Filling lines
Find innovative filling equipment and connect directly with world-leading technology suppliers
Filling lines are used extensively in all industries, such as food, pharmaceutical, chemical, and cosmetics, to accurately package different products into a container suitable for that product. Although the filling process is at the very end of the production line, it is no less important than the earlier steps. Last but not least, the idiom that dates back to 1382 when John Wyclif wrote the firste the laste, and the laste the firste, indicates just that the last things on a list are just as valuable as the previous ones. In this case, this idiom fits perfectly.
Innovative filling solutions
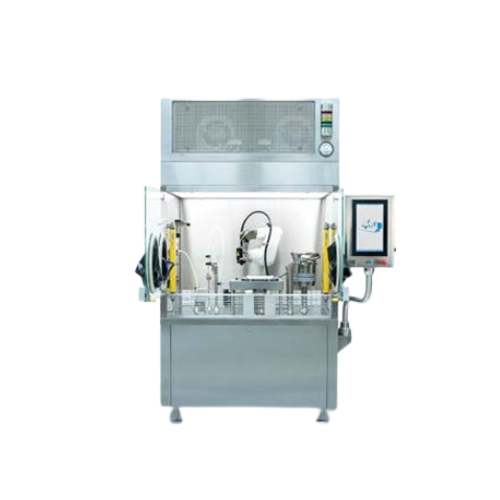
Aseptic filling line for biopharmaceuticals
Streamline your aseptic filling process with precision dosing and minimal spac...
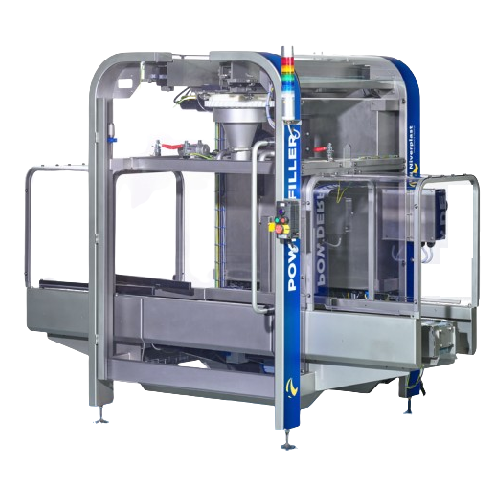
Accurate powder filling solution
When precision is paramount, this solution offers exceptional accuracy, filling powders up ...
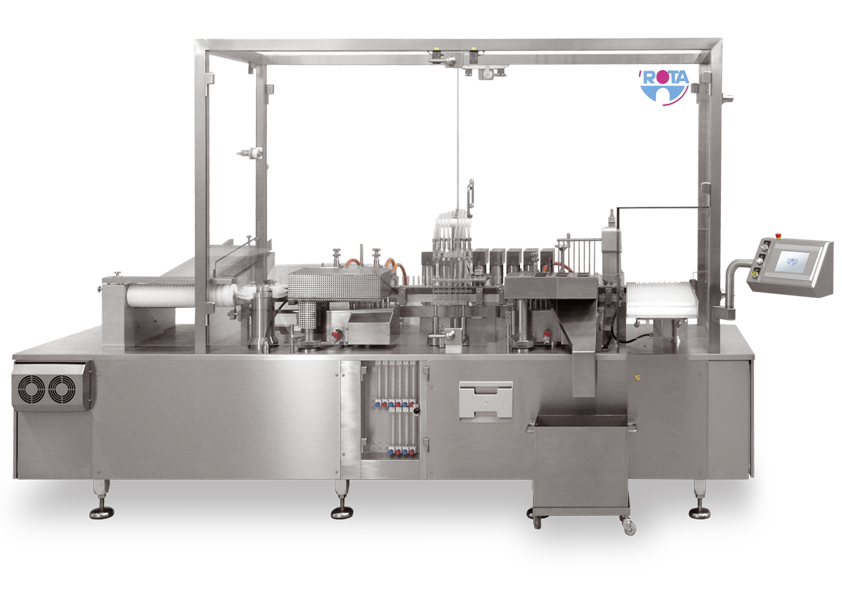
Ampoule filling machine
Filling ampoules or vials with parenteral fluids are an essential matter for which you need to consid...
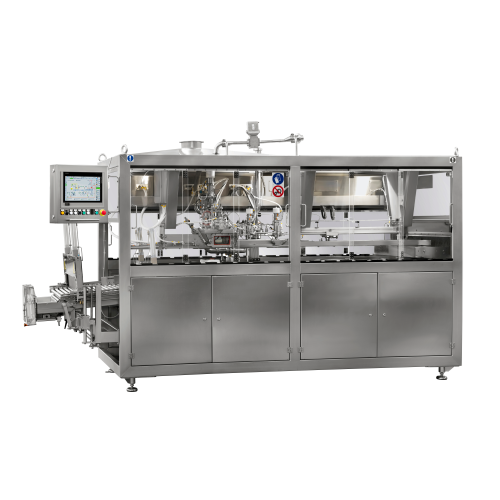
Aseptic filling system for bag-in-box packaging
Efficiently fill a range of liquid products into pre-sterilized bags while...
Based on product characteristics such as viscosity or its physical state – liquid or powder – and the technology they use, filling equipment can be categorized as rotary fillers, volumetric fillers, aseptic fillers, piston filling machines, net weight fillers, free-flowing or non-free-flowing and vibratory weigh filling machines.
Okay, that’s a long list, but no worries. Let’s try to take our time to understand the differences between them and which filling machine works best with which product.
Liquid filling – Choose your liquid fillers depending on the product viscosity
Liquid filling machines, also known as flow filling machines, are used extensively in the beverage industry for products such as mineral water, fruit juice, alcoholic beverages, and soft drinks. On the other hand, volumetric fillers, divided into gravity, pump, and piston fillers, are more suitable for packaging viscous substances. The significant difference between the two is that volumetric machines fill containers with the same product volume regardless of container size. In contrast, liquid fillers always fill containers to the same level, irrespective of volume.
What should you pay attention to when bottling your liquid product?
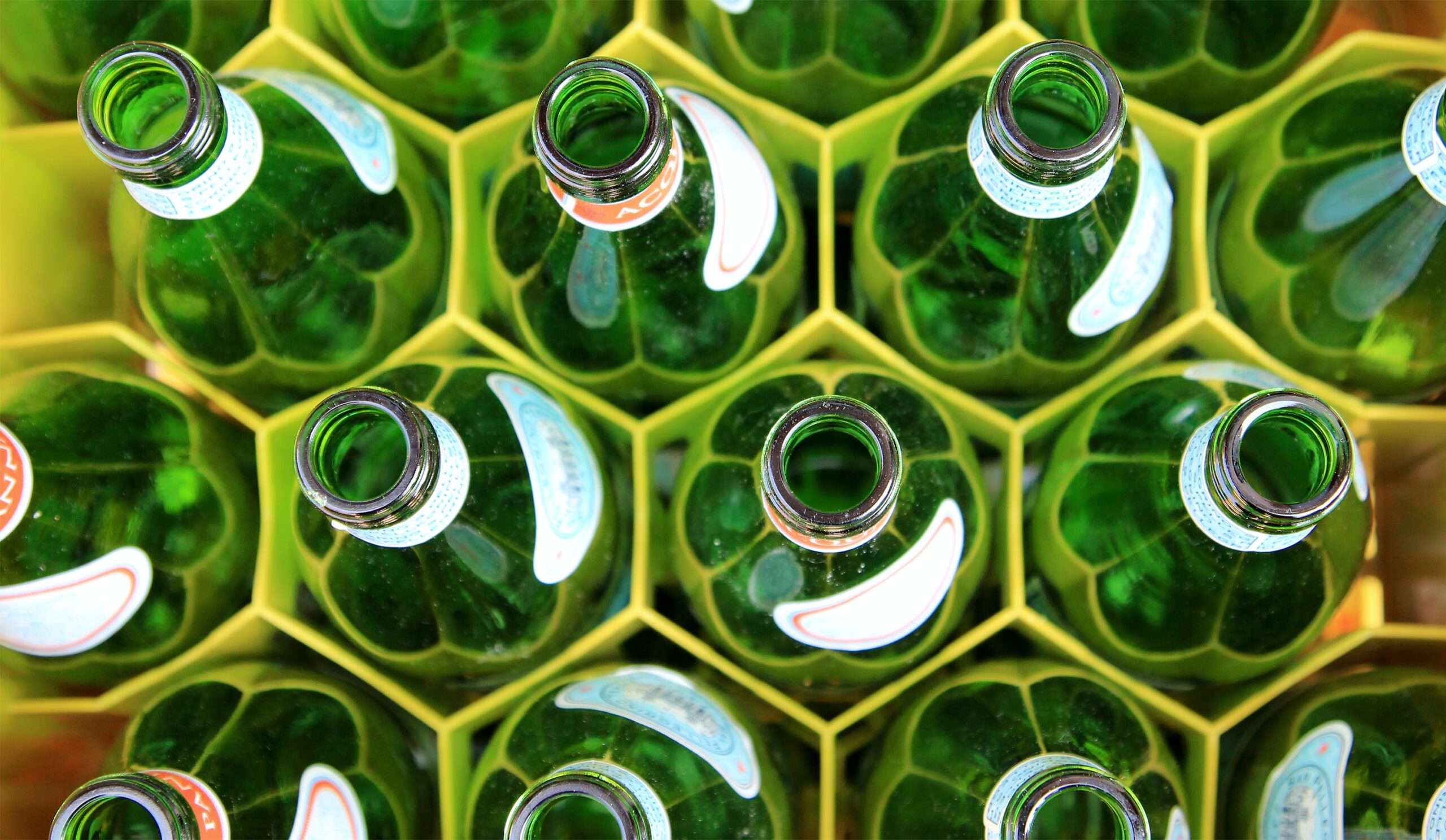
Whether tea, soft drinks, wine, or beer, the first thing that jumps out at you when choosing a drink is always its container. How your favorite beverages are bottled will depend on the beverage formulation and the nature of the liquid itself. During the bottling process, you need to transfer your product to the previously inspected bottle before capping it. Depending on your production scale and operation, you can adopt in-line or rotary fillers.
Inline liquid filling machines fill containers with both low- and high-viscosity substances. Rotary liquid filling machines are more complete consisting of several circular stations, each performing a different function, such as filling, sealing, and capping.
Bottling systems are also used in the beverage industry and food for different sauces such as ketchup, mayonnaise, or chili sauce.
Powder filling – Powder characteristics to consider

It would be too easy if the powder always had the same characteristics, wouldn’t it?
When packaging powdered products such as pharmaceutical powder, protein powder, or milk powder, you need to consider the physical properties of the powder itself. A powder product can be considered free-flowing, non-free flowing, and semi-free flowing. For example, products like granulated sugar are defined as free flowing because their particles are not cohesive. Instead, powdered milk is a non-free flowing powder because it can be easily compressed and retain its shape after adding pressure. Instant coffee can be categorized as semi-free flowing powder.
Auger filling machines belong to the volumetric fillers and are pretty popular in the industry. They don’t weigh the powder, unlike the net weight filling machine, which is the only piece of powder filling equipment to weigh the powder before dispensing it into the container.
The auger filling machine is suitable for powders such as flour but can handle free-flowing powders and some non-free flowing powders. The vacuum powder filling machines are used for powders that do not require any further breakdown or agglomeration because they work without using an auger or agitator. These types of filling machines are not suitable for granules.
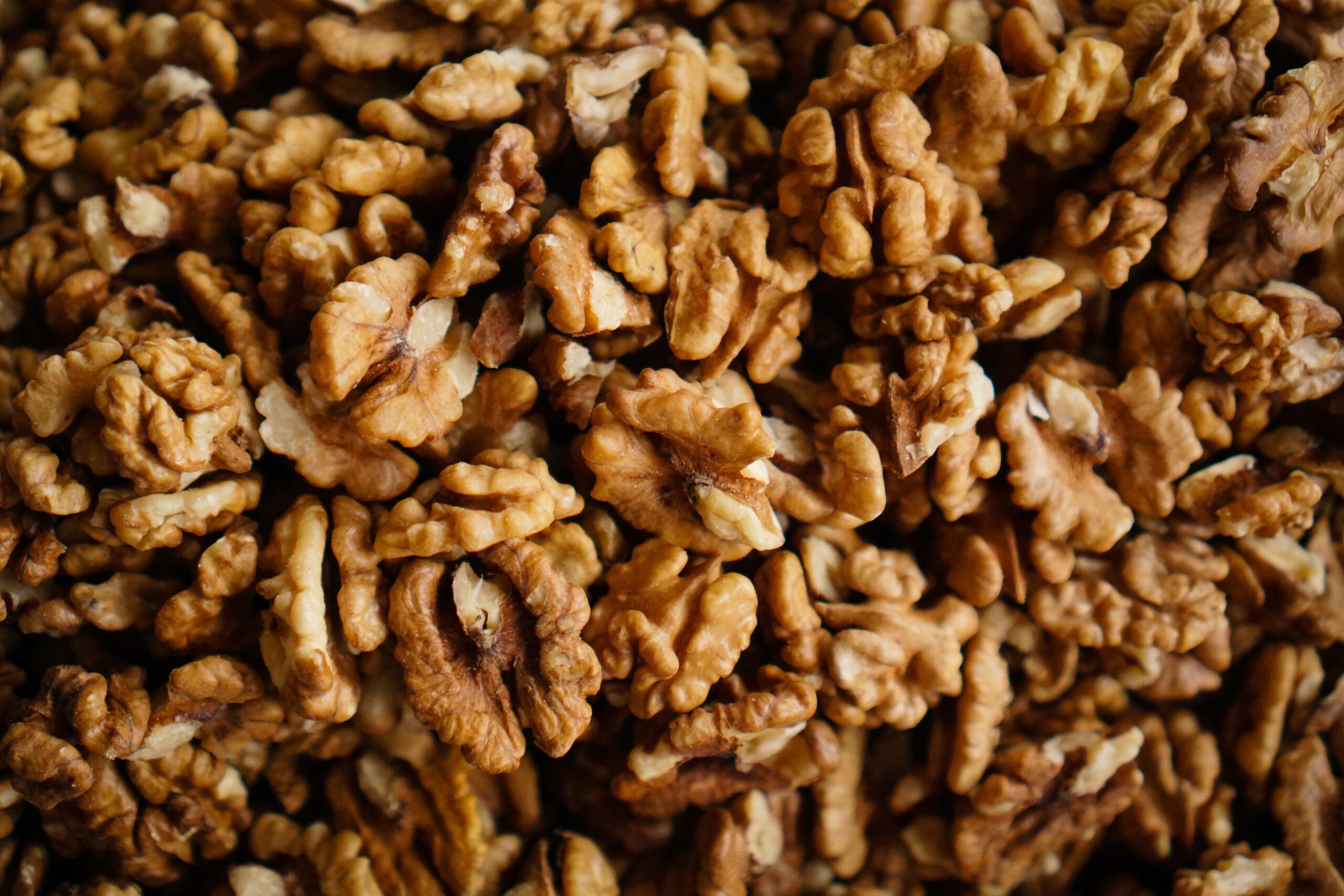
Bagging – not only for powders
Bagging is a packaging process that automatically inserts a measured amount of a product into a bag or a pouch. Powdered products such as coffee, cocoa powder, or baking powder undergo the bagging process. The choice of bagging equipment is critical since food products like coffee are pretty sensitive to air exposure.
Of course, the bag size varies depending on the product size and the production step. For example, semi-finished products such as nuts, seeds, or spices will be packed in flexible bulk containers for transportation and storage. Flexible intermediate bulk containers are used primarily in the chemical industry for fertilizers, dyes, or pigments.
Filling systems in the Pharma and Food industries
When it comes to pharmaceutical or food products, filling lines may require special precautions because these products are made specifically for human consumption and for being ingested. That’s why you will hear a lot about aseptic and sterile filling, especially in these two industries.
Aseptic vs. sterile – Is there any difference?
There has always been some confusion around these two terms. Both indicate techniques to create a sterile finished product, thus free of living microorganisms and as safe as possible. But although the two terms go hand in hand, they are different. After filling and sealing the container using sterile filling solutions, the product is subjected to a sterilization process using heat, radiation, or filtration. The product is sterilized in its final packaging.
Aseptic processing is reserved for products that cannot withstand heat exposure from the terminal sterilization process. It is a technique where the product, the container, and the container closure are first sterilized separately and then brought together. This method is meant to maintain the sterility of a product assembled from different sterile components. Since the product is not sterilized in its final container, it is essential that the filling and sealing take place in a highly controlled environment (aseptic filling).
Pharmaceutical filling for ensuring product safety and sterility
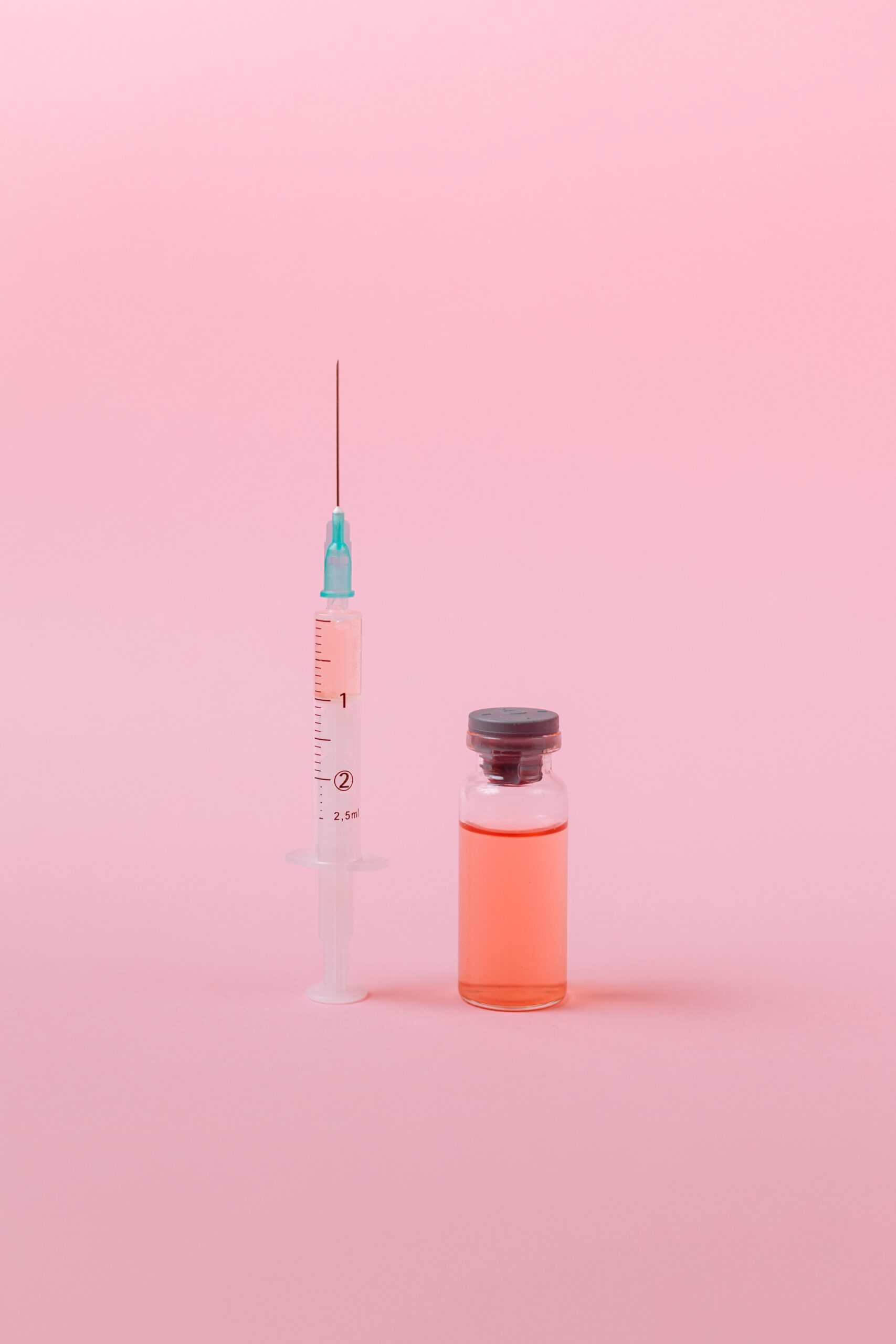
Vaccines or antibiotics are just two examples of drugs that cannot withstand heat sterilization, so they must be made through aseptic processing. When it comes to pharmaceutical filling, to ensure product safety and quality, aseptic fillers are widely used for filling and sealing drug containers such as vials, ampoules, and syringes. Aseptic filling is also used for parenterals since the entire process must be done in an aseptic environment to avoid contamination. The aseptic filling is very challenging since ensuring sterility is not easy, and failure can have dramatic consequences for the patients.
Aseptic filling in the food industry
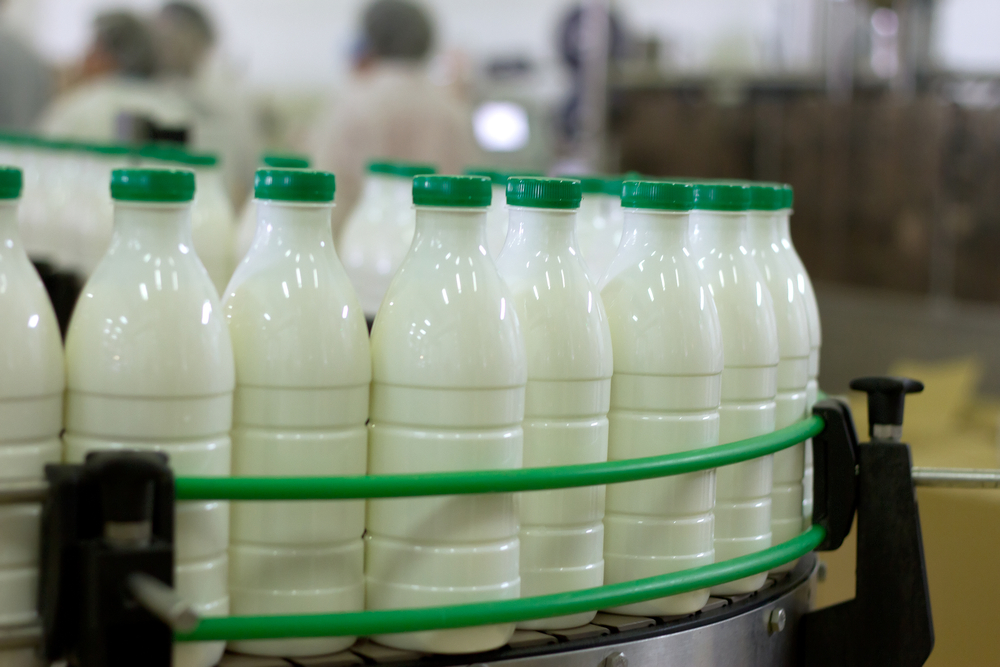
Aseptic filling is a food preservation method that ensures shelf-stable products, extending the food product shelf file and optimizing product quality. The important factors in the aseptic filling process are obtaining and maintaining sterile environment conditions for the filling and sealing process. It is used when producing dairy products, fruit juices, or sauces.
Tube filling equipment for viscous liquids or pastes
The packaging of choice is usually a tube made of plastic or metal when producers have to pack viscous liquid or pastes. In the food industry, tube filling equipment is used for packaging food pastes, while in the cosmetic industry for products such as toothpaste, ointments, gels, and creams.
Tube fillers consist of a pump injecting the product into the tube. The machine then crimps the end of the tube to seal it before packing the products into boxes for shipping.
What are you making?
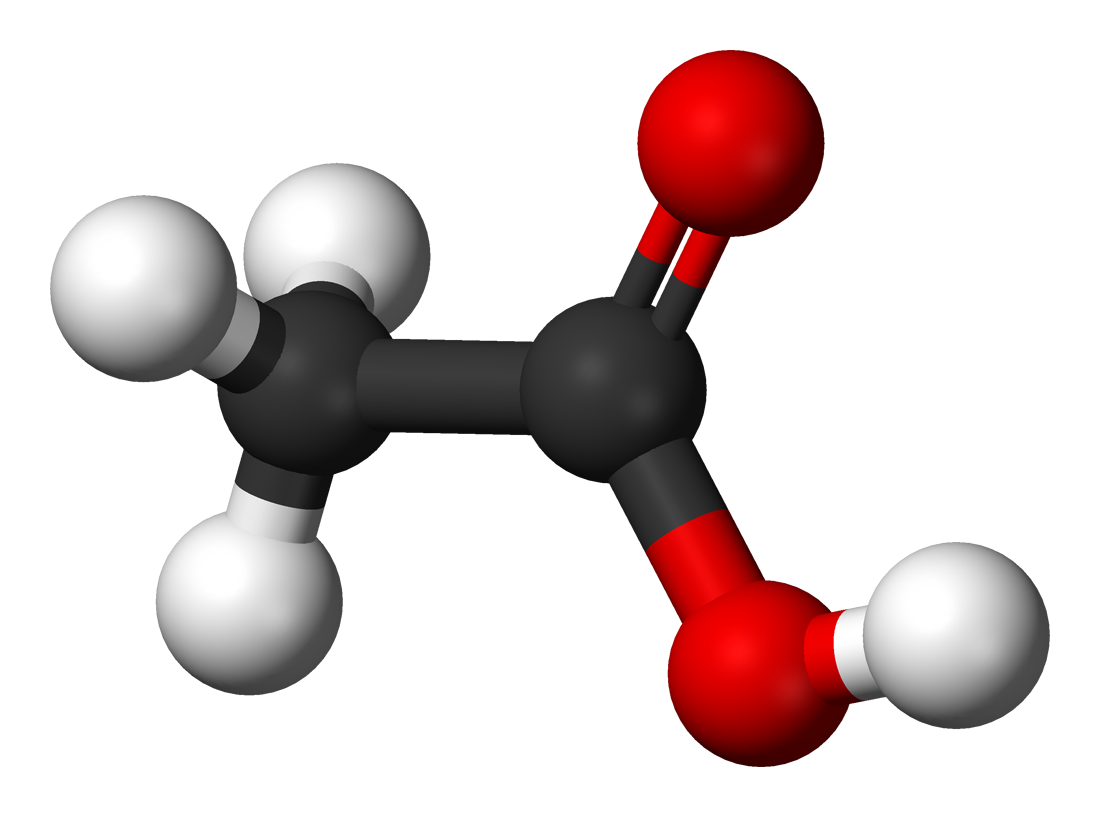
Acetic acid
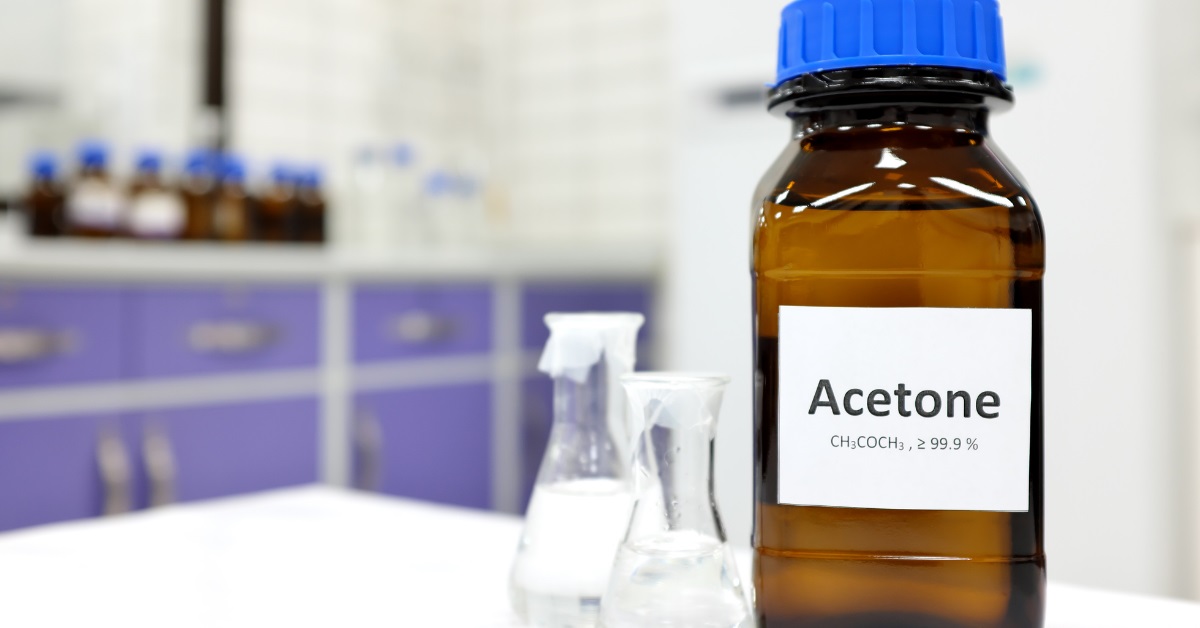
Acetone
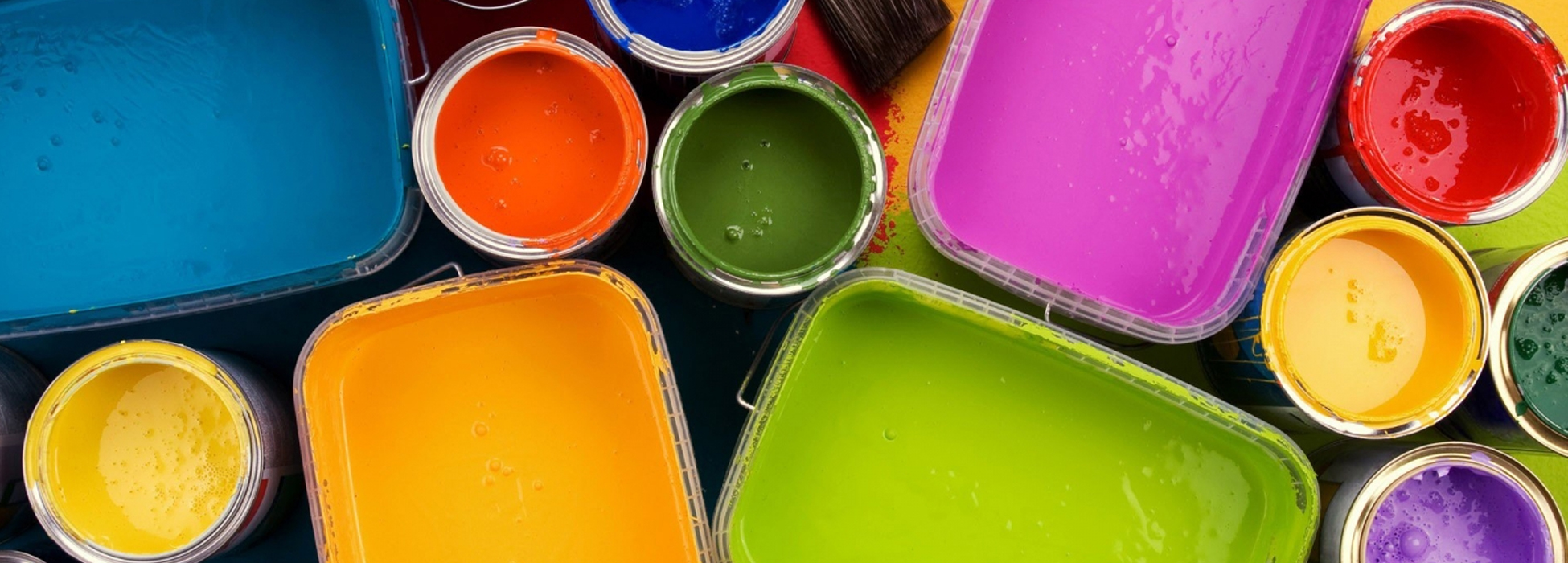
Acrylic coatings
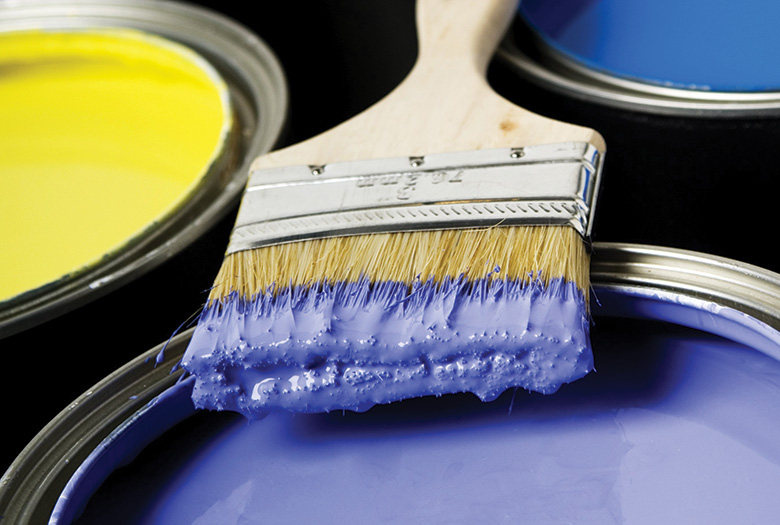
Acrylic emulsions
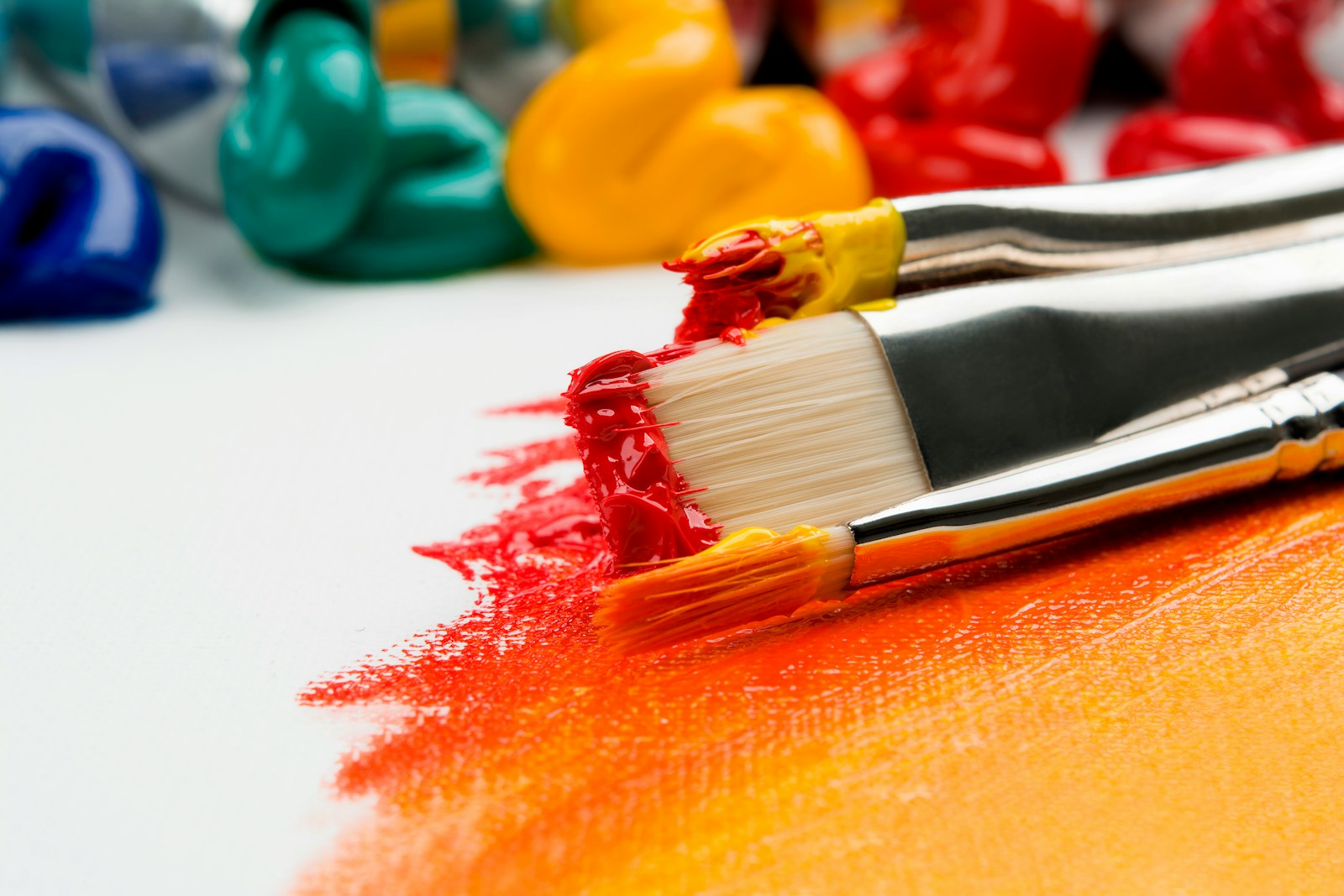
Acrylic paint
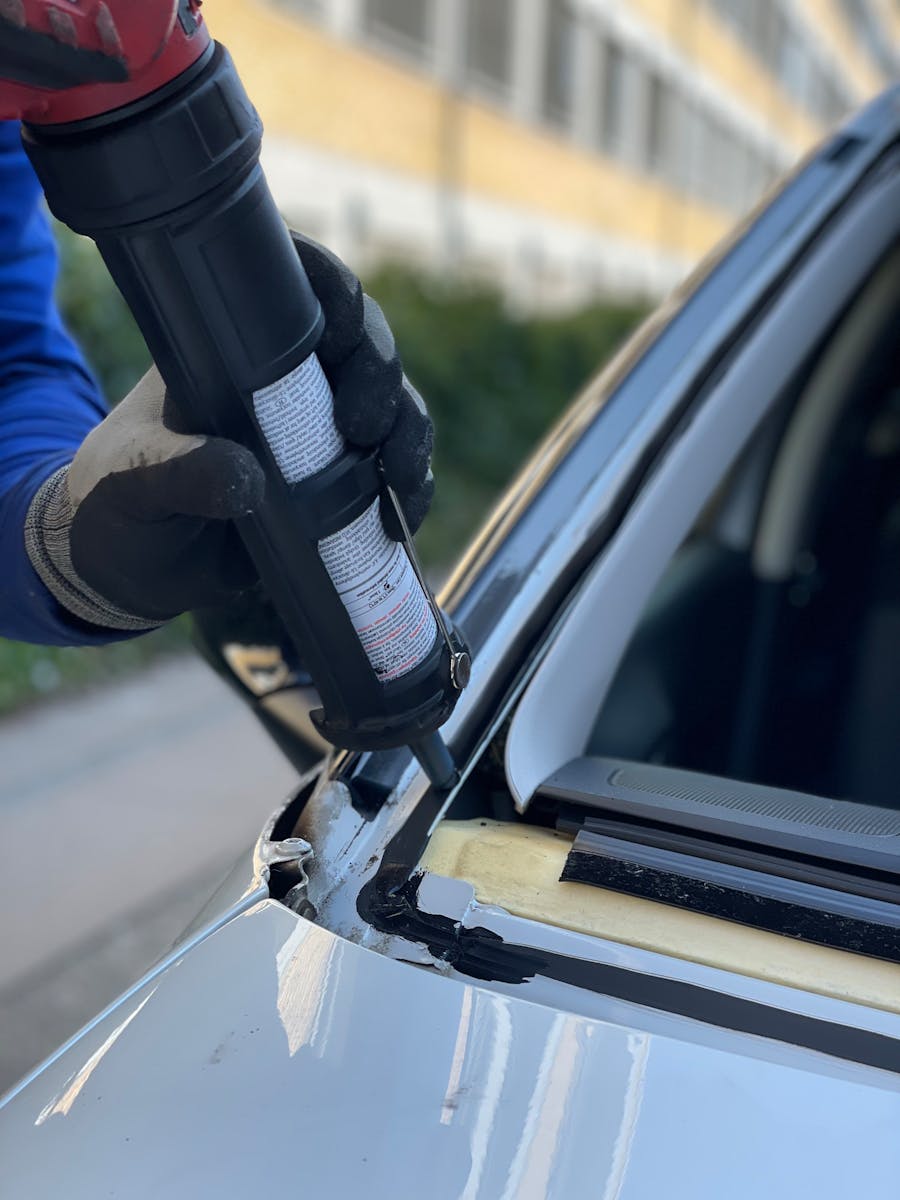
Acrylic sealants
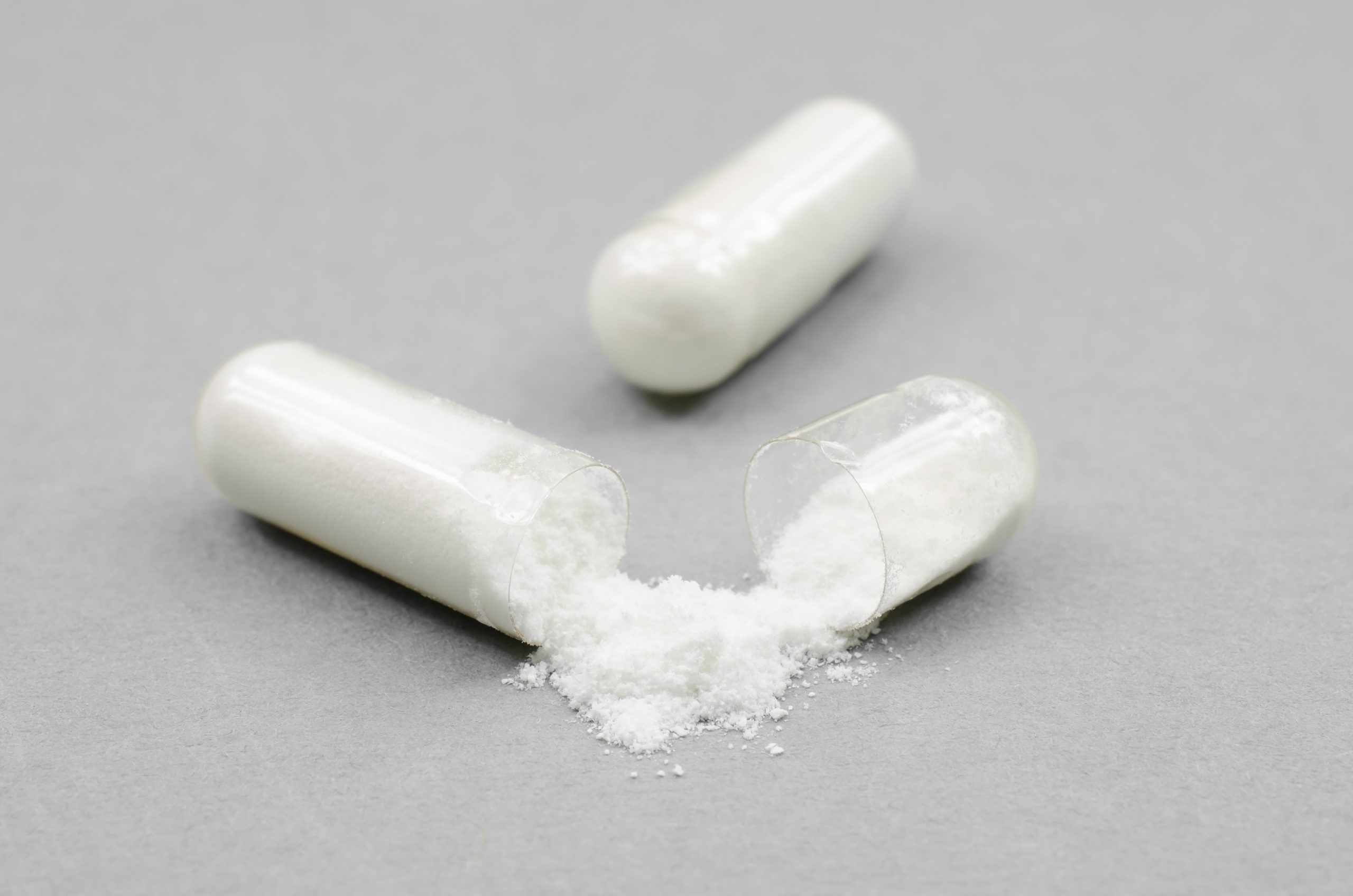
Active pharmaceutical ingredients (API)
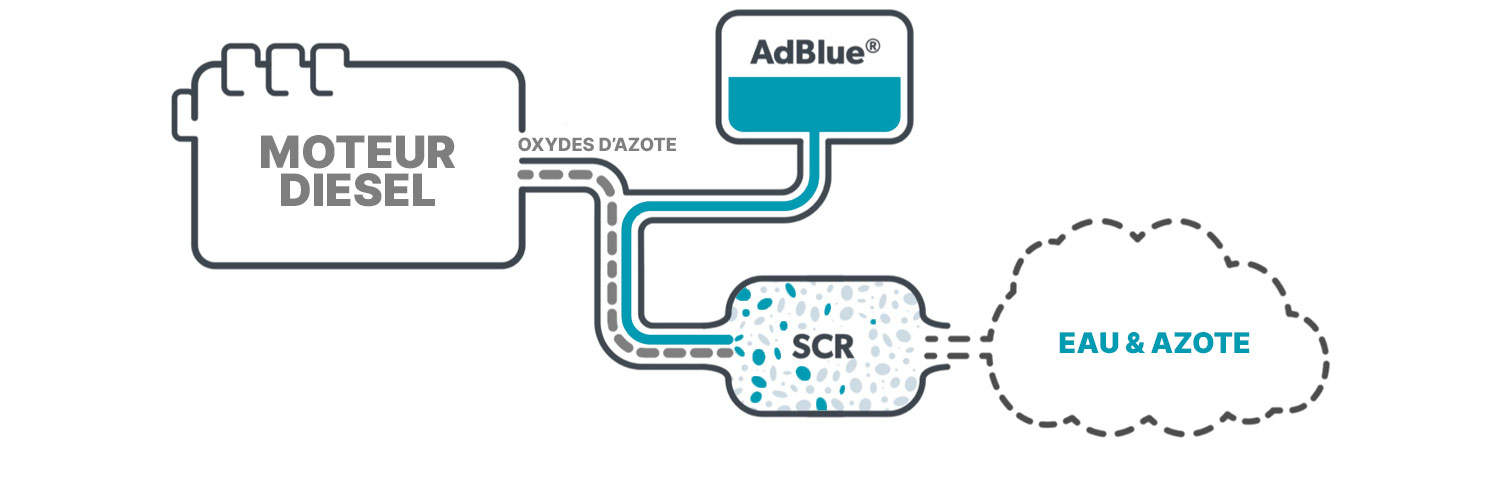
Adblue
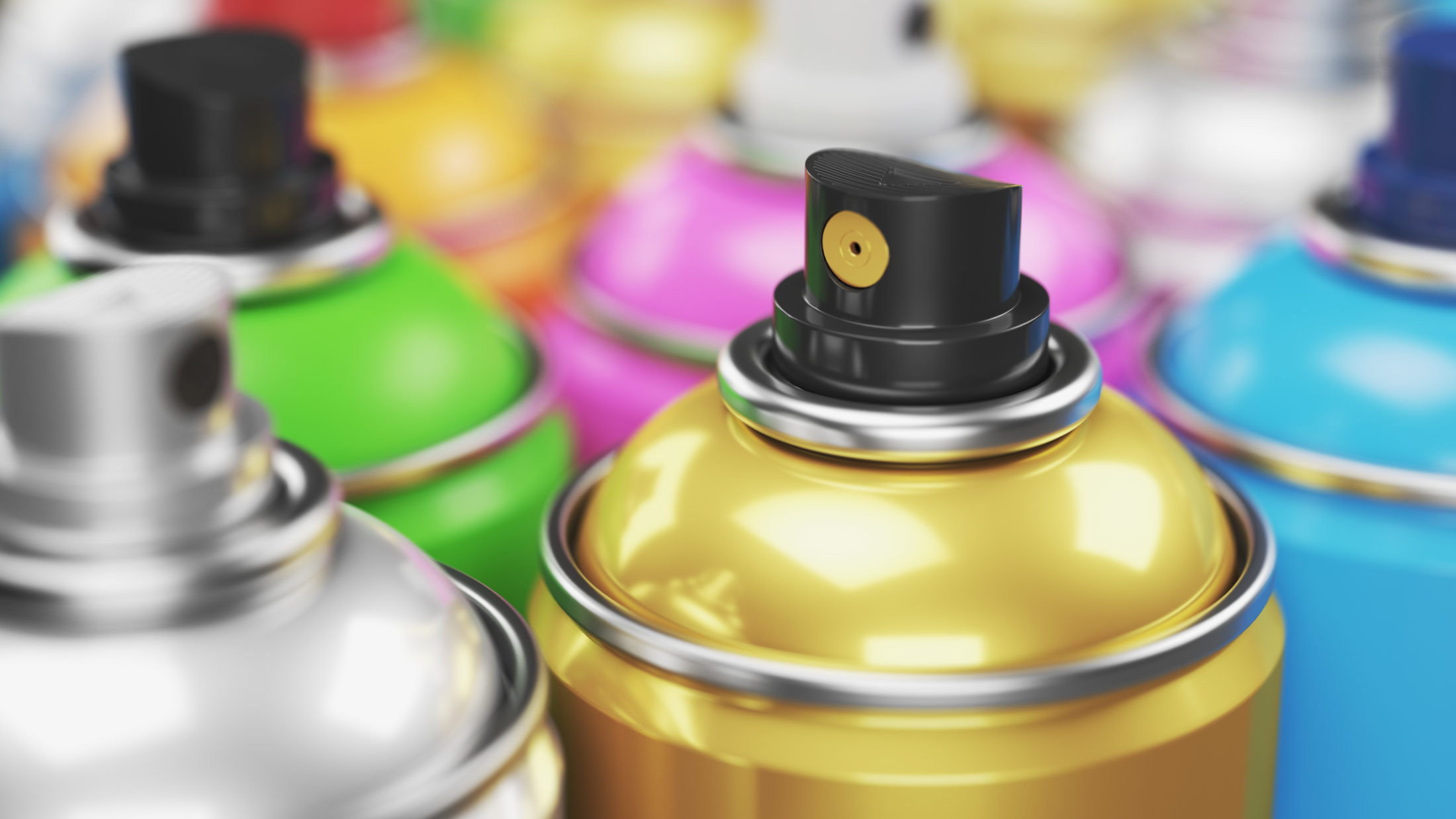
Aerosol cans
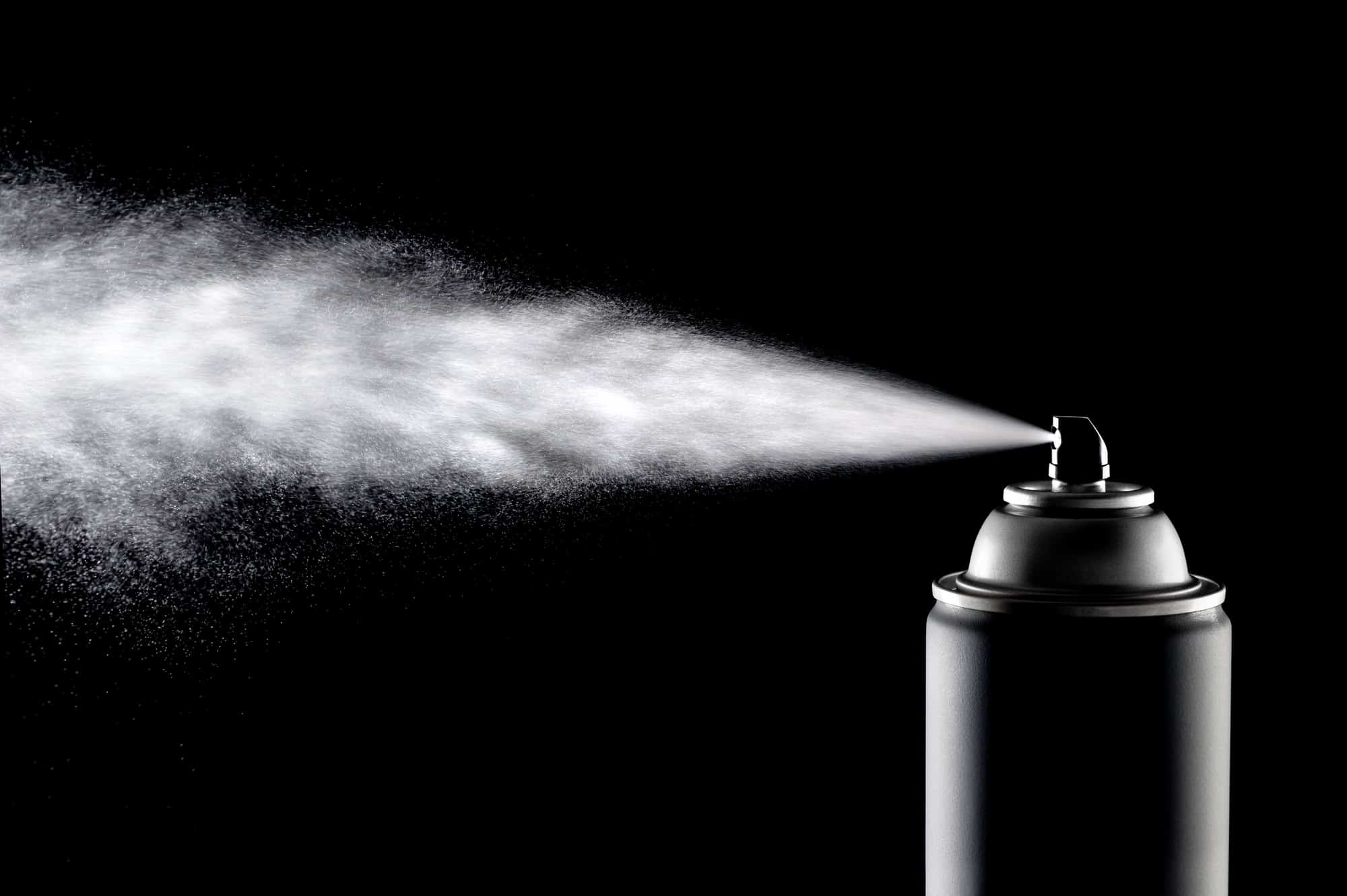
Aerosols

Aioli
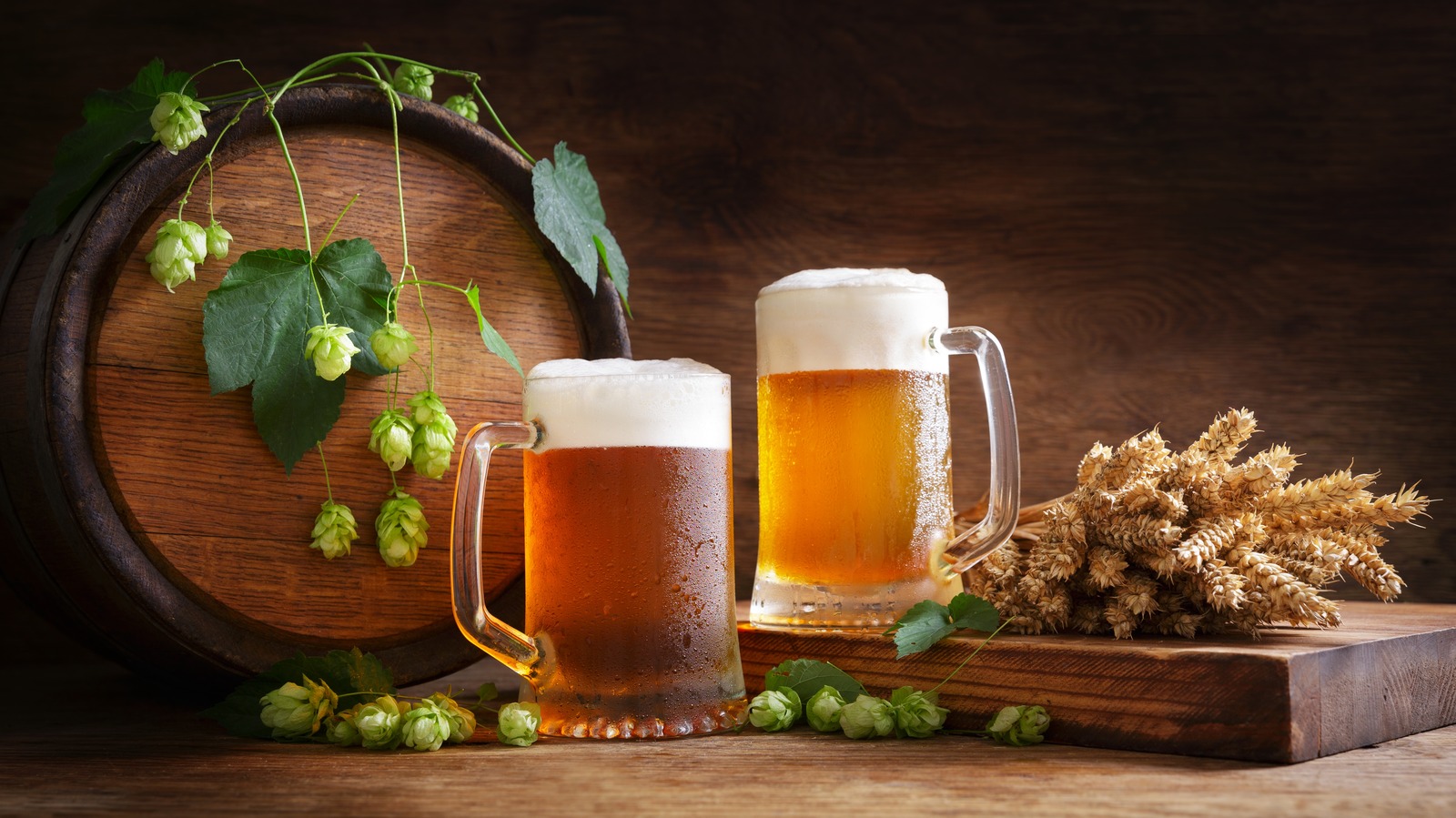
Ale beer
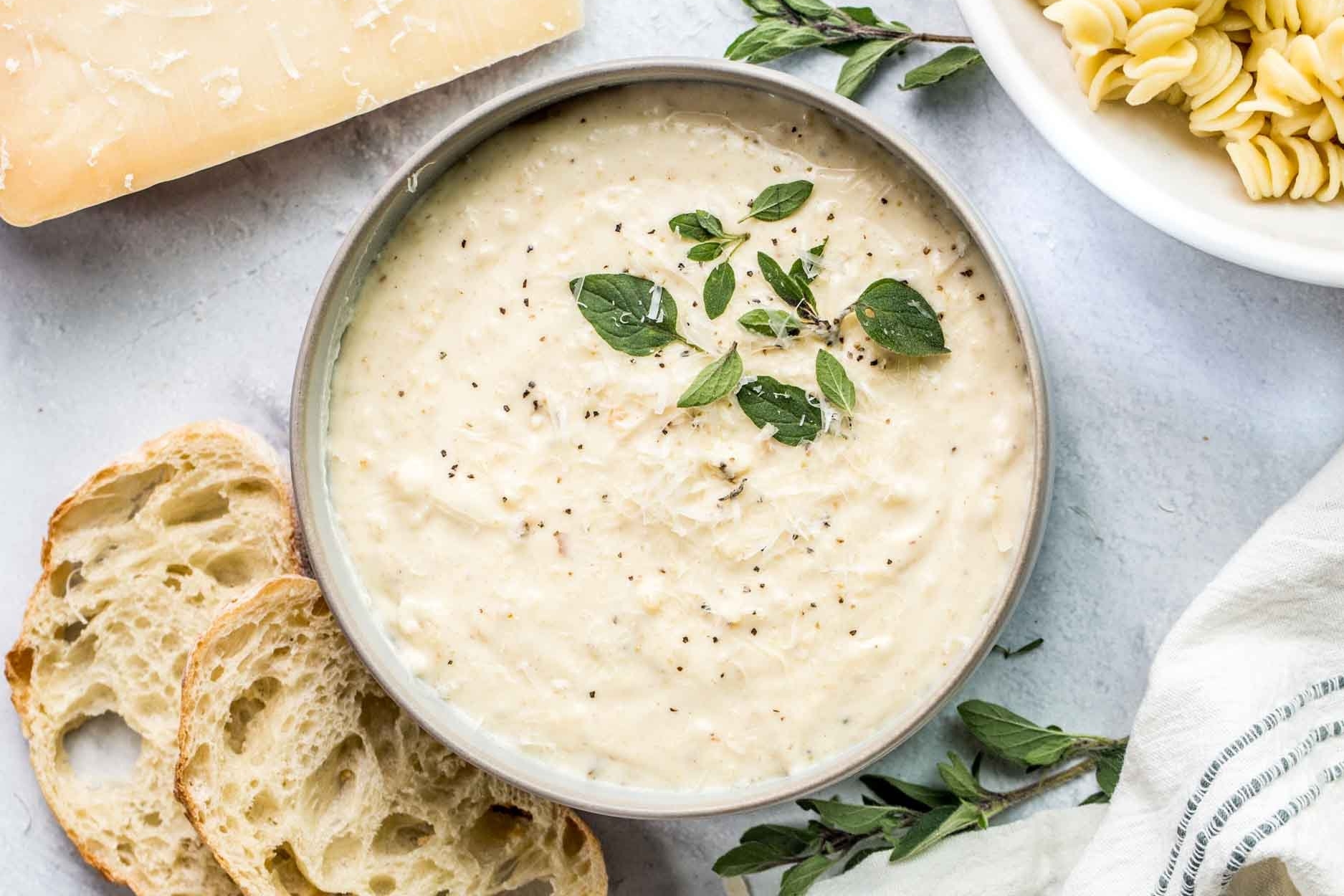
Alfredo sauce
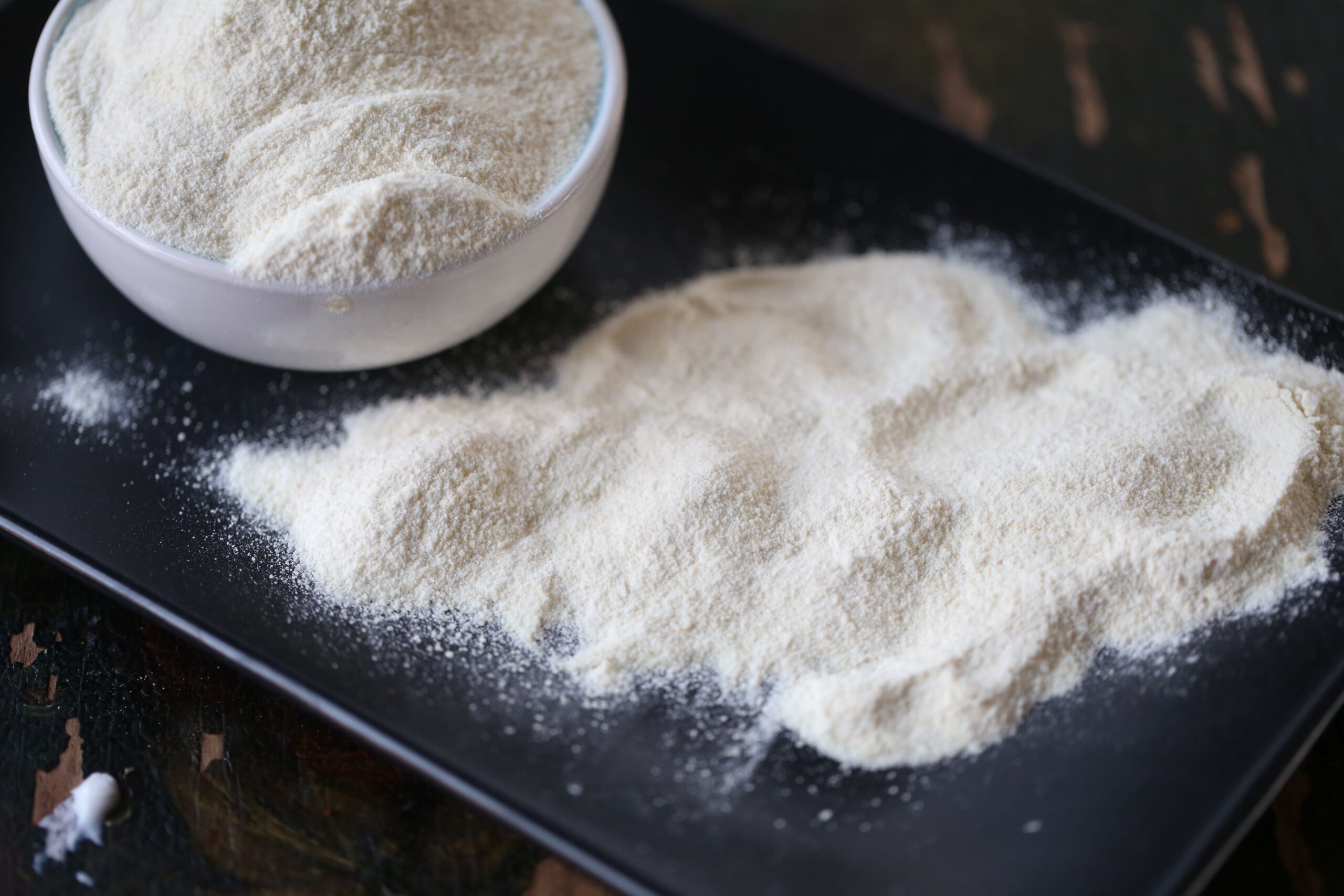
All-purpose flour
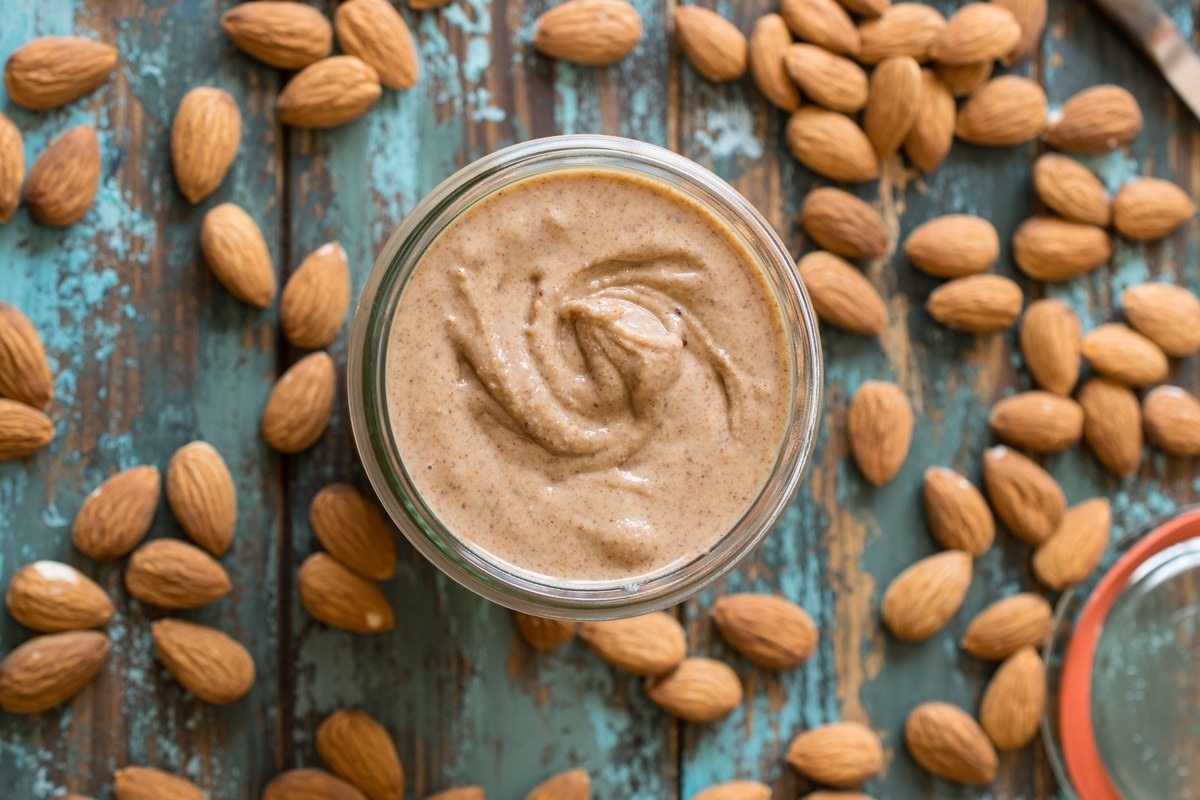
Almond butter
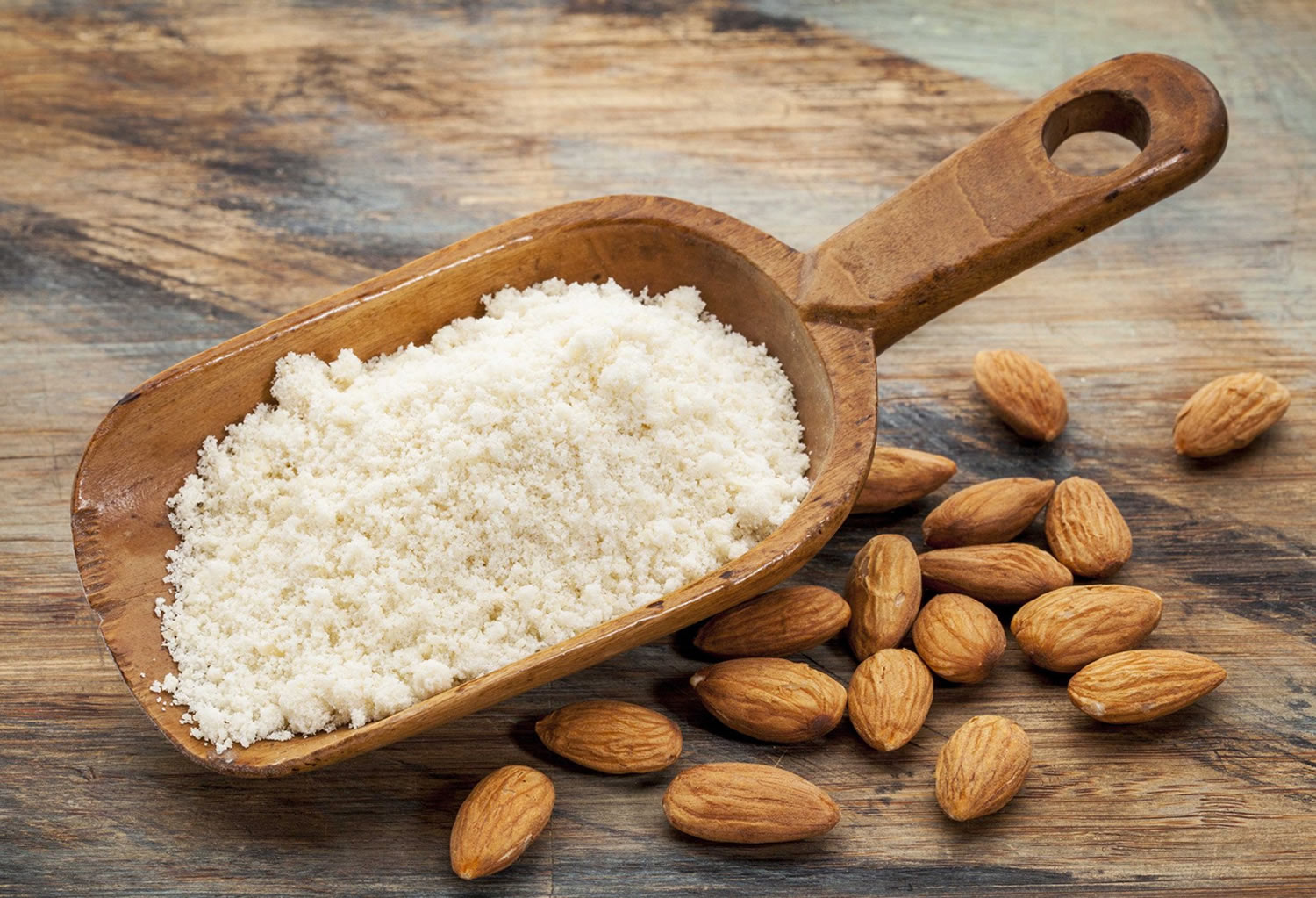
Almond flour
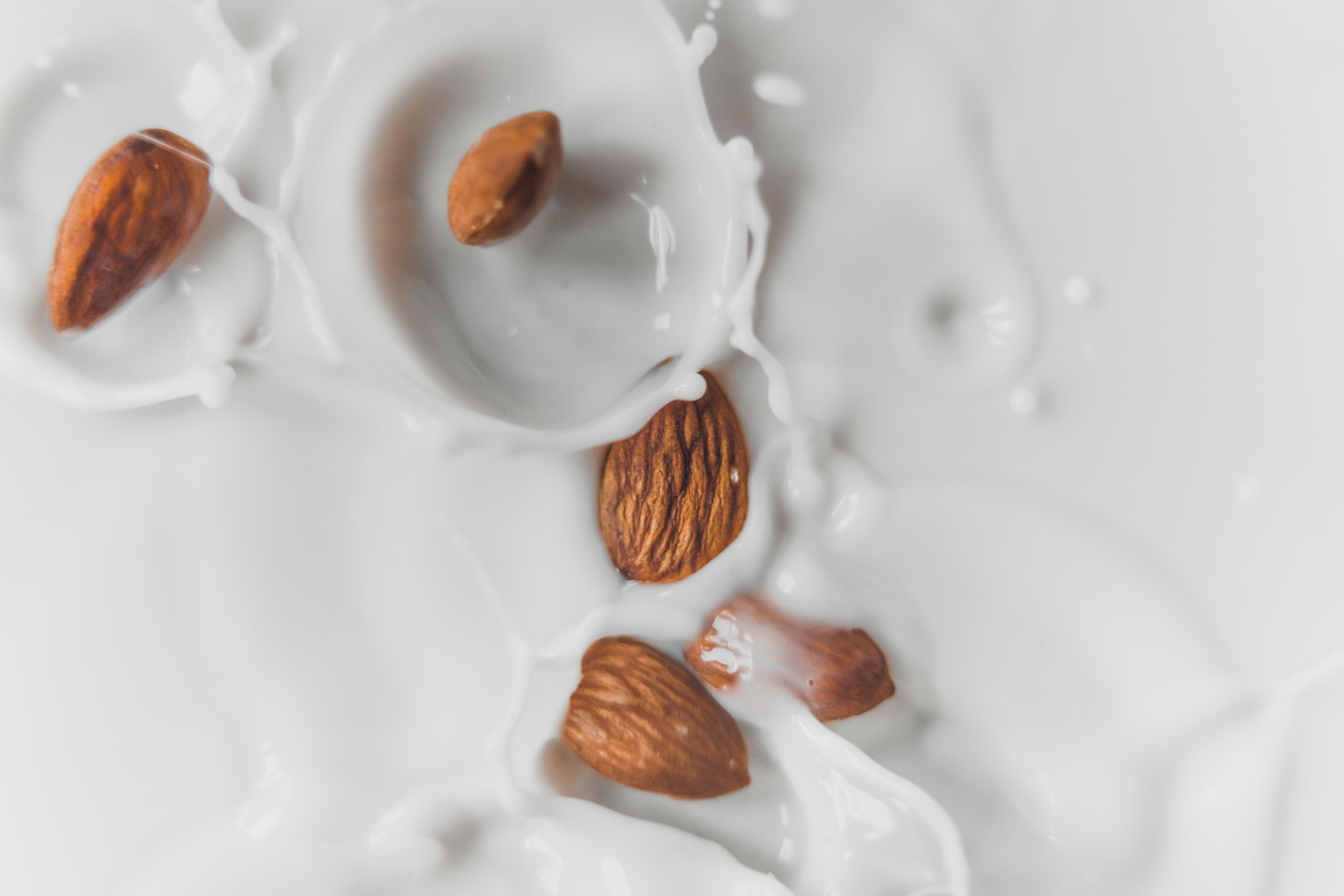
Almond milk
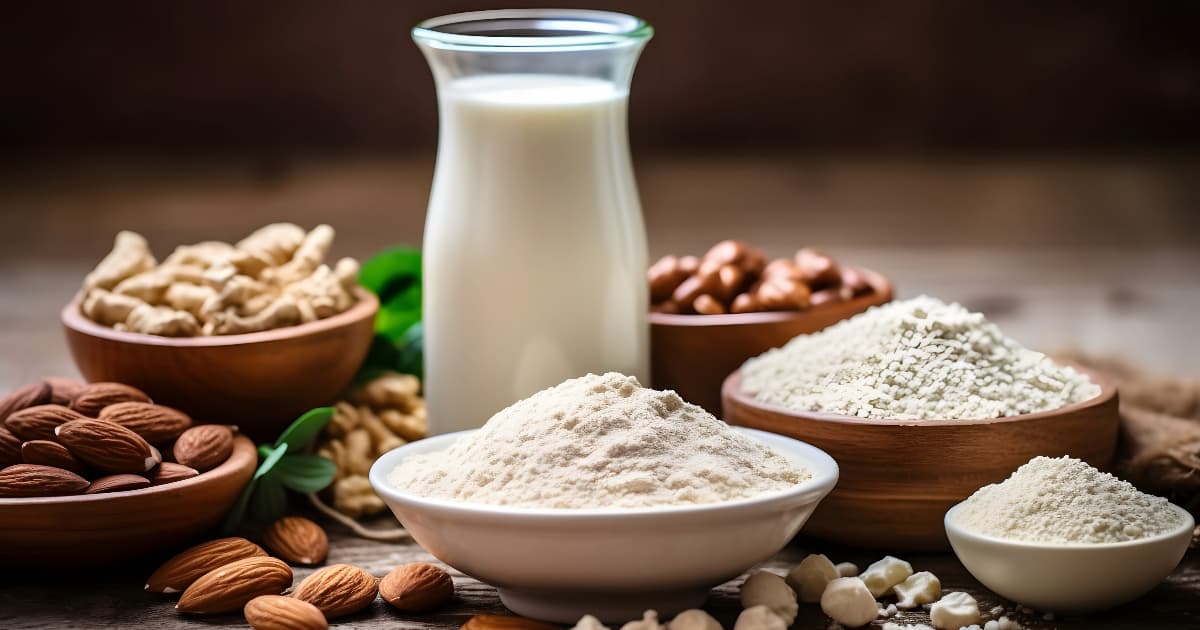
Almond milk powder
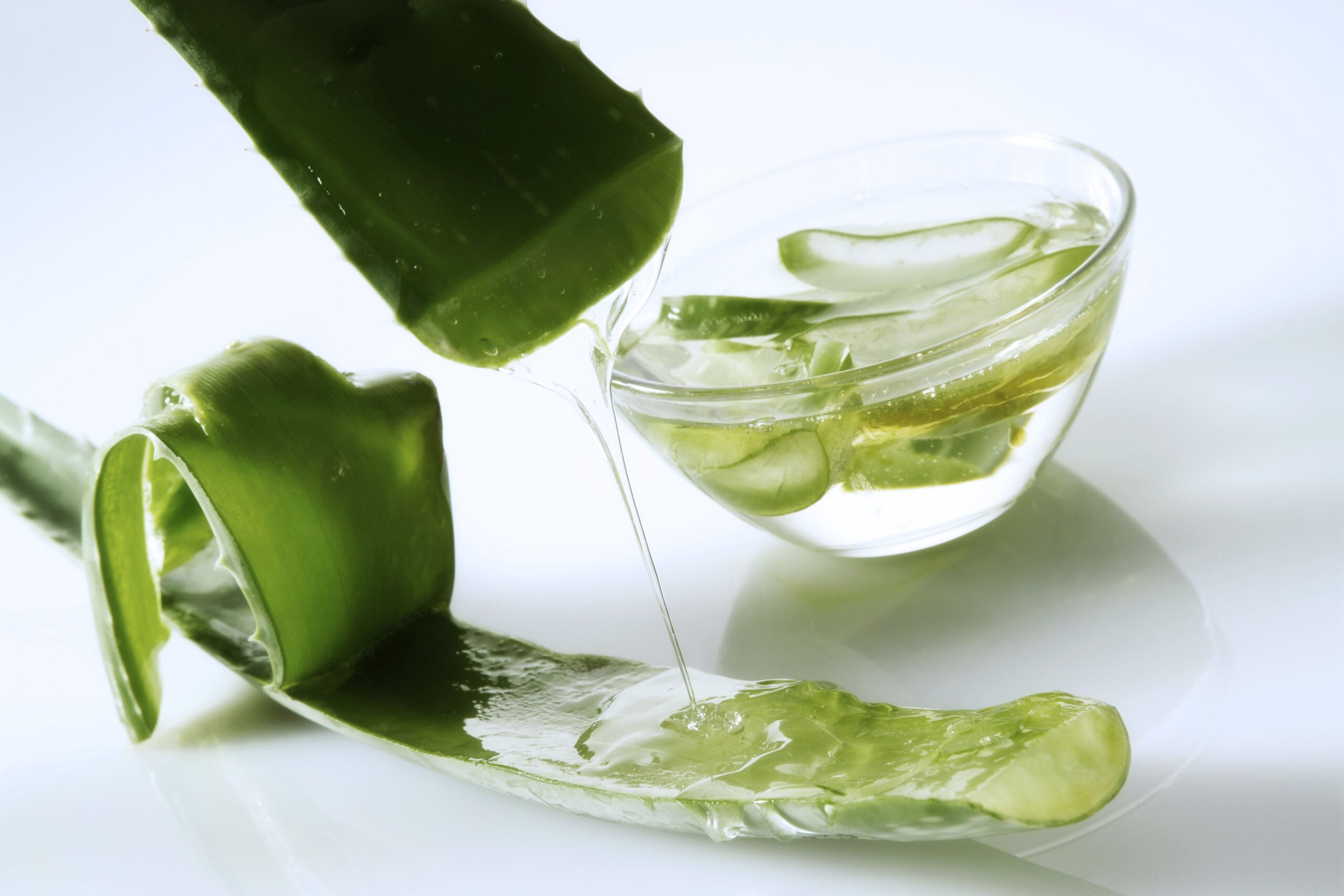
Aloe vera gel
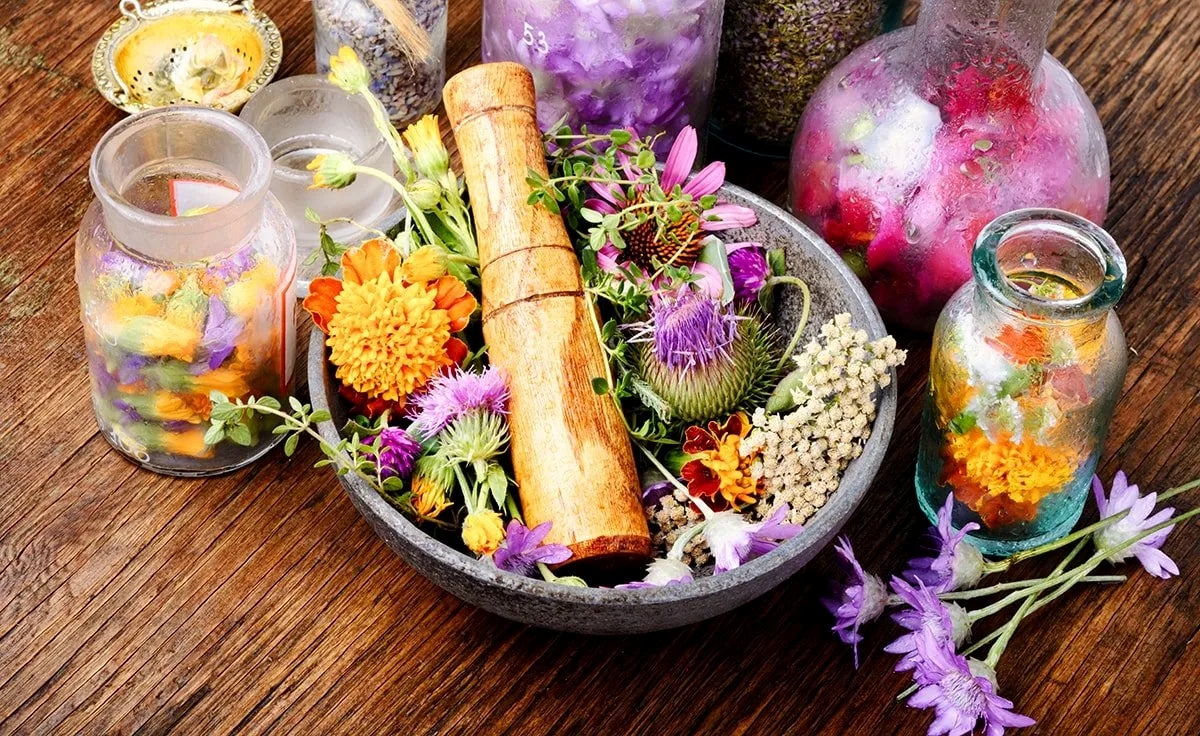
Alternative medicine
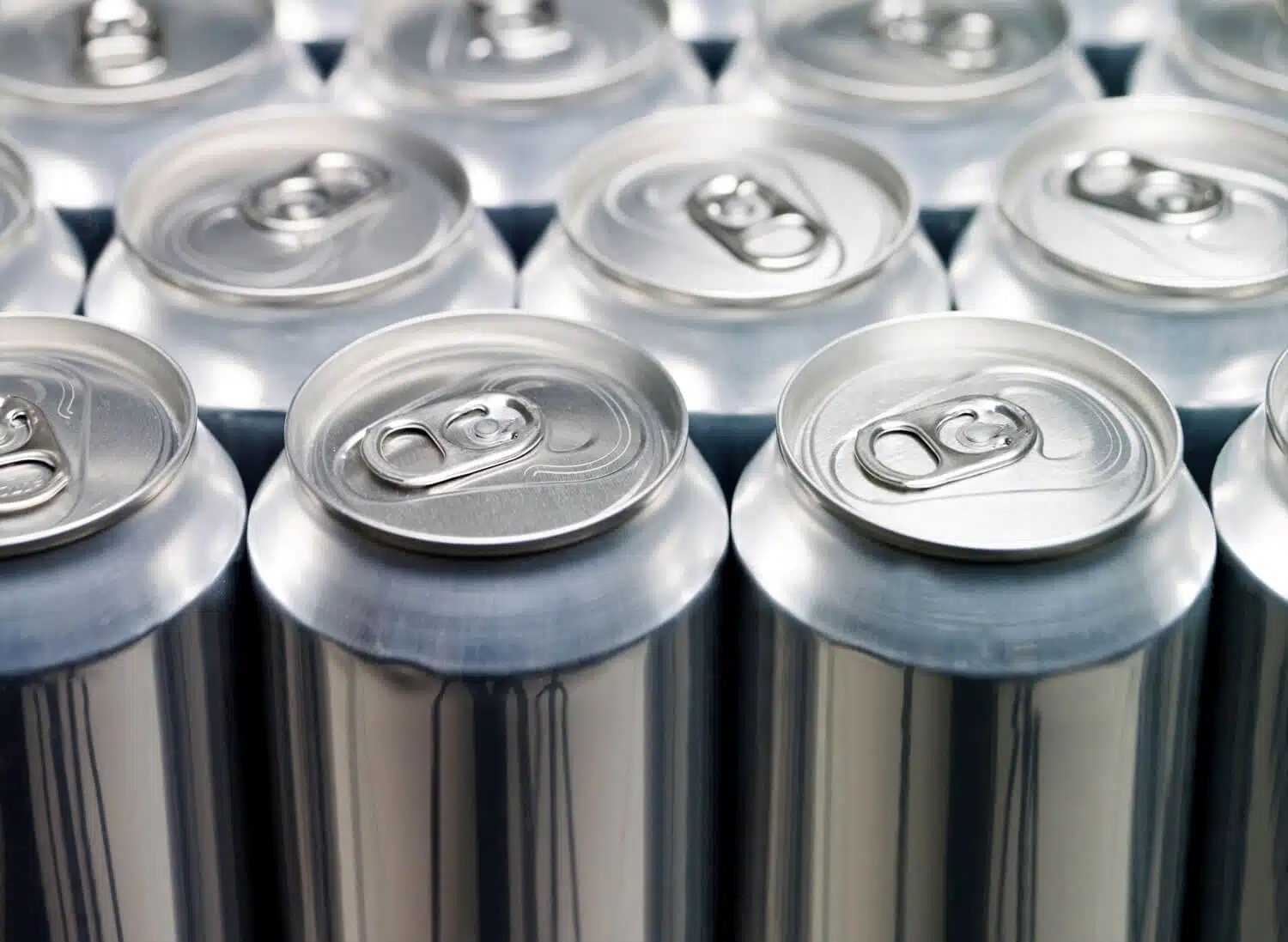
Aluminum beverage cans
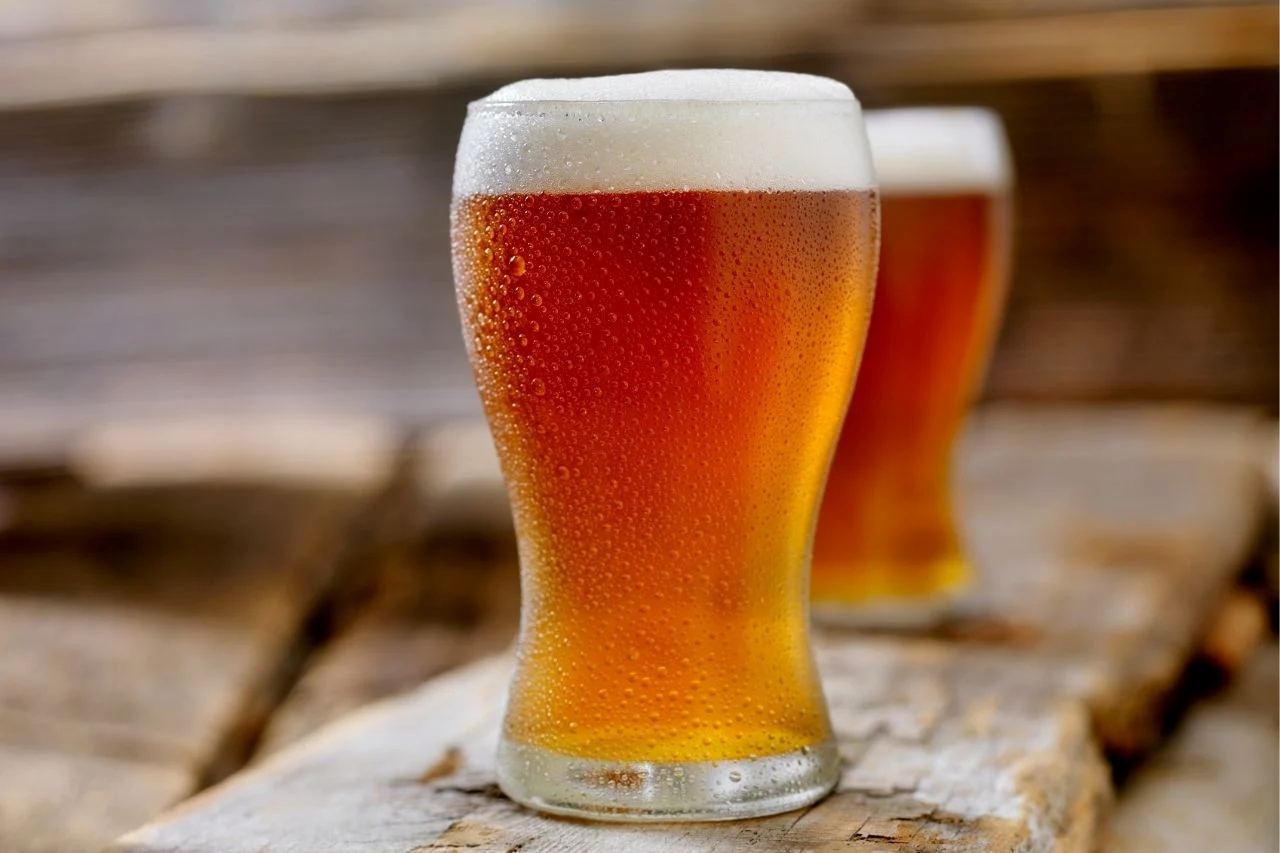
Amber ale
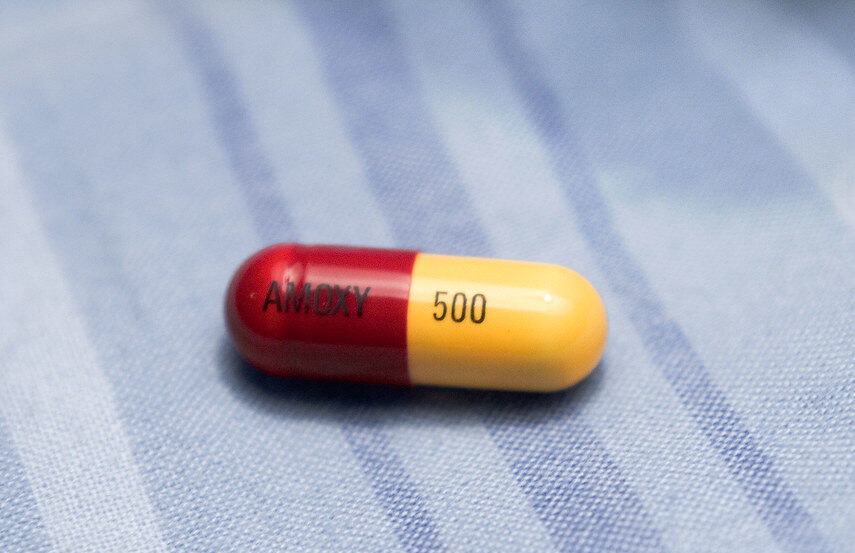
Amoxicillin capsules
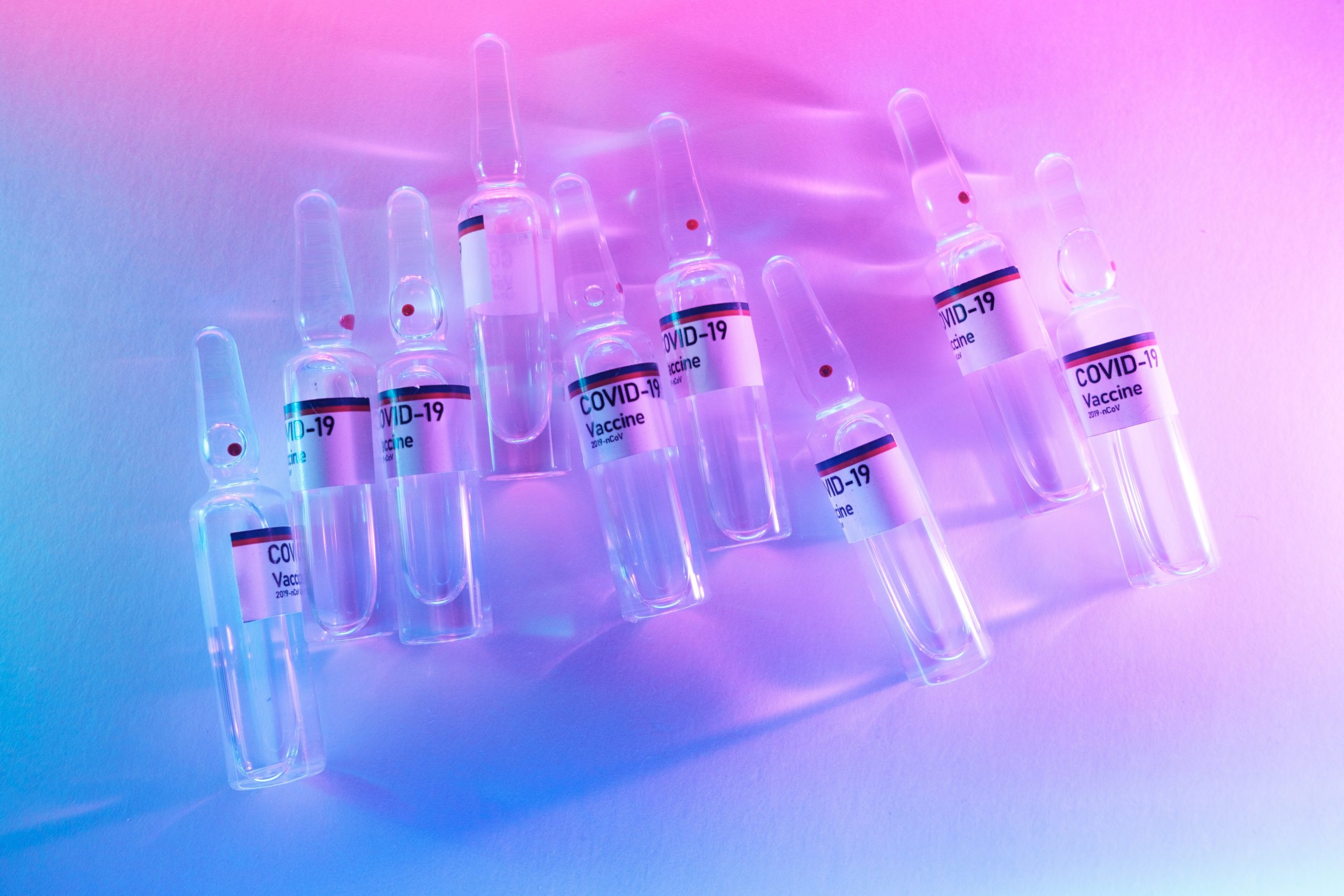
Ampoules
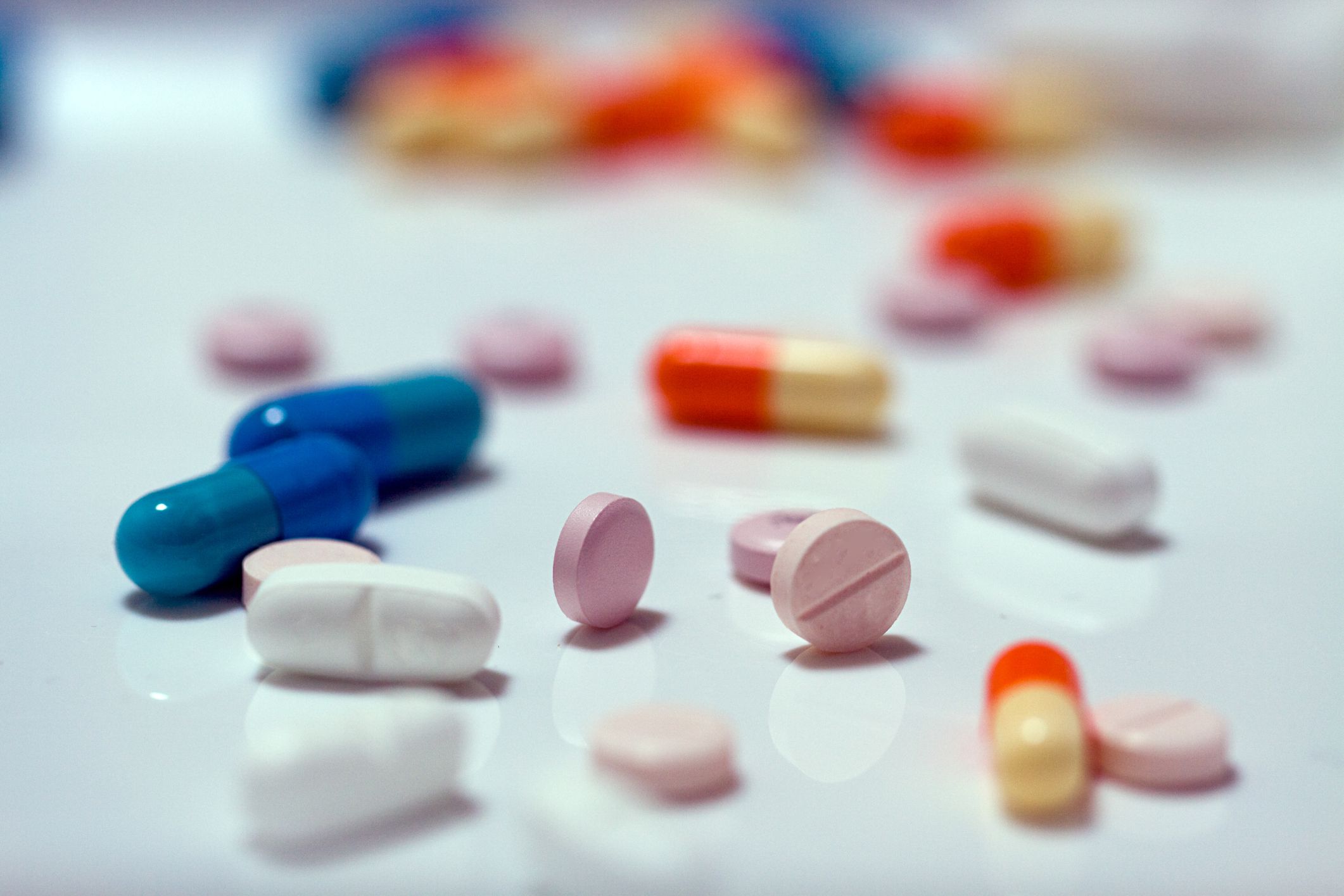
Analgesic tablets
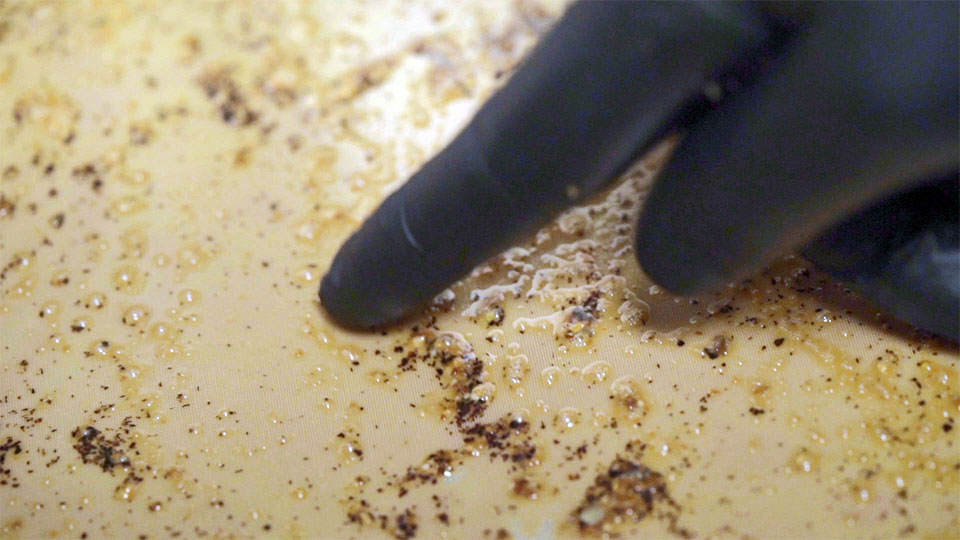
Anhydrous pastes
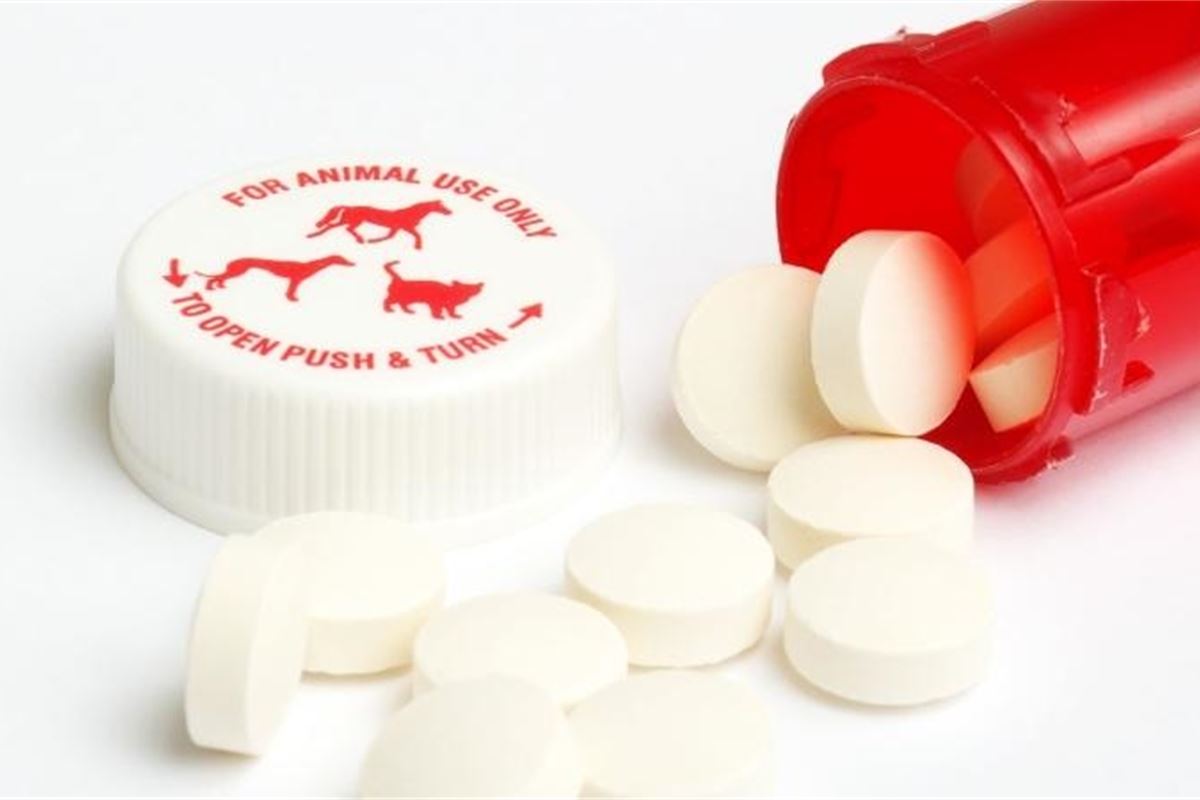
Animal health products
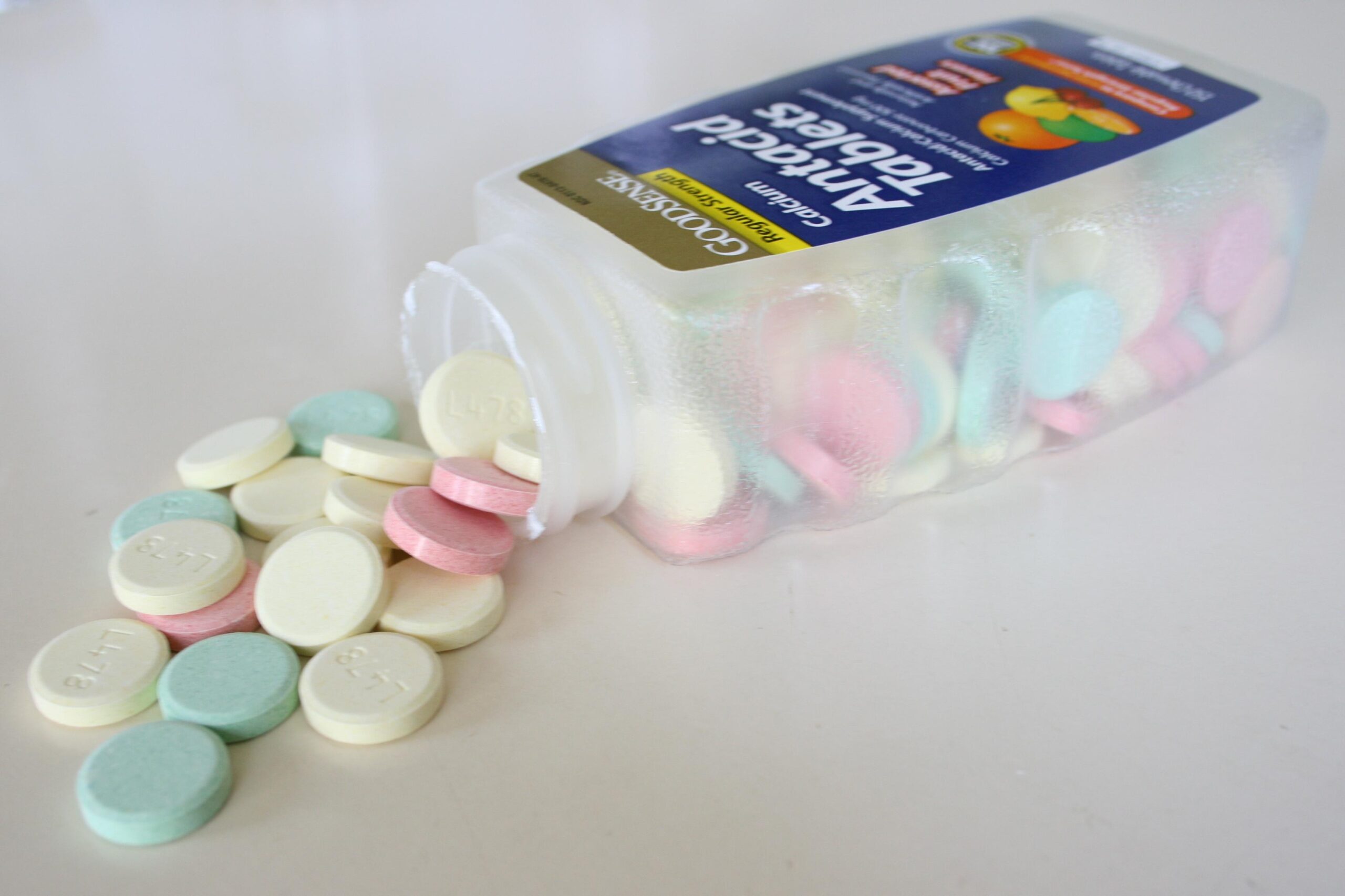
Antacid tablets
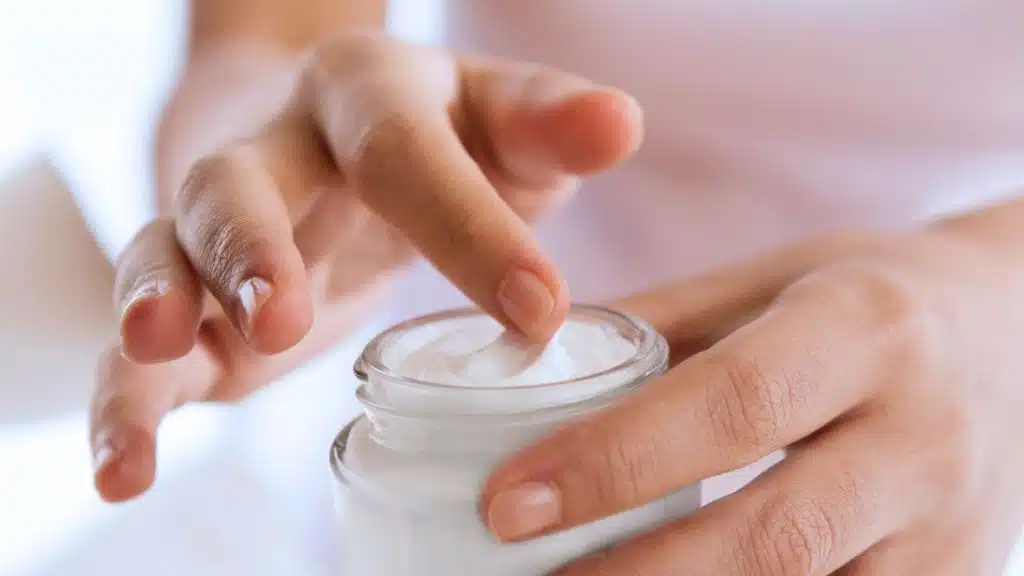
Anti-aging cream
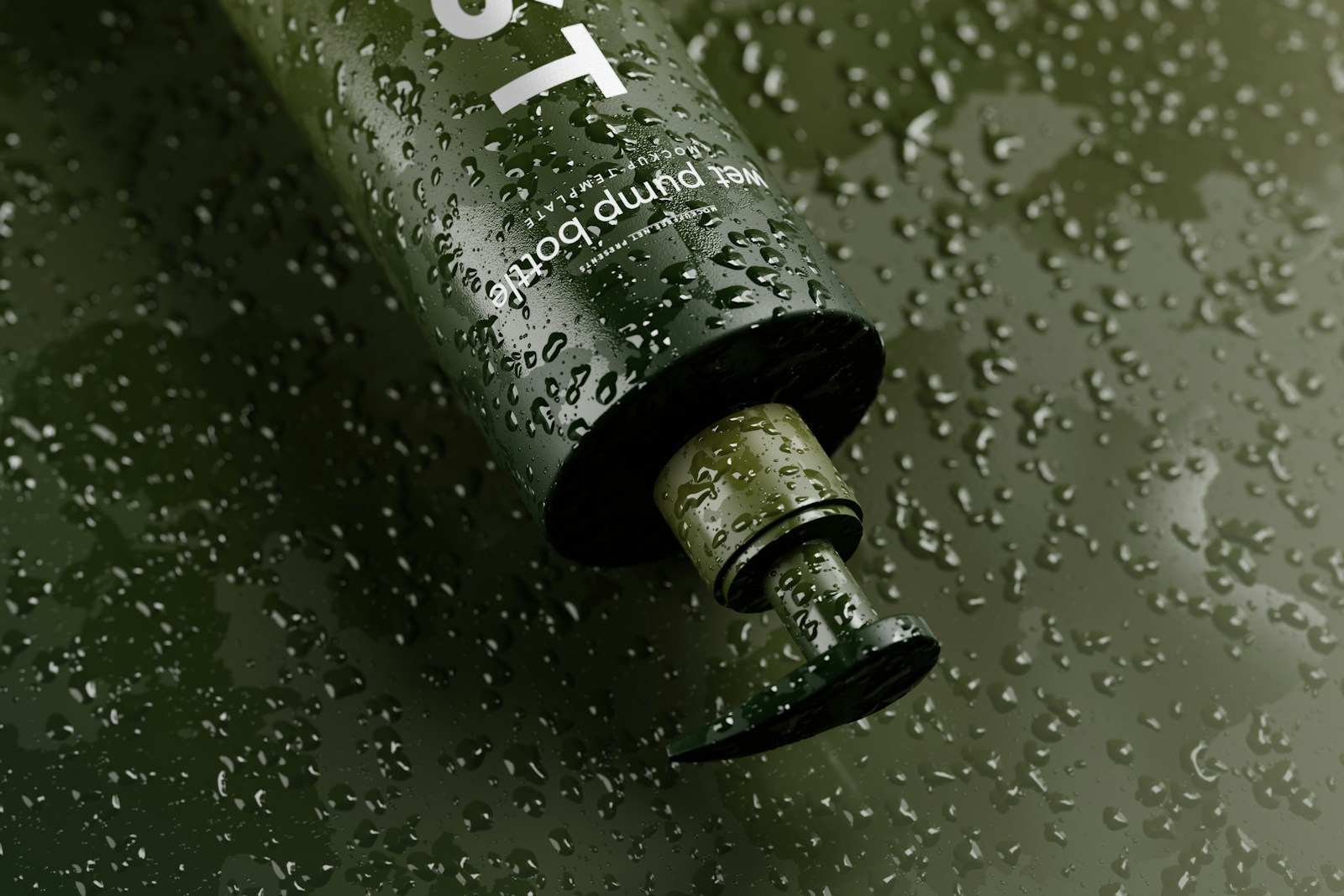
Anti-dandruff shampoo
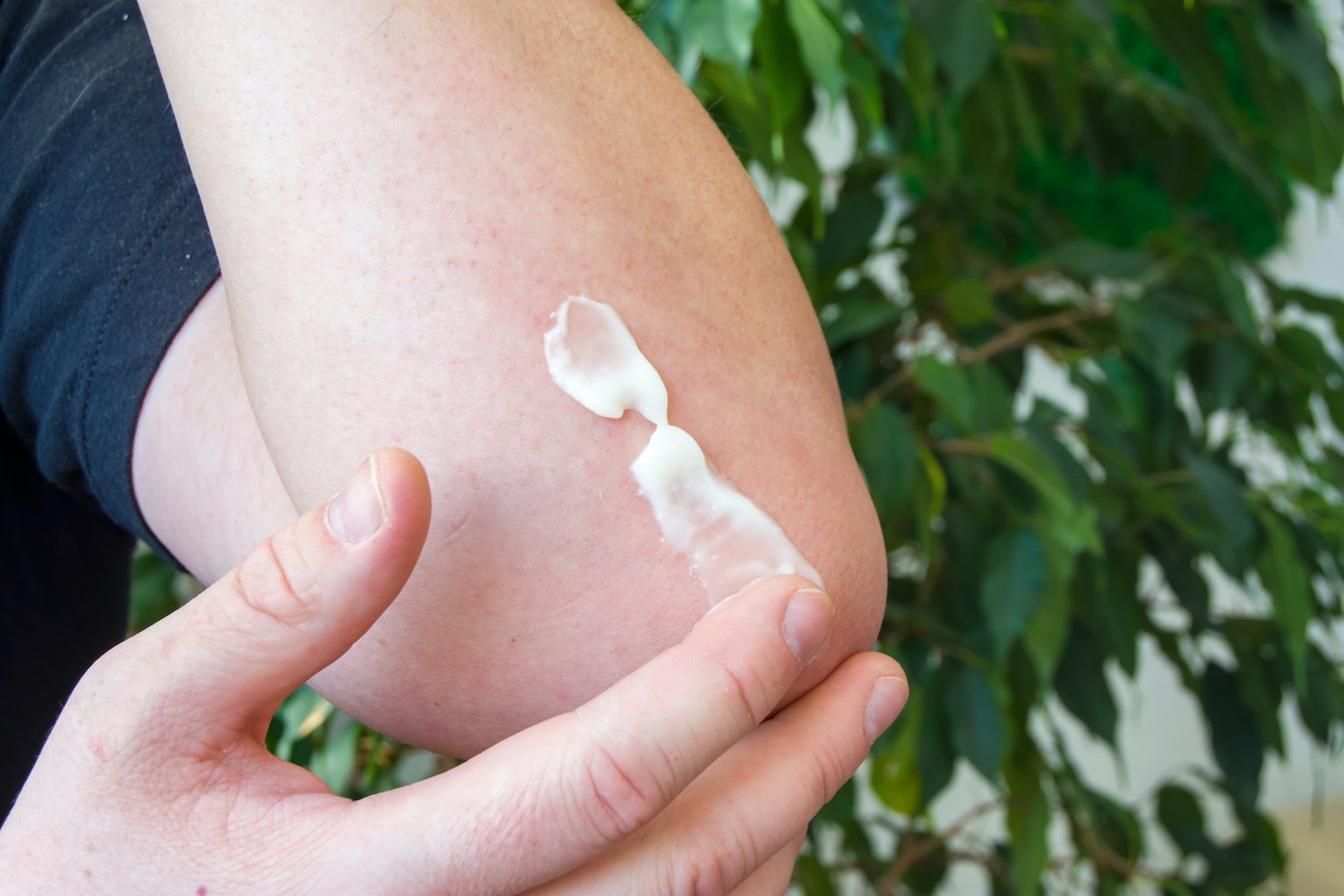
Antibacterial ointment
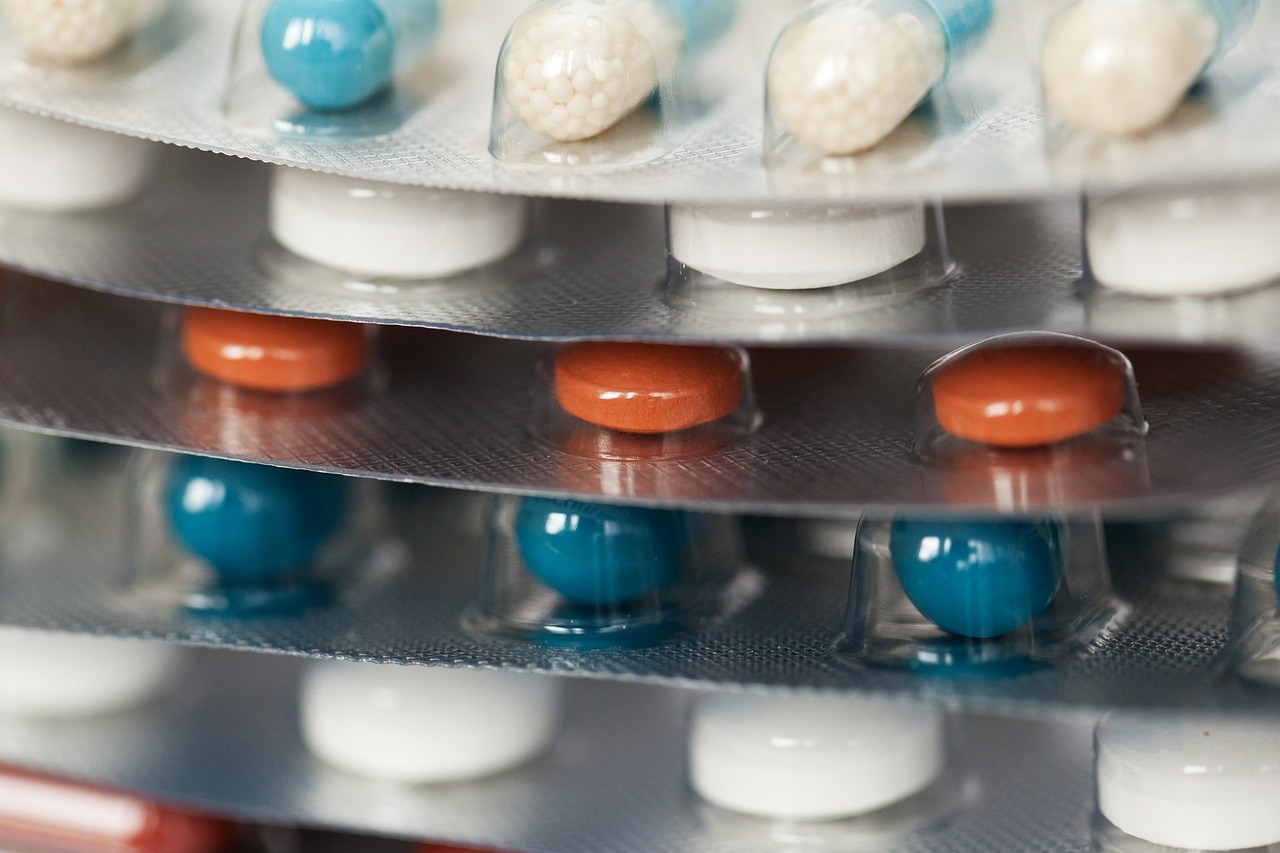
Antibiotics
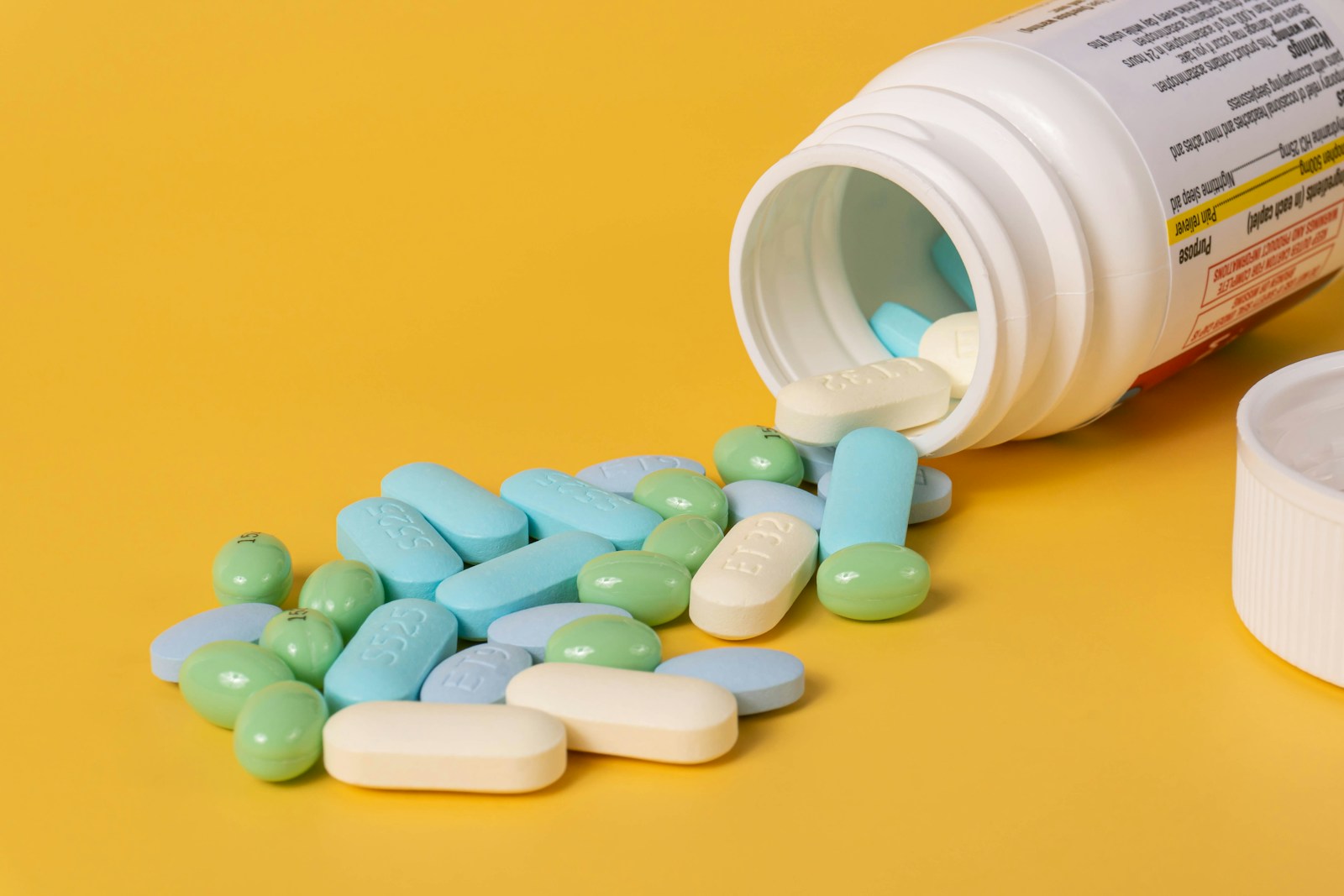
Antihistamine tablets
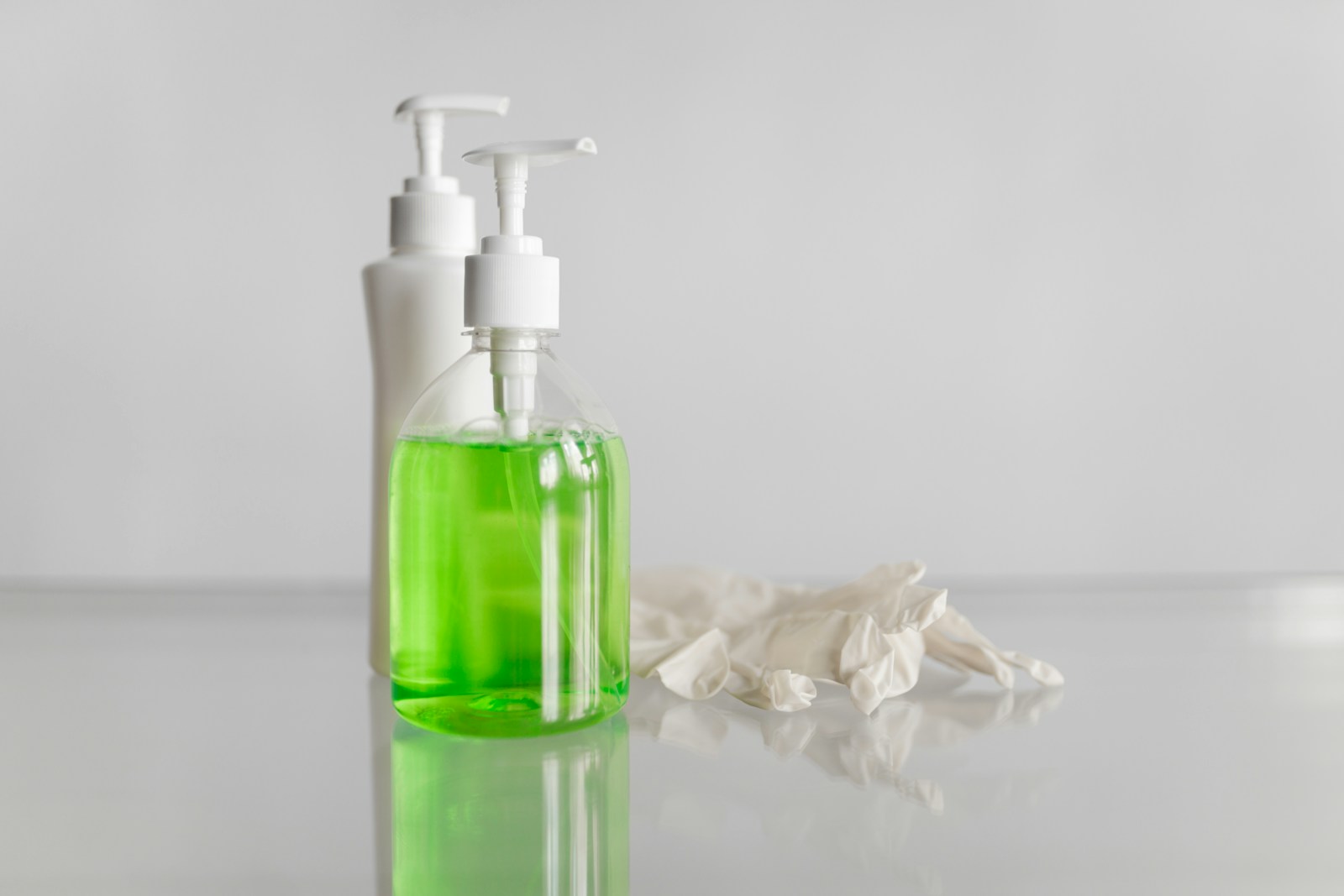
Antiseptic solutions
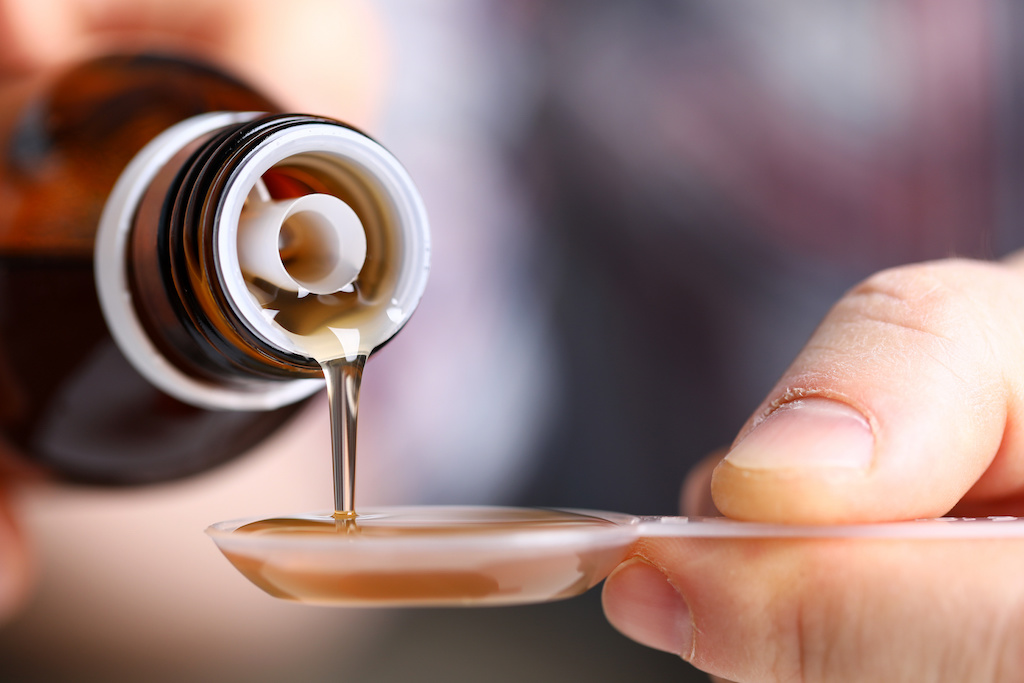
Api suspensions
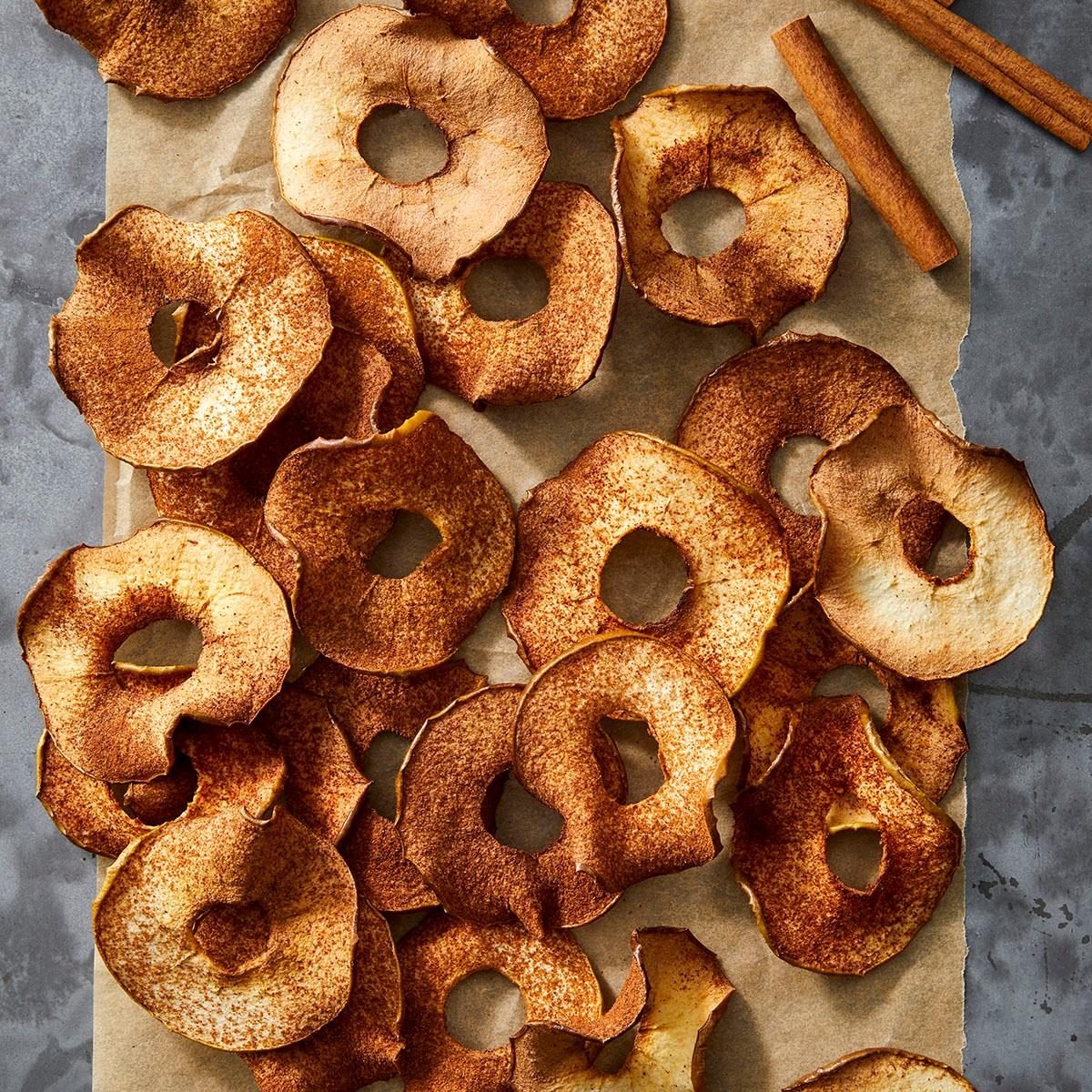
Apple chips
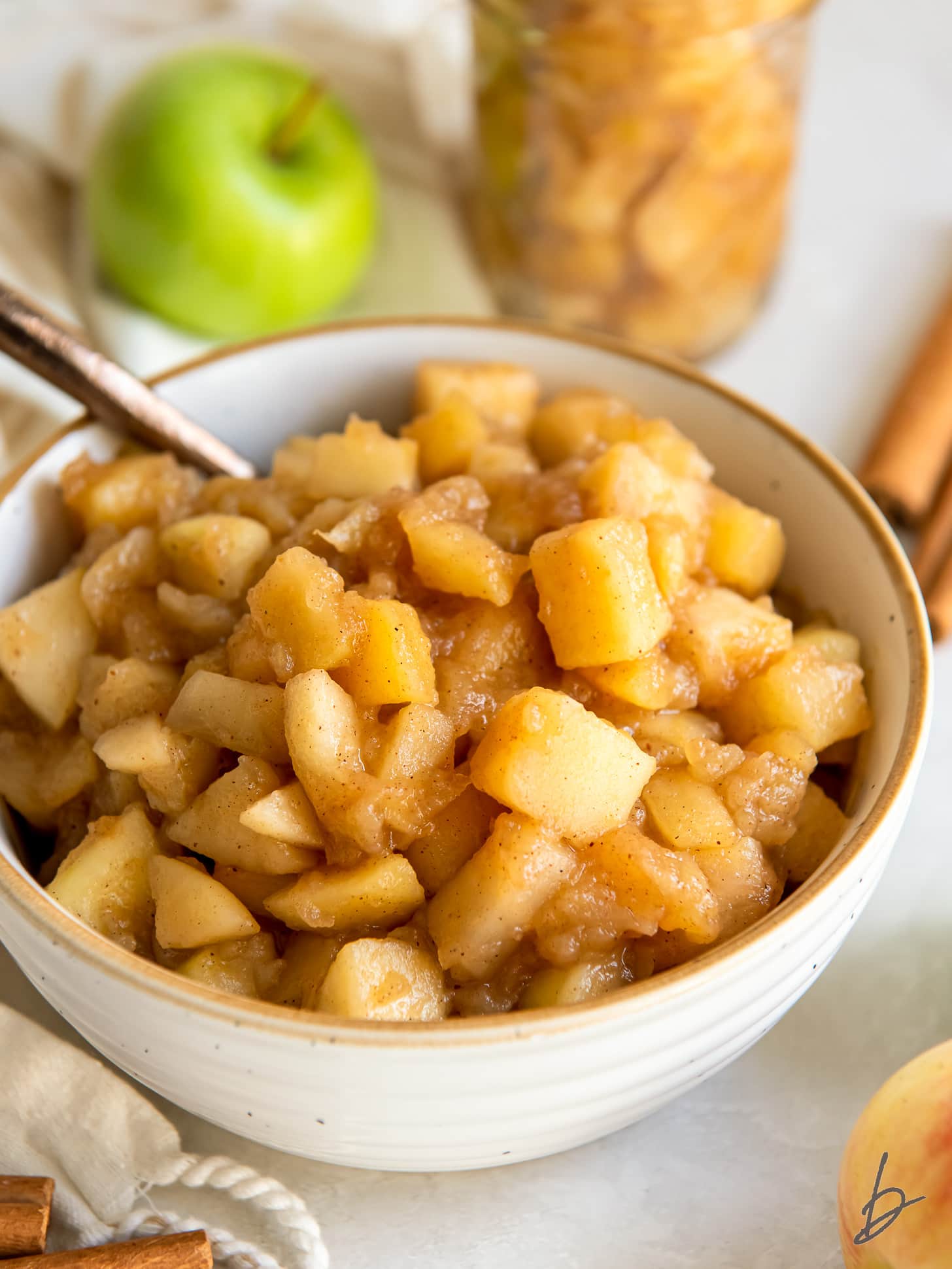
Apple compote
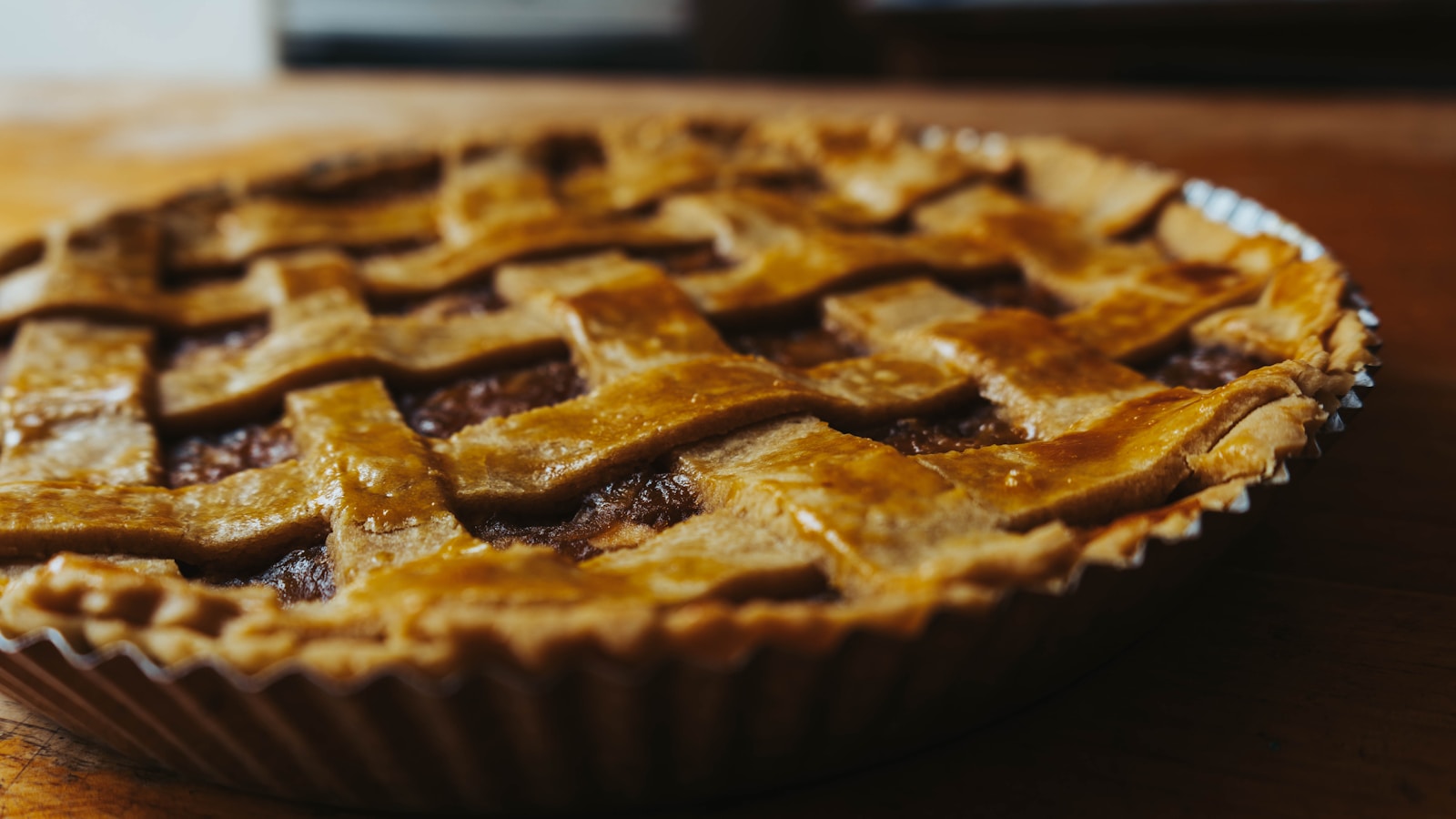
Apple pies
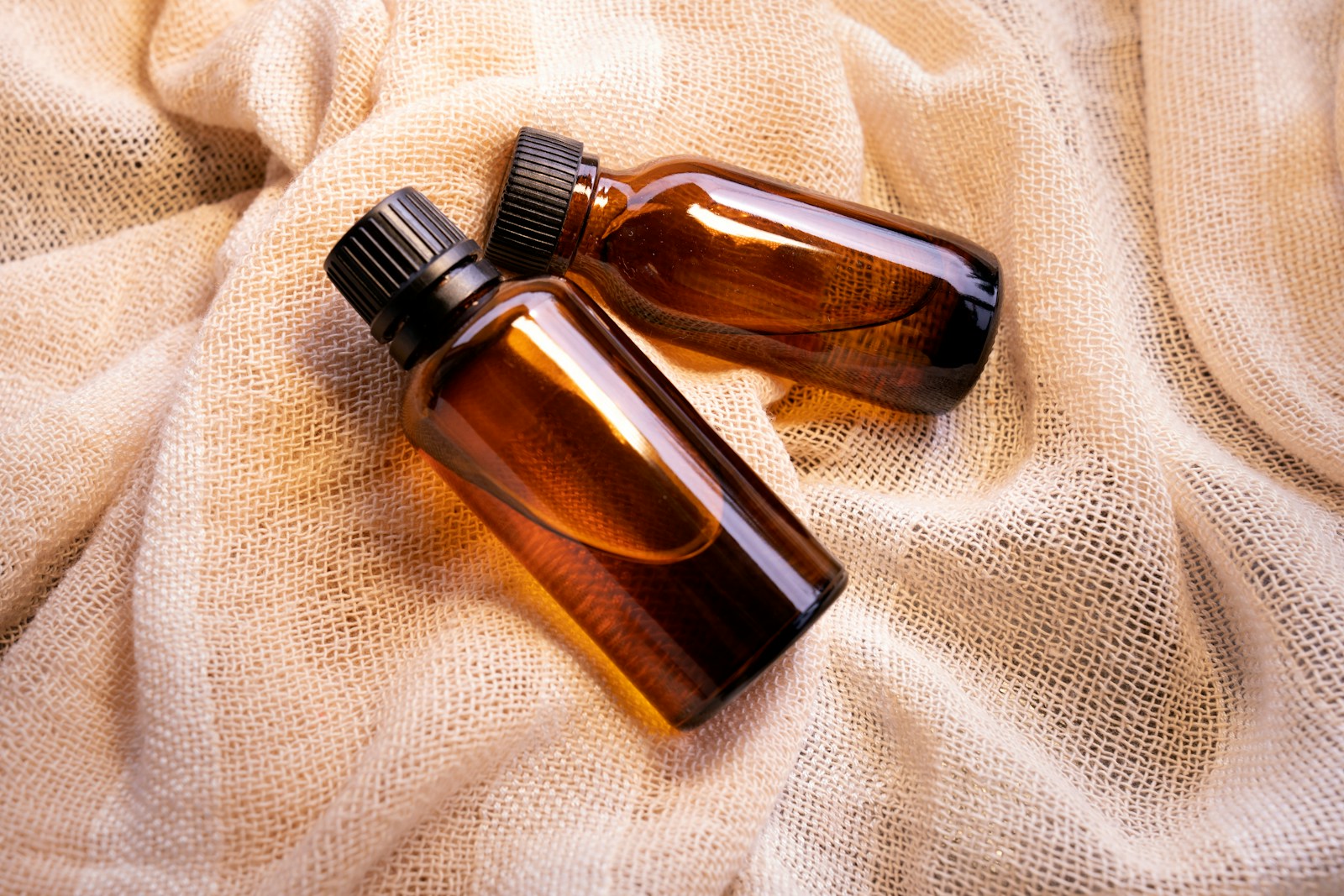
Aromatherapy oils
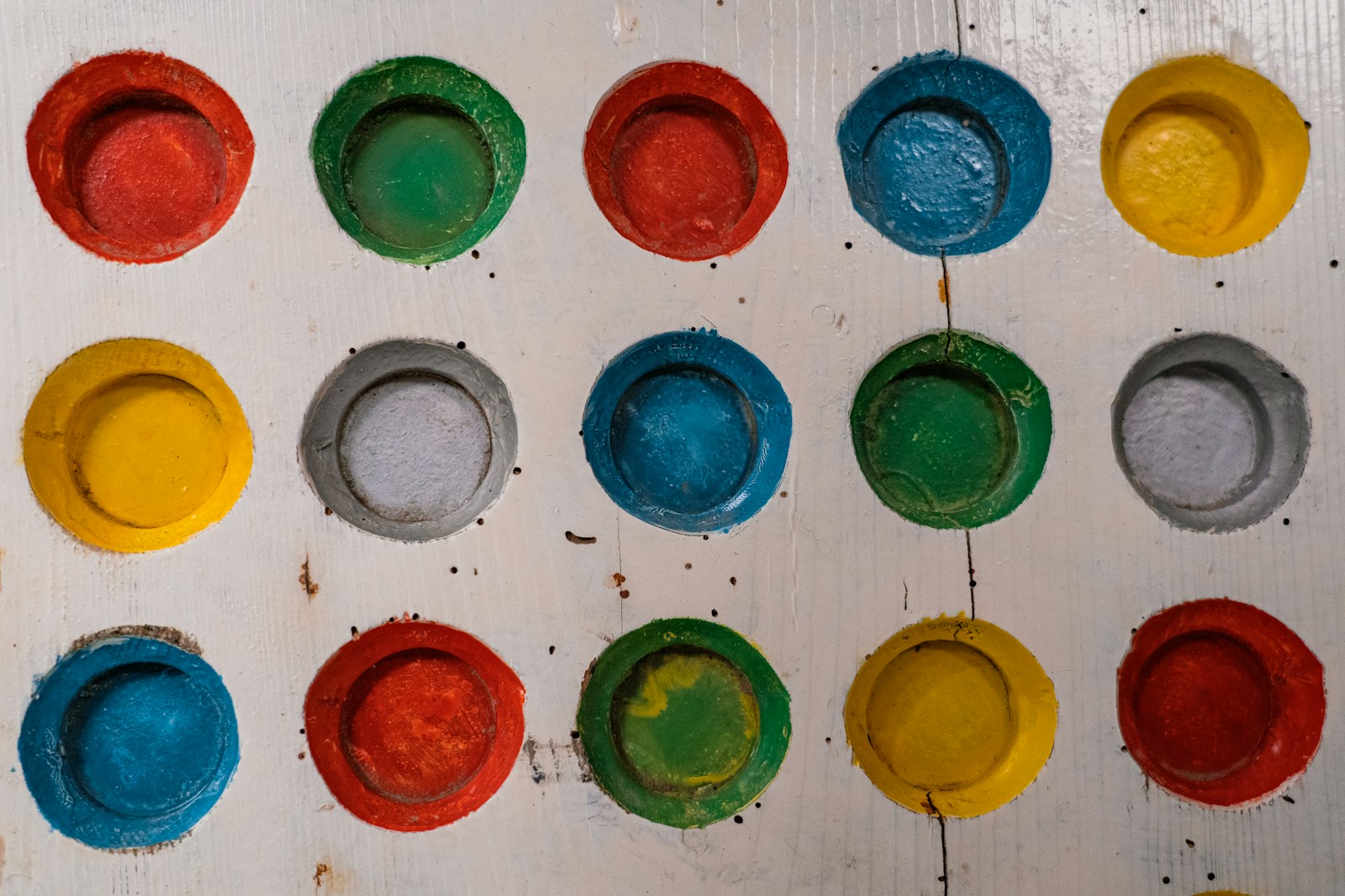
Artist colors
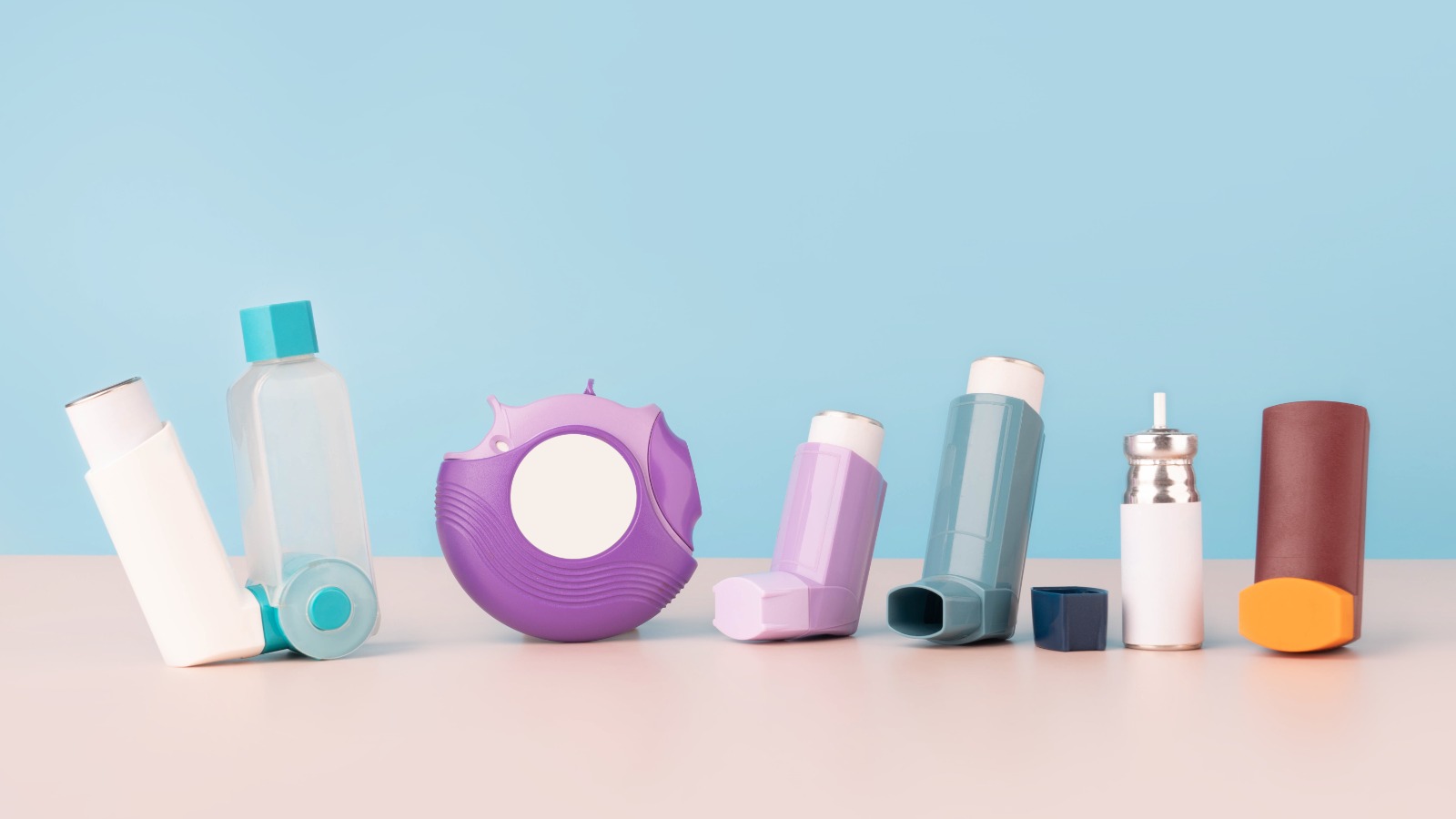
Asthma inhalers
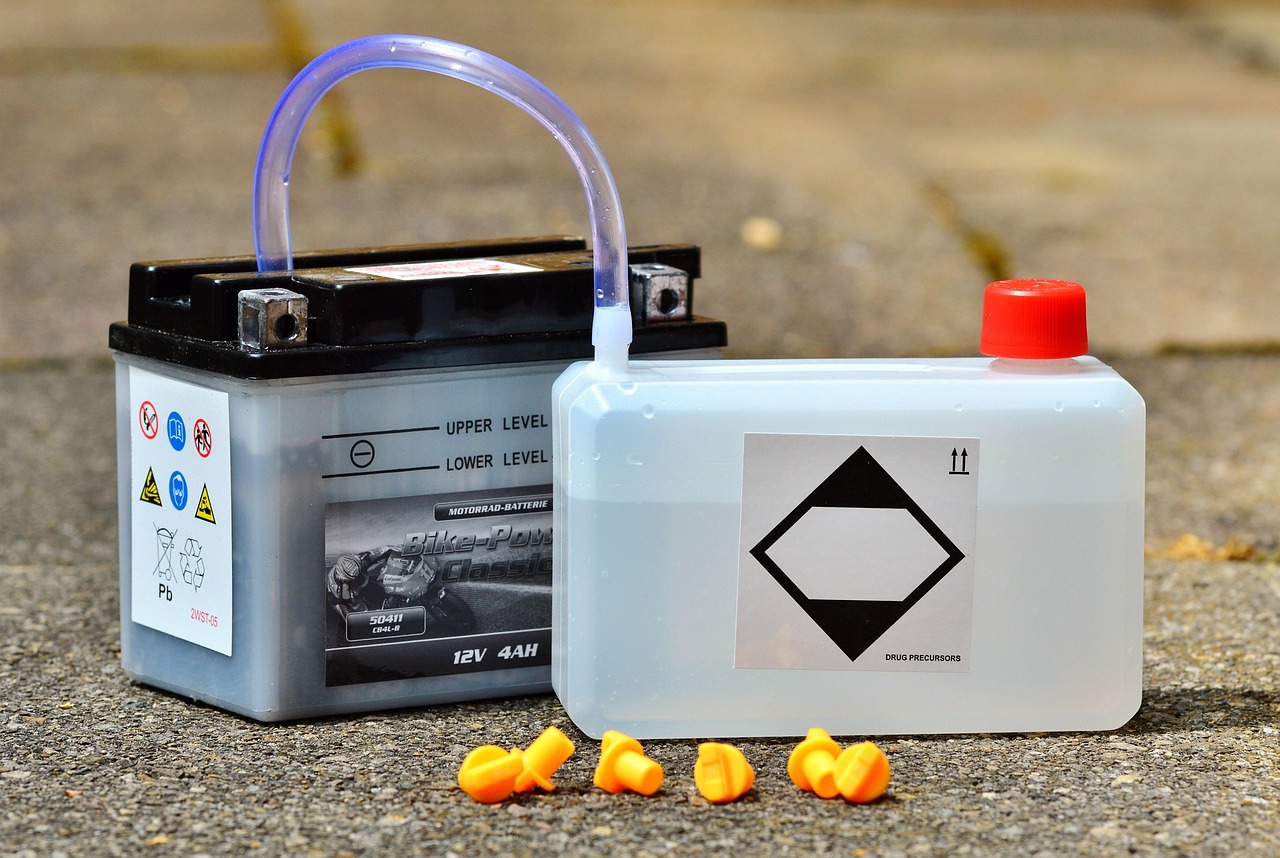
Automotive batteries
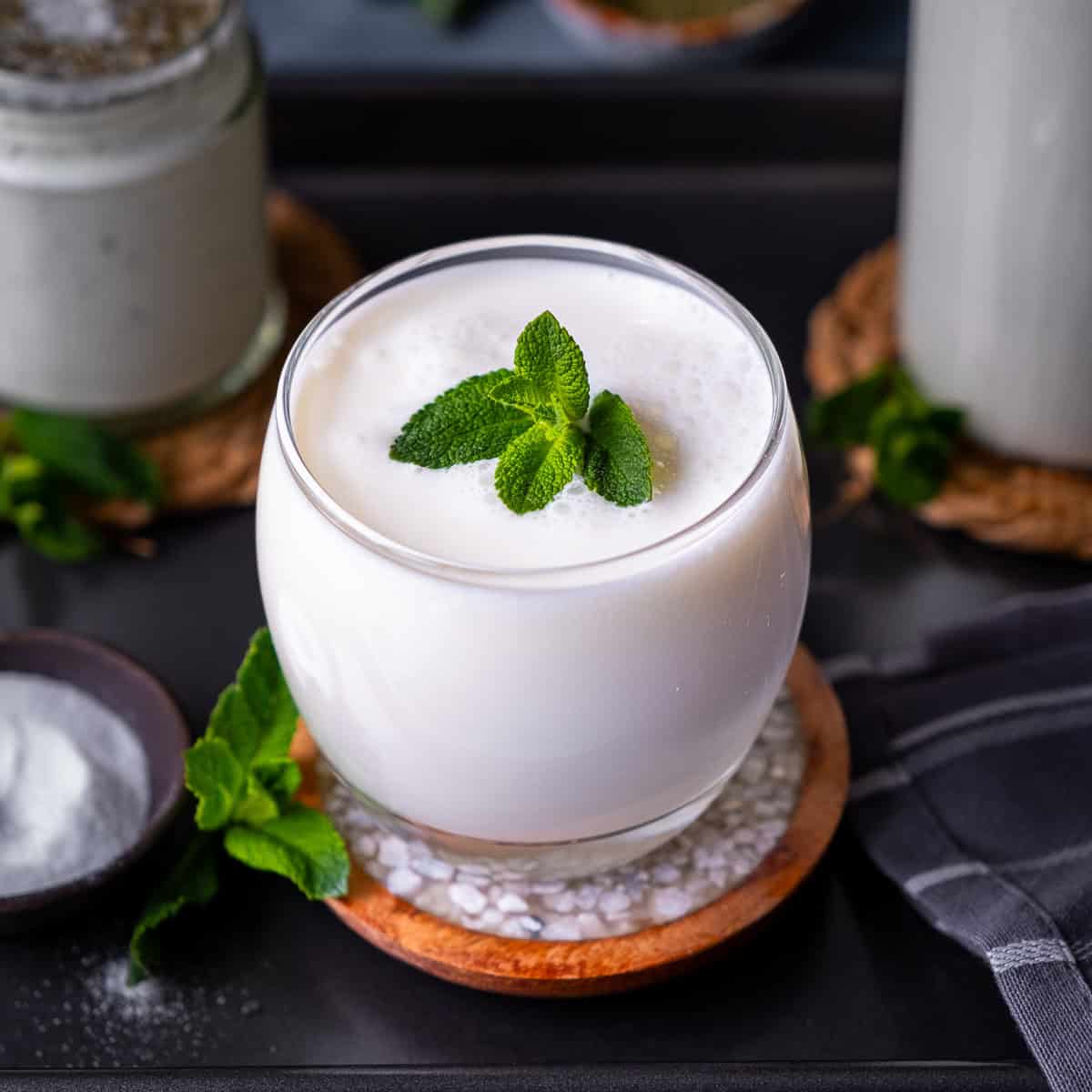
Ayran
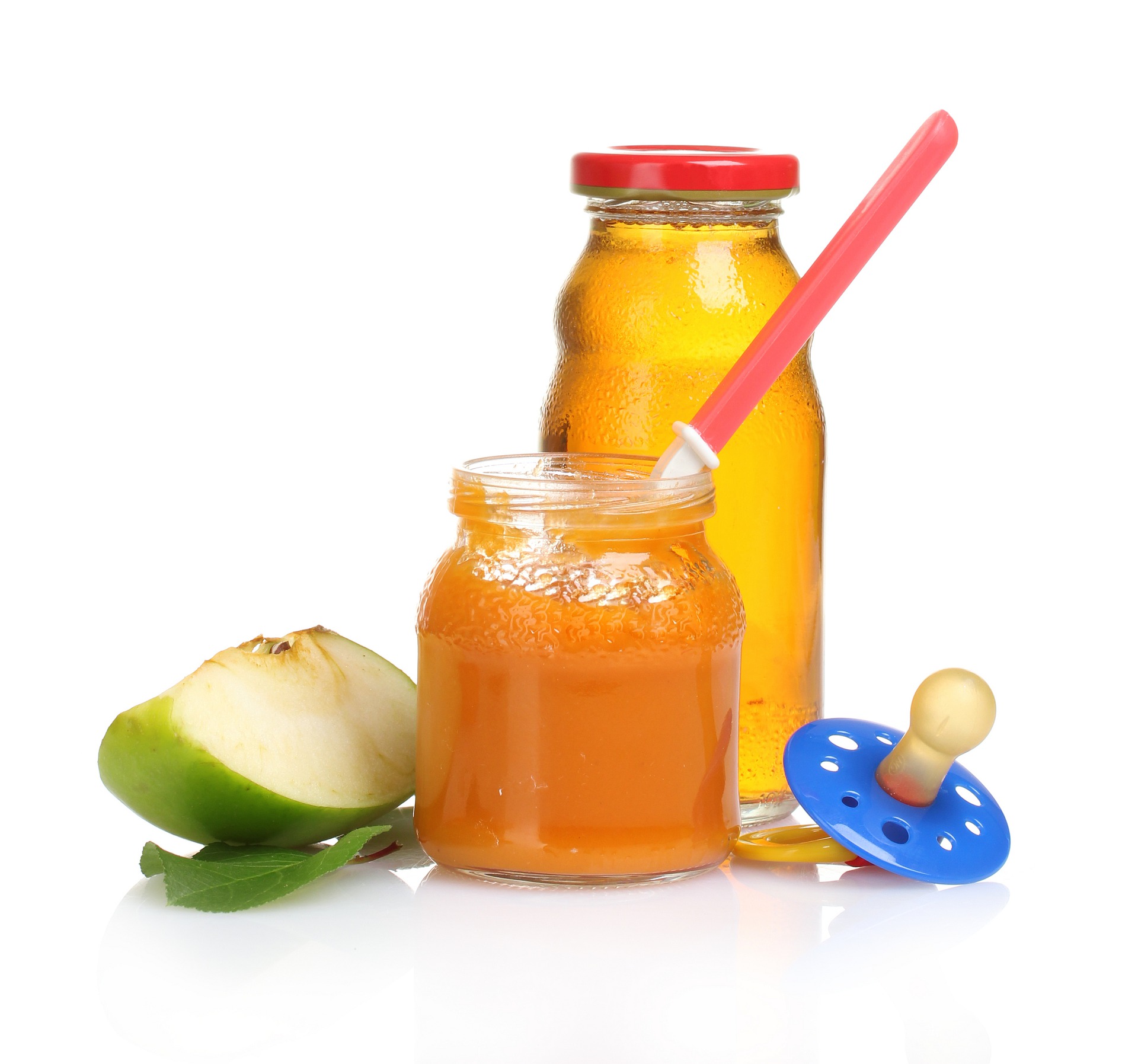
Baby Food
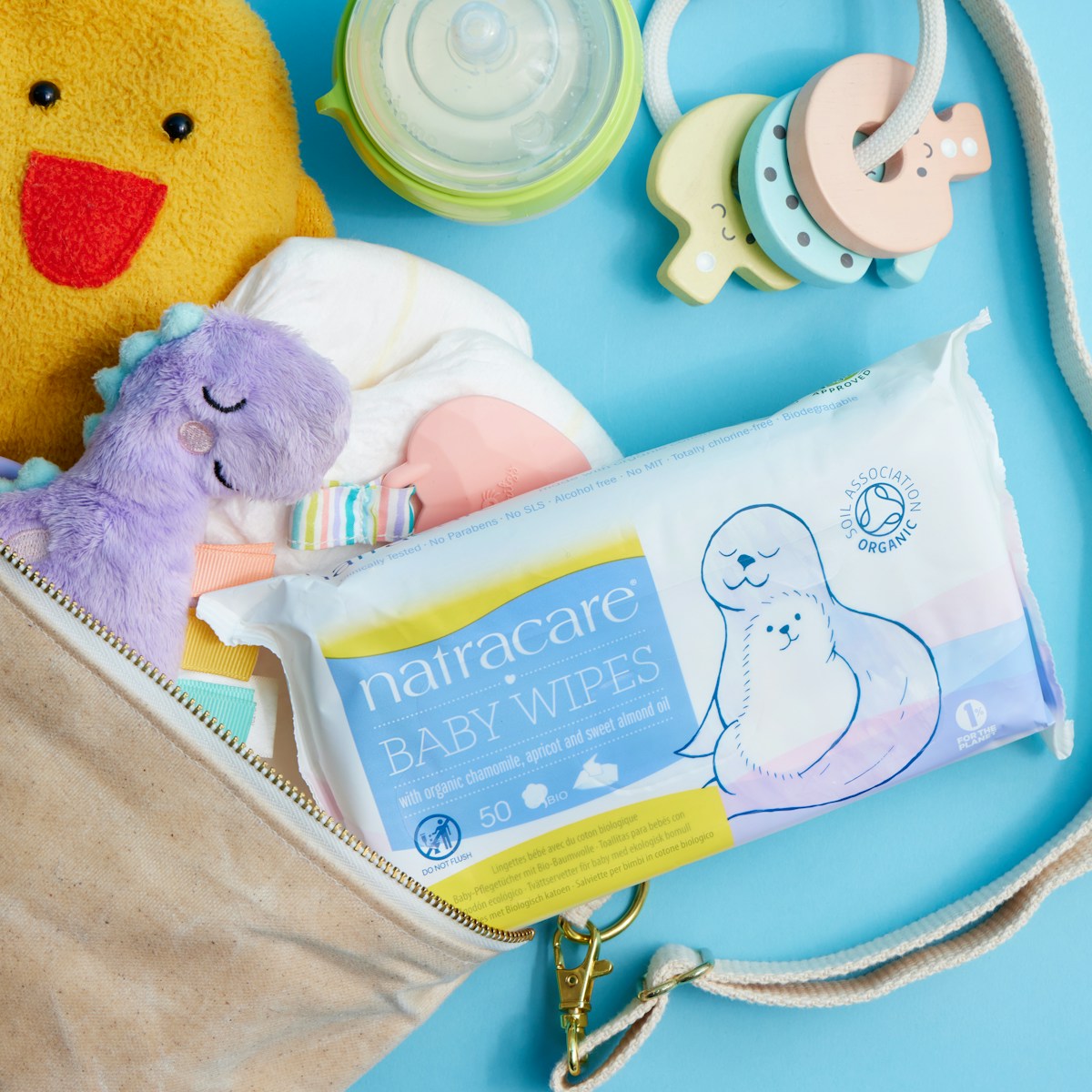
Baby wipes
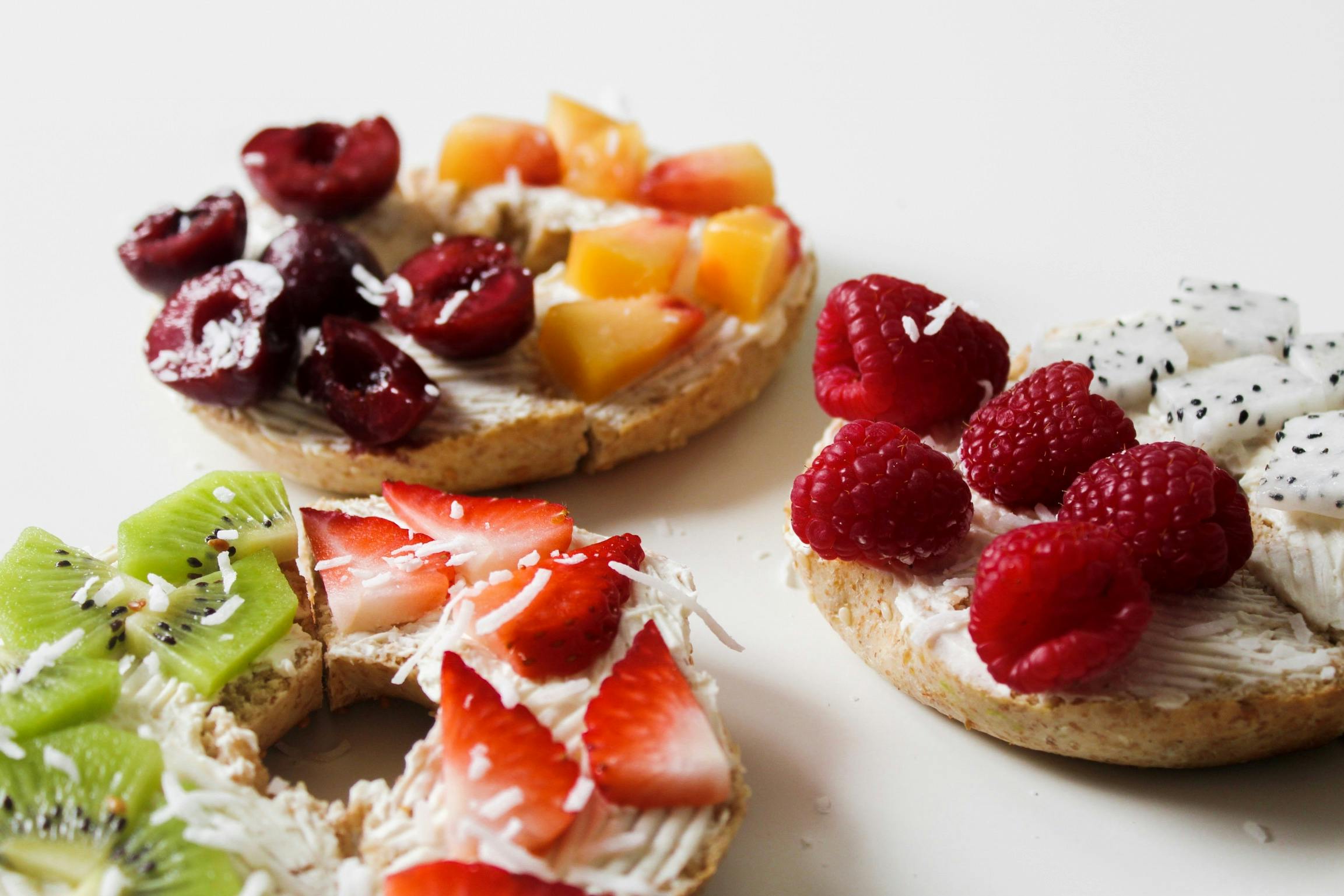
Bagels
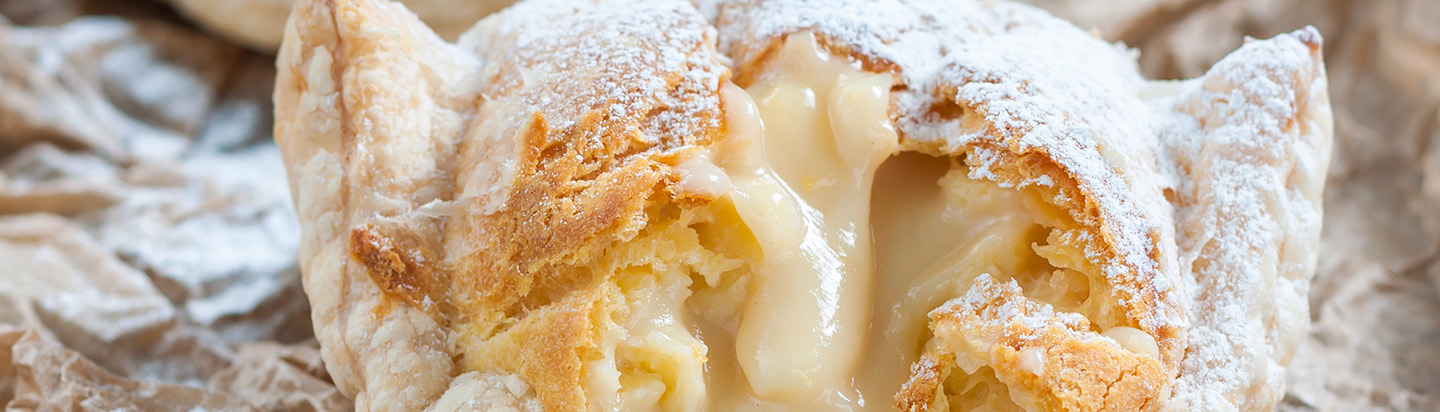
Bakery fillings
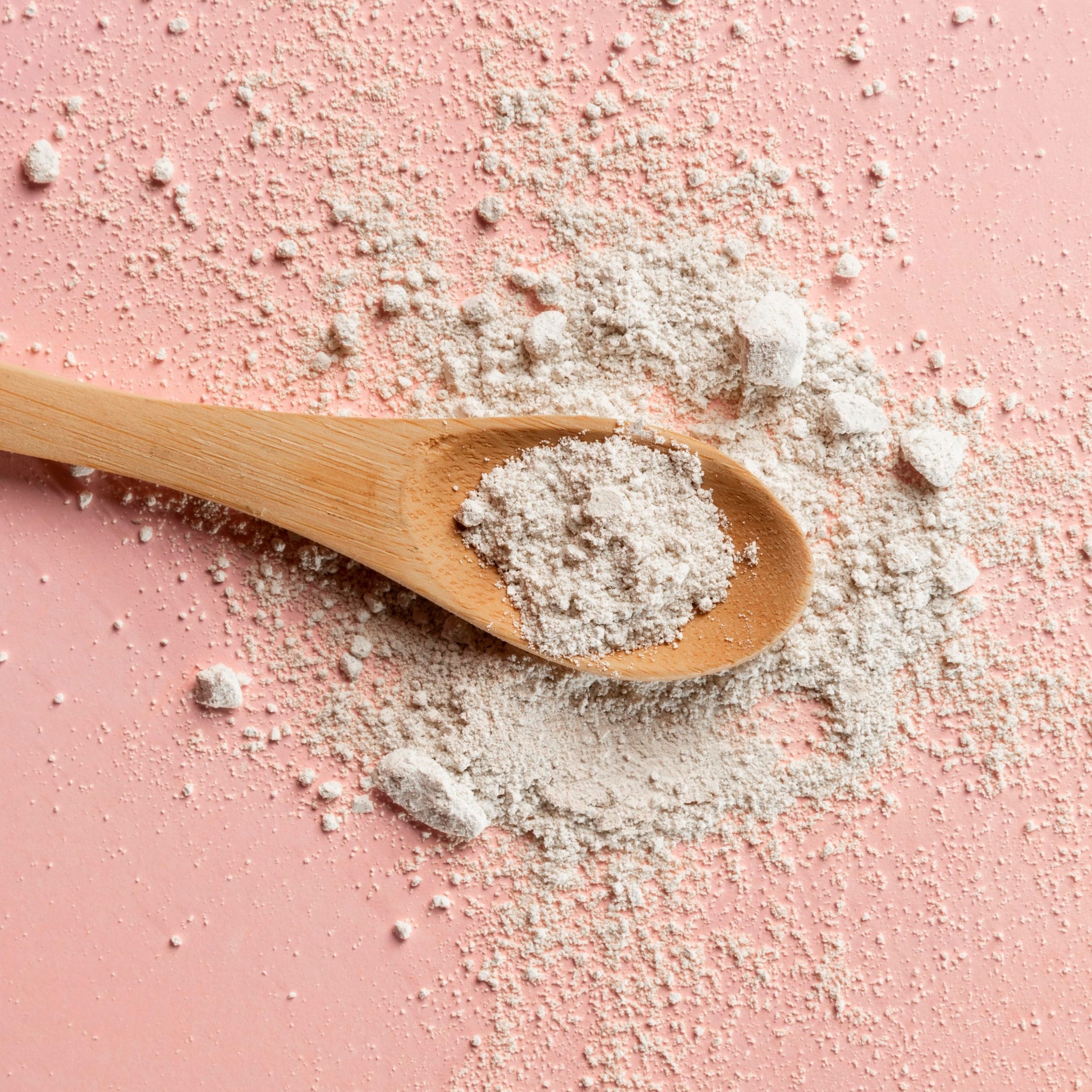
Baking powder
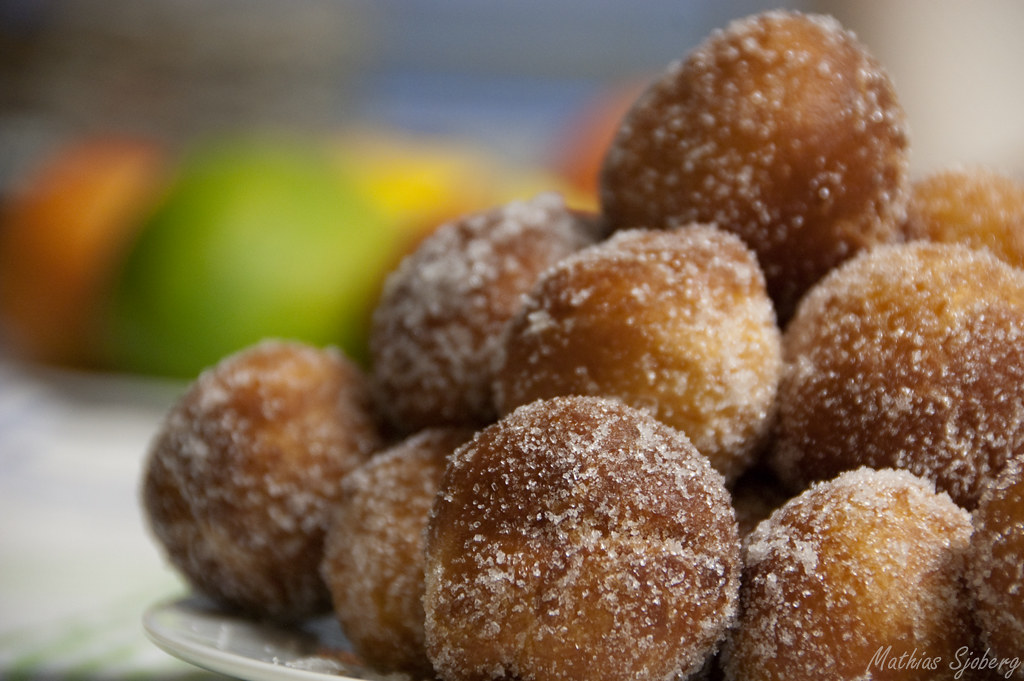
Ball donuts
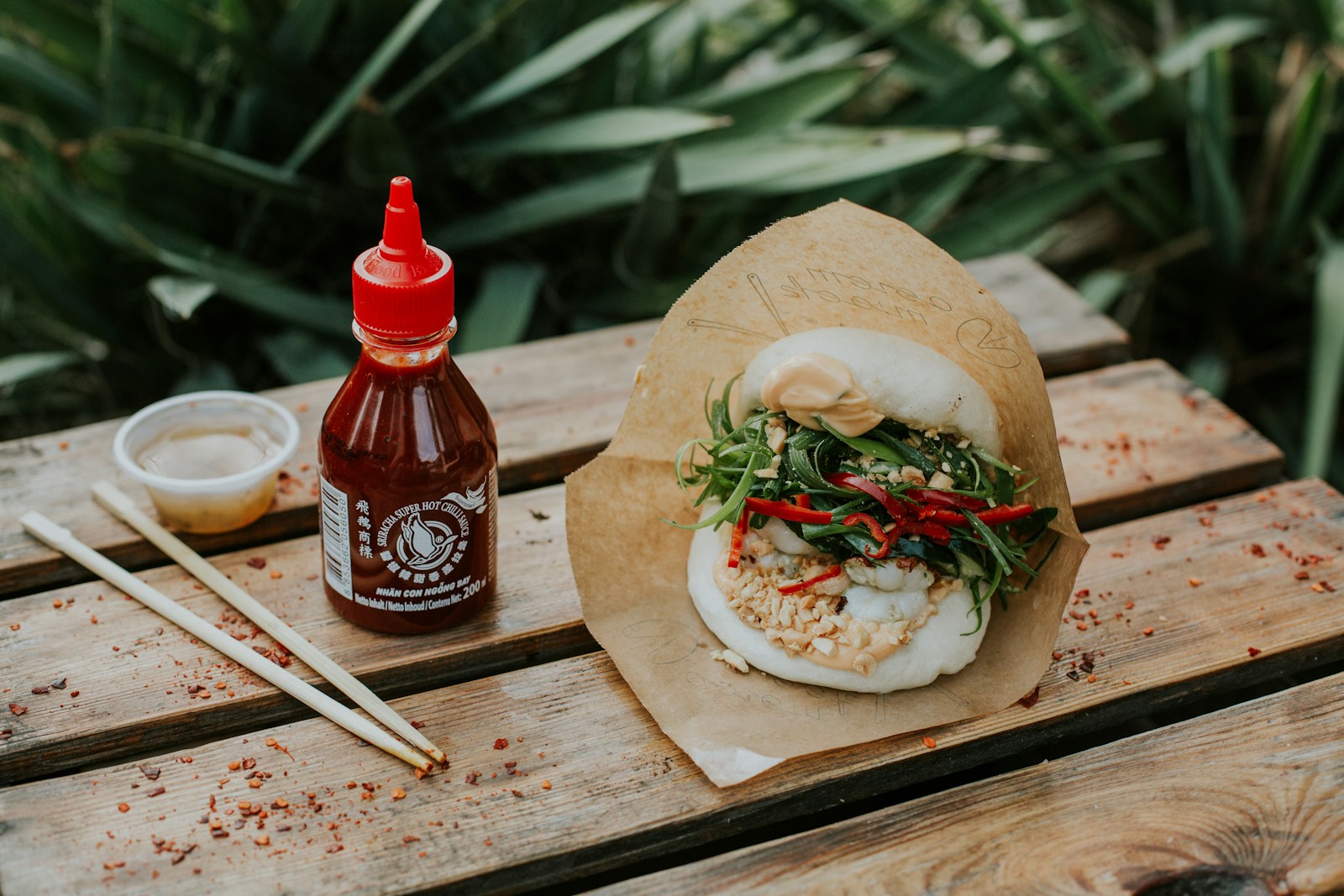
Bao
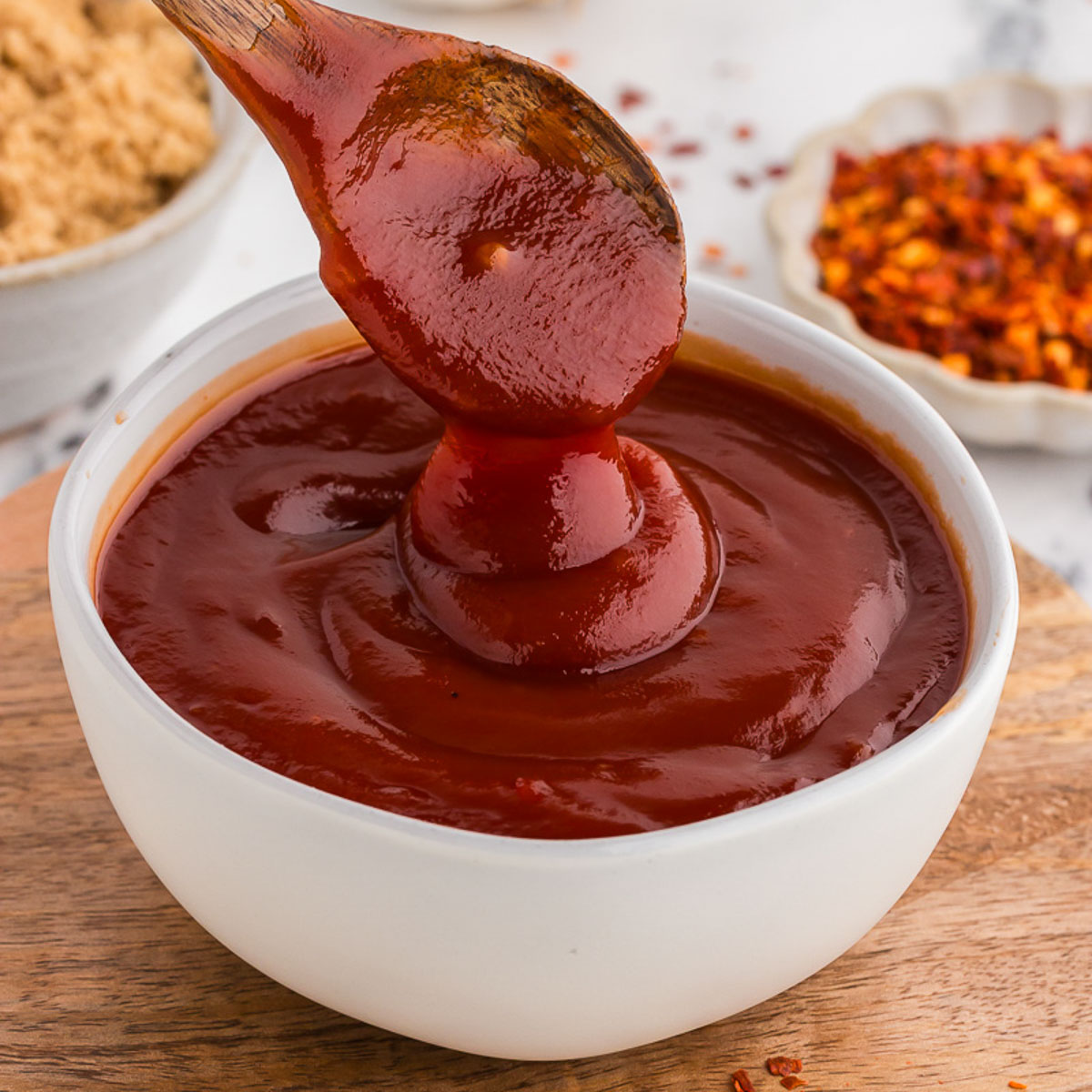
Barbecue sauce
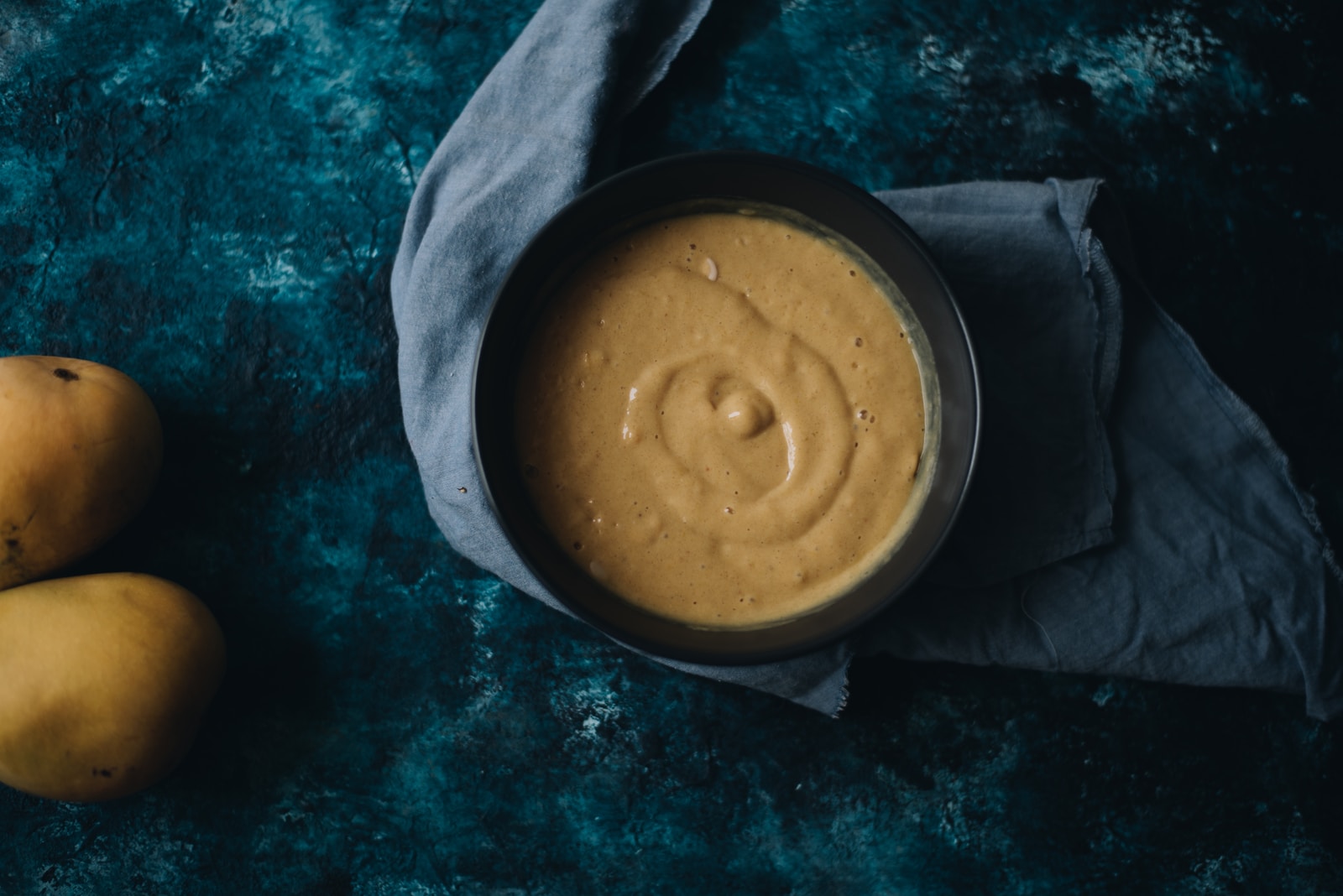
Batter
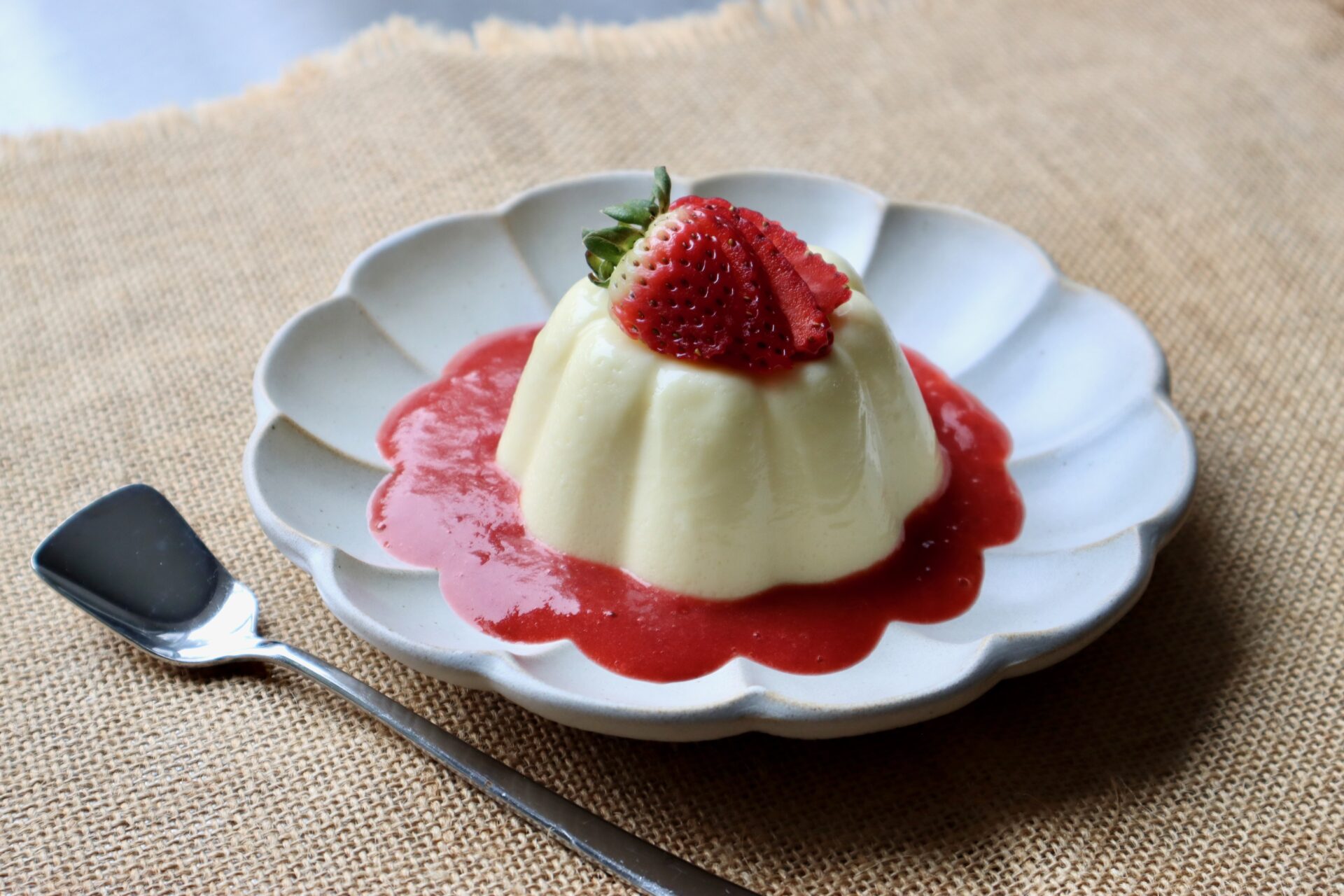
Bavarois
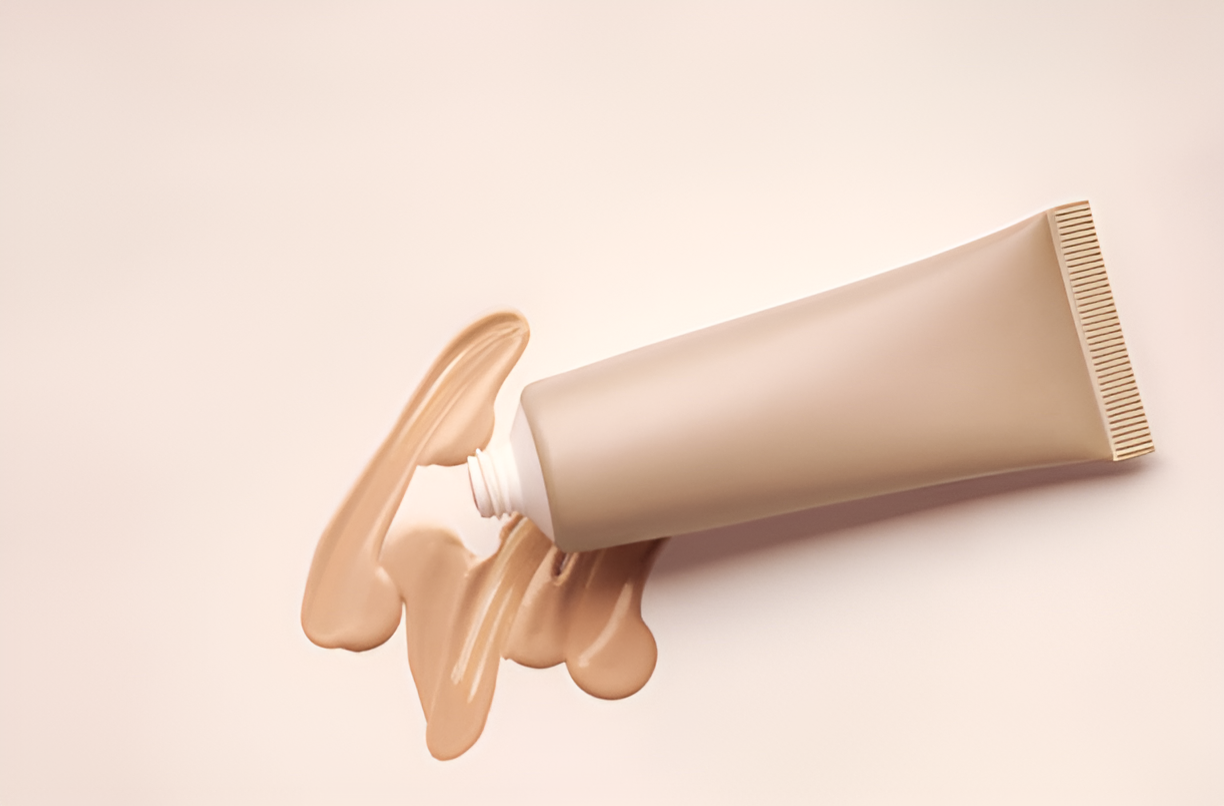
Bb cream
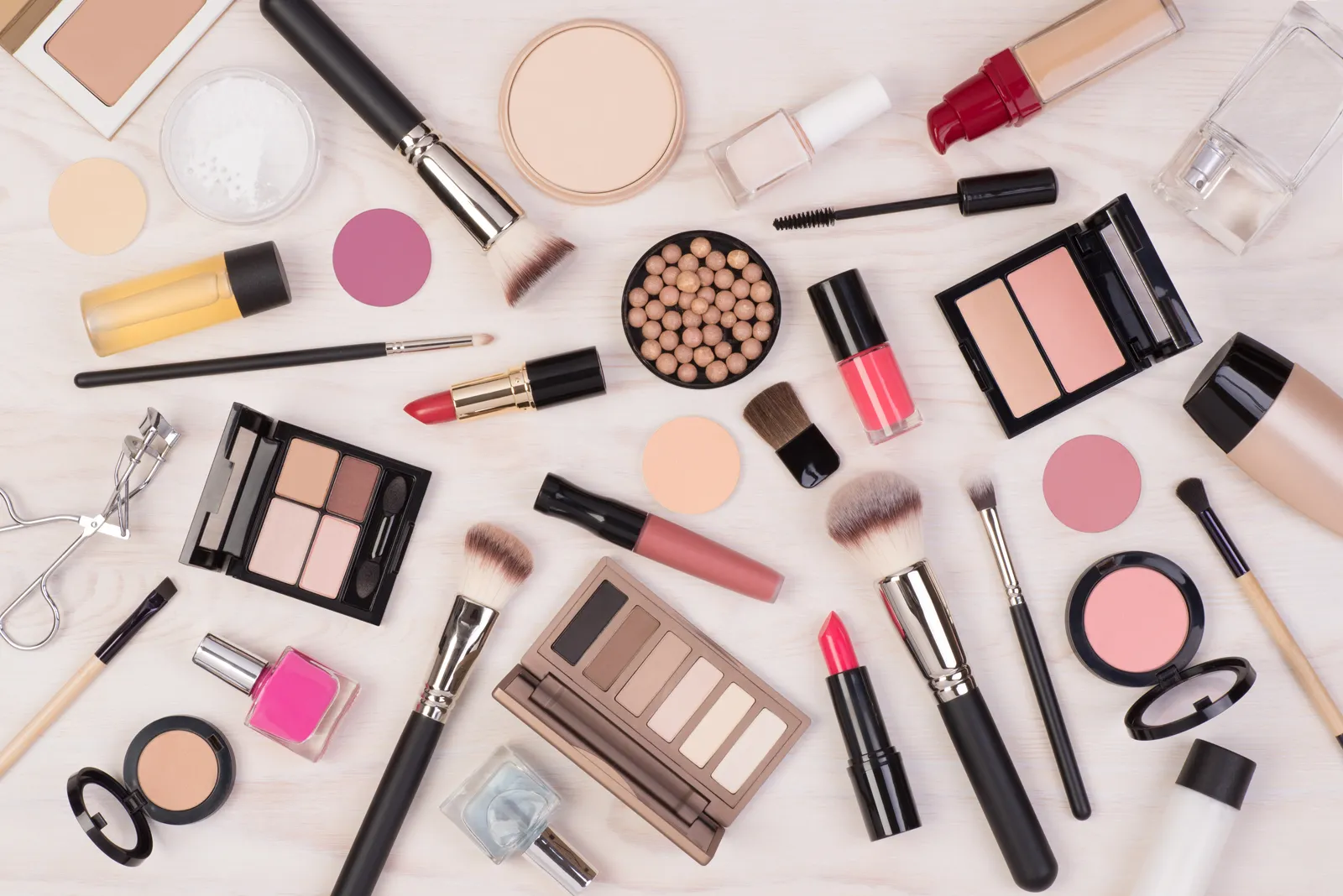
Beauty products
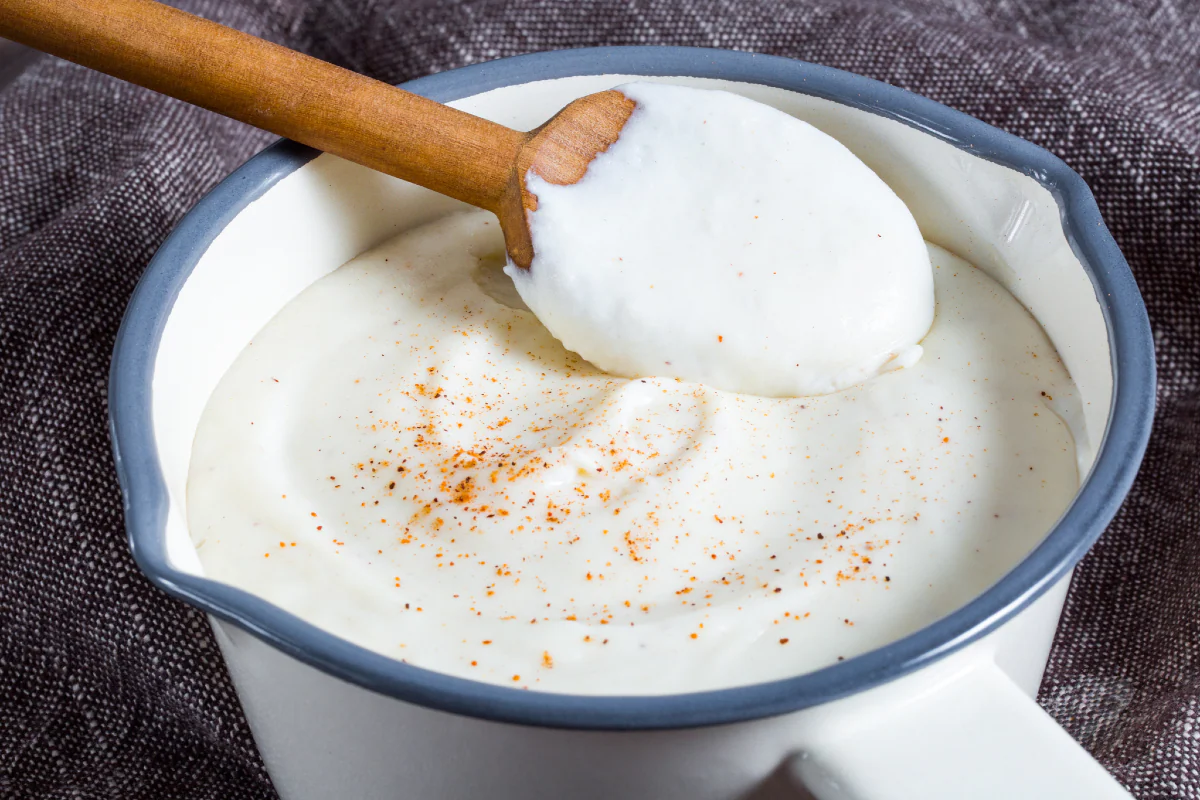
Bechamel sauce
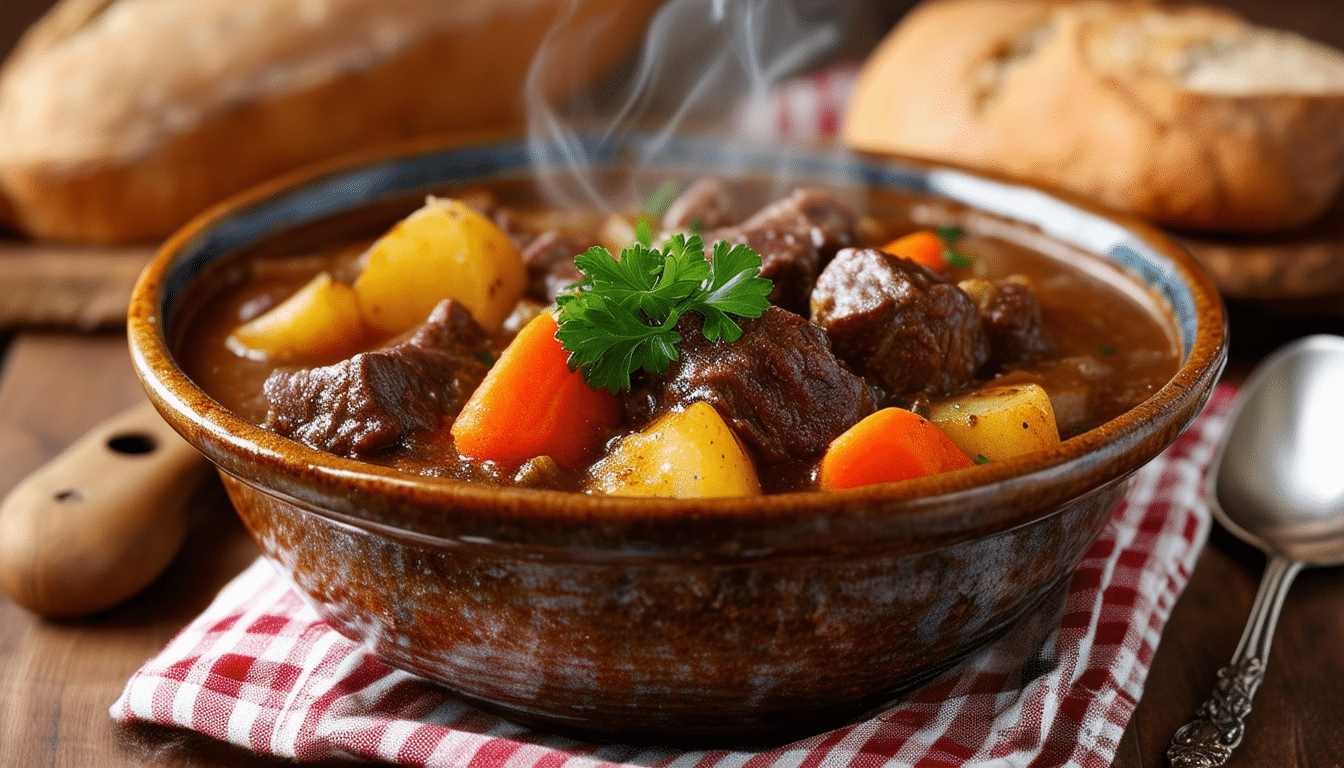
Beef gravy
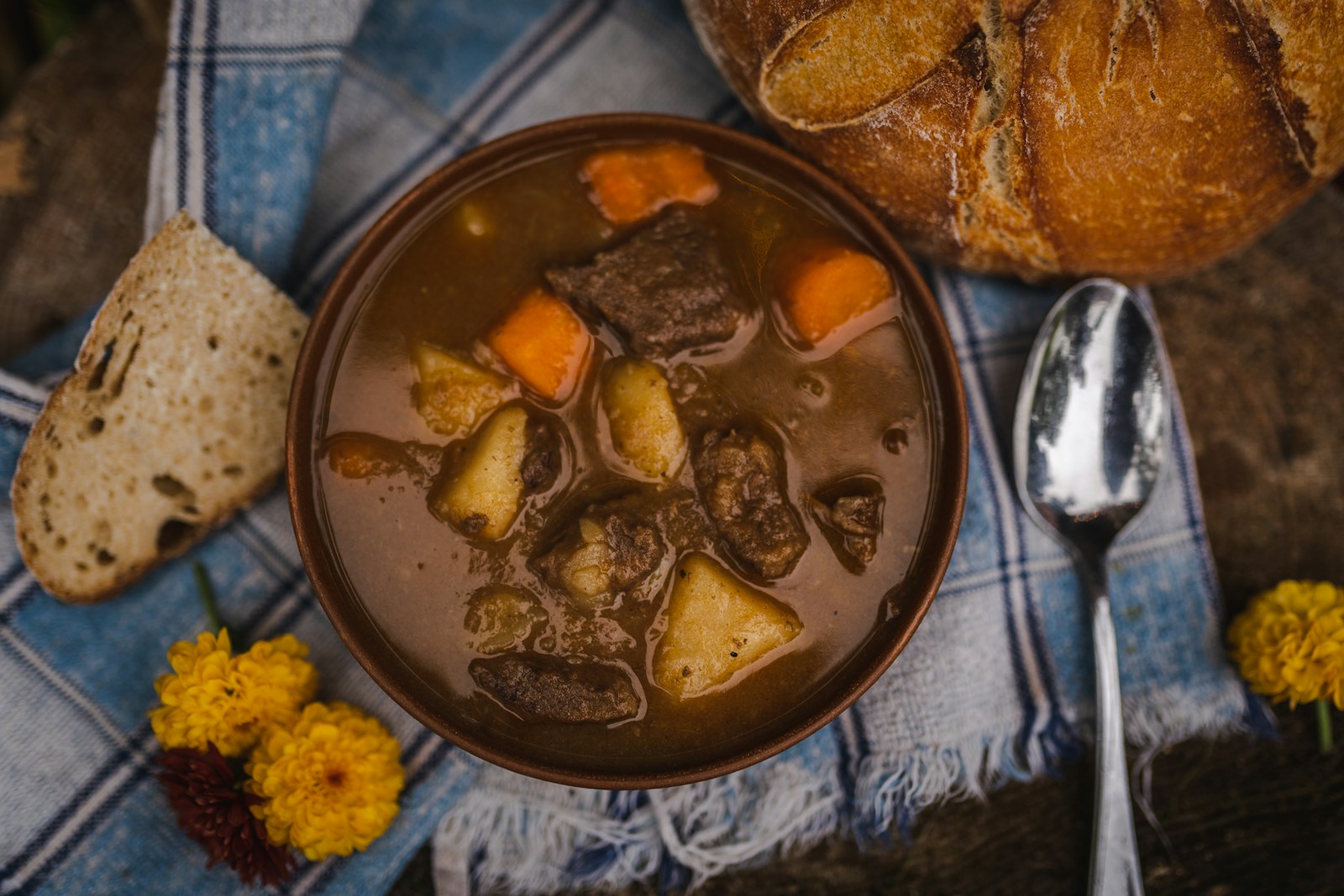
Beef stew
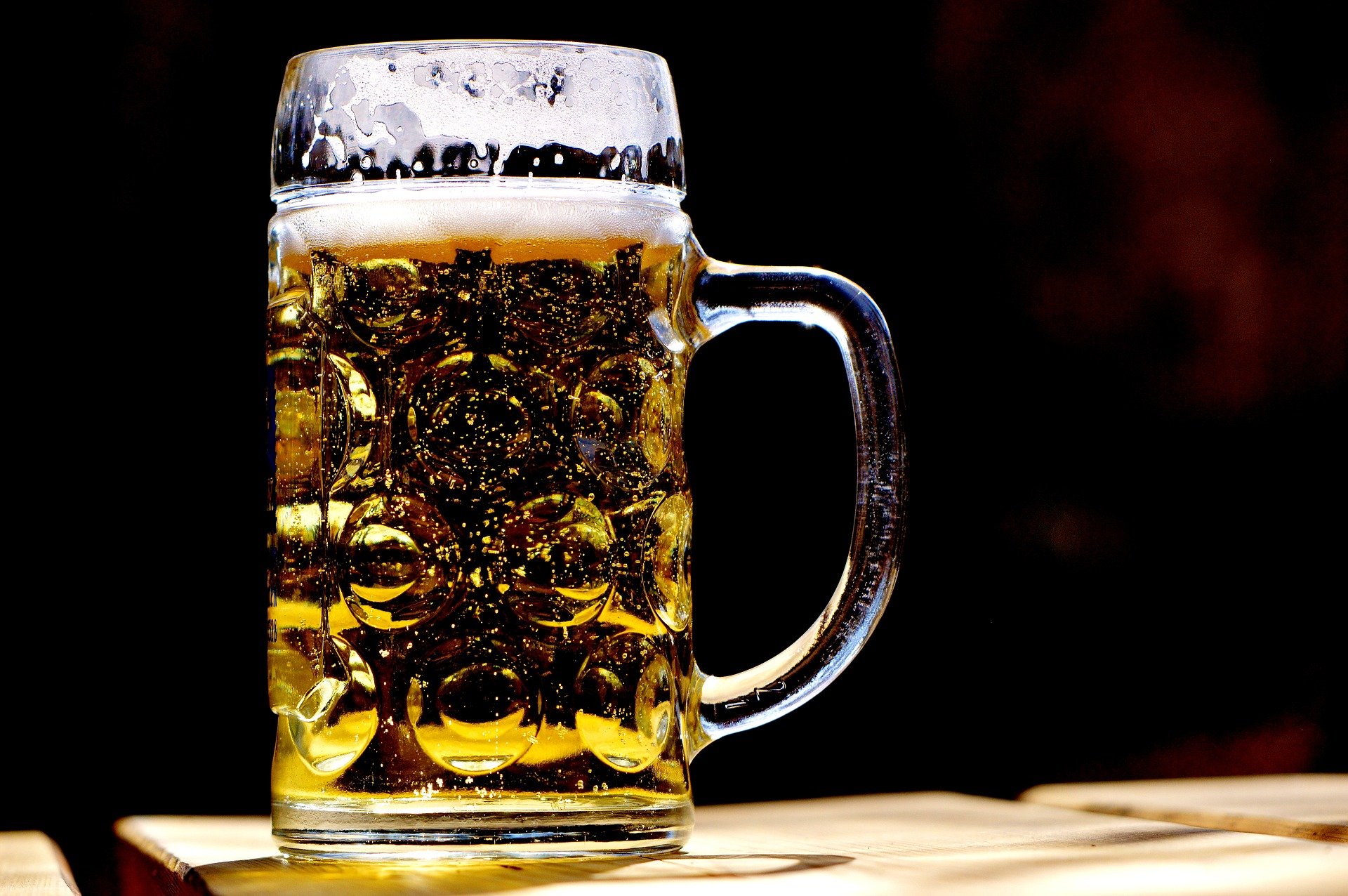
Beer
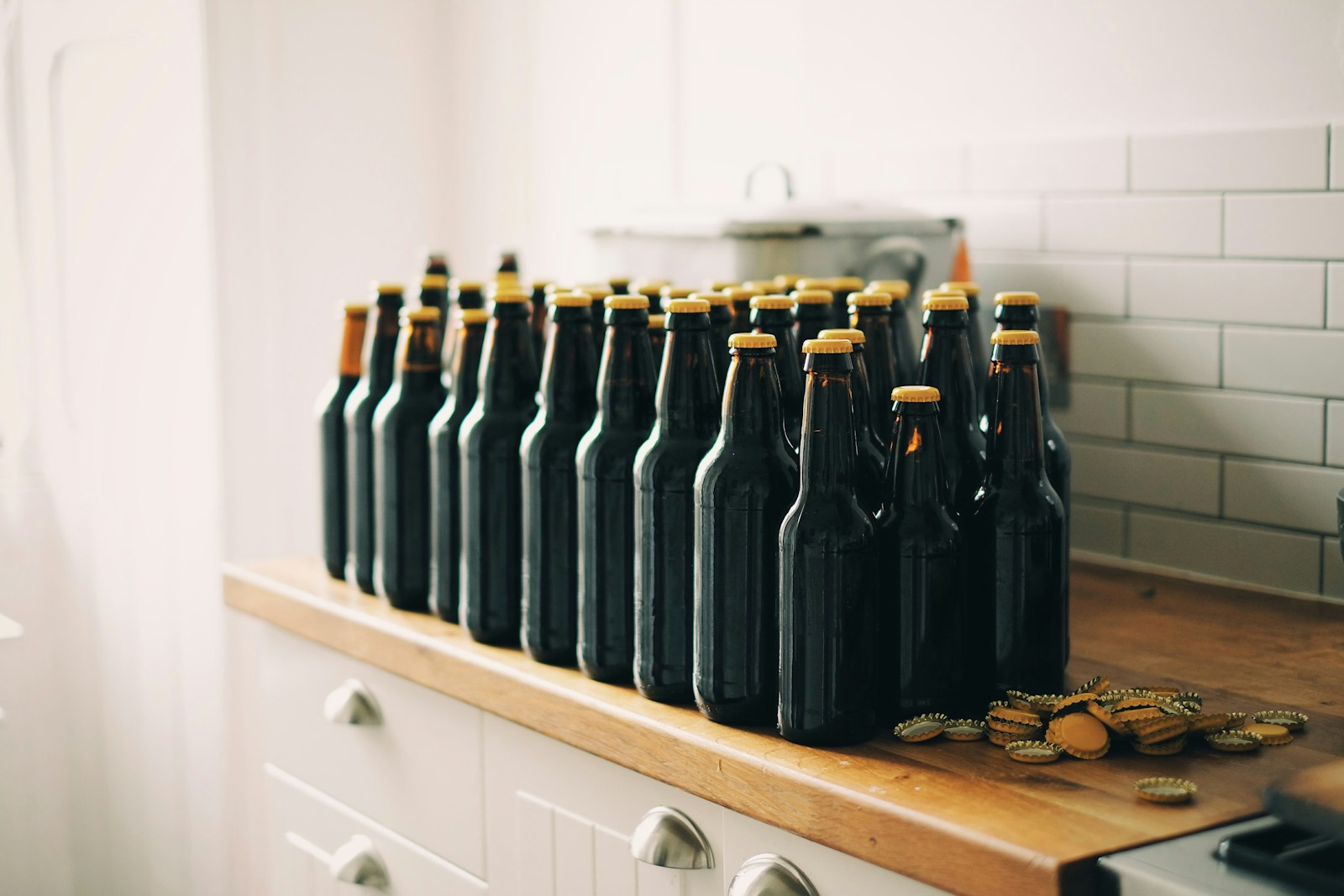
Beer bottles
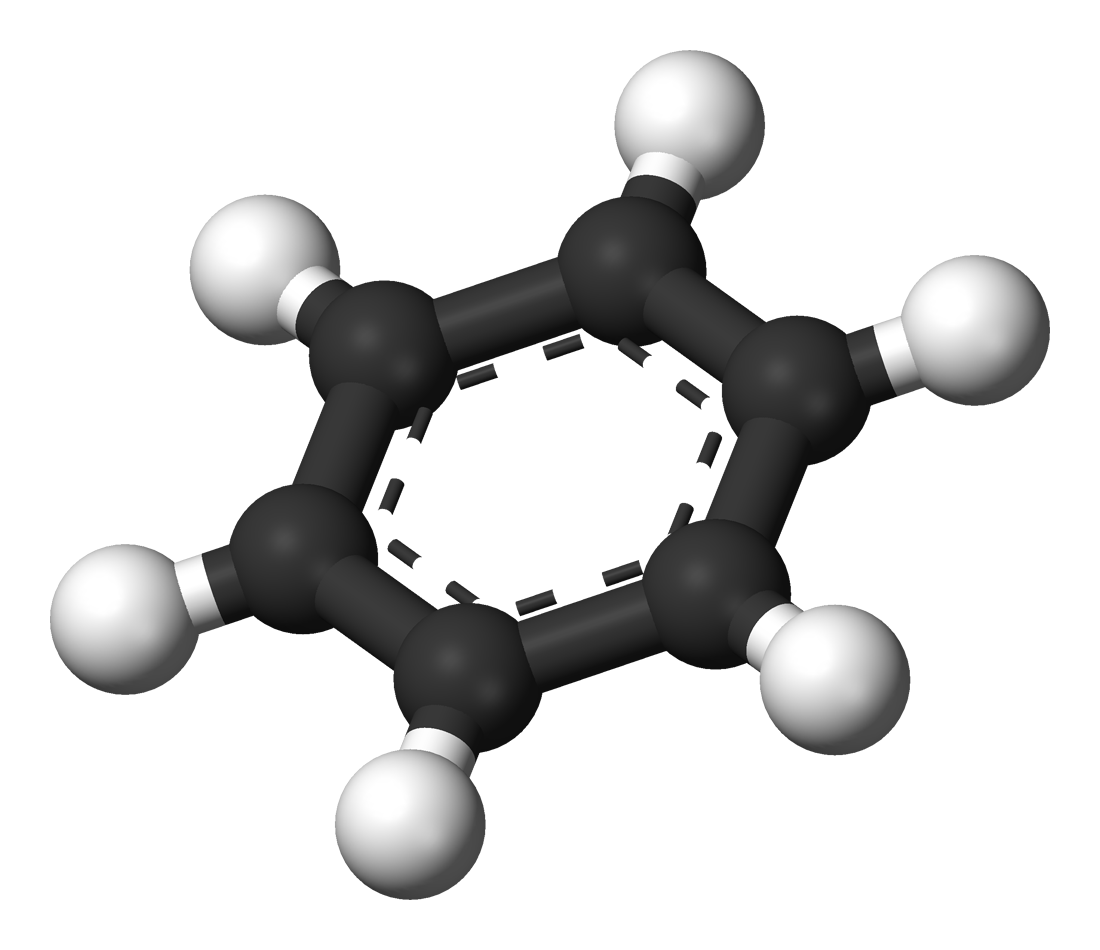
Benzene
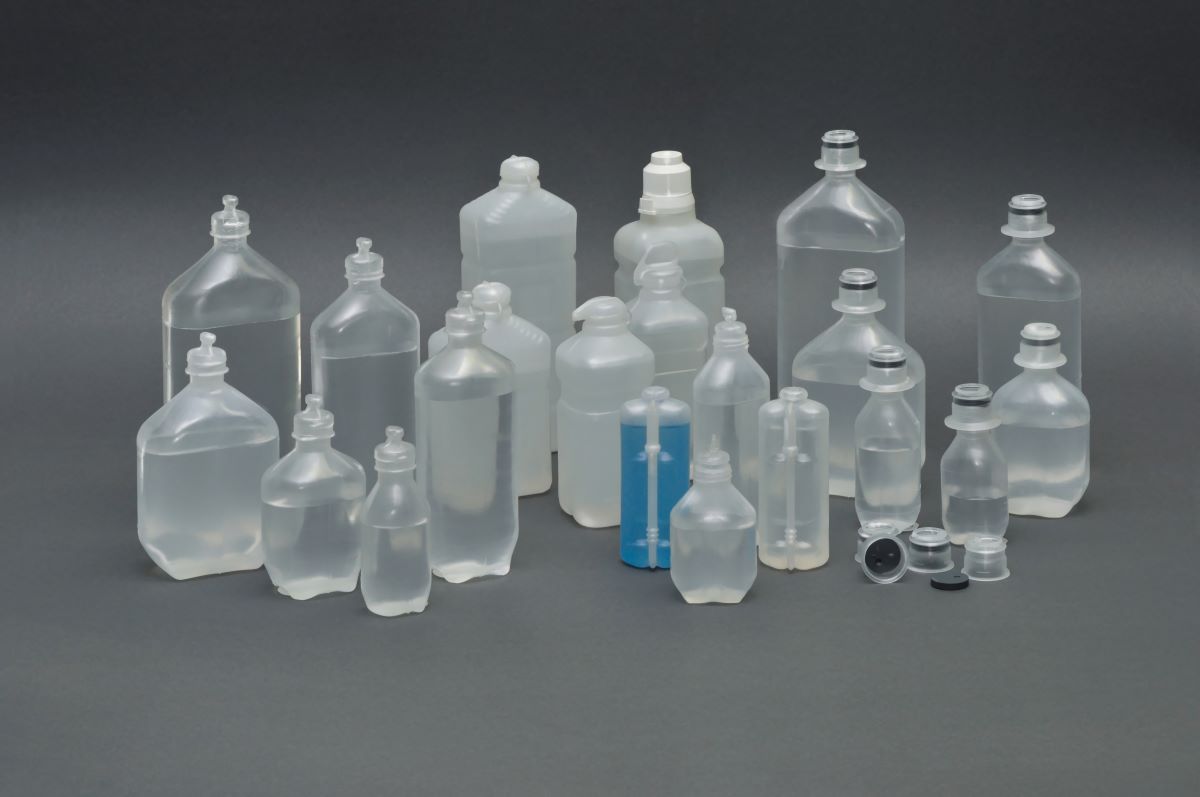
Bfs products
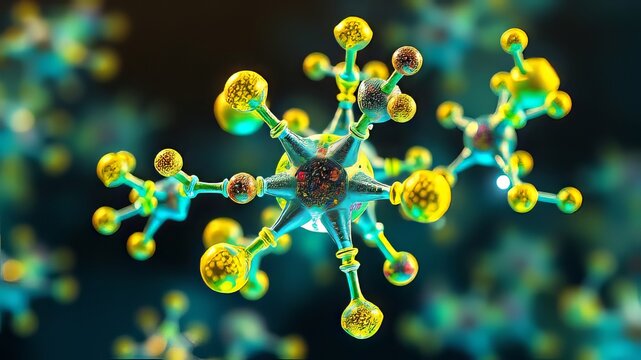
Biocides
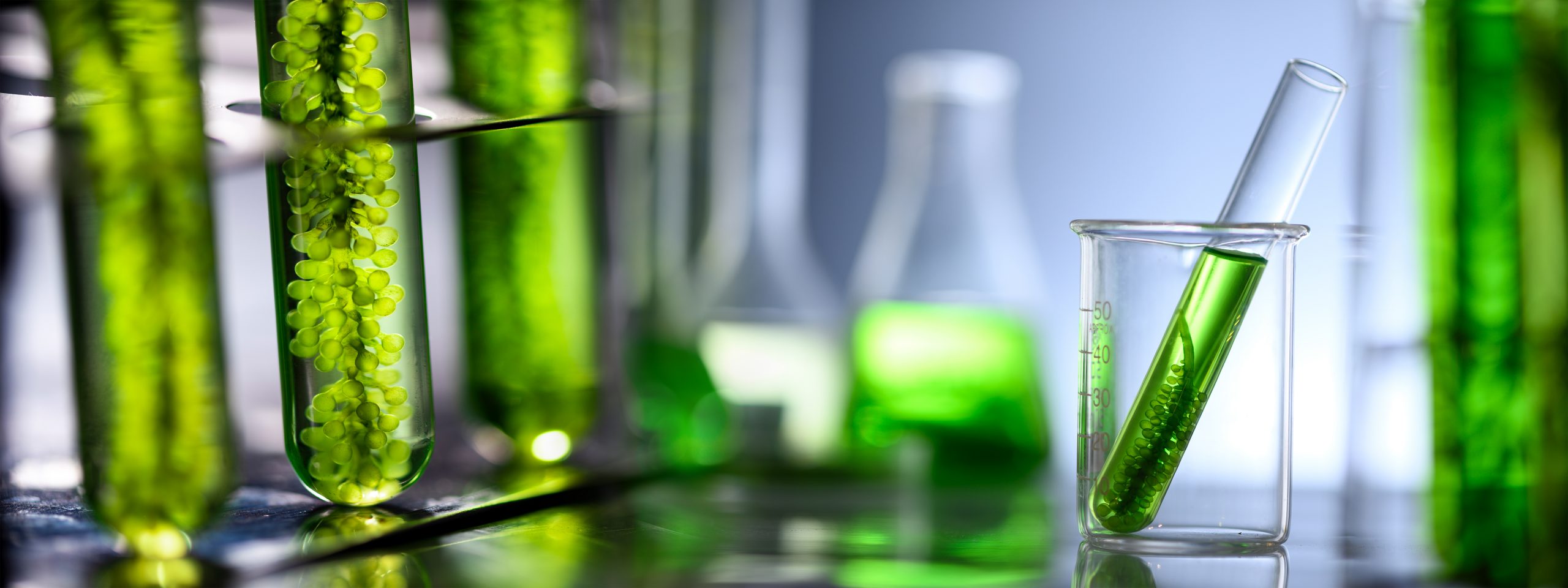
Biodiesel
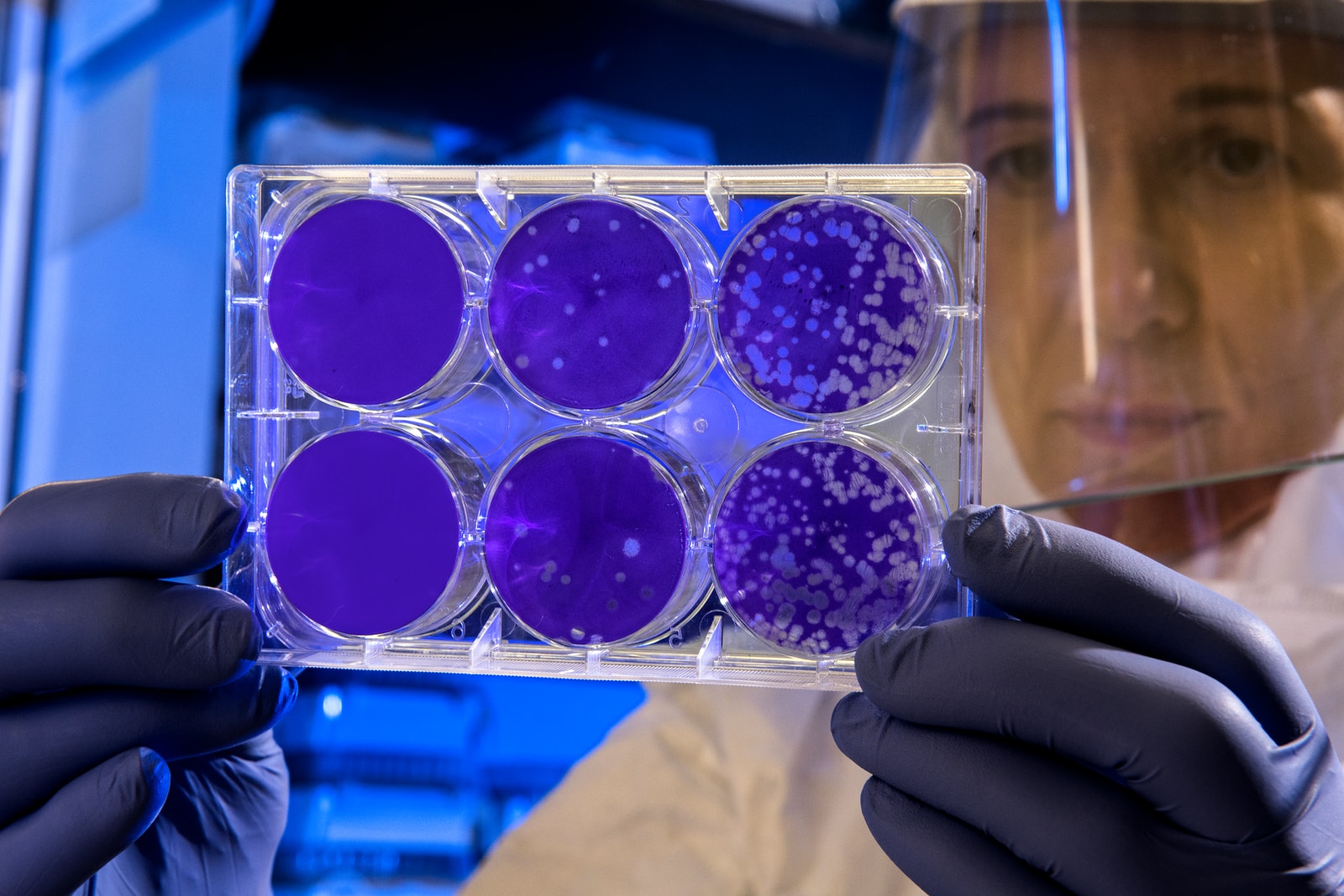
Biologics
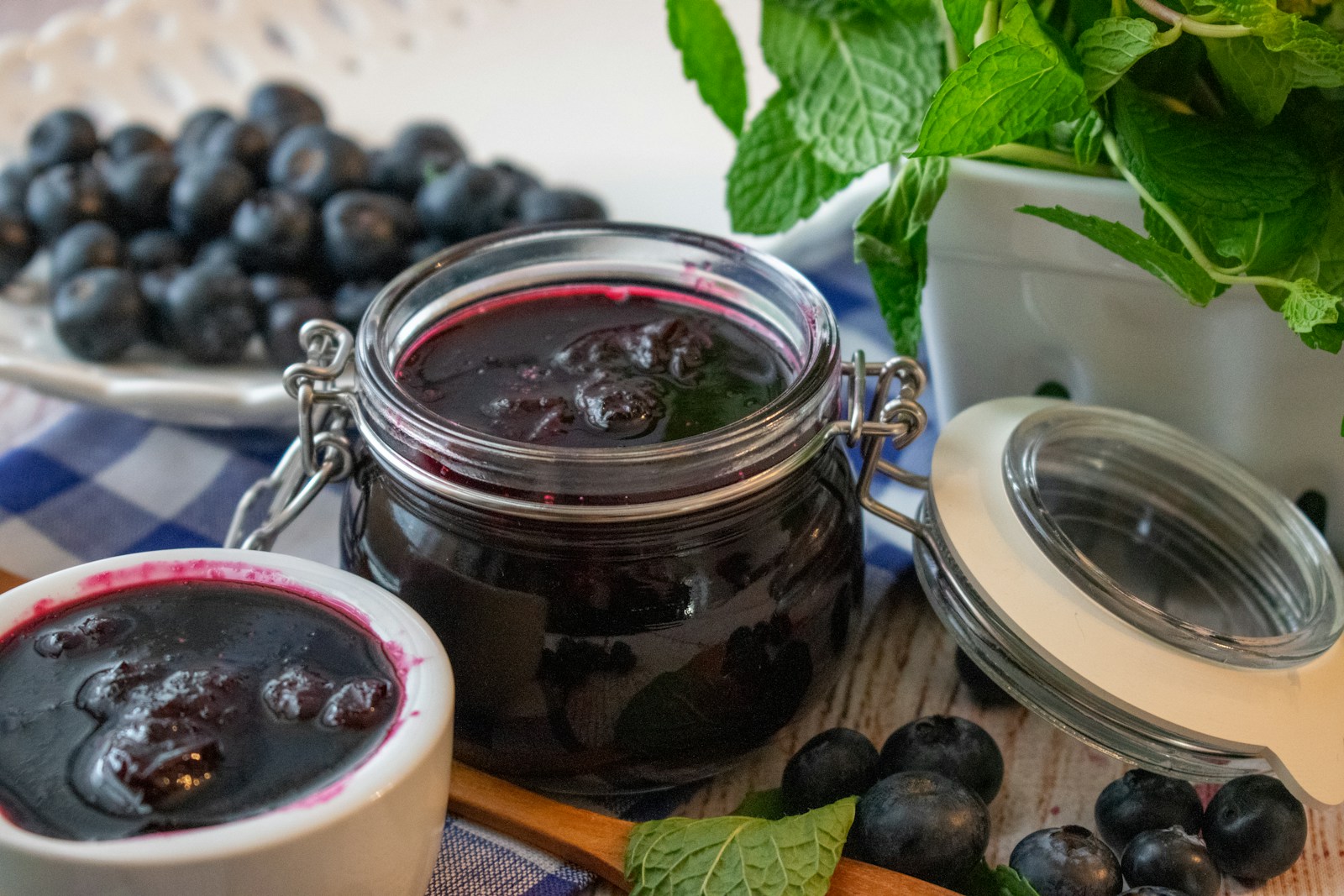
Blueberry jam
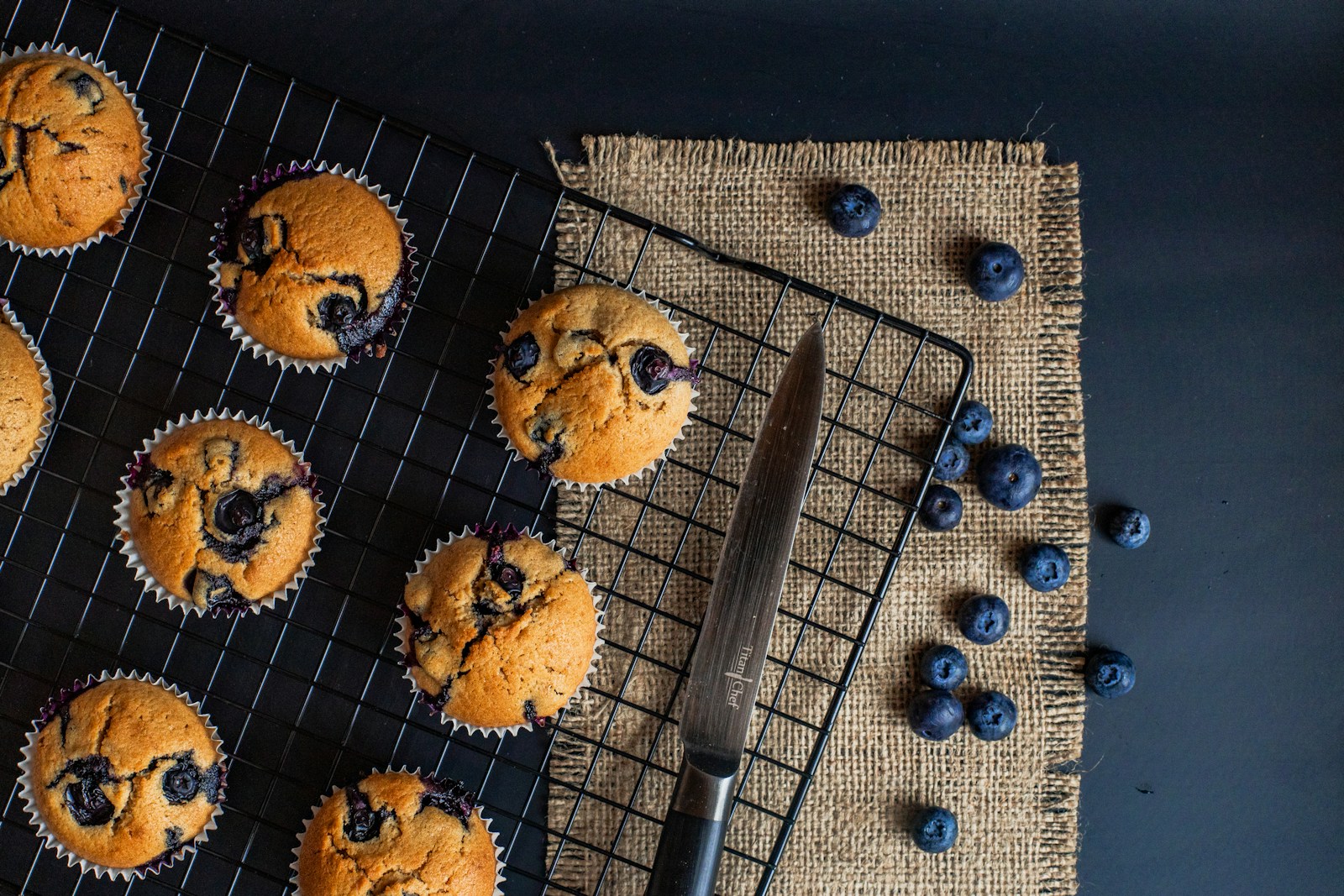
Blueberry muffins
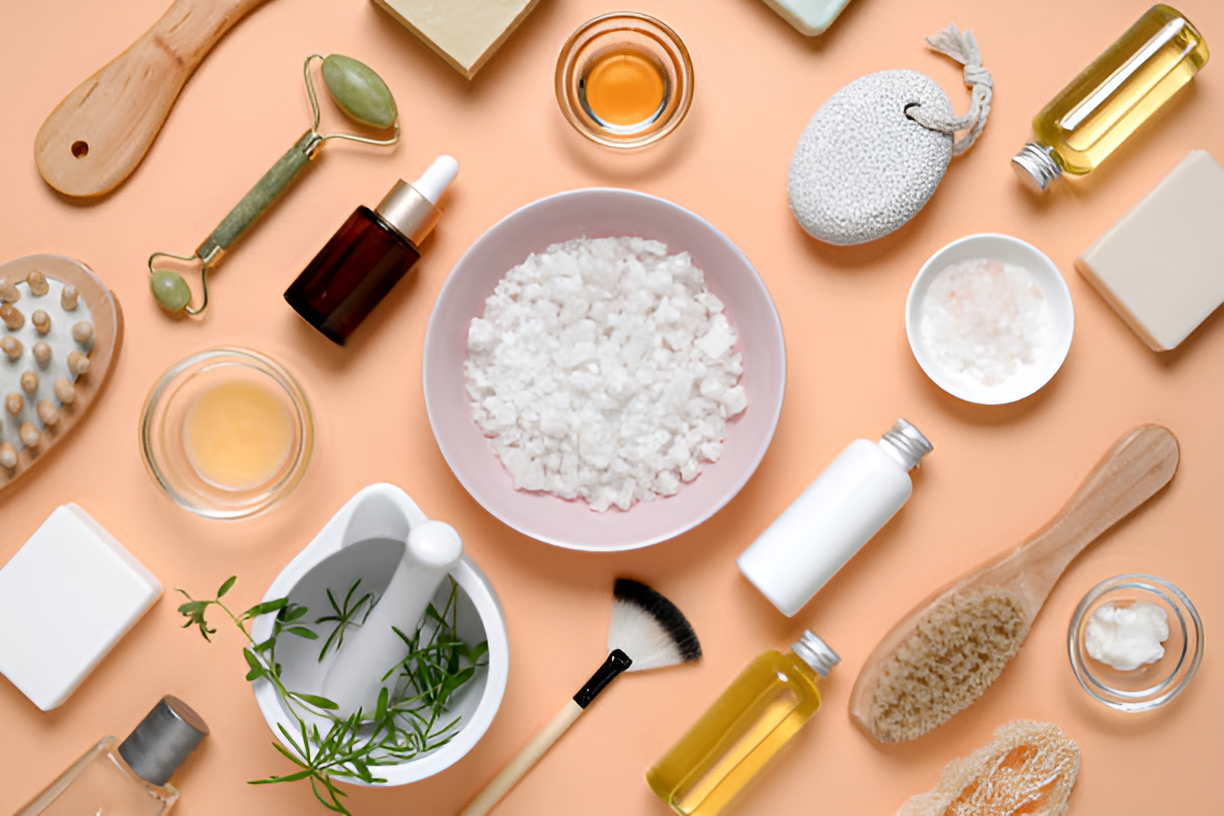
Body care
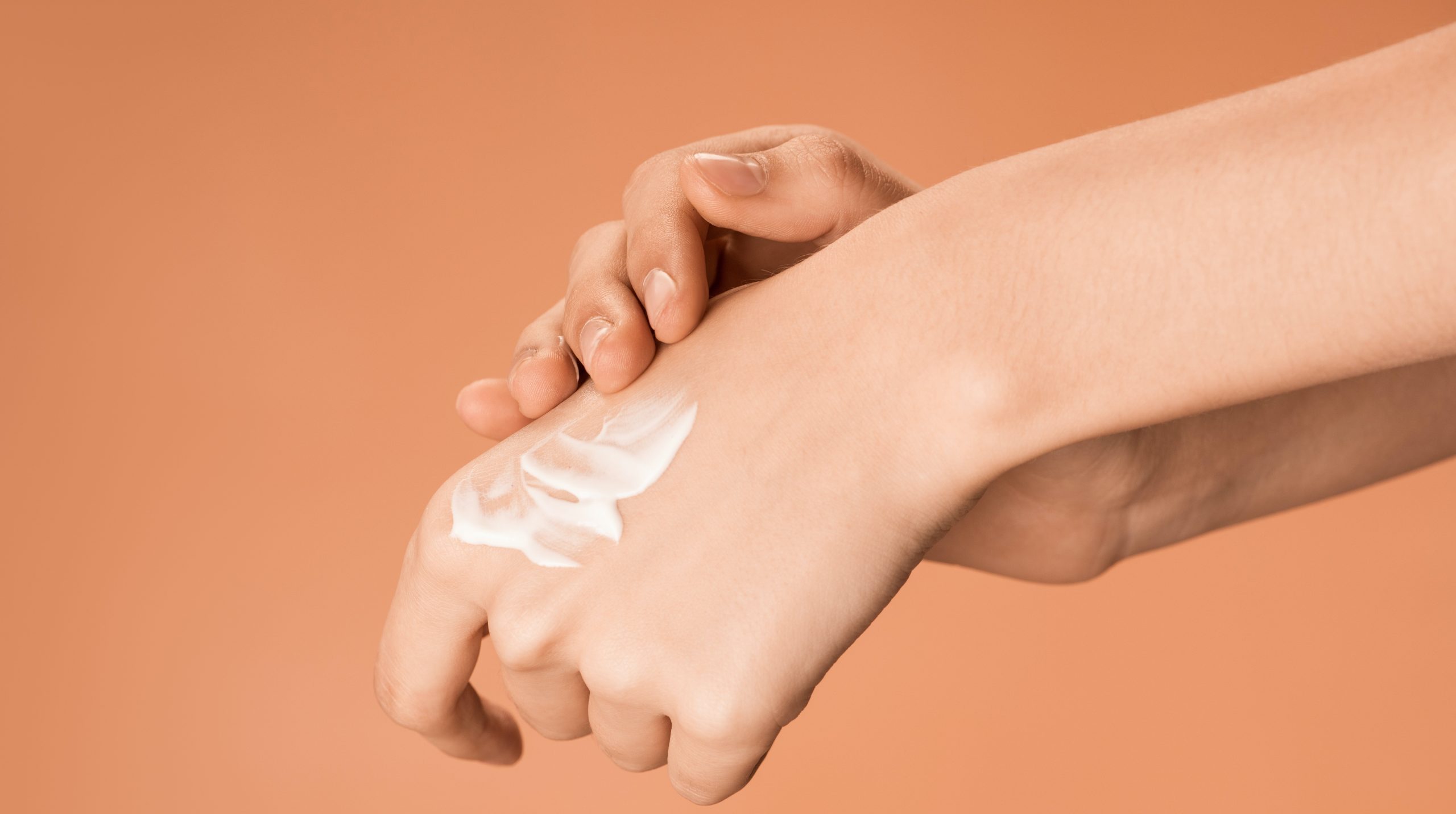
Body lotion
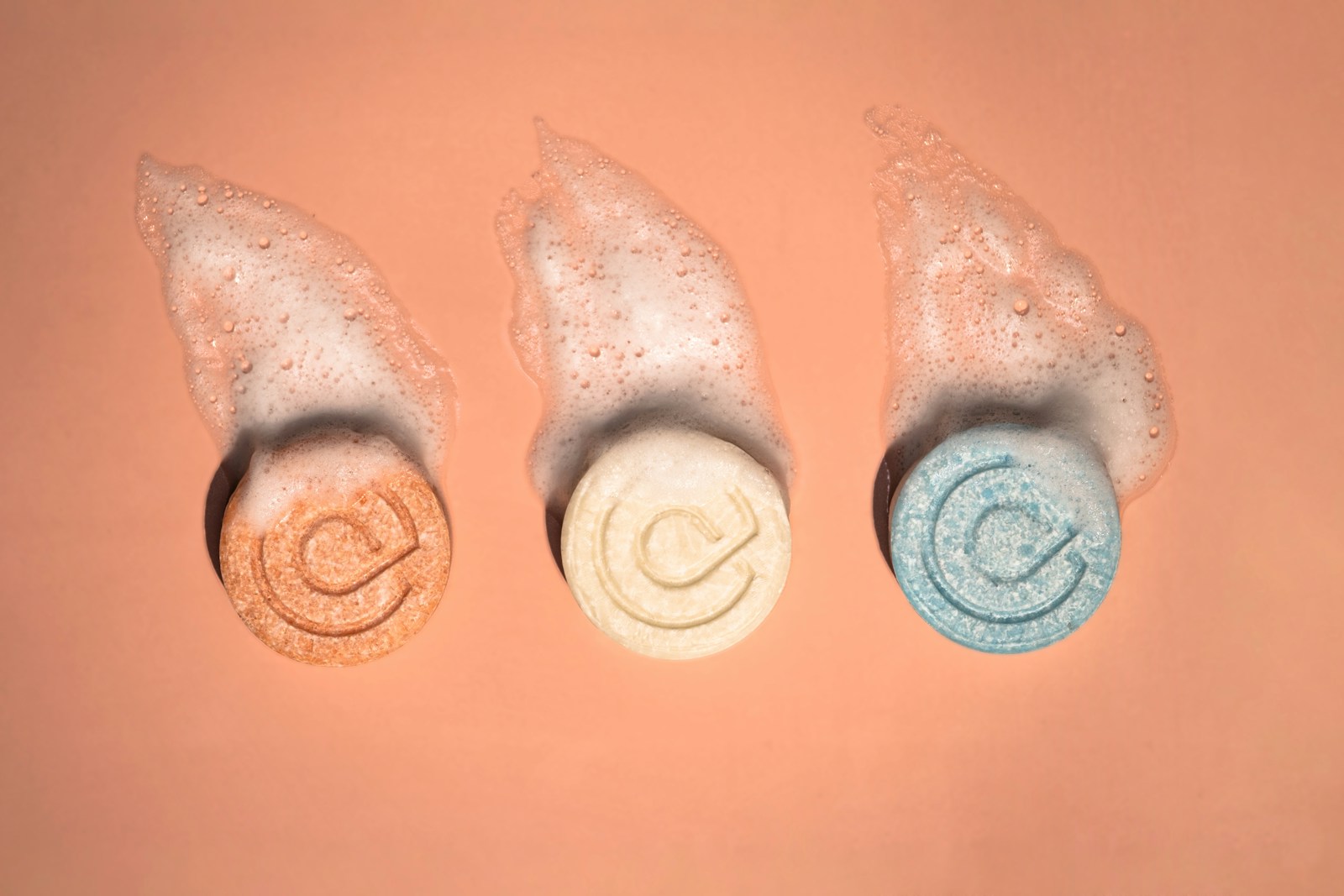
Body wash
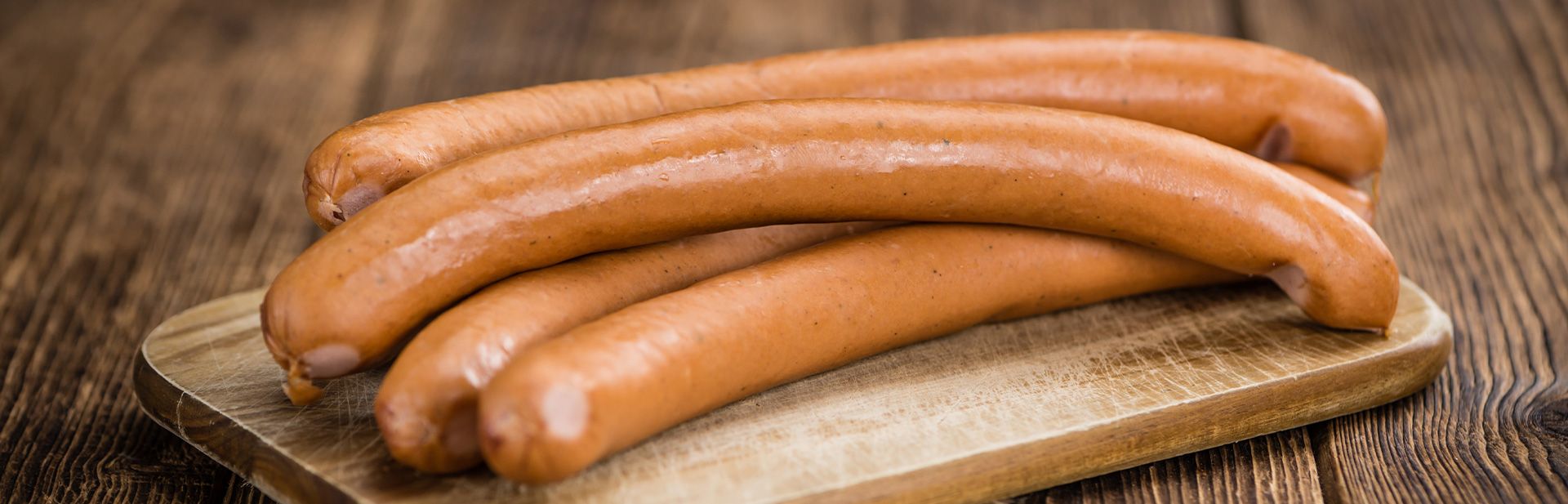
Boiled sausage
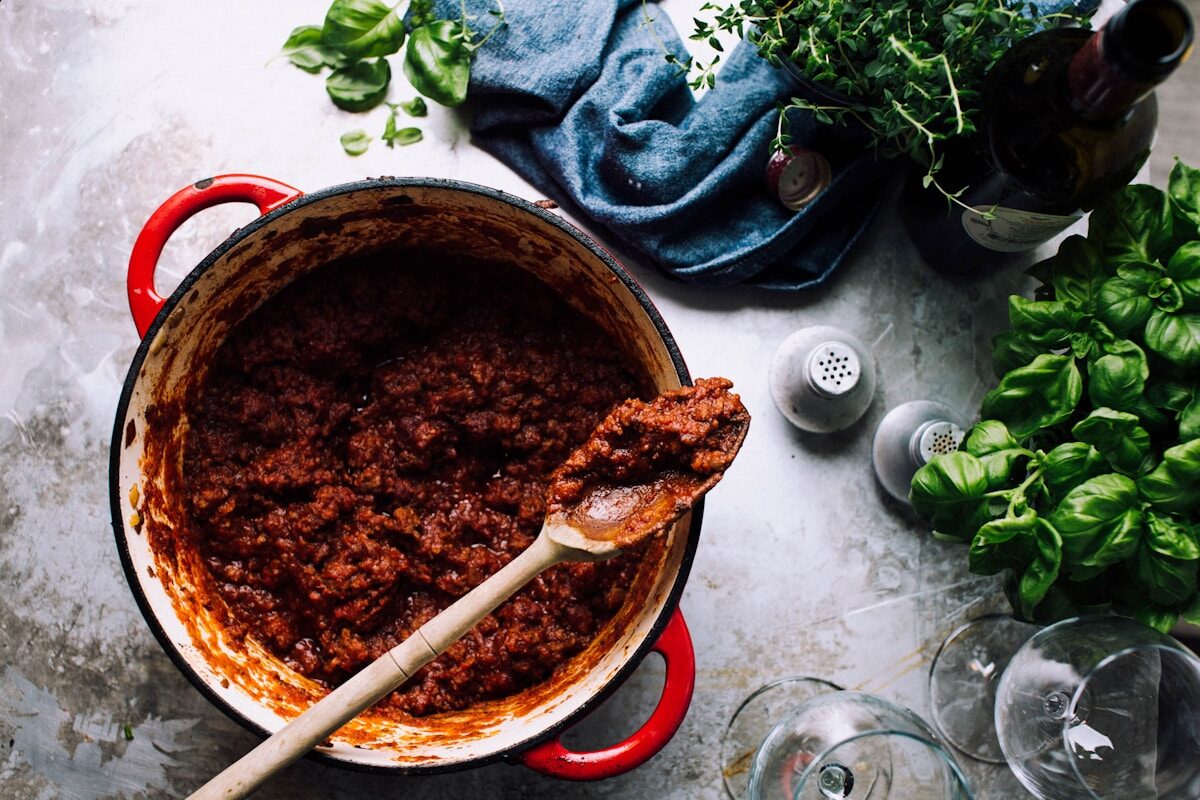
Bolognese sauce
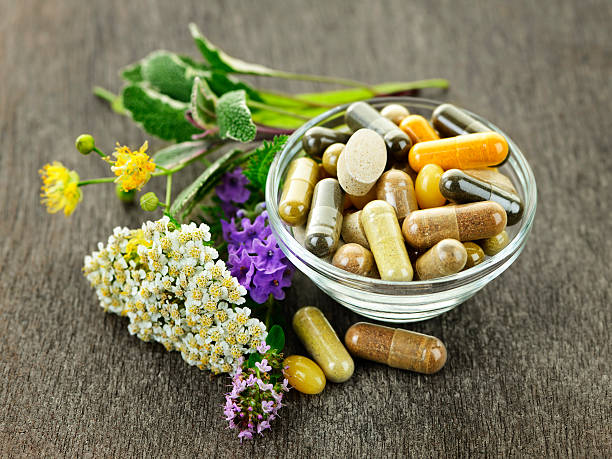
Botanical medicine
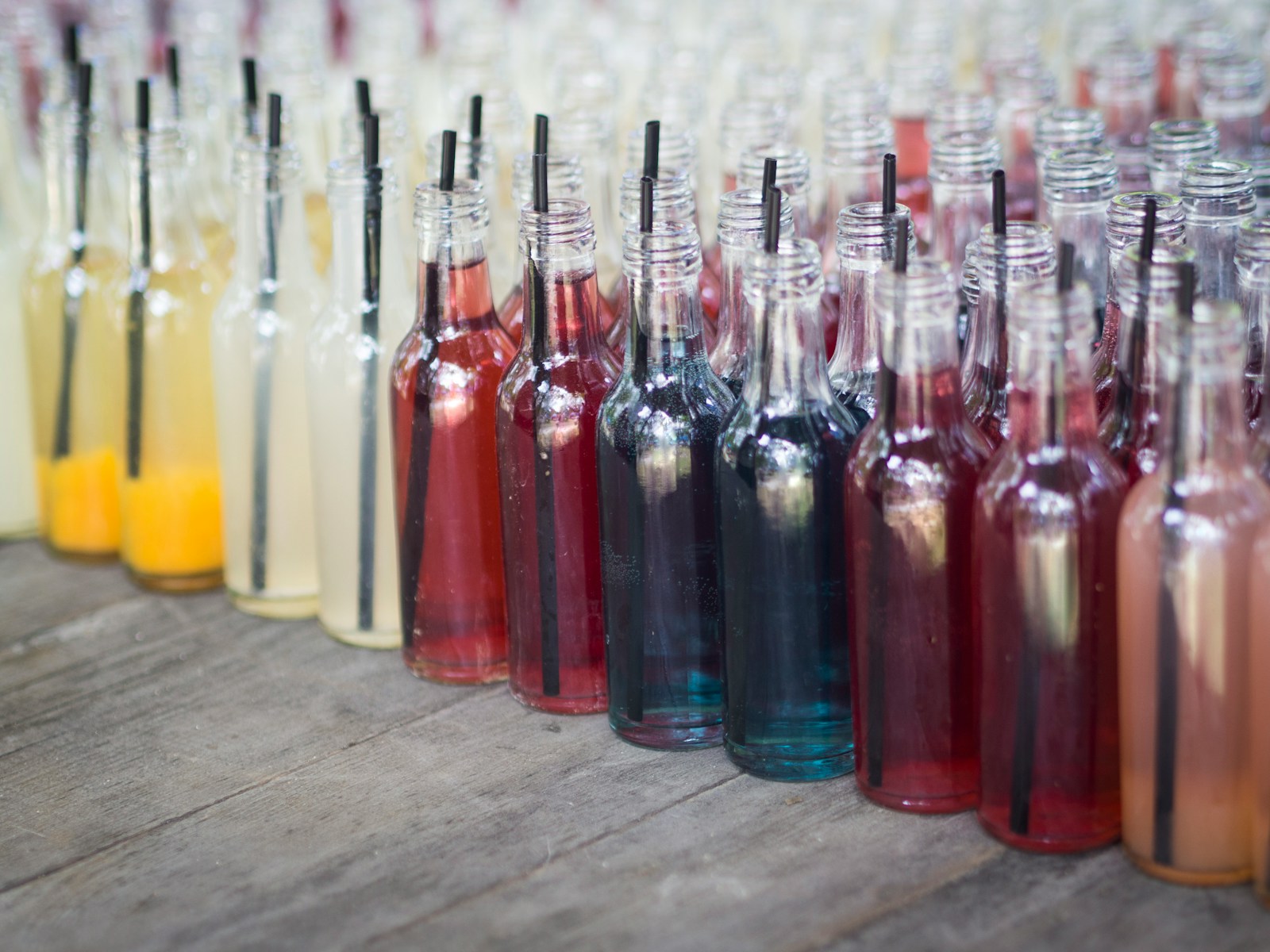
Bottled drinks
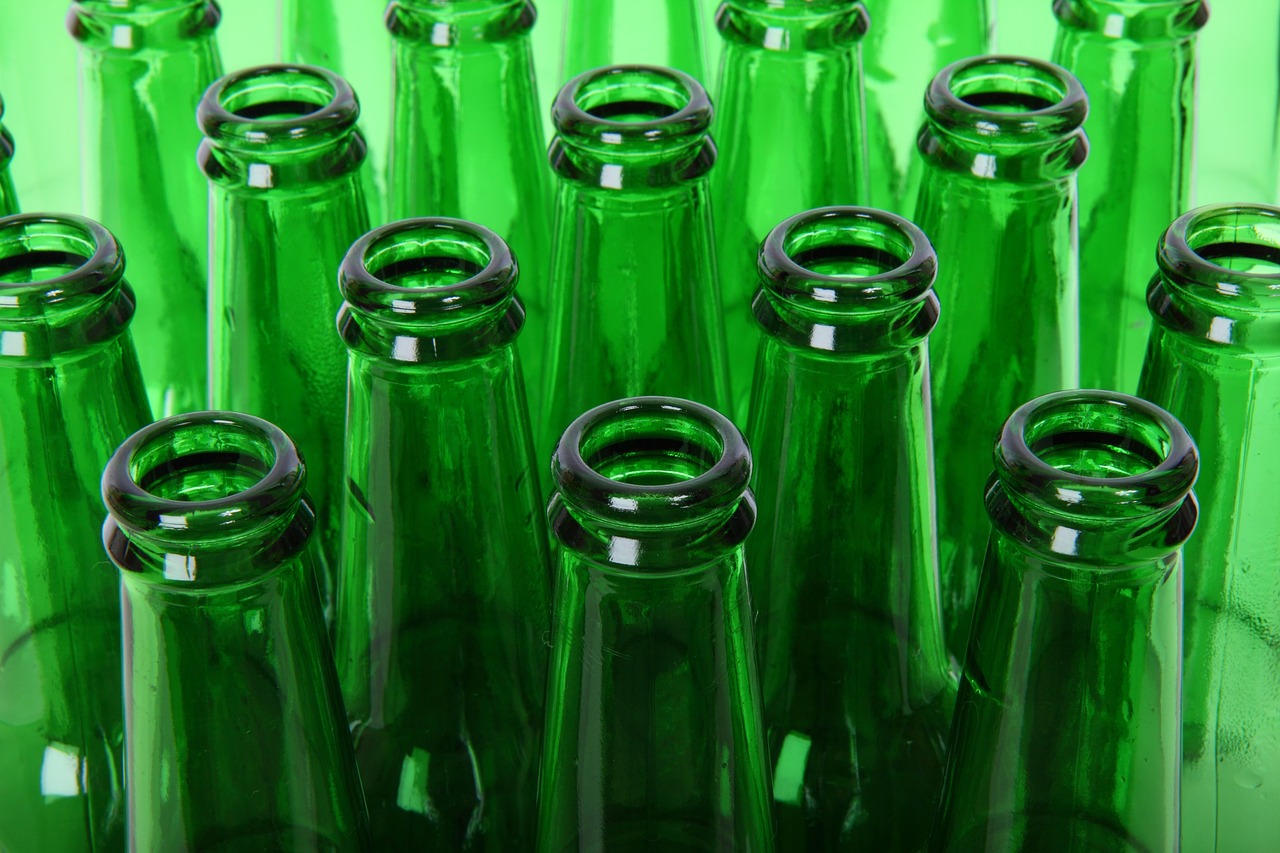
Bottles
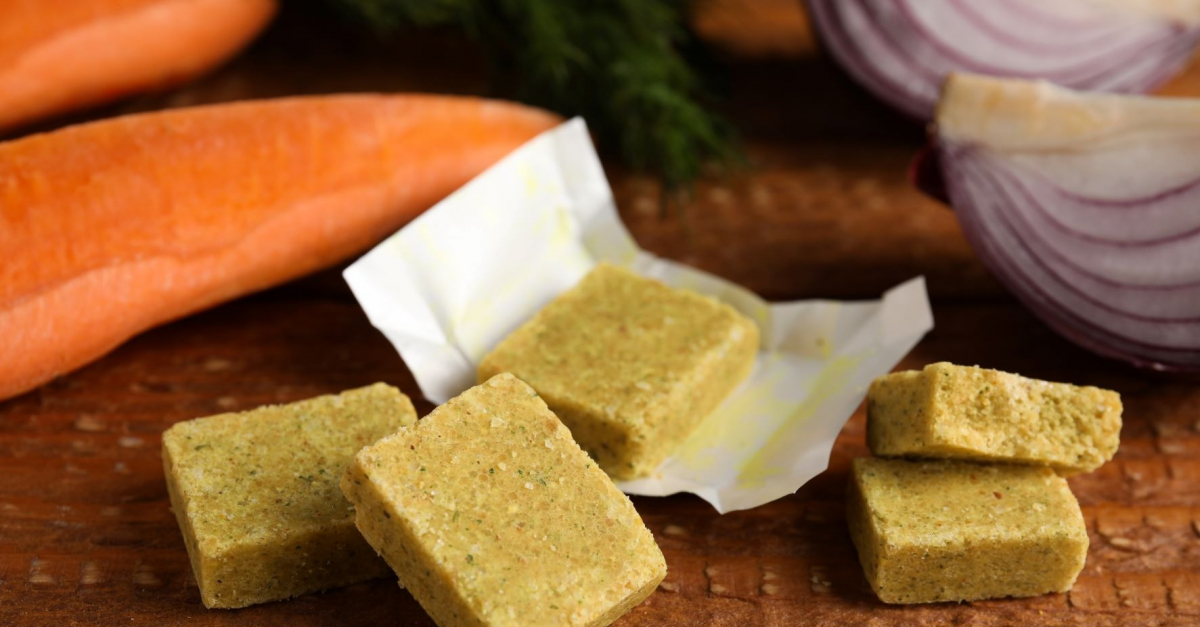
Bouillon cubes
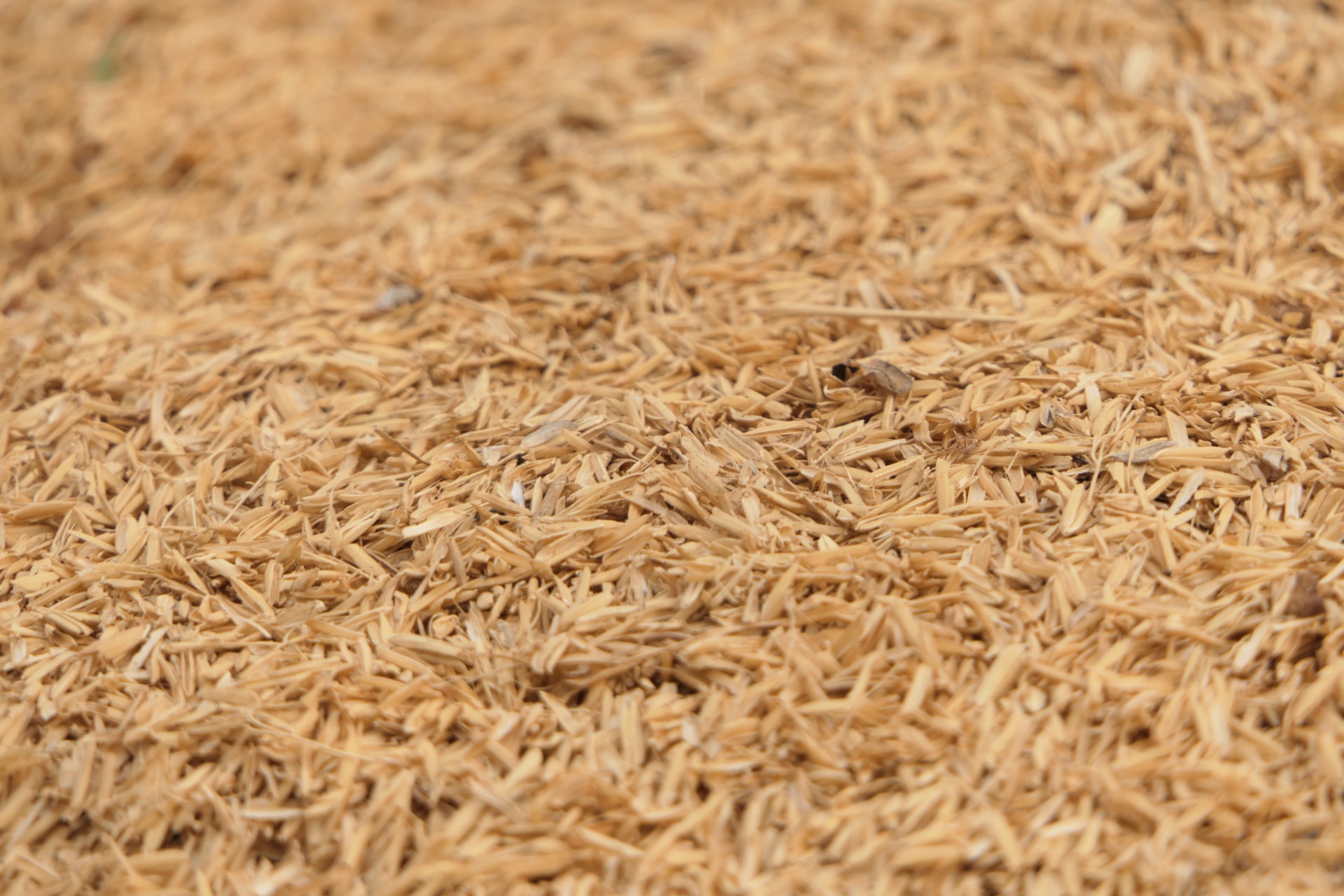
Bran
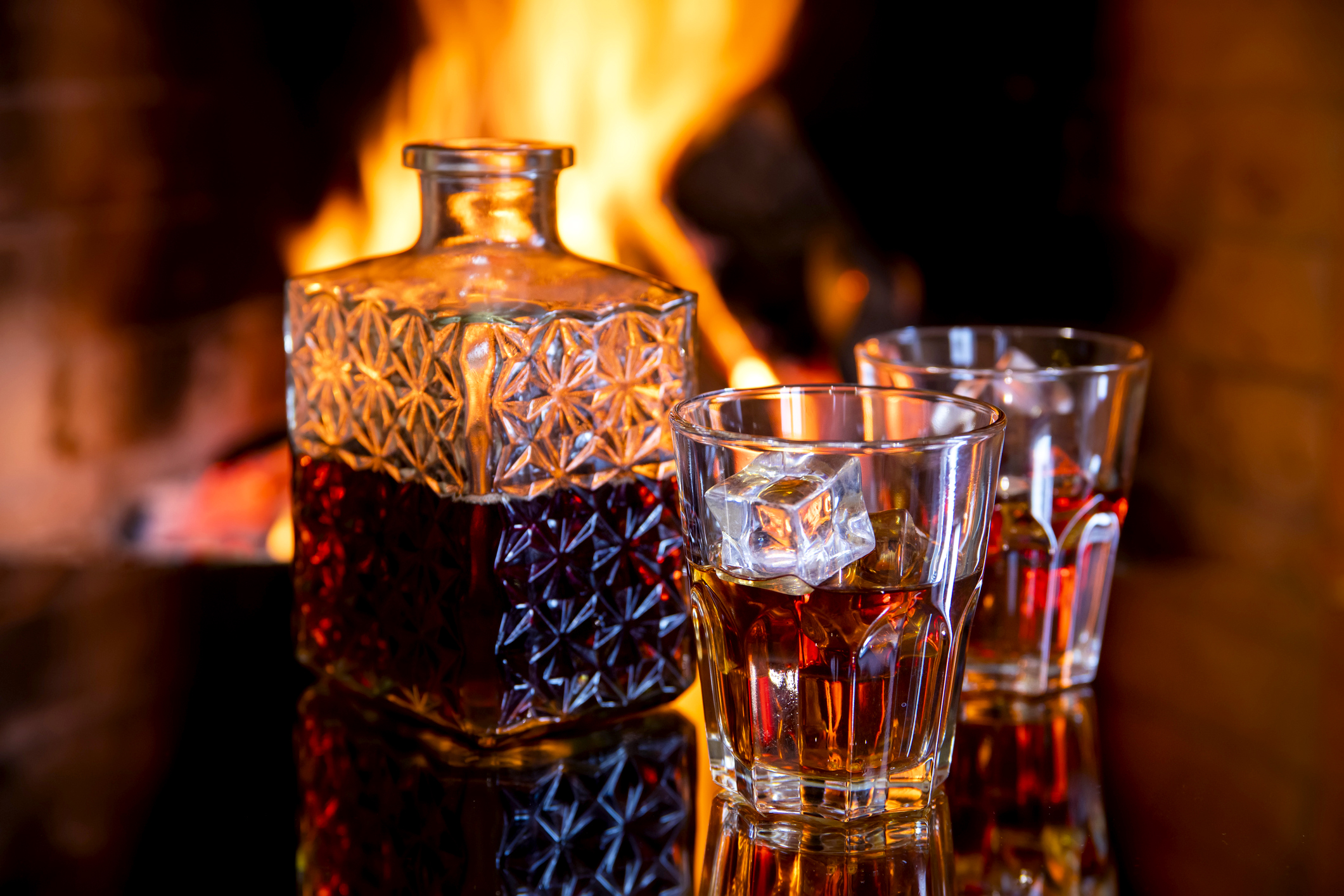
Brandy
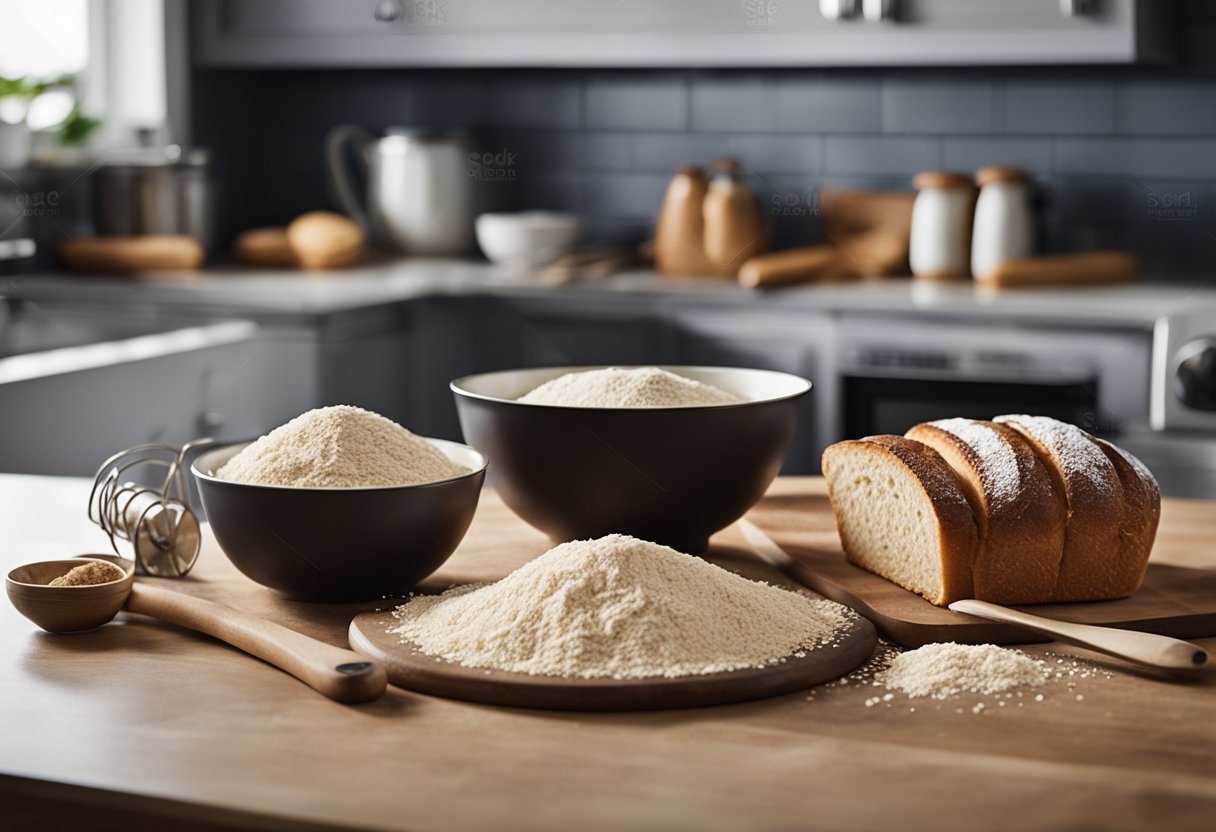
Bread mix
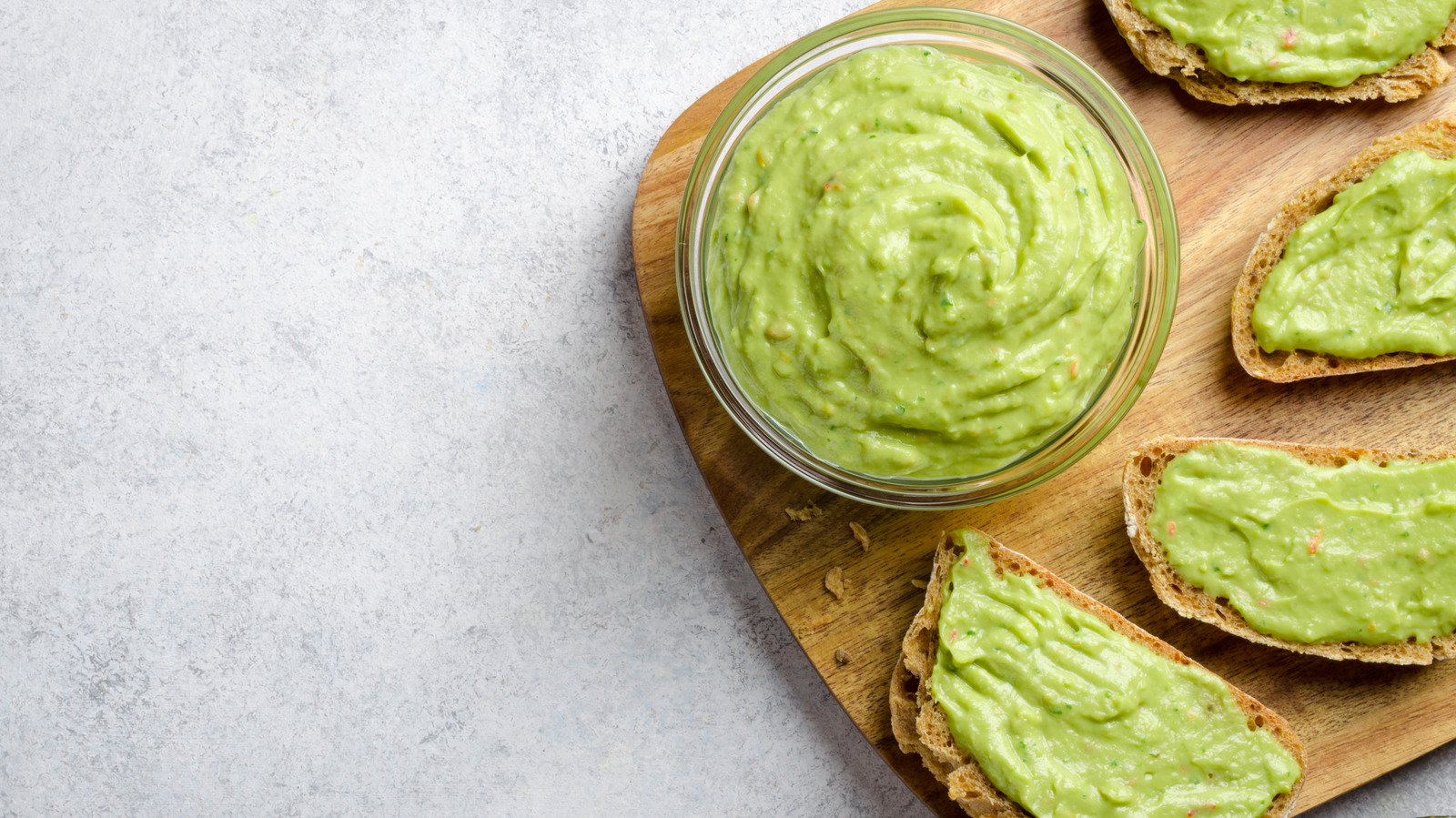
Bread spreads
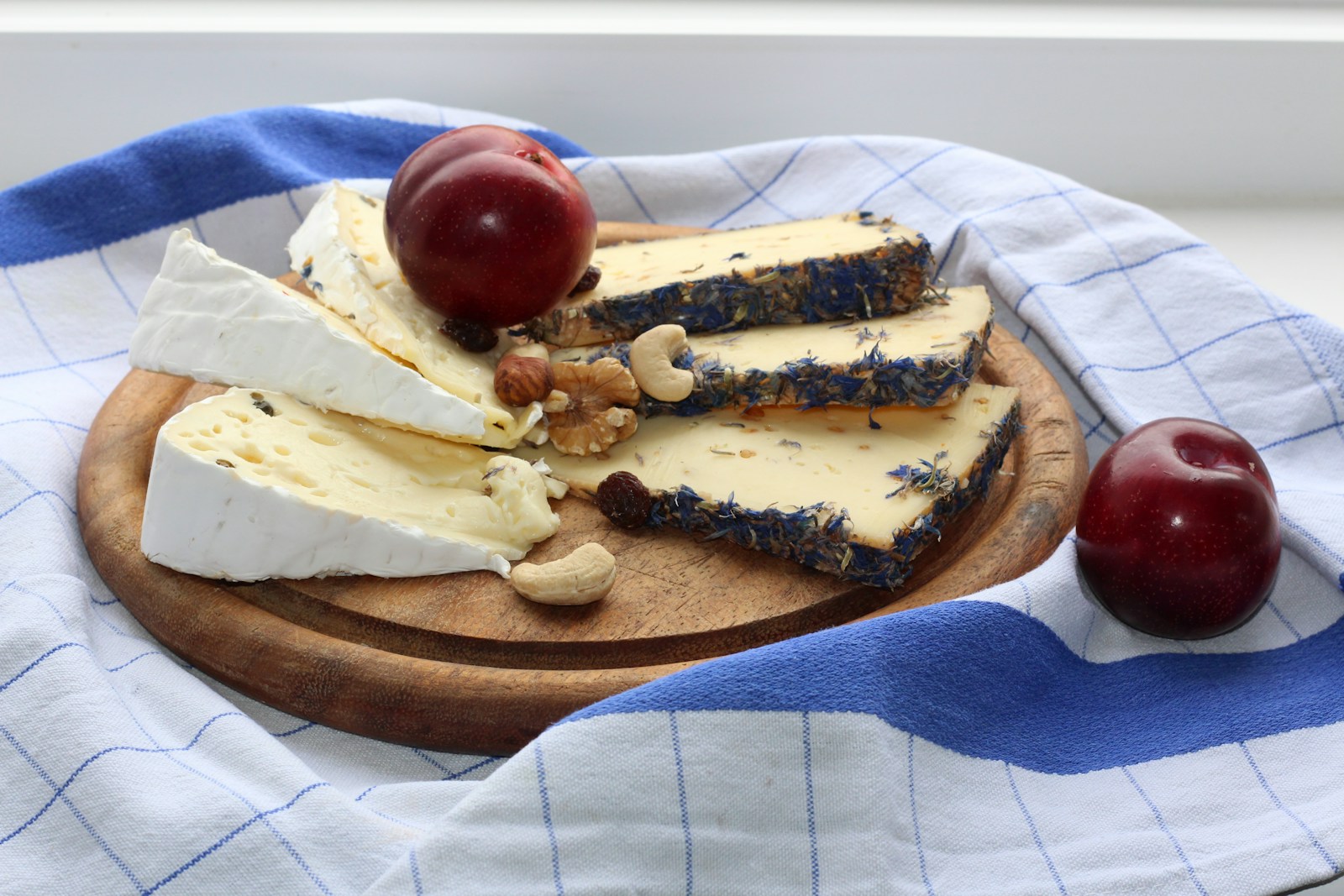
Brie cheese
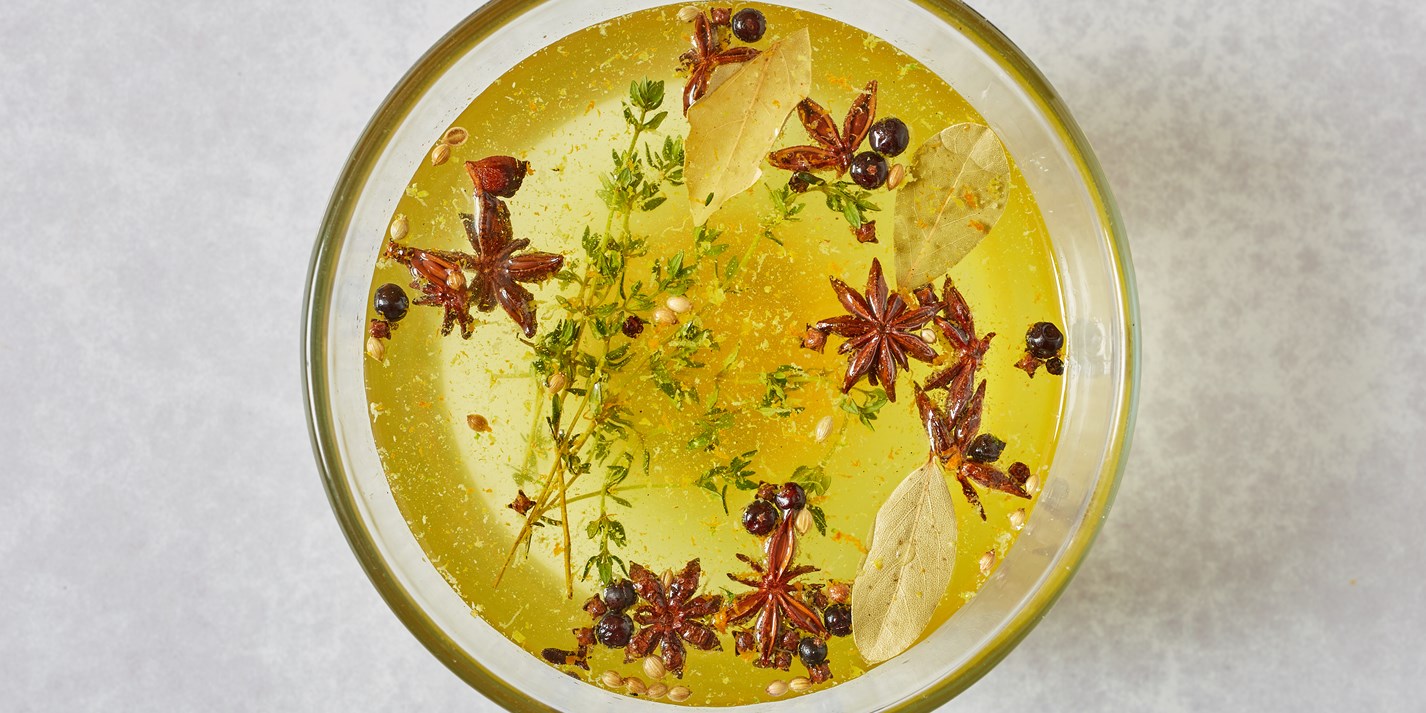
Brines
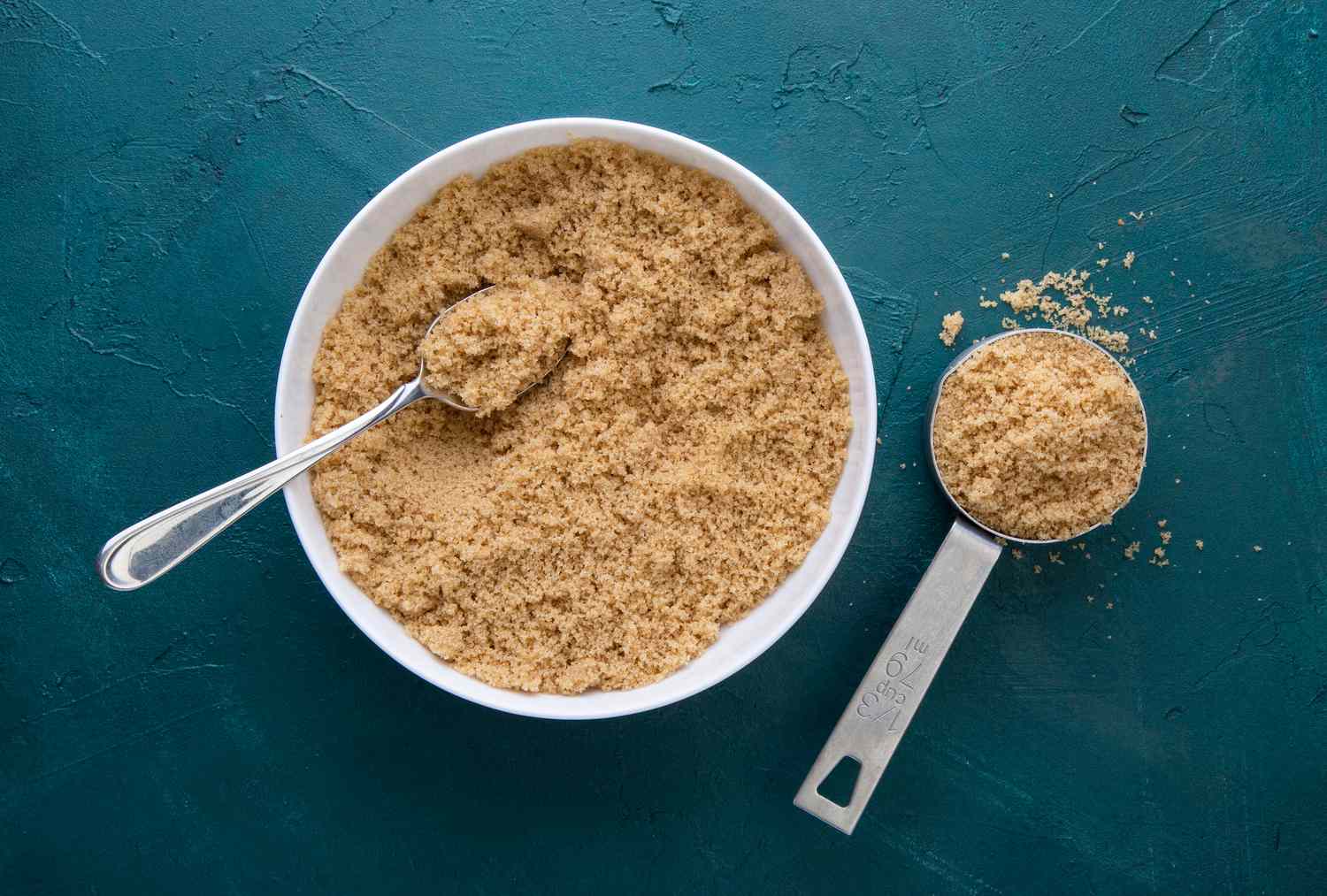
Brown sugar

Buffer solutions
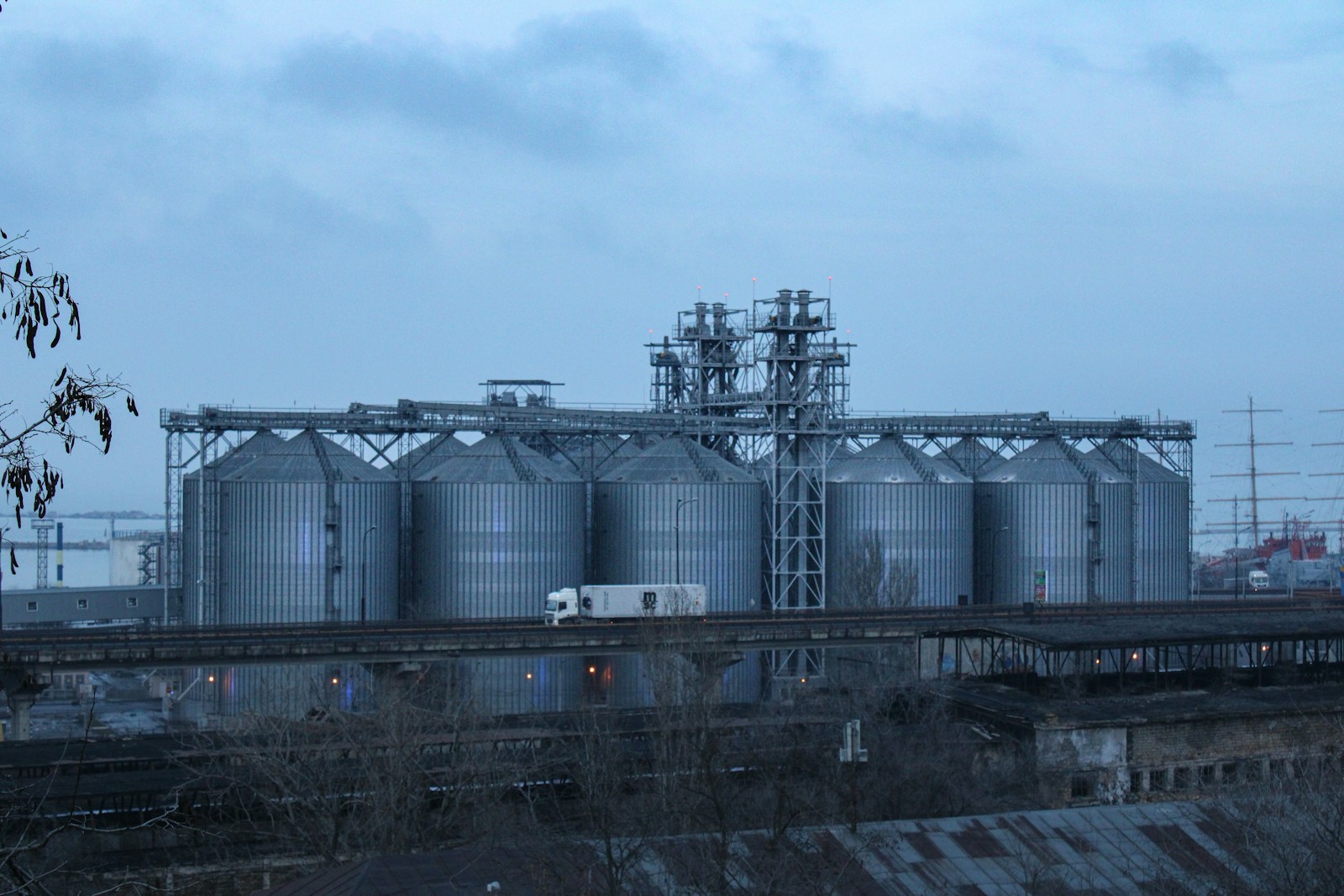
Bulk chemicals

Burrata
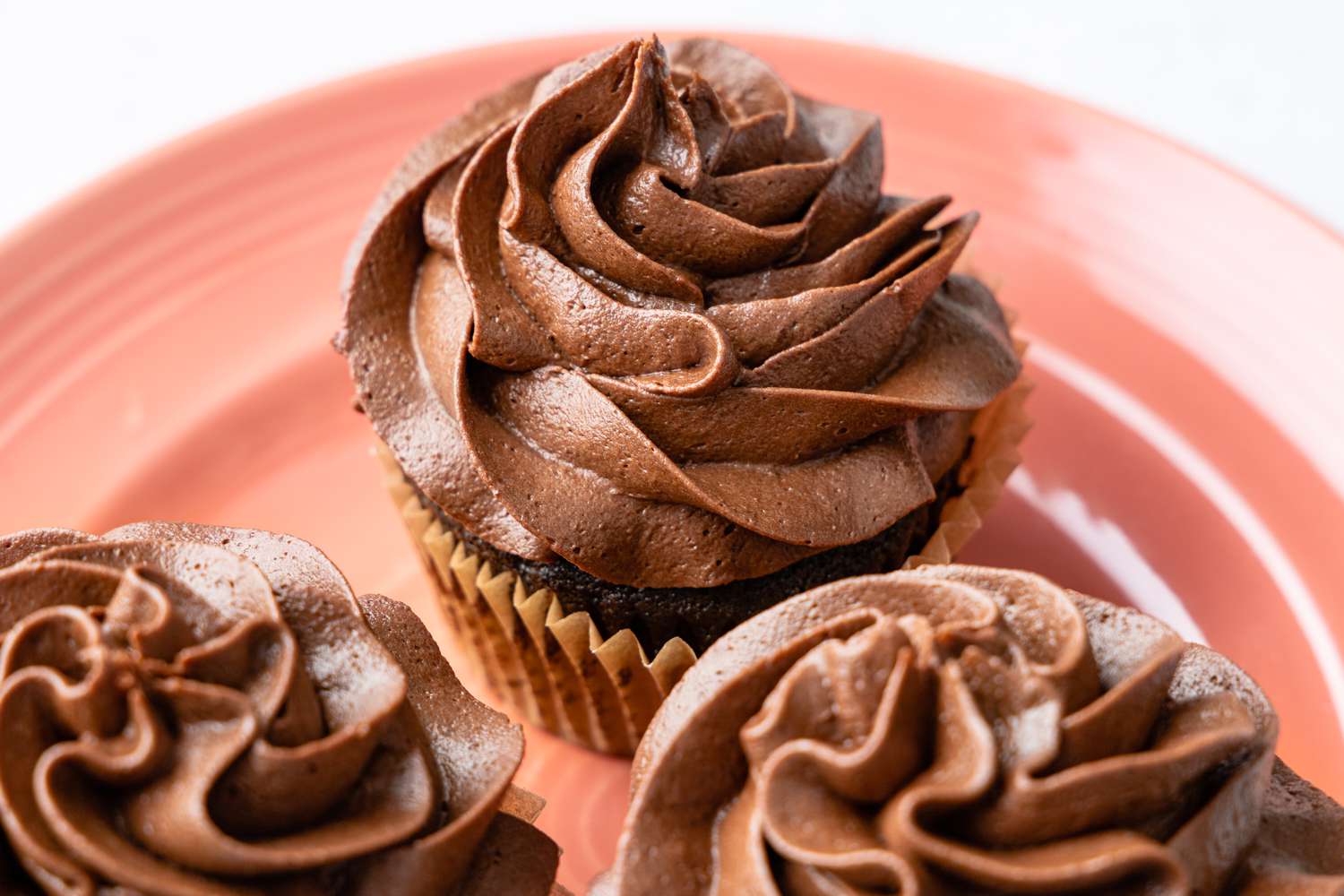
Buttercream
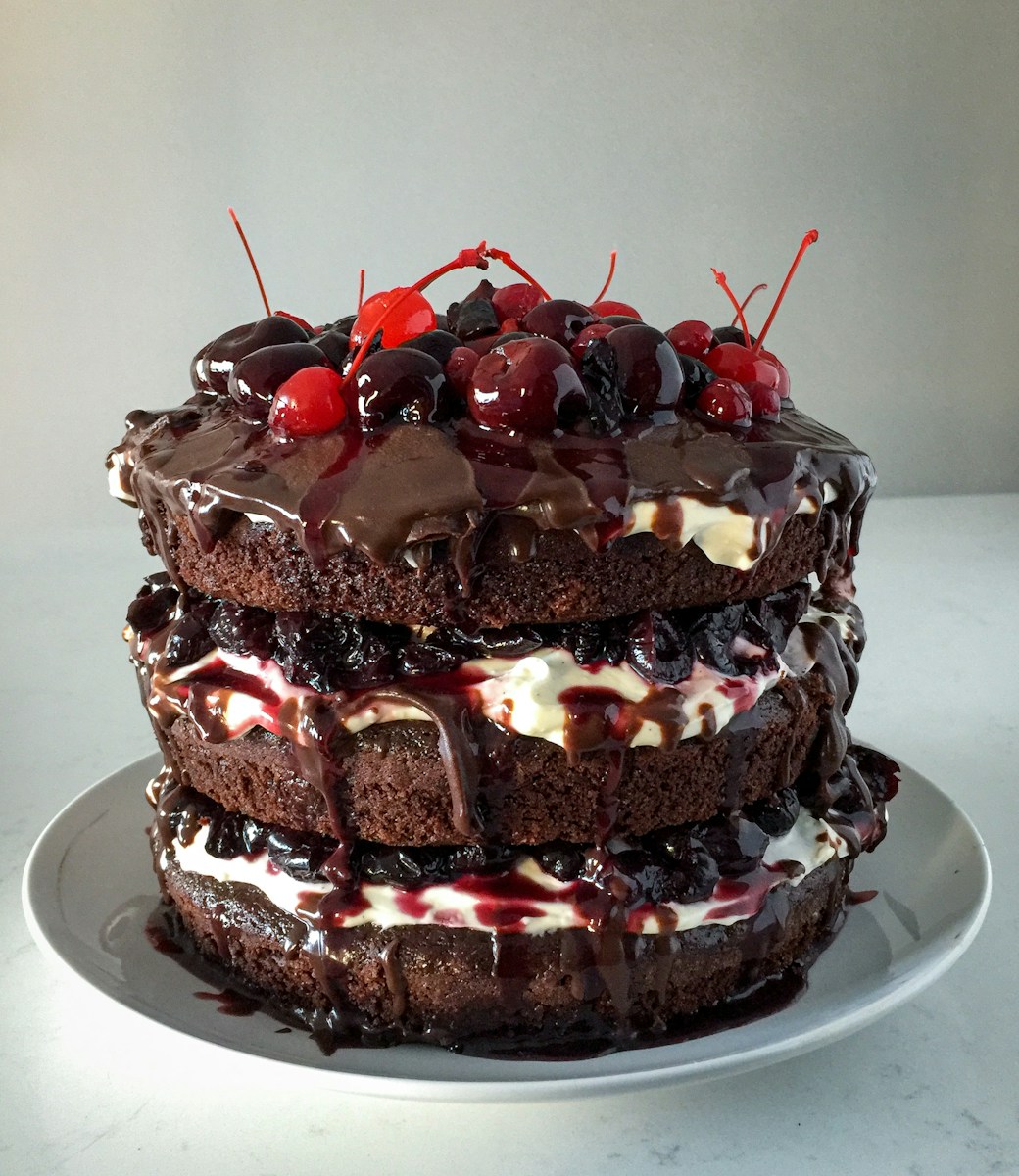
Cake

Calcium supplements
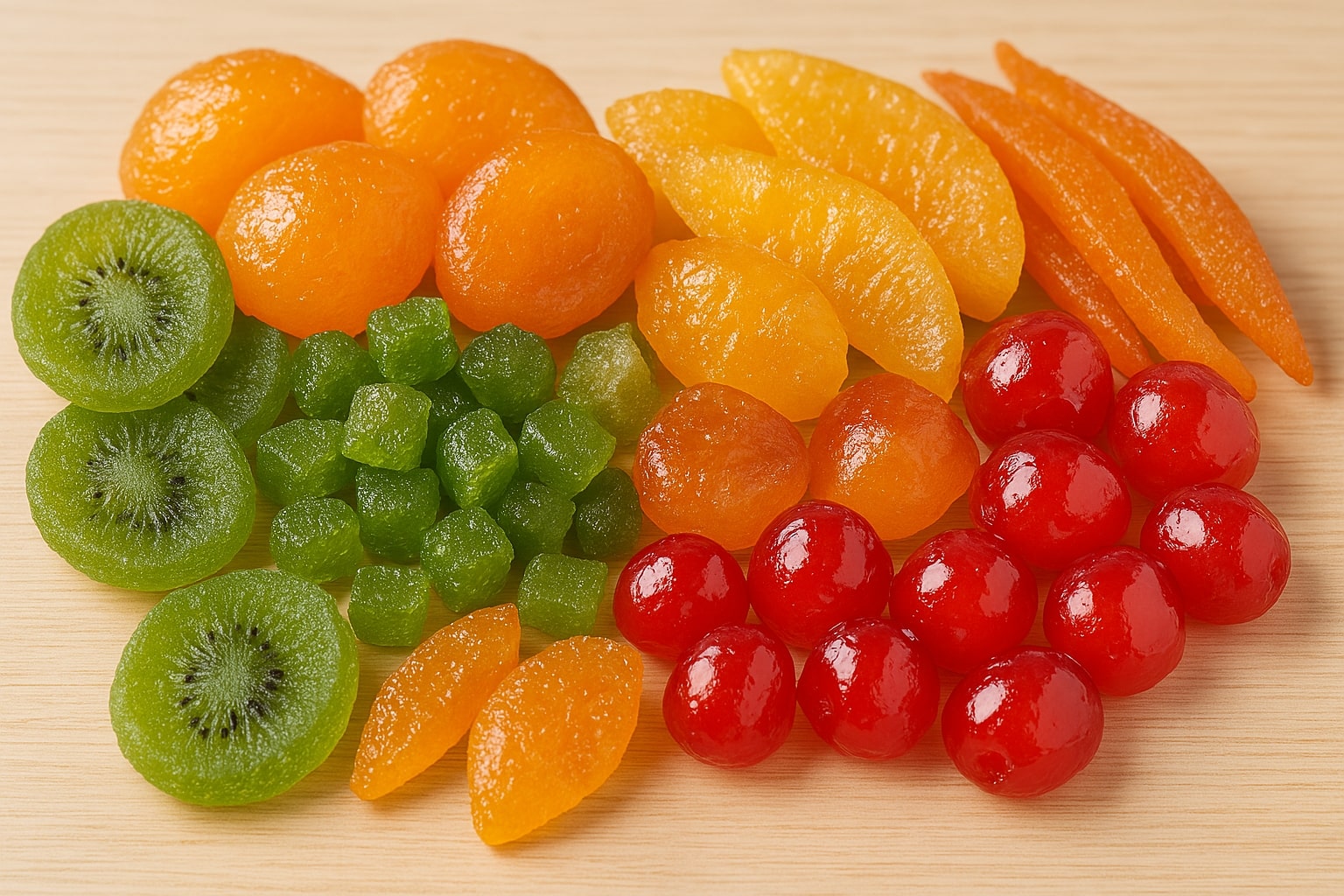
Candied fruits
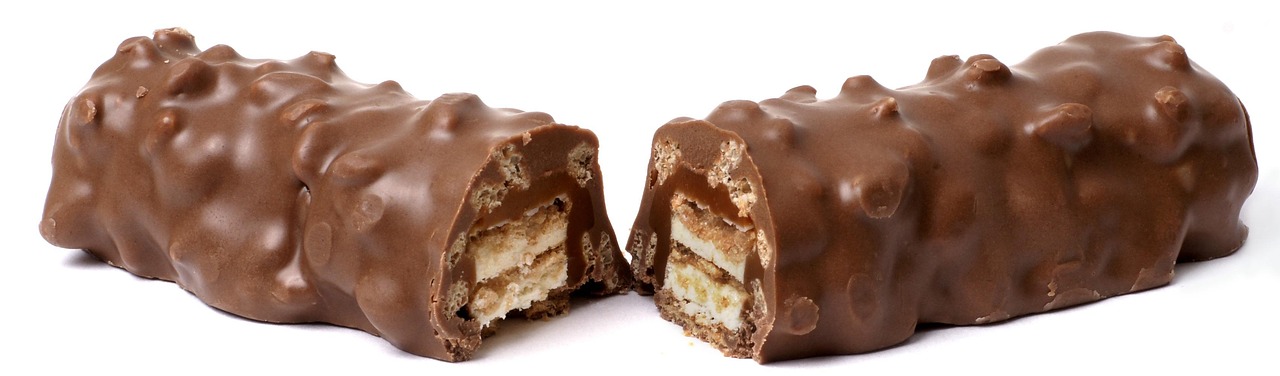
Candy bars
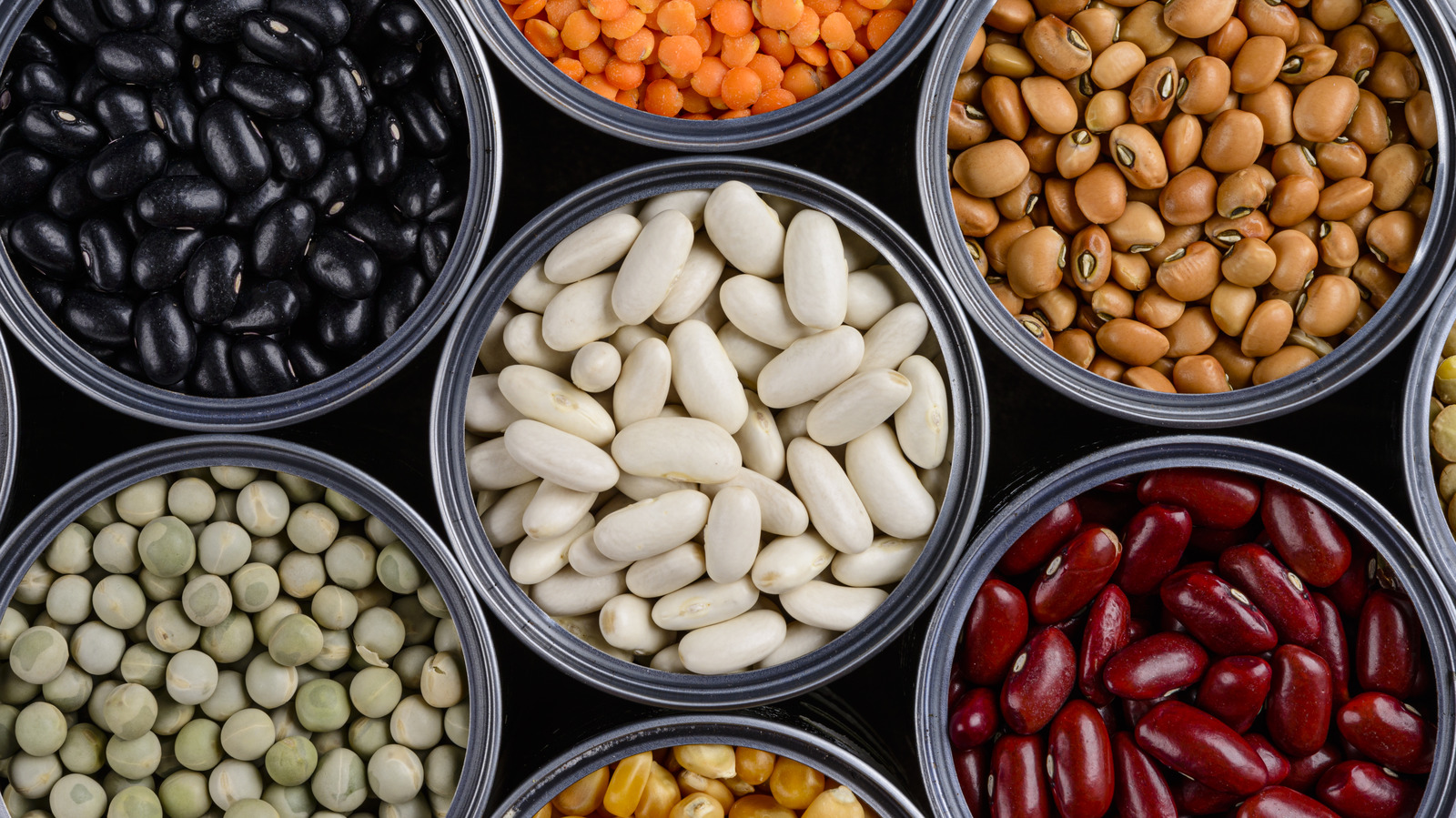
Canned beans

Canned beverages
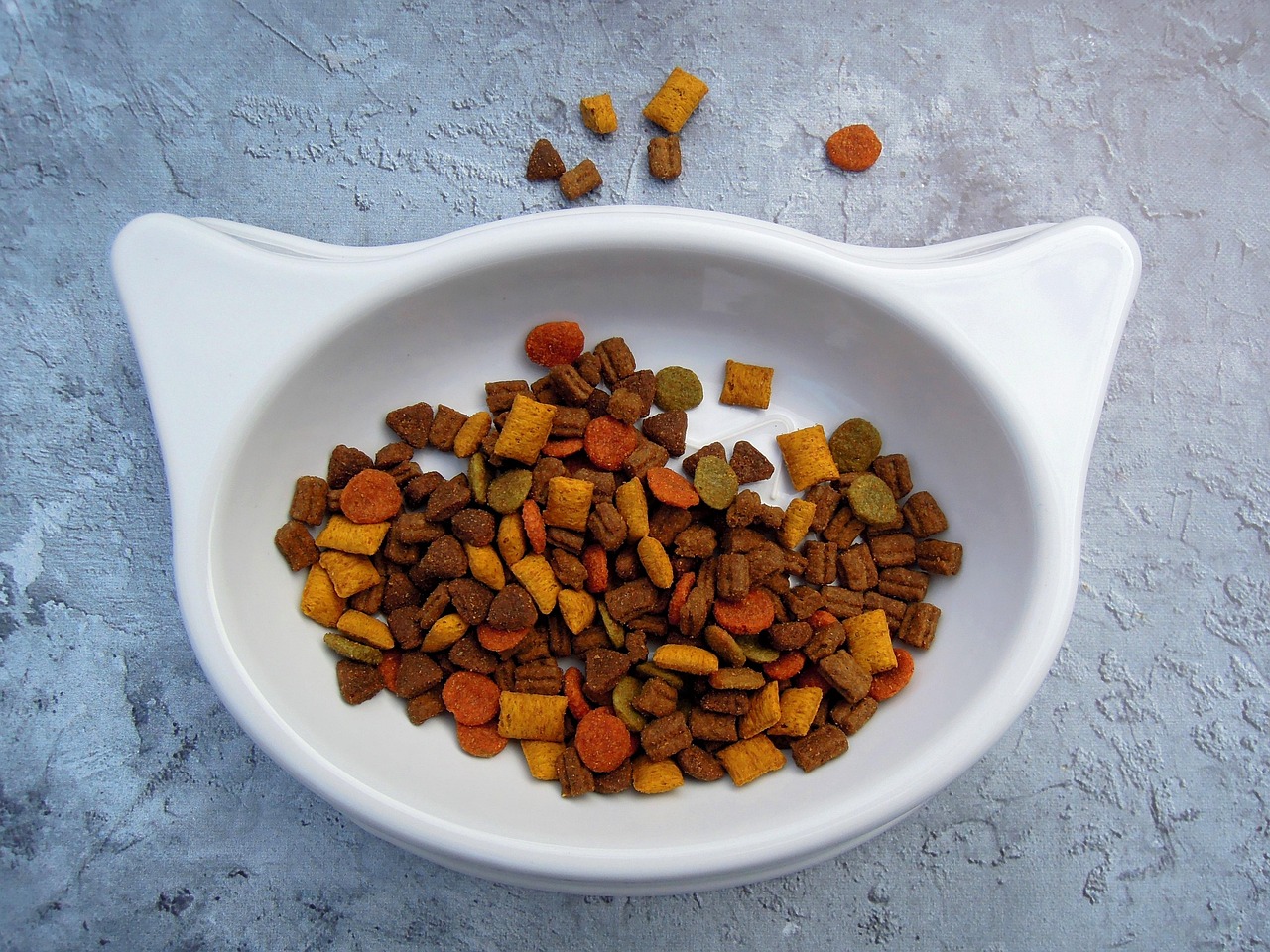
Canned cat food
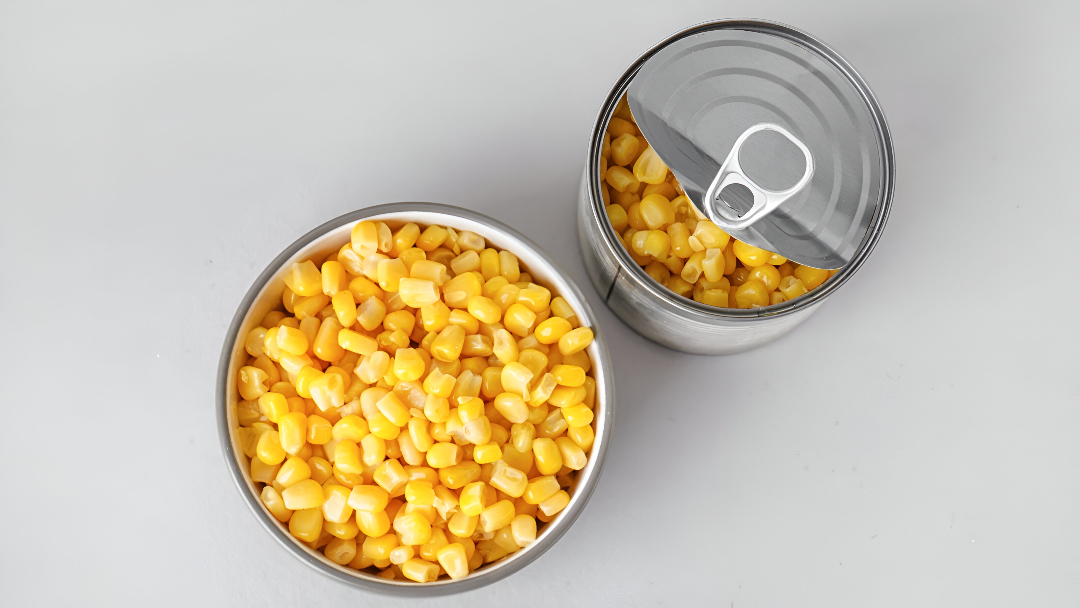
Canned corn

Canned dog food
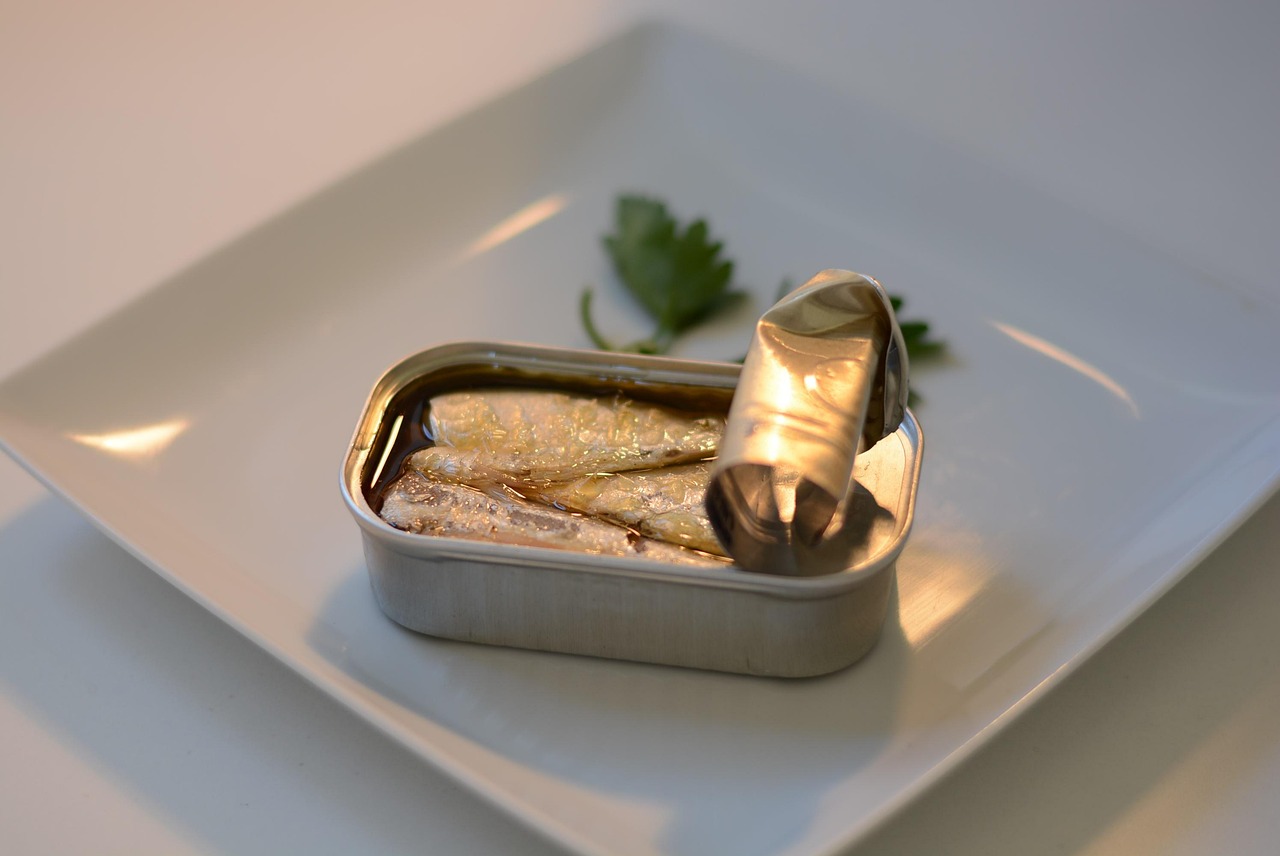
Canned fish

Canned fruits
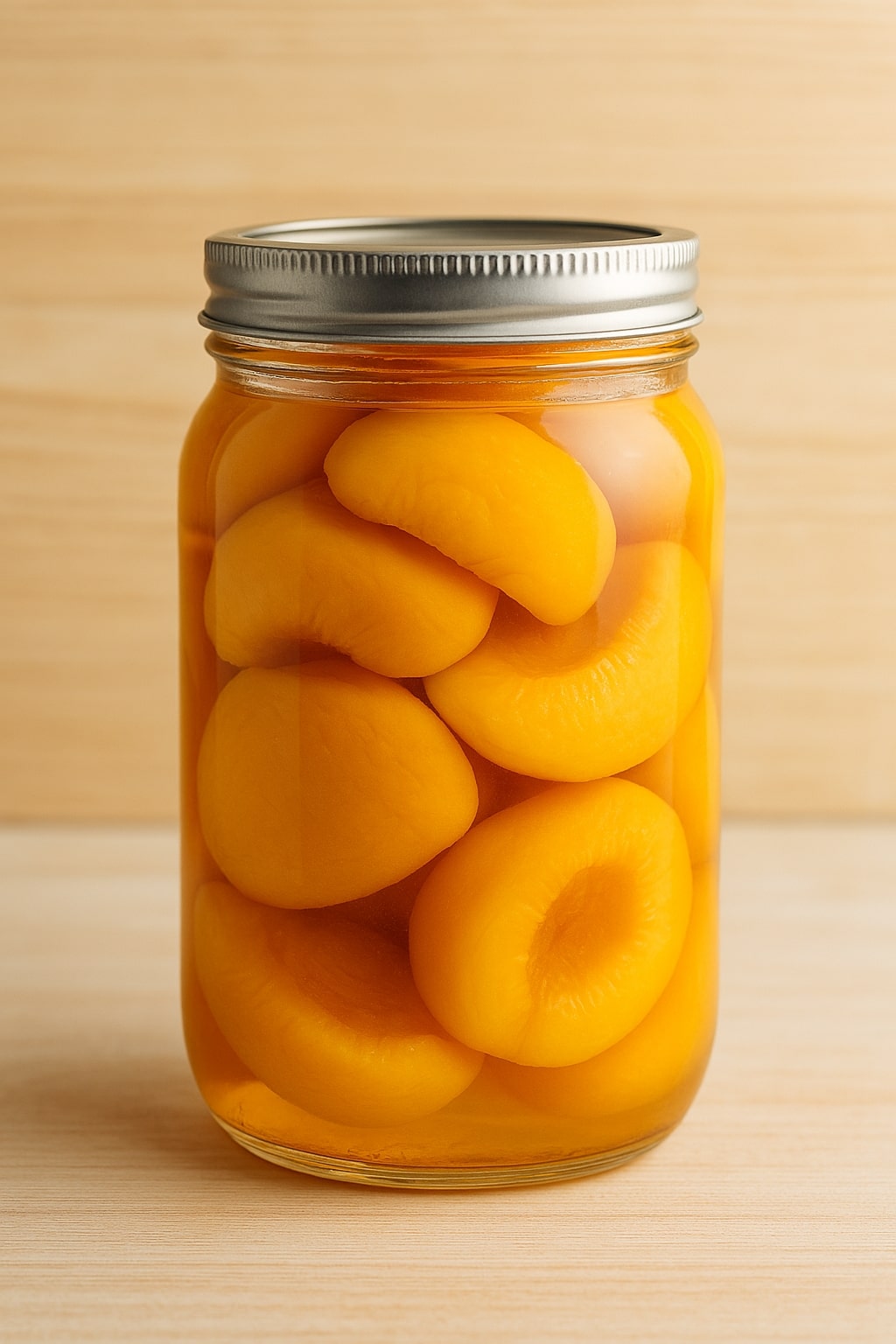
Canned peaches
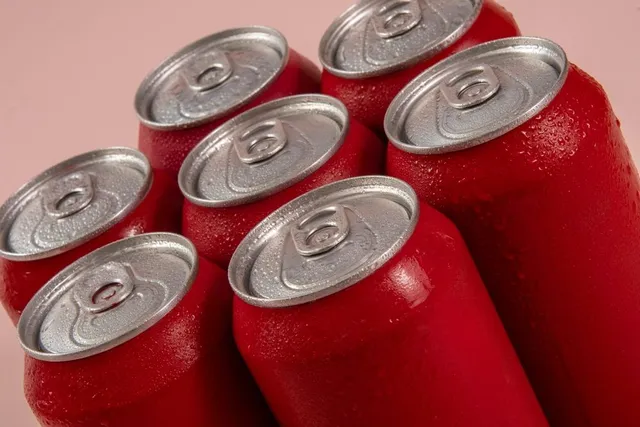
Canned soft drinks
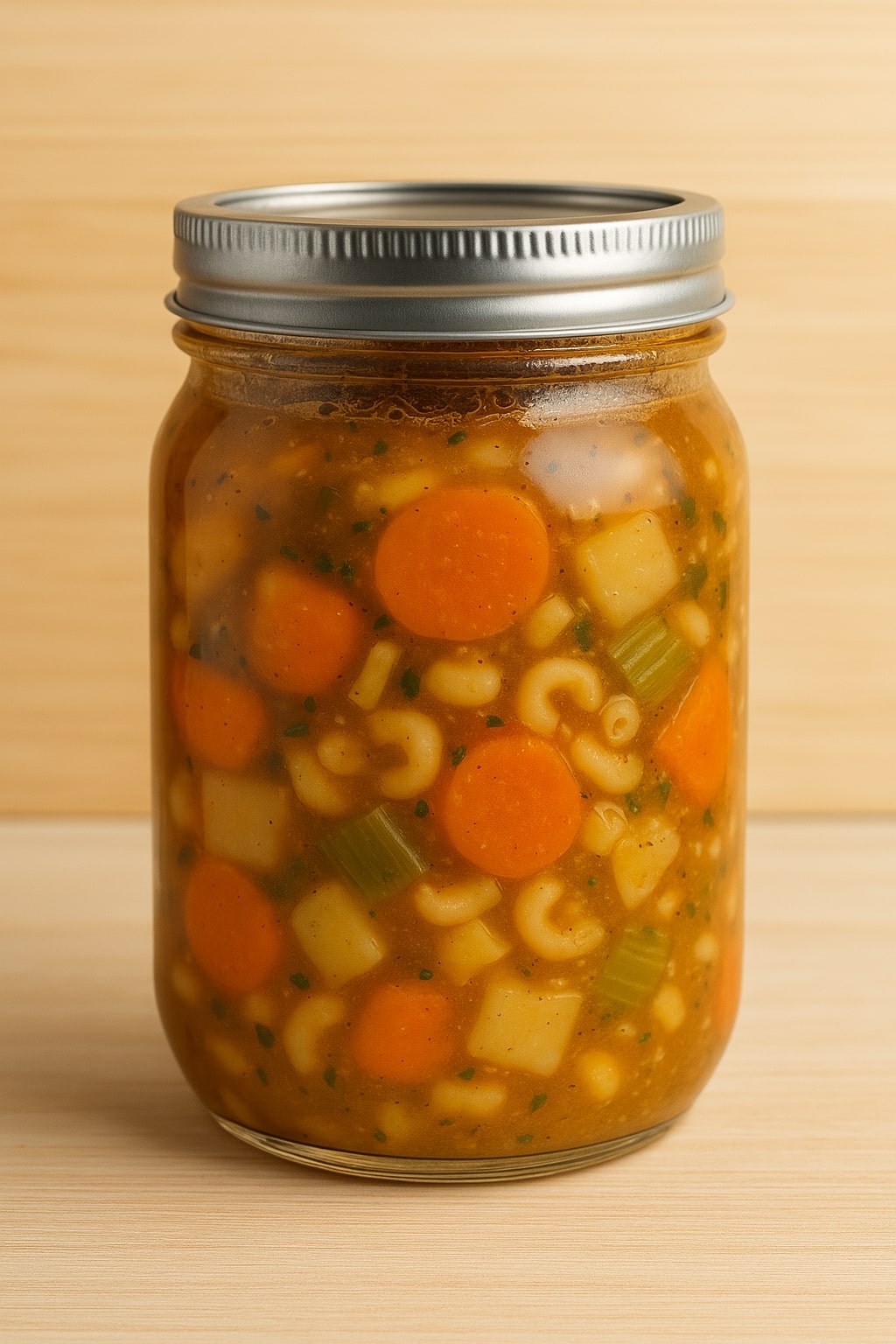
Canned soup
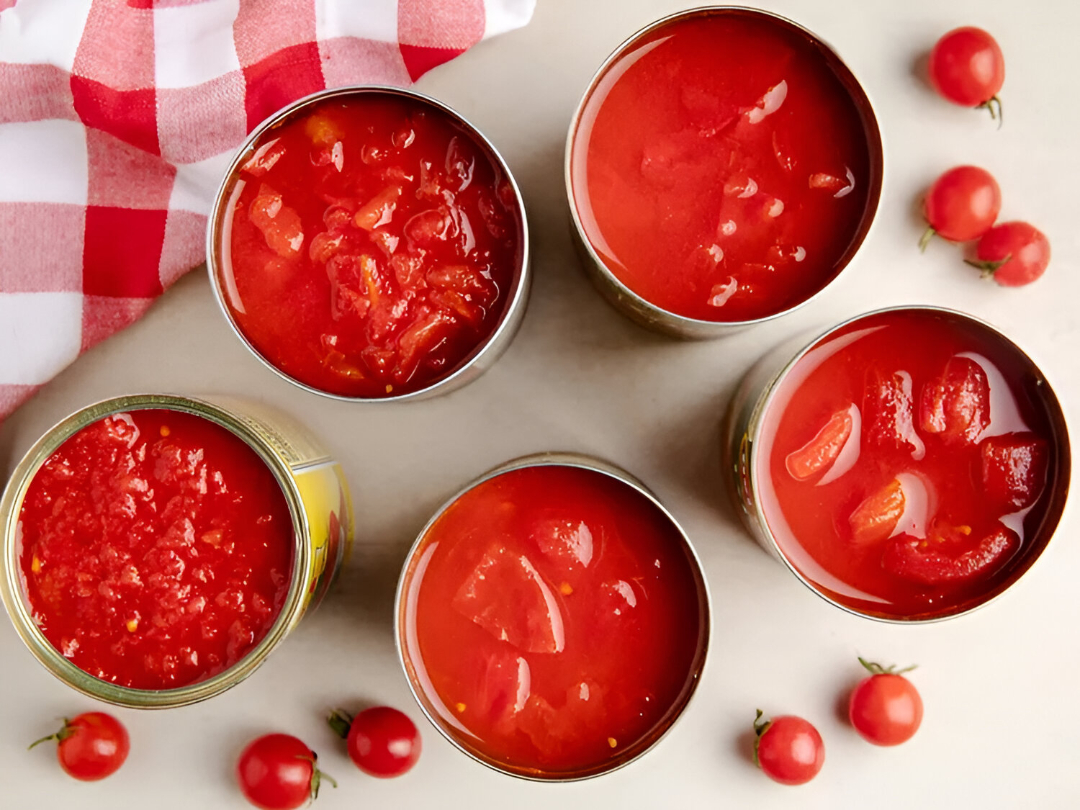
Canned tomatoes
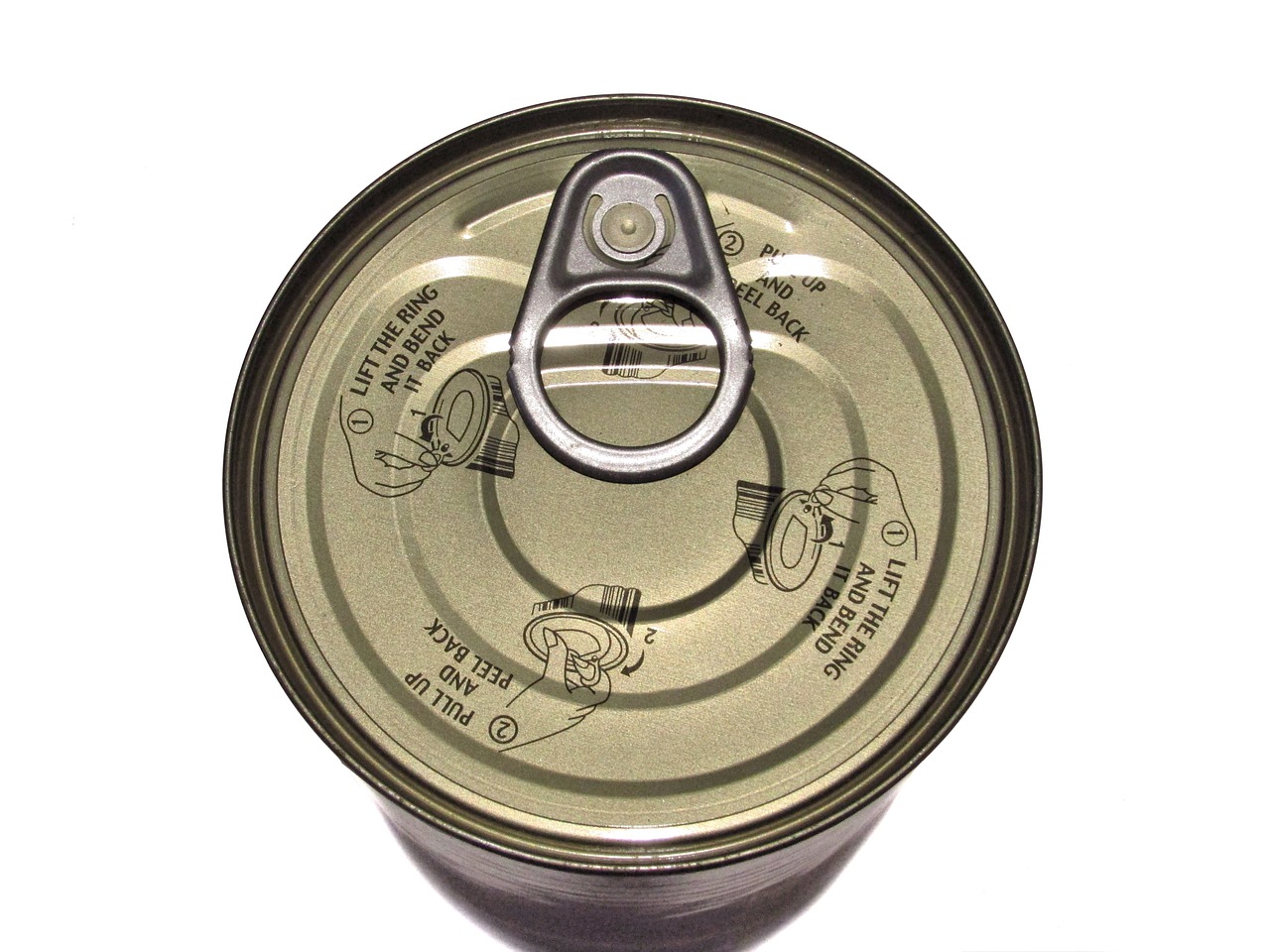
Cans
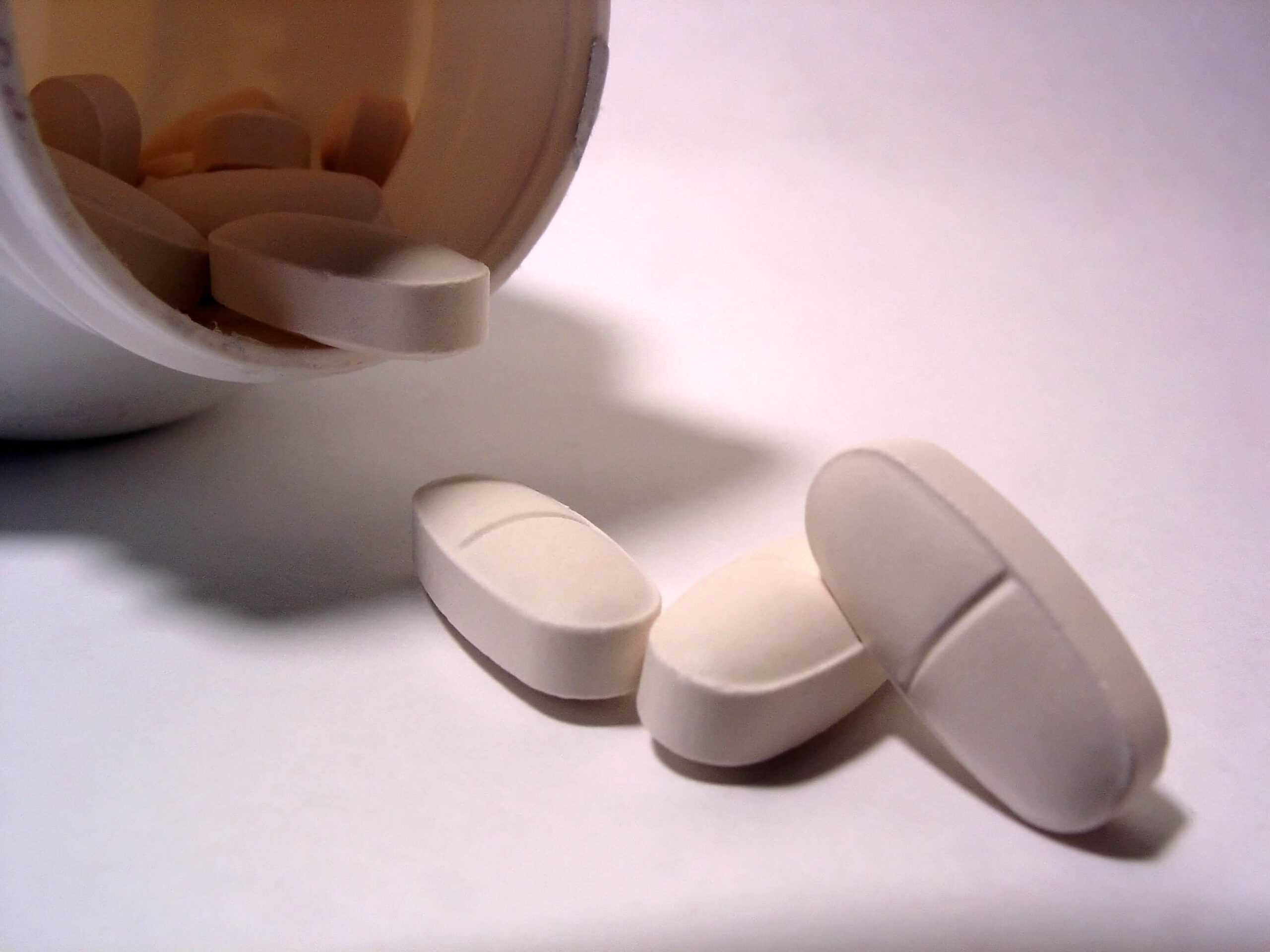
Caplets
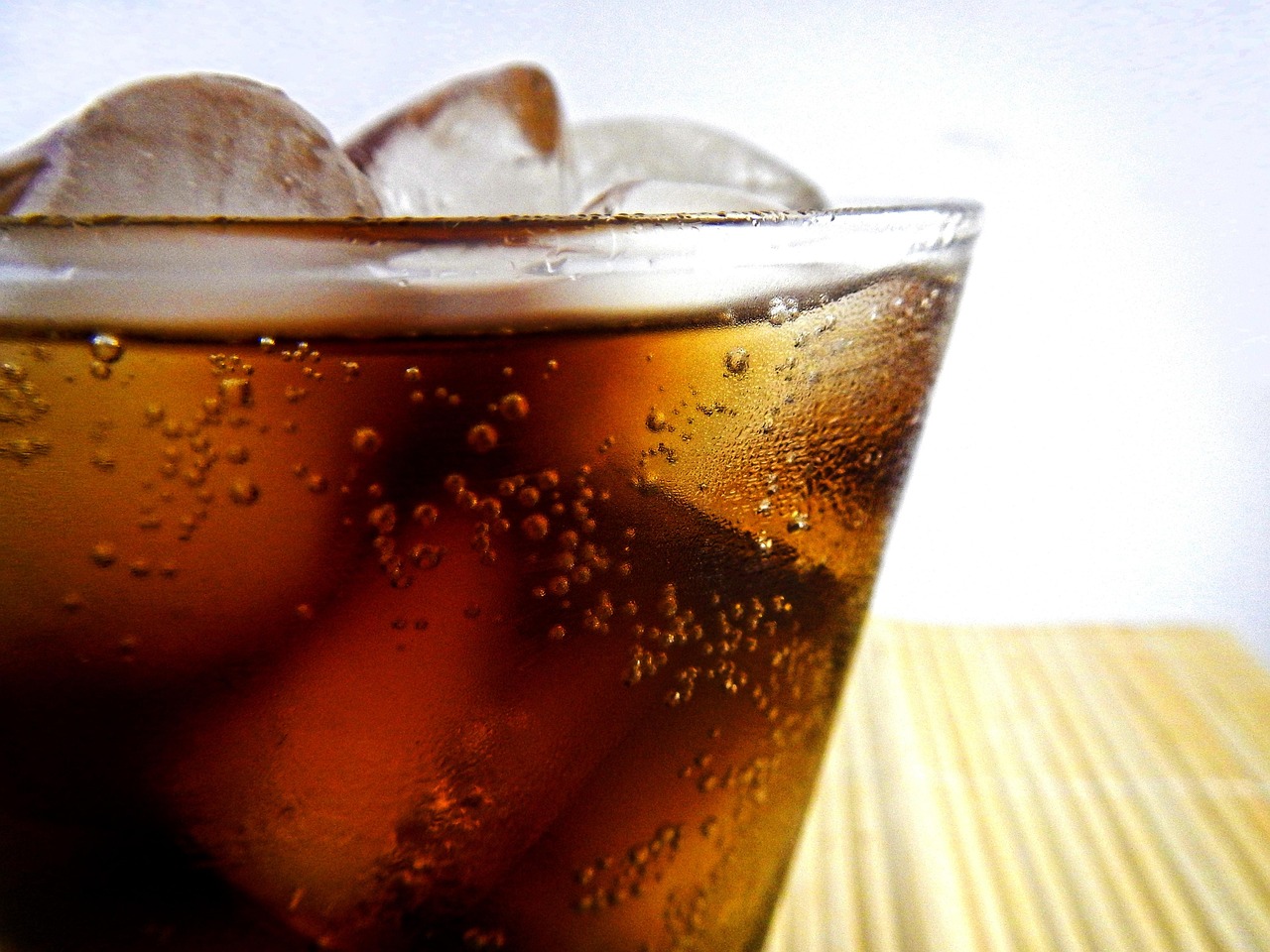
Carbonated beverages
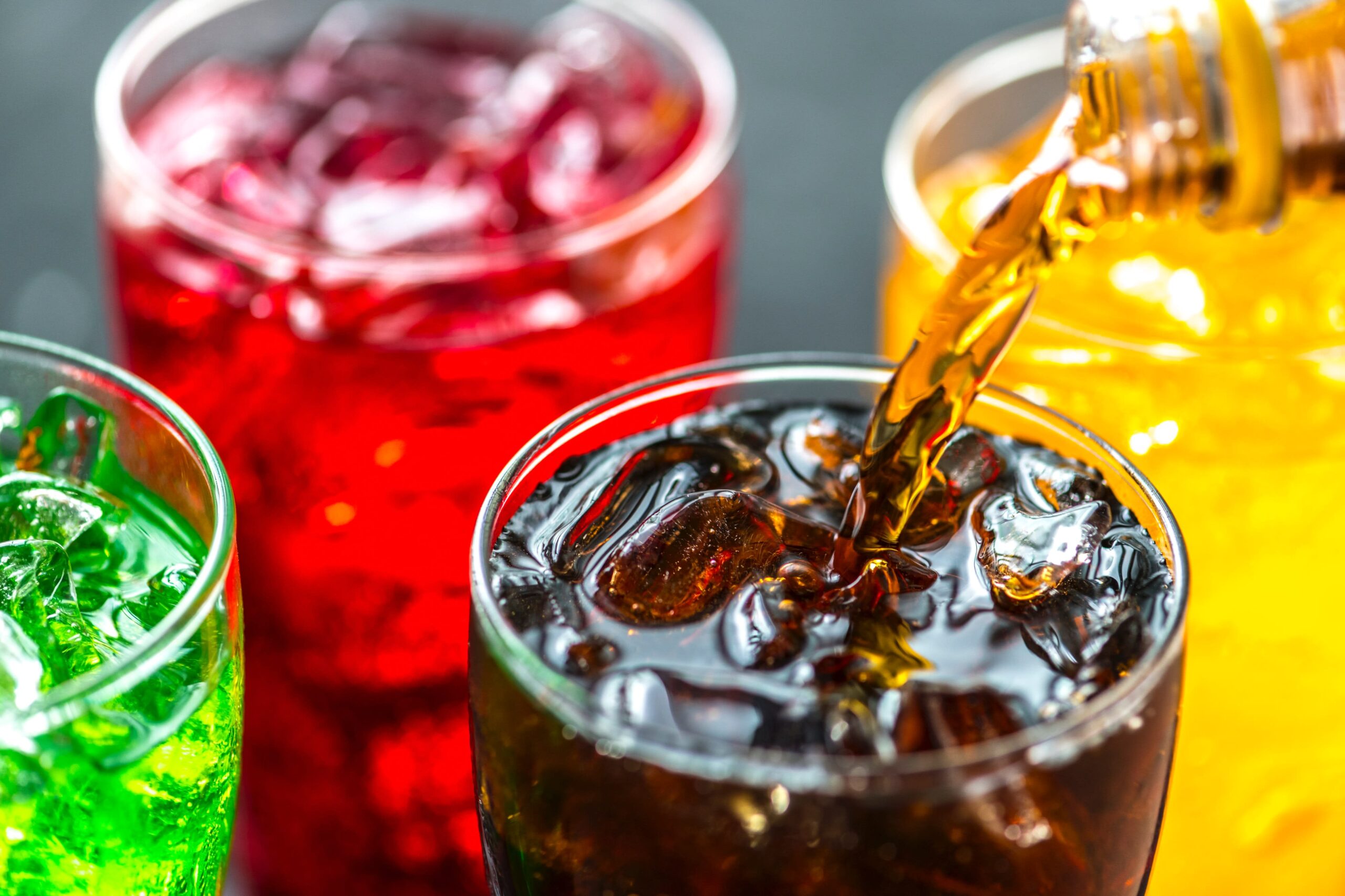
Carbonated soft drinks (csd)
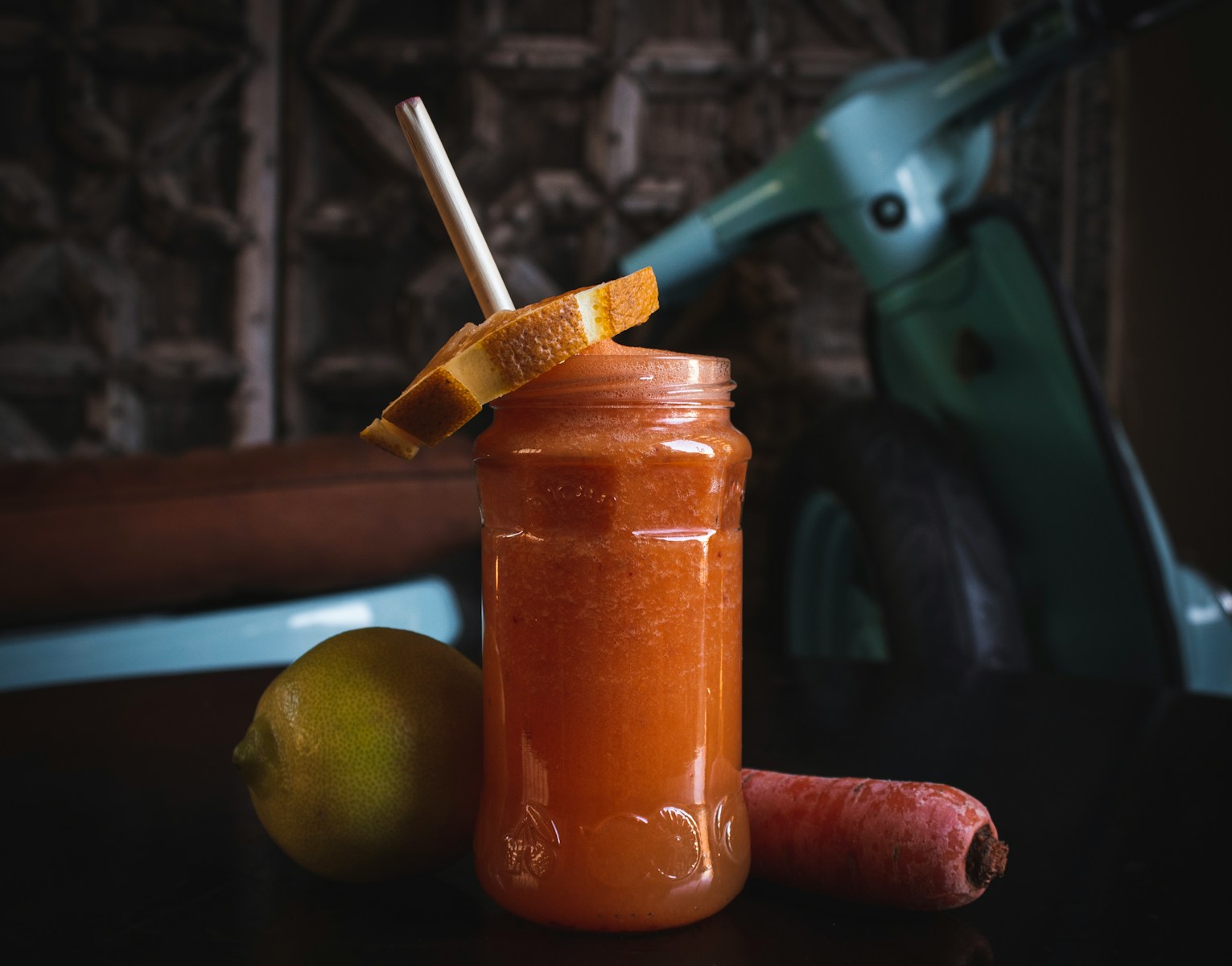
Carrot juice
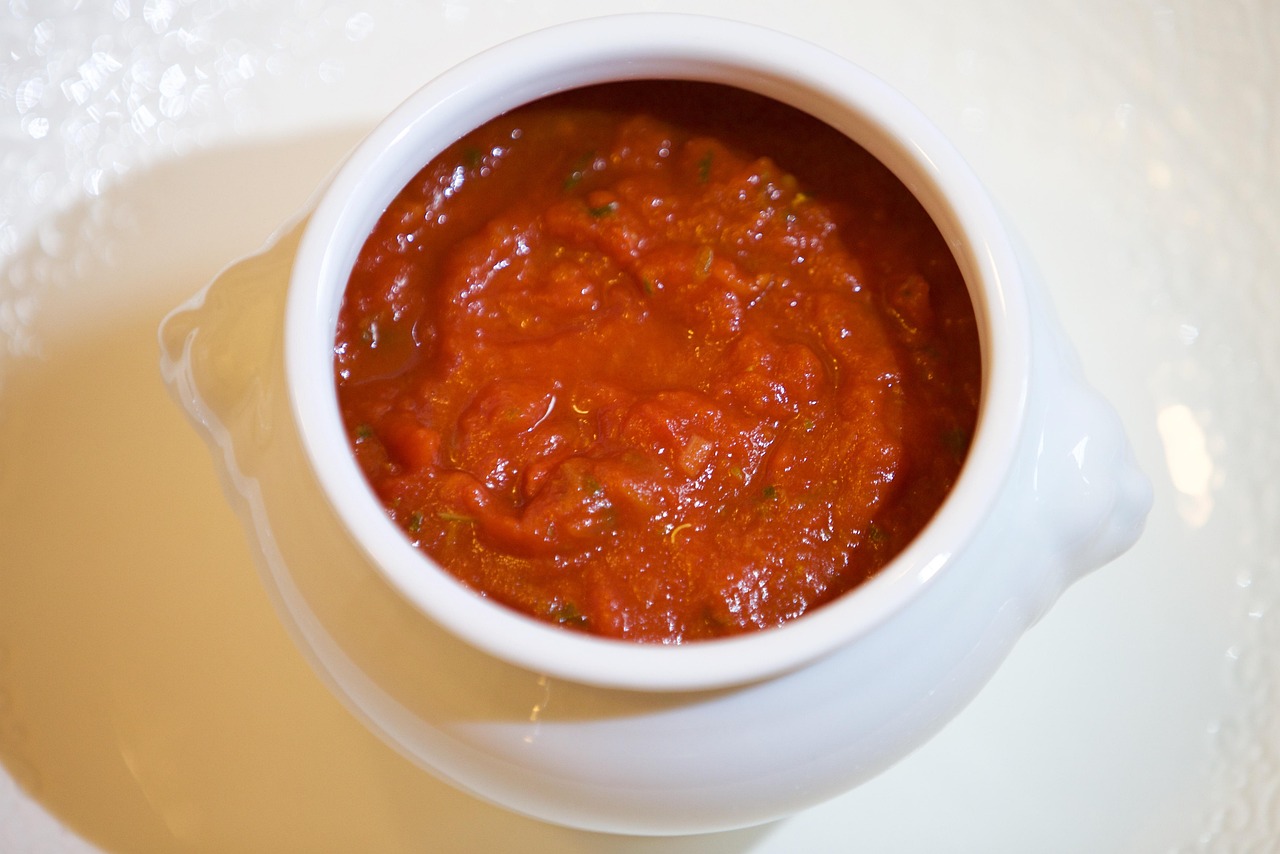
Carrot puree
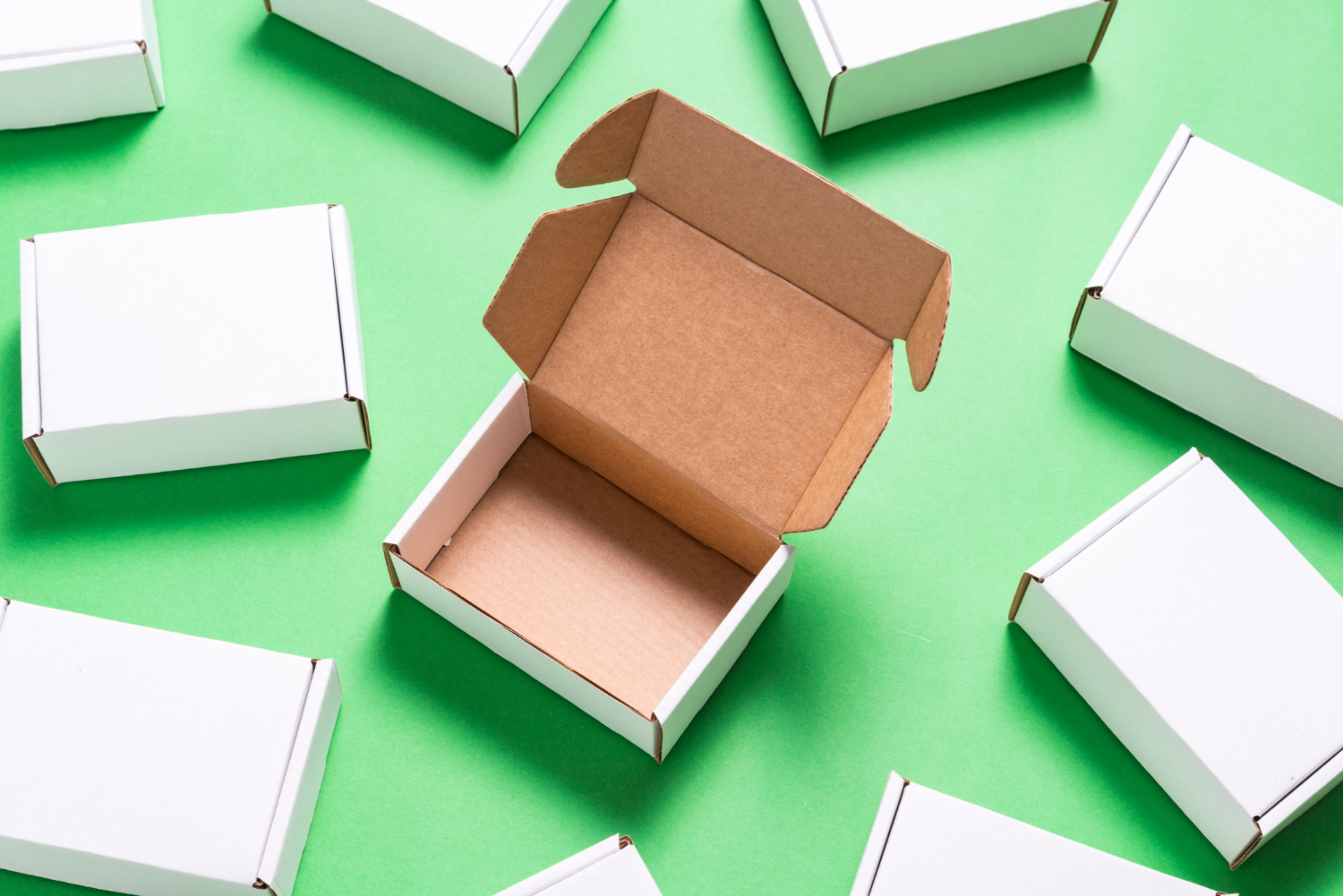
Cartons
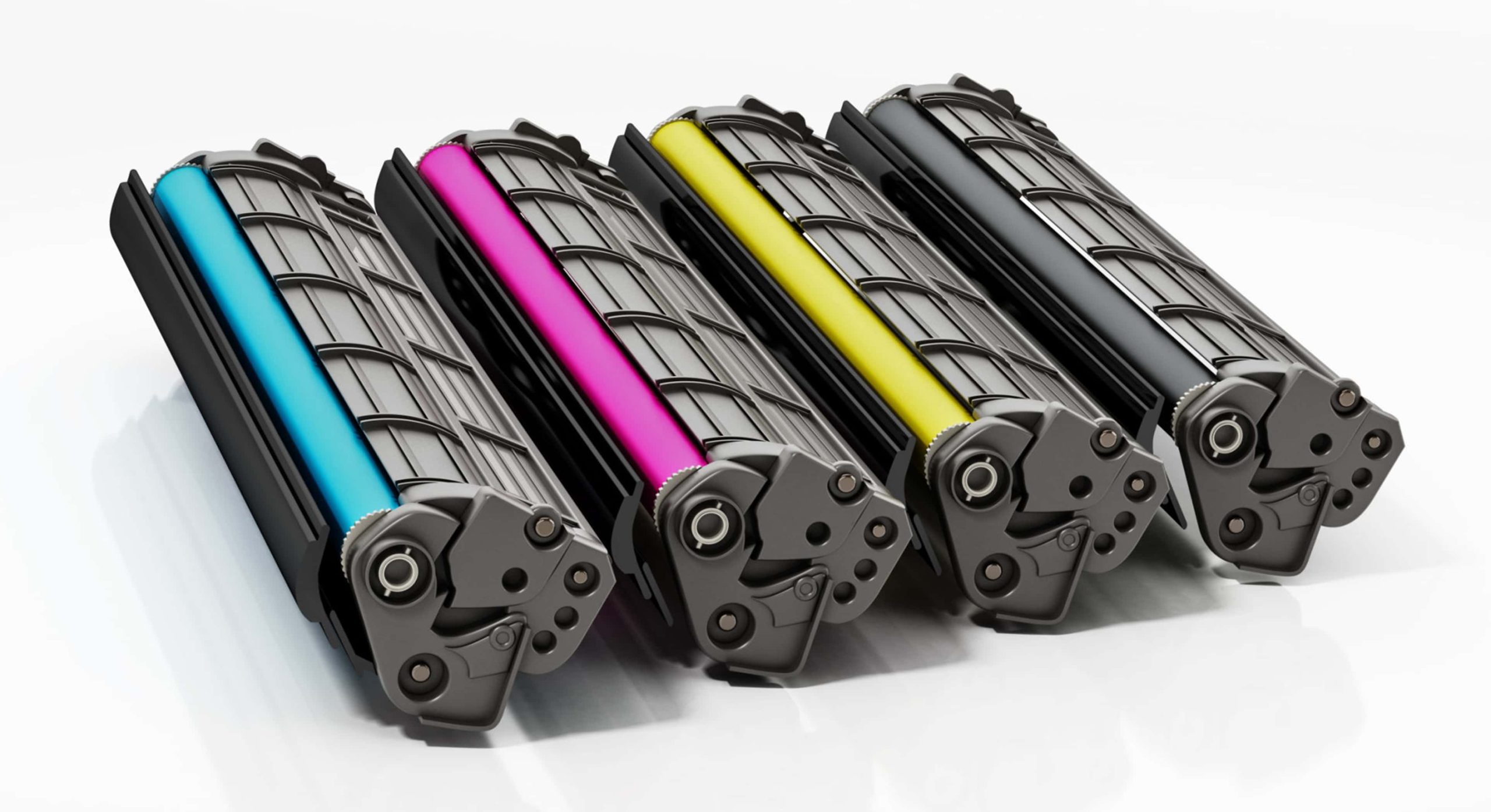
Cartridges
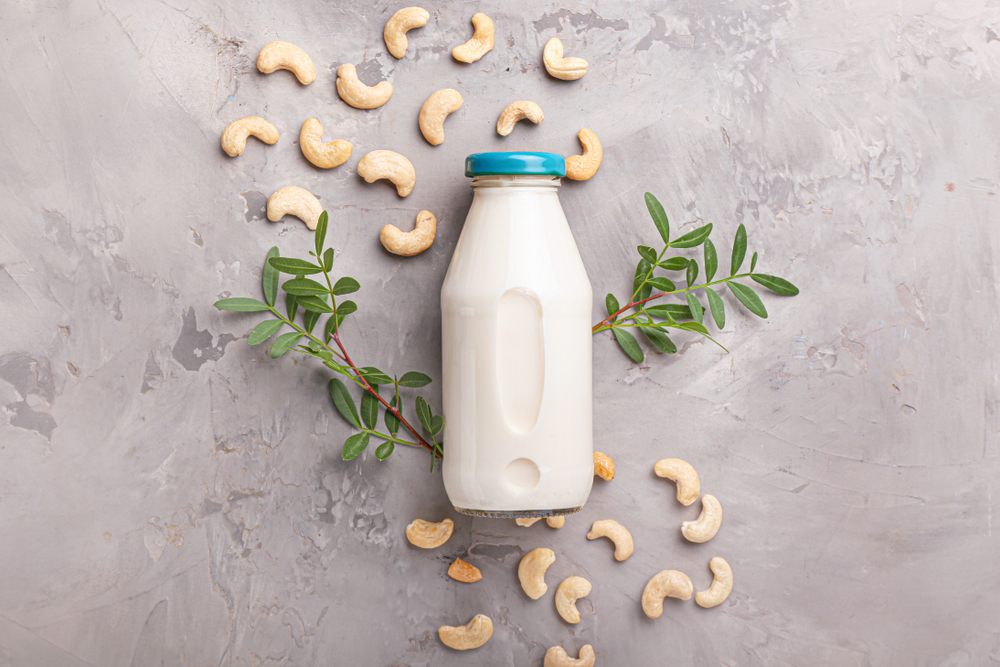
Cashew milk

Cat food
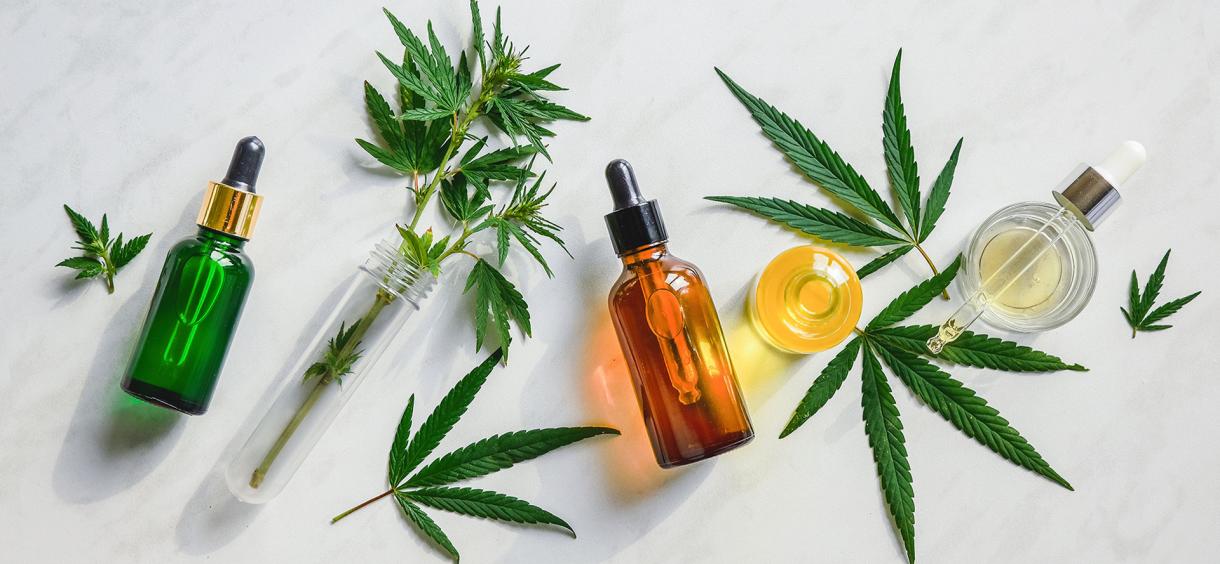
Cbd distillate
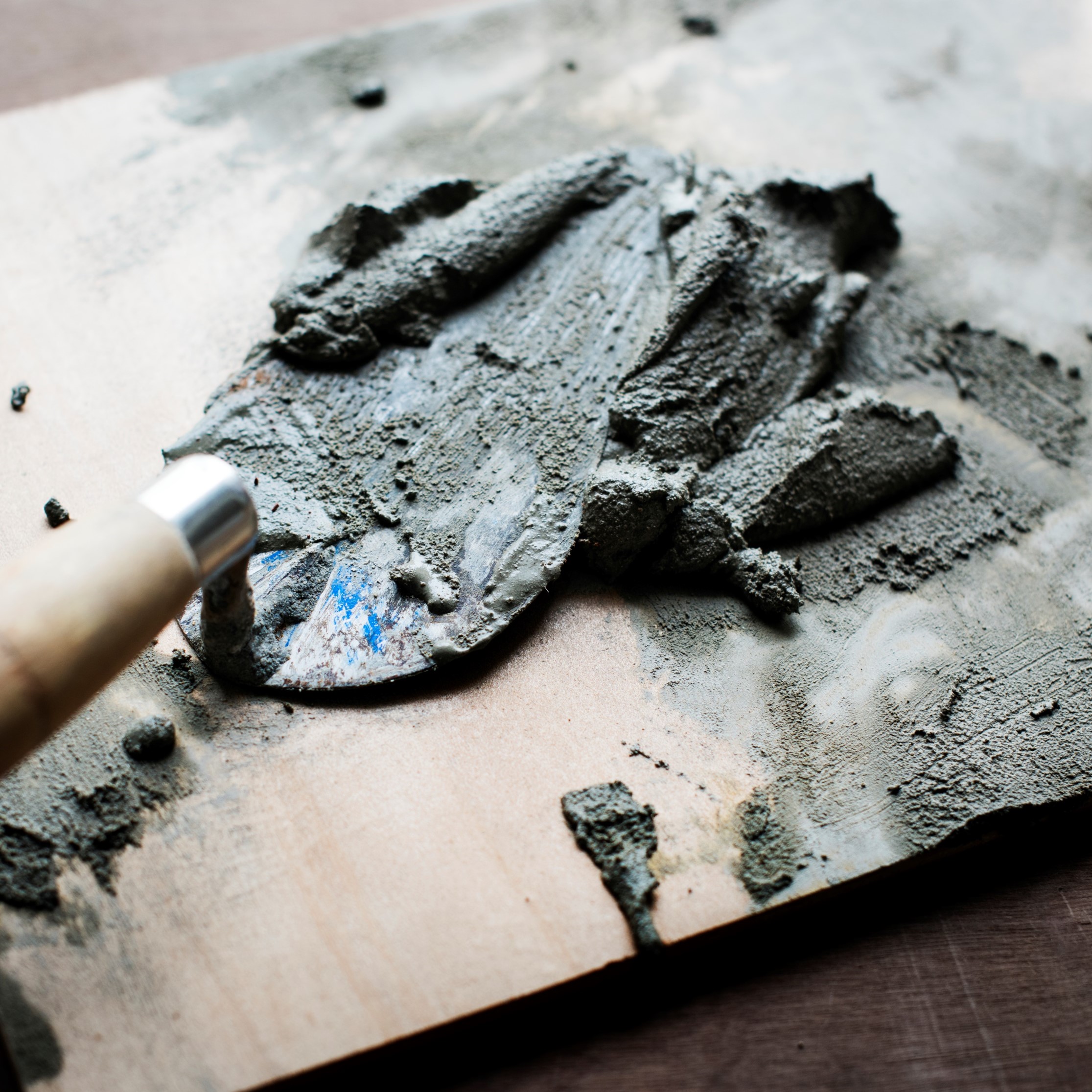
Cement
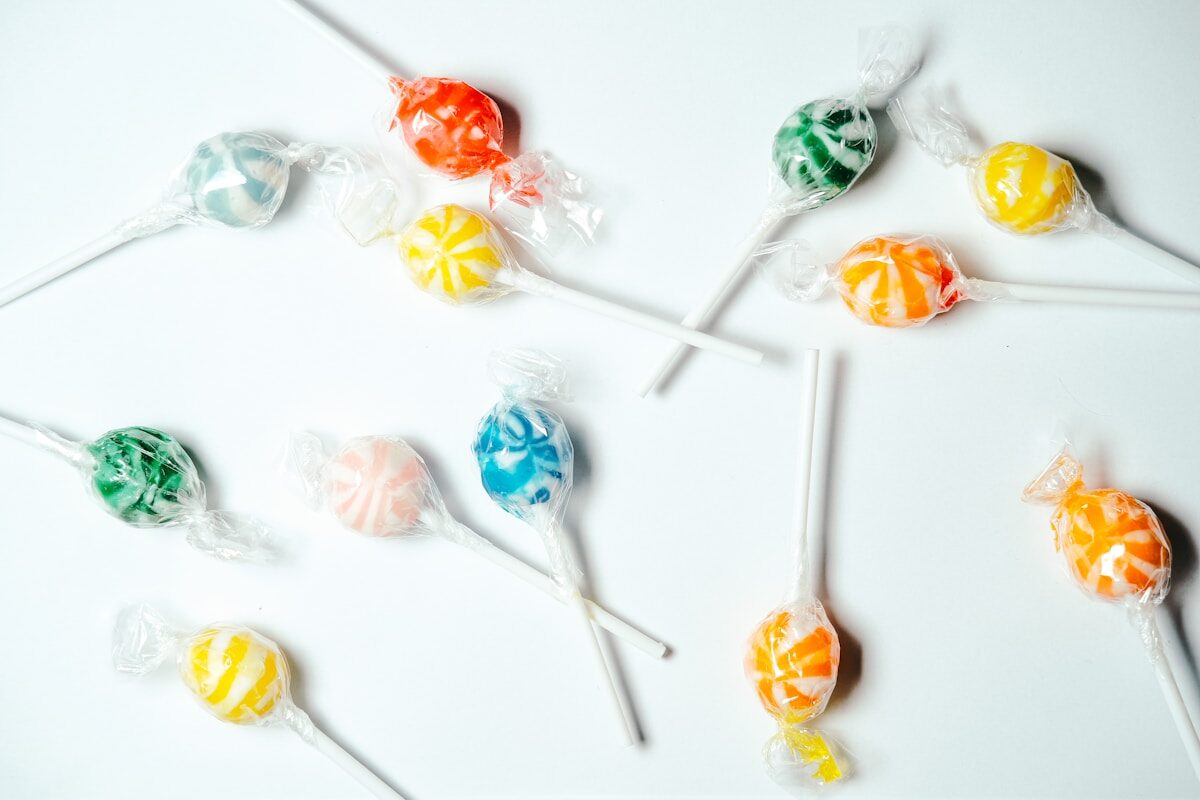
Center-filled lollipops
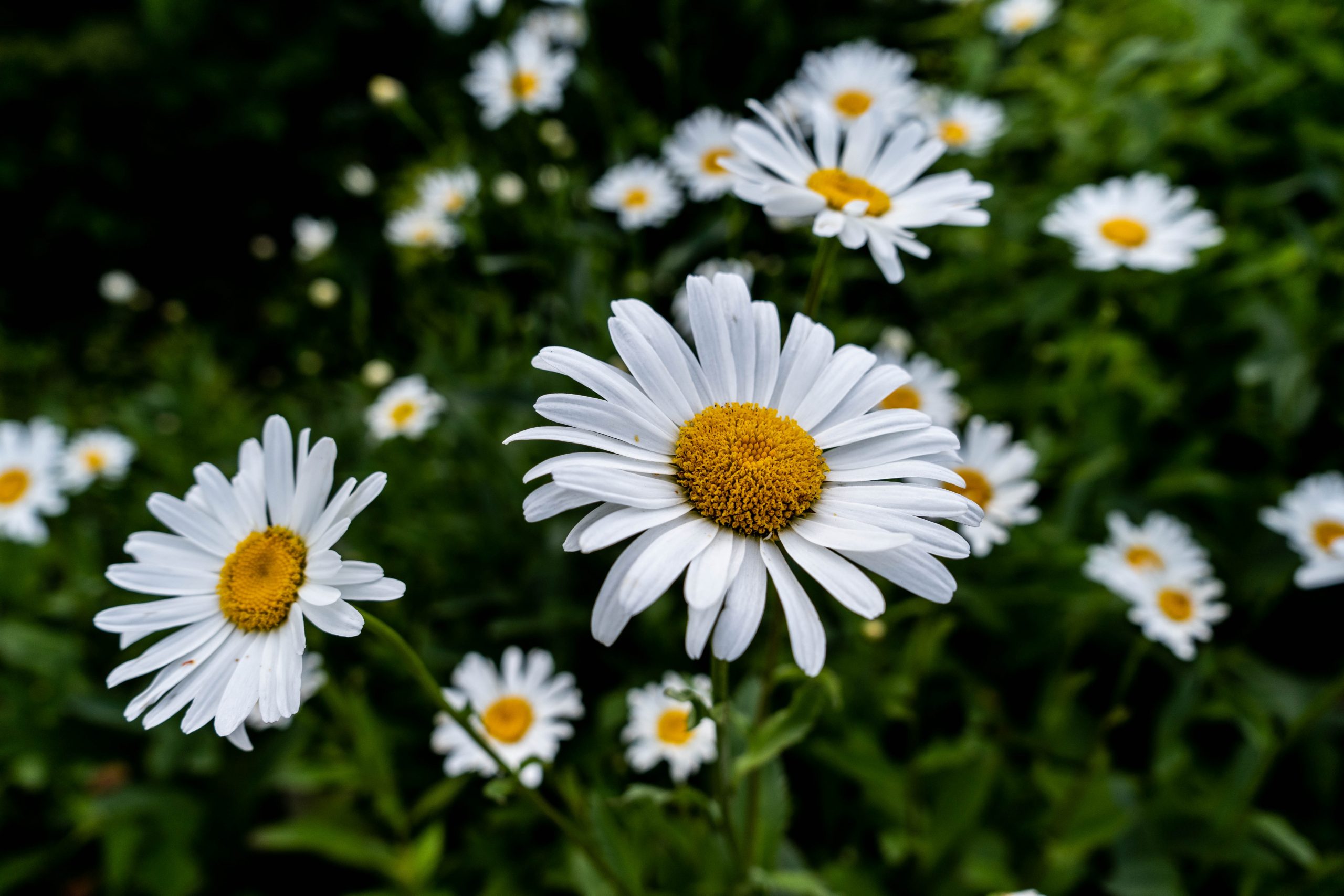
Chamomile oil
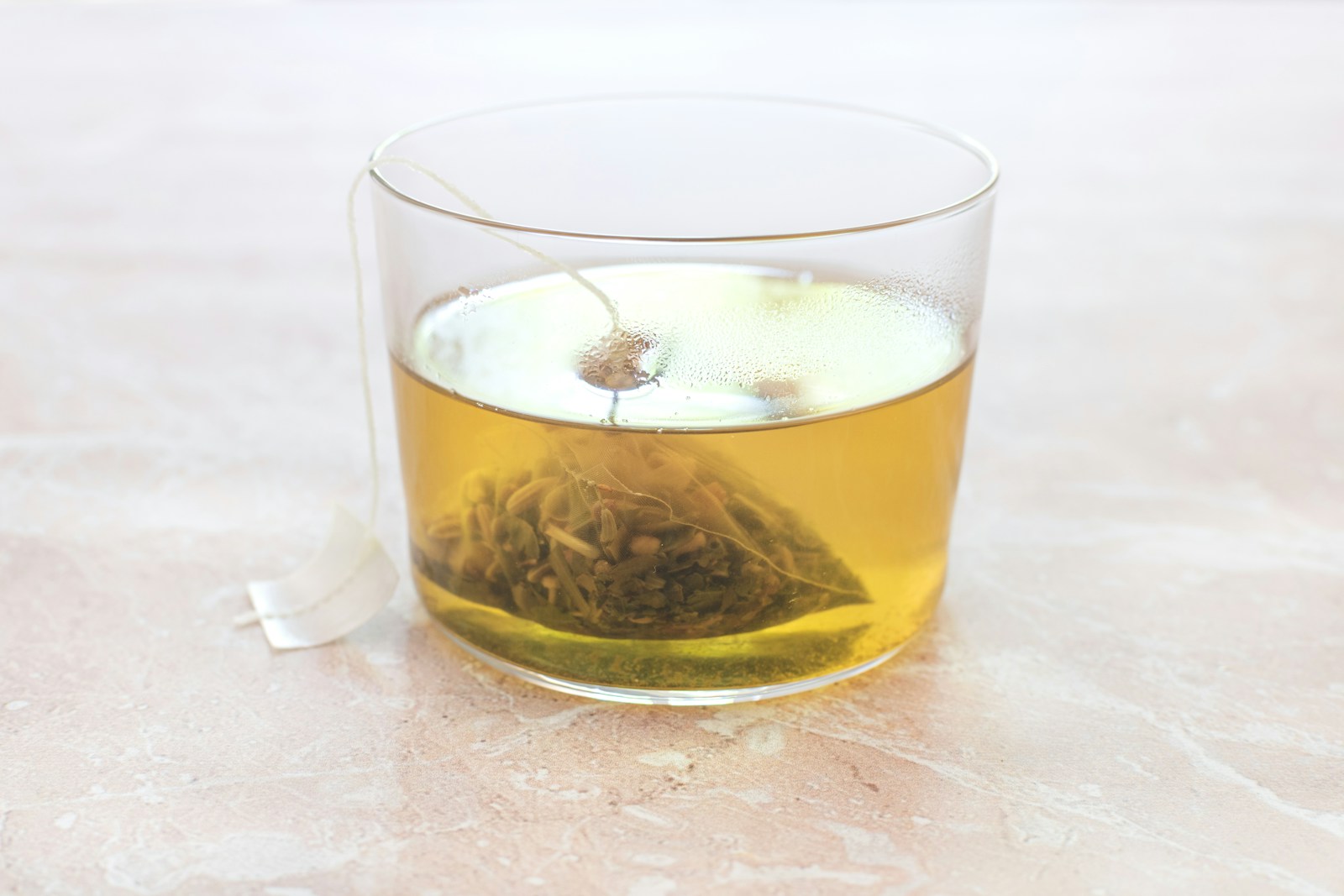
Chamomile tea bags
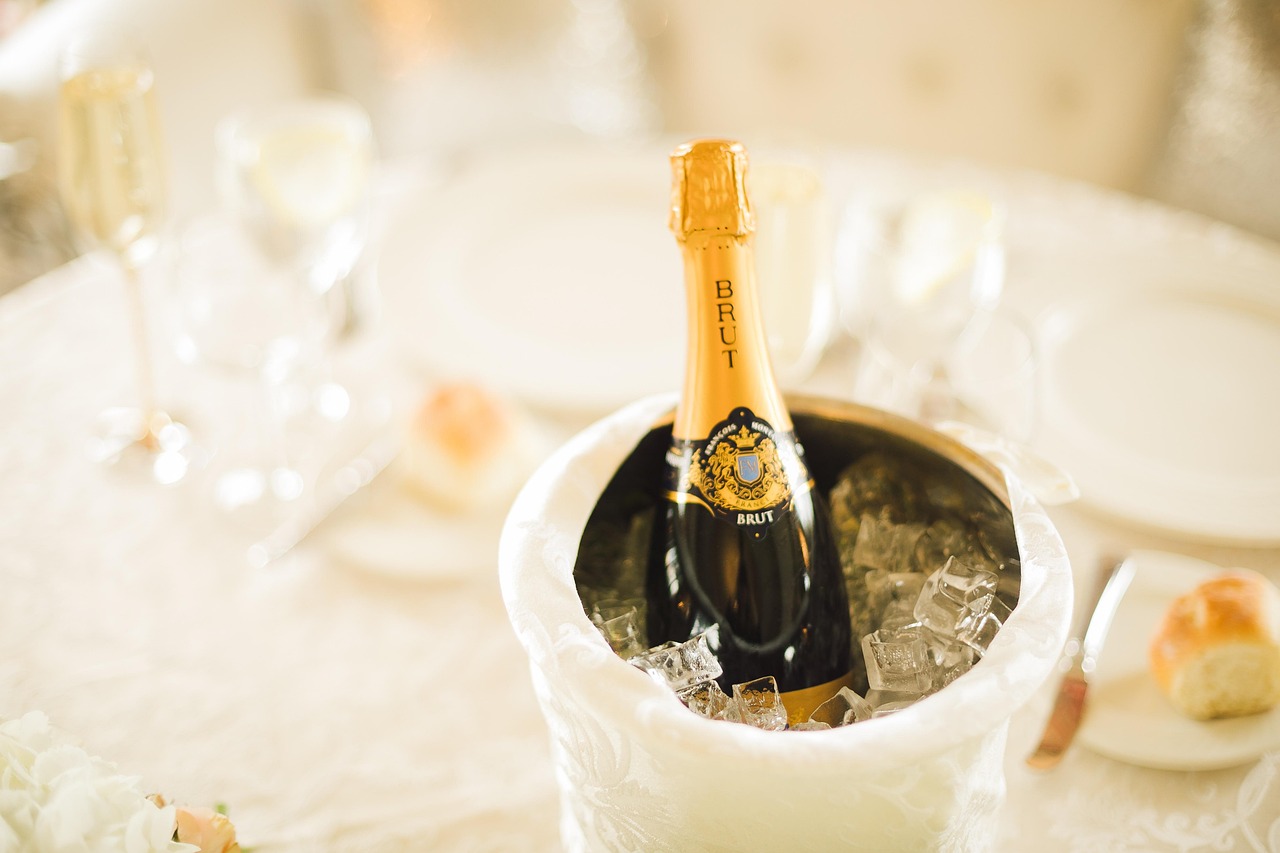
Champagne
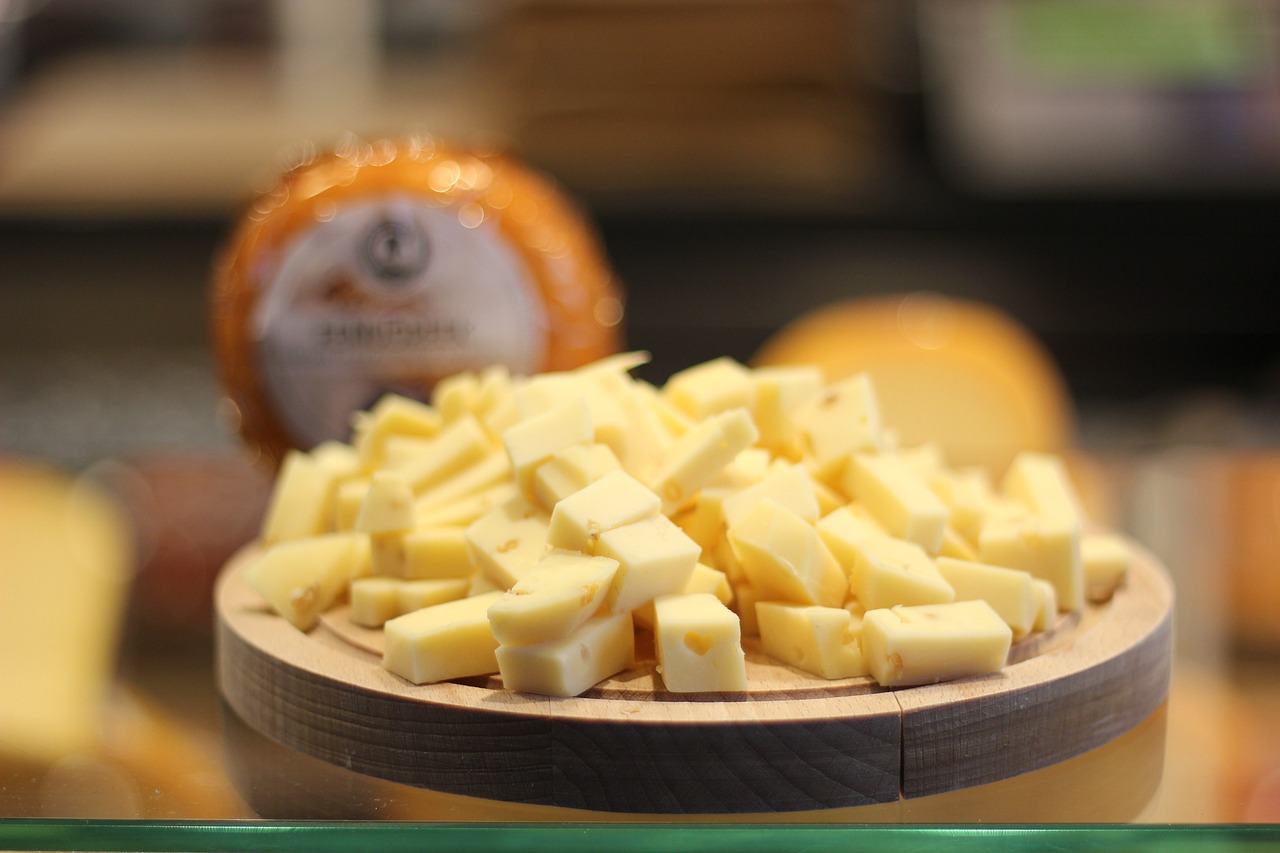
Cheese Blocks
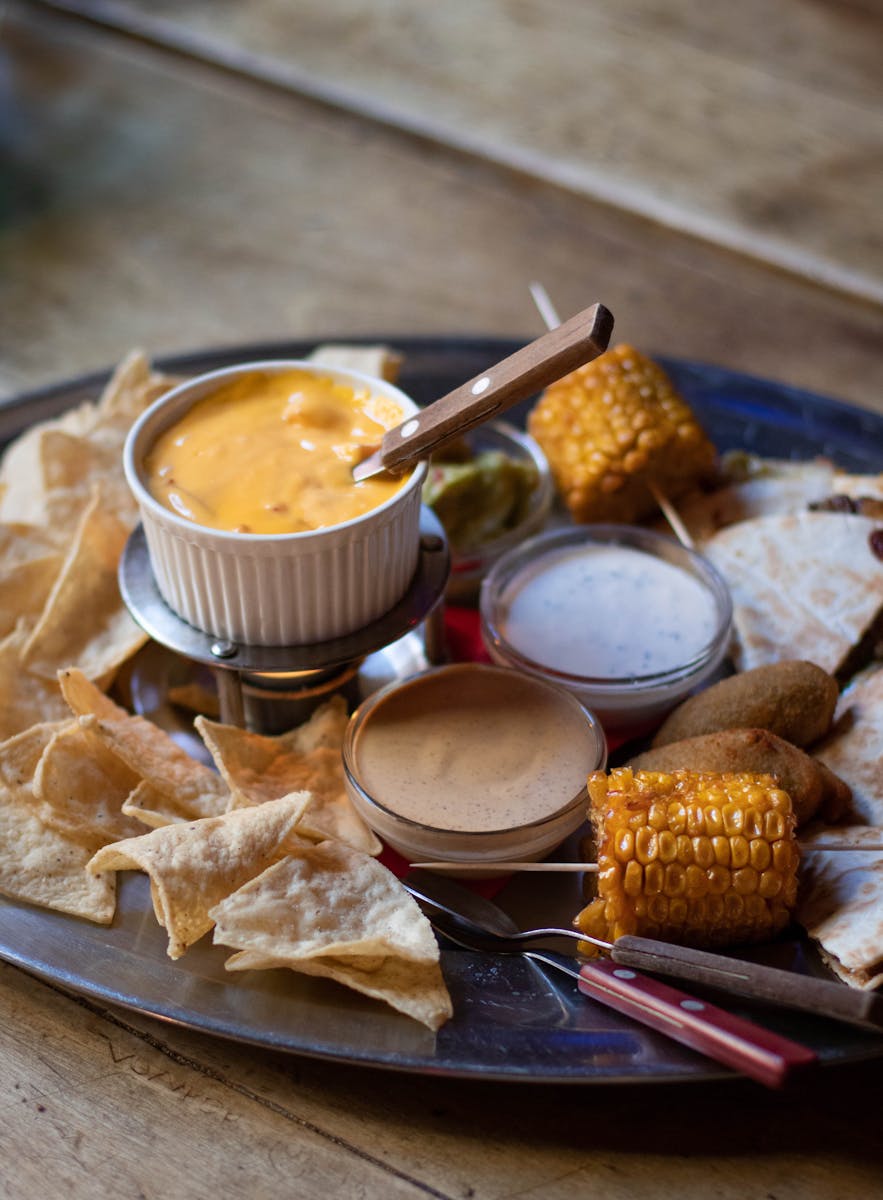
Cheese sauce
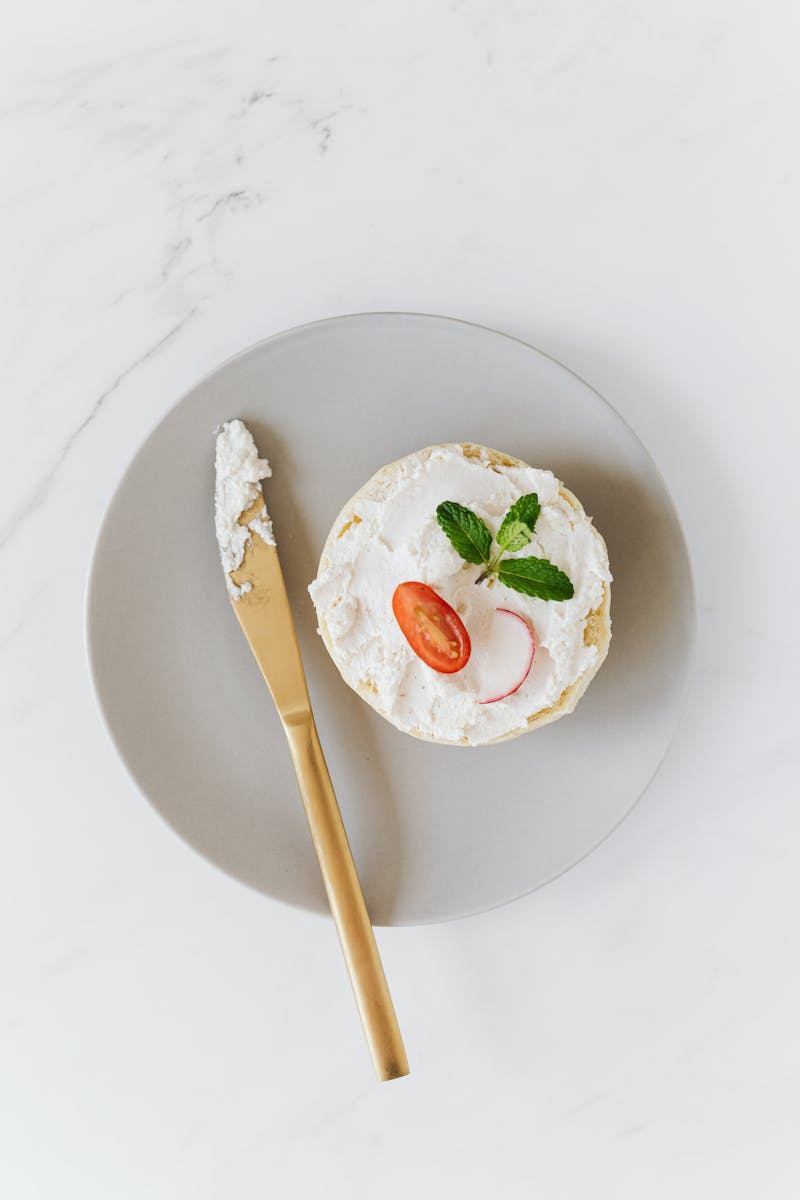
Cheese spreads
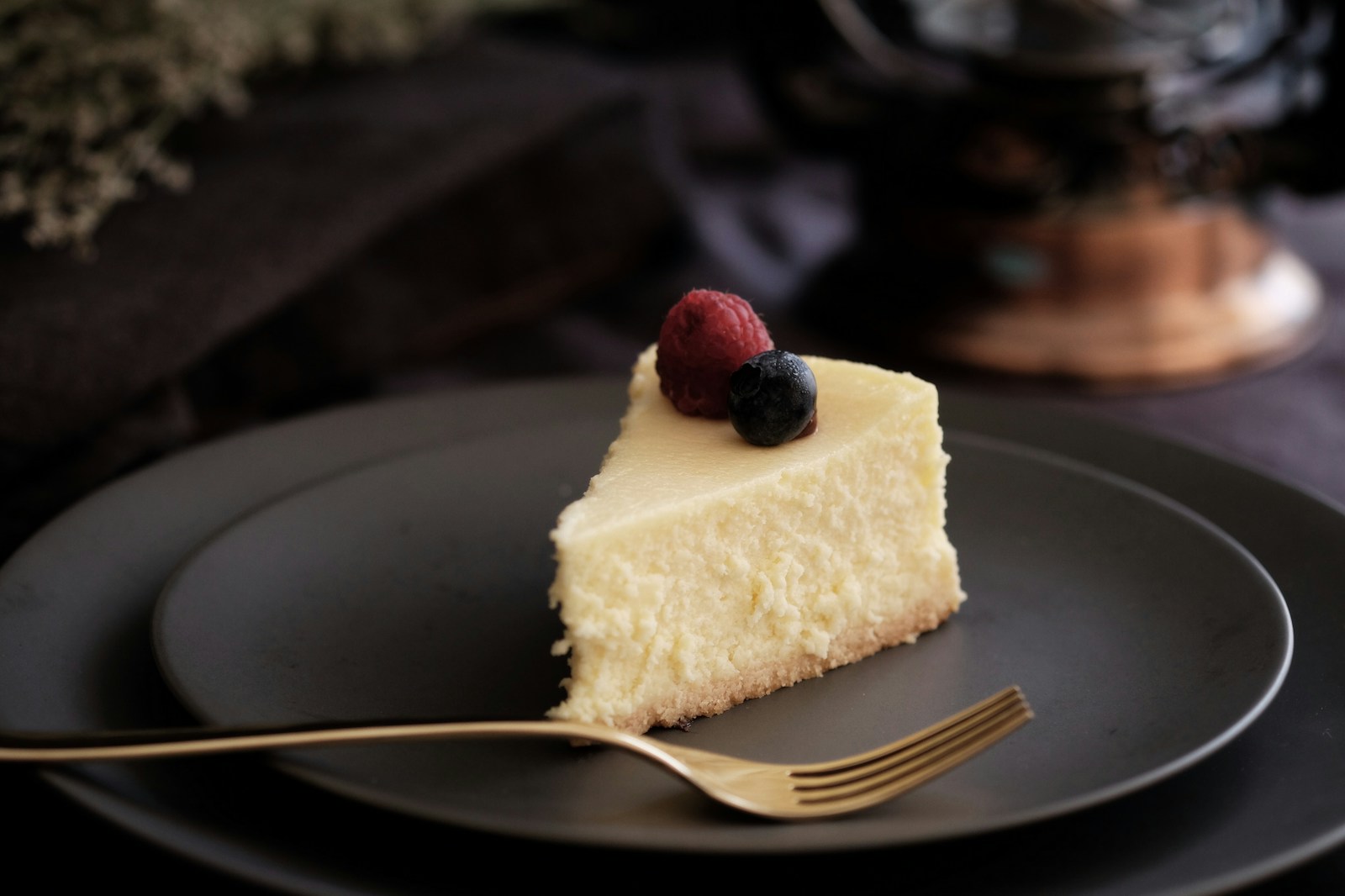
Cheesecake
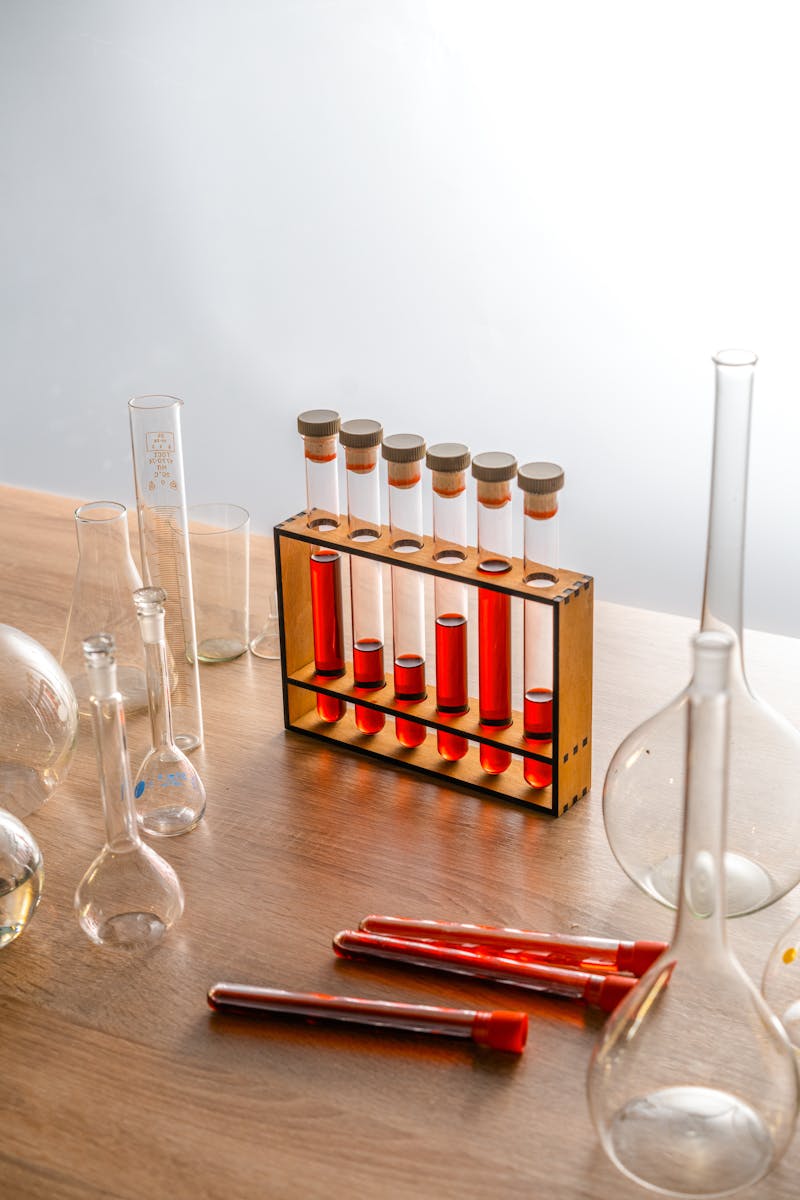
Chemical additives
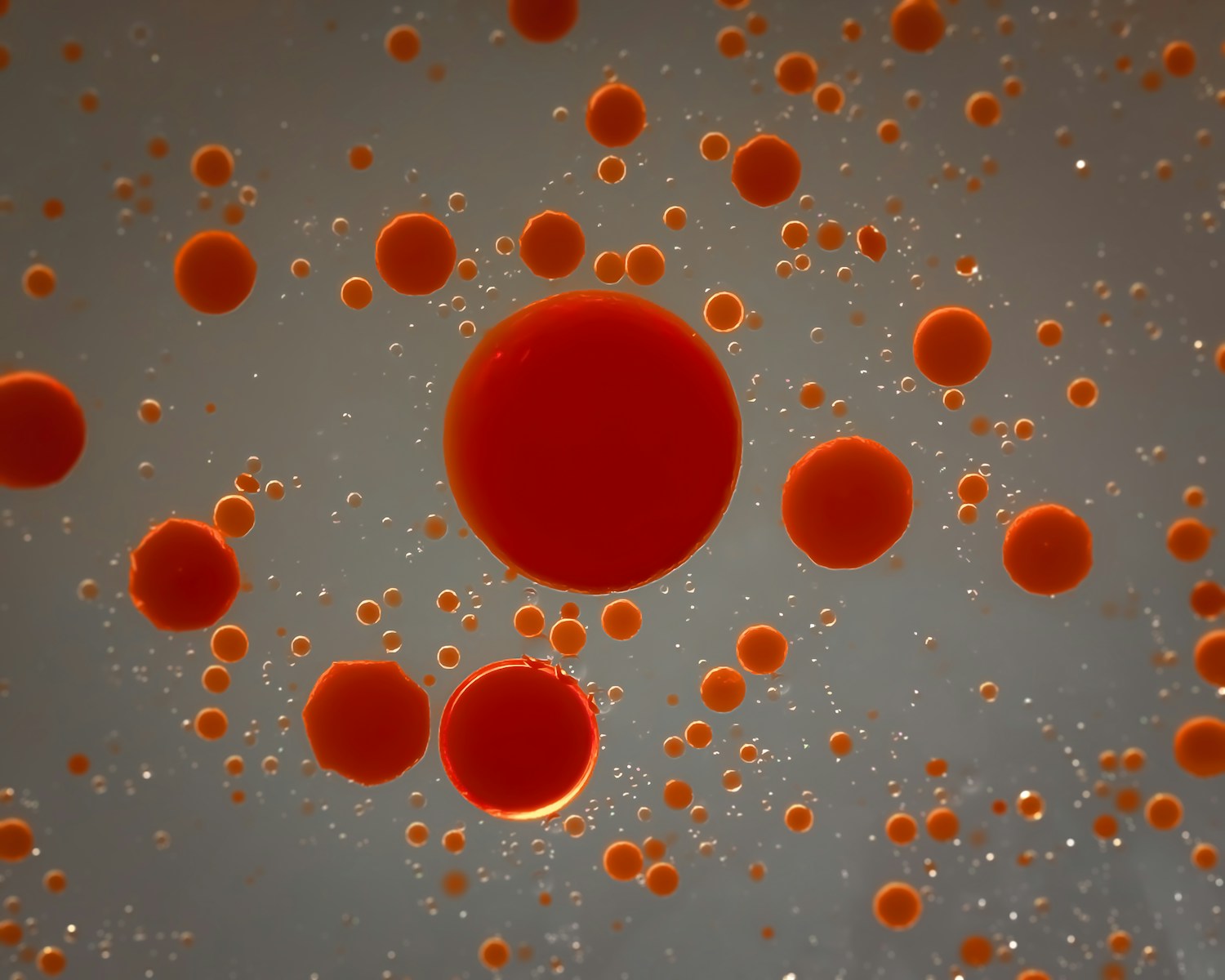
Chemical emulsions
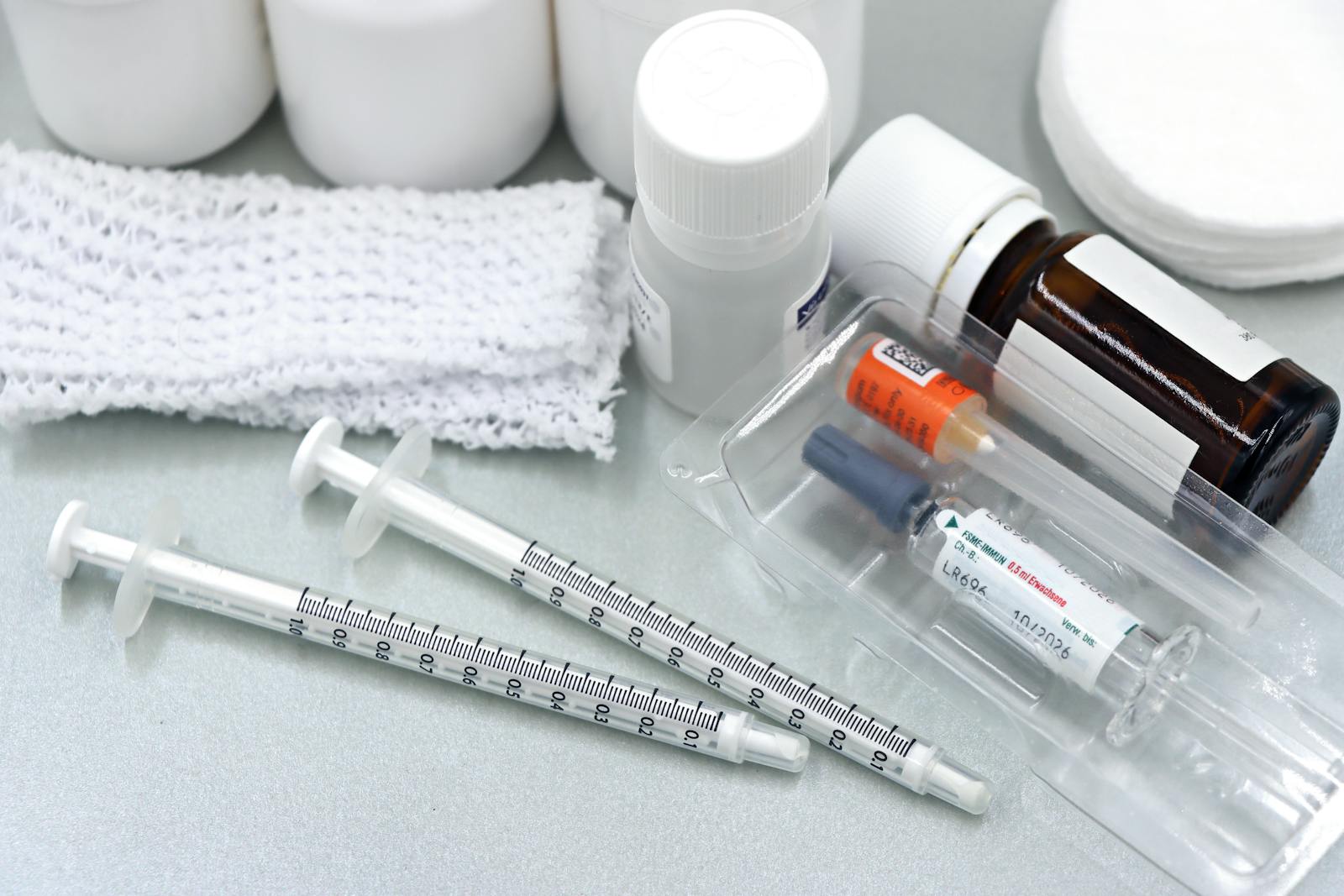
Chemotherapy drugs
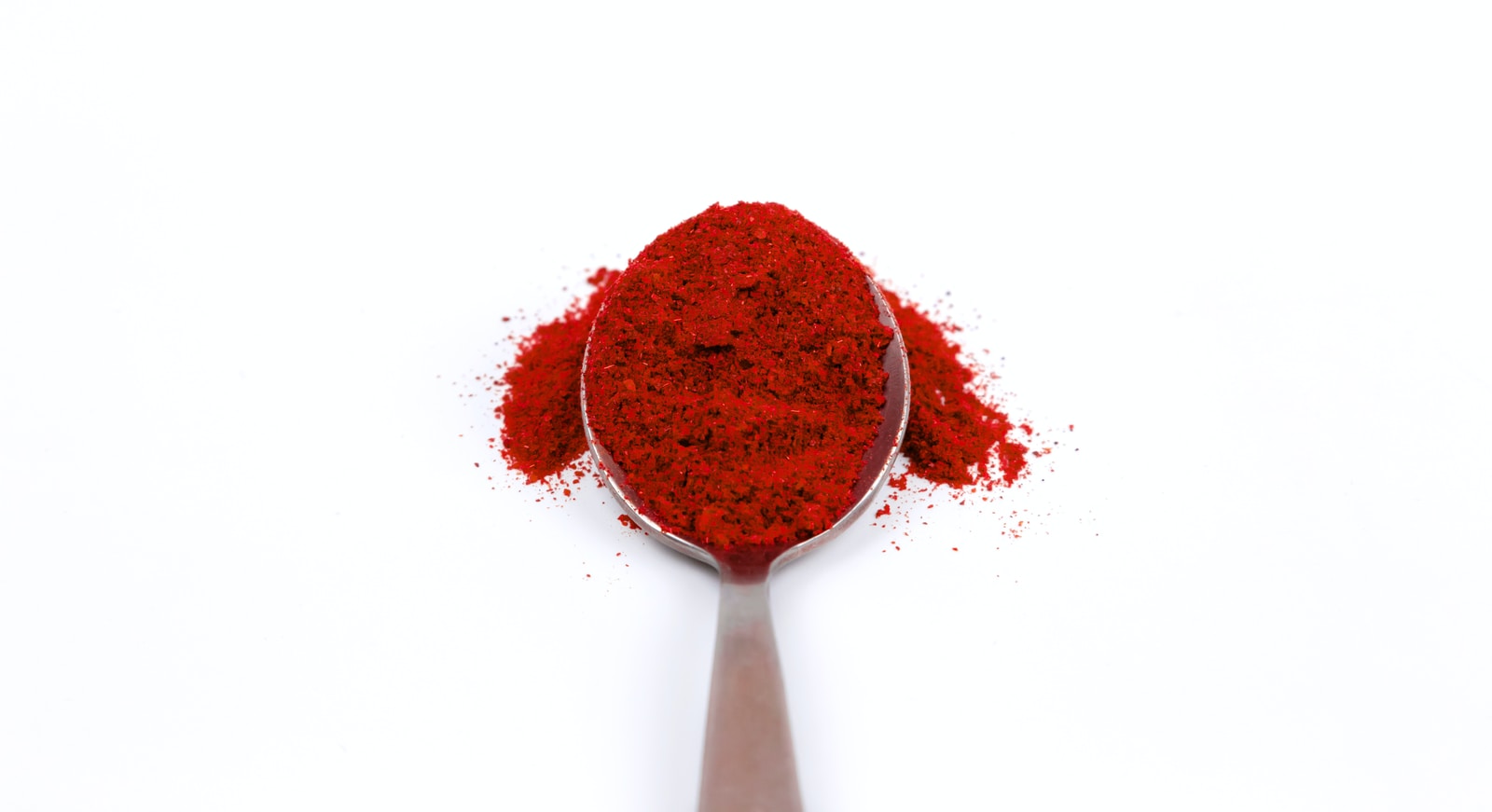
Chili powder
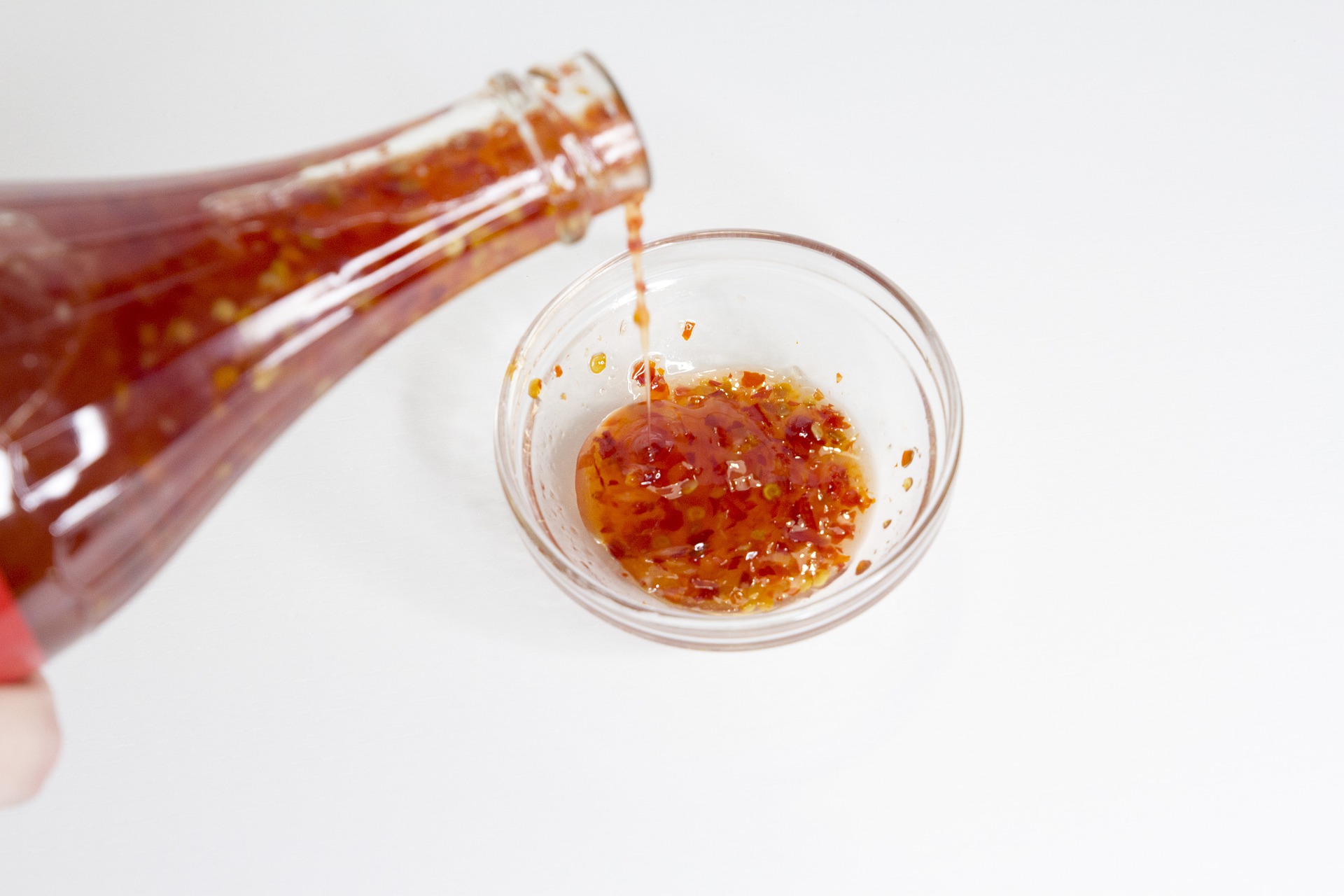
Chili sauce
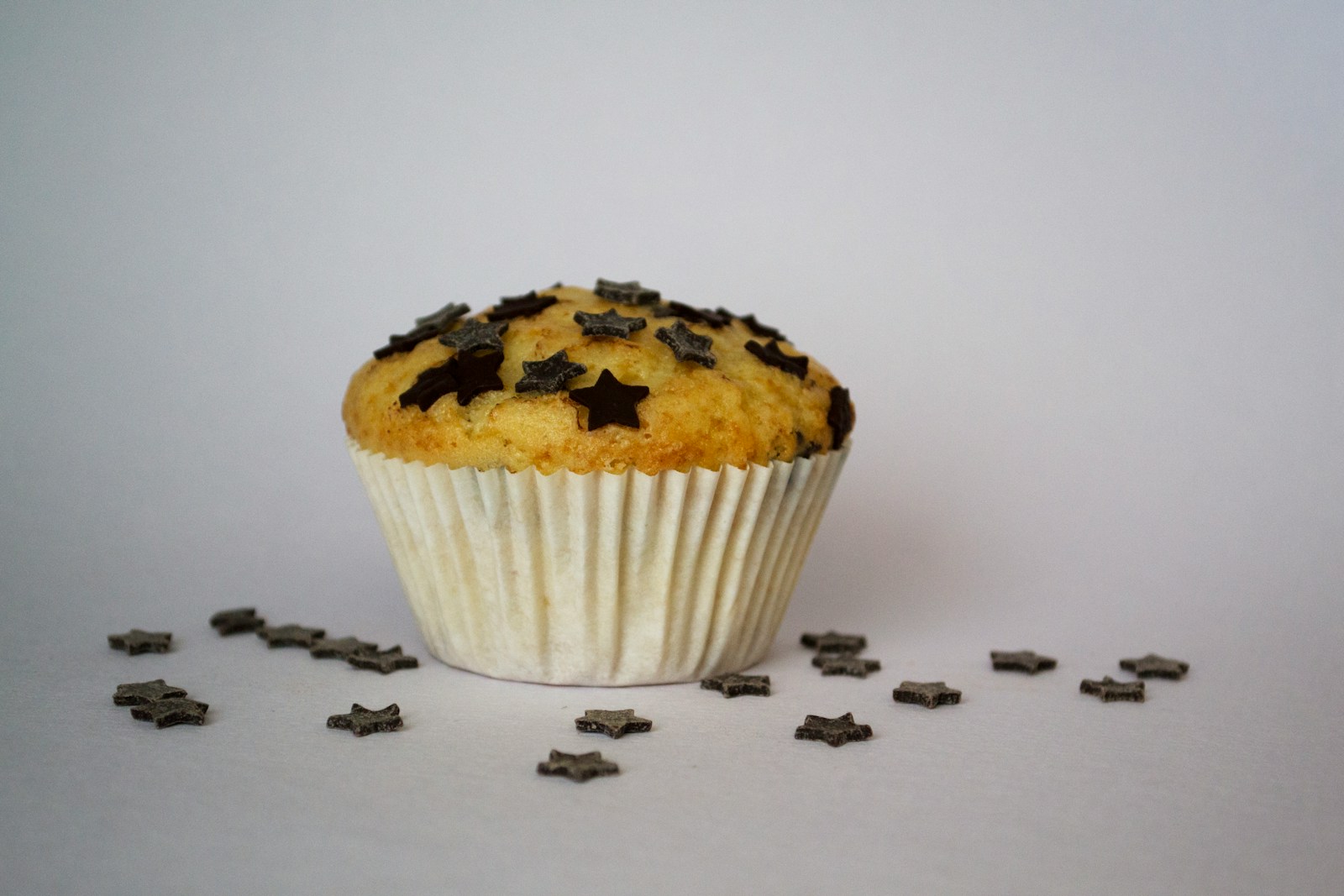
Chocolate chip muffins
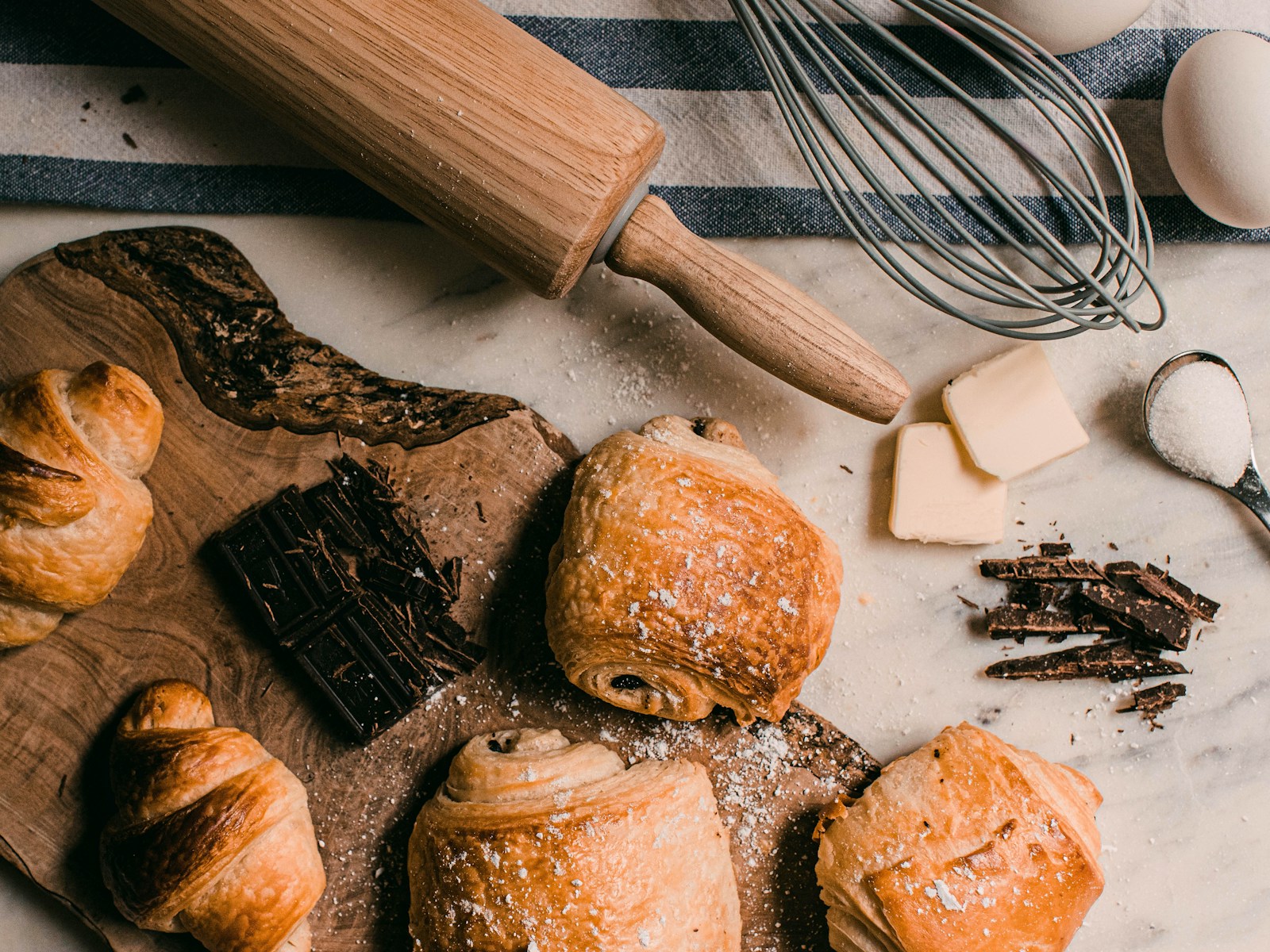
Chocolate croissants
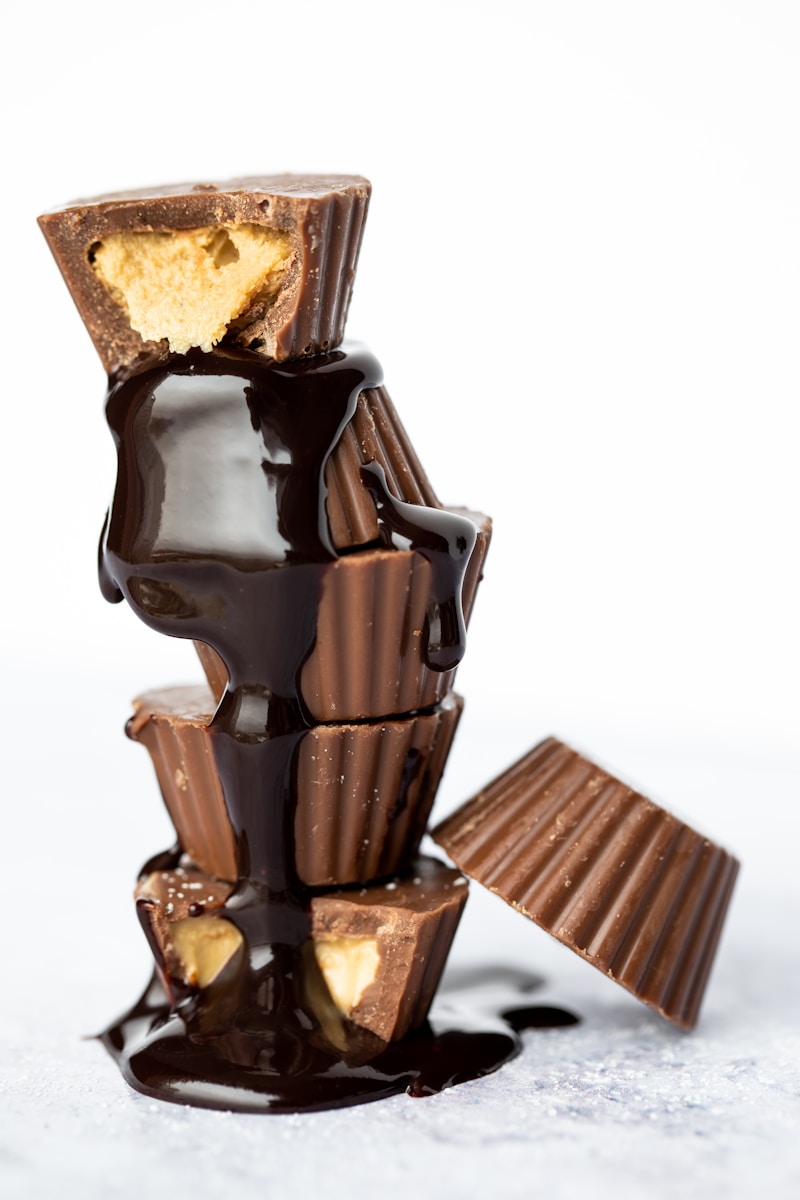
Chocolate ganache
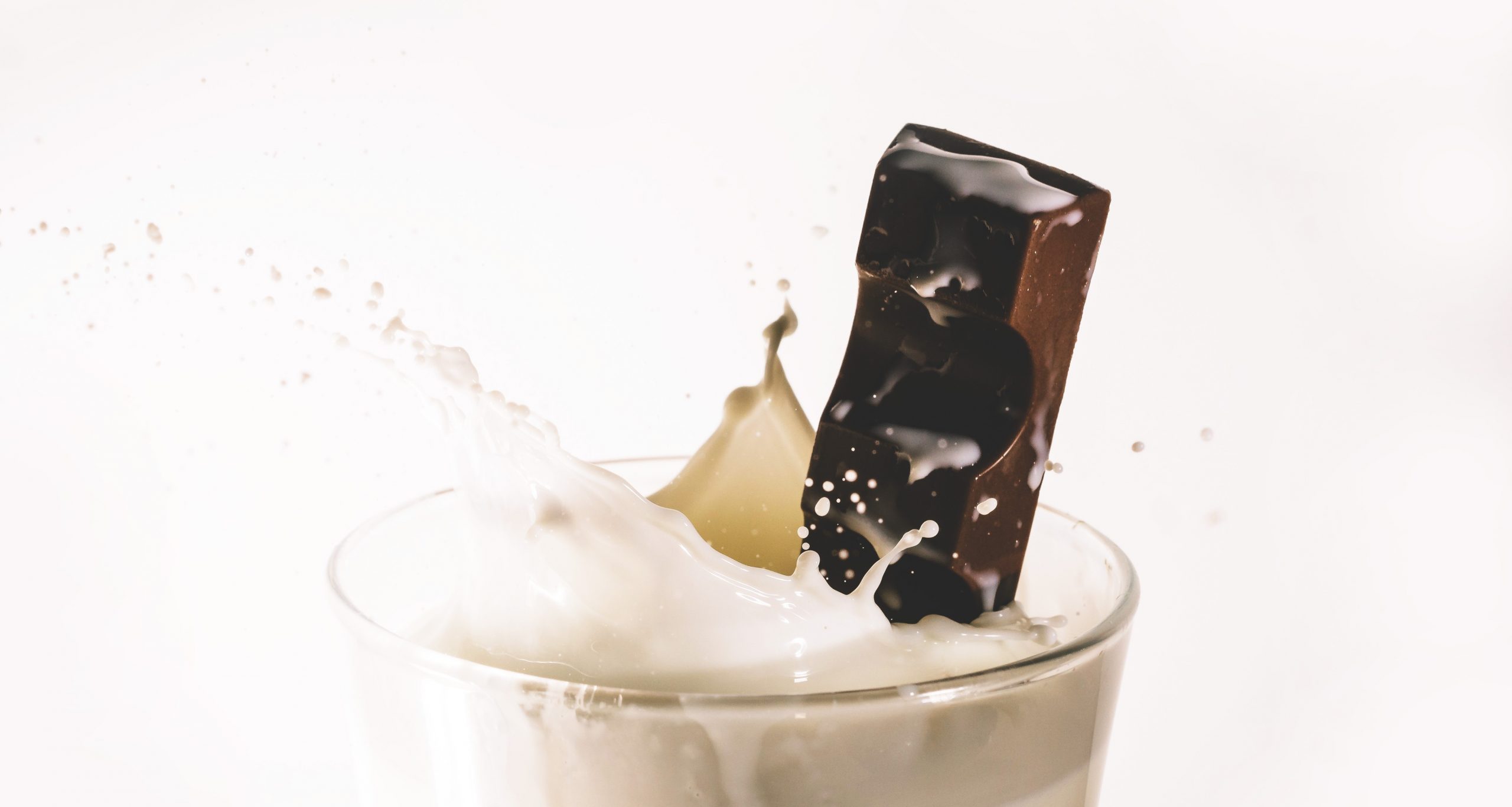
Chocolate milk
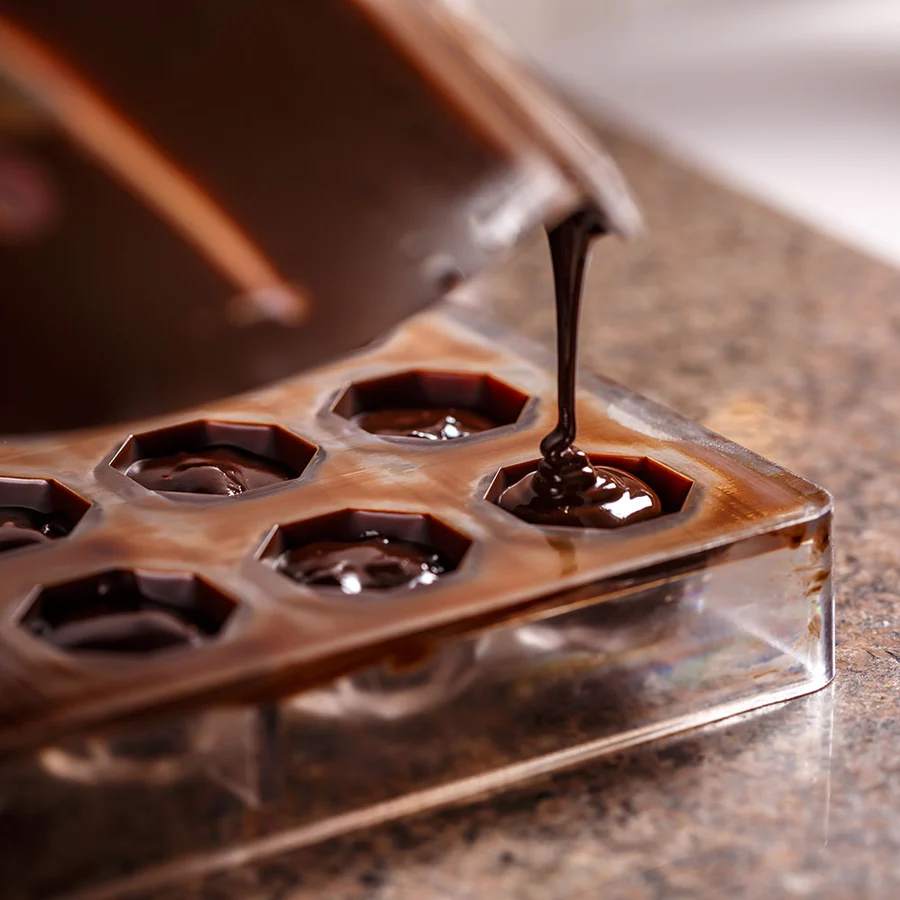
Chocolate molds
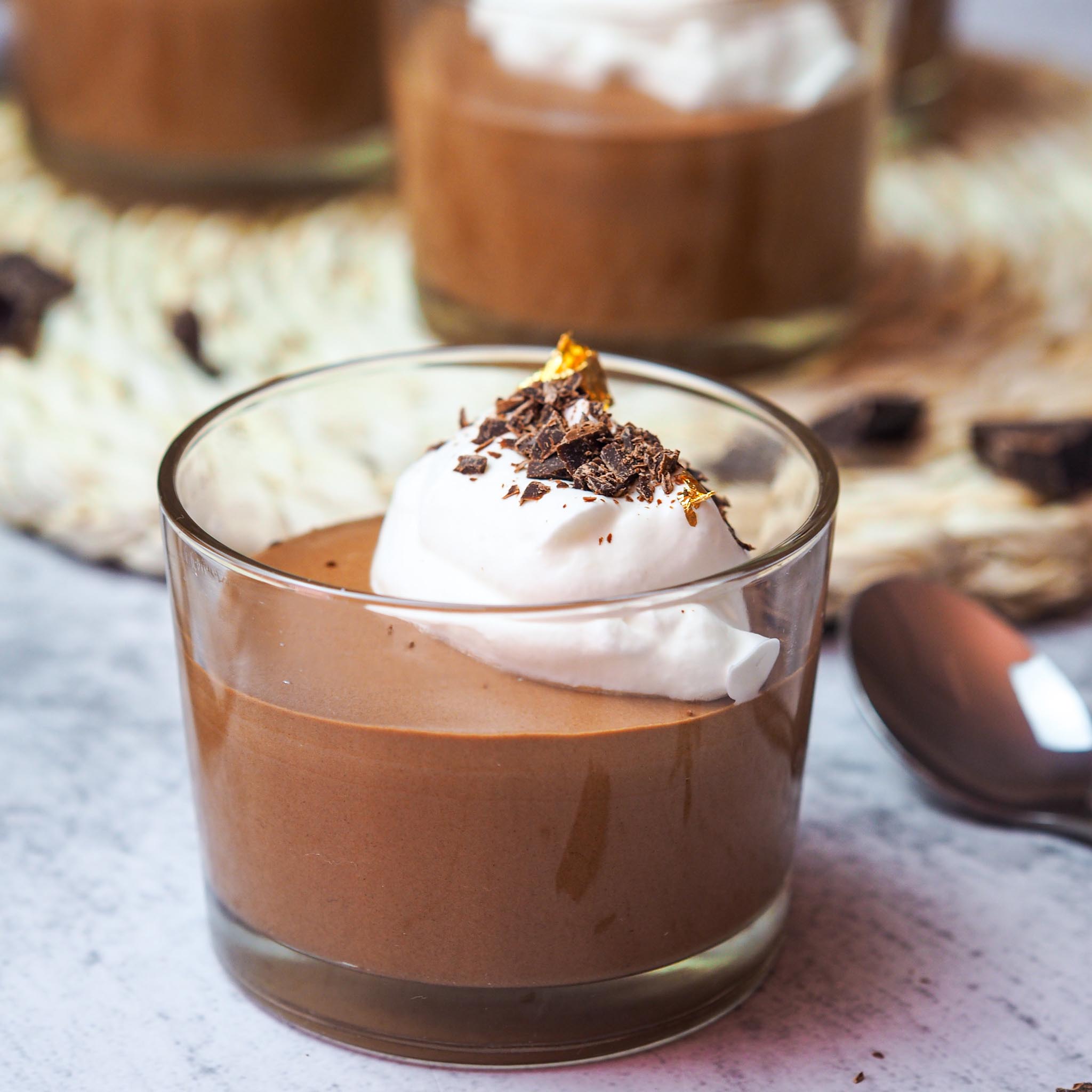
Chocolate mousse
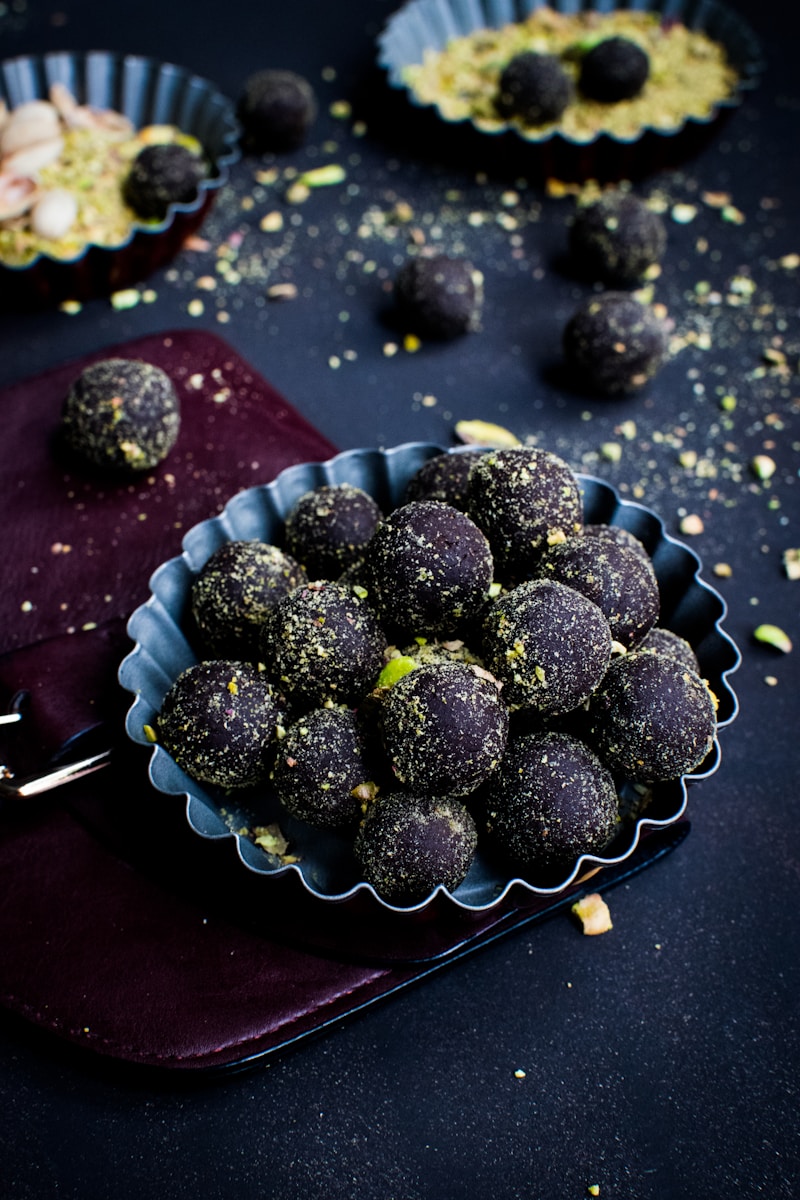
Chocolate truffles
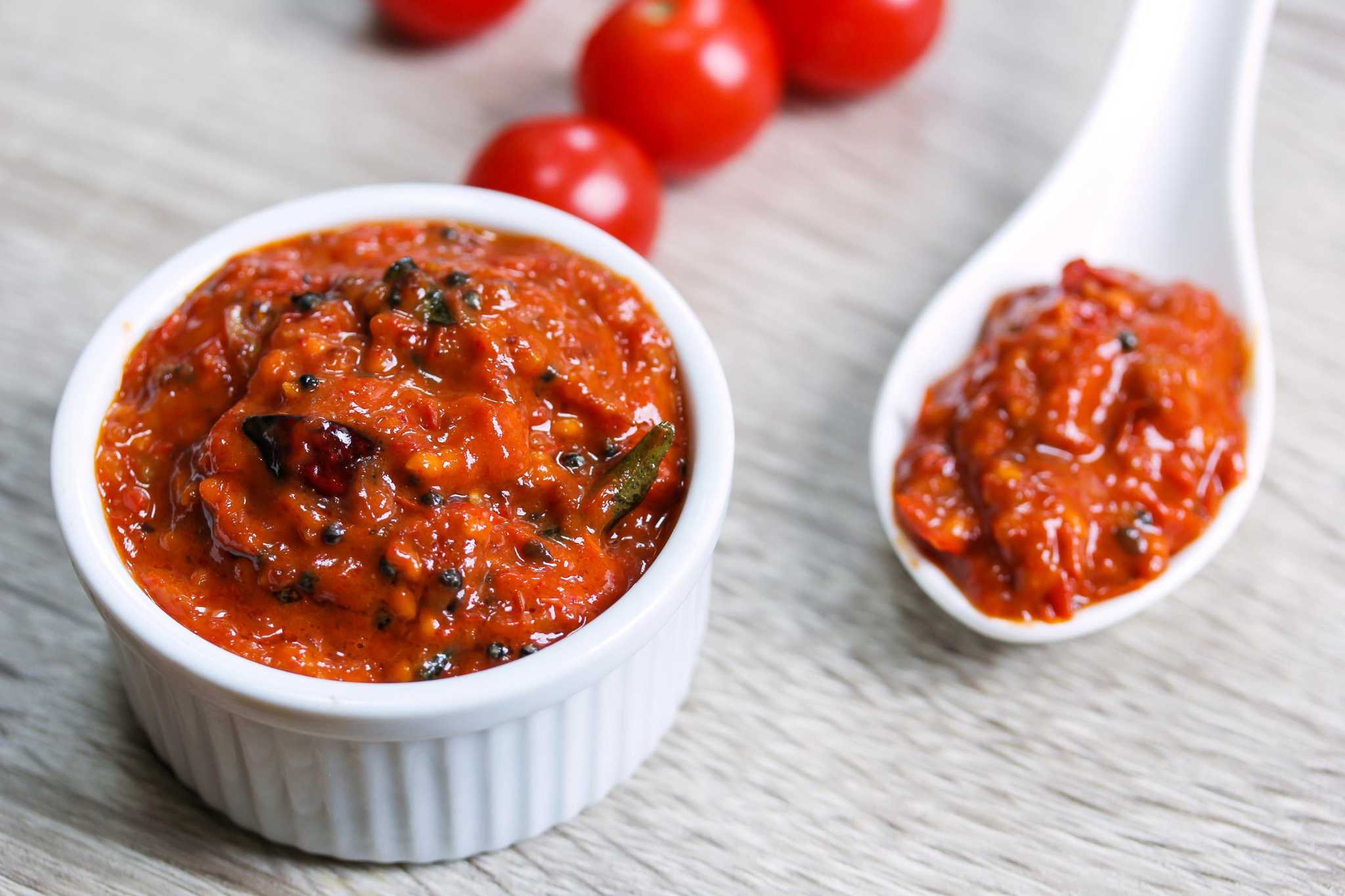
Chutneys
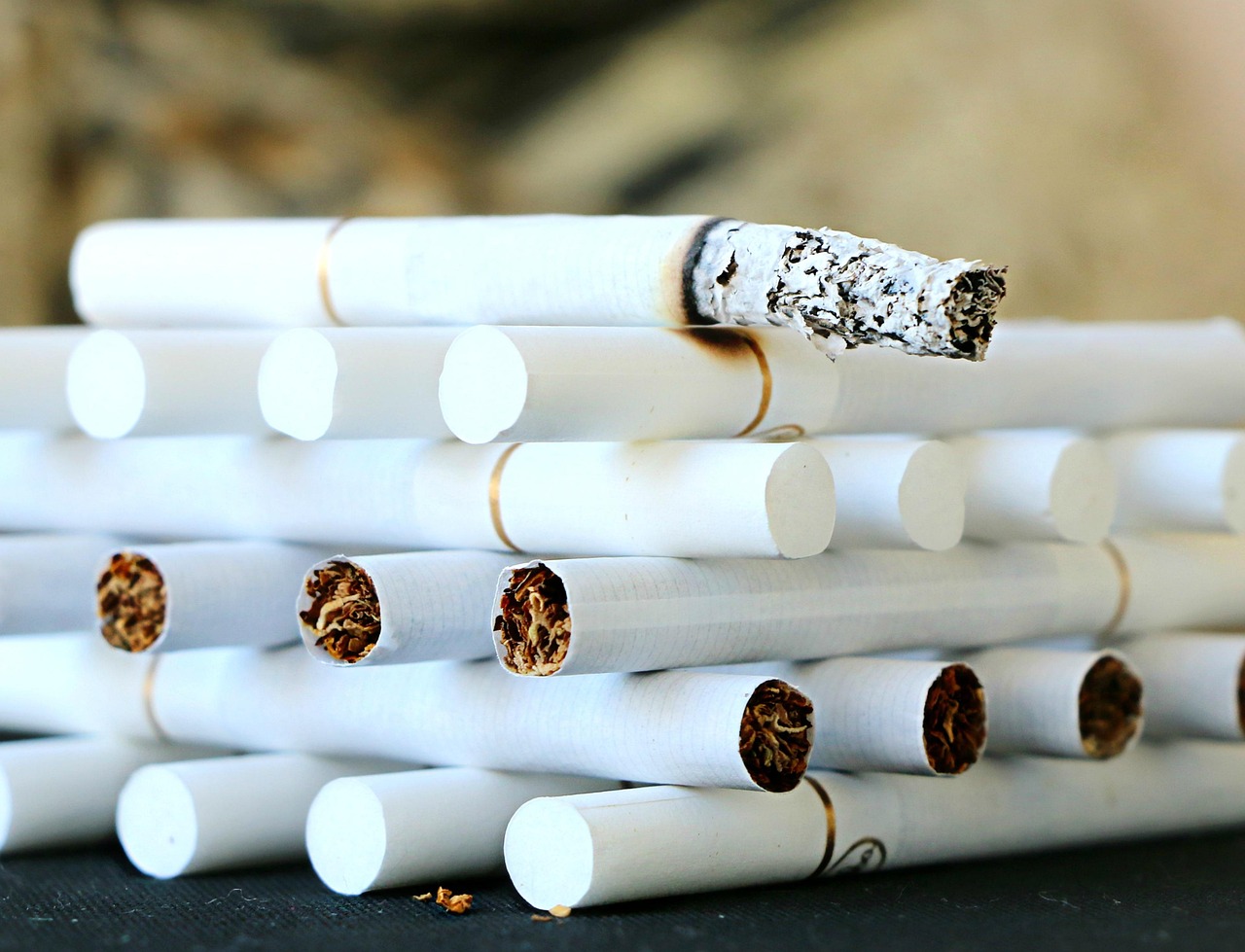
Cigarettes
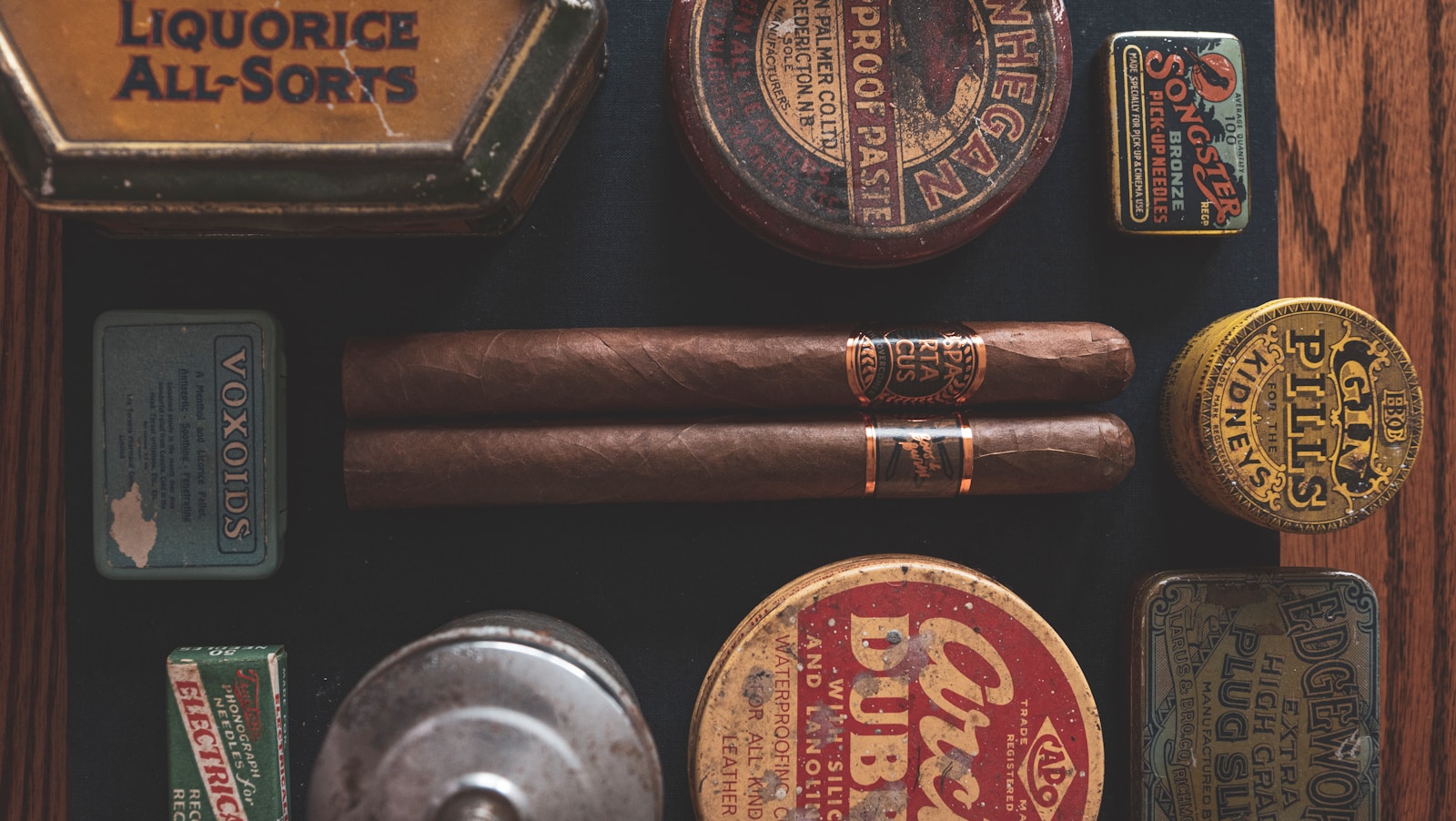
Cigars
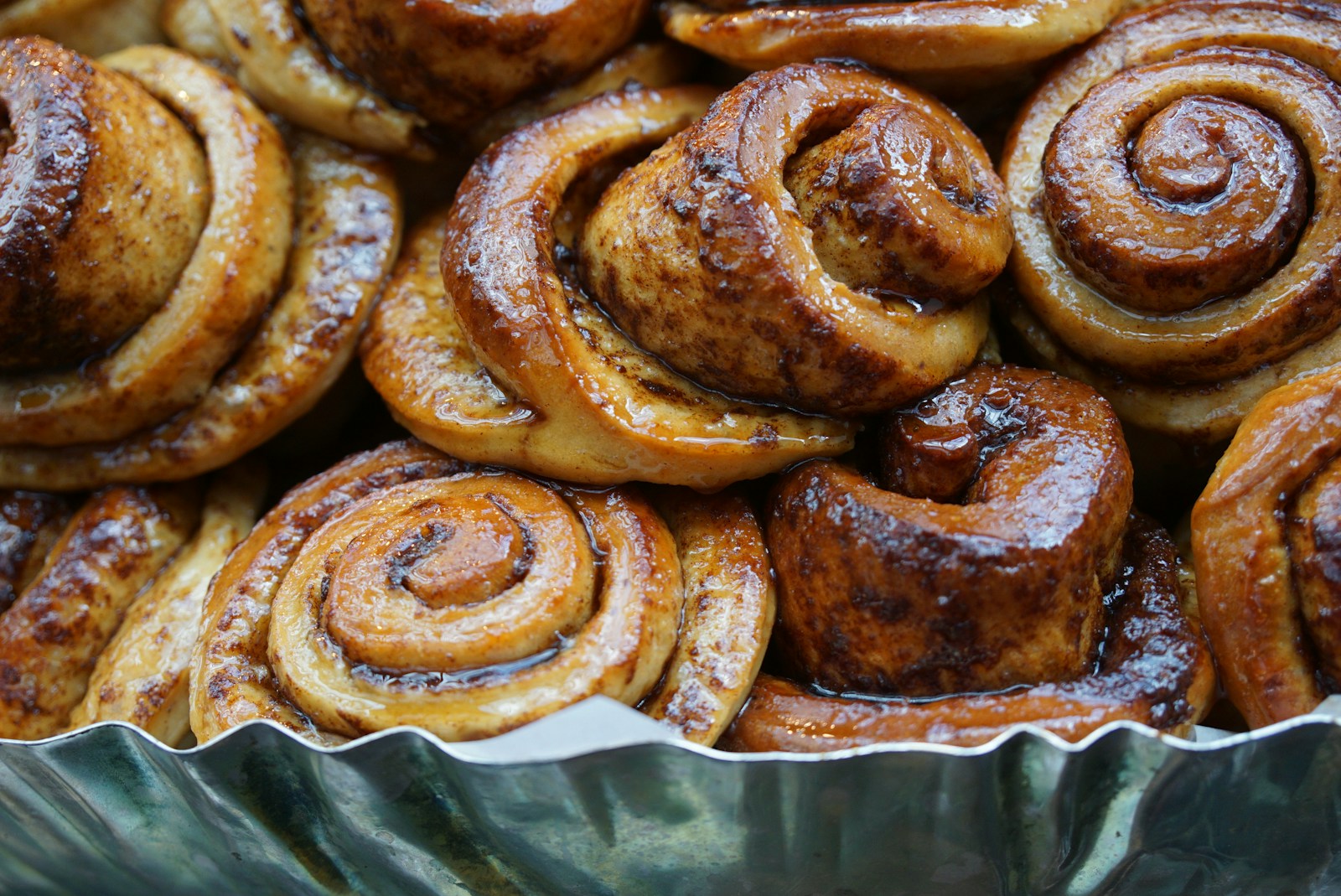
Cinnamon rolls
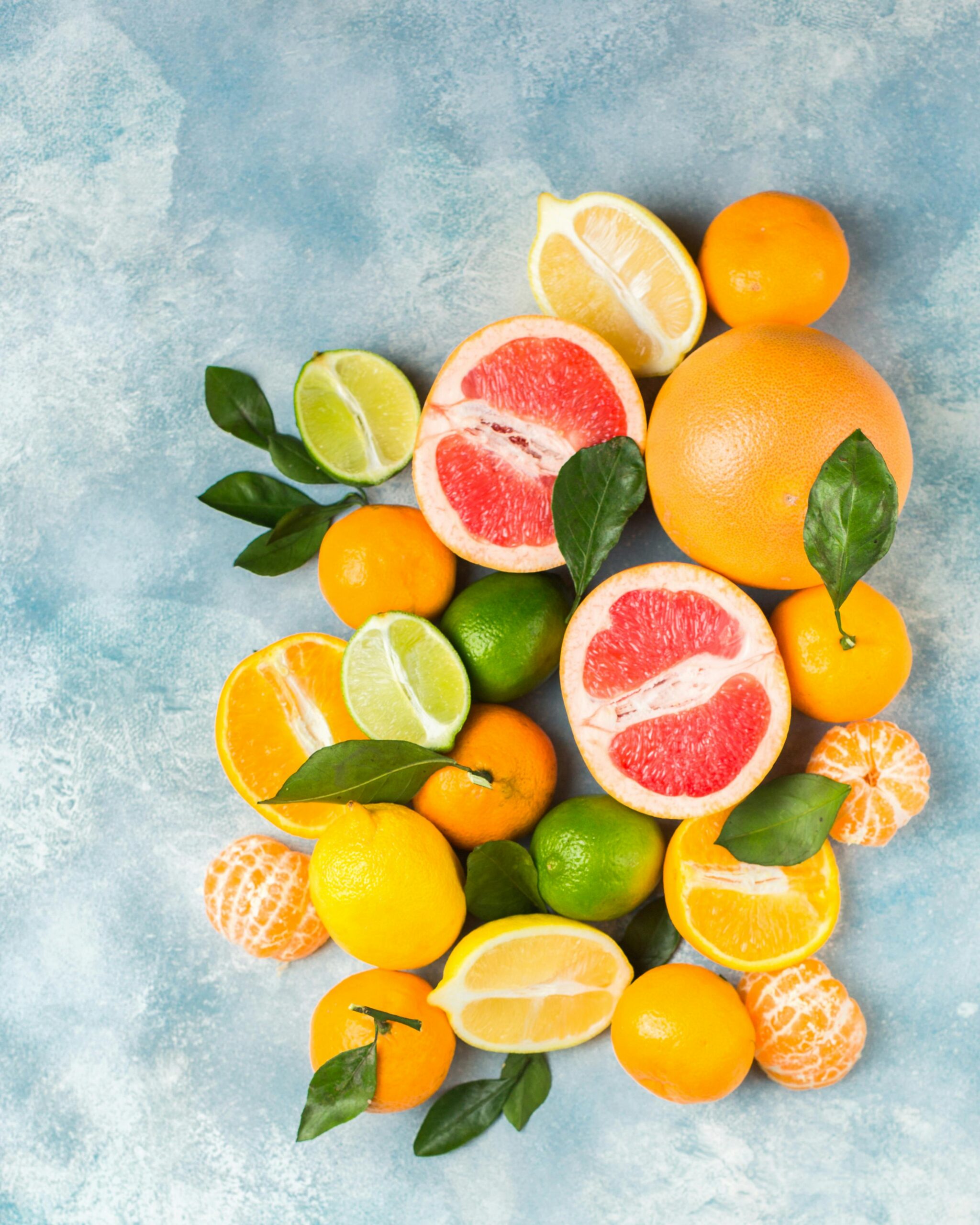
Citrus Fruit
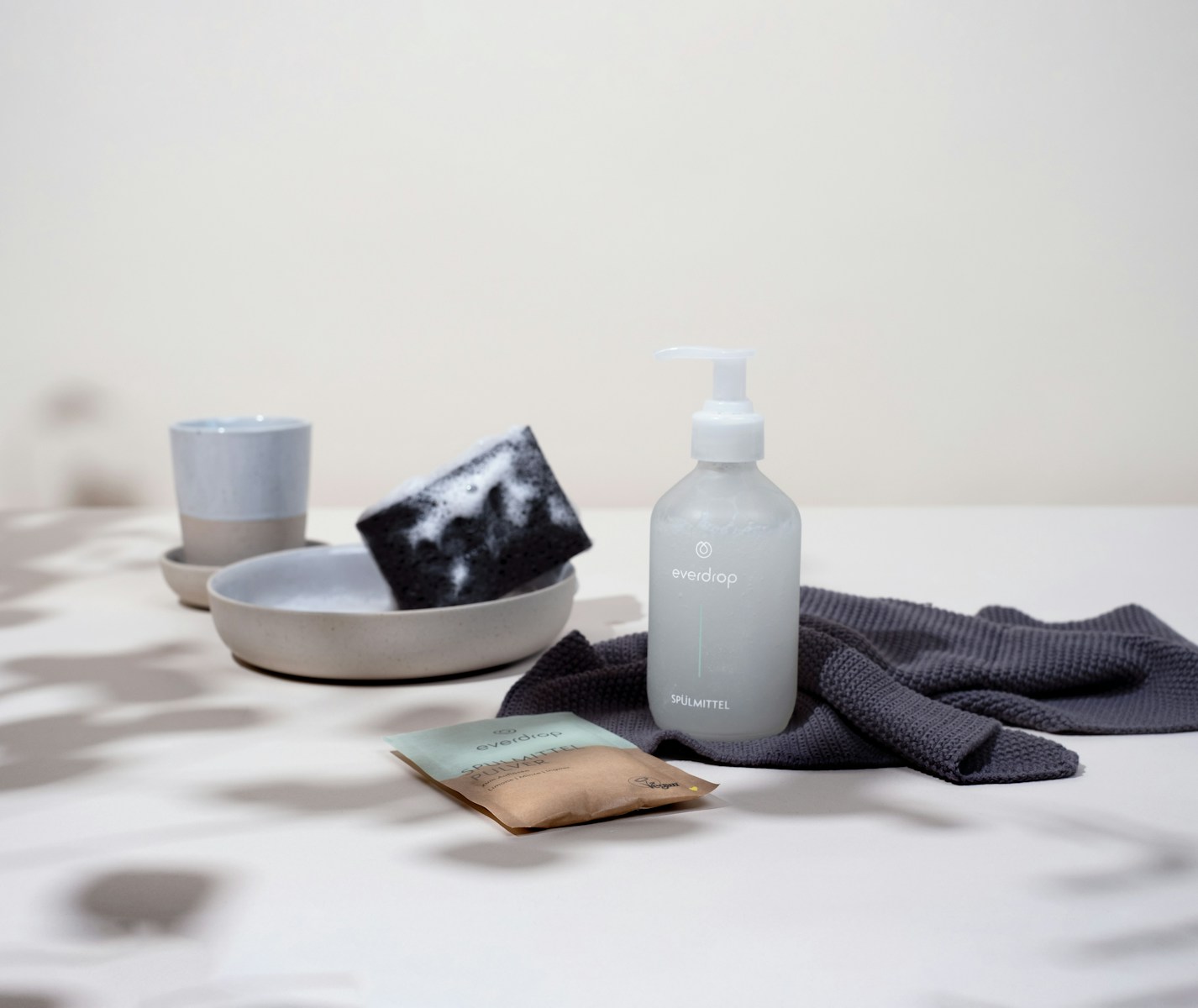
Cleaning agents
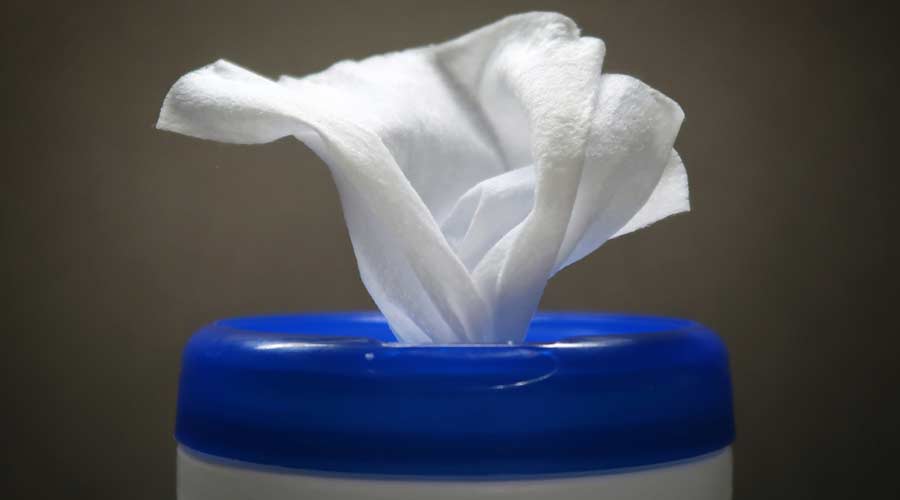
Cleaning wipes
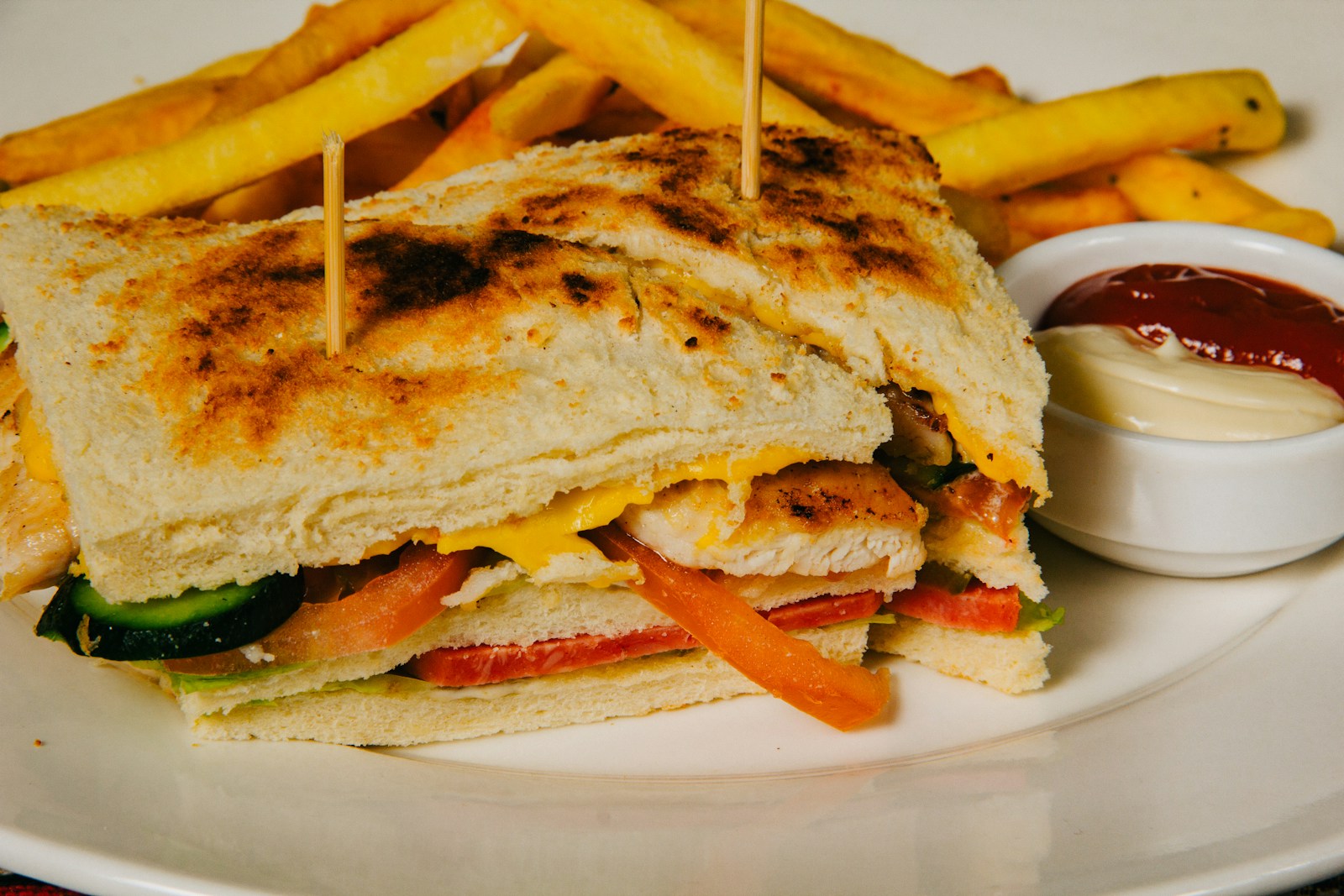
Club sandwiches
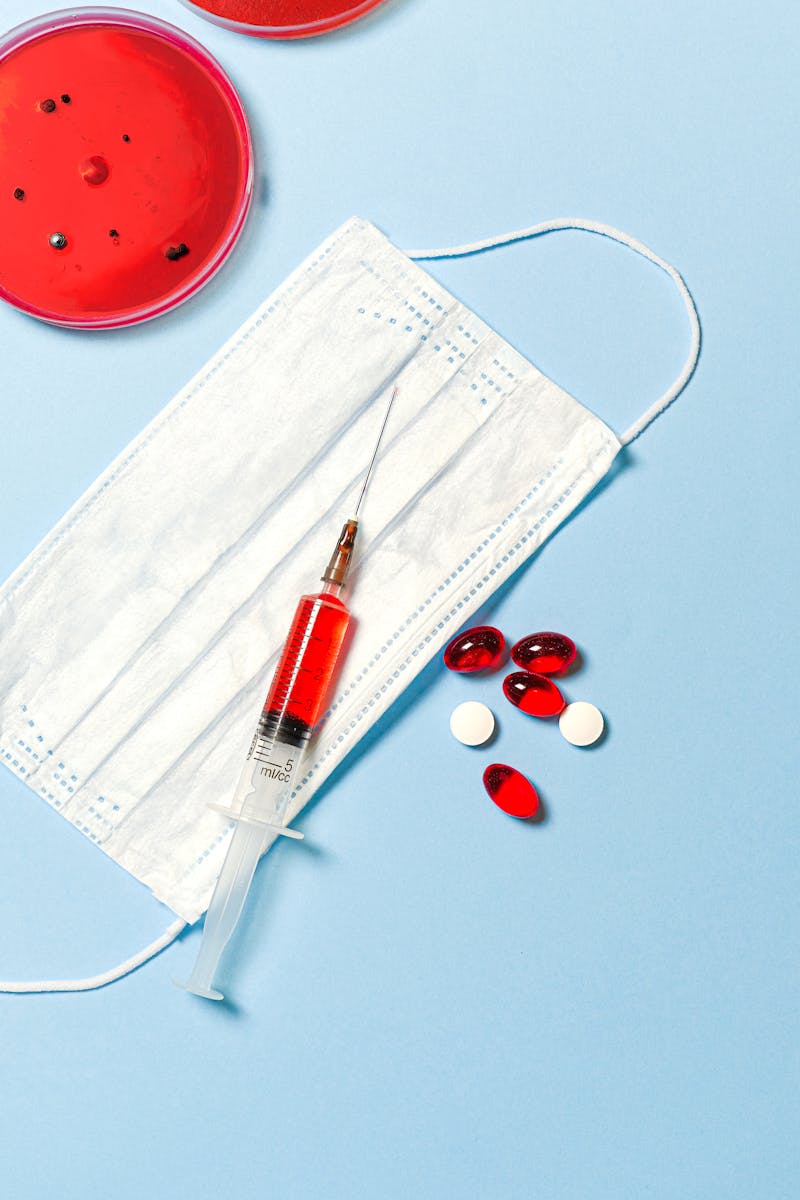
Coenzyme q10 capsules
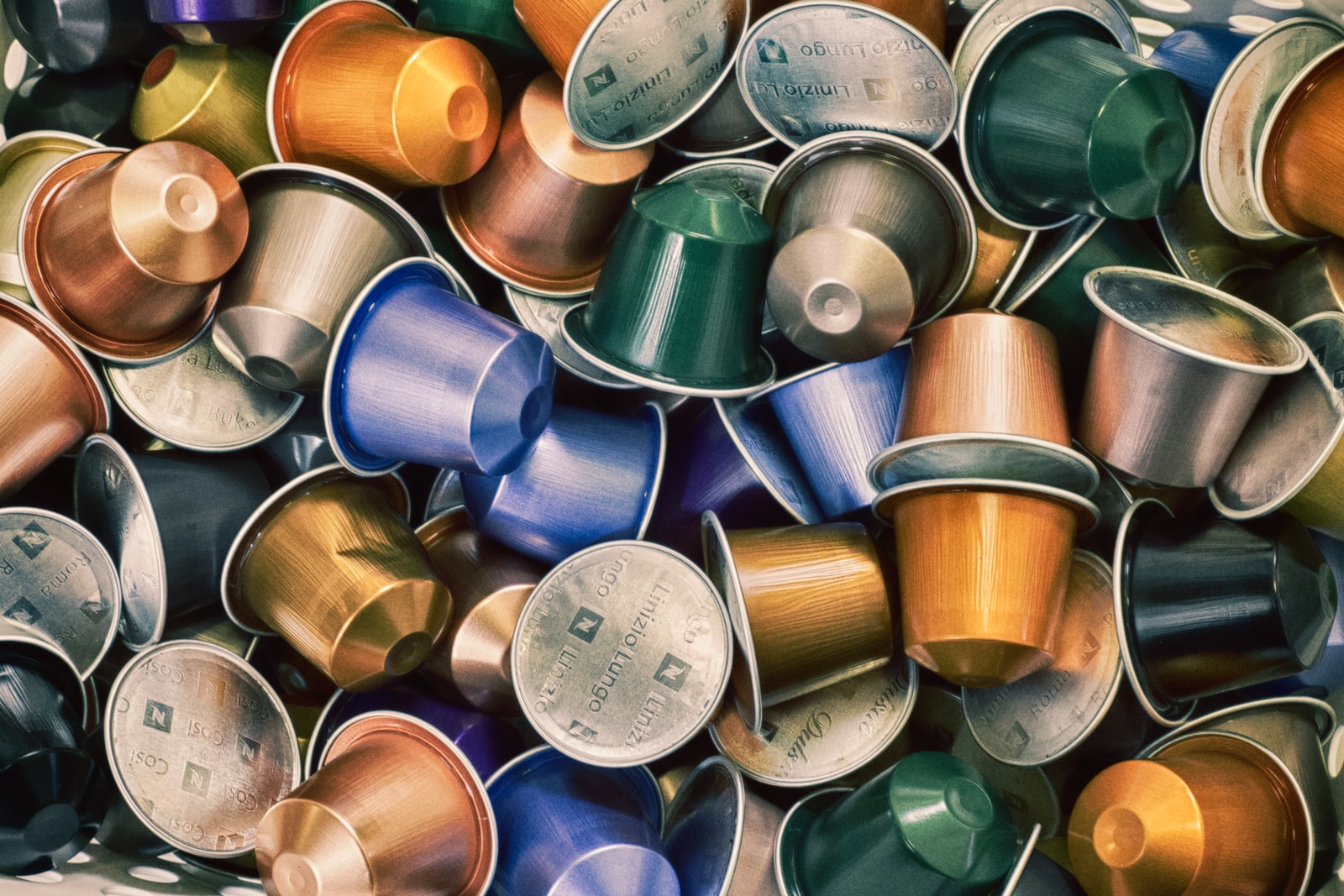
Coffee capsules
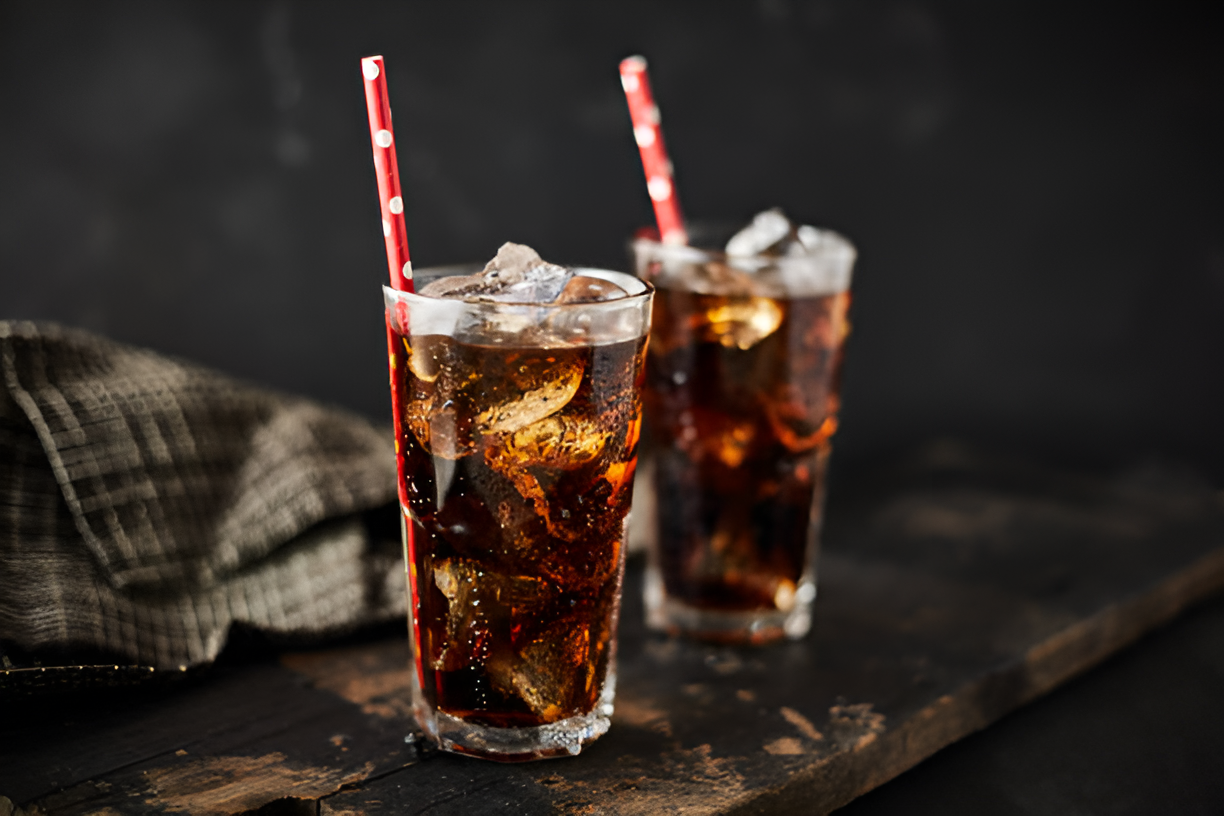
Cola soft drink
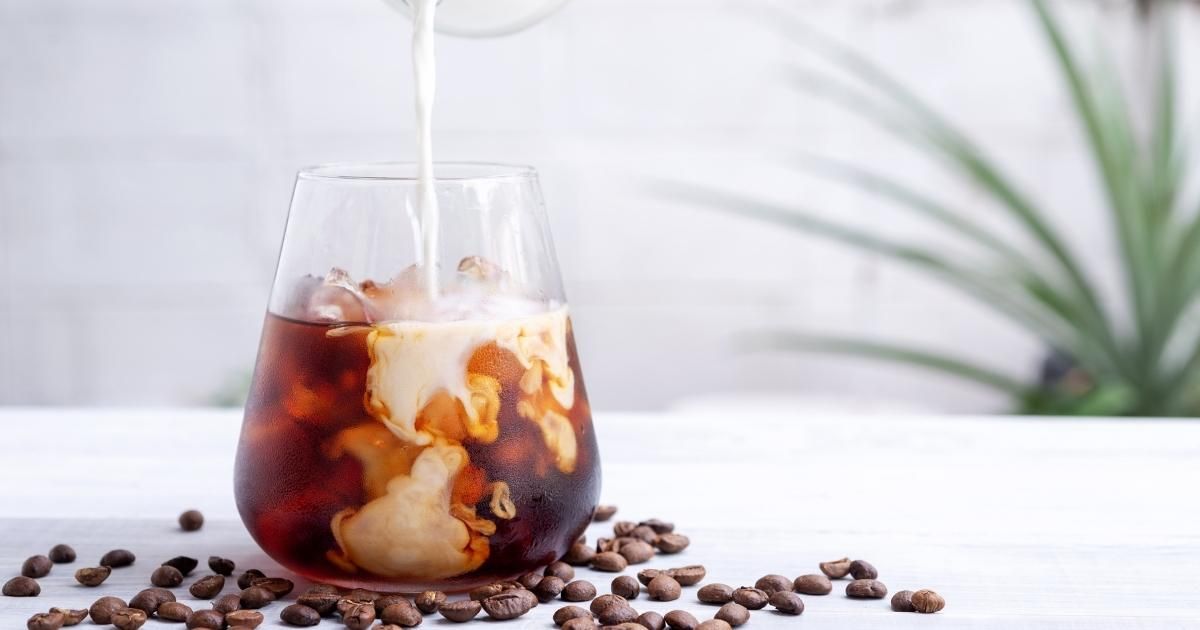
Cold brew coffee
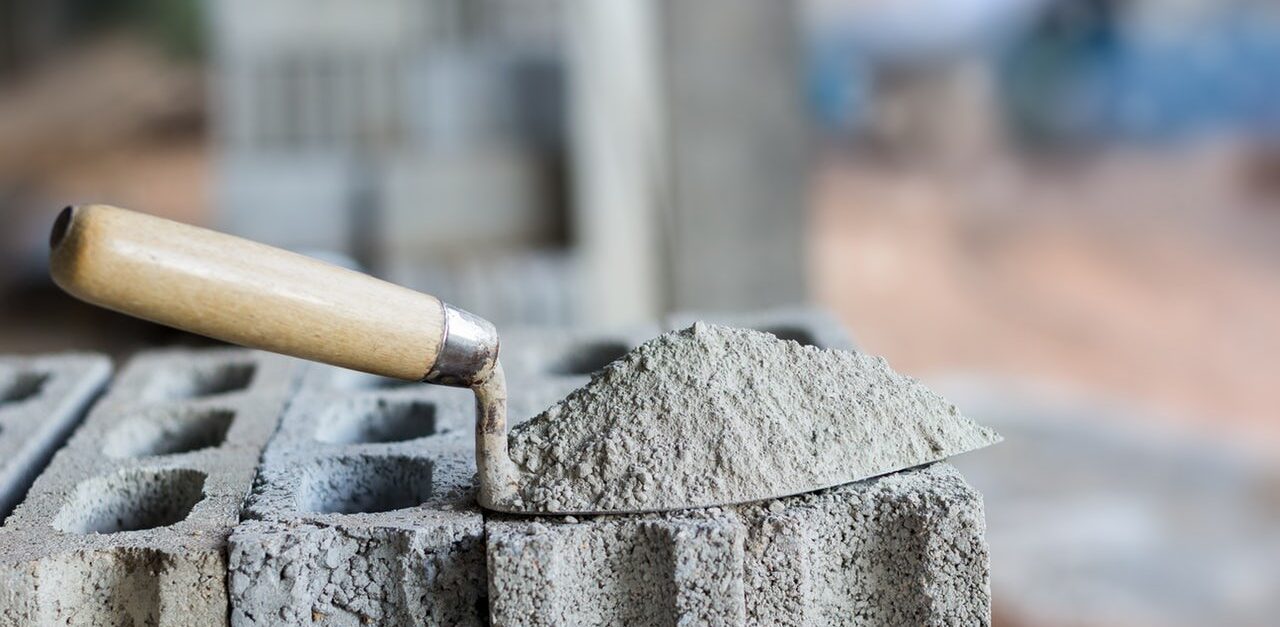
Concrete admixtures

Condensed milk
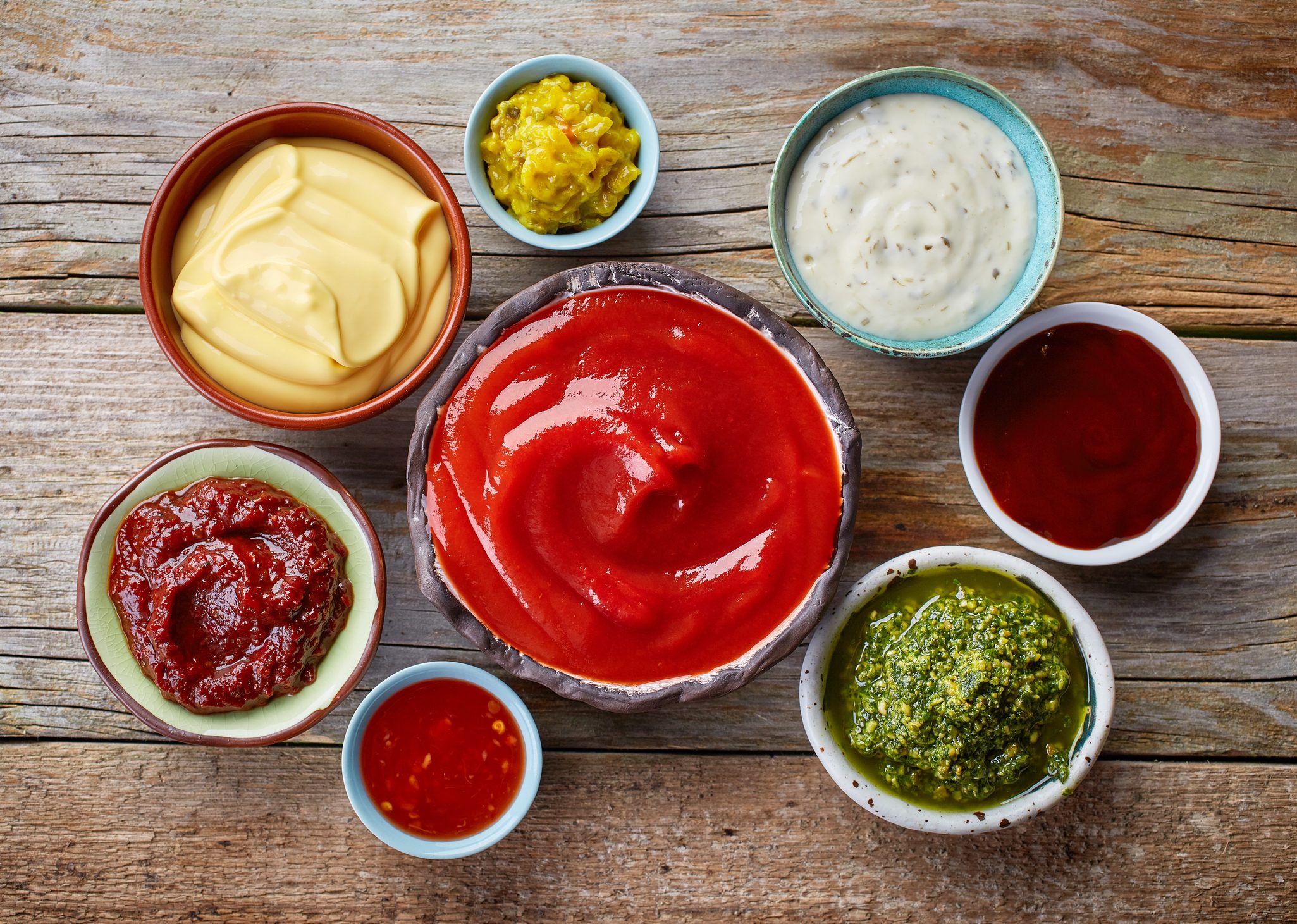
Condiments

Conditioner
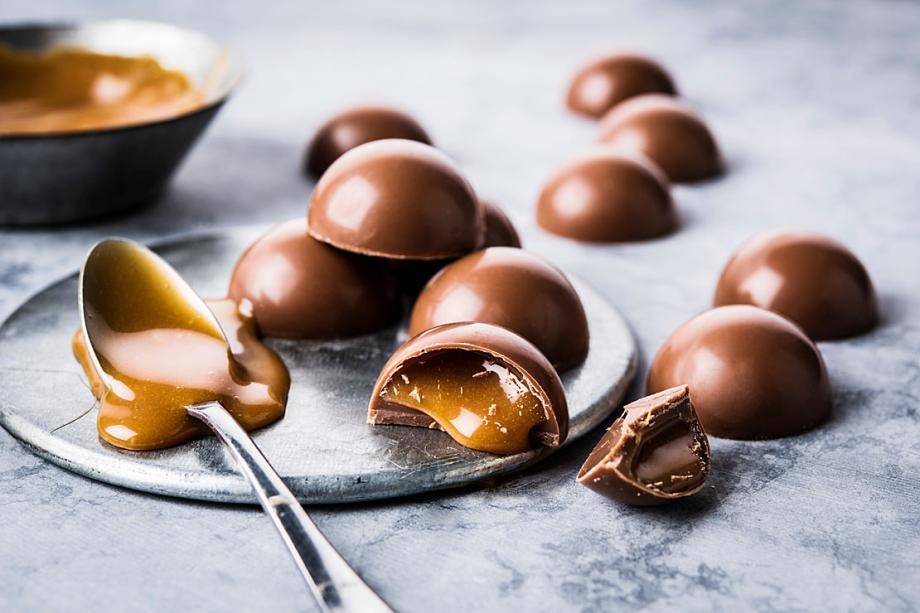
Confectionery fillings
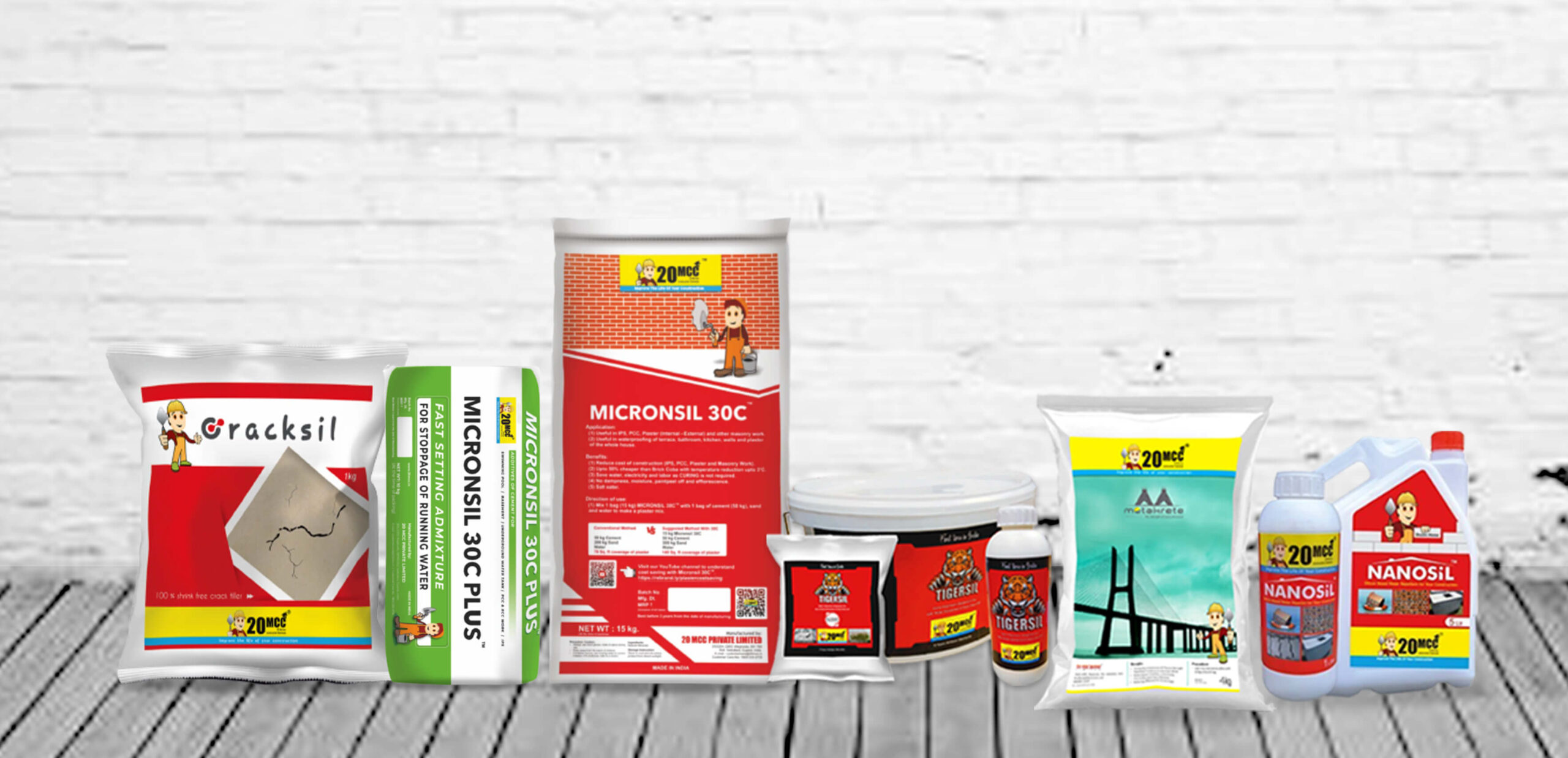
Construction chemicals
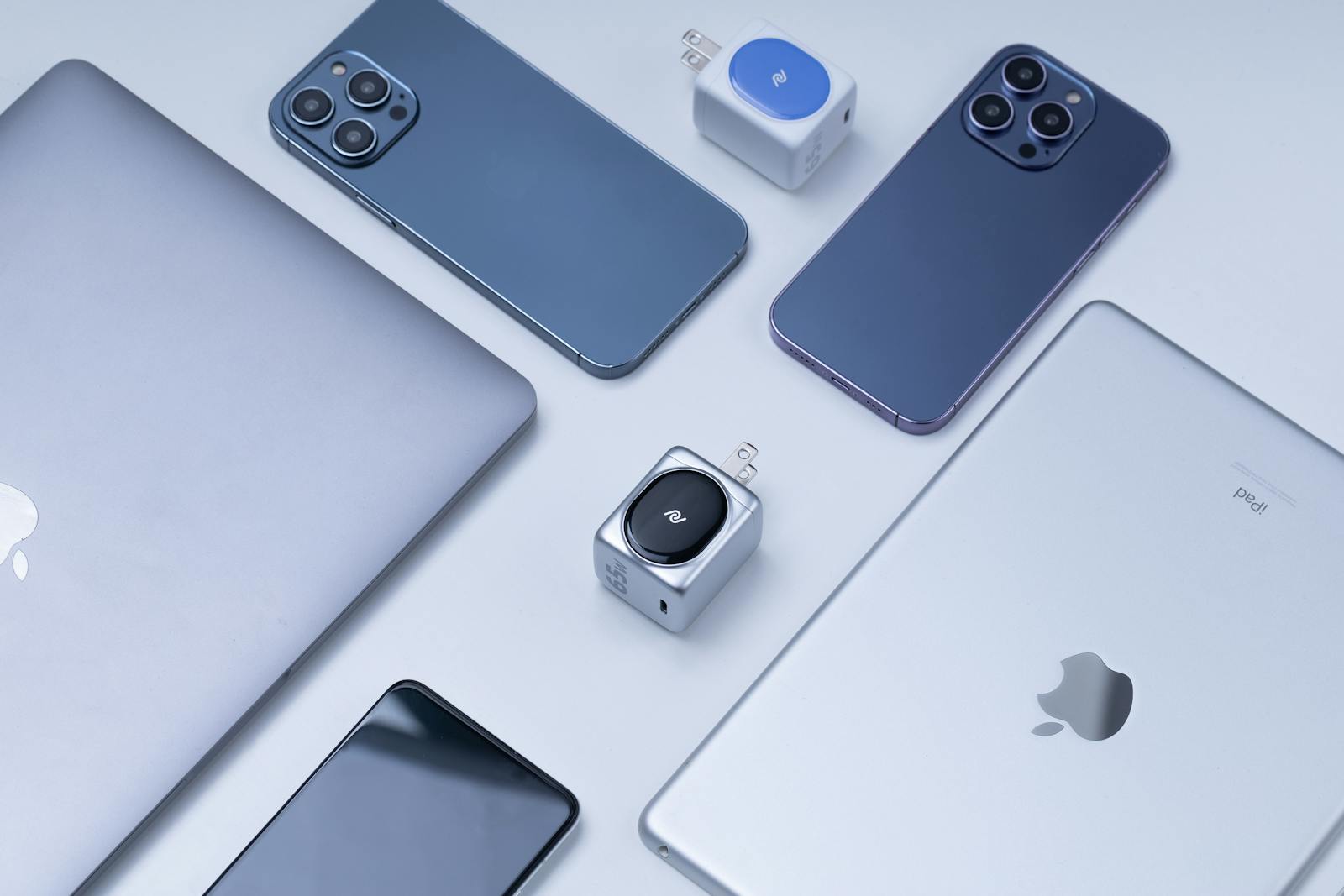
Consumer electronics
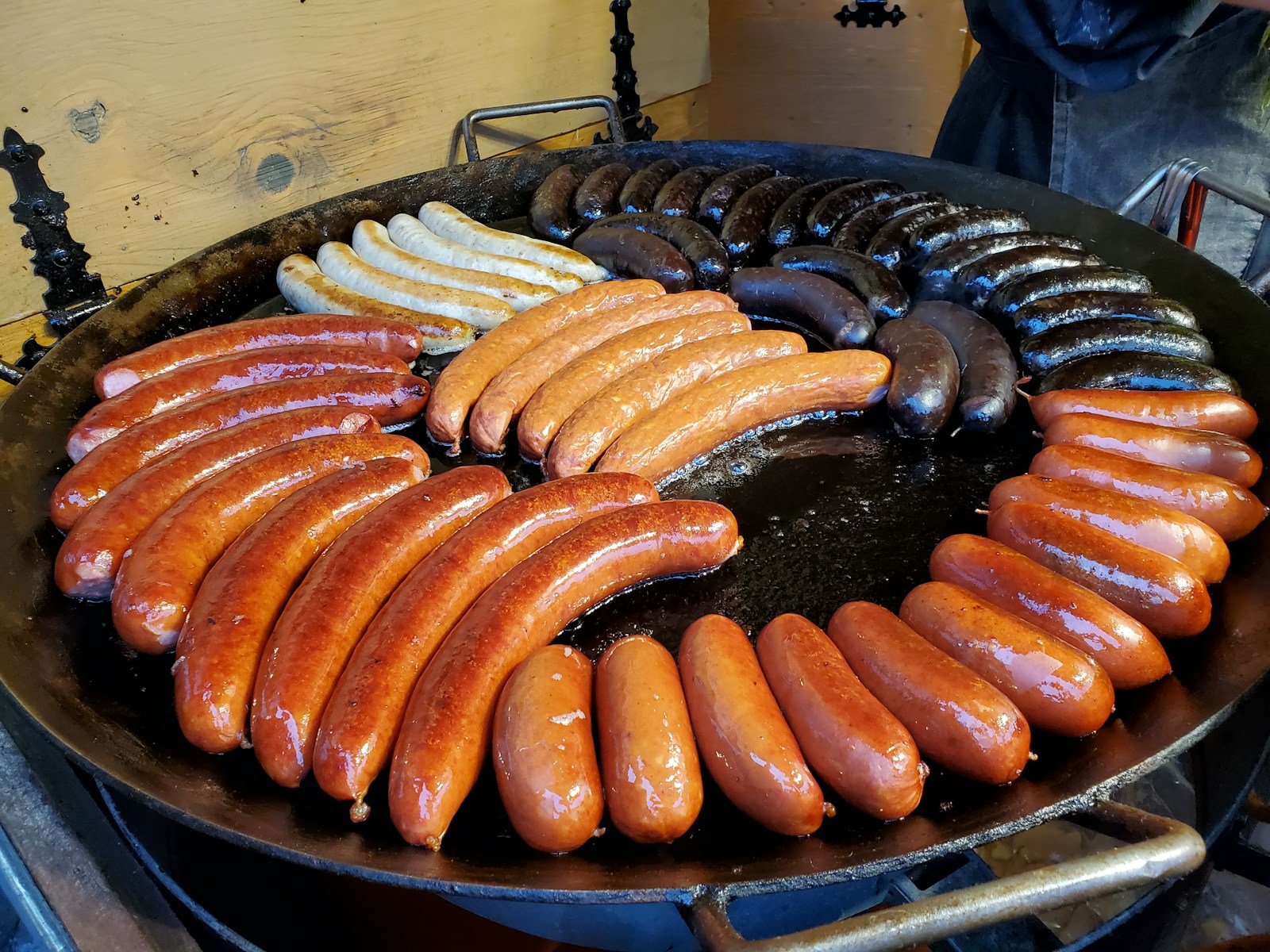
Cooked sausages
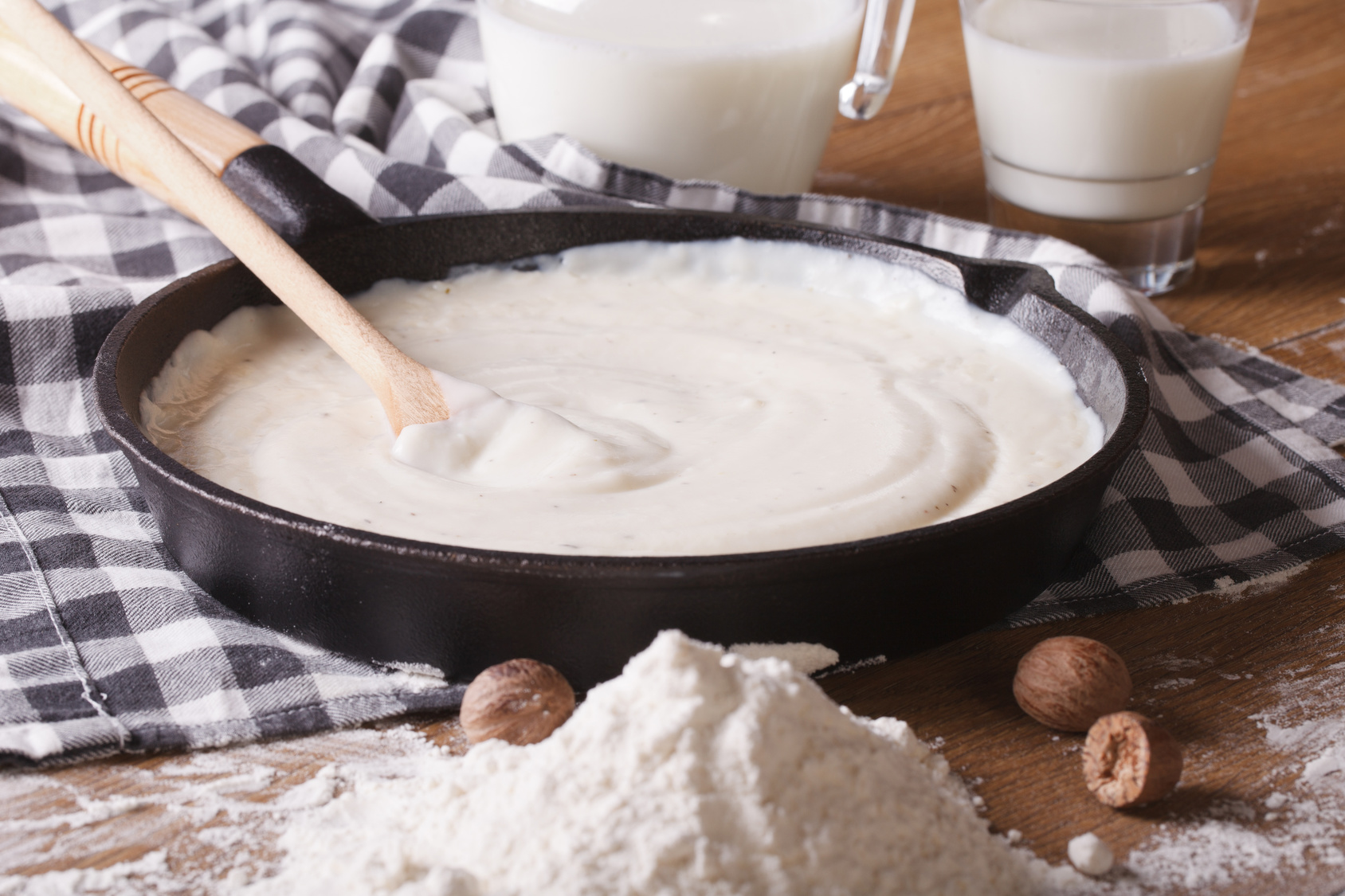
Cooking cream
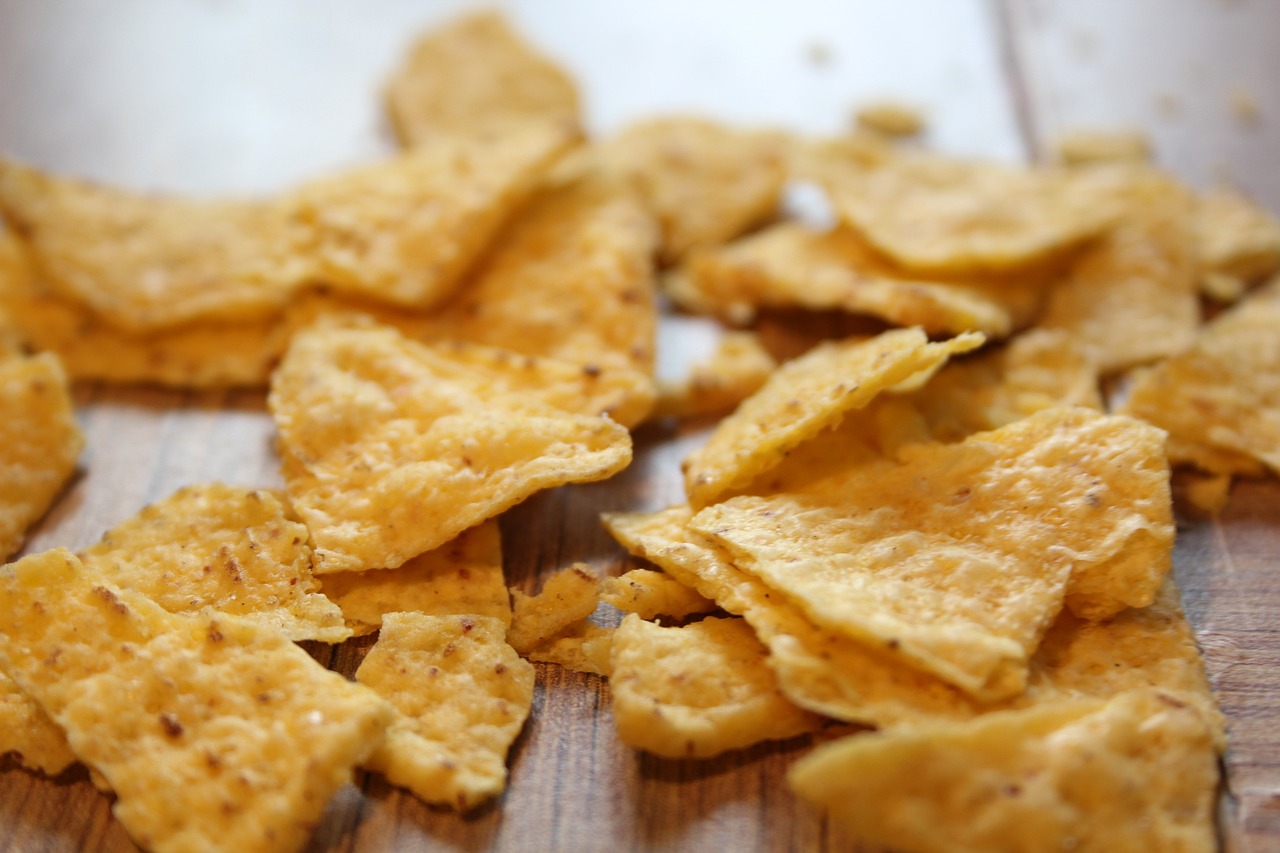
Corn Chips
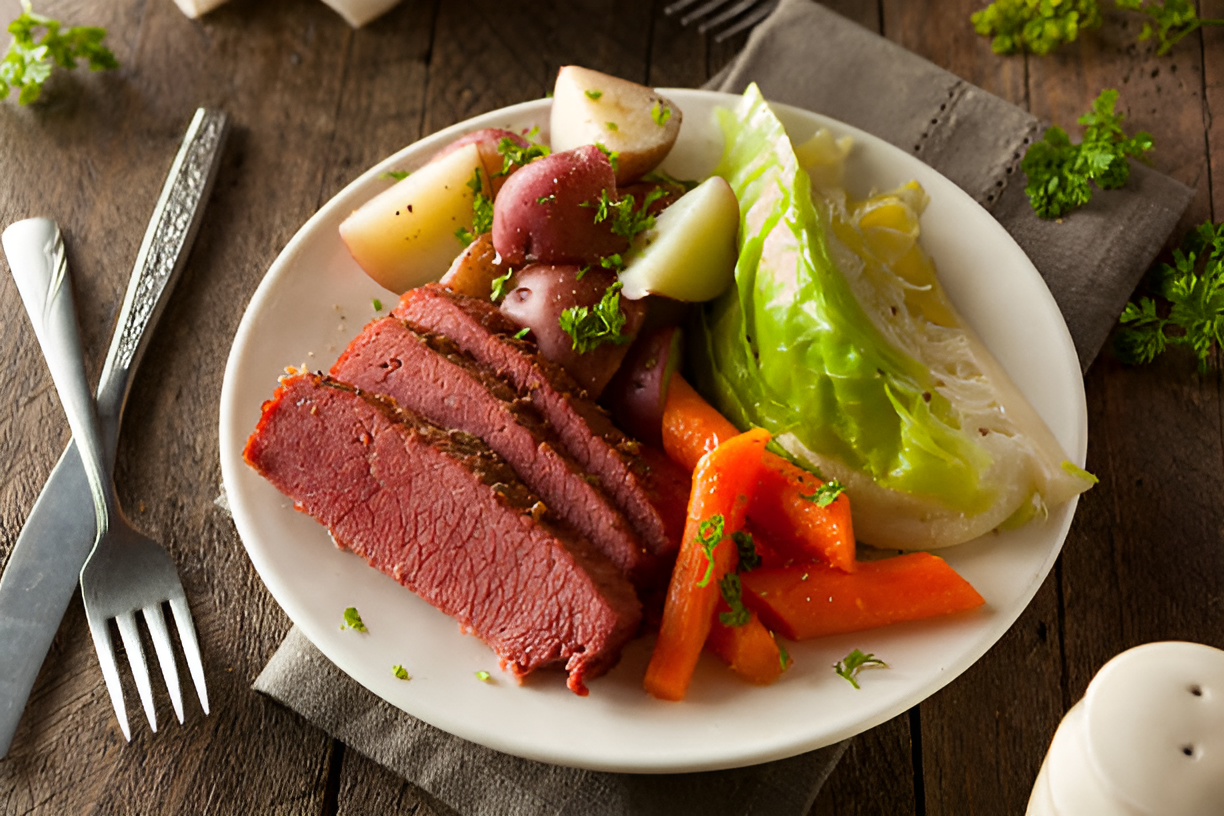
Corned beef
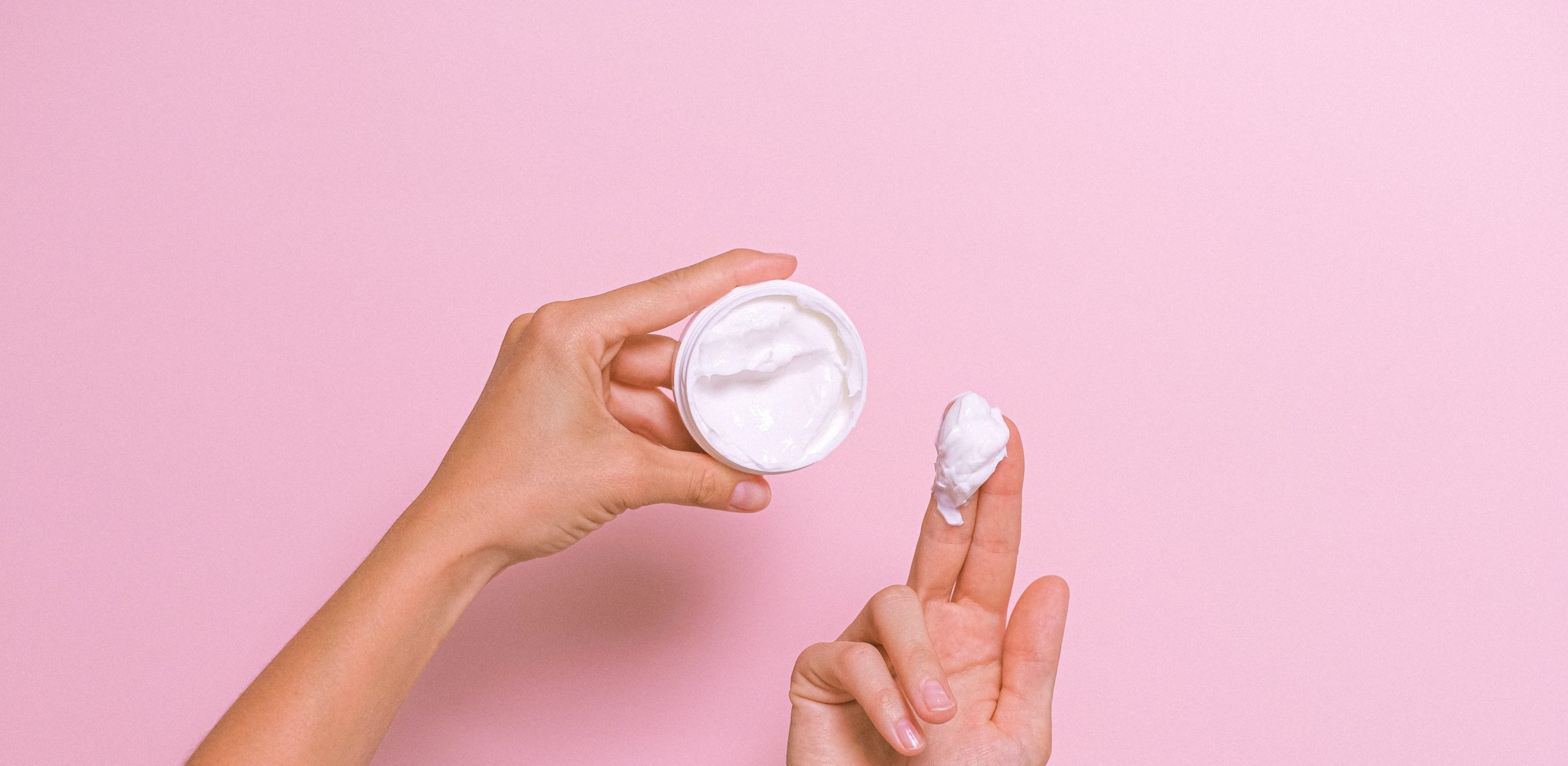
Cosmetic creams
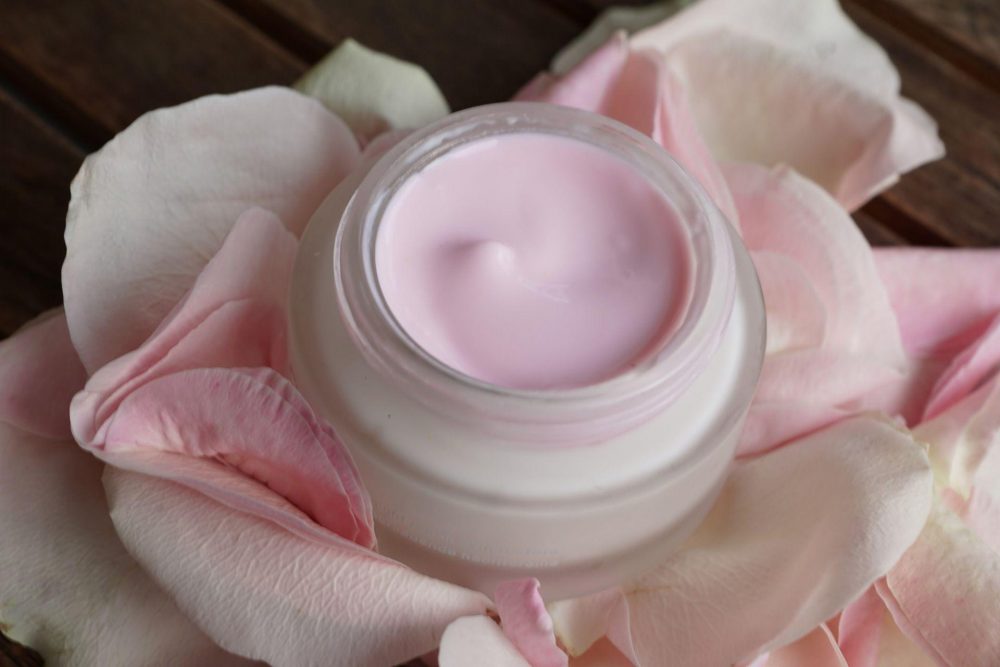
Cosmetic emulsions
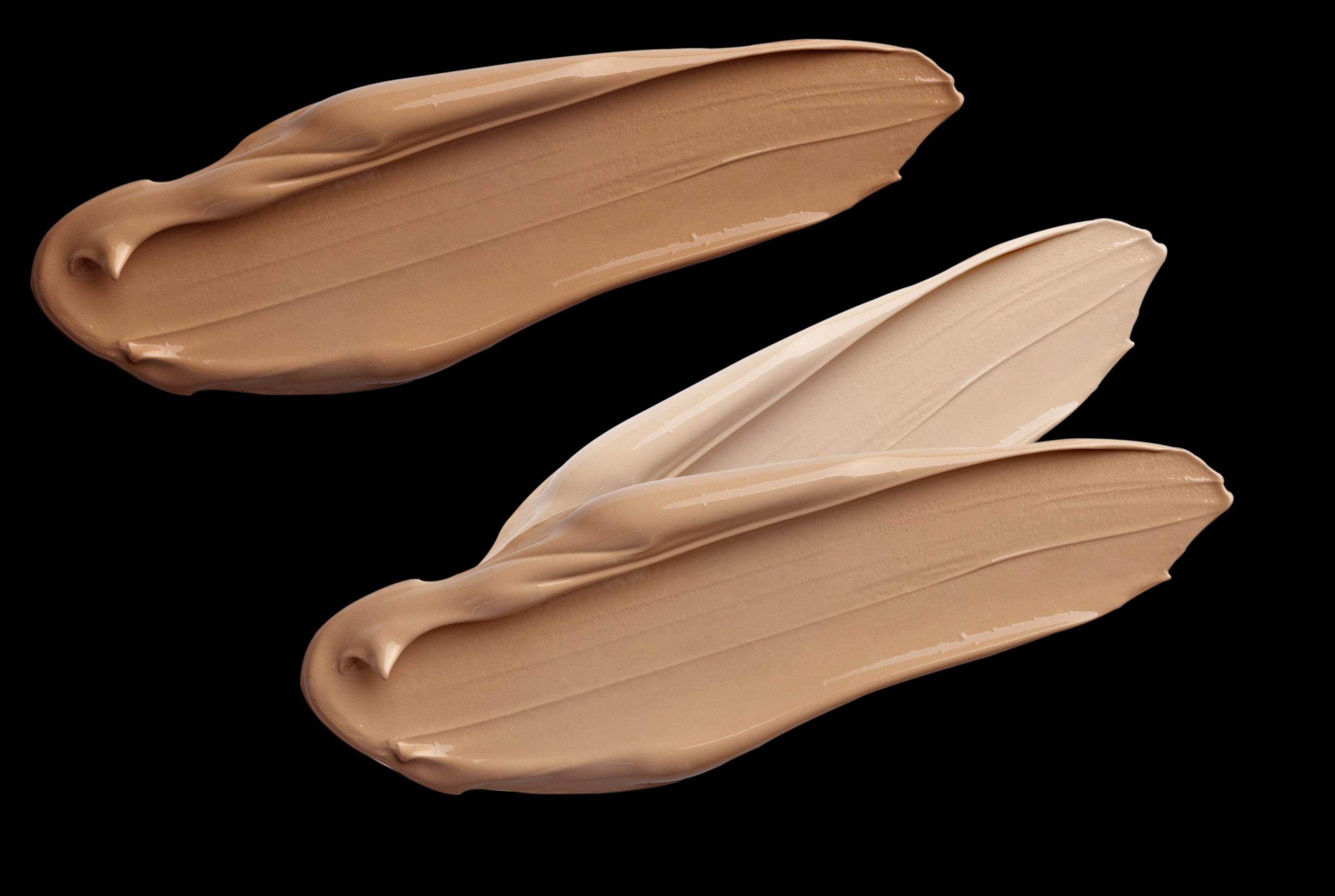
Cosmetic foundation
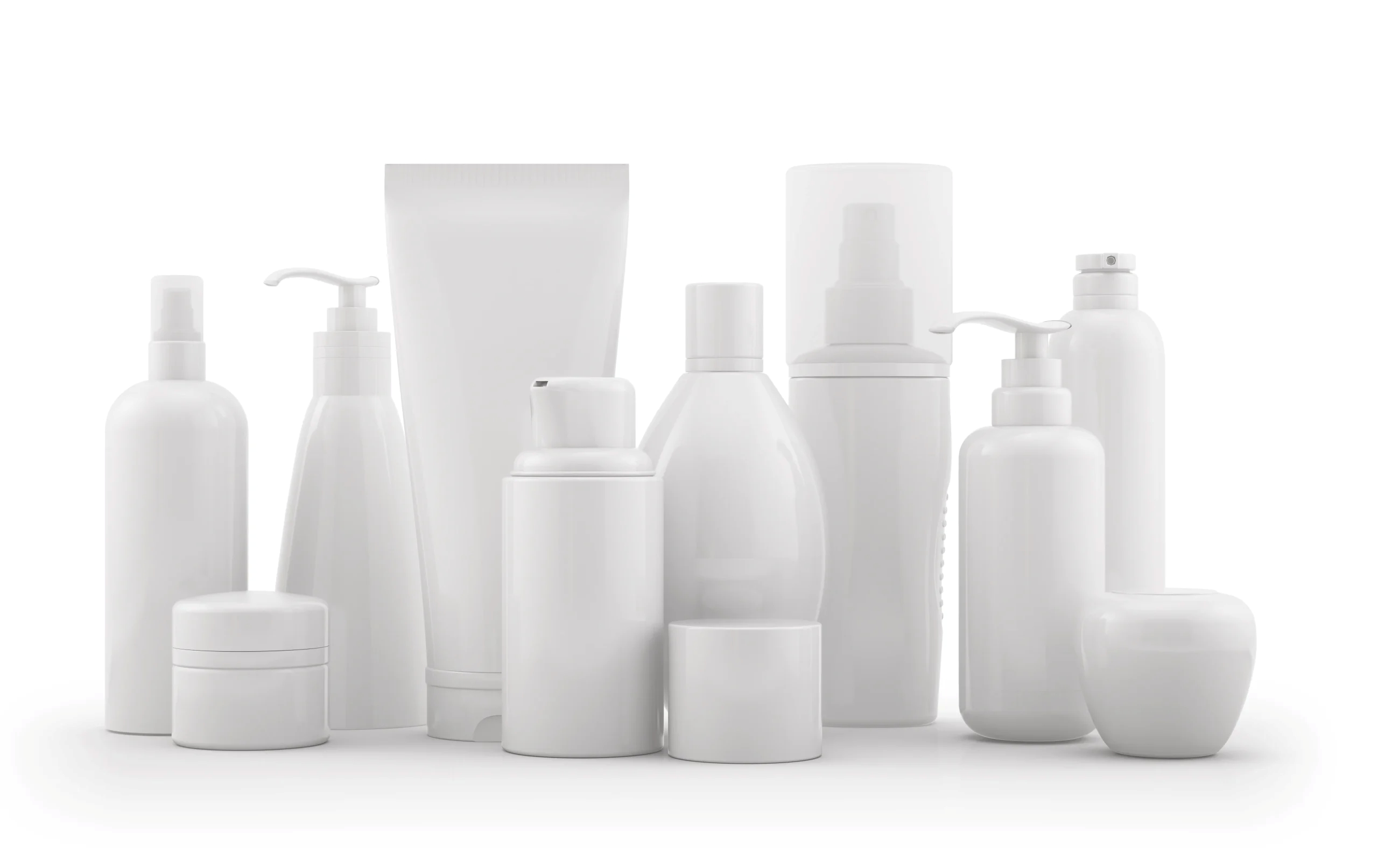
Cosmetic lotions
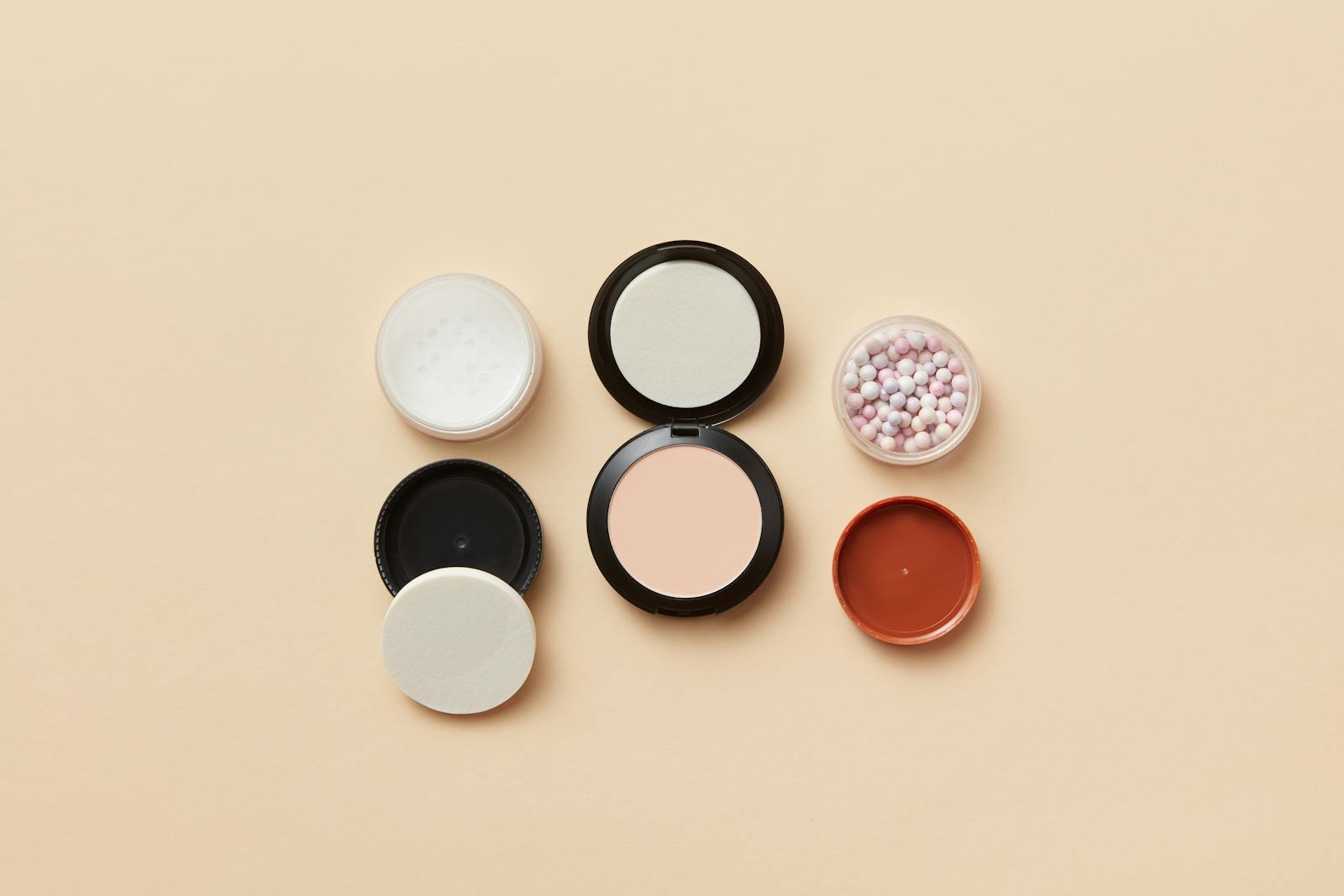
Cosmetic powders
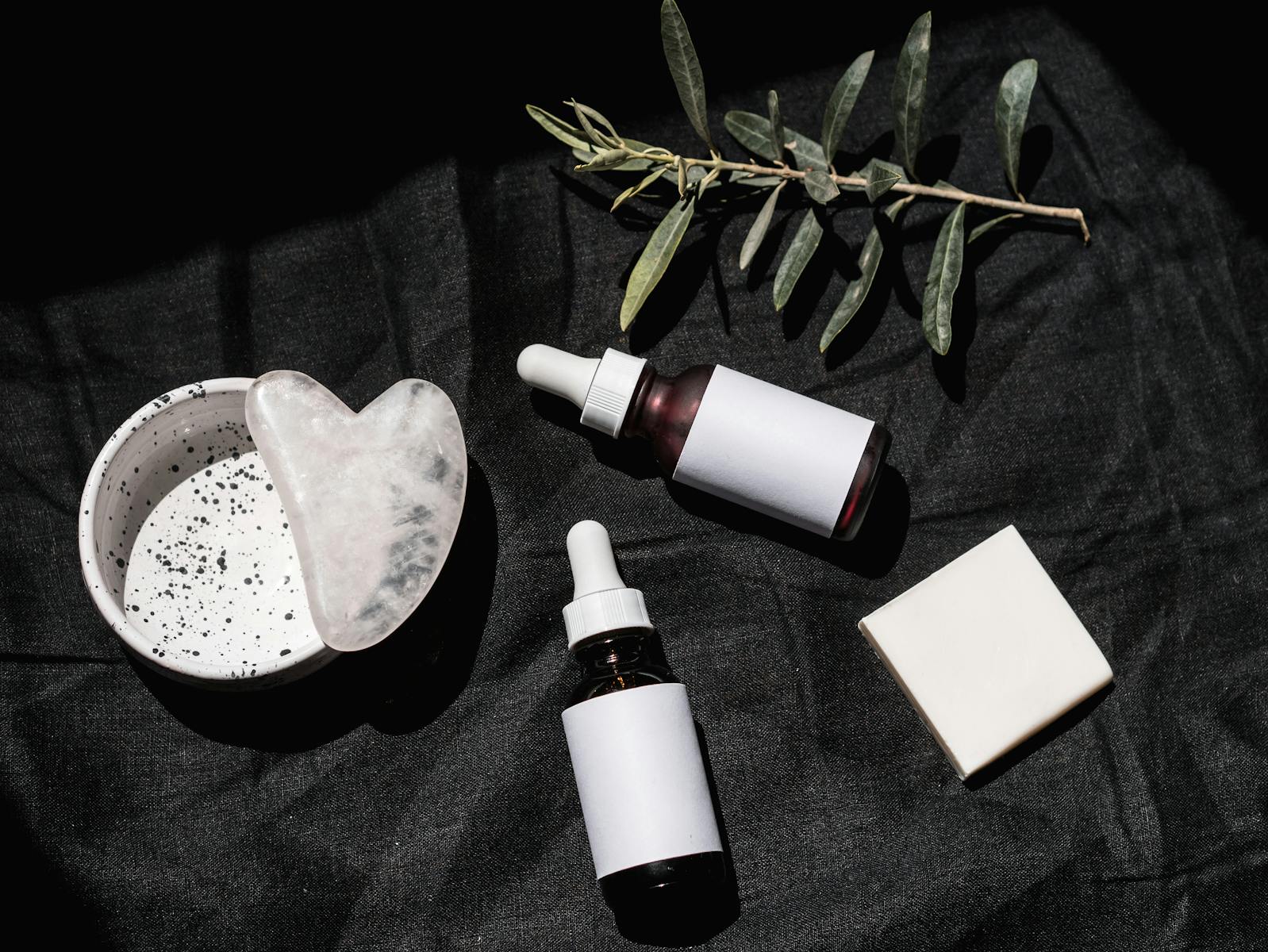
Cosmetic serums
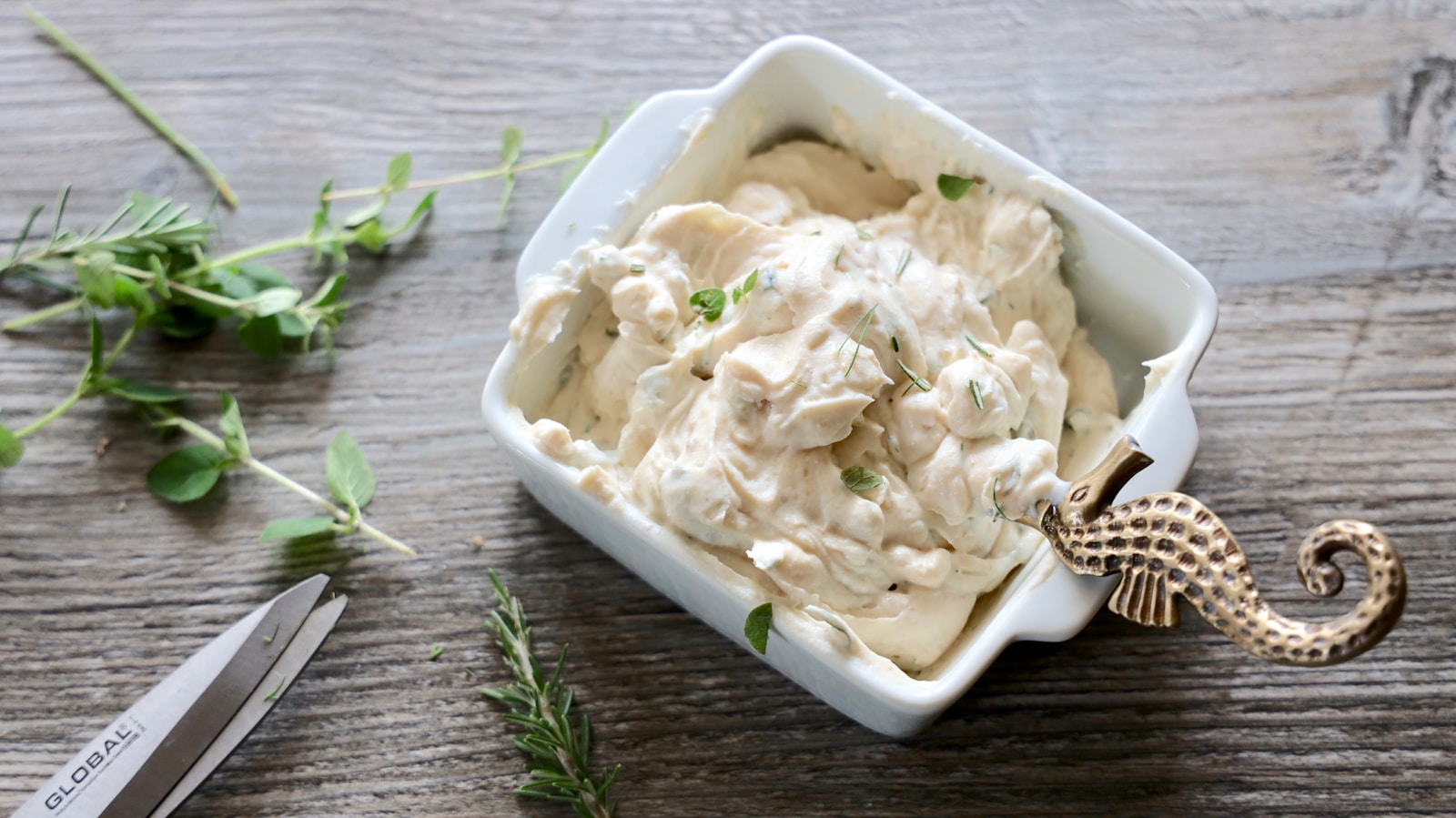
Cottage cheese
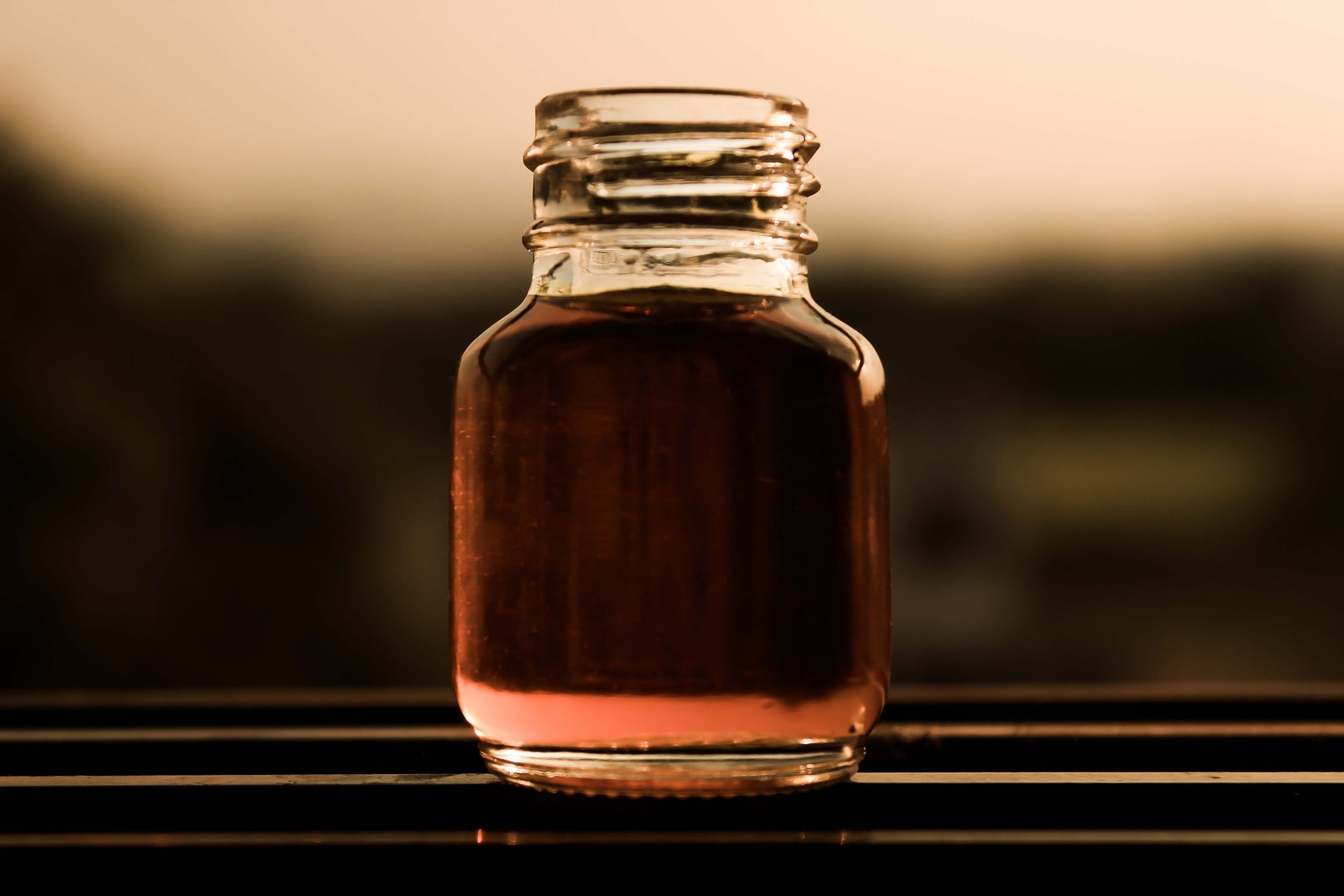
Cough syrup
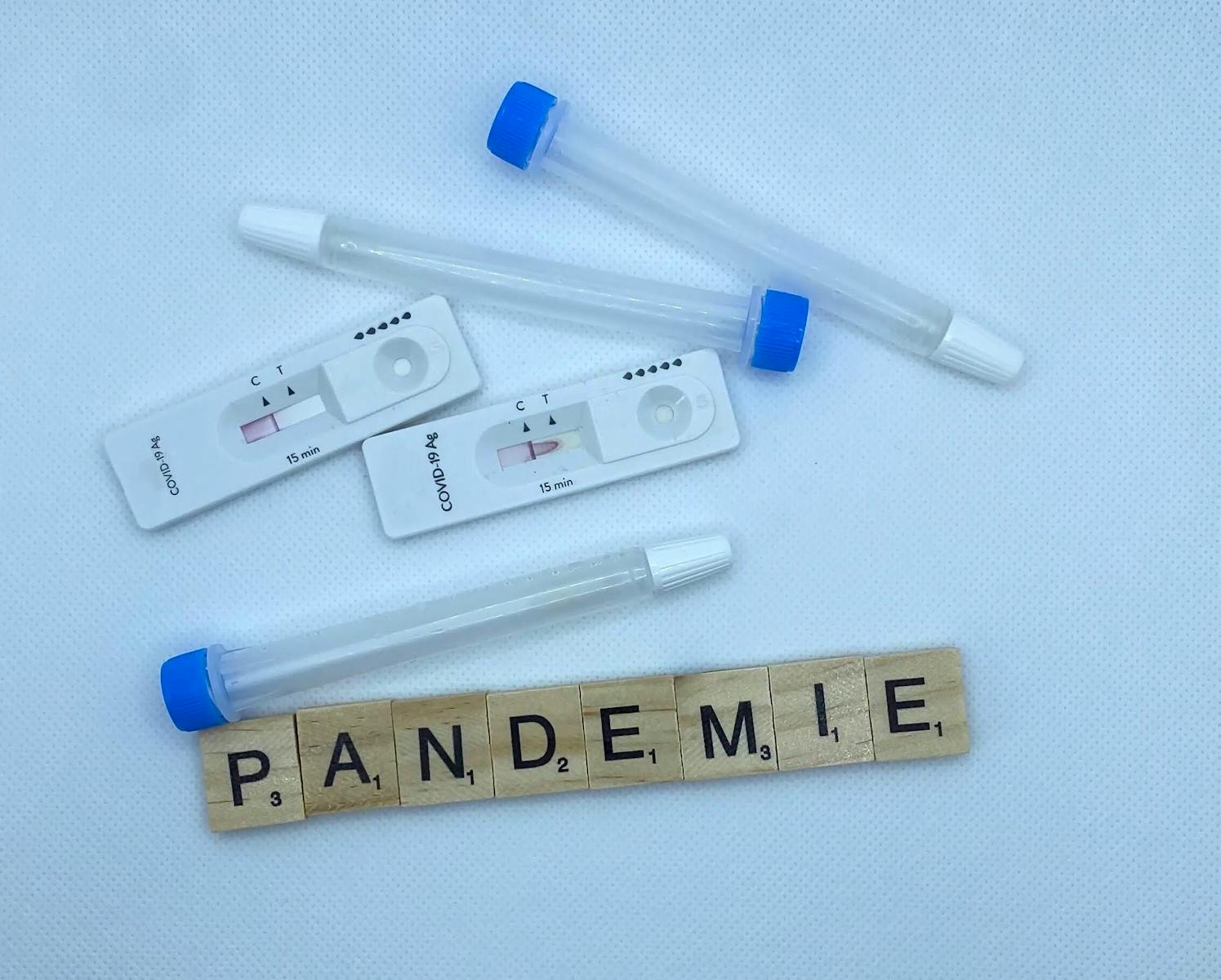
Covid-19 test kits
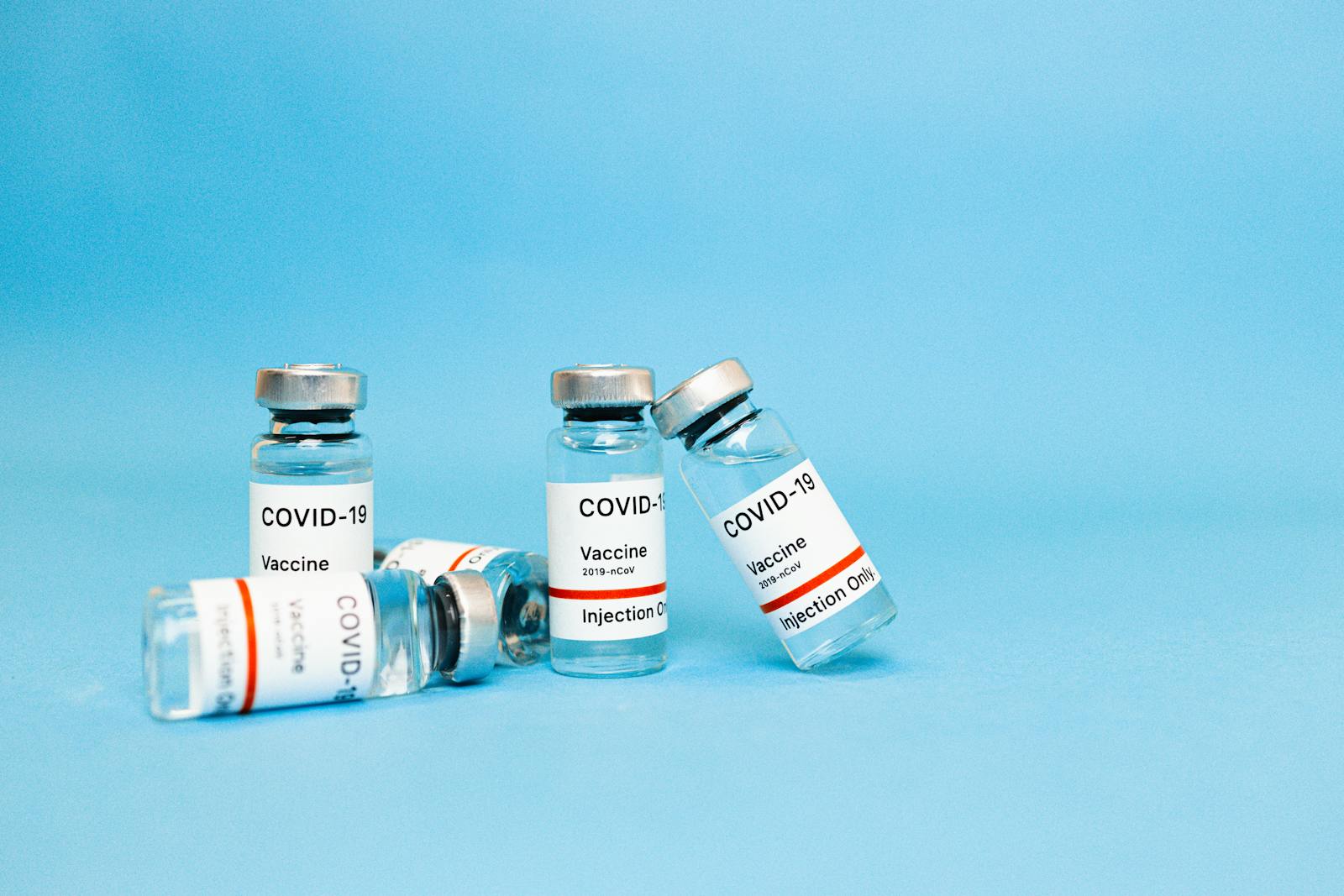
Covid-19 vaccines
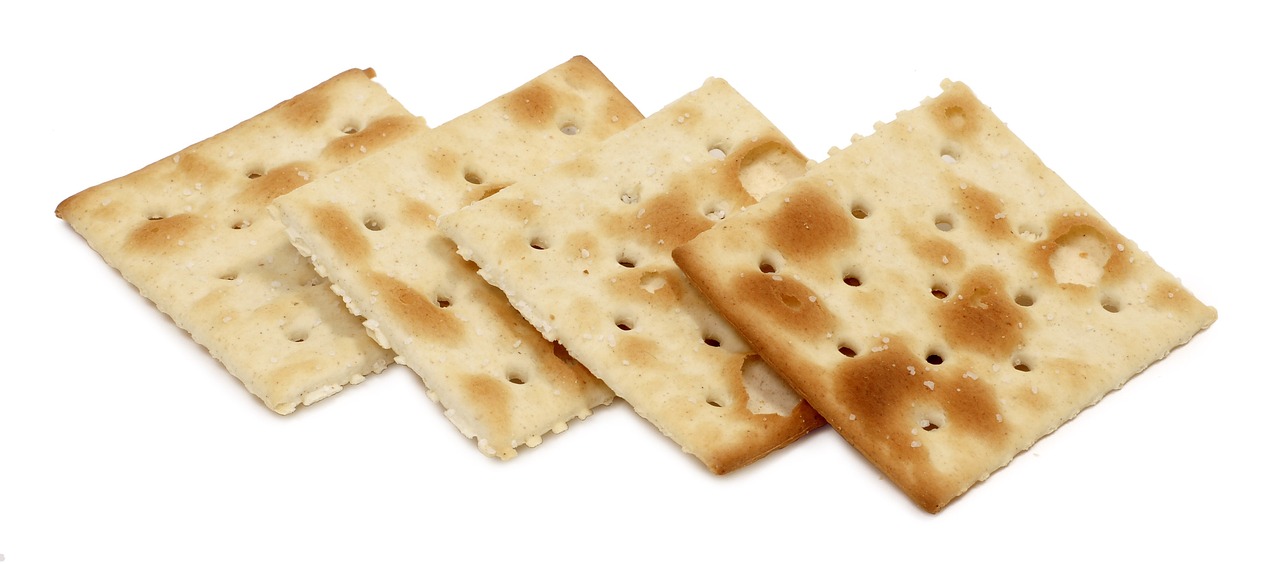
Crackers
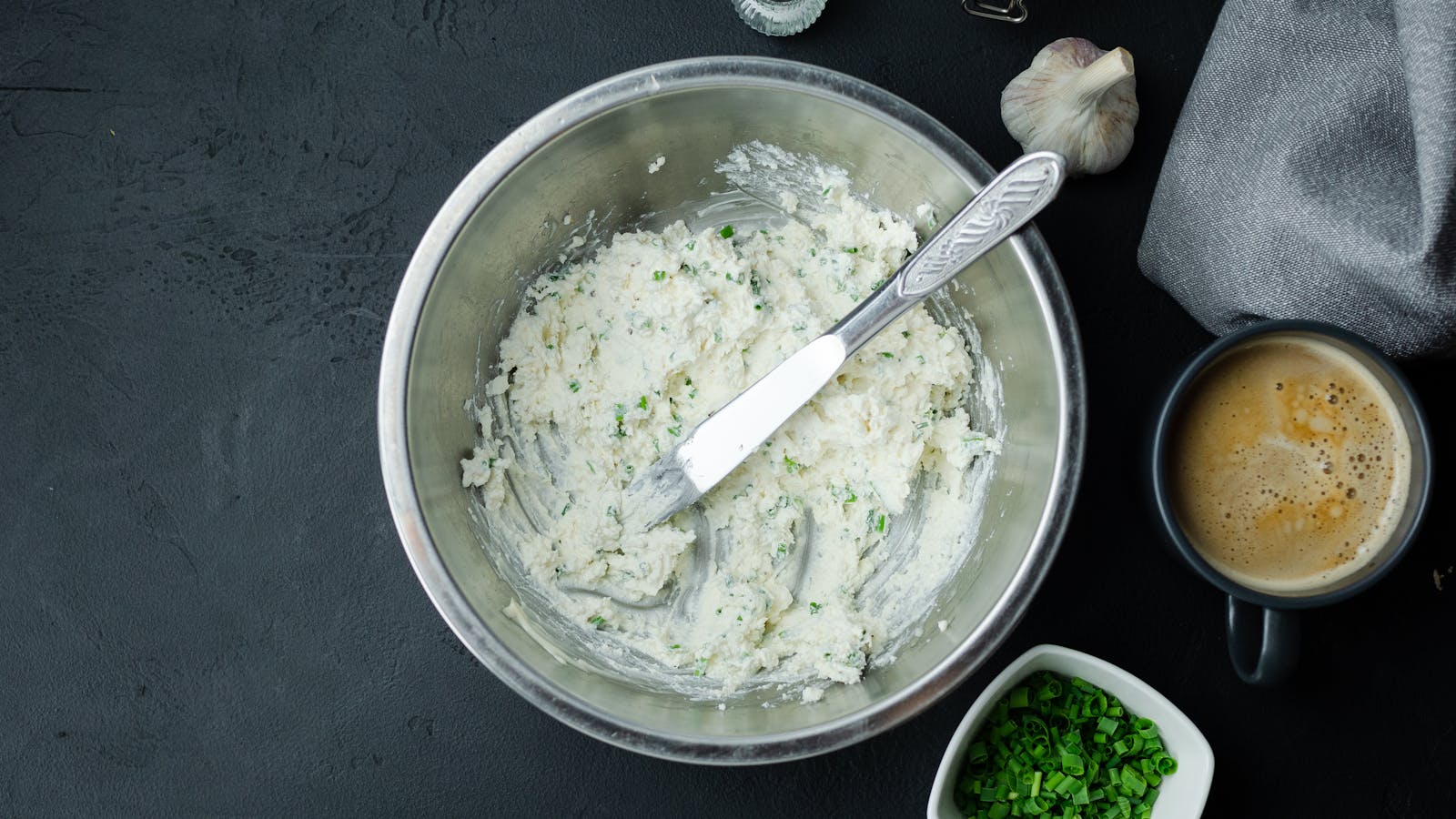
Cream cheese
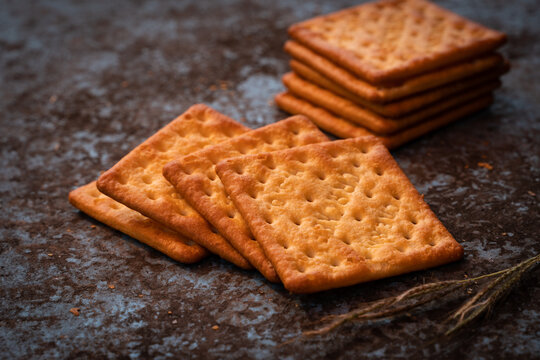
Cream crackers
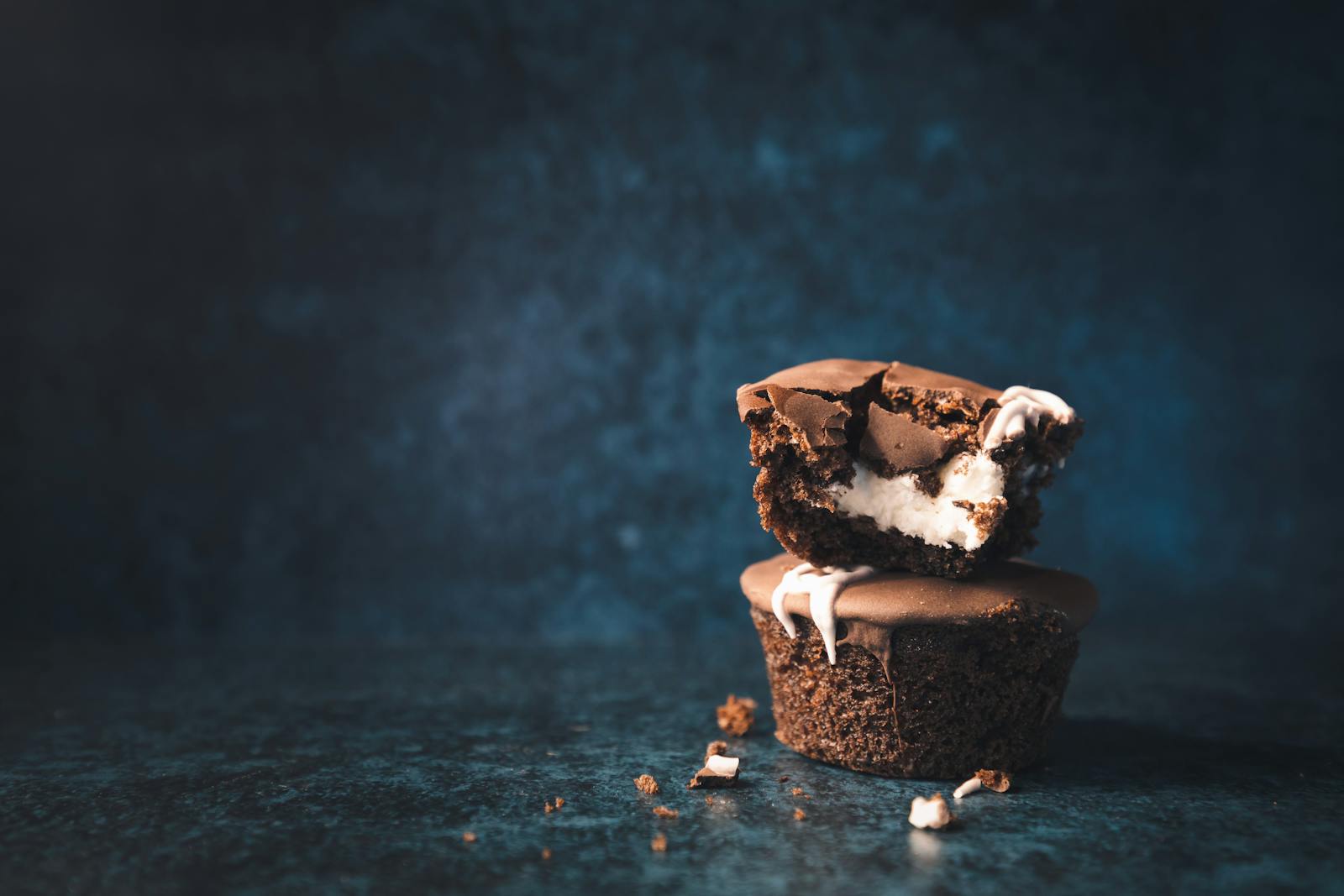
Cream fillings
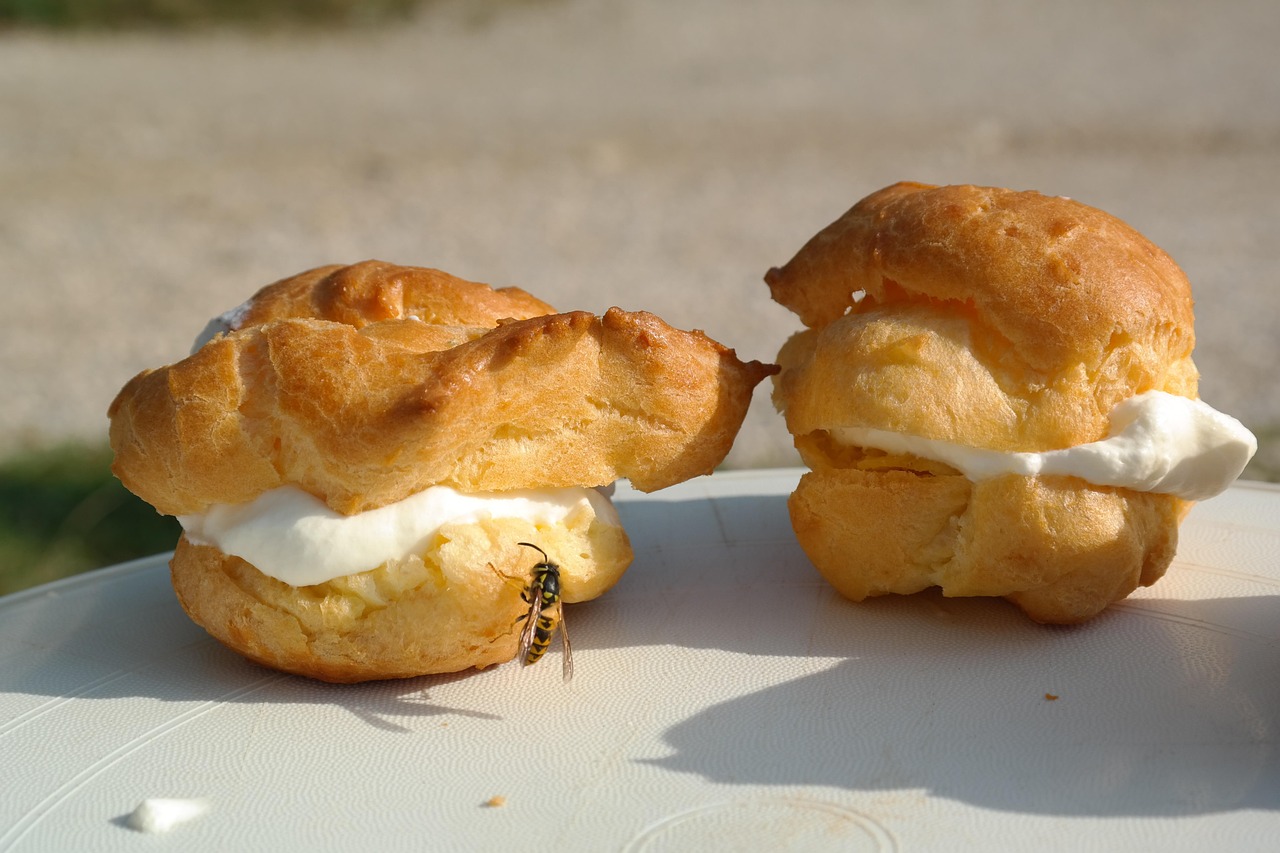
Cream puffs
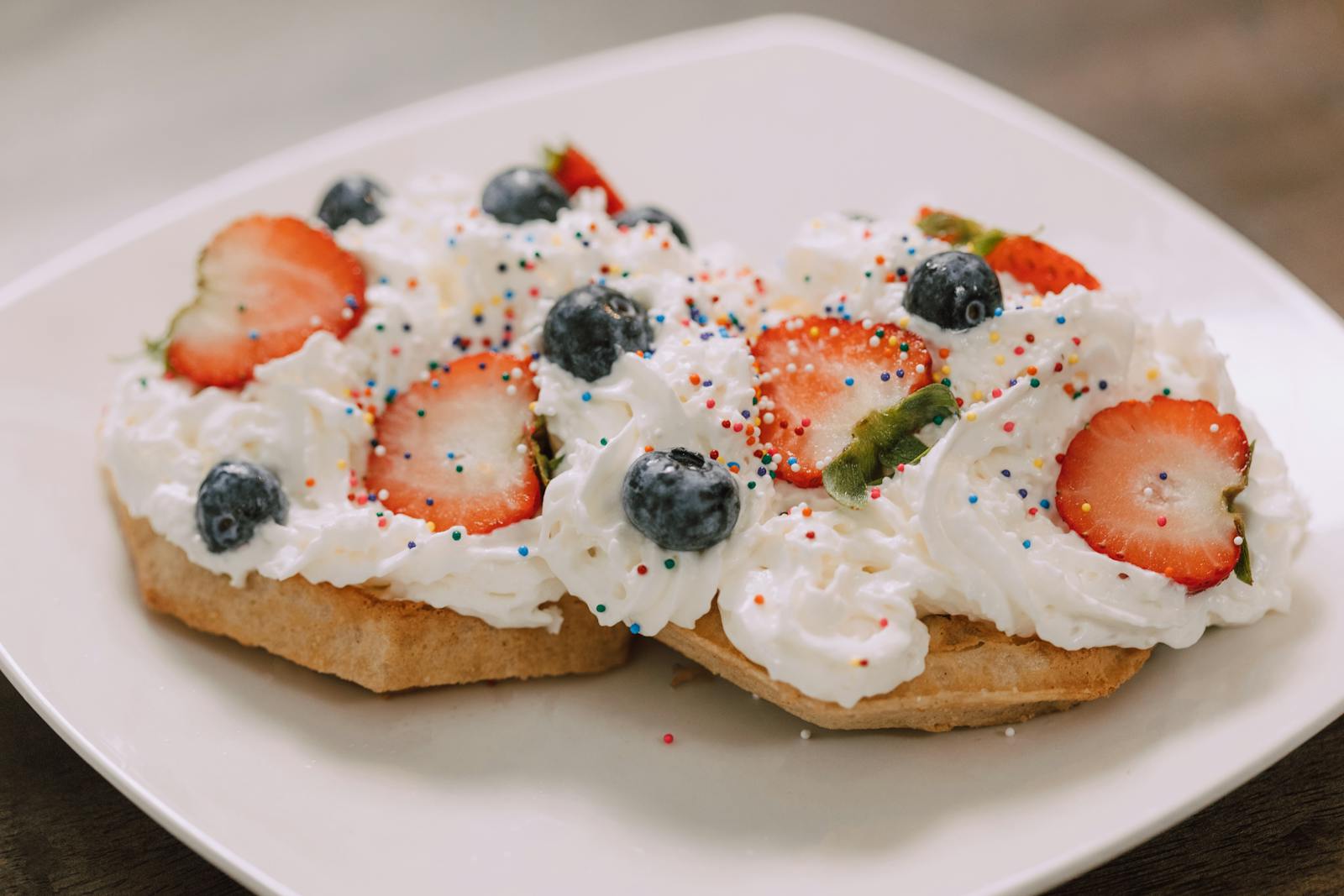
Creams

Croissants
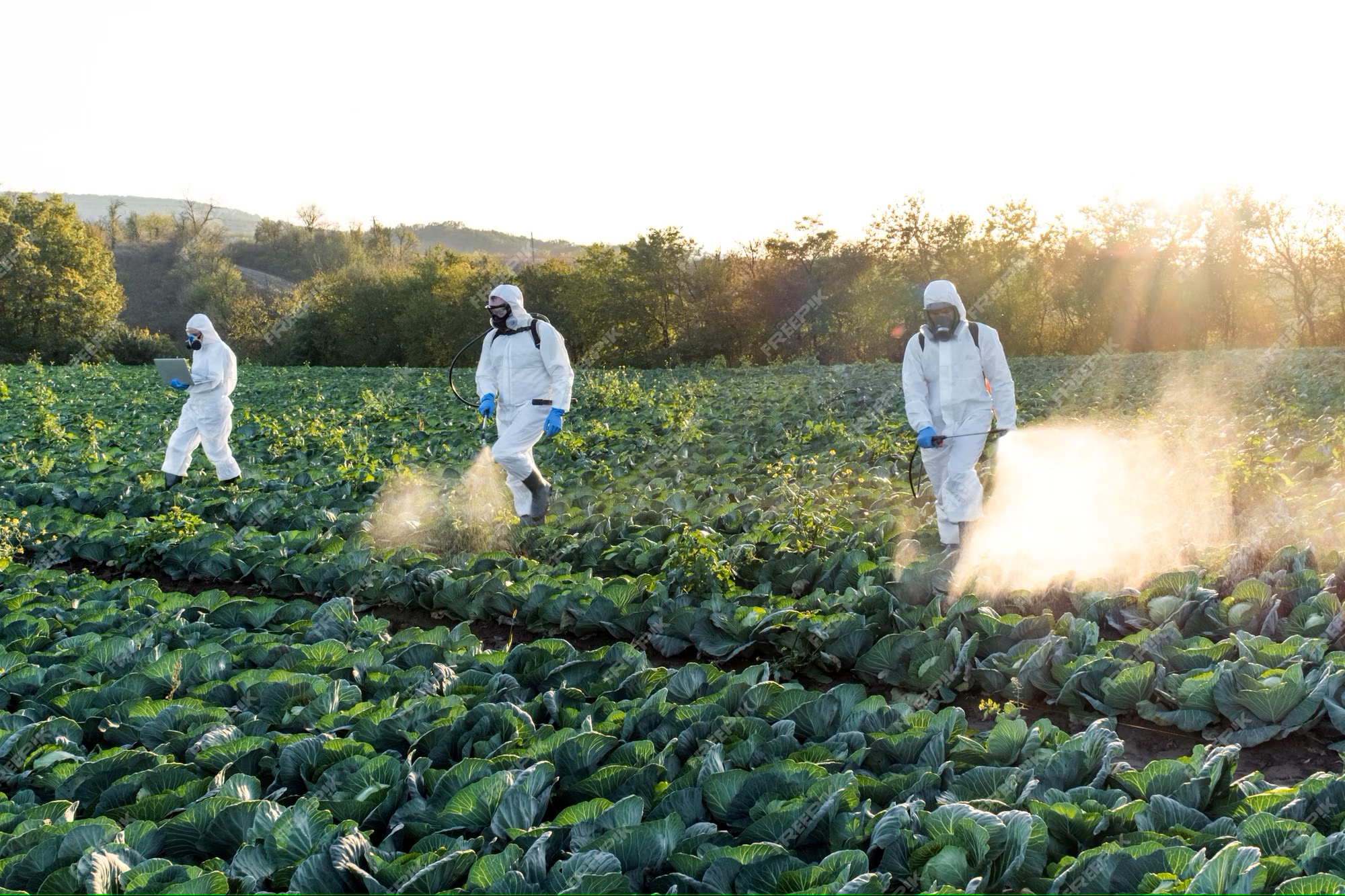
Crop protection agents
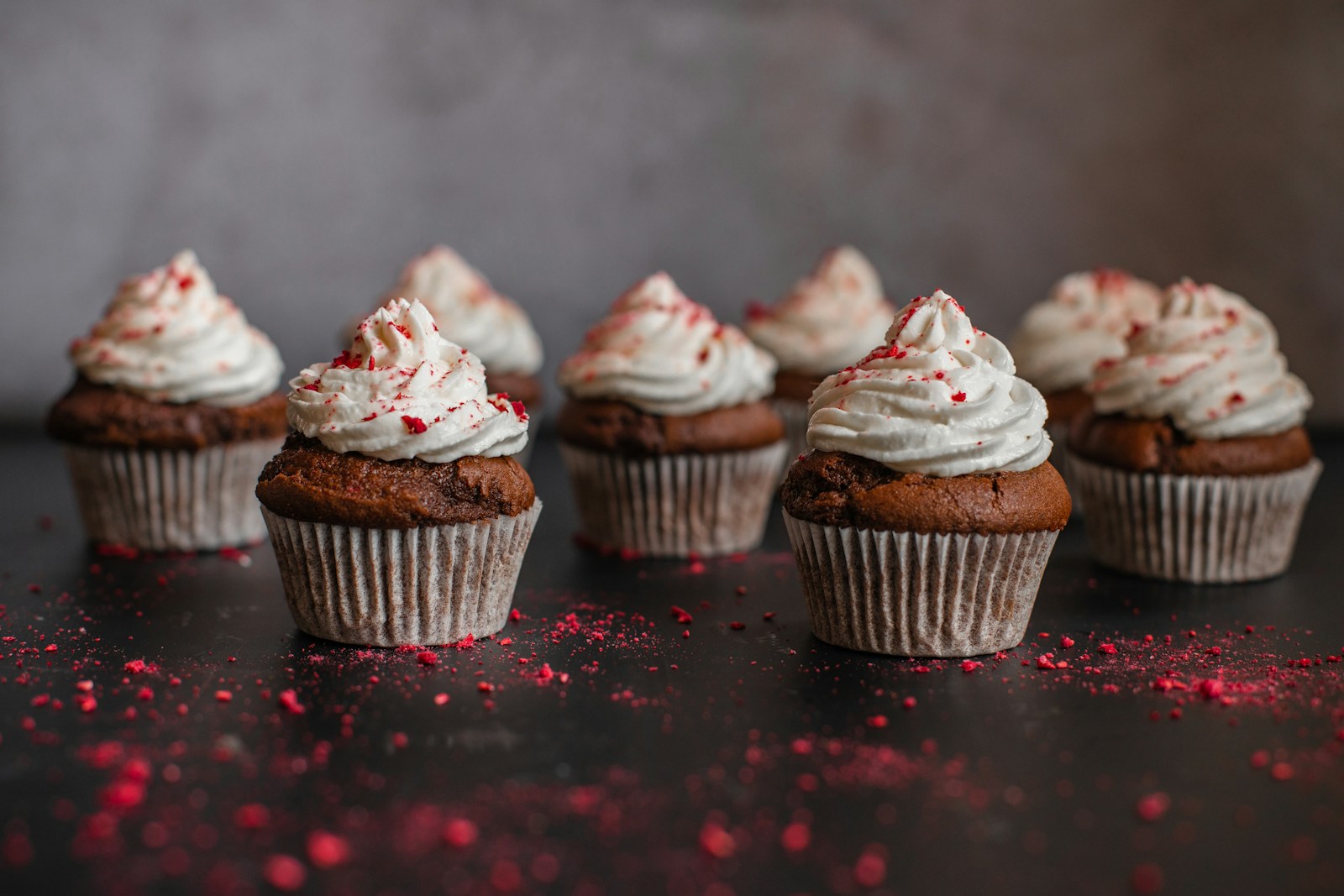
Cupcakes
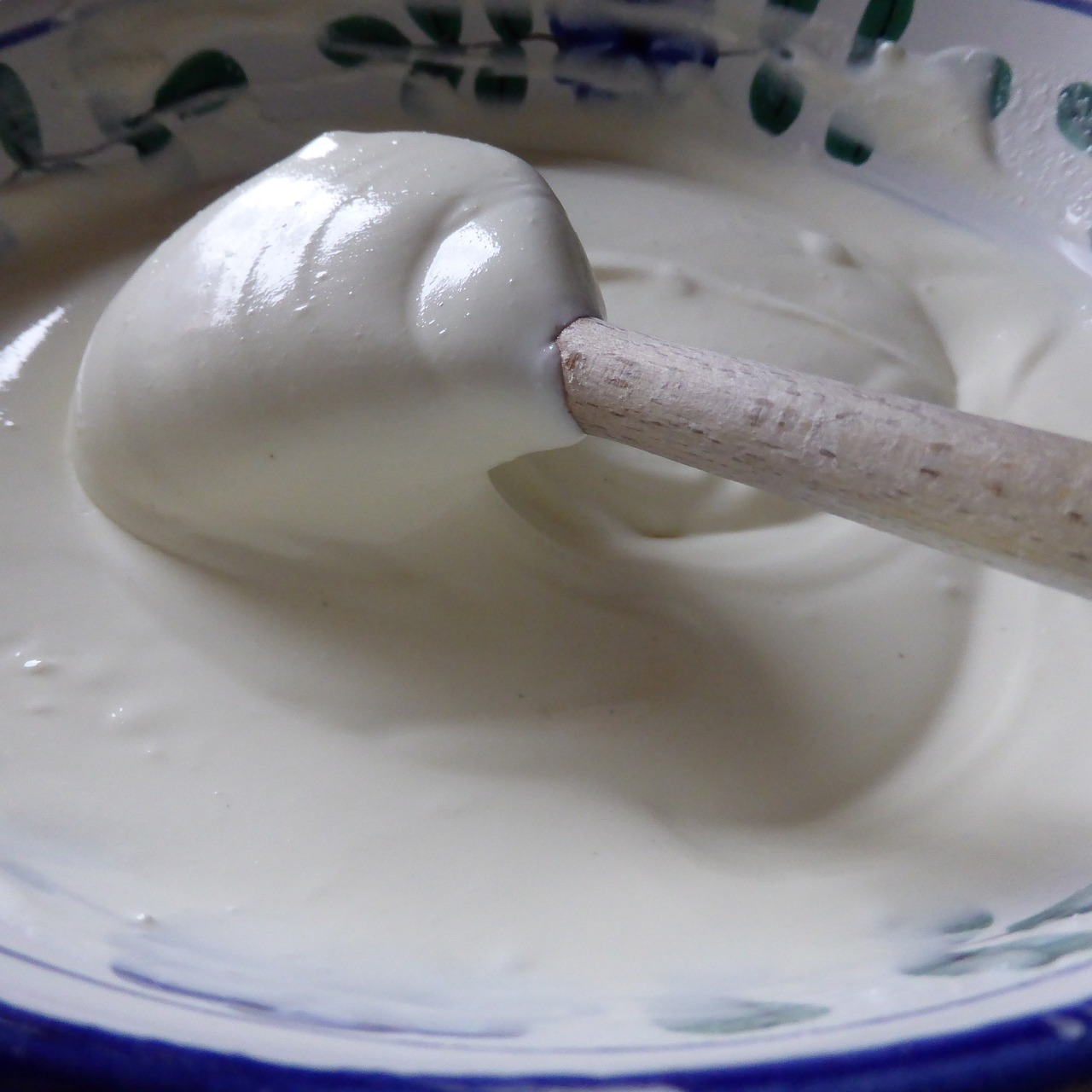
Curd
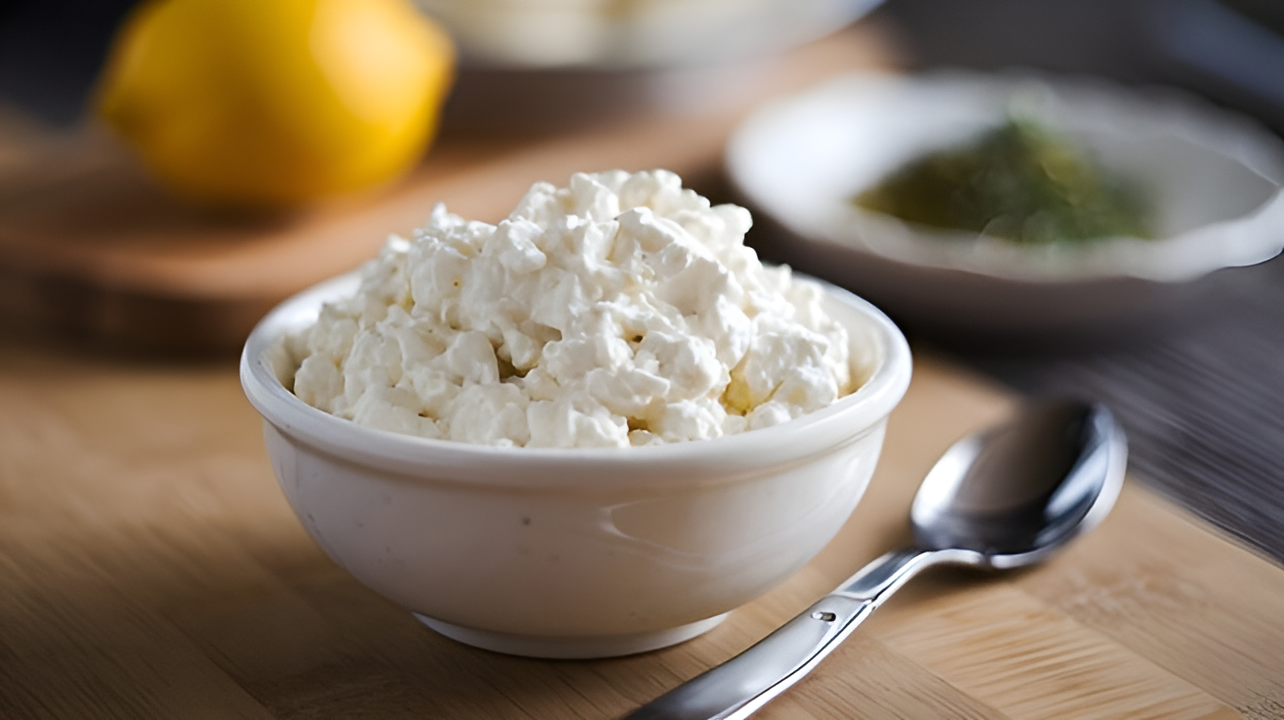
Curd cheese
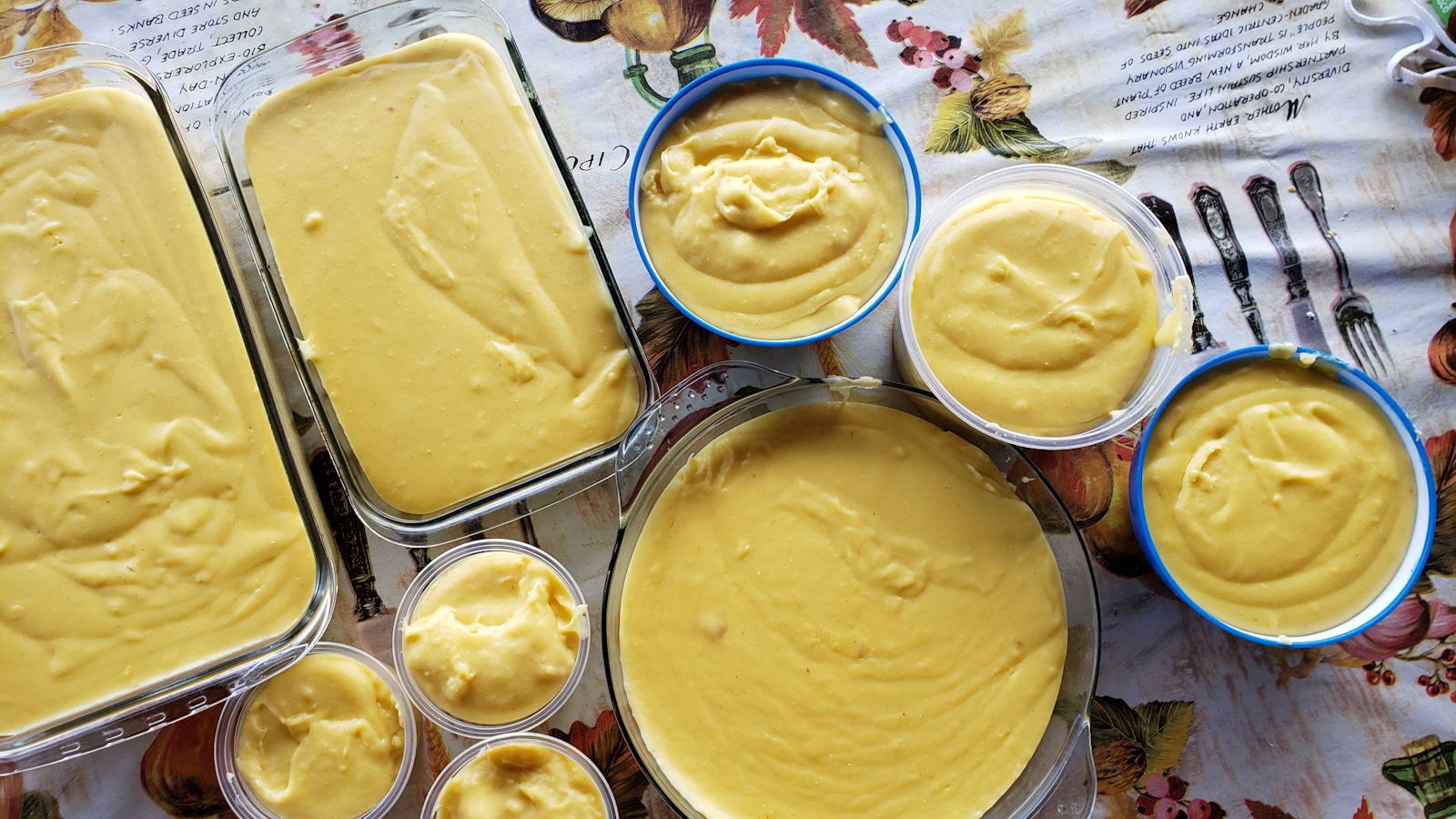
Custard
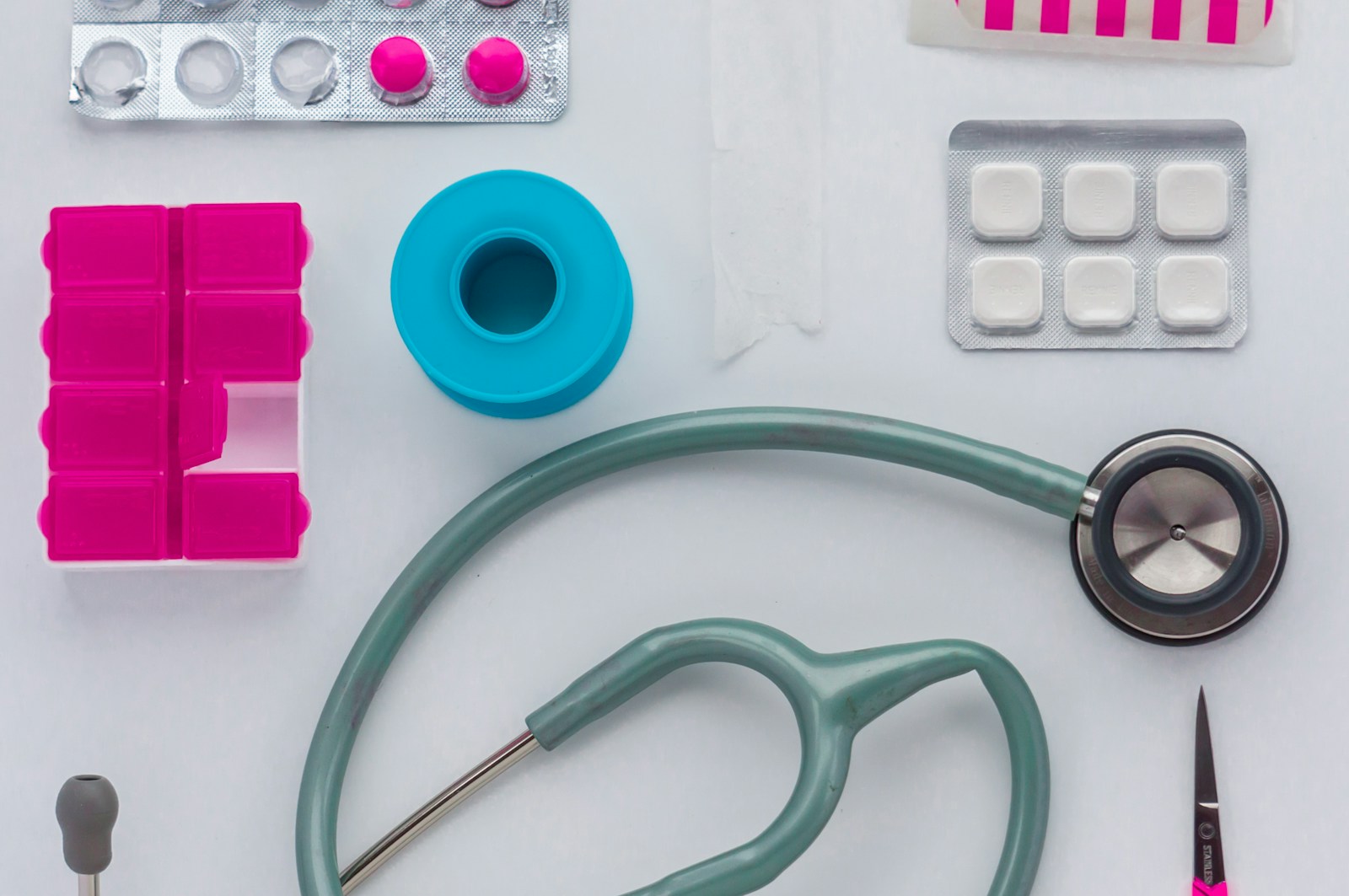
Cytotoxic drugs
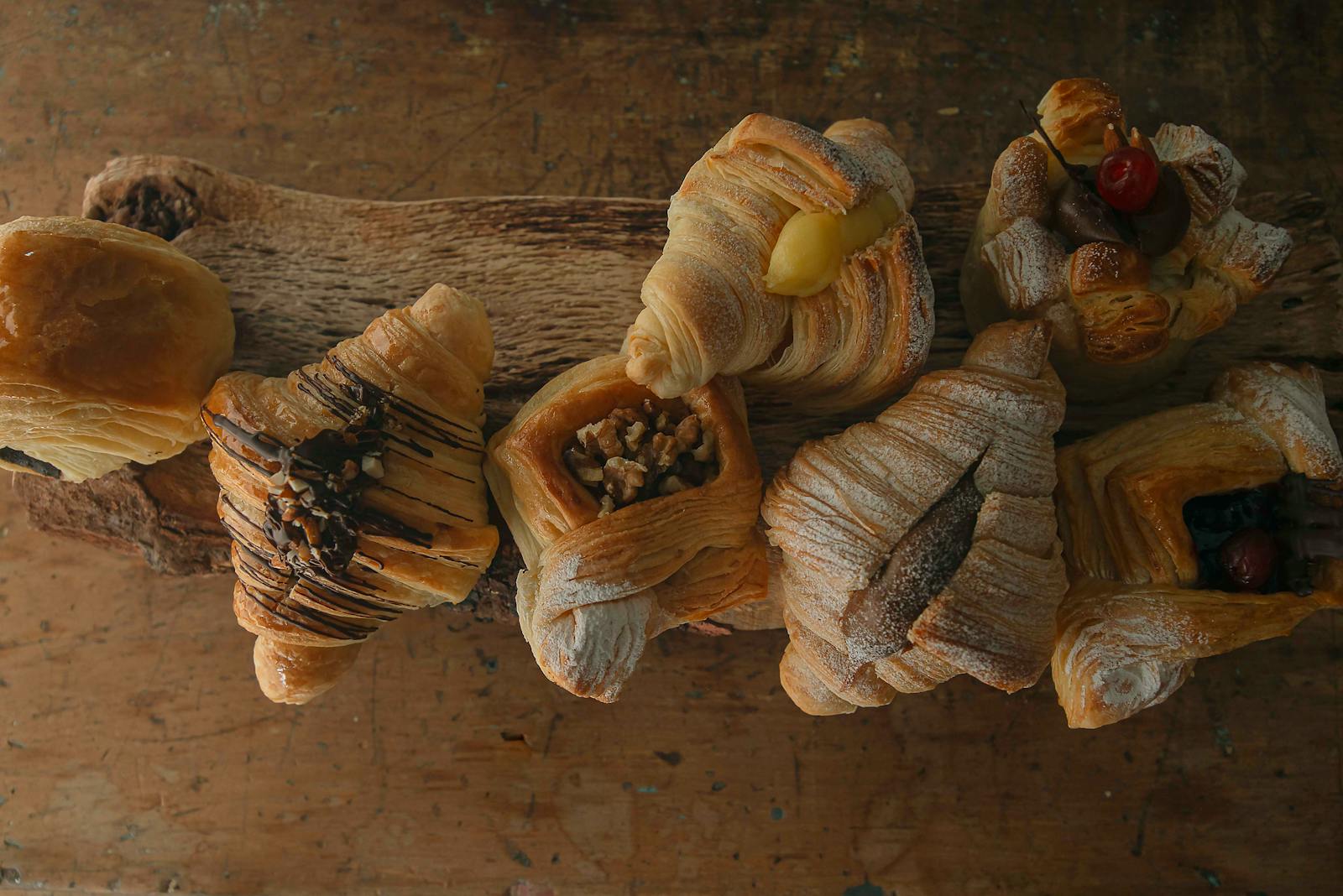
Danish pastries
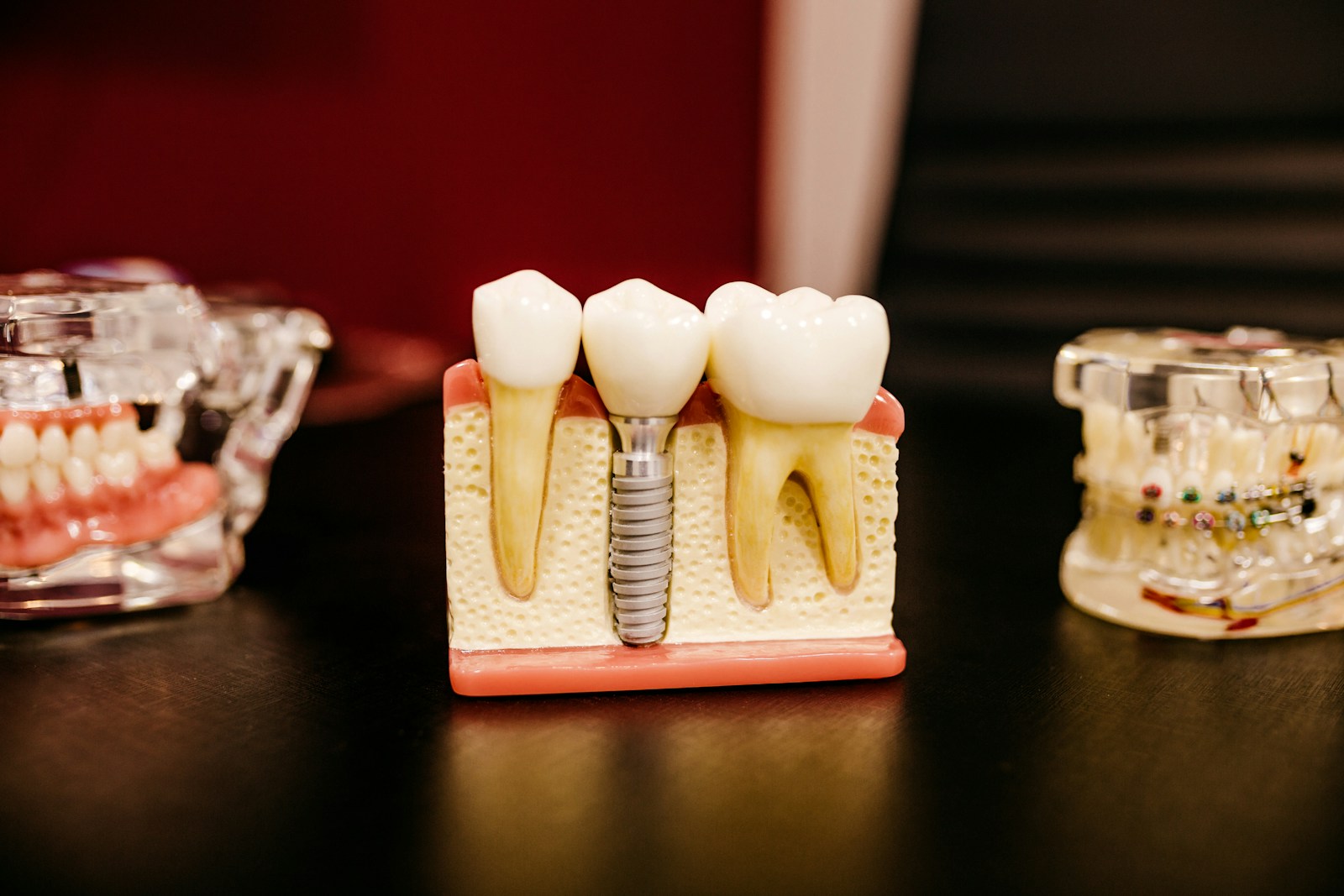
Dental
Deoderant
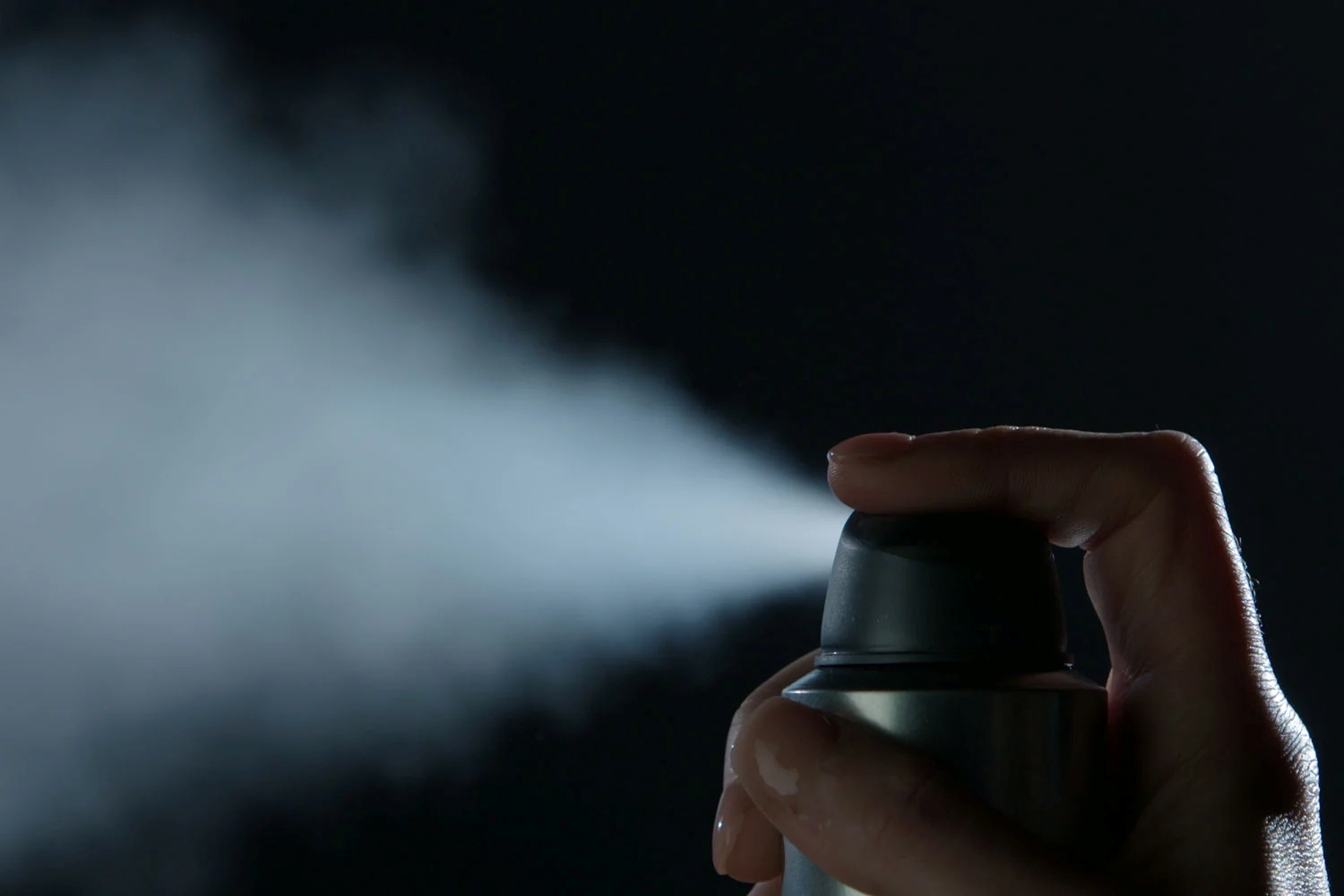
Deodorants
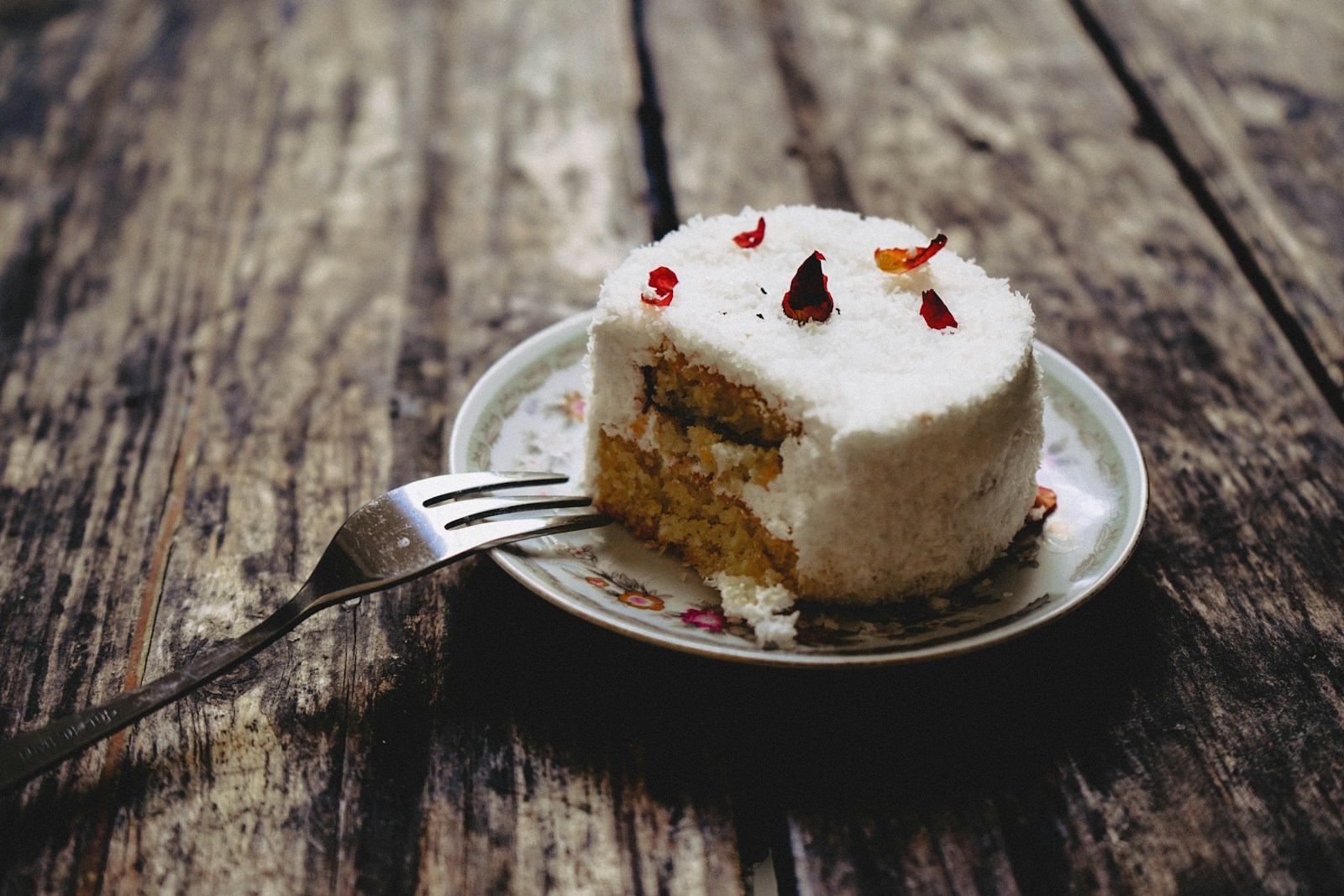
Desserts

Detergent bottles
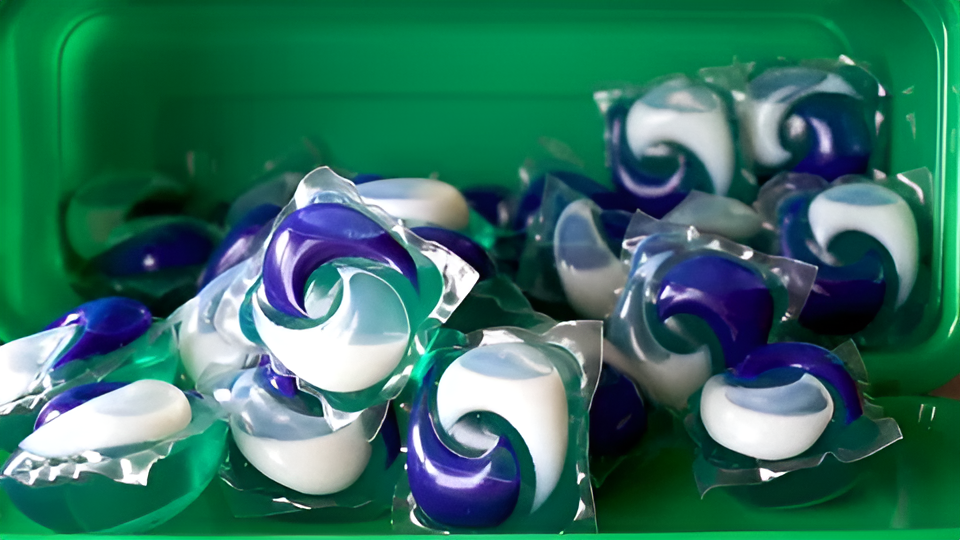
Detergent pods
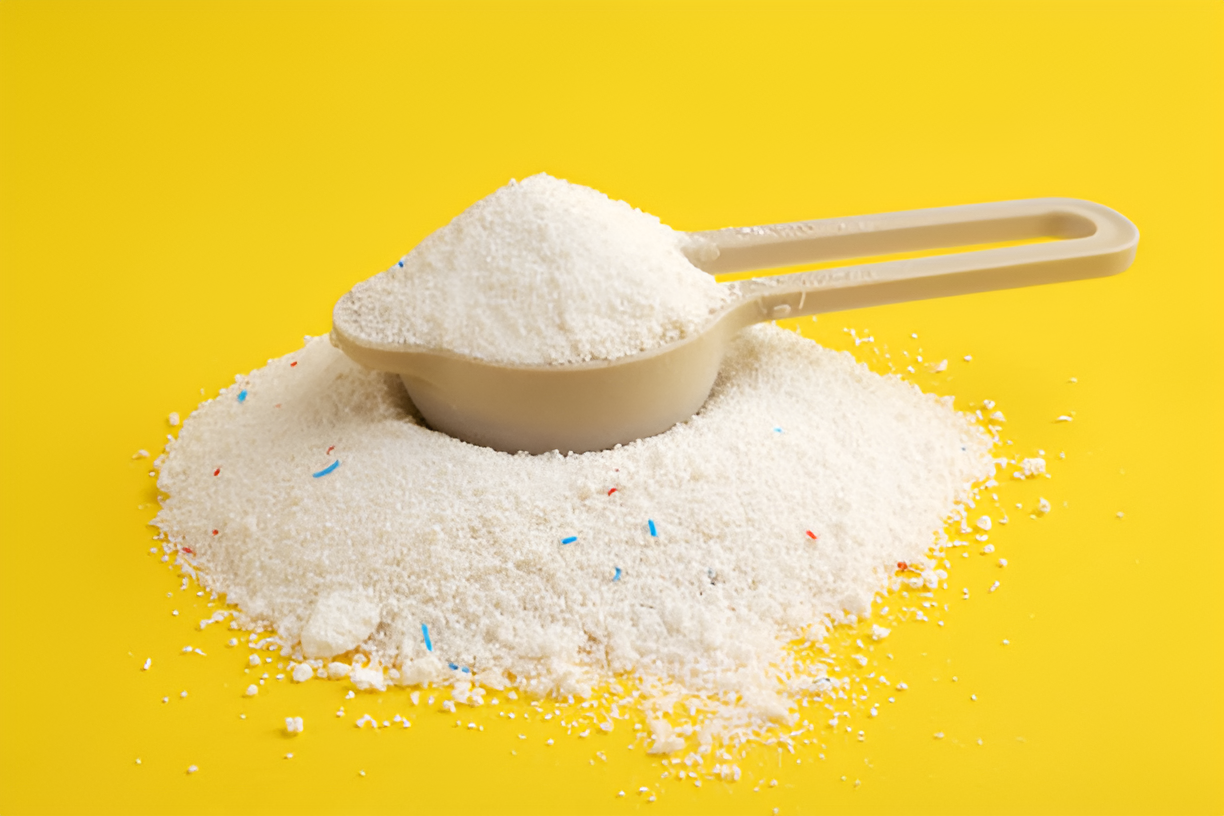
Detergent powder
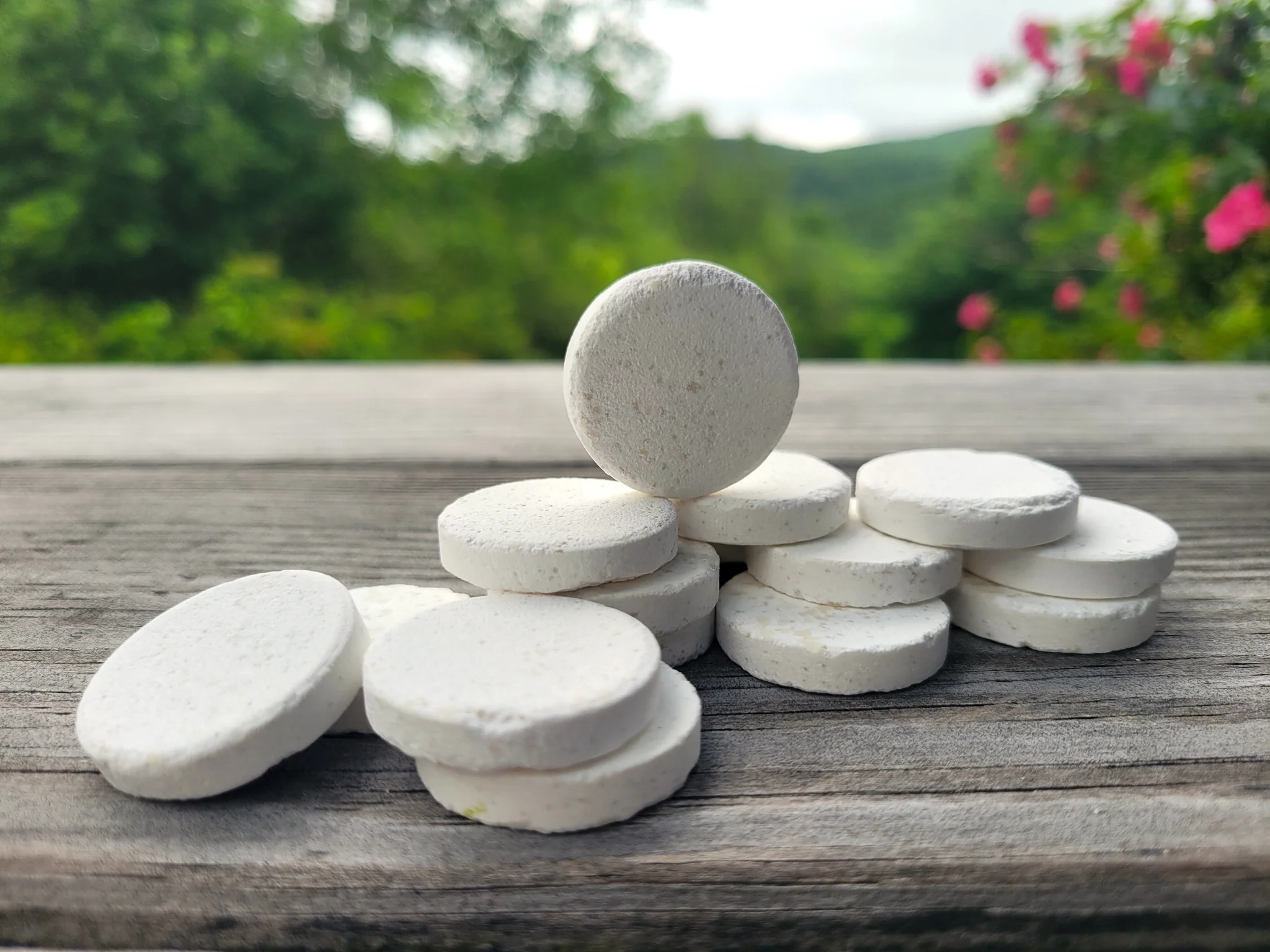
Detergent tablets
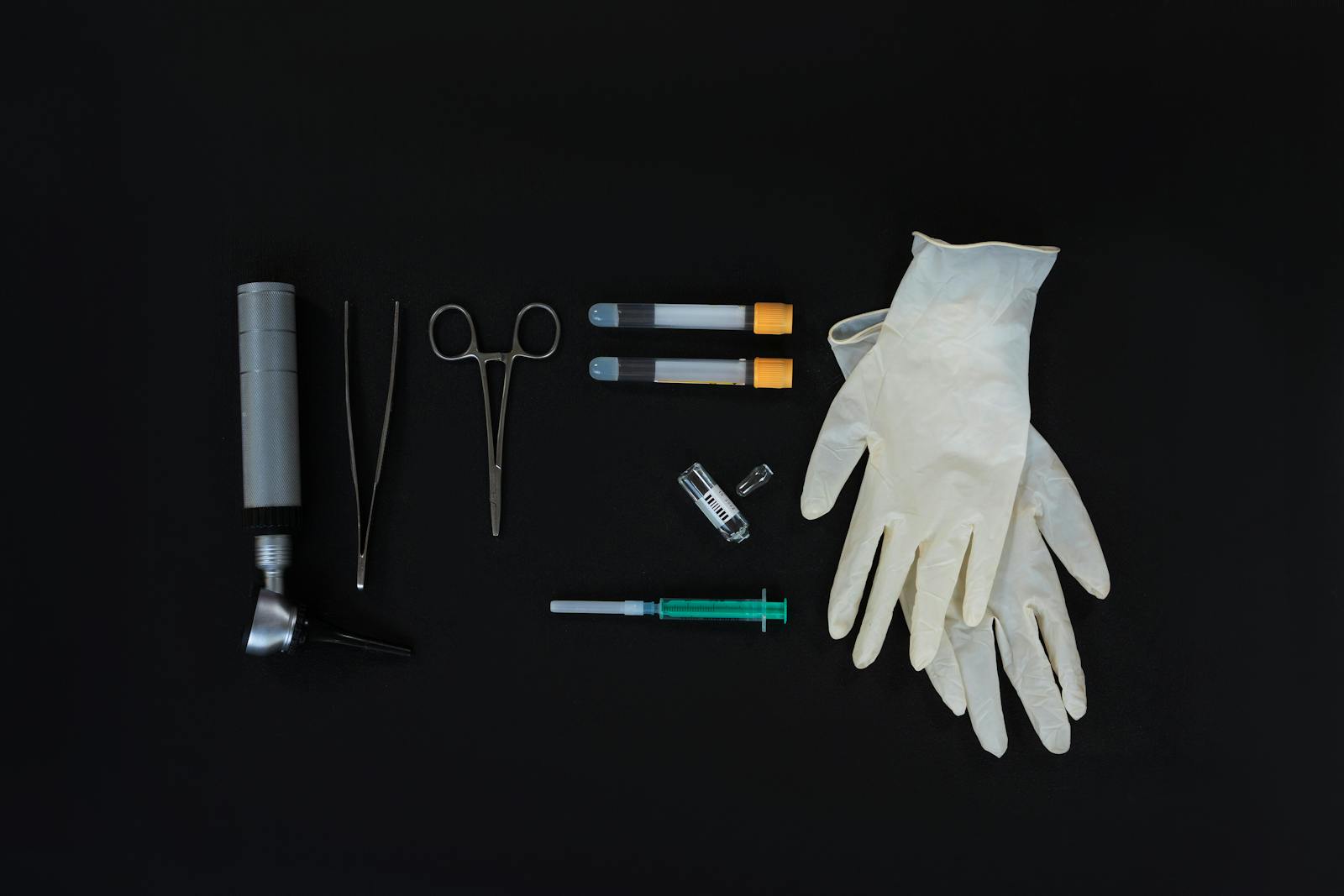
Diagnostic kits
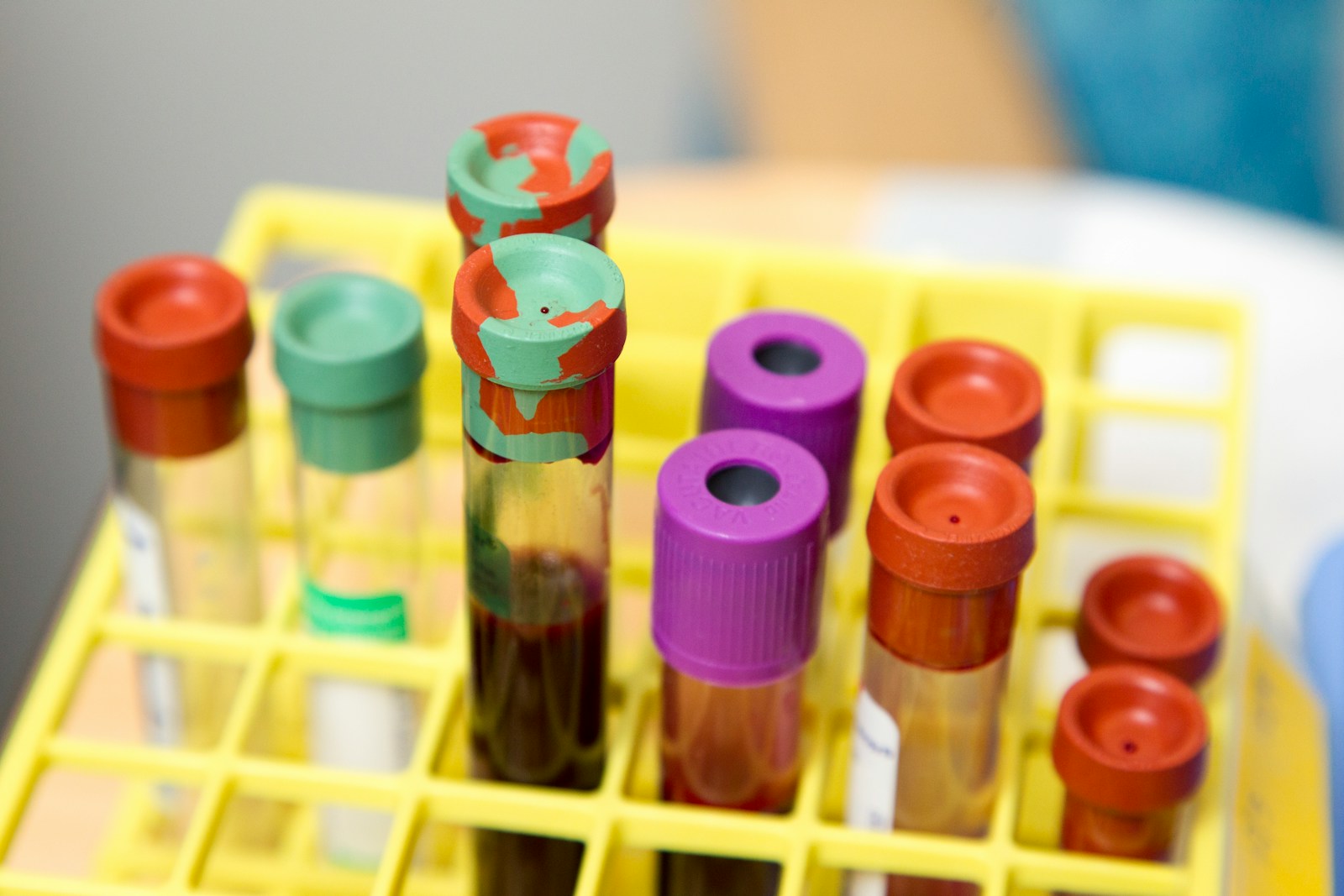
Diagnostic reagents
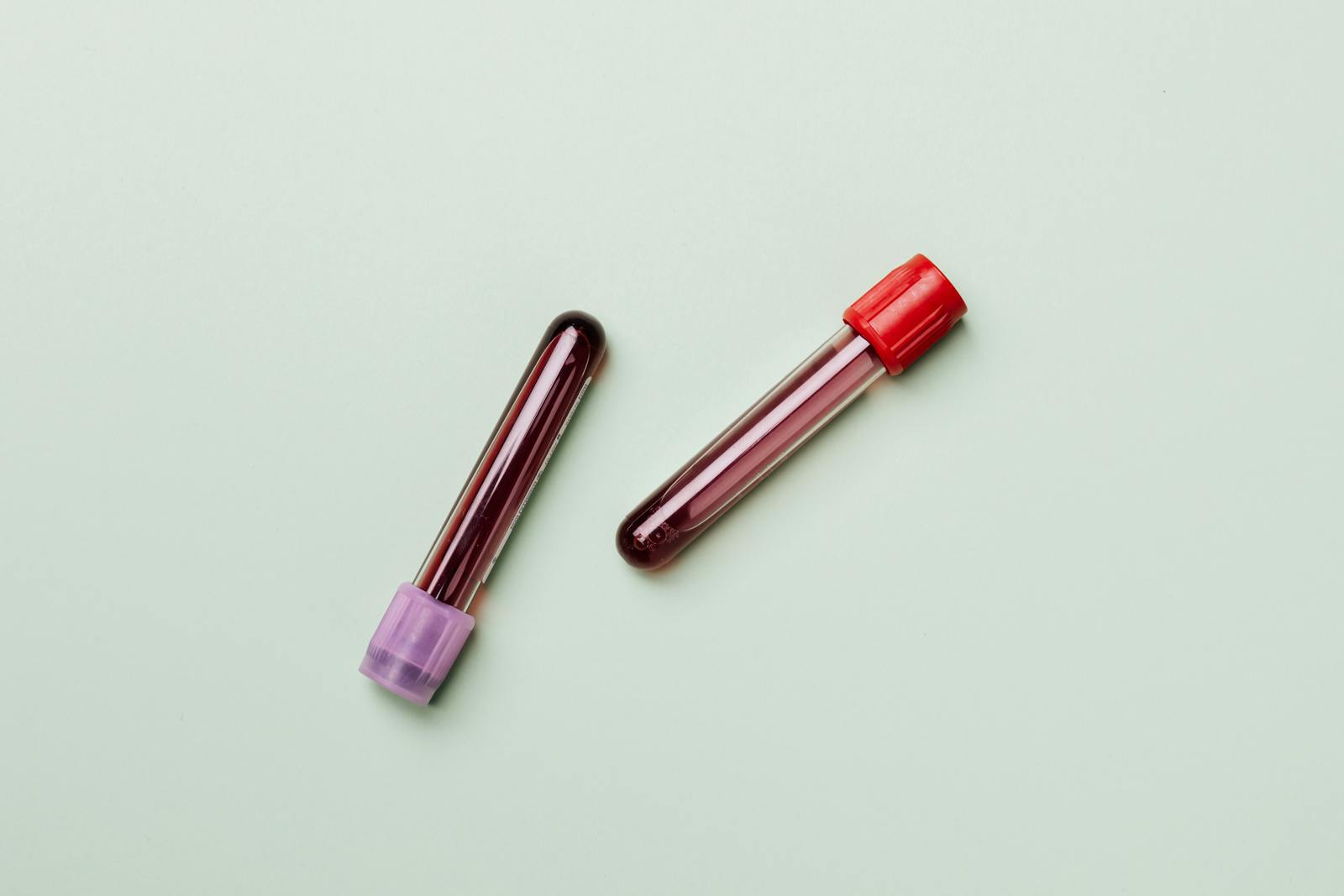
Diagnostics
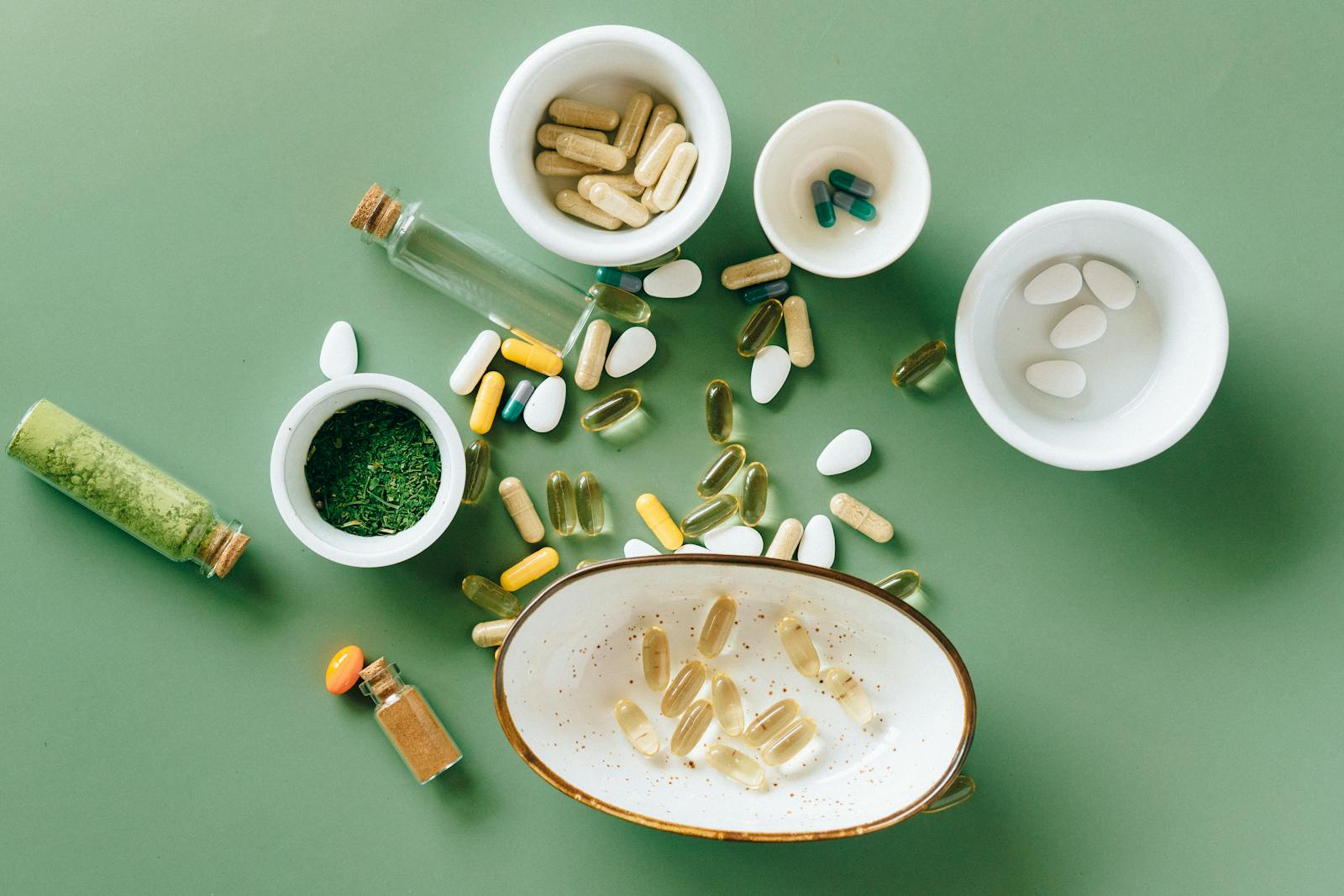
Dietary supplements
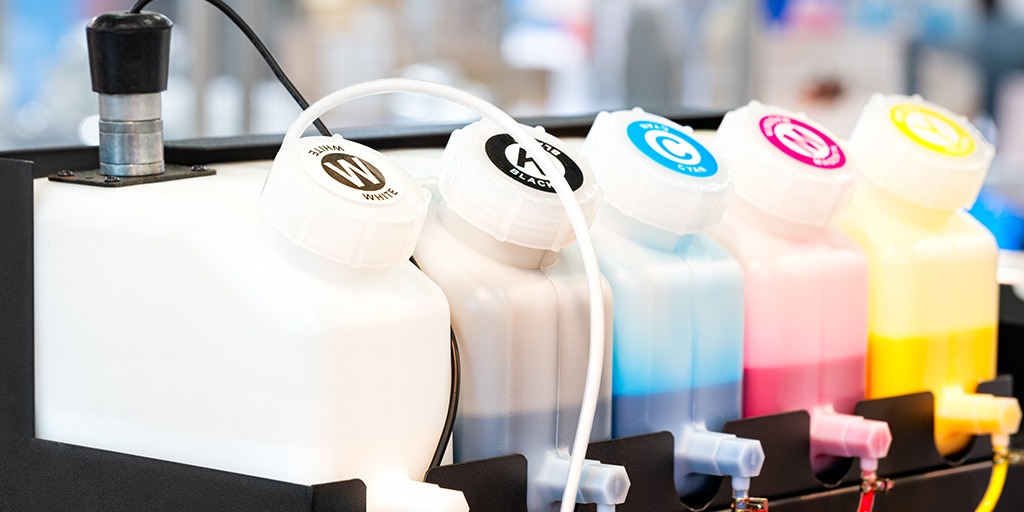
Digital printing inks
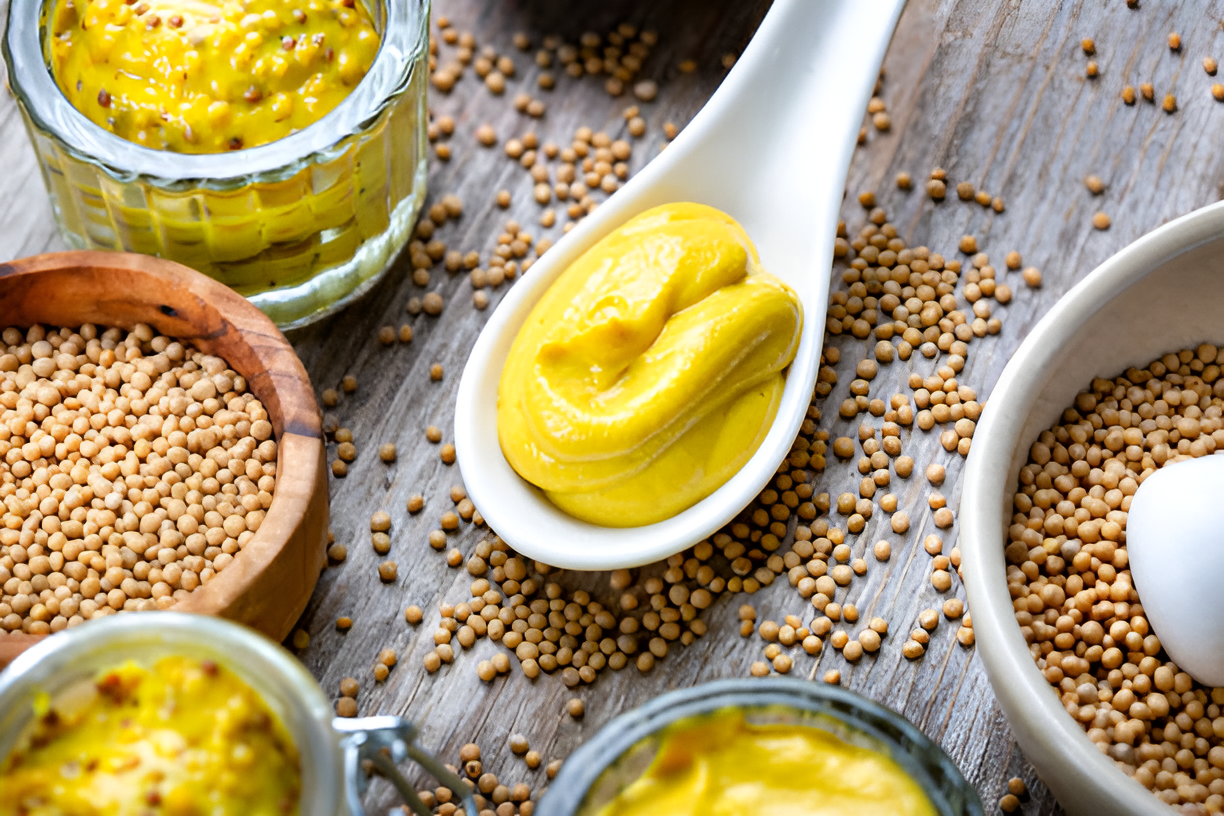
Dijon mustard
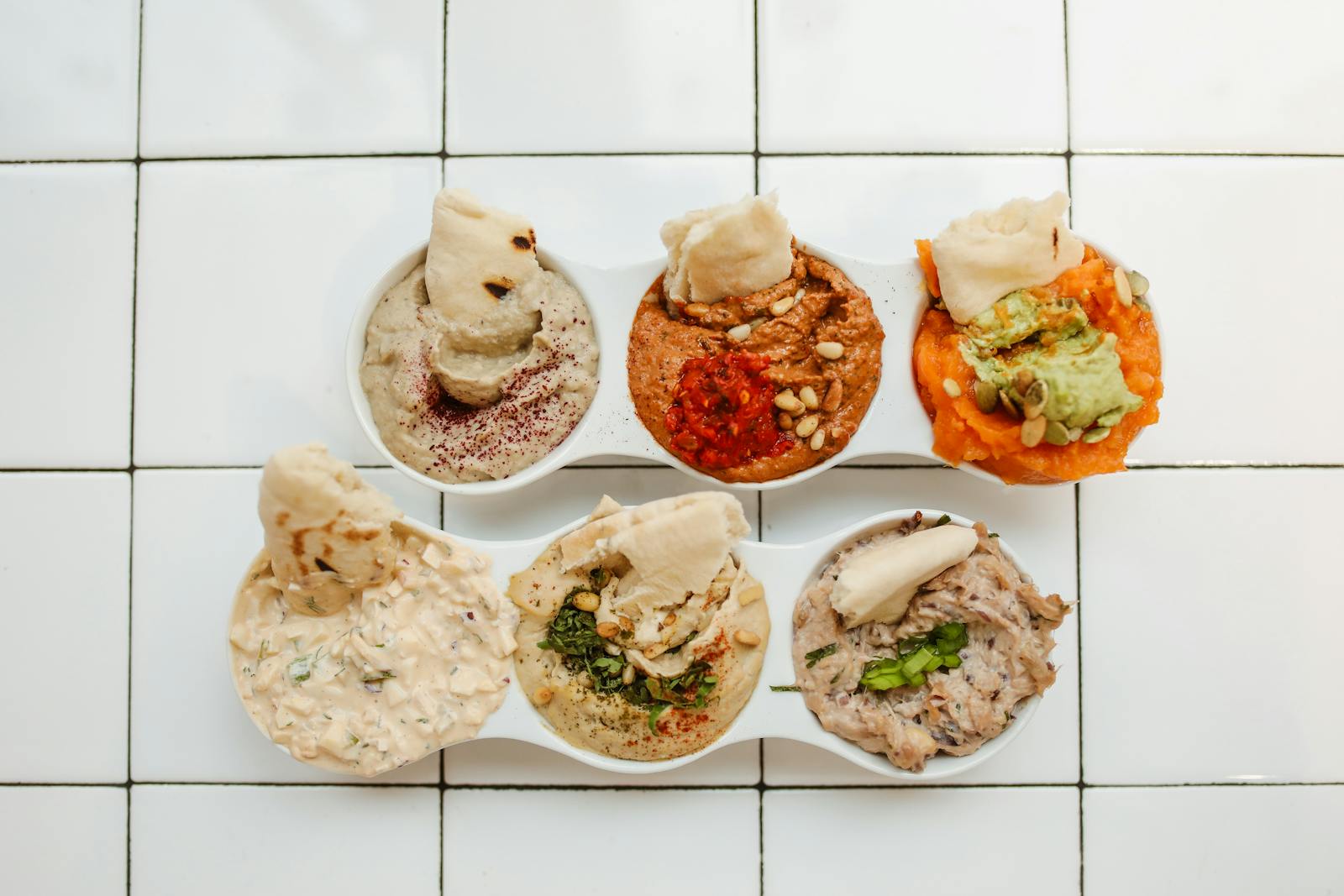
Dips
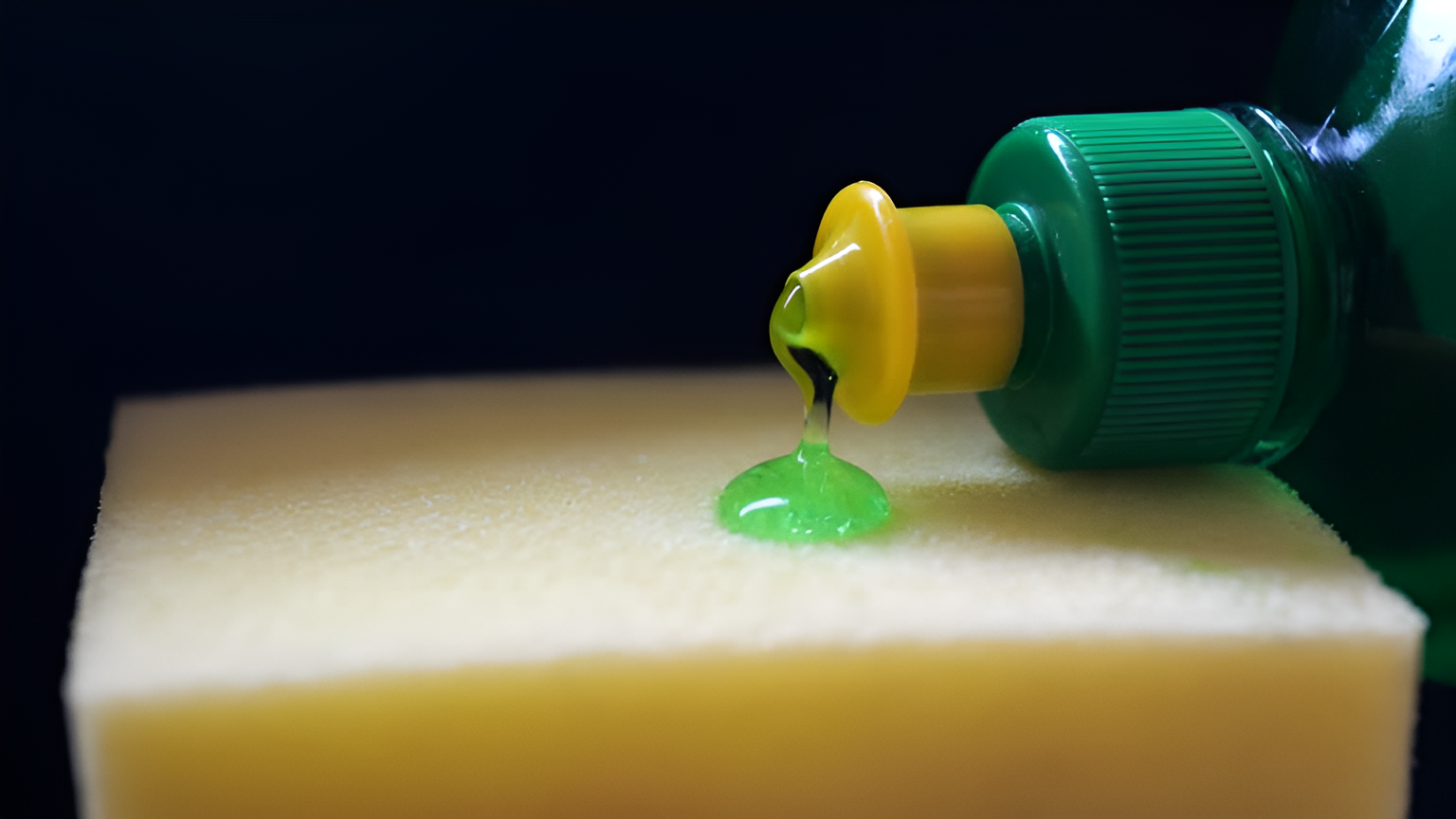
Dishwashing liquid
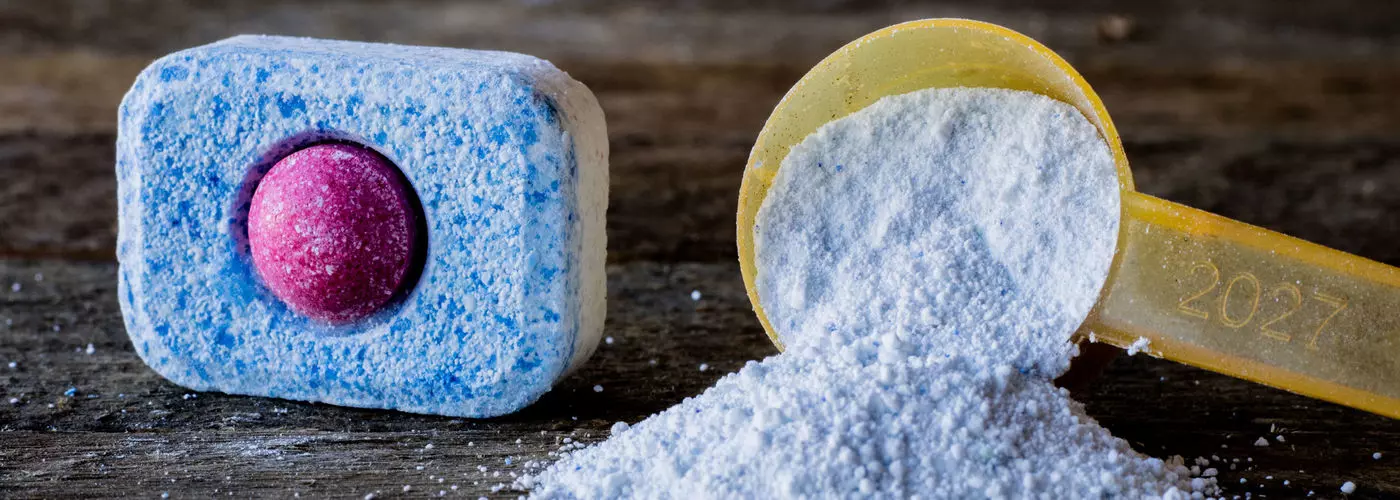
Dishwashing powder
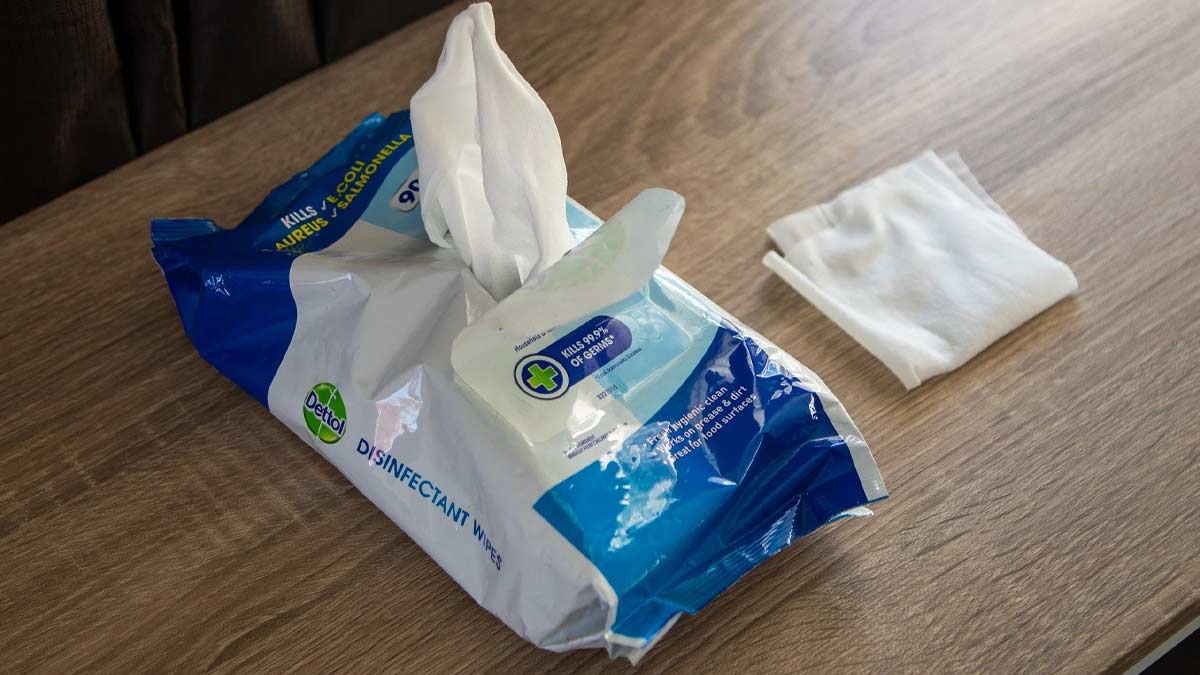
Disinfectant wipes

Disinfectants
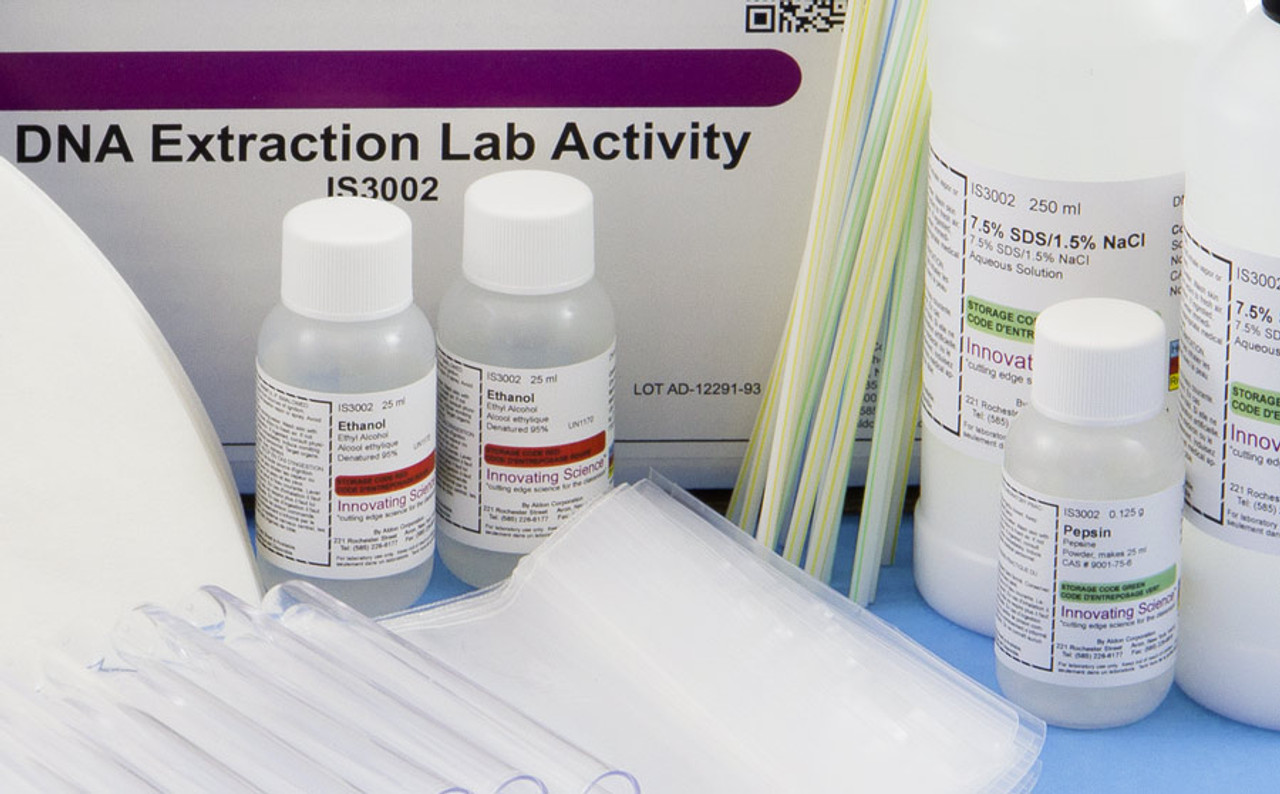
Dna extraction kits
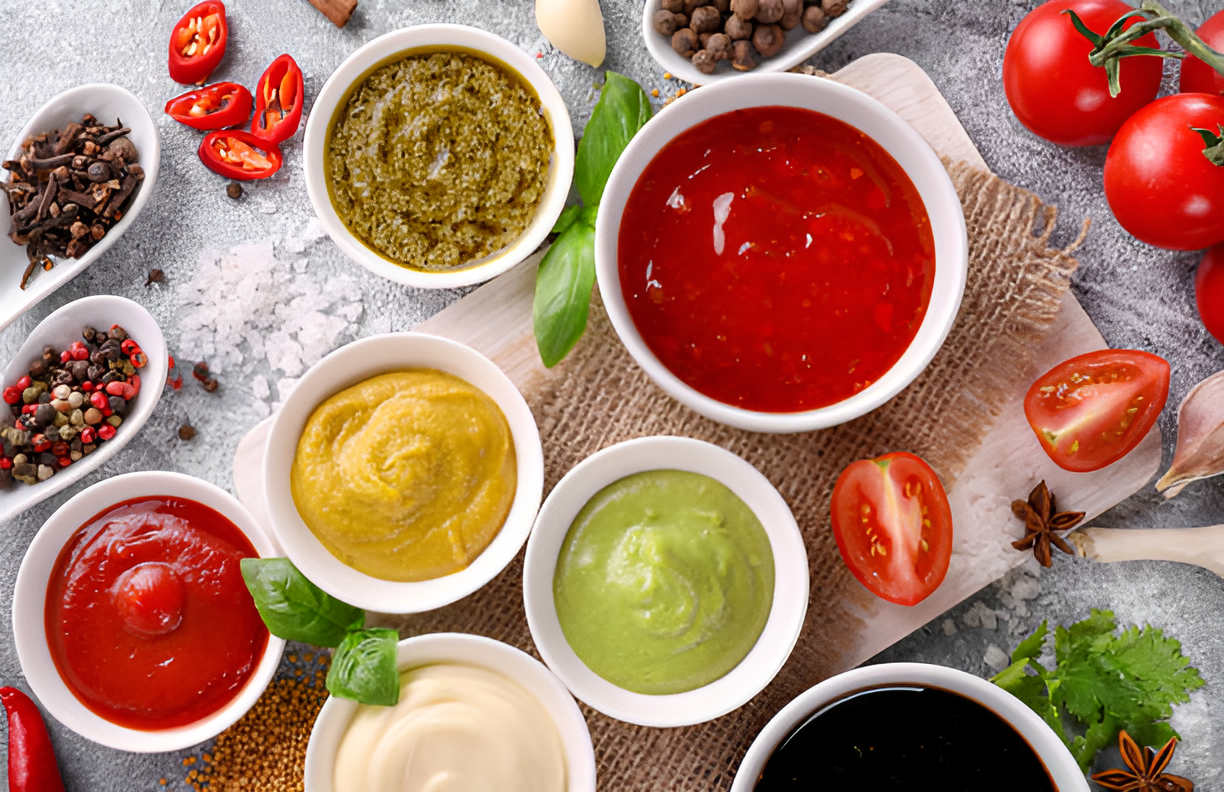
Dressings
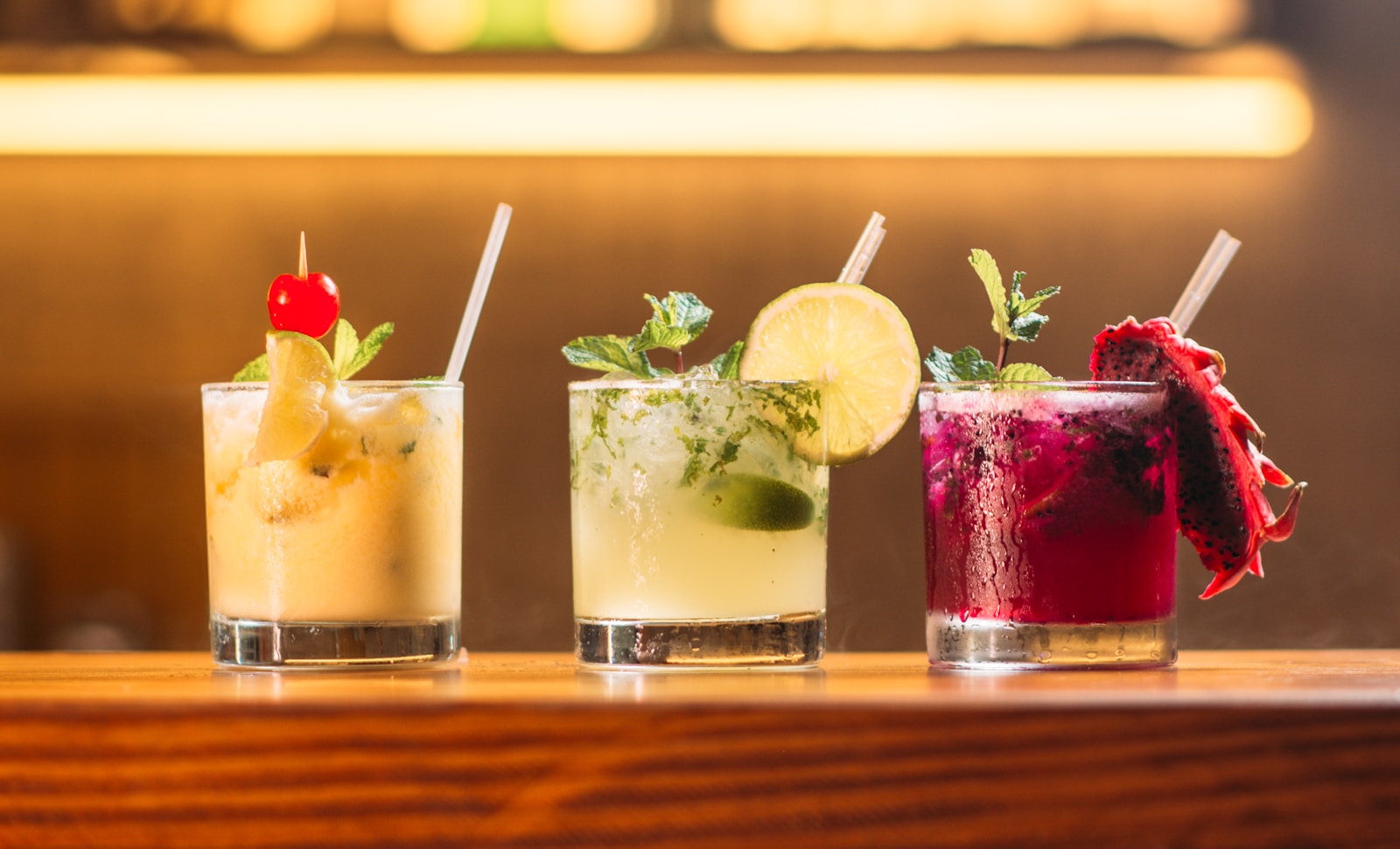
Drinks
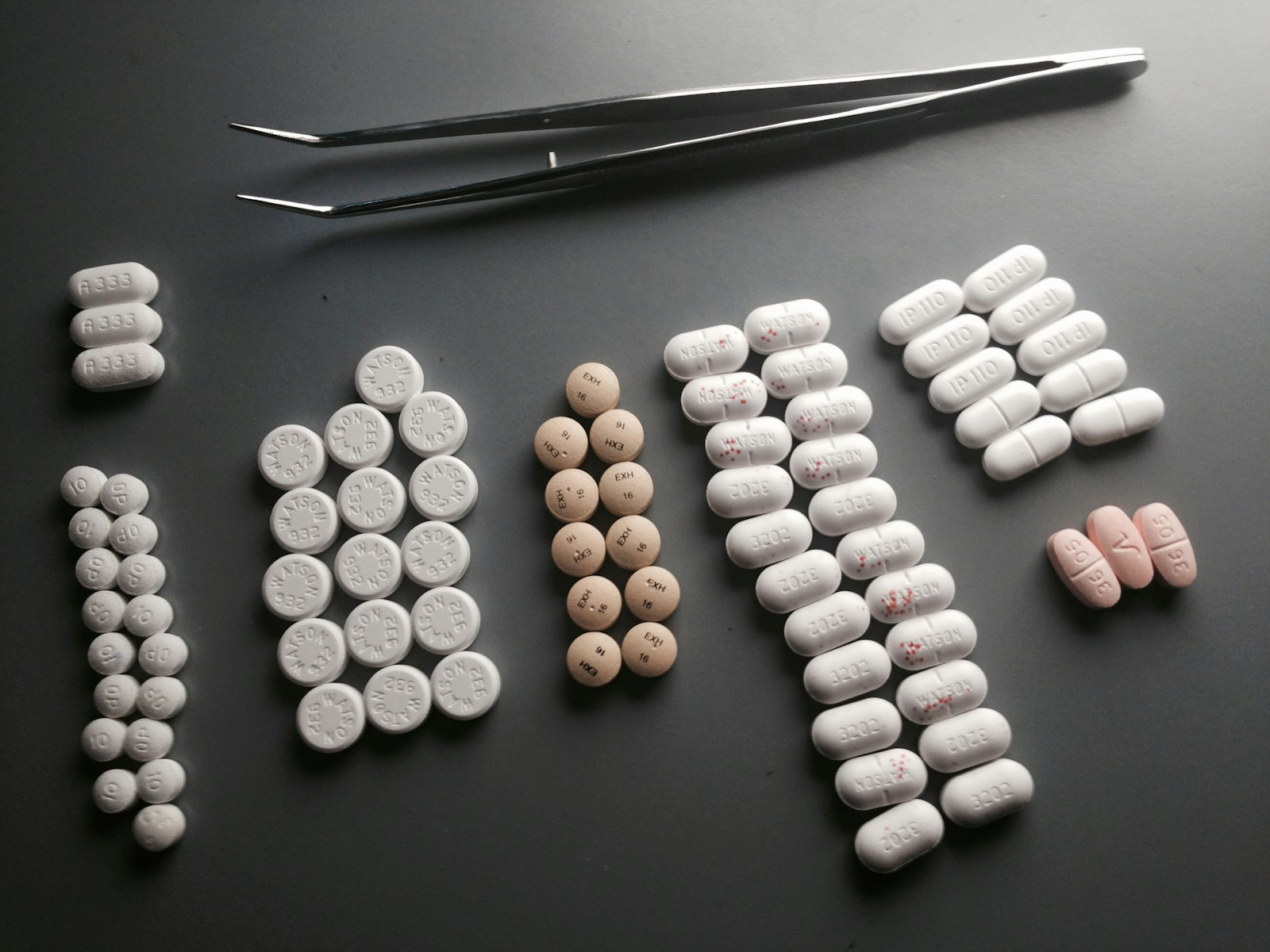
Drug formulations
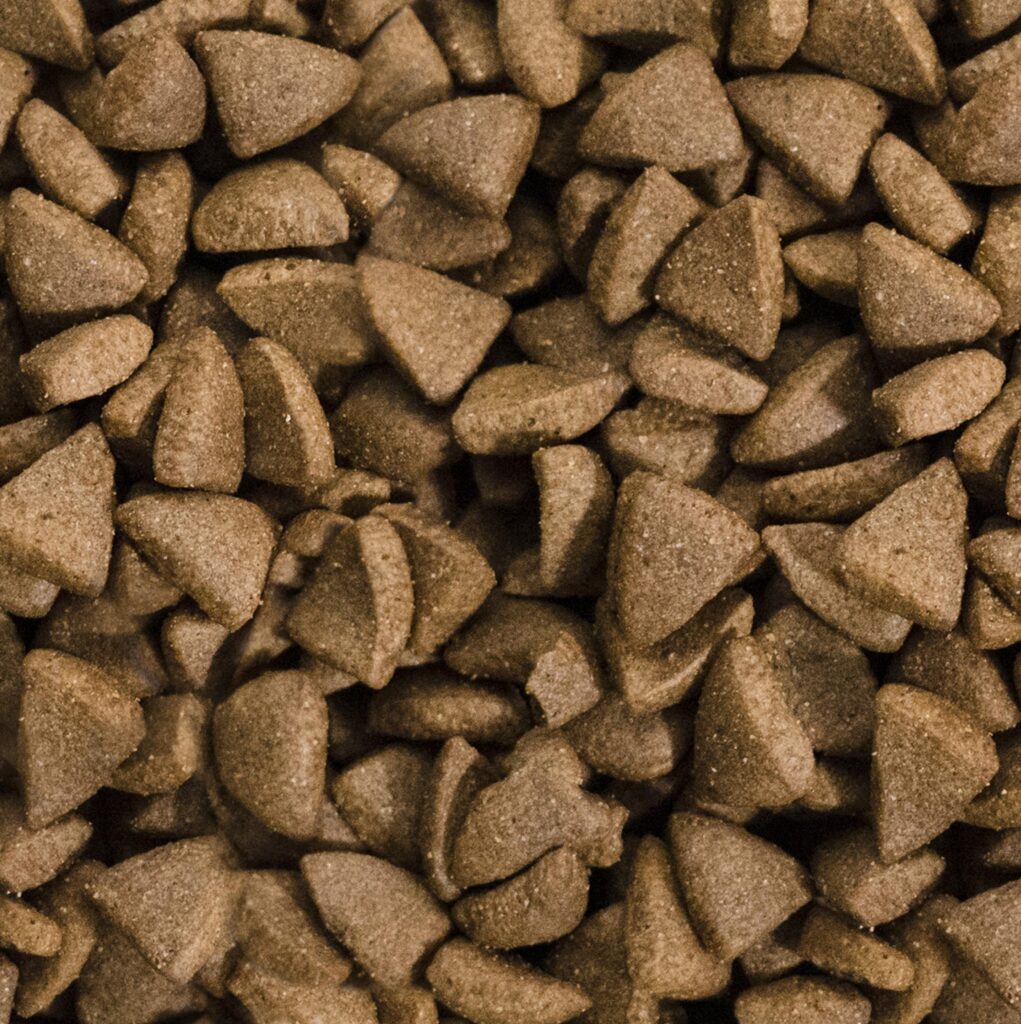
Dry pet food
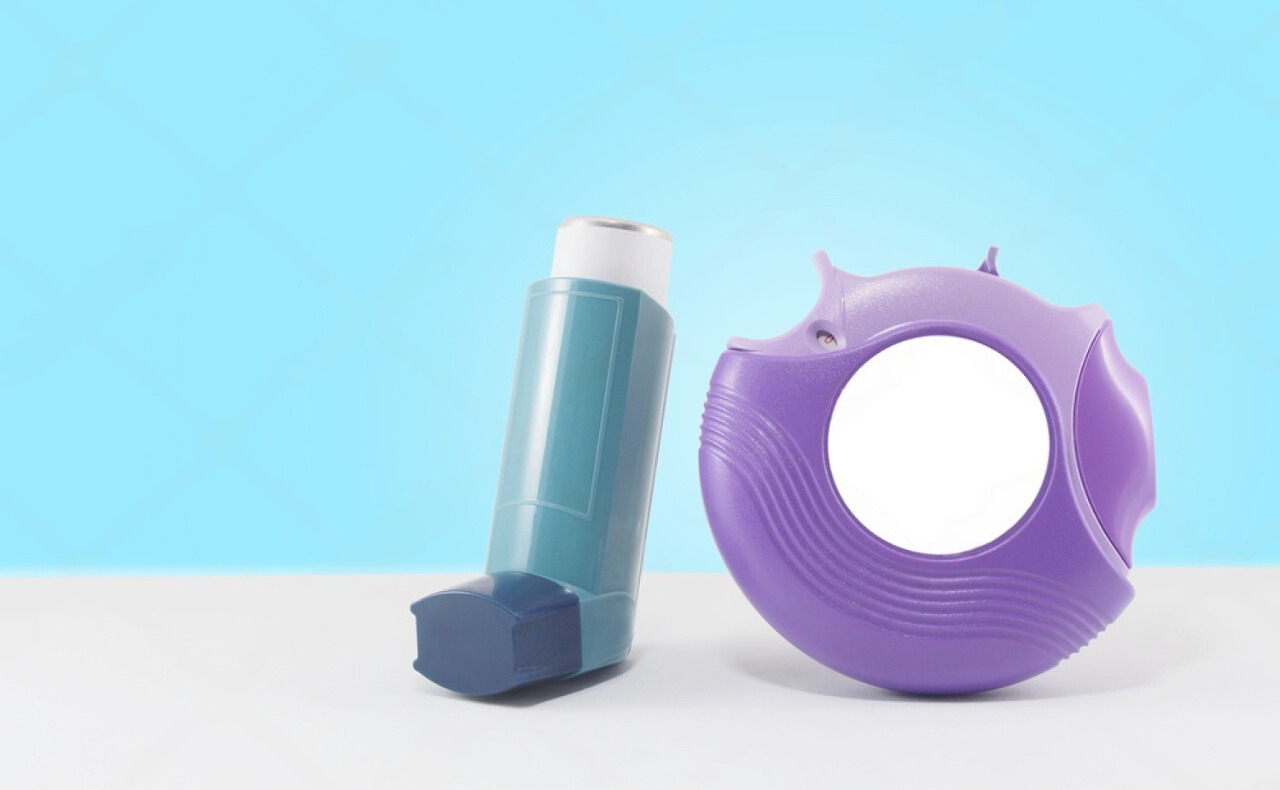
Dry powder inhalants (dpi)
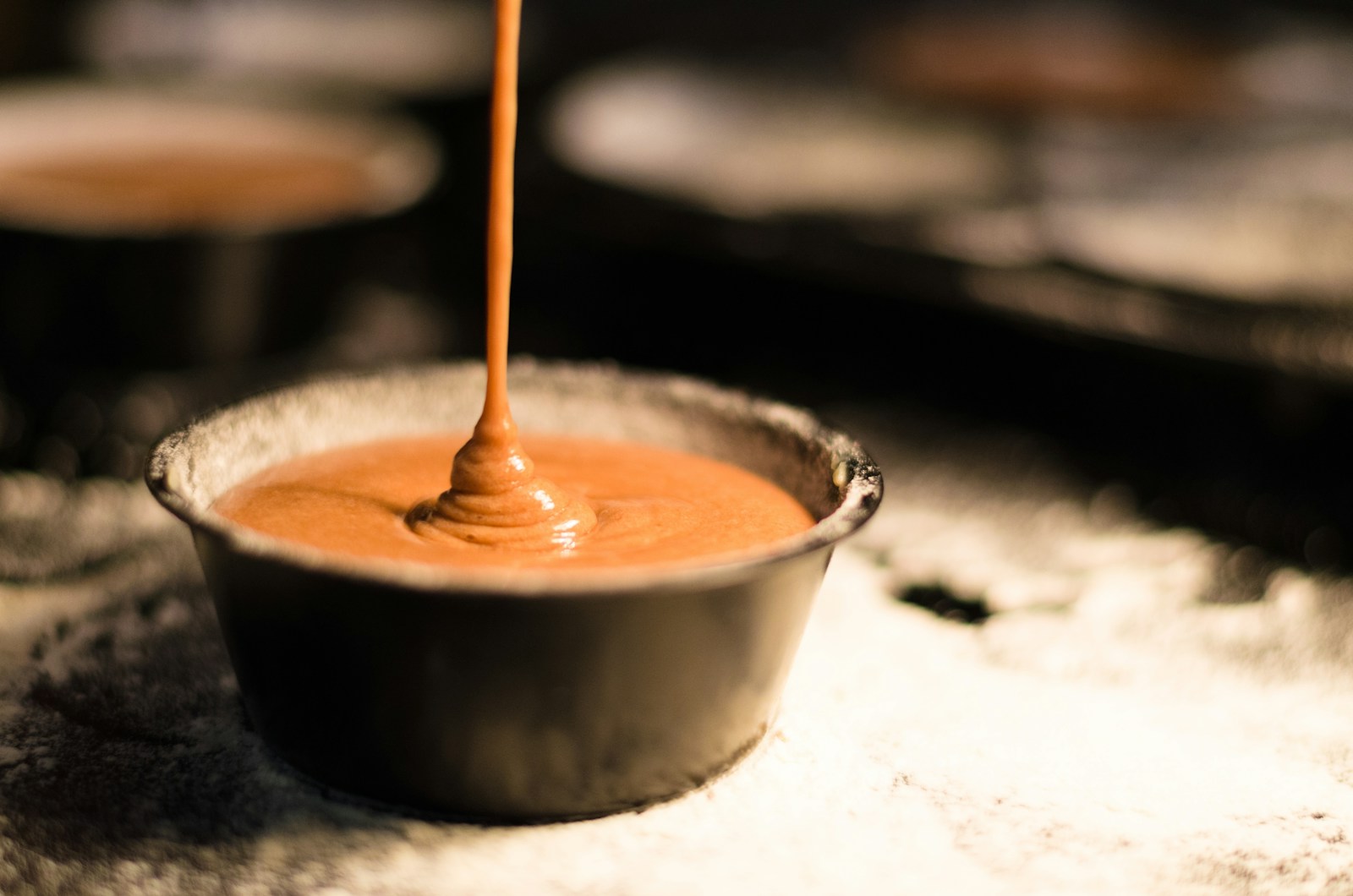
Dulce de leche

Eardrops
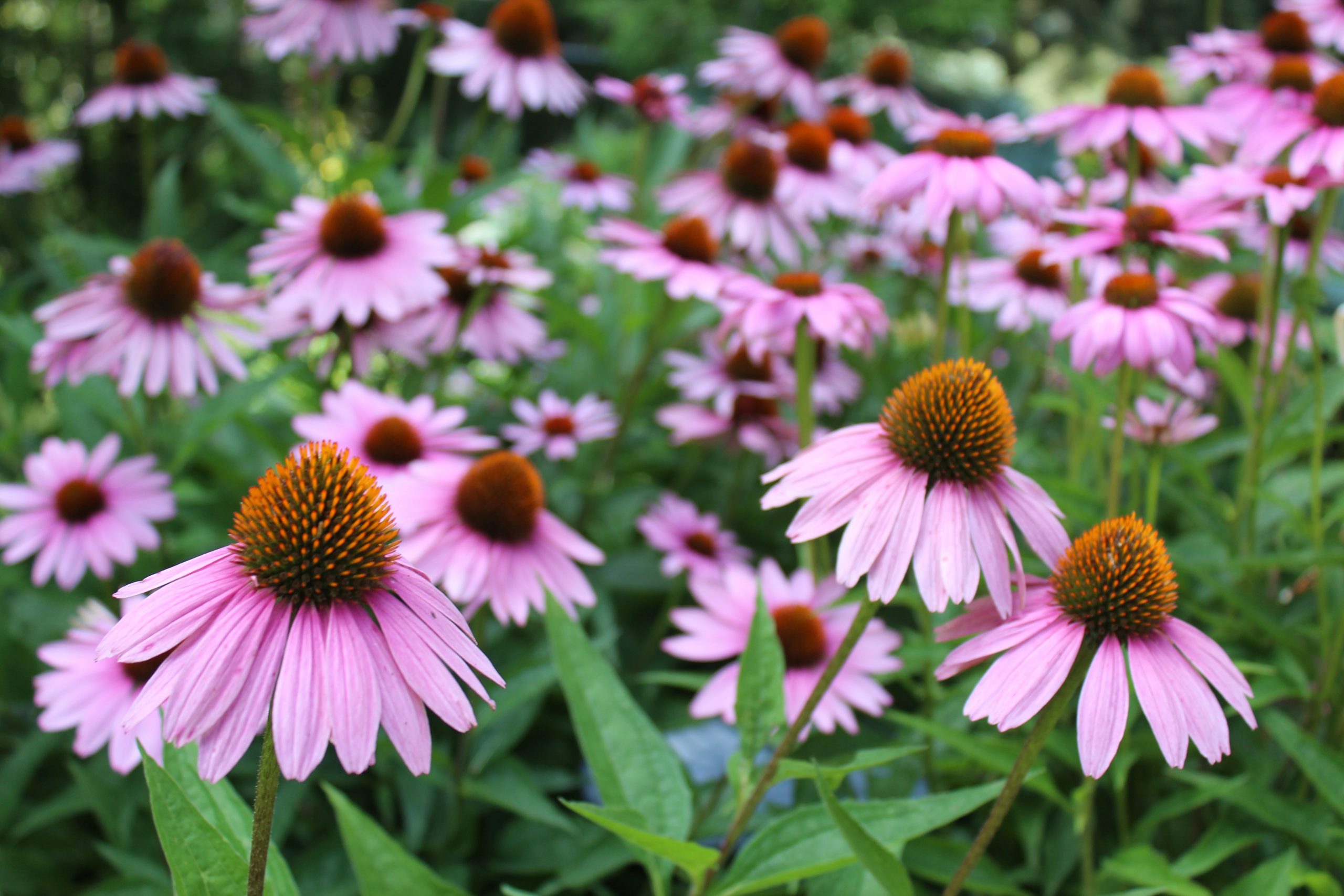
Echinacea extract
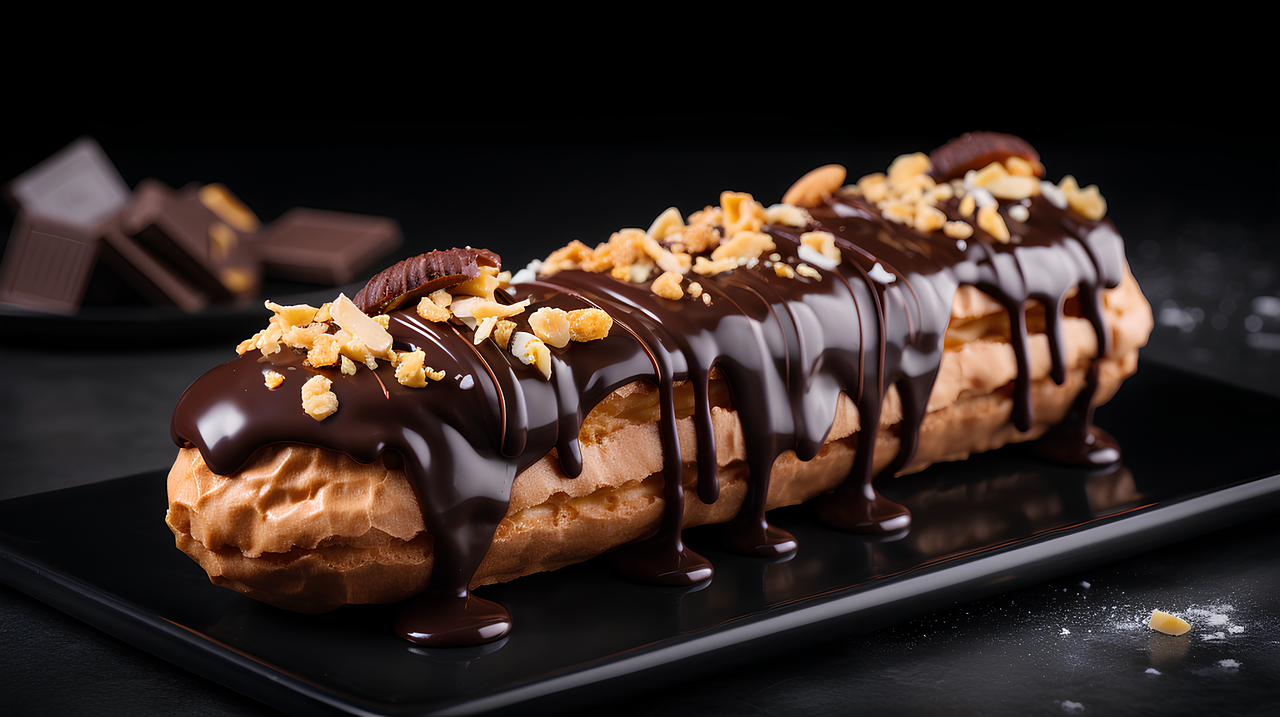
Eclairs
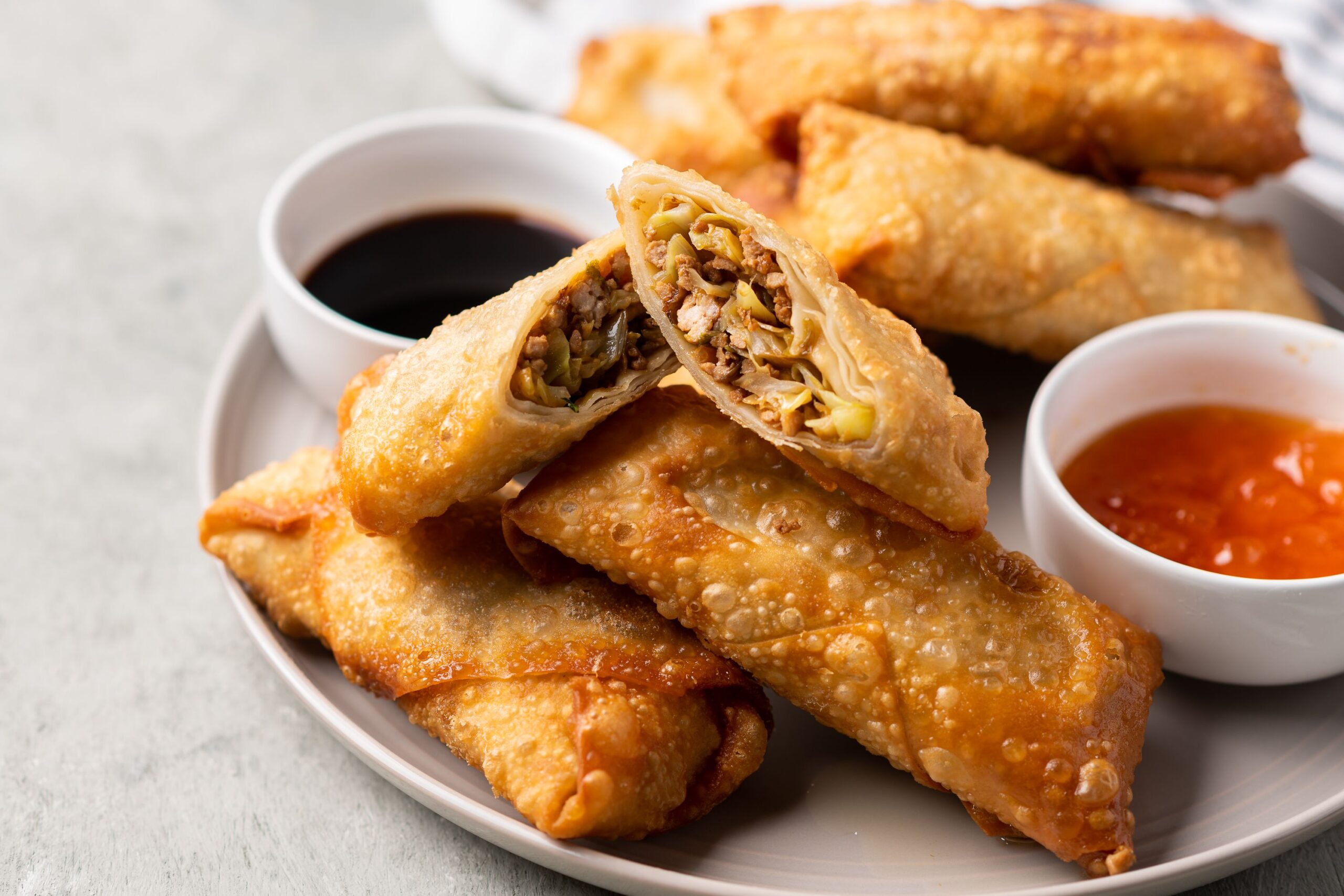
Egg rolls

Elderberry extract

Electrolyte drinks
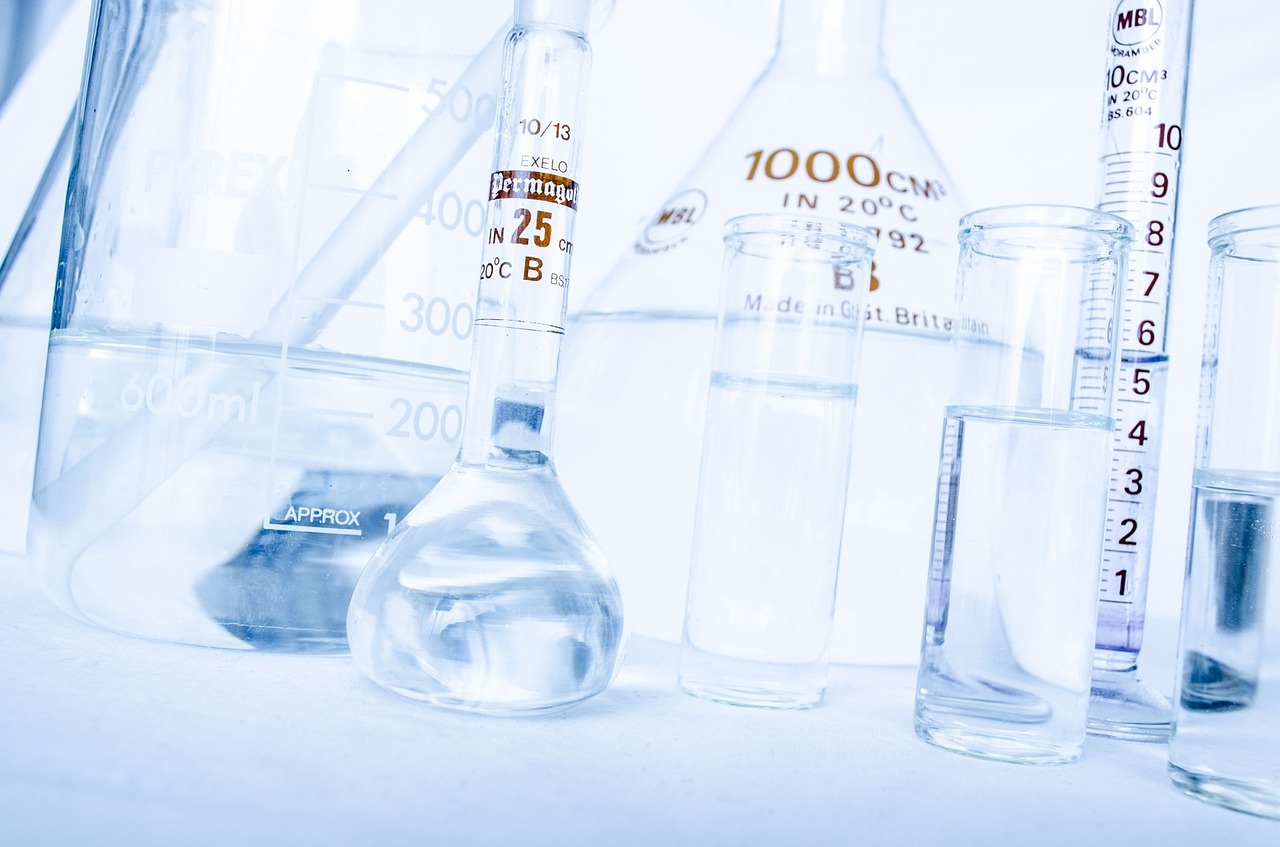
Electrolyte solutions
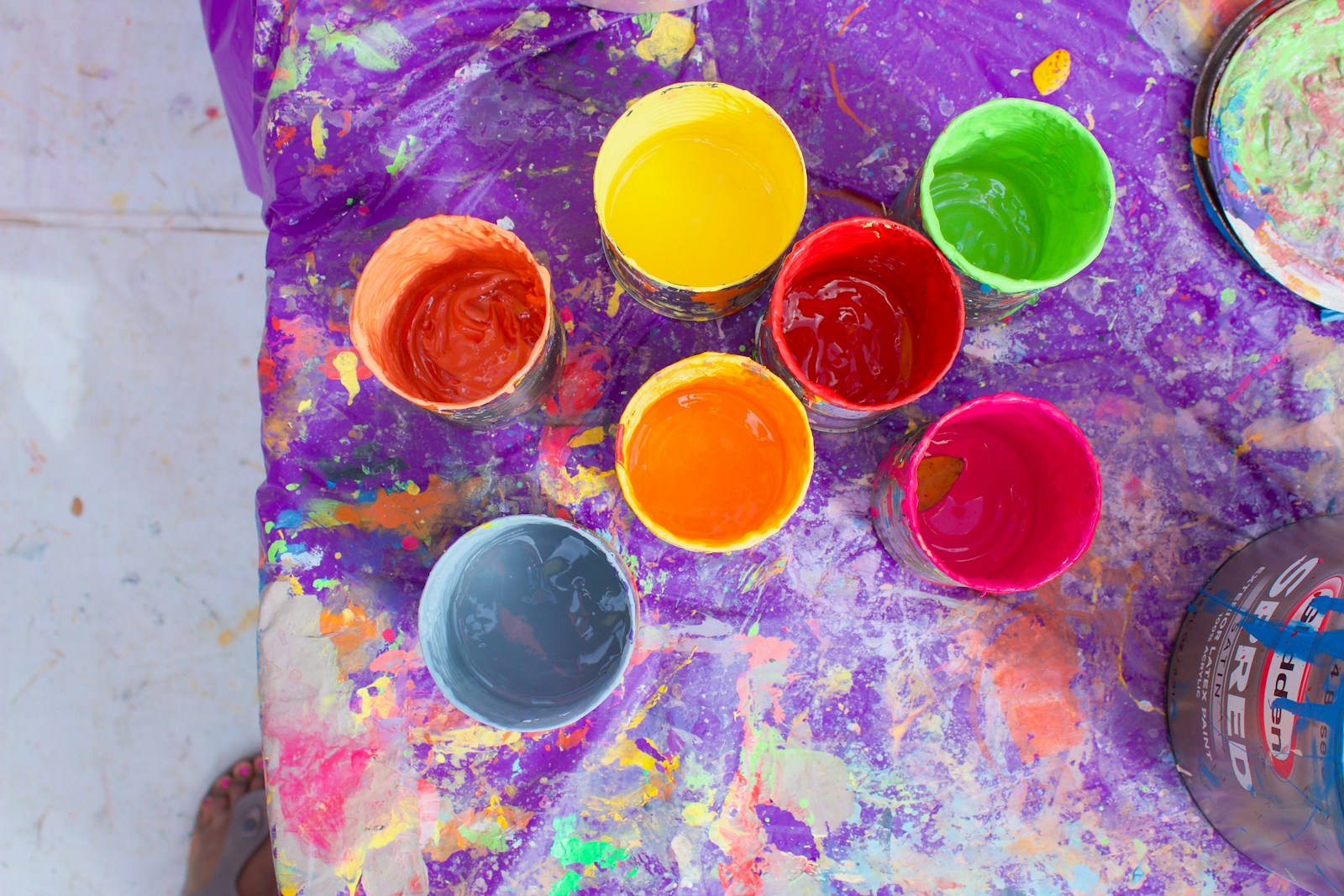
Emulsion paints
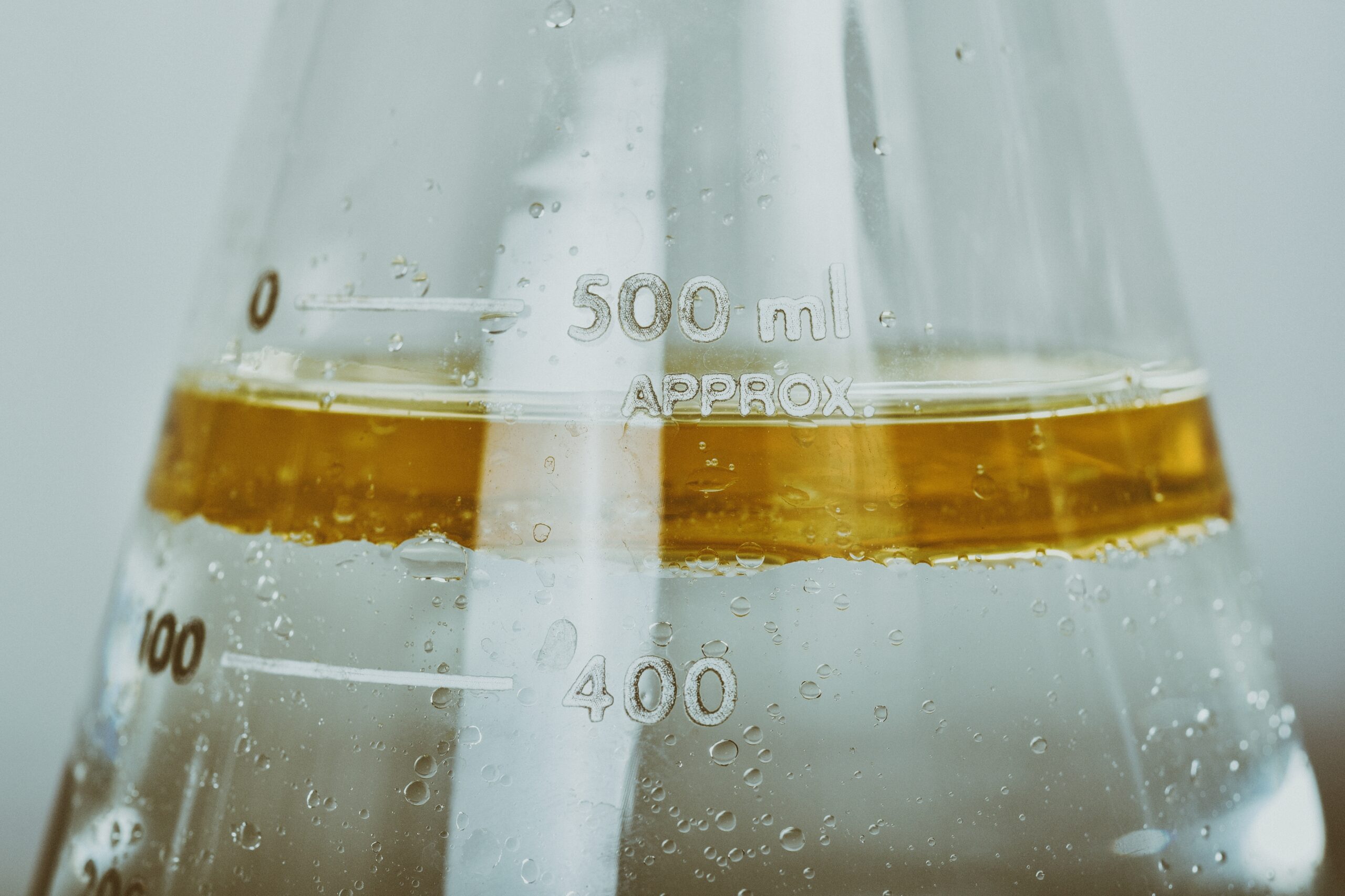
Emulsions
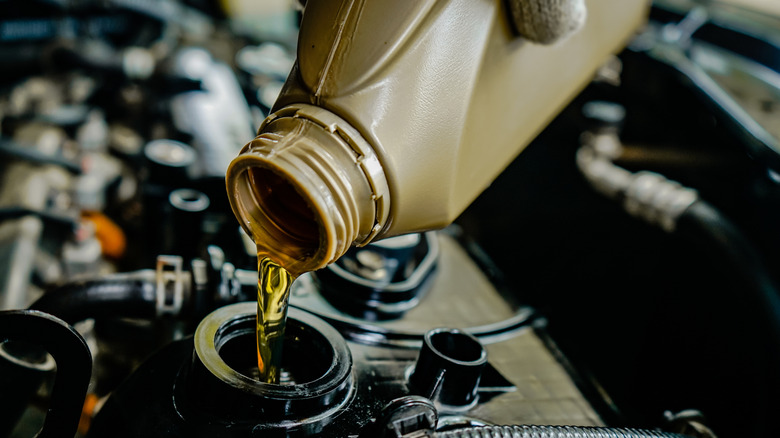
Engine oils
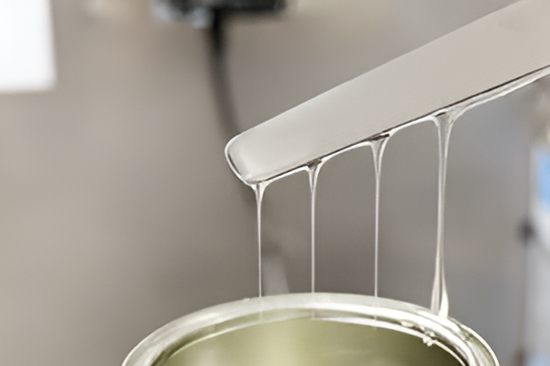
Epoxy adhesives
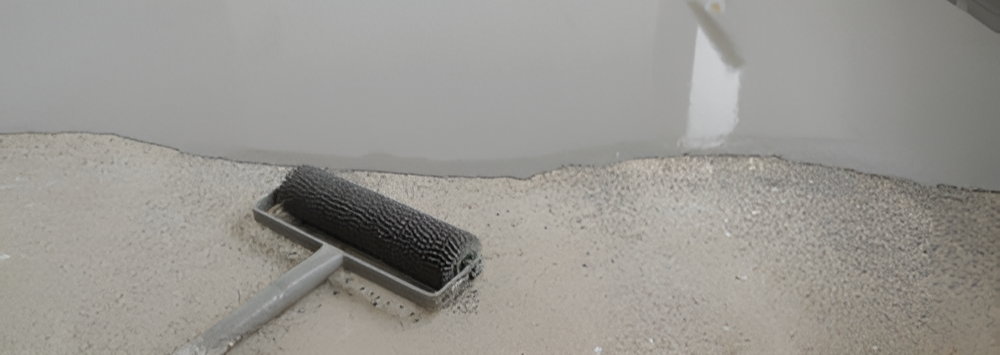
Epoxy coatings
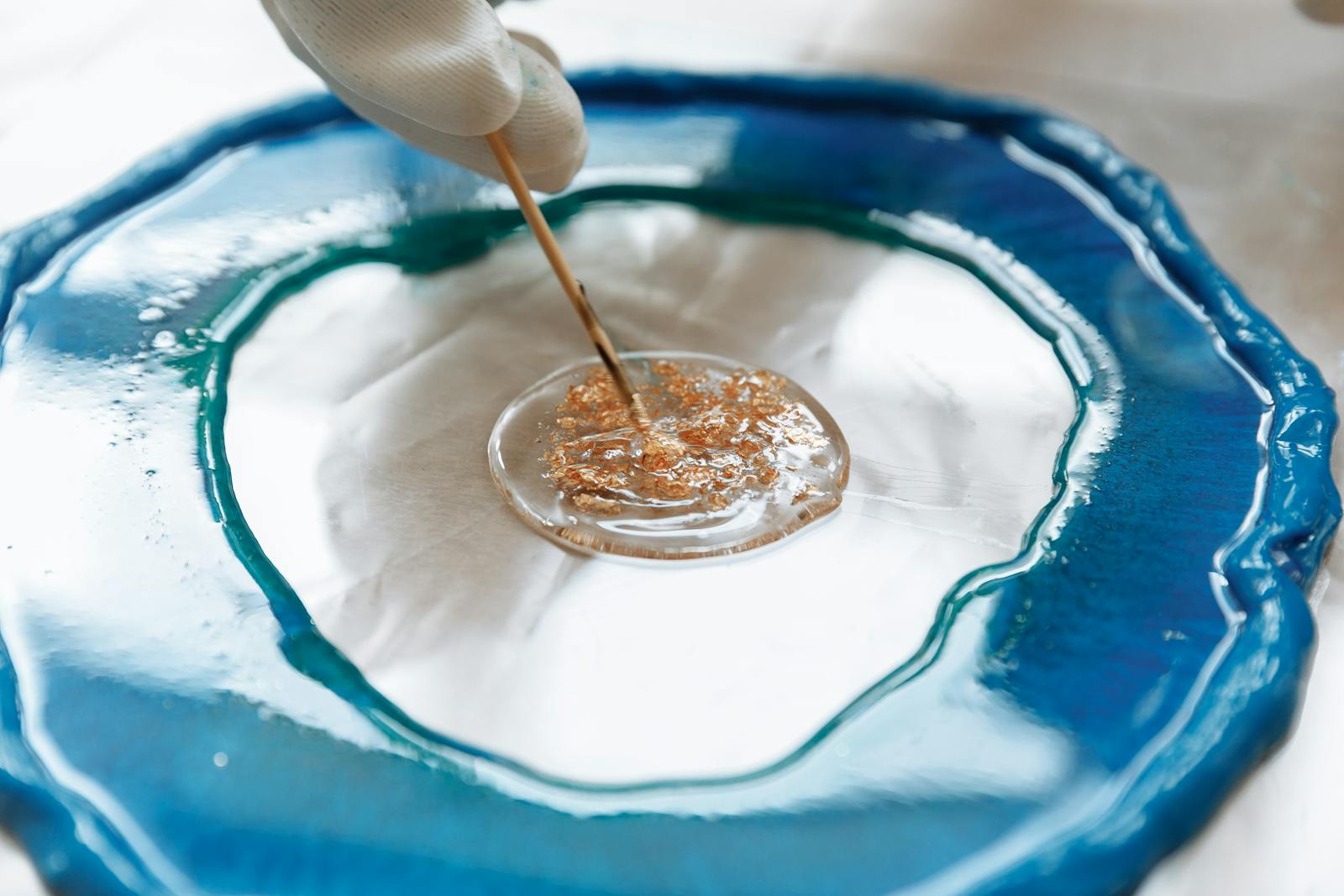
Epoxy resin
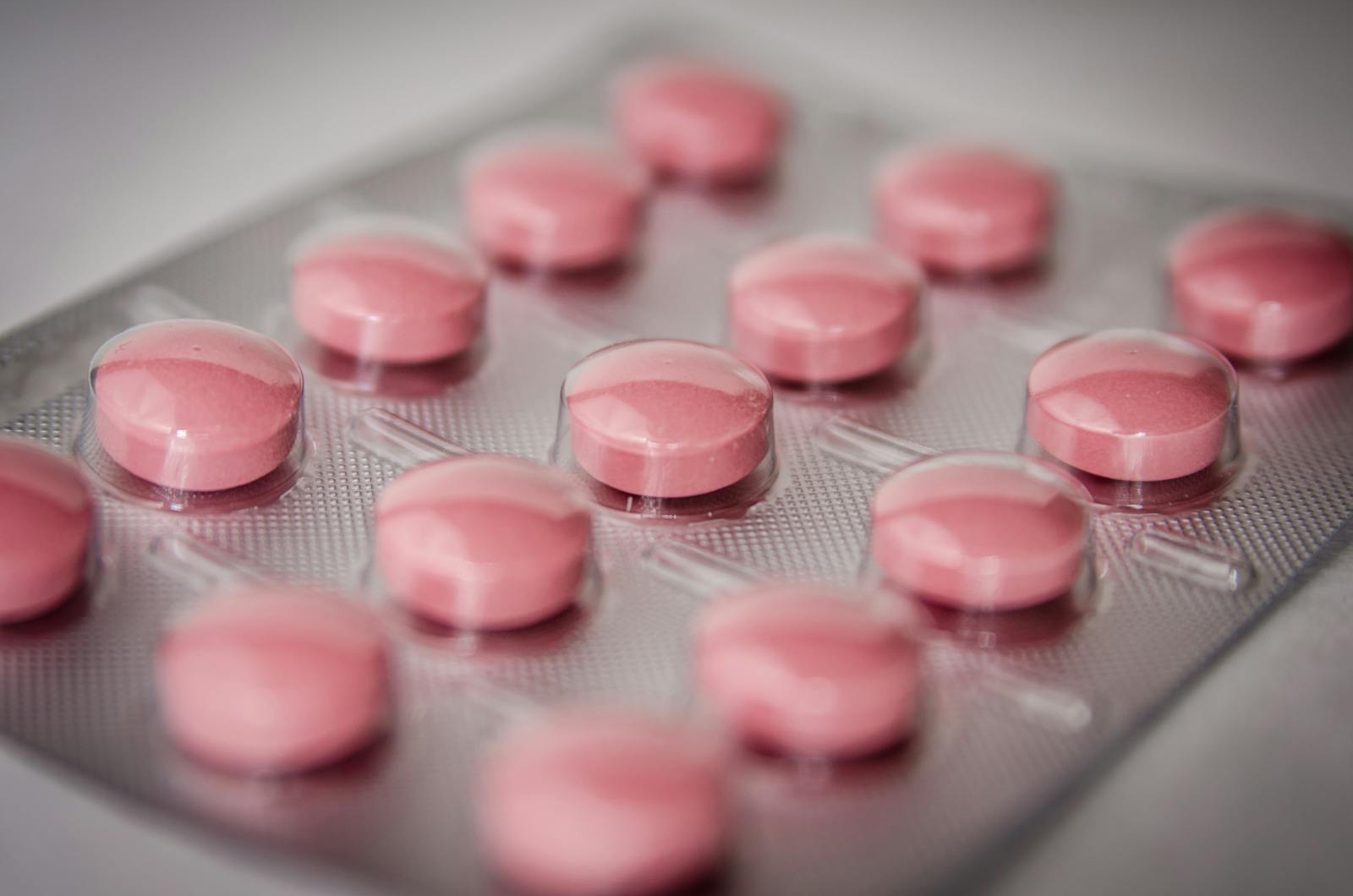
Er tablets
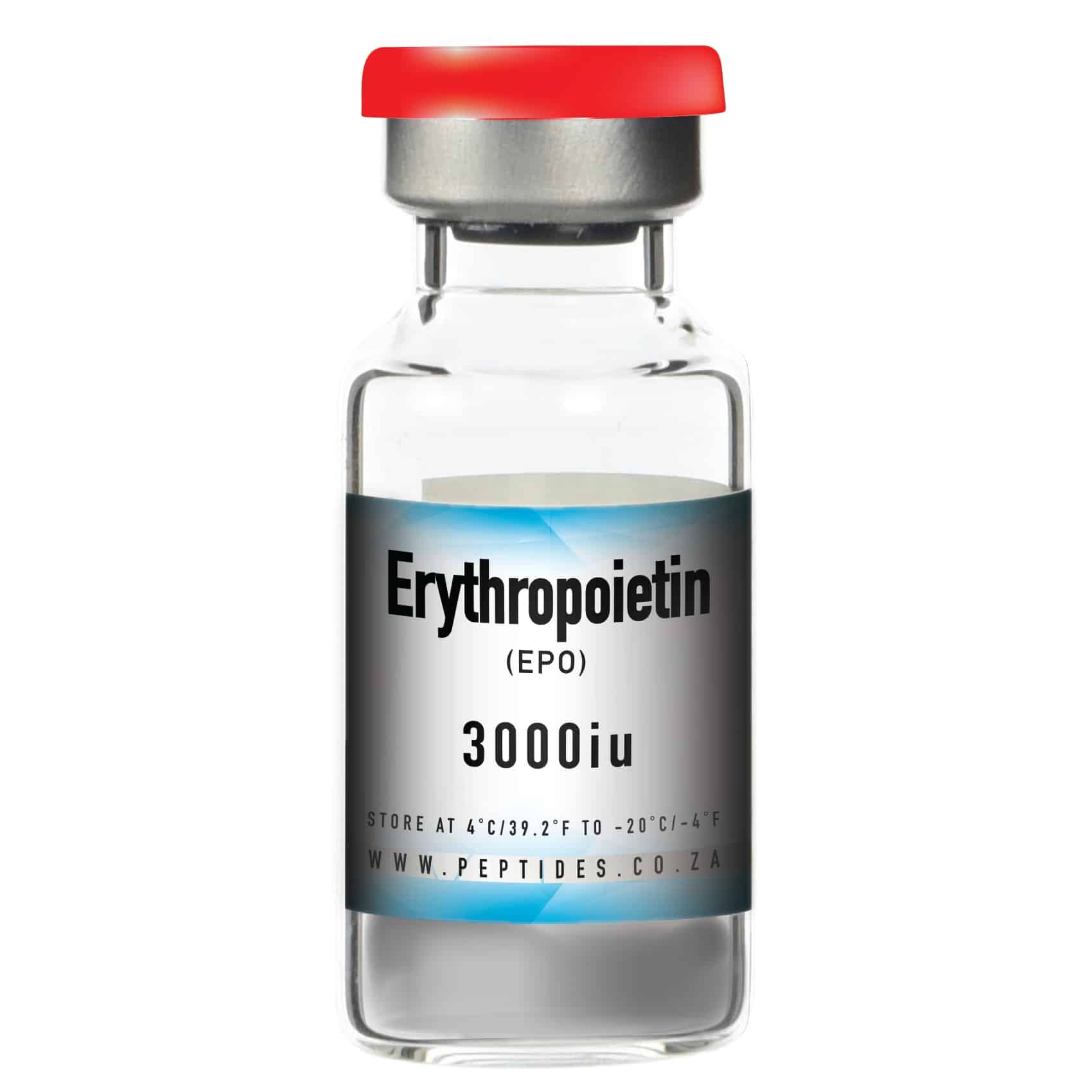
Erythropoietin
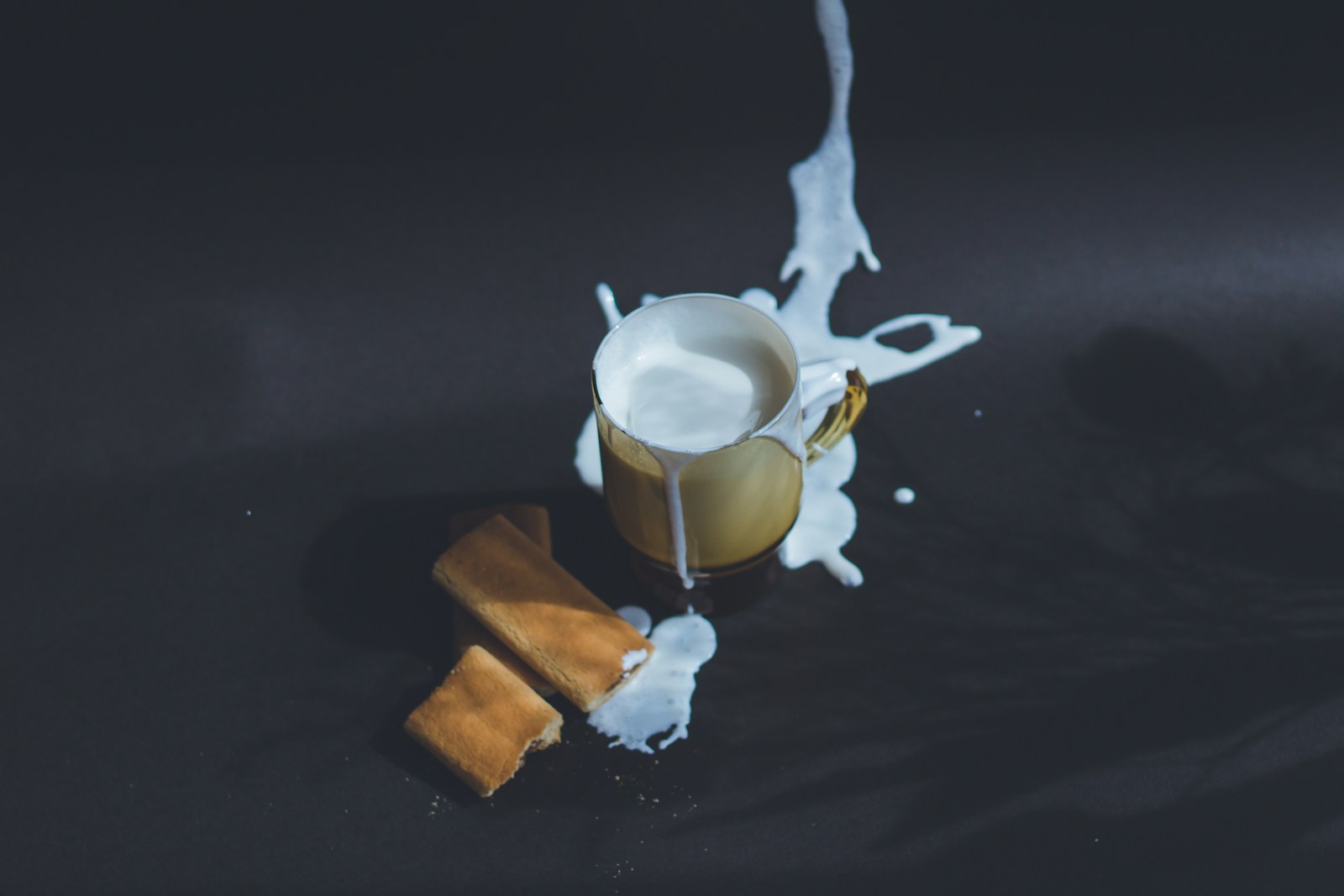
Esl milk
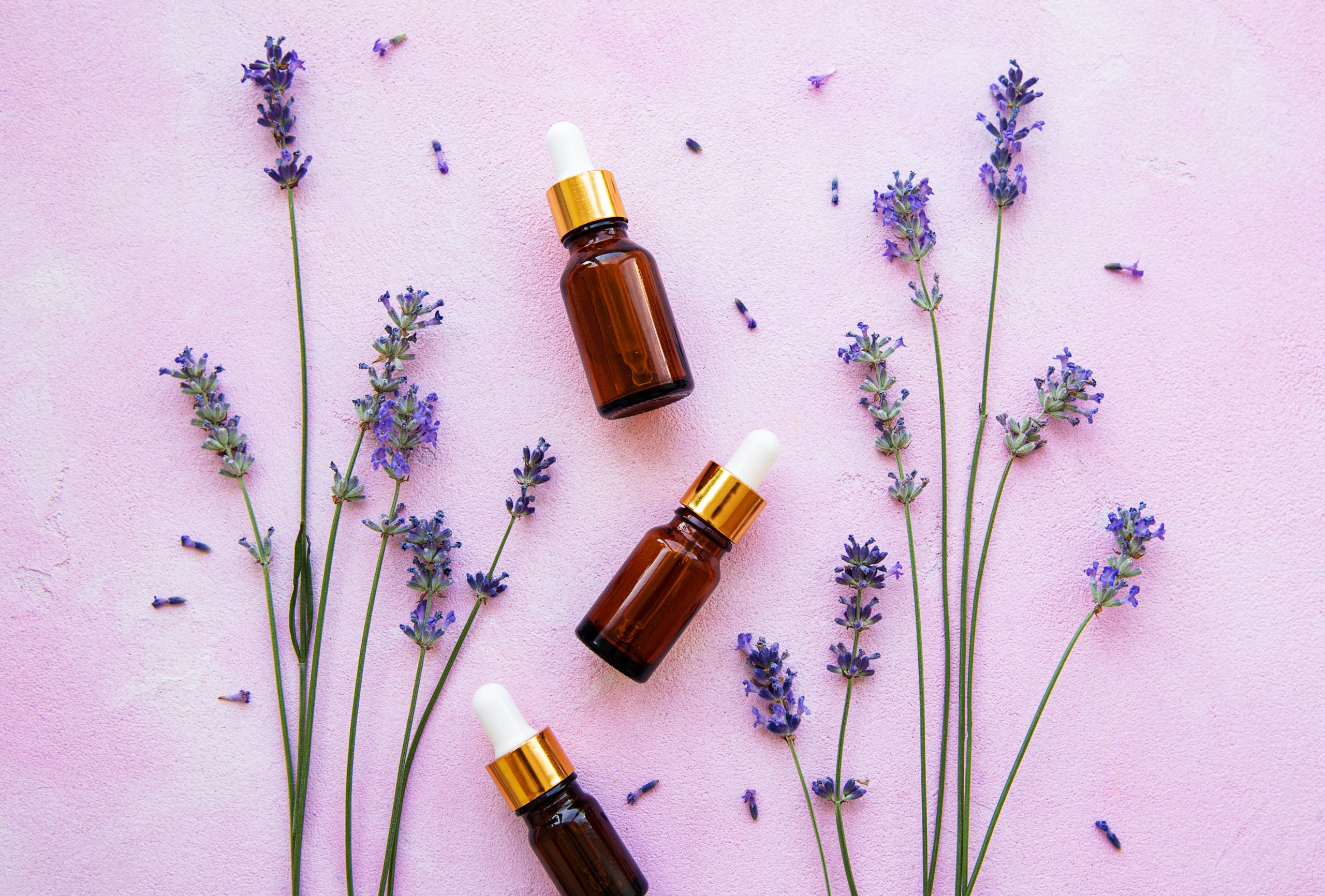
Essential oil blends
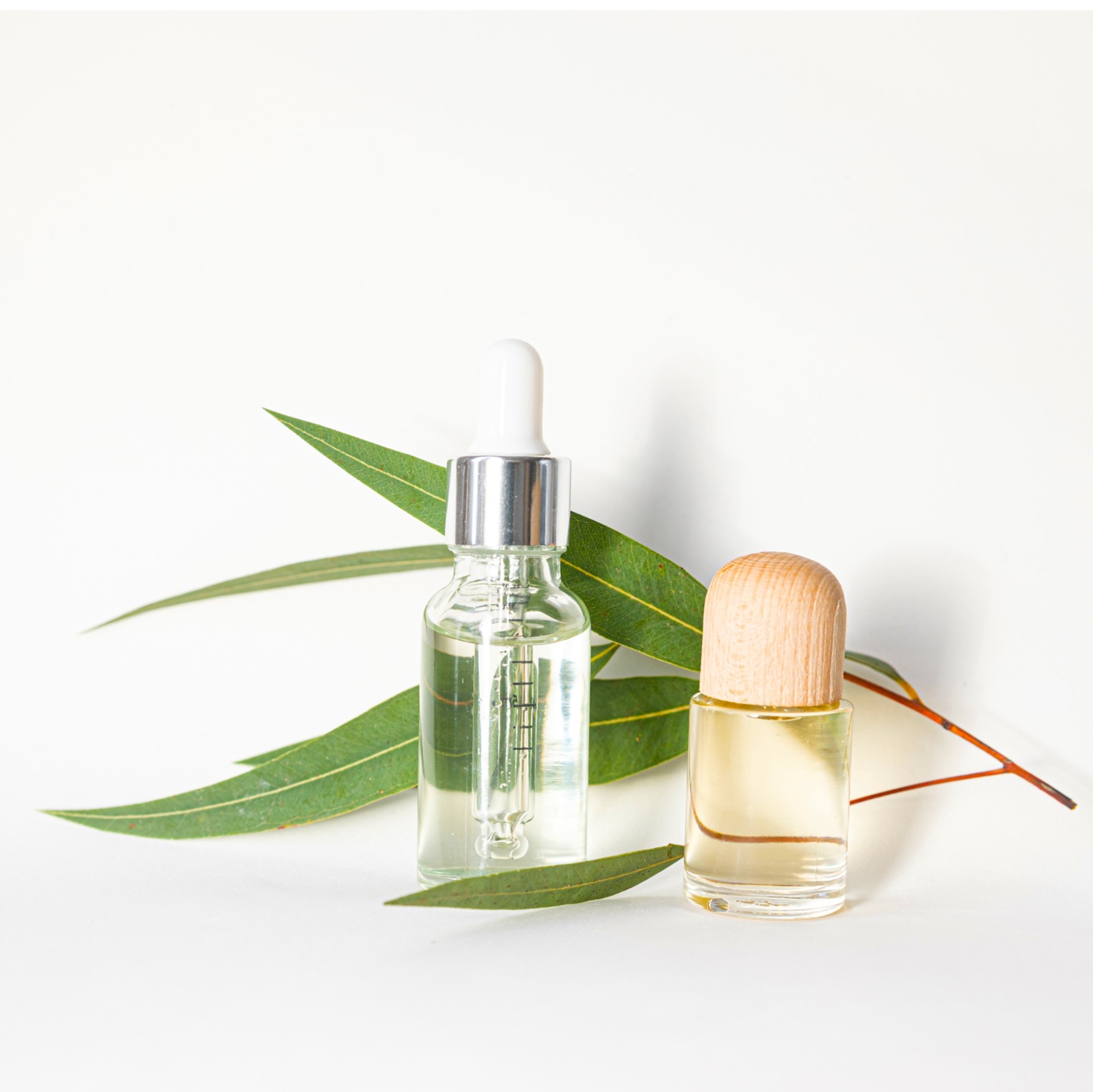
Eucalyptus oil
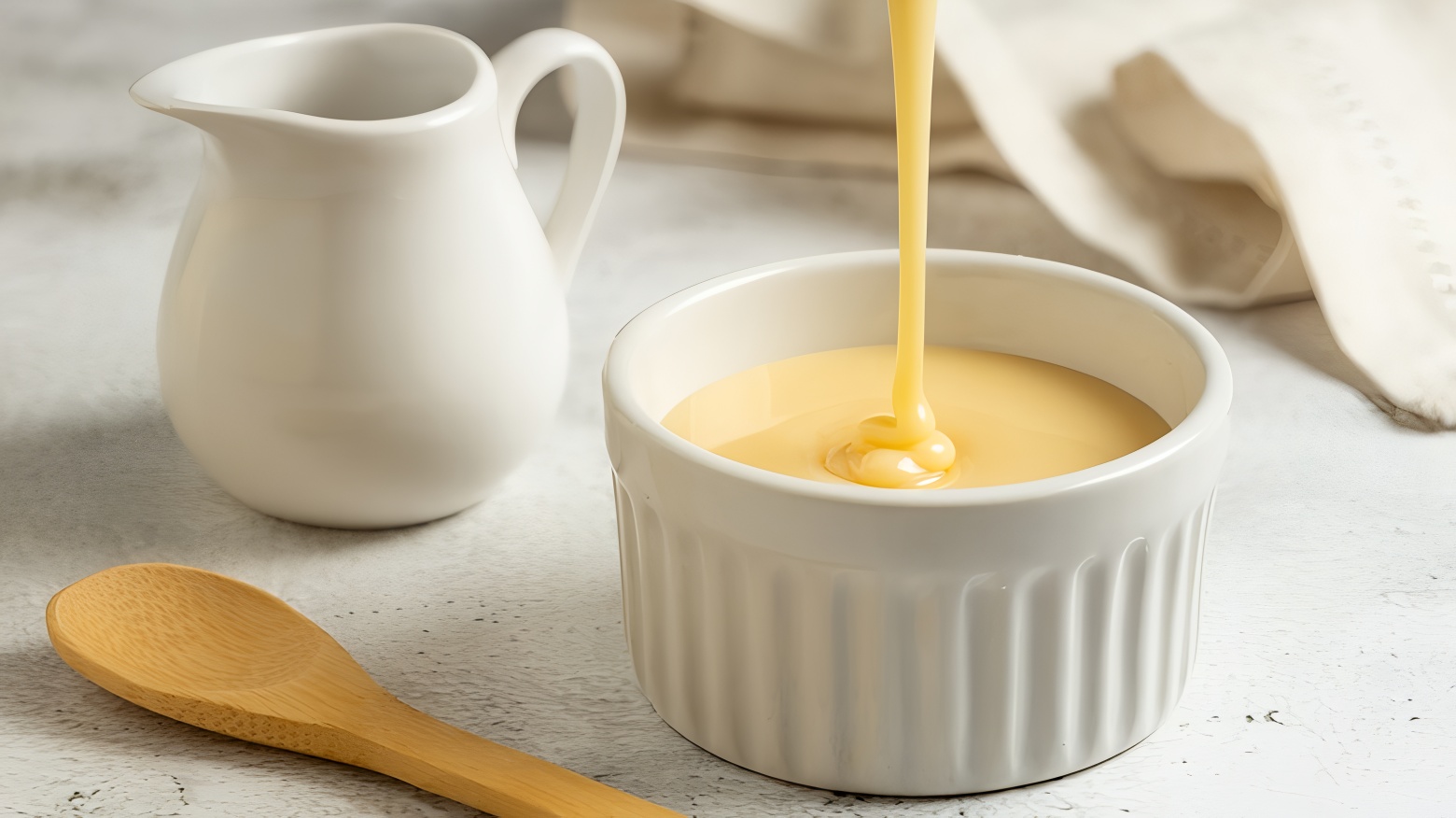
Evaporated milk
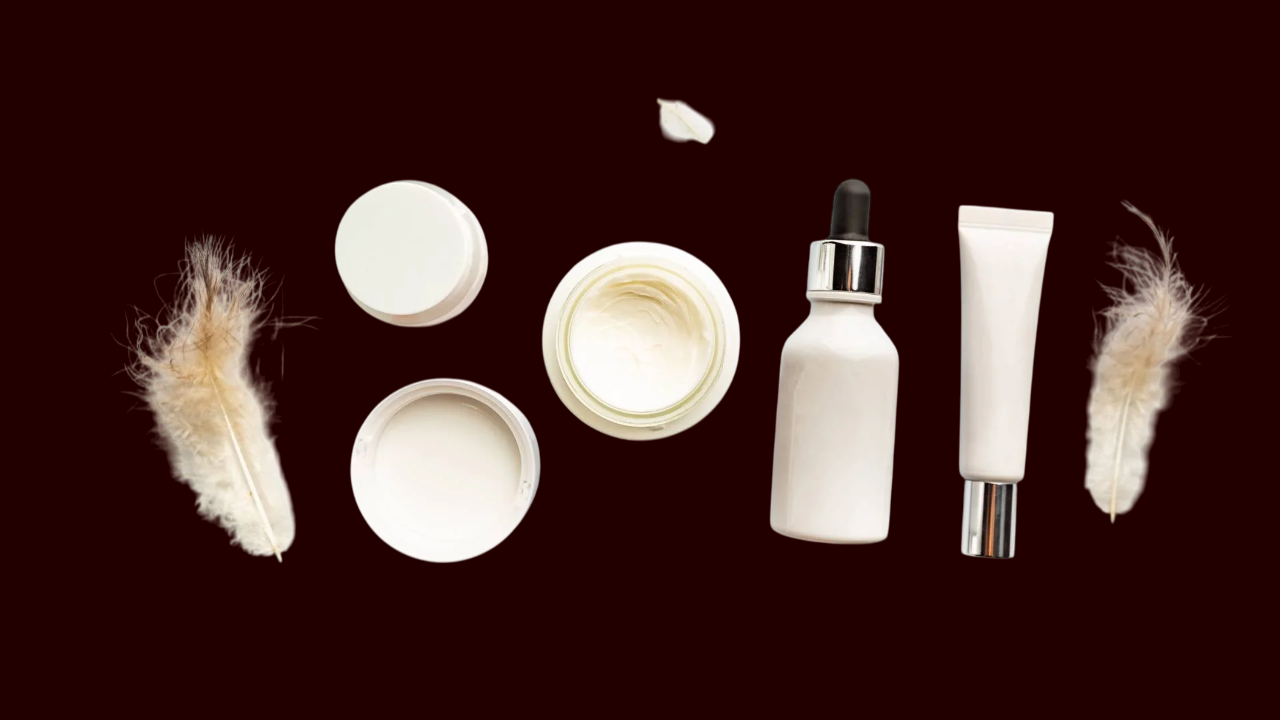
Eye care products
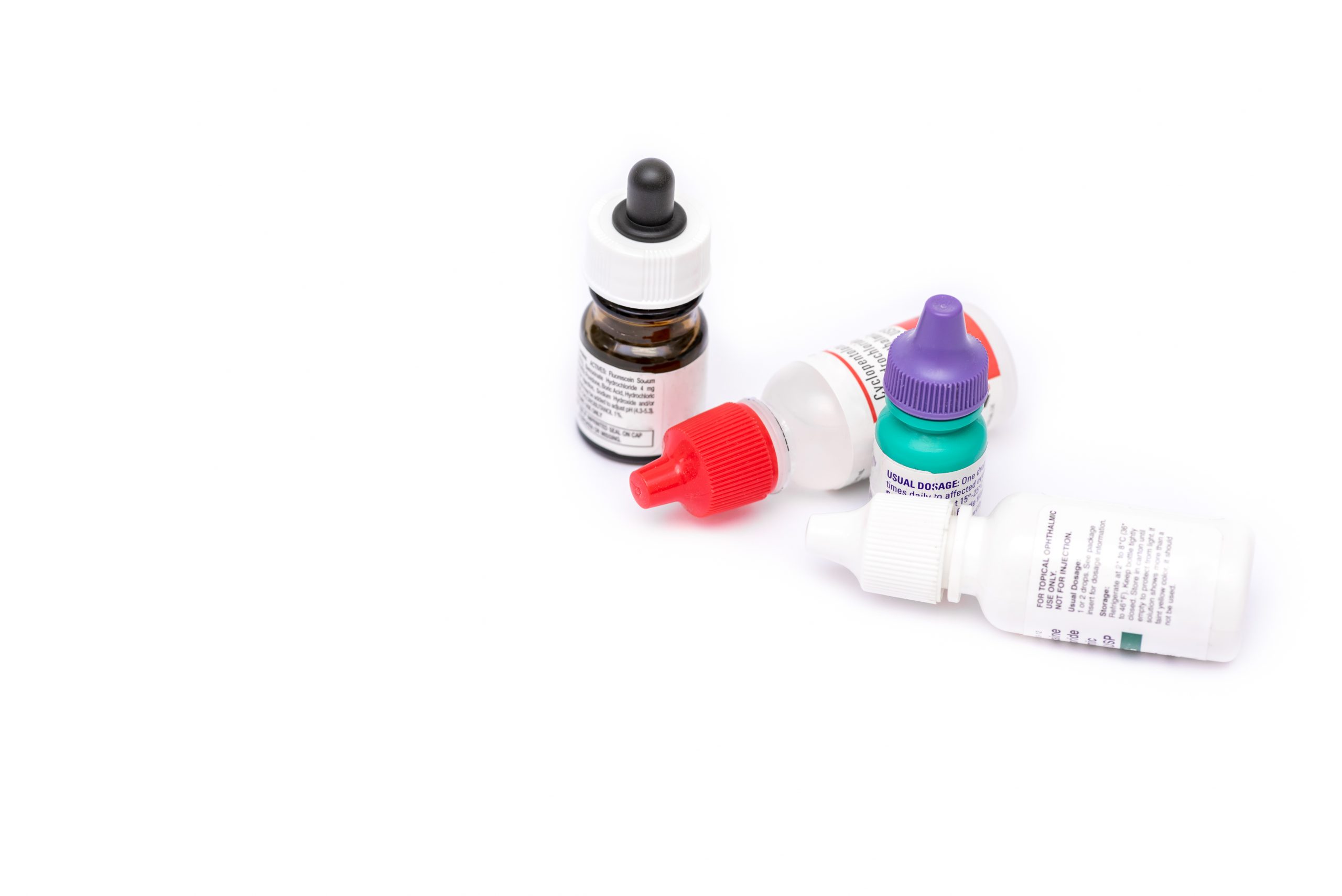
Eyedrops
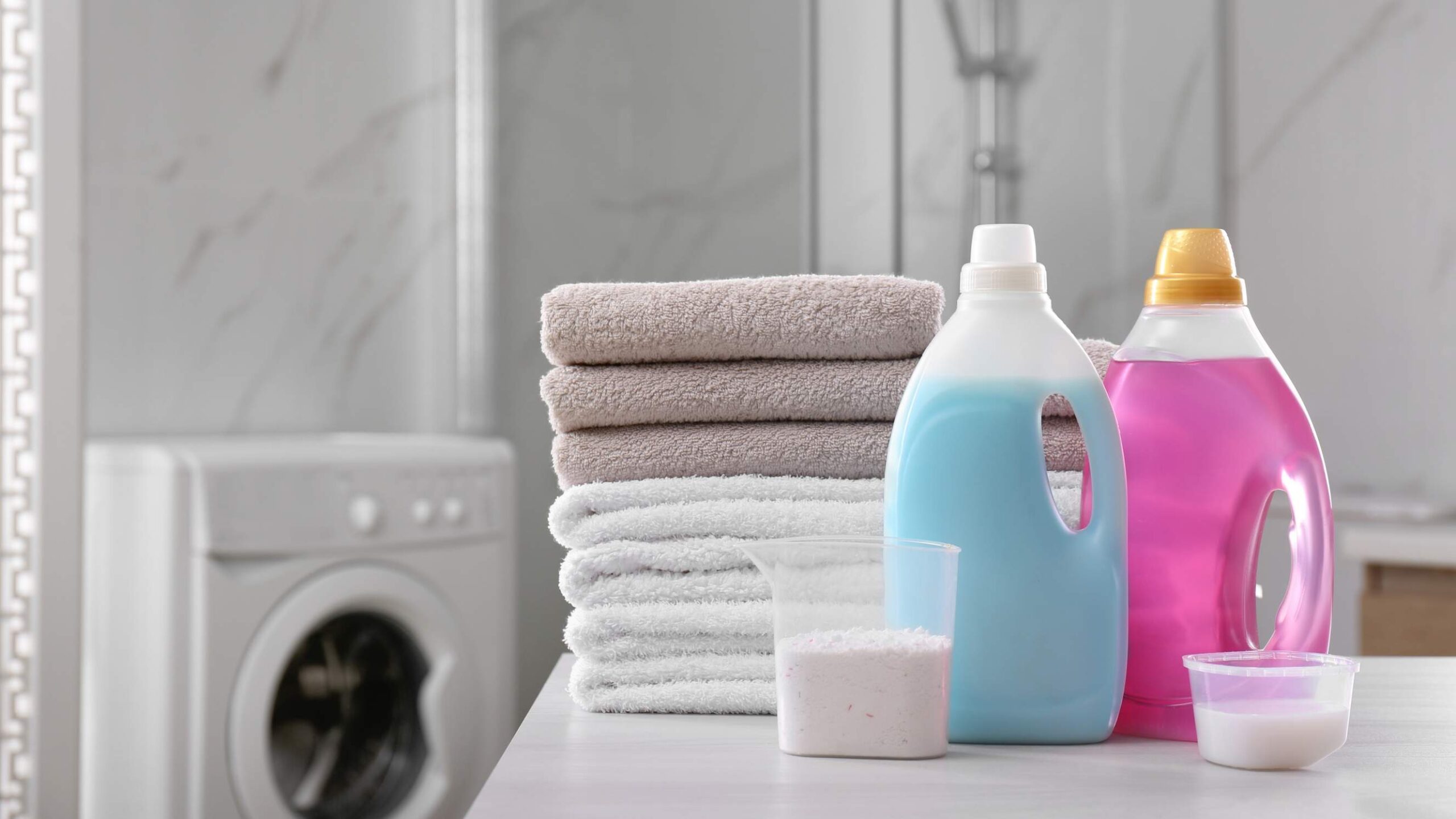
Fabric softener
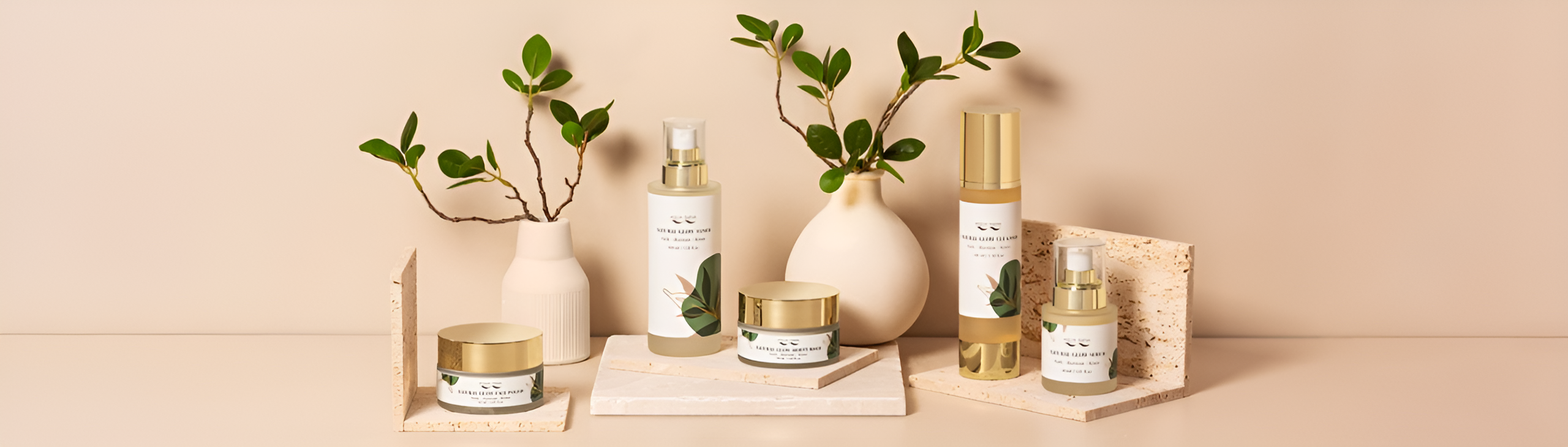
Face cream
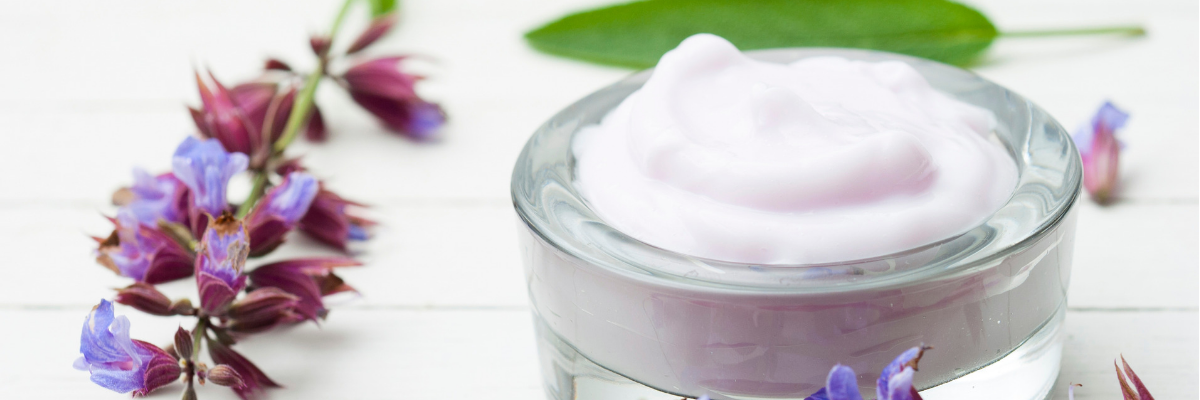
Facial moisturizers
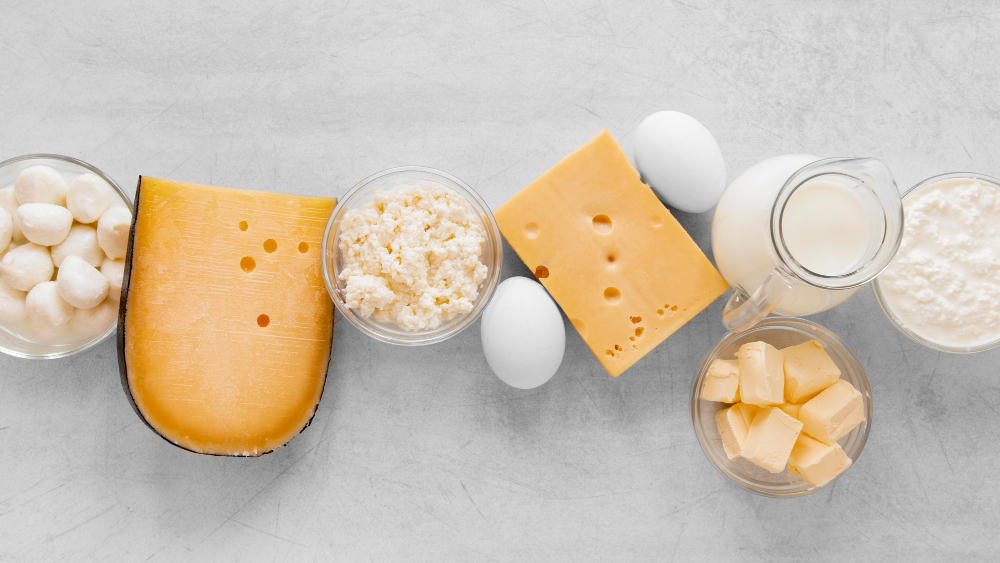
Fermented dairy products

Feta cheese
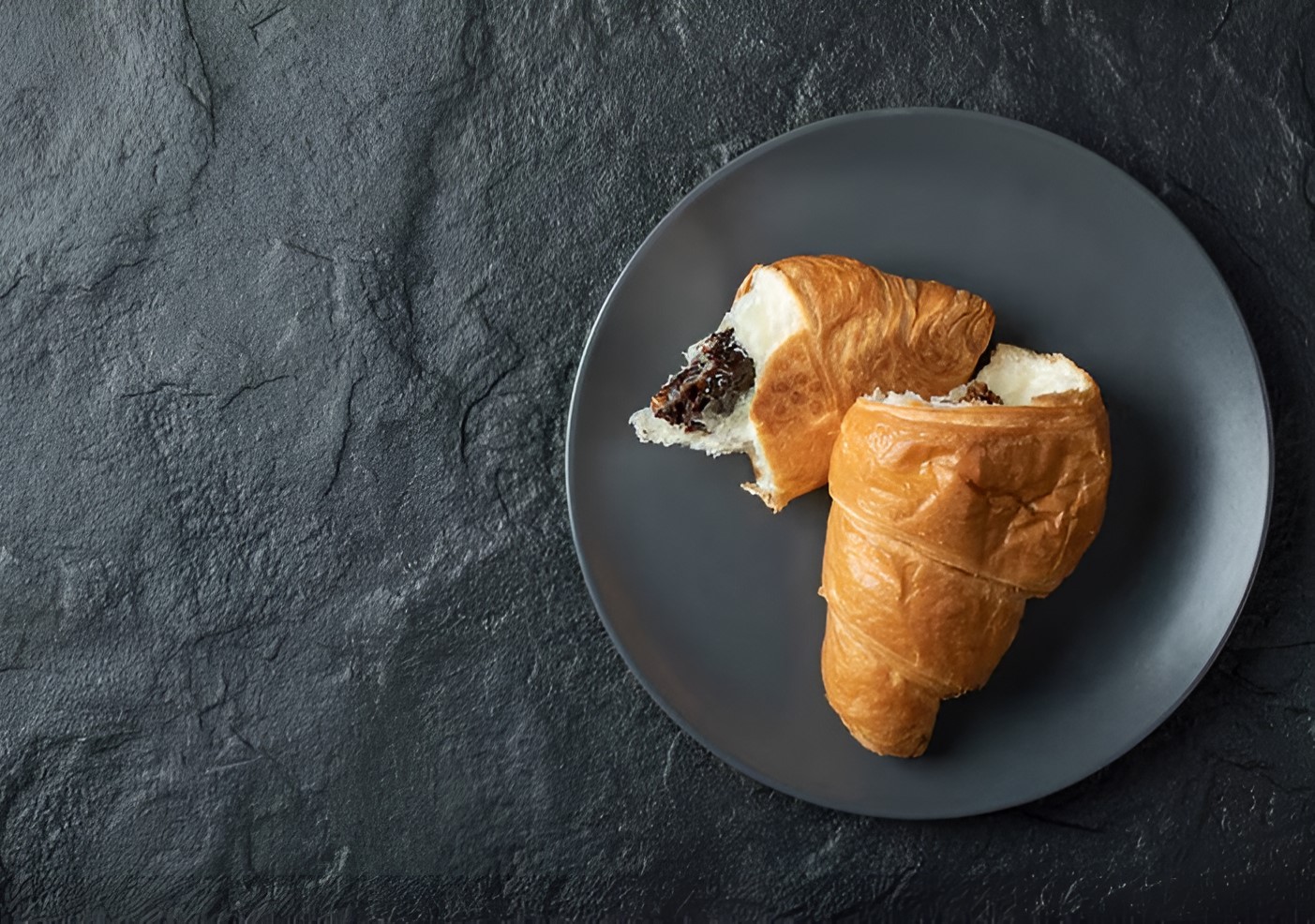
Filled croissants
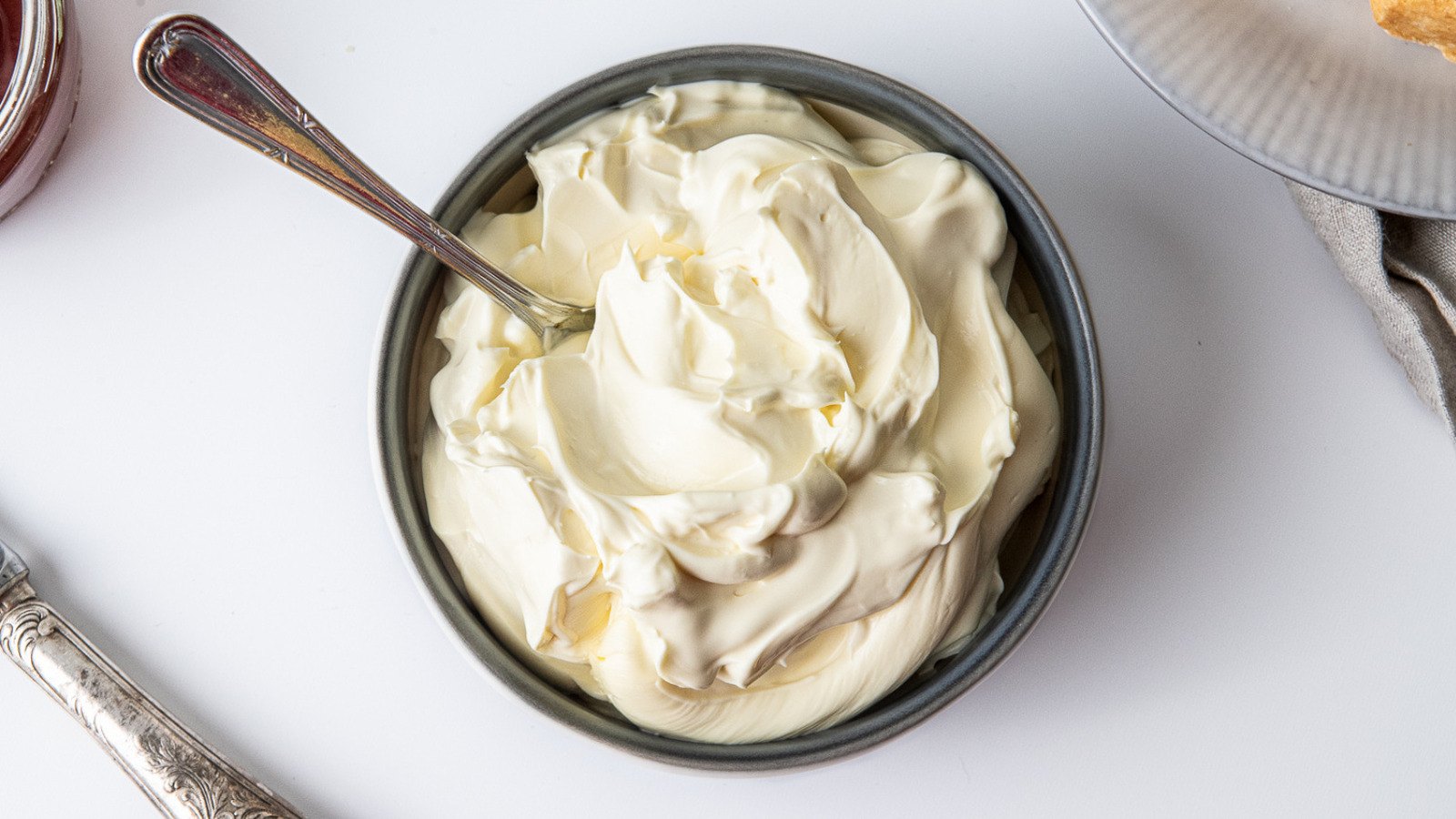
Fillings
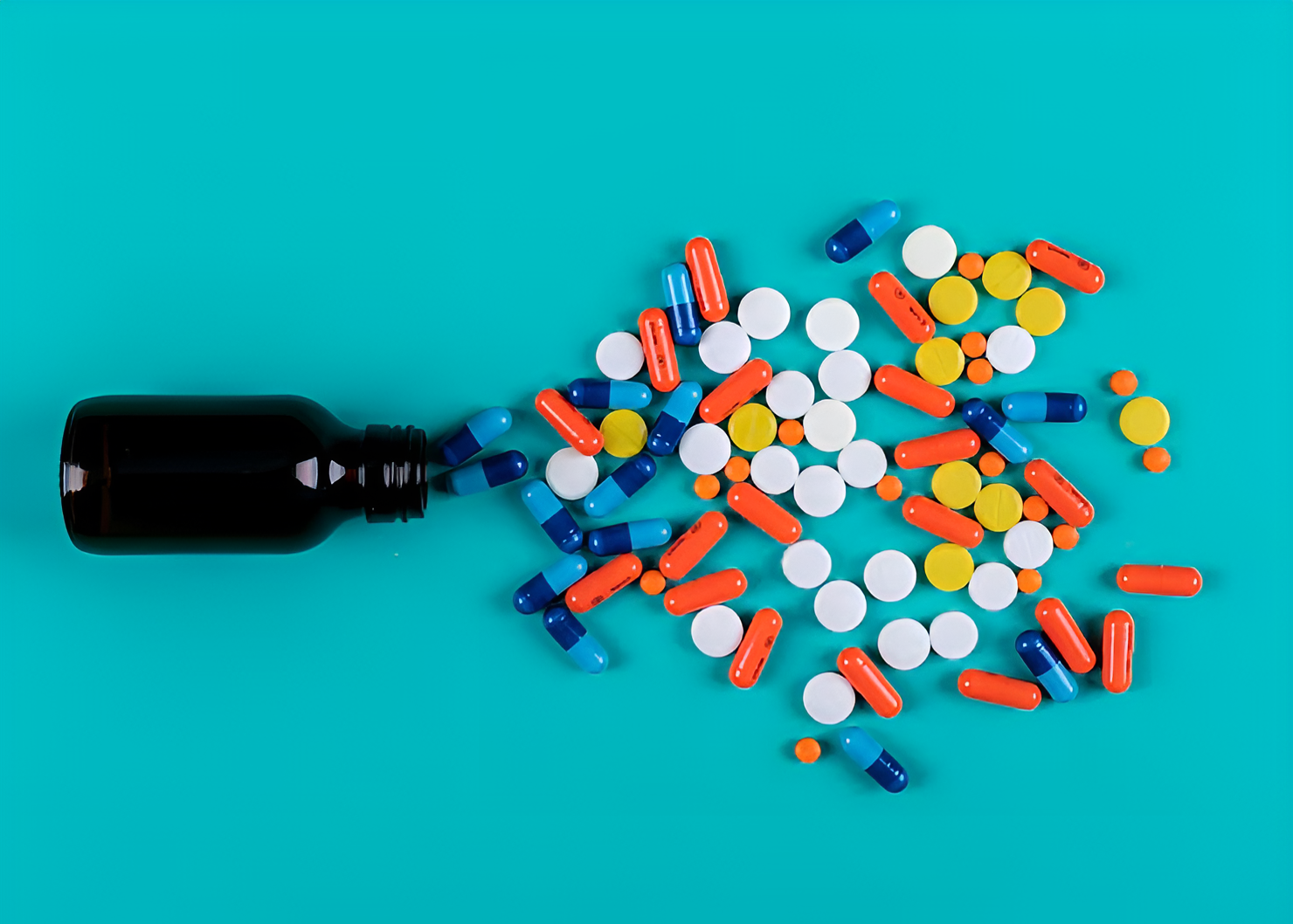
Film-coated tablets

Fish oil capsules
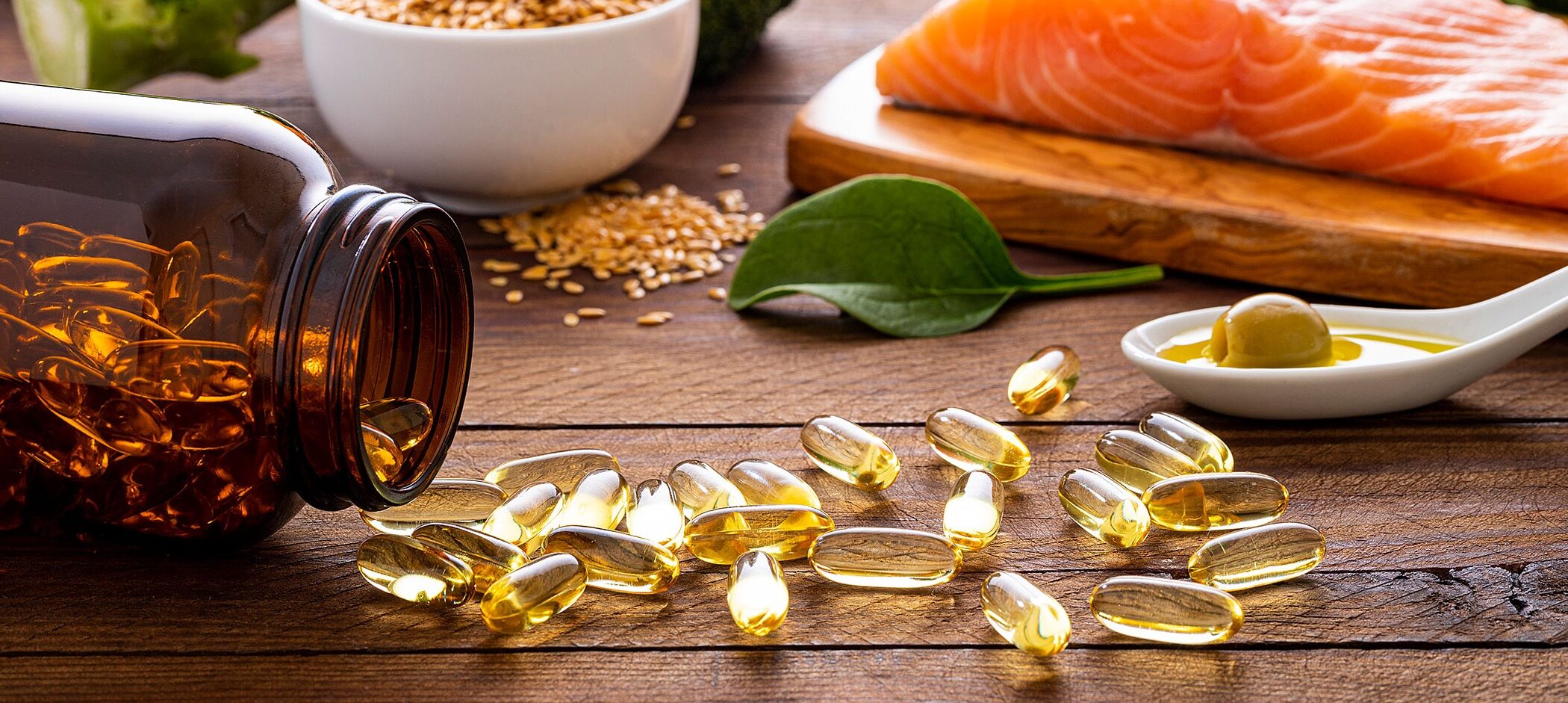
Fish oil supplements
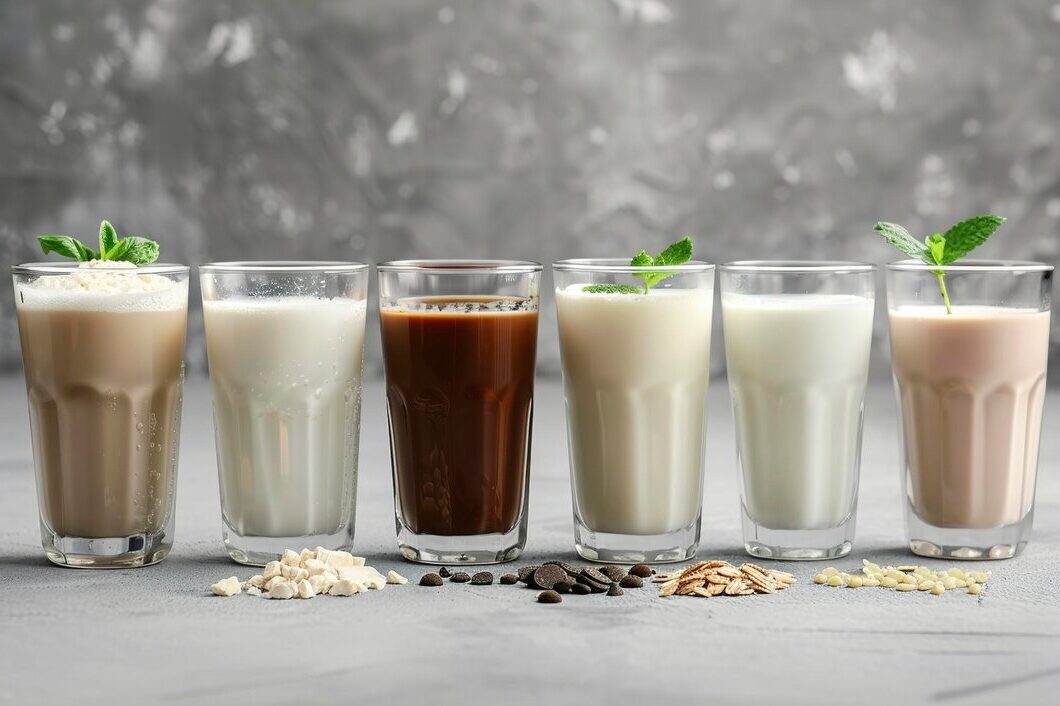
Flavoured milk
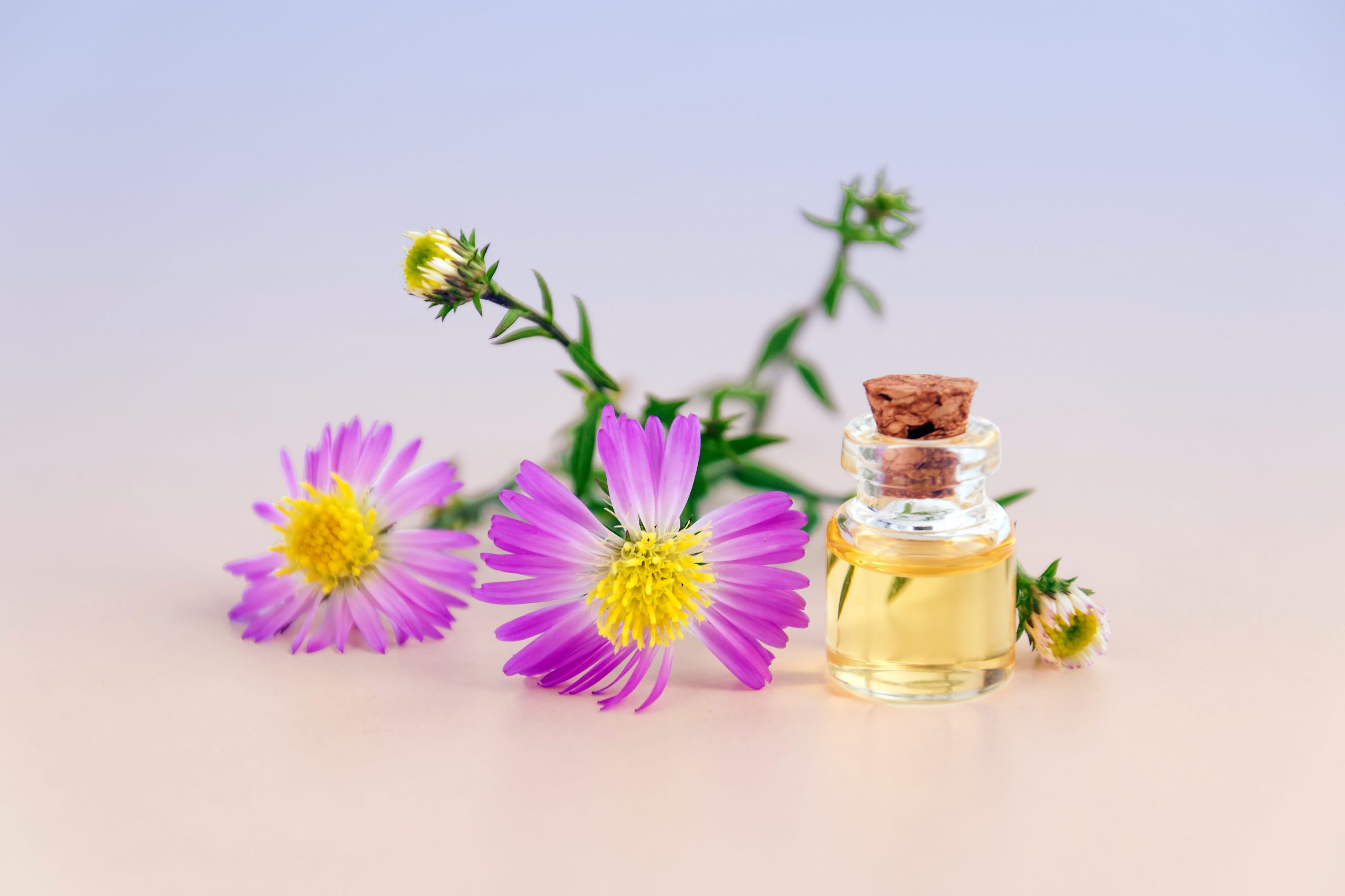
Flower extract
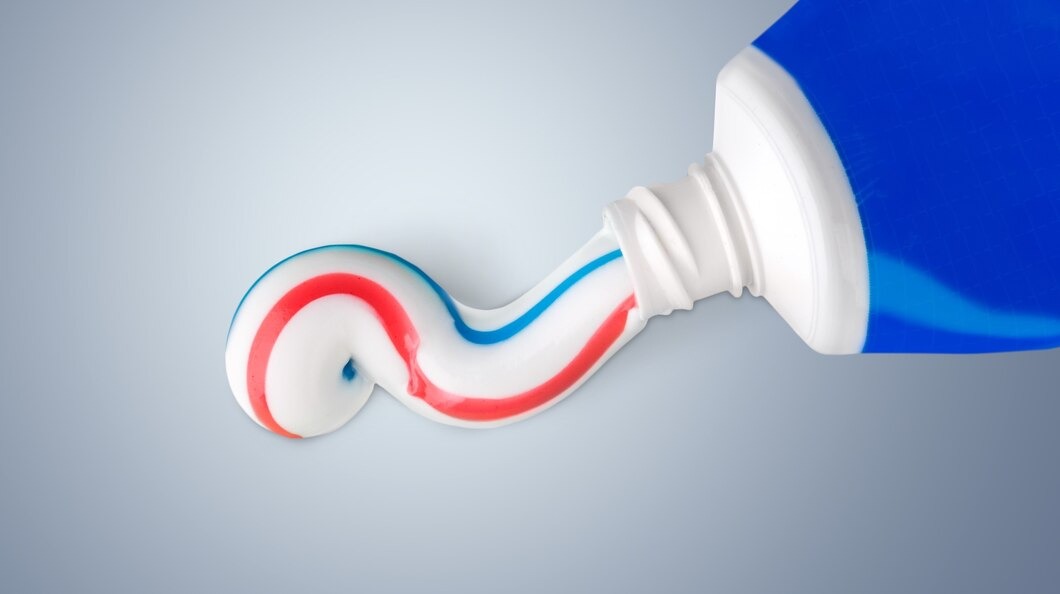
Fluoride toothpaste
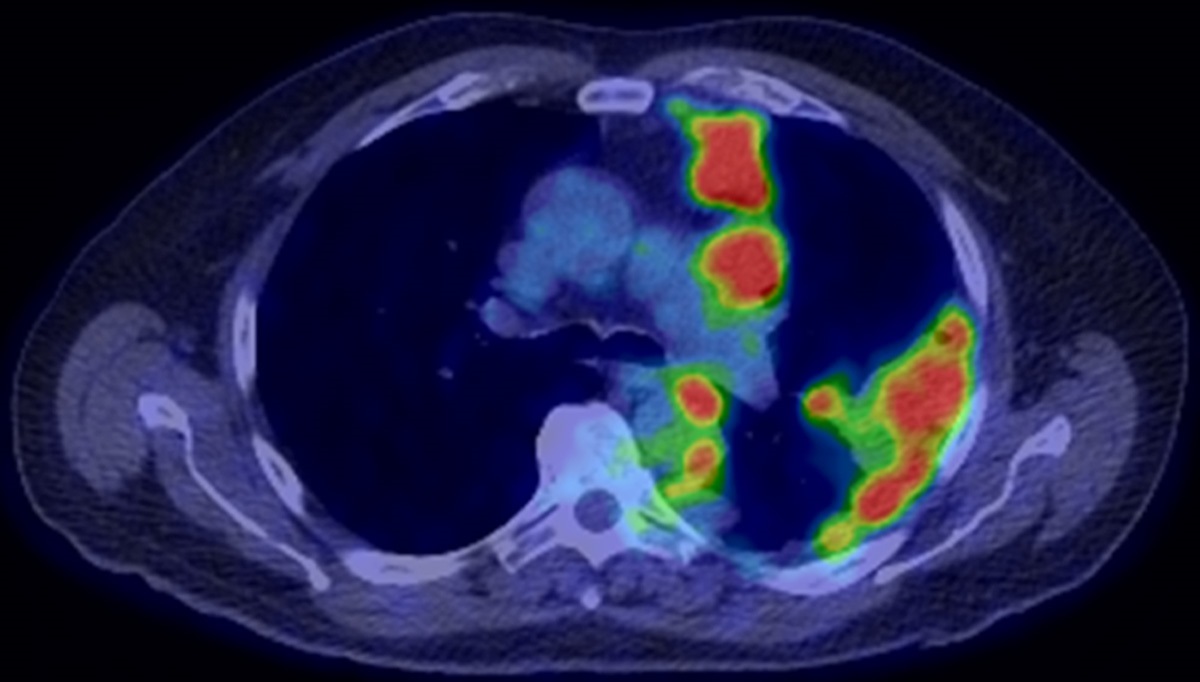
Fluorodeoxyglucose (fdg)
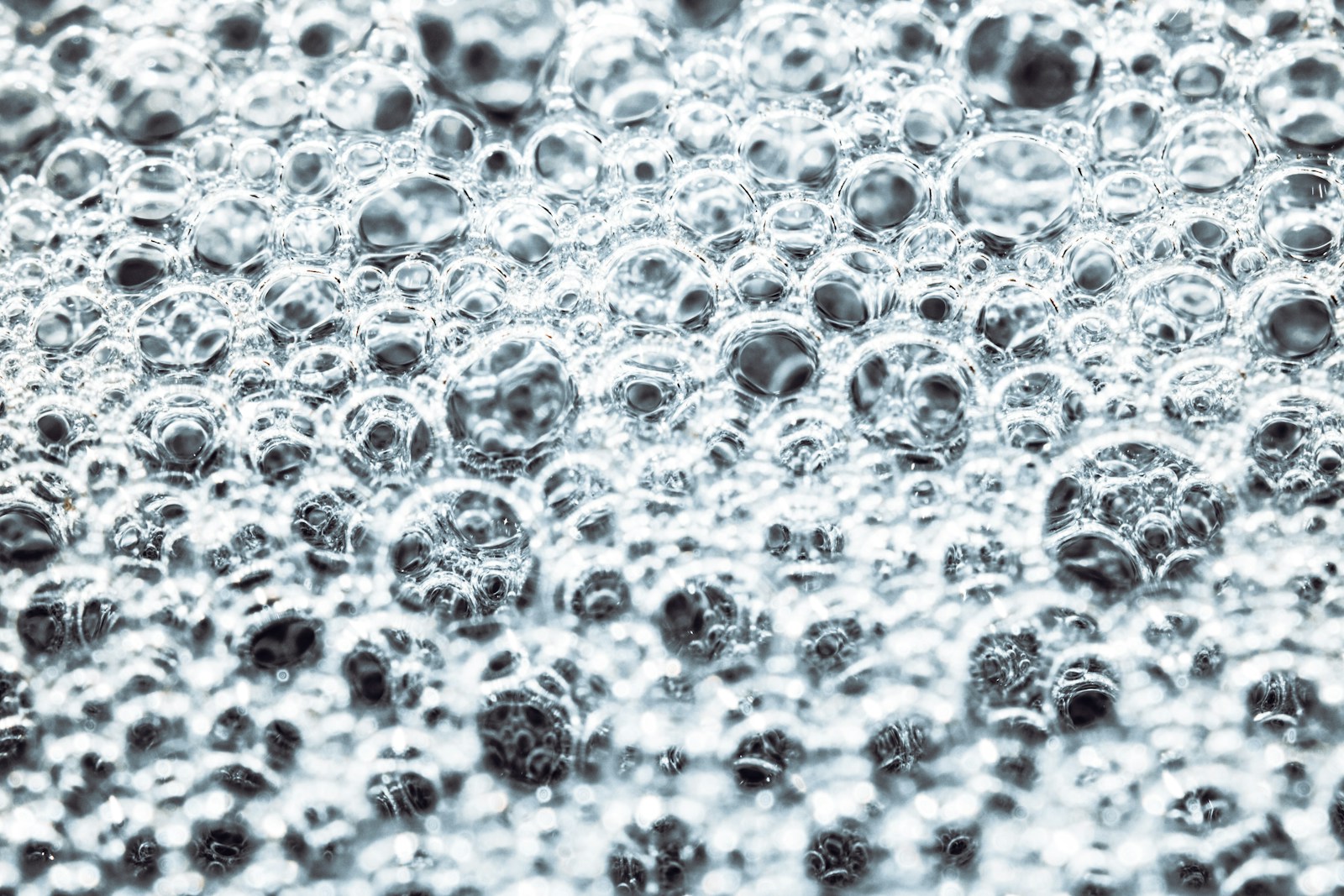
Foam
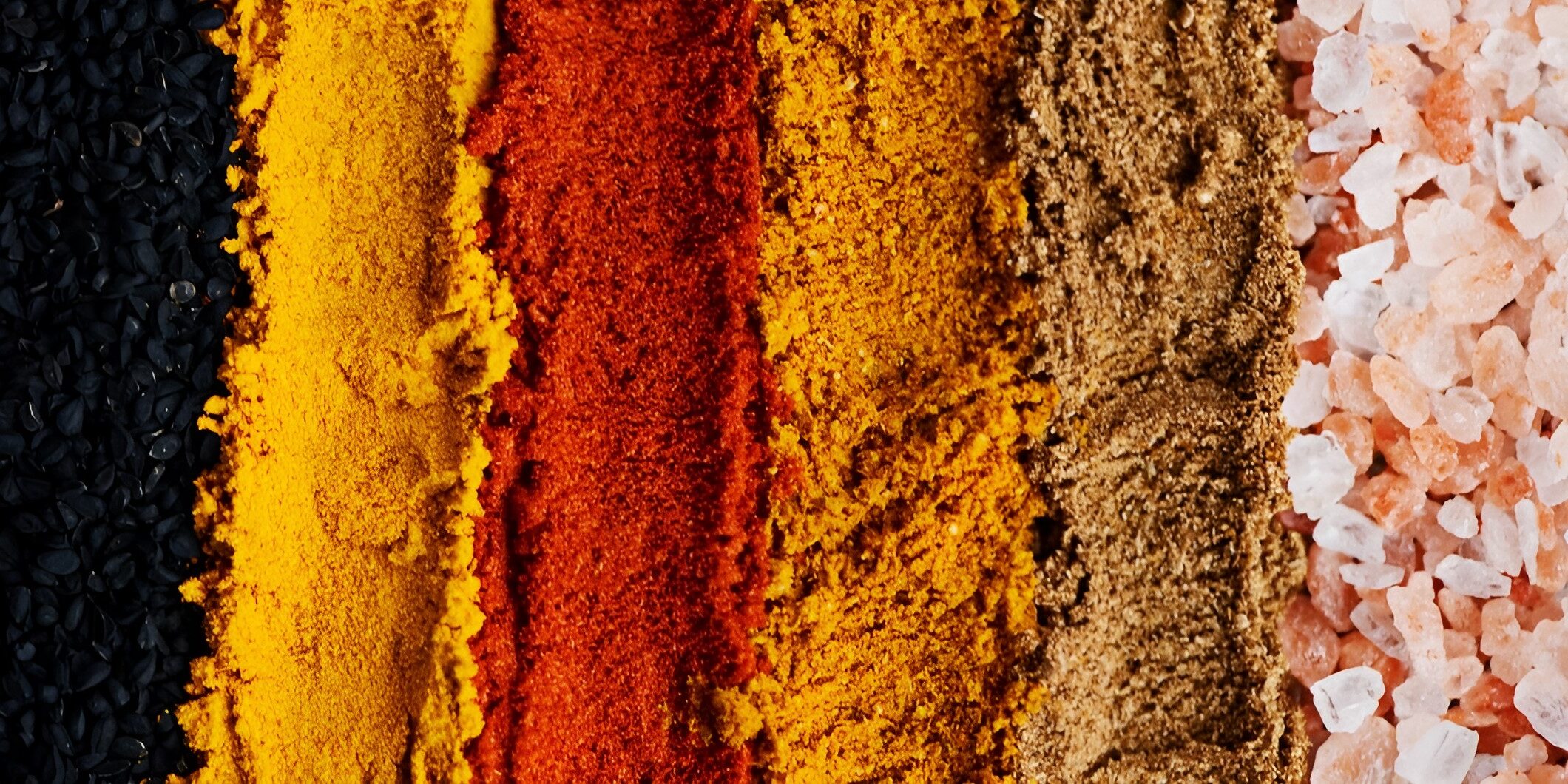
Food powders
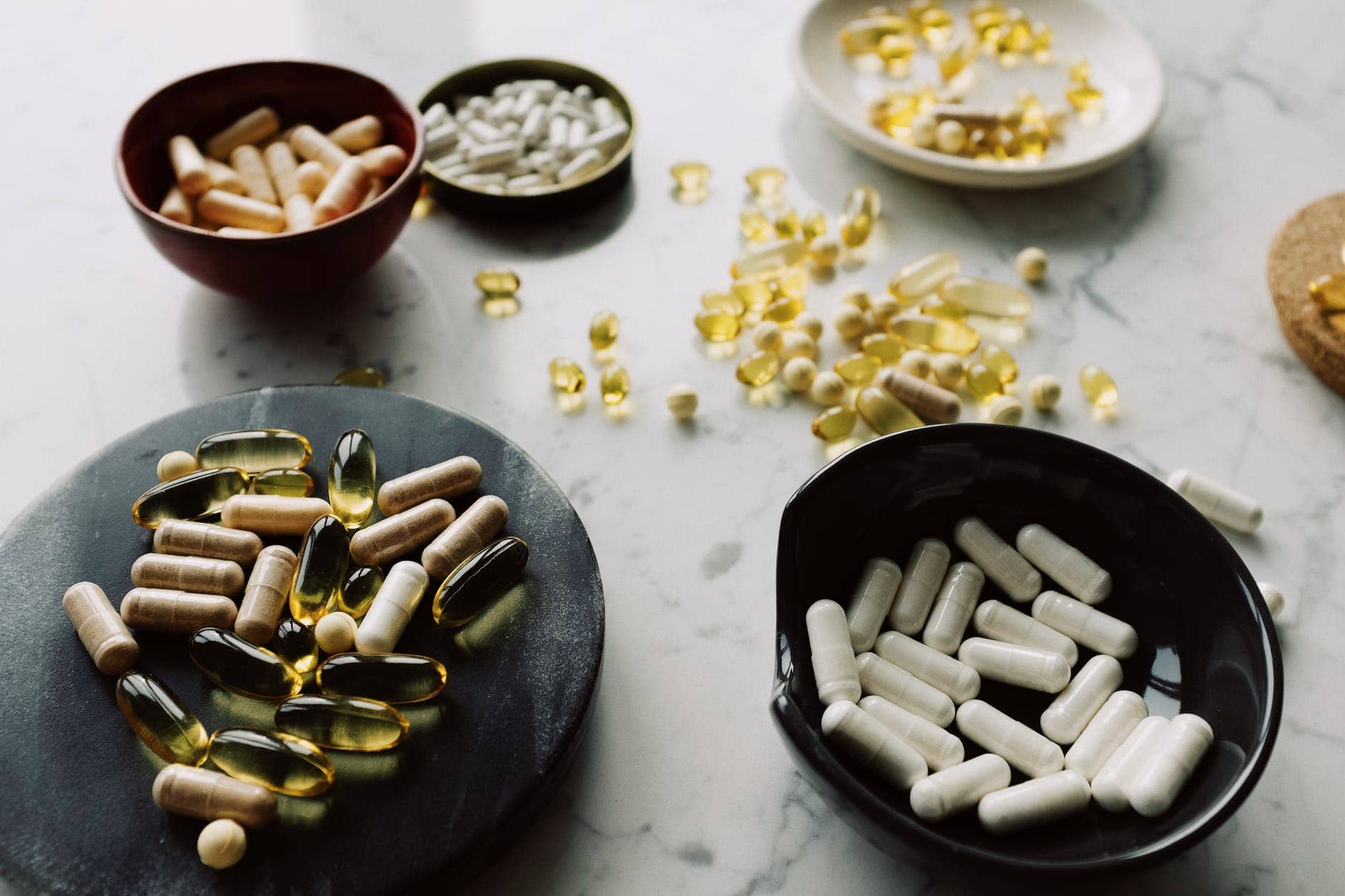
Food supplements
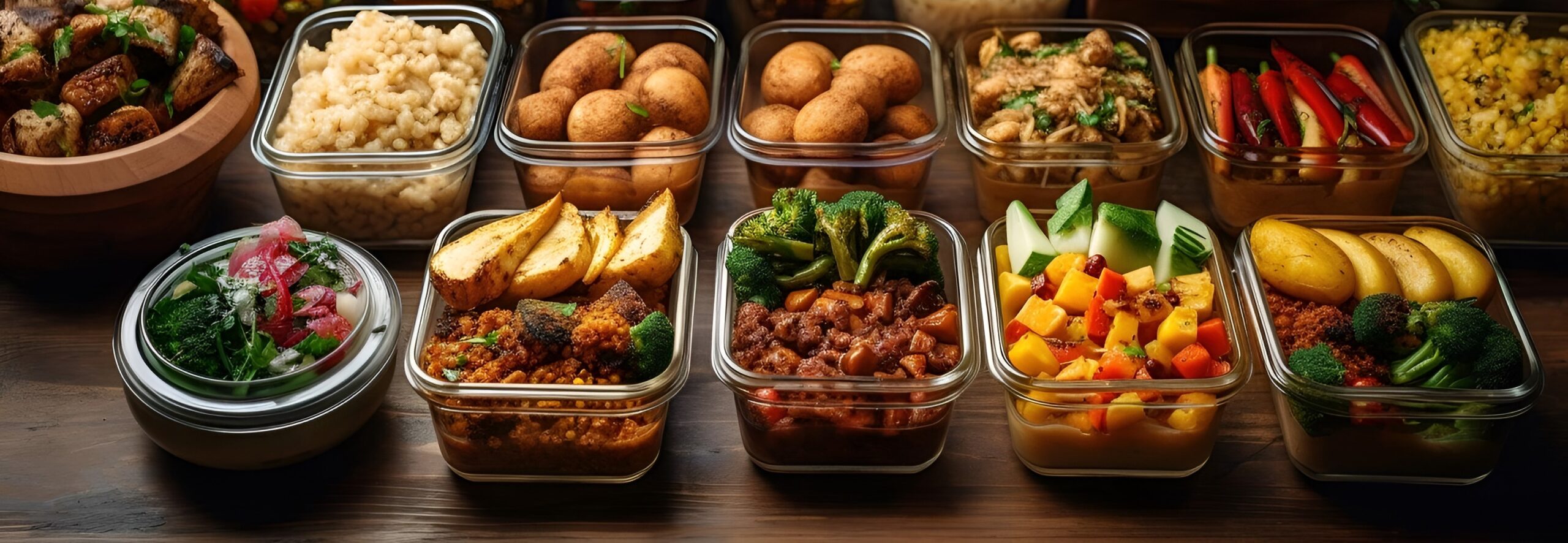
Food-to-go
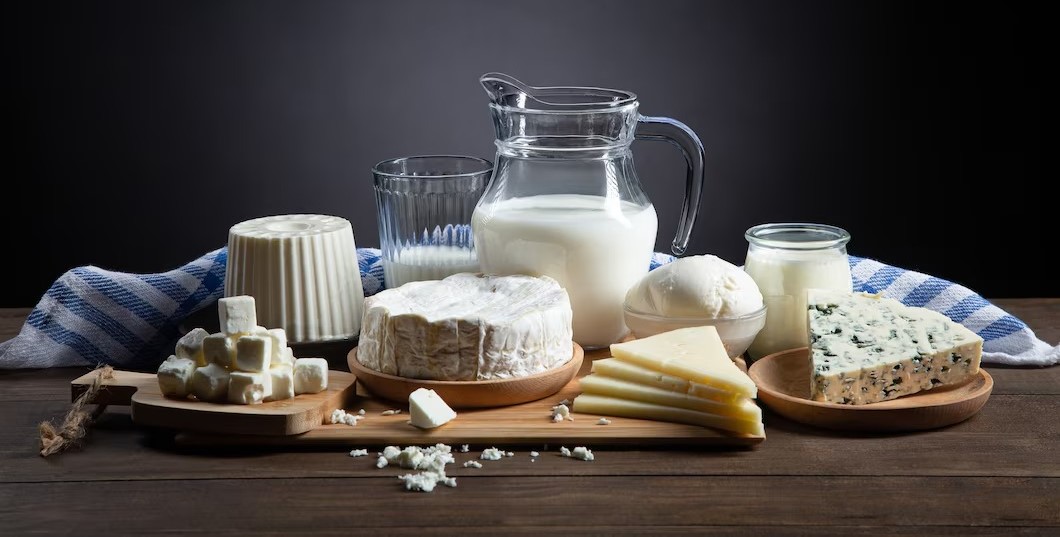
Formulated dairy products
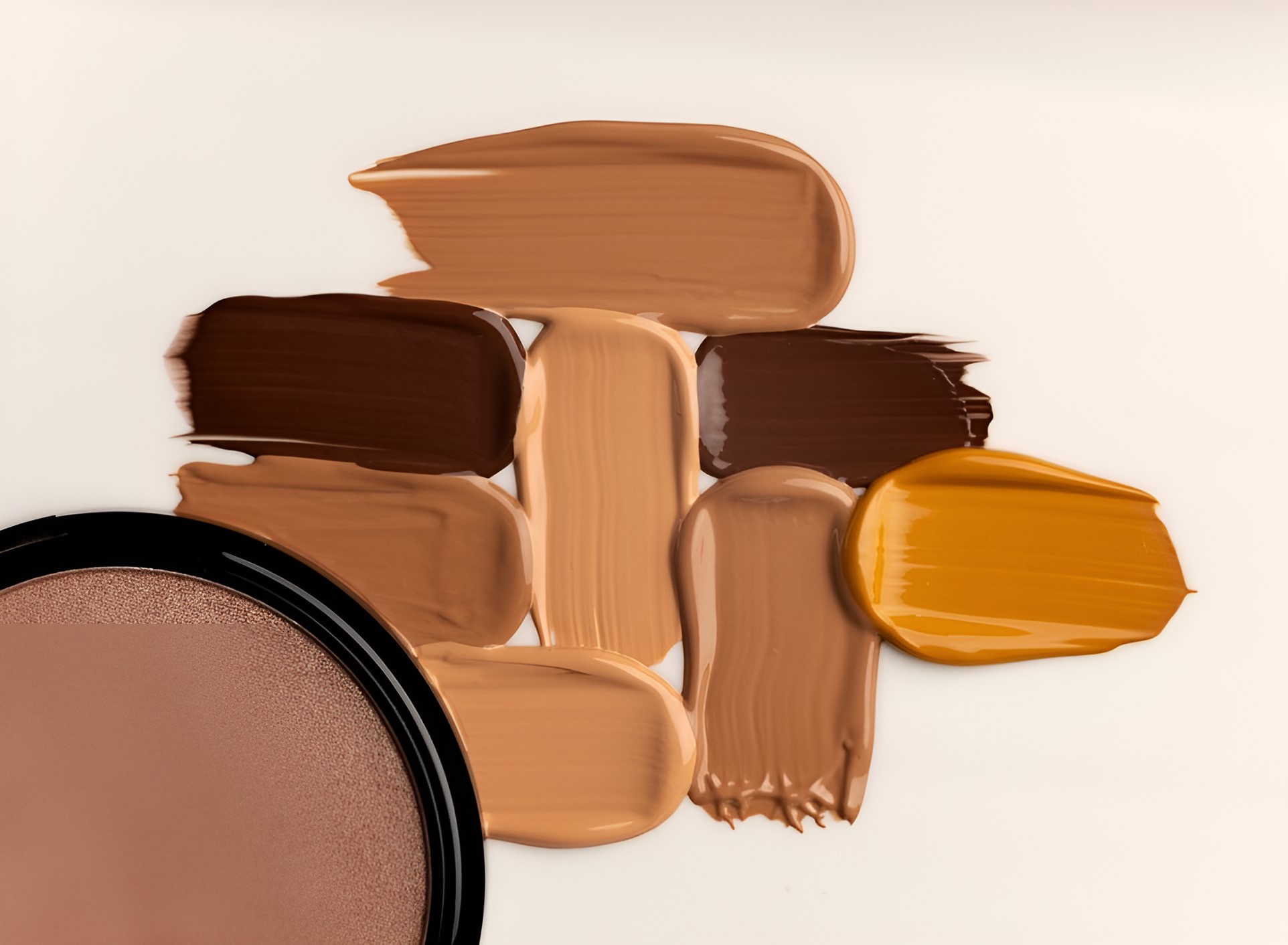
Foundation cream
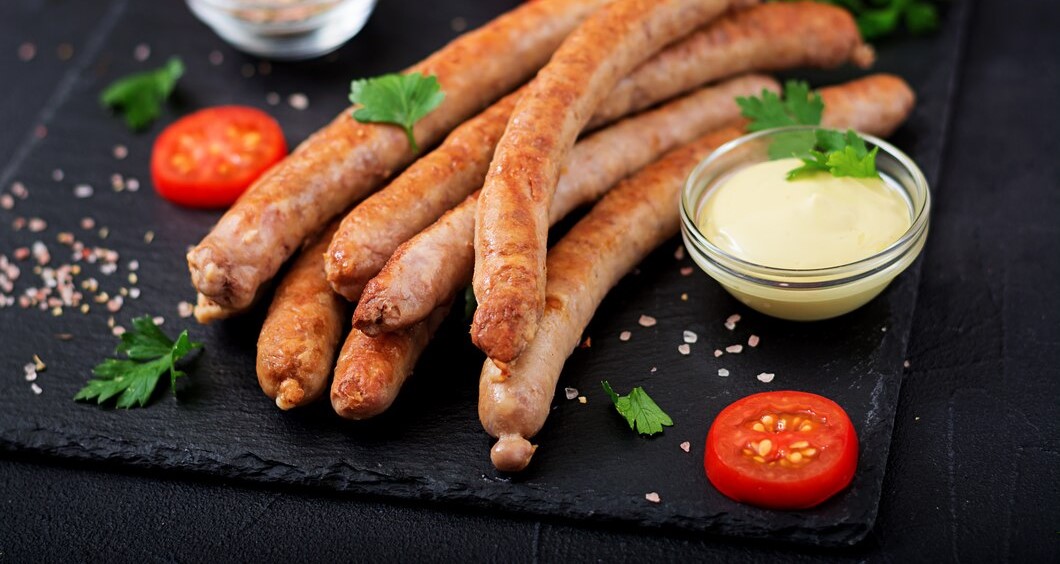
Frankfurters
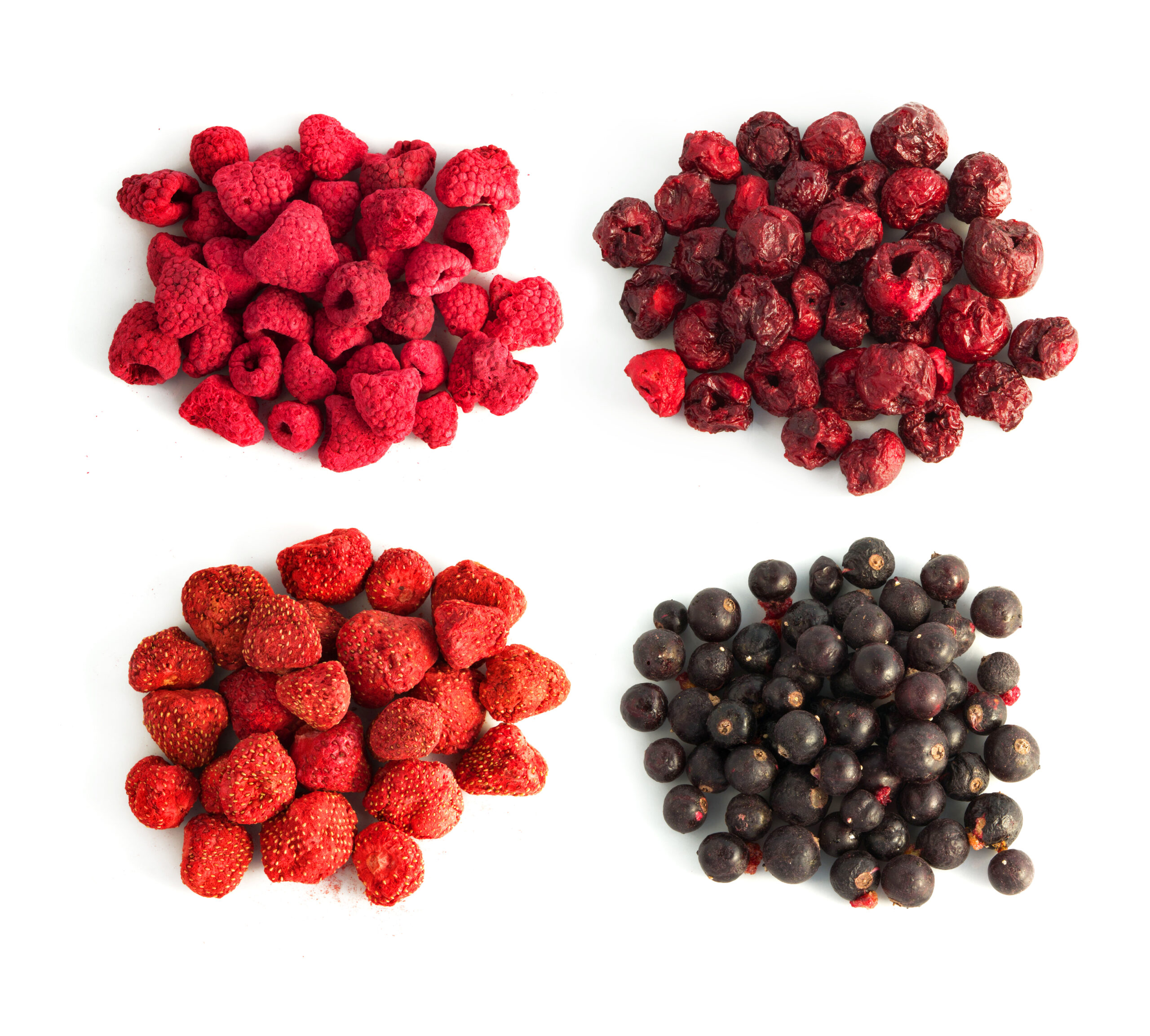
Freeze dried berries
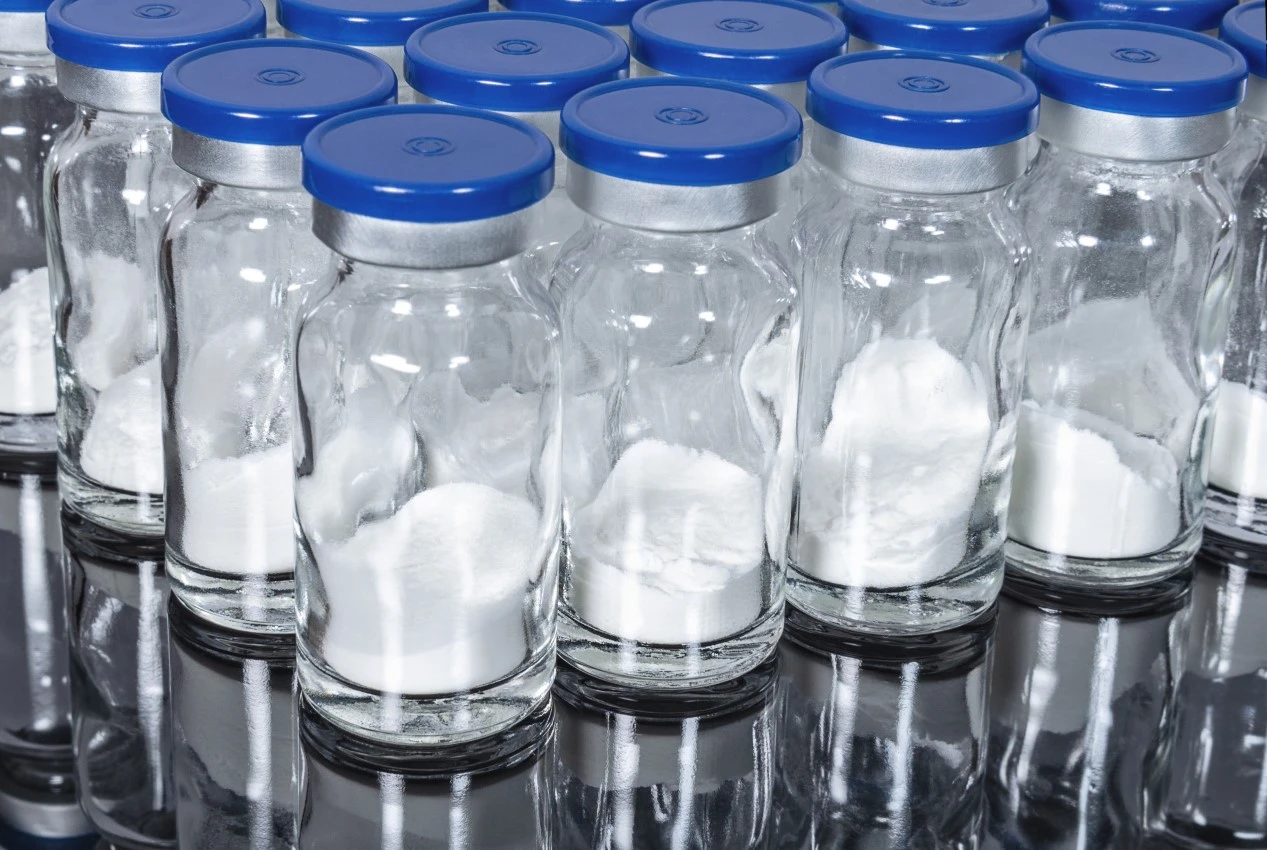
Freeze-dried pharmaceuticals
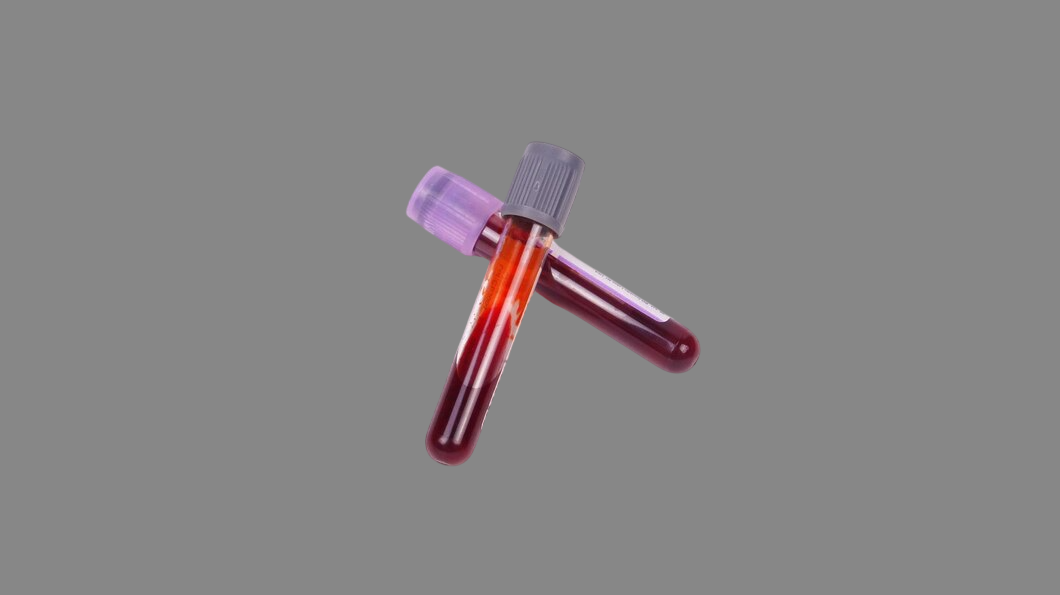
Freeze-dried plasma
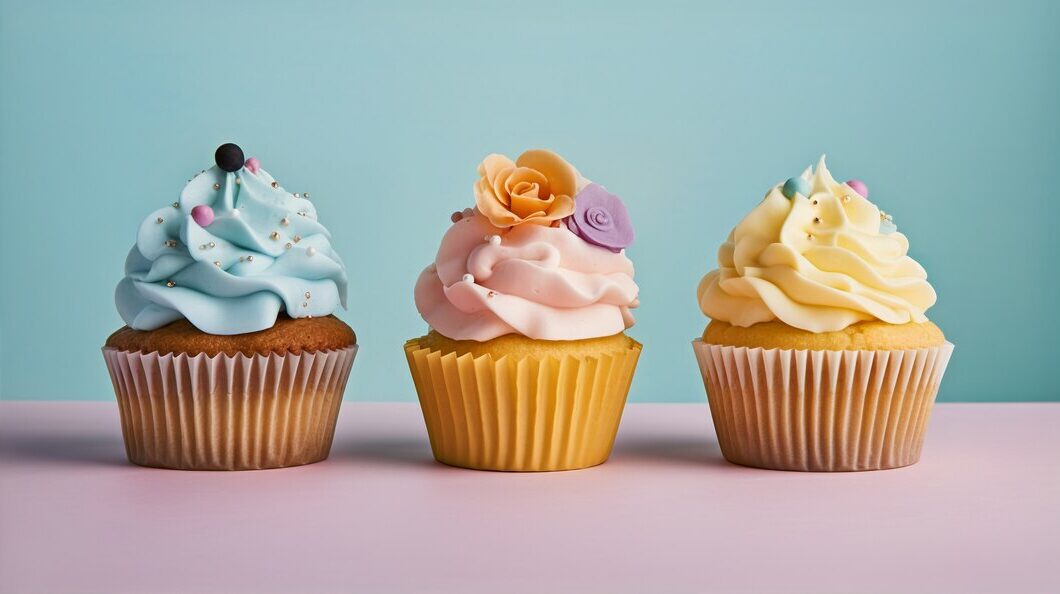
Frosting
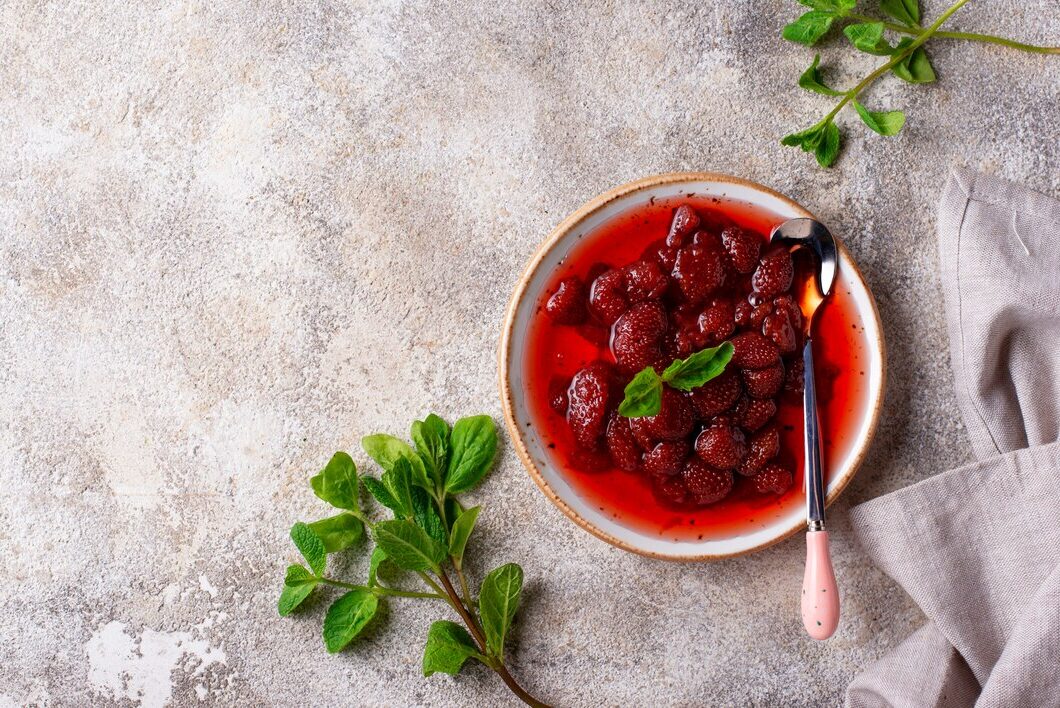
Fruit compote
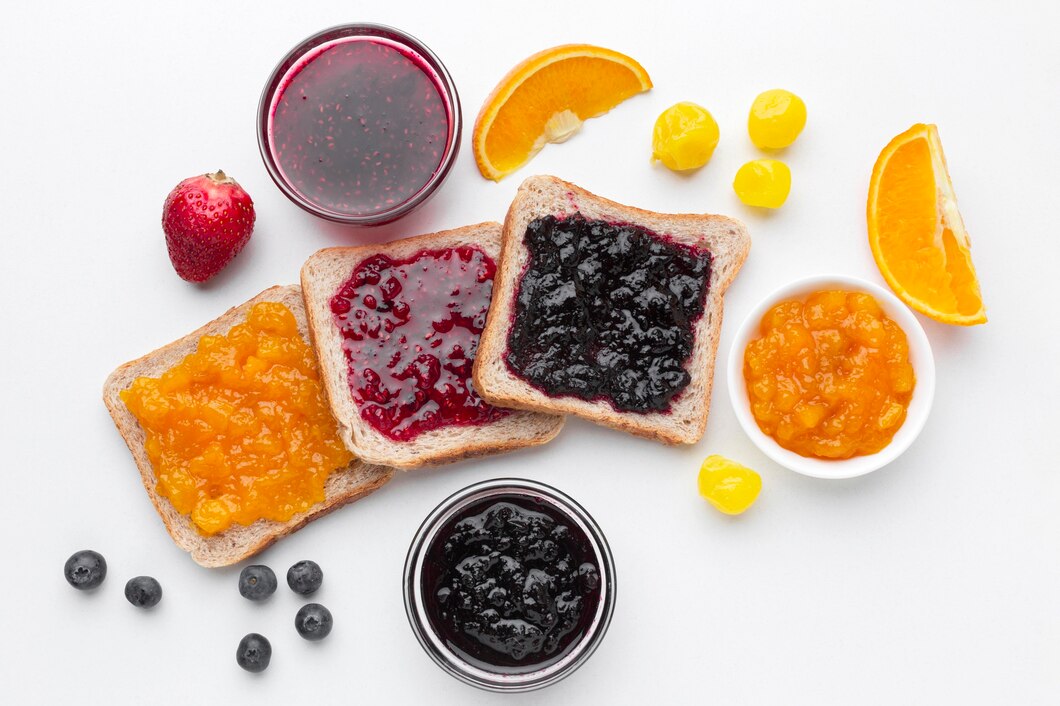
Fruit jam
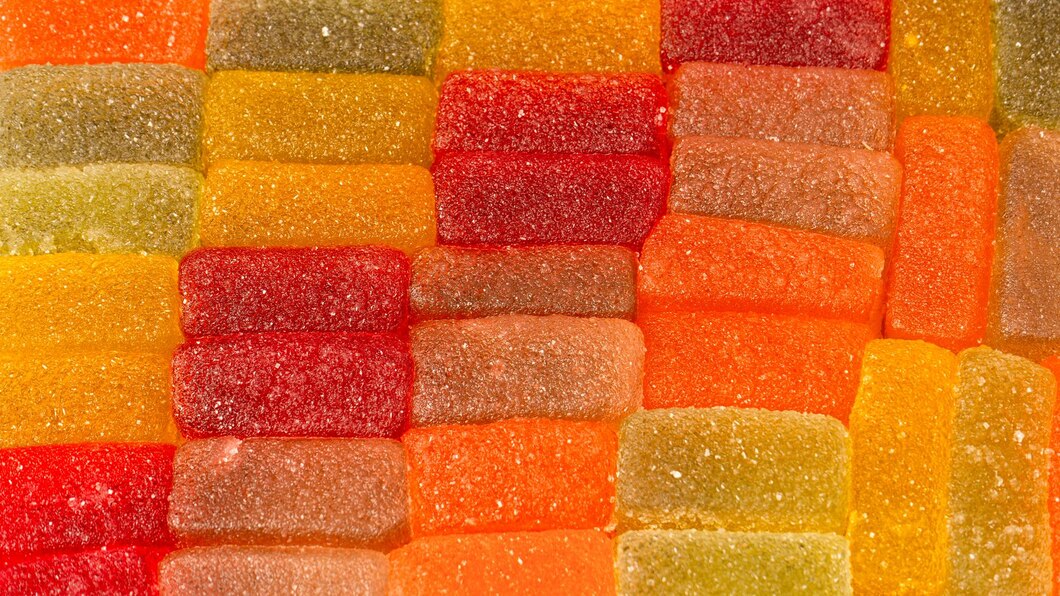
Fruit jellies
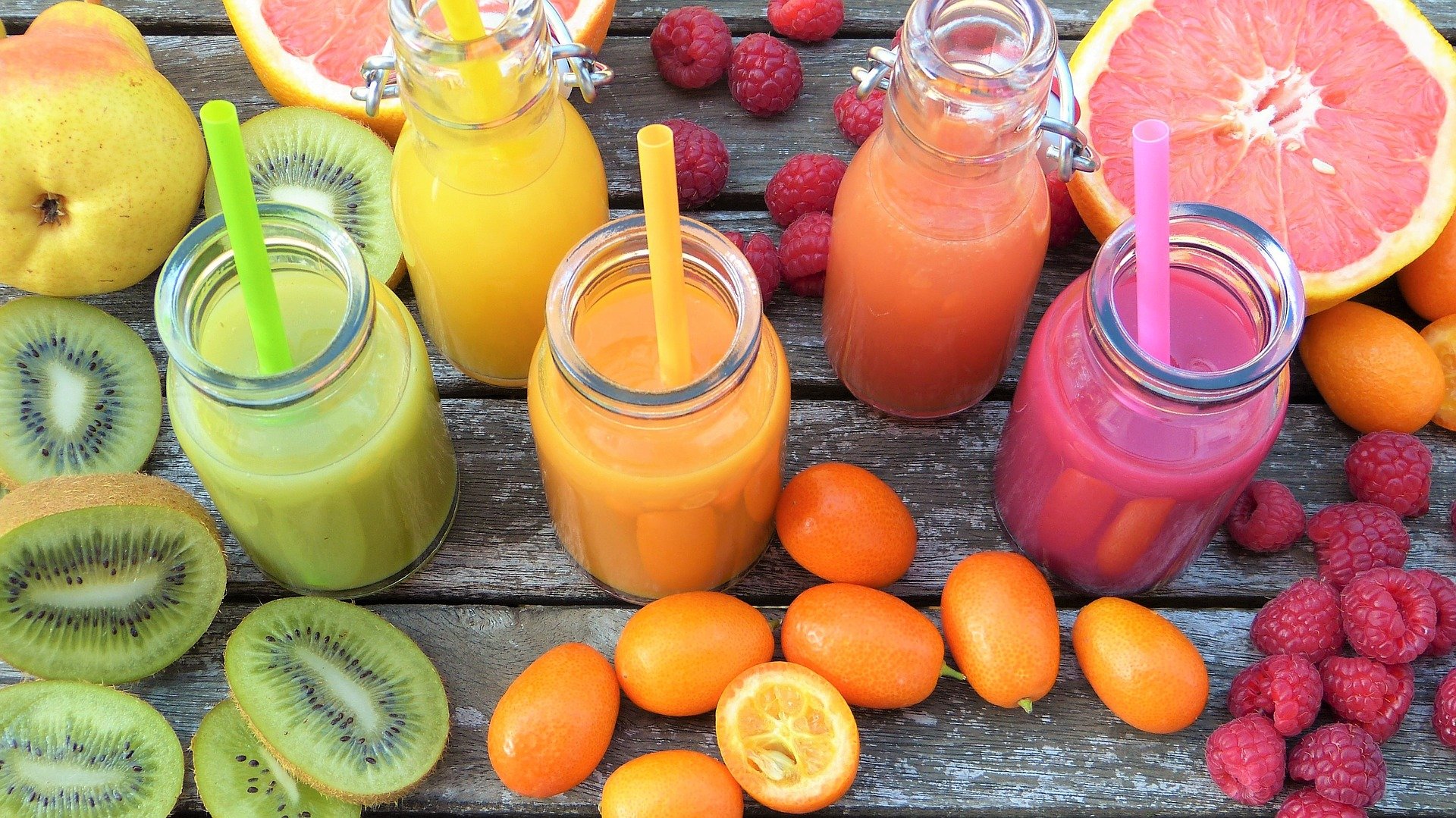
Fruit juice
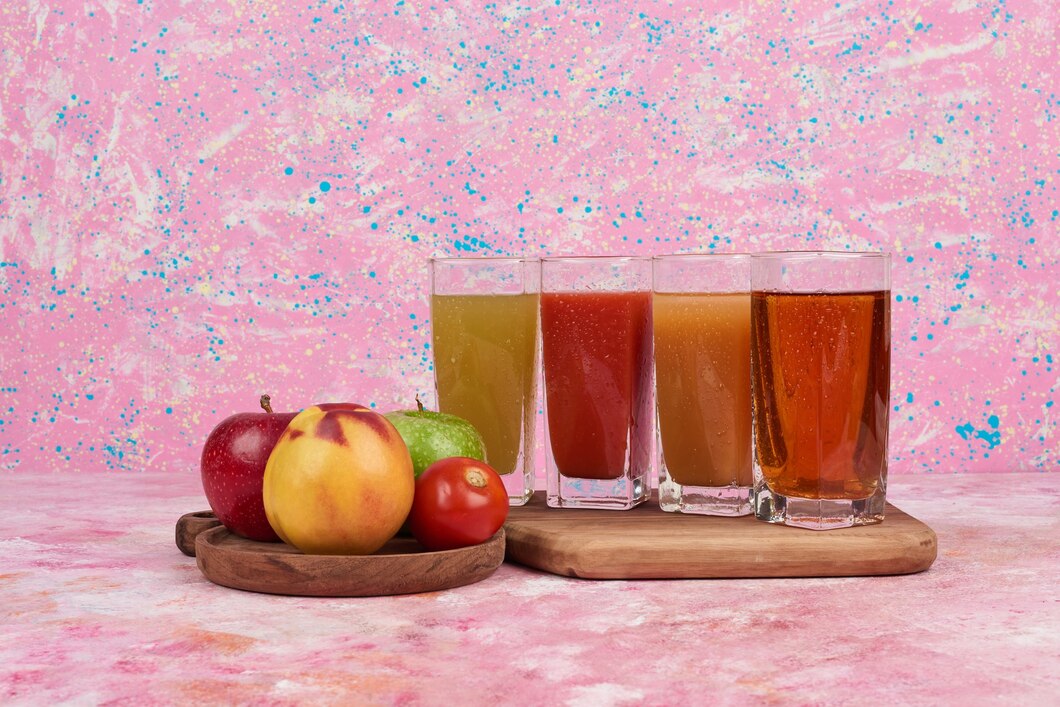
Fruit juice concentrate
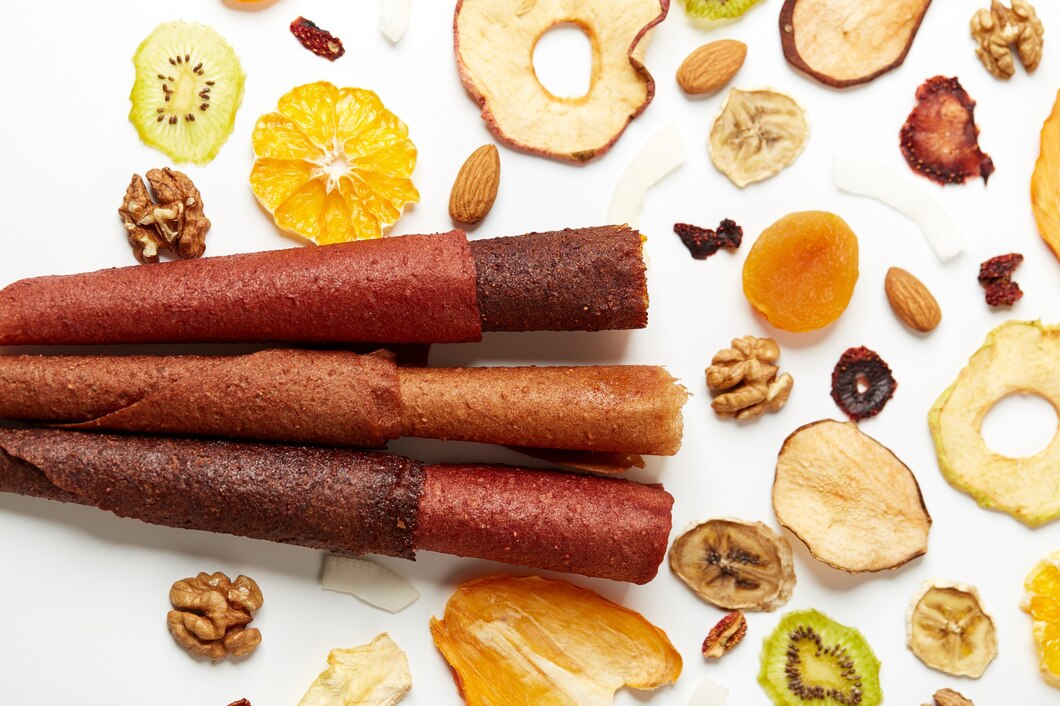
Fruit leather
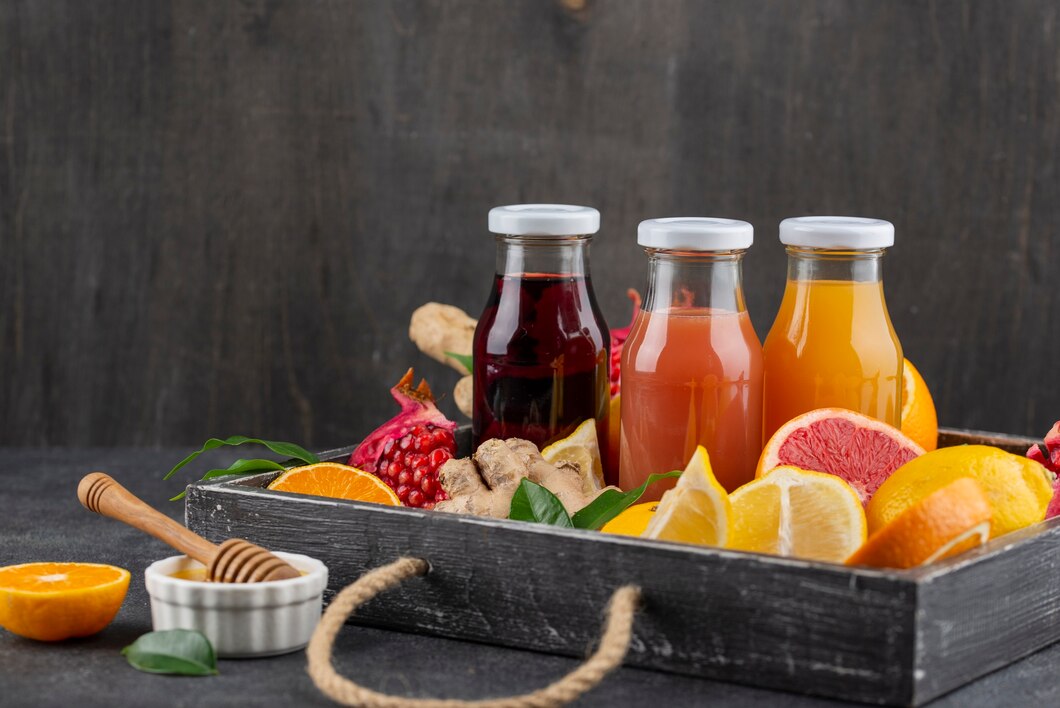
Fruit nectars
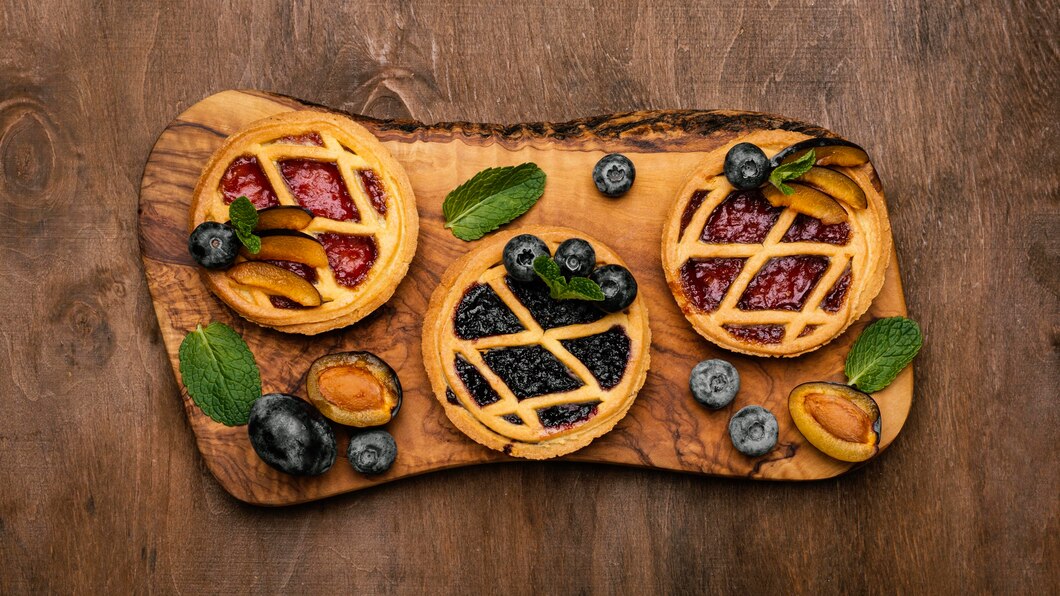
Fruit pies
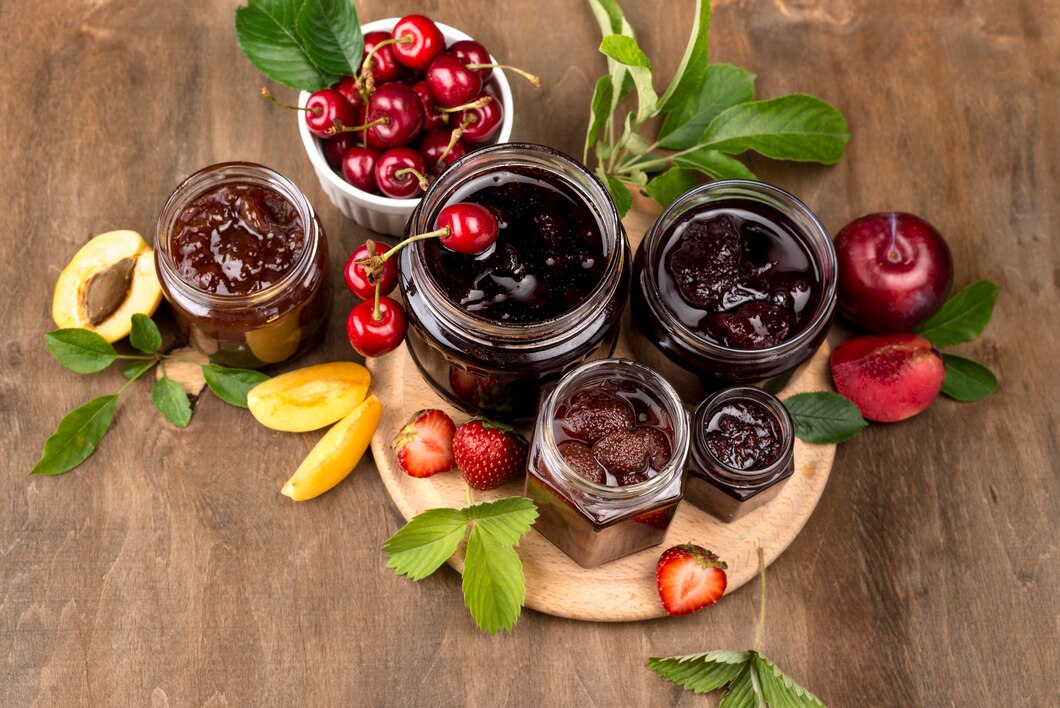
Fruit preserves

Fruit puree
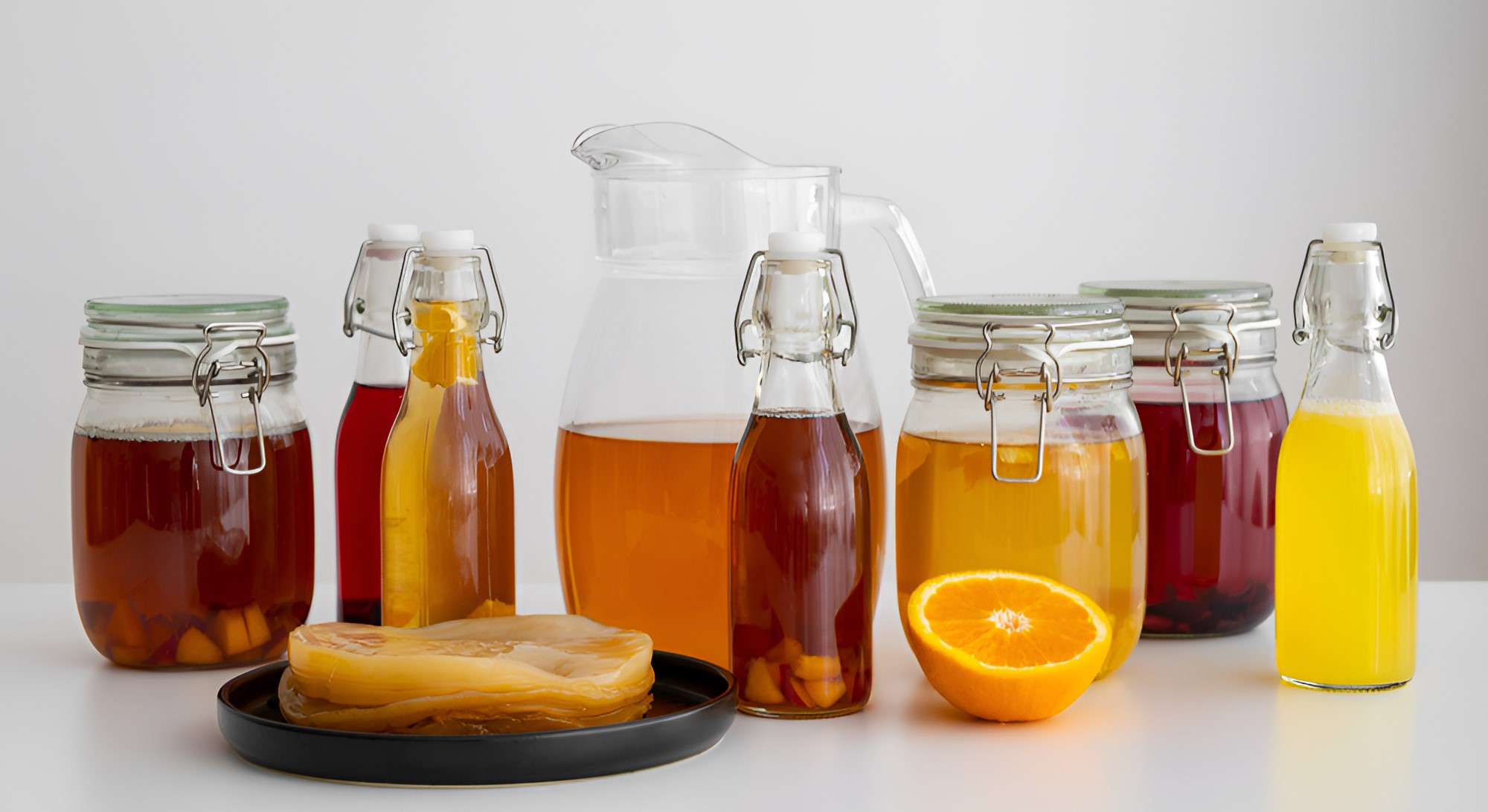
Fruit syrups
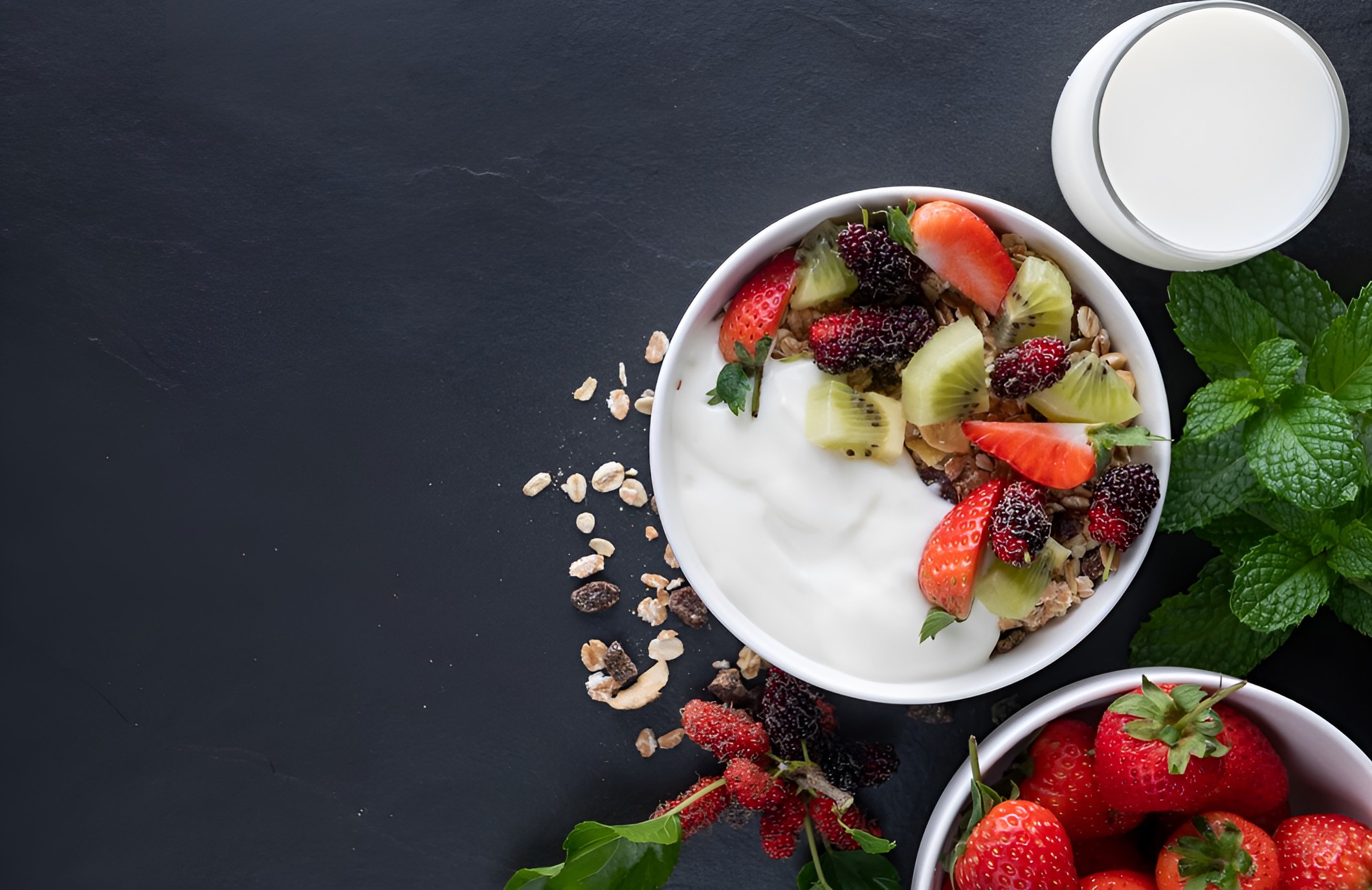
Fruit yogurt

Functional drinks
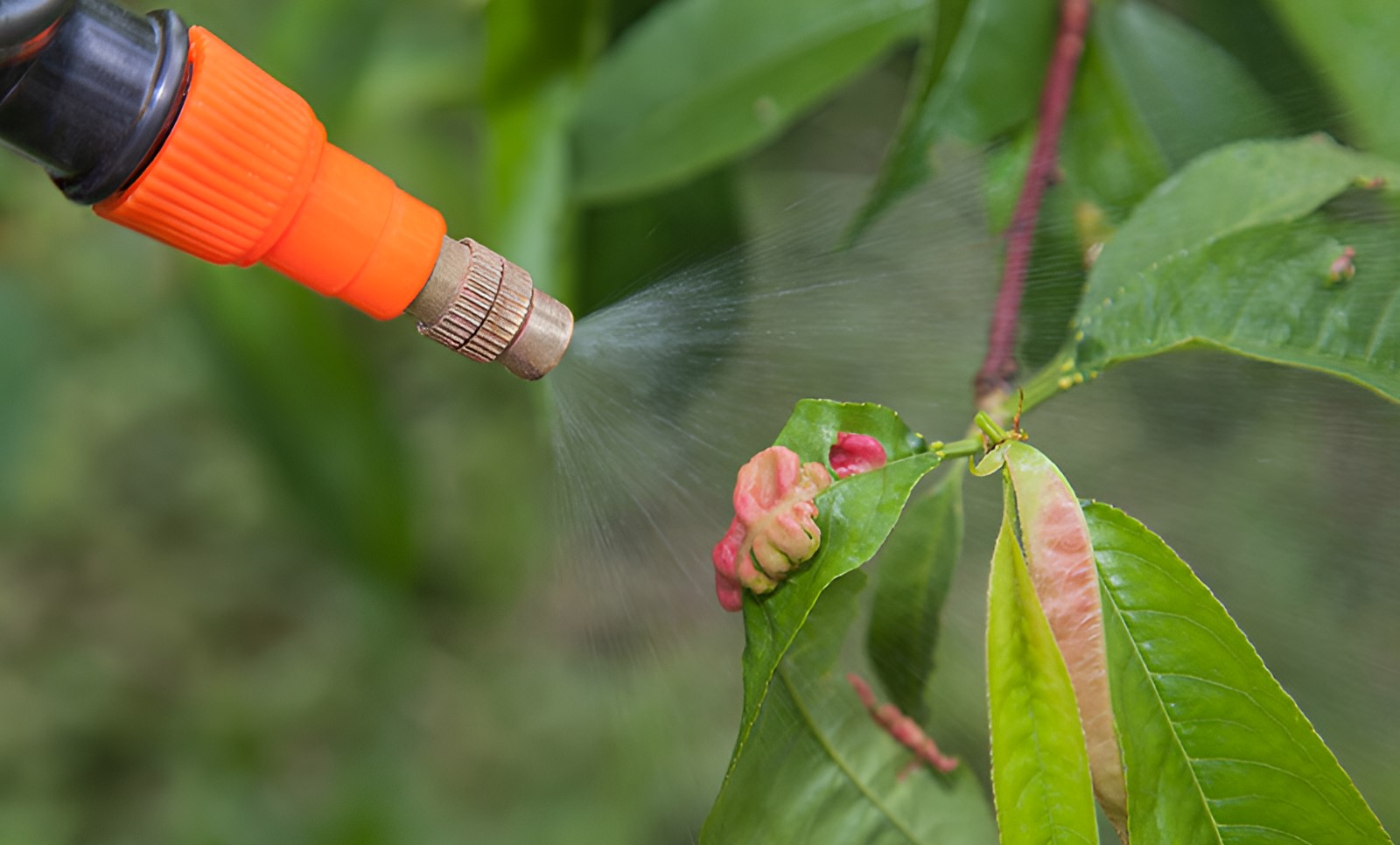
Fungicides
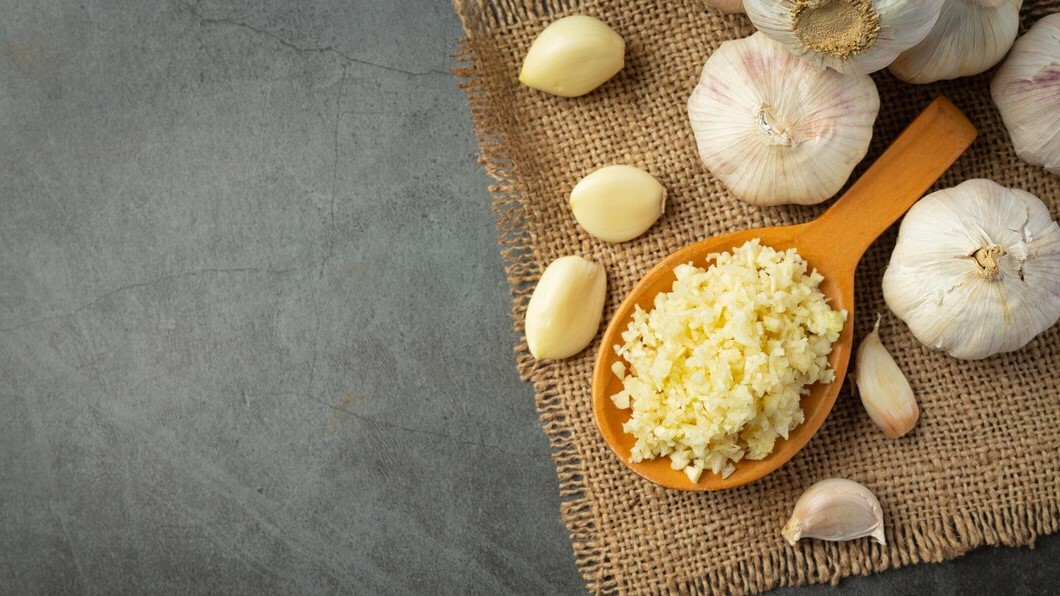
Garlic paste
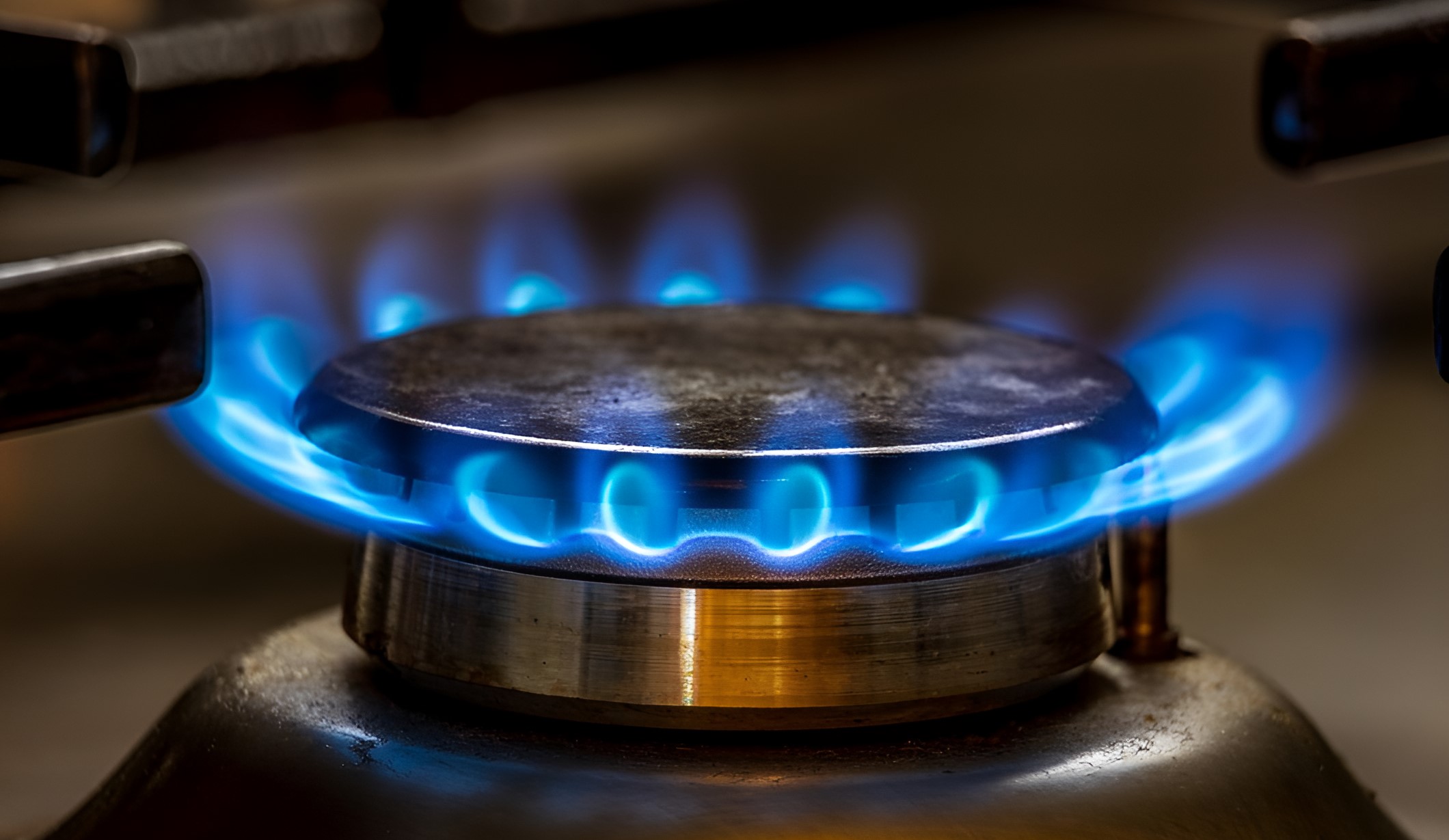
Gas
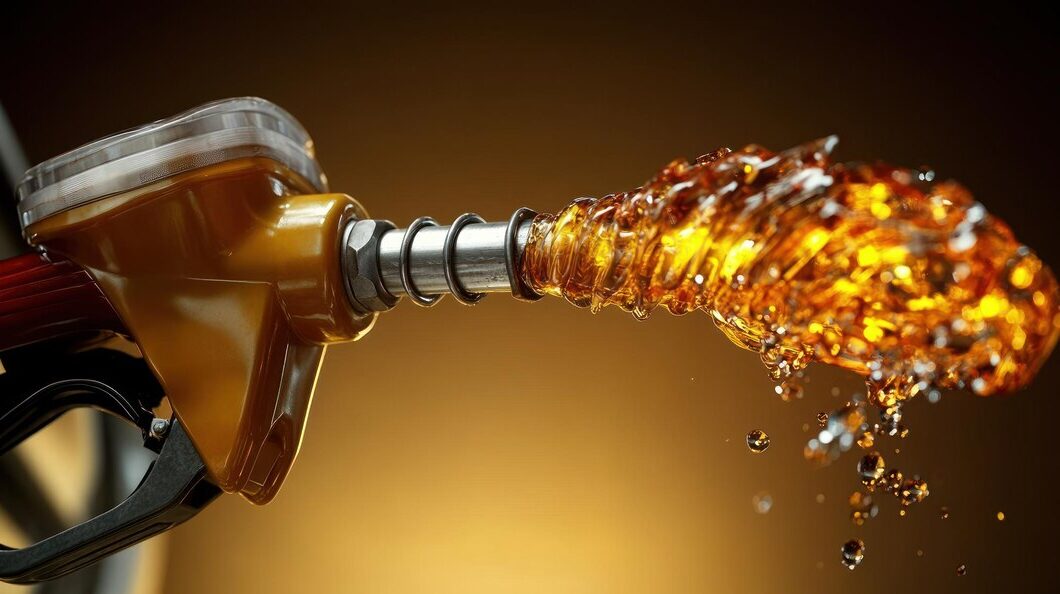
Gasoline
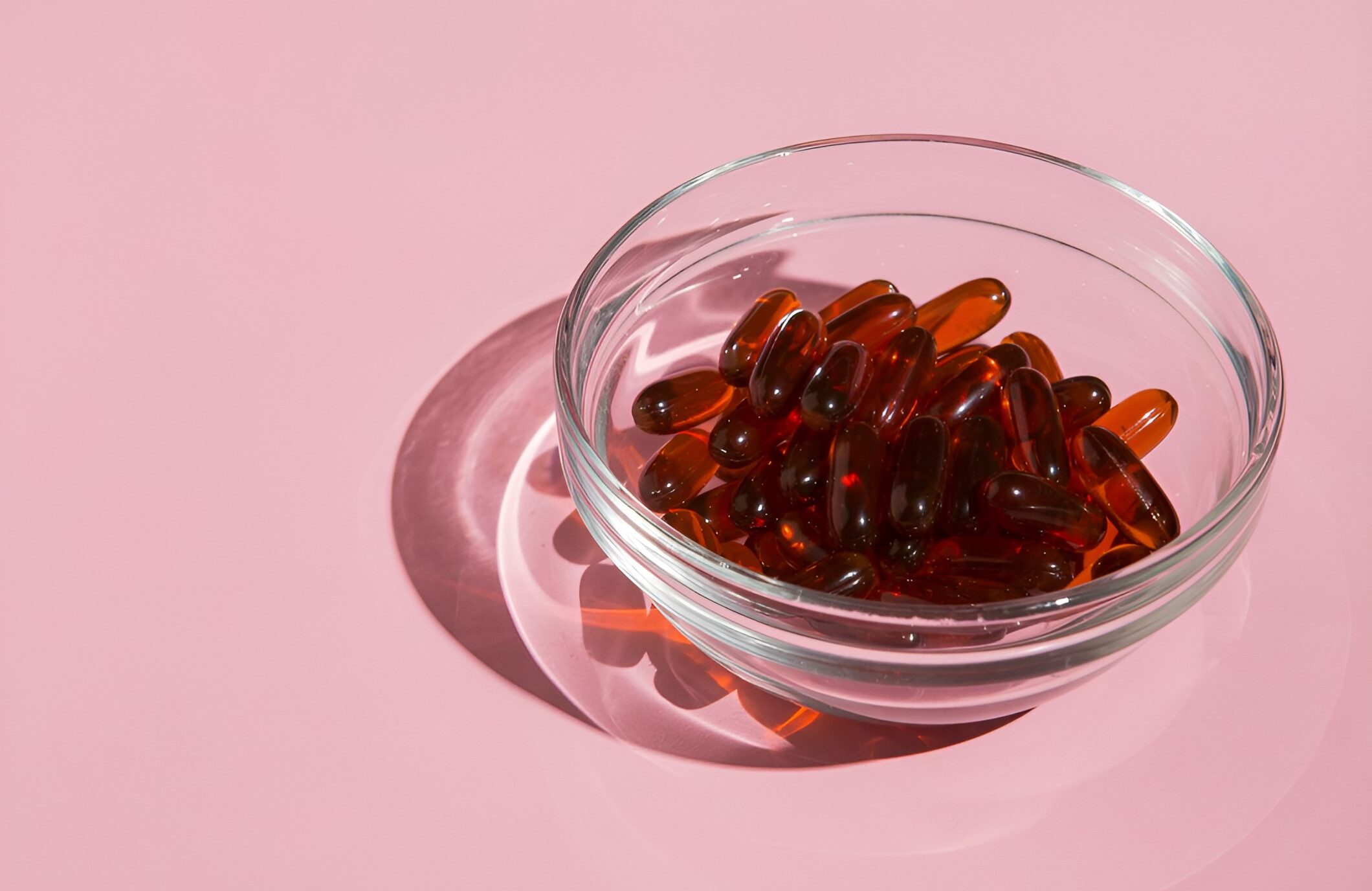
Gel capsules
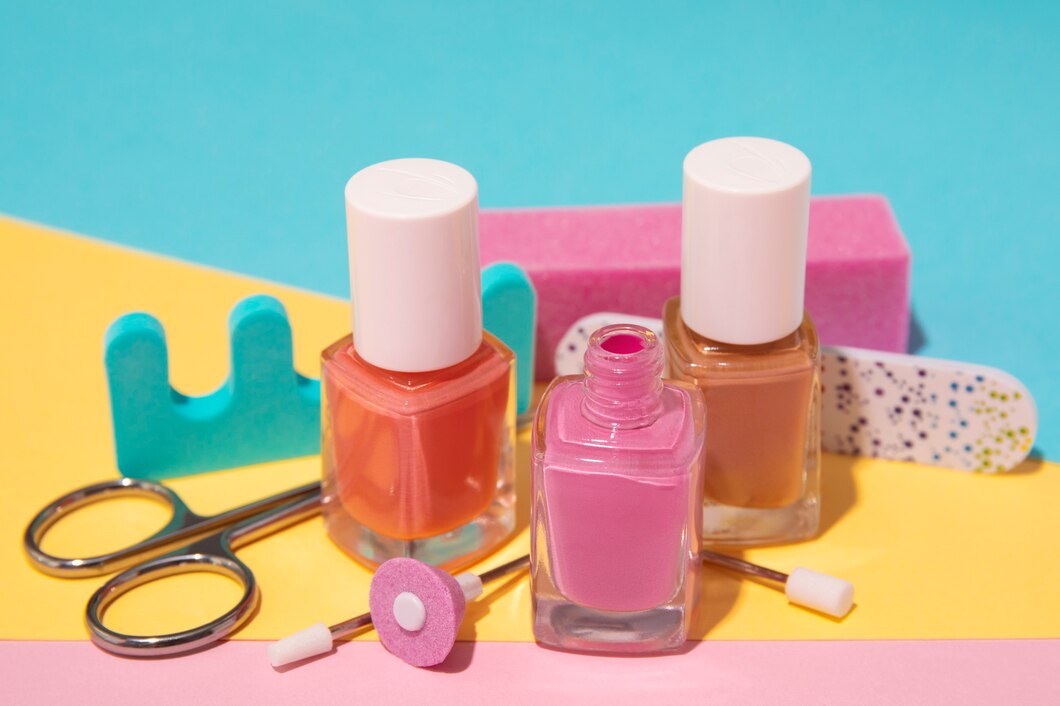
Gel nail polish

Gelatin capsules
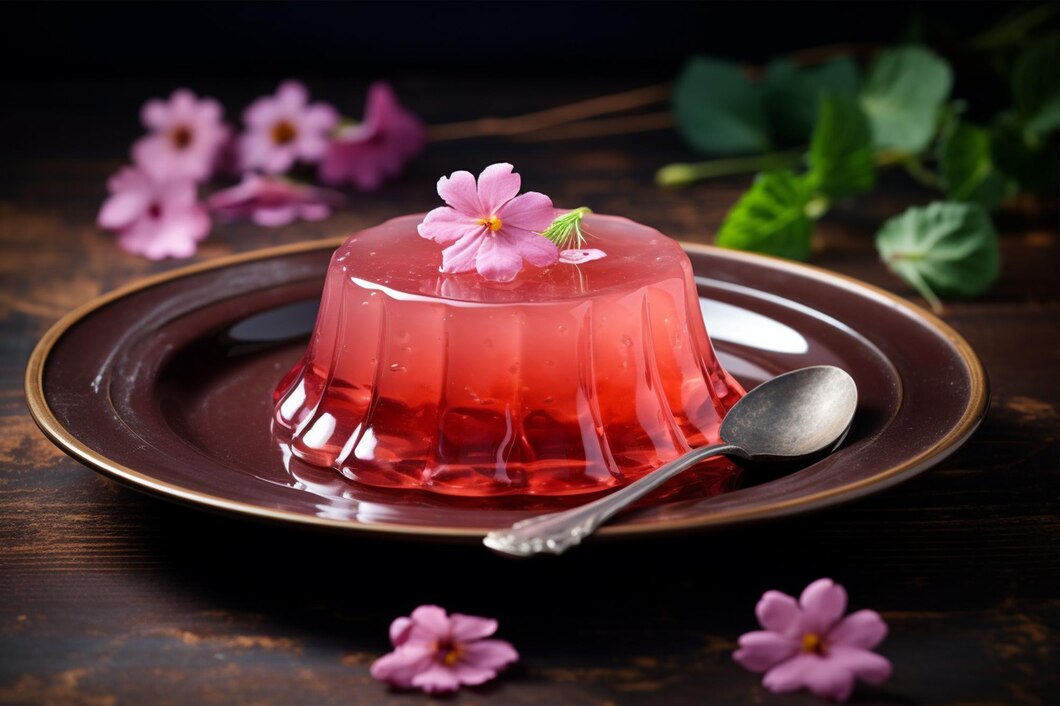
Gelatin desserts
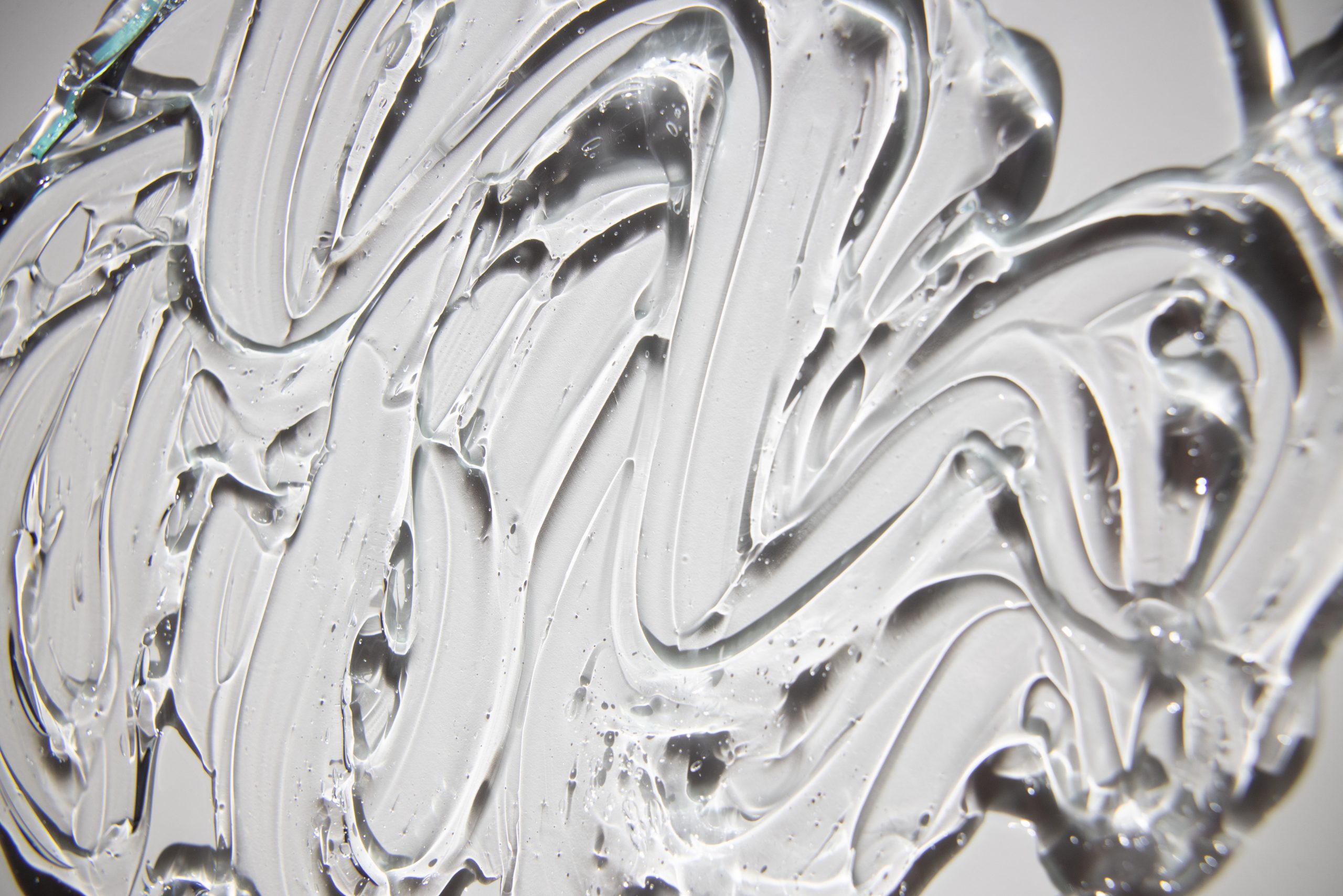
Gels
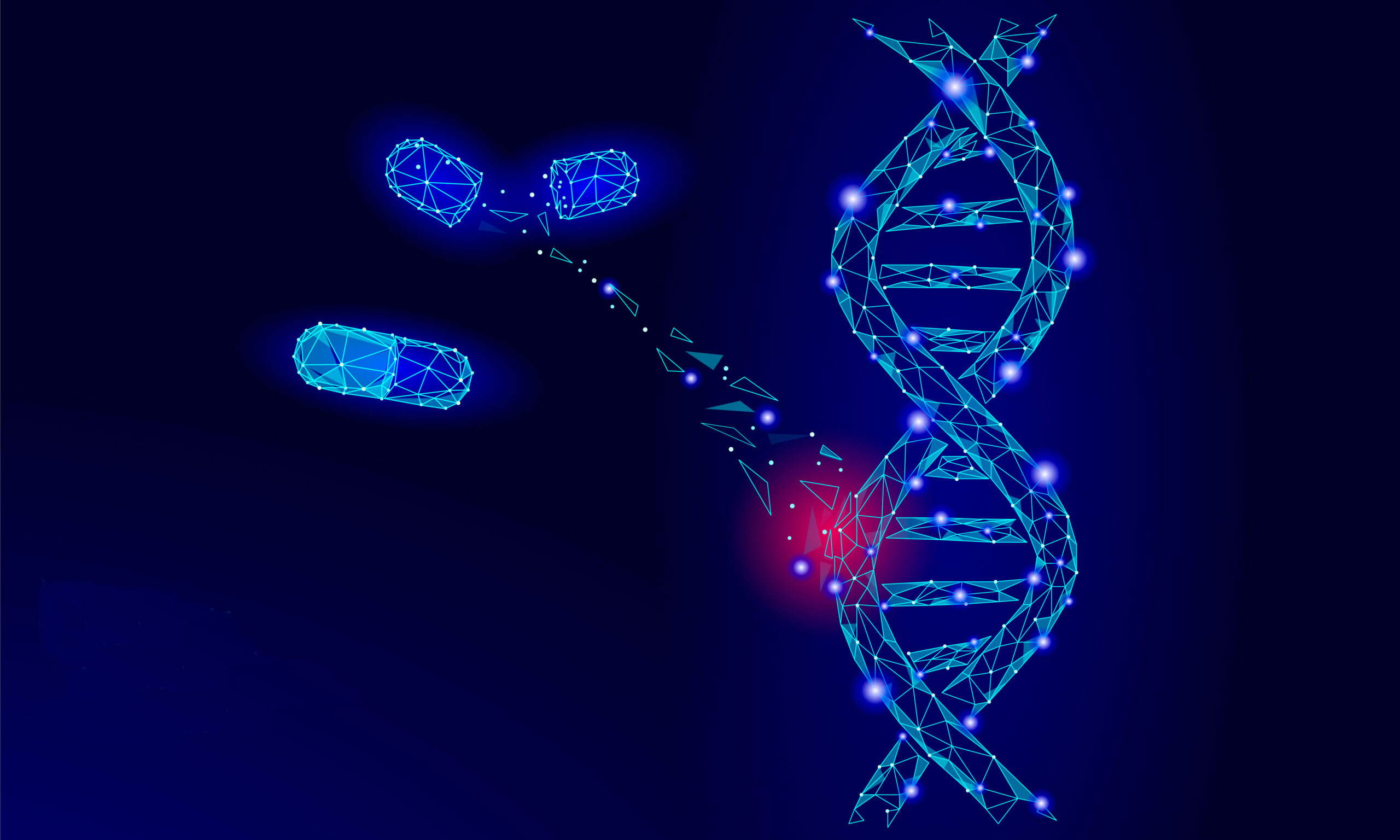
Gene therapy
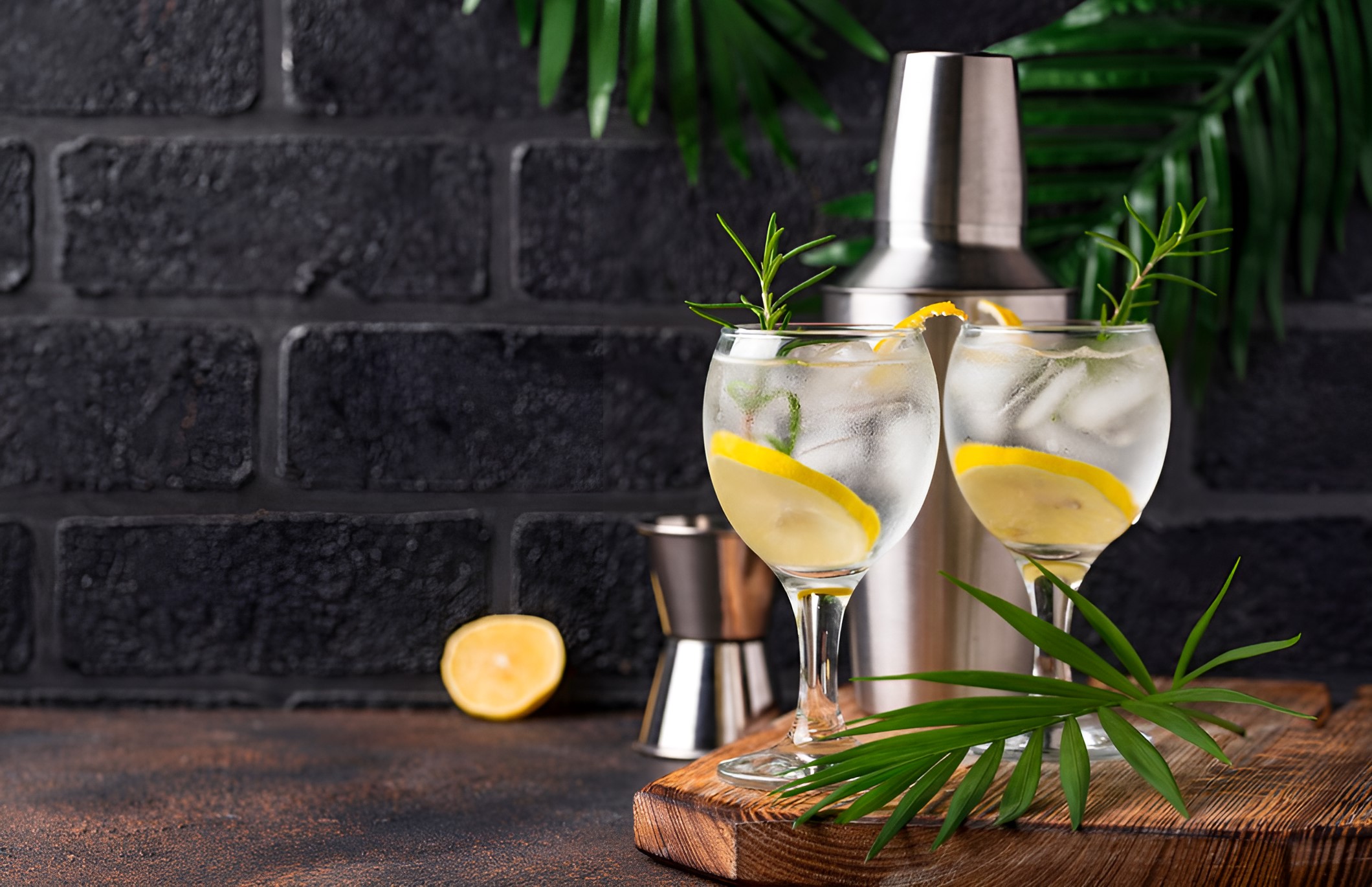
Gin
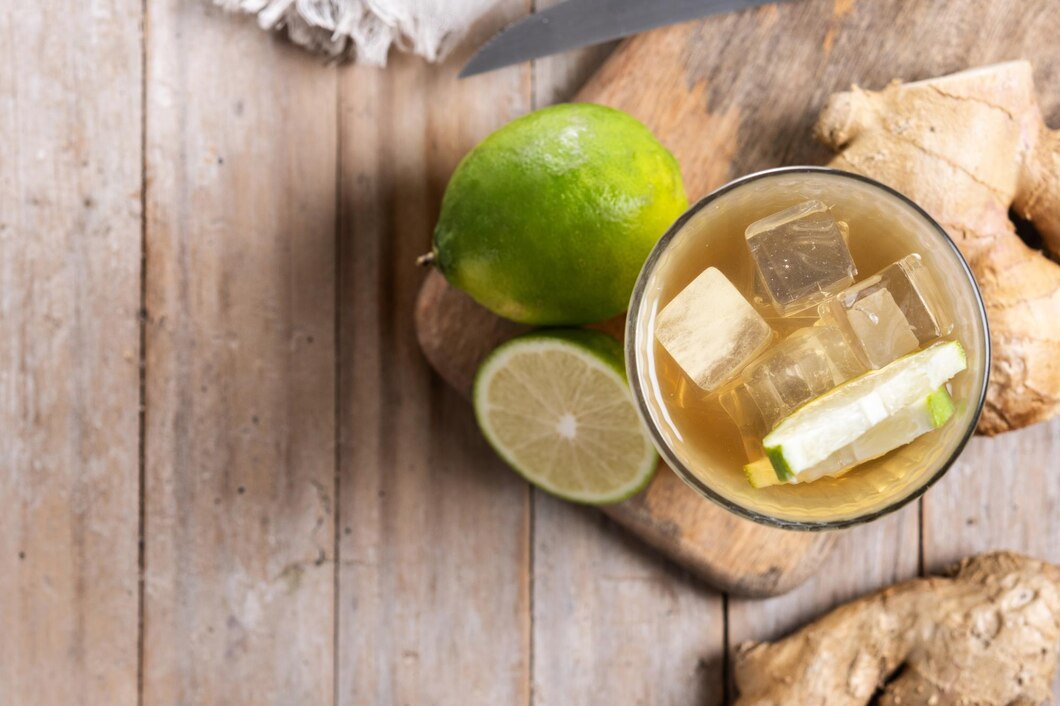
Ginger ale
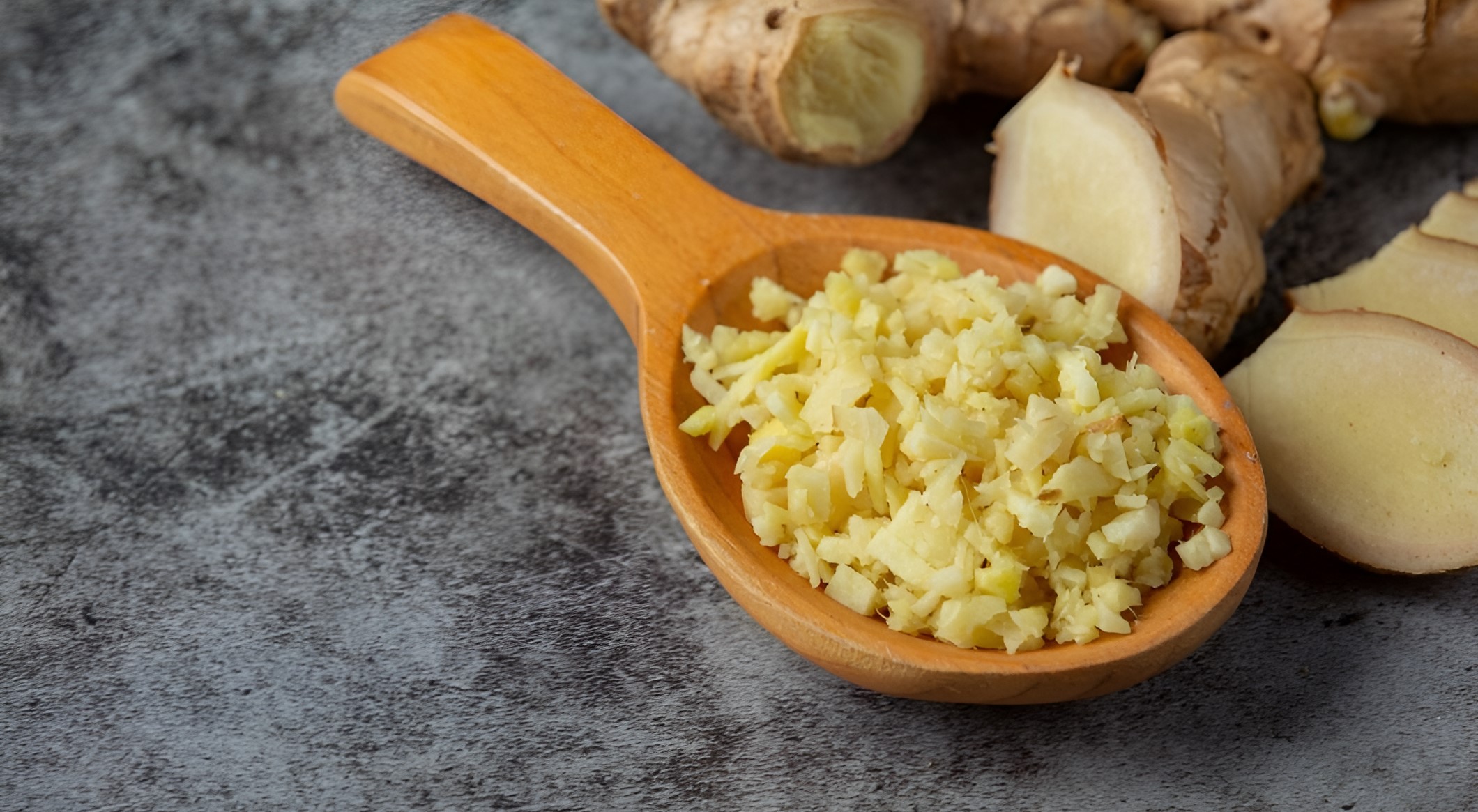
Ginger paste
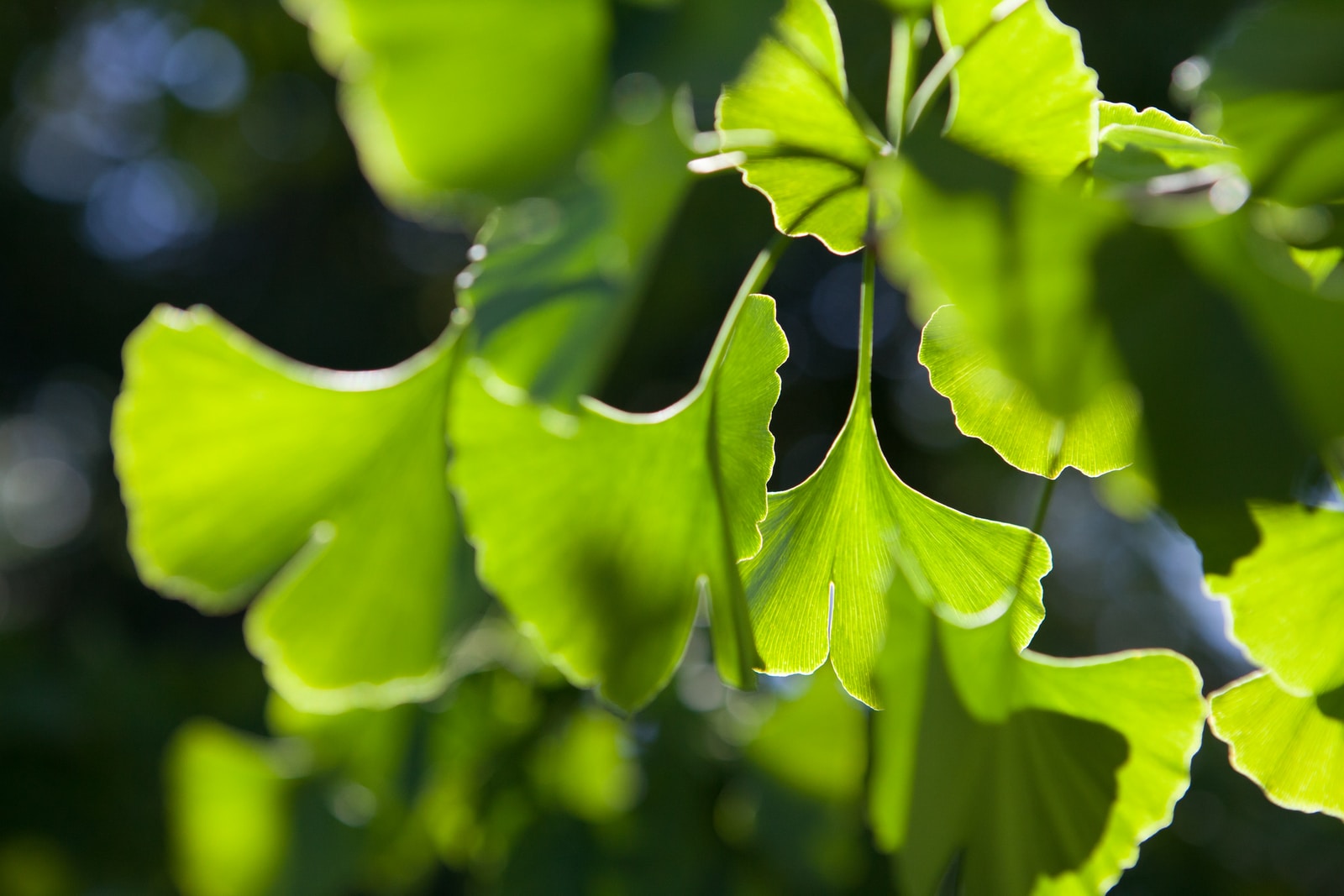
Ginkgo extract
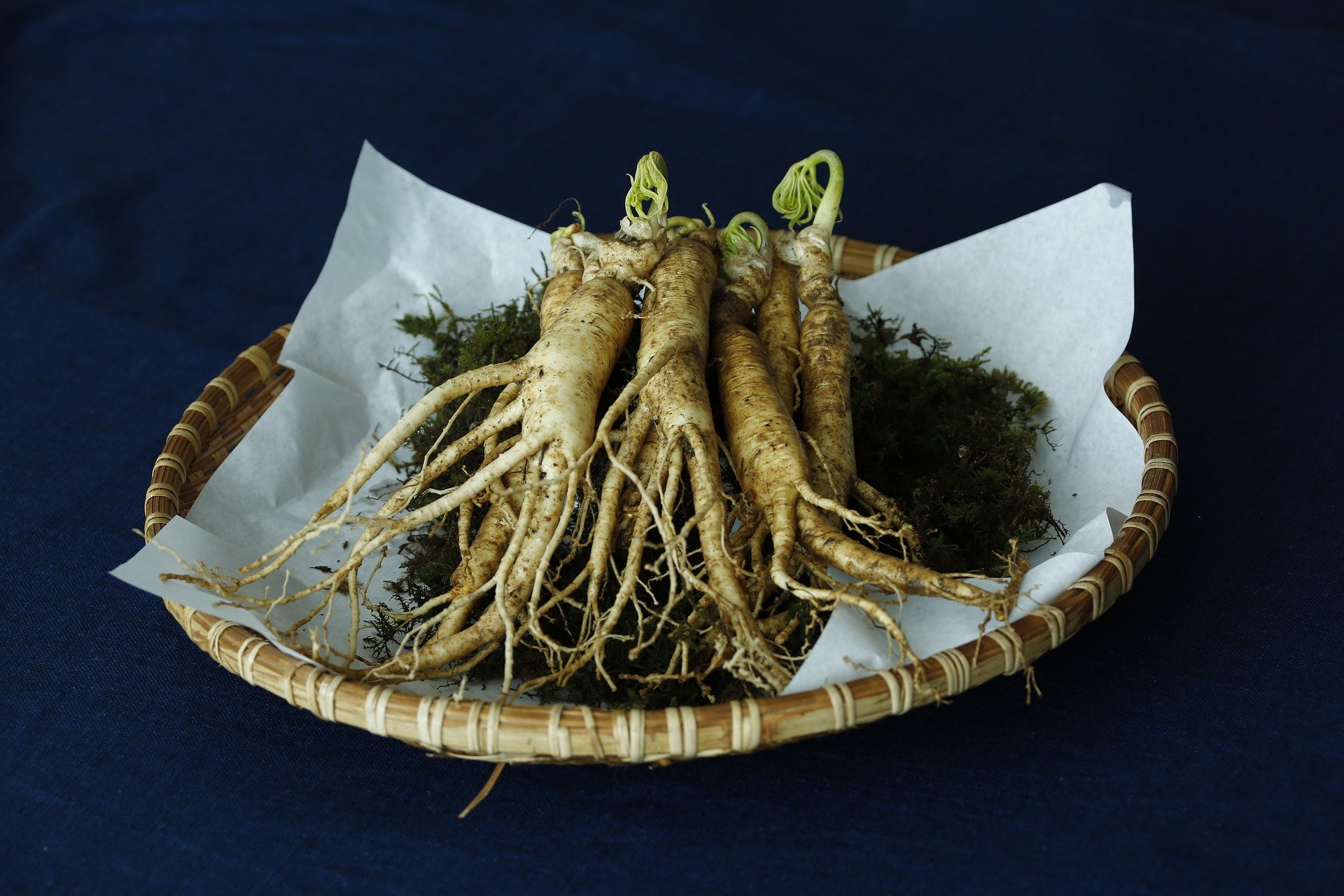
Ginseng extract
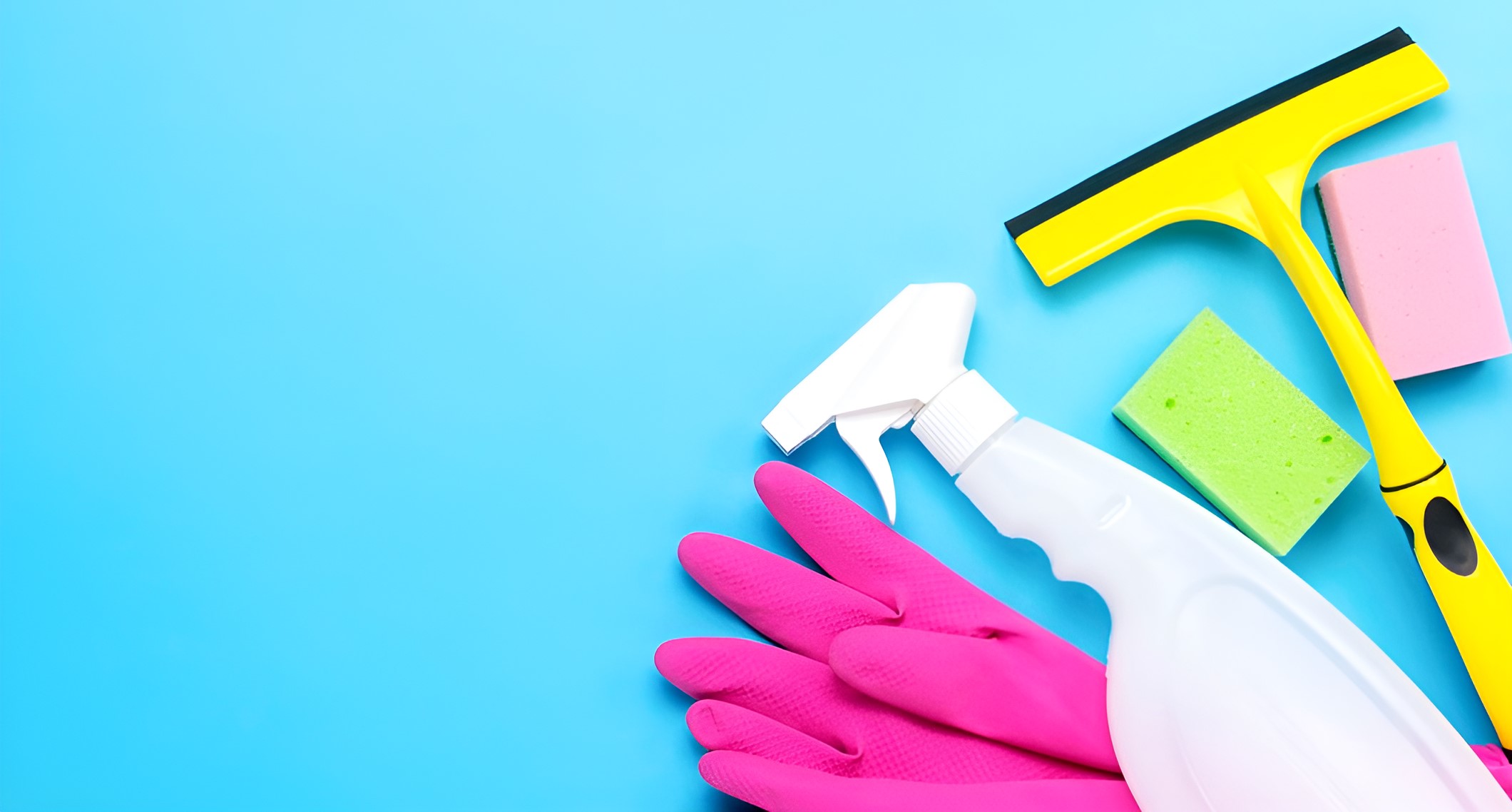
Glass cleaner
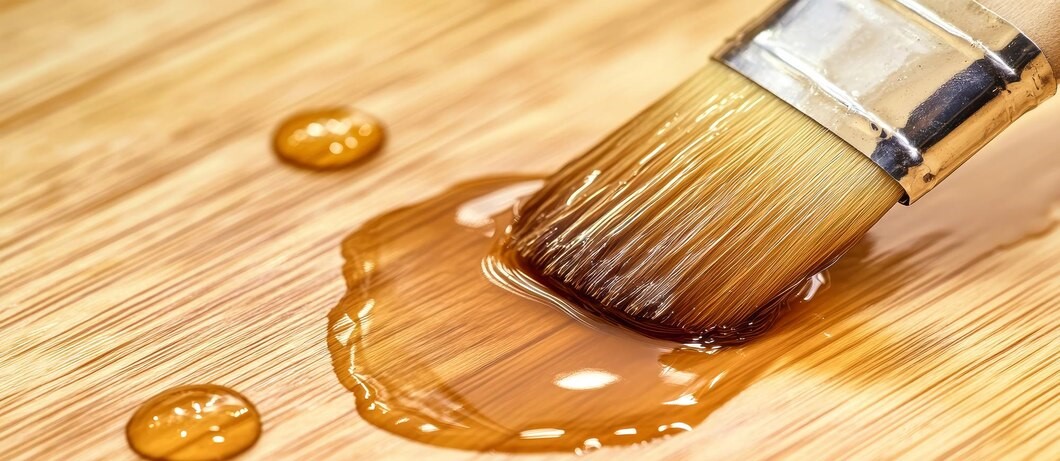
Gloss varnish
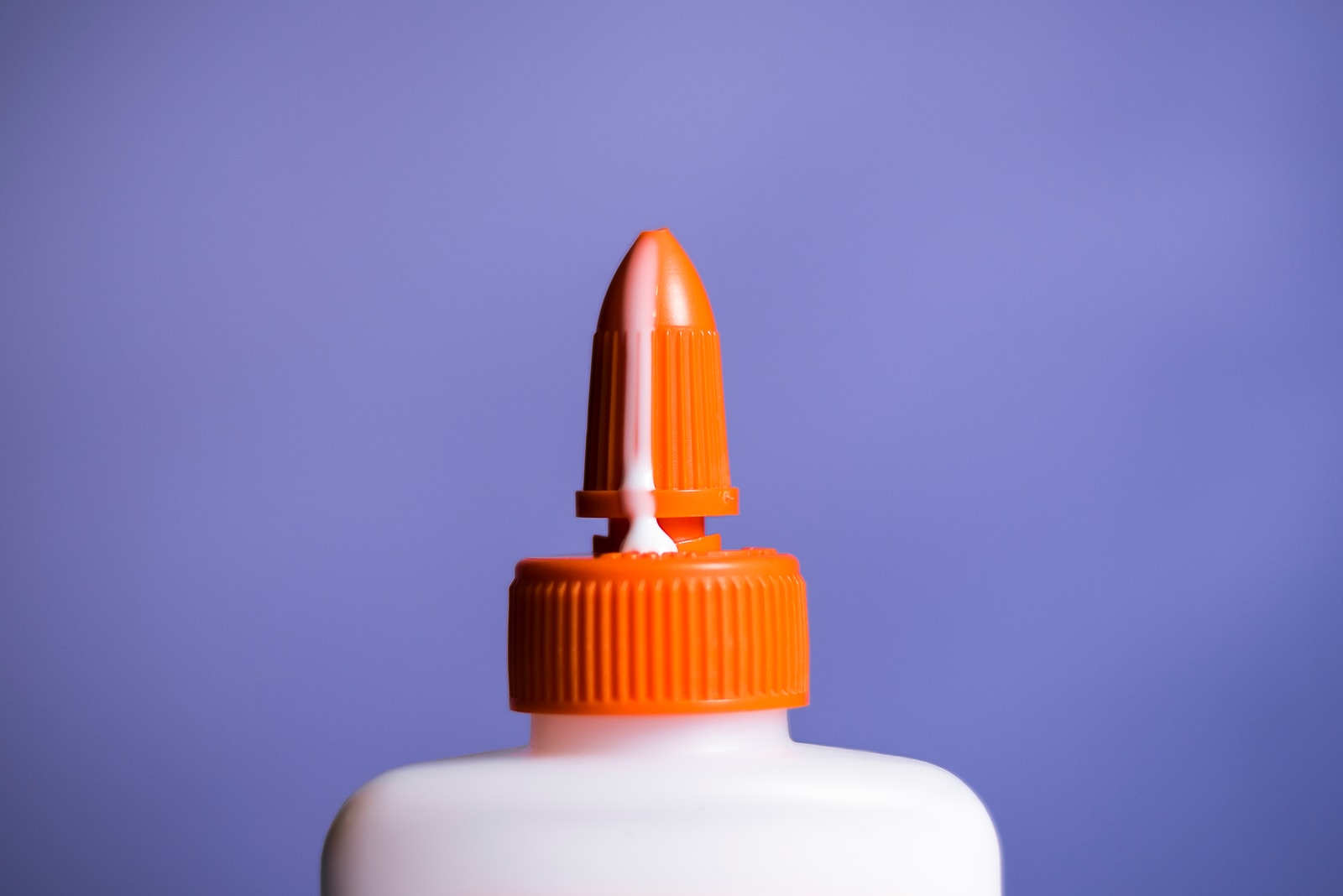
Glue
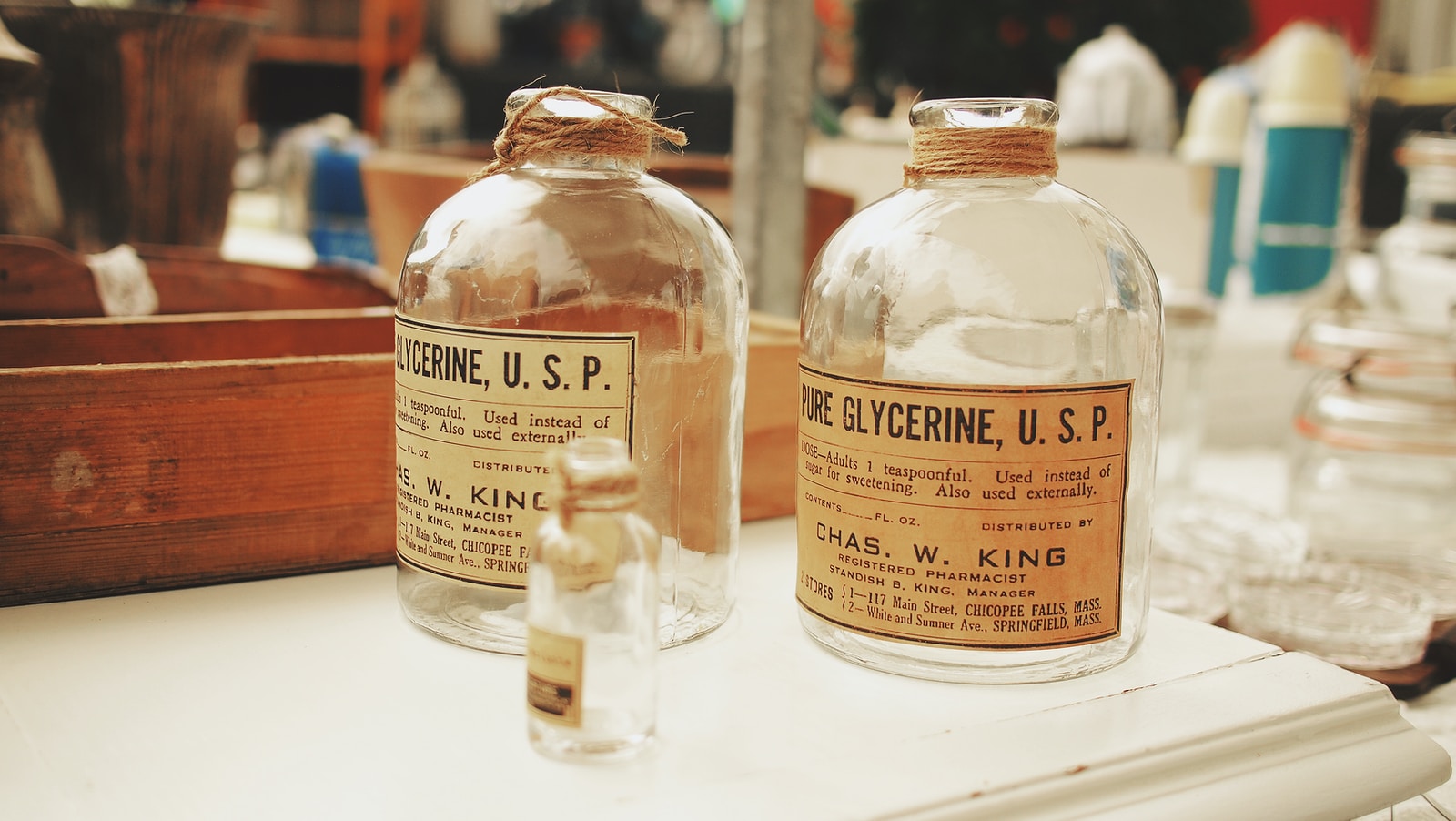
Glycerine
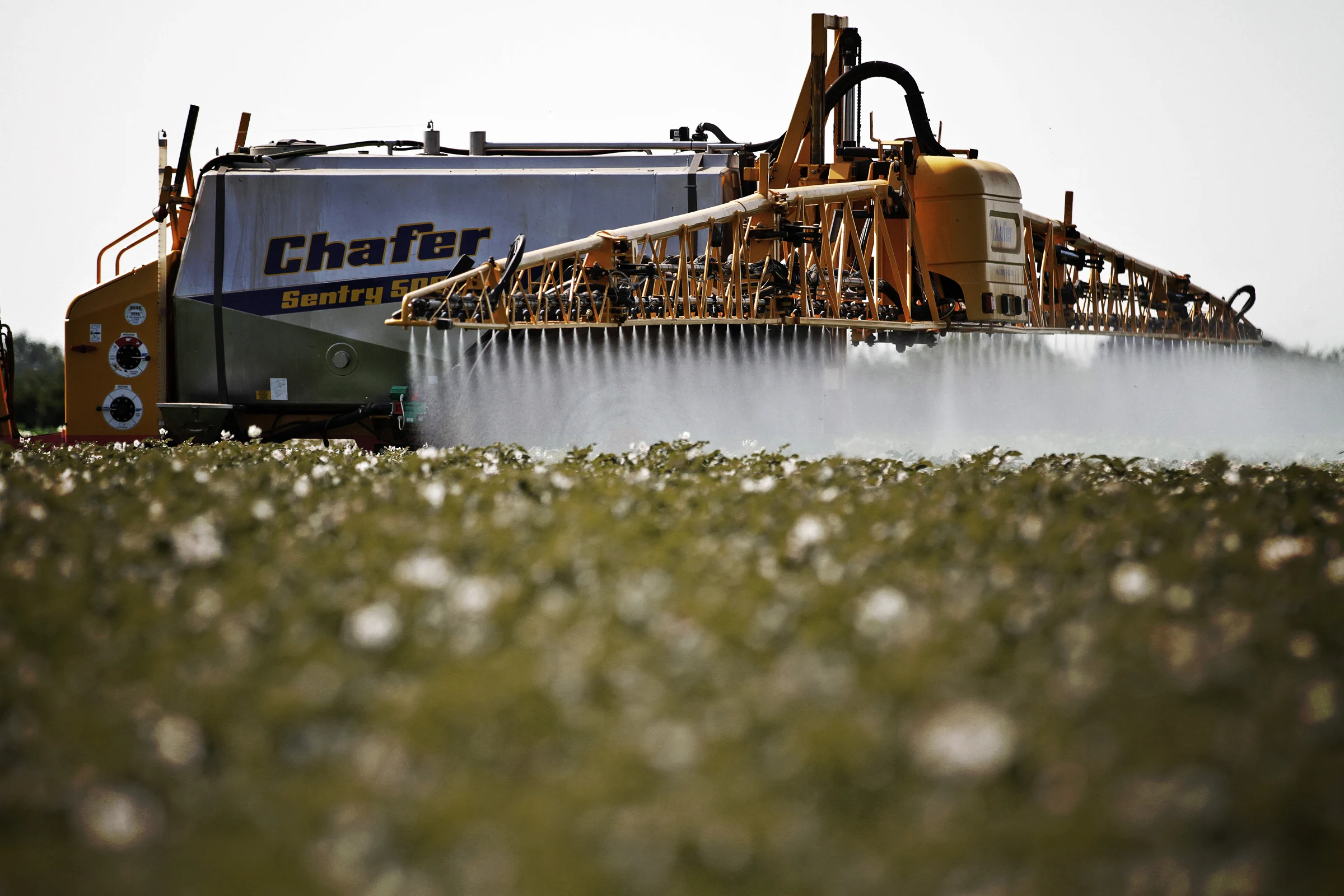
Glyphosate herbicides
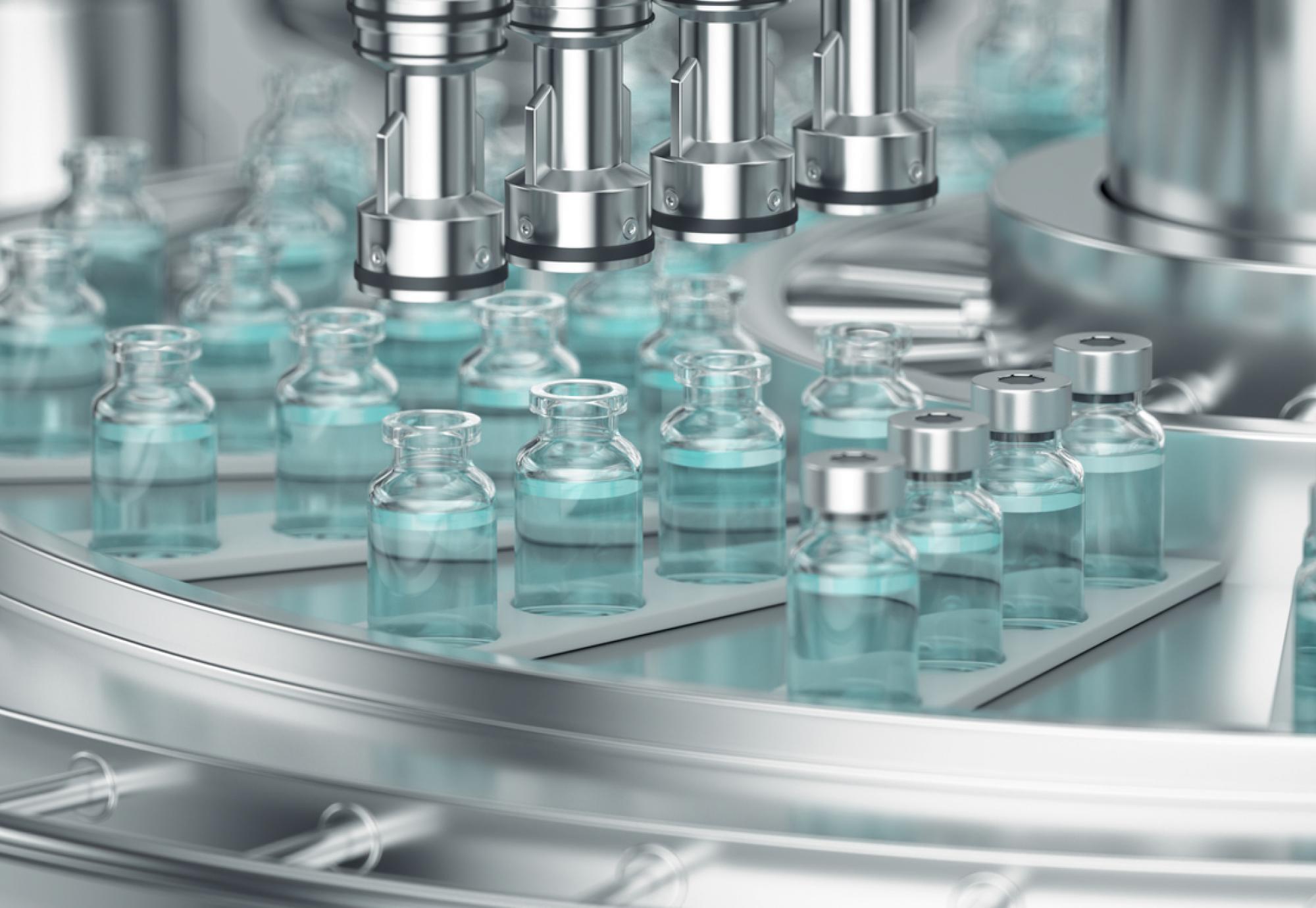
Gmp radiopharmacy
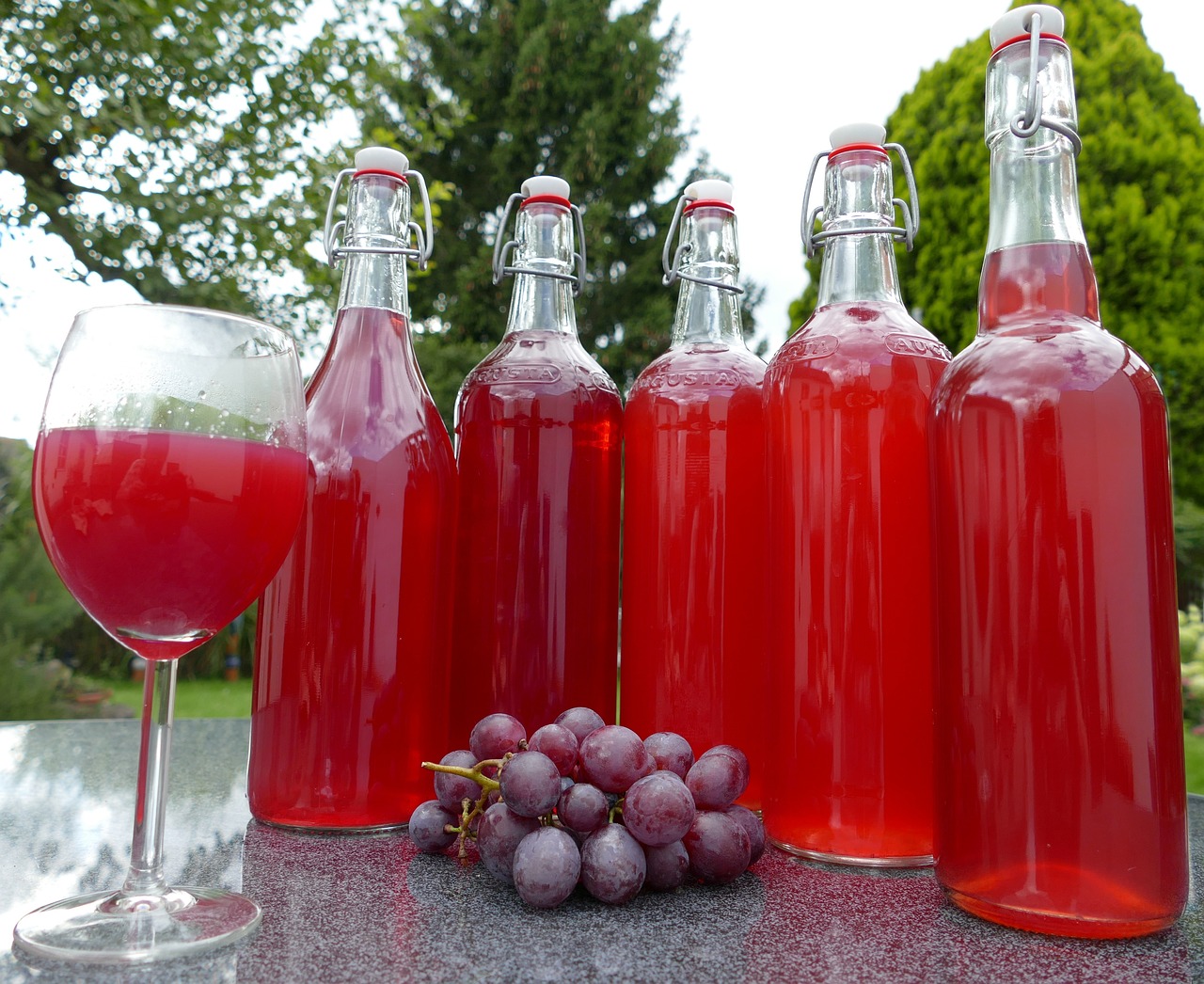
Grape Juice
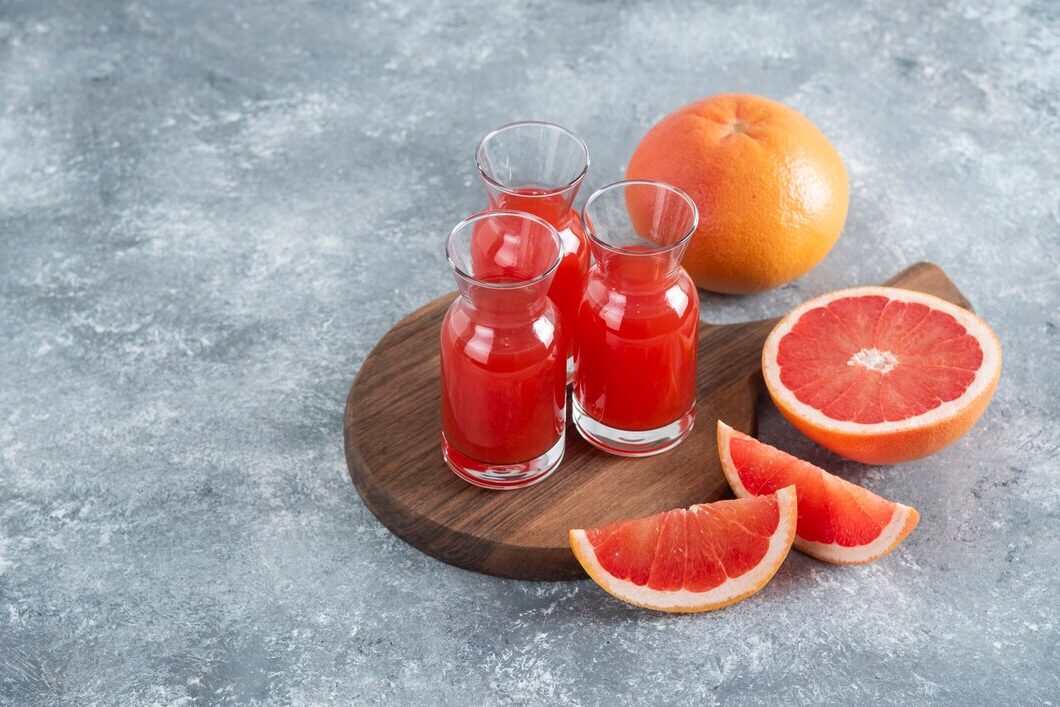
Grapefruit juice
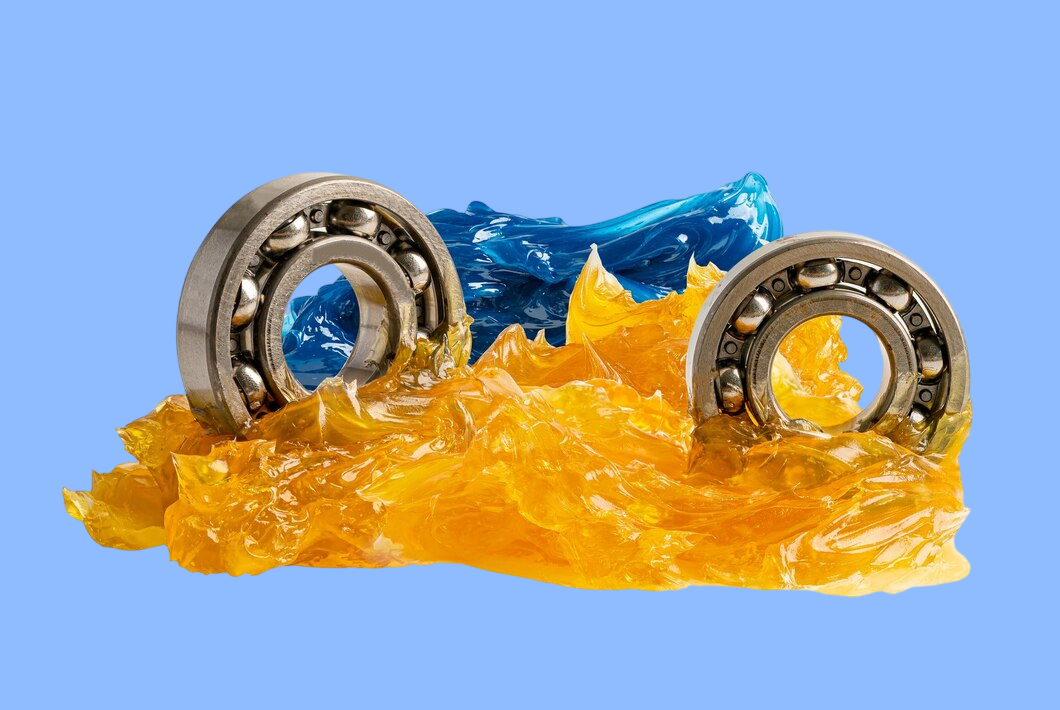
Grease
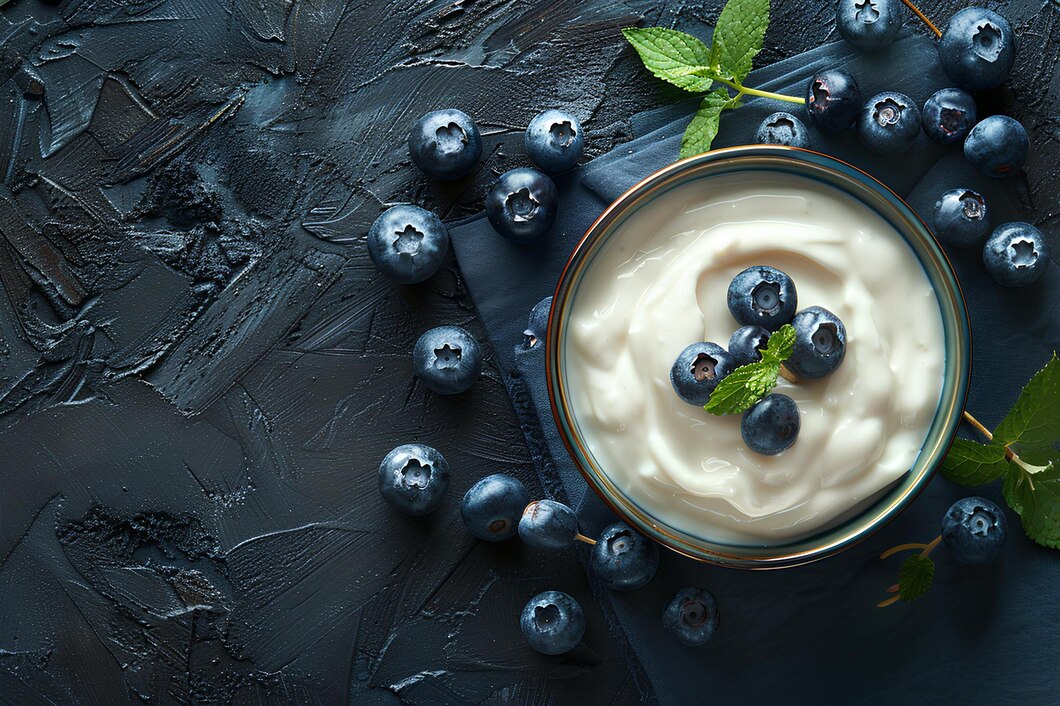
Greek yoghurt
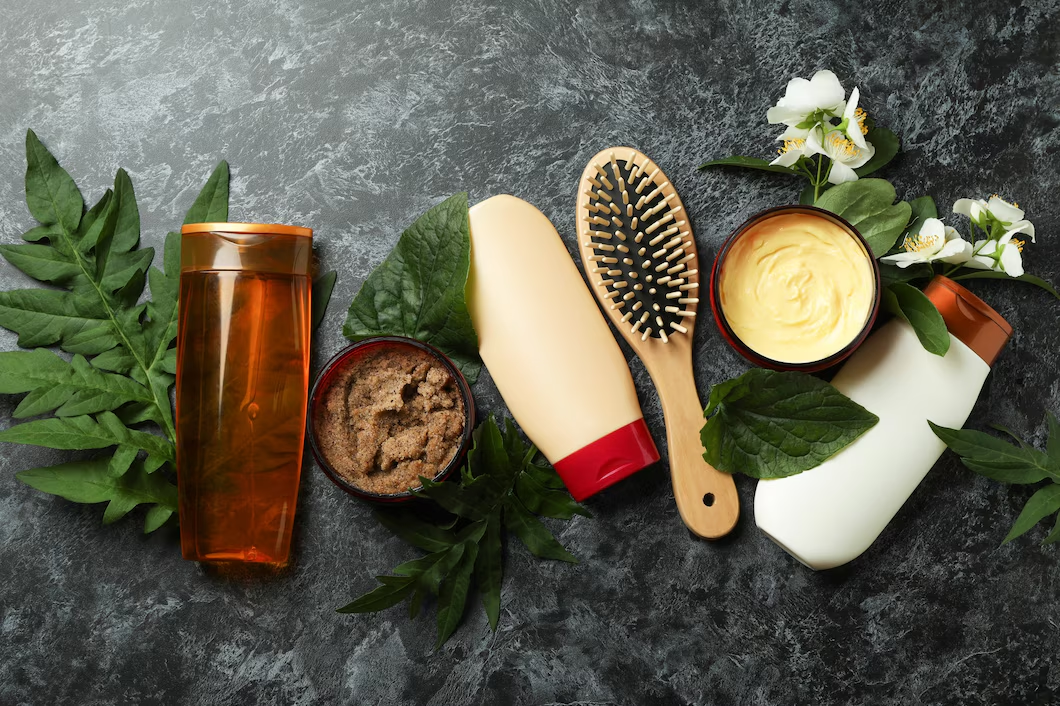
Hair care products
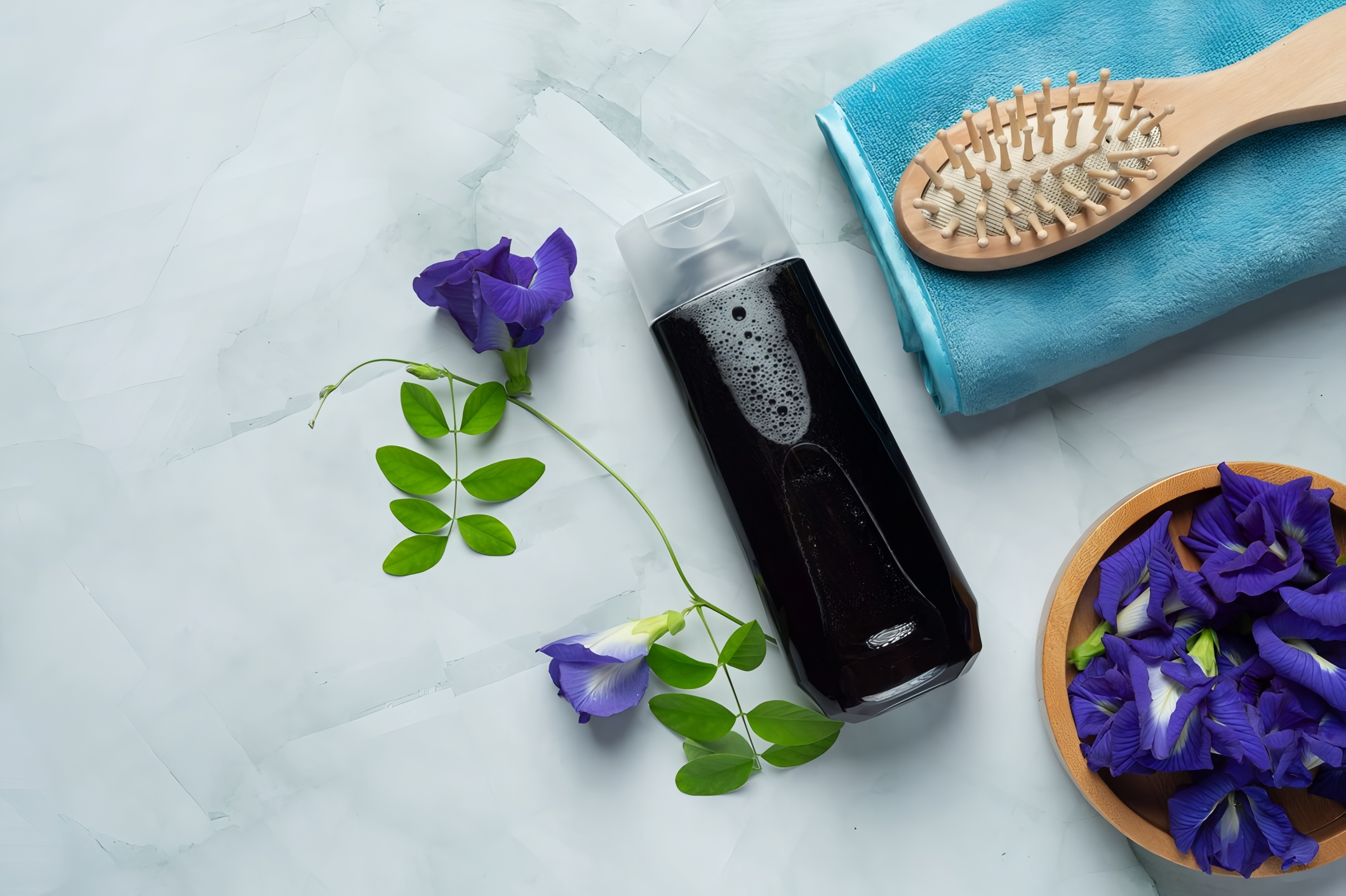
Hair conditioner
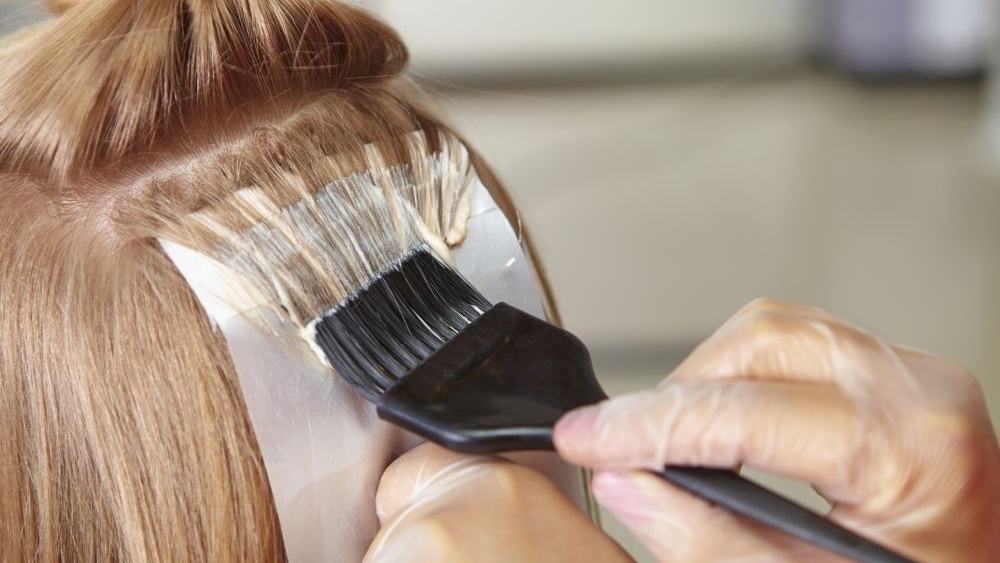
Hair dye kits
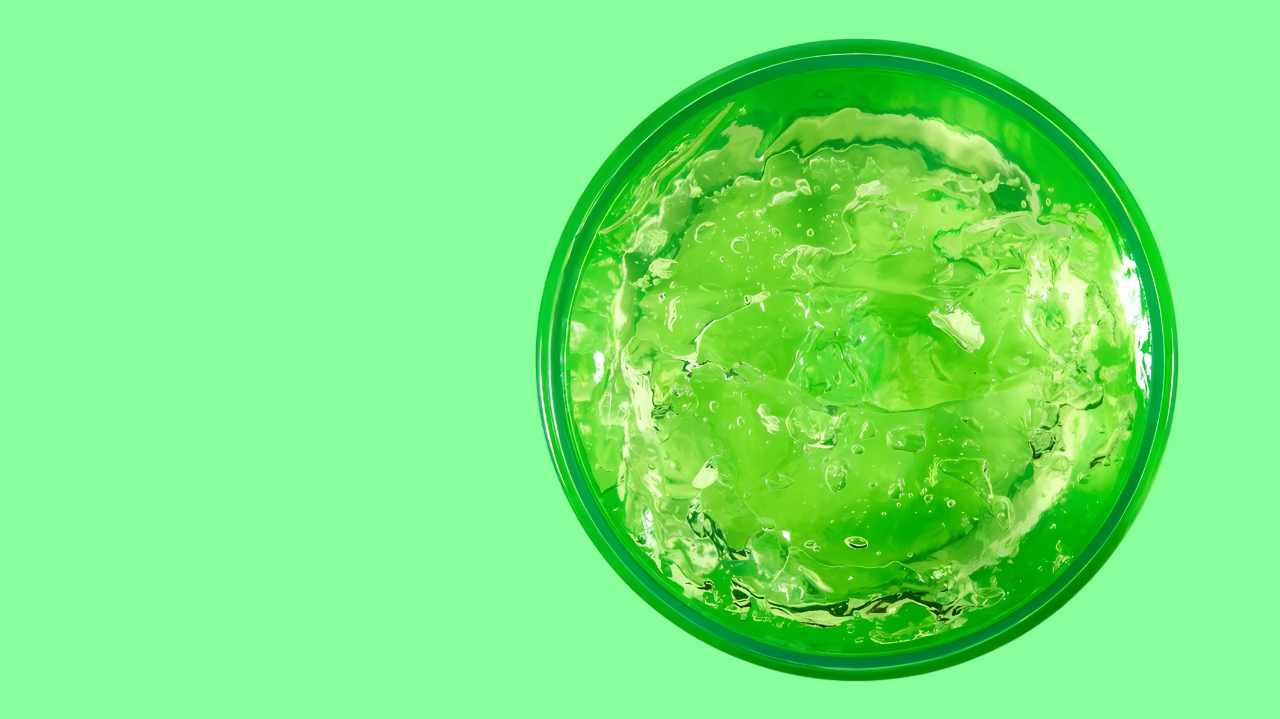
Hair gel
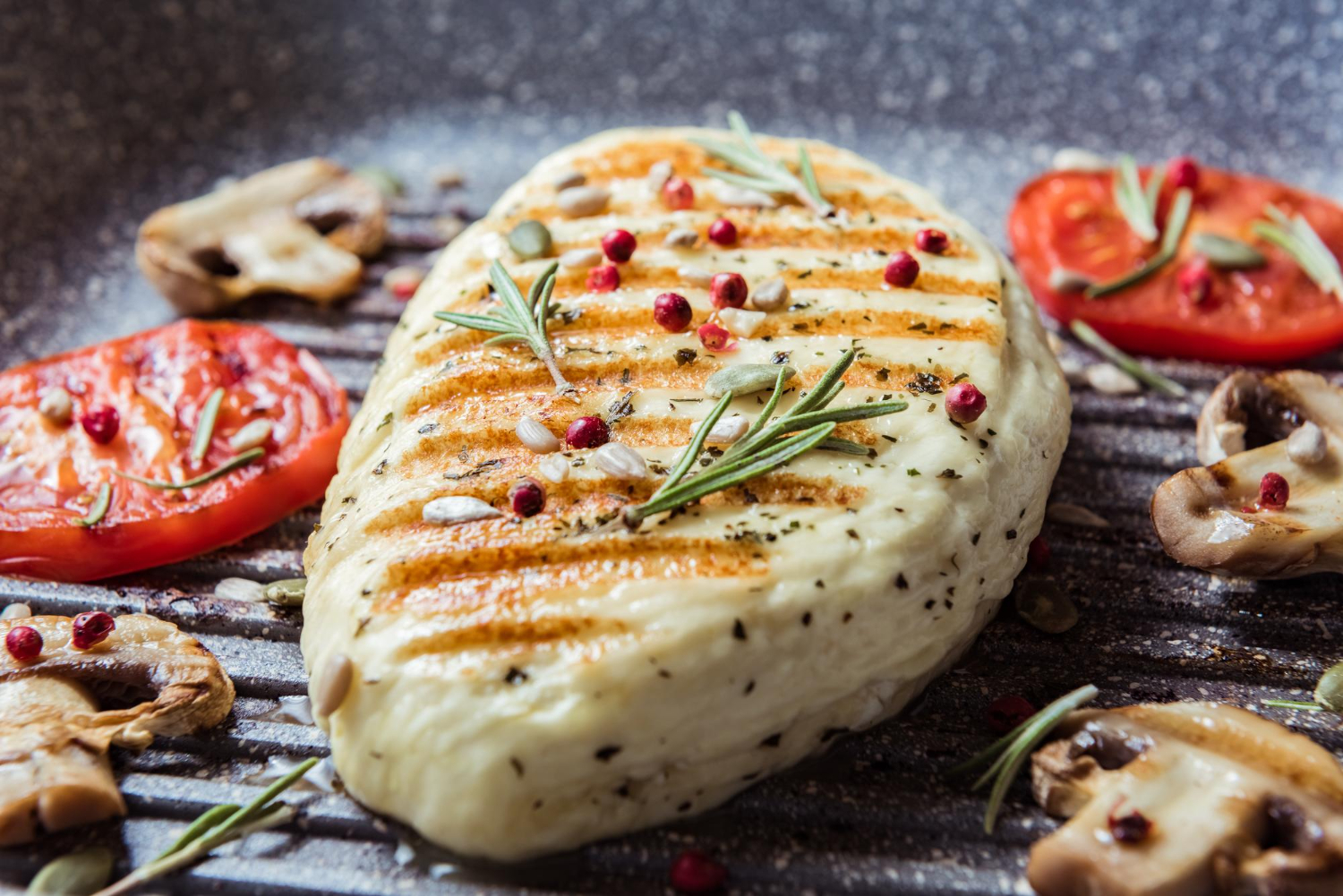
Halloumi

Halva
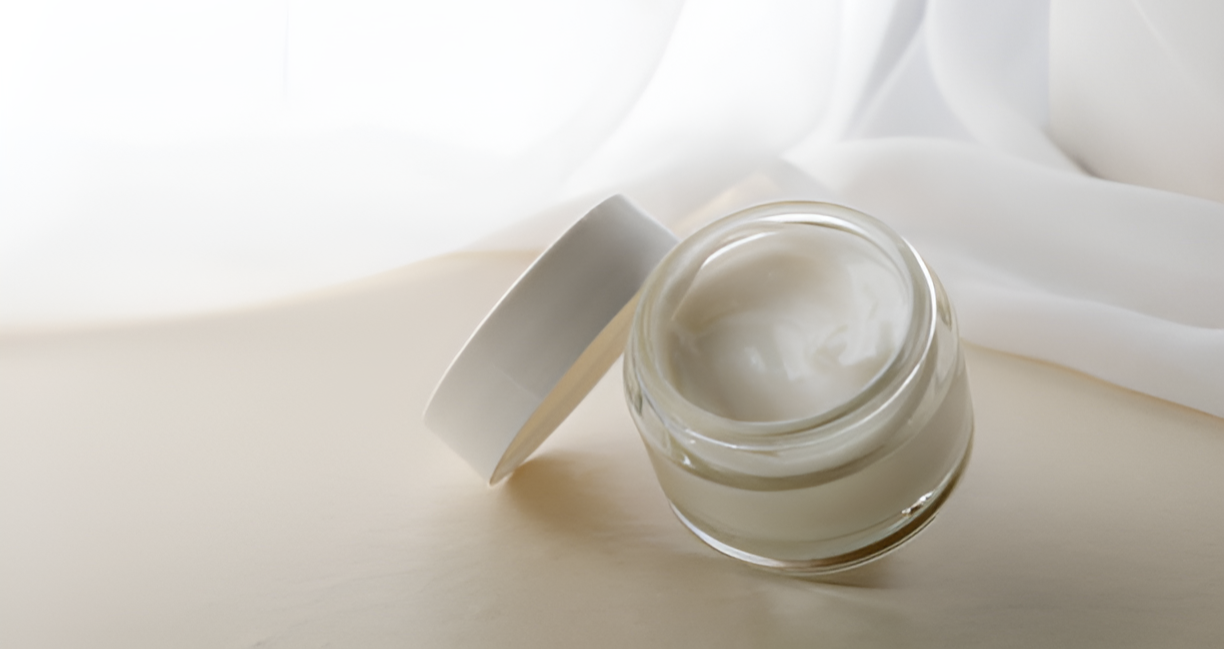
Hand cream
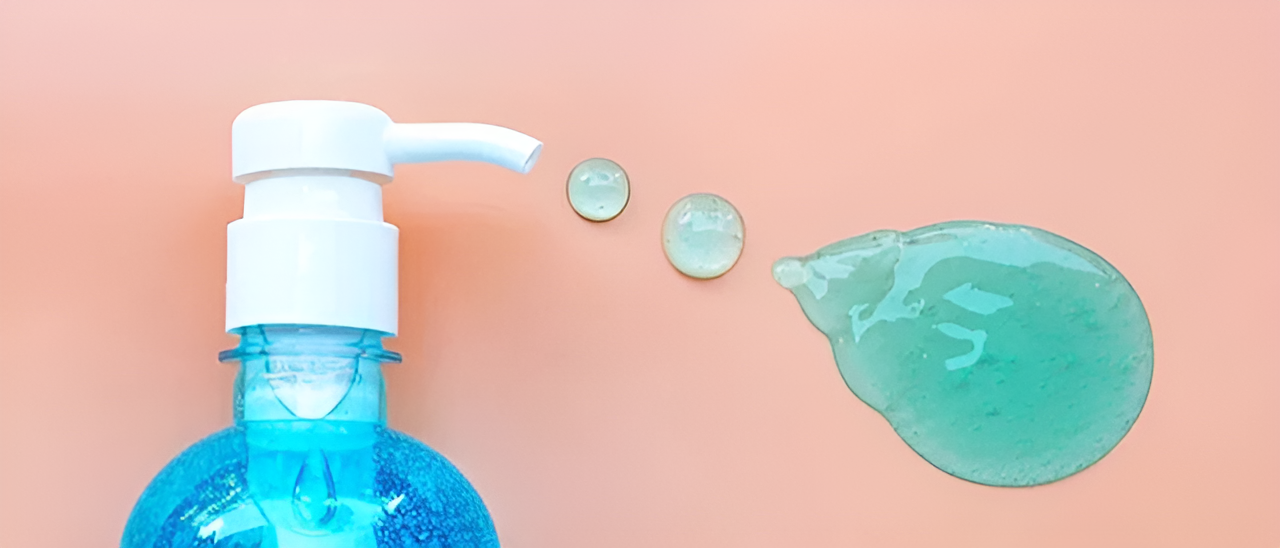
Hand sanitizer
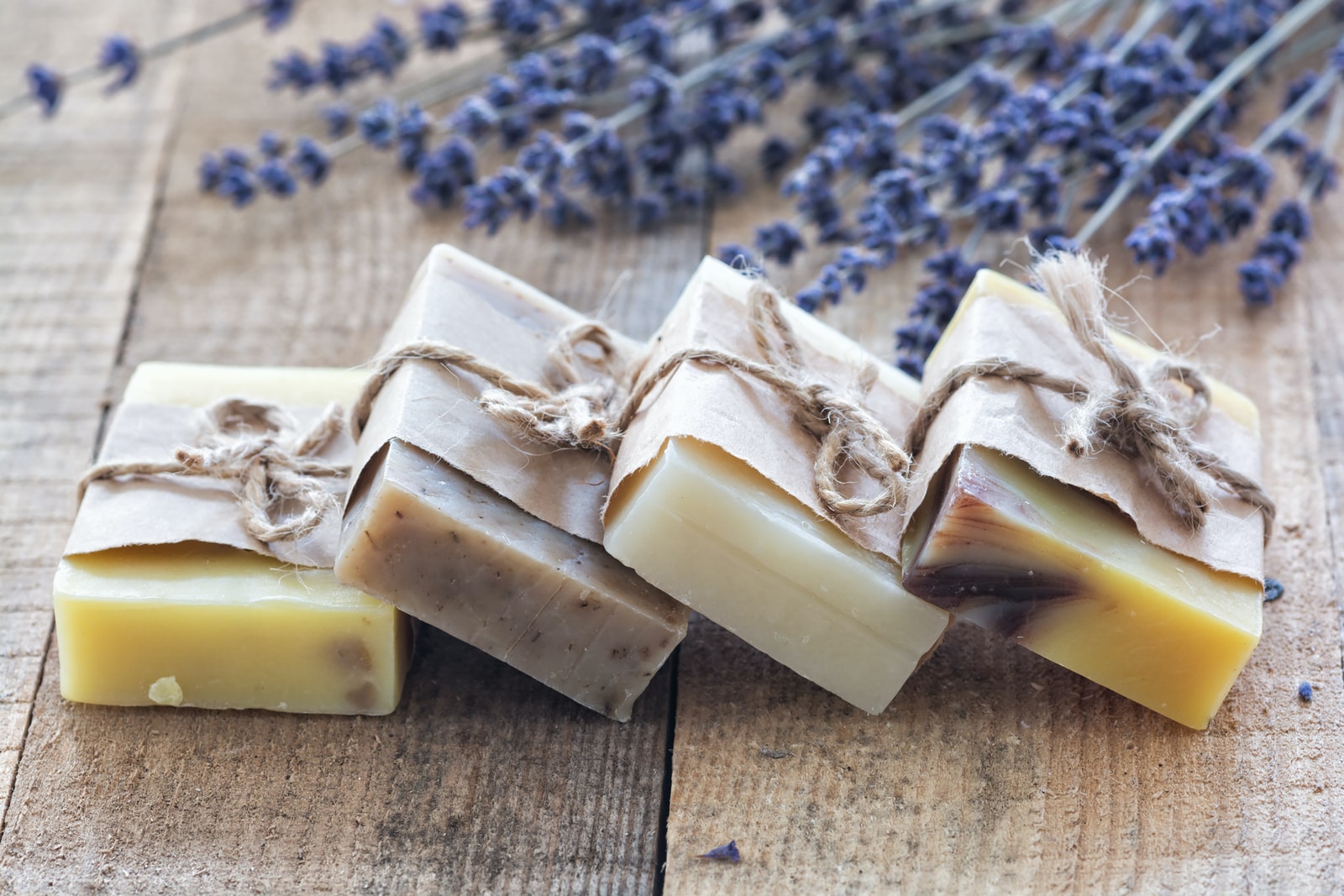
Hand soap
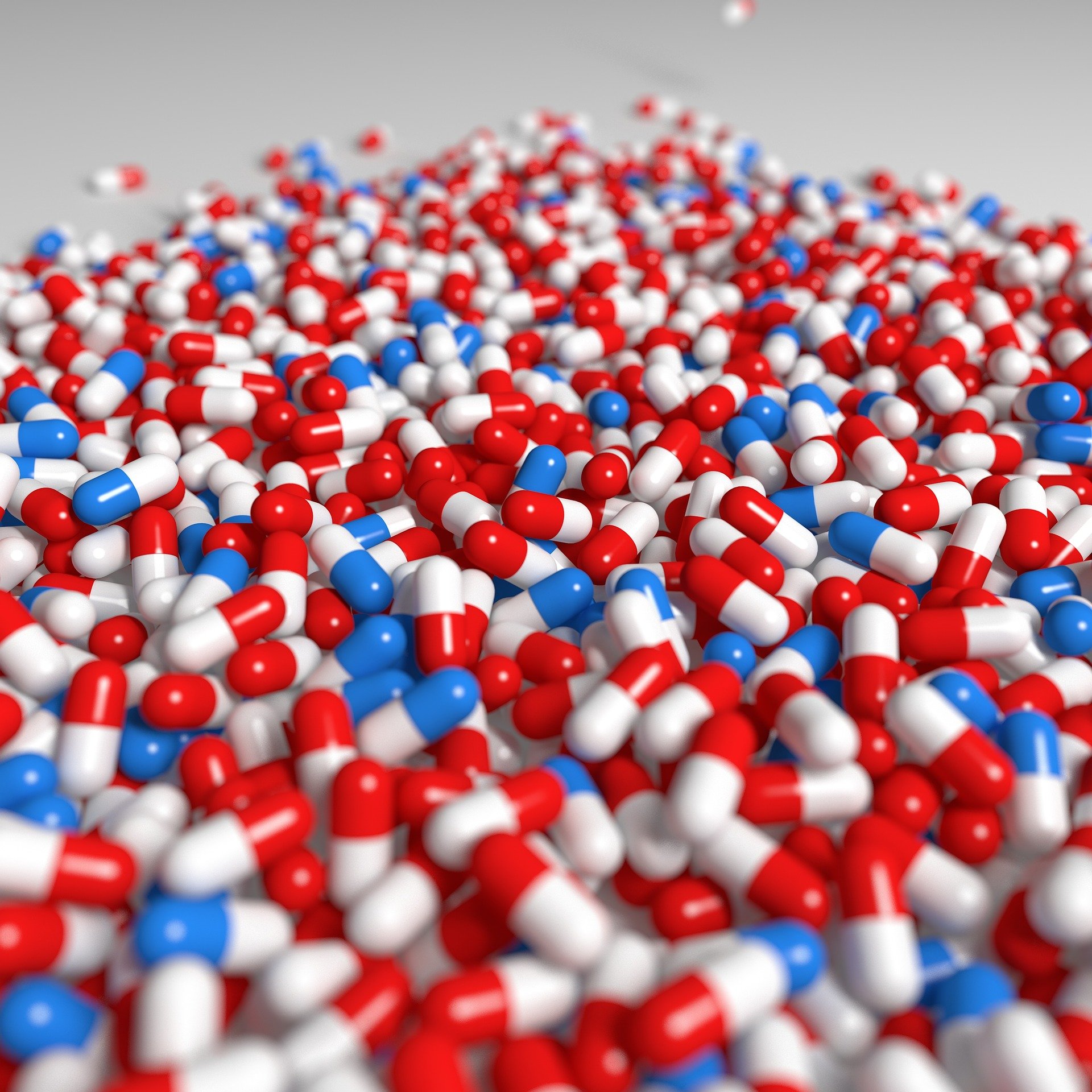
Hard gelatin capsules
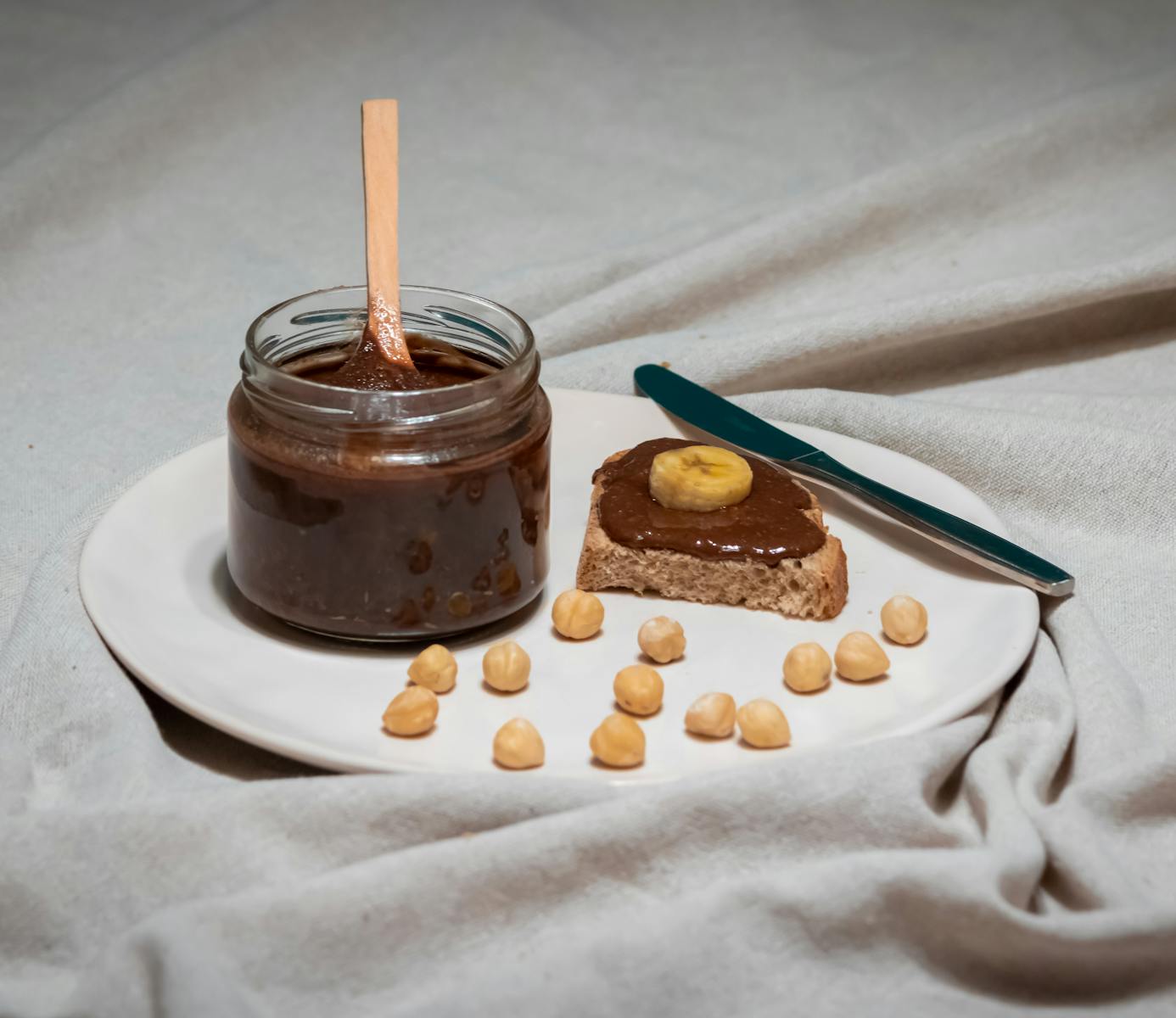
Hazelnut spread

Hazelnuts
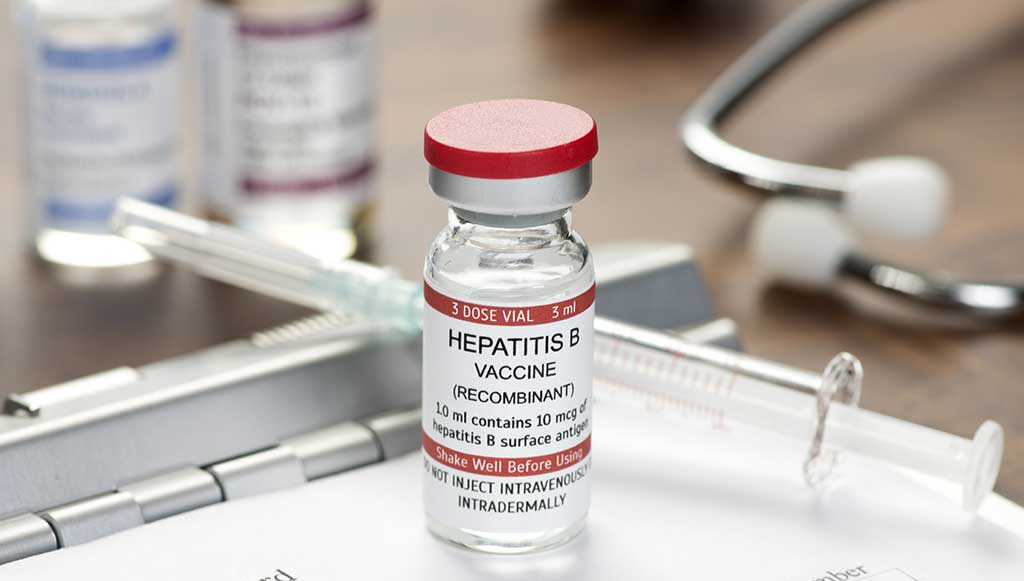
Hepatitis b vaccines
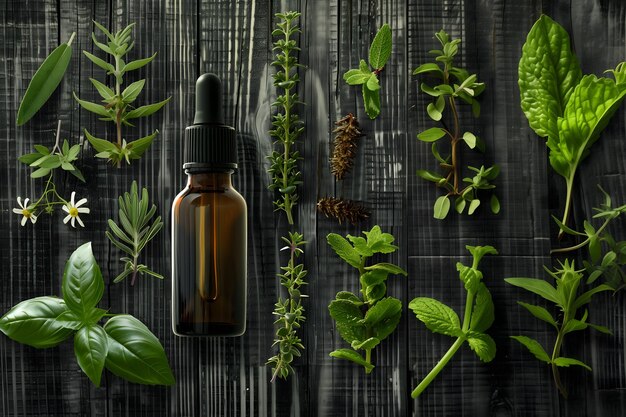
Herbal Extracts
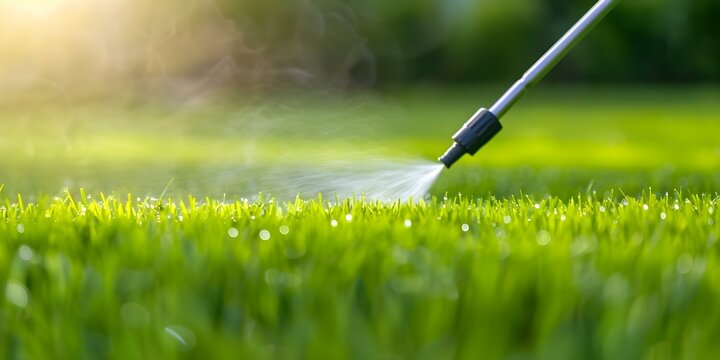
Herbicides
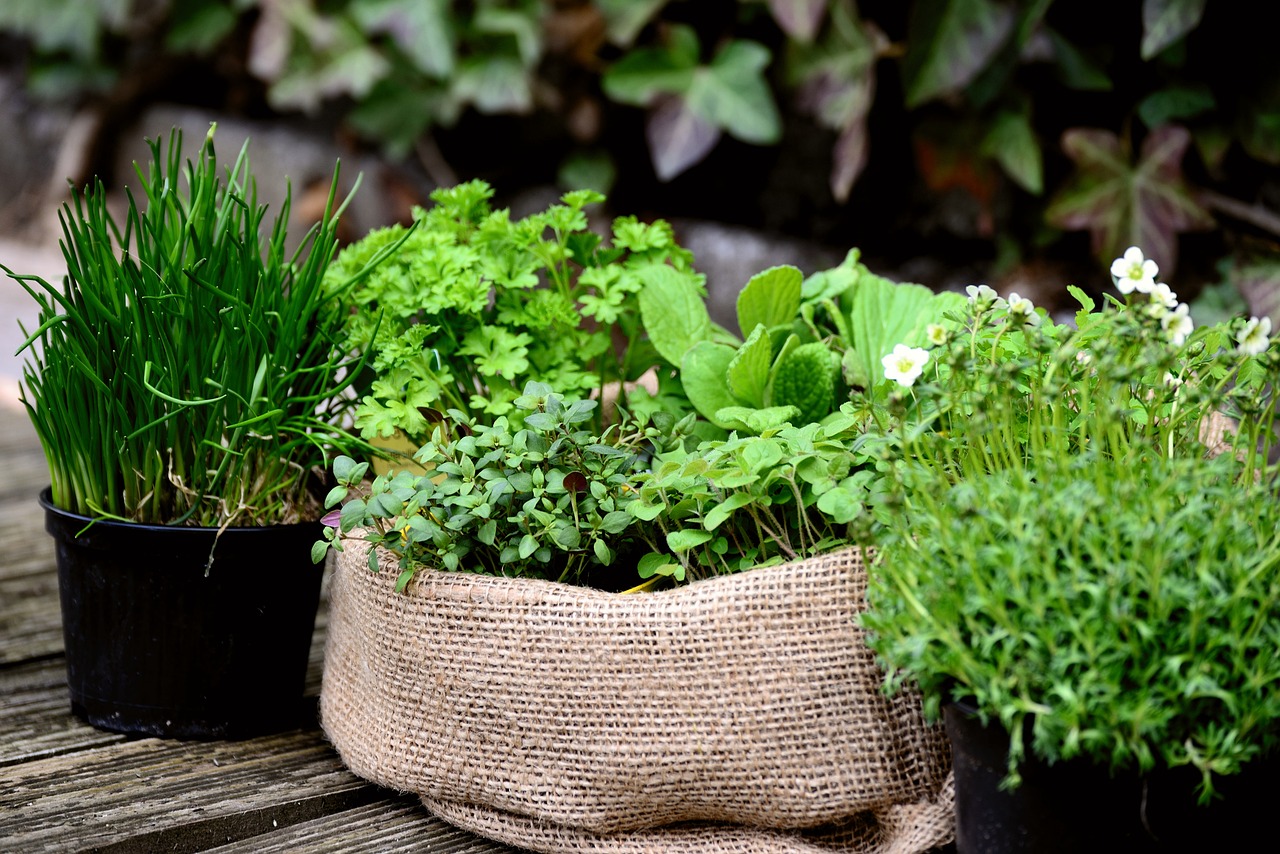
Herbs
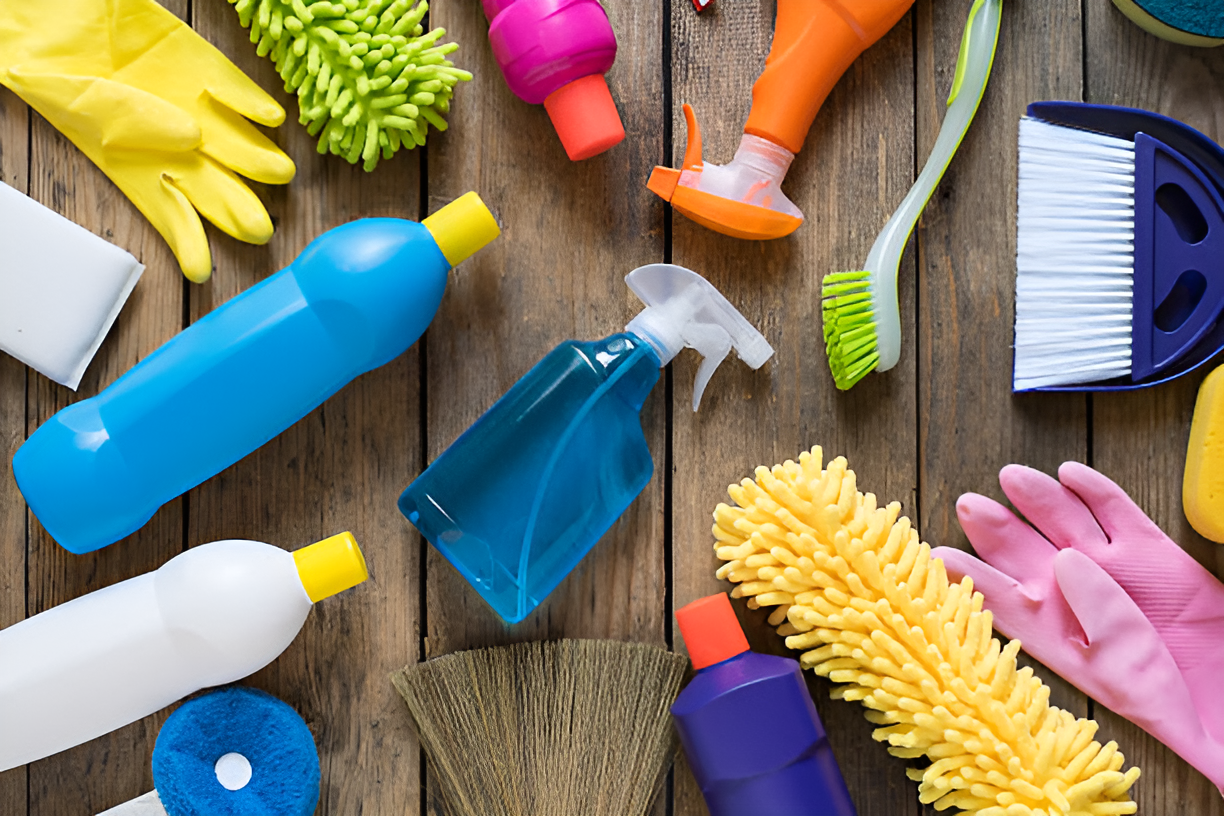
Home care products

Honey
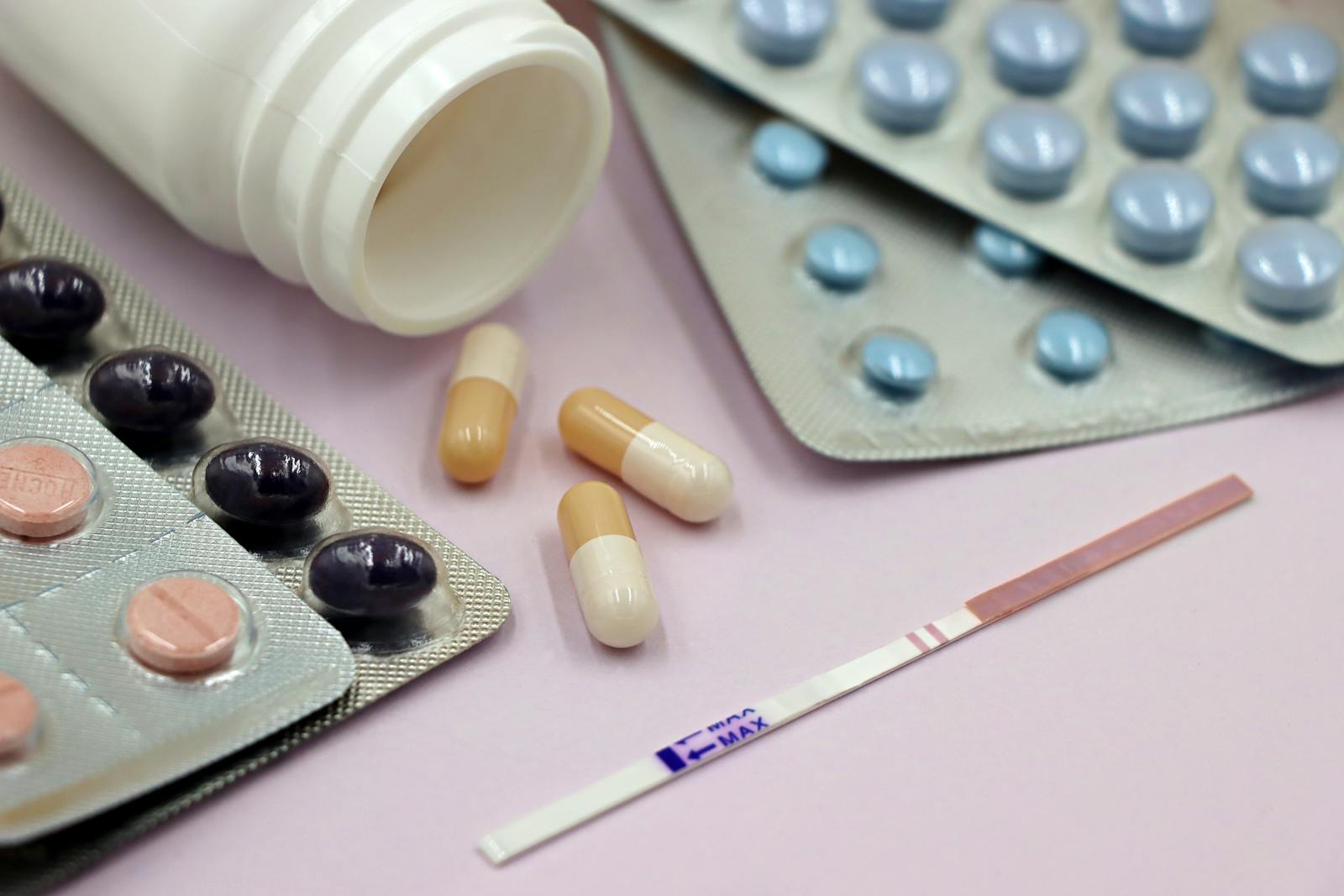
Hormone therapies
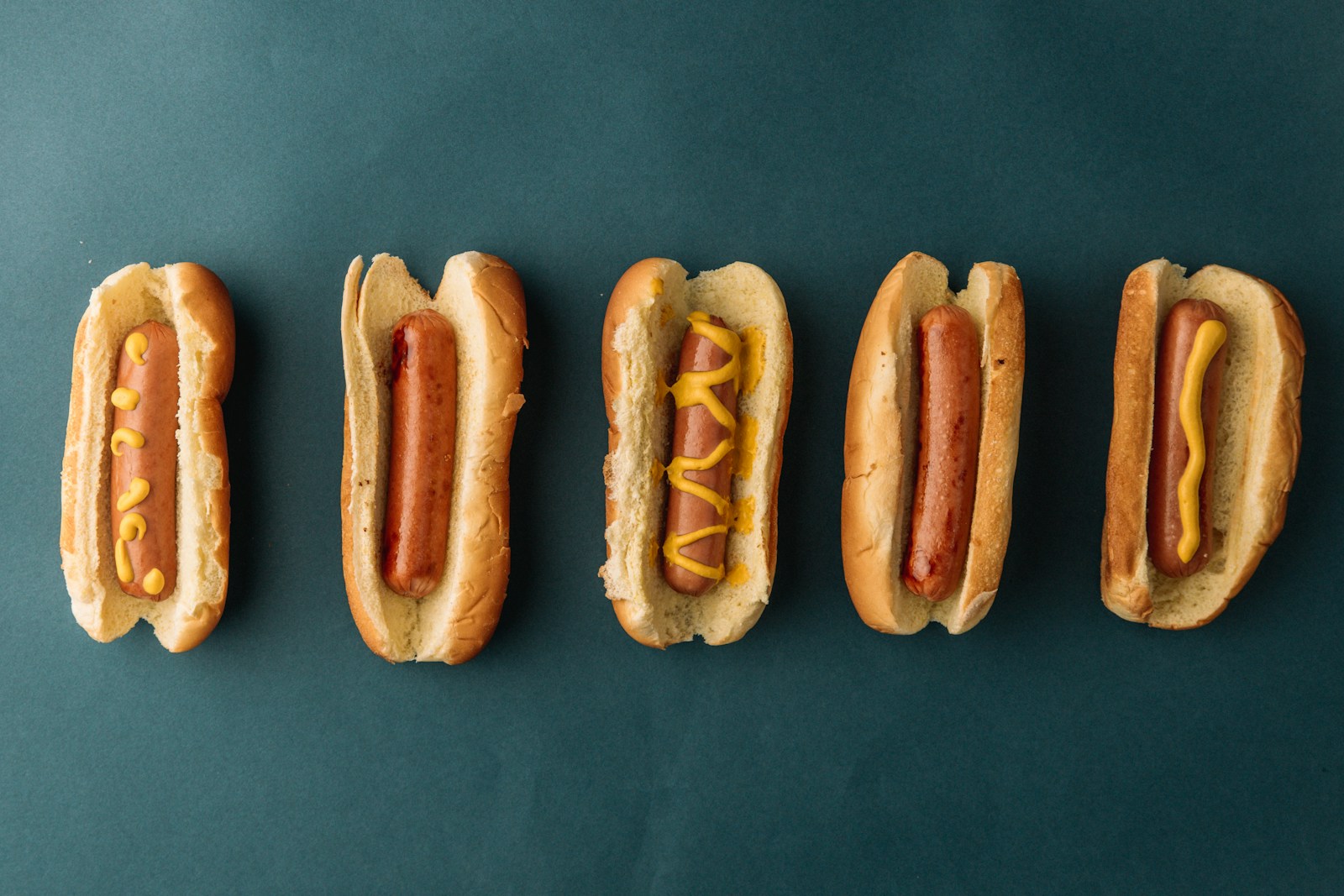
Hot dogs
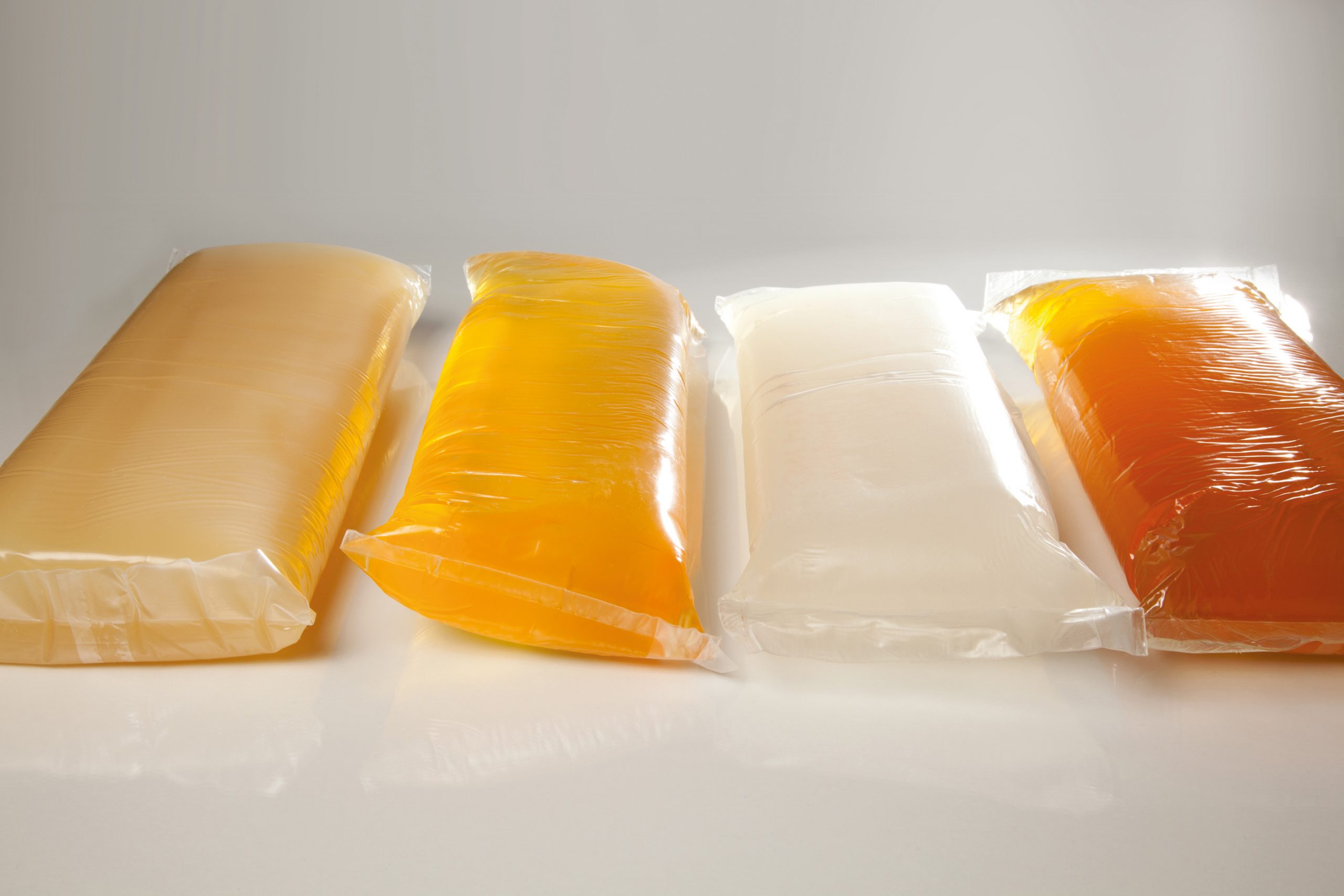
Hot melt adhesives
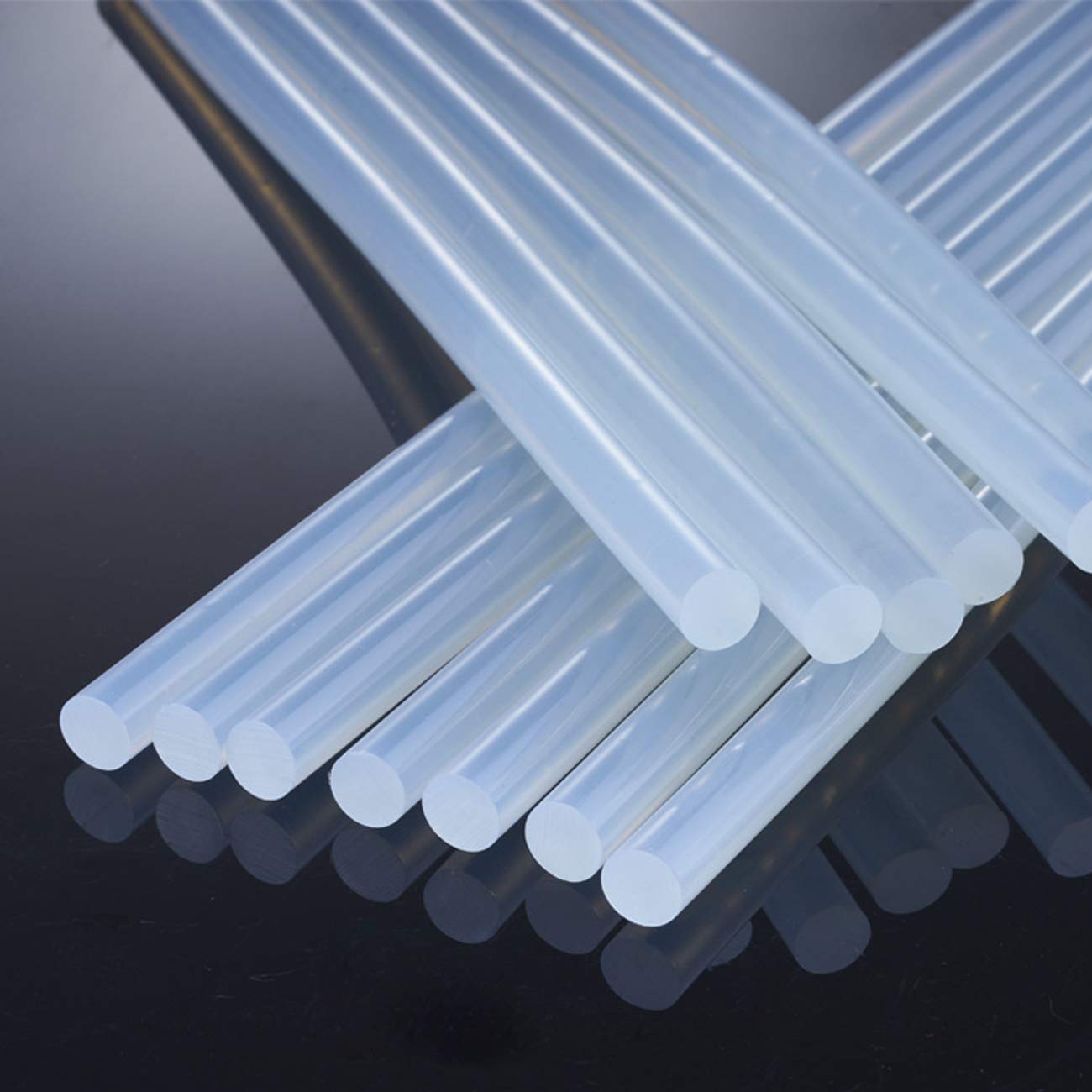
Hot melt glue sticks
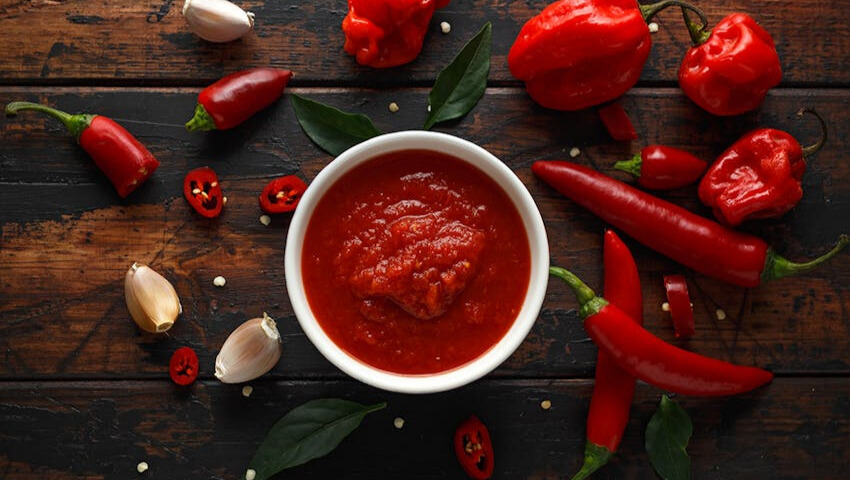
Hot sauce
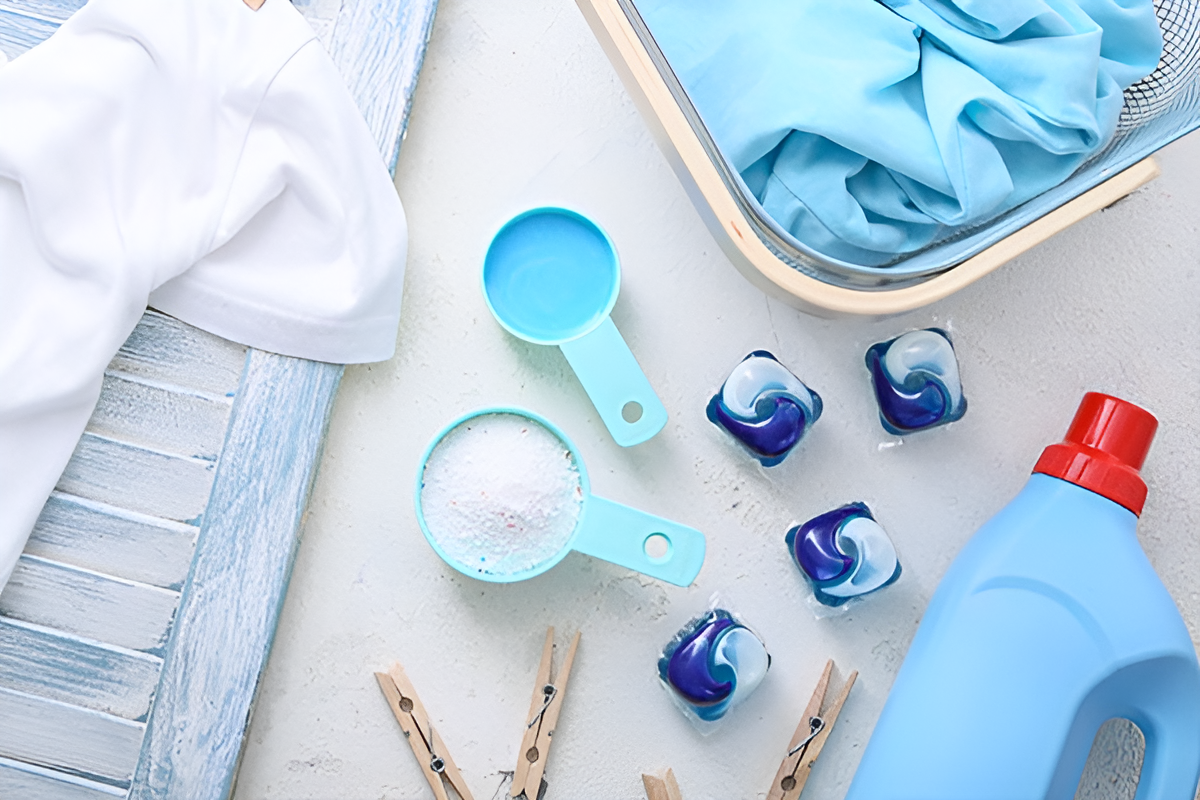
Household detergents
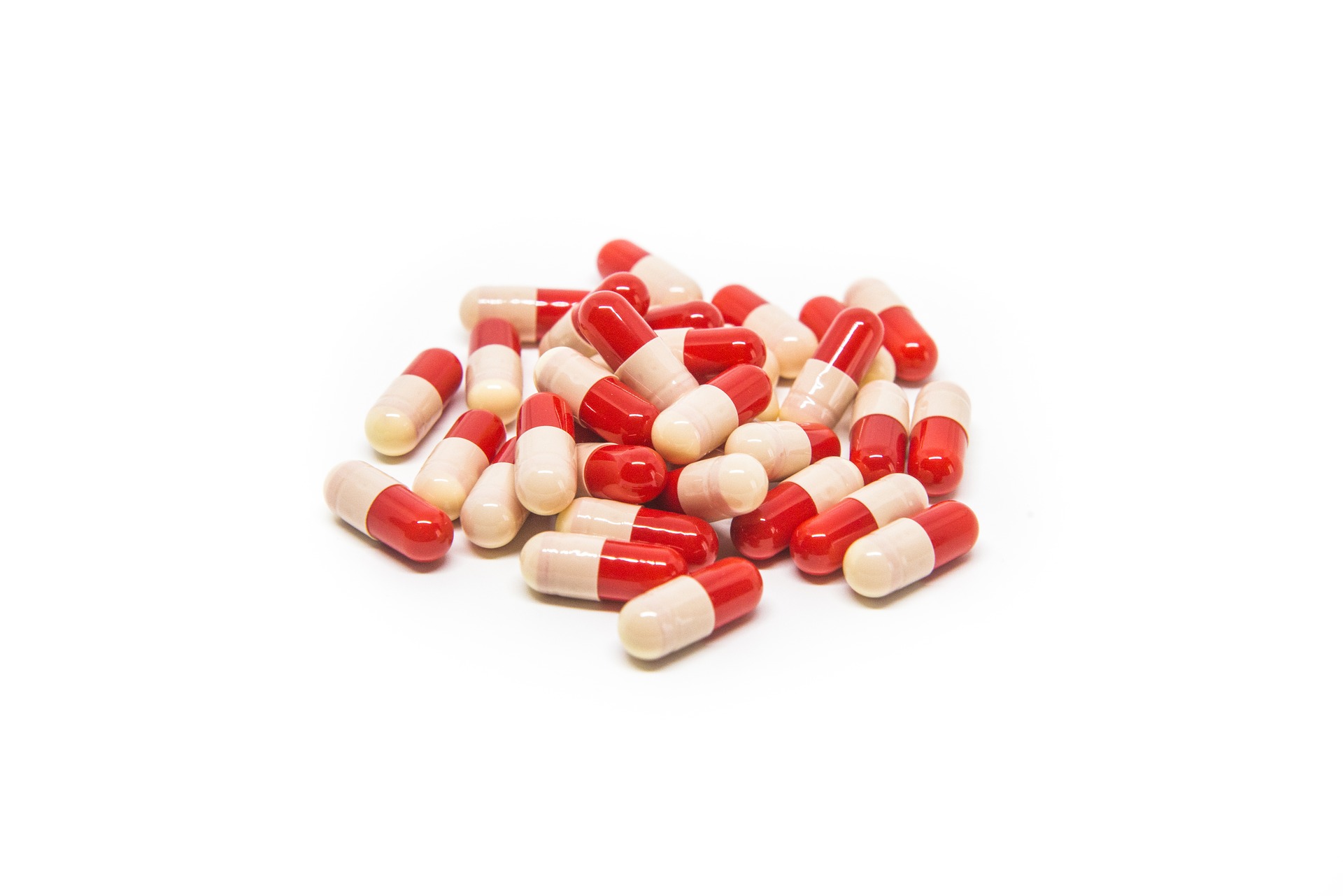
HPMC capsules
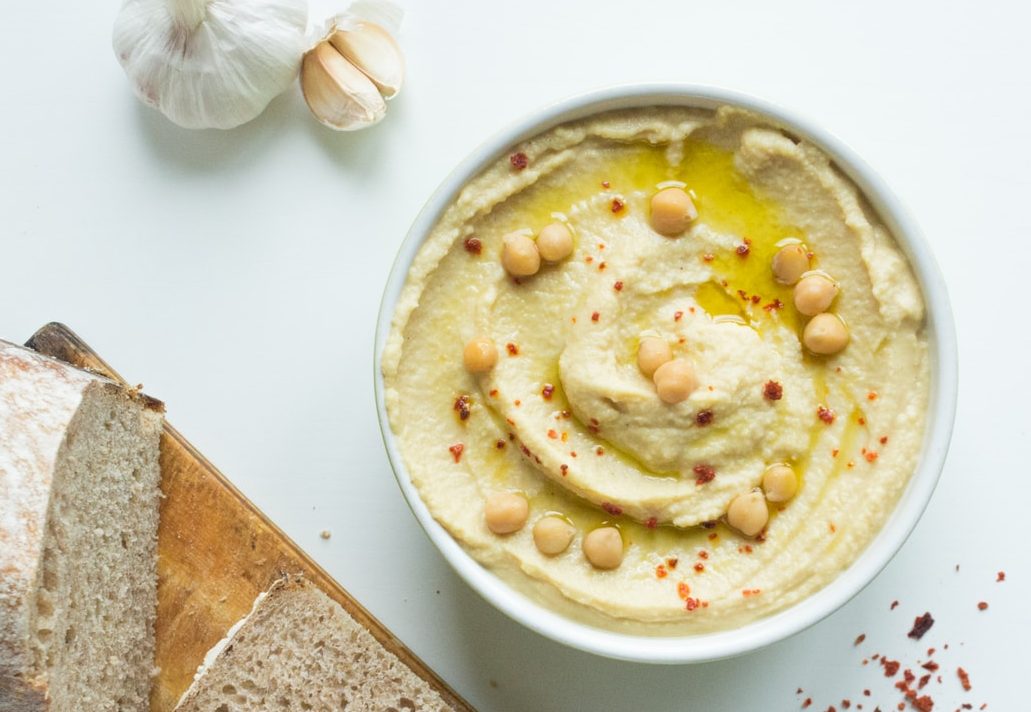
Hummus
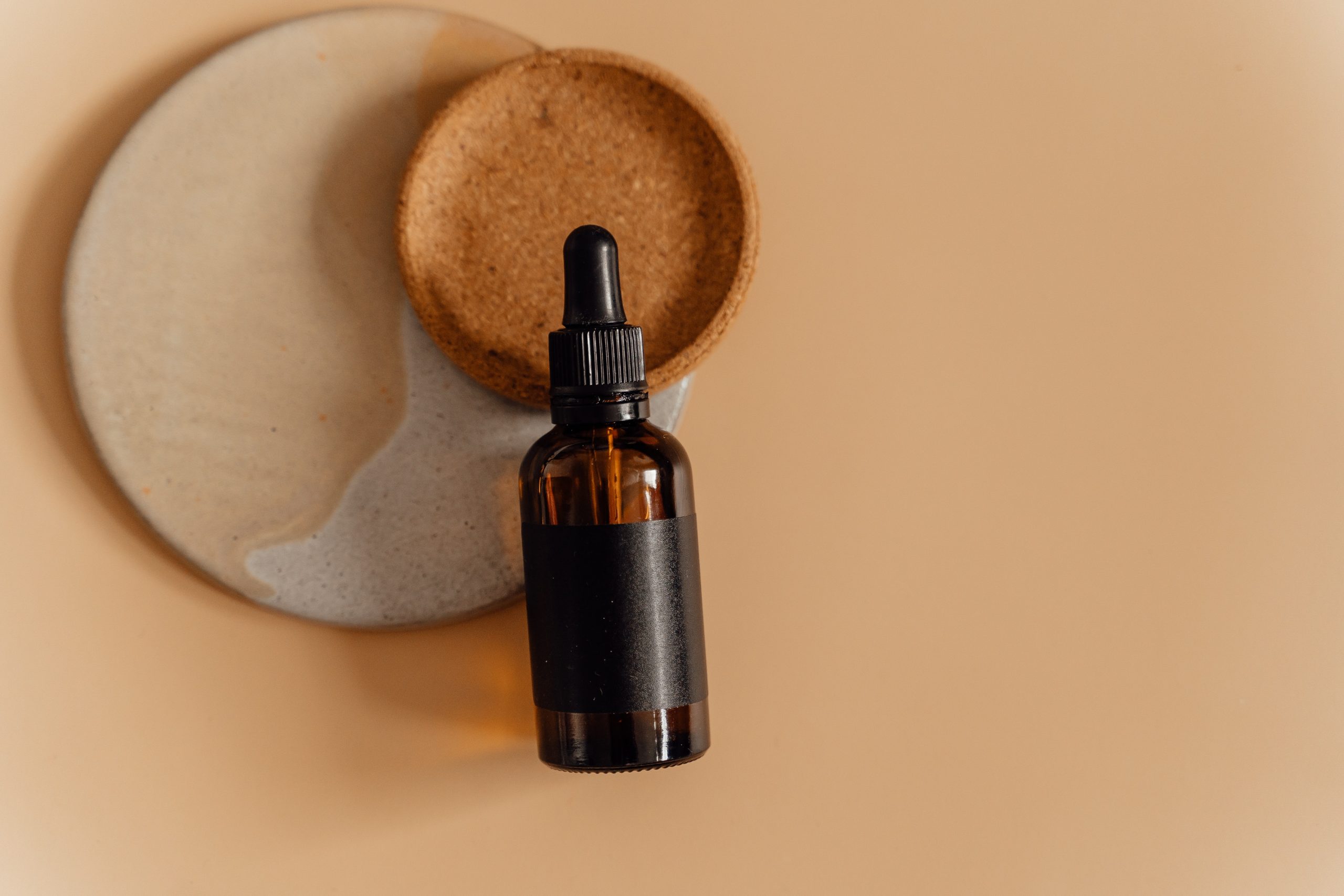
Hyaluronic acid
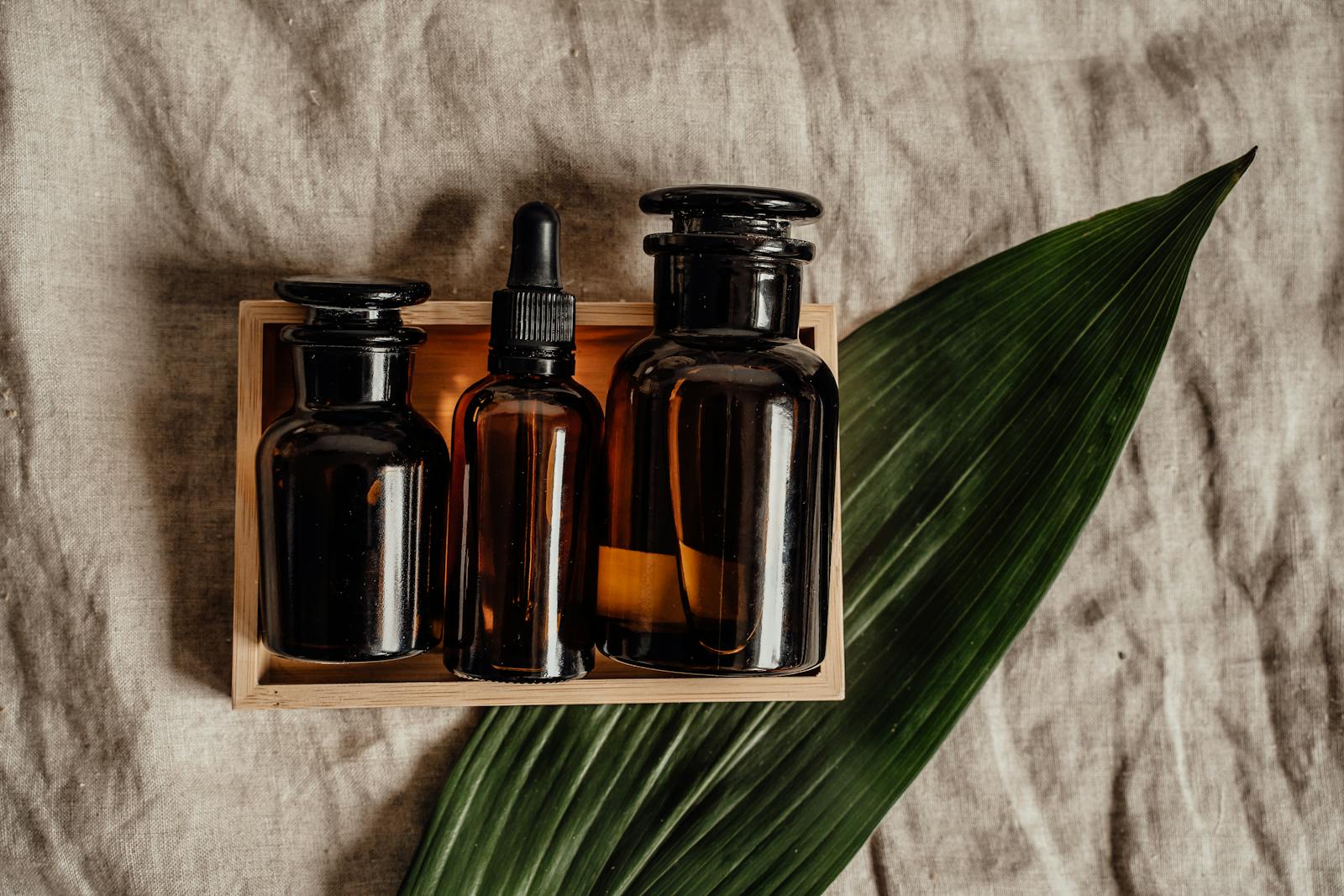
Hyaluronic acid serums
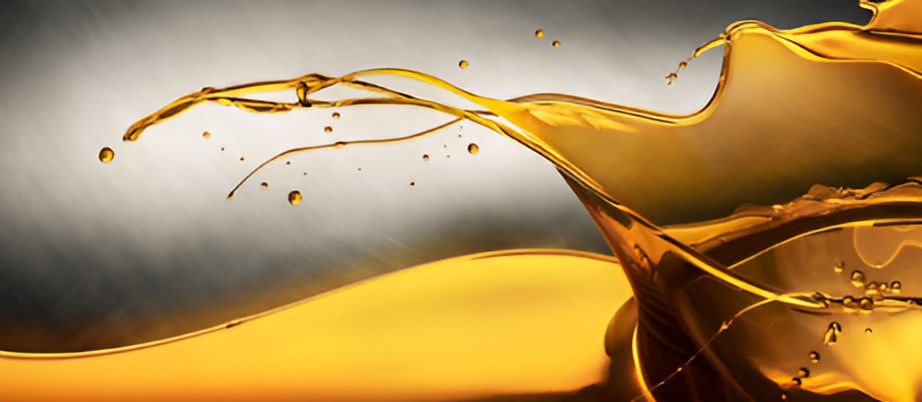
Hydraulic oil
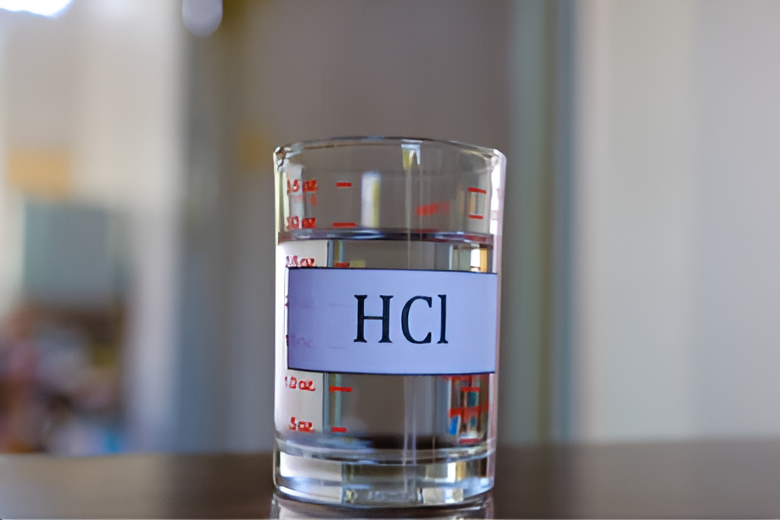
Hydrochloric acid
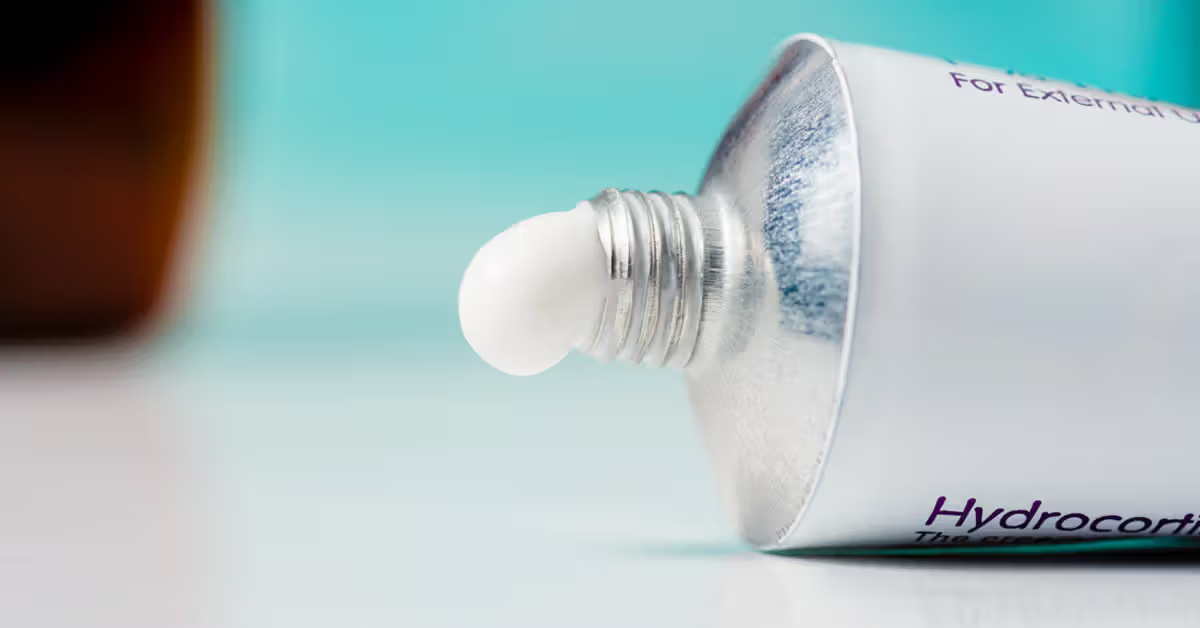
Hydrocortisone cream
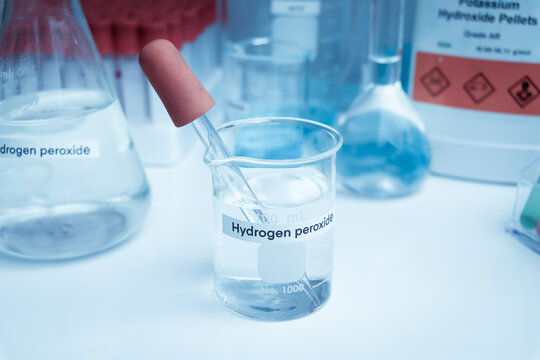
Hydrogen peroxide
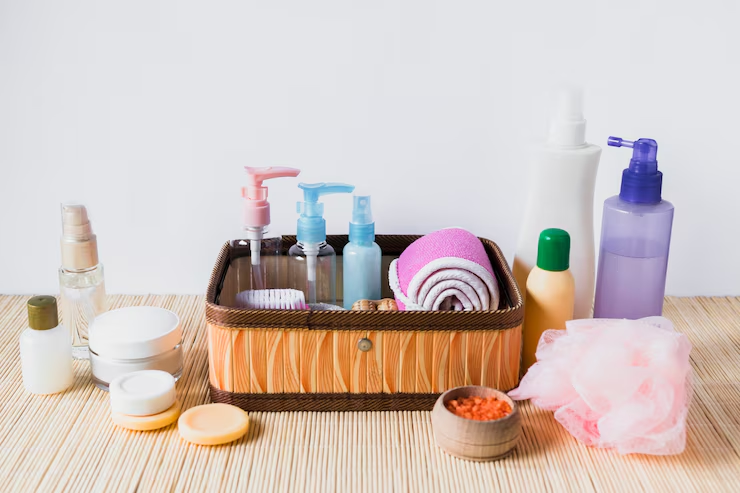
Hygiene products
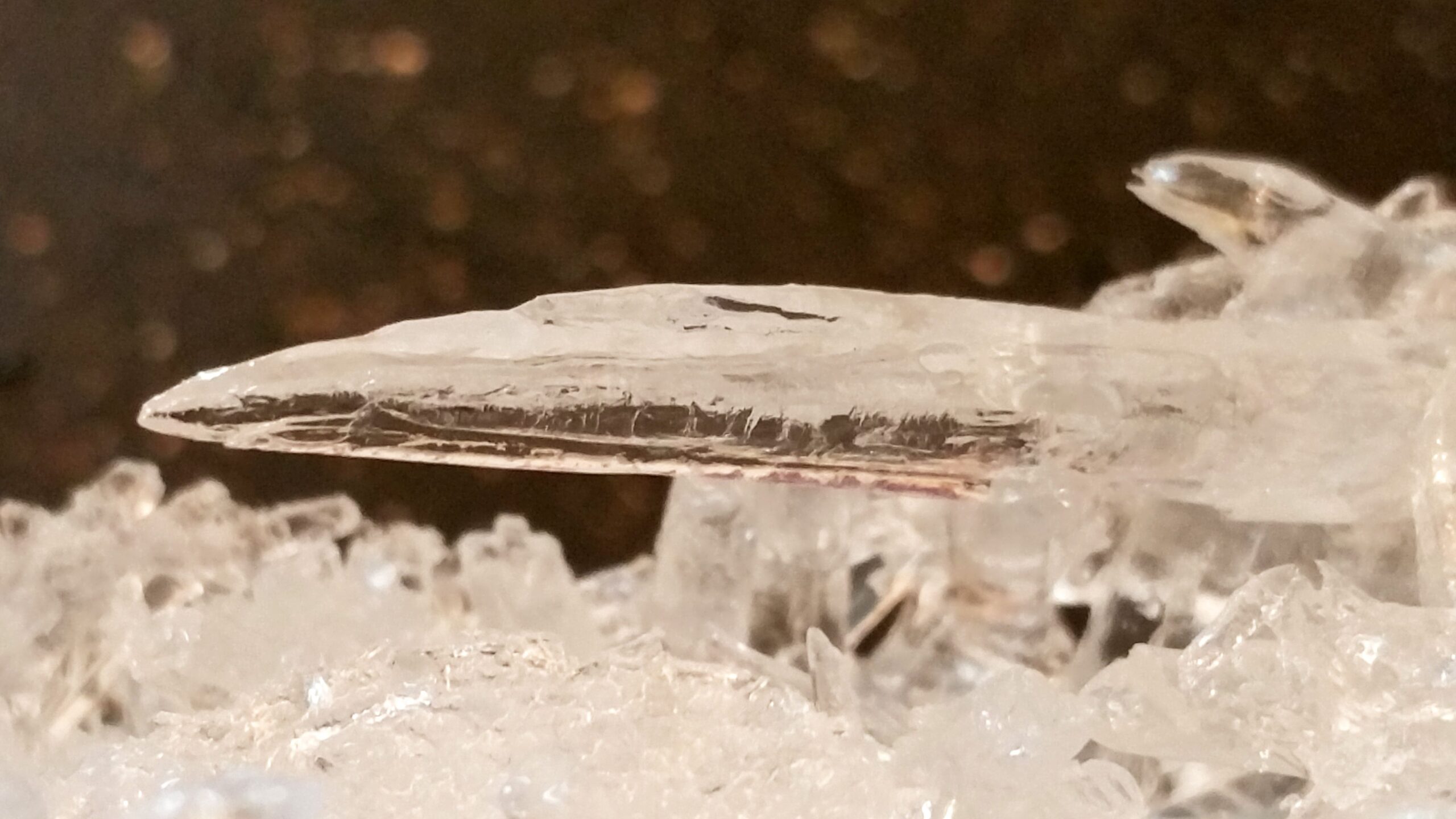
Hygroscopic products
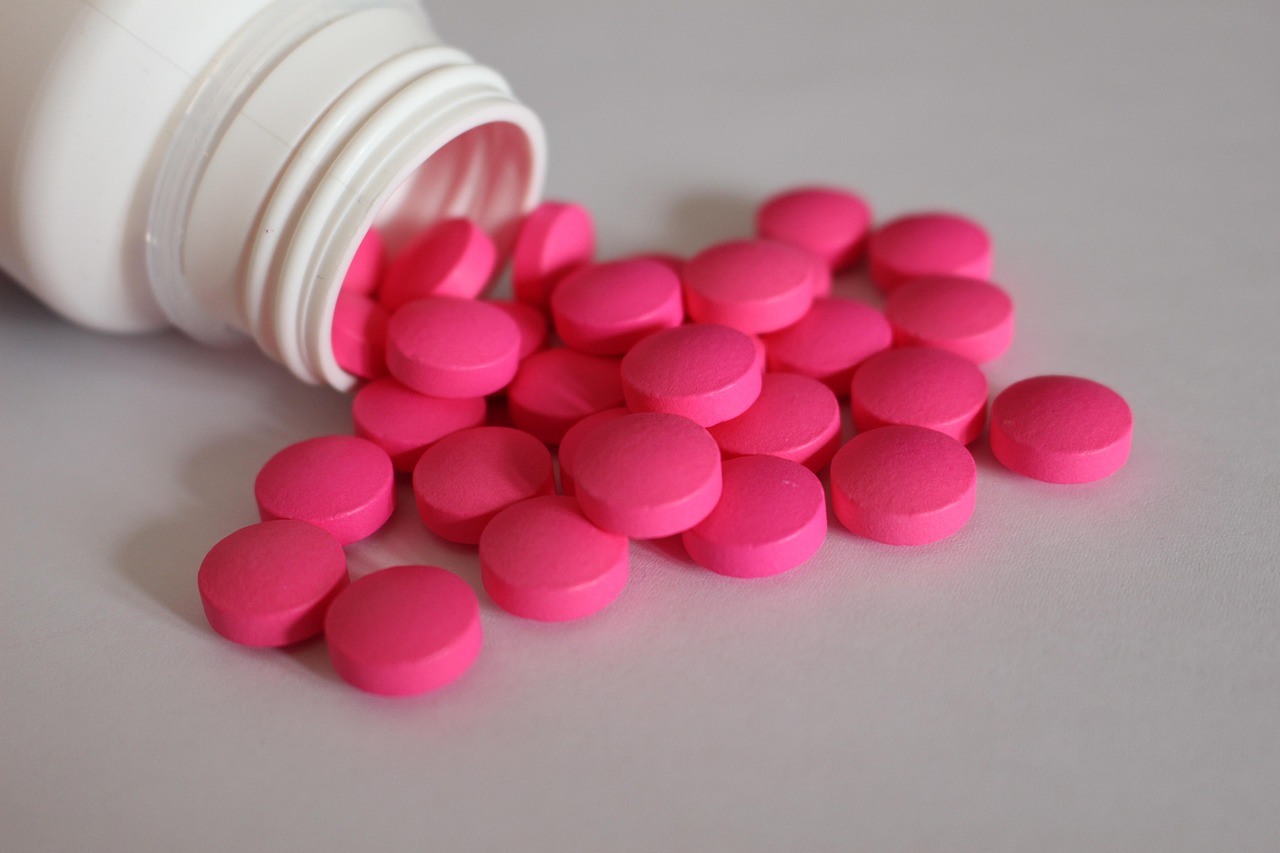
Ibuprofen
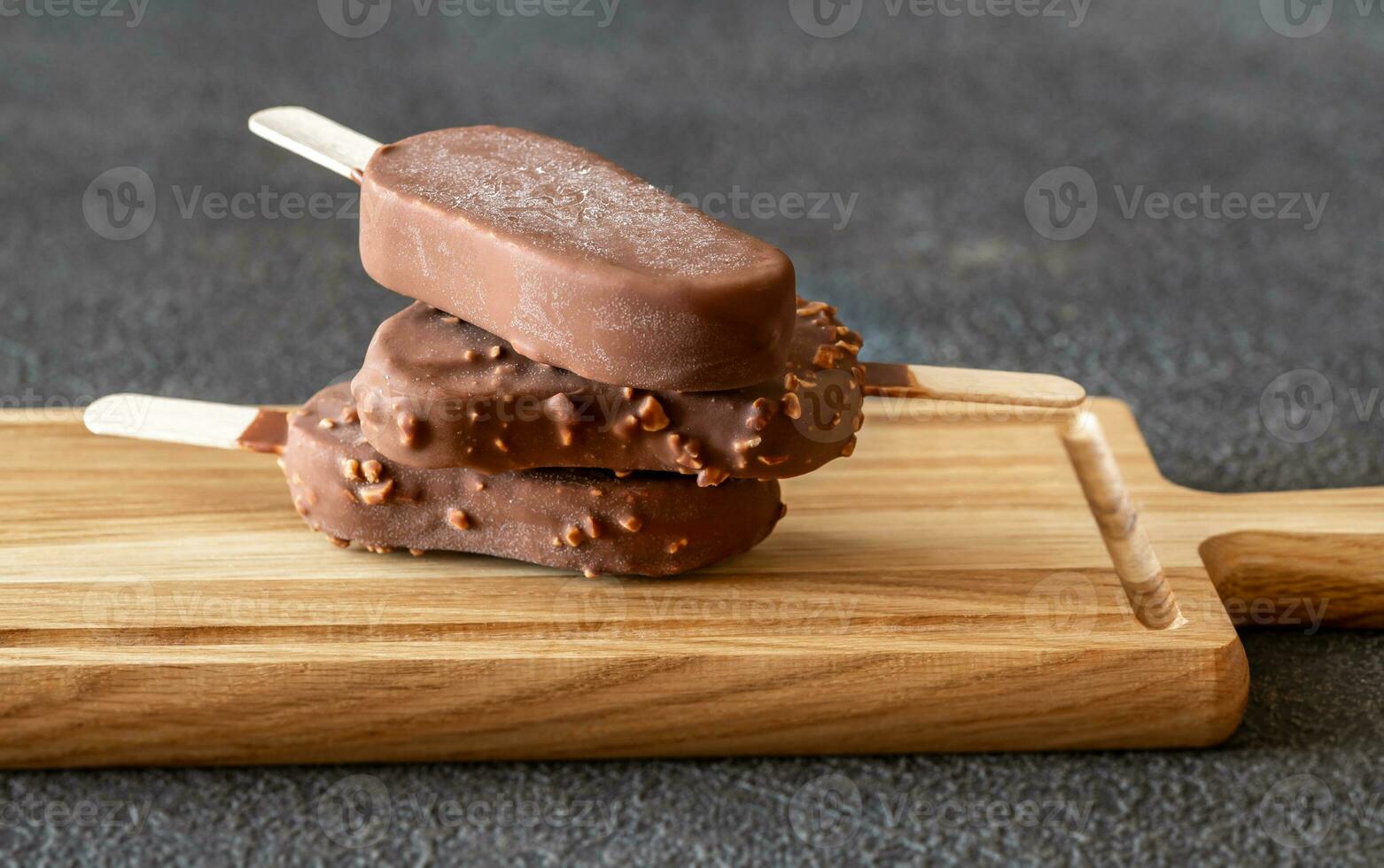
Ice cream bars
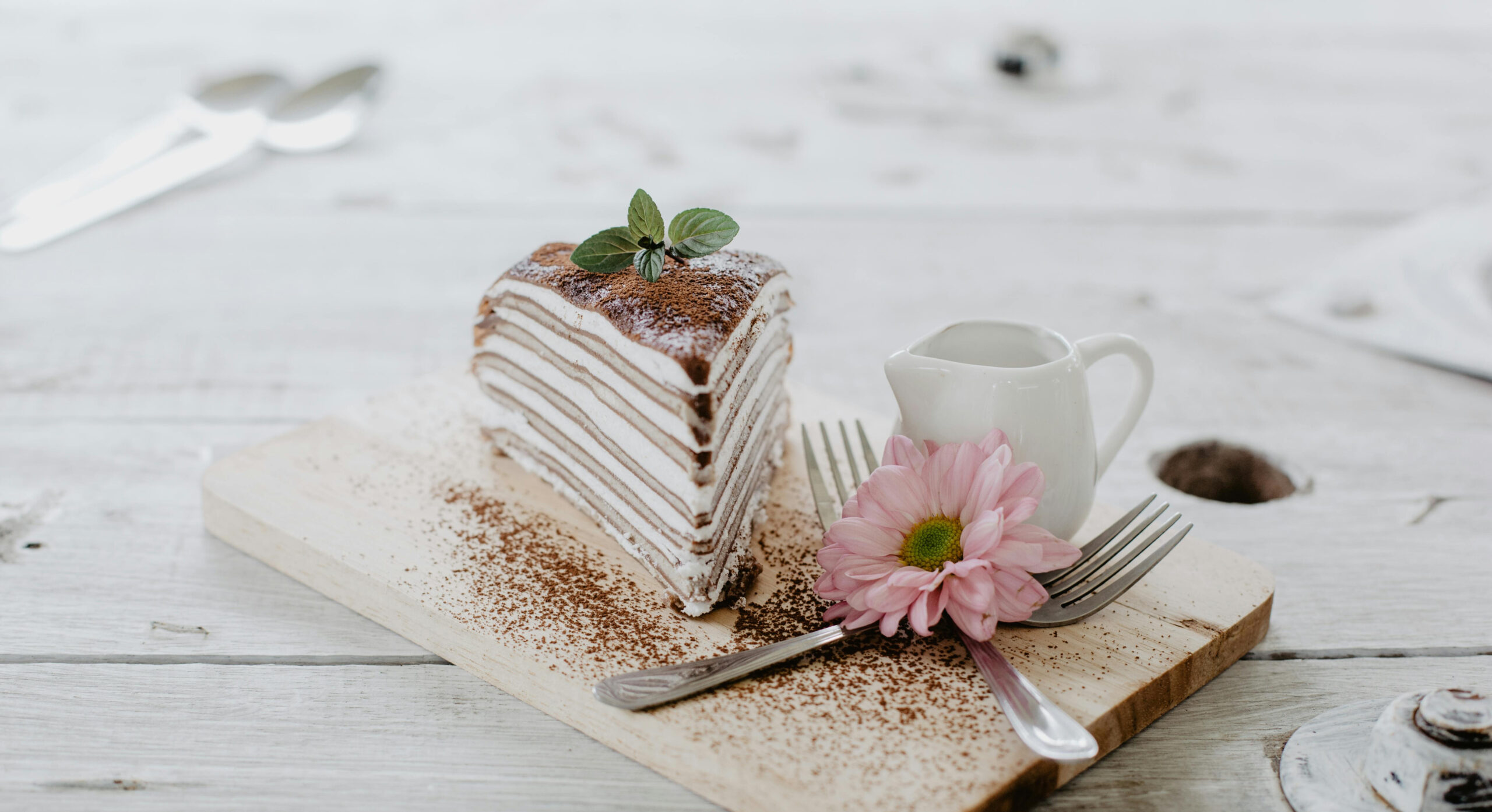
Ice cream cakes
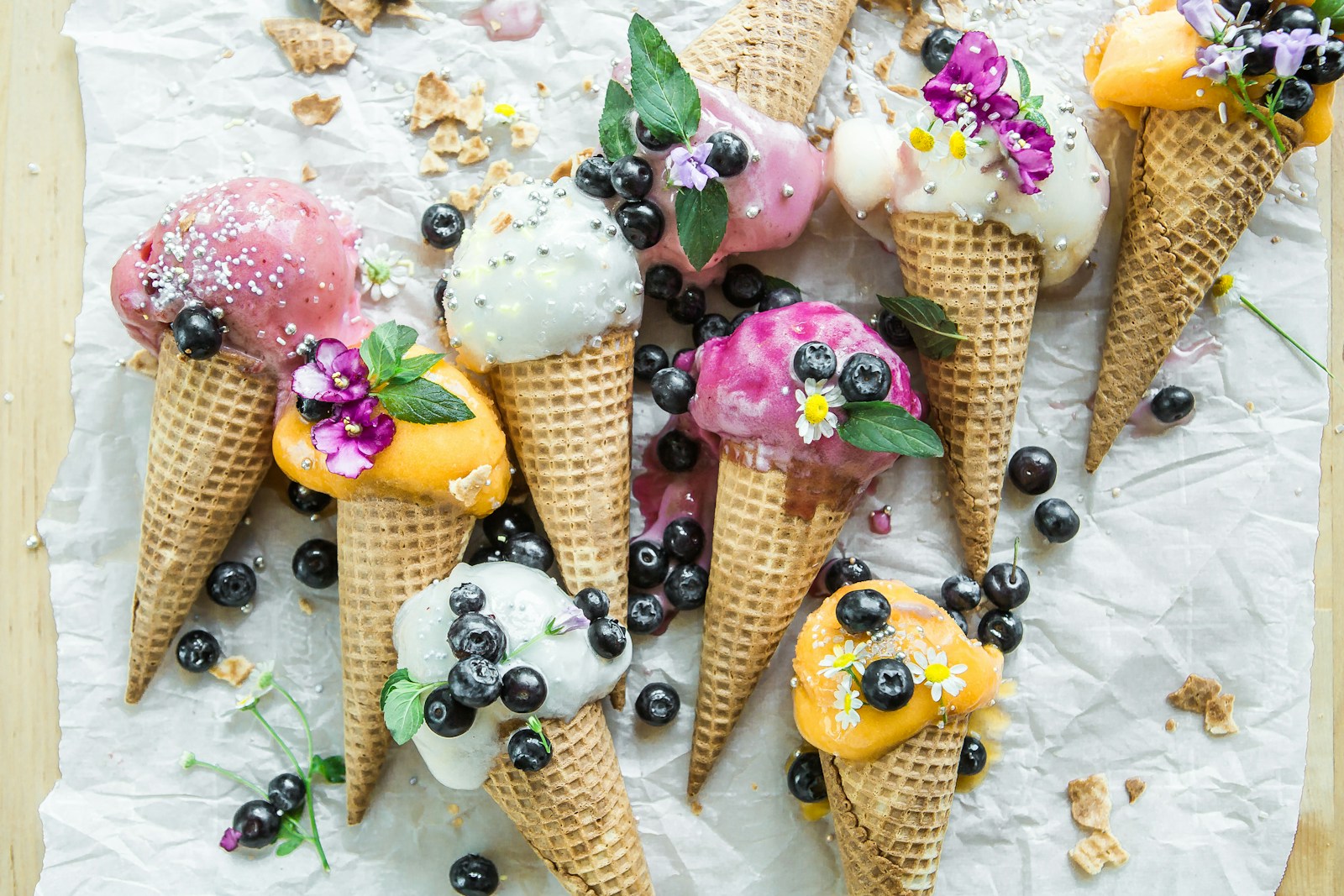
Ice cream cones
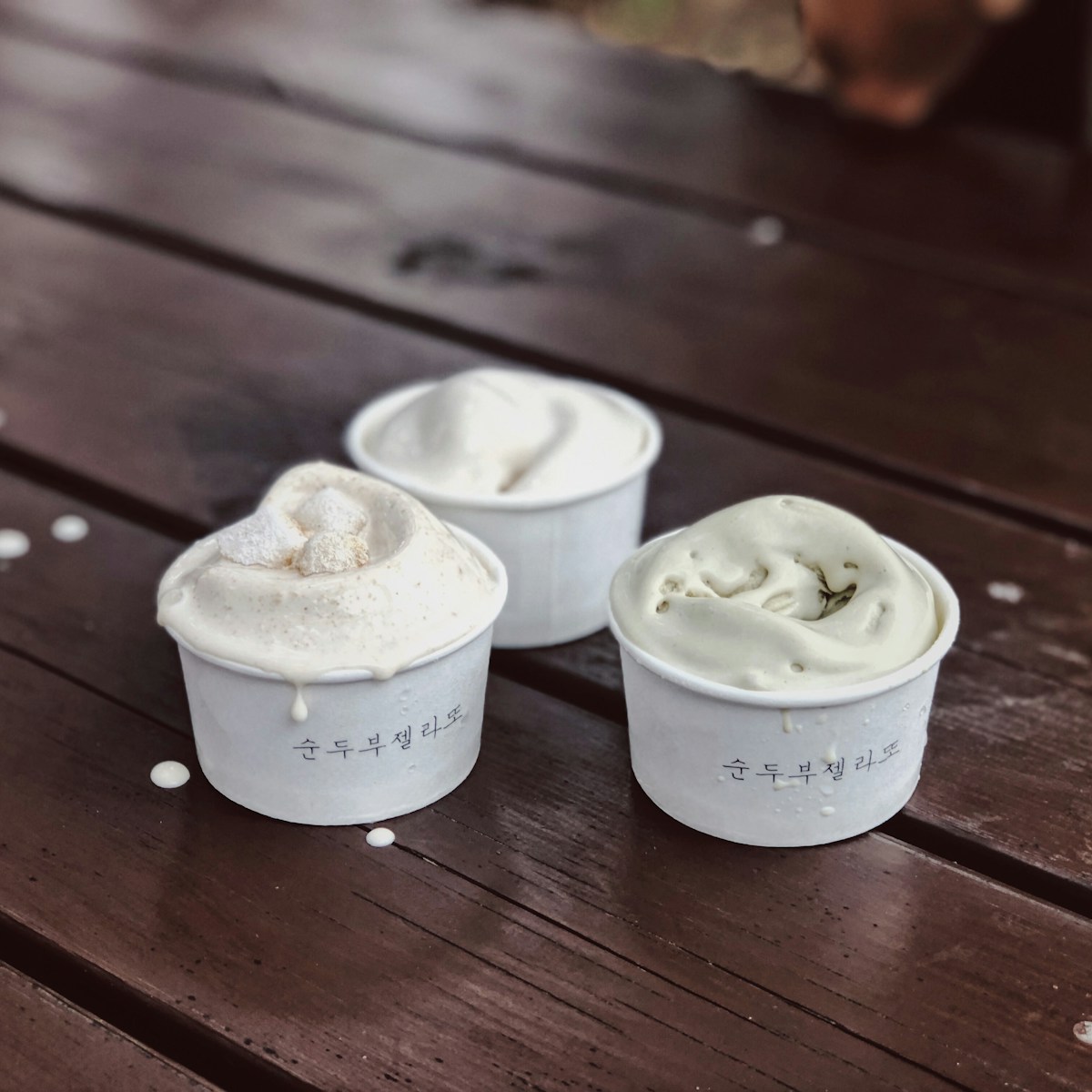
Ice cream cups
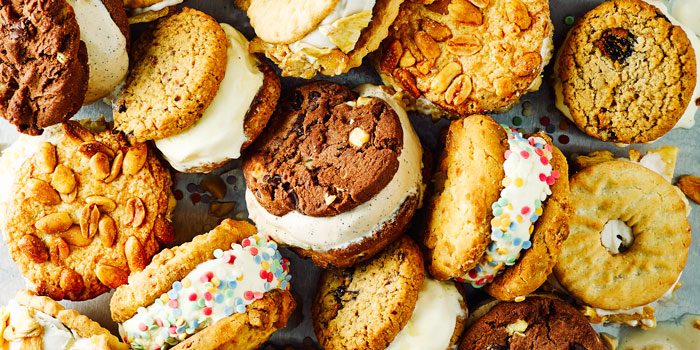
Ice cream sandwiches
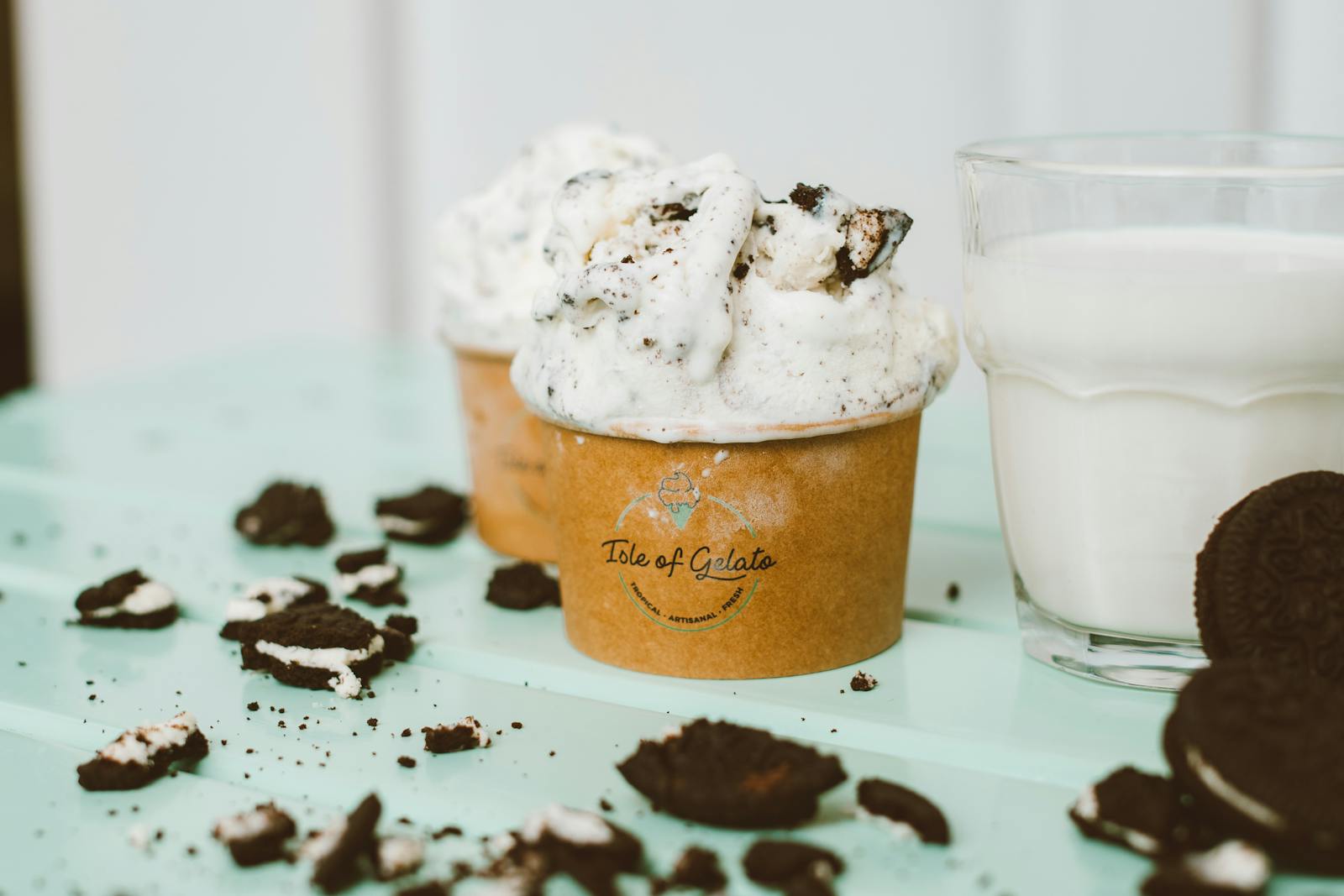
Ice cream tubs
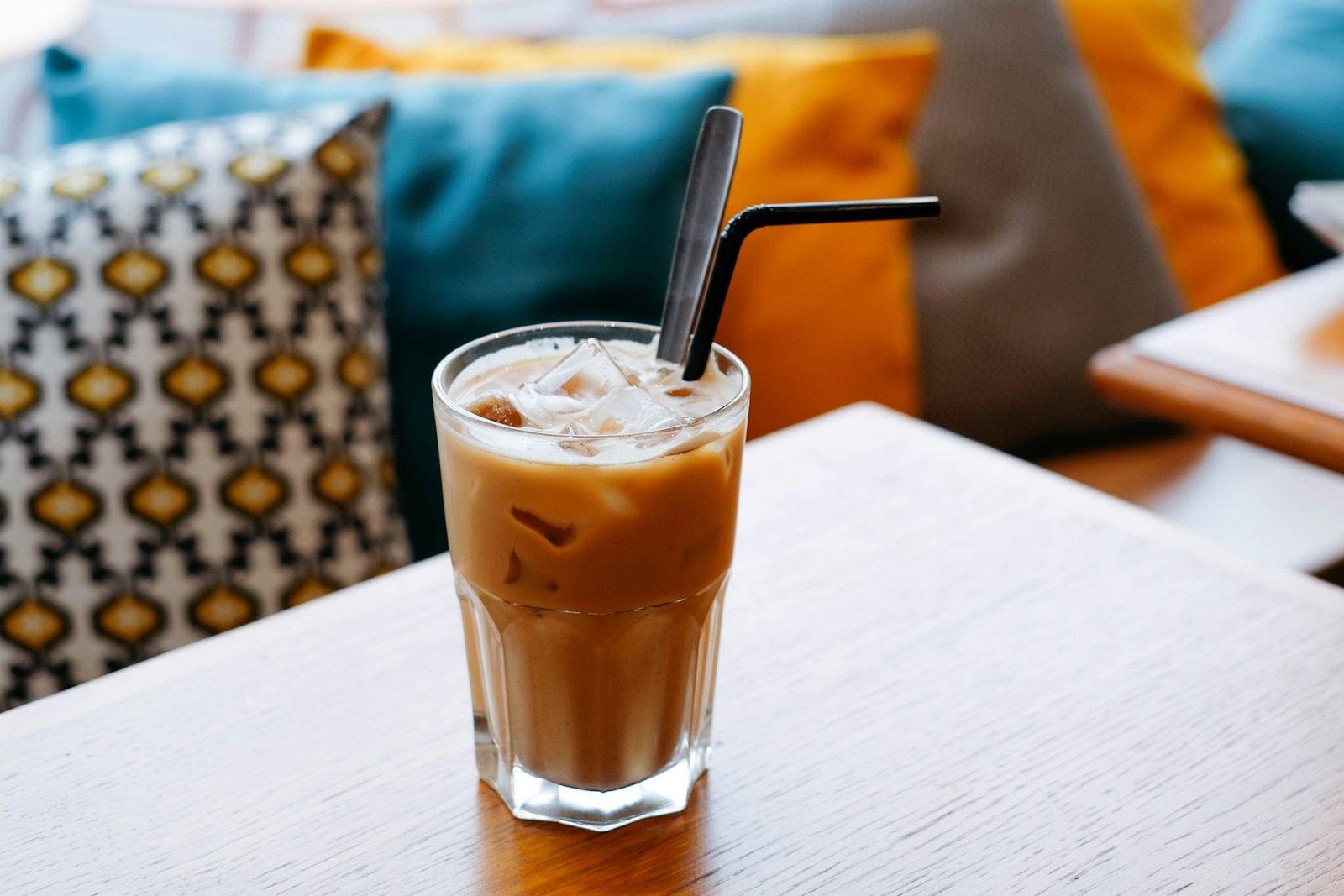
Iced coffee
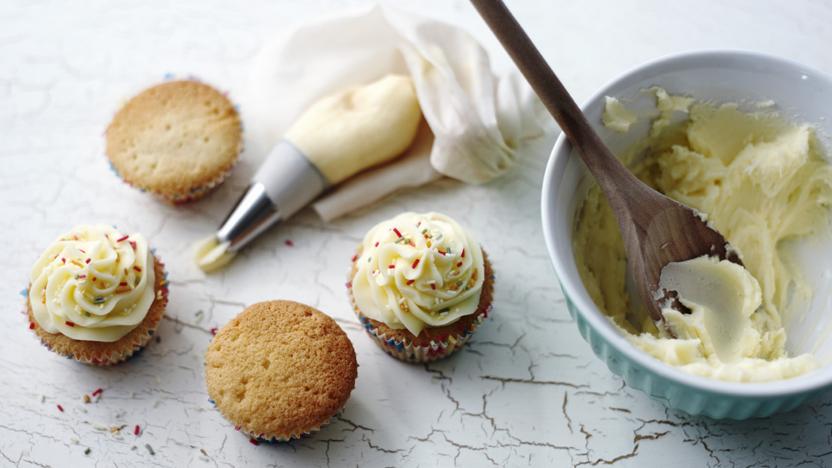
Icing
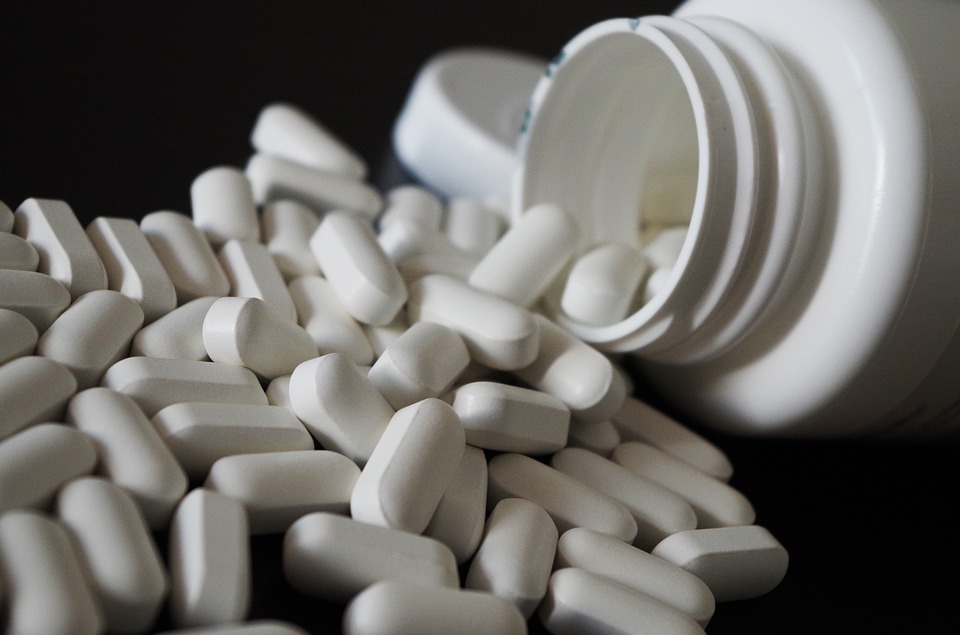
Immediate-release tablets
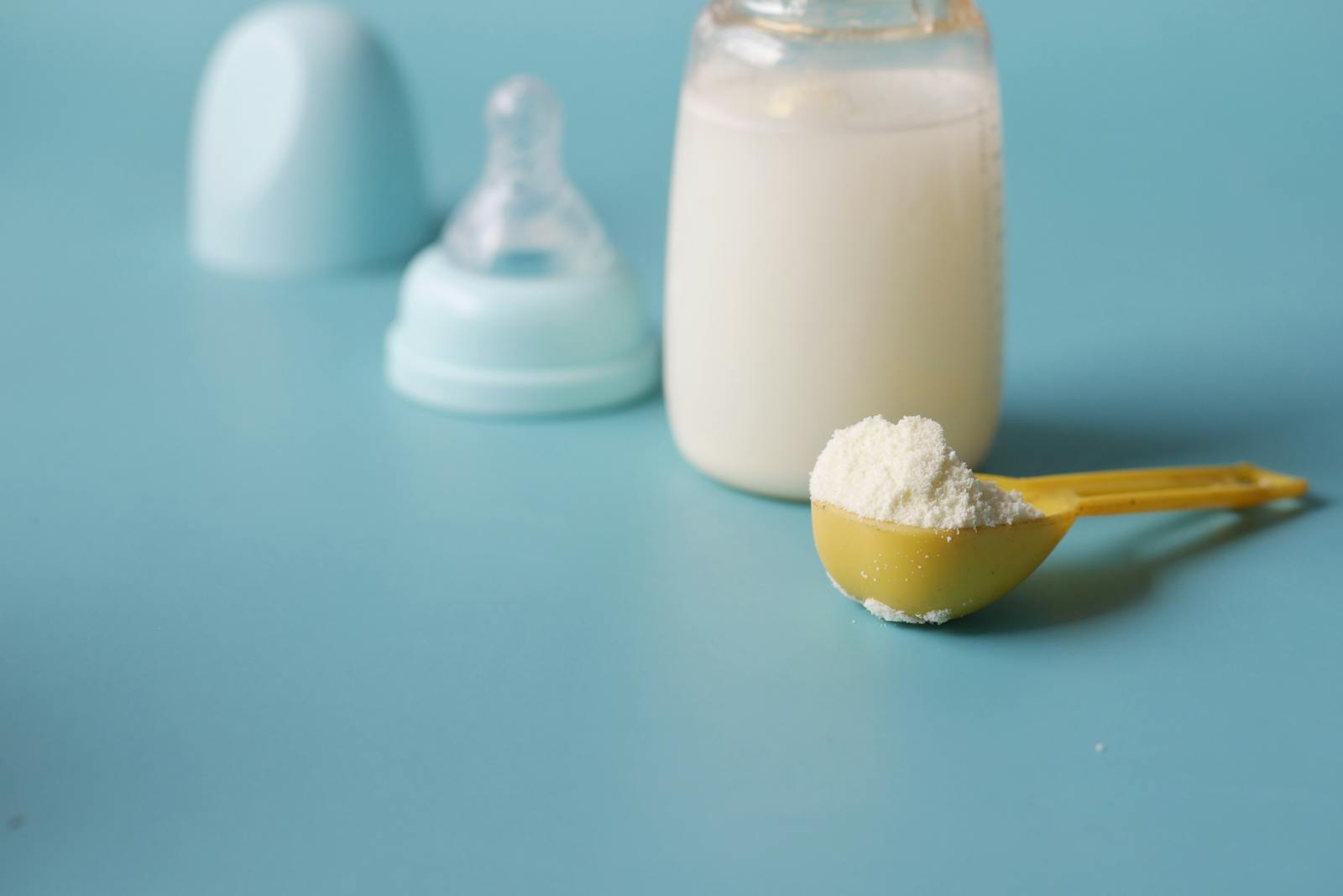
Infant formula
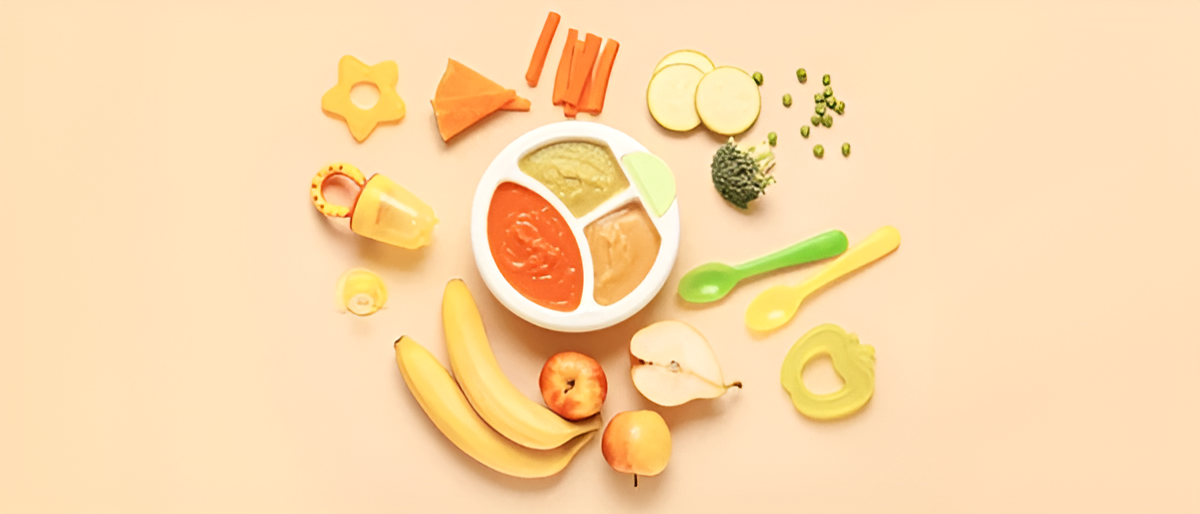
Infant nutrition
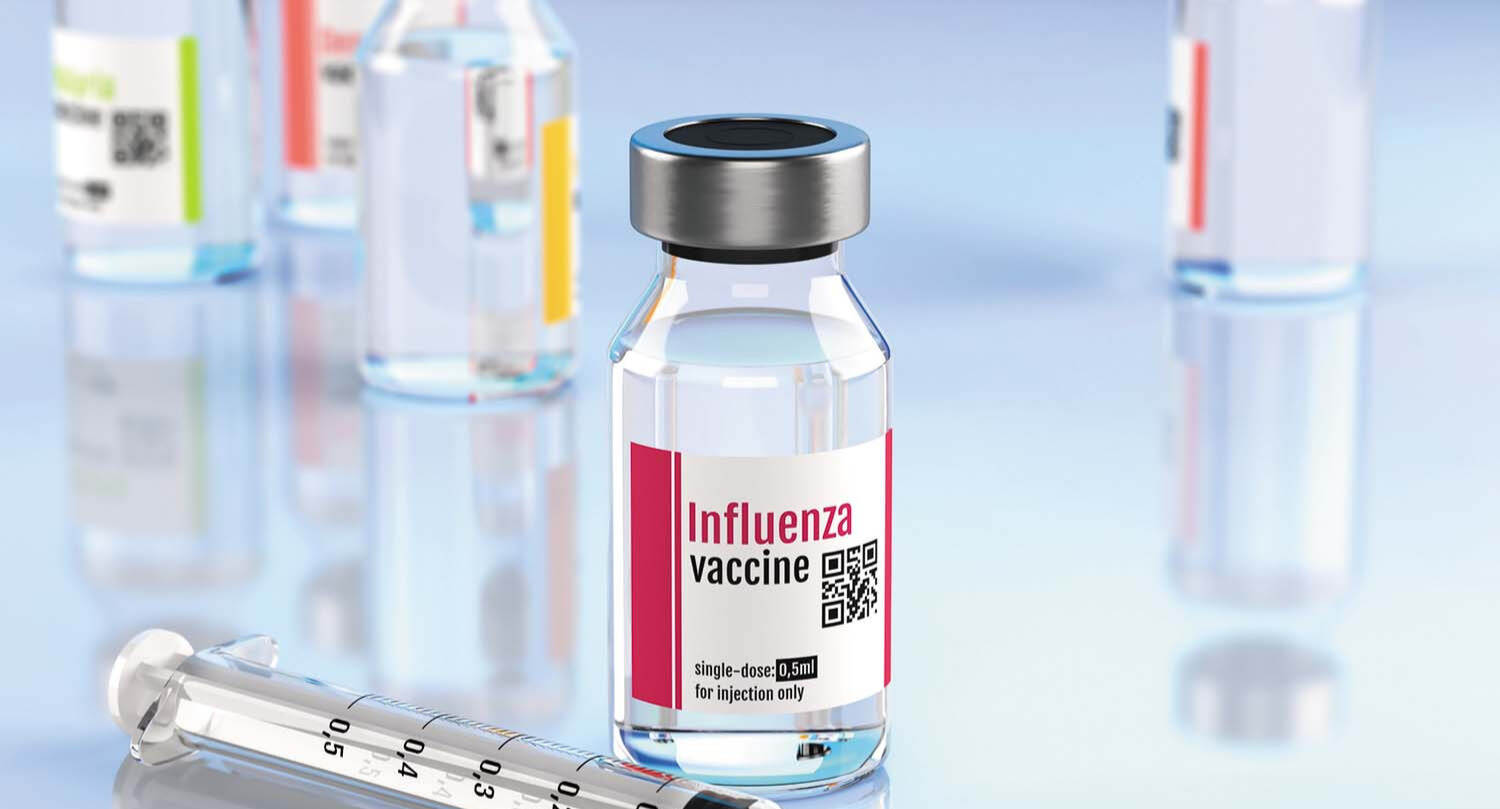
Influenza vaccines
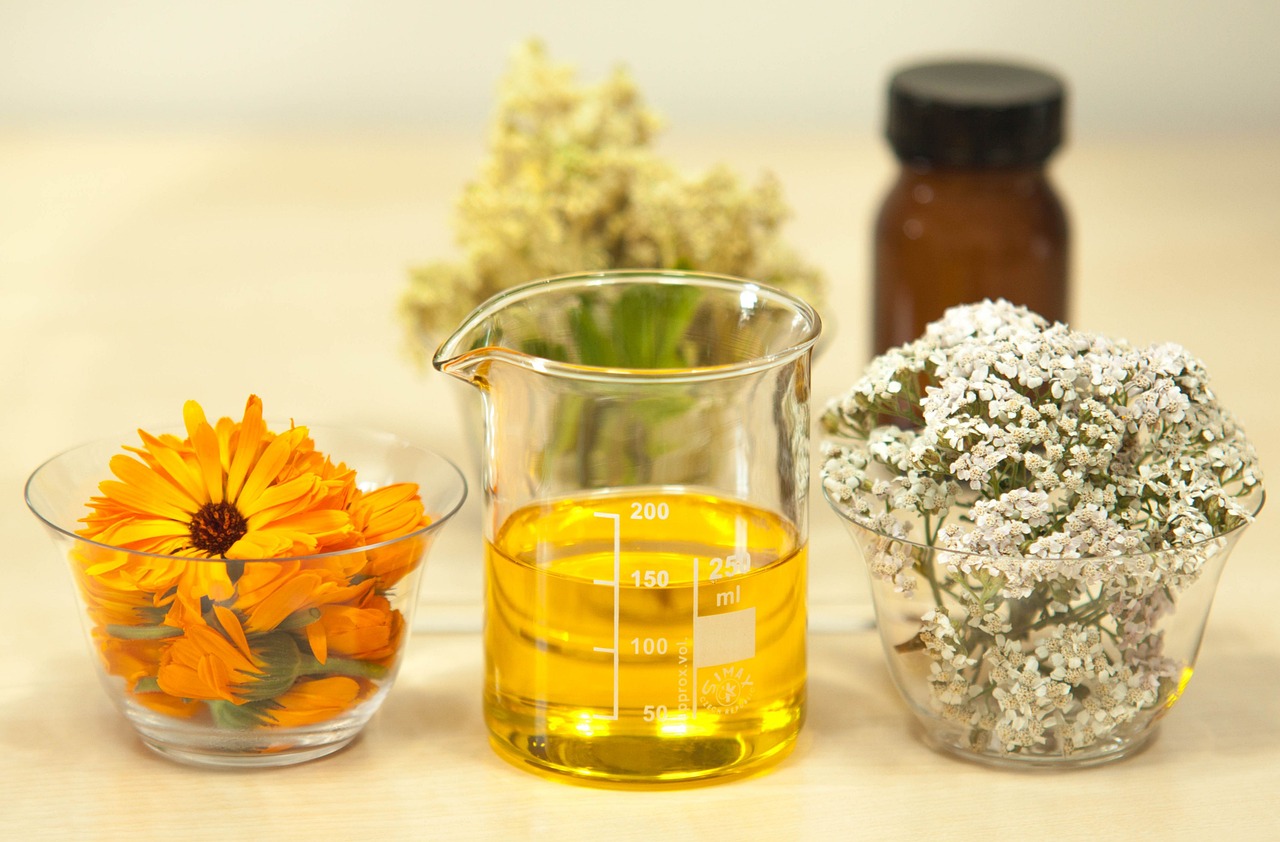
Infusions
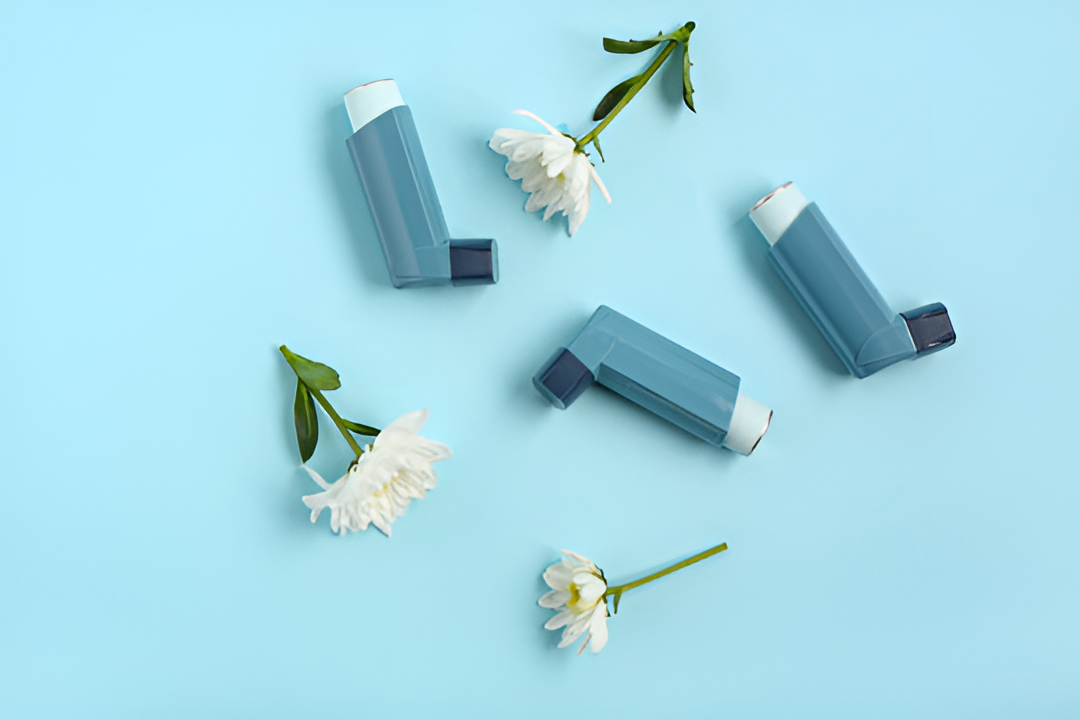
Inhalers
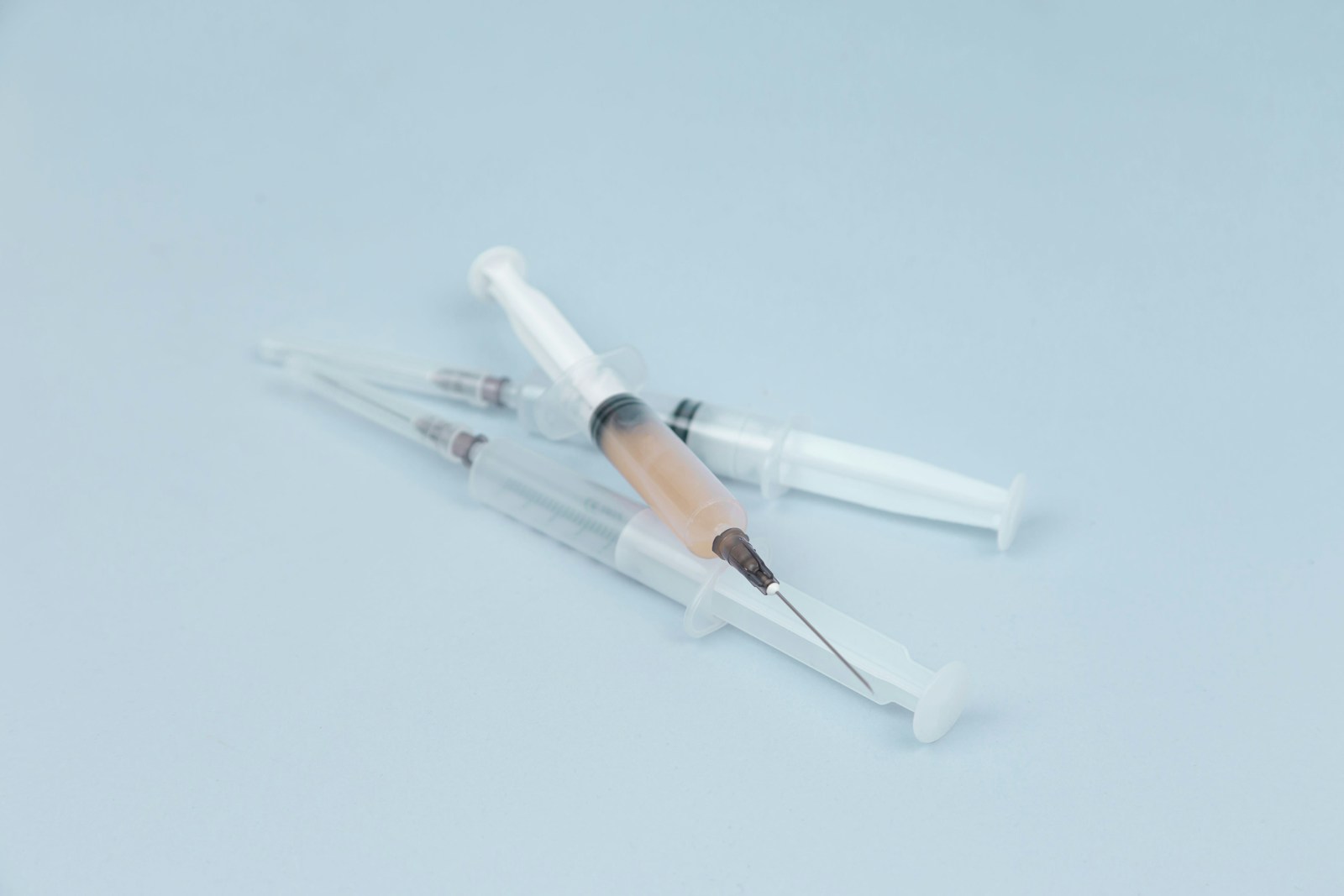
Injectable biologics
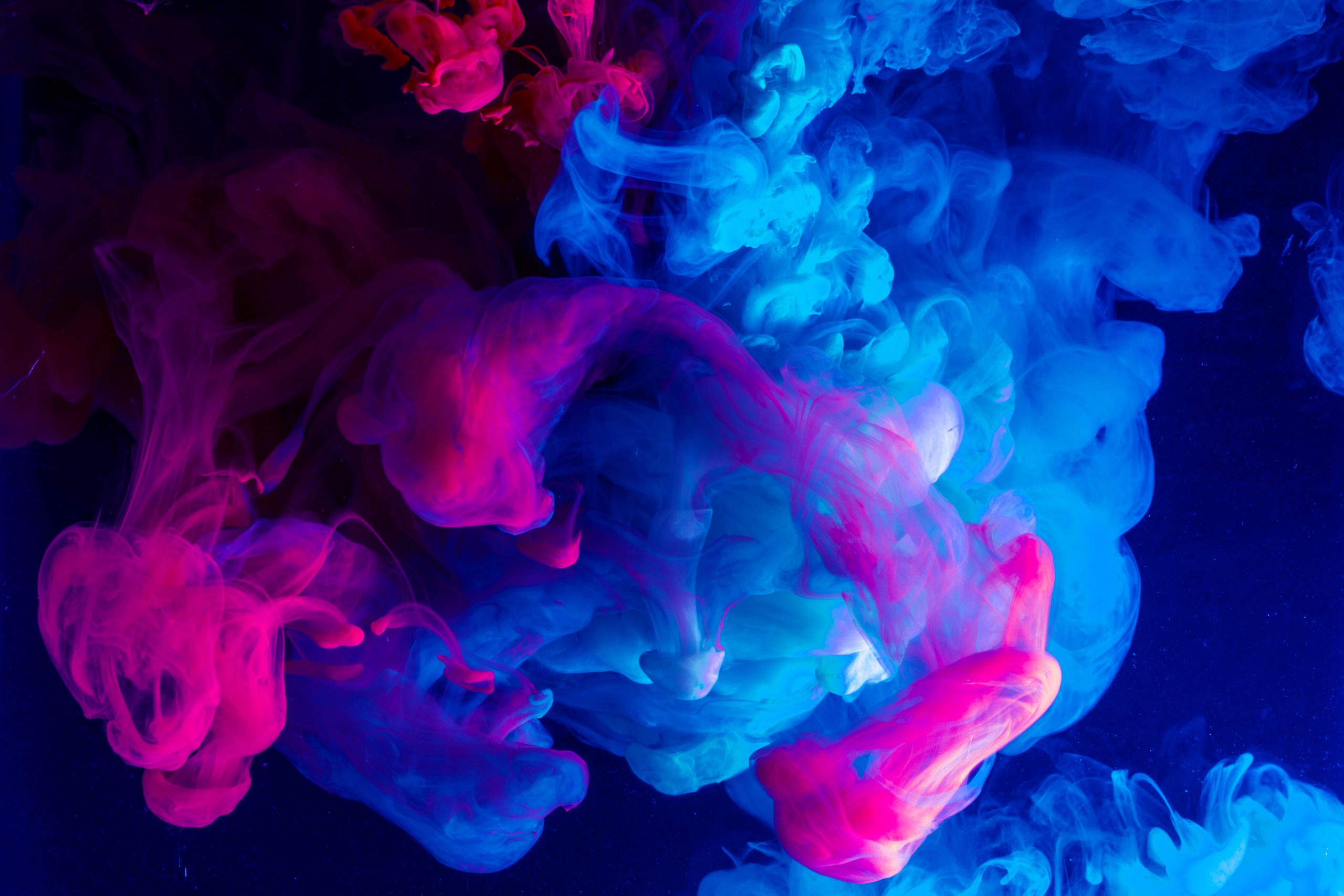
Ink
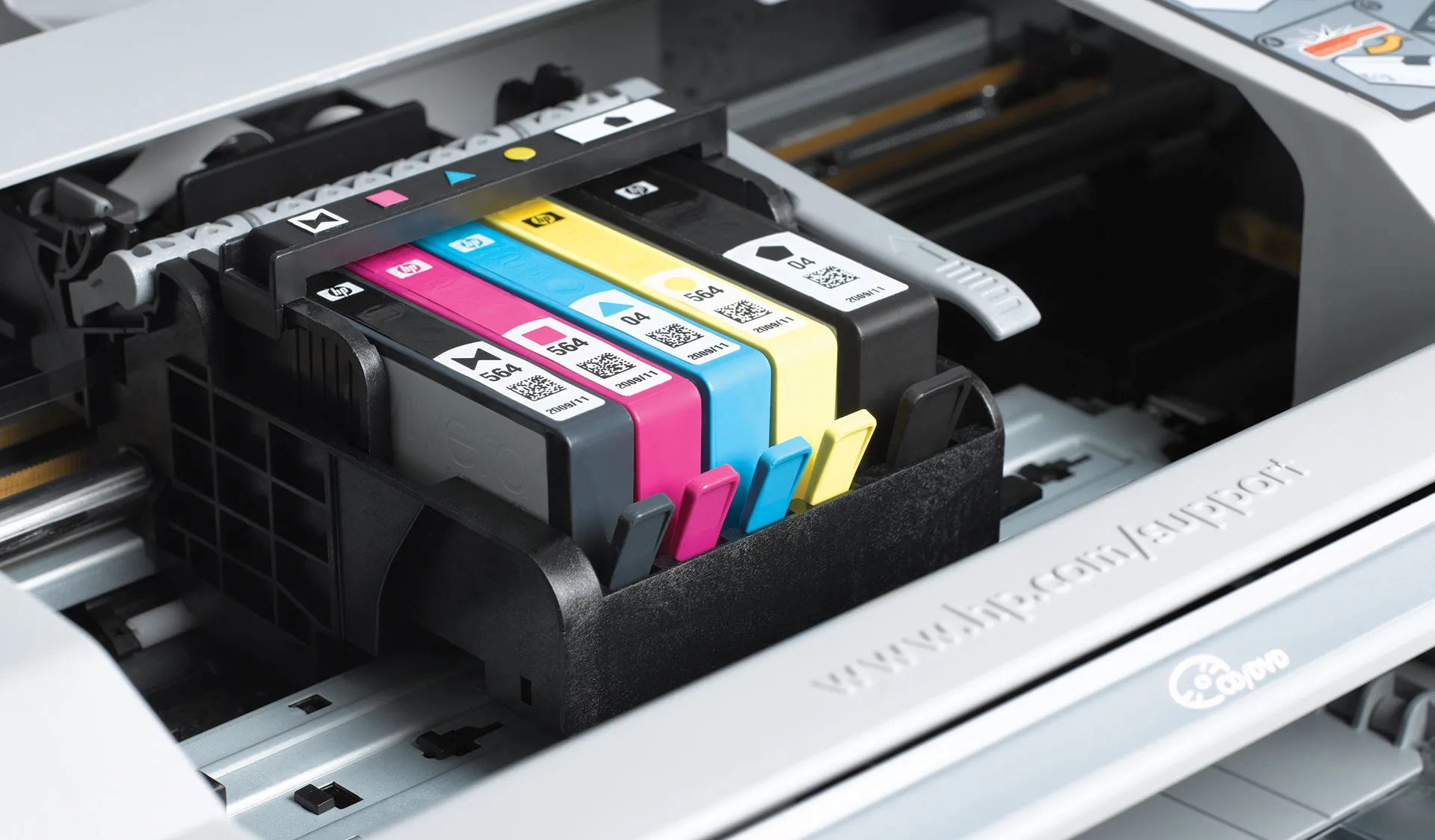
Inkjet printer cartridges

Insecticides
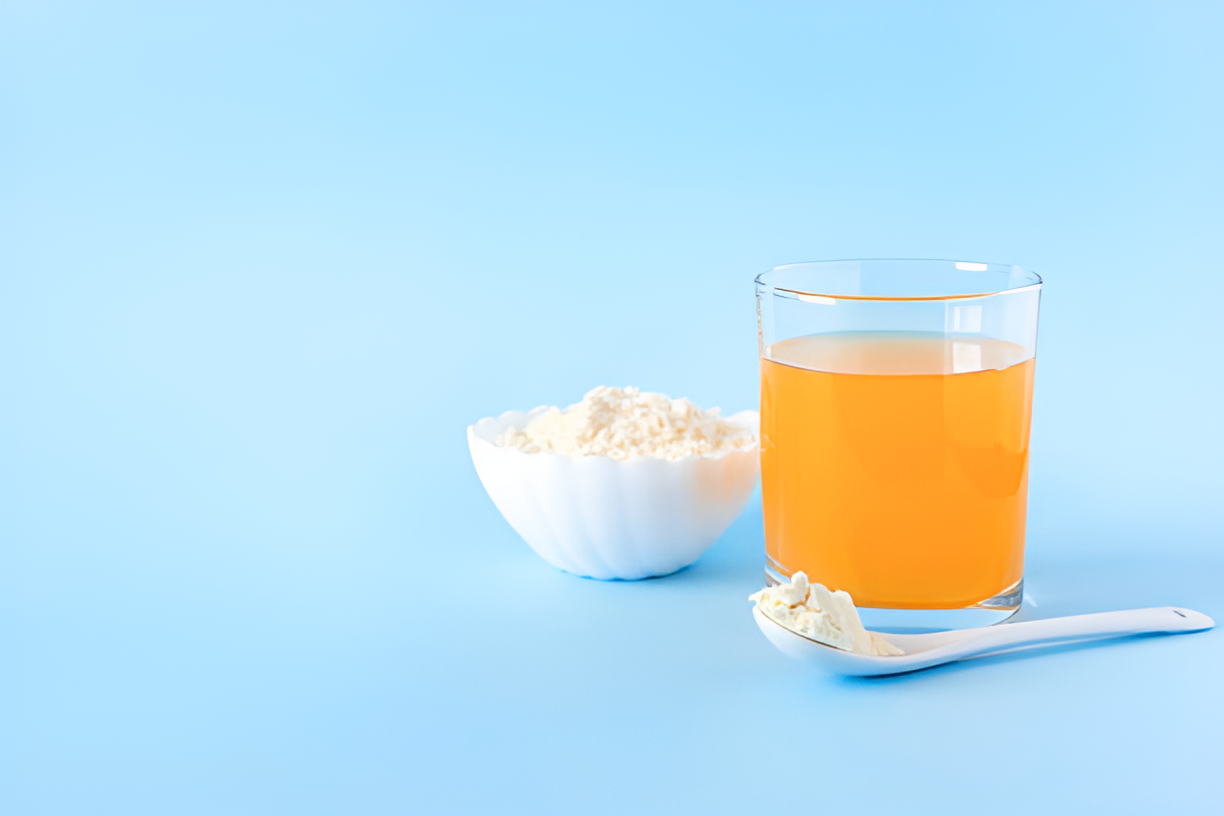
Instant drink powders
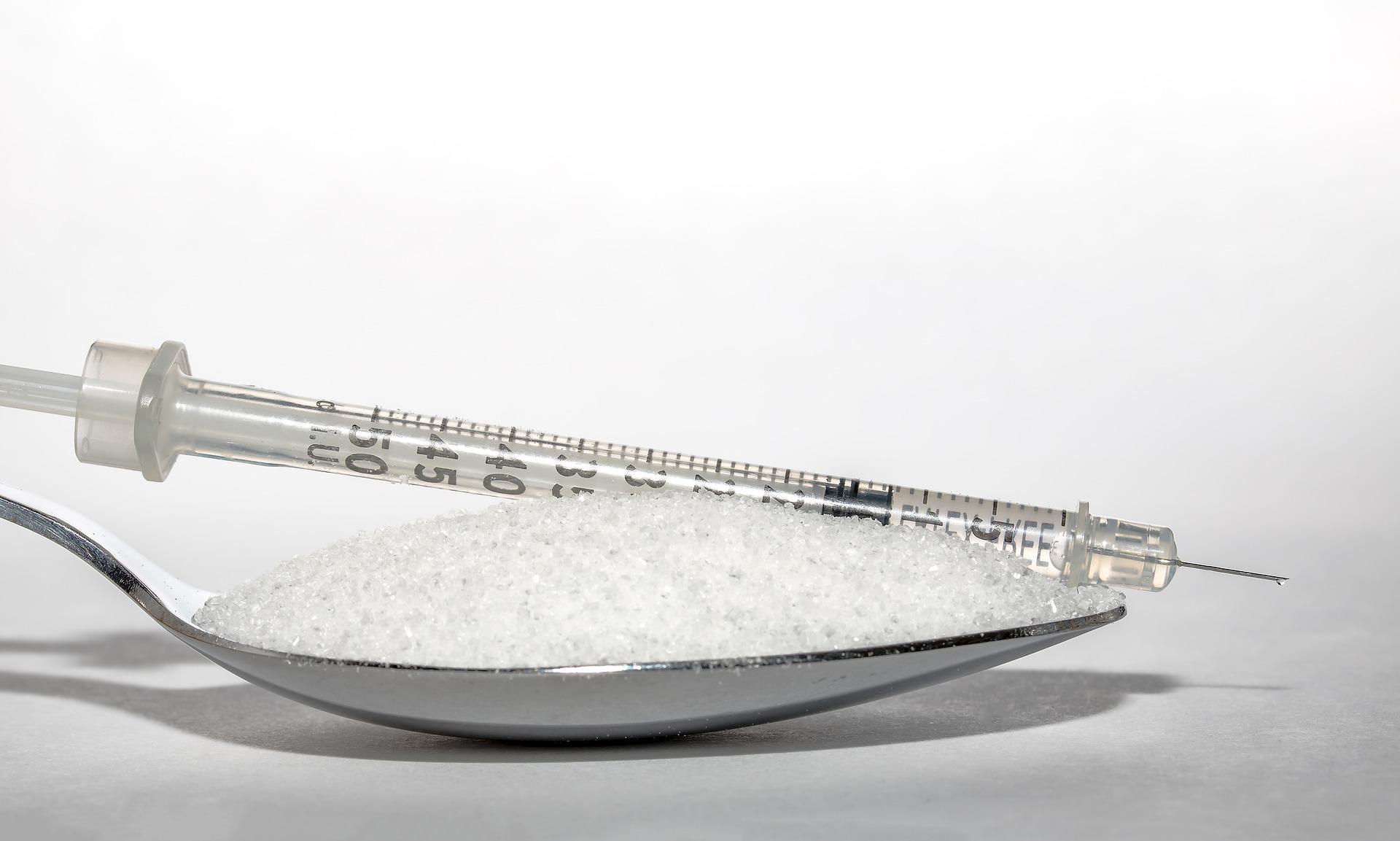
Insulin
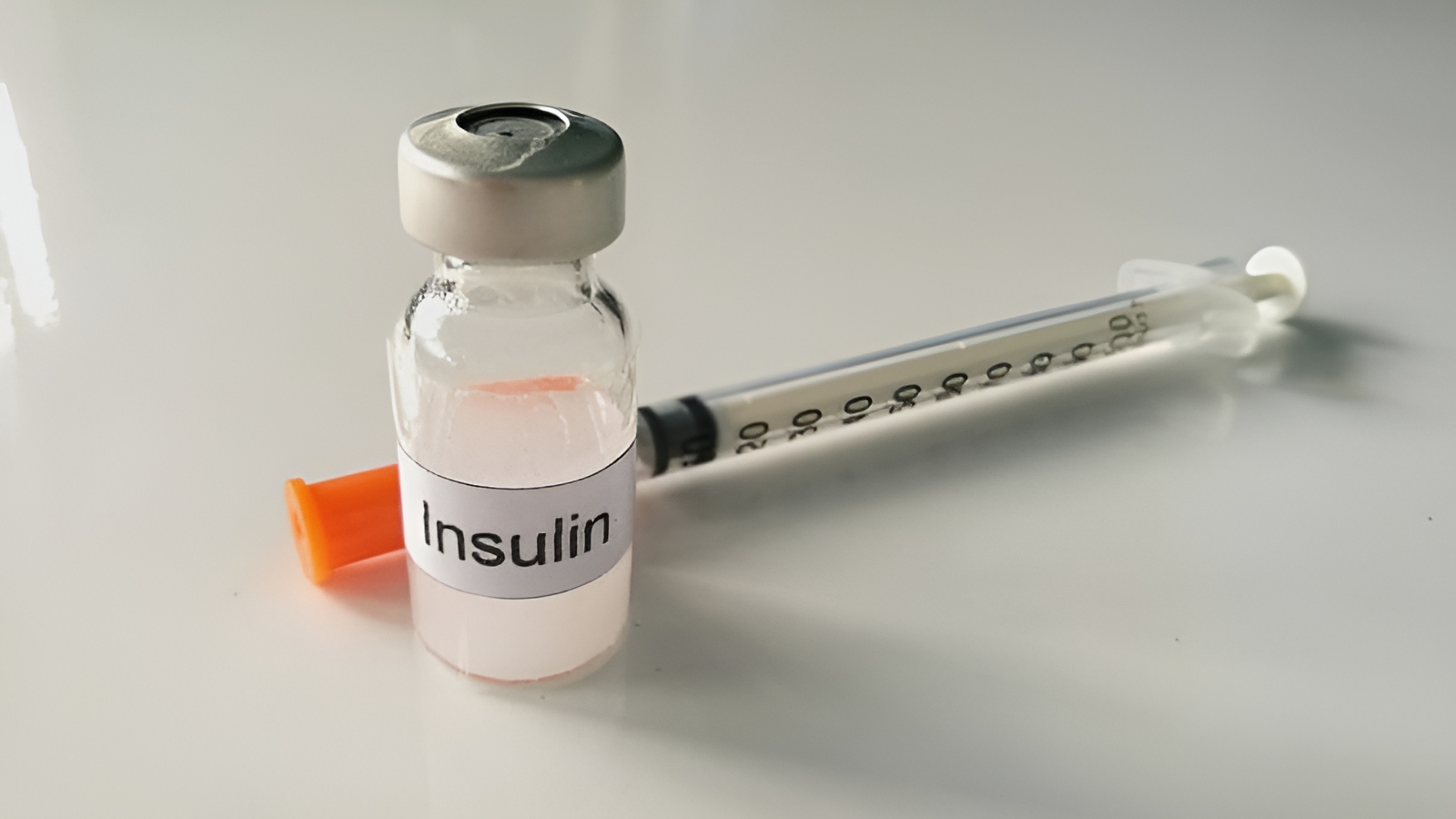
Insulin injections
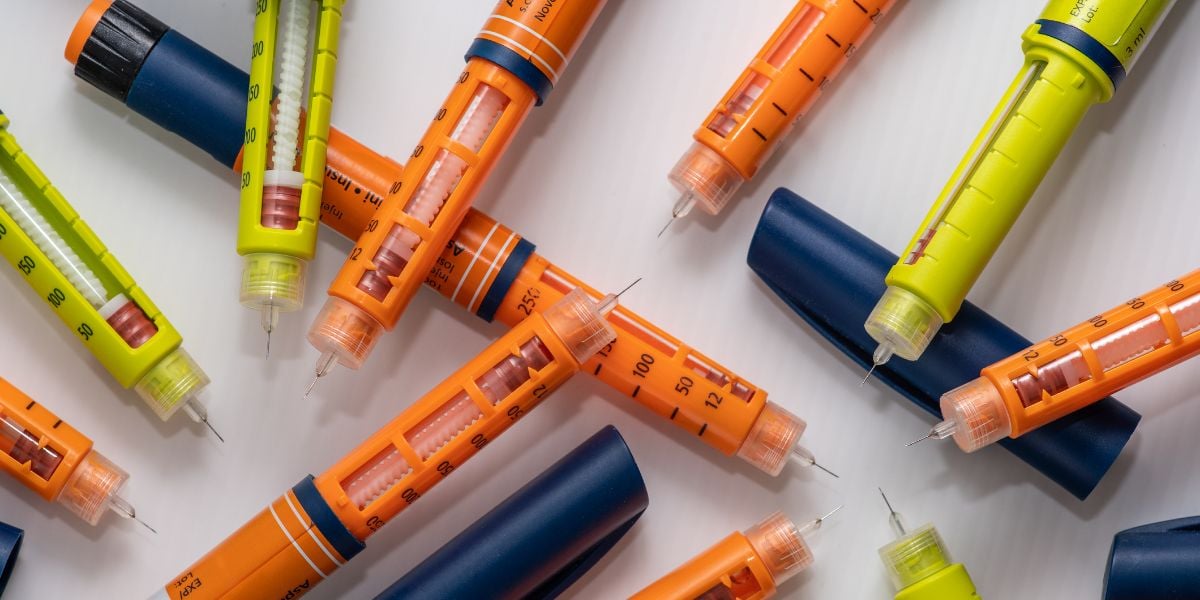
Insulin pens
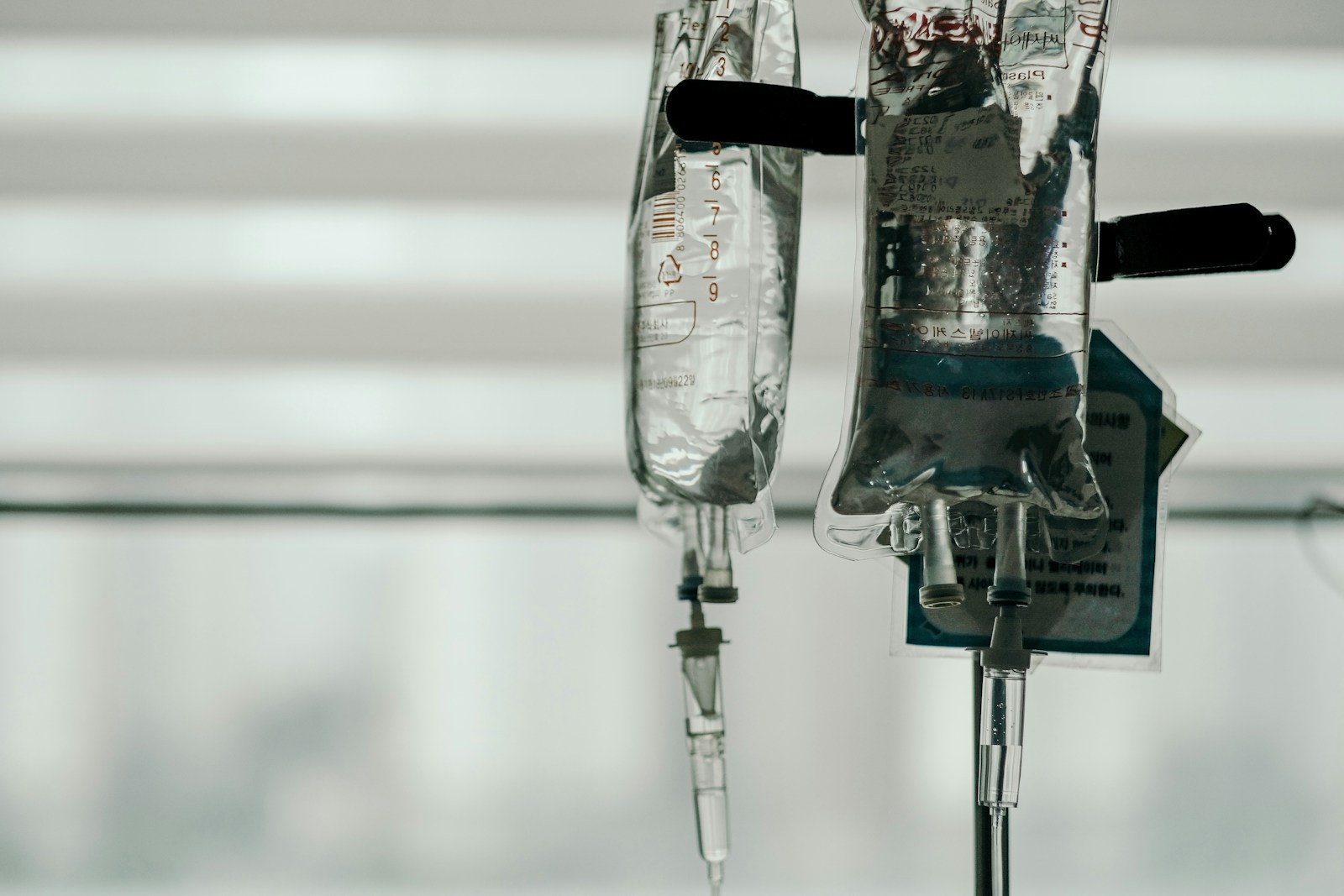
Intravenous solutions
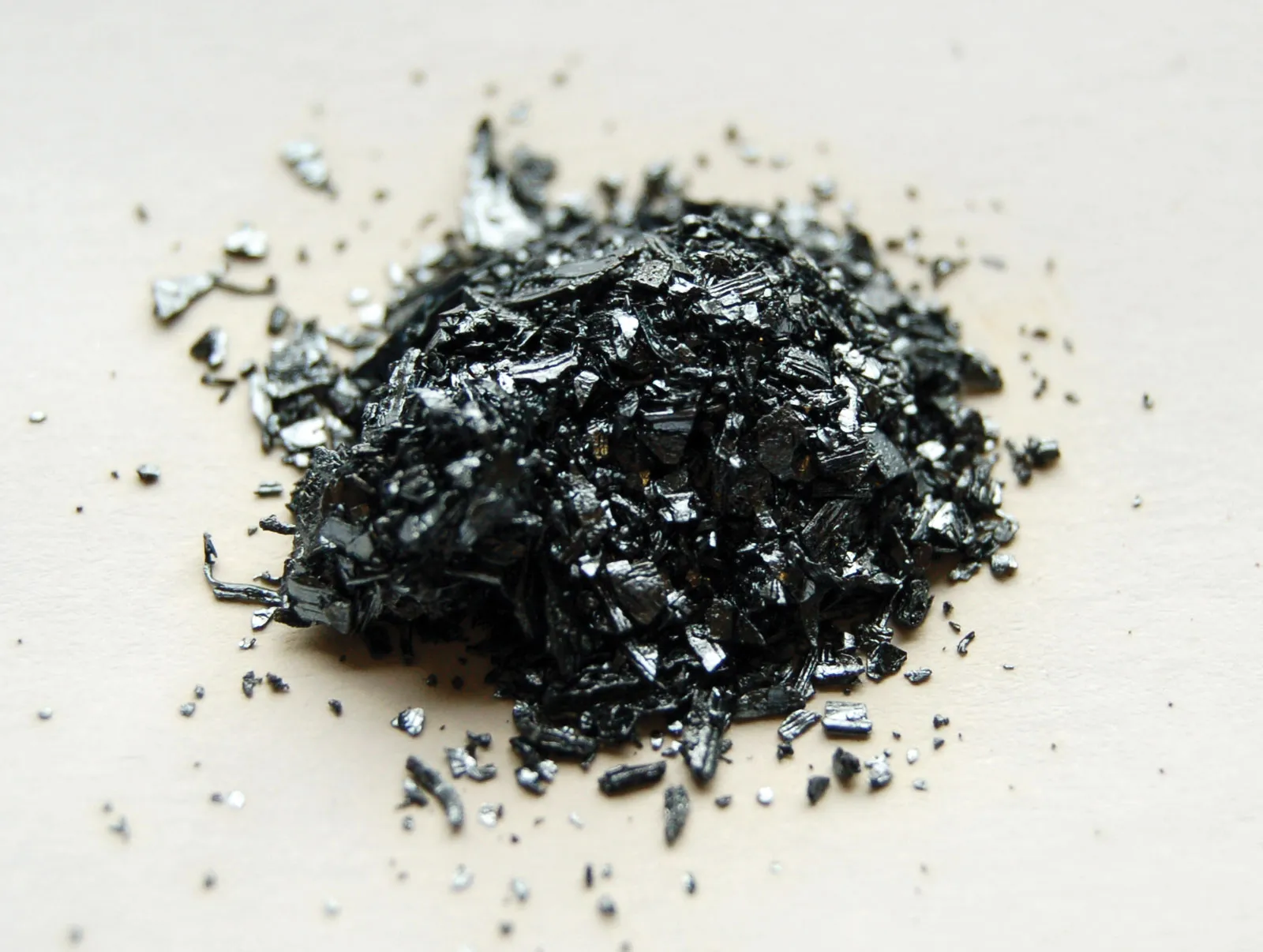
Iodine-131
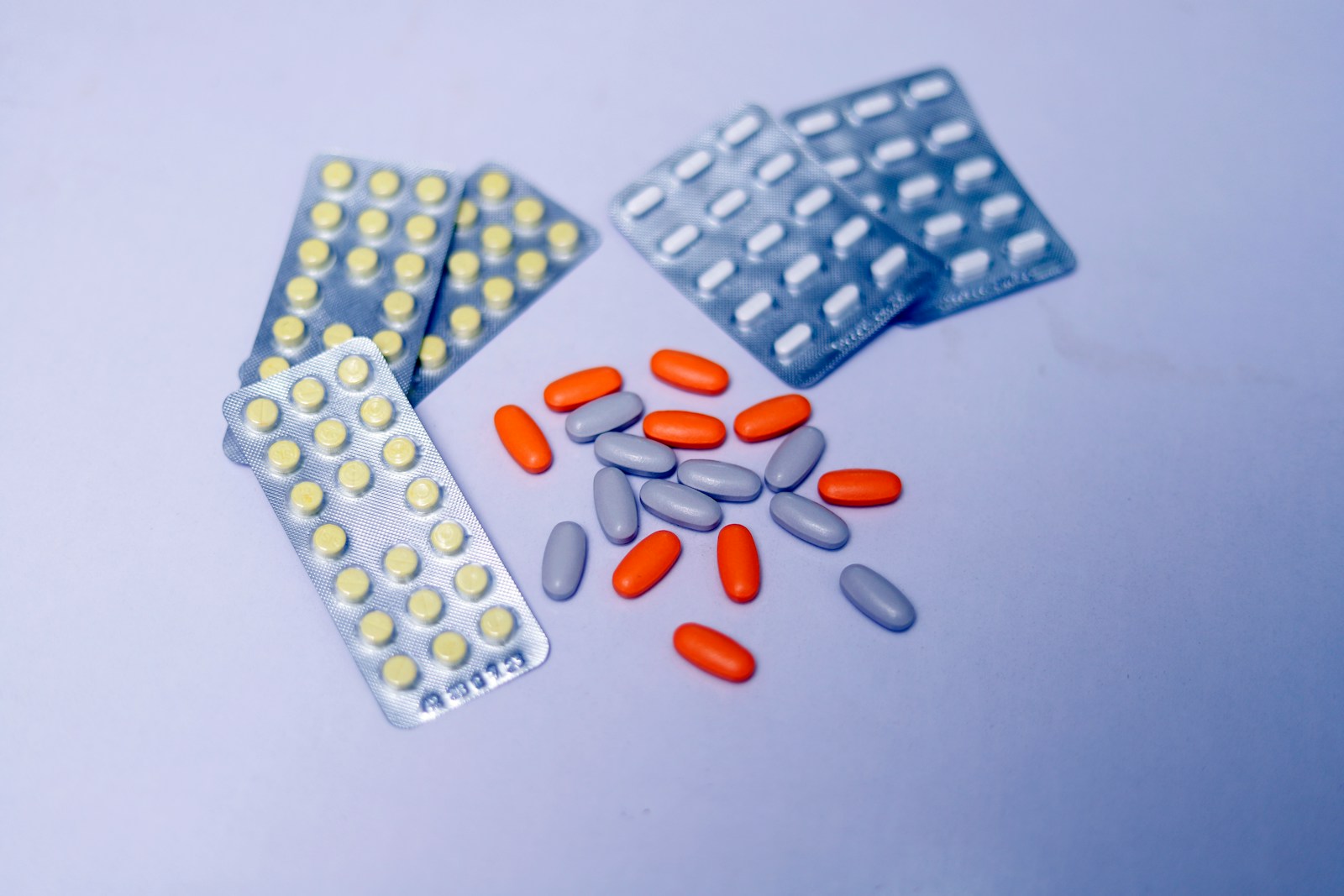
Iron supplements
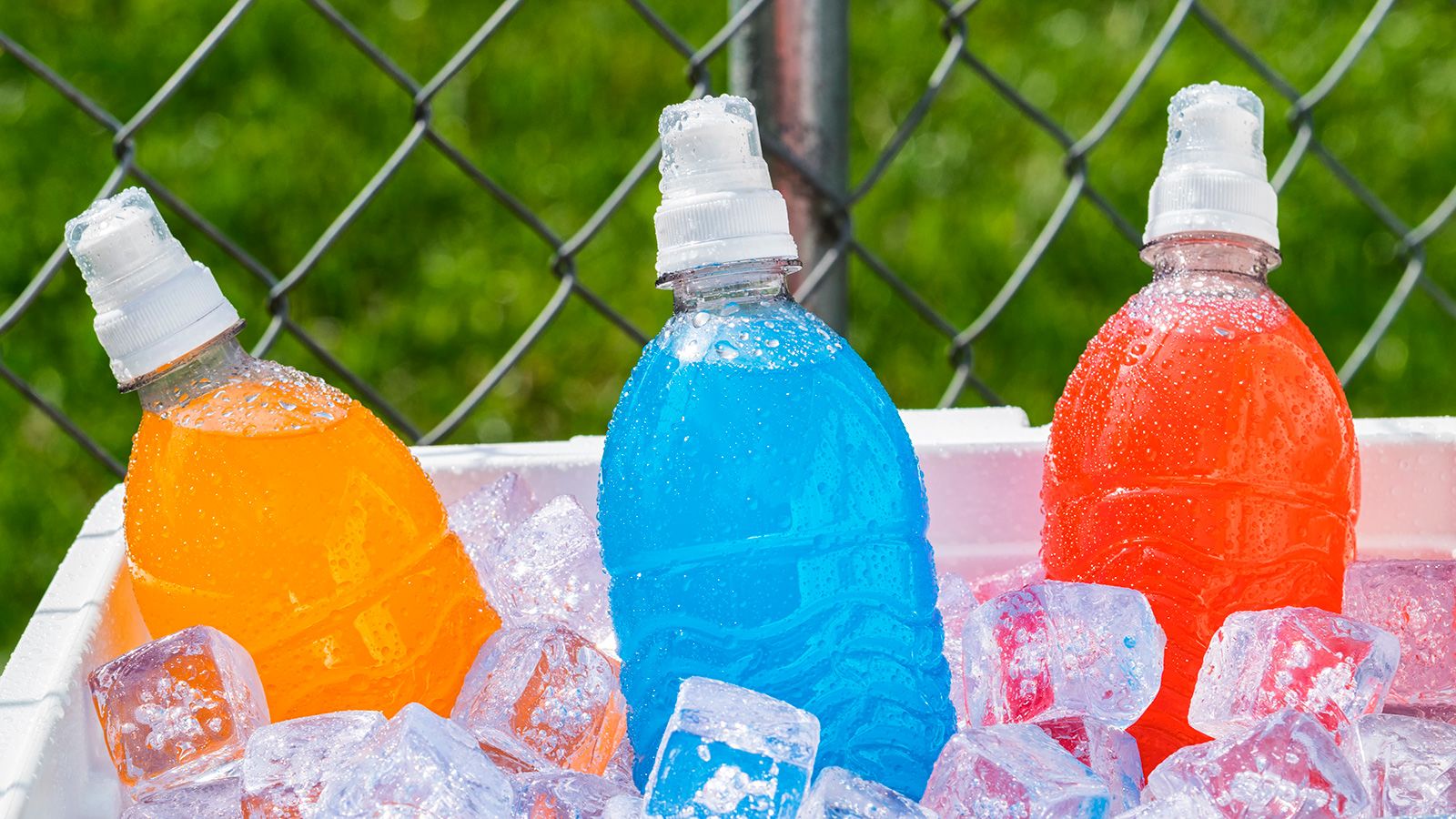
Isotonic drinks
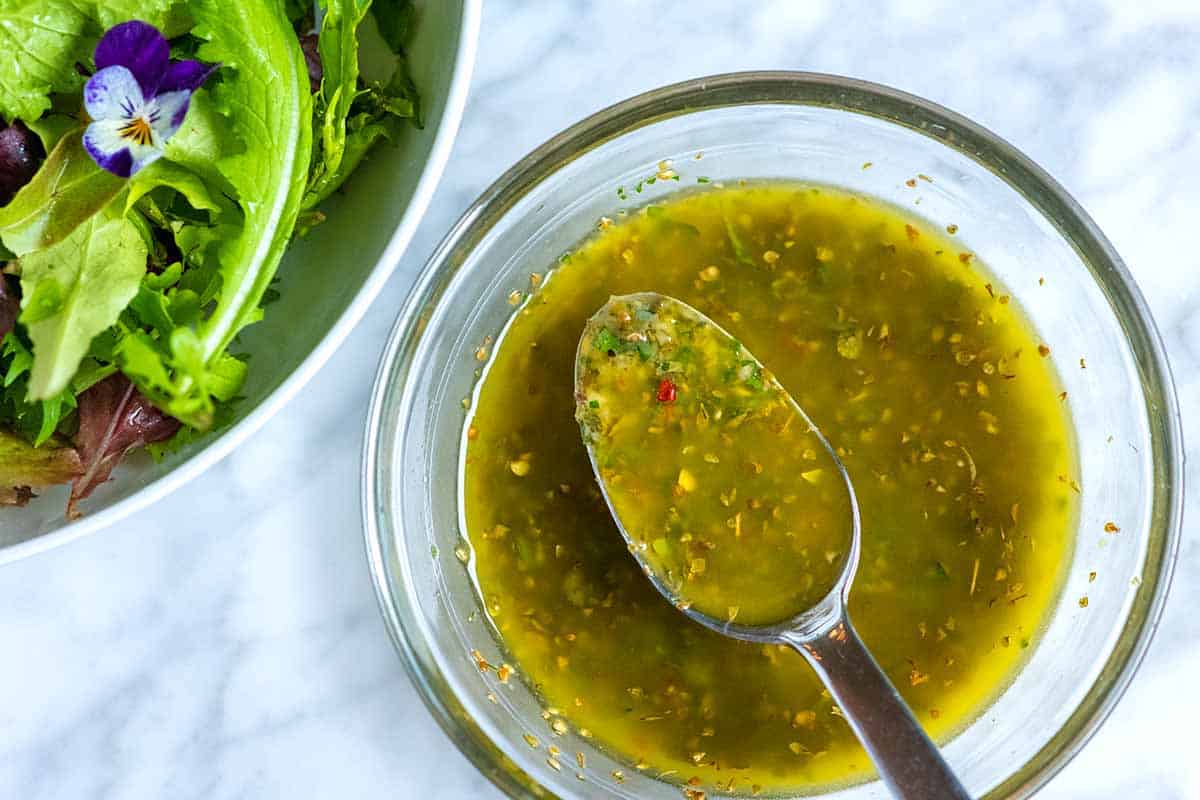
Italian dressing
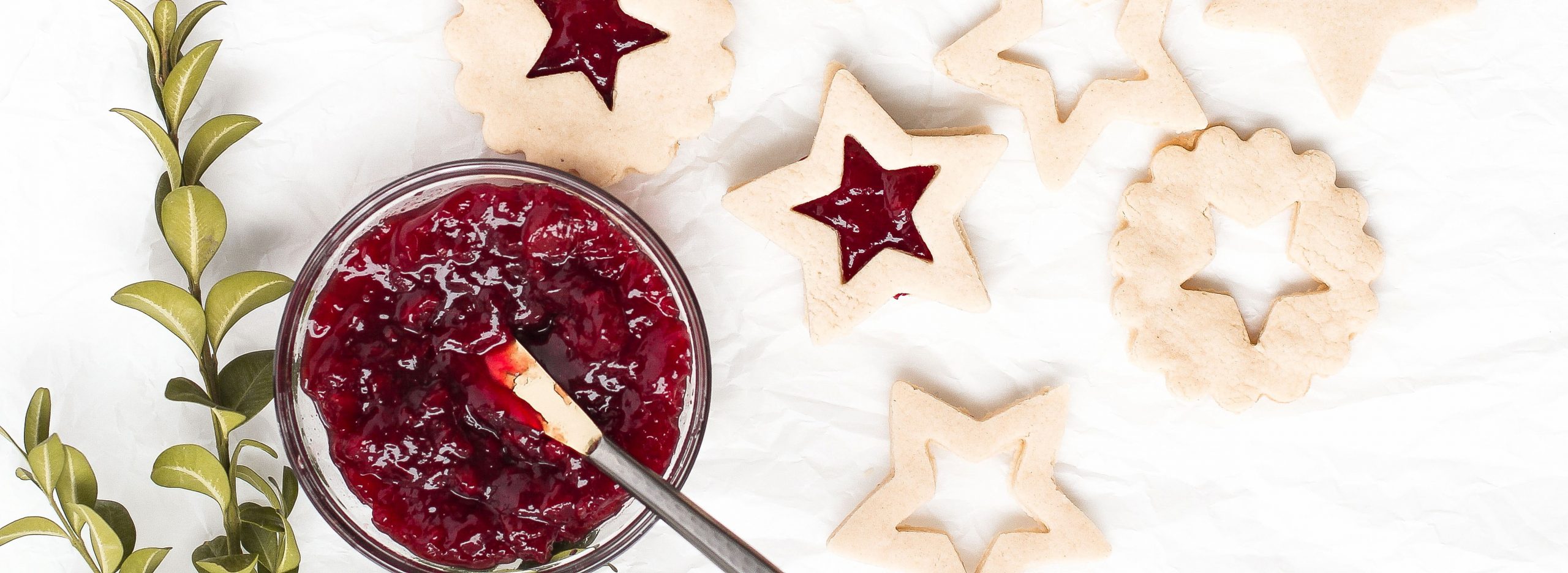
Jam

Jars
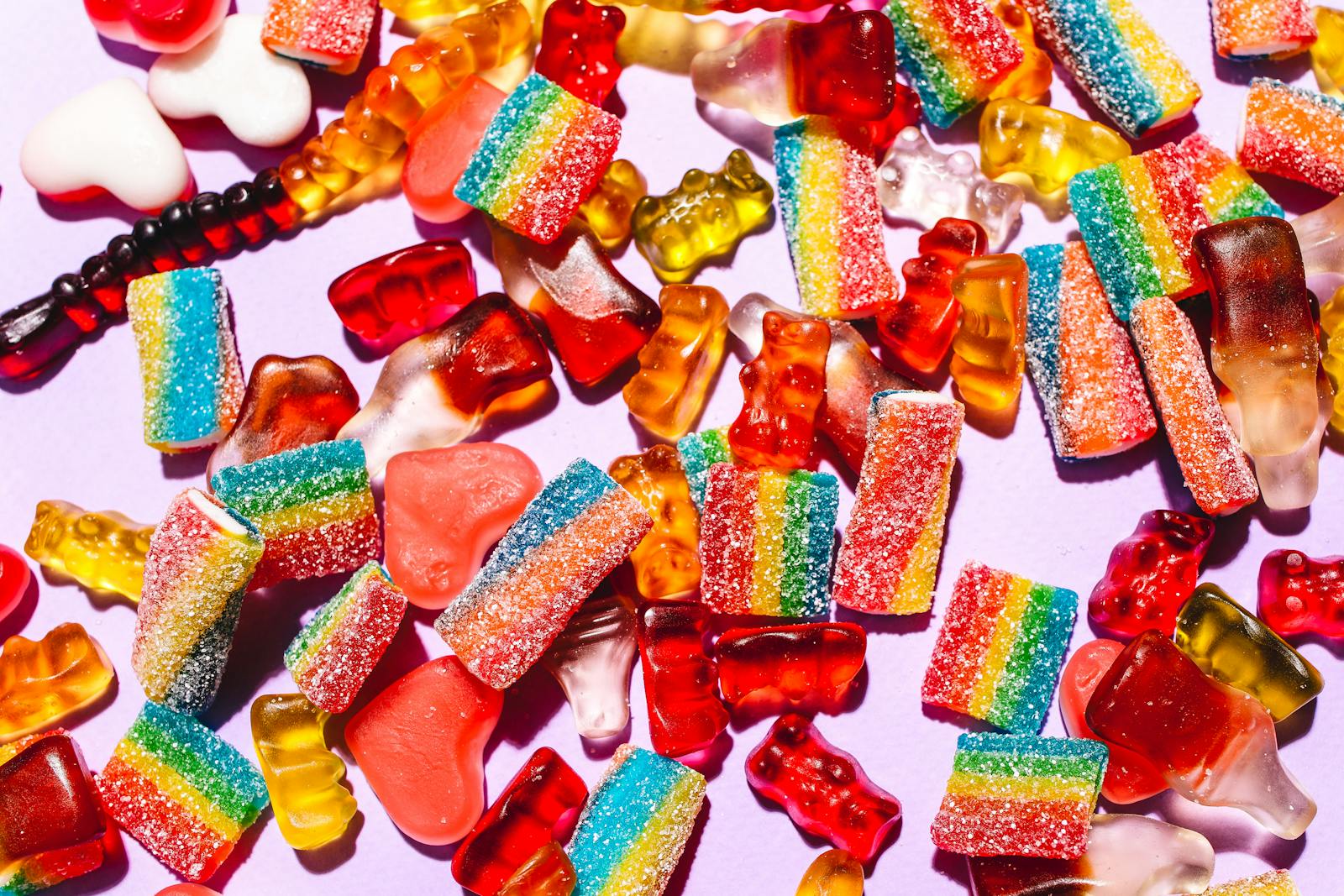
Jellies
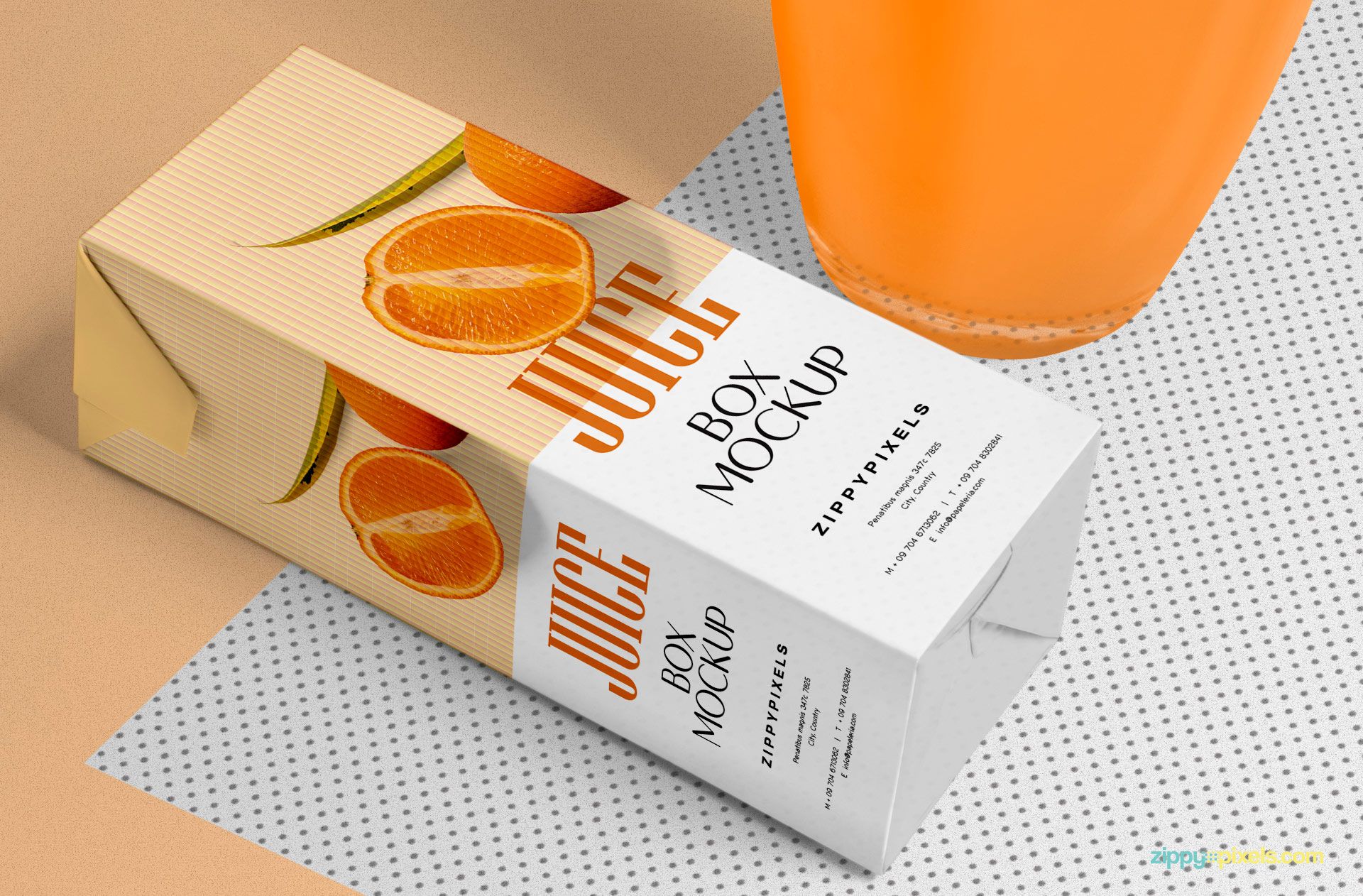
Juice cartons
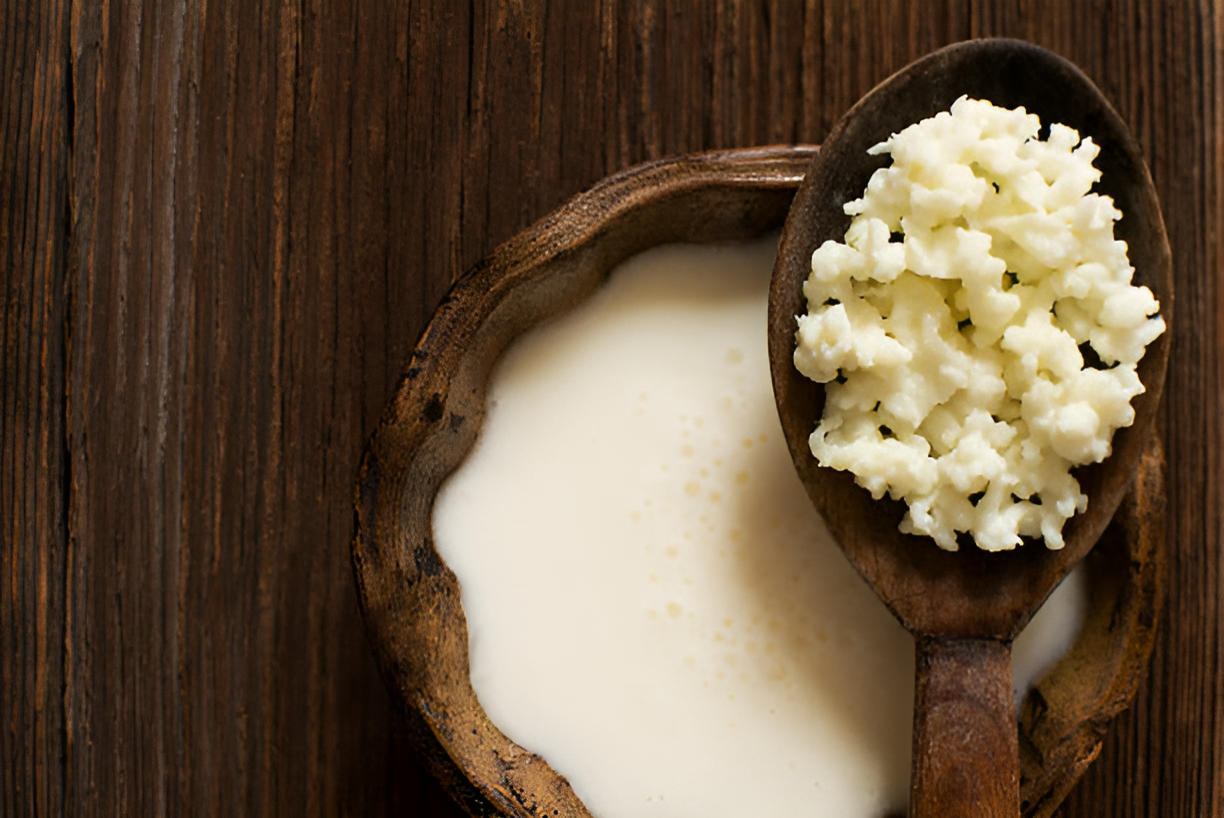
Kefir
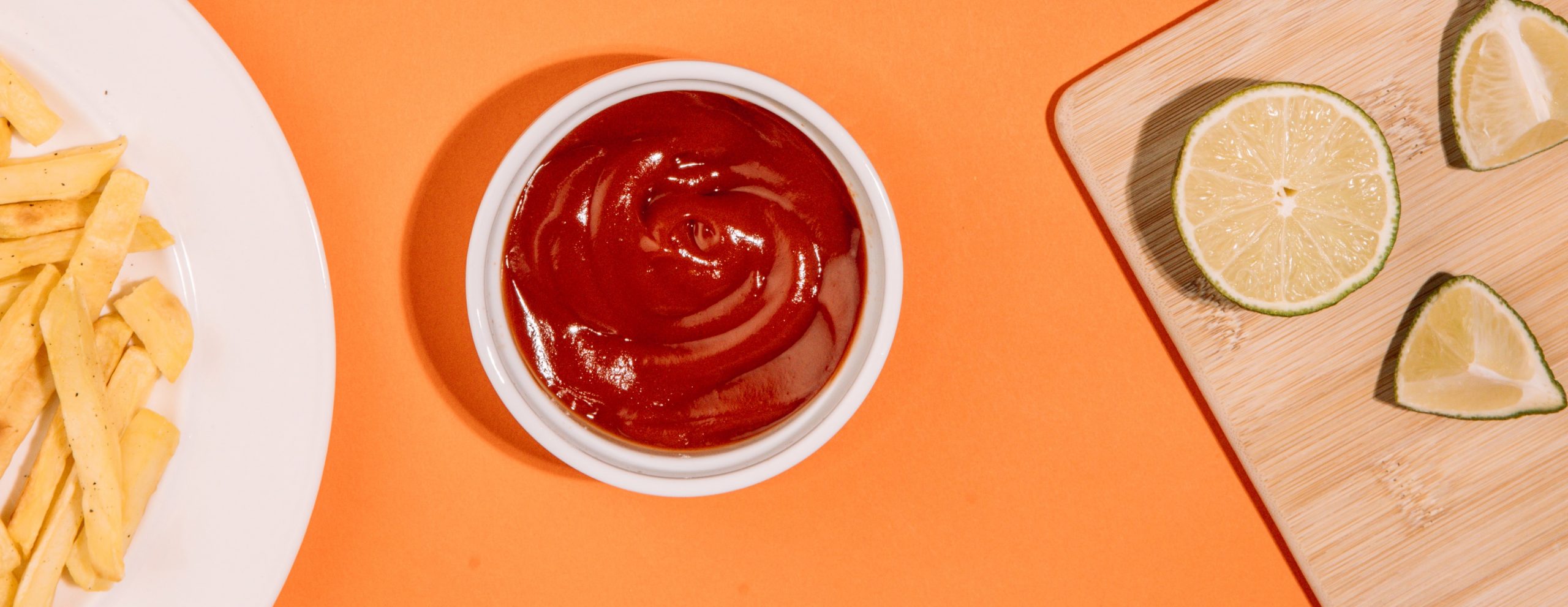
Ketchup
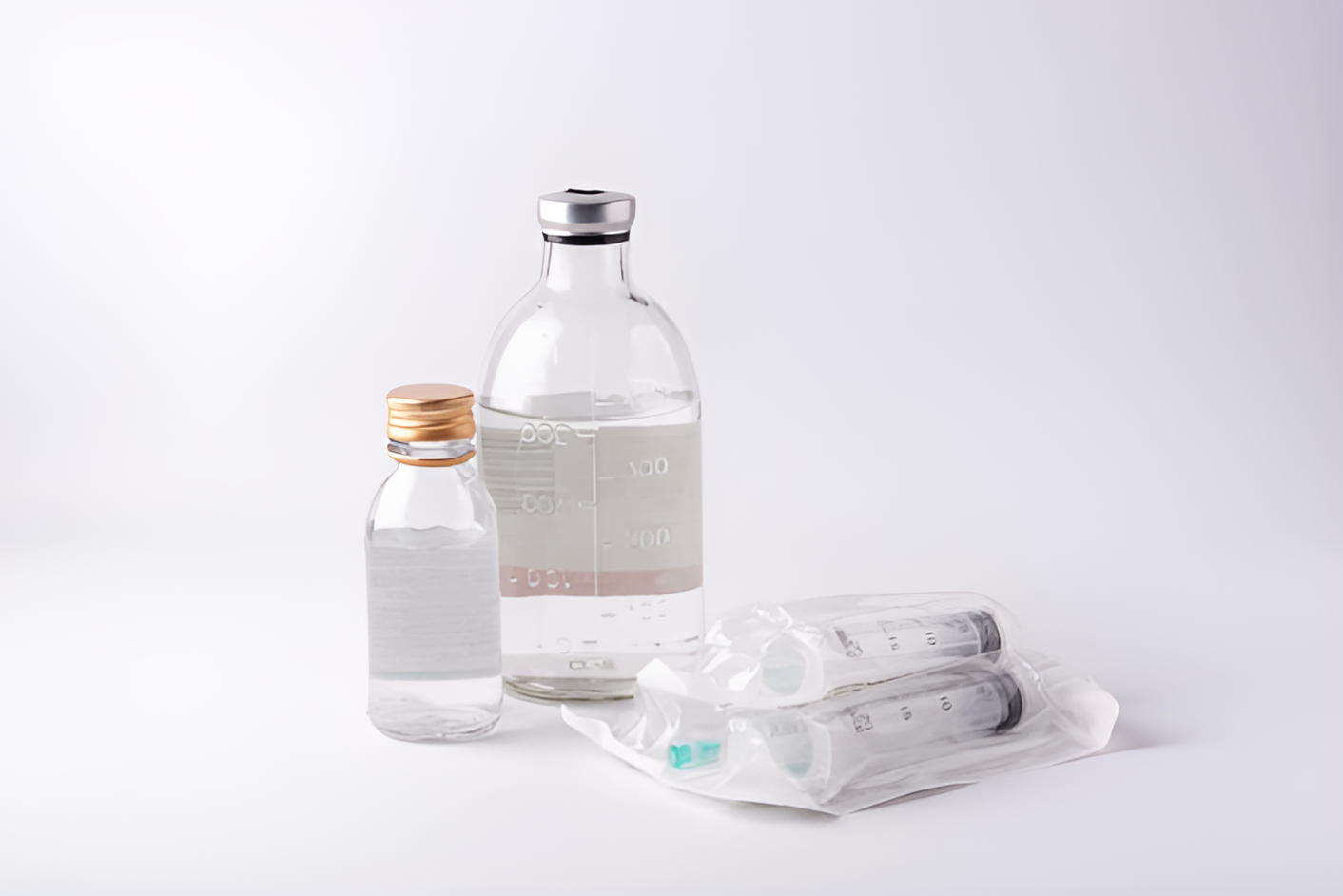
Large volume parenterals
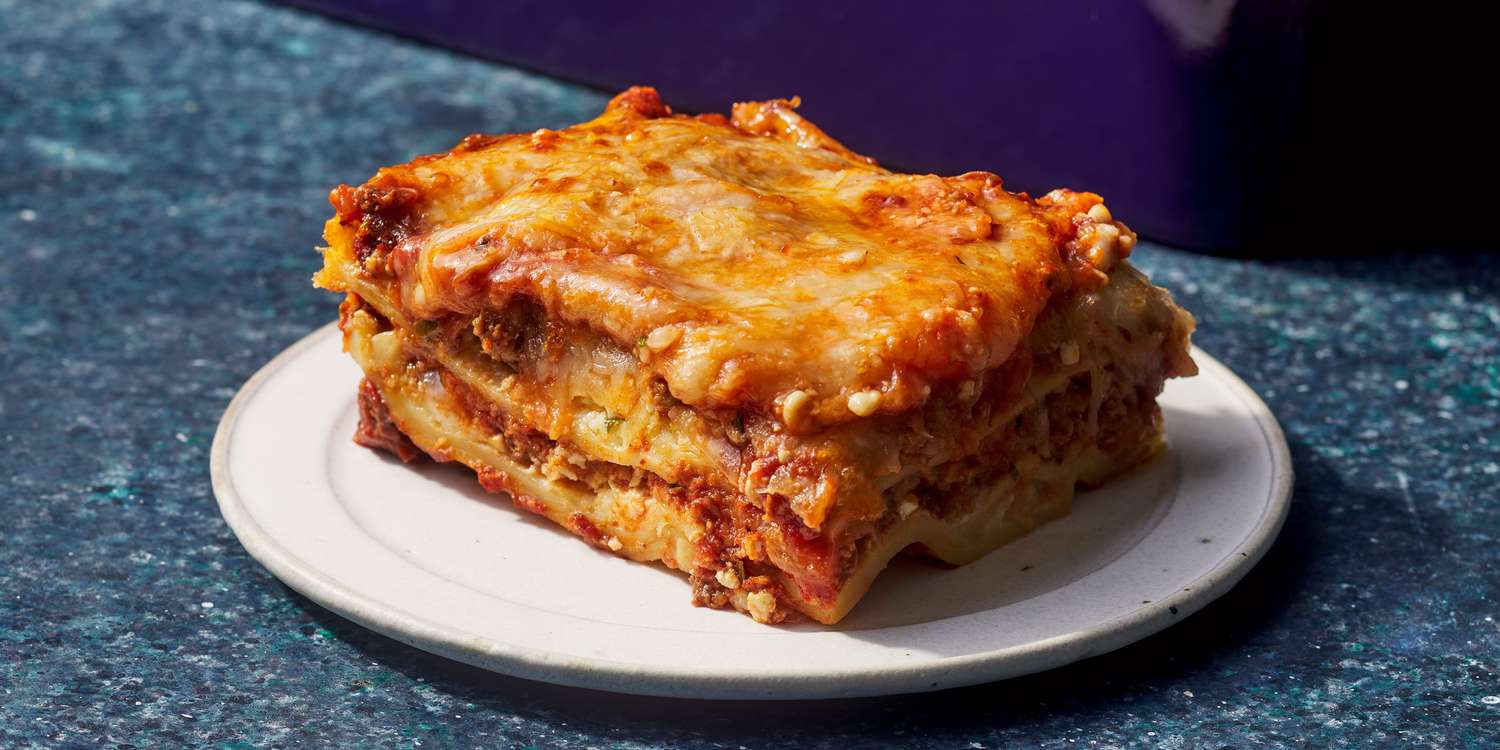
Lasagna

Latex
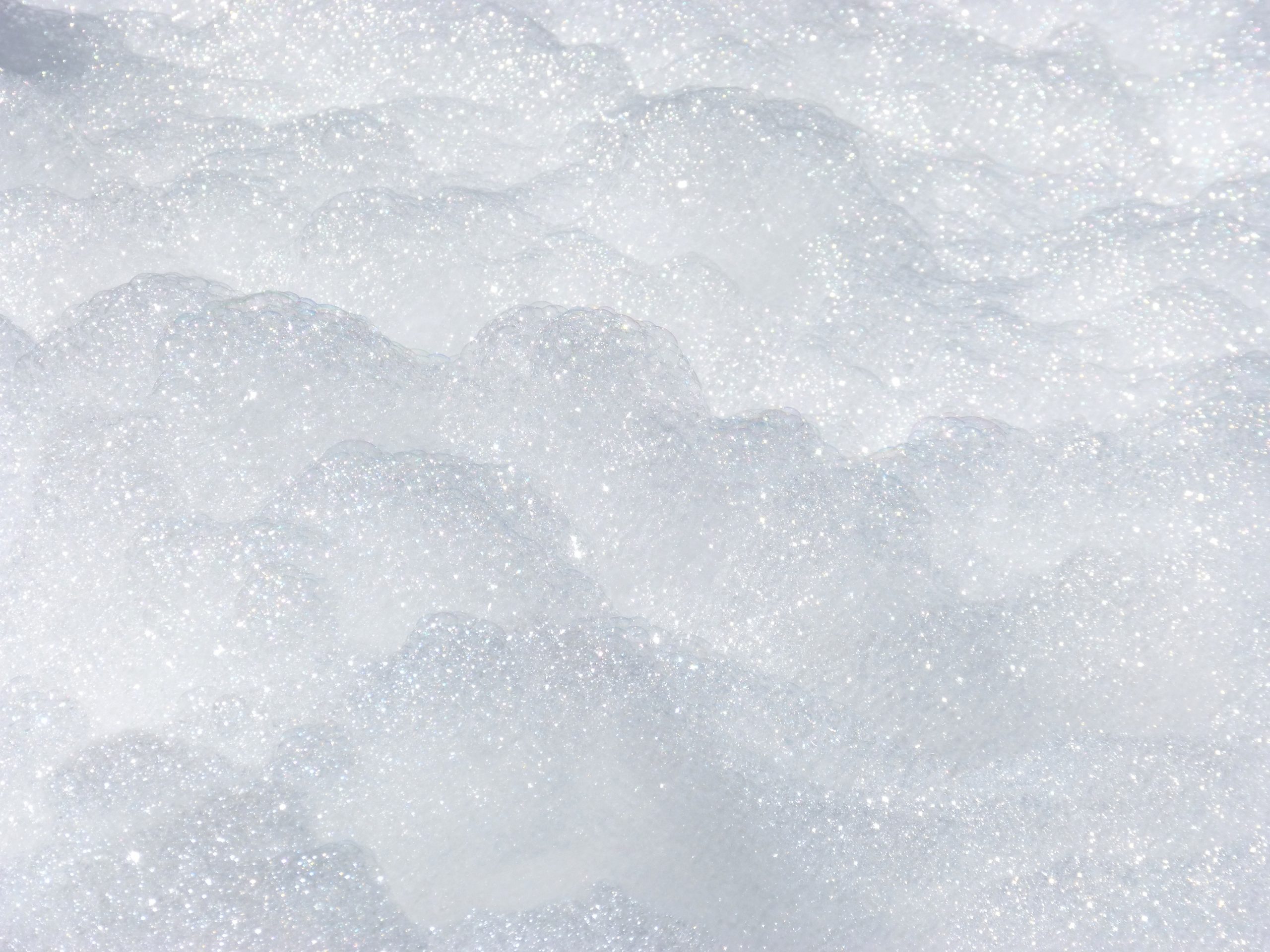
Laundry detergent
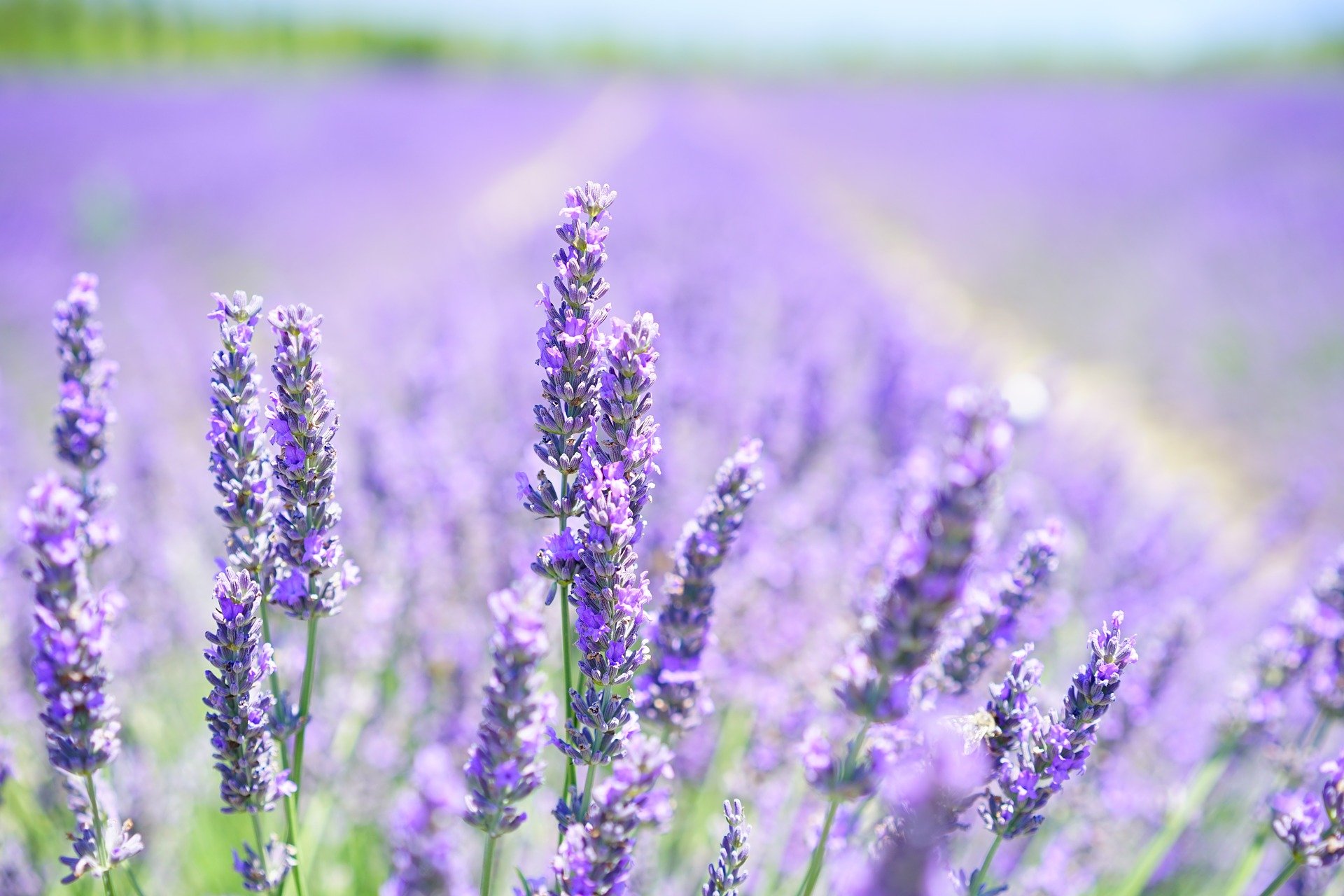
Lavender oil
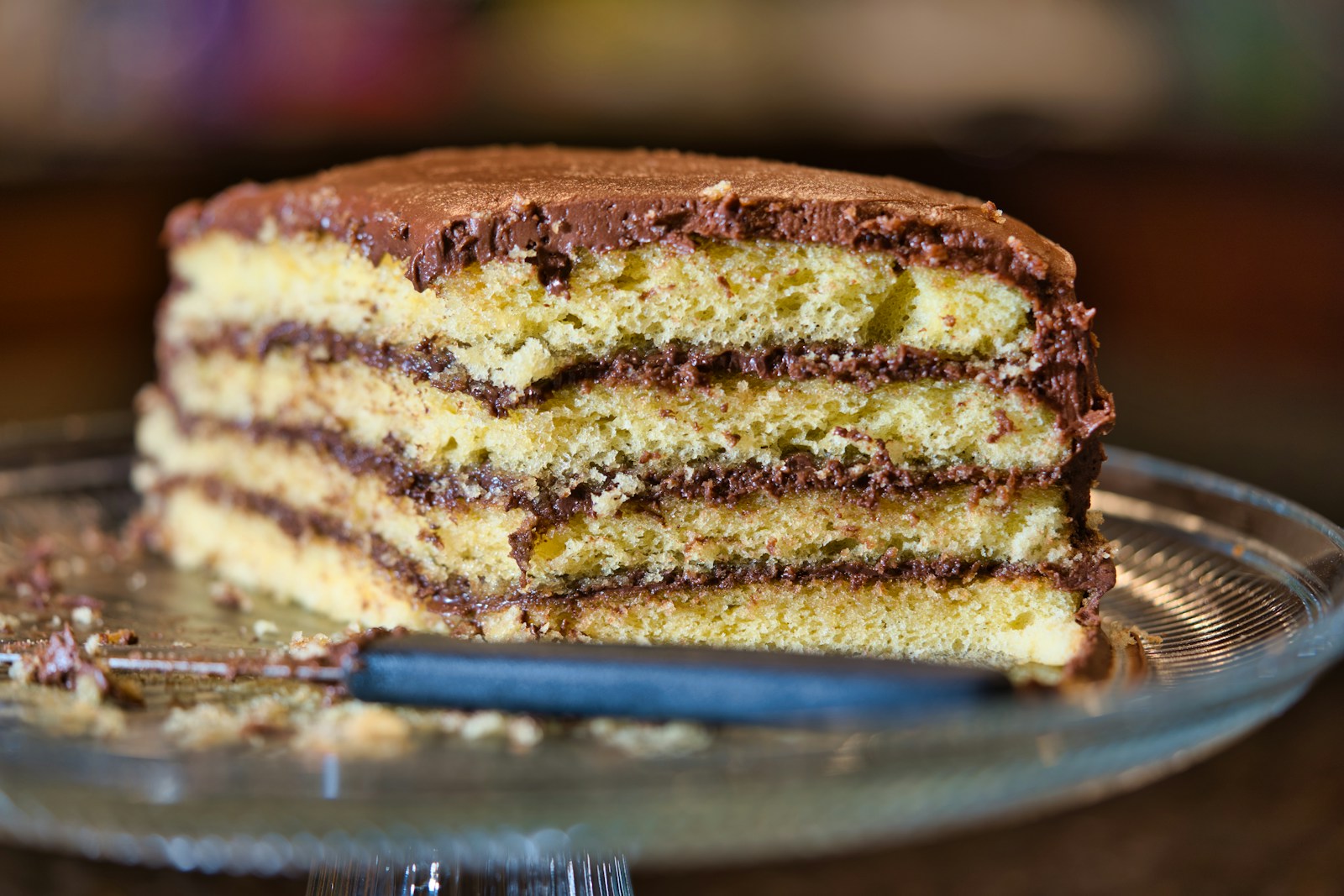
Layered cakes
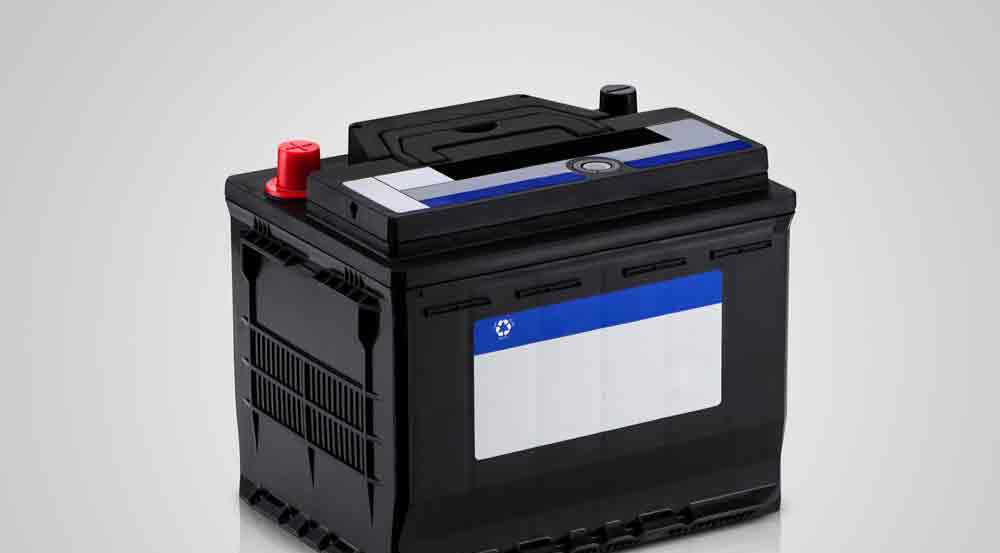
Lead-acid batteries
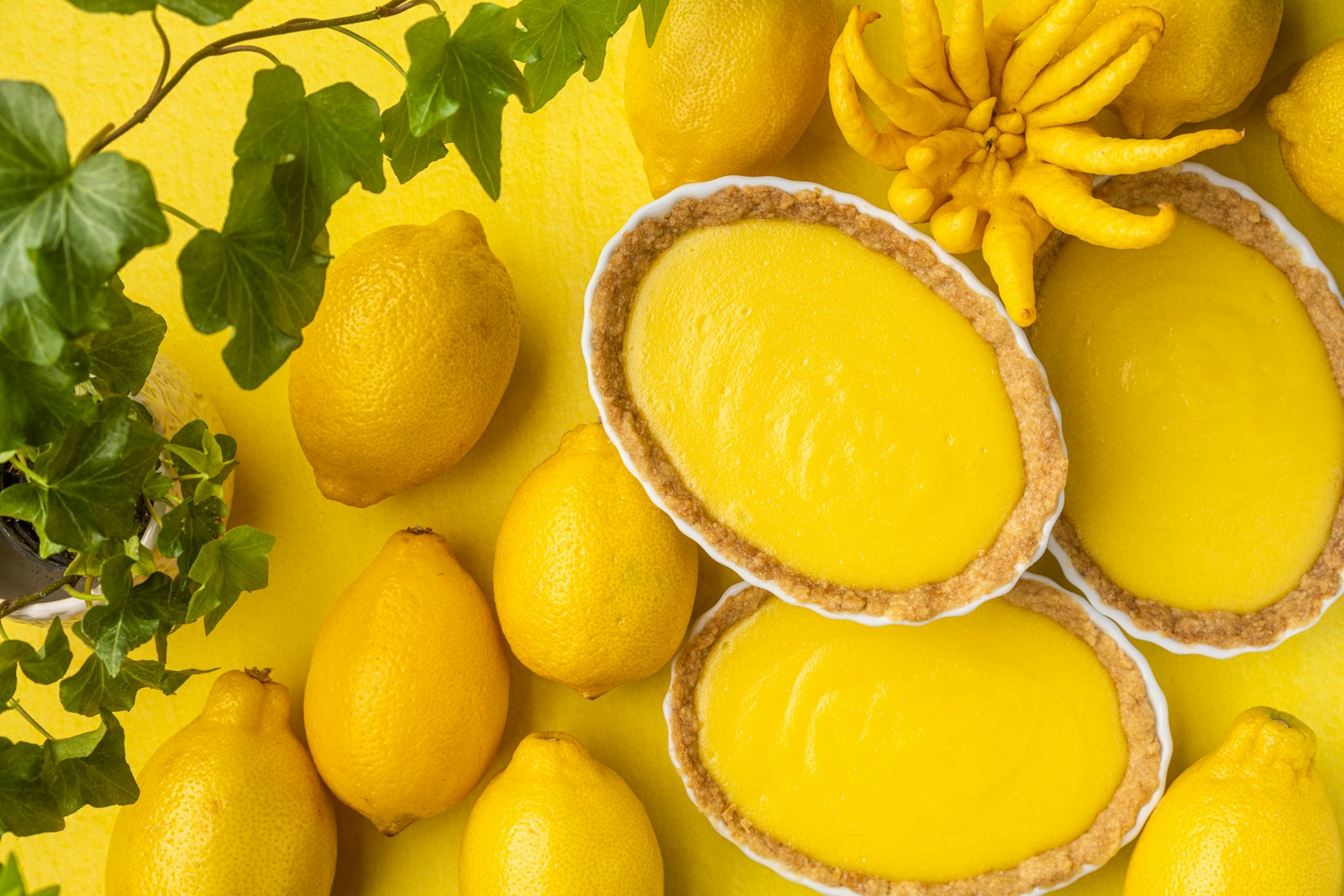
Lemon curd
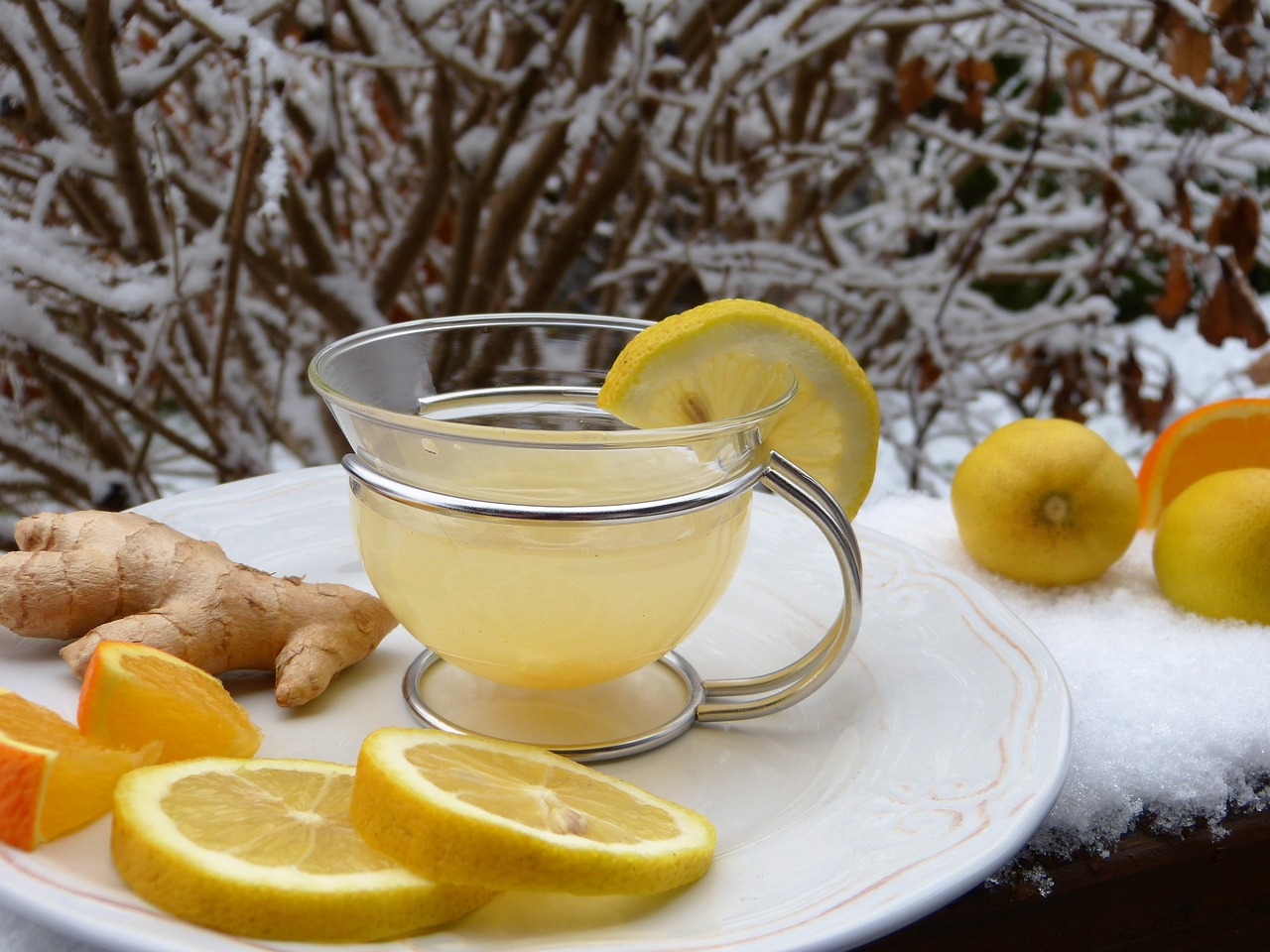
Lemon juice
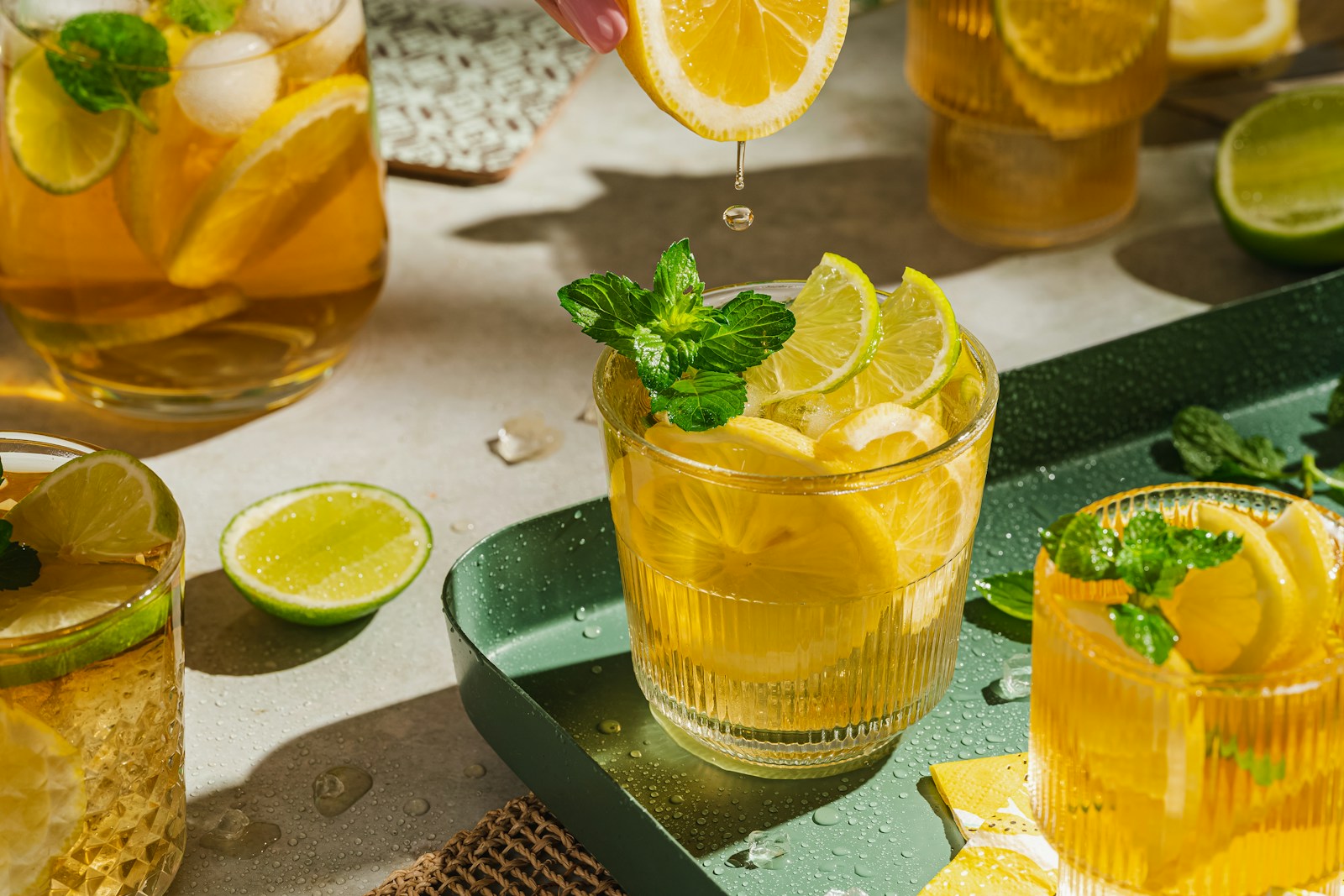
Lemonade
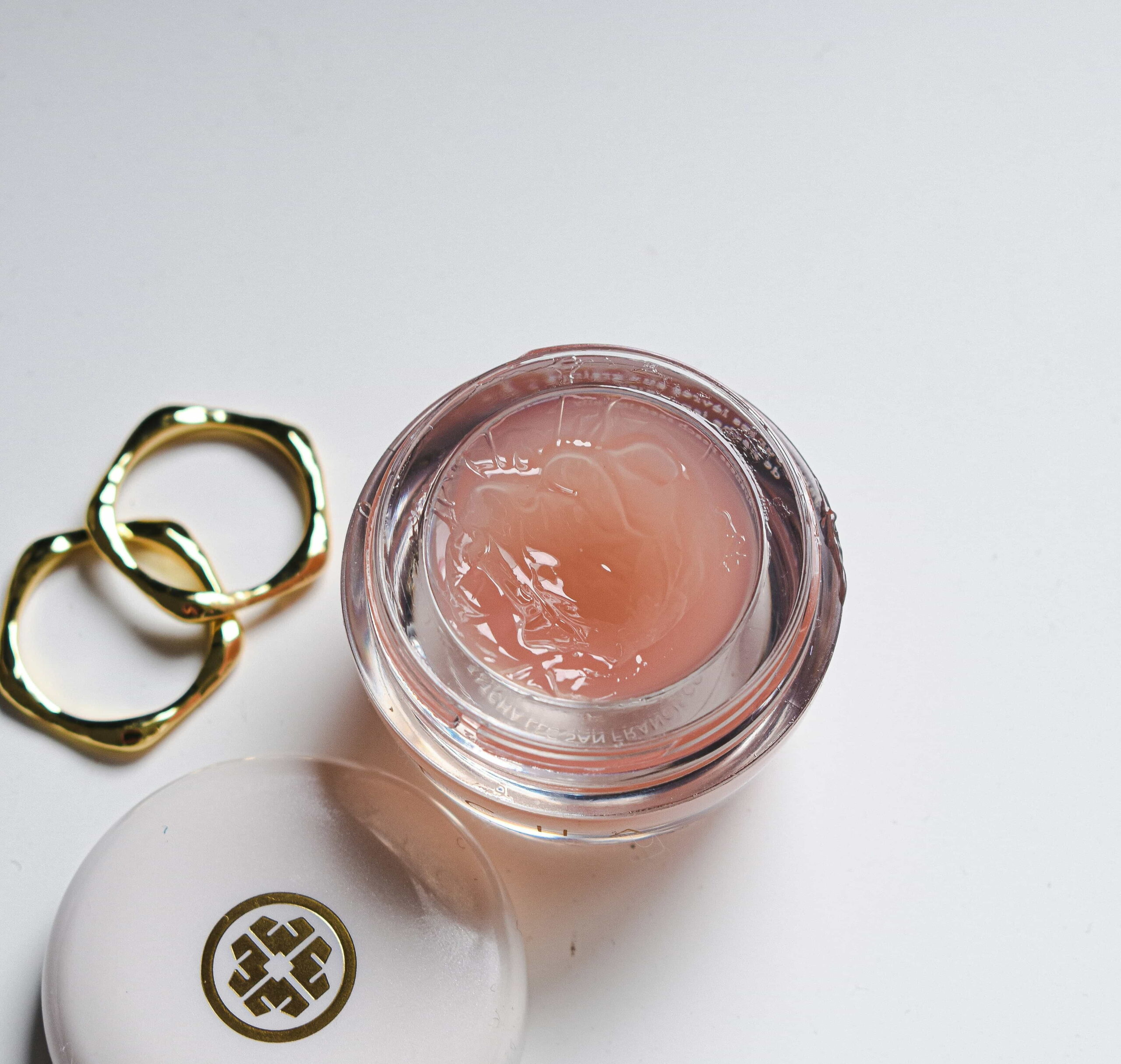
Lip balm
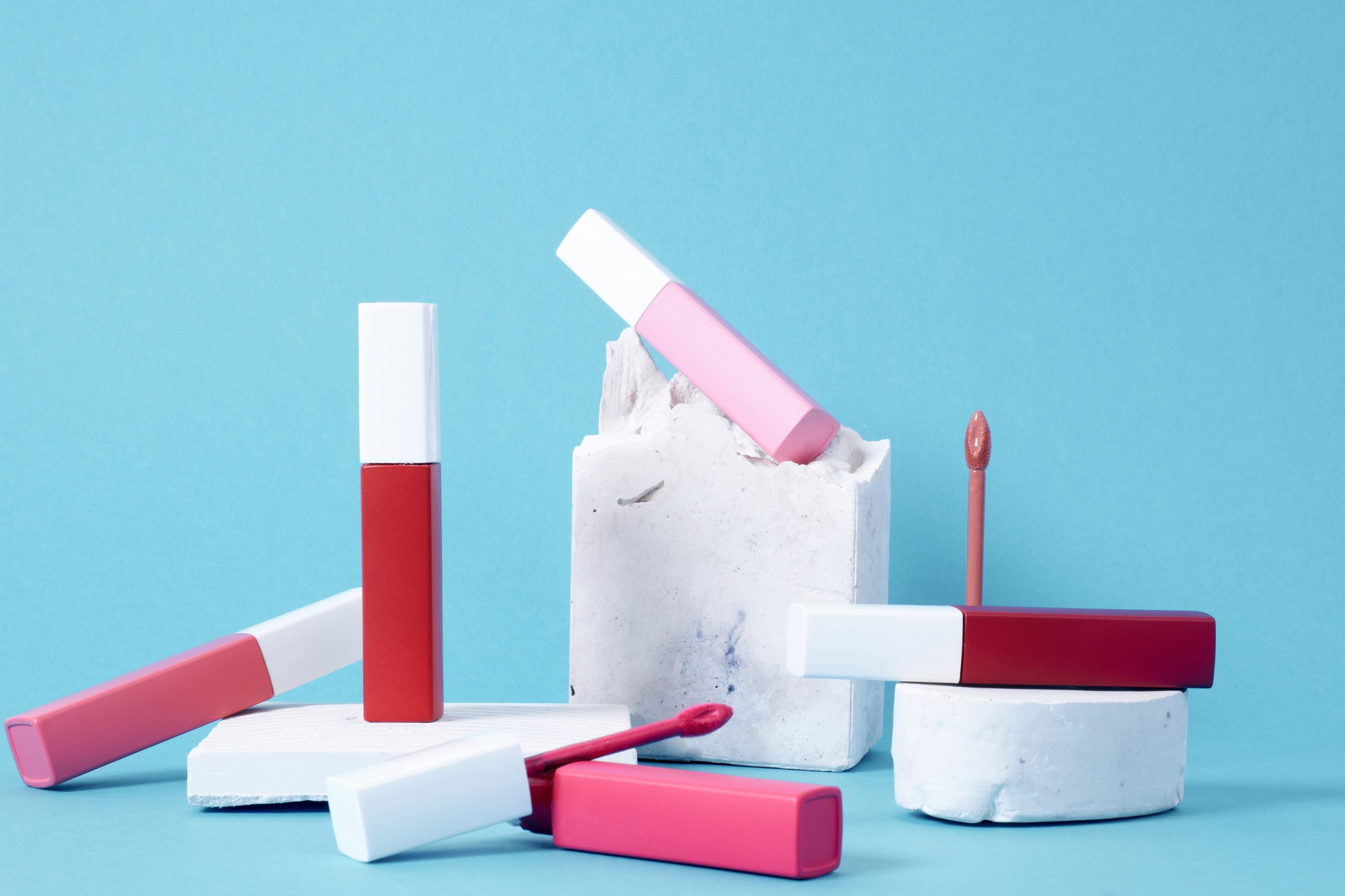
Lip gloss
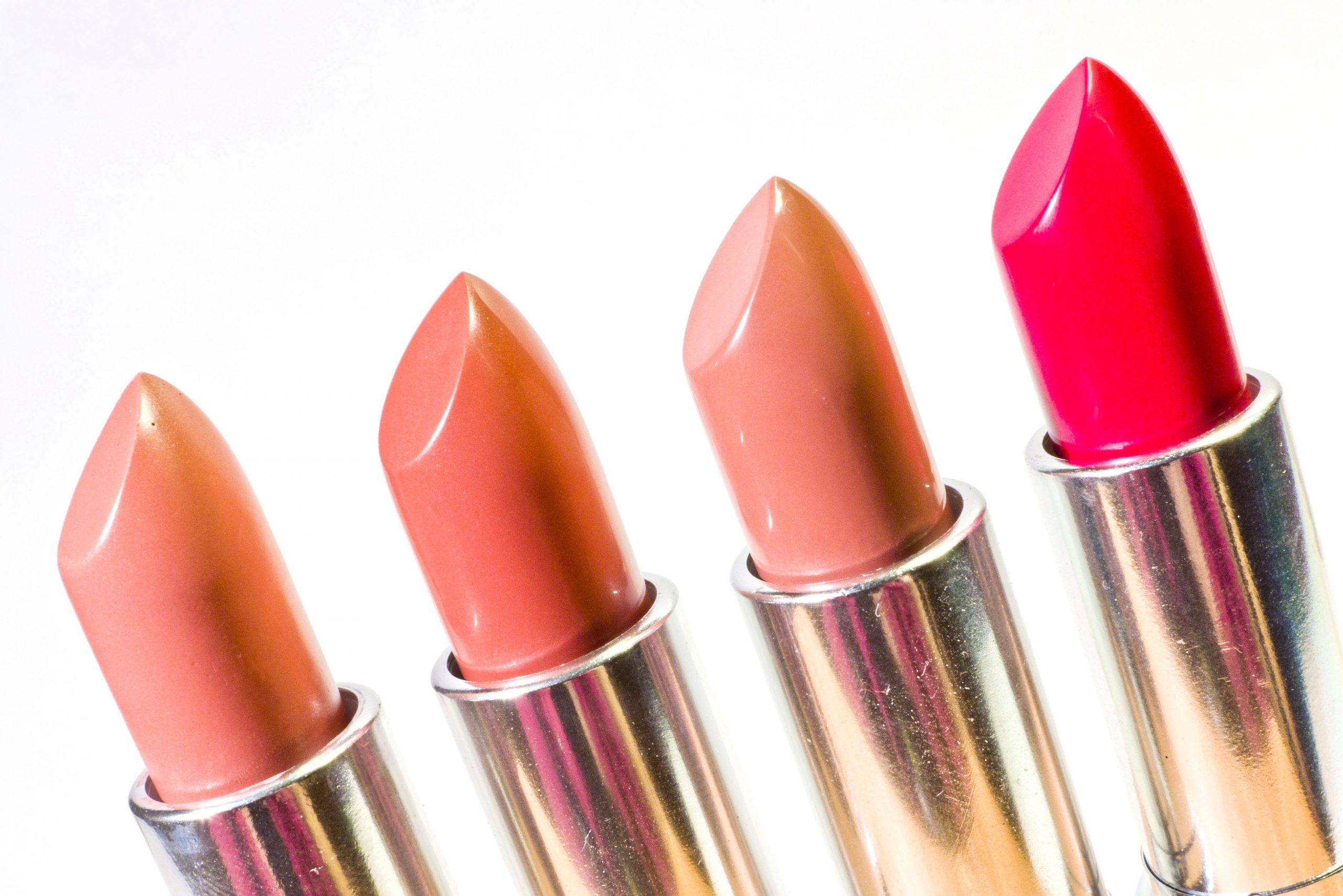
Lipstick
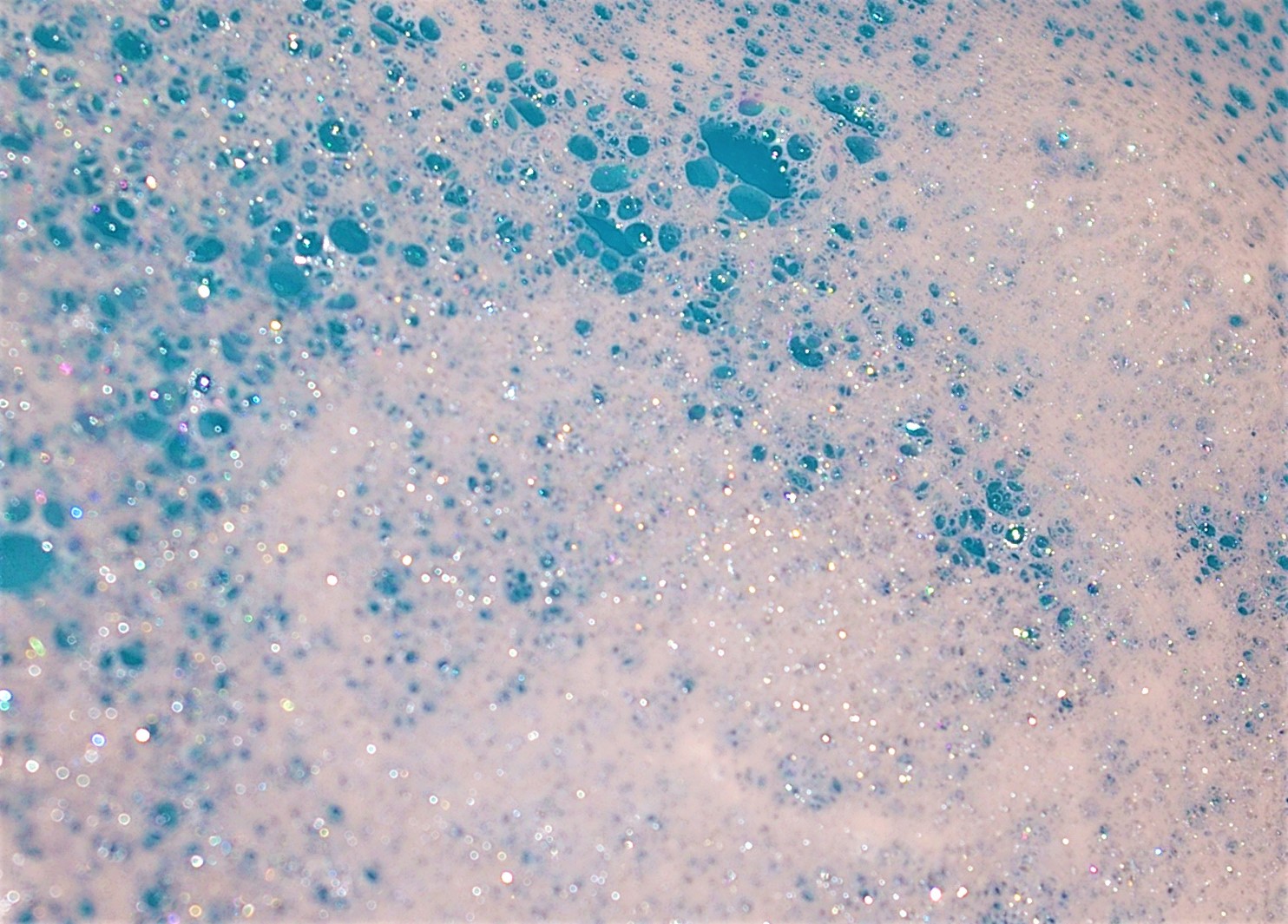
Liquid detergents
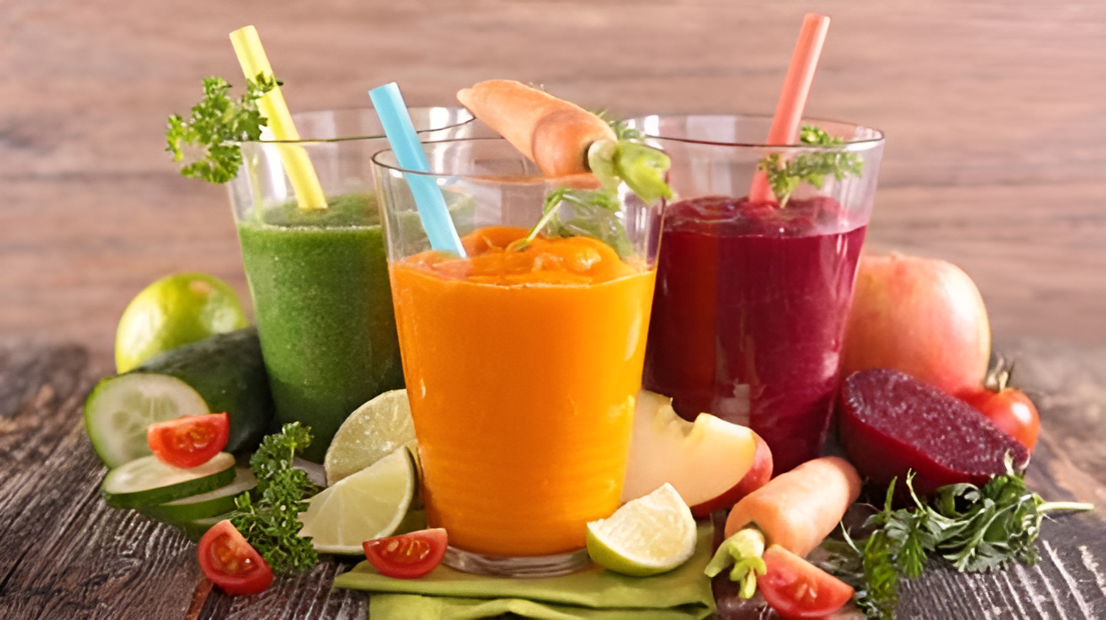
Liquid foods
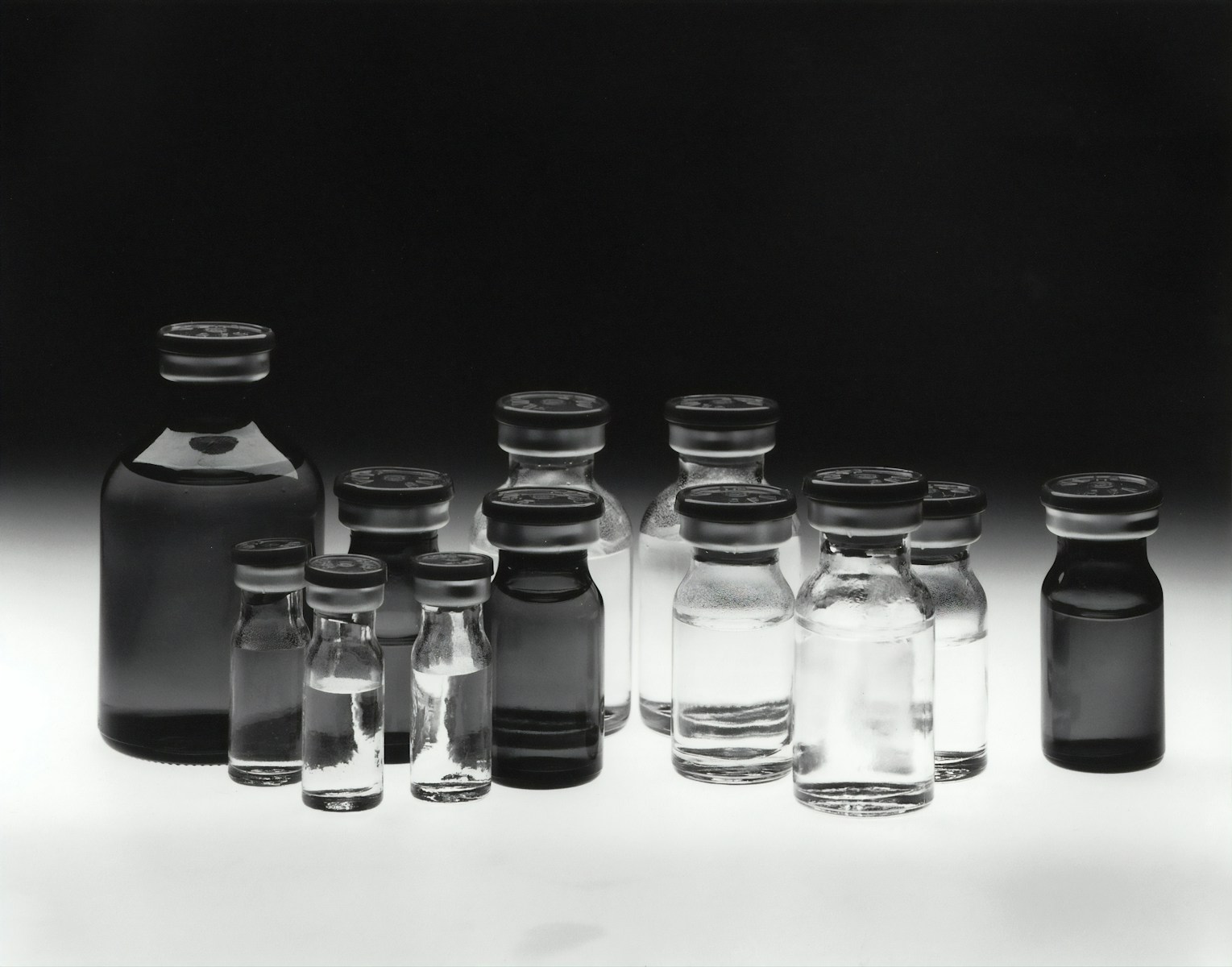
Liquid Formulations
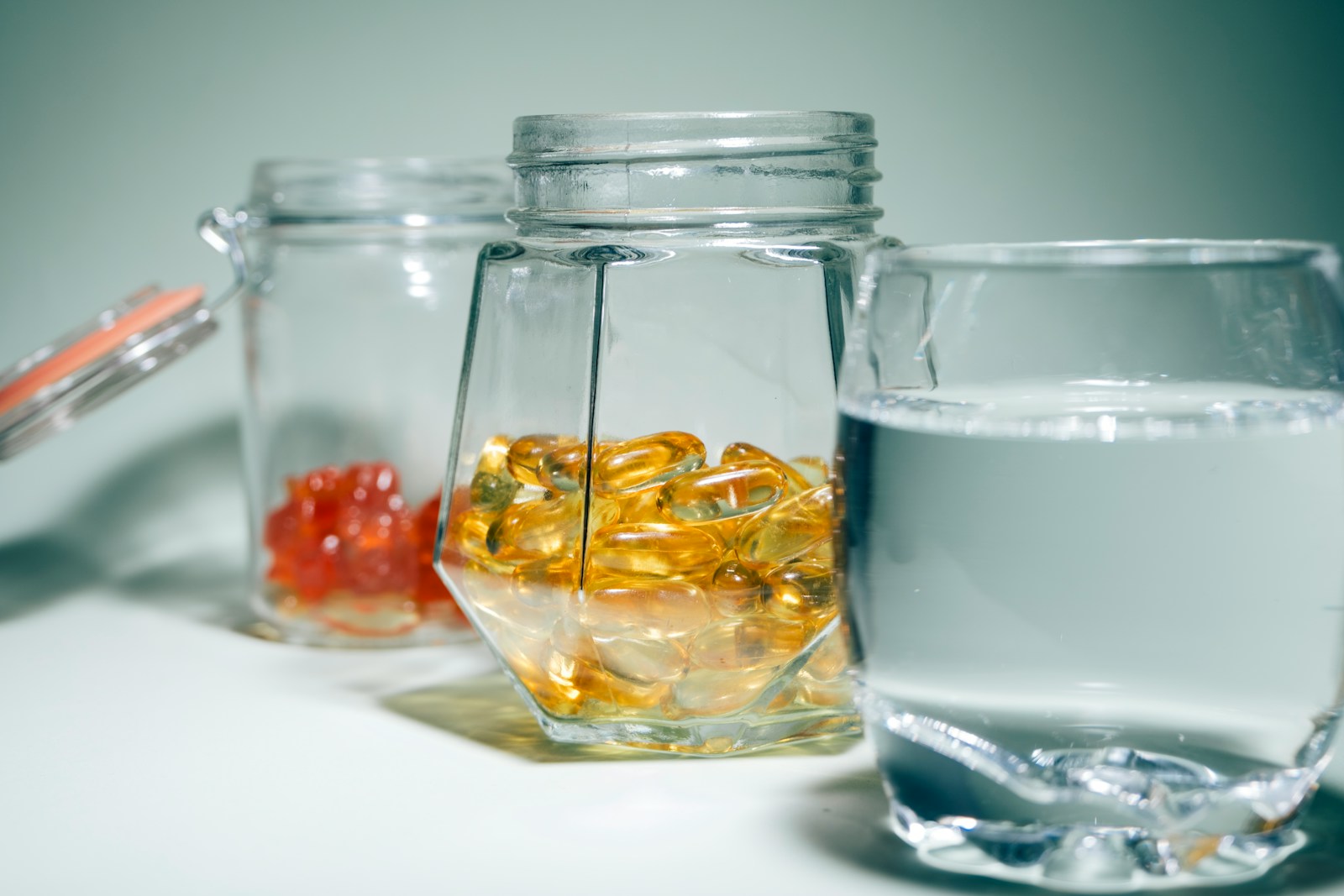
Liquid nutritional supplements
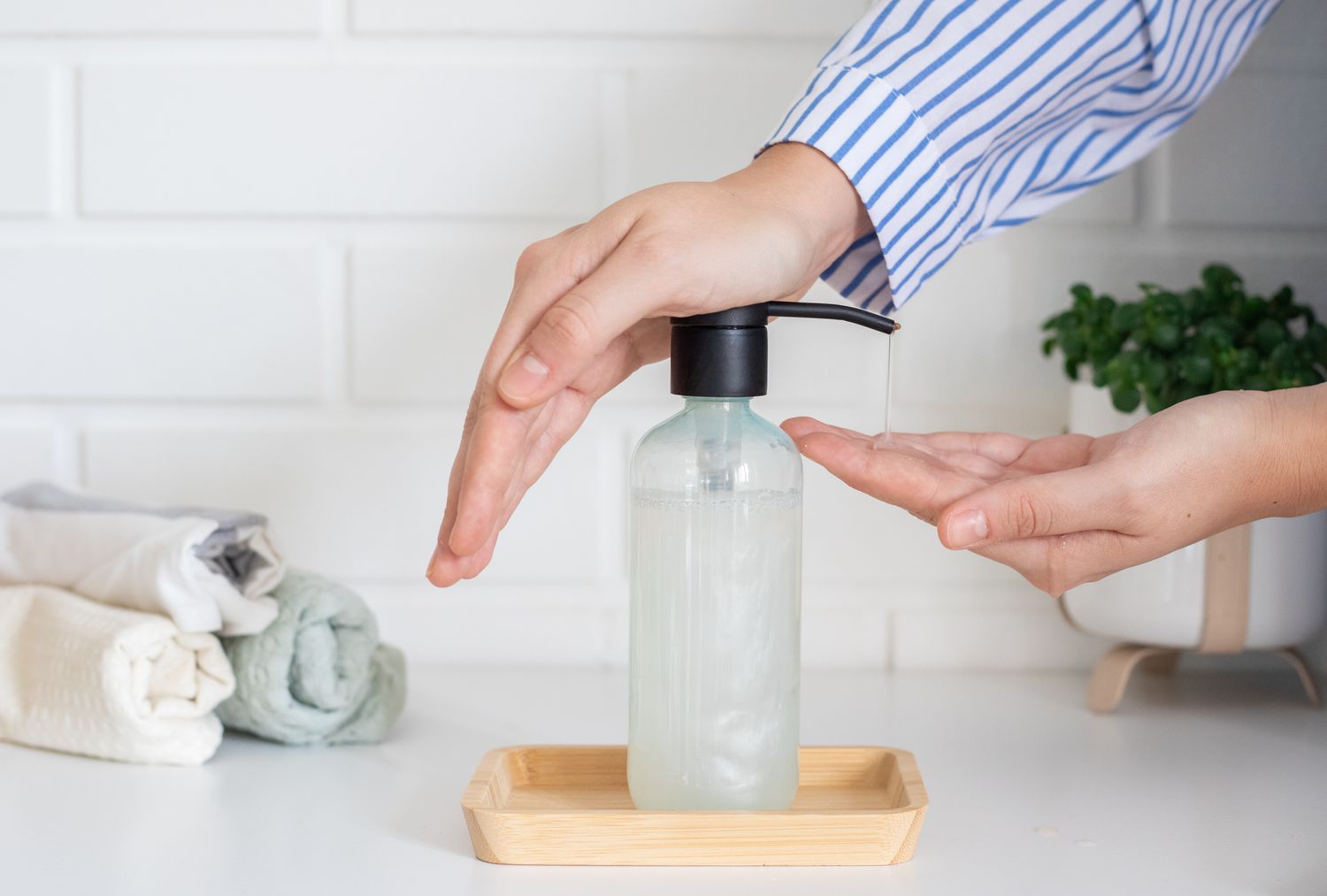
Liquid soap
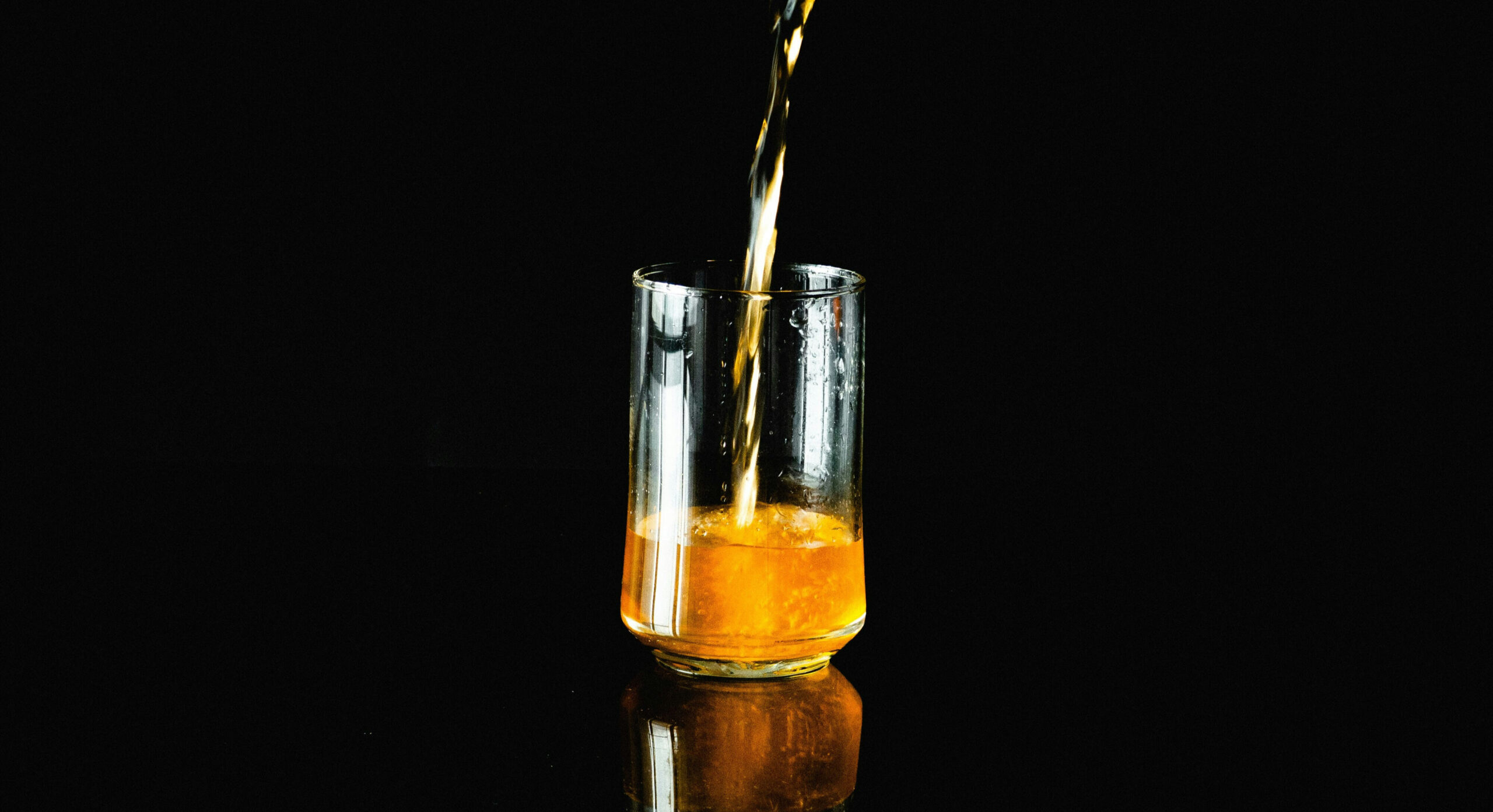
Liquid supplements
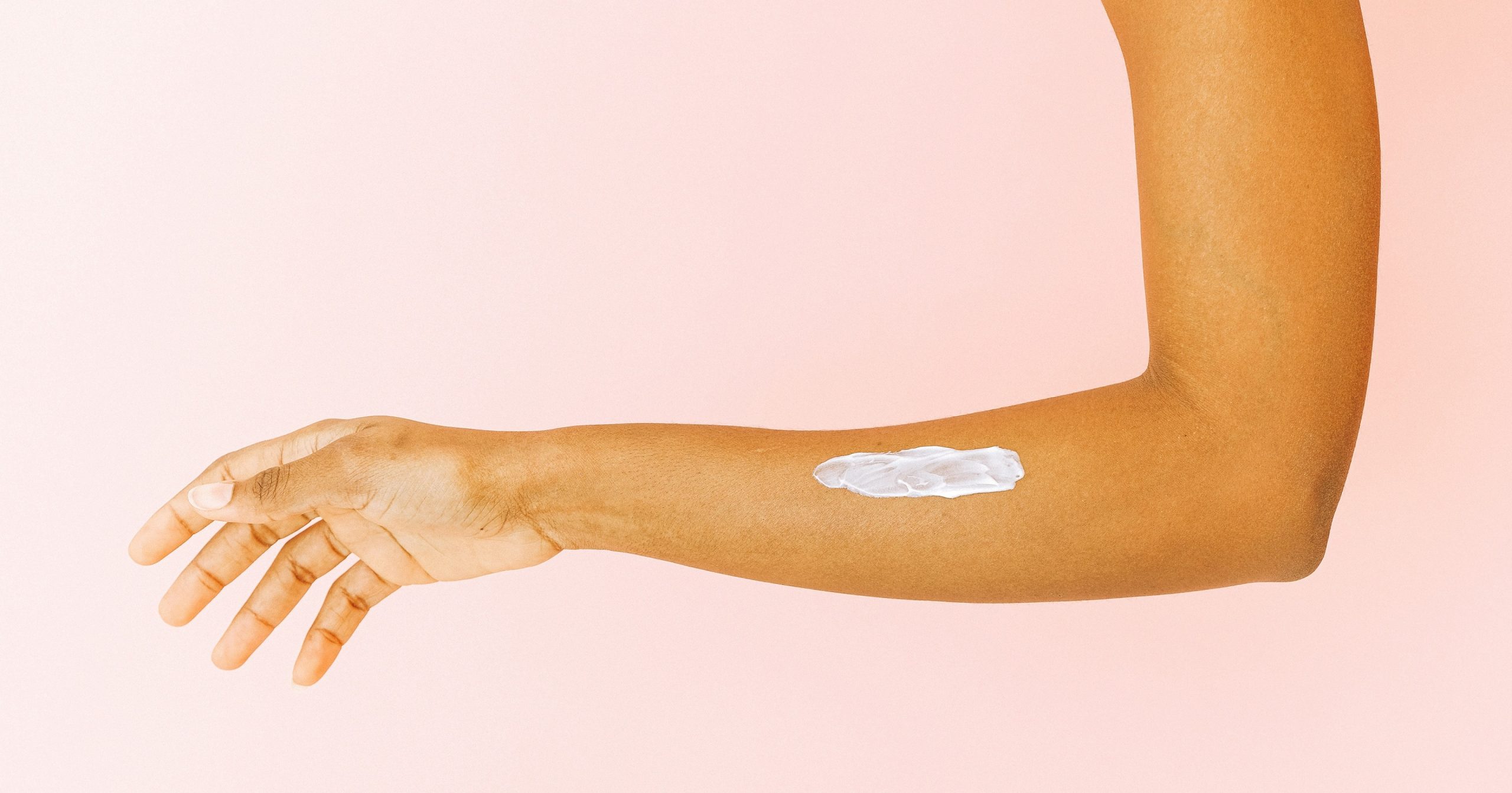
Lotions
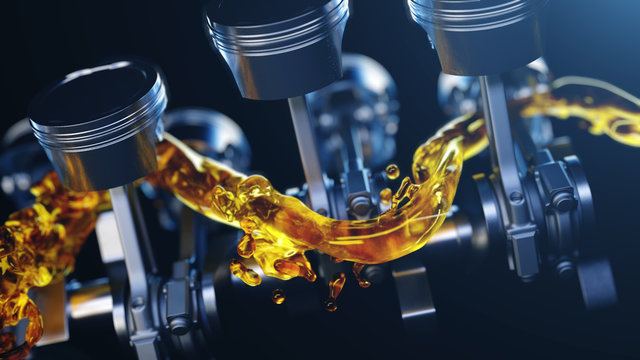
Lubricants
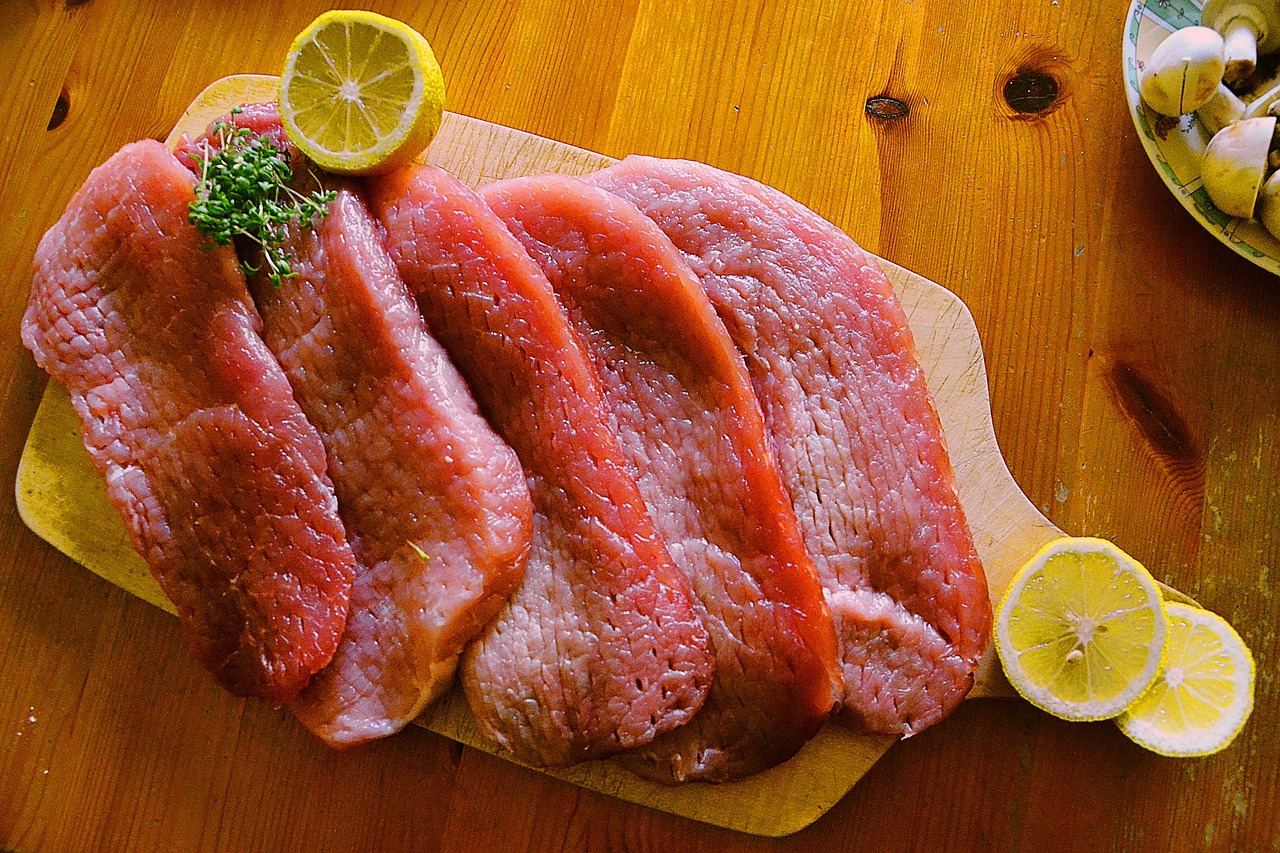
Luncheon meat
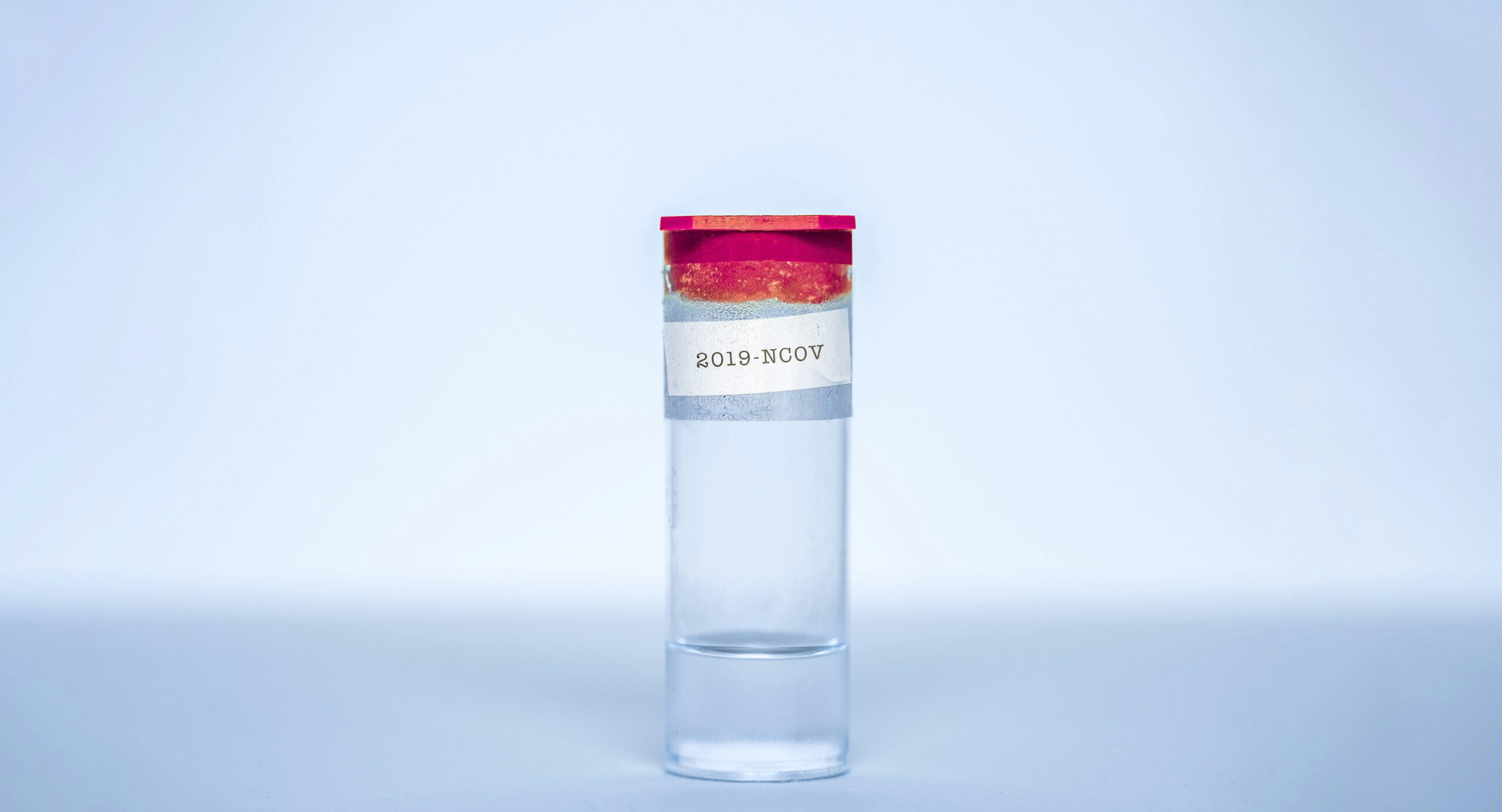
Lutetium-177
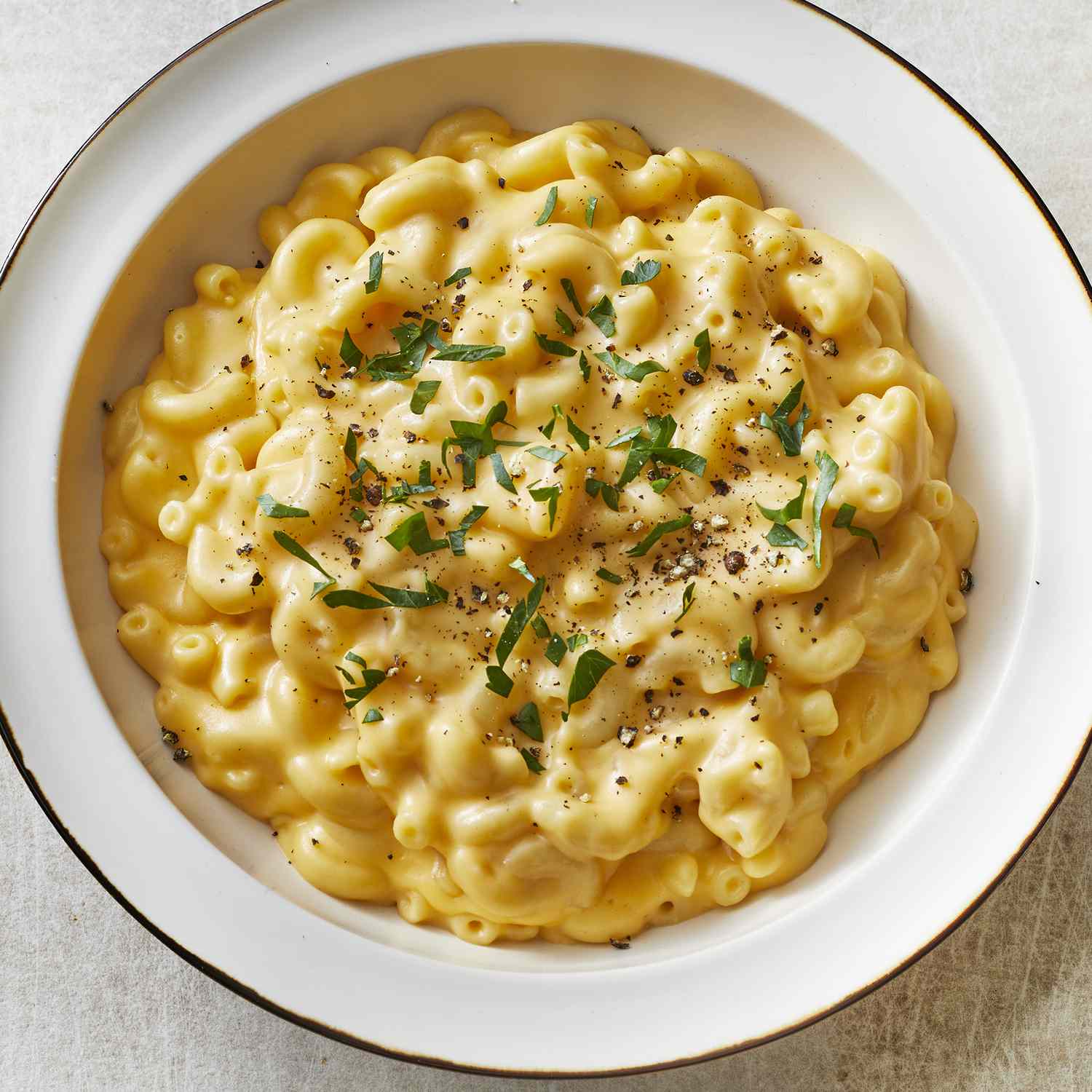
Macaroni and cheese
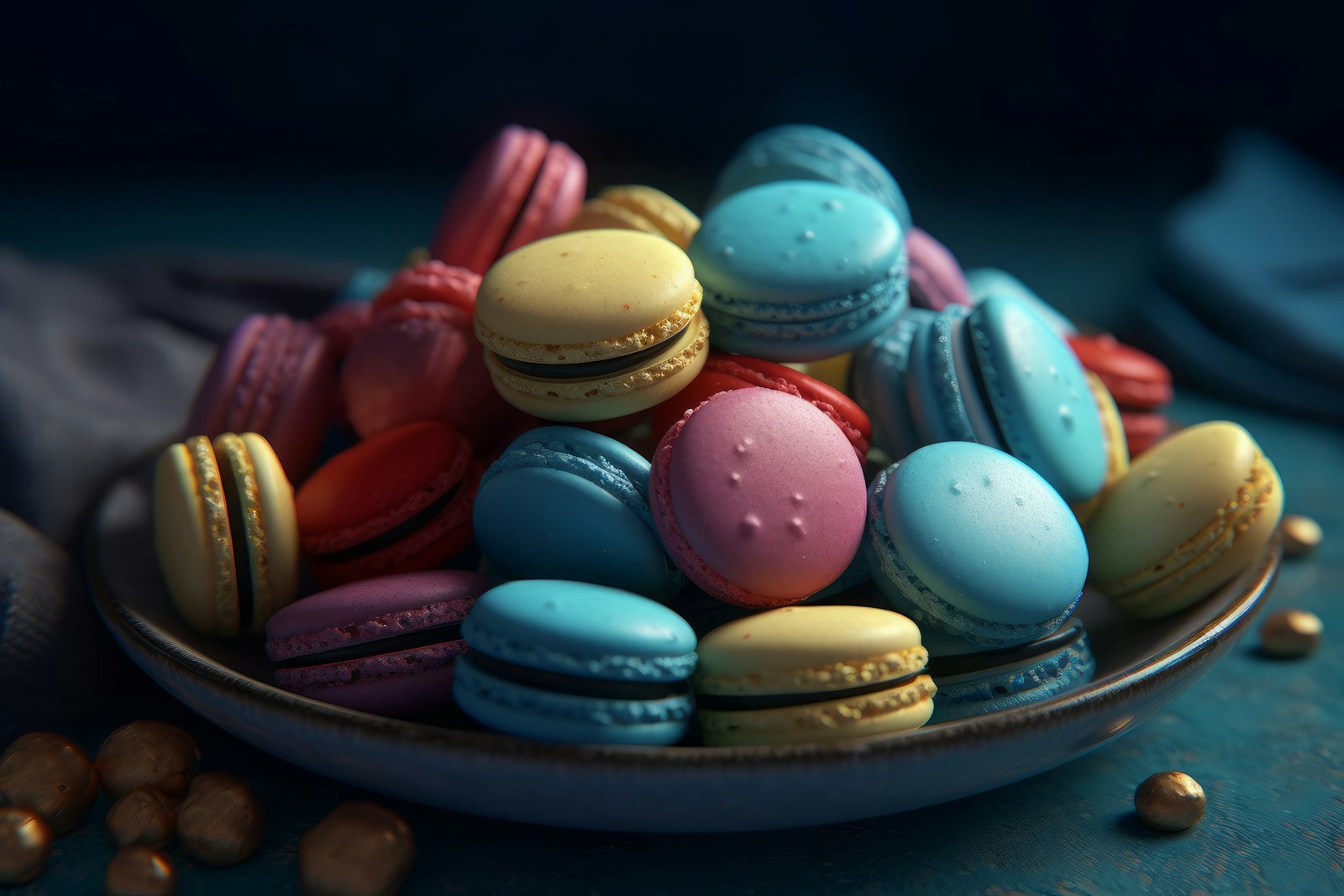
Macarons
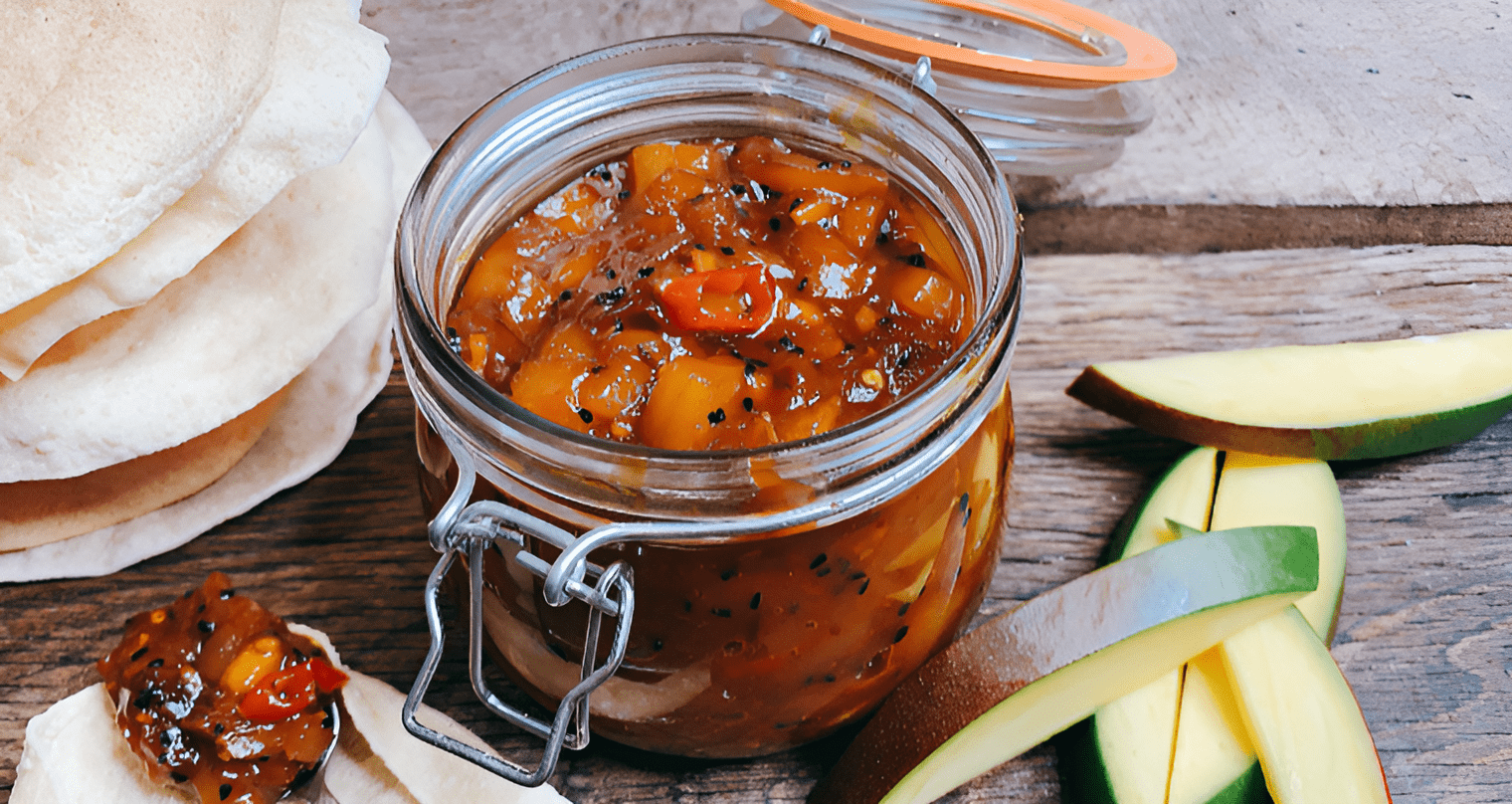
Mango chutney
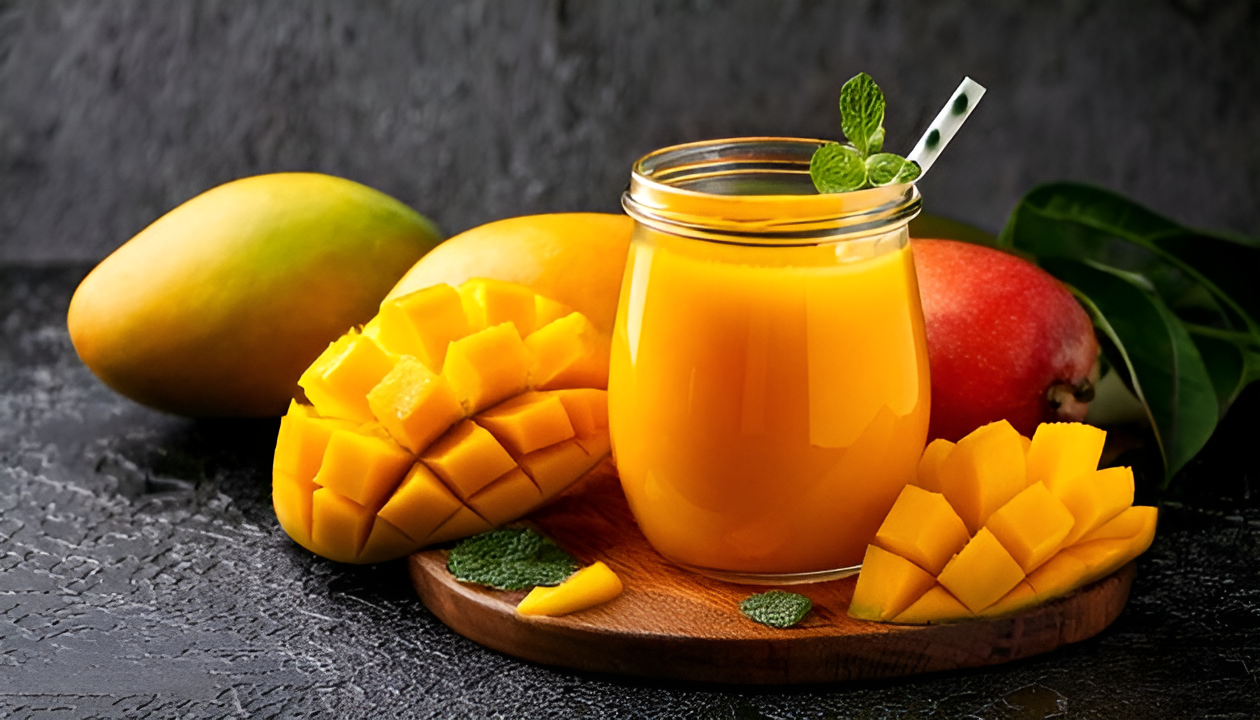
Mango juice
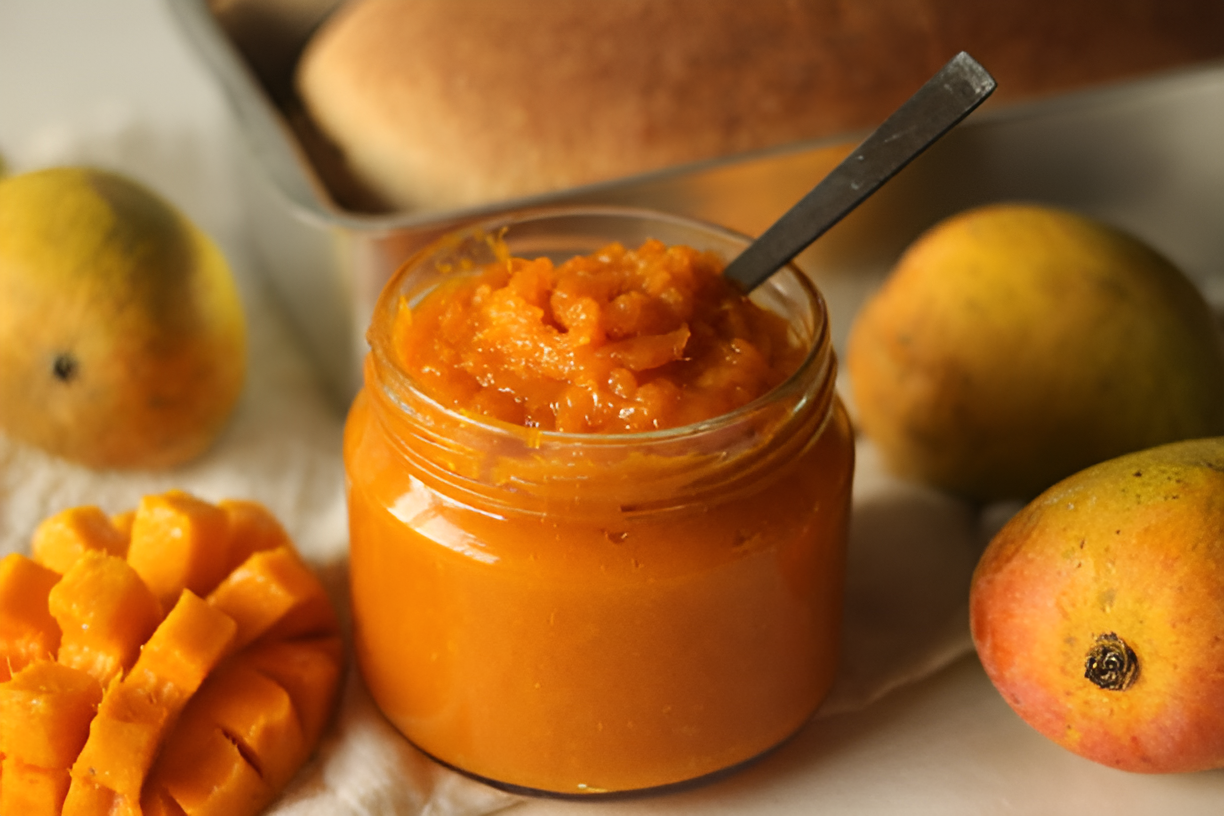
Mango pulp
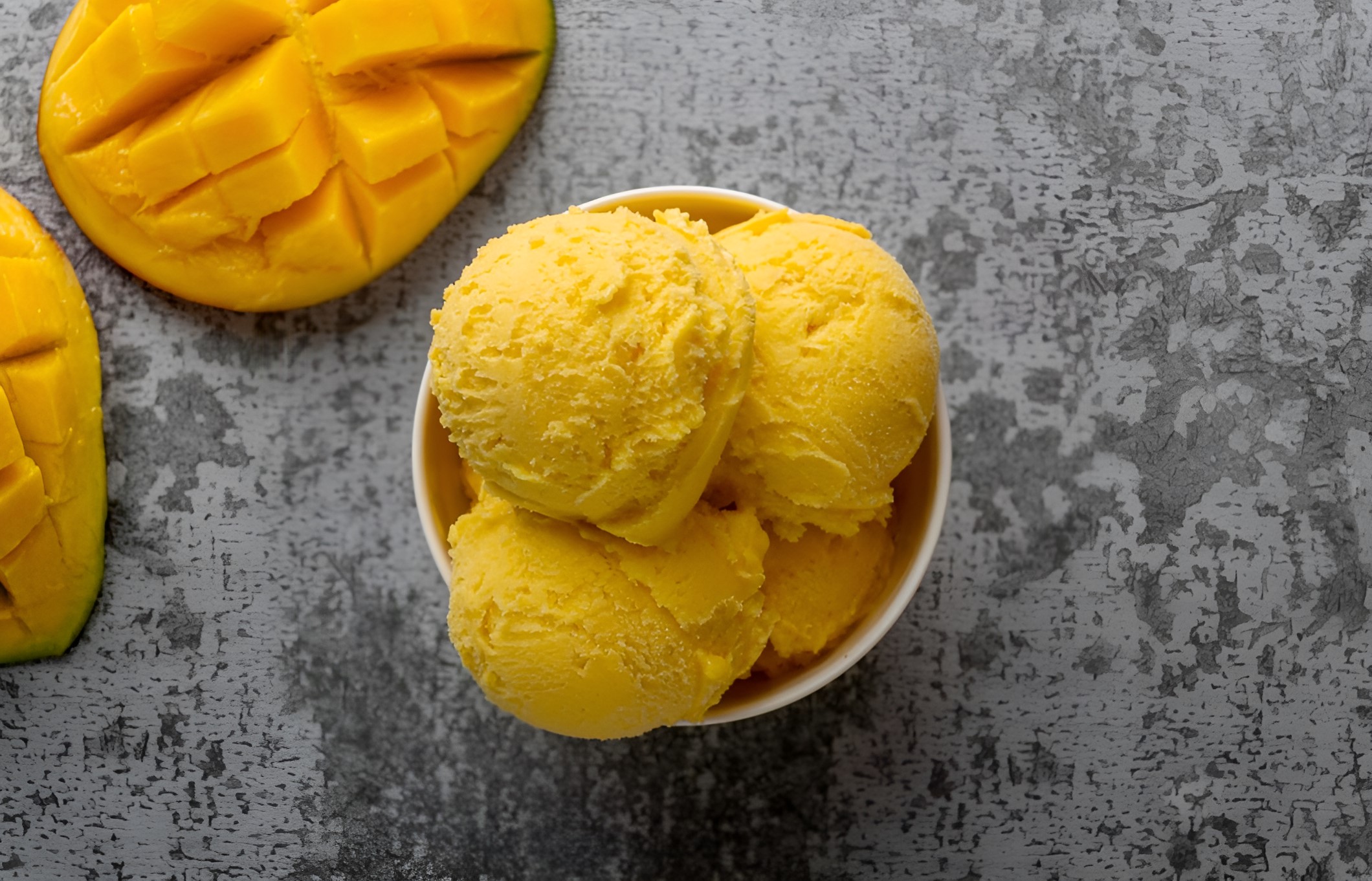
Mango sorbet
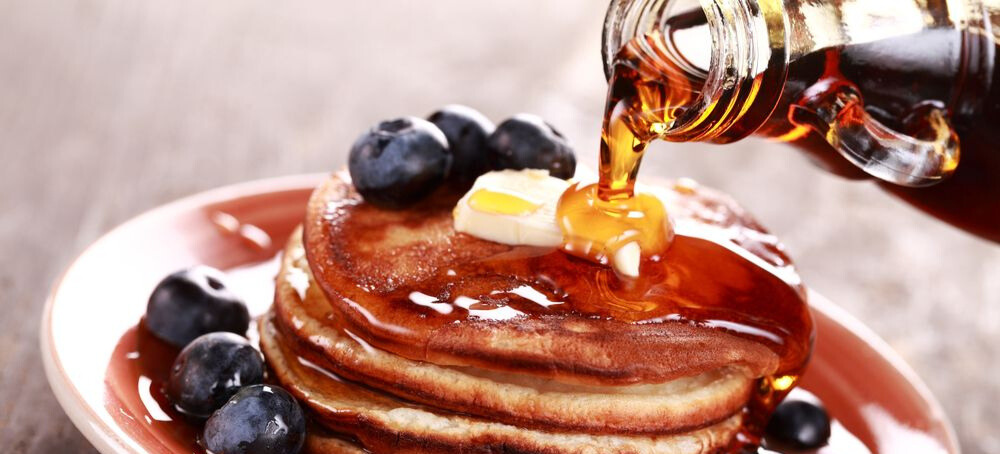
Maple syrup
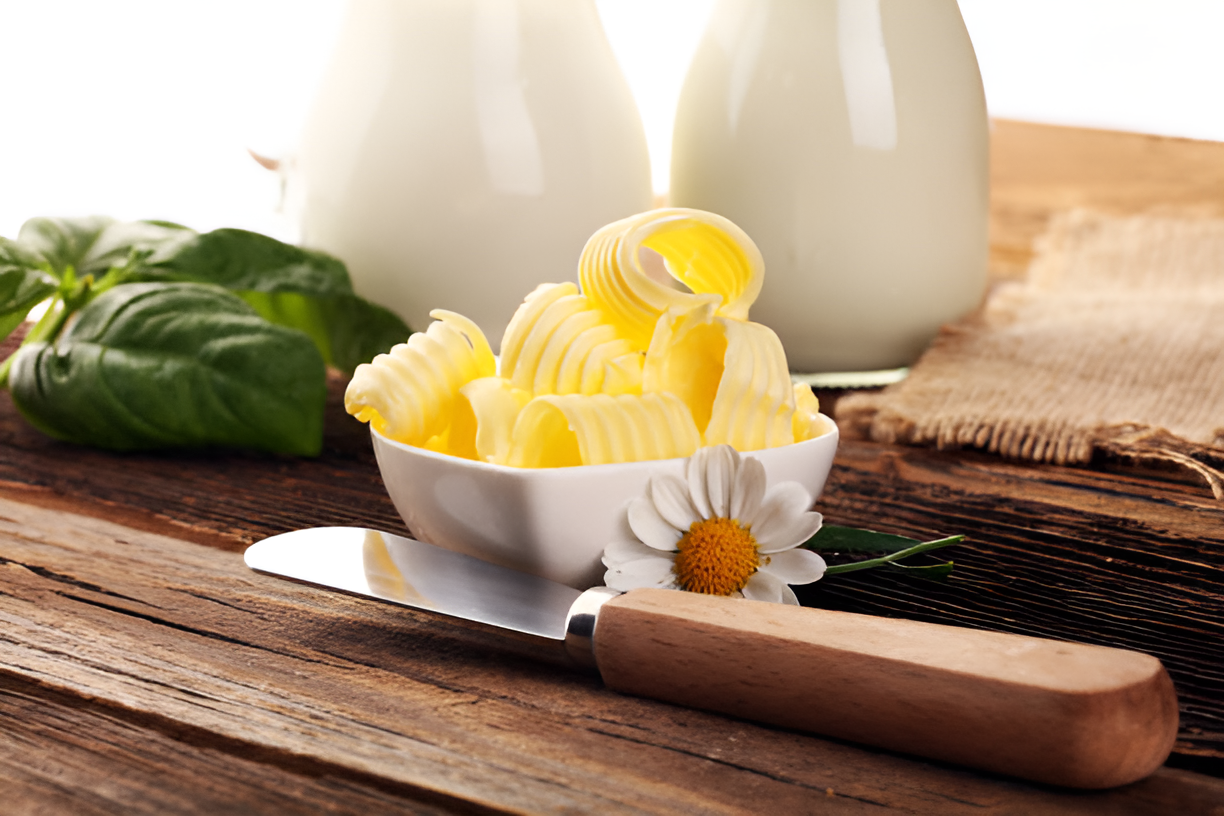
Margarine
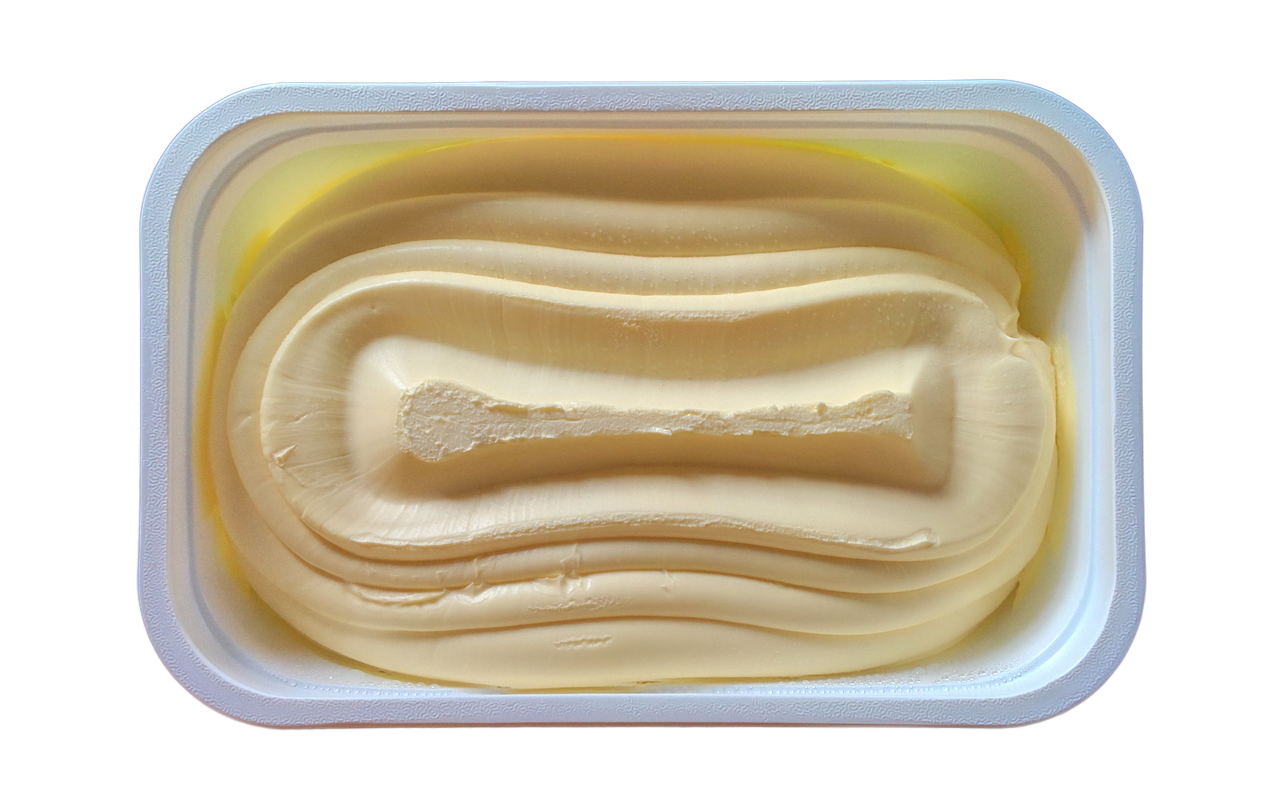
Margerine
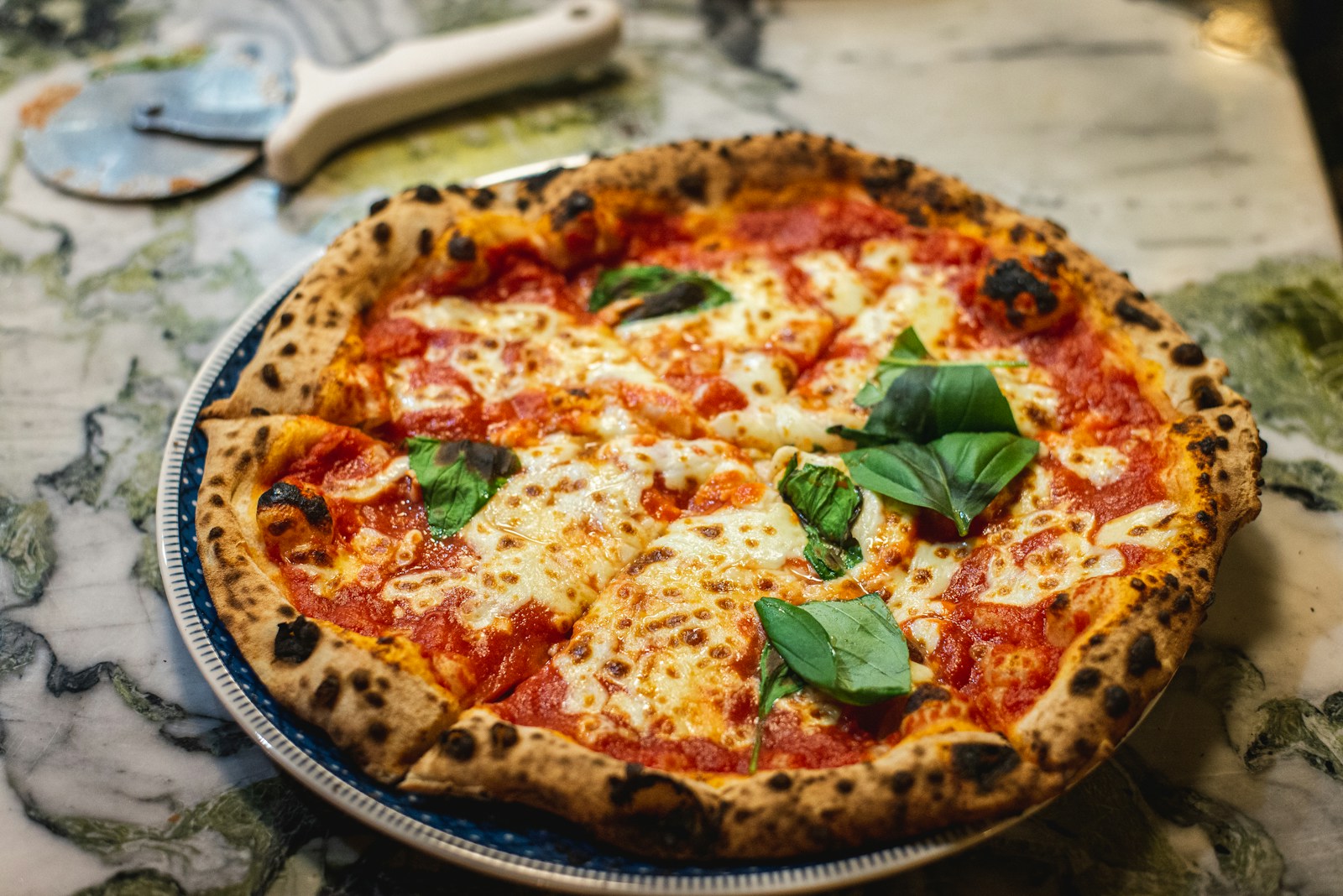
Margherita pizza
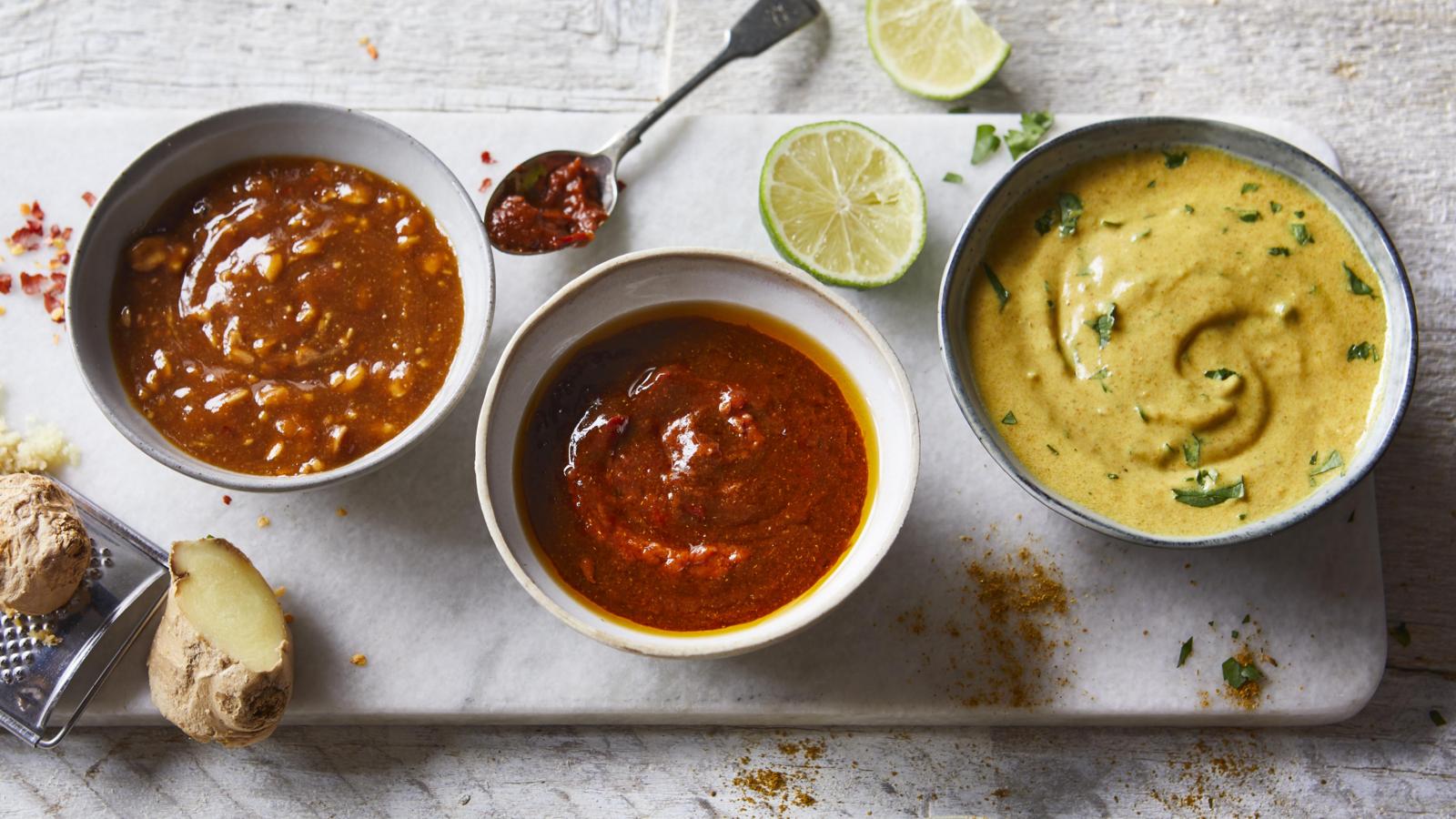
Marinades
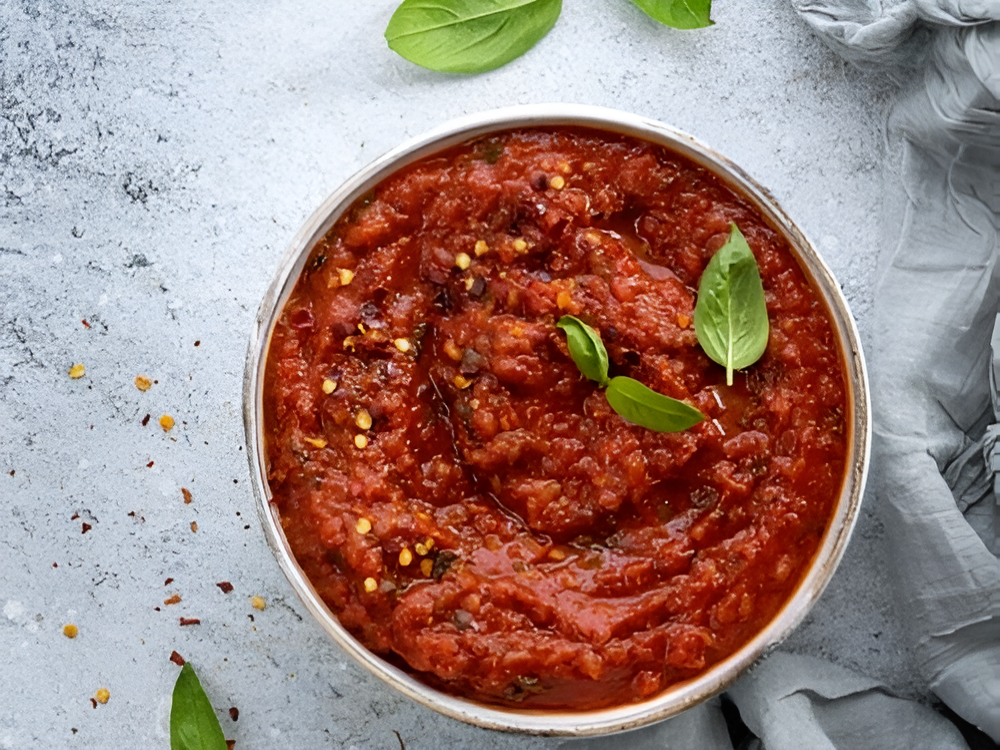
Marinara sauce
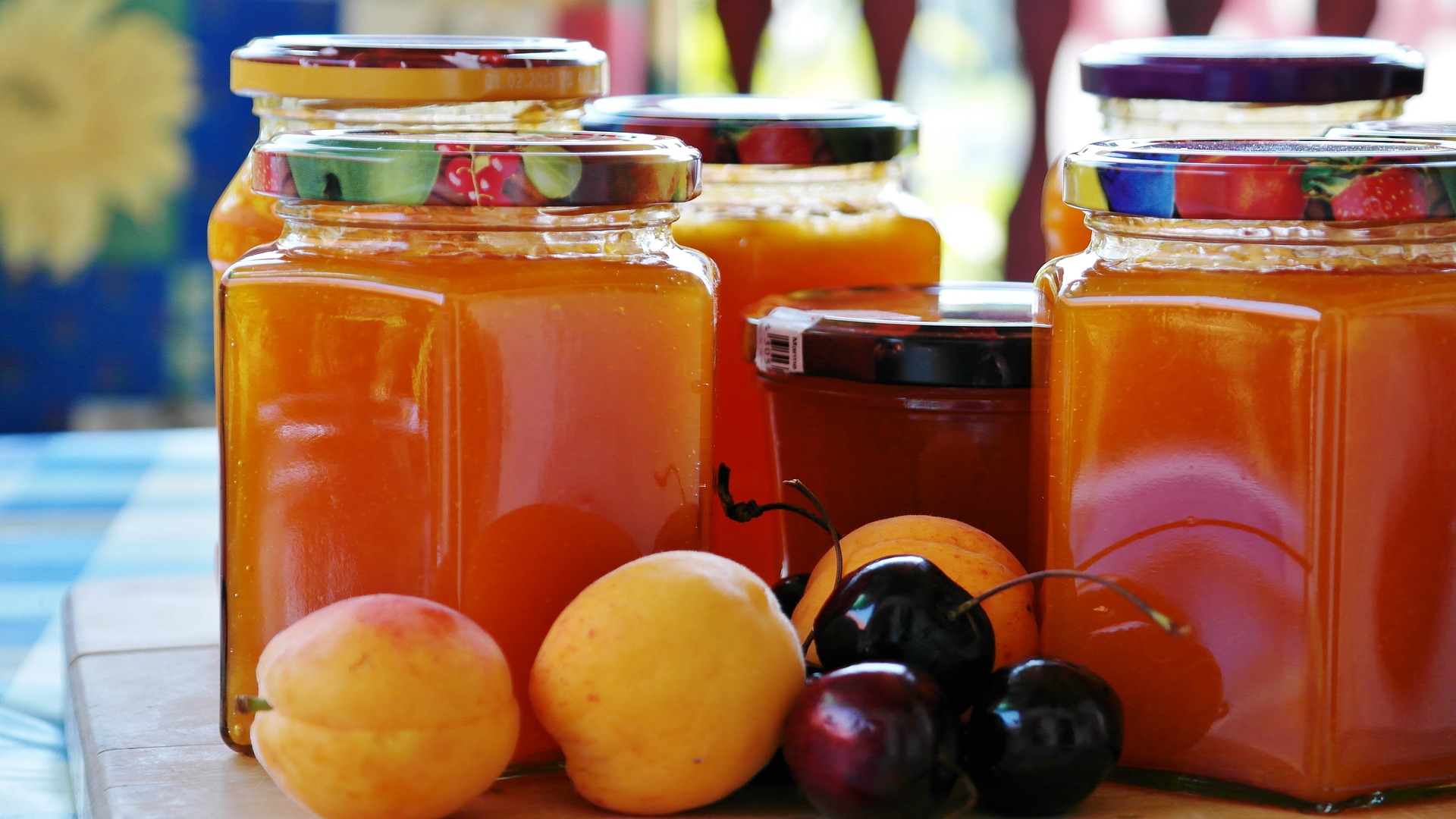
Marmalade

Mascara
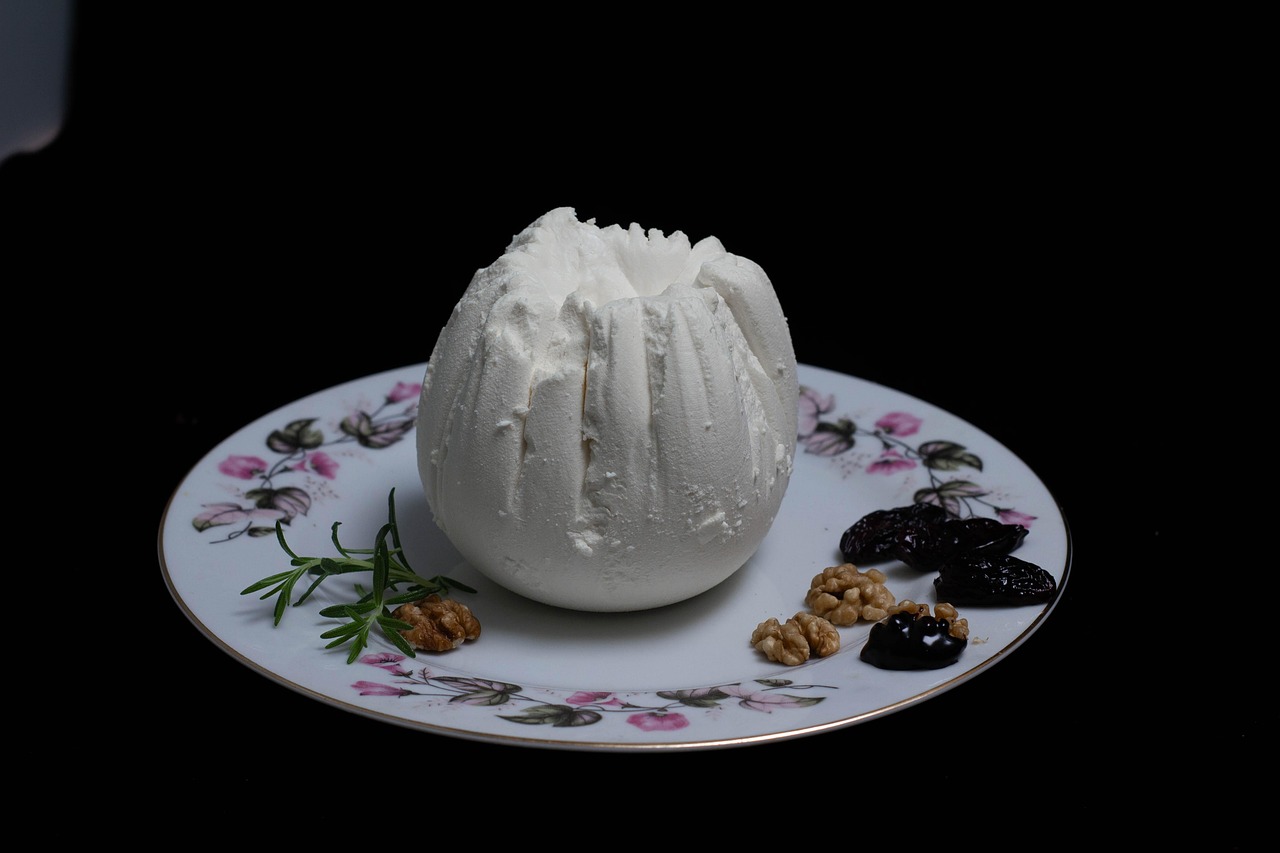
Mascarpone
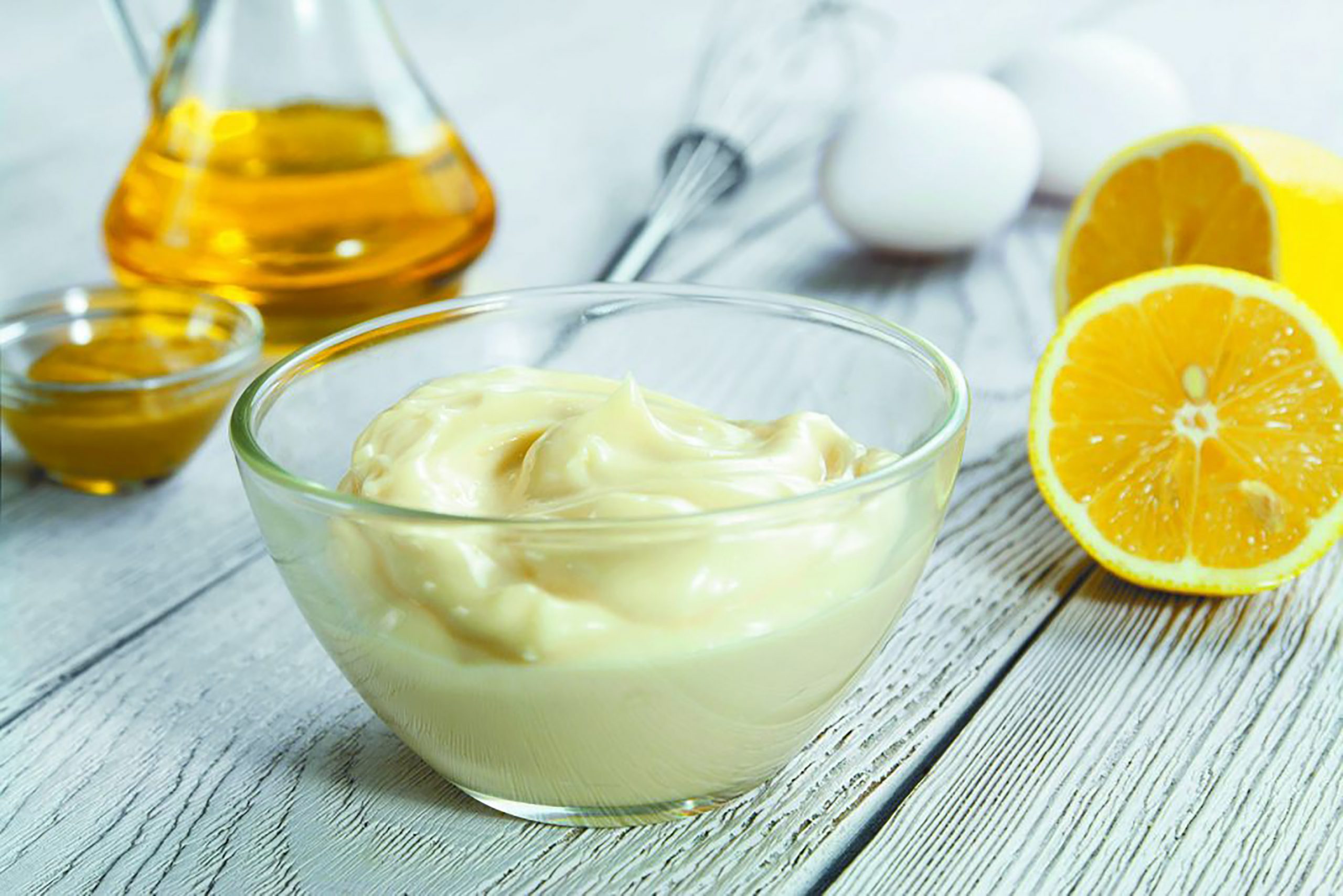
Mayonnaise
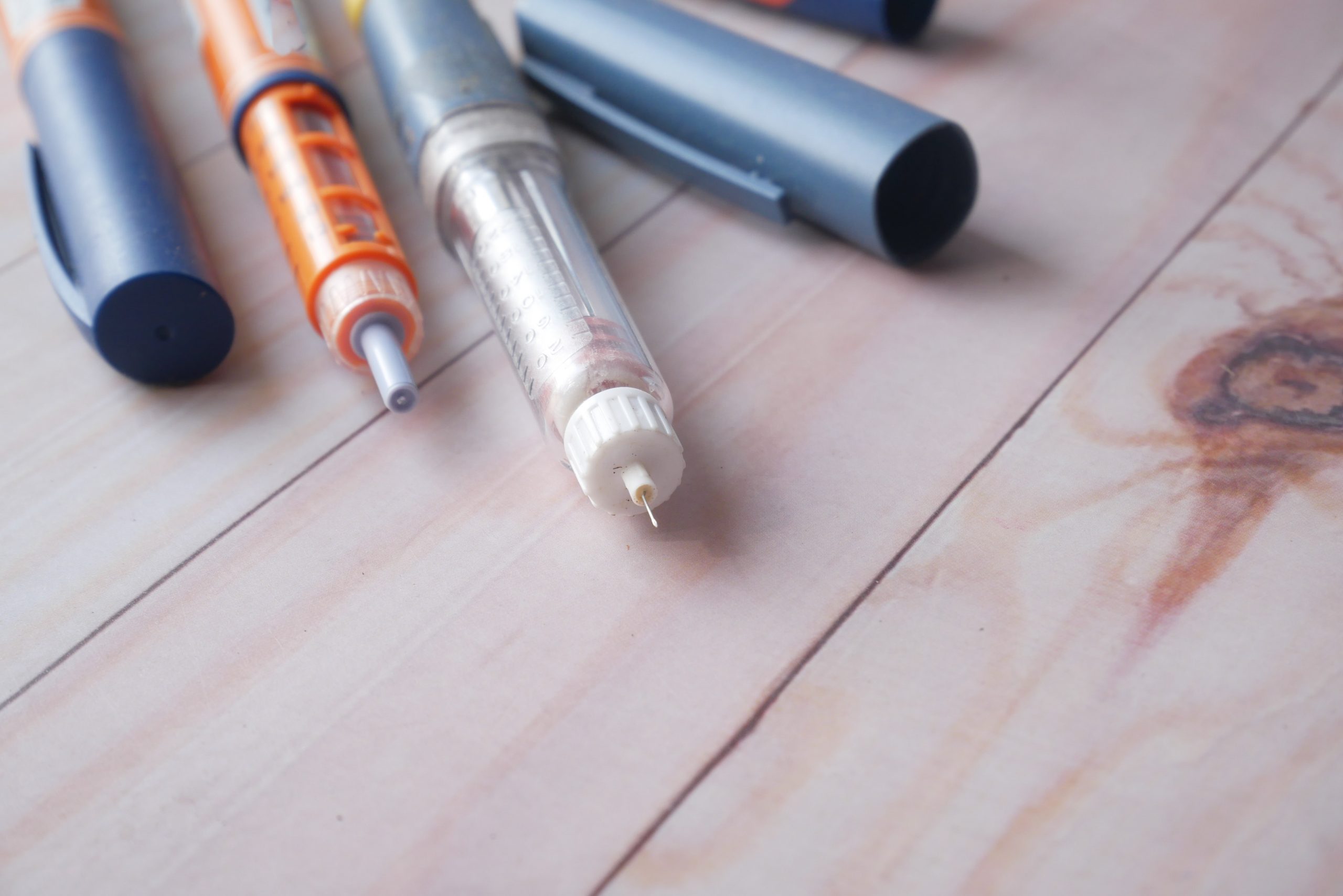
Medical devices
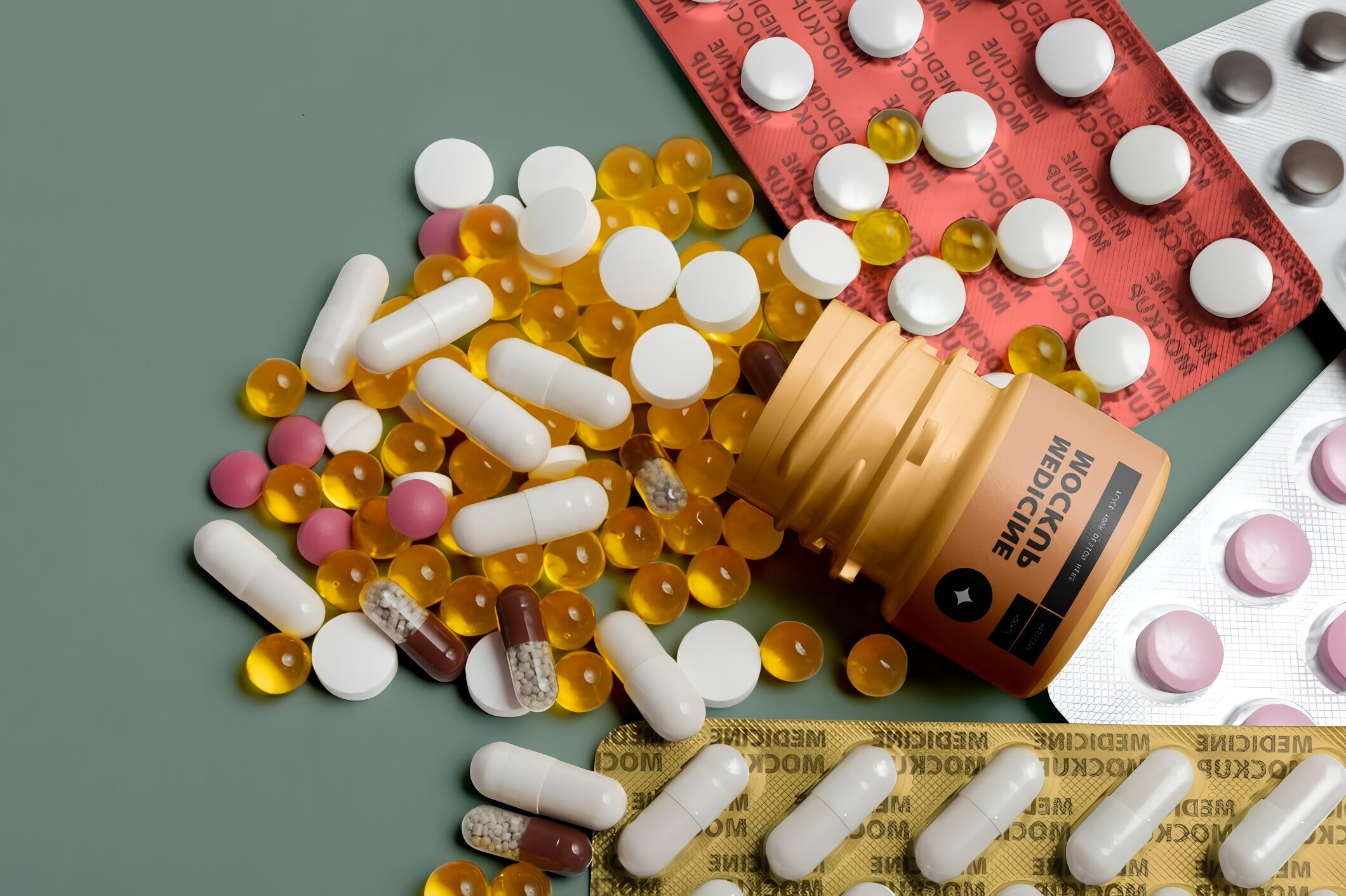
Medicine
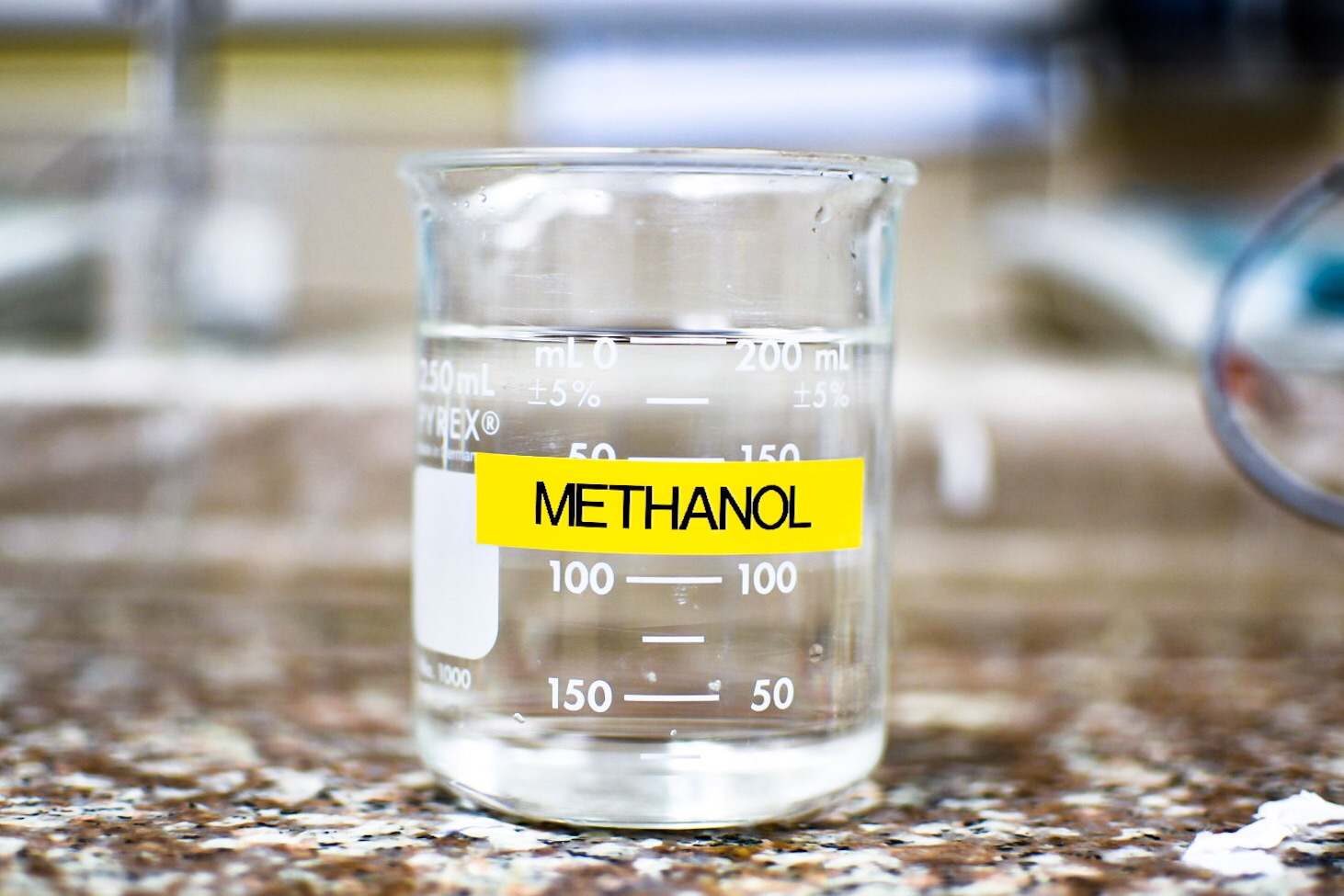
Methanol
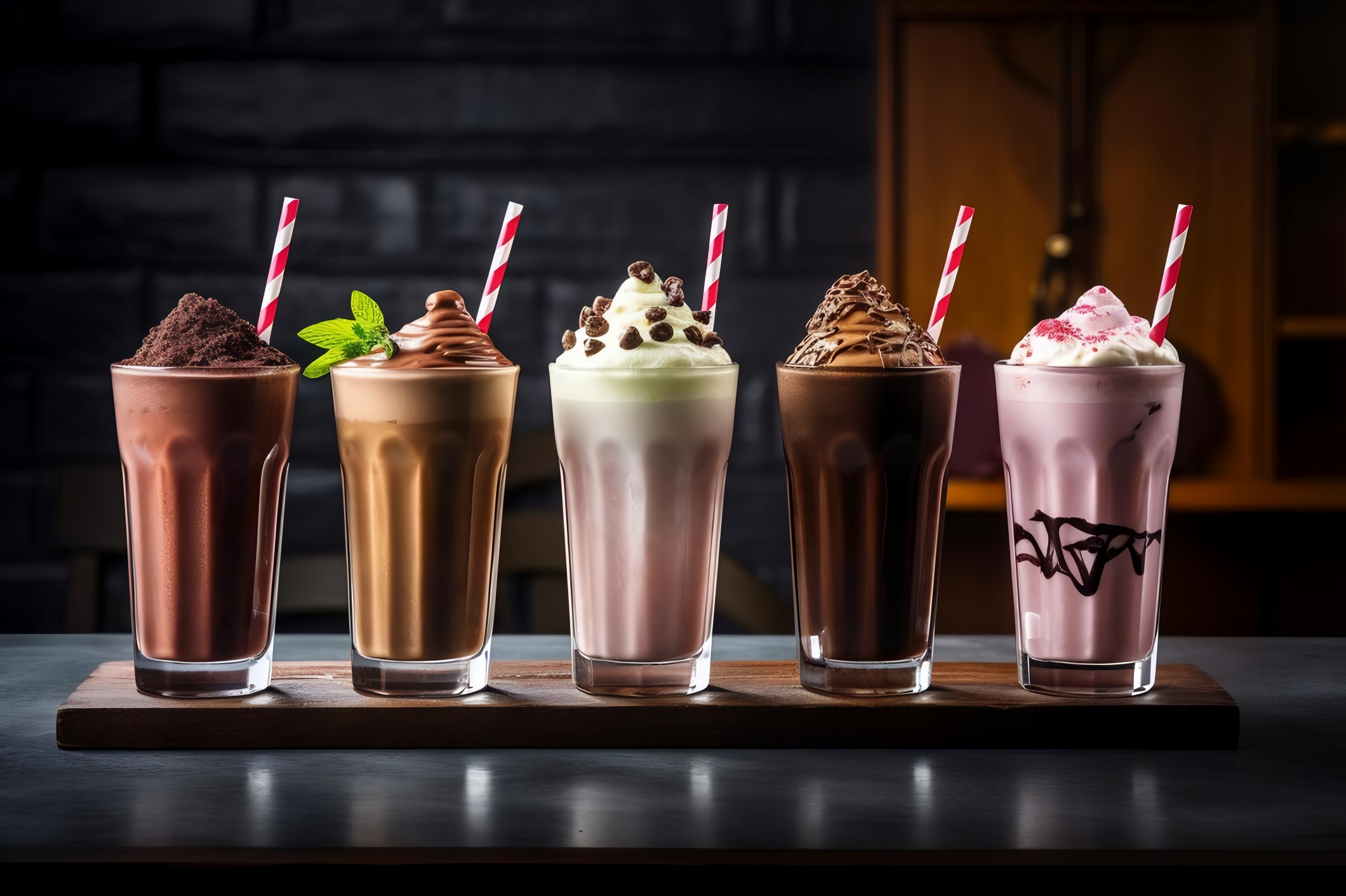
Milkshakes
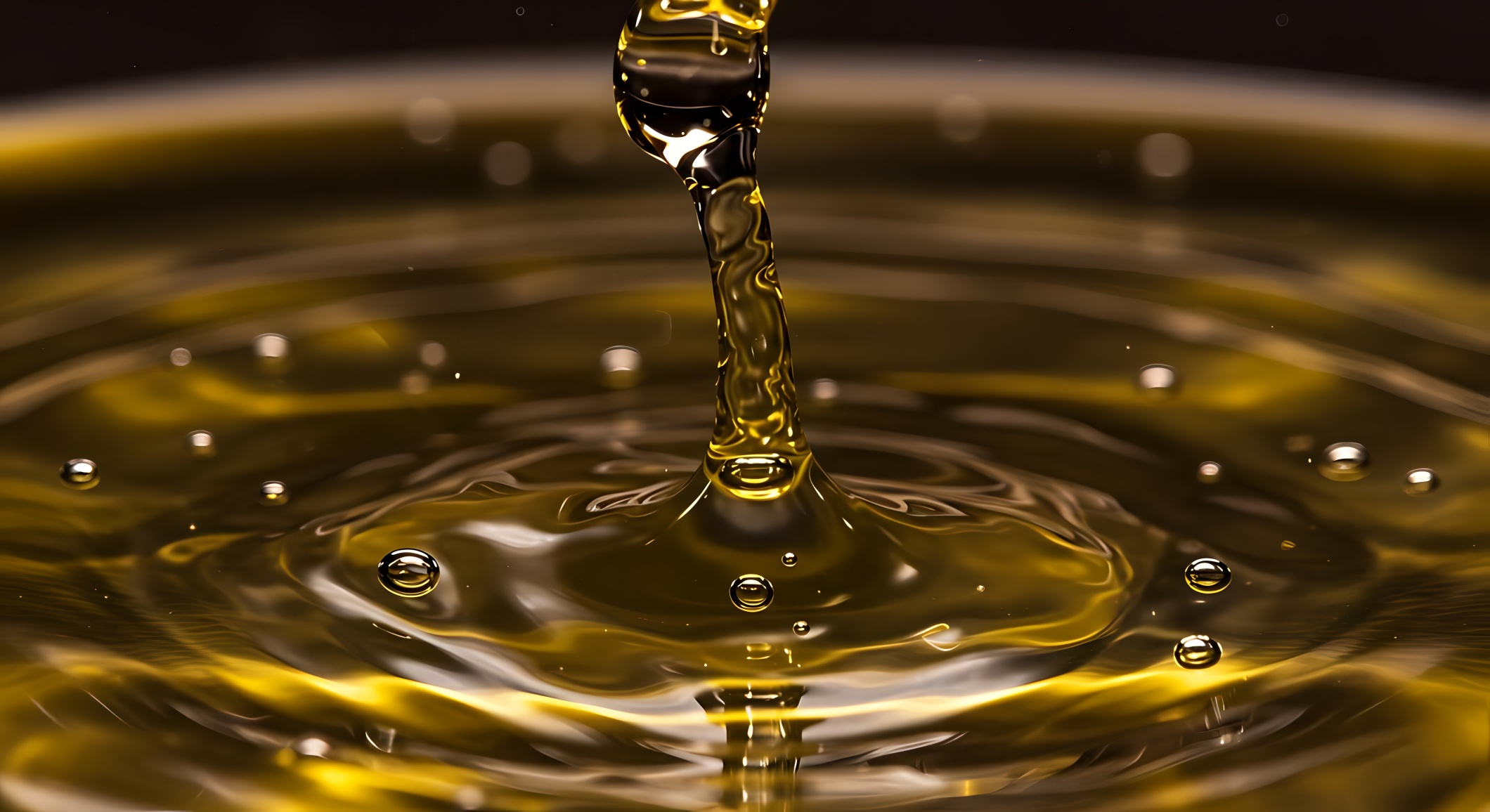
Mineral oils

Mineral water
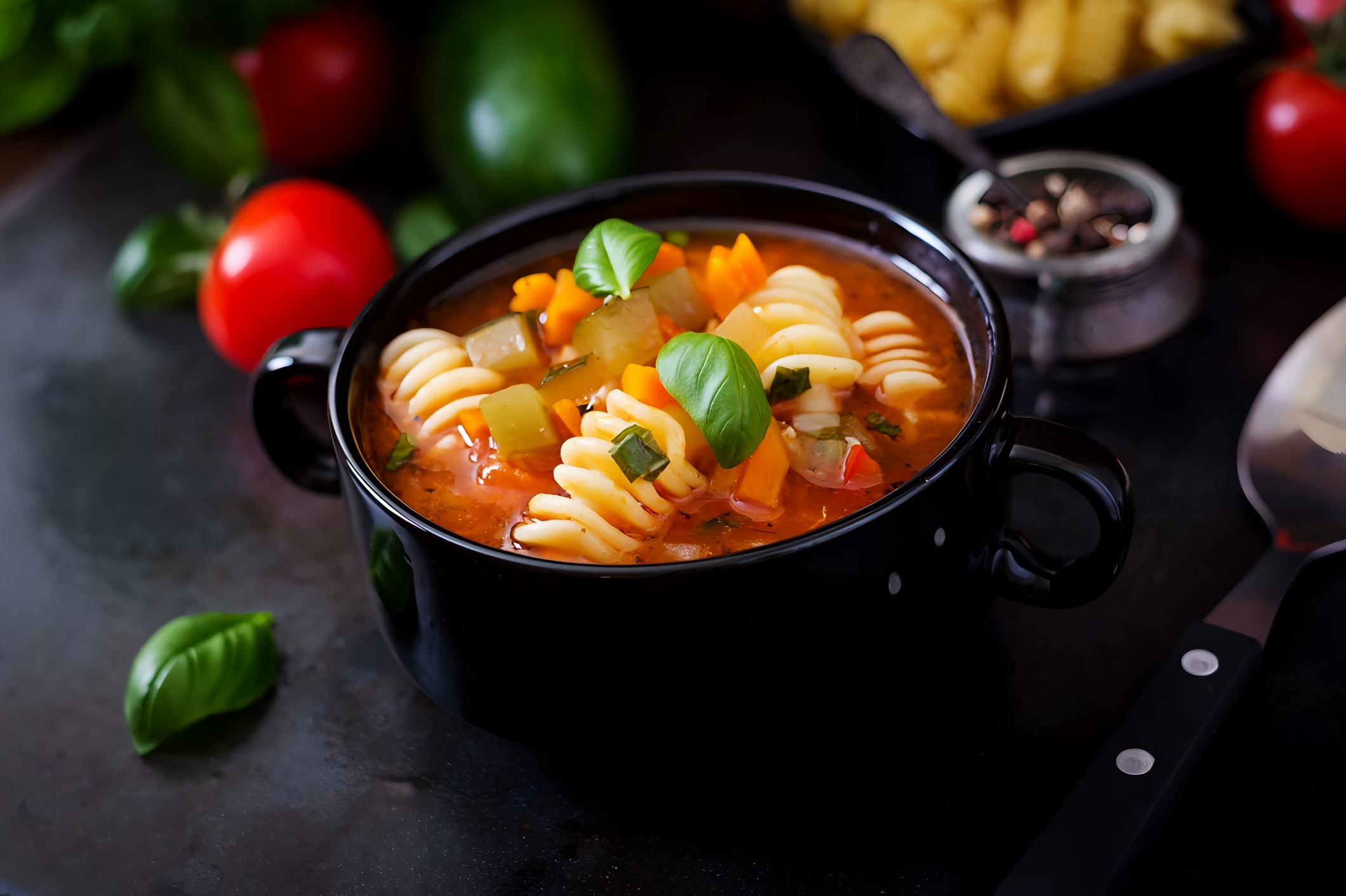
Minestrone soup
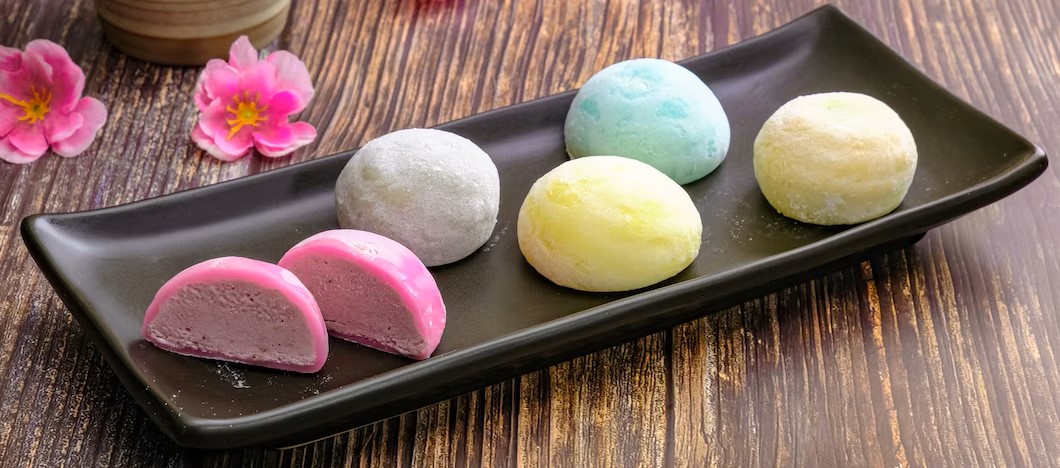
Mochi
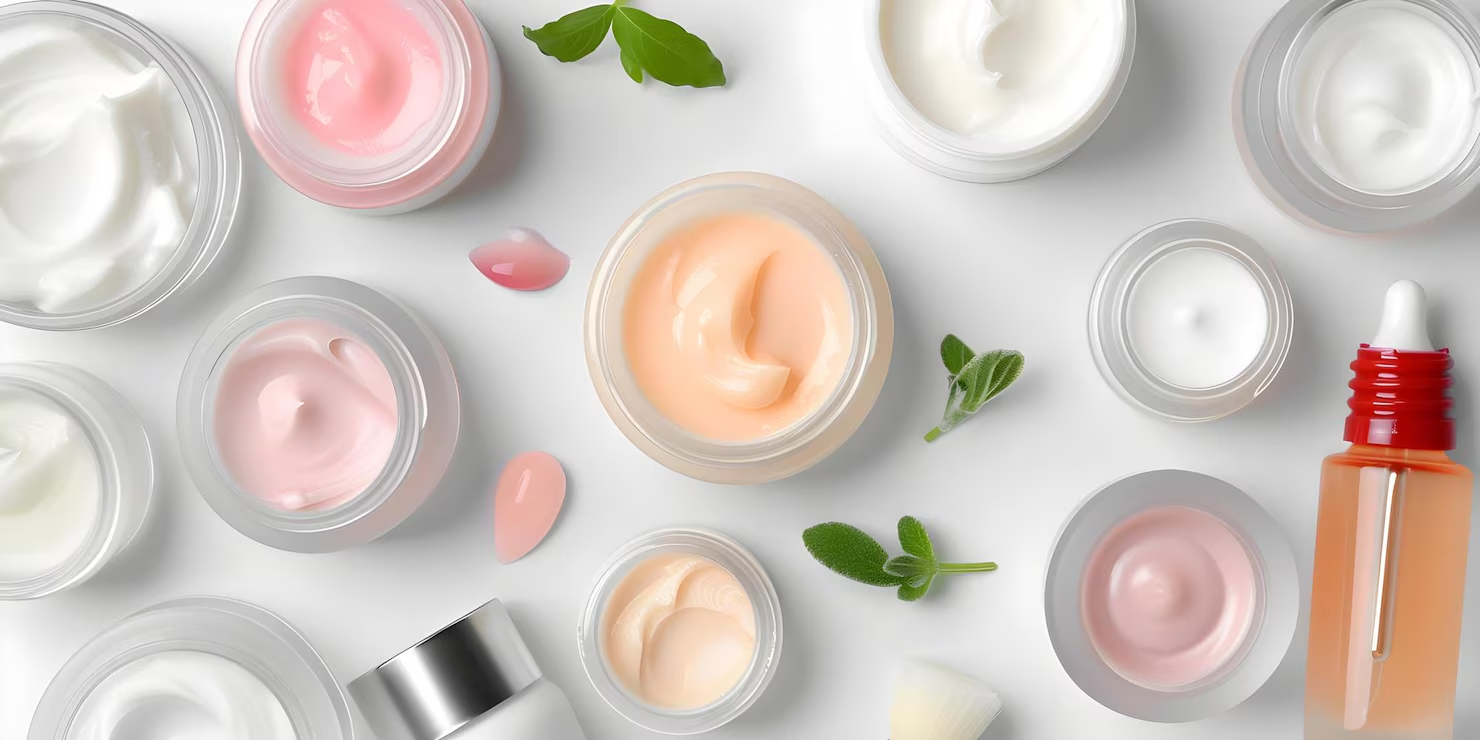
Moisturizers
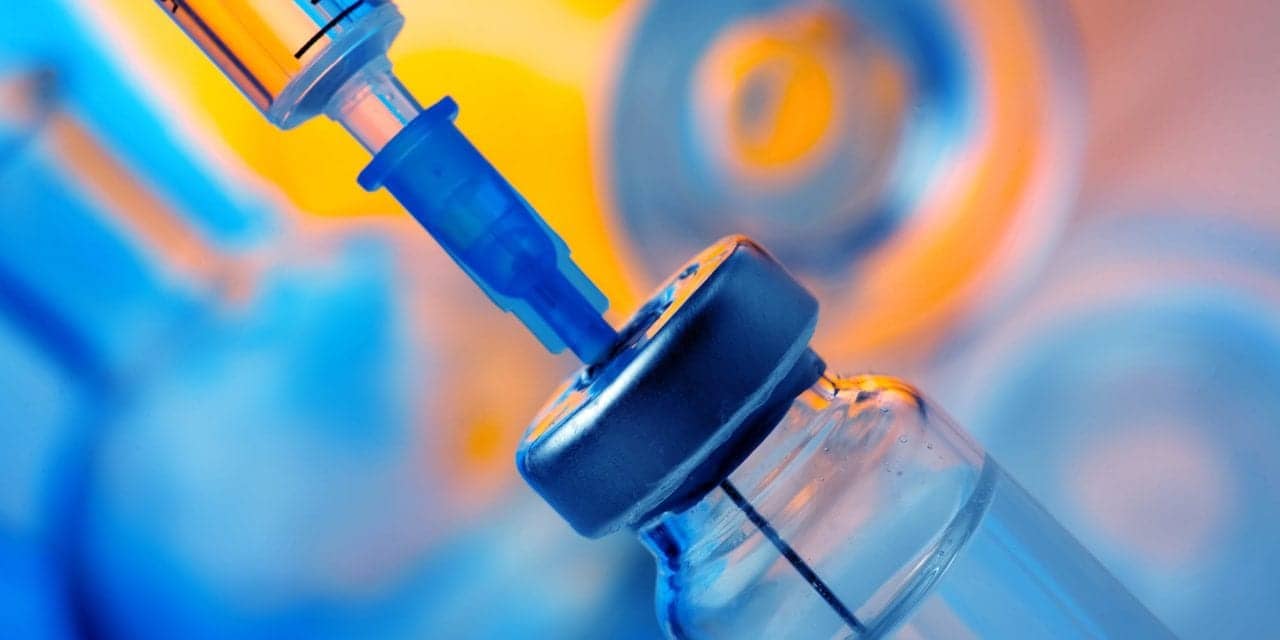
Monoclonal antibodies
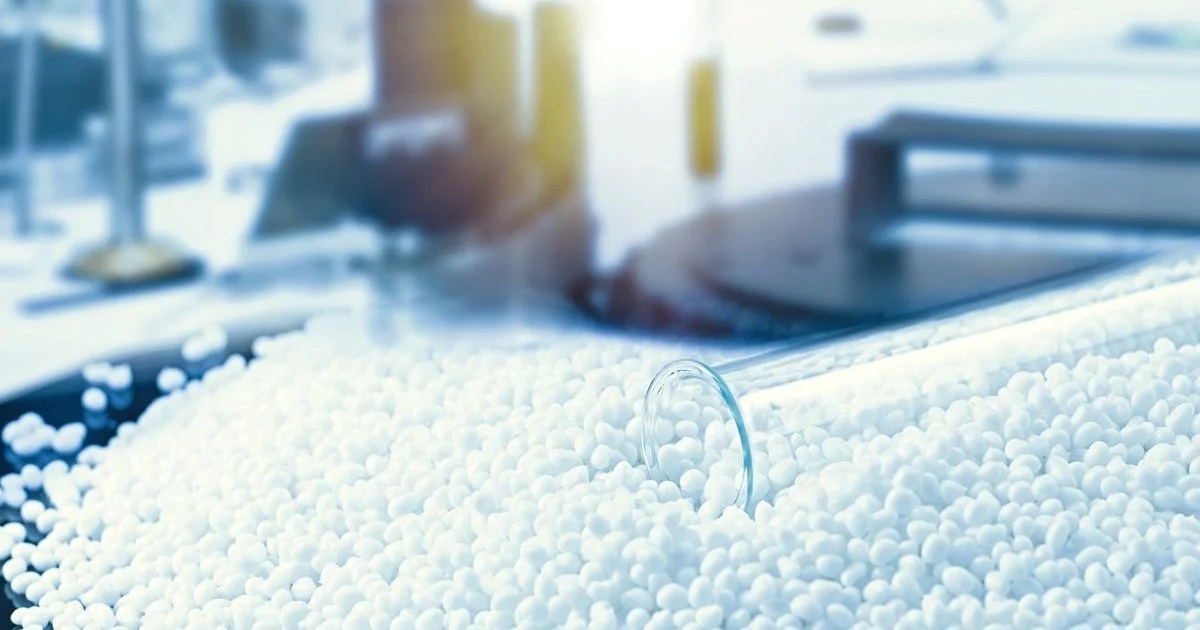
Monomers
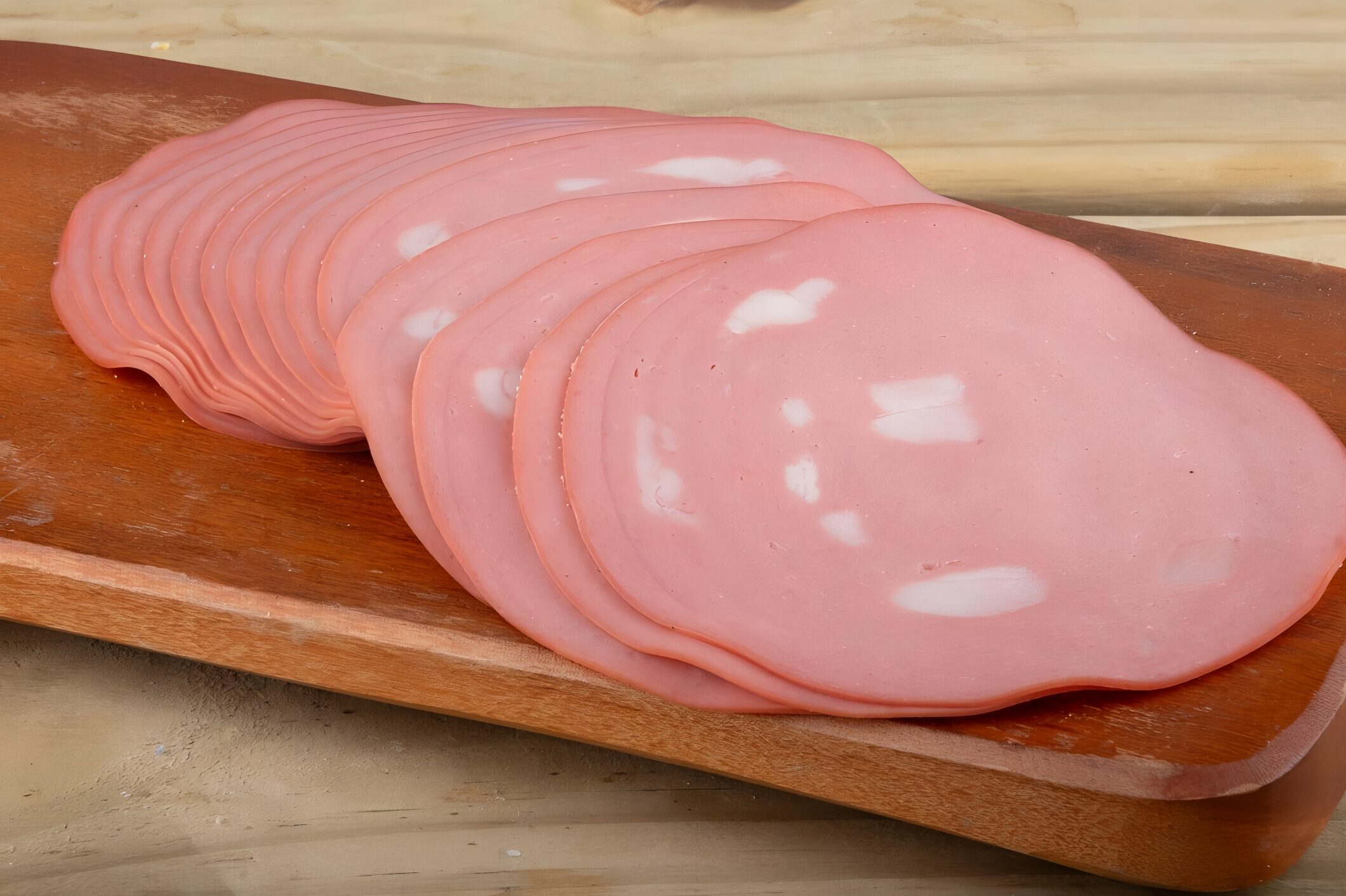
Mortadella
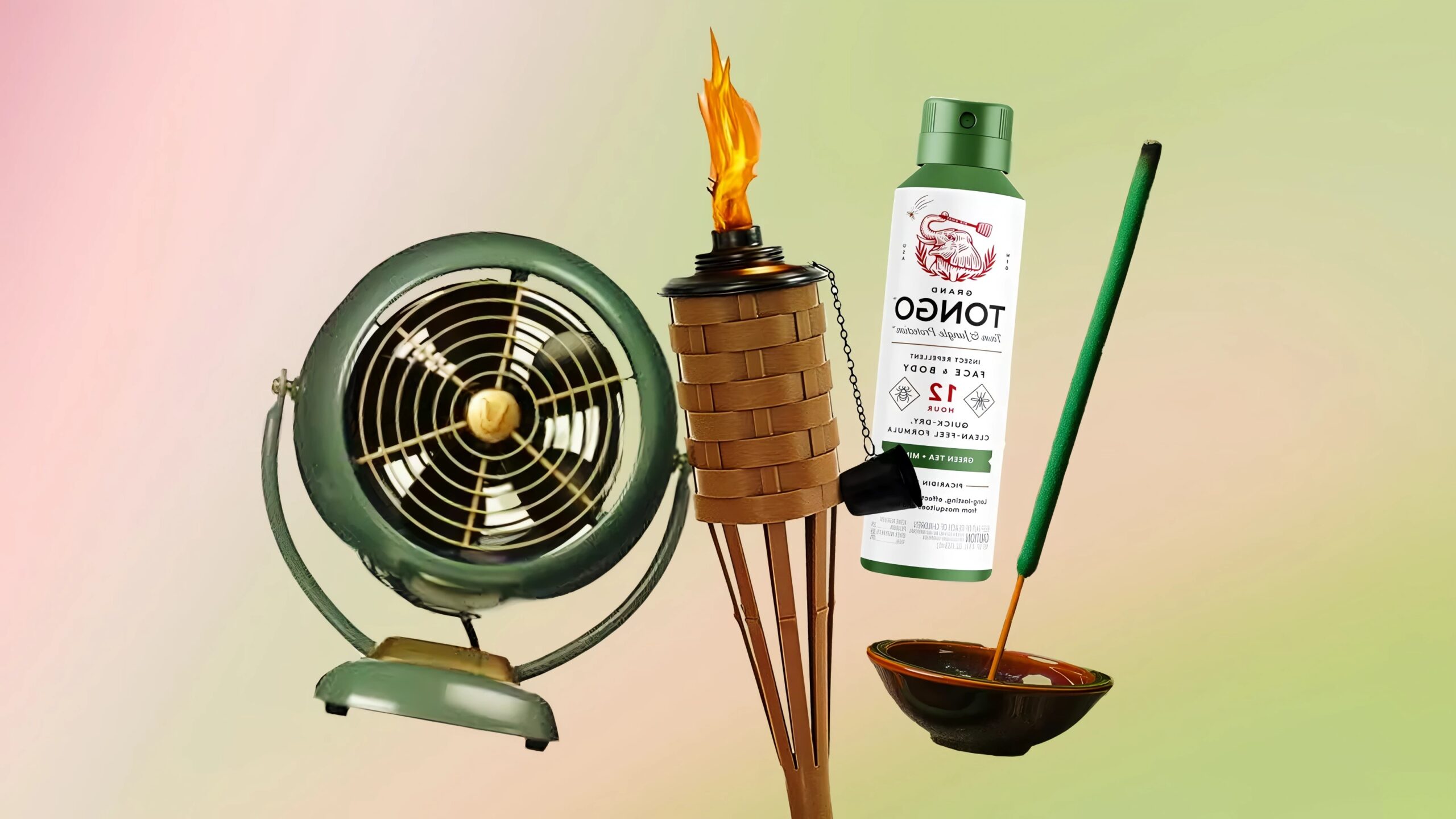
Mosquito repellent
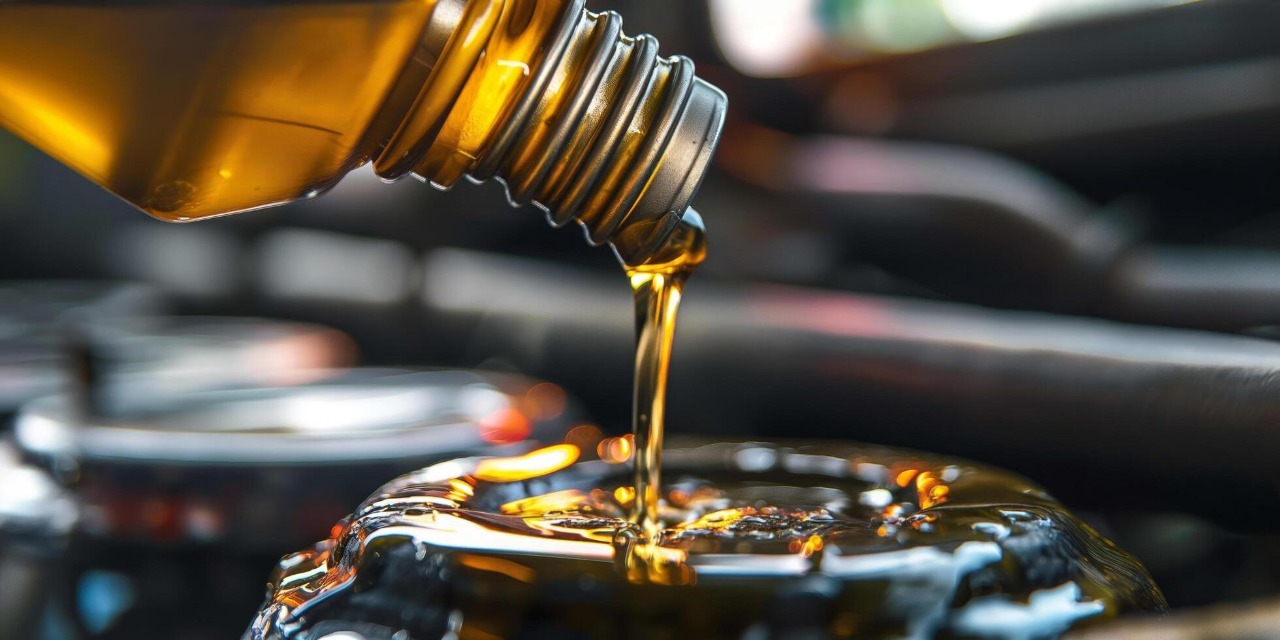
Motor oil

Mousses
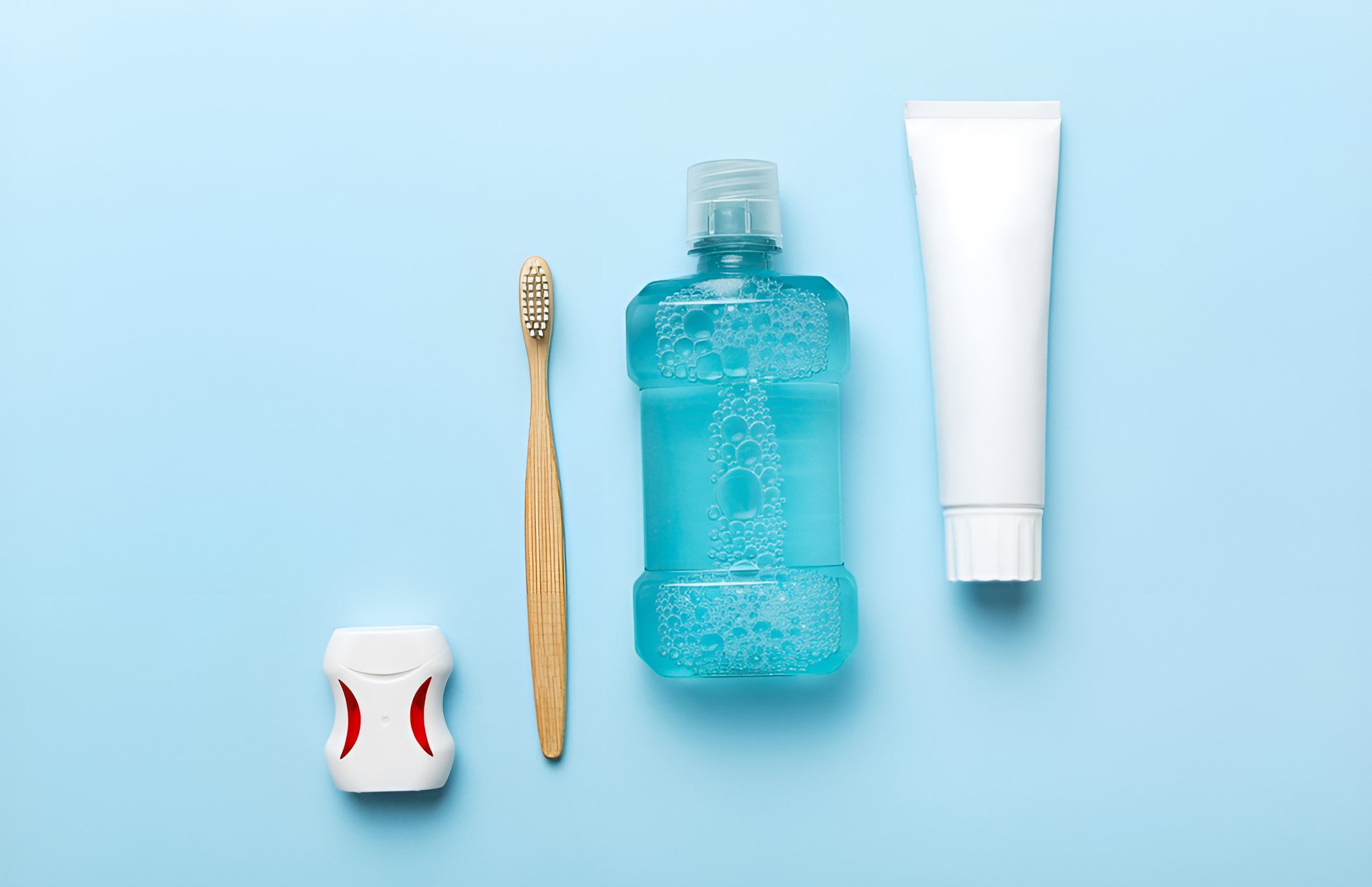
Mouthwash
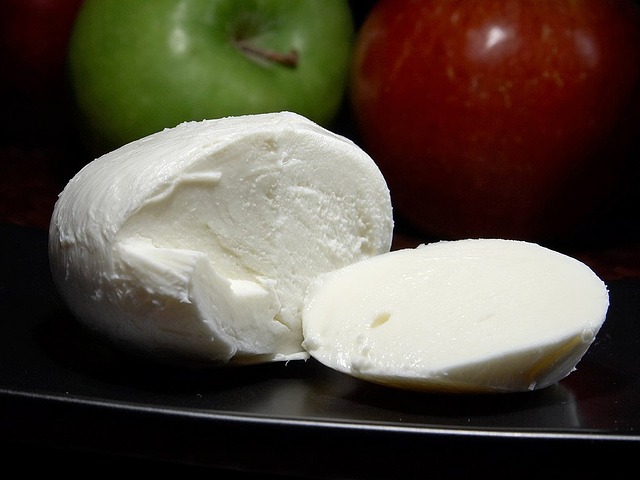
Mozzarella
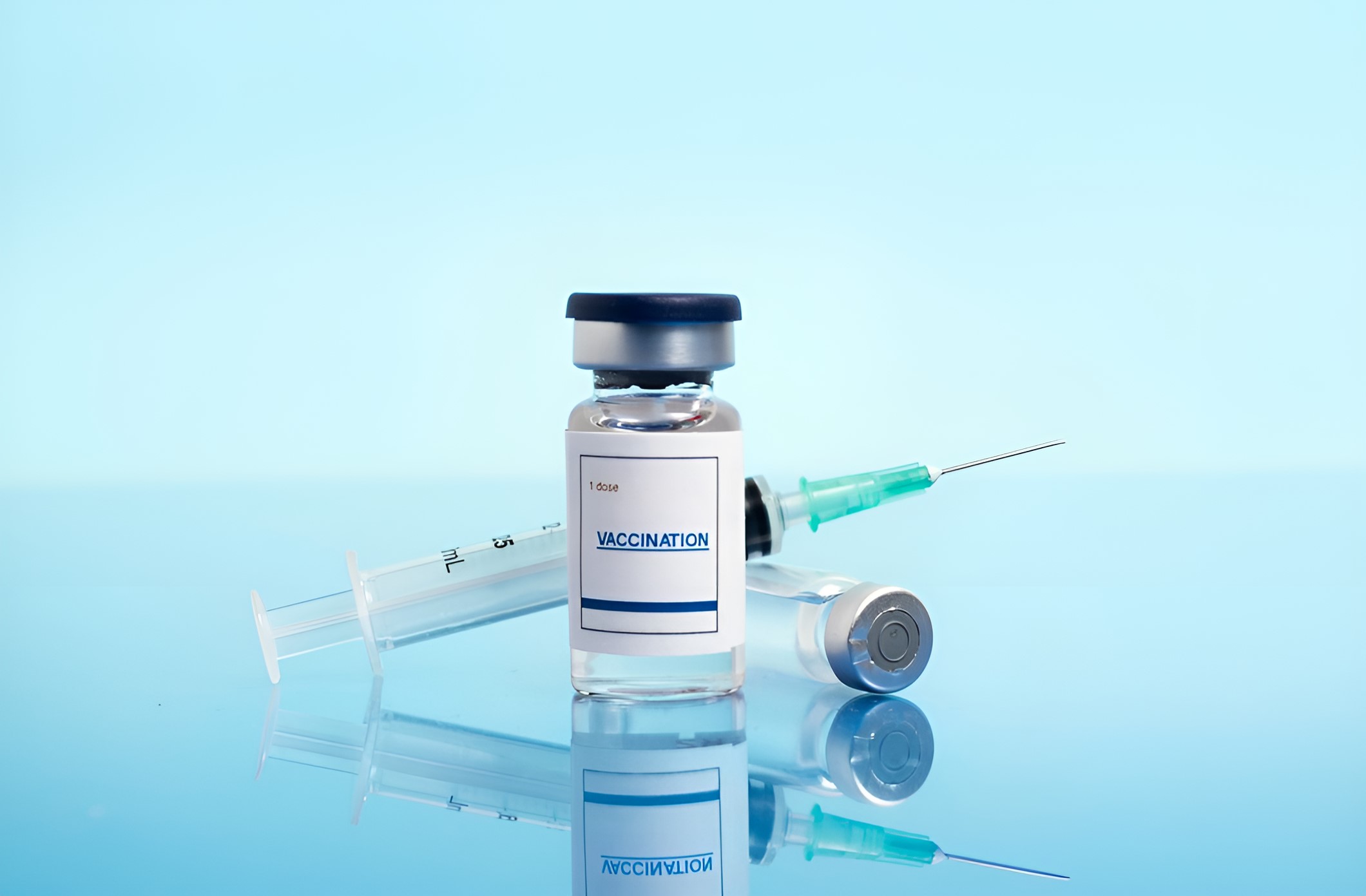
Mrna vaccines
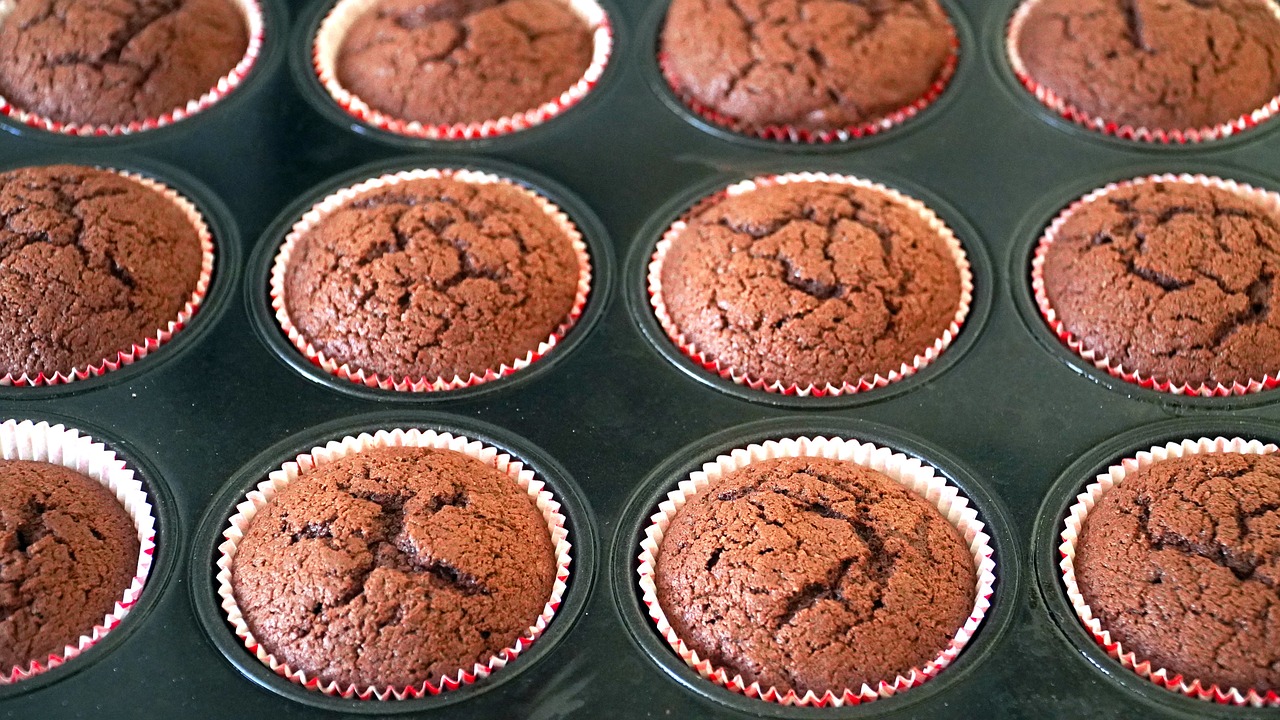
Muffins
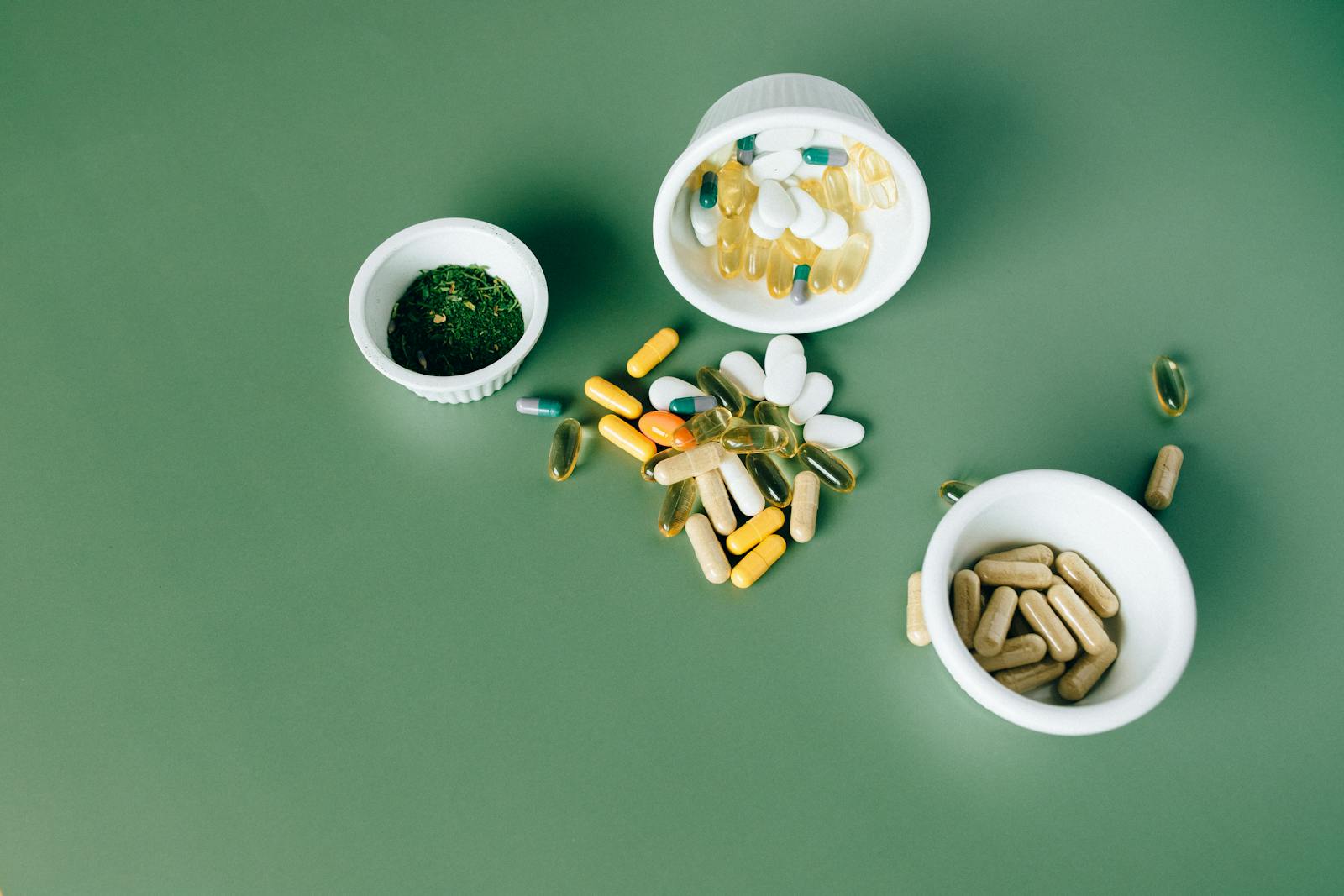
Multivitamin supplements
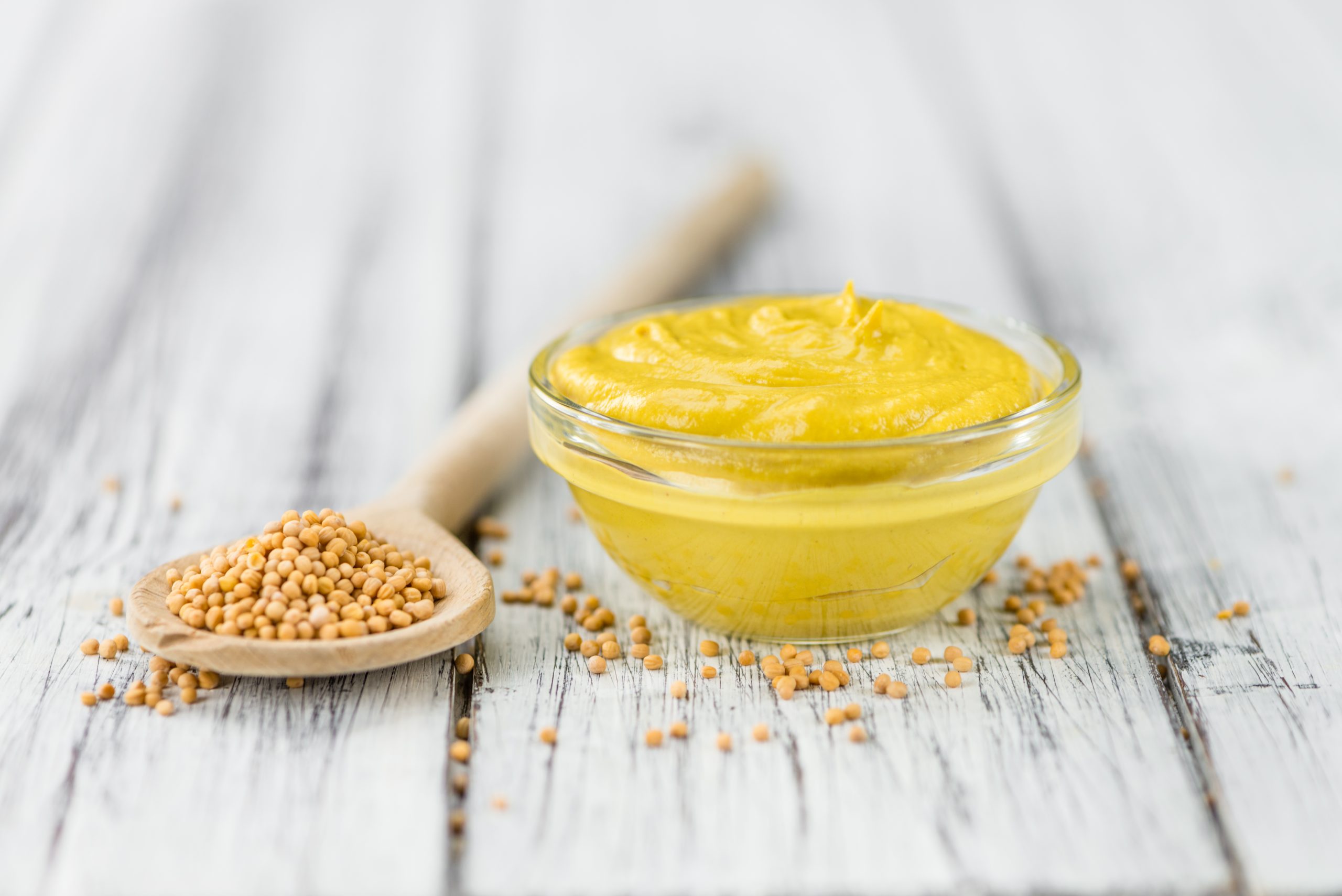
Mustard
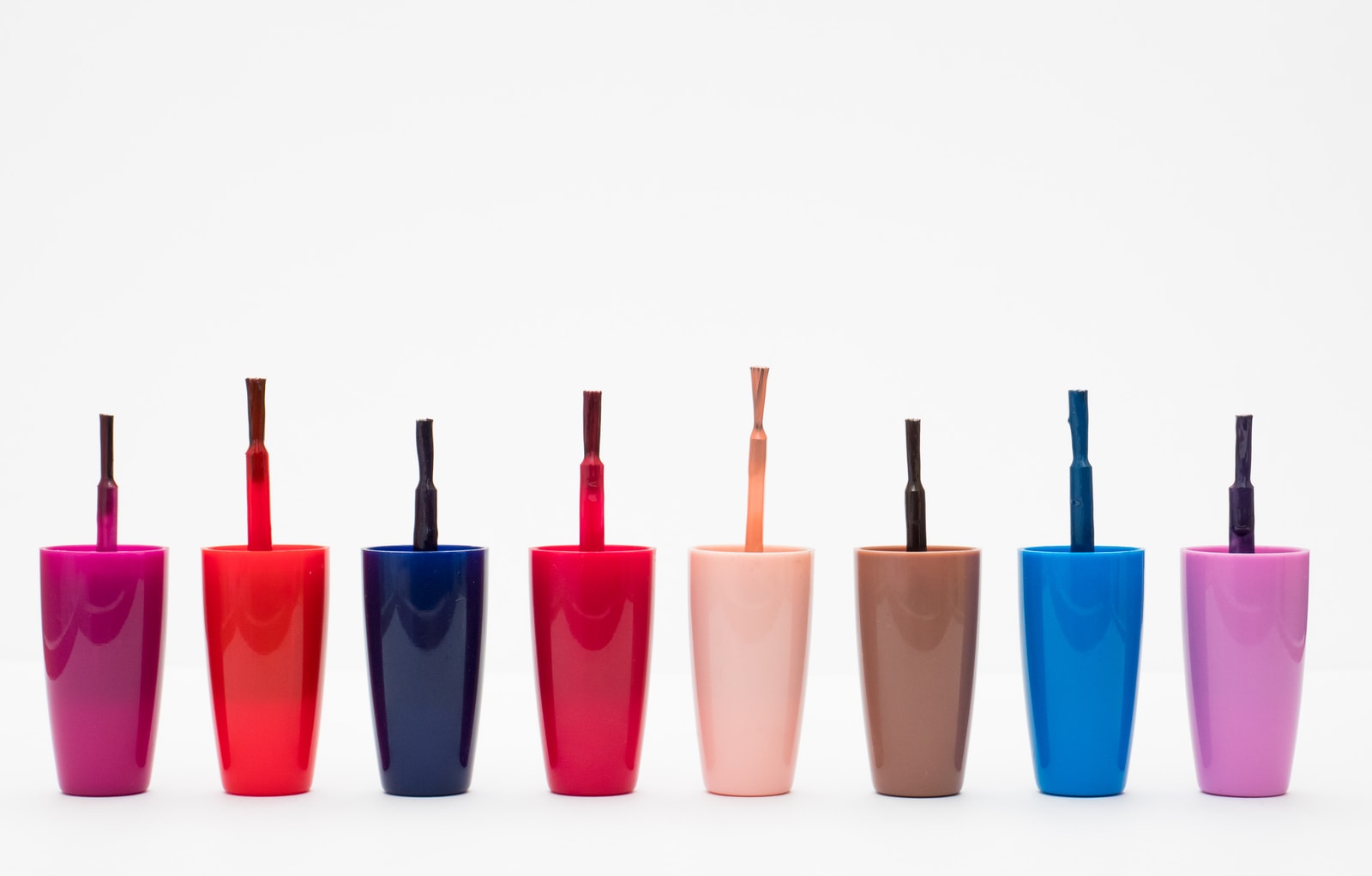
Nail polish
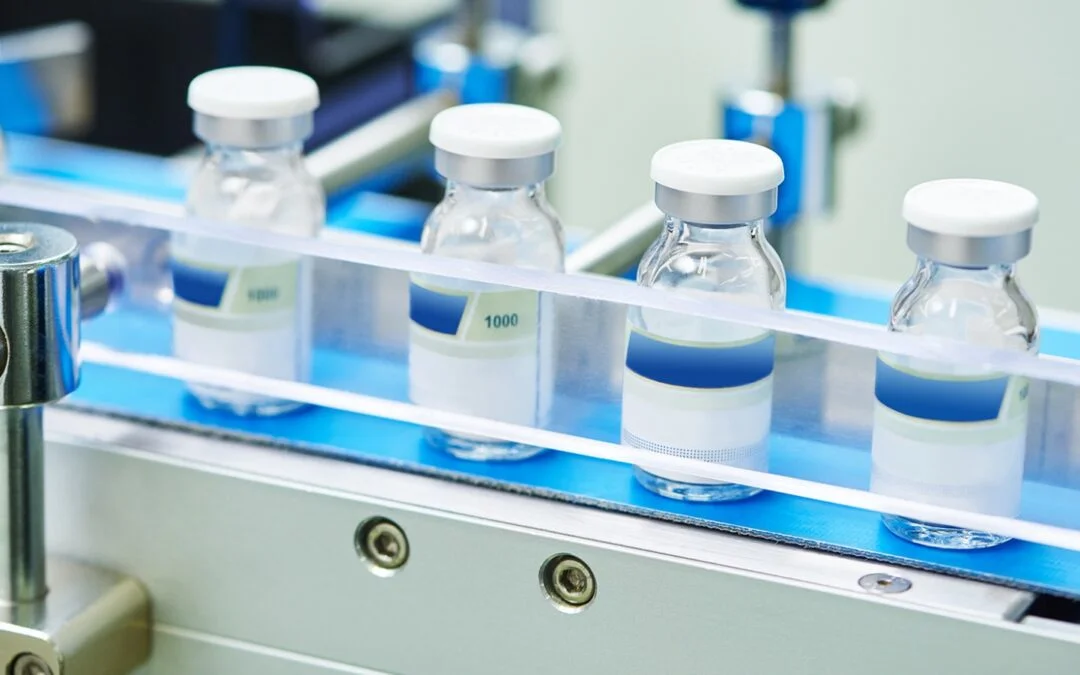
Nano suspensions
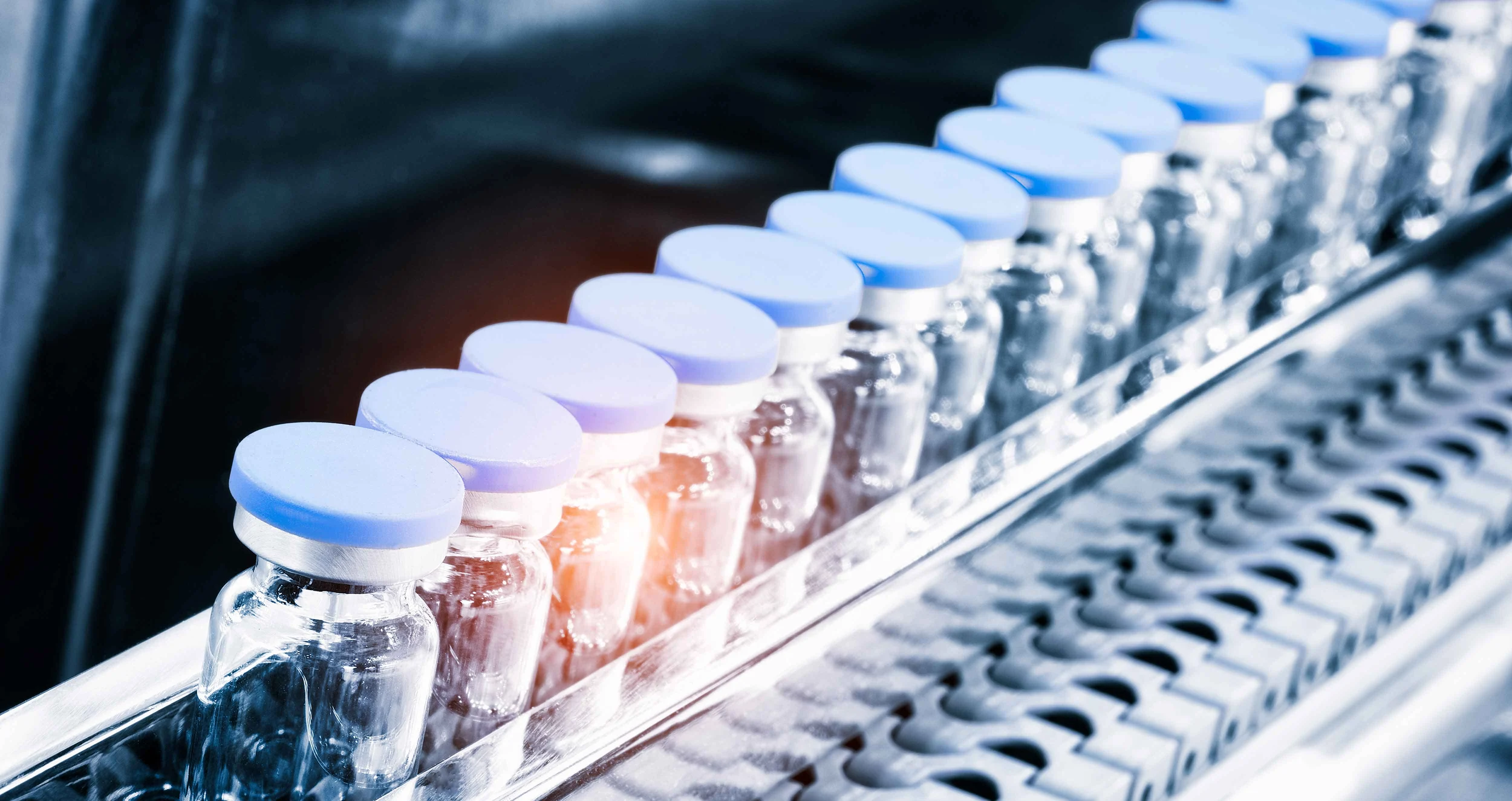
Nanoemulsions
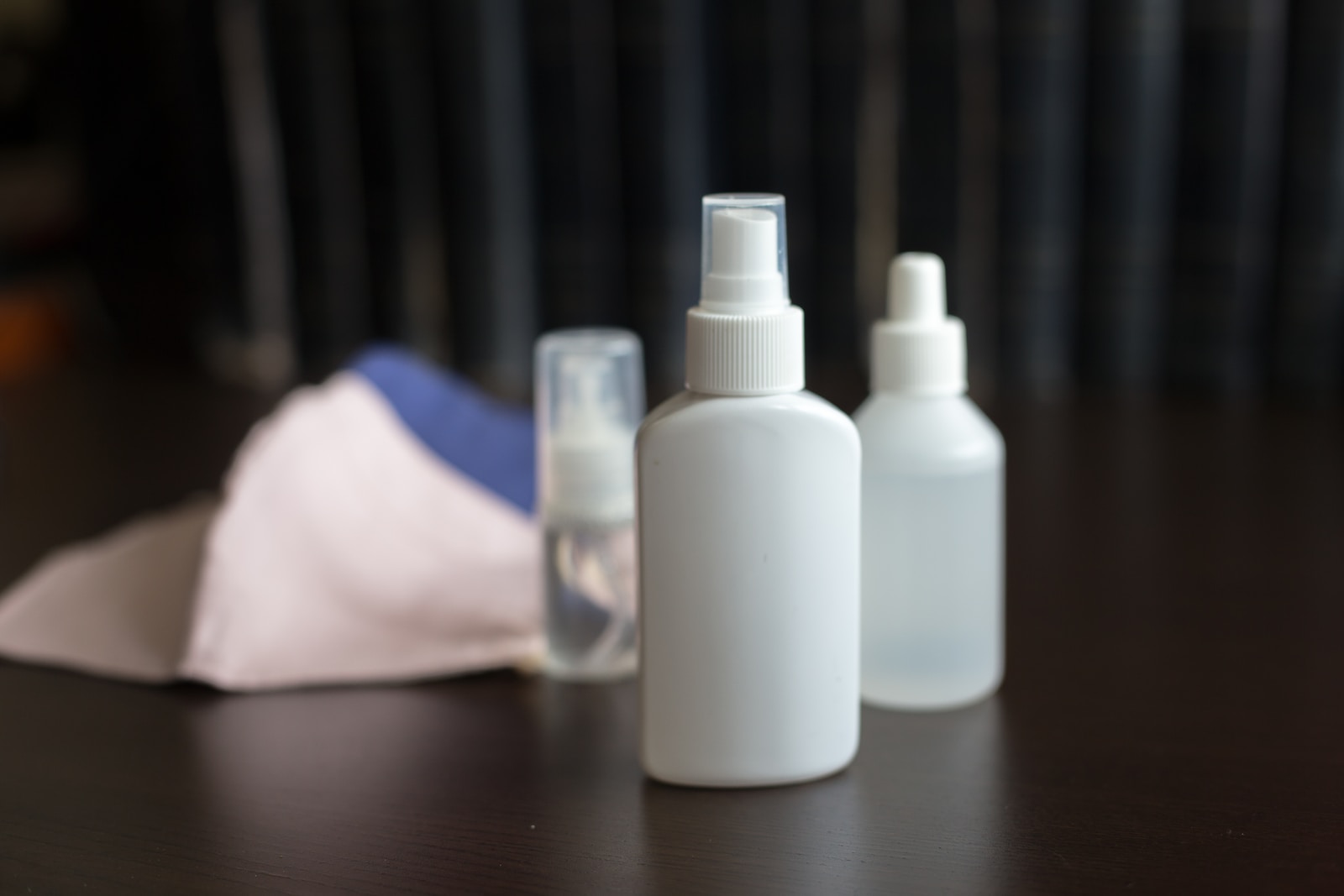
Nasal spray
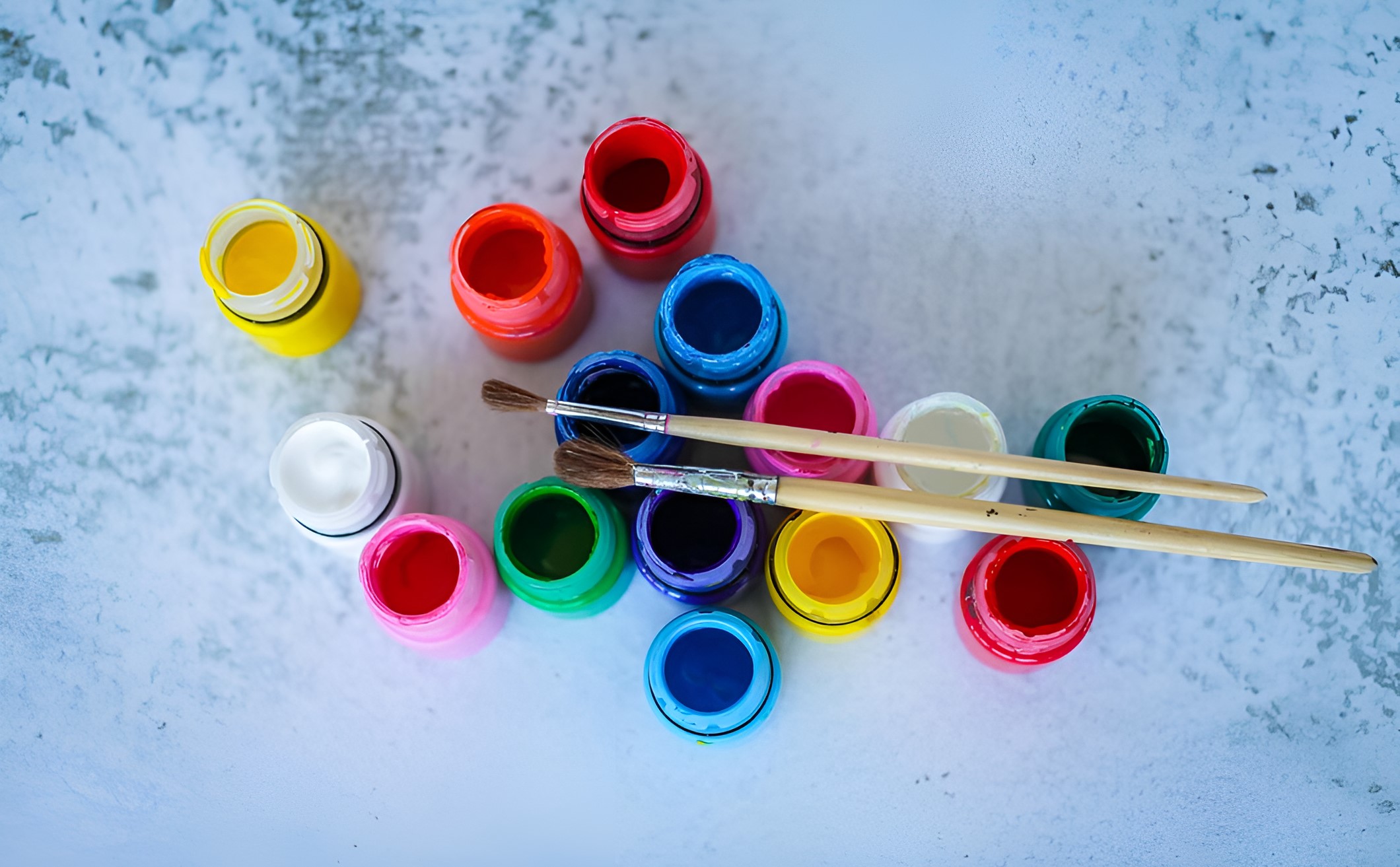
Natural paints
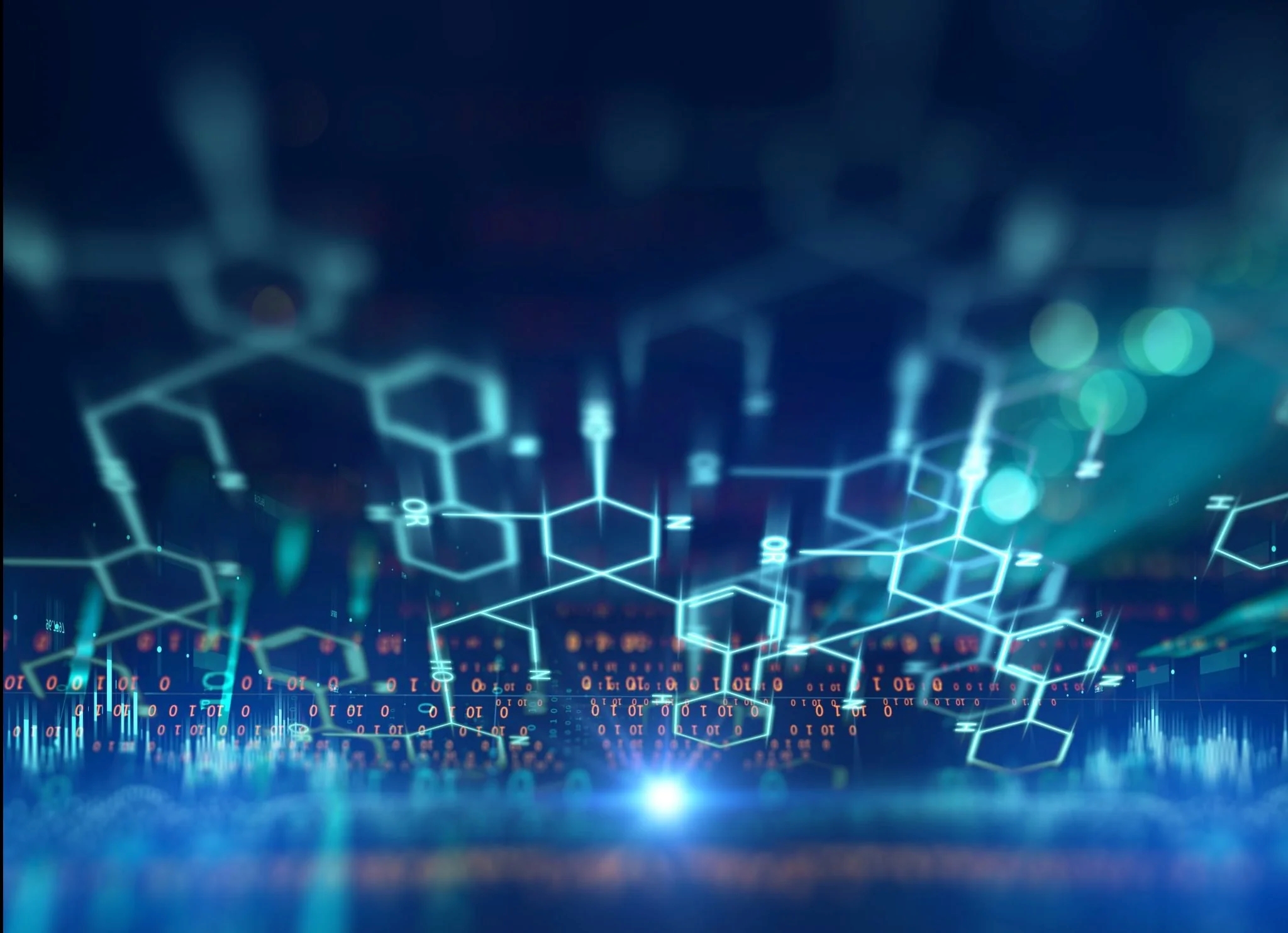
Next generation biologics
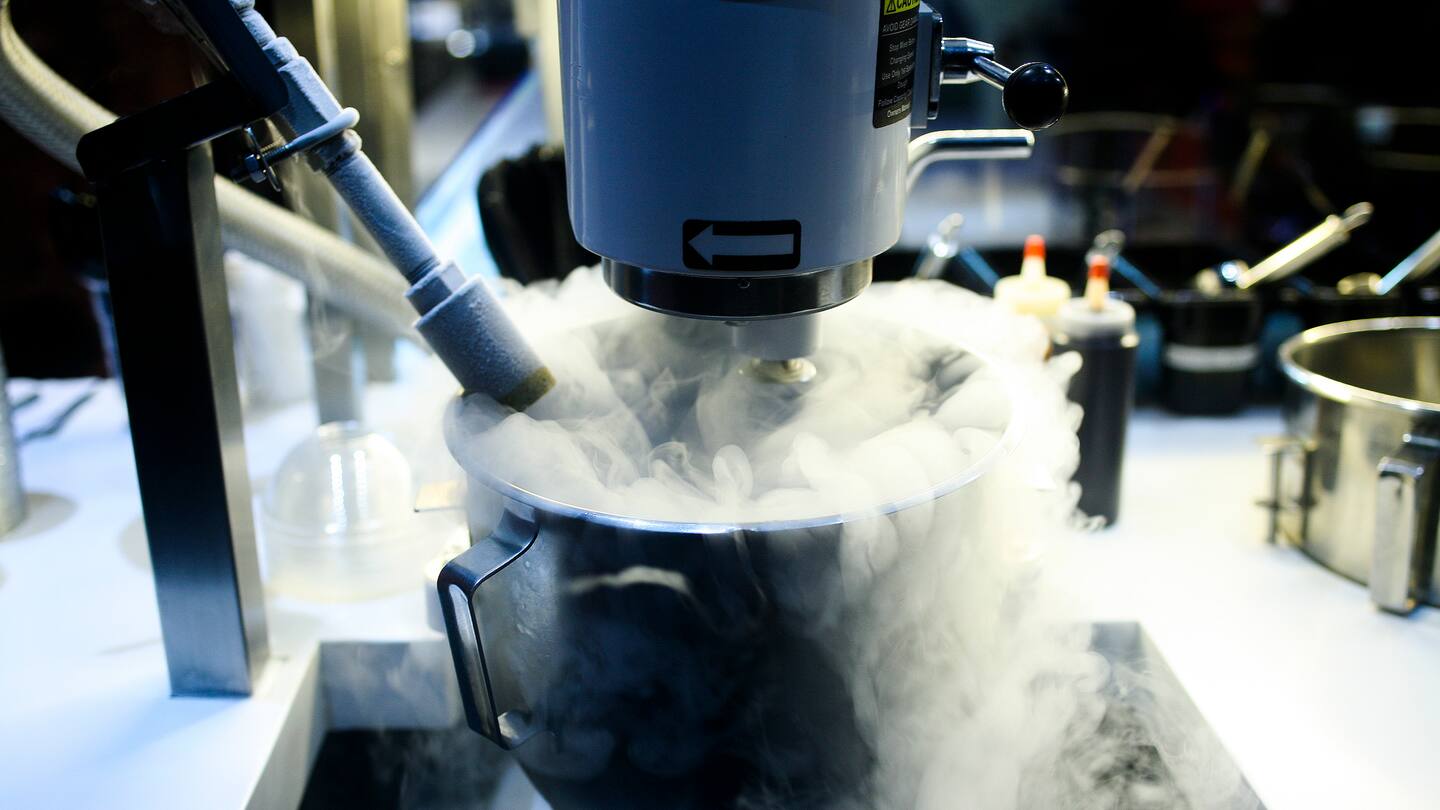
Nitrogen
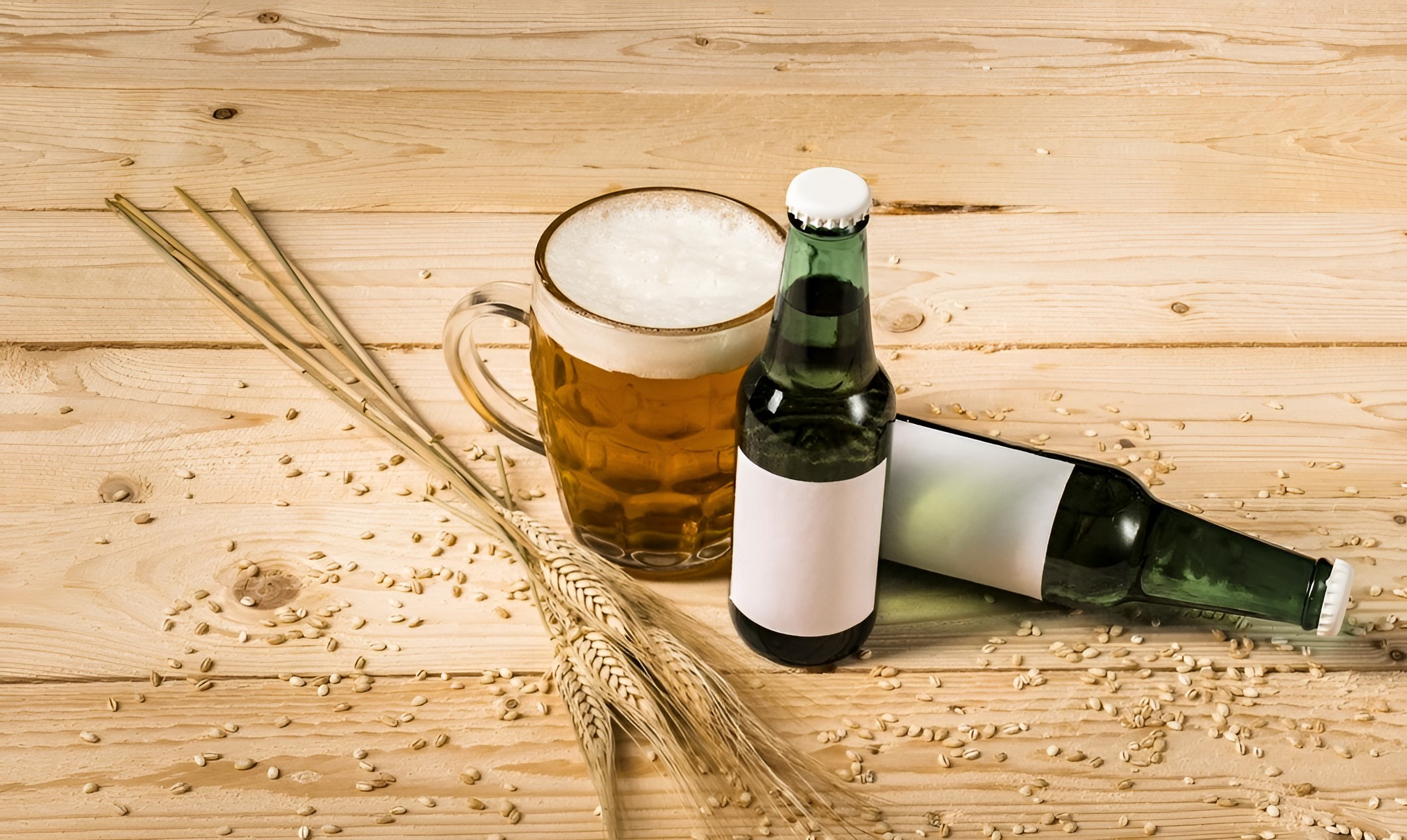
Non-alcoholic beer
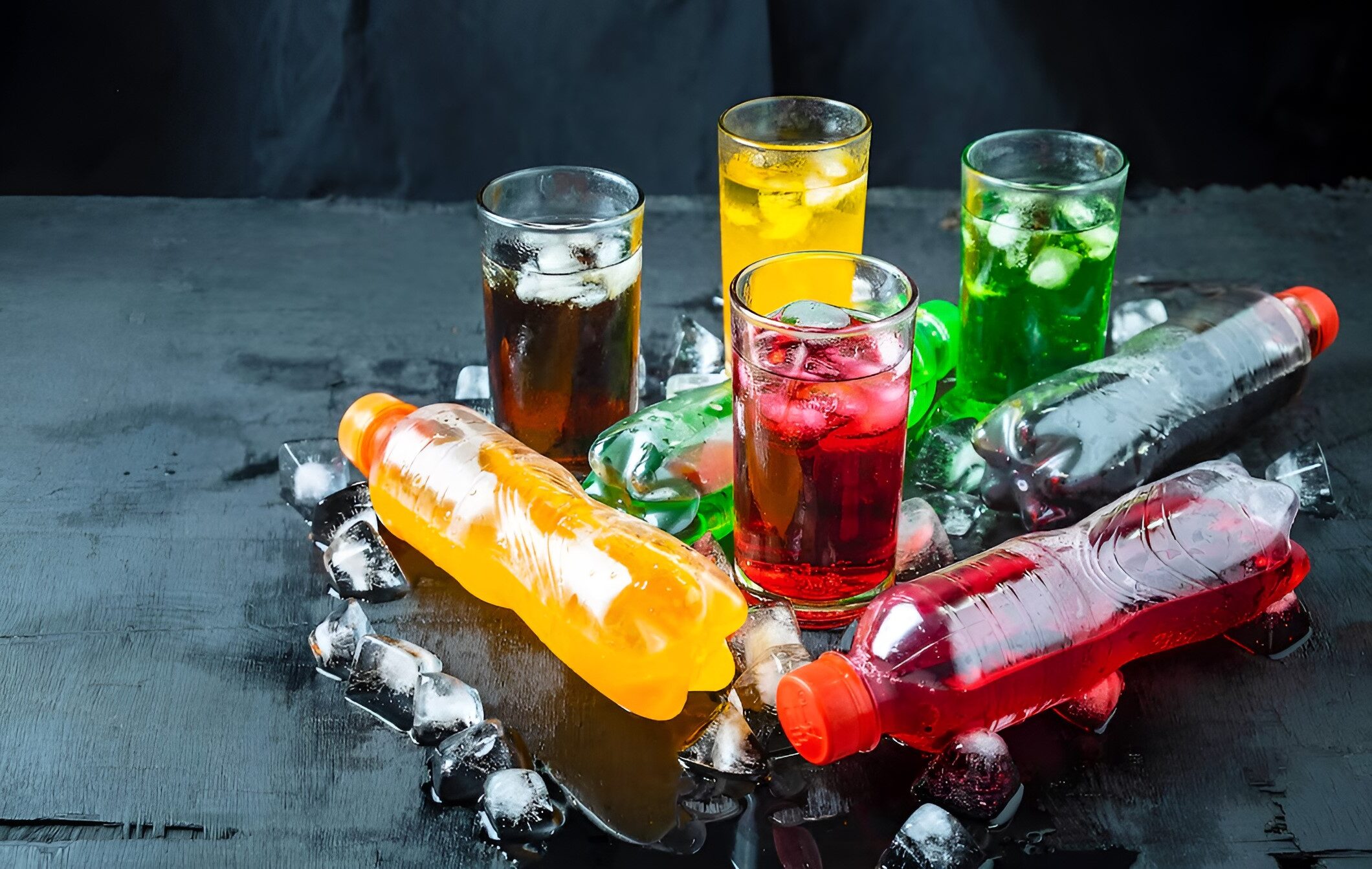
Non-carbonated beverages
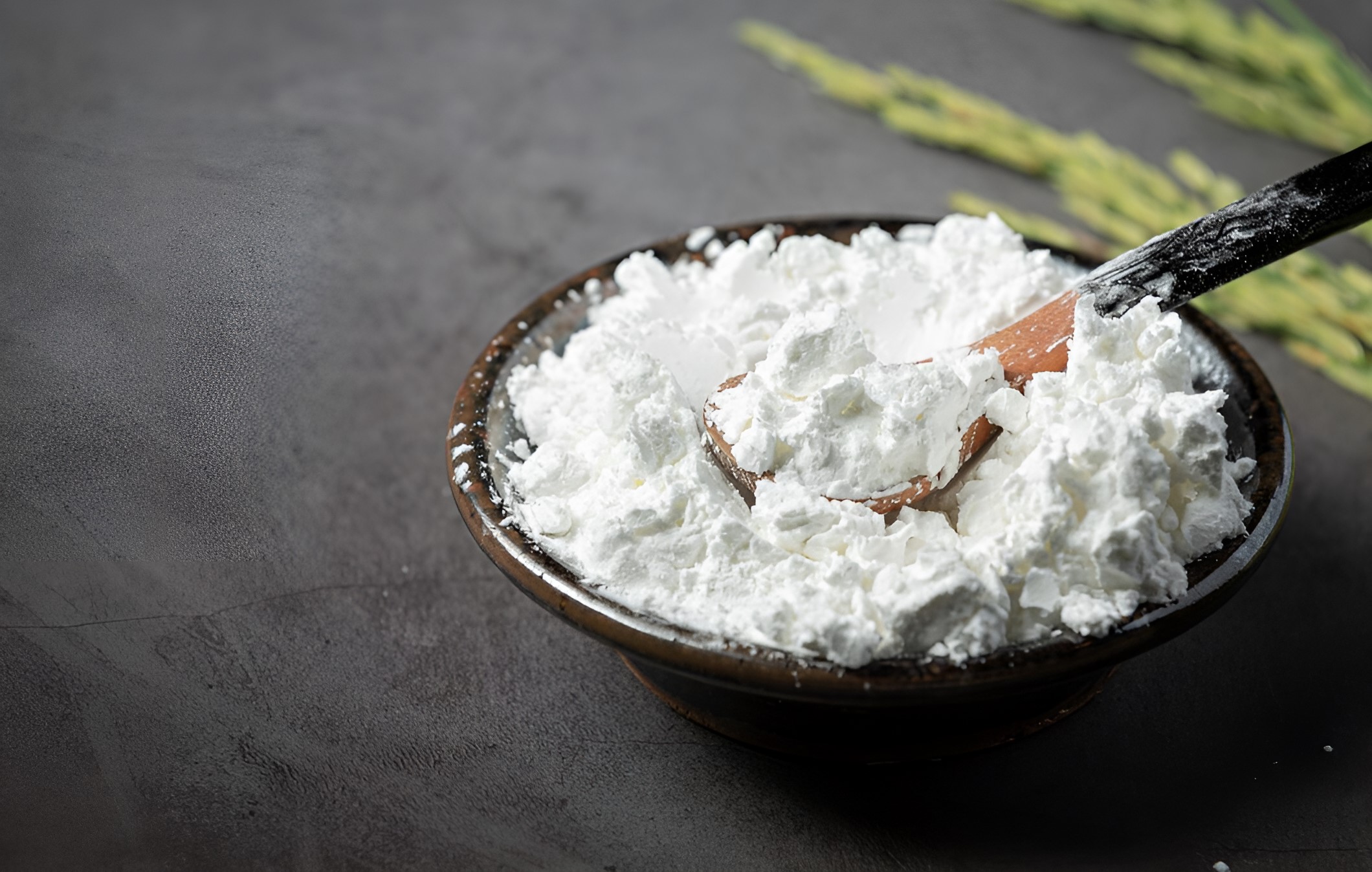
Non-dairy creamer
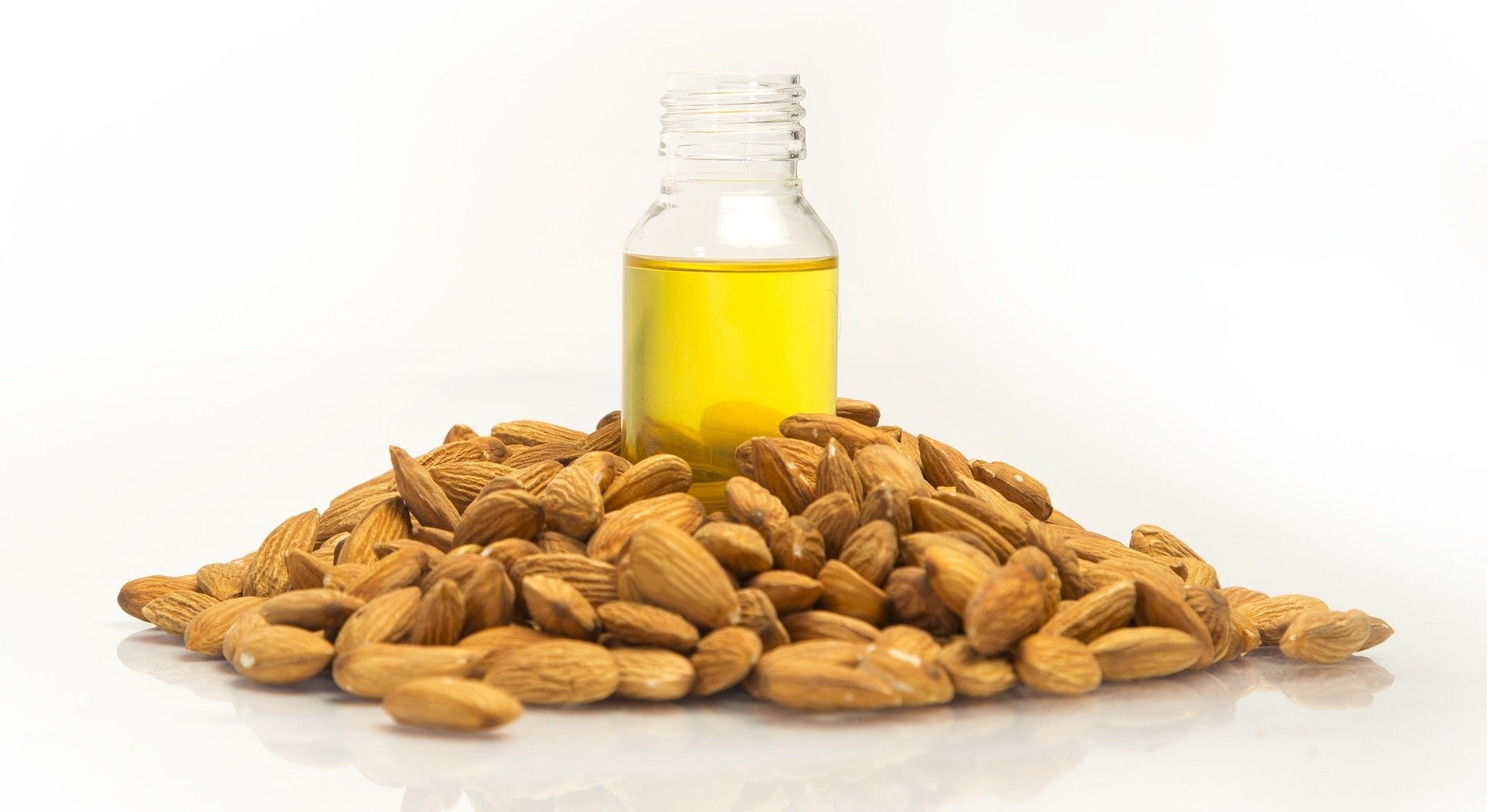
Nut oil
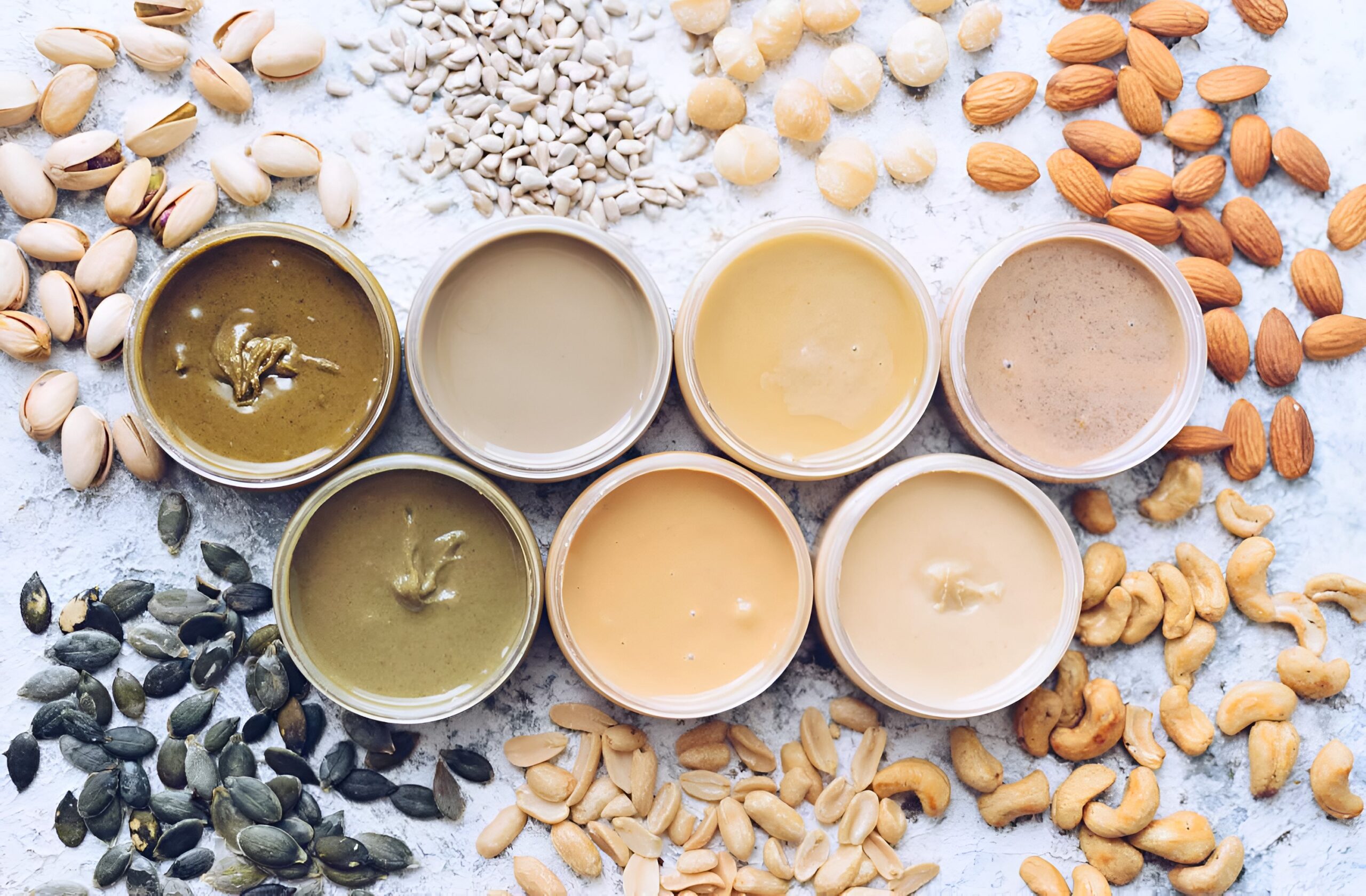
Nut paste
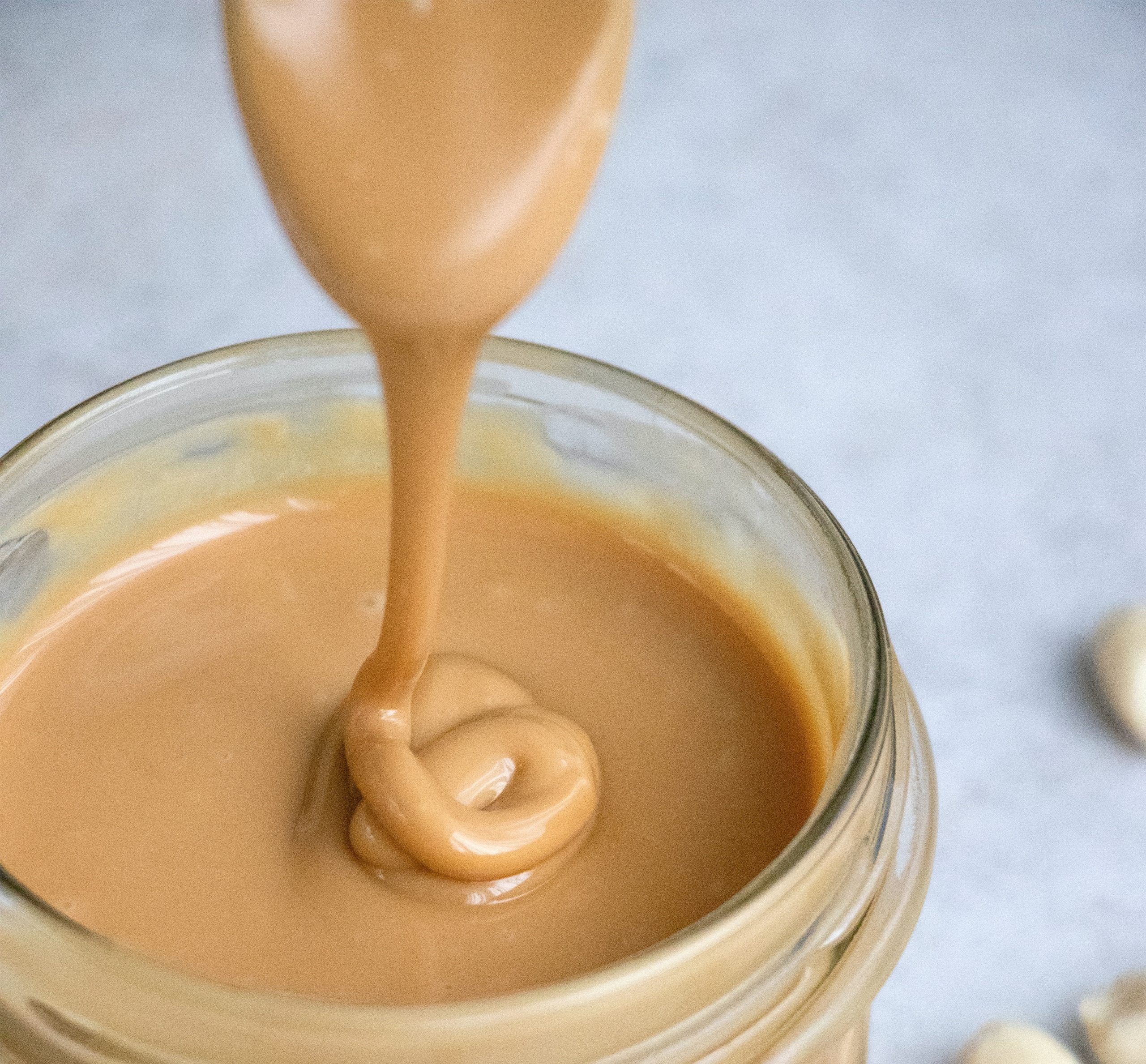
Nut butter
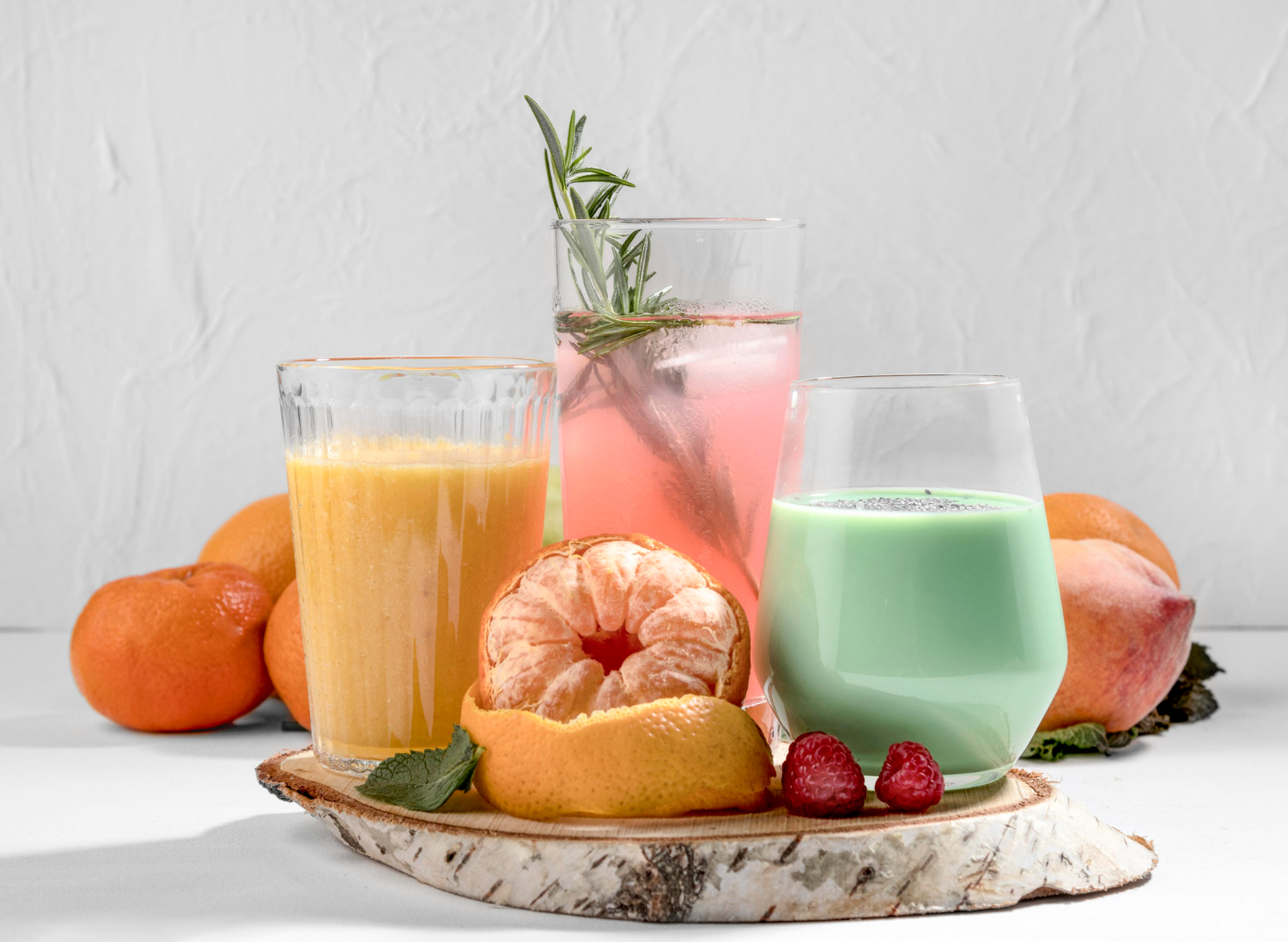
Nutritional drinks
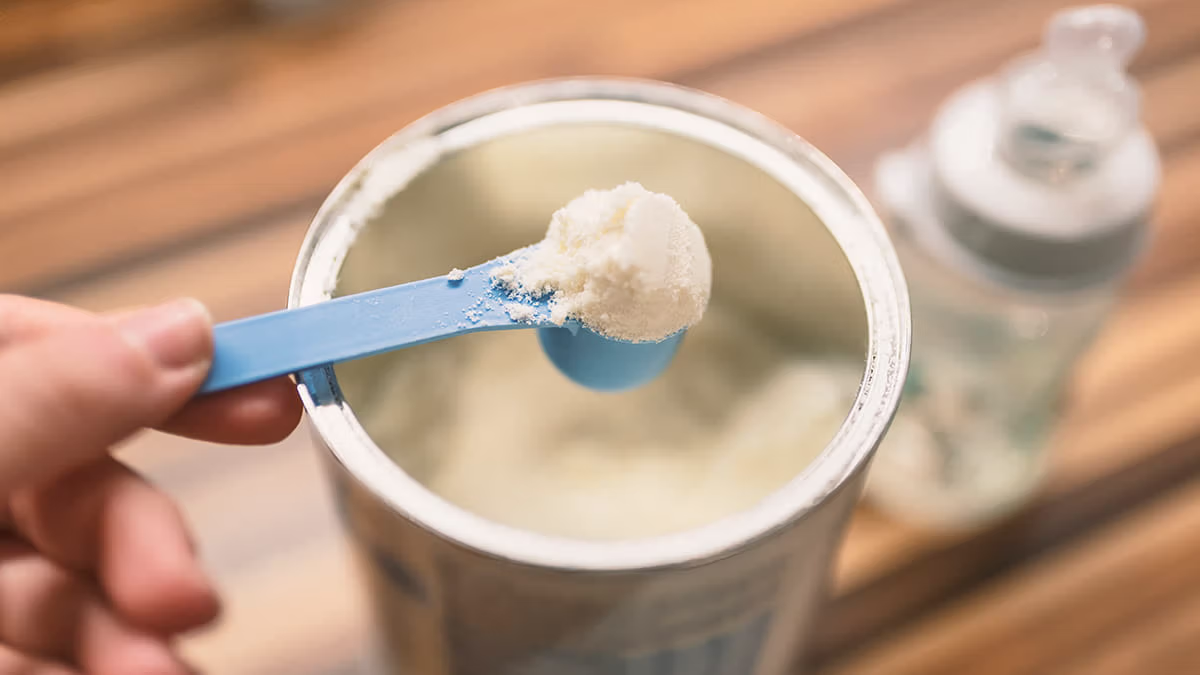
Nutritional formula
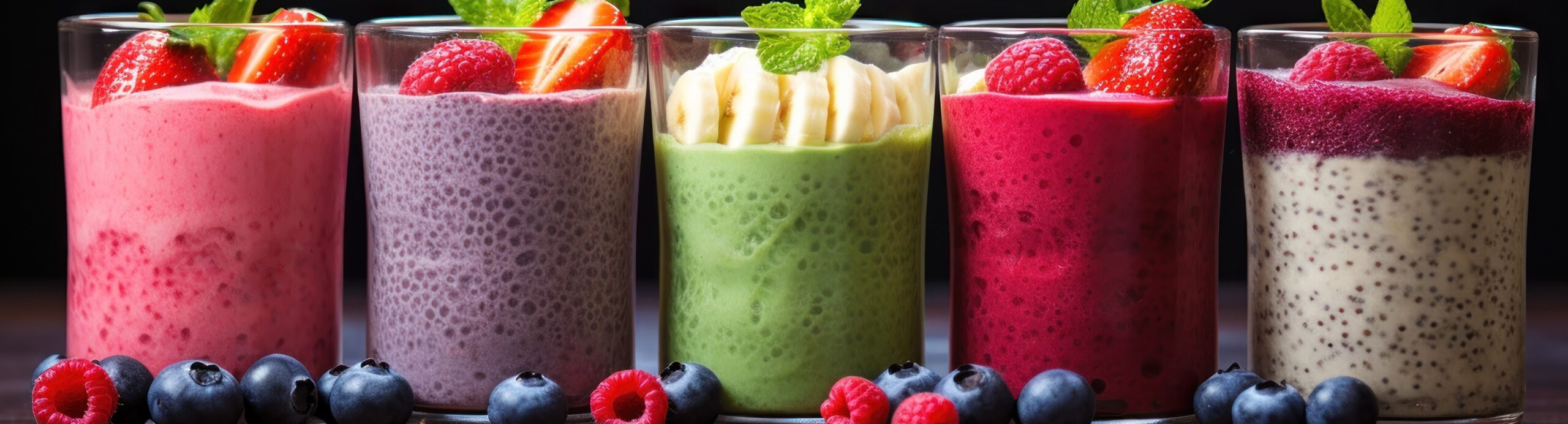
Nutritional shakes
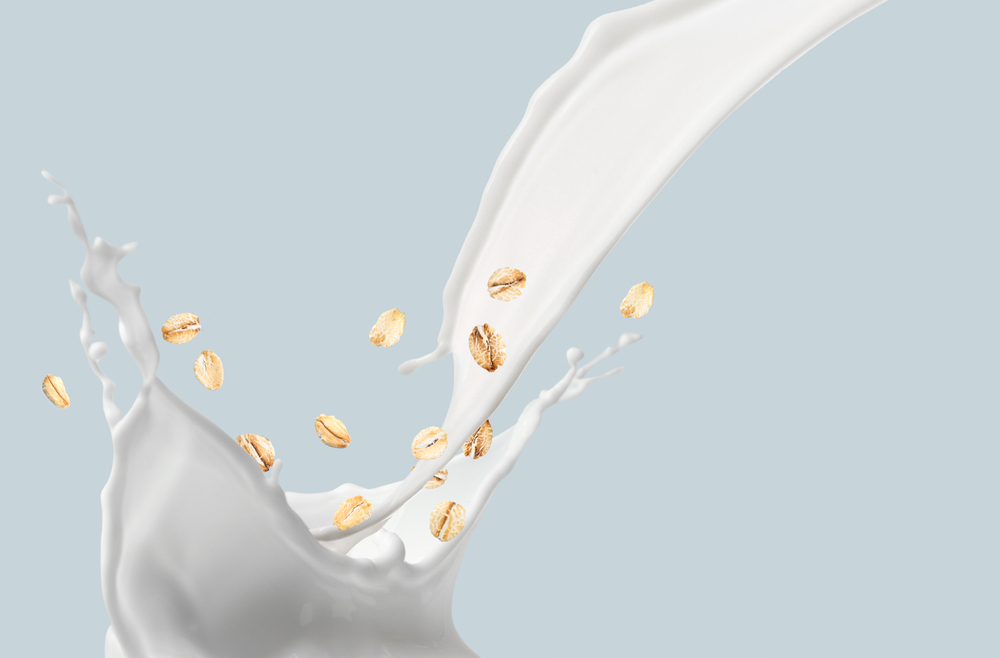
Oat milk
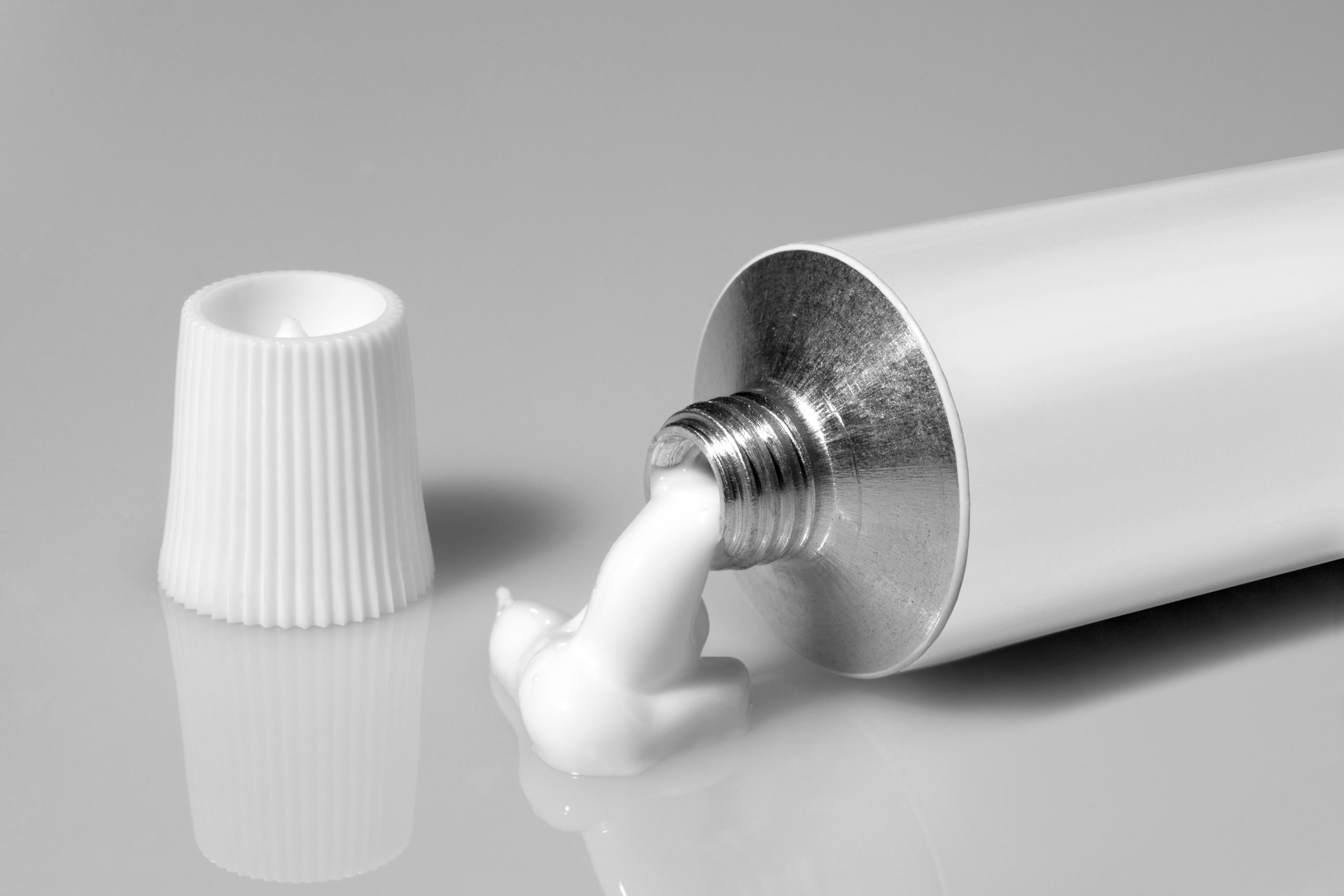
Ointment

Oleochemicals

Olives

Omega-3 capsules
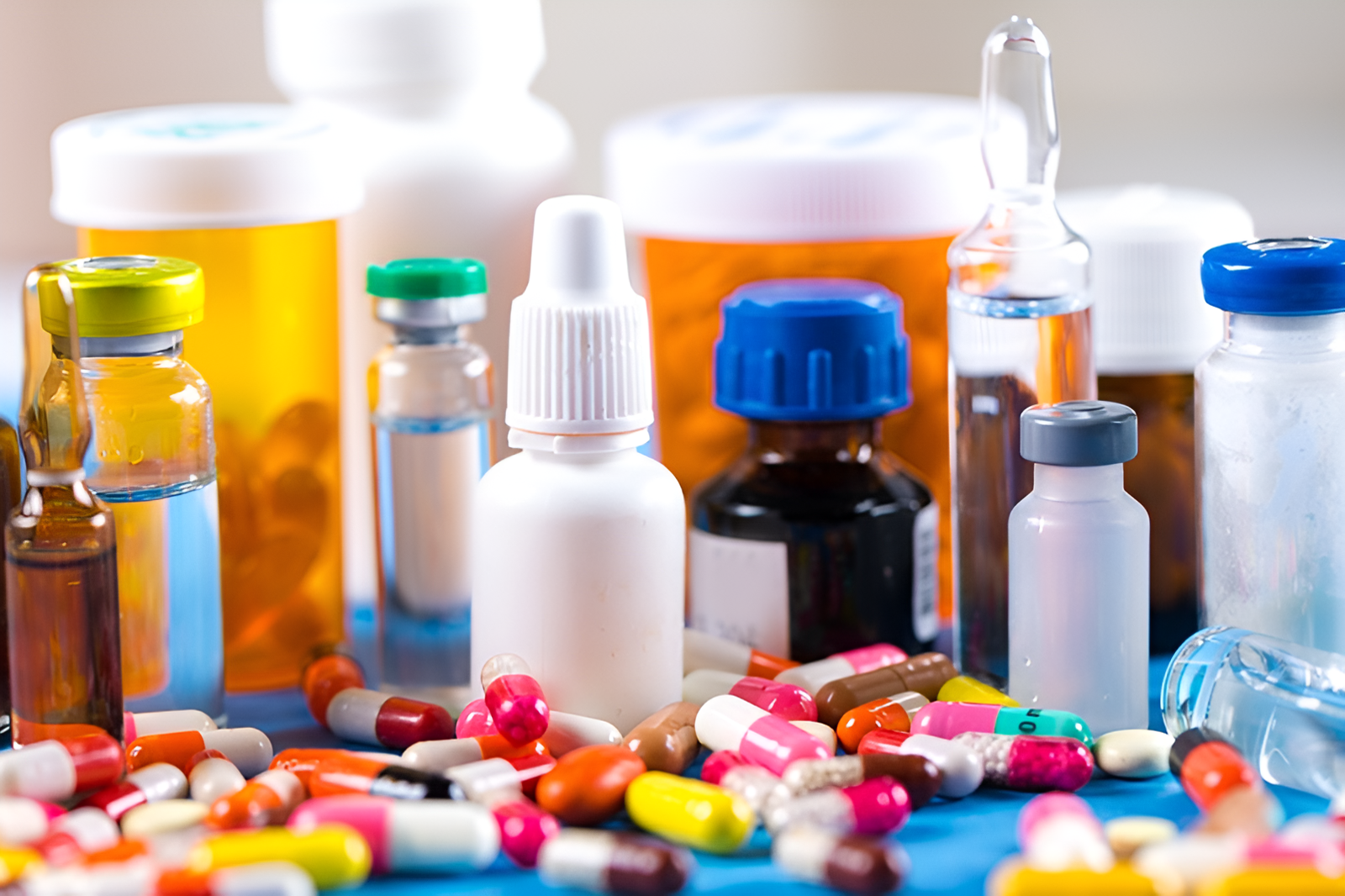
Oncology drugs
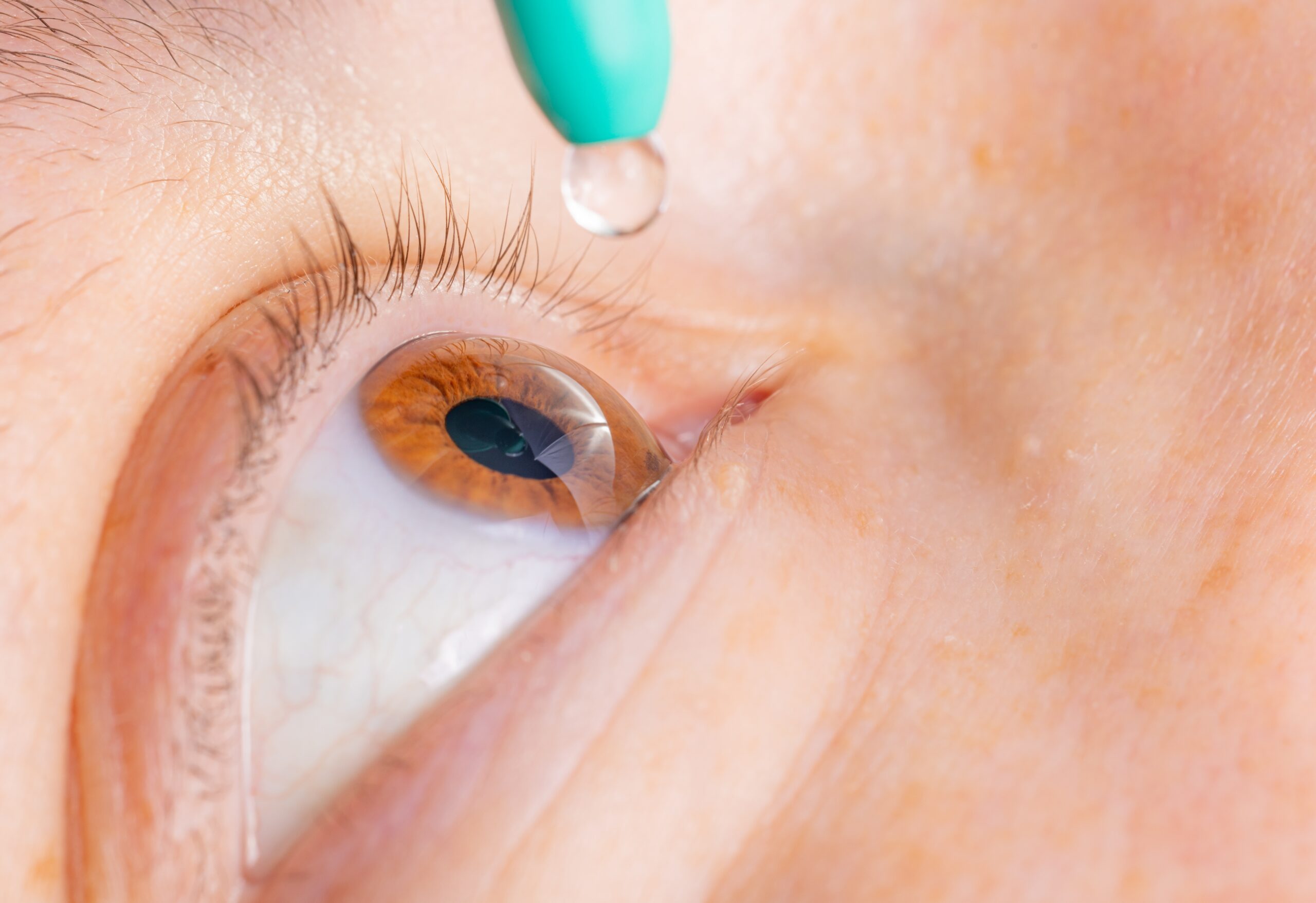
Ophthalmics
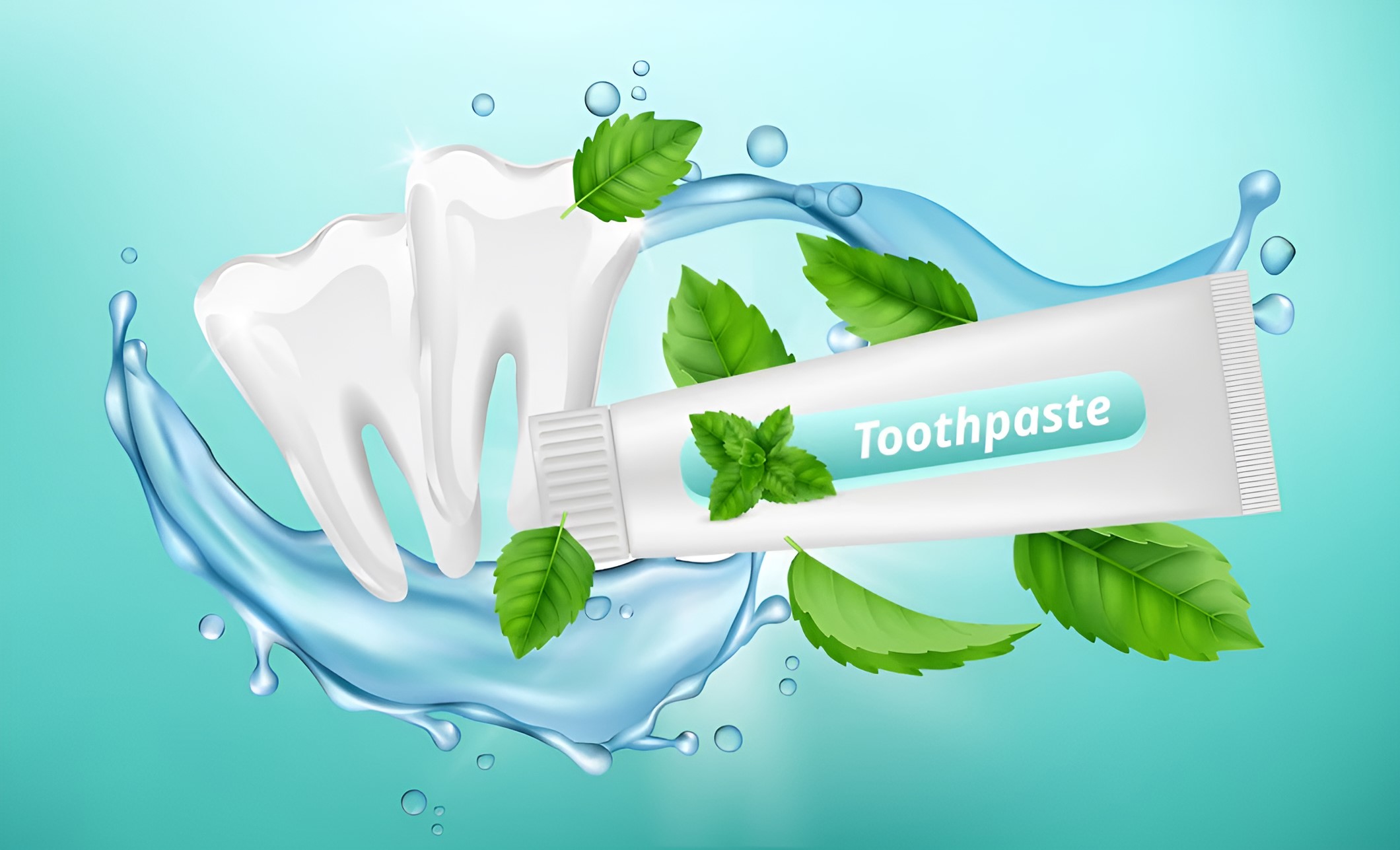
Oral care
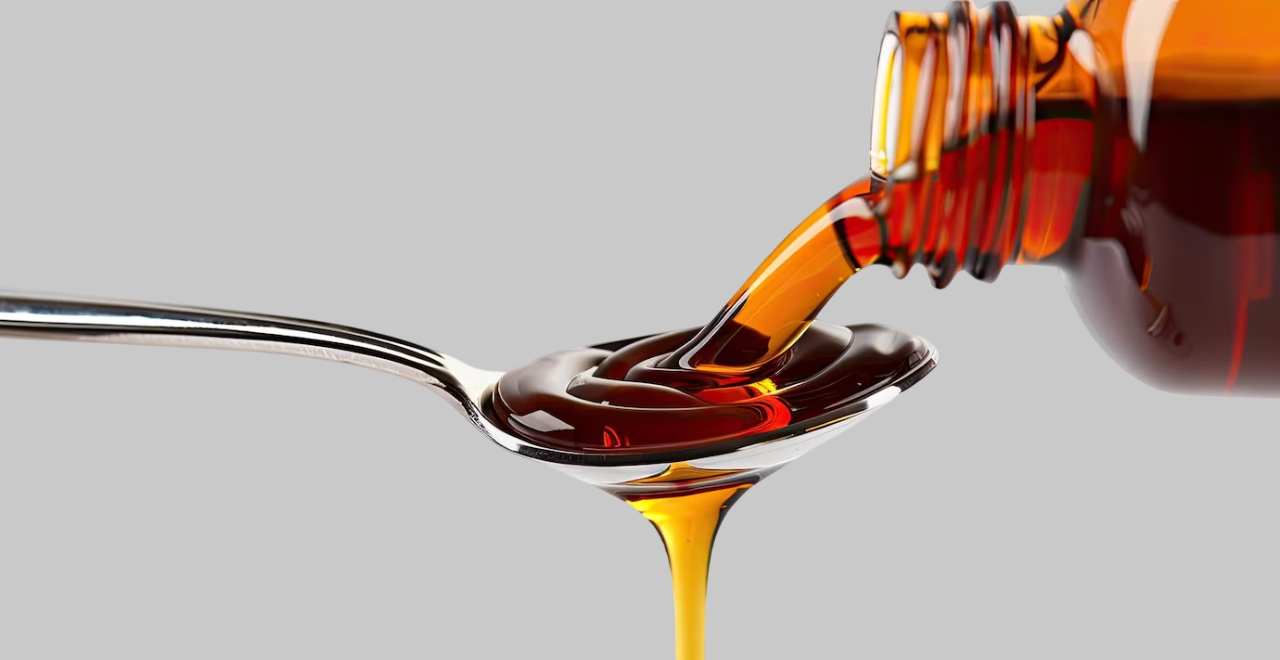
Oral liquid formulations
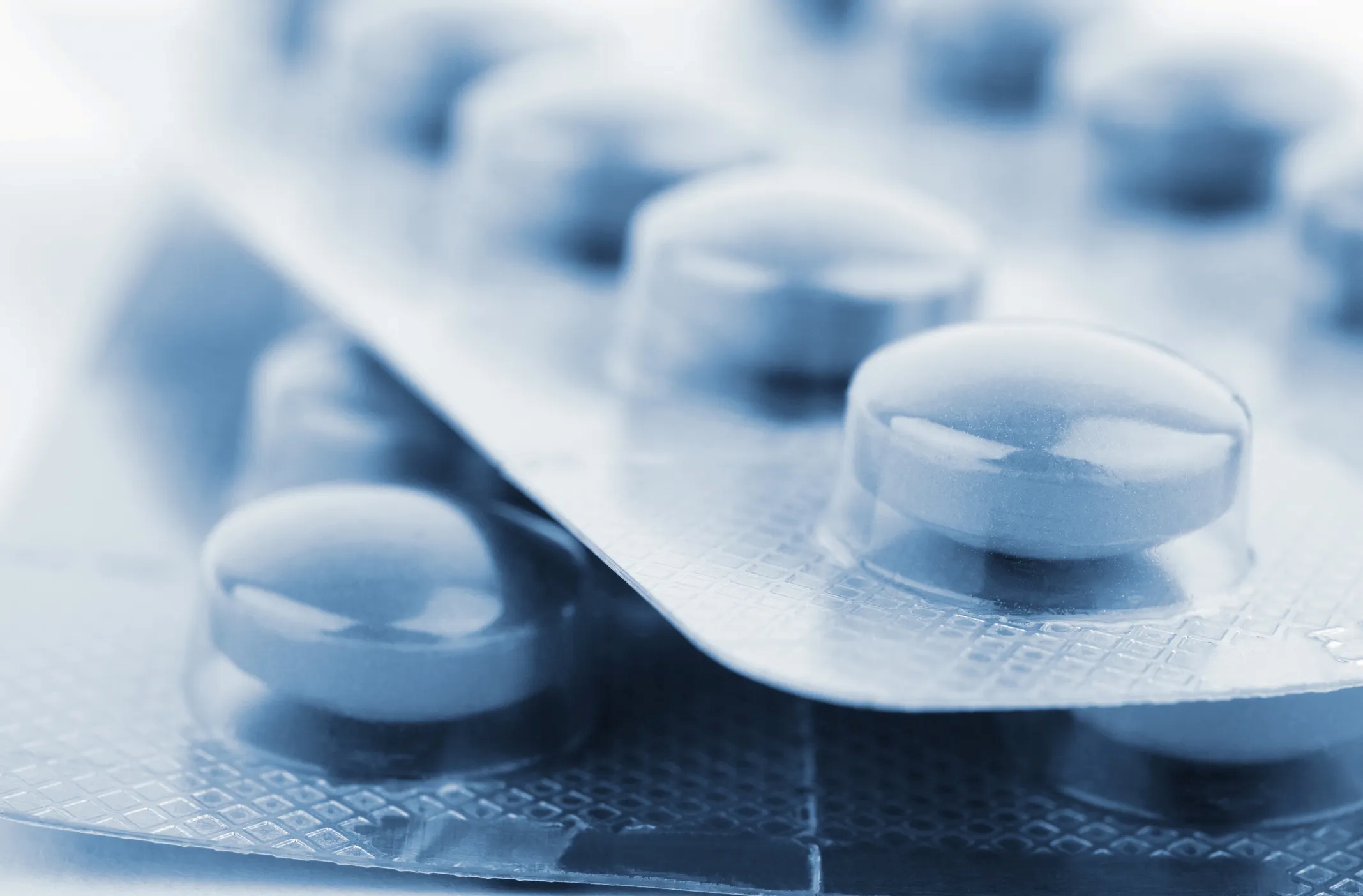
Oral vaccines
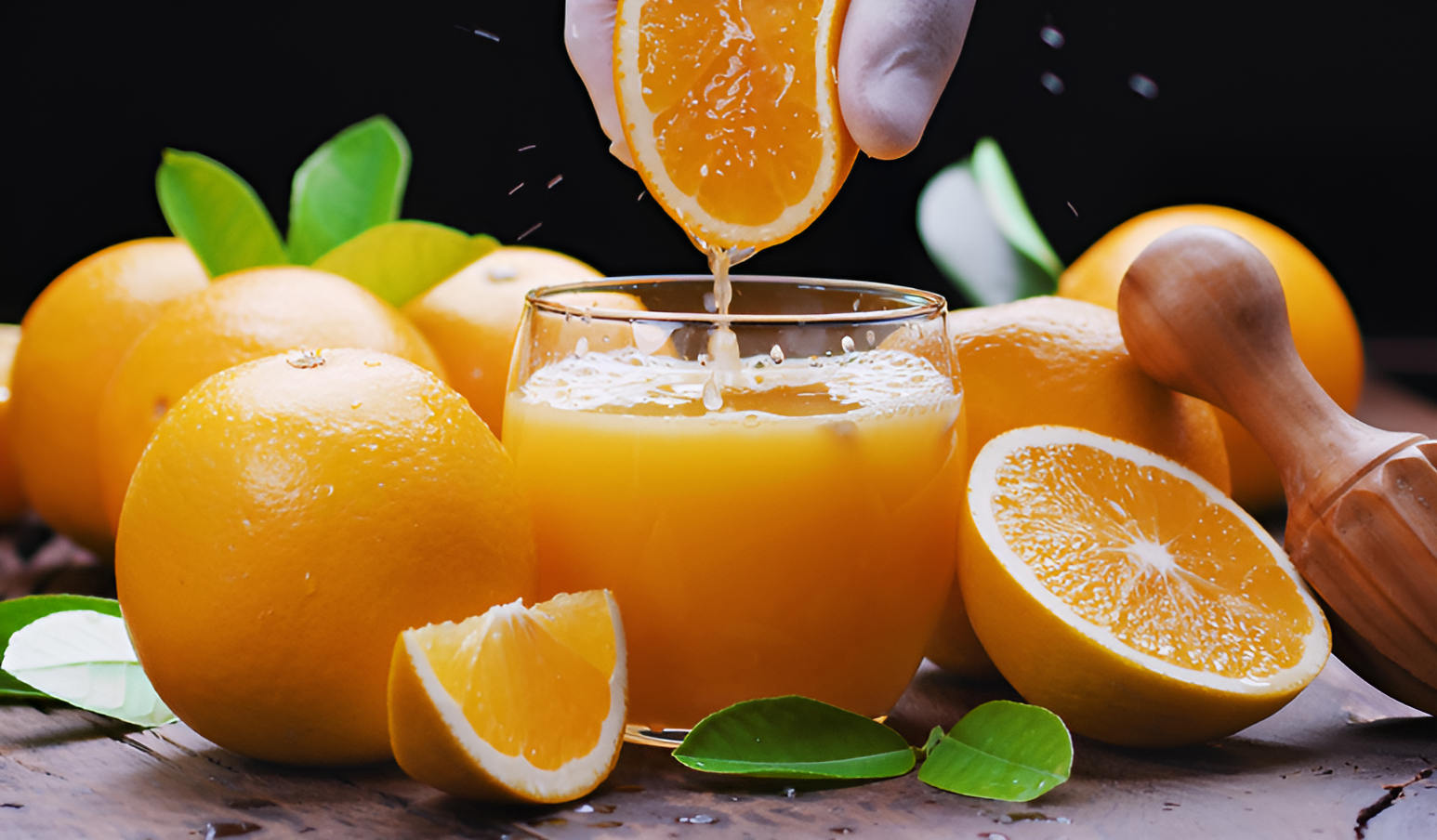
Orange juice
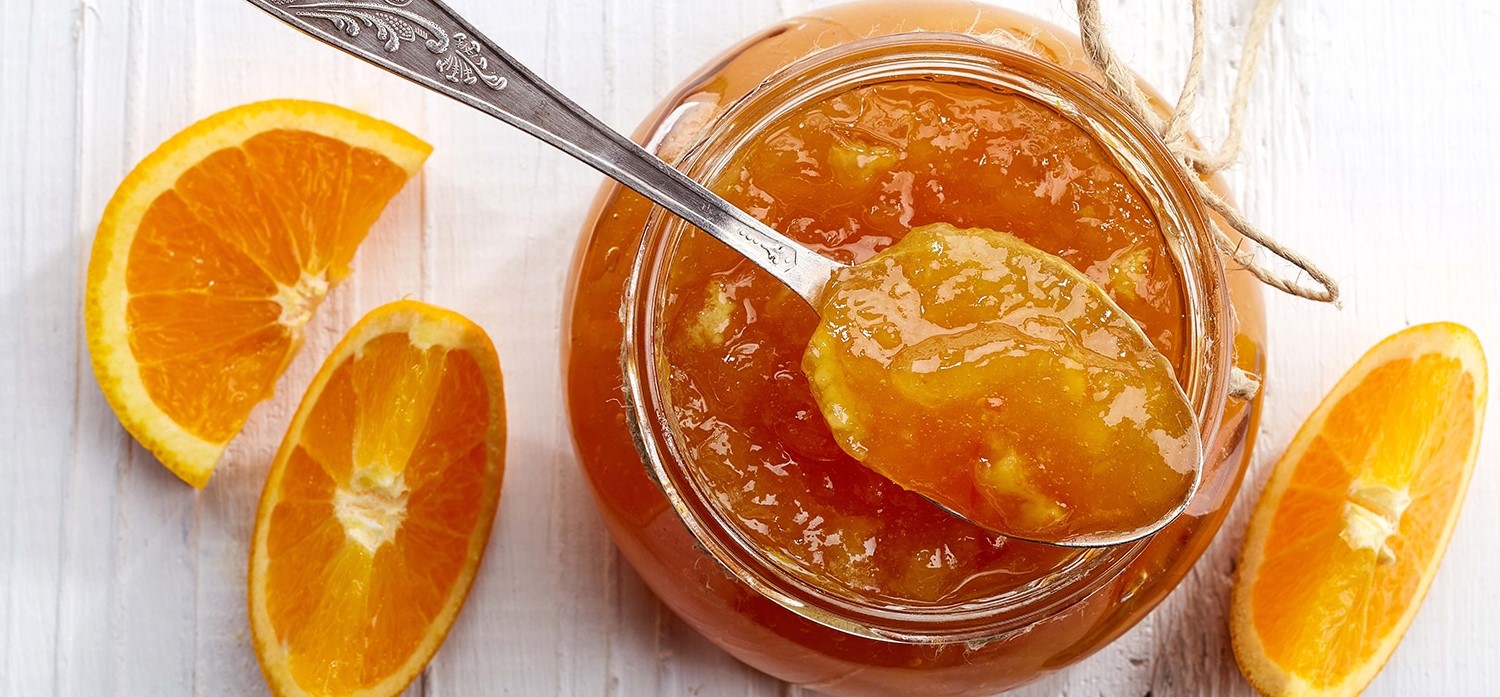
Orange marmalade
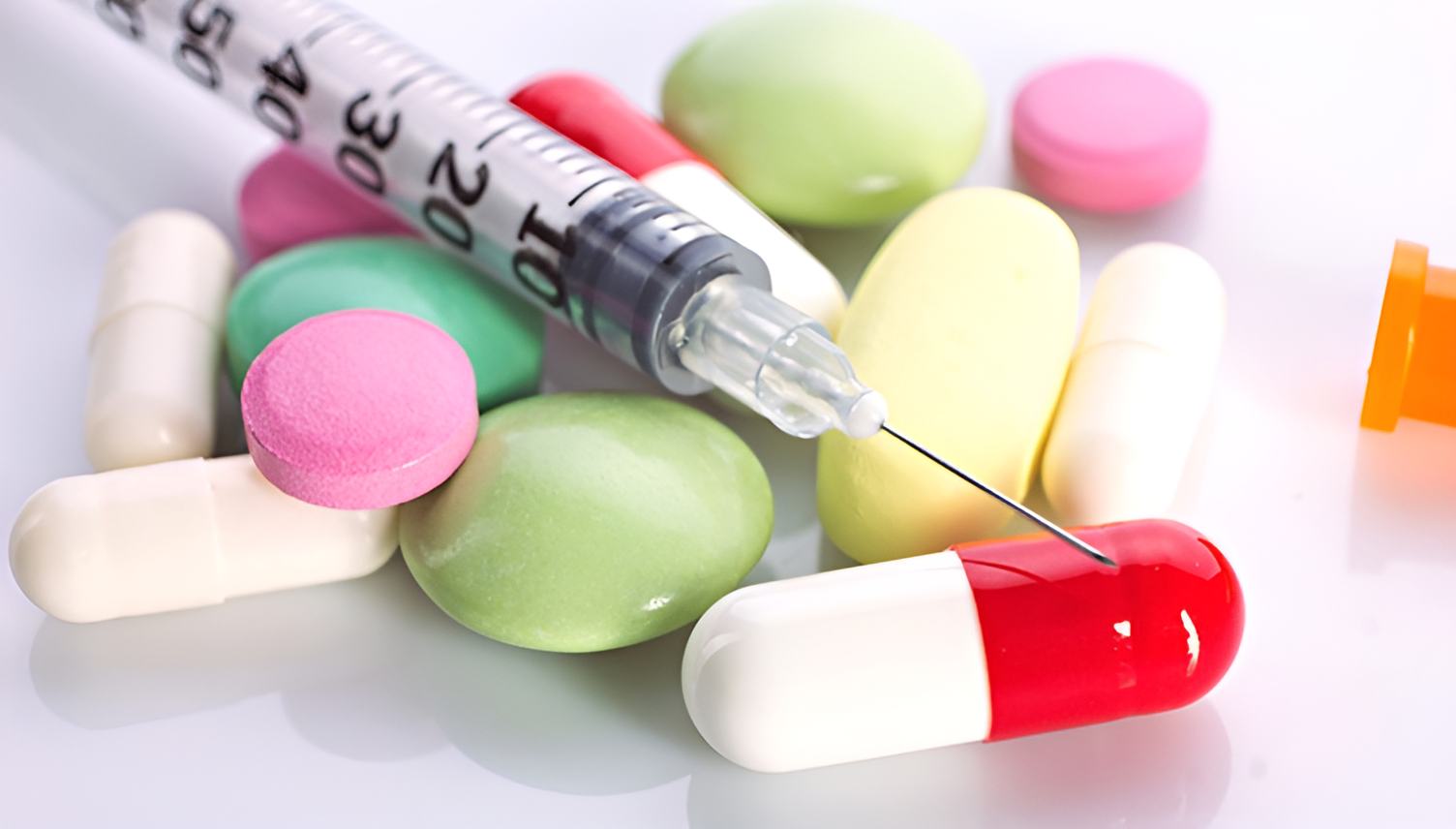
Orphan drugs
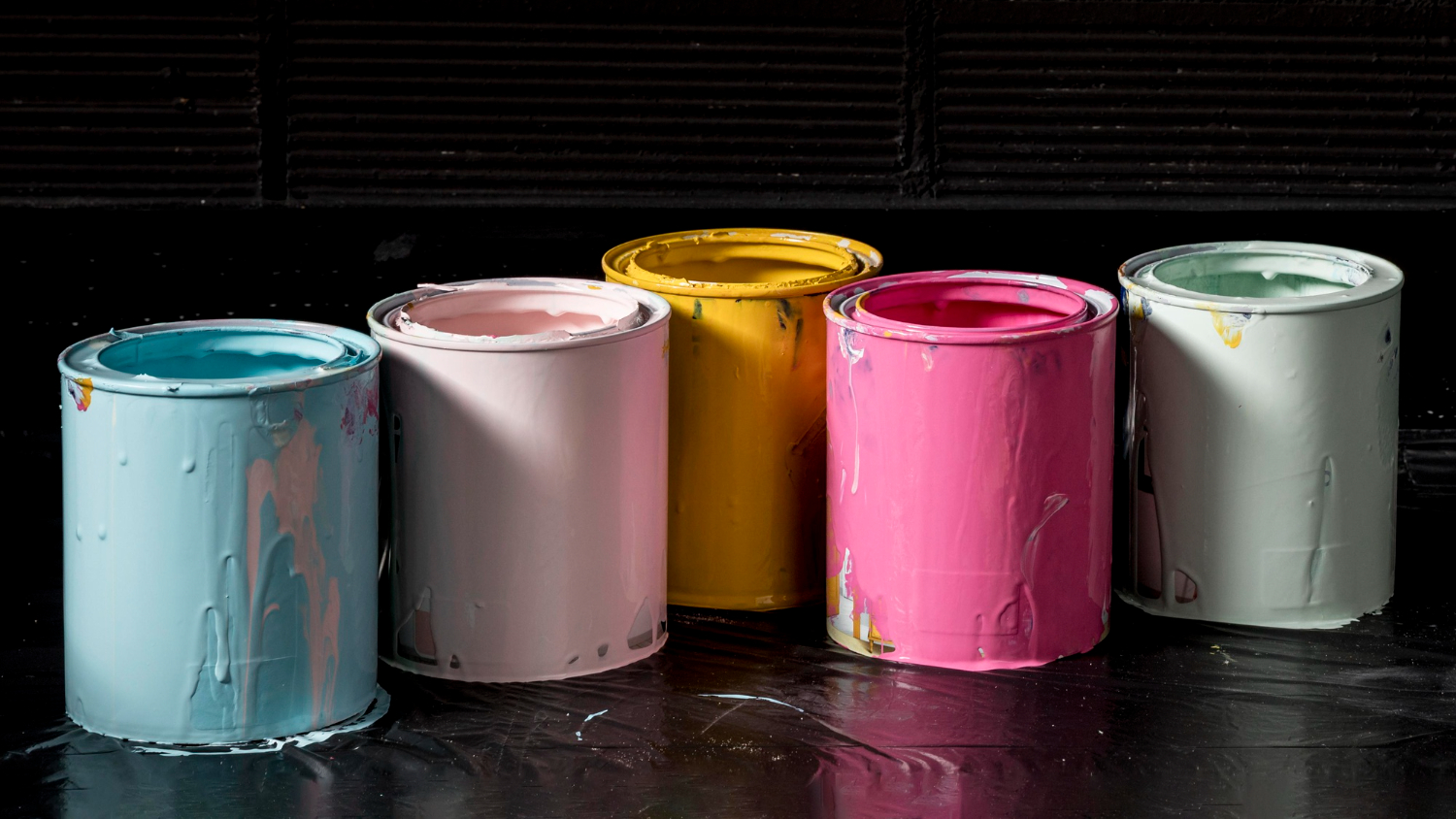
Paint cans
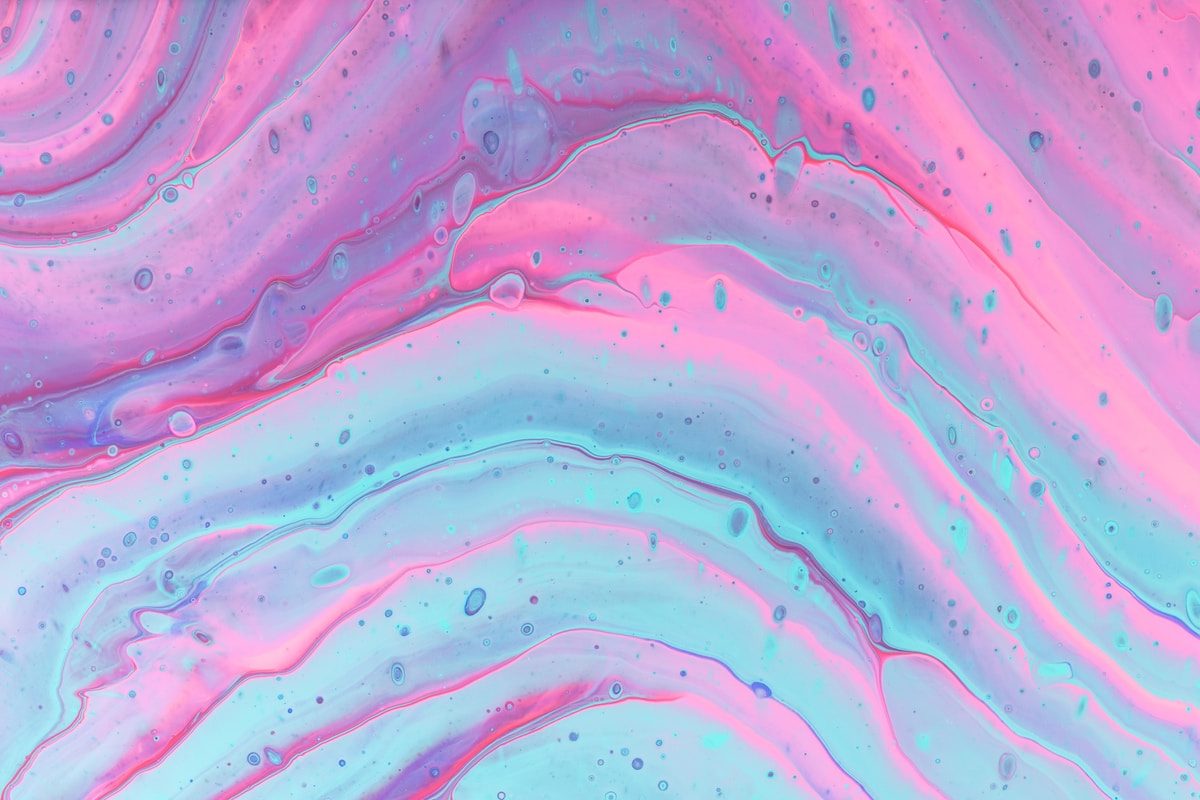
Paint
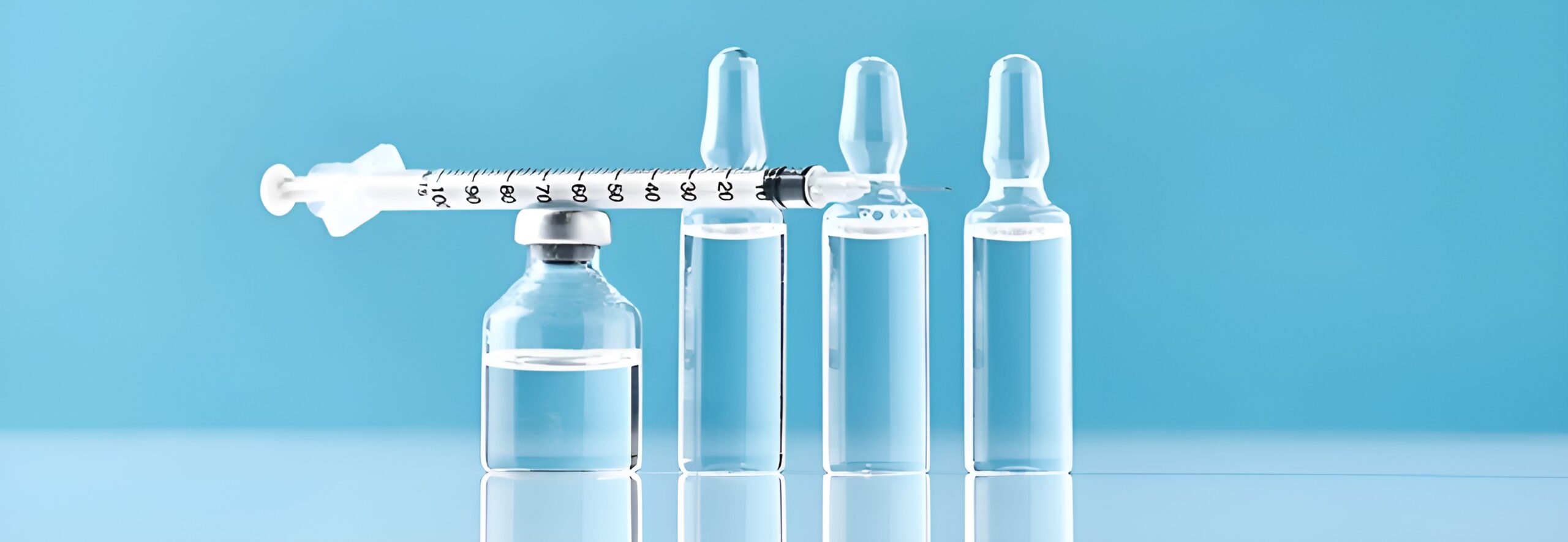
Parenteral drugs
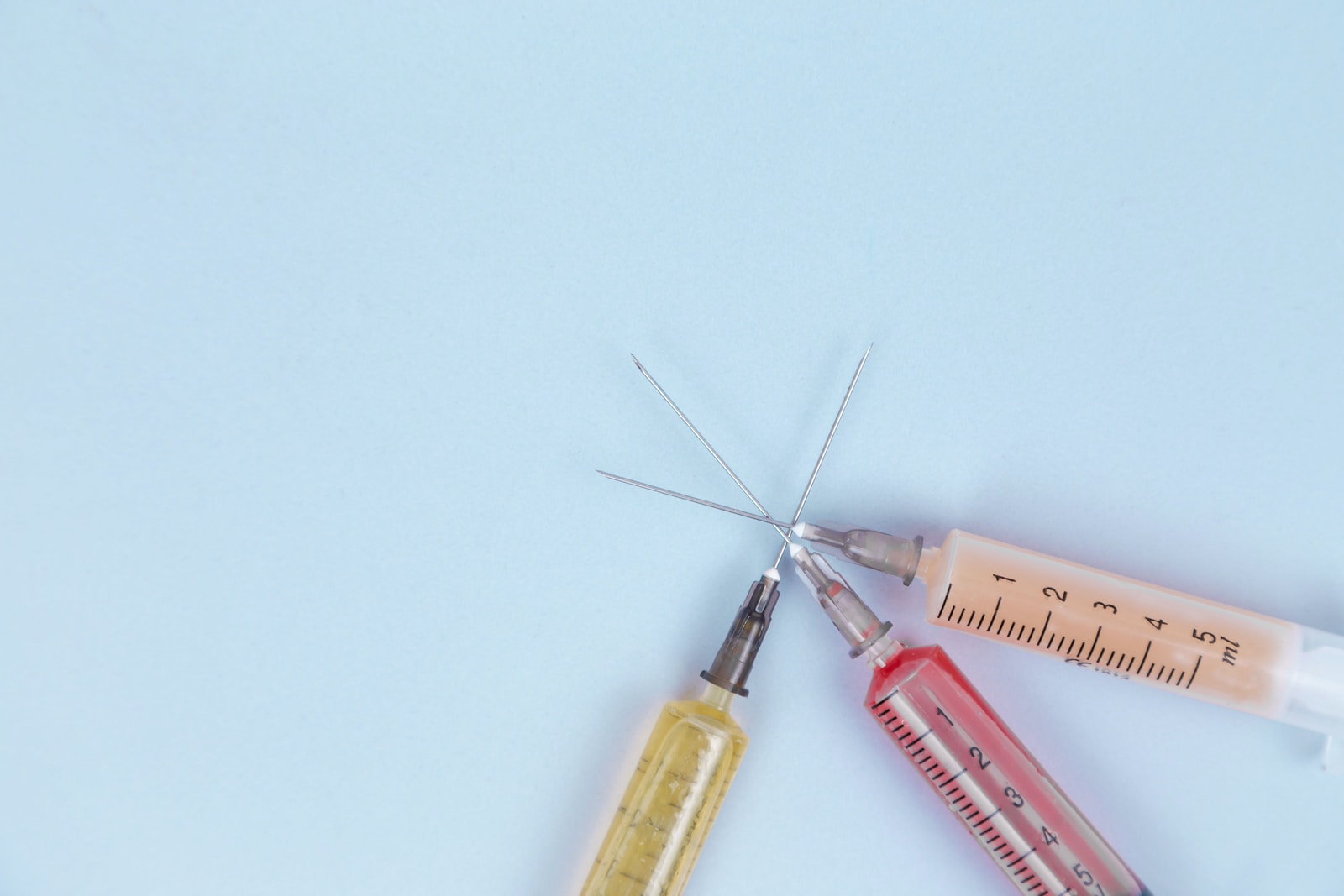
Parenterals
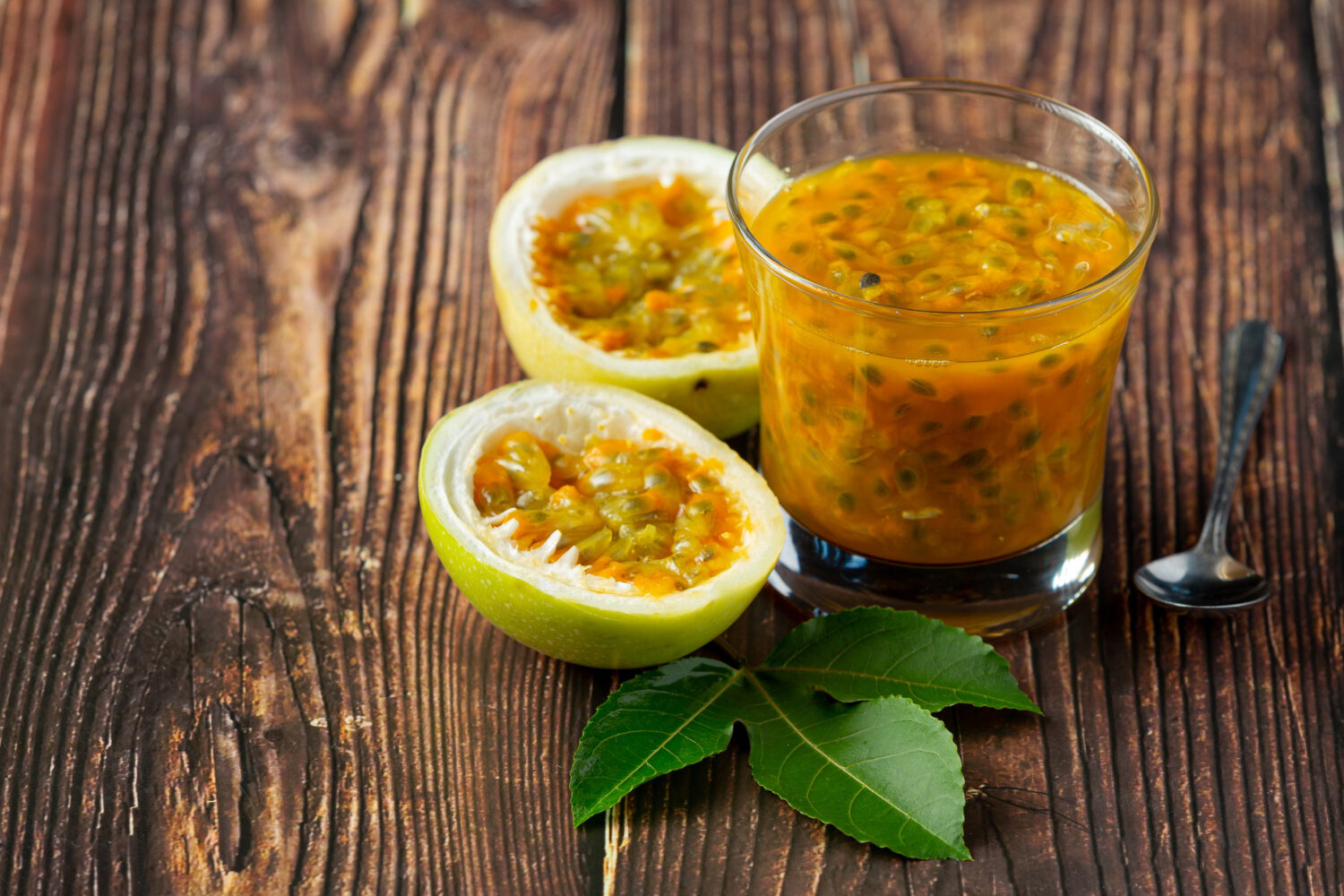
Passion fruit juice
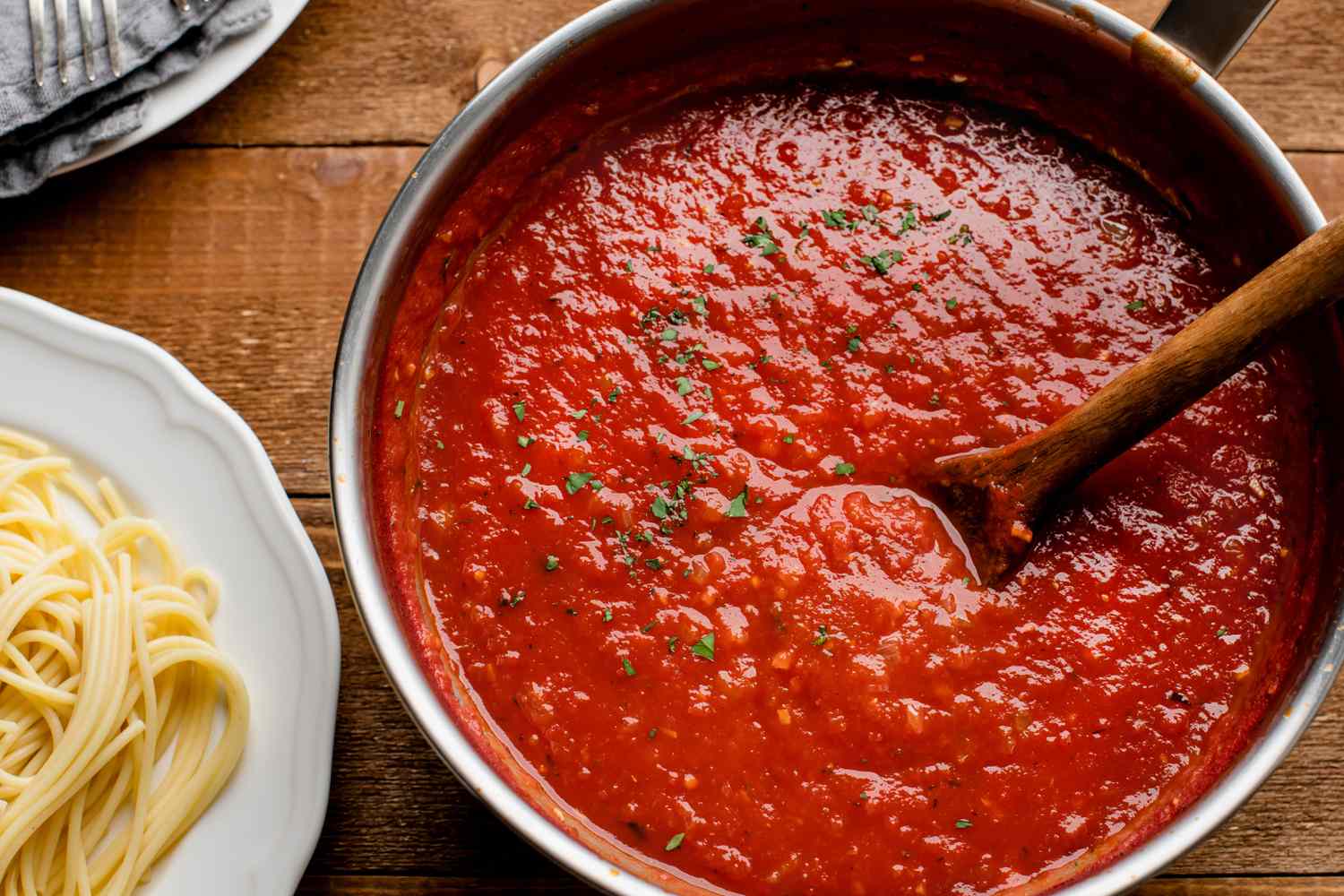
Pasta sauce
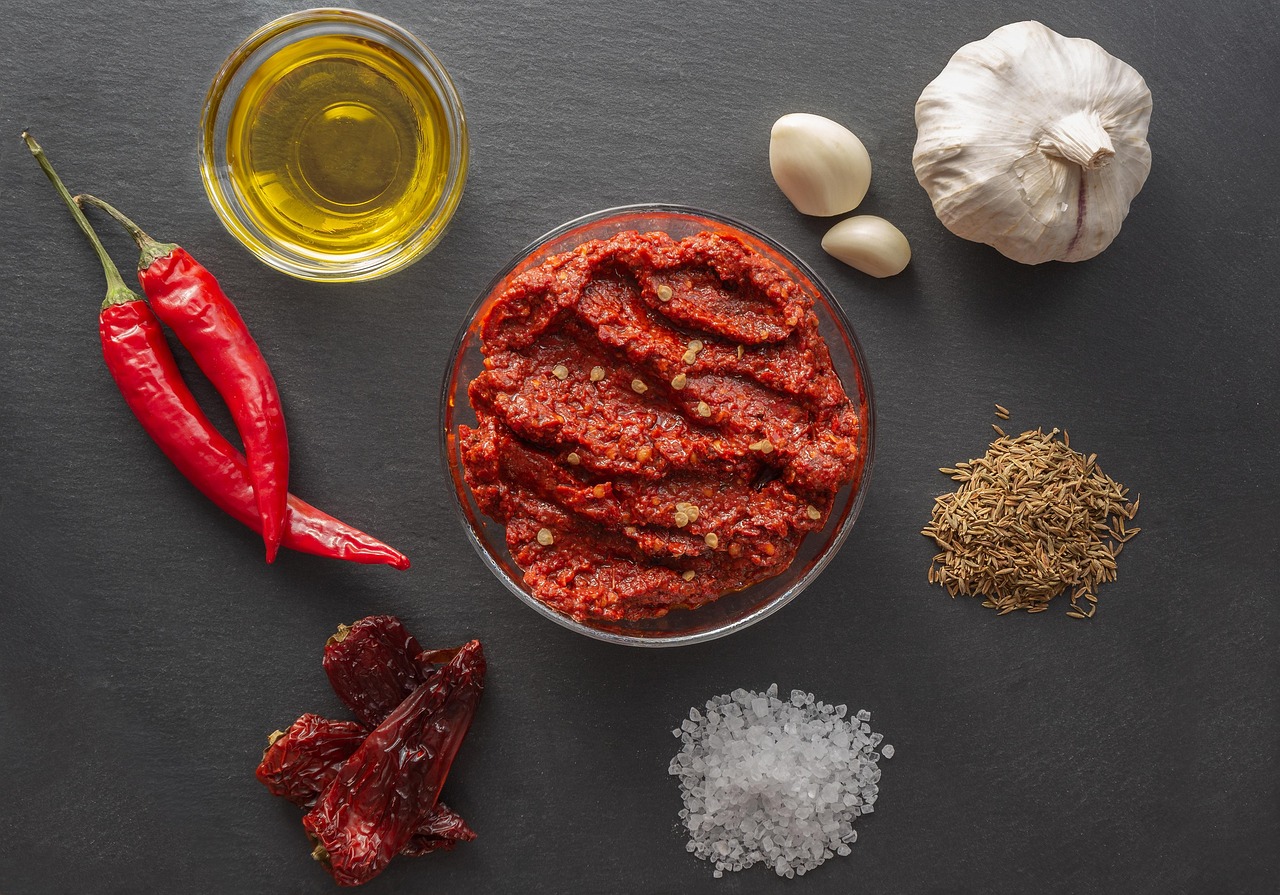
Pastes
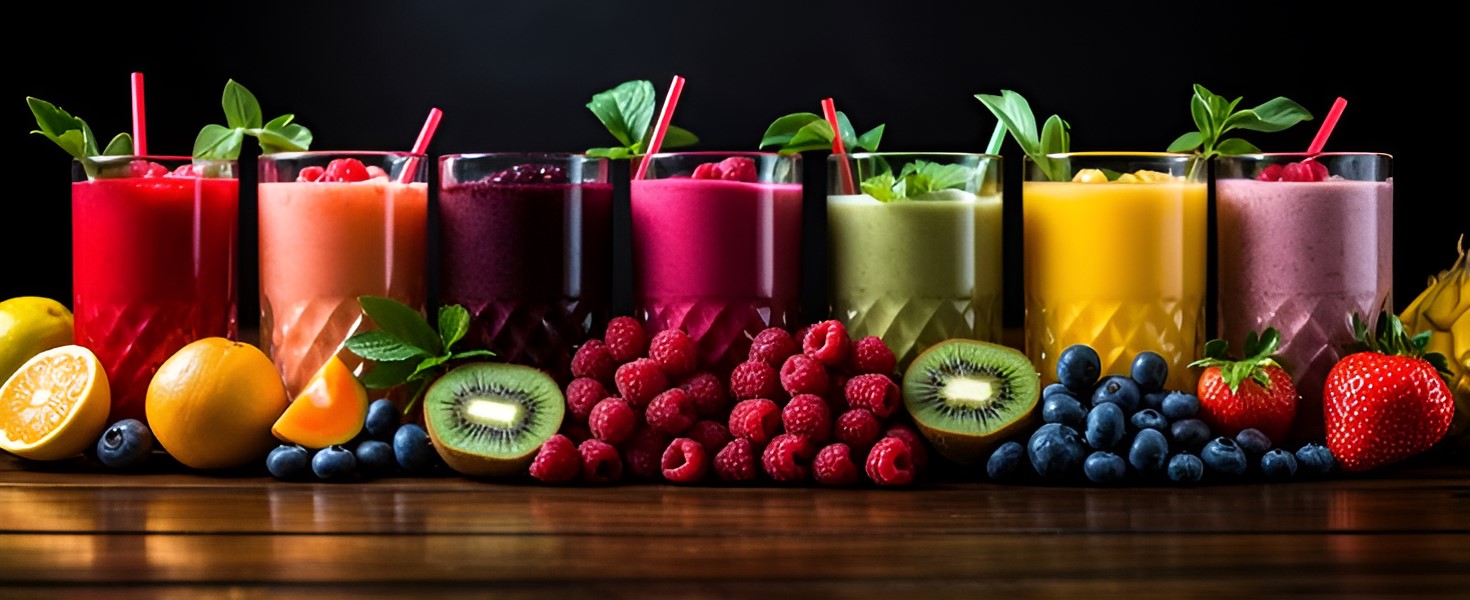
Pasteurized juice
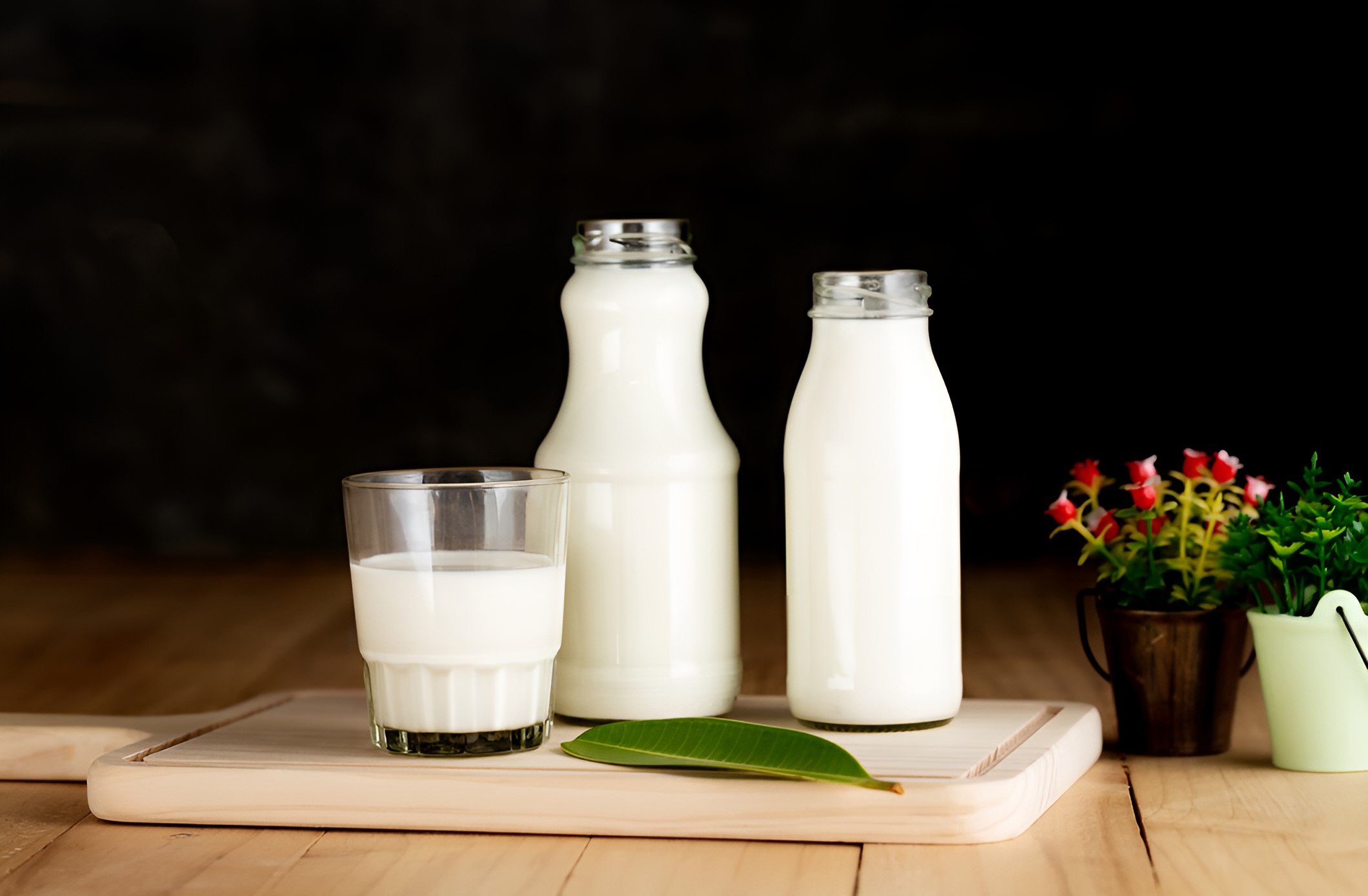
Pasteurized milk
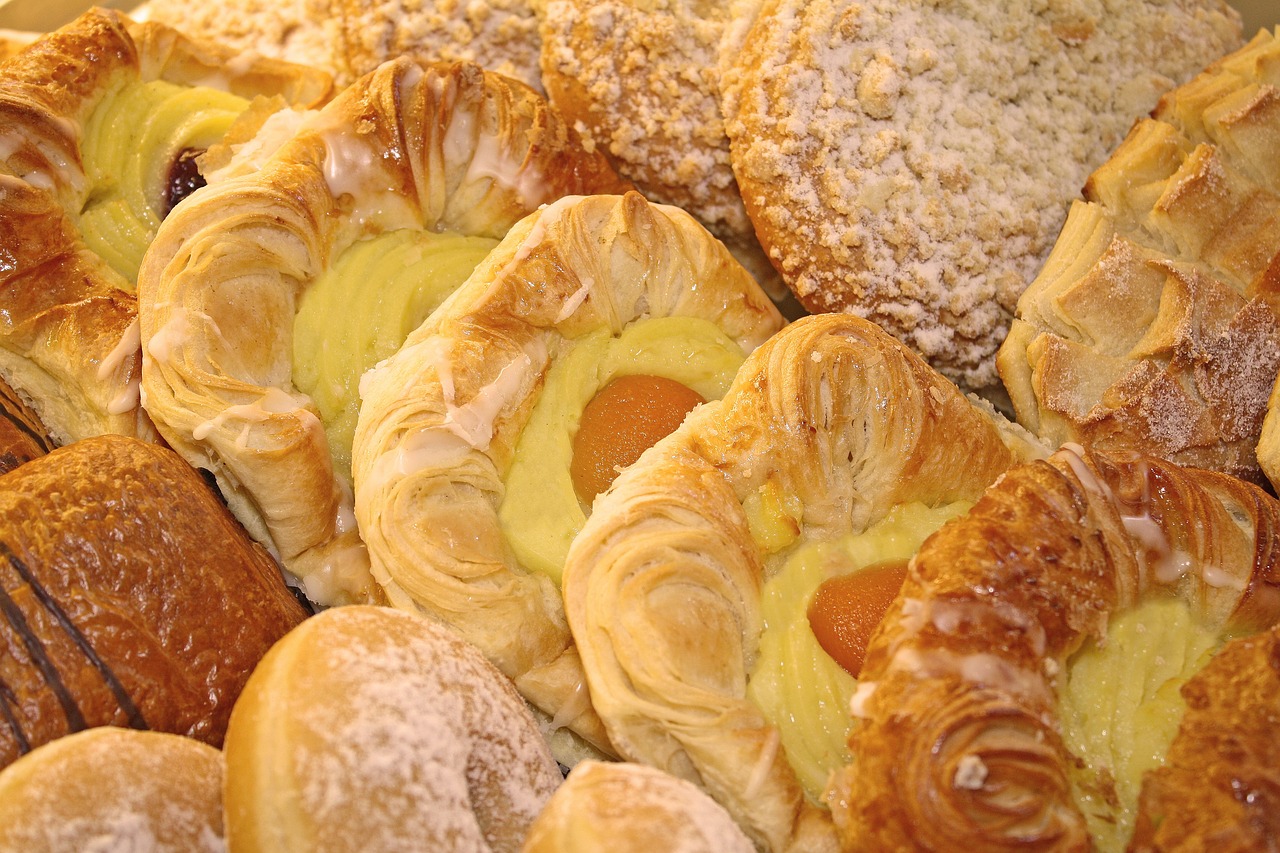
Pastries
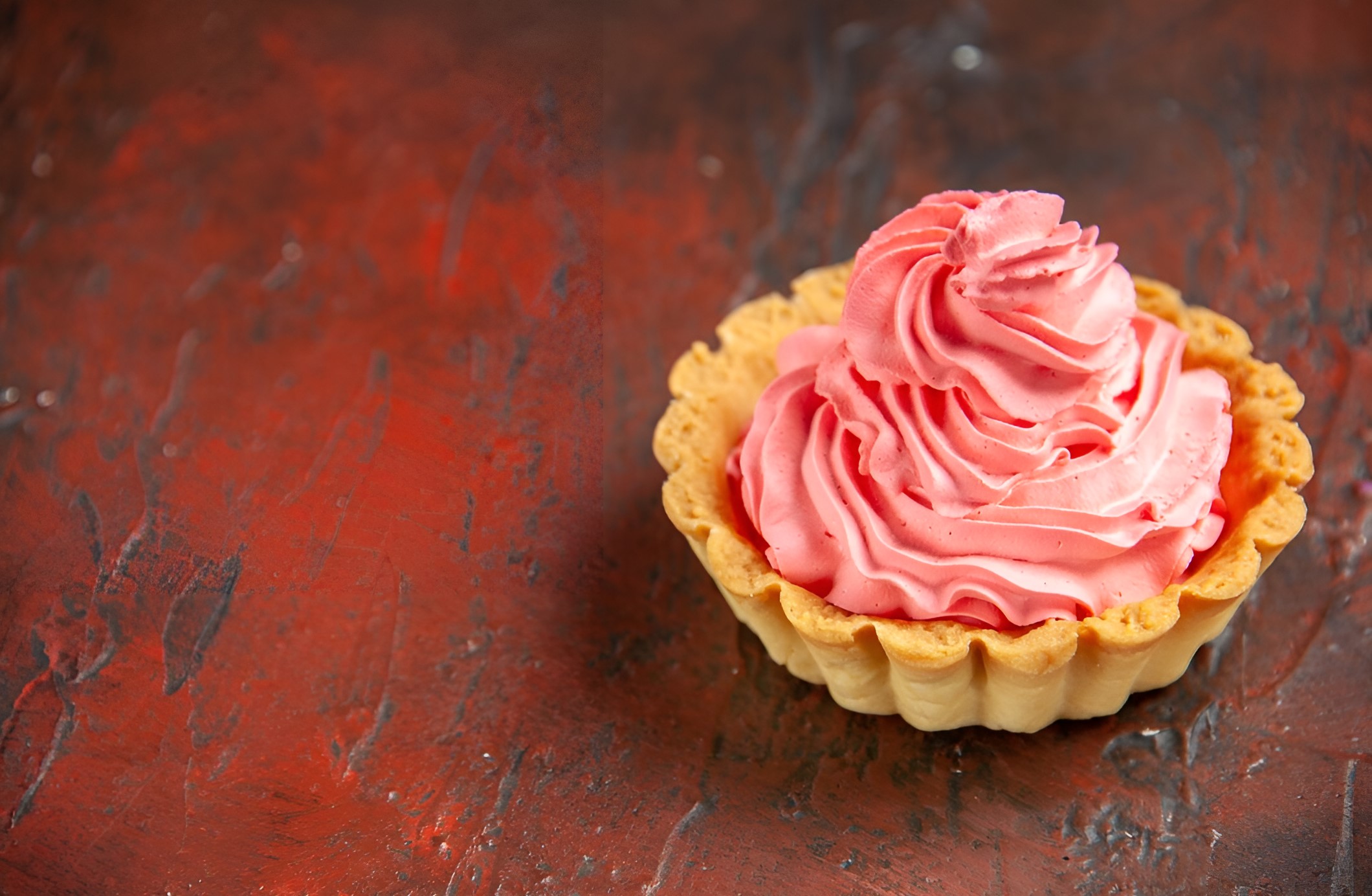
Pastry cream
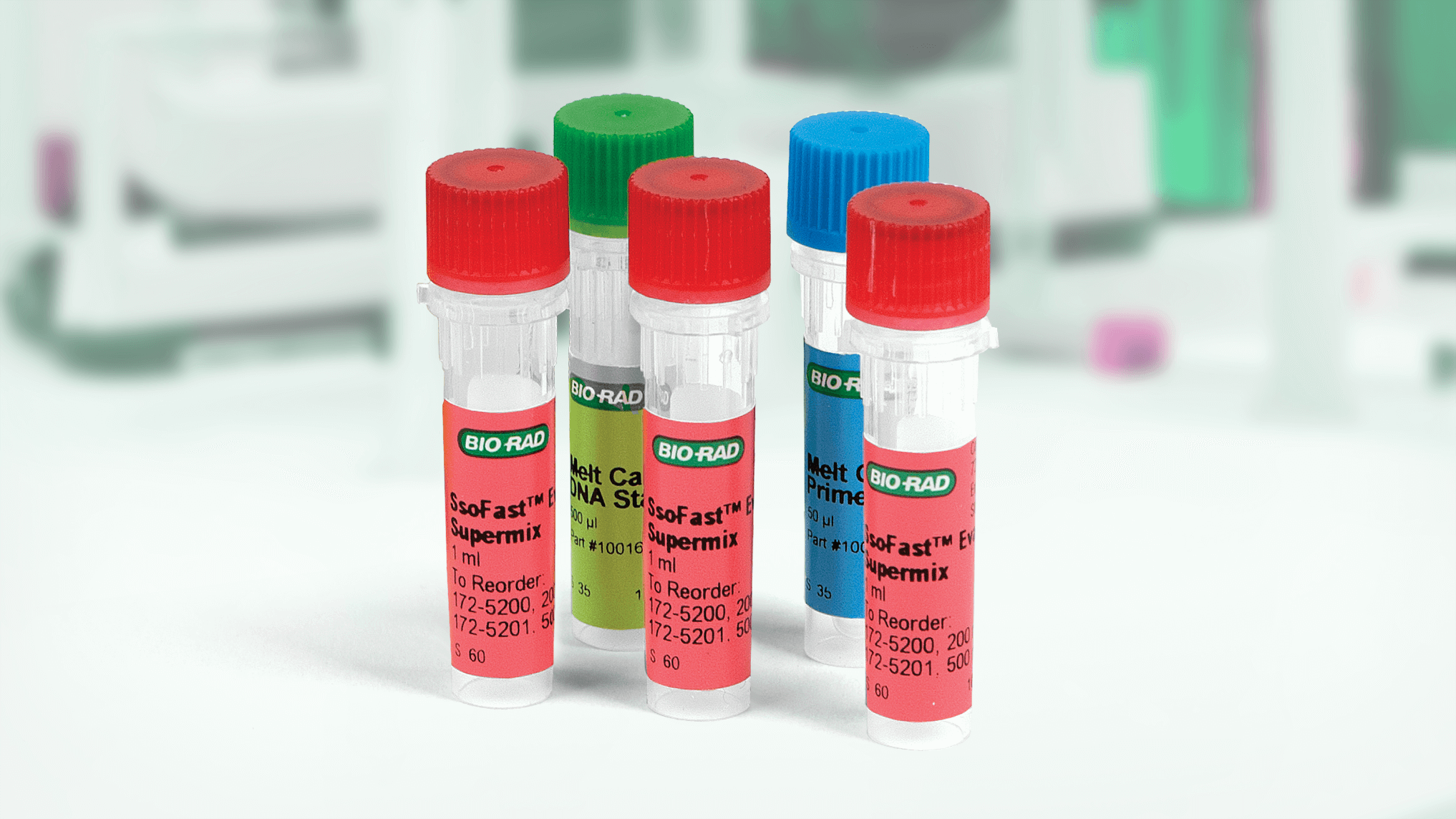
Pcr reagents
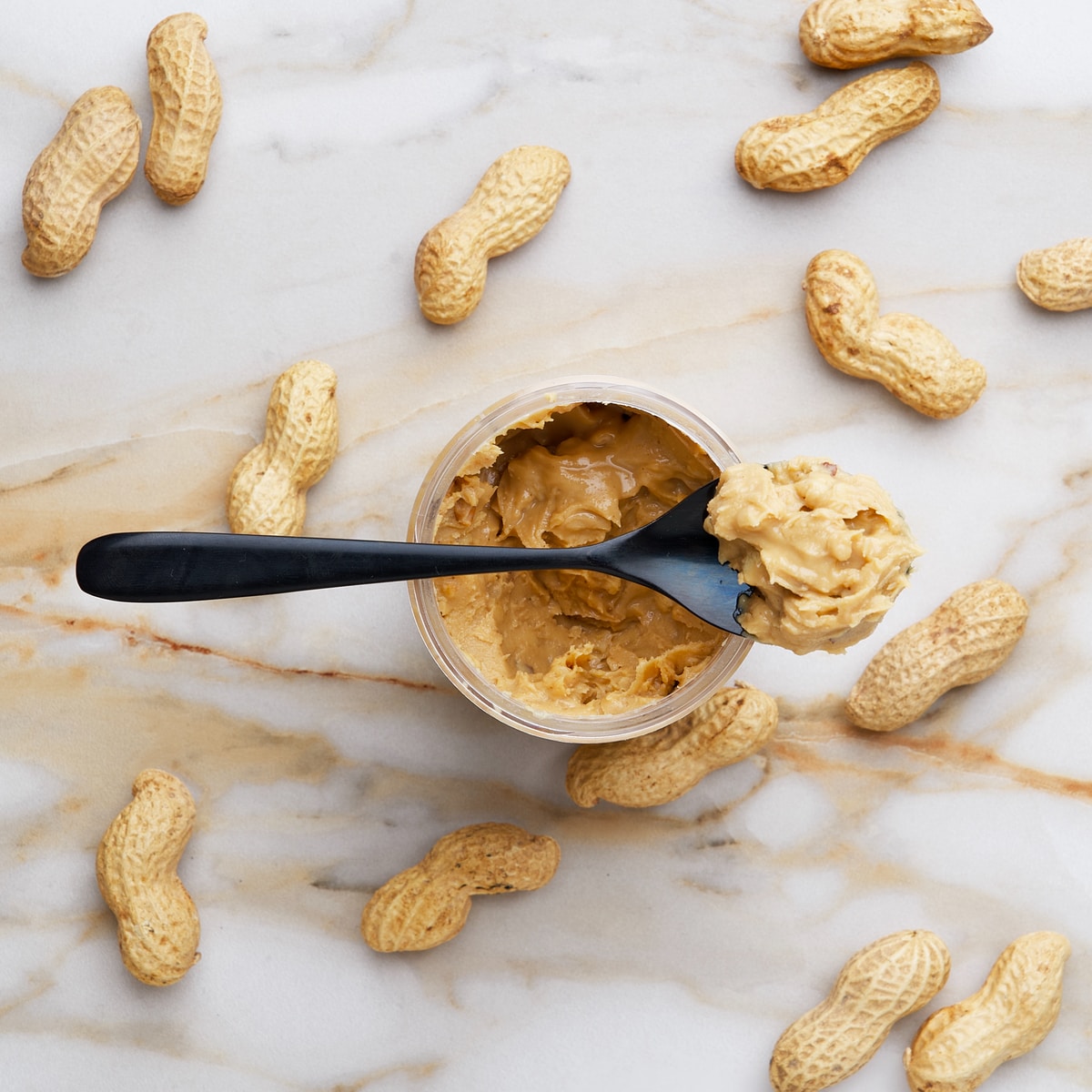
Peanut butter
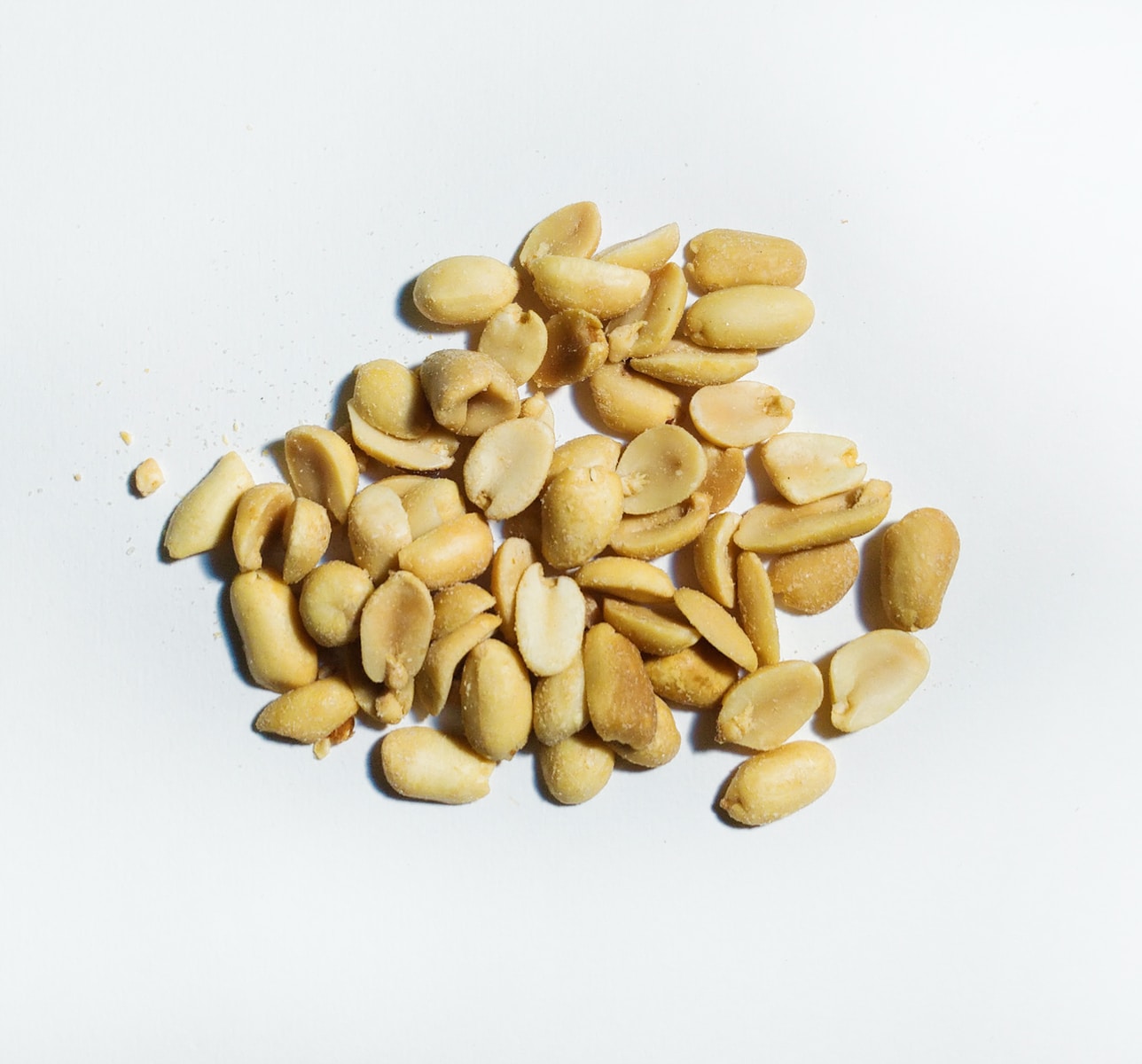
Peanuts
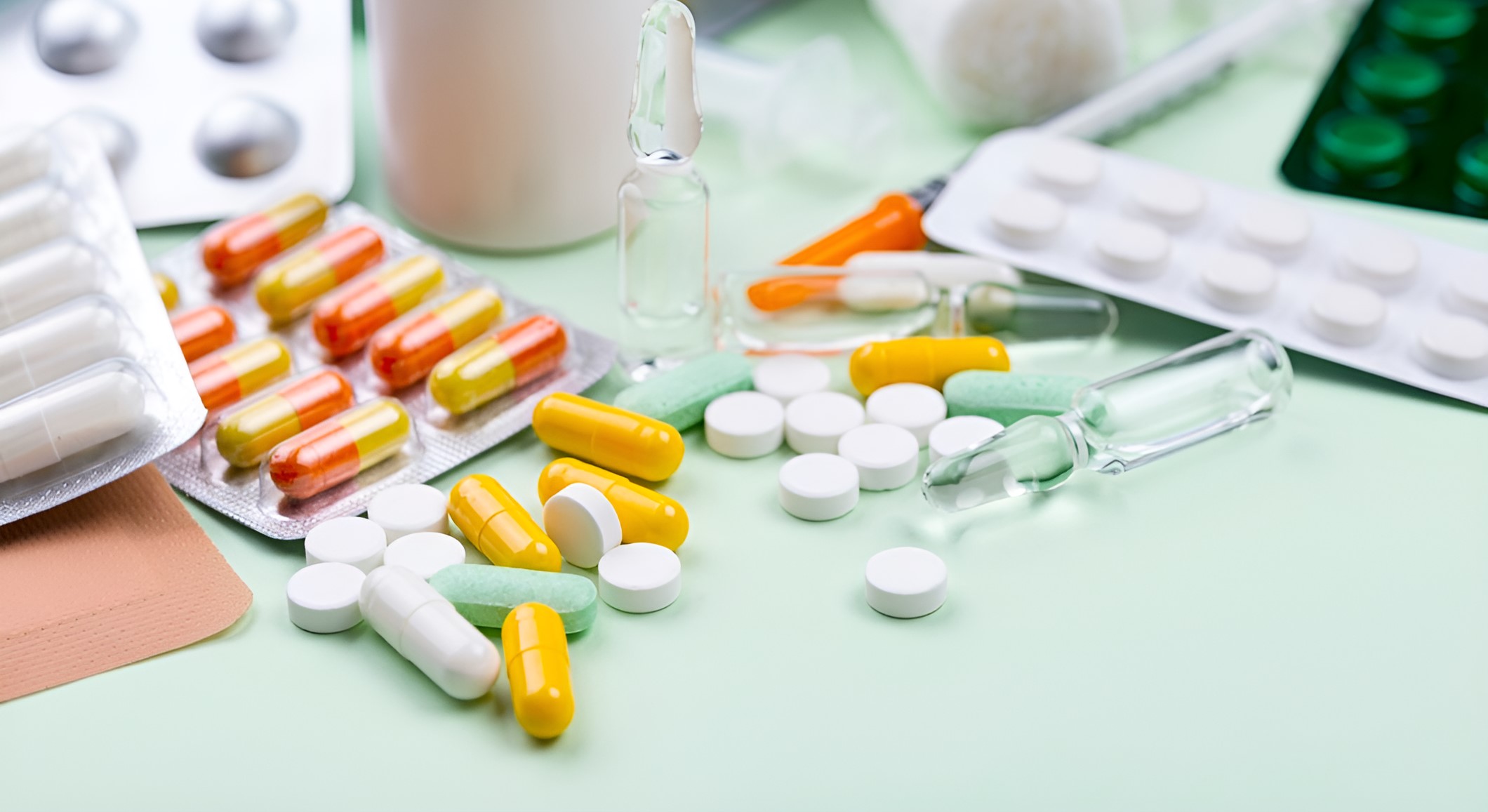
Personalized medicine

Pesticide
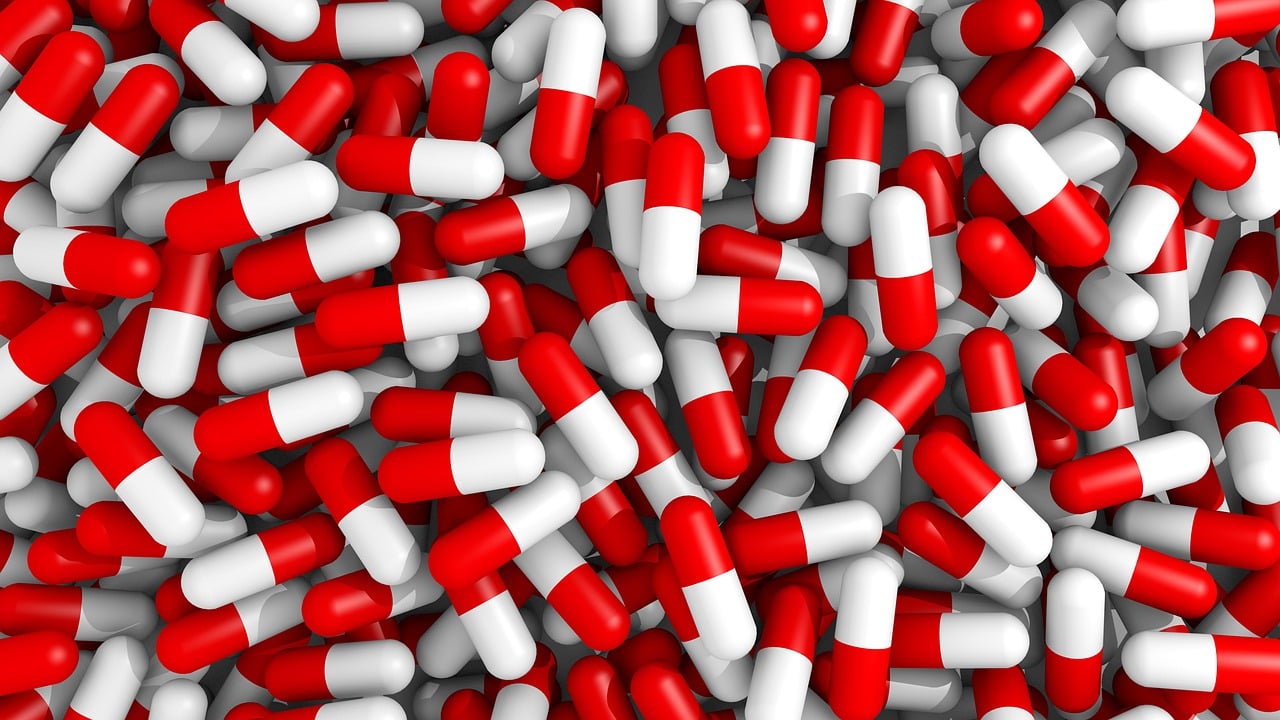
Pharmaceutical capsules
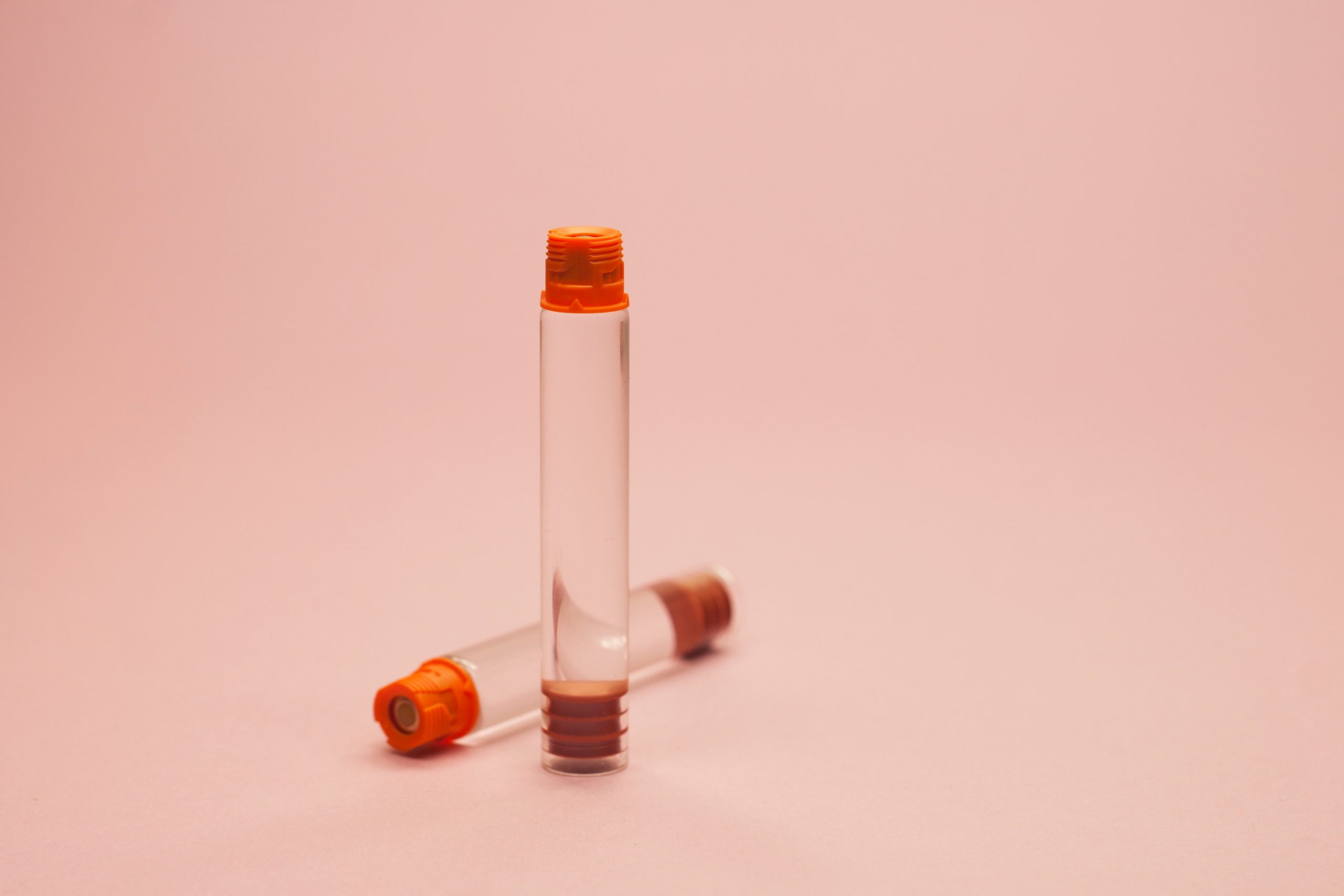
Pharmaceutical cartridges
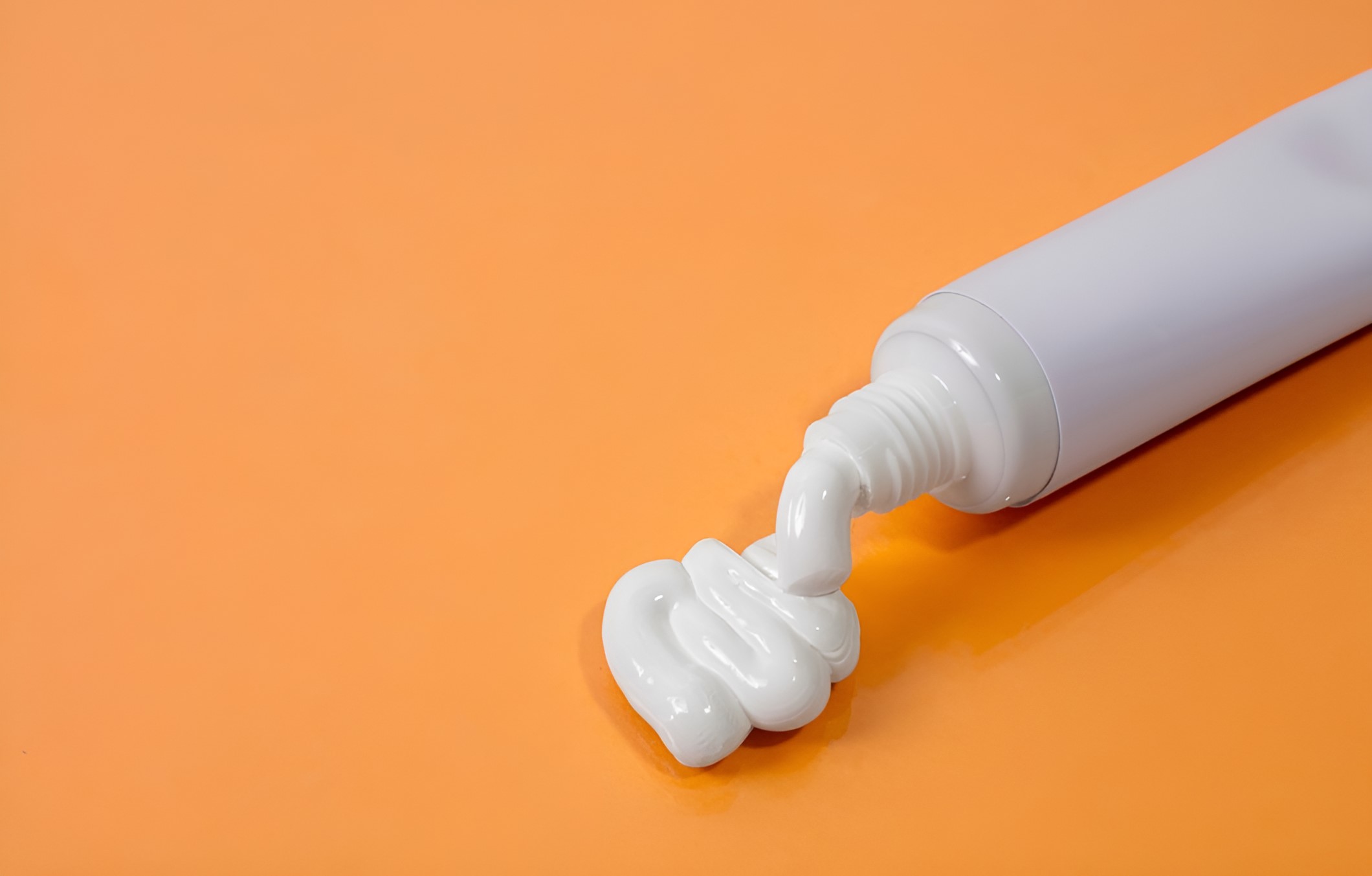
Pharmaceutical creams
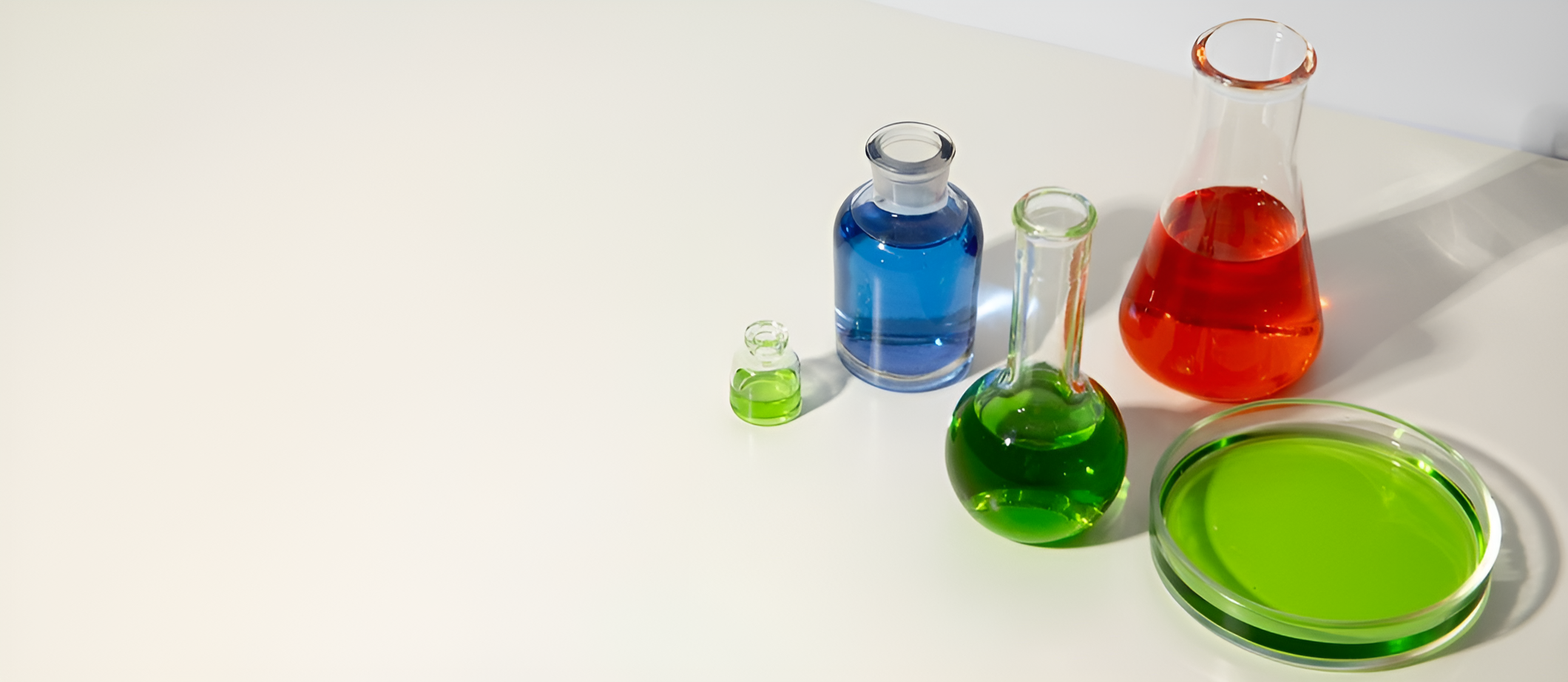
Pharmaceutical emulsions
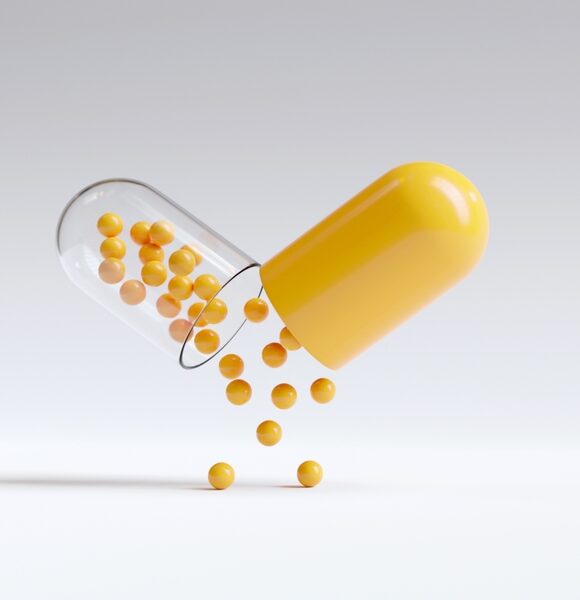
Pharmaceutical granules
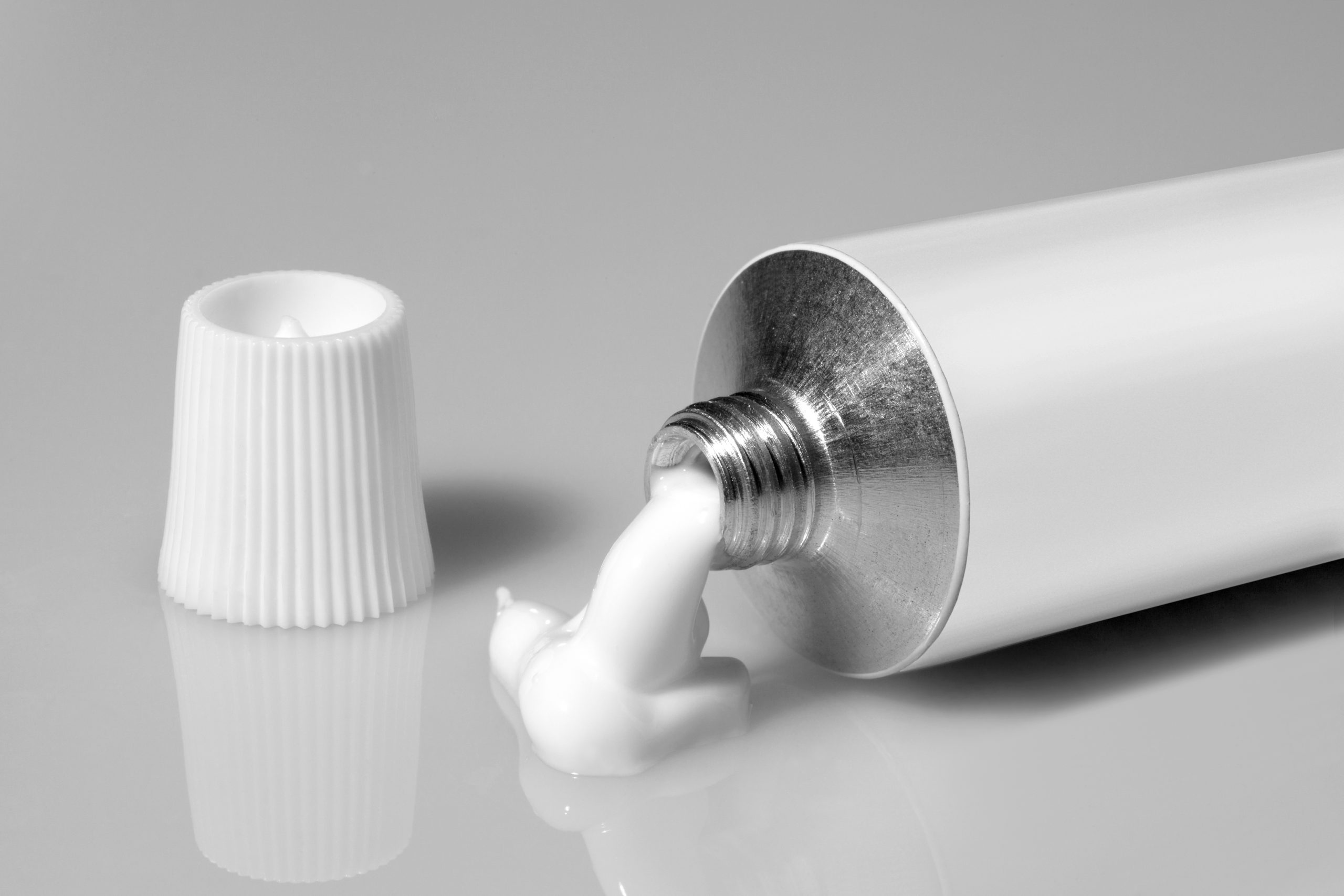
Pharmaceutical ointments
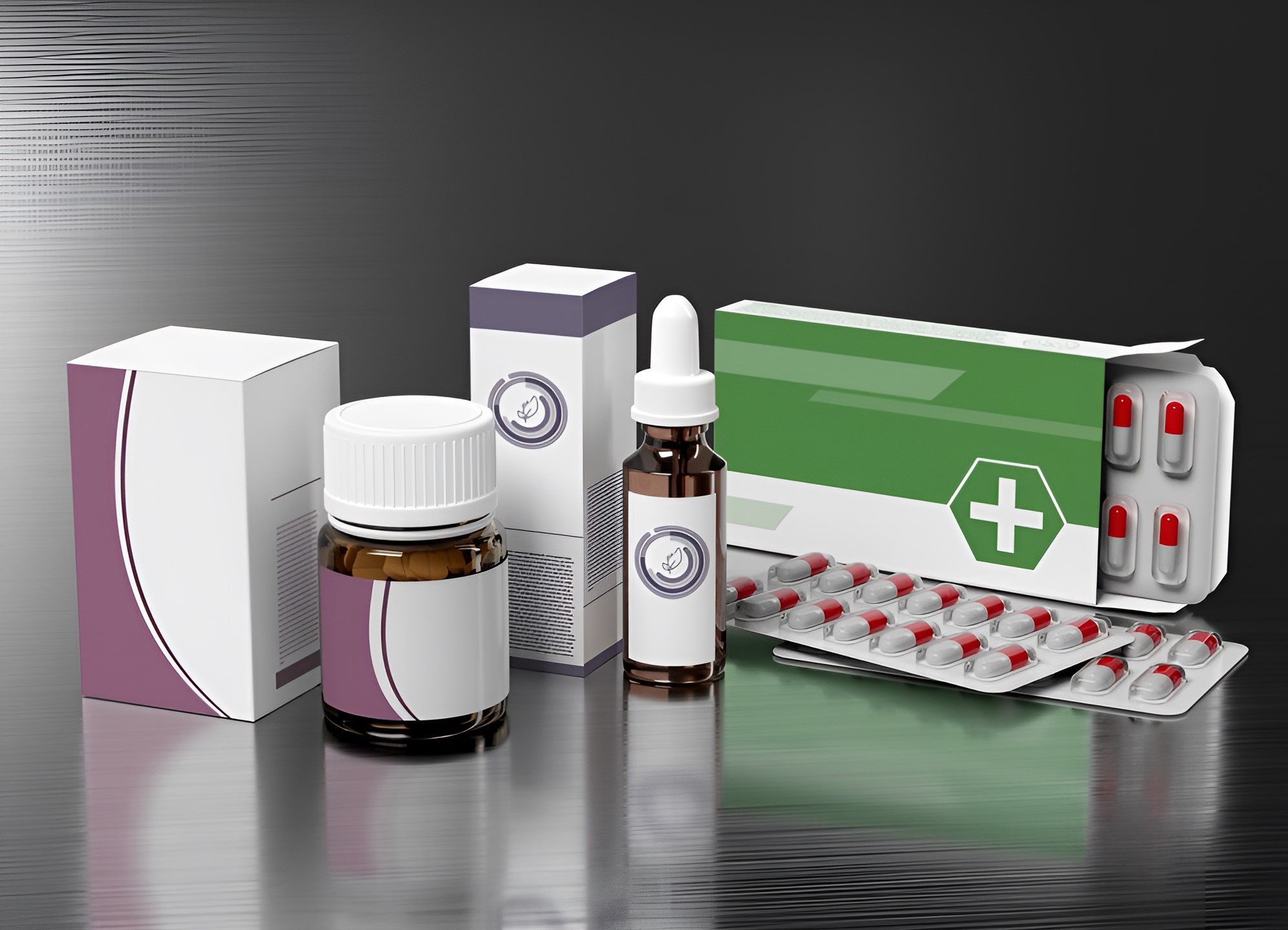
Pharmaceutical packaging
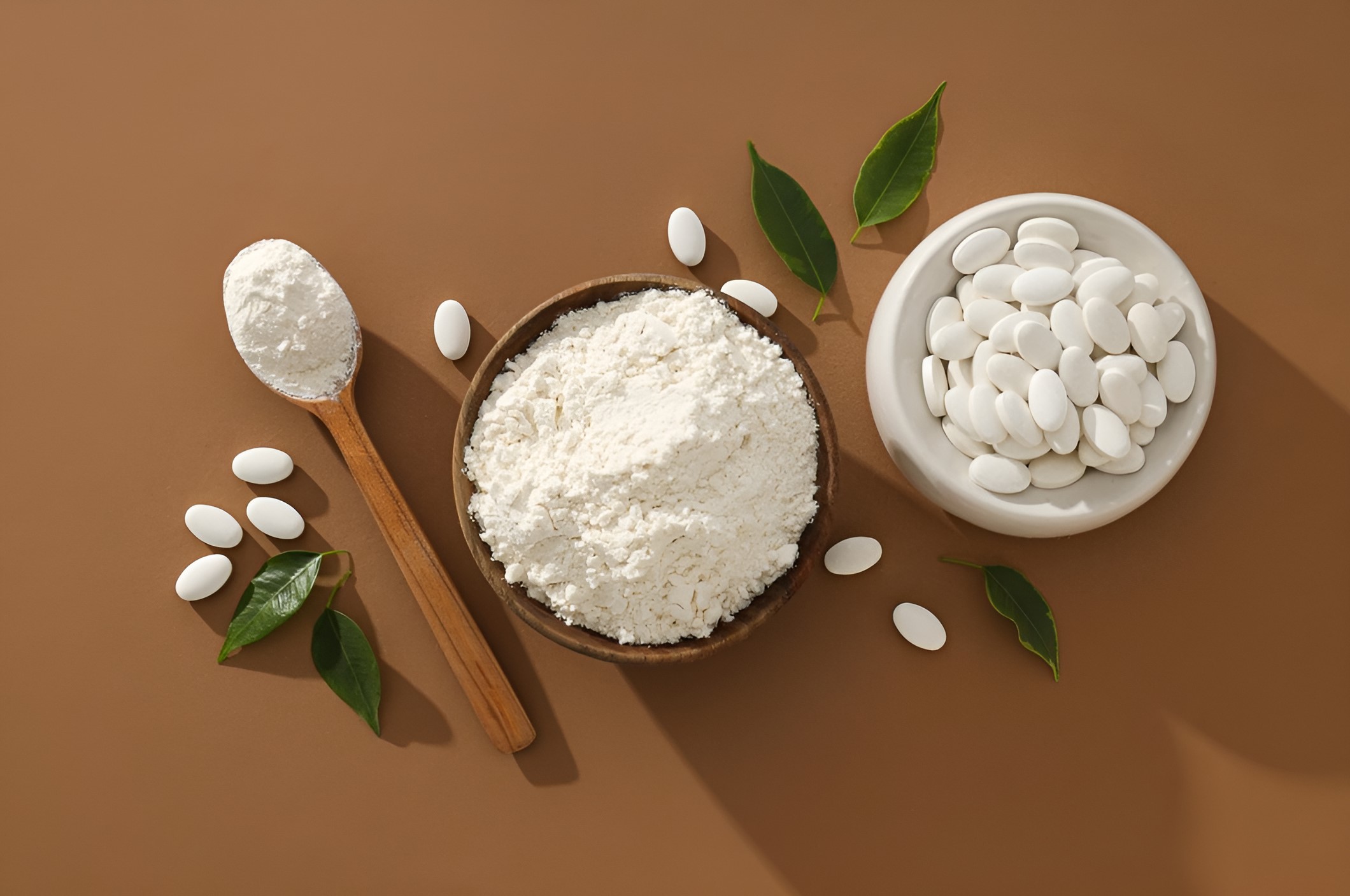
Pharmaceutical powders
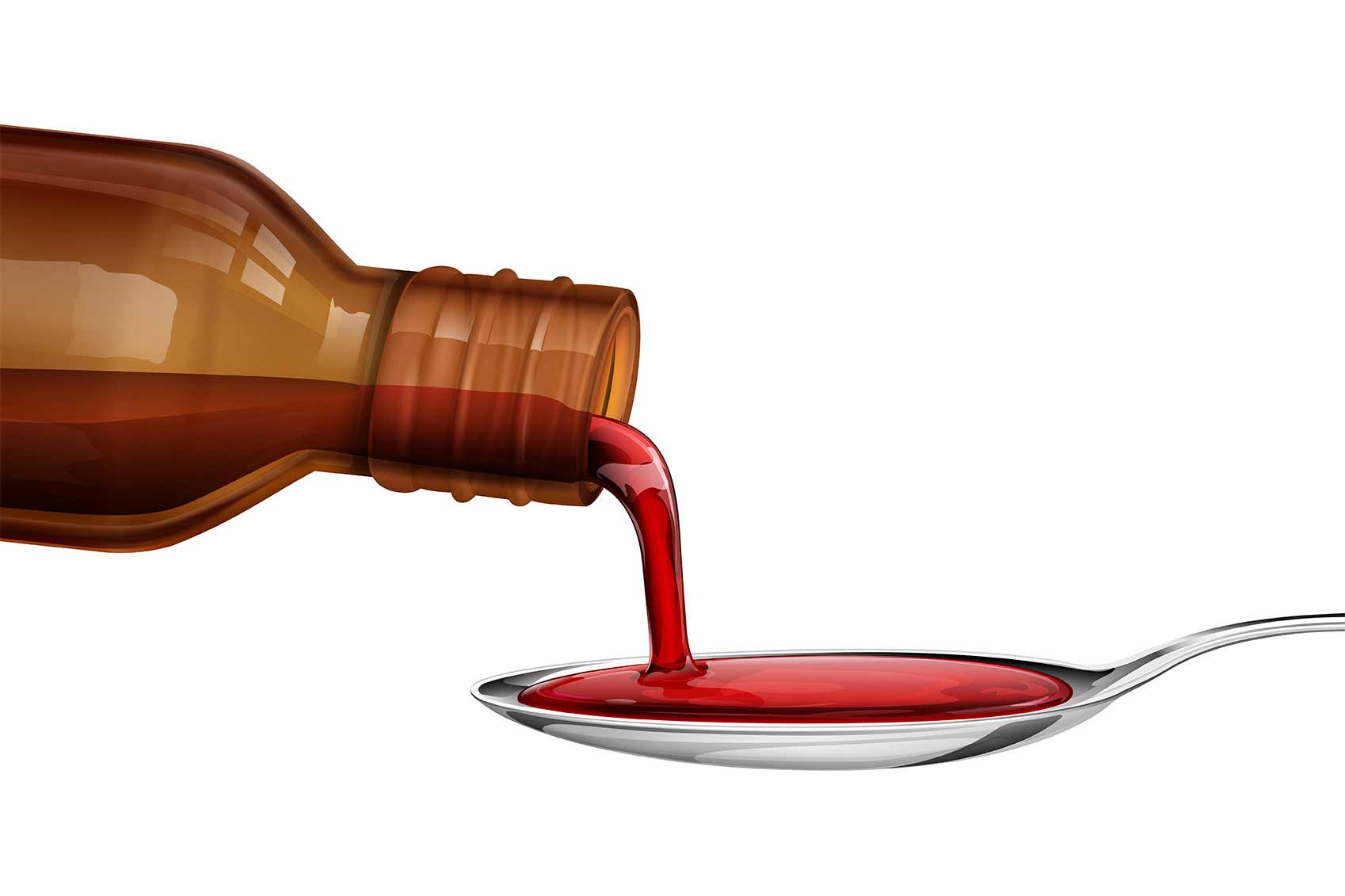
Pharmaceutical suspensions
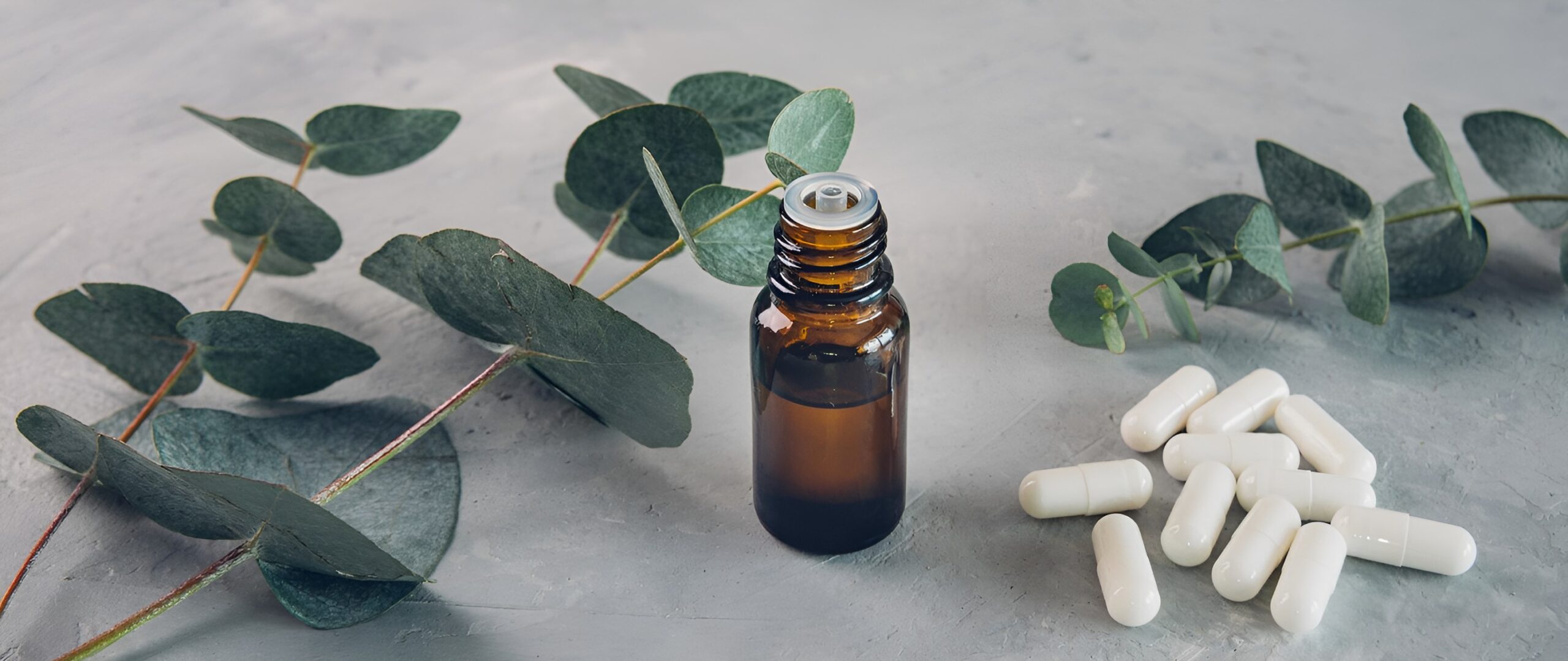
Pharmaceutical syrups
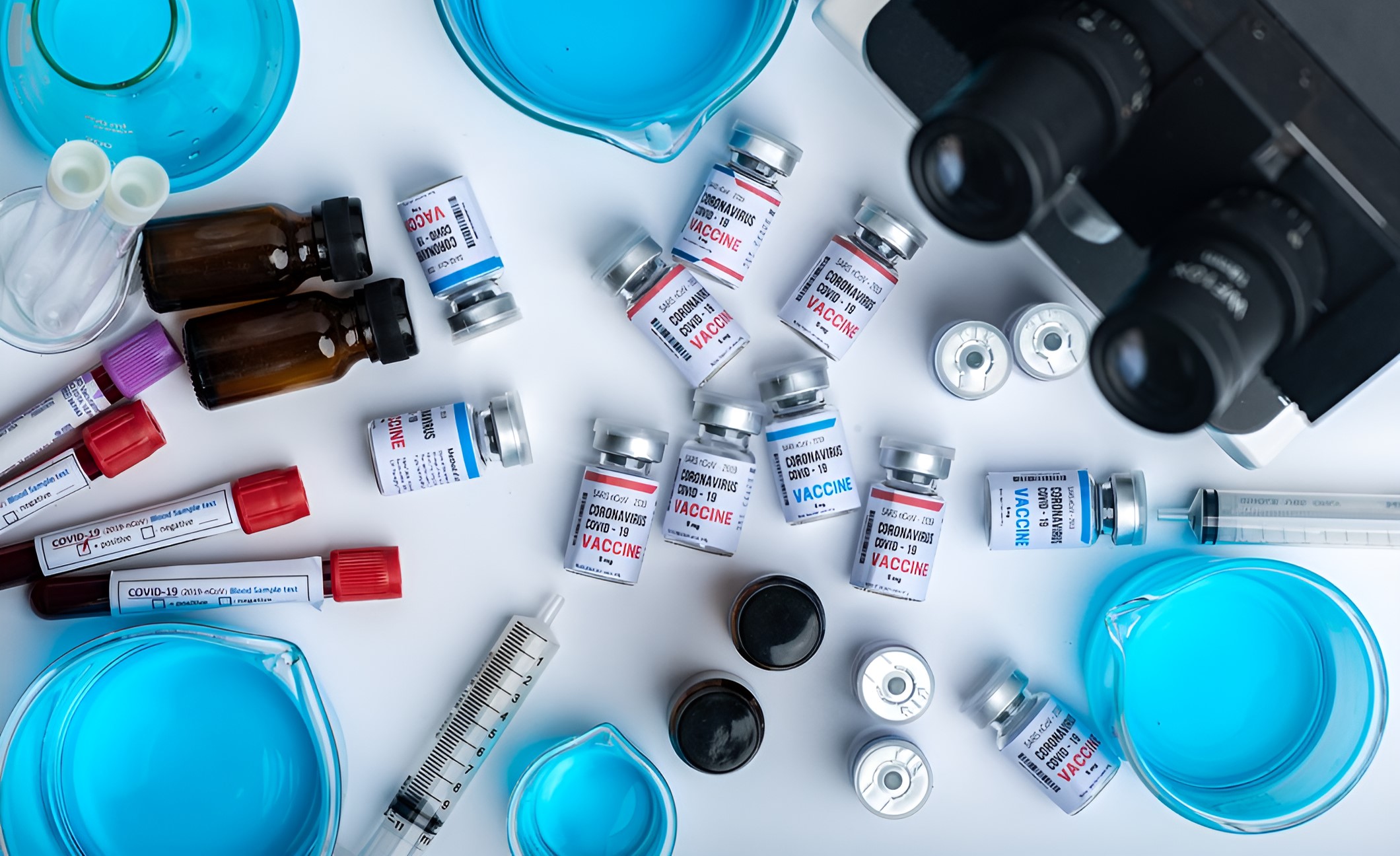
Pharmaceutical vials
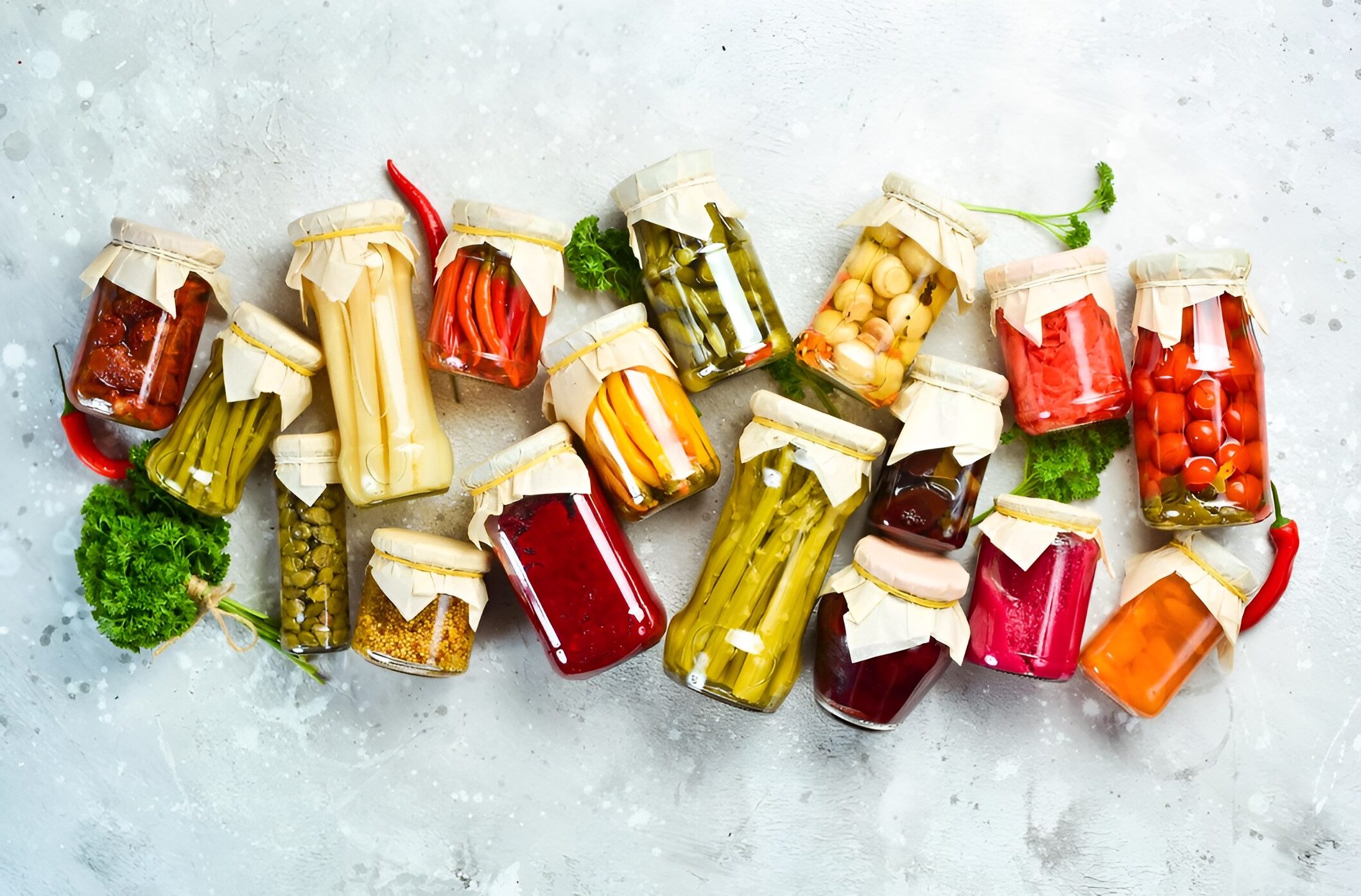
Pickled vegetables
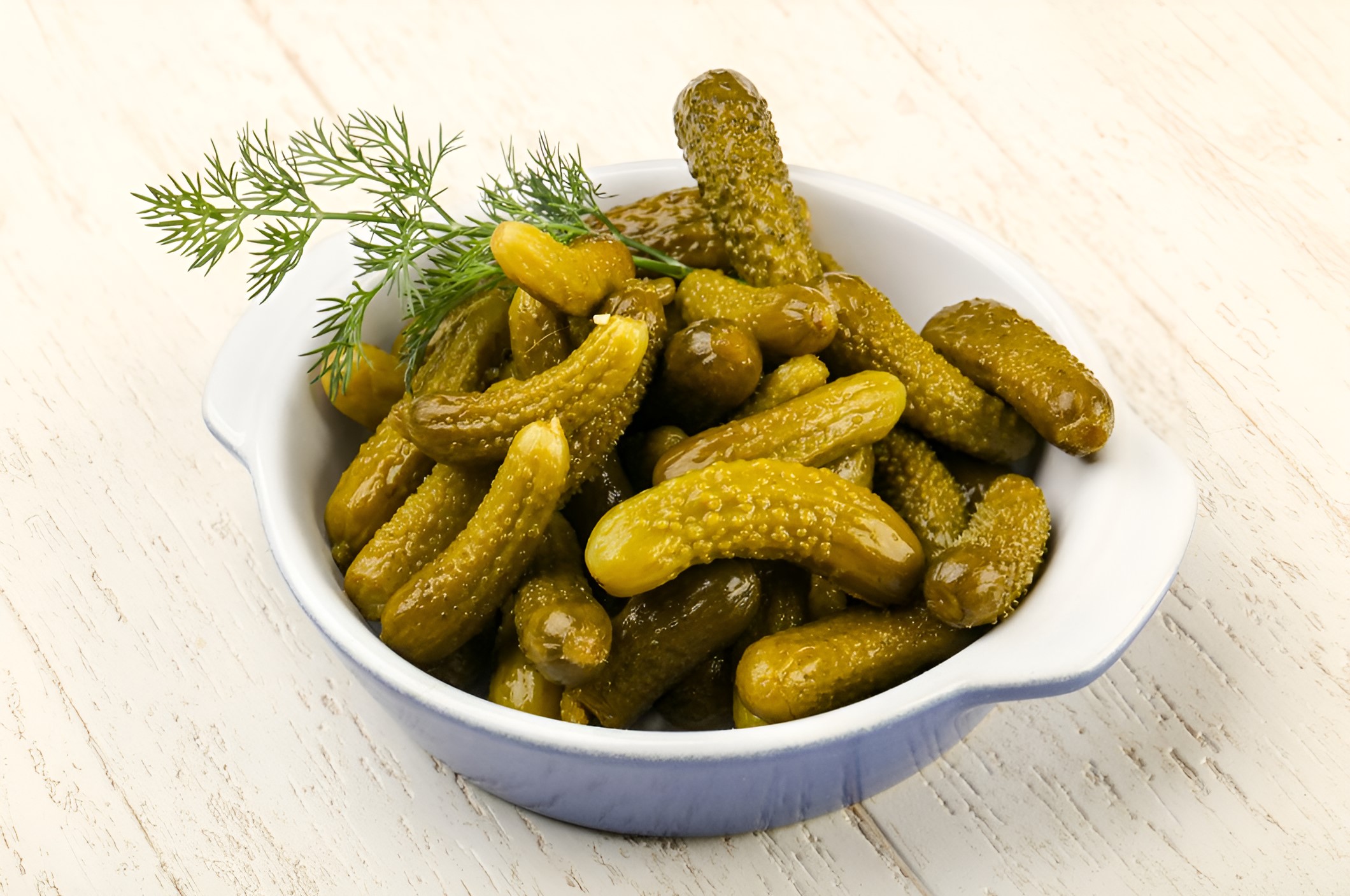
Pickles
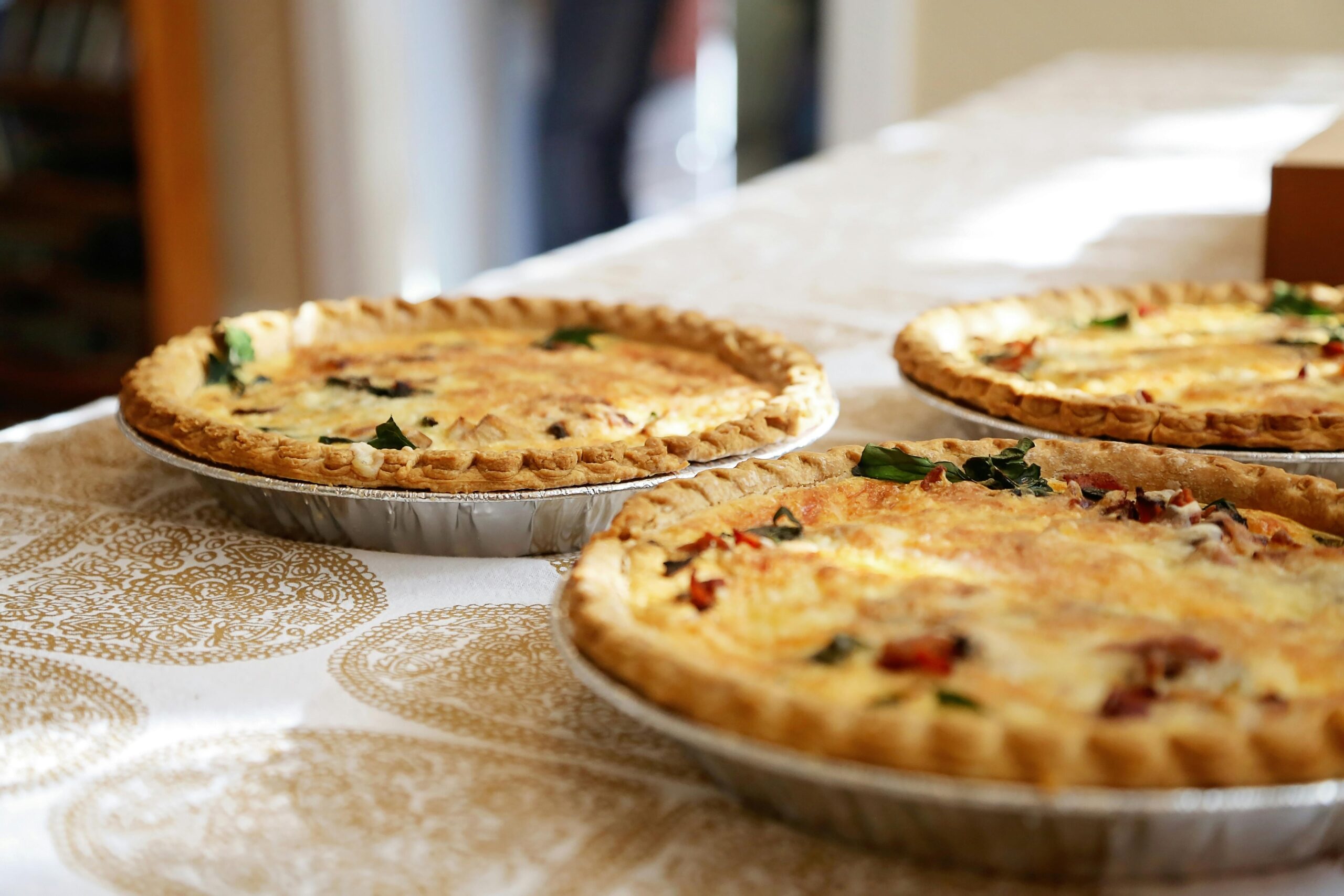
Pie
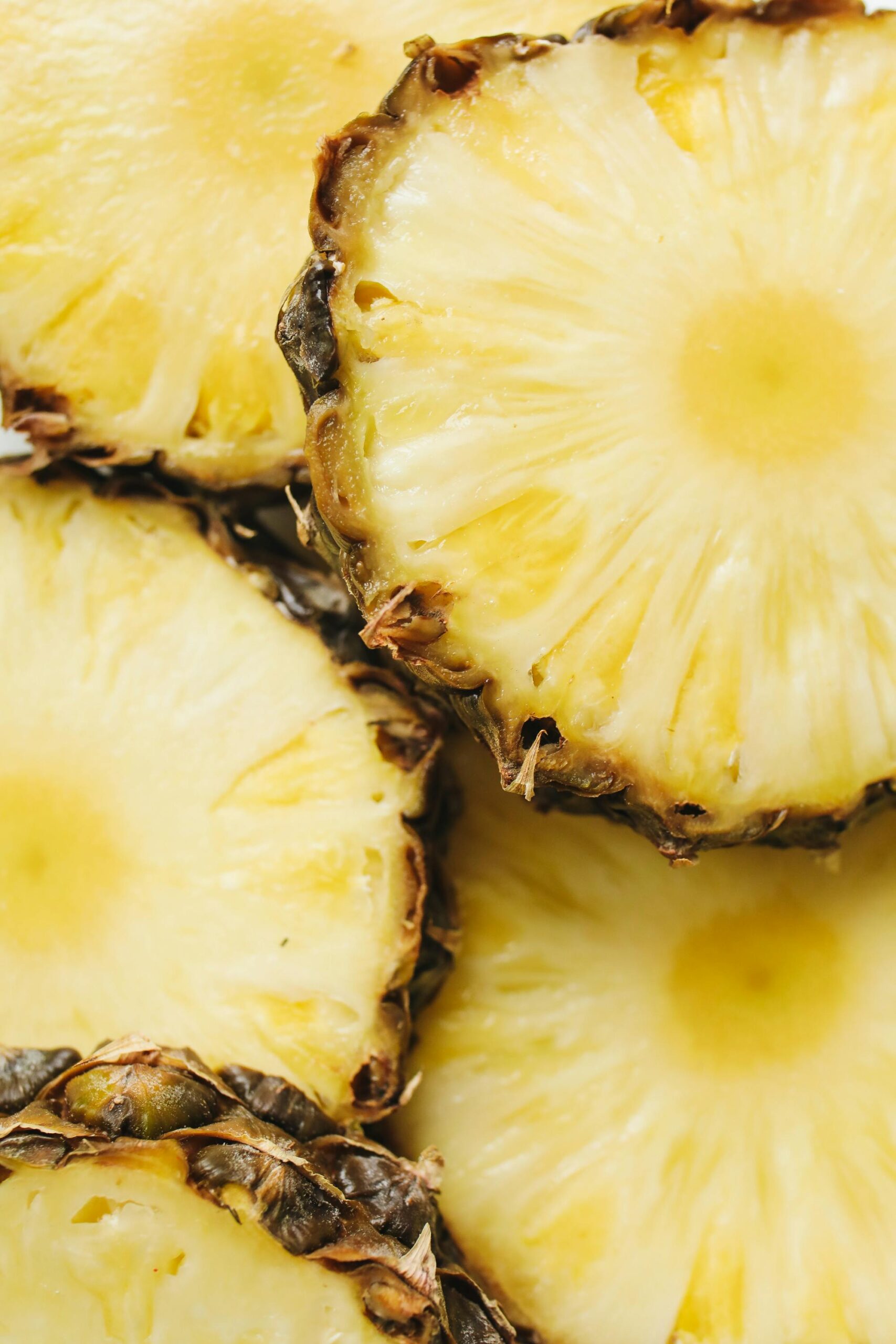
Pineapples
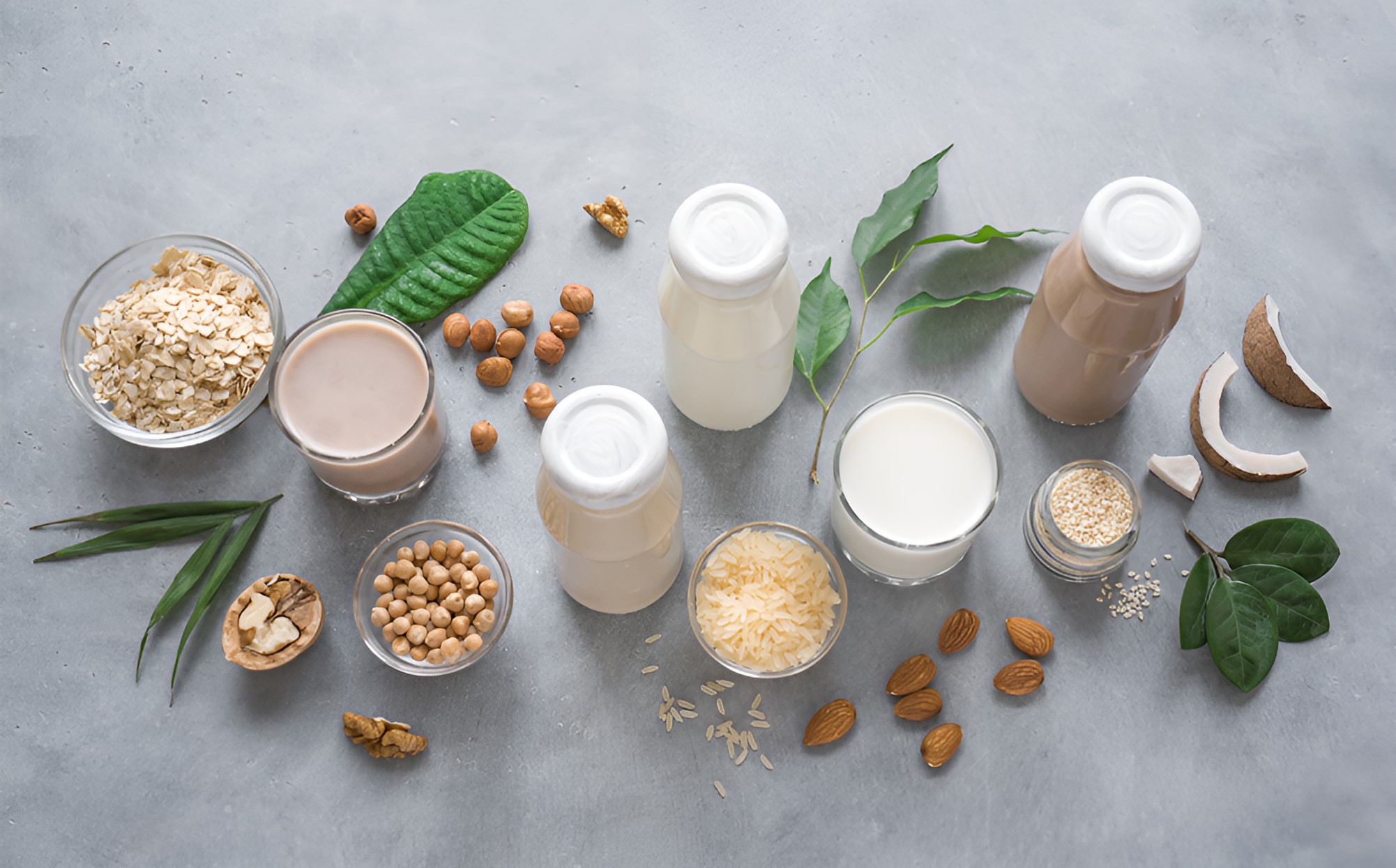
Plant-based beverages
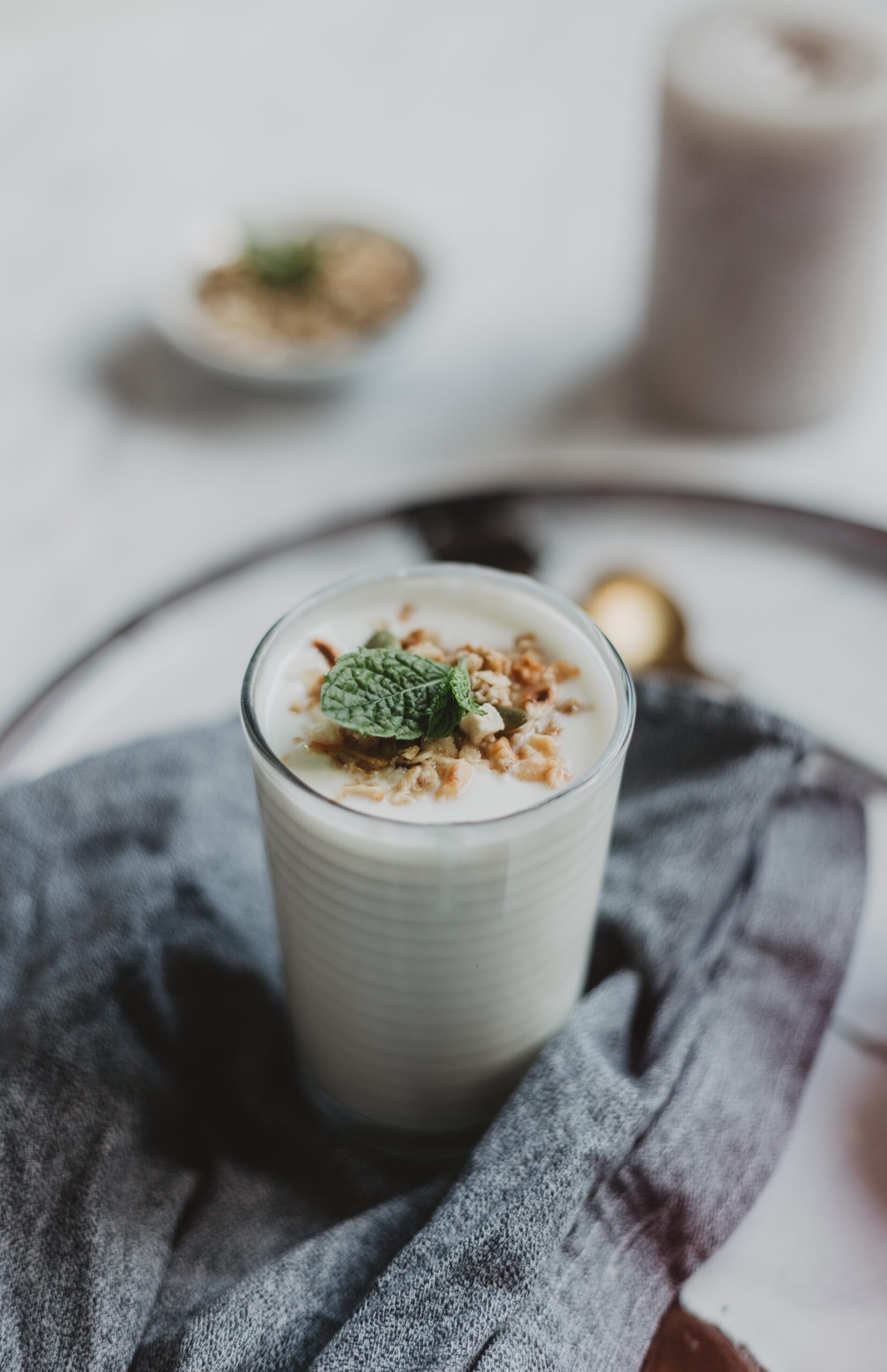
Plant-based yogurt
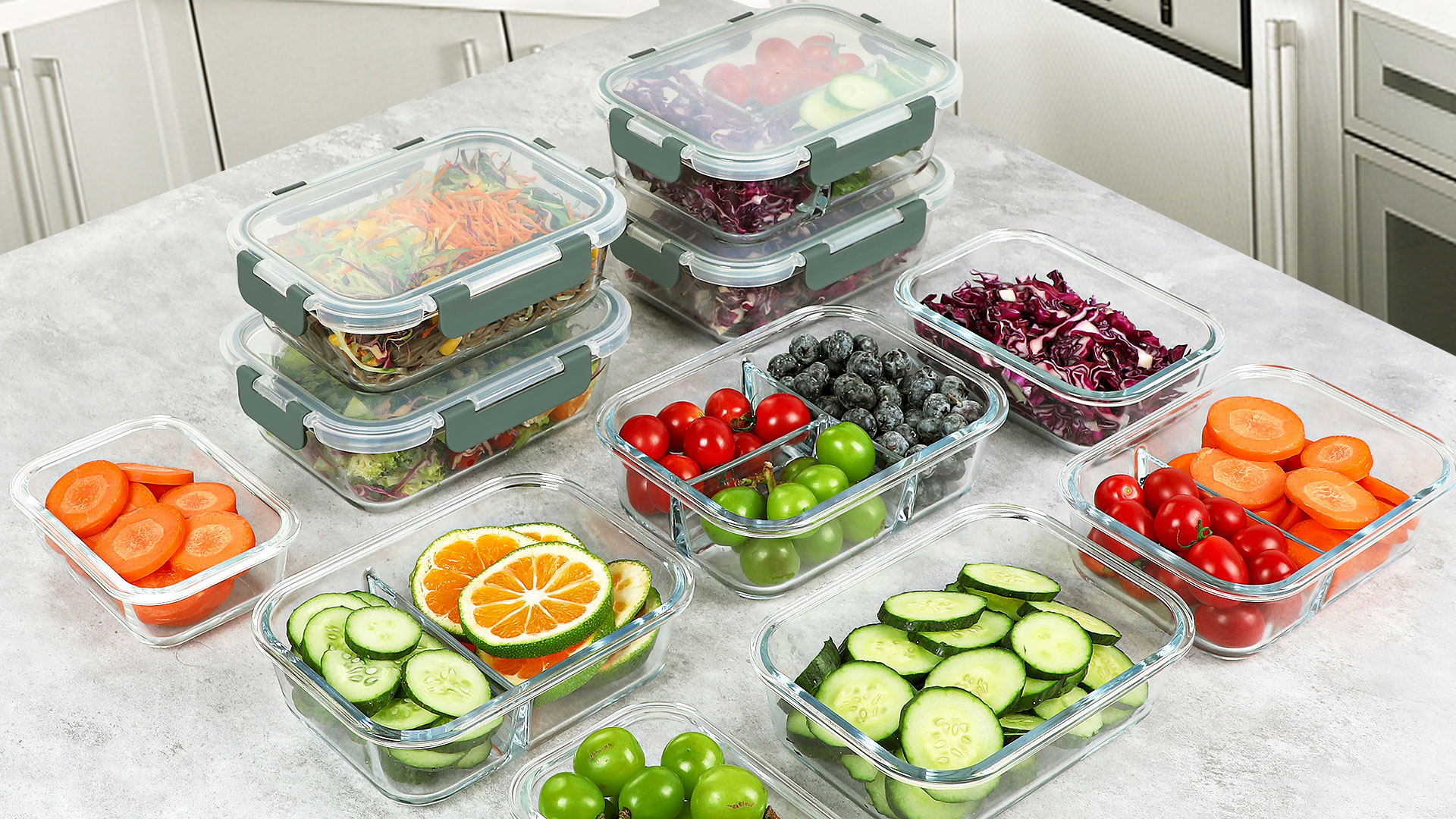
Plastic containers
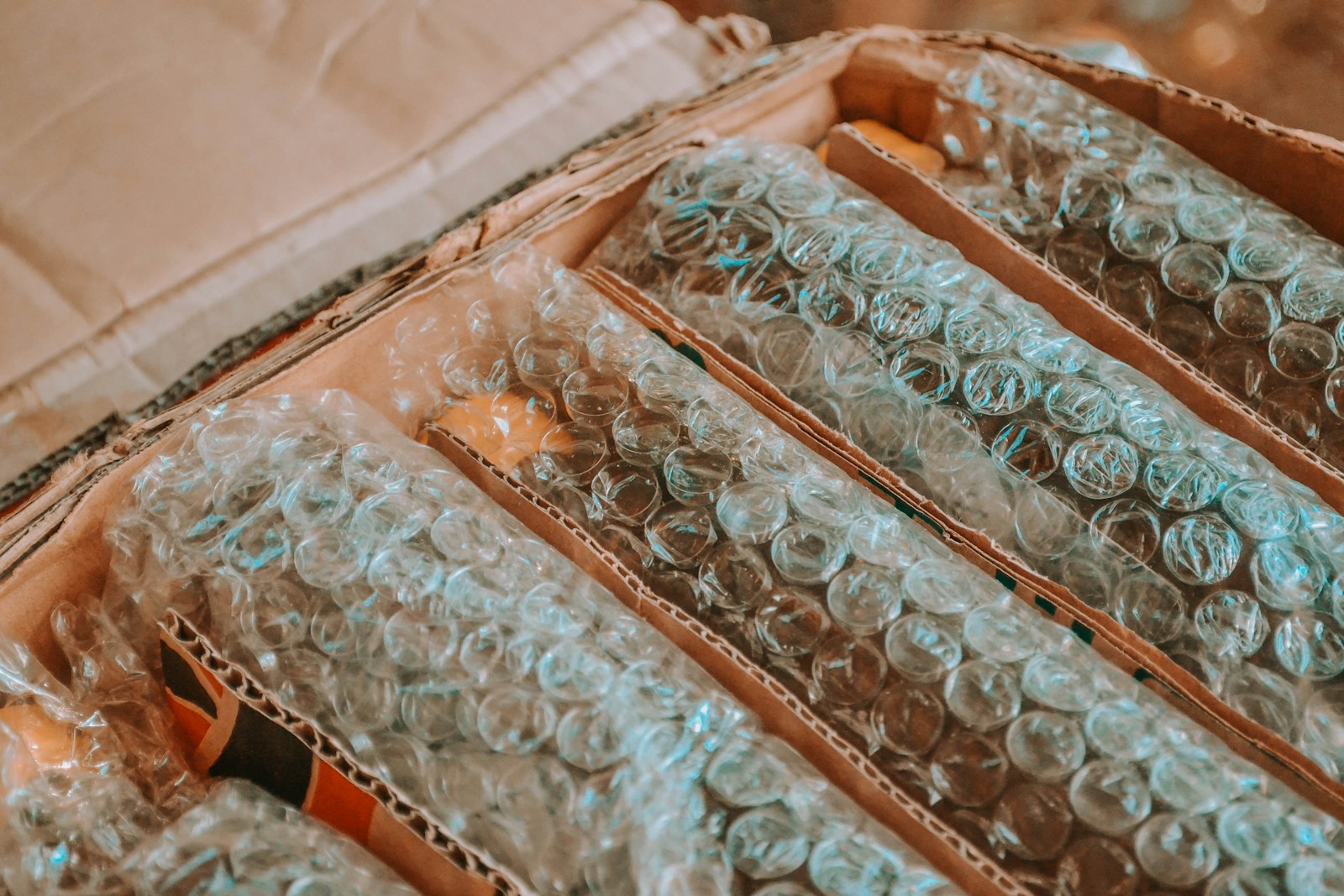
Plastic packaging
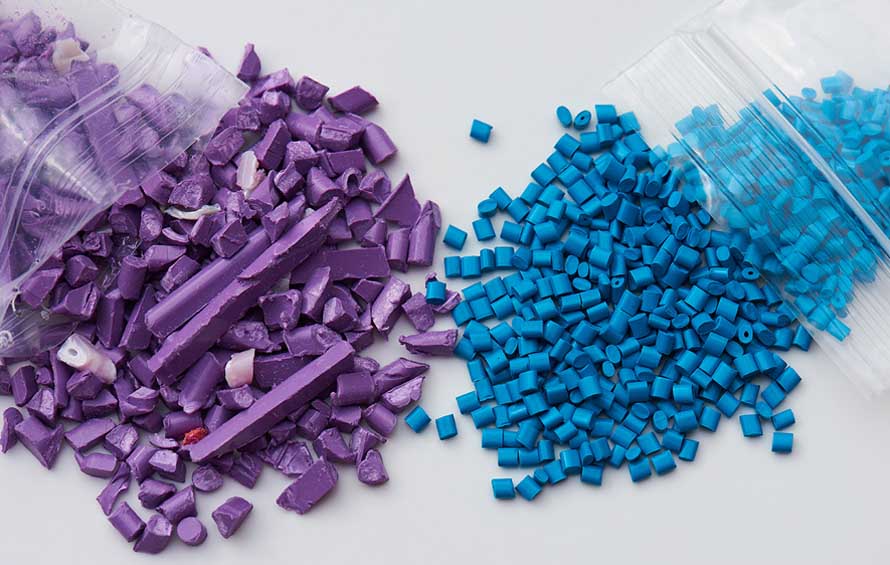
Plasticizers
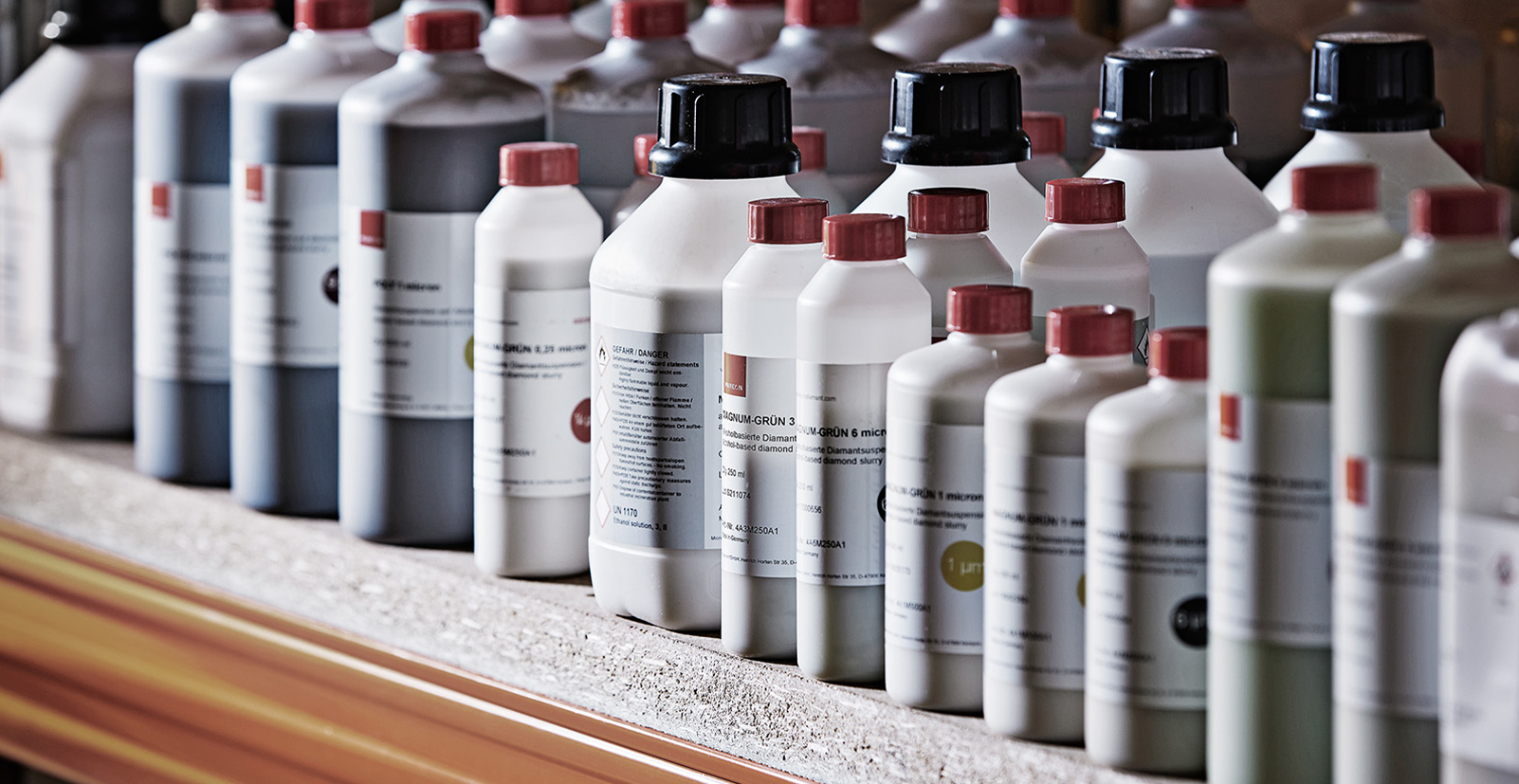
Polishing agents
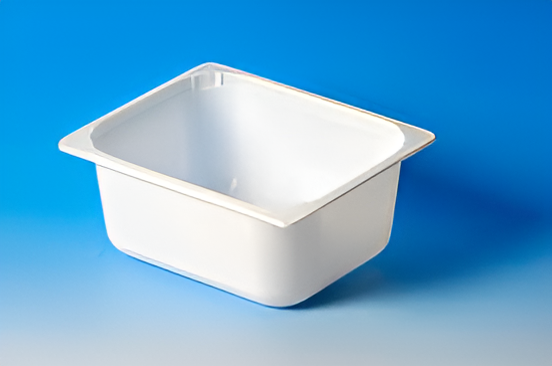
Polypropylene containers
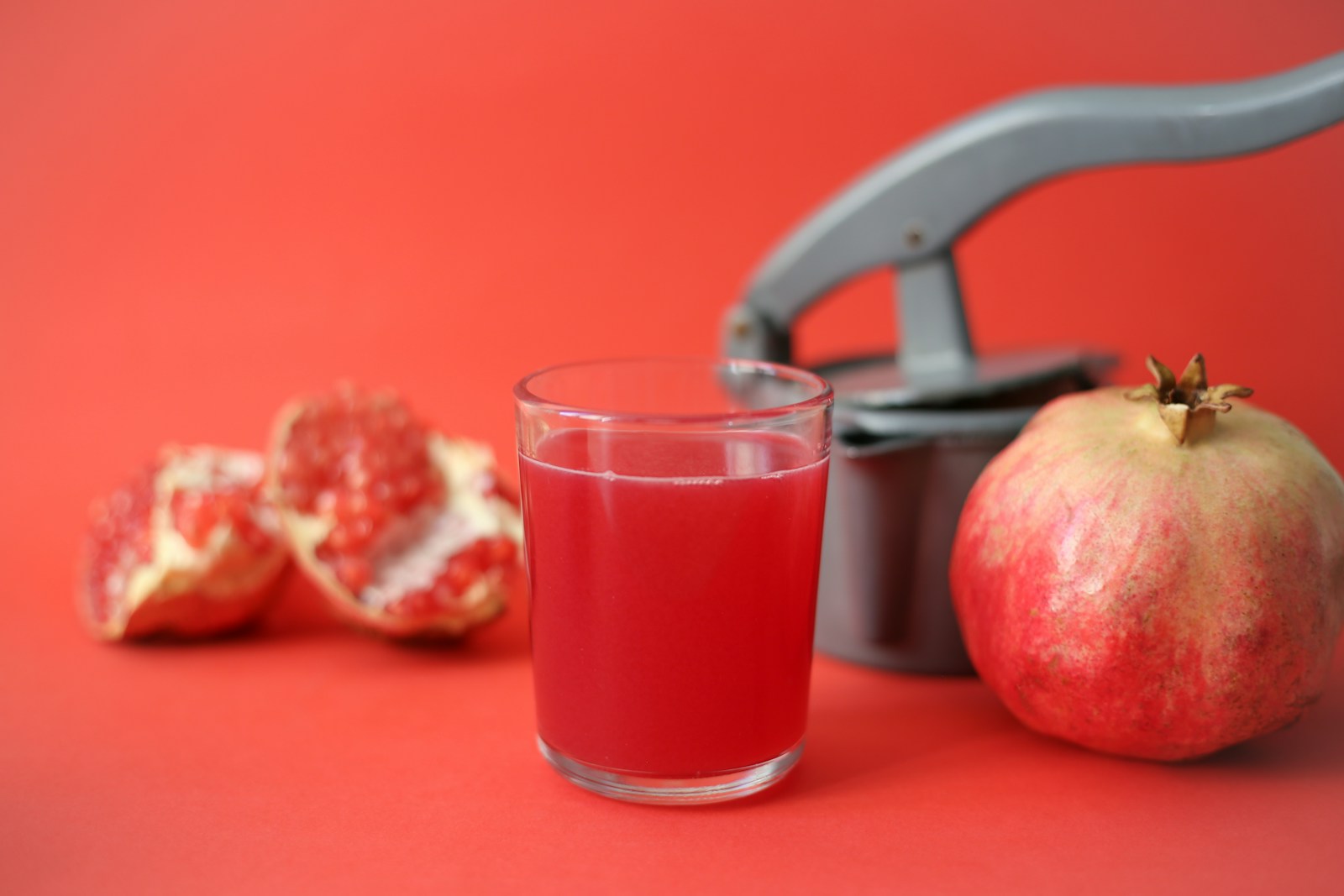
Pomegranate juice

Popcorn

Pouches
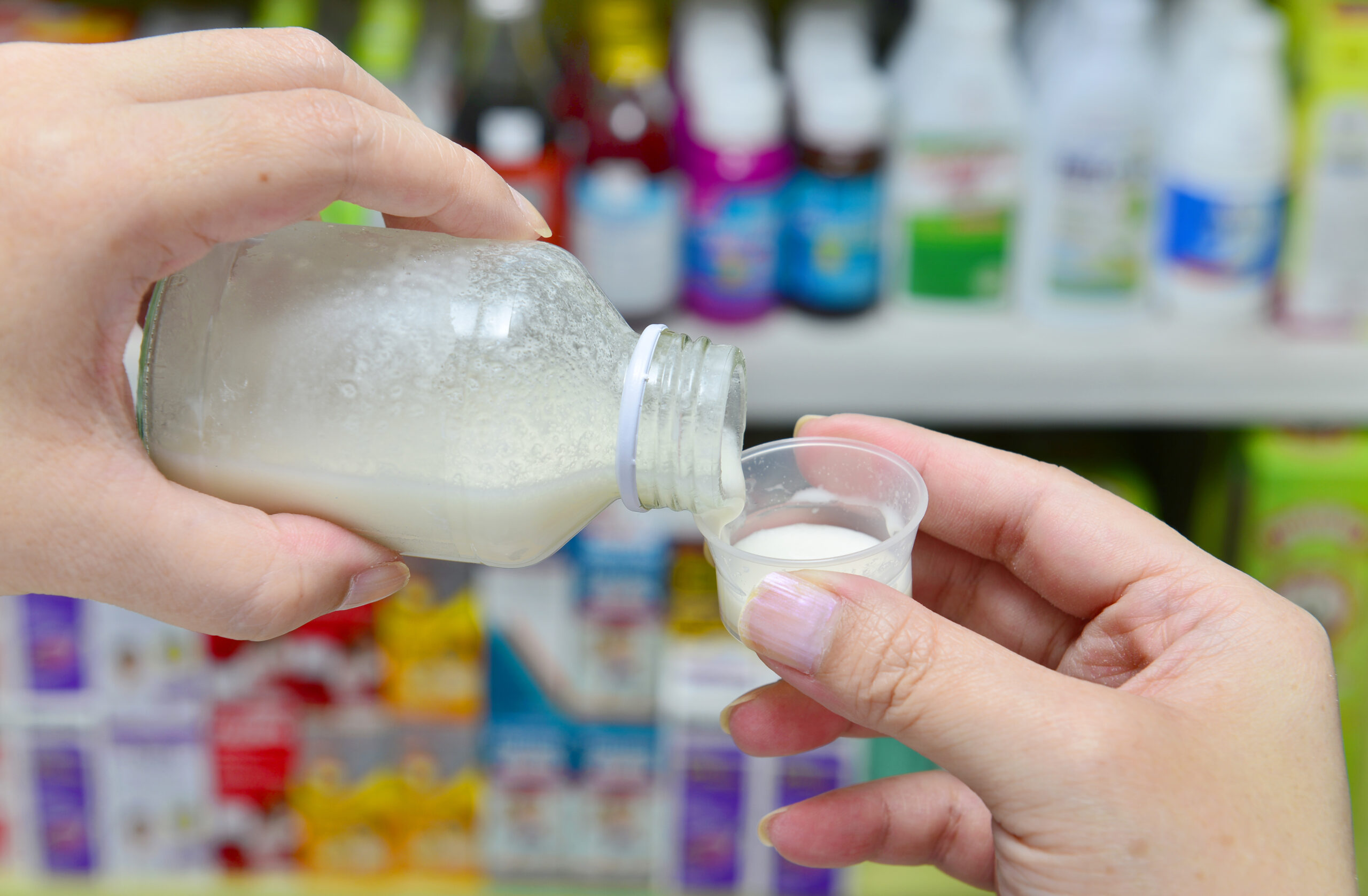
Powder for suspensions (PFS)
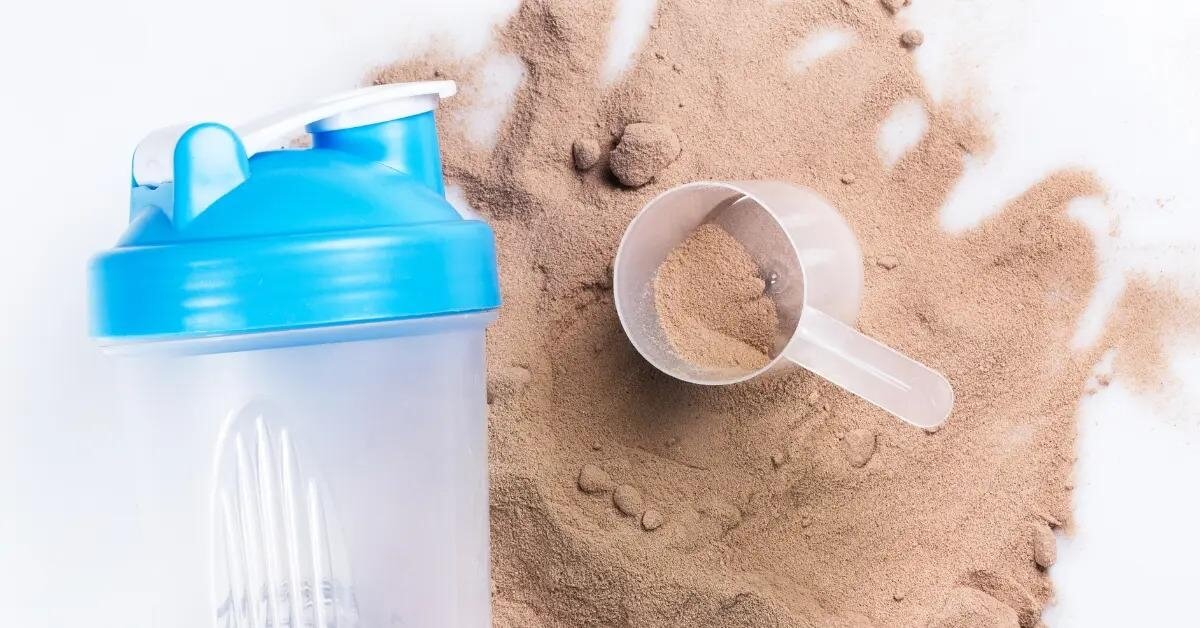
Powdered drink mixes
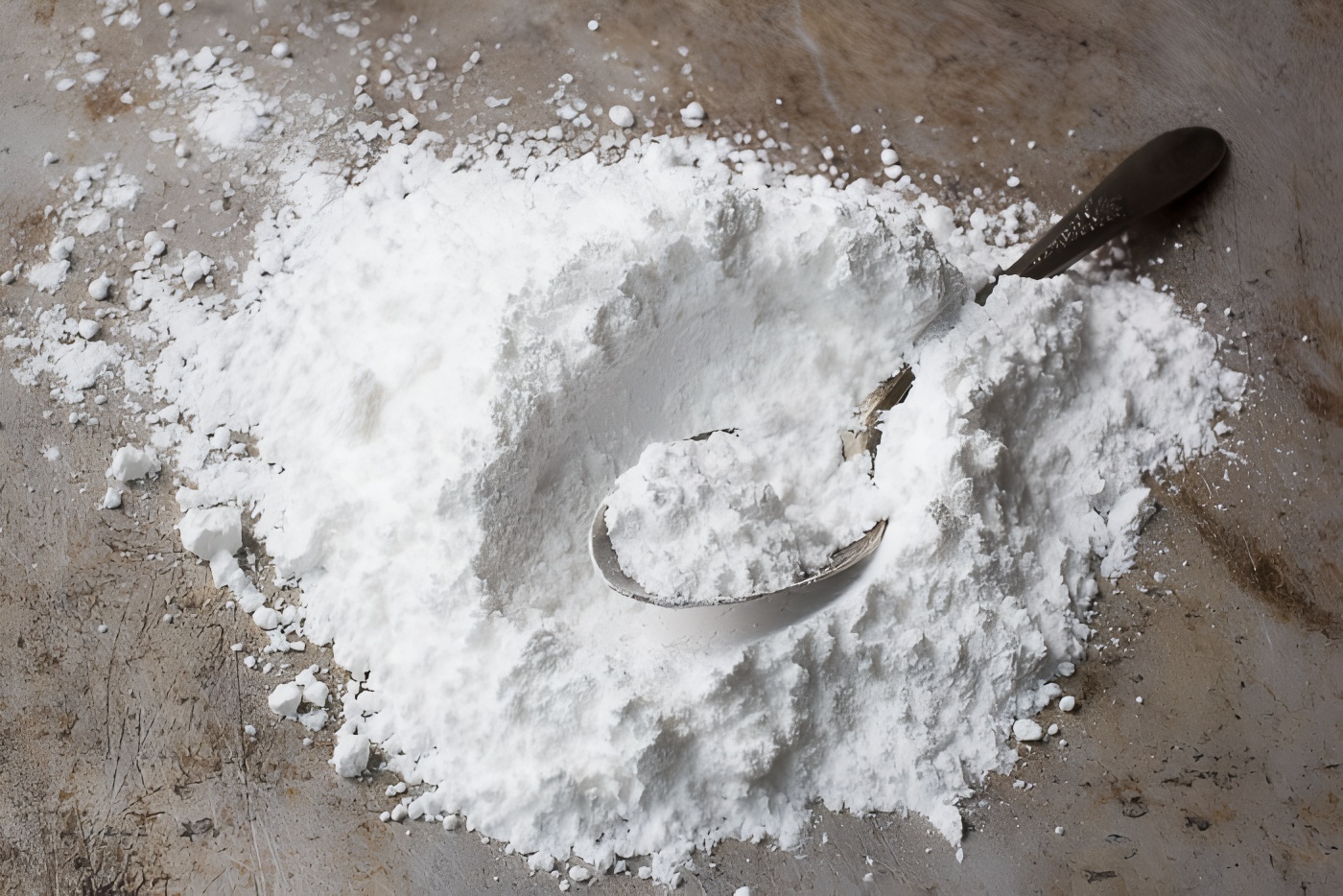
Powdered sugar
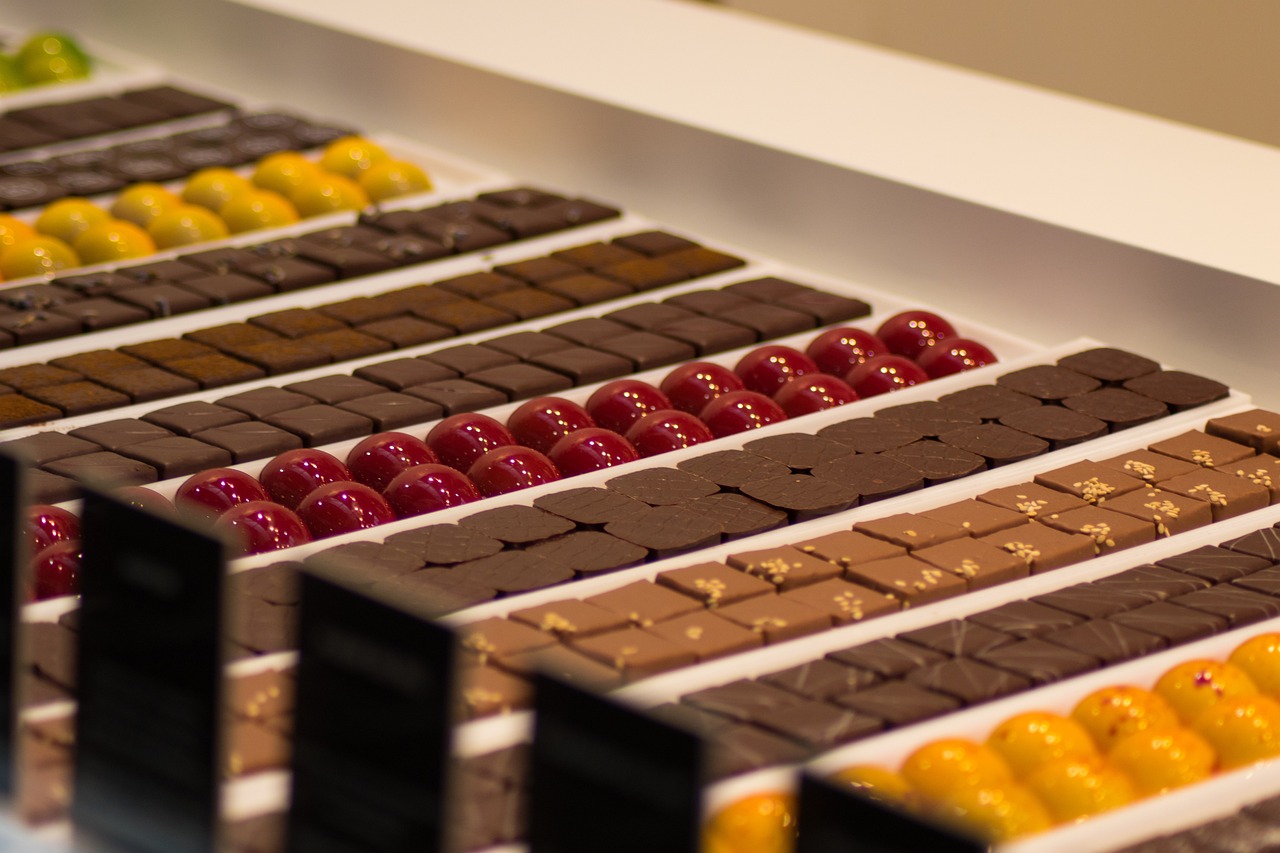
Pralines
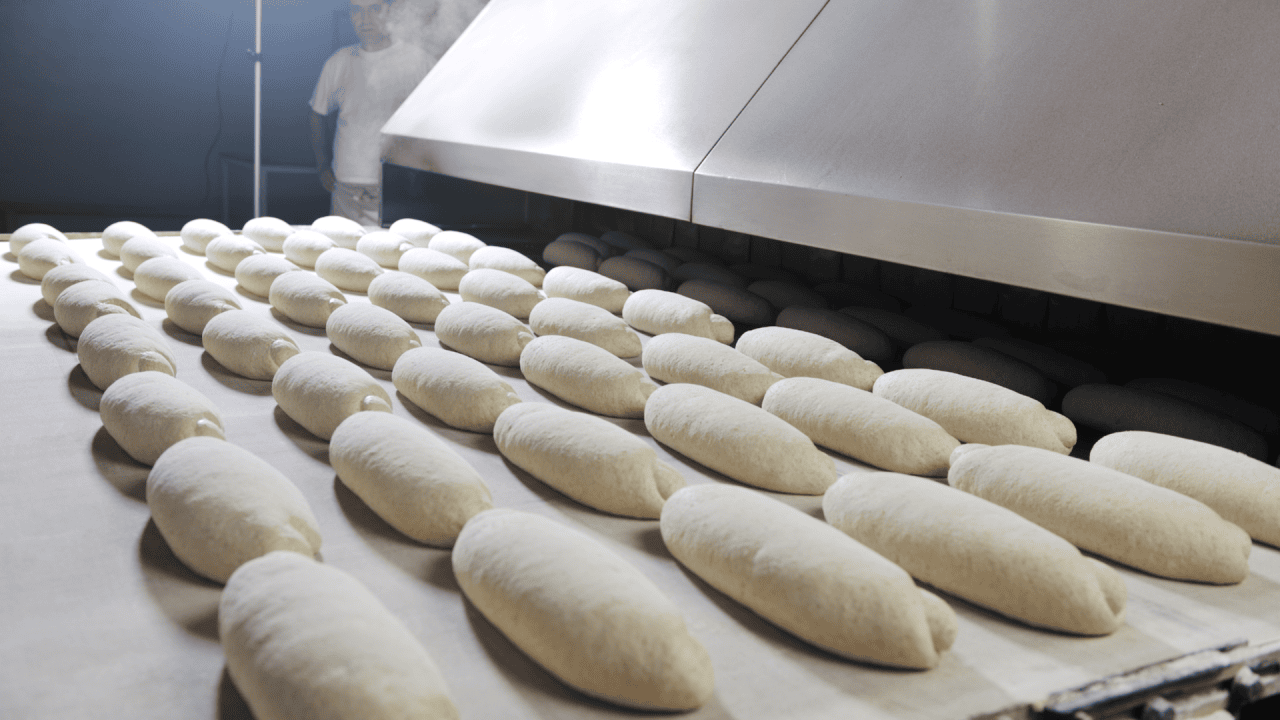
Pre-dough
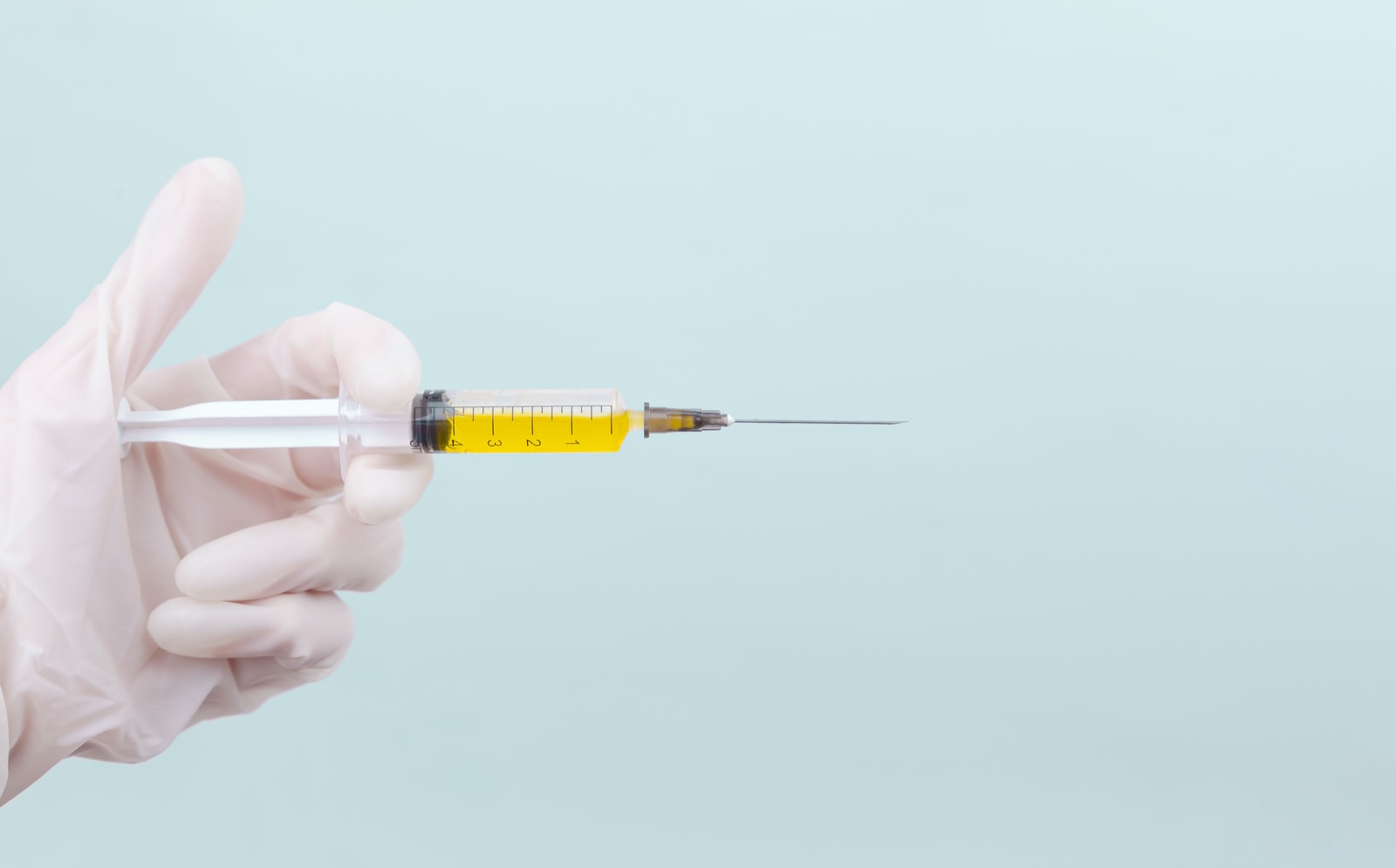
Pre-filled Syringes
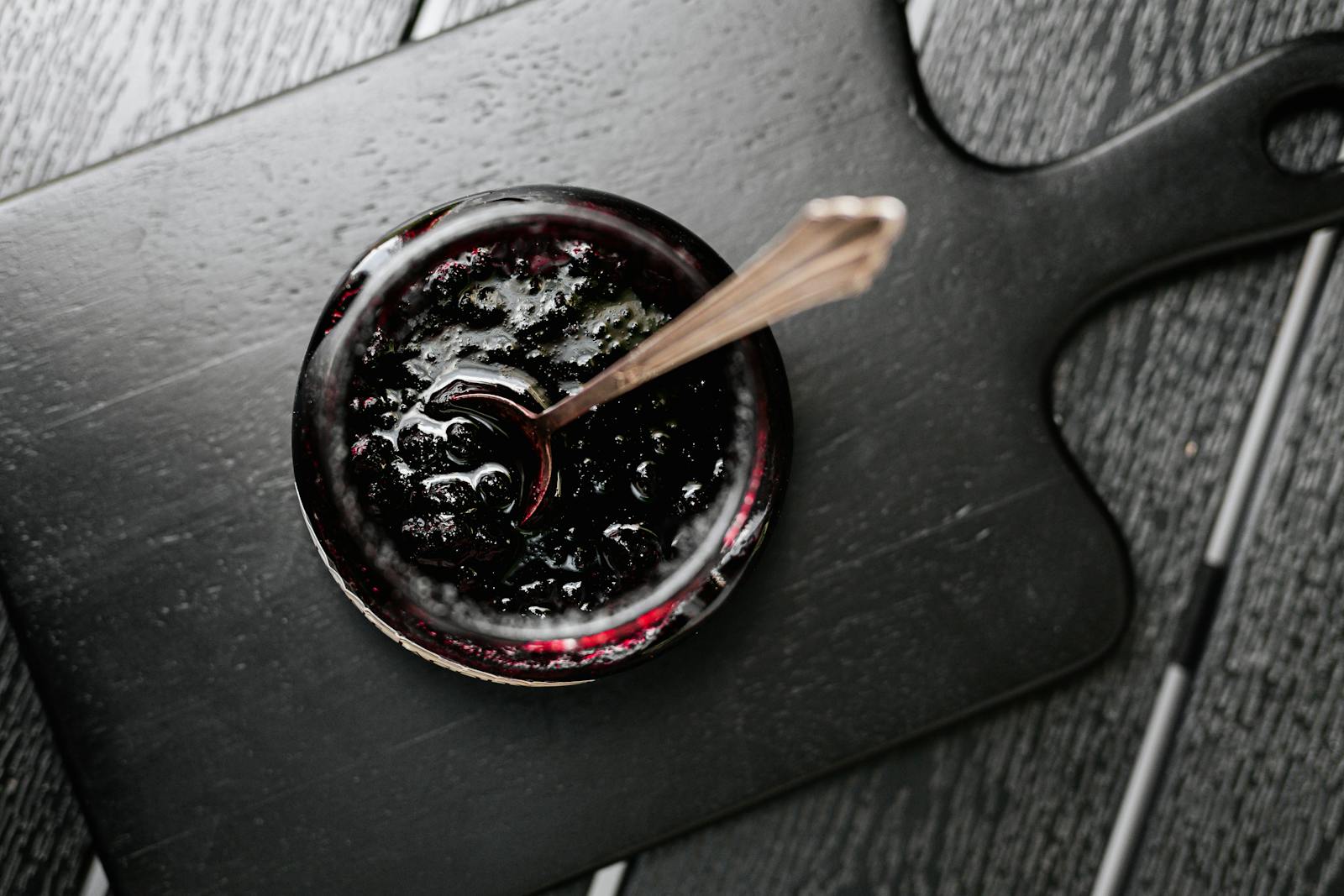
Preserves
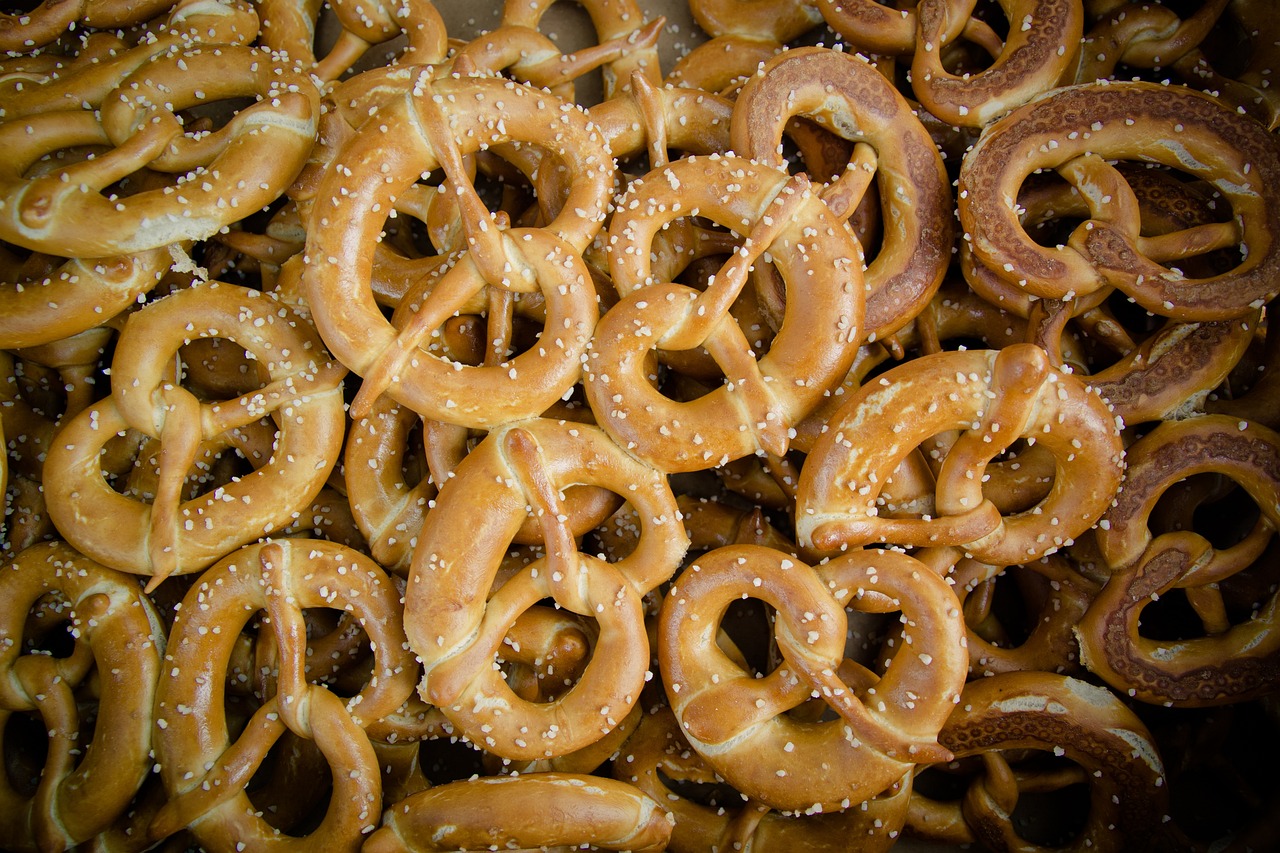
Pretzels
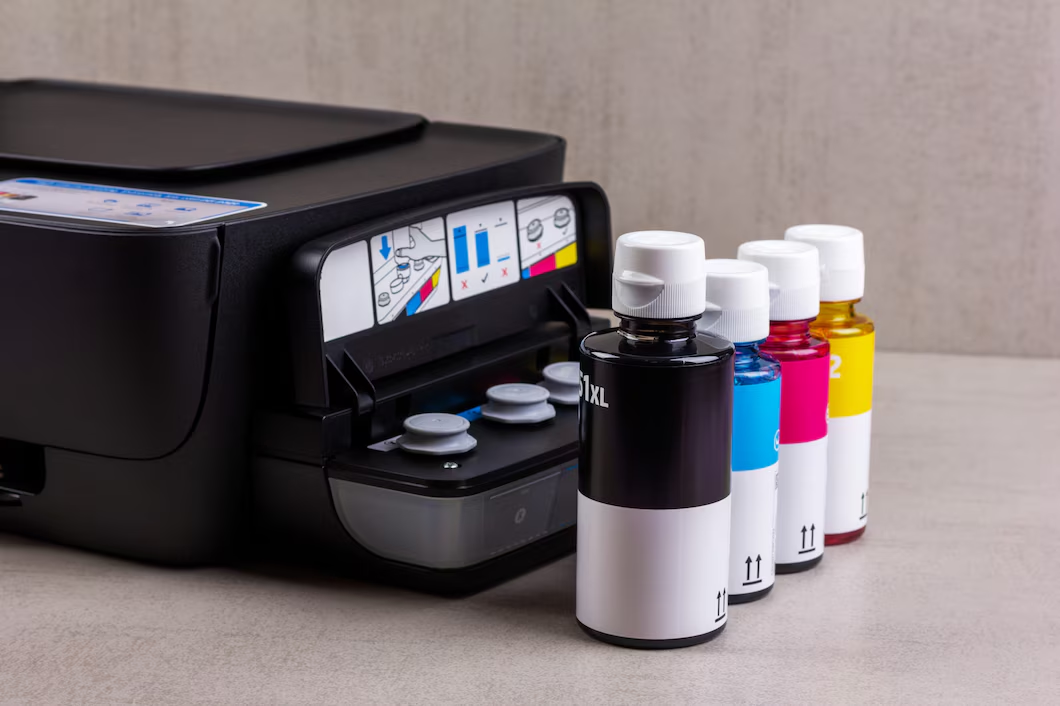
Printer ink
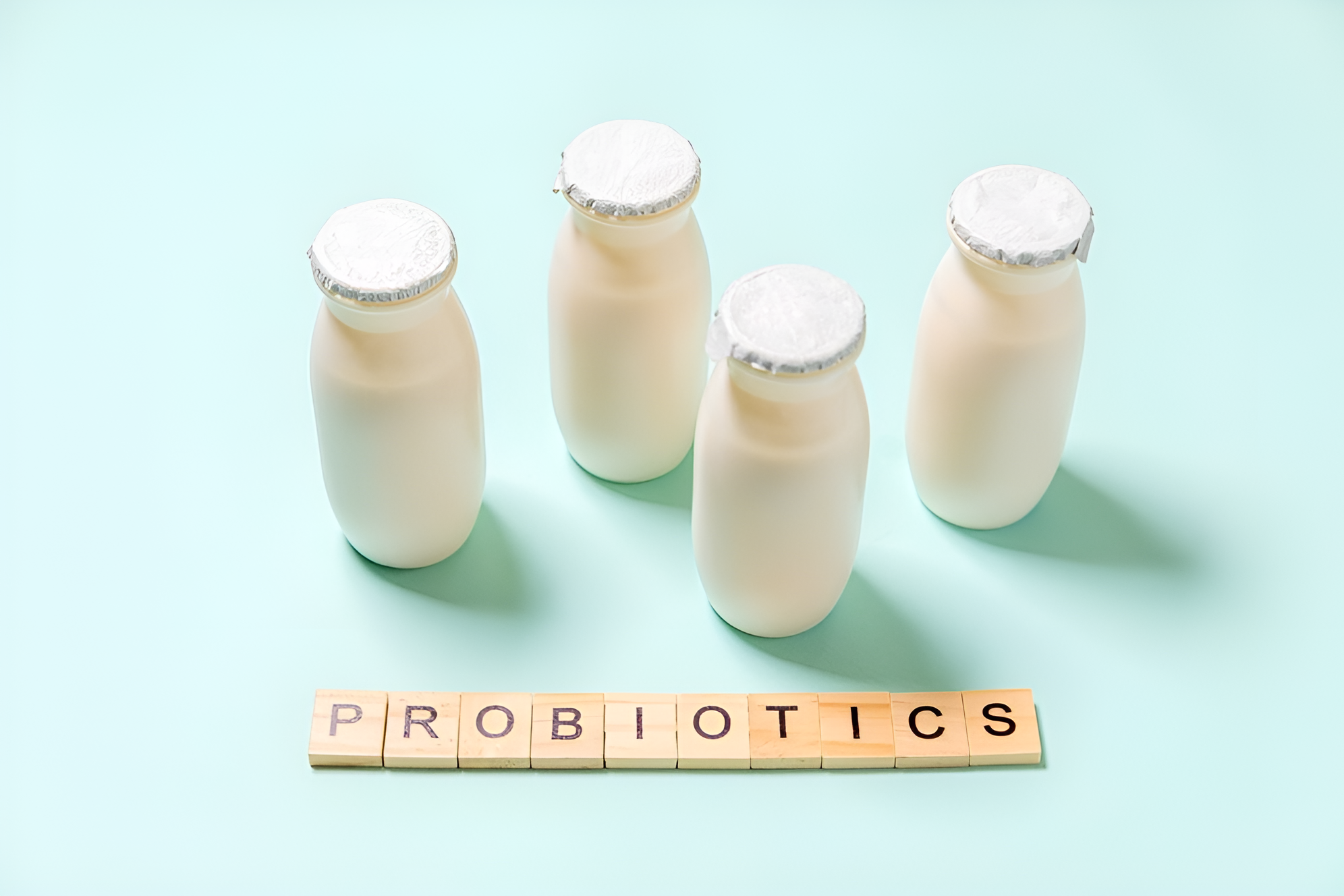
Probiotic drinks
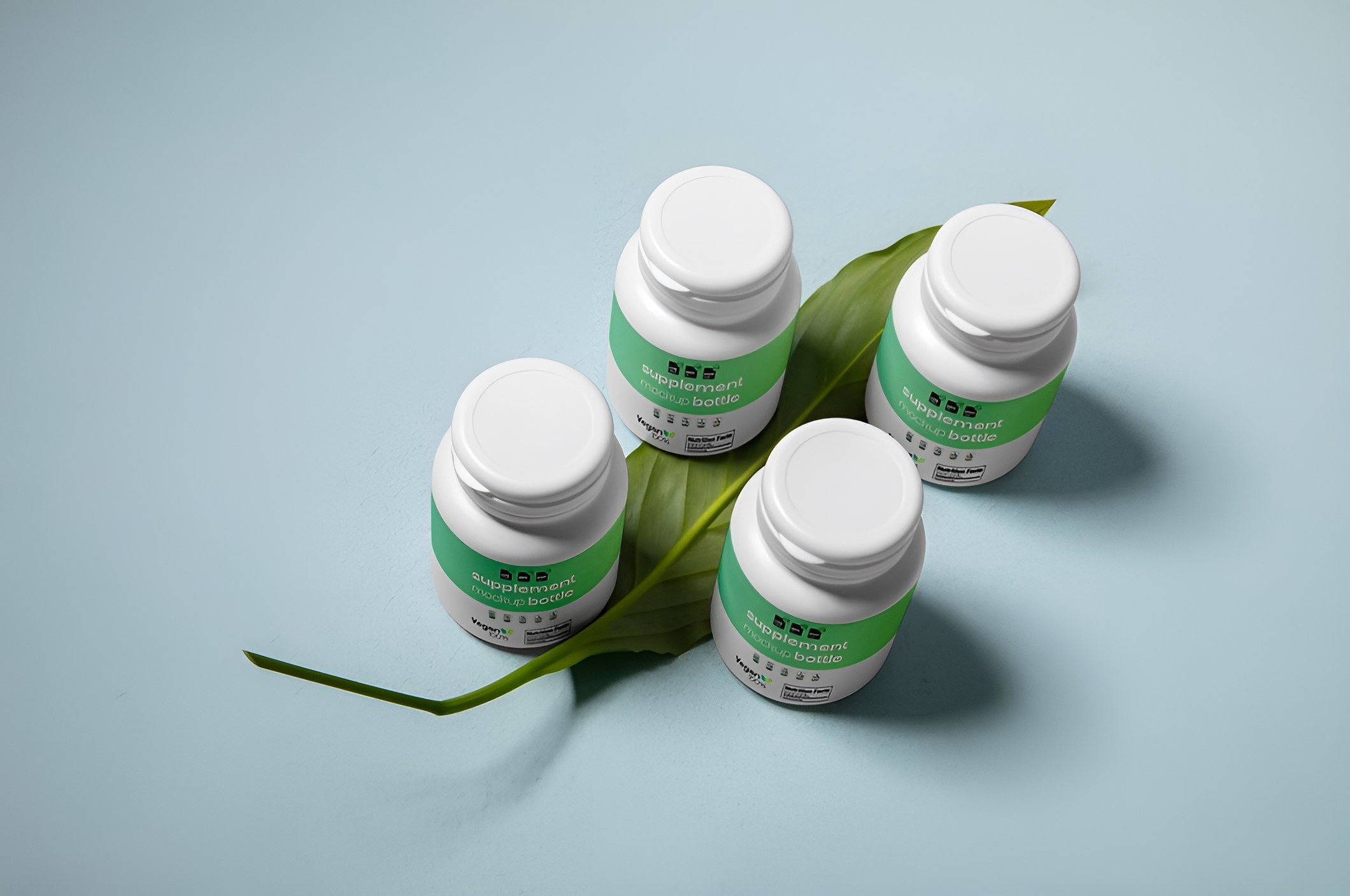
Probiotic supplements
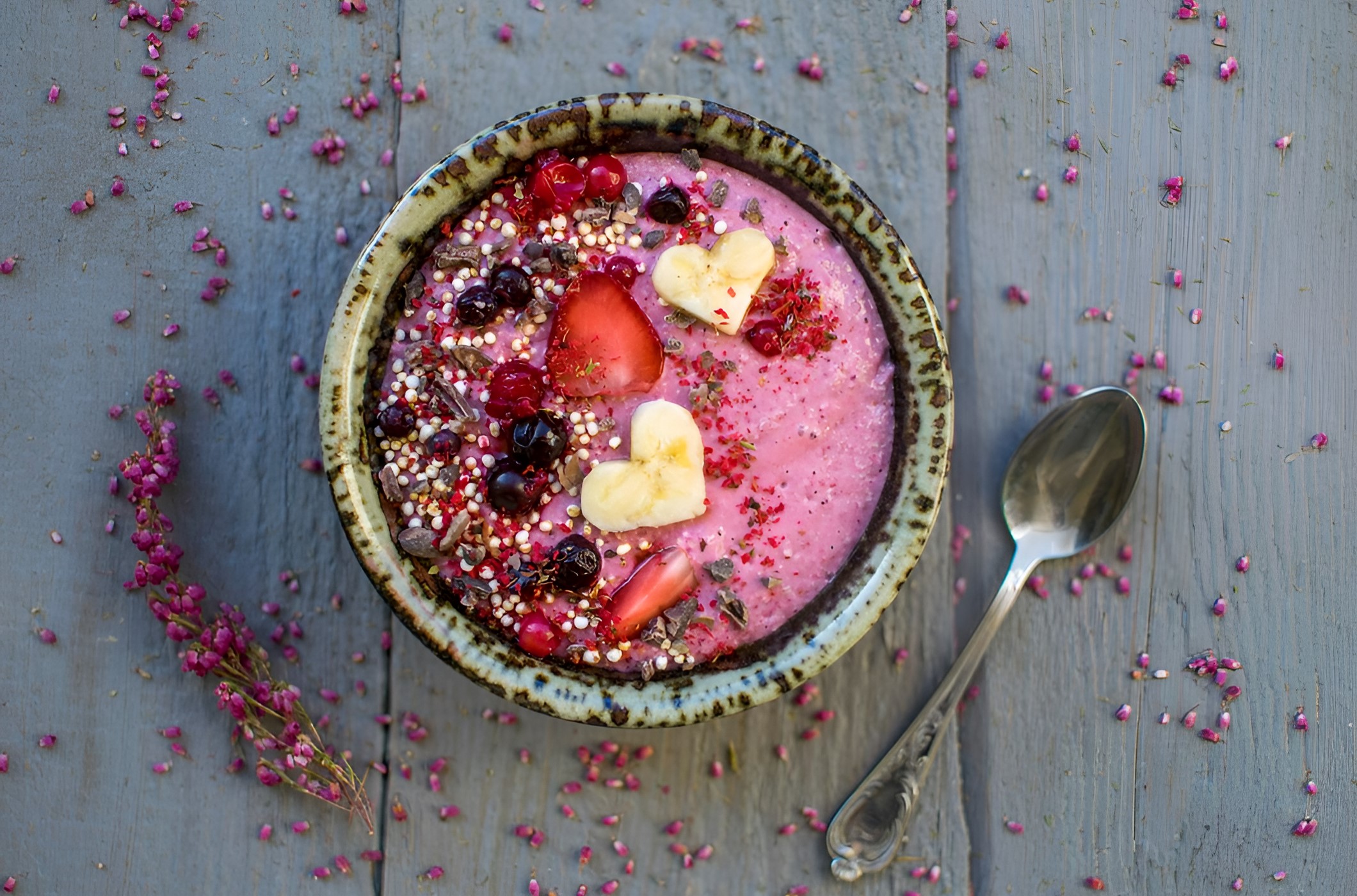
Probiotic yogurt
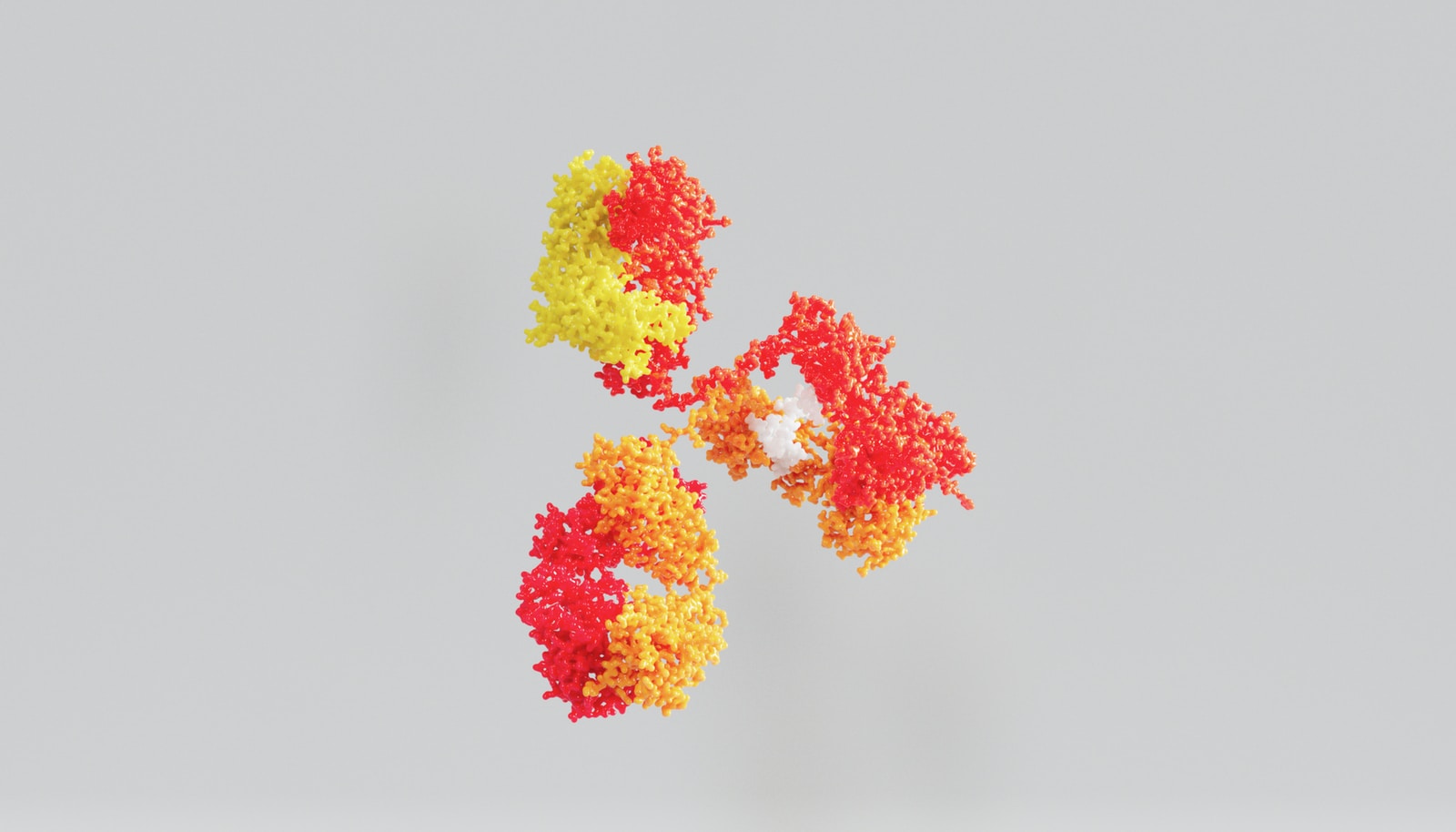
Probiotics
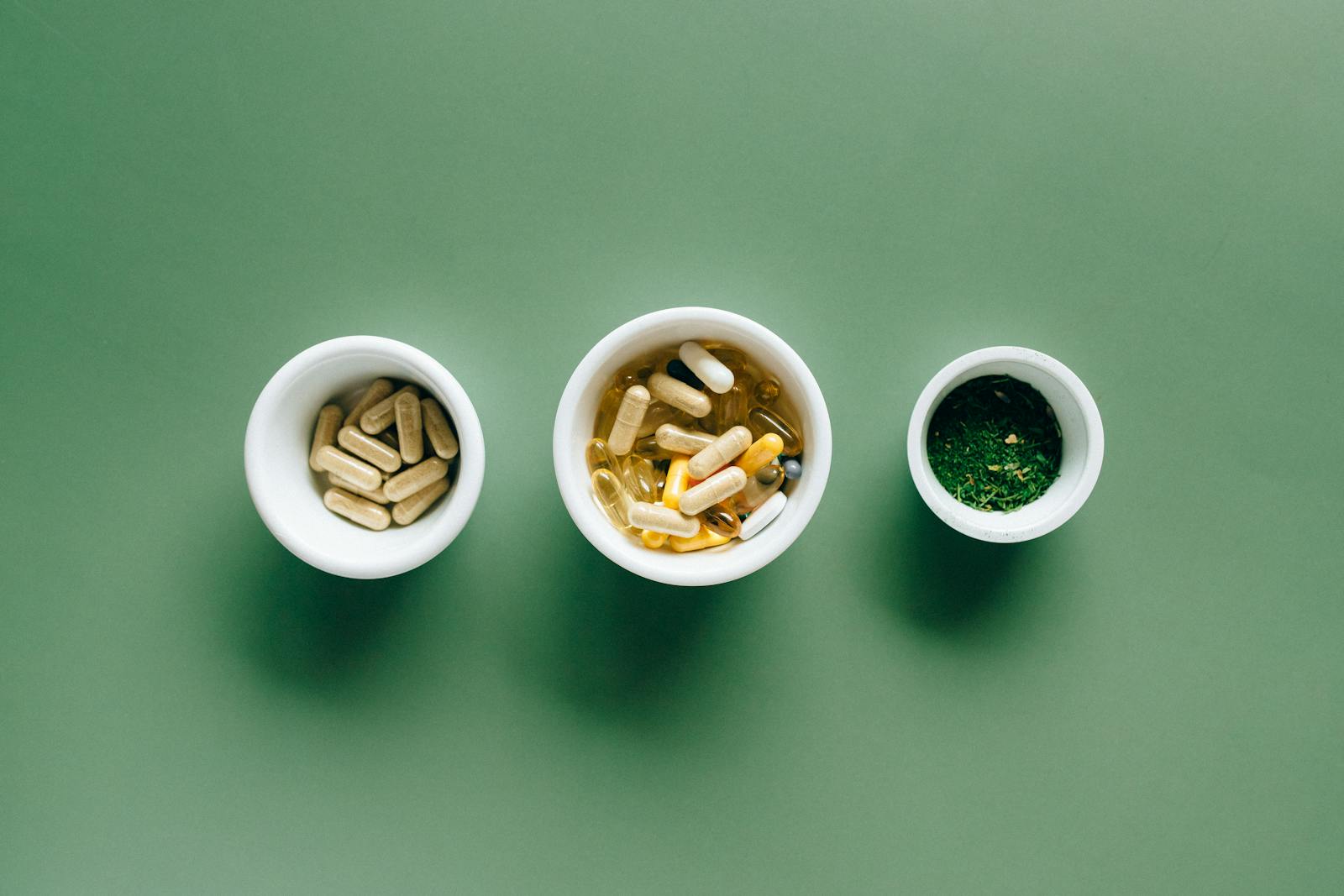
Protein-based drugs
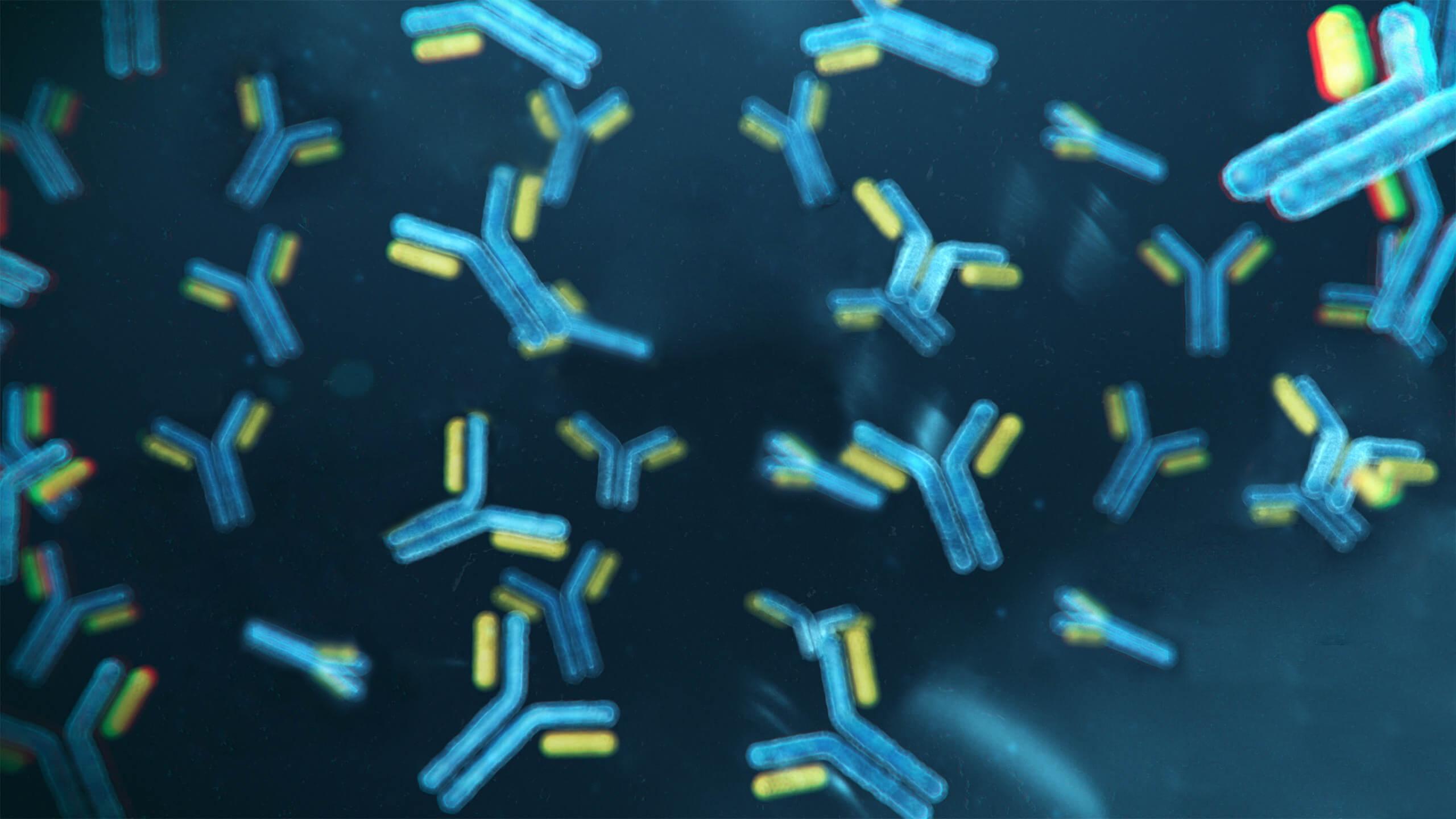
Protein therapeutics
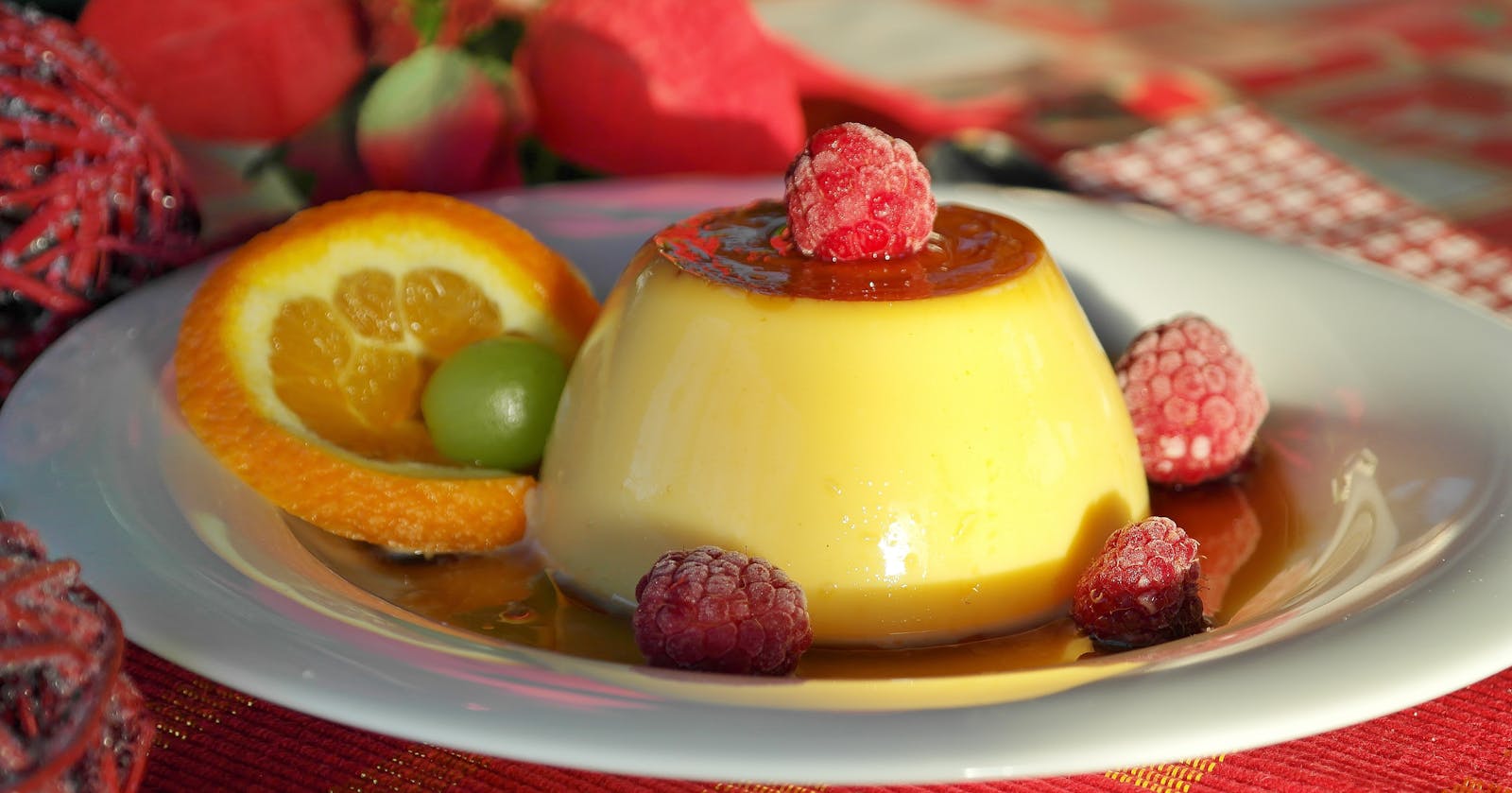
Pudding
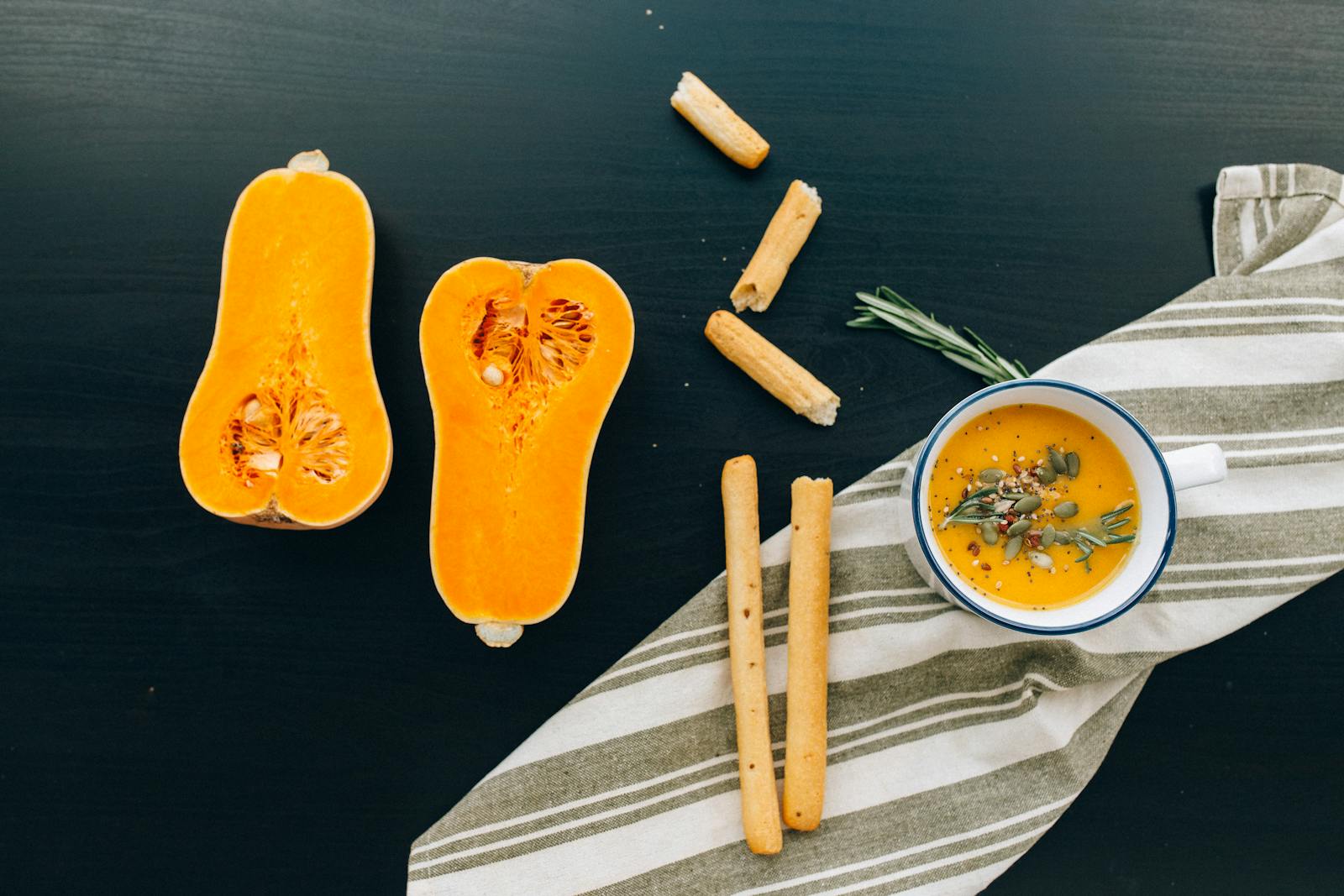
Puree
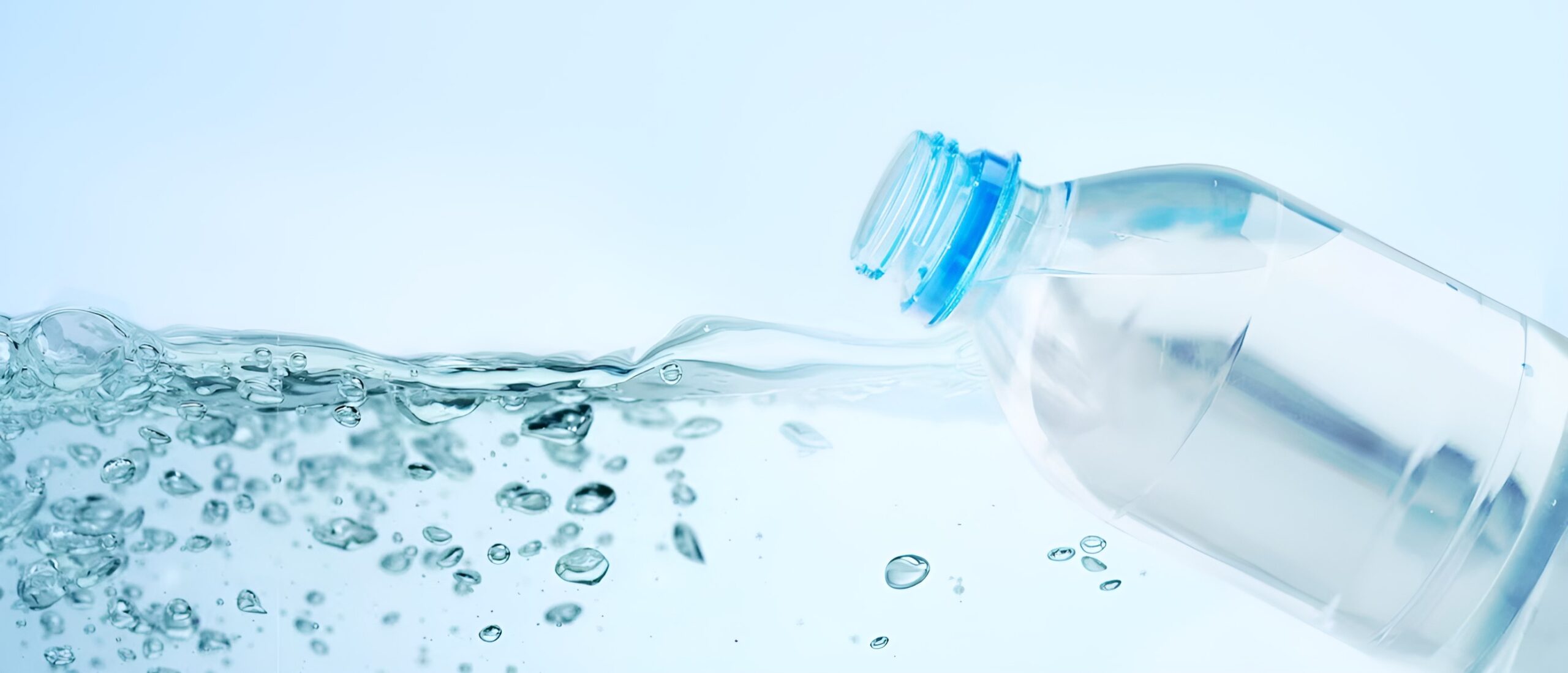
Purified water
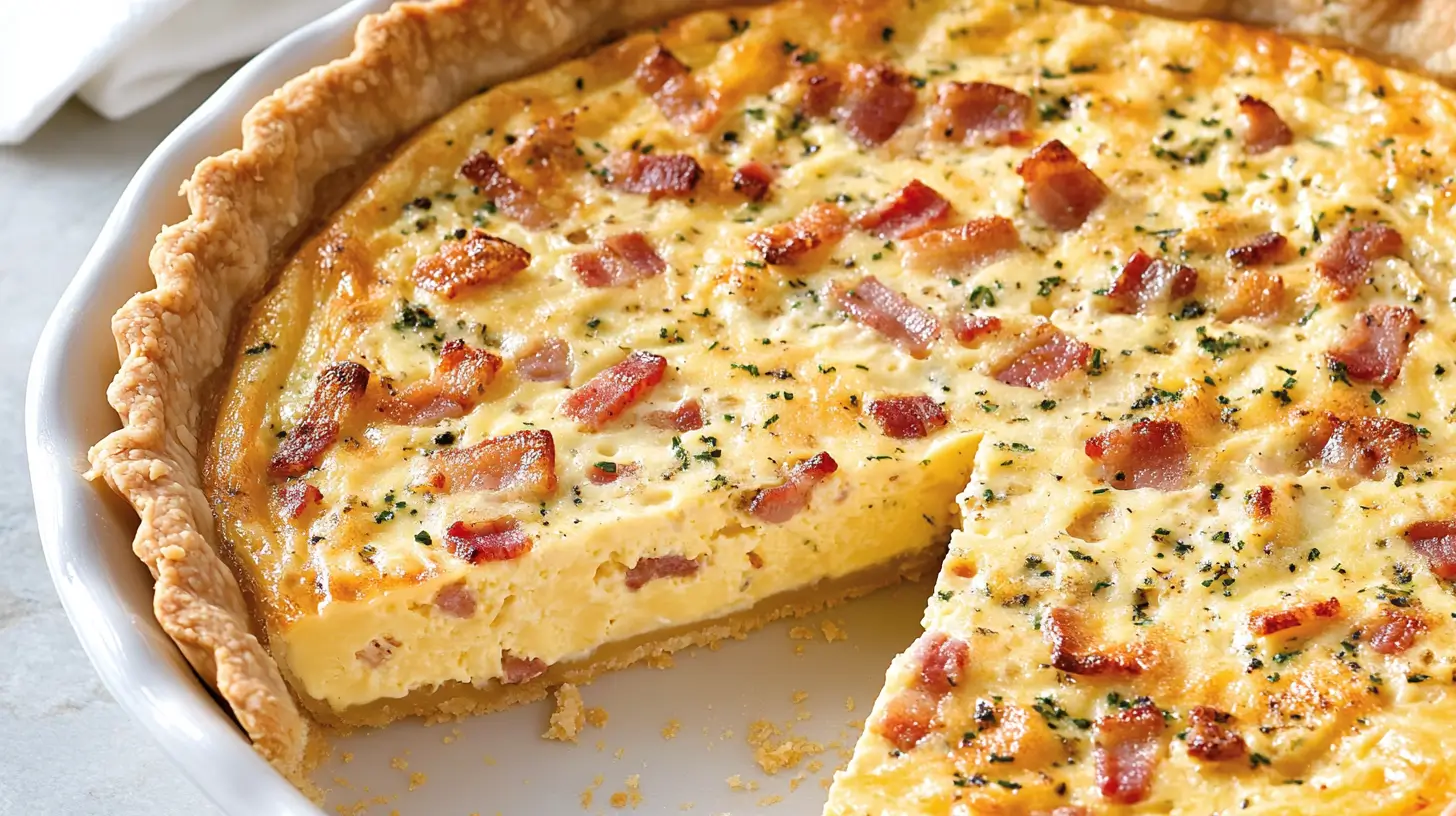
Quiche lorraine
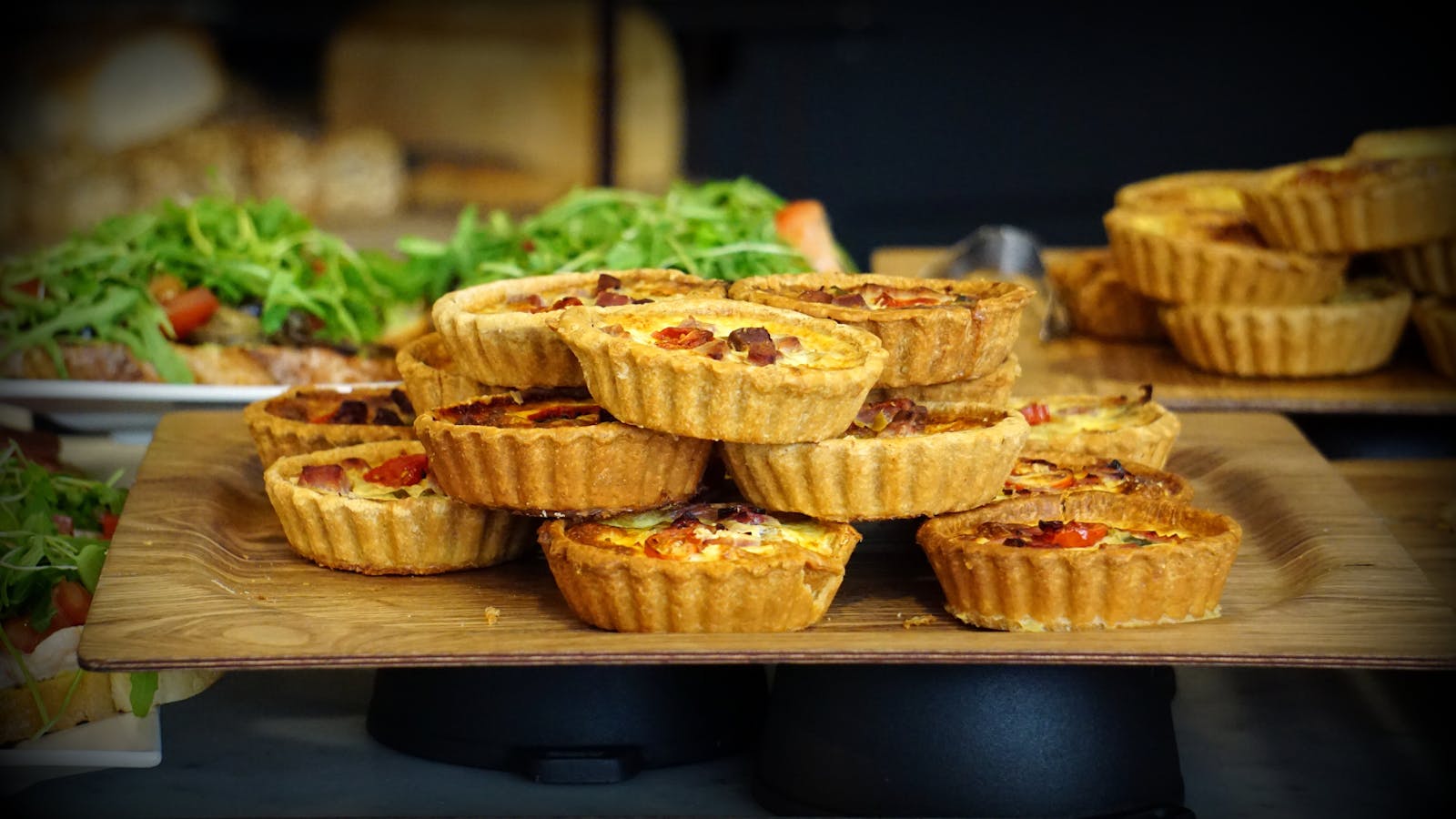
Quiches
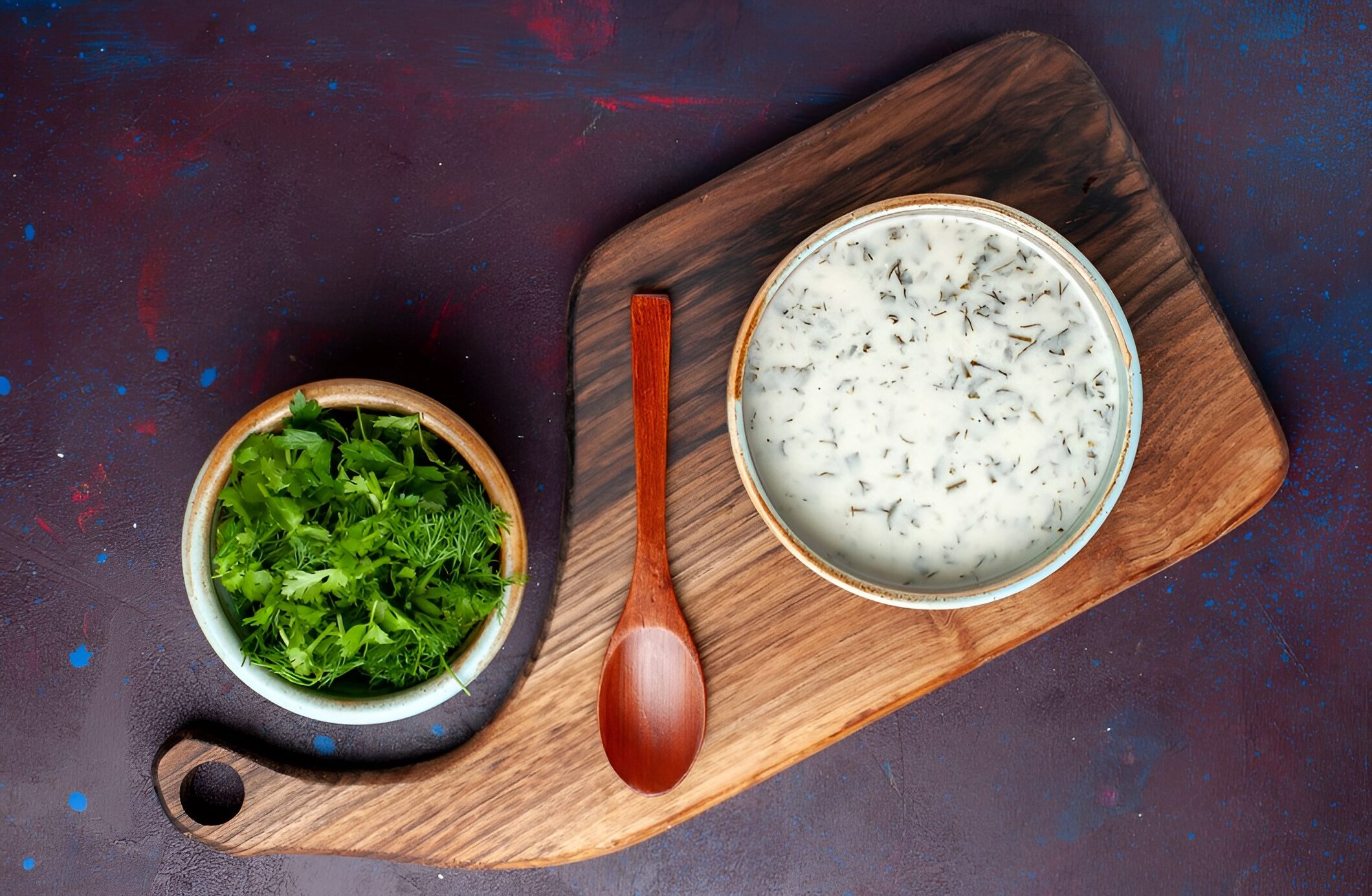
Ranch dressing
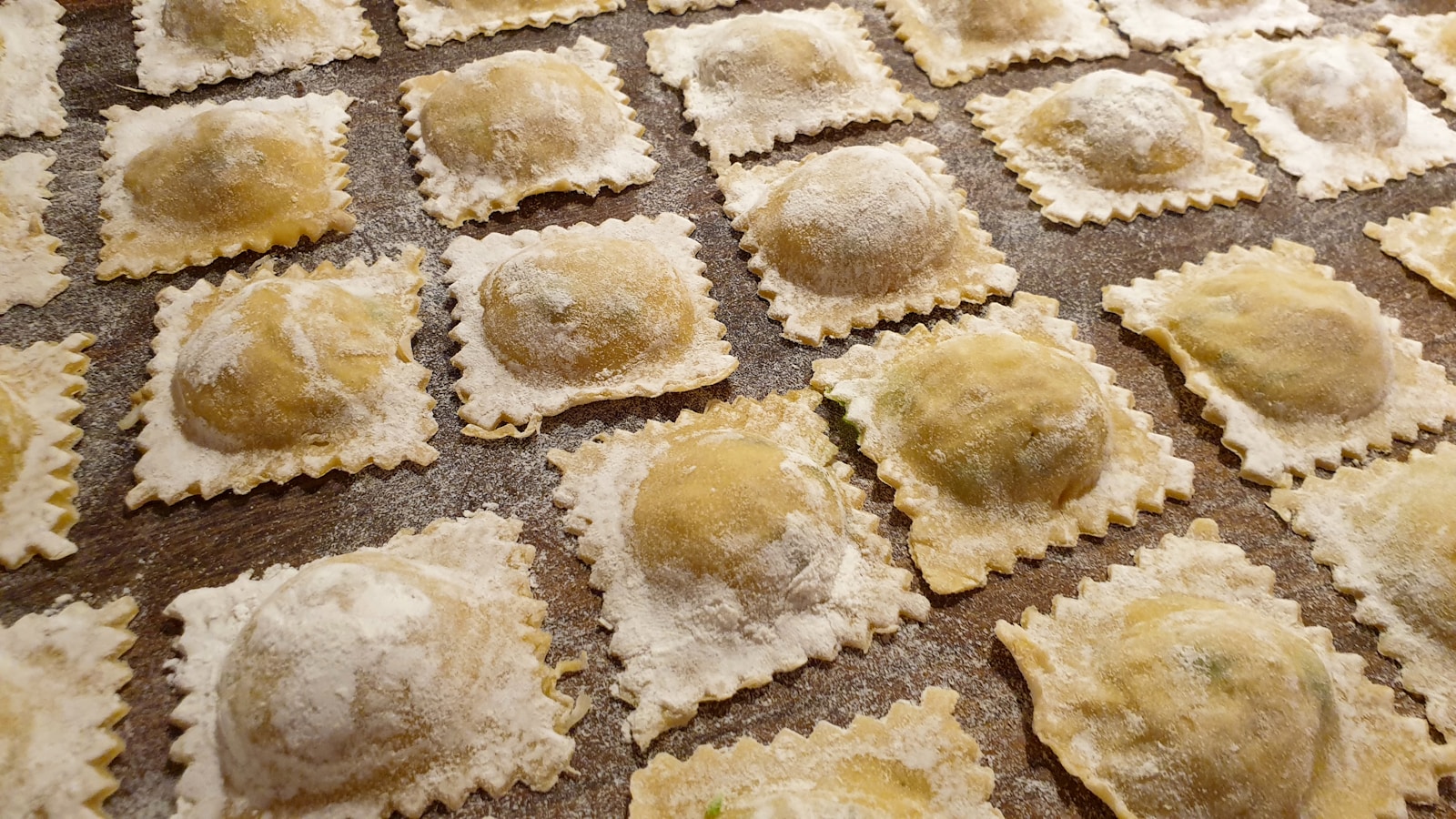
Ravioli
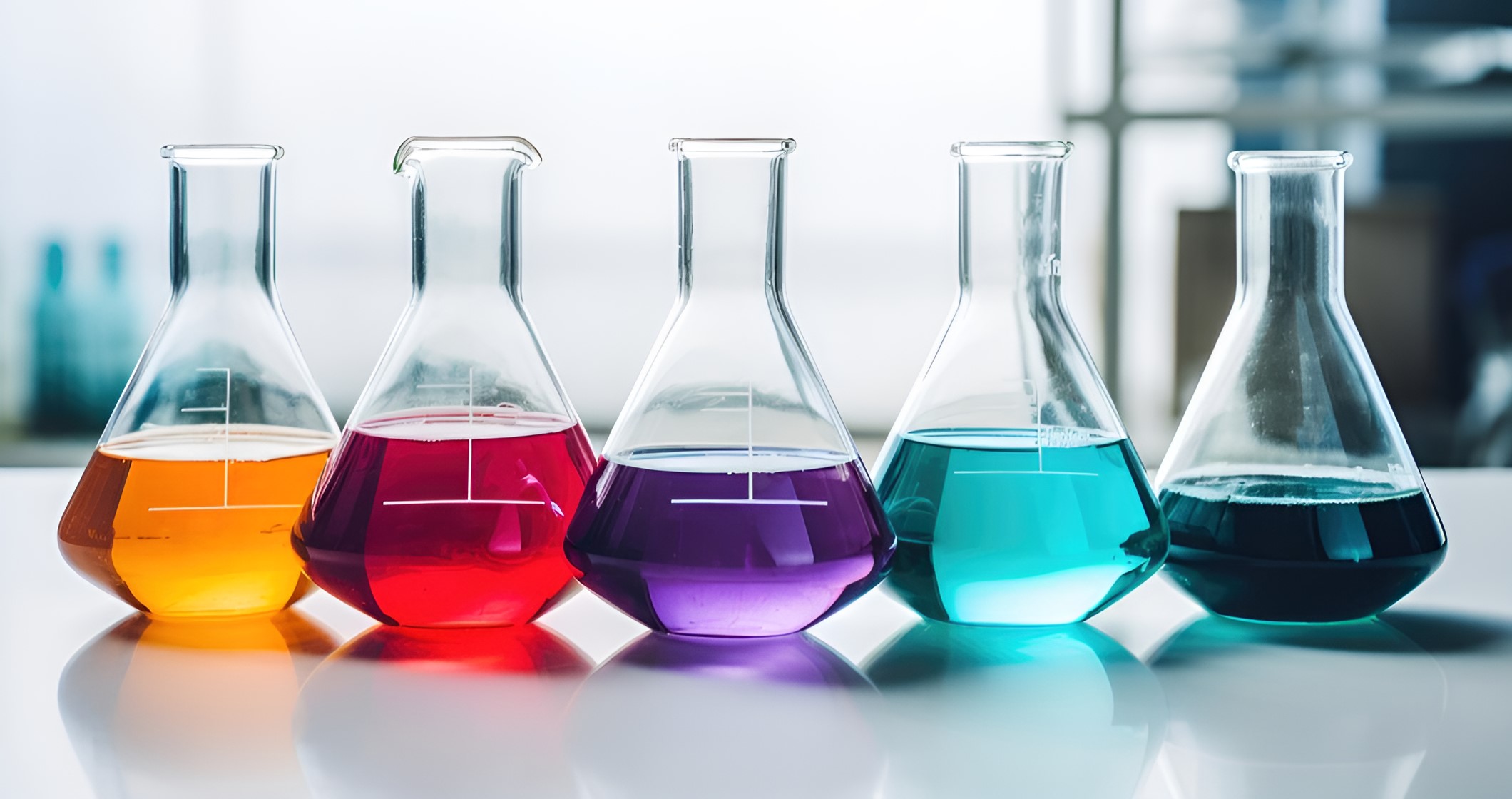
Reagents
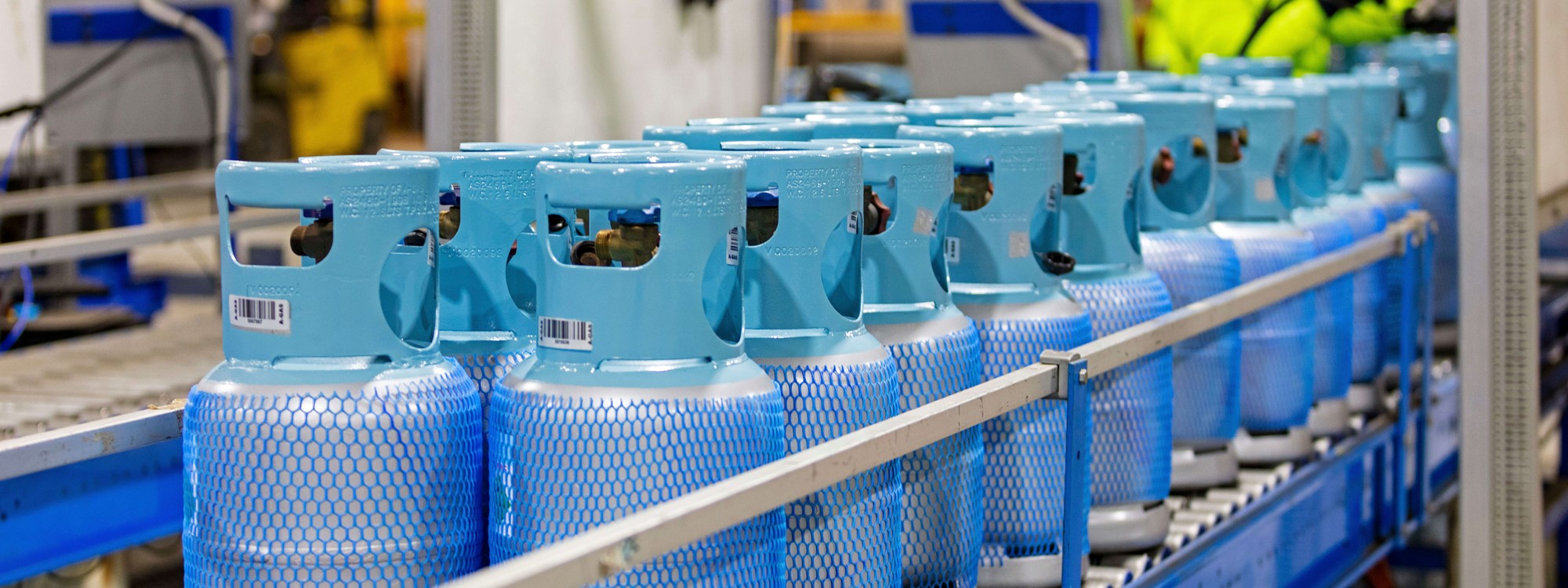
Refrigerants
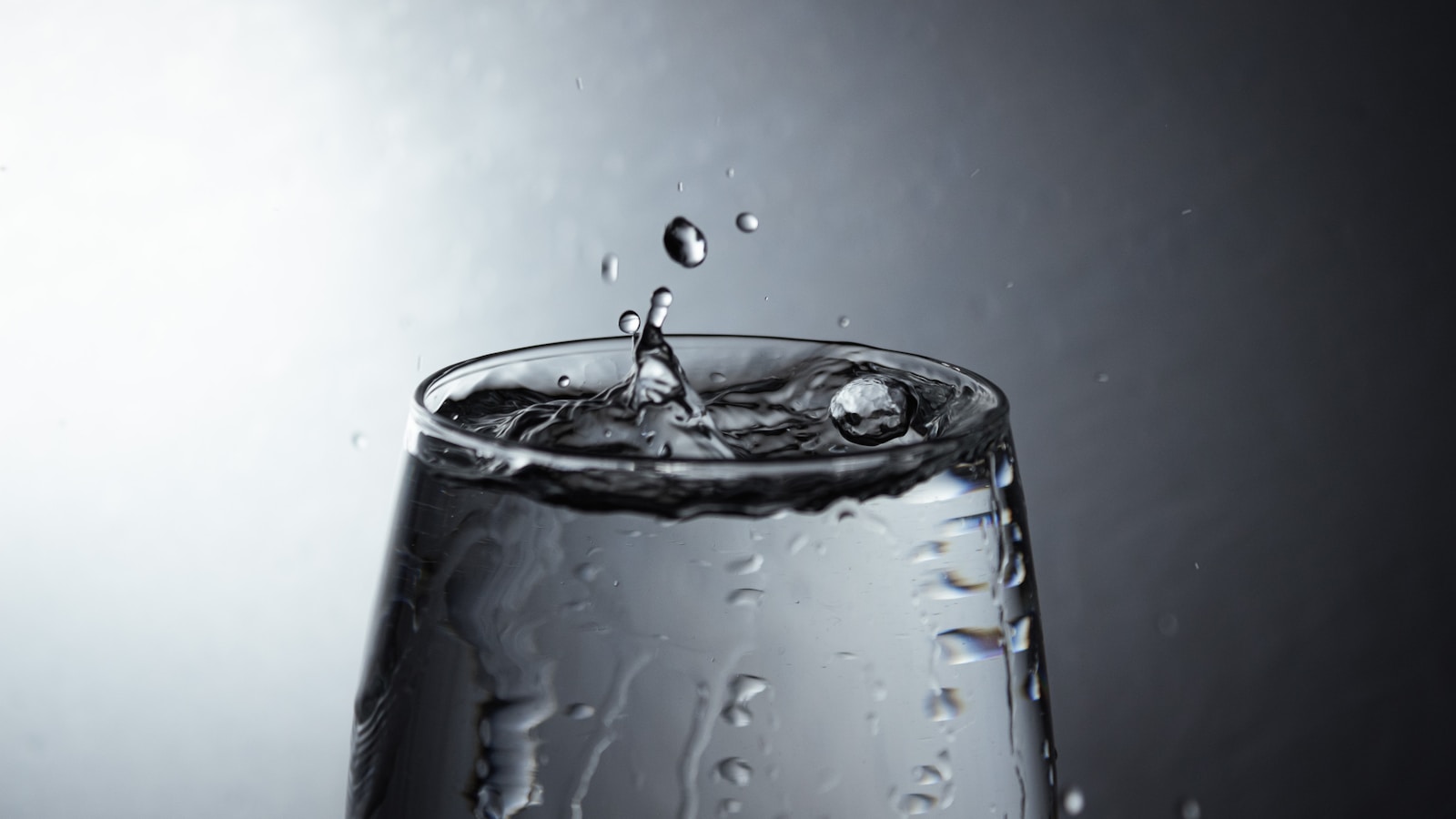
Rehydration solutions
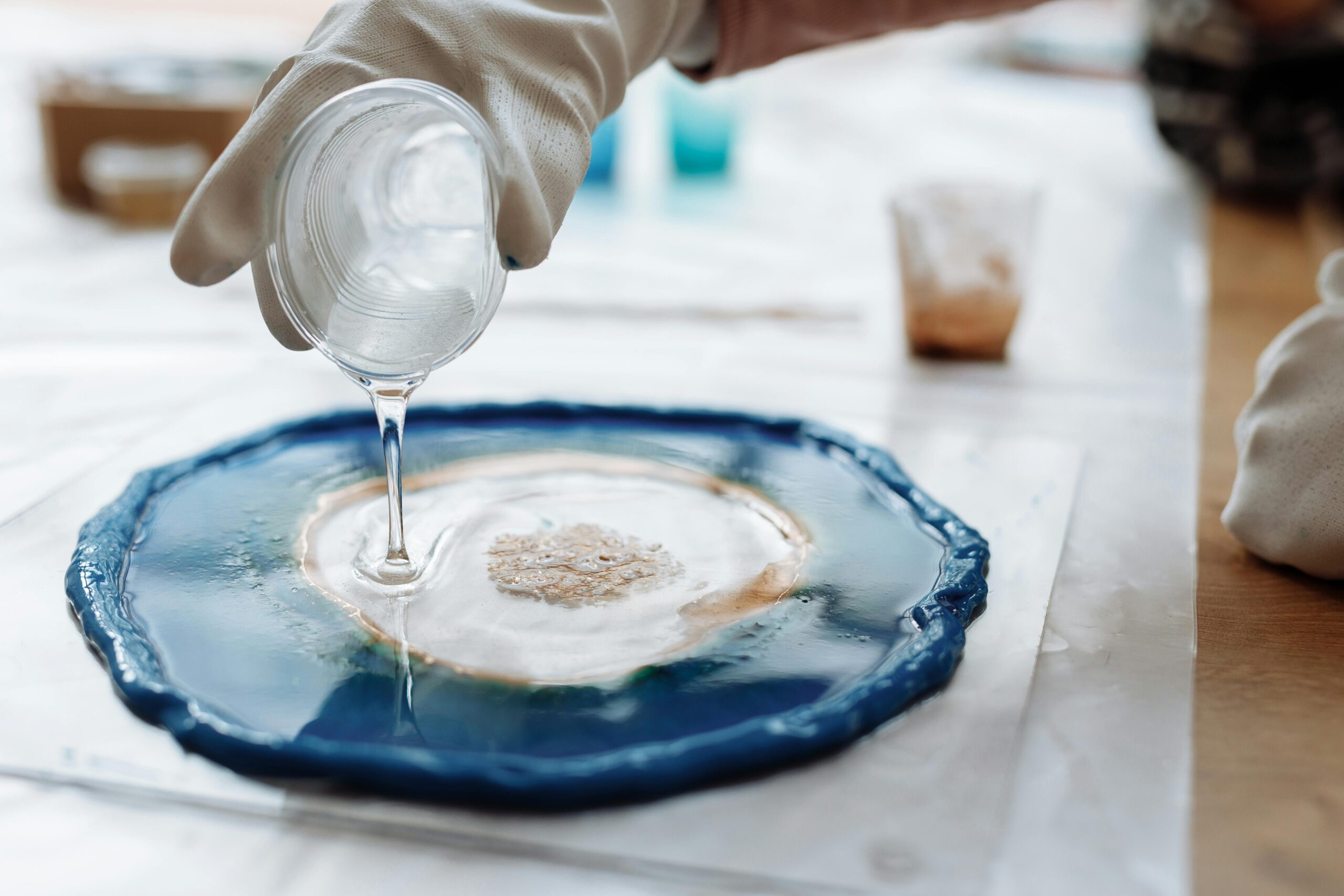
Resin
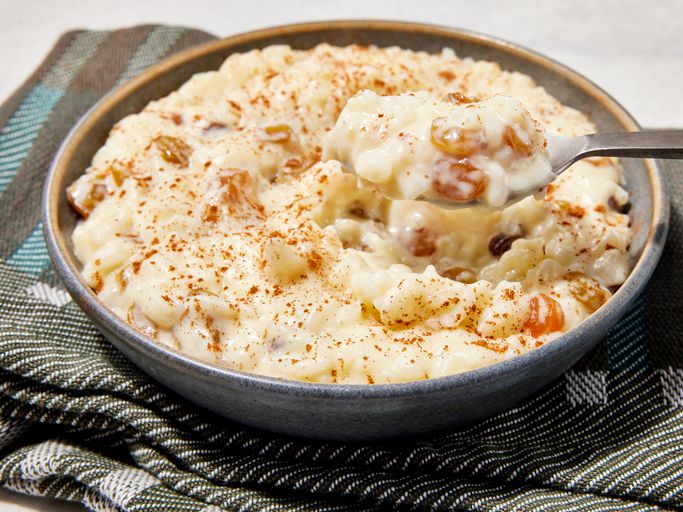
Rice pudding
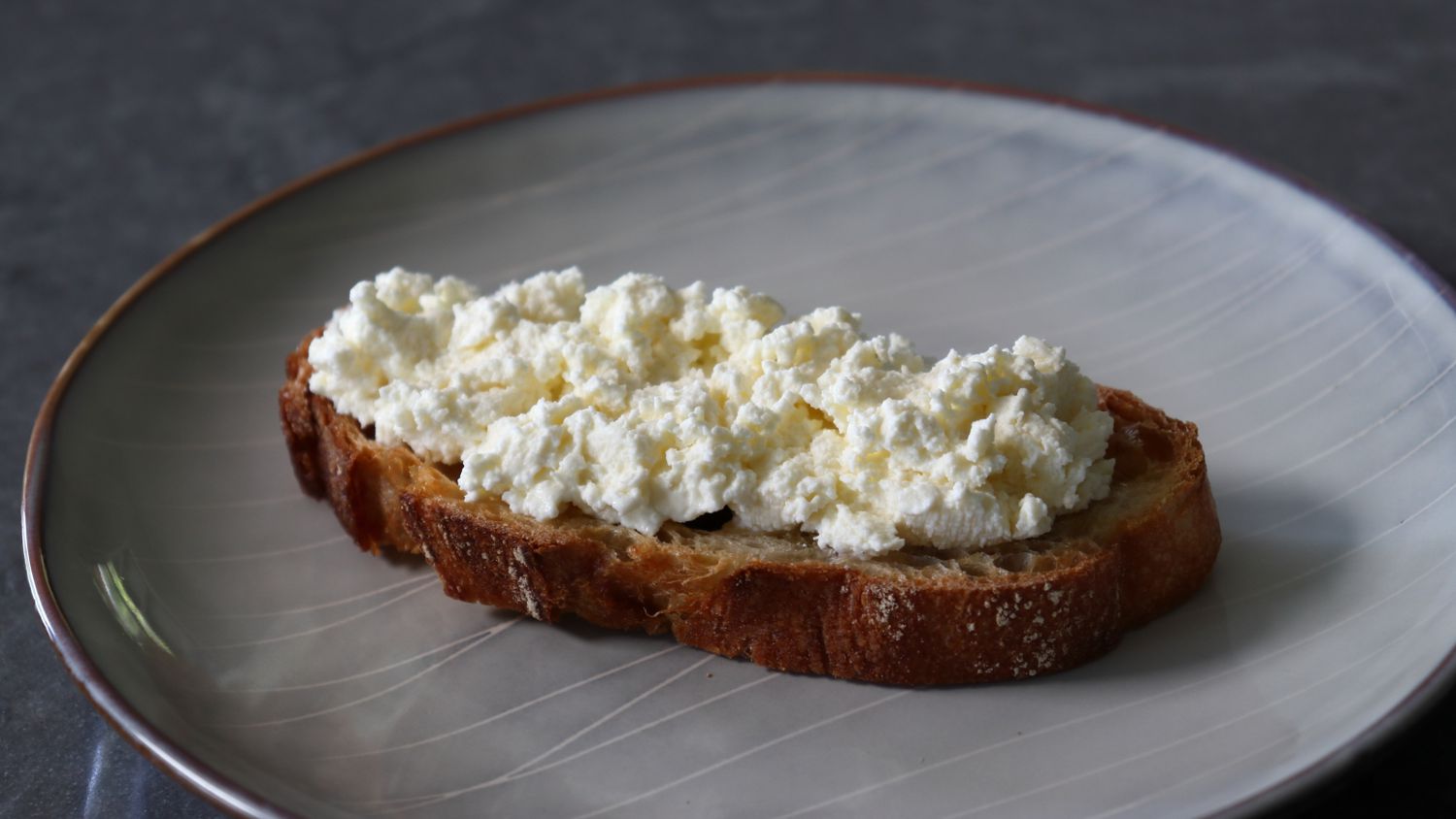
Ricotta
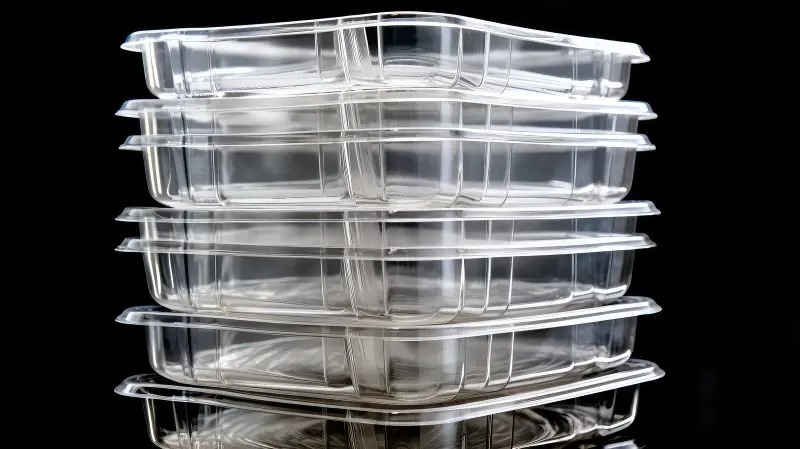
Rigid containers
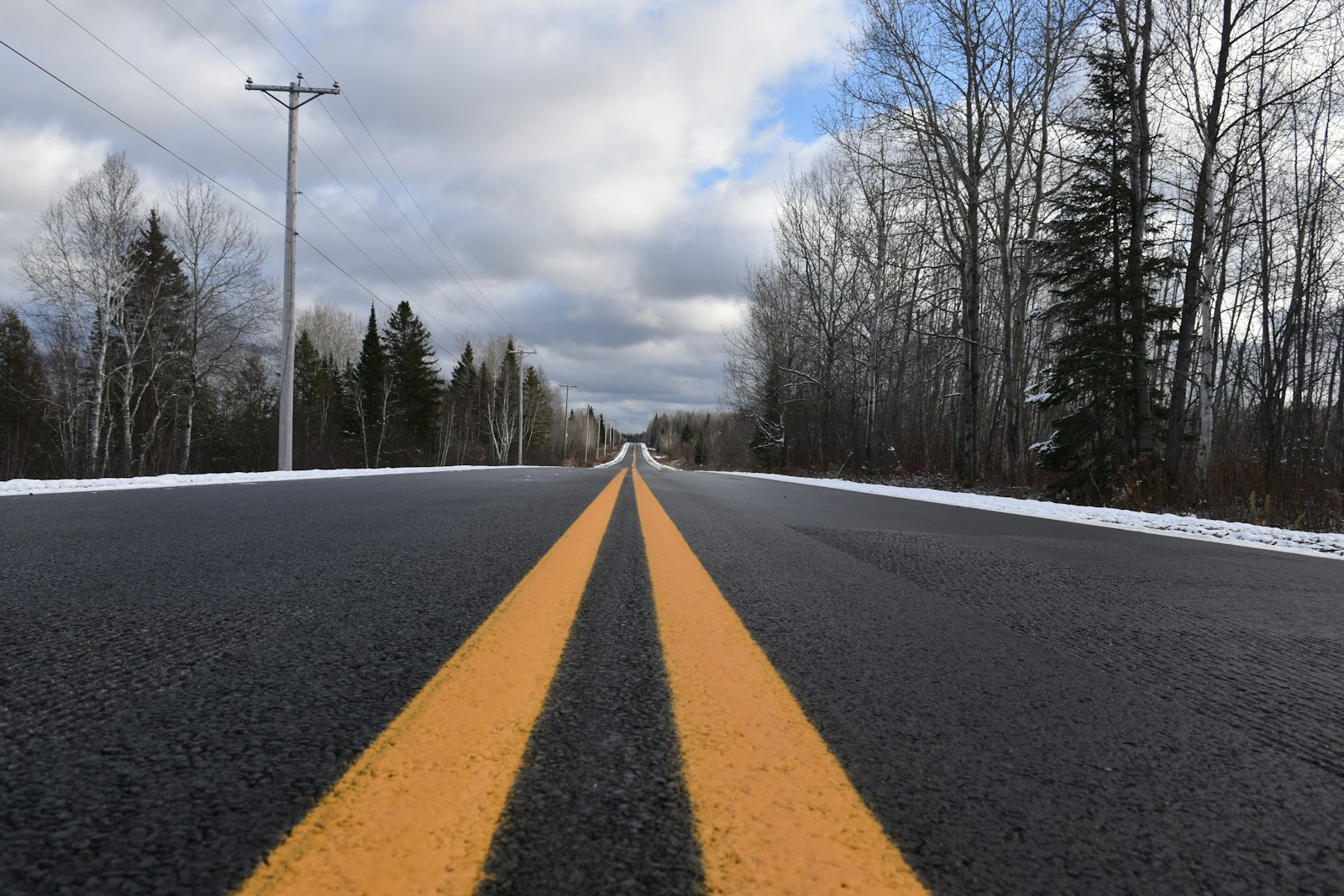
Road marking paints
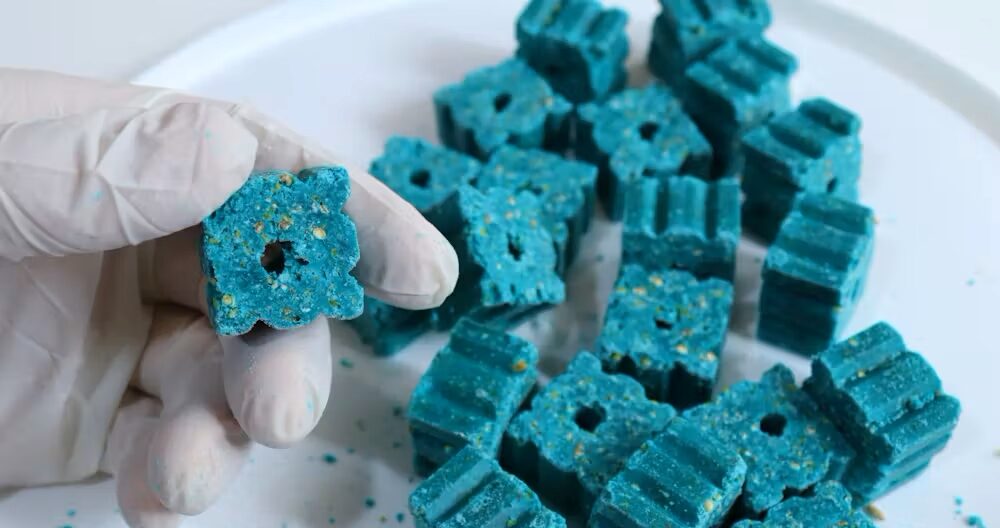
Rodenticides
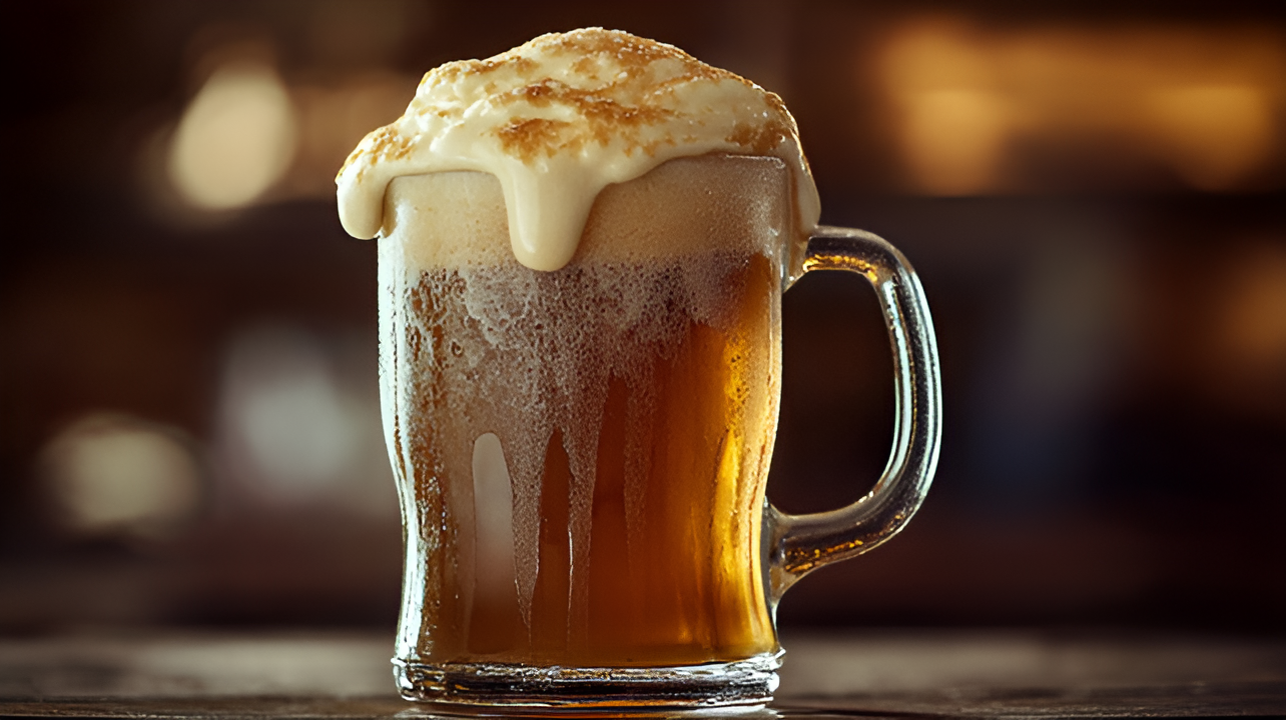
Root beer
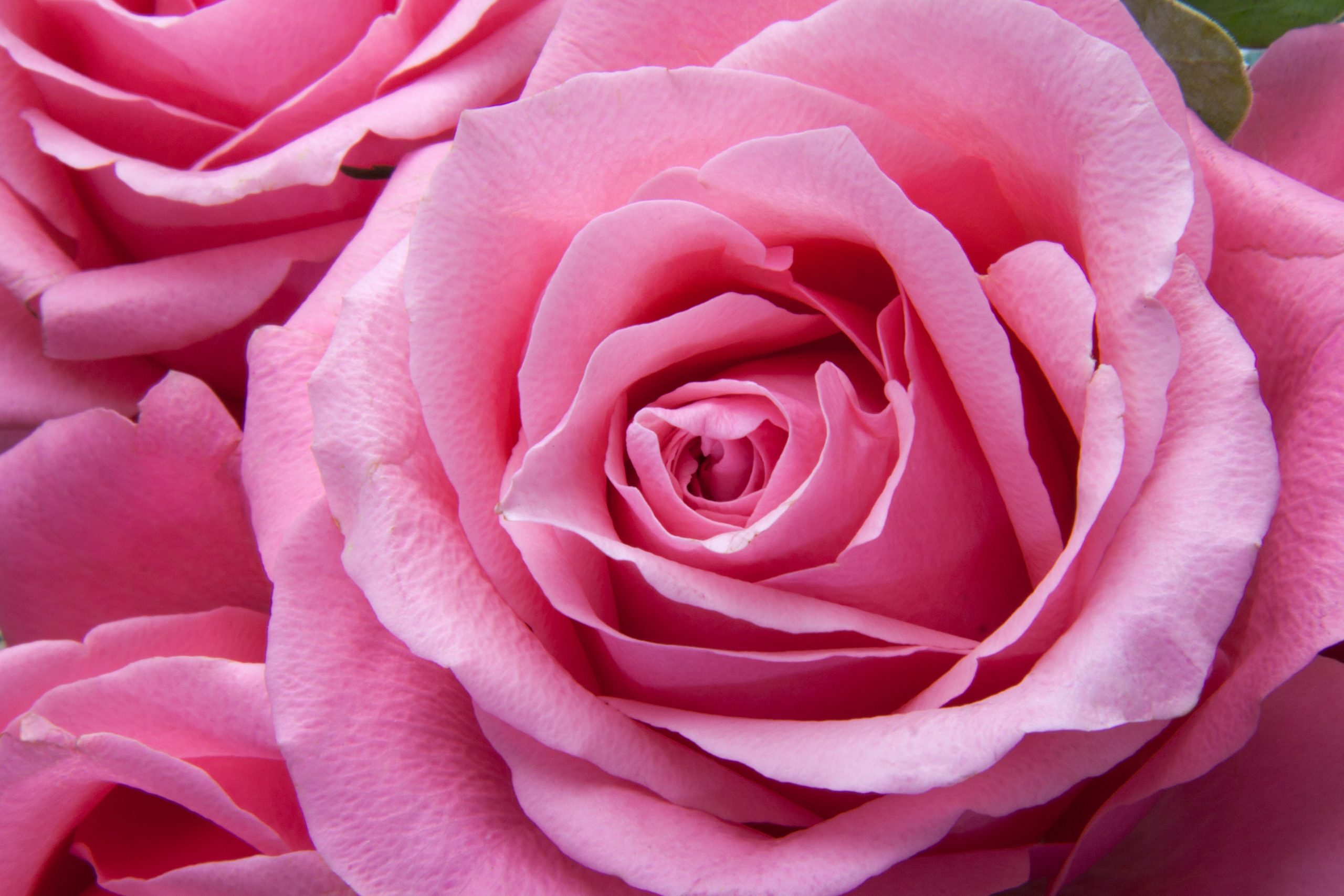
Rose oil
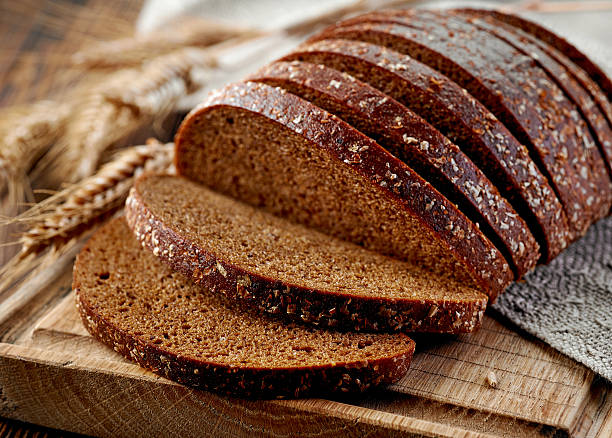
Rye bread
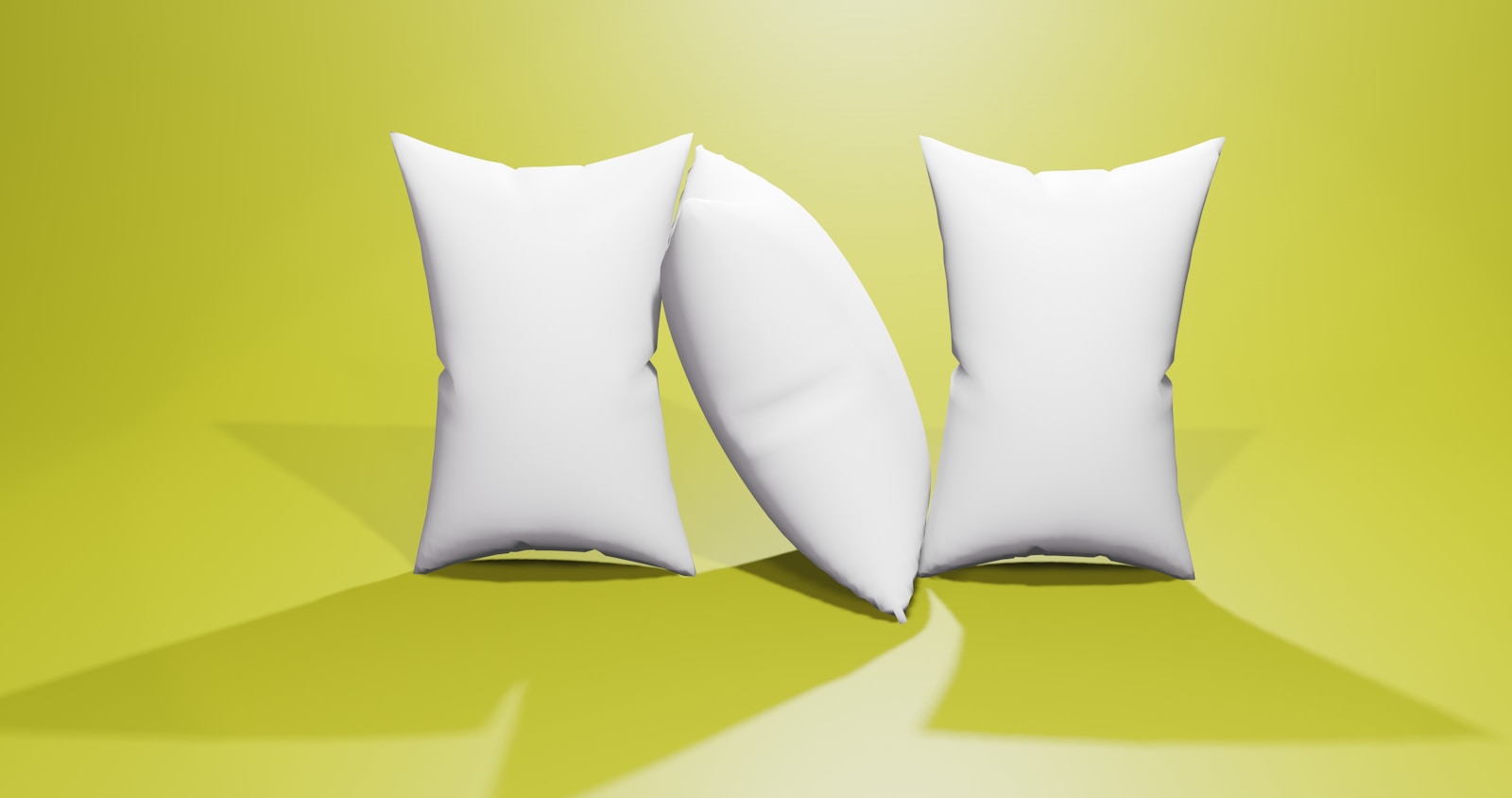
Sachets
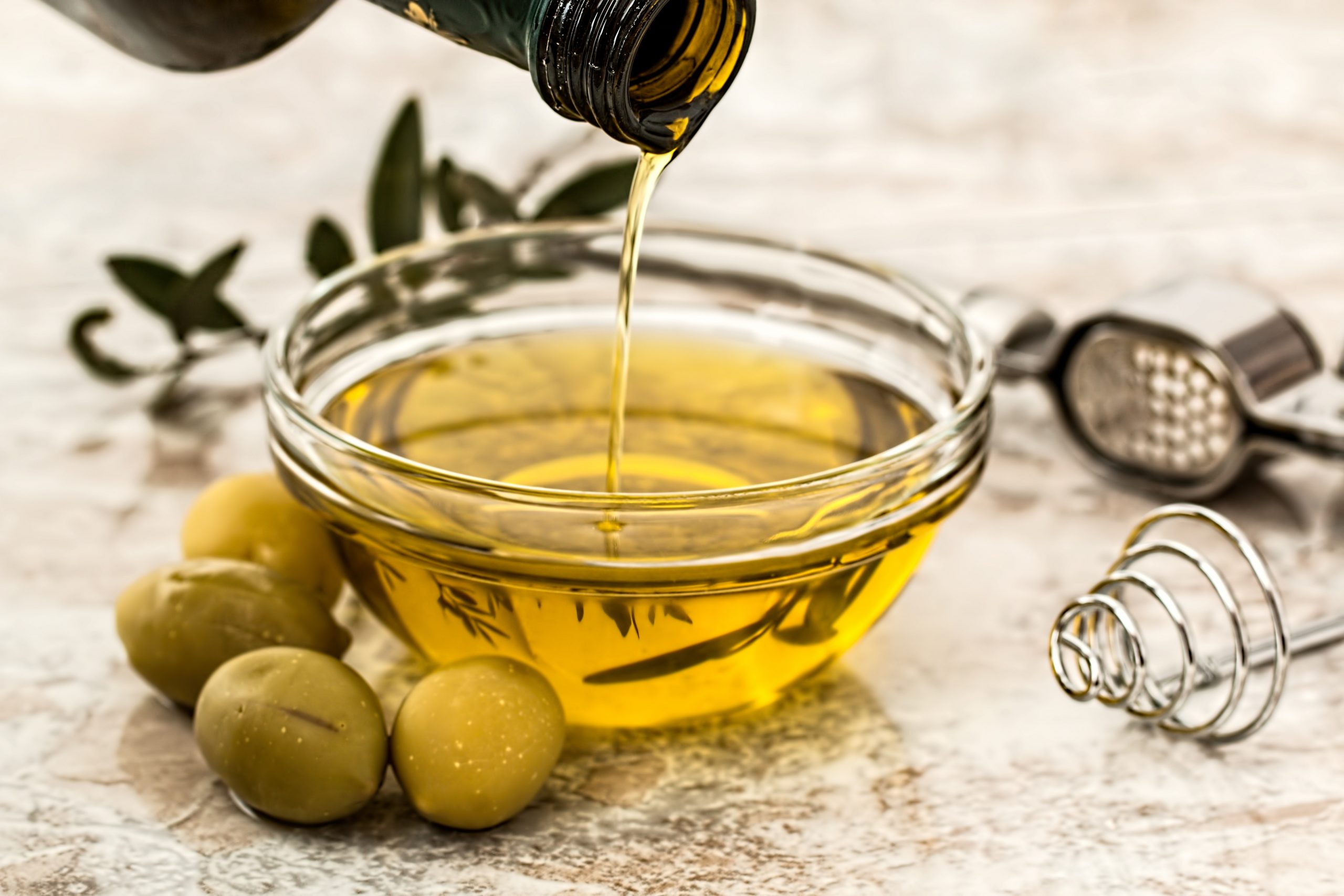
Salad dressing
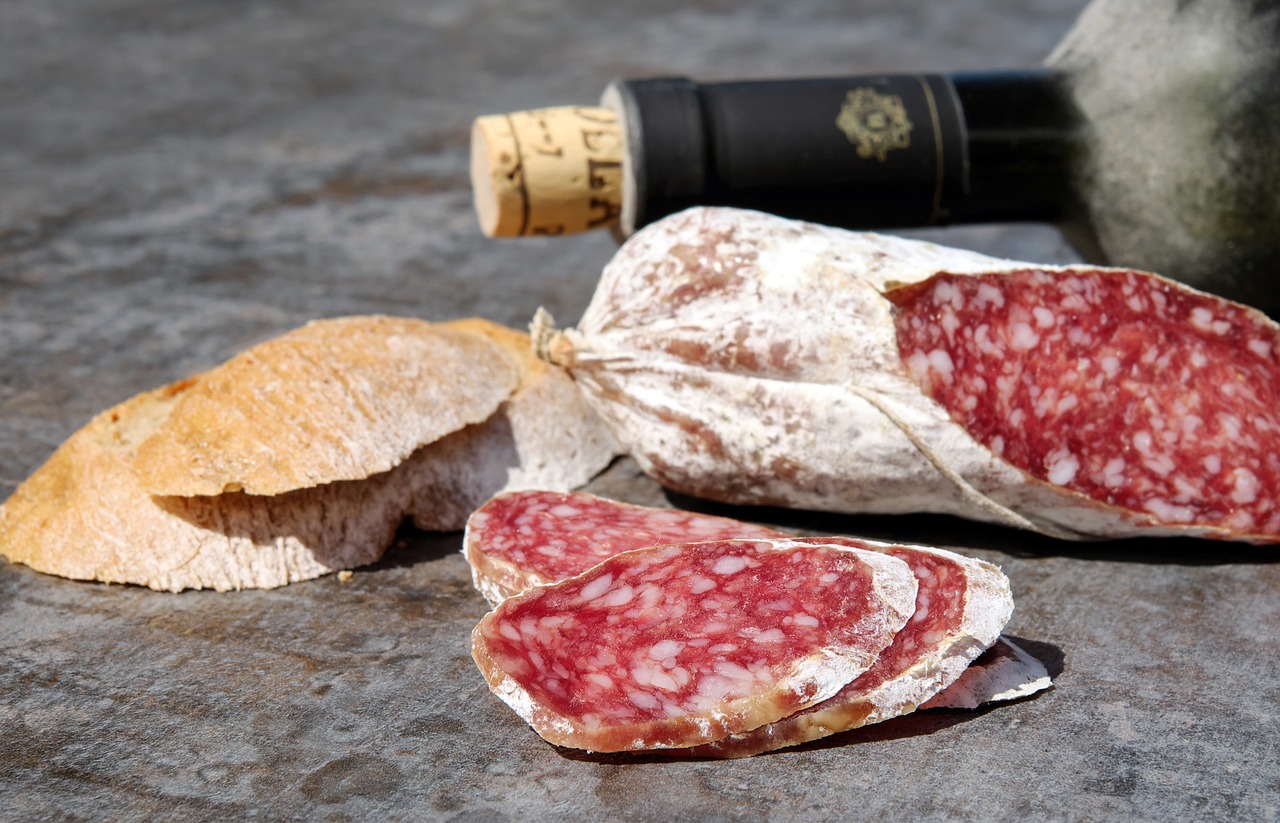
Salami
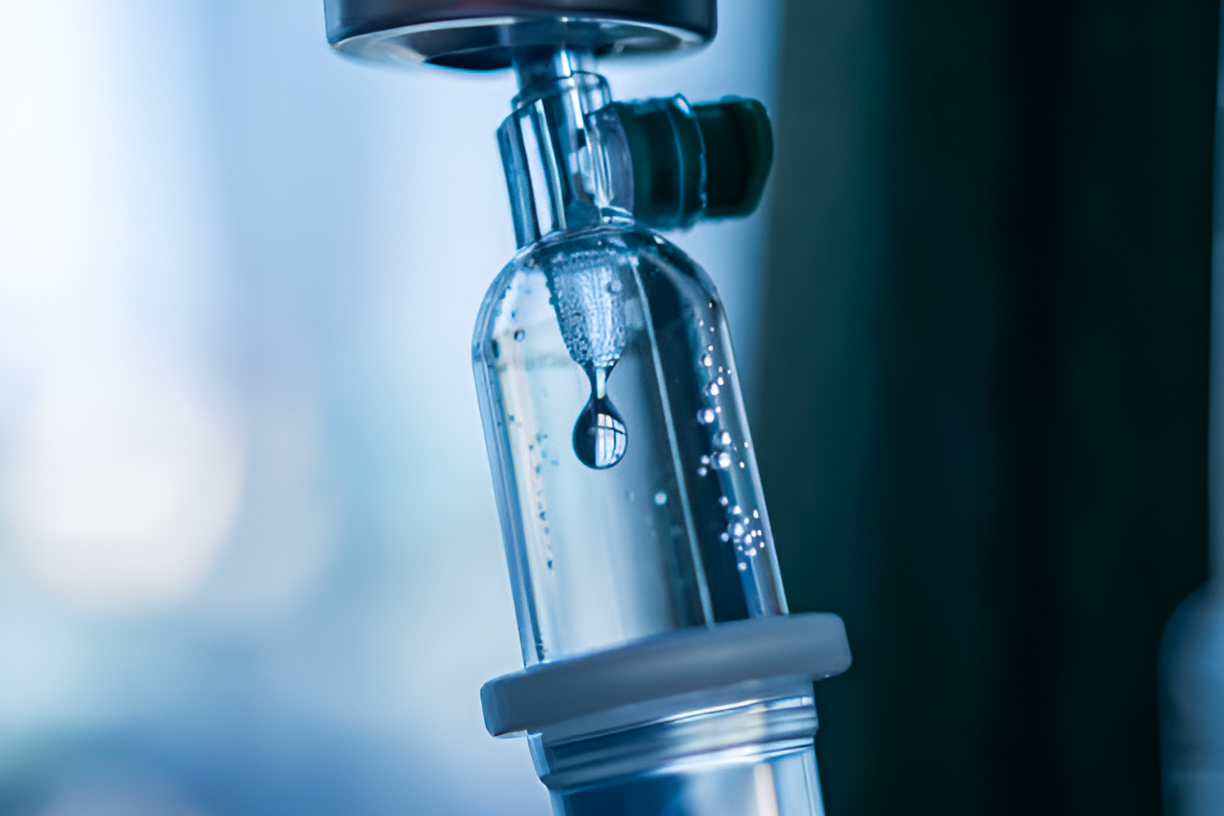
Saline solutions
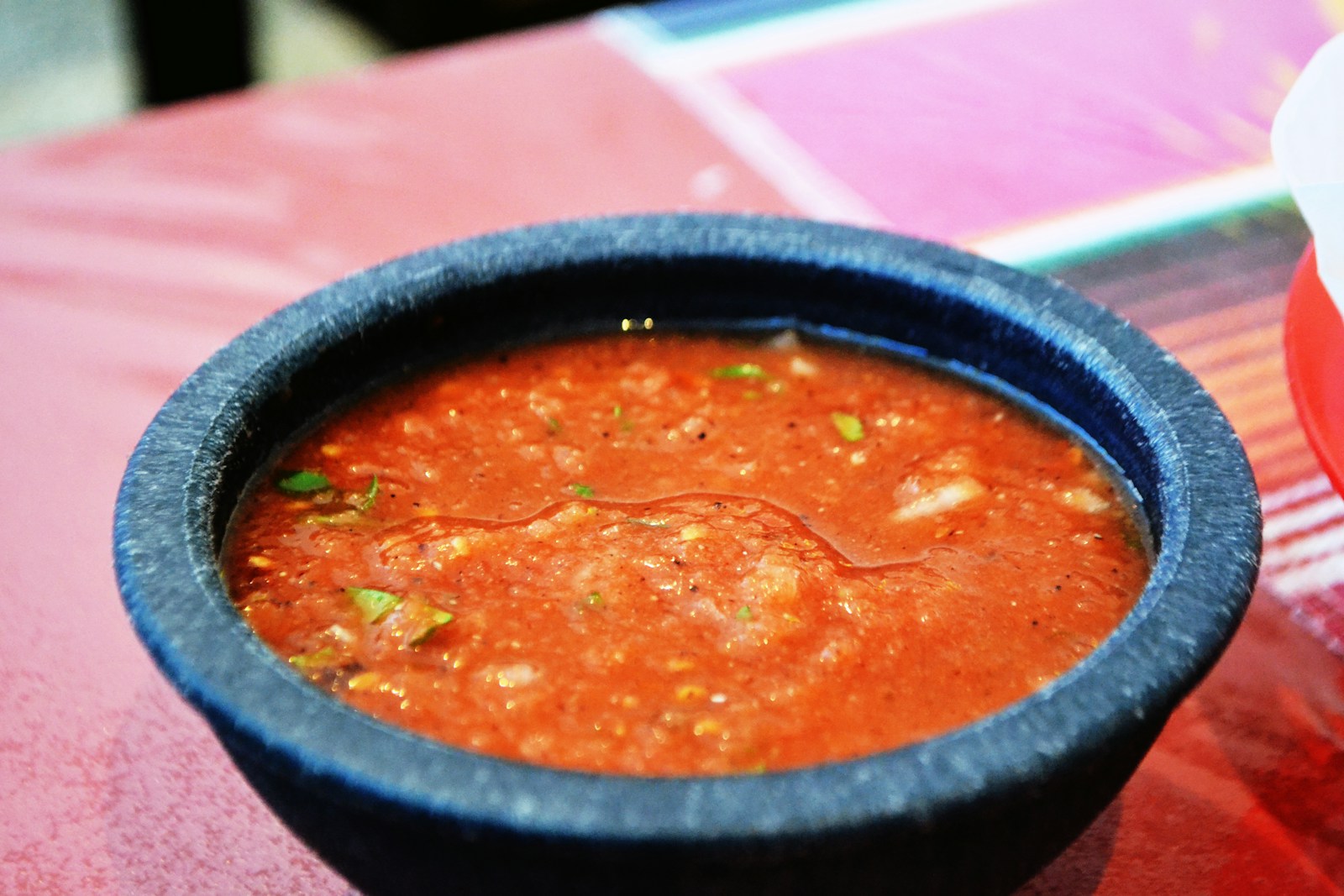
Salsa
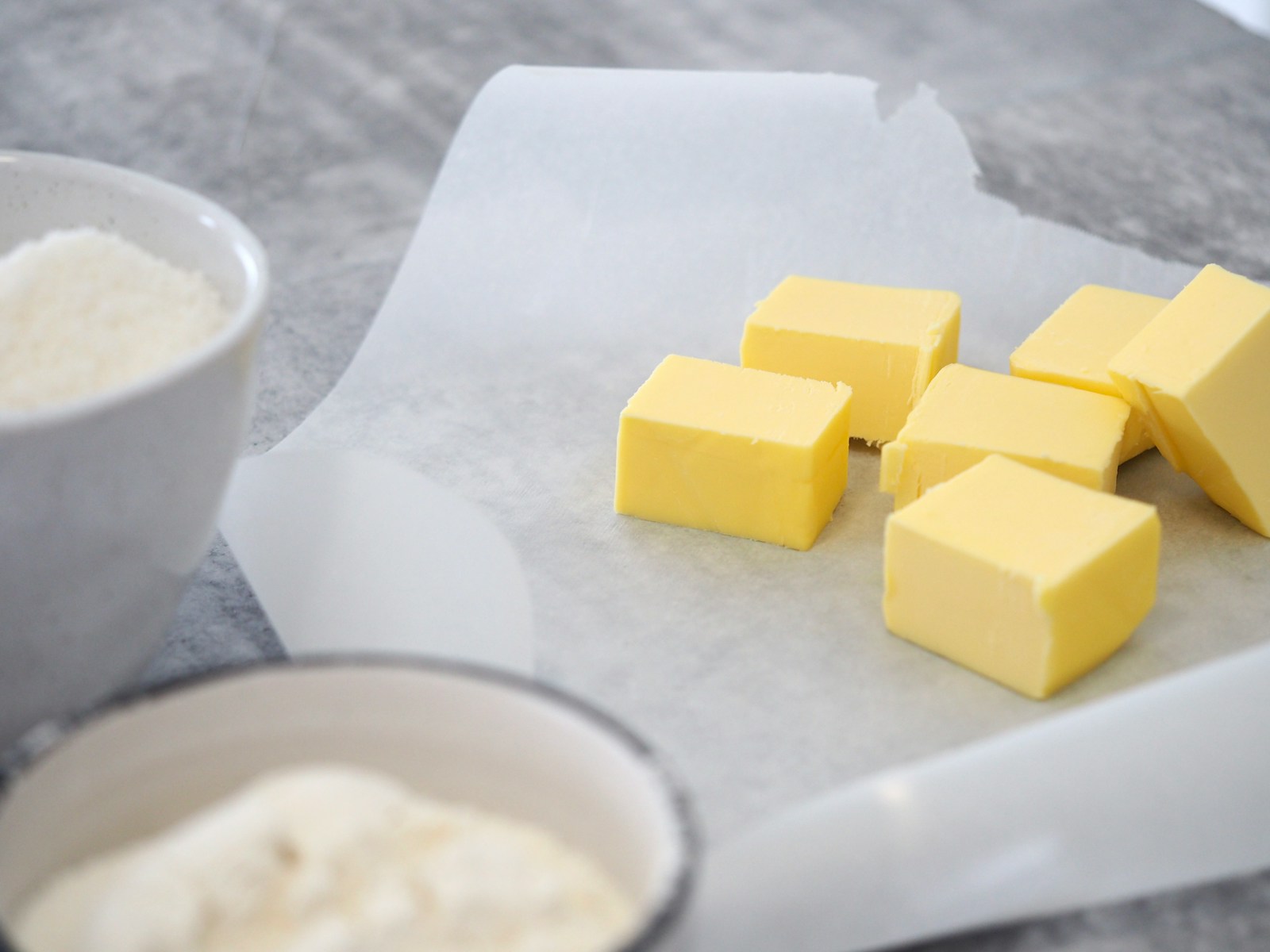
Salted butter
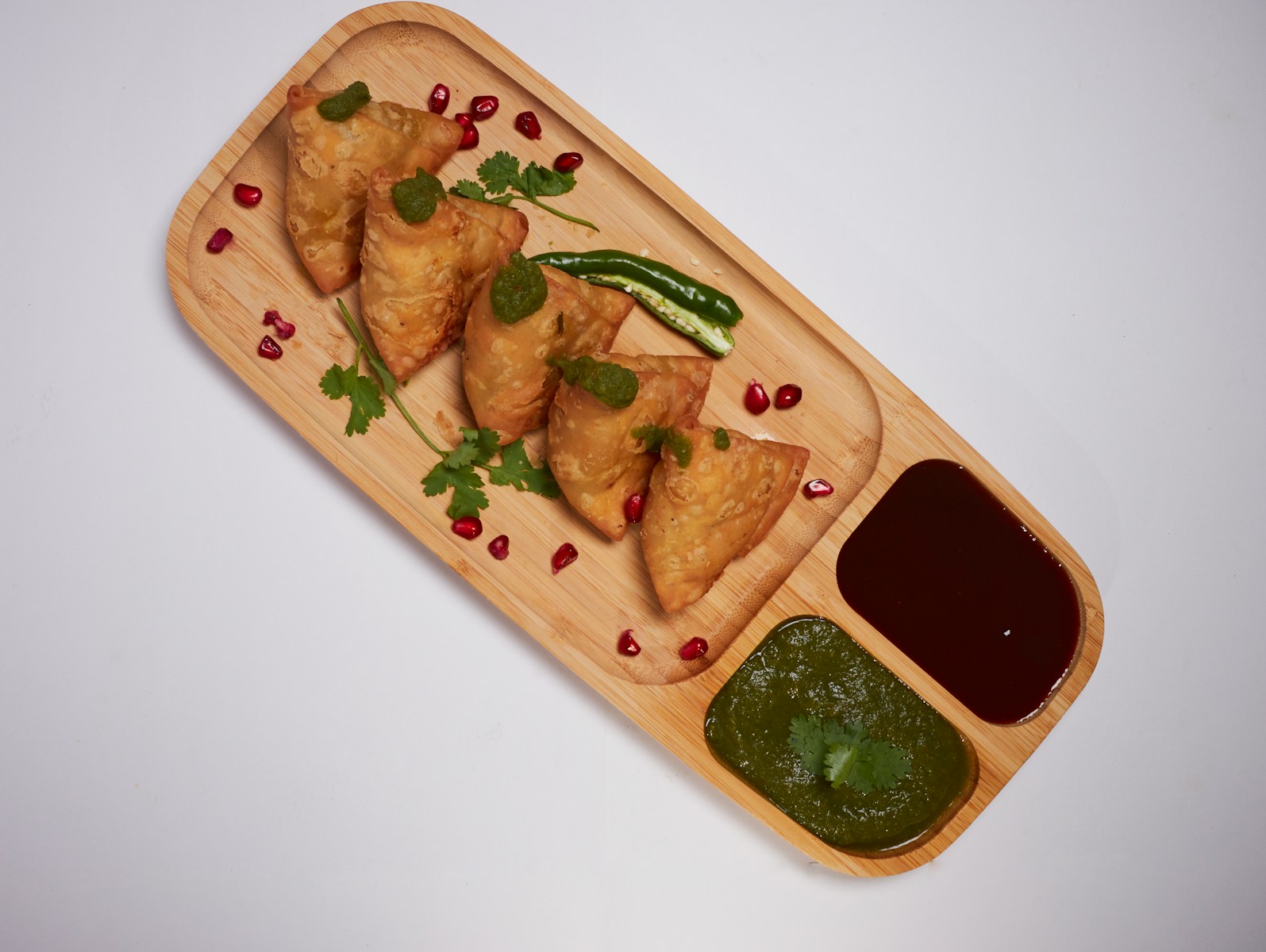
Samosas
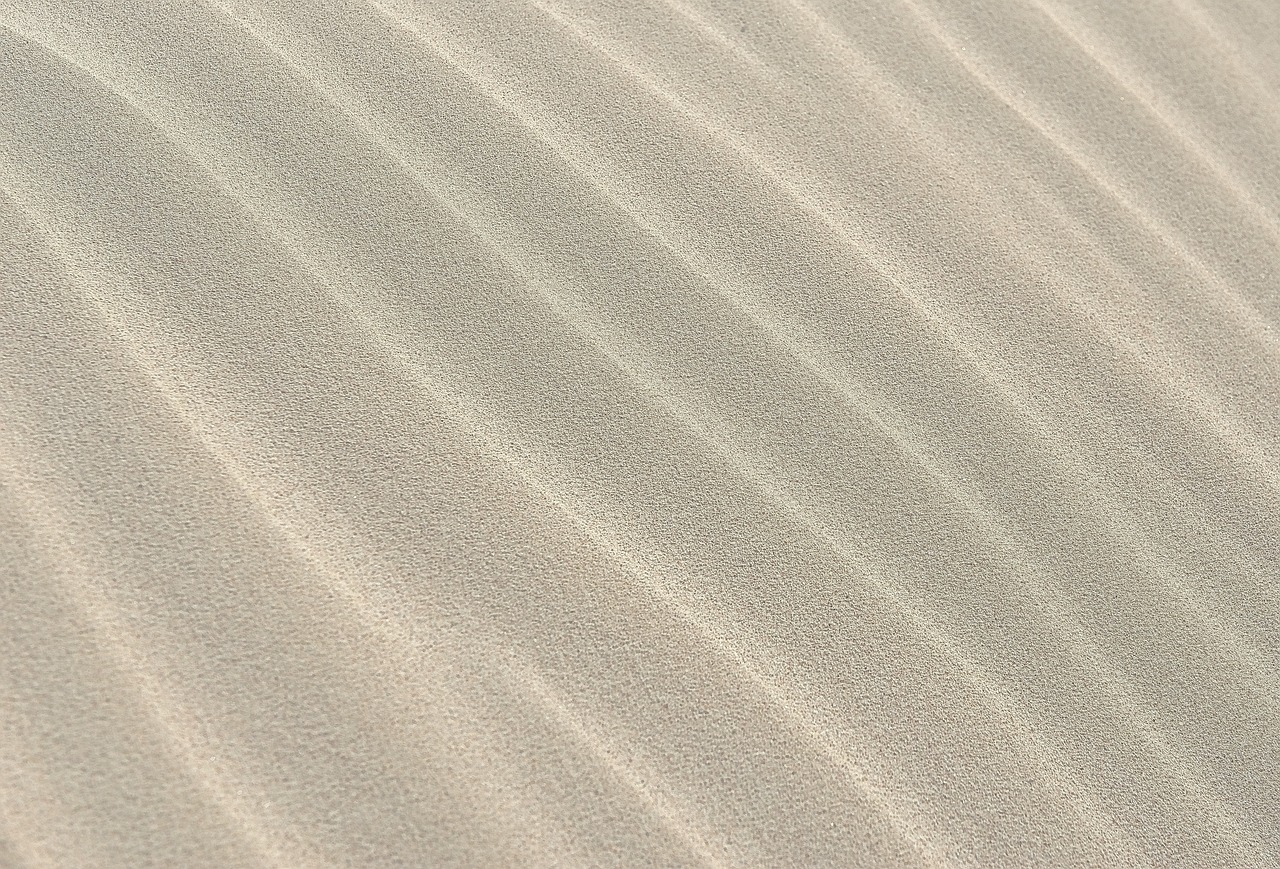
Sand
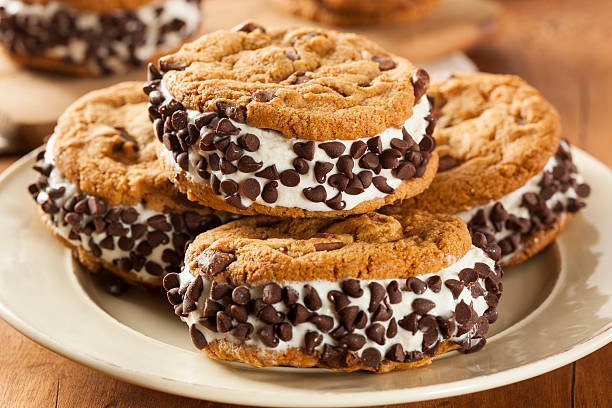
Sandwich cookies
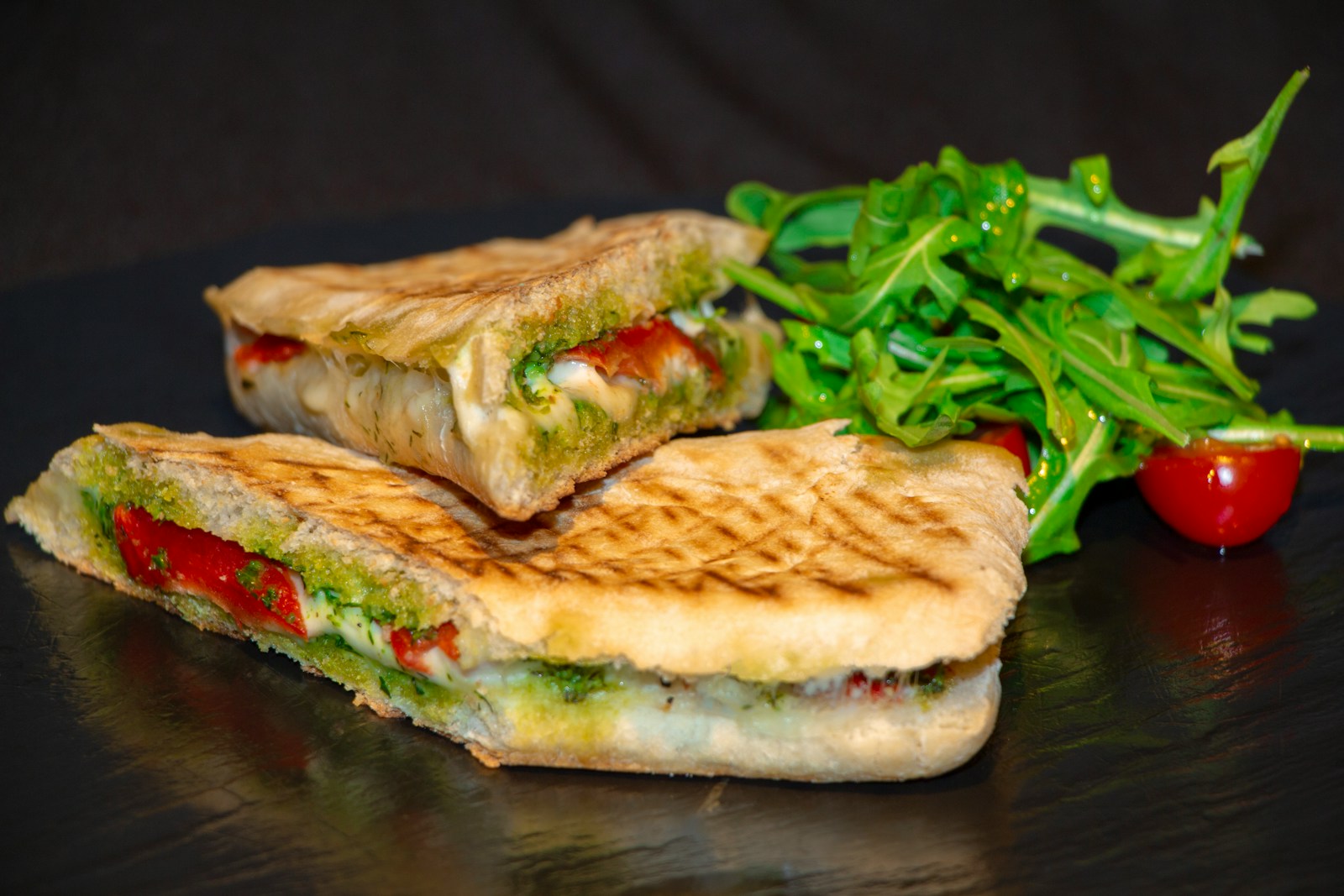
Sandwiches
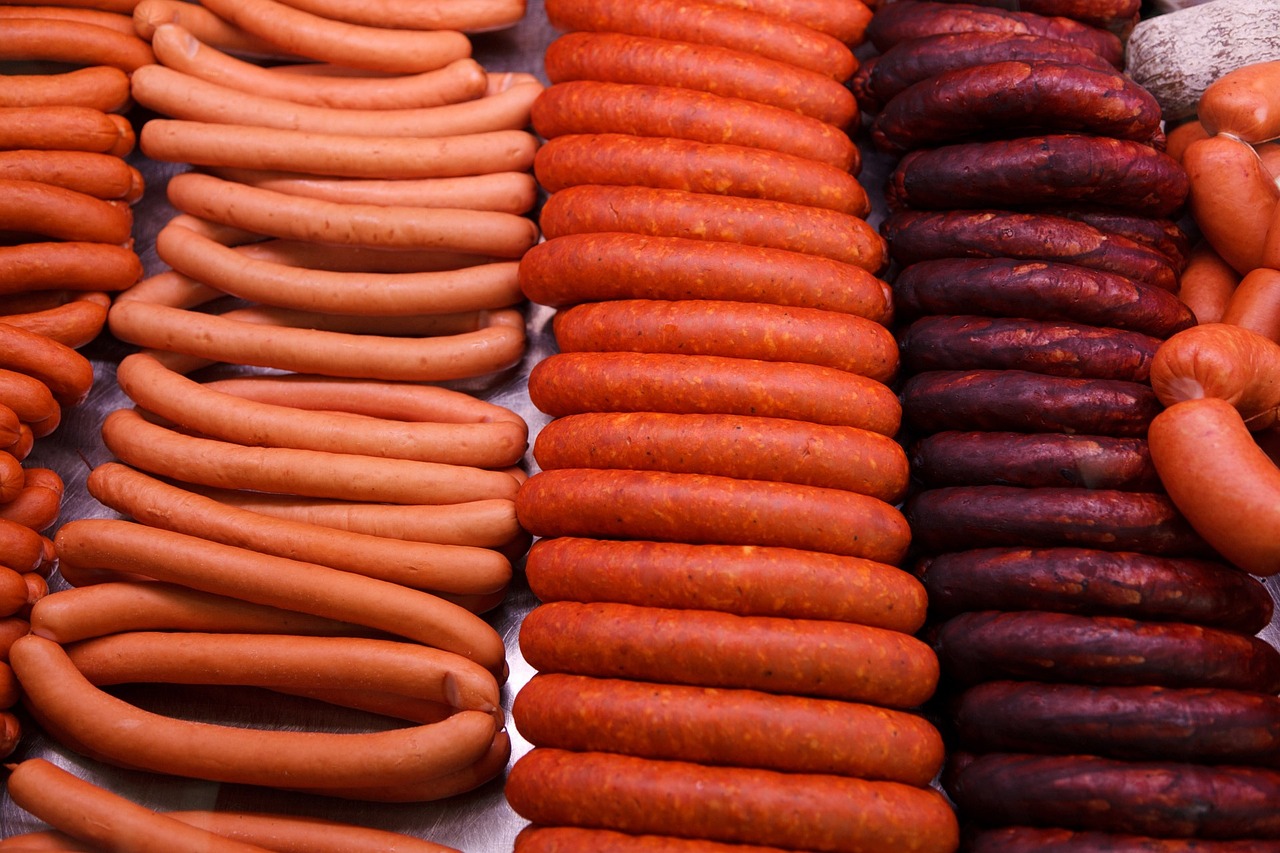
Sausages
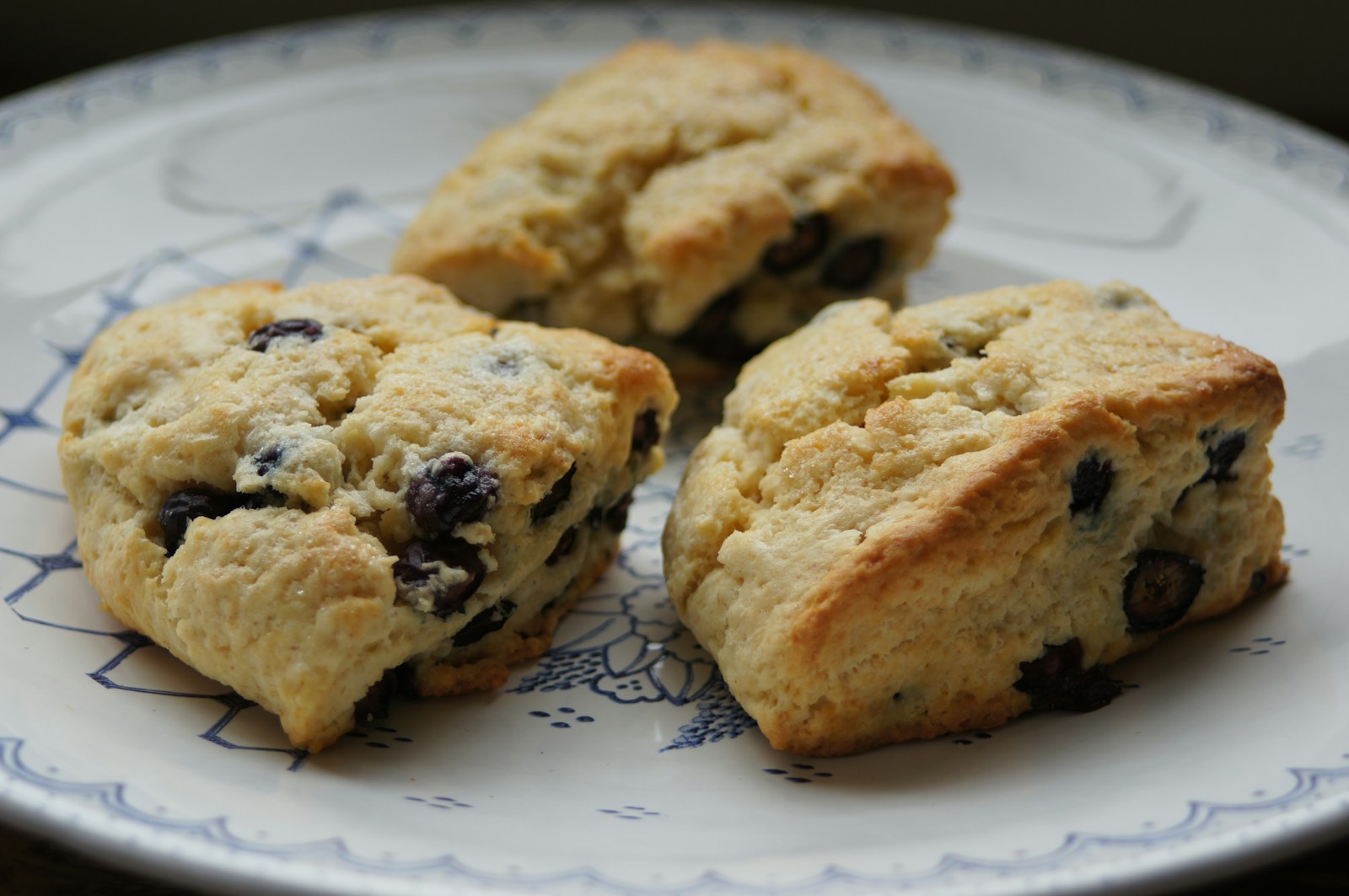
Scones
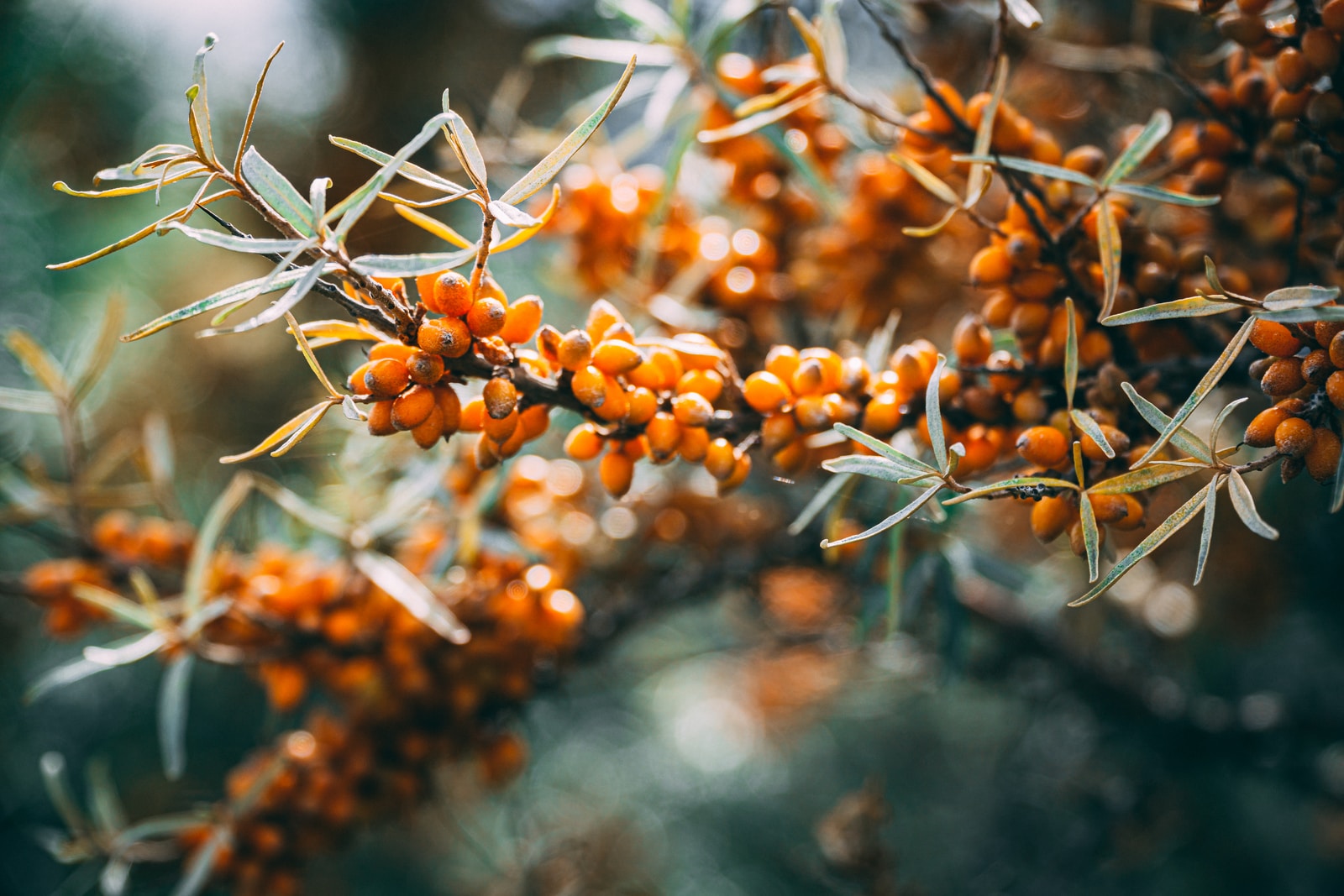
Sea buckthorn oil
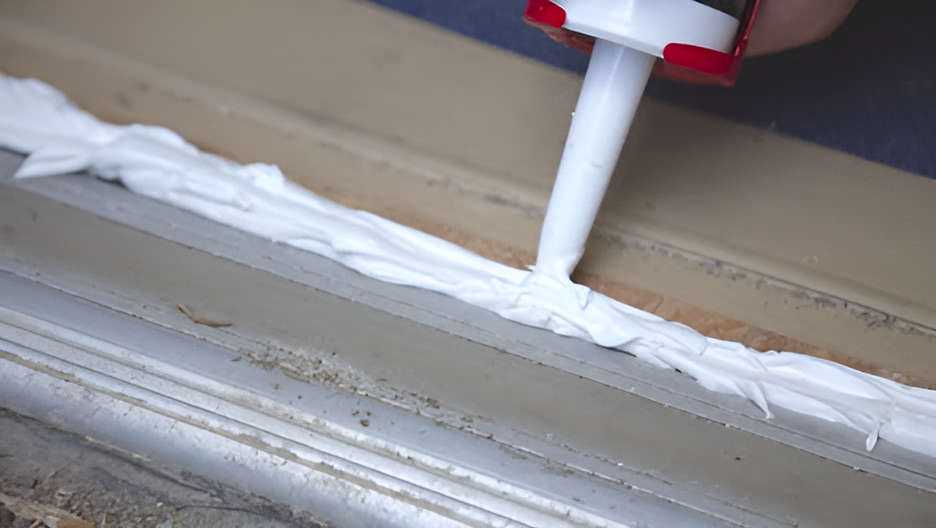
Sealants
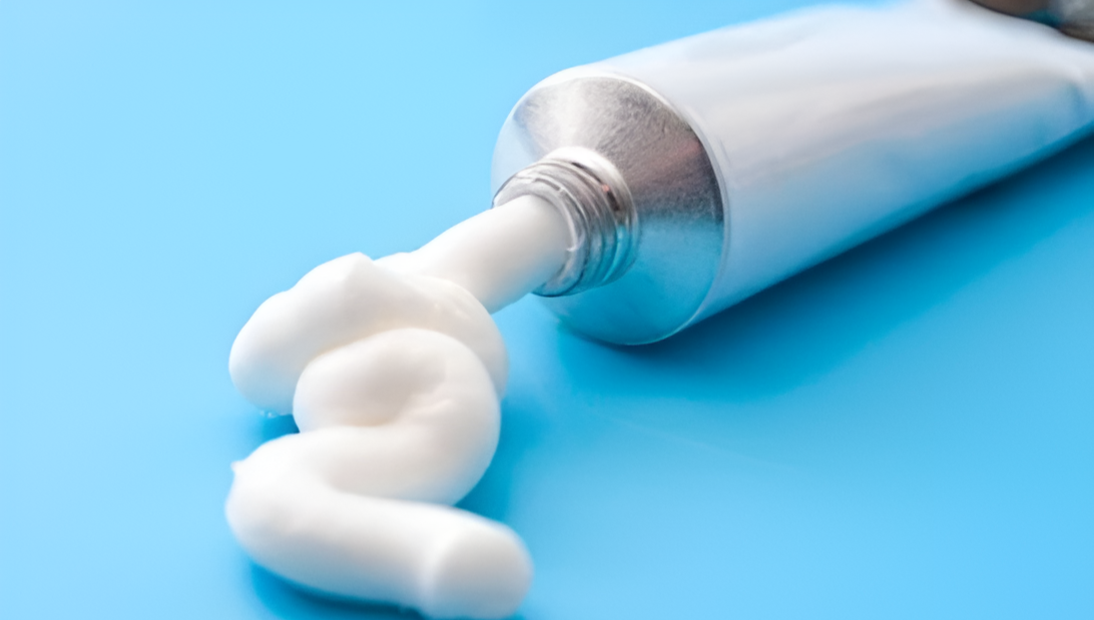
Semi-solids
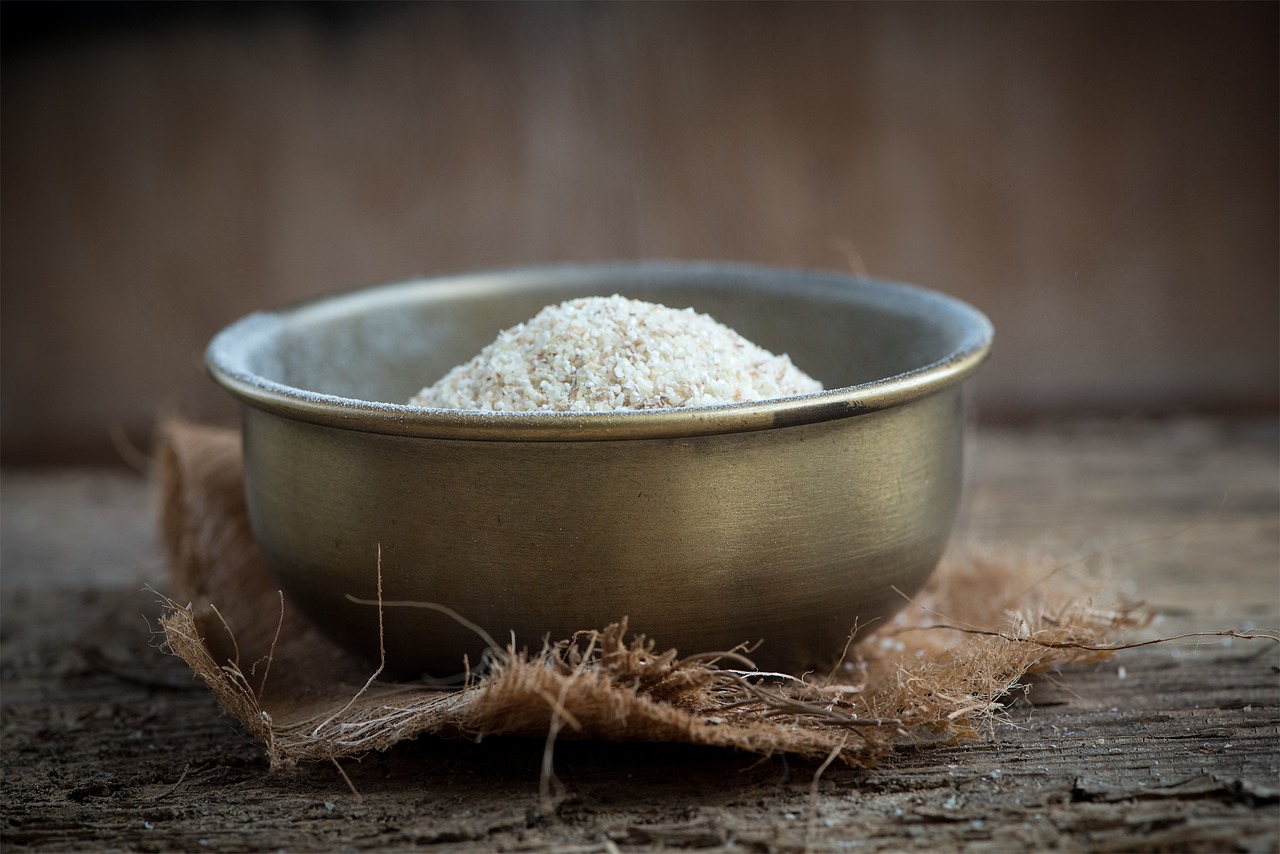
Semolina
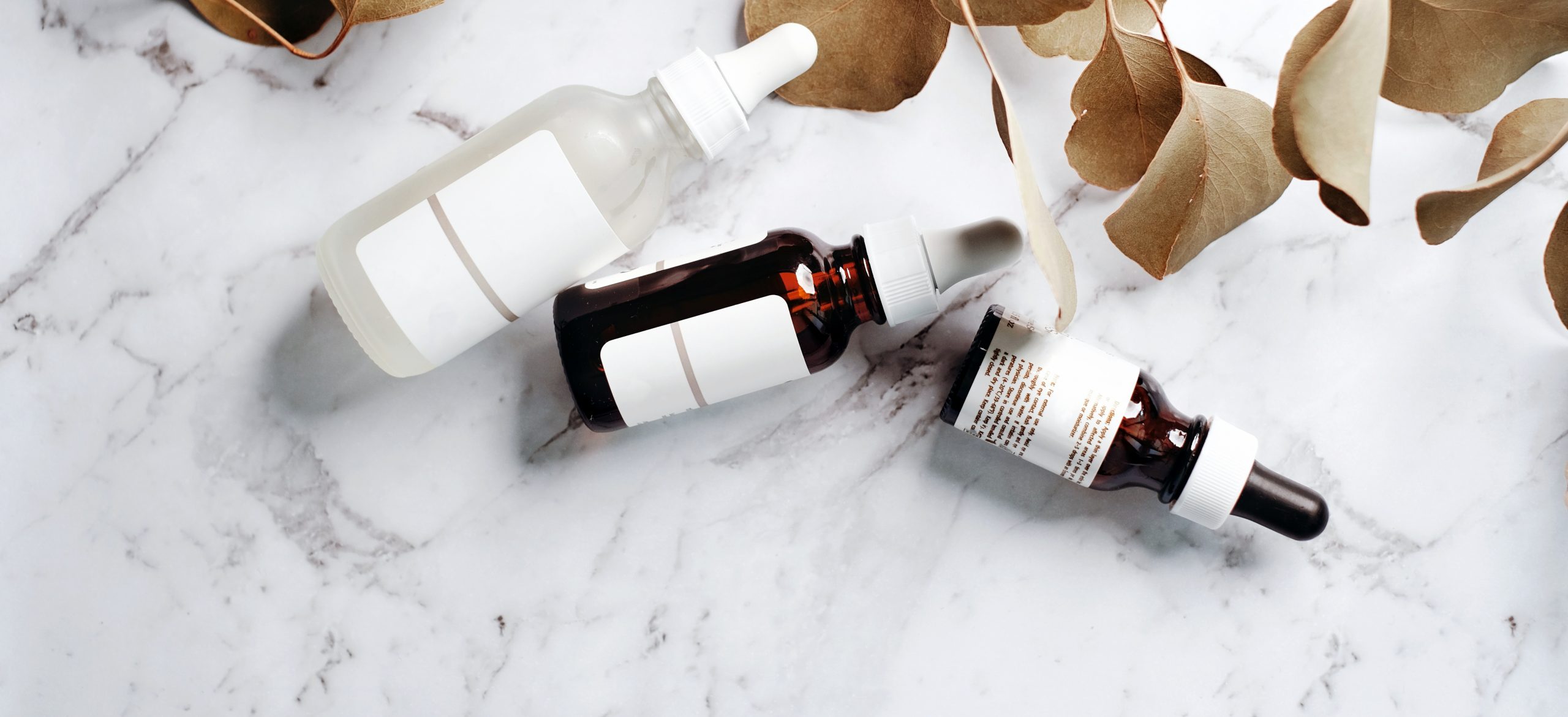
Serums
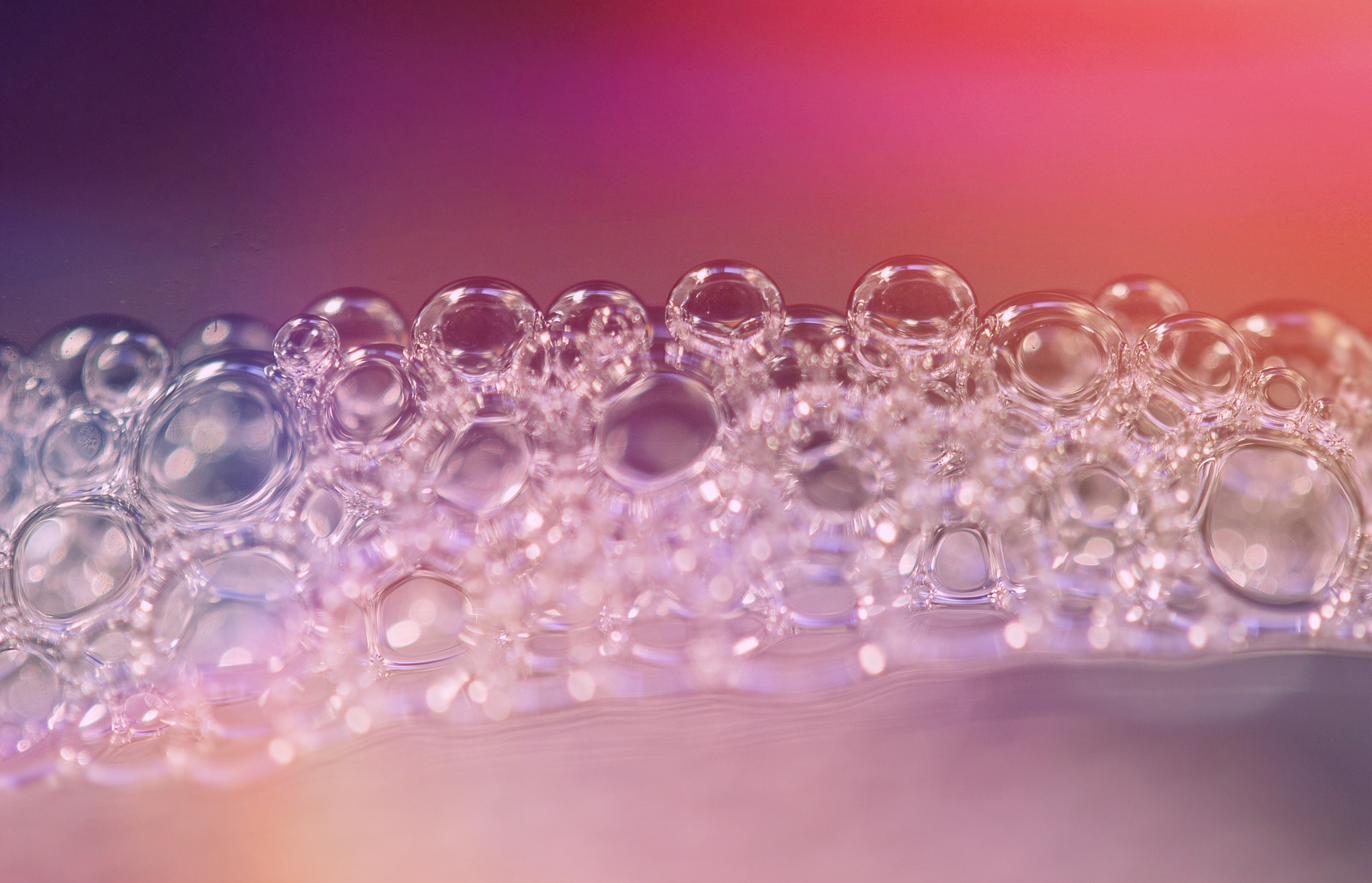
Shampoo
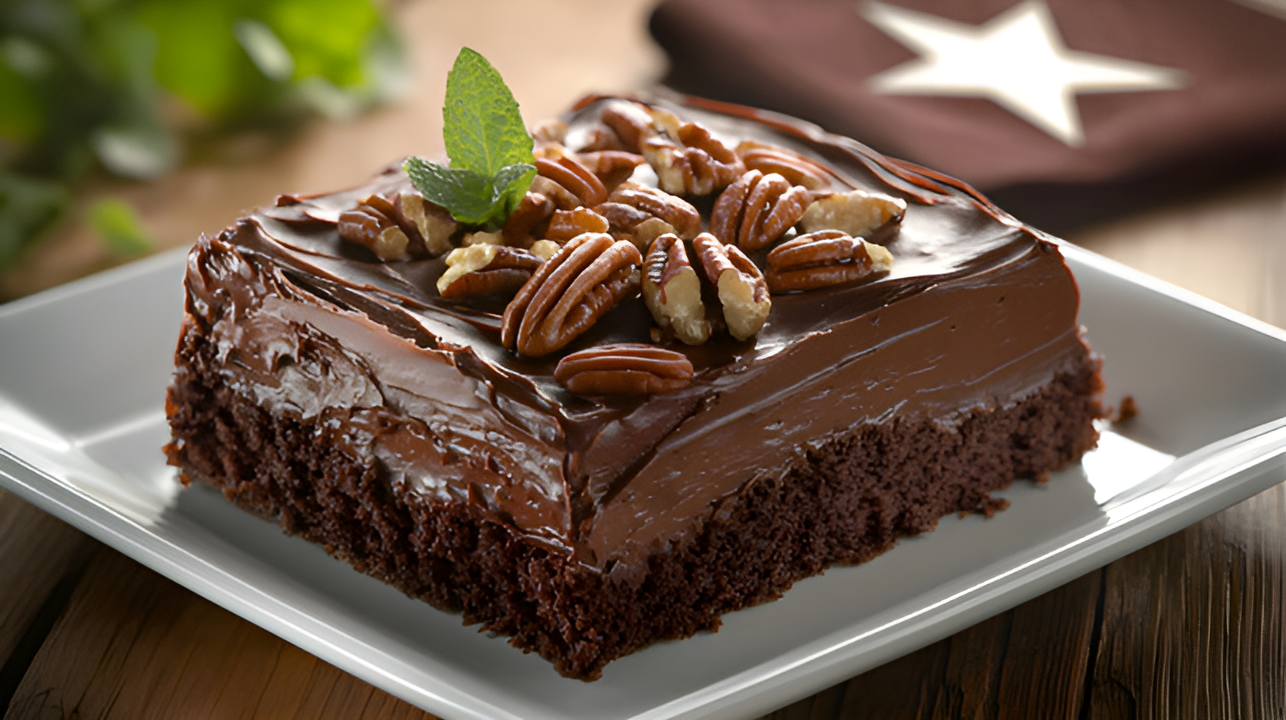
Sheet cakes
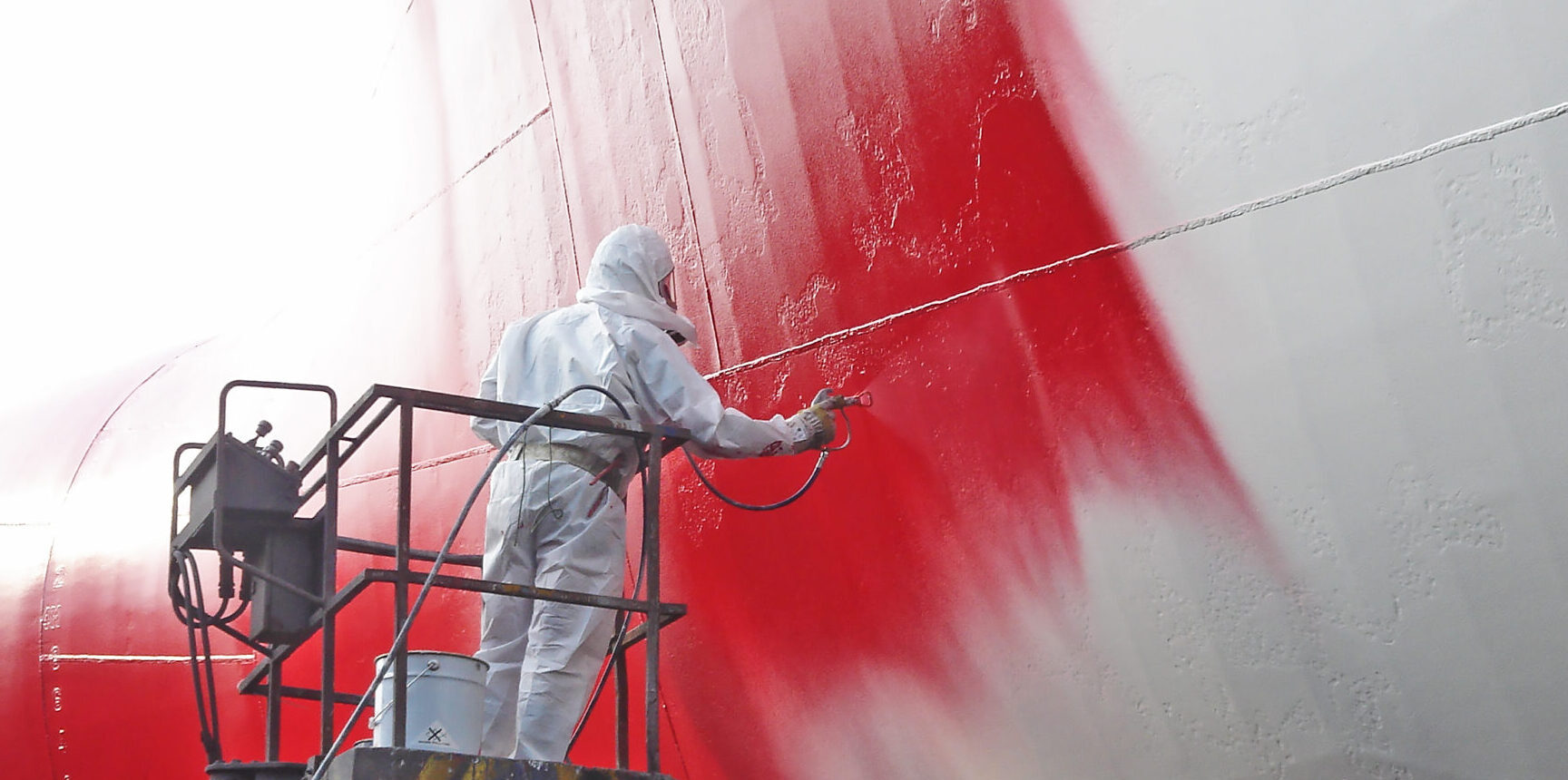
Ship paints
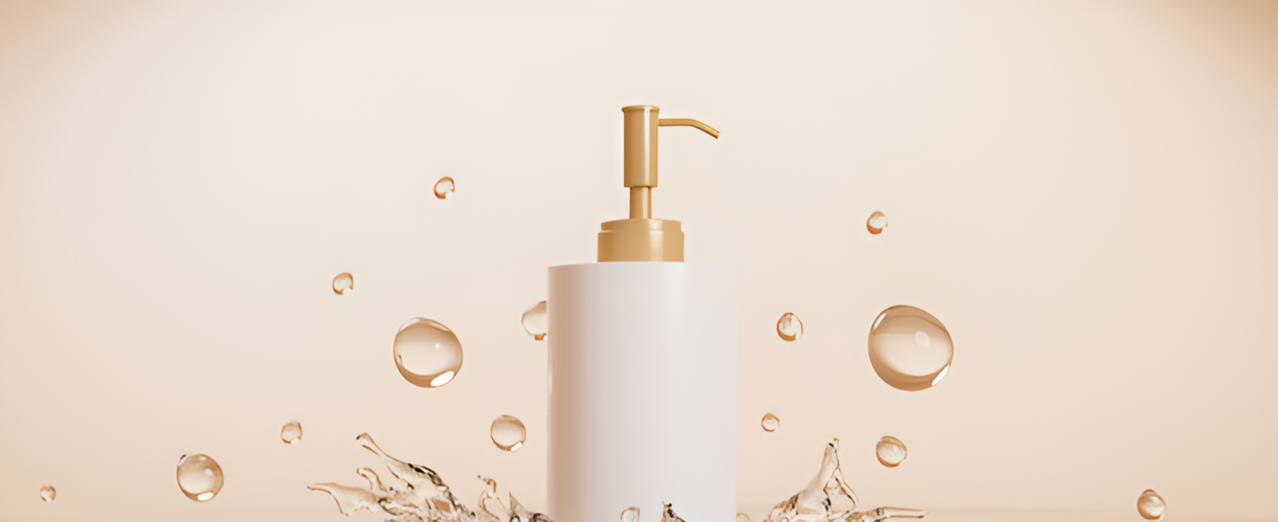
Shower gel
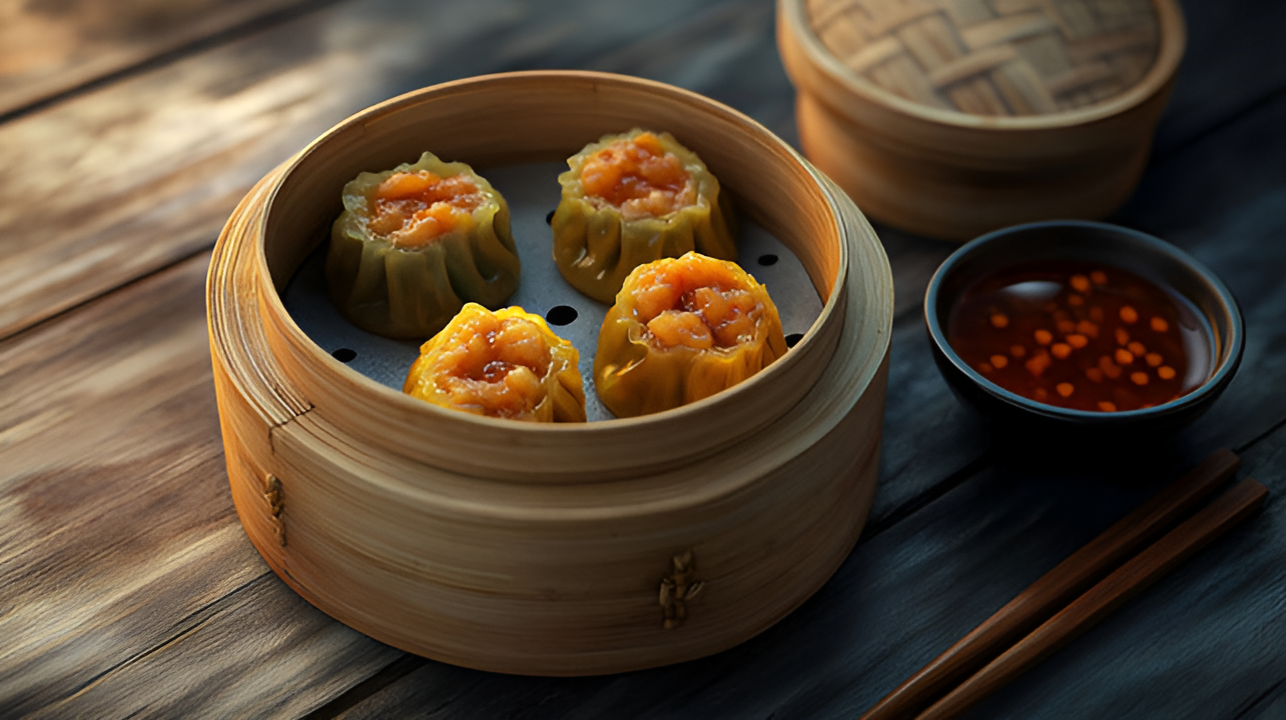
Shumai
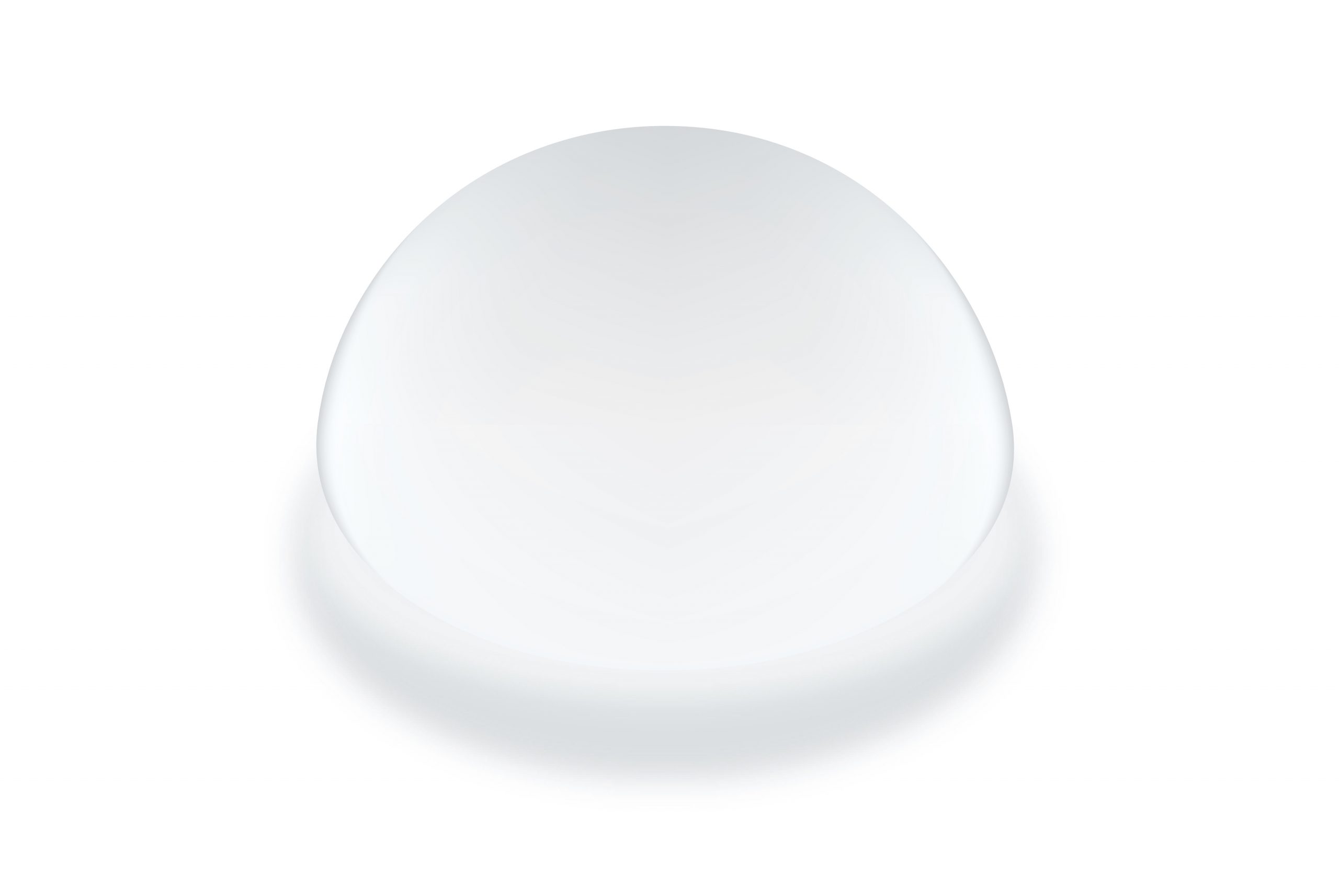
Silicone
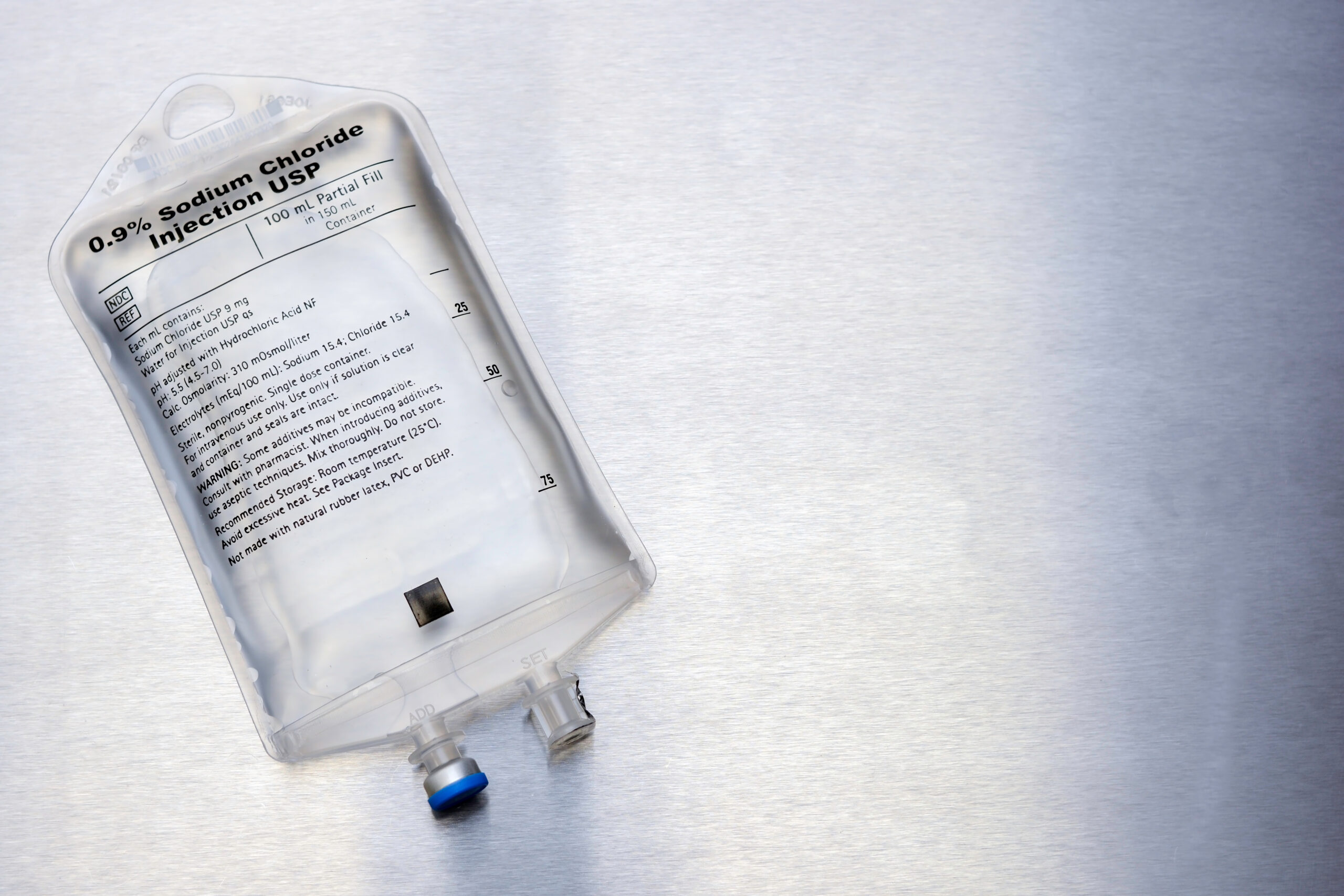
Single-use bags
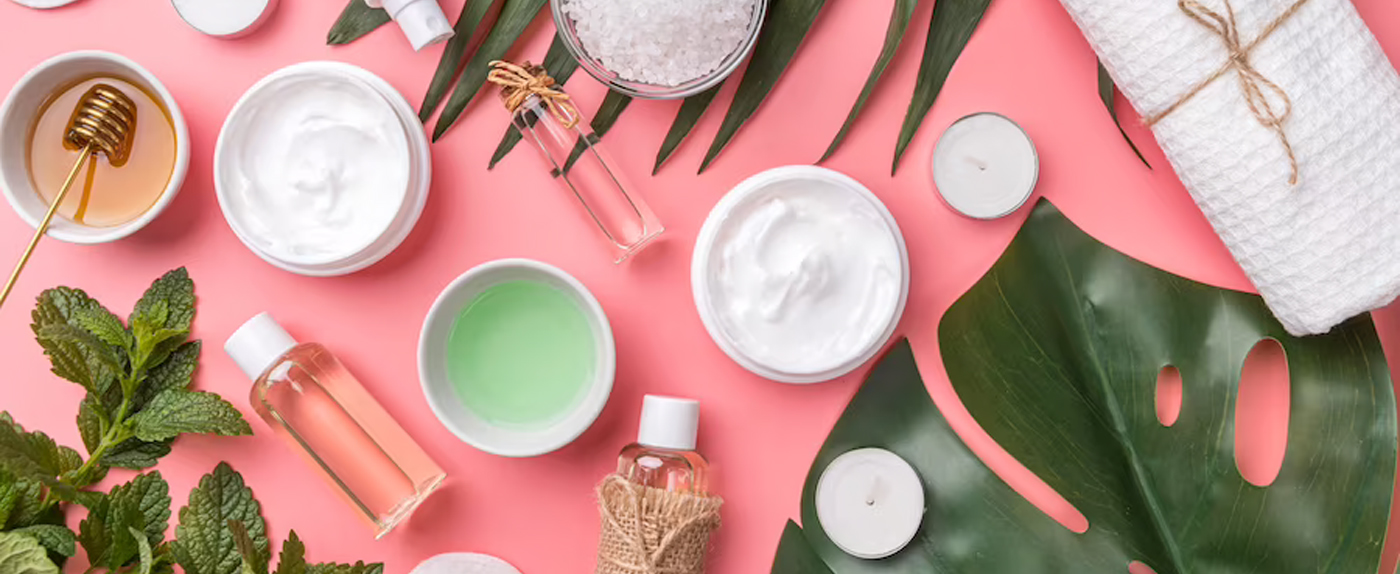
Skin care
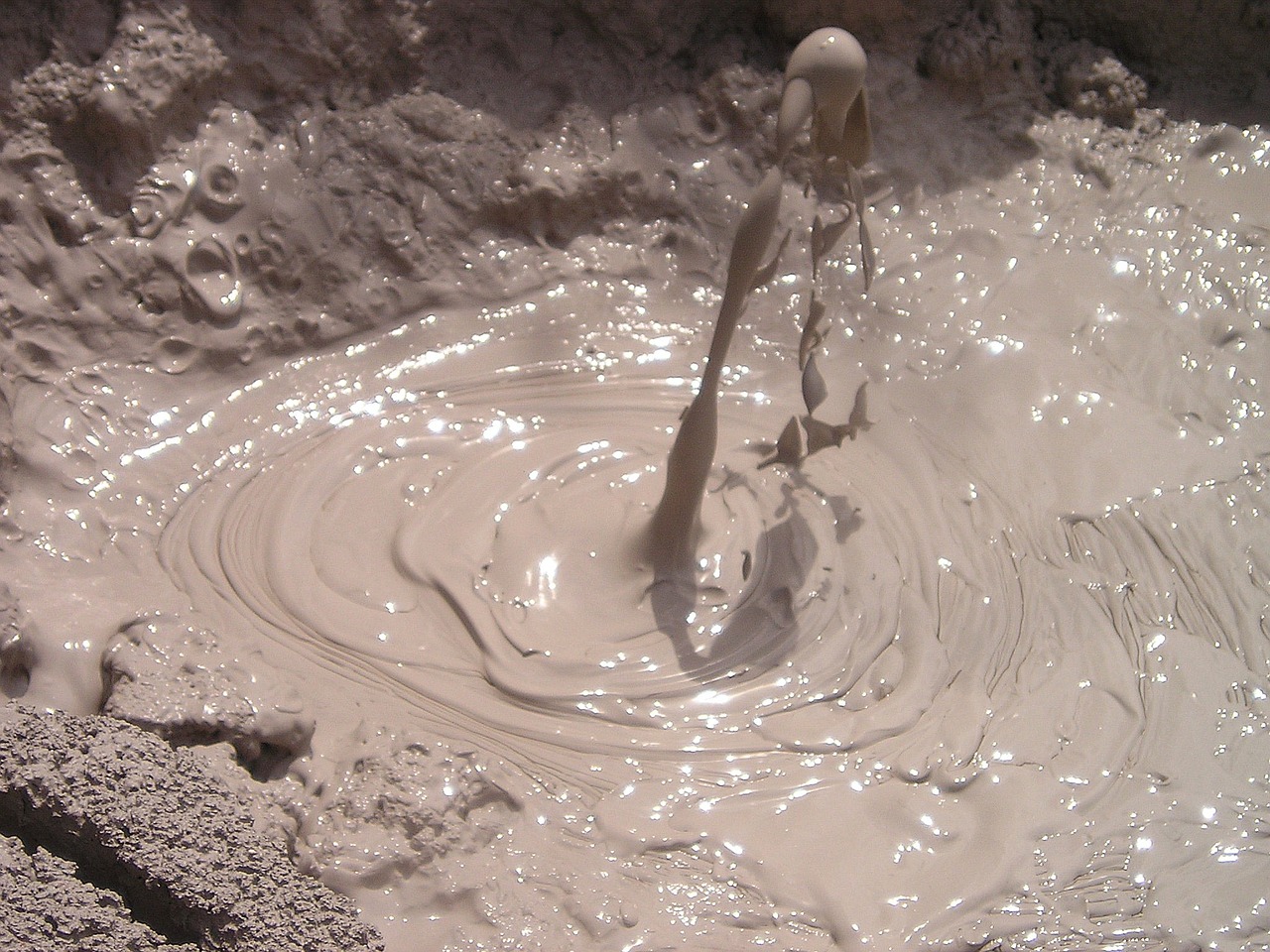
Slurry
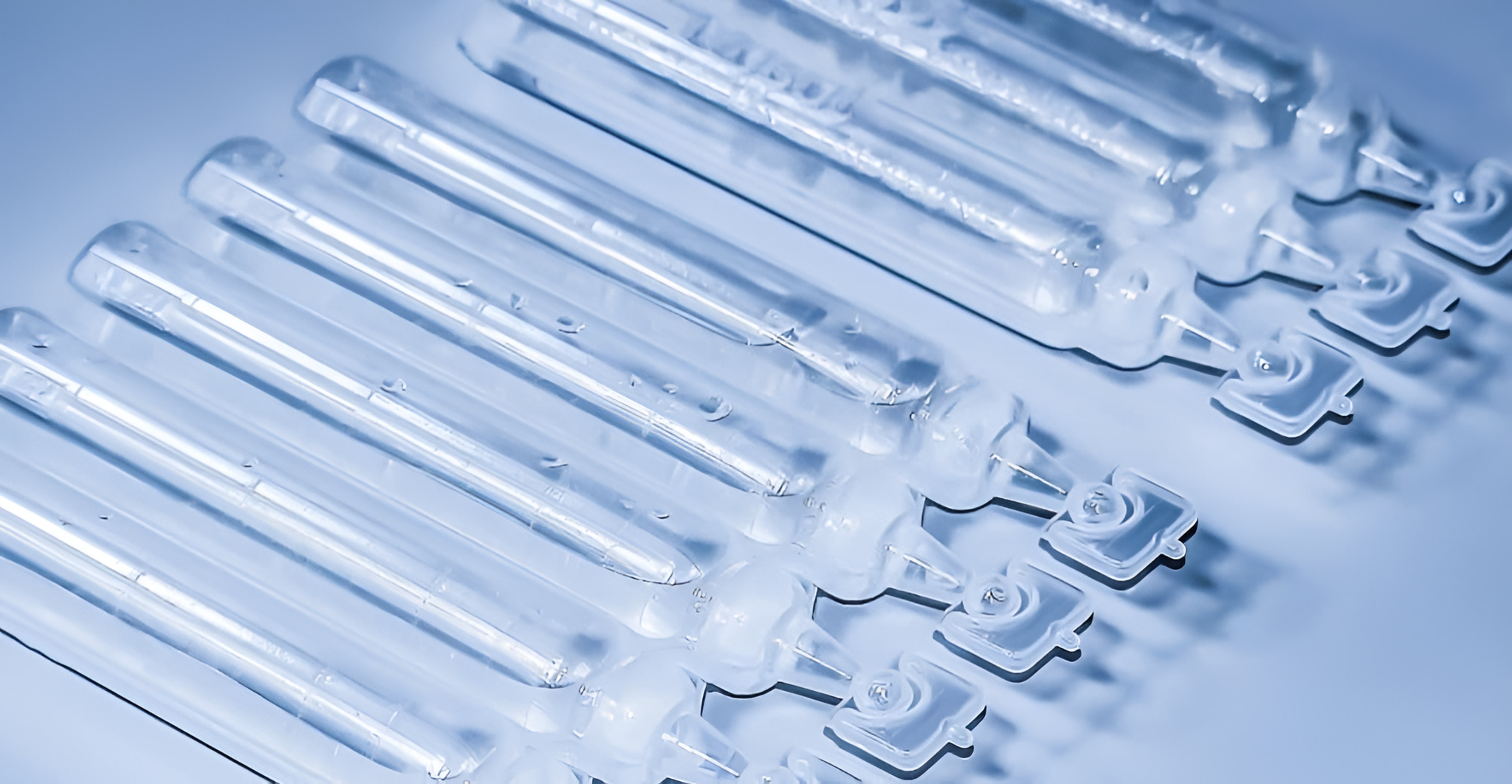
Small volume parenterals
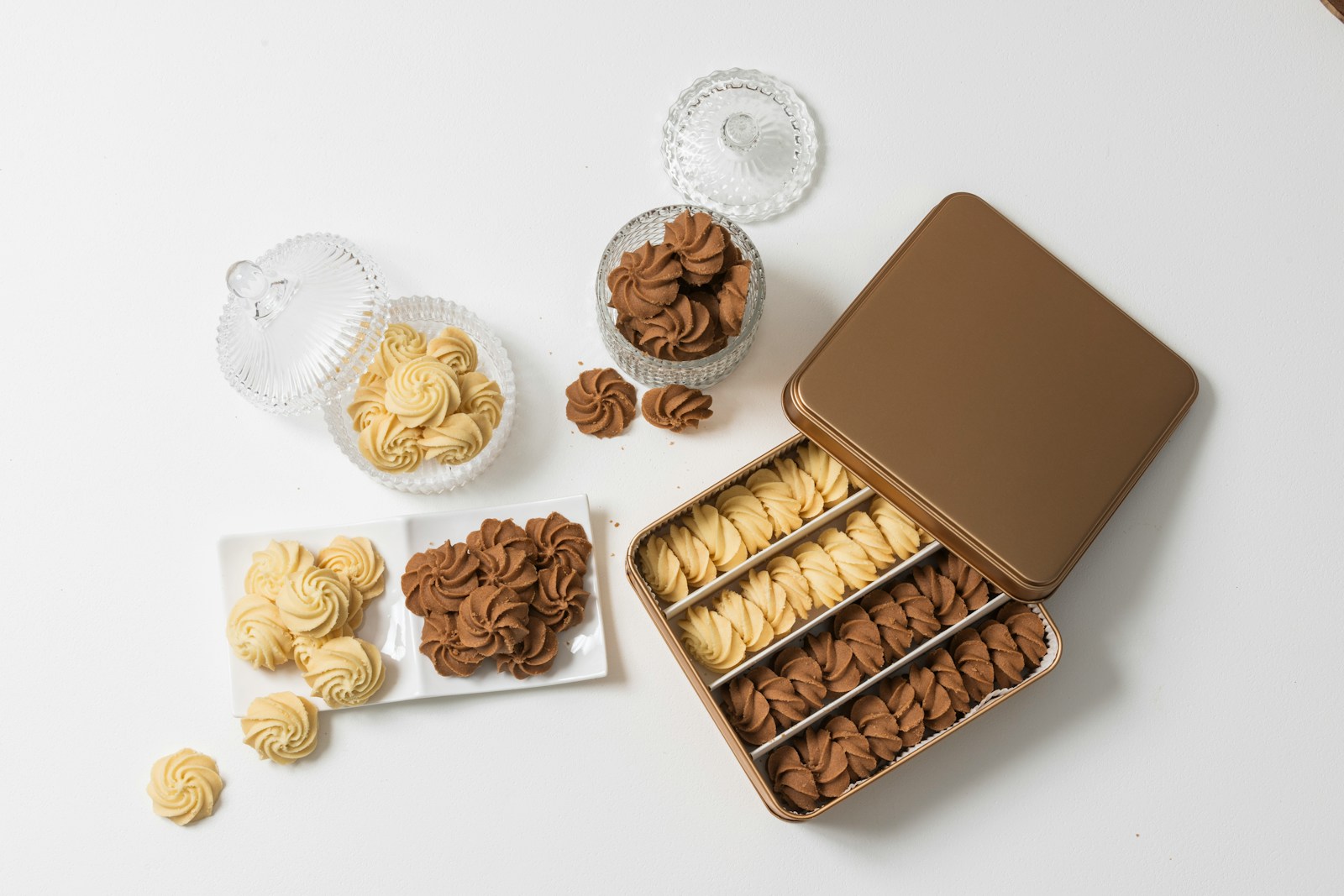
Snack packaging
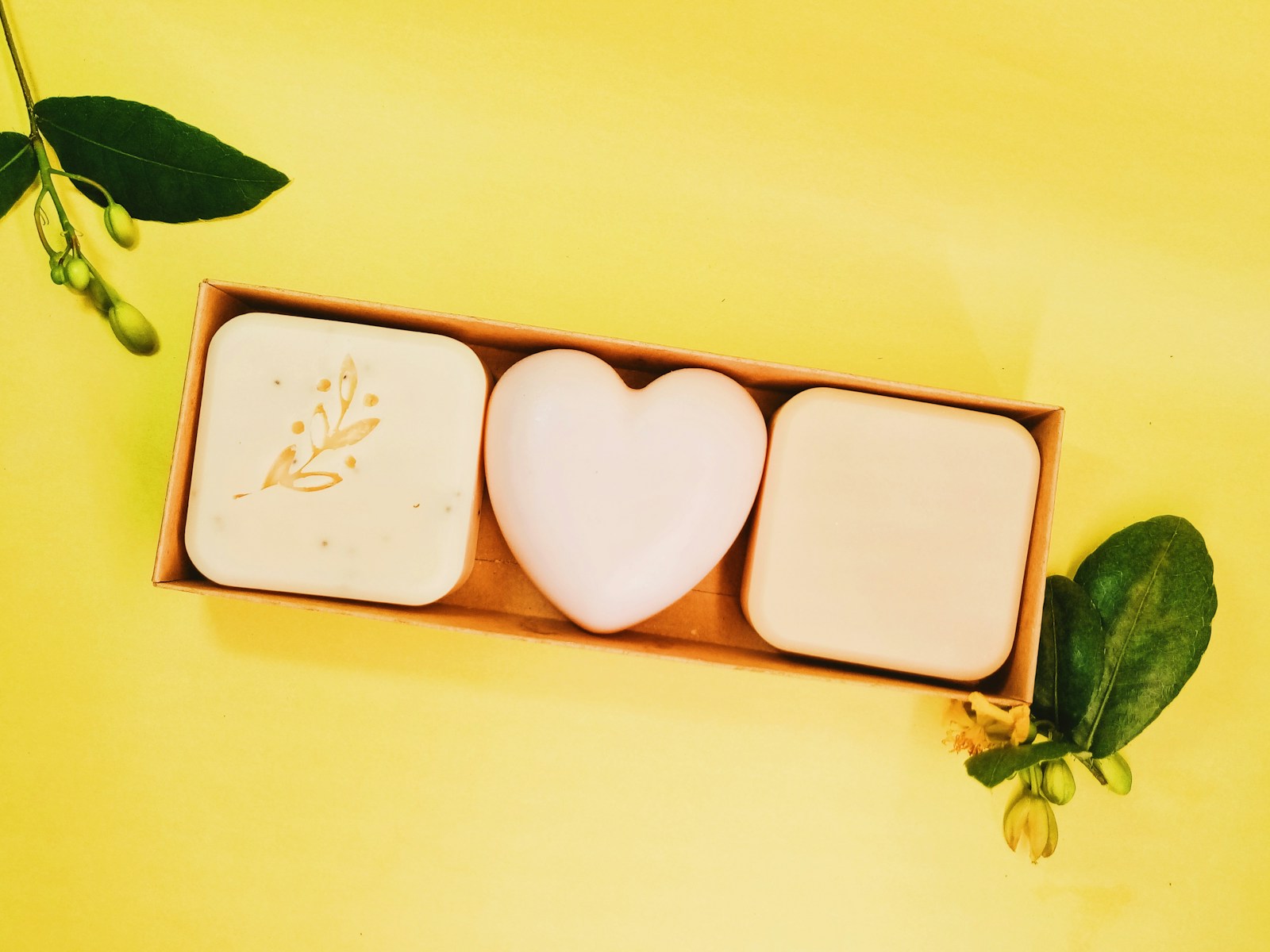
Soap
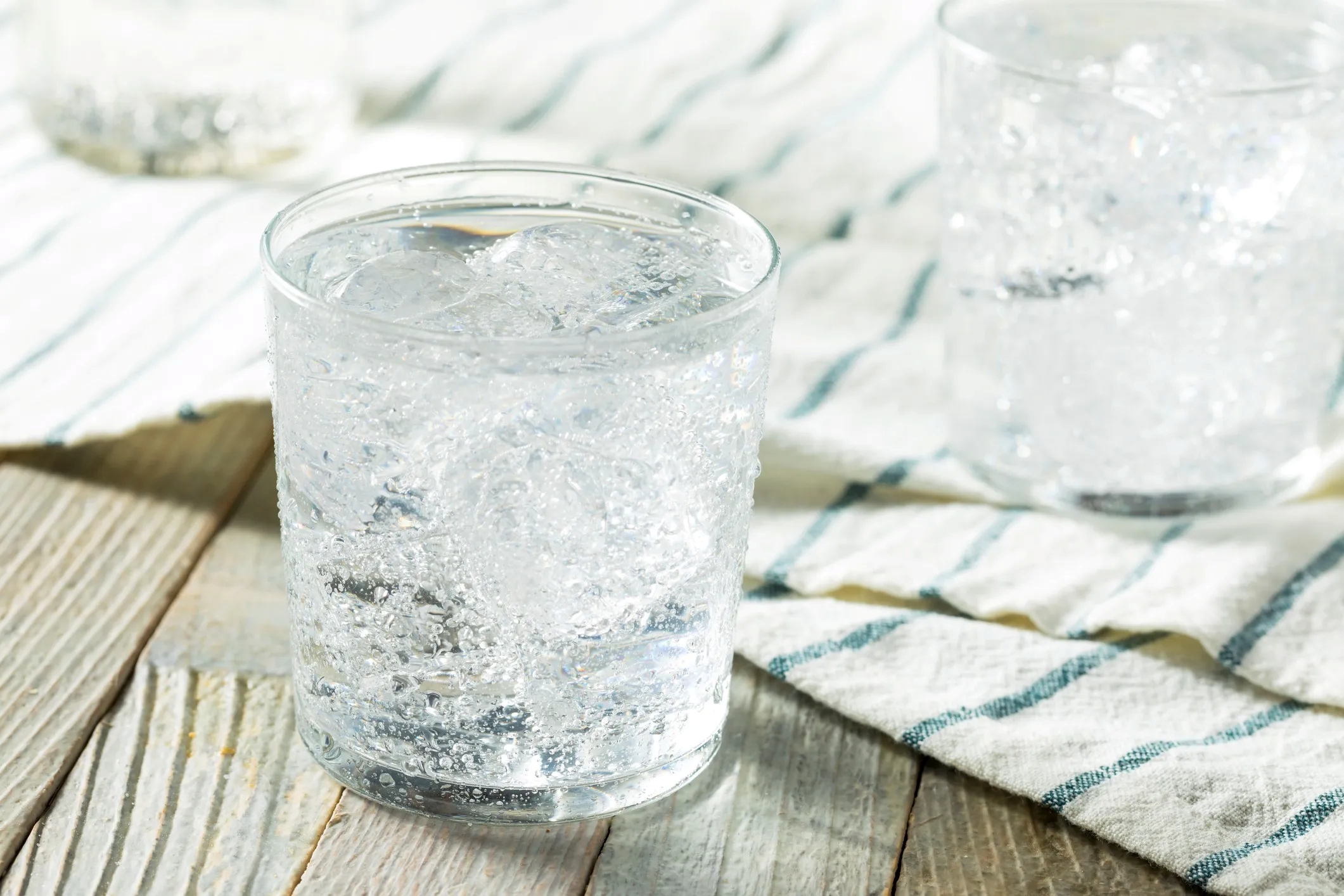
Soda
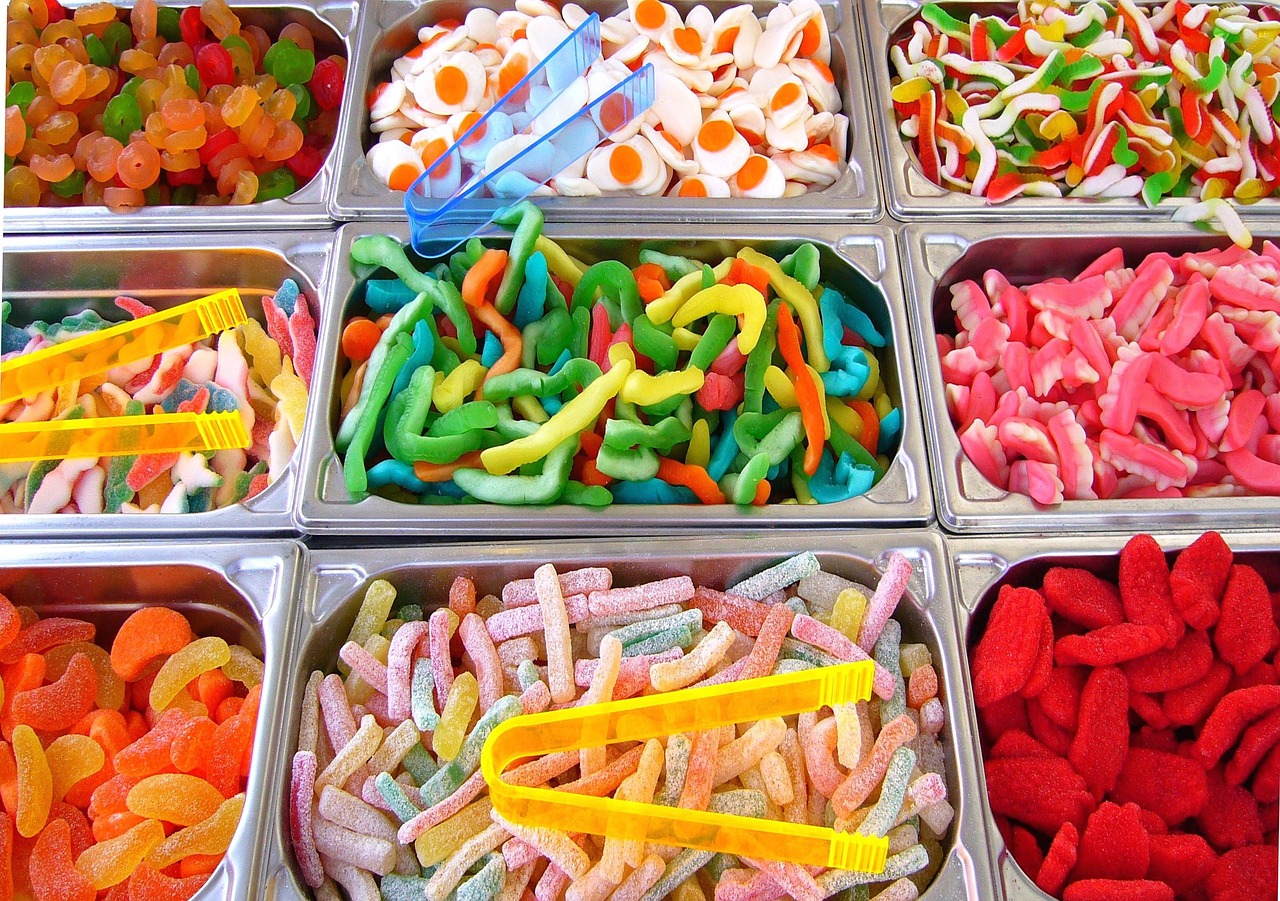
Soft Candy

Solvents
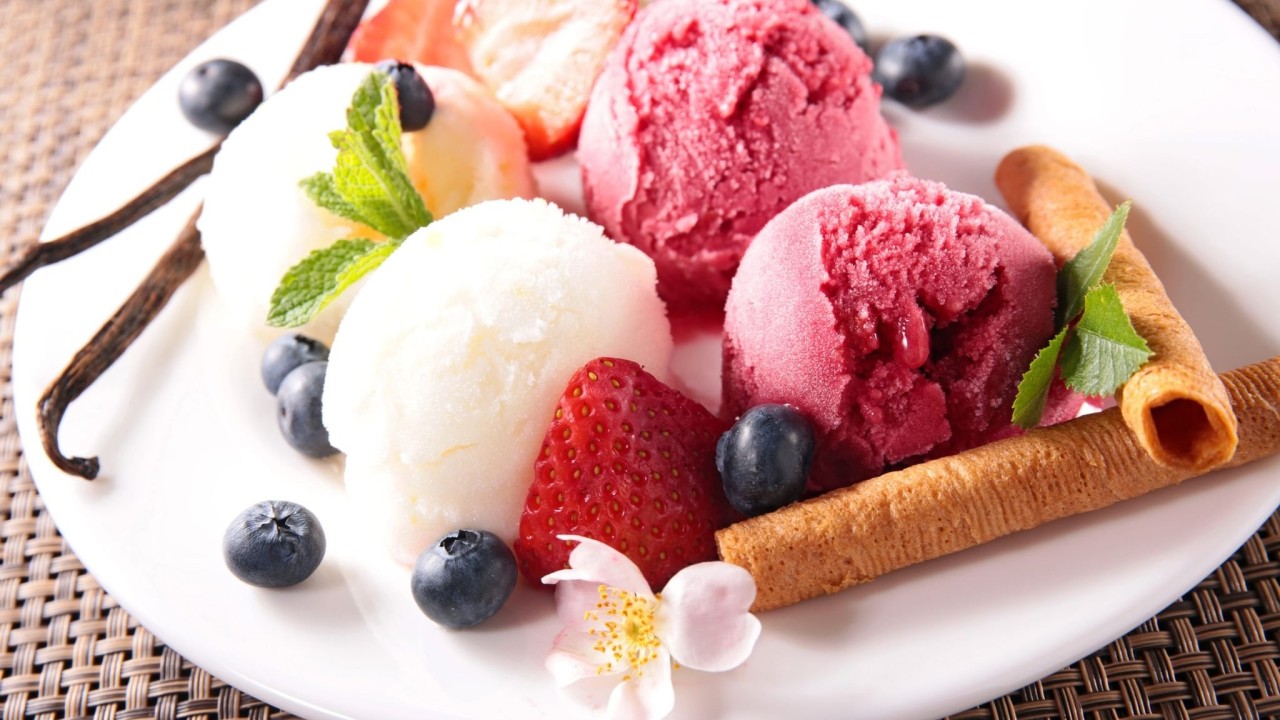
Sorbet
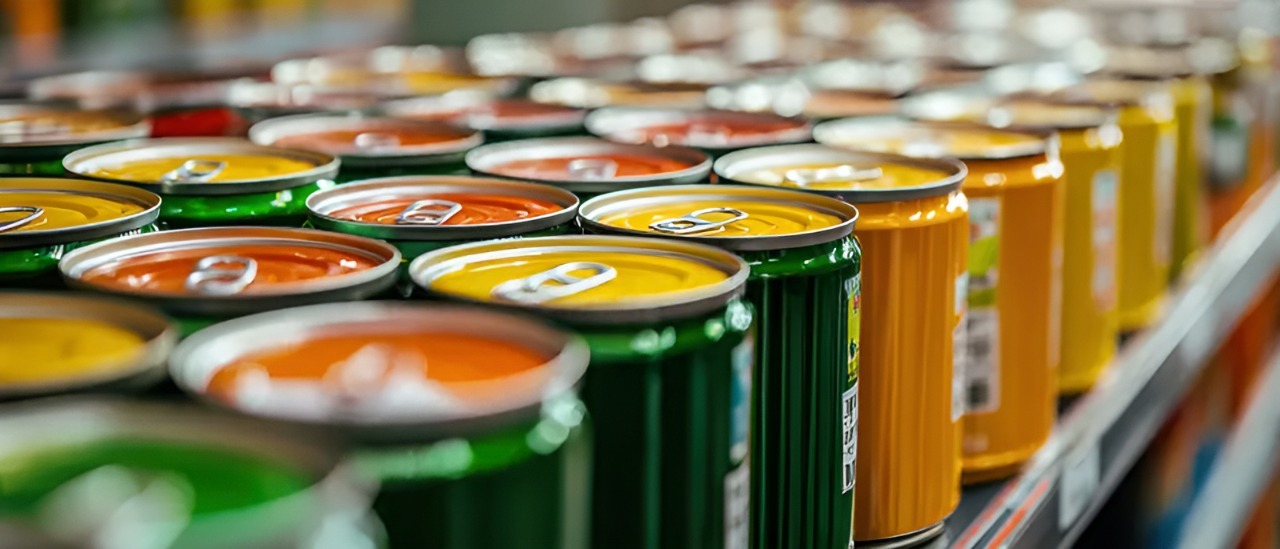
Soup cans
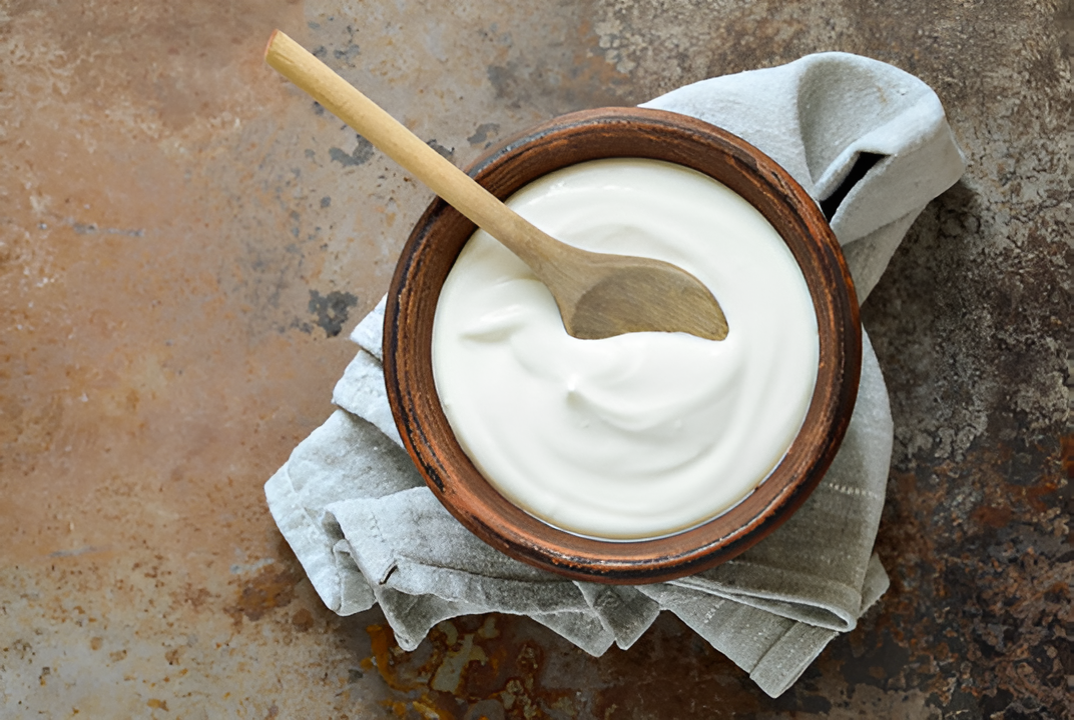
Sour cream
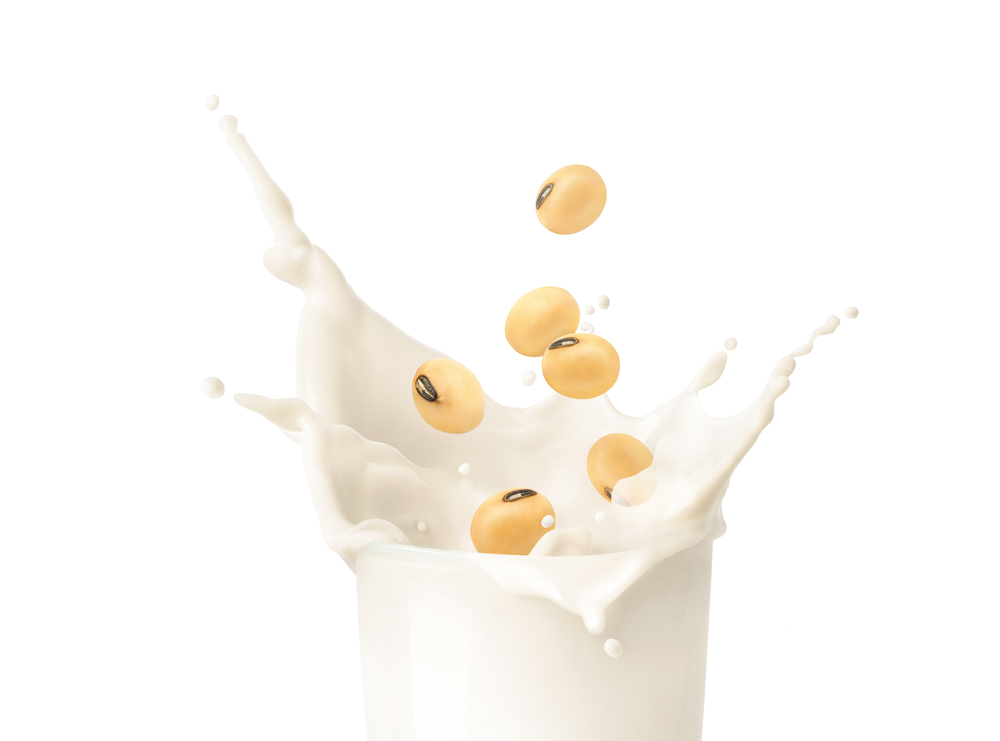
Soy milk
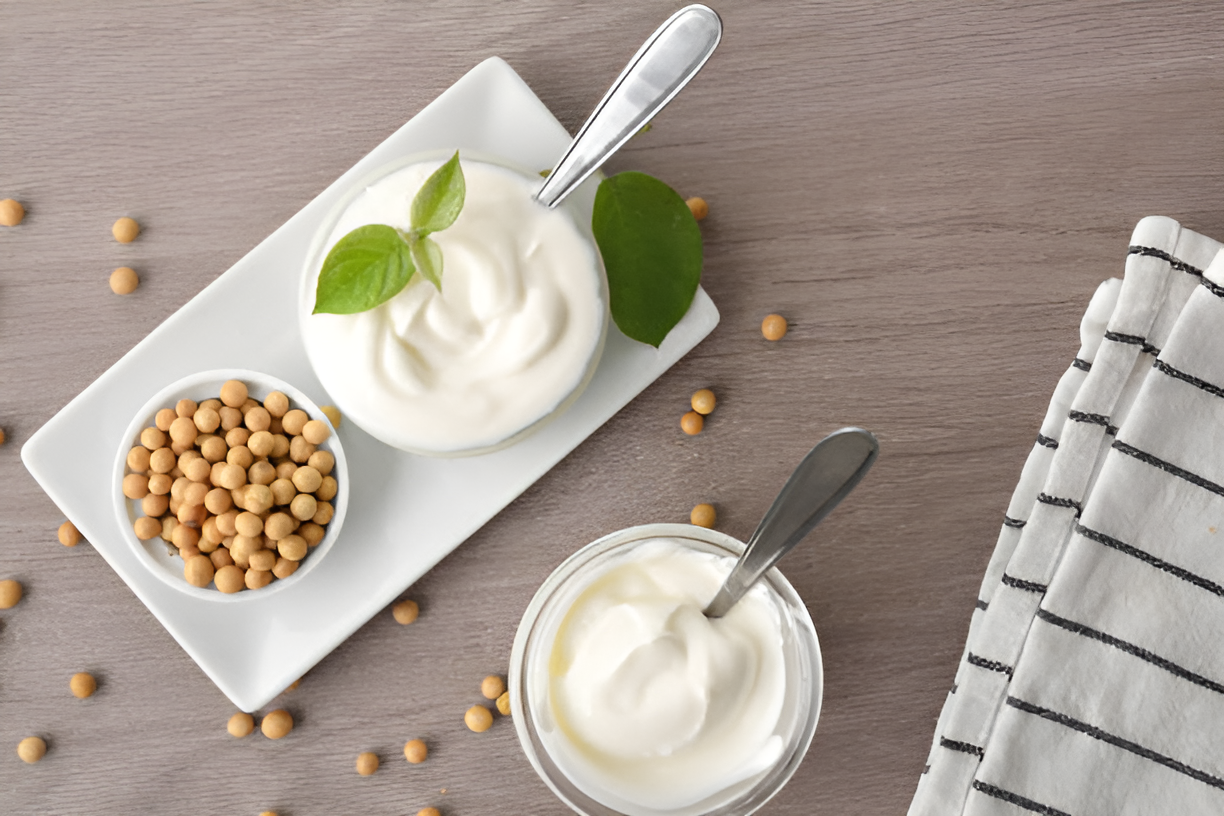
Soy yogurt
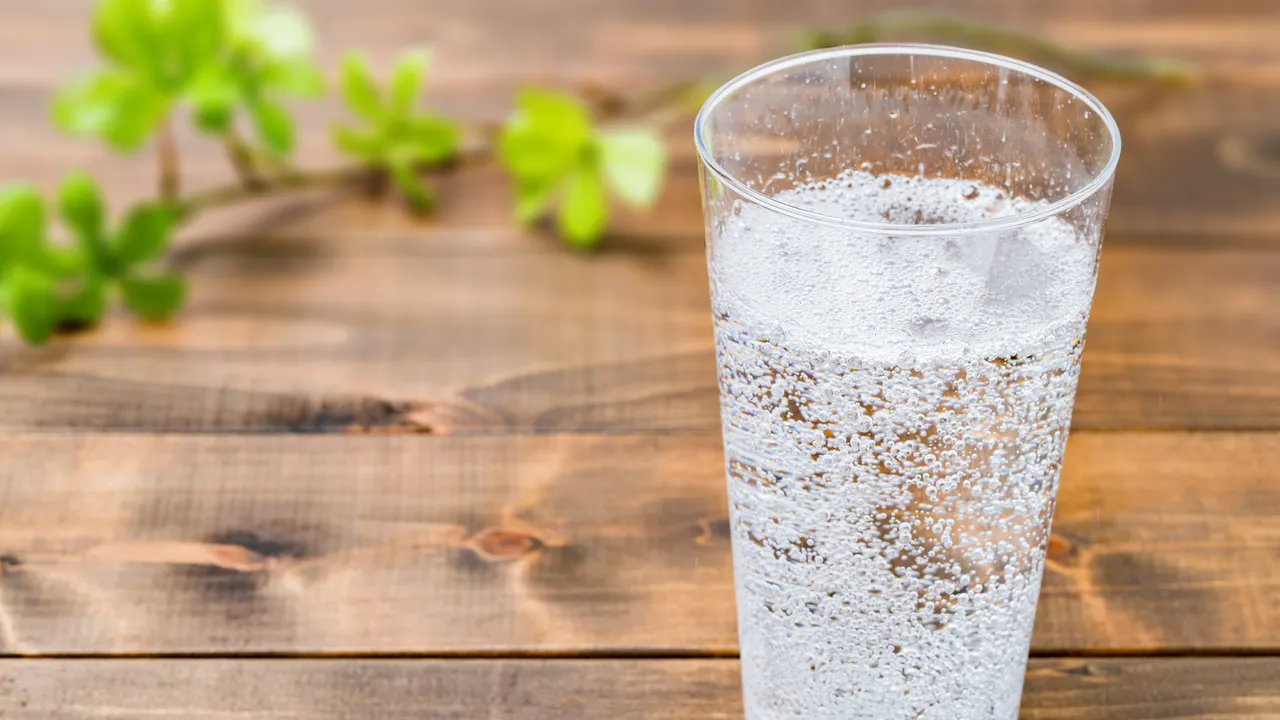
Sparkling water
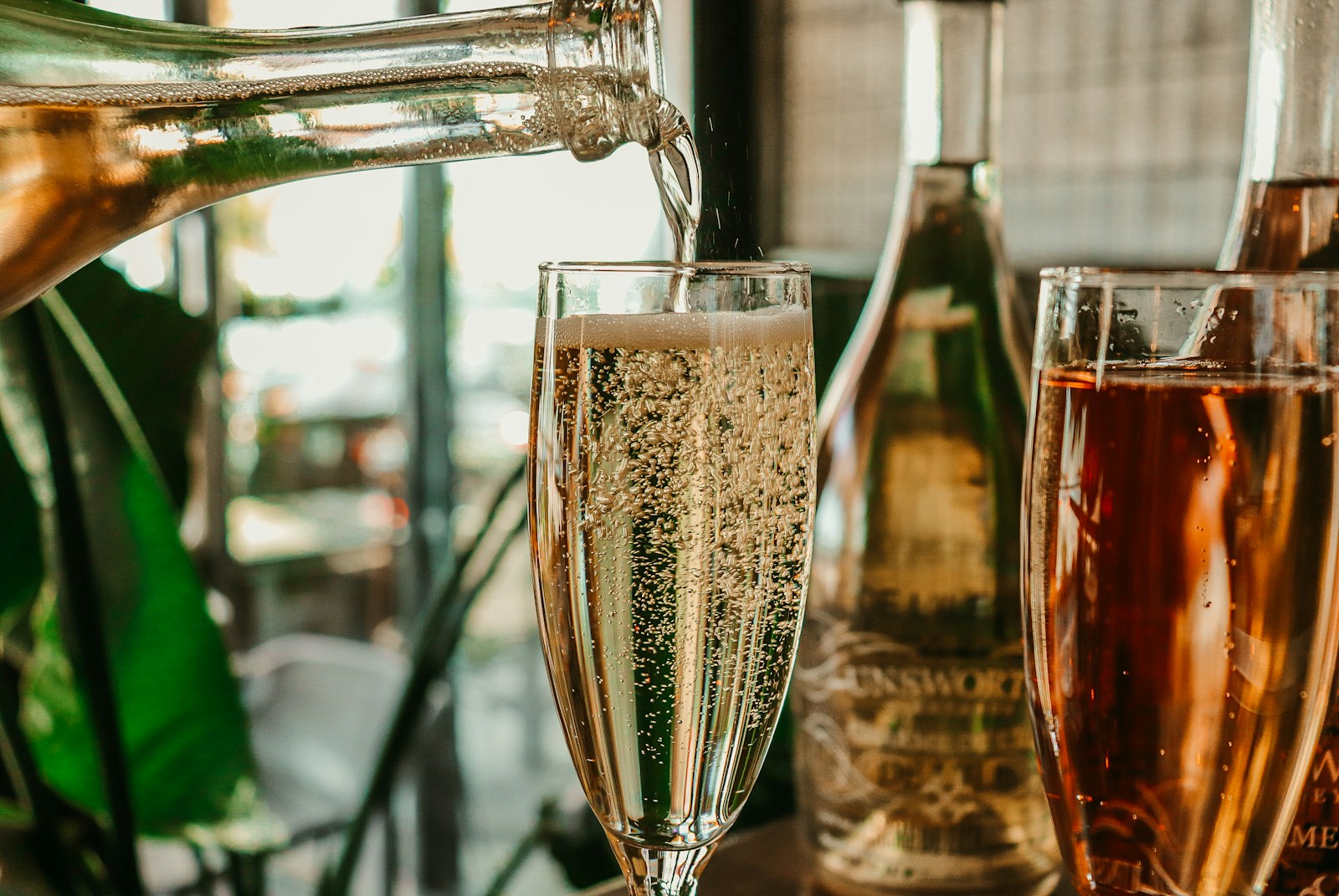
Sparkling wine
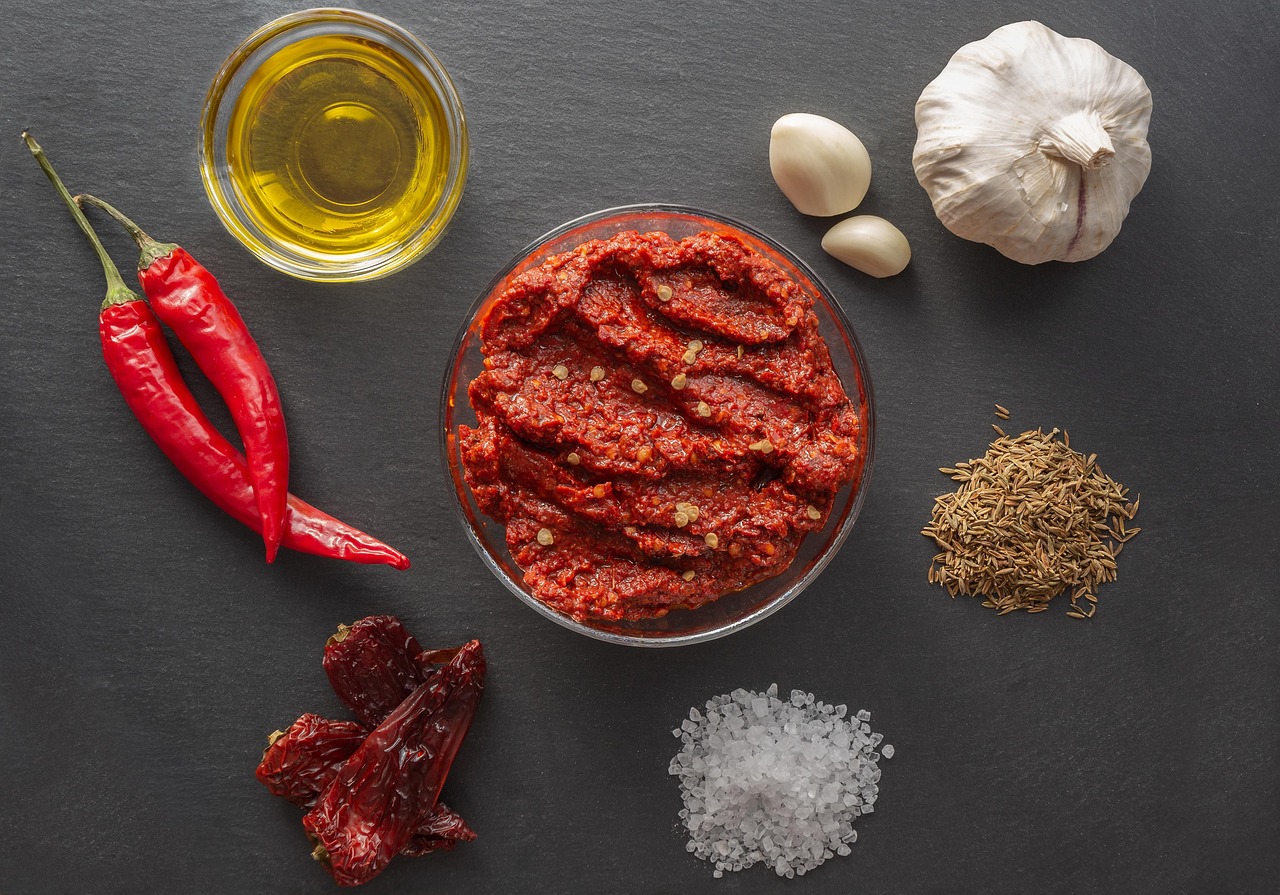
Spice pastes
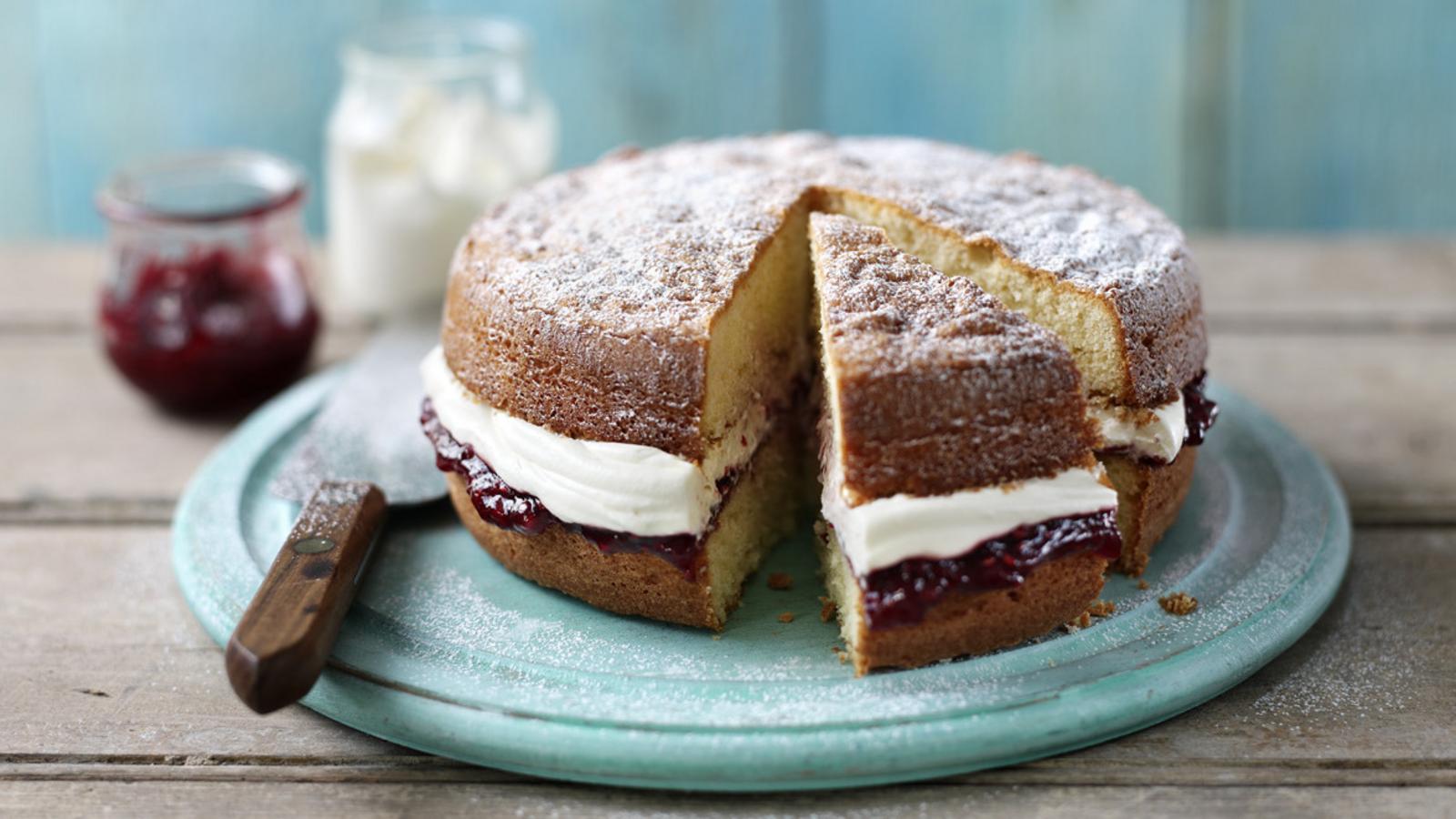
Sponge cake

Sport drinks
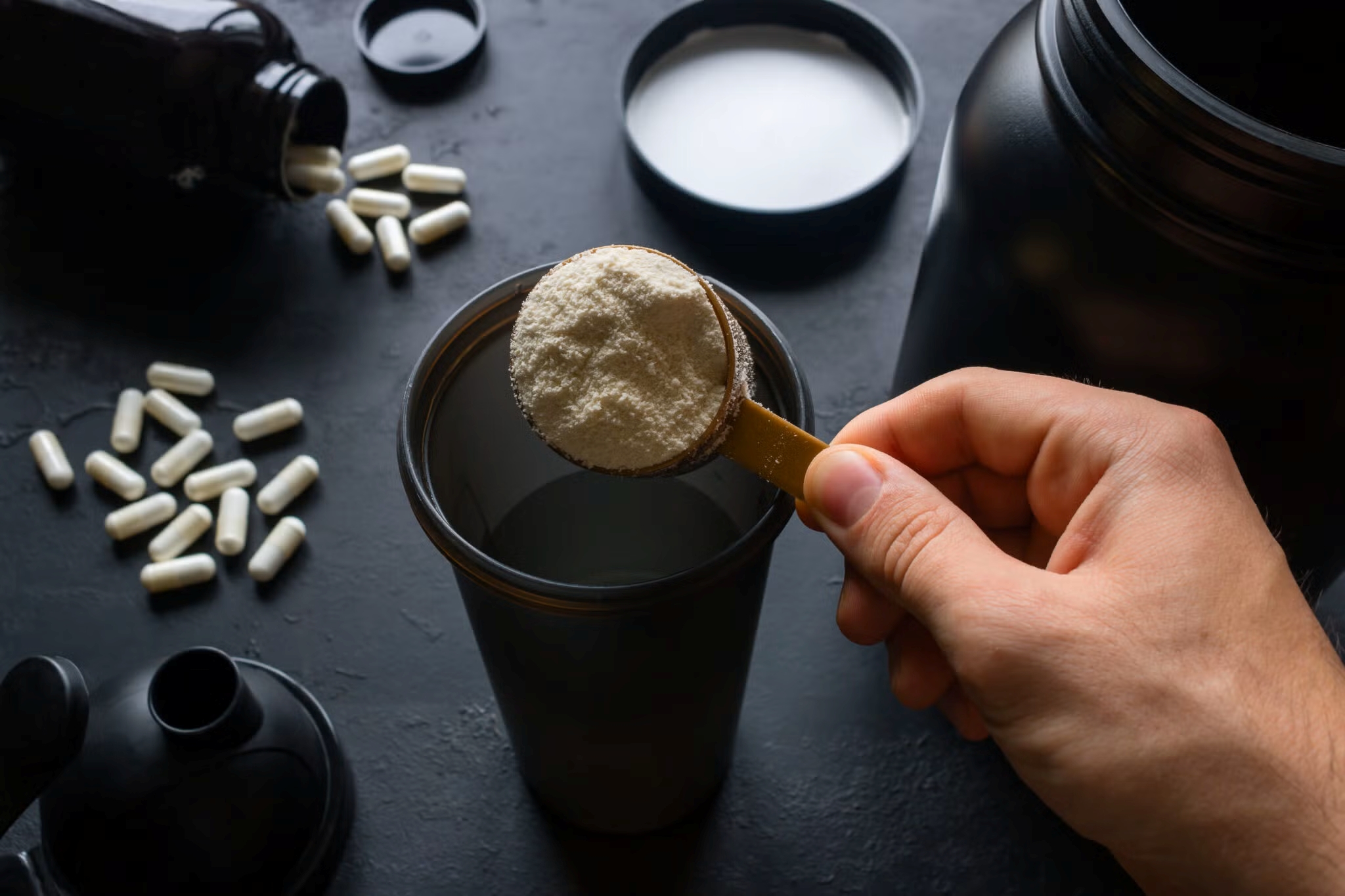
Sports nutrition
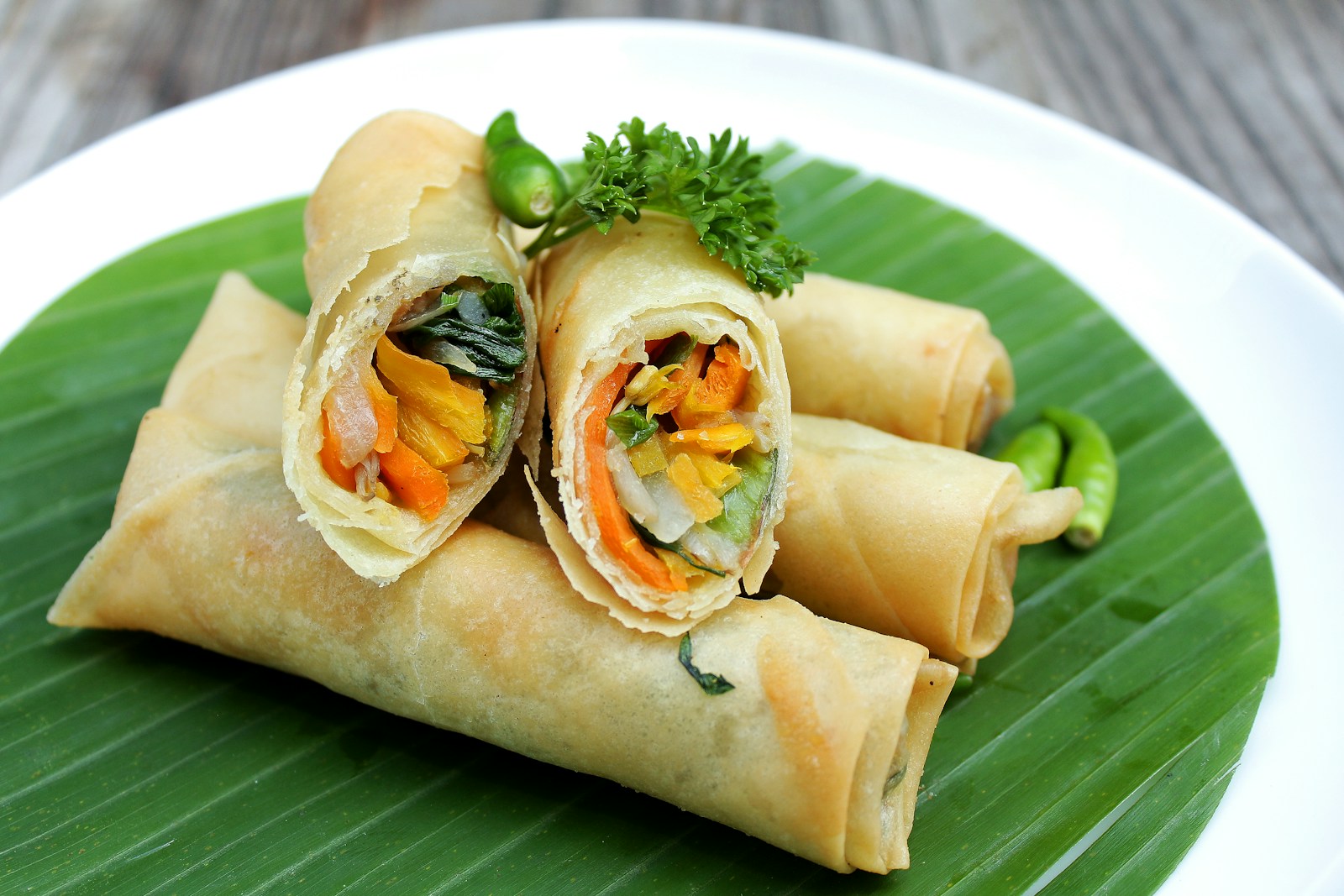
Spring rolls
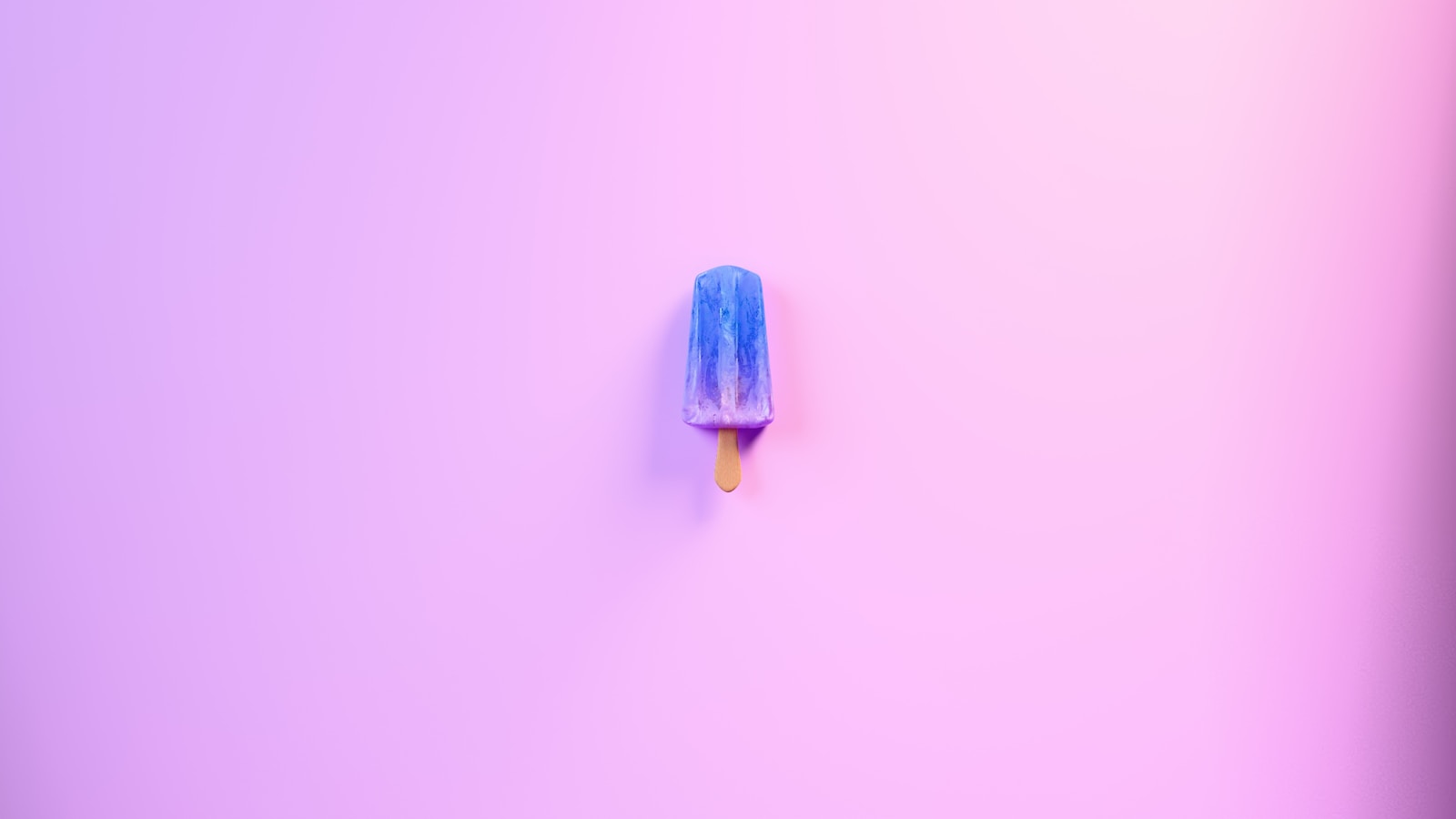
Stick ice-cream
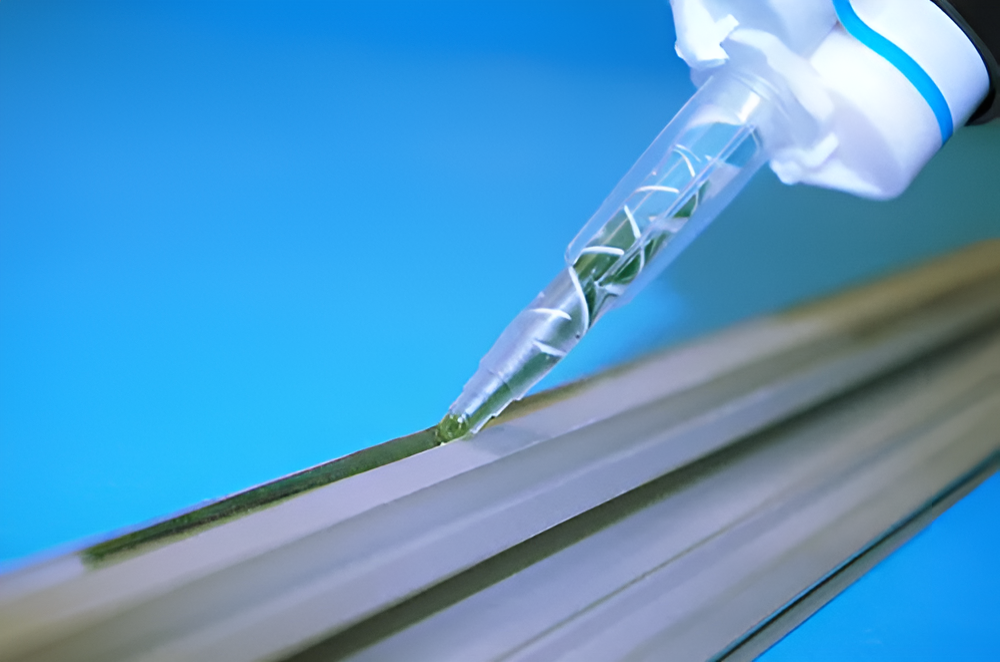
Structural adhesives
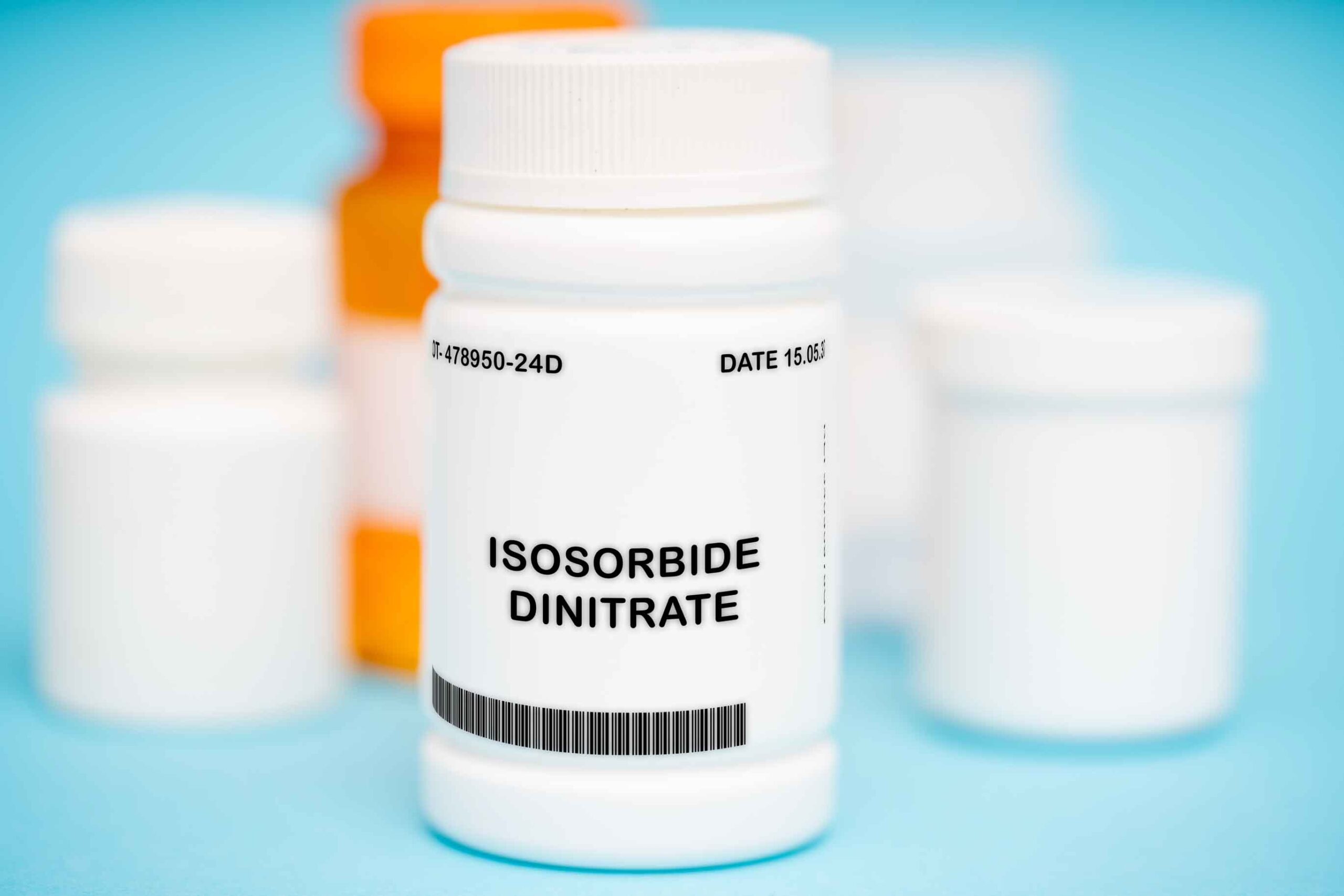
Sublingual spray
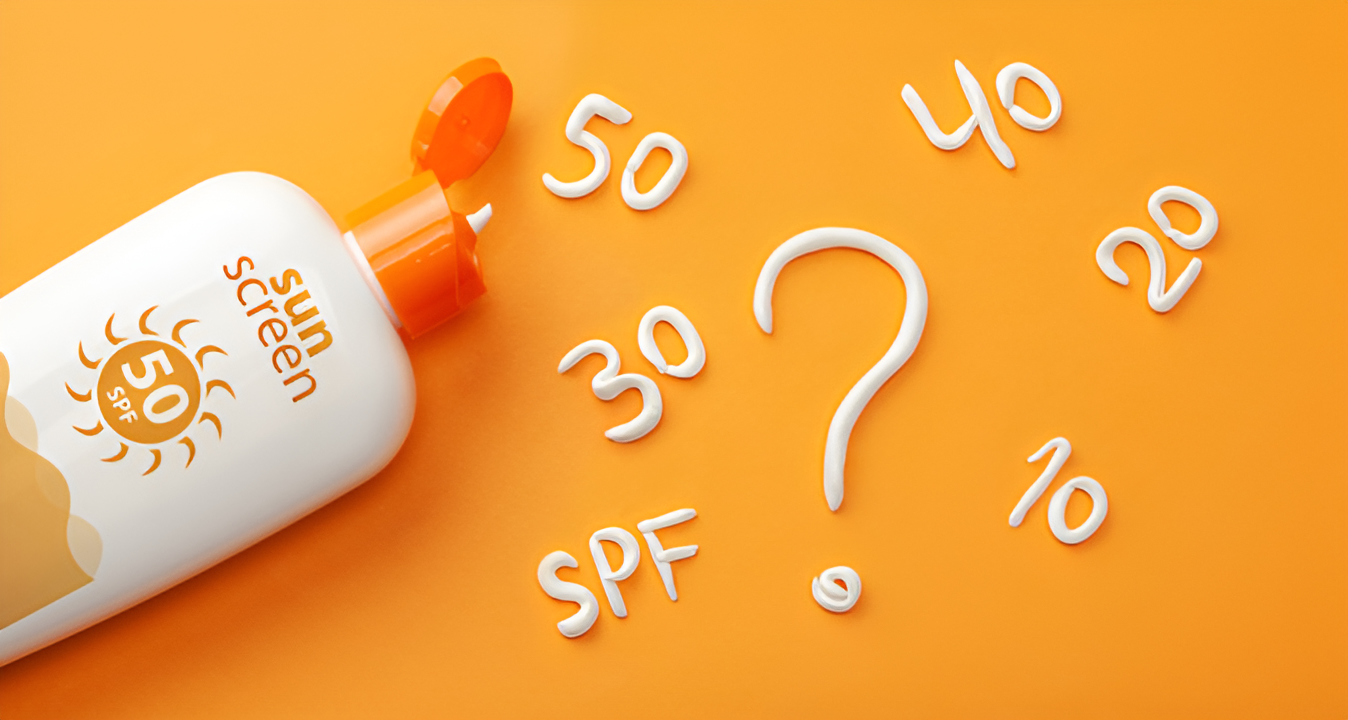
Sun care
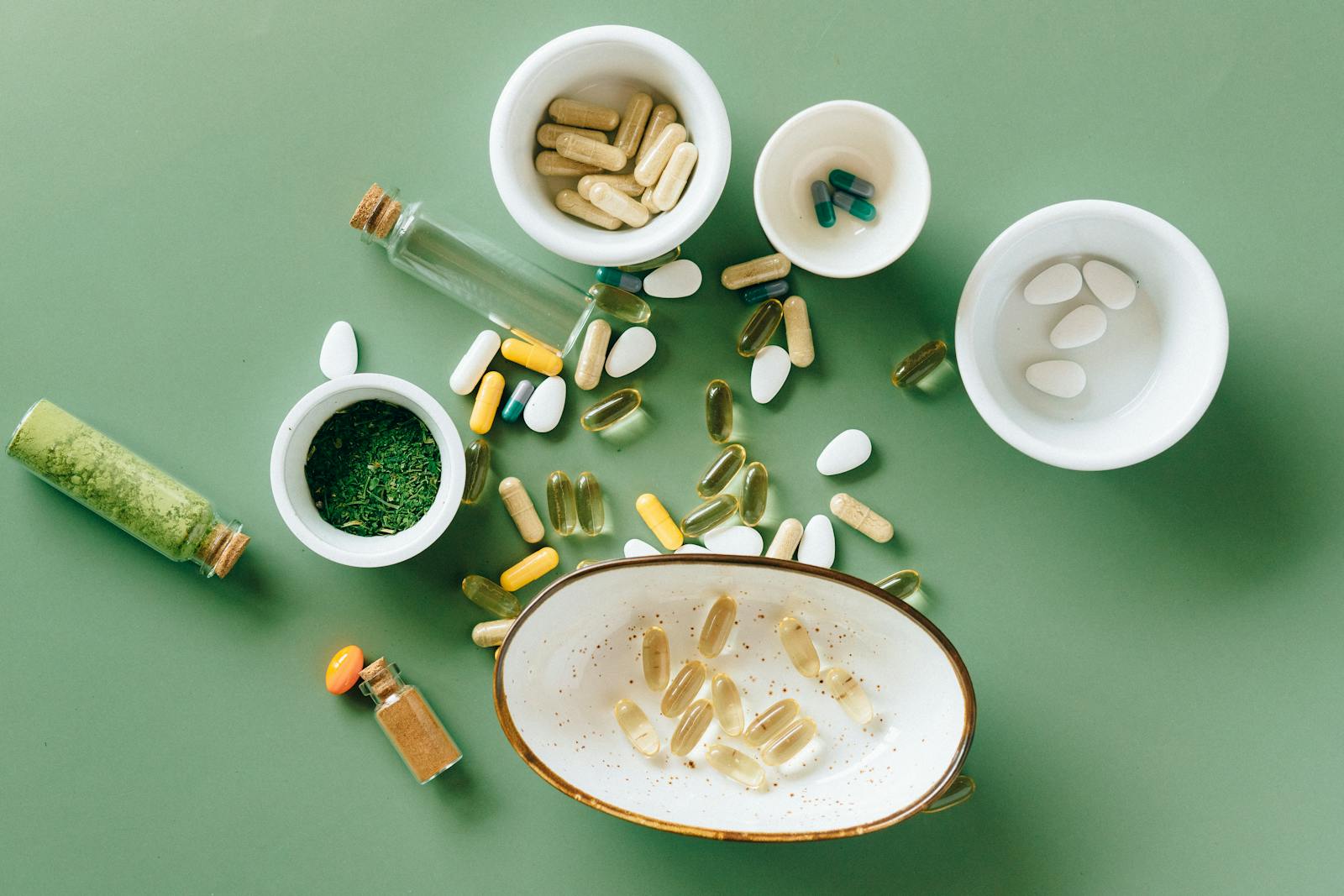
Supplements
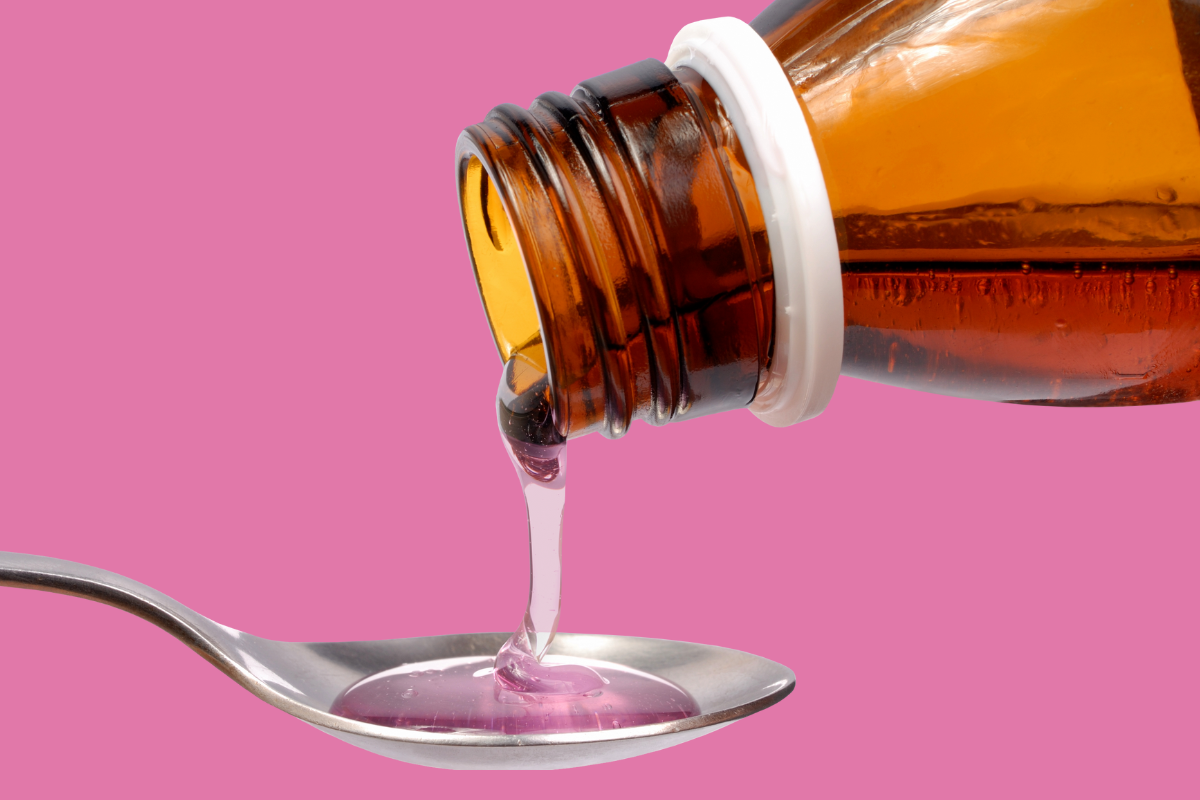
Suspensions
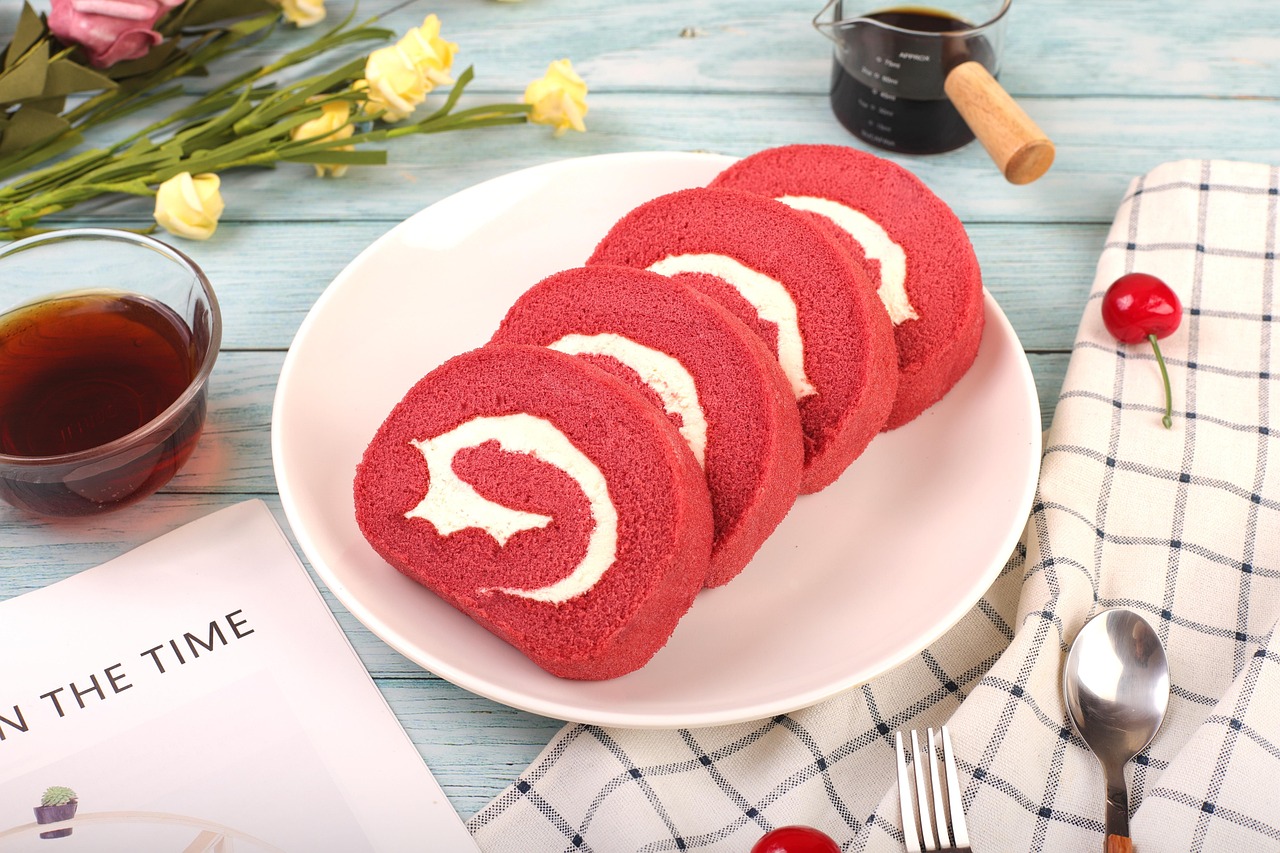
Swiss rolls
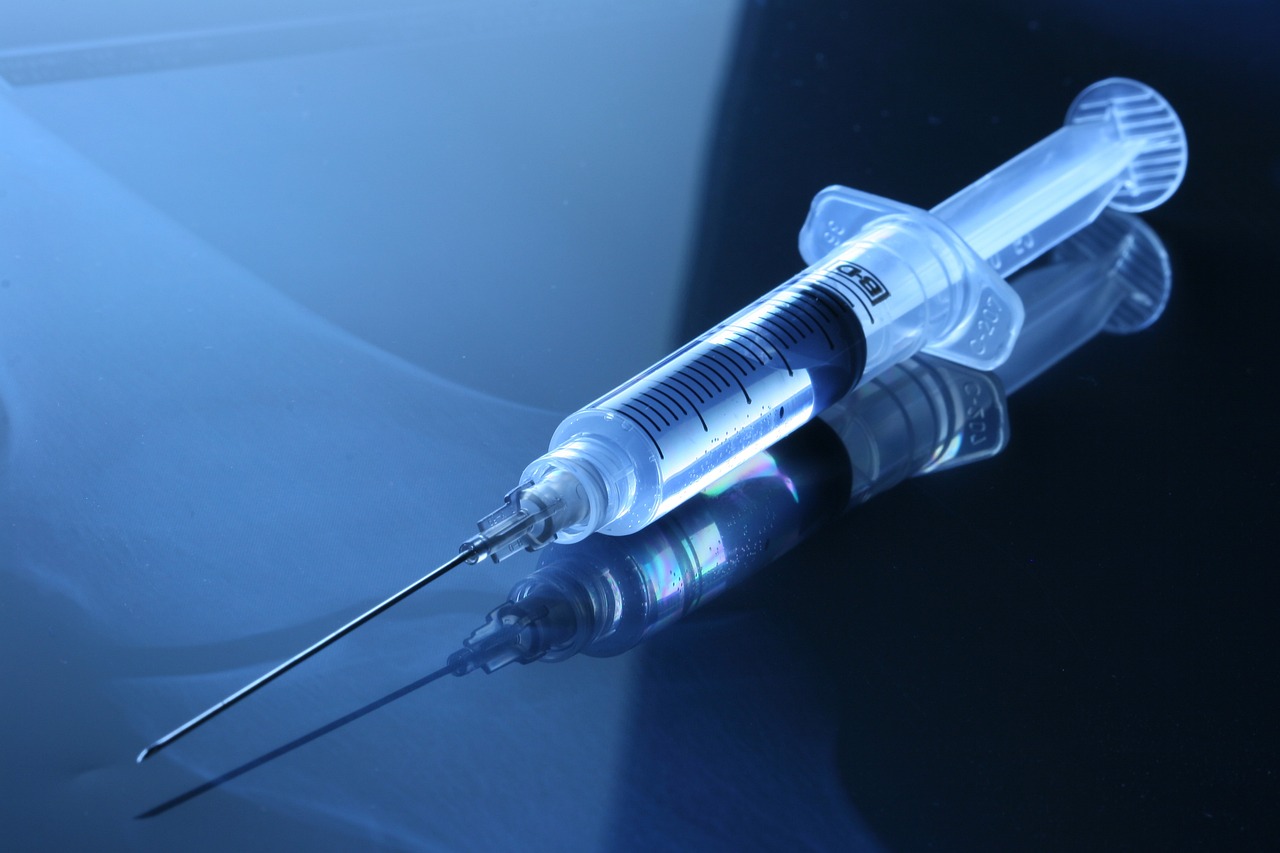
Syringes
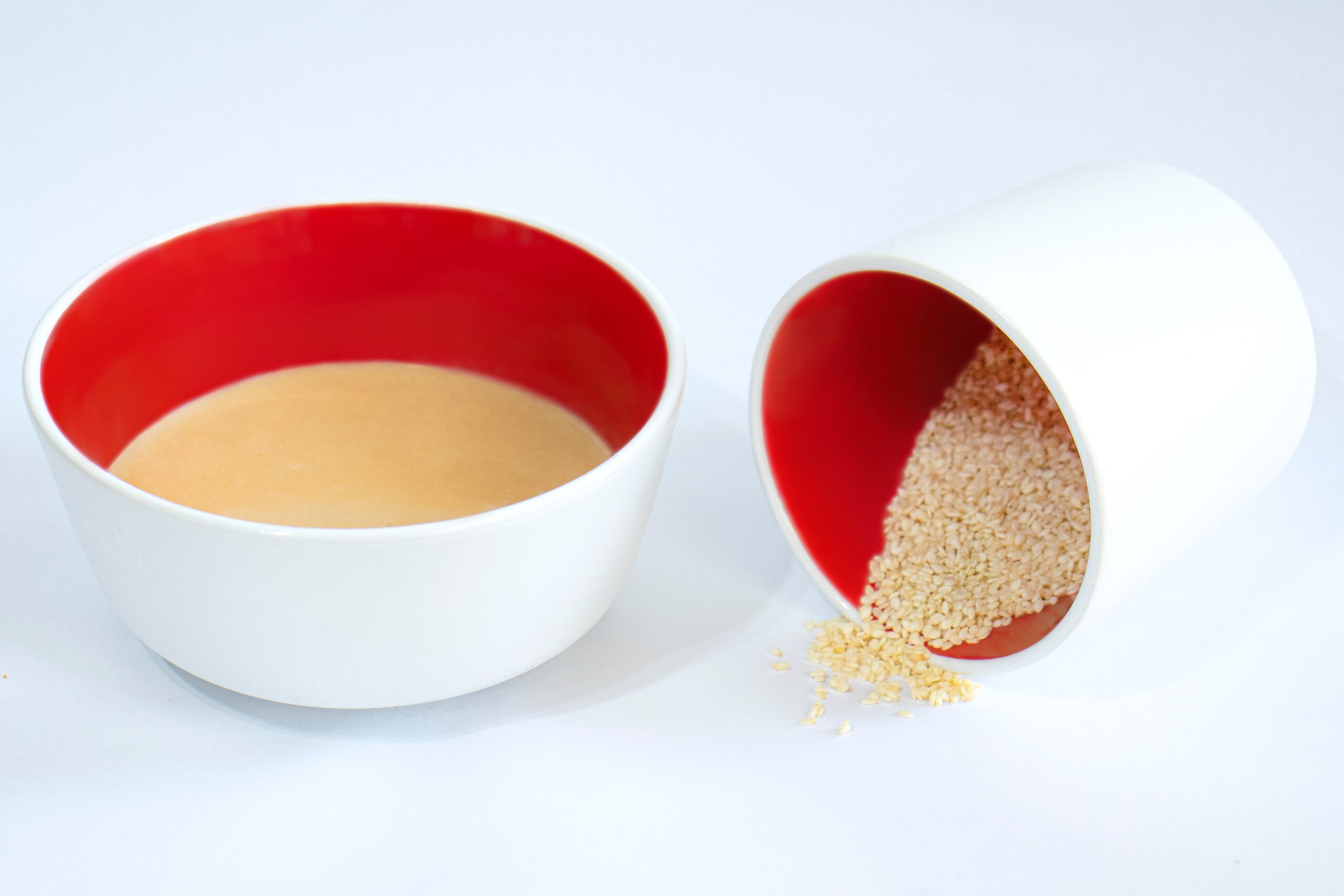
Tahini
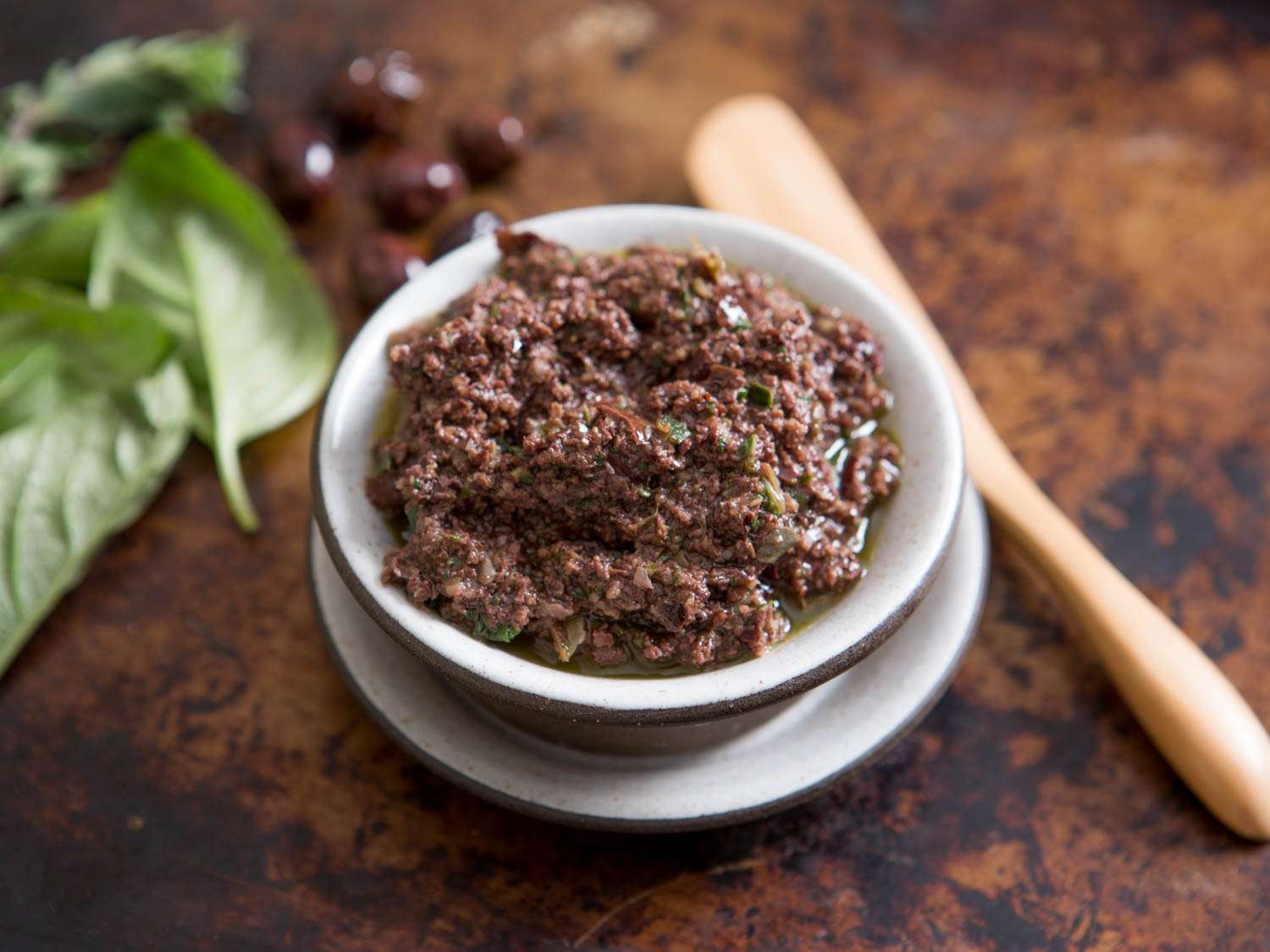
Tapenades
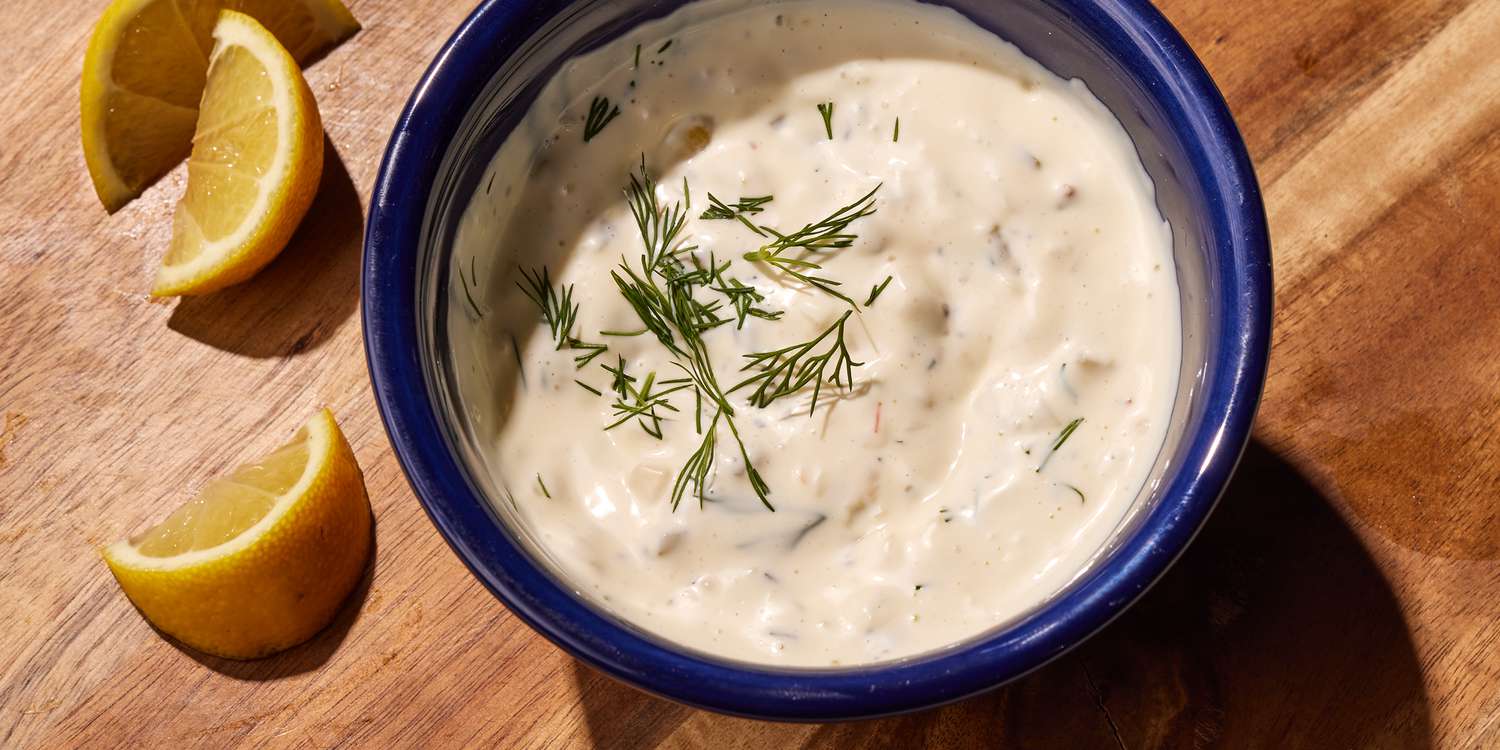
Tartar sauce
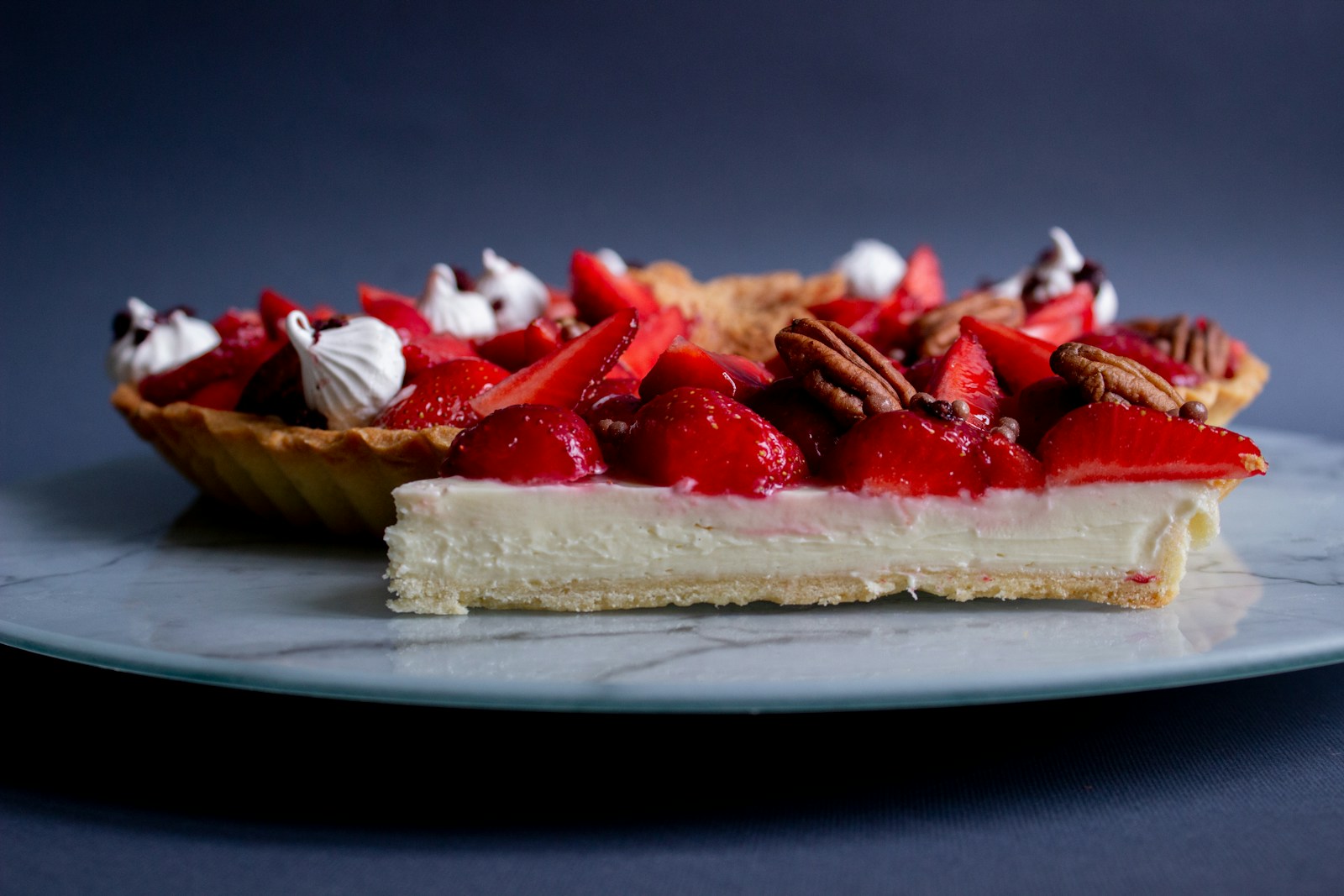
Tarts
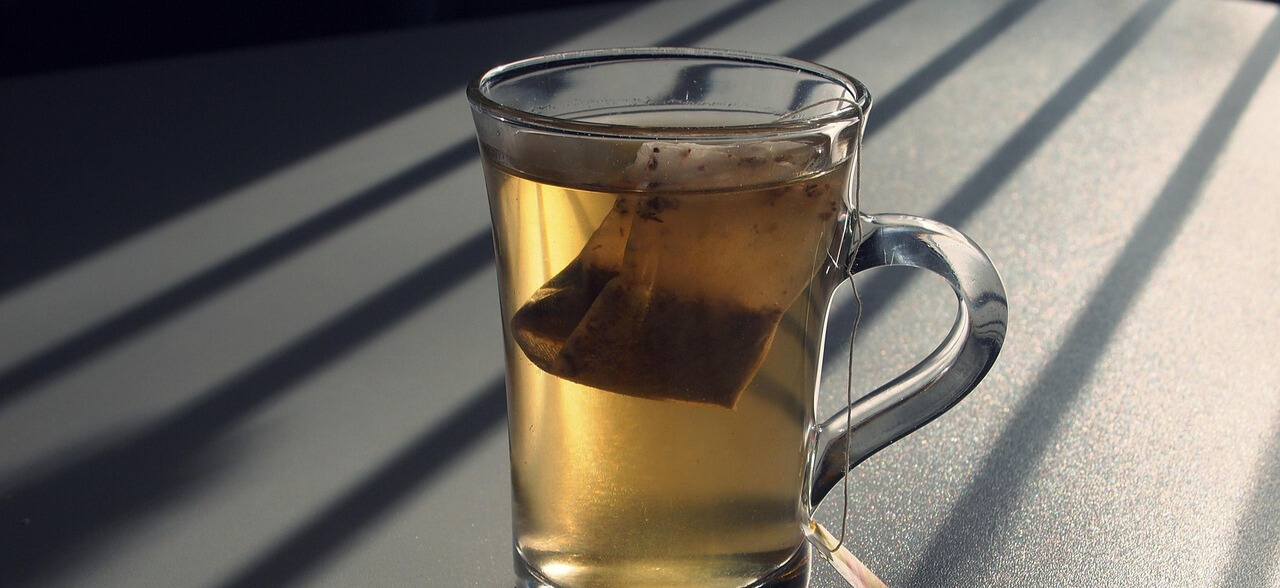
Tea bags
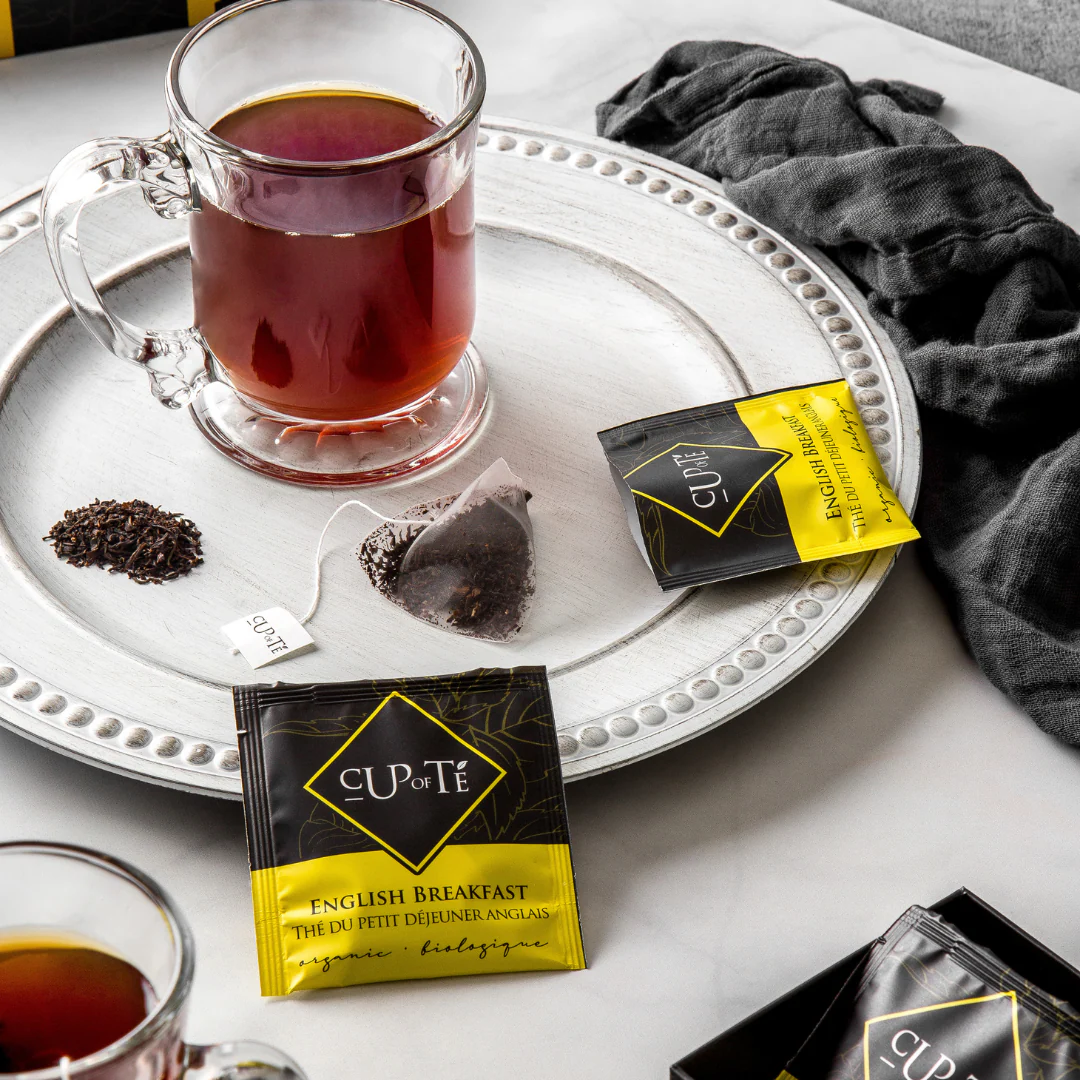
Tea sachets
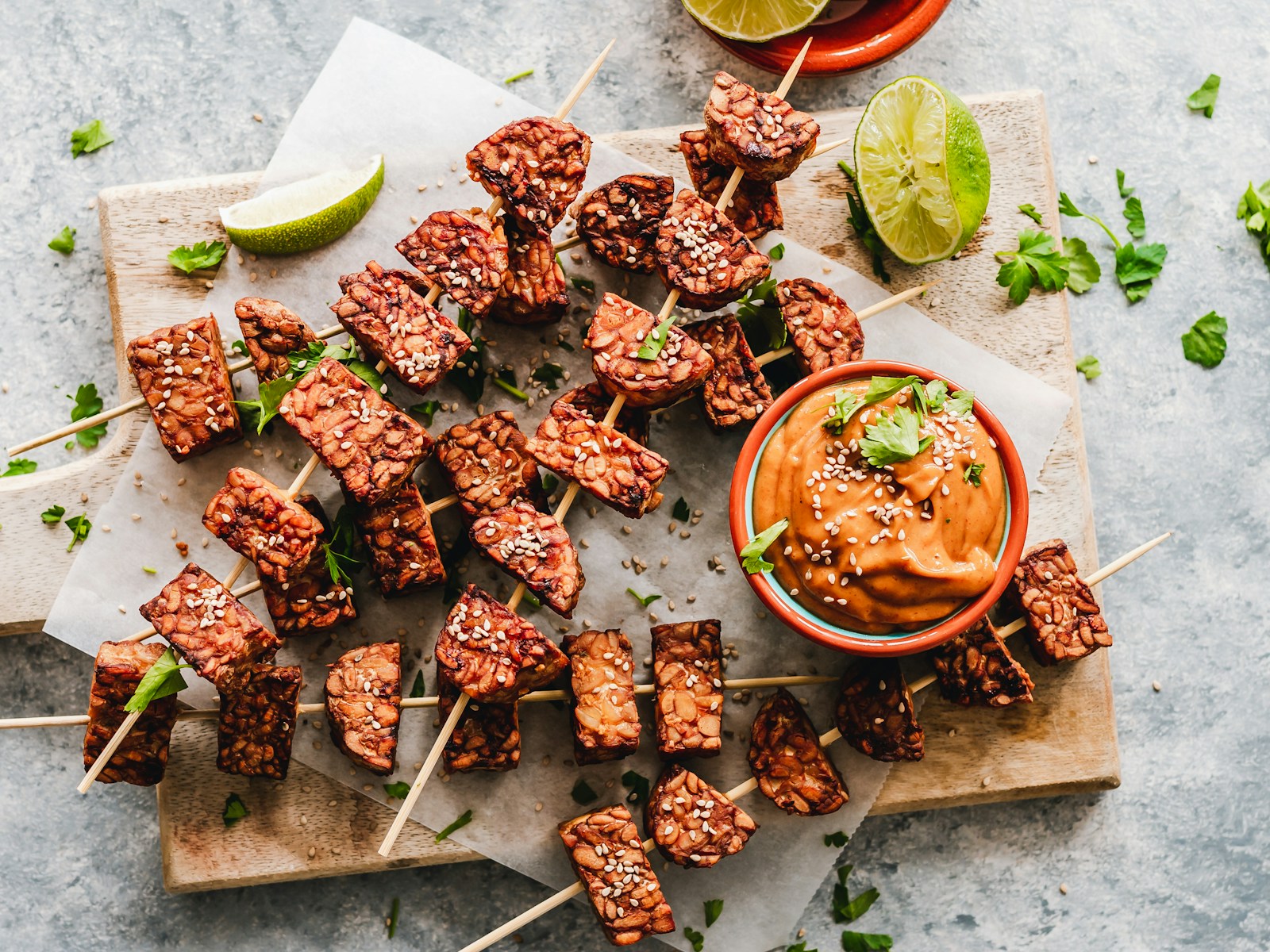
Tempeh
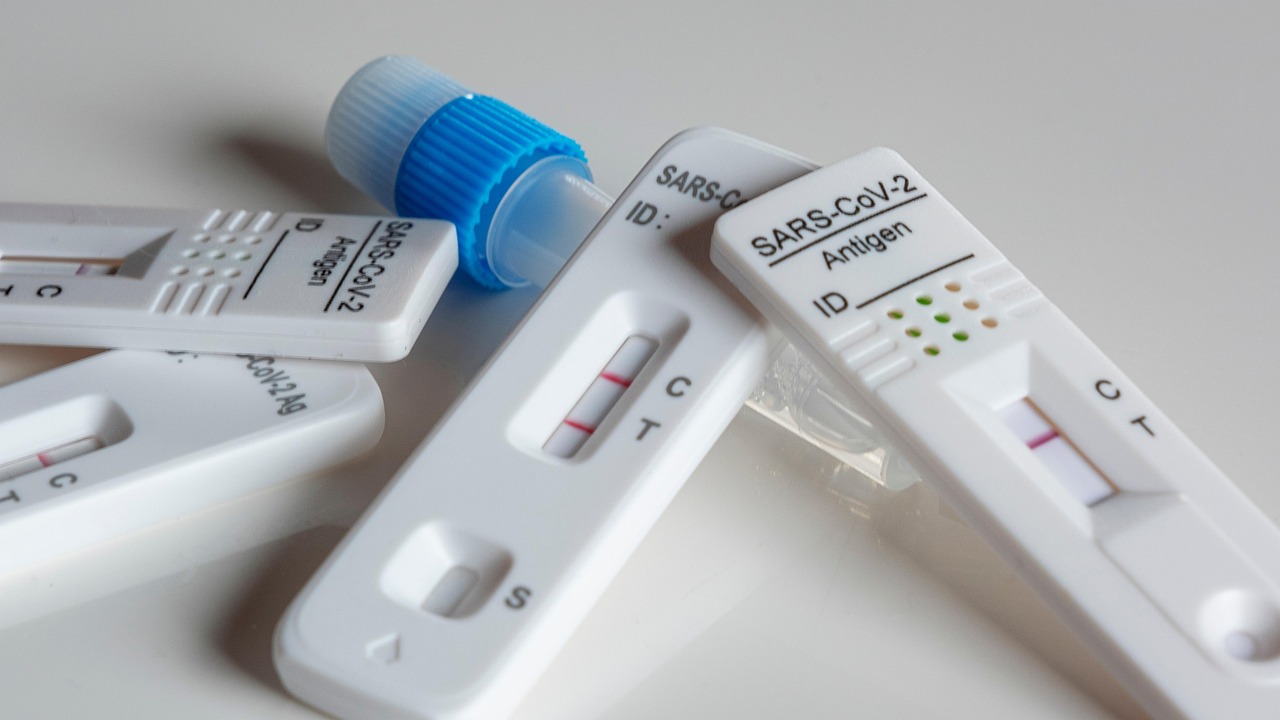
Test kits
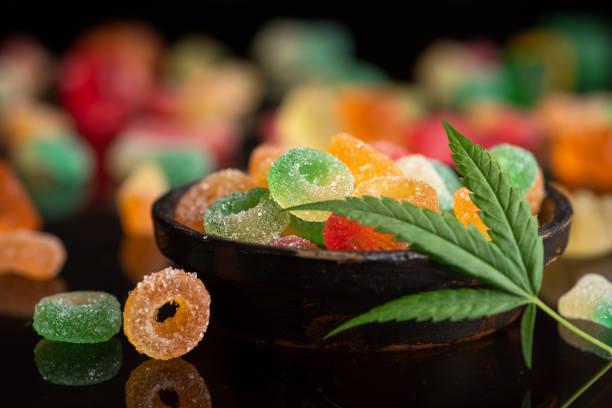
Thc gummies
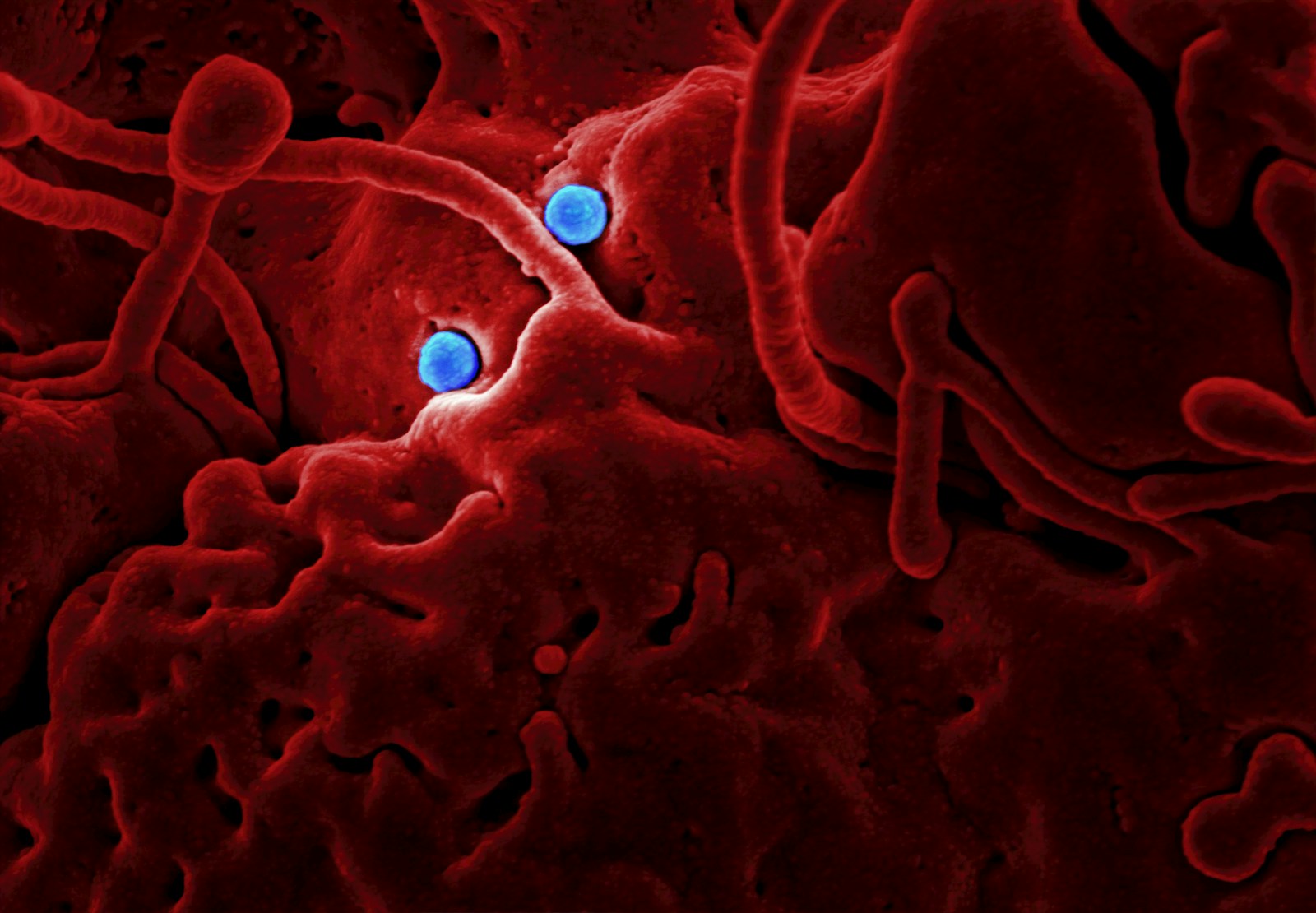
Therapeutic proteins
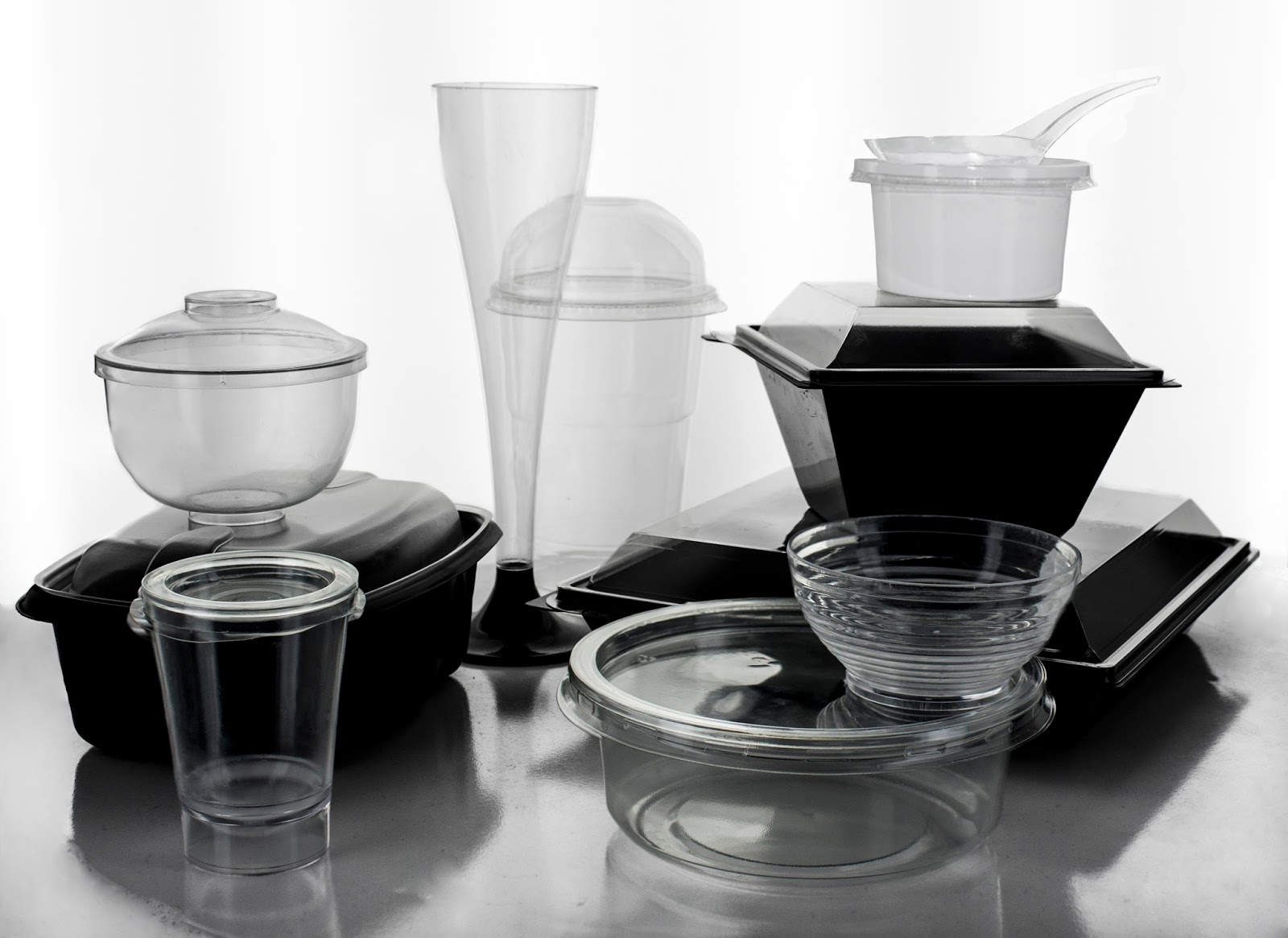
Thermoformed packs
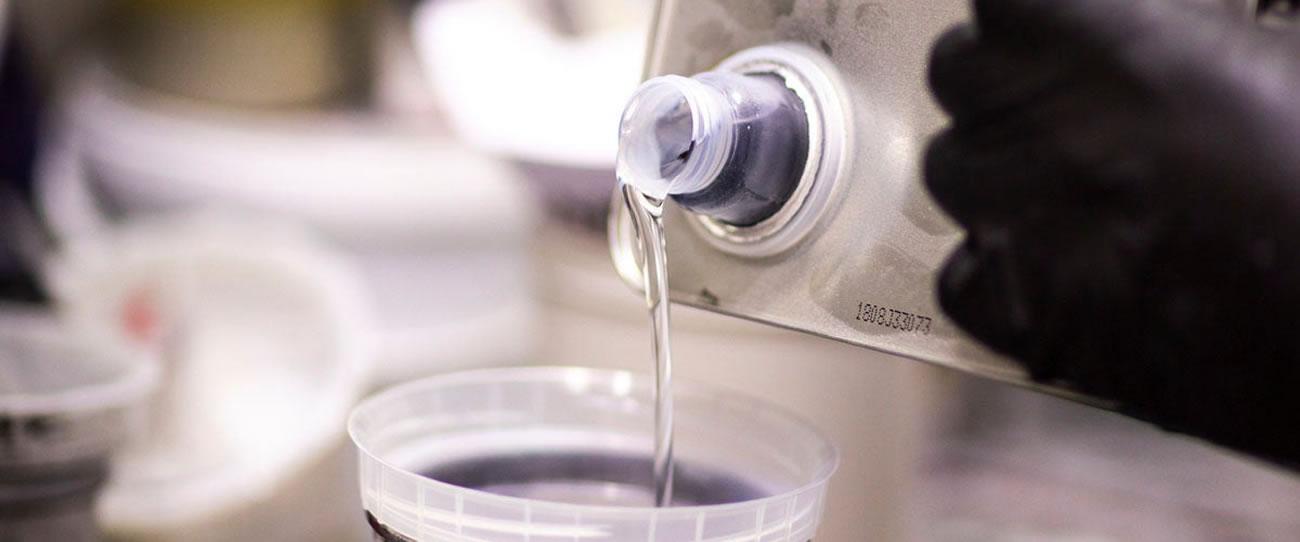
Thinners
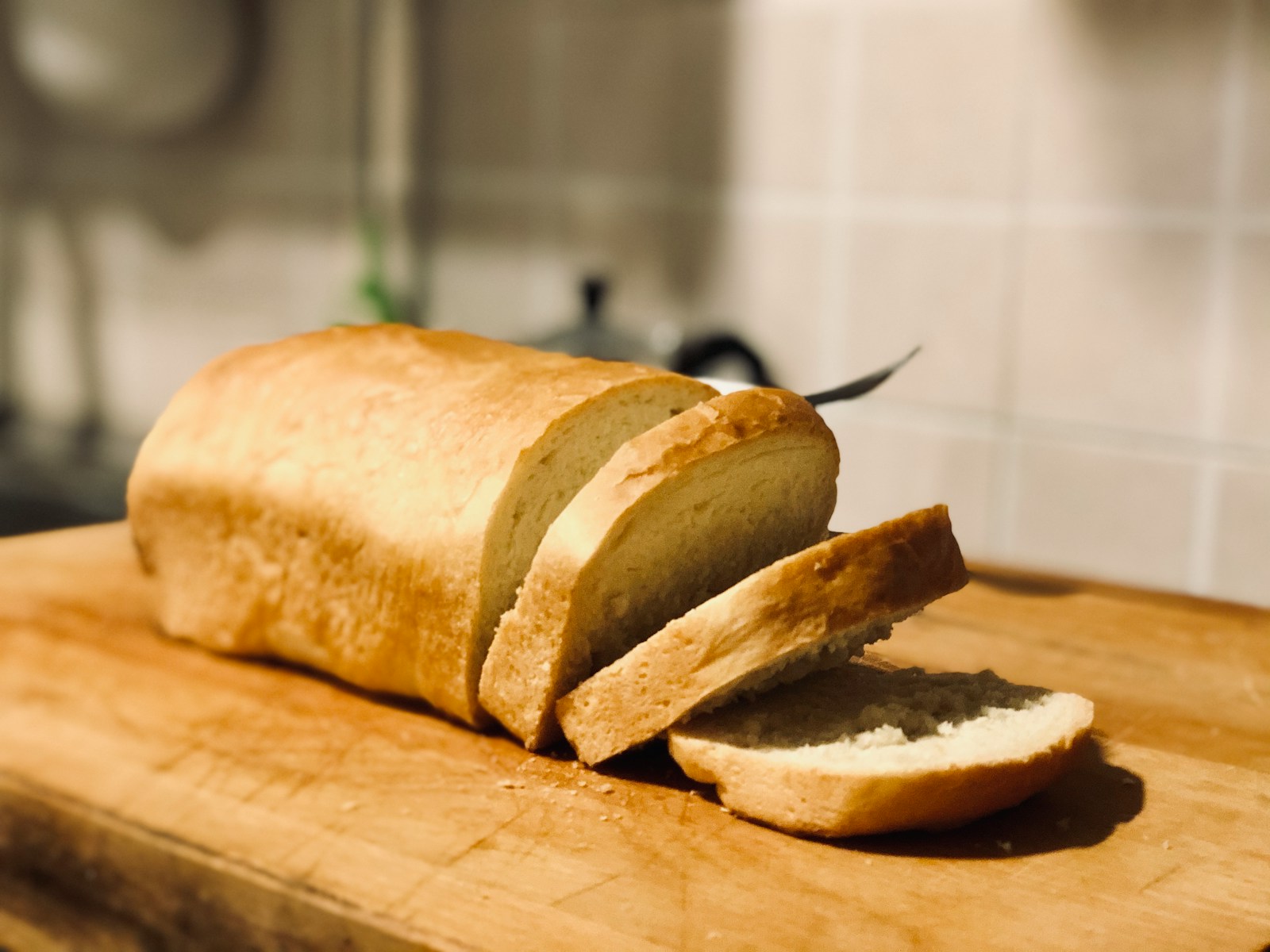
Tin bread
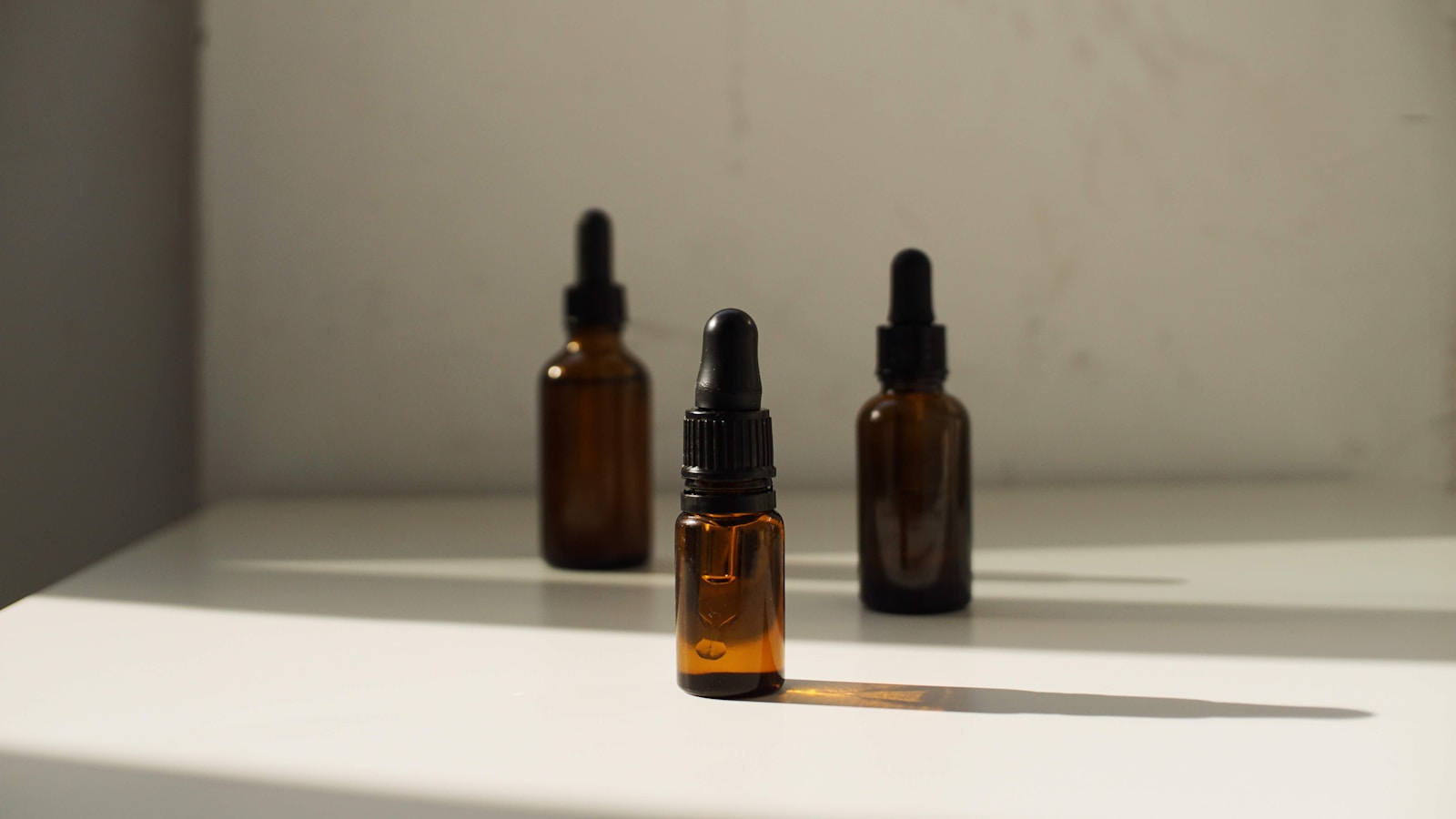
Tinctures
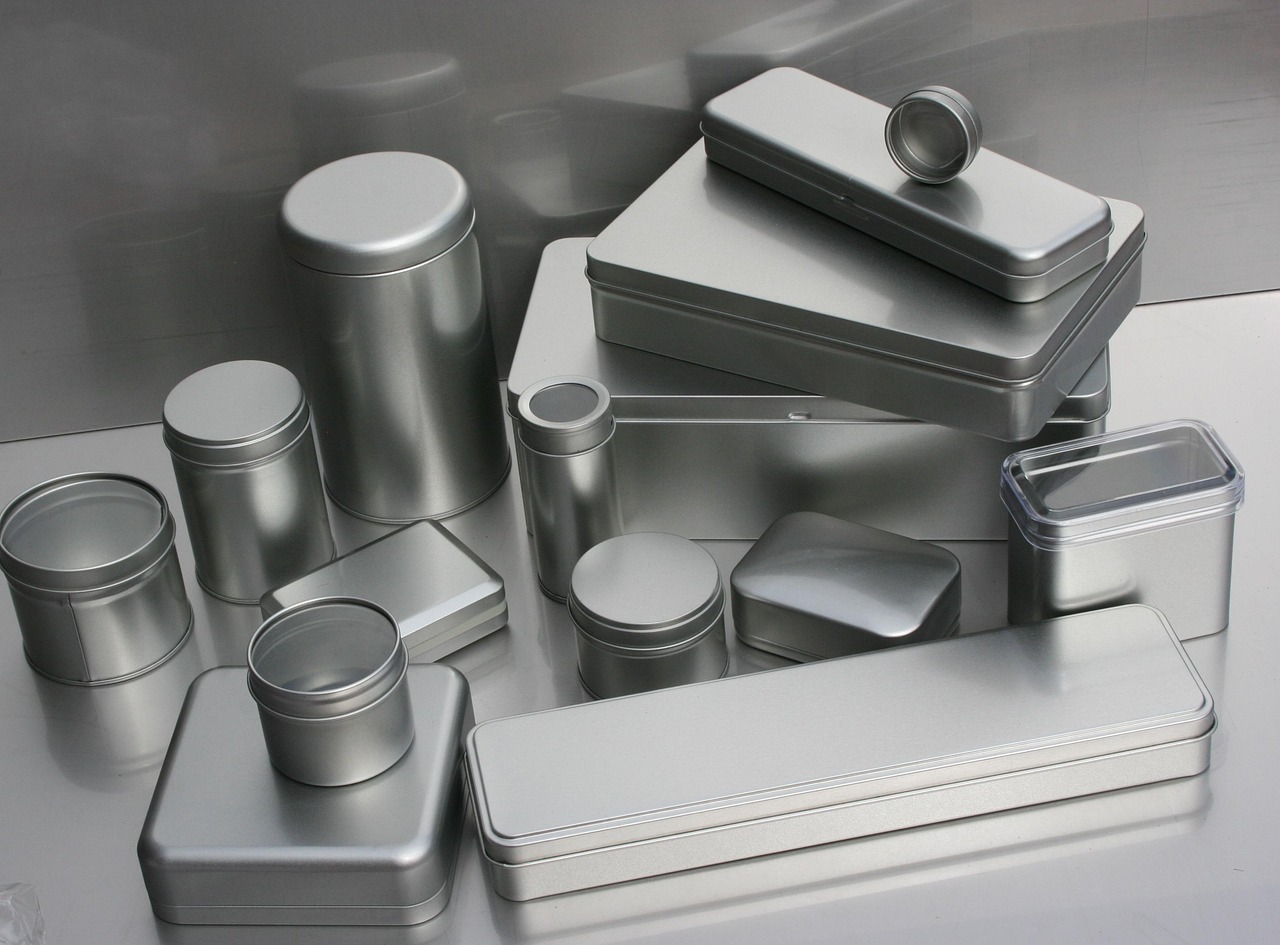
Tins
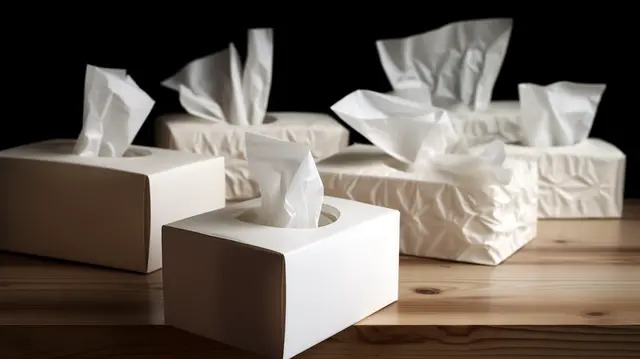
Tissue boxes
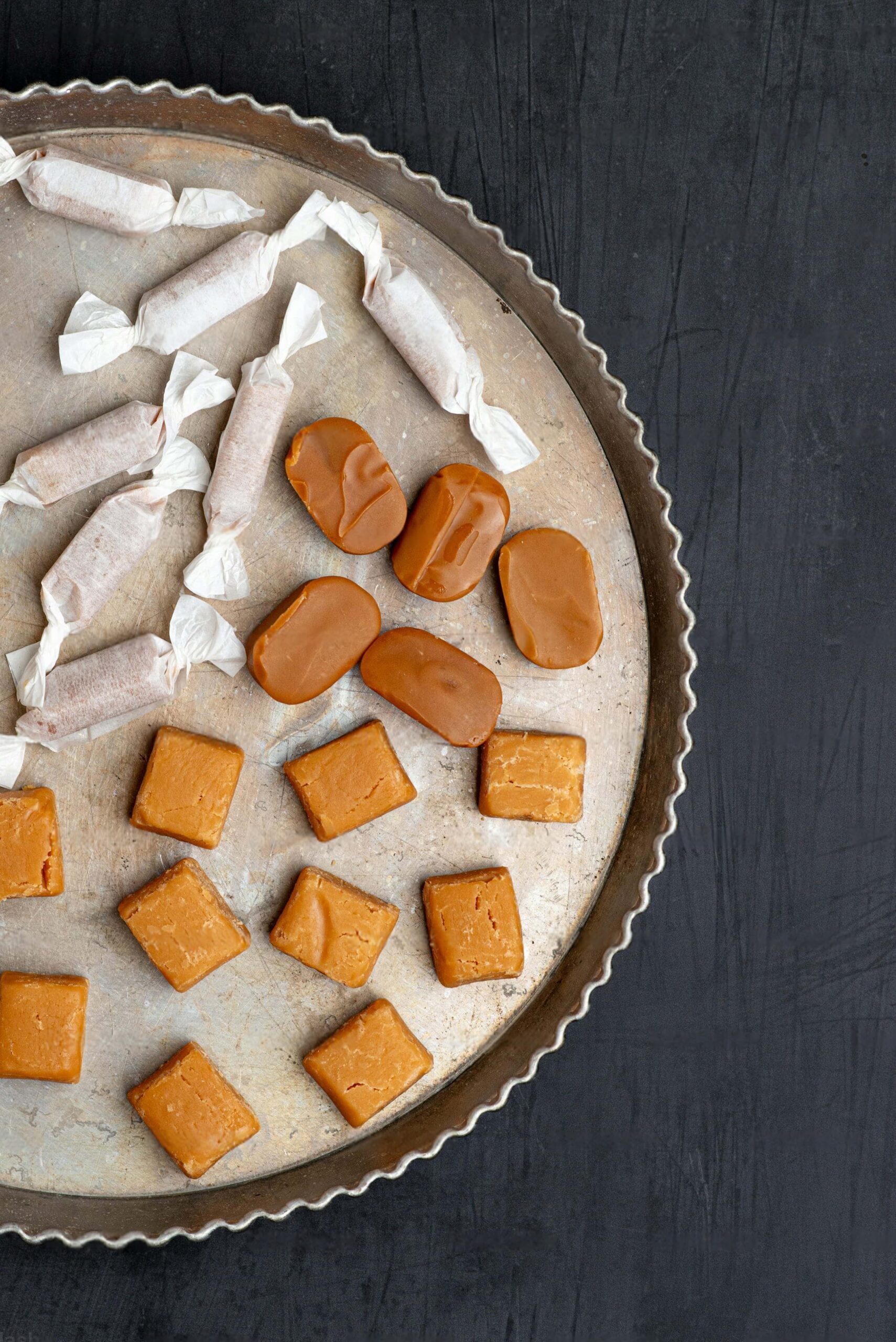
Toffees
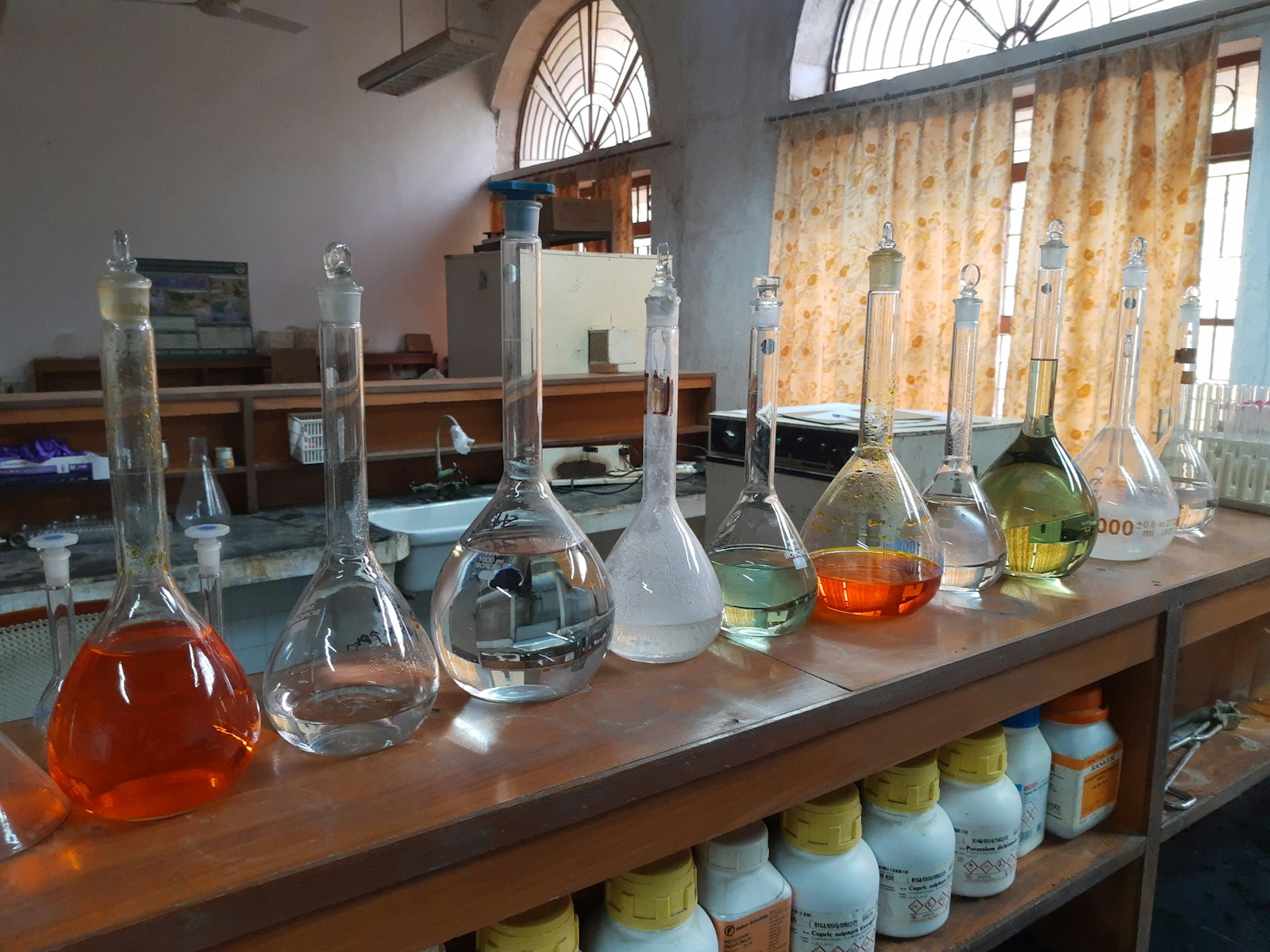
Toluene
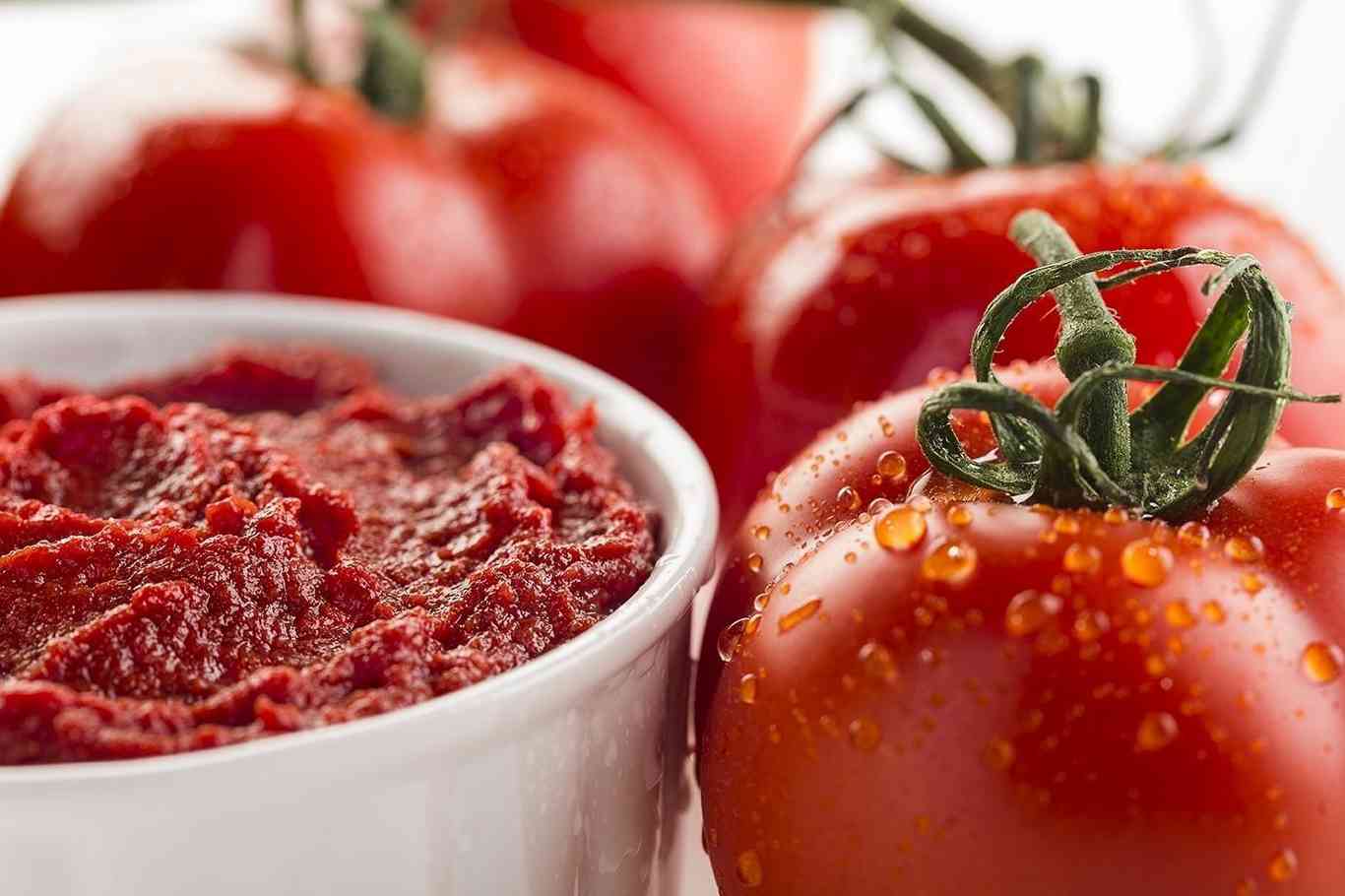
Tomato concentrate
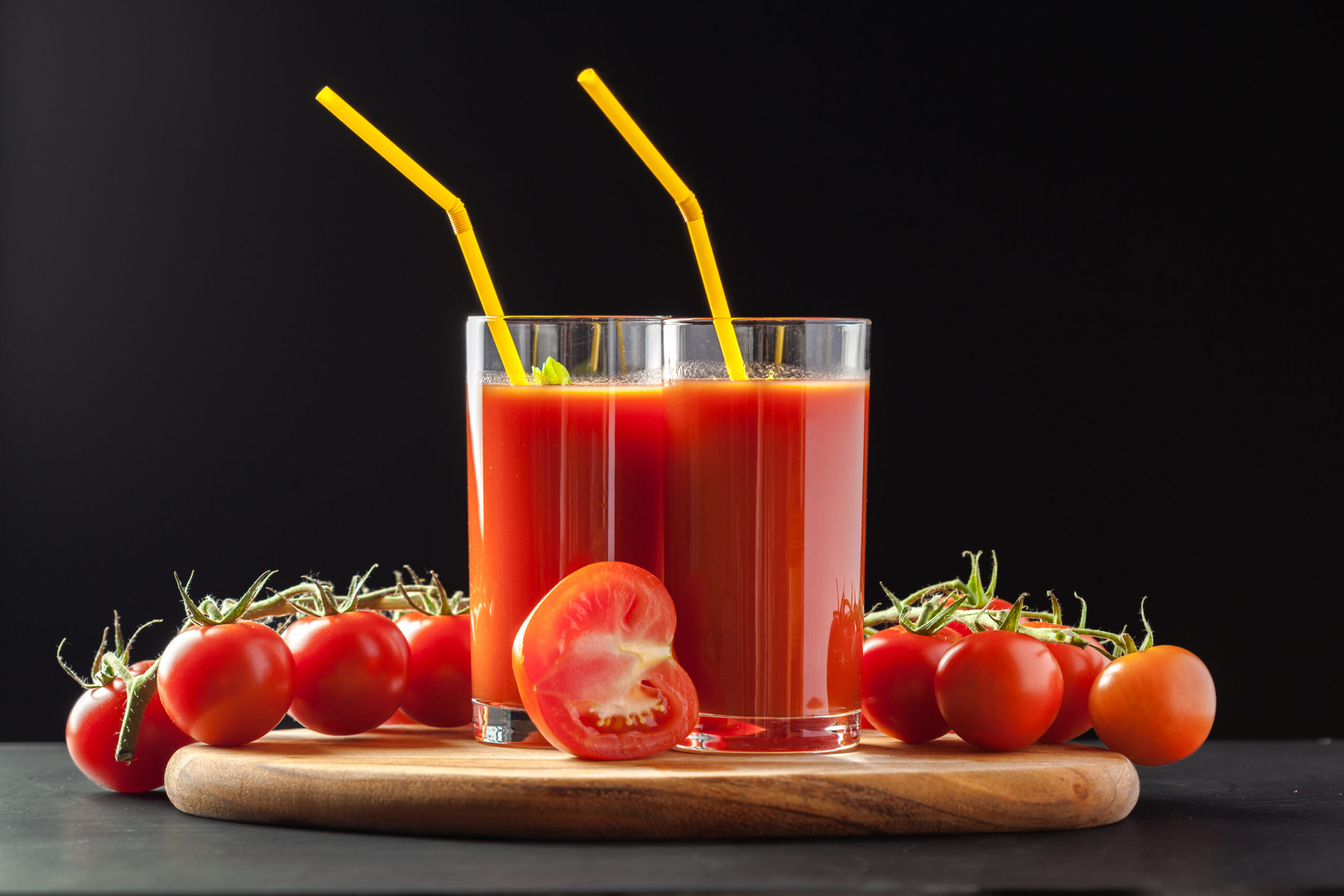
Tomato juice
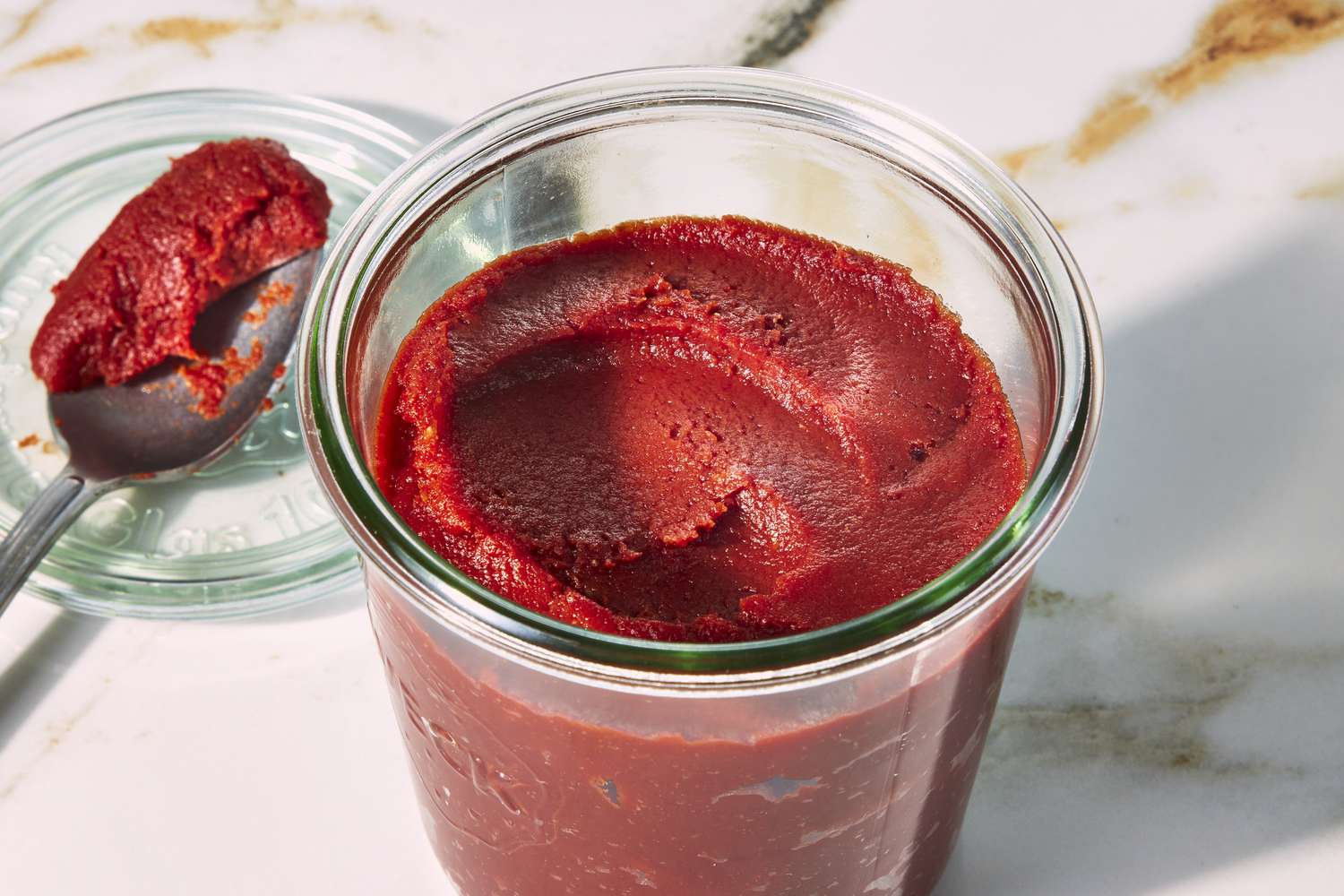
Tomato paste
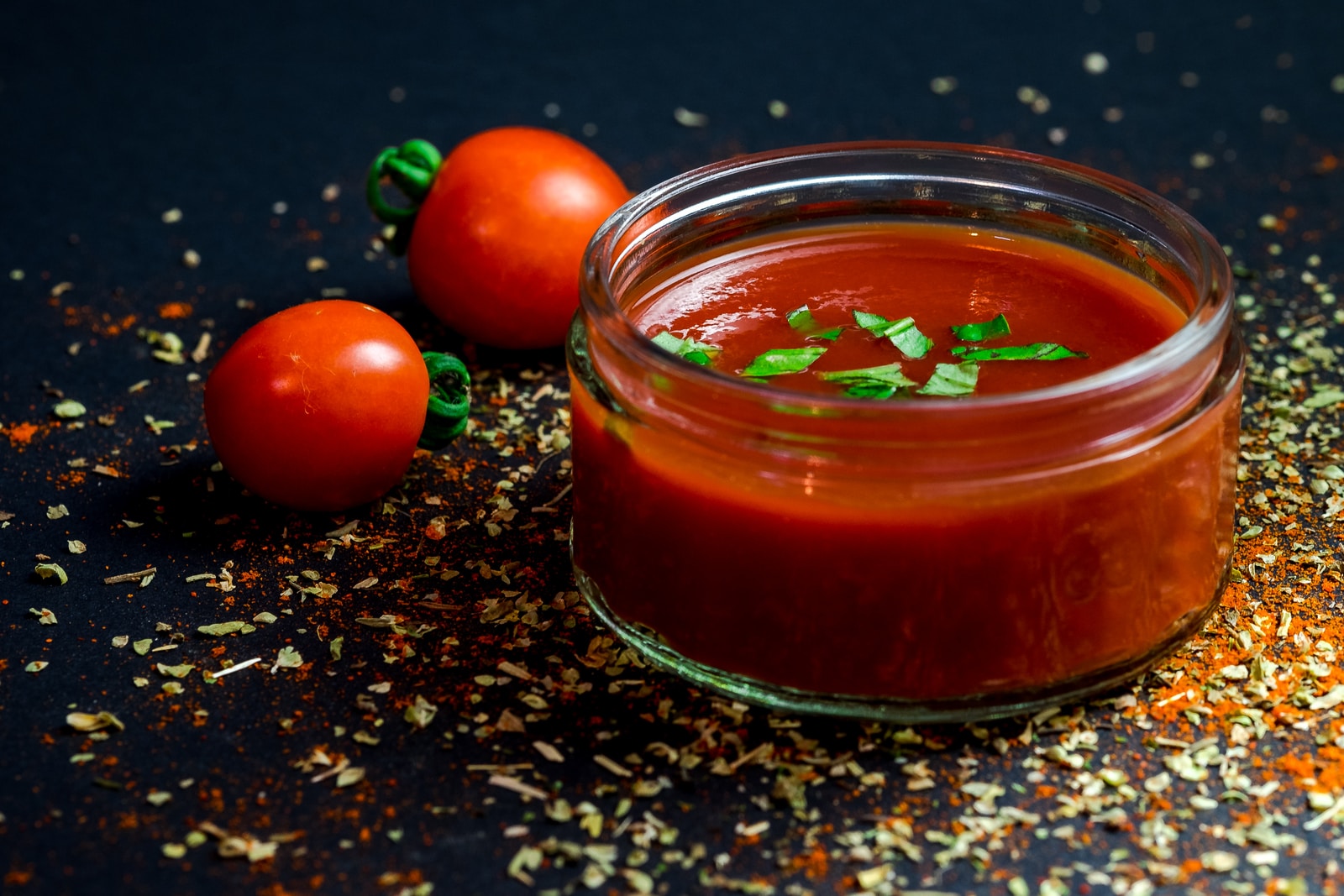
Tomato sauce
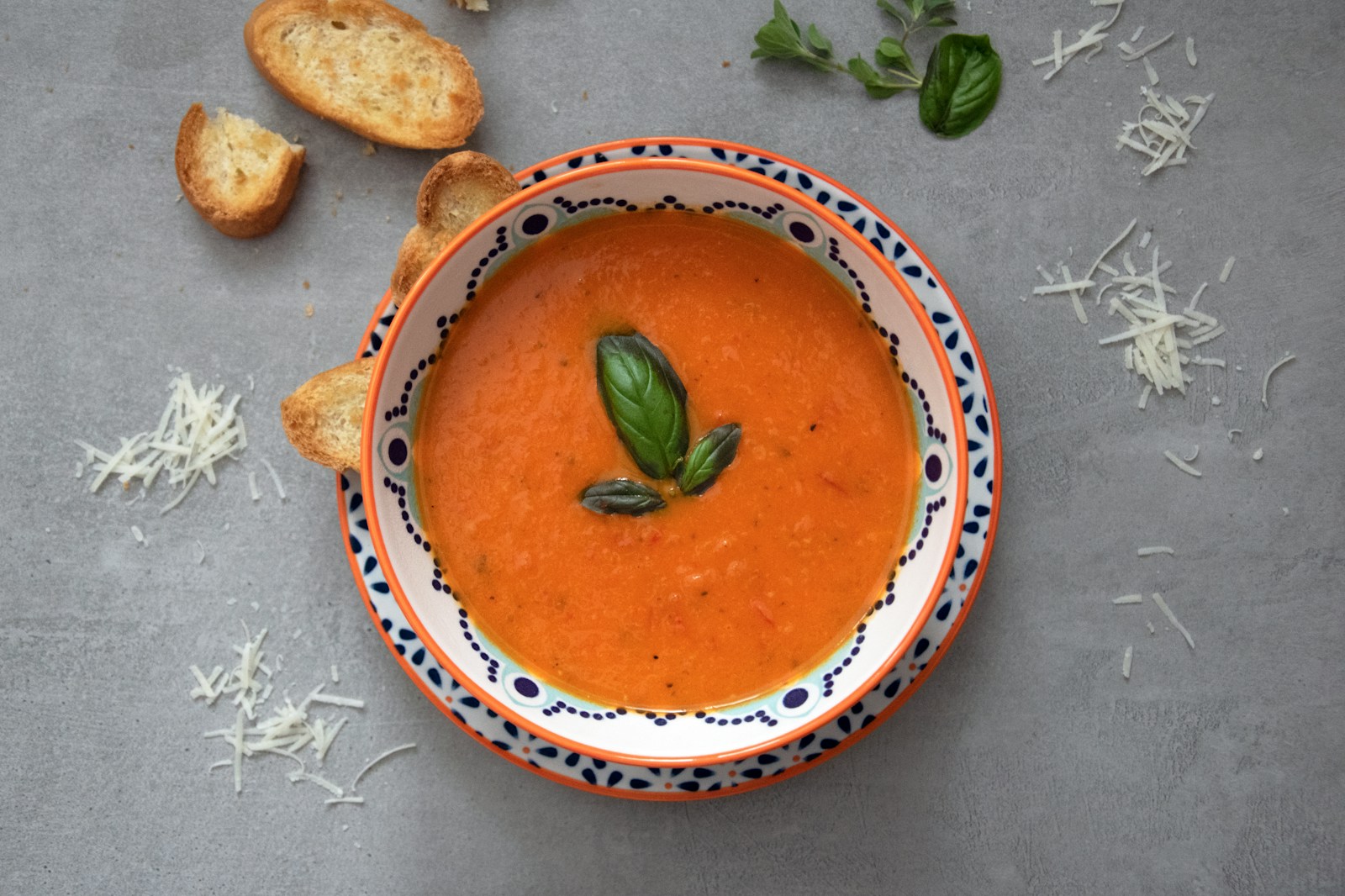
Tomato soup
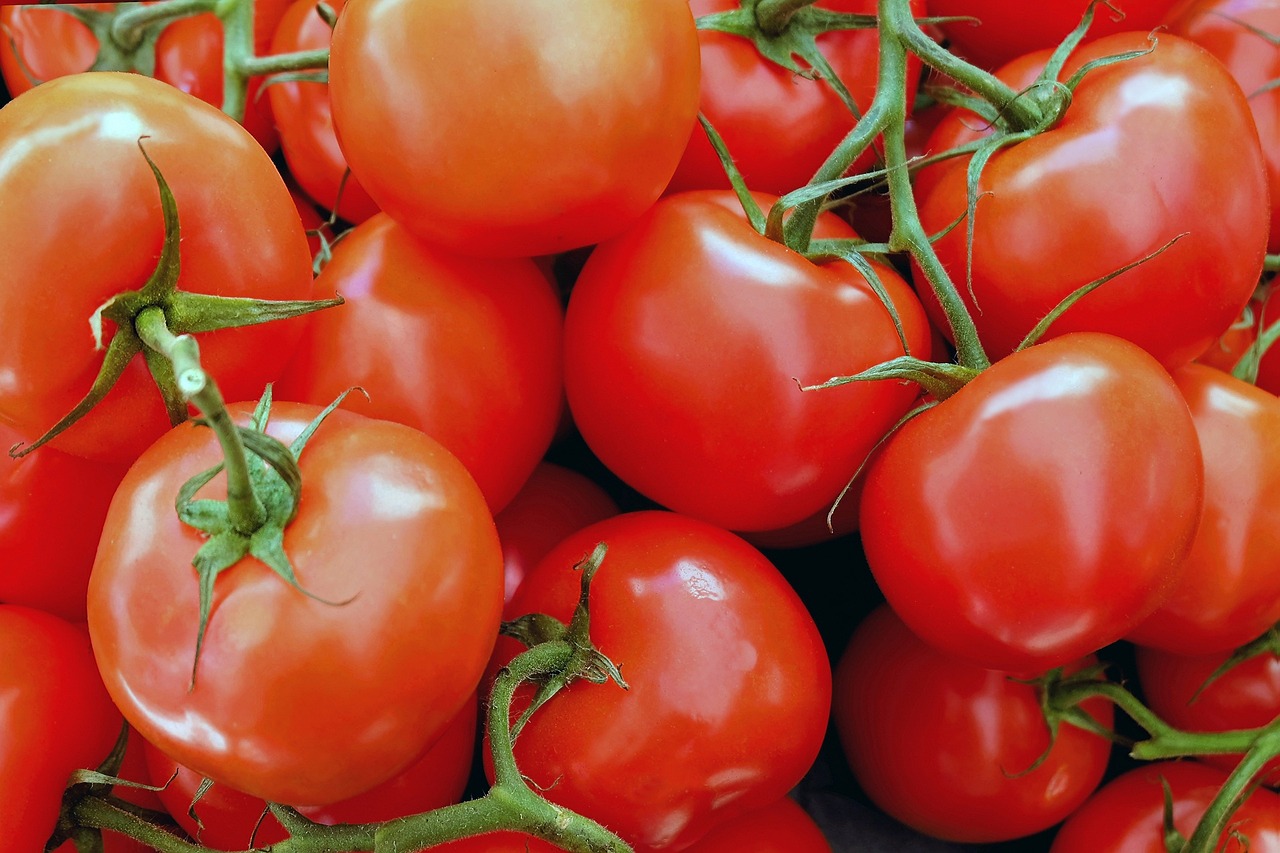
Tomatoes
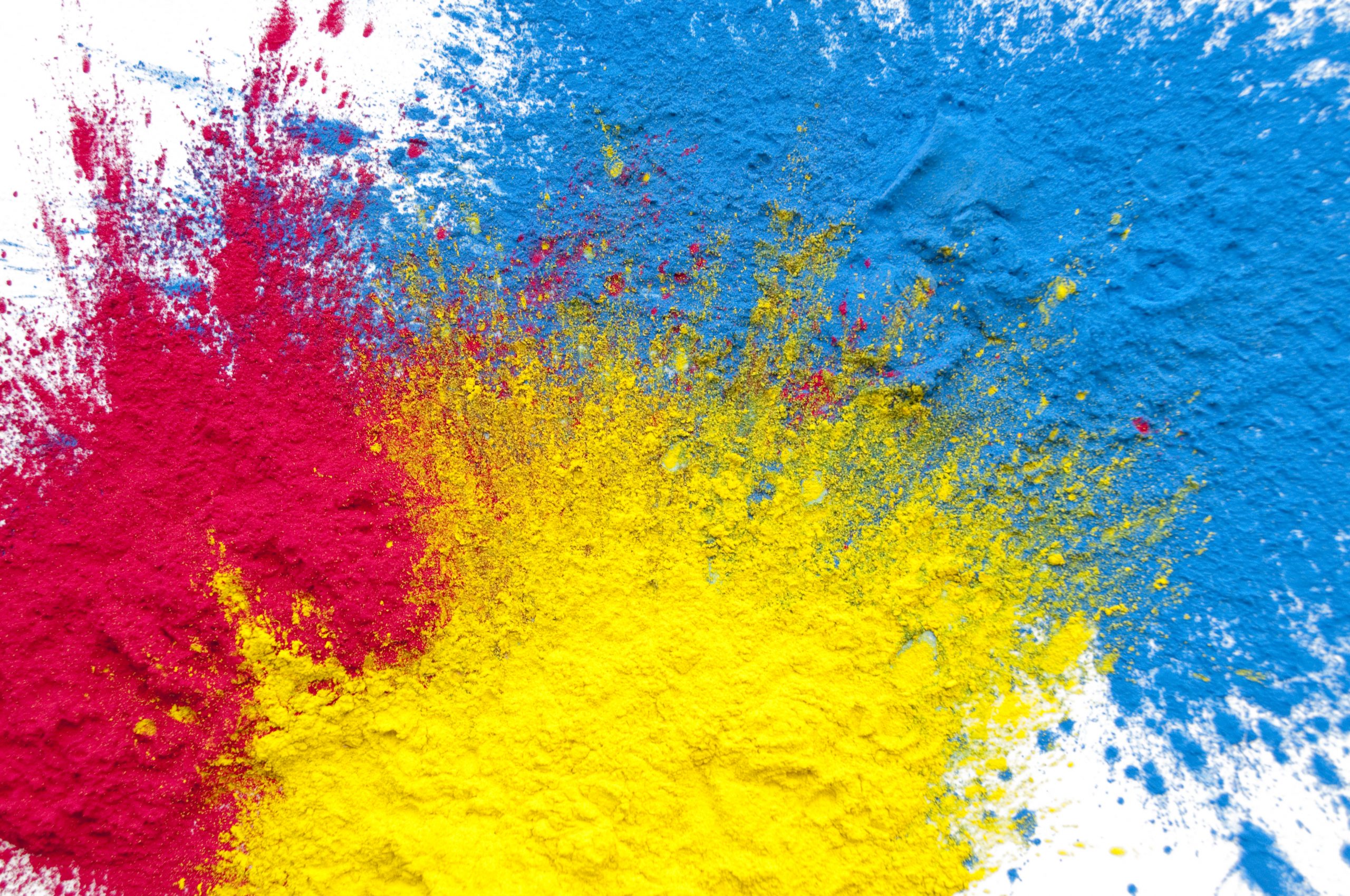
Toner
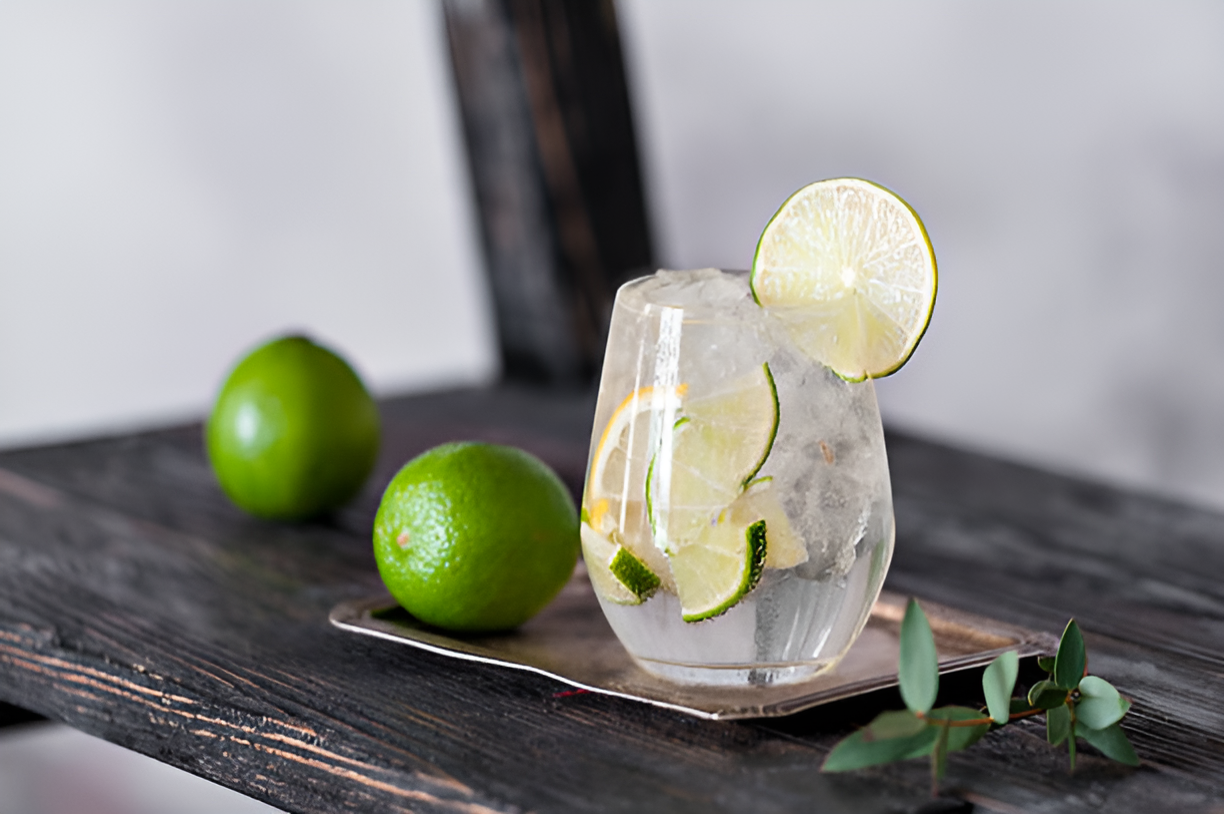
Tonic water
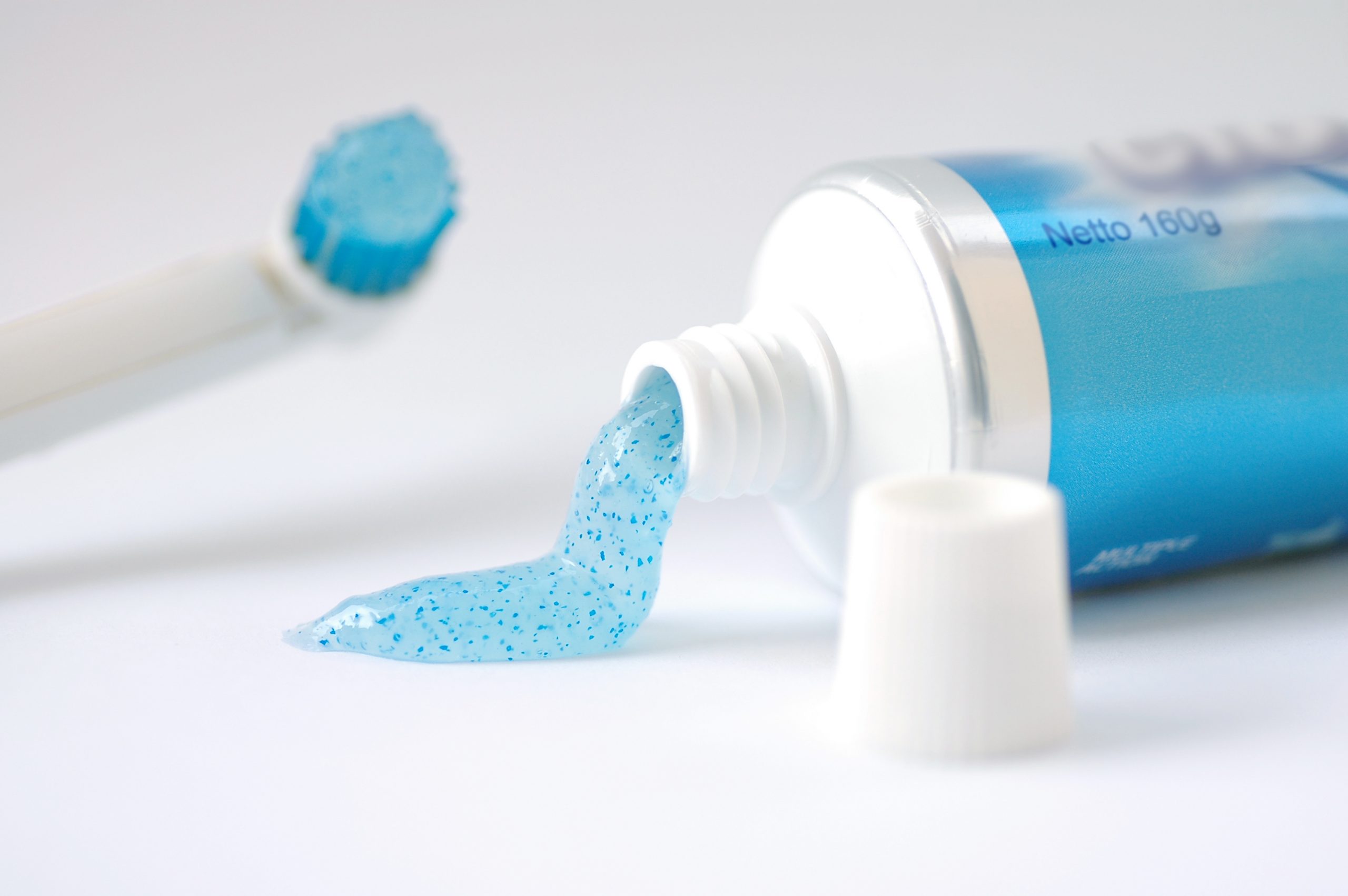
Toothpaste
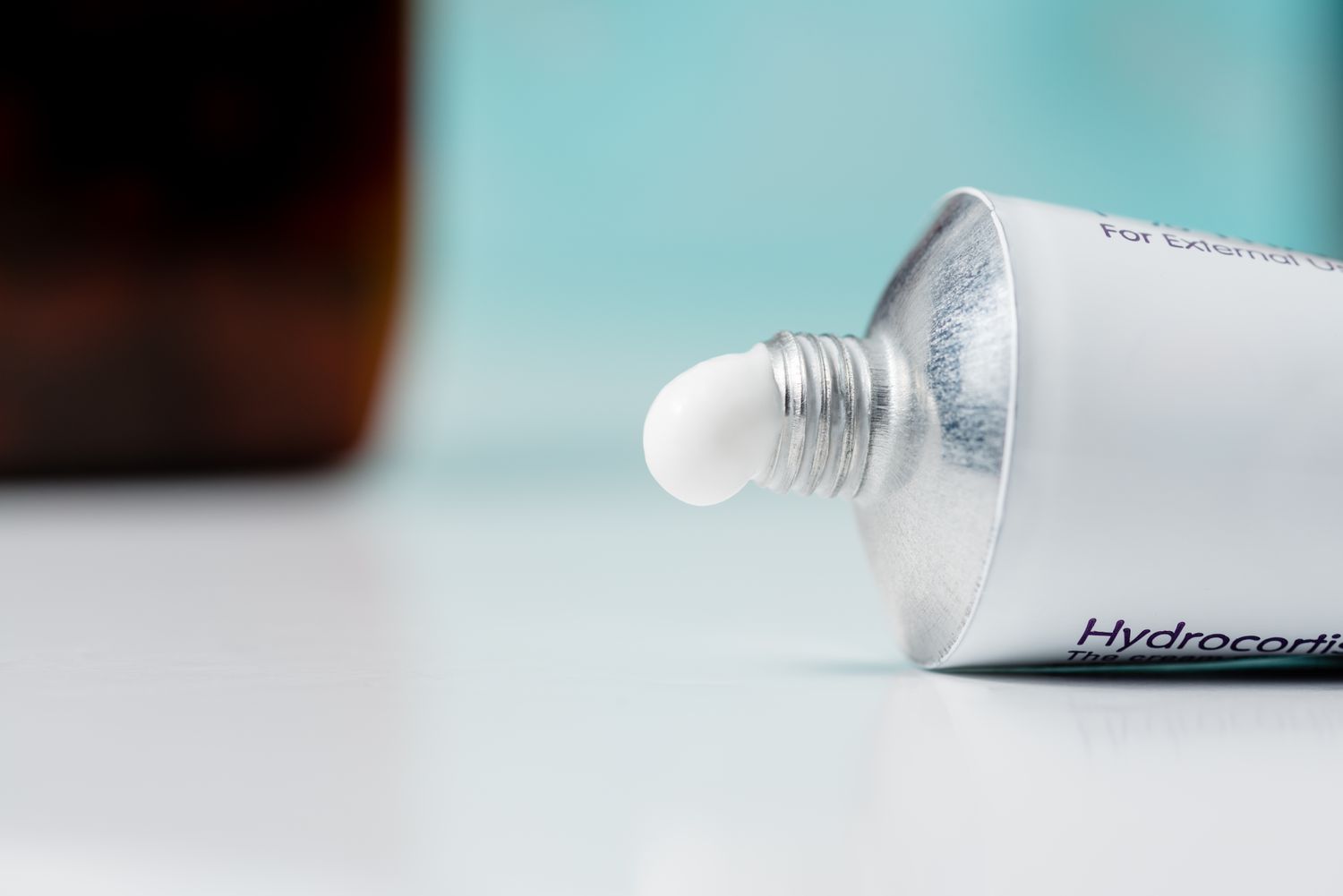
Topical creams
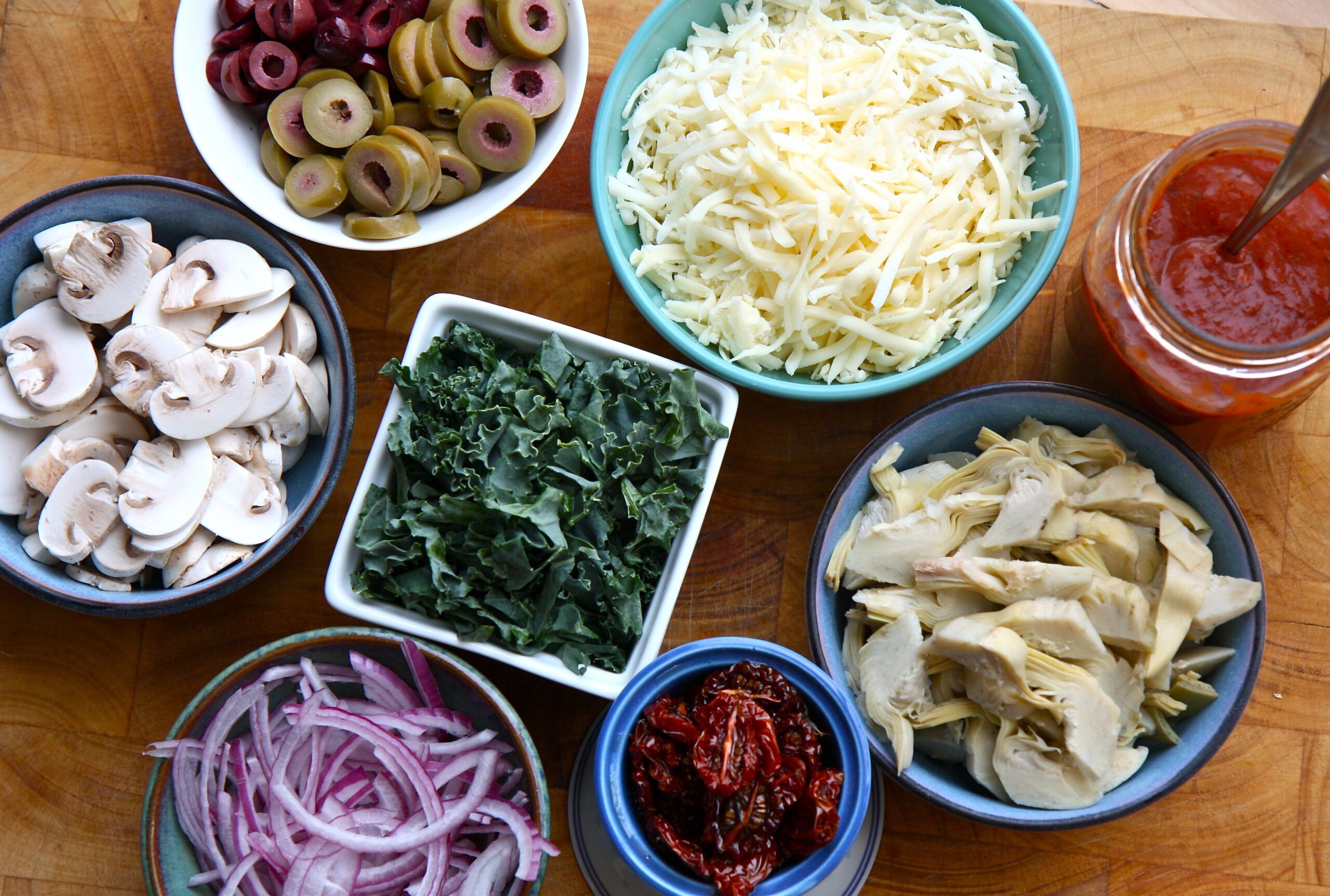
Toppings
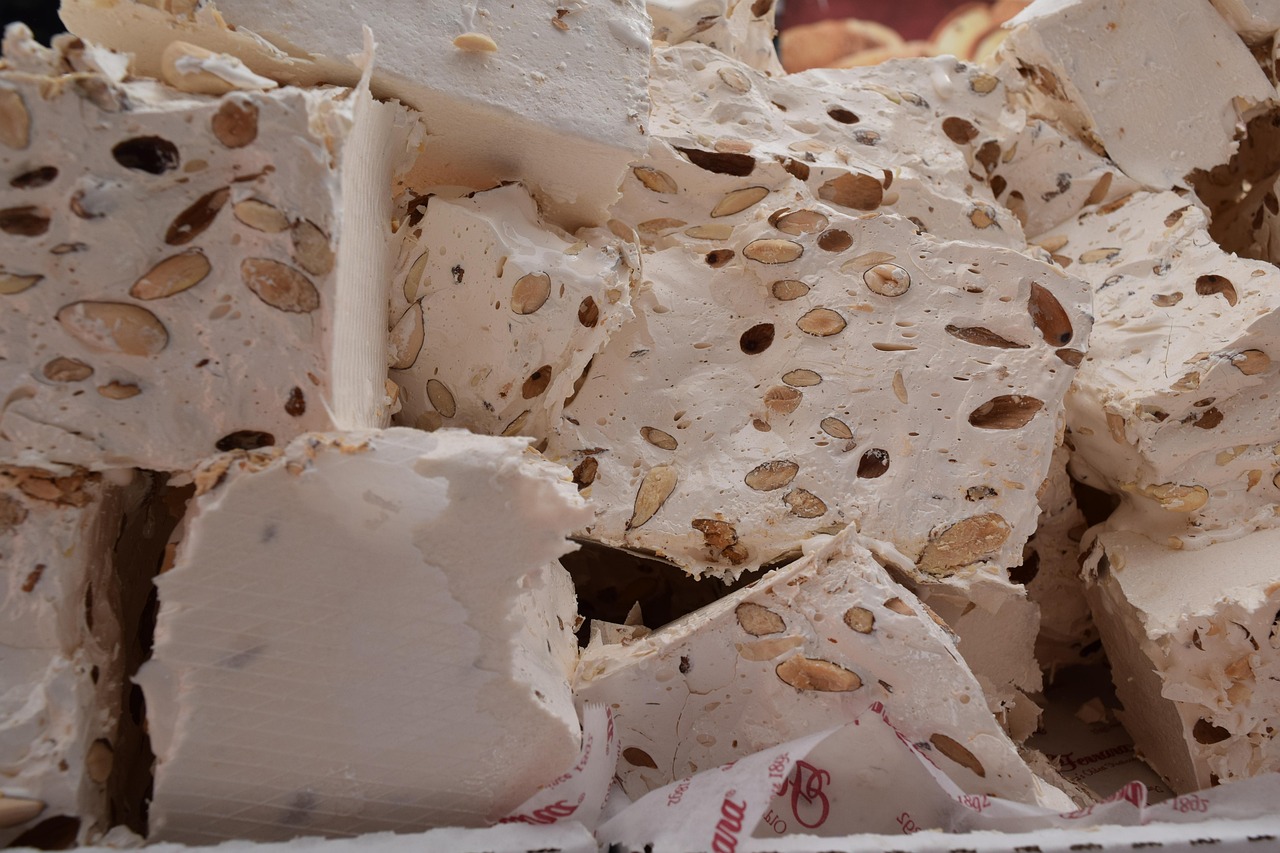
Torrone
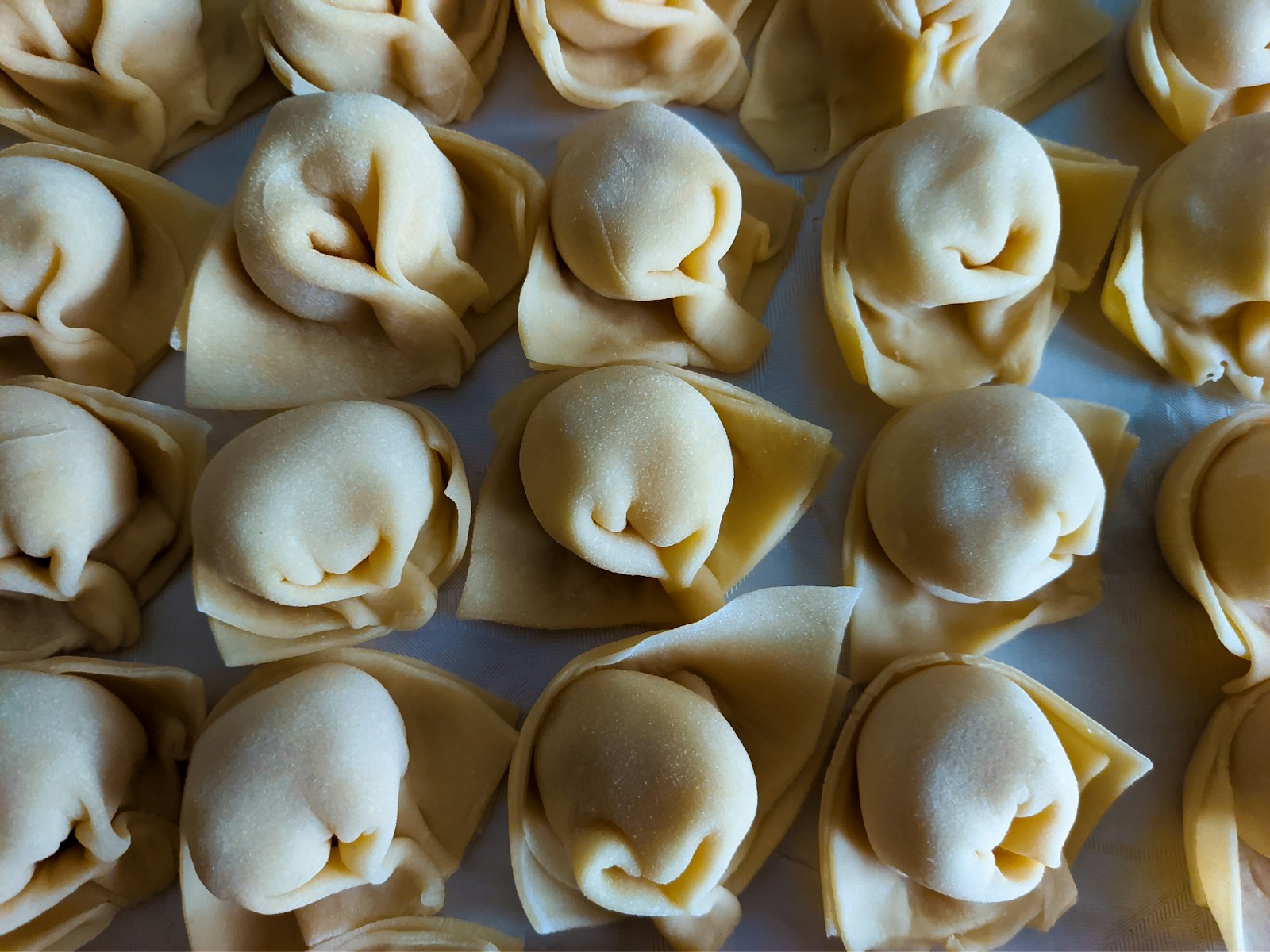
Tortellini
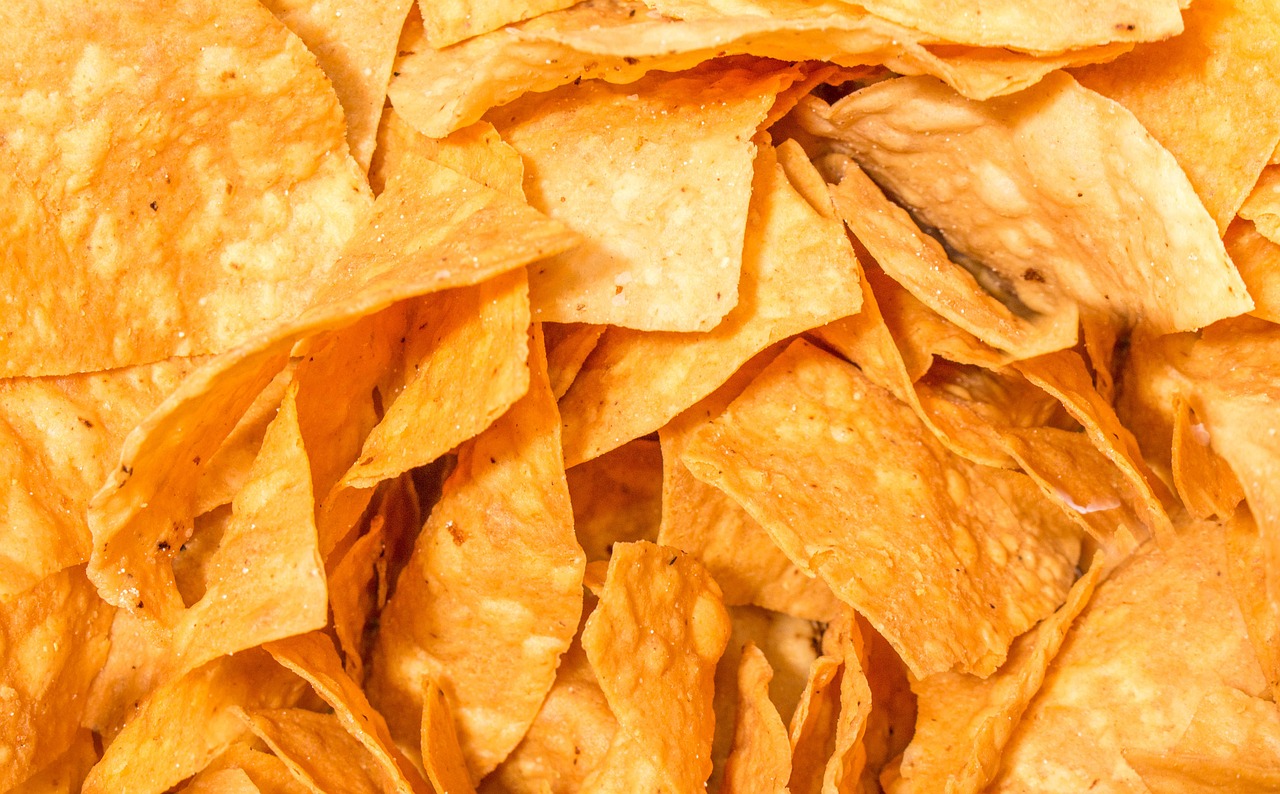
Tortilla Chips
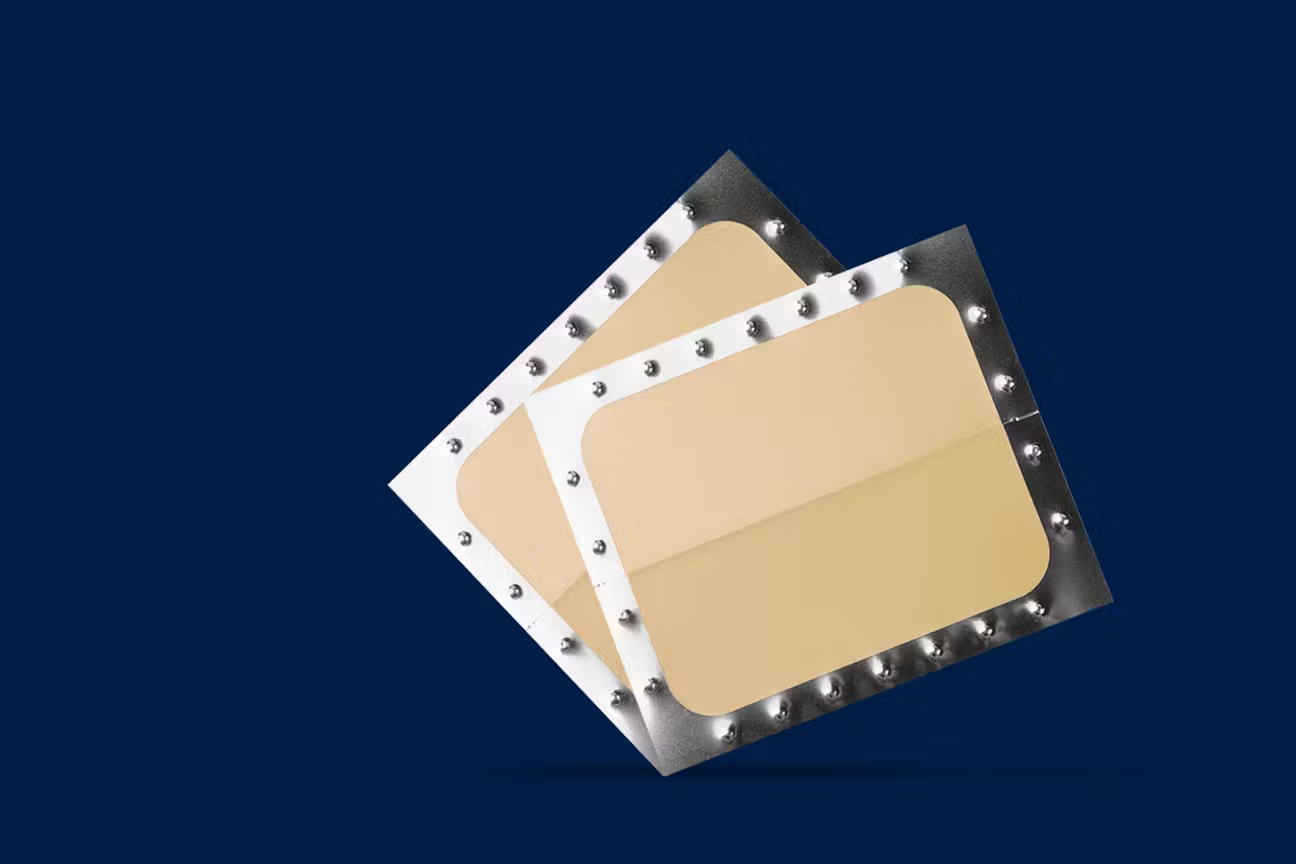
Transdermal patches
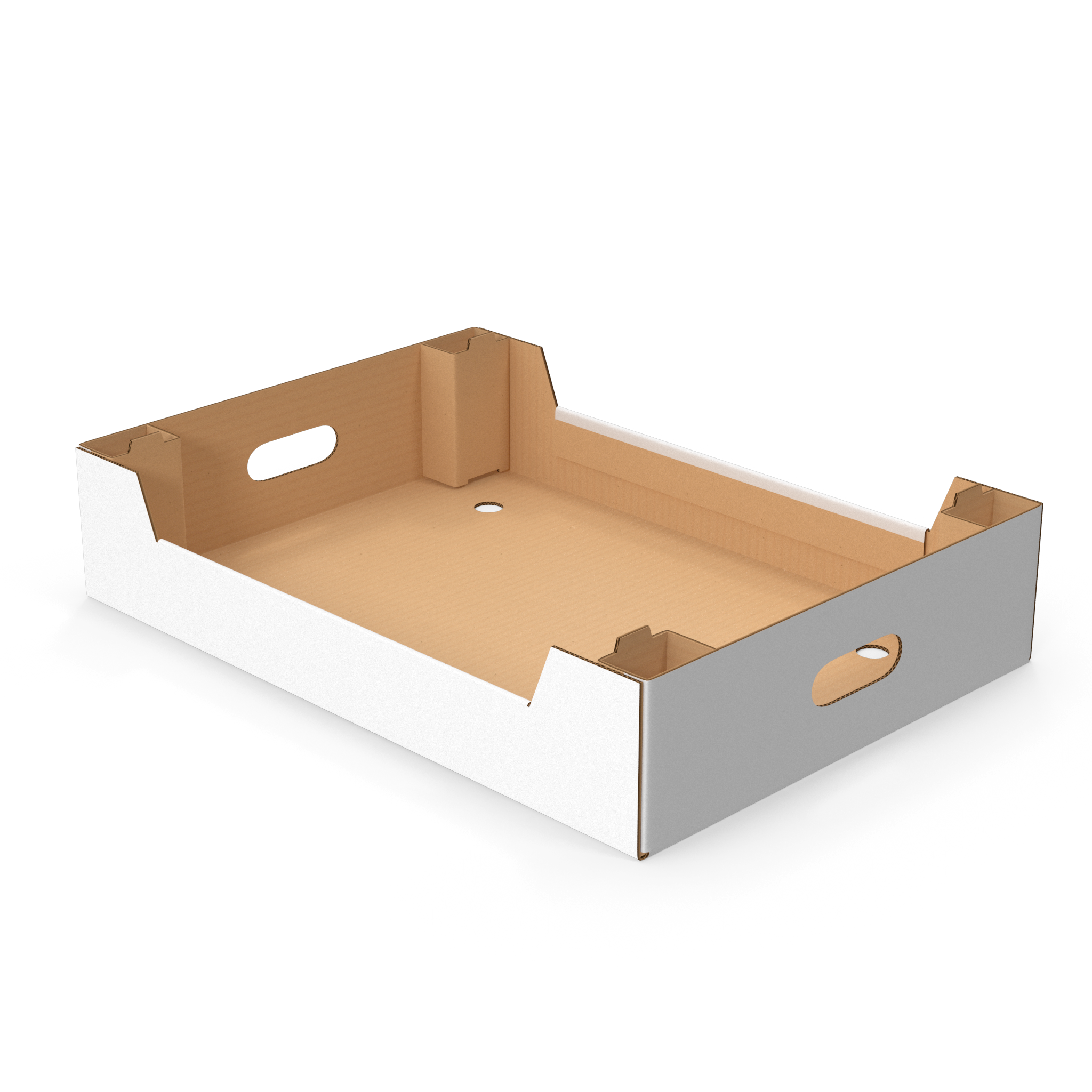
Trays
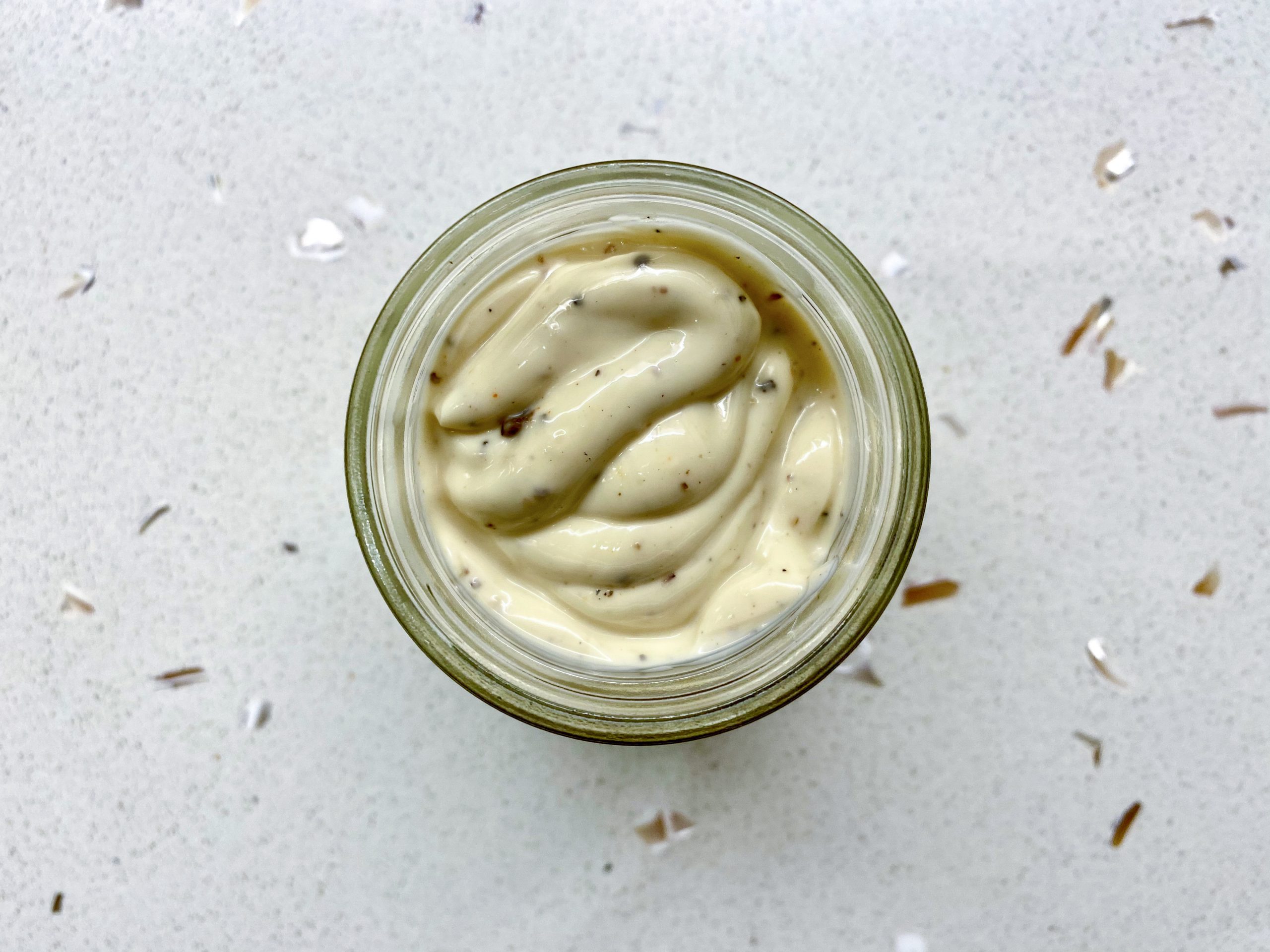
Truffle cream
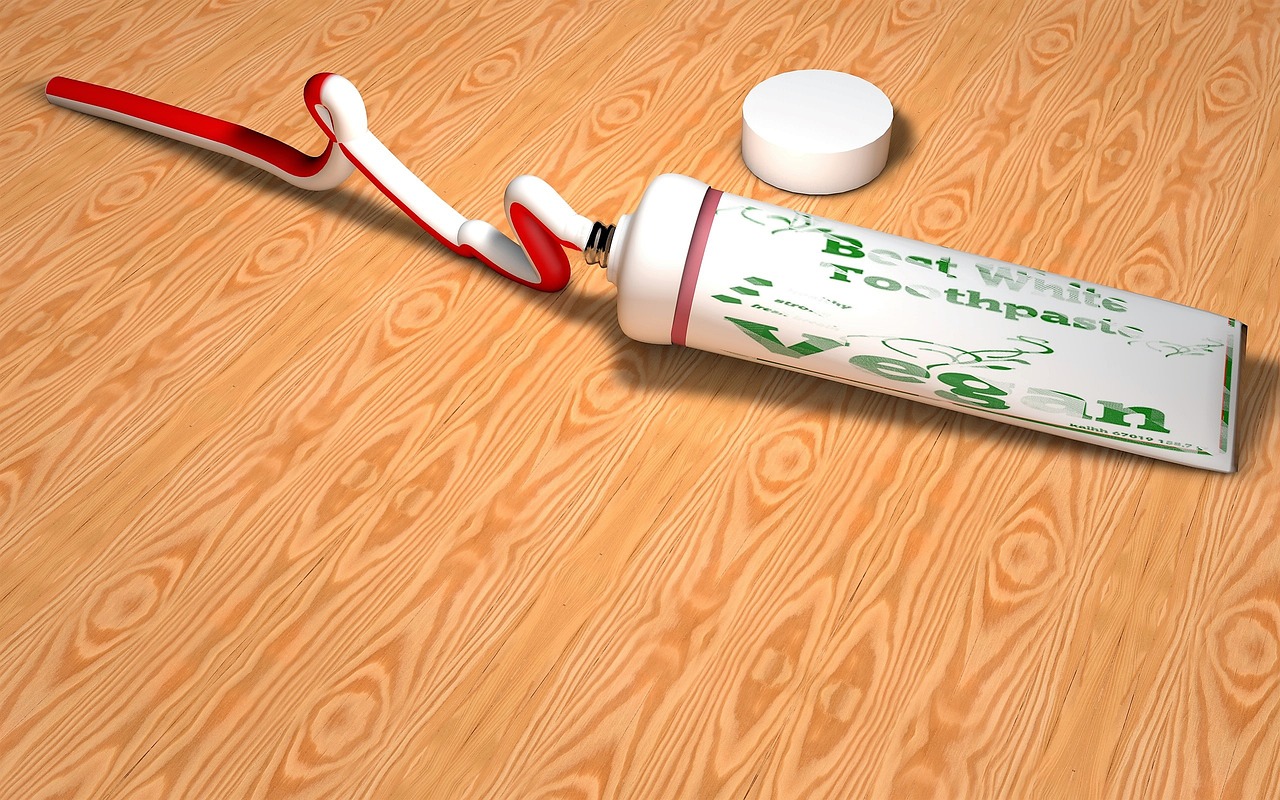
Tubes
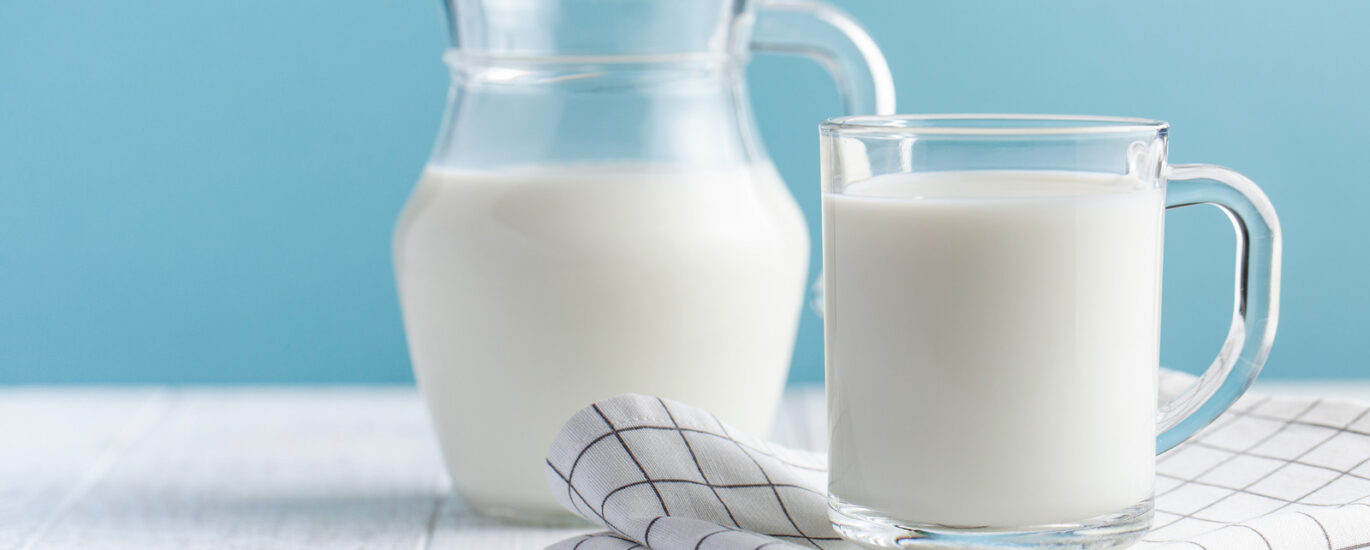
Uht milk
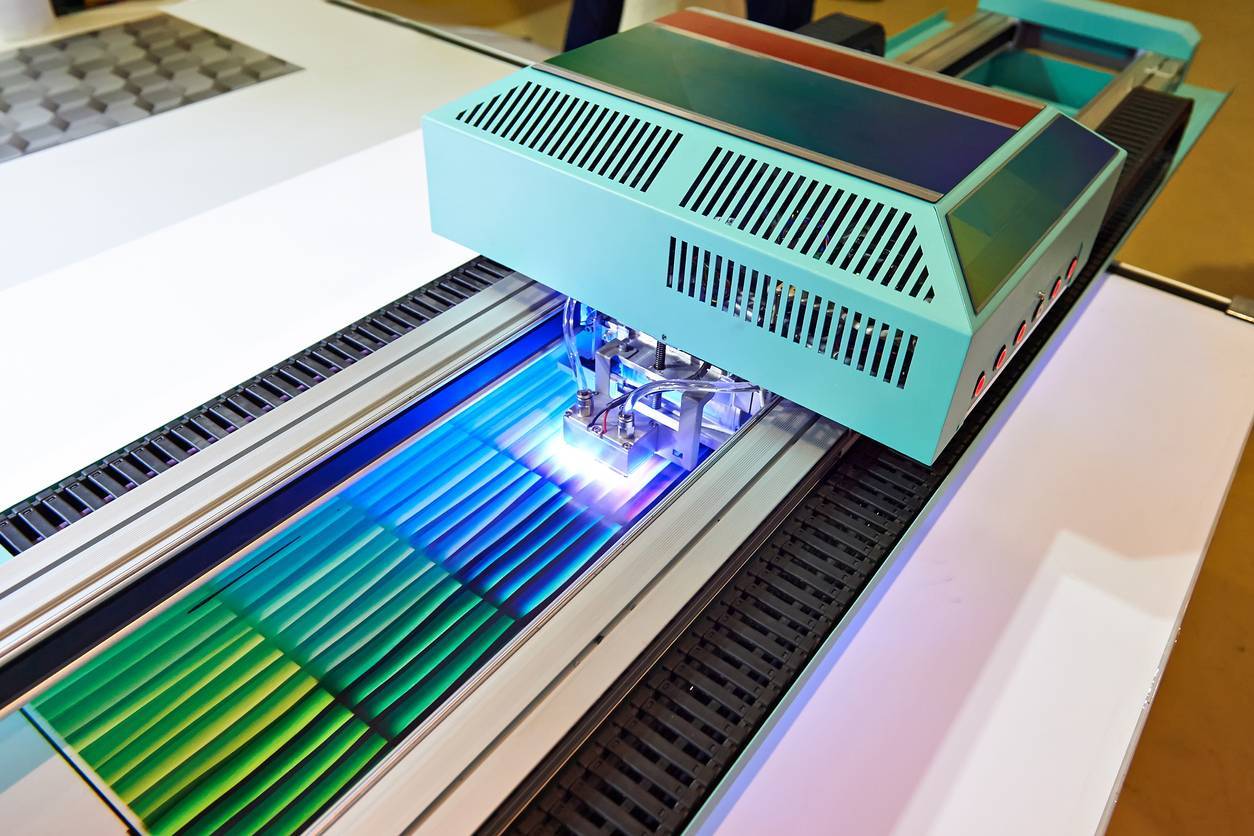
Uv-curable inks
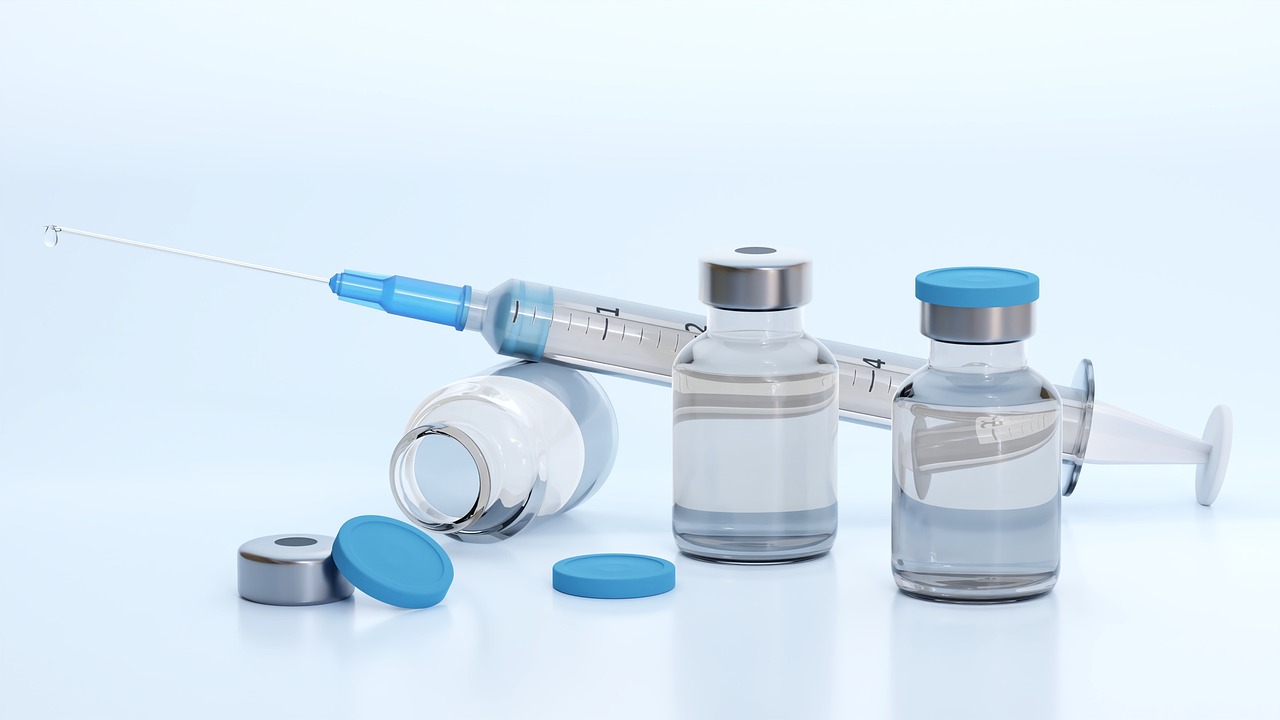
Vaccine vials
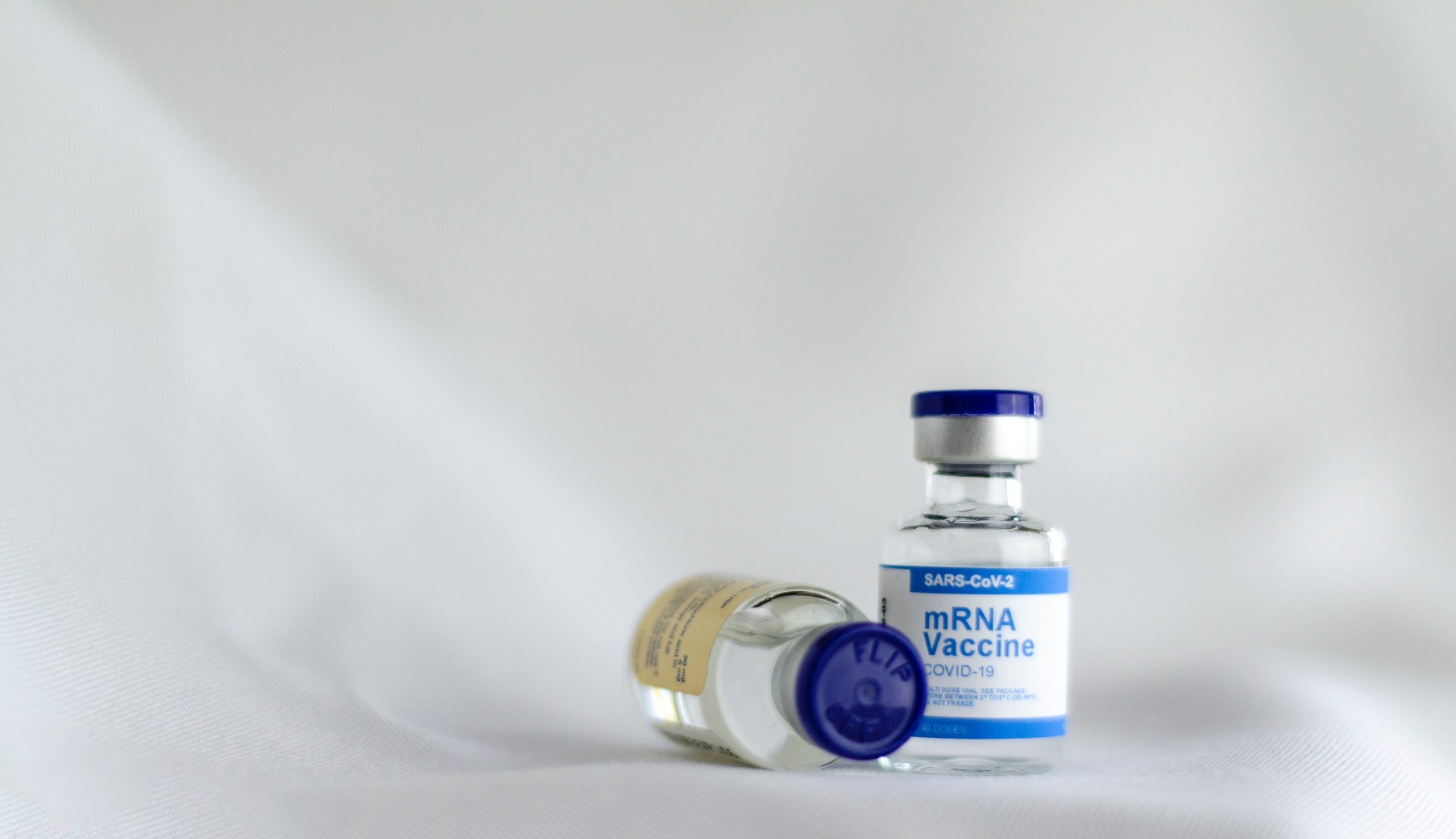
Vaccines
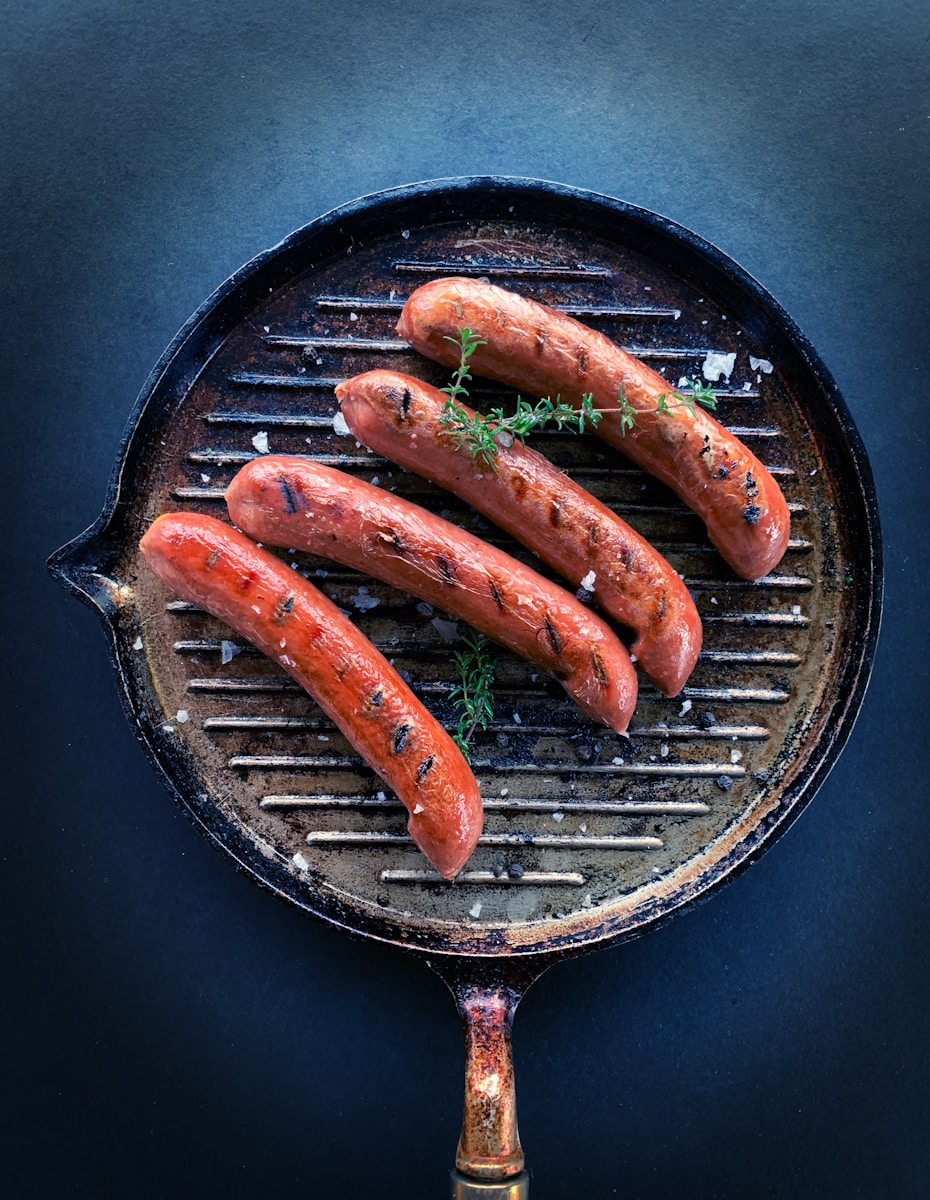
Vegan sausage
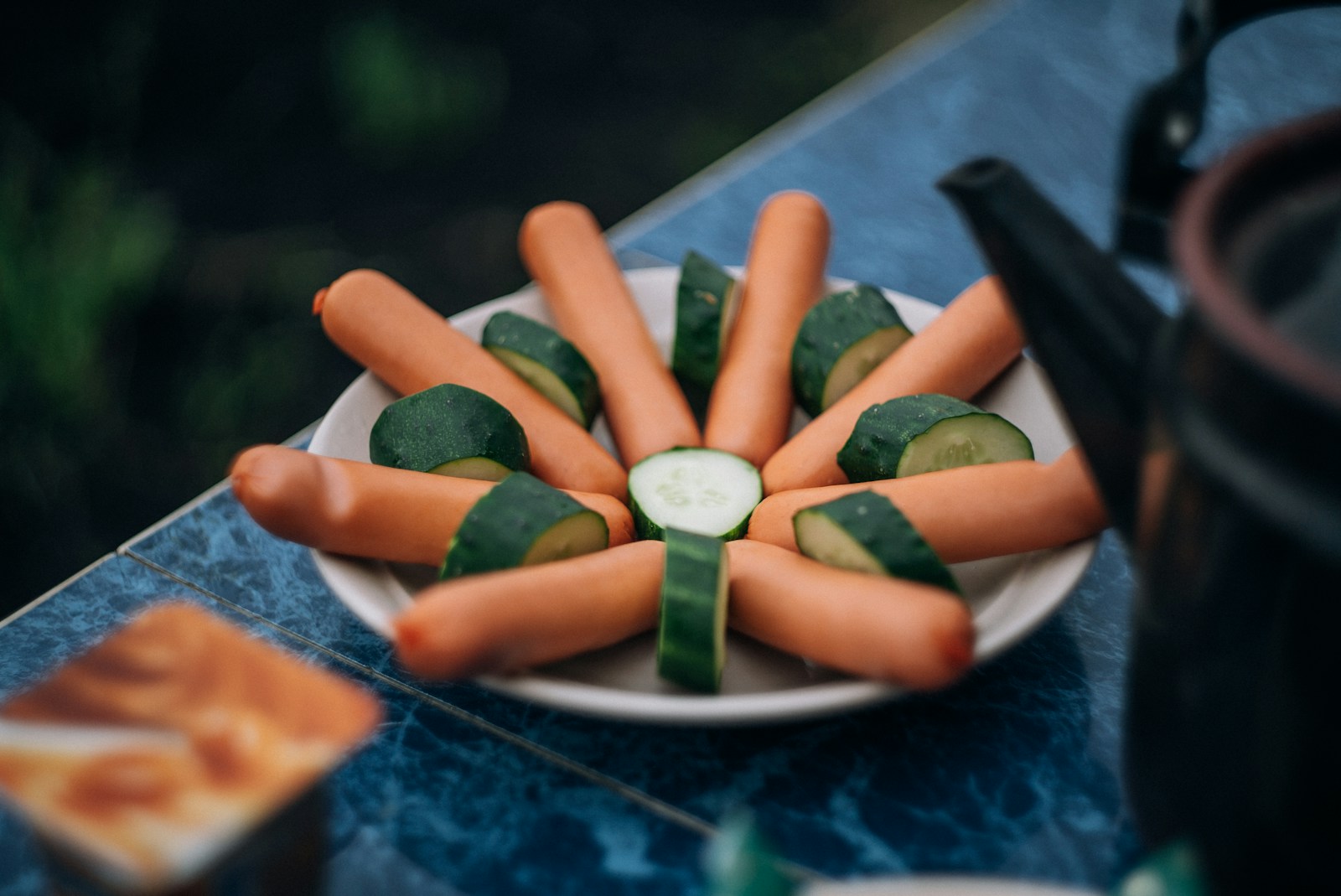
Vegan sausages
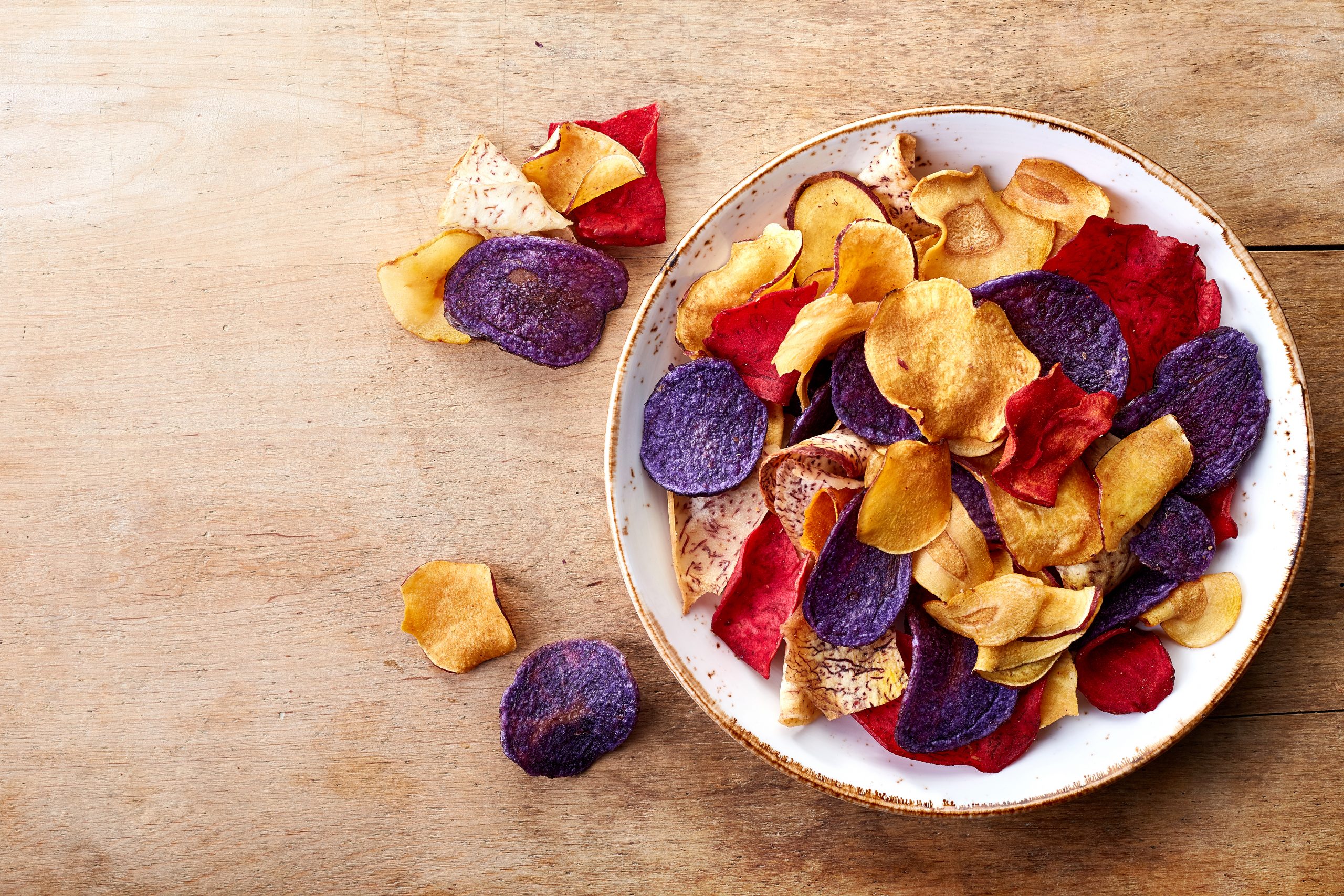
Vegetable chips
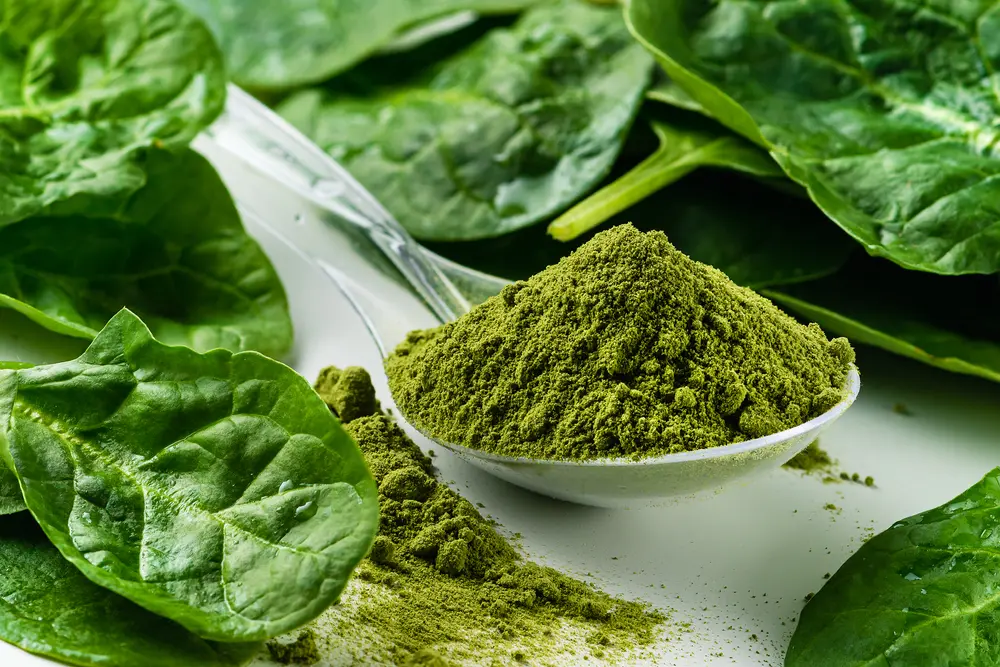
Vegetable powder
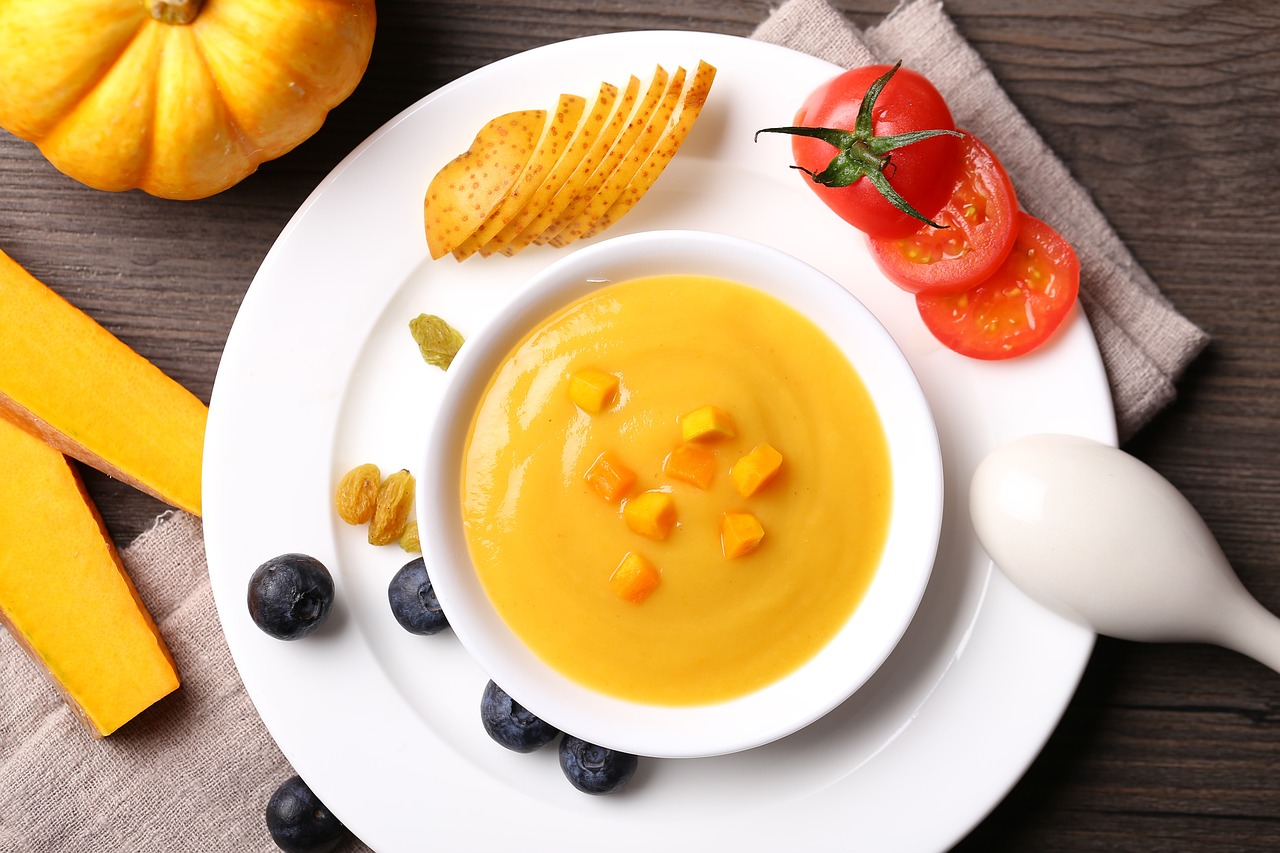
Vegetable Puree
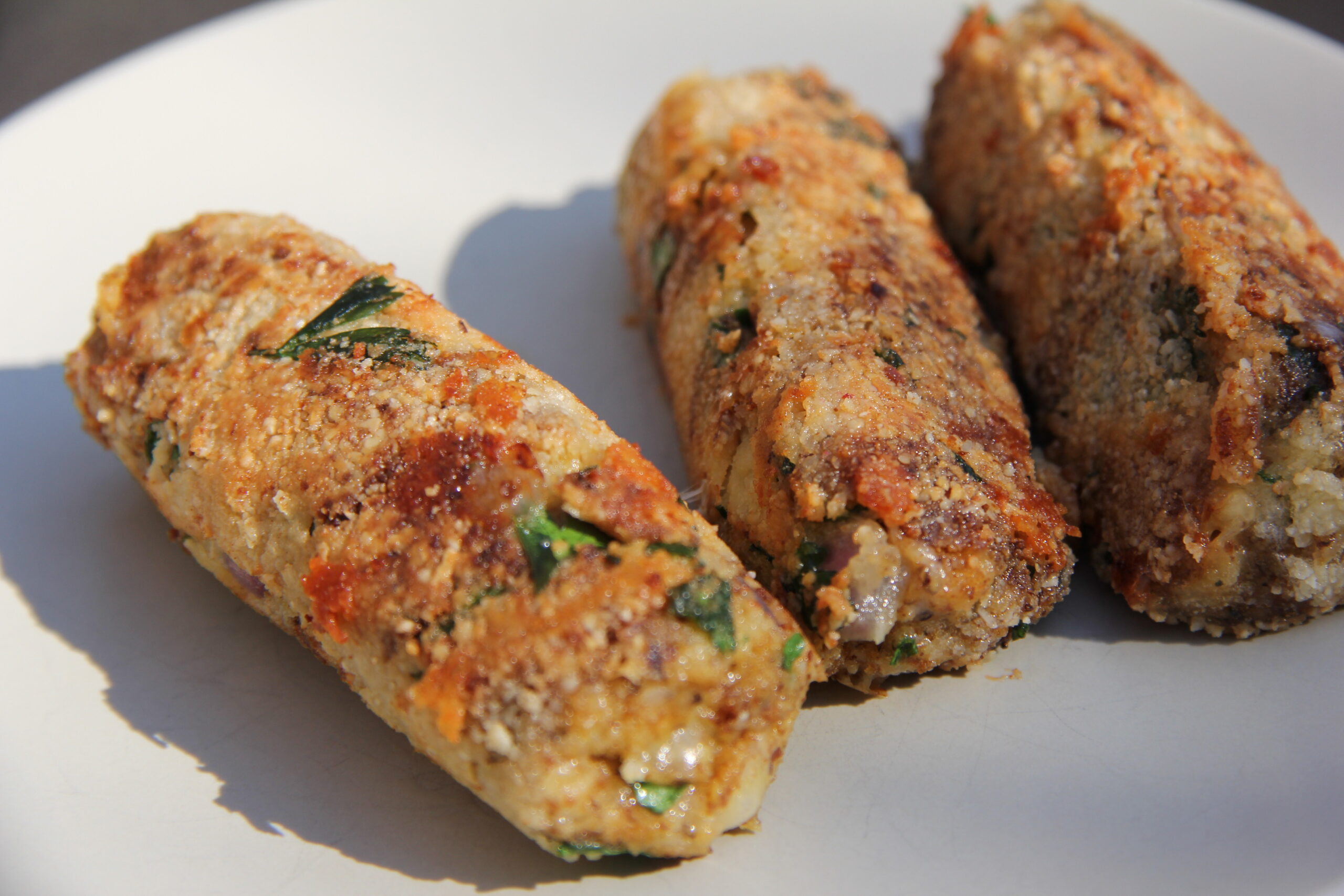
Vegetarian sausages
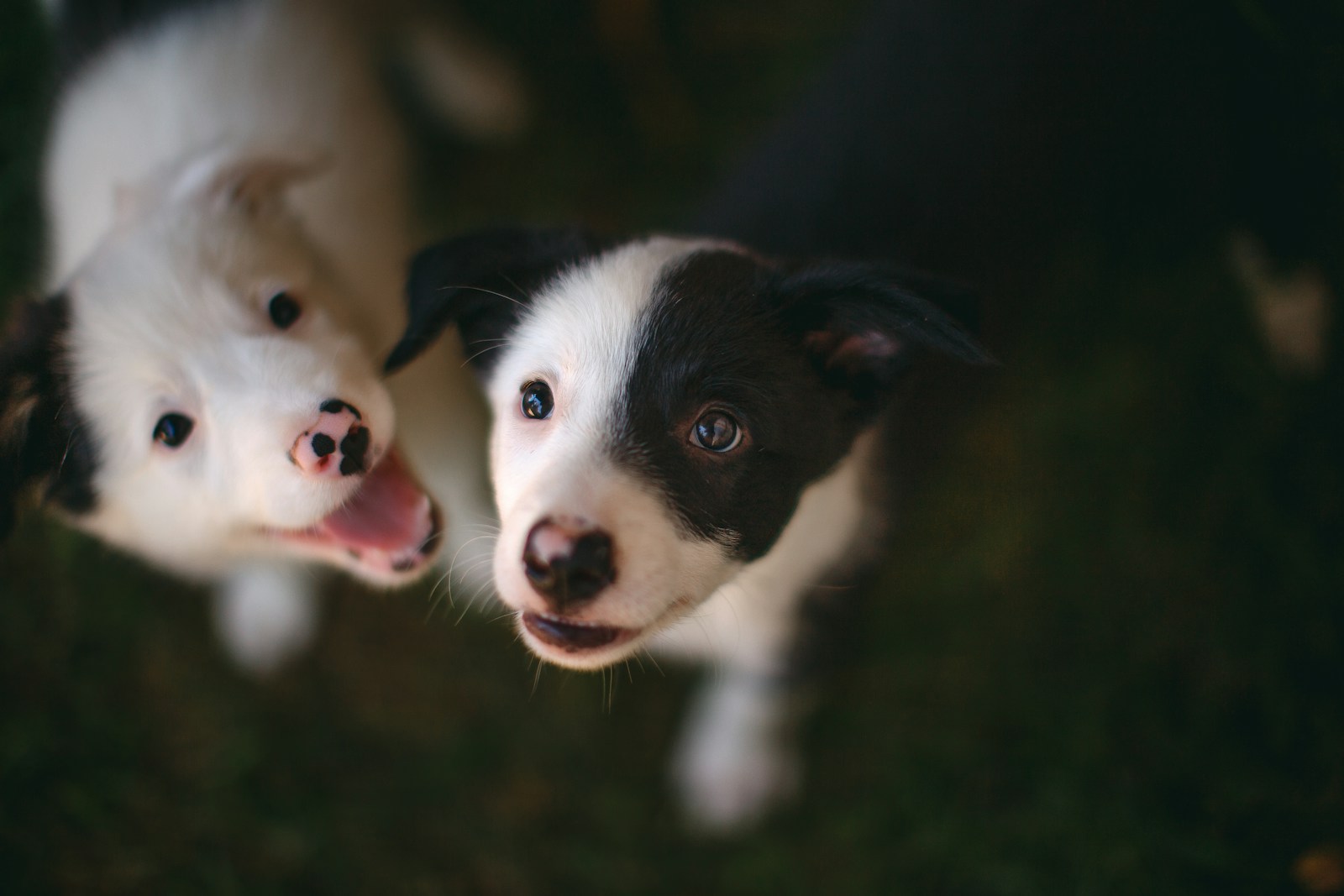
Veterinary
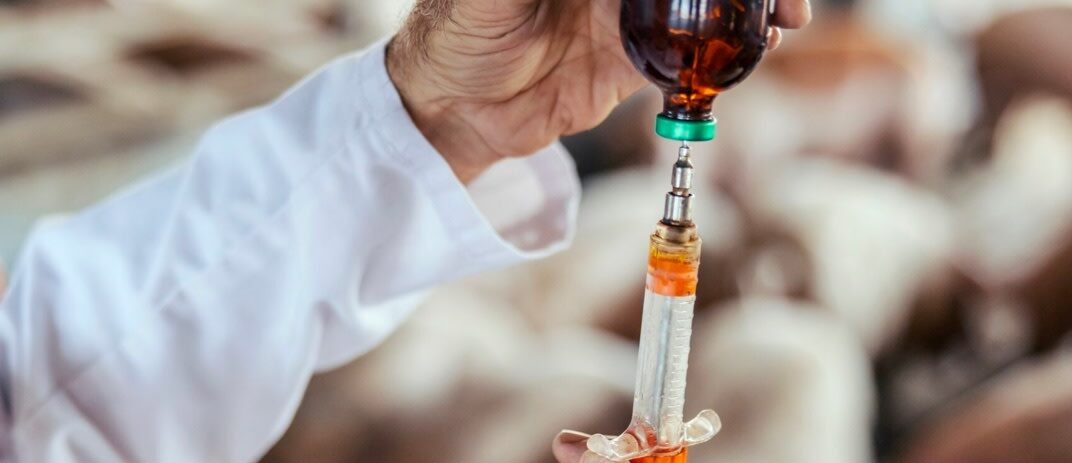
Veterinary antibiotics
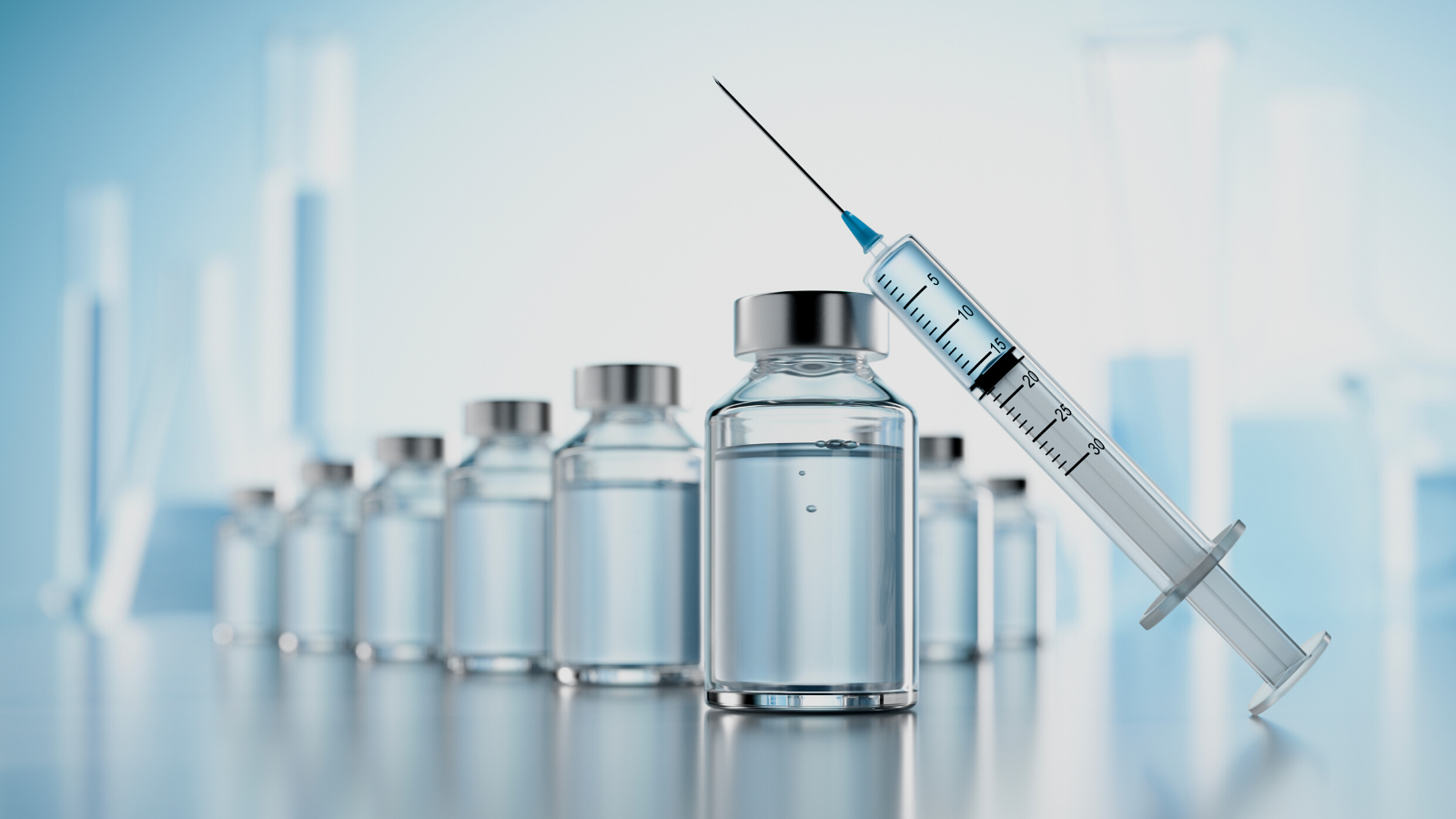
Veterinary vaccines
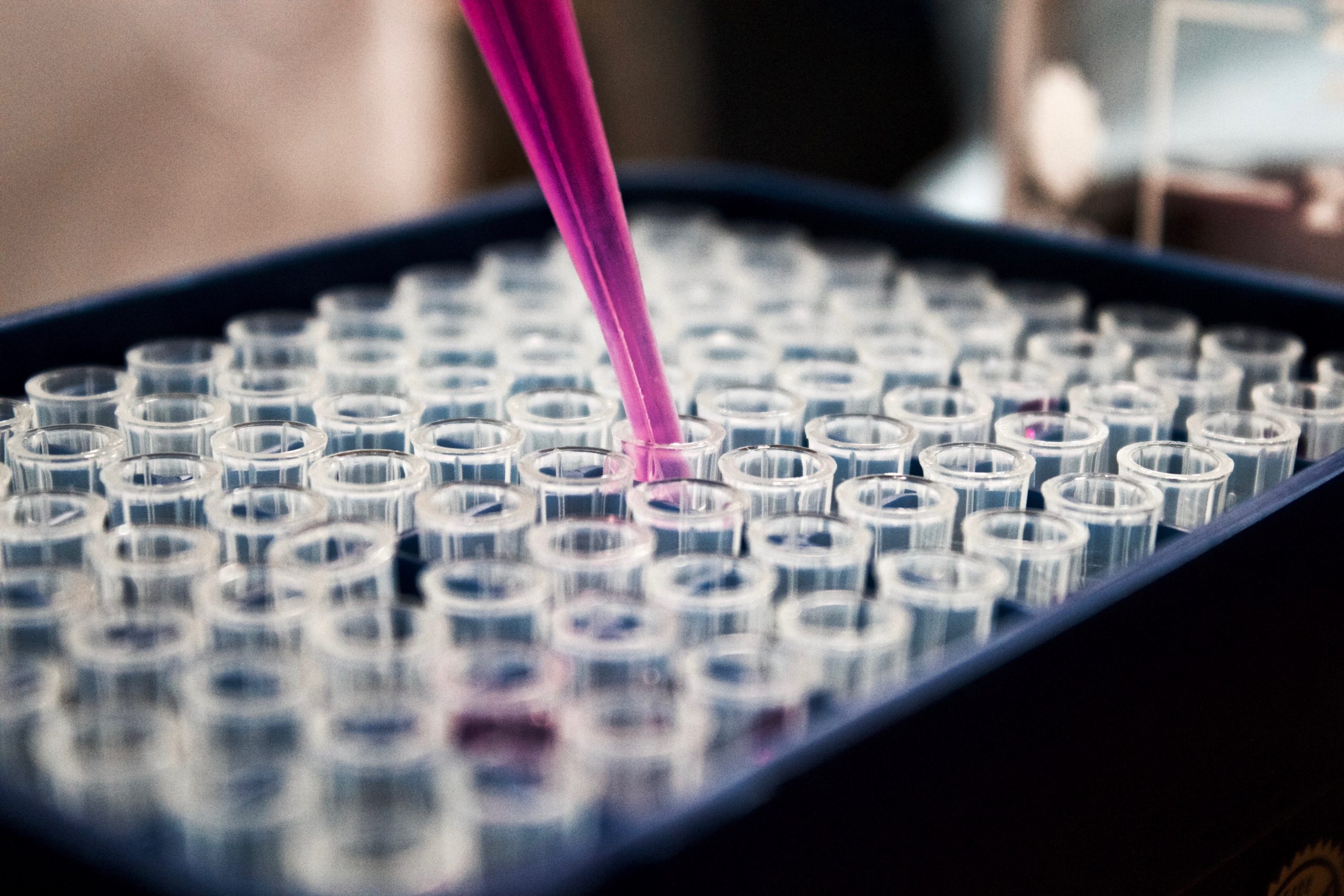
Vials
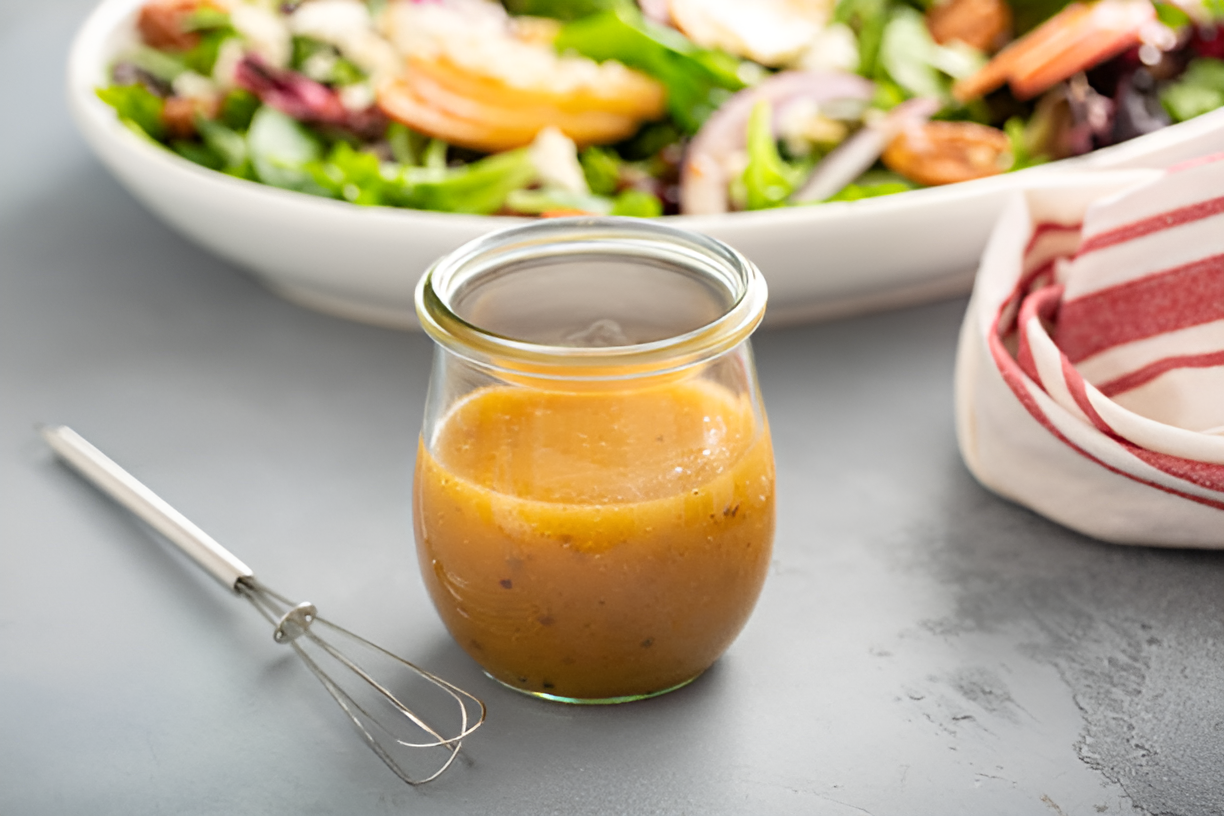
Vinaigrette dressing
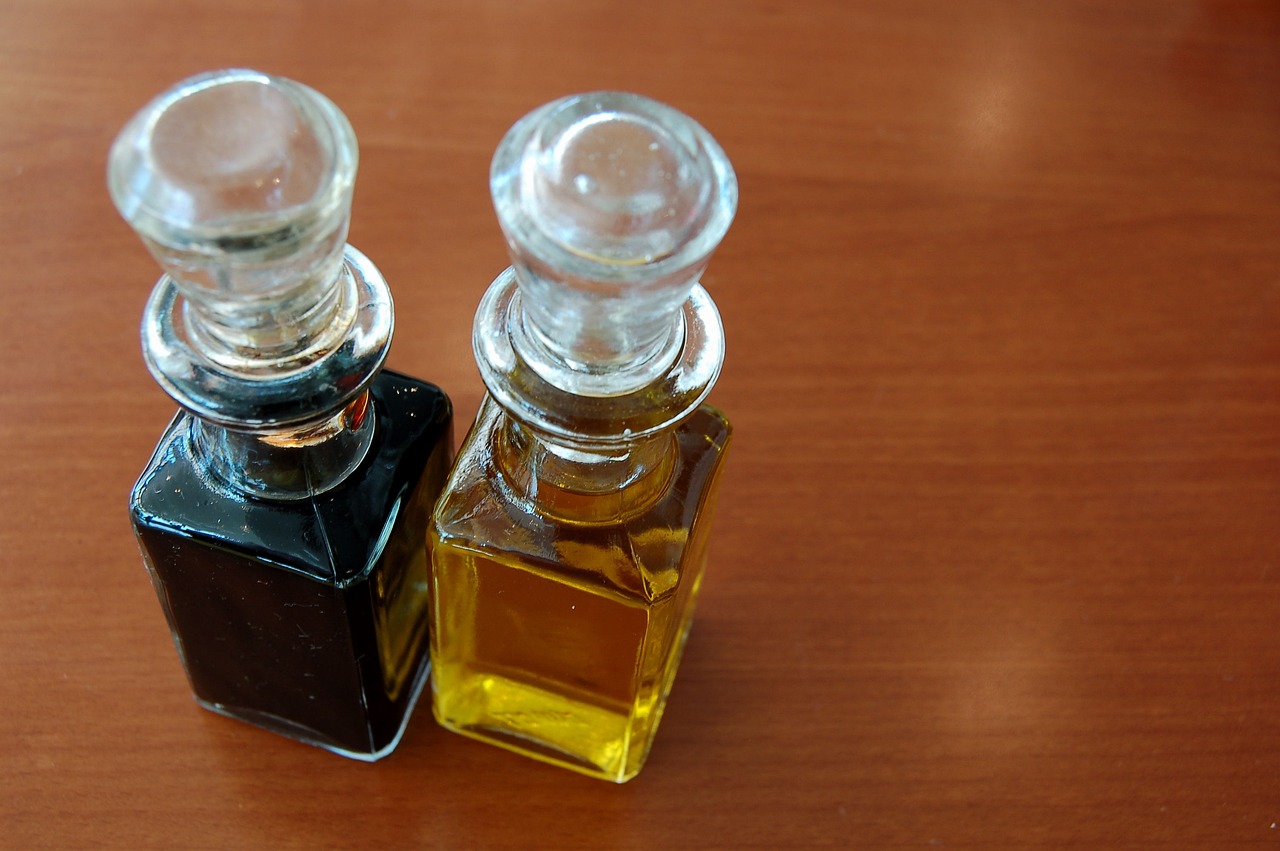
Vinegar
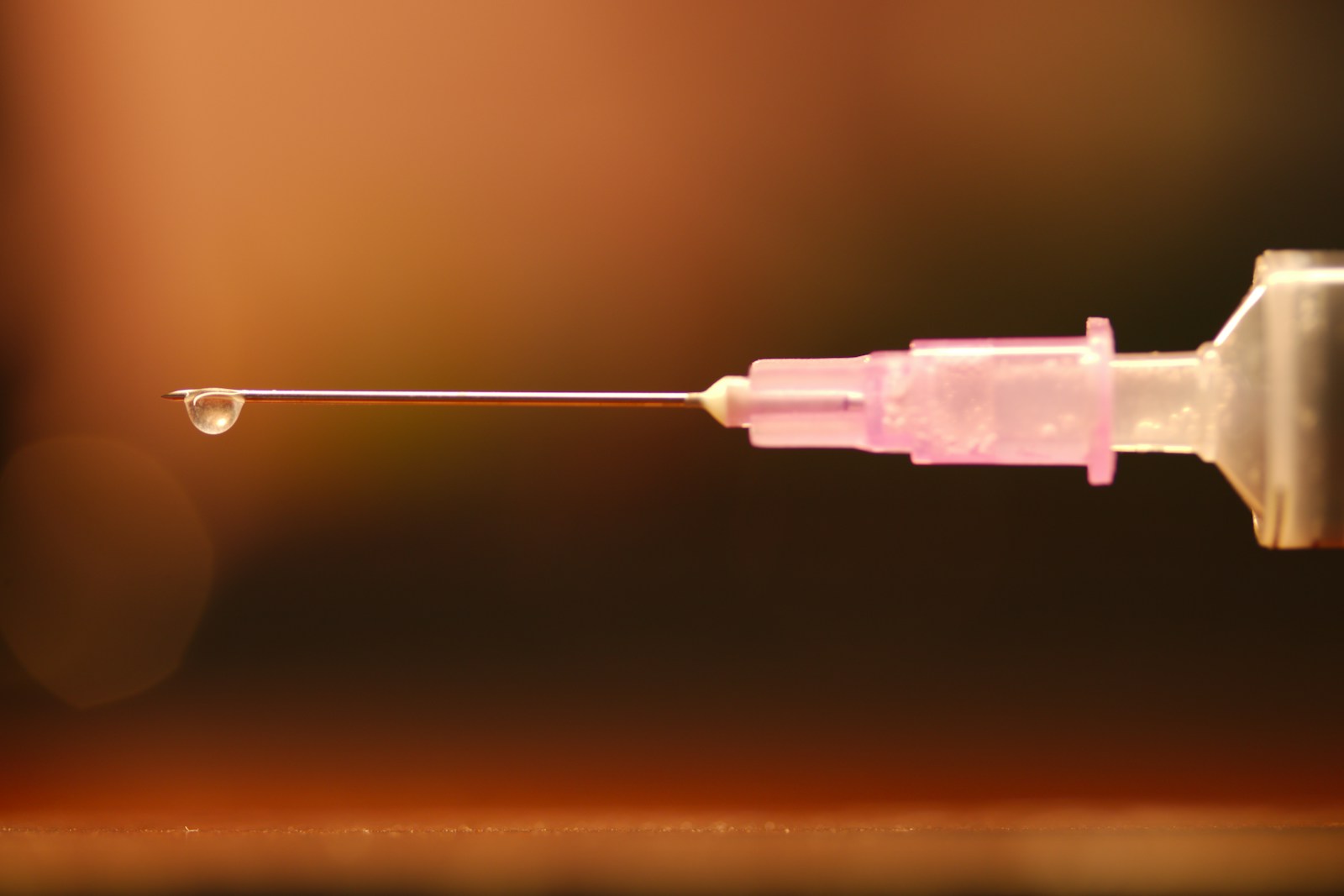
Viral vector vaccines
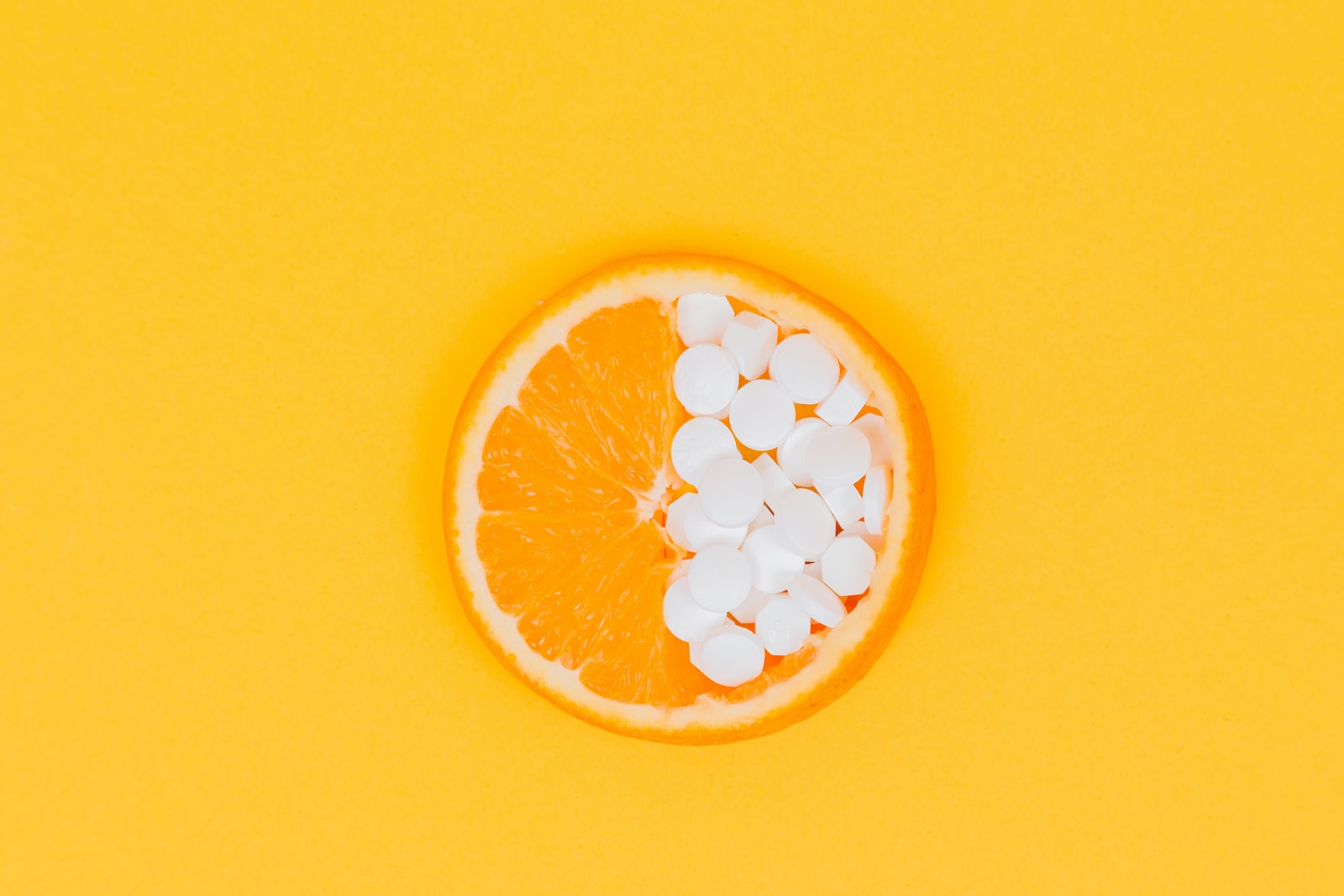
Vitamin C
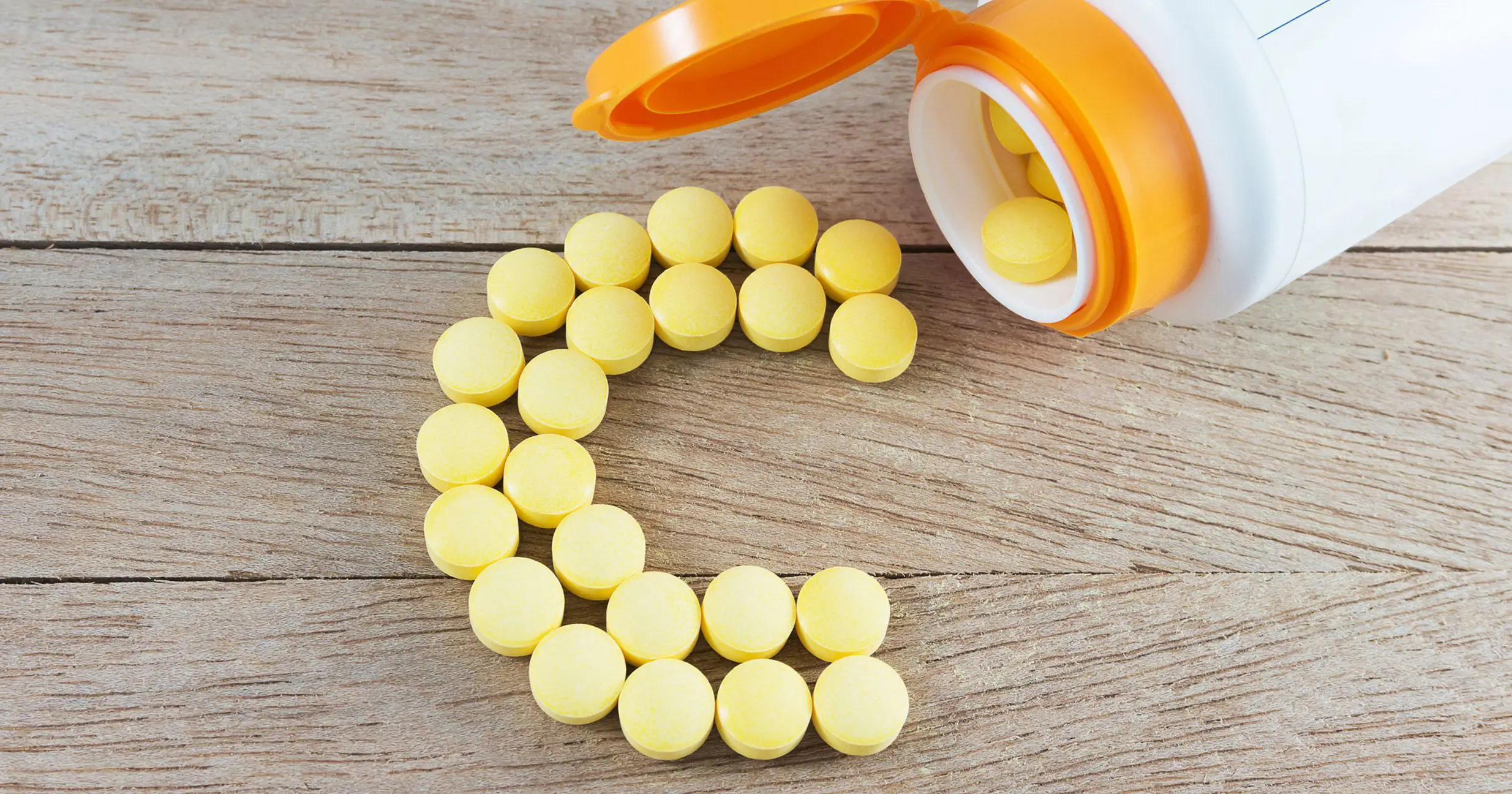
Vitamin c supplements
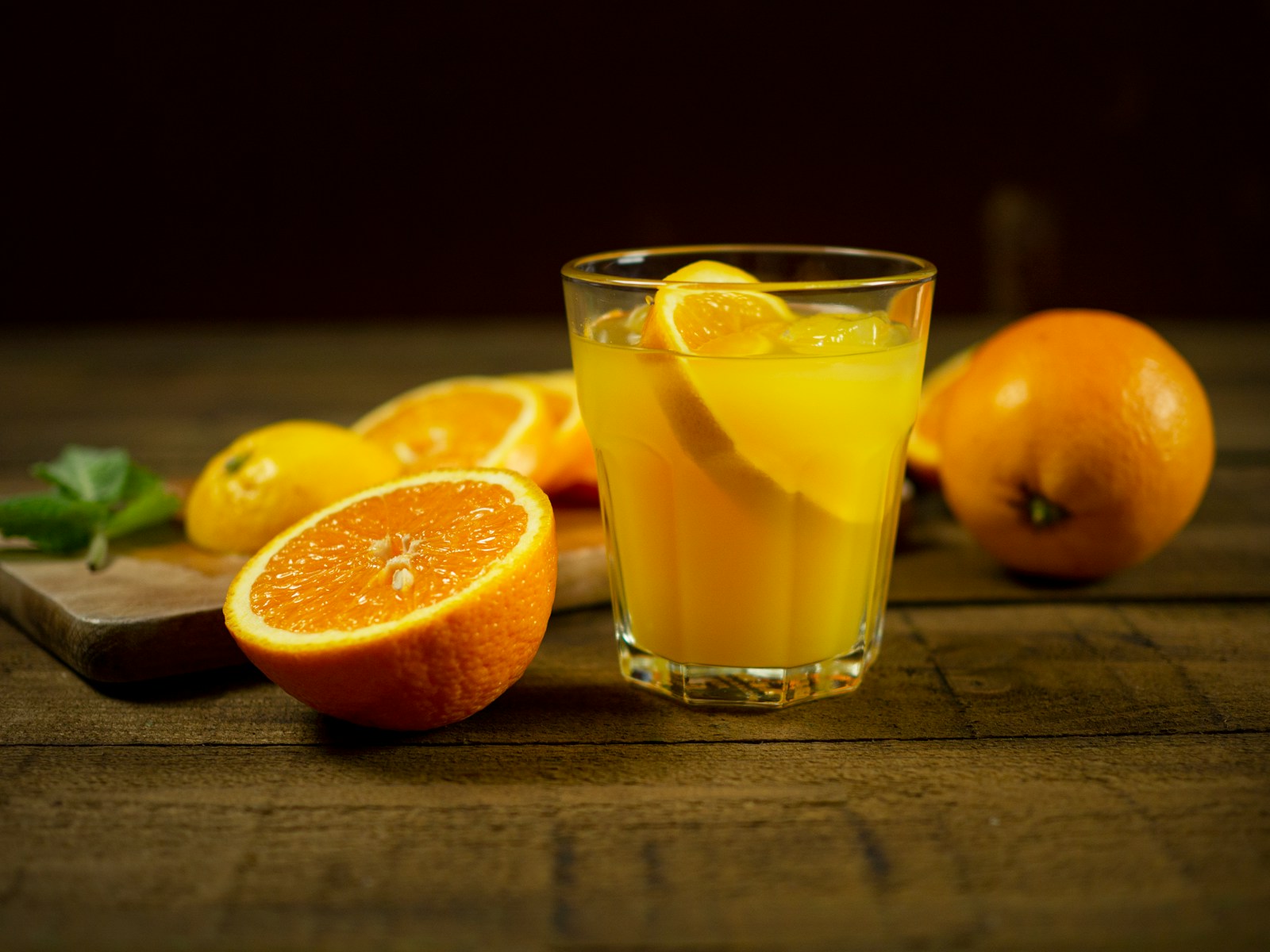
Vitamin-enriched beverages
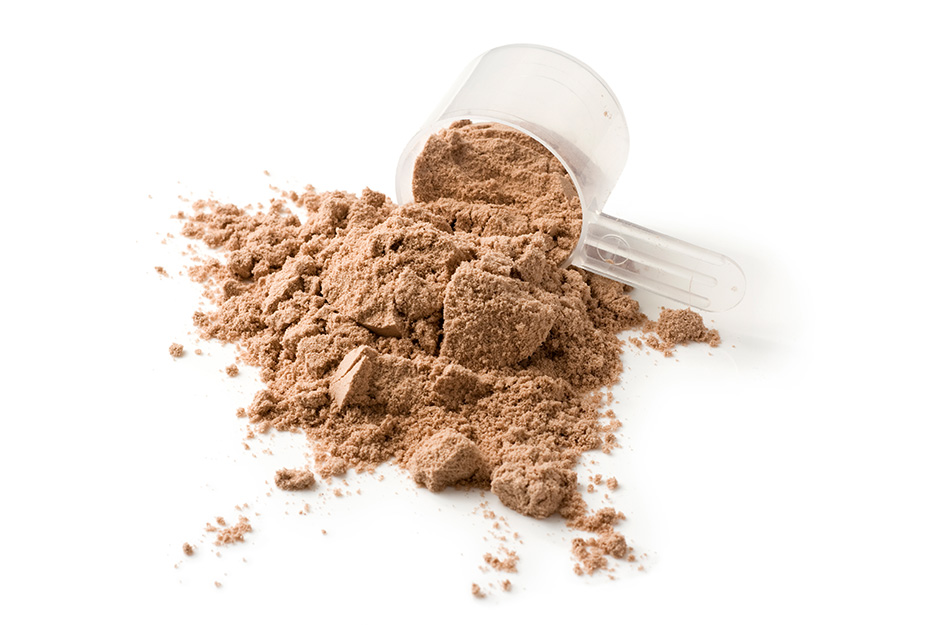
Vitamin premixes
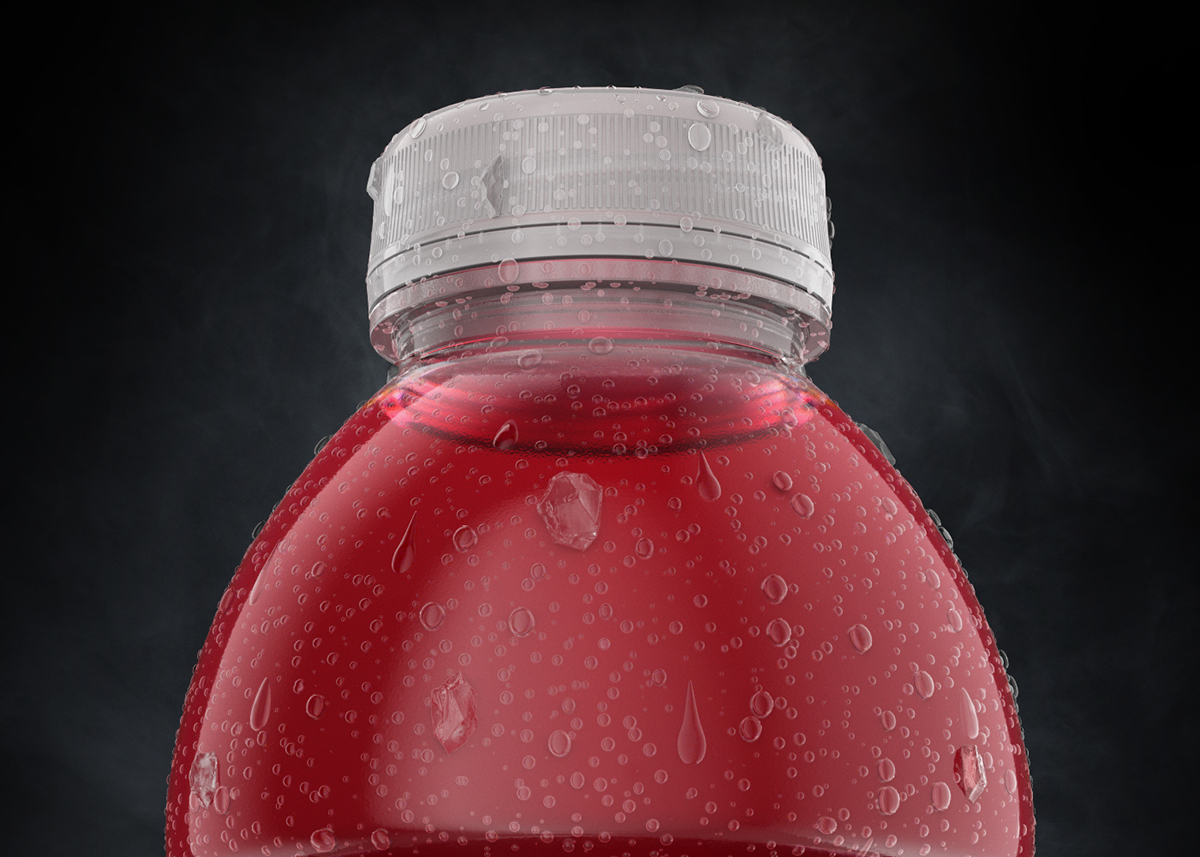
Vitamin water
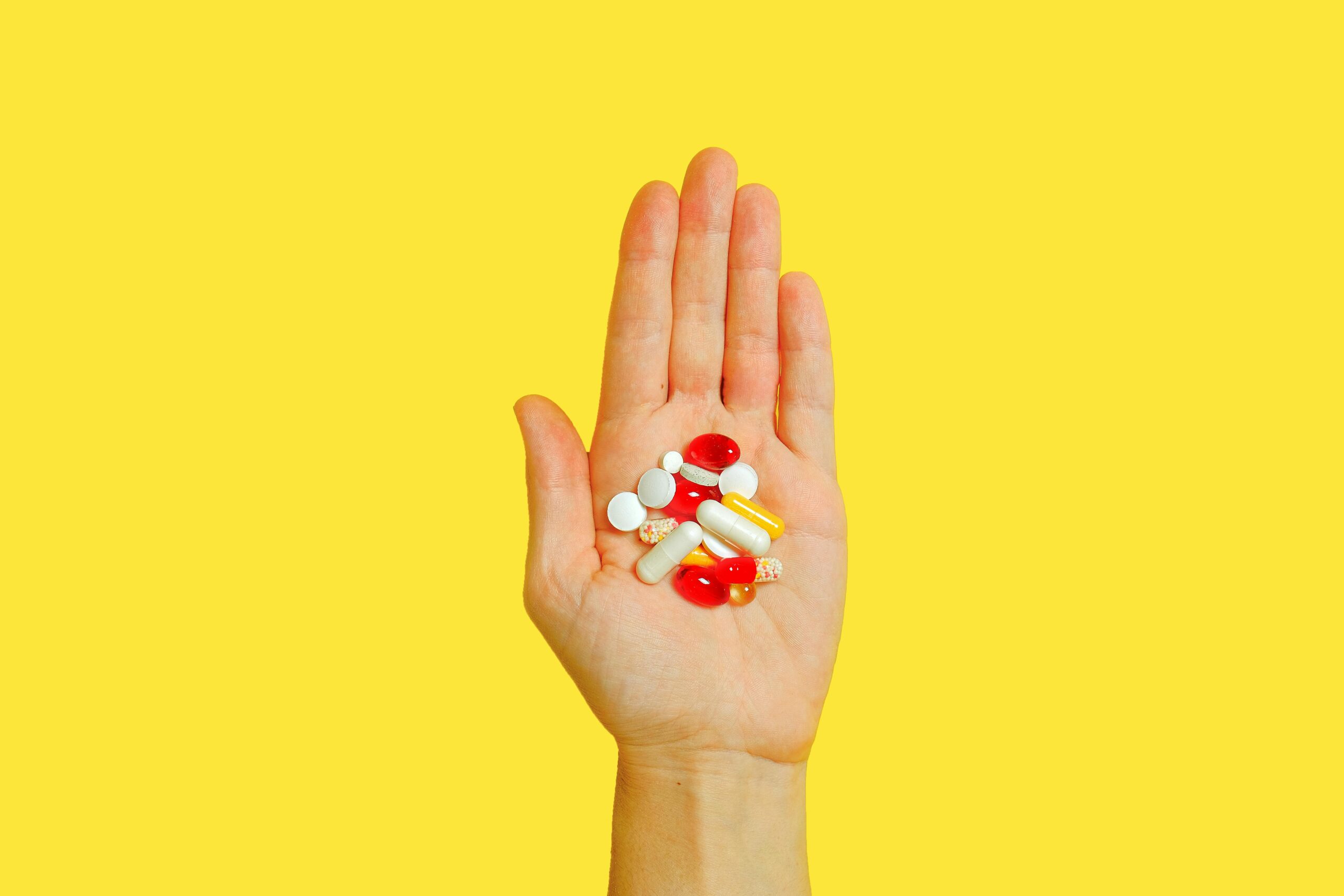
Vitamins
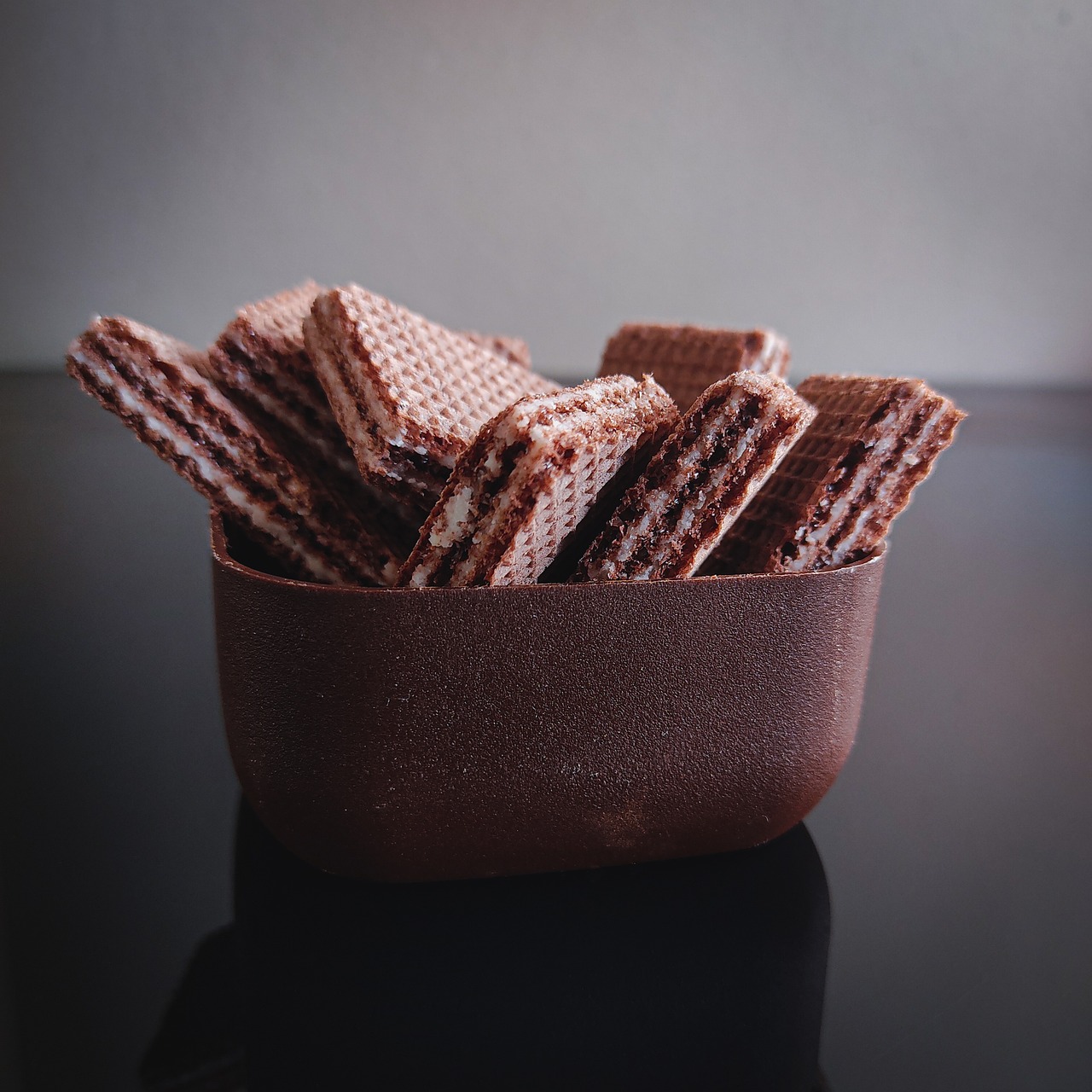
Wafer biscuits
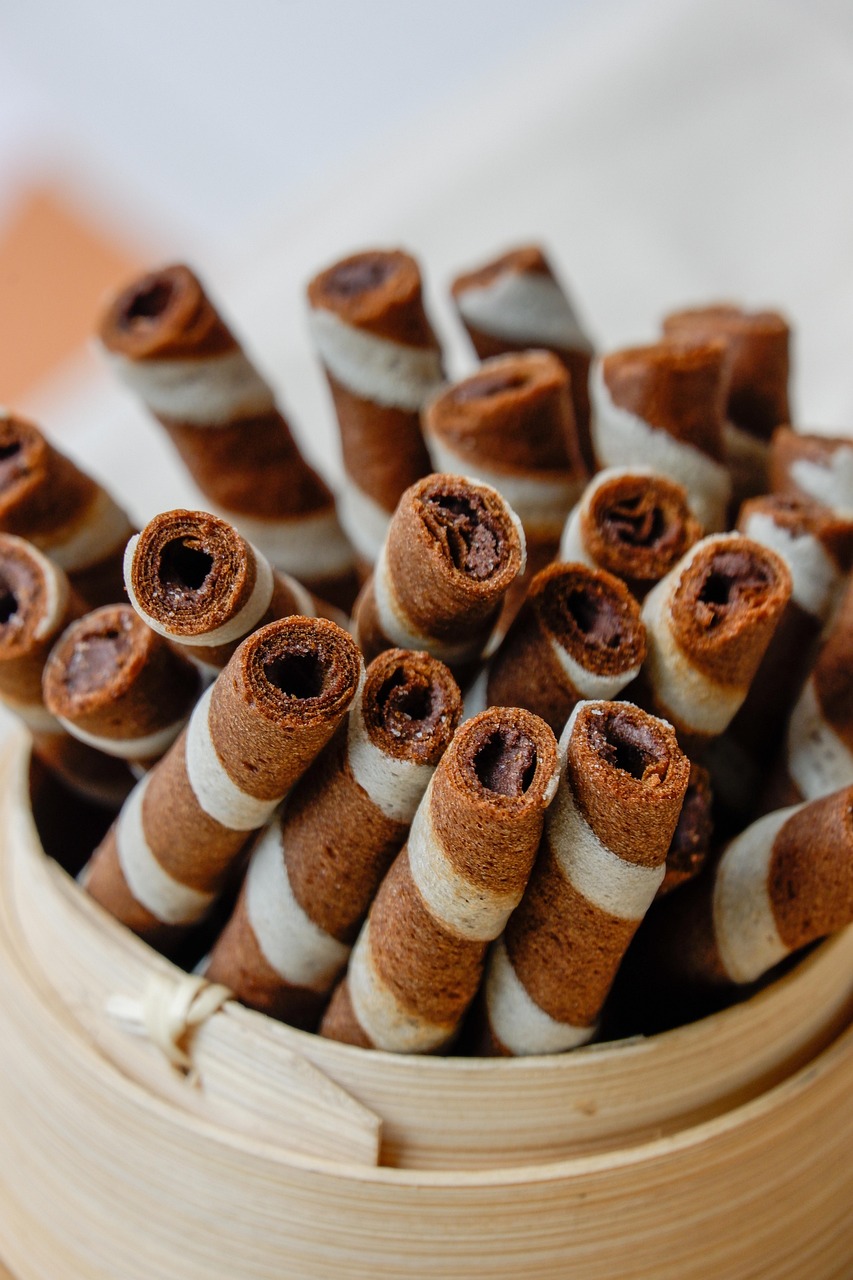
Wafer rolls
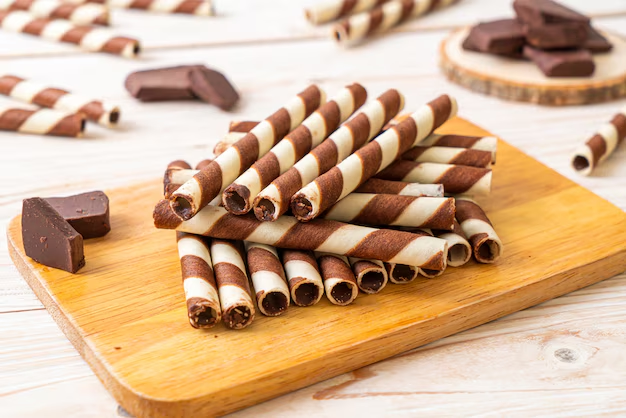
Wafer sticks
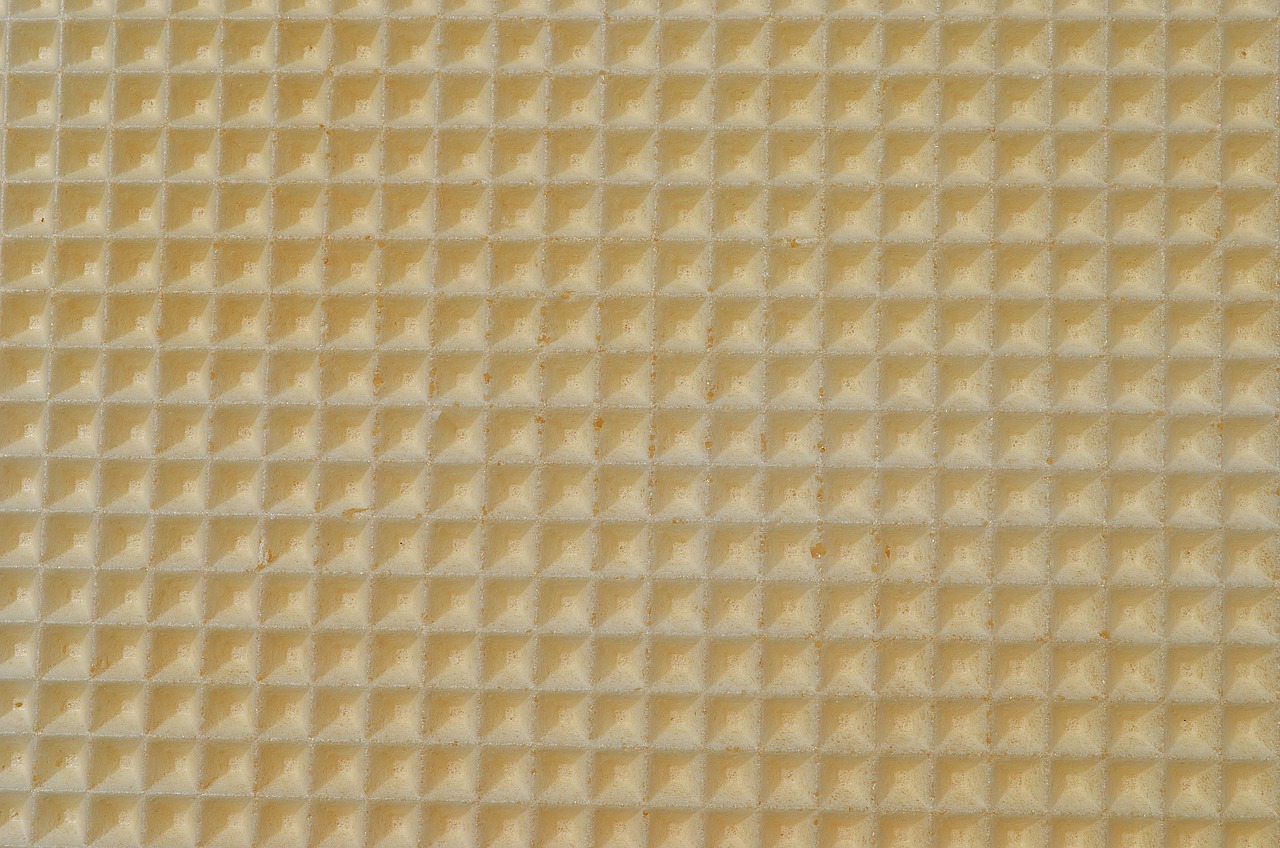
Wafers
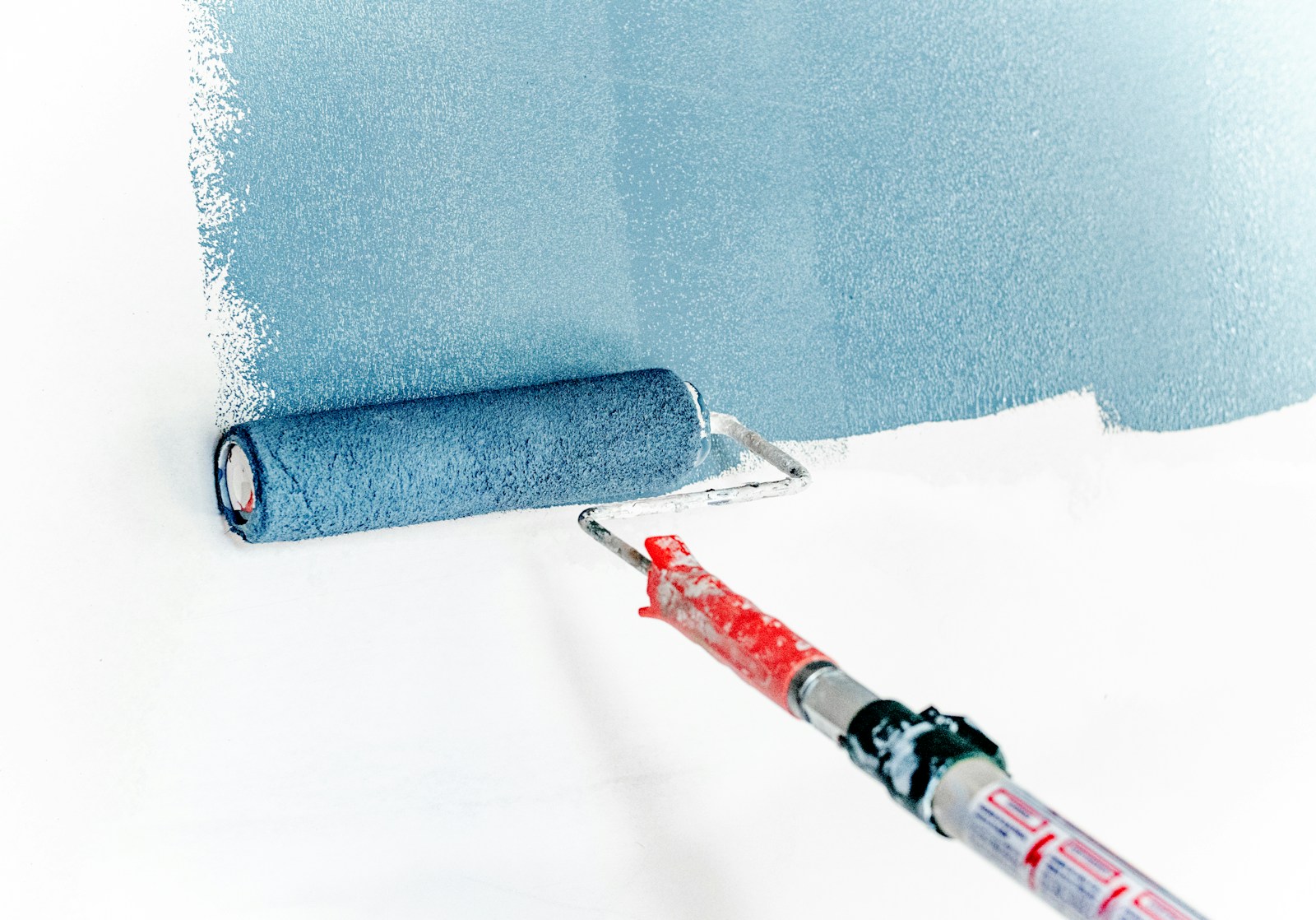
Wall paint
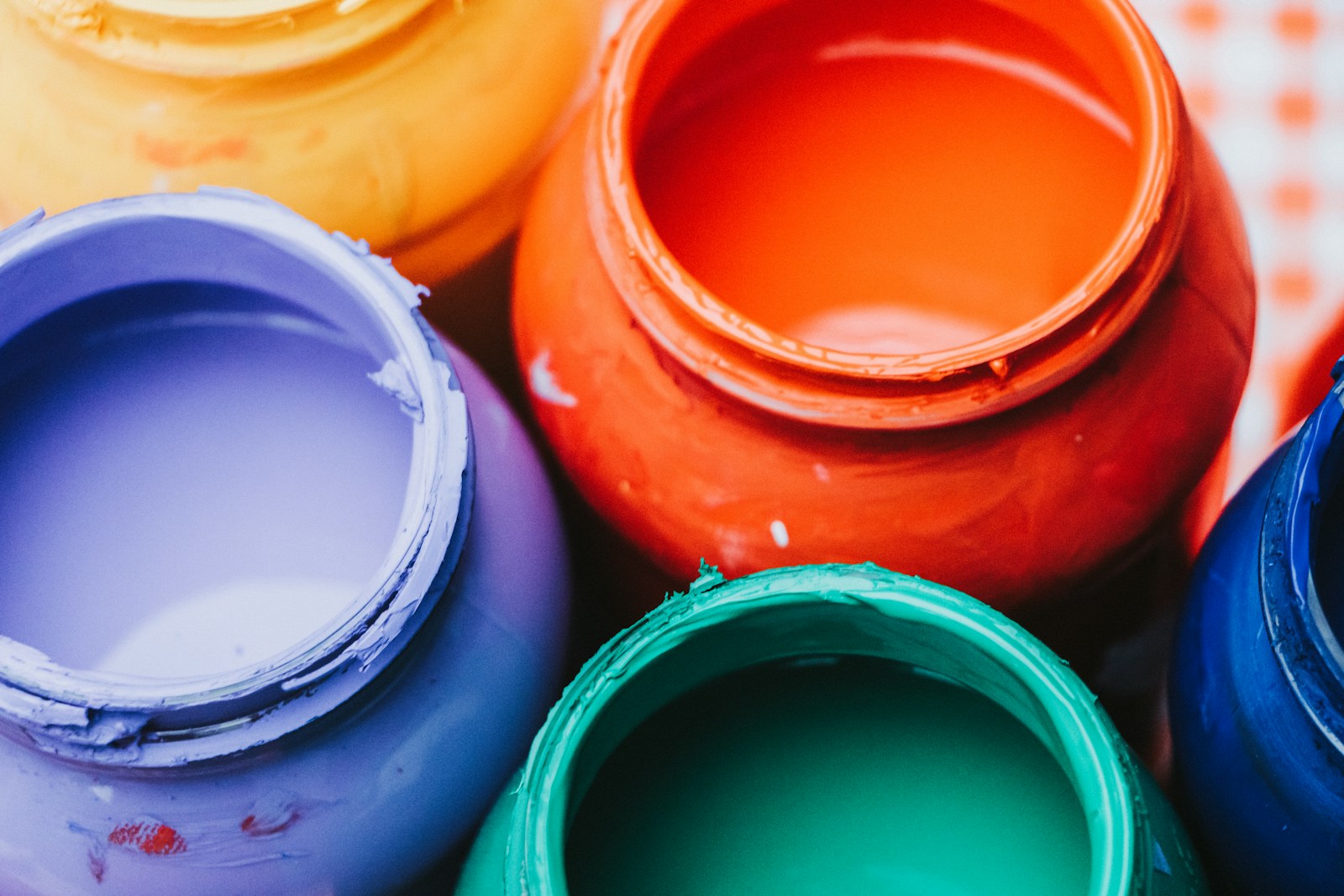
Water-based paints
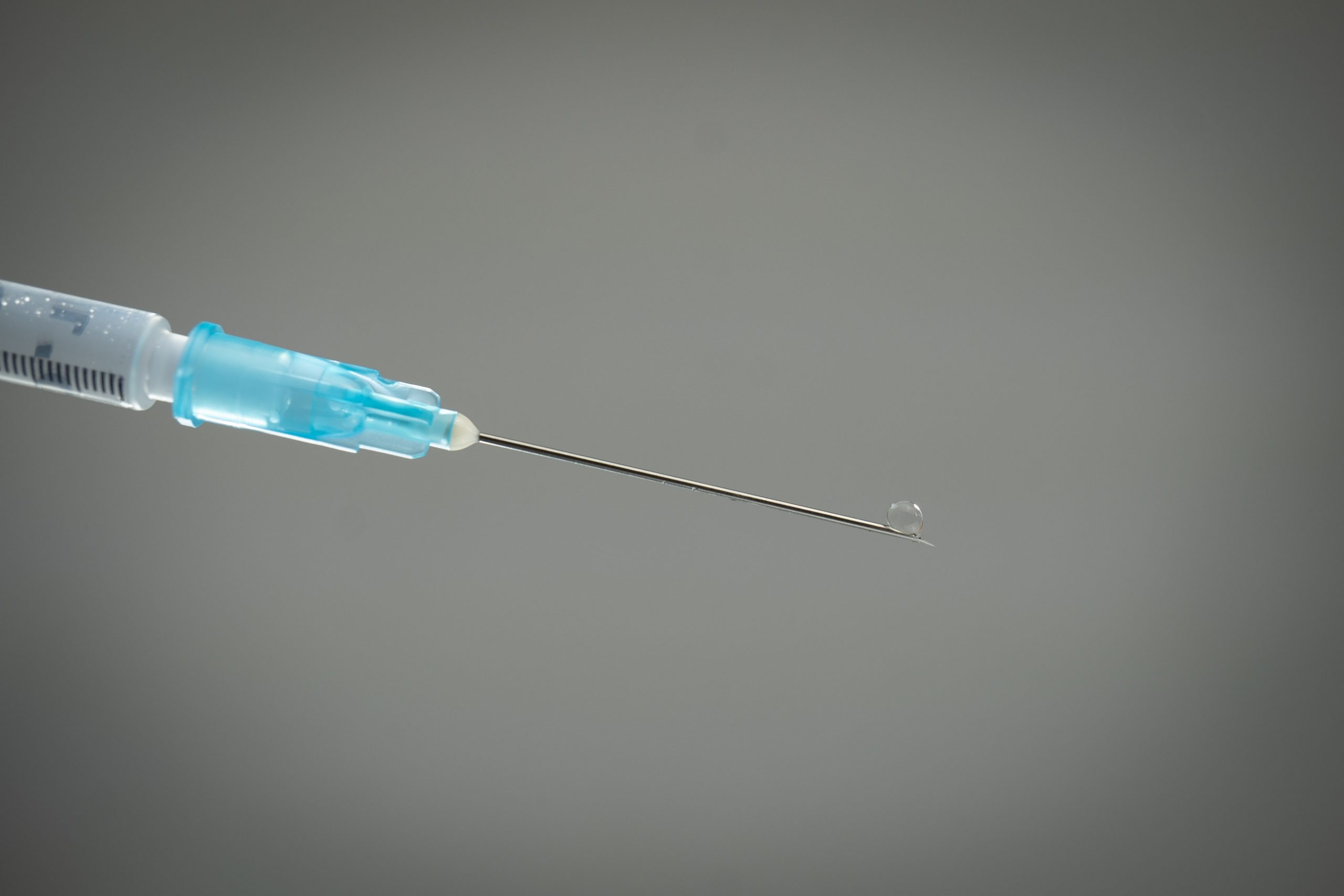
Water for injection
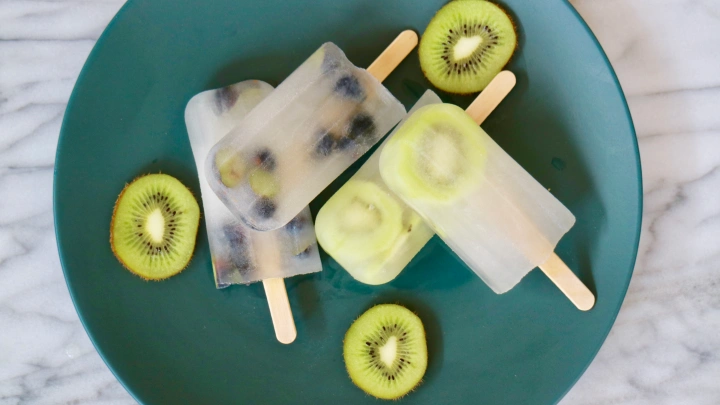
Water-ice lolly
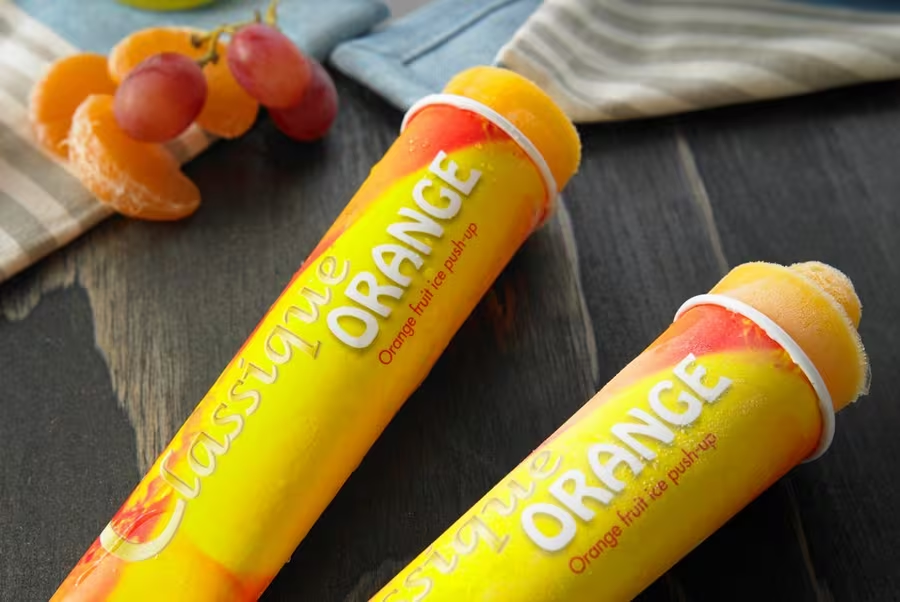
Water-ice push-up
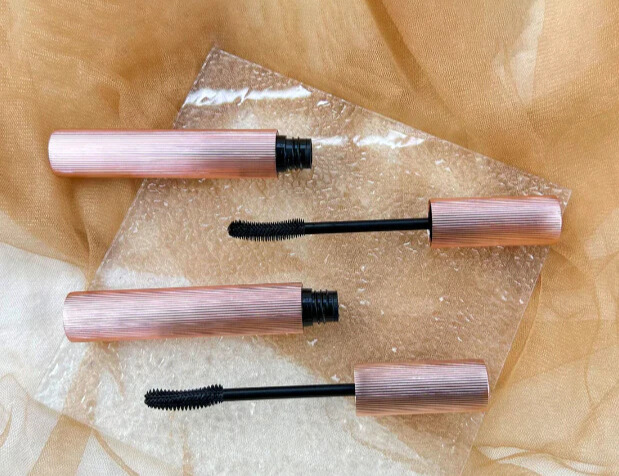
Waterproof mascara

Wet pet food
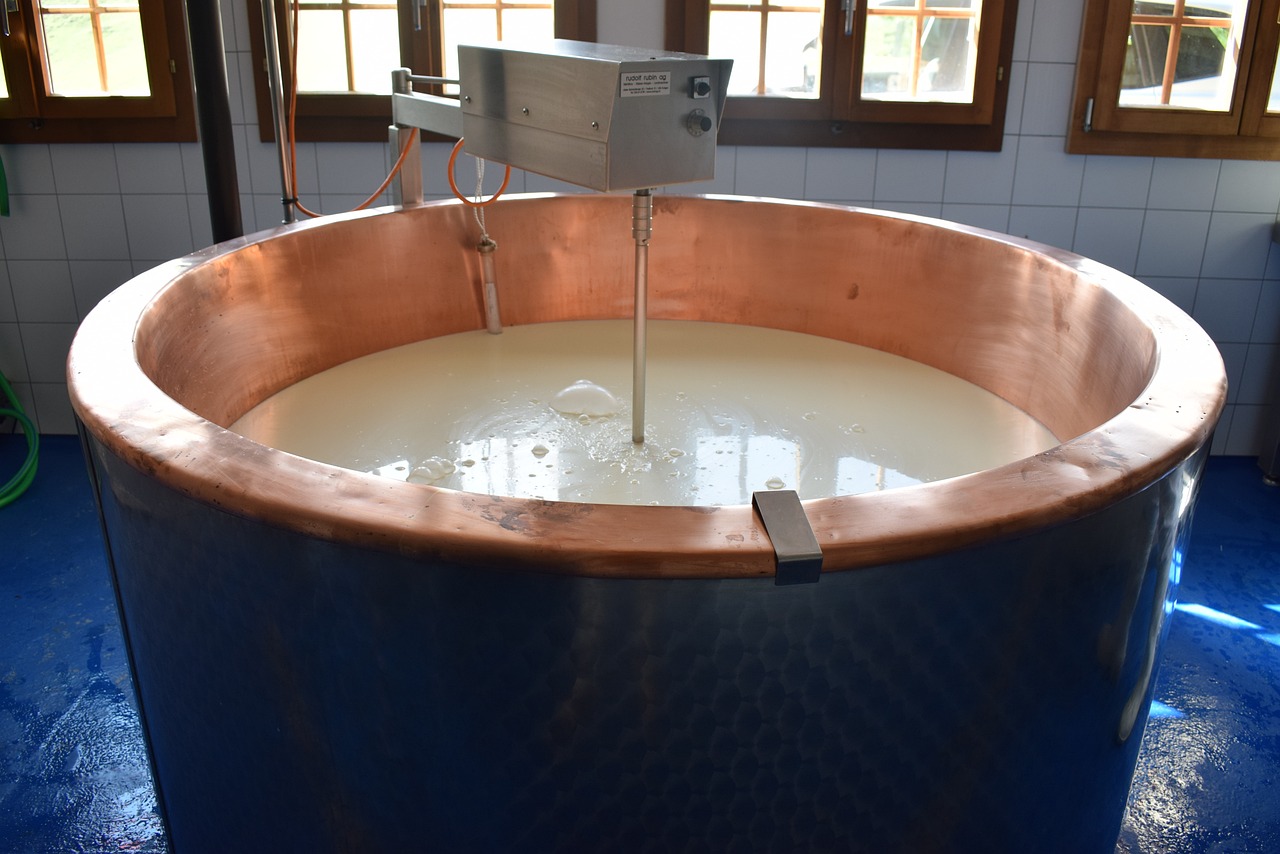
Whey
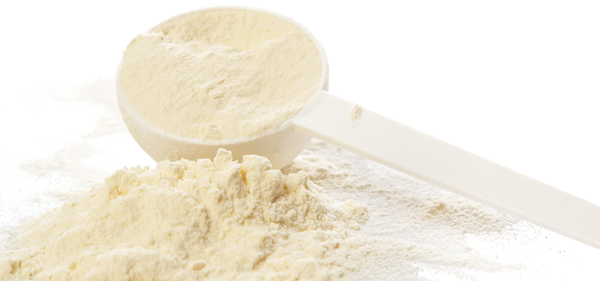
Whey protein
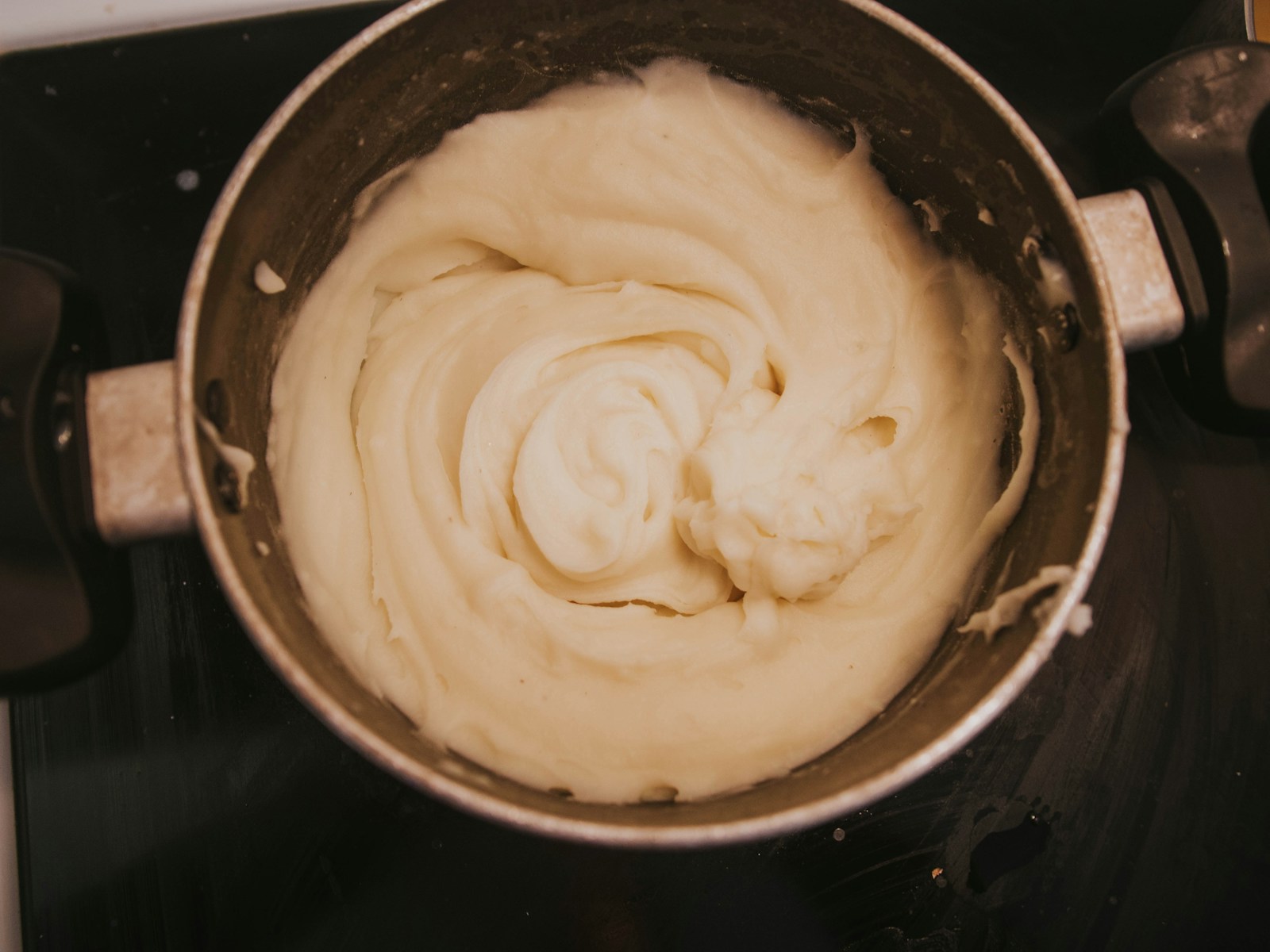
Whipped butter
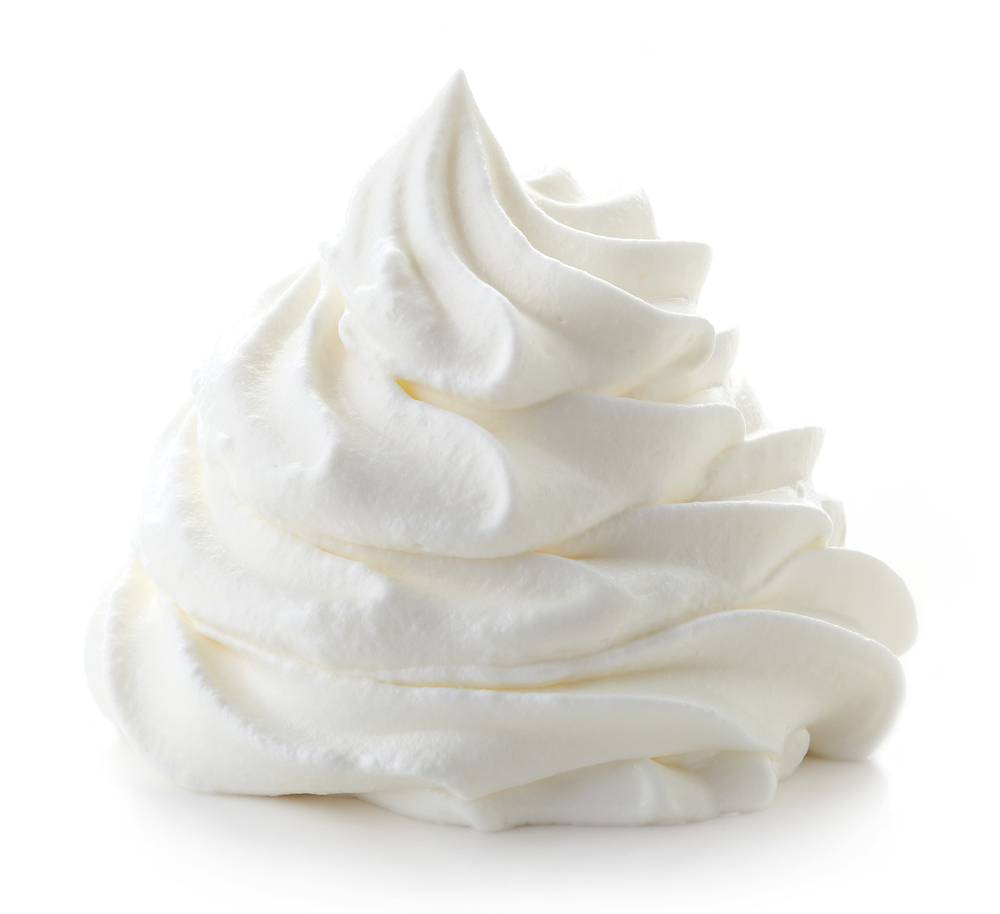
Whipped cream

Whisky
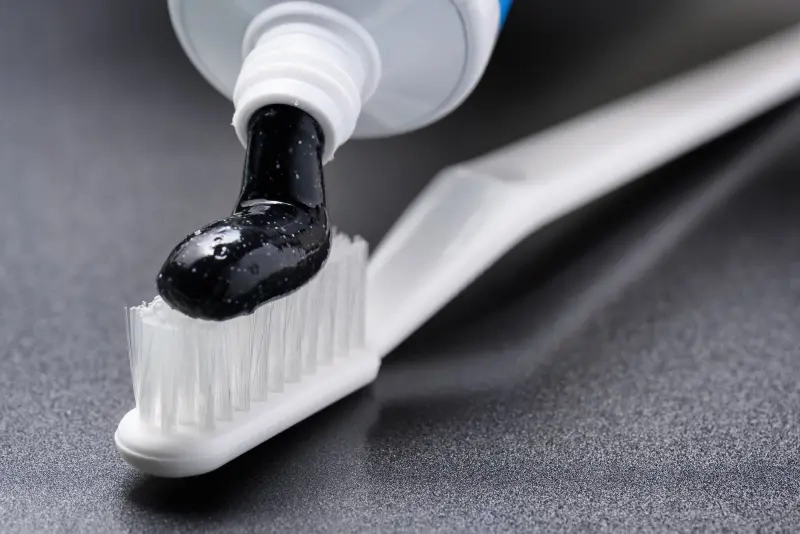
Whitening toothpaste
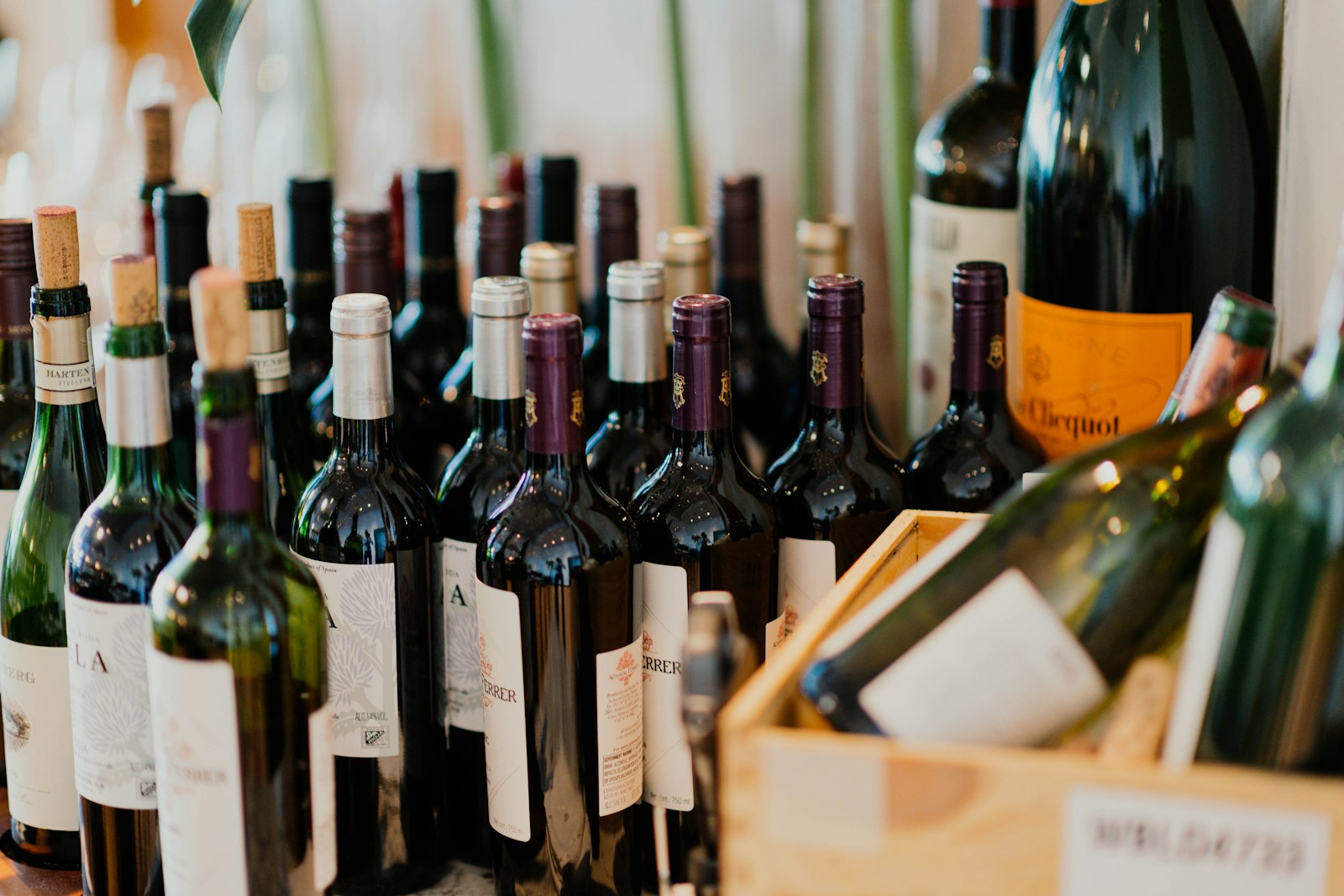
Wine bottles
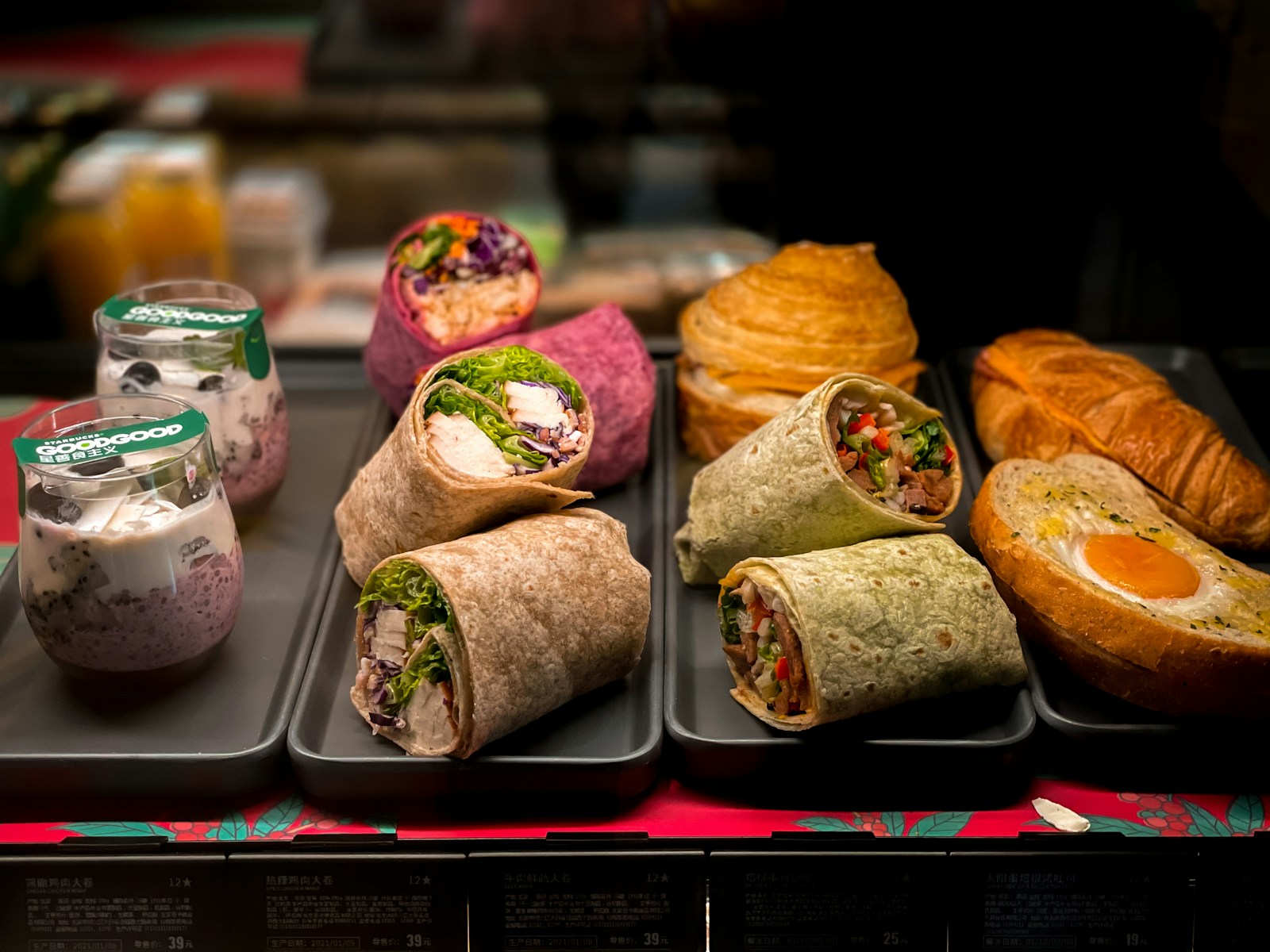
Wraps
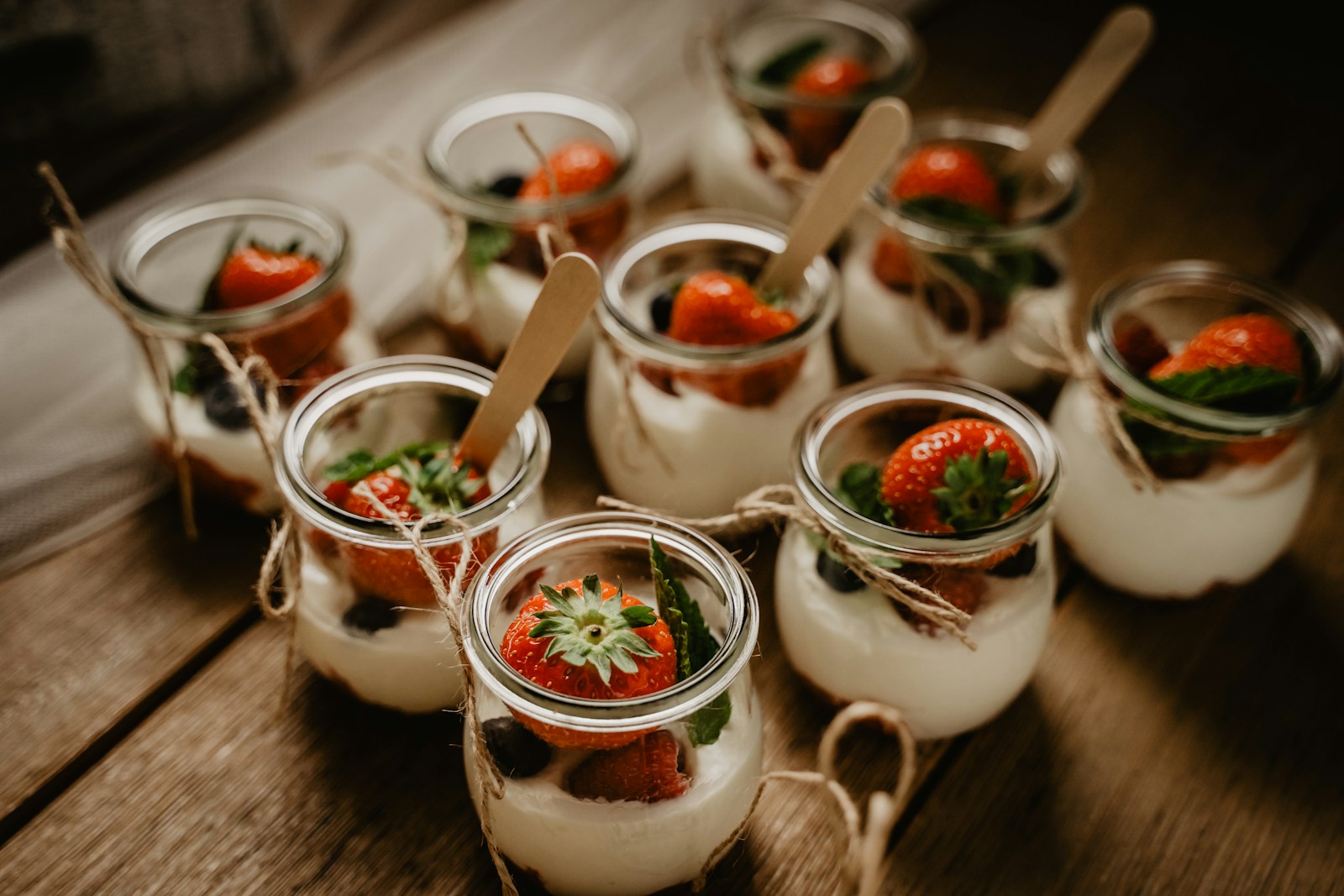
Yogurt cups
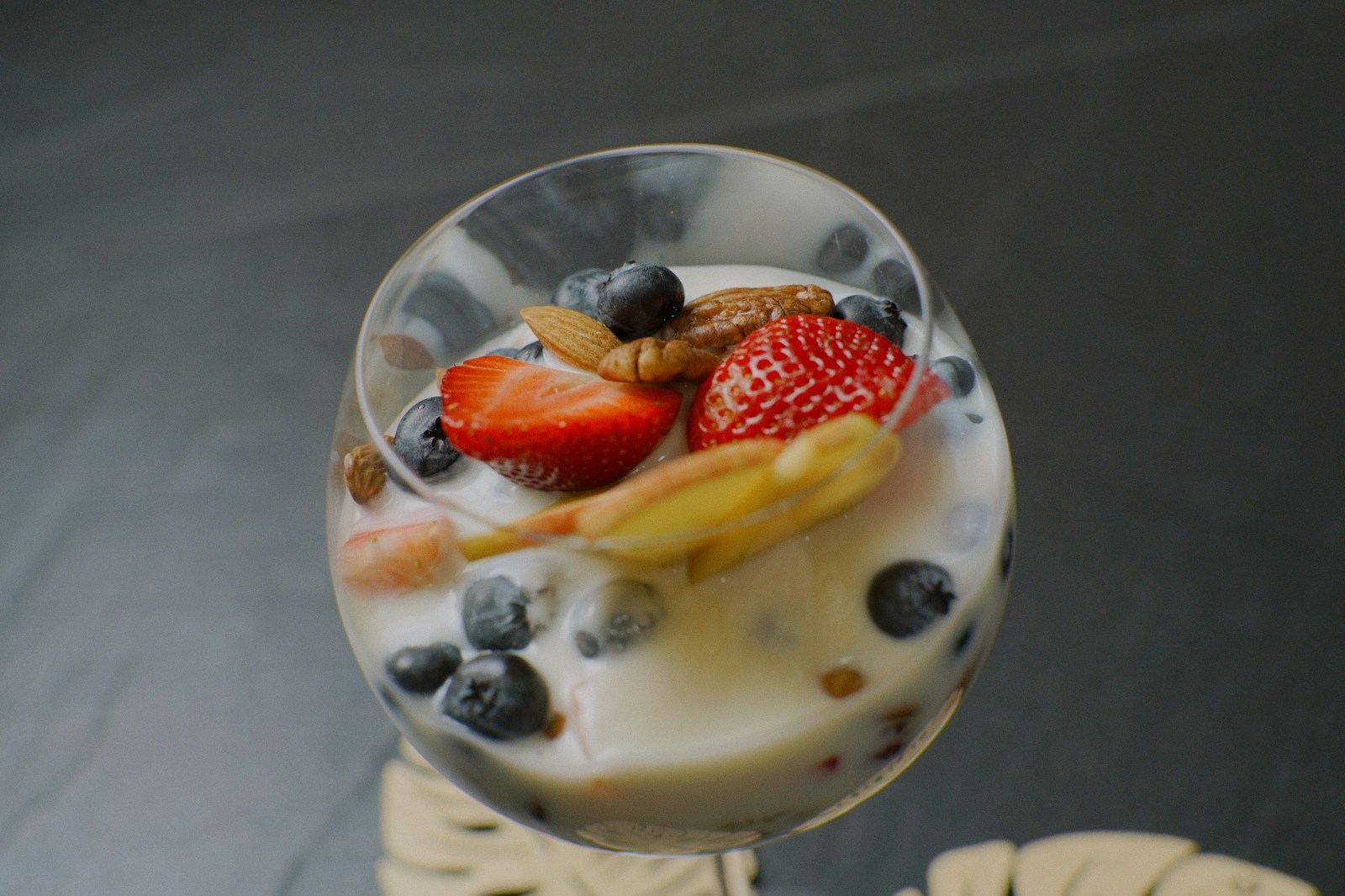
Yogurt parfaits
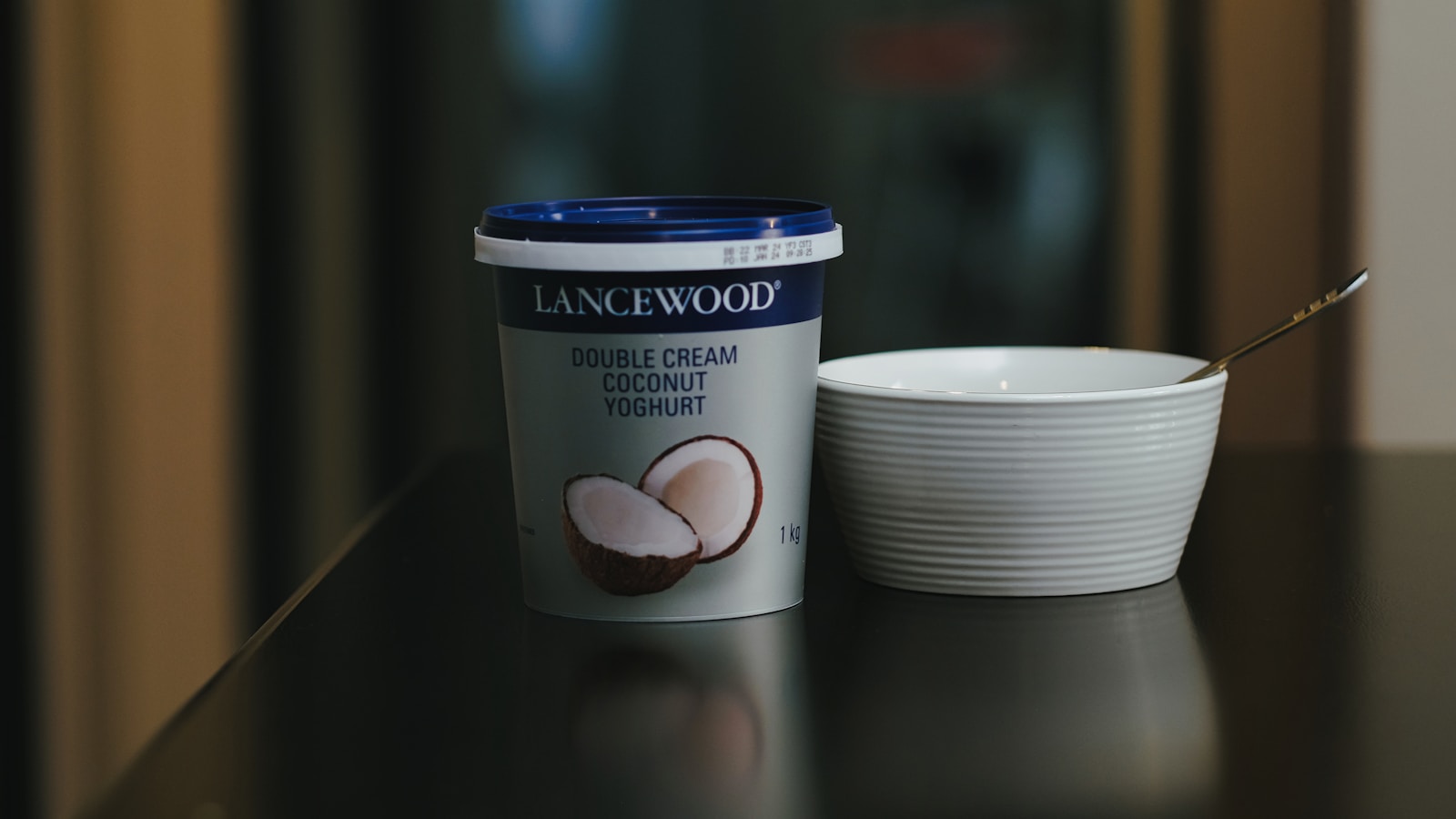
Yogurt tubs
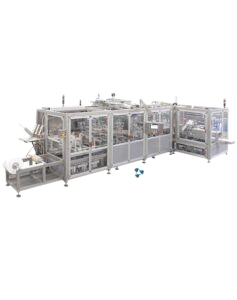
Aseptic filling equipment
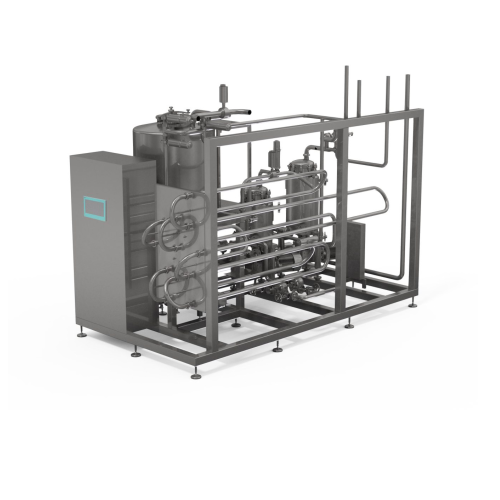
Aseptic processing systems
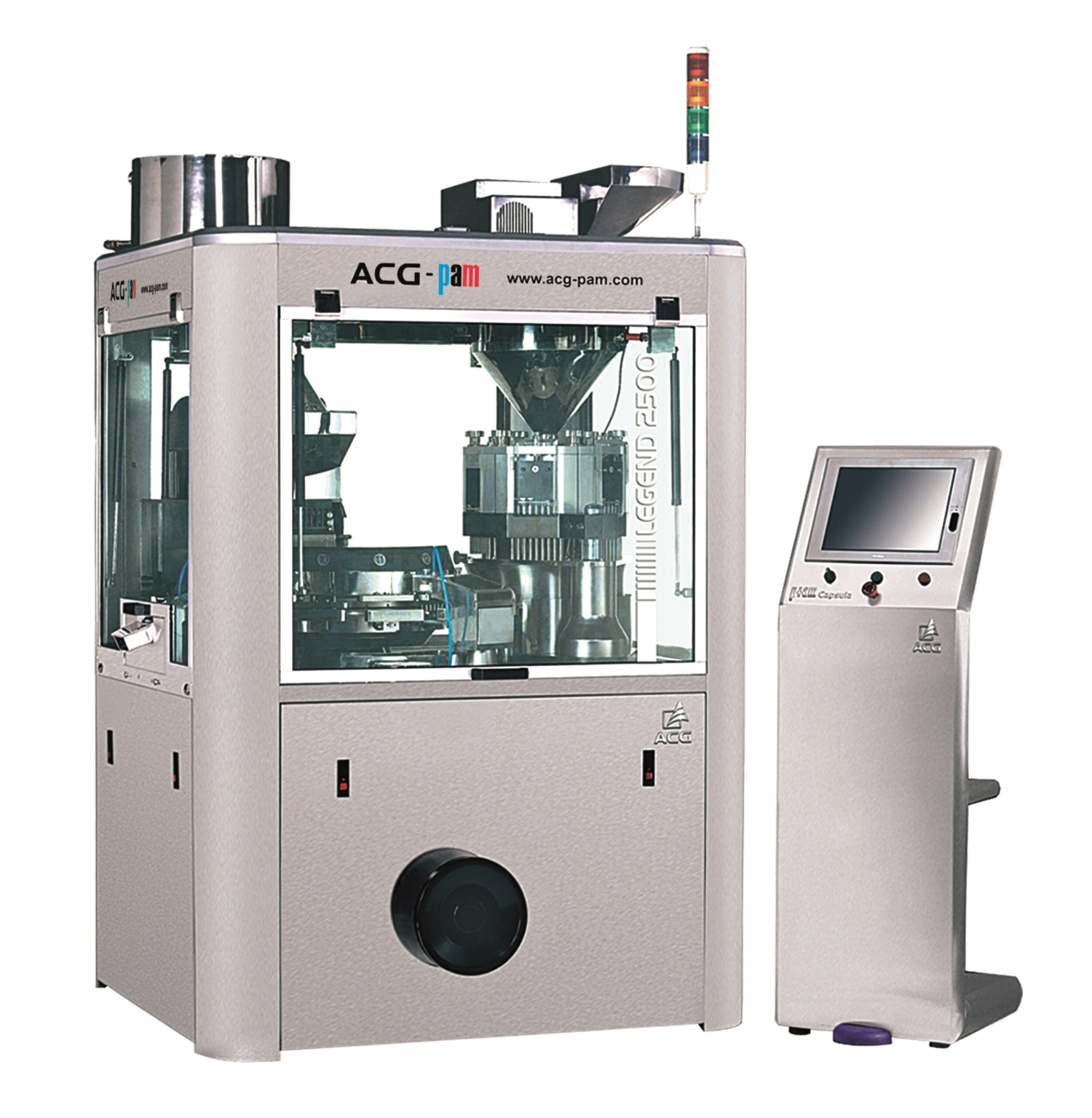
Auger filling machines
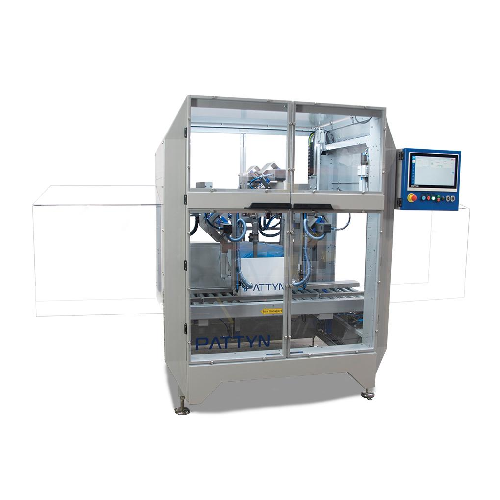
Automatic packaging systems
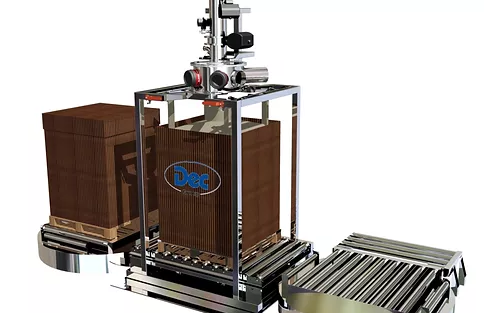
Bag filling machines
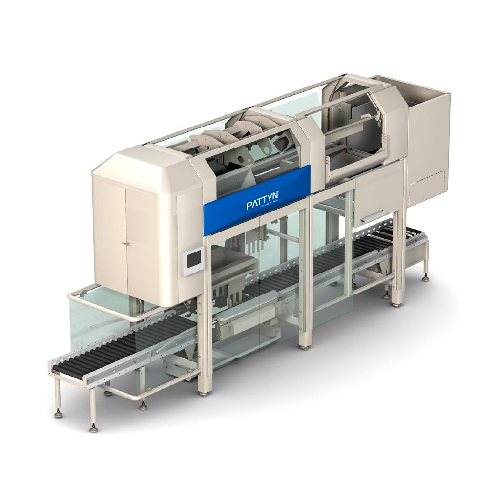
Bag inserters
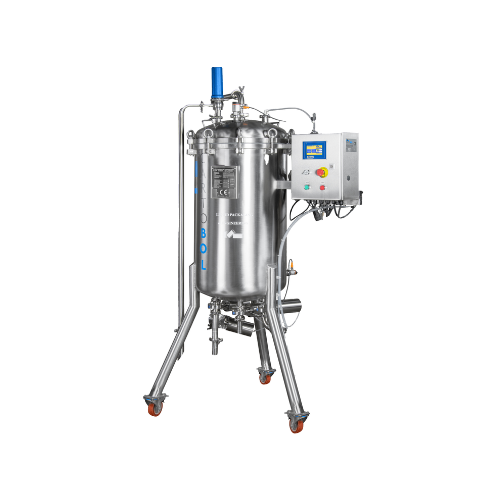
Bag-in-box fillers
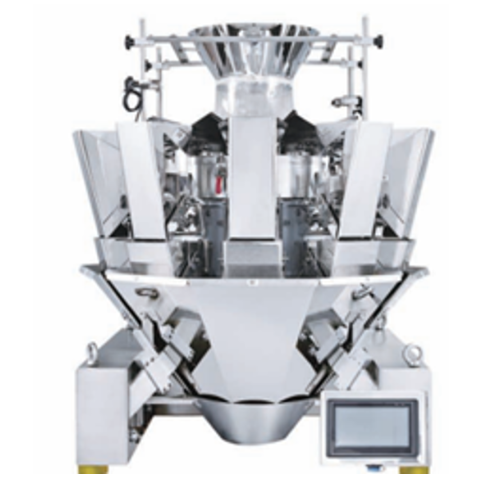
Bagging machines
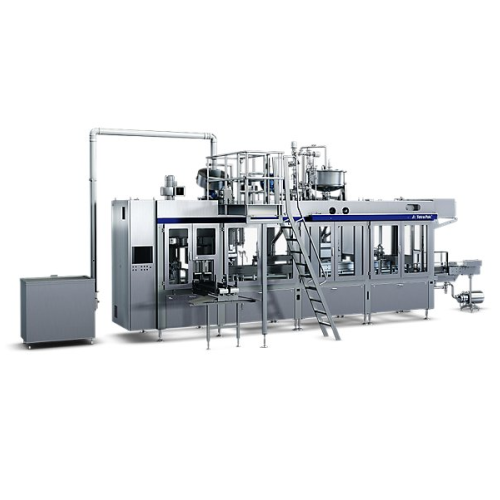
Beverage filling machines
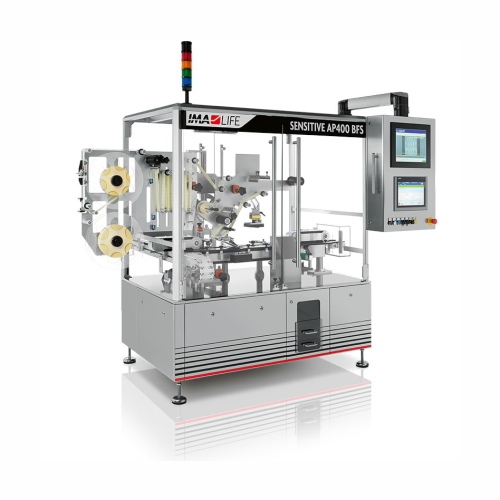
Bfs systems
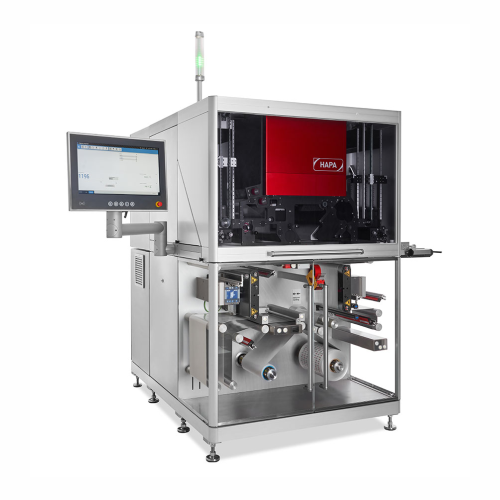
Blister packaging machines
Blow Molding Systems
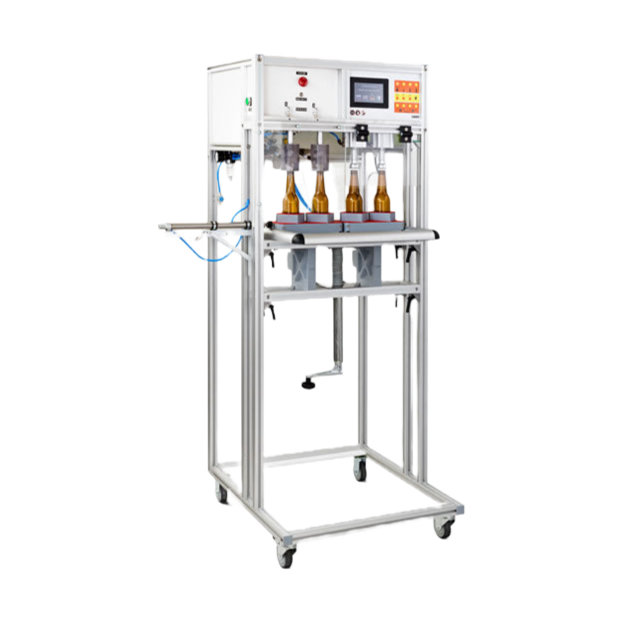
Bottle filling equipment
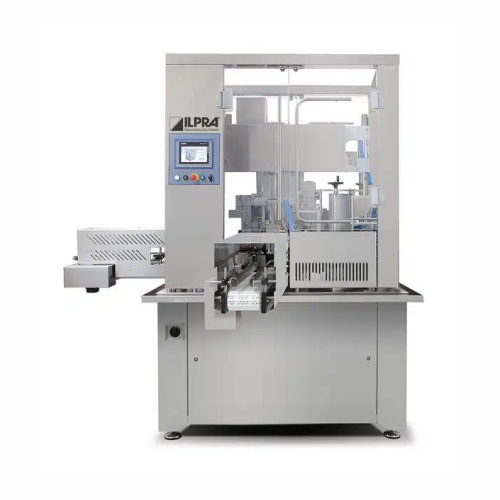
Bottle filling machines
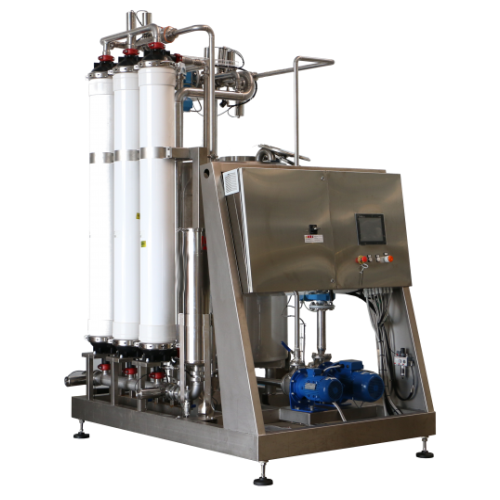
Bottling lines
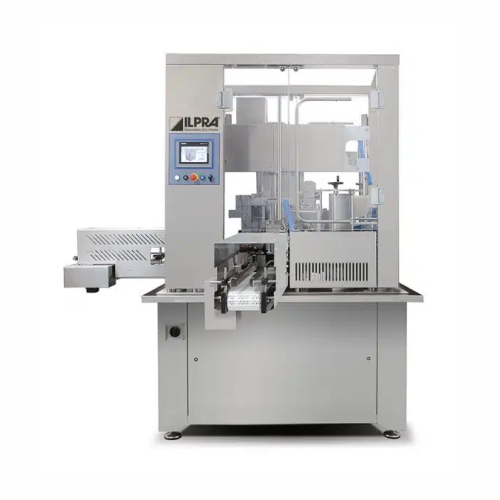
Box filling machines
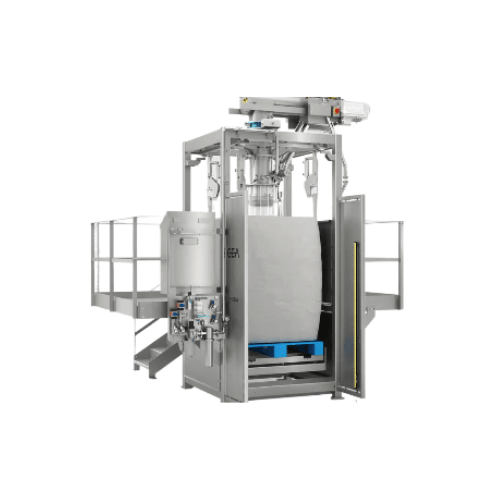
Bulk bag fillers
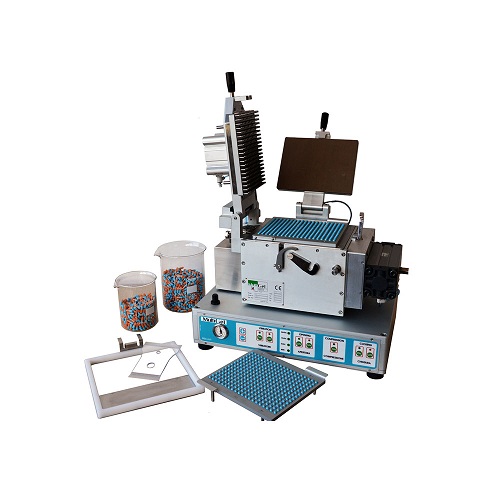
Capsule fillers
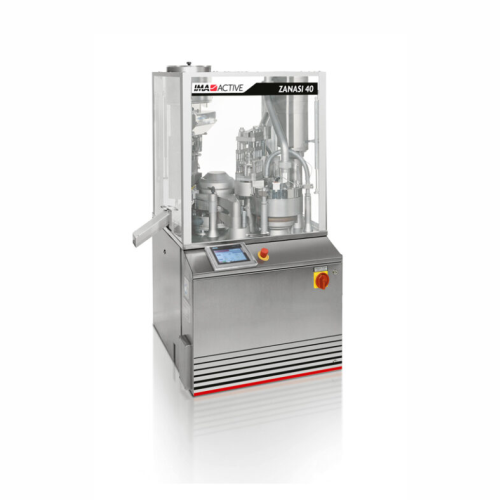
Capsule filling machines
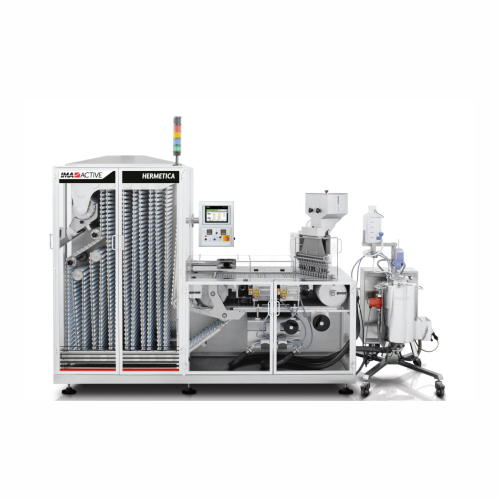
Capsule sealing machines
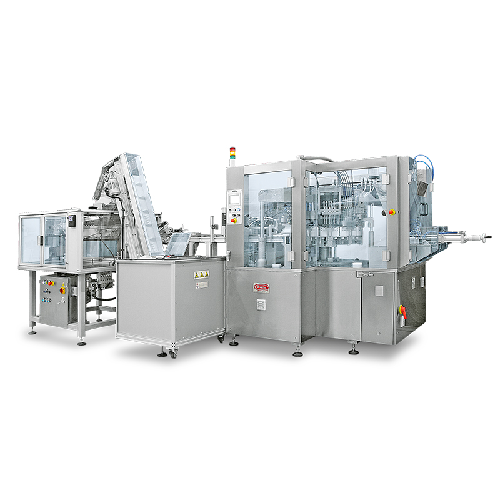
Cartridge filling machines
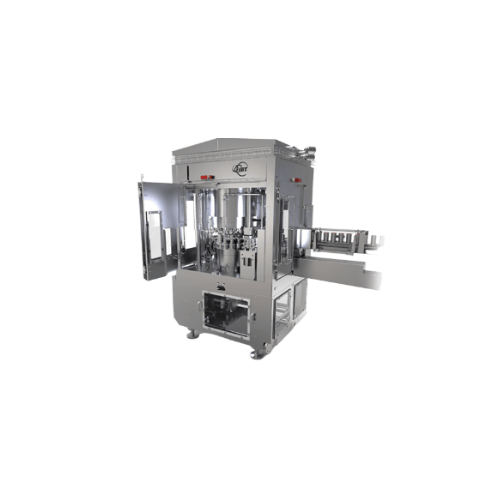
Corrosive filling machines
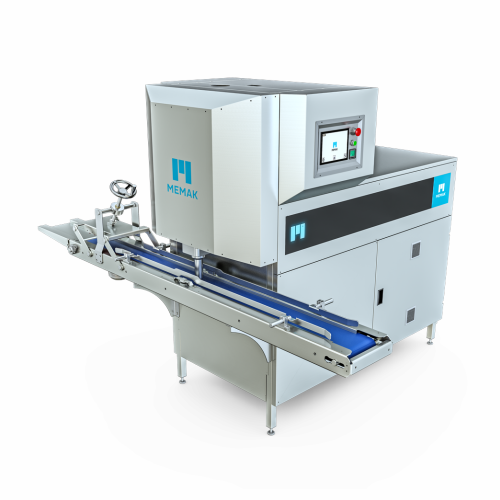
Cup filling machines
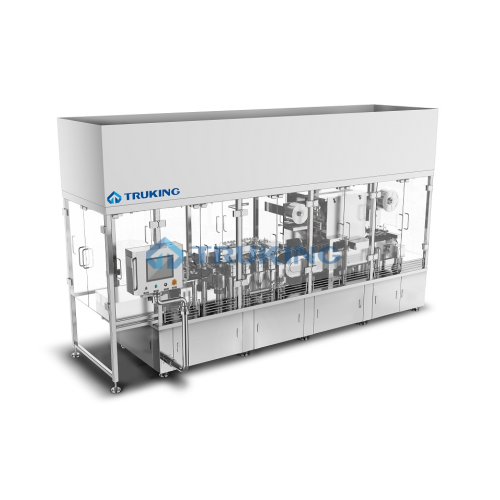
Diagnostic reagent filling systems
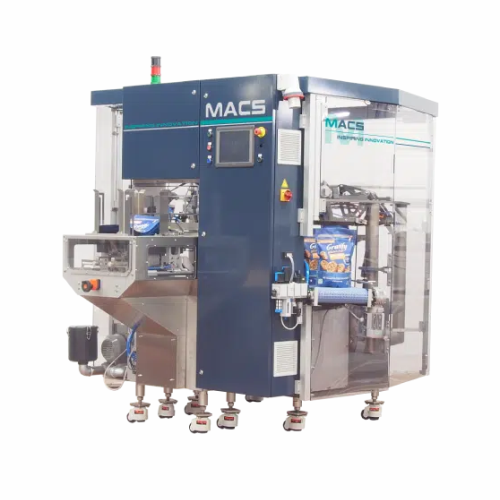
Doypack packaging machines
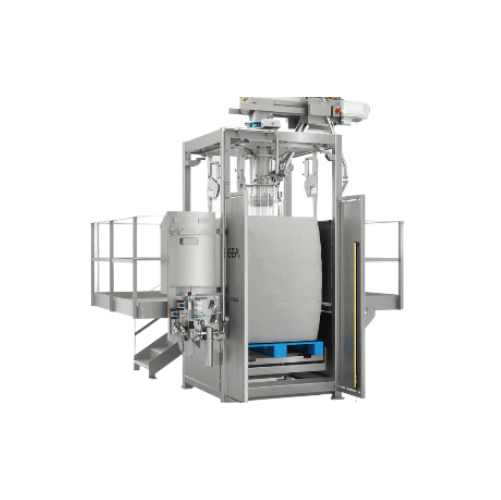
Fibc fillers
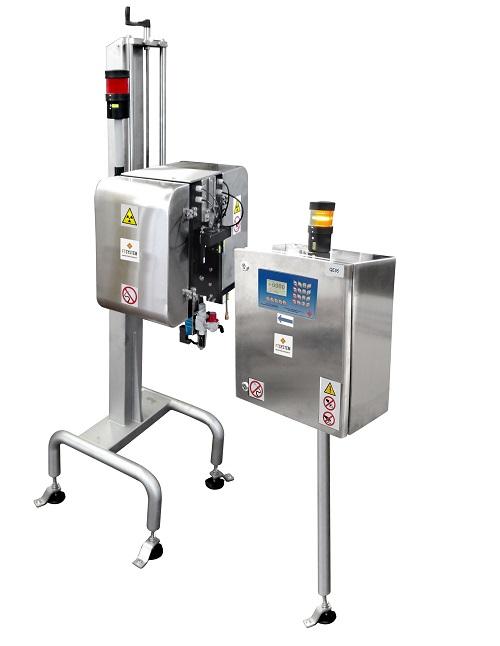
Fill level inspection systems
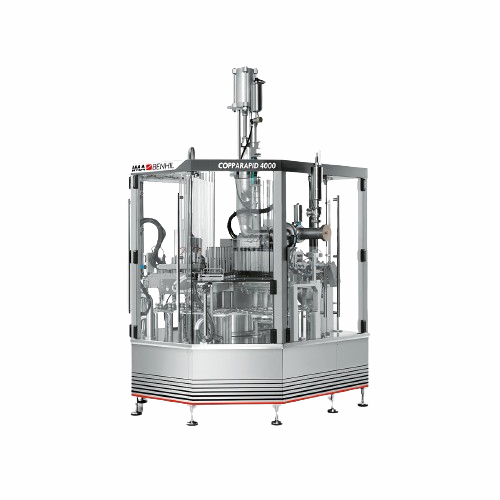
Filling stations

Filling systems for tins and jars
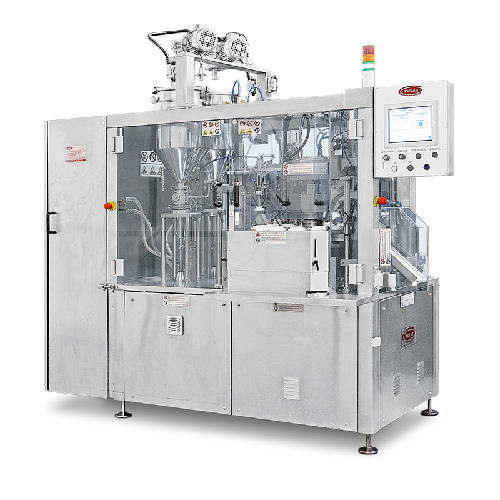
Flow meter filling machines
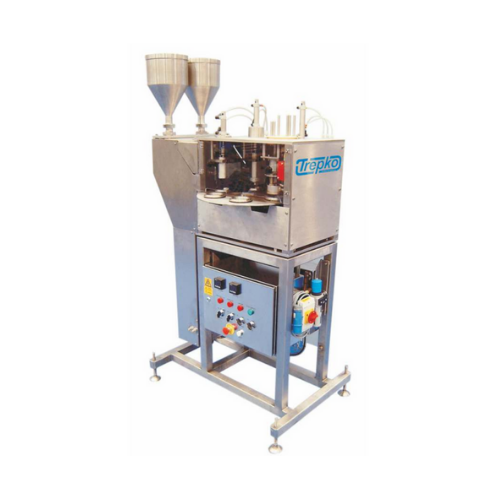
Form fill seal machines
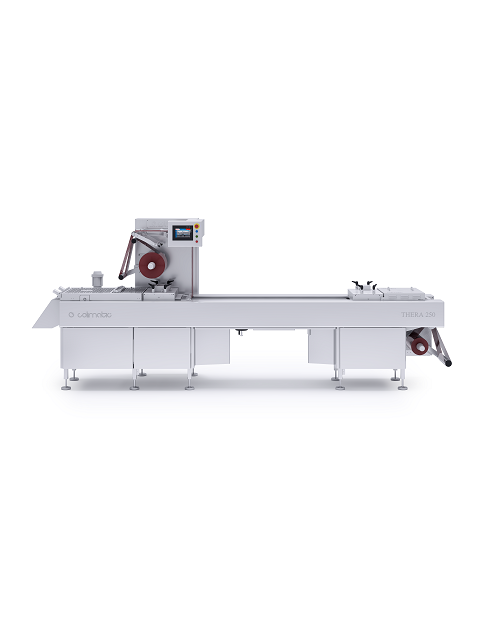
Form fill sealing equipment
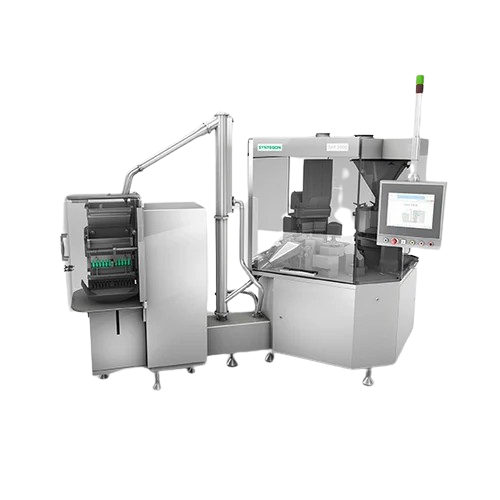
Gravimetric filling machines
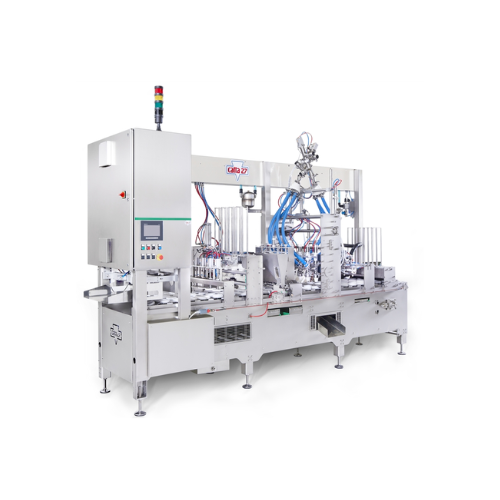
High-speed packaging machines
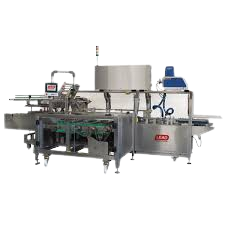
Horizontal flat pouching machines
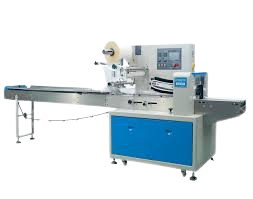
Horizontal form fill seal machines
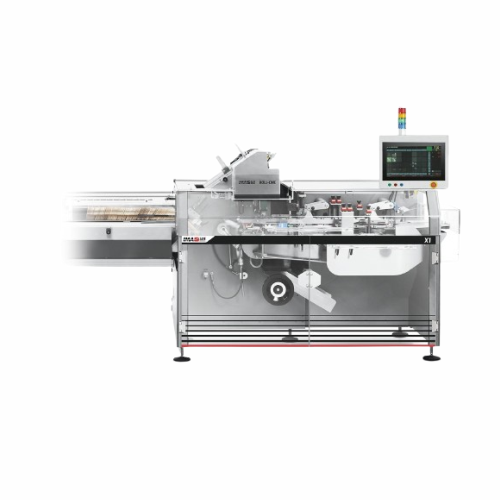
Intermittent motion cartoners
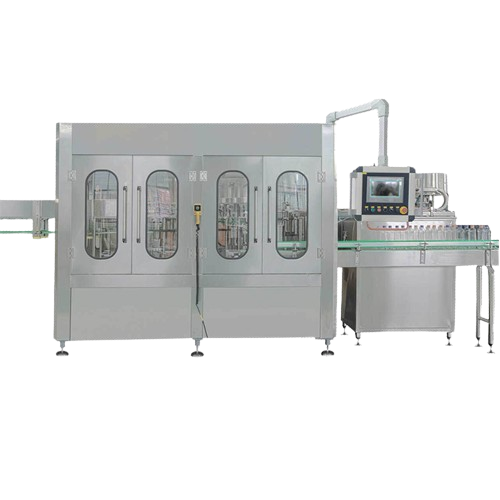
Isobaric filling machines
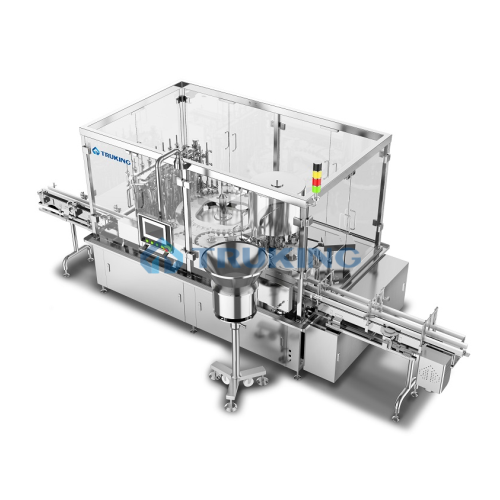
Large volume oral liquid filling systems
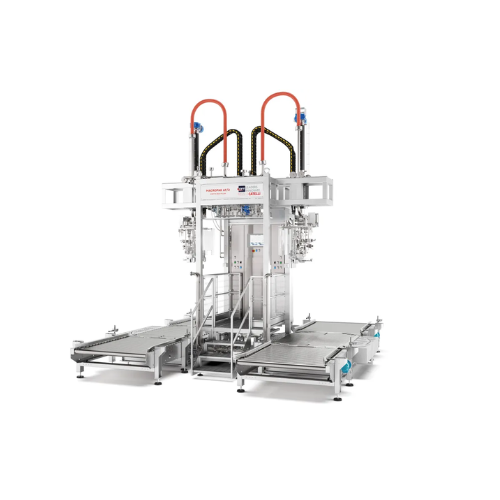
Liquid fillers
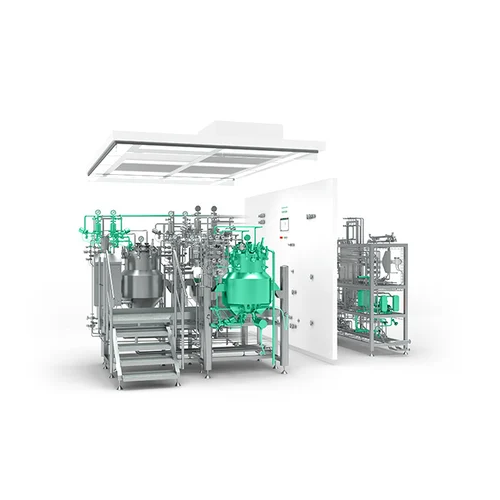
Lvp filling lines
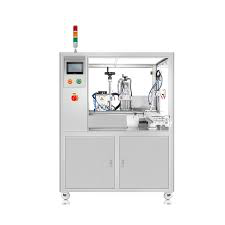
Mono-dose strips filling machines
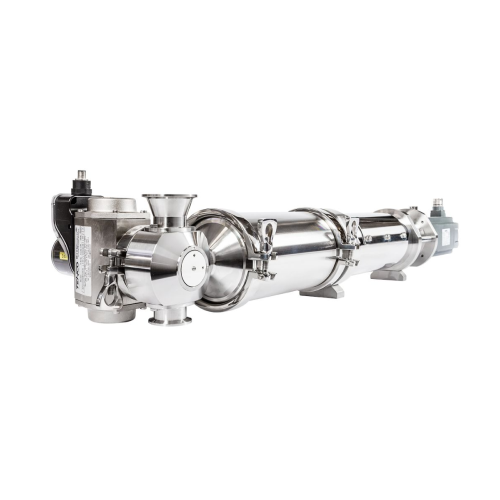
Piston fillers
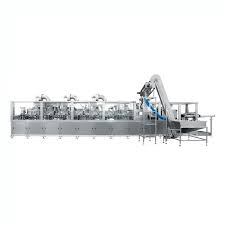
Plastic bottle bfs machines
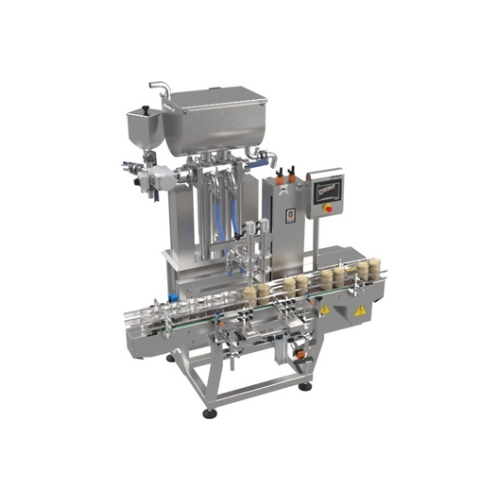
Pneumatic filling machines
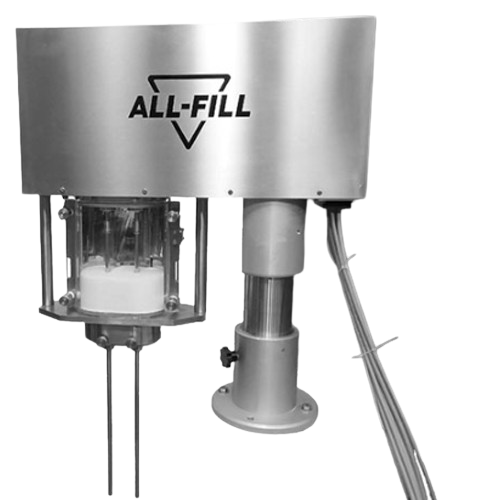
Pouch filling machines
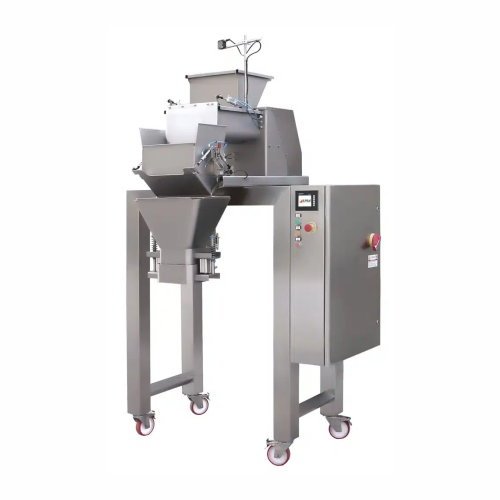
Powder auger fillers
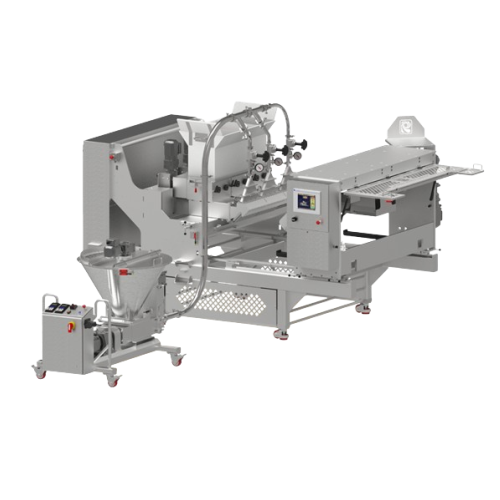
Precision filling scales
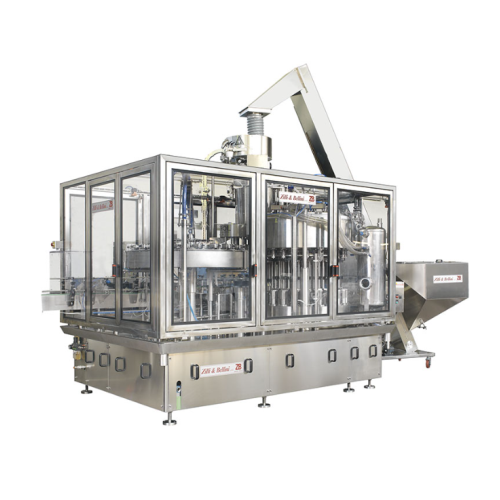
Rotary fillers
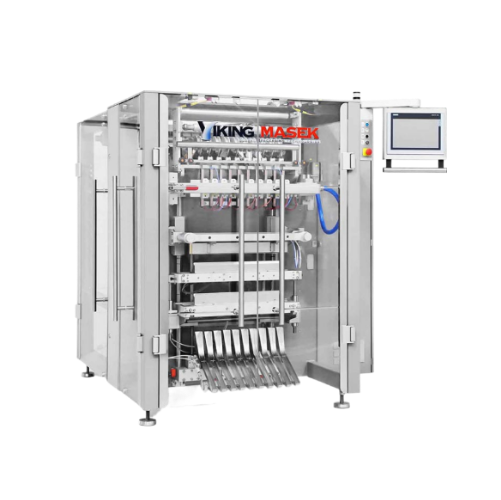
Sachet filling machines
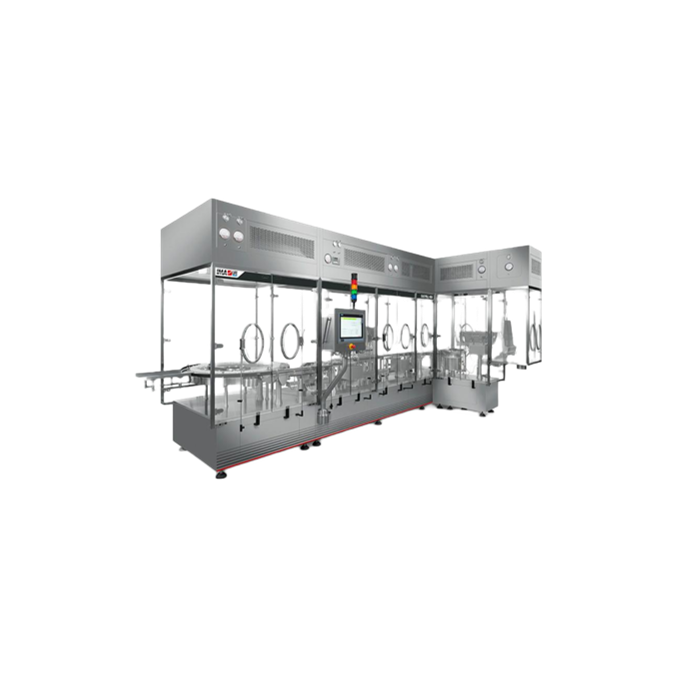
Sterile Filling Solutions
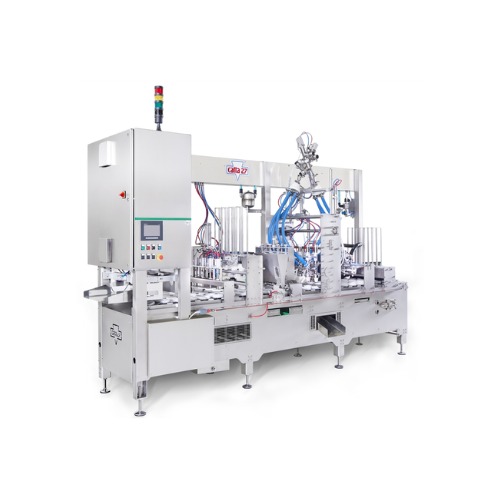
Stick pack machines
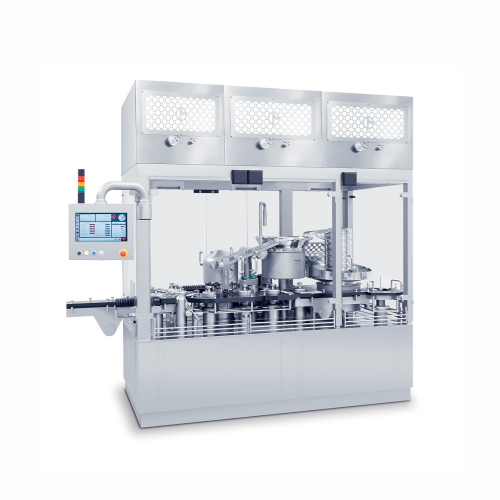
Svp filling lines
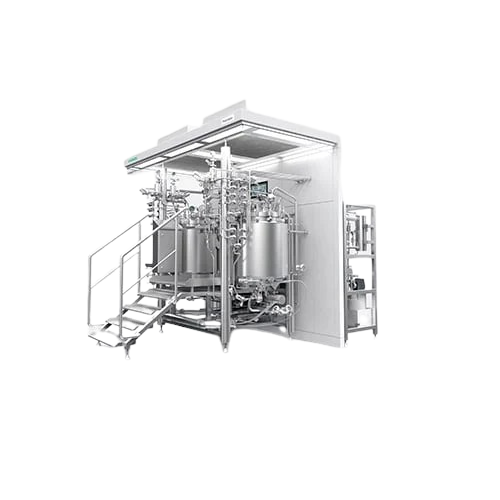
Syringe filling machines
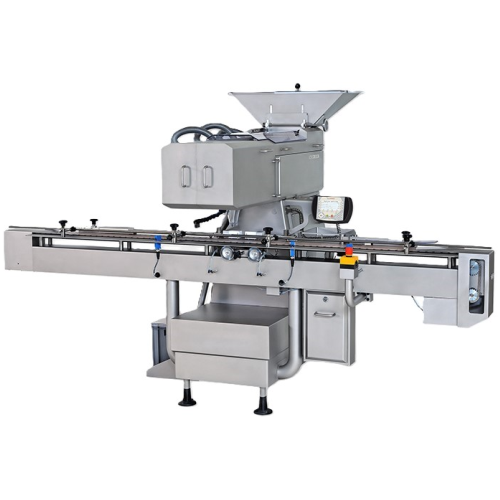
Tablet counter filling machines
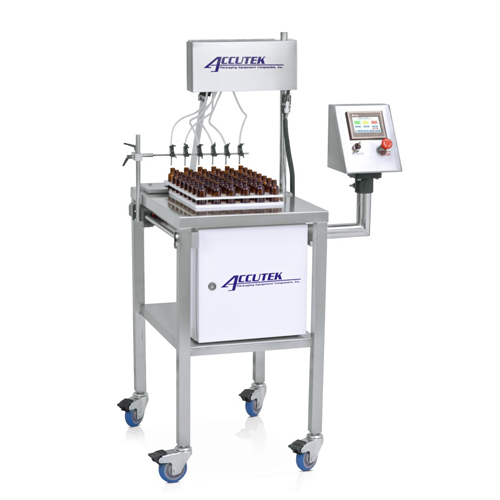
Timed fill filling machines
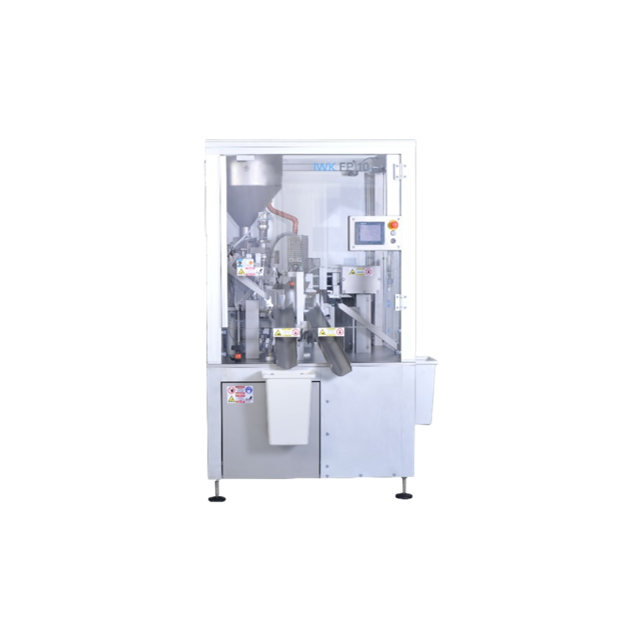
Tube filling equipment
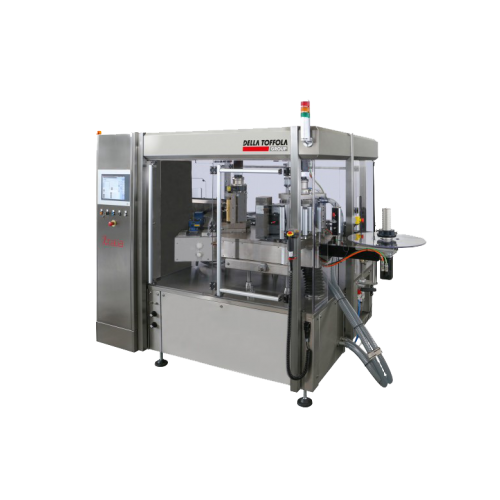
Vacuum bottling machines
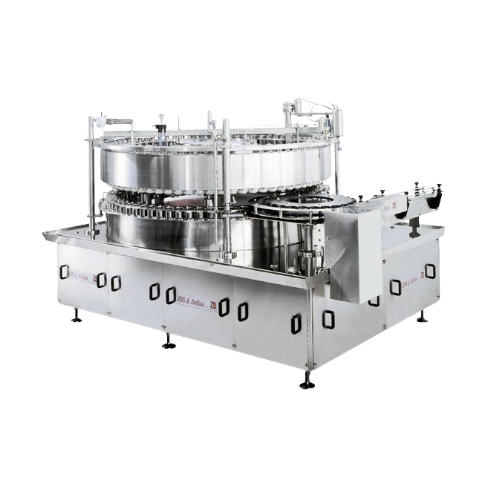
Vacuum fillers
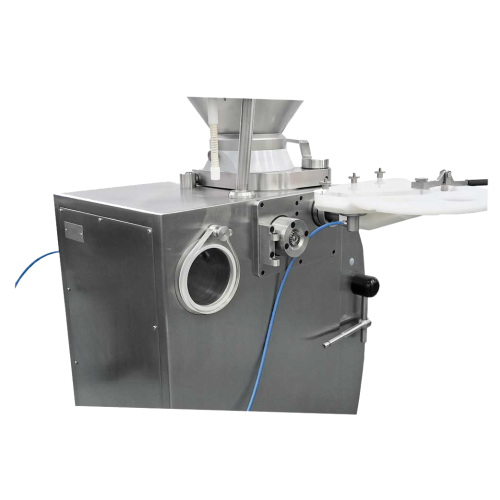
Vacuum stuffers
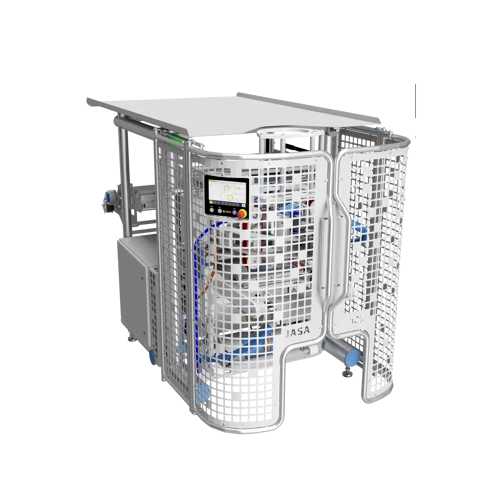
Vertical form fill seal machines
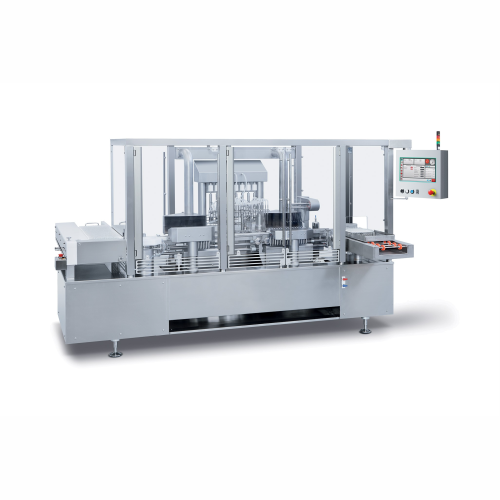
Vial filling lines
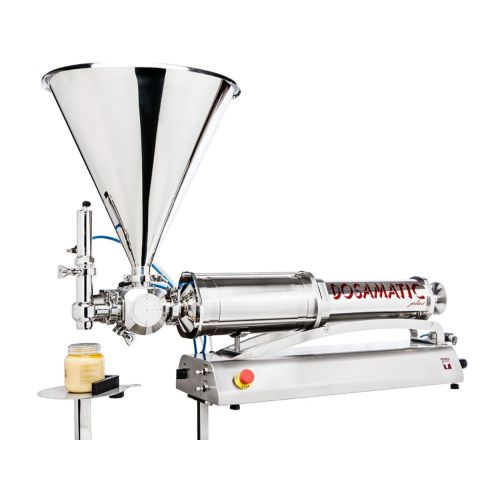
Volumetric fillers
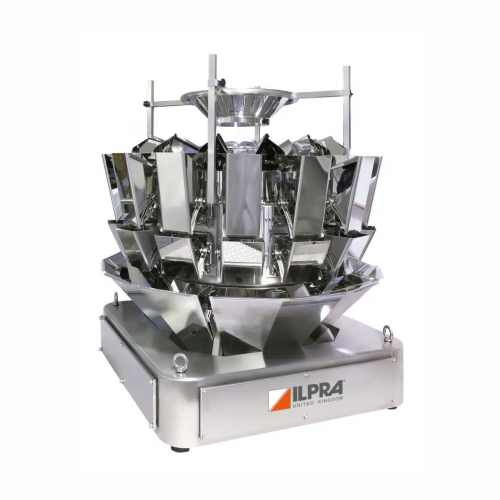
Weigh fillers
Which filling technology do you need?
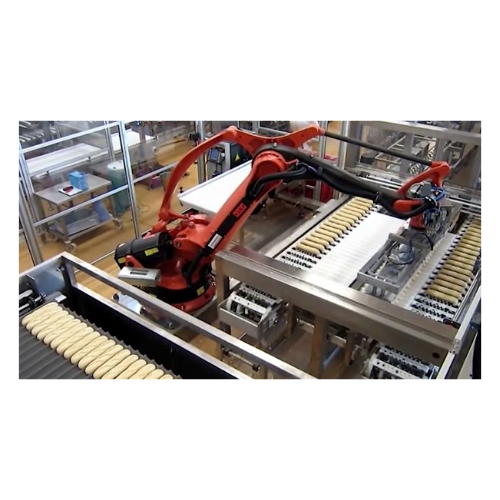
Baguette cutting and sauce filling system
Optimize your bakery production with an innovative system that seamlessly cuts a...
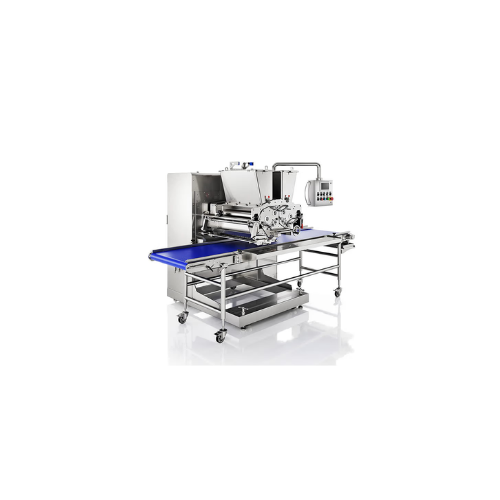
Lobe depositors and extruders for filled and decorated cookies
Optimize your bakery production with precision depositing...
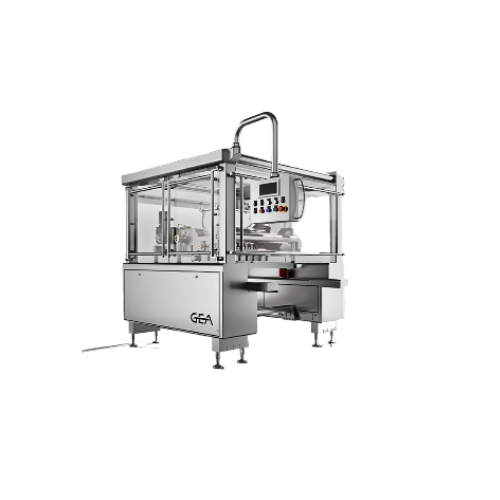
Volumetric piston depositors for cake and pie fillings
Achieve precise depositing and gentle handling of varied doughs an...
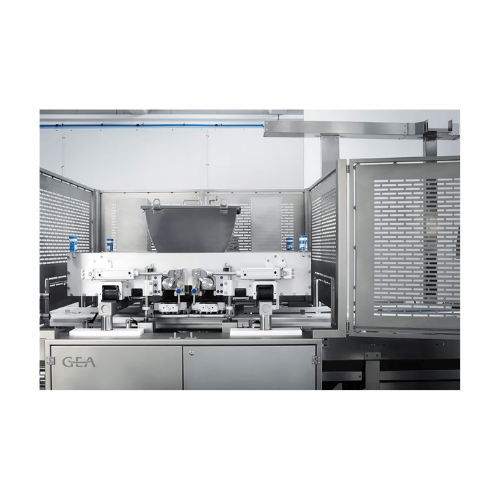
Cakes and pastry fill injector
Achieve precise and efficient filling of a variety of bakery products, minimizing waste and d...
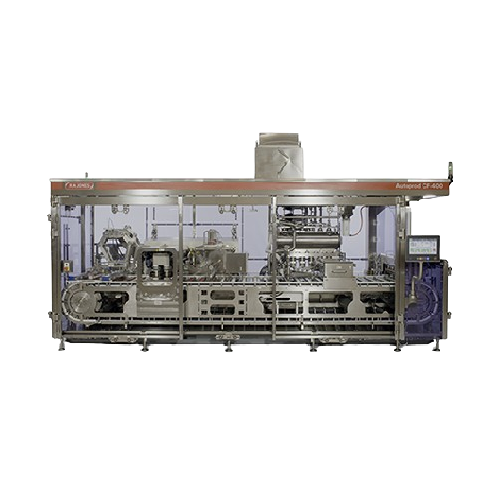
Cup filling and sealing system for dairy products
Optimize your production line with versatile cup filling and sealing ca...
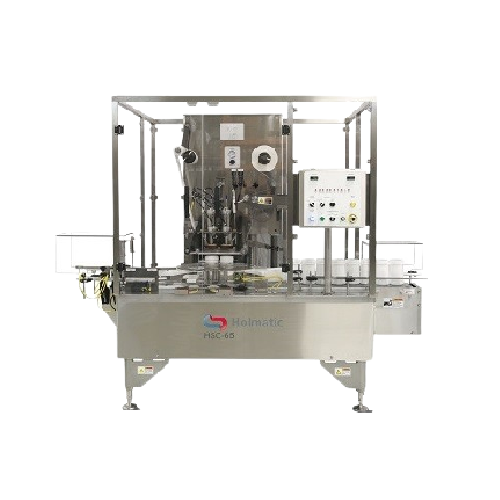
Rotary indexing sealer for cup filling
Streamline your production line with precise cup filling and sealing, ideal for a wi...
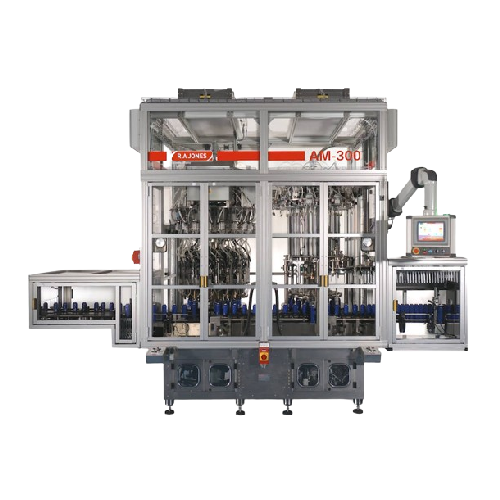
High-speed aerosol filling system for personal care products
Streamline your aerosol production with a multi-functional ...
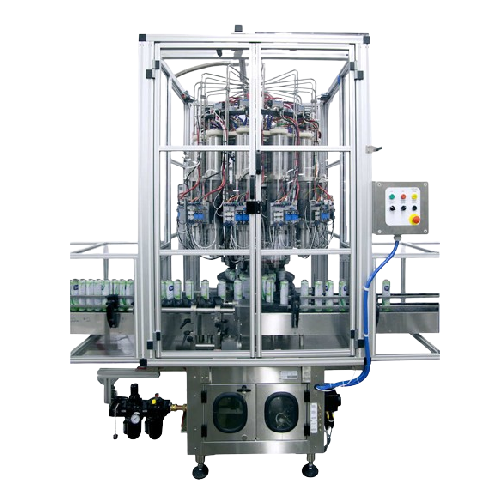
Rotary continuous aerosol product filler
Achieve precise aerosol filling with high-speed efficiency, designed for operation...
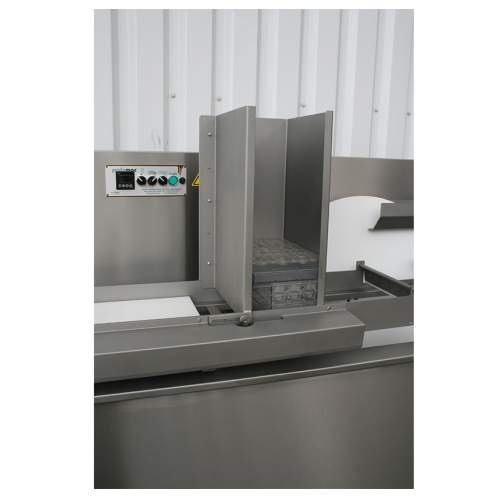
Pneumatic scrapers for chocolate mould filling
Achieve precise chocolate moulding with pneumatic scrapers that streamline ...
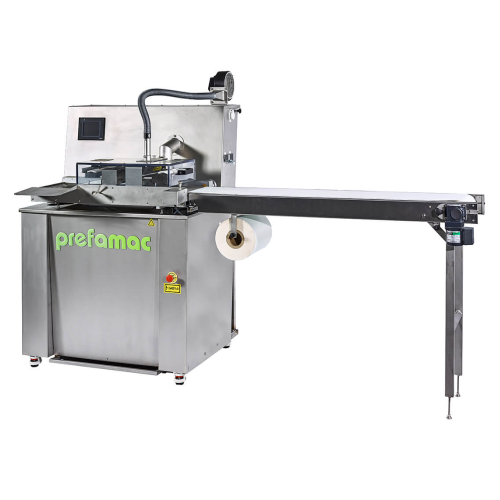
Chocolate tempering system for mould filling and vibrating
Ensure a flawless finish for chocolates and confections with ...
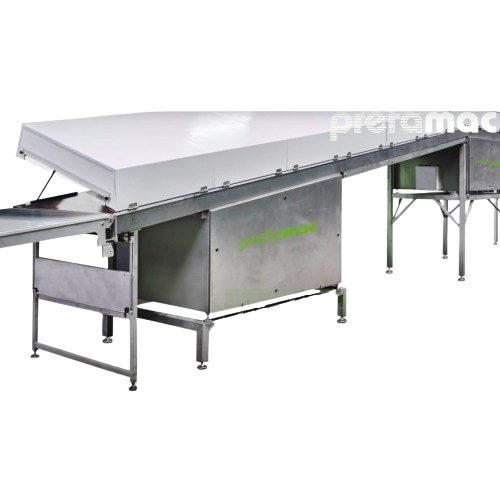
Buttercream filling applicator for chocolates
Enhance your confectionery process with precision dosing and moulding to cre...
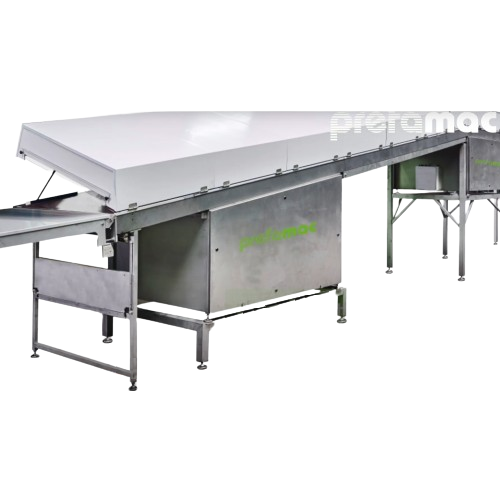
Chocolate filling application system for manons
Efficiently apply a variety of fillings, from delicate buttercream to rich...
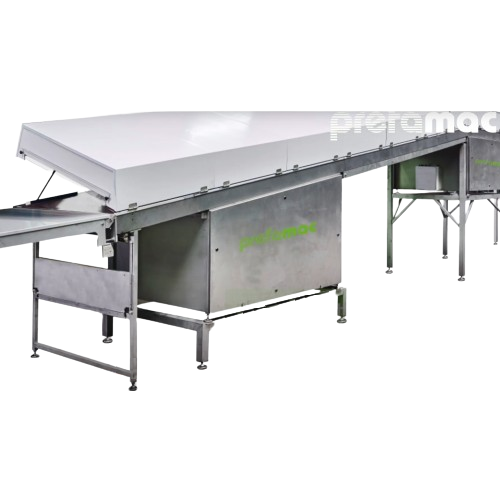
Filling system for chocolates and pralines
Efficiently dose, mold, and fill chocolates to create a variety of enticing con...

Semi-liquid weigh filler for edible oils & fats
Achieve precise weigh filling of semi-liquids while minimizing product was...
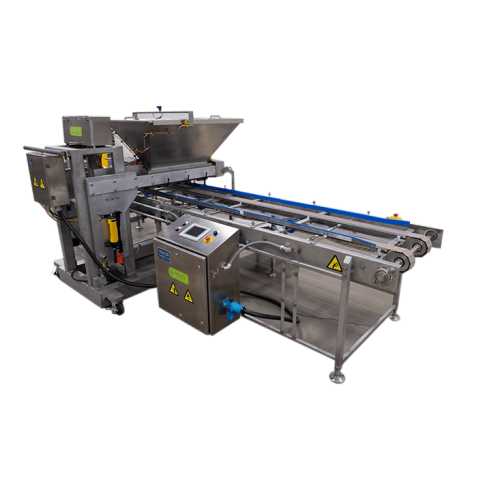
Depositors for bakery fillings
Achieve precise and high-speed depositing of bakery and pastry fillings to optimize your prod...

Linear belt vibratory weigh filler for solid chocolate
Optimize your chocolate production by minimizing product giveaway ...
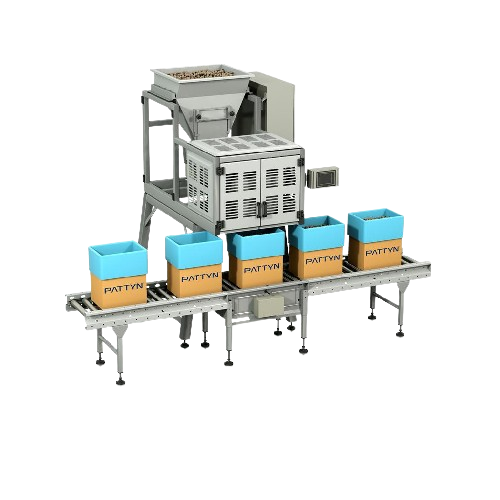
Linear vibratory weigh filler for fragile food products
Achieve precise and gentle filling of fragile food products with ...
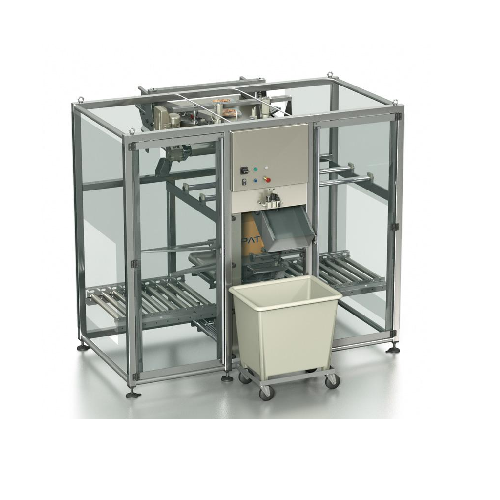
Bulk box filler for bakery and pastry products
Efficiently pack fragile bakery and pastry products with gentle handling an...
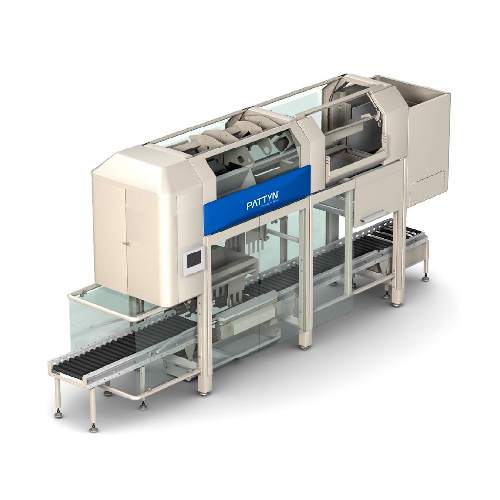
High-speed baguette case filling station
Effortlessly organize and pack bakery products into cases at high speed, ensuring ...
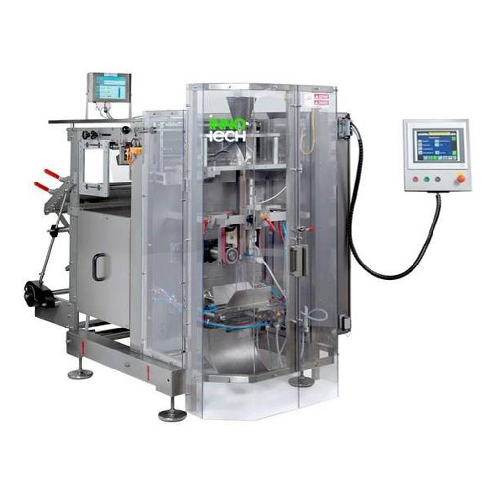
Vertical fill and seal bagging machine for bakery products
Streamline your bakery product packaging with this versatile ...
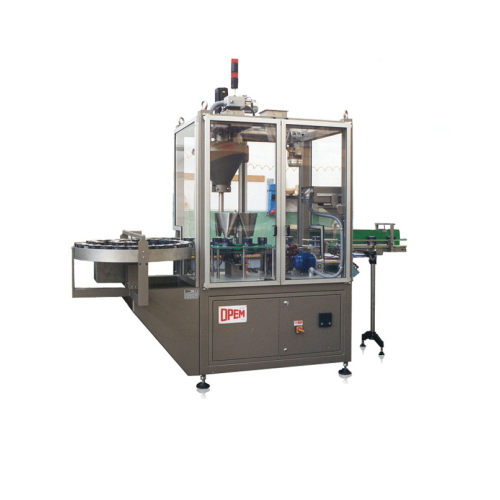
Coffee bean and ground coffee filling system
Efficiently fill tins and jars with coffee beans or ground coffee while ensur...
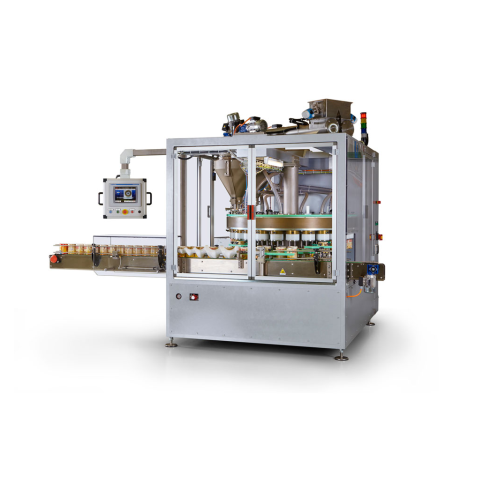
Filling system for ground coffee in tins
Achieve precise weight control and enhanced throughput with a high-speed filling s...
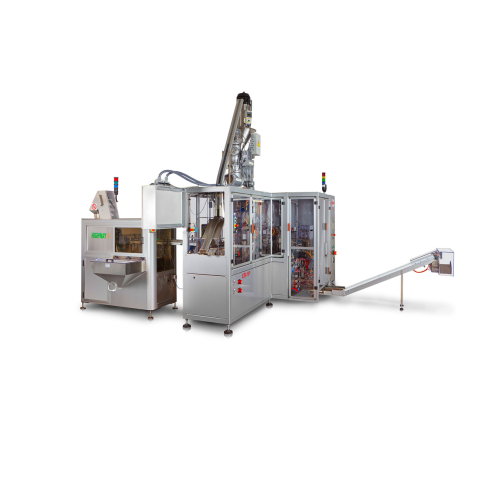
Capsule filling system with in-line weight control
Experience precise capsule filling with high-speed accuracy, designed ...
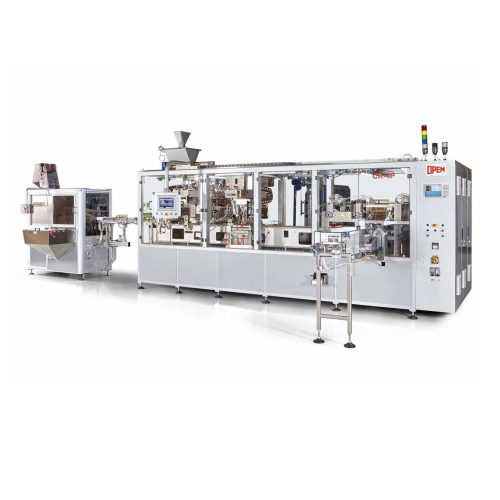
High throughput capsule filling system
Achieve precise, high-speed capsule filling with versatility, ensuring product integ...
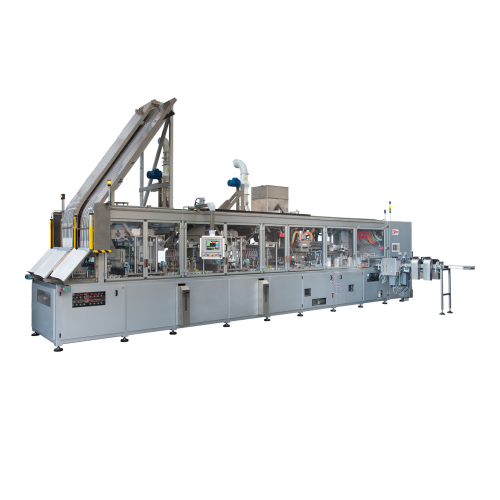
High-speed capsule filling system
Maximize production efficiency with high-speed capsule filling designed for precise dosin...

Capsule filling system for high volume production
Maximize your capsule production efficiency with a system designed to s...
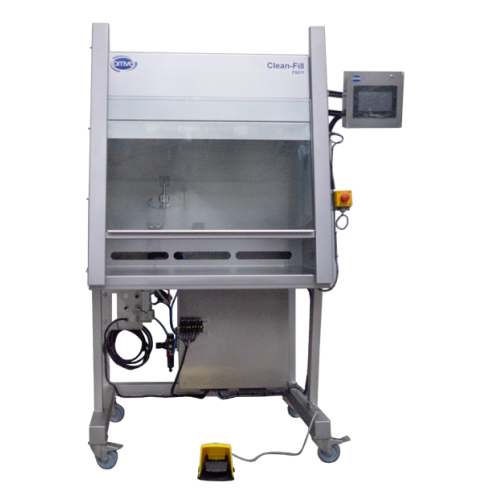
Sterile filling and closing bench for bottles and cups
Ensure precise and sterile filling for liquid products with a hygi...
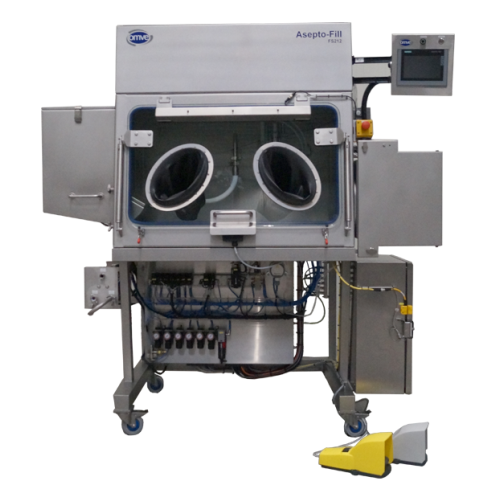
Cold aseptic filling solution for Uht samples
Ensure aseptic integrity and extend shelf life by securely filling and closi...
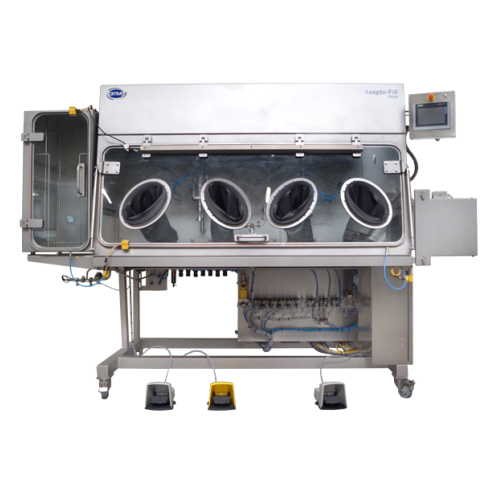
Aseptic filler for nutraceuticals
Ensure the sterility of your liquid nutraceuticals and beverages with a versatile solutio...
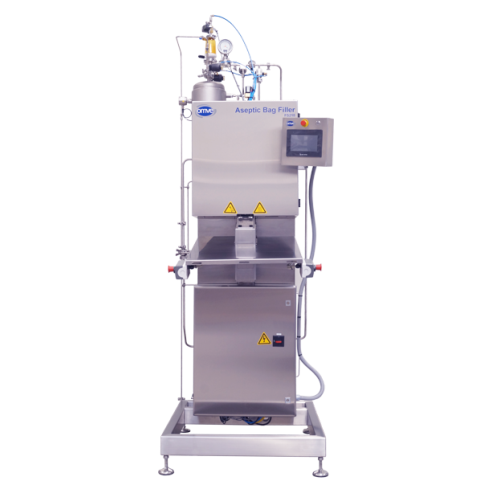
Aseptic bag-in-box filler for laboratory use
Achieve aseptic filling precision on a lab-scale with a compact solution that...
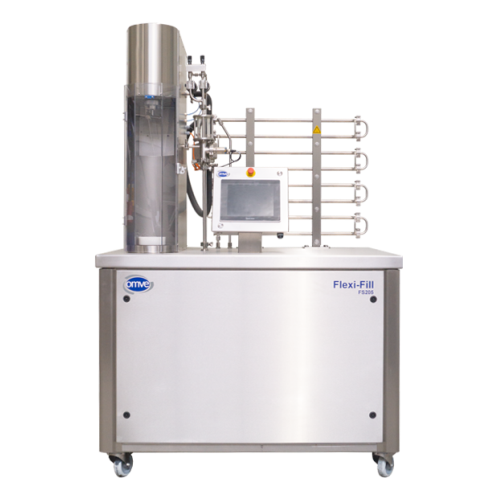
Counter-pressure filler for carbonated drinks
Enhance your carbonated beverage production with advanced counter-pressure f...

Lab-scale carbonation system for beverage filling
Streamline your beverage development with precision carbonation and ver...
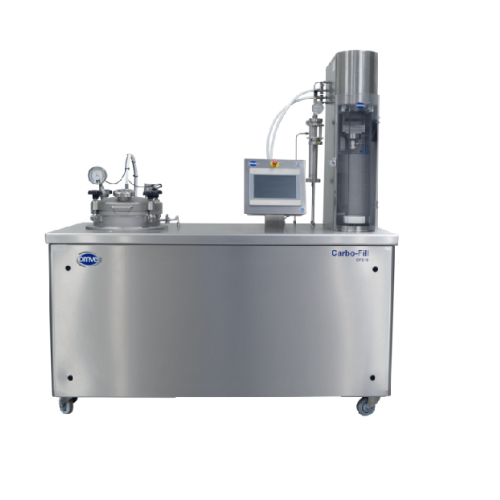
Carbonation and filling system for Pet and glass bottles
Optimize your beverage production with precise carbonation, fill...
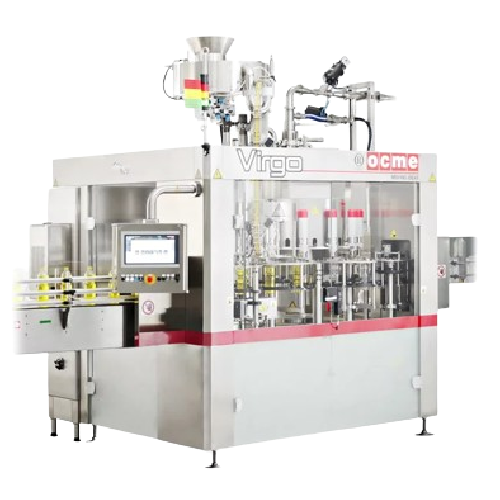
Rotary weight filler for edible oil
Optimize your liquid product filling with precise weight control, ensuring high accurac...
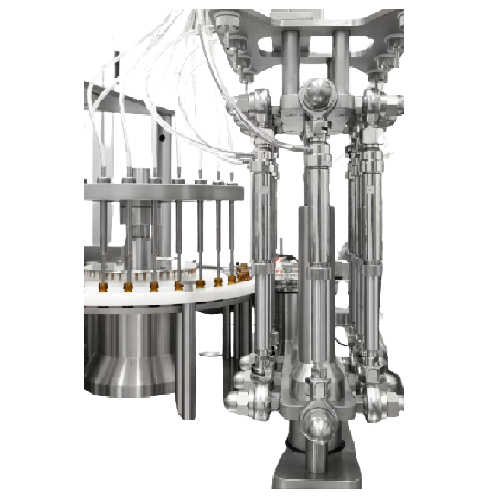
Filling and capping solution for oral liquid products
Achieve precise, high-speed filling and capping of oral liquids wit...

In-line weight filler for drums and kegs
Achieve precise and efficient weight-based filling for large liquid containers, en...
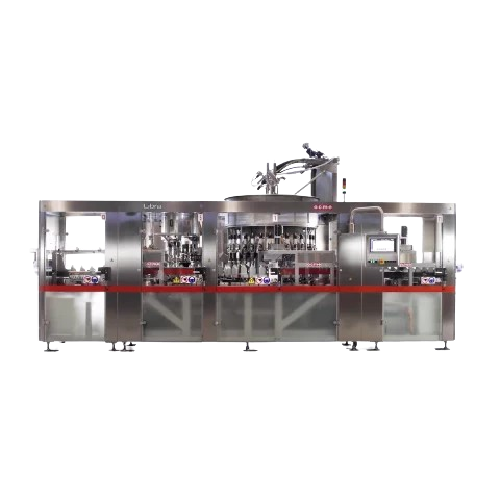
Rotary weight filler for Pet and Hdpe bottles
Enhance your production line with precise weight-based filling, ensuring rap...
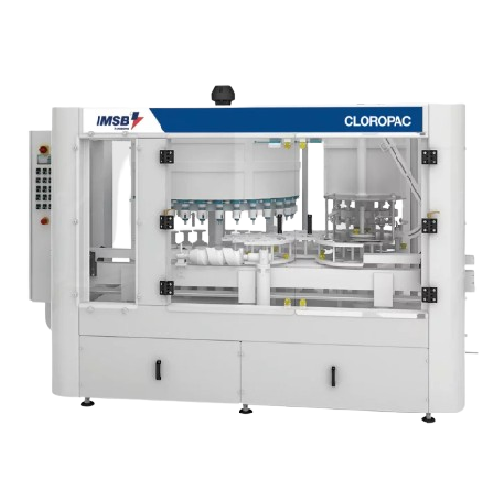
Gravimetric filling and capping system for chlorine solutions
Optimize your filling and capping processes for chlorinate...
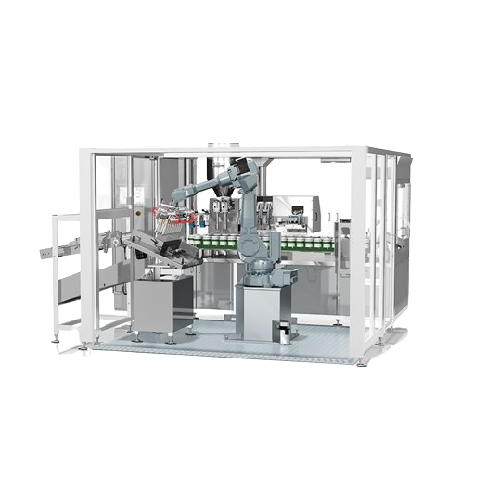
Tube filling machine for cosmetics and food products
Achieve precise and efficient packaging with this advanced twin-head...
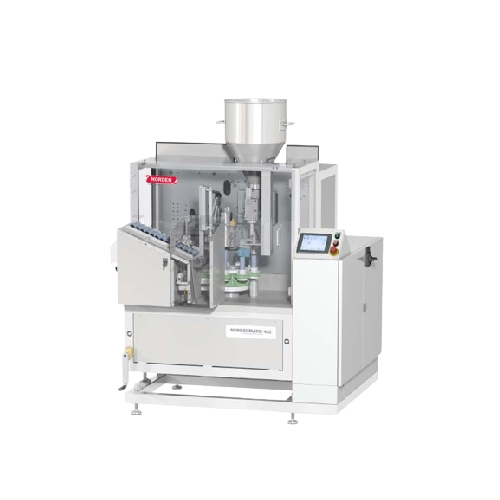
Tube filling solution for plastic and laminate tubes
Ensure precise tube filling and sealing with quick changeovers, enha...
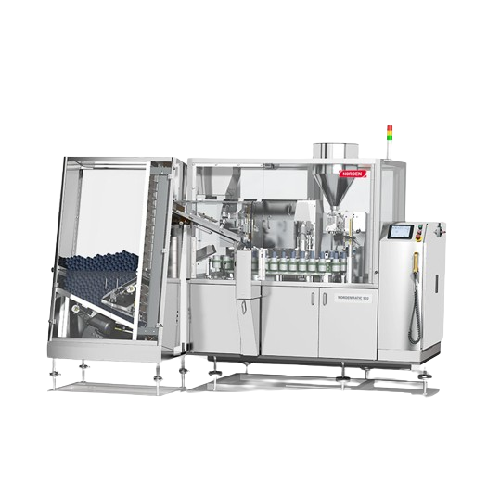
Tube filling solution for plastic, laminate, and aluminum tubes
Optimize your production line with a versatile tube fill...
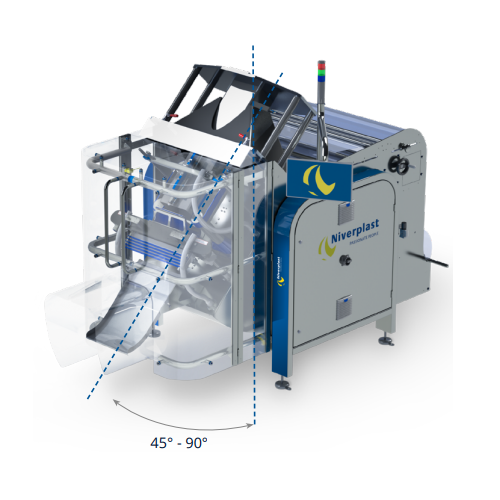
Vertical form fill seal packaging system
Enhance your packaging line with precision sealing and efficient throughput, ideal...
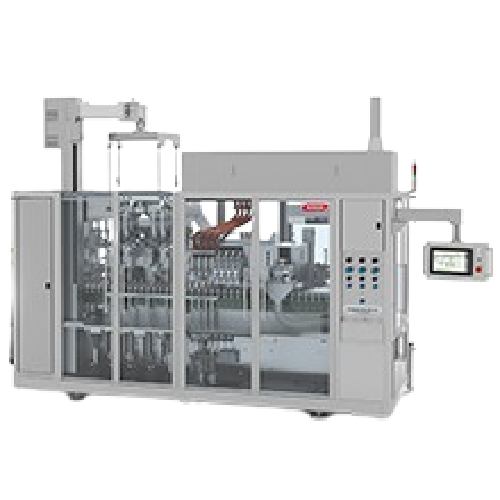
Tube filling station for plastic, laminate, and aluminum tubes
Efficiently seal and fill various tube materials, ensurin...
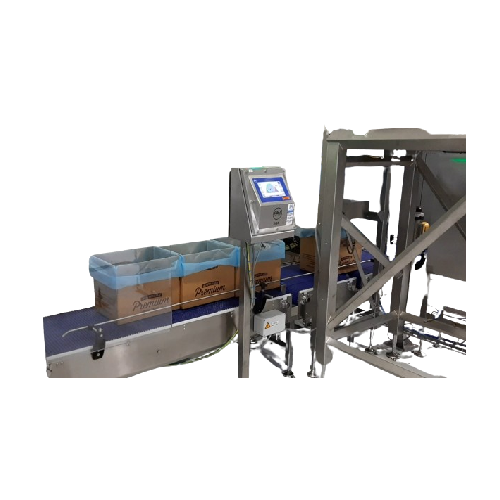
Linear weigh filler for accurate box packaging
Ensure precise weight-based filling for a variety of solid products, from d...
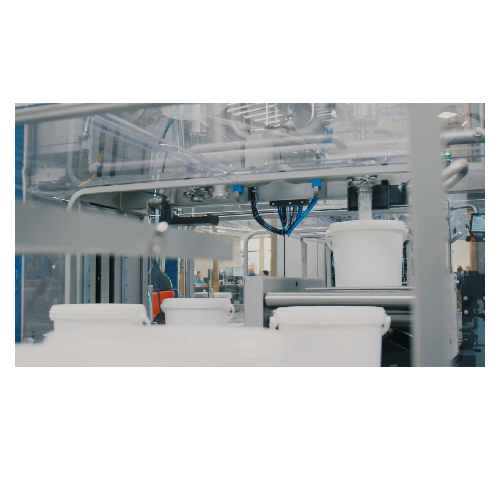
Oil and fat filling system for industrial use
Optimize your production line with this precise filling solution, designed t...
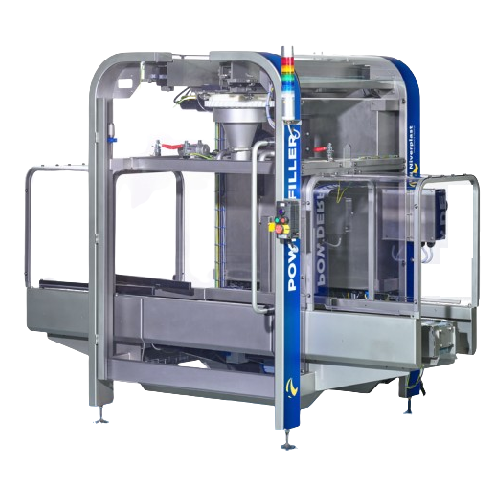
Accurate powder filling solution
When precision is paramount, this solution offers exceptional accuracy, filling powders up ...
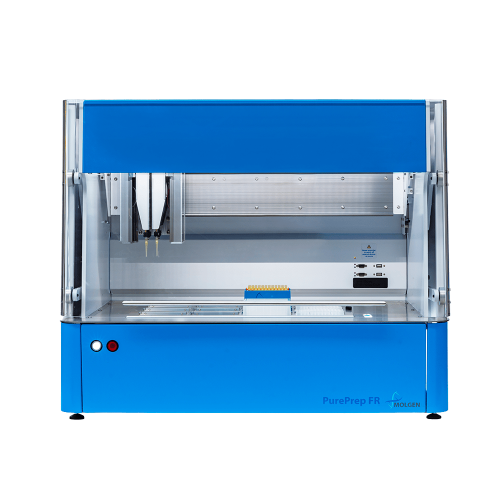
Automated liquid handler for high precision plate filling
Streamline your laboratory workflow with an intuitive system d...
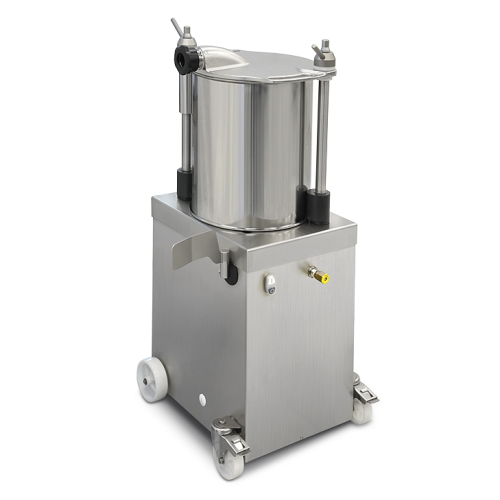
Upright stainless steel hydraulic sausage fillers
Streamline your sausage production with precise portioning and minimal ...
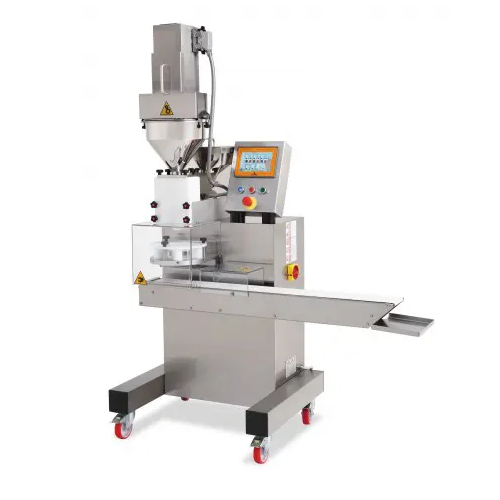
Co-extruder for filled sweet and savoury products
Effortlessly create a variety of filled sweet and savoury products, fro...
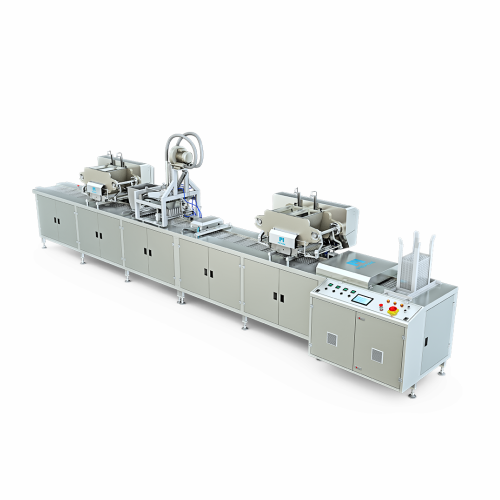
Chocolate moulding line for center-filled chocolates
Streamline your chocolate production with a versatile moulding line ...
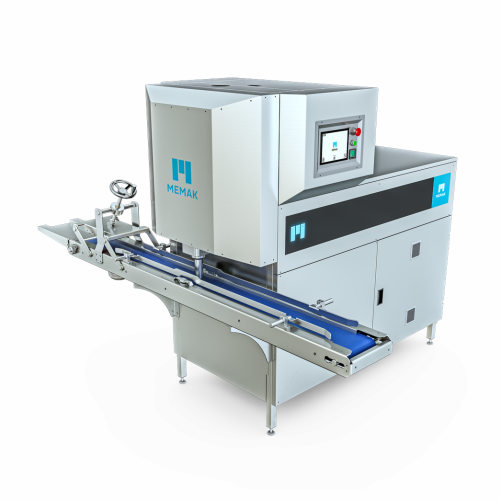
Cup filling system for jars and buckets
Optimize your confectionery and bakery filling processes with this high-speed cup f...
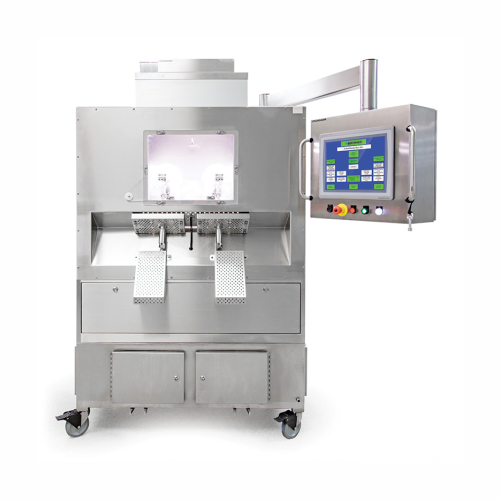
Aseptic filling system for biopharmaceutical products
This system ensures sterility in high-volume aseptic filling operat...
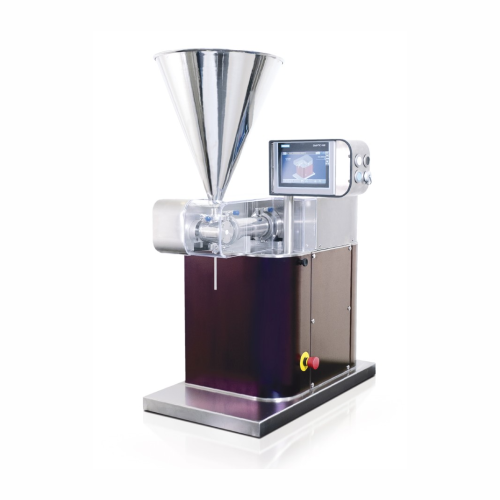
Lab-scale liquid and cream filling system
Streamline your lab production with precise filling of liquids, creams, and past...
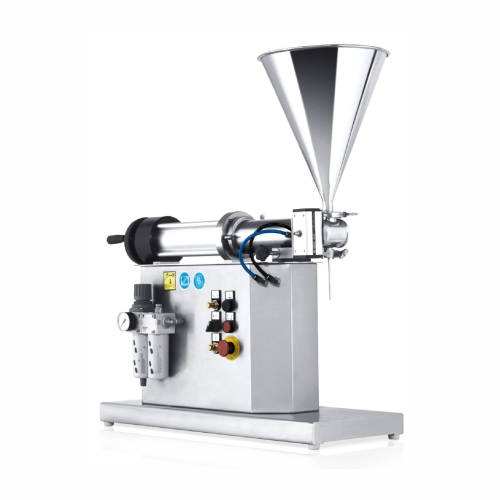
Laboratory filling system for liquid and creamy products
Optimize your laboratory processes by precisely handling liquid,...
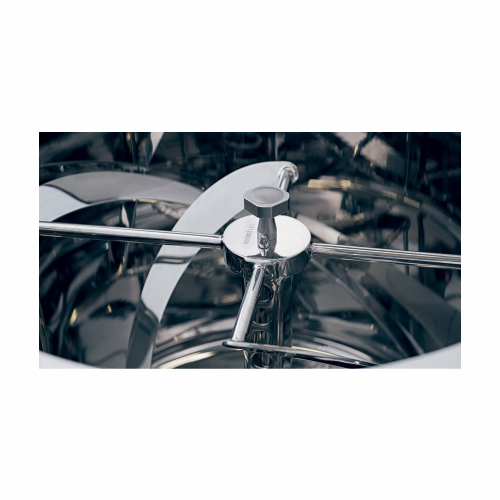
Mobile melting tank for hot filling lipstick
Optimize your cosmetics production with precise melting and hot filling techn...
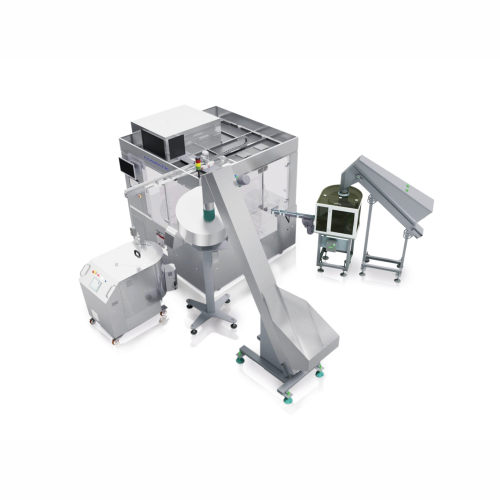
Lipstick filling solution for high output production
Achieve precision and efficiency in lipstick production with advance...
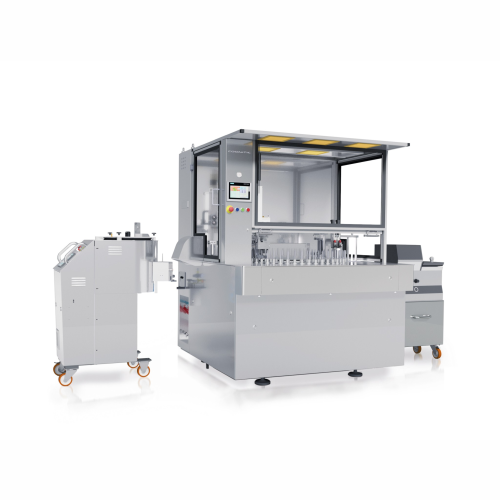
Cosmetic pencil filling system
Streamline your cosmetic production with high-speed filling and precise molding capabilities,...
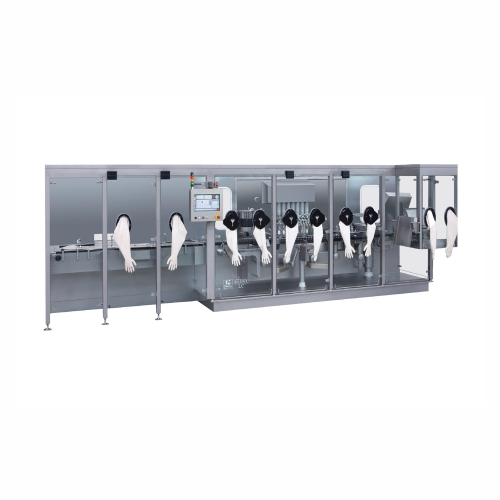
Vial filling and stoppering for aseptic liquid or lyo products
Ensure optimal aseptic conditions in your production line...

Rotary vial filling and stoppering
Ensure precise liquid formulations and lyophilized product consistency with a high-speed...
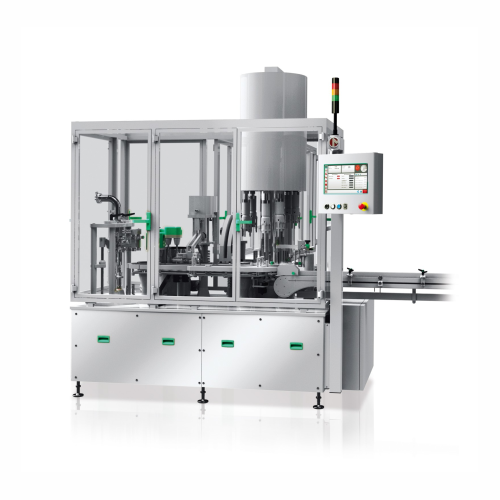
Mascara and lip gloss filling and capping system
Optimize your cosmetic production line with a high-speed system designed ...
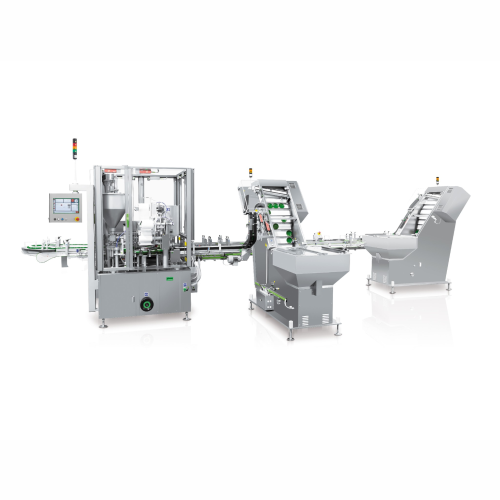
Automatic rotary jar filling and capping system
Optimize your personal care product line by efficiently filling and cappin...
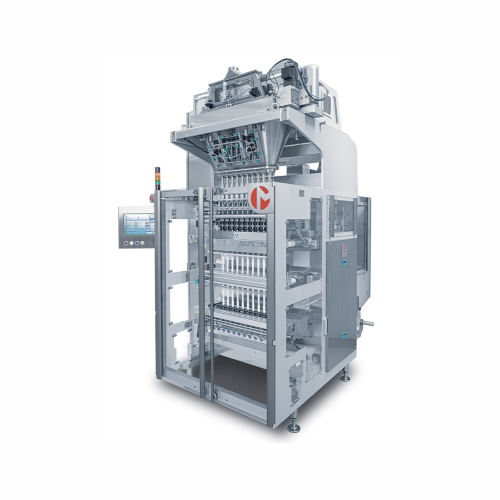
Stickpack filling and closing system for pharmaceutical powders
Achieve precise dosing and secure packaging for pharmace...
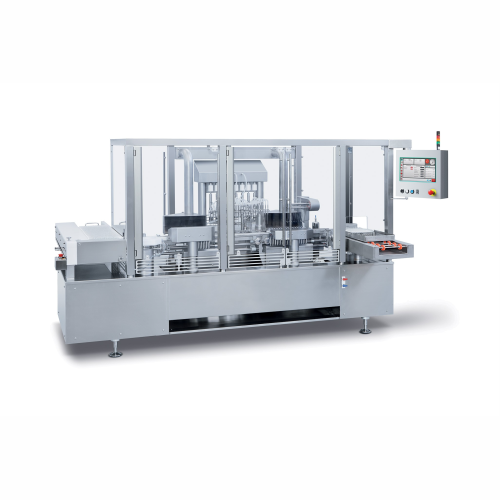
Aseptic ampoule filling and sealing solution
Ensure precise dosing and secure sealing of sterile liquid pharmaceuticals in...
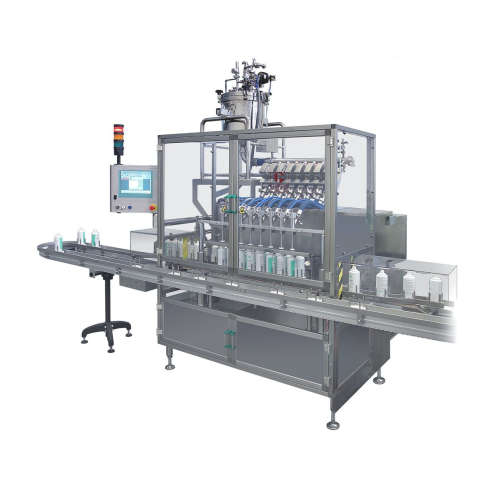
Bottle filler and capper
Achieve precise liquid filling and secure capping with high-speed, intermittent motion, ensuring con...
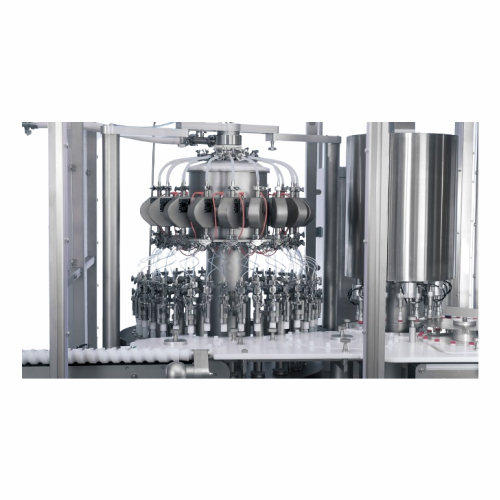
High-speed vial filling and capping system
Ensure precise vial filling and secure capping with this high-speed rotary solu...
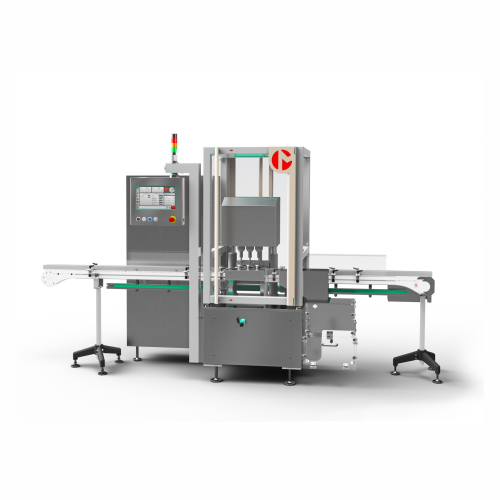
Filling and capping solution for bottles
Optimize your bottling efficiency with a robust solution designed to streamline fi...
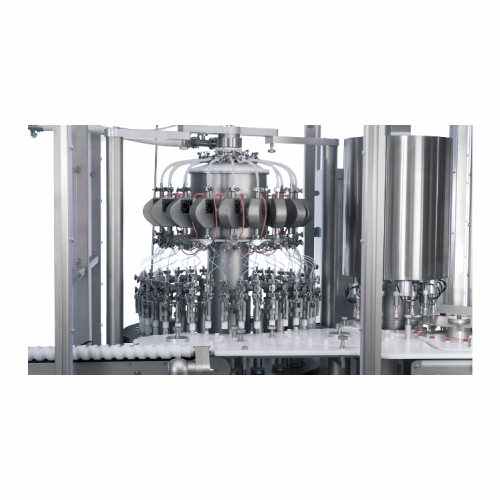
Aseptic vials filling and capping
Ensure precise vial capping and sealing for liquid pharmaceuticals with advanced aseptic ...
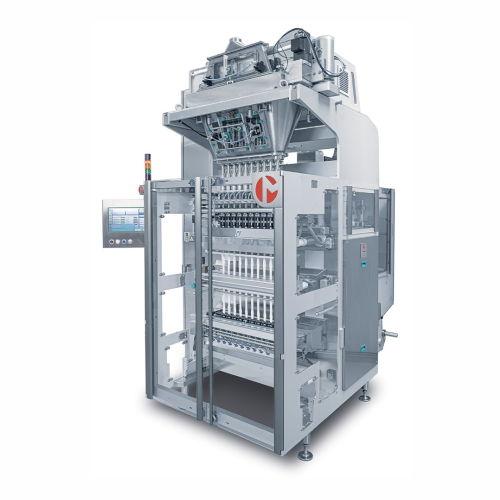
Stickpack filling and closing system
Optimize your stickpack production with precise dosing, uniform sealing, and seamless ...
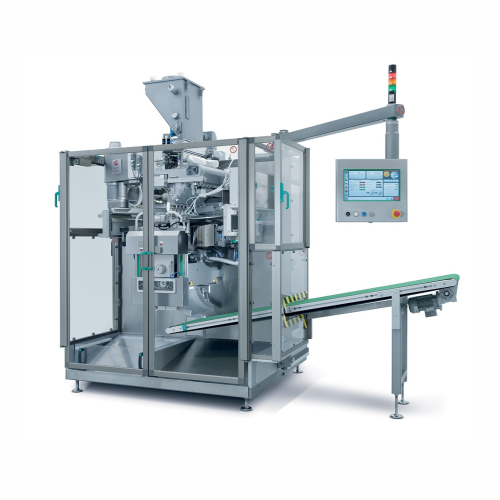
Sachet filling and closing system
Optimize your production line with a versatile solution designed to fill, seal, and count...
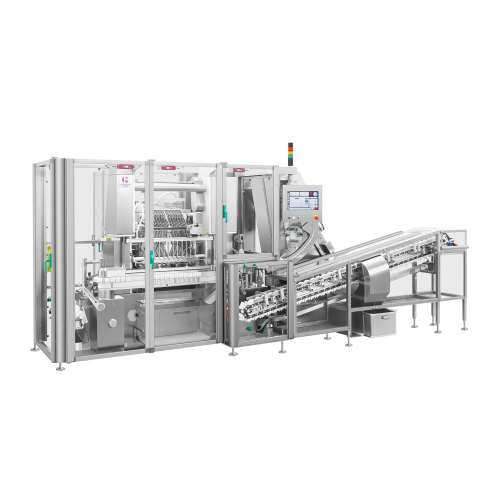
Rigid tube filling and capping system for tablets
Streamline your tablet production with an efficient solution that preci...
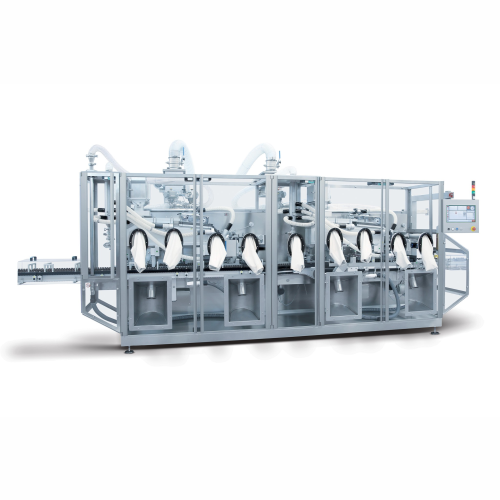
Electronic counting and filling system for vials
Efficiently streamline the packaging of solid dosage forms with a cutting...
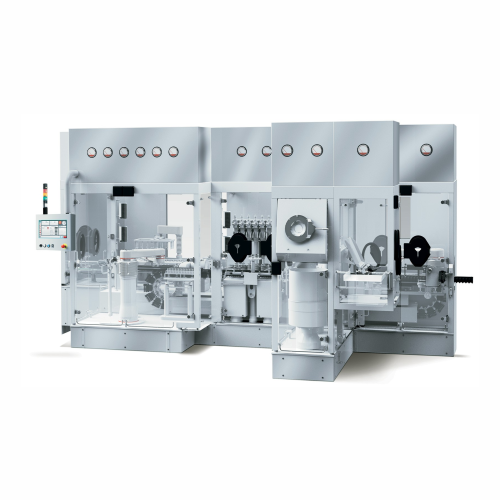
Filling and stoppering system for nested syringes
Ensure aseptic precision in syringe and vial preparation with a high-sp...
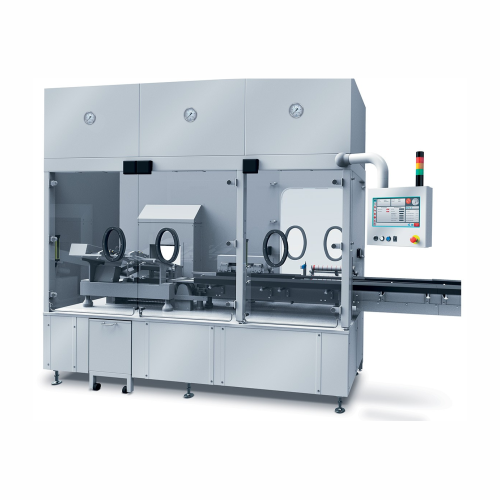
Nested syringe filling and stoppering line
Streamline your aseptic filling process with advanced machinery that handles ne...
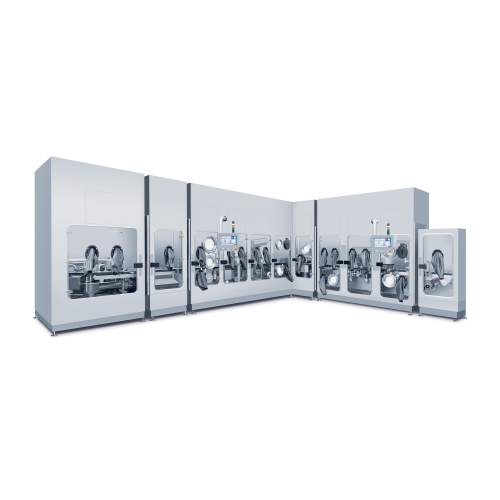
Aseptic filling and capping for vials and syringes
Ensure sterility and precision in vial and syringe filling with advanc...

Automatic tube filling and closing for metal, plastic, and laminate tubes
Enhance your production efficiency with a hi...
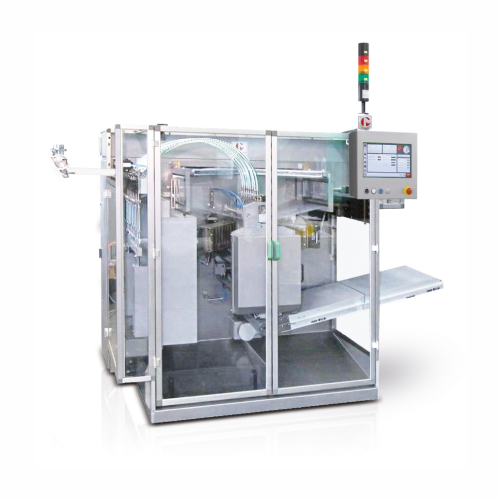
Automatic sachet filling and sealing system for liquids and creams
Optimize your cosmetic and personal care production ...
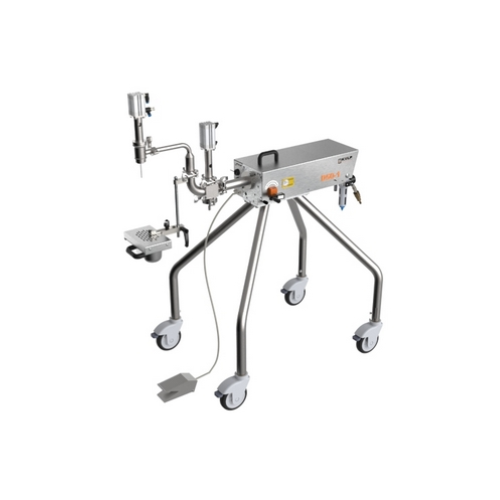
Volumetric filling system for cosmetic products
Streamline your production line with precise volumetric control, ensuring ...
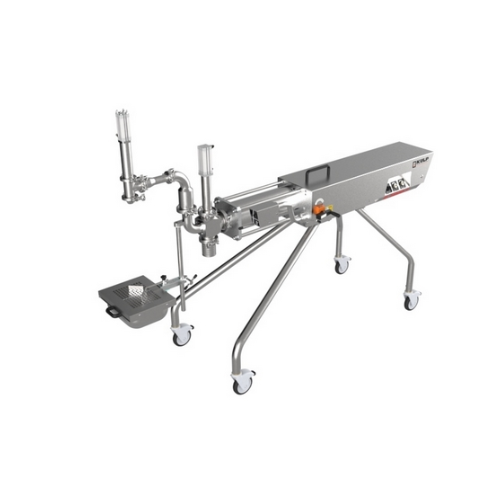
Volumetric filler for liquid and viscous products
Achieve precise and adaptable filling for a wide variety of liquid and ...
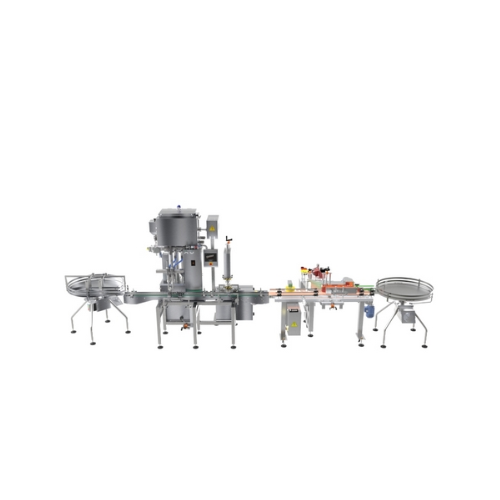
Medium capacity filling line for food and cosmetics
Streamline your production with a versatile filling line that seamles...
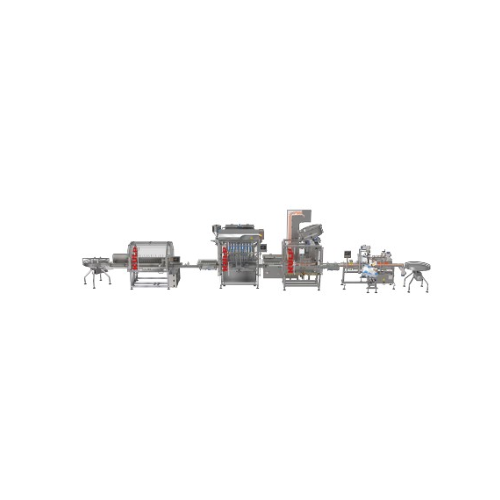
High capacity filling line for jars and bottles
Need to streamline your packaging line? This high-capacity solution proces...
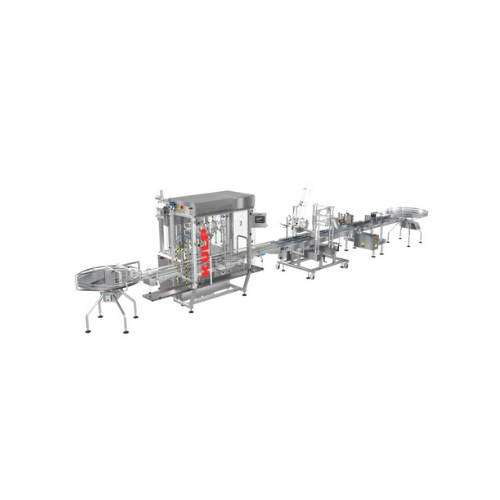
Large container filling line
Optimize your production line with a seamless solution for efficiently filling large containers...
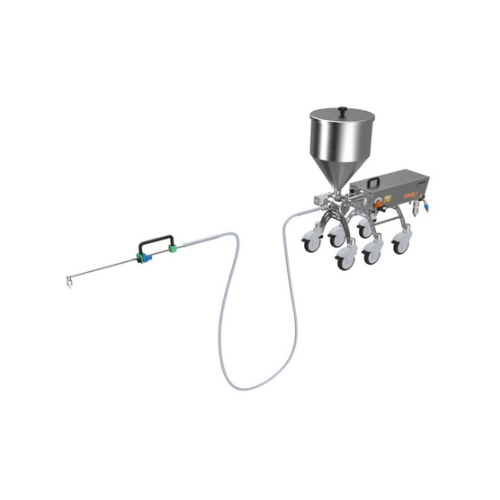
Volumetric filling technology for cosmetic and food products
Achieve precise and contamination-free filling of liquid an...
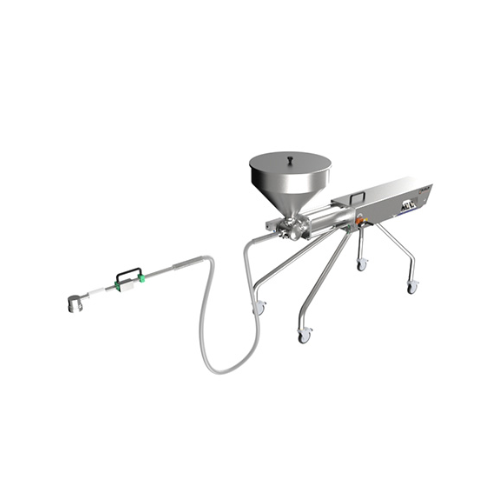
Volumetric filler for packaging liquids and semi-solids
Optimize your filling process with precision control and adaptabl...
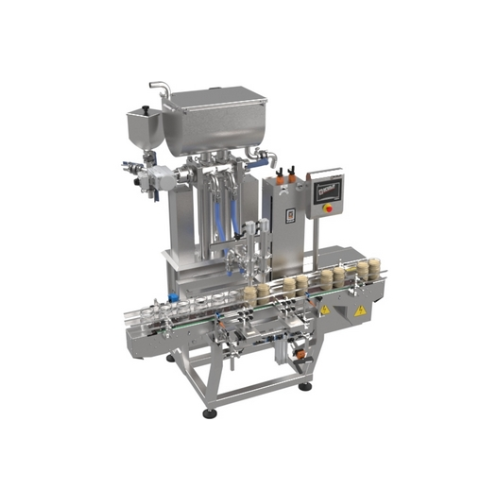
2-head liquid and viscous product filling system
Streamline your filling operations with precision and versatility designe...
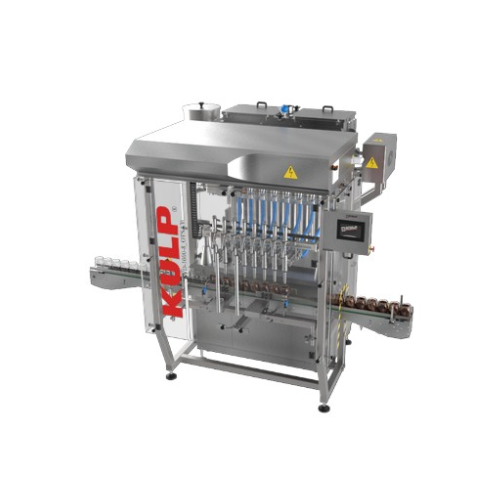
8 head liquid and viscous product filling system
When precision and speed are crucial, this 8 head filling machine ensures...

Paste filling system for high viscosity products
Efficiently fill high viscosity products with precision and speed, reduci...
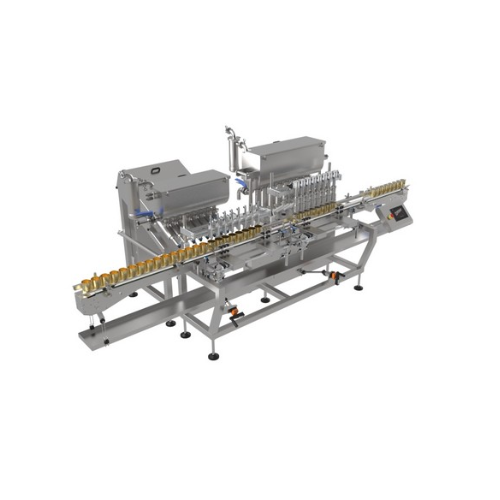
Two-component filling machines for food and beverage packaging
Streamline your filling process with precise two-componen...
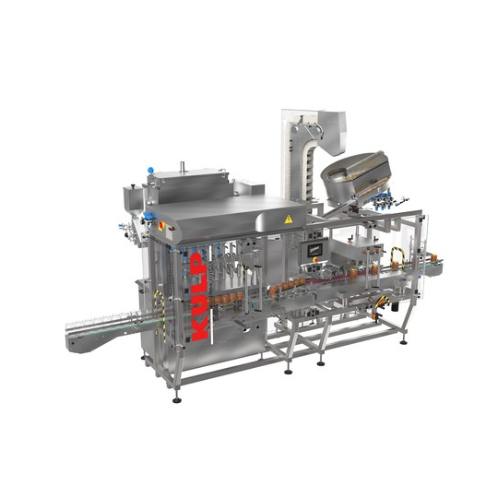
Volumetric filling and capping solution for liquids and viscous products
Effortlessly integrate high-precision filling ...
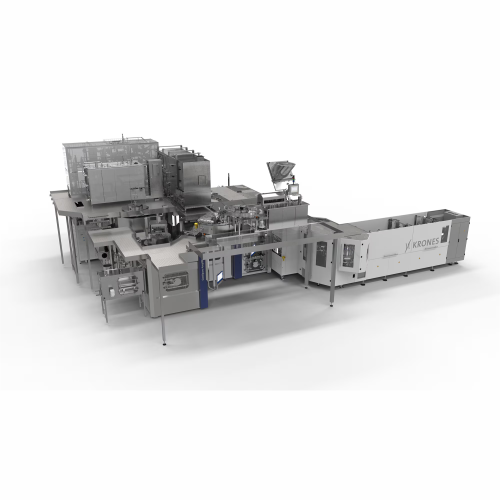
Ultrahygienic block for aseptic filling
When handling sensitive beverages, ensuring microbiological safety and quick produc...
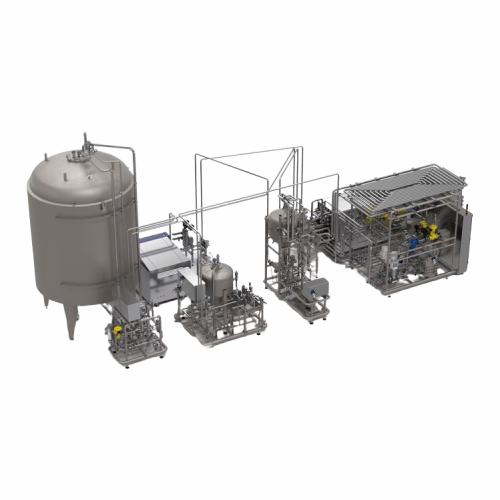
Uht system for aseptic filling of beverages
Ensure microbiological safety and retain natural flavors in your liquid produc...
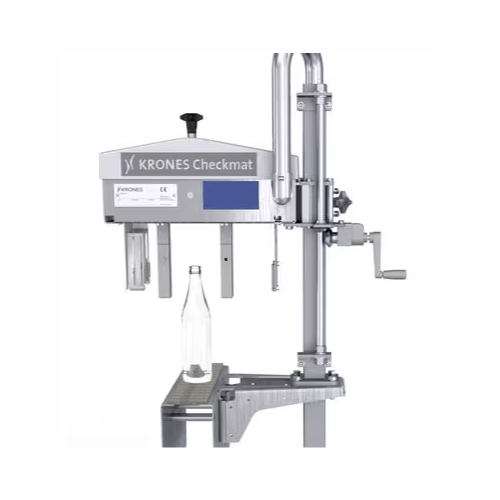
Inspection systems for fillers and cappers
Ensure precise fill levels and secure cap placements with advanced inspection s...
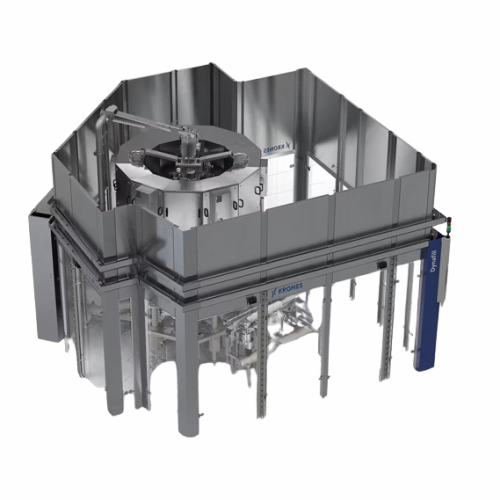
Innovative beer filling and capping technology
Revolutionize your filling process with an integrated system that combines ...
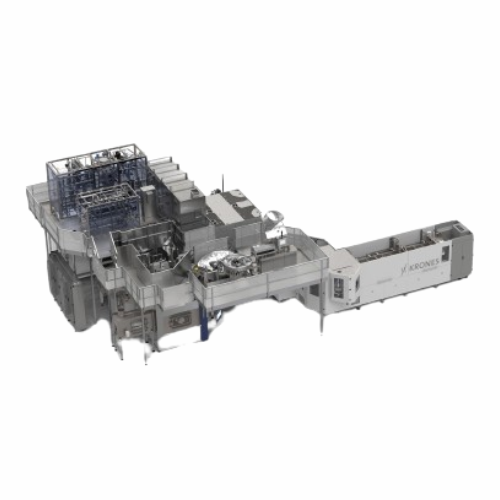
Aseptic filling system for Pet containers
Ensure your beverage products maintain sterility and longevity with a high-speed...
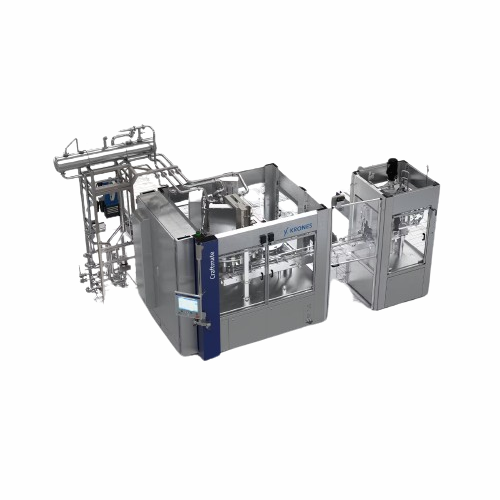
Low output can filler for craft beer
For beverage producers looking to efficiently fill cans with precision, this versatile...
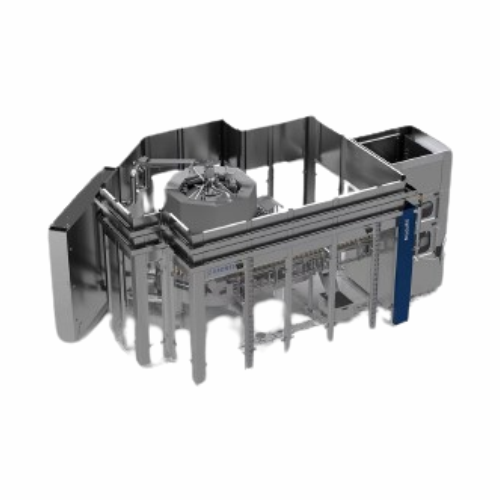
Filler-seamer block for cans
For high-speed beverage production, this solution integrates filling, seaming, and cleaning in ...

Vertical form, fill and seal packaging system for small bags
Maximize efficiency with small bag portioning for food and ...
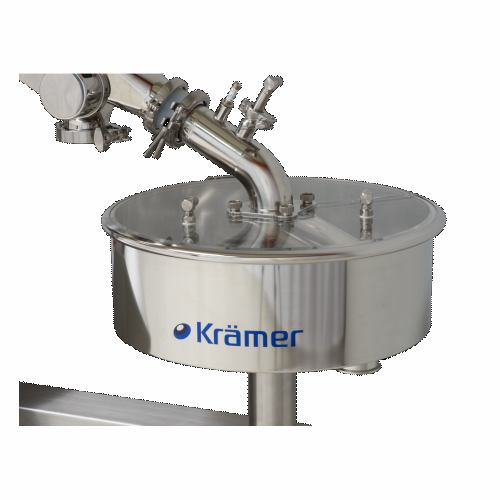
High-containment diverter for continuous tablet and capsule filling
Enhance your production line with a versatile solut...
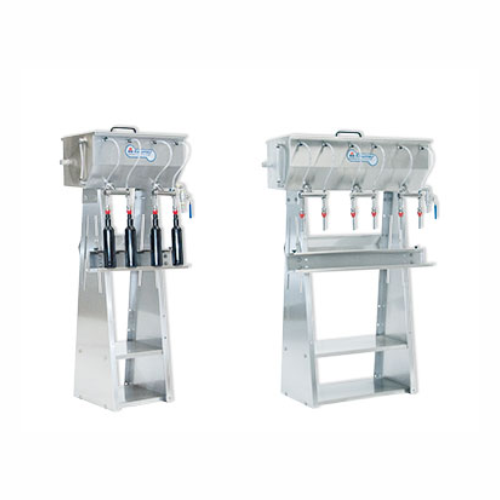
Juice bottle and bag-in-box filling systems
Streamline your juice production with versatile filling solutions that accommo...
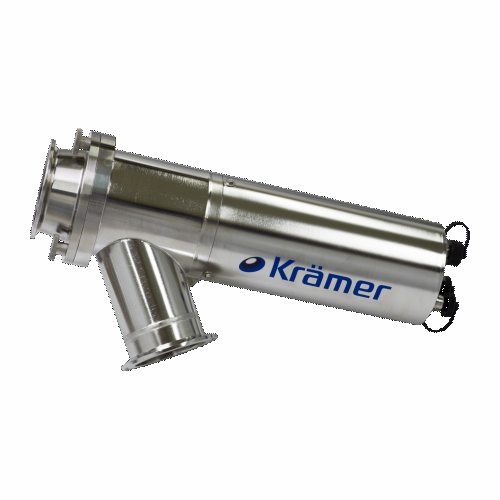
2-way diverter for tablet and capsule filling
Ensure precision in tablet and capsule filling with seamless batch switching...
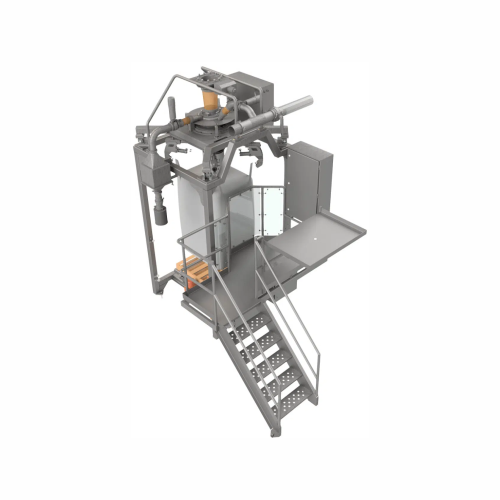
Sanitary bulk bag filling system
Streamline your powder handling process with a system designed to improve stability and acc...
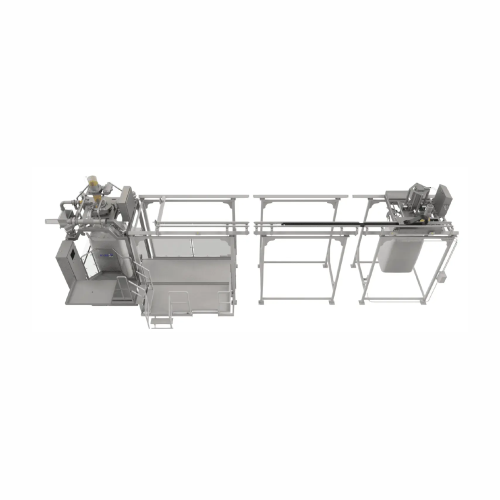
Bulk bag filler with integrated palletizing system
Optimize your powder packaging with a seamless system that fills and a...
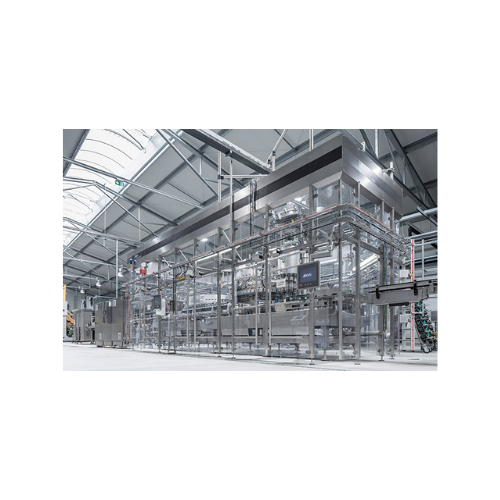
Wine and sparking wine filling system
Achieve precise filling and minimal oxygen pickup for high-value beverages with a rel...
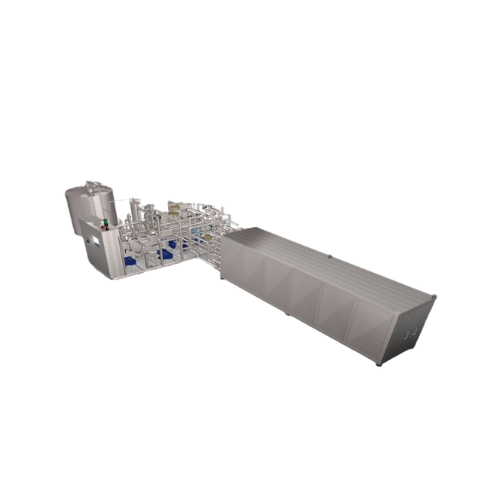
Energy-efficient hot filling system for beverages
Optimize your beverage filling processes with a system that ensures pre...
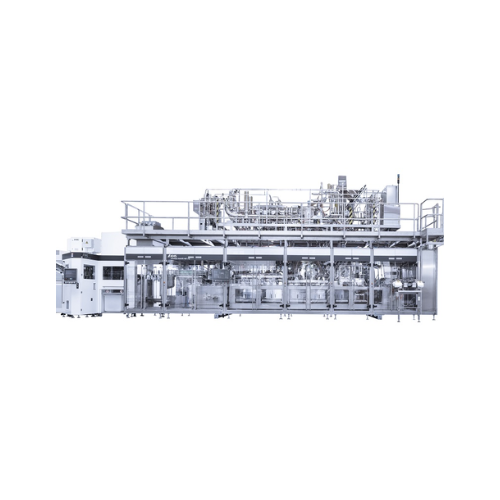
Aseptic linear filler for sensitive beverages
Experience unparalleled versatility and efficient aseptic filling with advan...

Pet bottle stretch blow molding with coating and filling
Extend the shelf life of your beverages and liquid products with...
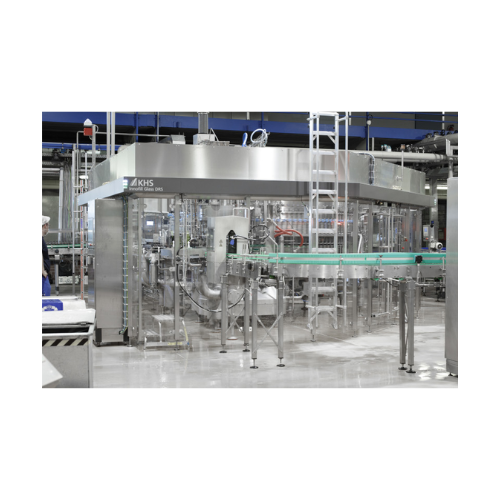
Glass bottle filler for beer and soft drinks
Optimize your beverage production with a high-speed filling solution that red...
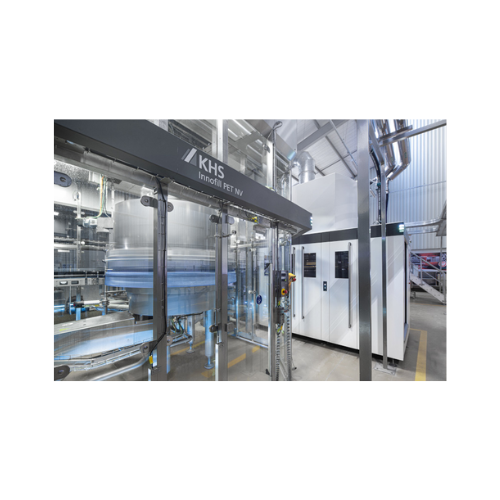
Pet bottle filler for hot and cold still beverages
Achieve high-speed precision in filling and capping for various bevera...
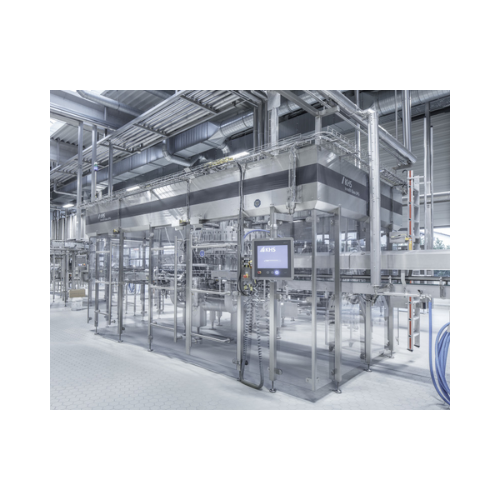
Bottle filler for beer and soft drinks in glass bottles
Achieve precision in bottling with reduced CO2 emissions and low ...

Hot-fill dosing system for soups and sauces
Efficiently dose hot soups, sauces, and porridges while ensuring workplace saf...
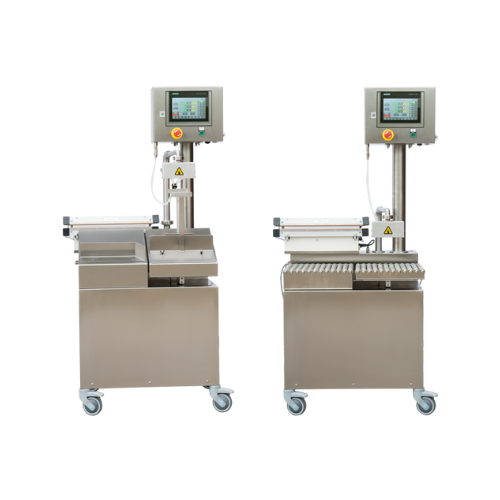
Hot-fill dosing system for soups and sauces
Ensure precise and efficient dosing of hot and cold liquid foods with integrat...
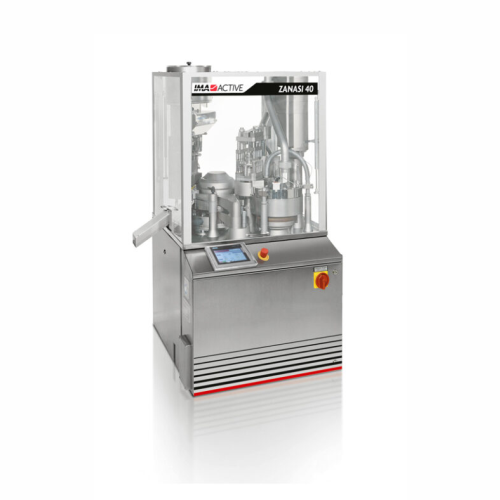
Automatic capsule filling machines
Efficiently fill capsules with precise doses of powders, liquids, and tablets to enhance...
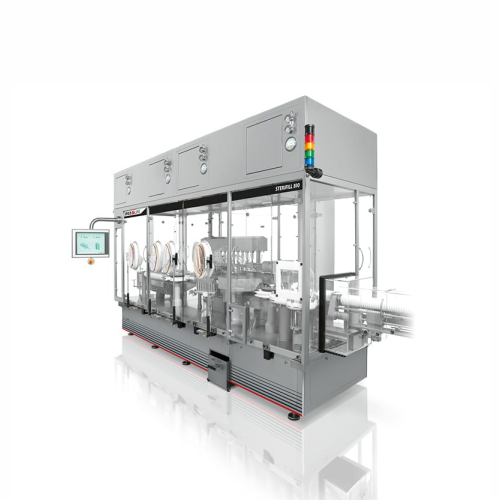
Ampoule filling and sealing system
Designed for high-speed sterile liquid filling and sealing, this system ensures precise ...
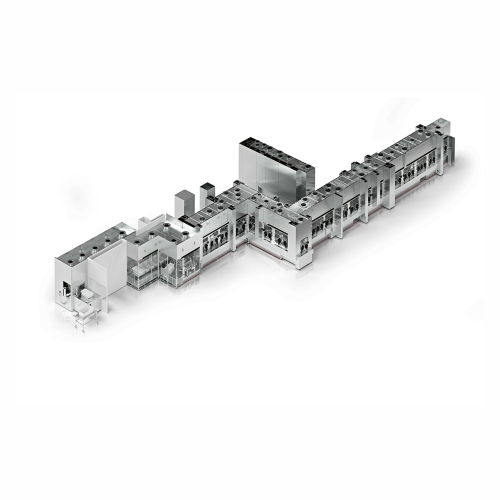
Sterile bag filling and closing system
Ensure precision and sterility in multi-chamber bag filling for liquid and powder ph...
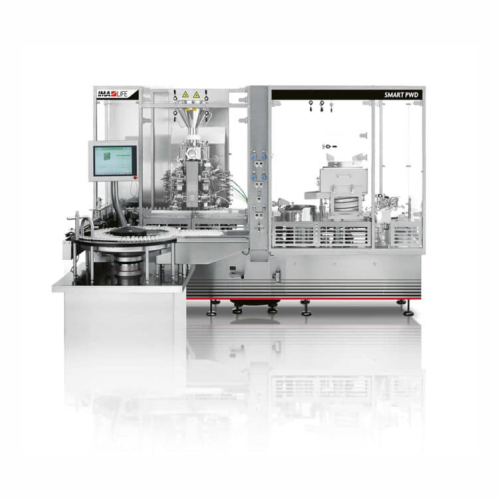
Powder filling and stoppering for antibiotic production
Tackle antibiotic resistance with precision powder filling and st...
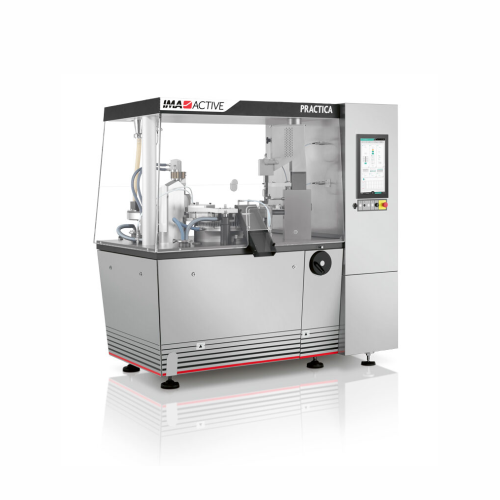
Capsule filler for pharmaceutical applications
Need precise capsule filling for pharmaceuticals and nutraceuticals? This s...
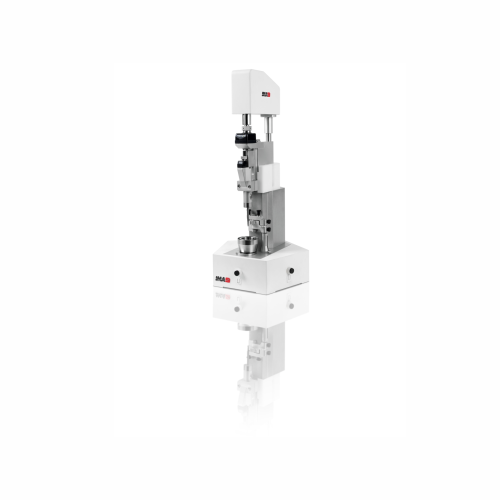
Table-top capsule filler for micro-dosing
Achieve precise micro-dosing for pharmaceutical powders and pellets with a user-...
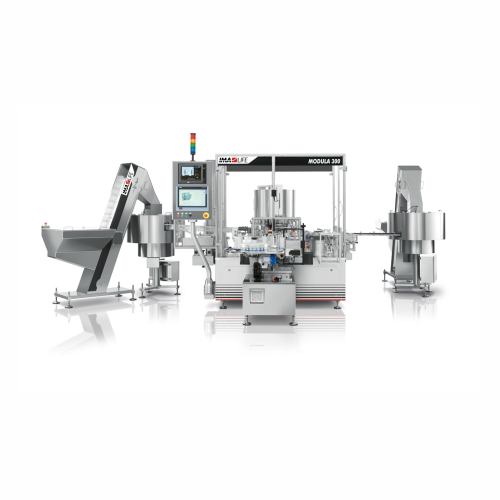
Syringe assembly for pre-filled glass syringes
In the precise world of pre-filled syringe production, ensuring seamless as...
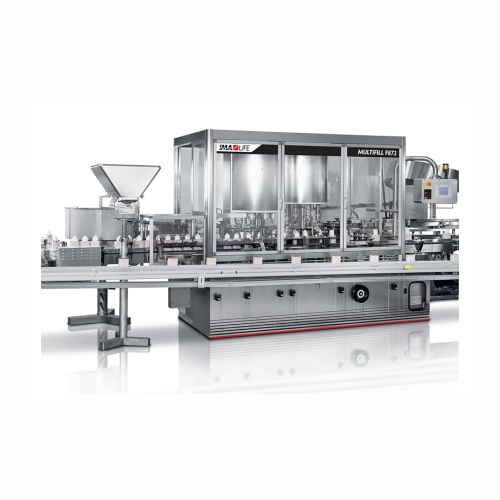
Rotary filling and closing system for pharmaceutical bottles
Optimize your large-batch liquid production with a high-spe...
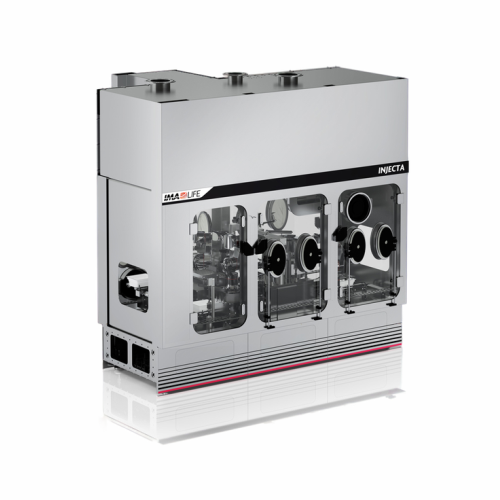
High-speed fill-finish system for ready-to-use components
Enhance aseptic fill-finish operations with a high-speed solut...
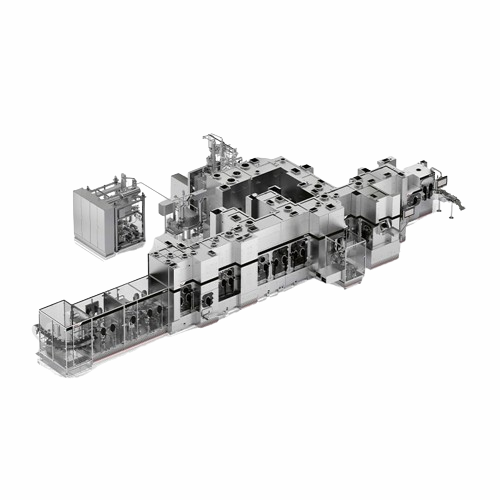
Isolation solutions for aseptic fill-finish lines
Achieve maximum product sterility with advanced isolation solutions, mi...
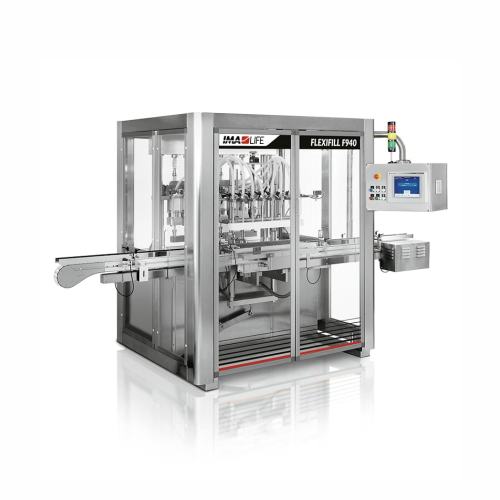
In-line filling system for pharmaceutical products
Ensure precise and flexible filling of liquids, from sterile saline to...
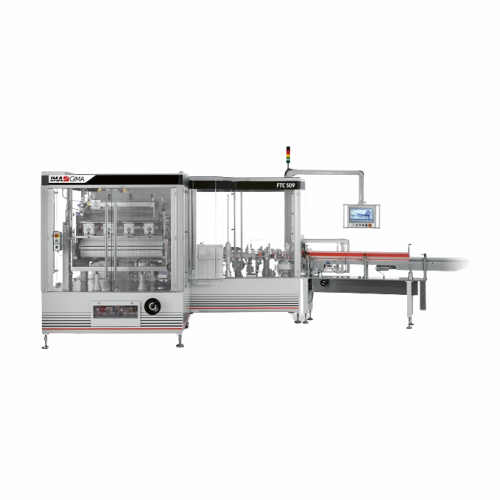
Vertical dosing and filling solution for confectionery packaging
Optimize your confectionery and nutraceutical packaging...
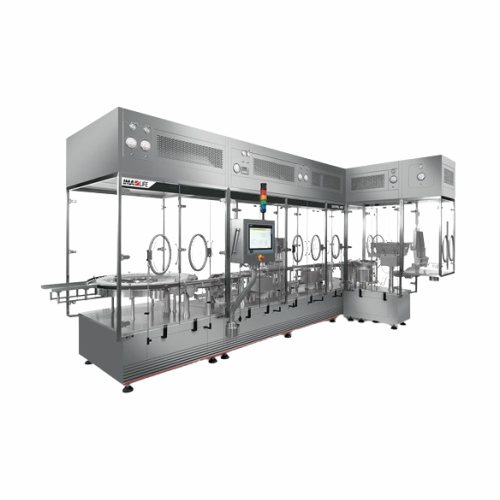
Aseptic filling and stoppering solution for vials
Ensure precise aseptic filling and stoppering of vials with enhanced fl...
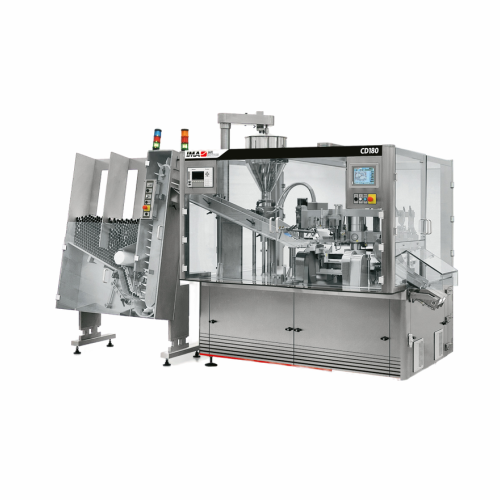
Automatic tubefiller for pharmaceutical tubes
Streamline your tube packaging process with this versatile solution, optimiz...
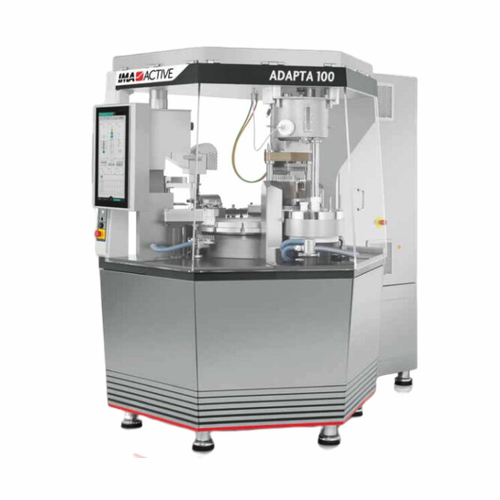
Capsule filler for multi-product dosing
Achieve precision and flexibility in capsule filling with a system designed for hig...
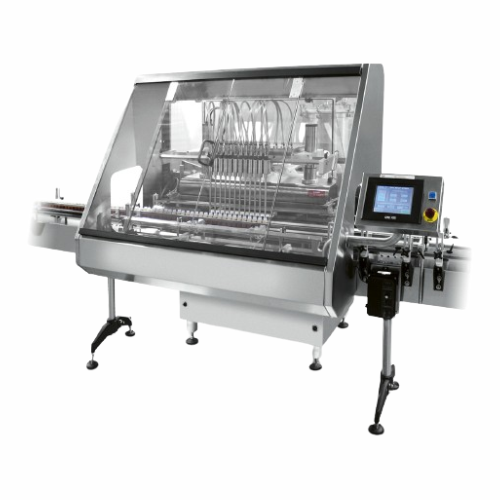
Positive displacement gear pump liquid filler
Optimize your liquid filling operations with precision gear pump technology,...
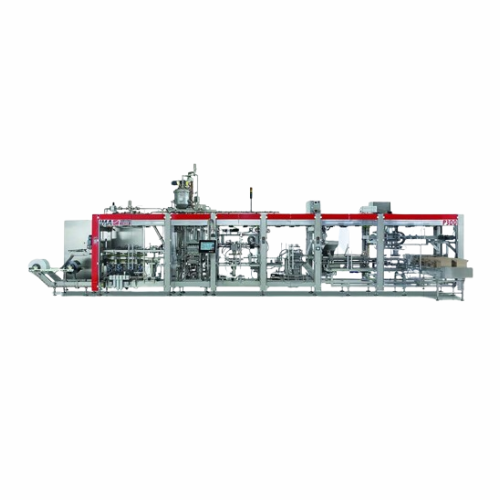
Form fill and seal machine for portion packs
Streamline your portion packaging with a compact system that efficiently form...
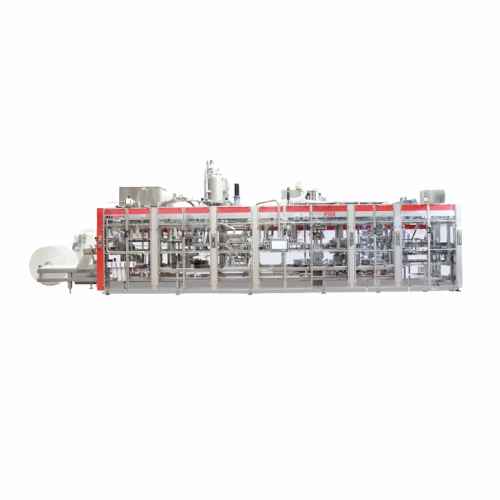
Form fill and seal solution for dairy portion packs
Optimize your production with precision portion packing, reducing mat...
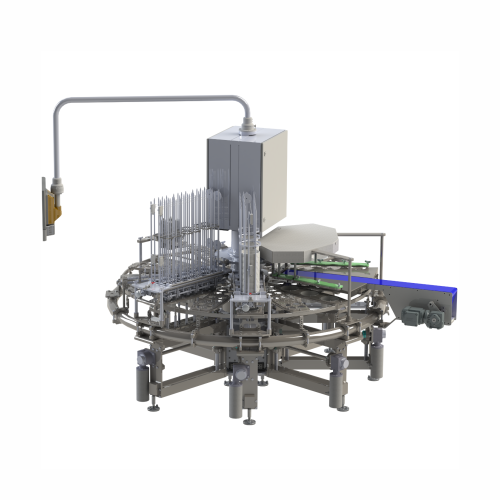
Rotary filling and sealing for liquid to pasty products
Boost production efficiency with a flexible rotary solution that ...
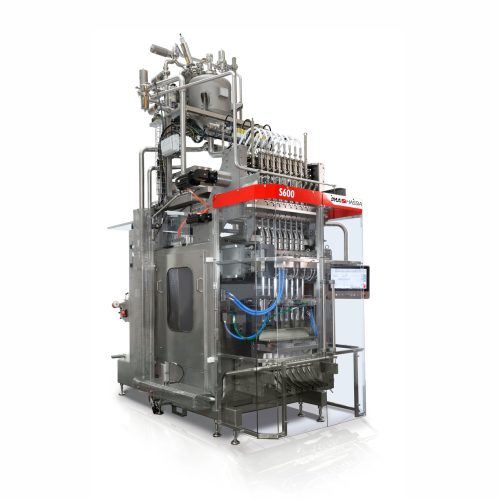
Stick pack forming, filling, and sealing solution
Enhance packaging efficiency with a high-speed solution designed for pr...
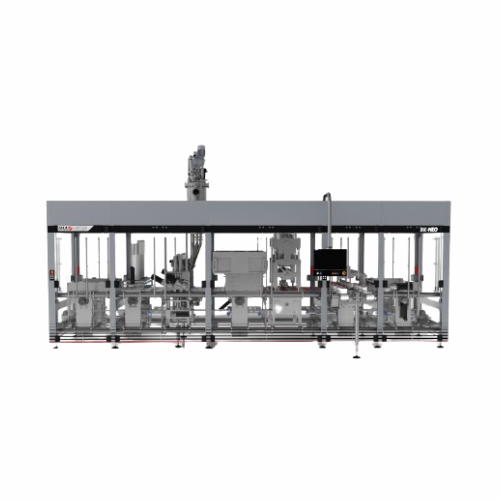
Filling and sealing system for pre-formed cups
Experience seamless integration of hygienic filling and sealing with adapta...
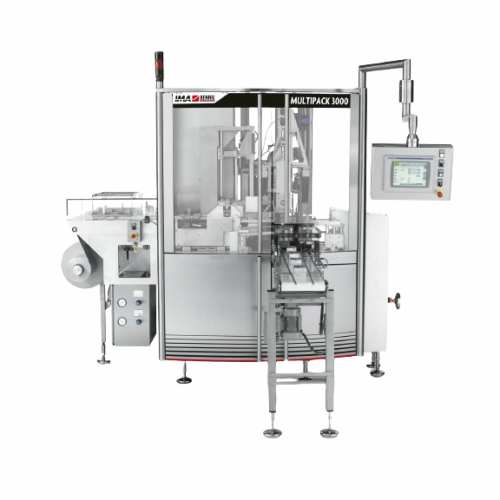
Filling and wrapping system for pasty products
Achieve precise dosing and flexible wrapping of diverse pasty products, ens...
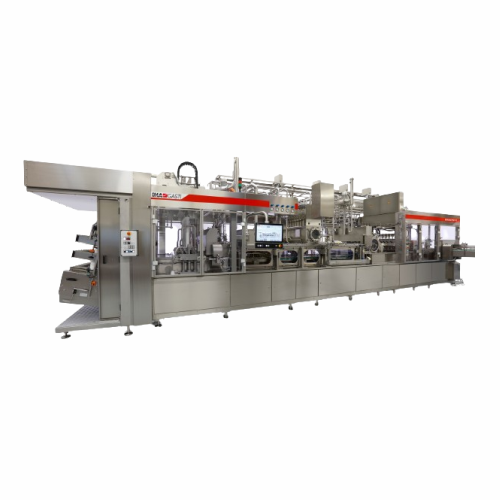
Filling and sealing pre-formed cups solution
Ensure ultra-clean and aseptic processing for pre-formed cups with a fully en...
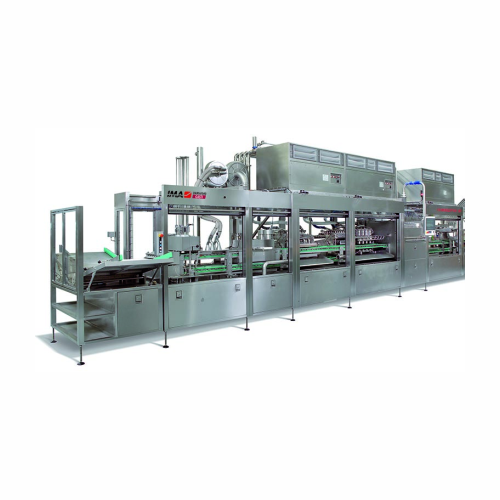
Filling and sealing solution for pre-formed cups
Optimize your liquid and solid product filling with a continuous-motion s...
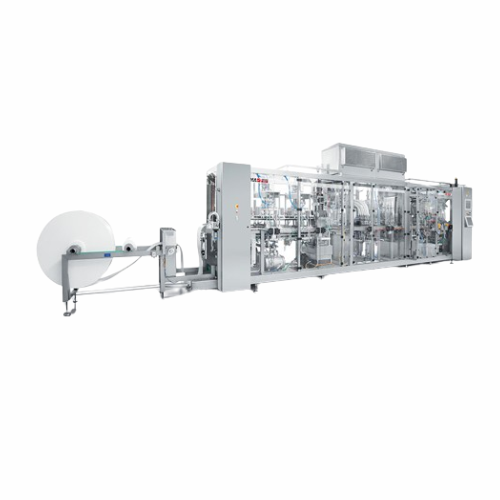
Form fill and seal solution for liquid and pasty products
Enhance your production efficiency with high-speed forming, fi...
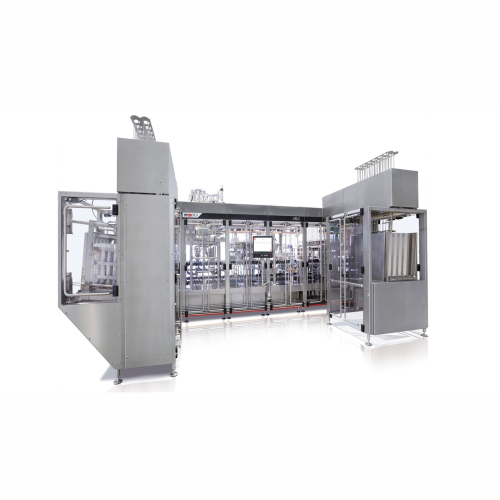
Flexible filling and sealing system for pre-formed cups
Achieve precise portioning and consistent quality in your product...
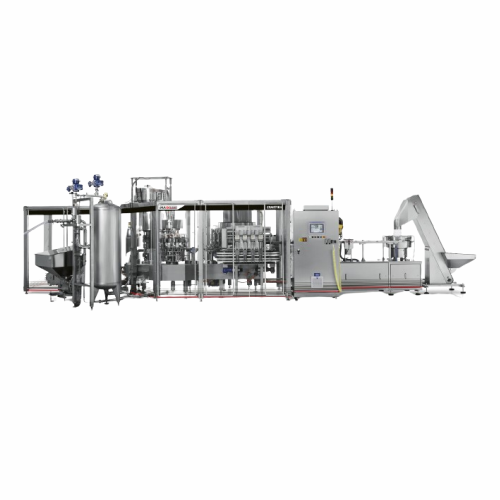
High-speed pouch filling and sealing system for food and dairy
Achieve precise spouted pouch filling with minimal waste ...
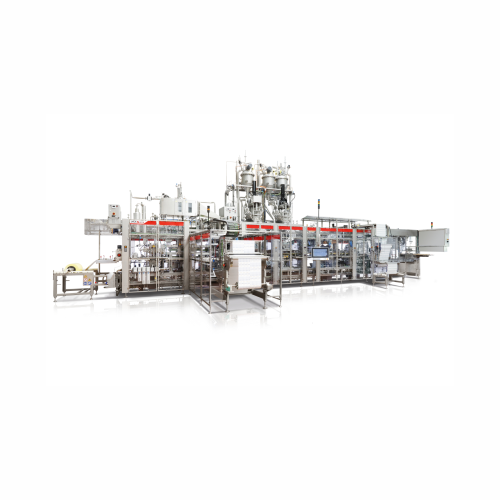
Forming, filling and sealing solution for cups
Maximize production efficiency and flexibility with a high-output machine d...
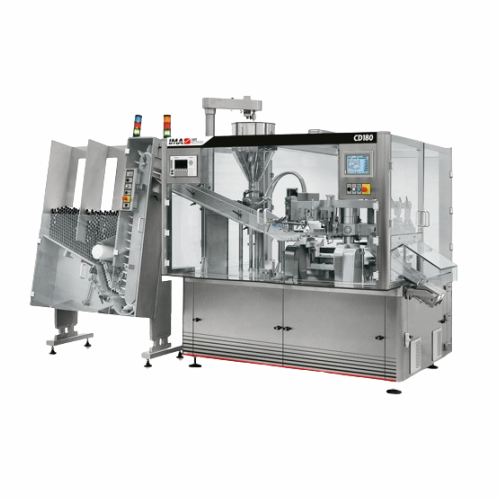
Automatic tubefiller for food and dairy products
Achieve precise dosing and seamless tube filling with high-speed efficien...
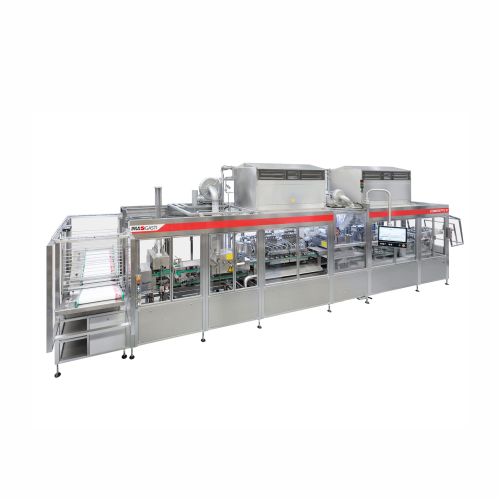
Filling and sealing system for yoghurts and desserts
Efficiently fill and seal a variety of dairy and dessert products wh...
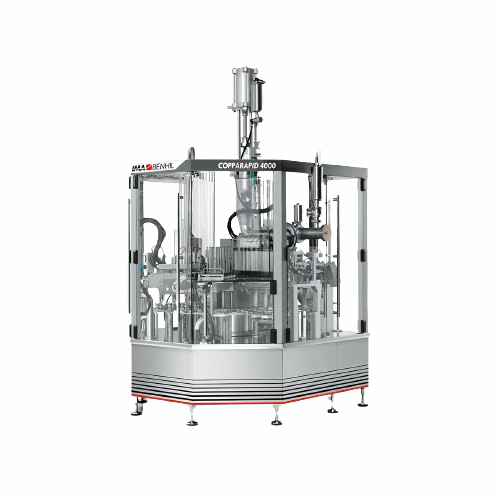
Rotary filling and sealing system for pasty products
Efficiently streamline your cup and tub packaging process with a ver...
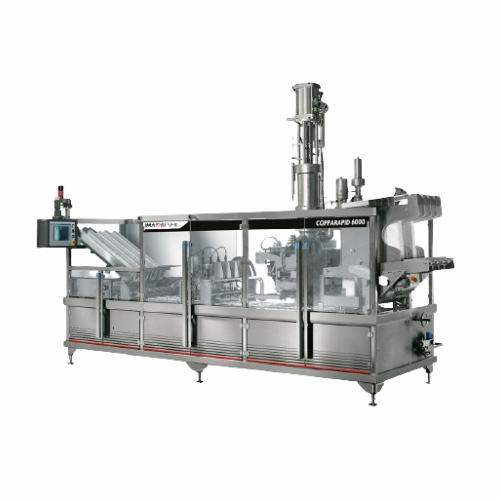
Tub filling and sealing for pasty products
Experience high-speed, precision tub filling and sealing designed for pasty pro...
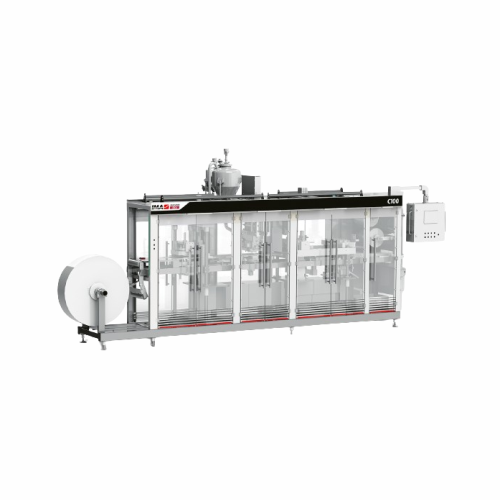
Cup forming, filling, and sealing solution
Optimize your cup production with a compact solution designed for precise formi...
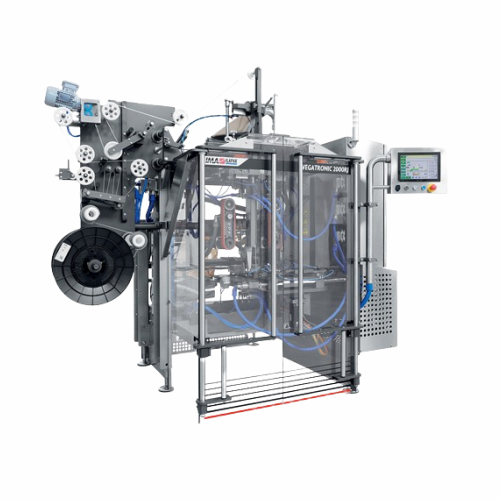
Intermittent vertical form fill seal for confectionery packaging
Optimize your packaging operations with this versatile ...
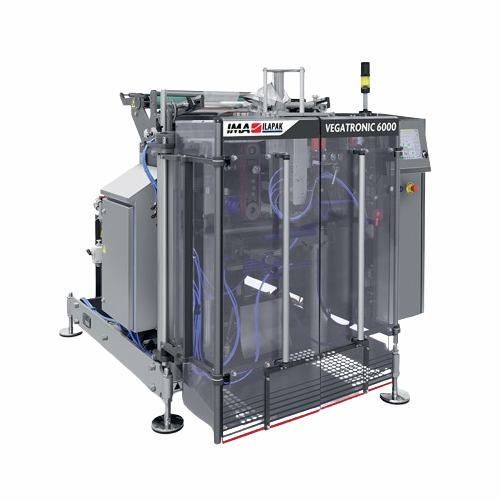
Continuous vertical form fill seal packaging solution
Experience unrivaled accessibility and efficiency in packaging fres...
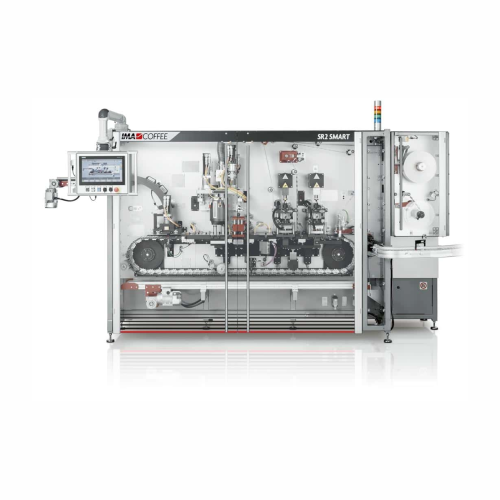
Capsule filling and sealing system for coffee production
Achieve precise coffee capsule production with a machine that se...
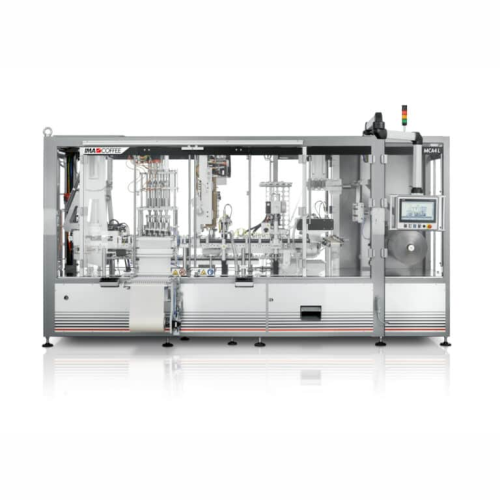
Capsule filling and sealing system for coffee
Optimize your capsule production with a system designed to enhance precision...
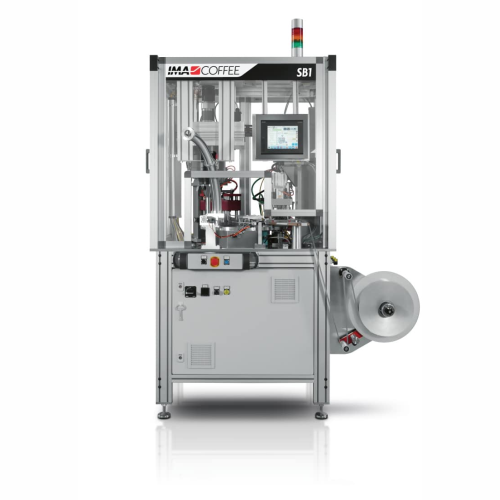
Capsule filling and sealing for lab purposes
Streamline your lab-scale coffee capsule production with a compact solution d...
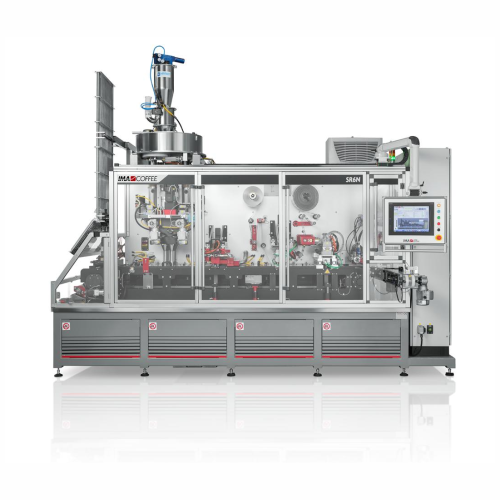
Capsule filling and sealing system for coffee products
Optimizing the precision of coffee and tea capsule production, thi...
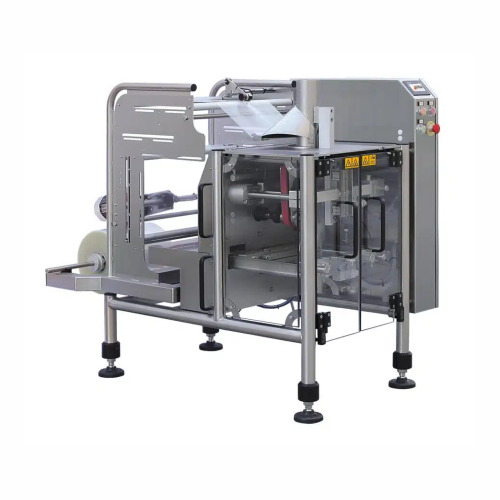
Vertical form fill seal for small to medium production runs
Ideal for scaling production, this compact packaging solutio...
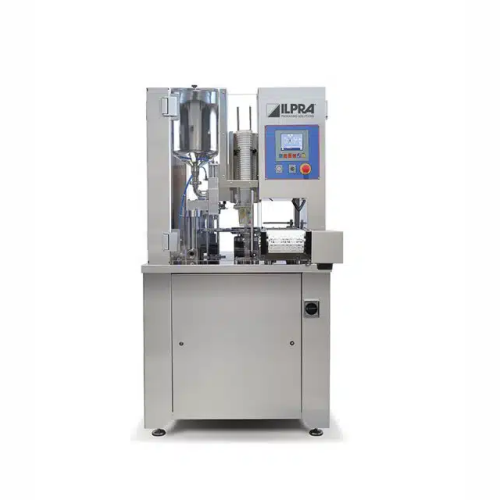
Rotary filler and sealer for dairy products
Optimize your filling and sealing needs with a compact solution designed for c...
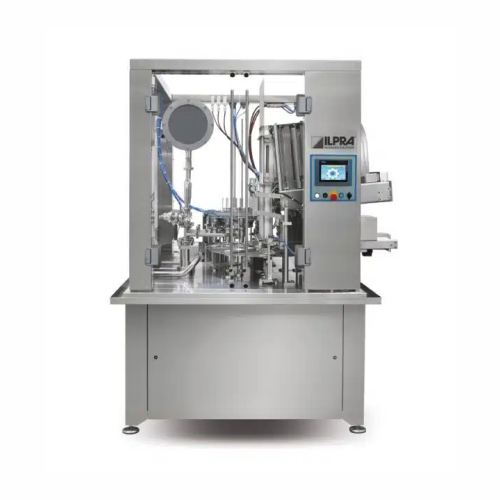
Automatic filling and sealing solution for medium to large production
Streamline your high-capacity filling and sealing...
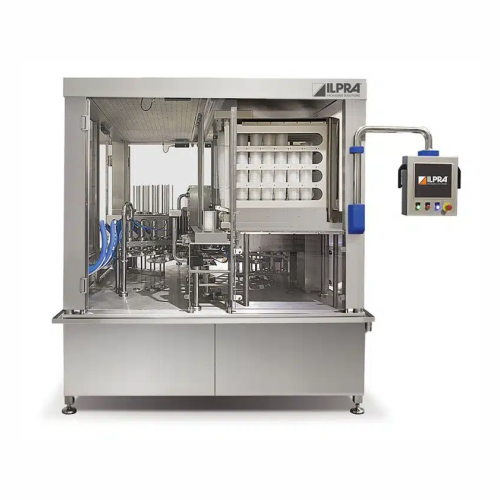
Rotary filler for optimized production processes
Streamline your fill and seal process with precise timing control and enh...
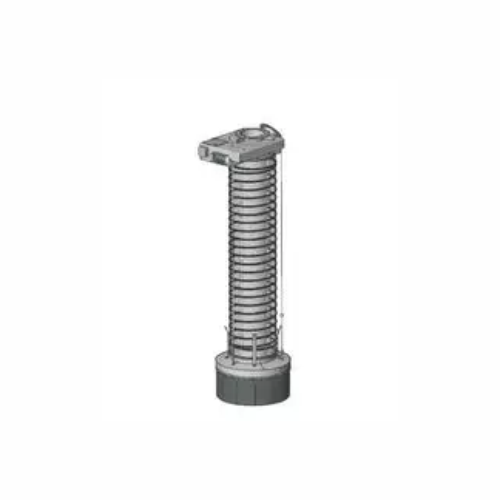
Automatic bulk material filling system
Ensure precise, contamination-free filling of various bulk materials with an advance...
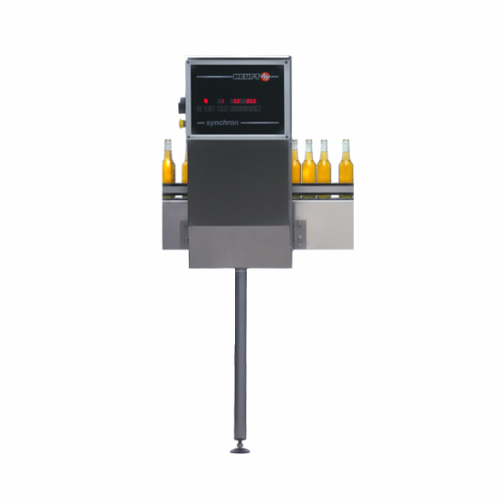
Conveyor control system for beverage filling lines
Optimize your production line’s efficiency by seamlessly managin...
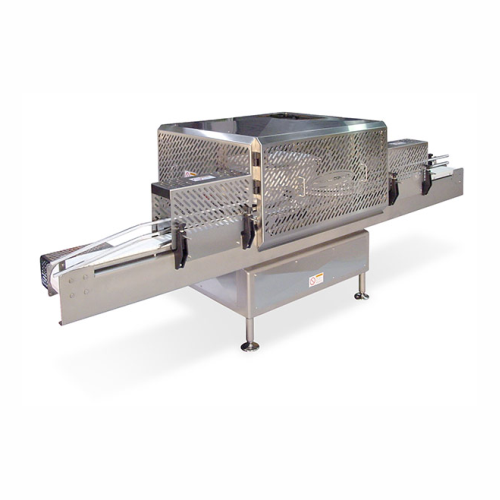
Rotary can filler for dry free-flowing products
Achieve precise, high-speed filling of dry free-flowing products like nuts...
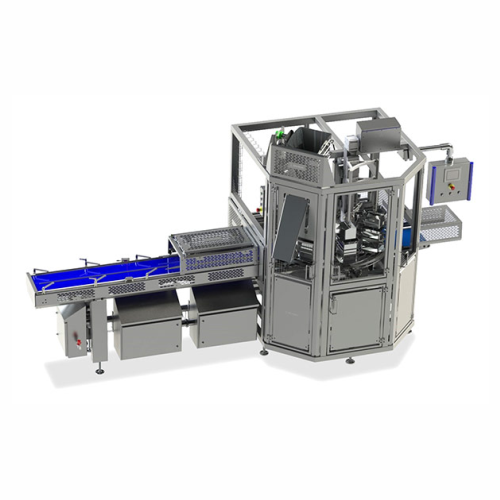
Automatic salad filler for preformed trays
Streamline your salad packaging process with this high-speed solution, ensuring...
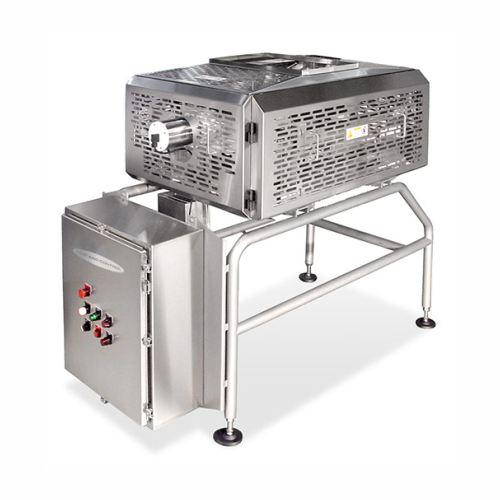
Product transfer shuttle for filling applications
Efficiently manage product flow with precise, customizable filling solu...
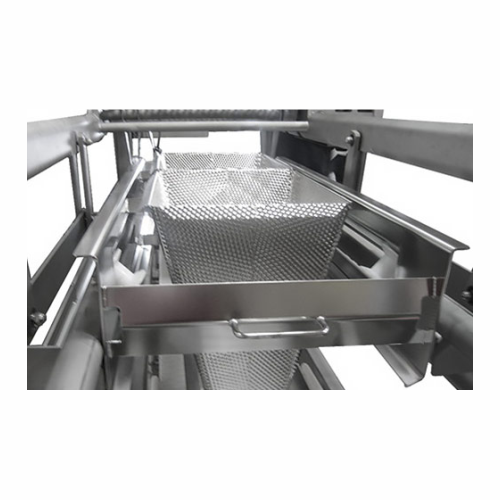
Versatile dual axis funnel filling system
Eliminate messy spills and maximize efficiency by synchronizing conveyor and tra...
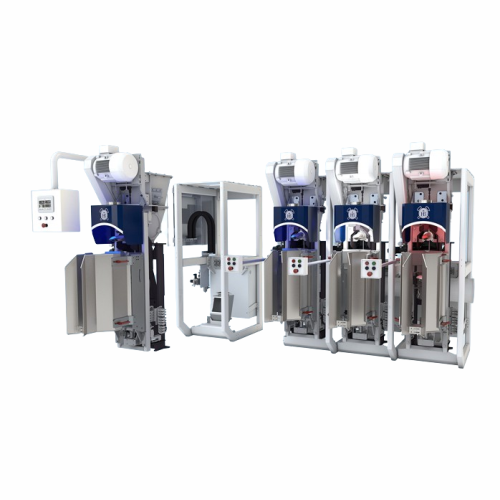
Valve bag filling system for cement and chemicals
Optimize your material handling with precision filling and sealing, ens...
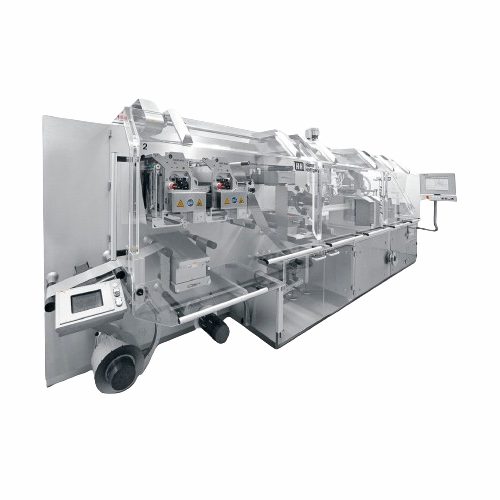
Pharmaceutical powder bag filling system
Ensure precision in pharmaceutical formulations with a system that fills high-spee...
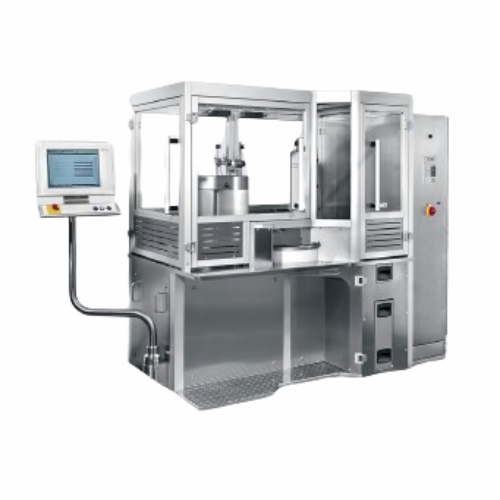
Liquid filling system for medical and pharmaceutical products
Enhance your production capabilities with high-speed liqui...
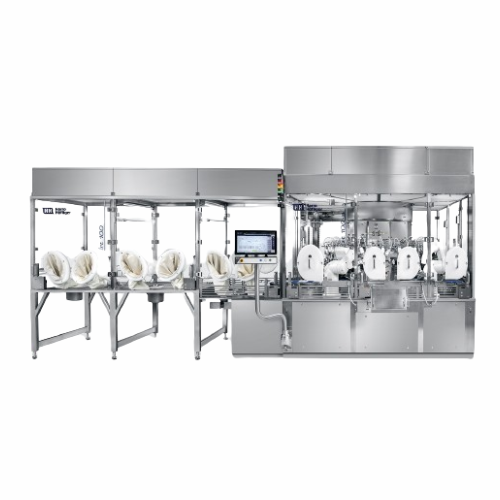
Sterile filling and sealing platform for infusion bags
Achieve reliable aseptic filling and sealing with a versatile plat...
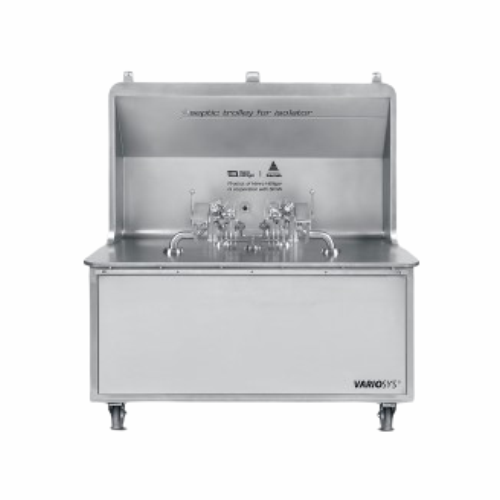
Sterile filling system for Iv bags
Ensure precise and sterile filling of IV and infusion bags with flexible, semiautomatic ...
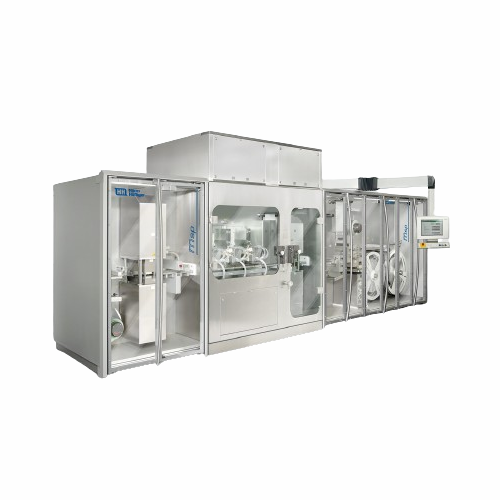
Commercial blister filling solution for dry powder
Efficiently fill and seal blister packs with precision, ensuring consi...
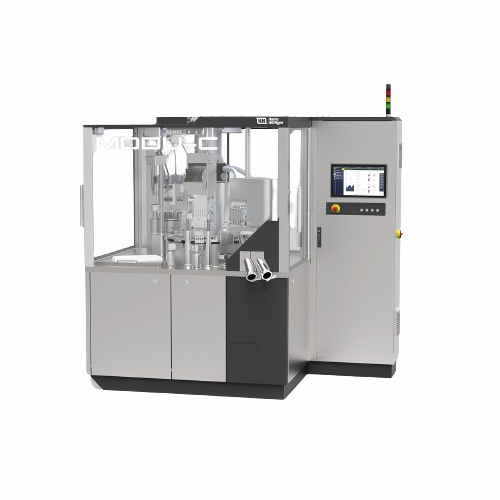
Commercial capsule filling for small scale production
Efficiently fill and dose capsules with precision, ensuring flawles...
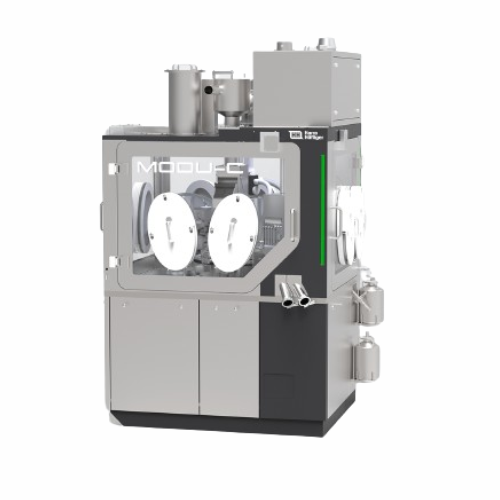
High-containment capsule dosing and filling system
Achieve precise dosing and optimal containment for pharmaceutical prod...

Capsule filling system for powder, pellets, and tablets
Optimize capsule production with rapid dosing changes, minimizing...
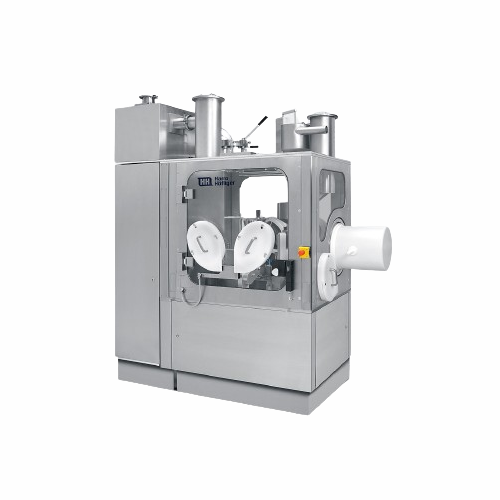
Containment capsule filling system for lab and small batch production
Designed to ensure maximum safety in pharmaceutic...
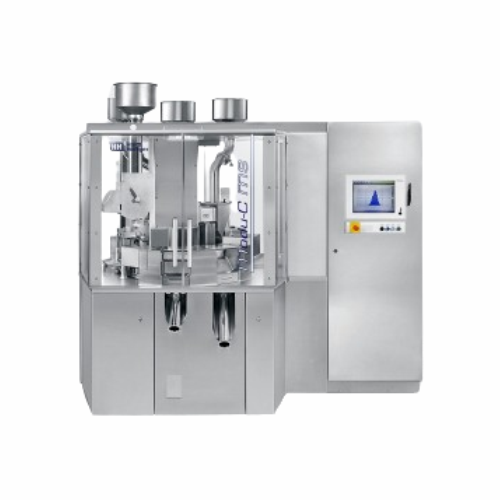
Versatile capsule filler for pharmaceuticals
Effortlessly switch between powder, pellet, and liquid dosing with this adapt...
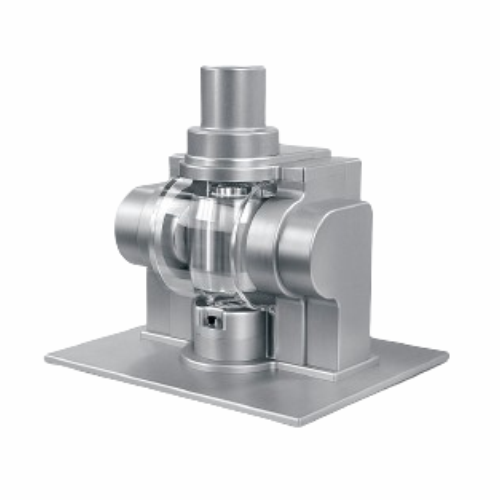
Disc filler for dry powder inhalers
Optimize your dry powder inhaler production with precision micro-dosing for diverse pow...
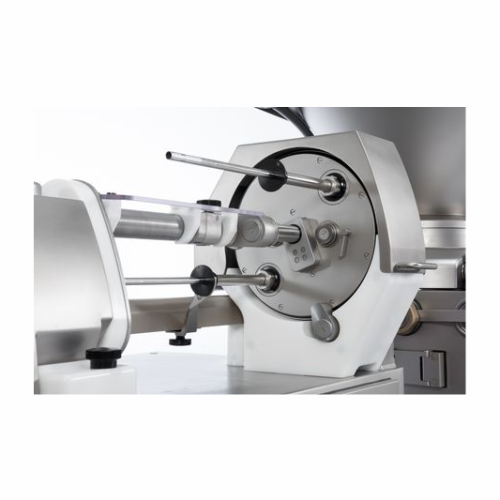
Sausage filling line for natural, collagen, and peel-off casings
Streamline your sausage production with rapid casing ch...
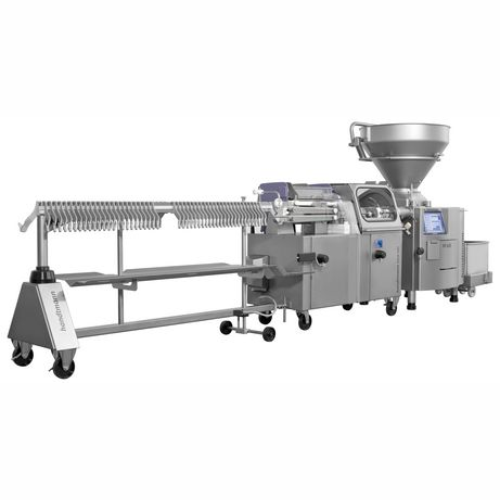
Automatic sausage filling and hanging system
Streamline sausage production with precise portioning and seamless integratio...
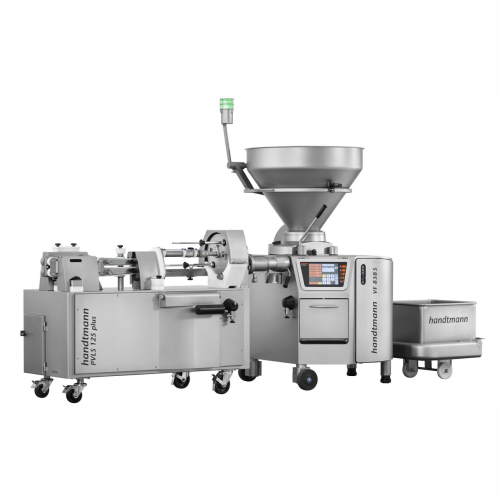
Sausage filling line for adjustable portions
Achieve precision in high-speed sausage production with rapid casing changes ...
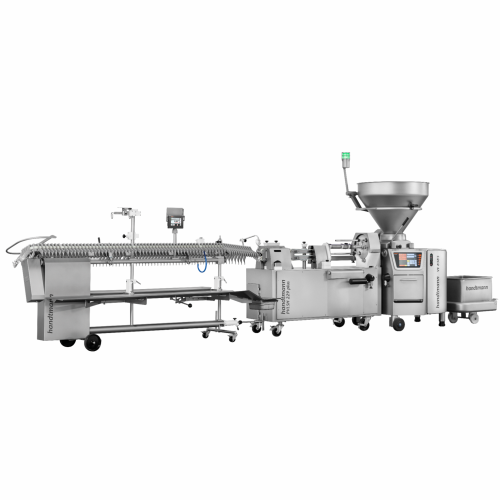
Automated sausage filling and portioning line
Boost your production efficiency with a versatile solution that seamlessly h...
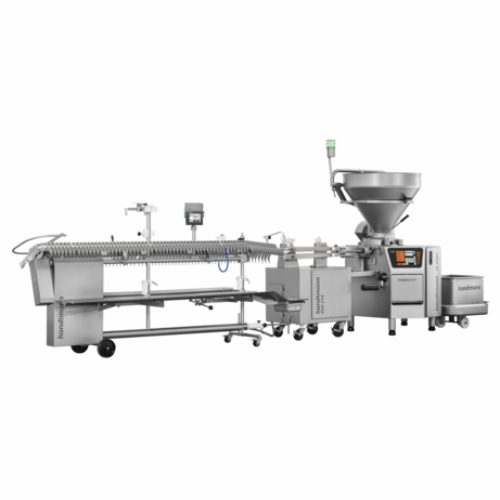
Automated sausage filling and portioning system
Streamline your sausage production with precision filling and versatile po...
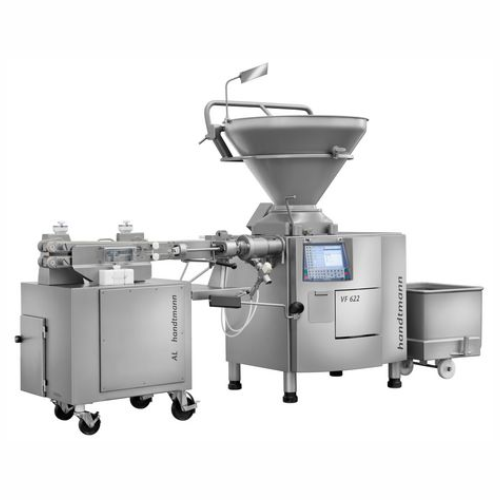
Automatic sausage filling and separating system
Achieve precise portioning with exact weights and lengths for sausages, st...
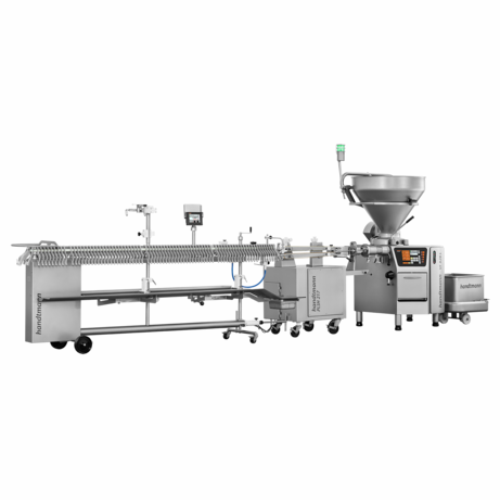
Sausage filling and portioning line
Streamline your sausage production with versatile equipment designed to seamlessly inte...
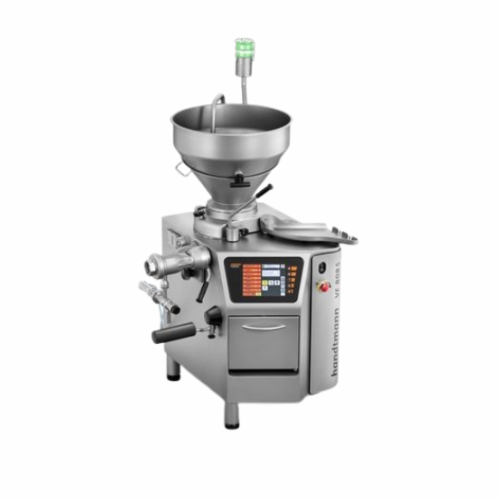
Compact vacuum filler for small to industrial scale food processors
Achieve precise portioning and high-speed productio...
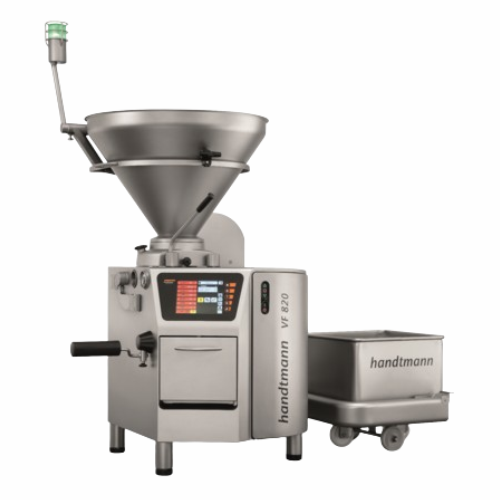
Vacuum filler for medium-scale sausage production
Achieve precise portion control and optimal hygiene with a versatile fi...
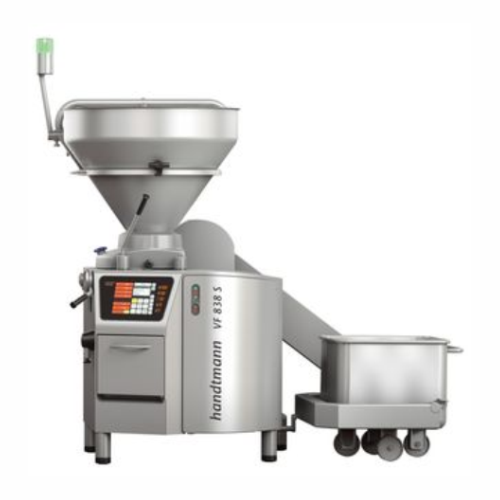
High-pressure vacuum filler for industrial sausage production
Effortlessly tackle high-pressure demands in sausage produ...

Vacuum filler for sausage and ham production
Achieve precision in filling and portioning pasty and fluid products with a s...
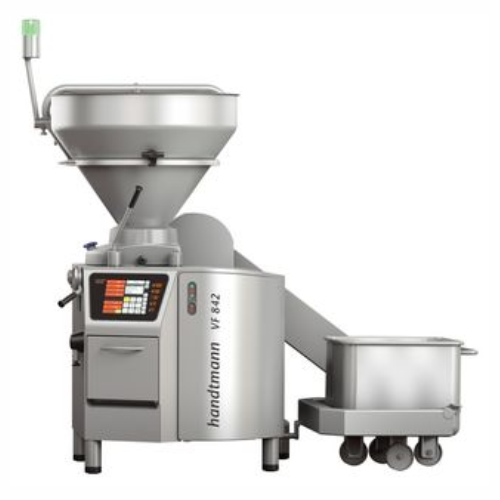
Industrial sausage and ham vacuum filler
Achieve unmatched precision in filling and portioning with high-capacity vacuum te...
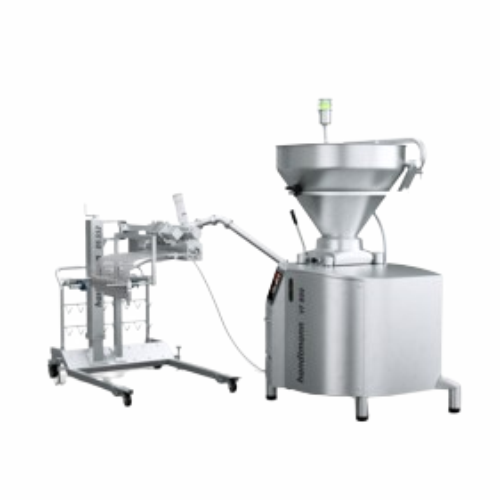
High-precision depositing system for fluid and viscous fillings
Achieve precise and efficient dosing for diverse food pr...
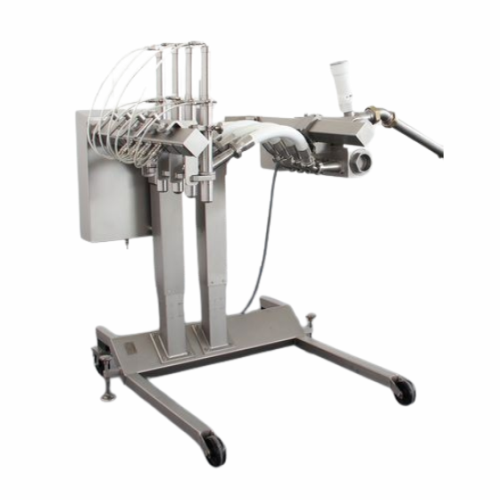
Filling flow divider for food and pet food applications
Optimize your production line with precision filling flow divider...
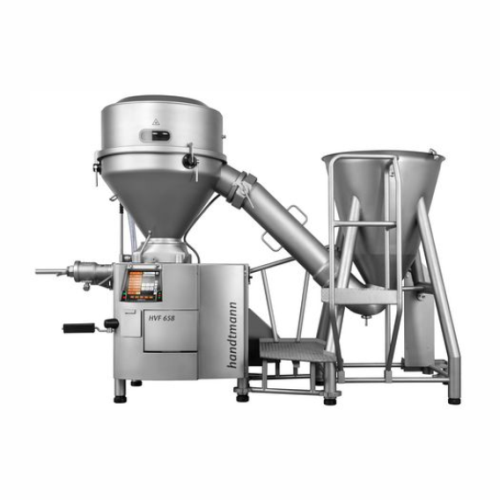
High vacuum filler for dry sausage products
Achieve pore-free, compact dry sausage products with superior evacuation perfo...
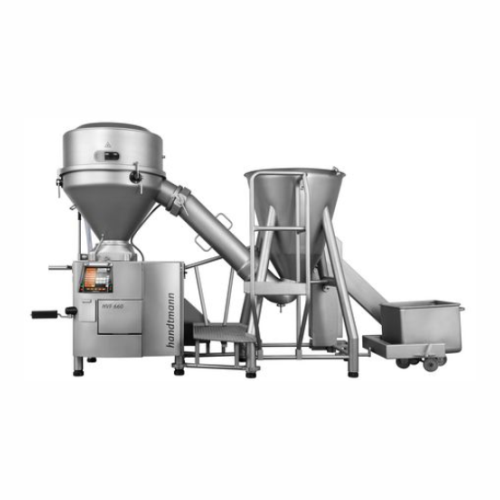
High vacuum filler for large-calibre sausages
Achieve pore-free, high-quality products with optimal portioning accuracy an...
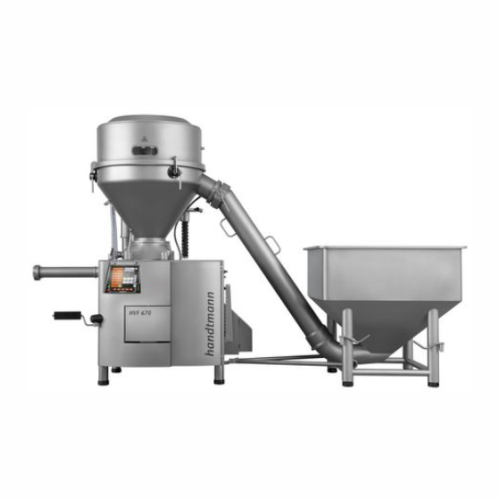
High vacuum filler for ham and ground material
Achieve unrivaled product quality and precision with high vacuum technology...
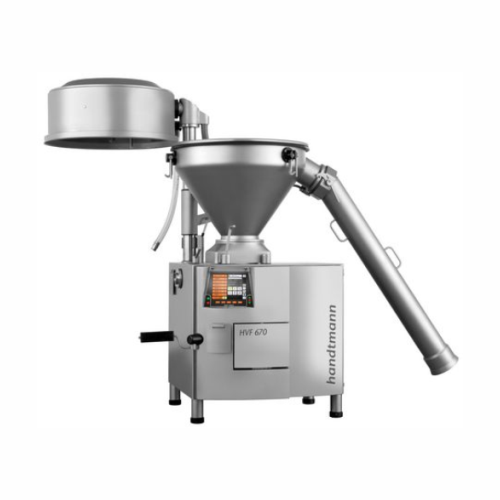
High vacuum filler for cooked ham with whole muscle pieces
Ensure precision and quality in cooked ham production with hi...
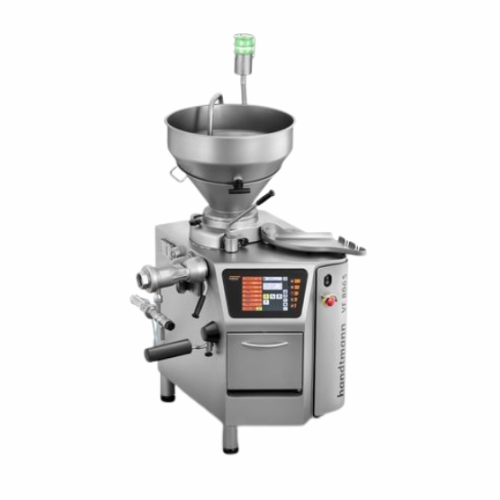
Vacuum filler for small and medium-scale meat producers
Achieve precise portioning with high-speed filling and grinding c...
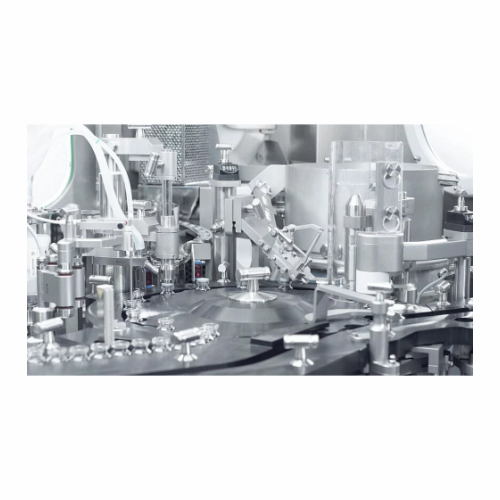
Integrated vial filling system for aseptic and toxic pharmaceuticals
Minimize product loss and ensure high sterility in...
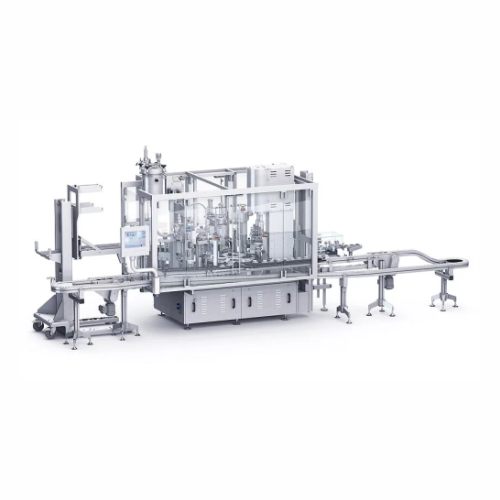
Filling and sealing system for creams and lotions
Achieve precise, high-speed filling and secure sealing of cosmetic cont...
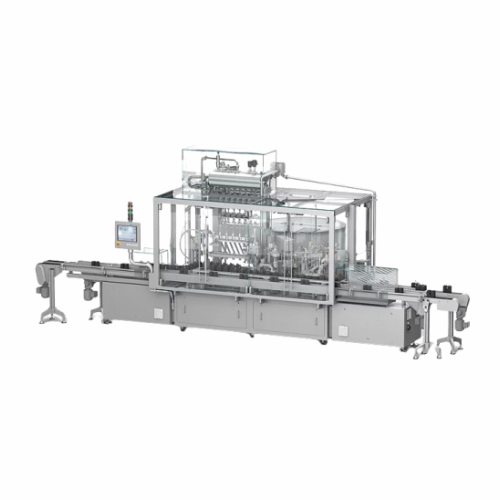
Automatic perfume filling line for cosmetic production
Ensure efficient and precise filling of perfume bottles and liquid...
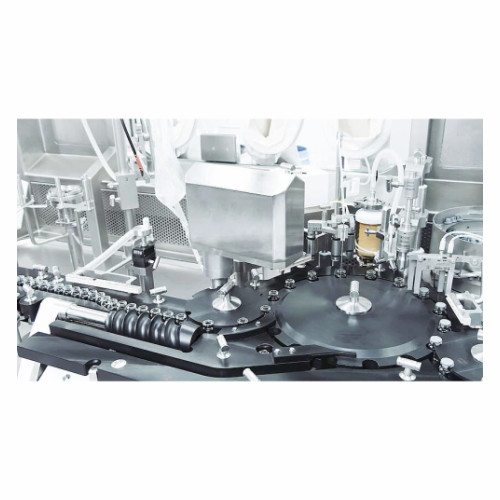
Aseptic filling solutions for Rtu vials, cartridges, and syringes
Optimize your aseptic filling processes with a system...
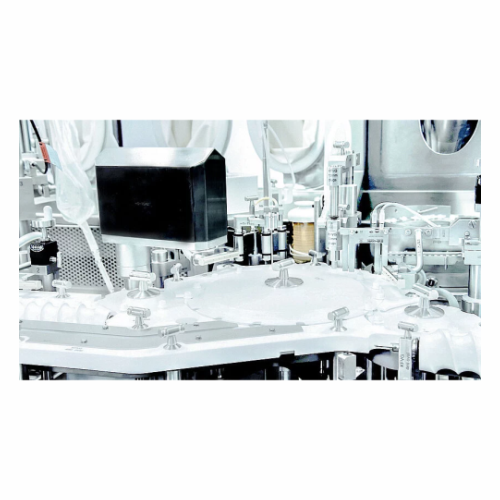
Nasal spray and eye drop filling solutions
Enhance the precision and flexibility of your liquid filling operations with ou...
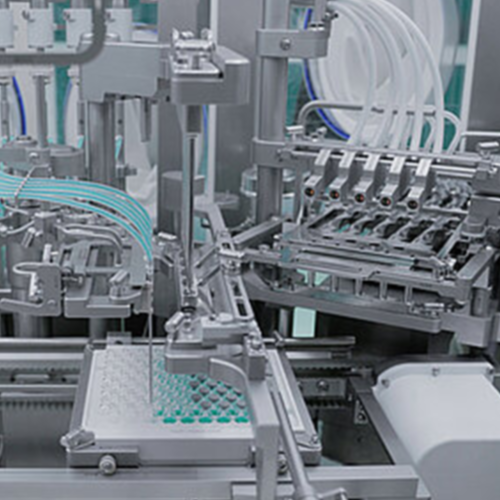
Vial and syringe filling system for pharmaceuticals
Ensure aseptic precision in liquid formulation filling with a modular...
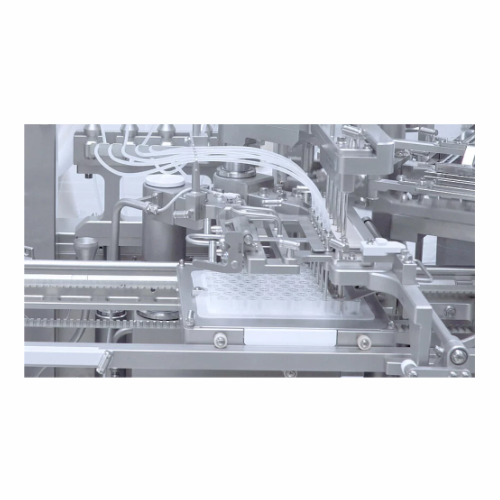
Aseptic syringe filling solution for Rtu containers
Streamline your pharmaceutical liquid filling operations with precise...
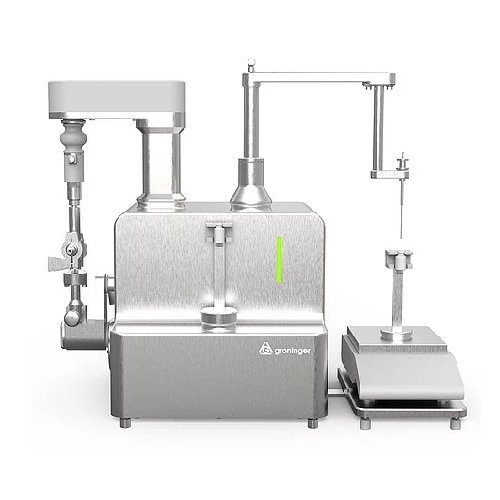
Benchtop filling solutions for small batch liquid medicine
Streamline your small batch liquid medicine production with p...
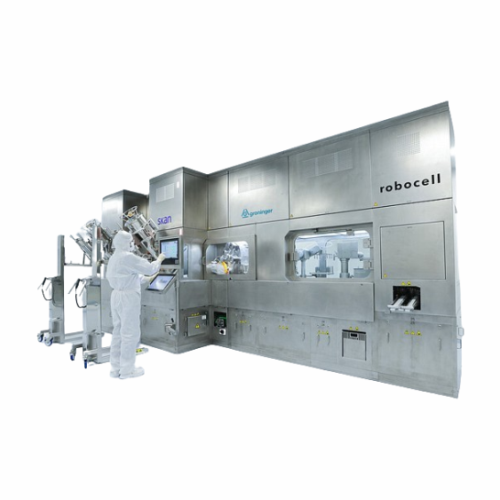
Gloveless robotic filling cell for aseptic pharmaceutical processing
Eliminate human intervention in aseptic filling wi...
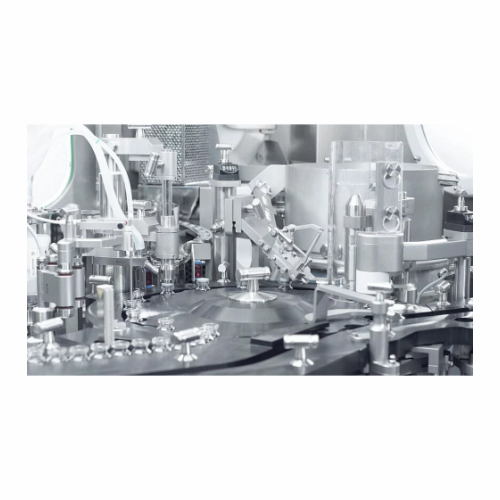
Vial filling for pharmaceuticals
Streamline your aseptic processing with vial filling machines that ensure sterile, precise,...
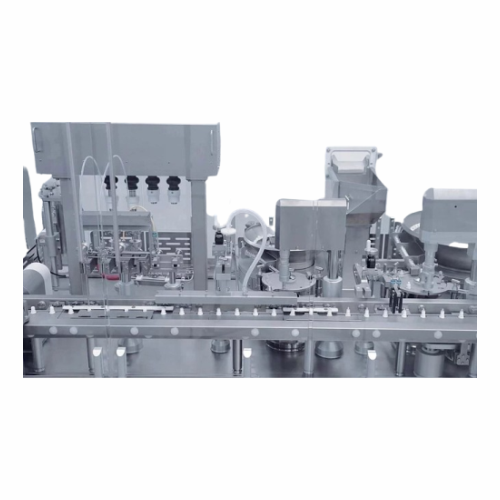
Filling system for consumer healthcare products
For small to medium productions needing versatile filling and sealing, thi...
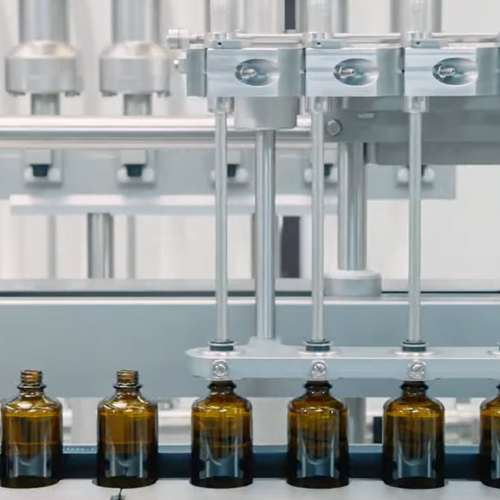
Filling solution for consumer healthcare products
Navigate complex liquid product formulations with a versatile filling s...
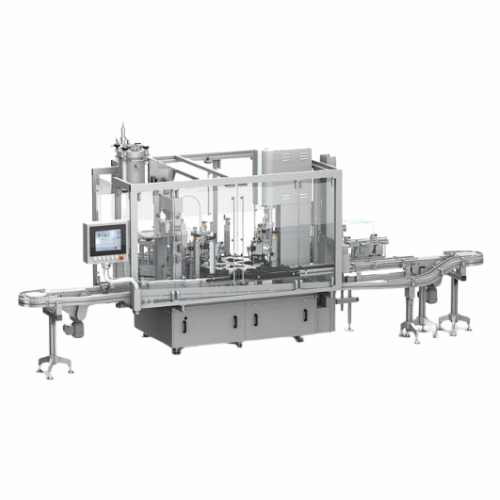
Mascara and lip gloss filling system for cosmetics
Optimize your cosmetic product filling operations with precision, hand...
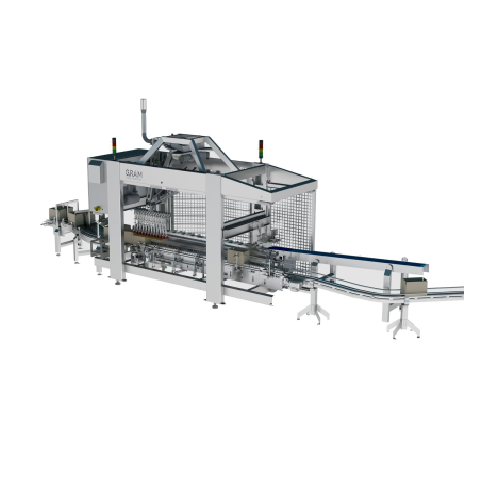
Automated in-line ice cream filling system
Enhance your ice cream production with precision filling, offering high-speed c...
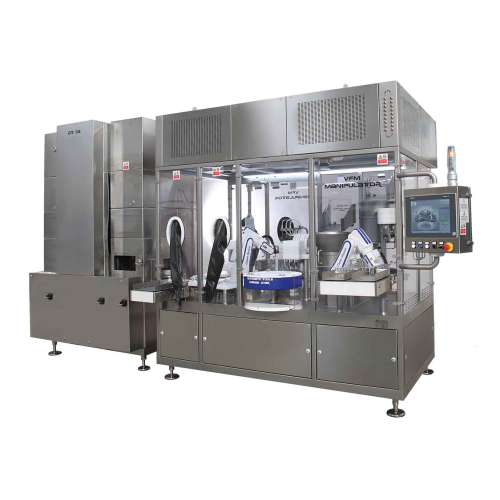
Industrial manipulator for sterile and nonsterile filling
Maintain the integrity of high-value pharmaceuticals with a hi...
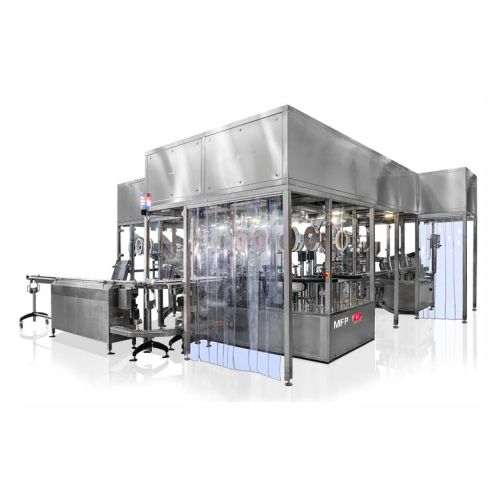
Sterile and nonsterile vial filling system for injectables
Achieve precision and safety in filling and stoppering with a...
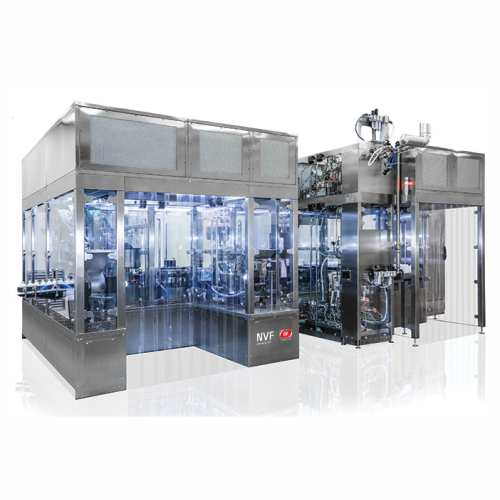
Sterile and nonsterile filling for injectable solutions
Efficiently fill and stopper injectable solutions in both sterile...
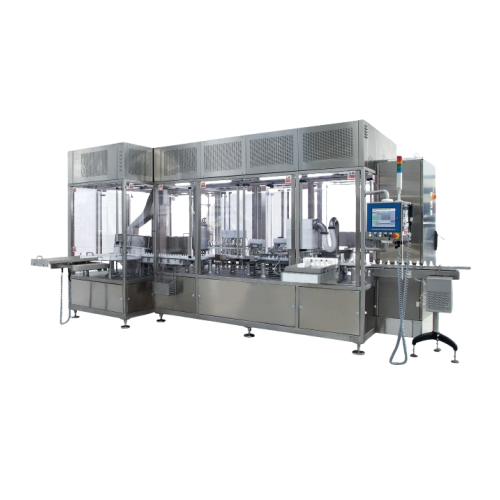
Filling solution for non-injectable pharmaceutical products
Streamline your pharmaceutical production with a versatile s...
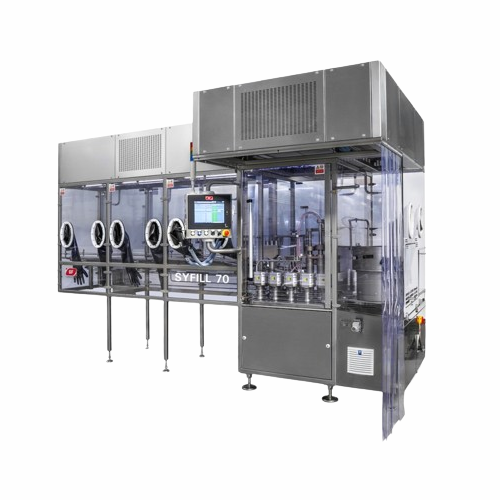
Vial filling system for sterile and nonsterile pharmaceuticals
Enhance precision in injectable drug preparation with a s...
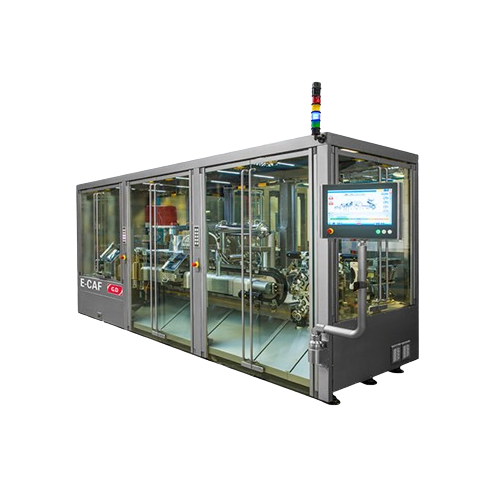
Cartridge assembler and filler for next generation tobacco products
Boost your production line’s efficiency with ...
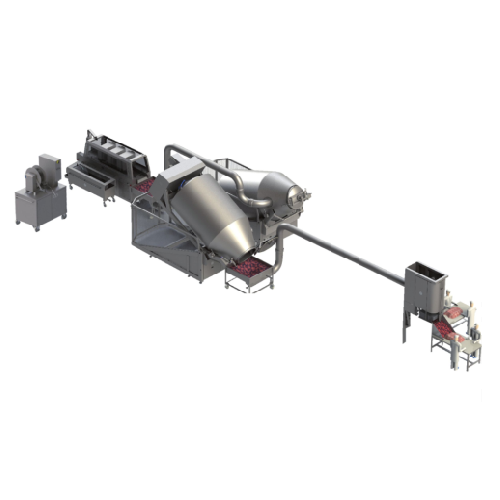
Vacuum filling system for automated food production
Eliminate manual handling with an advanced system that automates the ...
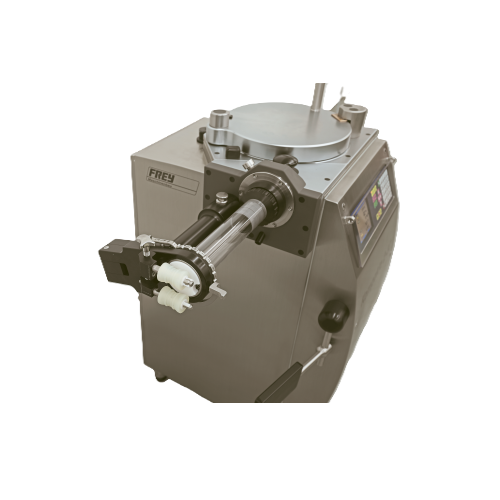
Piston stuffer casing holder for versatile filling applications
Optimize your filling operations with a solution designe...
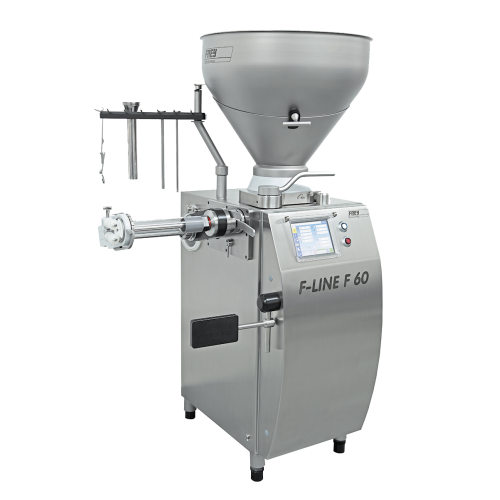
Continuous vacuum stuffer for efficient filling and portioning
Streamline your delicatessen and sausage production with ...

High-capacity piston stuffer for industrial filling and portioning
Streamline your production with high-speed, fully el...
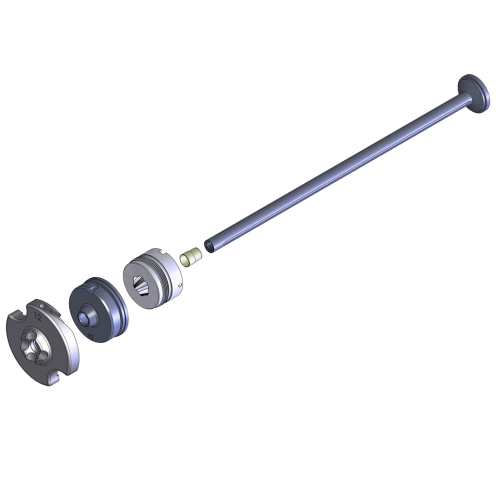
Linker filling tube for sausages
Optimize meat product consistency and reduce waste with precision filling and portioning de...
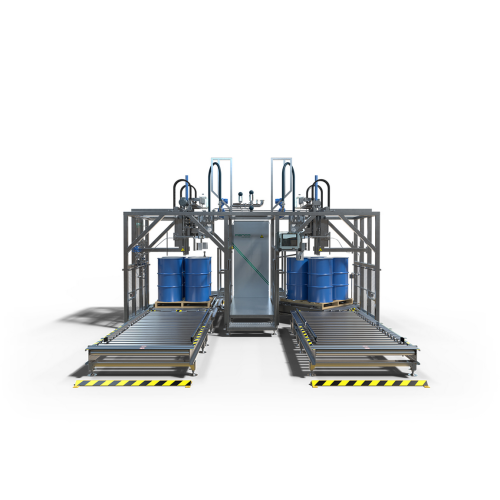
Industrial aseptic fillers for food processing
Ensure sterile packaging with advanced aseptic fillers, designed for precis...
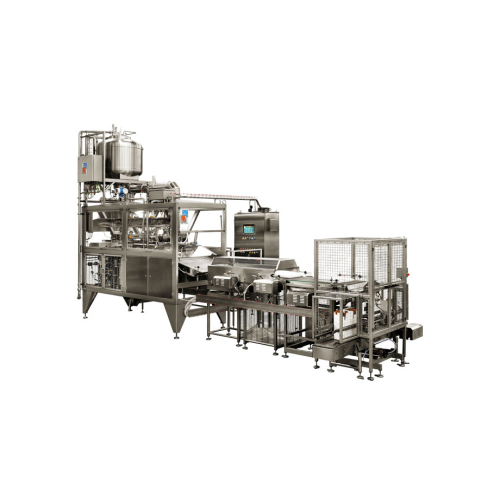
Aseptic filler for bag-in-box packaging
Achieve unparalleled product safety and quality in liquid packaging with our advanc...
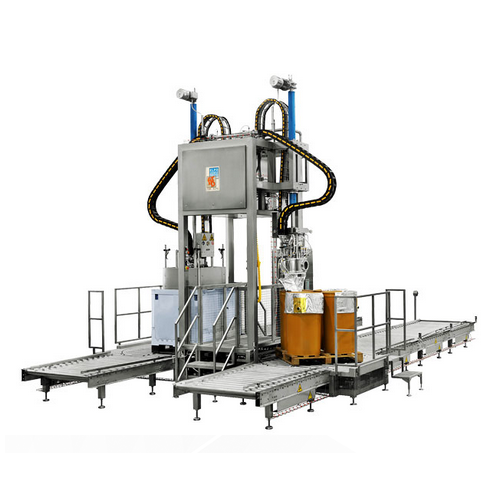
Aseptic filler for large bags
Ensure safe and sterile packaging of liquid and slurry products in large formats with this ase...
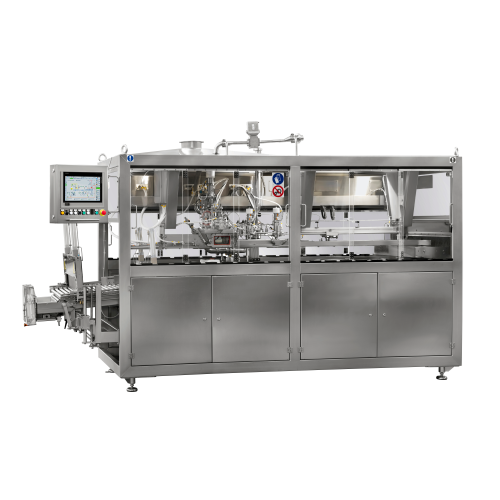
Aseptic filling system for bag-in-box packaging
Efficiently fill a range of liquid products into pre-sterilized bags while...
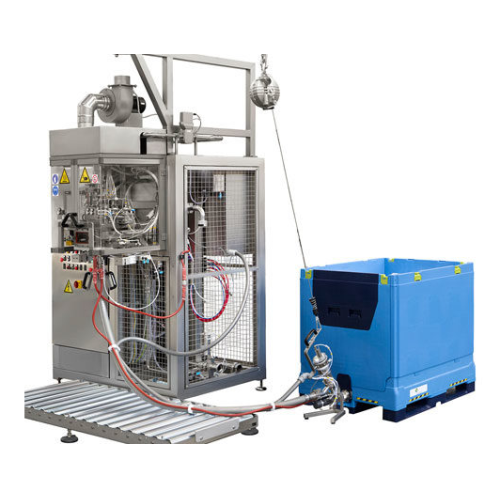
Aseptic filler for liquid and particulate products
Achieve precise, sterile filling of both liquid and chunky products wi...
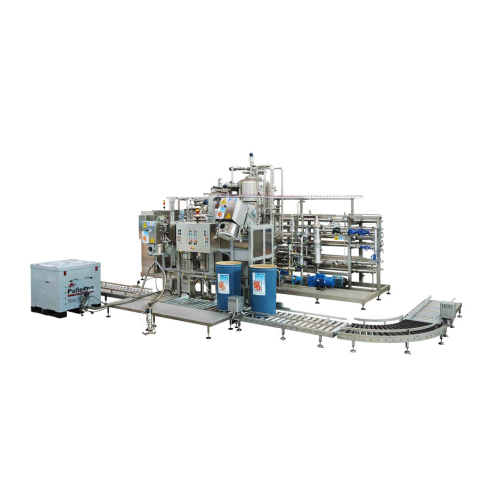
Aseptic treatment and filling for concentrates and purees
Optimize your processing line with a compact solution that com...
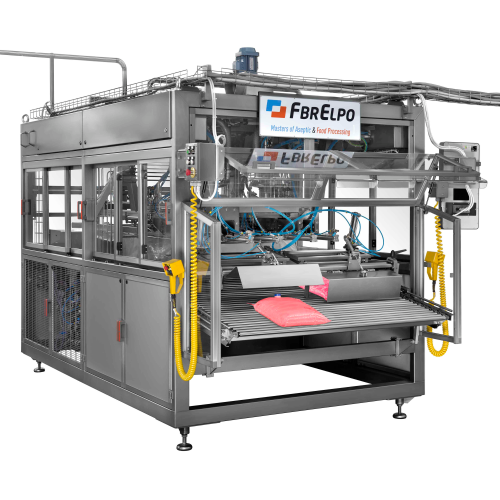
Aseptic filler for bag in box packaging
Optimize your bag-in-box packaging process with high-speed aseptic filling, ensurin...
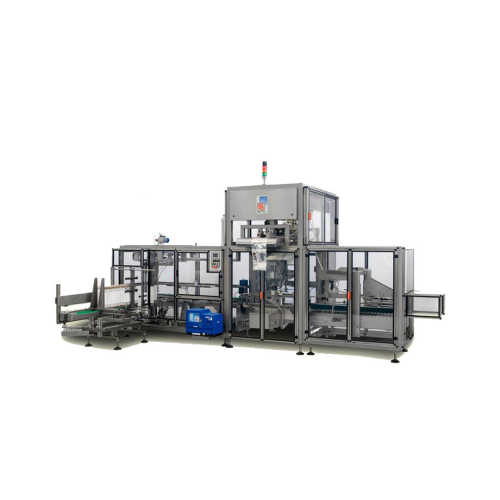
Ultra hygienic filler for non-aseptic products
Optimize your production with high-speed filling and sealing of liquid prod...
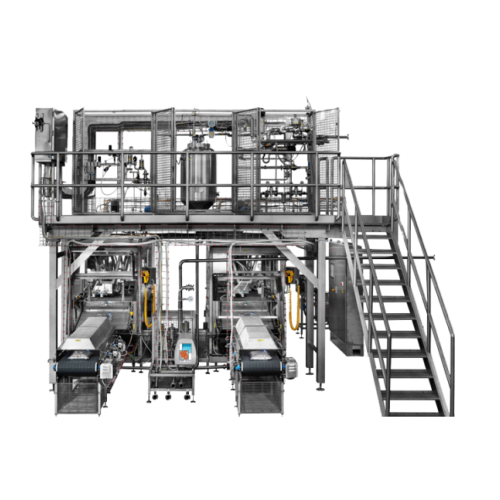
Aseptic bag-in-box filler for juices and purees
Enhance your filling operations with a high-speed aseptic solution designe...

Aseptic filler for liquids and semi-concentrates
Ensure maximum sterility and precision when filling liquids, concentrates...
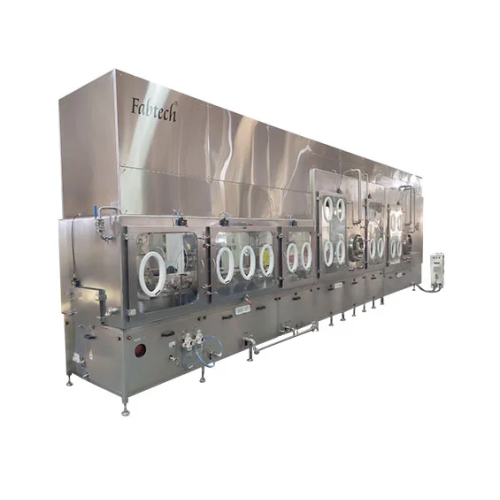
Aseptic filling isolator for vial / Pfs / cartridge
Ensure sterile and contamination-free filling of vials, pre-filled sy...
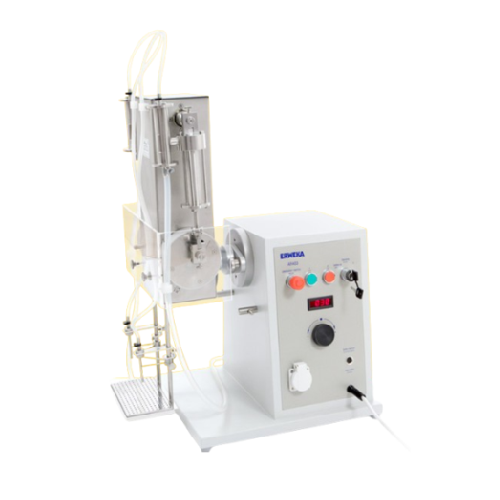
Industrial liquid filler for small to medium volume operations
Ensure accuracy and efficiency in liquid formulation with...
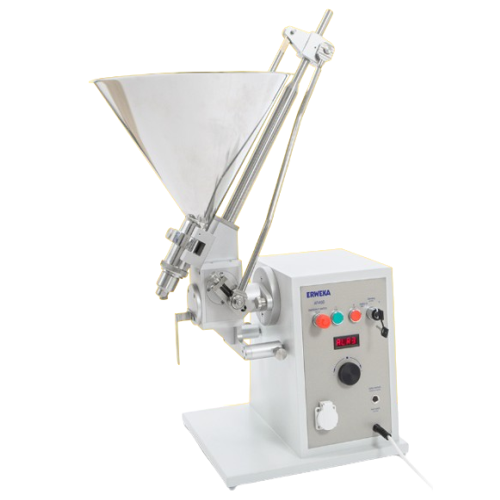
Precision ointment filling and dosing system
Achieve precise filling of liquid formulations with a versatile system capabl...

Liquid food filling solutions
Maximize efficiency in your packaging line with versatile filling machines designed for precis...
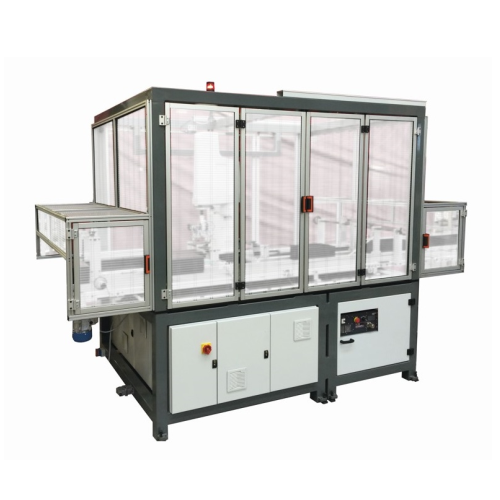
Automatic lidding-up and filling-up for luxury boxes
Enhance your luxury packaging lines with reliable precision, as this...
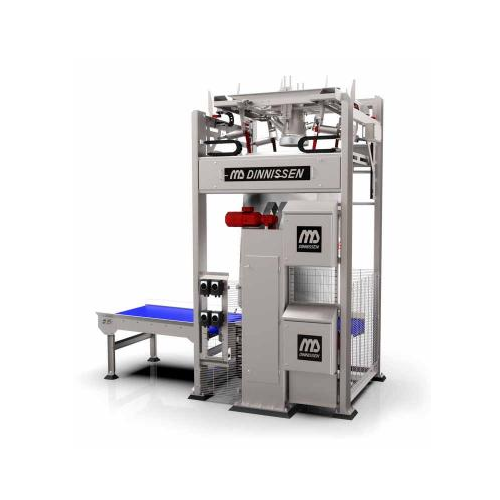
High-care big bag filling system for hygienic environments
Ensure precise hygienic filling of Big Bags in high-care envi...
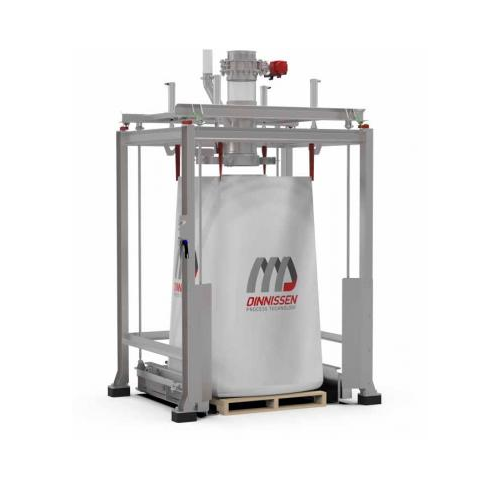
Calibratable big bag filling station for dust-free operations
Ensure precise, dust-free filling of bulk bags with ergono...
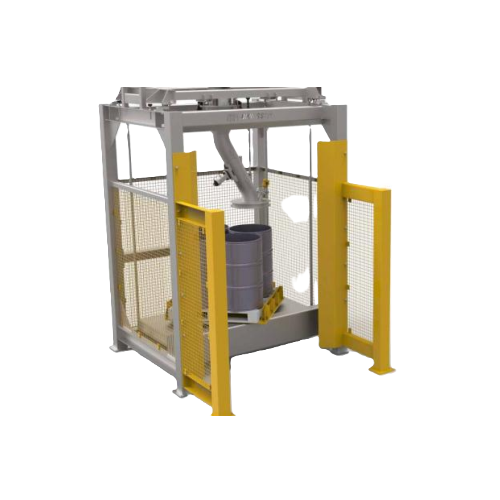
Ibc and drum filling system for chemical substances
Ensure safe and efficient handling of sensitive materials with a modu...

Bag-in-box filling system for packaging efficiency
Streamline your packaging process by integrating filling and boxing in...
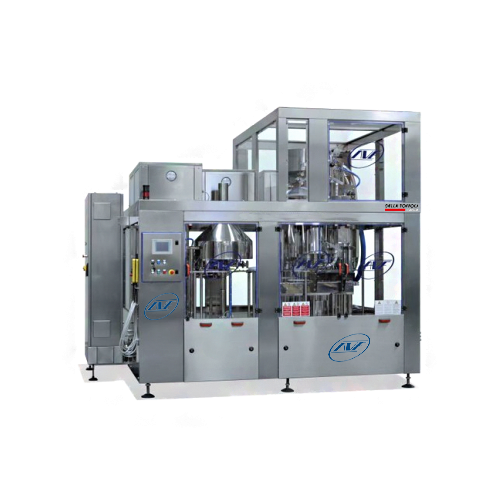
Electronic filling system for non-carbonated beverages
Optimize your bottling process with precision filling technology t...
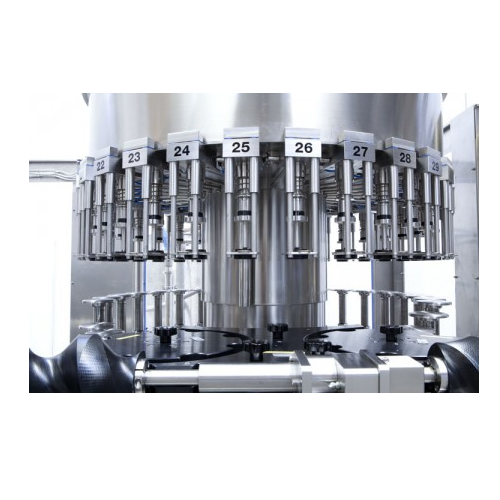
Gravity filling systems for still beverages
Ensure precise and clean filling for still beverages with gravity systems that...
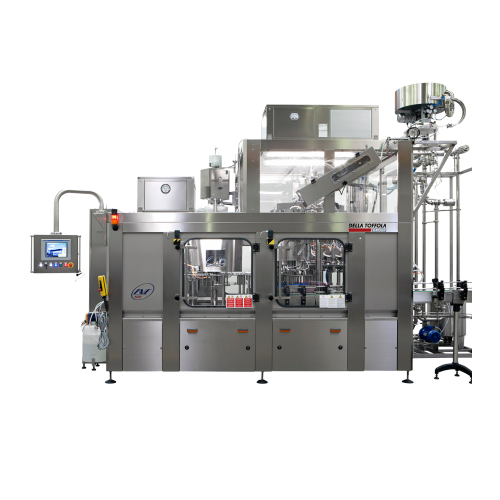
Hot beverage gravity filling system
Ensure precise hot filling of beverages with gravity-fed accuracy, handling liquid temp...
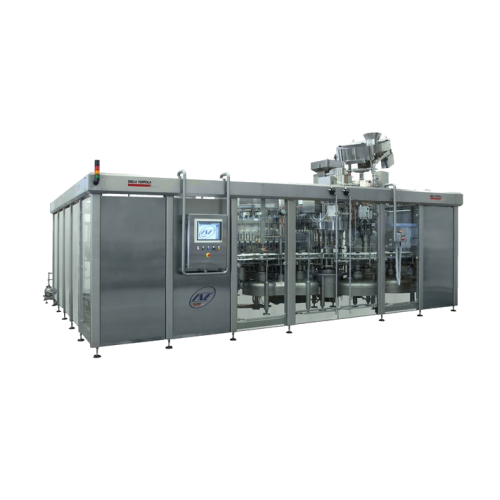
Isobaric filling solution for carbonated drinks
Achieve precision filling for carbonated and still beverages with advanced...
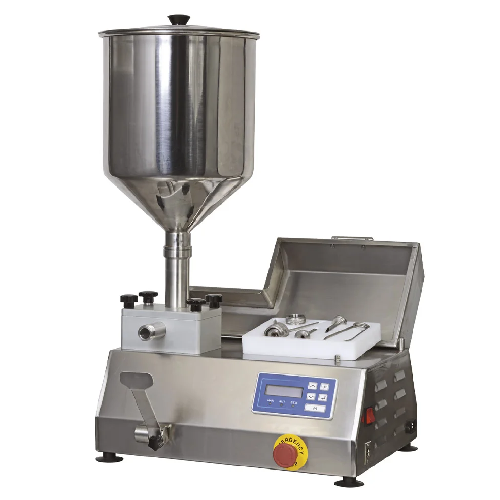
Gear or piston filling-dosing equipment for creamy and thick foods
Efficiently dose and fill dense and creamy products ...
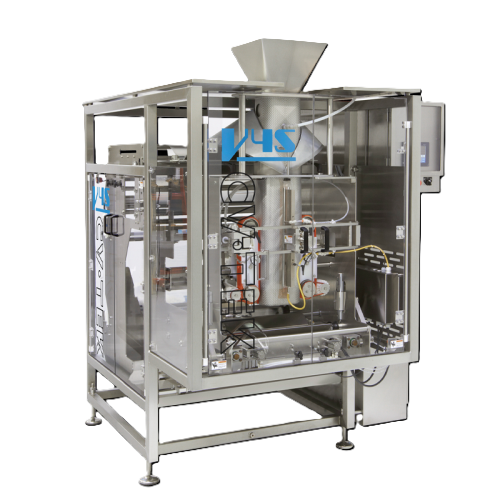
Vertical form fill seal packaging for high washdown environments
Ensure optimal packaging in demanding environments with...
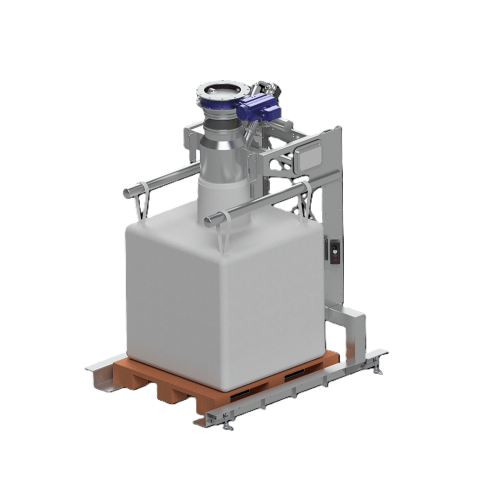
Bigbag filling system for powder and bulk materials
Ensure precise and dust-free bigbag filling with this versatile syste...
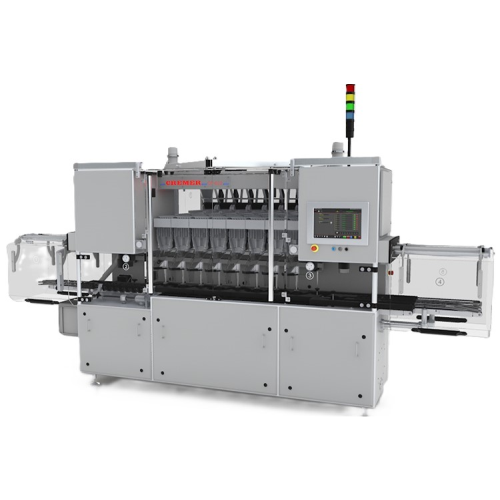
In-motion pharmaceutical bottle filler
Achieve up to 400 bottles per minute with this modular bottle filling solution, desi...
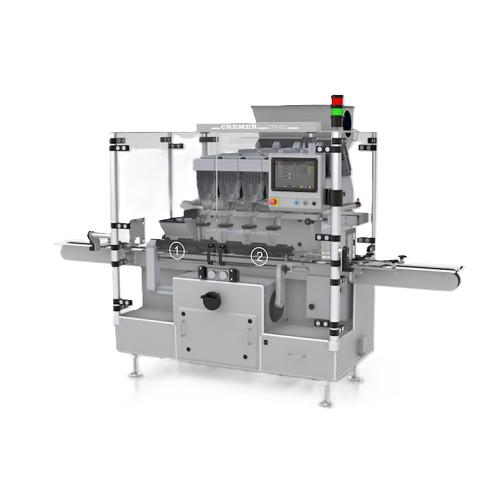
In-motion bottle filling system for pharmaceuticals
Boost your production efficiency with our high-speed bottle filling s...
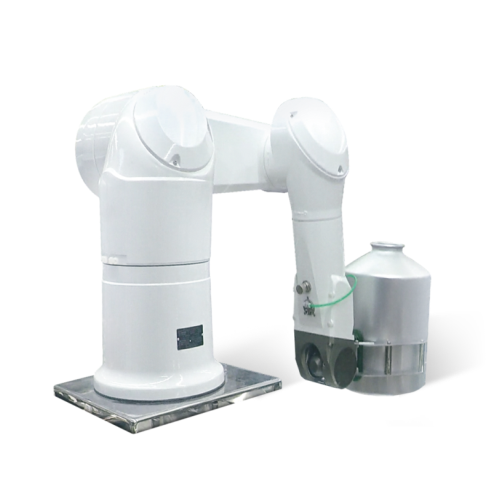
Tipping and filling line for bulk Api powder production
Ensure precise and aseptic handling of pharmaceutical powders wit...
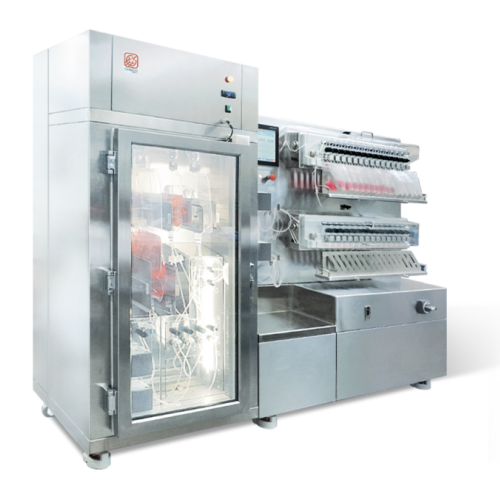
Semi-automatic filling system for cell and gene therapy
Optimize your cell and gene therapy processes with a modular fill...
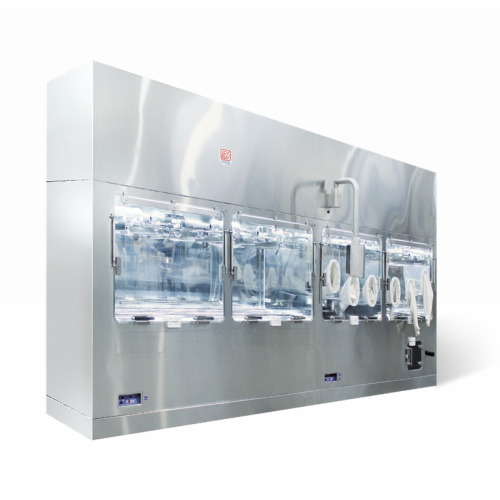
Custom automation for drug-device filling and assembly
Efficiently integrate precise filling and assembly for biopharmace...
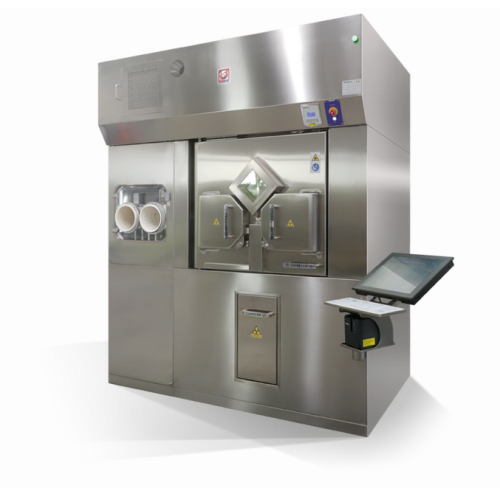
High-throughput aseptic isolator for syringes and vials filling
Streamline your aseptic filling process with a high-spee...
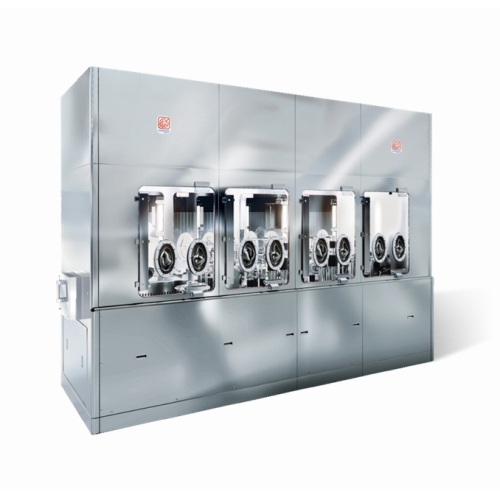
High quality sterile filling system
Experience unparalleled precision in aseptic filling with this advanced system, designe...
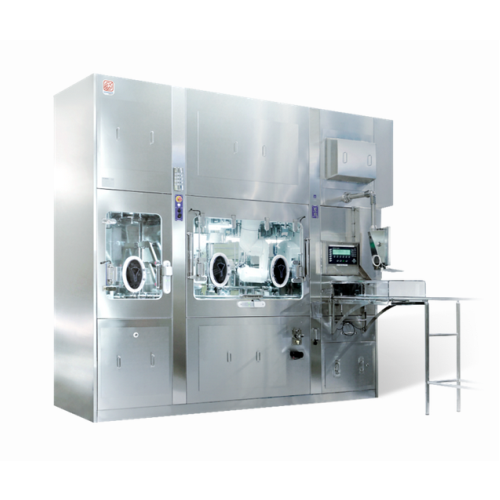
Dry powder filling isolator for cgmp production
Achieve precise powder dosage and secure containment for hazardous materia...
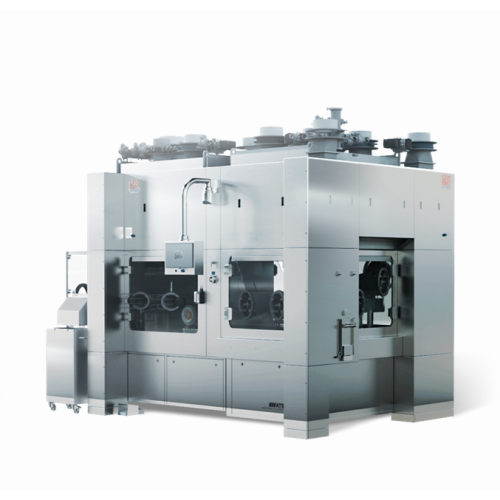
Sterile robotic filling for ready-to-use vials and syringes
Achieve precise and contamination-free filling for biopharma...
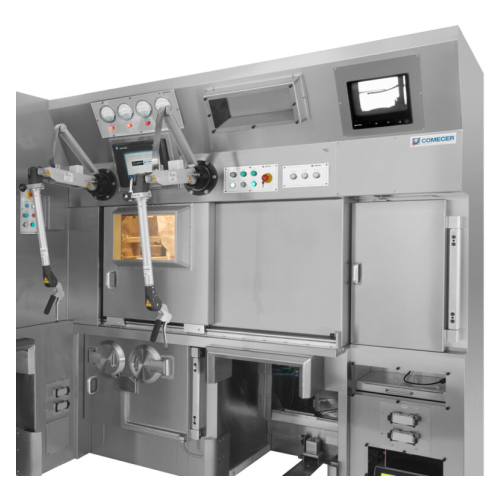
Aseptic filling line for 131i sodium Iodide
Ensure compliant production of iodine-131 radiopharmaceutical vials with preci...
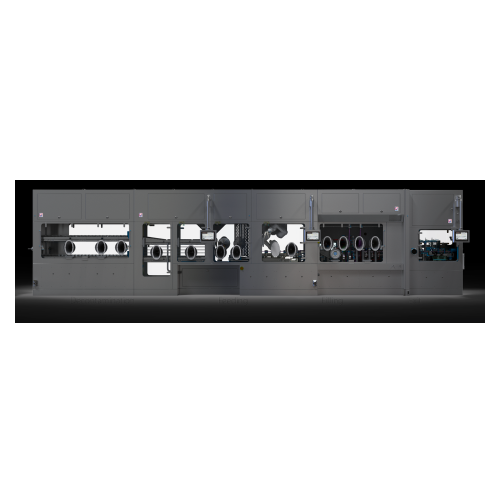
Automatic aseptic filling line for Iv bags
Ensure aseptic integrity and high-speed processing of IV bags with a filling li...
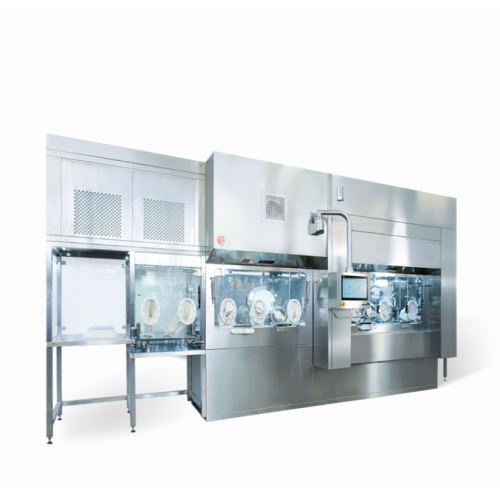
Compact aseptic vial filling system
Optimize your aseptic liquid filling with a compact system designed for seamless integr...

Rotary filling system for Rtu vials in pharma production
Optimize your sterile liquid and powder handling with a versatil...
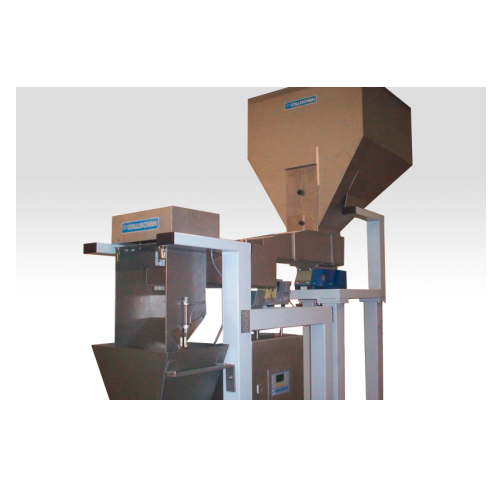
Weigh filler for bulk quantities 2-20kg
Optimizing your filling process with precision, this equipment handles bulk quantit...
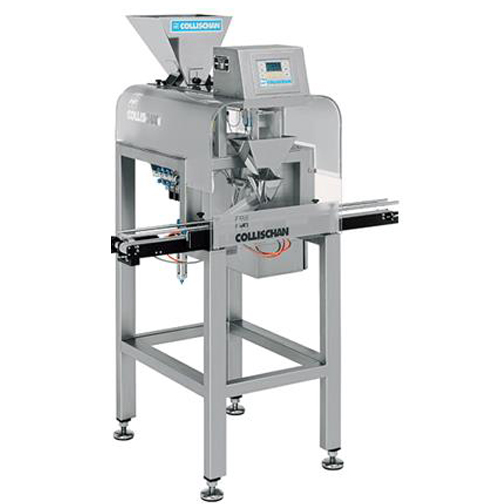
Weight filler for small batches in explosive areas
Efficiently handle and weigh small batch products with precision, even...
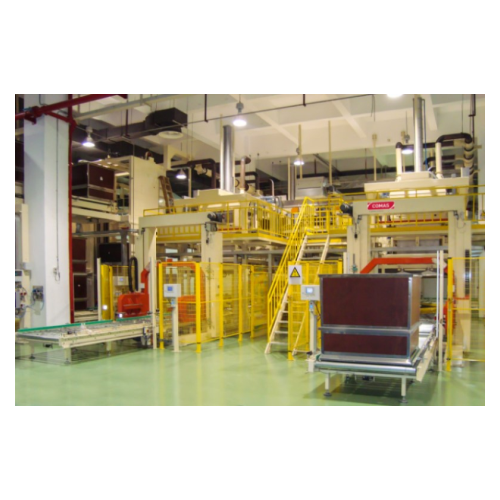
Bin and carton filling system for cut tobacco
Efficiently manage your tobacco product flow with a high-speed filling syste...
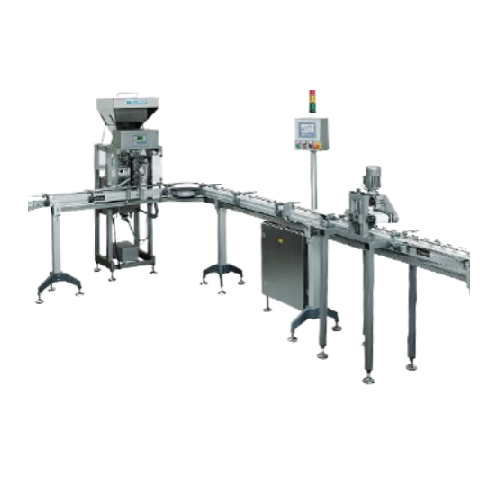
Precision weigh filler for food and pharma industries
Optimize precision in multi-component dosing with seamless integrat...
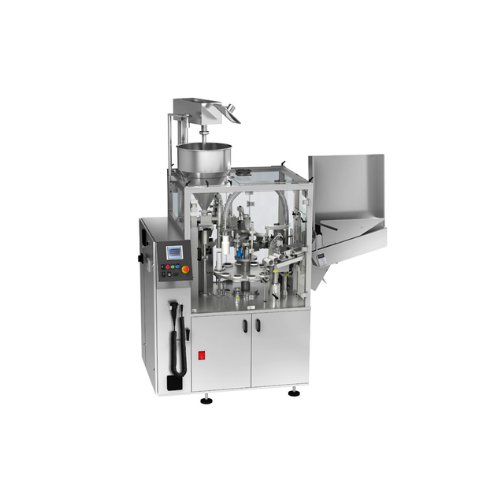
Tube filling solution for health and beauty applications
Achieve consistent quality and efficiency in tube filling operat...
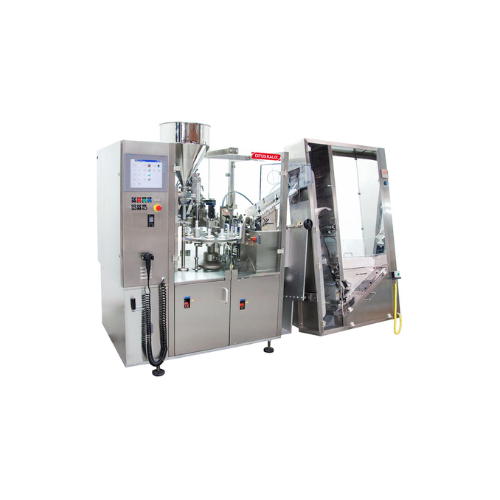
Tube filling solution for health and beauty products
Achieve rapid production with precision in tube filling for personal...
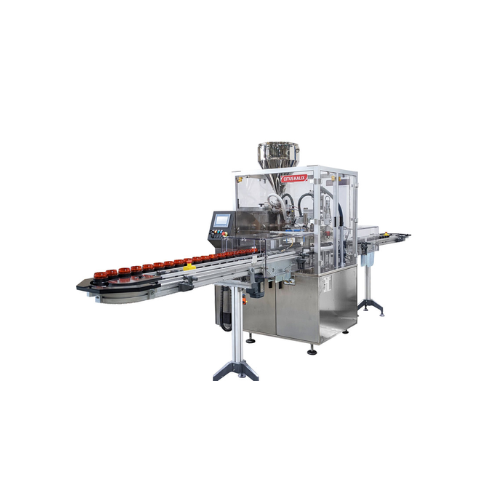
Cosmetic jar filling solution
Reduce product contamination and ensure precise filling with an intermittent jar filling solut...
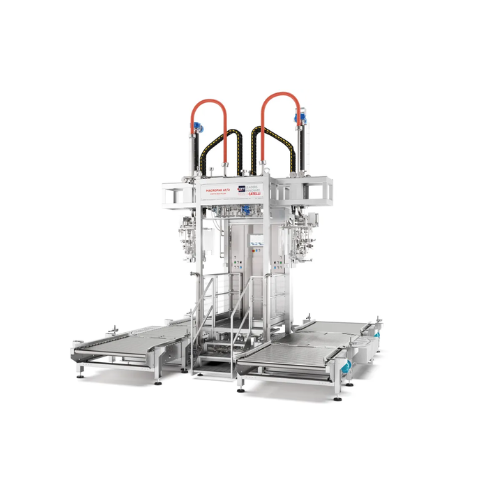
Aseptic fillers for liquid and viscous products
Ensure sterile and precise filling of liquid and viscous foods with adapta...
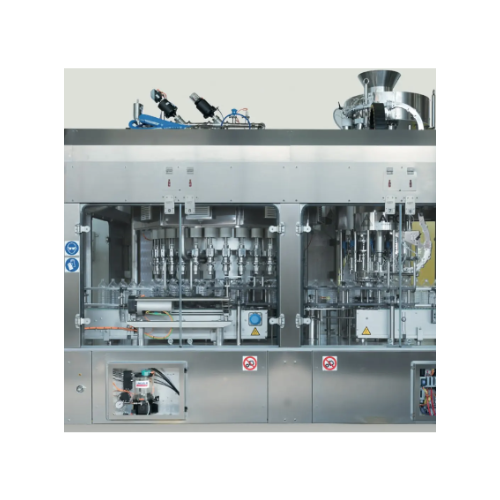
High-precision rotary weight filler for edible oils and sauces
Achieve exceptional filling precision with solutions desi...
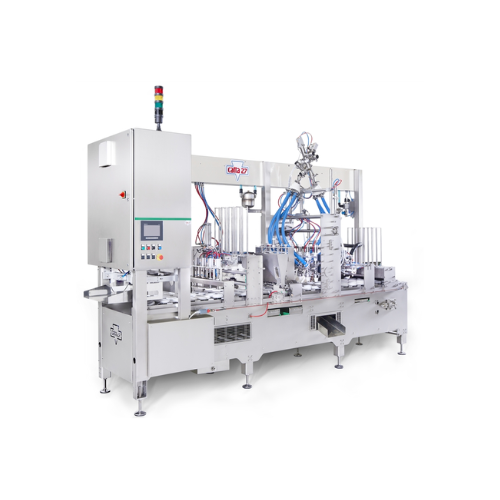
Linear filling machines for ice cream production
Enhance your ice cream production with modular filling machines designed ...
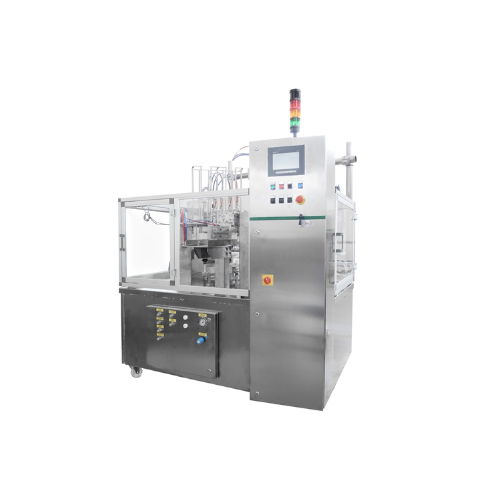
Rotary filling solutions for ice cream cups and cones
Optimize your ice cream production with customizable rotary filling...
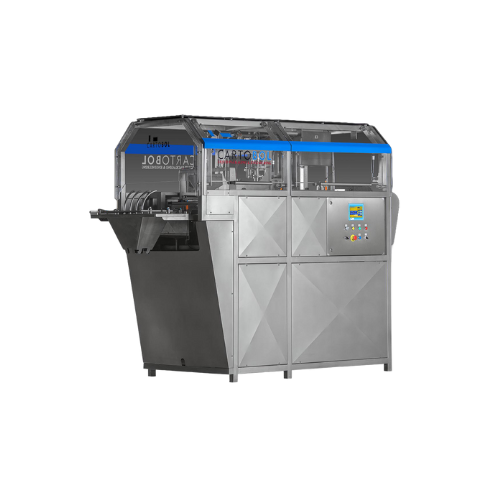
Automatic filling system for continuous bags
Ensure precision in liquid and gas handling with this high-speed system, desi...
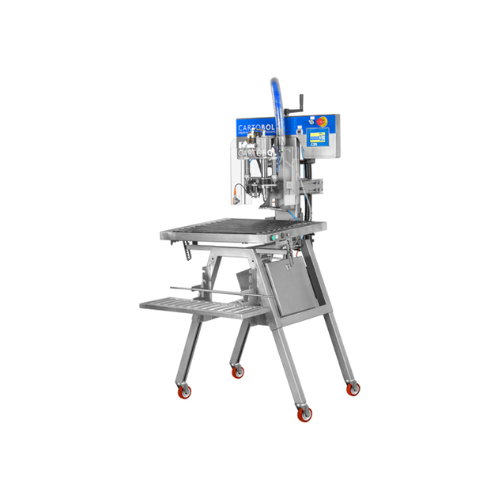
Semi-automatic filler for bag-in-box packaging
Streamline your liquid packaging process with a versatile filler that integ...
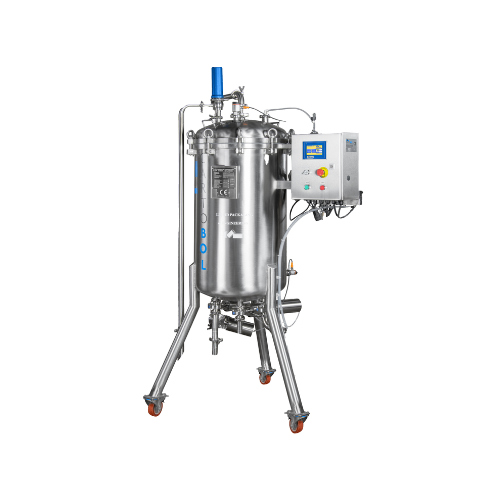
200l buffer tank for bag-in-box fillers
Ensure precise filling and consistent flow control with this stainless steel buffer...
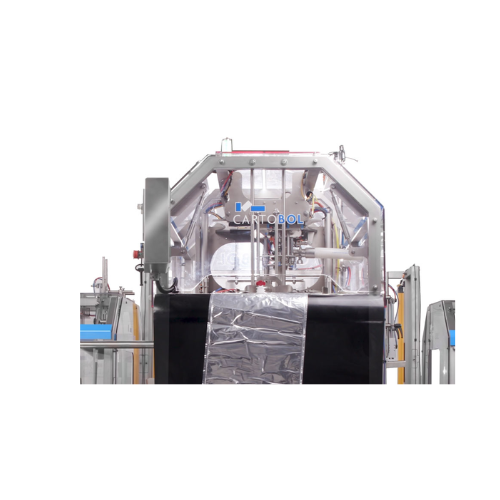
Bag-in-box fully automatic filling line
Streamline your liquid packaging operations with a modular system designed to enhan...
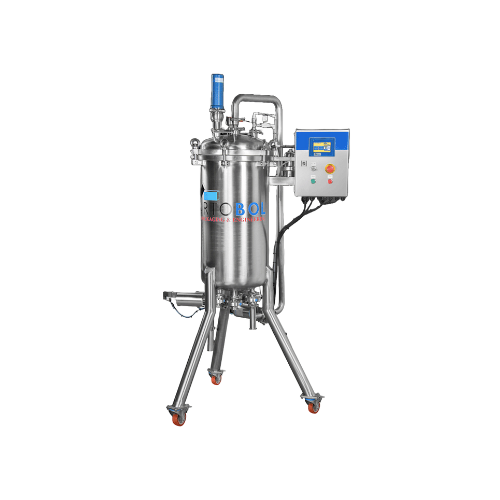
Buffer tank for bag-in-box filling
Optimize your liquid packaging with precise flow control and pressurization, ensuring st...
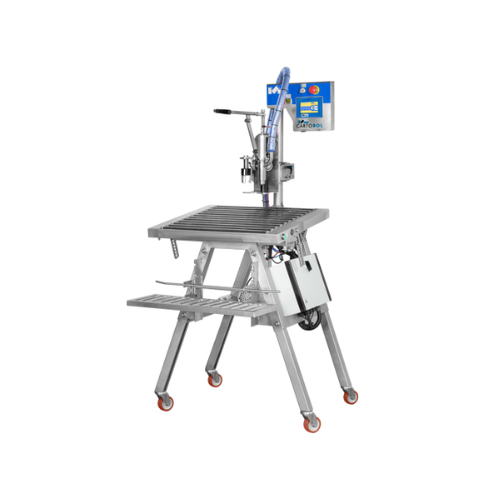
Manual bag-in-box filling solution
Streamline your liquid packaging with a compact, easy-to-operate filling system that sim...
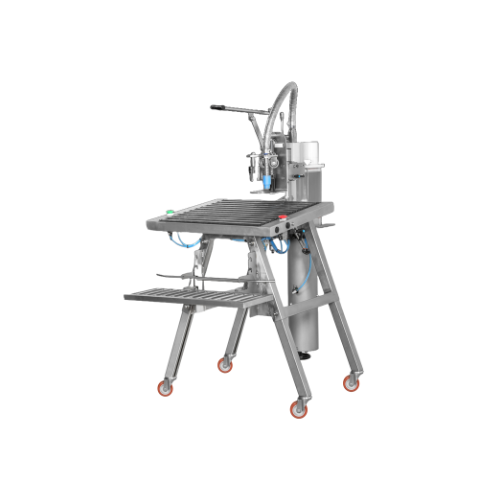
Manual pneumatic filler for bag-in-box
Experience seamless filling for liquid formulations with this pneumatic solution, en...
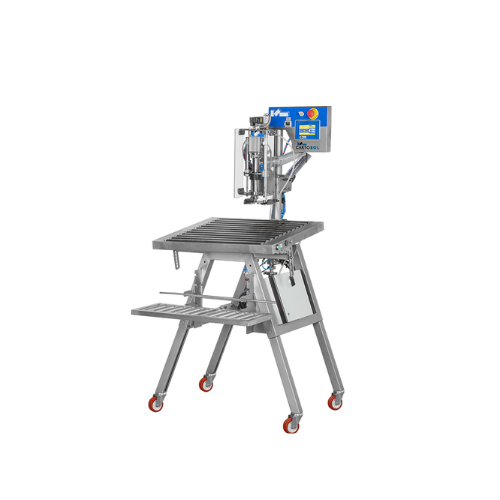
Manual filling system for bag-in-box packaging
Streamline your liquid filling process with a manual system designed for pr...
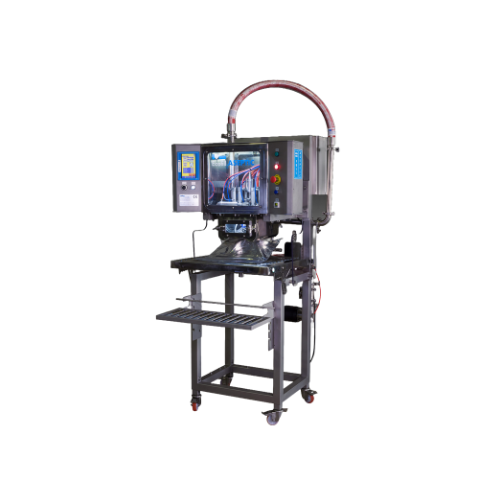
Semi-automatic aseptic filler for single bags
Ensure aseptic integrity and flexibility for your liquid and semi-liquid pro...
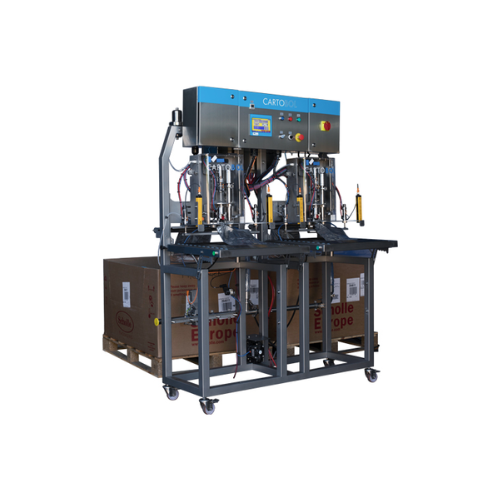
Bag-in-box filler with dual heads and automatic features
Boost your liquid production efficiency with a dual-head filling...
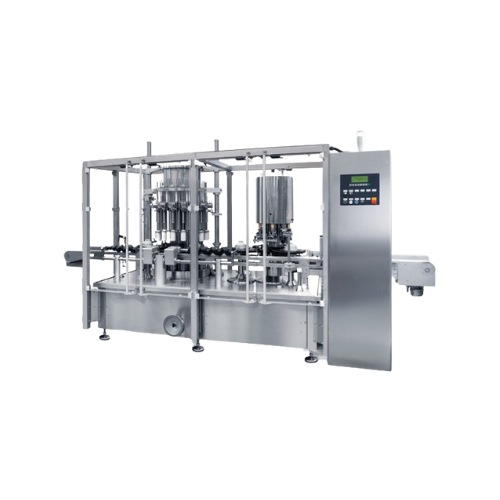
High speed continuous motion liquid filling and capping system
Achieve high-speed, precision filling and capping for liq...
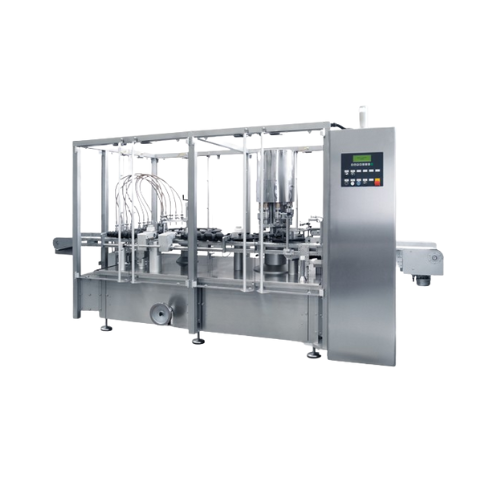
Continuous motion liquid filling and capping monobloc
Optimize high-speed liquid filling with seamless transitions from f...

Volumetric filling and capping system for pharmaceuticals
Optimize your liquid filling and capping operations with a ver...
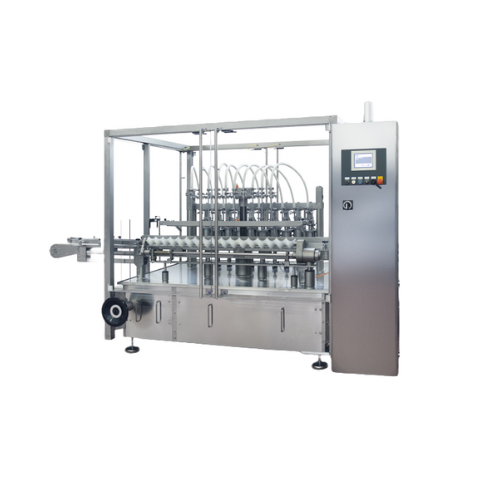
Linear intermittent motion filling system for high-density liquids
Ensure precise dosing of high-density liquids like c...
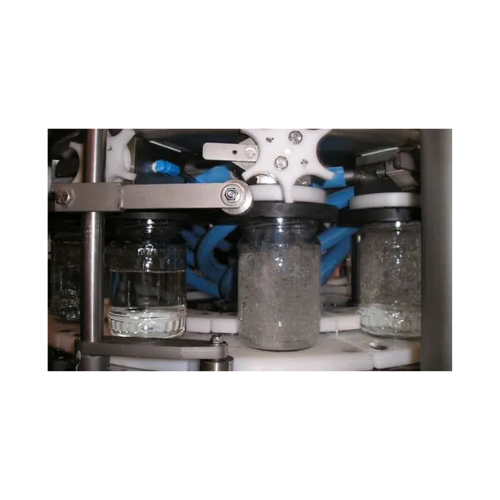
Vacuum filler for glass jars and cans
Ensure precise filling and equal headspace for your products with this vacuum filler,...
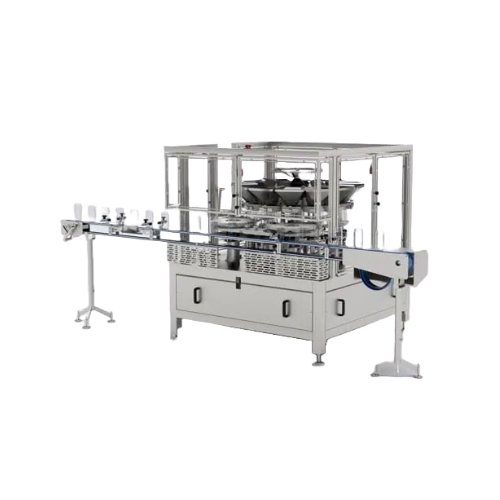
Vibratory rotary filler for accurate filling in food packaging
Achieve precise and efficient filling of diverse solid pr...
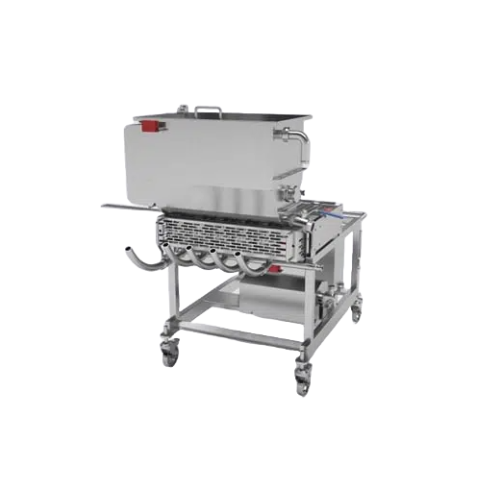
Automatic piston fillers for liquid products
Optimize your liquid filling process with high-precision piston fillers, engi...
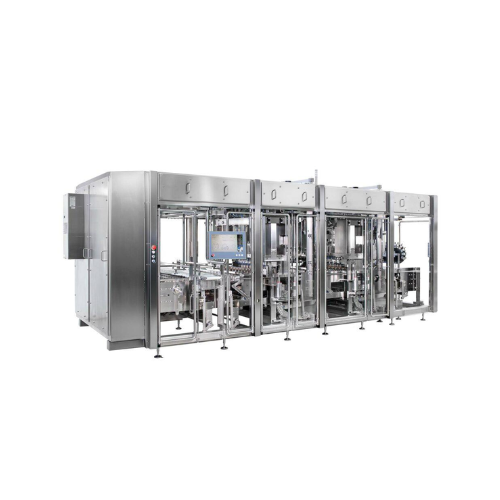
High-capacity filler and closer for pumpable products
Efficiently handle pumpable, flowable, and pasty products with this...
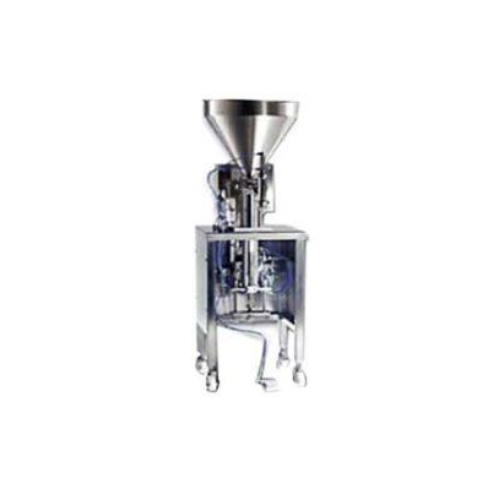
Dosing unit for semi-automatic filling and packaging extension
Streamline your filling operations with this dosing unit,...
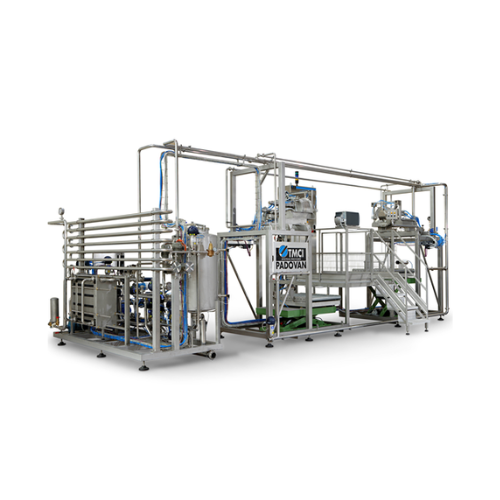
Aseptic filling system for fruit juices and nectars
Effortlessly integrate aseptic filling into your beverage production ...
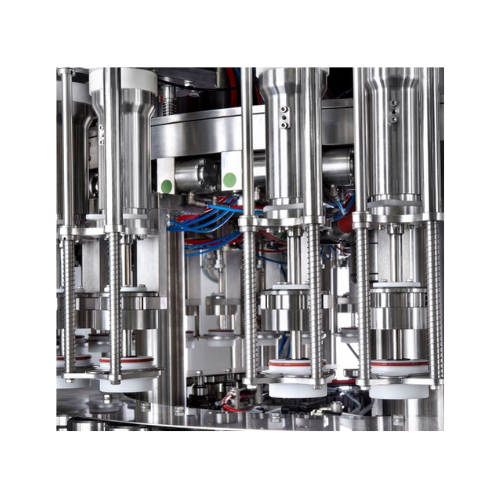
No-oxygen wine filler
Ensure product integrity with advanced no-oxygen filling systems, designed to preserve delicate flavors...
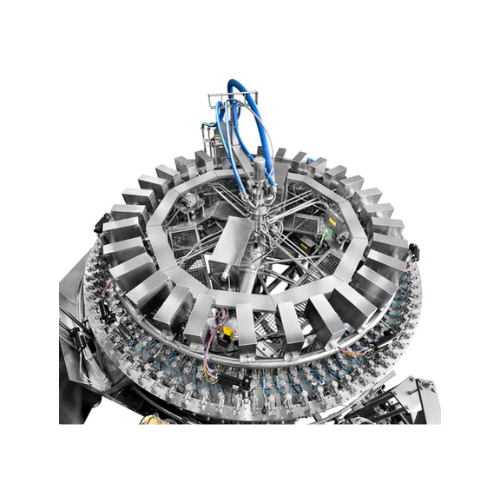
No-oxygen filler for wine bottling
Enhance liquid bottling with seamless integration that minimizes oxygen exposure, ensuri...
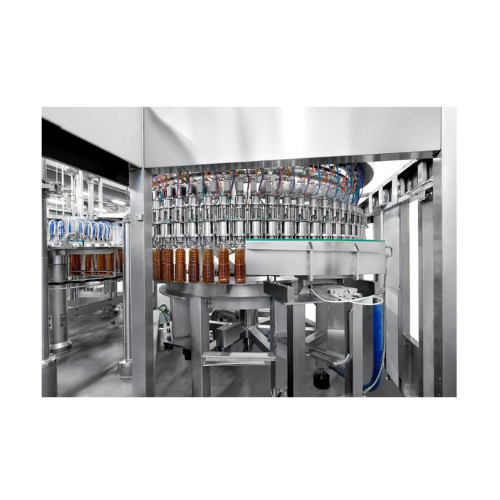
High-capacity no-oxygen wine filler
Ensure optimal flavor retention and prevent oxidation in your bottling process with adv...
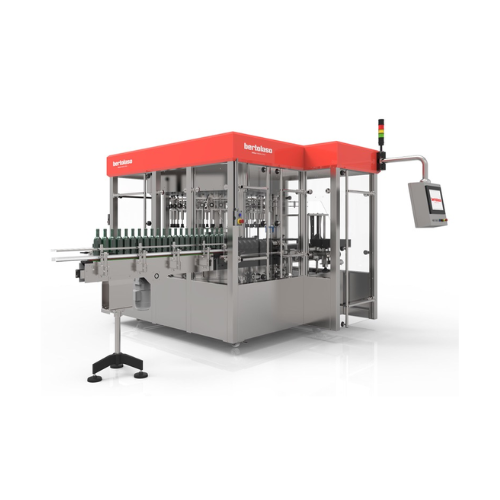
Inspection system for filled glass bottles
Ensure high-quality beverage bottling by detecting bottle faults, contaminants,...
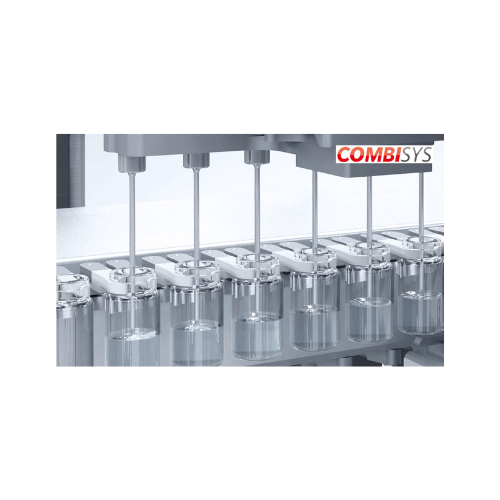
Combisys filling and closing system for pharmaceutical containers
Ensure precise filling and closing of pharmaceutical ...
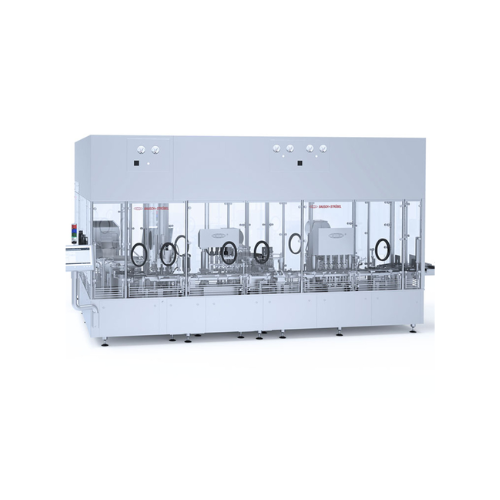
Filling and closing solution for plastic bottles
Efficiently sort, fill, and close a variety of plastic bottles with preci...
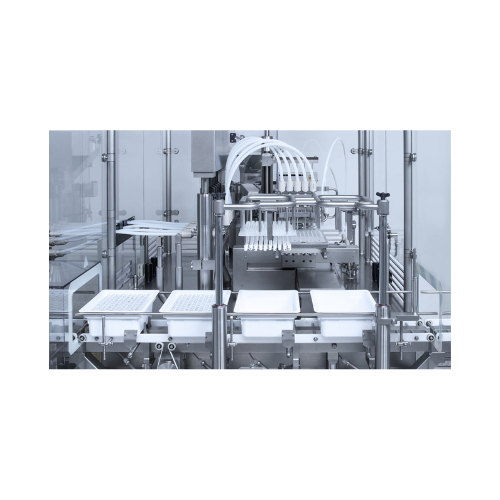
Filling and closing solution for nested containers
Streamline your vial, cartridge, and syringe production with precise d...
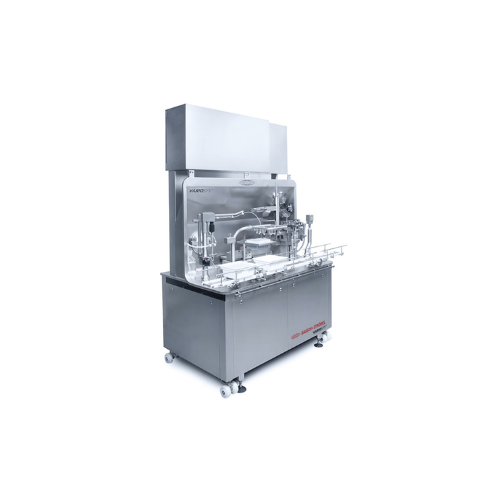
Filling and closing system for nested containers
Optimize liquid formulation packaging with a high-speed system designed f...
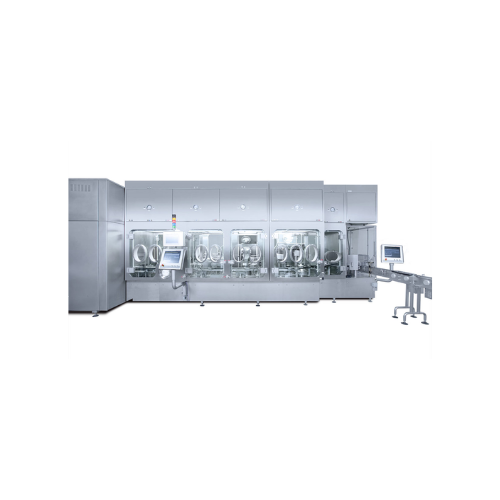
Filling and closing solution for vials and stable bottles
Optimize vial and bottle processing with a seamless solution d...
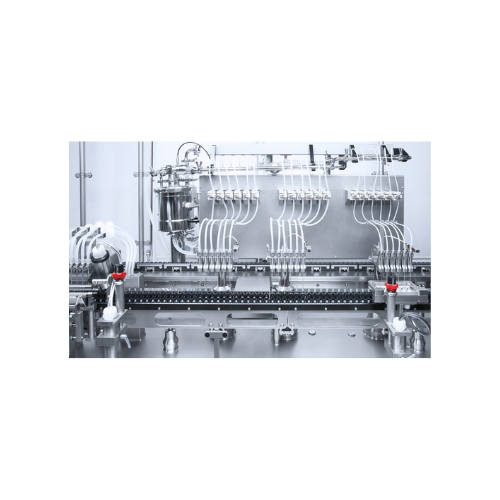
Filling and closing system for cartridges
Enhance your cartridge production with precise filling and closing technology de...
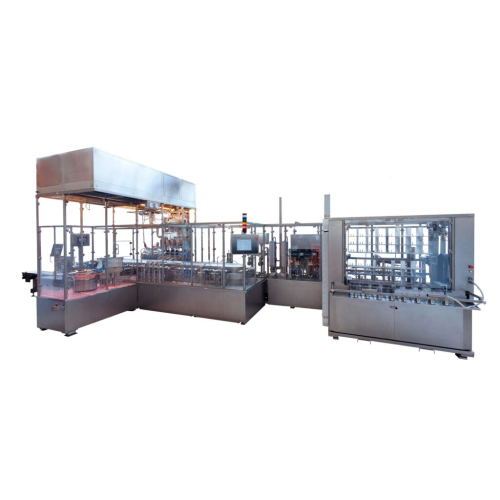
Aseptic filling and closing for flexible Iv bags
Streamline your production line with high-speed aseptic filling and seali...
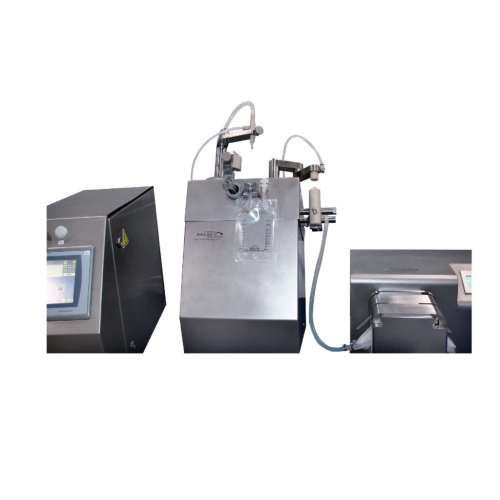
Semi-automatic filling and closing system for flexible bags
Ensure sterile and precise IV bag filling and closing with a...
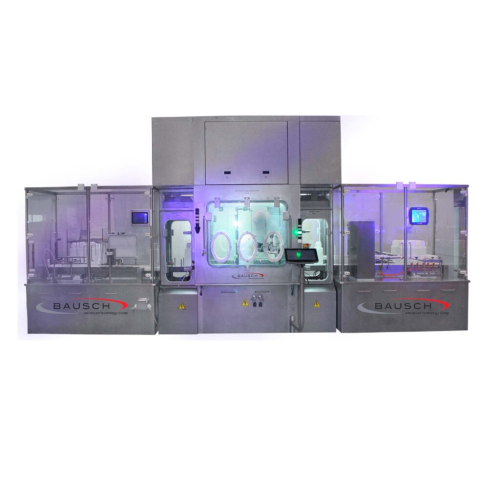
Automated filling and closing system for vials and bottles
Optimize your vial and bottle filling line with precise liqui...
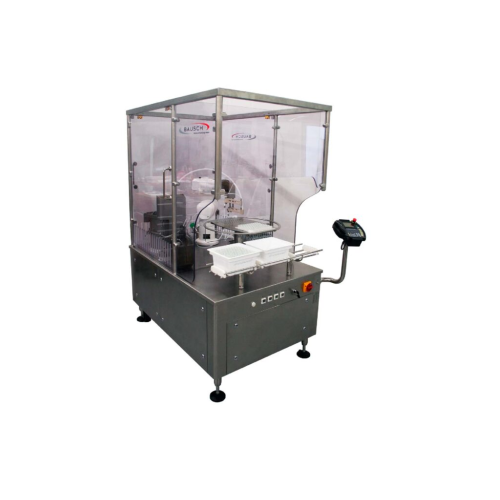
Nested vial and syringe filling and closing system
Achieve precise aseptic filling and closing for clinical products with...
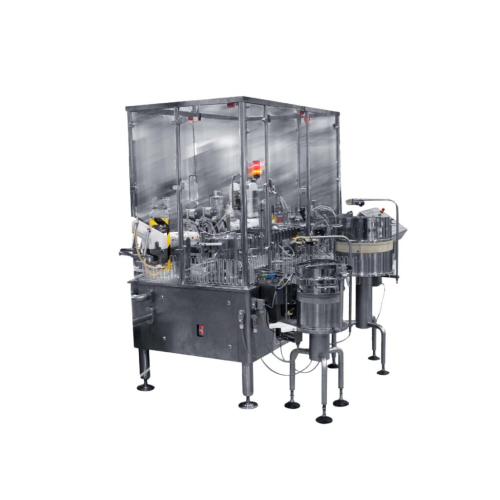
Filling and closing system for vials, syringes, and cartridges
Optimize your aseptic fill-finish operations with a versa...
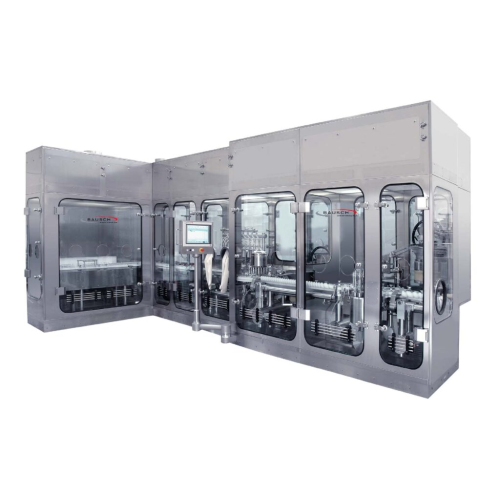
Vial and cartridge filling and closing system
Optimize your aseptic fill-finish process with high-speed, continuous operat...
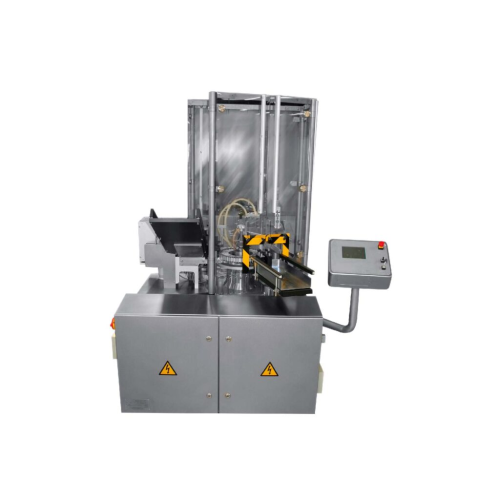
Filling and closing system for ampoules
Ensure precision and efficiency in your aseptic fill-finish operations with a compa...
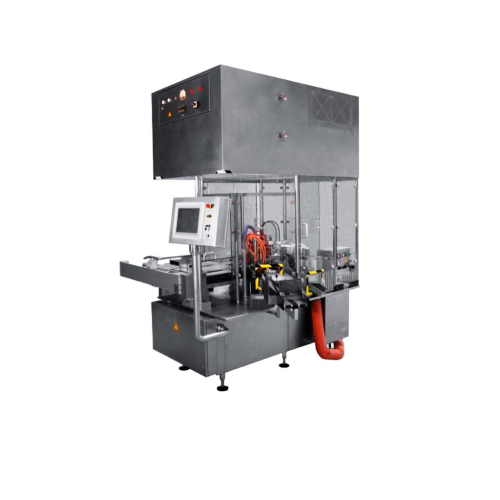
Ampoule filling and closing system
Optimize your production line with a high-speed system designed for seamless filling and...
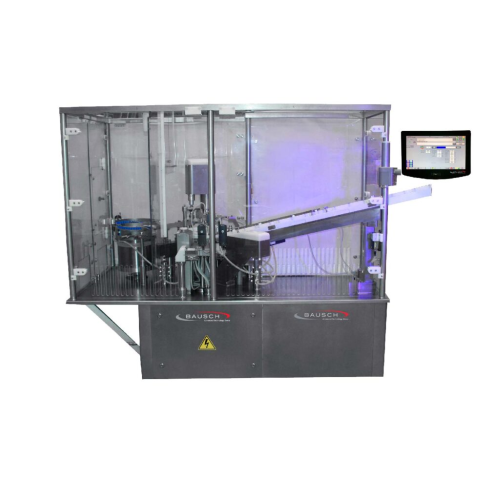
Filling and closing solution for vials and syringes
Achieve precise aseptic fill-finish of liquid formulations in vials a...
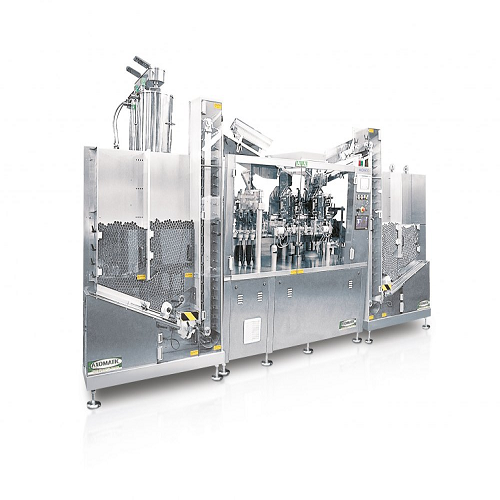
Automatic tube filling and closing system
Enhance production efficiency with a high-speed tube filling and closing system ...
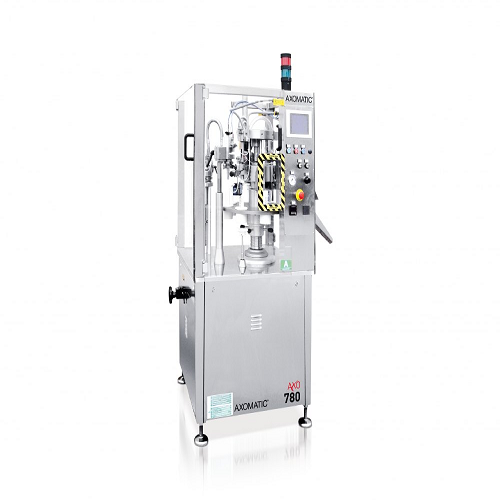
Semi-automatic tube filling and closing system
Achieve precise filling and secure closing for diverse tube types, optimizi...

Automatic bottle filling and capping line
Streamline your liquid product packaging with this high-speed solution, integrat...
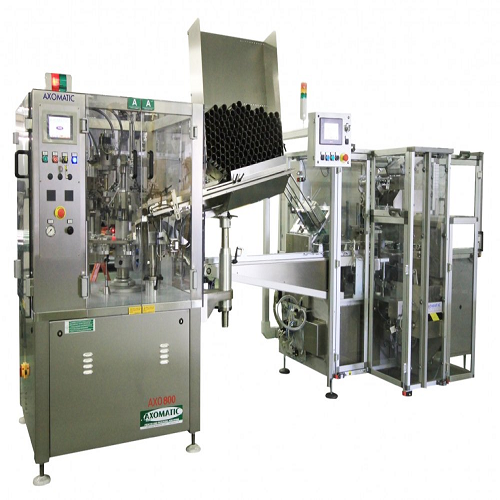
Filling, capping, labeling line for hair color products
Streamline your hair color production with an integrated line tha...

Linear filling and capping for stable bottles
Enhance your production efficiency with a solution designed for precise liqu...
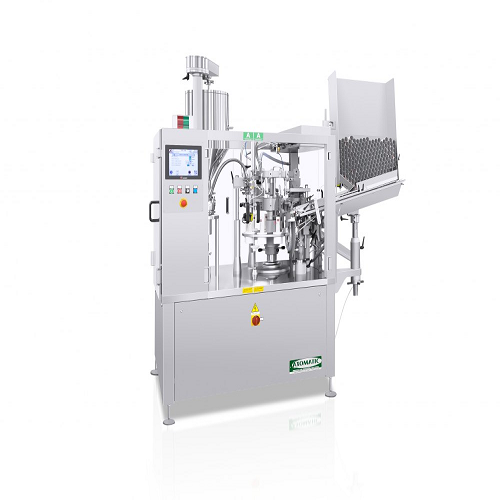
Automatic tube filling and closing solution
Optimize your production line with a high-speed machine for precise tube filli...
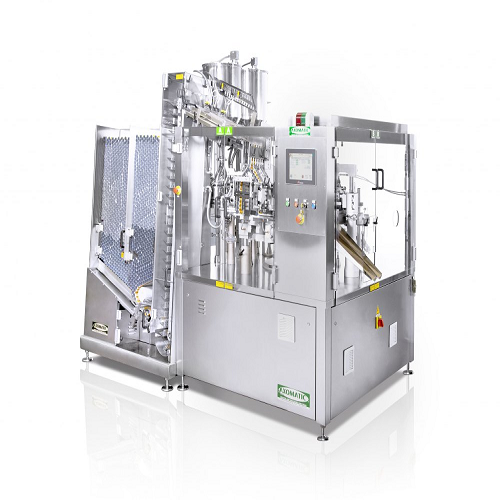
Automatic tube filling and closing system
Enhance your packaging efficiency with a high-speed tube filling and closing sol...
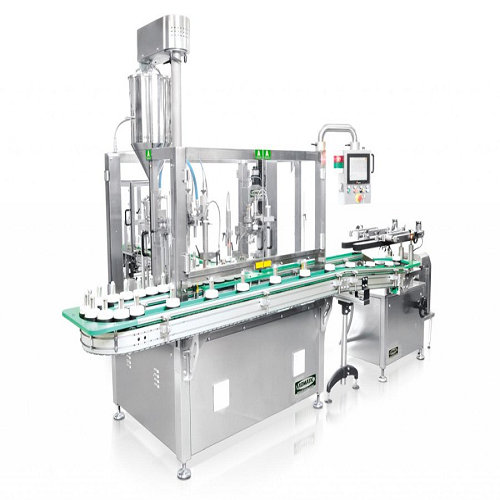
Alternate movement bottle filling and capping system
Enhance your production line with a versatile filling and capping so...
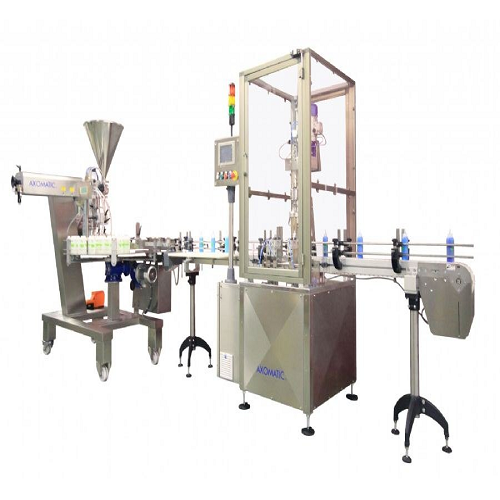
Automatic bottles and jars filling and capping line
Streamline your liquid product packaging with this high-speed solutio...

Sterile filling line for liquid and powder
Achieve seamless integration of filling, sterilization, and packaging with this...
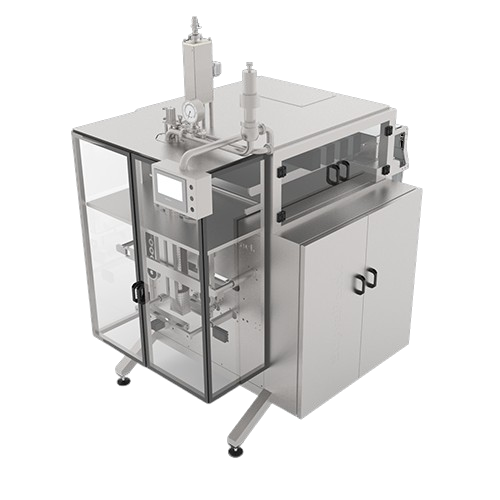
Ultra-clean vertical bag filler for viscous and particle-containing products
Streamline your viscous product packaging...
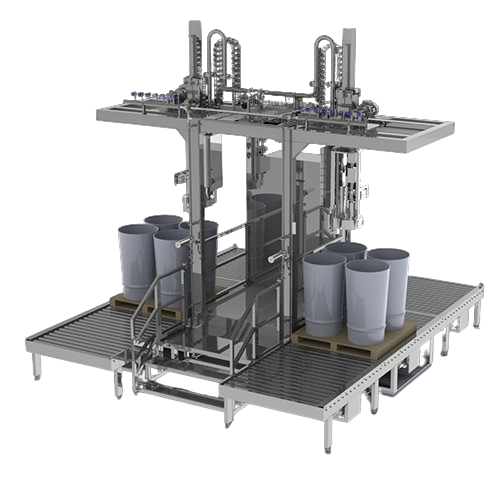
Aseptic filler for bag in drum or box
Enhance product shelf life and maintain quality without preservatives by employing as...
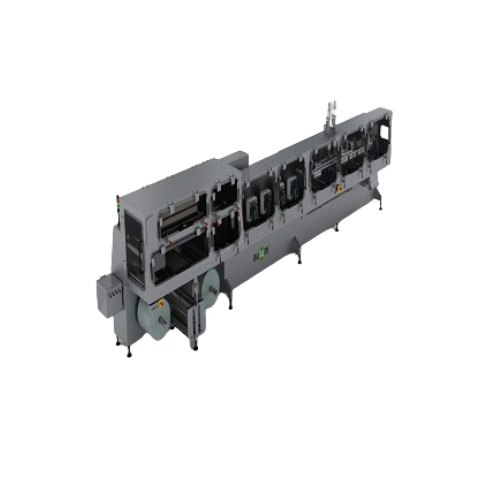
Aseptic linear doypack filler
Ensure extended shelf life and preserve quality in liquid food products with this high-speed a...
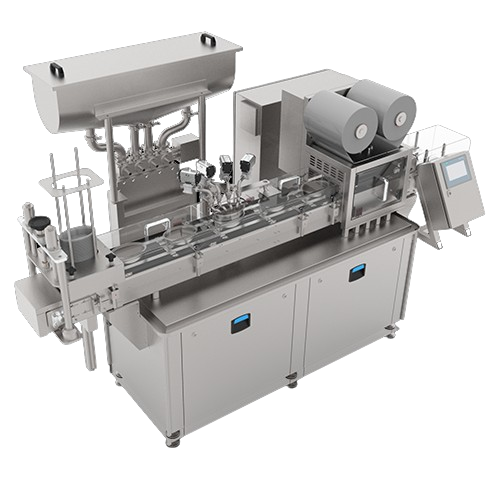
Linear filler for preformed containers
Streamline your packaging process with a compact solution that ensures precise filli...
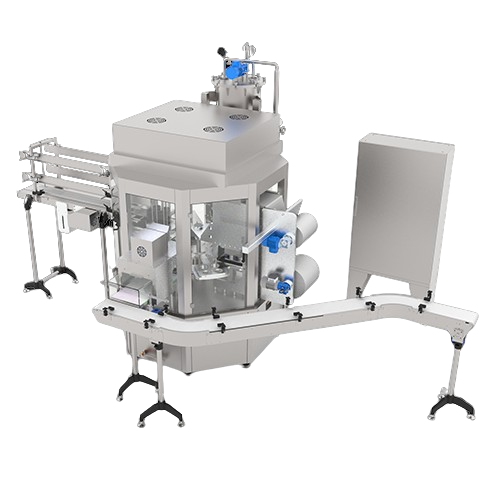
Rotary filler for preformed containers
Ensure microbiological safety and extended shelf life for your liquid products with ...
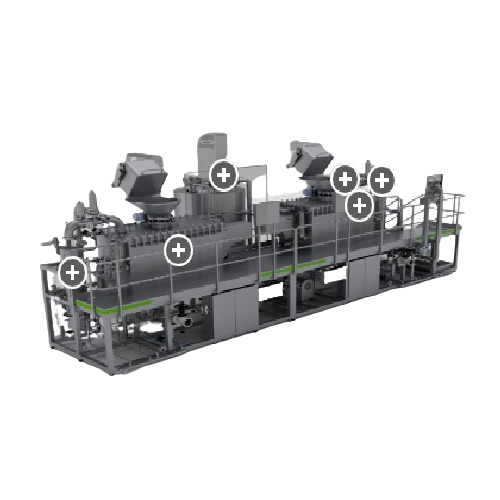
Aseptic cooking and filling line with two reactors
Streamline your production with a versatile line that combines high-ef...
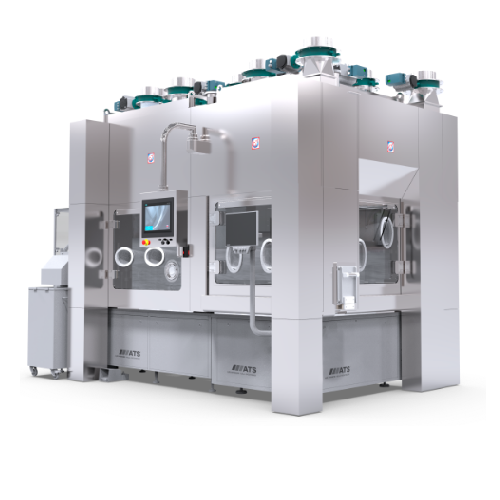
Robotic filler for aseptic pharmaceutical packaging
Effortlessly manage complex aseptic filling tasks with a system desig...
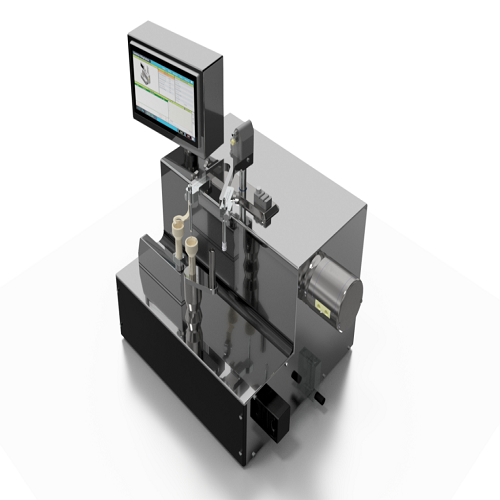
Tabletop vial and syringe filling system
Ensure precise dosing and maintain sterility in small batch production with a comp...
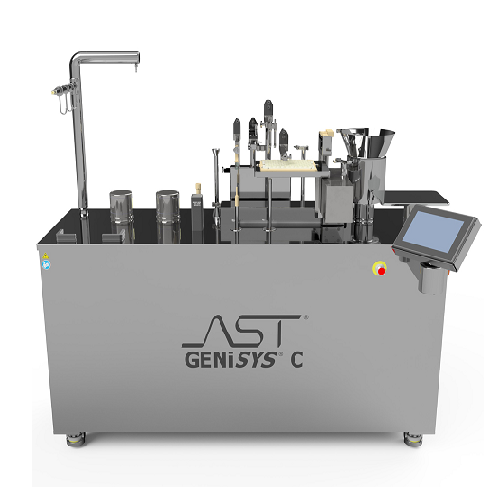
Automated aseptic filling and closing system for vials and syringes
Optimize small-batch production with precision fill...
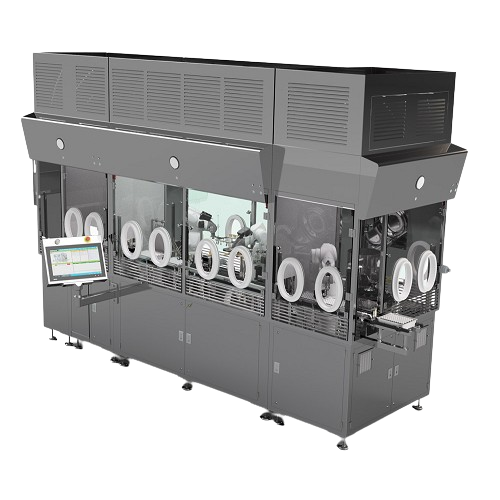
Aseptic small batch filling and closing system
Optimize your small-batch aseptic processing with this versatile system, de...
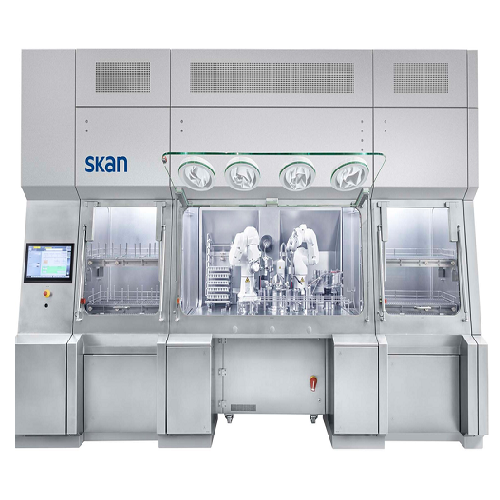
Aseptic vial filling system for gene therapy products
Elevate the sterility of your fill-and-finish process with a high-s...
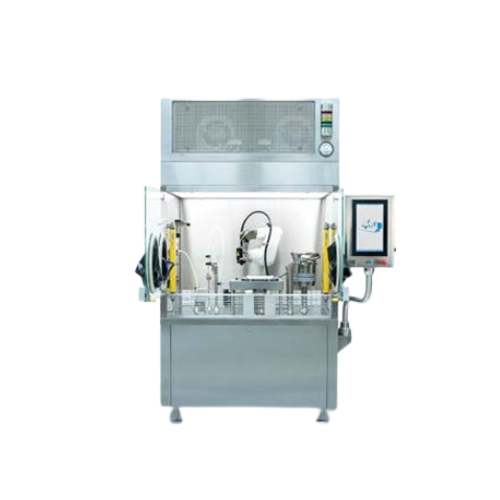
Aseptic filling line for biopharmaceuticals
Streamline your aseptic filling process with precision dosing and minimal spac...
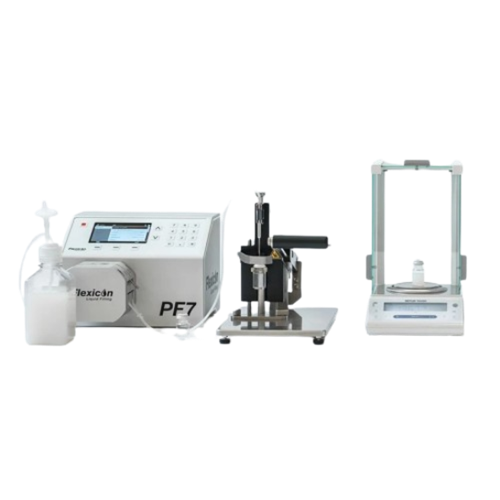
Aseptic filling station for small batch processes
Streamline small batch manufacturing with a tabletop filling station th...
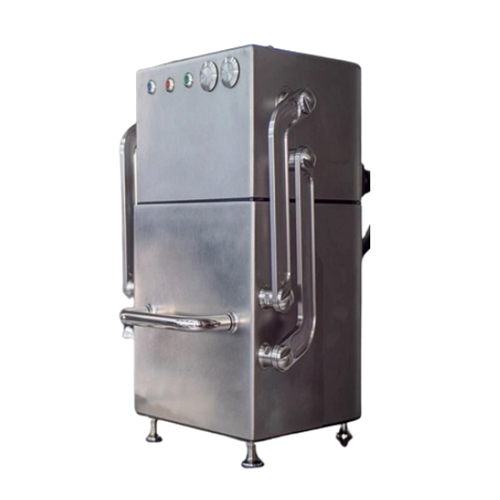
Aseptic filling isolator for small cgmp batches
Guarantee aseptic integrity for small-scale batches with this isolator, of...
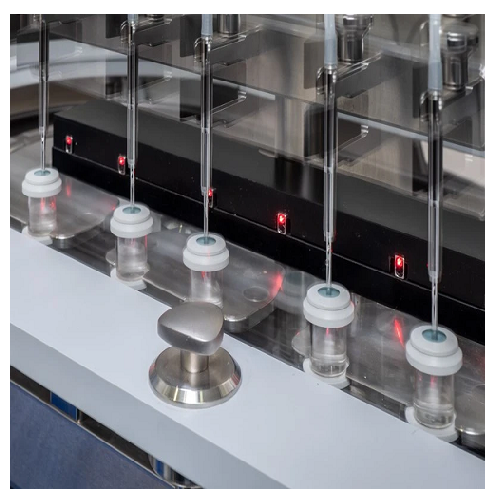
Aseptic filling line for biopharmaceutical products
Achieve precision and sterility in high-speed liquid filling operatio...
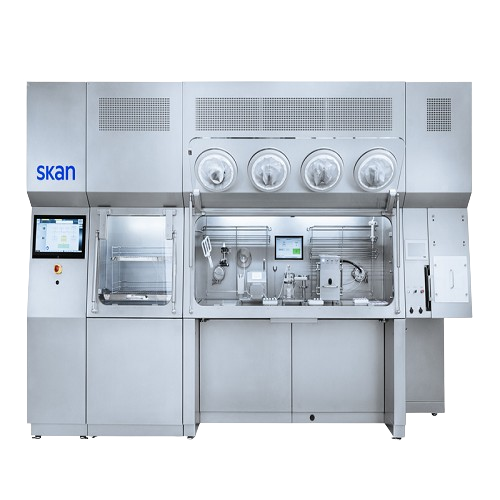
Aseptic filling solution for small cgmp batches
Ensure sterile and efficient filling of small-volume parenterals while mai...
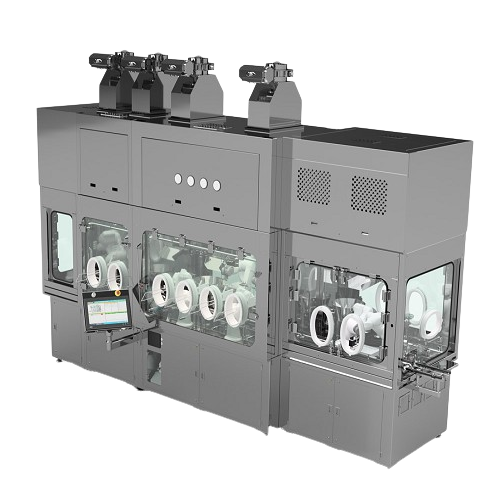
Aseptic small / medium batch filling and closing system
Ensure sterility in drug production by seamlessly integrating a v...
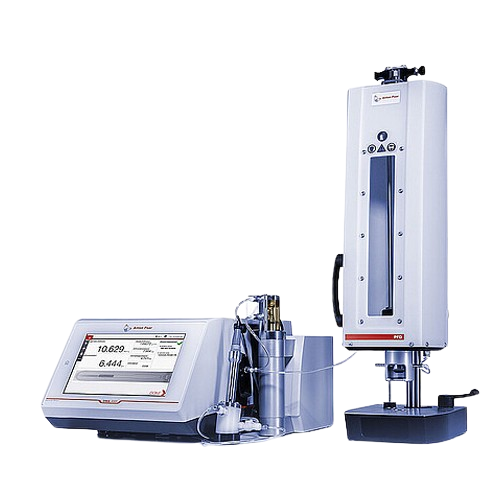
Co2/o2 beverage filling device
Ensure precise beverage analysis by maintaining carbonation integrity with a system that tran...
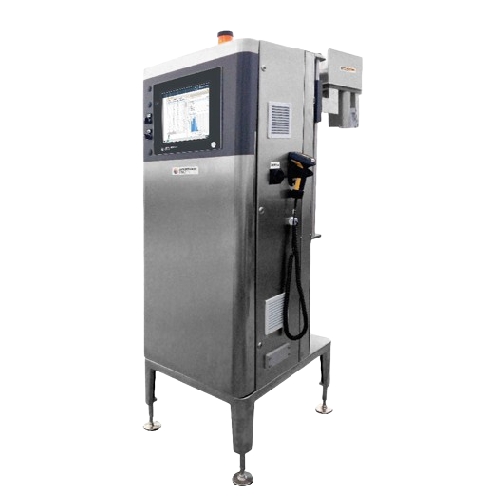
Fill level inspection system for beverage bottling
Ensure compliance and optimize quality control with a system that accu...

Multipurpose filling and forming solutions for dumplings
Enhance your food production with versatile equipment that trans...
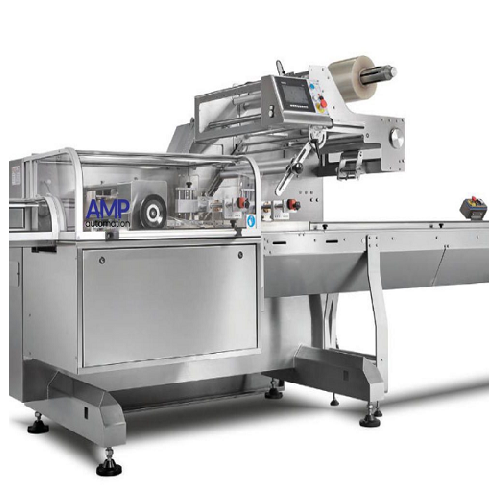
Pillow bag horizontal form-fill-seal solution
Optimize production efficiency with seamless integration of continuous, high...
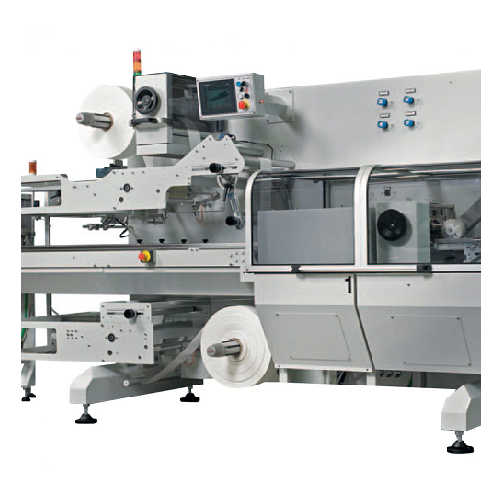
4-side seal horizontal form-fill-seal packaging system
Streamline your confectionery and snack packaging with high-speed,...

Linear big bottle water filling solution
Streamline your large-format water bottling process with integrated washing, filli...
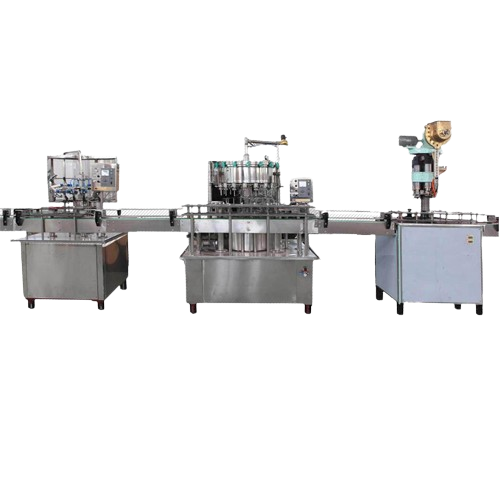
Small bottle linear type beverage filling production line
Optimize your bottling efficiency with a high-speed solution d...
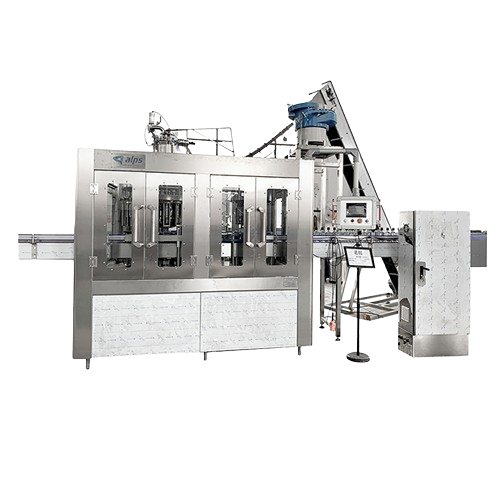
Glass bottle carbonated soft drink washer, filler, and capper
Streamline your bottling process with this machine that se...
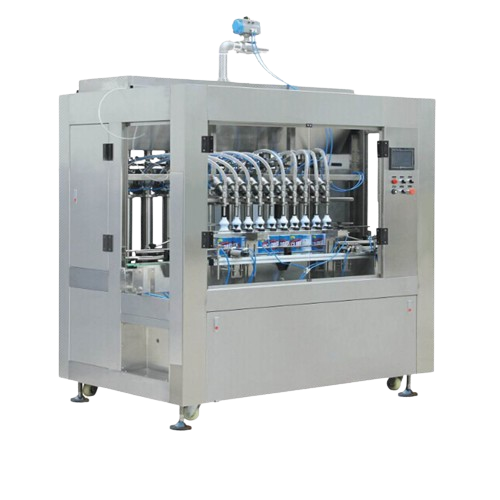
Automatic detergent shampoo filling solution
Streamline your filling process with precise volume control, achieving consis...
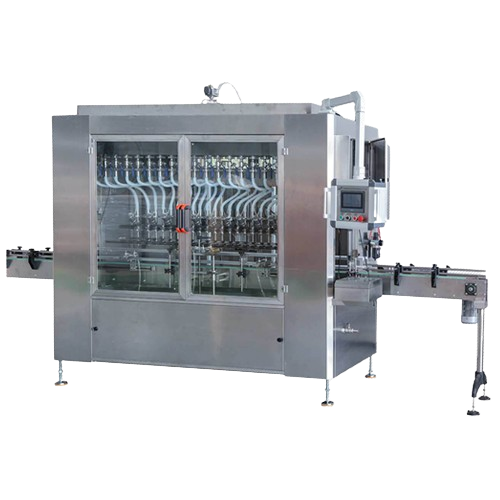
Automatic edible oil filling & capping solution
Streamline your liquid packaging operations with precise, high-speed filli...

High-capacity carbonated drink filling system
Optimizing your carbonated beverage production, this high-speed filling syst...
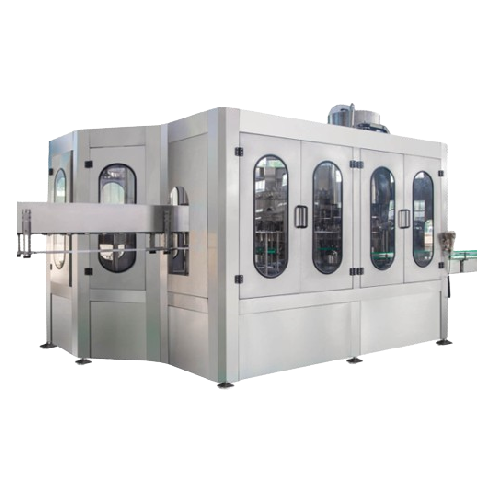
Automatic mineral water filling system
Optimize your bottling line with a machine designed for high-speed washing, filling,...
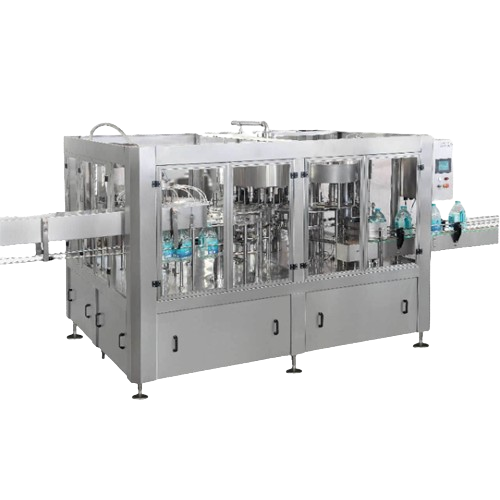
Large bottle water filling system
Streamline your bottled water production with an integrated solution that efficiently was...
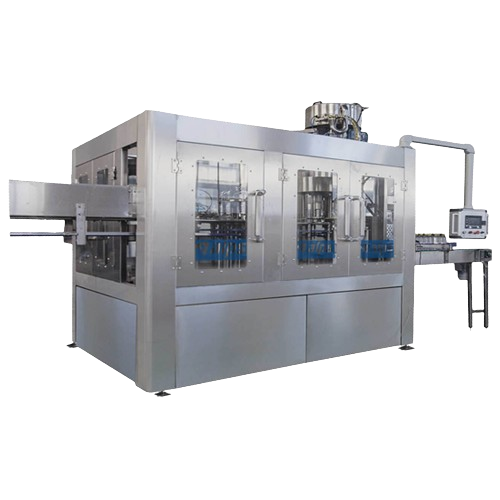
Automatic mineral water filling system
Enhance your bottling line with an advanced solution that seamlessly integrates wash...
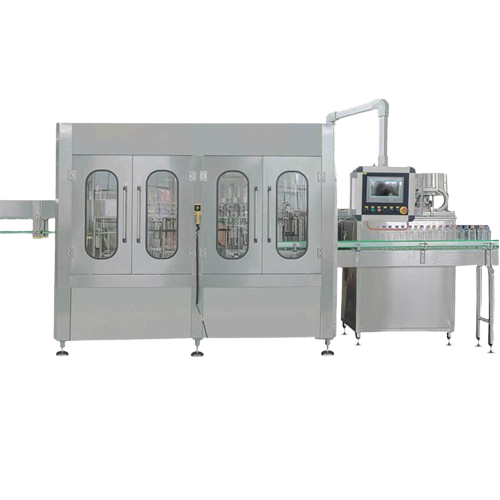
Carbonated drink filling solution for Pet bottles
Optimize your carbonated beverage production with an all-in-one filling...
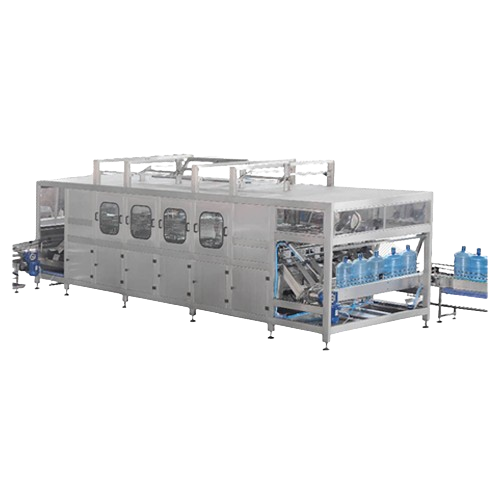
5 gallon water filling system
Streamline your bottling process with this integrated system, expertly combining rinsing, fill...
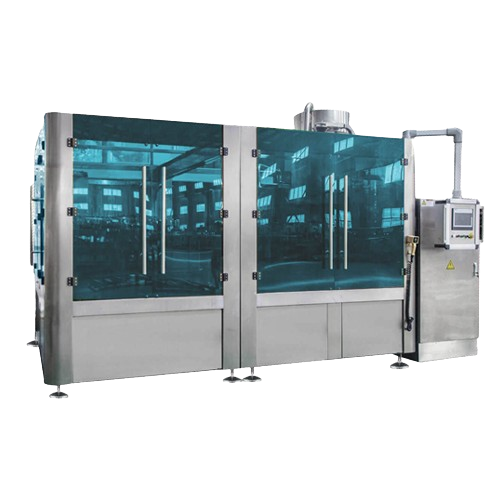
8000bph fruit juice filling system
Optimize your beverage production line with a high-speed fruit juice filling system, des...
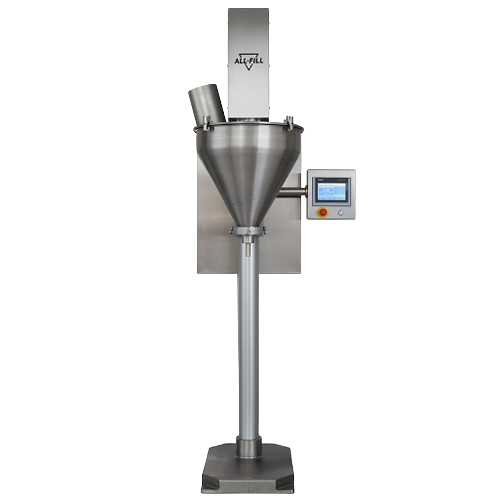
Volumetric filler for bags and rigid containers
Optimize precision filling of powders and granules with a versatile soluti...
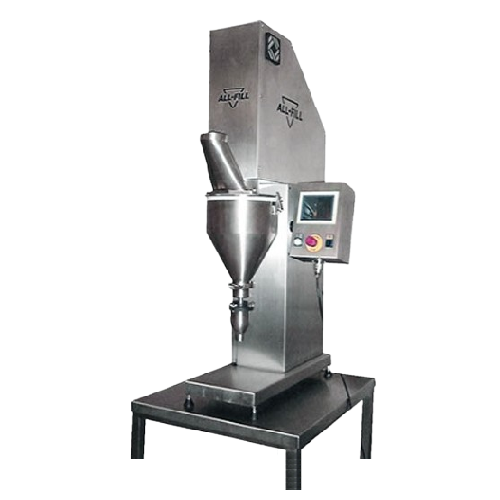
Miniature auger filler for precise powder filling
Achieve precision filling with a compact, bench-top auger solution desi...
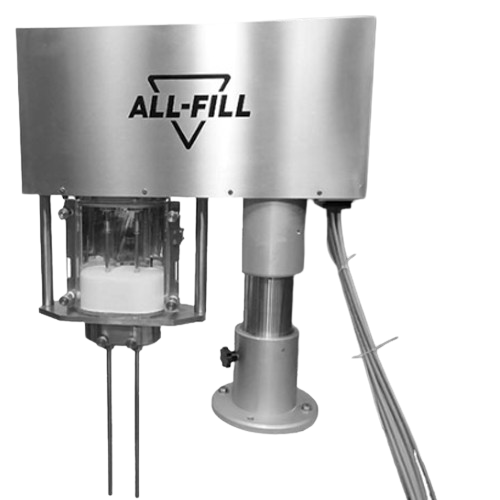
Multi-fill powder filling system
Achieve precise and consistent filling for your powdered and granulated products with a mod...
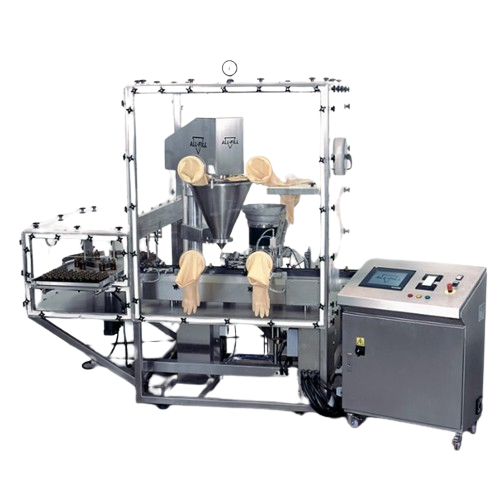
Special purpose auger filling systems for diverse industries
For manufacturers handling precise dosing, our advanced aug...
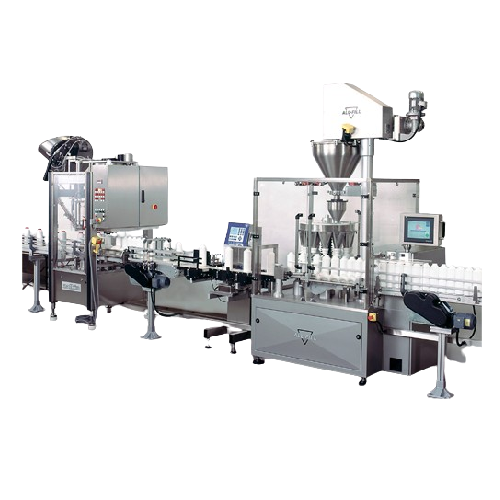
Turnkey filling lines for packaging solutions
Optimize your production line with our turnkey filling solutions, designed t...

In-line filling system for various container sizes
Streamline your production with versatile in-line filling solutions th...
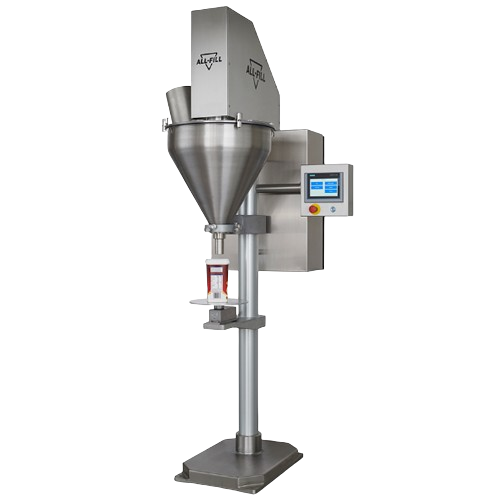
Gravimetric filling solution for inconsistent density products
Achieve precise weight accuracy in your filling processes...
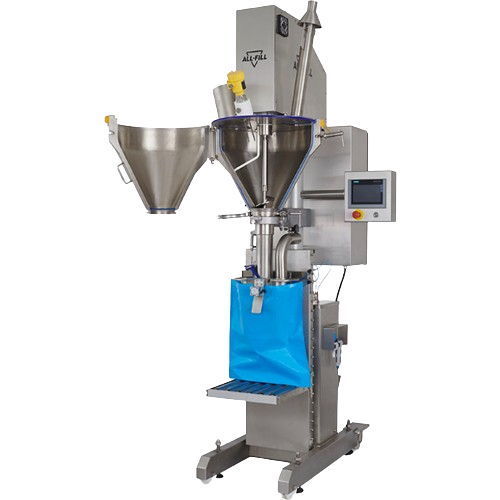
Industrial auger sack filler for large bags
Designed to efficiently fill large bags and sacks, this advanced filling machi...
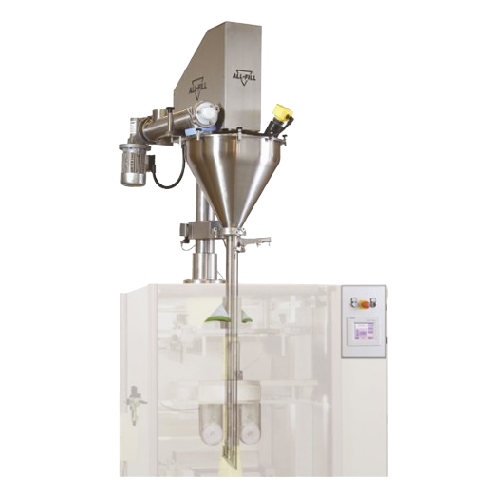
Vertical form fill seal filling system for auger applications
Effortlessly integrate precise powder and granule filling ...
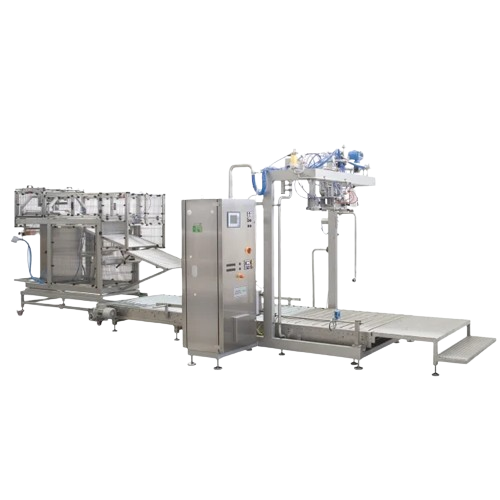
Flexible bag-in-box filler for liquid and viscous products
Optimized for flexibility and efficiency, this bag-in-box fil...
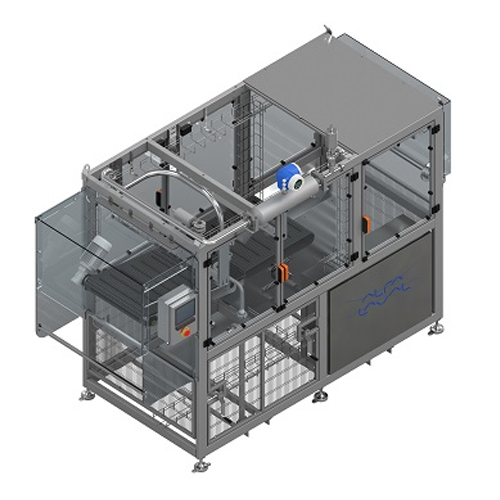
Bag-in-box filling solution for non-aseptic products
Maximize your production line’s efficiency with a high-speed f...
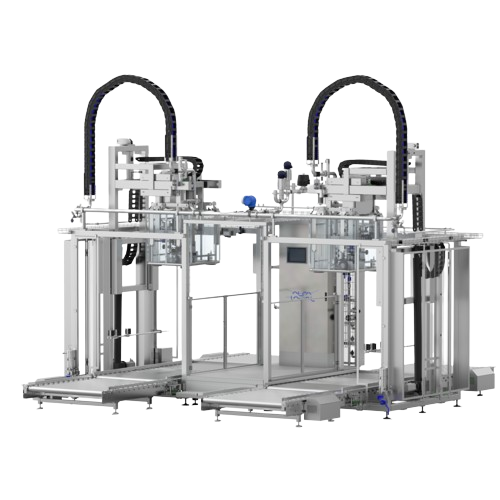
Thousand-litre aseptic filler
Ensure the aseptic filling of bulk liquid and viscous food products, reducing contamination ri...
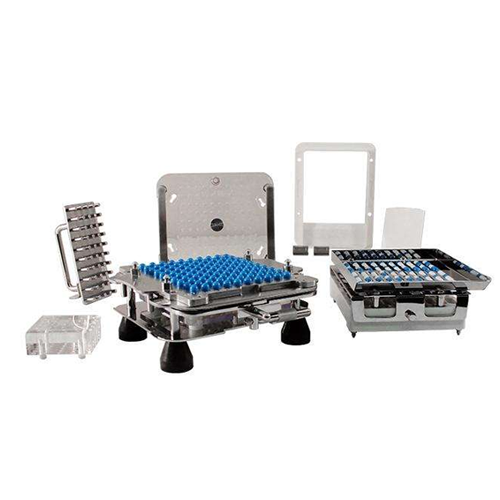
Capsule filling solution for small to medium batch sizes
Achieve precise and efficient capsule filling up to 3,400 units ...
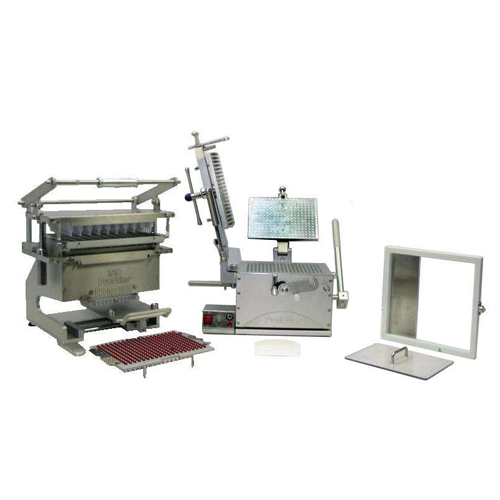
Capsule filling system for pharmaceutical production
Efficiently fill and lock capsules of various sizes with exceptional...
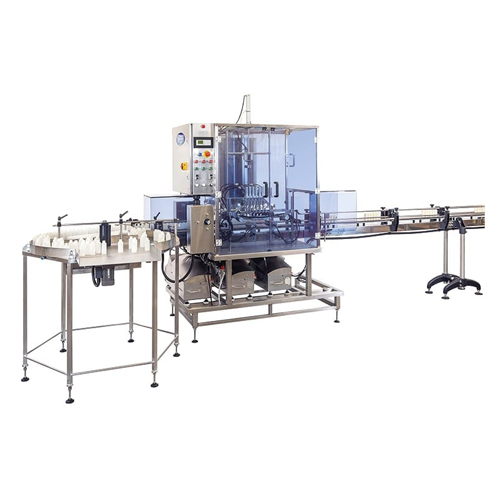
Automated bottle and jar filling solution
Streamline your production and minimize waste with a versatile filling solution,...
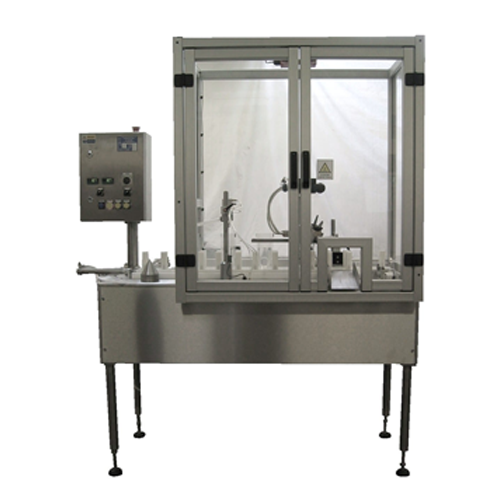
Bag and pouch filling solution for liquid products
Efficiently package diverse liquid products with precision and speed, ...
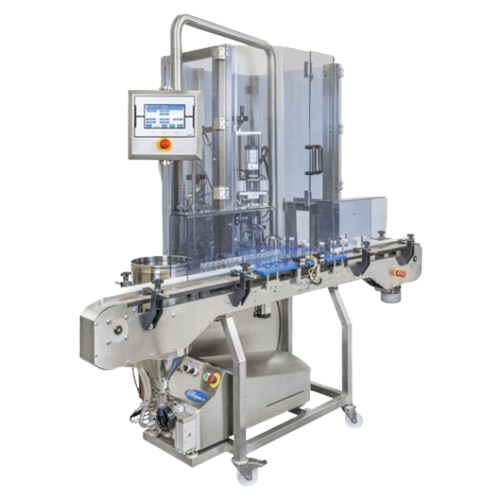
Filler and capper for bottles and jars
Optimize your production with a compact filling and capping solution that delivers f...
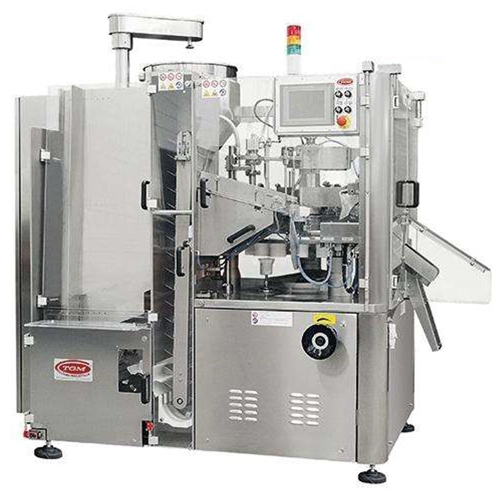
Tube filler & sealer for metal and plastic tubes
Streamline your production line by efficiently filling and sealing metal ...
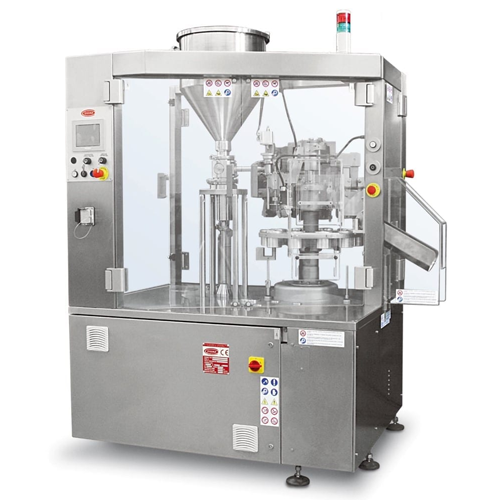
Efficient tube filler and sealer
Optimize your production line with a semi-automatic tube filling and sealing solution, desi...
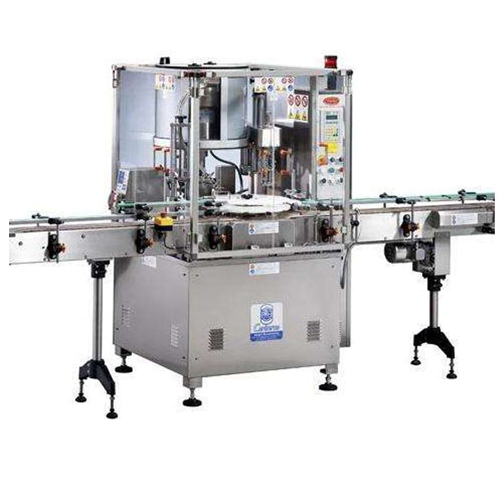
Compact filler and closer for vial processing
Efficiently streamline your vial filling and closing processes with a compac...
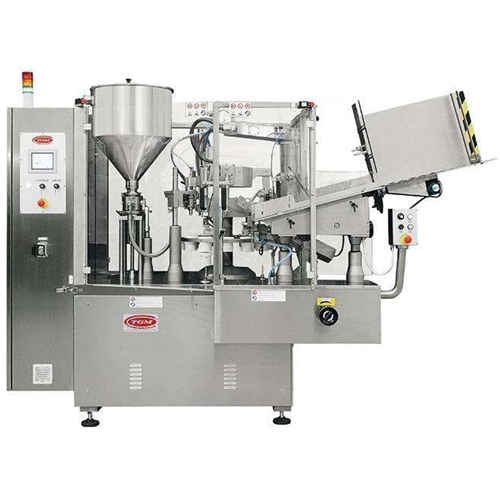
Tube filling and sealing for metal and plastic tubes
Achieve precise tube filling and sealing with high speed and efficie...
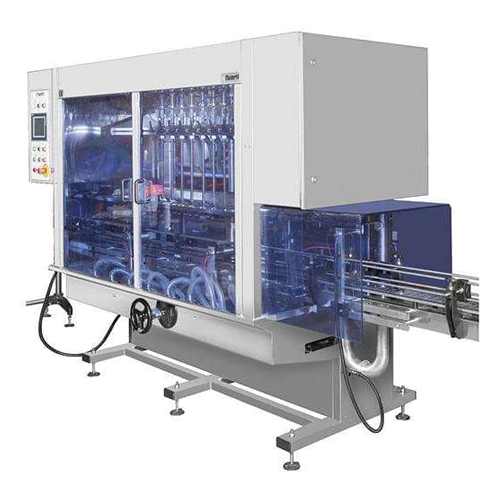
Automatic flowmeter filler for liquid packaging
Streamline your liquid production with precise filling capabilities, reduc...
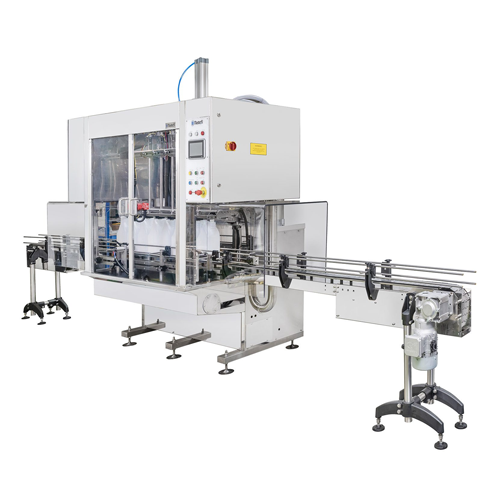
Automatic volumetric filler for liquid products
Optimize your production with this high-precision volumetric filler, desig...

Semi-automatic flowmeter boom filler for large volume containers
Effortlessly handle large volume liquid filling with pr...
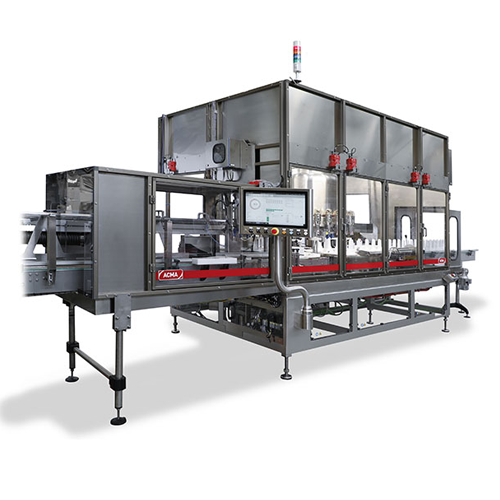
Rotary filler capper for personal care products
Ensure consistent filling and capping of liquid products with high-speed p...
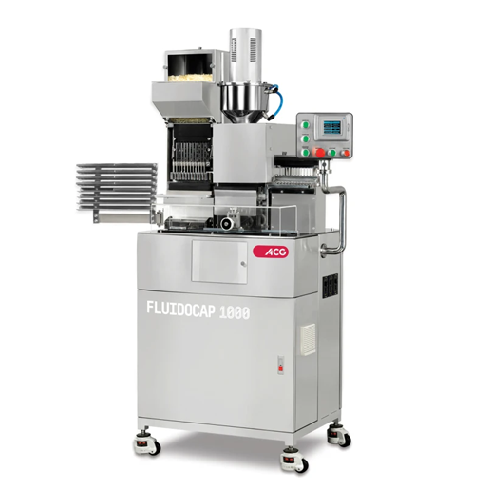
Liquid capsule filling for r&d and pilot-scale production
Optimize liquid capsule production with a compact machine that...
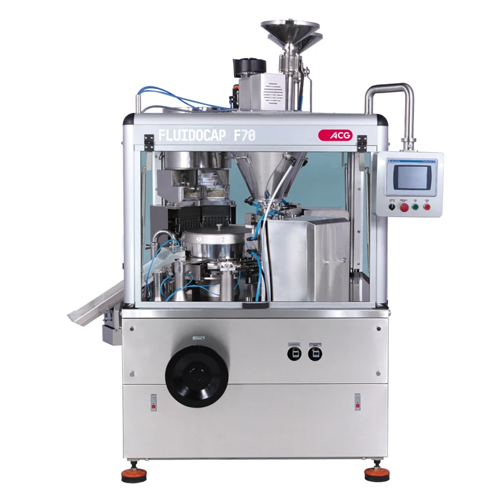
Liquid filling system for hard capsules
Easily fill two-piece hard capsules with liquids, pastes, and suspensions with prec...
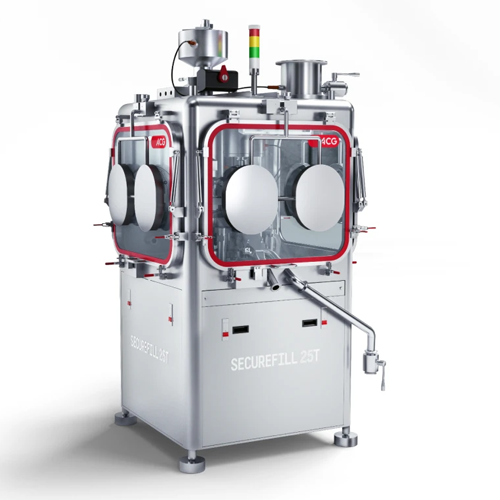
Containment capsule filler for highly potent drugs
Achieve complete operator safety while encapsulating potent pharmaceut...
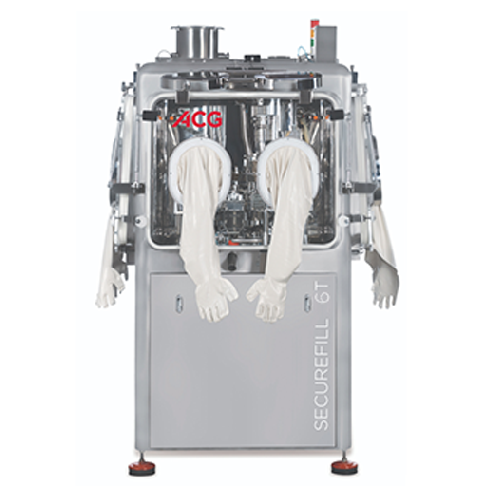
Containment capsule filling system for highly potent drugs
Ensure operator safety while filling capsules with high-poten...
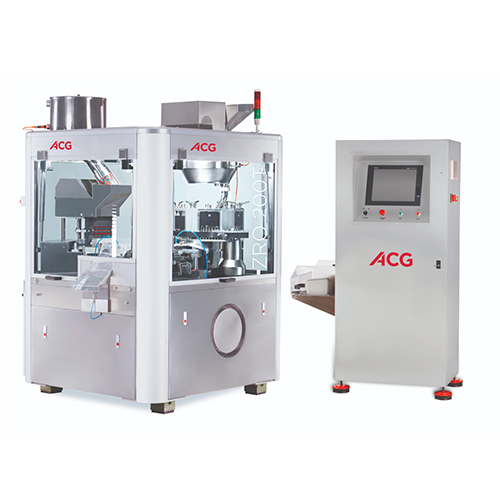
High-speed capsule filler for large batch production
Achieve higher yields and reduce powder waste with a capsule filling...
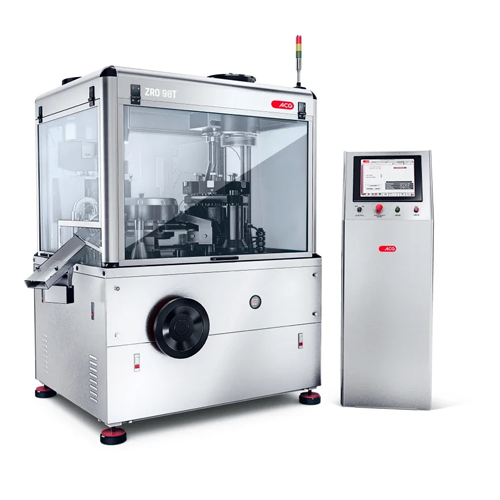
Capsule filler for high-speed, dust-free capsule production
Enhance your production efficiency with a solution designed ...
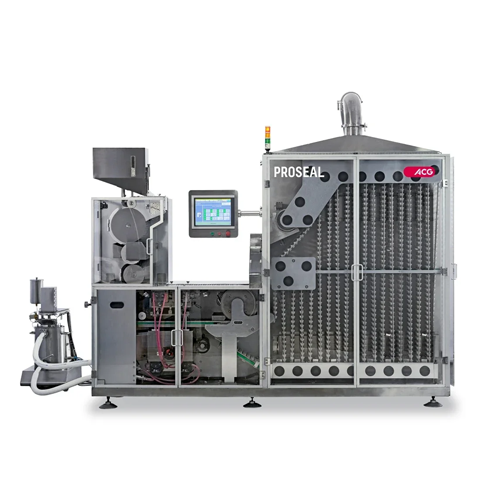
Capsule band sealer for liquid-filled hard capsules
Seamlessly seal liquid-filled hard capsules to enhance product integr...

Auto-indexing filler for aqueous solutions and light oils
Streamline your bottling process with this six-head filler, pe...
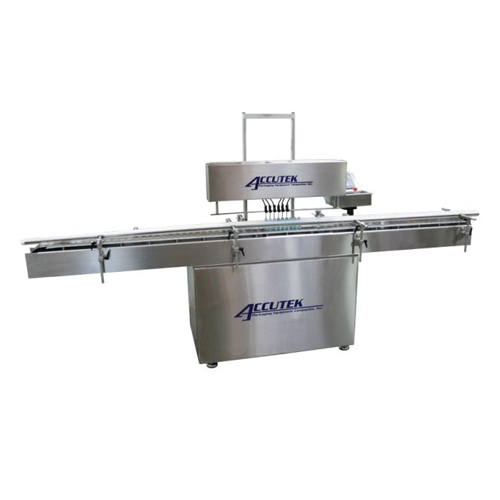
Automatic timed flow volumetric filling machine
Streamline your liquid packaging process with precise volumetric filling o...
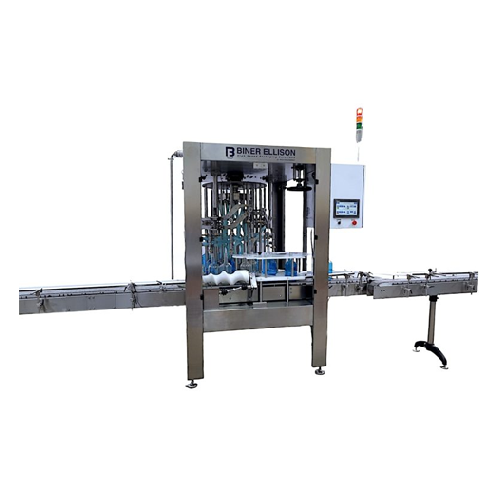
Rotary overflow filler for non-carbonated liquids
Achieve precise fill levels effortlessly with a high-speed rotary overf...
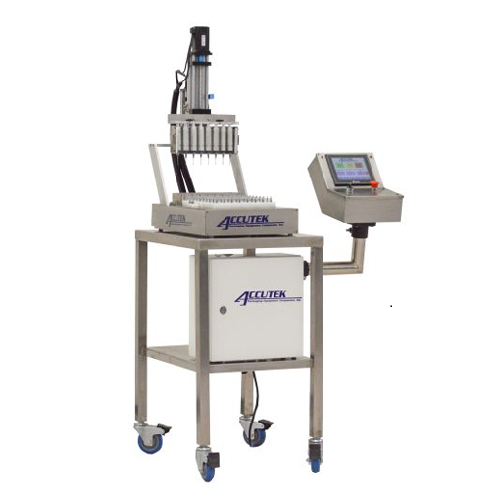
High precision automatic mini dose filler
Achieve unparalleled precision when filling small volumes, from 0.1 ML to 200 ML...

Rotary volumetric filling solution for viscous products
Achieve precision in volumetric filling with a machine designed f...
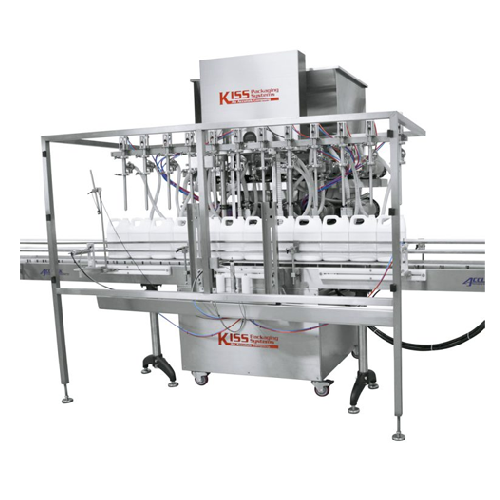
Automatic positive displacement filler for various liquids
Achieve precision and versatility in liquid filling operation...
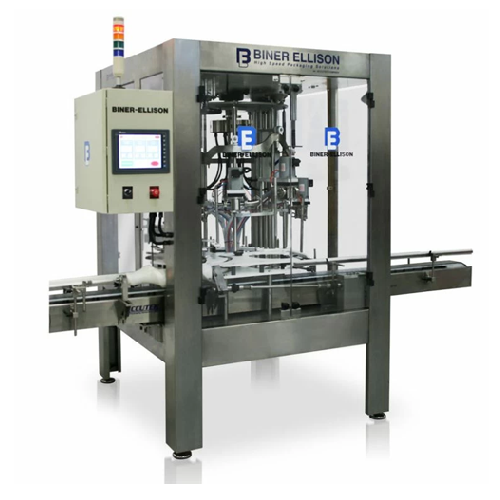
Automatic positive displacement bottle filler
Streamline your liquid filling operations with precision and flexibility, id...
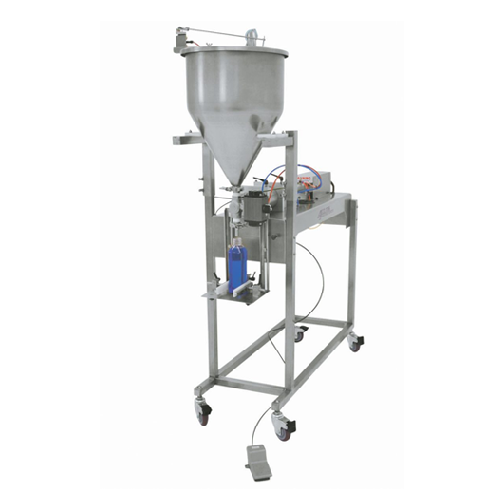
Semi-automatic volumetric piston filler
Achieve precise filling of diverse liquids and viscous products while minimizing wa...
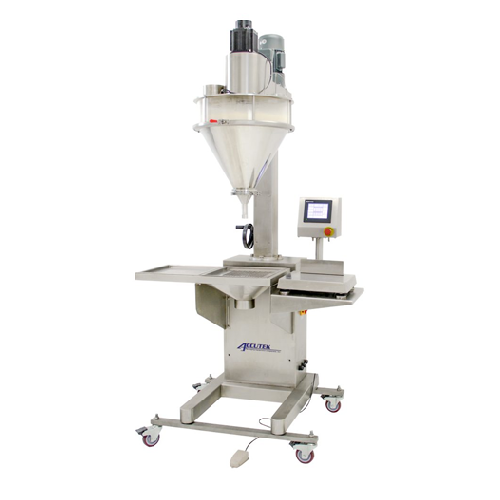
Powder filling machine for dry products
Achieve precision and consistency in filling dry powders and granules with a versat...
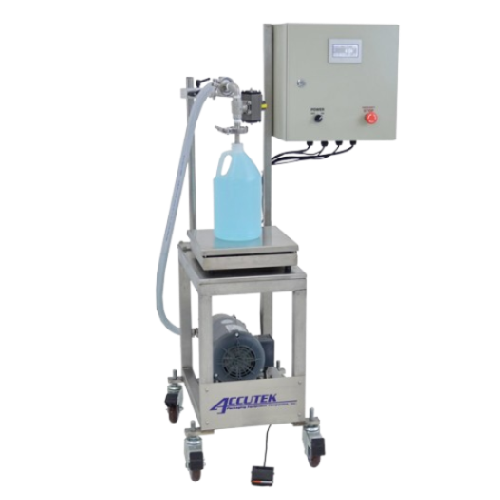
Accurate net weight filling for liquid and semi-liquid products
Ensure precise filling of diverse viscosities, from thin...
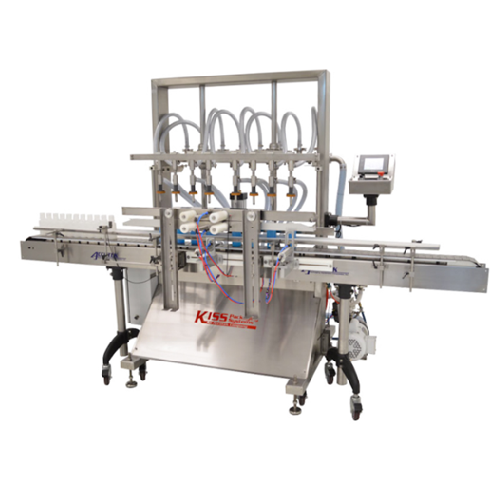
Automatic pressure overflow filler for low to medium viscosity liquids
Ensure consistent fill levels for low to medium ...
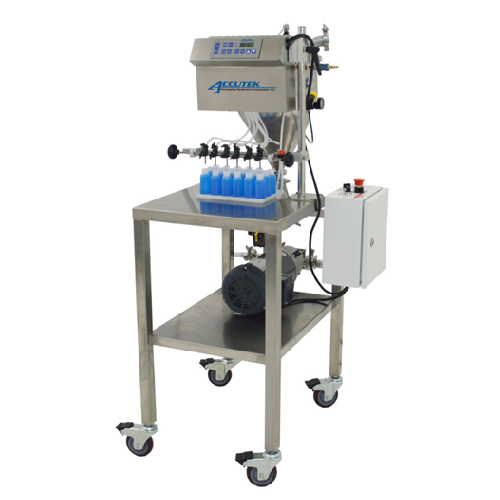
Semi-automatic timed flow filler for aqueous solutions
Handle diverse liquid filling needs with precision, from thin oils...

Semi-automatic overflow liquid filler
Optimize your production line with a reliable filling solution for low to medium visc...
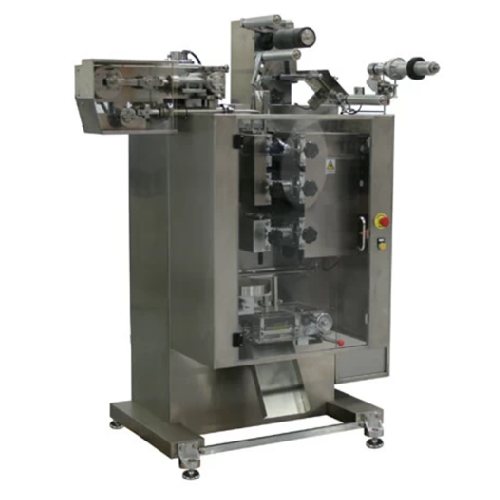
Form, fill, and seal system for single-use pouches
Achieve precise portion control and secure sealing with an integrated ...
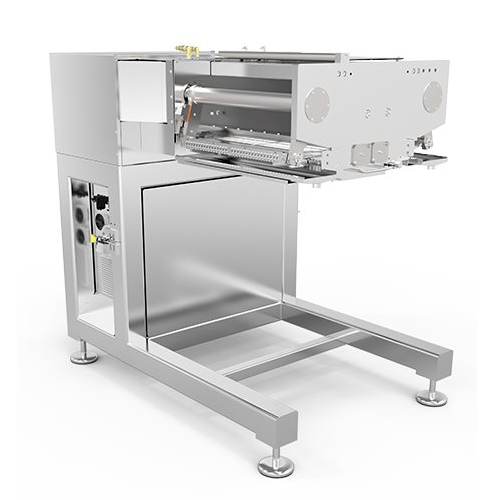
Depositing system for solid and filled chocolates
Enhance your chocolate production with a versatile depositing system, p...

Filling and weighing station for chocolate production
Ensure precise and efficient chocolate mass depositing with a stati...
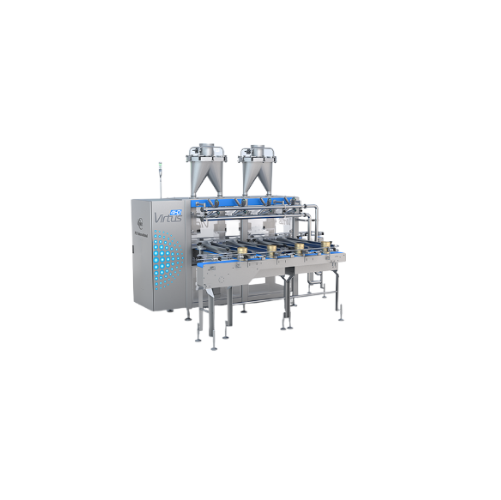
In-line vacuum powder filler
Optimize your production line with precise, contamination-free filling for nutritional powders,...
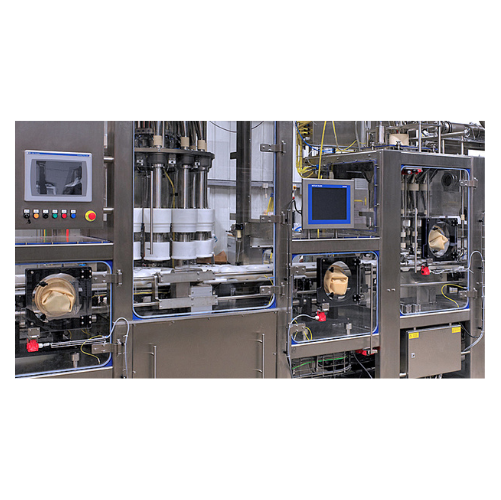
Vacuum powder filler for dairy and pharmaceutical products
Achieve precision and maintain product integrity with a versa...
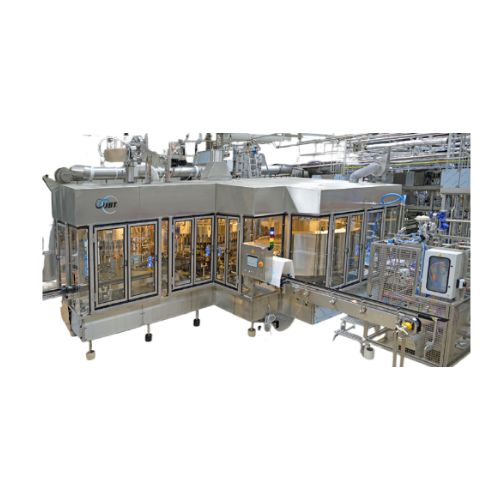
Rotary level filler for low to high viscosity liquid products
Ensure precise fill levels and enhance production efficien...
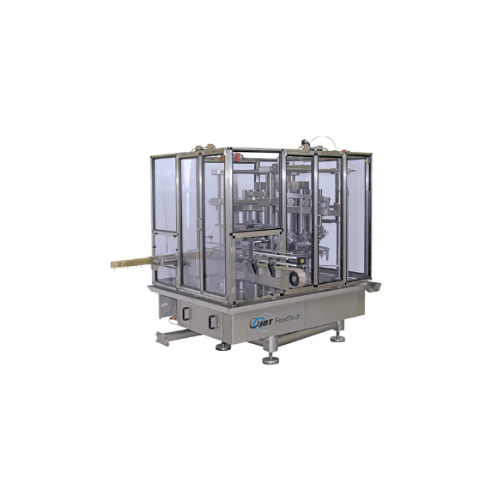
Volumetric piston filler for liquid and viscous products
Achieve precise volume control and enhance product integrity wit...
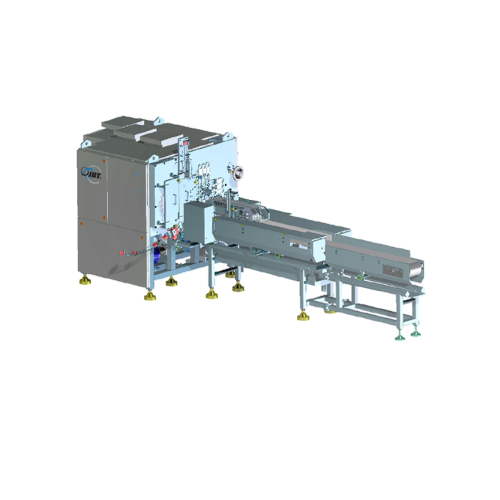
Automatic tuna can filler
Streamline your high-speed canning operations with precision-engineered fillers that maintain opti...
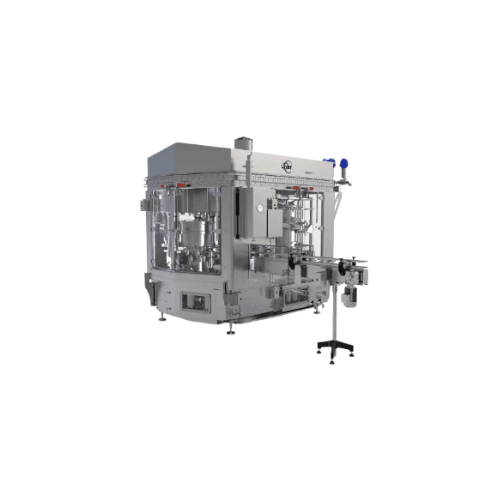
Rotary can filler and closer for metal cans
Achieve seamless integration in your production line with a solution that sinc...
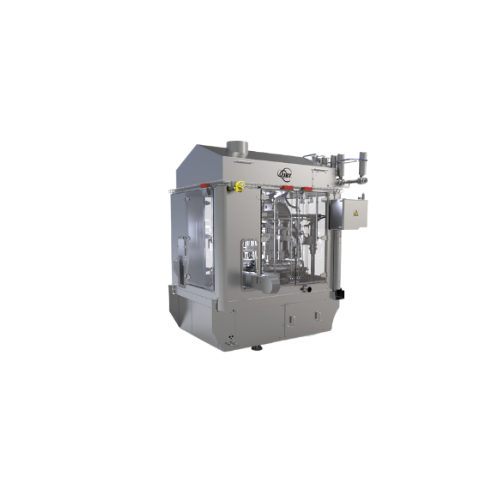
Volumetric filler for various food products
Achieve high precision and flexibility in your filling processes with a volume...
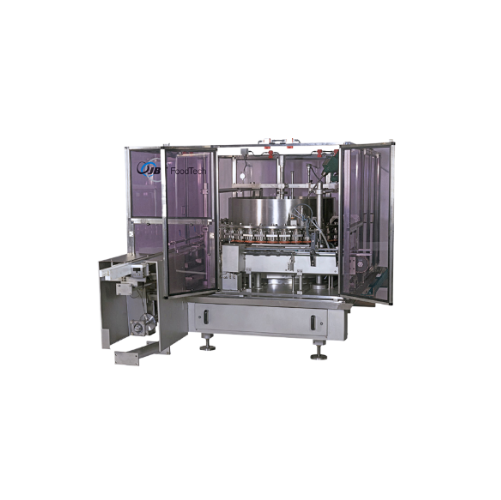
Vacuum filler for low viscous products
Achieve precise vacuum filling for liquid and granule products while effectively eli...
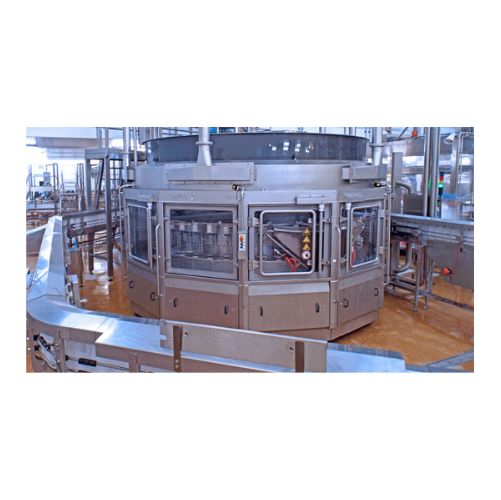
Industrial weight filler for bottles and jars
Achieve precise product filling with our weight filler system, expertly desi...
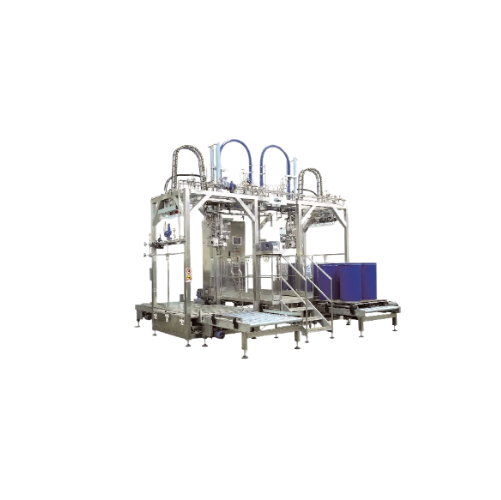
Aseptic filler for fluids, concentrates, and particulates
Optimize your fluid and concentrate filling process with a hig...
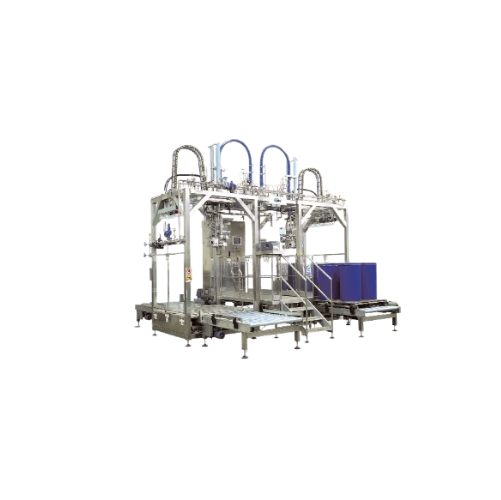
Aseptic filler for juices and beverages
Ensure sterile packaging with precision. This aseptic filler offers high-speed, con...
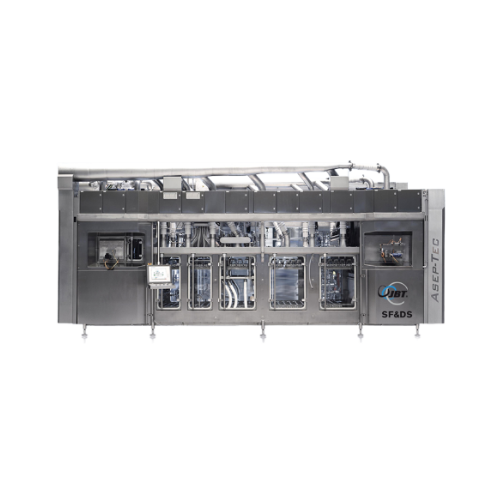
Aseptic filler for packaged dairy and beverages
Ensure product sterility and extend shelf life efficiently with high-speed...
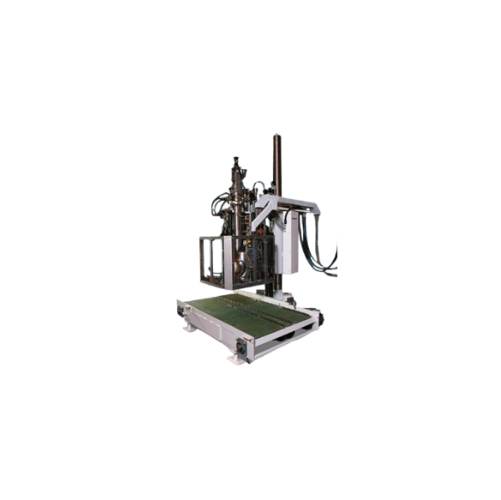
Aseptic bag filler for bulk containers
Eliminate spoilage events and ensure sterility in high-speed filling of bulk aseptic...
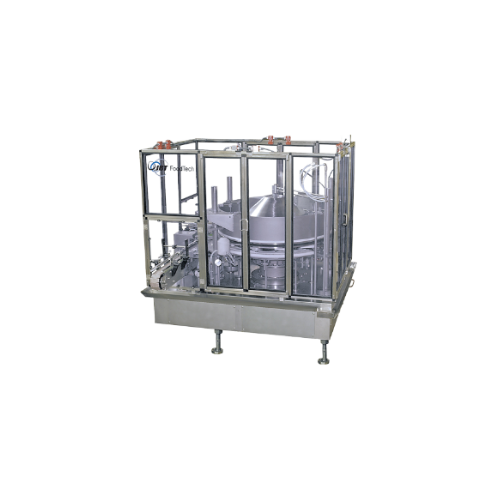
Granular filler for wide mouth containers
Ensure precise filling and minimize product loss with this granular filler, expe...
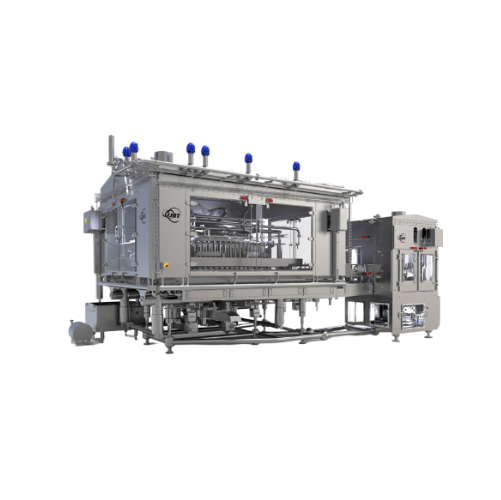
High capacity volumetric filler for pumpable products
When you need high-speed, precise filling for diverse liquid and sl...
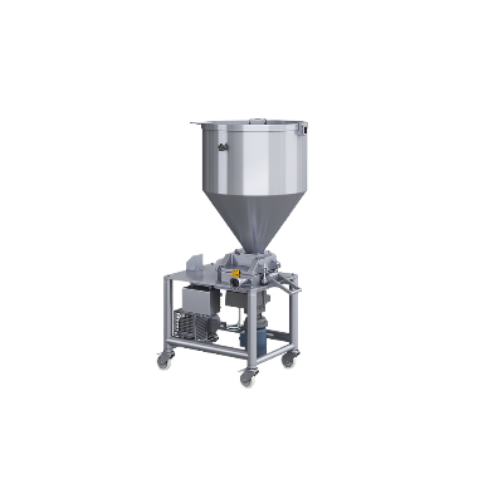
Creamy filling dosing system
Effortlessly dose creamy fillings into your production line with precision, ensuring chunk size...

Vertical form fill sealer for food packaging
Achieve high-capacity, flexible packaging for diverse food products with a ro...
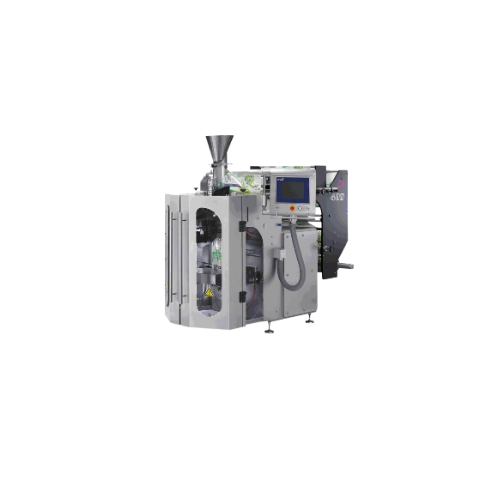
Vertical form-fill-seal packer for frozen vegetables
Efficiently streamline your packaging line with a versatile solution...

Hot fill gravity filler for beverages
Achieve precise hot filling with versatile gravity filling technology that maintains ...
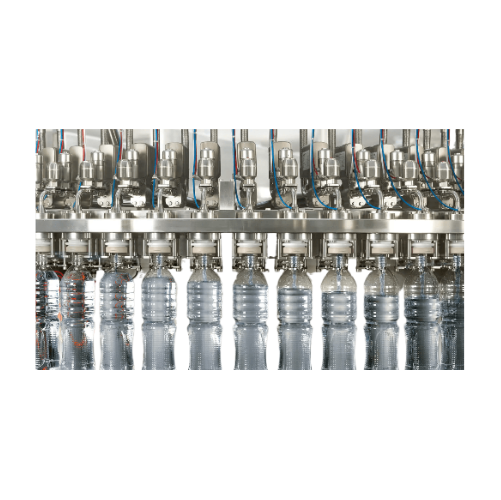
Rotary volumetric filler for still drinks
Optimize your bottling line with a versatile rotary volumetric filler, designed ...
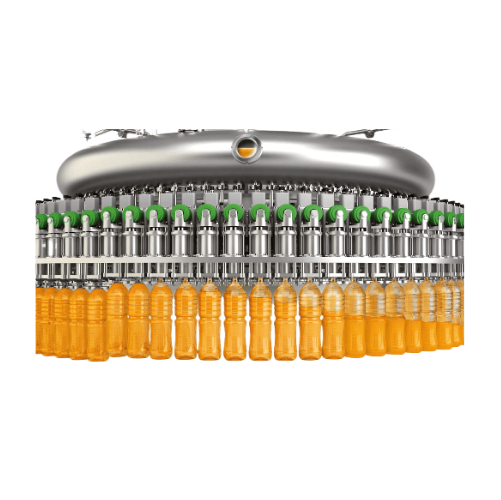
Bottle filler for still and carbonated drinks
Maximize efficiency in your bottling process by seamlessly filling both stil...
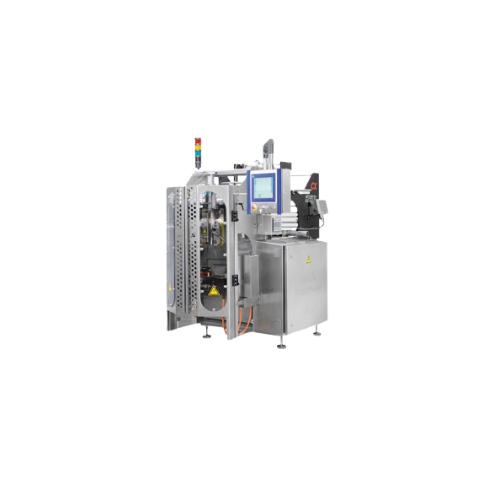
Vertical form fill sealer for high-speed packaging
Achieve consistent, high-speed packaging with flexible bag styles, per...
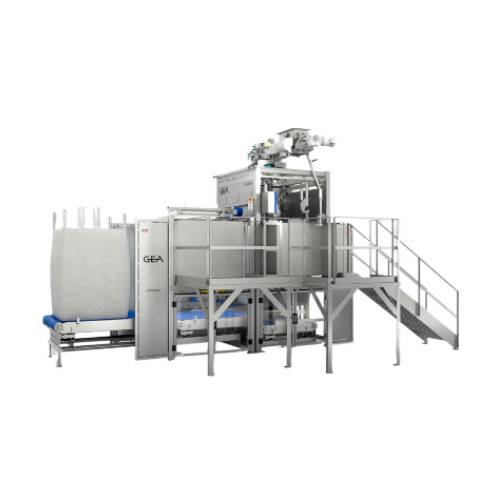
Bulk powder filler for food, dairy, and nutraceuticals
Optimize your bulk powder filling process with a system designed t...
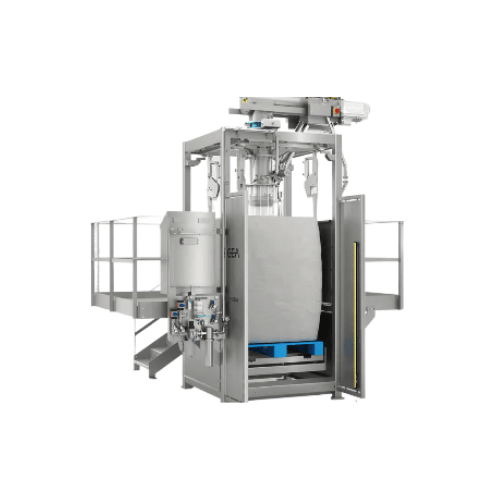
Low care bulk powder fillers
Optimize your production efficiency by accurately filling flexible bulk containers with dry pow...
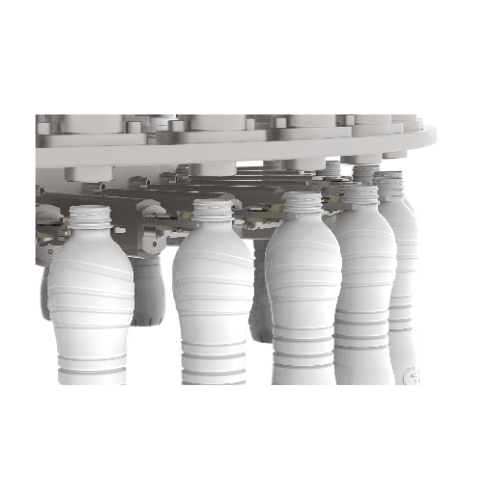
Hygienic filling system for short shelf life milk
Optimize your cold-chain distribution with a filling system engineered ...
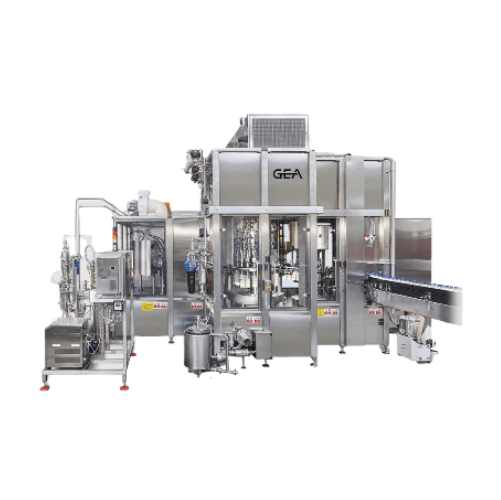
Esl beverage filling system
Ensure extended shelf life and maintain beverage quality with sterile filling and decontaminatio...
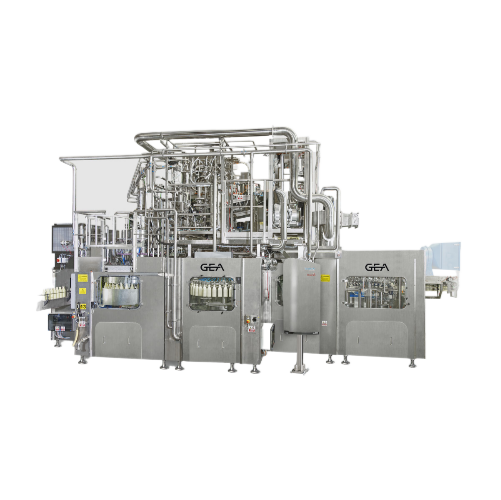
Cold chain filling system for sensitive beverages
Ensure extended shelf-life for liquid dairy and sensitive beverages wit...
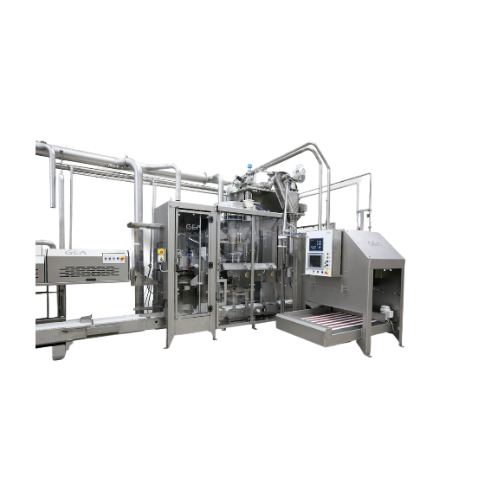
Inline automatic powder fillers for food and nutraceuticals
Ensure precise and efficient filling of sensitive powders in...
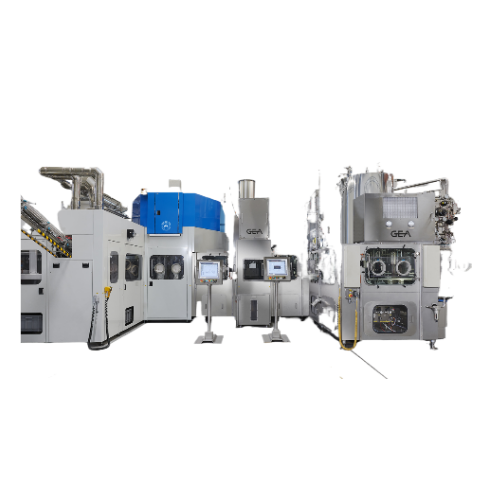
Aseptic blow fill system for beverage bottling
Designed for high-speed aseptic bottling, this system ensures sterility thr...
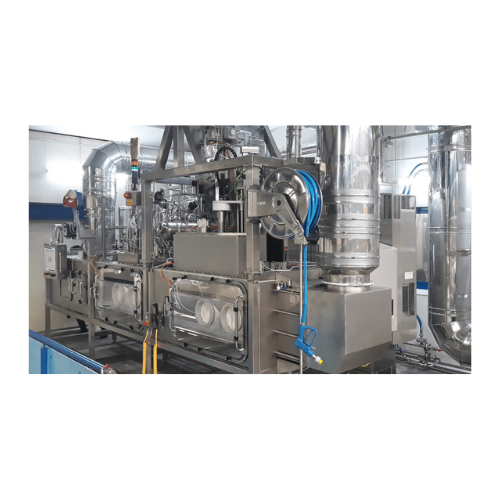
Aseptic filling system for sensitive beverages
Optimize your beverage production with an aseptic filling system that ensur...
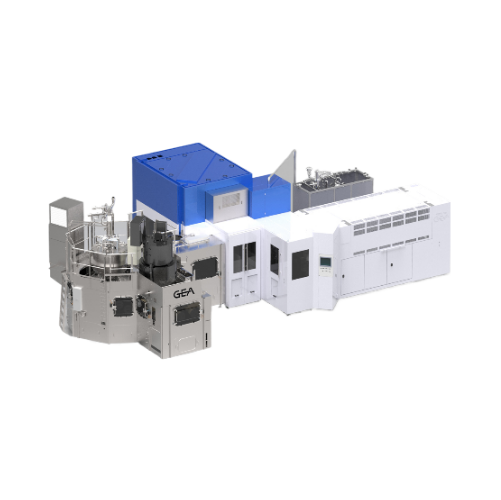
Decontamination blow fill system for beverages
Optimize your beverage production with a technology that integrates preform...
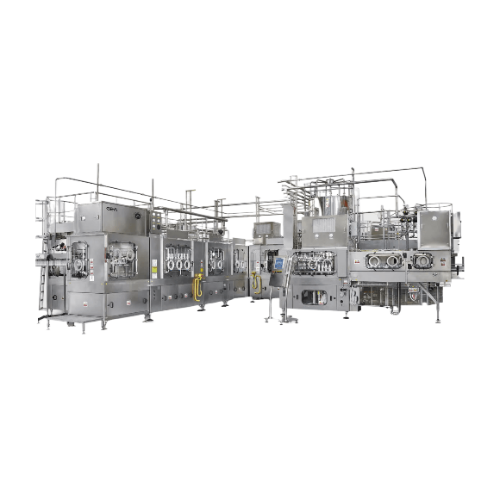
Advanced aseptic filling system for beverage bottles
Seeking a sterilization and filling system that maximizes sterilizat...
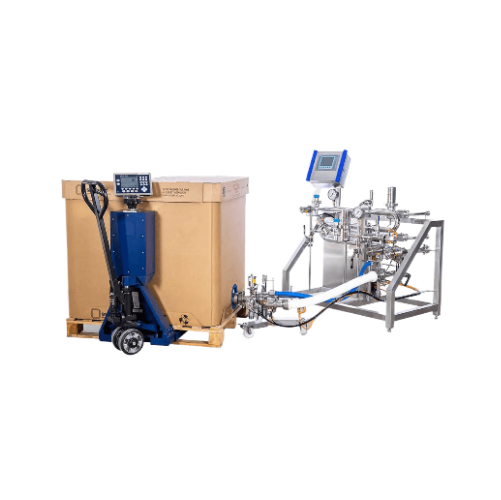
Aseptic filling system for bag-in-box containers
Ensure sterility and precision in filling aseptic liquid products, with s...
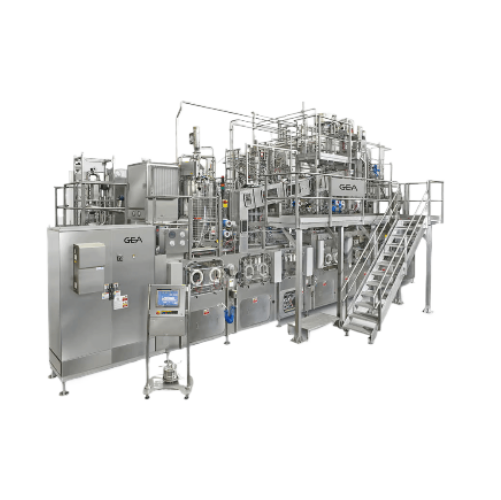
Aseptic filling for high and low acid beverages
Ensure aseptic integrity while maximizing operational efficiency with a co...
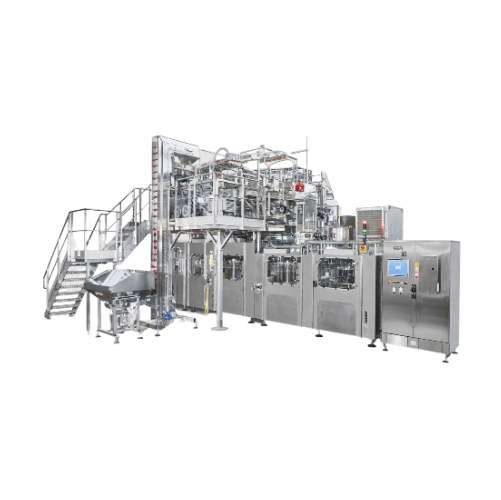
Aseptic filling system for milk-based drinks
Ensure sterile bottling of milk-based and sensitive beverages with this syste...
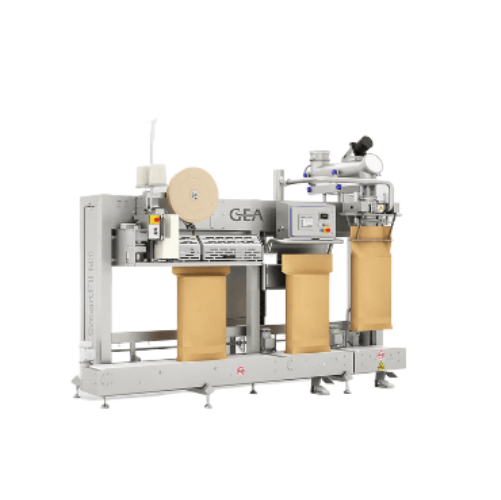
Semi-automatic powder filling system for food products
Achieve precise and flexible filling for food powders and granules...
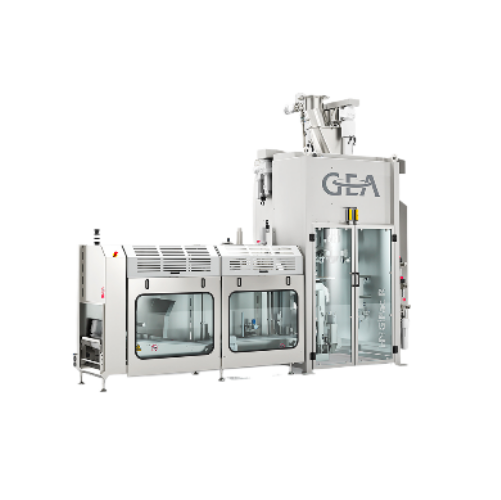
Hygienic powder filling system for low throughput
Ideal for compact production facilities, this filling system efficientl...
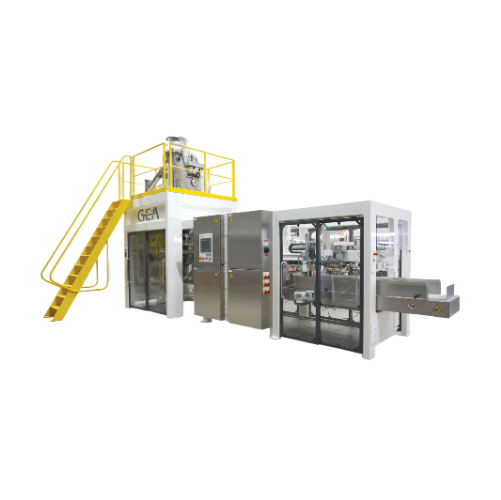
Automated powder bag filling system
Streamline your powder packaging operations with a fully integrated system that automat...
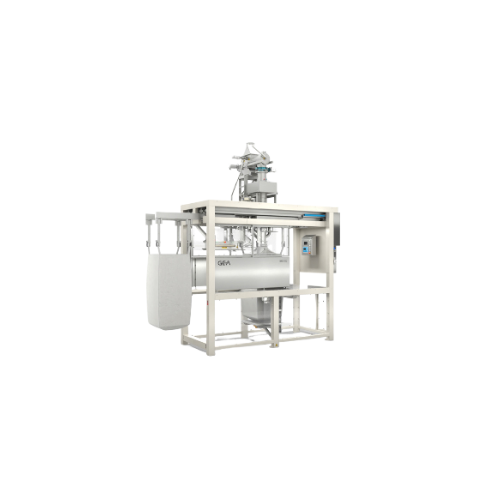
High care bulk powder fillers
Ensure hygienic packaging for your bulk powders with a system designed to enhance filling accu...

Semi-automatic filling solution for natural juices
For juice producers needing precision and adaptability, this semi-auto...
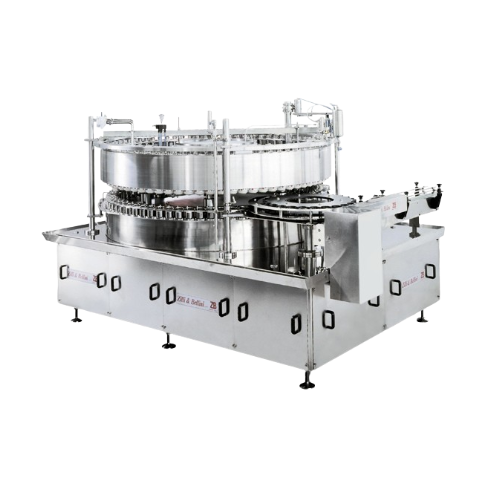
Rotary vacuum fillers for liquid and semi-liquid food products
Achieve precise filling of a wide range of liquid and sem...
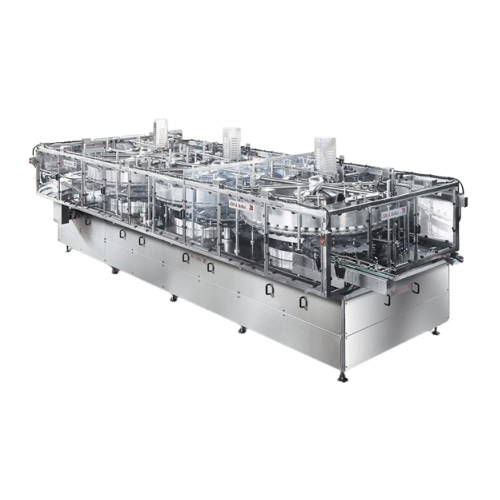
Fillers for solid products
Optimize your production line with versatile fillers that ensure precise handling and packaging o...

Handpack fillers for diverse food products
Streamline your canned food production by efficiently filling a wide range of c...

Industrial multifiller for fruit and vegetable salads
Need to efficiently fill diverse containers with fruit and vegetabl...
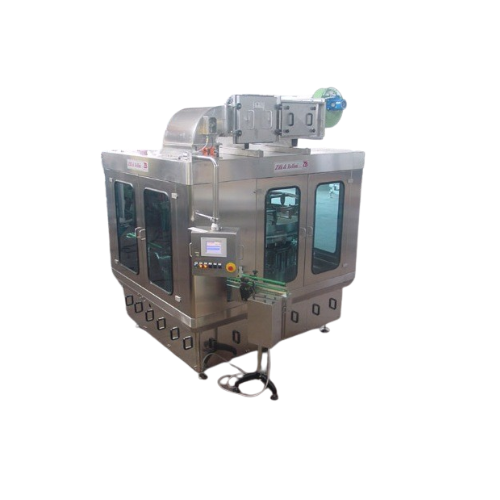
Industrial powder fillers for various containers
Optimize your packaging line with high-speed powder fillers that handle d...
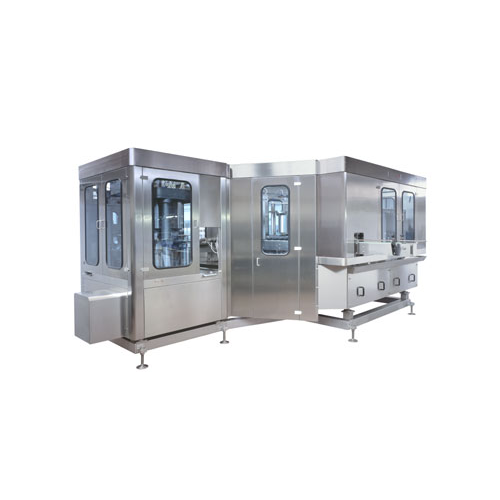
Filling and seaming groups for aluminium and tin plate cans
Smoothly synchronize filling and seaming of liquid and dense...
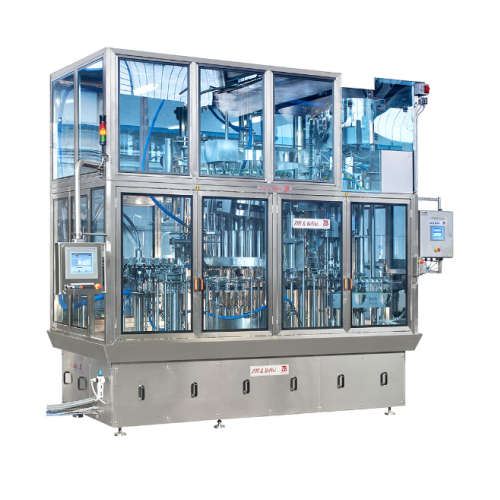
Integrated filling and capping system for food and soft drinks
Streamline your bottling operations with an integrated sy...
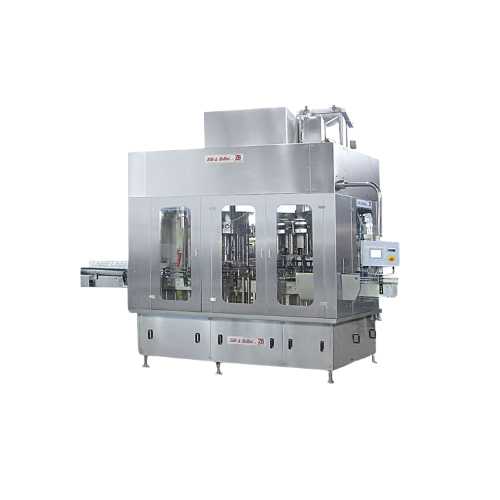
Ultraclean filling monoblocks for food industry
Enhance product safety and quality with monoblocks designed for ultraclean...
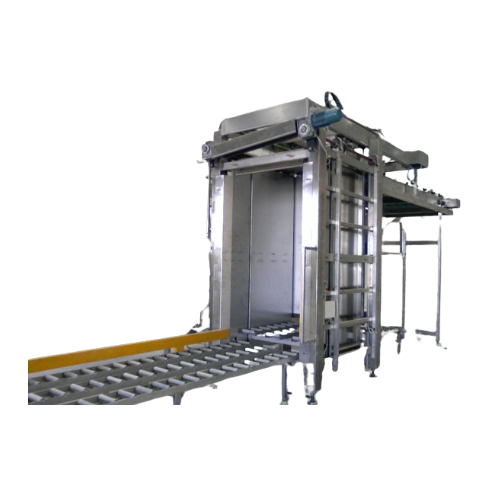
Complete filling and closing line for food containers
Optimize your production line with a versatile solution that ensure...
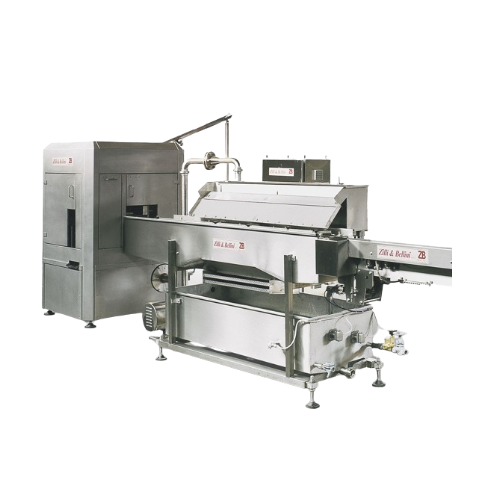
Linear gravity fillers for liquid products
Efficiently fill your liquid goods, from brine-filled olives to syrup-laden fru...
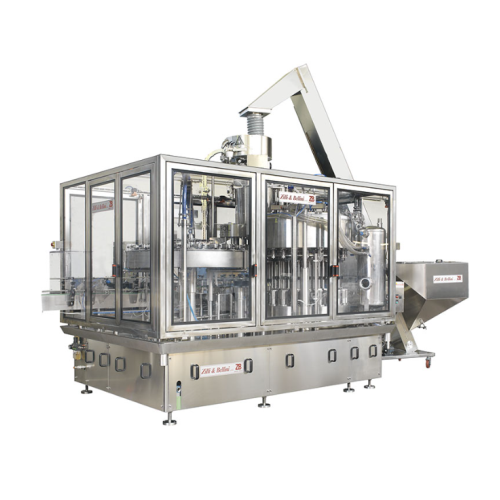
Rotary gravity fillers for diverse liquid products
Achieve precise filling and optimal packaging efficiency for a wide ra...
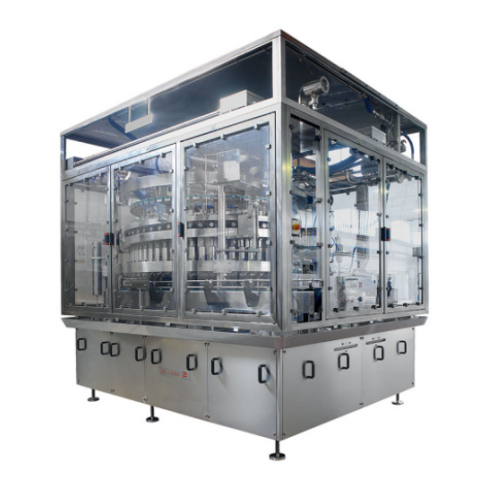
Rotary piston fillers for pumpable products
Optimize high-speed production lines with precision filling for diverse liquid...
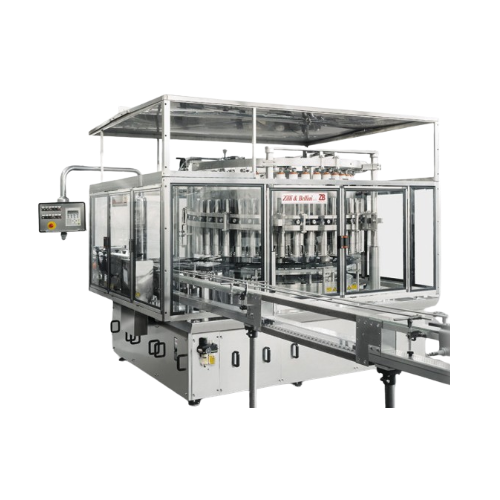
Rotary piston fillers with plunger for viscous products
Optimize your filling process with high-speed, rotary piston fill...
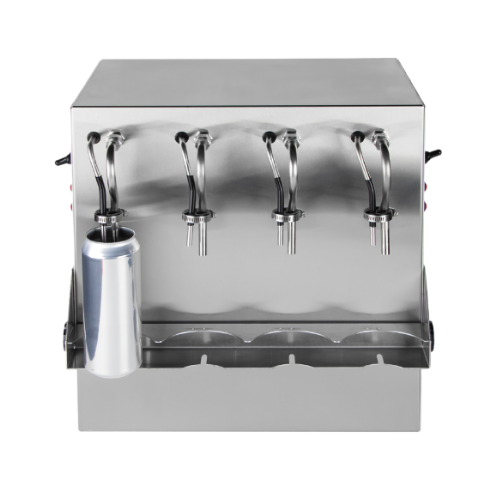
Carbonated beverage can filler - 4 spout open fill
Optimize canning carbonated beverages while minimizing CO2 loss with t...

Hot fill bottling unit for juices and isotonic beverages
Ideal for producers handling delicate or specialty liquids, this...
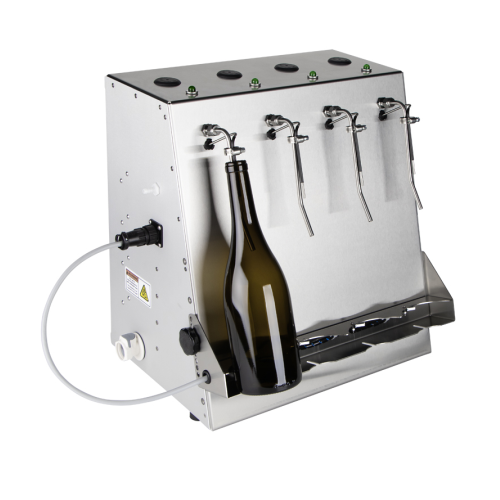
Level bottle filler for wine and spirits
Achieve consistent fill levels with precision sensor technology, ideal for ensurin...
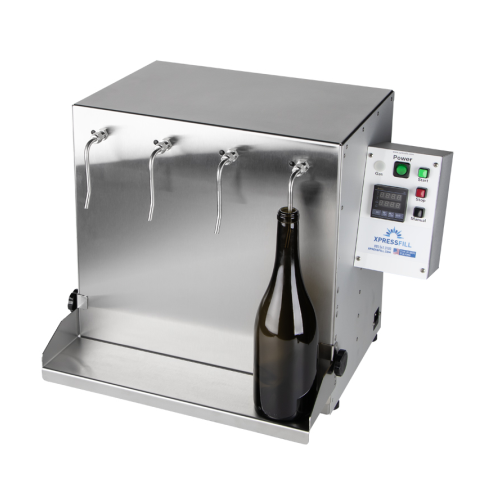
Volumetric bottle filler for distilled spirits
Ensure precise volume control and compliance with regulatory standards in y...
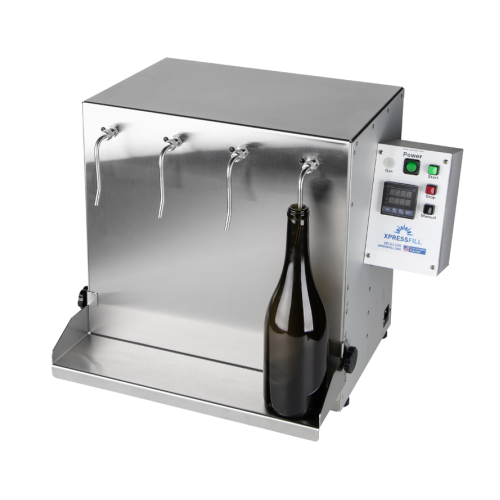
Volumetric bottle filler for high proof spirits
Ensure precise and consistent bottle filling for high-proof spirits with t...
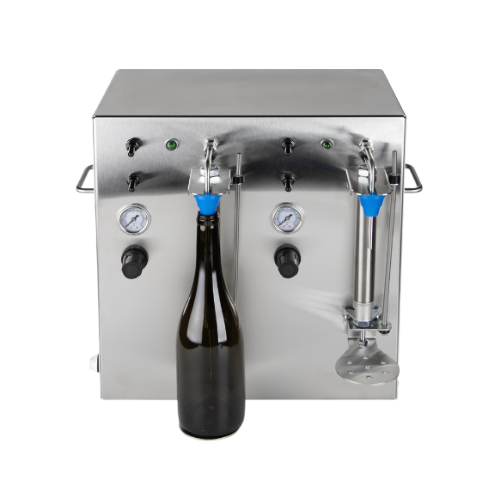
Counter pressure filler for carbonated beverages
Ensure optimal carbonation and minimal oxygen exposure during bottling, e...
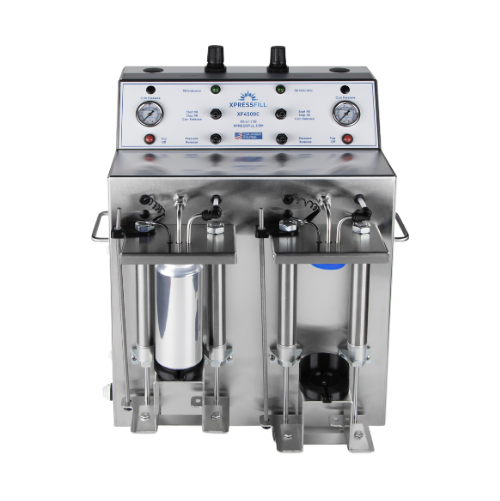
Counter pressure can filler for carbonated beverages
Achieve precise carbonation levels and minimal oxygen exposure in ca...
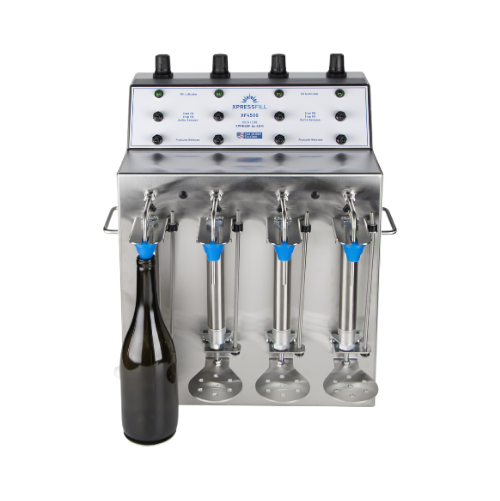
Counter pressure bottle filler for carbonated beverages
Maintain carbonation levels while filling bottles efficiently, en...
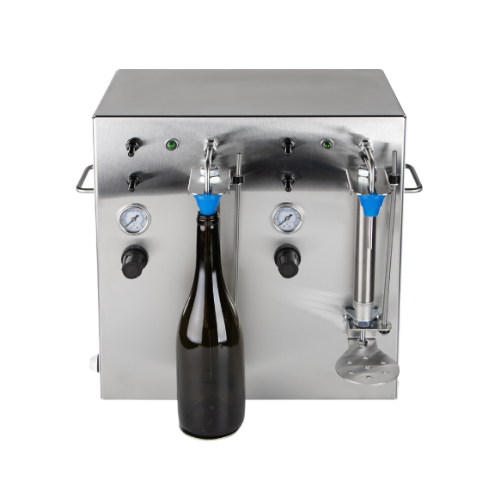
Counter pressure bottle filling system for carbonated beverages
Enhance your bottling efficiency with a versatile counte...
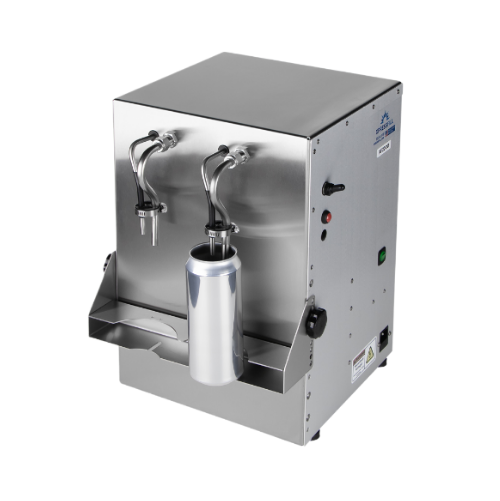
Carbonated beverage can filler for beer and kombucha
Looking to enhance your beverage production efficiency? This can fil...
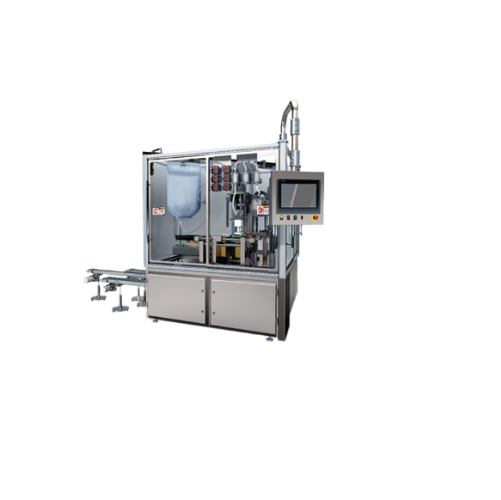
Blow/fill/seal packaging for laboratory and clinical trials
Streamline your small-scale pharmaceutical production with p...
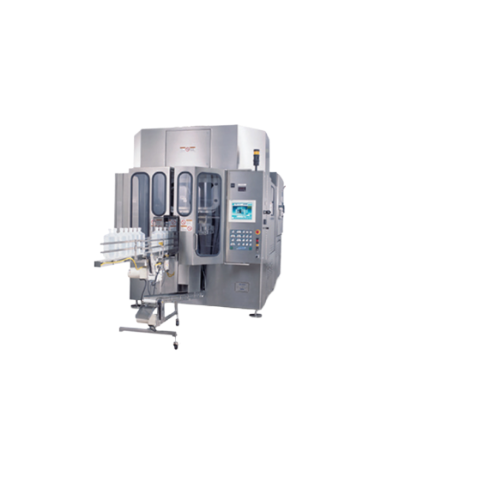
Large bottle blow/fill/seal packaging system
Achieve precise liquid filling and sealing for large-scale production with hi...

Blow/fill/seal packaging system for sterile liquid products
Streamline your liquid product manufacturing with high-speed...
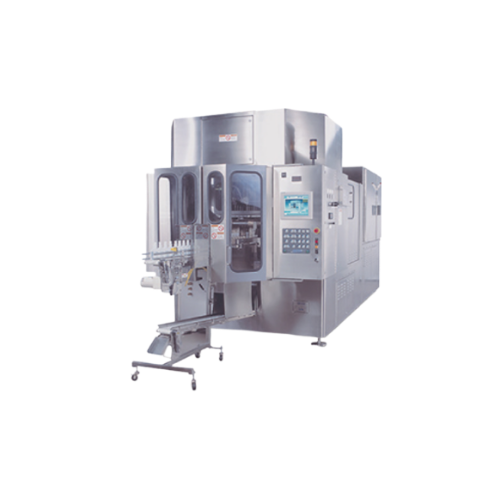
Blow/fill/seal system for aseptic liquid packaging
Achieve efficient aseptic packaging with a system that combines blow m...
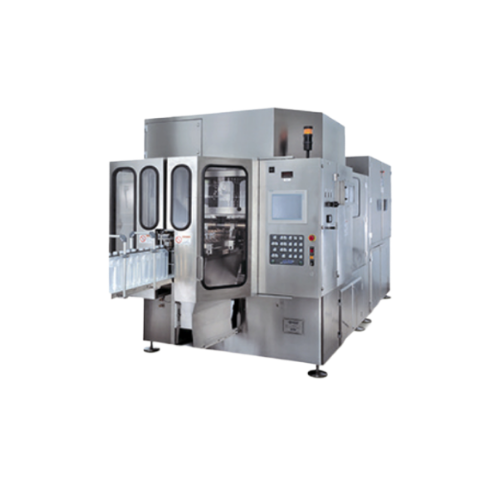
Blow/fill/seal packaging for large bottles
Need a high-speed solution for producing sterile liquid formulations in large v...
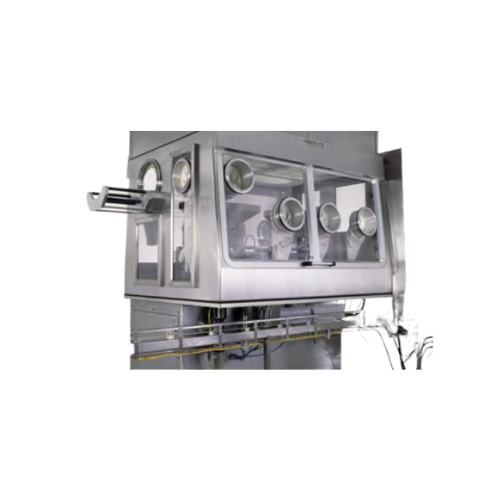
Insertion technology for sterile blow/fill/seal systems
Ensure sterility and precision in liquid pharmaceutical packaging...
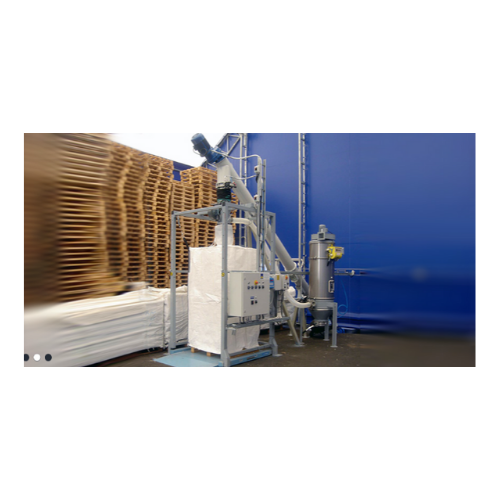
Dust-free bulk bag filling system
Achieve efficient, dust-free filling of bulk bags with our innovative system, ensuring se...
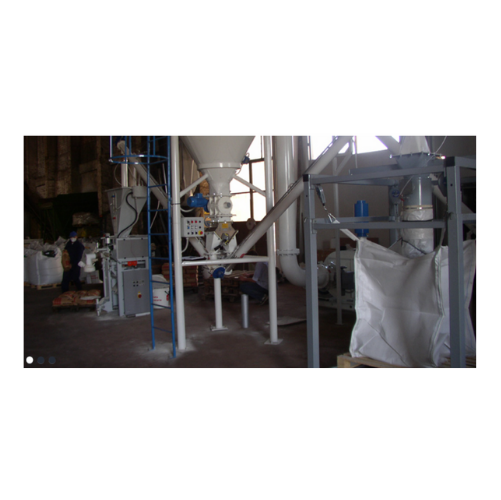
Manual Fibc bag filling station
Achieve dust-free filling of bulk bags with an efficient system designed to handle compacted...
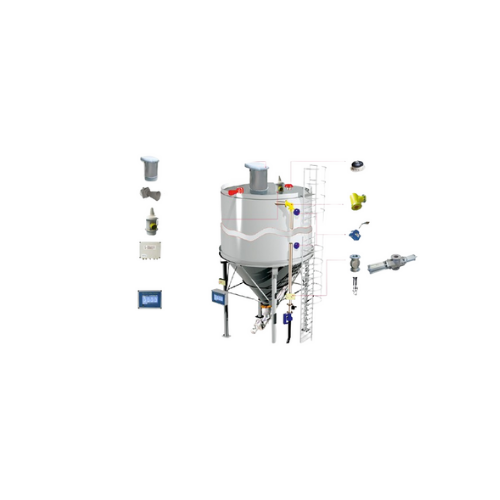
Silo overfill protection system
Prevent silo overfilling and excess pressurization with a system designed to safeguard silos...
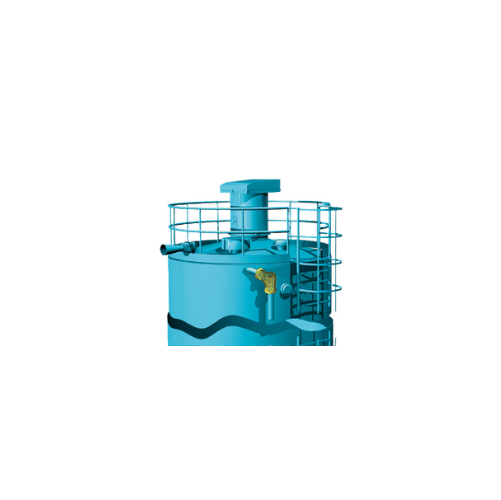
Silo overfilling safety system
Ensure safe silo filling with our system that prevents overfilling and excess pressurization,...
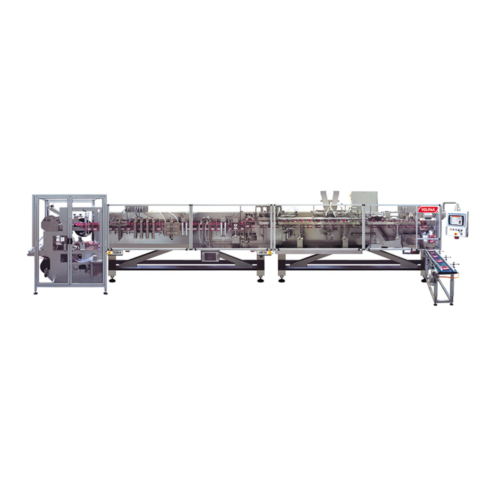
Stand-up pouch filling and sealing system
For packaging lines that demand quick, efficient, and flexible pouching, this hi...
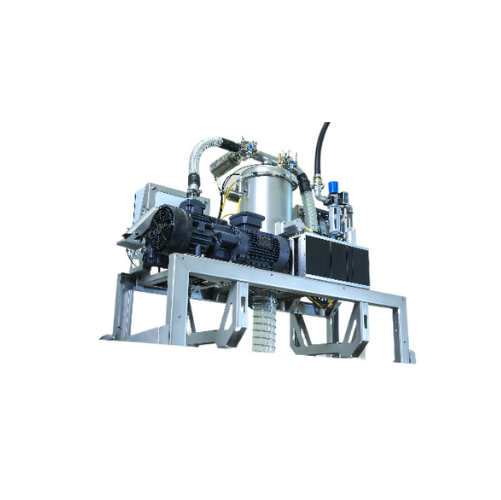
Automatic metal powder filling system for 3d printers
Ensure seamless operation of your 3D printing process with a system...

Dosing and filling pump for liquids and pastes
Achieve precise dosing and filling of liquids and pastes with compact, hygi...
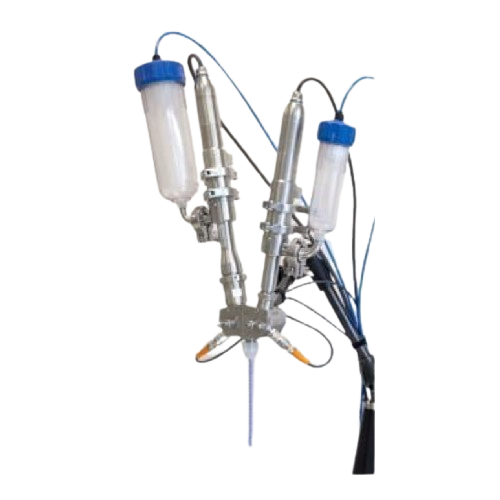
Continuous mixing and filling system for viscous materials
Experience precise, pulsation-free mixing and filling of visc...
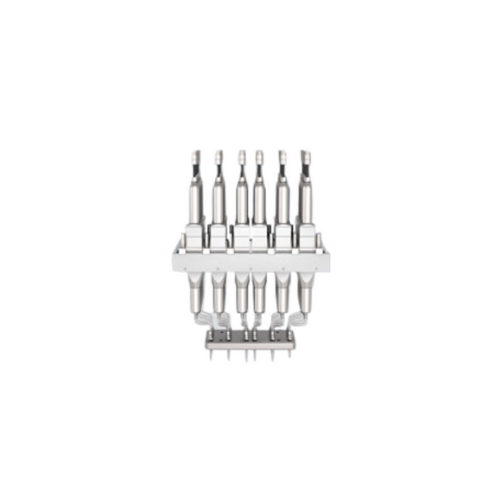
Fully automatic filling lines for liquids
Achieve precise dosing and filling of liquids with minimal cycle times using com...
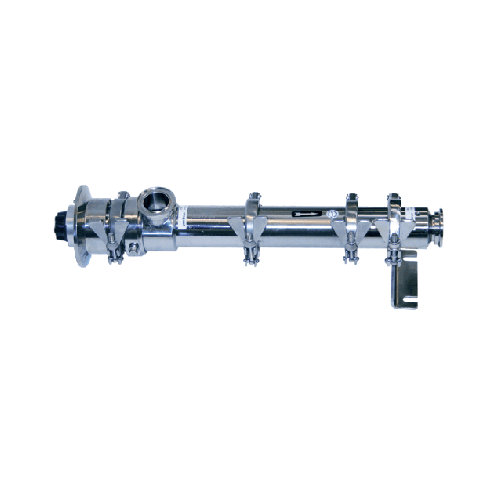
Dosing and filling pump for hygienic applications
Optimize your production line with this dosing and filling pump, design...
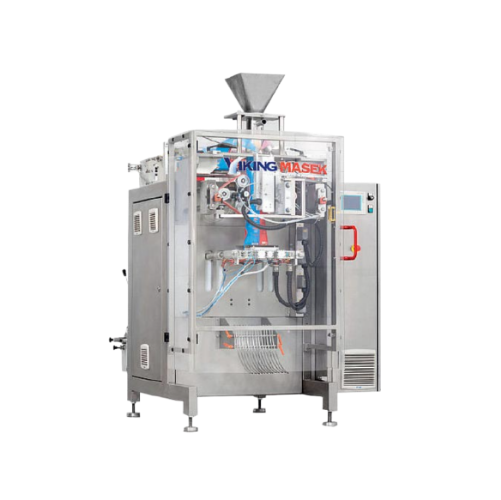
Continuous motion vertical form fill seal packaging system
Achieve high-speed, consistent packaging for diverse products...
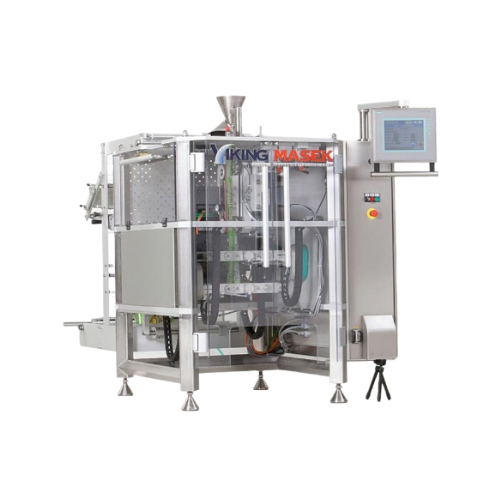
High-speed vertical form fill seal packaging machine
Optimize your packaging line with this high-speed vertical form fill...
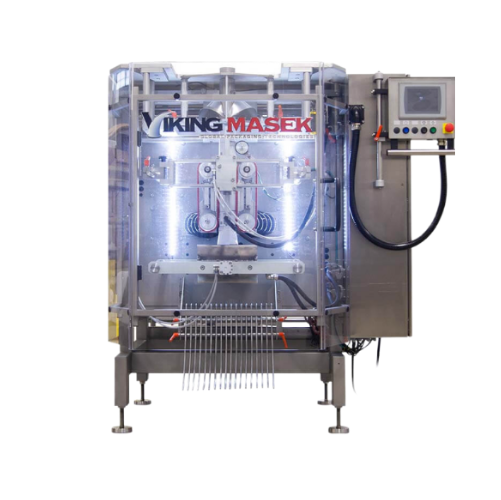
Vertical form fill seal for dusty and liquid products
Optimize your packaging line with a versatile solution designed to ...
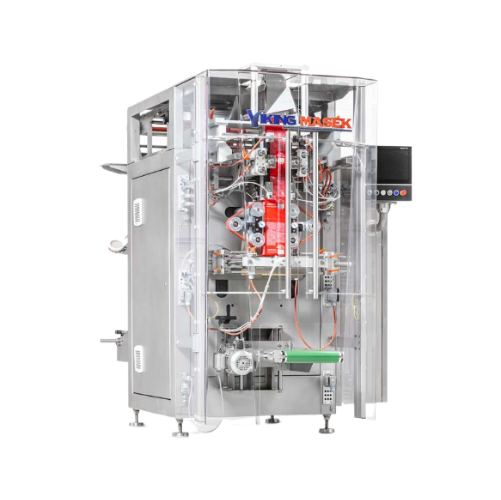
High-speed vertical form fill seal for various packaging needs
Streamline your packaging process with an advanced vertic...
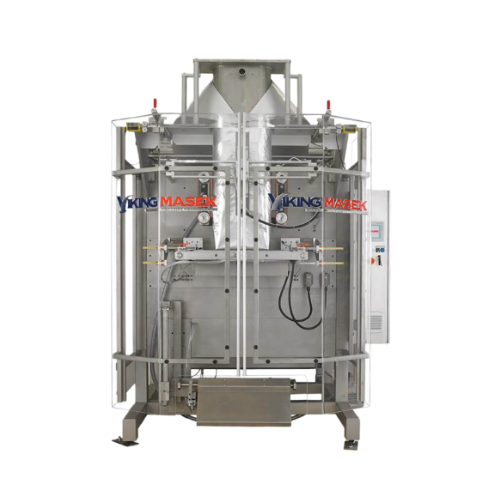
Vertical form fill seal for bulk bag packaging
Streamline your bulk bag packaging with efficiency and precision, ideal for...
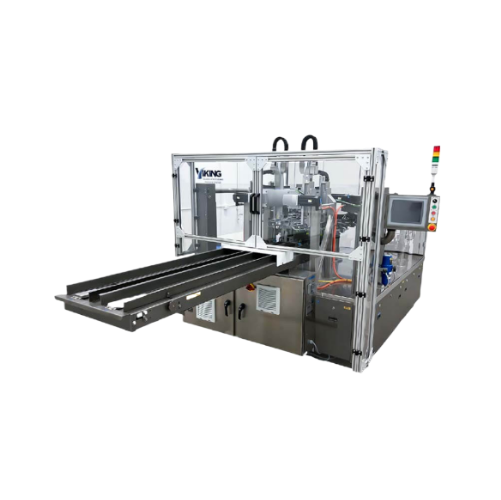
Rotary premade pouch filler and sealer
Maximize production efficiency by seamlessly filling and sealing diverse pouch sizes...
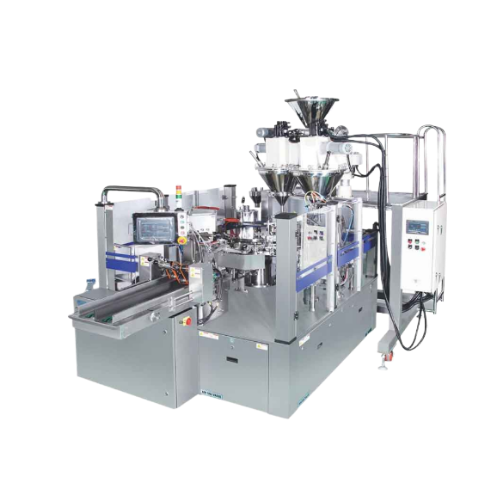
Automatic rotary filler and sealer for premade pouches
Enhance your production line efficiency with a dual-lane system th...
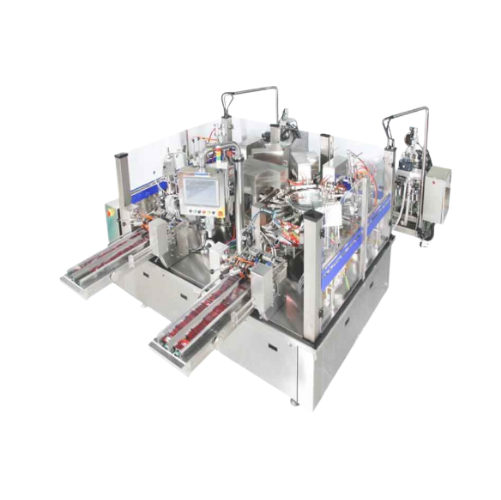
Automatic rotary premade pouch filler and sealer
Optimize your production line with high-speed pouch filling and sealing, ...
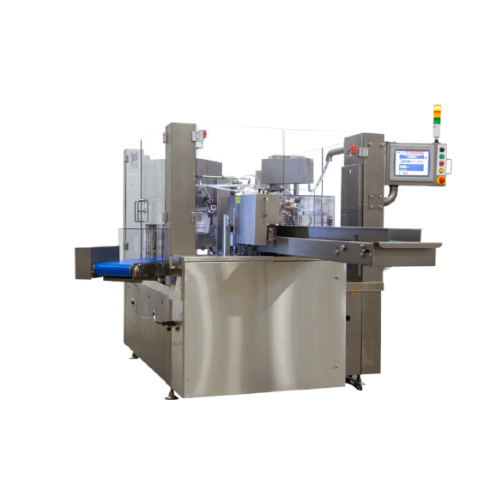
Automatic rotary premade pouch filler for various industries
Streamline your pouch packaging process with precision fill...
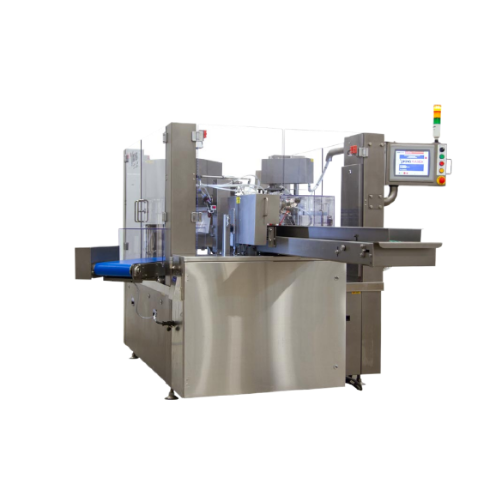
Premade pouch fill and seal solution
Effortlessly fill and seal various pouch sizes for streamlined packaging in diverse fo...
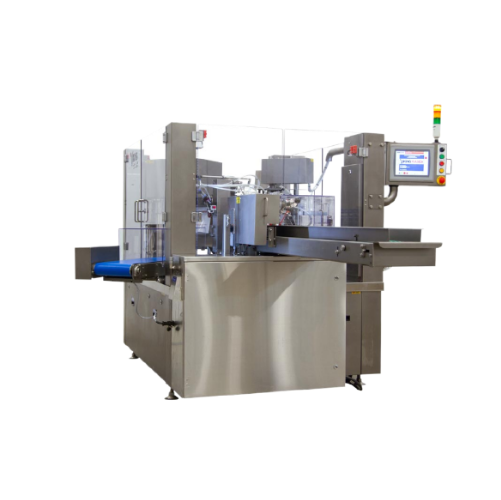
Automatic rotary premade pouch filler for food products
Enhance your packaging line with a high-speed solution designed t...
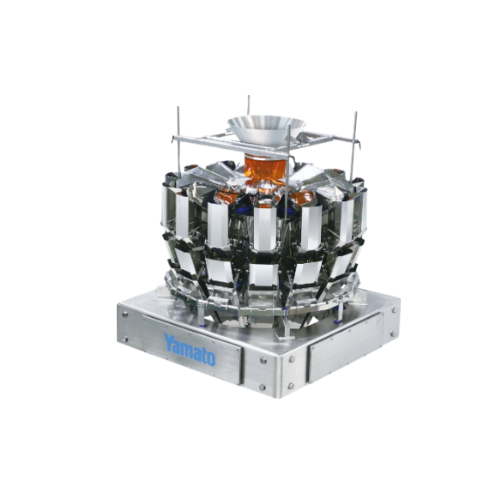
Industrial product fillers for precise packaging
Achieve consistent package weights and volumes with precision filling sol...
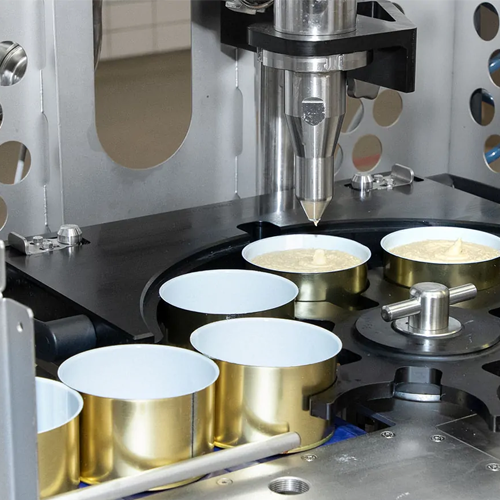
Container filling system for pasty and chunky products
Achieve precise, drip-free filling of diverse pasty and chunky pro...
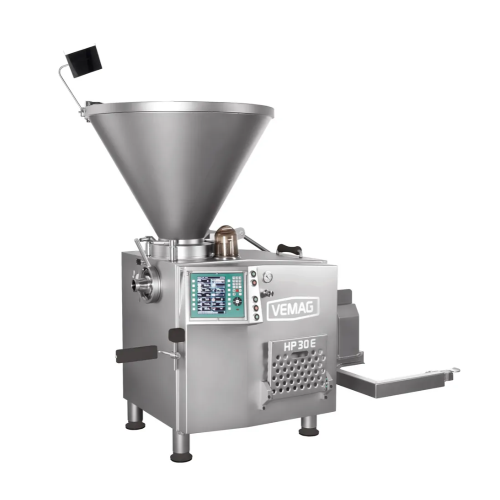
Vacuum filling machines for cooked ham & sausages
Achieve precise portioning and enhanced product quality with this advan...
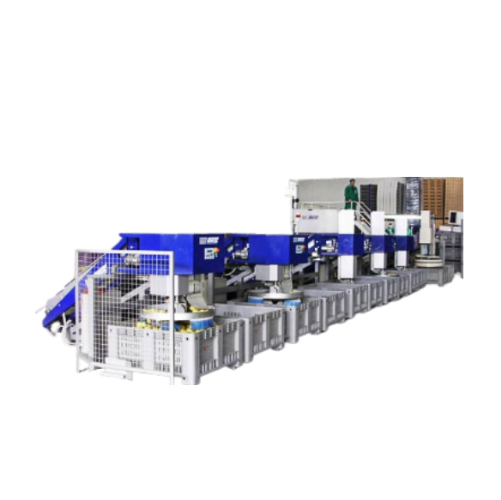
Bin fillers for fruit packing
Achieve precise and gentle handling of fruits and vegetables with flexible bin fillers that se...
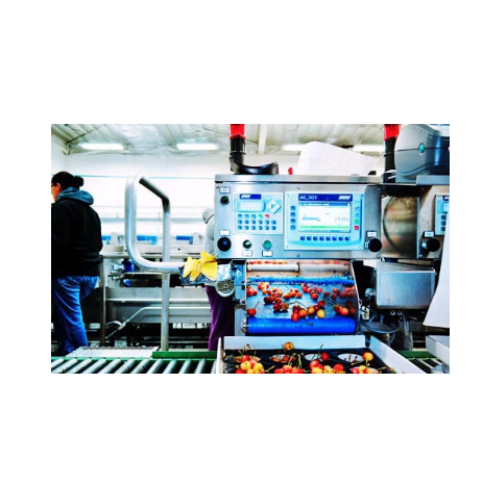
Automatic crate fillers for fruit packing
Elevate your fruit packing efficiency with precision crate fillers, designed to ...
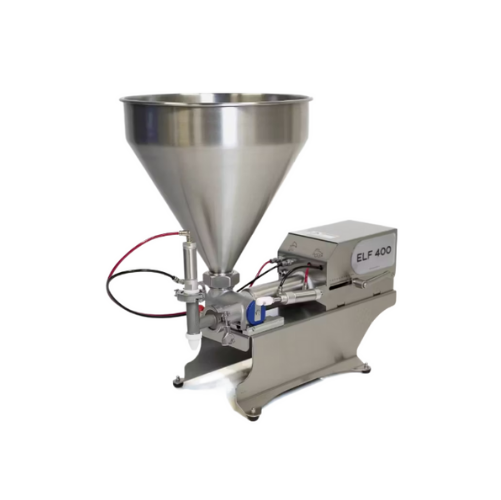
Single piston food filler
Achieve precise portioning and consistent product flow with a versatile solution perfect for handl...
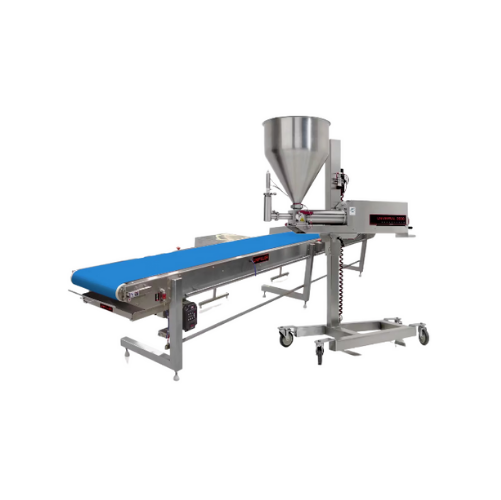
Industrial food filling and depositing equipment
Optimize your production line with precise, gentle depositing and filling...
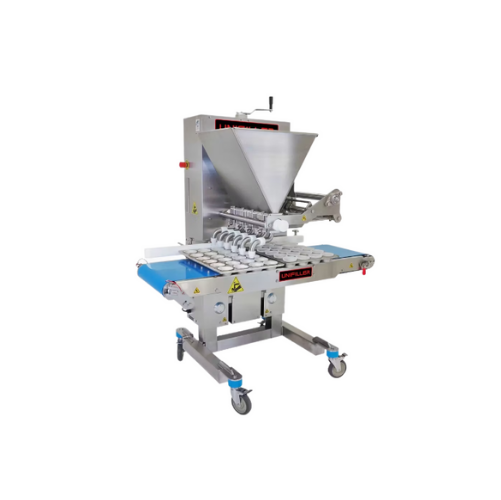
Multipiston food filling machine
Experience precise and versatile portion control with high-speed, servo-driven piston depos...
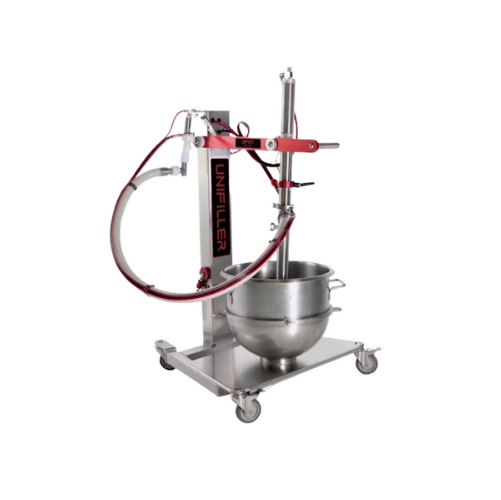
Compact bakery depositor for accurate filling
Streamline your bakery production with a compact depositor designed for prec...
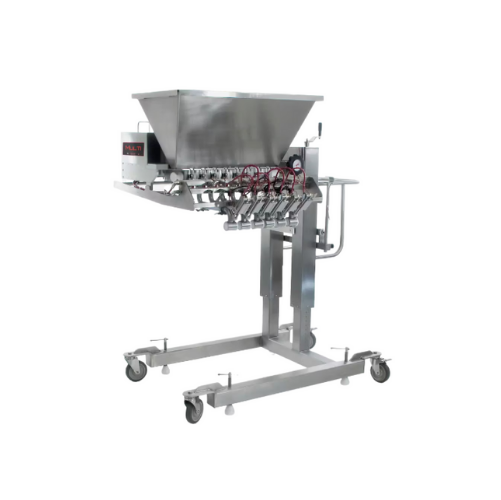
Multi piston depositor for automated bakery filling
Optimize your bakery production with precise portioning and filling, ...
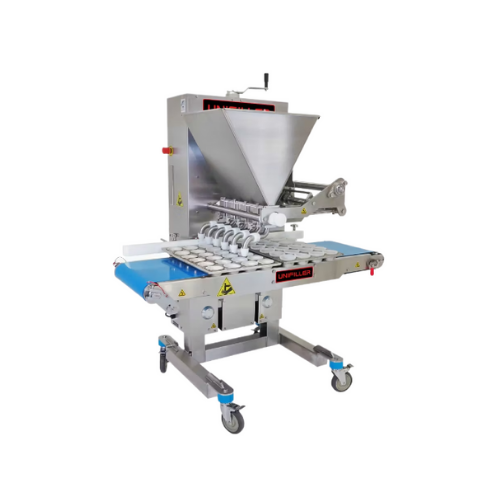
Servo driven multi-piston depositor for batters and fillings
Ensure precise portion control and maintain product integri...
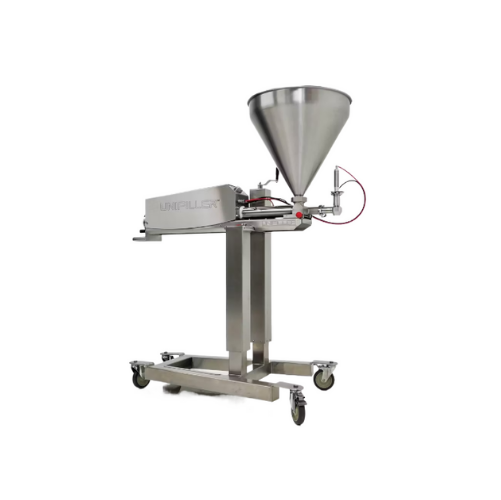
Industrial food filler for precise depositing over conveyors
Optimize your food production line with a versatile filler ...
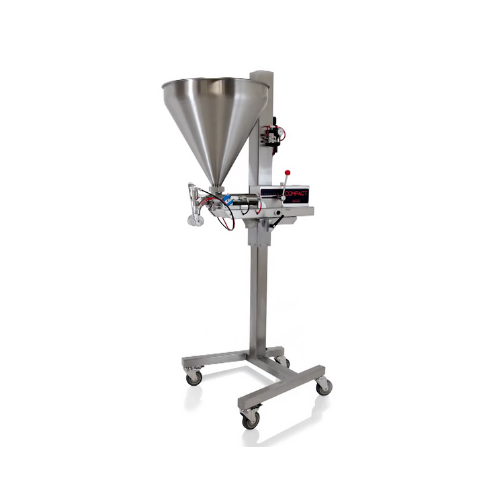
Compact food filling and portioning solution
Ideal for facilities needing precise portioning, this versatile filling machi...
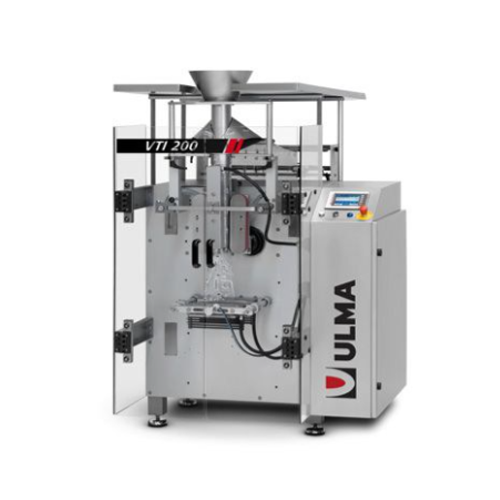
Vertical form fill seal packaging for medium-speed production
Achieve efficient and reliable packaging for diverse food ...
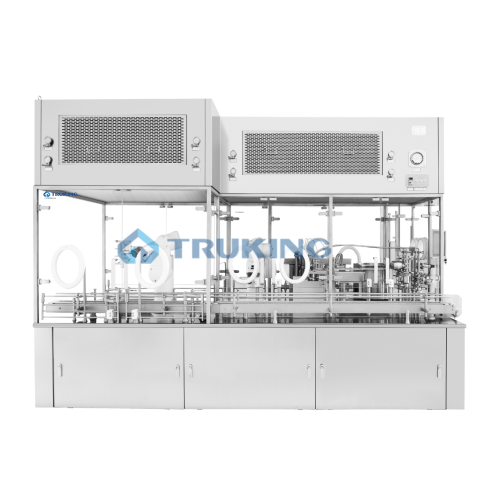
Nested fillers for vials, pre-filled syringes, and cartridges
Optimize your aseptic filling processes with precision dos...
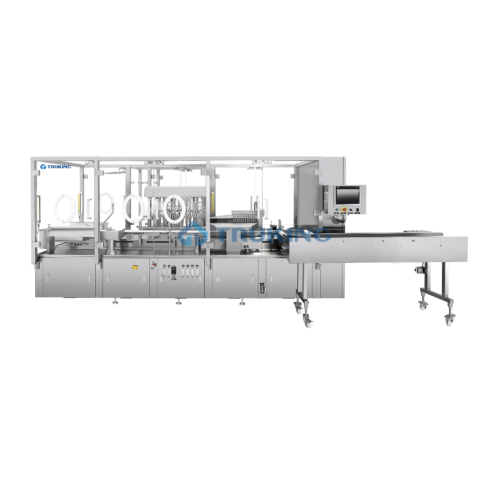
High-speed ampoule filling unit
Ensure precision and speed with this cutting-edge solution designed for efficient filling an...
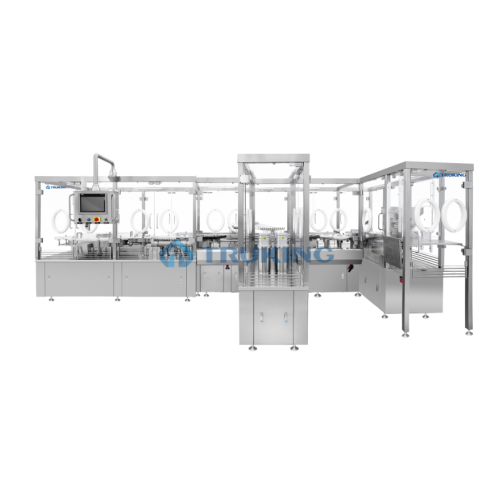
Vial filling and stoppering system for aseptic production
Streamline aseptic production by integrating high-speed vial f...
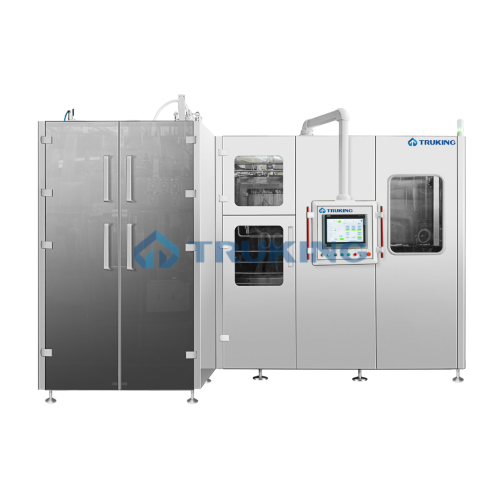
Aseptic blow fill seal system
Ensure sterile, high-speed production of liquid pharmaceuticals by integrating a cutting-edge ...
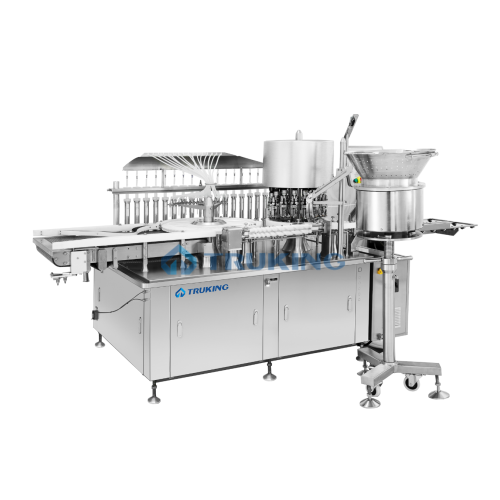
Oral liquid bottle filling & capping system
Streamline your liquid manufacturing processes with precise filling and secure...
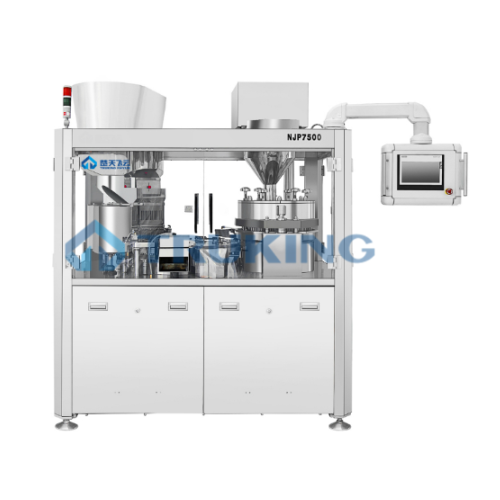
Fully automatic hard capsule filling machine
Enhance pharmaceutical production with precise capsule filling, ensuring opti...
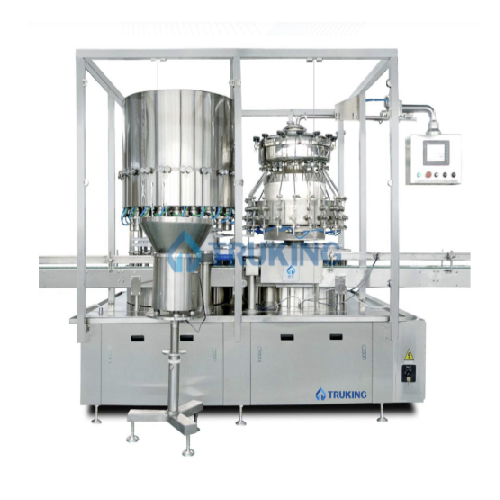
Gravity rotary filling for large infusion bottles
Ensure precise filling and secure stoppering of large infusion bottles ...
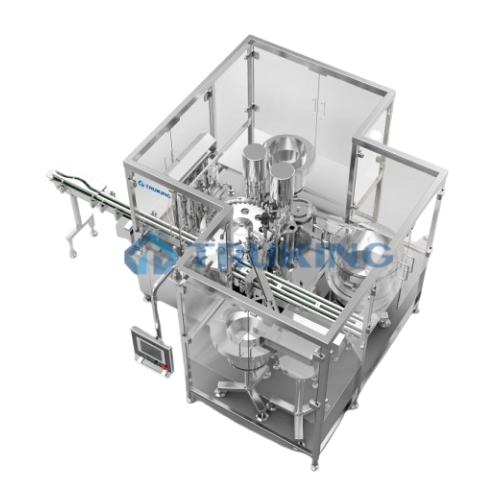
Pharmaceutical drops and sprays filling system
Streamline your liquid formulation process with precision filling and seali...

Large volume oral liquid filling system
Ensure precision and efficiency in liquid filling with a system designed to handle ...
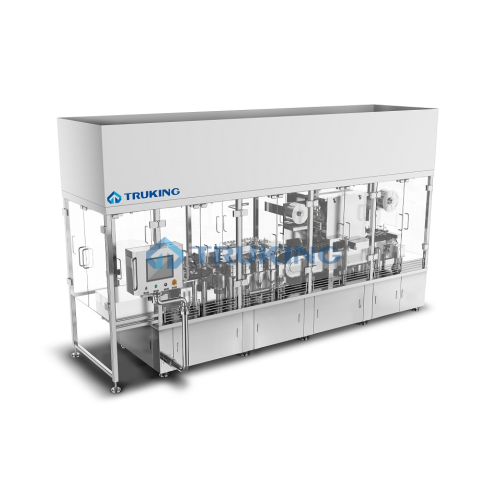
Diagnostic reagent filling system for accurate and efficient processing
Streamline the production of diagnostic reagent...
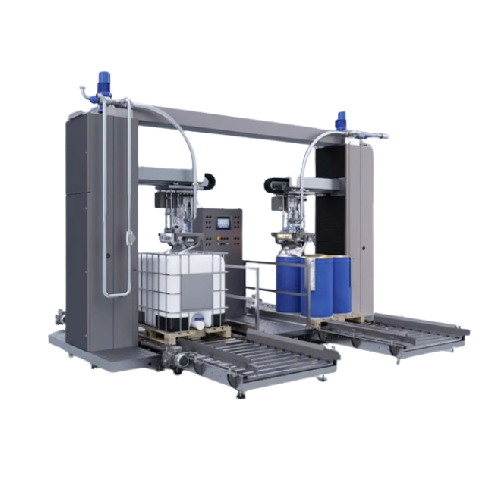
Aseptic filler for fruit juice and dairy products
Ensure sterile, high-speed filling of liquids and creams with precision...
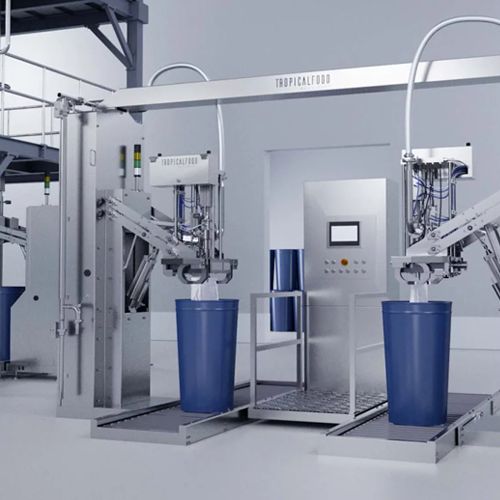
Aseptic filler for fruit juices and purees
Ensure product integrity and shelf stability with a versatile filler designed t...
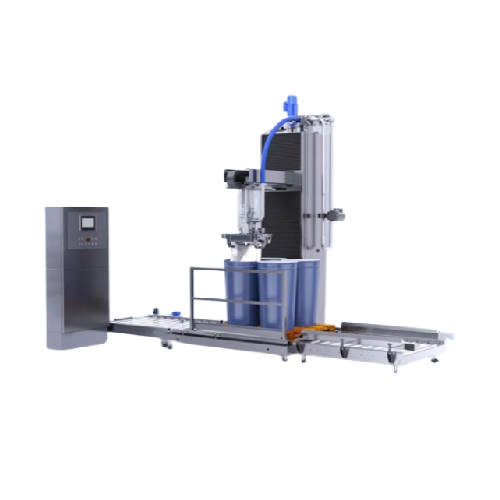
Aseptic filler for various liquid and semi-liquid food products
For manufacturers focused on quality, this aseptic filli...
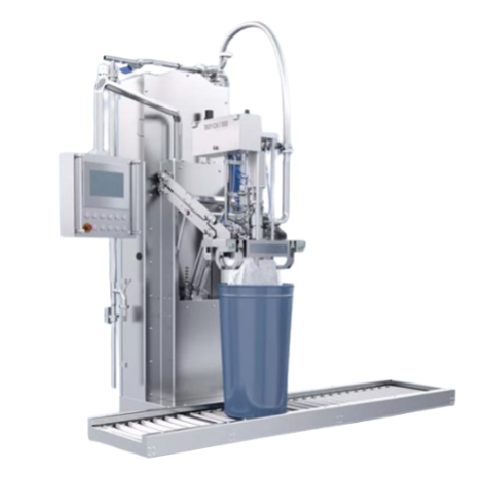
Aseptic filler for fruit juice and puree
Ensure optimal product safety and quality with this aseptic filler, designed to ha...
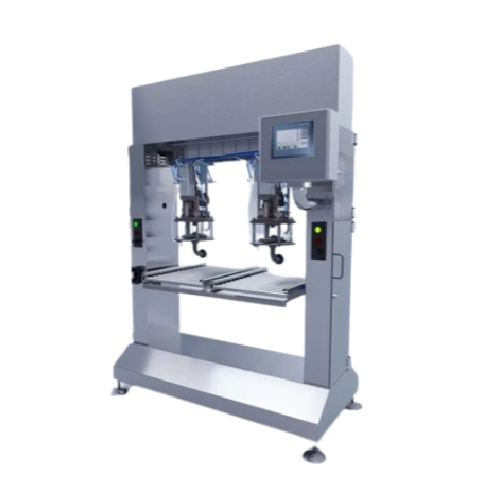
Aseptic filling solution for fruit juice and dairy products
Ensure product integrity and safety with this aseptic fillin...
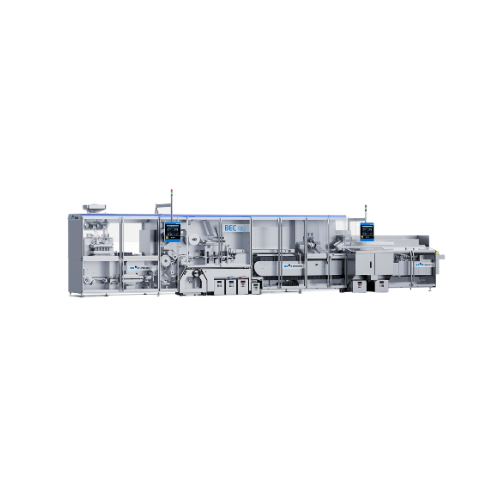
Semi-automatic butter bulk filling system
Optimize your dairy production with a seamless butter packaging solution that en...
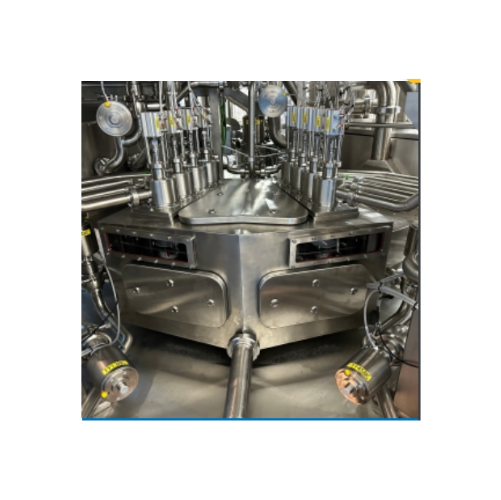
In-line filling and closing system for pre-formed containers
Looking to enhance production efficiency with a solution th...

Aseptic rotary cup filling and closing solution
Maximize your production capacity with this cutting-edge aseptic solution,...
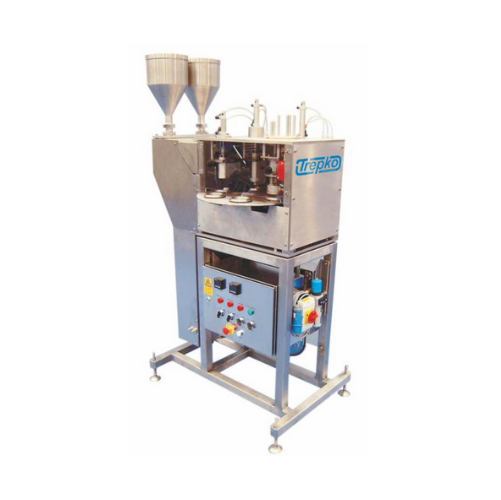
Rotary cup filling and closing system
Maximize production efficiency with a system that offers precision filling and secure...
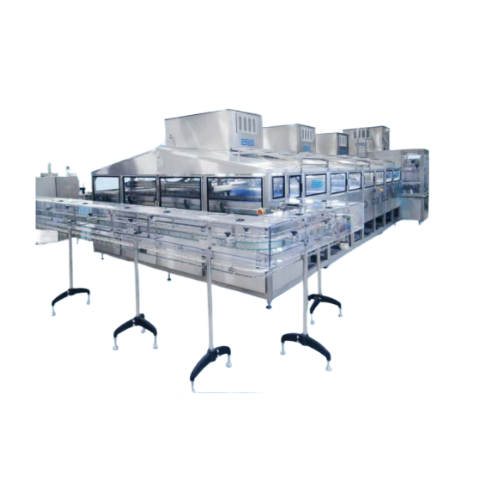
Semi-automatic filling and closing system for pre-formed containers
Streamline your packaging process with reliable sem...
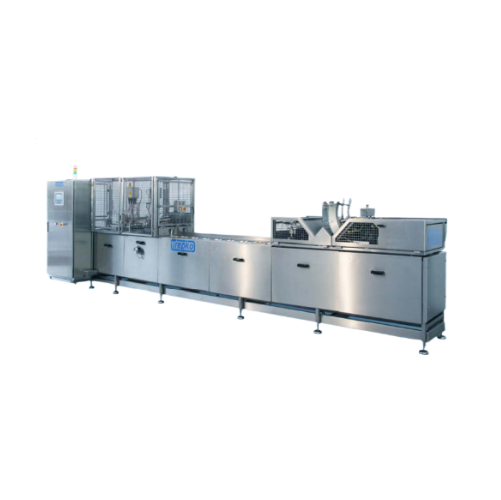
Automated filling and coagulation line for u.f. white cheese
Enhance your cheese production with a state-of-the-art syst...

Flexible container handling systems for high-speed filling and sealing
Optimize your packaging line with this servo-dri...
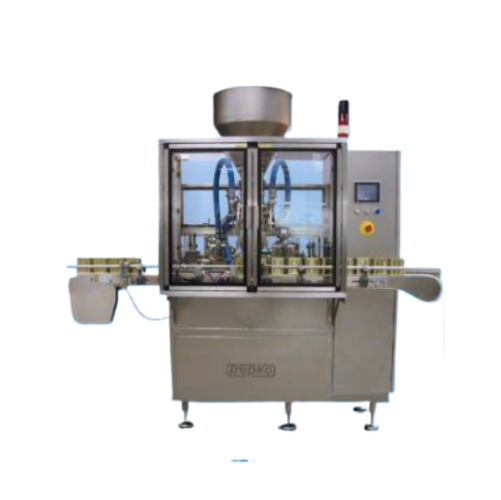
Pre-formed container filling system for multi-layer products
Efficiently handle a diverse range of products with this fl...

Glass jar filling system for processed cheese
Streamline your production line with a robust, high-speed filling solution d...
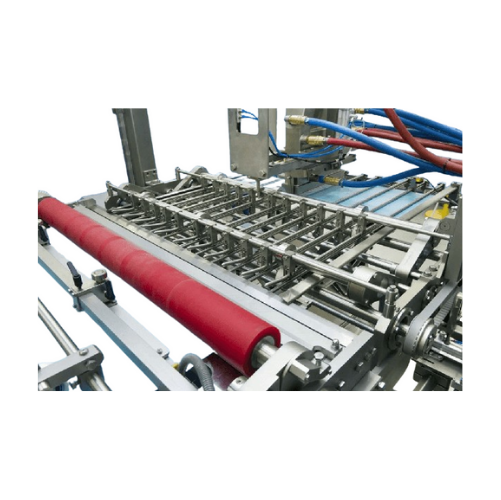
Bulk filling and wrapping for butter and margarine
Streamline your butter and margarine production with efficient bulk fi...
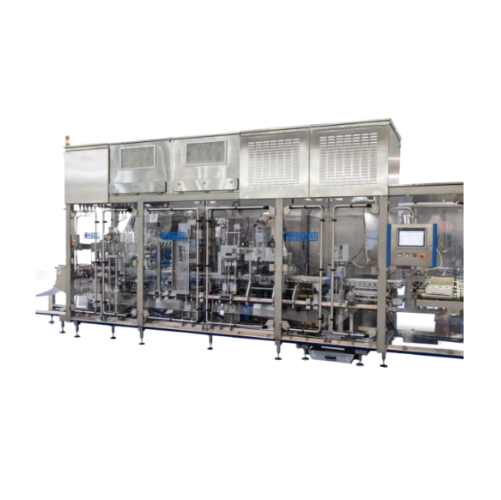
Forming, filling, and sealing solution for mini portions
Optimize your production line with a high-speed machine designed...
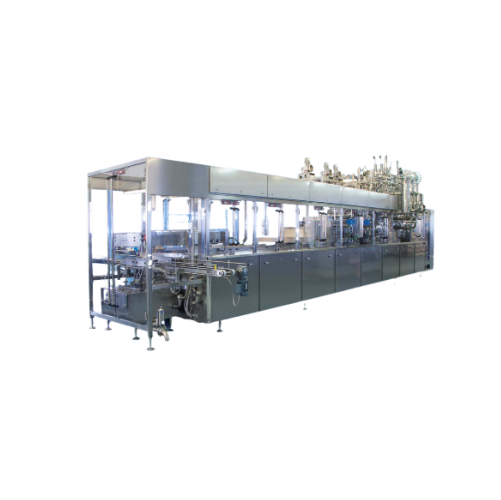
Forming, filling, and sealing system for liquid food products
Achieve precise portion control and versatile packaging wi...
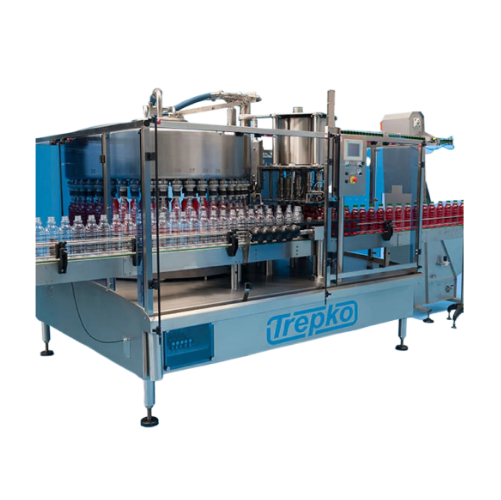
Bottle filling system for diverse specifications
Optimize your bottle-filling operations with a modular system that seamle...

Manual sausage filler for professional use
Achieve precise sausage filling with a manual solution designed to handle a var...
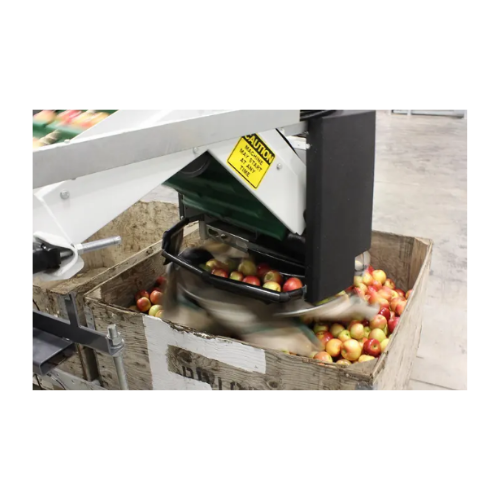
Dry bin filling for delicate fruit
Achieve gentle, high-throughput filling of delicate fruits with minimized manual interve...

High-speed filling system for cherries and blueberries
Streamline your packaging process with a system designed for rapid...
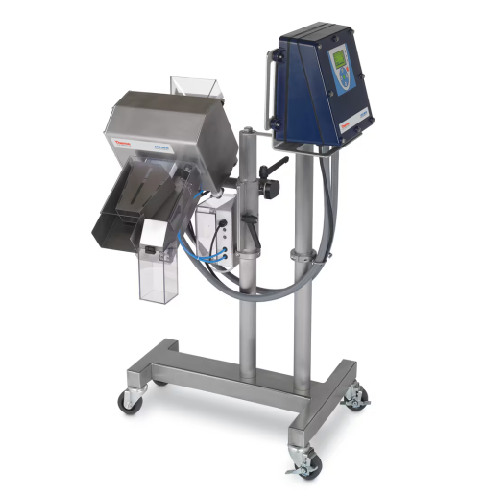
Pharmaceutical metal detector for tablet presses and capsule filling
Detect and eliminate metal contaminants in high-sp...

Volumetric auger filler for powder packaging
Streamline your powder packaging process with precise and efficient volumetri...
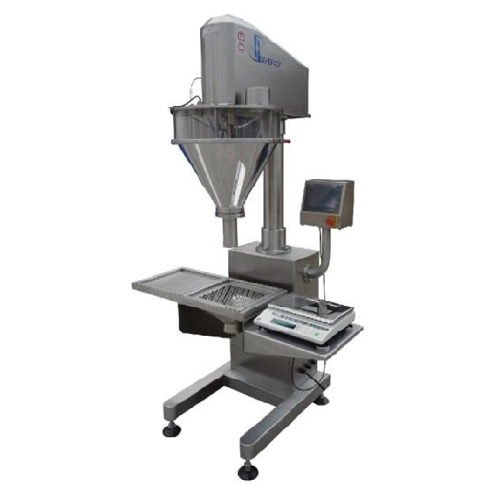
Volumetric auger filler for precise powder weighing
Optimize your production line with a high-speed volumetric auger fill...
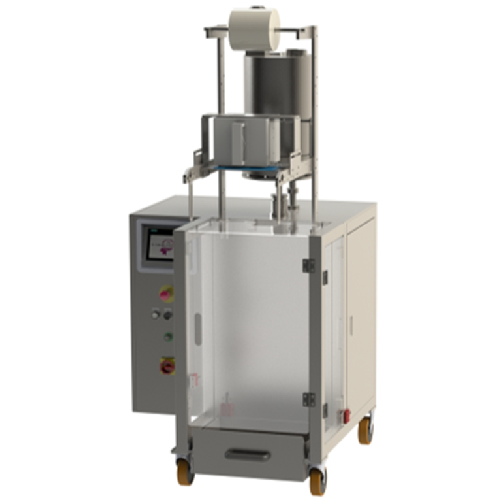
Granule filling sachet machine
Ideal for optimizing packing operations, this granule-filling sachet machine ensures precise ...
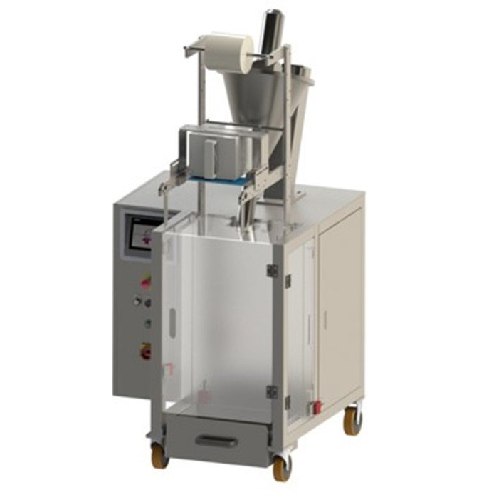
Sachet powder filling machine
Optimize your packaging line with this efficient solution for precise powder filling, ensuring...
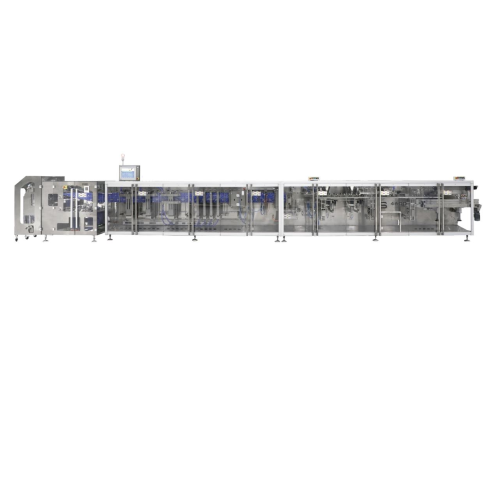
Horizontal form-fill-seal systems for pouch packaging
For production lines that demand efficient pouch creation, these hi...
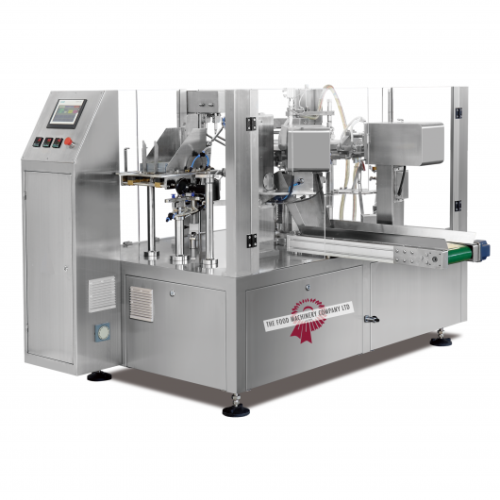
Rotary pouch filling system
Looking to efficiently manage pouch filling for diverse products? This rotary system seamlessly ...
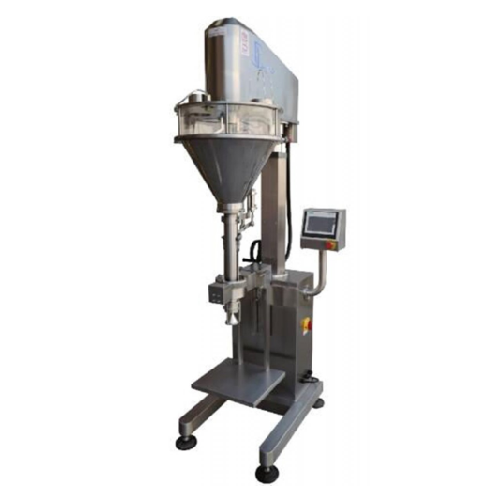
Gravimetric auger filler for powder weighing
Achieve precise powder filling with this gravimetric auger solution, ensuring...
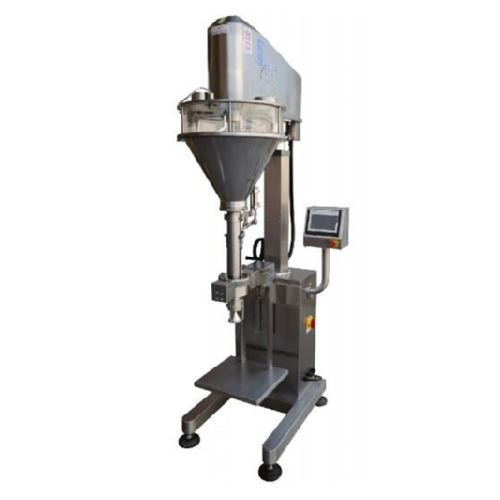
Powder auger filler for precise weighing and depositing
Ensure accurate and efficient powder filling with this innovative...
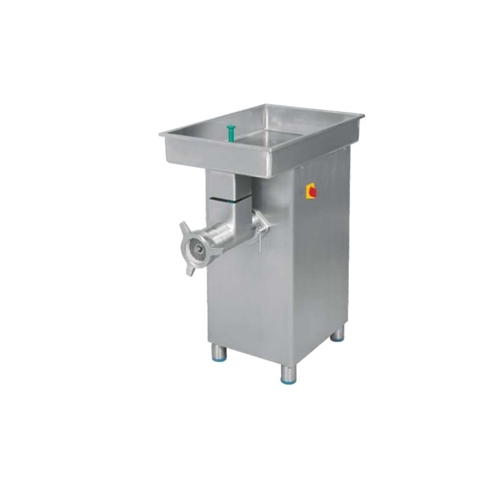
Commercial sausage fillers for butchery
Enhance your butchery workflow with specialized machinery designed for precise meat...
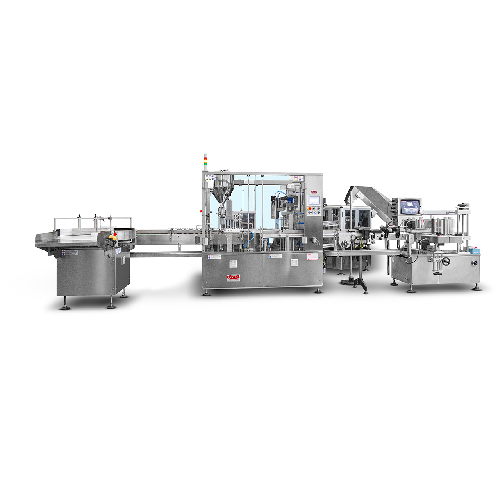
Medium volume bottle and jar filling system
Efficiently manage filling operations for diverse liquid and semi-dense produc...
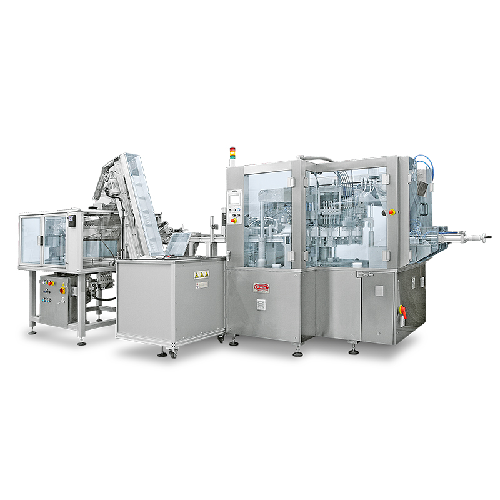
Automatic mono-dose strip filling system
Optimize your liquid product packaging with a multi-functional system designed for...
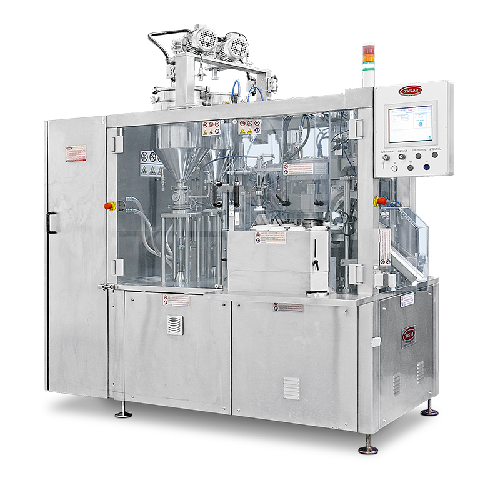
Automatic tube filling for multi-color products
Achieve precision in multi-color product packaging with seamless co-extrus...
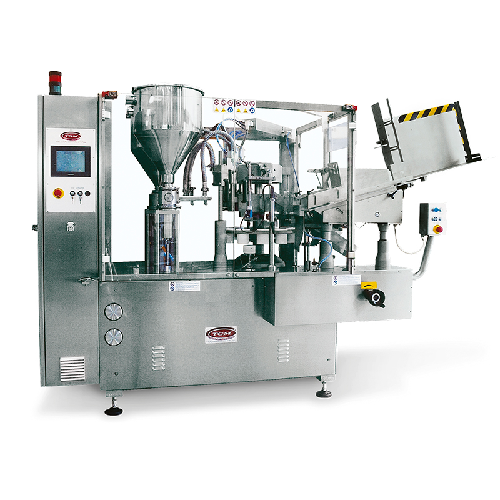
Automatic tube filler for multi-color coextruded products
Achieve precise dual- or tri-color product designs with except...
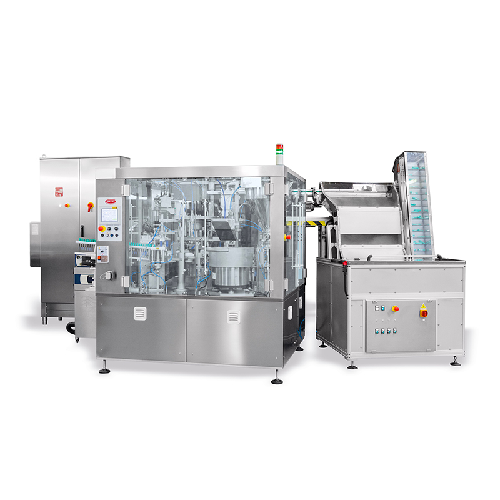
Automatic bottle filling and capping solution
When dealing with fragile or unstable bottles, precise filling and capping a...
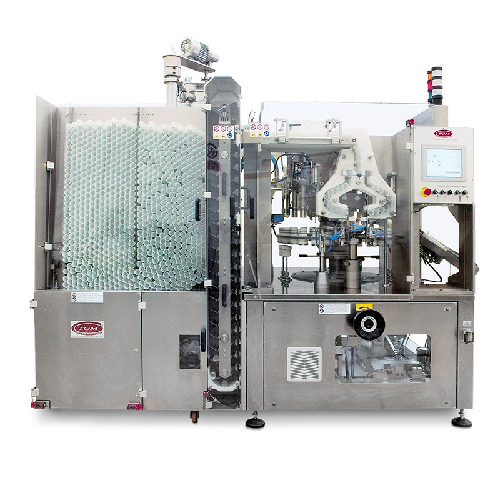
Automatic tube filling for coextruded products
Maximize efficiency in high-volume production with precision co-extruding c...
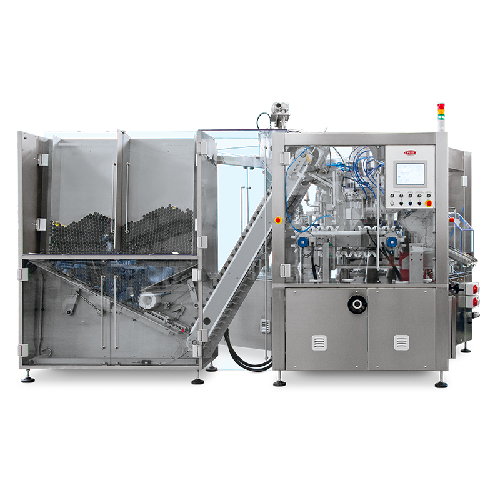
Automatic tube filling solution for high-volume production
Effortlessly streamline your production with this high-speed ...
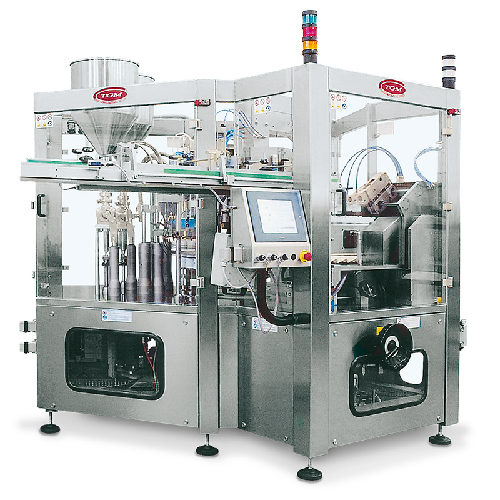
Automatic tube filler for co-extruded products
Achieve precise multicolor co-extrusion filling with high-speed accuracy, o...
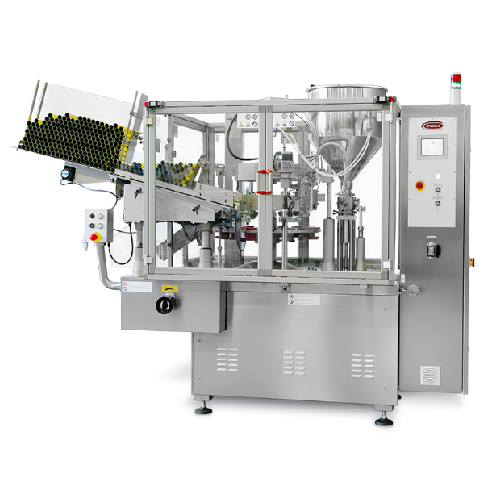
Automatic tube filling solution for medium to high volume production
Boost your production line efficiency with a robus...
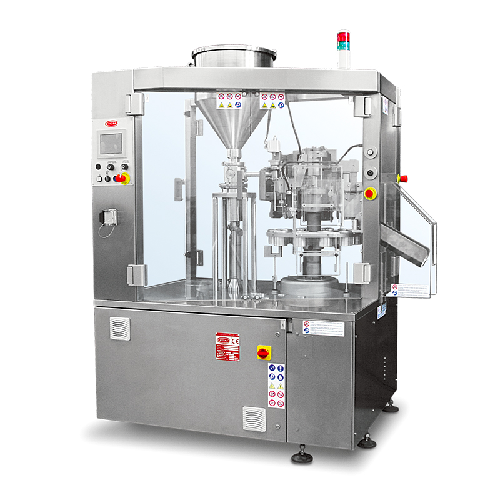
Small batch tube filling system for metal and plastic tubes
Optimize your small-batch production with precise tube filli...
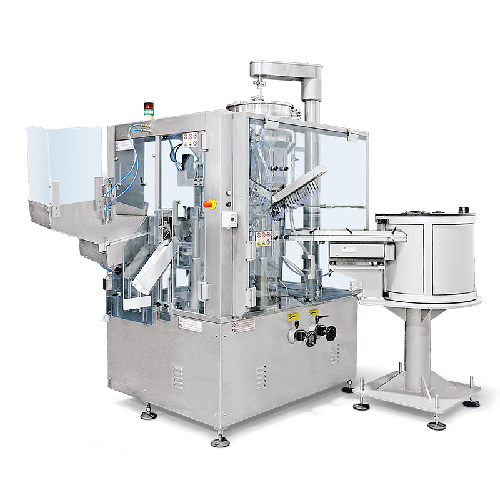
Semi-automatic mascara bottle filling and capping
Streamline your production line with a solution designed for precision ...
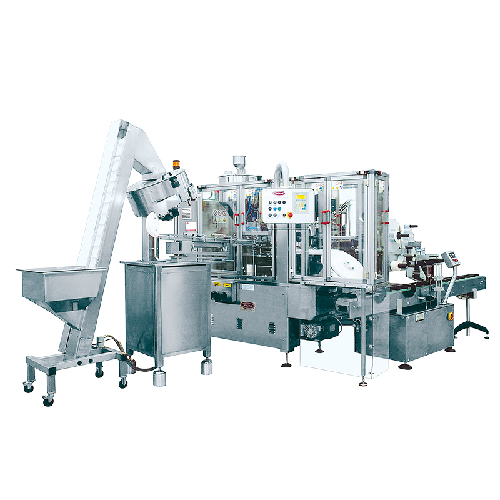
Syringe filling and capping system for pharma industry
Enhance your production line with precise syringe filling and capp...
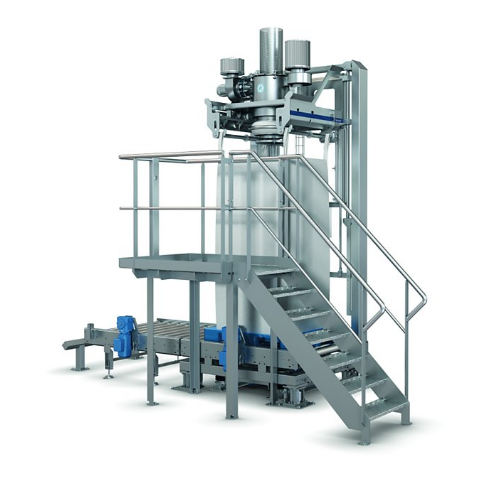
Big bag filler for granulated or powder components
Ensure precise and dust-free filling of large bags with a unit designe...

Volumetric bottom filler for ice cream
Achieve precise distribution and inclusion integrity in moulded ice creams and froze...
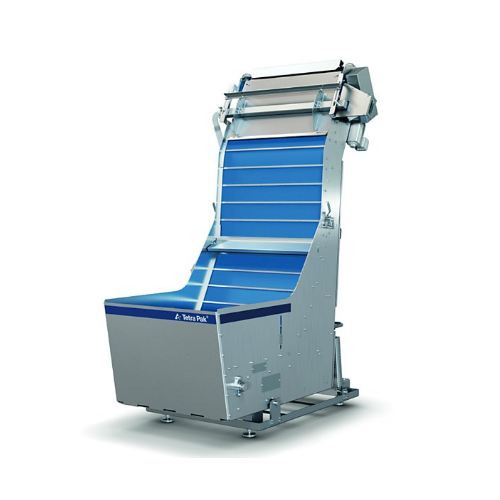
Ice cream filling solution for cups and cones
Optimize your ice cream production with a compact filling solution capable o...
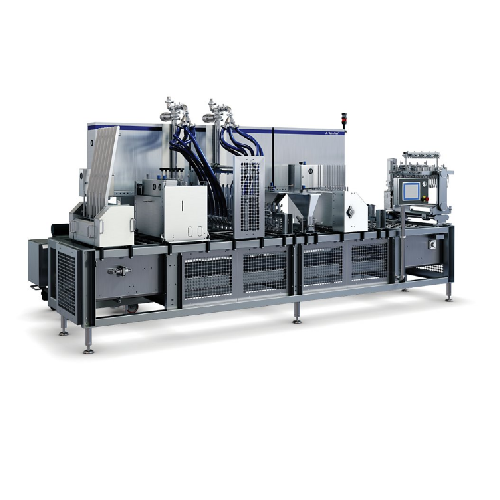
Ice cream filler for consistent and efficient production
Achieve precision in ice cream production with a system that off...
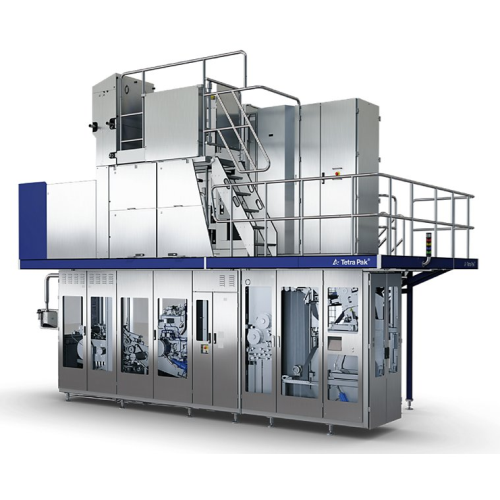
High-speed aseptic carton filling solution
Maximize production efficiency and meet growing demand with this high-output fi...
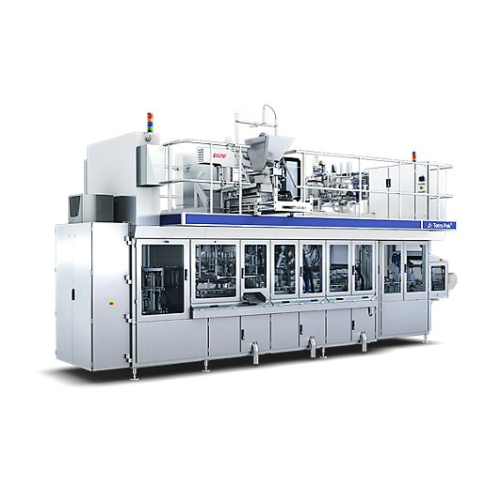
Compact filling system for retortable carton packages
Simplify your production of ready meals and soups with a space-savi...
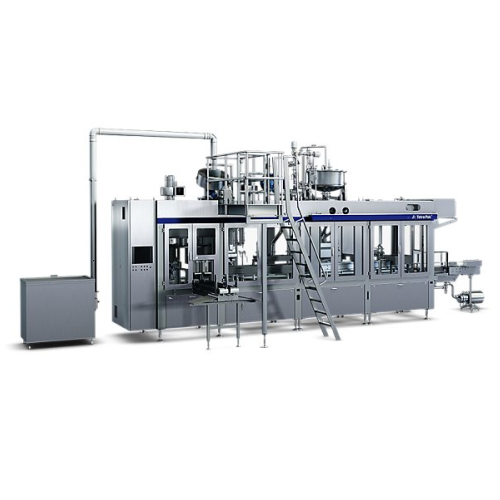
Filling system for gable top packages
Achieve precise, cost-effective filling with reduced energy consumption for chilled l...
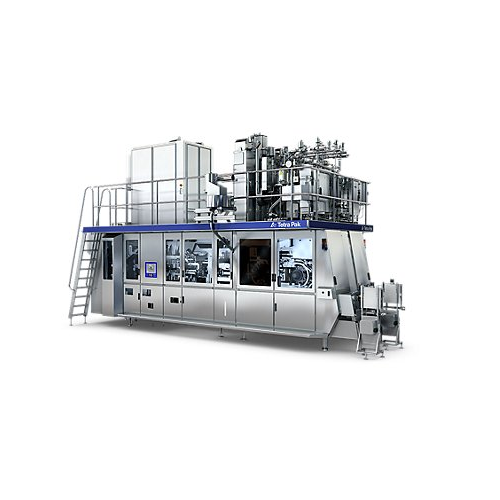
Filling solution for water packaging
Achieve efficient packaging for a variety of beverages with this high-speed filling so...

Dual-line filler for tetra top packages
Maximize your production flexibility with a high-speed, dual-line filling solution ...
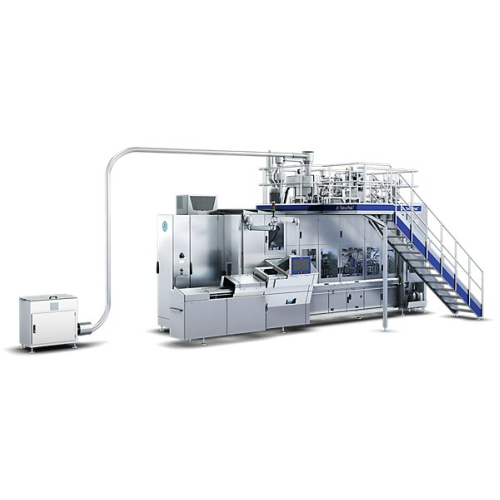
Filling machine for tetra rex® gable top cartons
Maximize efficiency and food safety in high-speed liquid filling with pre...
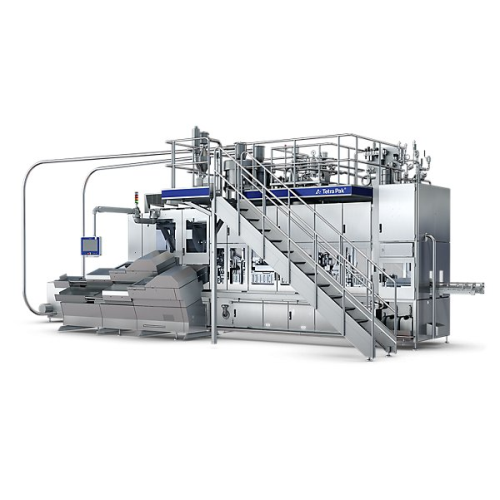
Filling system for gable top cartons chilled products
Achieve precise filling and reliable sealing for chilled beverages ...
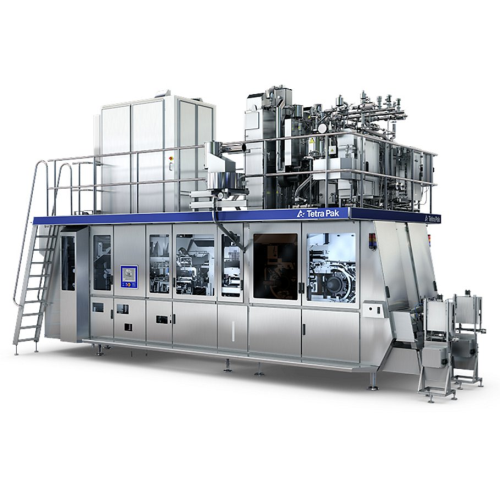
Dual filling solution for tetra top packages
Boost production flexibility by simultaneously filling different liquid produ...
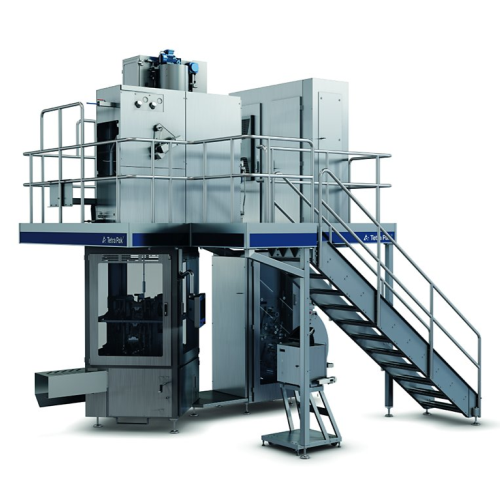
Aseptic filling solution for tetra classic packaging
Experience efficient aseptic packaging with high-speed operation, of...
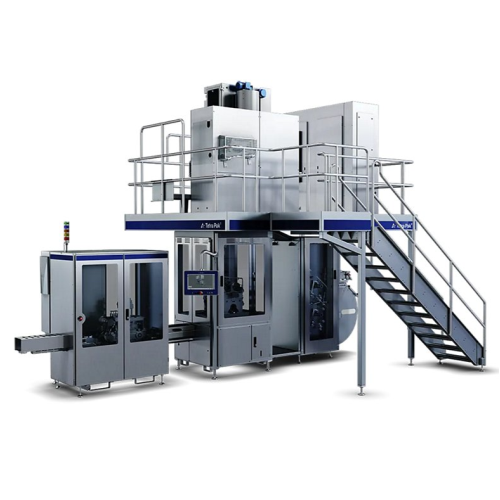
Filling system for tetra brik 100 slim packages
Optimize your chilled product packaging with a high-speed filling system d...
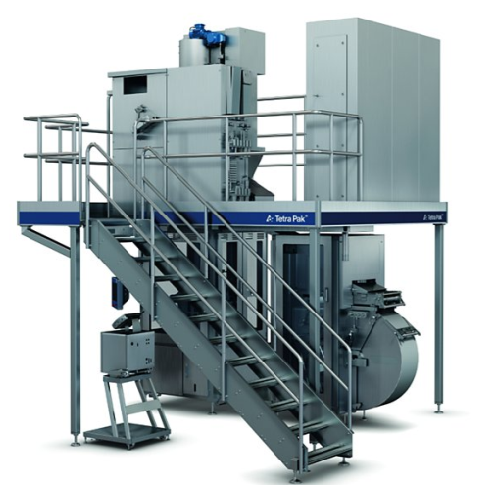
Aseptic carton filling system for tetra fino packaging
Elevate your production efficiency with a high-speed aseptic filli...
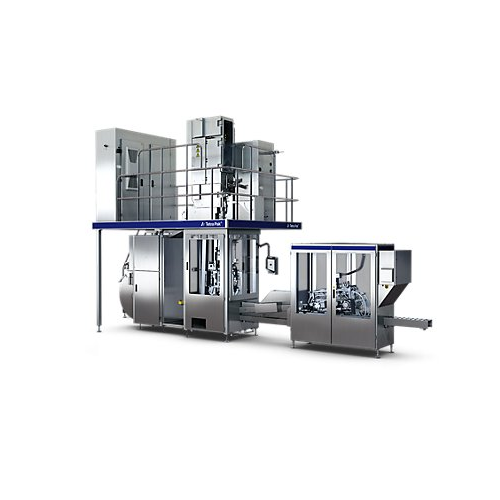
Filling system for tetra wedge aseptic packages
Optimize your production line with a reliable filling system designed to e...
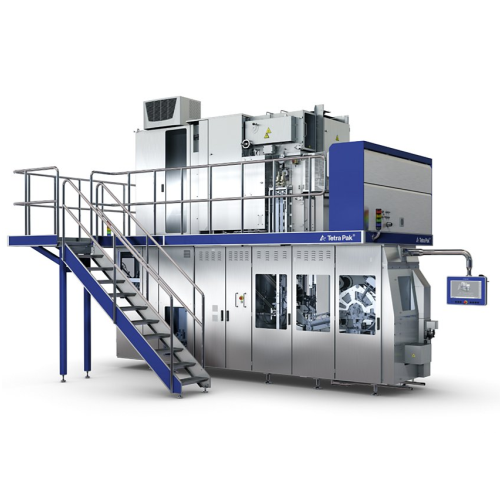
Compact aseptic filling solution for versatile production
Maximize production line efficiency with a compact filling sys...
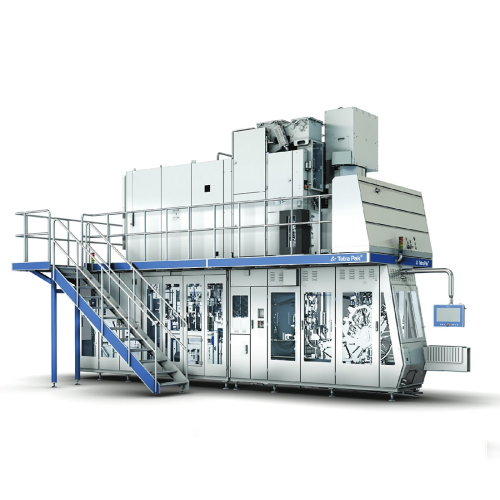
Versatile filling system for aseptic packaging
Achieve seamless integration in high-speed aseptic packaging with this flex...
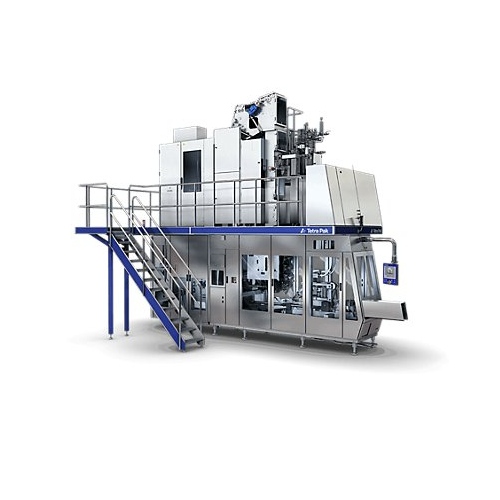
High-speed carton filler for aseptic packaging
Maximize production efficiency with this high-speed filling solution that e...
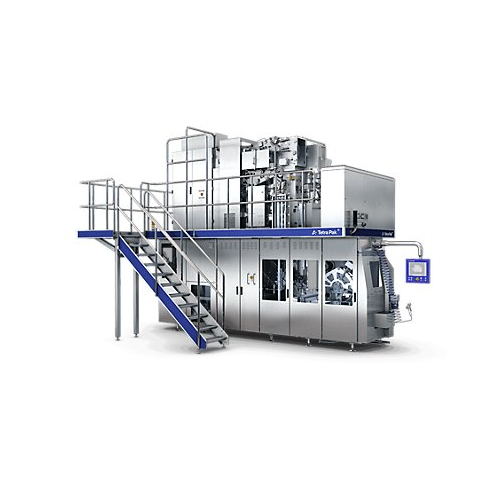
Carton filling system for tetra brik portion packs
Achieve high-capacity portion filling with innovative electron beam st...
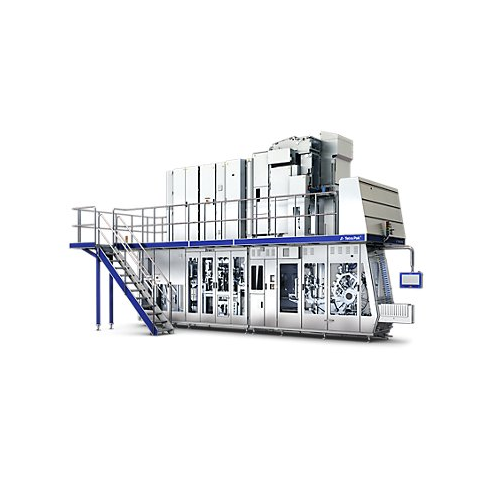
Filling solution for tetra brik® packages
Optimize your filling and packaging process with a system that seamlessly switch...
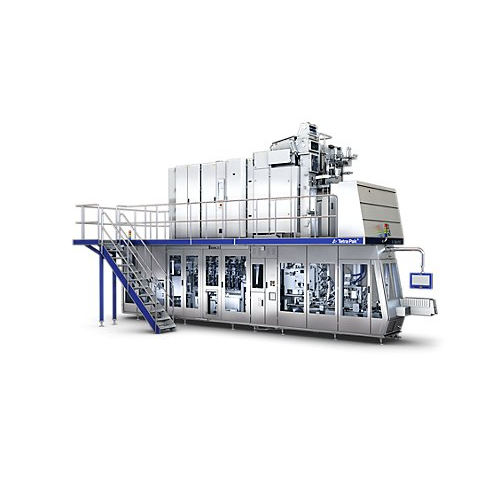
Aseptic filling solution for liquid food packaging
Optimize liquid food production with advanced aseptic filling, ensurin...
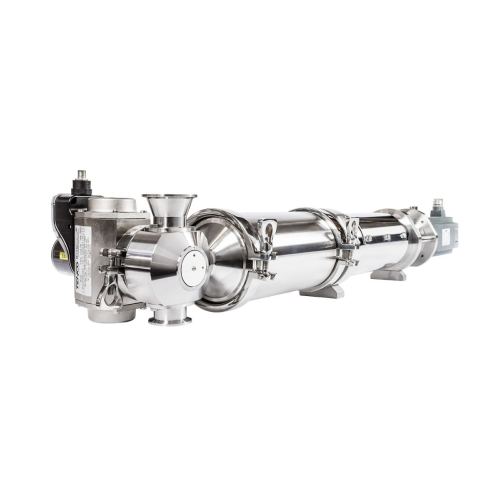
Volumetric piston fillers for liquid and dense products
Perfect for diverse packaging needs, these volumetric piston fill...

Automatic liquid filling solutions for various containers
Ensure precise liquid packaging for diverse container types, e...

Volumetric piston fillers for dense liquid products
Ensure precise filling of liquids and dense products with versatile i...
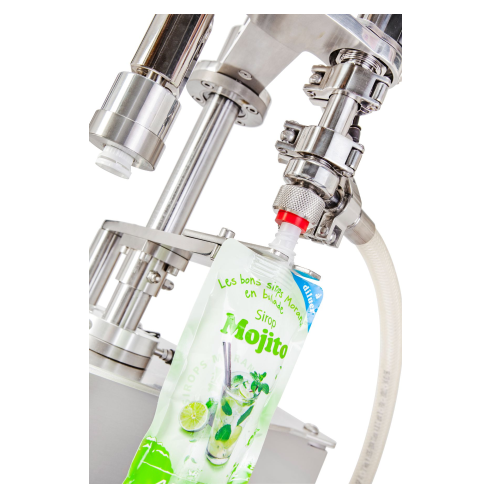
Manual monoblock for filling and capping spouted pouches
For those handling liquid or semi-dense products, this manual mo...
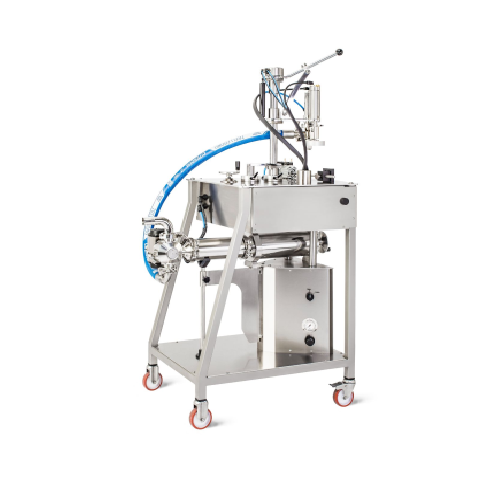
Manual monoblock for filling and capping jars
Optimize your jar filling and capping processes, even with high-temperature ...
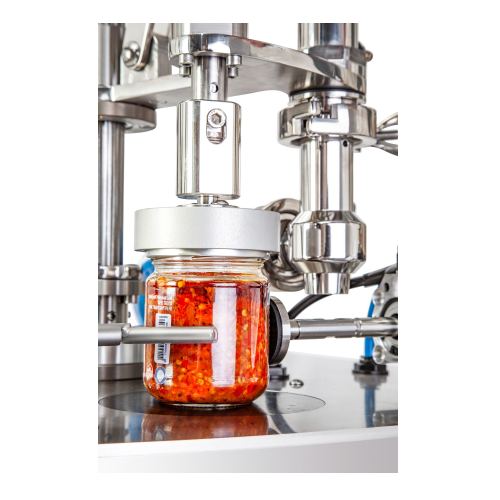
Manual system for filling and capping jars
Ideal for efficiently handling liquid and semi-dense products, this manual syst...
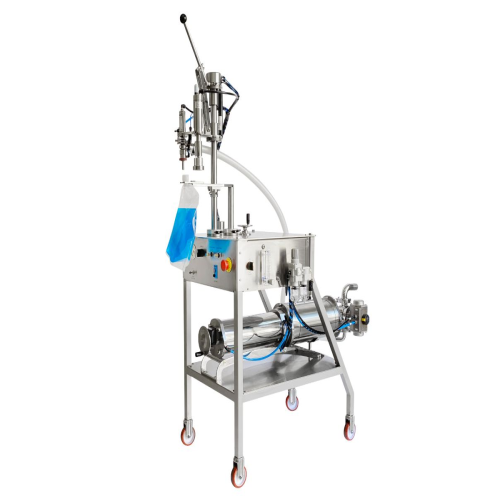
Manual filling and capping for spouted pouches
Optimize your production line with a versatile solution for filling and cap...
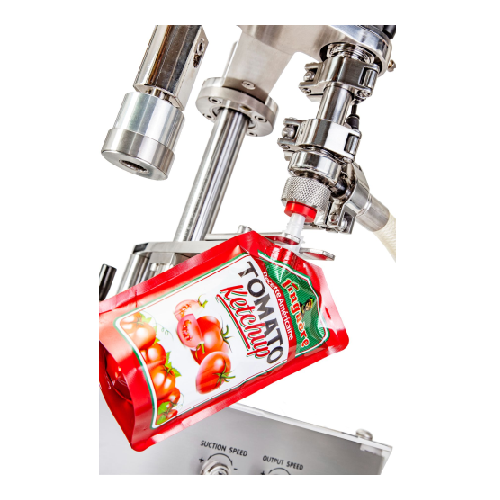
Manual filler and capper for spouted pouches
Easily manage filling and capping for flexible pouches with precise volumetri...
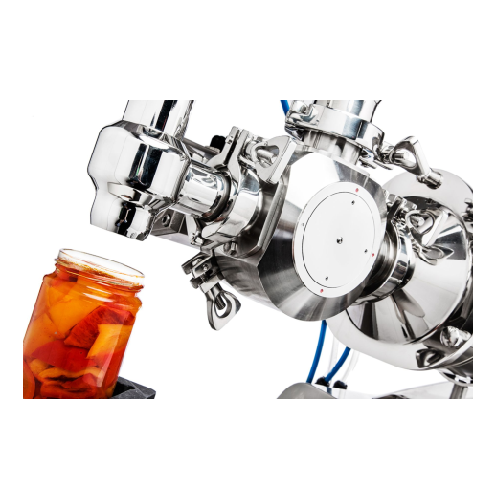
Filling solution for various container types
This versatile filling solution optimizes liquid packaging by accommodating a...
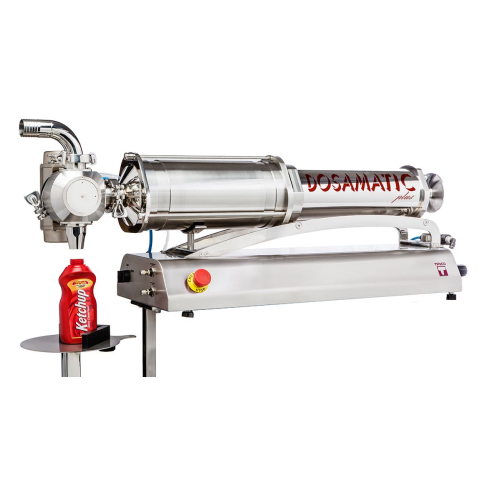
Accurate volumetric filler for liquid and semi-dense products
Achieve precise dosing and filling of various liquid and s...
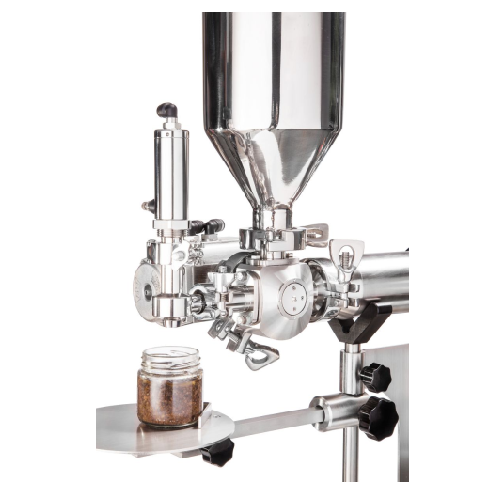
Bench-top piston filler for liquid and semi-dense products
Optimize your filling precision with a versatile piston fille...
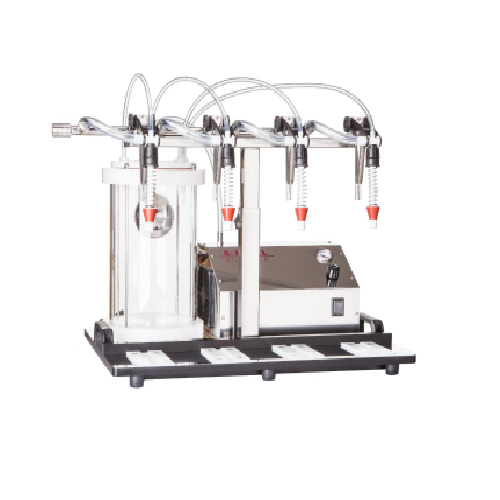
Interchangeable kits for enolmaster filling system
Achieve precision and versatility in liquid filling with adaptable kit...
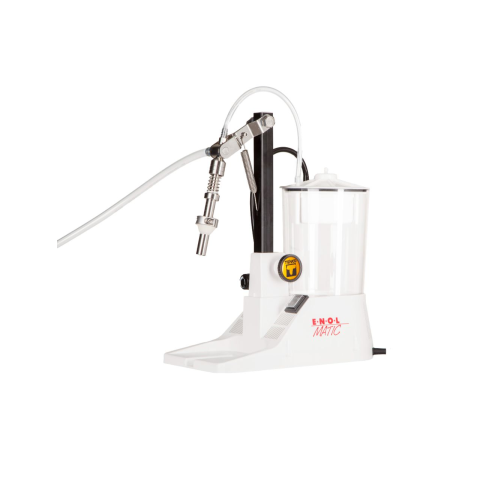
Vacuum filler for wine and oils
Optimize your beverage bottling process with a compact vacuum filler designed for precise le...
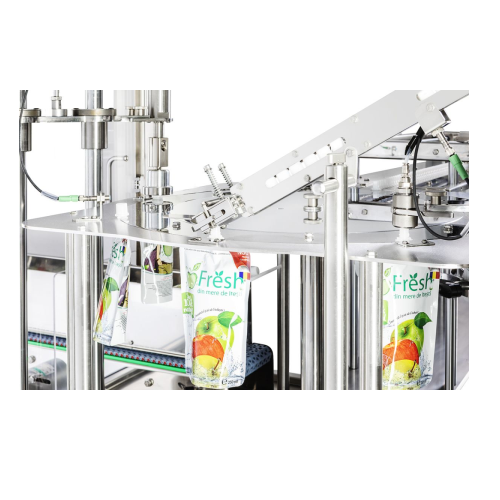
Automatic line for filling and capping spouted pouches
Streamline your production line with high-speed filling and cappin...
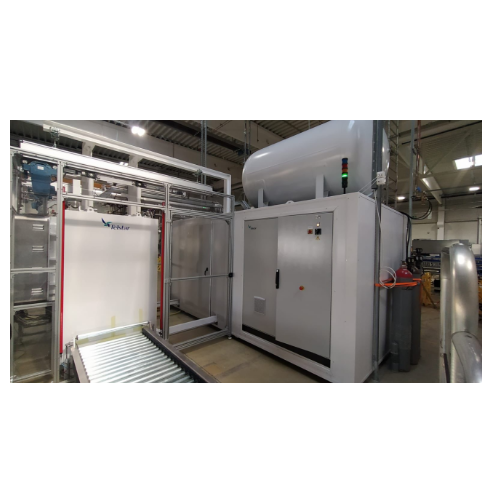
Leak detection and gas filling for electric switchgears
Achieve precise leak detection and efficient gas filling for elec...
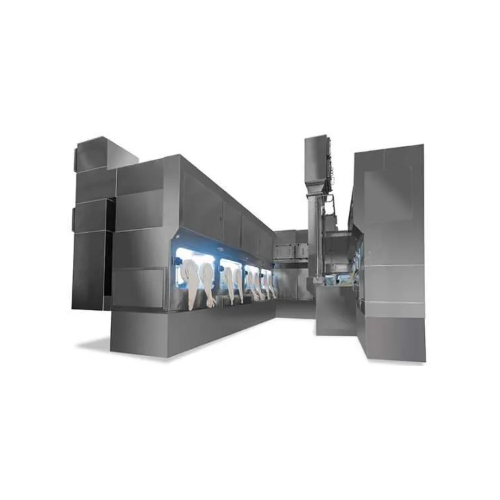
Freeze dryer & filling line aseptic isolator for cytotoxic products
Handle cytotoxic and high-potent drugs with precisi...
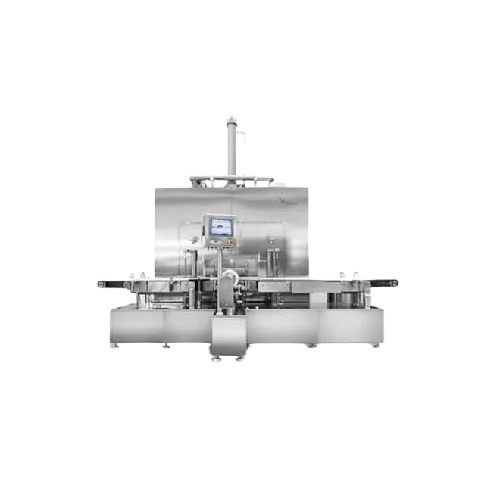
Sterile lyophilisation and filling line
Ensure aseptic conditions while freeze-drying biopharmaceuticals and high-potent dr...
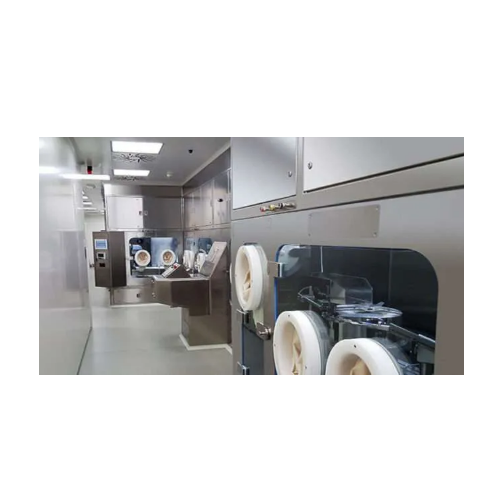
pharmaceutical lyophilised filling line
For high-precision production of moisture-sensitive drugs, this aseptic system ensu...
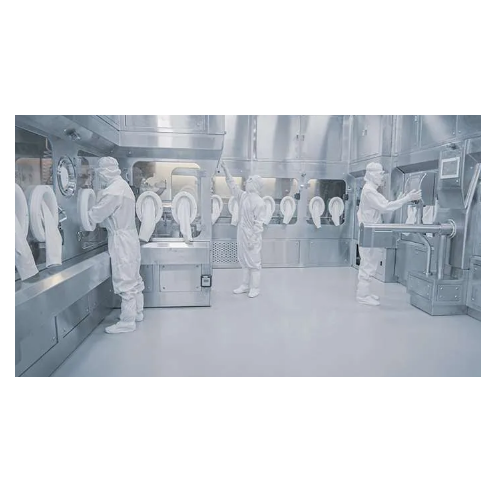
Vial filling line and freeze dryer system
For seamless drug production, integrate reliable vial filling with precision fre...

Sterile lyophilised filling line
Ensure precision in filling and sterilization with an integrated system designed for stream...
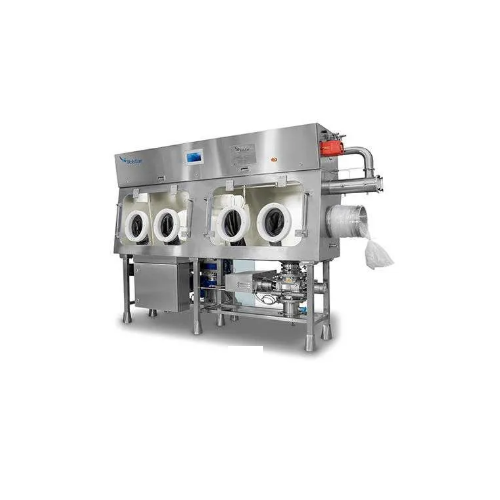
Sterile lyophilised filler
Achieve precise weighing and contamination-free lyophilisation with our cutting-edge sterile fill...
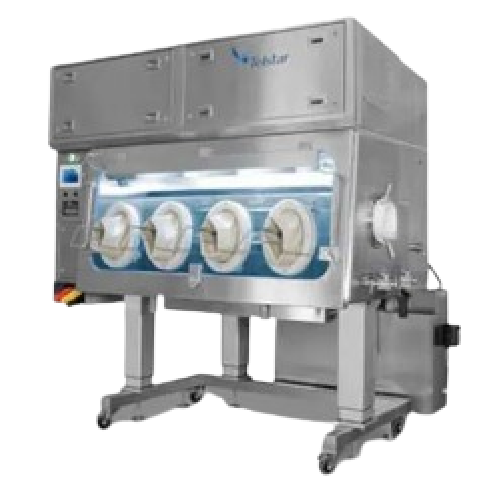
Aseptic ophthalmic filling isolator
Ensure sterility and precision in ophthalmic solutions with a controlled aseptic enviro...
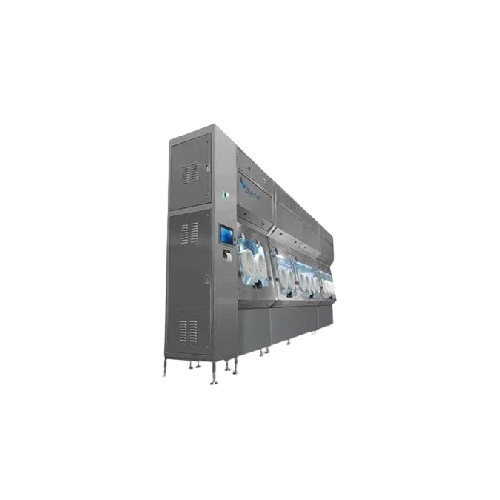
Aseptic syringe filling isolator system
Ensure product sterility and precision with a cutting-edge solution for aseptic syr...
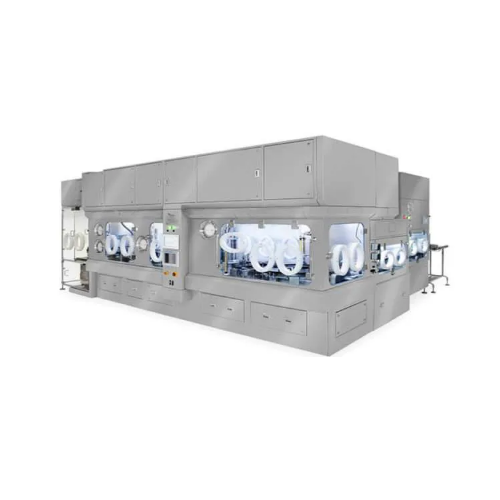
Sterile lyophilized filling line
Ensure sterility and precision in filling pharmaceuticals with advanced isolator lines desi...
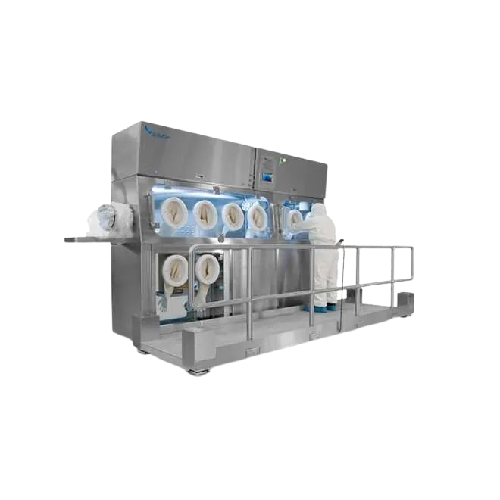
Sterile lyophilised filling solution
Achieve precise filling and control of moisture-sensitive pharmaceuticals while ensuri...
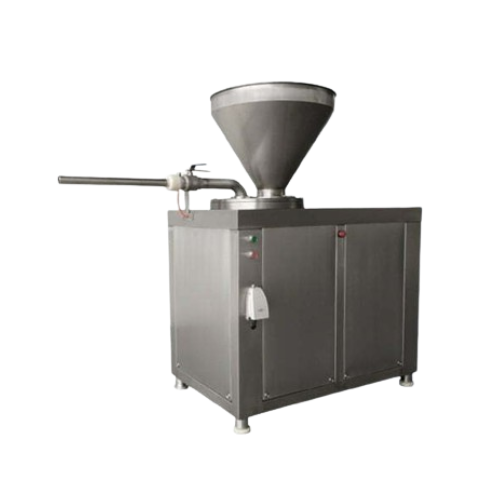
Hydraulic sausage stuffer for continuous filling
Streamline your sausage production with our hydraulic stuffer, designed f...
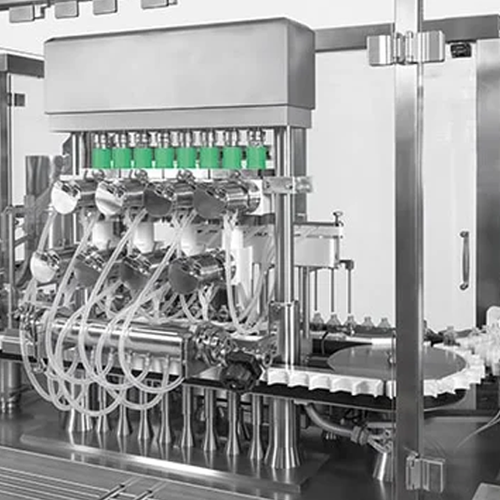
Bulk vial liquid filling system
Ensure reliable and efficient processing of critical biopharmaceutical and pharmaceutical li...
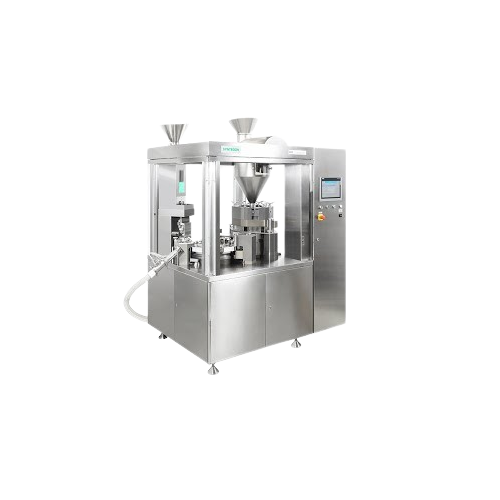
Capsule filling for nutrition and health products
Optimize your production line with advanced capsule filling capabilitie...
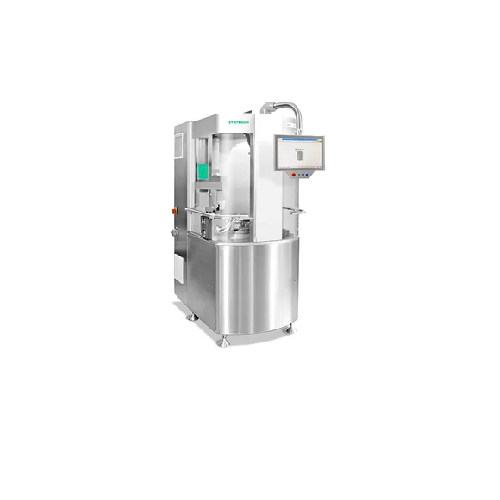
Capsule filling for pharmaceuticals and nutraceuticals
Enhance your capsule production capabilities with modular filling ...
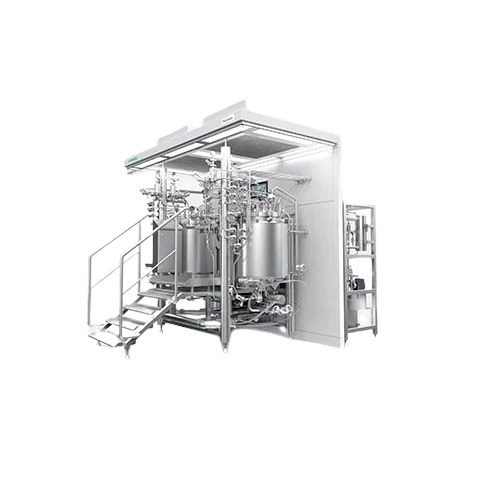
Syringe filling line for parenteral drugs
Ensure precise dosage and sterility with this high-speed syringe filling line, i...
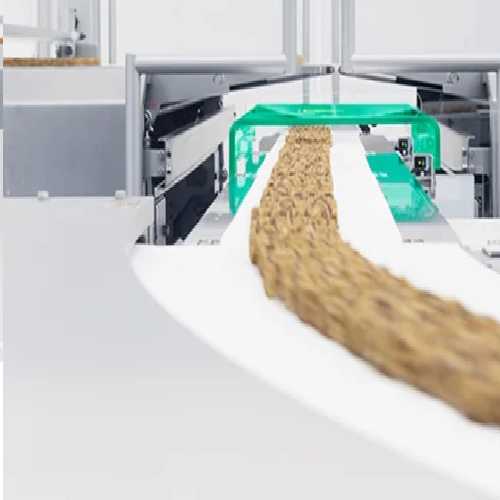
Automated cup filling solutions for liquid and viscous products
Ensure precise and hygienic filling of dairy, baby food,...
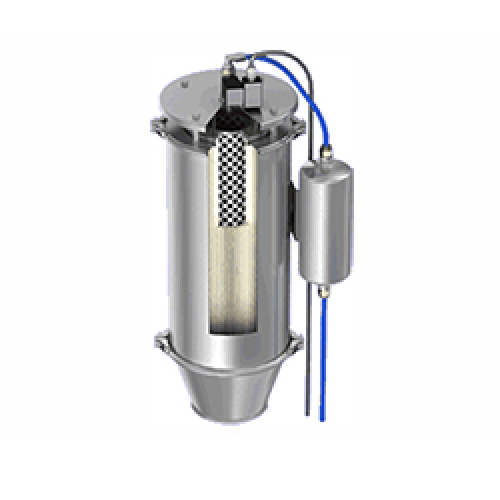
Dust filter for loss-in-weight feeder refill
Optimize your feeder operations by effectively filtering displaced air and mi...
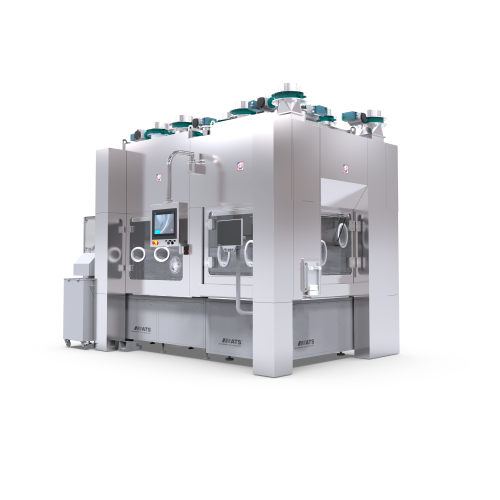
Robotic filler for aseptic pharmaceutical production
Streamline your aseptic filling process with high-speed robotic prec...
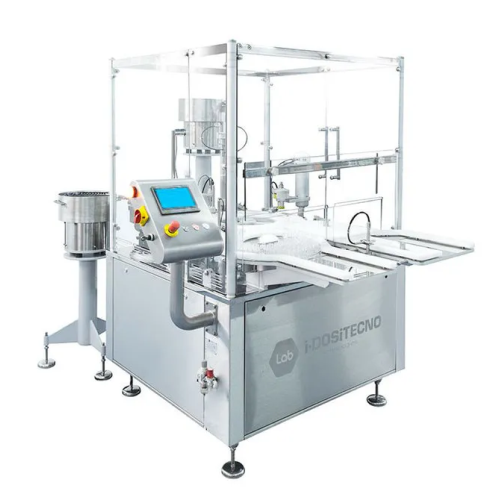
Rotary filler for pharmaceutical vials
Optimize precision and efficiency in fill-finish operations with a rotary system des...

Nasal spray filling solution
For precise nasal spray production, achieve seamless filling, stoppering, and capping to ensure...
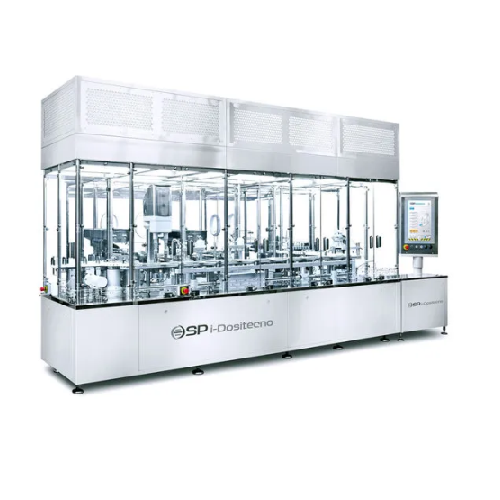
Ophthalmic filling solution for eye drops
Enhance your ophthalmic production line with a solution designed for precision f...
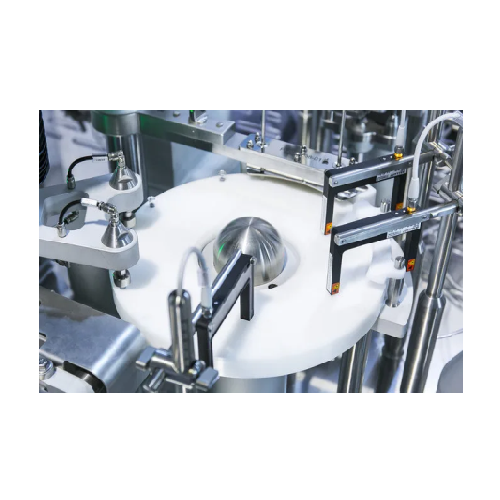
Robotic syringe filling system for sterile pharmaceutical production
For high-precision liquid dosing in sterile enviro...

Pharmaceutical liquid and powder filling solution
Achieve precise filling and capping of diverse formulations with a vers...
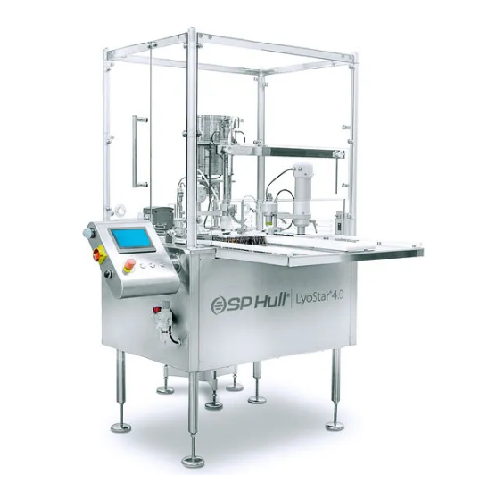
Small scale pharmaceutical filler and stoppering system
Optimize your R&D operations with a versatile filling and st...
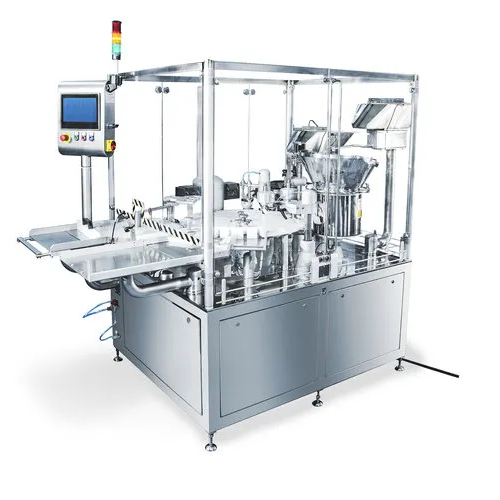
Micro-line vial filling solution for biopharmaceuticals
Ensure batch consistency and sterility in fill-finish operations ...
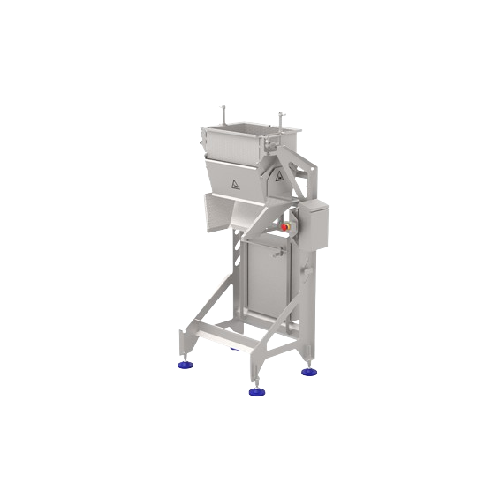
Weighing and crate filling station for cut vegetables
Optimize your vegetable processing workflow by accurately weighing ...
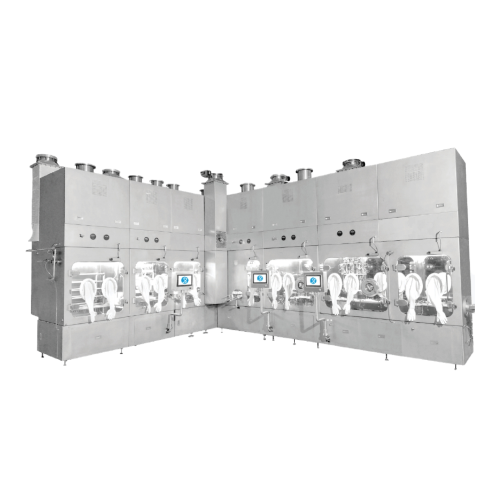
Ampoule filling and sealing line
Streamline your ampoule production with an integrated solution that expertly handles everyt...
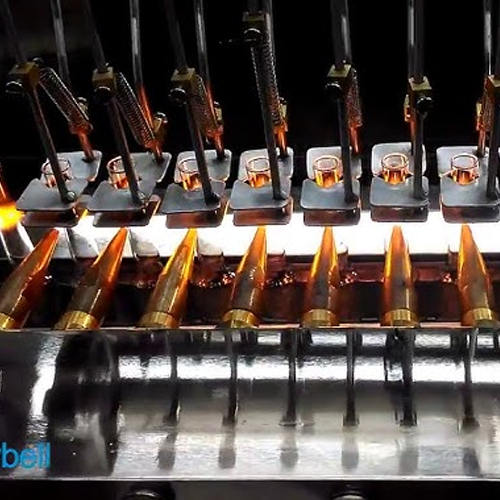
Triple combi filling and stoppering system for vials and ampoules
Optimize your liquid formulation process with a versa...
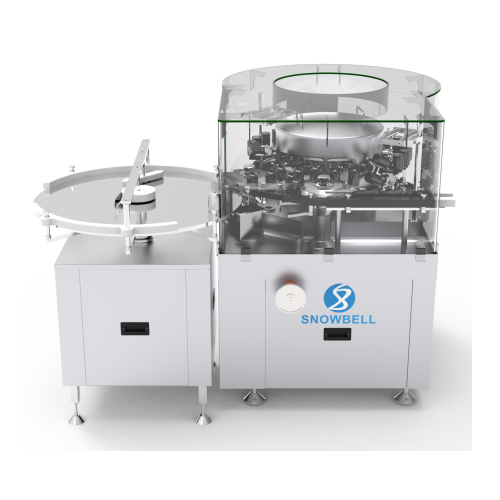
Automatic filling, nozzle placing, and capping line for ophthalmic solutions
Ensure precise dosing and secure sealing ...
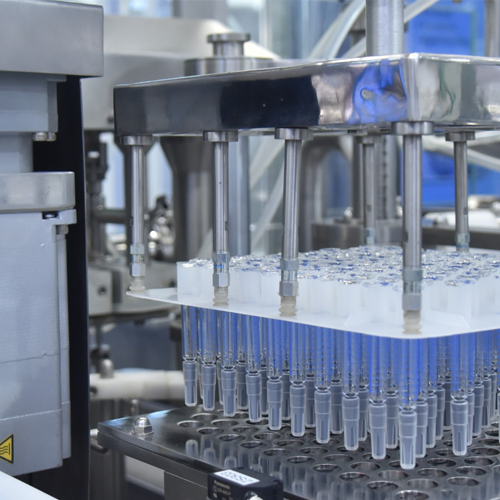
Prefilled syringe filling and stoppering system
Achieve precision in drug administration with this integrated system for f...
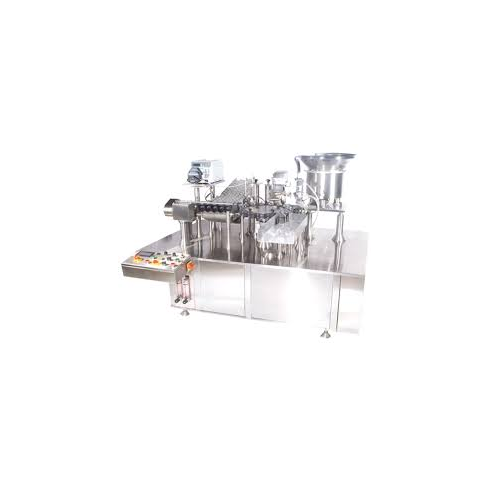
Combi r&d ampoule and vial filling equipment
Optimize your R&D operations with a versatile machine designed for preci...
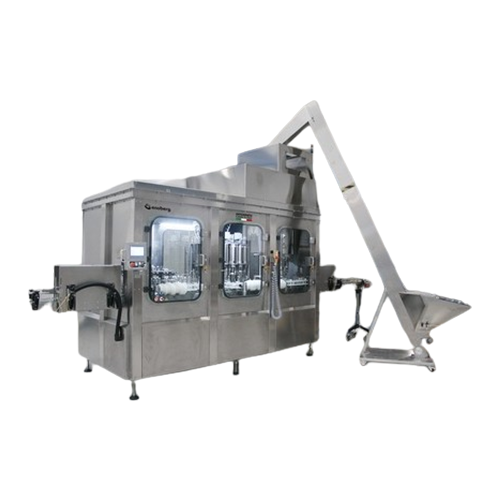
Hyper-clean electronic volumetric filler for Pet bottles
Enhance your liquid filling operations with precision and hygien...
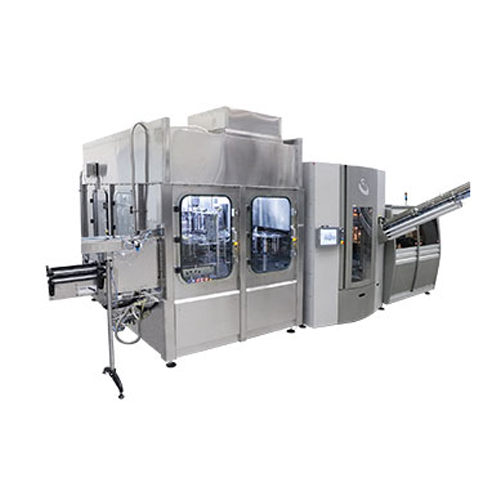
Integrated stretch-blow moulding, filling, and capping system for still liquids
Streamline your bottling process with ...
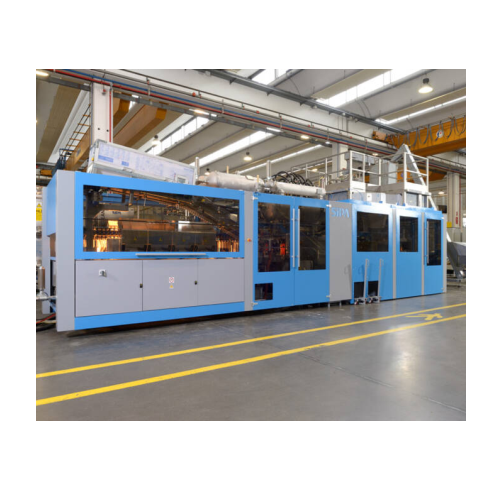
Integrated linear blowing and filling system for Pet containers
Streamline your PET container production with integrated...
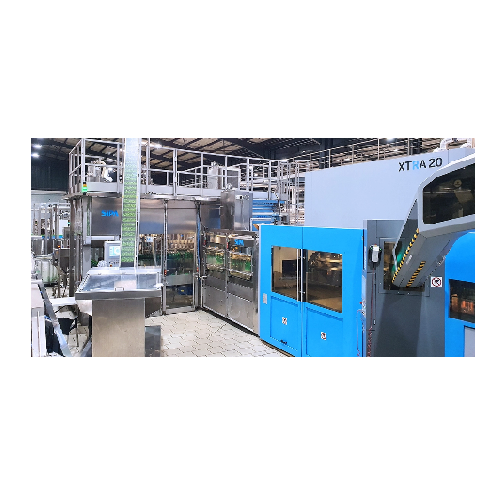
Integrated rotary blowing and filling system for Pet bottles
Optimize your beverage production with an integrated rotary...
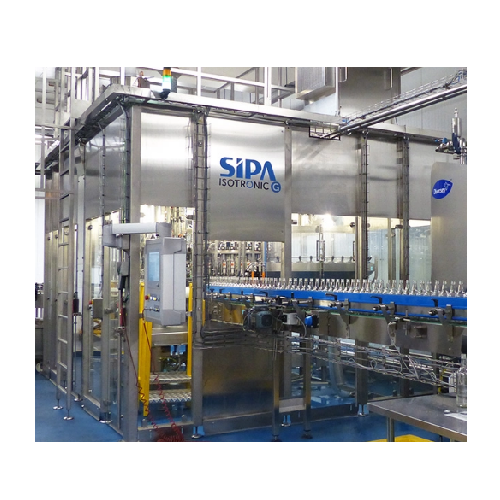
Isobaric filler for glass and Pet bottles
Achieve precise liquid filling with enhanced operational flexibility and hygiene...
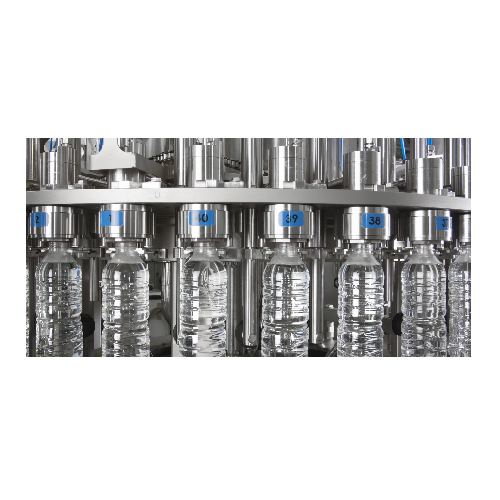
Gravity filling system for Pet bottles
Optimize your beverage production with an advanced gravity filling system, designed ...
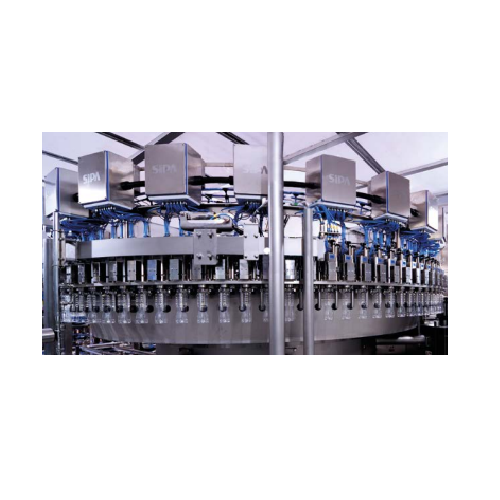
Volumetric gravity filler for large Pet bottles
Optimize your production line with a high-speed volumetric gravity filler,...

Volumetric filler for Pet bottle beverages
Experience seamless integration into your bottling line with this advanced volu...
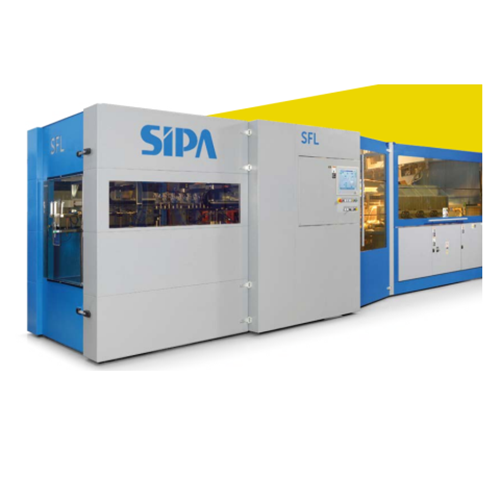
Isobaric filling system for carbonated beverages in Pet bottles
Achieve precise carbonation levels and seamless integrat...
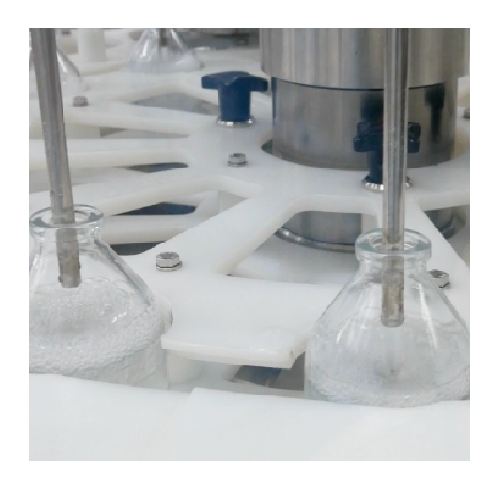
Rotary vial filling and stoppering system
For high-speed production of sterile injectable vials, this continuous motion ro...
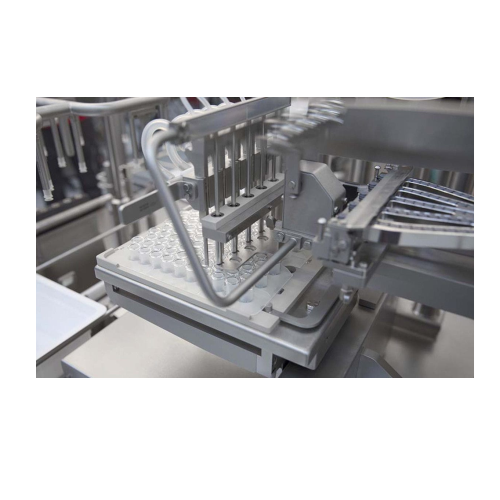
Nested syringe filling and stoppering system
Optimize your syringe production with precise filling and stoppering, ensurin...
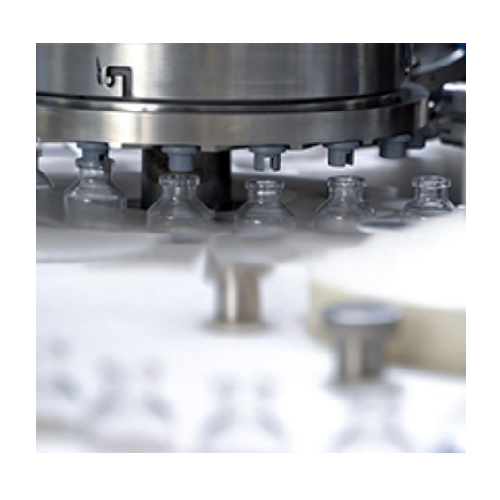
Continuous motion rotary vial filling and stoppering solution
Optimize your vial production with a high-speed, continuou...
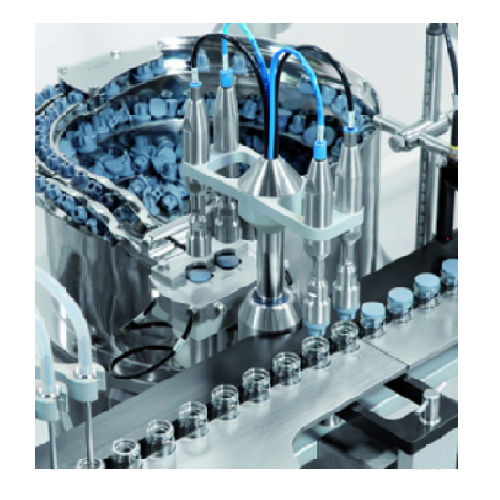
Automatic linear filling stoppering system for large volume vials
Ensure precise vial filling and secure sealing with a...
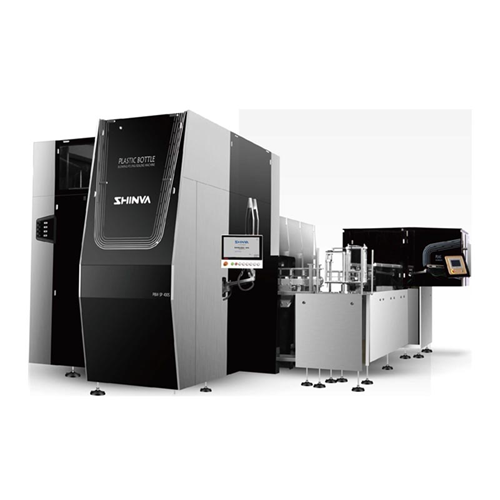
Reciprocating plastic bottle blow-fill-seal system
Achieve seamless integration of bottle forming, filling, and sealing w...
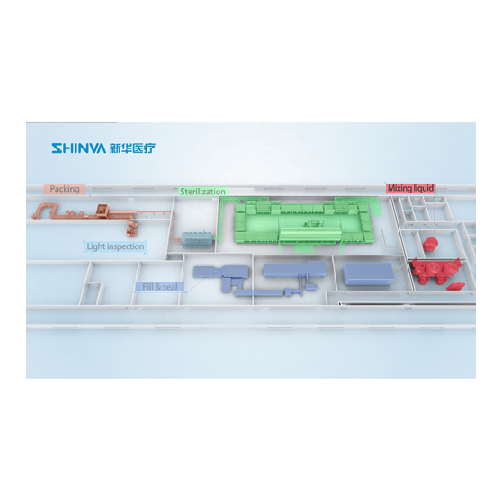
Plastic bottle blowing-filling-sealing system
Optimize sterile liquid packaging with integrated blowing, filling, and seal...
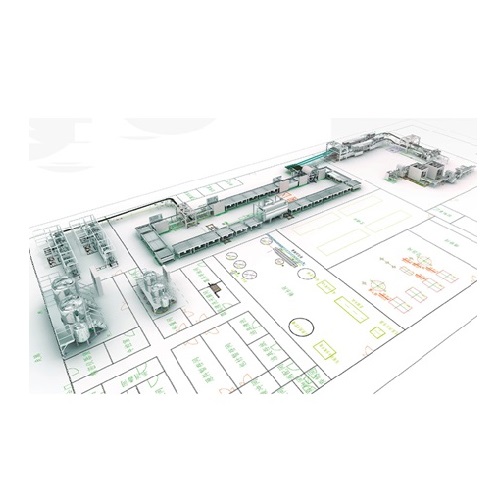
Soft bag form-fill-seal system for large volume injection
Streamline your production of intravenous and nutritional flui...
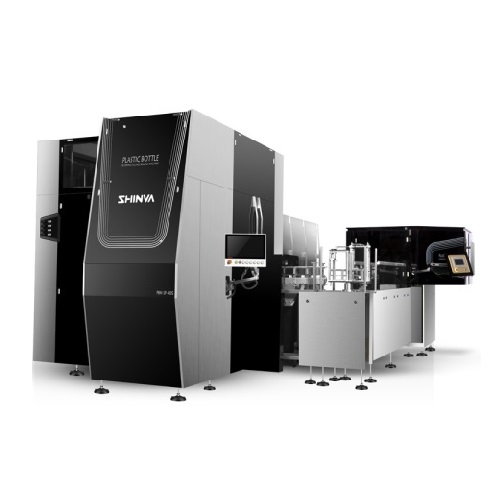
Blow-fill-seal system for small volume injection production
Ensure precise aseptic liquid packaging with integrated blow...
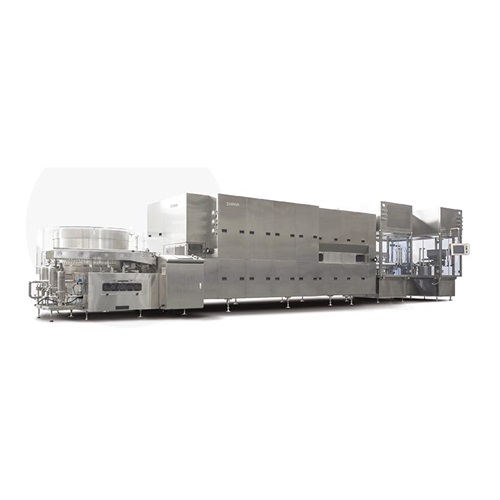
Vial washing drying filling sealing line for pharmaceutical production
Streamline your vial production with this integr...
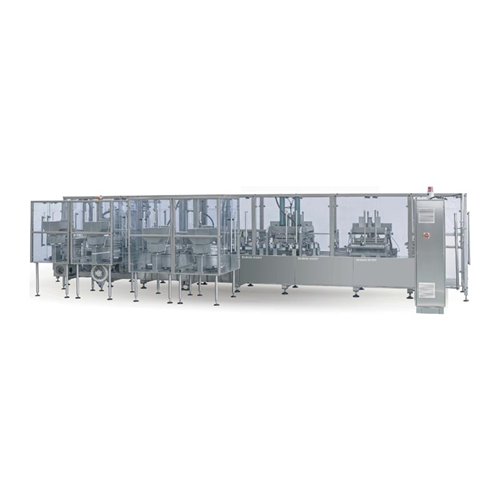
Non Pvc soft bag form fill seal system
Efficiently form, fill, and seal non-PVC infusion bags while ensuring precision and ...
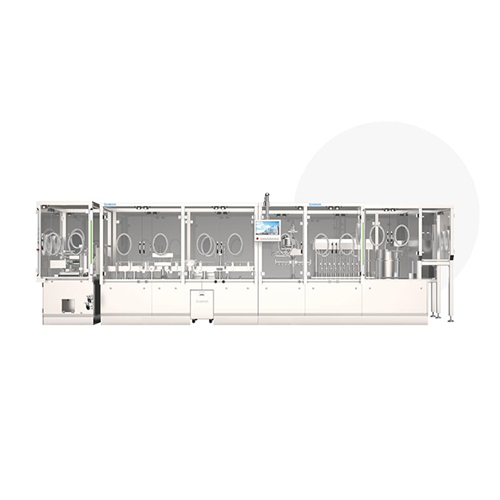
Intelligent pre-filled syringe production line
Optimize your sterile liquid medication production with a streamlined pre-f...
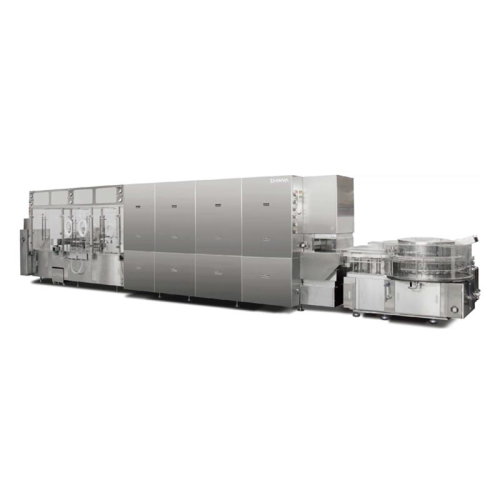
Ampoule washing, filling, and sealing line
Streamline your ampoule production with an integrated washing, filling, and sea...
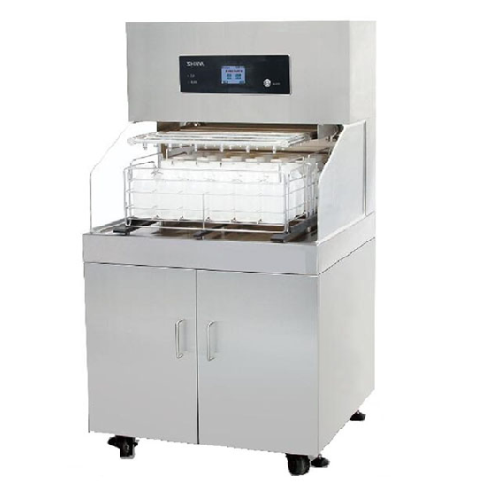
Automatic bottle filling system for animal drinking water
Streamline your laboratory bottling process with a high-effici...
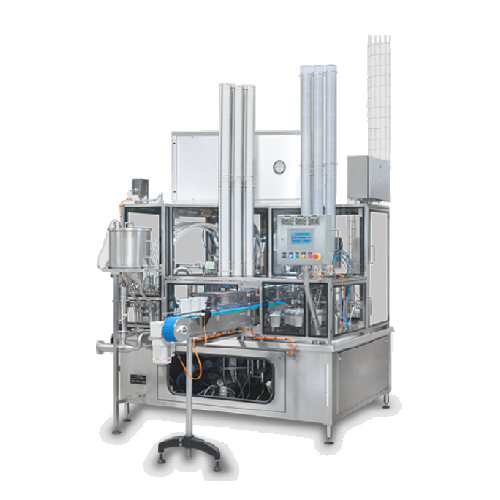
Filler for yoghurt and white cheeses
For manufacturers seeking efficient, versatile filling for products like yoghurt and s...
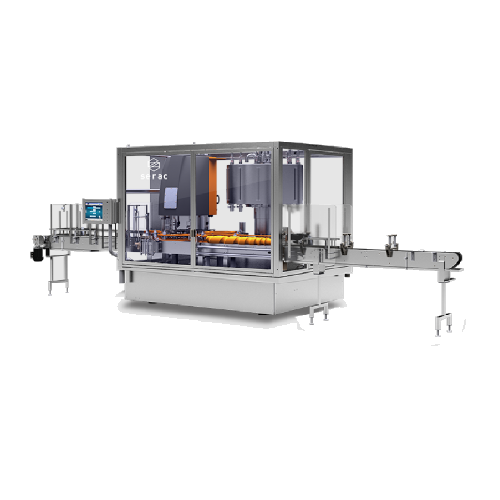
Versatile rotary filler-capper for liquid products
Optimize your liquid product production with a versatile solution that...
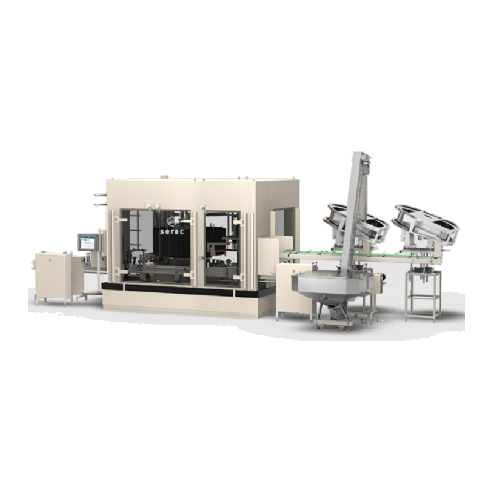
Anti-corrosion filling system for aggressive liquids
When dealing with corrosive liquids, ensure durability and safety wi...
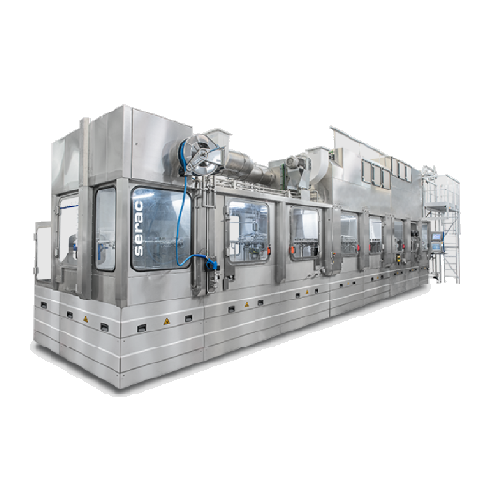
Aseptic filling technology for dairy products
Ensure product integrity and extend shelf life with a high-speed aseptic fil...
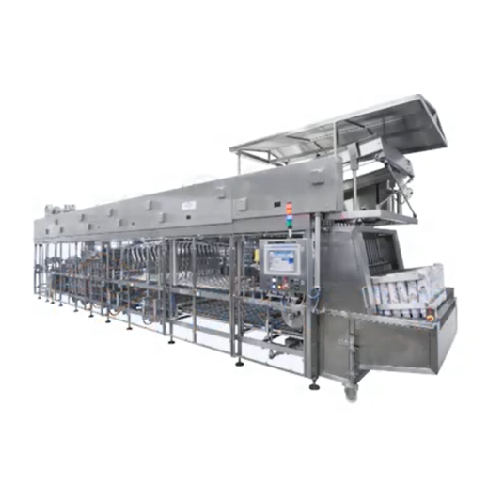
Dairy product filling solutions
Optimize your dairy production with advanced filling systems designed to enhance product saf...
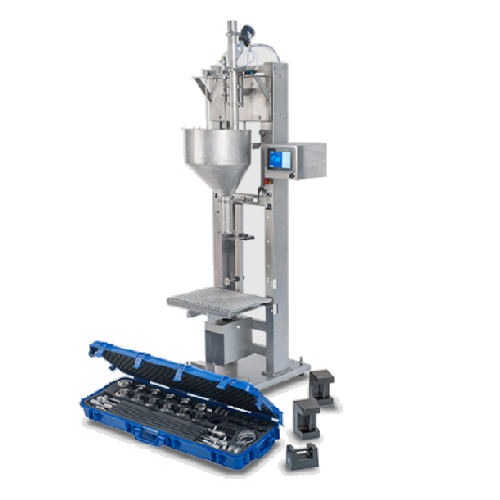
Semi-automatic weight filling system for liquid products
Achieve precise and versatile liquid filling performance with th...
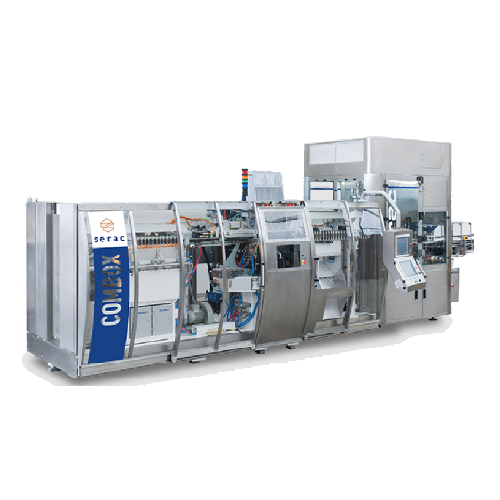
Blow-fill-cap solution for low/medium batch production
Streamline your production line with a compact blow-fill-cap syste...
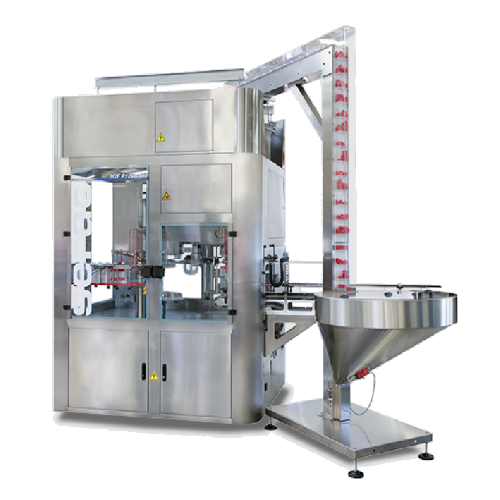
High hygienic filler for chilled beverages
Enhance cold beverage production with a modular, hygienic filler offering chemi...

Yoghurt and dairy desserts filling solution
Maximize efficiency in filling and sealing multi-product dairy desserts and be...
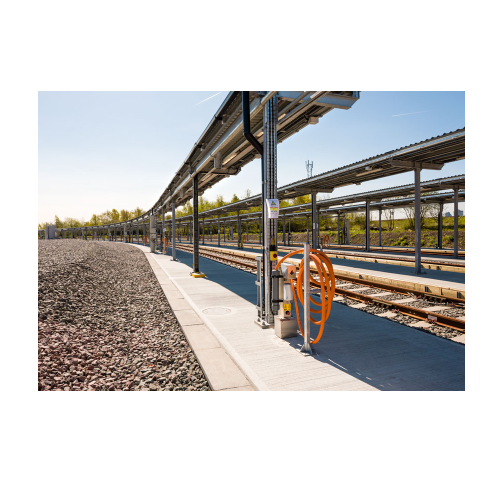
Static sand filling system for train and tram sand boxes
Ensure optimal train and tram braking performance with efficient...
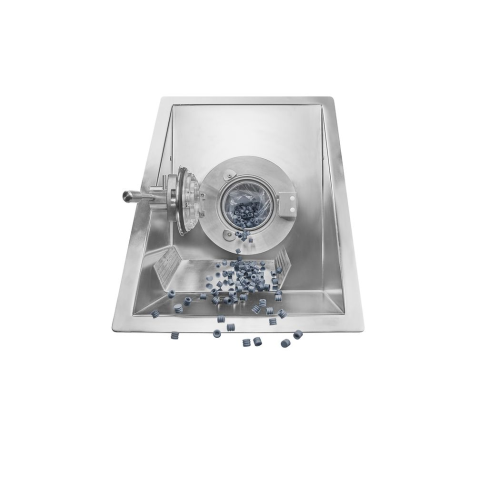
Single-use transfer and filling solutions in barrier isolated filling lines
Ensure sterile, high-volume liquid transfe...
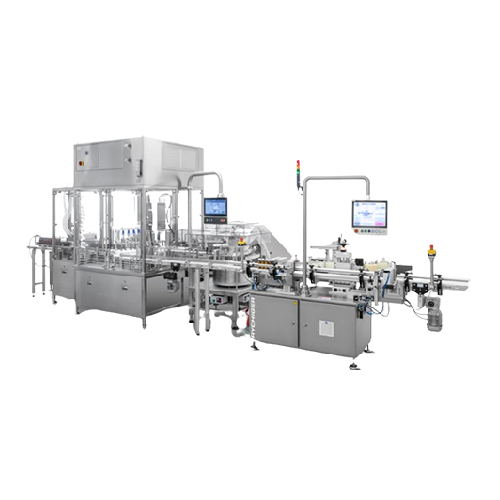
Rotary transfer system for pharmaceutical product filling
Ensure precise and hygienic filling of diverse pharmaceutical ...
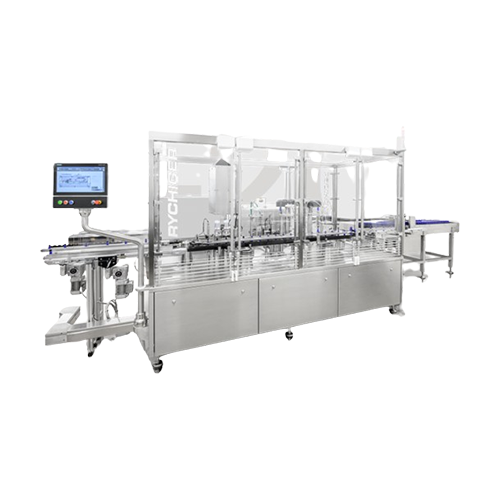
Sterile filling platform for pharmaceuticals
Achieve precise, high-speed aseptic filling and packaging with advanced compl...

Aseptic handling and fill-finish platform for Rtu syringes, vials, and cartridges
Ensure aseptic precision and high t...

Semi-automatic filling solution for syringes and vials in isolators
Achieve precise aseptic fill-finish operations for ...
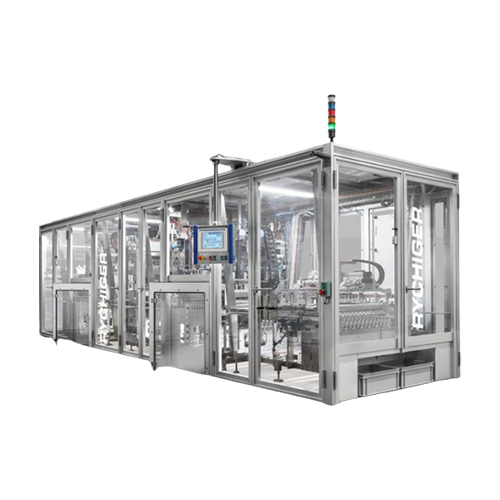
Coffee capsule filling and sealing solution
Optimize your production with a high-speed solution designed to fill and seal ...
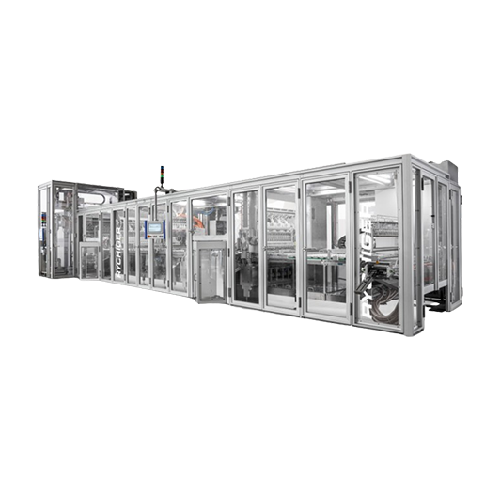
Coffee capsule filling and sealing system
Boost capsule production efficiency and reduce downtime with a high-speed system...
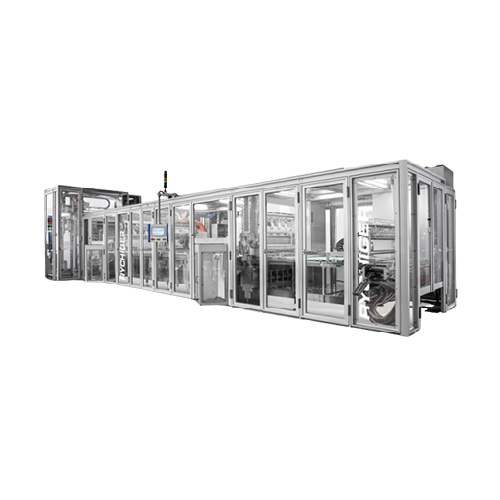
Coffee capsule filling and sealing line
Elevate your capsule production with a high-speed filling and sealing solution that...
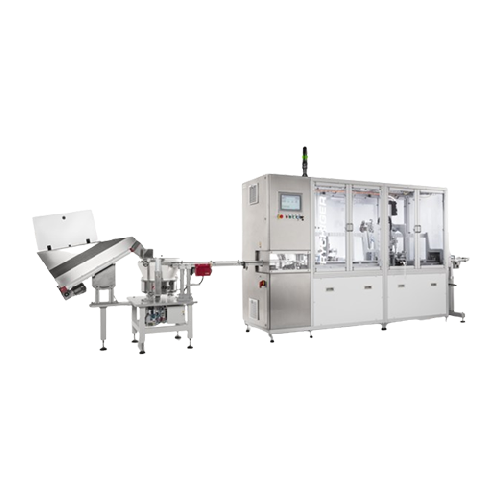
Filling and sealing multi-well cassettes for molecular diagnostics
Streamline your small to medium-scale diagnostic pro...
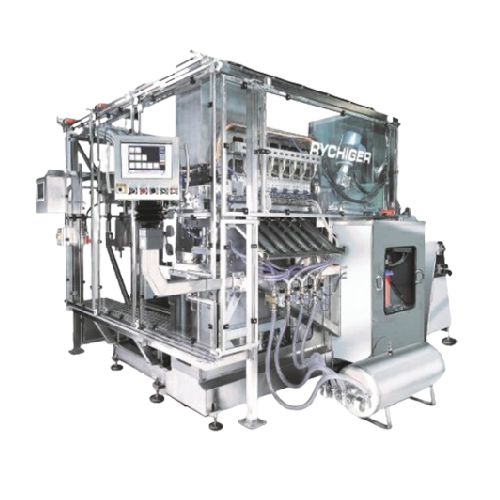
Convenience and pet food filling solution
Optimize your production line with high-speed, hygienic filling of diverse food ...
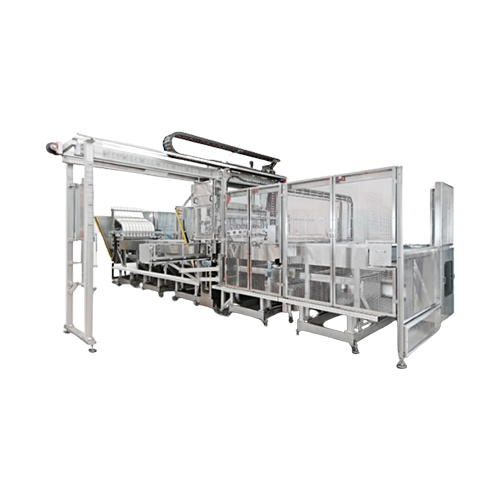
Precision filler for convenience and pet food
Achieve unparalleled precision and efficiency in filling solids, powders, li...
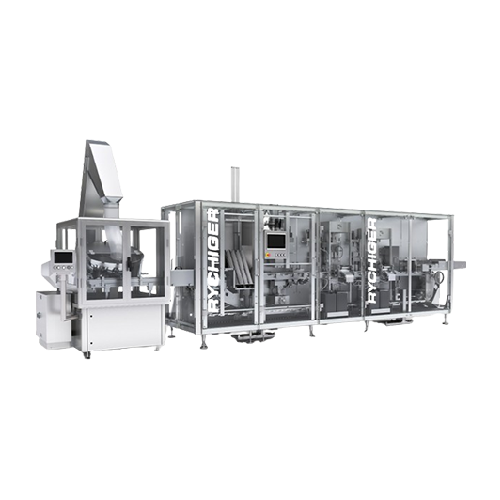
Filling and sealing solution for beverage capsules
Optimize your production with a modular capsule filling and sealing so...
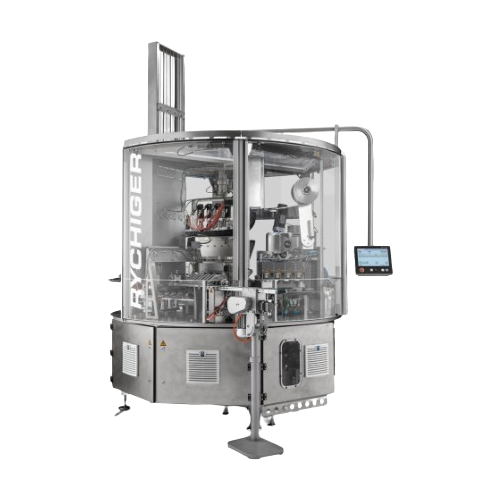
Coffee capsule filling and sealing machine
For producers seeking a compact yet powerful machine, this system efficiently f...
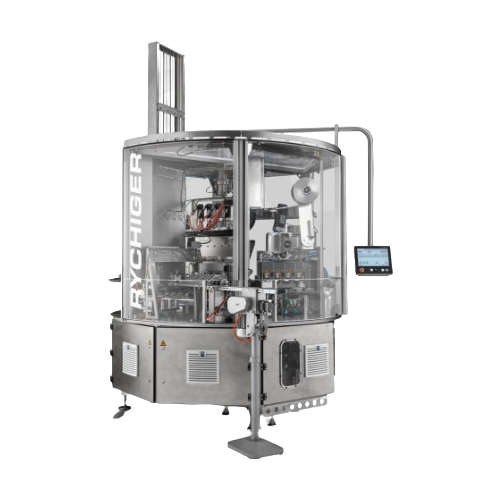
High-speed coffee capsule filling and sealing system
Streamline your capsule production with a high-speed solution that e...

Filling and assembling solution for Ivd and Poc products
Optimize precision and efficiency in cleanroom environments with...
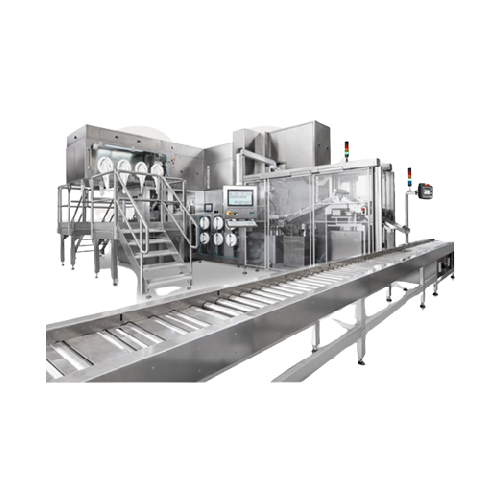
Filling solution for powders and liquids in diagnostics
Simplify precision filling of diverse products, from freeze-dried...
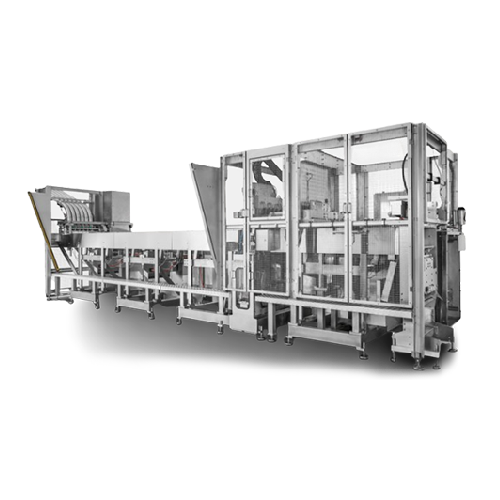
Filling system for solids, pastes, and liquids
Eliminate contamination risks while achieving high-speed, precise filling o...

Vacuum filler for coarse and dry sausage products
Optimize your sausage production with a machine that ensures consistent...
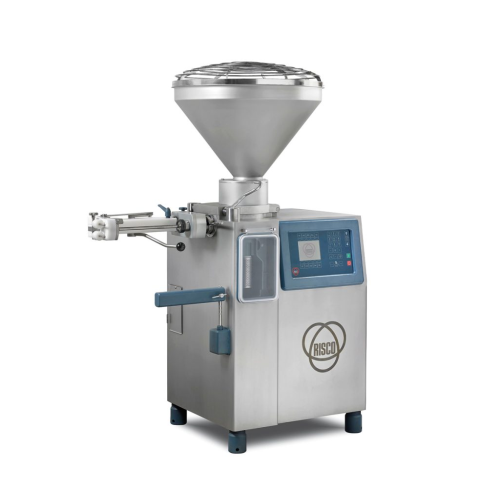
Portioning and filling system for sausage production
Achieve precise portioning and efficient filling for a diverse range...
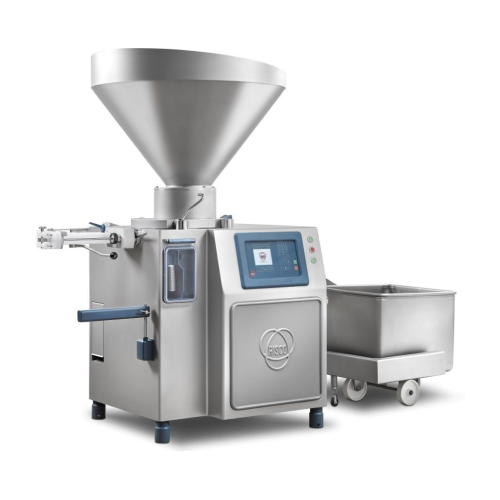
Industrial vacuum filler for large-scale food production
Enhance your production efficiency by integrating a vacuum fille...
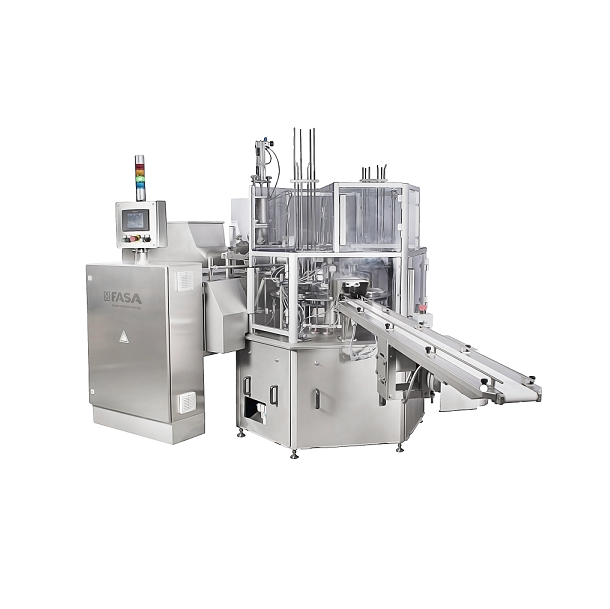
Butter Tub Filling And Sealing Machine
When packing paste-like products such as butter, spreads or margarine you need flexi...
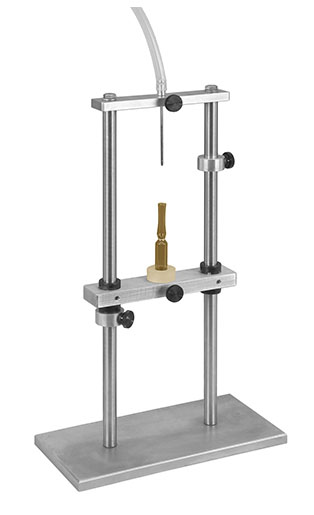
Manual ampoule filler
When you fill ampoules it is essential to avoid wetting the inside walls of the container, as it may af...
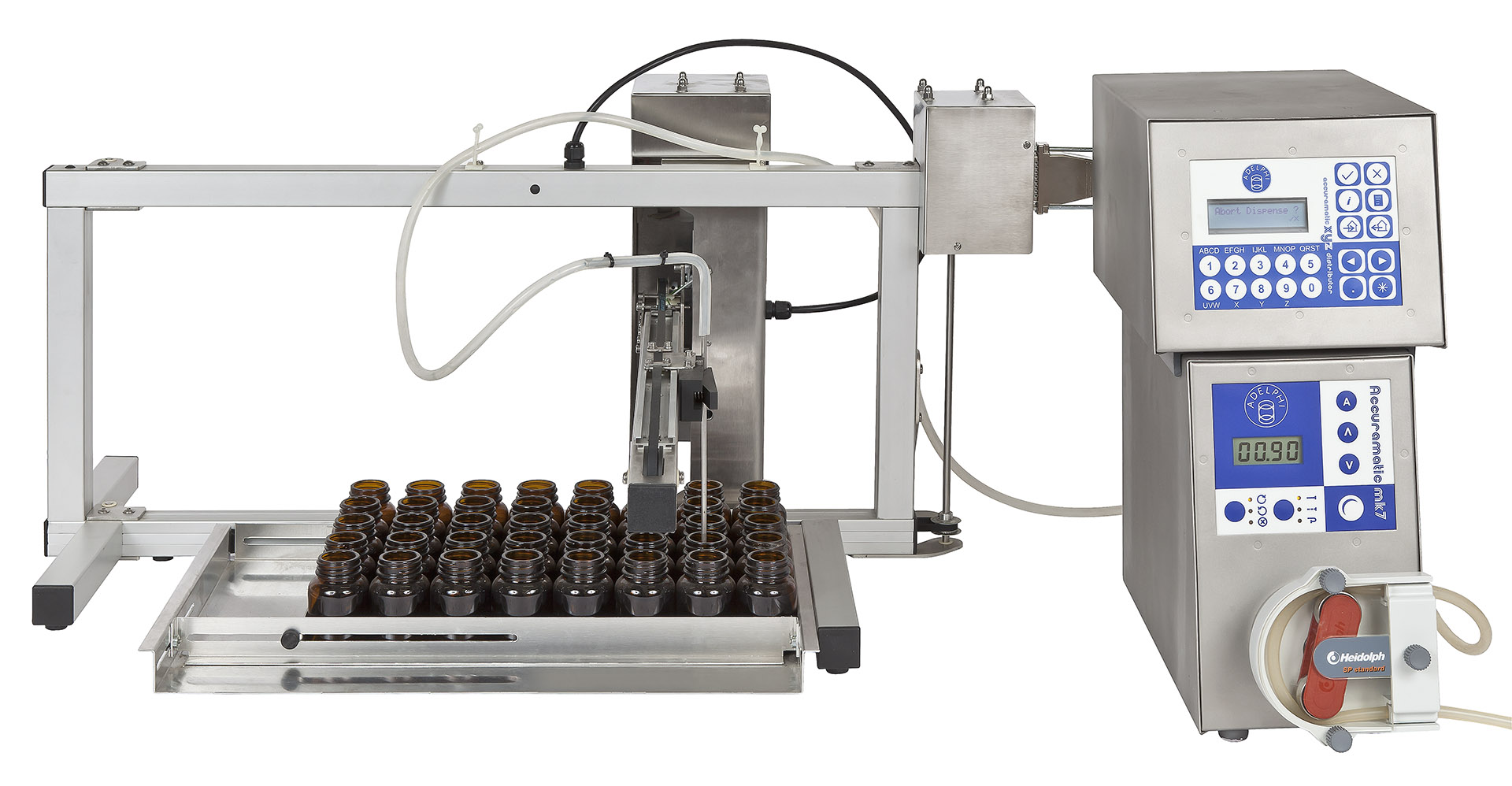
Benchtop piston filling equipment for vials in trays
Vials are difficult to fill individually through manual methods due ...
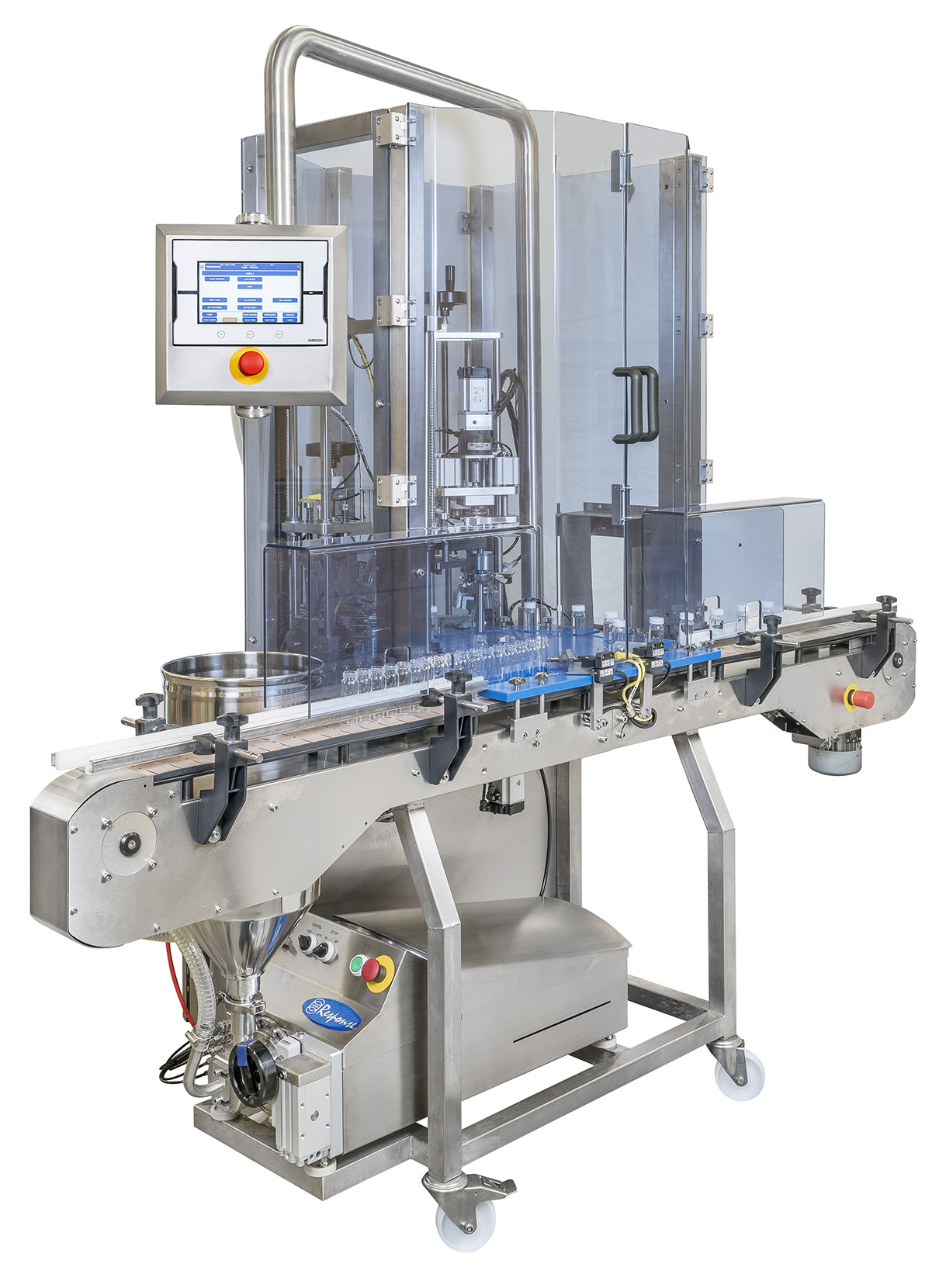
Monobloc filler and capper
If you have separate filling and capping stations you may experience lower throughput rates due t...
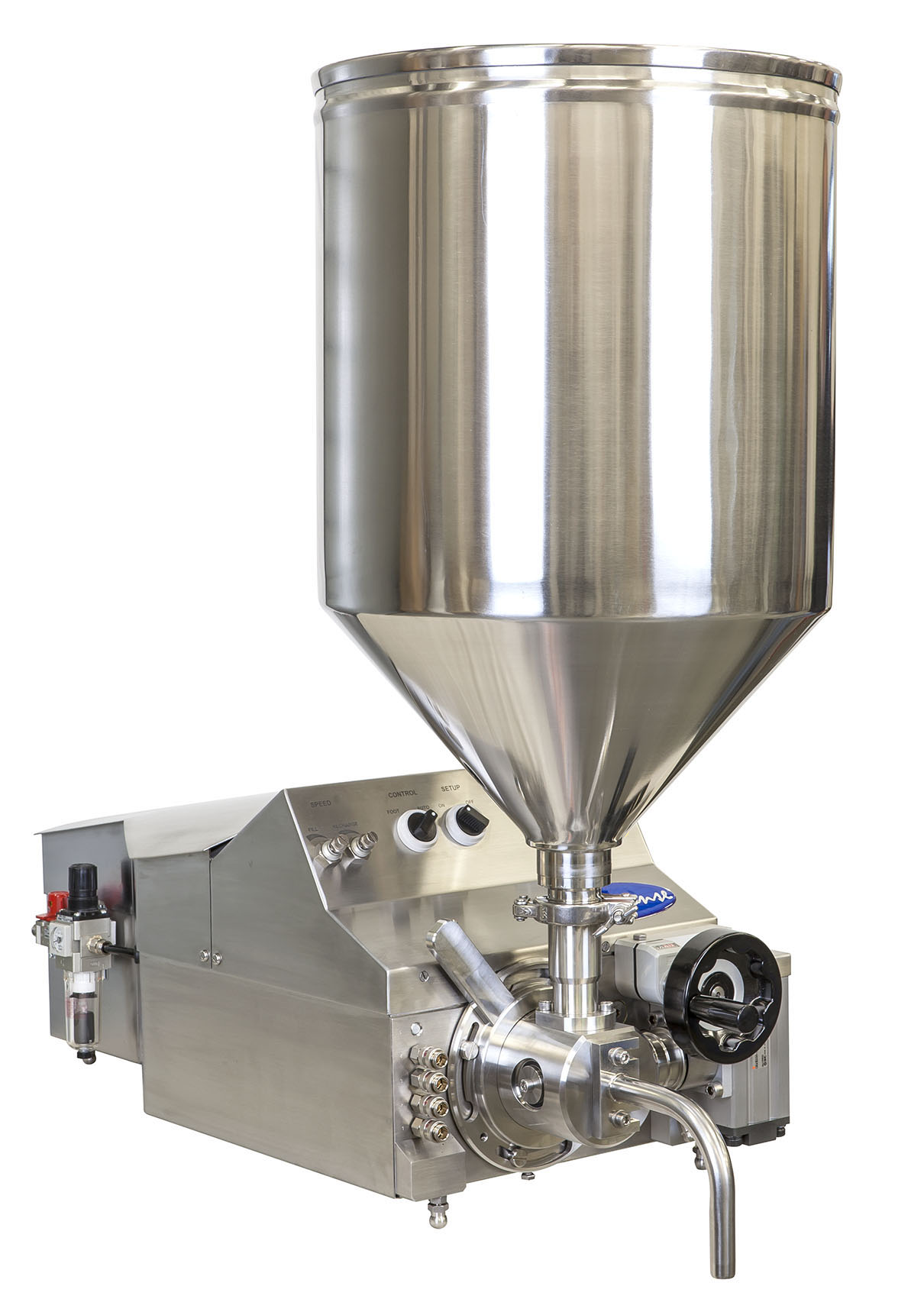
Semi-automatic filler
When you are a small or a medium-sized manufacturer the manual filling processes might often lead to in...
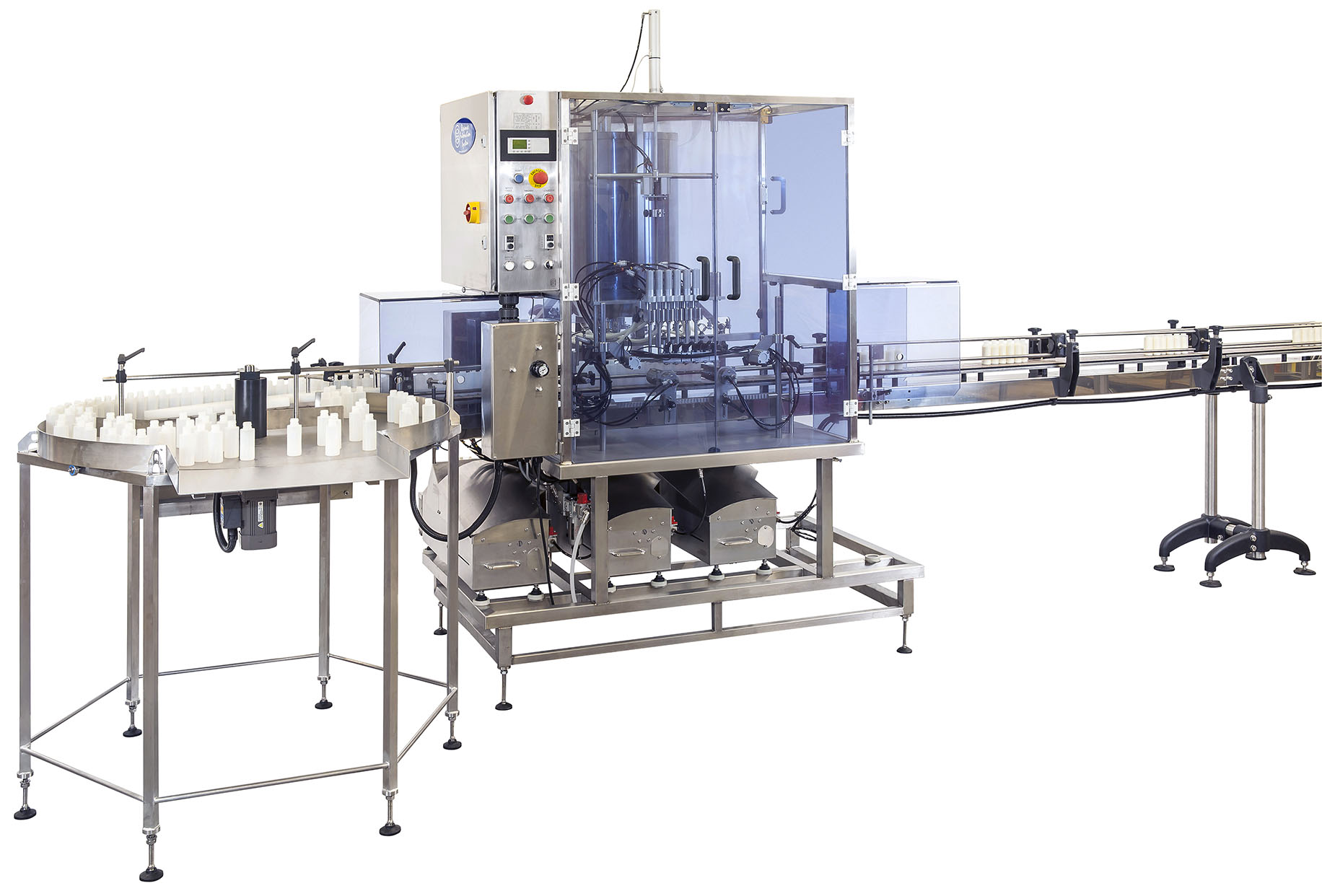
Up to four head automatic filling machine
When your consumer demand is increasing you will need new and more effective pac...
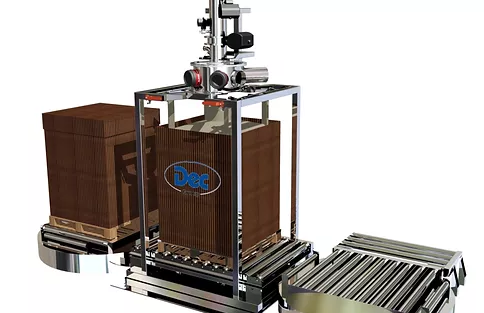
Big bag filling machine
Active pharmaceutical ingredients demand high handling standards to prevent cross-contamination. More...
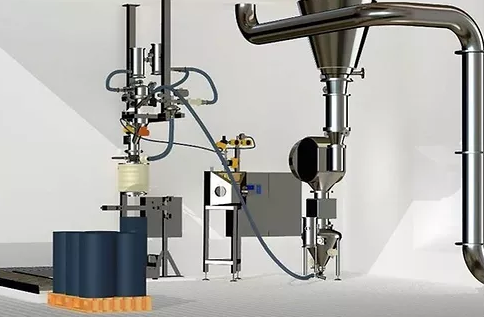
Contamination free filling system
Liners for powder handling across industries must prevent contamination of materials to c...
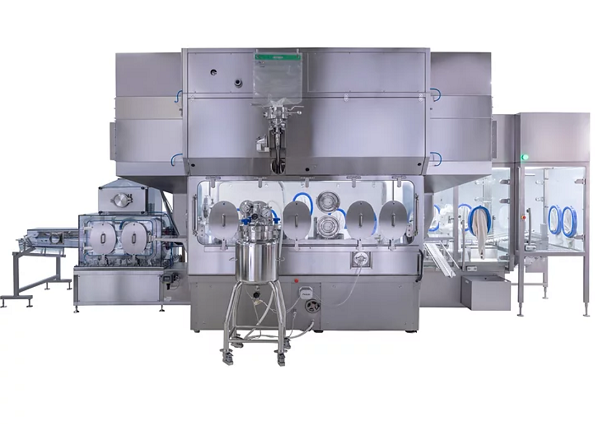
Aseptic filling machine for liquids and powders
Aseptic filling of containers such as vials, syringes, bottles, and cartri...
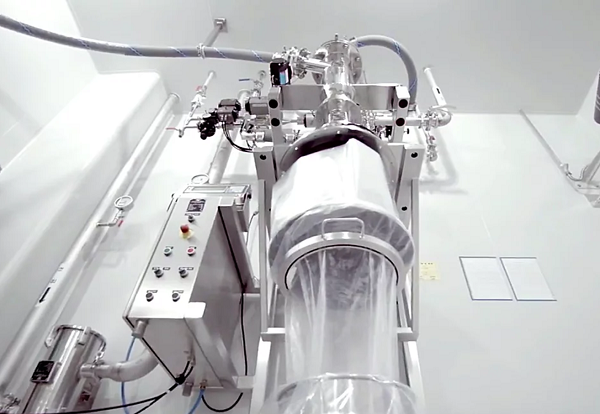
Drum filling system
Pharmaceutical and chemical products may be toxic or prone to contamination from environmental exposure. ...
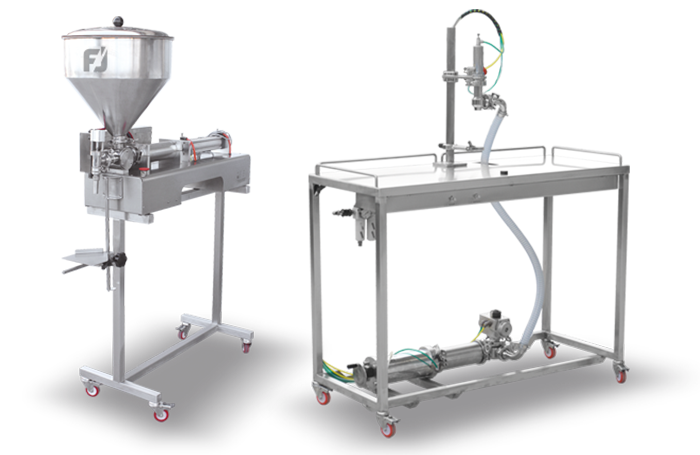
Semi-Automatic Volumetric Liquid Filling Machine
Filling containers manually with liquid and viscous products is the metho...
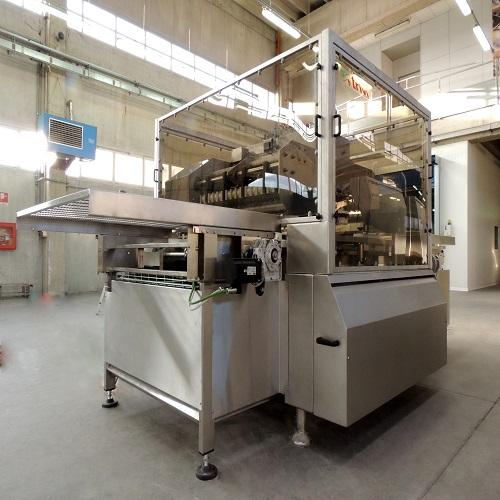
Cream filling machine for bakery industry
Cream and other fillings in bakery products must be injected in the right volume...
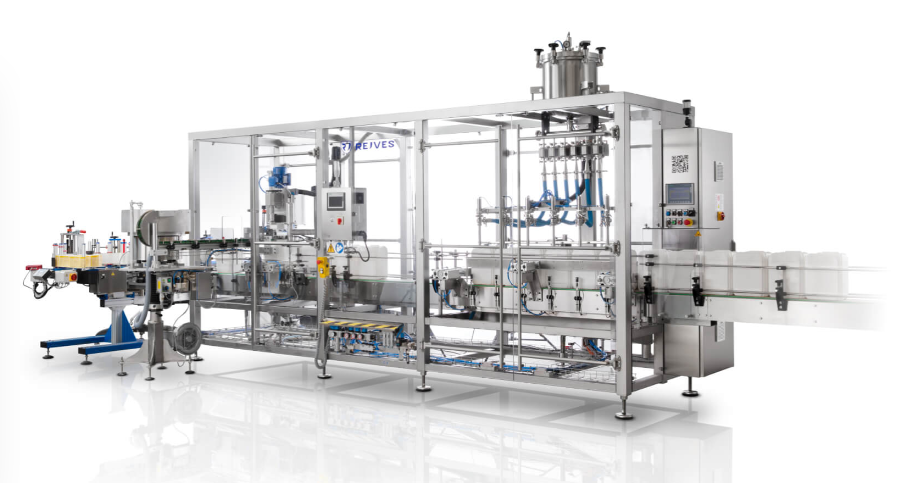
Liquid fertilizer filling and capping monobloc
Production lines for bottling liquid products such as liquid fertilizer, re...
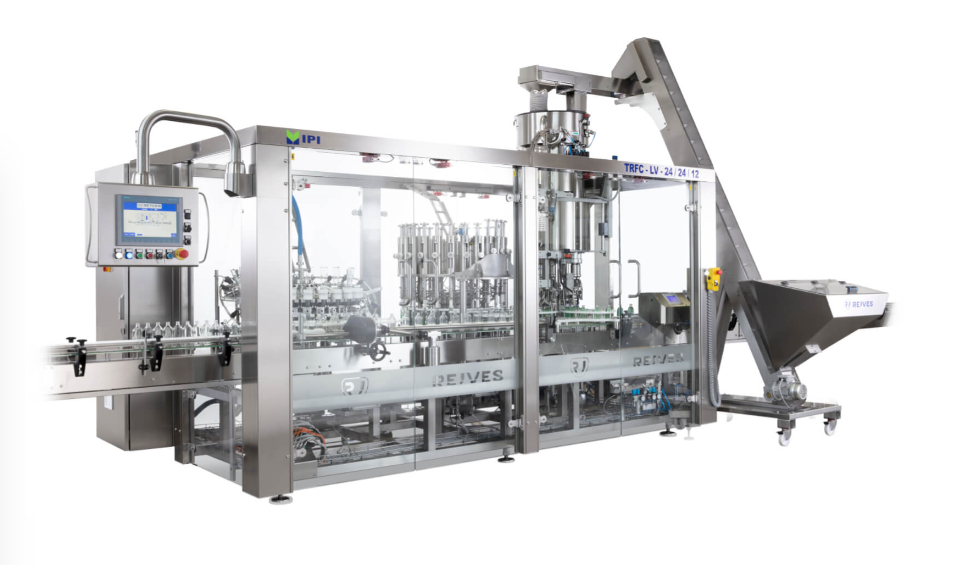
Bottle filling and capping monobloc
Spillage and overfilling are common problems in most production lines for bottled produ...
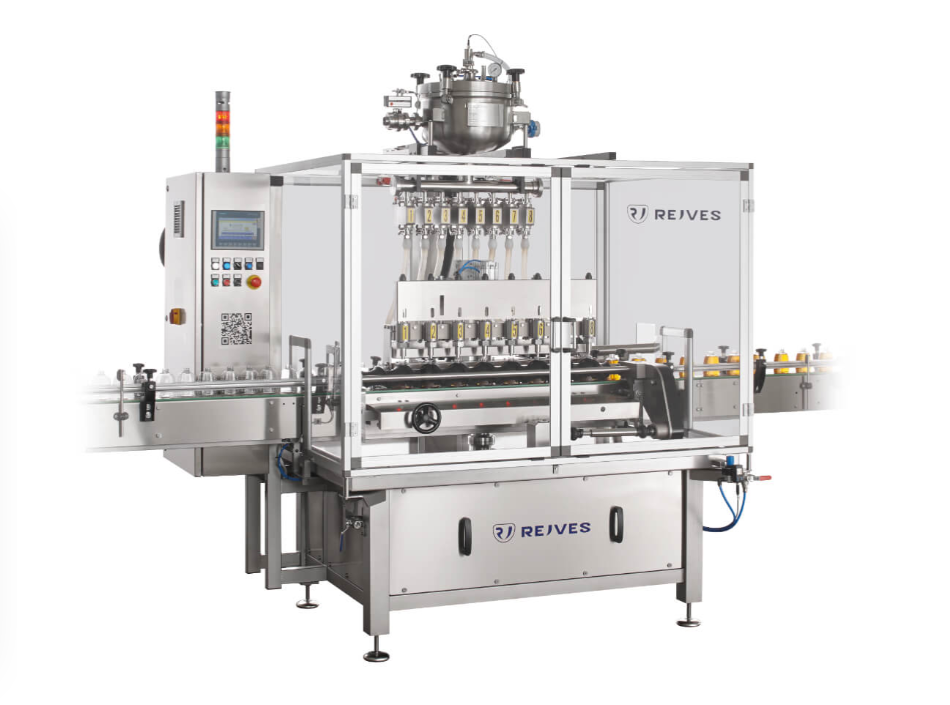
Automatic syrup filling machine
For large production of liquid products, whether in the food industry, home use, industrial,...
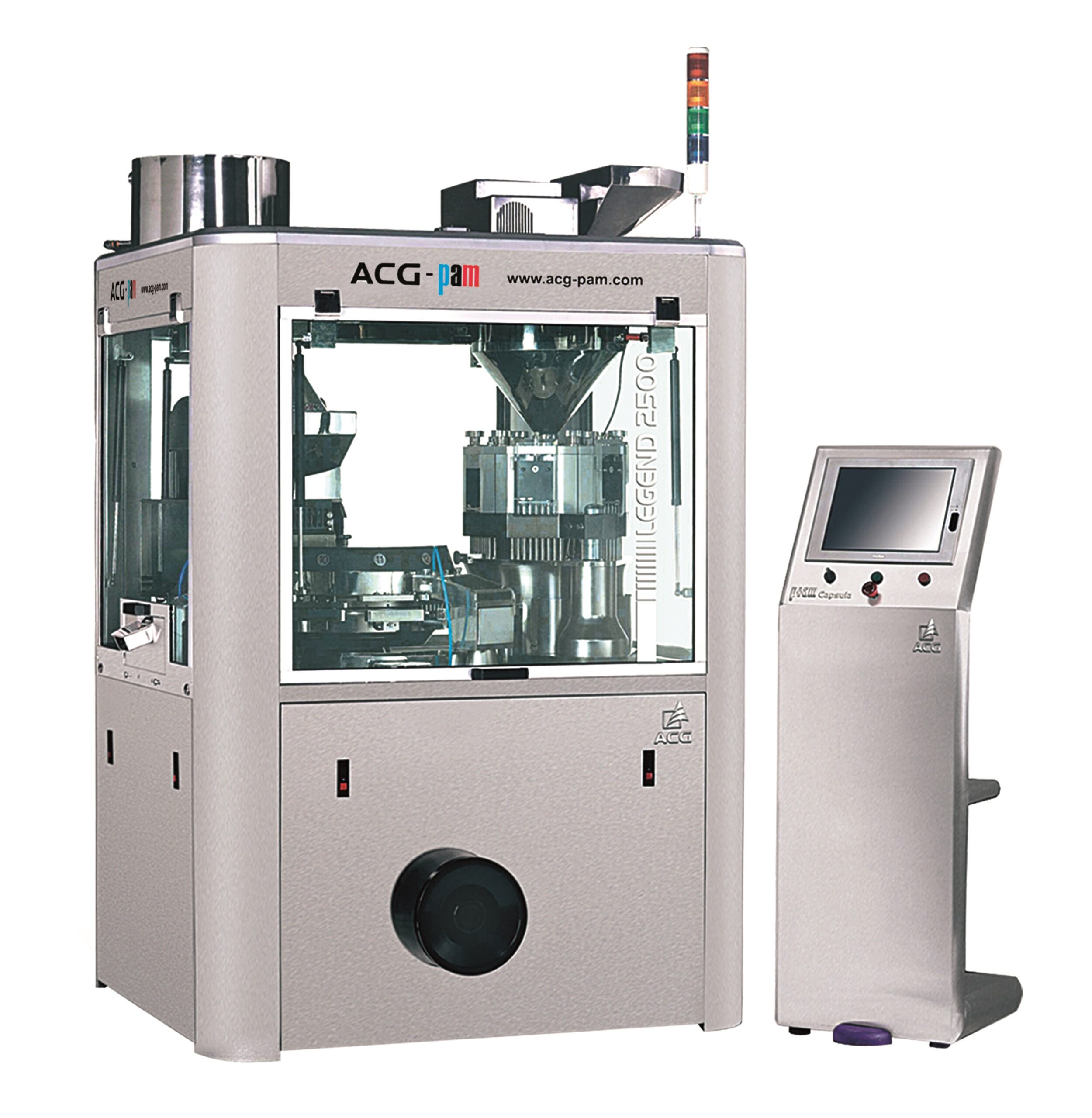
Easy to validate capsule filler
Staying competitive in today’s highly dynamic and highly regulated pharmaceutical prod...
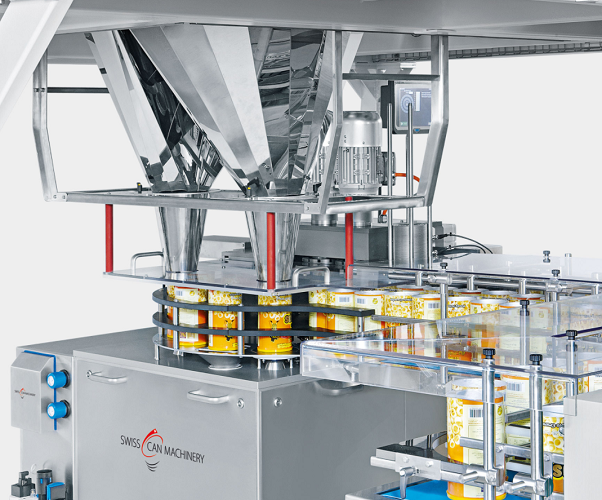
Filling and weight checking machine for food cans
Making sure the right quantity of product is in the packaging can be a ...
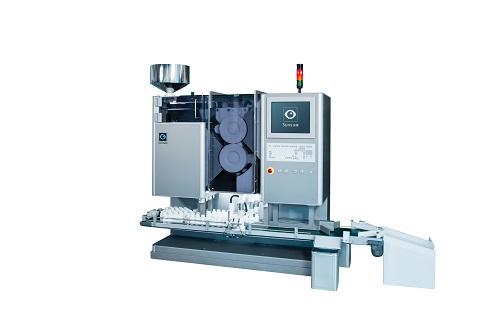
High speed bottle filler with inspection
Medicines in tablet, capsule, or soft gel forms undergo various processes before r...
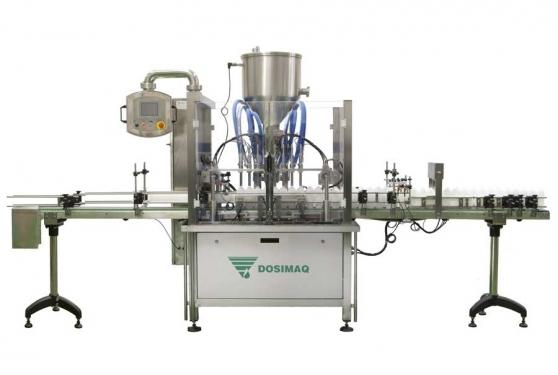
Automatic filling machine for sauce
Traditional sauce filling units can struggle to maintain a high quality of output in ca...
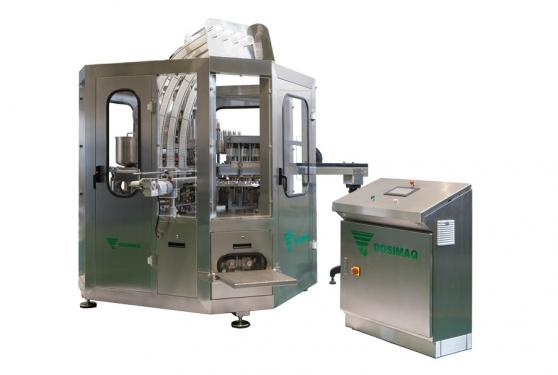
Automatic filling and sealing machine for yogurt
One of the biggest challenges when filling yogurt in containers is that t...
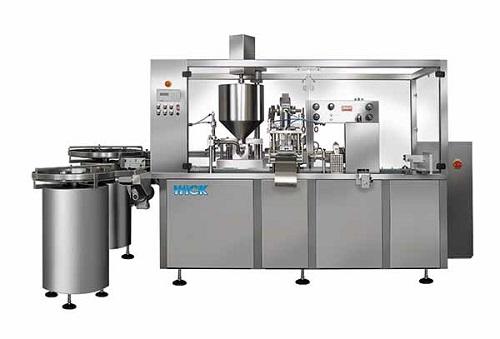
Cosmetic cream filler
From thin liquid baby oils and perfumes to thicker lotions and creams for hair and skincare, cosmetic p...
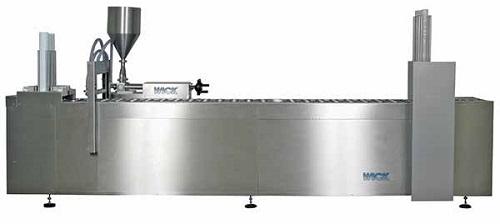
Pre-made cup filler for salad dressings
Pre-made cup fillers are mostly used by food companies to assist in the mass produc...
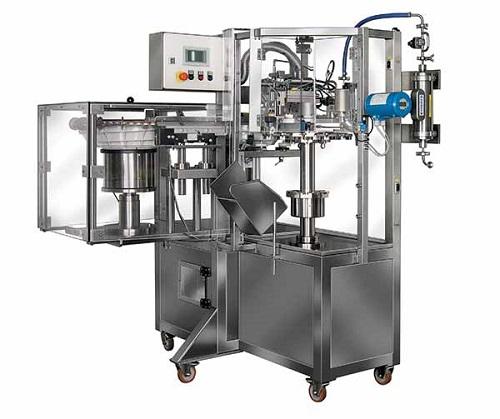
Low speed Filler for large-volume parenterals
Large-volume parenteral bottles are usually manufactured with a resin that c...
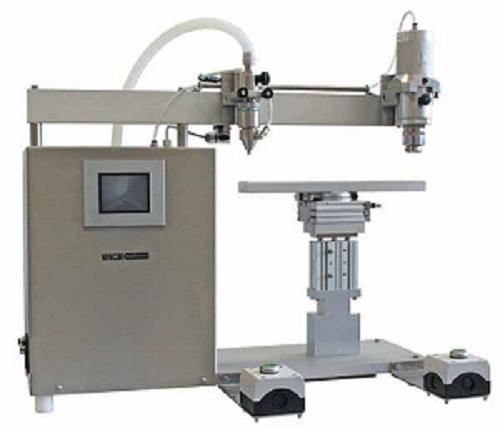
Entry-level filler for large-volume parenterals
Large volume parenterals are unit-dose containers that are larger than 100...
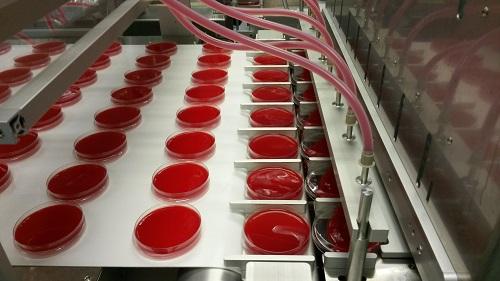
High speed petri dish filling machine
Traditional petri dish filling machines take up a large amount of space in the cleanr...
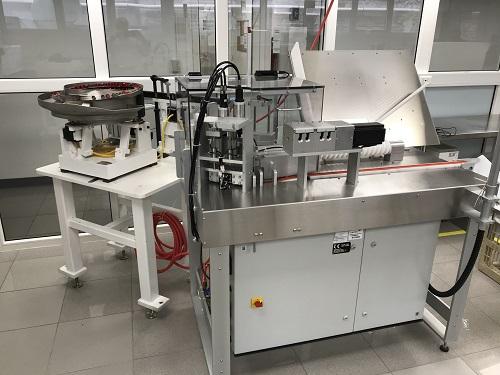
Laboratory test tube filling machine
Test tube filling needs to be accurate and efficient. Moreover, large laboratories tes...
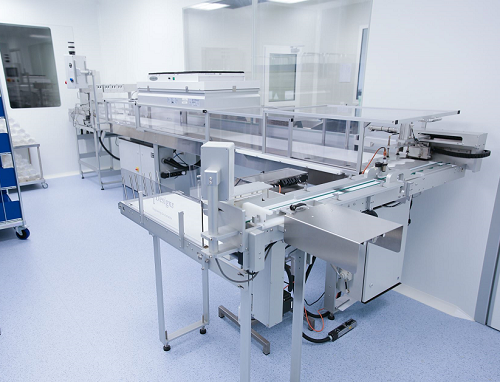
Industrial petri dish filling machine
High throughput petri dish filling machines are traditionally slow and require a larg...
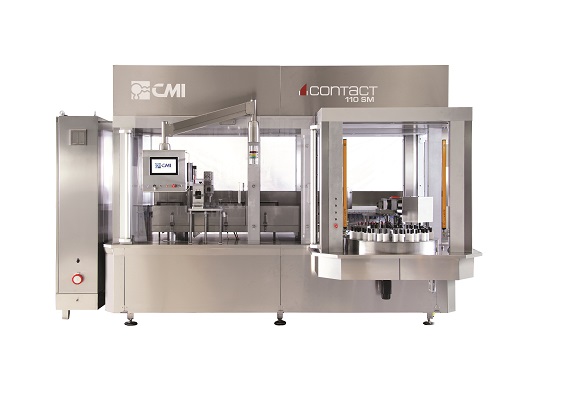
Automatic lipstick filling machine
Lipsticks, lip balms and lip glosses are very popular cosmetic products that require hig...
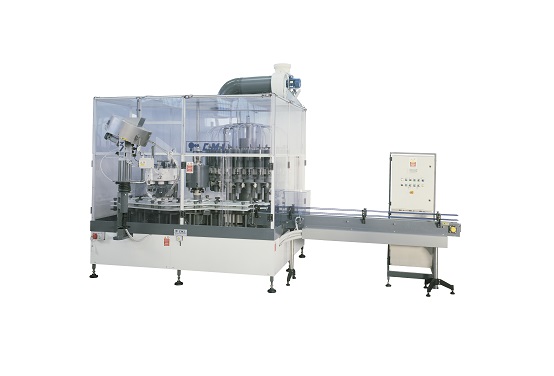
Acid filling machine
Traditional filling solutions are not appropriate for corrosive substances as they make extensive use of...
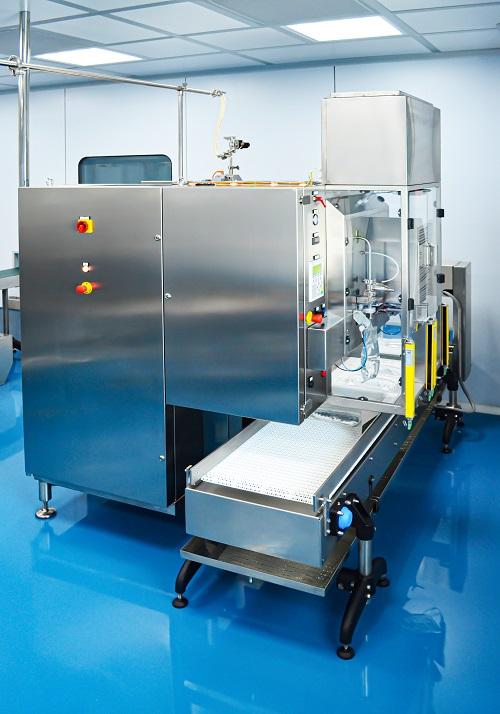
IV bag filling machine
Filling machines for intravenous bags require highly polished surfaces where they contact the bags or ...
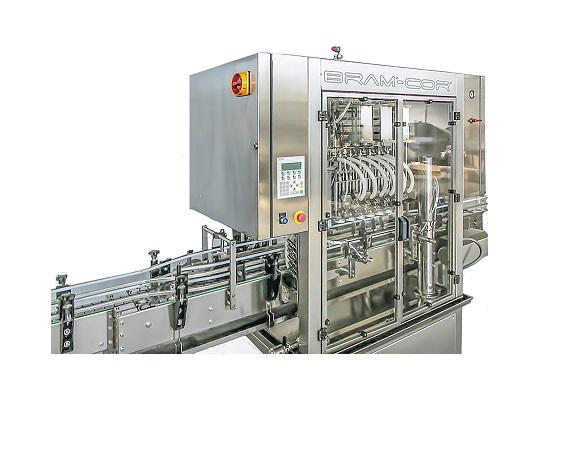
Pharmaceutical bottle filling machine
Filling machines for pharmaceutical bottles must achieve high production speeds while...
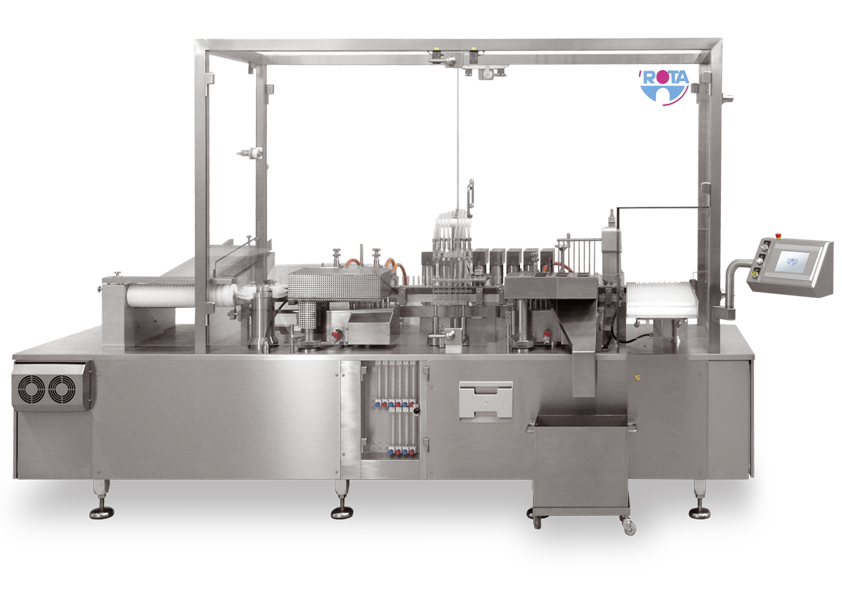
Ampoule filling machine
Filling ampoules or vials with parenteral fluids are an essential matter for which you need to consid...
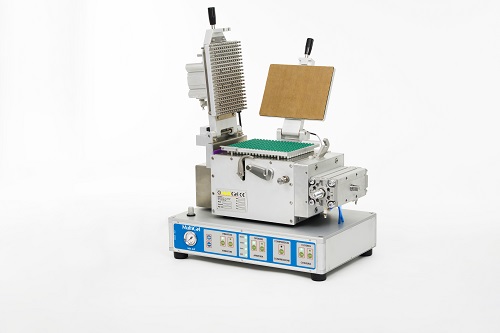
Semi-automatic capsule filler
Hard gelatin capsules are a popular format for delivering a wide variety of pharmaceutical dos...
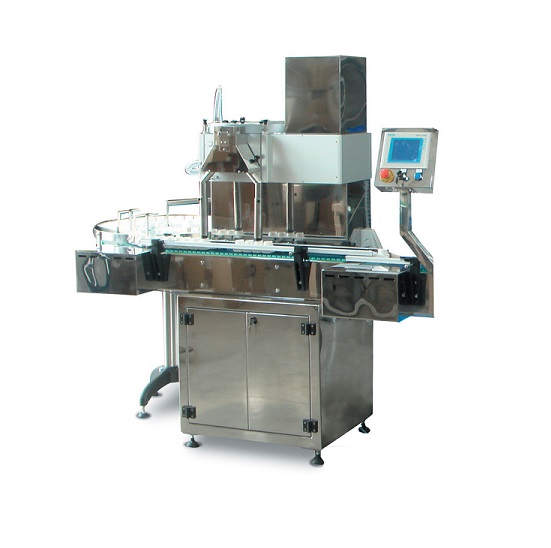
Automatic filling line for solid doses
For medium-scale production of solid doses such as tablets, capsules, and softgels t...
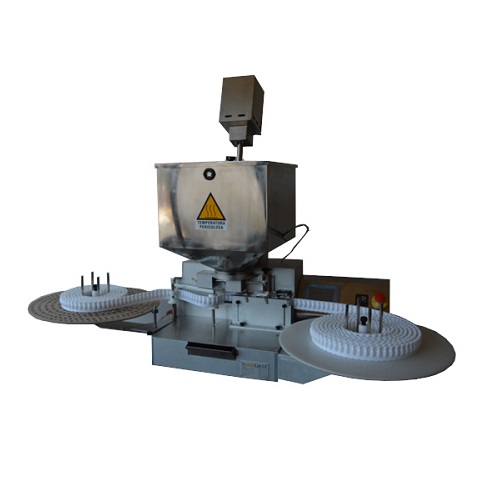
Suppository filling machine
Small-to-medium scale production of suppositories using pre-formed shells can be slow where manu...

Laboratory capsule filler for liquid solutions
A recent important change in the industry is the trend toward providing liq...
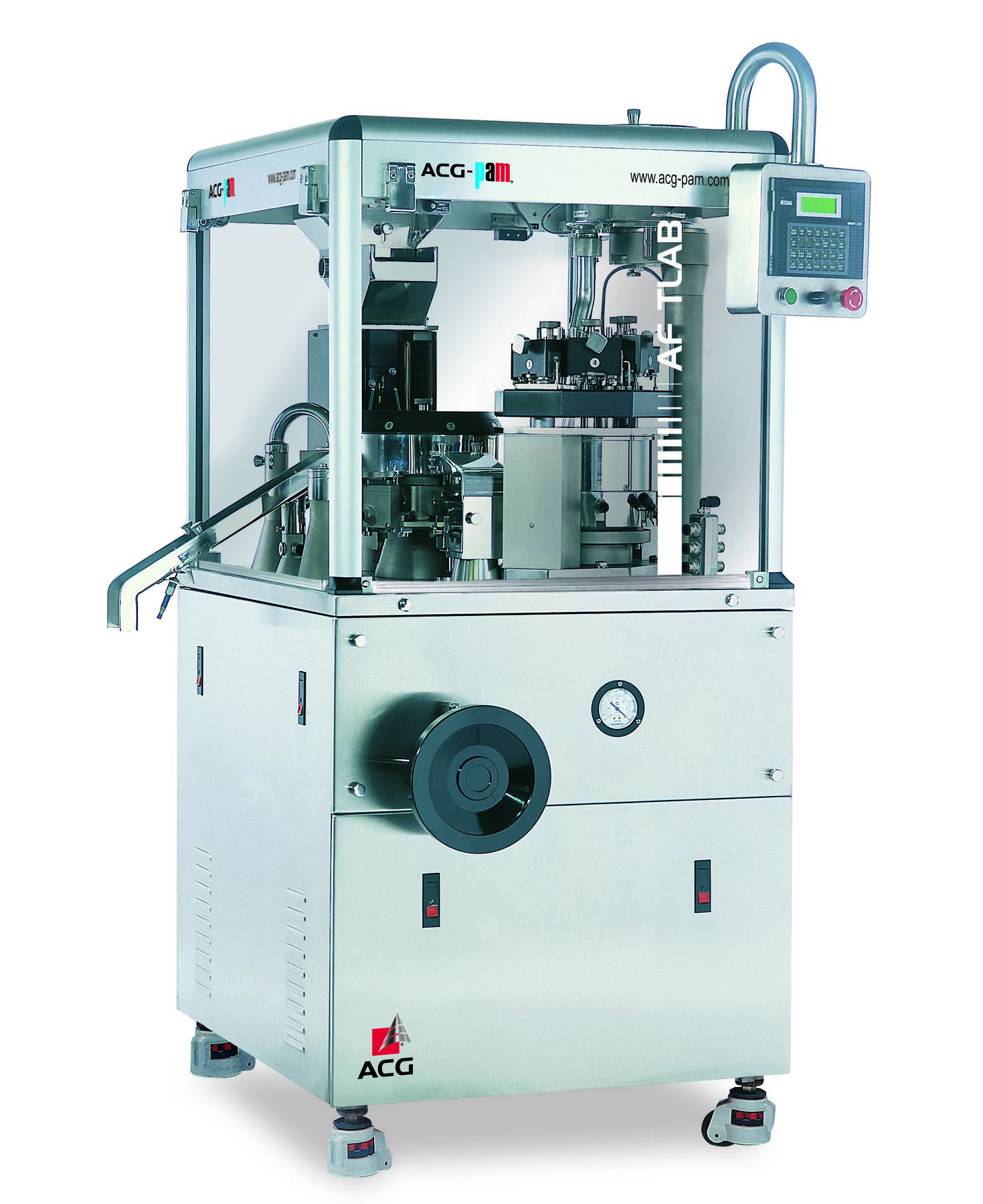
Automatic laboratory capsule filler
Innovators in the highly regulated and highly dynamic pharmaceutical market place need ...
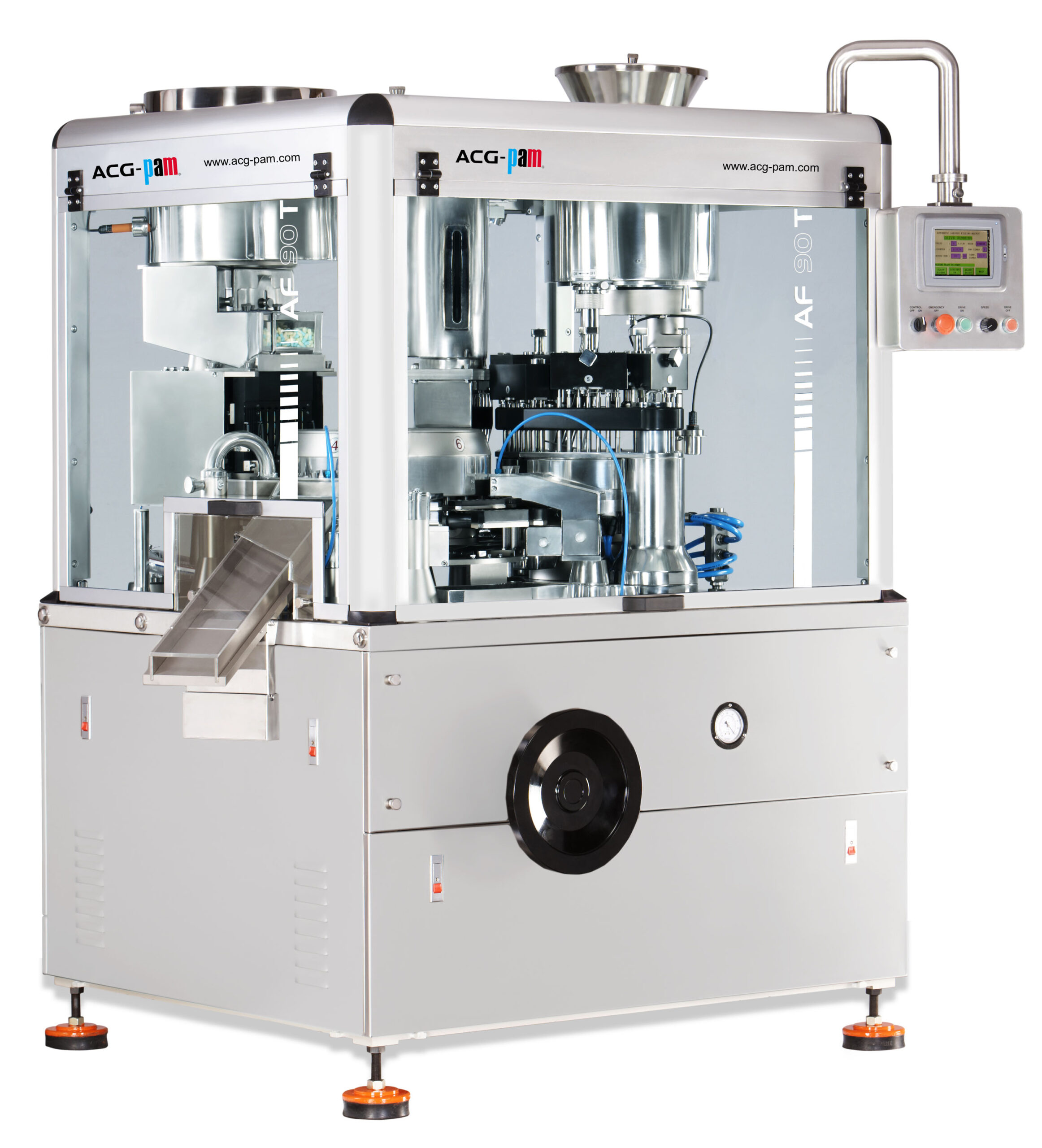
Automatic capsule filler
Capsule filling should be a worry-step in pharmaceutical and nutraceutical manufacturing. The right...
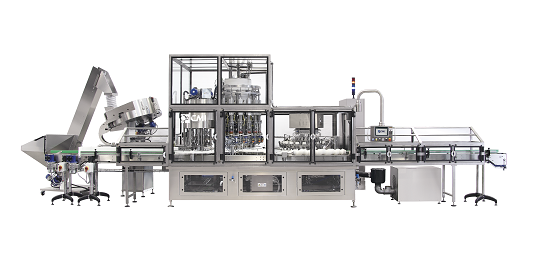
Filling machine for viscous products
Chocolate paste and other viscous liquids require special handling to obtain the optim...
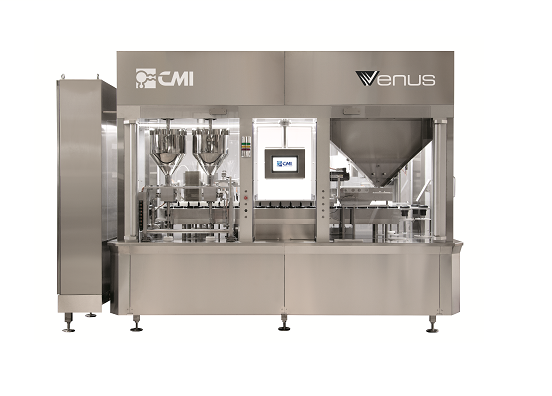
Mascara filling machine
For smaller production volumes, a fully automatic filling solution for mascara, eyeliner, lip gloss a...
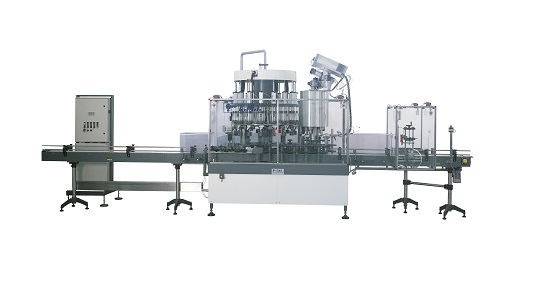
Liquid detergent filling machine
Filling of liquid detergents requires specialised equipment because of the foaming nature o...
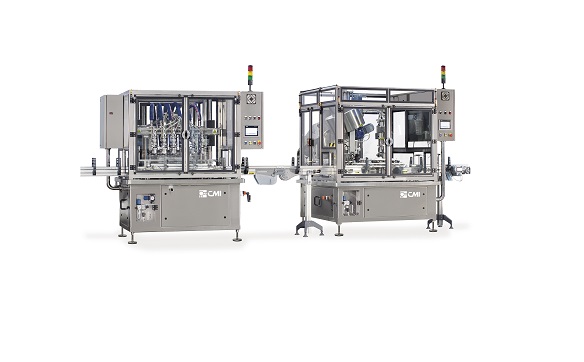
Filling machine for creams
Liquid cosmetics have particular requirements when it comes to filling and capping containers. Mo...
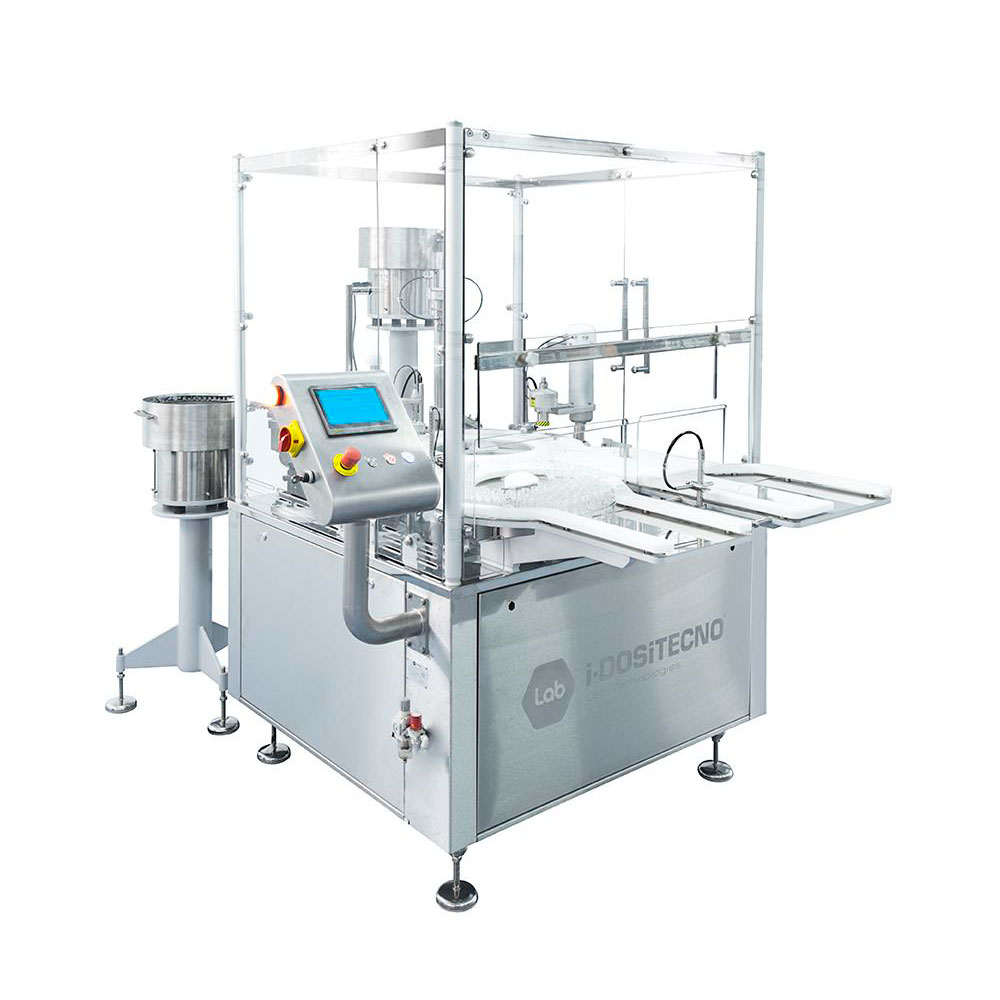
Start-up sterile filling line for injectables
For smaller-scale production of vials and syringes for the injectables marke...
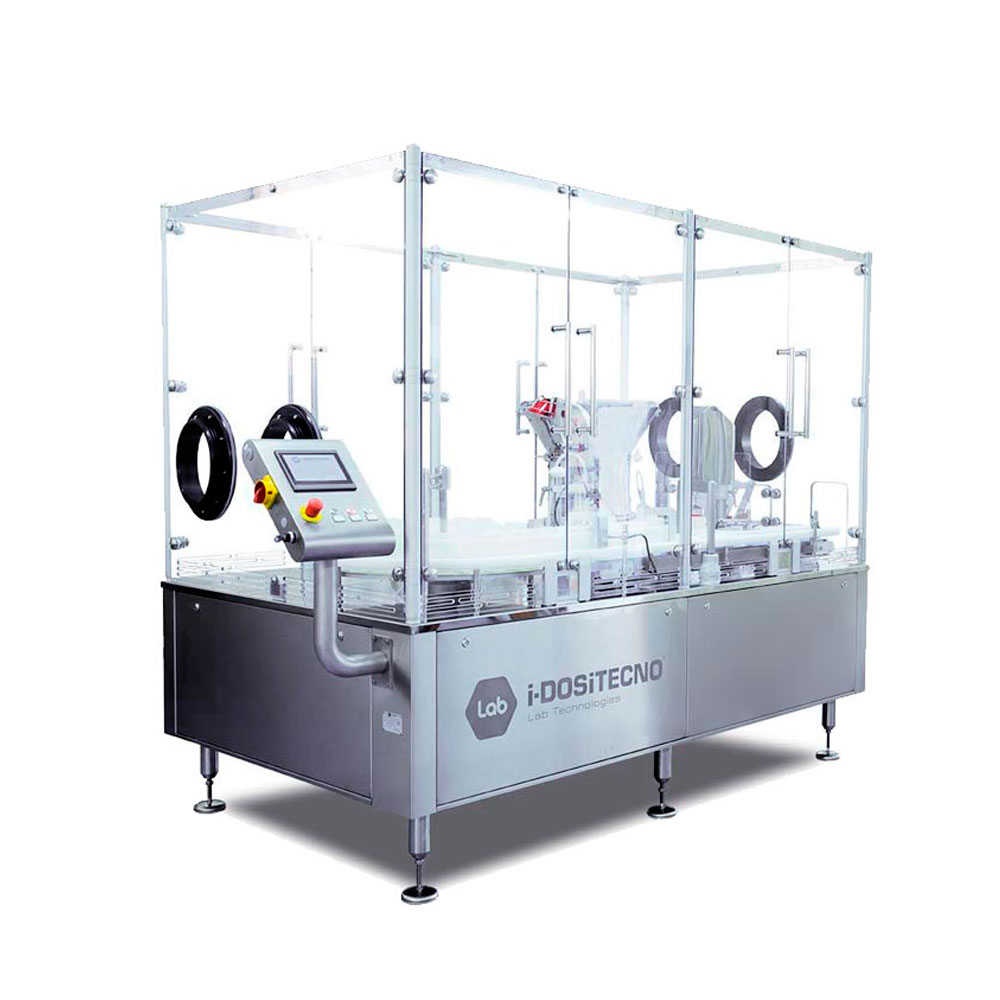
Start-up sterile filling line for ophthalmics
Commencing ophthalmic production requires sterile conditions and accurate me...
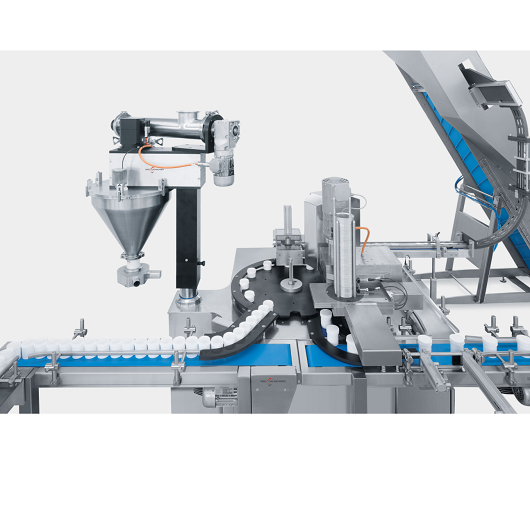
Can filling equipment
Having separate equipment for different process steps like filling and closing, can put a brake on grow...
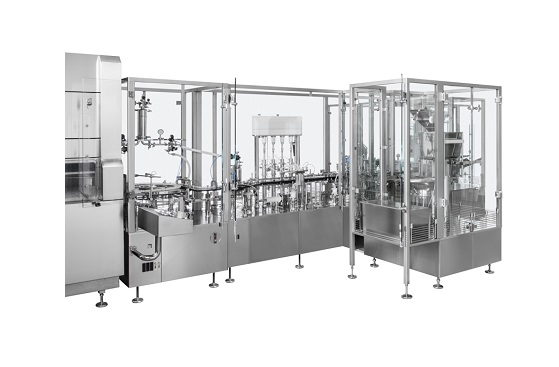
Vial filling machine
The volume filling of vials, cartridges and syringes is a vital part of the production of a wide range o...
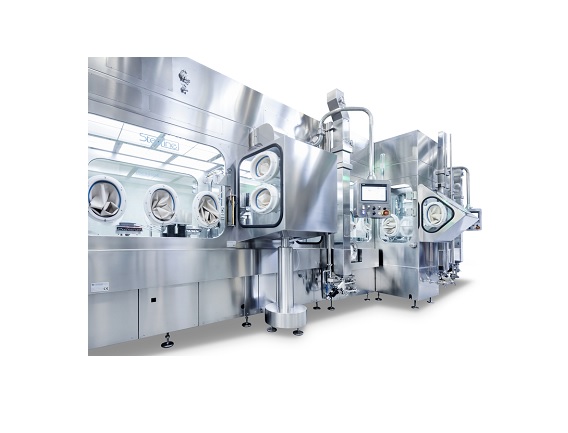
Aseptic automatic vial filling machine
Current and future developments in pharmaceuticals increasingly rely on aseptic prod...
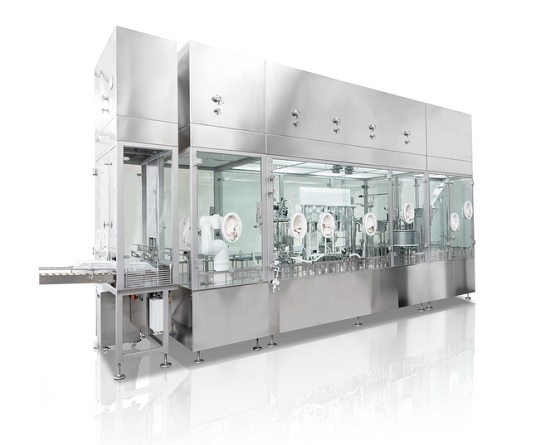
Nested syringe filling machine
Increasingly, pre-sterilized Ready To Use (RTU) nested vials, cartridges and syringes are the...
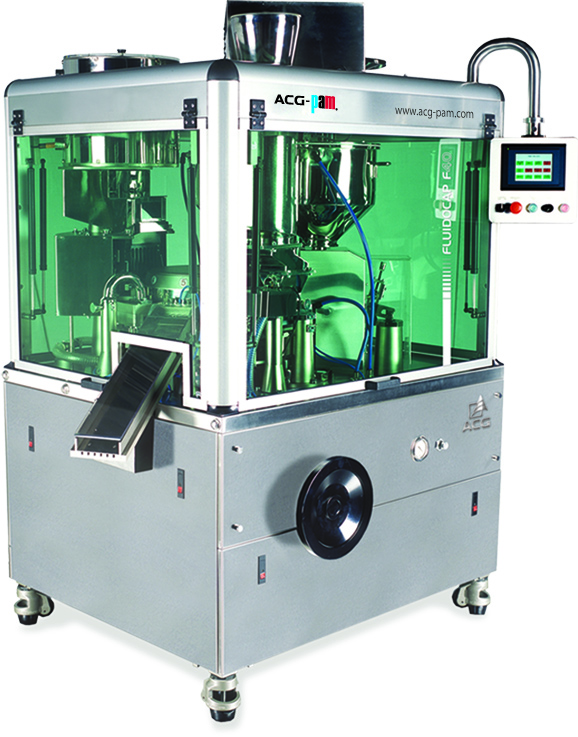
Automatic capsule filler for liquid solutions
Use of liquid filled hard capsules is increasingly popular with today’...
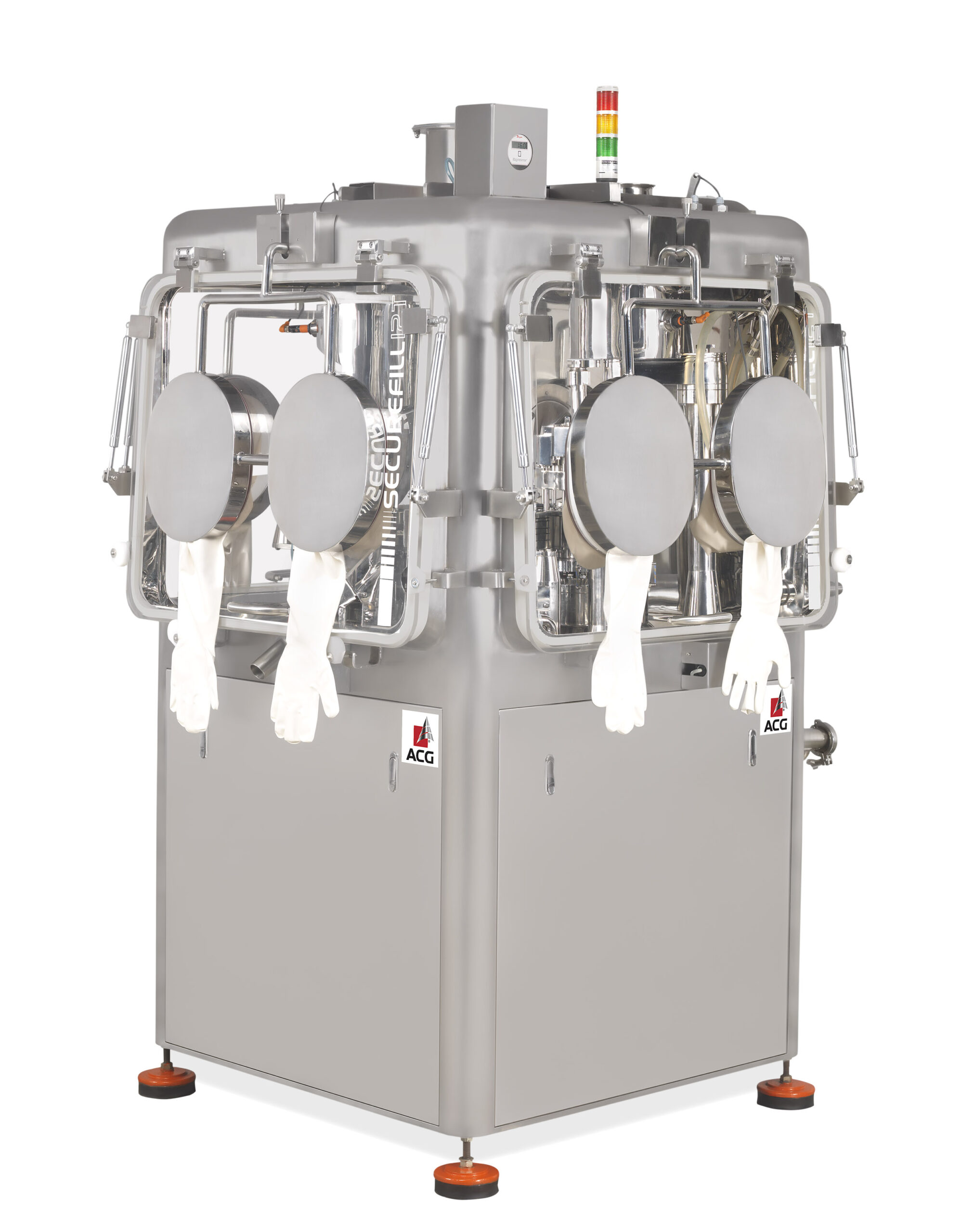
Contained capsule filler
For pharmaceutical formulations that are highly active specialized capsule filling equipment is ofte...
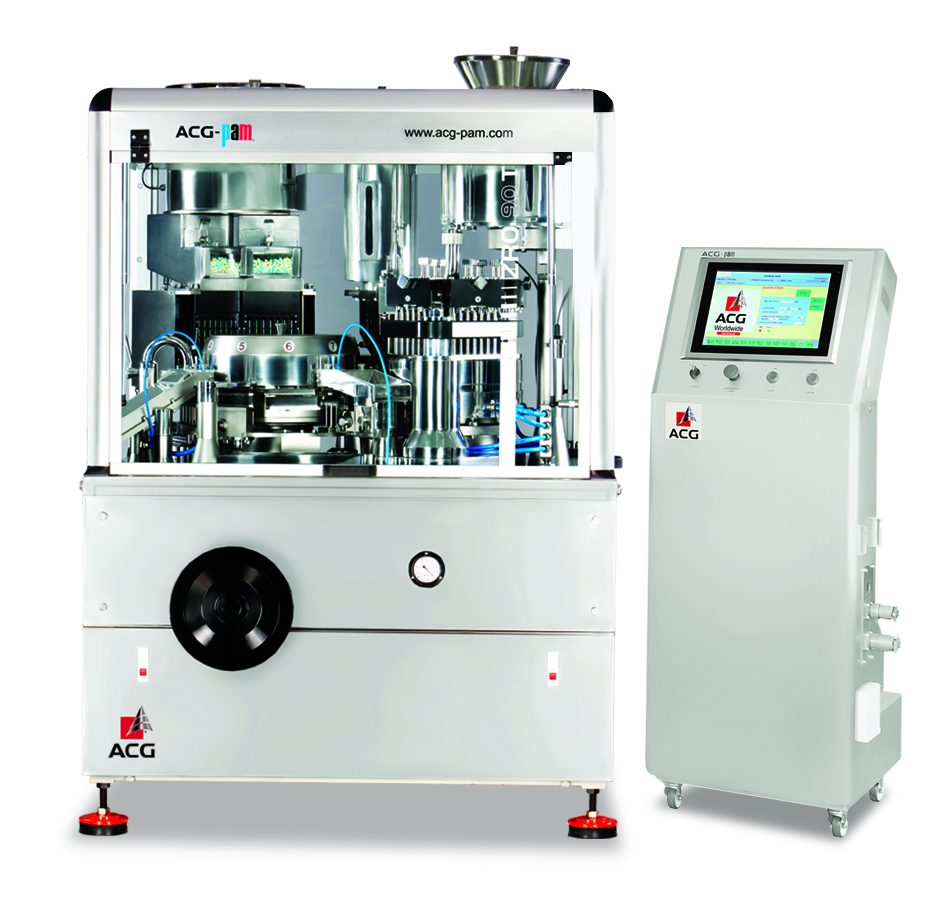
High-yield capsule filler
Pharmaceutical manufacturers require maximum yield from their encapsulation process for efficient ...
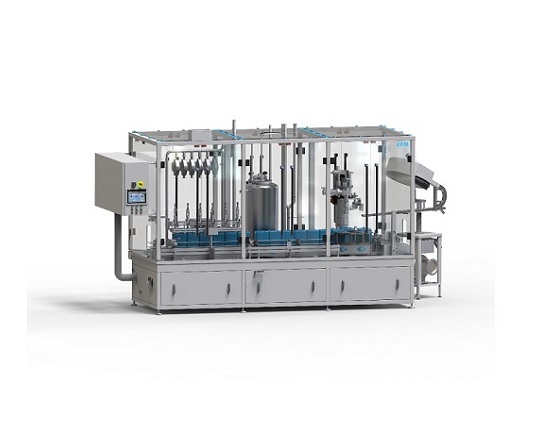
In-line monoblock linear filler & capper
In many food, chemicals and cosmetic industry processes it is vital to have a...

Flowmeter filler
For larger production runs of food, non-food and cosmetics industries, where accuracy and volume of filling i...
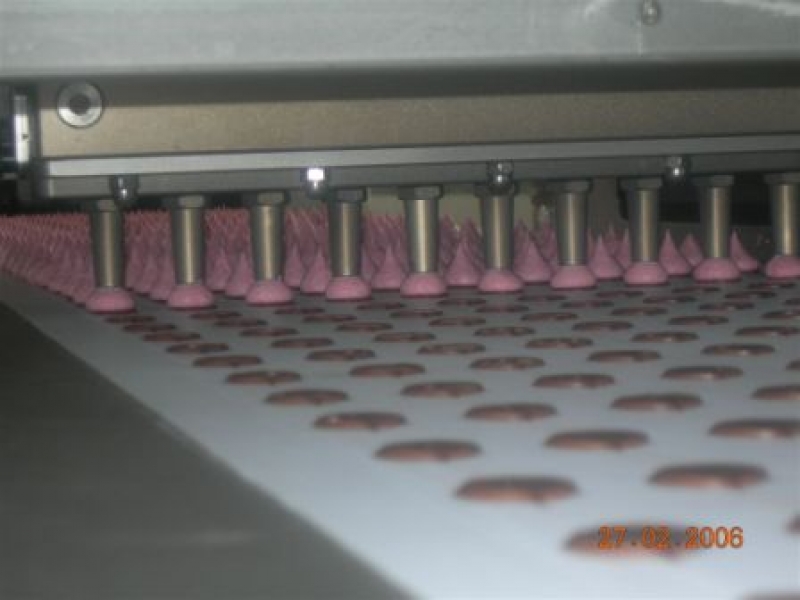
Single row piston depositor for soft fillings
For depositing soft fillings directly onto the cooling belts.
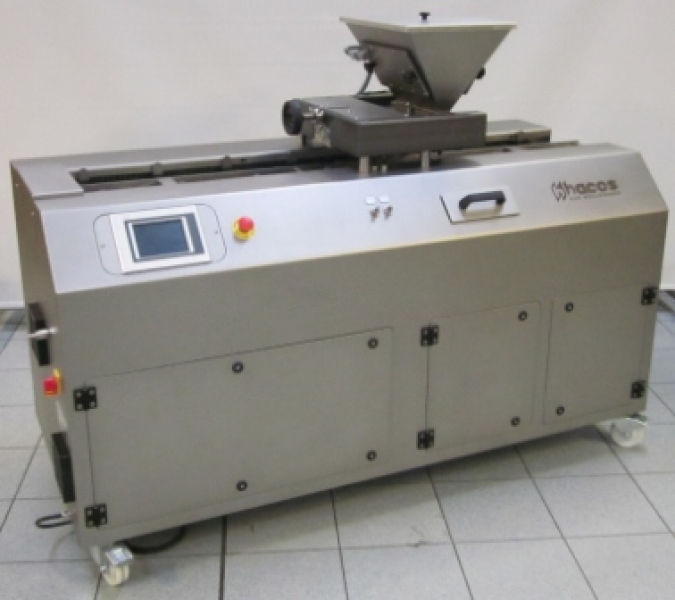
Piston filler for creams into moulds
The perfect cream filler, which the main feature is its accuracy and that can contain ...
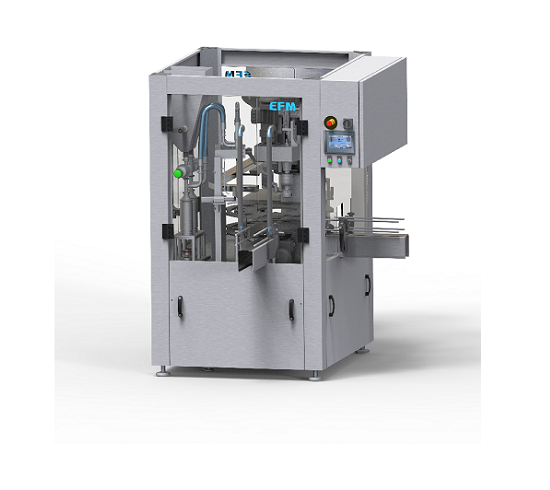
Compact monoblock filler
Filling and capping bottles and pots for food, chemical and cosmetics industries using separate mach...
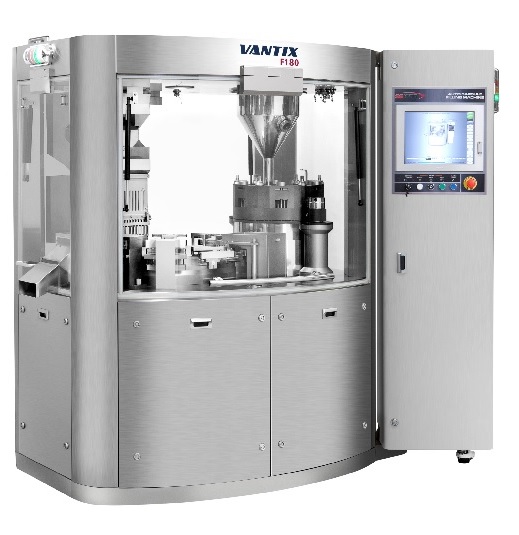
High capacity capsule filler
In the highest volume pharmaceutical production environments, capsule filling needs to be extre...
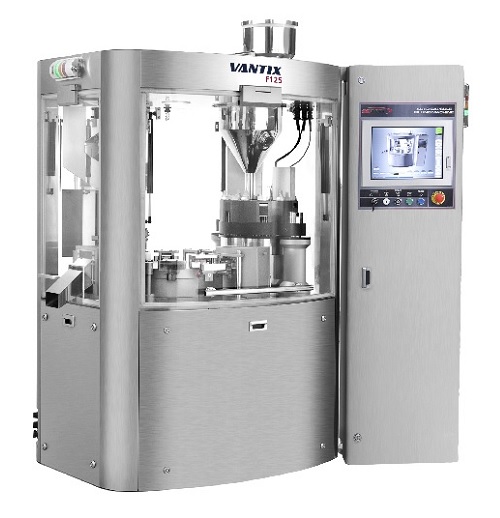
Scale up capsule filler
For higher production volumes of pharmaceutical capsules, speed, accuracy and reliability of producti...

Entry level capsule filler
For the production of pharmaceutical doses in capsule form complete accuracy of fill is paramount...
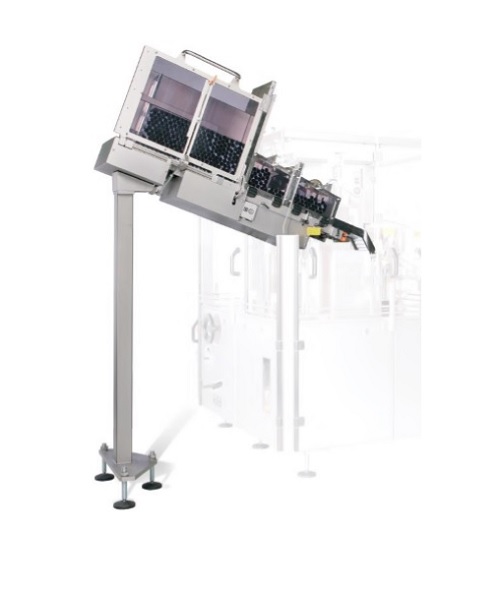
Loading cassette for a tube filler
High performance tube-filling machines are used in the pharmaceutical and cosmetic indus...
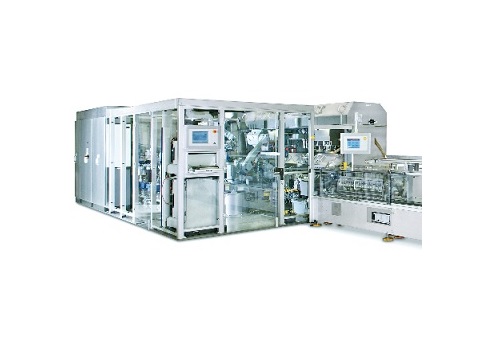
High speed automatic tube filler
For high-volume lines filling pharmaceutical, cosmetic or food products into tube container...
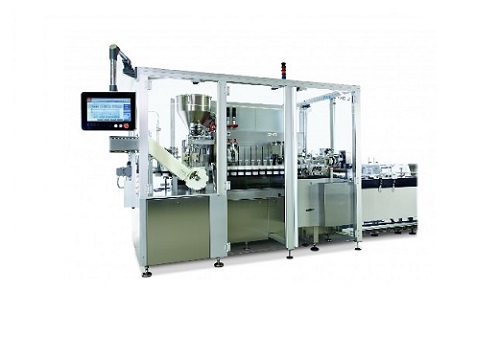
Medium speed tube filler and sealer
For scale-up filling of tube packaging for pharmaceuticals, cosmetics and food products...
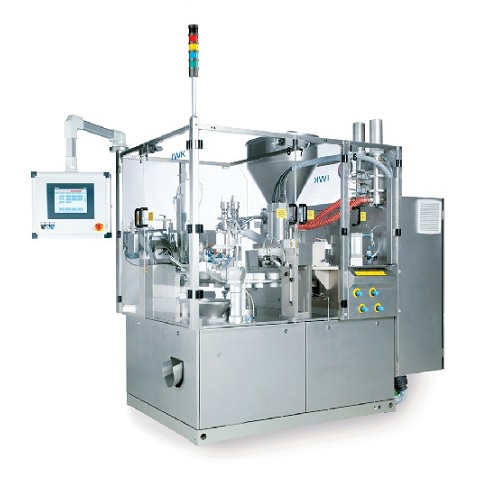
Medium and high speed range automatic tube filler
When scaling up production of pharmaceutical, food or cosmetic products...
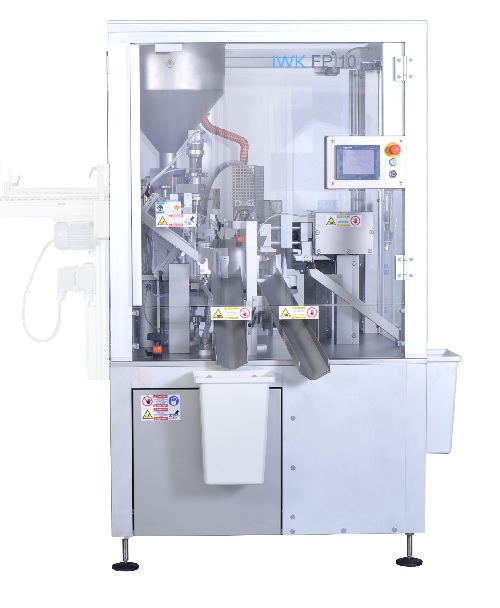
Low speed tube filler
Increasing numbers of products in the pharmaceutical, cosmetic and food industries are delivered in fle...
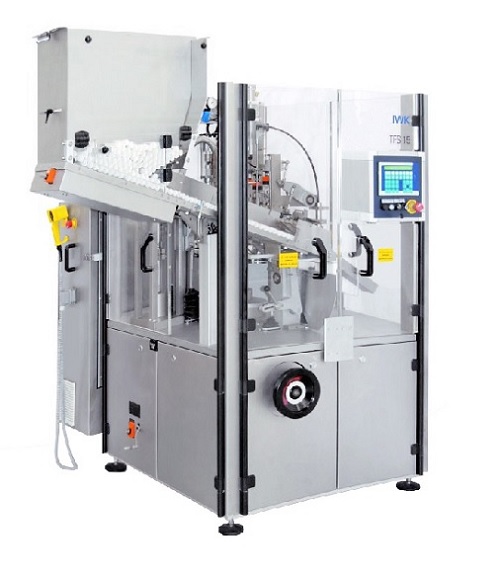
A two-component filling application tube filler
A wide variety of pharmaceutical, cosmetic and food products require tube-...
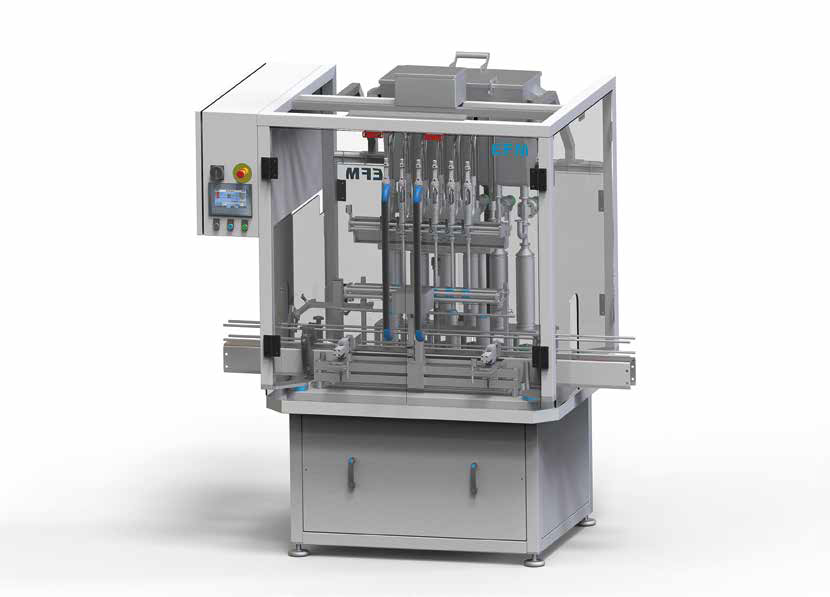
Servo controlled filler
For food and non-food liquid products that are high foam or have a high viscosity a specialist fillin...
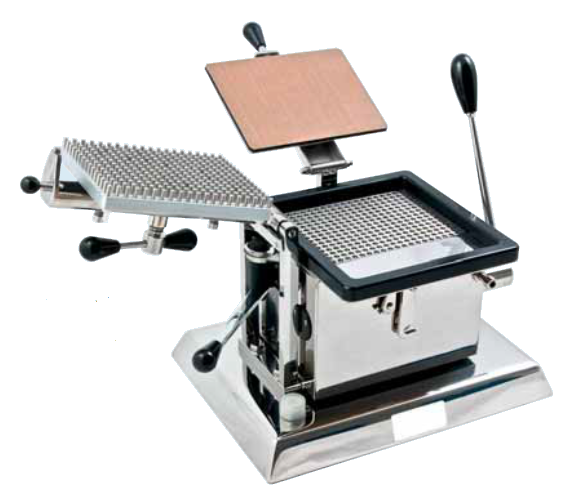
R&D semi-automatic capsule filler
Semi-automatic filling machine suitable to open, fill and close empty hard gelatin capsul...
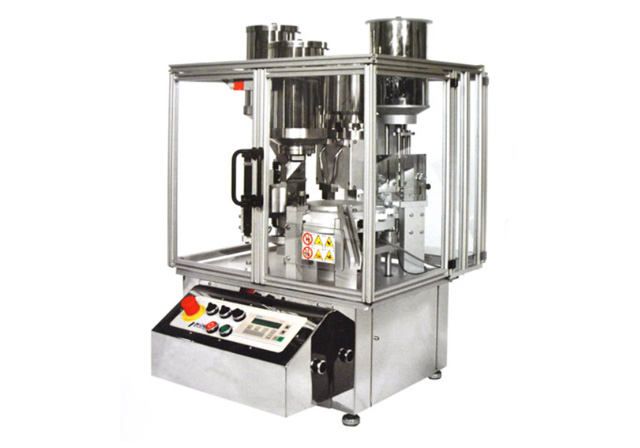
R&D automatic capsule filler
Automatic capsule filling machine for powders, pellets, tablets, mini-tablets, capsule in capsu...
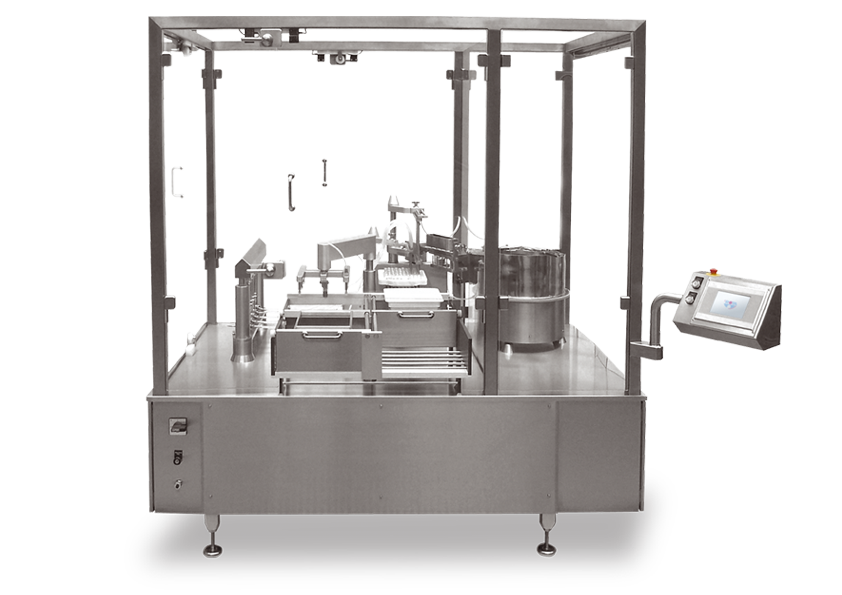
Filling and closing machine for parenterals
Any pre-filled syringe can be filled and closed with this fast and easy machin...
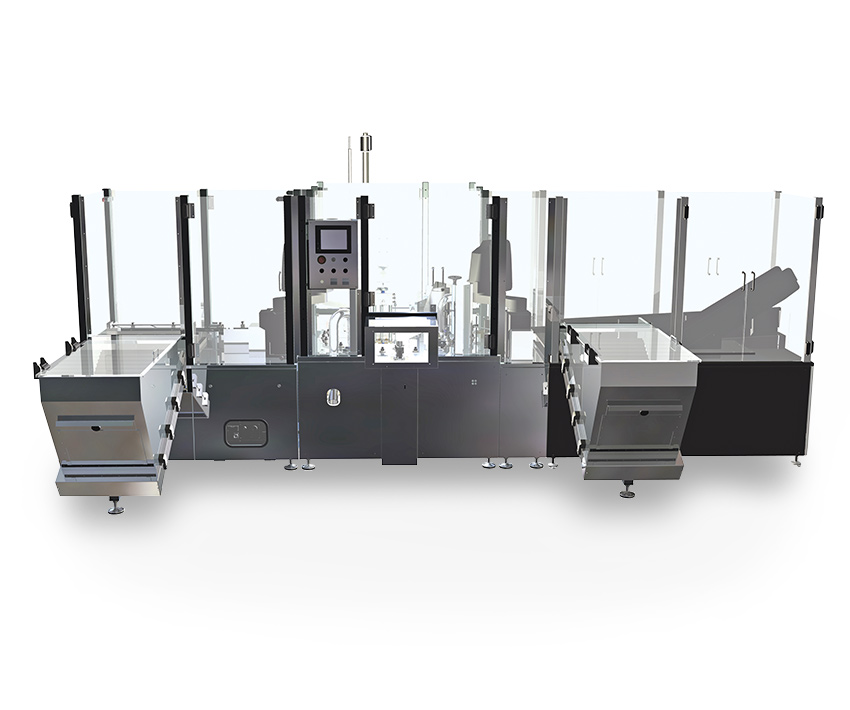
Automatic mascara filling machine
Do you need to increase your efficiency and production volumes whilst reducing your costs...
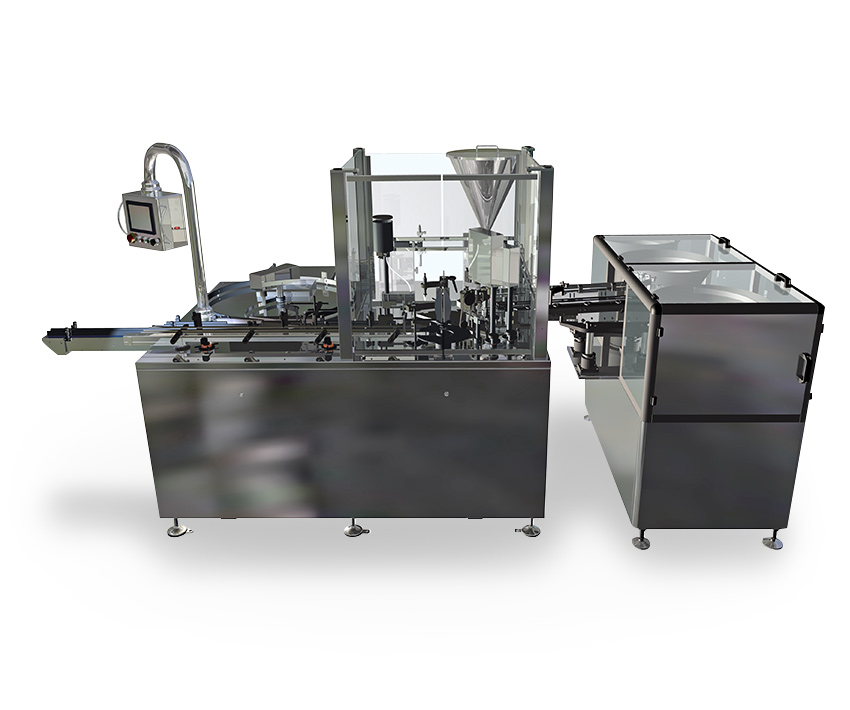
Automatic nail polish filling machine
Do you need to increase your production volumes in the most efficient way possible? A...
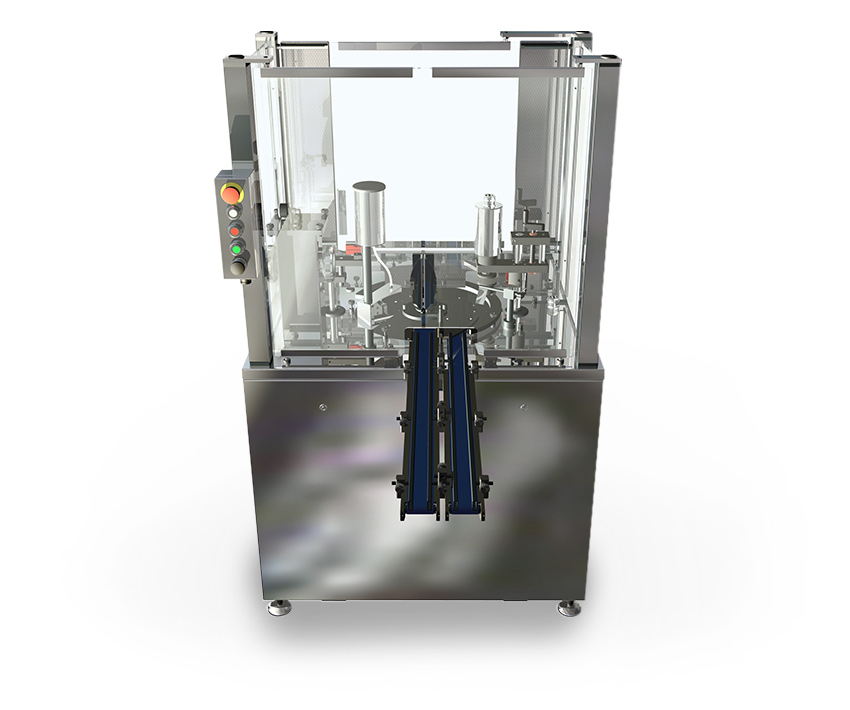
Semi-automatic filling machine for nail polish
Do you need to automate a smaller cosmetic line without the large costs ass...
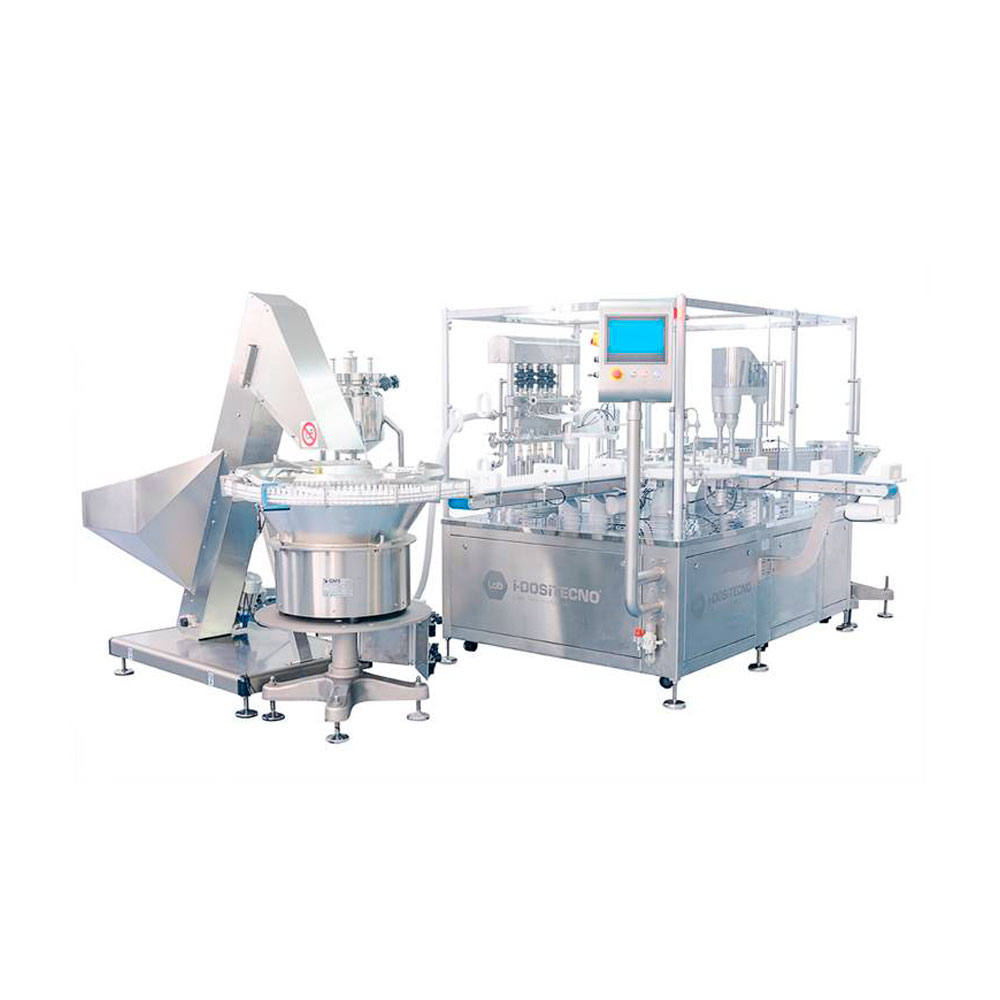
Sterile filling line for ophthalmics
Demanding very high standards, the ophthalmic market requires quality solutions for fi...
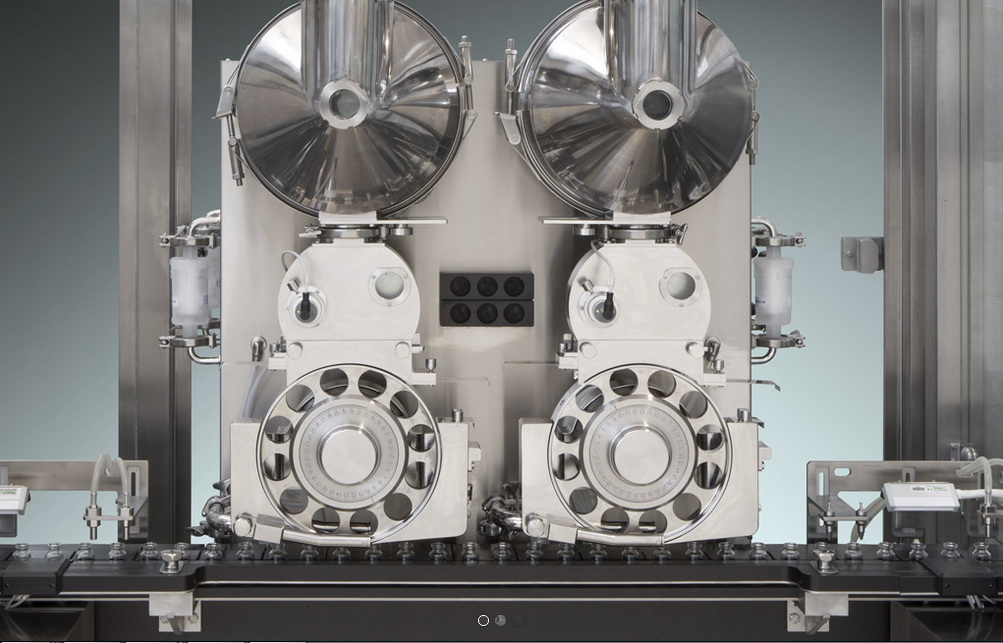
High-speed aseptic injectable vial filling machine
Fill up to 24,000 vials per hour with pharmaceutical powders or liquid...
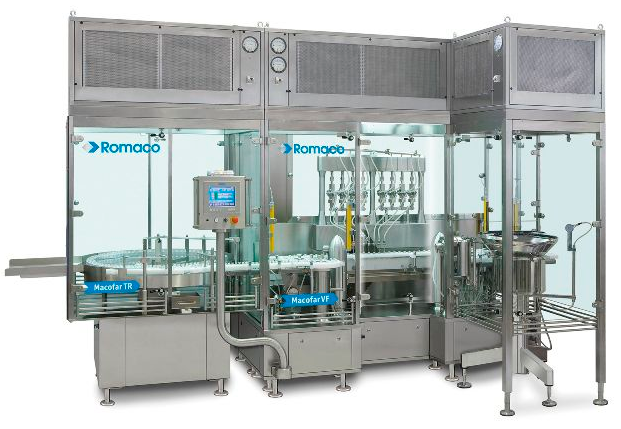
Aseptic liquid filler for vials
Compact modular aseptic filler of vials with parenteral medicines and freeze-dried products.
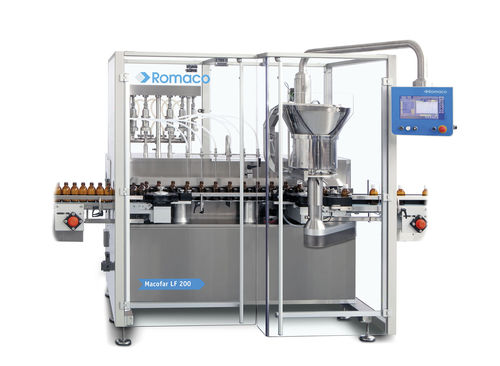
High-speed small volume liquid filler
Fill liquid pharmaceutical, nutraceutical and cosmetic products in ampoules and bottl...
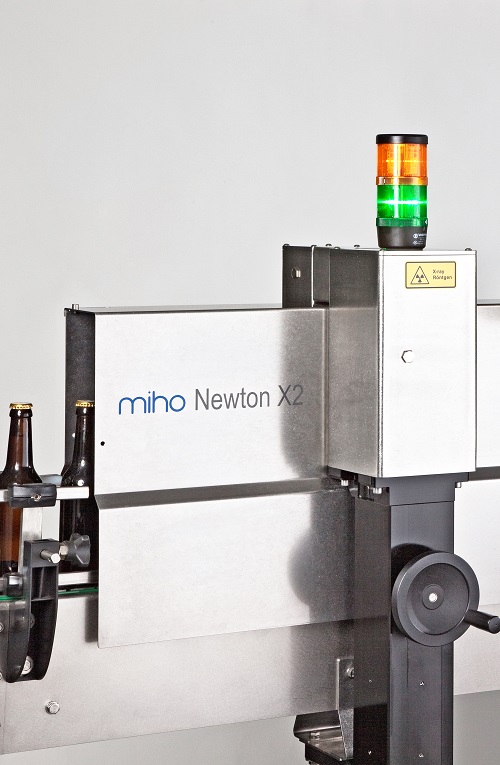
High-precision X-ray fill level controller
High-speed, high precision X-ray system to inspect containers that are difficul...
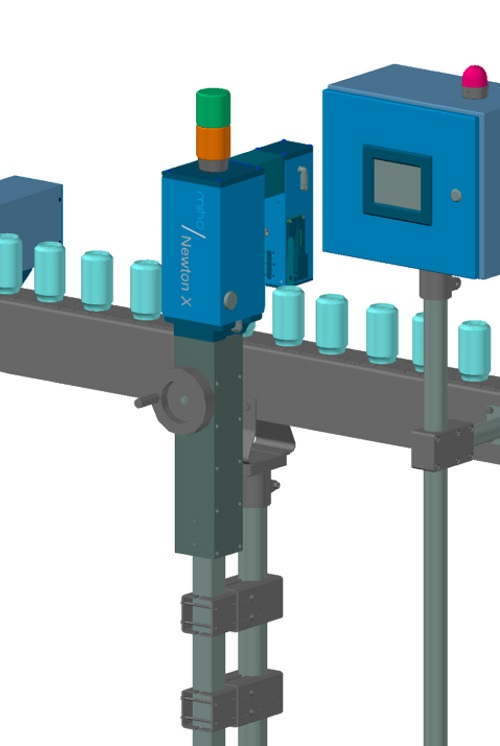
X-ray fill level controller
For containers that are difficult to see through, such as cans or cartons lined with aluminium, ...
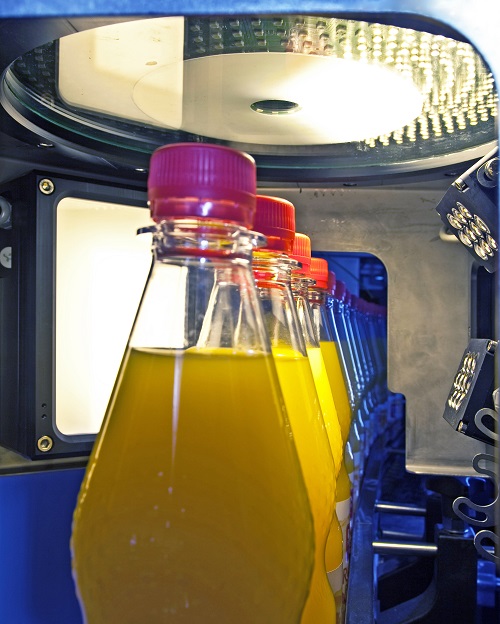
Optical fill level controller
Accurate fill level inspection for transparent, opaque and foaming liquids, that makes sure th...
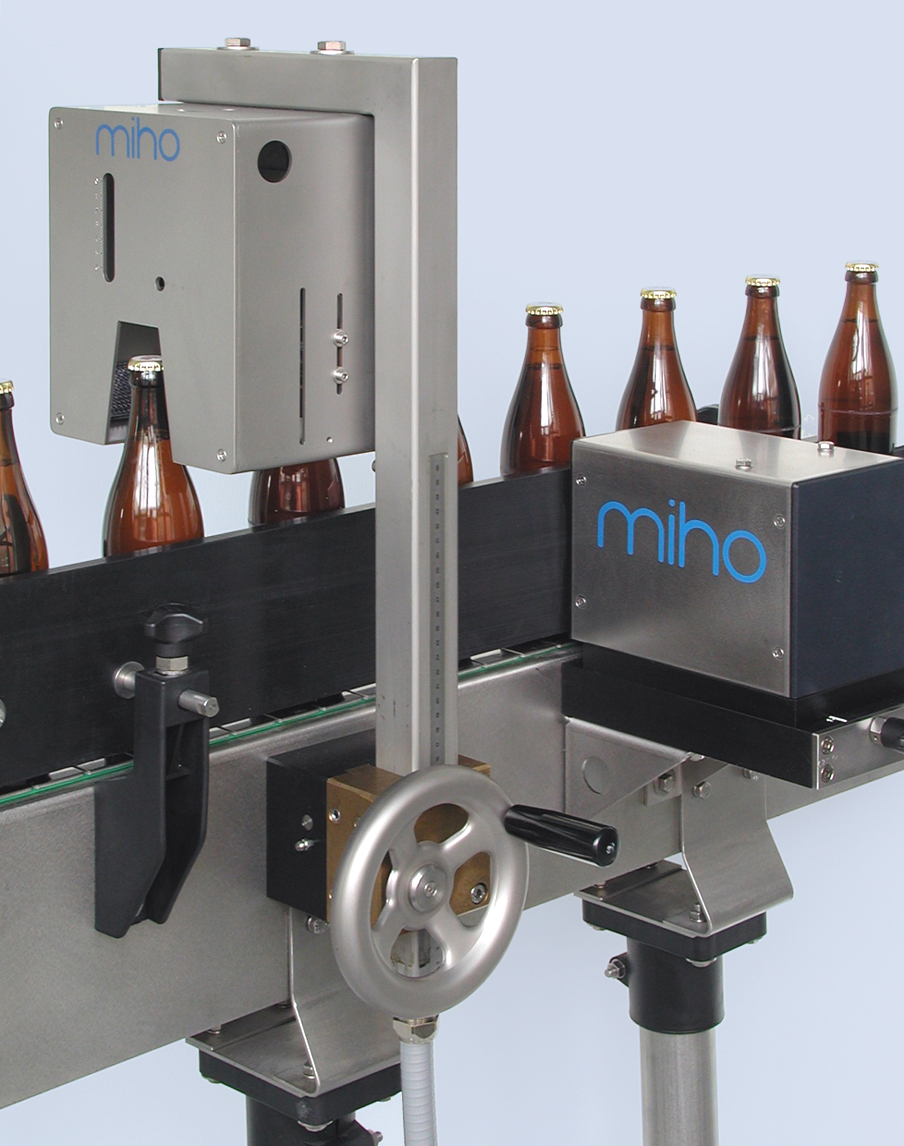
High-frequency fill level controller
In terms of high-frequency technology, the fill level detection is considered a standa...
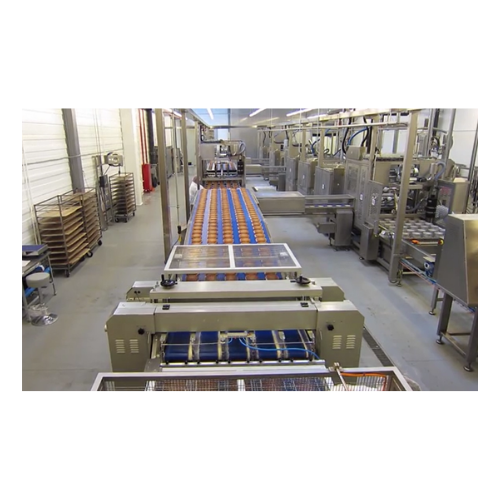
Layer cake production system
Effortlessly streamline your bakery production with a system designed for precise layering and ...
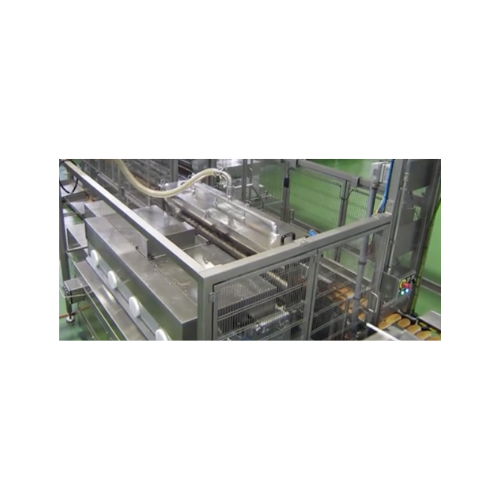
Cakes and pastry side injector
Enhance your bakery production with precision side injection technology that efficiently fill...
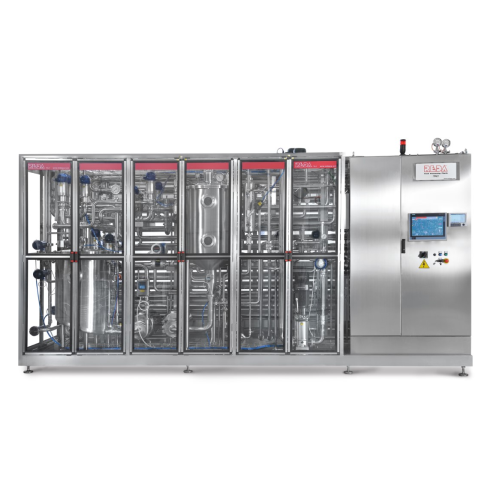
Uht sterilization for milk
Enhance your production line with advanced UHT sterilization, ensuring extended shelf-life and un...
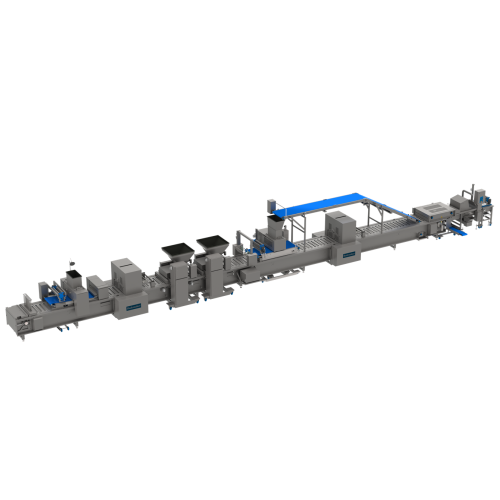
Pie and quiche production line
Optimize your bakery’s capacity with a versatile production line that seamlessly integr...
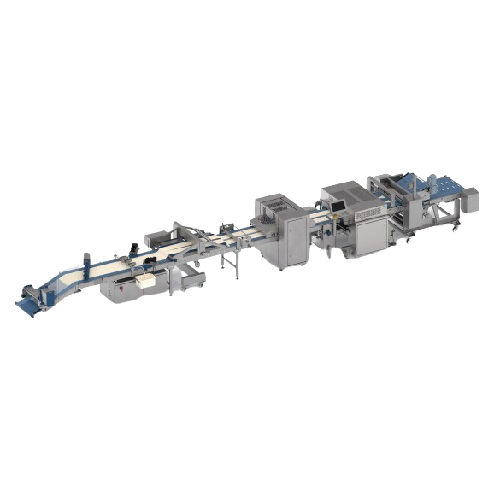
Croissant production module for pastry make-up lines
Enhance your bakery’s product range with a versatile module de...
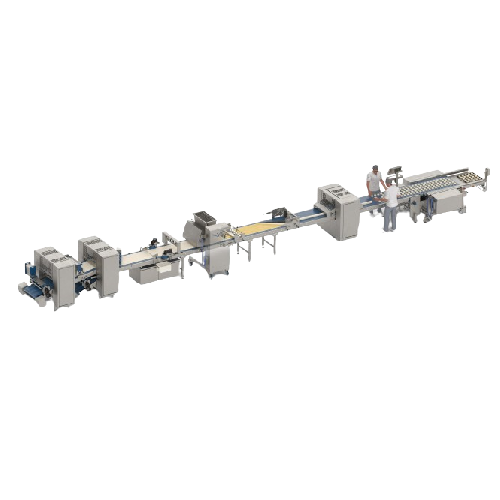
Pastry production line for large-scale bakeries
Streamline your bakery production with a versatile line designed to effici...

Beverage multi-pack cartoner for cans and bottles
Optimize your beverage production line with high-speed, continuous mult...
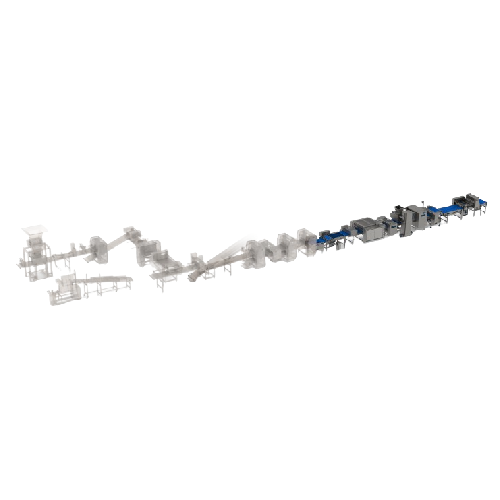
Industrial croissant production line
Streamline your bakery’s operations with a versatile solution capable of produci...

Intermittent motion end load cartoner for baked goods and home care products
Streamline your packaging line with high-...
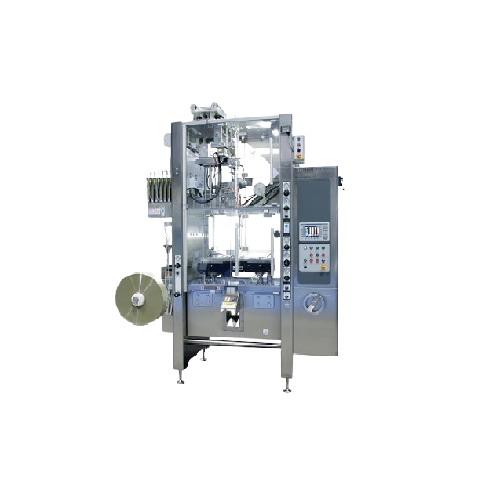
Chub packer for resin bolt packages
Optimize high-speed packaging of liquid resin products with precise filling and wrappin...
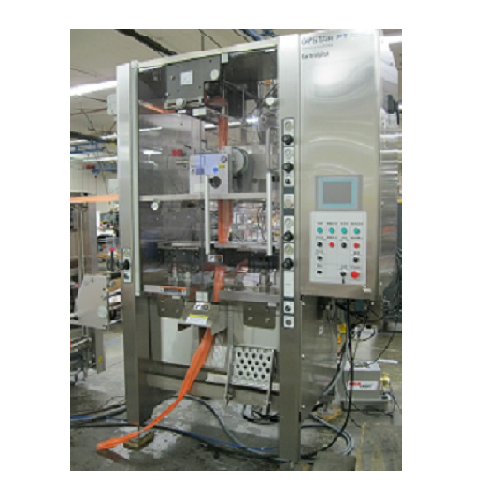
Chub packing system for chemical emulsions
Effectively pack and fill chemical emulsions with precision to enhance the safe...
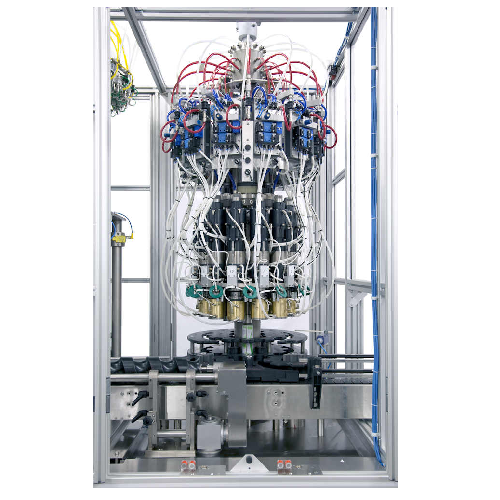
High-speed aerosol can crimper
Optimize your aerosol production with a continuous high-speed crimping solution designed to h...
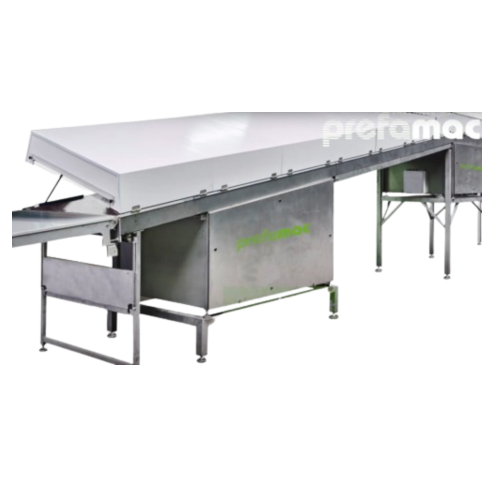
Precise dosing technology for praline and chocolate production
Streamline the production of pralines, chocolate bars, an...
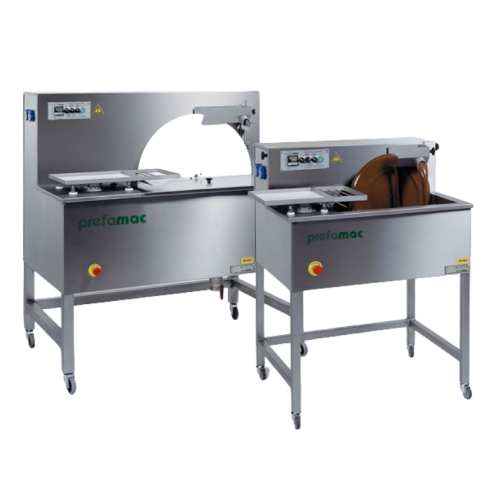
Chocolate moulding system for small-scale production
Optimize your chocolate production by efficiently melting, tempering...
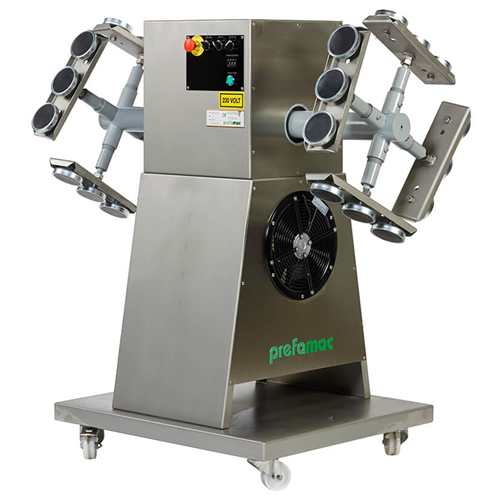
Double spinning machine for hollow chocolate figures
Achieve perfect distribution of chocolate in molds with precision sp...
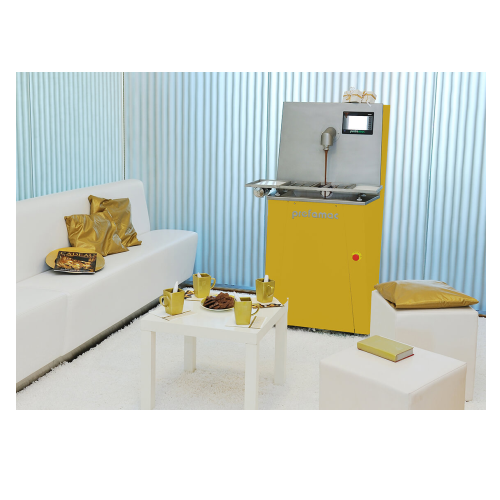
Compact chocolate tempering solution
Enhance your chocolate products’ finish and efficiency: this compact solution en...

Dosing system for kügel chocolate moulds
Automate your chocolate production with precision dosing, seamlessly integrating m...
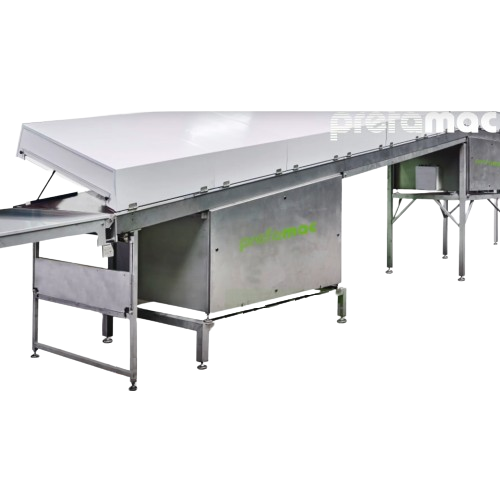
Mini praline dosing system
Achieve precise dosing and versatile moulding for mini pralines and chocolate creations, streamli...
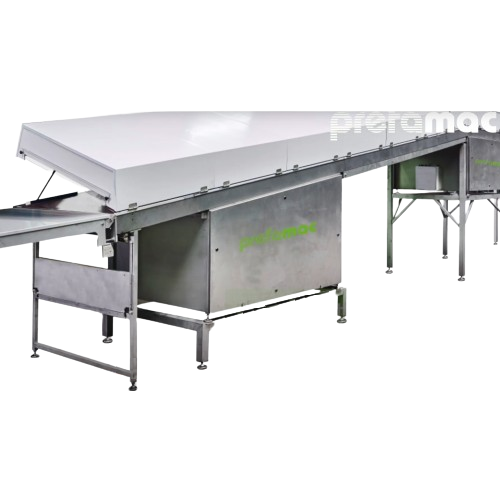
Dosing system for chocolate tablets
Enhance your confectionery production with a versatile solution for precise dosing and ...
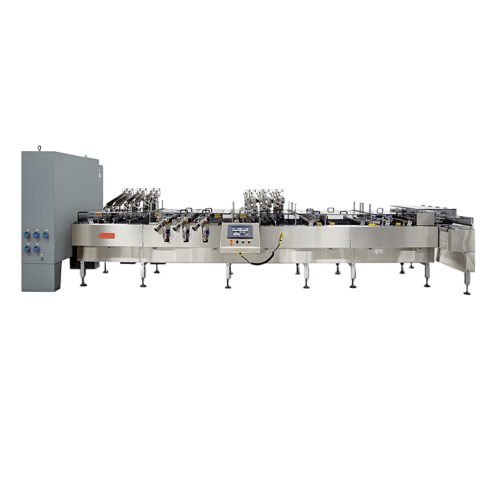
High-speed sandwiching machine for bakery production
Streamline your baking operations with a machine designed to efficie...
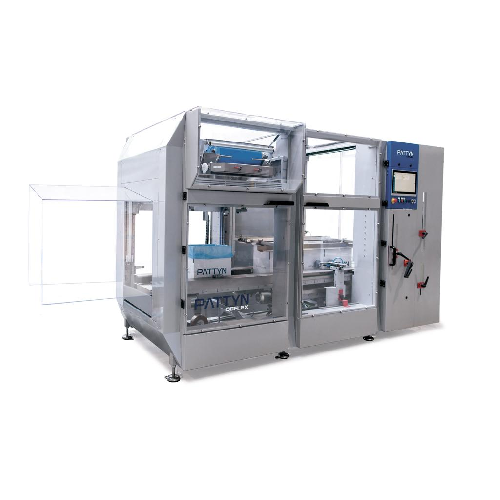
Combined case erector with bag inserter for packaging lines
Streamline your packaging process by integrating case erecti...
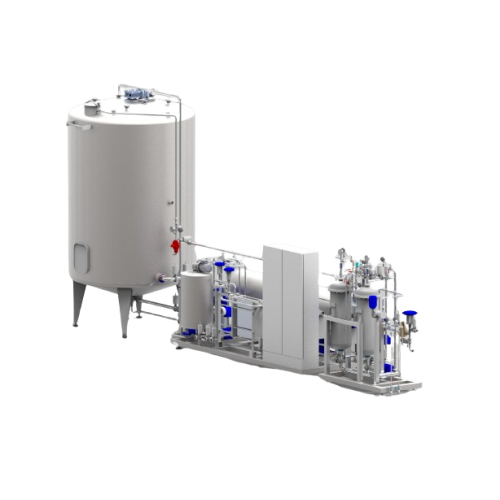
Continuous tartaric stabilisation for wine
Ensure your wines are free from unwanted crystals with a continuous solution th...
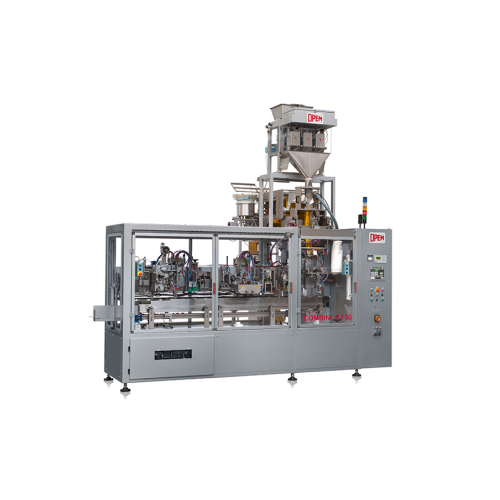
Vertical bagging system for four corner seal bags
Optimize your coffee pod and capsule production with a high-speed, cont...
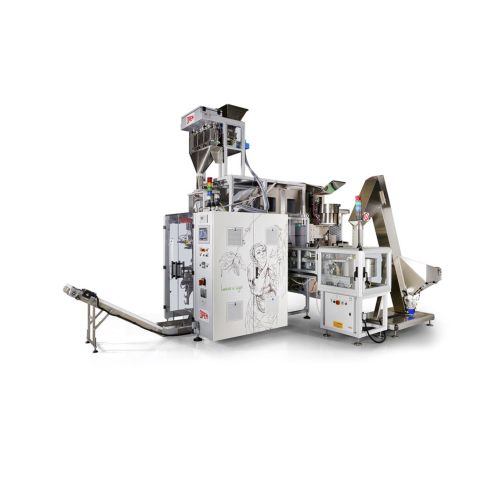
Vertical packaging system for pet food
Streamline your production line with high-speed packaging capabilities, handling var...
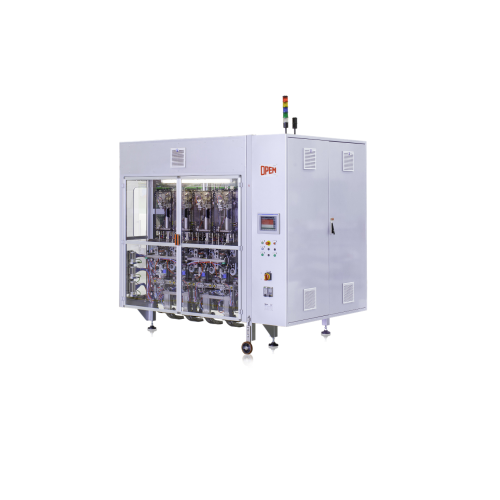
Automated capsule packaging system
Streamline your high-speed packaging operations with a system designed for precision fil...

Vacuum packaging system for food products
Optimize your packaging process with high-speed vacuum technology designed to pr...
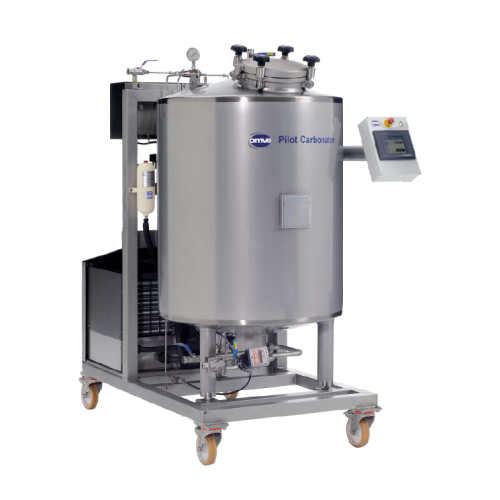
Hygienic buffer tanks for process optimization
Enhance your production flow with hygienic buffer tanks that ensure consist...
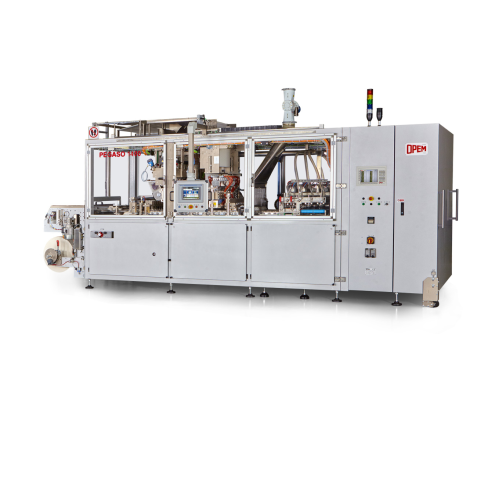
High-capacity filter paper pod production system
Optimize your pod production line with a high-speed solution that ensures...
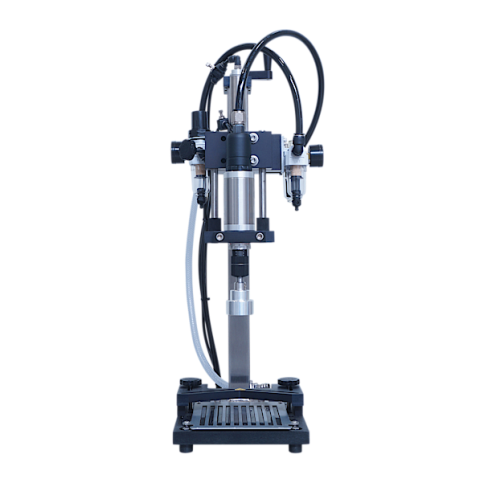
Fs closing devices for industrial packaging solutions
Streamline your packaging process with versatile closing devices, d...
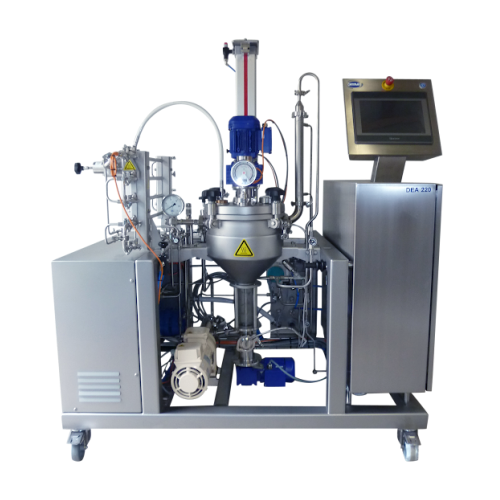
Continuous deaeration solution for laboratory and pilot systems
Achieve superior product stability and minimize foaming ...
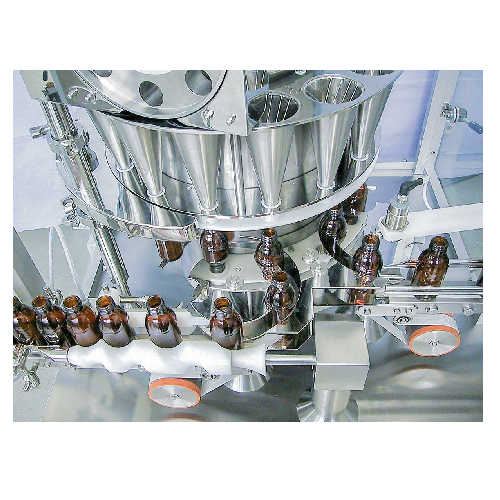
Vacuum pressure macro dosing system for dry syrups
Ensure precise dosage and minimal powder spillage with a high-speed va...
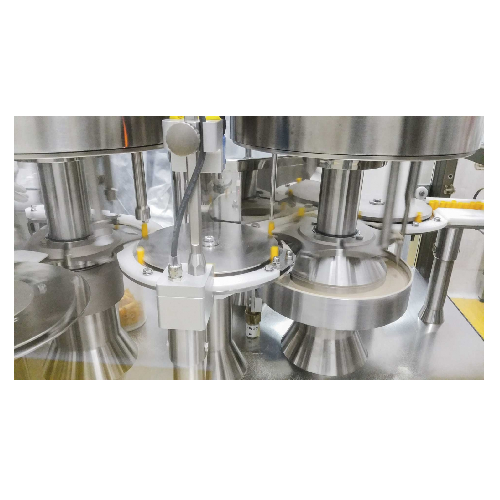
Continuous motion micro dosing system for nutraceutical powders
Streamline your powder processing with a high-speed, con...
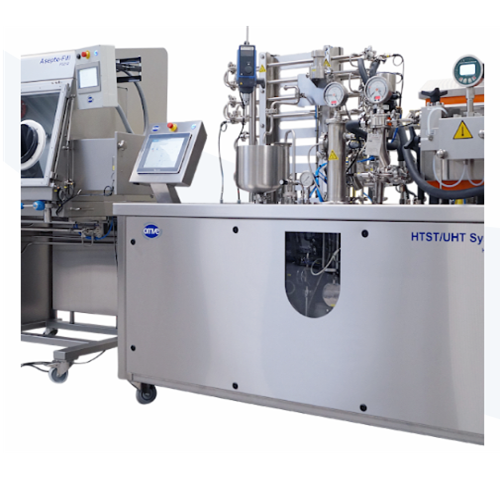
Customized process plants for plant-based beverages
Efficiently scale your production of plant-based beverages with modul...
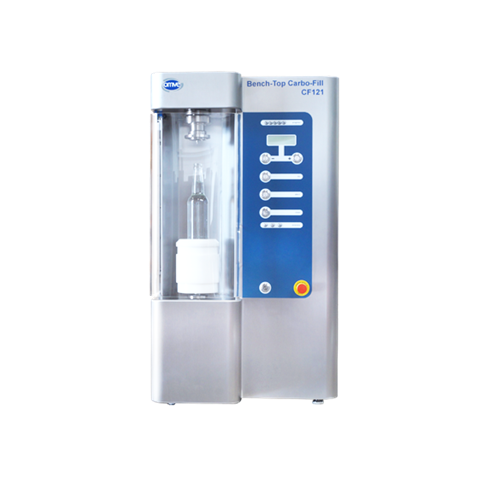
Bench-top carbonation system for postmix drink production
Achieve precise carbonation in small batches with a reliable b...
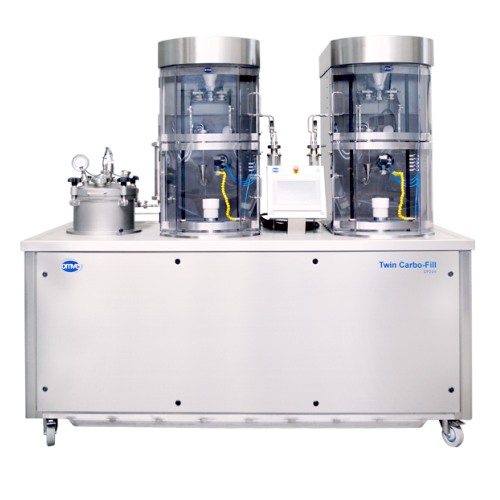
Carbonation and can seaming solution for beverages
Optimize your beverage production with a seamless integration that sim...
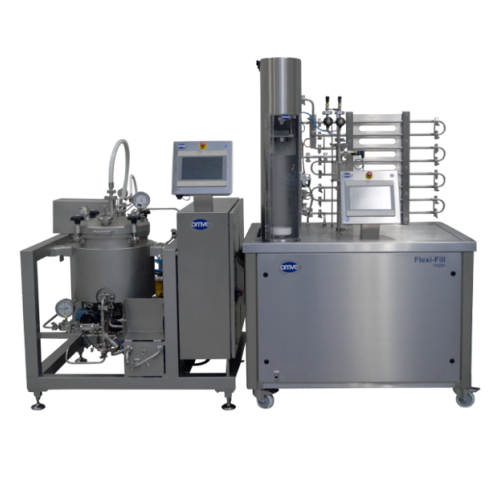
Sterile carbonation system for beverages
Achieve precise carbonation for both common and specialty beverages with this vers...
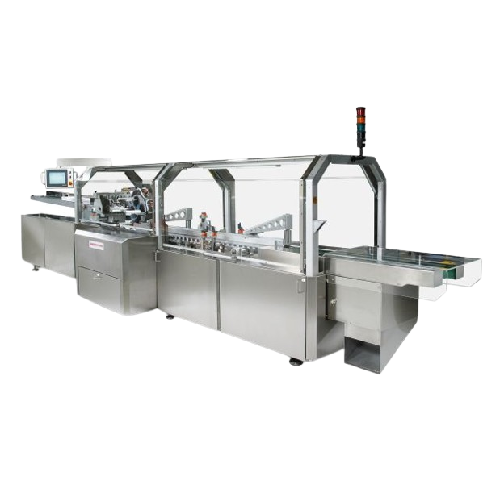
Hig Speed Tube Cartoner
Achieve seamless integration into your high-speed packaging line with a cartoning solution that ensur...
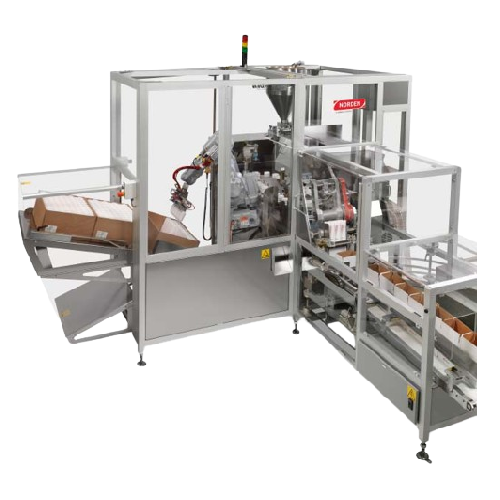
Pick & place robot for packing tubes in boxes
Efficiently streamline your packaging line with this compact case packer, de...
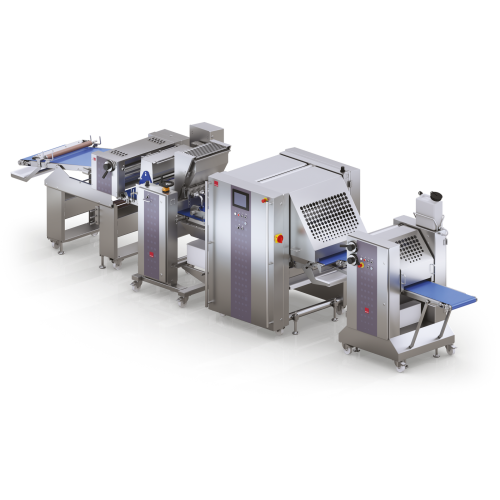
Production line for coiled bakery products
Enhance your bakery’s efficiency with a versatile system designed to crea...
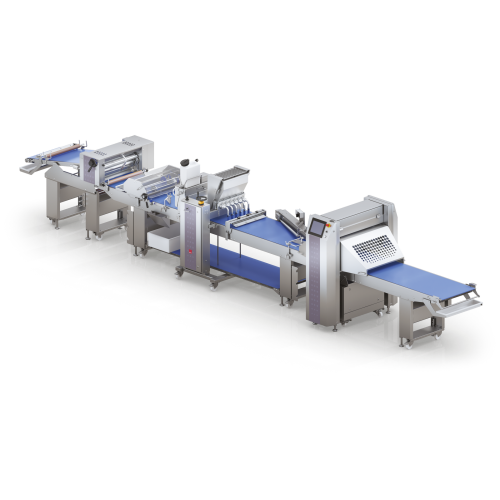
Flexible pastry production line
Maximize your bakery’s output with a versatile pastry line that handles everything fro...
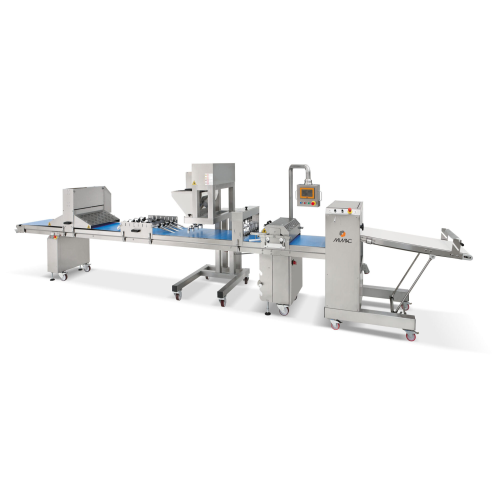
Compact pastry kneading line
Optimize your pastry production with a flexible system designed to knead, cut, fill, roll, and ...
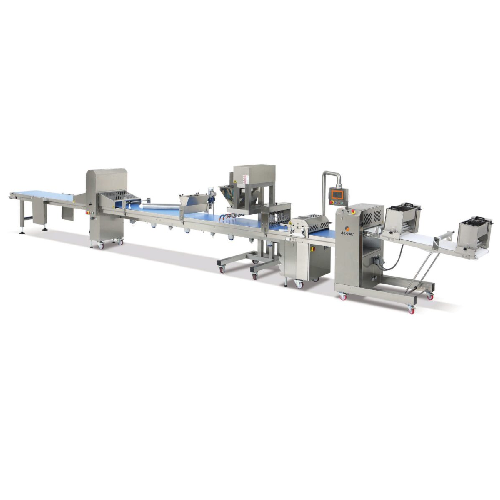
Semi-automatic pastry production line
Elevate your pastry production with a solution that seamlessly combines cutting, fill...
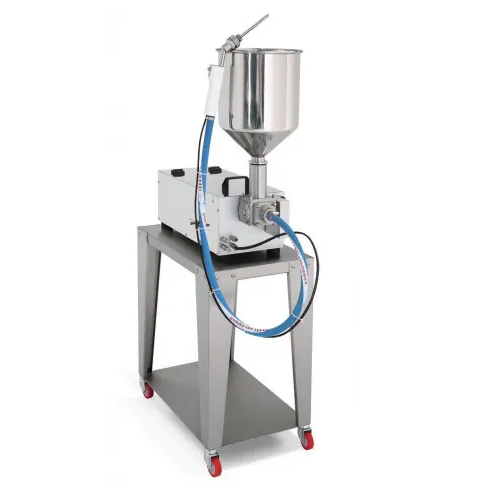
Industrial cream doser for pastry applications
Efficiently dose and fill a variety of bakery and confectionery mixtures wi...
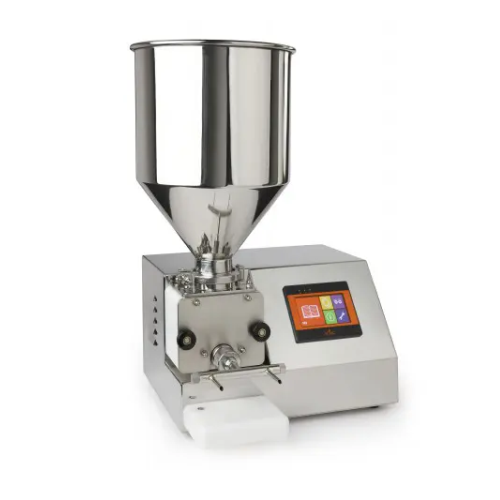
Professional dosing system for creams and sauces
Streamline your production with precise dosing of creams and sauces, tail...
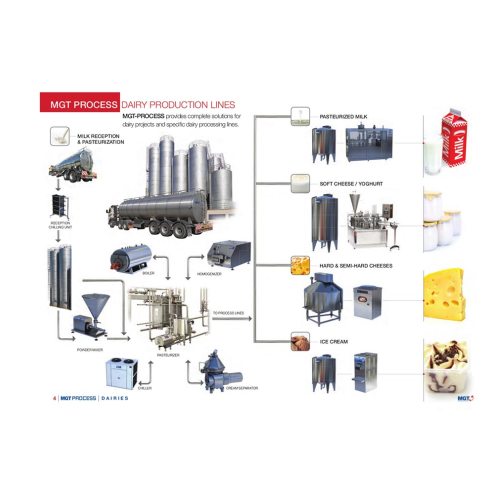
Homogenizer for dairy products
Achieve precise texture and quality in dairy products with this versatile homogenizer, design...
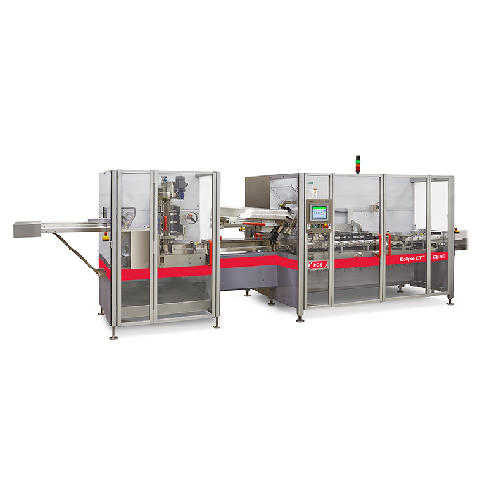
Horizontal cartoner for diverse industries
Streamline your packaging process with precise cartoning capabilities, effectiv...
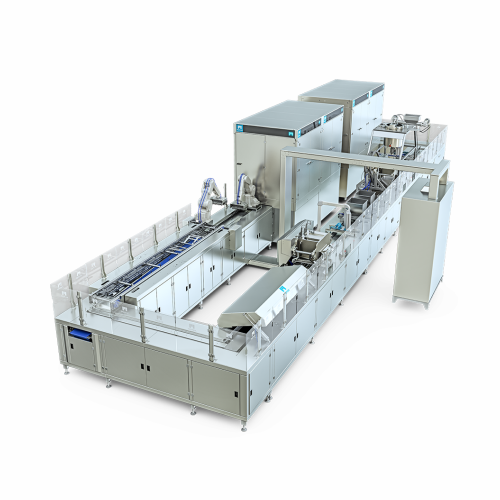
Automatic one-shot moulding line for chocolate production
Streamline your chocolate production with a versatile line tha...
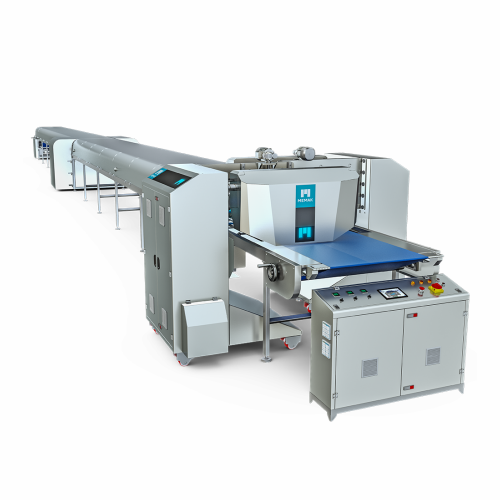
Chocolate drop production line
Enhance your chocolate processing capabilities with precision depositing and moulding, delive...

Automatic chocolate shell moulding line
Enhance your production capabilities with a cutting-edge moulding line that deliver...
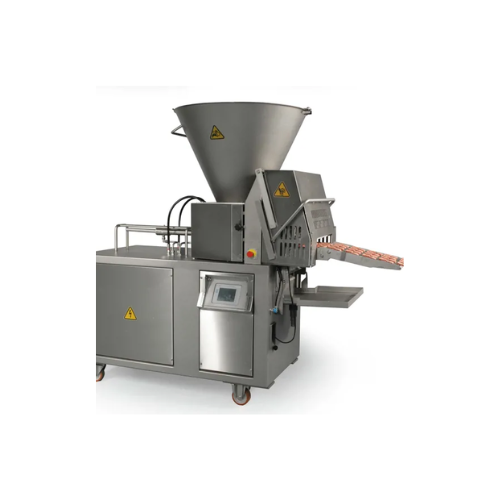
High-pressure forming solution for plant-based and meat products
Experience precision forming with versatile application...
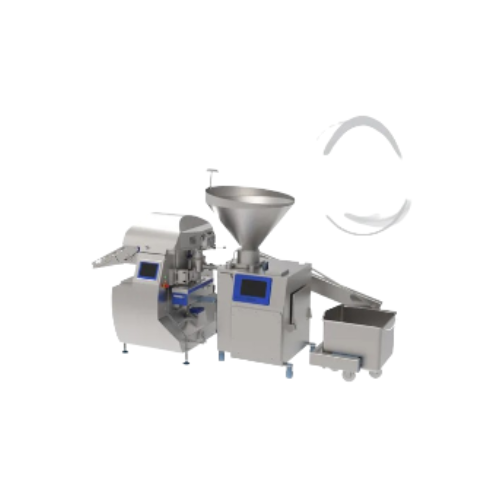
High-quality burger forming system
Effortlessly form a variety of burgers and proteins with consistent texture and shape, t...
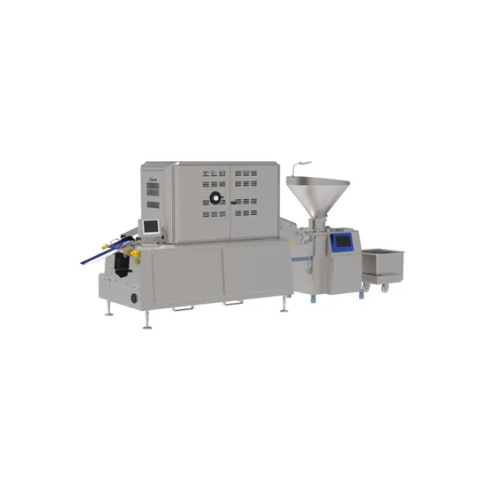
Low-pressure forming solution for plant-based products
Achieve a handcrafted look and precise texture retention for plant...
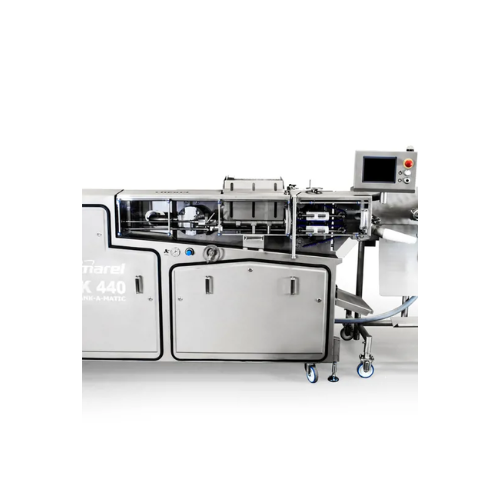
Sausage linking system for consistent weight and length control
Achieve precision in sausage production with high-speed ...
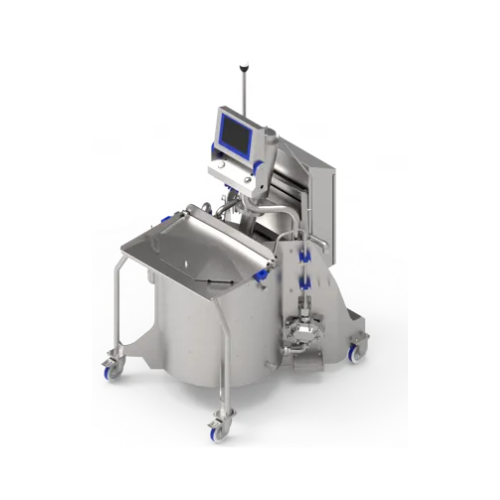
Semi-automatic batter mixer for prepared food production
Achieve consistent, high-quality batter for a variety of conveni...
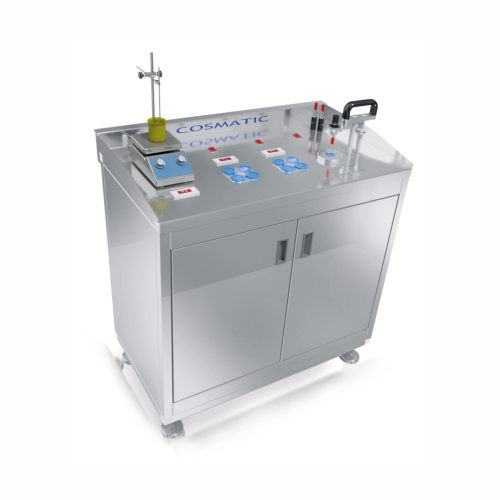
Preparation system for lipstick production in stores
Streamline your cosmetic production by transforming raw ingredients ...
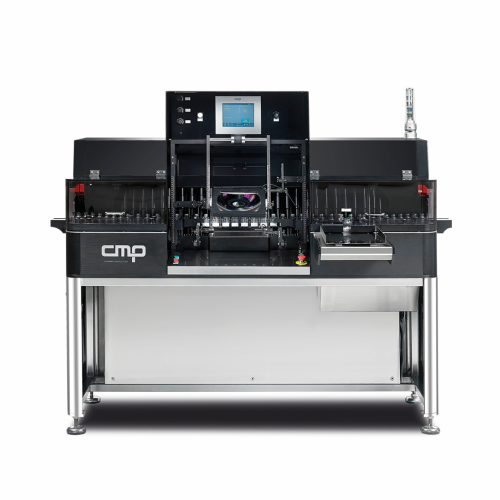
Inspection system for glass containers
Ensure precise inspection of liquid, freeze-dried, and powdered products in glass co...
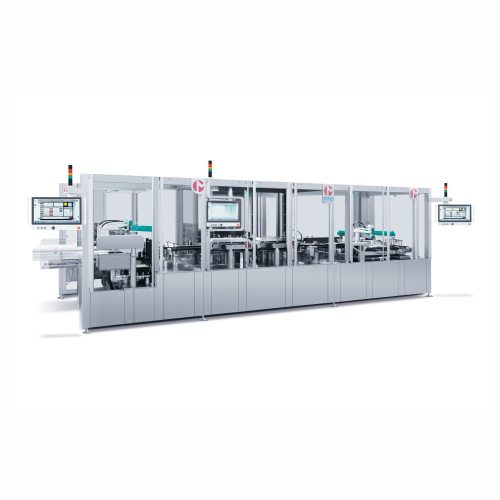
Inspection for glass syringes
Ensure comprehensive quality control for syringe-based medical products with high-speed, no-co...
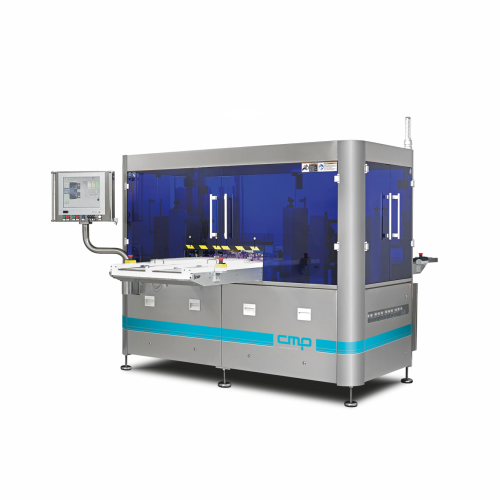
Inspection for glass containers
Ensure the integrity and quality of your liquid formulations with high-speed inspection and ...
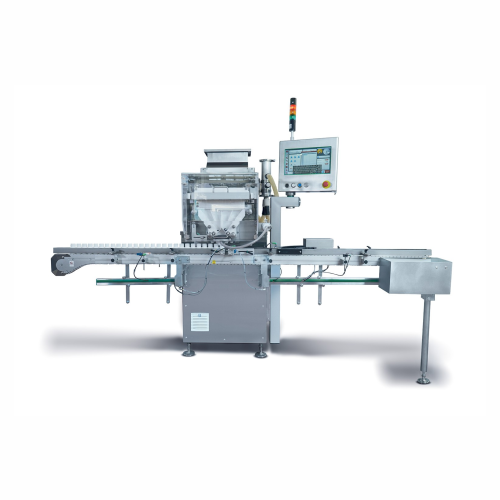
Tablet and capsule counting system
Need precise counting and filling of solid doses like tablets and capsules in your produ...
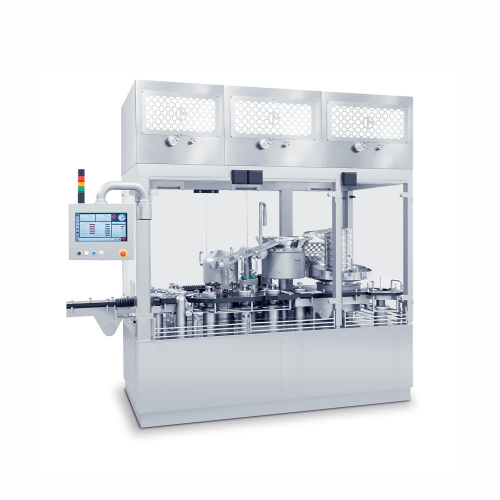
Vial capping for small volume parenteral
Ensure precise sealing and contamination-free environments for small volume parent...
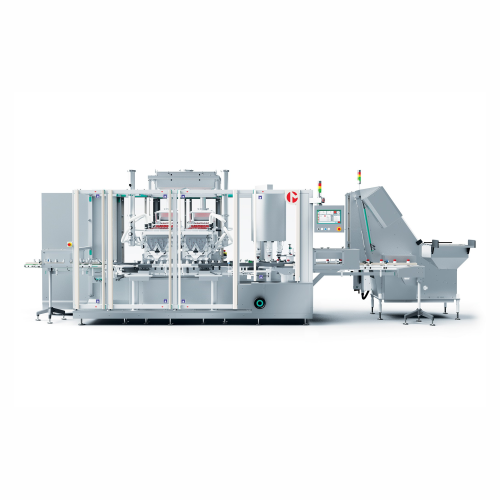
Counting and capping solution for tablets and capsules
Streamline your tablet and capsule production with a high-speed so...
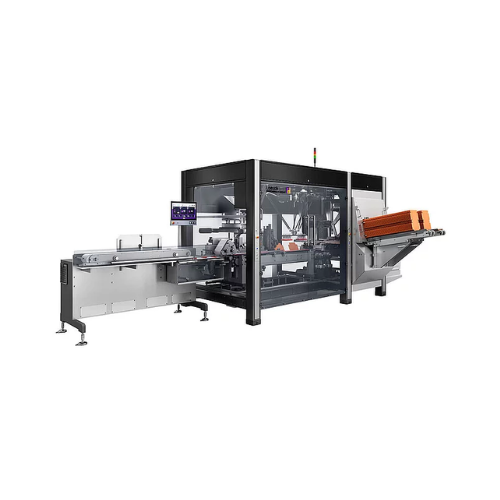
Top-loading cartoner for bar and confectionery packaging
Optimize your high-speed packaging operations with a flexible ca...
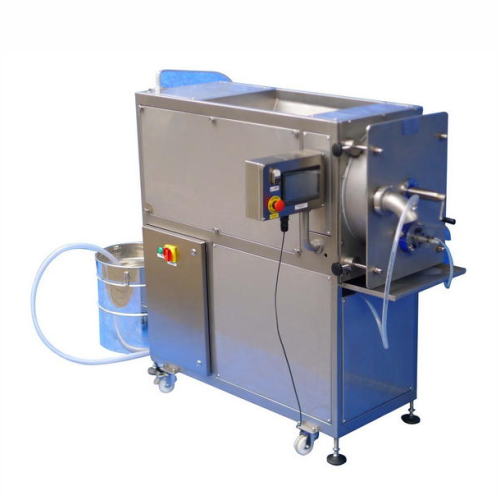
Semi-automatic packaging system for sauerkraut and vegetables
Efficiently tackle the challenge of packing sticky product...
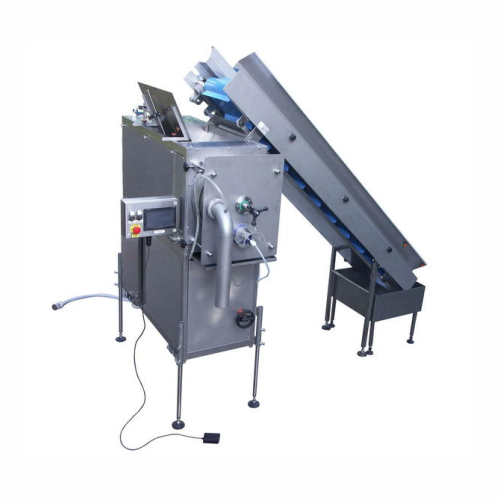
Automatic dosing and packing system for cabbage and sauerkraut
Streamline your vegetable processing line with a robust, ...
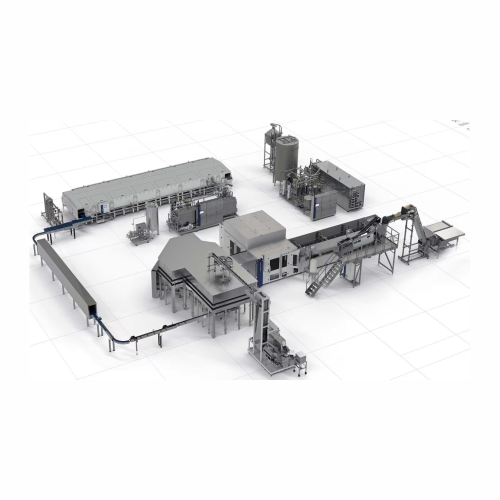
Intelligent pre-dosing system for fruit juices
Optimize your beverage production by minimizing fruit piece damage and ensu...

High-performance stretch blow moulding and labelling system
Maximize space and efficiency with this compact system that ...
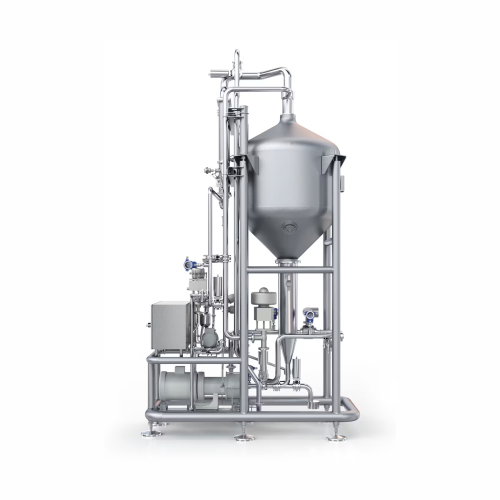
Juice product deaerator
Ensure high-quality filling without foam formation through efficient deaeration, perfect for manufact...
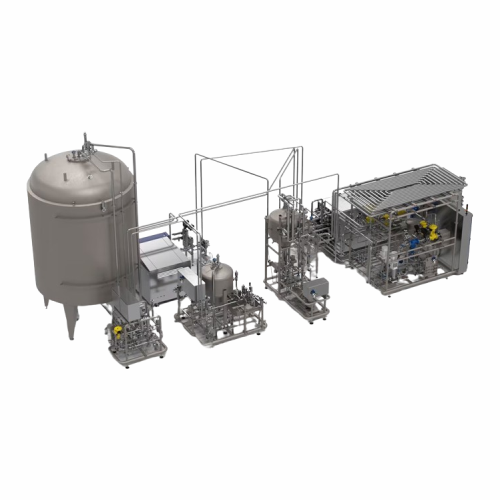
Uht system for milk products
Achieve optimal product safety and quality for dairy and plant-based beverages with precise UHT...
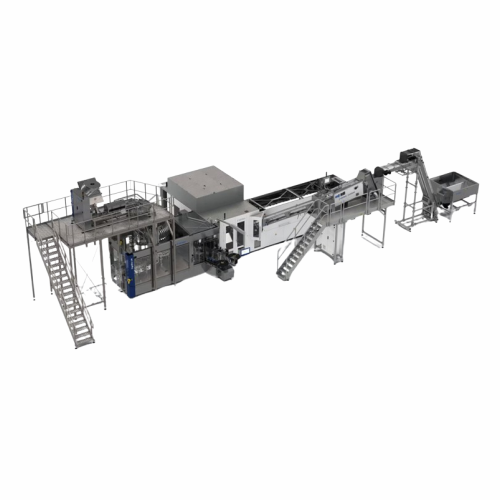
Wet-section block solution for non-carbonated water
Streamline your bottling operations with a compact solution that effi...
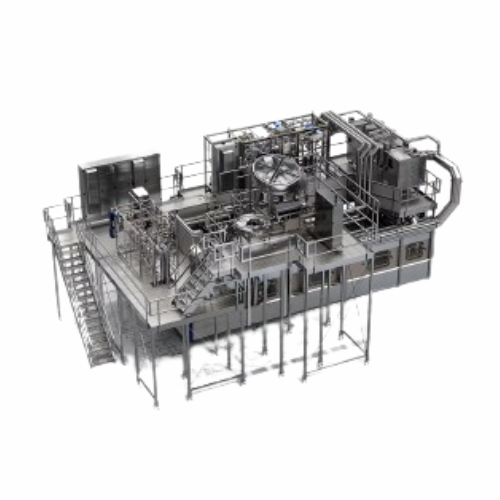
Aseptic bottle sterilisation system for Pet containers
Ensure aseptic integrity and high-speed efficiency in beverage pro...
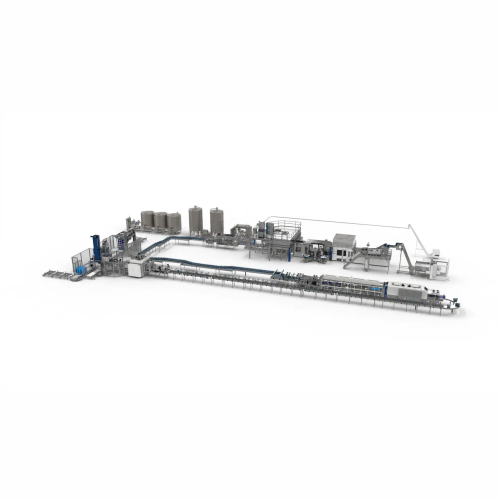
Automated product change-over system
Maximize your production line efficiency by reducing downtime during product changeove...
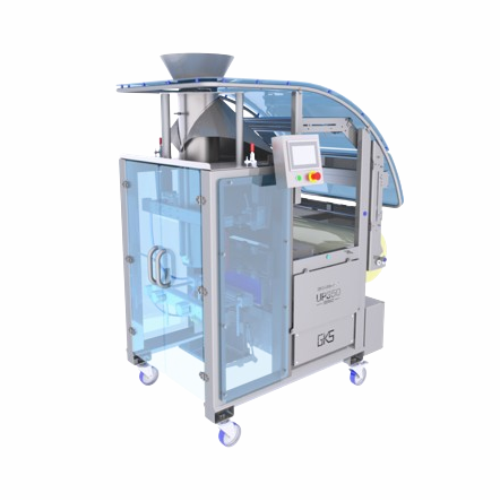
Continuous packaging solution for free-flowing food products
Streamline your production with a high-speed packaging mach...
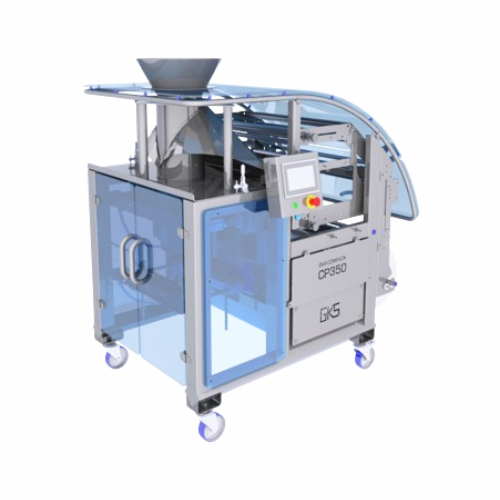
Packaging solution for bulk vegetables and fruits
Ensure precise, high-speed packaging for diverse product sizes with a f...
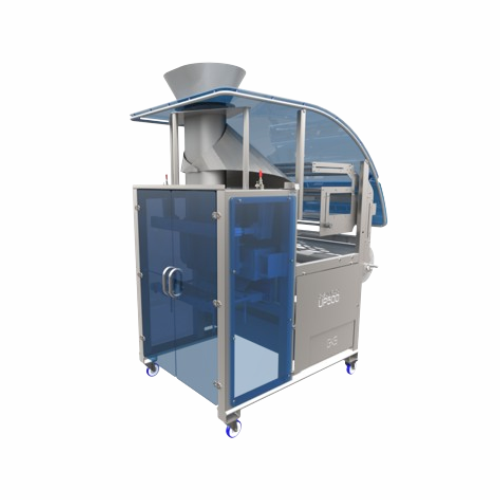
Flexible packaging solution for large food volumes
For high-volume food packaging, achieving consistent bag sizes and red...
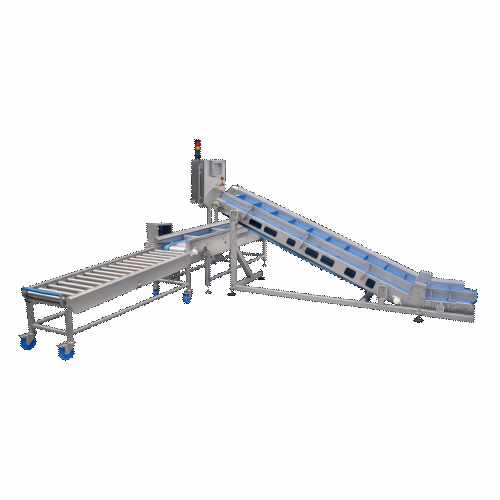
Automatic crate weighing system for fresh produce
Streamline your fresh produce processing by precisely weighing and fill...
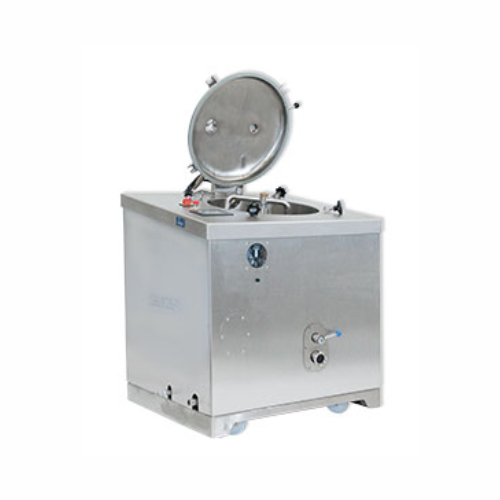
Jam kettle for preserve and marmalade production
Ensure consistent flavor and texture in your jams and marmalades with pre...
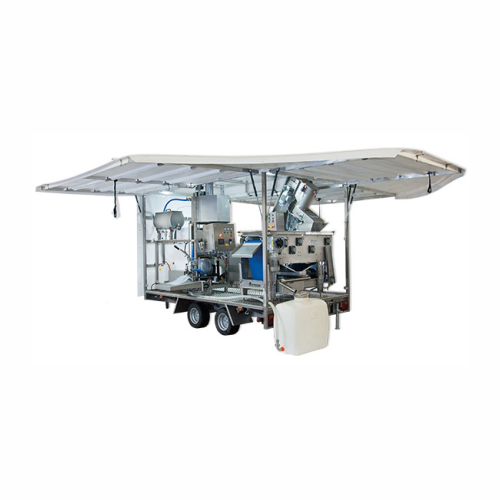
Mobile juice processing units
Transform your fruit harvest into fresh, pasteurized juices directly on-site, ensuring optimal...
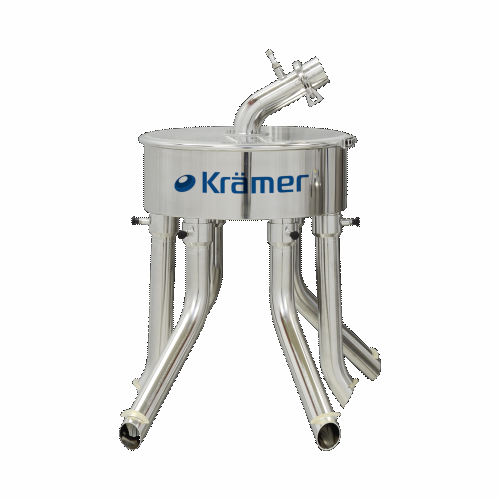
Tablet and capsule diverter
Streamline your tablet and capsule production with precise container filling and flexible config...
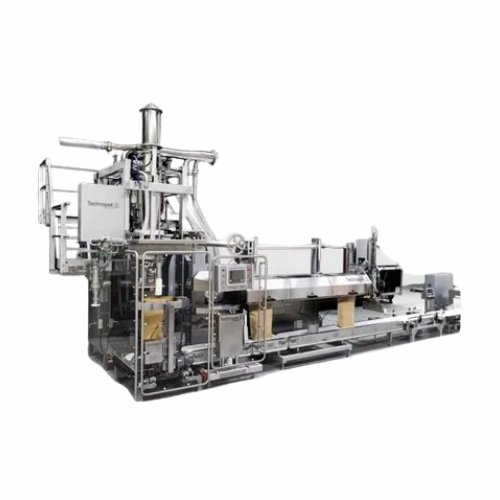
25kg automatic dry powder packaging system
Optimize your packaging line efficiency with precise, high-speed handling for 2...
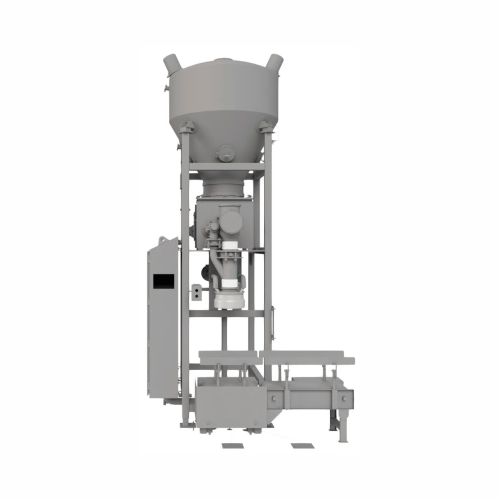
25kg powder packaging system for sanitary applications
Achieve high accuracy and hygiene in powder packaging with a syste...
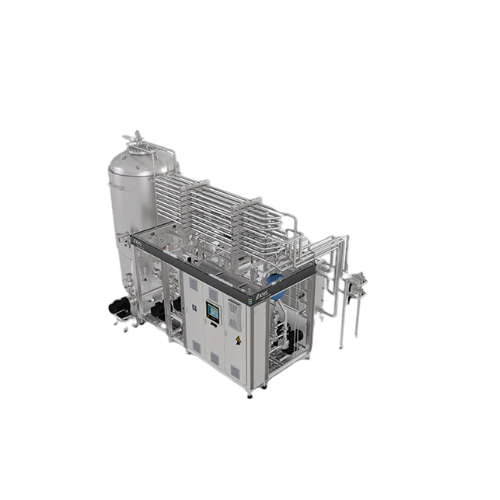
Continuous flash pasteurizer for beverage shelf life extension
Maximize beverage shelf life with precise microbial and e...
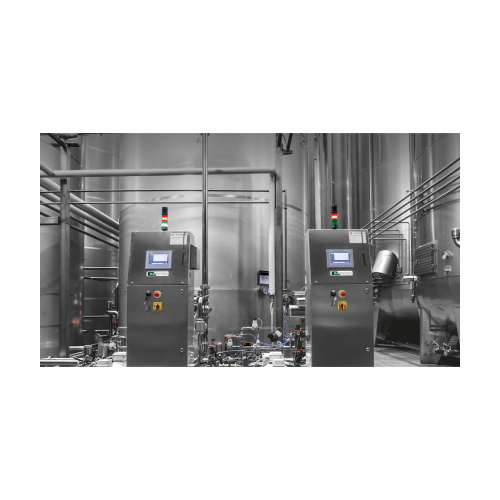
Piping discharge system for product separation in transfer lines
Optimize your beverage production by preventing product...
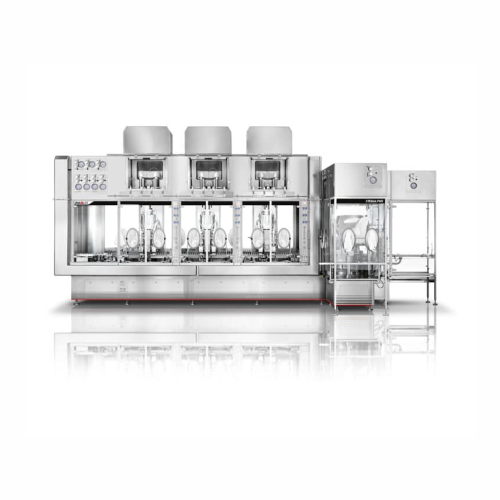
High speed powder dosing and stoppering for antibiotics
Address the threat of antibiotic-resistant bacteria with precisio...
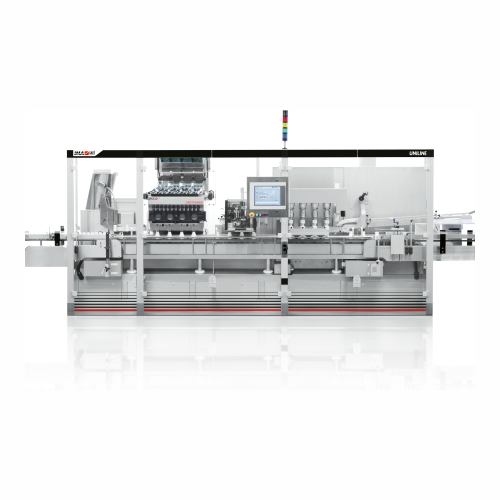
Integrated counting system for tablets and capsules
Streamline your packaging line with a highly versatile system that se...
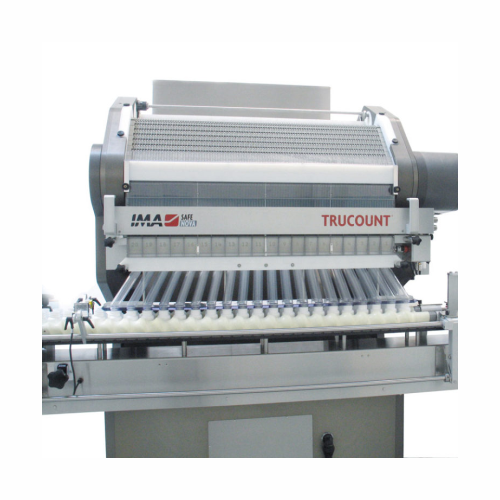
High-precision slat counter for tablet bottling
Optimize your tablet bottling with a low-energy, high-speed counter design...
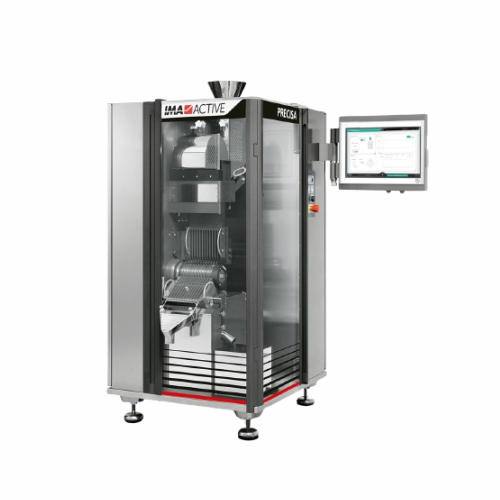
Precision weight-checking for pharmaceutical capsules
Ensure exact capsule and tablet dosage with high-speed precision we...
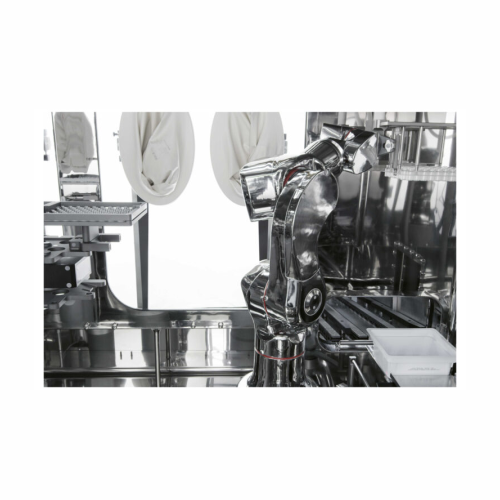
Robotic denesting system for Rtu vials
Streamline vial handling in aseptic environments with a fully robotised system that ...
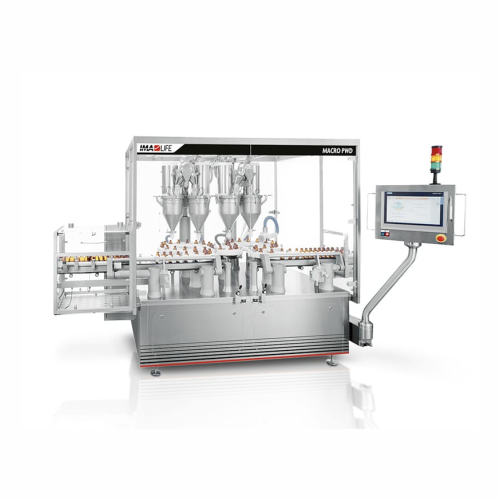
Pharmaceutical powder dosing system
Ensure precise dosing and contamination-free filling with this machine designed for eff...
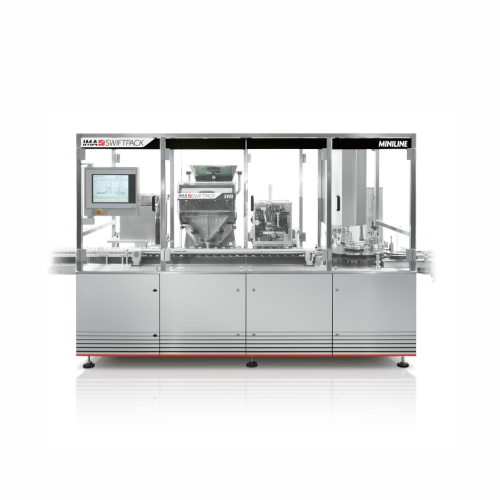
Integrated counting system for tablet and capsule bottling
Optimize your production line with a compact solution designe...
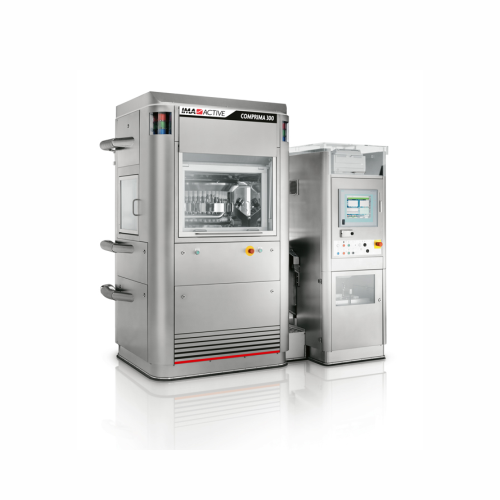
Tablet press for high-quality pharmaceutical tablets
Ensure optimal tablet quality and yield with an advanced compression...
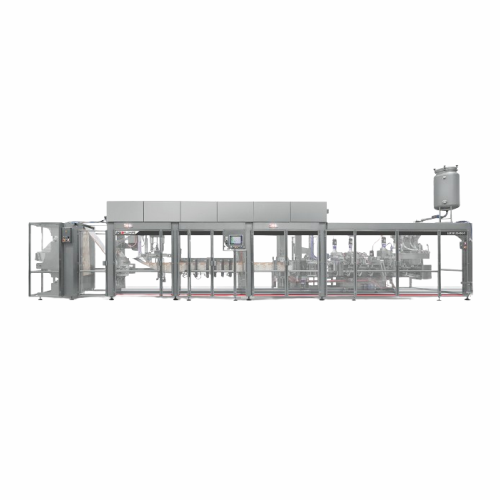
High-speed drift-dwell motion doypack forming system
Optimize your liquid packaging efficiency with a dual-motion system ...
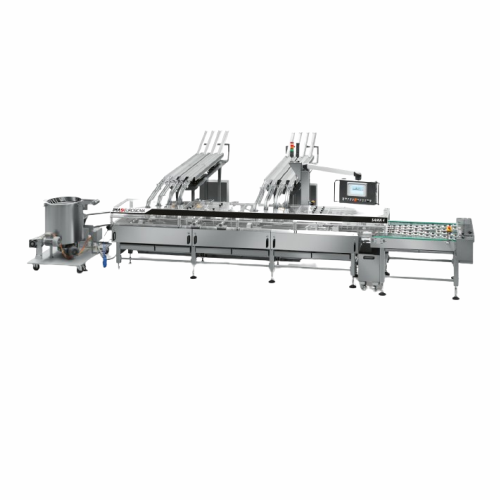
Automatic biscuit sandwiching equipment for high-volume production
Optimize your biscuit production line with high-spee...

Vertical bagging system for heat sealing films and Lpde
Achieve unparalleled flexibility with a versatile vertical baggin...
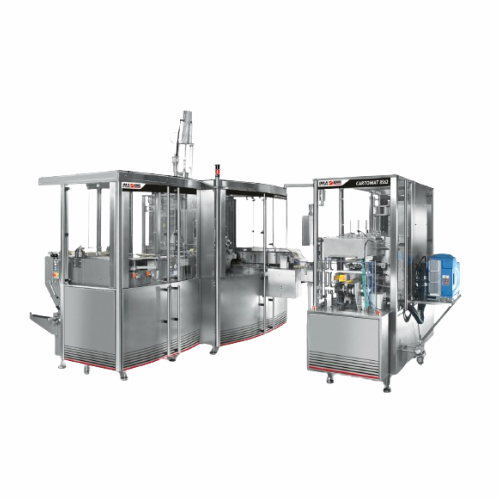
Dosing and wrapping solution for pasty products
Achieve precise dosing and efficient wrapping of pasty products with high-...
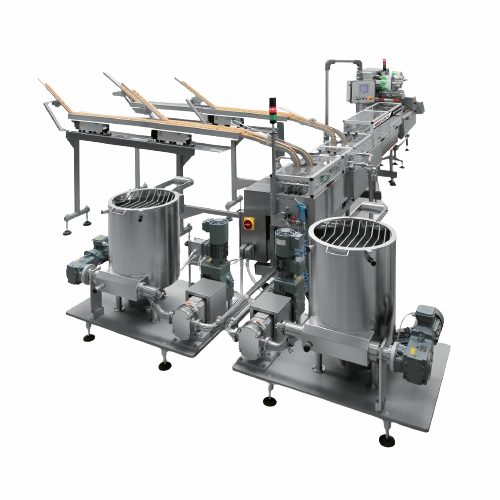
Automatic sandwich biscuit production system
Elevate your biscuit production line with high-speed sandwiching capabilities...
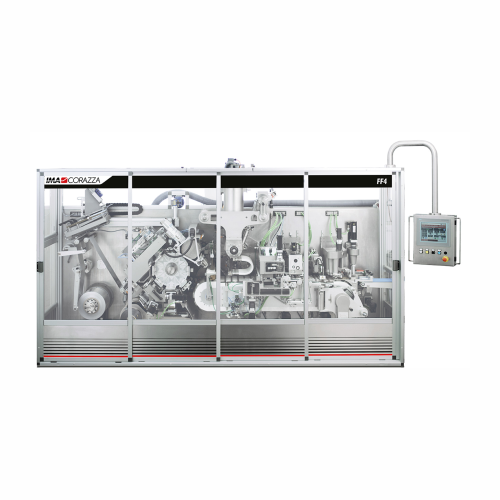
High speed cheese dosing and wrapping solution
Achieve precise dosing and efficient wrapping of cheese portions with versa...

High-speed dosing and wrapping for butter and margarine
Achieve precision in butter and margarine packaging with a high-s...
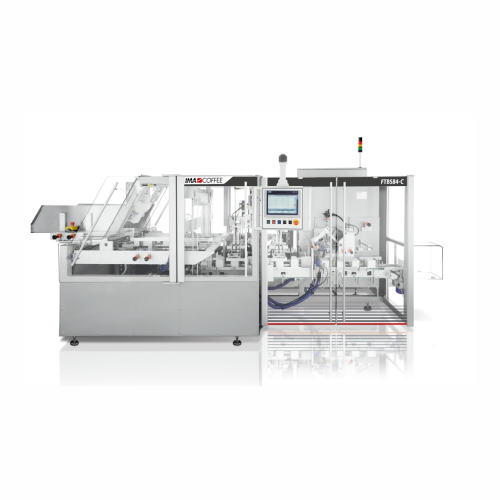
Cartoning system for coffee capsules
Optimize your production line with a space-saving cartoning system designed specifical...
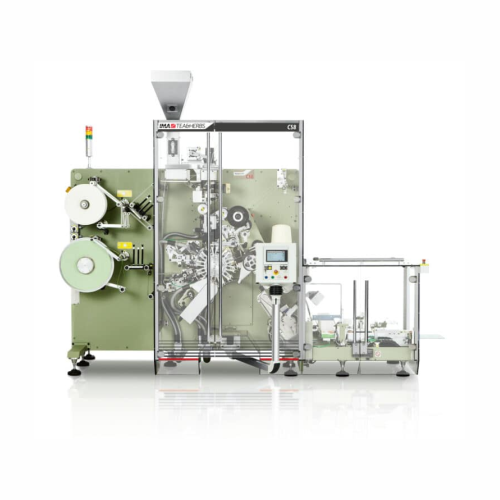
High-speed tea bag packaging system
Enhance your tea production with fast and flexible packaging that infuses superior flav...
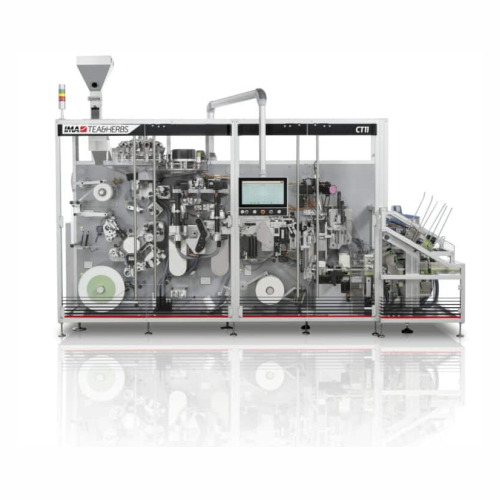
Tea bag packaging system for long-leaf and premium tea
Optimize your tea bag production with a versatile system designed ...

Rotary doypack packaging system for various materials
Enhance your packaging line with versatile doypack machines designe...
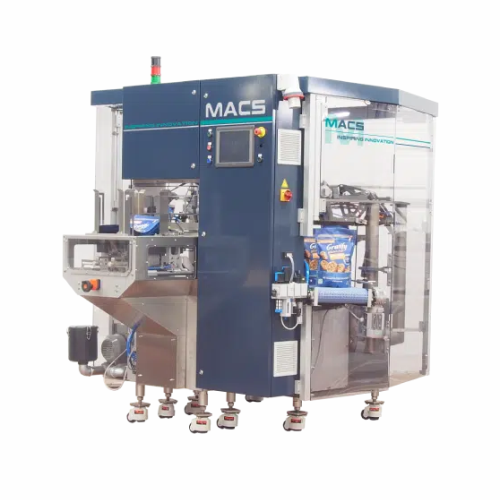
Rotary doypack for granules, liquids, and powders
Enhance your packaging line with a rotary doypack system designed to ef...
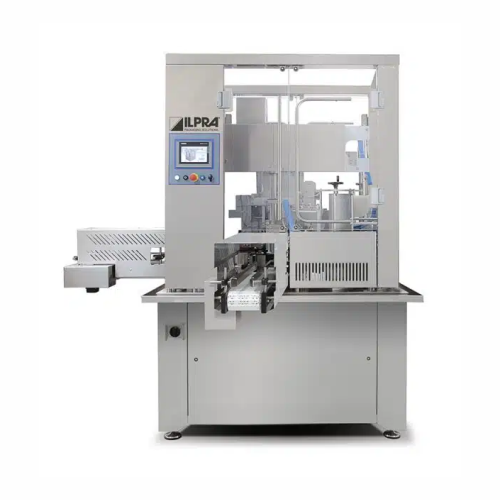
Packaging solution for small bottles and jars
Effortlessly seal and fill non-stackable containers, ensuring precision for ...
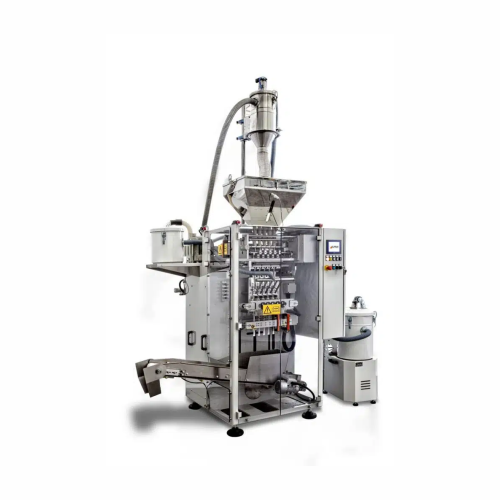
Vertical stick pack sachet packaging solution
Ideal for mid-scale operations, this vertical stick pack machine streamlines...
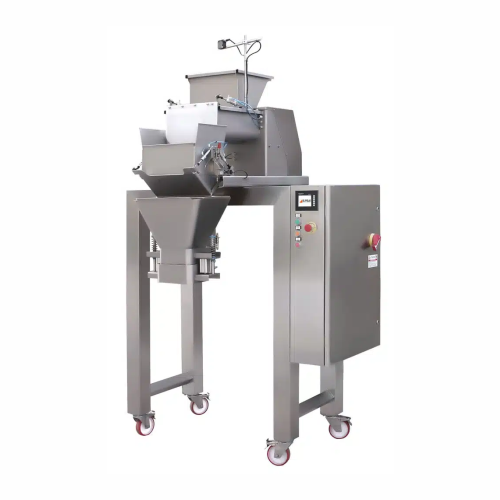
Linear and auger weighing systems for non-free-flowing products
Optimize your production line with precise weighing and ...
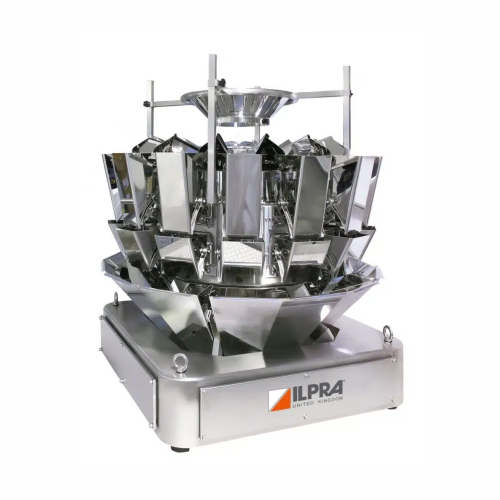
Multi head weigher for precise portioning
Ensure consistent product portions with our multi head weigher, ideal for high-s...
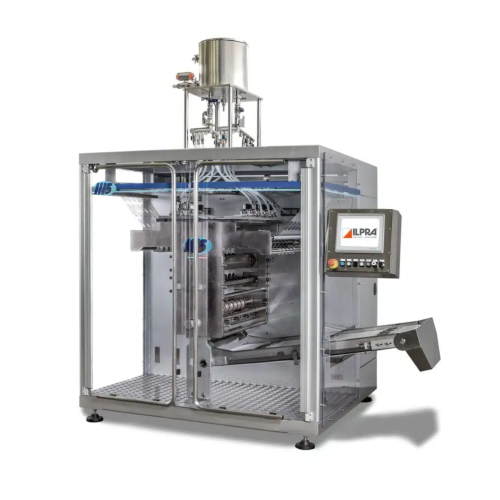
High-speed continuous rotating packaging solution
Transform your packaging efficiency with versatile operations, accommod...
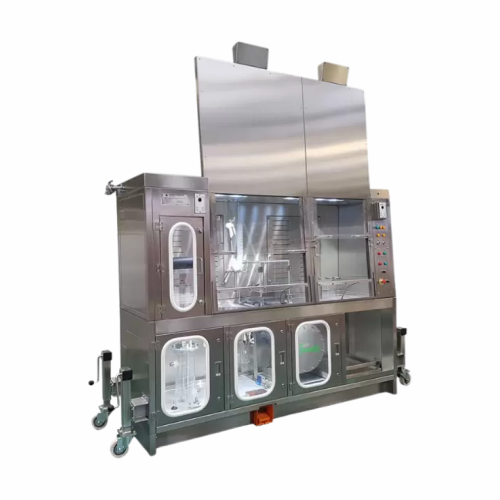
Containment solutions for hazardous material processing
Ensure safe and efficient processing of hazardous materials with ...
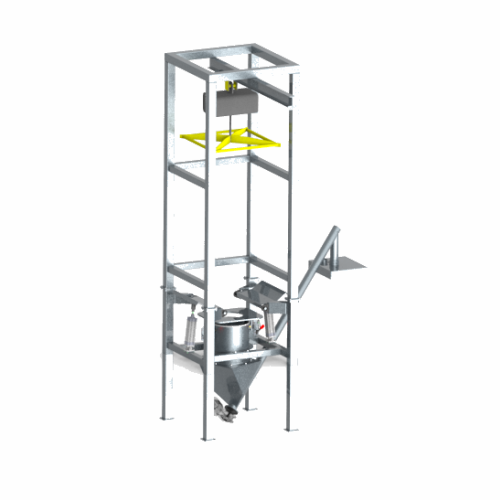
Powder dosing system for big-bags
Efficiently dose and fill various powdered materials directly from big-bags into your pro...
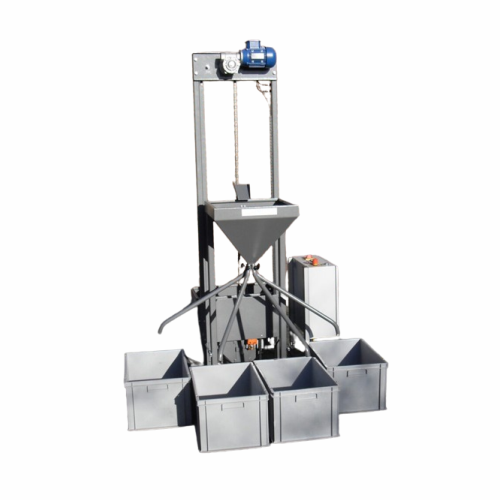
Single bucket elevator for seed handling
Optimize your seed processing efficiency by seamlessly transporting and splitting ...
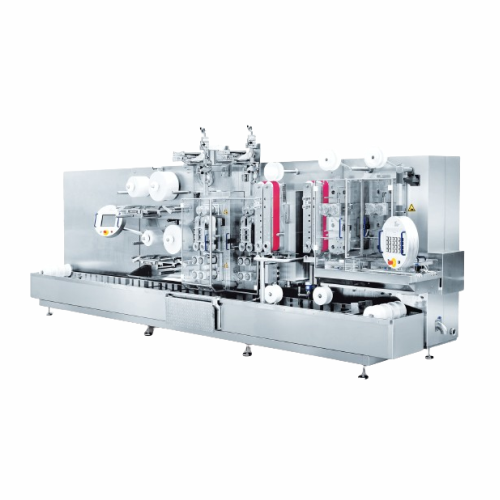
High-speed cheese slice wrapper
Achieve unparalleled efficiency with the high-speed wrapping machine that securely packages ...
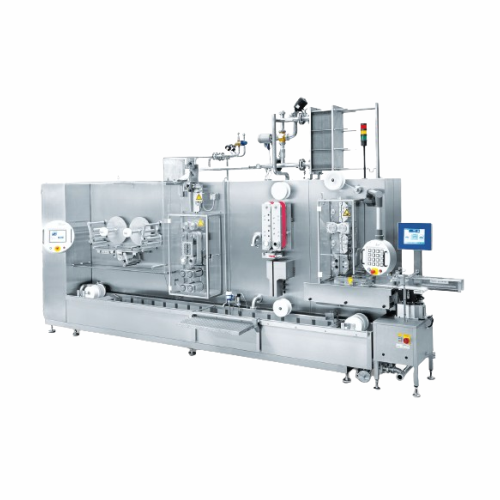
Individually wrapped processed cheese slice production line
Efficiently produce consistent, individually-wrapped cheese ...
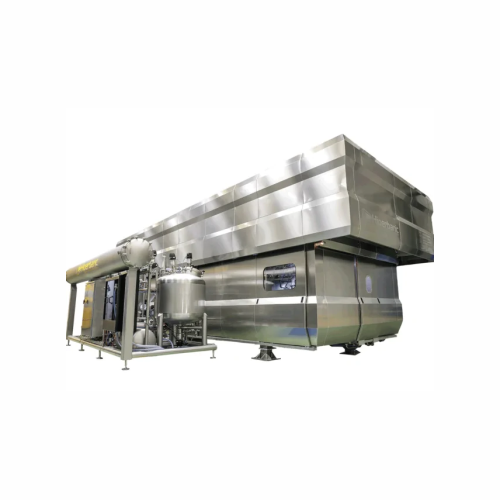
High pressure processing for bulk liquid beverages
Streamline your liquid processing with high-pressure in-bulk technolog...
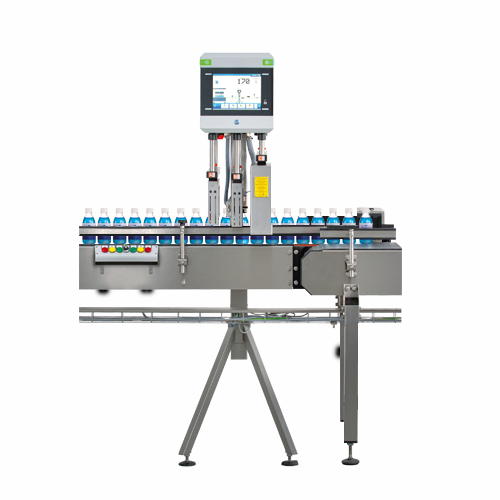
Compact full product inspection system for pharmaceuticals
Easily detect fill level inaccuracies, closure misalignments,...
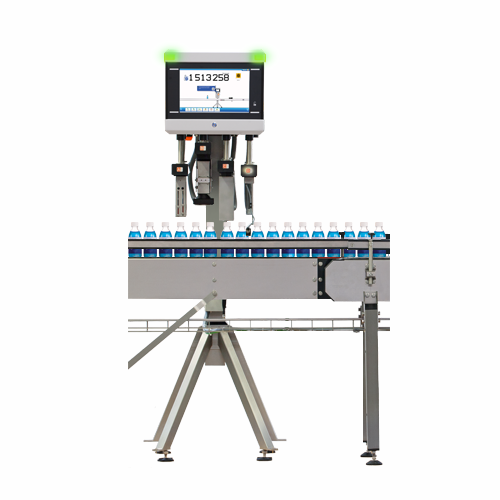
Full container inspection for pharma and food industries
Ensure precise fill levels and secure closures in your productio...
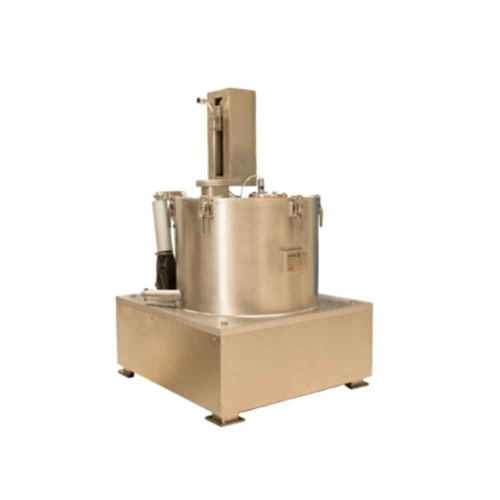
Vertical centrifuge for plasma fractionation
Achieve high-purity plasma derivatives with precision; this vertical centrifu...
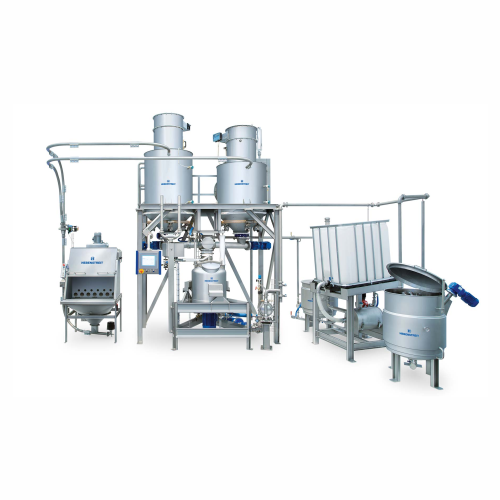
Automatic wafer batter preparation system
Optimize wafer production with precision dosing and homogeneous mixing, ensuring...
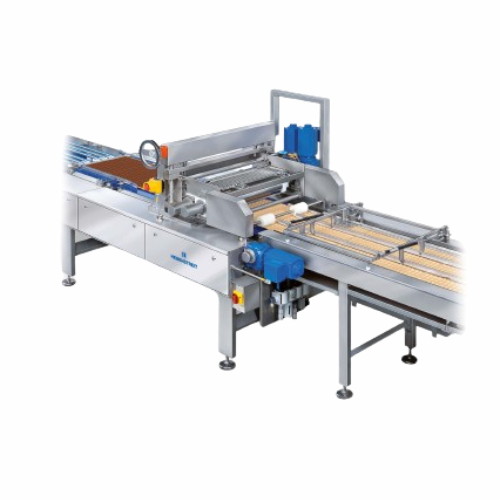
Hollow wafer spreading machine for consistent coating
Optimize your snack production with precise spreading—achieve unifo...
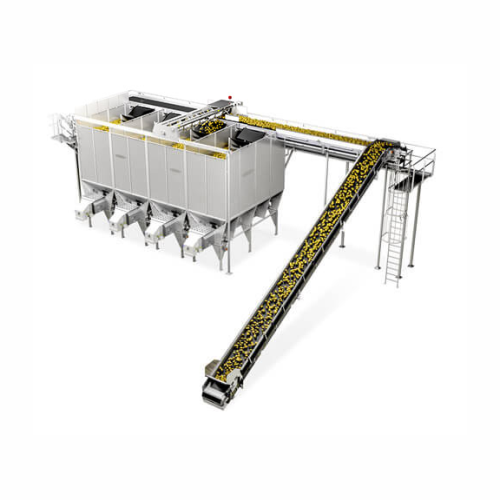
Gentle-flo storage and handling system for fresh produce
Ensure gentle handling and precise control of fresh produce stor...
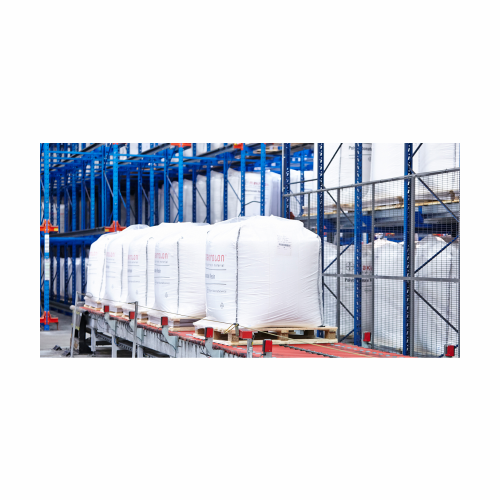
Stationary entry packaging system for valve bags
Optimize your packaging workflow with a high-speed, modular filling syste...
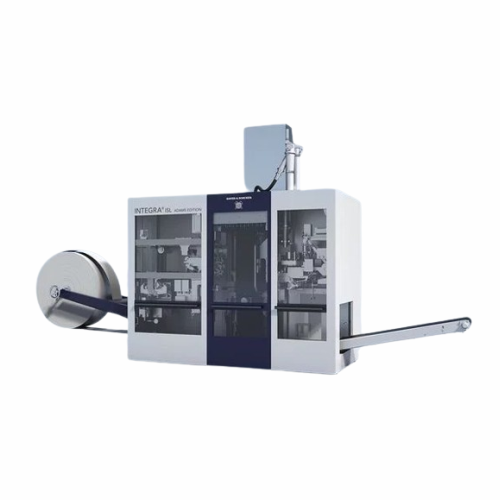
Integrated packaging system for cement and building materials
Streamline your packing operations with a fully enclosed s...
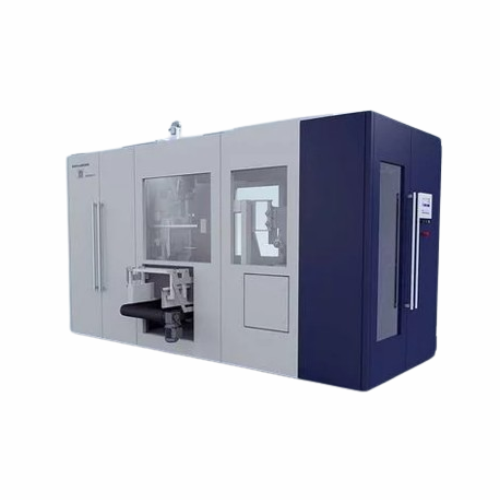
Integrated packaging system for valve and Ffs bags
Streamline your packaging operations with a versatile system designed ...
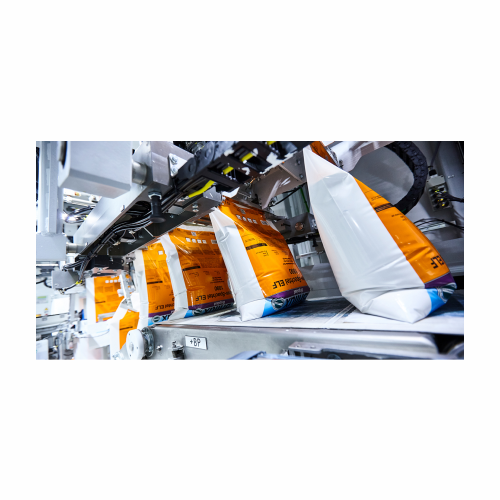
Integrated packaging system for valve and tubular film bags
Achieve precision and efficiency in your packaging line with...
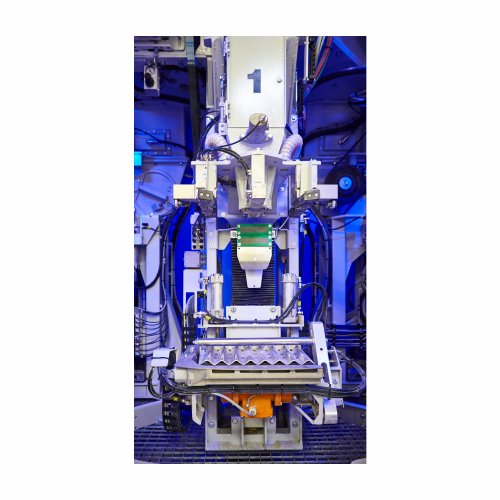
Rotating packaging system for cement and chemicals
Streamline your packaging line with a high-speed, rotating solution th...

Rotating packaging system for bulk materials
Optimize your bulk material packaging with high-speed, precise rotary packers...
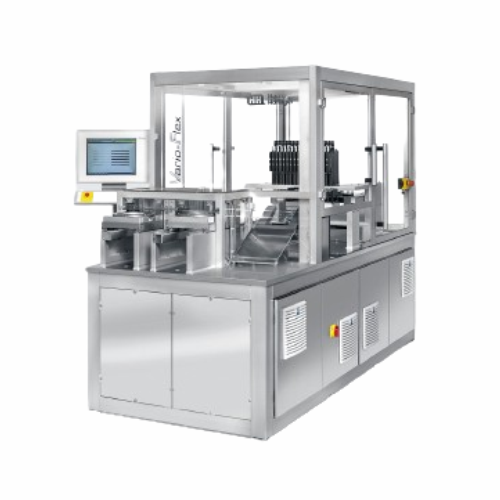
Automated assembly system for lab diagnostics
Streamline your lab diagnostics production with a flexible assembly system, ...
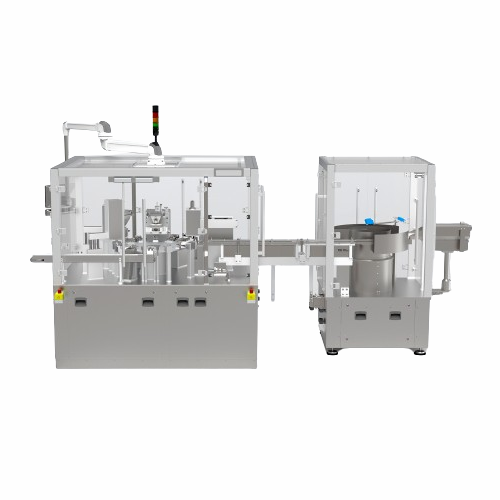
Rotary indexing table for dosing and assembly
Optimize production efficiency with a compact rotary indexing table that str...
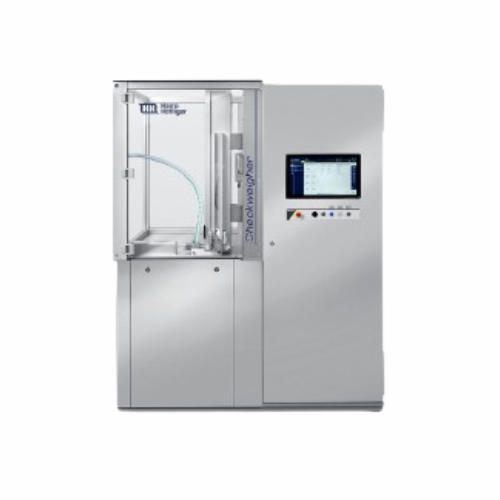
Dpi blister strip weighing system
Ensure precision in your inhalation product lines with a system designed for real-time we...
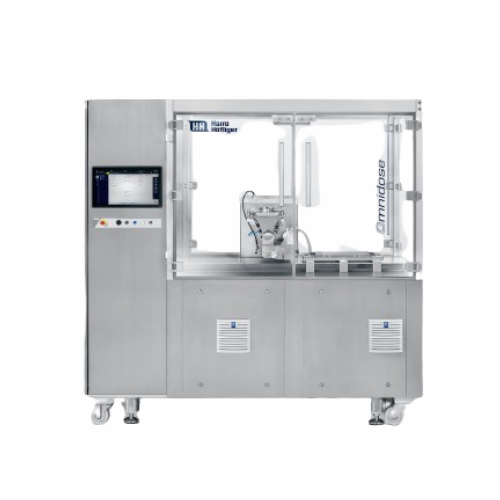
Powder dosing system for development and small batches
Streamline lab-scale pharmaceutical production with a versatile po...

Powder dosing machine for laboratory applications
Achieve precise powder dosing and streamline your R&D processes wi...
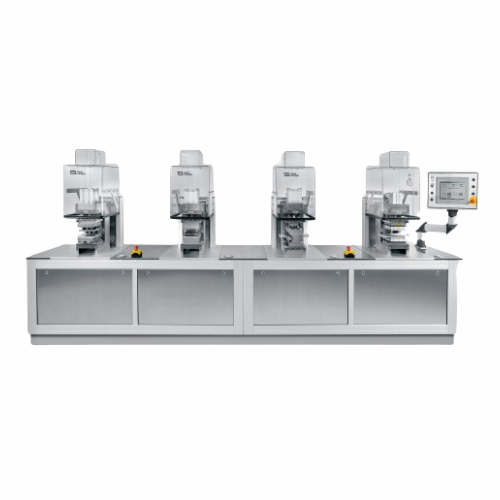
Lab machine for producing portion packs
Efficiently form, fill, seal, and punch portion packs in laboratory settings with c...
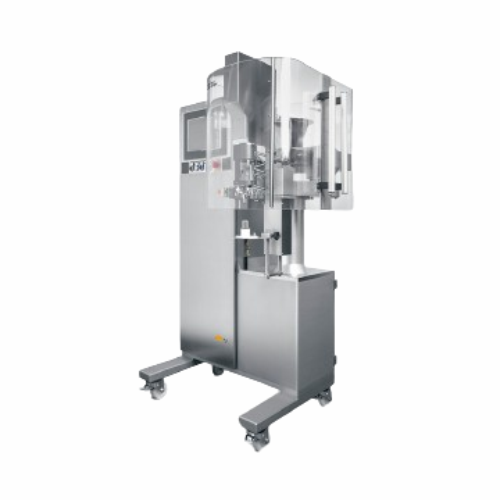
Auger dosing unit for powder dosing in pharmaceuticals
Ensure precise and flexible dosing of pharmaceutical powders with ...
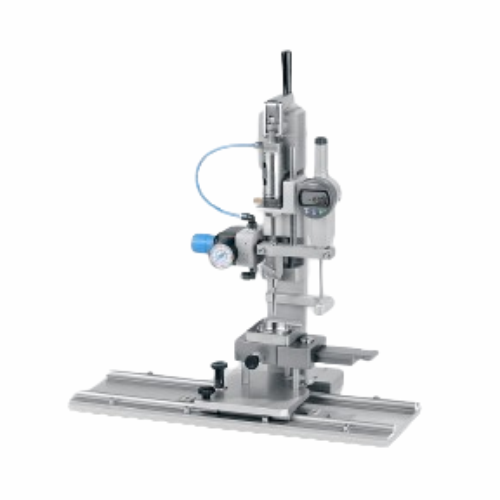
Powder dosing for lab and galenics
Ideal for precise dosing needs, this compact lab device streamlines powder filling proce...
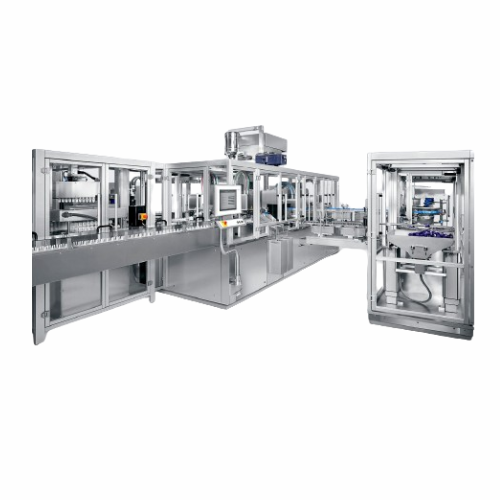
Dpi inhaler production system
Enhance your inhaler production with precision assembly and integrated dosing, filling, and ca...

Micro-dosing system for inhalation blisters
Streamline your inhalation product production with precision micro-dosing, for...

Liquid dosing and assembly platform for pharmaceutical products
Optimize your production line with a seamless solution f...
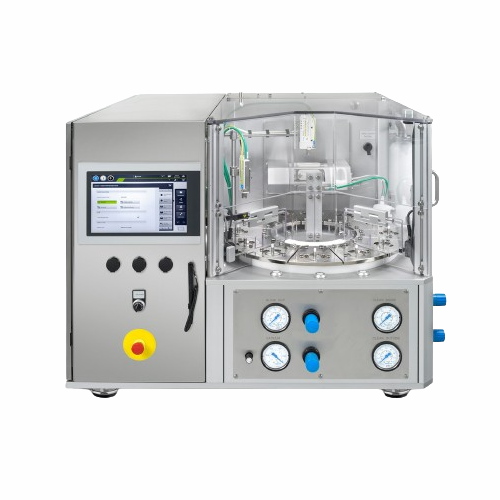
Semi-automatic powder dosing system
Achieve precise micro-dosing for pharmaceutical powders with a flexible system ideal fo...
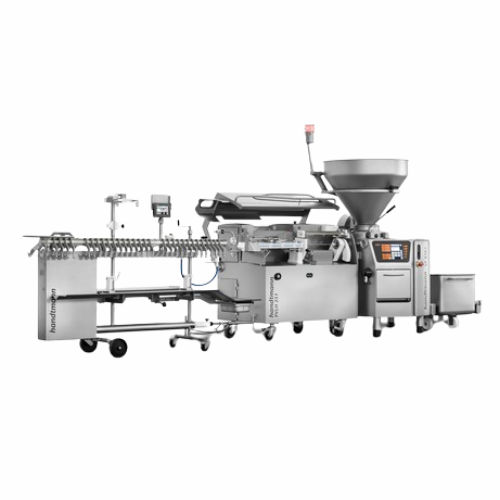
High-performance sausage linking and hanging line
Boost your production efficiency with a high-speed line designed for se...
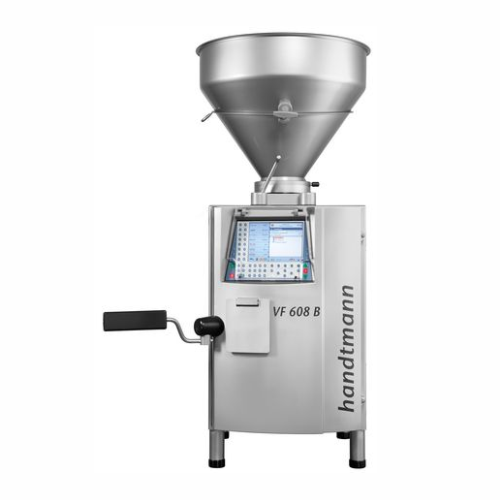
Dough portioning system for bakery operations
Achieve precise dough portioning with minimal waste using our advanced syste...
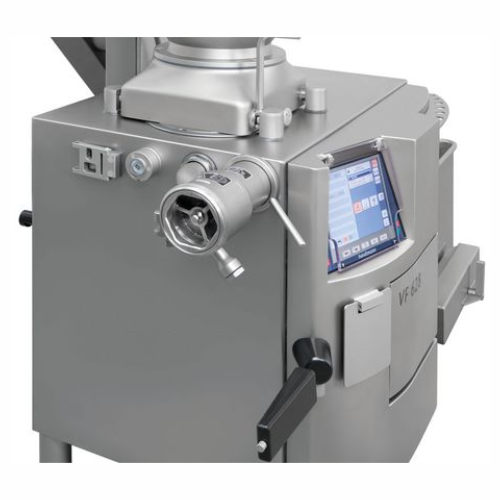
Inline grinding system for sausage and minced meat production
Streamline your production line by simultaneously grinding...
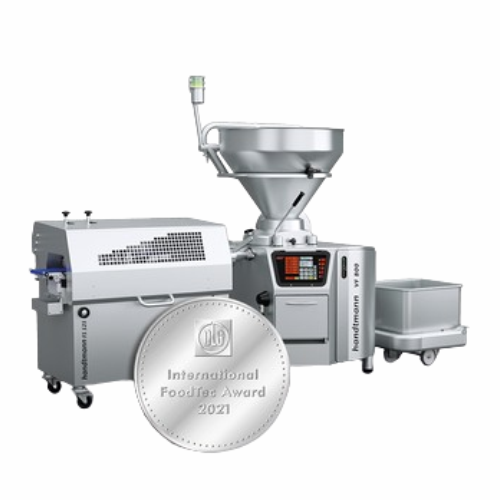
Industrial forming and cutting system for diverse products
Maximize product versatility with a system that effortlessly ...
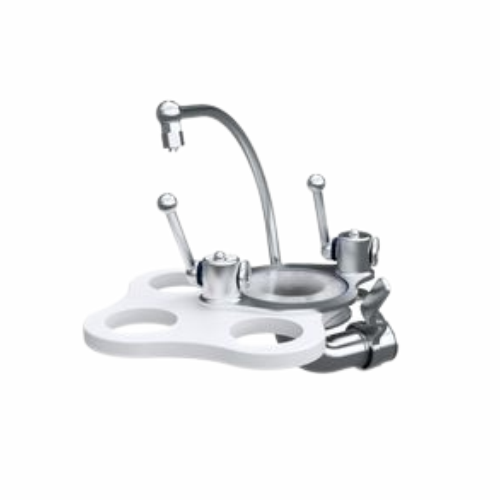
Manual forming unit for burger patties
Produce up to 30 perfectly shaped burger patties per minute with consistent quality ...
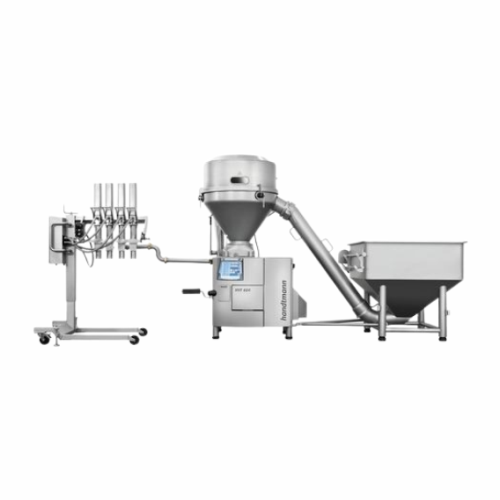
Cutting valve for chunky food portioning
Achieve precise portioning of chunky products, reducing waste and increasing effic...
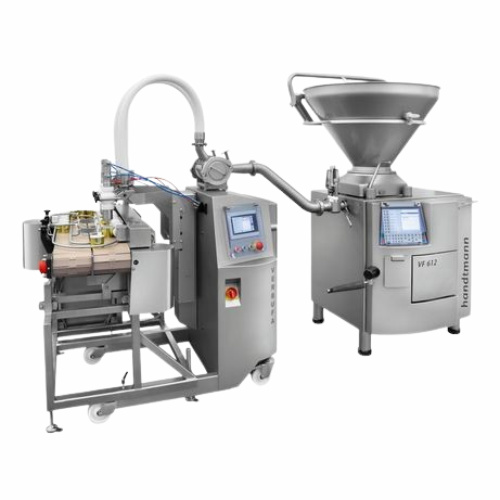
Automatic multi-lane dosing system for fluid to pasty products
Streamline your production with precise multi-lane dosing...
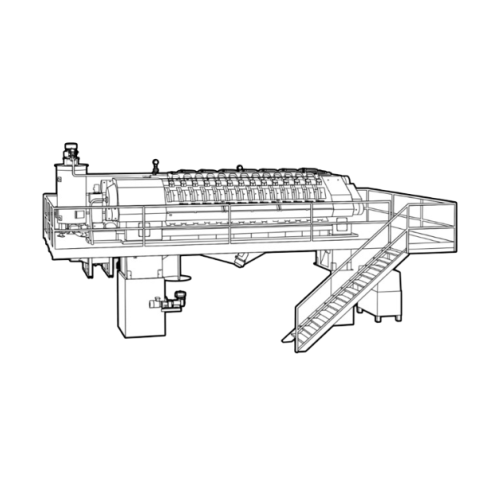
Cocoa pressing plant for high-capacity cocoa liquor processing
Optimize your cocoa processing by converting cocoa liquor...
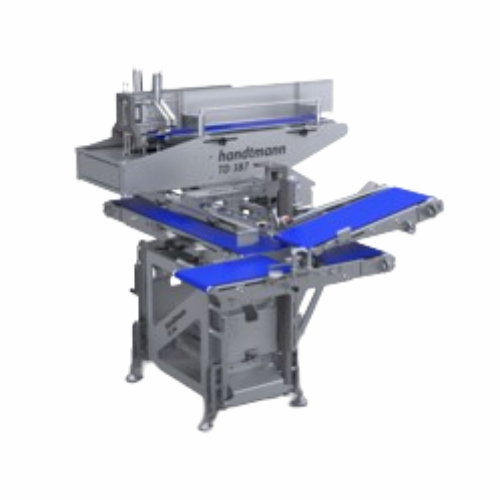
Automatic tray loader for minced meat portions
Streamline your tray loading process by integrating a flexible and fully au...
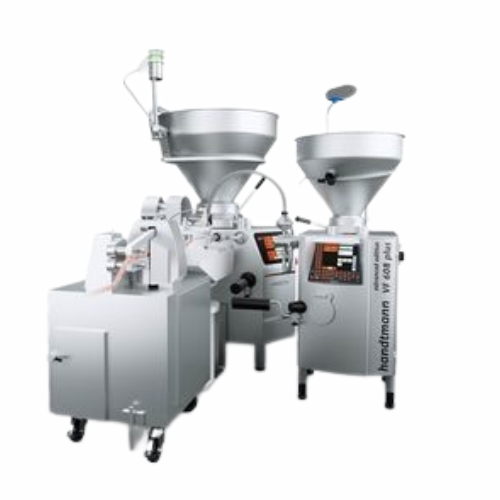
Industrial co-extrusion system for sausages with alginate casing
Eliminate the need for traditional sausage casings with...
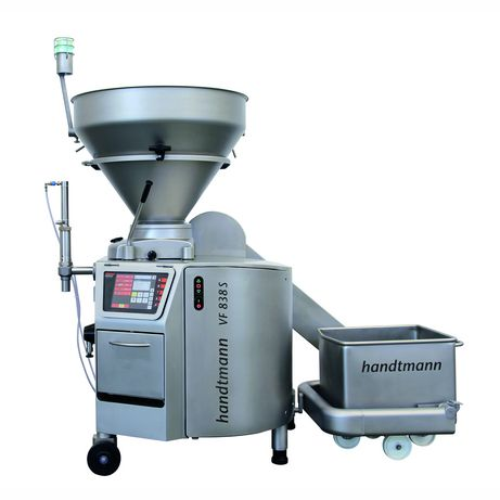
Precise dosing valve for pasty products
Achieve precise, gram-accurate dosing for a wide array of pasty and semi-viscous pr...
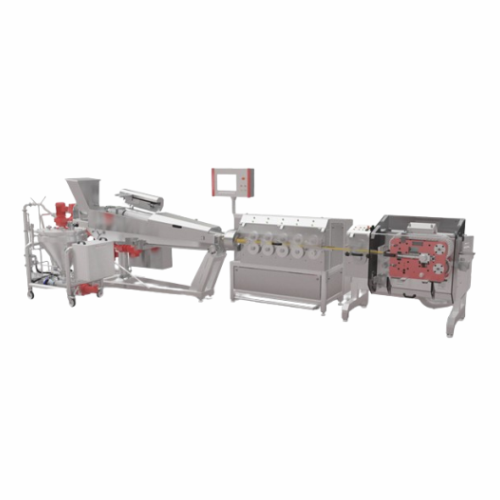
Hard candy forming line for manufacturing
Experience seamless candy production with advanced forming technology, ensuring ...
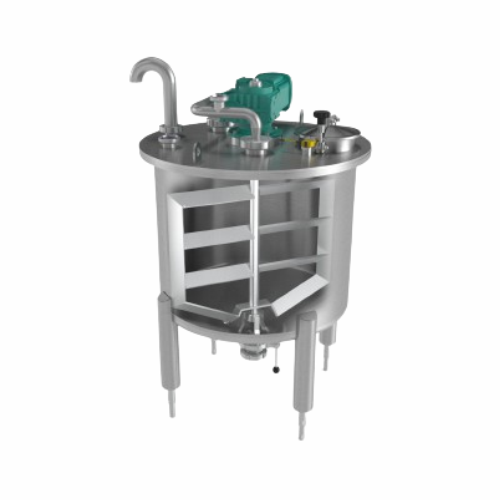
Stainless steel buffer tanks for food, pharma, and cosmetics
Ideal for maintaining process fluidity, these stainless ste...
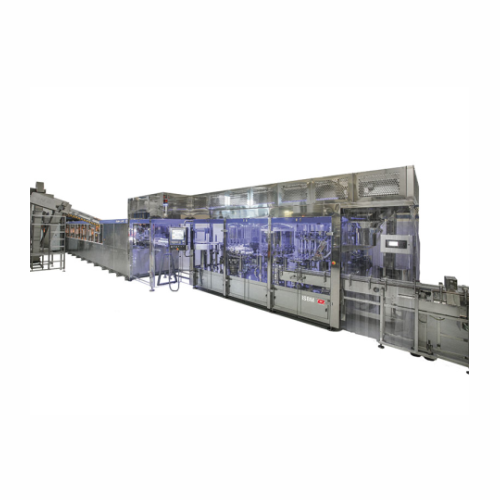
Injection stretch blow moulding line for pharmaceutical solutions
Optimize sterile solution production by forming, fill...
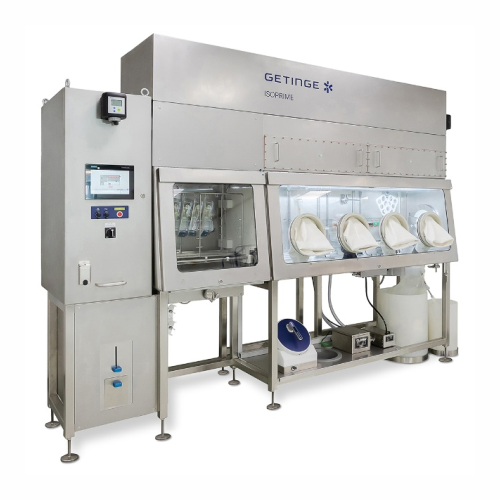
Cost-effective rigid-wall isolator for aseptic applications
Ensure sterility and safety with a versatile isolation and d...
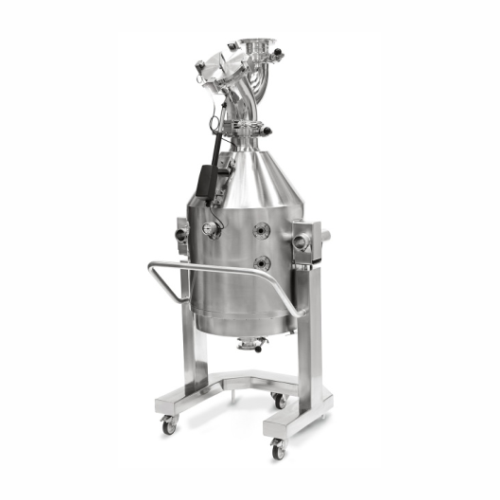
Sterile closure processing system for pharmaceutical production
Ensure your pharmaceutical closures remain sterile and i...
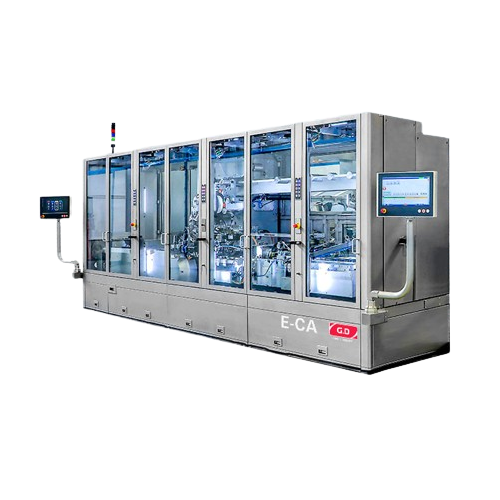
Cartridge assembler for next generation vapour products
Optimize your production of vape cartridges and e-cigarette pods ...
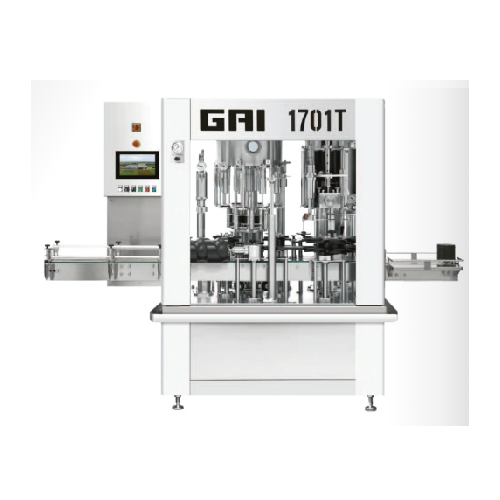
Complete bottling lines for beverage industries
Optimize your bottling process with high-speed, precision-engineered lines...
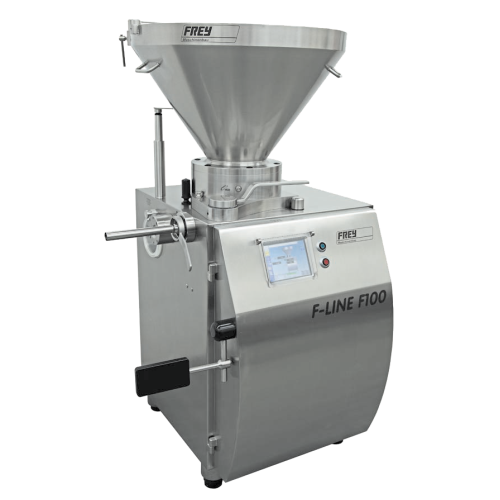
Industrial vacuum stuffer for high-volume food production
Streamline your sausage production with precision filling and ...
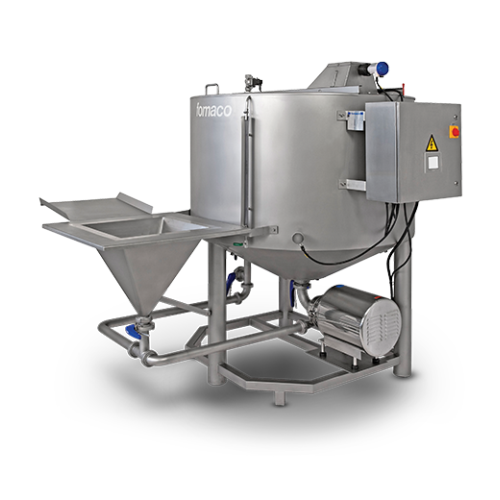
Industrial brine mixers for meat and poultry processing
Optimize your production line with brine mixers that ensure homog...
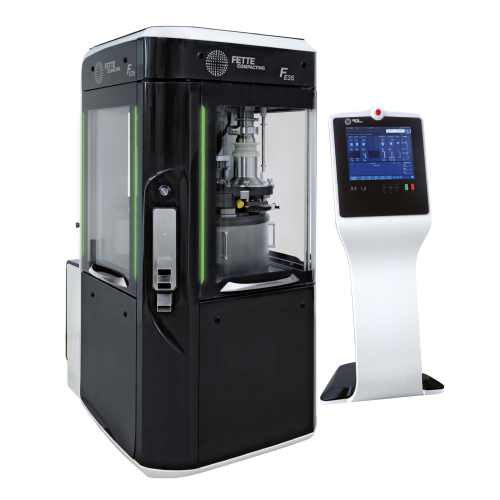
High-capacity tablet press for pharmaceutical production
Achieve precise compression and consistent tablet density with a...
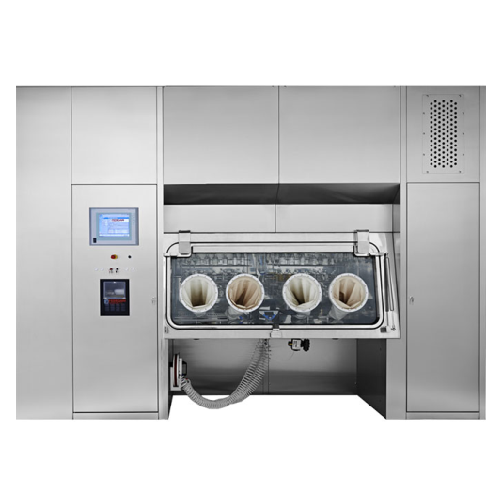
Pharmaceutical isolator for contamination control
Ensure sterility and safety in pharmaceutical manufacturing with advanc...
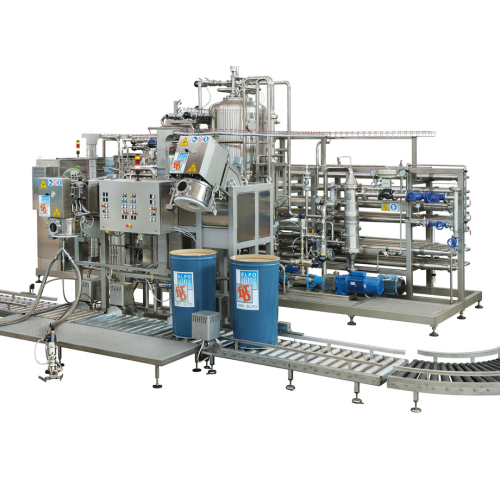
Aseptic sterilizer for fruit-based products
Ensure product safety and extend shelf life with advanced sterilization techno...
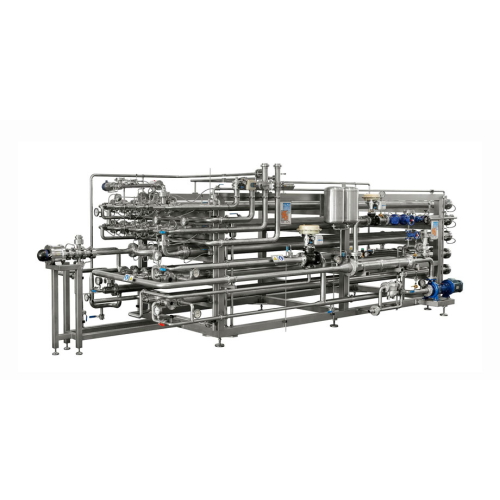
Aseptic sterilizers for tomato products
Ensure your tomato-based and fruit products remain safe and shelf-stable with advan...
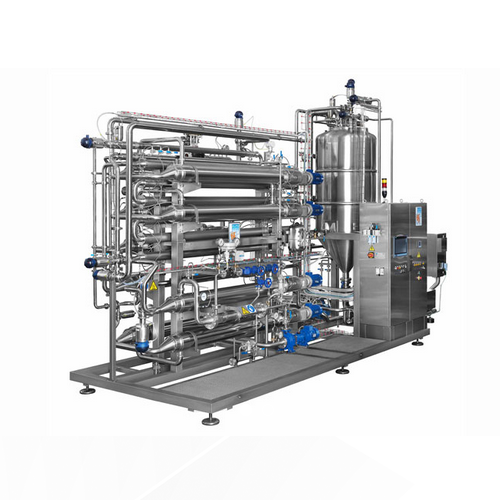
Scraped surface sterilizers for food industry products
Optimize your food processing line with high-efficiency sterilizat...
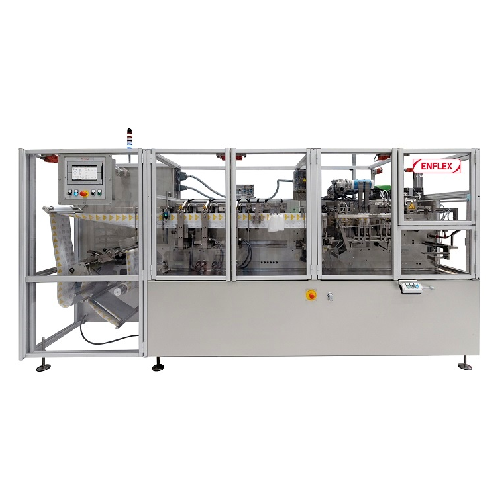
Horizontal flat pouching system for liquid soaps
Optimize your liquid packaging with high-speed, continuous operations tha...
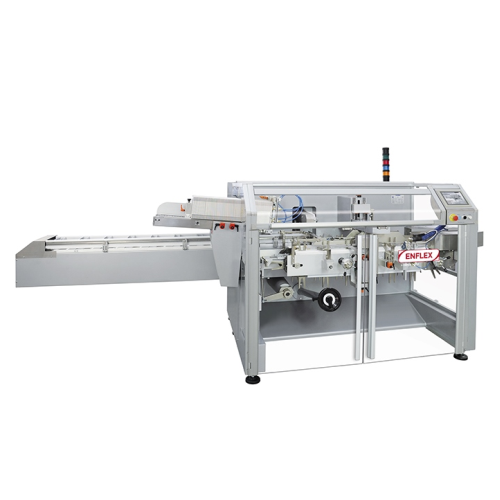
Intermittent side-load cartoner for pouches or stick packs
Optimize your packaging process with an intelligent side-load...
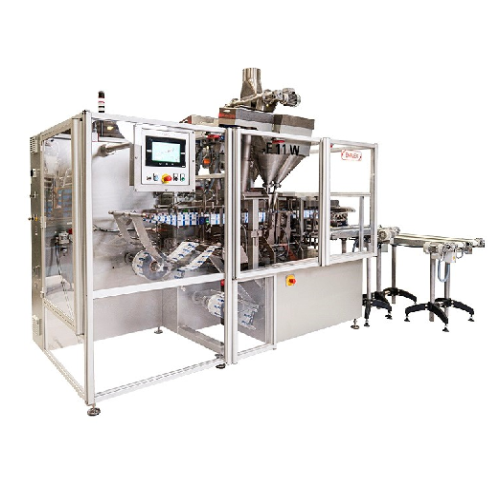
Horizontal flat pouching line for liquid soaps
Streamline your liquid product packaging with a dual-lane flat pouching lin...
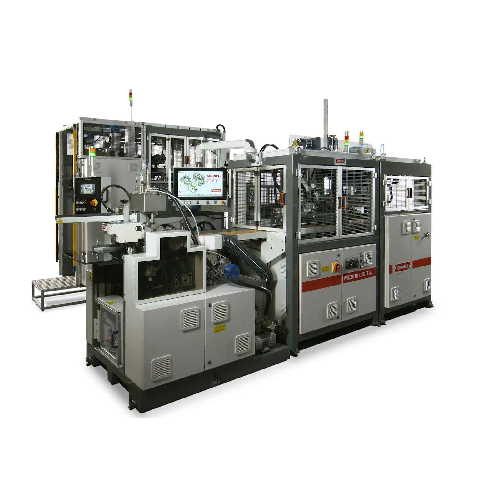
Digital box making line
Optimize your packaging capabilities with a versatile, digital box-making line designed to efficientl...
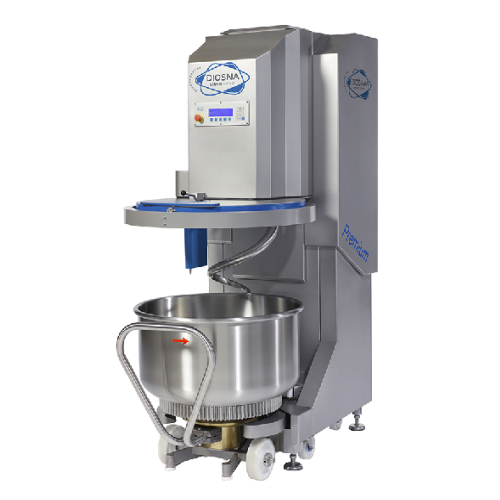
Interchangeable tool stainless steel kneader
Streamline your batch processing with this flexible mixing technology that of...
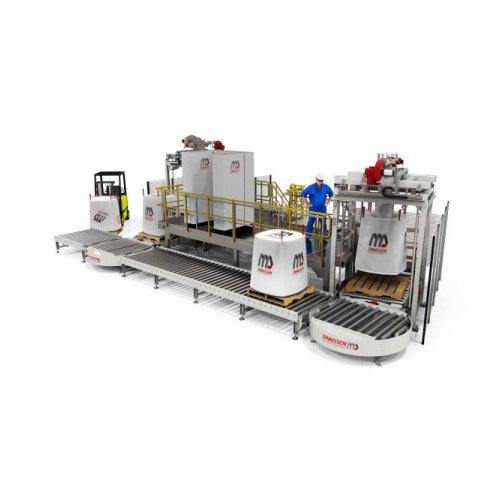
Product handling system for big bags and containers
Optimize your production line with a comprehensive system for transpo...
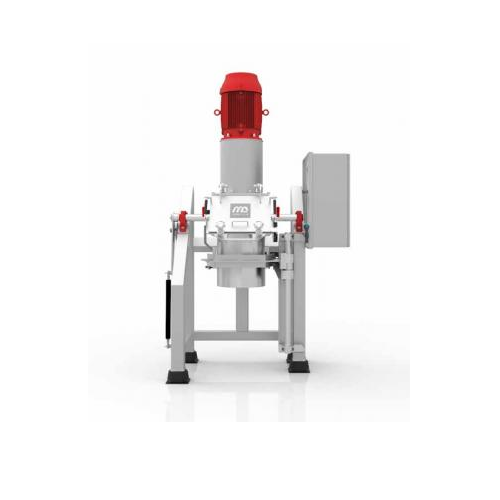
Industrial pulper for fresh produce
Achieve ultra-fine purees and pastes with this high-speed industrial pulper, designed t...
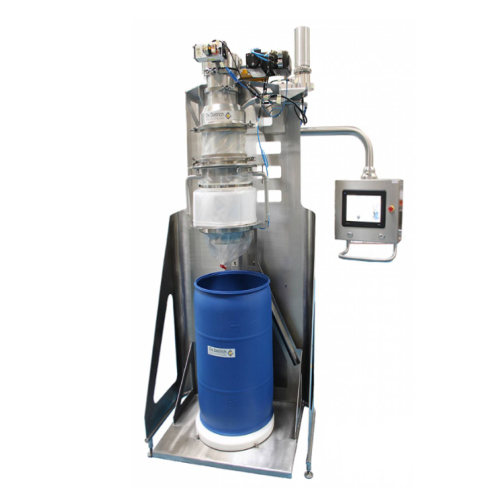
Powder conditioning station for high containment applications
Ensure safe and precise handling of hazardous powders with...
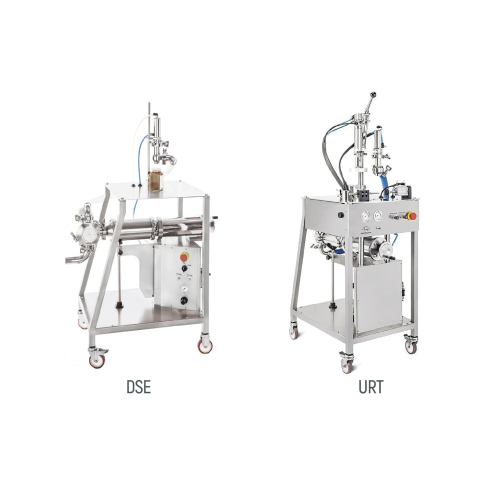
Pneumatic dosers for variable density products
Achieve precise dosing for liquid to dense products with versatile pneumati...
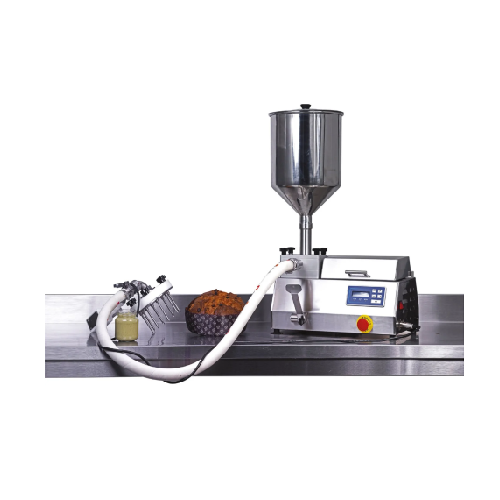
Multi-injection plate for leavened bakery foods
Optimize your bakery production line with precise and customizable filling...
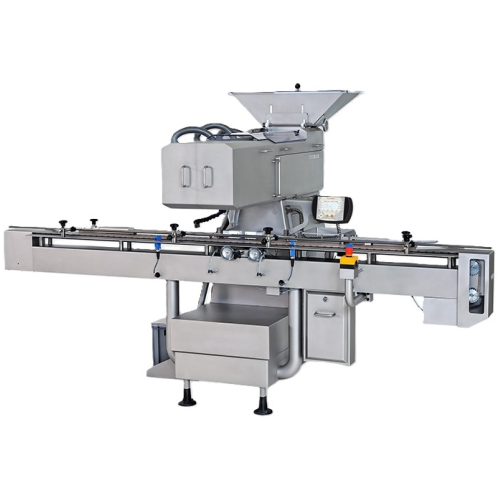
Linear tablet and capsule counter
Ensure precise and efficient bottle filling with a cutting-edge counting system that guar...
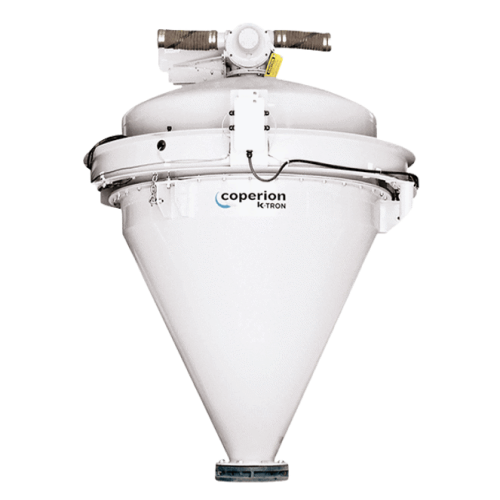
Scale hopper for bulk material processing
Optimize your bulk material handling with precise control in separation, filling...
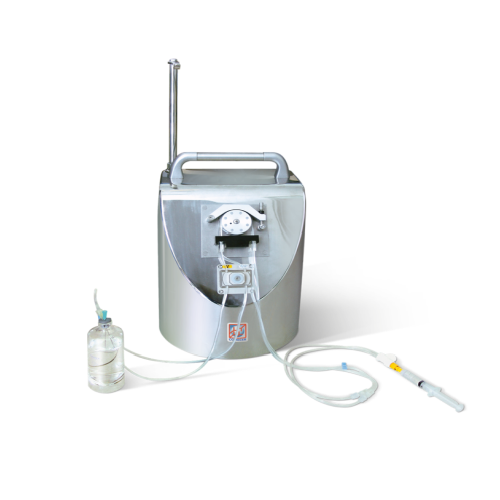
Syringe dispensing system for nuclear medicine
Optimize your radiopharmaceutical workflows with a system designed to preci...
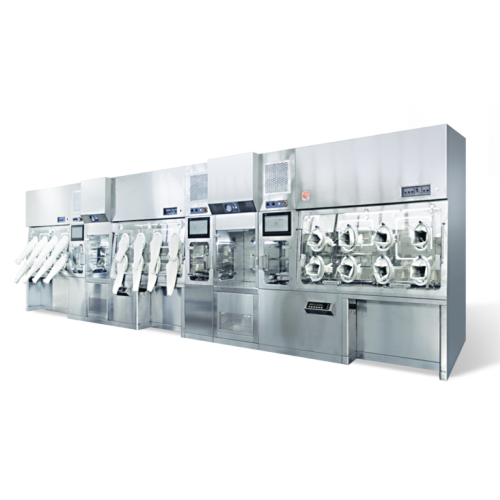
Cell and gene therapy modular isolator
Enhance your cell and gene therapy production with a modular isolator that integrate...
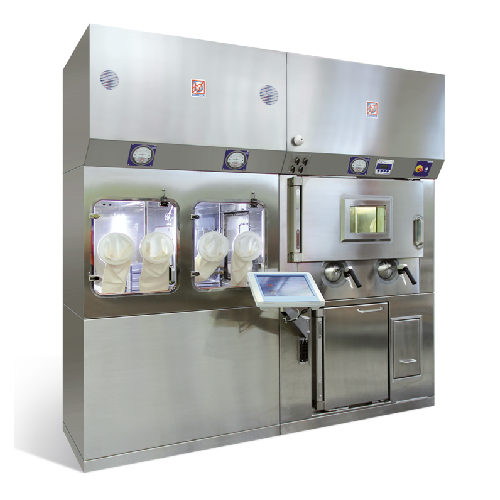
Radiopharmaceuticals dispensing isolator
Ensure precise and sterile dispensing of radiopharmaceuticals and other liquid for...
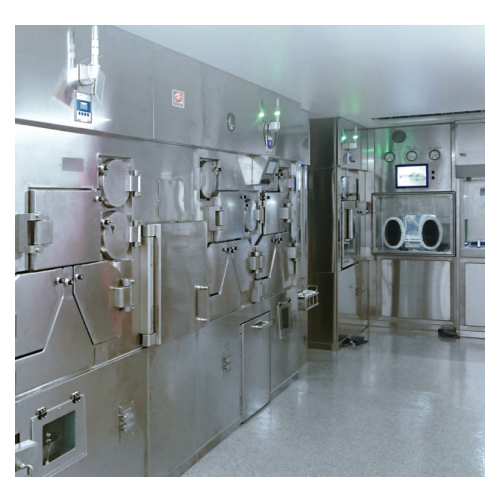
Ra-223 dichloride production and dispensing suite
Ensure precise production of Ra-223 dichloride and related radiopharmac...
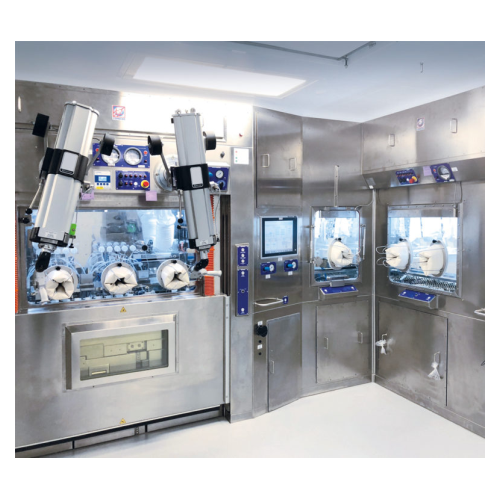
Rb-82 generators production plant
Ensure stringent aseptic conditions and efficient Sr-82/Rb-82 generator production with a...
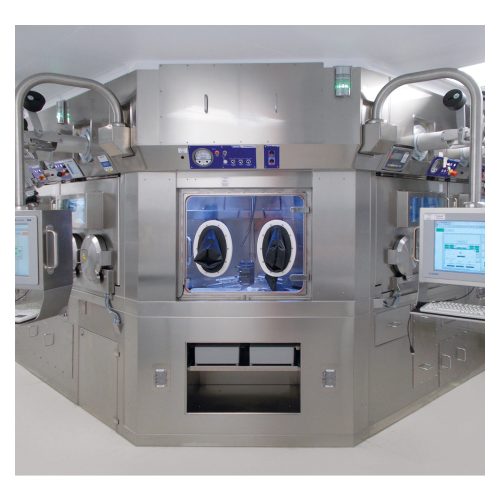
Automated ioflupane i-123 injection dispensing solution
Ensure precision and efficiency in radiopharmaceutical production...
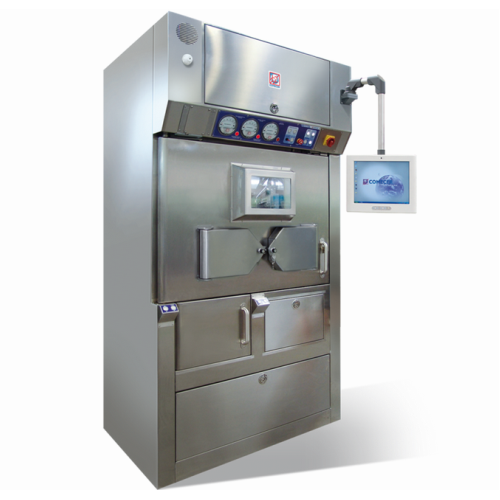
Automatic dispenser for radiopharmaceutical syringes
Streamline your radiopharmaceutical syringe preparation with precise...

Closed vial dispensing system for radiopharmaceutical production
Ensure precise radiotracer dosages and maintain sterili...
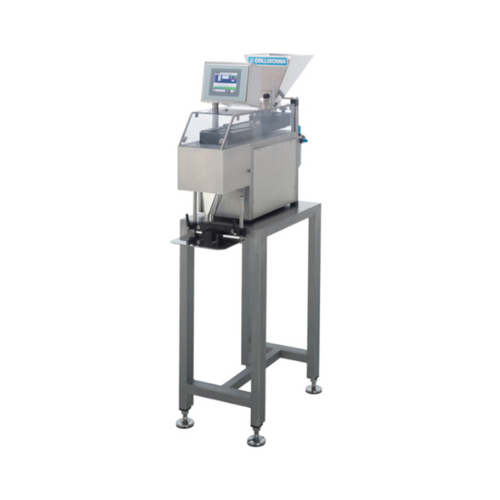
Counting system for tablets and capsules
Effortlessly count a variety of tablets, capsules, and dragées with precision, ens...
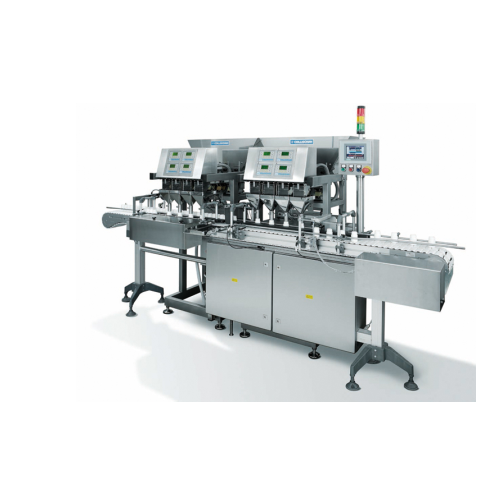
Complete packaging lines for various containers
Streamline your packaging process with versatile equipment capable of hand...
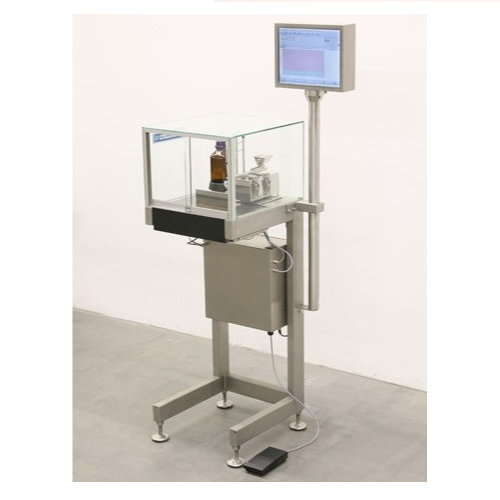
Microdosing system for granules and powder
Achieve precise dosing with minimal variance across all fills, ensuring consist...
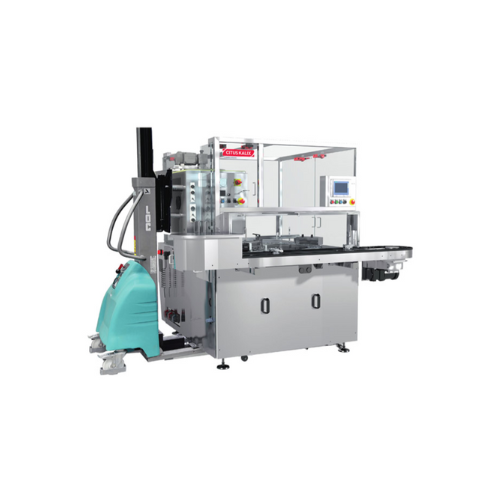
Lipstick moulding solution for cosmetics manufacturing
Streamline lipstick production with high-speed molding and flexibl...

Thin chocolate shell forming
Create gourmet confections with precision by forming delicate chocolate shells, perfect for ver...
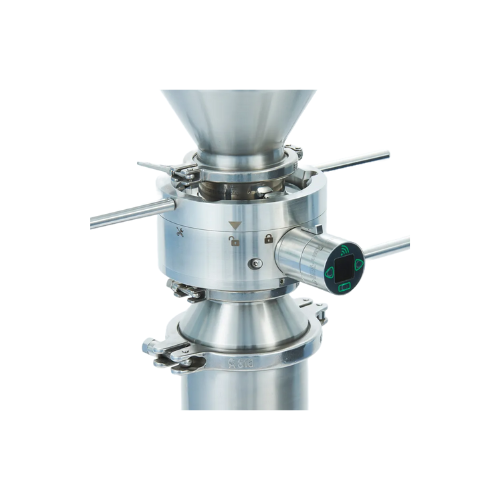
Aseptic transfer valve for sterility assurance
Ensure sterility and safety in your critical production processes with adva...
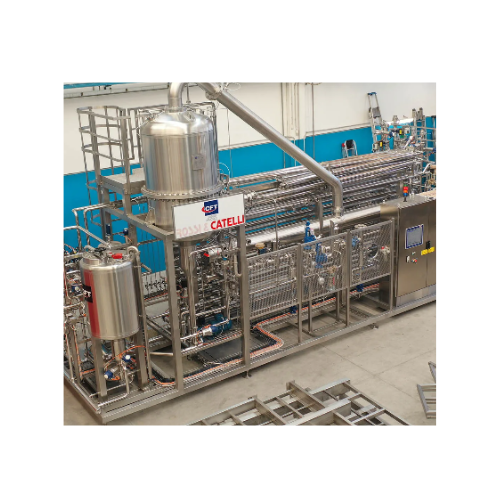
Sterilizers and pasteurizers for industrial food processing
Optimize thermal processing for viscous foods and beverages ...
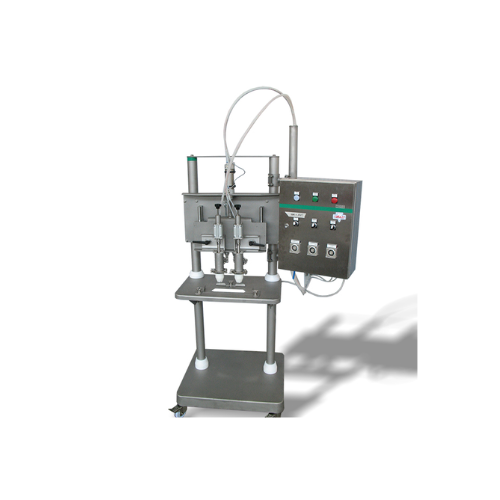
Semi-automatic dosing table for ice cream cups and bulks
Ensure consistent and precise dosing for various ice cream produ...
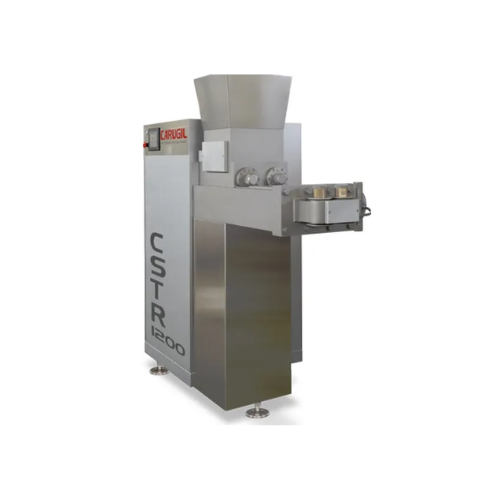
Food and confectionery twin-screw extruder
Enhance your confectionery production with a versatile twin-screw extruder desi...
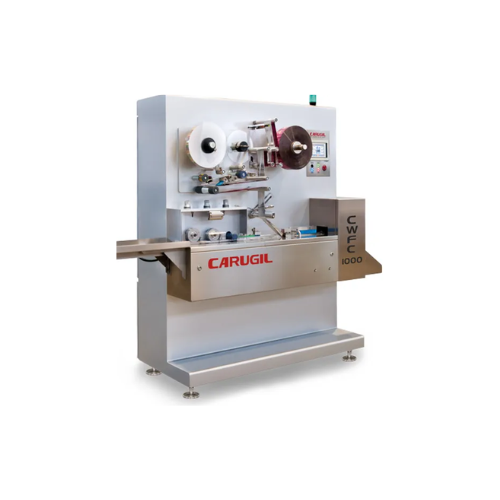
Cut and flow pack system for cylindrical and rectangular pieces
Enhance your confectionery production with a high-speed ...
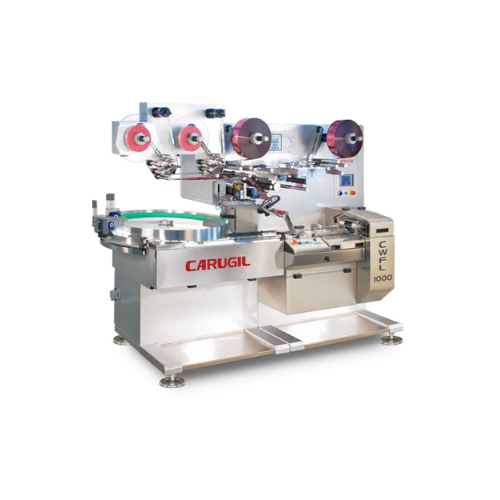
Flow wrapper for lollipops packaging
Achieve precise and high-speed lollipop packaging with continuous-motion flow wrapping...
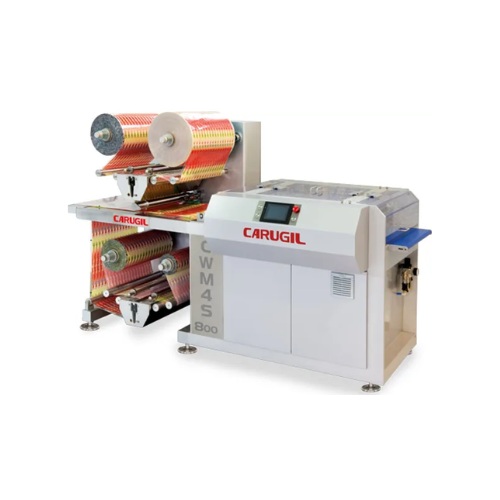
Multilane wrapping solution for food and confectionery products
Enhance your packaging line efficiency with high-speed m...
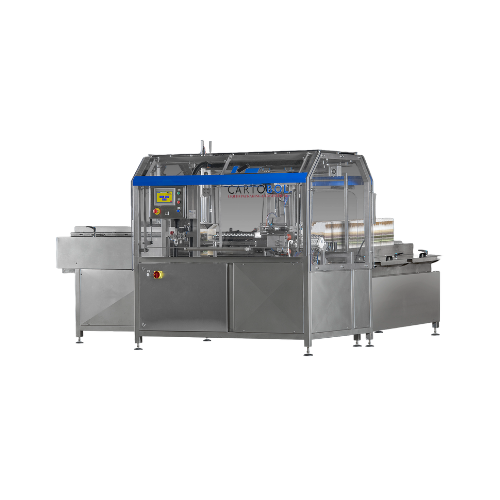
Bag-in-box carton erector
Experience seamless carton erection with advanced servomotor technology, enhancing both efficiency...

Ball former for bubble-gum and soft candy production
Achieve precise ball forming for bubble gum and soft candies with cu...
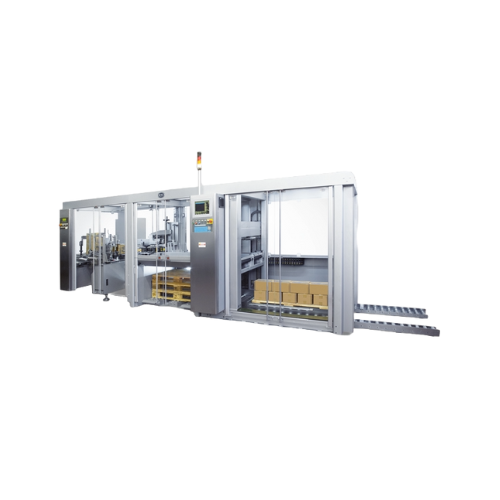
Integrated case-packing and case-palletizing system
Streamline your production line with an all-in-one system that seamle...
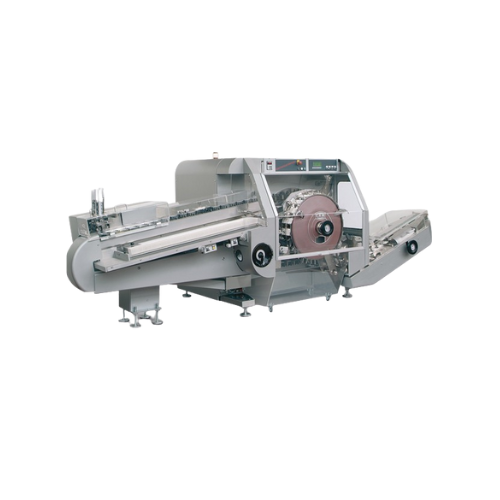
High-speed continuous motion horizontal cartoner
Achieve seamless high-speed cartoning with precision cartoner systems des...
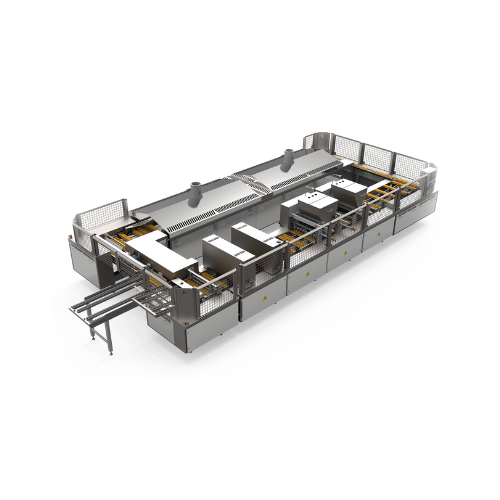
Industrial manju cake production system
Transform traditional treats into innovative 3D cakes with precise filling and perf...
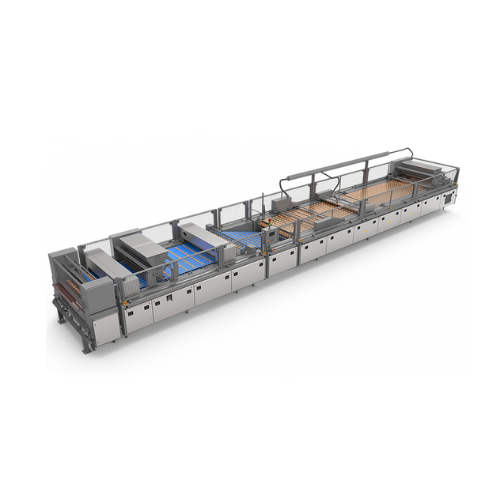
Industrial sandwich pancake system
Streamline your production with a machine that seamlessly integrates baking, filling, pr...
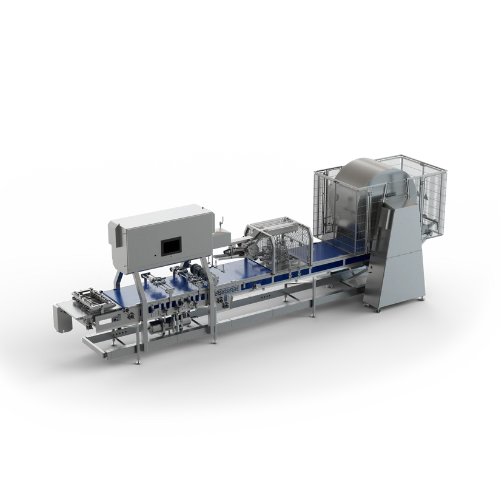
Processing line for spring rolls
Streamline your spring roll production with a compact machine designed to minimize downtime...
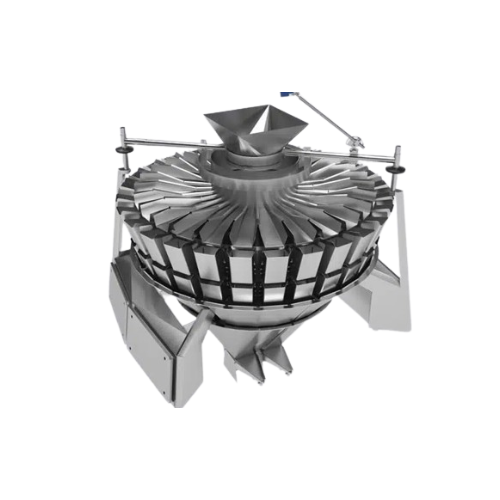
Multihead weigher with vibratory feeding
Experience precise and efficient weighing with a multihead system designed for com...
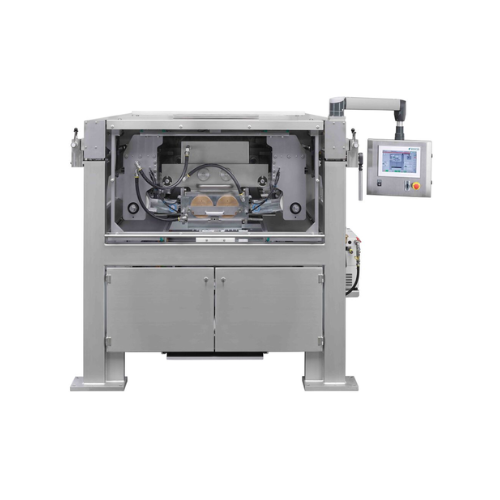
One-shot chocolate depositing system
Enhance your confectionery line with precise, high-speed depositing technology designe...
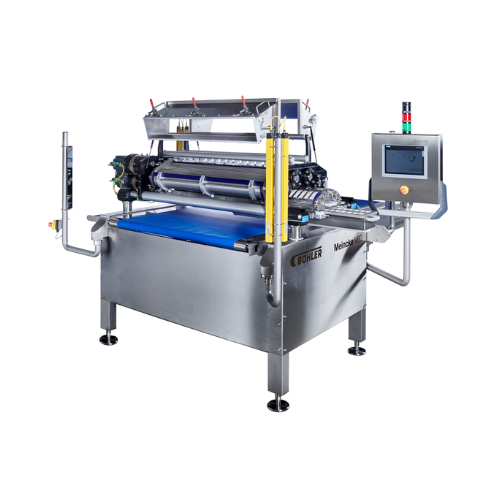
Biscuit wire cutter and depositor for confectionery production
Streamline your production of intricately designed cookie...
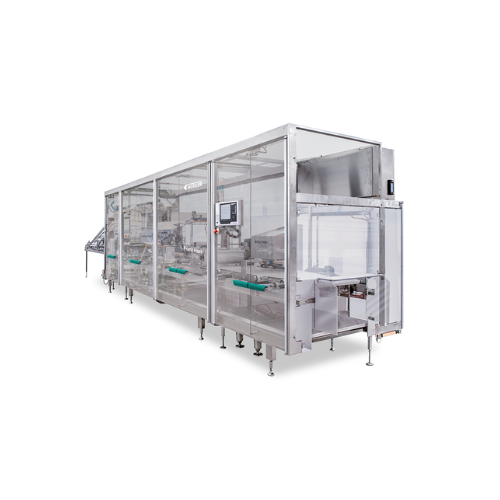
Hollow wafer film-spreading machine for confectionery
Achieve precise and uniform cream distribution on hollow wafer shee...
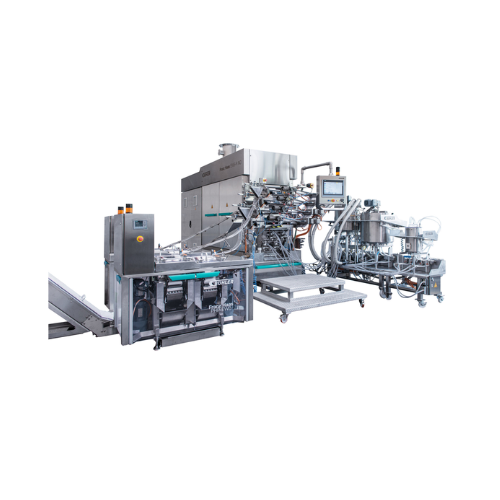
Wafer stick baking oven
Enhance your confectionery production with precision, from forming to filling and coating, achieving ...
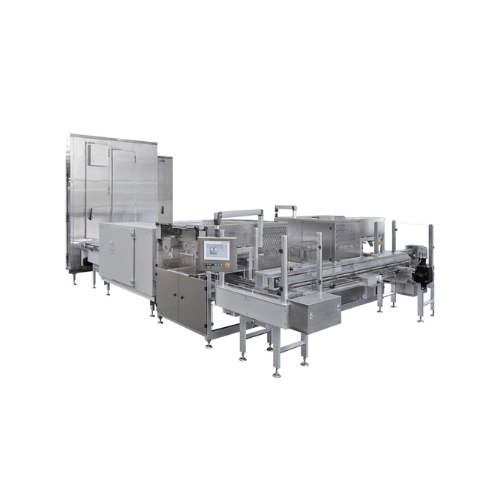
Loose mould line for chocolate production
Streamline your chocolate production with a high-throughput line that seamlessly...
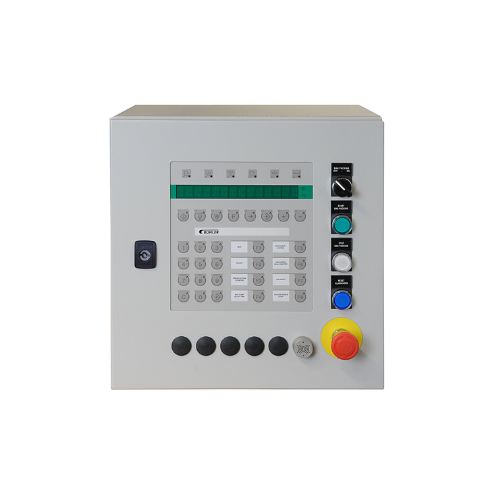
Bagging control system for centralized operations
Streamline your bagging operations with a centralized control system, d...
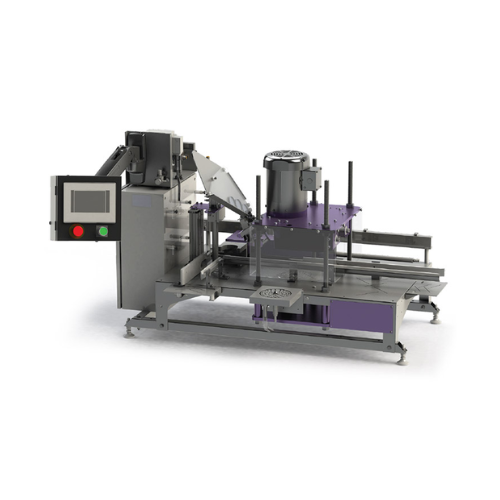
Automated beverage canning line
Optimize your beverage packaging with a high-speed canning line that seamlessly integrates f...
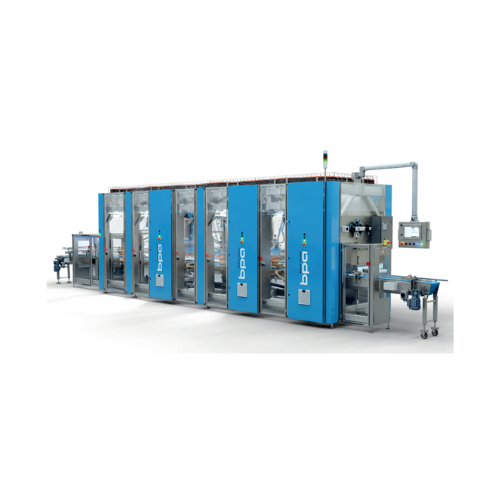
Case packing system for bags and cases
Streamline your secondary packaging process with a compact, fully integrated system ...
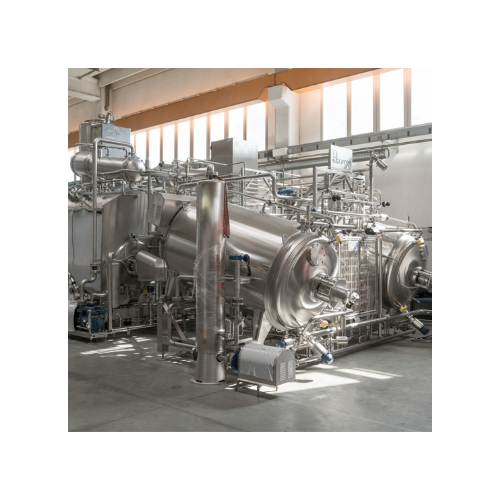
Sterile cooling system for fruit preparations
For manufacturers seeking aseptic conditions, this cooling system ensures ra...
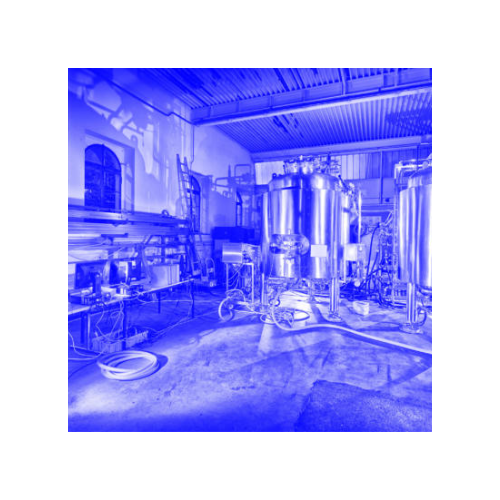
Formulation vessel for biopharmaceutical homogeneity
Achieve precise homogeneity in liquid formulations with vessels opti...
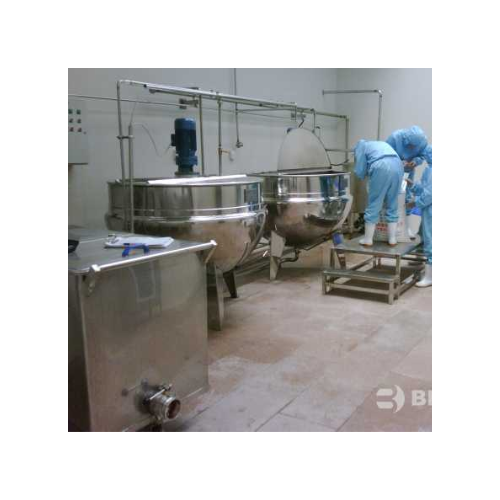
Fruit base processing technology for yoghurt and bakery
Ensure the integrity of fruit preparations while maximizing varie...
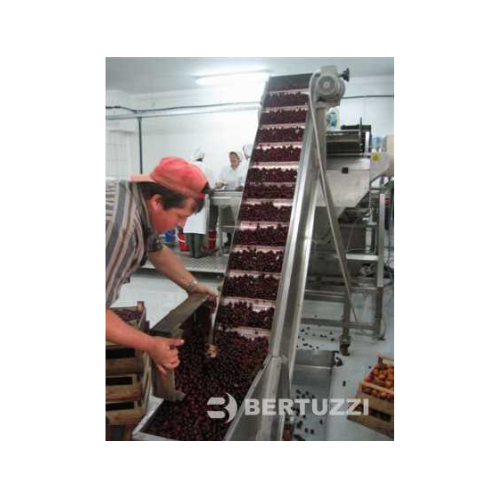
Industrial jam processing line for fresh fruit or puree
Streamline your jam production with a versatile line capable of p...
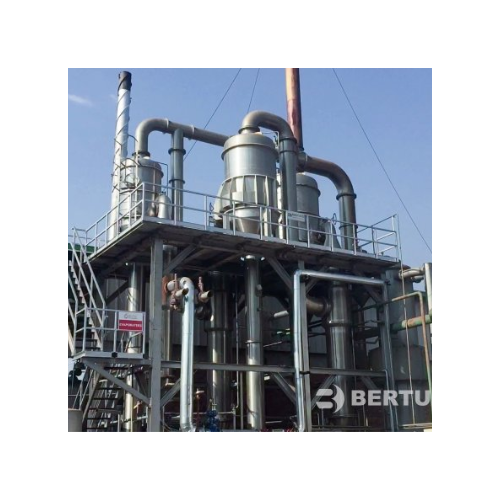
Tomato processing plant for sauce and paste
Efficiently transform raw tomatoes into a variety of high-demand products, fro...
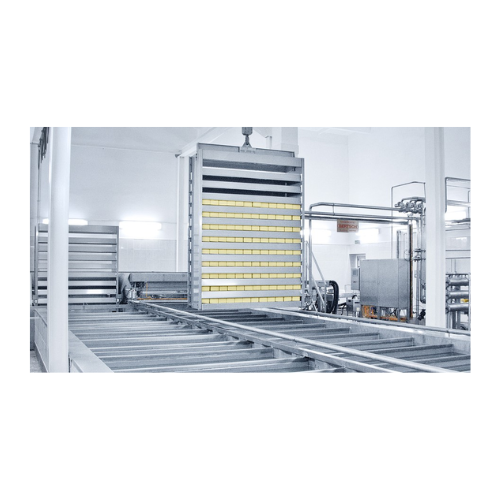
Cip cleaning systems for dairy processing plants
Optimize cheese production with precise curd handling and exceptional sti...
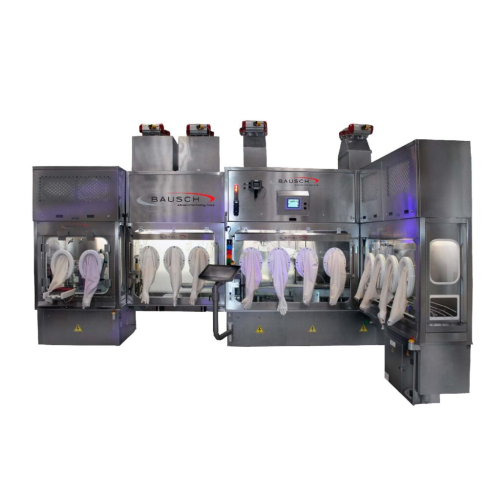
Cell and gene therapy packaging system
Streamline cell and gene therapy packaging with a versatile system that accelerates ...
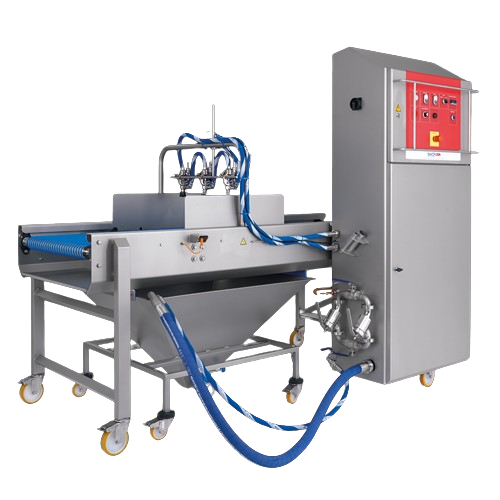
Industrial glaze sprayer for high-volume bakery production
Enhance product appeal and extend shelf life with precise gla...
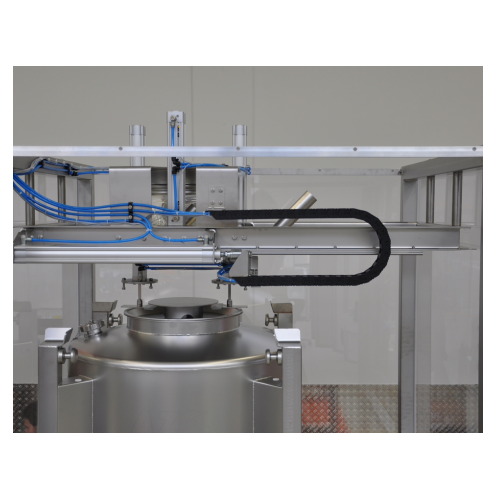
Dust-tight docking for dosing units to bulk solids containers
Ensure seamless, dust-free transfer and dosing of bulk sol...
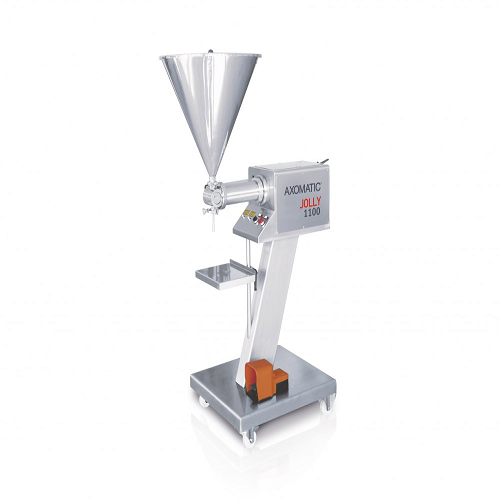
Pneumatic dosing system for dense and semi-dense products
For precise dosing of dense and semi-dense liquids, this pneum...
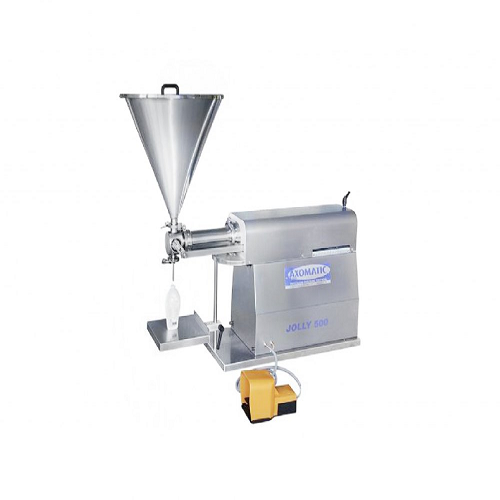
Pneumatic dosing system for dense and semi-dense products
Easily handle dense and semi-dense products with precision dos...
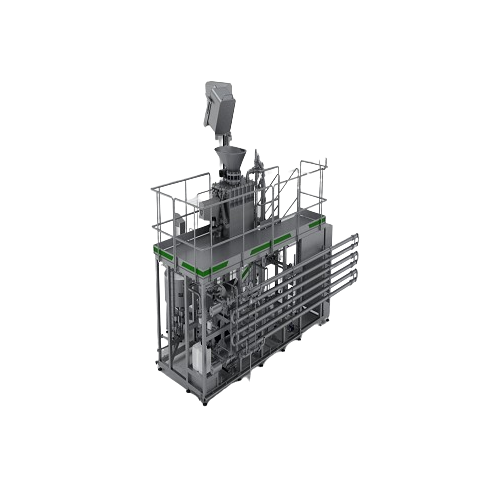
Aseptic cooking line for industrial food processing
Achieve seamless aseptic cooking and filling for diverse food product...
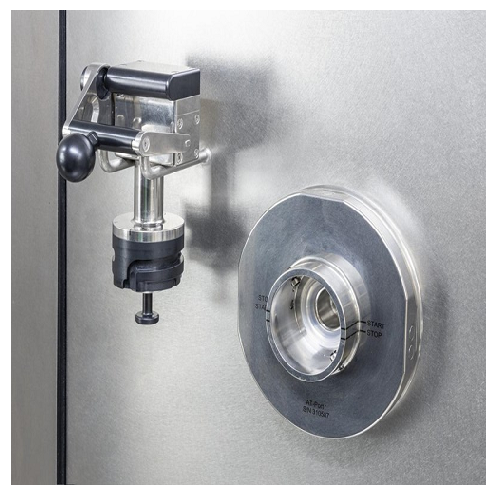
Aseptic liquid transfer connection system
Ensure sterile liquid transfer between containment areas with minimal product lo...
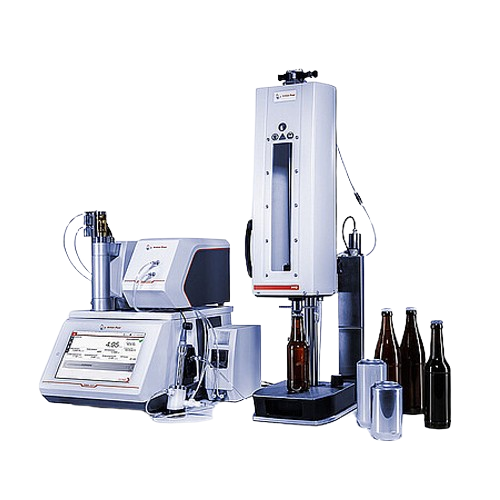
Packaged beverage analyzer for alcohol and Co2
Ensure precise beverage analysis with a streamlined solution that integrate...
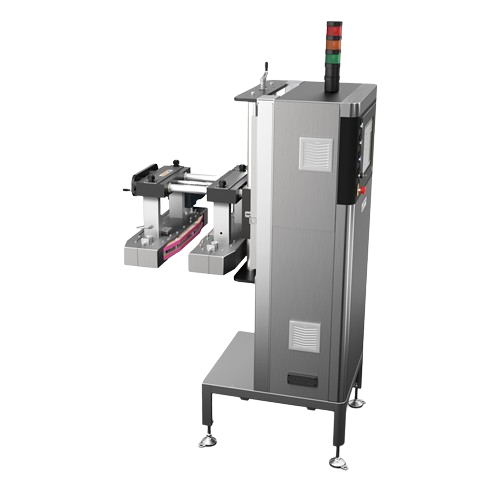
Leak detection system for cans
Ensure the integrity and shelf-life of canned goods with precise leak detection, pressure mea...
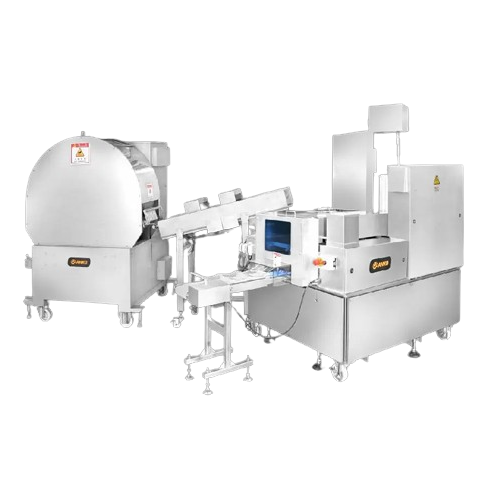
Spring roll production line
Efficiently produce diverse spring rolls with a machine that optimizes filling and wrapping, str...
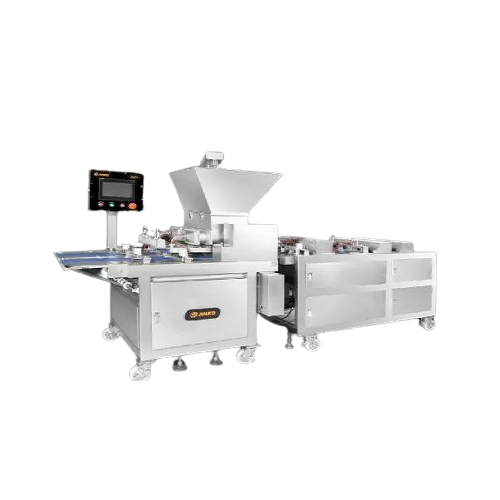
Automated quesadilla production system
Streamline your quesadilla production with a high-speed system designed to efficient...
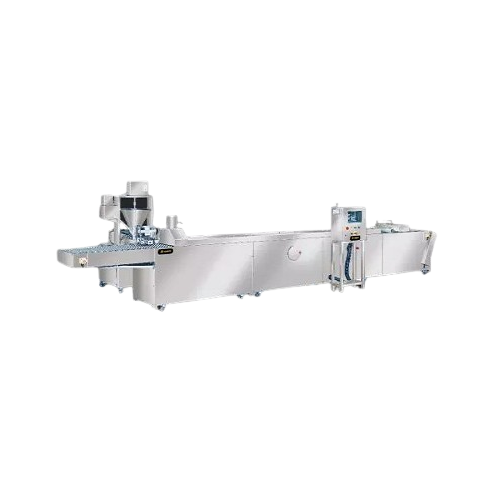
Vietnamese rice paper spring roll production system
Efficiently transform rice papers into delicious spring rolls with a ...
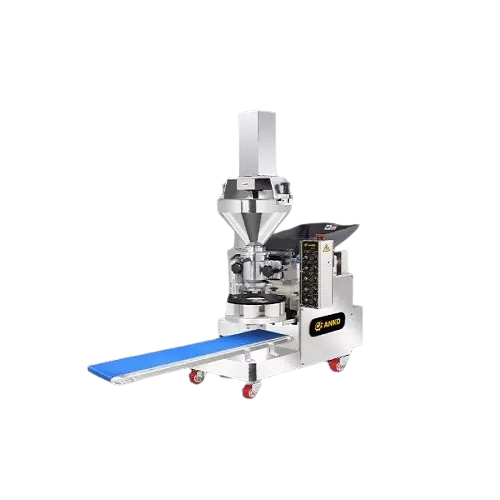
Automatic table-type encrusting and forming machine for diverse ethnic foods
Optimize your food production with a comp...
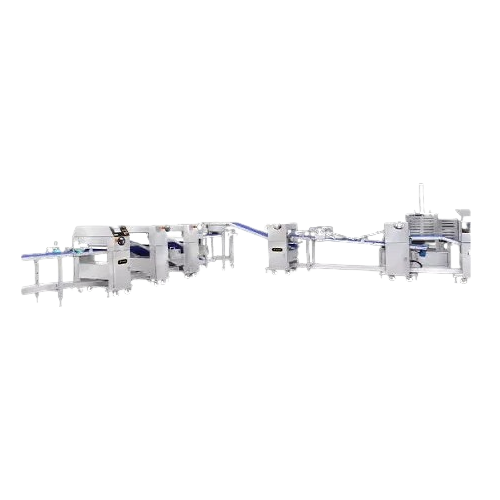
Customized puff pastry production line
Streamline your pastry production process with this customizable solution, capable o...
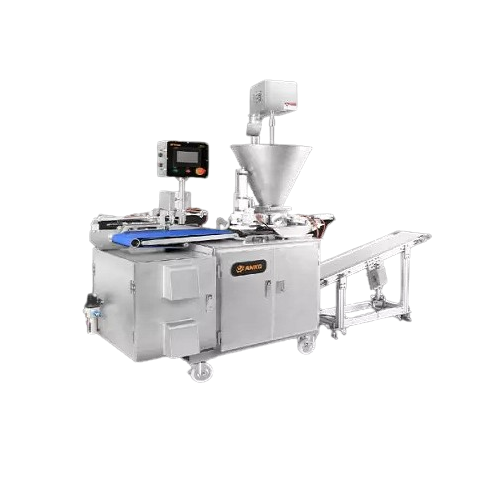
Empanada production line
Streamline your snack and pastry production with a compact solution that seamlessly integrates filli...
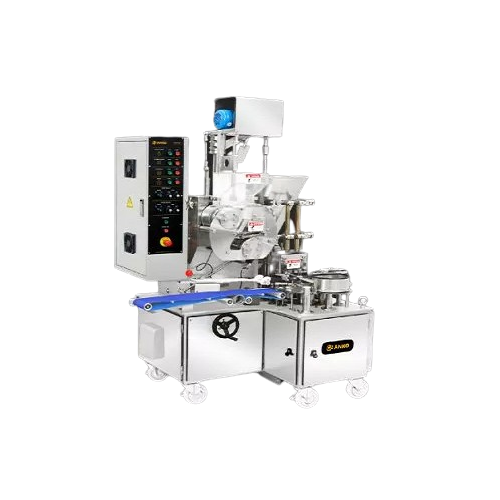
Automatic shumai production equipment
Boost your production capacity with high-speed shumai equipment, offering adjustable ...
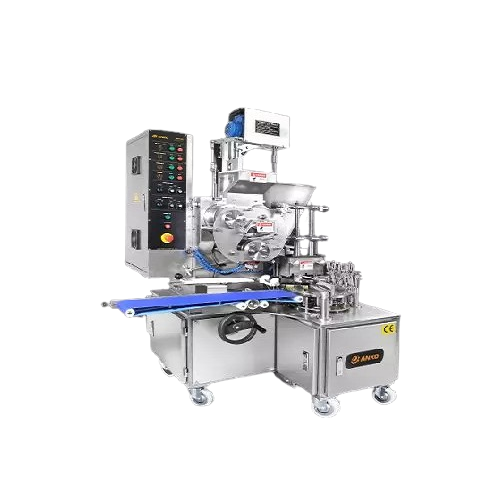
Automatic wonton production system
Streamline your production of high-quality wontons with this efficient system, which mai...
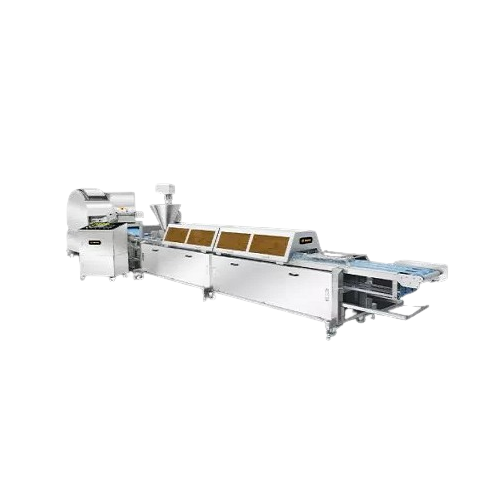
Automated blini production line
Enhance your food production efficiency with a blini solution that combines precise filling,...
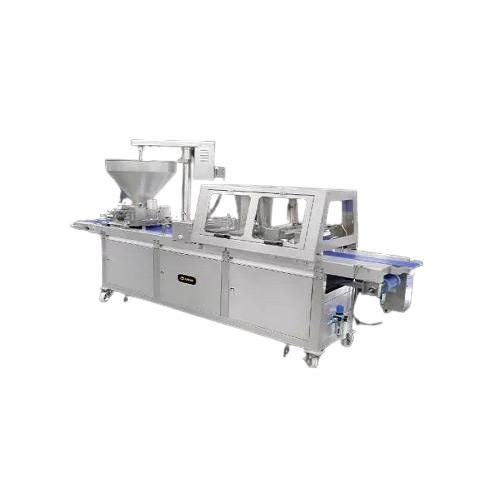
Burrito forming equipment
Streamline your burrito production by automating the delicate tasks of filling, folding, and wrapp...
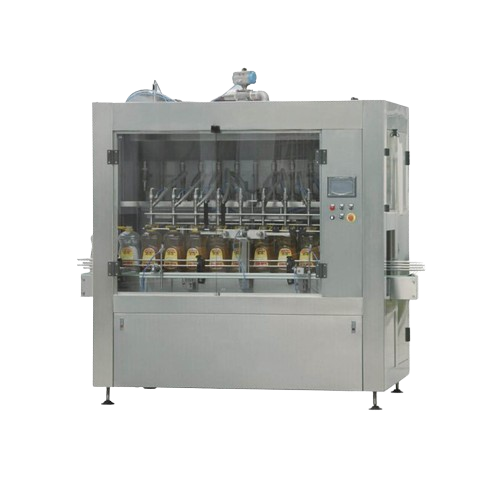
Automatic food cooking oil bottling solution
Ensure precise volumetric filling for a range of liquid products, enhancing y...
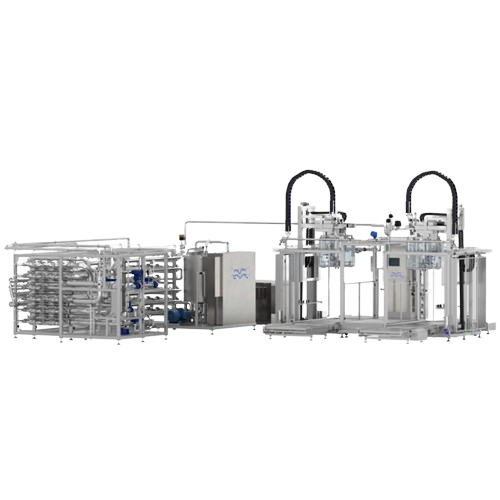
Aseptic processing equipment for food products
Optimize aseptic processing to ensure microbiological stability and product...
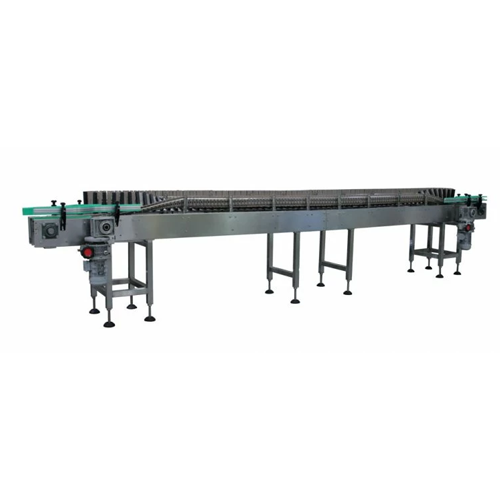
Inversion sterilizing conveyor for hot beverage bottle sanitation
Ensure sanitary filling of hot beverages by utilizing...
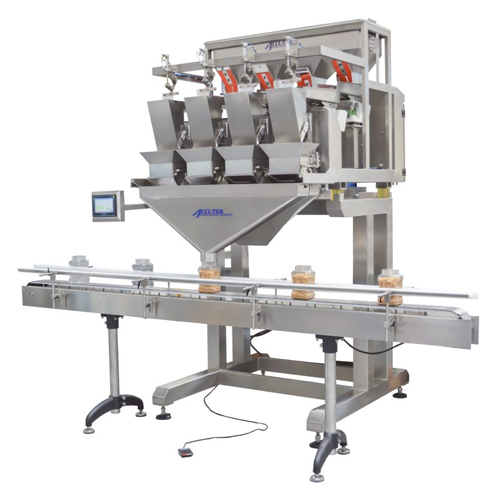
Automatic granular product weighing system
Effortlessly achieve precise fills for dry granular products and powders while ...
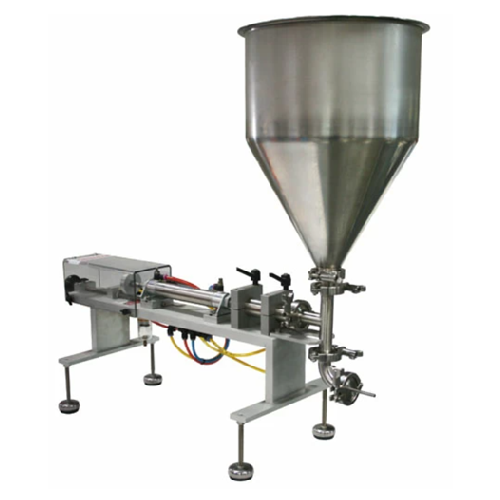
Semi-automatic piston injector for bakery products
Enhance your bakery production with precise delivery of a wide range o...
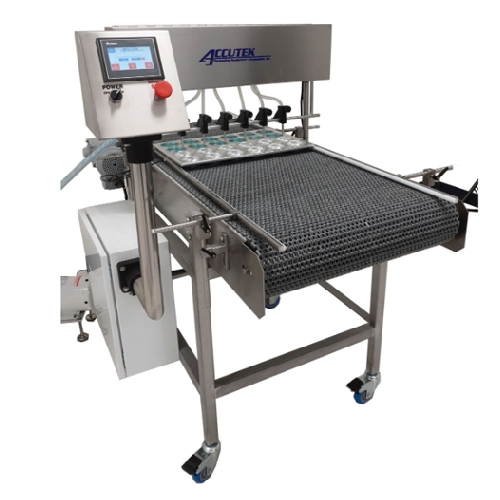
Servo bakery tray depositor
Enhance production efficiency with precise dough placement, reducing manual labor and ensuring c...
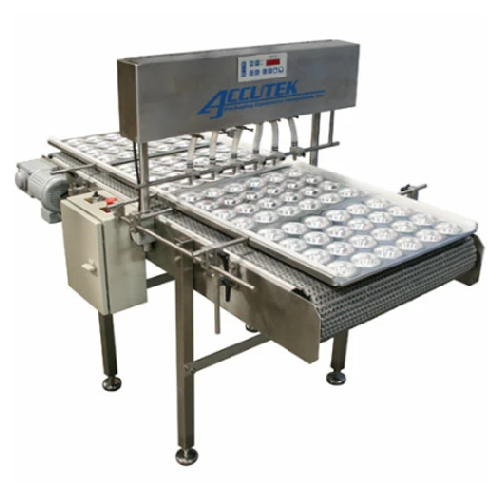
Auto bakery tray depositor for creams and batters
Efficiently deposit precise quantities of creams and batters with high-...

Retractable spiral chute for bulk material handling
Enhance the integrity of your products by gently transferring bulk ma...
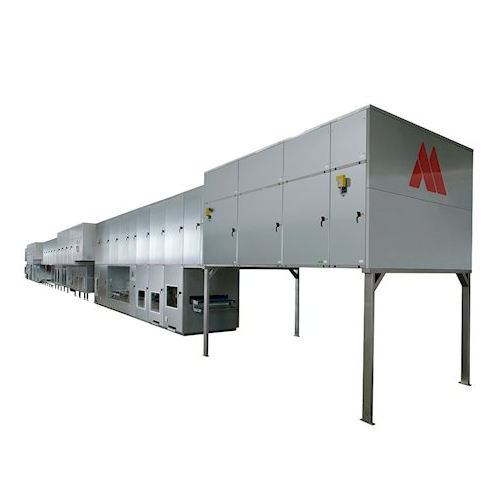
High capacity chocolate moulding line
Maximize your production capacity with a tailor-made moulding line designed for versa...
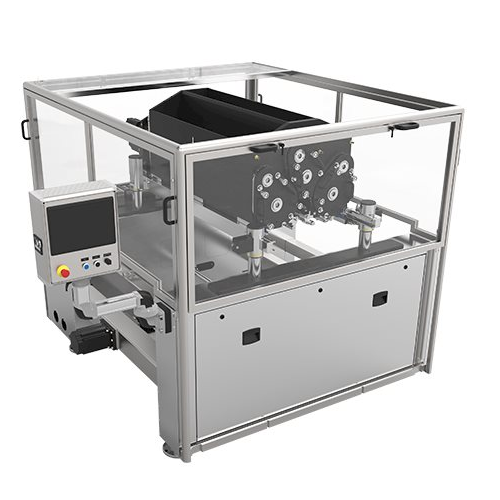
Extruder and depositor for confectionery production
Ideal for producing sophisticated confectionery and bakery items, thi...
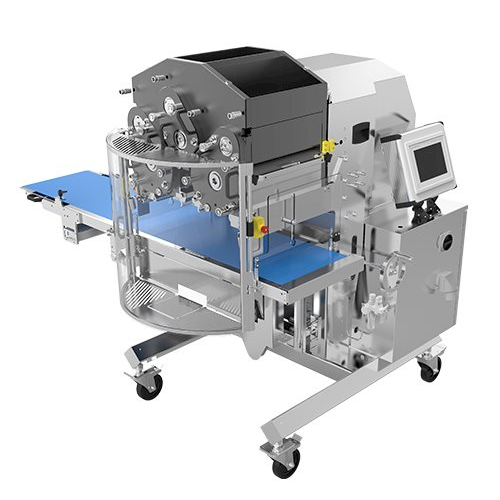
Small-scale depositor and extruder for bakery production
Revolutionize your confectionery and bakery production with a fl...
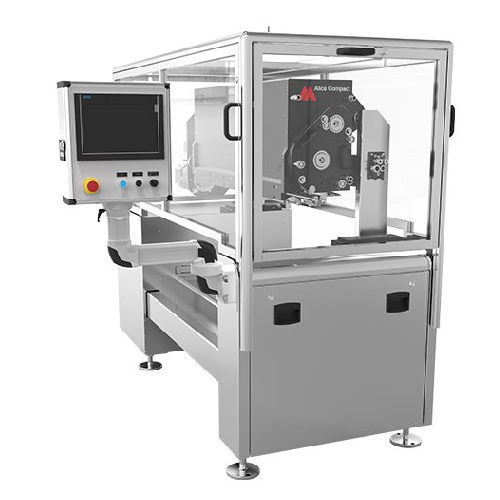
Compact extruder and depositor for confectionery and bakery production
Streamline your confectionery and bakery product...
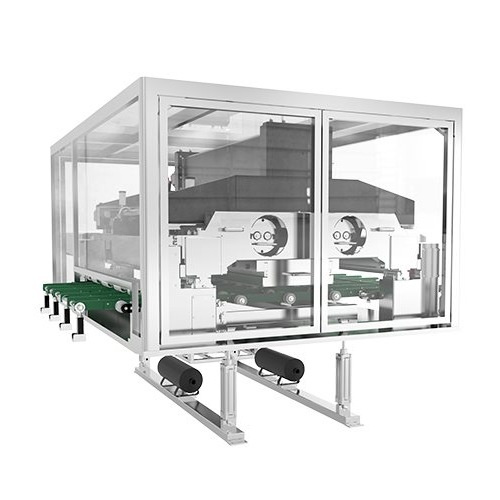
High-viscosity mass depositor
Efficiently deposit high-viscosity masses like caramel and jam with precision, while the integ...
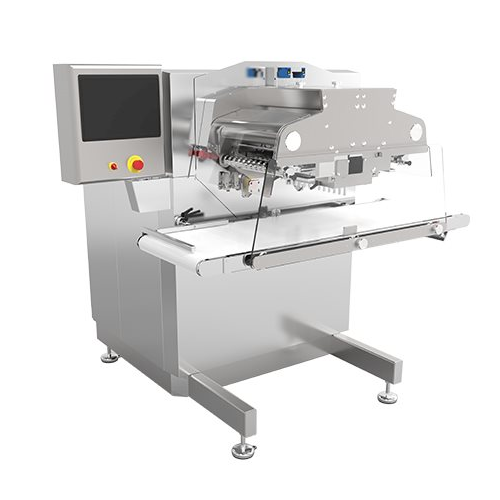
Chocolate depositor for small to medium production
Optimize your confectionery production with a versatile depositor that...
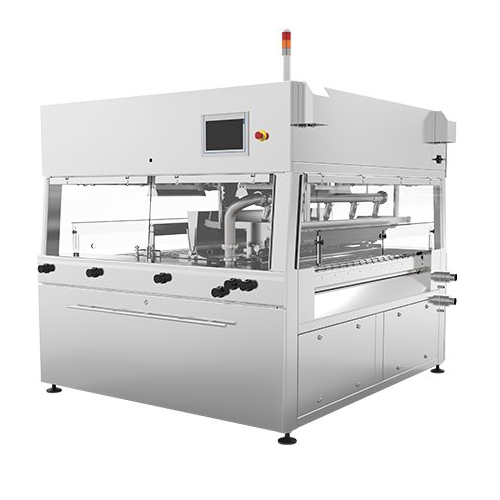
Industrial chocolate enrober
Achieve exceptional chocolate coating consistency and efficiency with this advanced enrobing te...
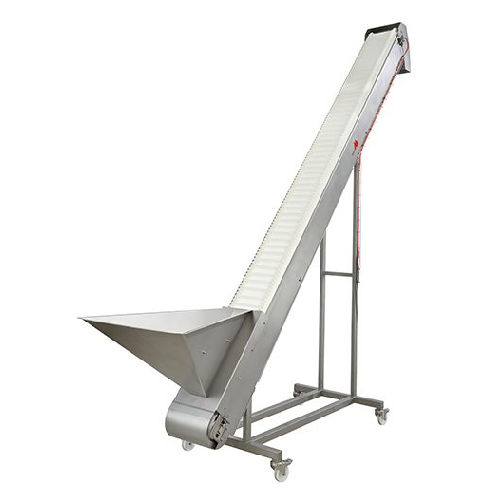
Conveyor system for chocolate production lines
Streamline your production flow with this conveyor system, ensuring efficie...
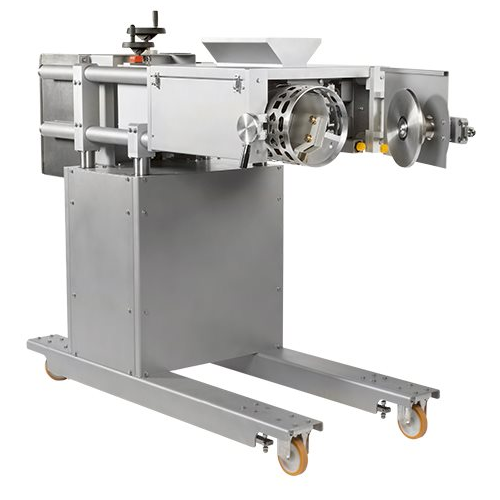
Rotating stencil depositor for confectionery products
Streamline your confectionery operations by precisely depositing in...
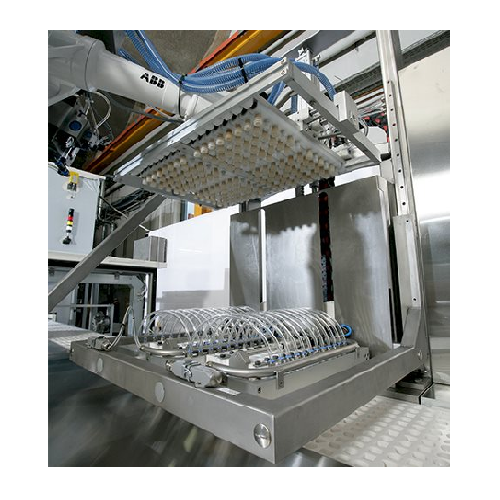
Robotic chocolate assortment system
Streamline your chocolate production by precisely assorting various filled chocolate ar...
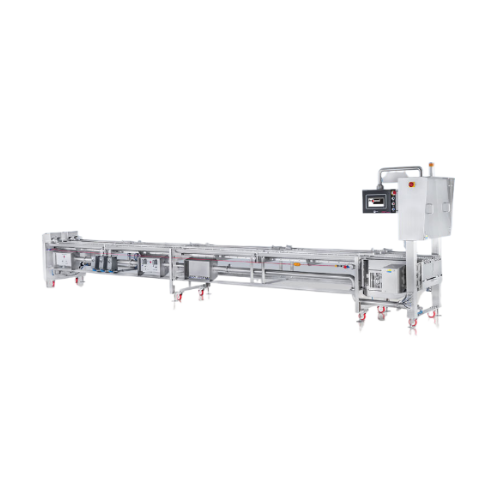
High throughput tray conveyor system
Looking to streamline your tray sealing process? This modular conveyor system integrat...
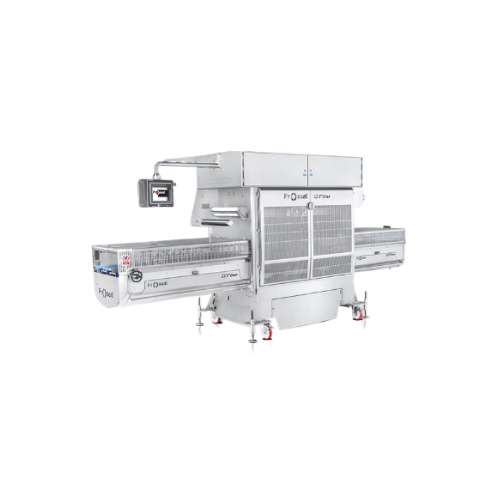
In-line tray sealing system
Streamline your packaging line by implementing a high-speed, in-line tray sealing system designe...
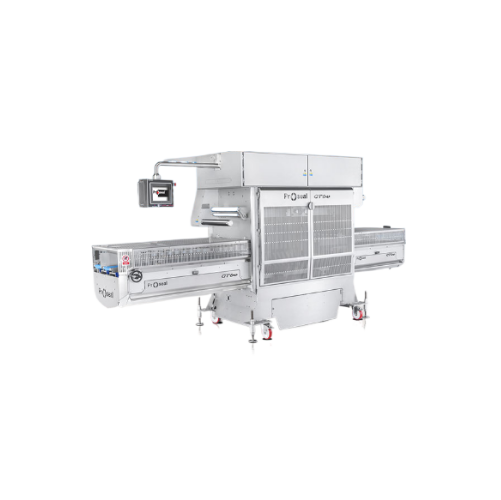
High-capacity tray sealer for poultry, meat & seafood
Optimize your high-speed packaging line with this large-capacity tr...
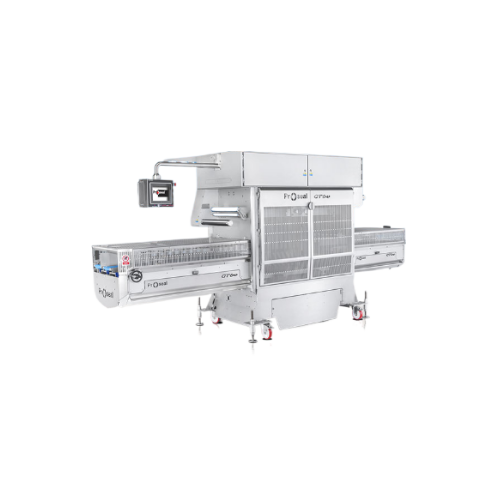
Large-capacity automatic tray sealer
Optimize your production line with this tray sealer, designed for high-speed sealing a...
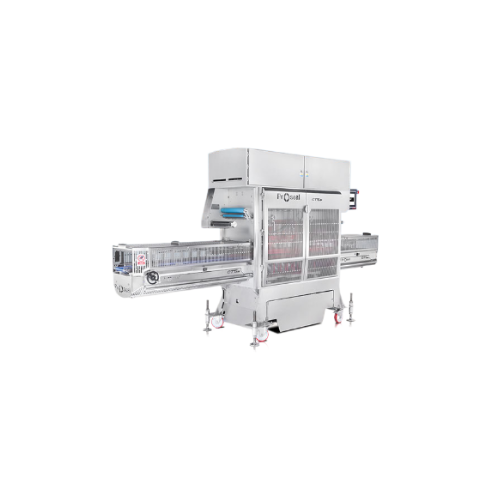
Automatic inline tray sealer for food packaging
Streamline your packaging process with high-speed, reliable tray sealing t...
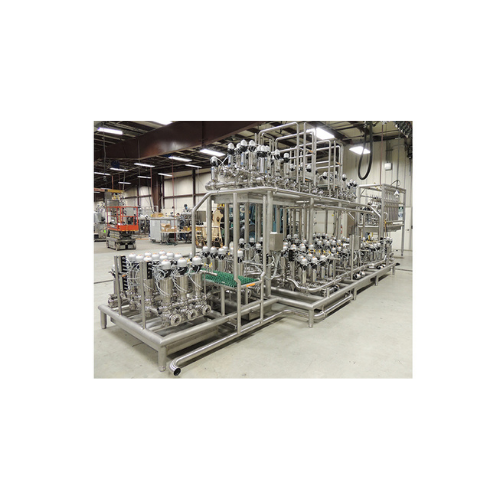
Automated valve manifolds for clean-in-place solutions
Optimize your production efficiency with automated valve manifolds...
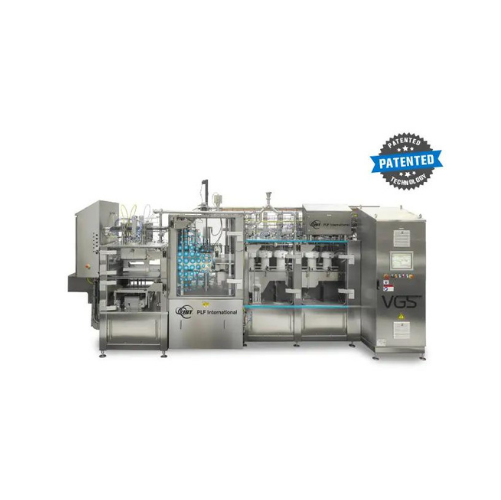
Vacuum gassing seamer for infant formula packaging
Ensure low residual oxygen levels in your powdered products with a spe...
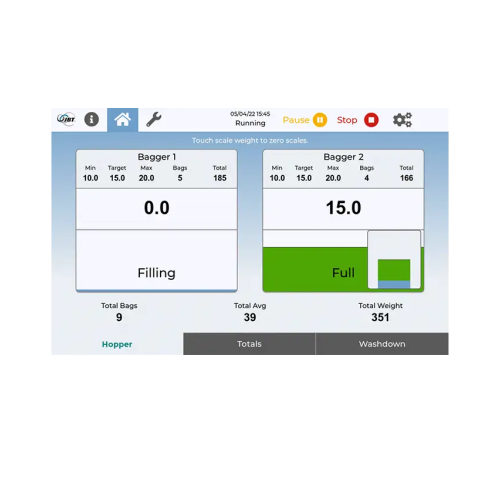
Weighing and distribution system for poultry processing
Optimize your production line by ensuring precise product weight ...
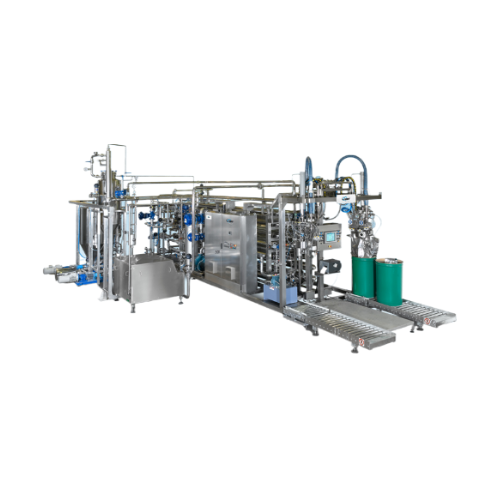
Aseptic processing system for food products
Streamline your food processing line with an efficient aseptic processing syst...
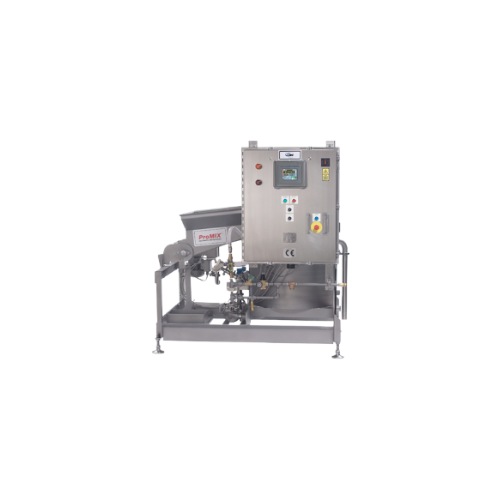
Automatic batter mixer for coating applications
Achieve consistent batter viscosity for precise coating in high-demand foo...
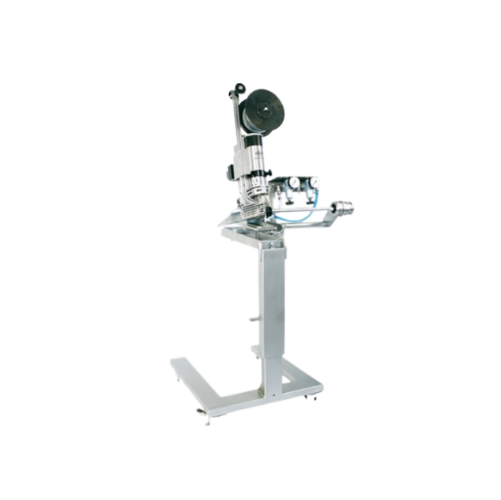
Automatic single clipper for sausage production
Streamline your sausage and cheese packaging with high-speed, reliable clo...
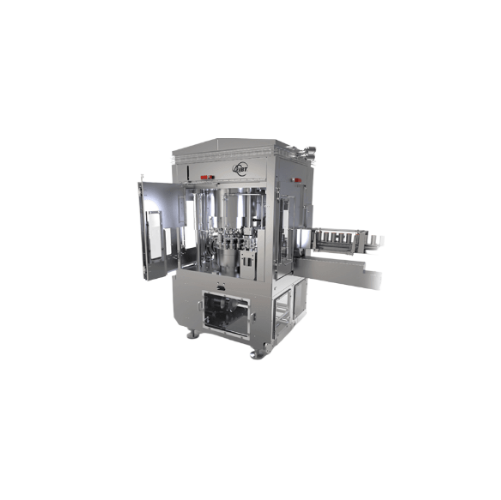
Can seamer for high-speed liquid applications
Ensure consistent seal integrity and maximize throughput with this advanced ...
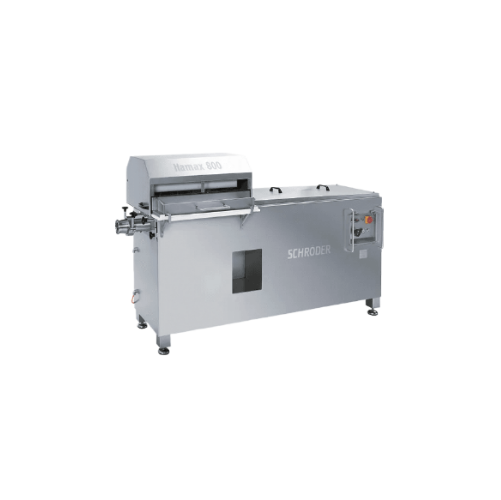
Whole muscle stuffer for slicing efficiency
Streamline your meat production with a hydraulically driven stuffer designed t...
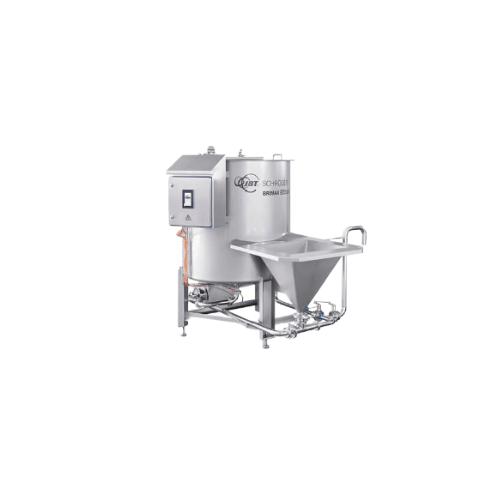
Seafood brine preparation system
Optimize your meat and seafood production with this versatile brine preparation system, ens...
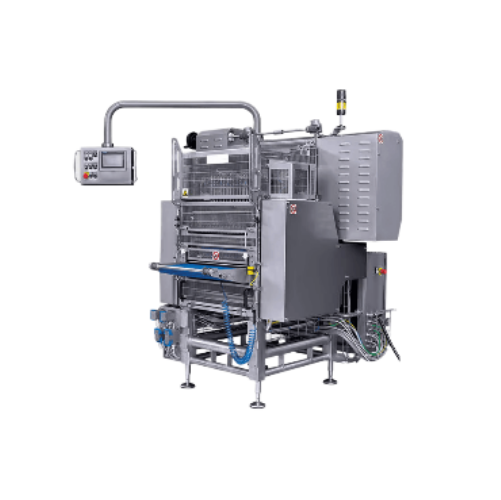
Double sheet forming system for ravioli production
Streamline your production with high-speed forming and sealing, achiev...
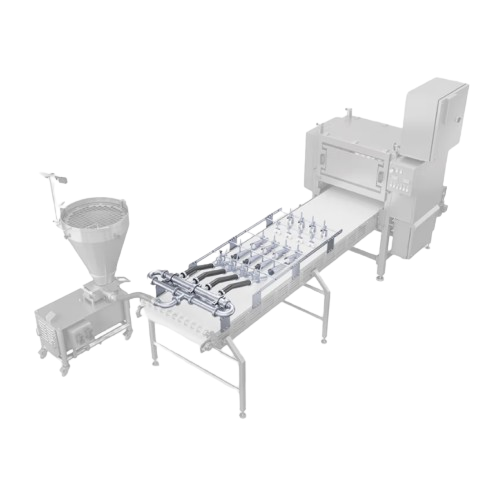
Pasta folding system for cannelloni production
Streamline your production by precisely folding pasta around filling to cre...
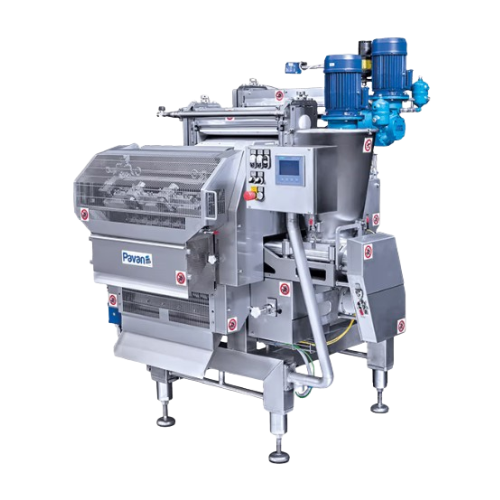
Single sheet former for fresh pasta production
Optimize your production line with a versatile machine designed to precisel...
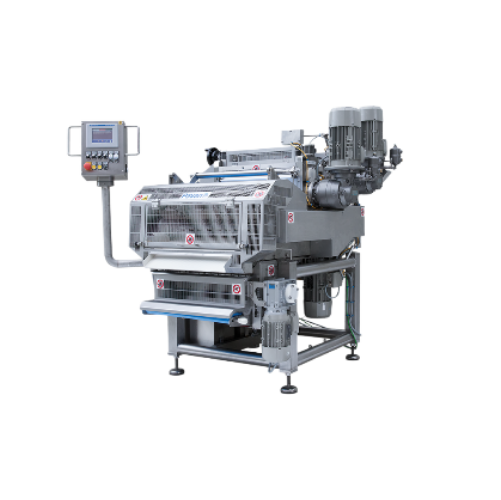
Pasta sheet forming machine for ravioli and cappelletti
Achieve precision pasta forming with consistent thickness and hig...
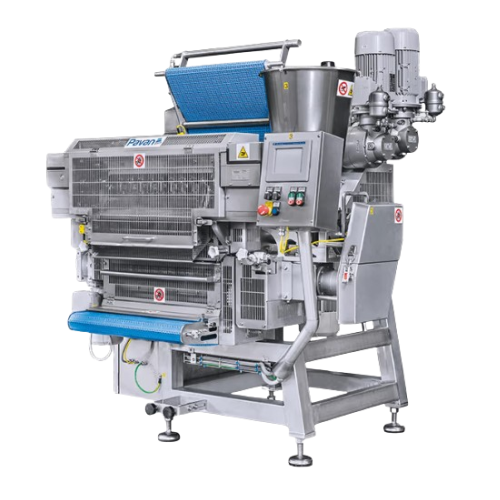
Tortellini forming machine
Optimize your tortellini production with a high-speed forming machine that ensures precise thickn...
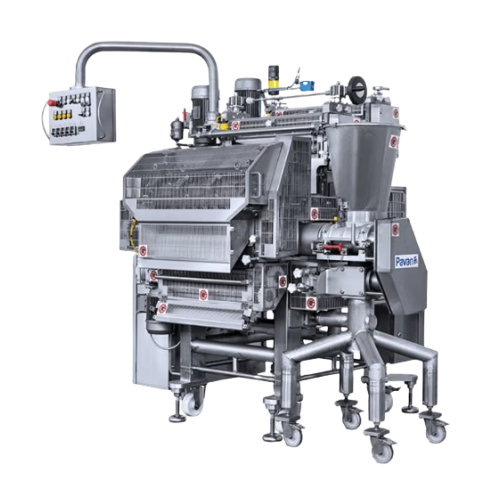
Single sheet fresh pasta forming solution
Effortlessly form diverse pasta varieties with precision, ensuring each shape ac...
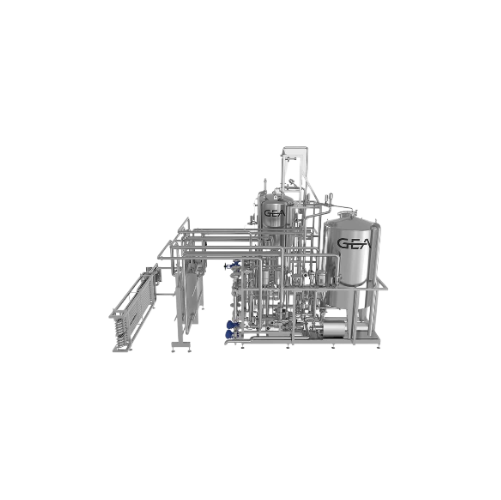
Pasteurizer for non-alcoholic beverages
Ensure microbiological safety and extend shelf life of your non-alcoholic beverages...
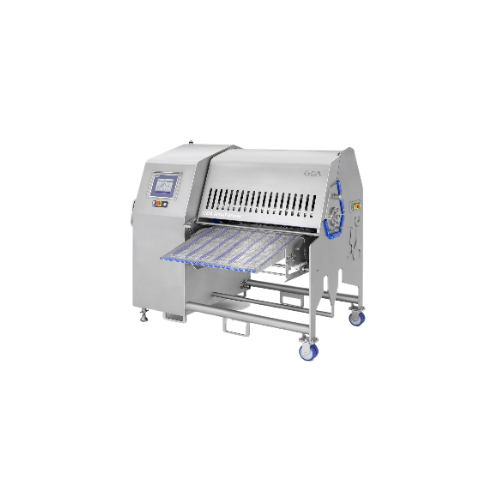
High volume forming solution for poultry, pork, and vegetarian products
Optimize your production with a robust forming ...
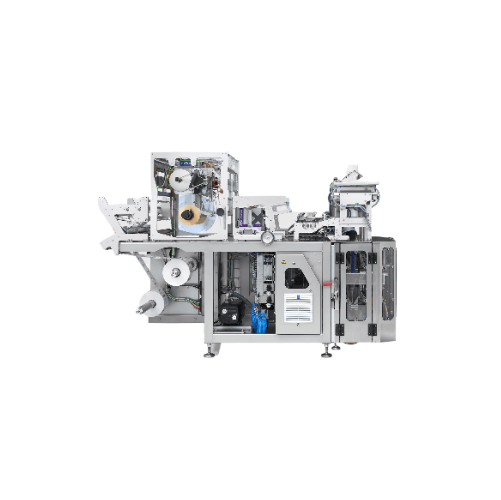
High-speed vertical packaging system for candy and snacks
Achieve up to 500 pillow bags per minute with our high-speed p...
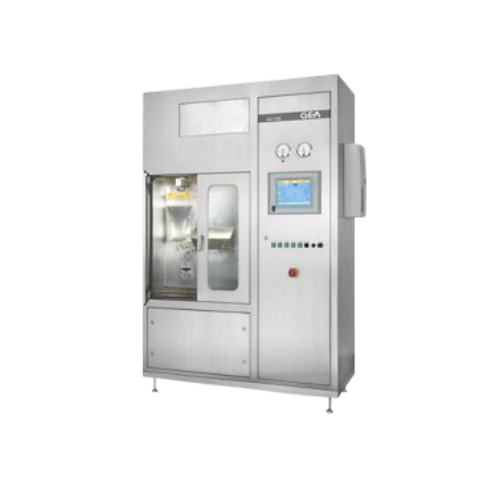
Aseptic liquid dosing system
Ensure precise, sterile dosing of aseptic liquid products, enhancing product integrity and exte...

Continuous leveler and sealer for powder packing
Enhance efficiency in powder packaging with a system that ensures precise...
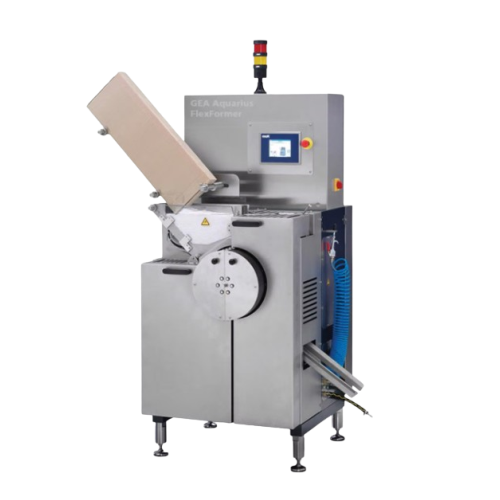
Lollipop forming system for various shapes
Create perfectly shaped lollipops with precise control over size and design whi...
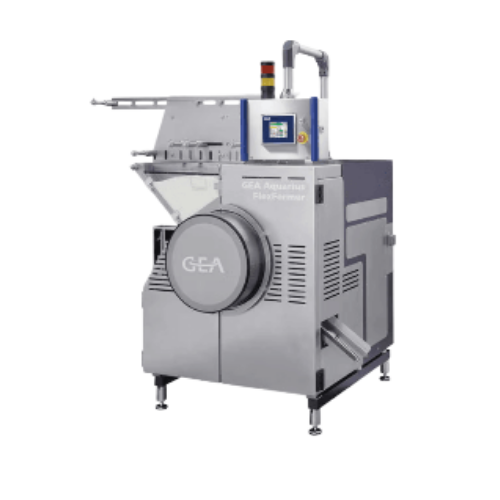
Advanced lollipop forming system
Craft diverse lollipop shapes with precision and efficiency, reducing downtime with rapid c...
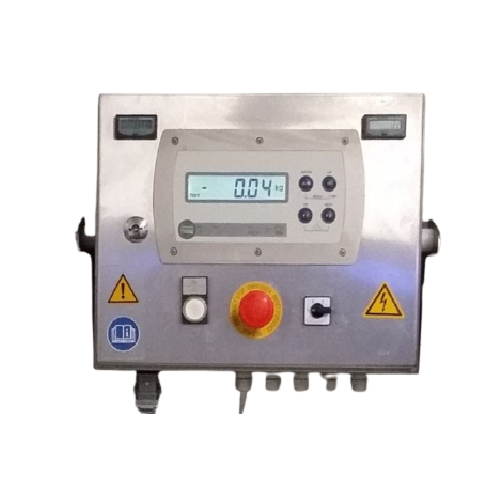
Bag in box bottling system for fruit and vegetable juice
Streamline your juice production with precise filling and packag...
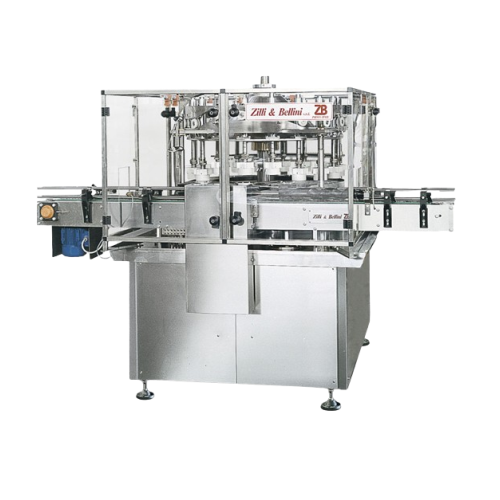
Rotary tampers for metal and glass containers
Optimize your food production line with high-speed rotary tampers, designed ...
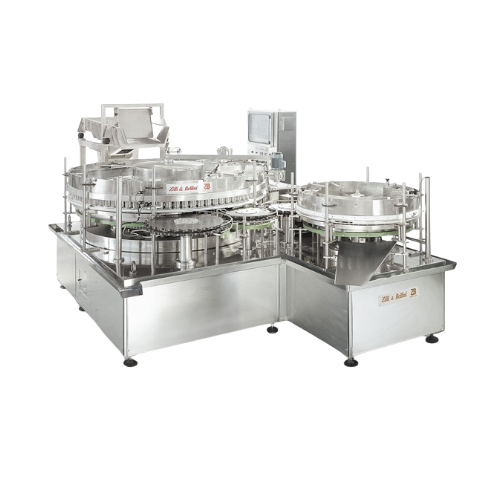
Spice doser for powdered and free-flowing dry vegetables
Optimize spice and dried vegetable packaging with precise dosing...
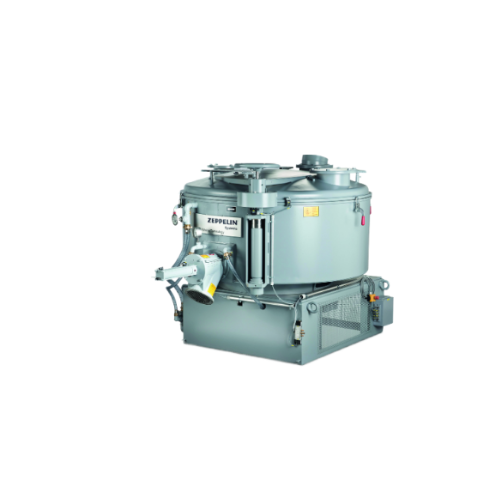
Vertical cooler mixer for industrial cooling mixing
Enhance your production line with efficient temperature control and r...
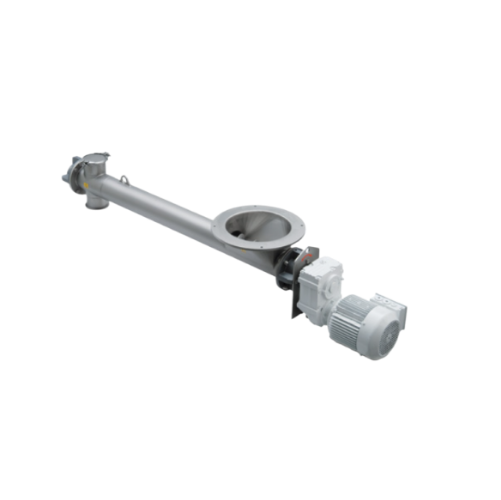
Dosing and conveying screw for dry bulk materials
Efficiently manage the precise dosing and conveying of dry, powder, and...
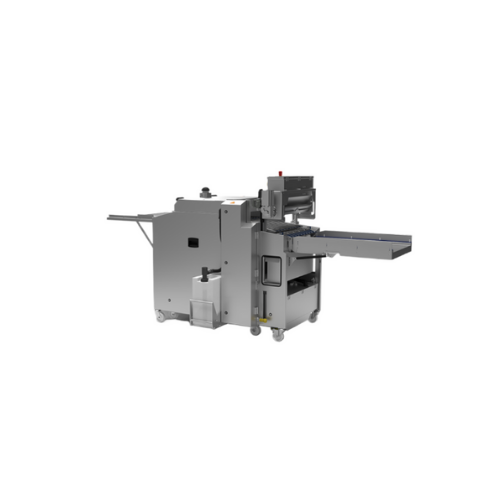
Automatic lye dosing system for pretzel production
Enhance your bakery’s efficiency with a lye dosing system that e...
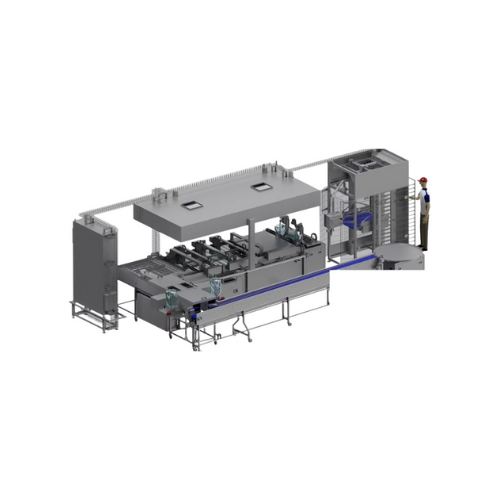
Industrial deep fryer for high-volume donuts
Streamline your high-volume pastry production with an advanced fryer system d...
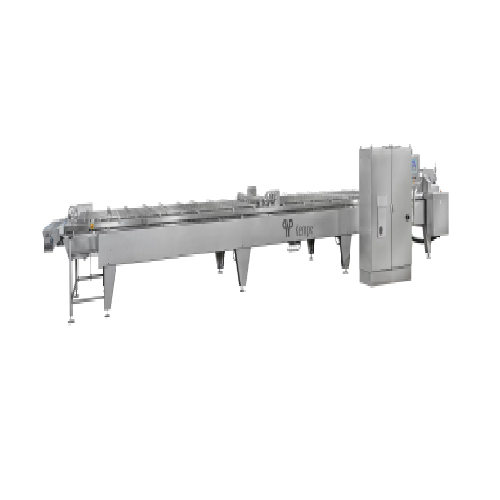
Industrial fryer for donuts and ball donuts
Maximize your deep-fried pastry output with precise control over frying condit...
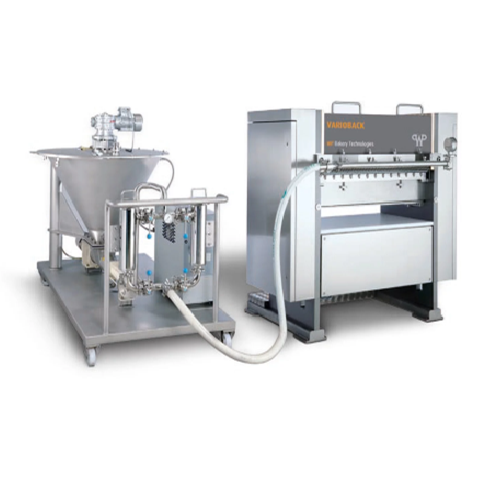
Stick press for pretzel and biscuit production
Transform your snack production with a versatile solution that presses, fil...
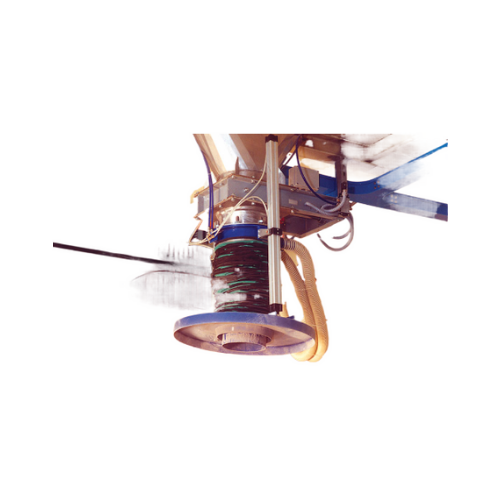
Loading bellows for drums and Ibcs
Ensure dust-free loading of bulk solids into confined spaces with compact, pneumatically...
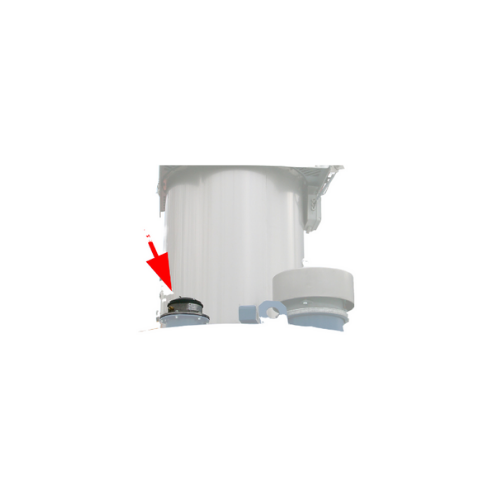
Electronic pressure meters for silo safety monitoring
Ensure precise pressure management in your systems with this advanc...
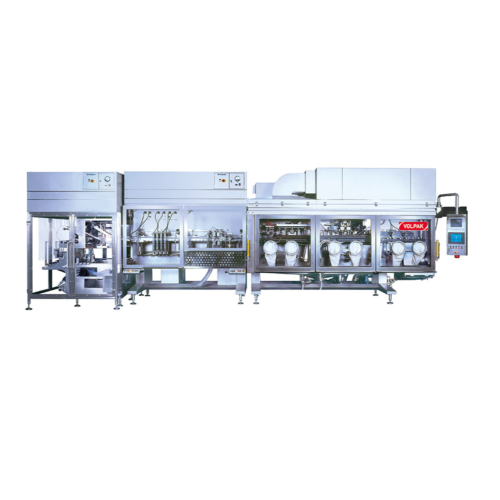
Horizontal stand-up pouching for beverages, dairy, and pet care
Optimize your liquid product packaging with rapid, high-...
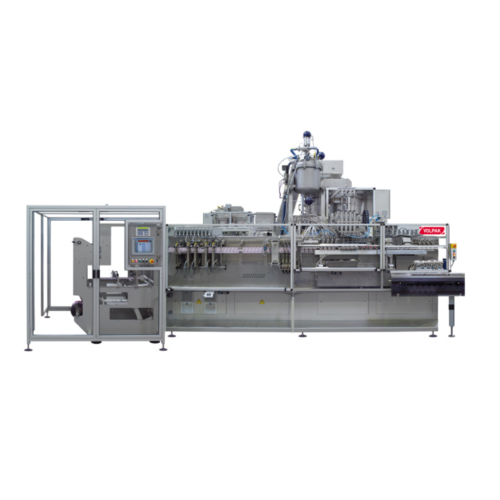
Horizontal flat pouching for top-cap pouches
For manufacturers aiming to streamline pouching operations, this high-speed h...
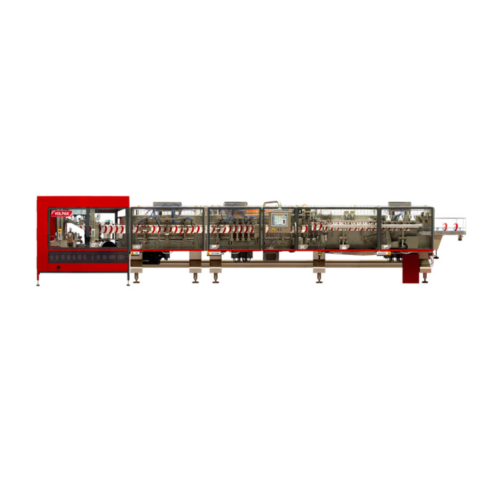
Horizontal stand-up pouching system for liquids and solids
For producers aiming to optimize efficiency and precision, th...
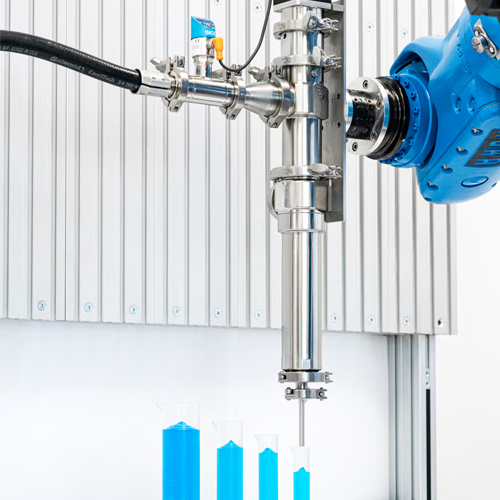
Dosing pump for liquids and pastes
Achieve precise dosing and filling of liquids and pastes with flexibility in dosing volu...
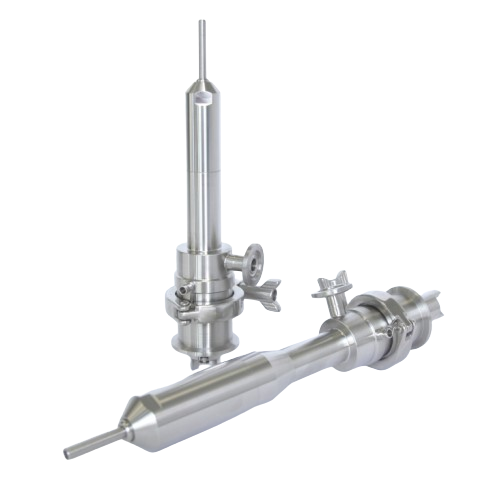
Accurate pharmaceutical dispenser for high-viscosity fluids
Achieve precise liquid dosing with ease, designed to handle ...
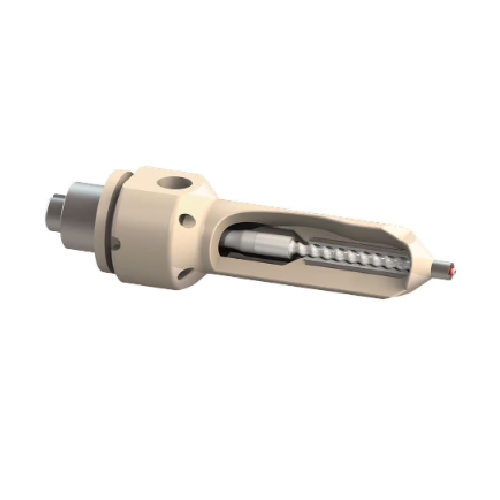
Dispenser for reactive material applications
Ensure precise dispensing of reactive materials without metal contamination, ...
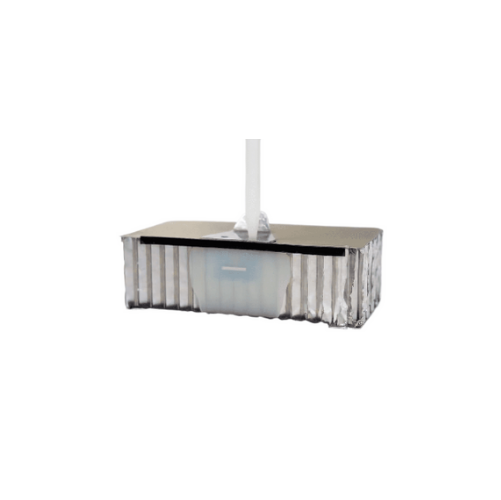
High-precision dosing systems for aerospace applications
Achieve unmatched precision and reliability when dosing complex ...
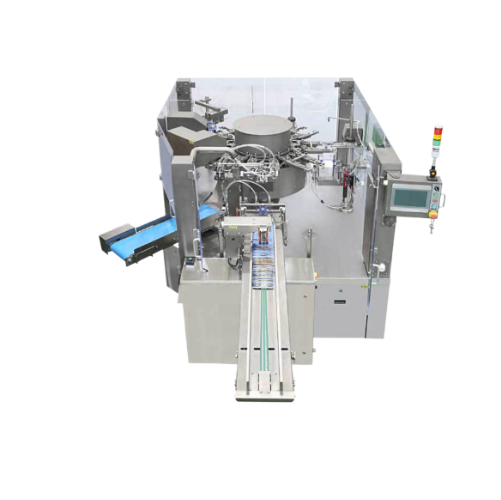
Rotary pouch packaging system for food and powder products
Streamline your packaging process with a rotary system that e...
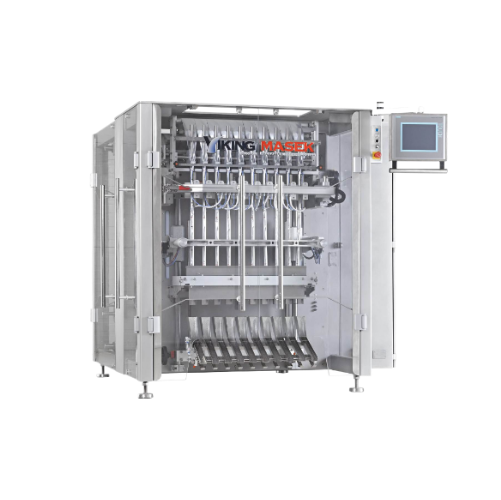
High-capacity stick pack packaging solution
Enhance your production efficiency by packaging diverse products like powders ...
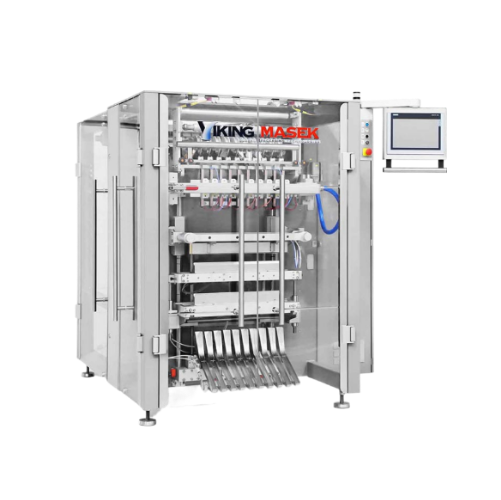
Stick pack packaging for powders and liquids
Streamline your packing process with high-speed, servo-driven stick pack mach...
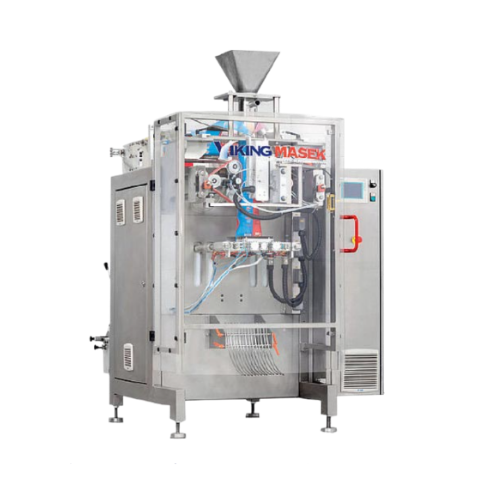
Continuous motion liquid packaging system
Achieve precise and clean liquid packaging with advanced servo-driven squeegee s...
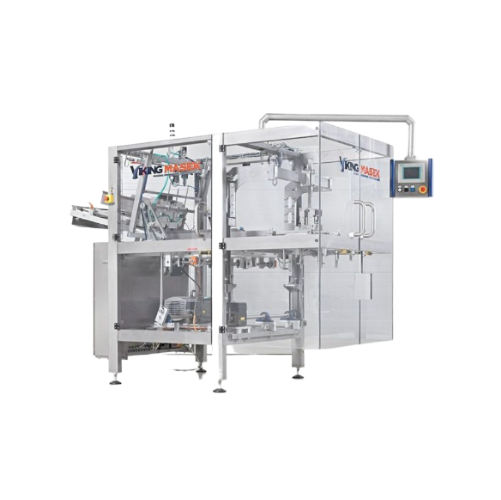
Top load cartoner for various carton shapes
Optimize your production line with a versatile cartoning solution, perfect for...
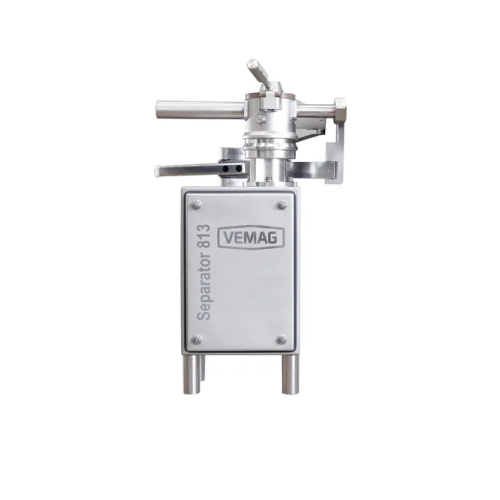
Grinding and separating solution for meat processing
Optimize your meat and plant-based production lines by integrating a...
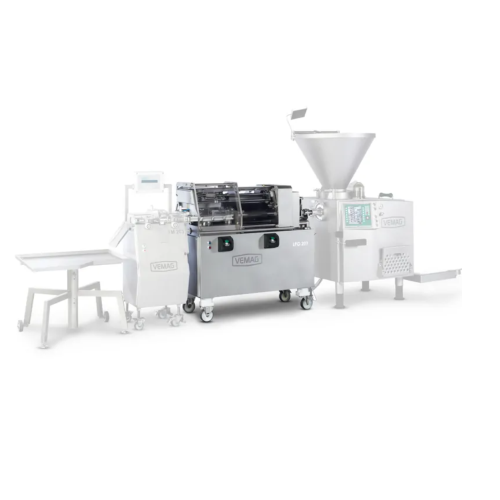
Sausage linking and portioning solution
Optimize your sausage production with precise linking, hanging, and cutting technol...
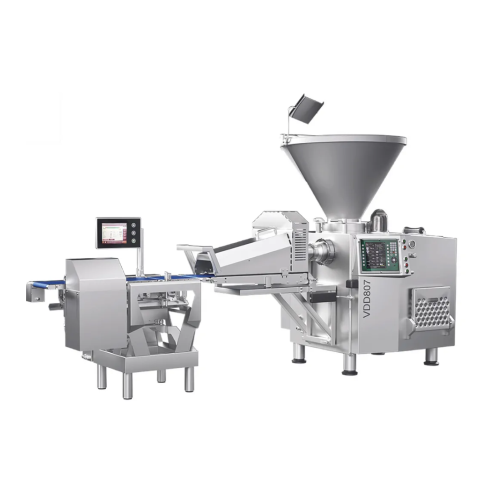
Dough portioner for baked goods applications
Achieve precise and gentle portioning with advanced dough portioning technolo...
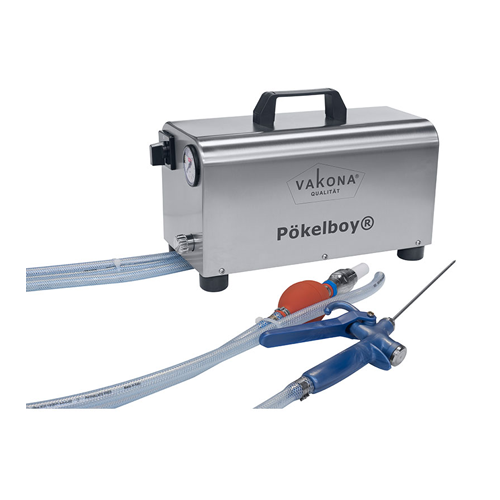
Meat brine injection system
Achieve precise brining and tenderizing with minimal energy consumption, ensuring your meat, pou...
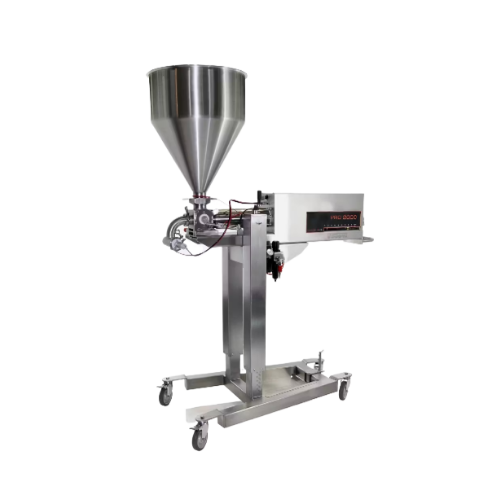
Single piston depositors for bakery and food production
Optimize your depositing and filling processes with versatile equ...
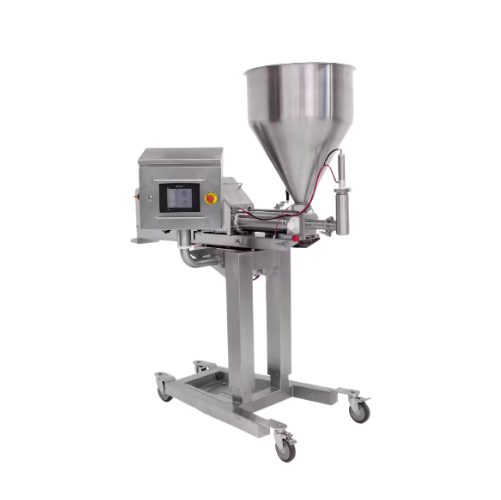
Industrial depositor for automated recipe management
Effortlessly streamline your production with precise depositing cont...

Automated sandwich production line
Optimize your sandwich production with high-speed automation that effortlessly handles d...
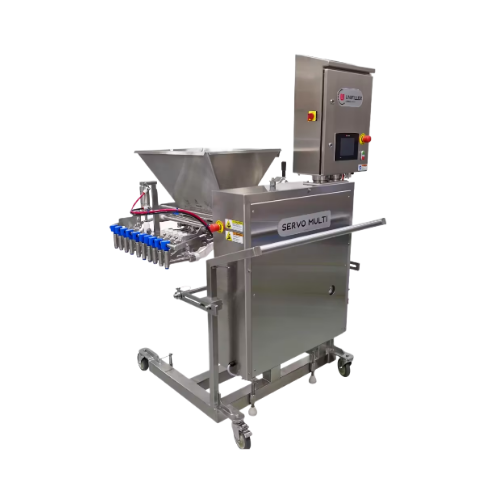
Servo multi food portioner
Achieve precise portion control and high-speed depositing for diverse applications with this adva...
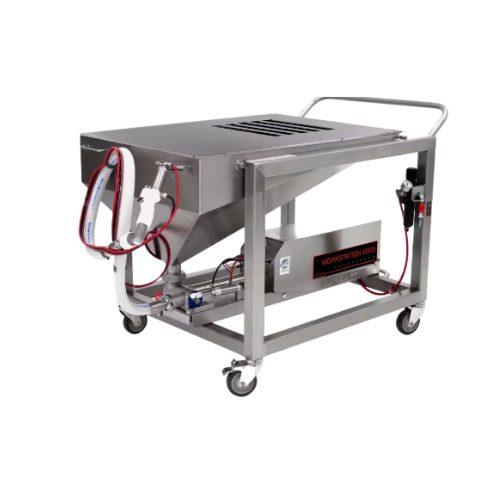
Industrial food depositor for large volume applications
Efficiently handle diverse food textures with precise portion con...
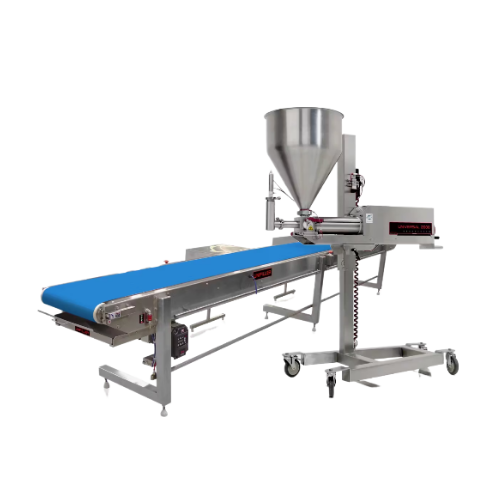
Industrial food portioning system
Optimize your production flow with precision portioning equipment designed to handle a di...
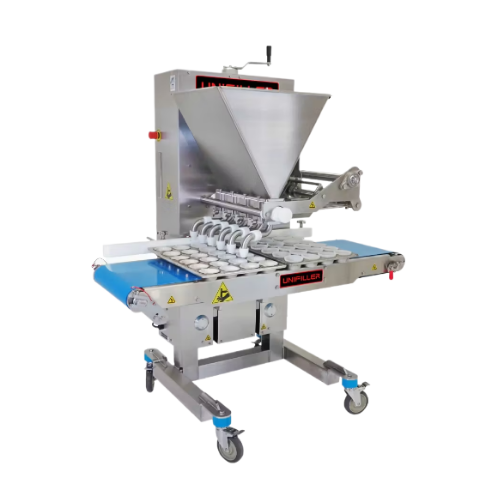
Multi piston depositors for bakery production
For bakeries seeking precision in depositing and filling, these multi piston...

Multi piston depositors for high-volume baking production
Optimize your high-speed production line with precision deposi...
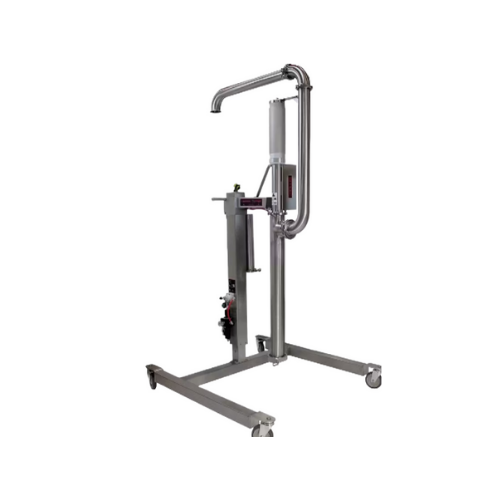
Food transfer and dosing pumps for bakeries
Enhance efficiency in food processing with pumps designed for precise transfer...
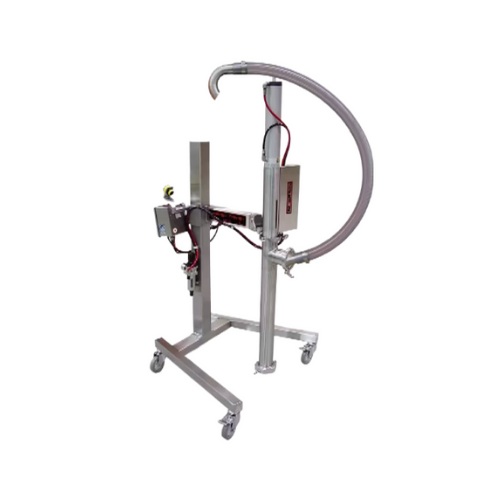
Food grade transfer pump for semi-solid products
Streamline your production with a high-speed transfer pump designed for s...
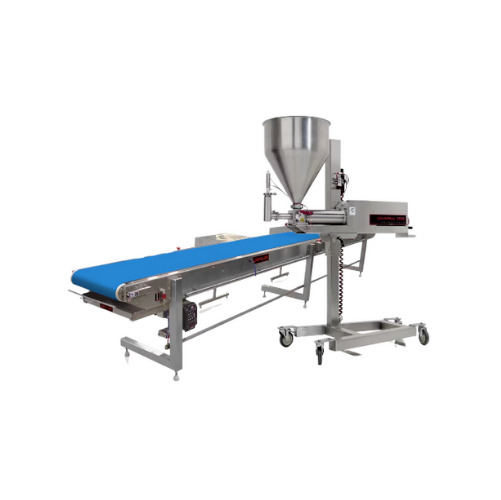
Layered food production line
Effortlessly streamline your production of layered foods with versatile technology that pumps, ...
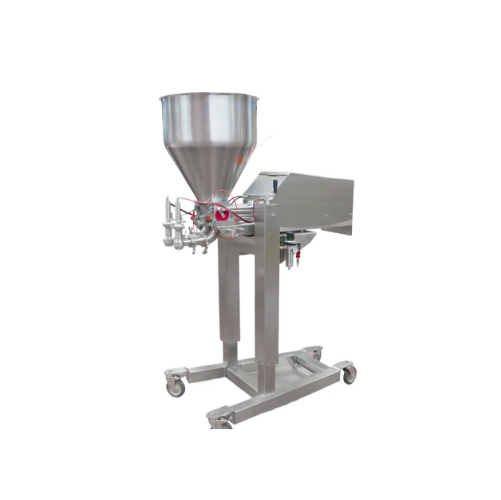
Dual or triple lane food depositor
Enhance your production efficiency with a depositor that seamlessly handles a variety of...
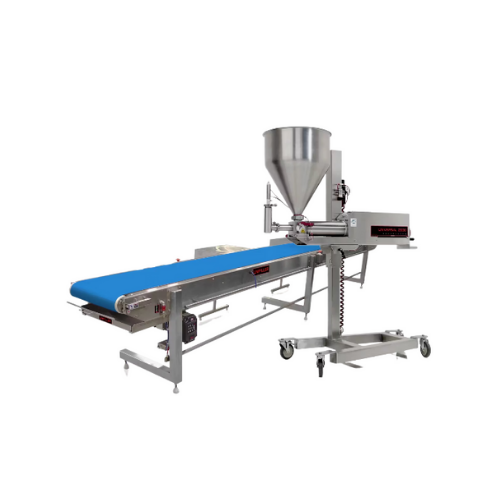
Parfait production line equipment
Optimize your dessert production with advanced depositing technology, perfect for creatin...
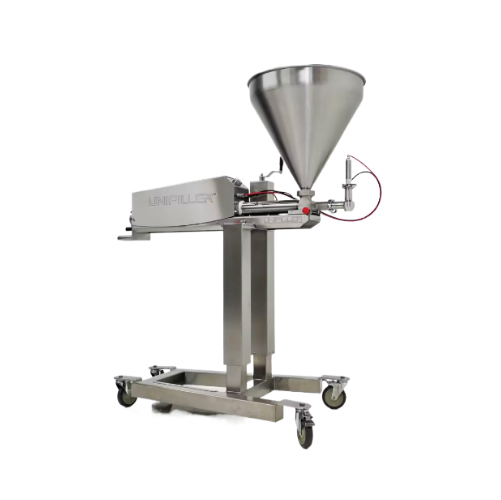
Food depositor for large chunk applications
Need precise depositing of chunky food products like stew or salsa? This versa...
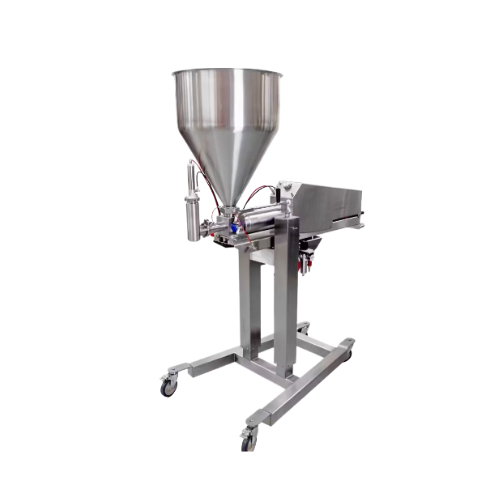
Large portion depositor for food production
Achieve precision and efficiency in depositing large portions with versatile s...
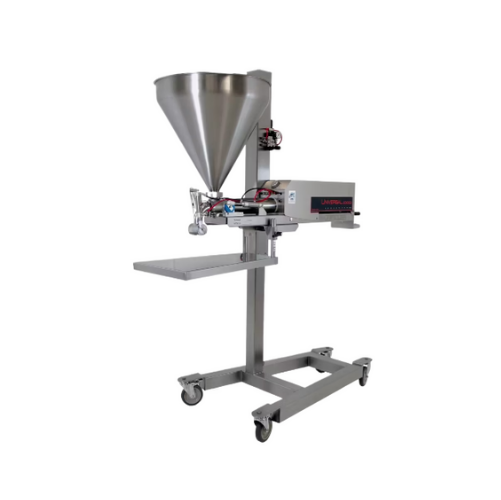
Industrial depositor for bakeries
Enhance your bakery production with precision depositing and filling, designed to handle ...
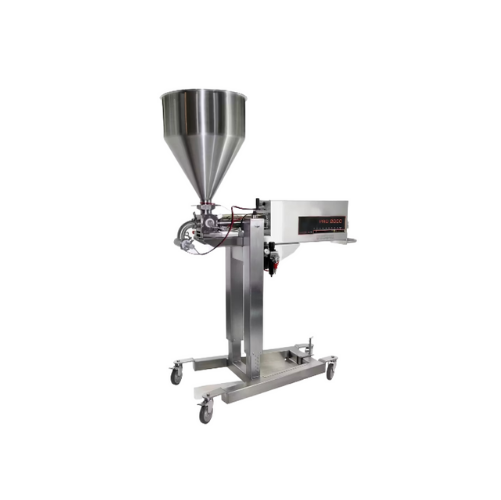
Industrial depositor for large volume bakery products
Achieve precise and high-speed depositing for bakery items with sea...
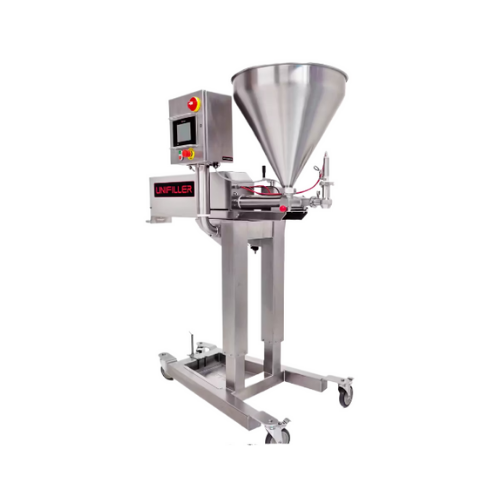
Industrial servo-based depositor for cake production
Effortlessly manage diverse depositing tasks across high-speed baker...
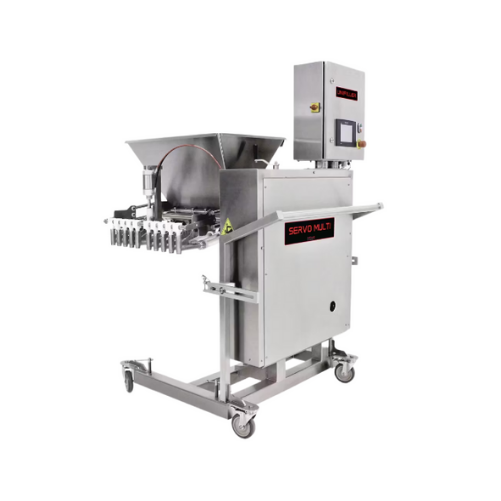
Servo multi piston depositor for bakery production
Streamline your bakery production with precise portion control and hig...
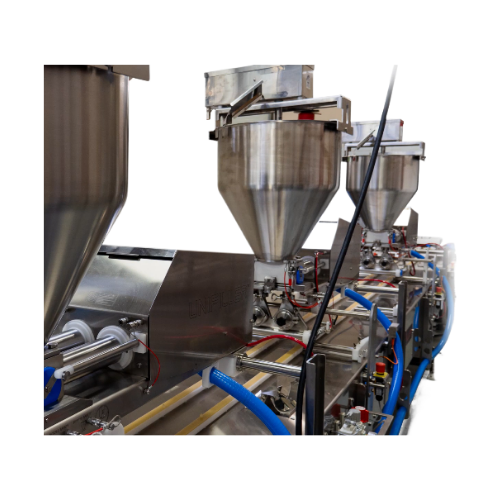
Sheet cake icing system for bakeries
Enhance your bakery’s efficiency with a high-speed icing system, expertly design...
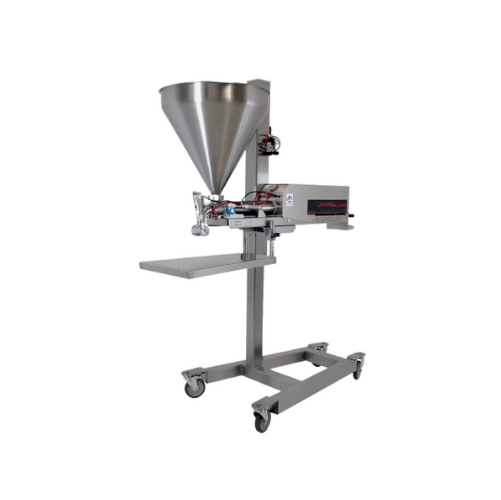
Bakery batter depositor for efficient, consistent depositing
Enhance your bakery production with precision depositing fo...
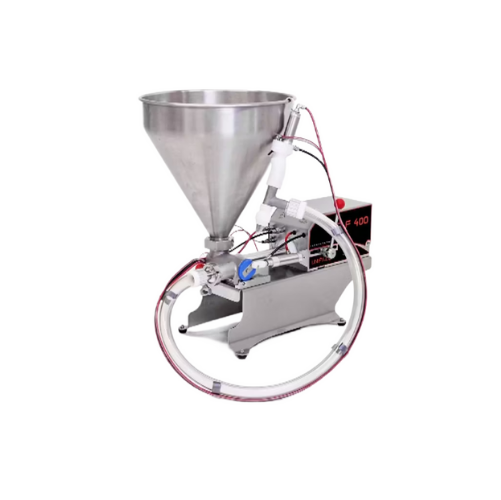
Portable table top bakery depositor
Optimize your baked goods production with precise portioning and rapid depositing, all ...
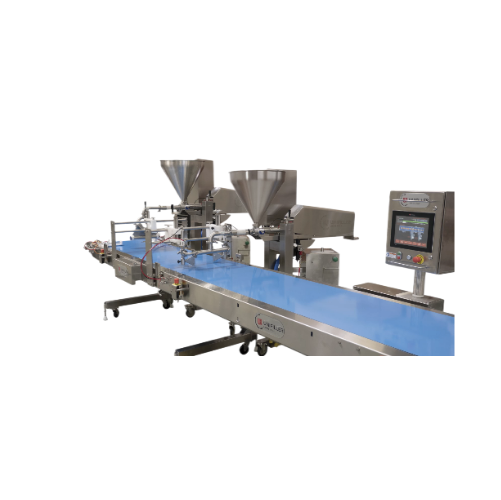
Industrial cake icing system
Enhance cake production efficiency with technology designed for high-speed icing and filling, s...
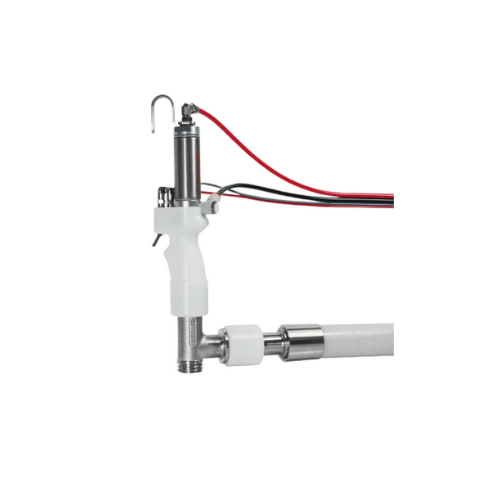
Hand depositing nozzle for precise portion control
Ensure consistent product quality and reduce ingredient waste with thi...
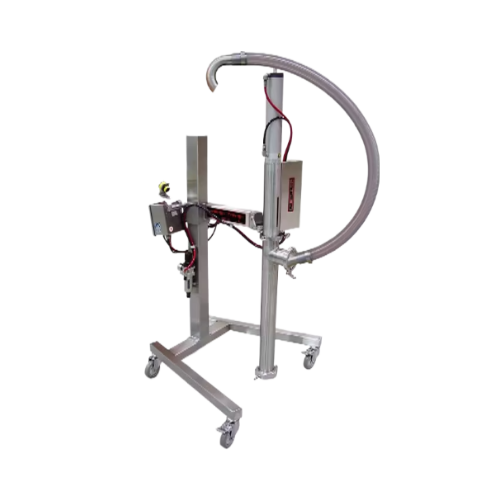
Hopper transfer pump for bakery production
Effectively transfer and maintain the integrity of various food products, from ...
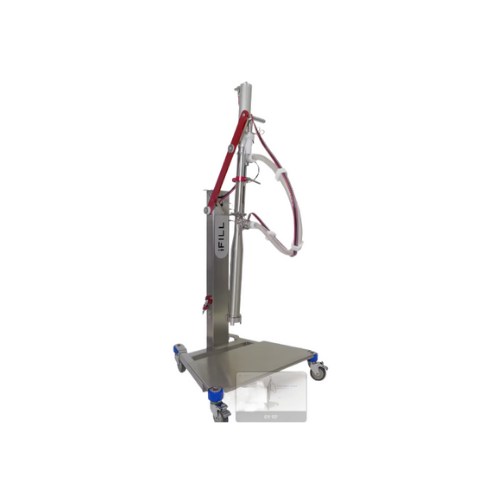
Compact depositor for viscous and liquid products
Easily transition between depositing viscous and liquid products with p...
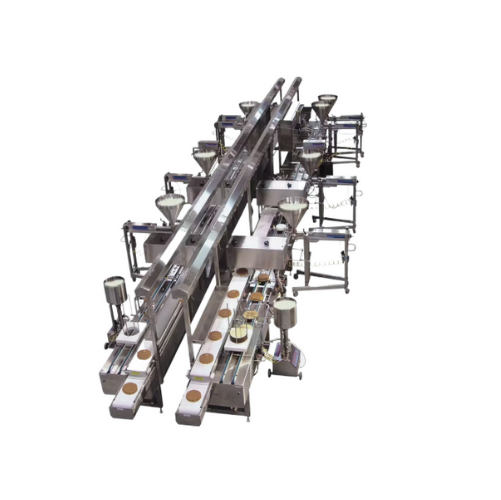
Automated cake icing system
Enhance your cake production efficiency by seamlessly integrating high-speed icing and decoratio...
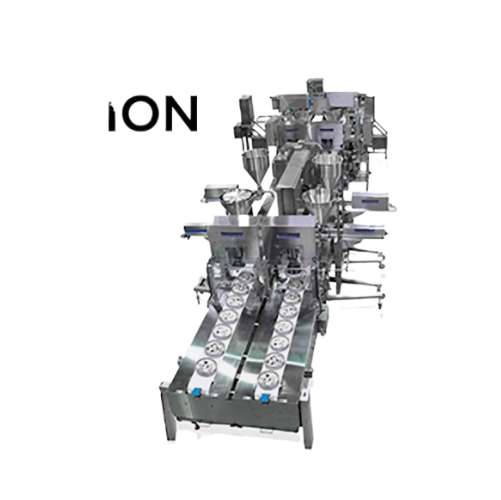
Cheesecake production line
Streamline your cheesecake production with integrated processes for oiling, crumbing, and marblin...
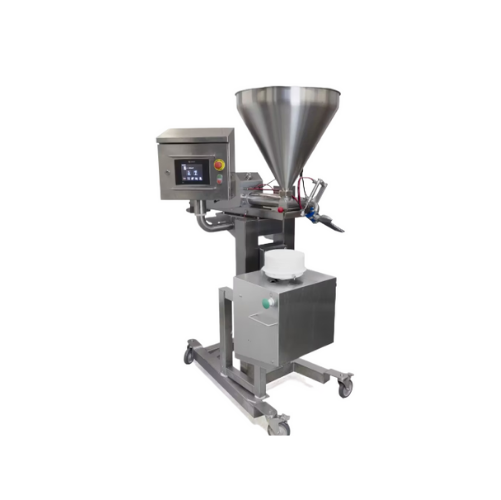
Cake icing and decorating system
Streamline your cake production with this system that adjusts to icing texture changes, ens...
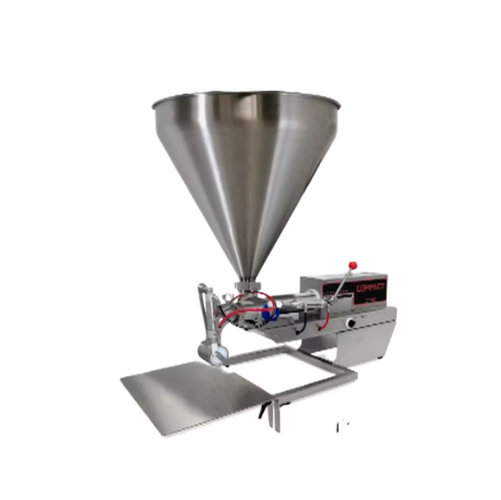
Compact bakery depositor for versatile applications
Streamline your bakery production with a high-speed, versatile deposi...
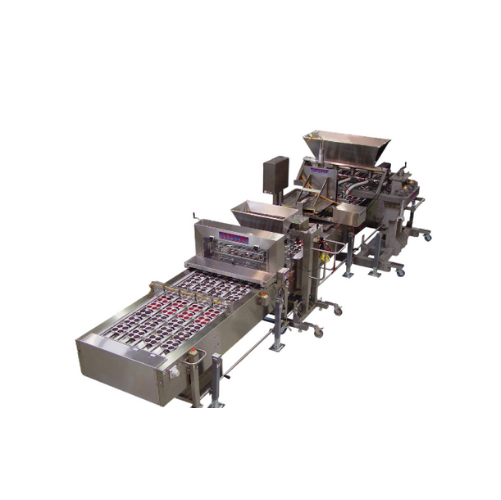
Cupcake production line for automated depositing and decorating
Streamline your cupcake production with high-speed depos...
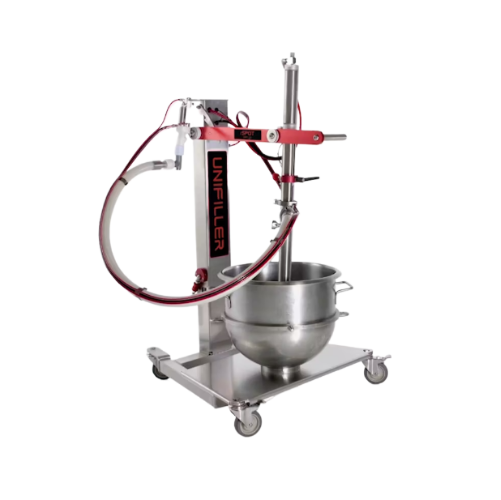
Compact food depositor for direct container use
Streamline your depositing process with a versatile solution that handles ...
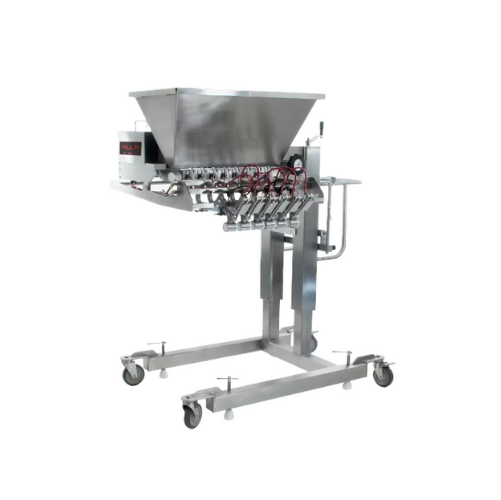
Multi piston food depositor for sauces and dips
Efficiently fill and deposit sauces, dips, and more with precision across ...
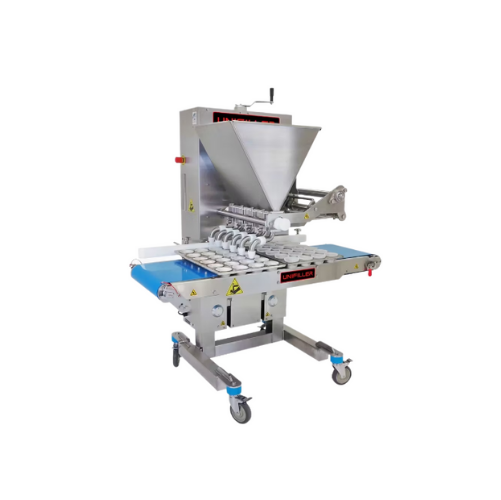
High-speed piston depositor for food applications
Achieve precise portioning and rapid depositing of diverse food product...
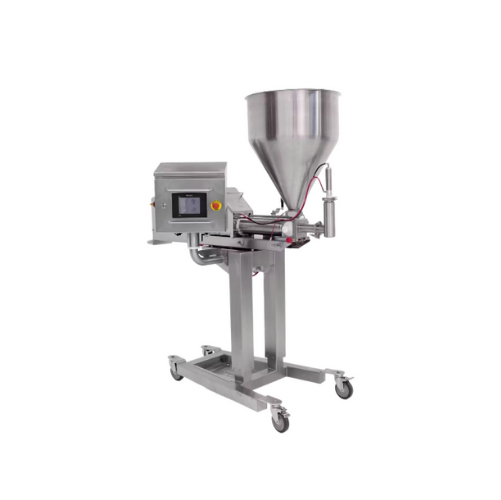
Industrial depositors for flowable food products
Enhance your production line’s efficiency with precision depositing...
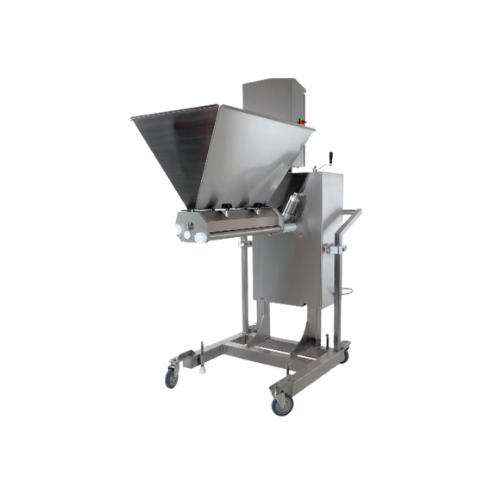
Pneumatic Rp depositor for bakery and food plants
Optimize your production line with a high-speed depositor designed to d...
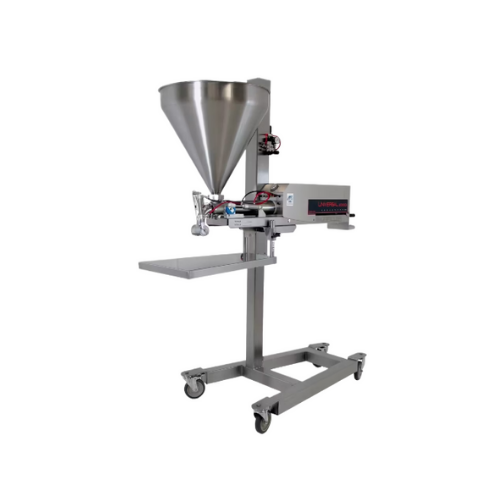
Single piston food depositor
Achieve precise portion control for diverse food products, from soups to chunky fillings, with ...
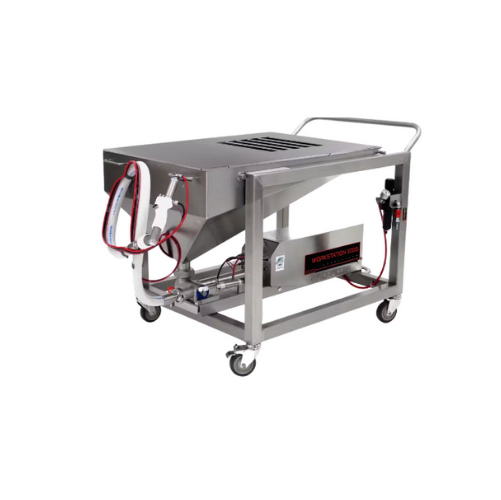
Industrial food portioning depositor
Optimize portioning precision and streamline your production with this advanced deposi...
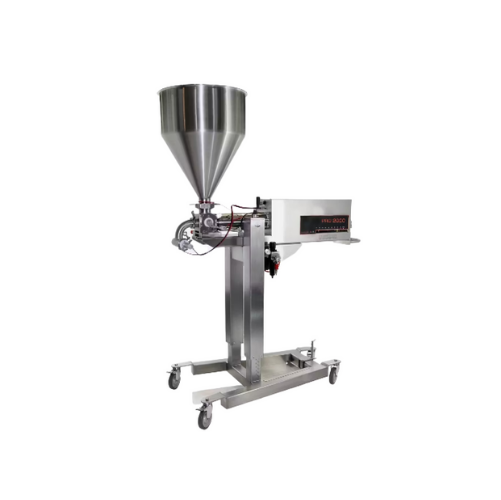
Automated production lines for cakes and cupcakes
Streamline your bakery’s production line with a versatile automat...
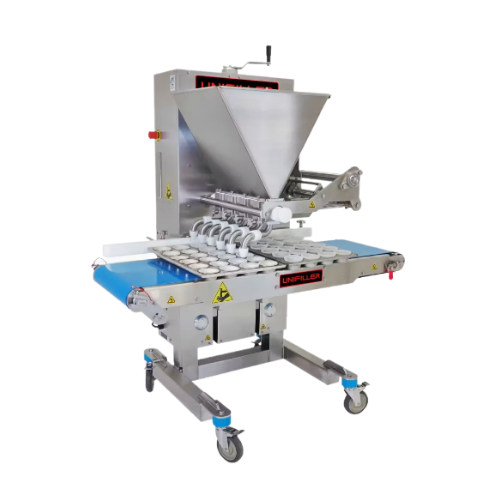
Servo driven multi-piston depositor
Experience precise control and high-speed depositing with the latest servo-driven techn...
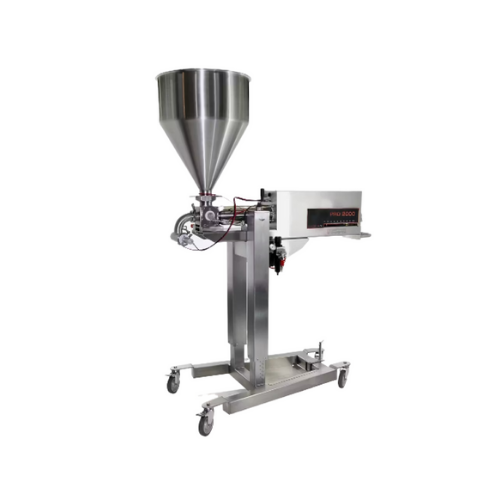
Industrial food production depositor for bakery applications
Optimize your bakery production with precision depositing a...
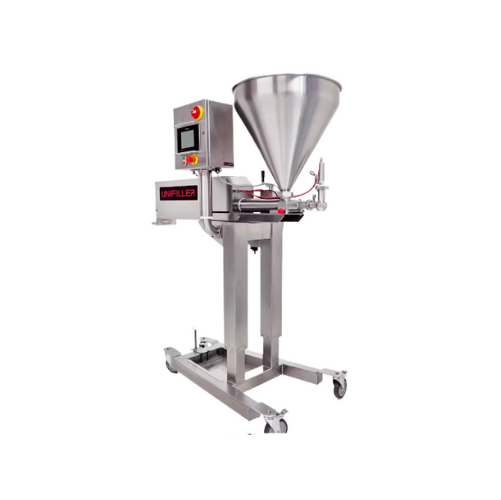
Servo deposition system for industrial cake production
Effortlessly streamline your food production process with precise ...
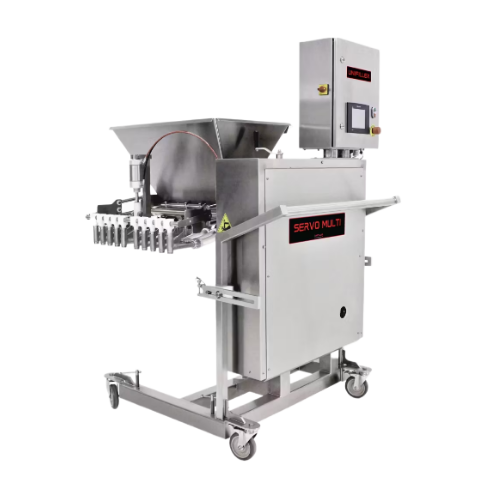
Servo multi-piston depositor for bakeries
Achieve precision and consistency in baked goods production with this solution, ...
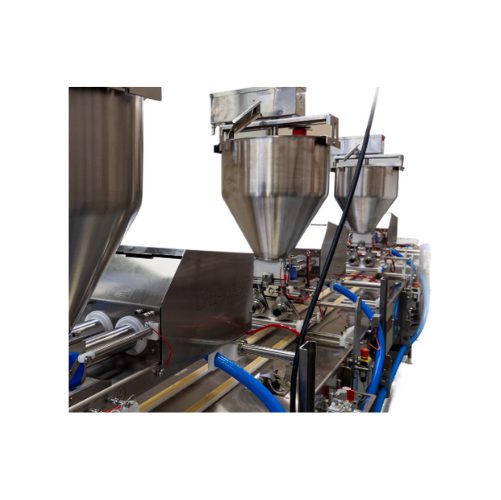
Automated sheet cake icing line for bakeries
Enhance your bakery’s efficiency with a powerful sheet cake icing line ...
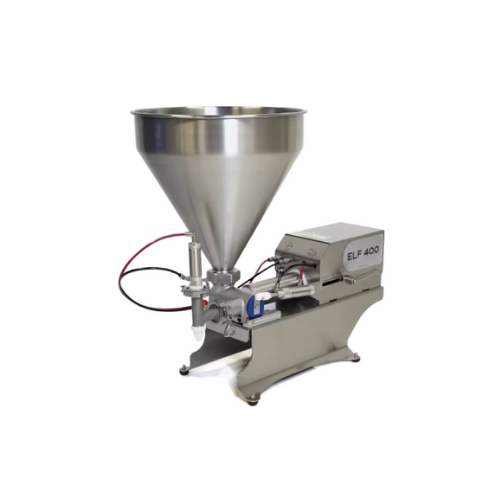
Tabletop food depositor for portion control
Streamline your food production with precise portion control, reducing waste a...
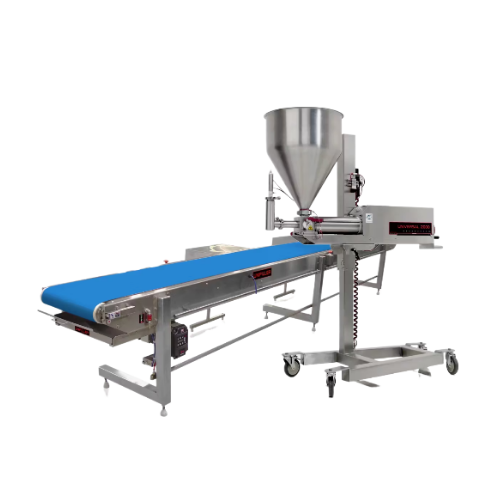
Single piston food depositor for temperature-sensitive environments
Optimize your production with a versatile depositor...
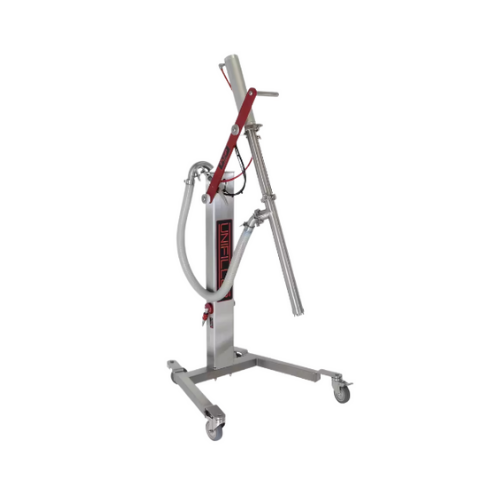
Compact food transfer pump
Effortlessly maintain your production flow with a compact transfer pump designed to handle a wide...
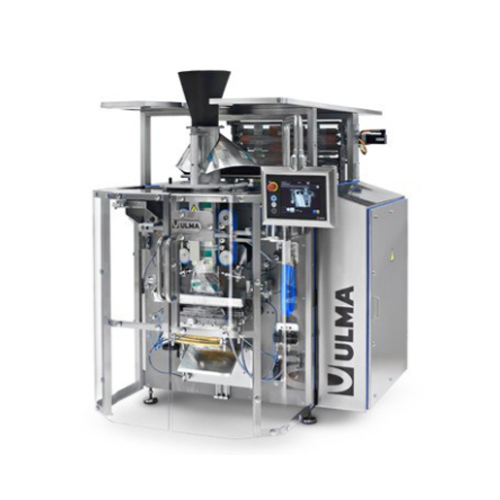
Vertical packaging system for medium-high speed applications
Optimize your packaging line with a system that delivers pr...
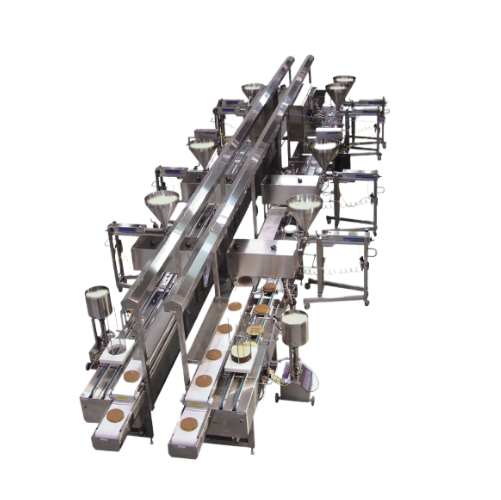
Automated icing system for cakes
Efficiently layer, fill, and ice various cake types with precision and speed, securing cons...

Cupcake production line automation
Streamline your cupcake production with high-speed automation, enabling precise depositi...
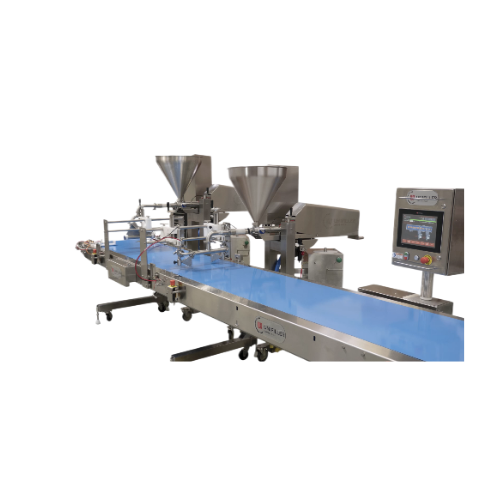
Automated cake icing line
Enhance your cake production with precision icing and efficient layering, ensuring each product me...
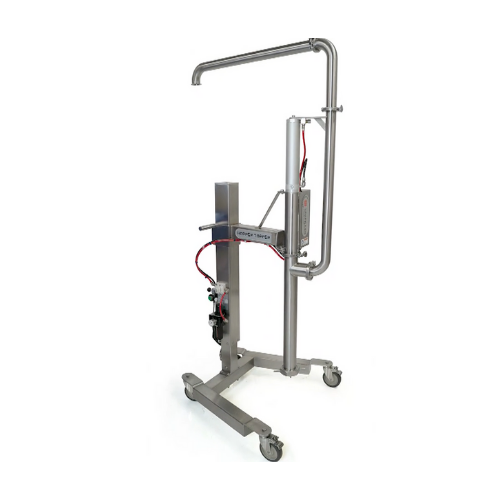
Bakery transfer pump for smooth and chunky products
Ensure consistent product quality with this transfer pump that gently...
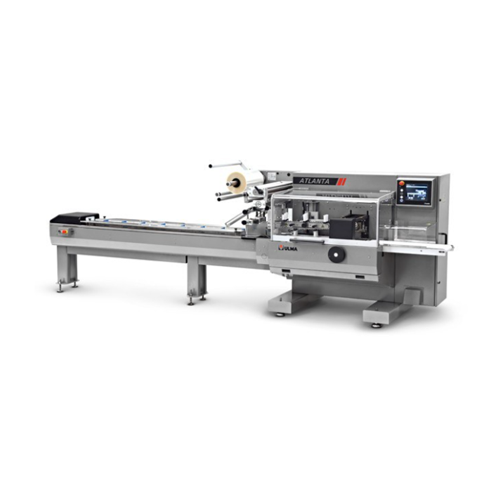
Horizontal flow wrapper for medium to high production
Optimize your packaging line with a versatile horizontal flow wrapp...
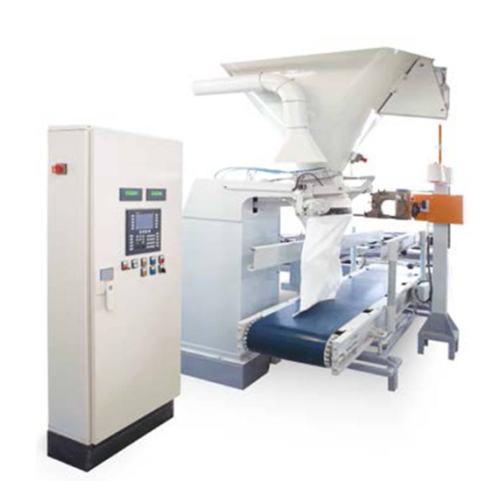
Automatic packaging machine for open-mouth bags
Optimize your packaging line with precision weighing and high-speed baggin...
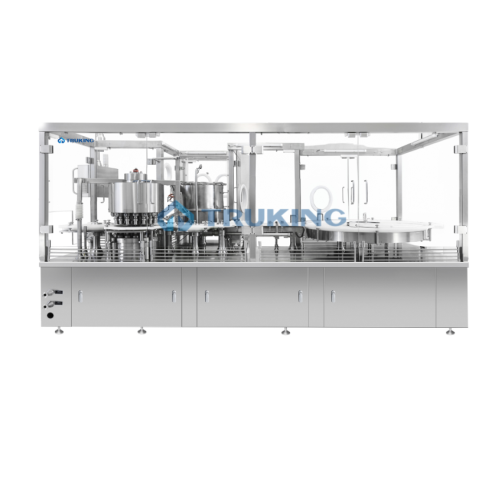
Vial capping machine for pharmaceutical production
Ensure precise and reliable vial sealing in high-throughput pharmaceut...
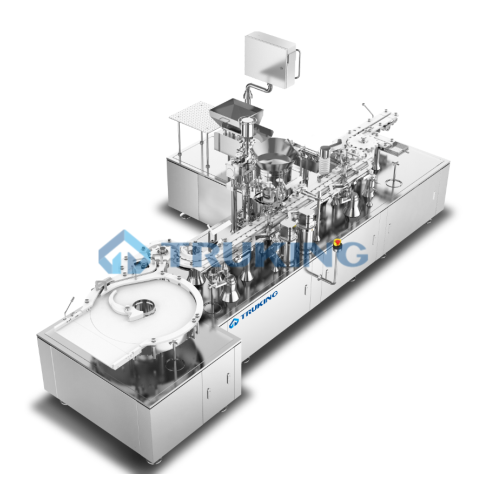
Vial powder dispensing system
Optimize your aseptic fill process with high-precision powder dispensing that minimizes contam...
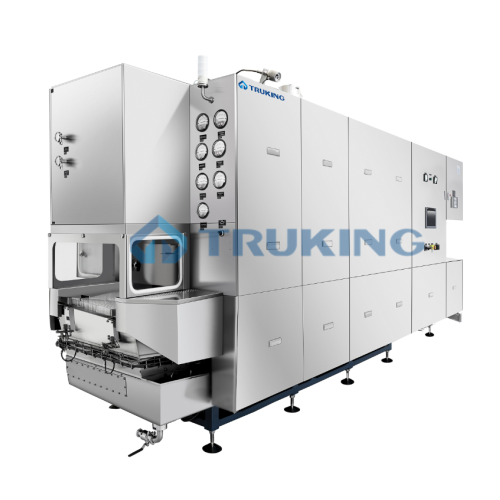
Sterilizing and depyrogenization tunnel for ampoules
Ensure sterile and pyrogen-free ampoules with precision control in d...
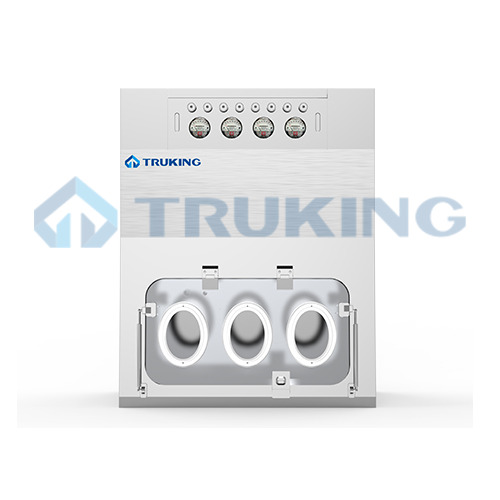
Feeding isolator for liquid preparation in pharmaceuticals
Ensure precise and contamination-free preparation of liquid p...
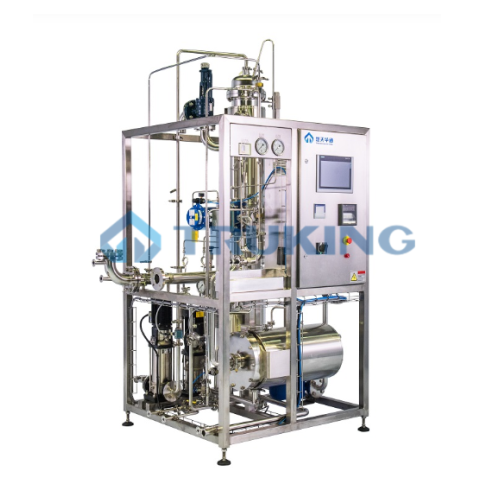
Pure steam generator for pharmaceutical and biotech industries
Ensure optimal steam quality and compliance with stringen...
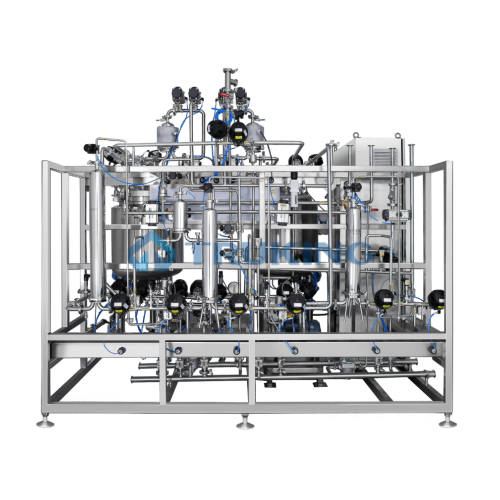
Pharmaceutical preparation system
Achieve seamless integration in pharmaceutical processes with a preparation system that o...
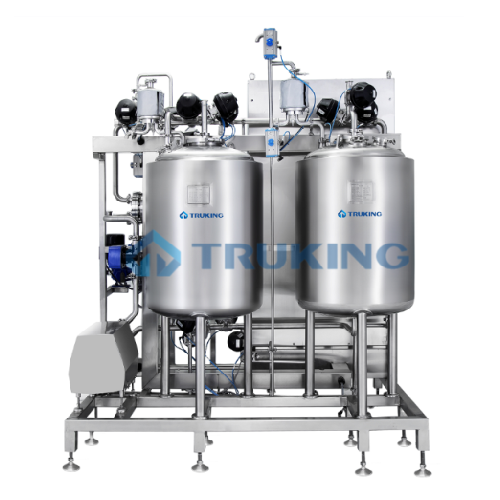
Comprehensive auxiliary system for online cleaning and temperature control
Ensure reliable and precise control in phar...
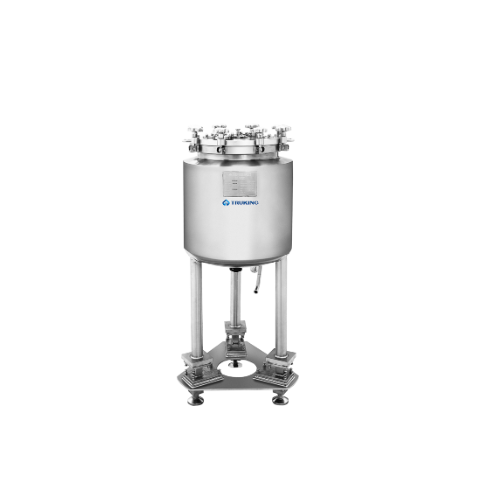
Sanitary vessels for pharmaceutical applications
Ensuring the highest standards of aseptic processing, these sanitary vess...
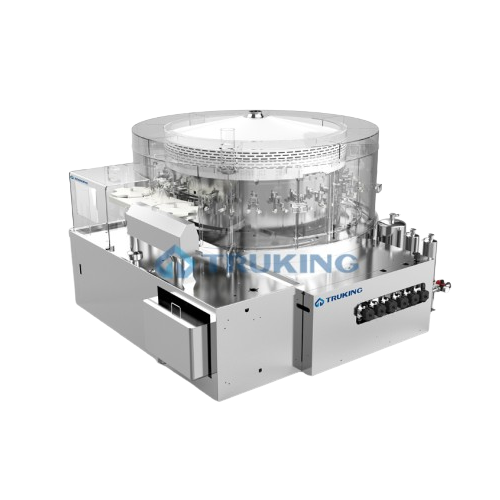
Industrial freeze dryer for pharmaceutical applications
Enhance your production line with precision cleaning solutions fo...
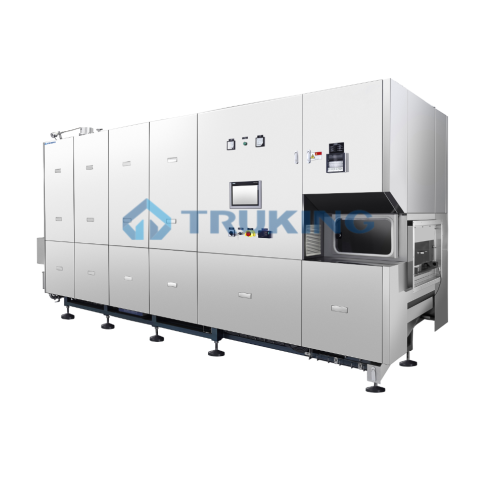
Sterilization and drying tunnel for glass bottles
Ensure aseptic integrity and regulatory compliance in injectable produc...
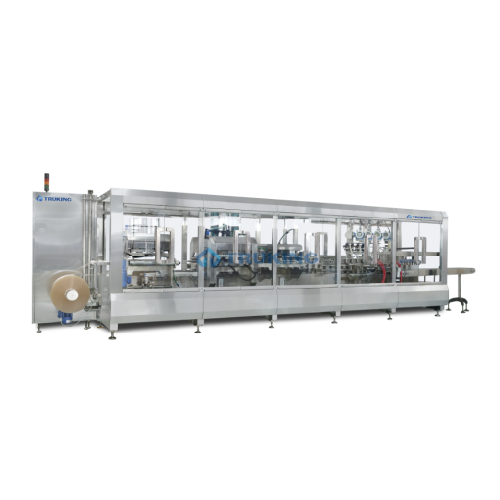
Non-pvc film large infusion compact line
Streamline your infusion production with a compact line designed for high-speed, p...
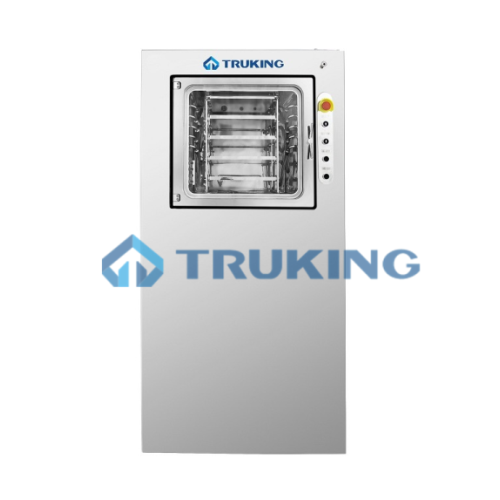
Laboratory freeze dryer for research and development
Optimize moisture removal with precision control during research and...
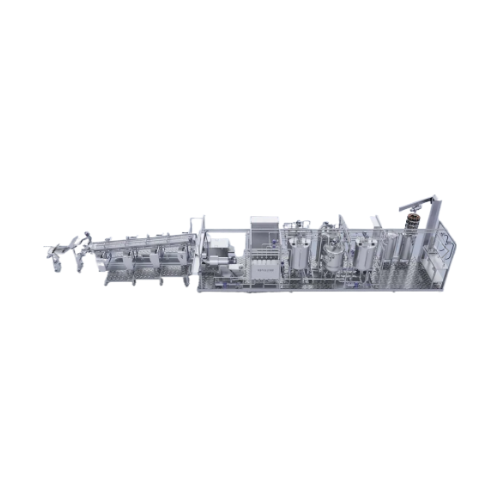
Small-scale fruit processing line for juices and sauces
Streamline your small-scale production with a versatile line that...
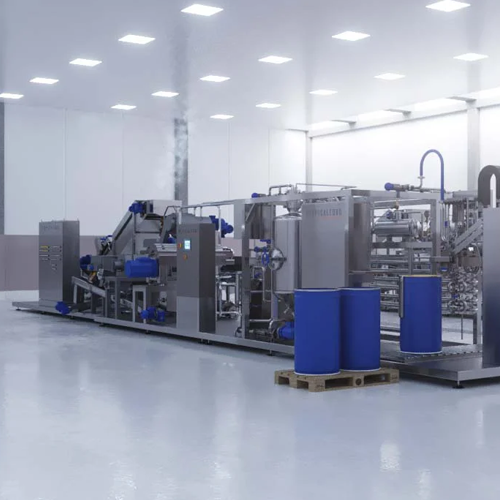
Multifruit processing line for wholemeal pulps and juices
Optimize your fruit processing capabilities with a skid-based ...
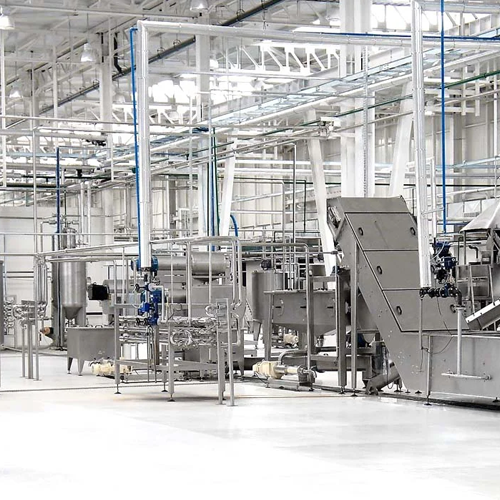
Multifruit processing line for tropical and temperate fruits
Optimize your fruit processing operations with a versatile ...
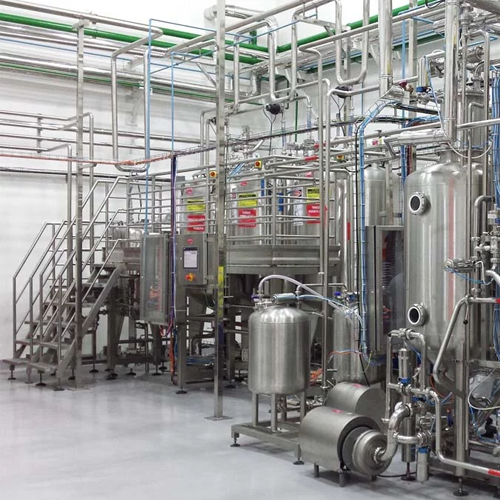
Nectar formulation line for fruit juices
Optimize your fruit-based product lines with a seamless process that integrates hi...

Peach, plum, and apricot juice processing line
Optimize your fruit processing capabilities with a multifunctional solution...
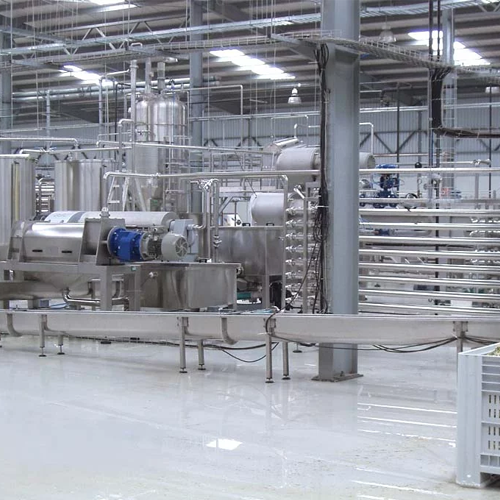
Pineapple juice extraction line
Streamline your pineapple processing with a complete solution designed to efficiently transf...
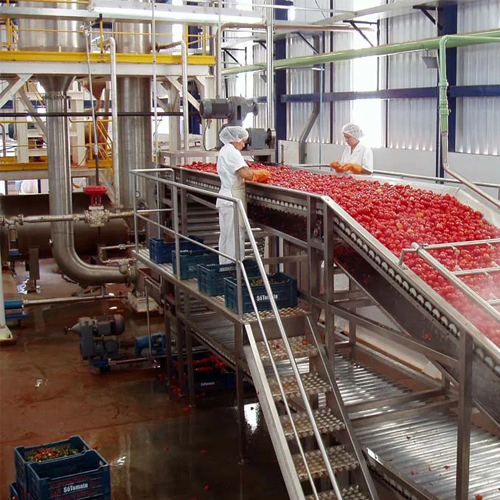
Tomato paste production line
Maximize tomato yield and flavor retention with this robust processing line designed to ensure ...
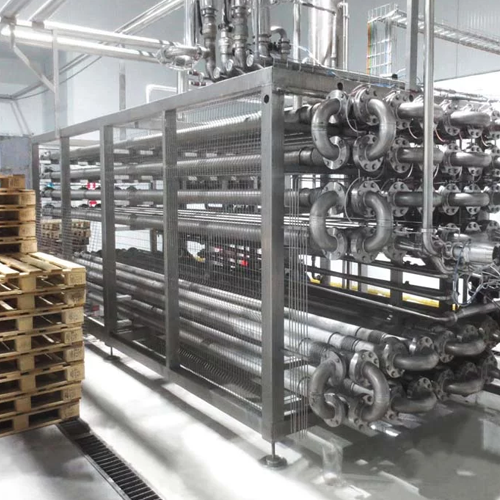
Banana purée production line
Maintain banana pulp quality by processing in a nitrogen atmosphere, ensuring fresh, oxidation-...
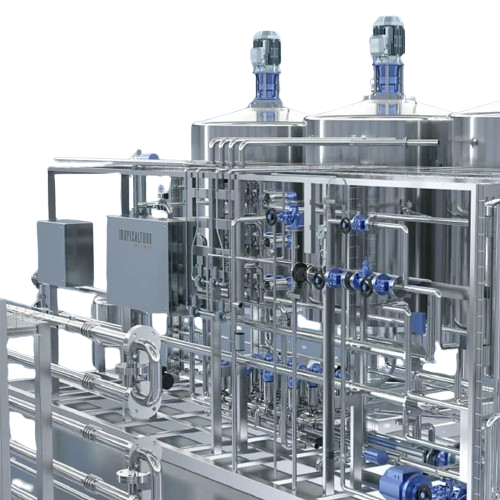
Coconut processing line for green coconut water and cream
Enhance your coconut processing with a fully automatic line th...
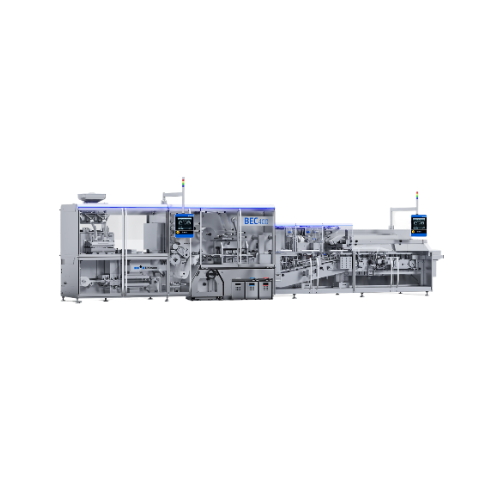
Fully automated packaging lines
Streamline your production with versatile packaging lines designed to handle a range of good...
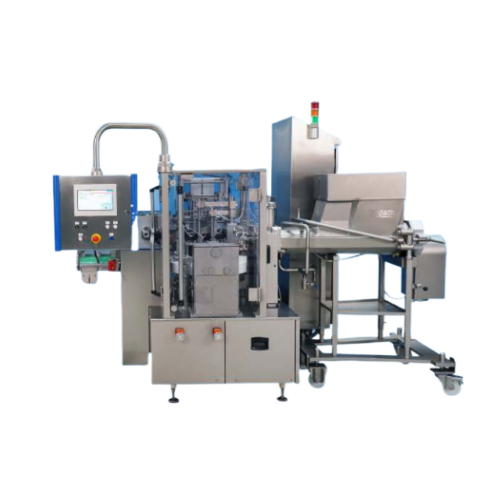
Brick forming and wrapping system for food products
Optimize your production line with seamless forming and wrapping of v...
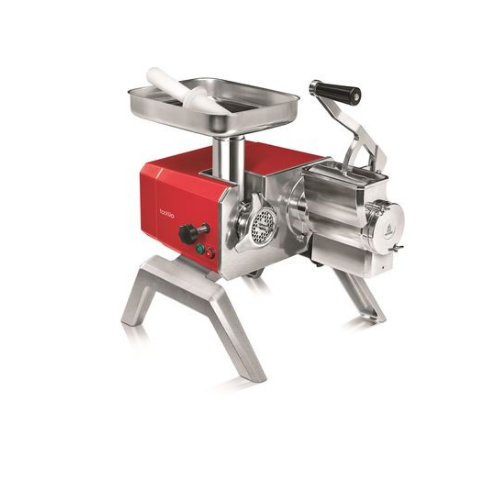
Grinder and grater combination for professional kitchens
This versatile meat processing and cheese grating solution integ...
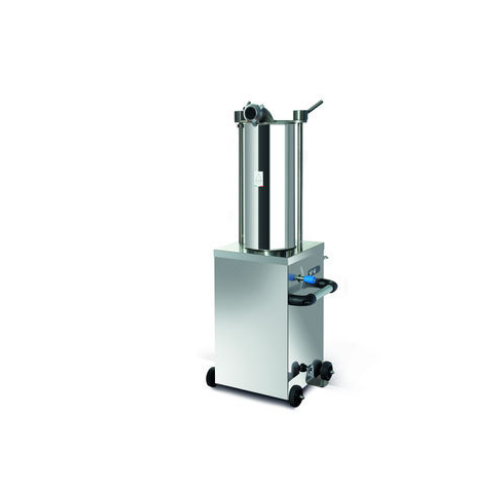
Hydraulic sausage stuffer for professional use
Maximize efficiency in your meat processing line with a solution designed f...
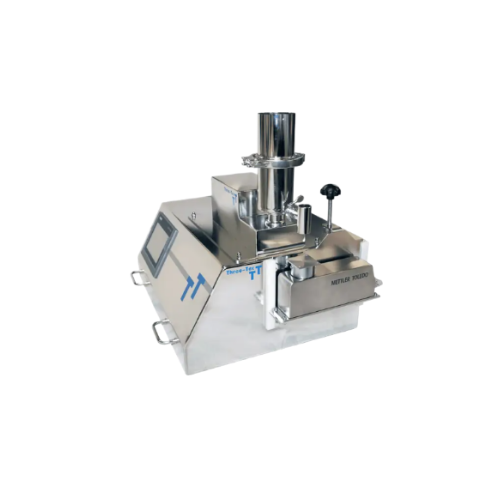
Table-top gravimetric feeding solution for precision batches
Achieve high-precision batch filling with integrated gravim...
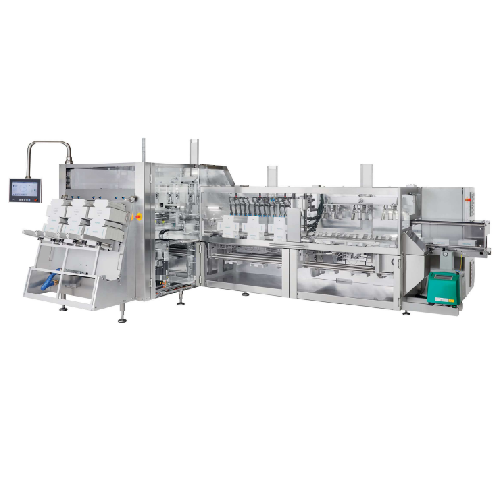
High-speed cartoning system for primary wrapped products
Optimize your packaging line with this high-speed cartoning syst...
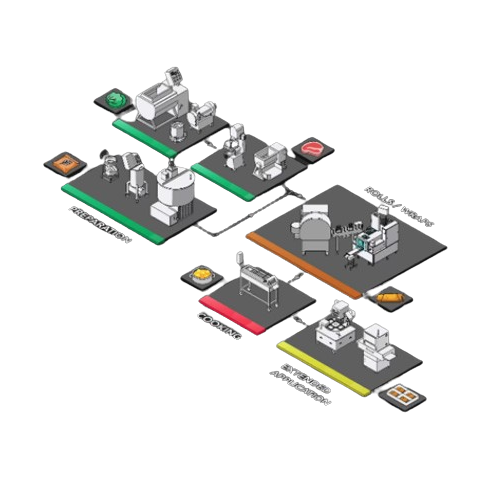
Spring roll manufacturing line
Optimize your spring roll production with an advanced manufacturing line that ensures consist...
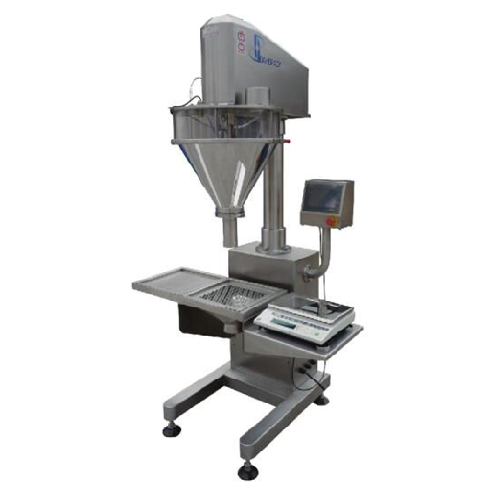
Volumetric auger for powder weighing and depositing
Ensure precise powder weighing and depositing for consistent product ...
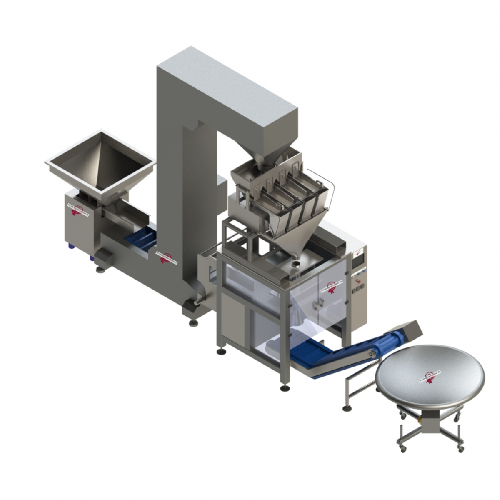
Modular linear packing system for granular products
Streamline your packing operations with a versatile system that integ...
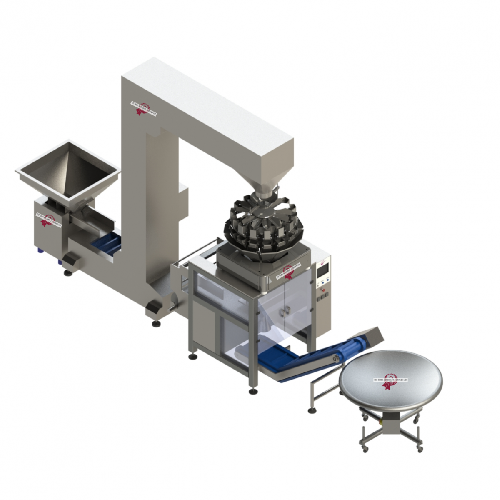
Modular packing system for multihead weighing
Streamline your production with a versatile multihead system designed for pr...
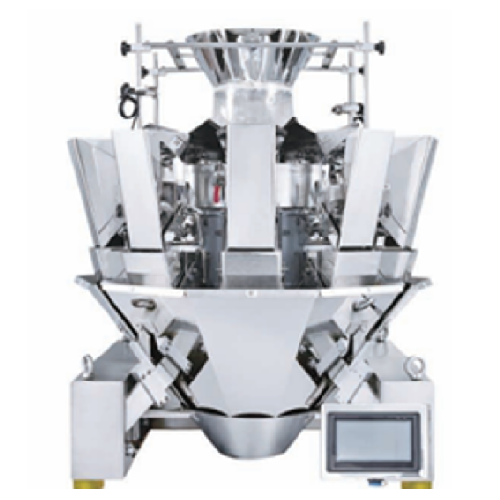
Multihead weighing system for dry free flowing products
Optimize your packaging line with precise weight measurements for...
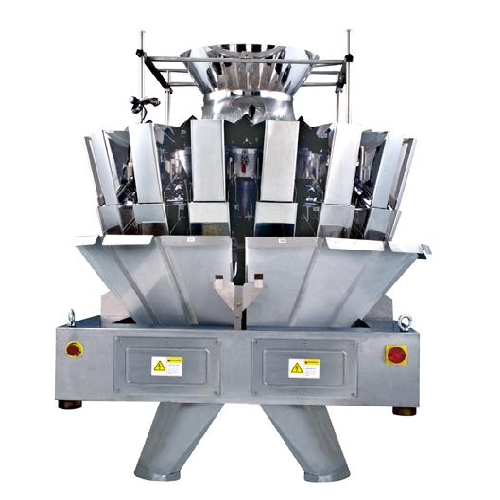
Multihead weighers for food production
Optimize your food production line with precision and speed by integrating advanced ...
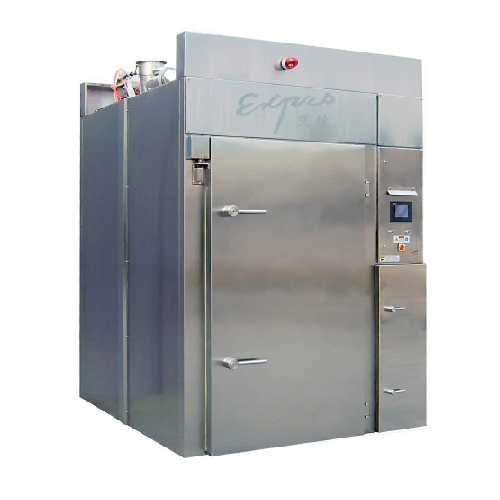
Commercial rice cooking systems
Maximize efficiency in high-volume rice production with precision cooking, soaking, and cool...
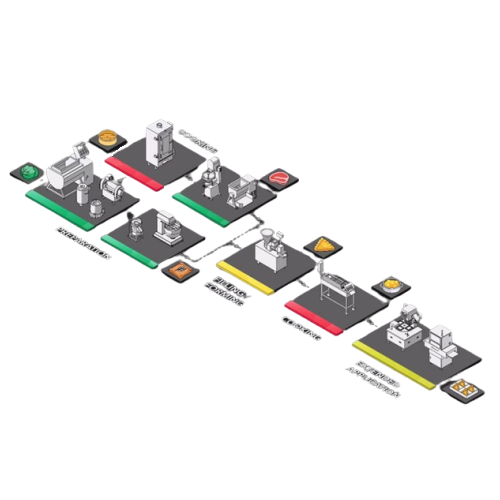
Automatic samosa production system
Optimize your ethnic food production with a machine that seamlessly forms and shapes var...
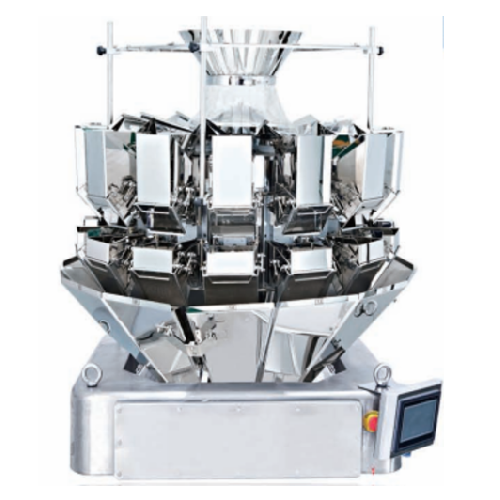
10 head multihead weigher for dry products
Optimize your weighing and packaging operations with precise and rapid handling...
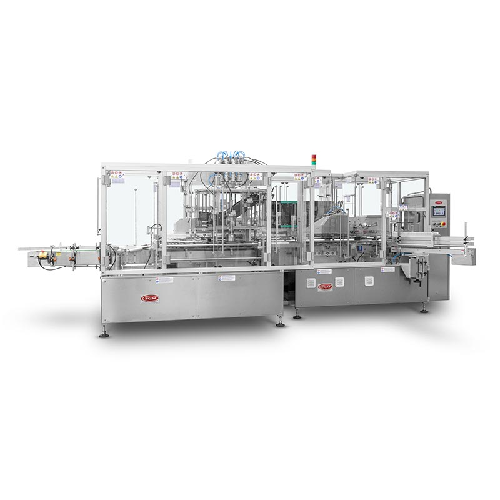
Vertical cartoner for fast and efficient packaging
Streamline your high-speed production by seamlessly integrating vertic...
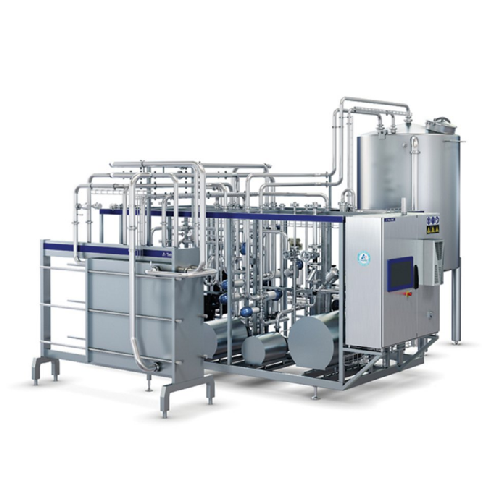
Continuous sugar dissolver for beverage and food production
Efficiently dissolve crystalline sugar in water up to 65°Bri...
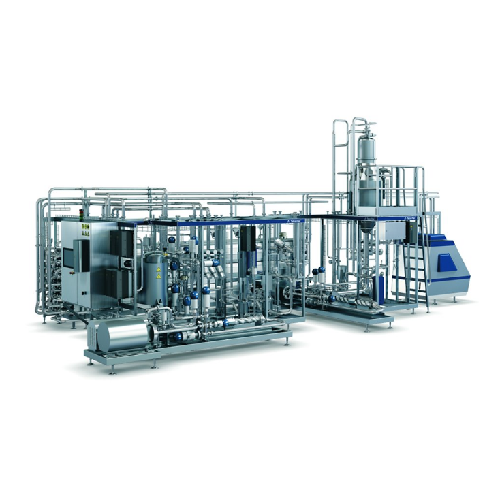
Food pasteurizer for prepared foods
Optimize your prepared food production with precise temperature control and automated o...
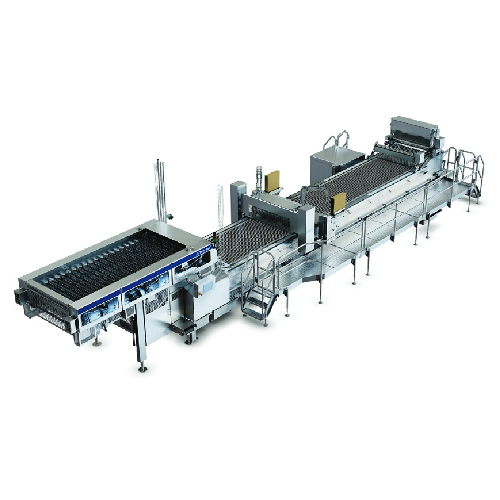
High-capacity ice cream stick production line
Maximize production efficiency with a high-speed, continuous ice cream moldi...
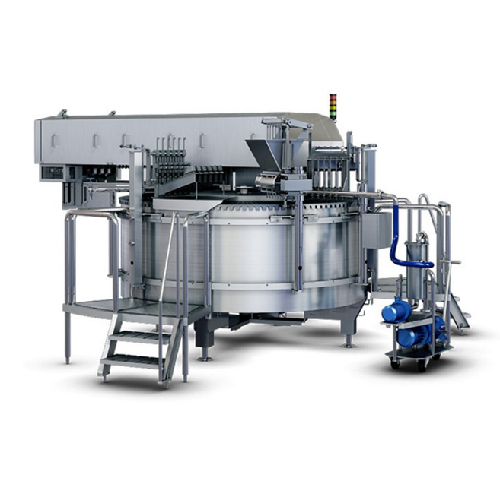
Rotary moulder for ice cream production
Achieve high-speed, precise ice cream moulding with seamless integration into your ...
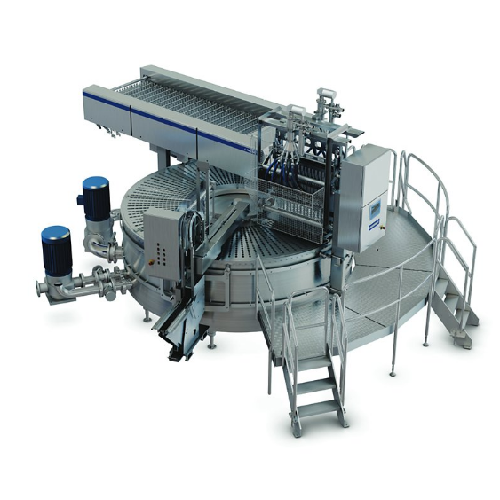
Ice cream rotary moulder 35 a2
Streamline your frozen treat production with high-capacity moulding that supports a variety o...

Ice cream cone production system
Streamline your ice cream production and enhance product quality with a continuous system t...
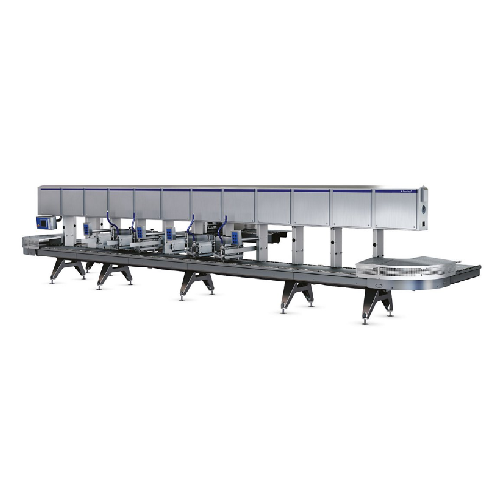
Ice cream extrusion system
Optimize your ice cream production with a versatile system designed for efficient extrusion, shap...
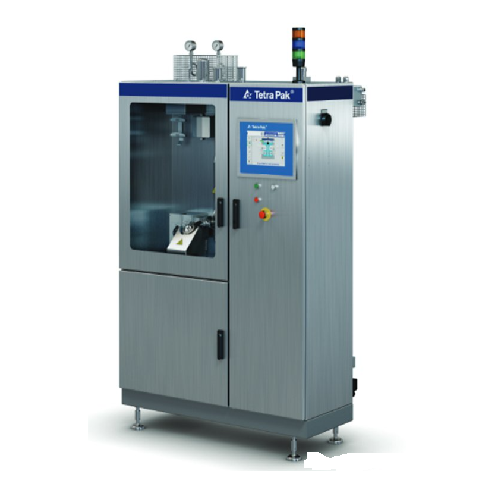
Aseptic dosing system for heat-sensitive ingredients
Enhance product quality and reduce ingredient waste by precisely inj...
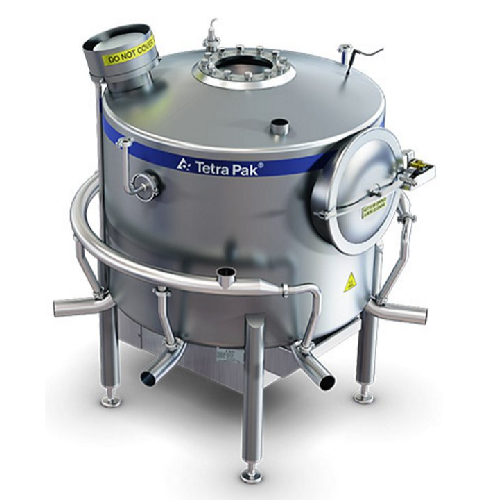
Curd distribution system for cheddar production
Ensure consistent curd distribution for optimal cheese quality with our ad...
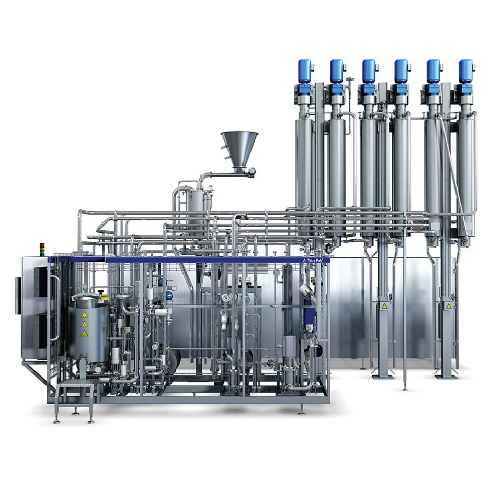
Indirect Uht treatment unit for viscous food products
Ensure uniform heat treatment and consistent product quality in you...
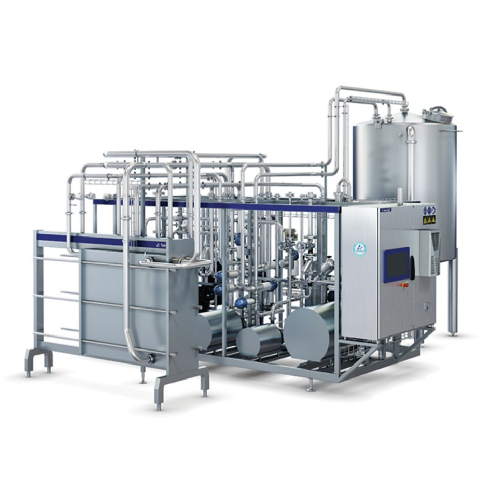
Continuous sugar dissolver for beverage production
Optimize your production line with a system that efficiently dissolves...
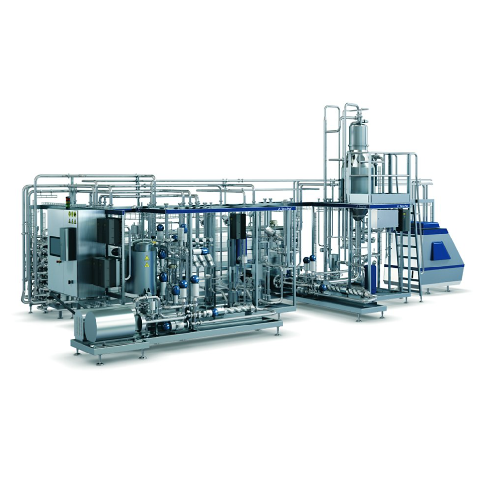
Efficient pasteurizer for prepared foods
Achieve precise heat treatment and reduce product waste with a modular pasteurizat...
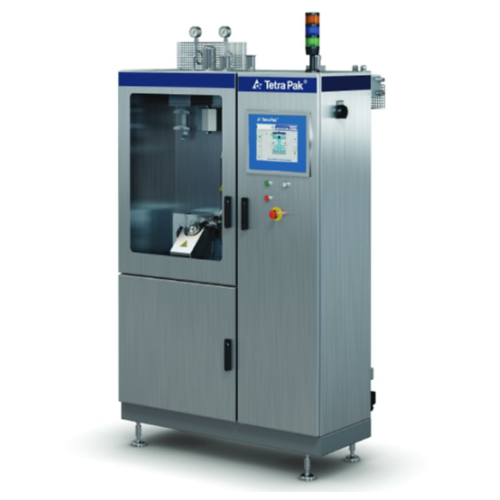
Aseptic dosing unit for sensitive ingredients
Ensure the stability of heat-sensitive ingredients with precise in-line dosi...
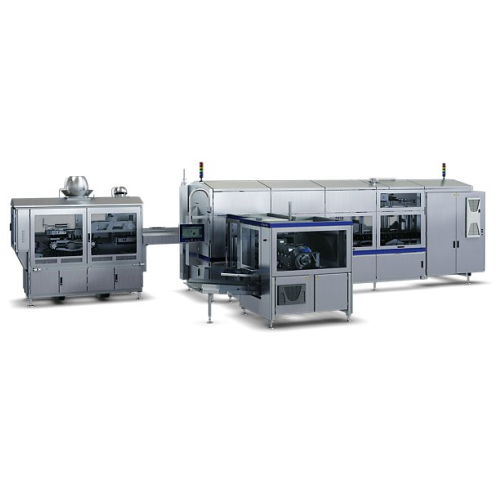
High-speed form and seal machine for retortable food packages
Streamline your production with a machine engineered for h...
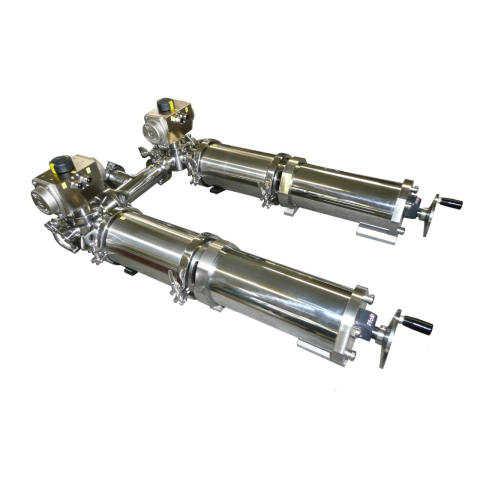
Pneumatic dosing syringes for precise liquid dispensing
Achieve precise and reliable liquid dosing with pneumatic syringe...
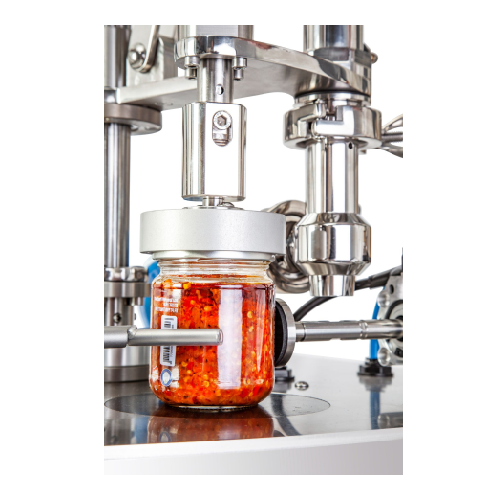
Manual dosing and capping for semi-dense products
Enhance your production line efficiency by seamlessly integrating manua...

Pneumatic syringe dosing system
Streamline your liquid dosing process with precision and efficiency, ensuring each applicati...
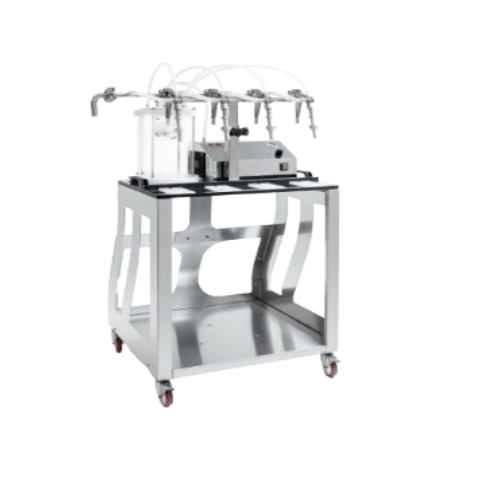
Vacuum bottling equipment for wineries and breweries
Optimize your bottling process with a vacuum solution that fills up ...
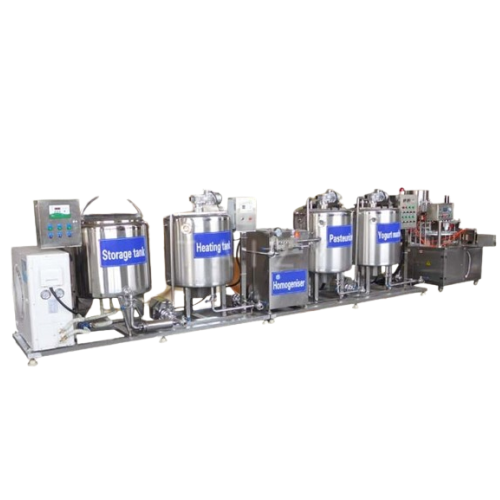
Yogurt production line
Optimize your dairy production with a comprehensive solution that seamlessly transforms milk into a di...
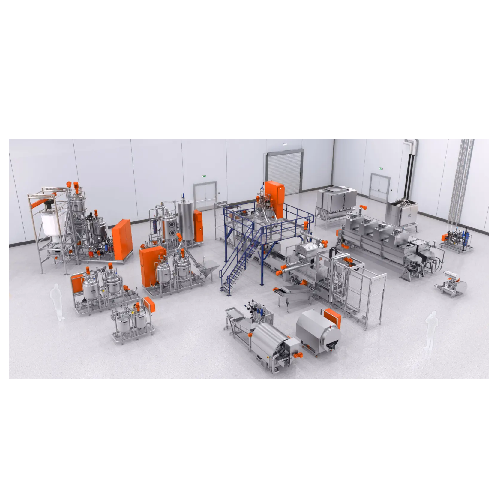
Automatic production line for gummies and nutraceuticals
Maximize the versatility and efficiency of your production space...
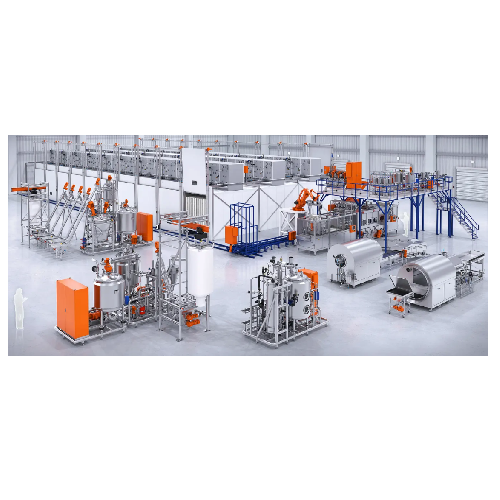
Robotic production line for gummies and nutraceuticals
Streamline your gummy and nutraceutical production with a versatil...
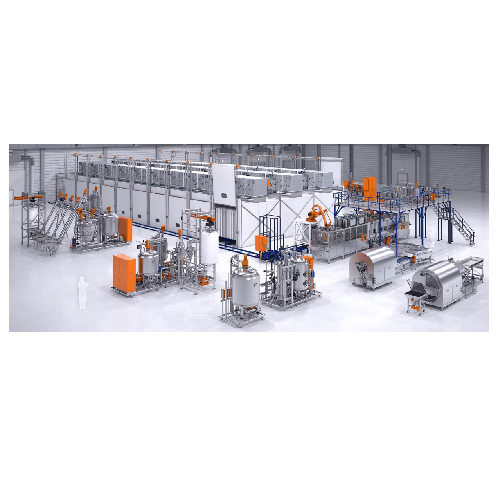
Robotic high capacity production line for gummies and jellies
Optimize your gummy and jelly production with a high-capac...
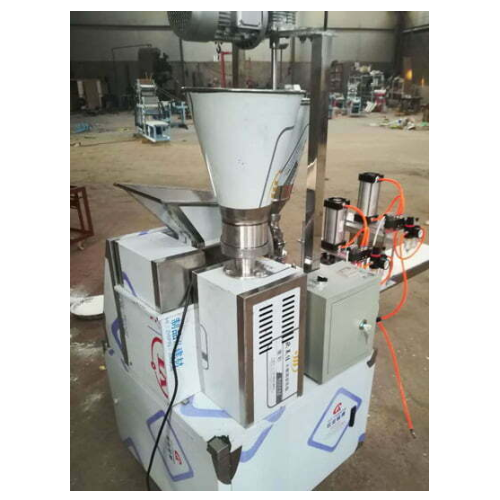
Stuffed paratha making system
Efficiently produce a variety of stuffed parathas with consistent quality by integrating seaml...
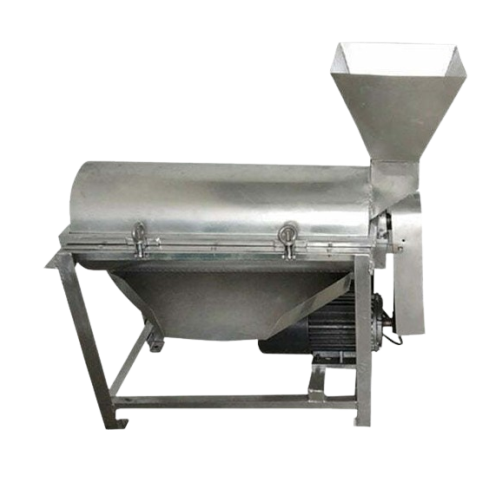
Tomato paste processing line
Streamline your tomato processing with our comprehensive production line, ensuring high-quality...
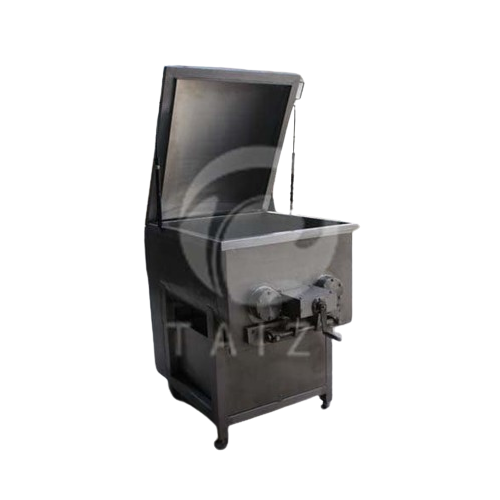
Sausage production line for efficient sausage manufacturing
Streamline your sausage manufacturing with an integrated pro...
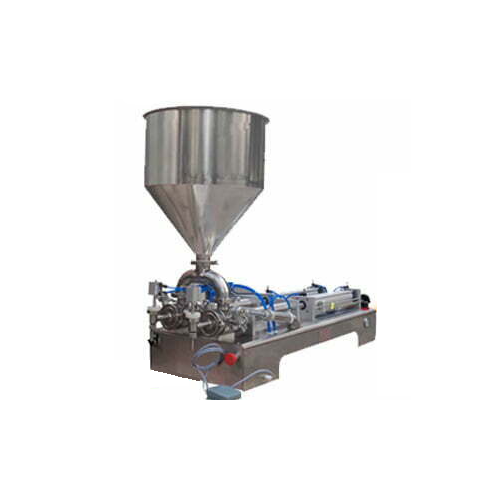
Industrial peanut butter production line
Enhance your production line with this comprehensive peanut butter processing solu...
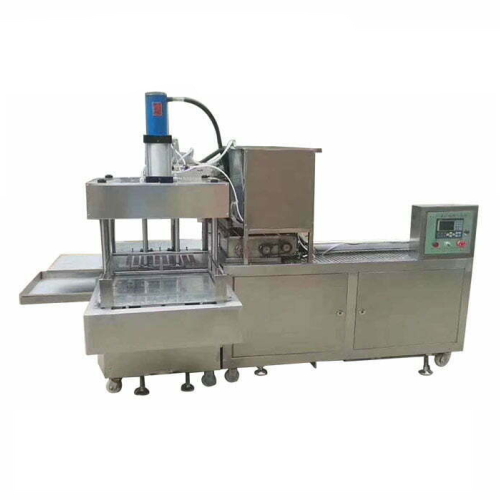
Polvoron and mung bean cake moulding system
Efficiently mold and shape your confectionery creations with this versatile sy...
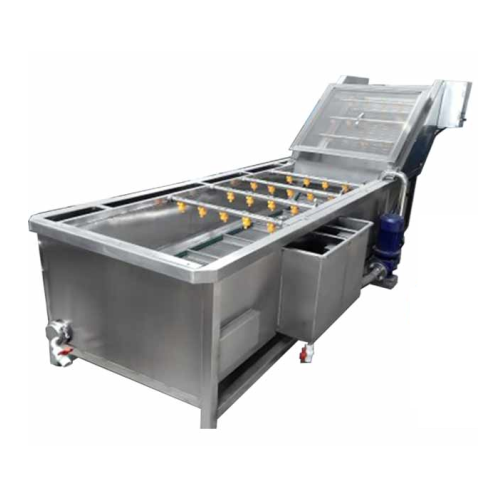
Mango juice production line
Streamline your mango juice production with a complete solution that efficiently transforms fres...
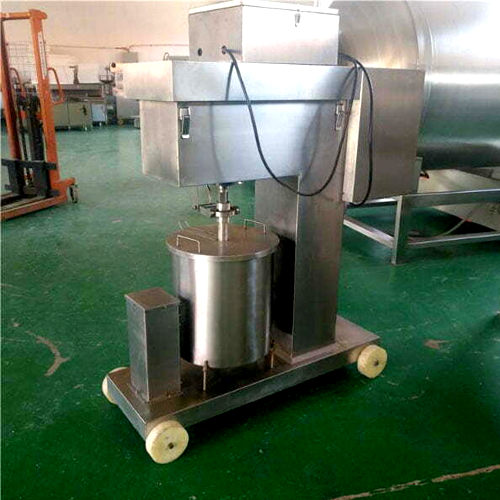
Cupcake production line for automated bakery solutions
Streamline your bakery operations with this comprehensive solution...
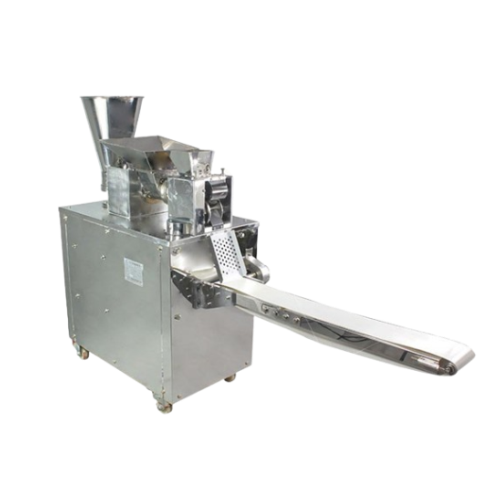
Curry puff and samosa making machine for dumplings and empanadas
Streamline your production of filled dough products lik...
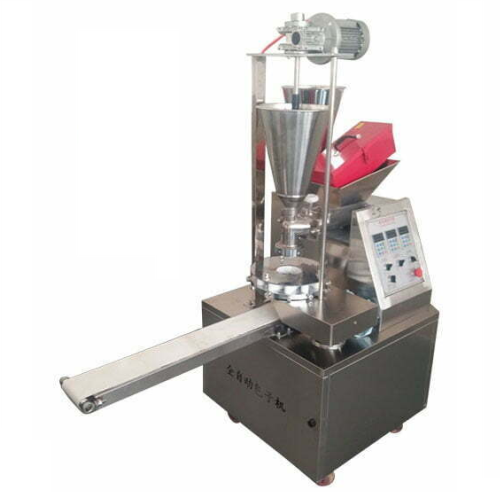
Commercial momo making equipment
Streamline your dumpling and bun production with equipment designed to enhance precision, f...
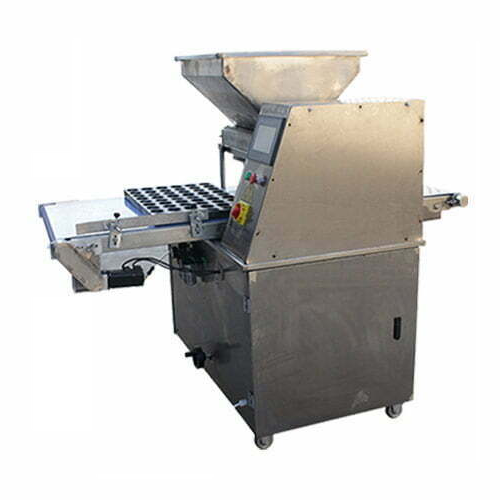
Automatic cake depositor
Streamline your cake production with precision depositing, ensuring consistent batter distribution, ...
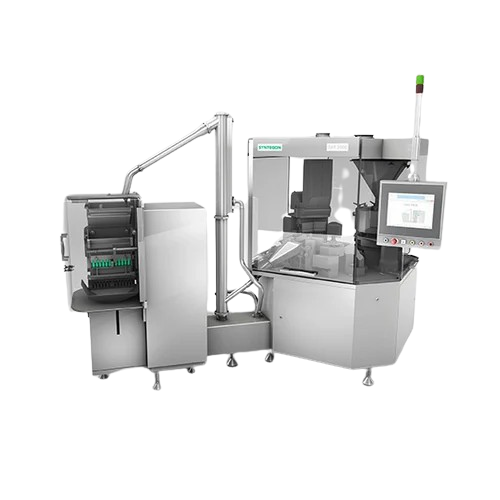
Capsule checkweighing system for pharmaceutical production
Ensure every capsule meets your precision weight standards wi...
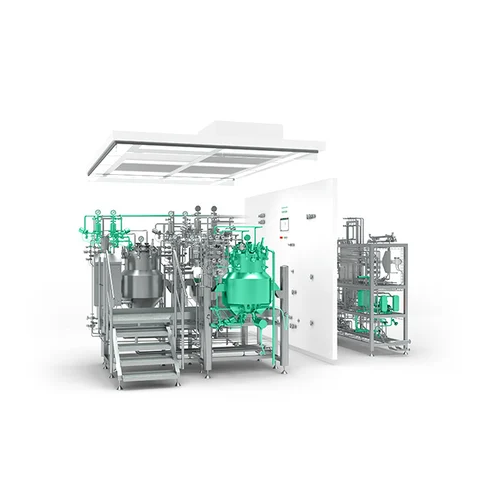
Modular pharmaceutical formulation systems
Achieve unparalleled flexibility and efficiency in liquid pharmaceutical formul...
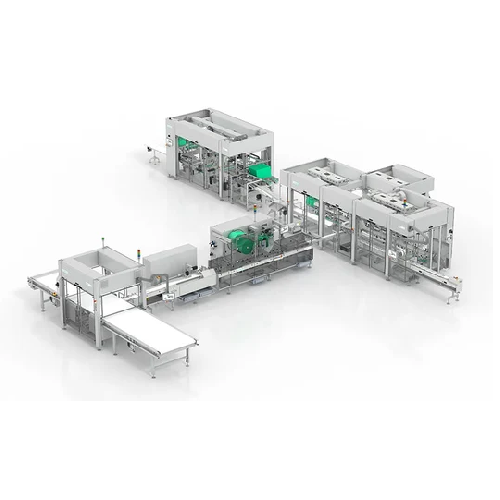
Horizontal flow wrapper for food packaging
Simplify your packaging process with our high-speed horizontal flow wrapper tha...
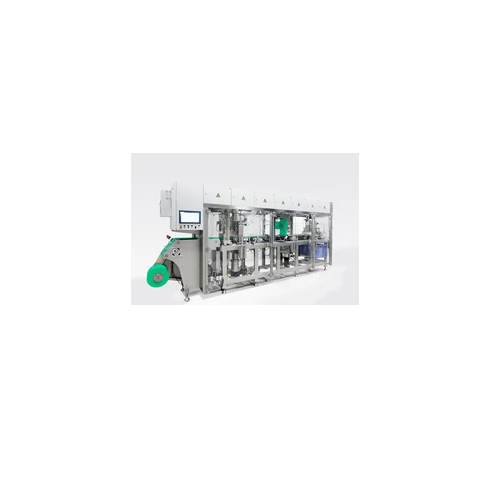
Paper forming technology for sustainable packaging
Elevate your product’s sustainability with advanced paper formin...
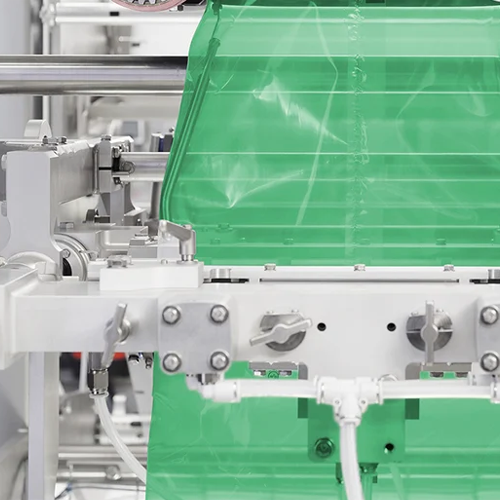
Vffs packaging solution for diverse bag styles and high hygiene standards
Enhance your packaging operations with high-...
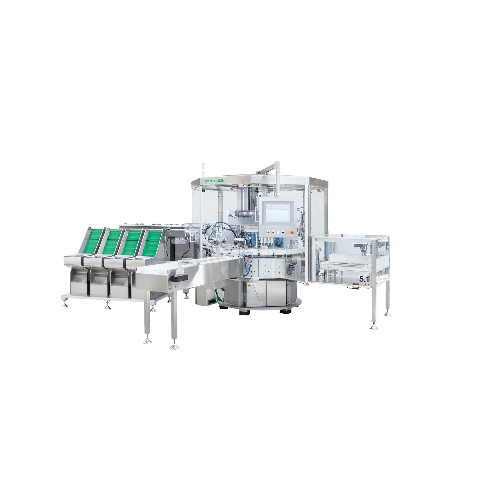
Assembly solutions for medical devices
Optimize your medical device production with specialized assembly solutions that ens...
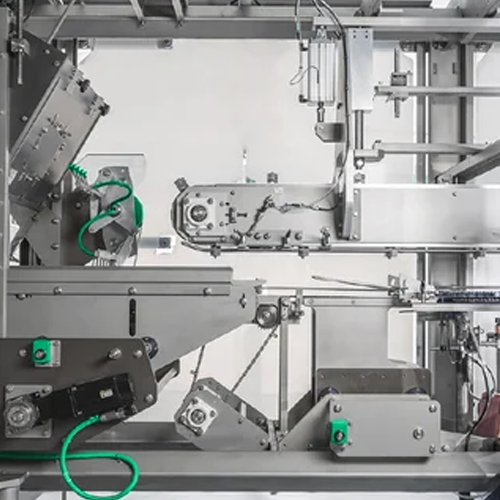
Nutraceutical products processing and packaging
Streamline your nutraceutical production with versatile equipment capable ...
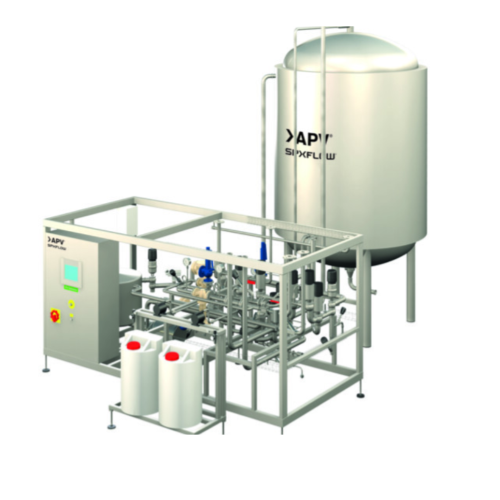
Aseptic storage tank for aseptic products
Ensure uninterrupted aseptic product storage with this advanced tank system, des...
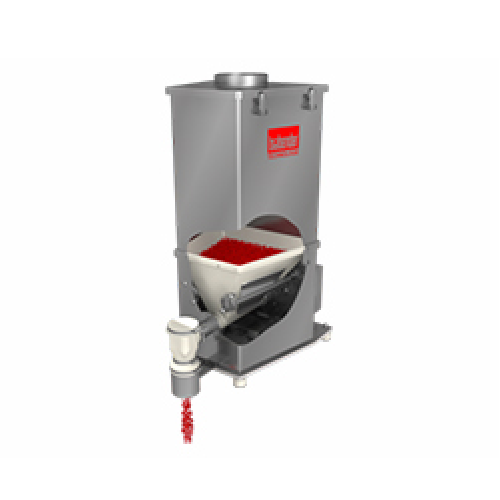
Precision batch feeder for flowable ingredients
Achieve precise ingredient control with a batch feeder designed for versat...
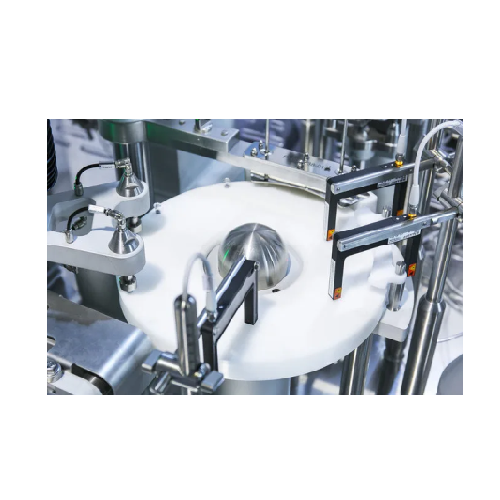
Sterile syringe plunger placement system
Ensure precision in syringe assembly with enhanced plunger placement, maintaining ...
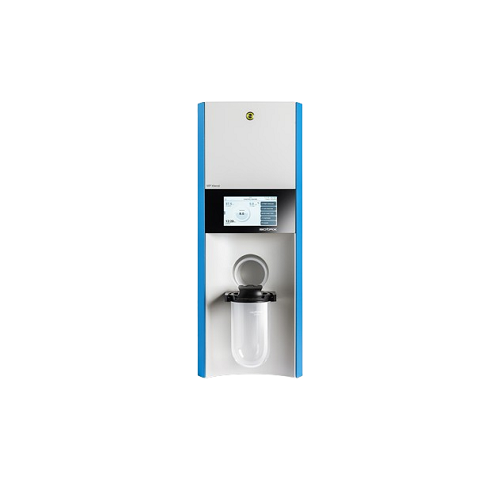
Dissolution medium preparation system
Streamline your laboratory workflows with a system that prepares and manages dissolut...
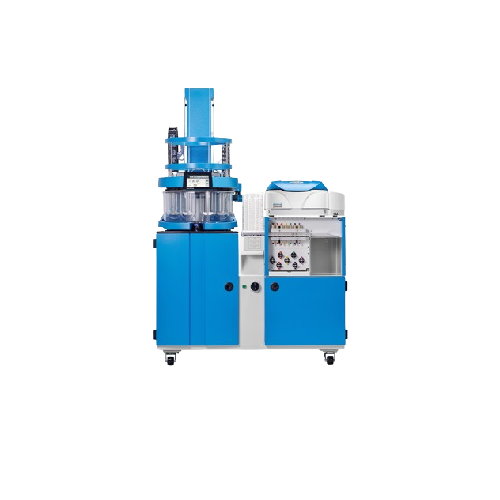
Advanced dissolution tester for pharmaceutical laboratories
Achieve consistent and reproducible dissolution results with...
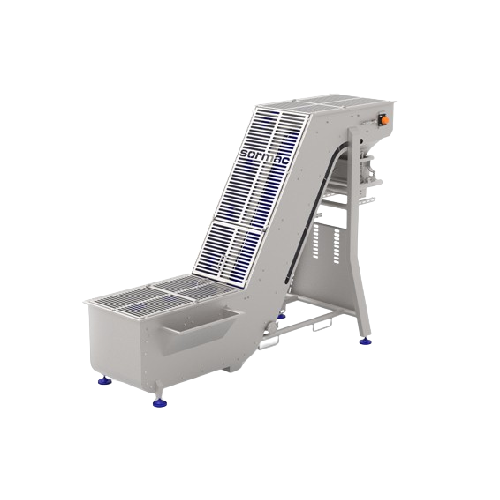
Potato weighing solution for high-precision processing
Achieve precise portioning for packaged vegetables and potatoes wi...
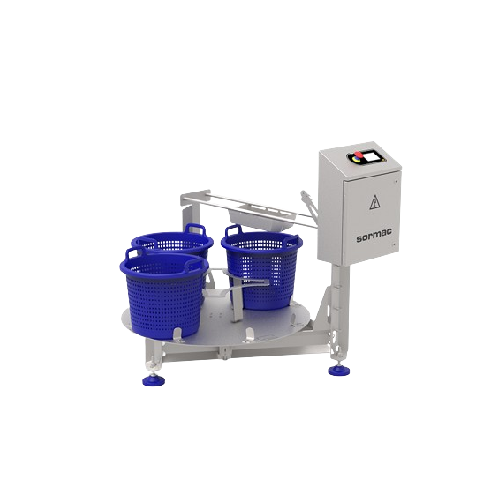
Automatic basket carousel for vegetable washers
Streamline your vegetable processing with a solution that efficiently fill...
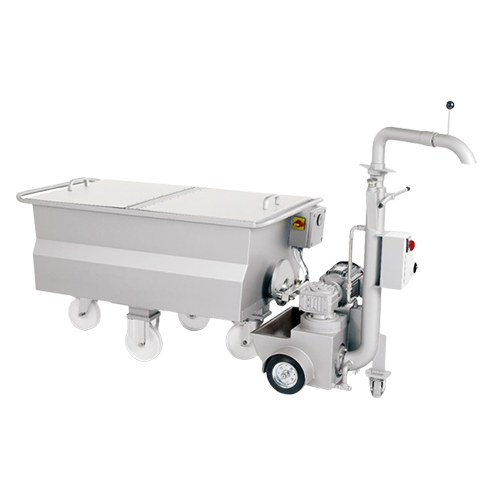
Bulk chocolate storage for confectionery production
Maximize space efficiency while maintaining product quality with our ...
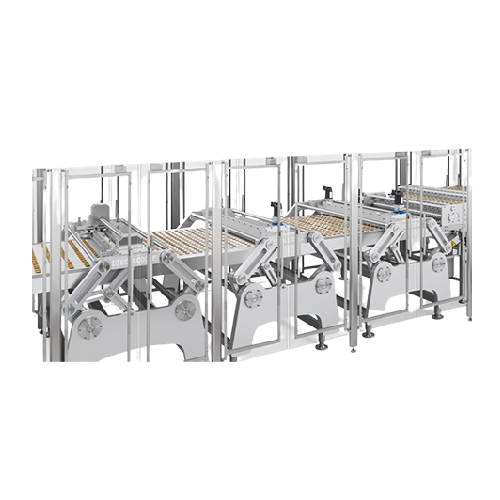
High-precision biscuit sandwiching system
Efficiently align, fill, and sandwich high-speed biscuit rows while ensuring pre...
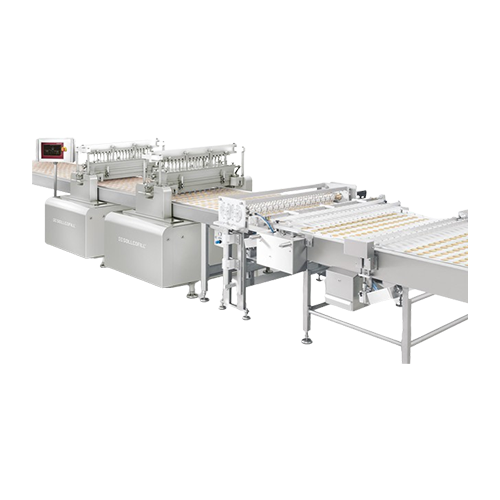
Weight-accurate depositor for confectionery refinement
Achieve precise filling and refinement of biscuits and confections...
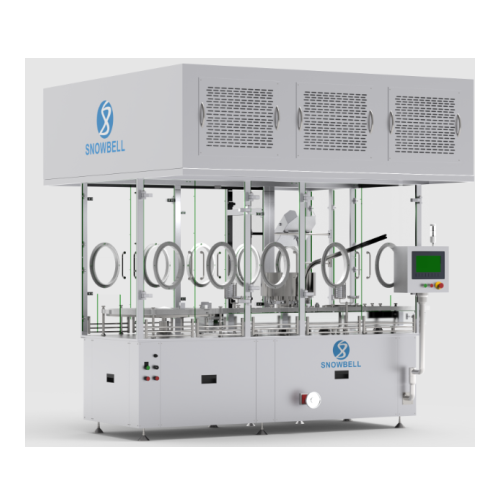
Vial washing system for internal and external cleaning
Streamline vial preparation with comprehensive washing, sterilizin...
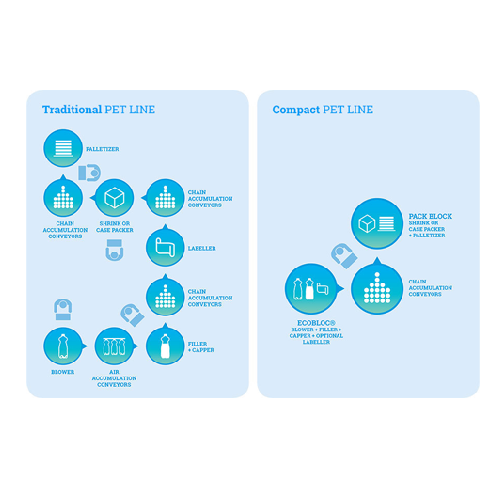
Compact bottling line for water
Revolutionize your bottling process with a compact solution that integrates multiple operati...
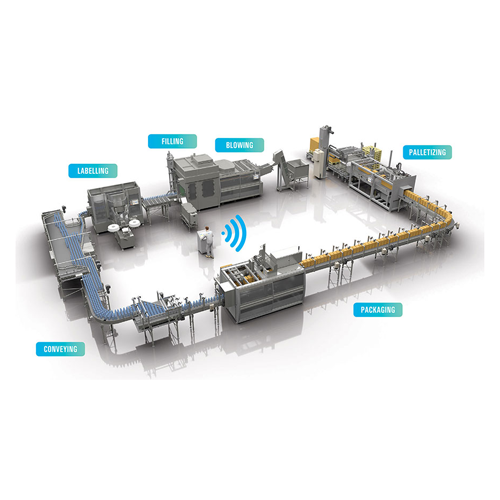
Complete bottling lines for beverages
Achieve seamless integration and high-speed efficiency in your liquid product packagi...

Dosing system for bakery and convenience food
Achieve precise dosing and filling of liquids and slurries with this versati...

Integrated preform production and bottling system for Pet bottles
Achieve seamless production of PET bottles, from pref...
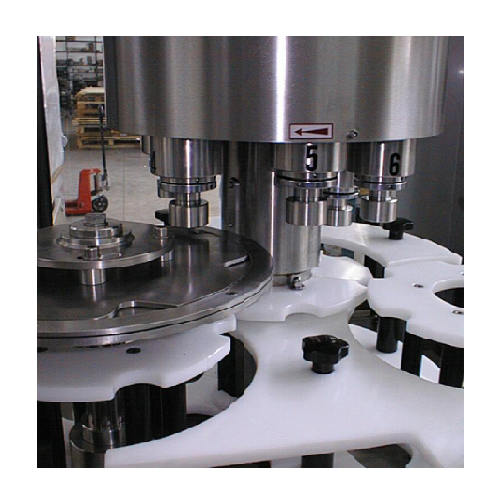
Automatic counting and capping system for tablets and capsules
Ensure precise tablet and capsule counting and seamless c...
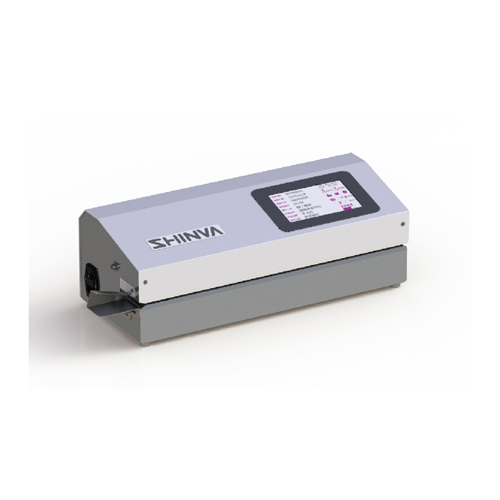
Cutting and sealing solution for medical packaging
Optimize your sterile packaging process with precision cutting and sea...
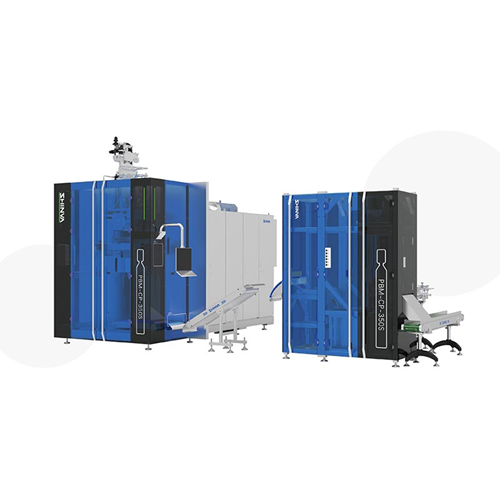
Single-mold continuous bottle Bfs solution
Optimize aseptic production with this advanced solution, offering superior ster...
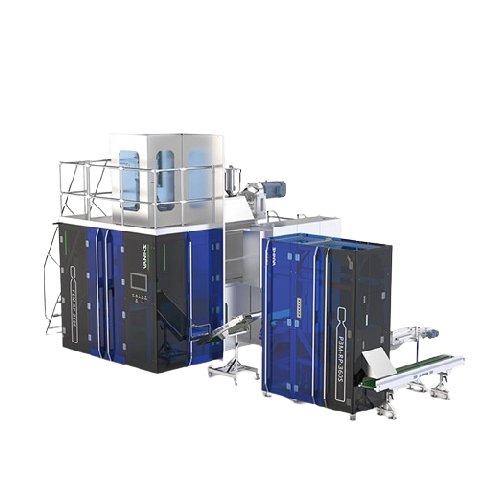
Multi-mold continuous plastic bottle Bfs solution
Optimize your aseptic product operations with a high-efficiency solutio...
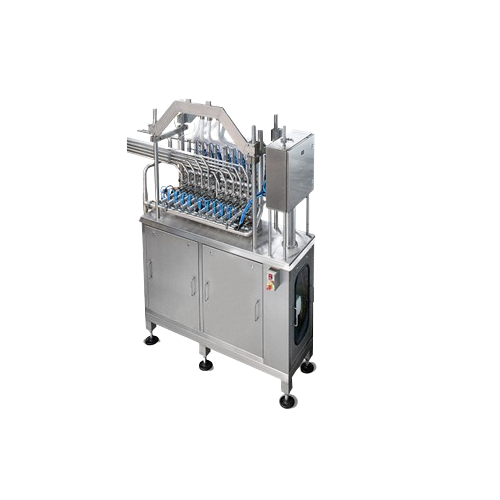
Dosing system for packaging lines
For producers looking to optimize their packaging lines, this dosing system offers precis...
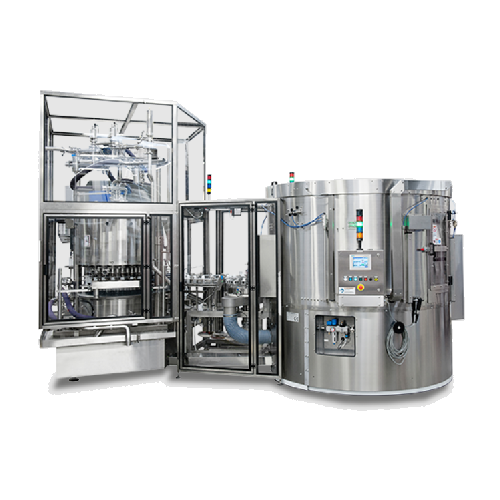
Space-saving packaging solution for high-velocity production
Optimize your manufacturing floor space with a versatile in...
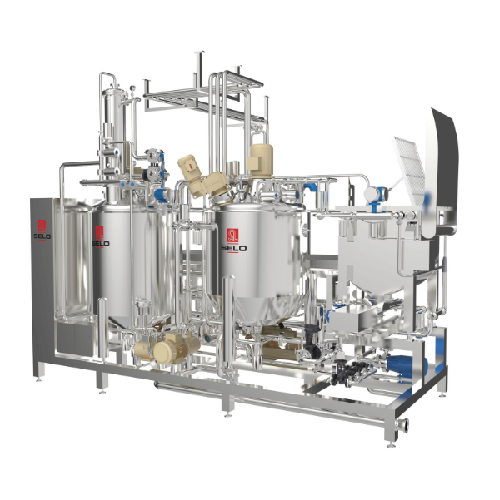
Automated soup production line
Transform your soup production with a high-efficiency, fully automated line, seamlessly integ...
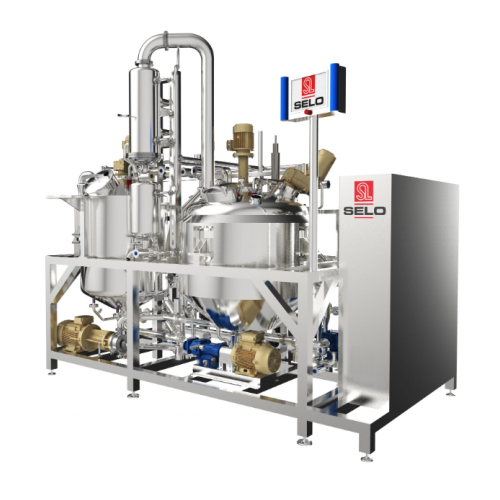
Efficient jam and marmalade production line
Optimize your fruit and bakery product lines with equipment designed for high-...

Simultaneous chocolate dosing solution
Achieve high-precision chocolate and ganache filling in a single step with this effi...
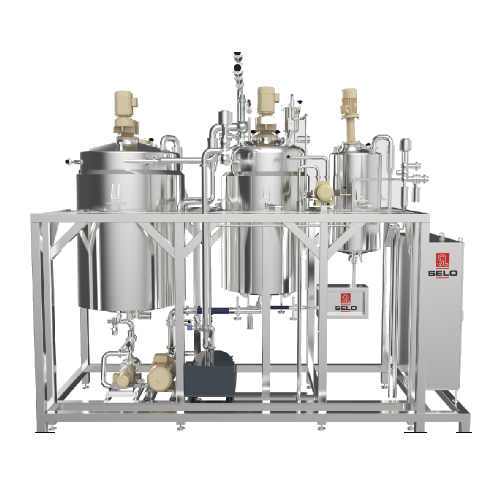
Baby food production line
Ensure optimal safety and precision with this production line, designed for processing delicate ba...
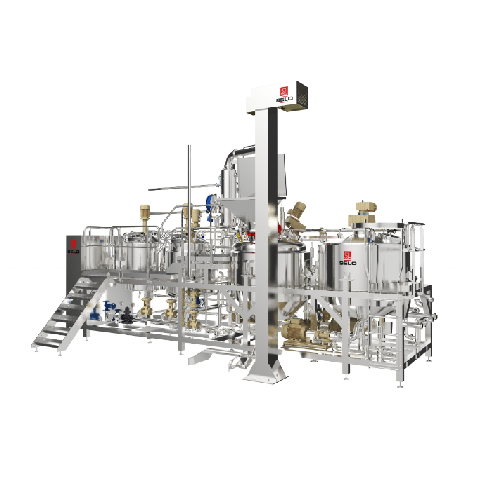
Jam production line
Optimize your jam production with our sophisticated line that ensures high capacity, consistent quality, ...
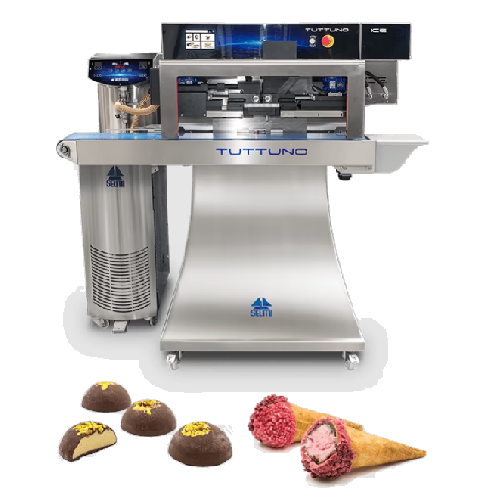
Simultaneous chocolate and ice cream dispenser
Unite the worlds of chocolate and ice cream with a machine capable of seaml...
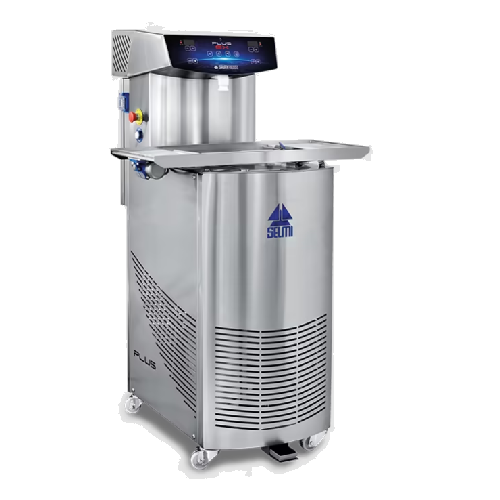
Professional chocolate tempering system for artisan chocolatiers
Achieve precise chocolate tempering with quick changeov...

Automatic heated mould loader for chocolate production
Streamline your chocolate production with this heated mould loader...
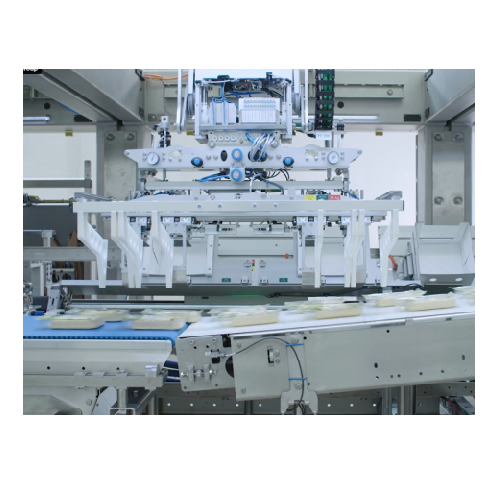
Case packer for diverse packaging needs
Optimize your production line with this modular case packer, designed to handle div...
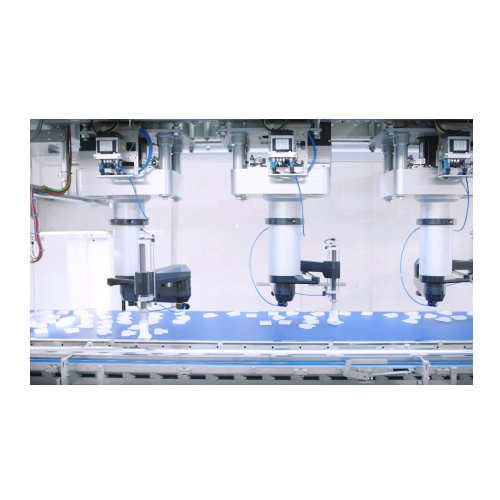
Compact carton packing solution for standardized tasks
Streamline your packaging workflow with a preconfigured solution d...
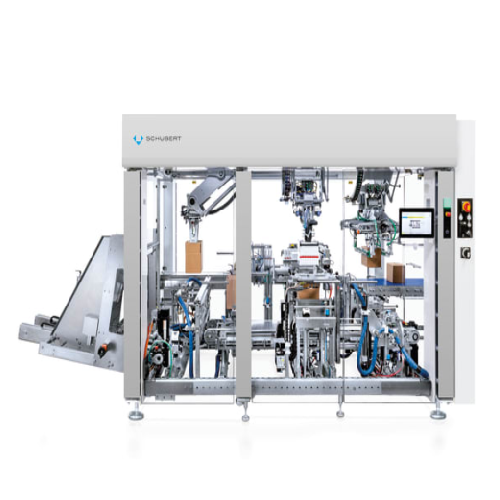
Ultra-compact case packer for consumer goods
Maximize efficiency on your production floor with a compact case packer desig...
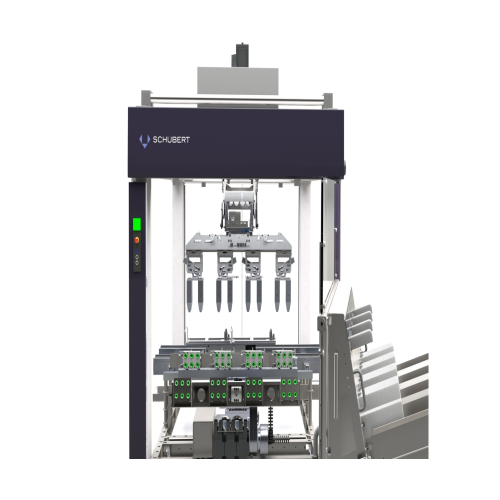
Modular packaging systems for diverse industries
Effortlessly adapt to market demands with versatile packaging systems, de...
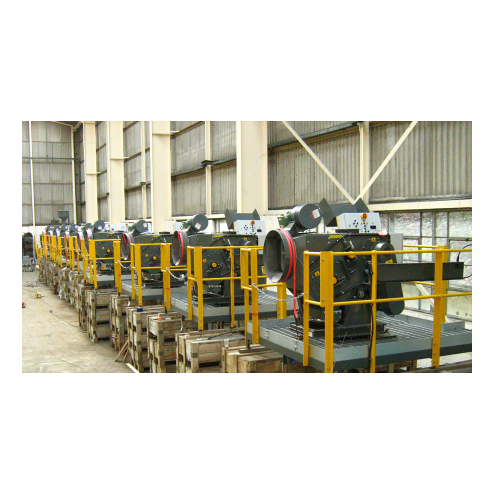
High-speed container loading system for granulated bulk materials
Optimize your loading operations with a robust system...
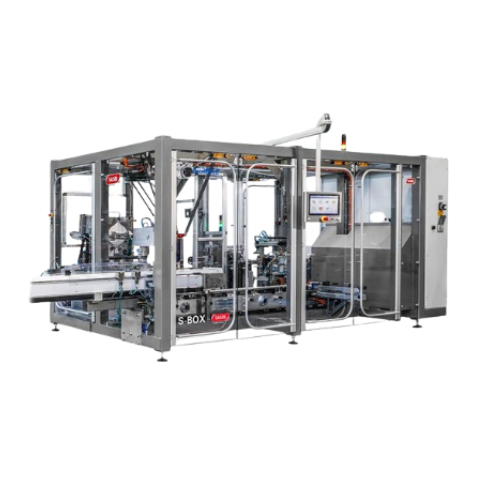
Wrapper and cartoner for e-commerce packaging
Streamline your packaging line with efficient cartoning and wrapping solutio...
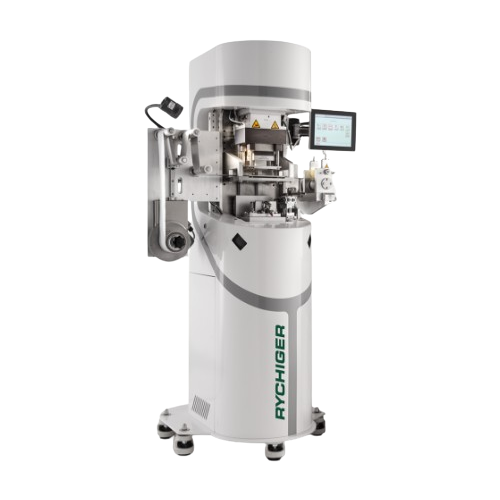
Lab punching and sealing system for cleanroom conditions
Test and refine your packaging processes with precision, ensurin...
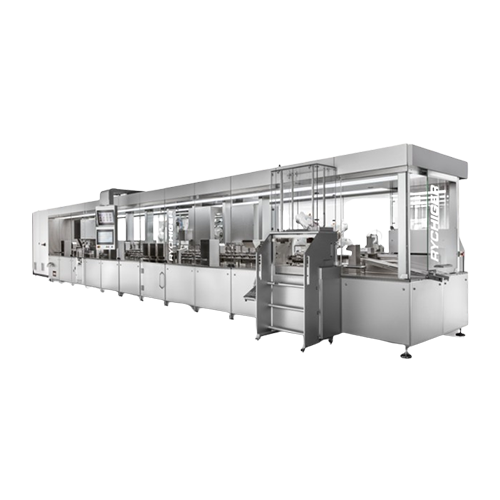
Production system for molecular diagnostics
Eliminate bottlenecks in molecular diagnostics production with a versatile sys...
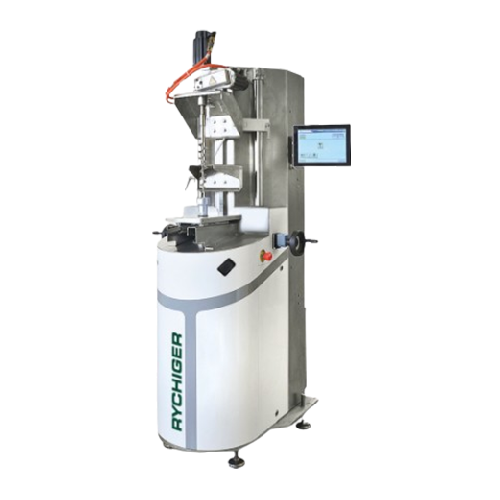
Lab device for testing coffee capsules
Achieve precise testing and reproducibility of coffee capsule parameters crucial for...
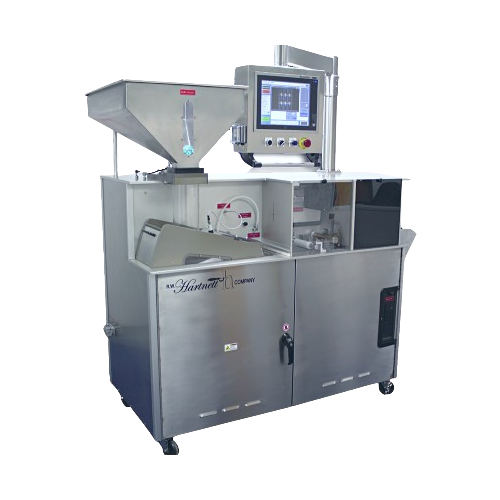
Flatbed laser drilling for tablet manufacturing
Optimize your tablet production with high-speed laser drilling, ensuring p...

Tablet and capsule ink printing and laser writing solution
Maximize efficiency in marking and coding with a high-speed s...
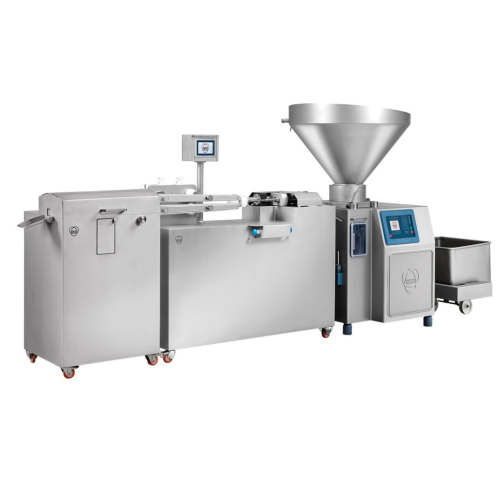
Sausage production line with in-line cutting system
Efficiently achieve precise portion control and separation in sausage...
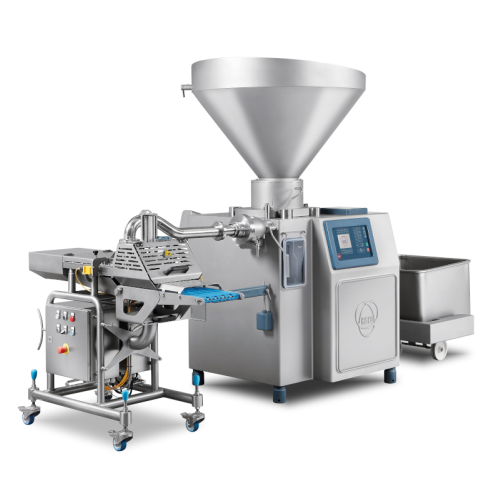
Double head forming system for burger production
Streamline your burger production with a high-speed forming system that e...
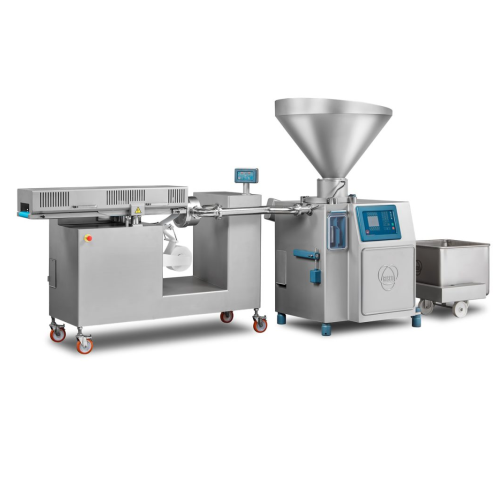
Portioner for ground meat production
Effortlessly streamline your high-volume meat processing with a versatile system desig...
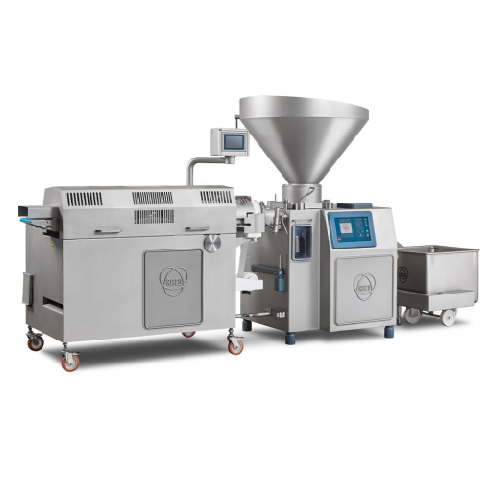
High speed portioner for minced meat and burgers
Optimize your production speed and portioning precision with this high-pe...
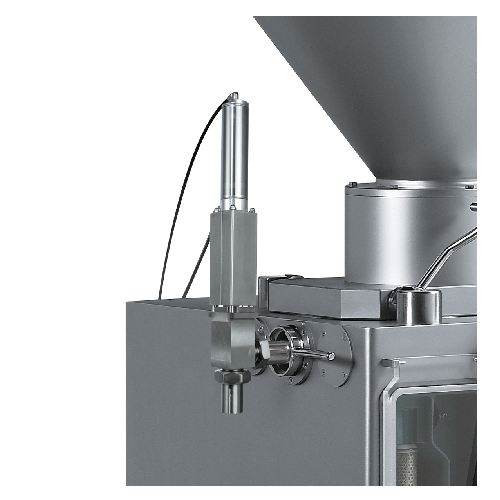
Vertical dosing valve for accurate food portioning
Ensure precision in portioning liquid and semi-liquid food products wi...
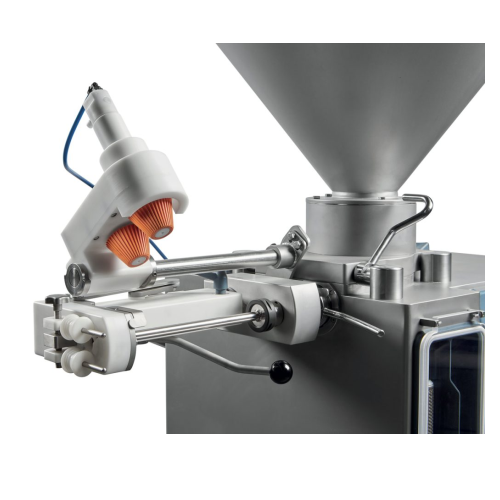
Casing spinner for natural sausage casings
Improve efficiency in your sausage production by seamlessly integrating natural...
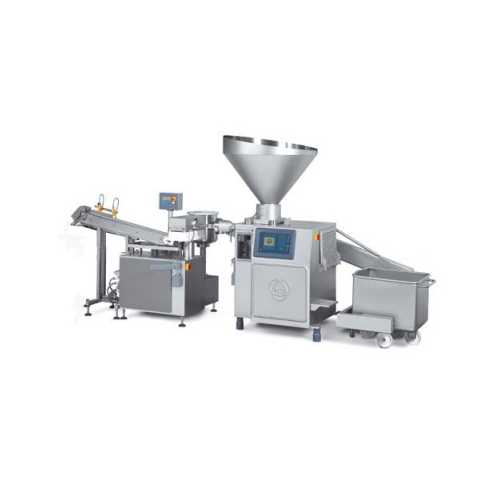
Innovative sausage production with vegetable coating
Optimize sausage production with a vegetable-based alginate coating,...

Automatic butter wrapping machine
Do you pack your butter wraps in aluminium foil, parchment paper or ecoline solutions? An...
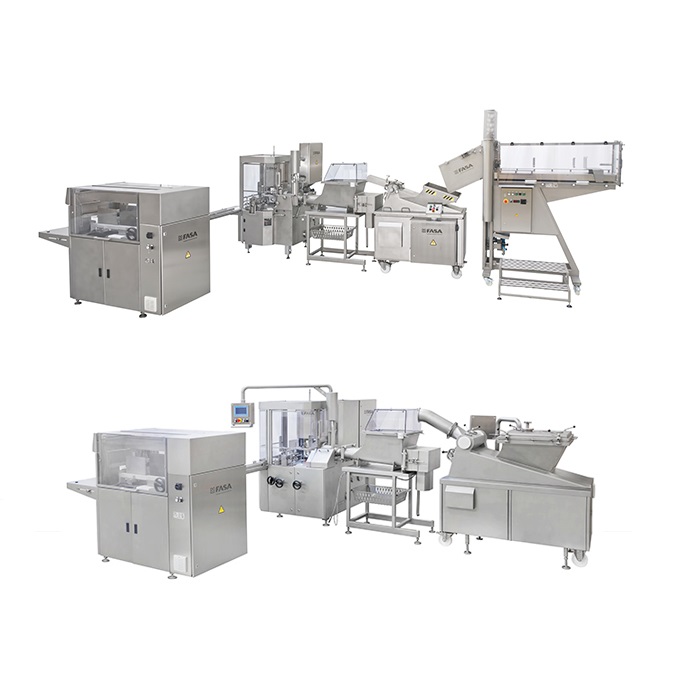
Butter Re-packaging Line
Although bulk butter blocks are commonly used in commercial food production, they are heavy and diff...

Foil wrapping machine for cream cheese
When producing cream cheese and selling them in foil wrapped bricks you need a relia...
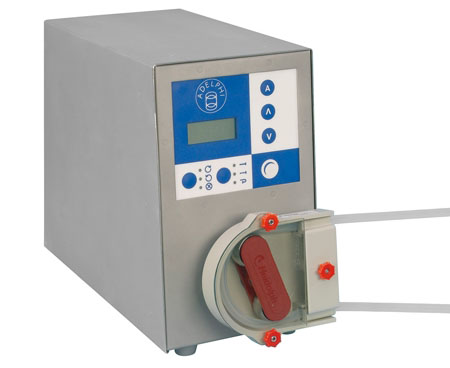
Benchtop peristaltic dispenser
When you fill vials and ampoules, high standards of hygiene are required to avoid the risk of...
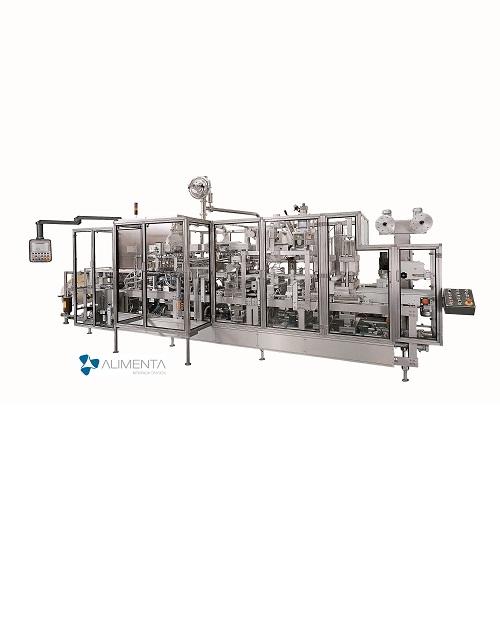
High-speed FFS machine for water cups
Packing water in cup containers, asks for good hygiene in order to avoid contaminatio...
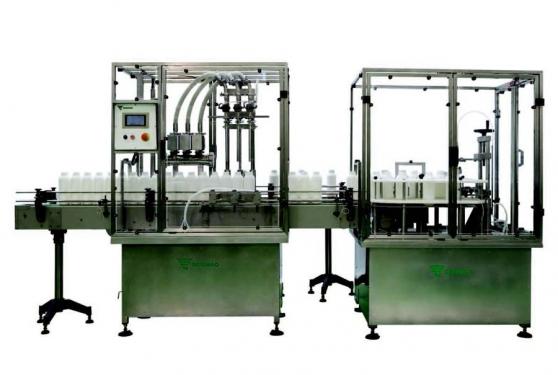
Linear automatic bottling machine for liquids
Autonomous filling systems are a very widely utilized solution for the consi...
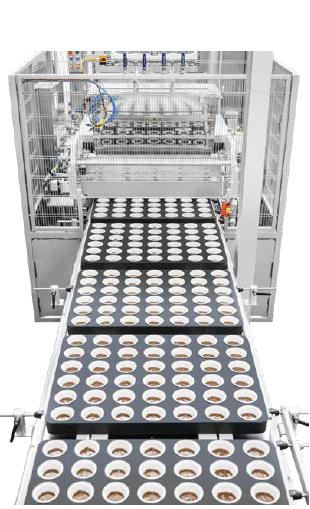
Cake batter and cream depositing machine
Whether you’re making muffins or cupcakes, you need just the right amount of...
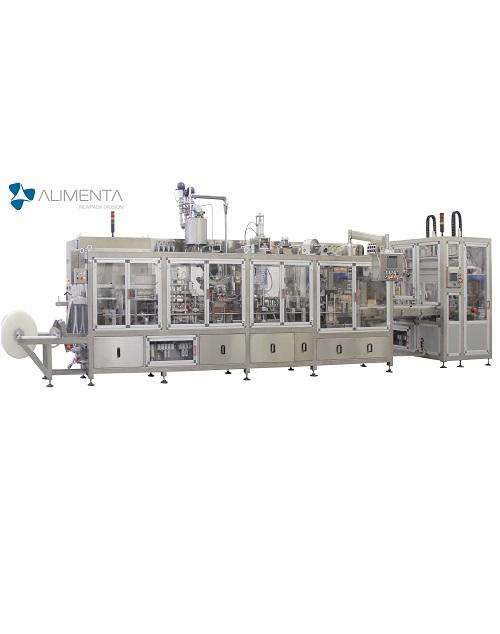
High-clean FFS machine for butter in mini portions
With the production of dairy products such as butter in mini portions ...
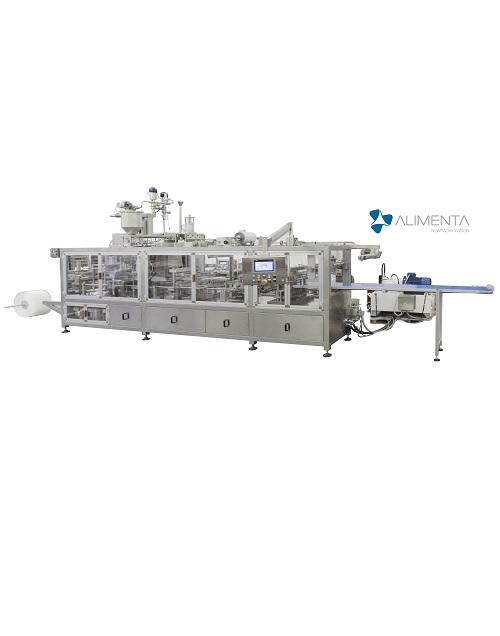
Ultra-clean FFS machine for yoghurt in cups
Dairy products like yoghurt are very susceptible to spoilage. Yeasts and mould...
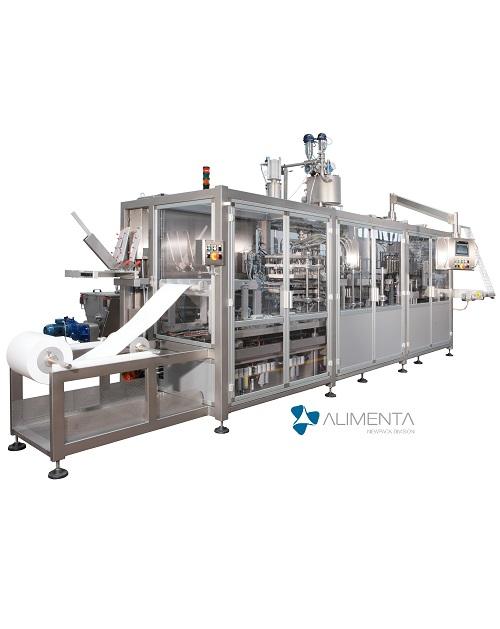
Standard FFS machine for spreads and sauces in mini portions
In the food industry, from a microbiological point of view,...
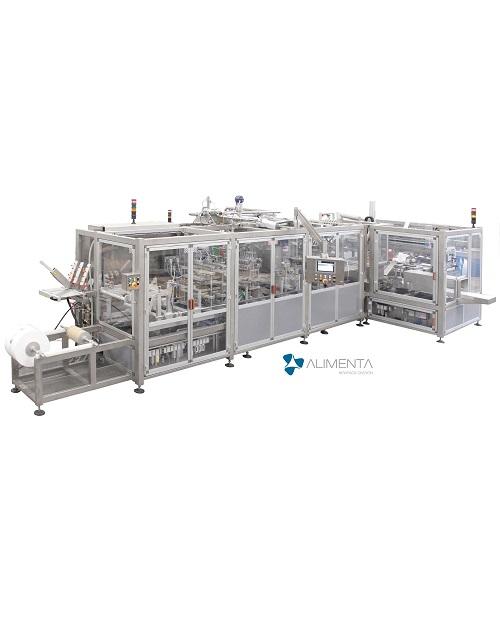
Aseptic FFS machine for UHT products
UHT products (ultra high temperature processing) such as sterilized milk, are products...
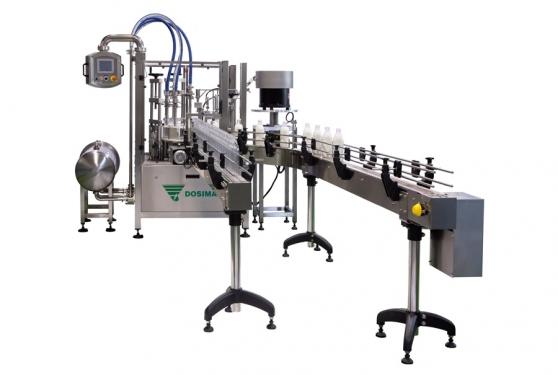
Automatic bottling machine for beverage
One of the biggest challenges when bottling beverage drinks is that many of the bot...
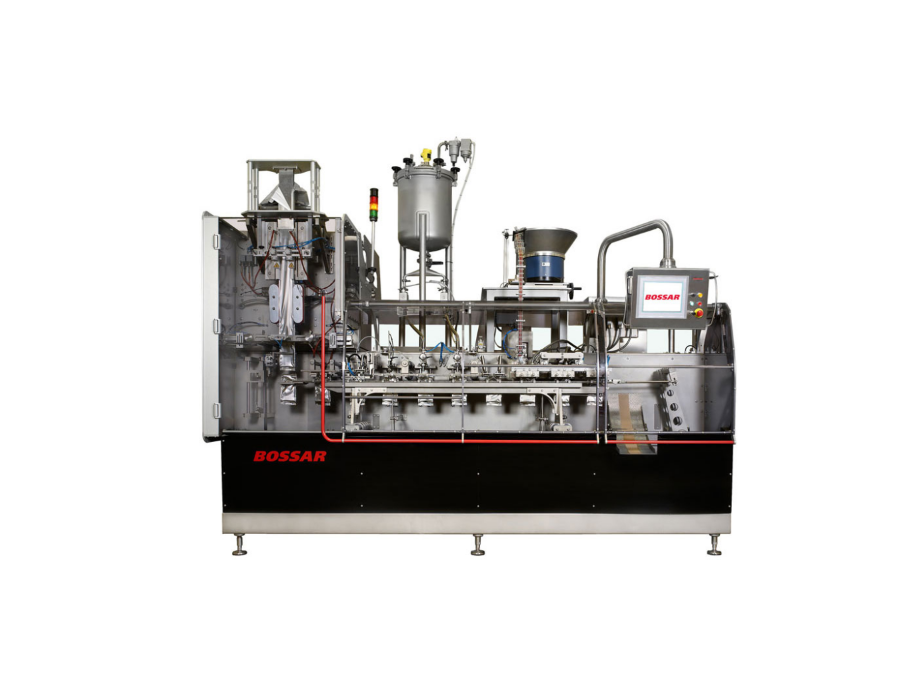
Economical Pouch Packaging Machine
The side gusset pouch is a popular packaging solution for medium formats, particularly f...
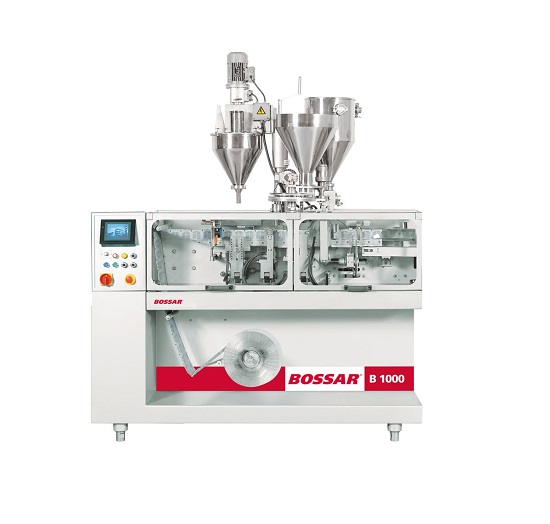
Wet Wipes Packaging Machine
Sachet packaging is a convenient and popular wrapping method for a wide range of products in the...
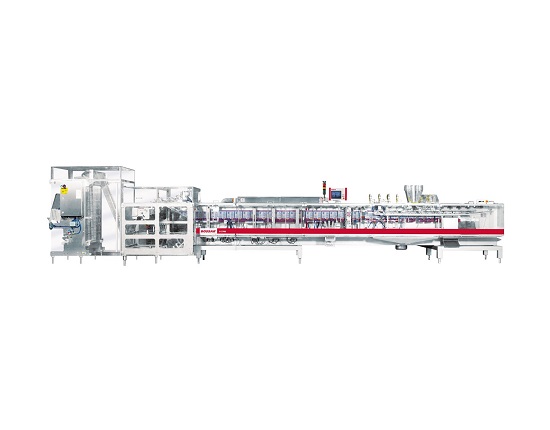
Dairy Packaging Machine
The use of sachets and pouches for powdered or shredded dairy products is an increasingly popular for...
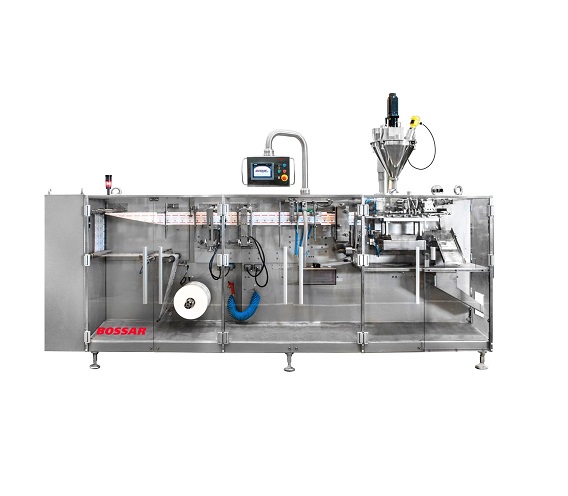
Entry level HFFS Machine for flat sachets
Traditional horizontal form fill and seal sachet machines for lower volume lines...

High-Speed Pouch Packaging Machine
For large scale production of powders and liquids in a wide range of industry sectors, a...
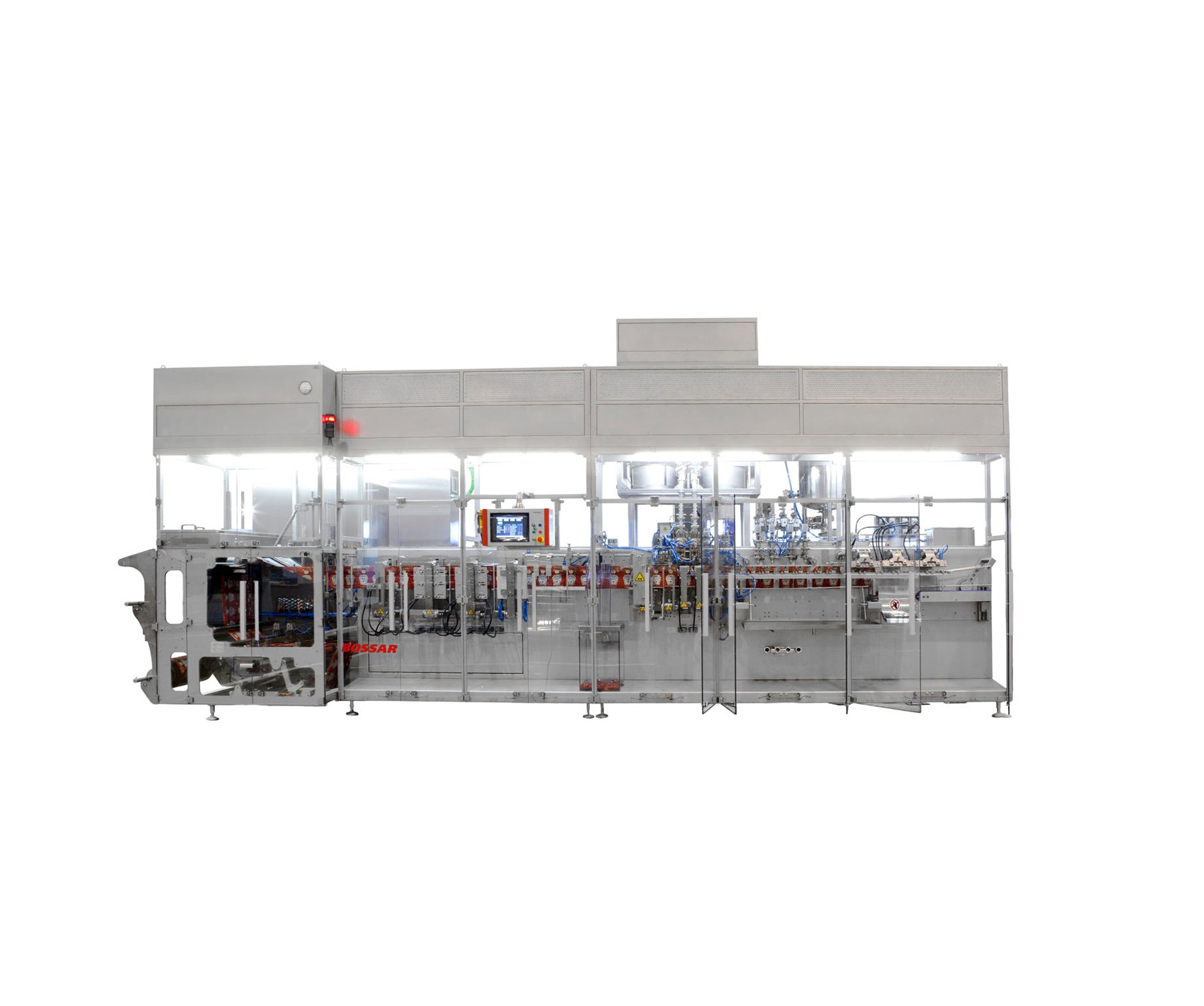
Modular HFFS Machine
A large range of sizes and types is available, with traditional horizontal form fill and seal machines b...
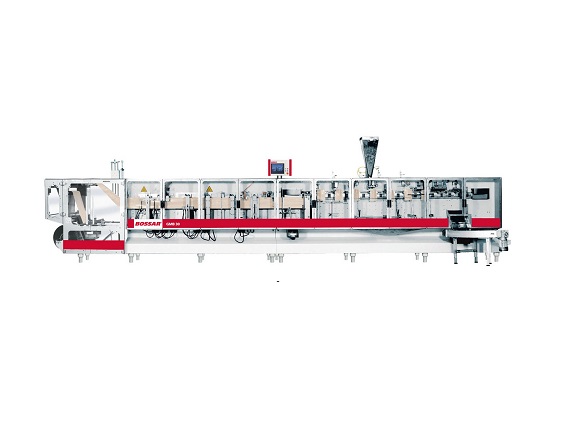
HFFS Machine for Large or Heavy Pouches
Traditional pouch-forming machines can struggle to maintain the position of the pac...
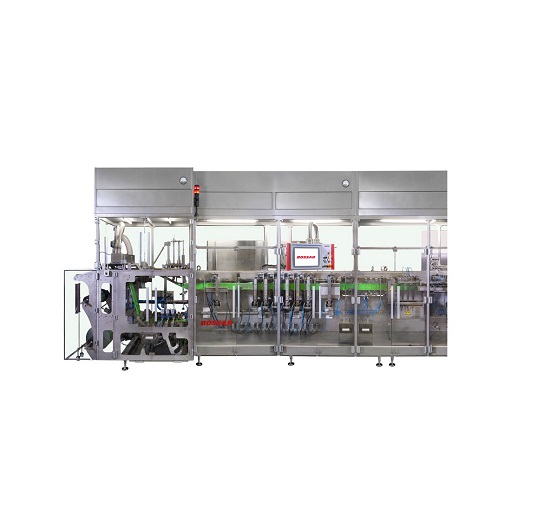
HFFS machine with servo-control system
Traditional HFFS machines use mechanical cams to drive the production path through t...
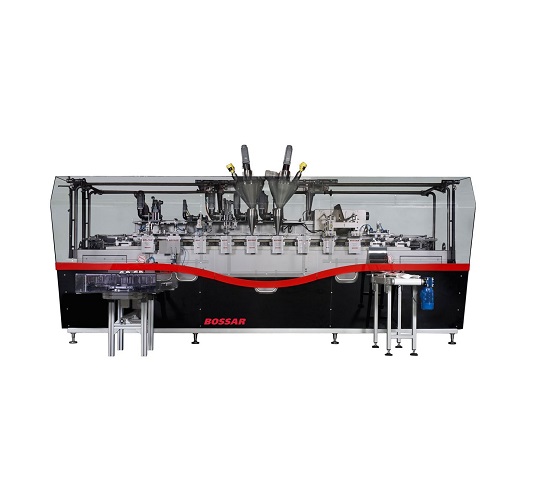
High Speed Premade Pouch Packaging Machine
Pre-made pouches can be problematic for traditional cam-driven mechanical HFS m...
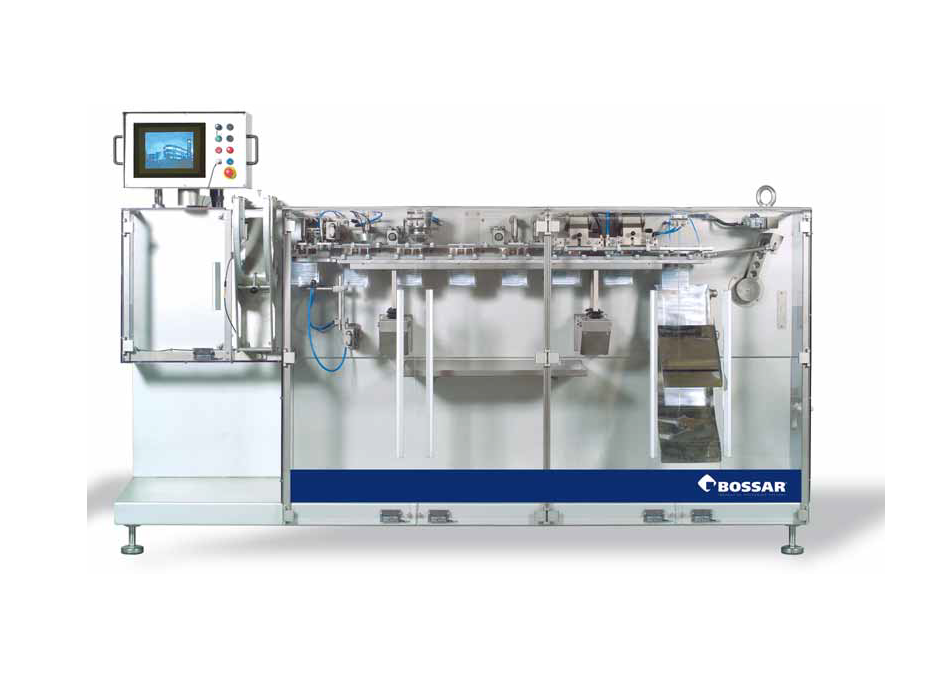
Retort Pouch Packaging Machine
A wide variety of products that were previously canned are now able to be more economically p...
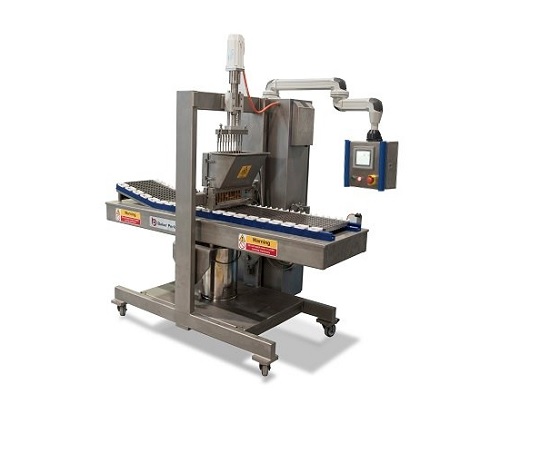
Production machine for deposited candies and jellies
For smaller production volumes, fully automated depositors for produ...
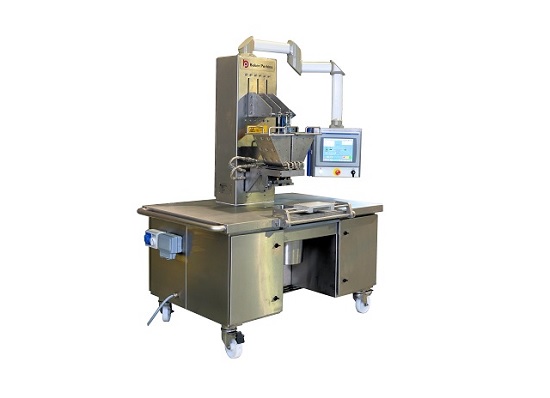
Laboratory confectionery depositors
When designing new confectionery products, the ability to experiment on lab-scale equip...
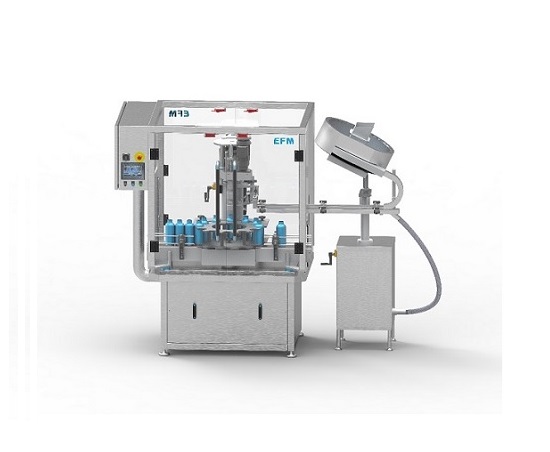
Single head capper
For the stand-alone capping of bottles of up to 30 litre capacity for smaller-scale production you need a ...
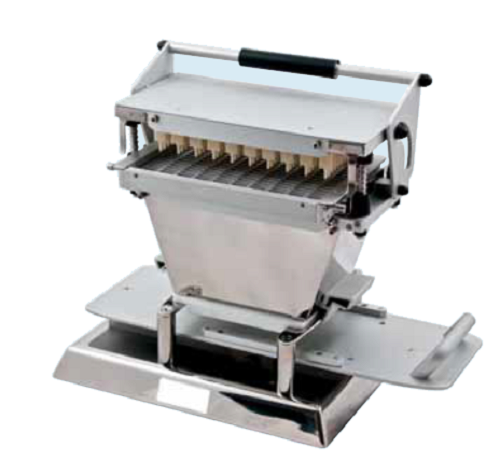
R&D capsule orientater
A semi-automatic orienter for capsules with an output speed up to 6000 capsules.
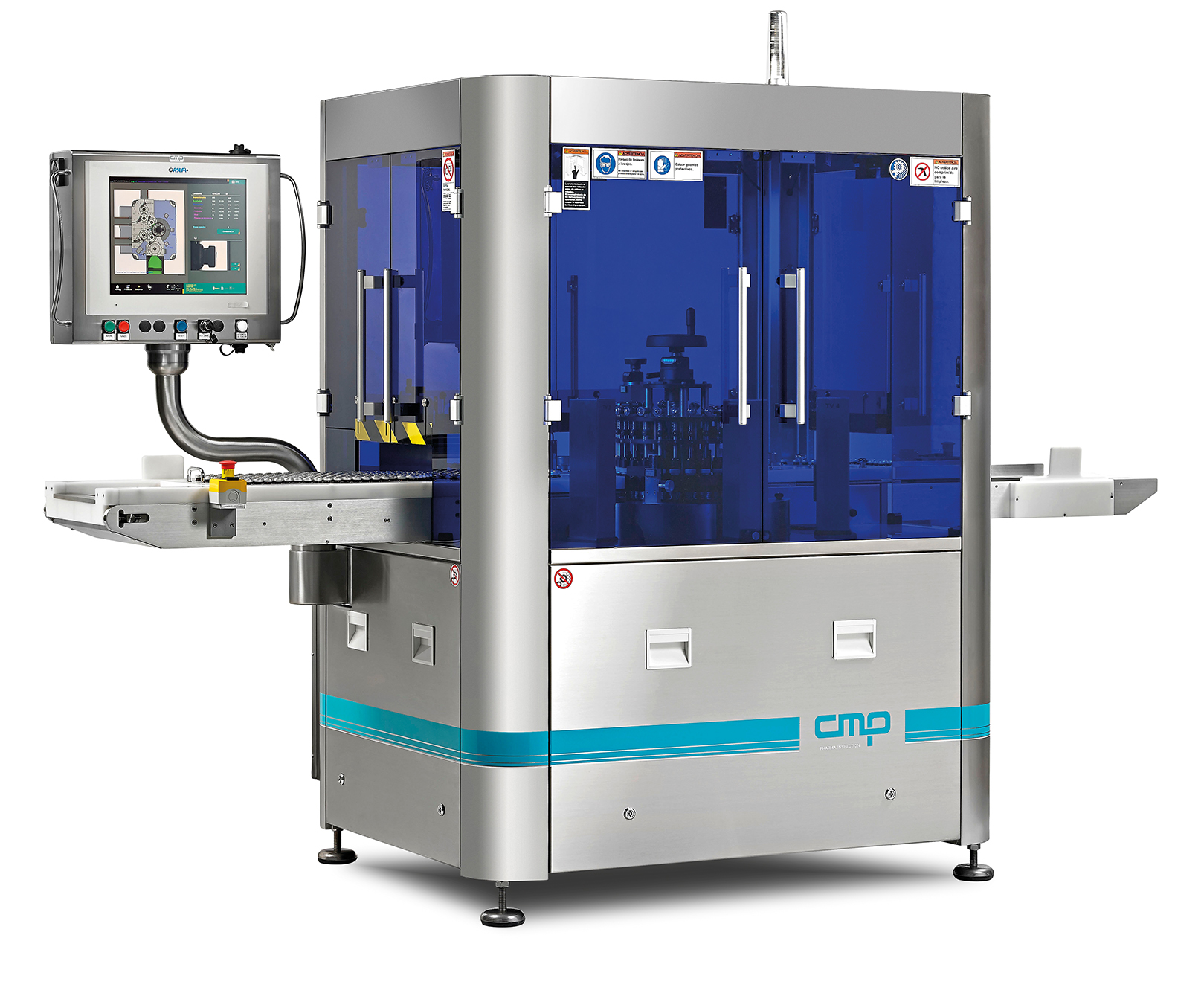
Small automatic inspector for ampoules, vials, or cartridges
Inspect small batch production of ampoules, vials, or cartr...
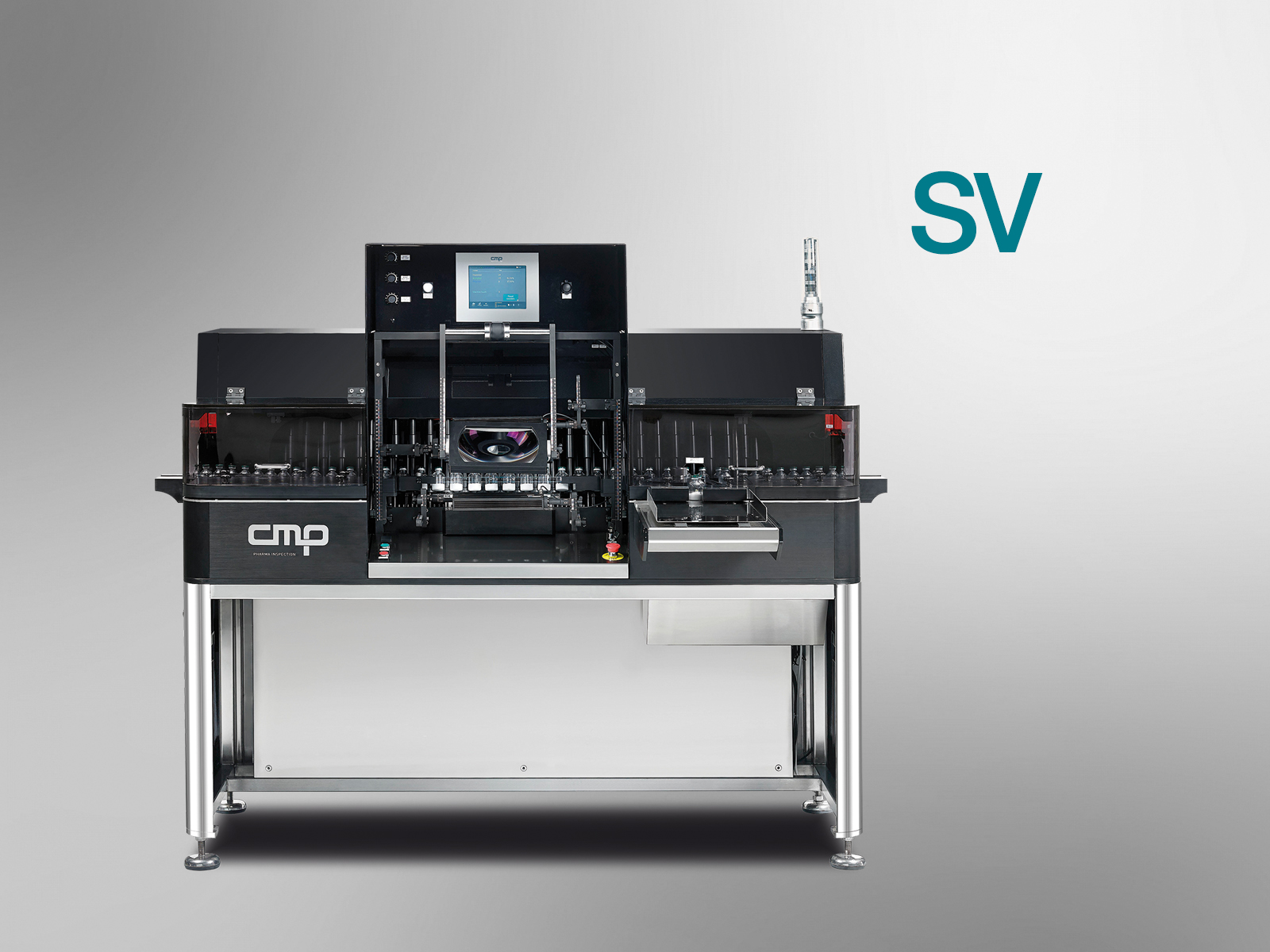
Semi-automatic inspection machine for ampoules, vials or cartridges
If you need to increase the efficiency of your manu...
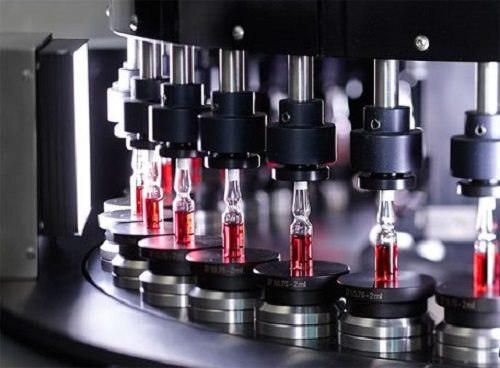
Visual and HVLD inspection for ampoules, vials and cartridges
Do you need to improve the efficiency and capability of yo...
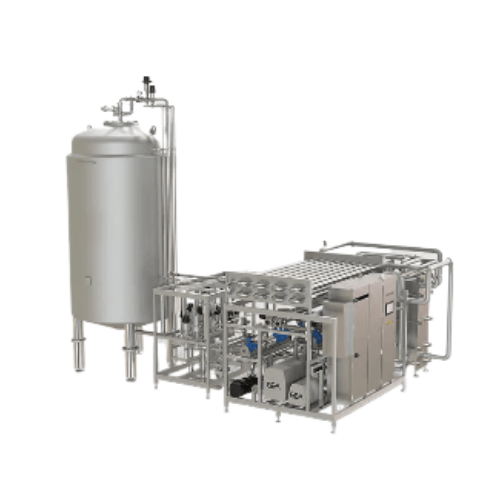
Flash pasteurizer for beer and carbonated beverages
Ensure optimal flavor and safety in your beverages by integrating a c...
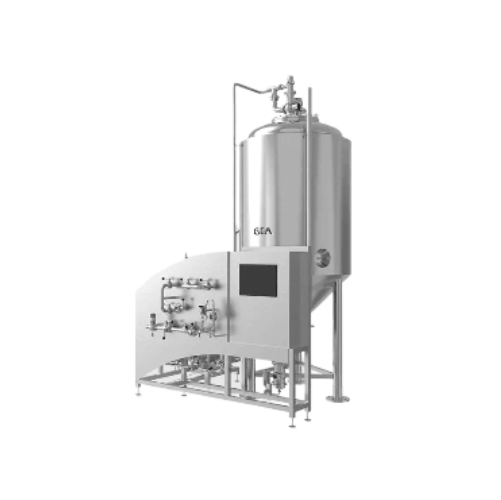
Skid-mounted yeast propagation system for craft breweries
Enhance your brewing capabilities with a versatile propagation...
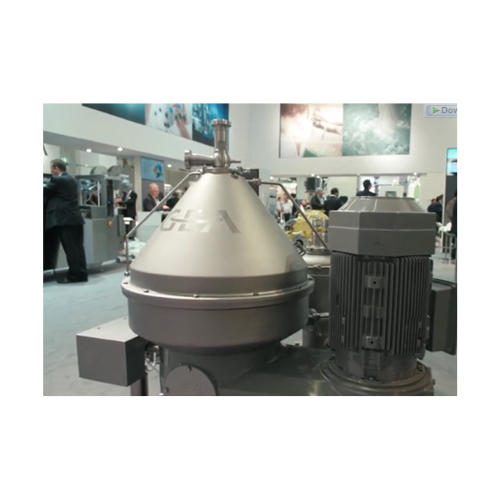
Clarifiers for plant protein recovery
Maximize protein yield and minimize waste with advanced clarification technology desi...
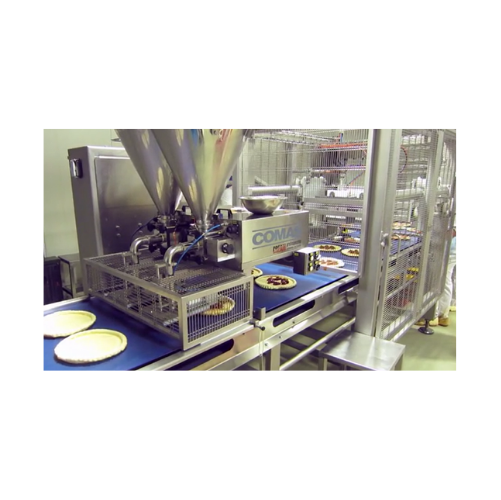
Pizza topping system for tomato sauce and ingredients
Streamline your pizza production with precise depositing of sauces ...
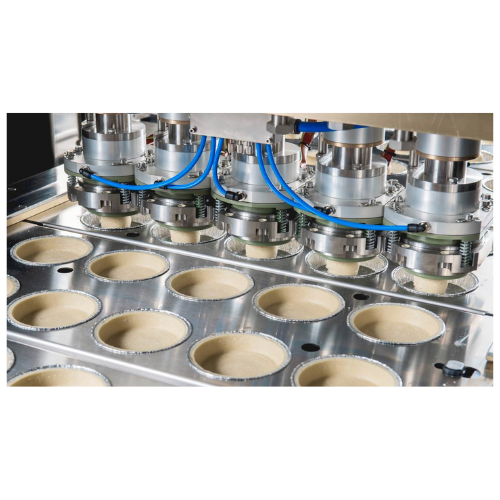
Industrial pie making systems for high-volume bakeries
Elevate your bakery operations with a versatile solution that seam...
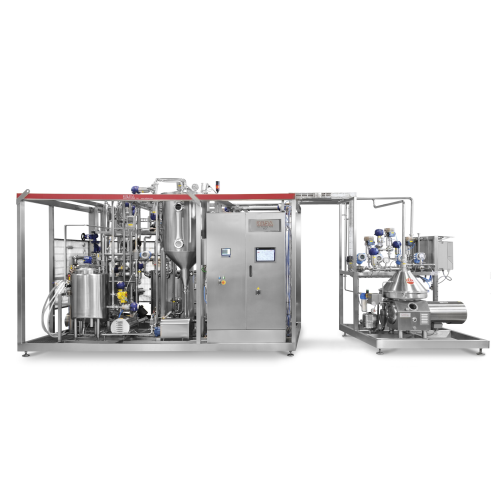
Complete milk processing lines
Optimize liquid product quality with a comprehensive processing line that integrates pasteuri...
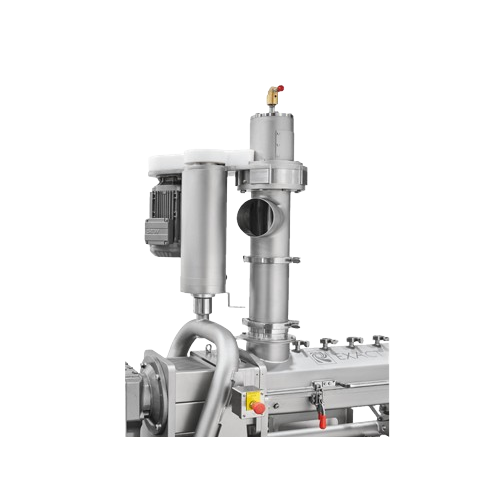
Instant dough hydration system
Efficiently hydrate dry ingredients instantly with minimal heat increase, streamlining your m...
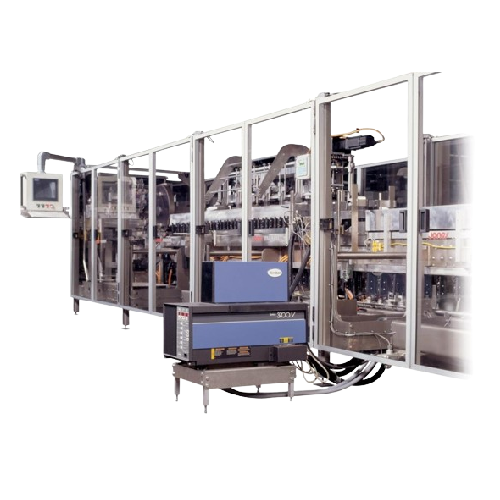
Horizontal end load cartoner for facial tissues
Achieve seamless and efficient cartoning for your tissue products with thi...
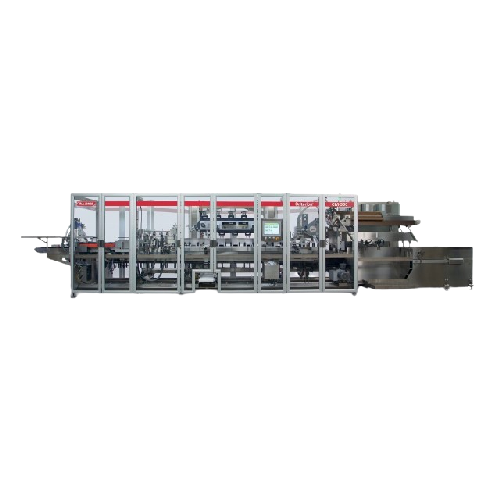
Medium-speed end load cartoner for food and beverage packaging
Streamline your packaging line with versatile cartoning c...
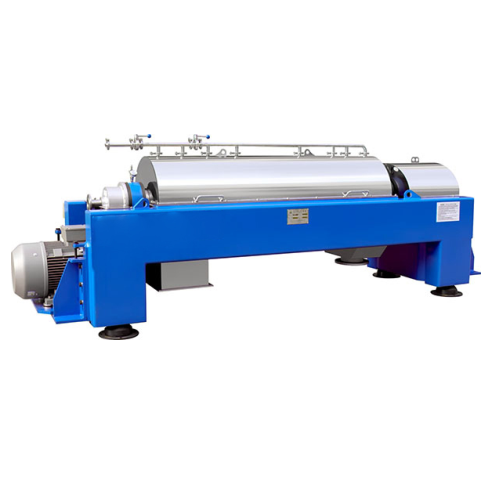
High-performance decanter centrifuge for dewatering
Achieve efficient and reliable dewatering by integrating a decanter c...
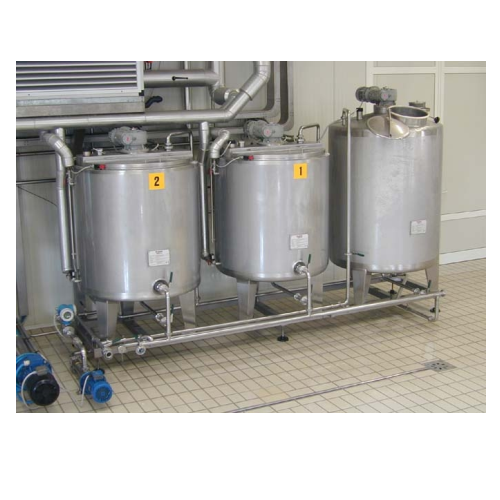
Refrigerated fermentation tank with cold water jacket
Enhance the precision of your cheese production with advanced therm...
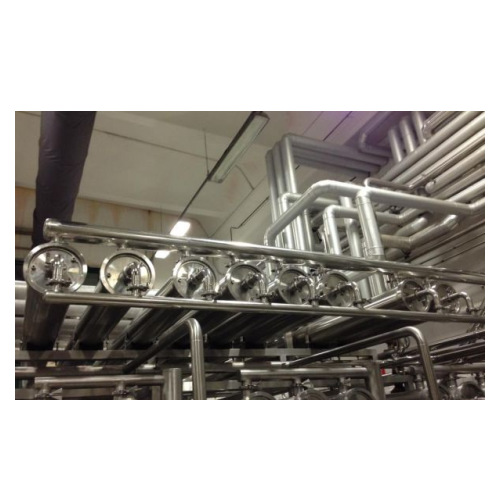
Whey concentration system with reverse osmosis
Optimize your cheese and dairy production with our reverse osmosis concentr...
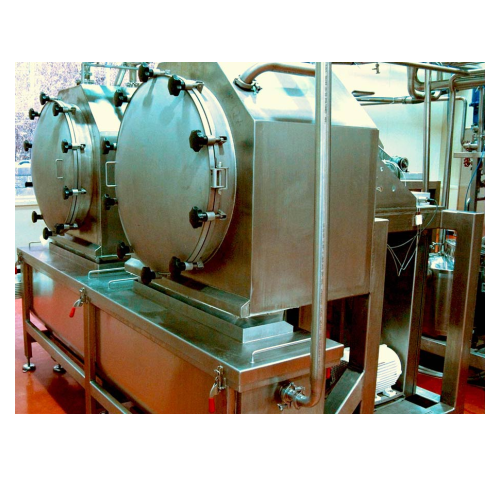
Almond milk production system
Streamline your plant-based beverage production with a comprehensive system designed to finely...
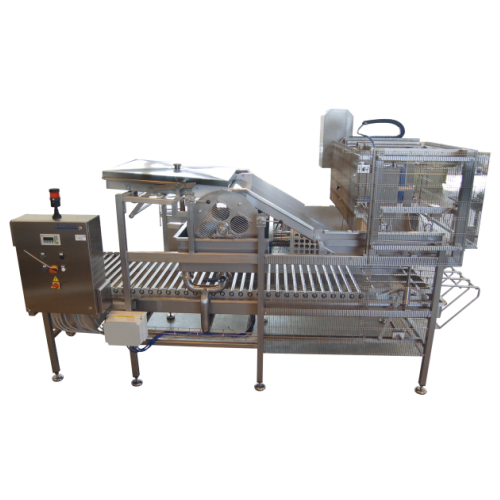
Curd drainers and portioners for cheese production
Enhance your cheese production with precise curd draining and portioni...
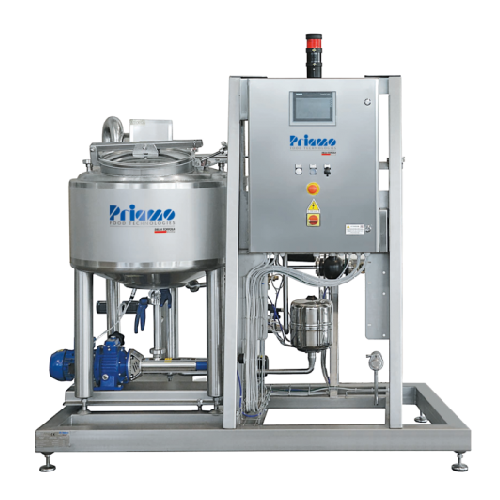
Industrial yogurt production line
Streamline your yogurt production with precise process control to ensure consistent quali...
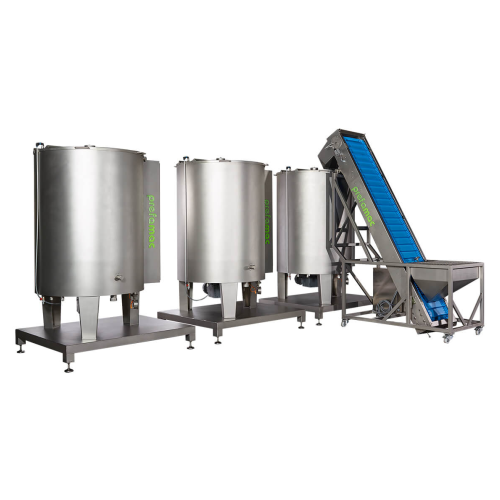
Chocolate transport system for feeding and packaging
Enhance your chocolate production with a versatile transport system ...
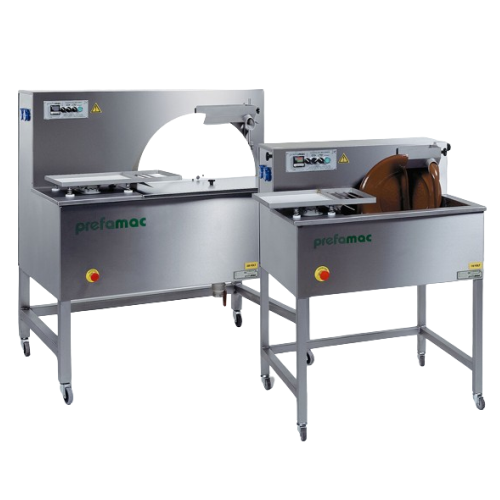
Chocolate moulding system for small batch production
Streamline your chocolate product line with precision moulding and t...
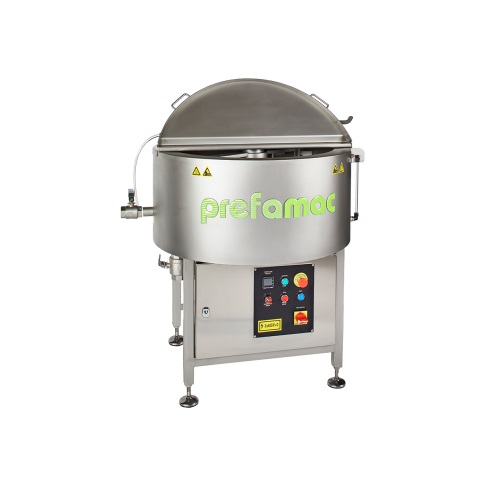
Chocolate melting and mixing kettle for small-scale production
Streamline your confectionery production with a compact k...
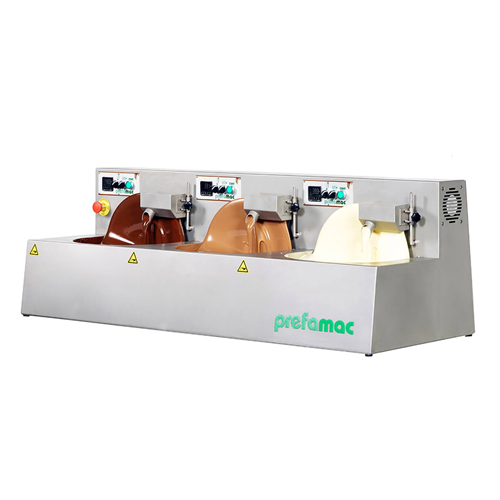
Compact chocolate moulding solution 3-in-1
Streamline your confectionery creations with a versatile 3-in-1 machine that se...

Bottom valve for cheese vats
Enhance your cheese production efficiency with a flush-mounted bottom valve, designed for optim...
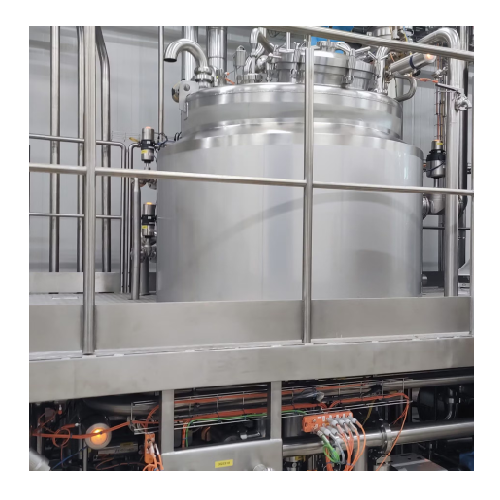
Batch processing systems for industrial applications
Optimize batch production with versatile systems that enhance energy...
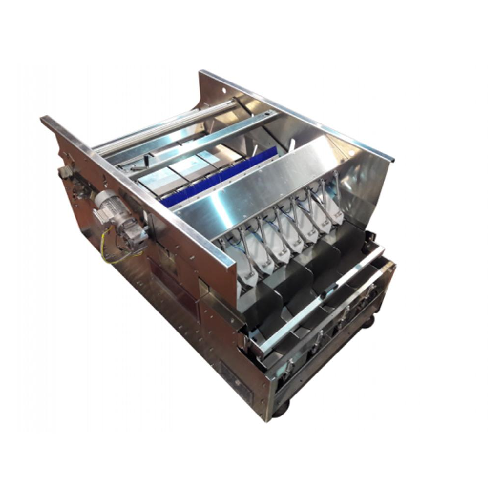
Vibrating counting system for small bakery products
Optimize counting precision and efficiency for your bakery production...
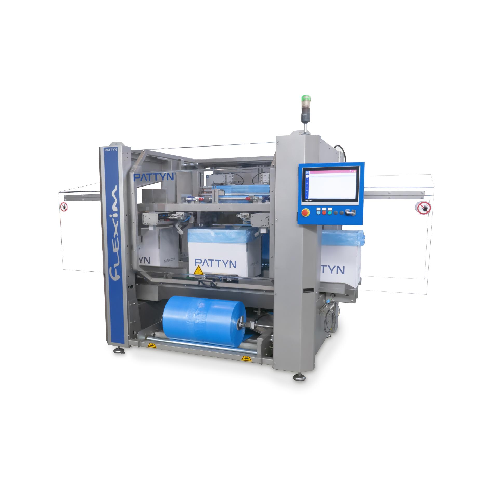
Automatic bag inserter for various containers
Optimize your packaging process with a high-speed bag inserter that perfectl...
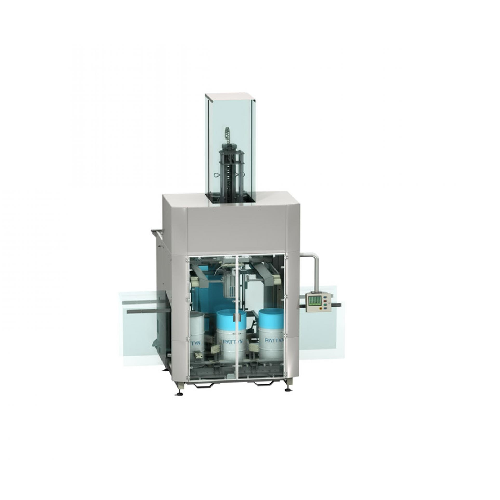
Bag inserter for drums
Effortlessly streamline your packaging process by automatically inserting custom-made bags into drums,...
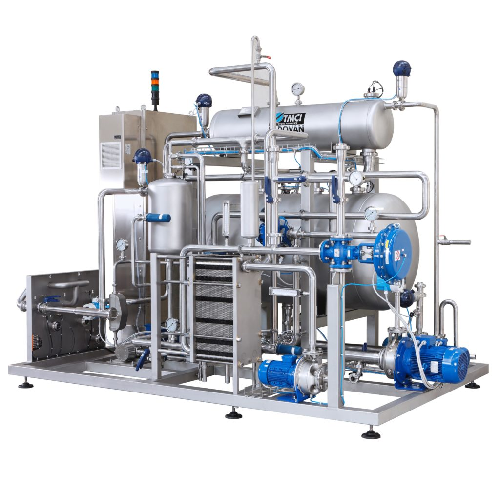
Premix system for alcoholic beverage preparation
Enhance your beverage production with precision mixing and carbonation, e...
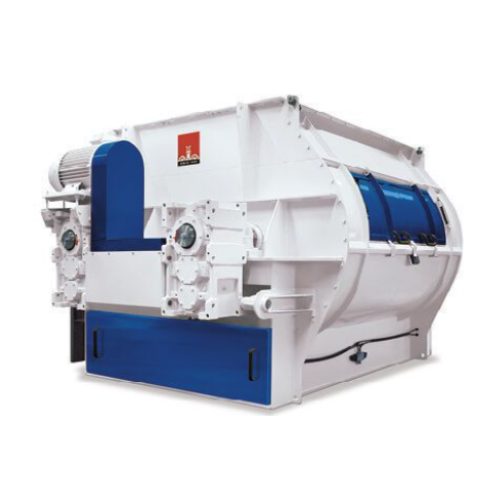
Double shaft paddle mixers for industrial powders and granulates
Achieve precise mixing and homogenization of dry powder...
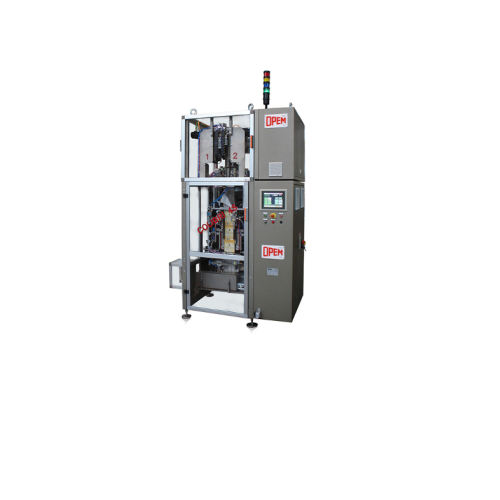
Packaging system for stacked coffee pods
Efficiently package your pods with precise counting and sealing, ensuring optimal ...
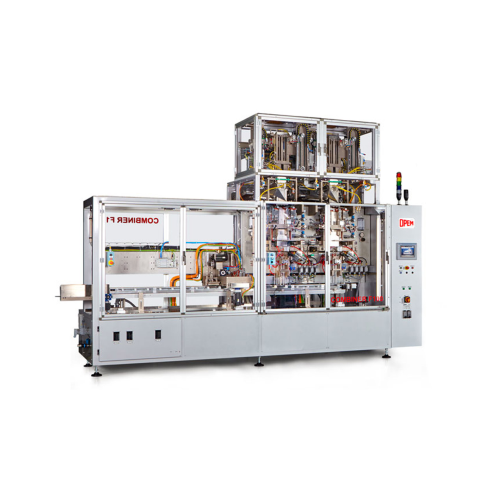
System for packaging stacked coffee pods in filter paper
Streamline your pod production with precision bagging and sealin...
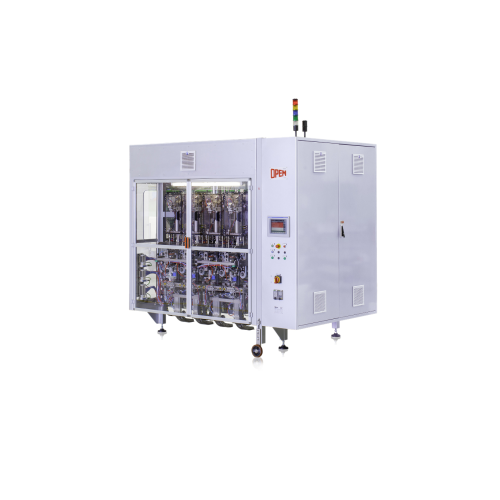
Capsule packaging system for individual gusseted bags
Streamline your coffee capsule production with high-speed, precisio...
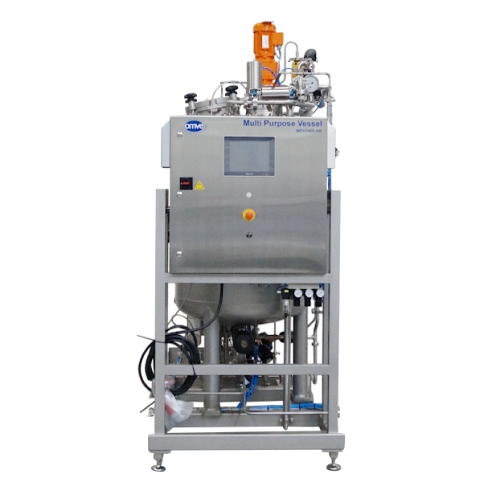
Aseptic buffer tanks for pilot scale process lines
Ensure seamless production flow and quality control in sterile environ...
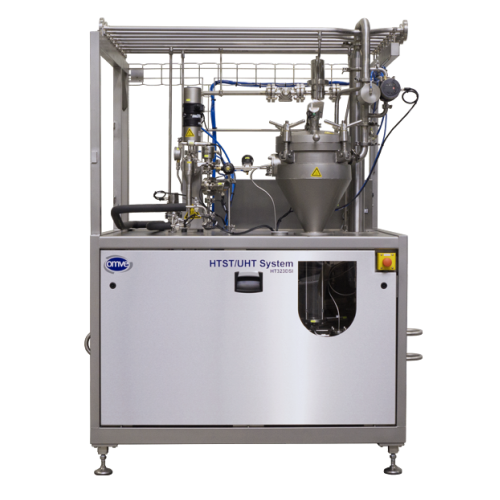
Direct steam injection Uht pilot system
Elevate your production capabilities with a sanitary UHT pilot system designed for ...
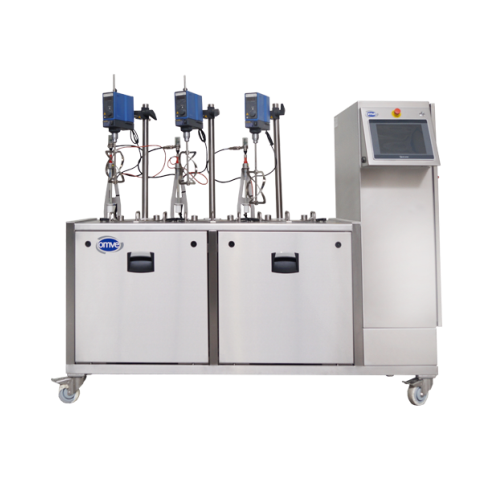
Lab-scale fermenter for simultaneous batch processing
Optimize your lab-scale fermentation process with a versatile solut...
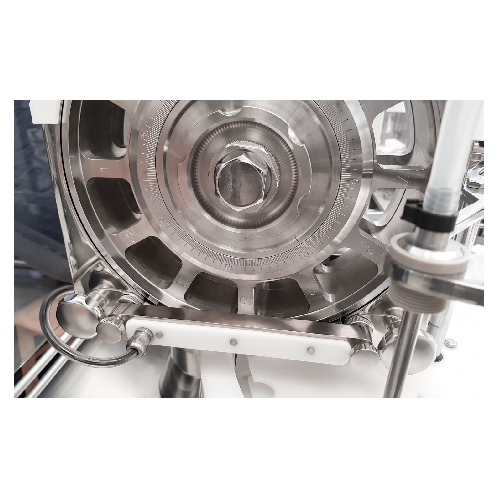
Micro-dosing system for pharmaceutical powders in vials
Ensure accurate aseptic dosing of sensitive pharmaceutical powder...
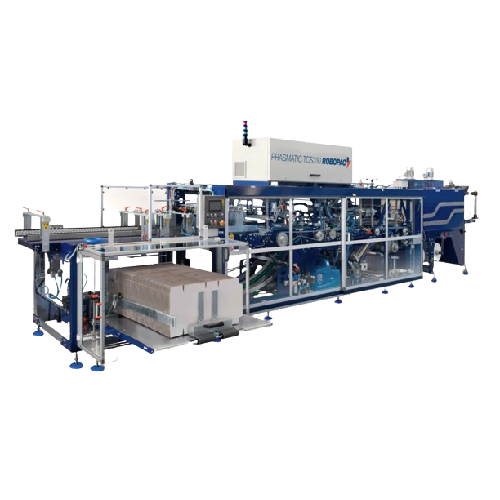
Medium-speed shrink wrapper and case packer for food industry
Optimize your packaging line with a combined solution that...
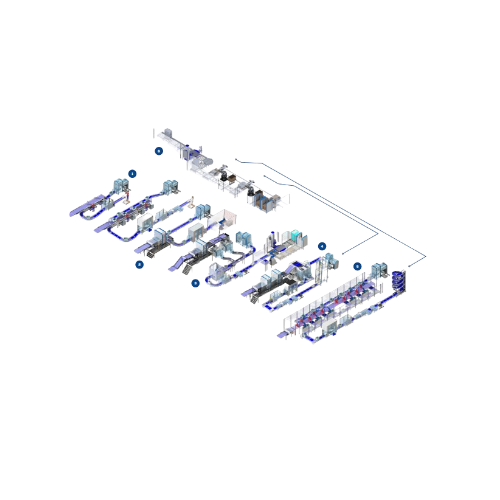
Automatic box loader for fragile products
Ensure precise and gentle handling of delicate bakery goods with a compact case ...
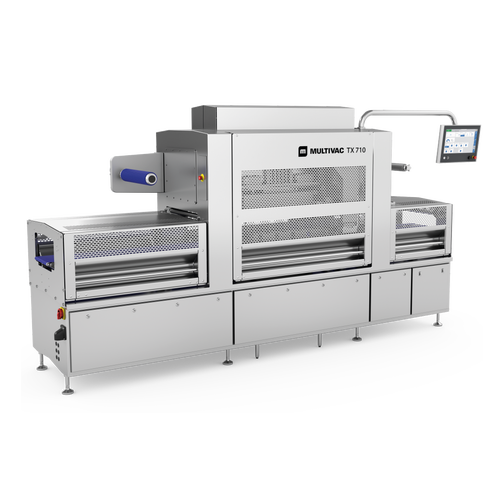
Automatic traysealer for food packaging
Optimize your packaging efficiency with this advanced traysealer, designed to enhan...

Belt loaders for automated food packaging
Streamline your packaging line with precision-engineered belt loaders, designed ...
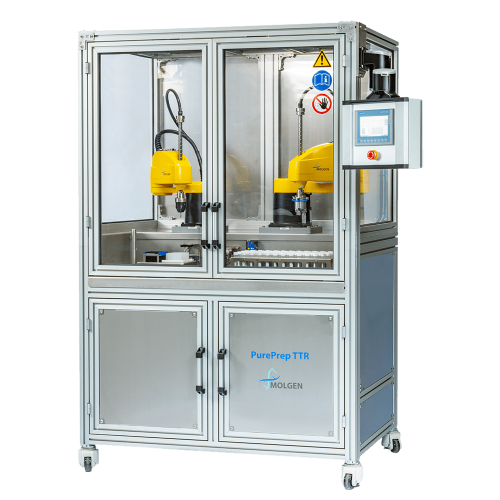
High-throughput tube transfer system for lab automation
Streamline laboratory workflows by automating high-throughput tub...
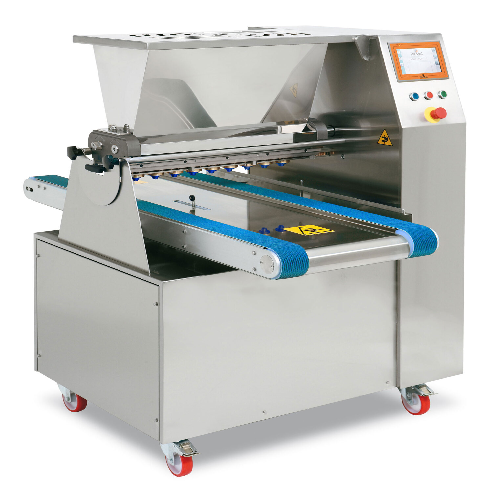
Rotating nozzle depositor for pastry production
Optimize your pastry production with precise dosing and shaping capabiliti...
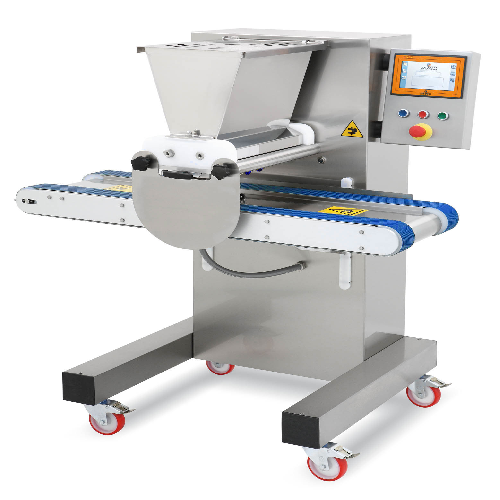
Depositing system for fixed deposited biscuits
Optimize your bakery production with a versatile depositing system designed...
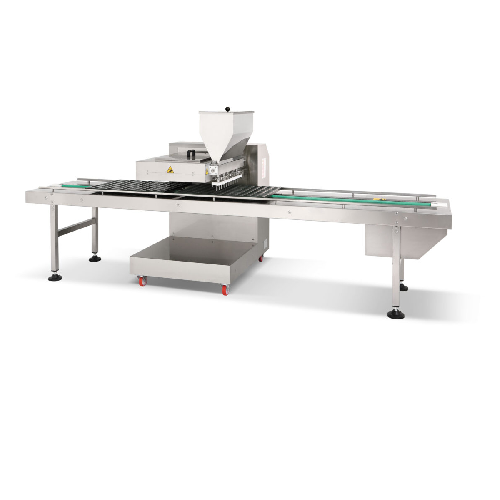
Industrial muffin production line
Maximize your bakery’s efficiency with a high-performance line engineered for preci...
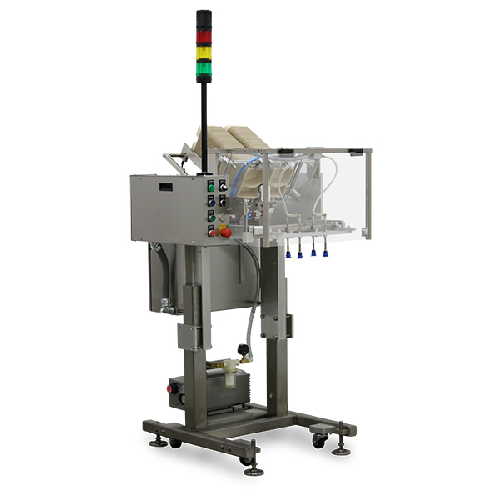
Intermittent pick and place solution for stackable items
Optimize your production line with high-speed, intermittent oper...
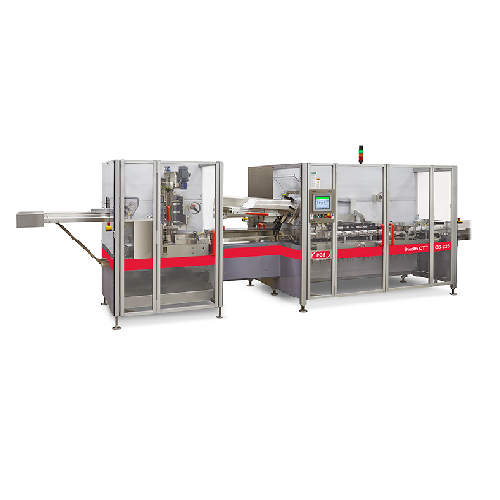
Horizontal continuous motion cartoner
Streamline your packaging process with a high-speed cartoning solution that ensures p...
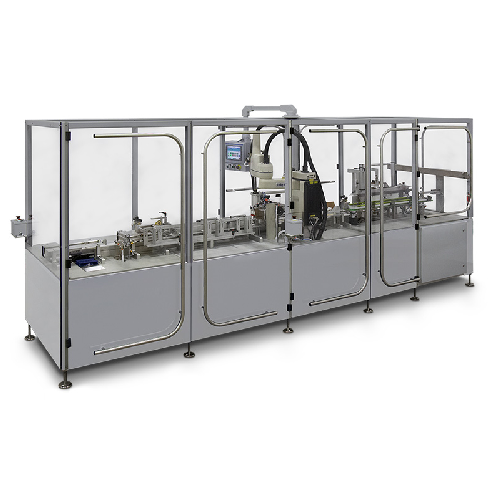
Top load cartoning system for pharmaceuticals
Optimize your packaging line with precision top-load cartoning, designed for...
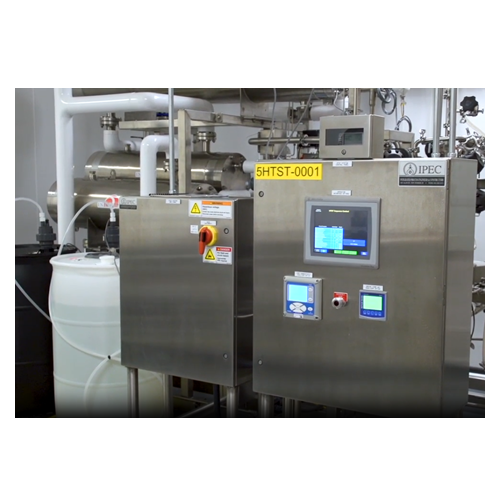
Bioprocessing liquid cell culture media
Streamline your bioprocessing with sterile liquid media solutions that ensure optim...
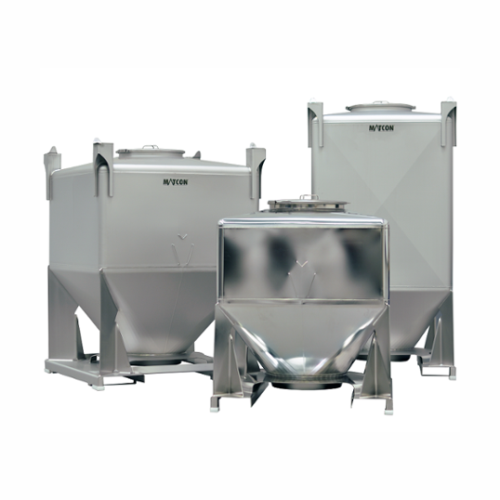
Intermediate bulk containers for powder and materials handling
Optimize your material handling processes with containers...
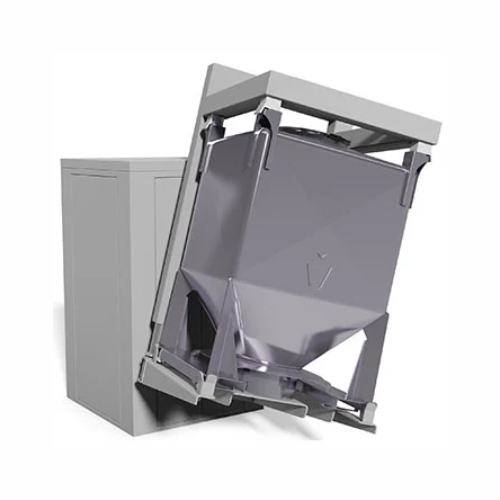
Ibc blender for industrial powder mixing
Streamline your powder mixing with rapid batch changeovers and reduced cleaning do...
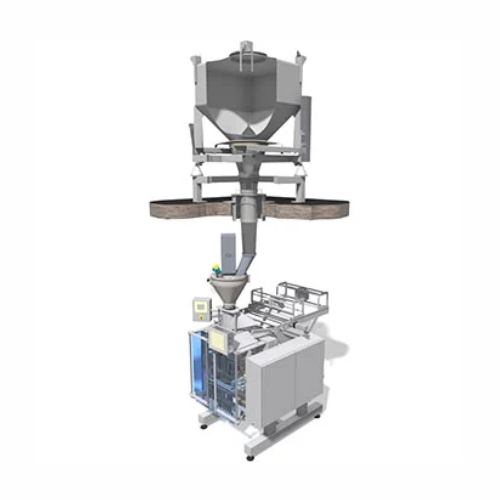
Powder packing module for consistent flow
Enhance your production efficiency with streamlined powder packing that ensures ...
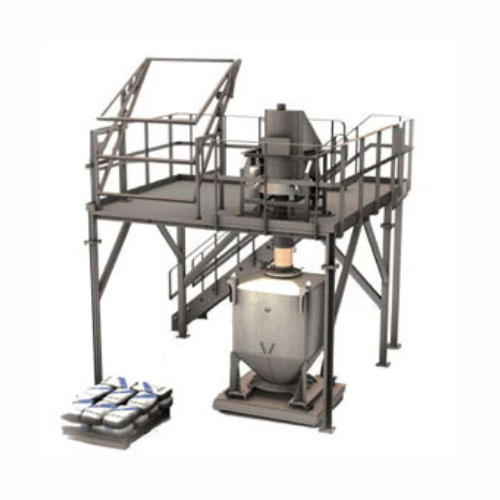
Small powder recipe formulation system
Streamline the formulation of diverse powder recipes with seamless integration into ...
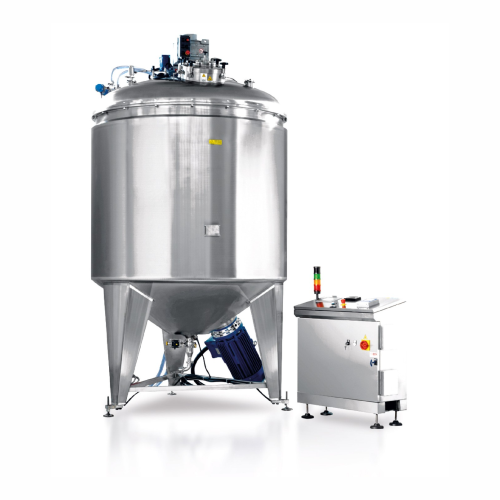
Vacuum turboemulsifier for liquid and creamy products
Achieve precise emulsification and mixing of liquid and creamy form...
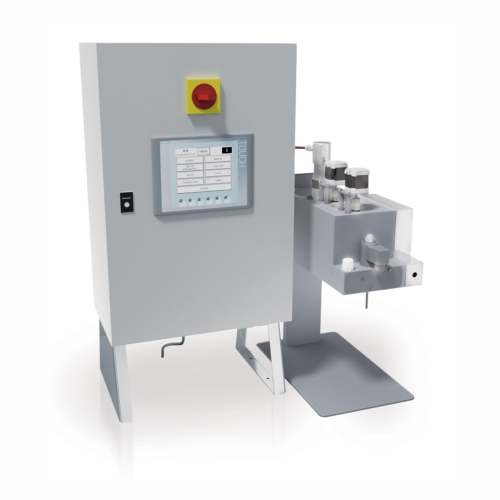
Melting tank for cosmetic production
Achieve precise and consistent melting and dosing of cosmetic liquids, from face cream...
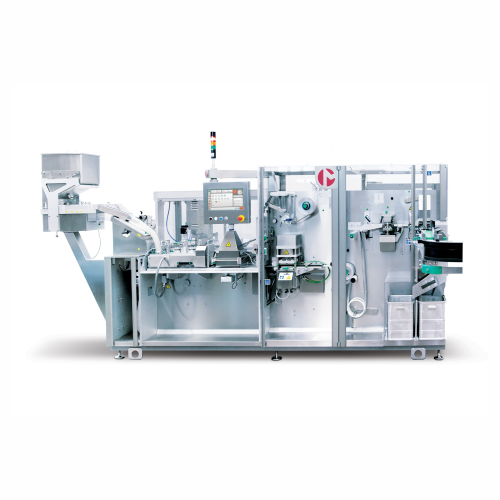
Blister thermoforming for Pvc/alu
Effortlessly mold and seal blister packs for a range of solid products, optimizing packag...
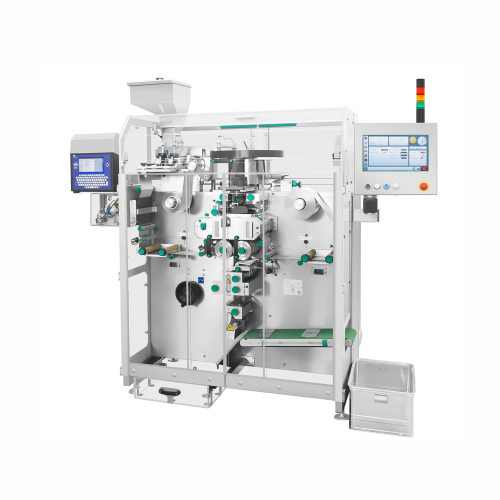
Compact strip packaging for solid products
Efficiently package a variety of solid pharmaceutical products with precision a...
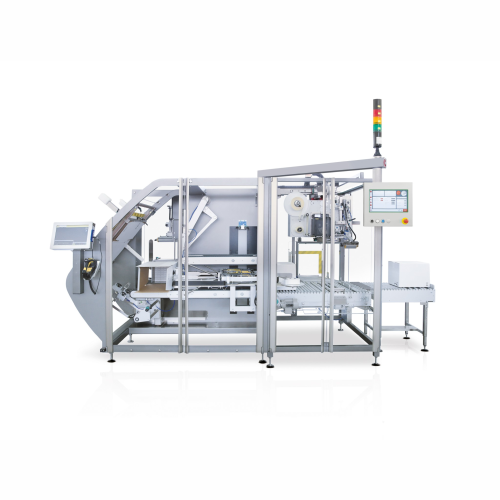
Automatic case packing solution for cosmetic products
Streamline your cosmetic production line with efficient case packin...
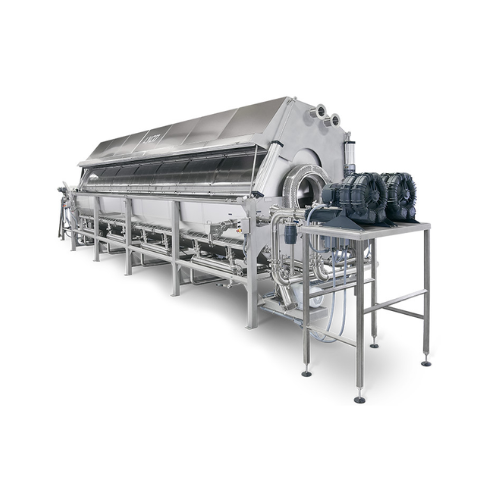
High-capacity pouch cooling system
Move pouched foods swiftly through critical temperature zones, ensuring rapid cooling fo...
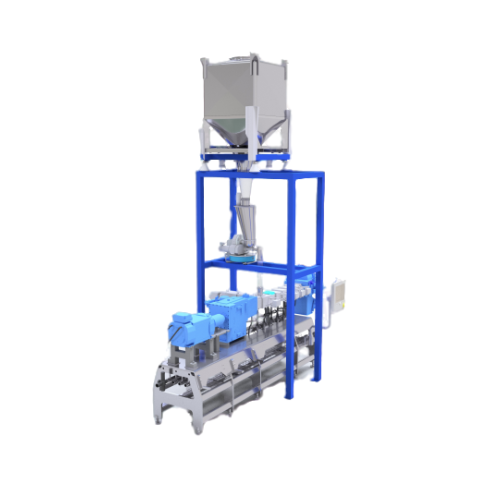
Powder handling systems for battery production
Optimize your battery production with a versatile powder handling system th...
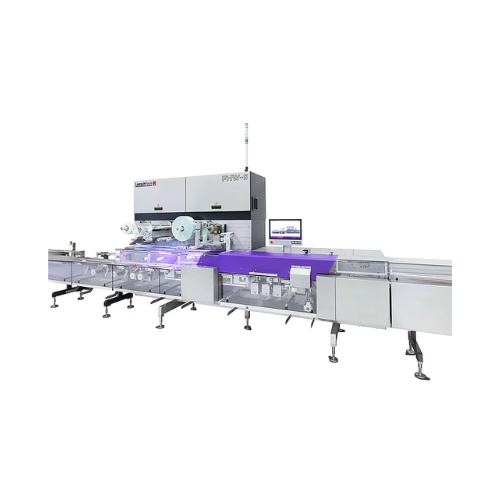
Horizontal flow wrap solution for chocolate bars
Achieve high-speed precision in packaging with a machine designed to hand...
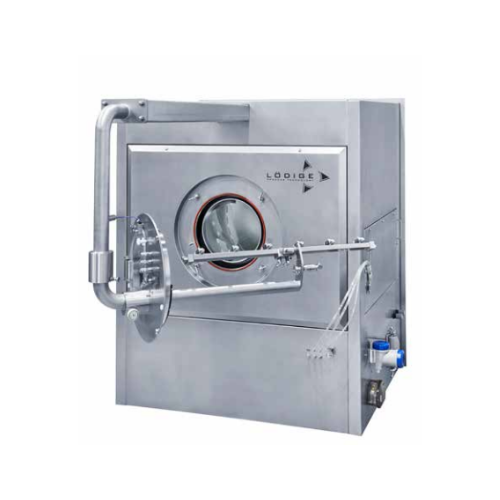
Film coater for Otc and food supplements
Achieve optimal film coating for tablets and capsules with precision-engineered so...
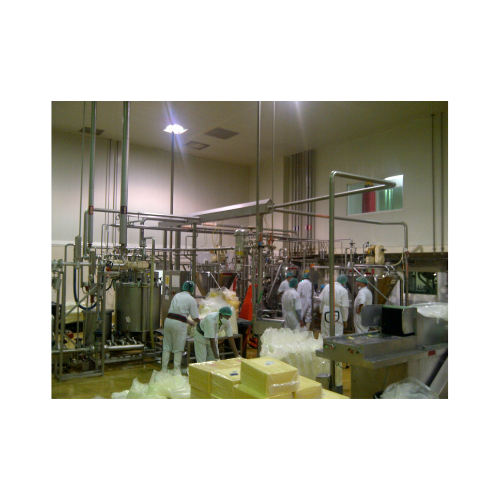
Ultra high temperature treatment system
Achieve extended shelf life and product stability with ultra high temperature treat...
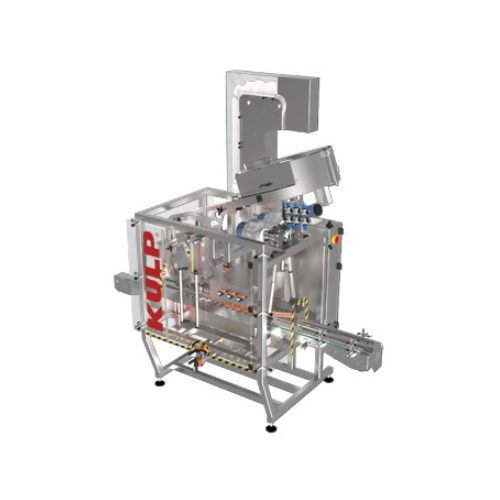
Continuous inline capping system
Perfect for high-speed operations, this system ensures precise capping of diverse container...
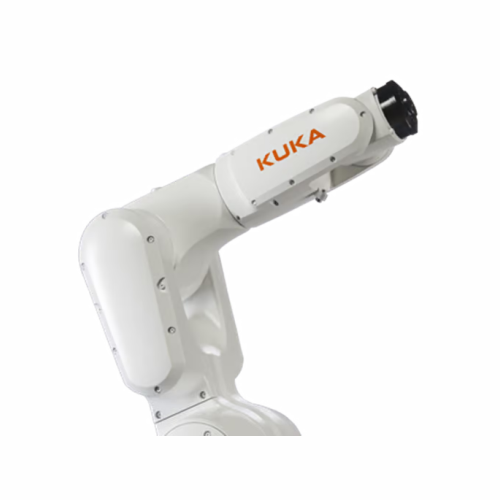
Six-axis industrial robot for high-speed precision tasks
Designing compact automation systems? This solution excels in hi...
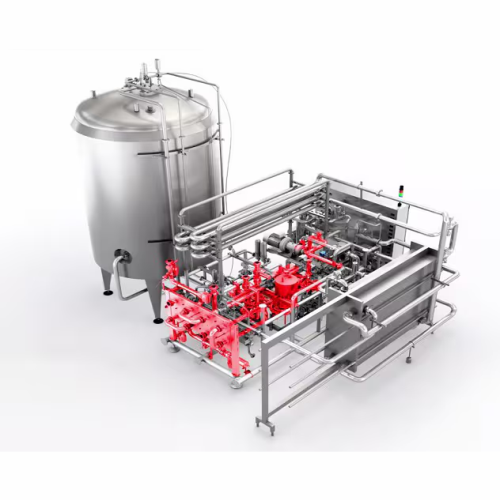
Flash pasteuriser for beer
Ensure superior beverage quality with precise pasteurisation and carbonation while minimising ene...
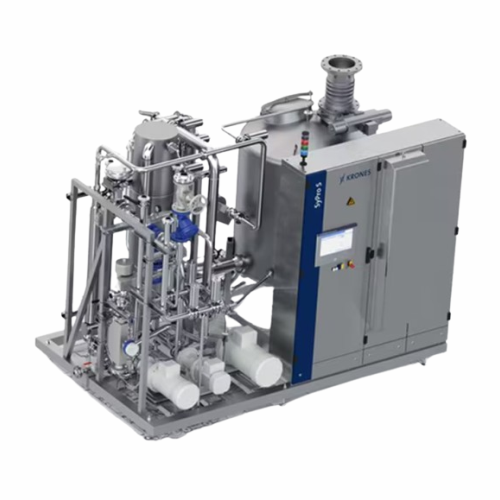
Syrup room for customized beverage ingredient preparation
Achieve unparalleled flexibility in beverage production with a...
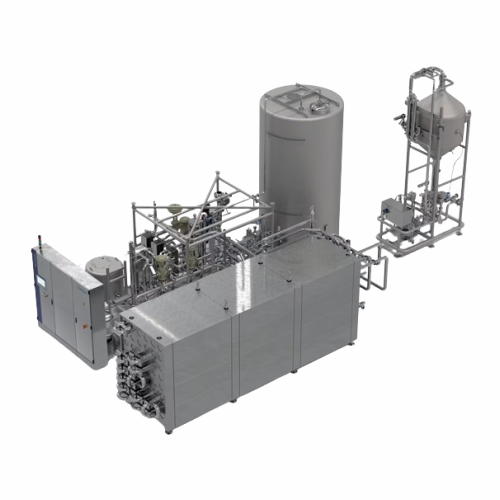
Flash pasteuriser for juice production
Ensure the microbiological safety and quality of your juice products with precise th...
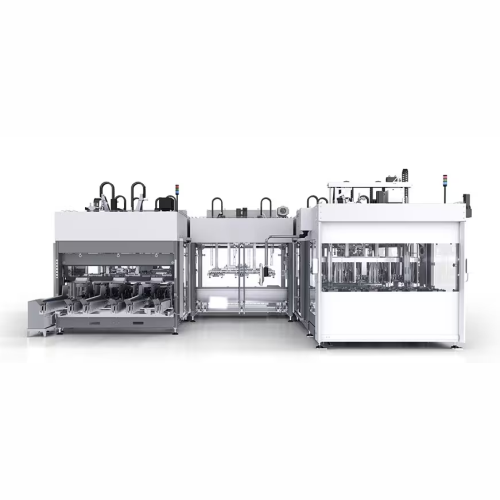
Flexible packaging line for beverage production
Streamline your beverage production with a flexible system capable of hand...
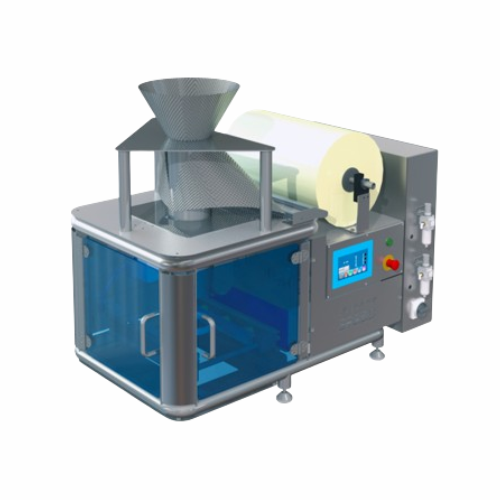
Entry-level food packaging machine for pillow bags
Achieve space-saving packaging versatility with a machine designed for...
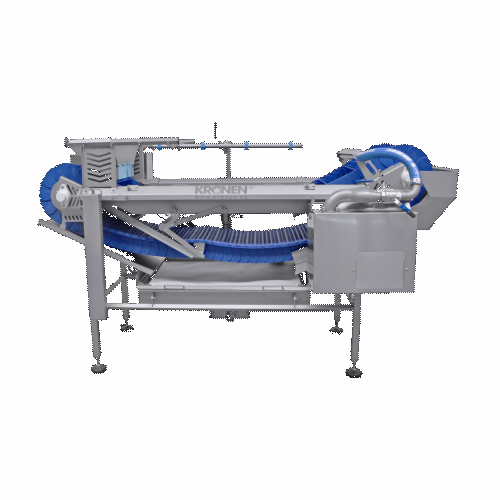
Industrial dipping bath for prolonging shelf life of cut fruits and vegetables
Enhance the shelf life and hygiene of y...
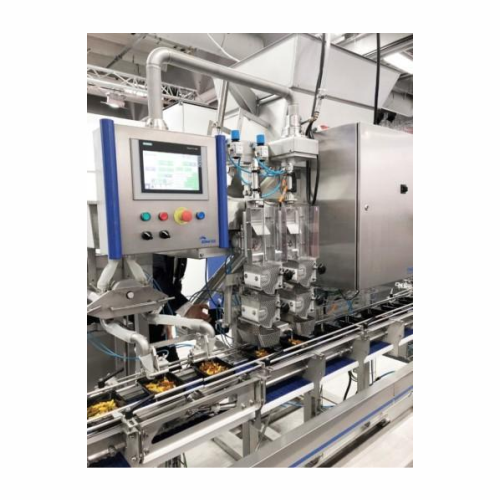
Food dosing systems for industrial applications
Optimize your food production efficiency by minimizing waste with precisio...
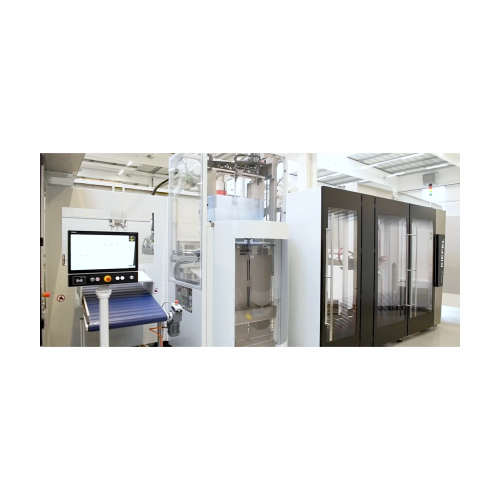
Modular stacking and automation for polymer packaging
Addressing the needs of flexible food packaging, this solution offe...
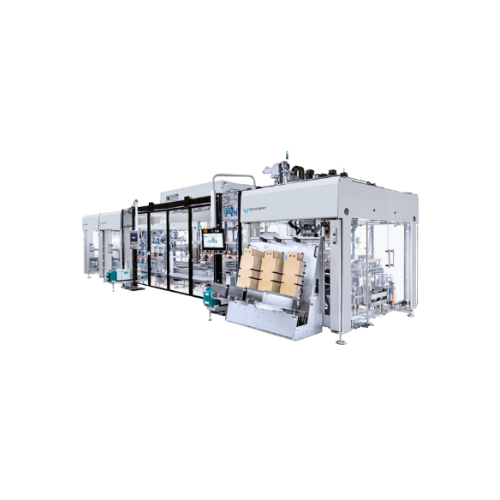
Flexible packaging system for beverage containers
Streamline your packaging process with a modular system that adapts sea...
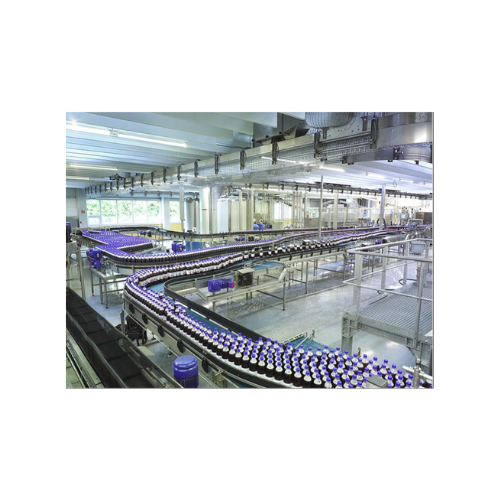
Gentle container conveyor for bottles and cans
Achieve seamless container flow with minimal noise and enhanced precision, ...
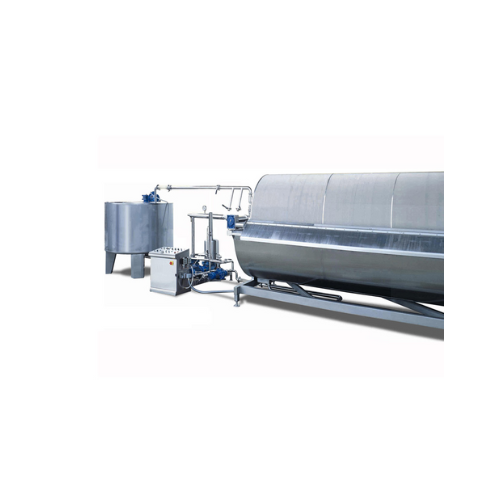
Vacuum rotary filter for liquid filtration
Enhance your production line’s efficiency with precise filtration, ensuri...

Automated Cip system for small facilities
Ensure impeccable hygiene with a mobile cleaning system designed to efficiently ...

Oxygen and carbon dioxide monitoring and elimination system
Achieve precise control over dissolved gases with a system t...
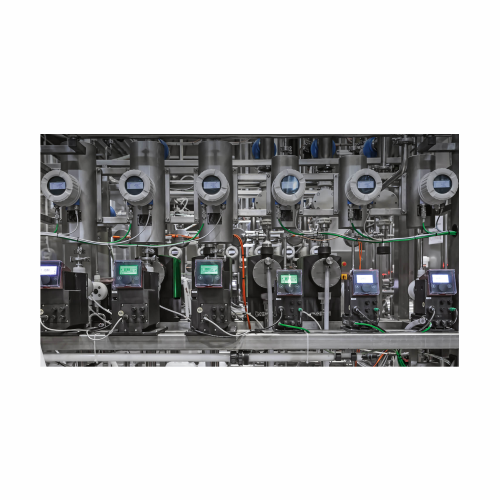
In-line additive dosing systems for beverages
Ensure precision and safety in beverage production by integrating in-line do...

Industrial cooking kettle for food processing
Achieve seamless integration of cutting, mixing, and cooking processes to cr...
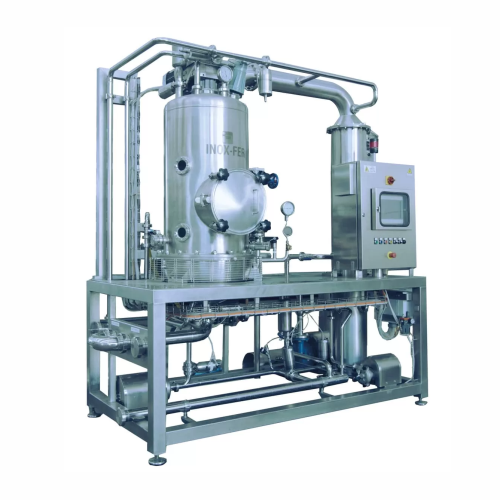
Industrial vacuum kettle for sauce production
Achieve optimal flavor retention and nutrient preservation with an industria...
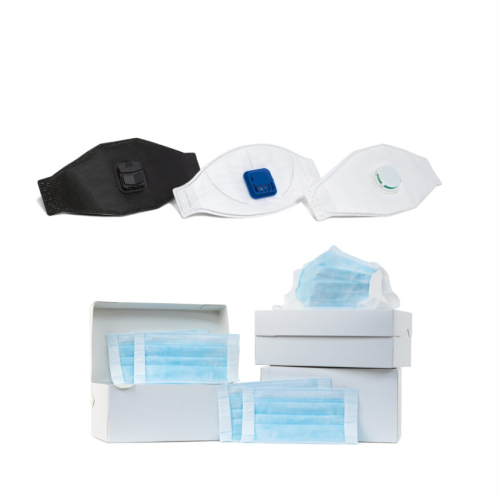
Complete line for manufacturing face masks and respirators
Achieve high-speed production of various masks and respirator...
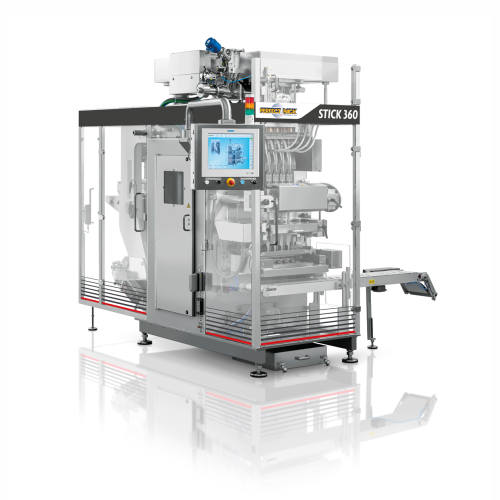
Vertical intermittent motion stick packaging
Experience seamless packing for diverse products, from powders to dense paste...
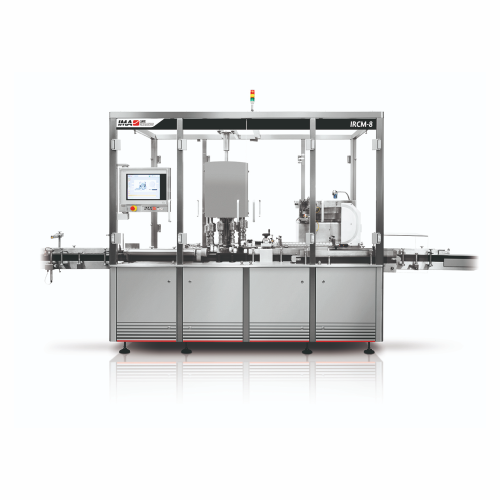
Rotary capper for round and irregular shaped containers
Efficiently cap round and irregular containers with precision and...
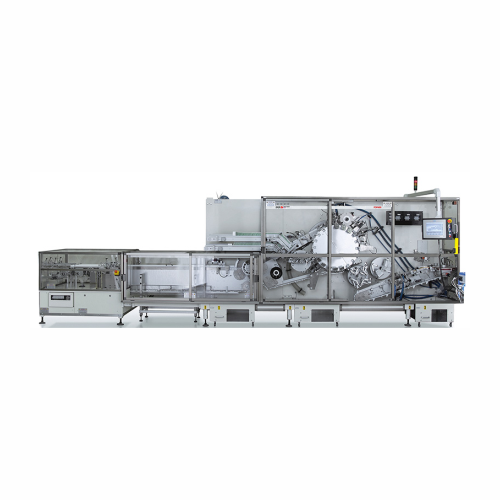
Horizontal cartoning solution for pharmaceutical packaging
Streamline your confectionery packaging with high-speed, cont...
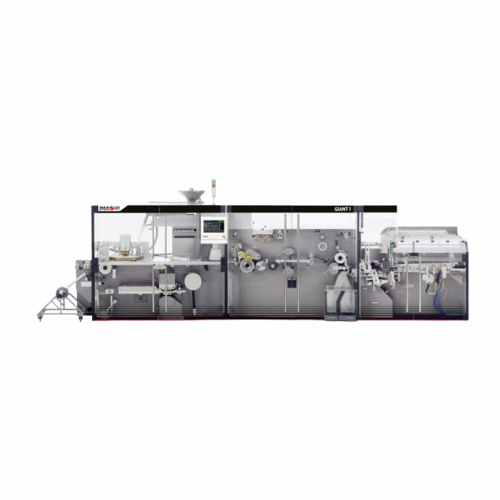
Blister packaging solution for small-medium batches
Achieve unparalleled versatility and efficiency in blister packaging ...
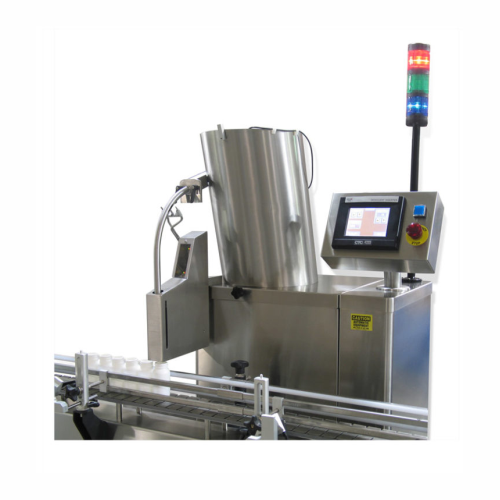
Desiccant inserter for pharmaceutical bottles
Ensure your products remain moisture-free and preserved by integrating this ...

Flow wrapper for high-speed confectionery packaging
Achieve gentle, high-speed packaging for delicate confectionery items...
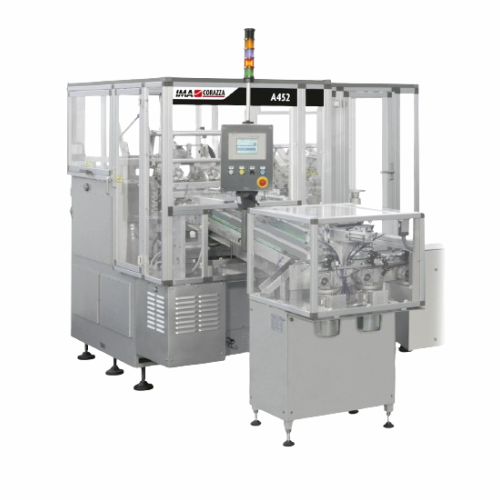
Cartoning solution for cheese portions
Optimize your cheese packaging with a flexible cartoning solution designed to accomm...
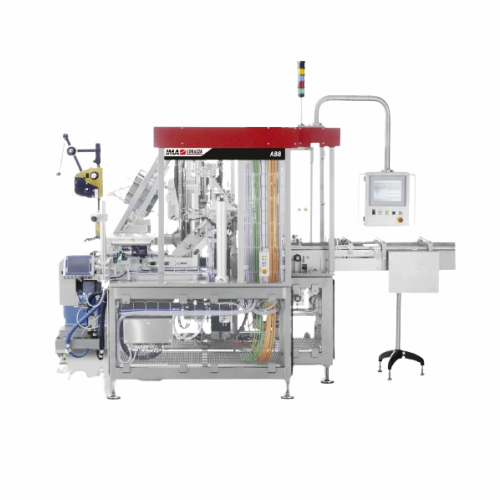
Wrap-around cartoning solution for butter and yeast
Optimize your packaging line with a high-speed cartoning system that ...
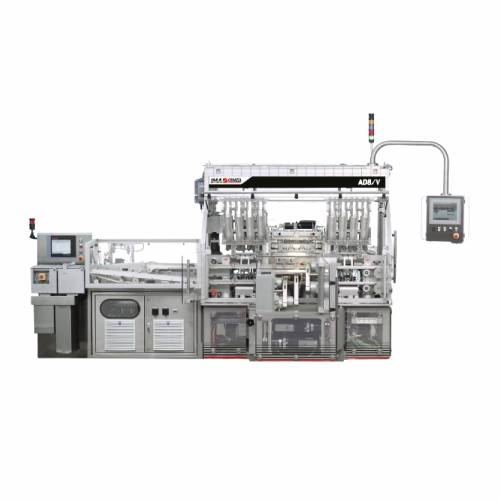
Cartoning solution for soup cubes
Optimize your soup cube packaging process with a compact, high-speed wrap-around solution...
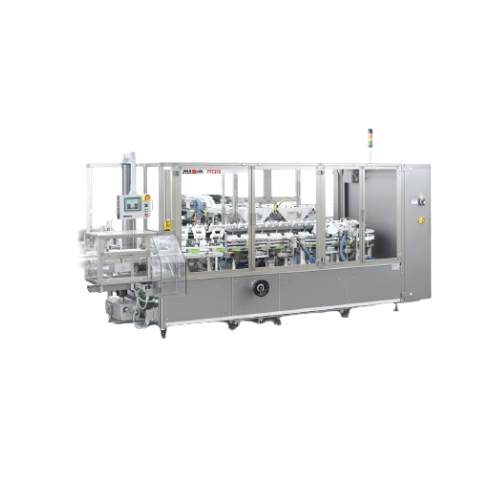
Vertical cartoning system for confectionery products
When you need high-speed, versatile cartoning capabilities for varie...
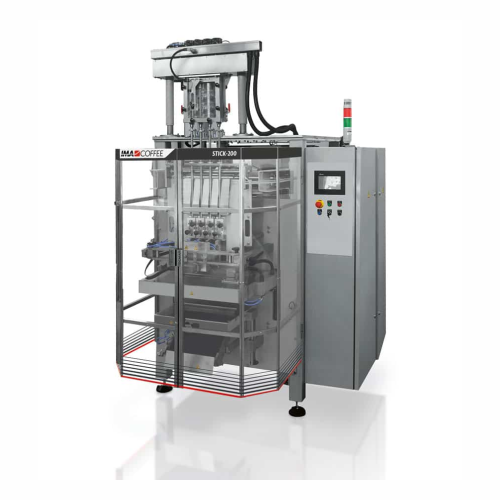
Multilane vertical packaging for stick sachets
Optimize your packaging line with high-speed, multilane machines designed f...
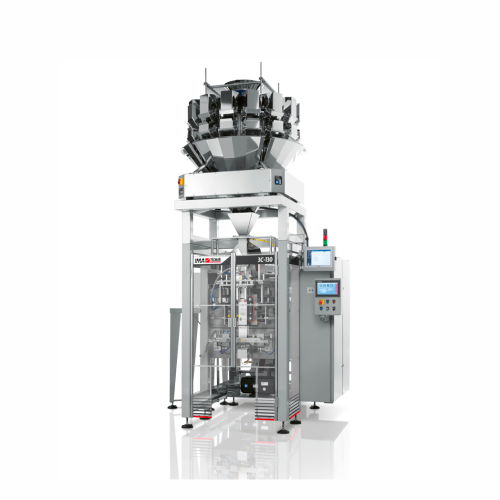
Vertical baggers for confectionery packaging
Streamline your packaging operations with high-performance vertical baggers d...
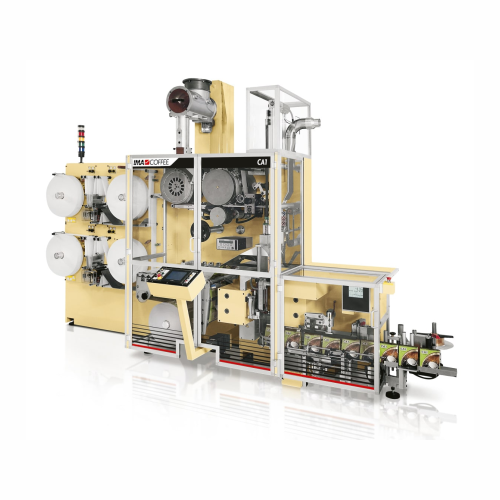
Soft pod packaging solution for coffee
Streamline your coffee production with a compact, high-speed solution that ensures p...
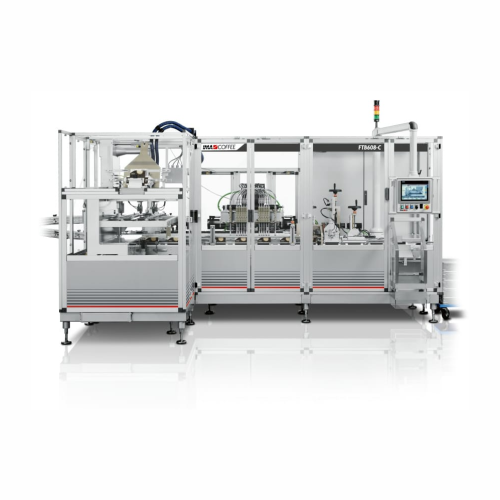
Capsule cartoning system for coffee and tea
Streamline your capsule packaging with a high-speed cartoning solution that ef...
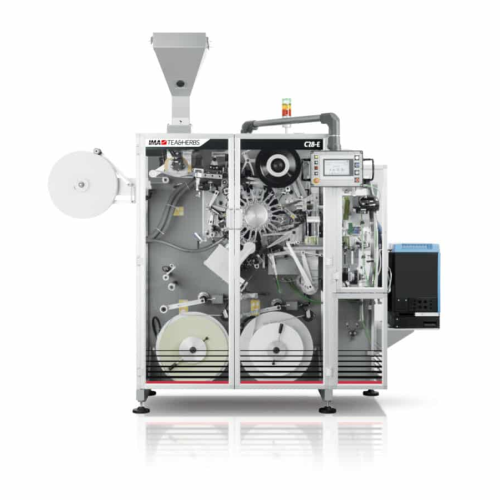
Tea bag packaging system for small production runs
Streamline your tea packaging efficiency with precision knotting techn...
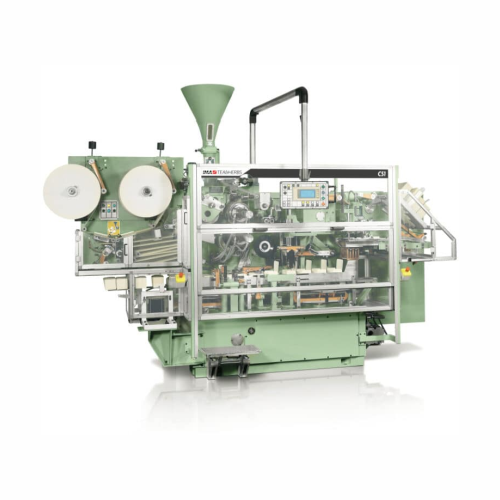
Overhauled tea bag packaging system for black tea
Streamline your tea packaging line with this high-speed solution, desig...
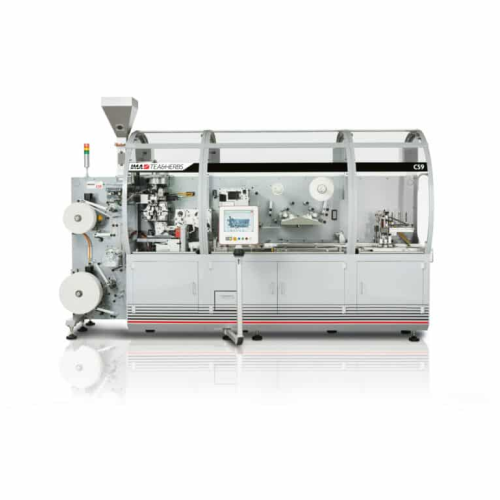
Tea bag packaging solution for single-chamber bags
Achieve efficient, high-speed tea packaging with a compact system that...
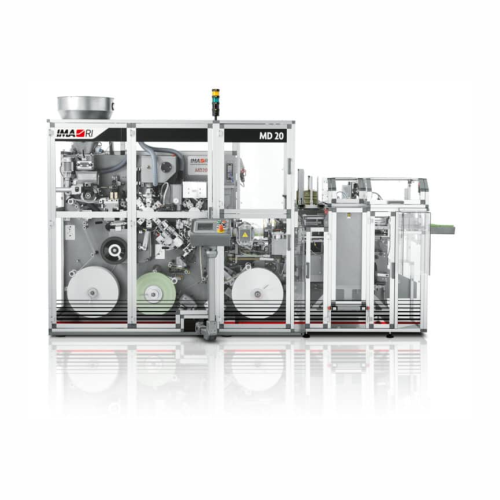
High-speed tea bag packaging for naked or heatsealed envelopes
Need to enhance production efficiency in tea packaging? D...
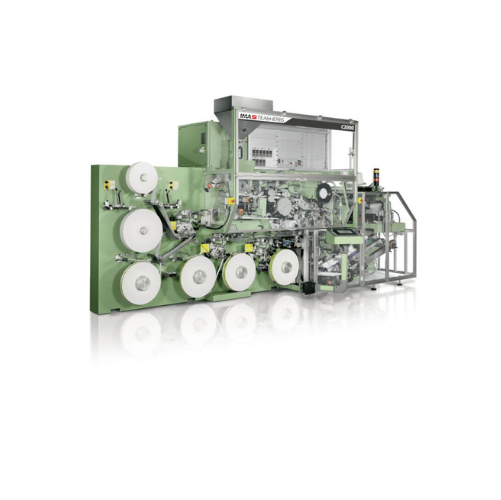
High-speed heatsealed tea bag packaging
Achieve unparalleled efficiency in your tea packaging line with a high-speed system...
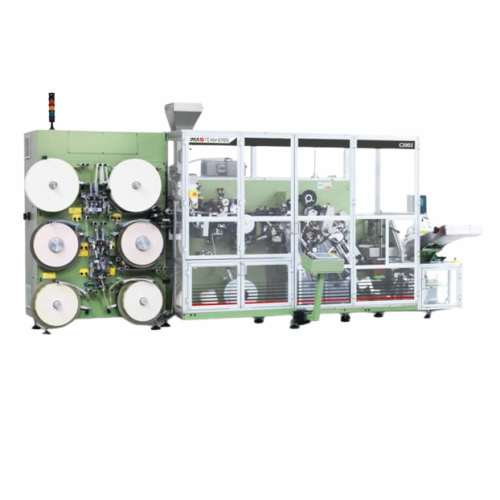
Heatsealable double-chamber tea bag packaging system
Achieve unmatched speed and versatility in tea bag production, deliv...
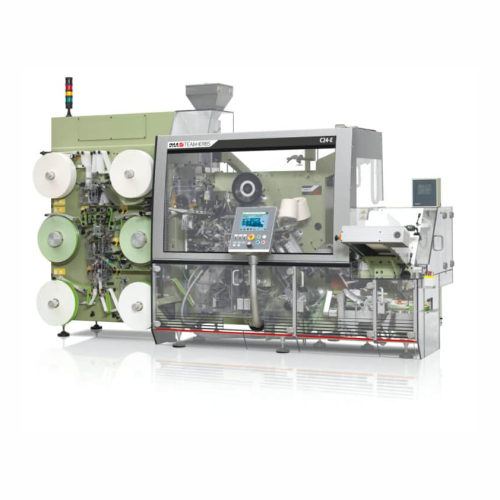
High-speed tea bag knot packaging line
Achieve precision and efficiency in tea packaging with a system designed for high-sp...
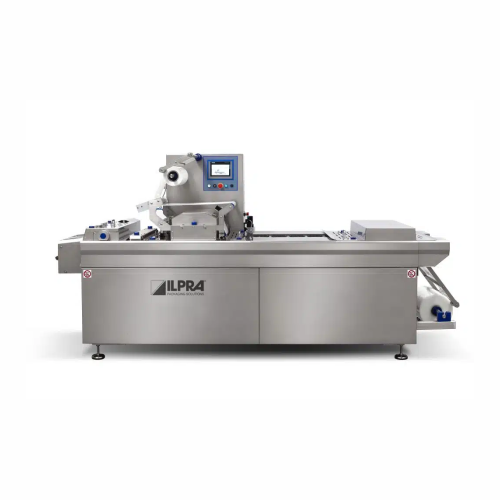
Compact thermoforming packaging system for food industry
Revolutionize your packaging line with a space-saving solution t...
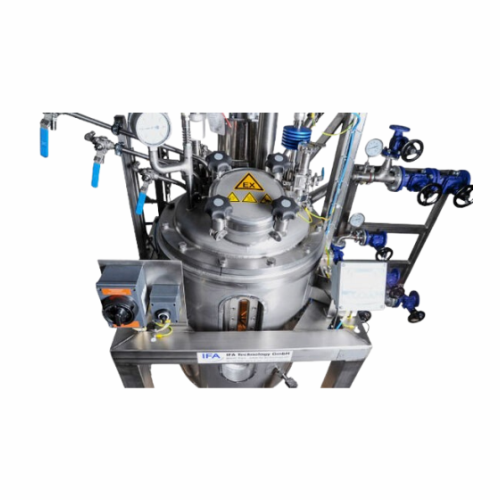
Wastewater treatment system for industrial applications
Optimize resource management and environmental impact by integrat...
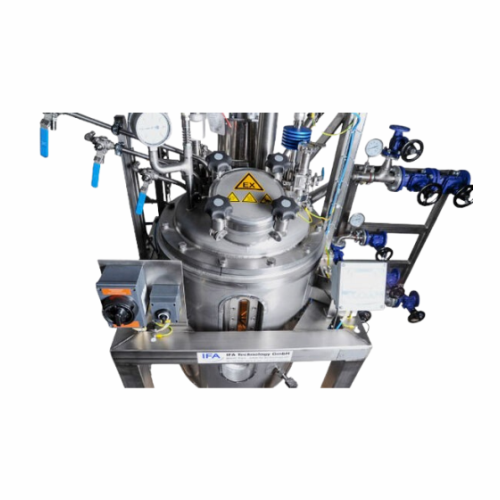
Turnkey resin synthesis plant system
Streamline resin production with a comprehensive turnkey system designed to efficientl...
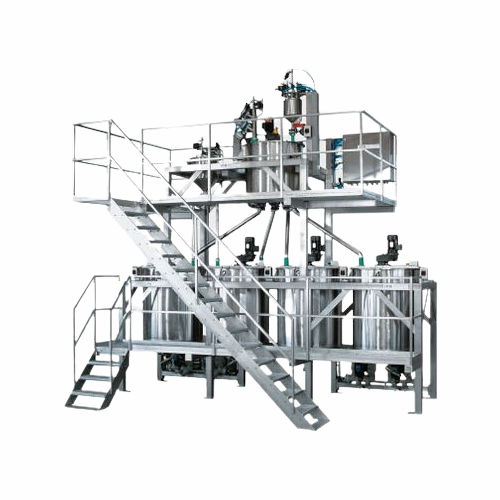
Gravimetric dosing systems for precise material measurement
Achieve precise material measurement with gravimetric dosing...
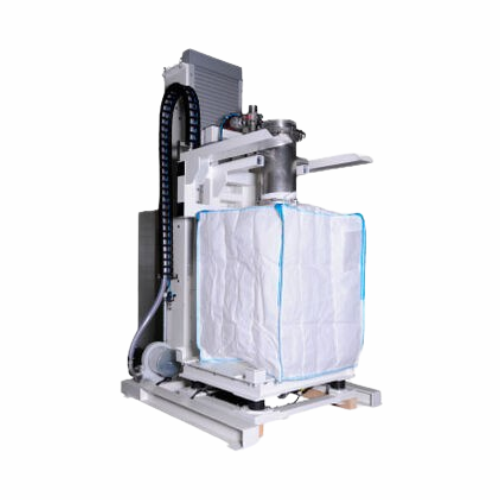
Customised tank systems for liquid and bulk material storage
Ensure safe and compliant storage of liquids and bulk mater...
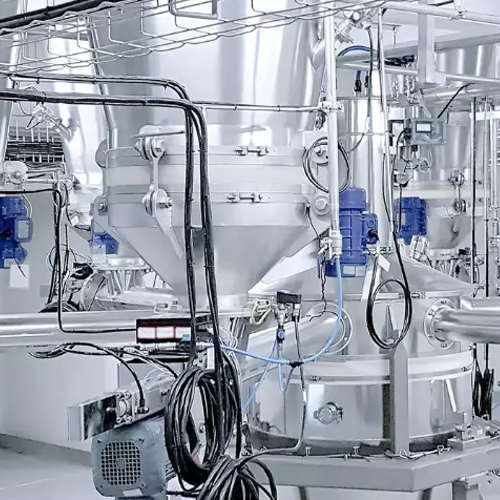
Conical screw mixer for powder blending
Achieve precise and homogeneous blending with the conical screw mixer, ensuring uni...
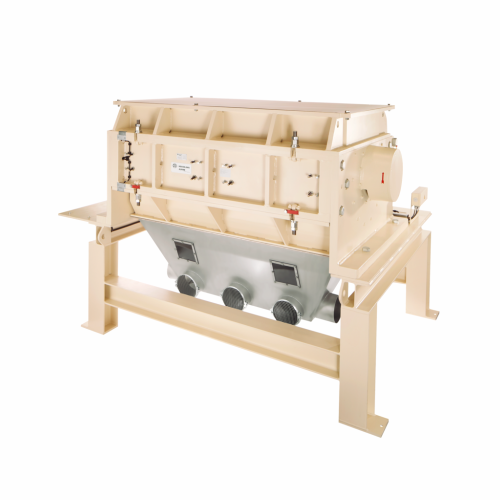
Compact granulator for plastic comminution
Optimize your plastic recycling operations with a compact granulator designed t...
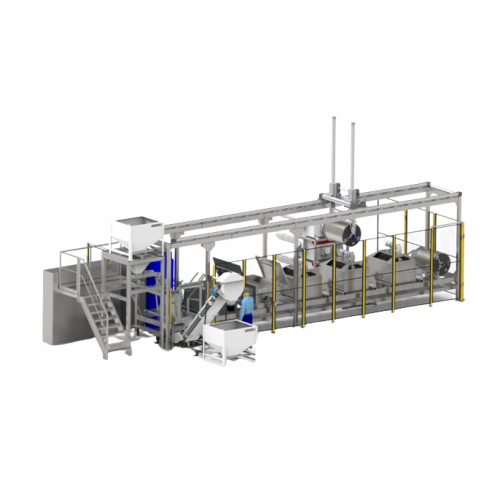
Modular system for liquid treatment protocols
Streamline your seed treatment process with a versatile system capable of ha...
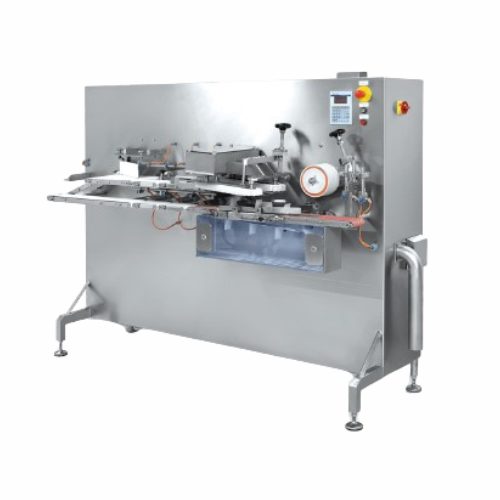
Cheese packaging system for mixed cheese types
Optimize your cheese production line by seamlessly integrating a system des...
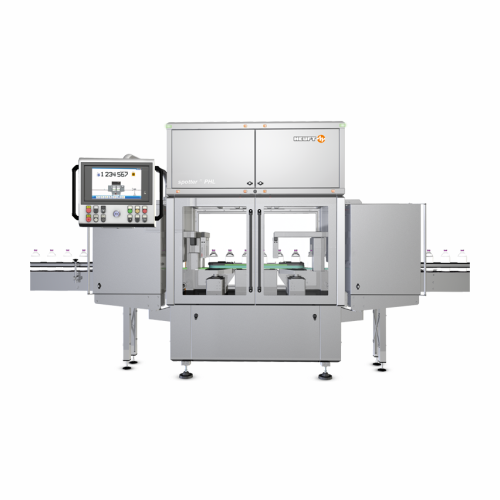
Vial inspection system for pharmaceutical industry
Ensure vial integrity by detecting and rejecting contaminants, glass d...
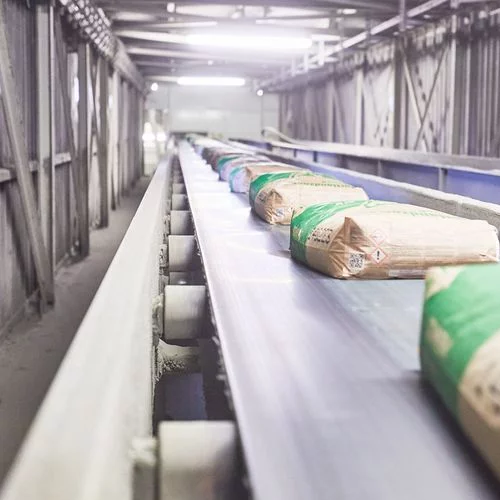
Industrial wire screens for efficient material separation
Streamline your packaging and production process with custom-e...
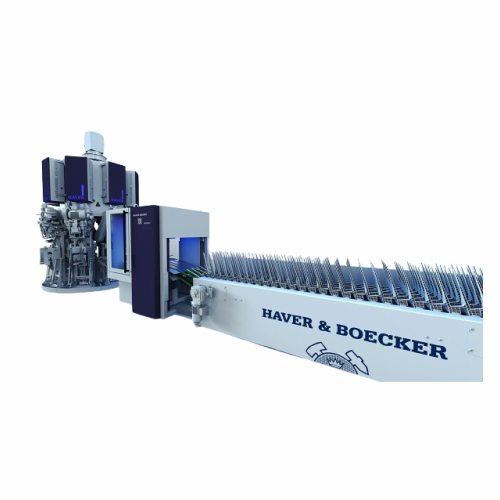
Fully automatic bag applicator for valve bags
Maximize your packaging line efficiency with a high-speed system that seamle...
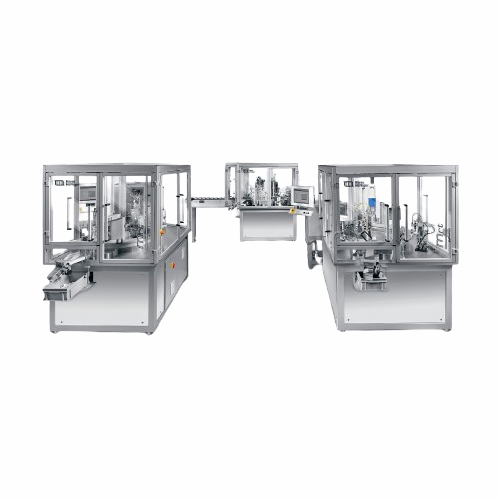
Round motion assembly platform for inhalers
Achieve high-efficiency assembly and inspection of inhalers and diagnostic dev...

Production system for multi-chamber portion packs
Efficiently produce multi-chamber portion packs with high precision for...
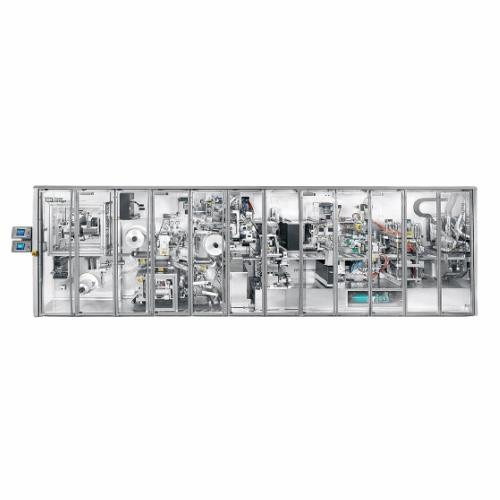
Production of sterilized aluminum blister packs
Optimize your medical product packaging with our high-speed solution for p...
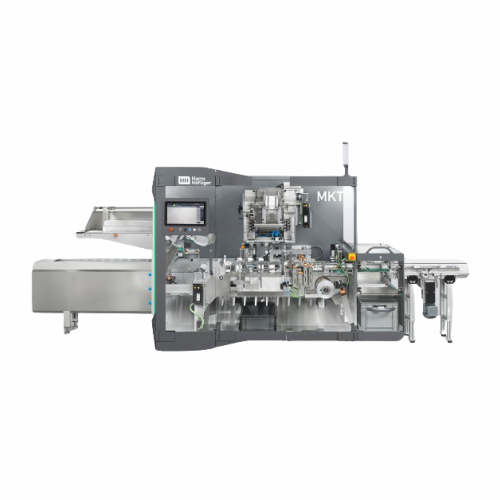
High-performance cartoning system for pharmaceutical products
Optimize your packaging line with a flexible cartoning sol...
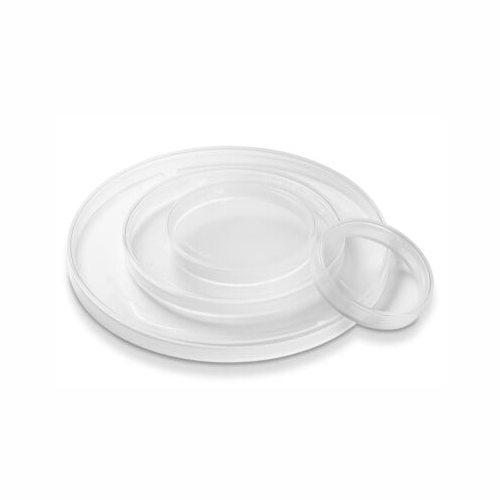
Silicone dust caps for dust-tight powder transfer
Achieve dust-tight containment and efficient powder transfer with flexi...
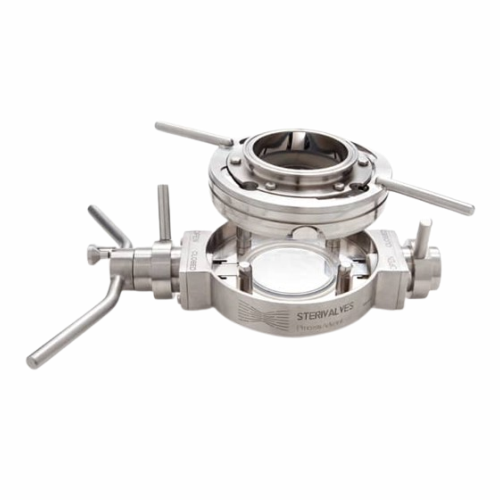
Split butterfly valve for sterile powder transfer
Ensure safe and sterile transfer of powders with unparalleled containme...
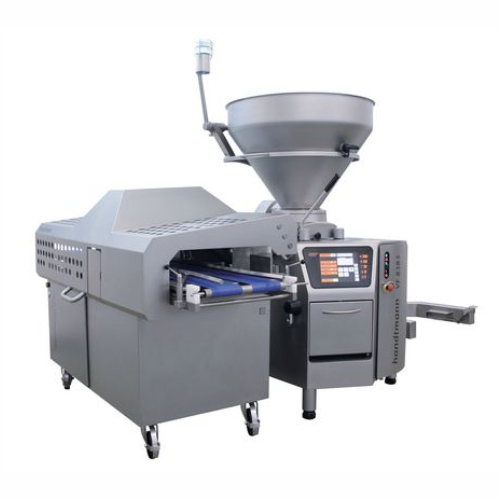
Cutting unit for high-yield tin loaves
Experience precision and efficiency in dough portioning with our high-capacity cutti...
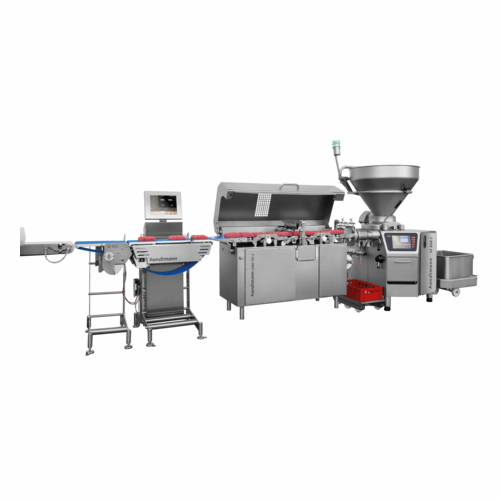
Minced meat portioning line
Optimize your production line with precise portioning and packaging of minced meat, enhancing ef...
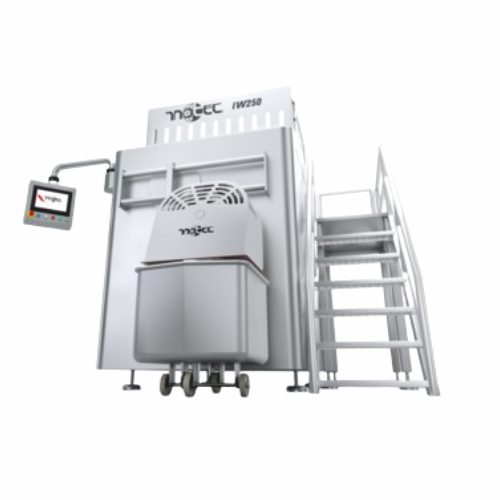
High-capacity industrial grinder for frozen and fresh raw materials
Effortlessly grind both deep-frozen blocks and fres...
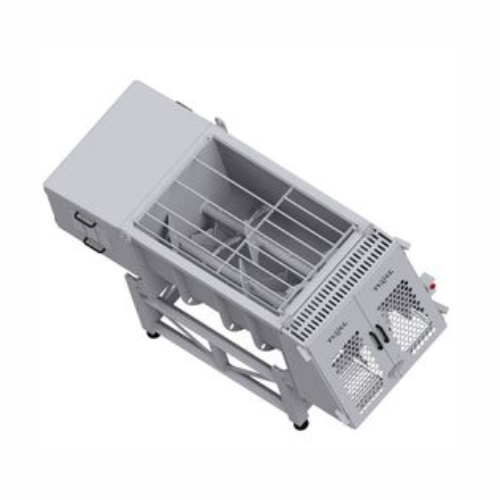
Industrial mixer for food and pet food production
Achieve precise and efficient mixing of viscous to highly viscous produ...
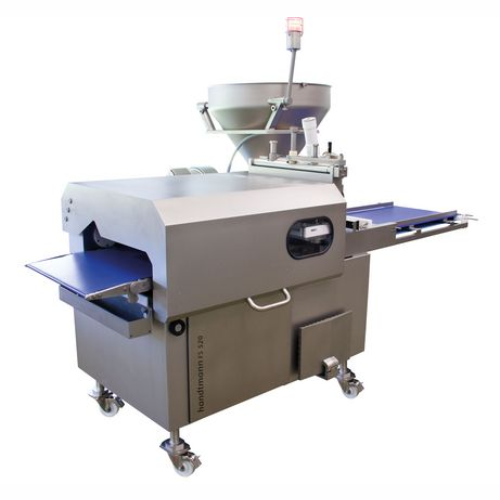
Multi-lane forming system for 3d food product shapes
Achieve precise weight accuracy and high-speed production of diverse...
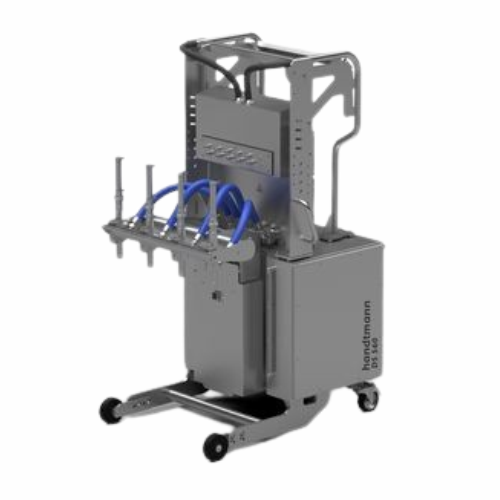
Depositing system for multi-lane dosing with vertical traversing
Achieve precision dosing and flexible portioning with t...
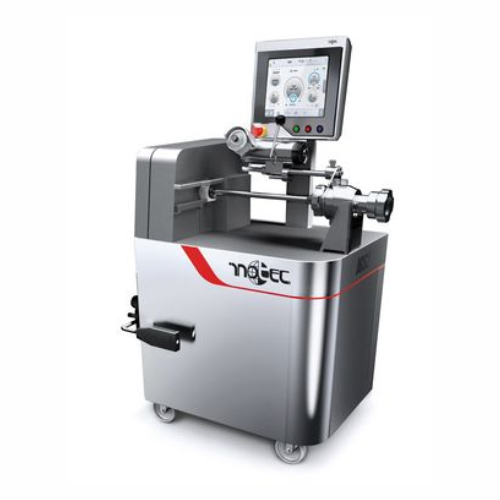
Tying solution for sausage products in natural and collagen casings
Efficiently portion and tie sausage products to per...
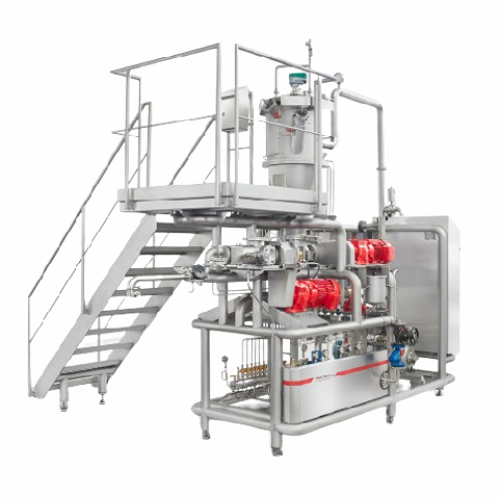
Integrated process system for hard caramel production
Optimize your candy production with a fully integrated system desig...
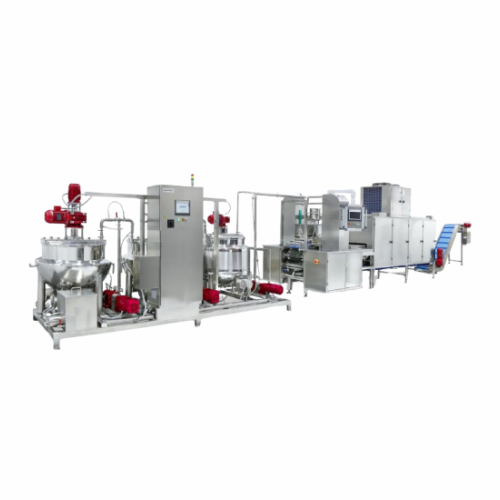
Automatic gummy production system
Achieve precise control in gummy production with systems that cater to diverse formulatio...
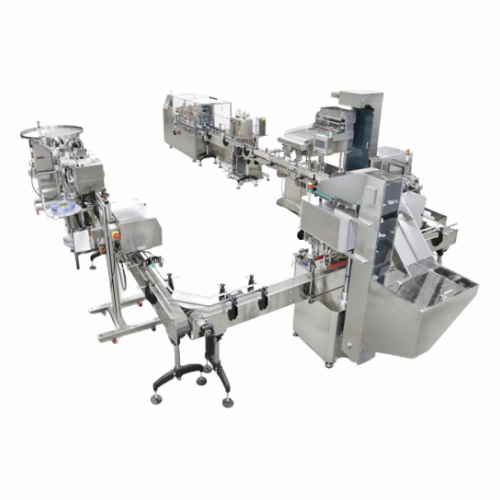
Packaging system for gummy products
Optimize your gummy production with a flexible packaging system that safeguards product...
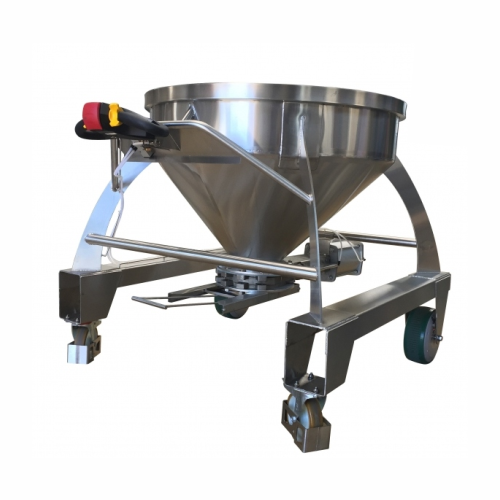
Mobile stainless steel tank for grape harvest transfer
Facilitate efficient grape harvest transfer with a motorized mobil...
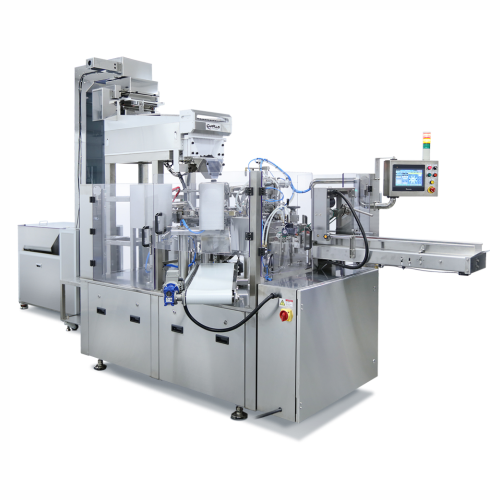
Gummy counter for gusseted bags
Optimize your gummy production line with precise counting and packaging into re-sealable gus...
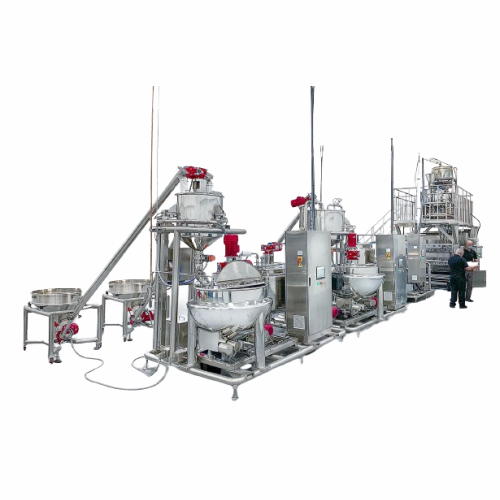
High-capacity gummy production system
Optimize your gummy production with a starchless system that deposits up to 240,000 g...
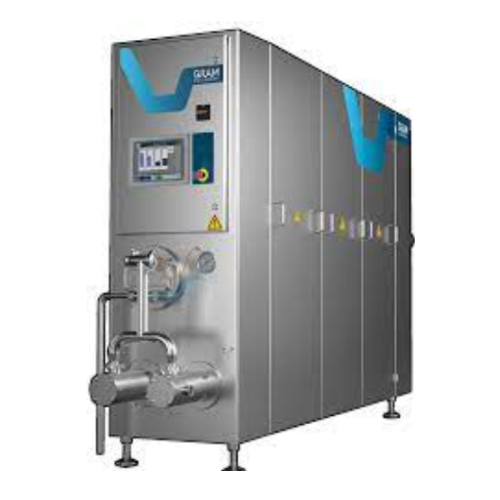
Continuous ice cream freezer
Enhance the consistency and texture of frozen desserts with this self-contained solution, strea...
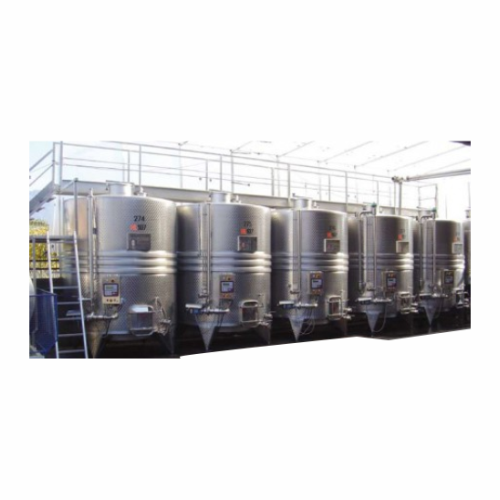
Vertical red winemaking tanks
Streamline your red wine vinification with advanced vertical tanks that optimize oxygen manage...
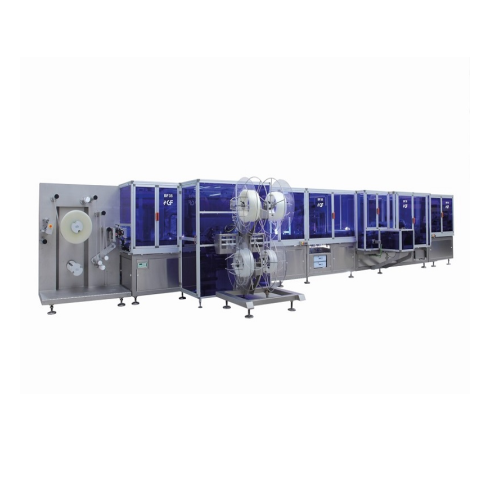
Bag forming system for pharmaceutical industry
For fluid pharmaceutical production, ensure precise formation and sealing o...

Aseptic transfer port for secure bi-directional transfer
Ensure seamless and contamination-free transfer of sterile mater...
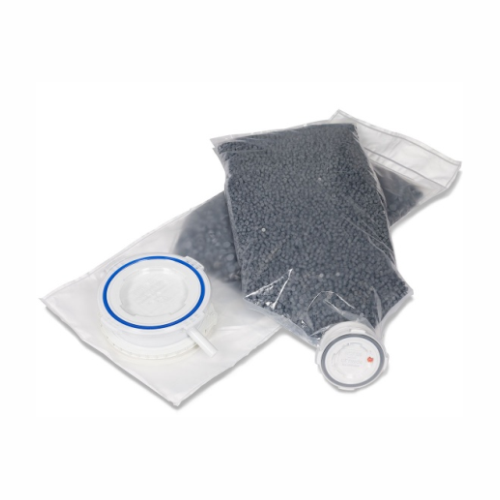
Sterile transfer bags for aseptic production
Ensure contamination-free and efficient component transfer in high-speed asep...
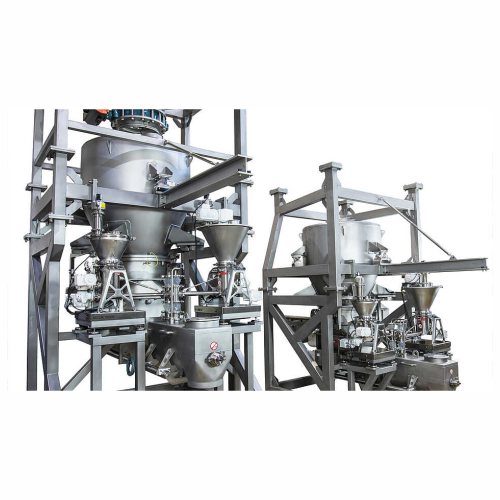
Continuous inline mixing for late product differentiation
Achieve seamless product differentiation with compact inline m...
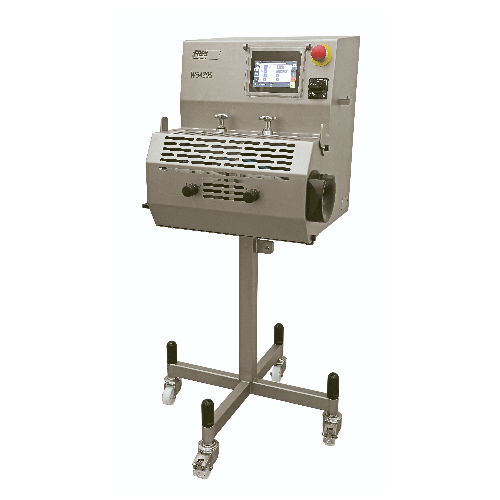
High-speed sausage cutter
Streamline your sausage production with precision cutting technology, ensuring consistent product ...
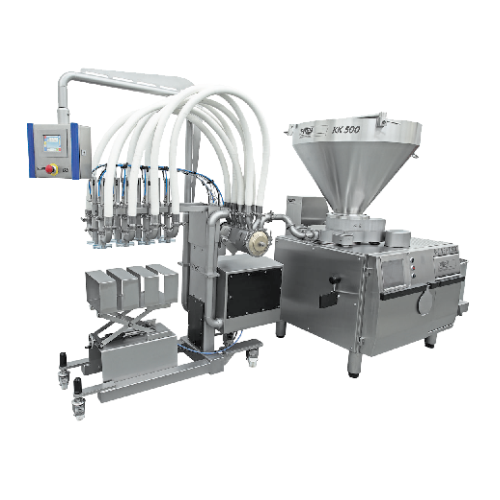
Servo-driven dosing and portioning system
Optimally dose and portion a wide range of food products with precise weight acc...
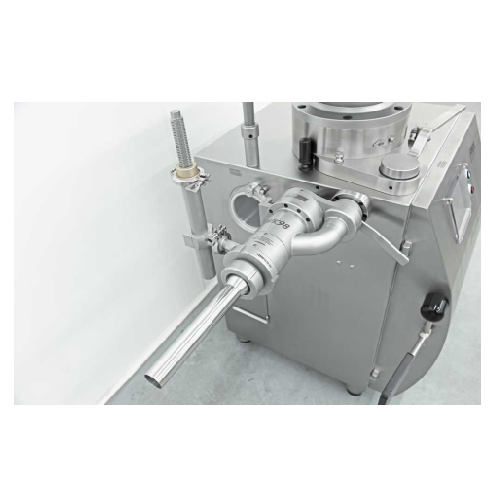
Grinding head system for raw sausage production
Optimize your raw sausage production with a grinding head system designed ...
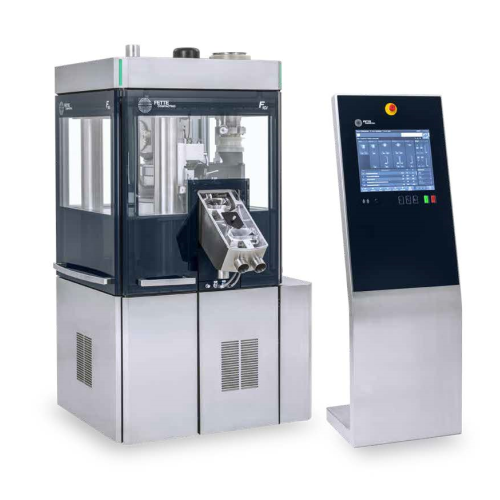
Industrial tablet press for high output production
Achieve precise control and efficient production with advanced rotary ...
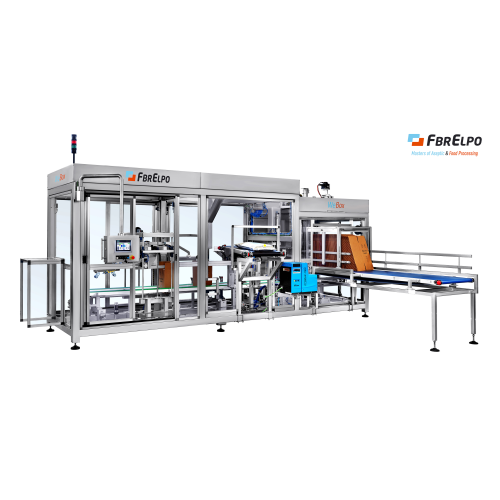
Automatic cartoning solution for 3-20l aseptic bags
Streamline your aseptic packaging with an integrated cartoning soluti...
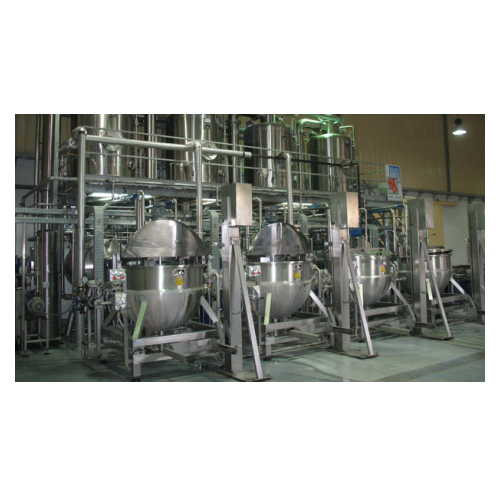
Marmalade, sauces, nectars, and baby food processing solution
Maximize flexibility in your production line with a system...
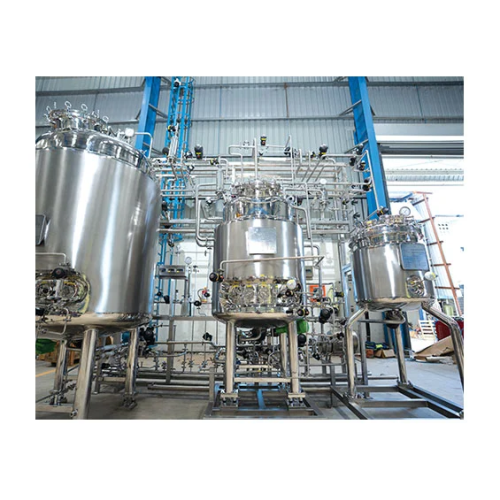
Pharma manufacturing process vessels
Ensure contamination-free production of sterile liquid formulations with process vesse...
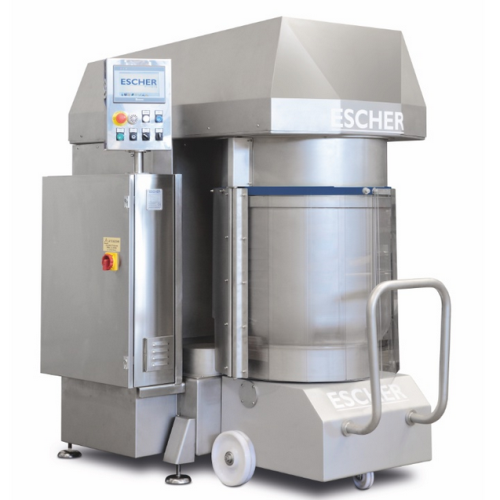
Planetary mixer with double tool for pastry dough
Optimize your pastry production with precise mixing capabilities that e...
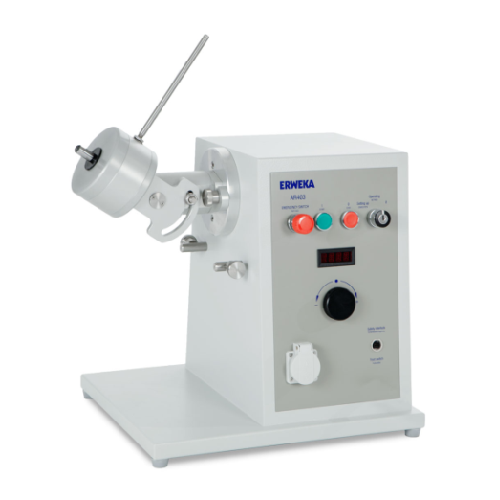
All-purpose mixer and processor for laboratory and small scale production
Optimize your small-scale production with a ...
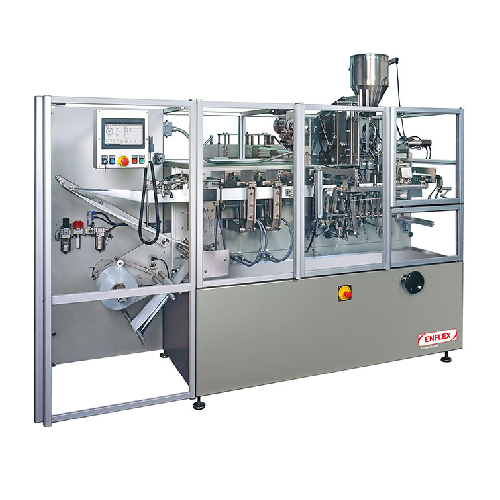
Flat pouch packaging for towelettes
Design high-speed precision packaging to enhance towelette freshness and efficiency on ...
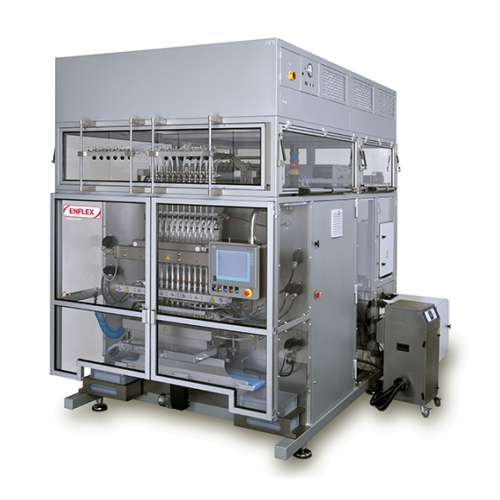
Intermittent stick pack machine for pharma and healthcare
Looking to streamline your packaging operations with high-spee...
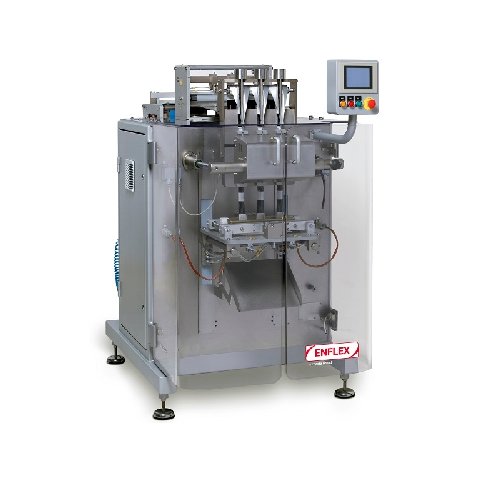
Intermittent stick pack packaging system for pharma products
Achieve precise dosage and packaging of pharmaceutical and ...

High-speed multi-lane flat pouch packaging system
Boost your packaging efficiency with a high-speed solution designed for...
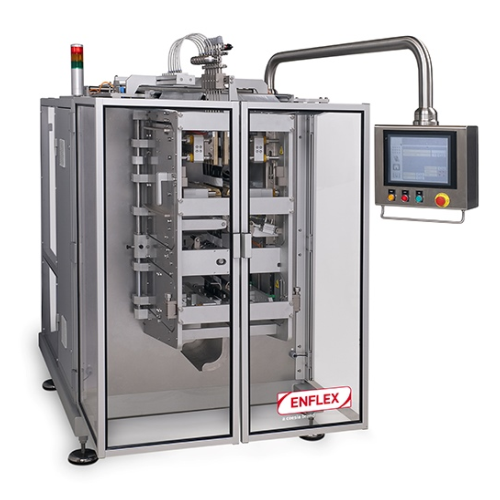
Multi-lane vertical pouching solution for pharma industry
Achieve precision and high-speed efficiency in single-dose liq...
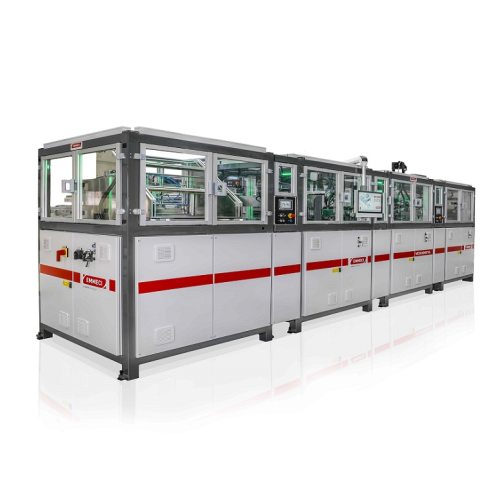
Digital luxury box making line
Elevate your luxury packaging with precision-engineered digital technology designed to craft ...
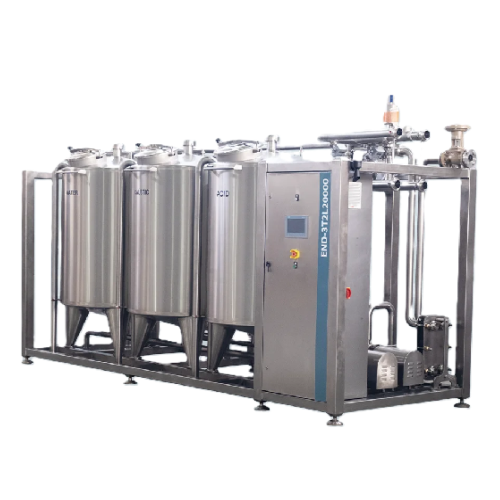
Automated cleaning in place (cip) systems for beverage processing
Optimize your production with automated CIP systems t...
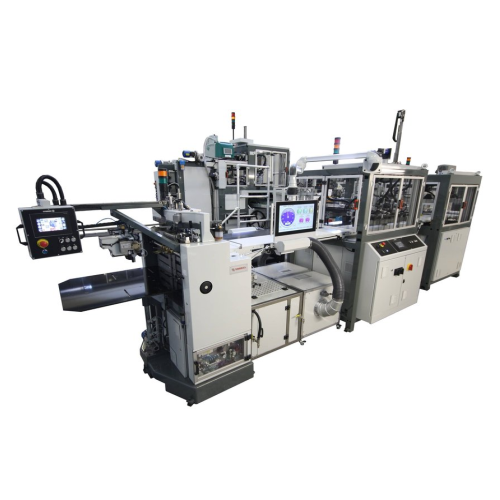
Medium to large-size box making line
Streamline your packaging process with a versatile box making line that efficiently ha...
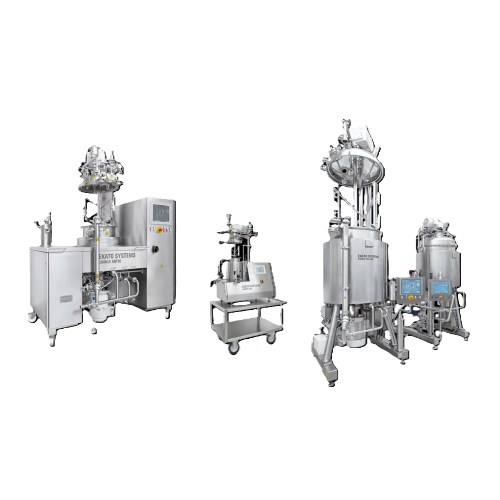
Vacuum processing units for high-viscosity products
For manufacturers seeking to streamline production of high-viscosity ...
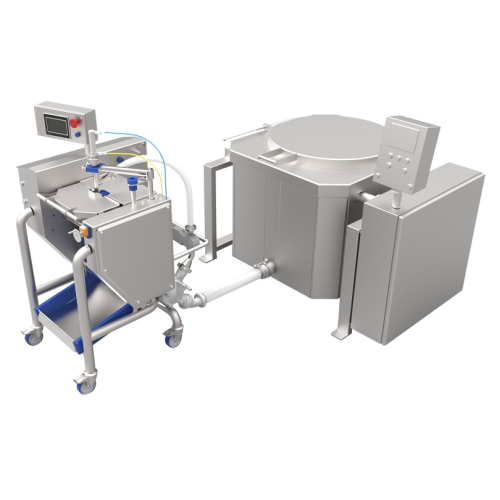
Production solutions for convenience foods
Effortlessly transform your innovative recipe ideas into consistent, high-quali...
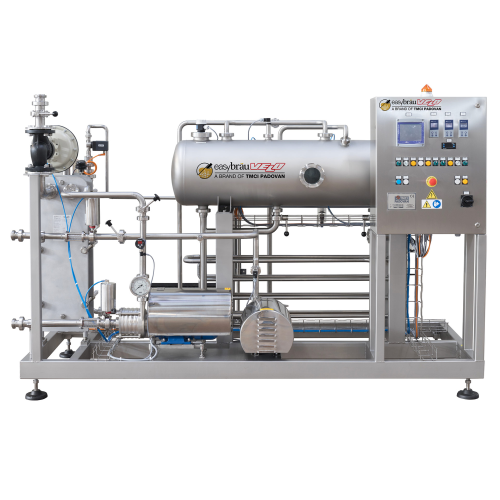
Carbonation system for Co2 dosing in beer production
Achieve precise carbonation in every beverage batch with seamless CO...
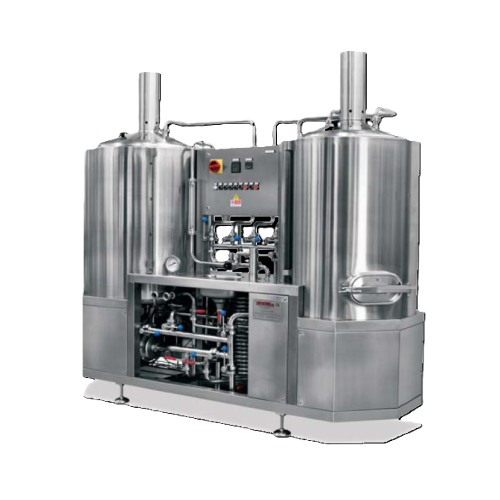
Compact brewhouse for microbreweries and brewpubs
Designed for seamless integration into microbreweries, this compact bre...
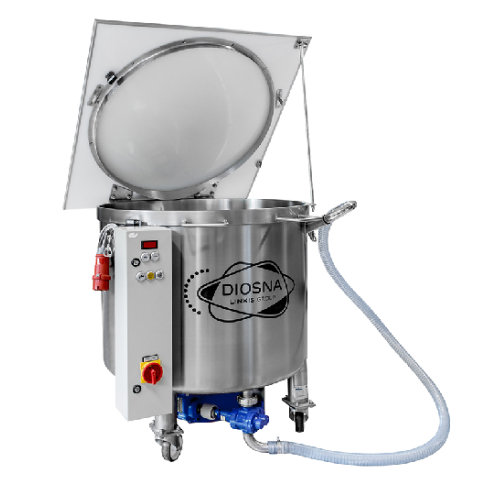
Wheat and spelt pre-dough system
Optimize your bakery production with a flexible system designed for rapid, lump-free mixing...
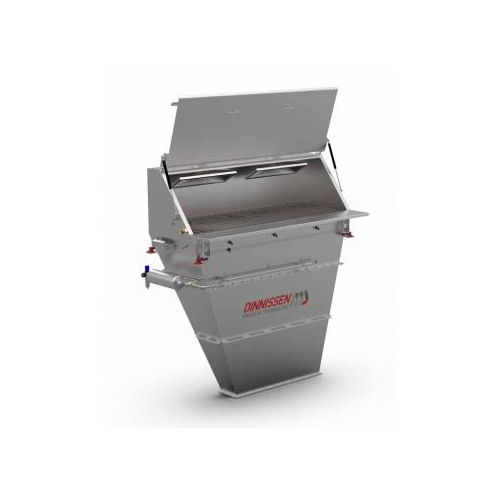
Bag emptying system for bulk material handling
Streamline your material processing operations with a versatile solution de...
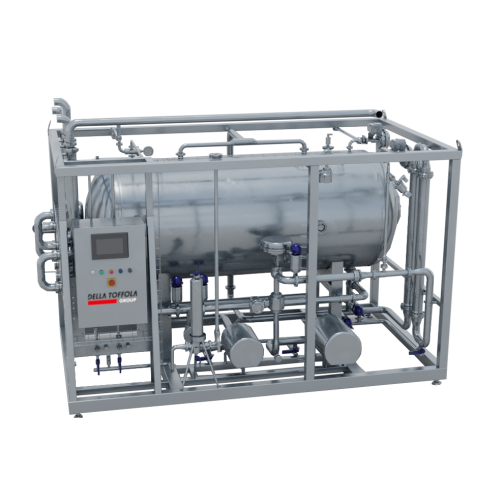
Inline carbonation solution for beverages
Achieve precise carbonation control and consistency in your beverage production ...
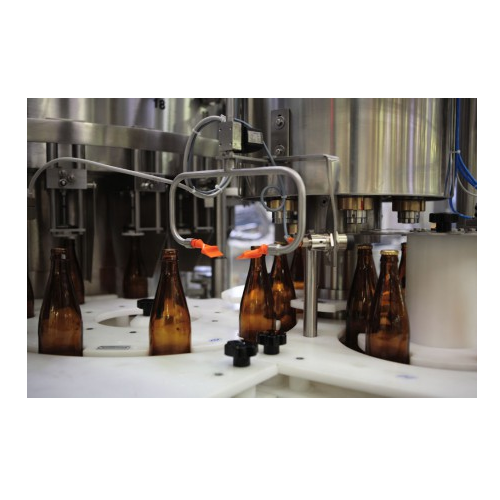
Crown capping solution for beverage bottles
Ensure perfect sealing for beverage containers with a high-speed crown capping...
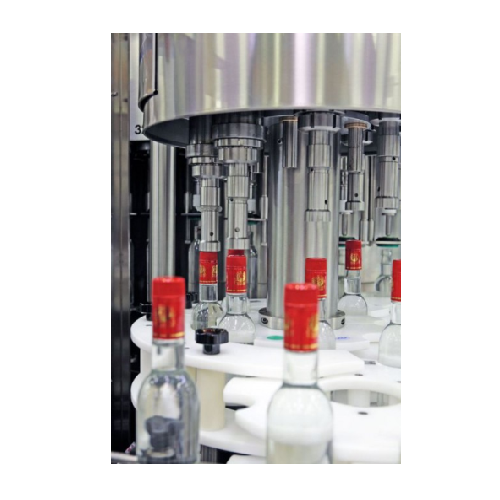
Press-on capping system for bottles
Ensure precise and secure closure of various bottle types with our versatile press-on c...
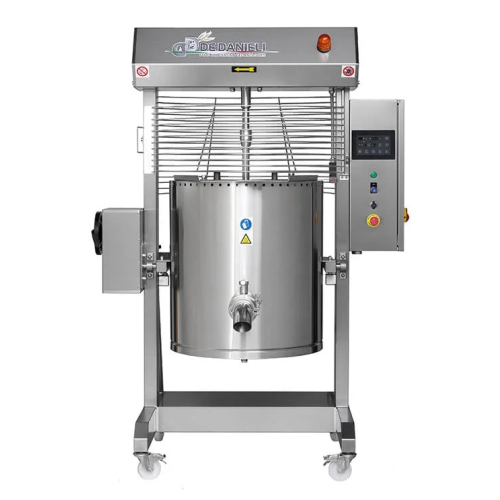
Electric cooker for preserved food preparation
Efficiently streamline your preserved food production with a multifunction ...
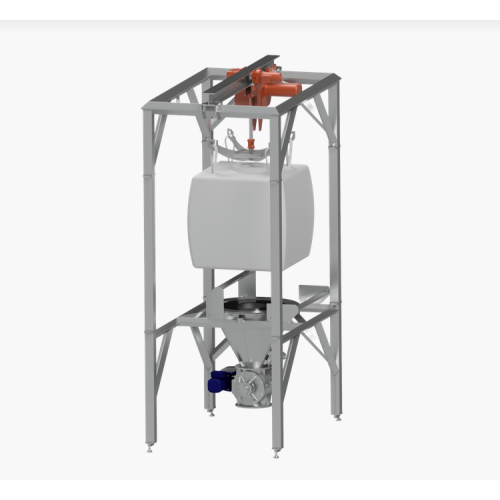
Bigbag discharge system for food, chemical, and pharmaceutical industries
Ensure precise and dust-free handling of bul...
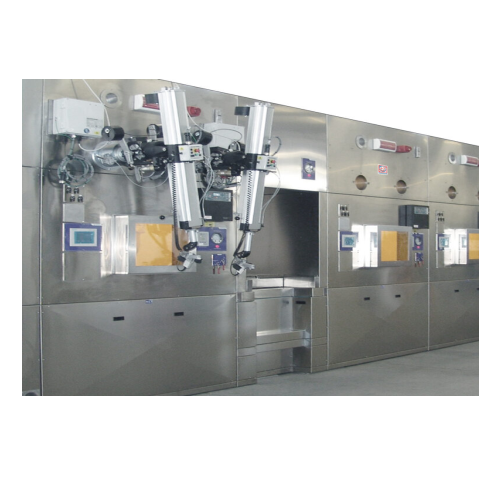
Hot cell system for solid target manipulation in radiopharma
Optimize radiopharmaceutical synthesis with precise manipul...
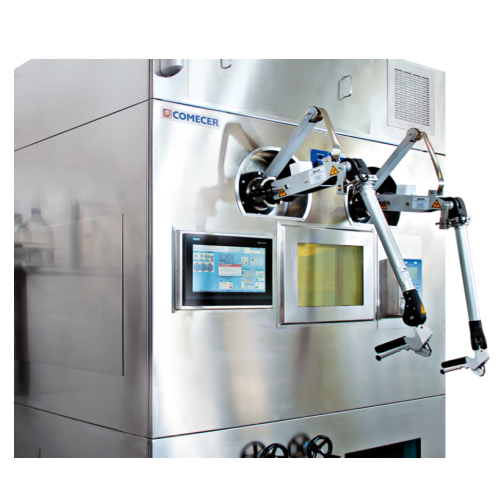
Technetium-99m generator production line
Streamline your radiopharmaceutical production with our solution, ensuring precise...
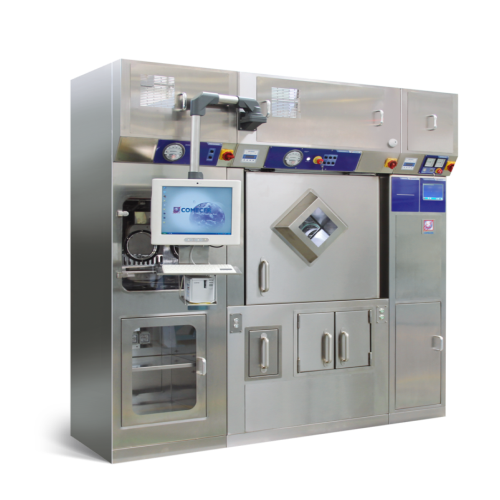
Robotic dispenser for radiopharmaceuticals
Ensure precise and safe handling of radiopharmaceuticals with a fully automated...
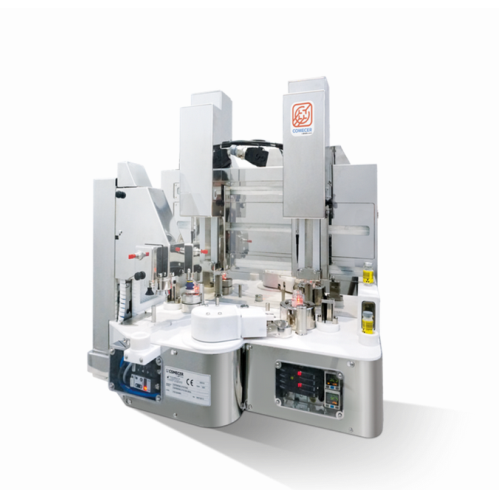
Micro-dispenser for lu-177 and ac-225
Efficiently dispense precise volumes of radioisotopes for diagnostic and therapeutic ...

Volumetric dispensing system for radiopharmaceuticals
Ensure precise dosing of radiopharmaceuticals like FDG and tracer i...
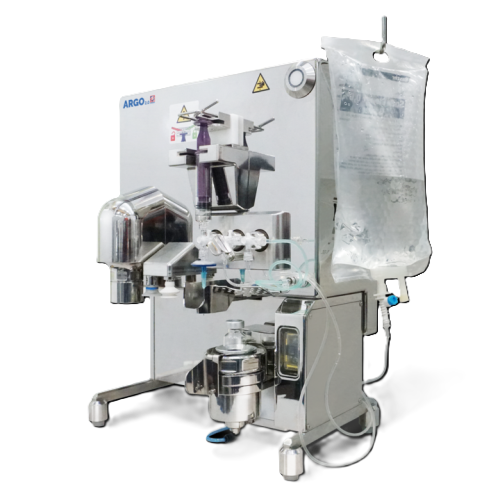
Automatic vial dispensing system for nuclear medicine
Ensure precise, compliant dispensing of radiopharmaceuticals with a...
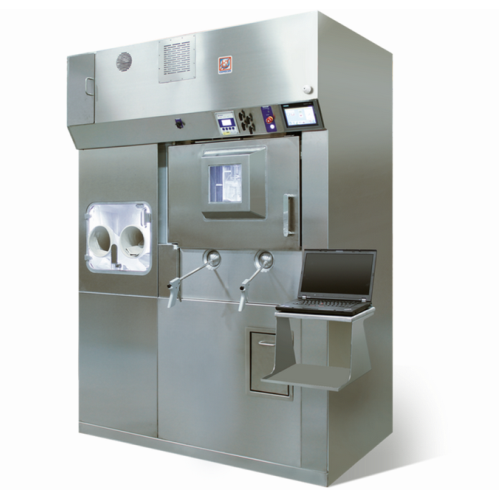
Shielded isolators for radiopharmaceutical dispensing
Ensure precise radiopharmaceutical dose preparation with complete o...
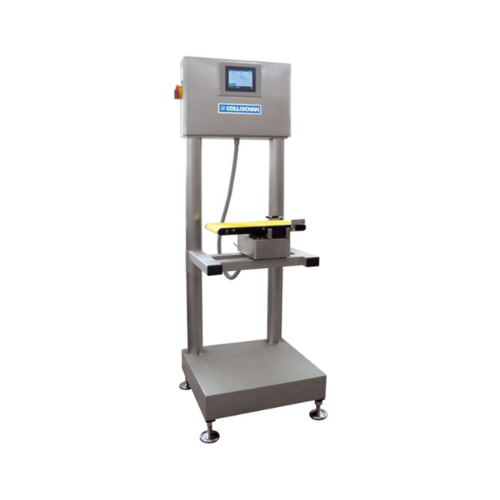
Basic checkweigher for weight control in low to medium performance
Ensure accurate weight control with a versatile chec...
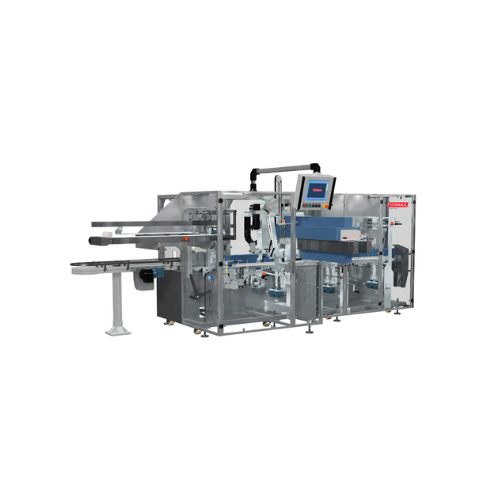
Vertical cartoning solution for fragrance and skincare products
Effortlessly carton even the most delicate cosmetics wit...
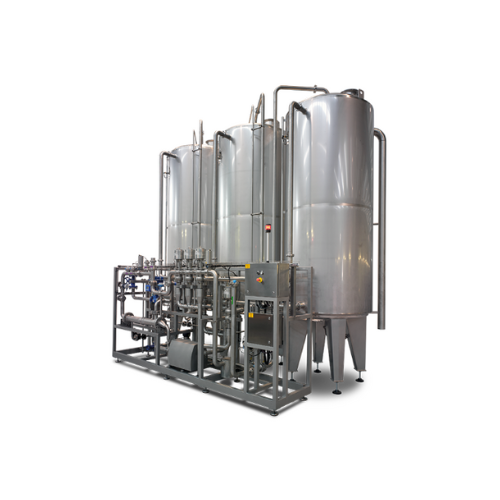
Cleaning solution tanks for beverage production
Achieve superior internal cleaning of beverage containers with our advance...
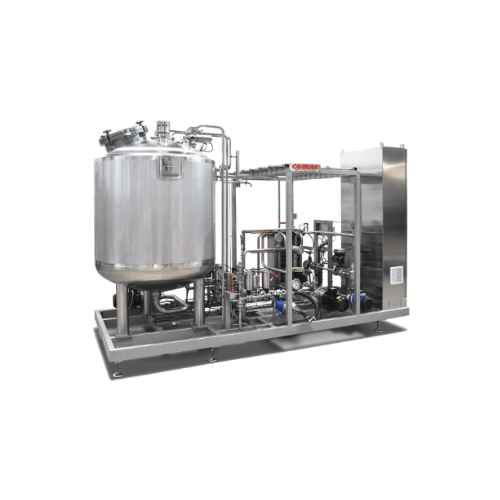
Flash pasteurizer for beverage production
Ensure beverages maintain quality and safety with precise temperature control an...
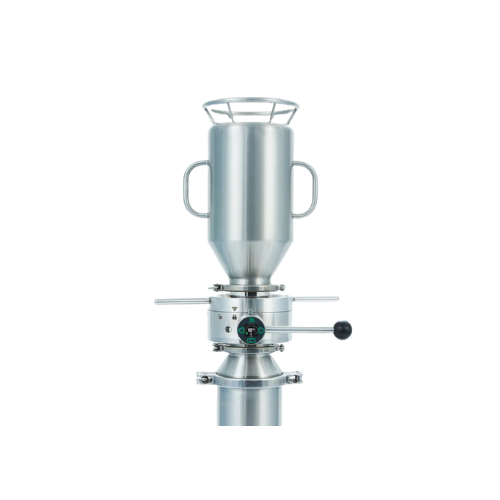
High containment powder transfer valve
Ensure high containment for potent powders in your production line, reducing contami...

High containment powder transfer valve for bulk material
Ensure operator safety and prevent cross-contamination with robu...
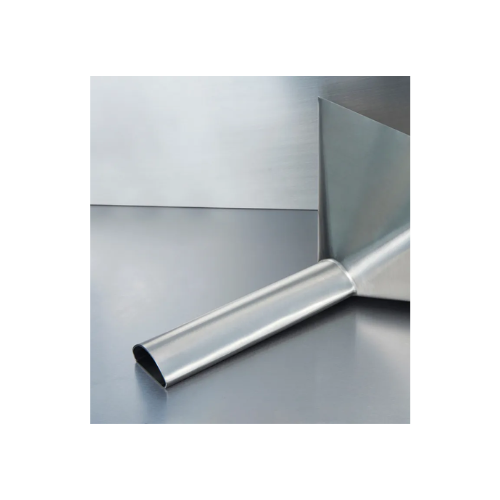
Powder dispensing funnel
Enhance powder handling accuracy while minimizing product loss with a precision-engineered dispensin...
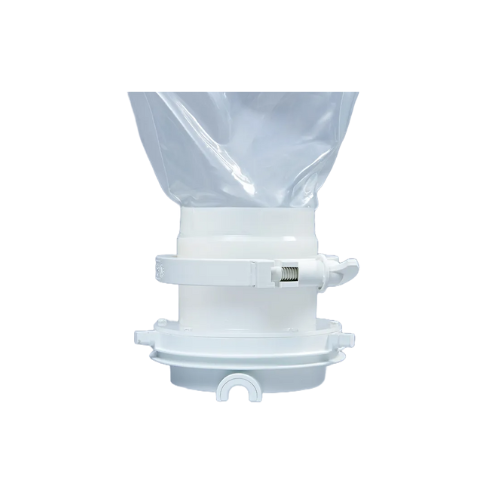
Single use valves for powder transfer
Efficiently transfer powder ingredients with a single-use containment solution, ensur...
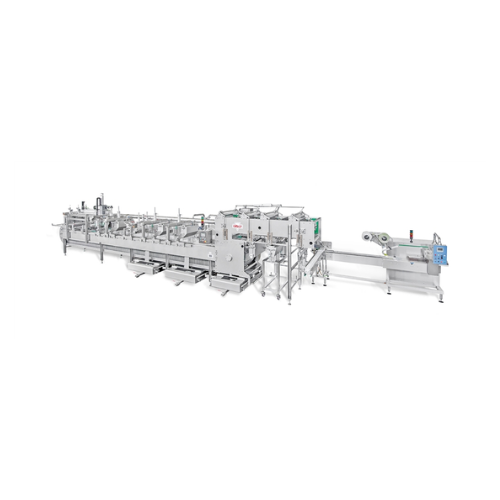
Linear mould system for ice cream production
Optimize your ice cream line with modular flexibility, allowing seamless adap...
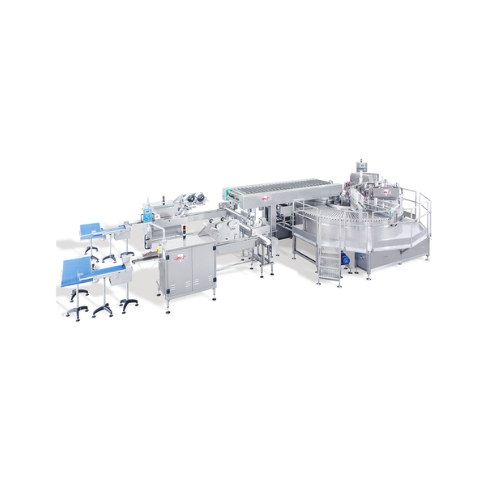
Rotary mould machine for ice cream production
Streamline your ice cream production with a rotary mould machine designed fo...
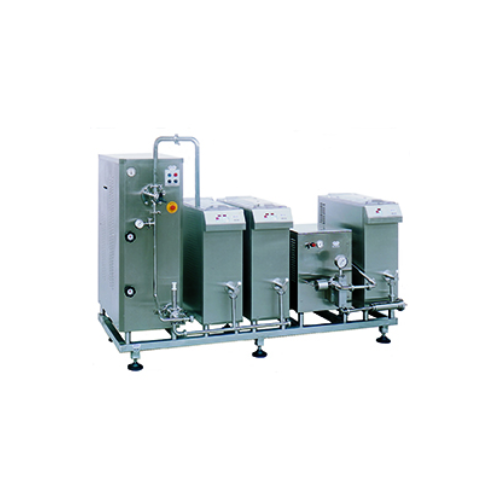
Pilot plant for ice cream production
Optimize your ice cream production with a flexible pilot plant that seamlessly integra...
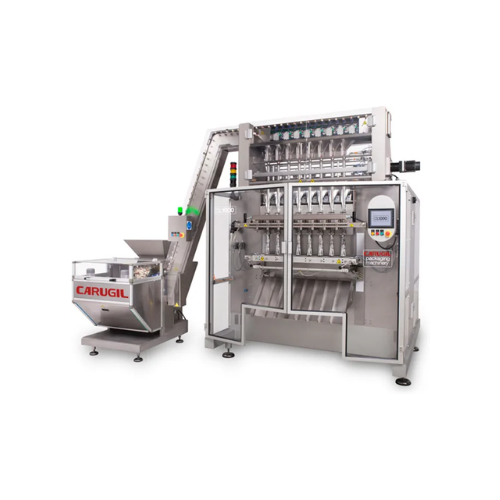
Stickpack wrapper for lollipops
Enhance your confectionery line’s efficiency by wrapping up to 480 lollipops per minut...
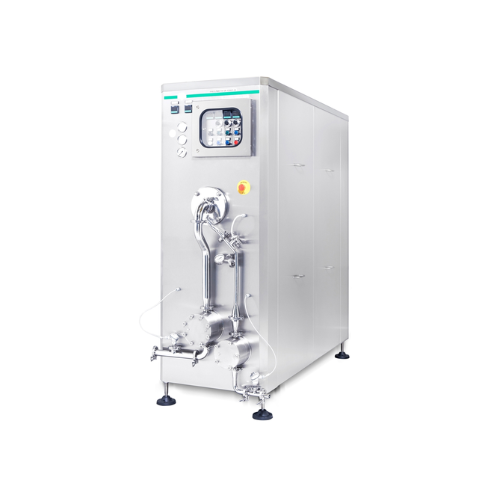
Lobe pump freezer for industrial ice cream production
Streamline your ice cream production with a semi-automatic lobe pum...
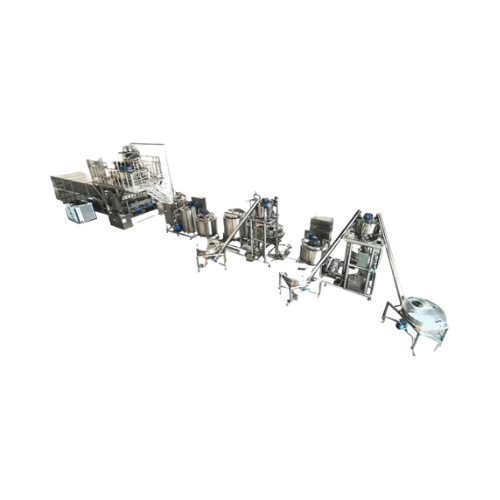
Automatic gummy candy production system
Maximize your confectionery output with a high-speed system capable of producing up...
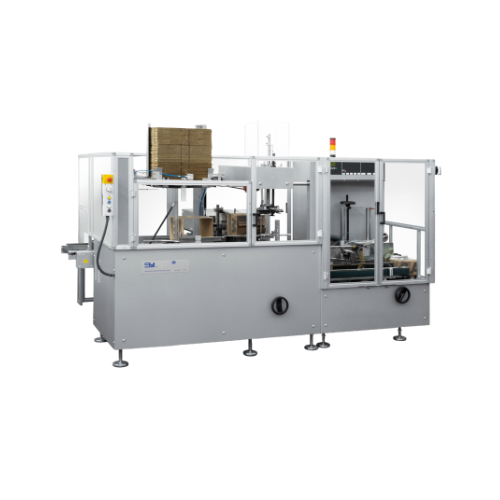
High-speed horizontal case packer for shipping cases
For high-demand production lines, this modular case packer streamlin...
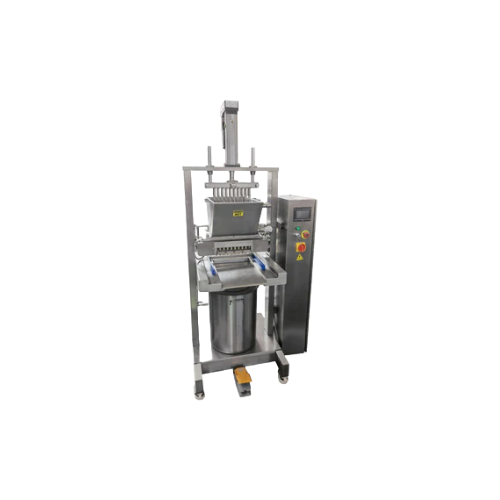
Gummy candy depositor for precision manufacturing
Achieve consistent gummy size and shape while maintaining precise weigh...
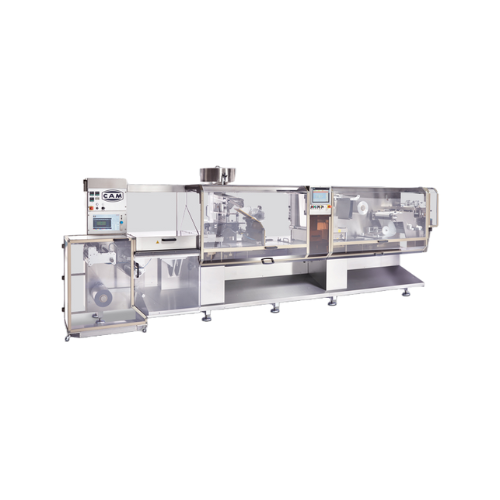
High speed blister packaging for pharmaceutical industry
Ensure precision and speed in pharmaceutical packaging with a hi...
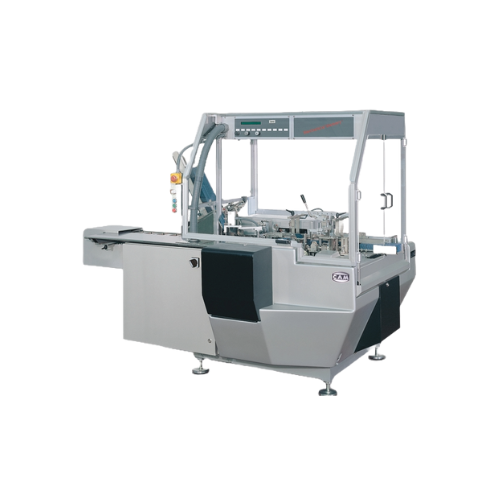
Intermittent motion horizontal cartoning system
Streamline your packaging operations with a high-speed cartoning solution ...
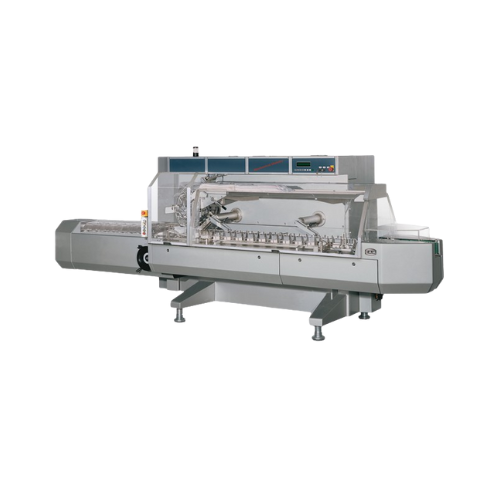
High-speed continuous motion cartoner
Streamline your packaging line with precise cartoning operations, ensuring secure and...
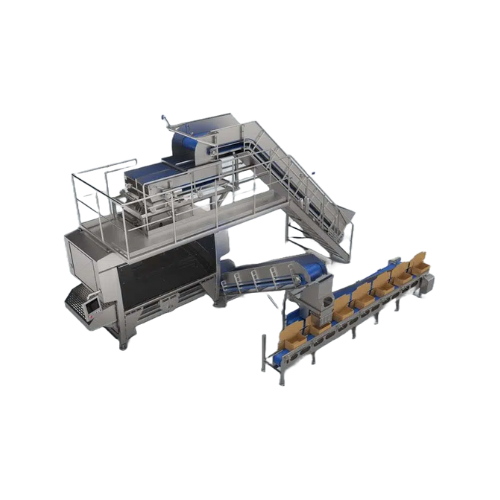
High-speed weighing system for large batch sizes
Maximize yield and minimize waste with a high-speed batching solution des...
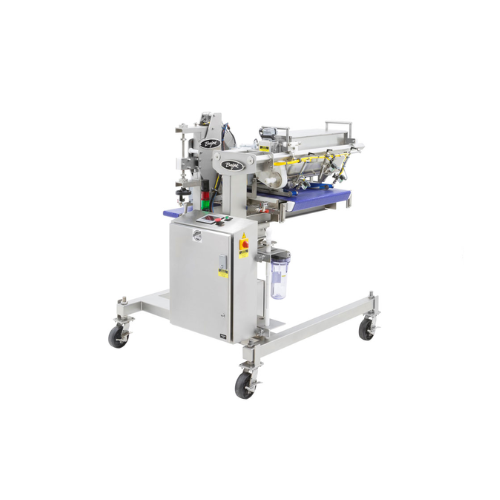
Enrober for complete dry topping coverage on dough pieces
Ensure consistent, high-speed enrobing of dry toppings on doug...
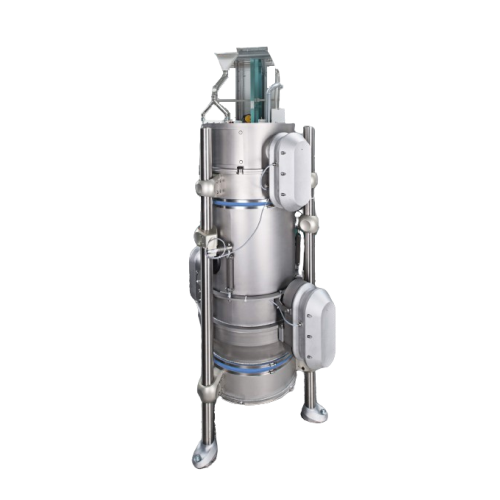
Advanced superheated steam drying solution
Harness the power of consistent drying technology to achieve optimal moisture c...
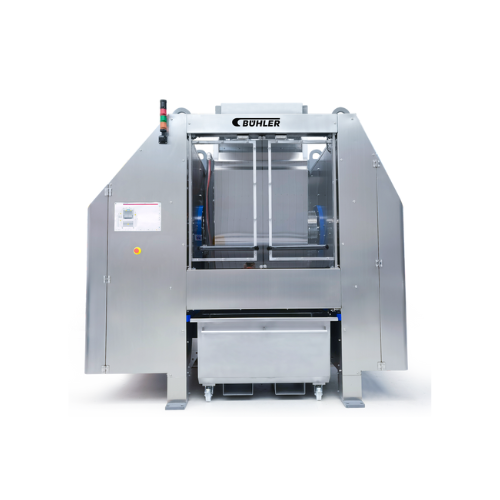
High-speed mixer for dough production
Achieve consistent dough quality and streamline your production process with this ver...
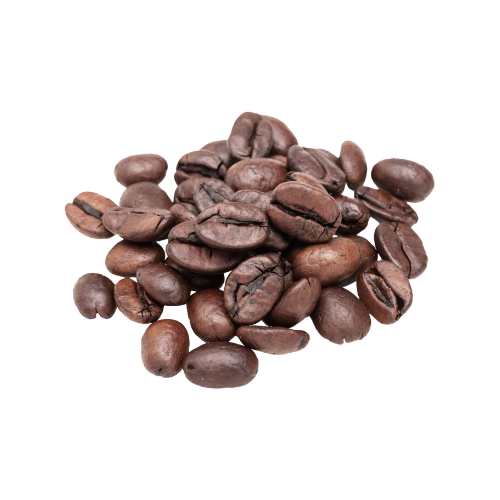
Coffee processing system for integrated coffee production
Enhance your coffee production with a versatile system that in...
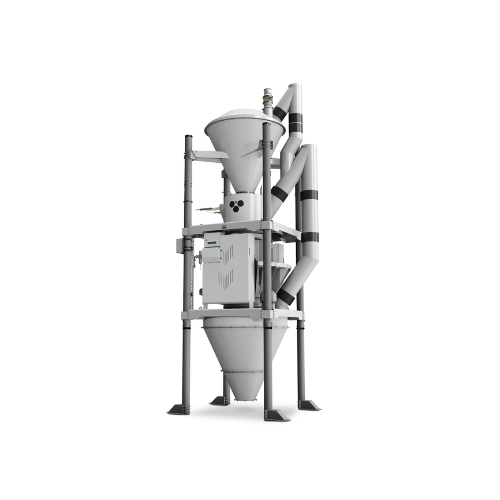
Fully automatic batch scale for powdery and granular products
Achieve precise and repeatable dosing for powdery and gran...
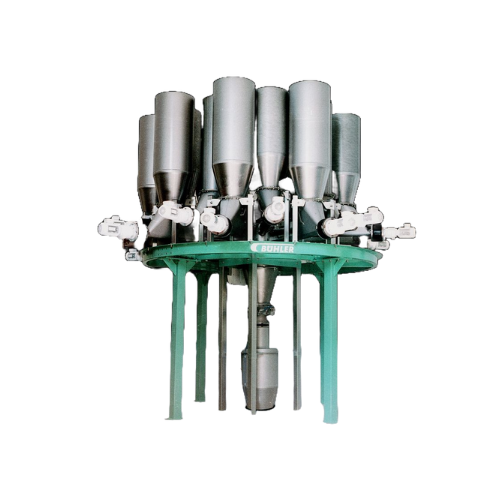
Micro-dosing system for animal feed additives
Achieve precise and consistent feed formulation with high-precision micro-do...
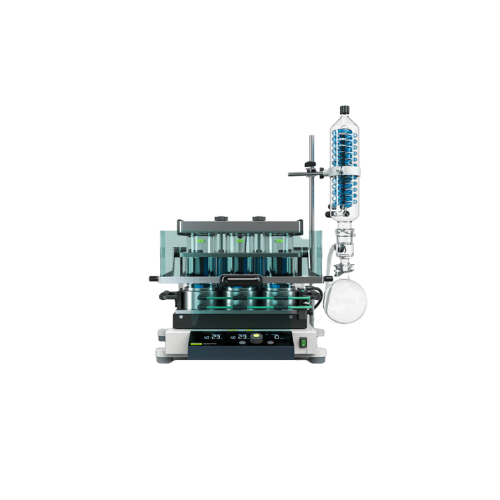
Parallel evaporation system for laboratory sample preparation
Achieve precise sample concentration and drying with autom...
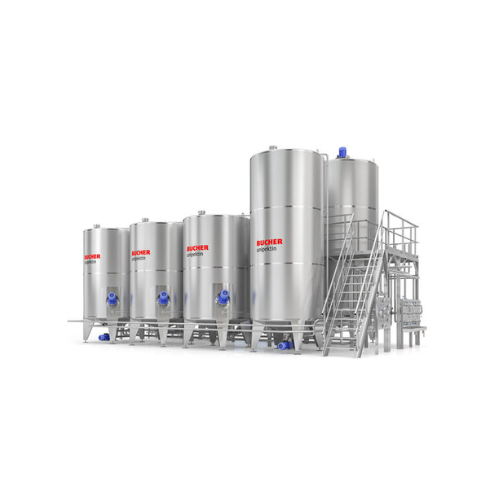
Commercial juice mixing station
Streamline your beverage production with precise mixing and dosing, ensuring consistently hi...
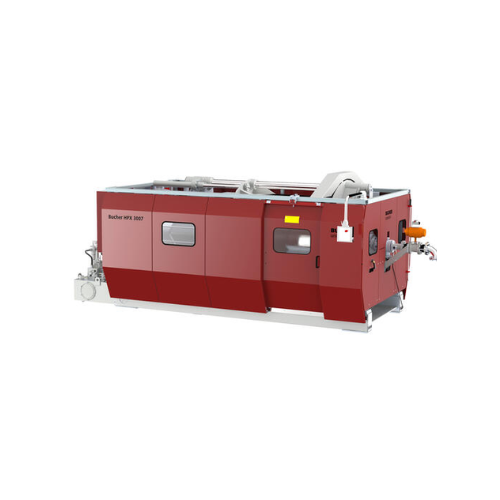
Hydraulic press for juice extraction from apples
Optimize juice yield and purity with a robust hydraulic pressing system, ...
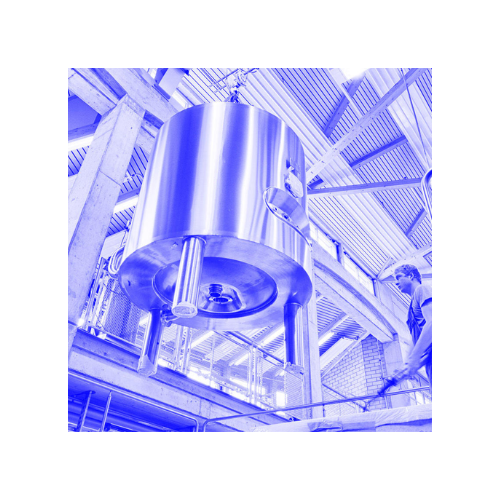
Sterile media and buffer storage tanks
Ensure uninterrupted bioproduction with our tanks designed for secure storage and pr...
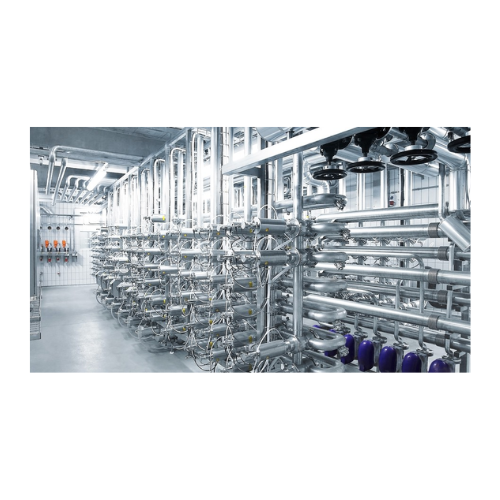
Industrial cheese processing plants
Streamline your cheese production with custom-engineered systems designed to enhance ef...
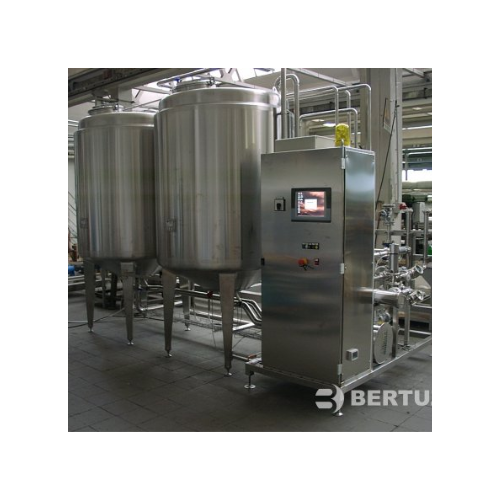
Apple processing equipment for juice and puree production
Efficiently process apples and pears into high-quality juice a...
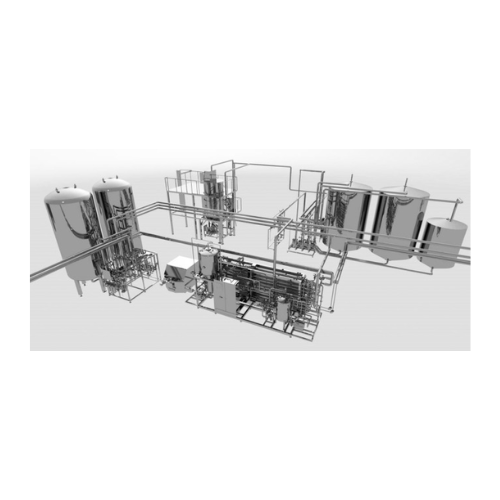
Juice reconstitution equipment for concentrated juice
Revolutionize your beverage production with advanced equipment desi...
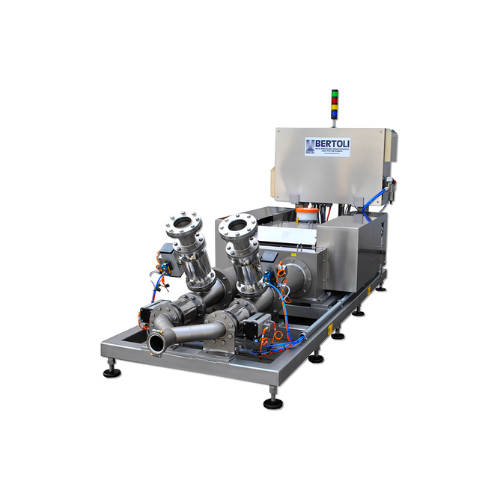
Industrial homogenizer for food and beverage applications
For manufacturers seeking consistent quality, this homogenizer...
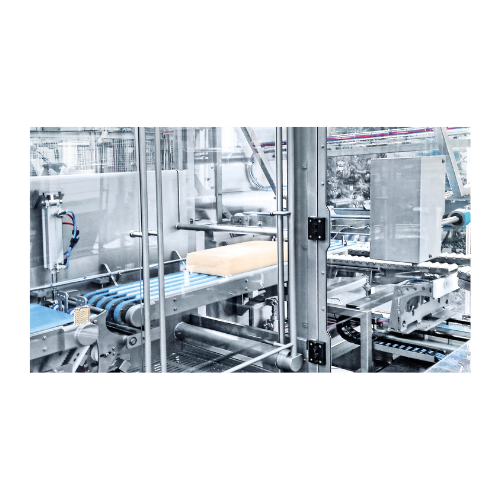
Cheese processing plant
Transform your dairy processing with comprehensive, tailored systems designed to optimize production ...
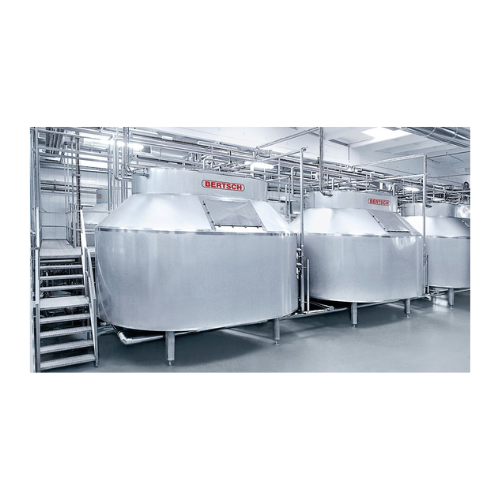
Cheese processing plant for hard and semi-hard cheese
Optimize your cheese production with a versatile solution designed ...

Cheese vat for varied cheese types
Ensure consistent high-quality cheese production with a vat that accommodates multiple c...
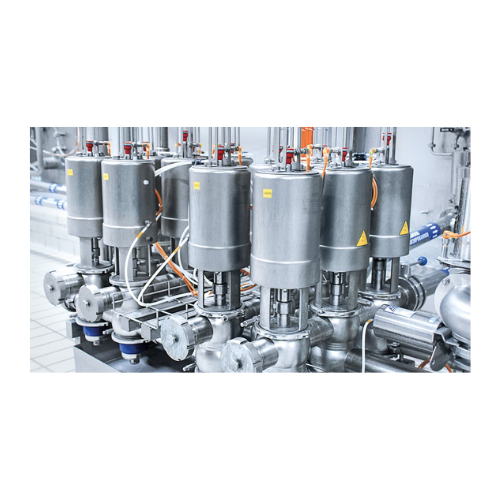
Cheese vat for diverse cheese production
Optimize your cheese production with a versatile cheese vat designed for precision...
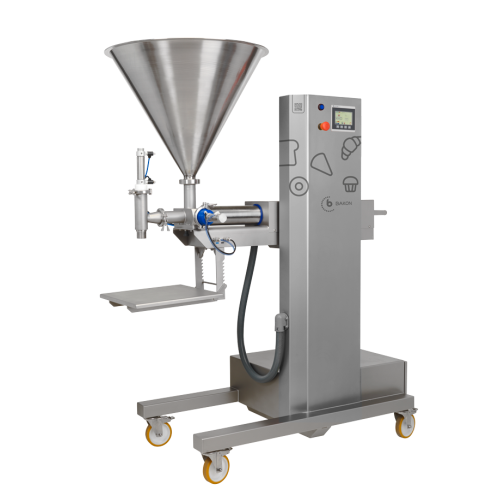
Depositing solutions for liquid and semi-liquid foods
Ensure consistent portioning and minimize waste with advanced depos...

Depositing line for cake production with paper cup denester
Optimize your cake production by seamlessly depositing marbl...
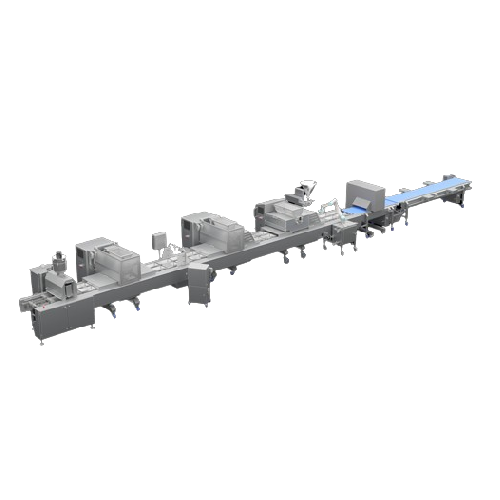
Multifunctional depositing line for bakery production
Optimize your bakery and food production with a modular depositing ...
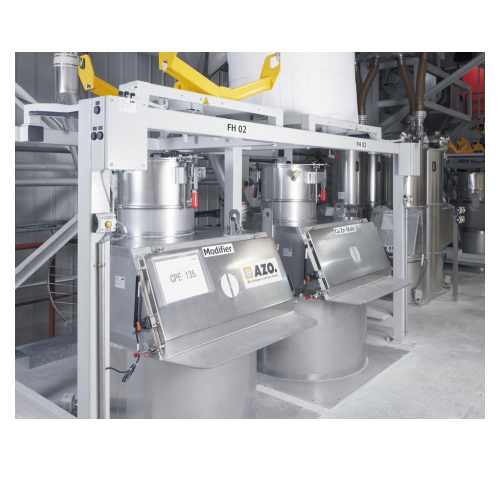
Integrated pickup station for bagged products and big bags
Streamline the handling and transition of bulk materials with...
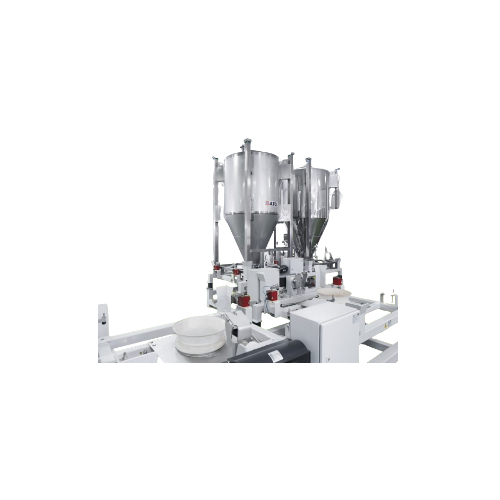
Dust-free docking collar for containers and bins
Achieve seamless, dust-free connections between containers and processing...
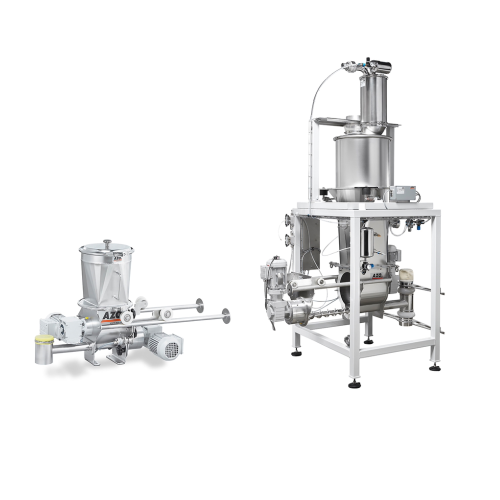
Accurate dosing for powder products
Ensure precise dosing and consistent flow of bulk powders in your production line to en...
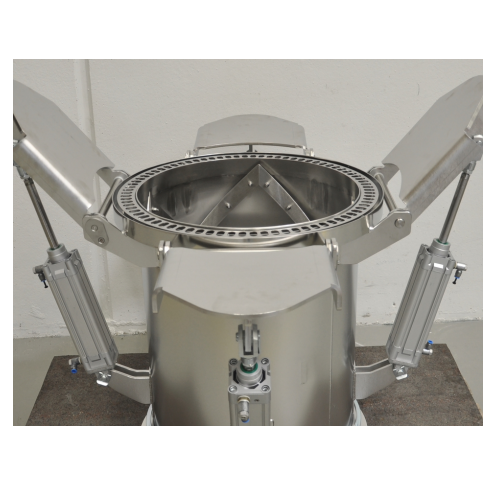
Dust-free big bag connection system for bulk solids
Eliminate dust and ensure reliable discharge with this vacuum docking...
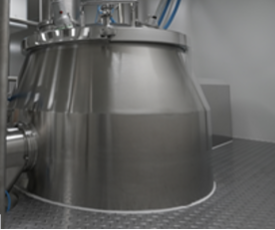
Continuous wet granulation equipment
Achieve optimal particle size and uniformity in pharmaceutical production with our con...
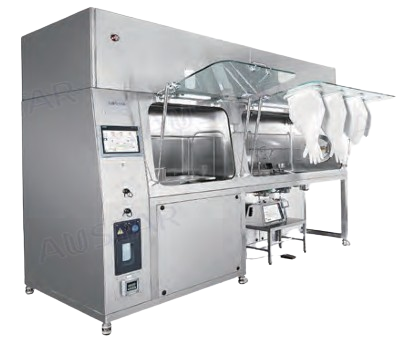
Sterilisable isolator workstation for aseptic containment
Ensure precise contamination control and sterile conditions du...
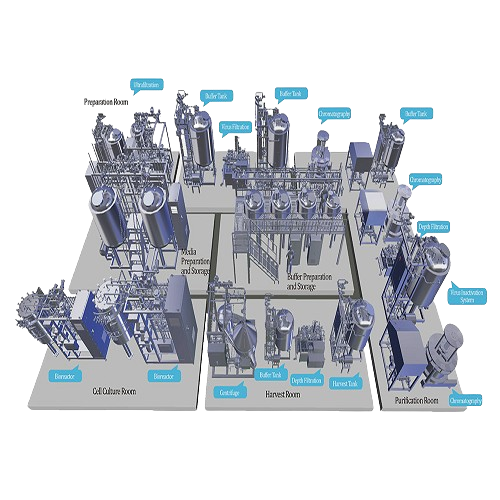
Bioprocess system for protein and antibody drugs
Streamline biopharmaceutical production with a system engineered to optim...
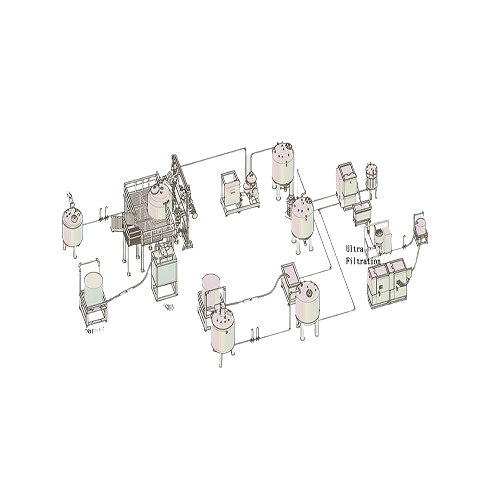
Hybrid bioprocess system for cell culture and purification
Streamline your bioprocessing operations with a versatile sol...
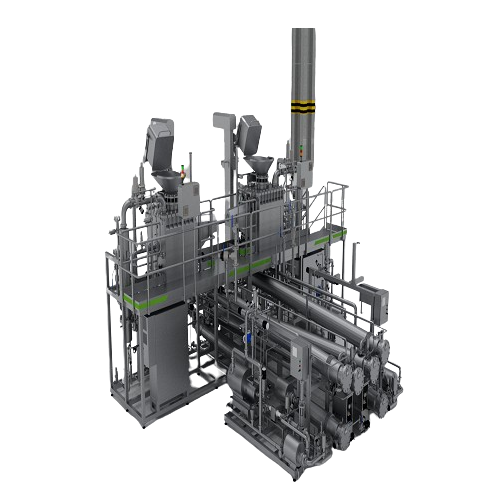
Aseptic cooking line for plant-based products
Enhance your production efficiency and product quality with an advanced doub...
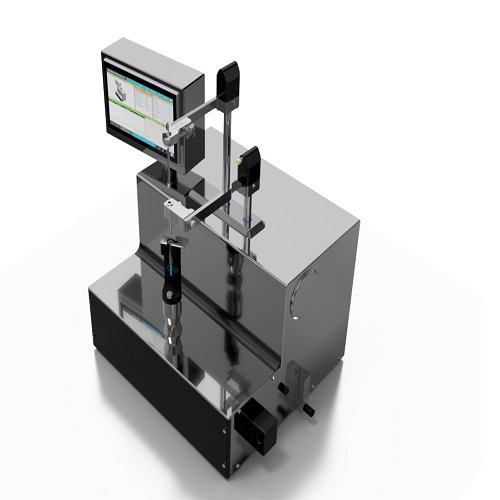
Bench-top syringe & cartridge closing system
Ensure precise and repeatable syringe and cartridge closure with this versati...
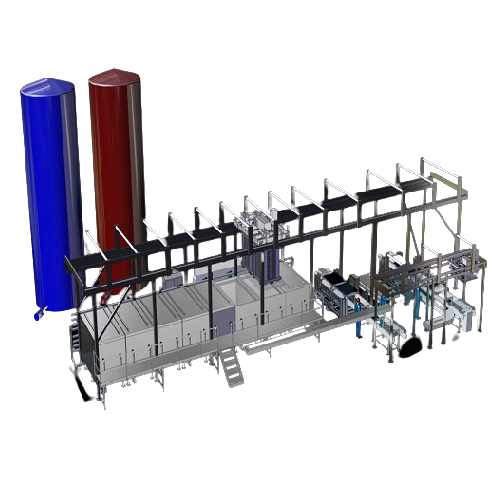
Automated sous vide cooking and chilling system
Optimize your cooking process with a system that ensures consistent temper...
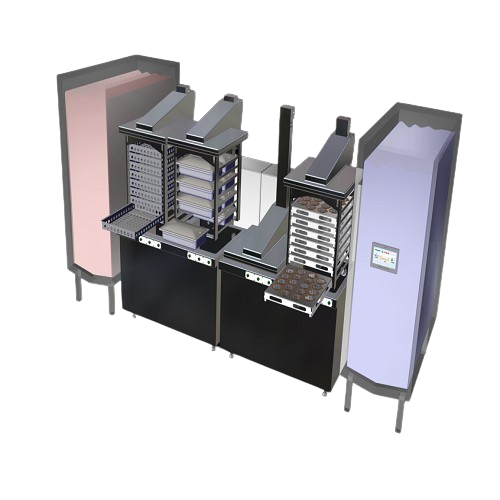
Sous vide water cook & chill system
Achieve precision in Sous Vide cooking with a system that ensures optimal temperature c...
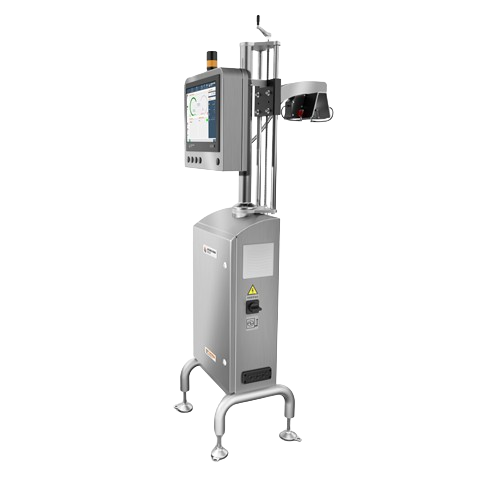
In-line leakage detection for sealed water bottles
Ensure the integrity of your bottled beverage products with reliable i...
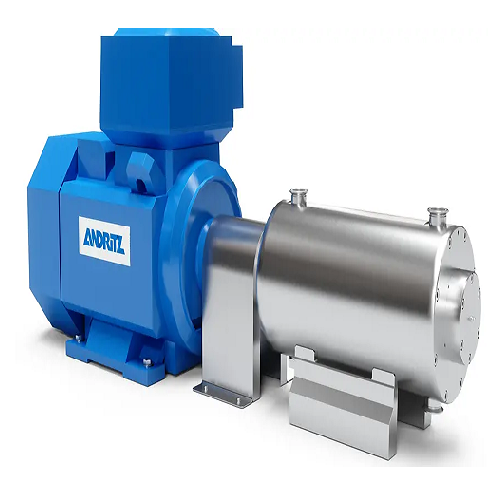
Solid/liquid extractor for high-yield functional nutrient extraction
Maximize extraction efficiency and elevate product...
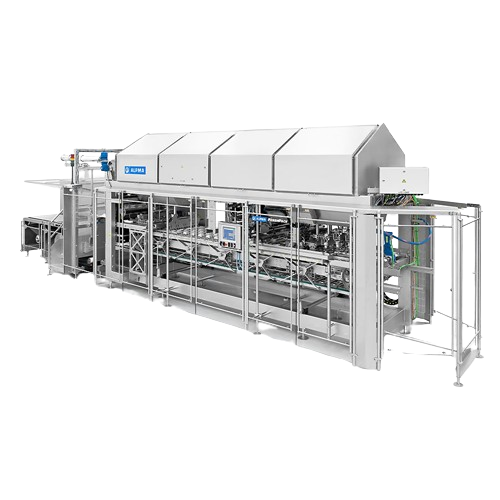
Fully automatic packaging solution for butter and pasty products
Streamline your production line with this versatile pac...
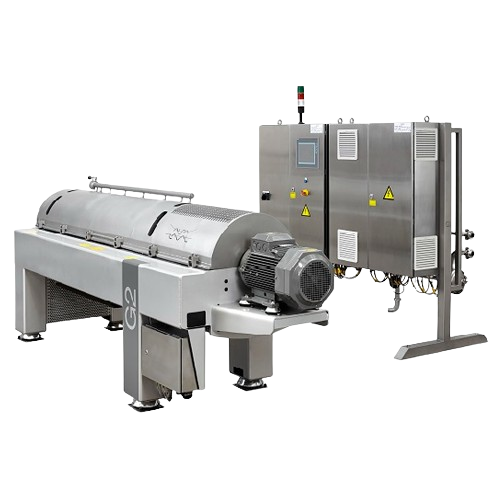
Intelligent whirlpool system for breweries
Increase your brewery’s yield and efficiency by integrating our advanced ...
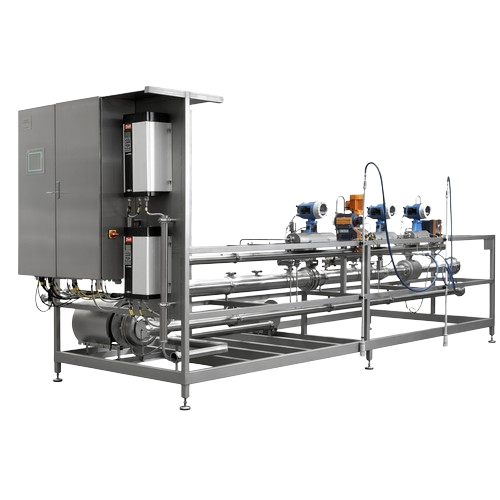
Modular dosing system for brewing and beverage industry
Ensure precise formulation of beverages by seamlessly integrating...
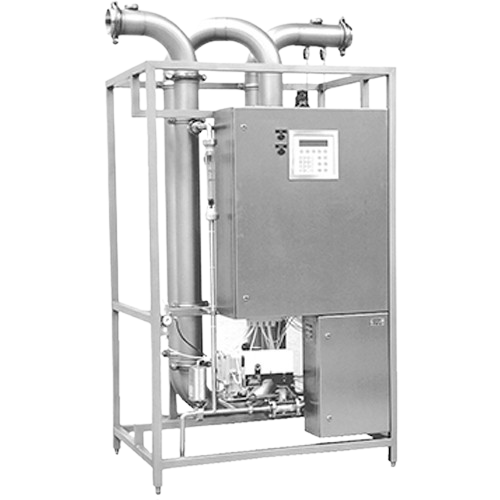
Beer carbonation system
Achieve consistent and precise carbonation in beverages, ensuring optimal gas dissolution for enhance...
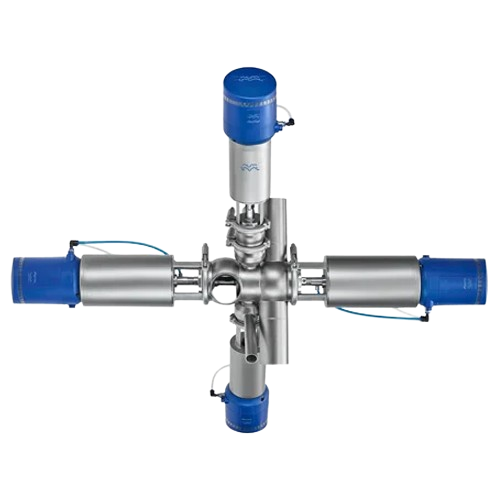
Aseptic mixproof valve for sterile processing
Ensure absolute product safety and optimize cleaning efficiency in sterile p...
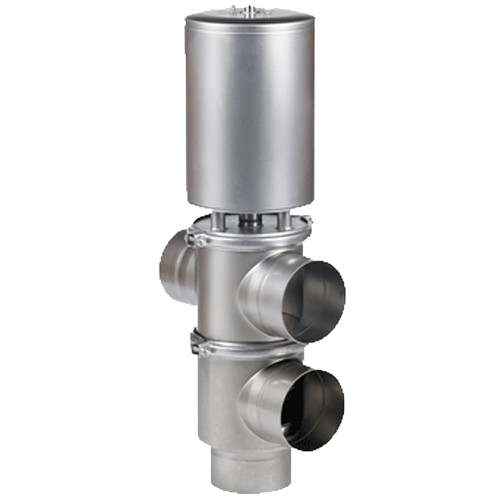
Single seat valve for hygienic applications
Ensure optimal hygiene and safety with a versatile pneumatic valve designed to...
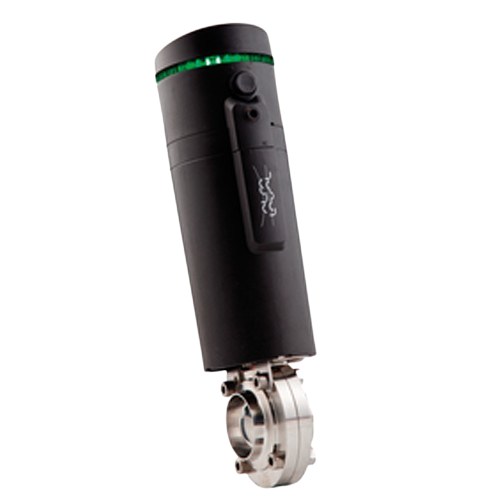
Automated butterfly valve actuator for hygienic processing
Streamline your flow control operations with a robust and mai...

Powder dosing and weighing system
Optimize precision in pharmaceutical processing with a system designed to ensure accurate...
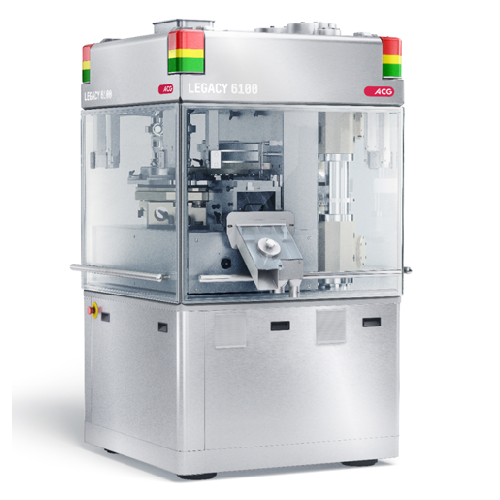
Single rotary tablet press
Streamline your tablet production with enhanced efficiency and precision, ensuring consistent tab...
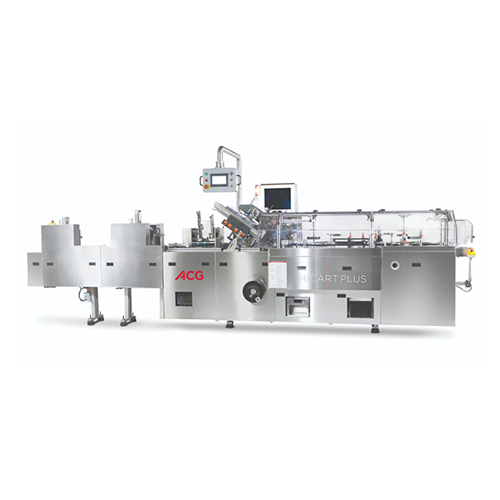
Continuous cartoning solution
Enhance your production line with efficient high-speed cartoning, designed to streamline packa...
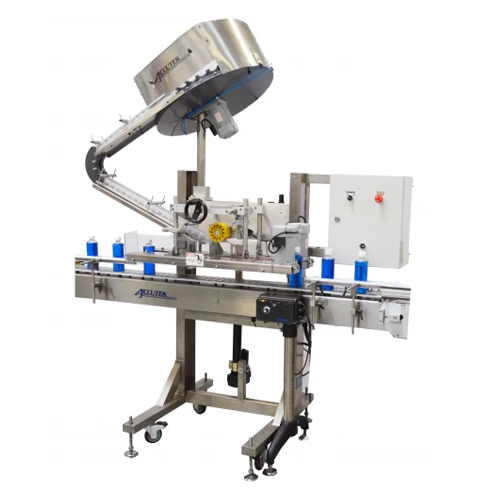
Automated snap capper for various container types
Eliminate manual errors and repetitive strain with this high-speed snap...
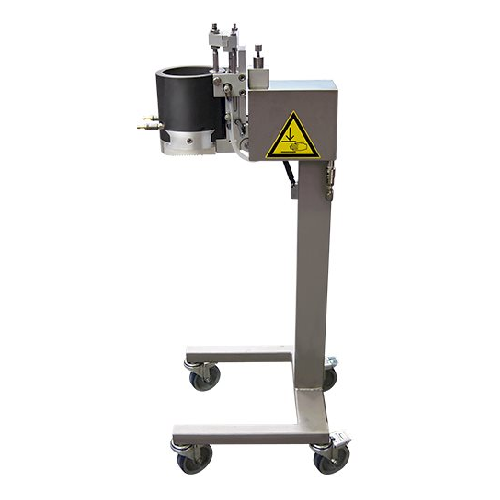
Lab-scale chocolate chip depositor
Enhance your R&D capabilities with precision depositing of chocolate masses, allowi...
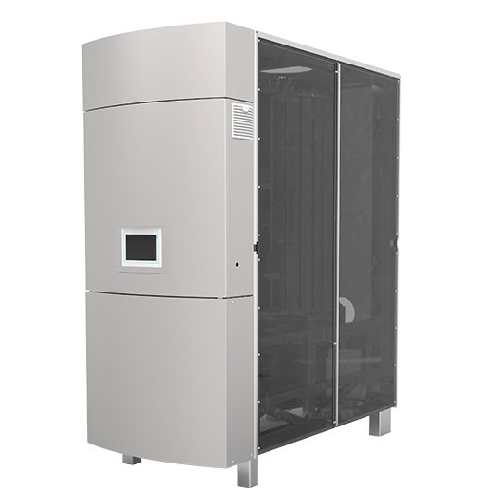
Advanced chocolate tempering system
Achieve flawless chocolate and confectionery products with precision tempering, ensurin...

Chocolate enrober for large scale production
Efficiently enrobe a wide range of products, from chocolate bars to delicate ...
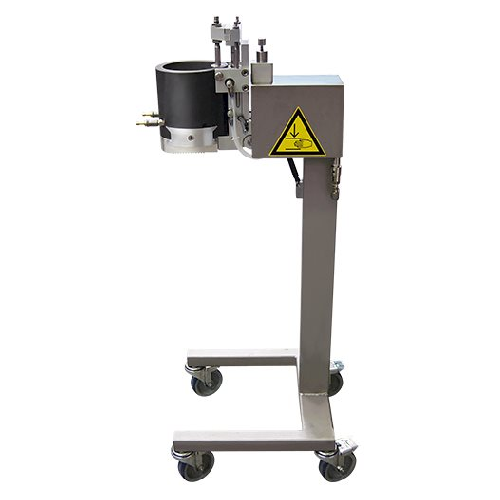
Small scale chip depositor for confectionery production
Efficiently deposit a variety of confectionery and snack products...
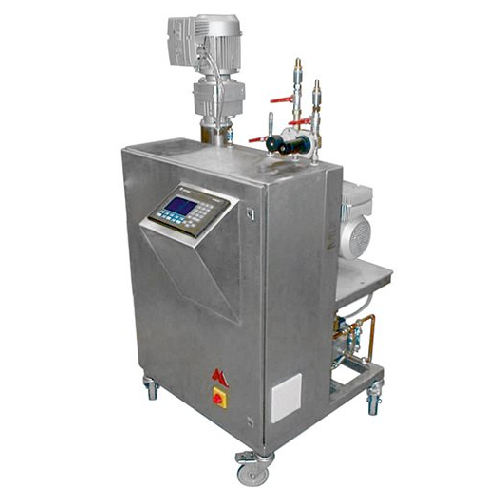
Aeration and aroma mixing system for chocolate production
Optimize your chocolate and confectionery production with prec...
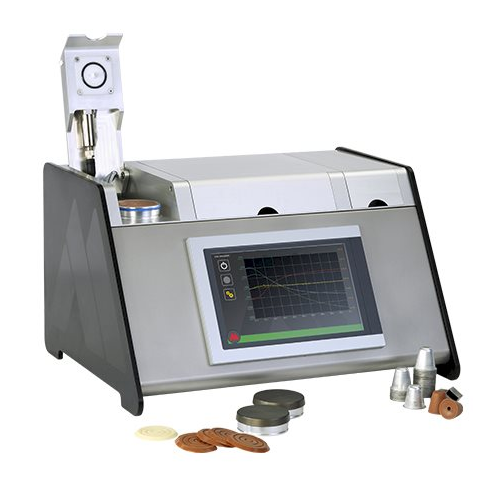
Chocolate quality measuring instrument
Ensure consistent chocolate quality by accurately measuring contraction, expansion, ...
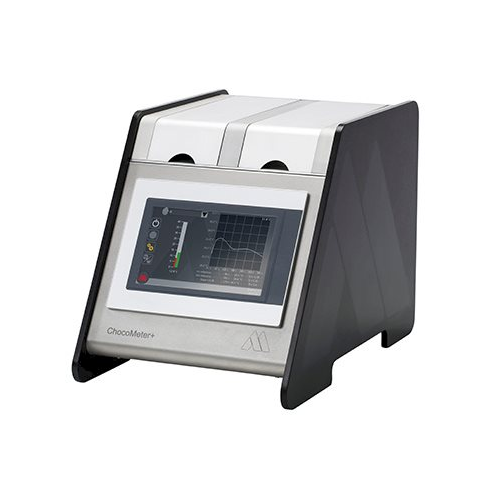
Accurate chocolate tempering measurement tool
Ensure precise chocolate tempering with real-time accuracy, enhancing qualit...
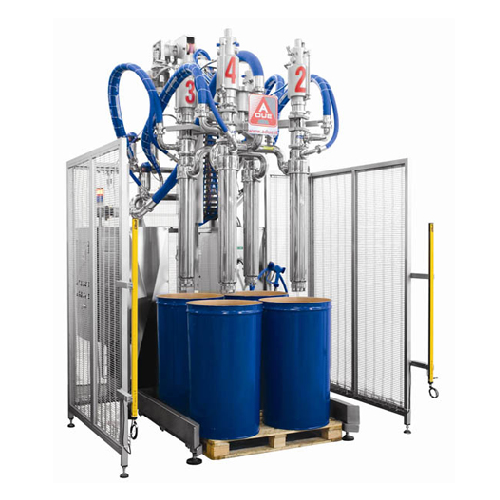
Fruit pieces handling for juice production
Achieve perfect fruit piece integration in juice with a system designed to prev...

Linear conveyor tray sealing
Experience unparalleled flexibility and efficiency in tray sealing with high-speed integration,...

Industrial high speed tray sealer
Enhance your production line efficiency with precision sealing capabilities, accommodatin...
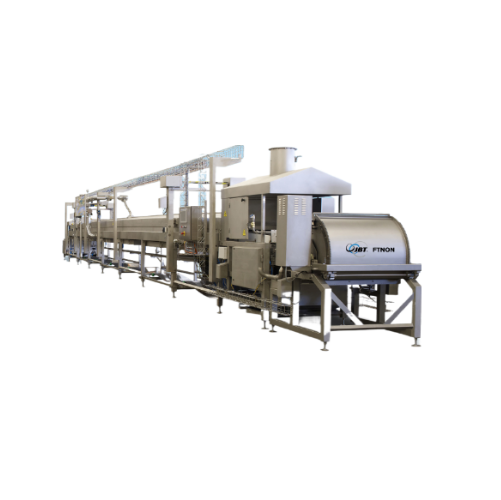
Wet pet food processing system
Optimize your wet pet food production with a system that integrates steaming, cooling, mixing...
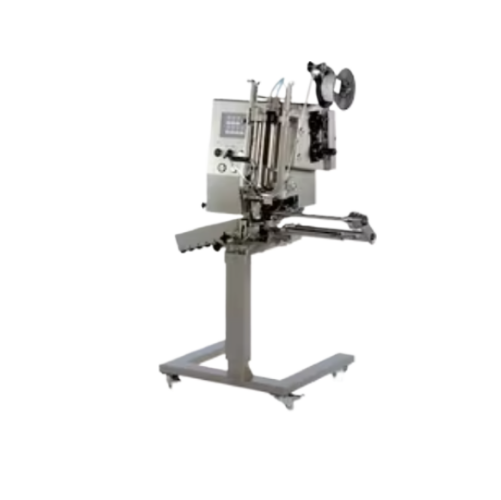
Semi-automatic clipper for sausage and meat packaging
Optimize your packaging operations with a modular solution that ens...
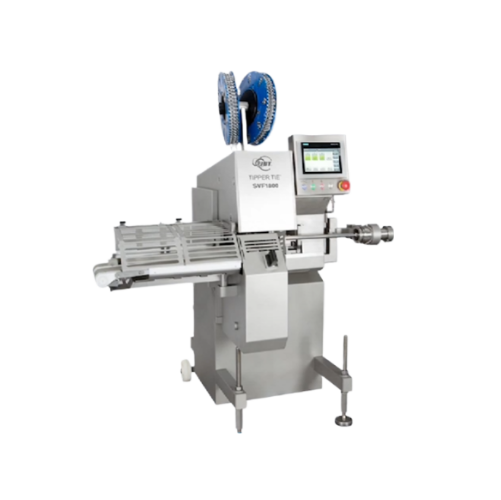
Automatic double clipper for sausage production
Optimize your production line with a high-speed double clipper that secure...
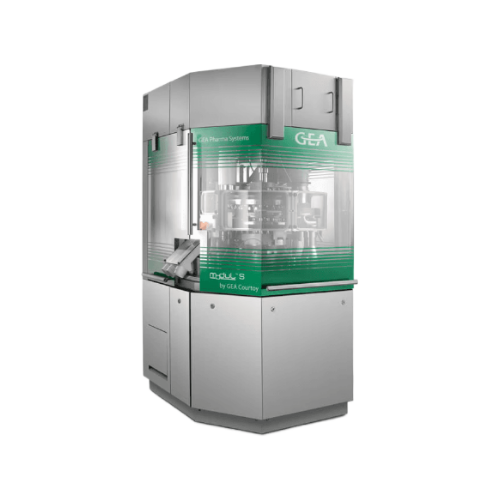
Rotary tablet press for small to medium scale production
Optimize your tablet production with a versatile rotary press, o...
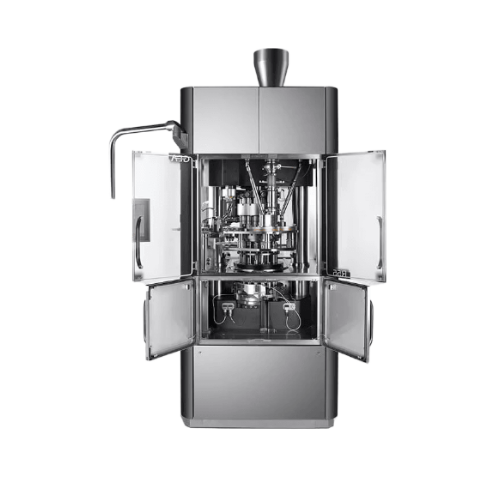
Industrial rotary press for single-layer tablet production
Optimize your tablet production with precision-engineered rot...
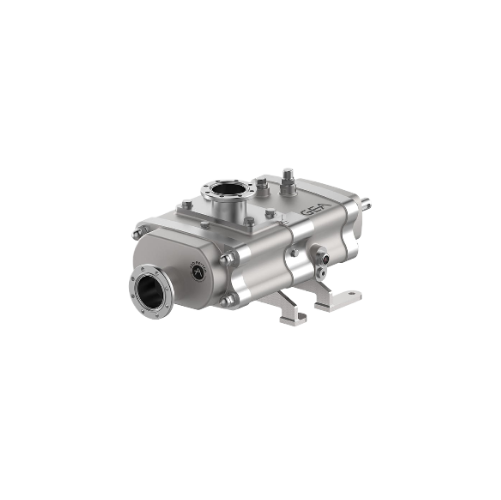
Twin screw pump for viscous media
Streamline your production with a twin screw pump that effortlessly handles viscous media...
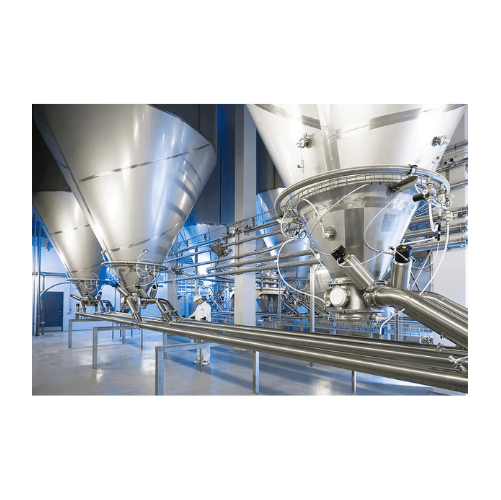
Bulk storage silos for food products
Ensure optimal powder storage and handling with versatile silos designed for efficient...
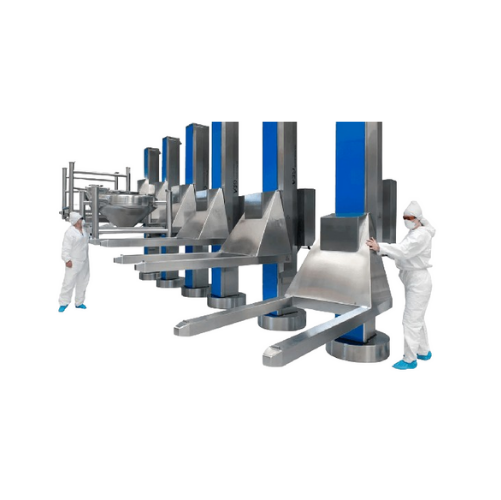
Ibc post hoists for pharmaceutical manufacturing
Ensure precise material handling with advanced lifting solutions designed...
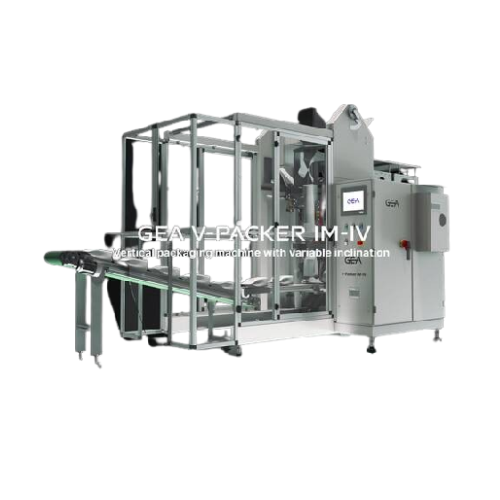
Packaging system for short-cut pasta and dry granular food
Streamline your packaging process with a versatile system des...
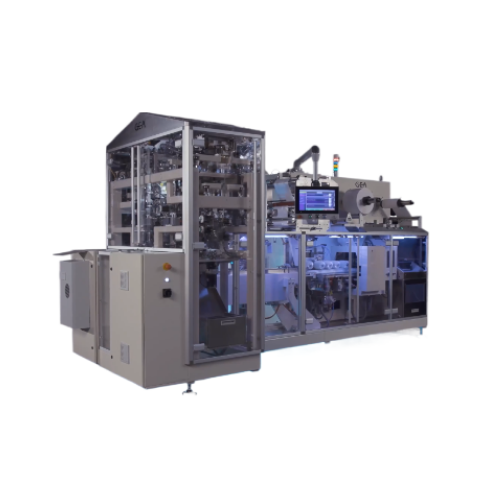
High-speed packaging system for long-cut pasta
Achieve seamless high-speed packaging with enhanced accuracy and minimized ...
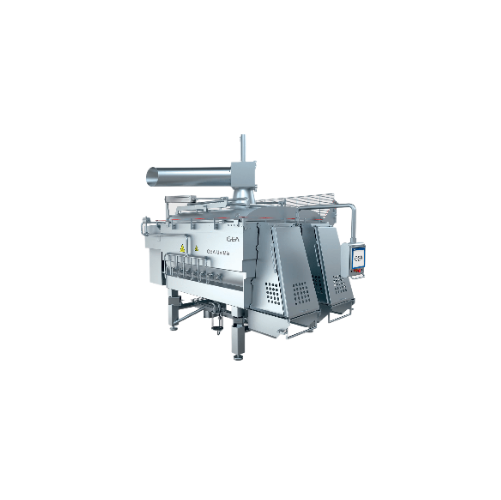
Twin-shaft mixer for meat mix preparation
Achieve consistent texture and flavor in your meat and plant-based products with...
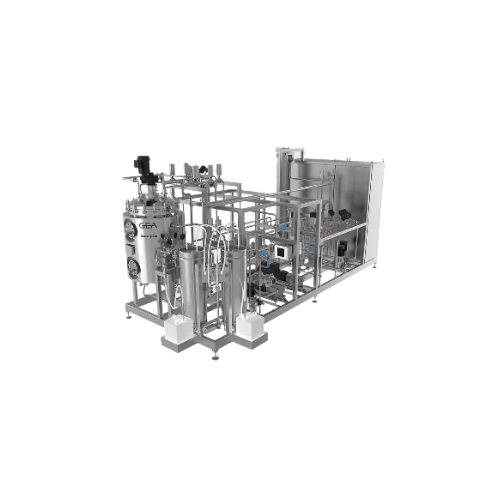
Sugar reduction skid for fresh juice
Transform the way you produce juice with enzymatic technology that reduces sugar conte...
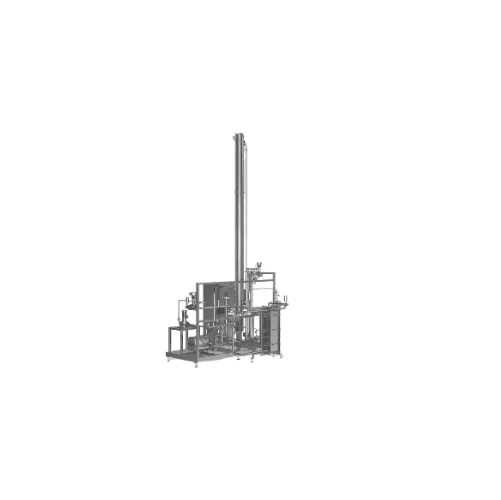
Hot water deaeration system for beverage production
Achieve superior product quality by efficiently removing oxygen from ...
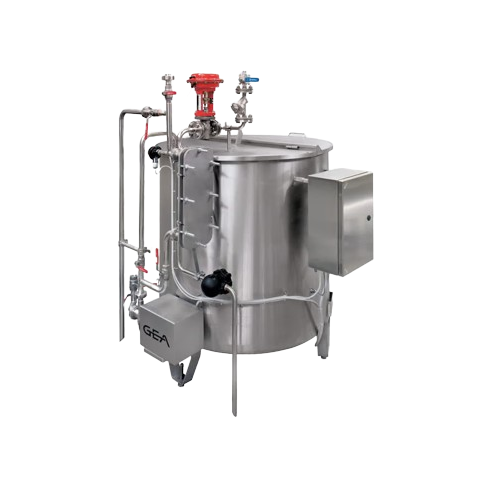
Liquid salt dosage systems for pasta filata-type cheeses
Achieve precise salinity control and optimal temperature for you...
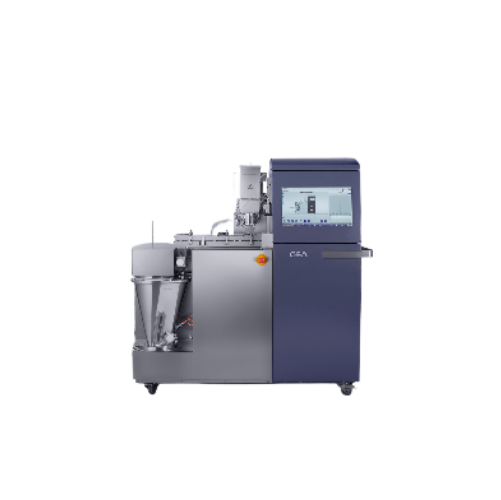
Continuous granulation and drying system for r&d
Develop precise pharmaceutical granules with this compact system, tailore...
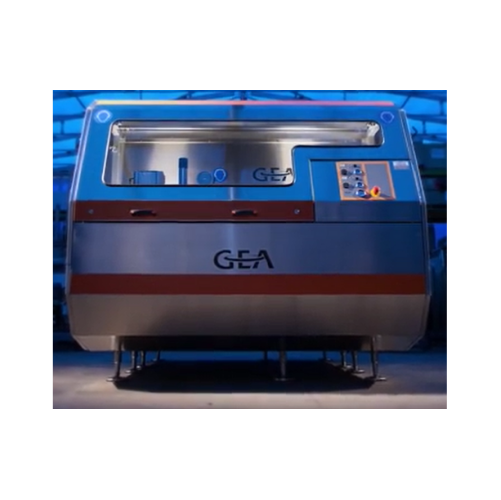
Industrial high-pressure homogenizer
Achieve precise homogenization with superior flow rates and efficiency, ensuring optim...
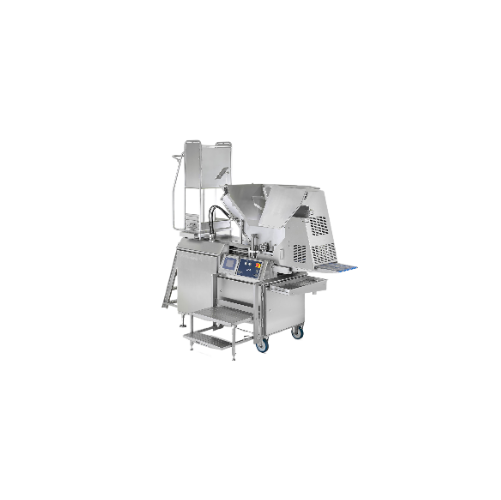
Flexible plate former for meat products
Achieve precise shaping and portioning with a highly adaptable plate former, design...
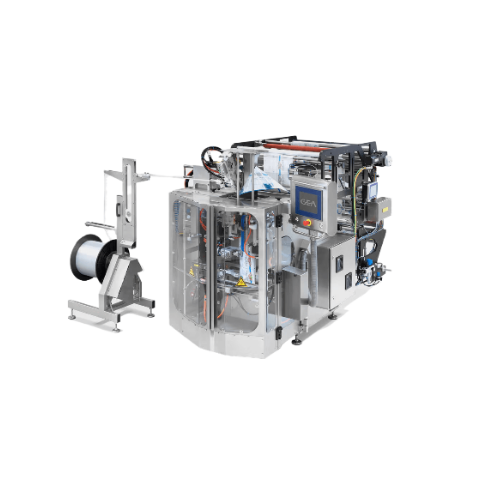
Vertical pouch packaging system for food products
Achieve high-speed, precise packaging with our vertical pouch system, i...
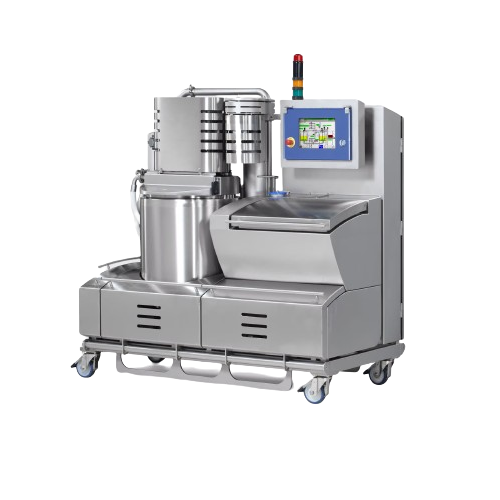
Automated tempura batter mixer
Achieve consistent tempura batter quality with automated mixing control that ensures precise ...
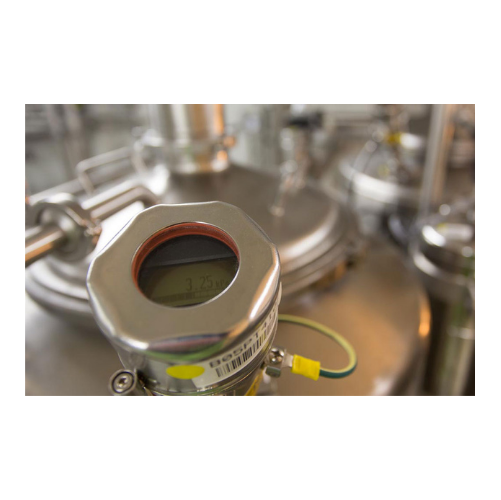
Powdered product shelf-life enhancement through inert gas packing
Extend the shelf life of sensitive powder products by...
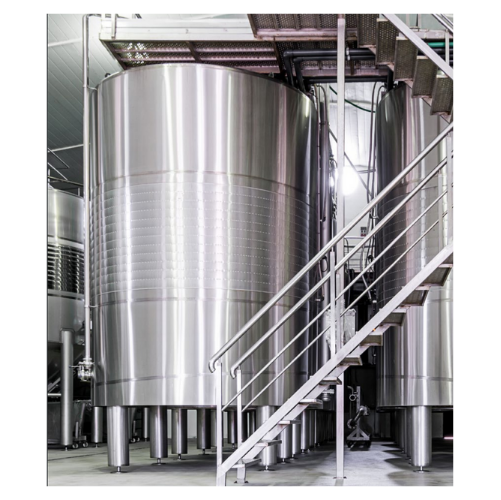
Reverse osmosis dealcoholization technology
Elevate your beverage production capabilities with advanced dealcoholization t...
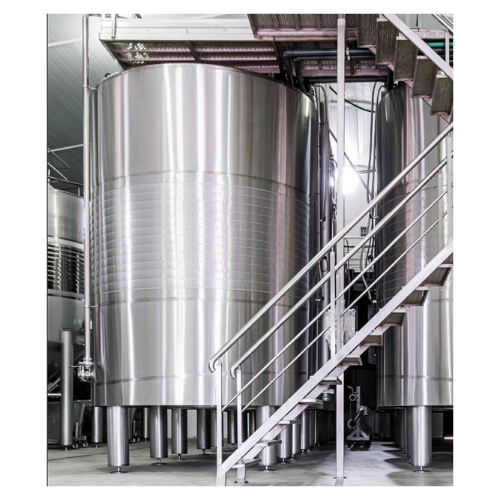
Centrifuge for beverage clarification
Elevate your beverage production with enhanced clarification, ensuring your drinks me...
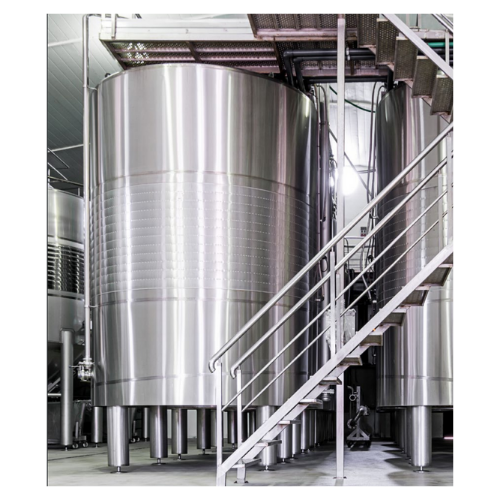
Reverse osmosis dealcoholization technology for beer
Achieve consistent flavor profiles in your non-alcoholic beer produc...
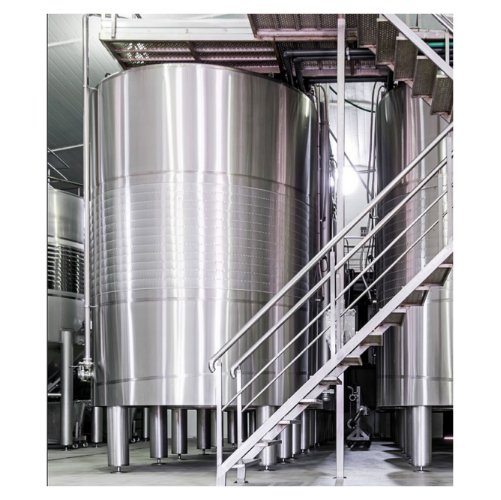
Reverse osmosis beer dealcoholization technology
Achieve precise alcohol removal from beer while preserving flavor integri...
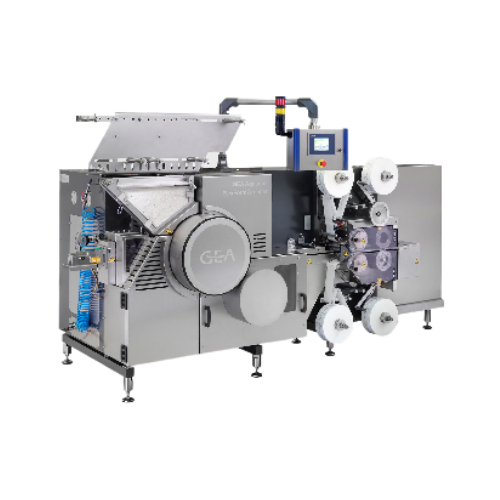
Lollipop forming and wrapping solution
Streamline your confectionery production with this innovative system designed to eff...
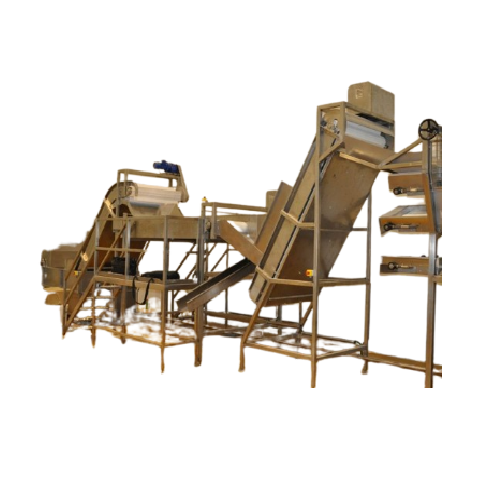
Fruit treatment lines for juice and pulp extraction
Optimize your juice production line by efficiently extracting, proces...
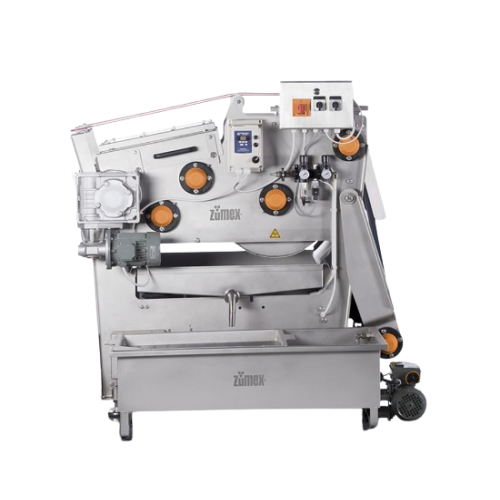
Industrial fruit juice extractor
Maximize juice yield from a wide range of fruits and vegetables with precise extraction and...
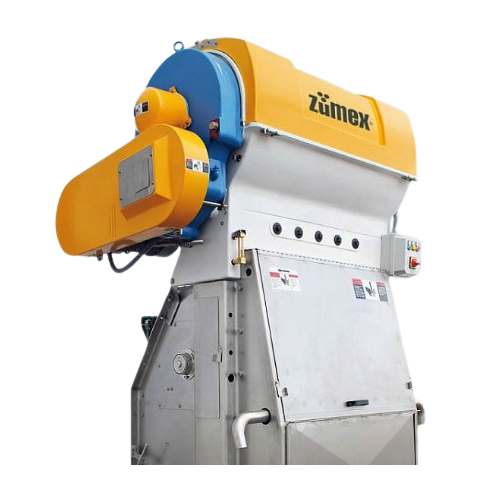
Industrial citrus juice extractor
Achieve high-yield juice extraction with reduced oil content, delivering premium quality ...
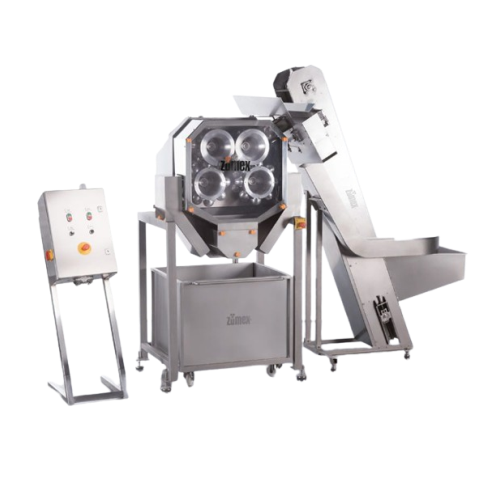
Industrial citrus juice extraction system
Streamline your juice production with a versatile system that efficiently extrac...
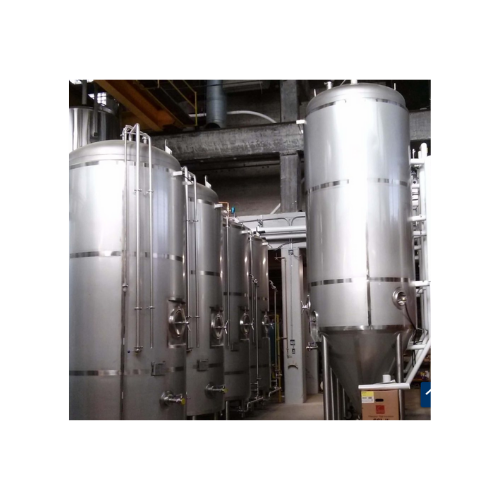
Bright beer tanks for breweries
Enhance your beverage production with precise carbonation and conditioning, ensuring excepti...
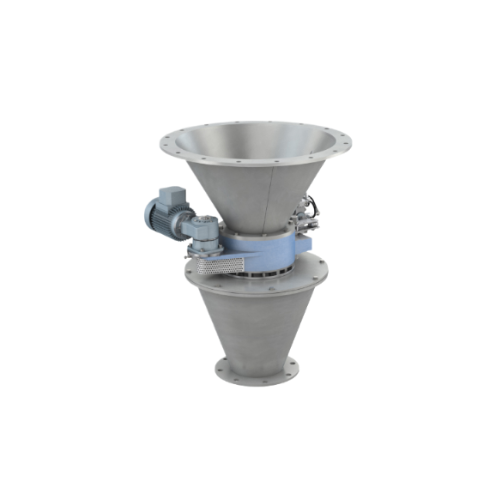
Industrial discharge and dosing module
Optimize material flow and prevent blockages in silo discharge and dosing processes,...
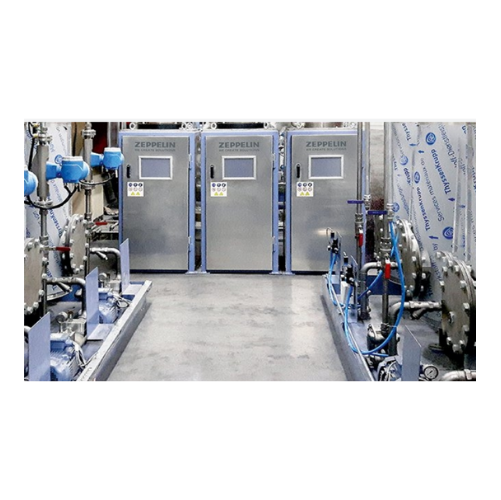
Liquid additive dosing system for industrial mixers
Achieve unparalleled precision in liquid ingredient integration with ...
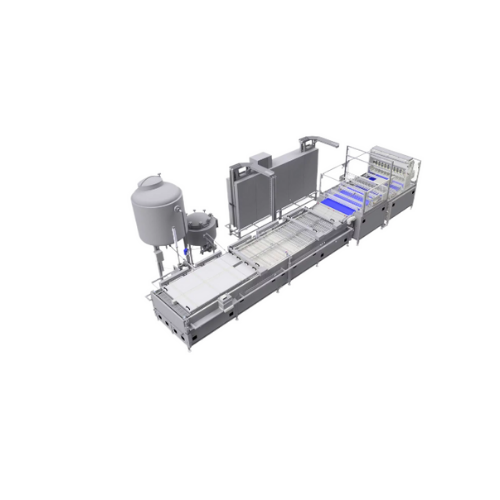
Industrial continuous frying system for donuts and pastries
Achieve artisanal-quality frying with high-volume efficiency...
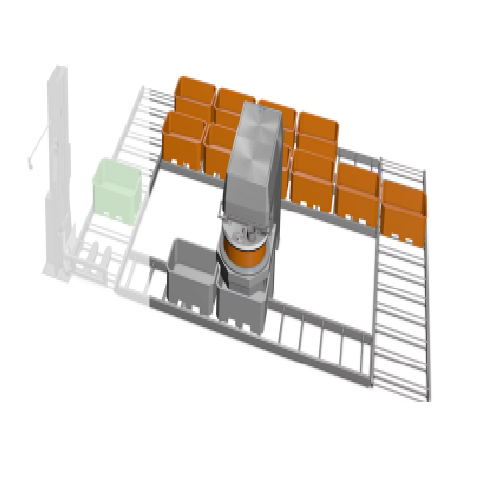
Mixing system for long dough resting times
Achieve consistent dough quality with extended resting times, optimizing water ...
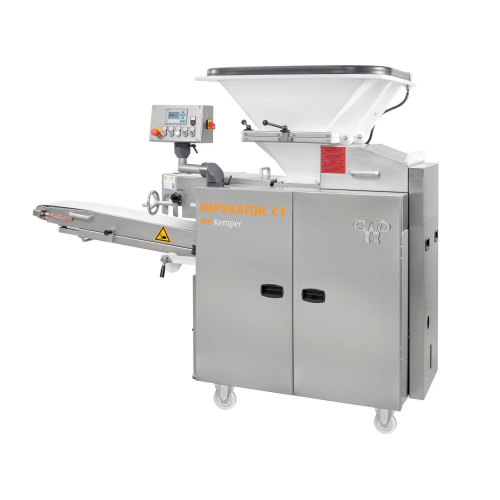
Industrial bread dough divider for accurate weight control
Achieve precise weight accuracy and gentle handling for a var...
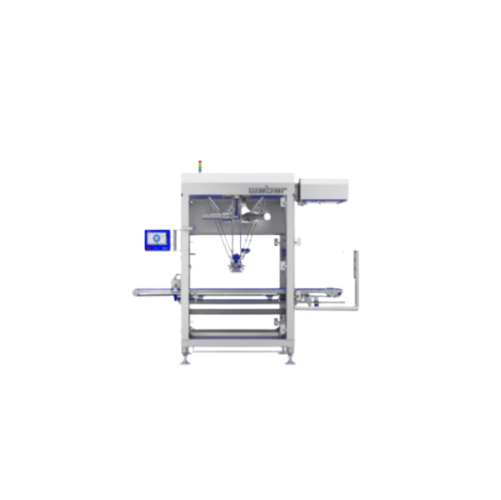
Automated cold cuts loading system
Optimize your production line with a flexible side loading solution designed for precise...
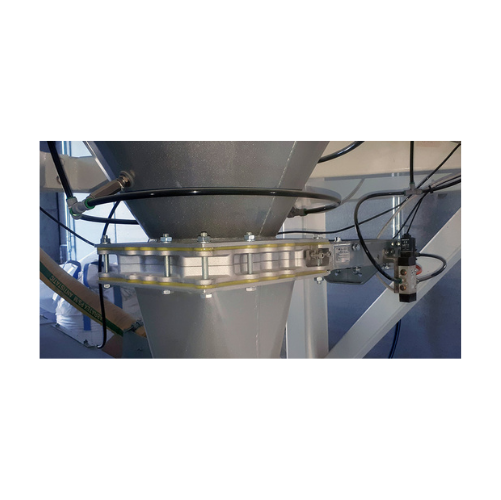
Slide valves for flow interception in powder and granular materials
Effectively manage the flow of powdery and granular...
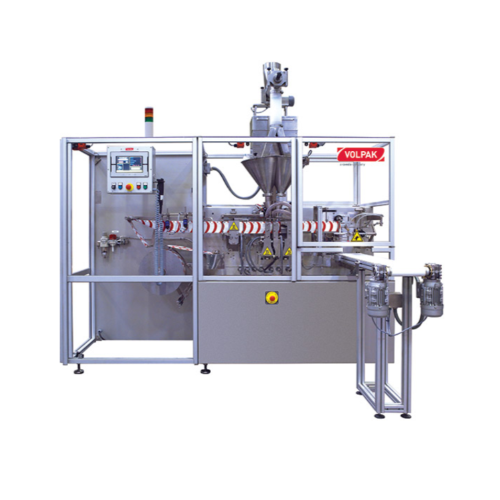
Horizontal flat pouching solution for foods and chemicals
Achieve precision in pouching liquids and powders with high-sp...
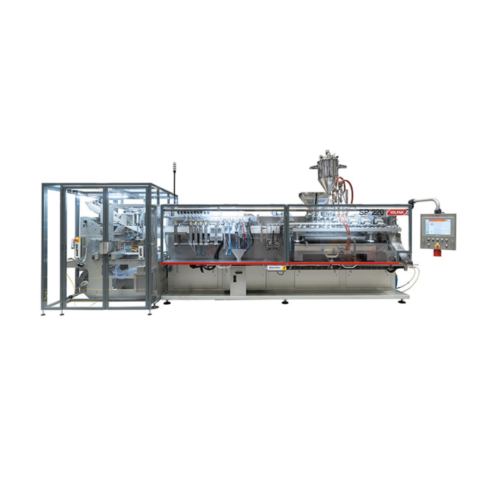
Stand-up pouch packaging for various industries
Elevate your packaging capabilities with a high-speed horizontal pouching ...
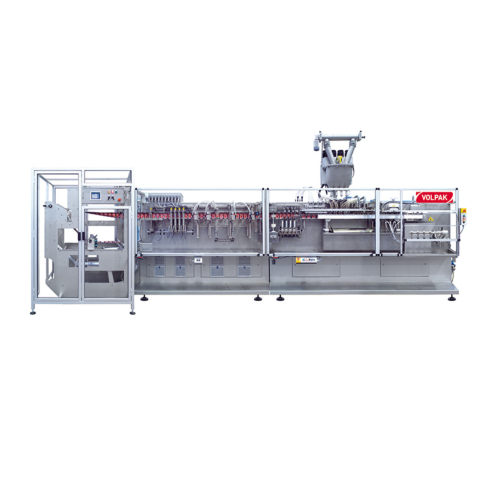
Horizontal flat pouching system for up to 180ml capacity
Optimize your packaging process with a high-speed solution desig...
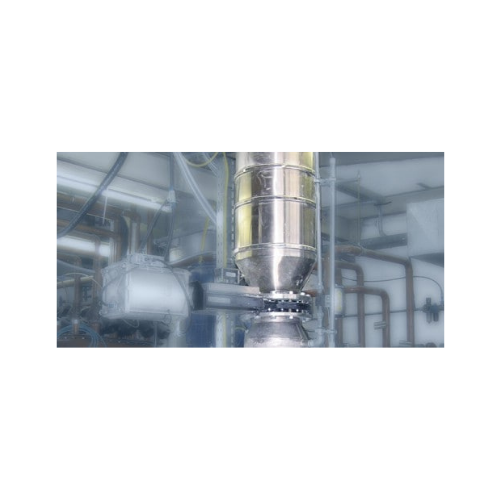
Powder locks for safe bulk material handling
Ensure containment and prevent contamination while processing sensitive bulk ...
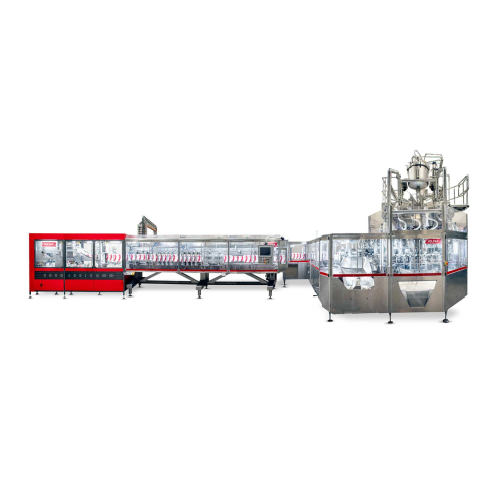
Continuous stand-up pouching solution for up to 1000ml
Maximize efficiency in high-speed production lines with precise st...
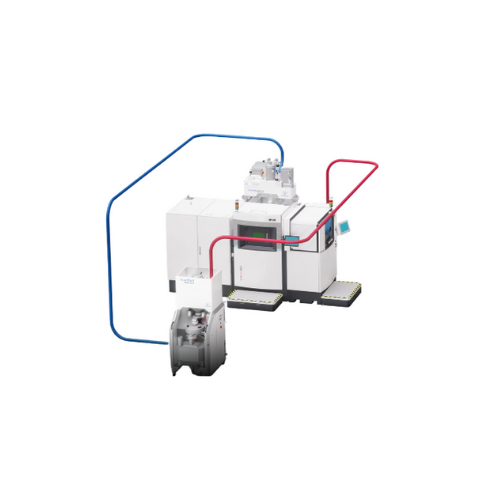
Closed powder handling loop for Eos metal Am printers
Effortlessly manage metal 3D printing powders with a solution that ...
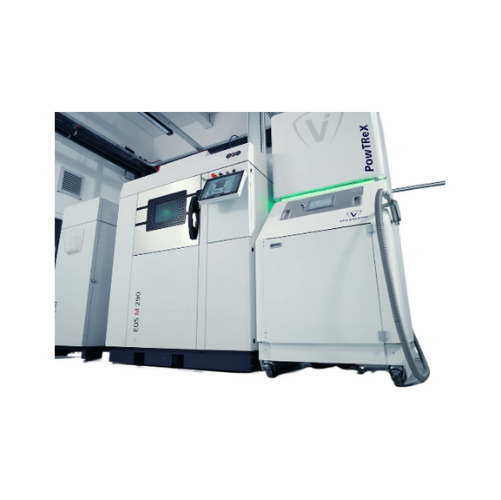
Metal powder recovery system after 3d printing
Effectively reclaim and purify metal powders after 3D printing to enhance c...
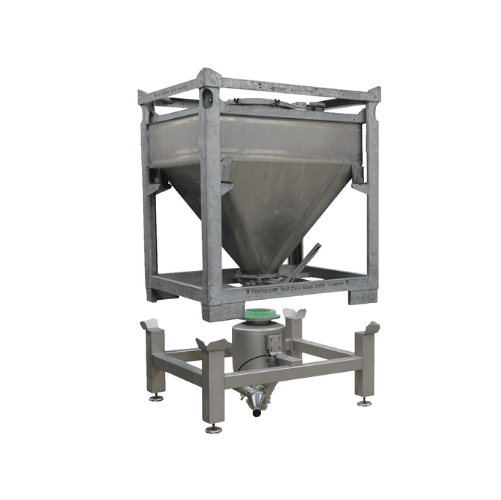
Ibc docking and discharge stations
Ensure seamless material transfer with dust-free docking and effective discharge, mainta...

Modular dispenser for dosing adhesives and abrasive media
Streamline your production line with a modular dispenser desig...
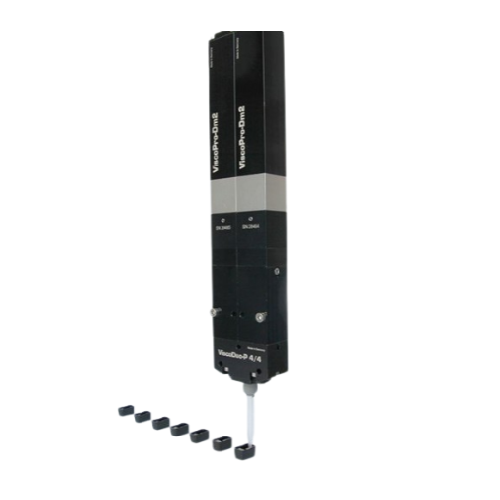
Precision 2k dispenser for automated systems
Achieve precise mixing and dispensing of two-component materials with minimal...
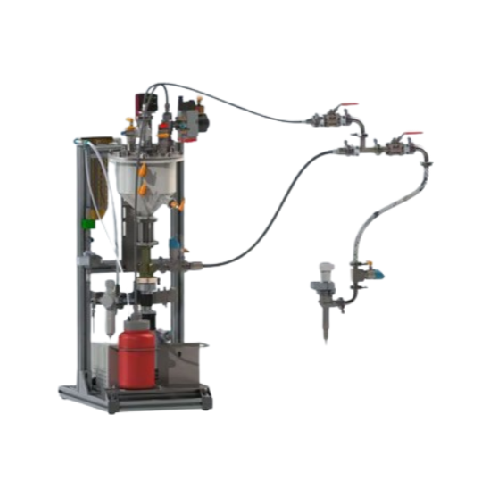
Fluid and paste dosing systems for industrial applications
Achieve precise dosing and mixing for high-viscosity liquids ...
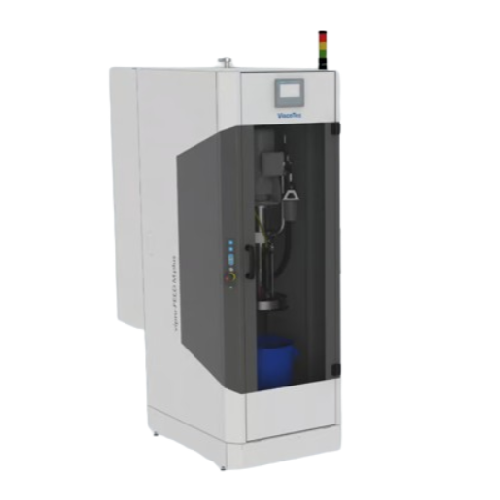
Emptying systems for high viscosity fluids and pastes
Efficiently empty high-viscosity fluids and pastes with precision, ...
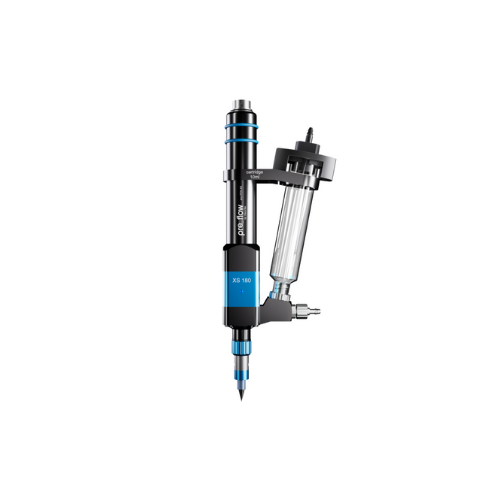
1-component industrial dispenser for precision dosing
Achieve unparalleled precision in microdispensing across diverse ap...
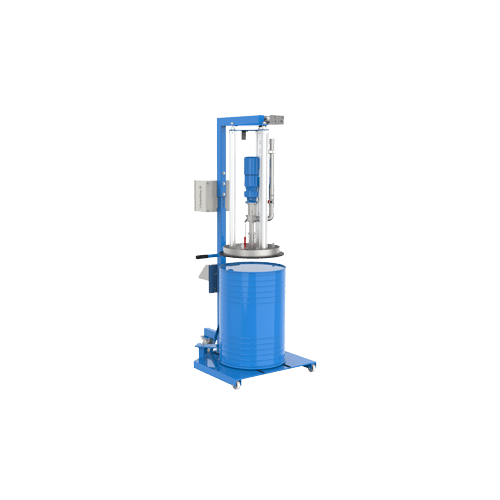
High-volume dispensing for single-component fluids and pastes
Enhance your production line with a pump that delivers lar...
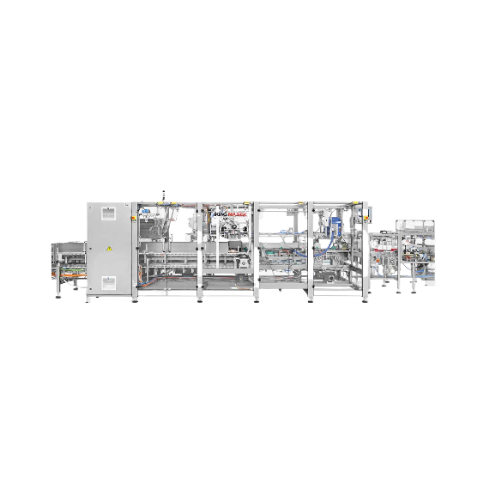
Endload automatic cartoning solution
Streamline your packaging line with this versatile cartoning solution, perfect for eff...

Robotic packaging integration for automated systems
Enhance your production line efficiency with seamless robotics integr...
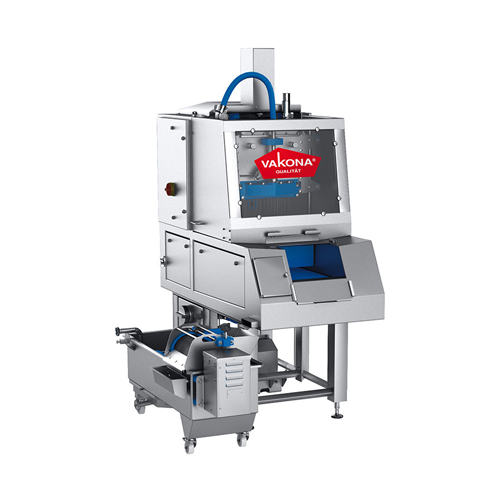
Industrial pickle injector for precise brine injection
Achieve unparalleled brine distribution and consistency in meat an...
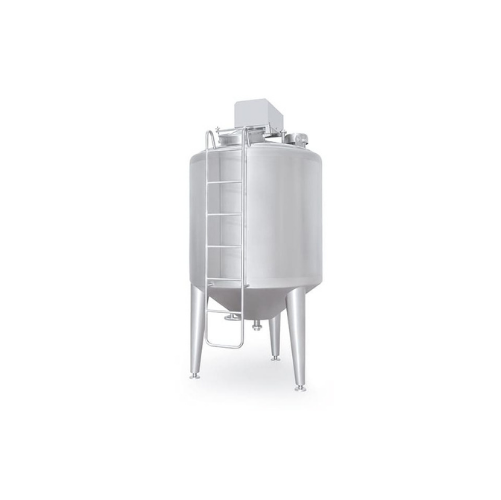
Industrial buffer tank for temperature and texture control
Achieve precise temperature control and optimal texture with ...
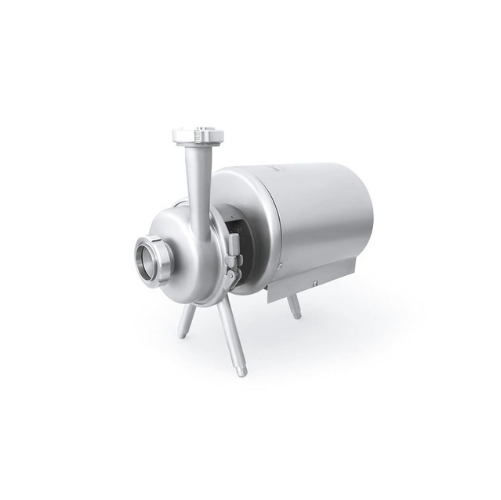
Stainless steel centrifugal pump for liquid transfer
Optimize your food and dairy production with a reliable centrifugal ...
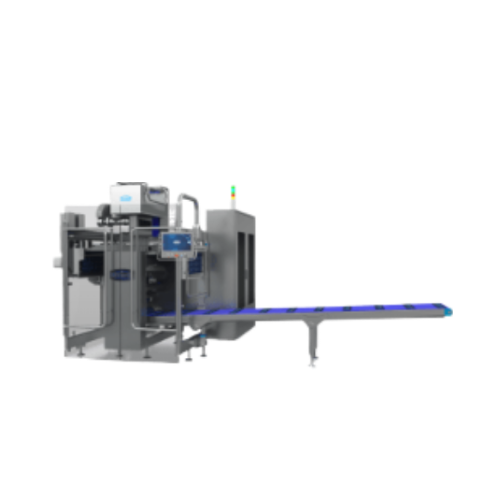
Sachet packaging for pharmaceuticals
Streamline your pharmaceutical packaging with high-precision sachet solutions, ensurin...
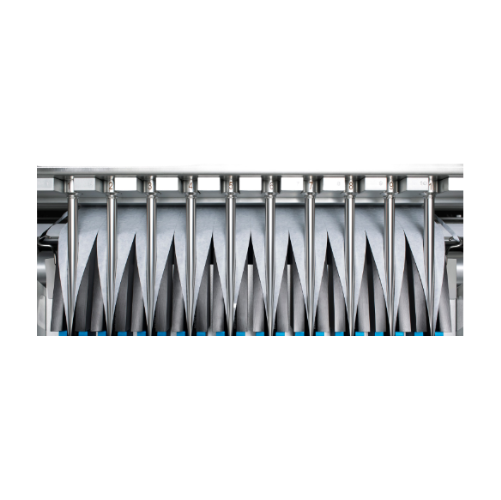
Stick pack packaging for pharmaceutical products
Enhance your production efficiency with compact stick pack solutions, off...
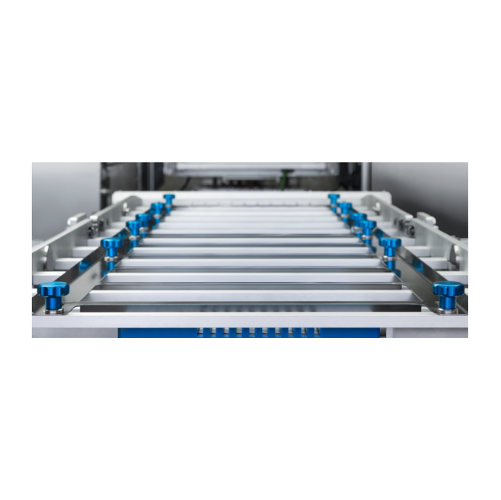
Stick pack packaging line for pharmaceuticals
Optimize your pharmaceutical production with stick pack packaging lines that...
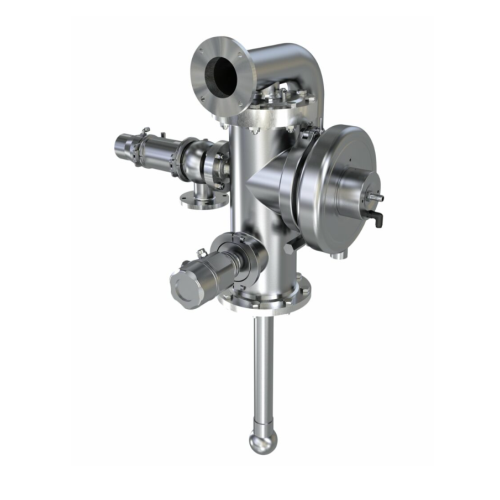
Vessel dome fittings for tank protection
Ensure seamless production by preventing tank damage due to overpressure or vacuum...
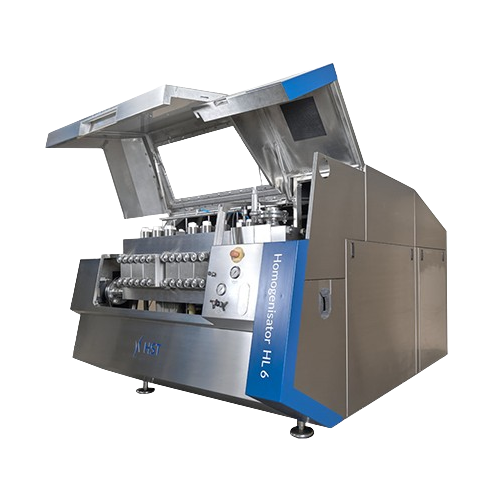
Industrial homogenizers for liquid processing
Achieve consistent product quality and energy efficiency in liquid processin...
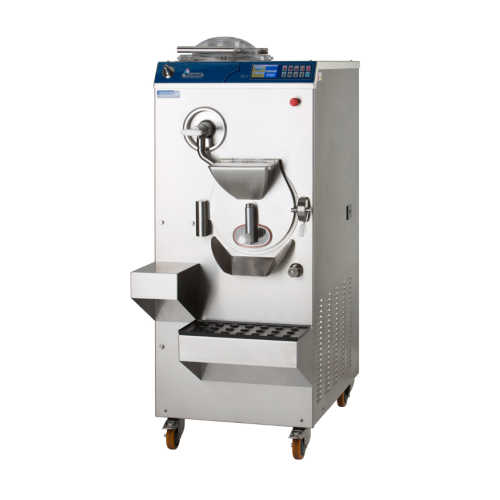
Artisan ice cream processing equipment
Transform your ice cream production with high-efficiency equipment designed to strea...
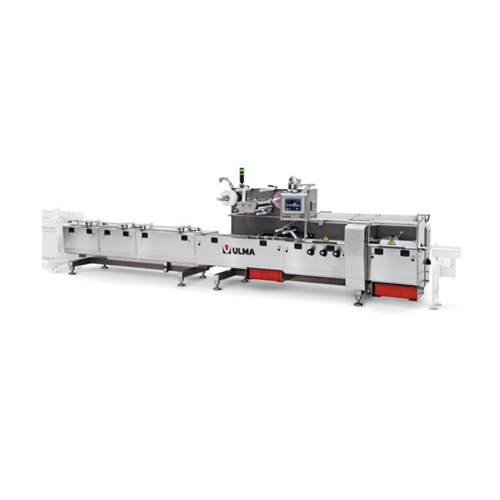
Horizontal flow wrapper for bakery and chocolate
Achieve seamless integration in high-speed production lines with a horizo...
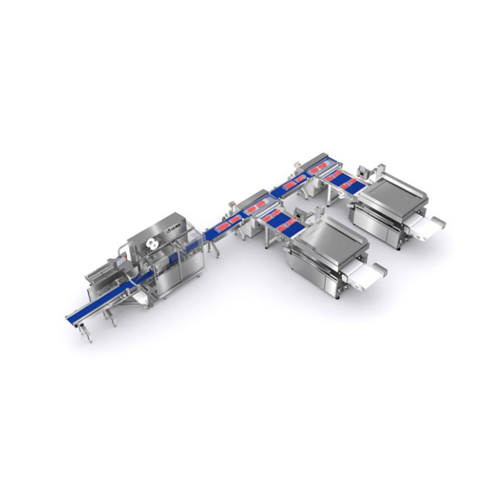
Vacuum packaging for industrial cuts of meat
Enhance production efficiency and packaging integrity with a system designed ...
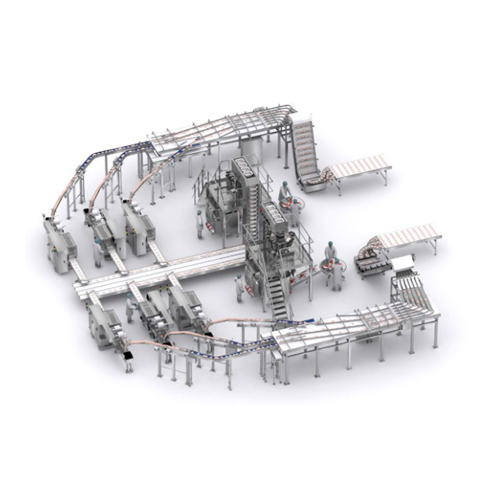
Frozen hamburger packaging solution
Streamline your frozen burger production with a fully automated system that efficiently...
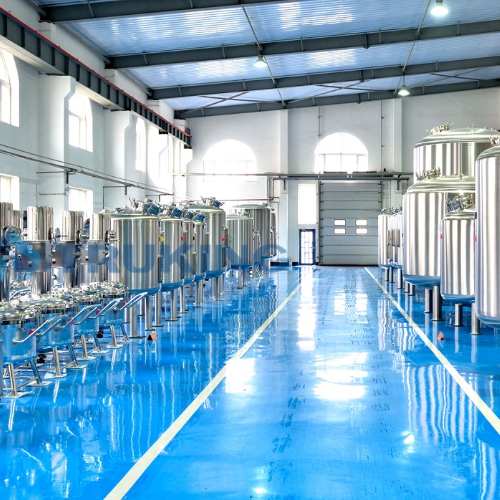
Stainless steel craft tanks for biopharmaceuticals
Ensure precise temperature control and customized capacity for your fo...

Robotic sterilization logistics system
Ensure seamless aseptic transfers across production stages with this robotic logisti...
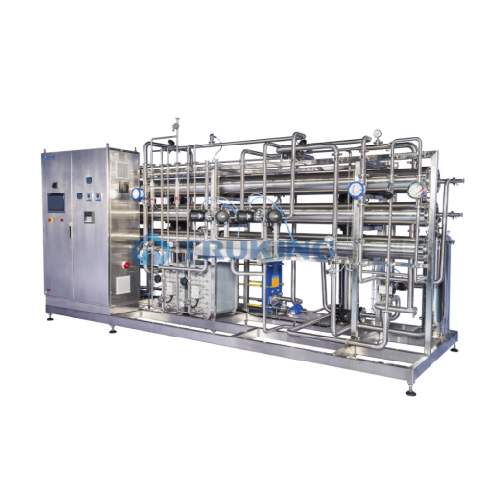
Ultra-pure water preparation system for pharmaceutical industry
Ensure your pharmaceutical production line meets stringe...
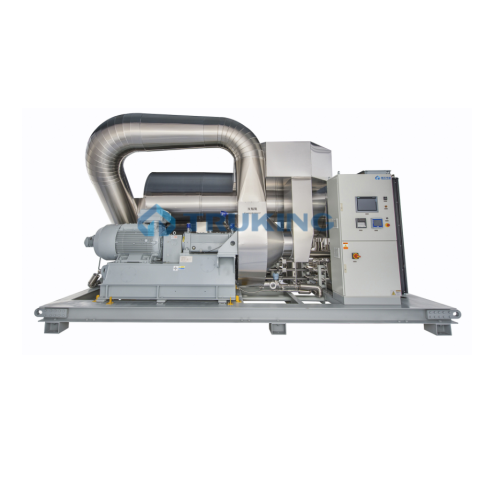
Hot press distilled water unit for pharmaceutical applications
Ensure superior water purity in pharmaceutical production...
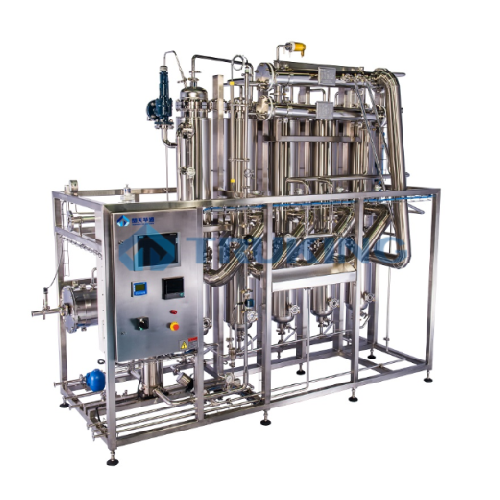
Multi-effect water distillator for pharmaceutical applications
Ensure your production line meets stringent regulatory st...
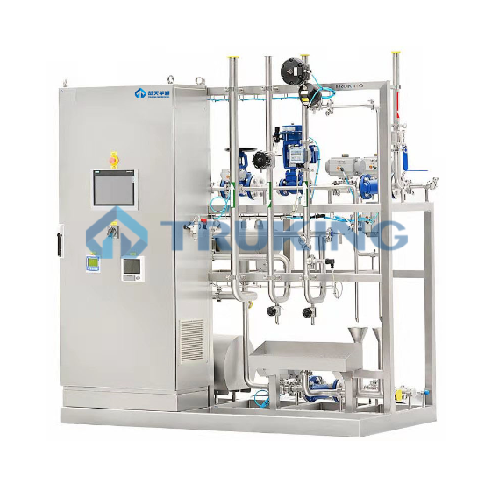
Pharmaceutical ultra pure water distribution system
Ensure stringent purity standards with a modular water distribution s...
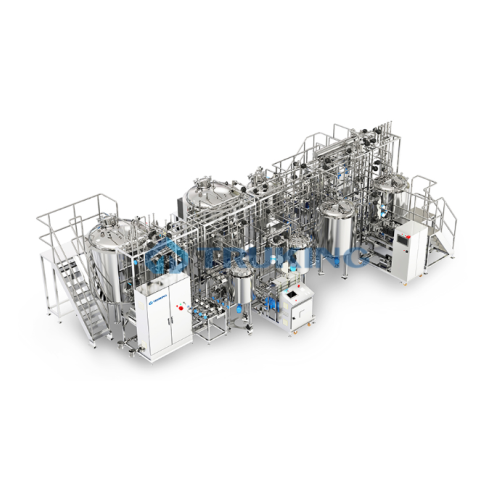
Complex preparation system for industrial microsphere production
Achieve precise particle size and uniform drug encapsul...
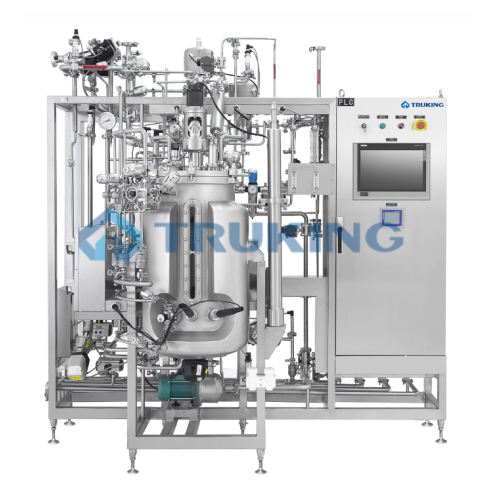
Bioreactor system for protein and enzyme reaction
Ensure precise control in biopharmaceutical production with a bioreacto...
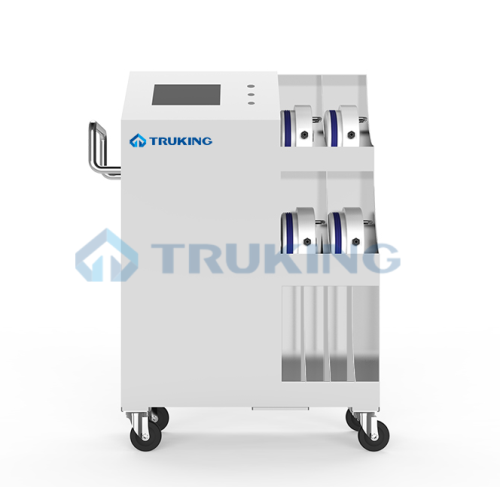
Isolator for sterility testing in pharmaceutical manufacturing
Ensure precise sterility testing with advanced isolators ...
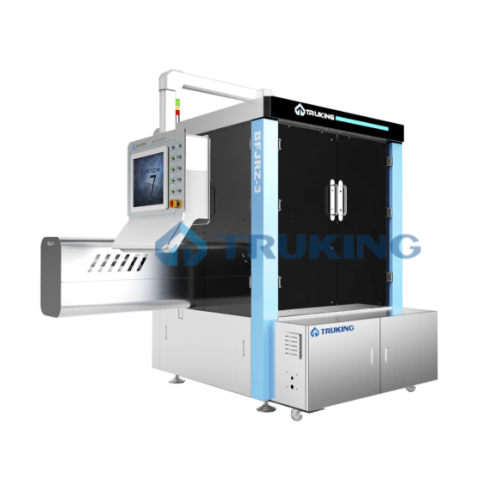
X-ray inspection for pharmaceutical vials
Ensure product purity by detecting contaminants in pharmaceutical vials with adv...
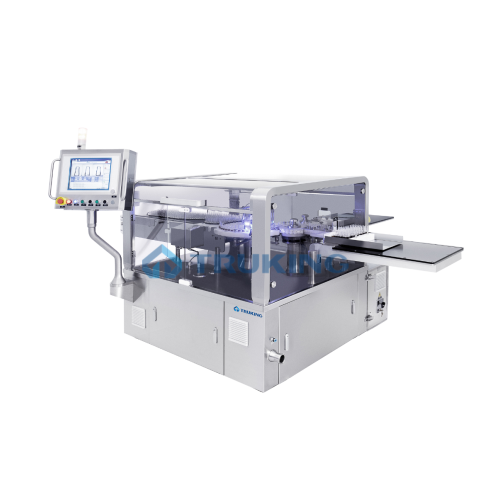
Automatic inspection system for sealing defects in ampoules
Ensure flawless ampoule sealing with a high-precision inspec...
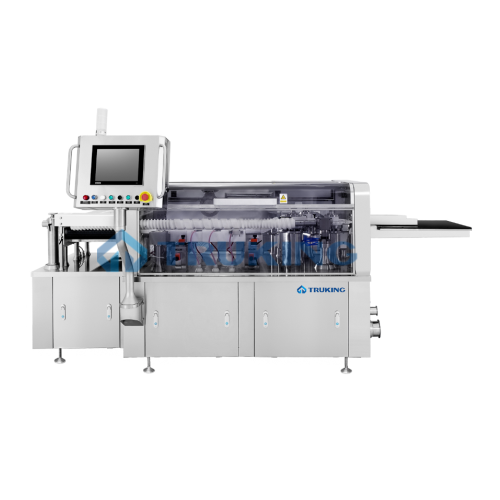
Automatic leak detection system for pharmaceutical containers
Ensure the integrity of pharmaceutical containers with pre...

High capacity automatic blister packaging system
Streamline your production line with a high-speed blister packaging syste...
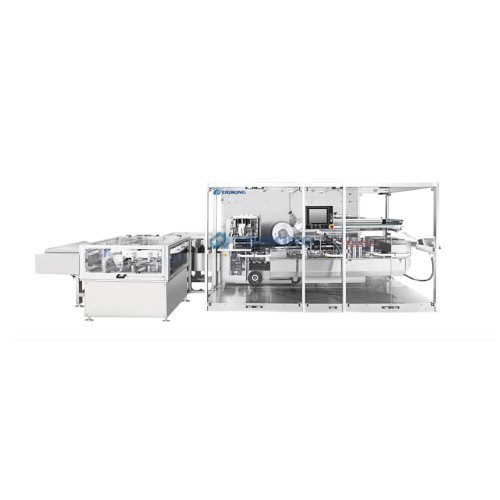
Secondary packaging cartoner for ampoules and vials
Optimize your aseptic production with efficient high-capacity carton ...
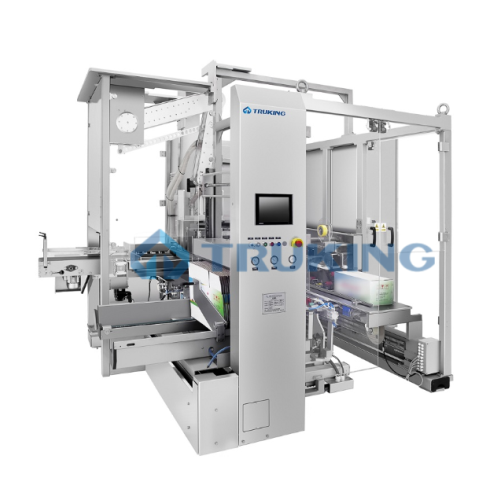
Automatic case packer for pharmaceutical industry
Optimize your packaging process with a versatile case packer designed t...
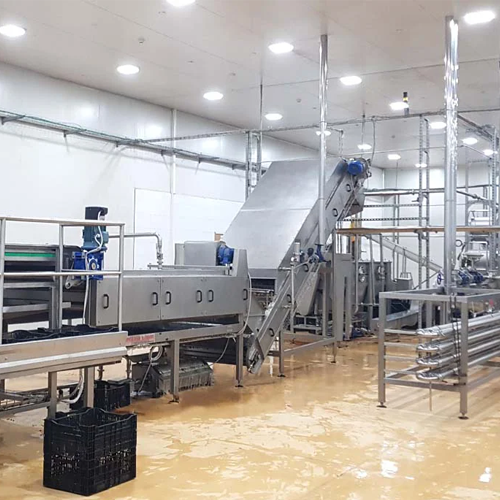
Multi-fruit extraction line for mango, guava, and passion fruit juice
Optimize your fruit processing with high-yield ex...
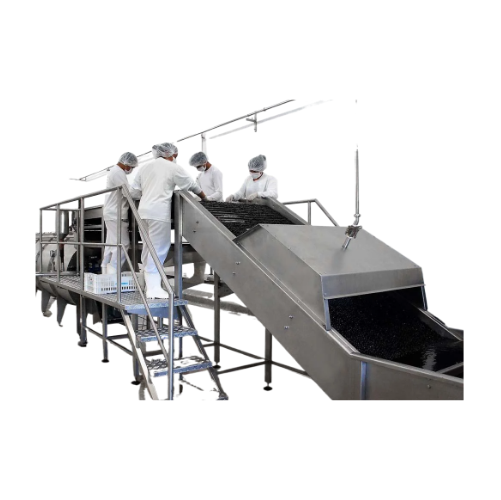
Acai berry processing line
Enhance your acai berry production efficiency with an automated line that transforms traditional ...
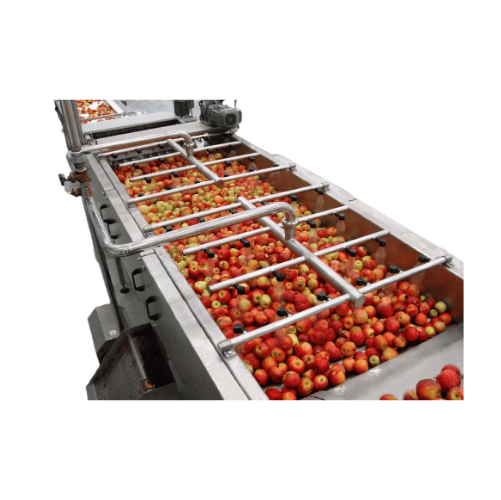
Apple, pear, and kiwi juice extraction line
Achieve high-yield juice production from apples, pears, and kiwis while retain...
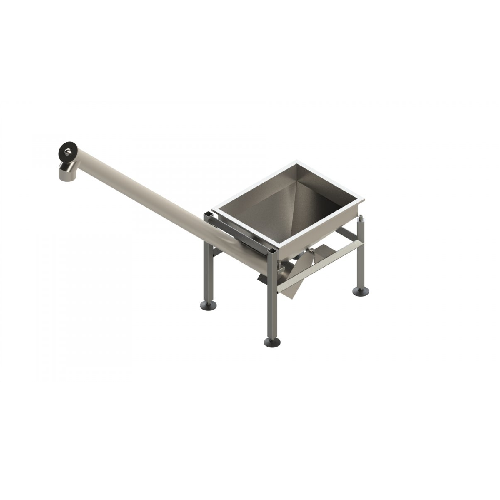
Vibratory storage hopper with inclined screw conveyor
Enhance your production line efficiency with a vibratory storage ho...
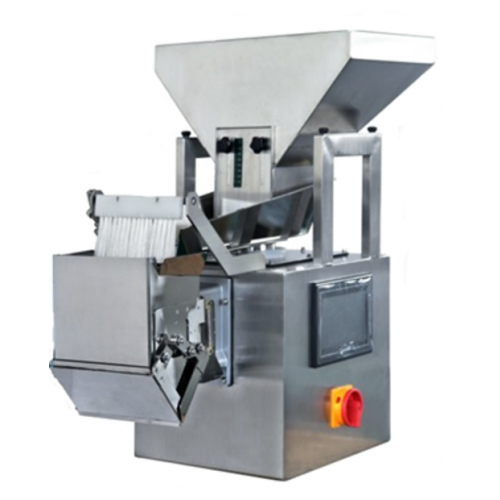
Linear weigher for dry free flowing products
Streamline your packaging process with precise weighing capabilities, ensurin...
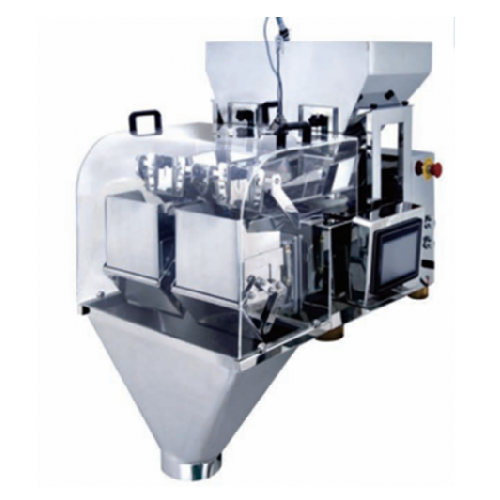
Linear weigher for accurate food portioning
Ensure precise weight control for snacks and confectioneries with our advanced...
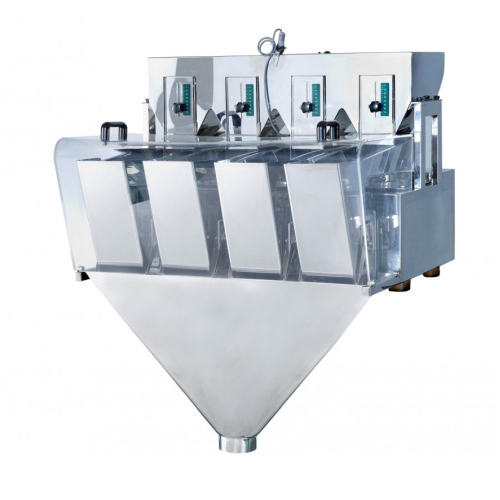
Linear weigher for dry free-flowing products
Optimize your packaging line with precise weighing for snacks, sweets, and gr...
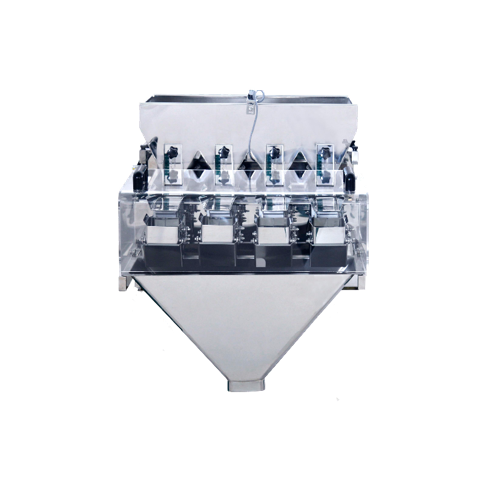
Linear weigher for dry free flowing powder
Optimize your packaging line with precise weighing for free-flowing granular pr...
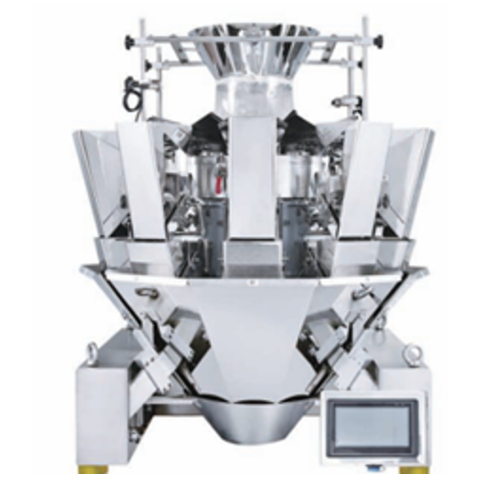
14 head multihead weigher for dry products
Achieve precise and rapid weighing for a variety of dry, free-flowing products ...
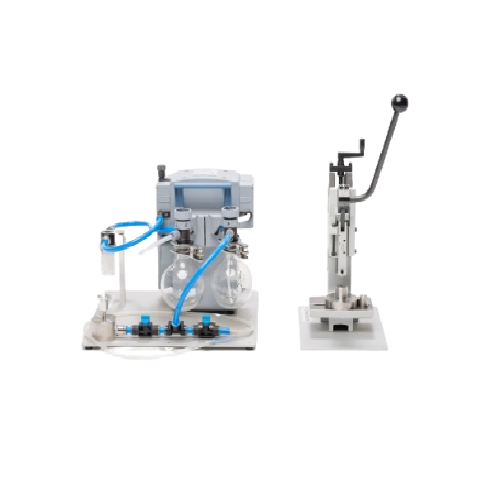
Catalyst cartridge packing system
Efficiently pack and seal catalysts into cartridges with precision, ensuring reliable and...
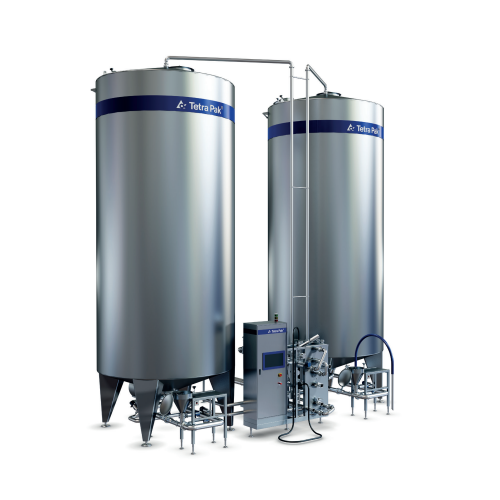
Beverage preparation system for large-scale production
Ideal for producers looking to scale up, this versatile system eff...
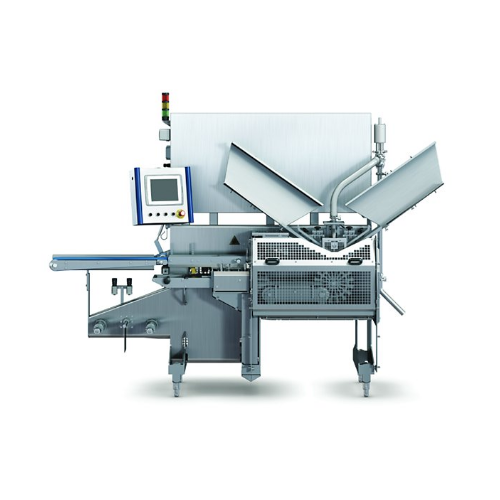
Ice cream sandwich production unit
Achieve consistent production of high-quality ice cream sandwiches with rapid, precise o...
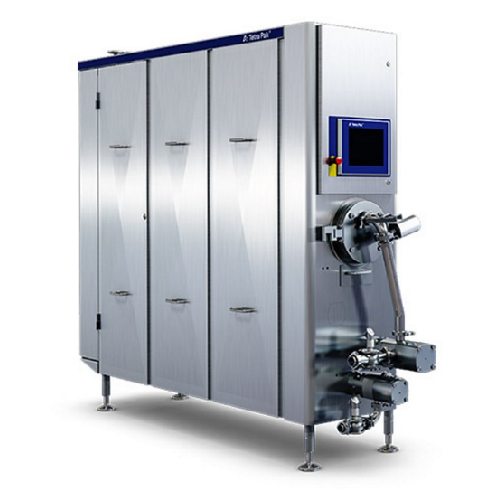
Continuous freezer for ice cream production
Optimize your ice cream production with precision freezing, mixing, and air in...
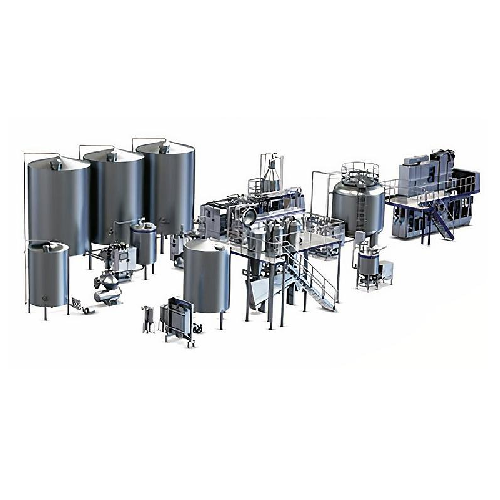
Single-pass tea extraction system
Achieve consistent, high-quality ready-to-drink tea extraction with a streamlined, semi-c...
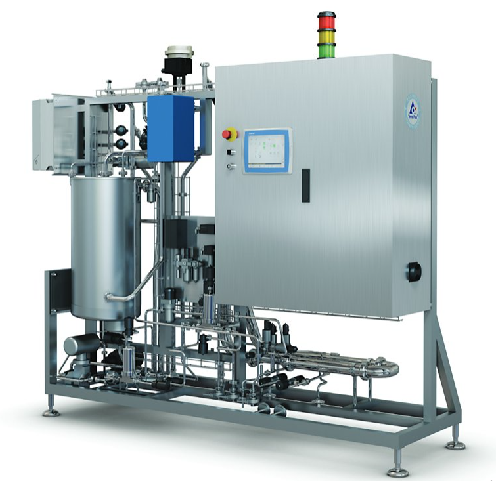
Aseptic dosing unit for enzymes and vitamins
Efficiently integrate precision ingredient dosing for enzymes and vitamins in...

Cheese curd production vat for semi-hard cheese
Optimize your cheese production with a vat designed to ensure precision in...
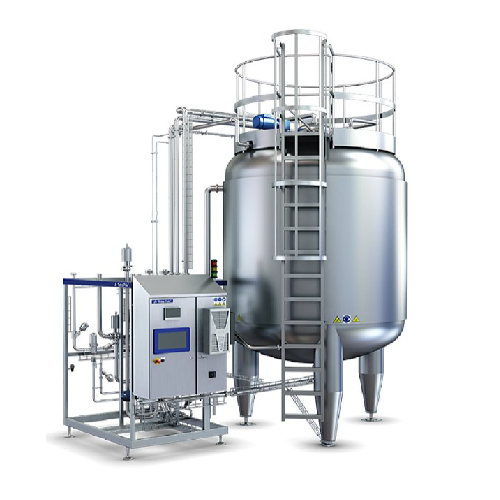
Aseptic tank with blending function for liquid food storage
Achieve seamless integration of aseptic buffering and in-lin...
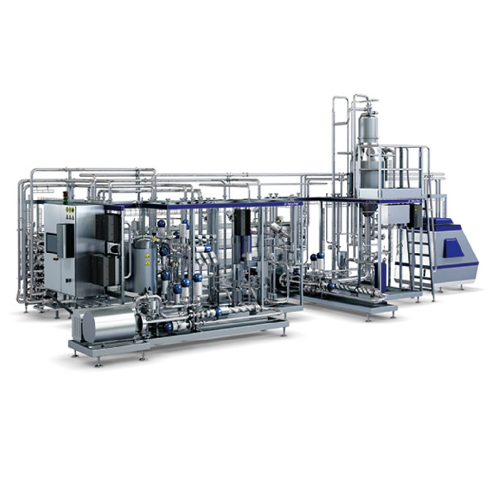
Continuous ultra-high temperature treatment for prepared food products
Optimize your prepared food production with cont...
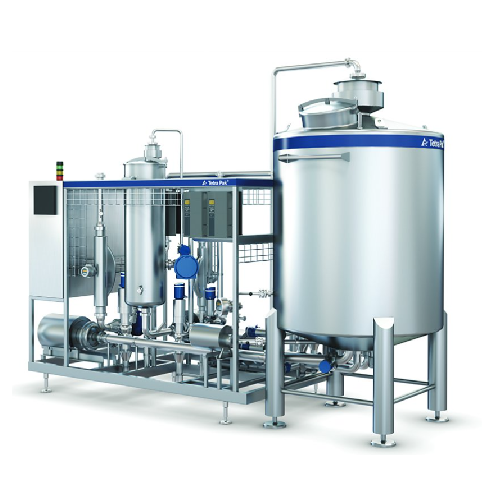
In-line blender for beverage production
Enhance beverage production with a versatile solution that offers precise blending,...
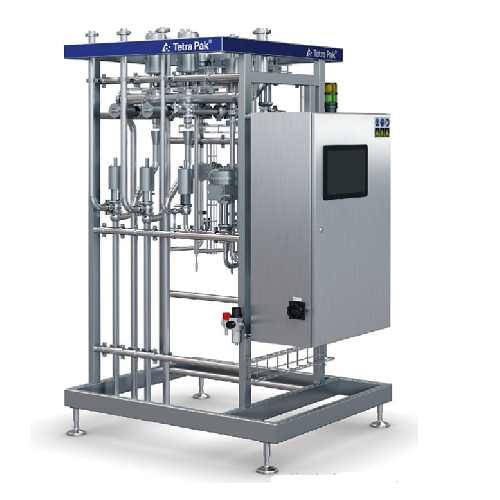
Automated milk standardization unit
Achieve precise in-line standardization of milk components, ensuring optimal quality an...
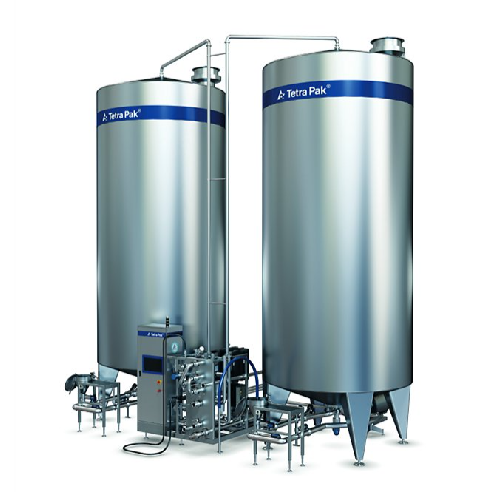
Final syrup and beverage preparation system
Optimize your beverage production with a modular system designed for flexibili...
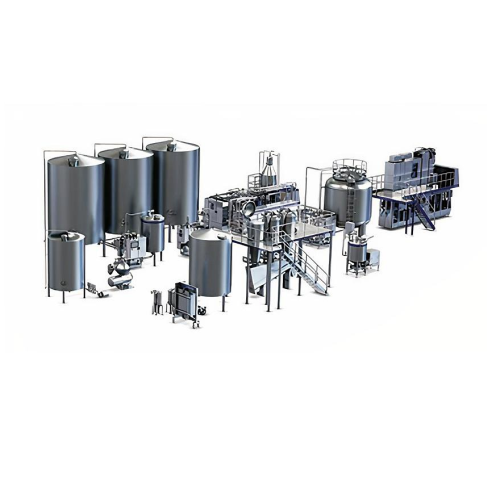
Single-pass extraction system for tea
For tea producers seeking consistent, high-quality extraction, this semi-continuous s...
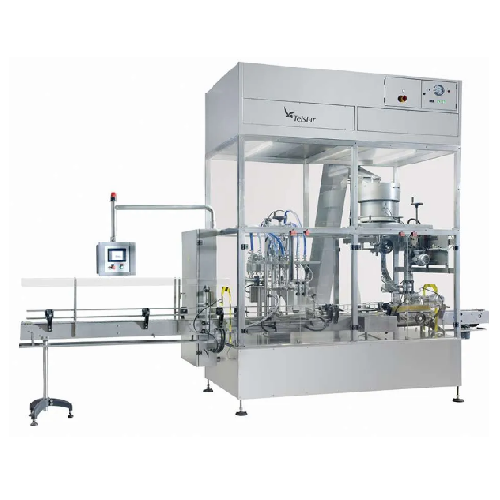
Laminar air flow systems for pharmaceutical production
Ensure contamination-free production by maintaining unidirectional...
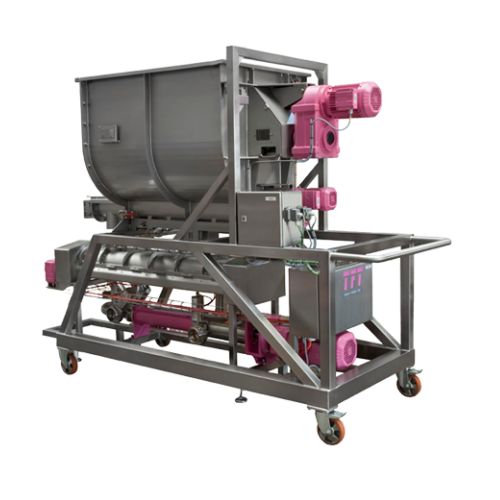
Dry ingredient blending solution for confectionery and bakery products
Achieve seamless integration of dry inclusions i...
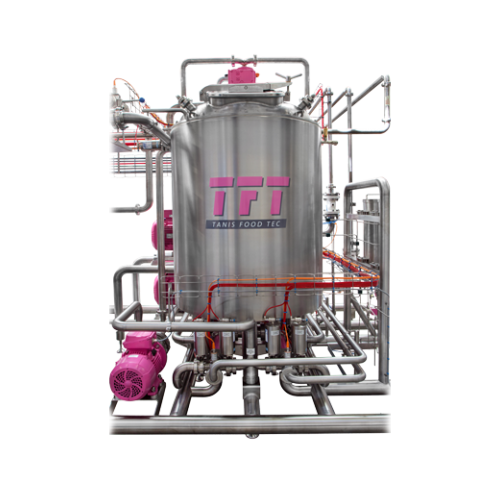
Buffer tank for consistent product temperature control
Ensure consistent product temperatures and streamline your product...
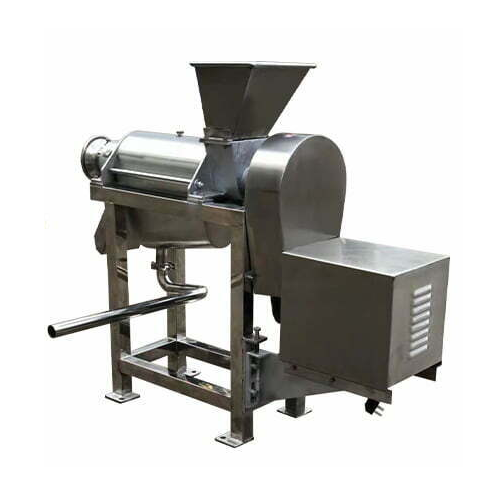
Spiral fruit juicer for apples and oranges
Enhance juice production efficiency by seamlessly integrating this spiral fruit...
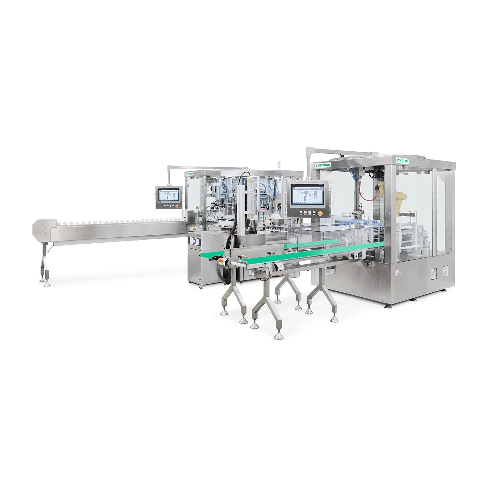
Medical device assembly and labeling solutions
Streamline assembly and labeling processes for medical devices with technol...
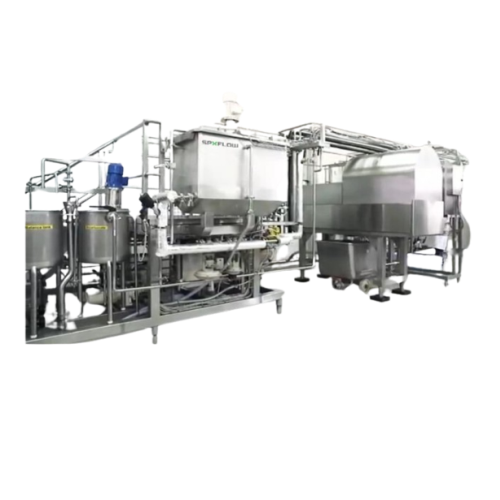
Soymilk processing plant
Enhance your plant-based production with our tailored soymilk processing plants, designed to efficie...
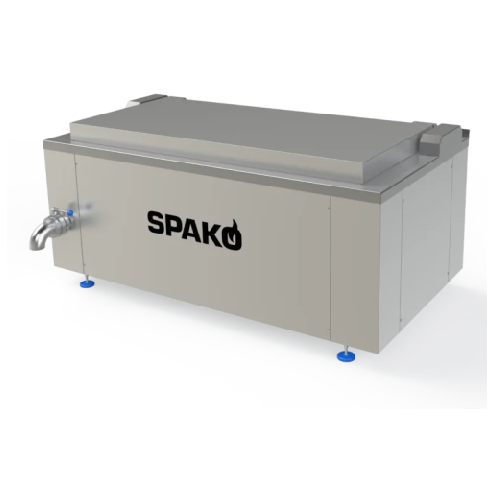
Industrial cooking kettle for meat processing
Optimize your batch cooking operations with a versatile solution designed fo...
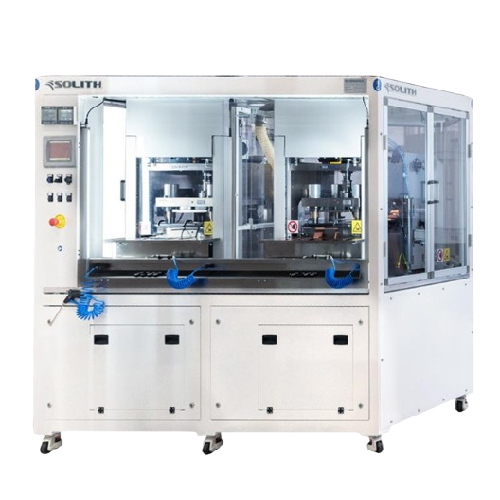
Pouch li-ion cell assembly line
Efficiently assemble high-performance lithium-ion pouch cells crucial for powering electric ...
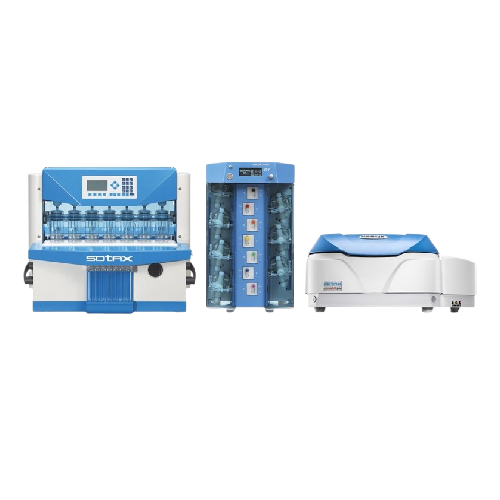
Flow-through cell dissolution testing with Uv analysis
Effortlessly monitor real-time dissolution with flow-through cell ...
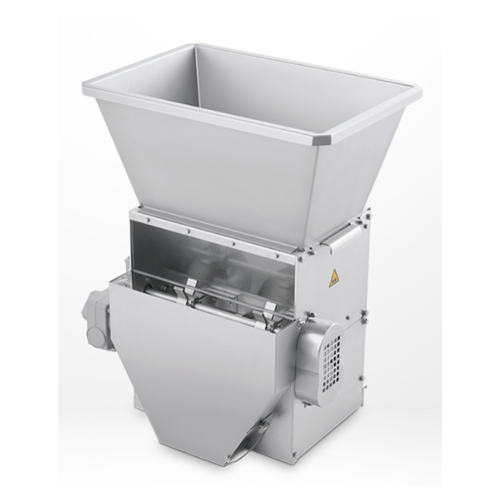
Precise metering system for dry confectionery ingredients
Achieve precise dosing of granular and dry ingredients like nu...
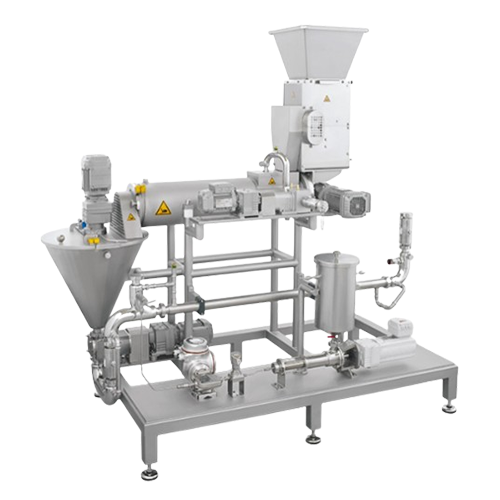
Flavour and colour dosing system
Simplify production by efficiently incorporating various flavors, colors, and solid inclusi...
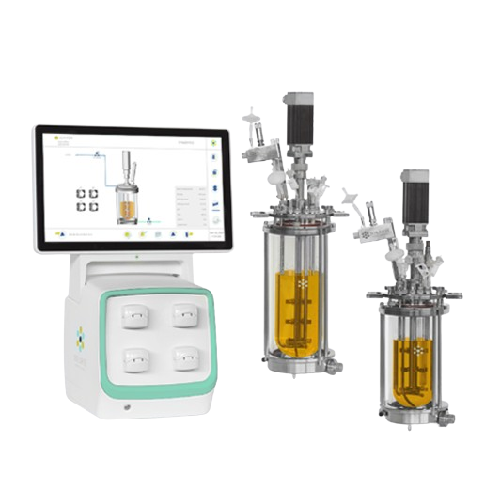
Autoclavable fermenters for small scale bioprocessing
Optimize your bioprocesses with configurable fermenters offering pr...
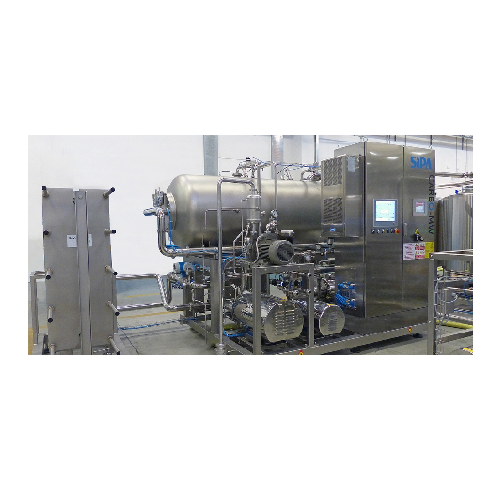
Degassing and carbonation system for mineral water
Optimize your carbonation process with a compact system that ensures p...
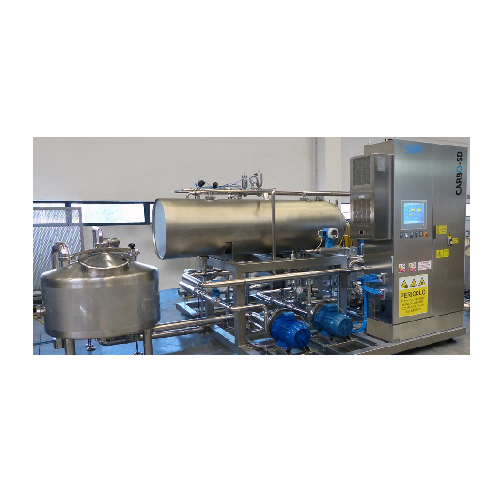
Compact carbonation unit for carbonated beverages
Enhance beverage quality with precise carbonation, ensuring consistent ...
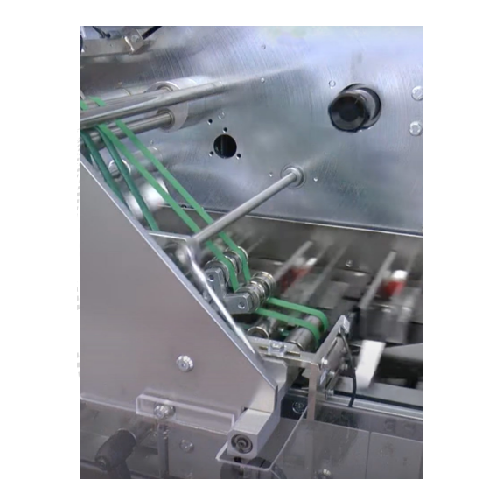
Automatic cartoning system for pharmaceuticals
Simplify your cartoning process with high-speed, continuous motion that boo...
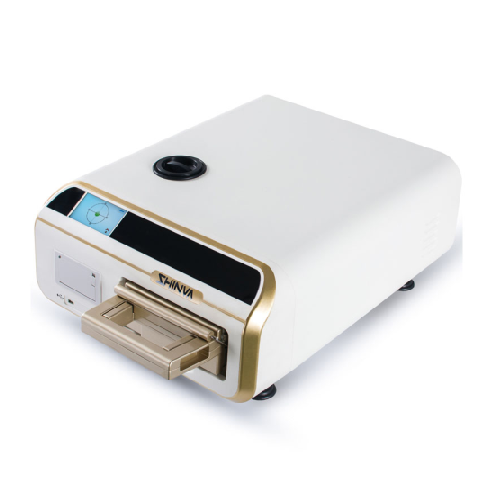
Cassette autoclave for sterilization in medical settings
Ensure the reliable sterilization of medical and laboratory inst...
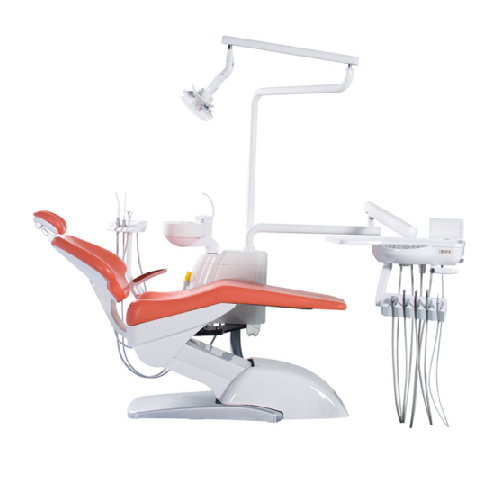
Dental equipment sterilizer
Ensure complete infection control and safety with advanced sterilization and cleaning capabiliti...
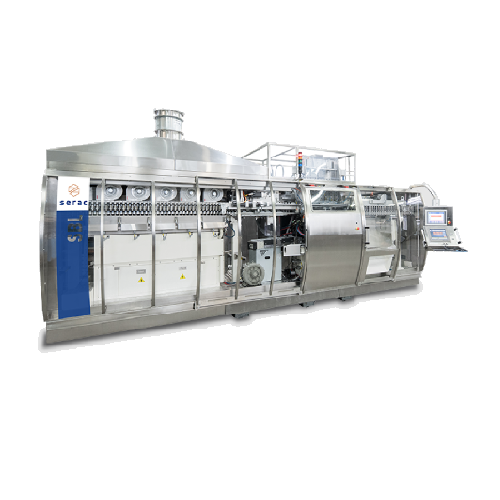
Pet bottle production for small and medium outputs
Optimize your production line by manufacturing PET bottles in-house, r...
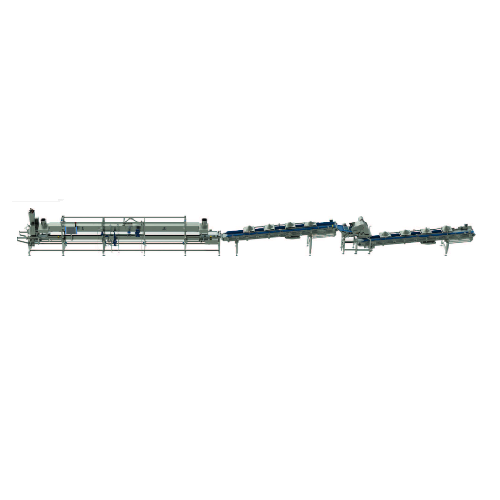
Pet food production line
Enhance your pet food production with a seamless, efficient system that emulsifies, extrudes, and pa...
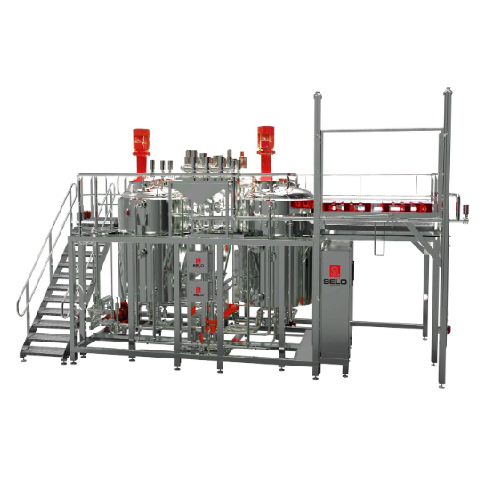
Automated sauce production lines
Streamline your sauce production with flexible lines designed for rapid recipe changeovers,...
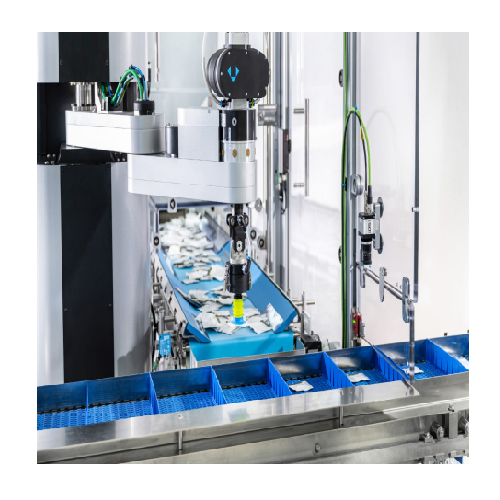
Automated pick and place cobot for packaging
Overcome packaging bottlenecks with an advanced cobot designed for high-speed...
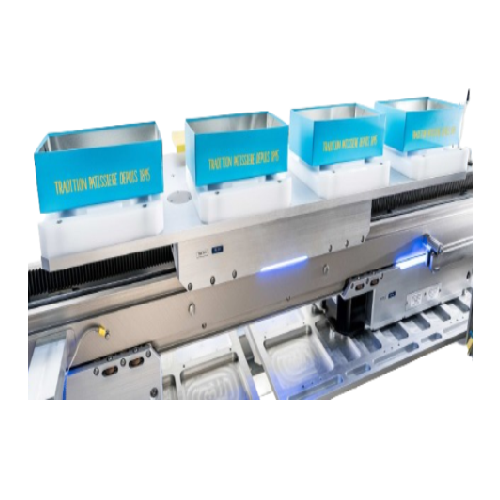
Flexible transport robot for packaging lines
Enhance your packaging efficiency with a transport robot engineered to seamle...
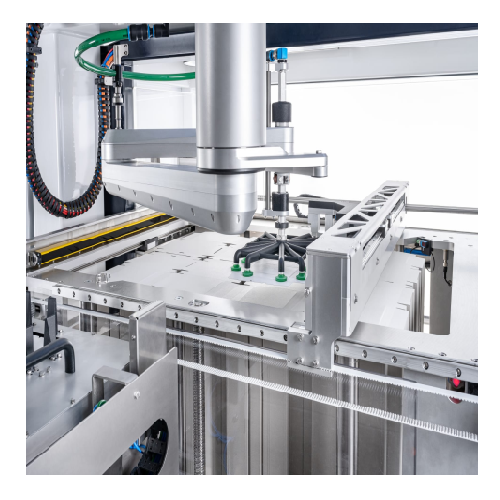
Compact carton blank feeding system
Maximize your production efficiency with a solution designed to streamline carton blank...
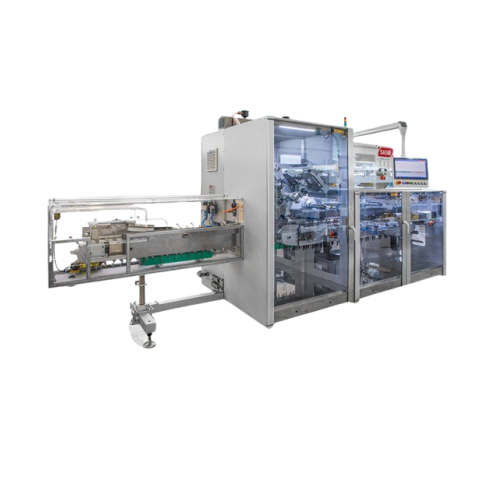
Cartoner for tobacco and hemp products
Streamline your production line with high-speed cartoning and packaging for cigars, ...
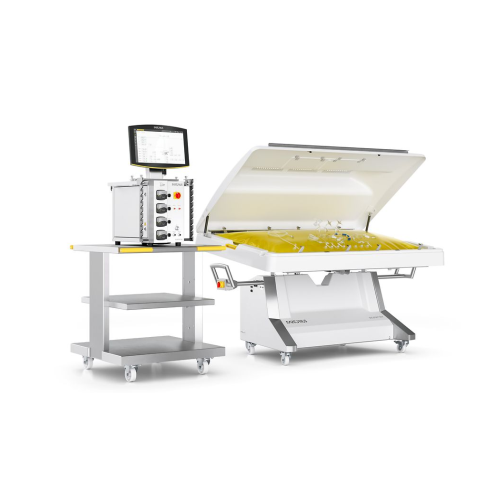
Cell culture bioreactor for mabs and vaccines
Optimize your biopharmaceutical production with advanced cell culture capabi...
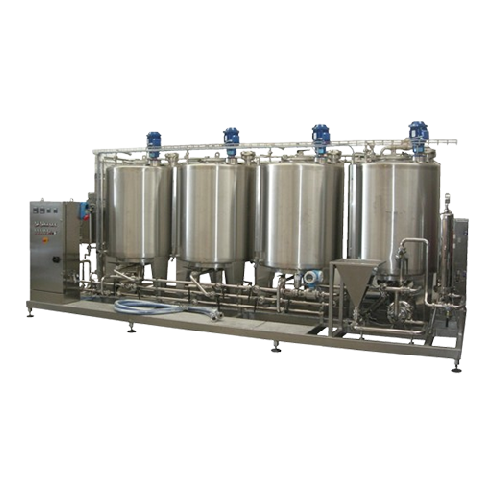
Custom syrup preparation systems
Optimize your beverage production with precision-engineered syrup preparation systems desig...
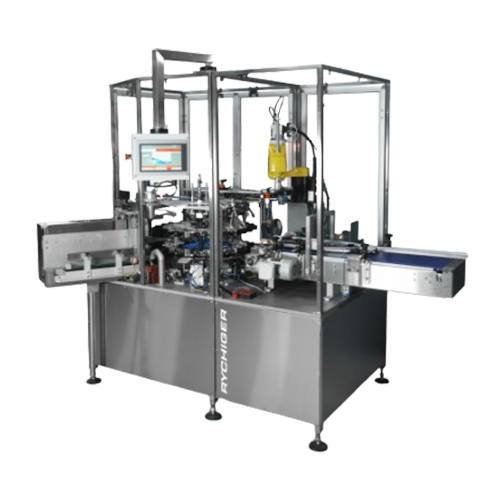
Cartoner for pharmaceutical products
Effortlessly streamline your packaging line with compact cartoning capabilities, ensur...
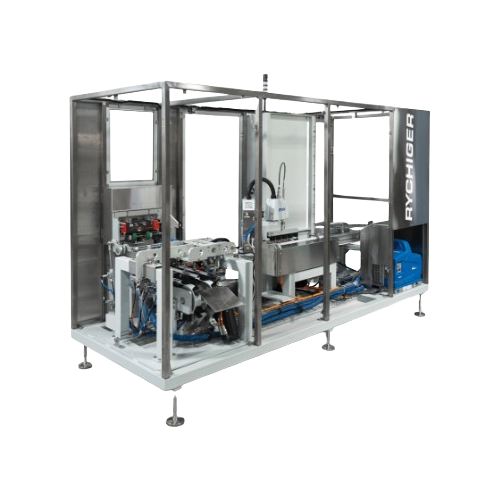
Horizontal cartoning system for coffee pods
Enhance your packaging line efficiency with a system designed for gentle handl...

Batch cooker and mixer for food and pet food production
Streamline your cooking and mixing processes with a versatile bat...
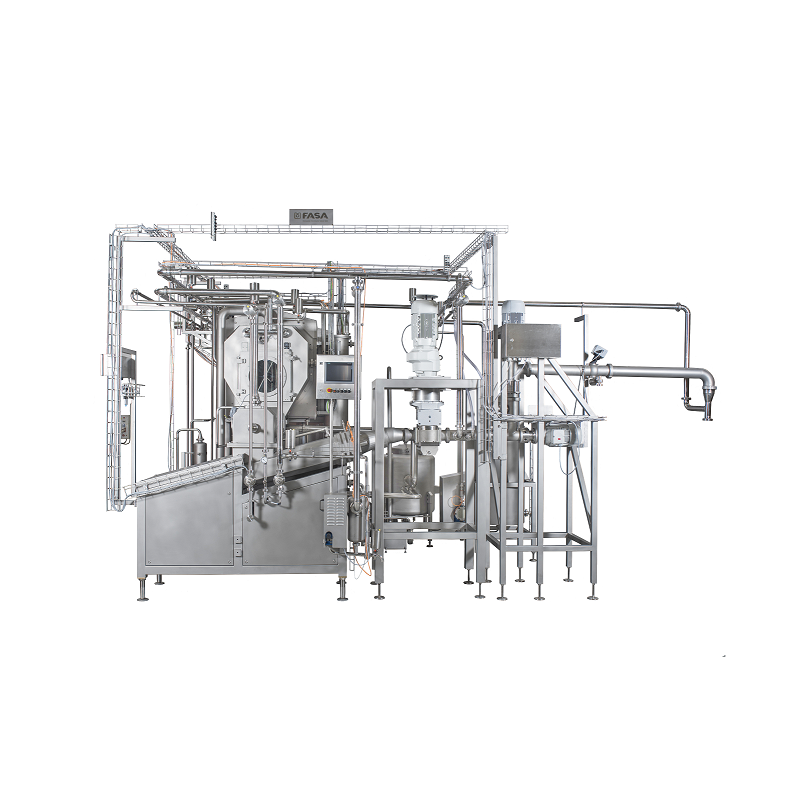
Continuous butter production line
When producing large volumes of butter in consistent quality, taste and appearance you ne...
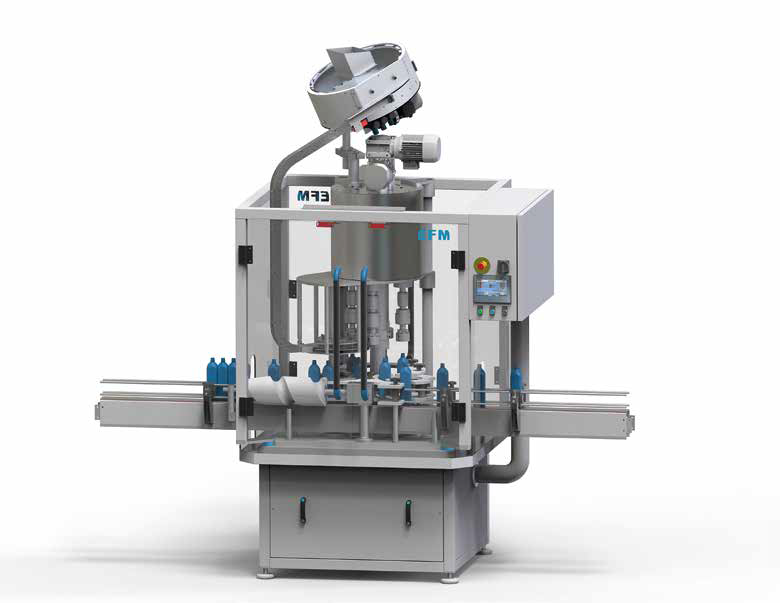
Multi-head capper
For the stand-alone capping of bottles of up to 2.5litre capacity you need a robust and flexible machine wi...
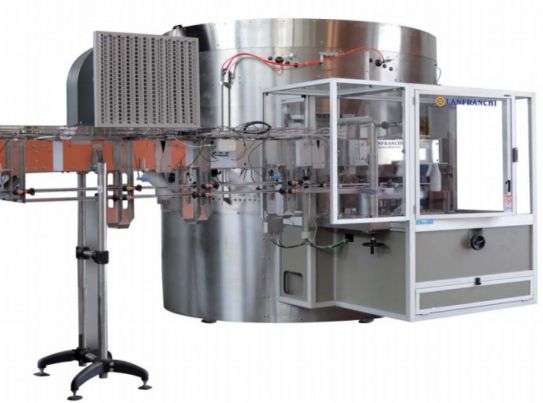
High-speed unscrambler for large bottles
Large volume plastic bottling plants need high-speed unscramblers suitable for lar...
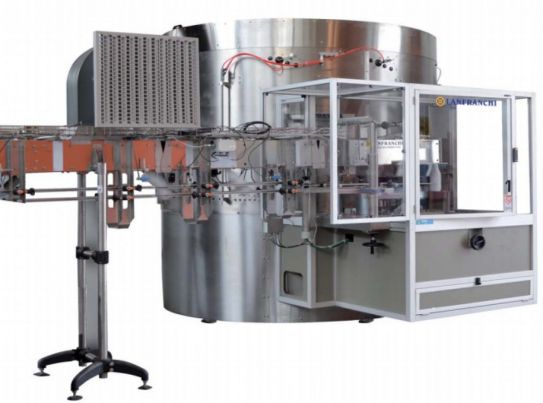
High-speed unscrambler for small bottles
Large-scale production of smaller volume bottled product needs a gentle, accurate ...
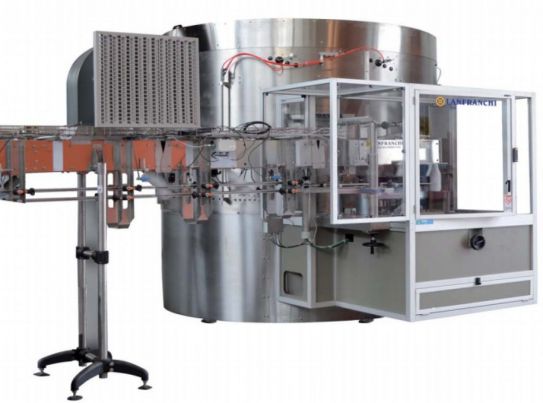
Low-speed unscrambler
Smaller plastic bottling lines need a lower cost, lower volume unscrambling machine that maintains gent...