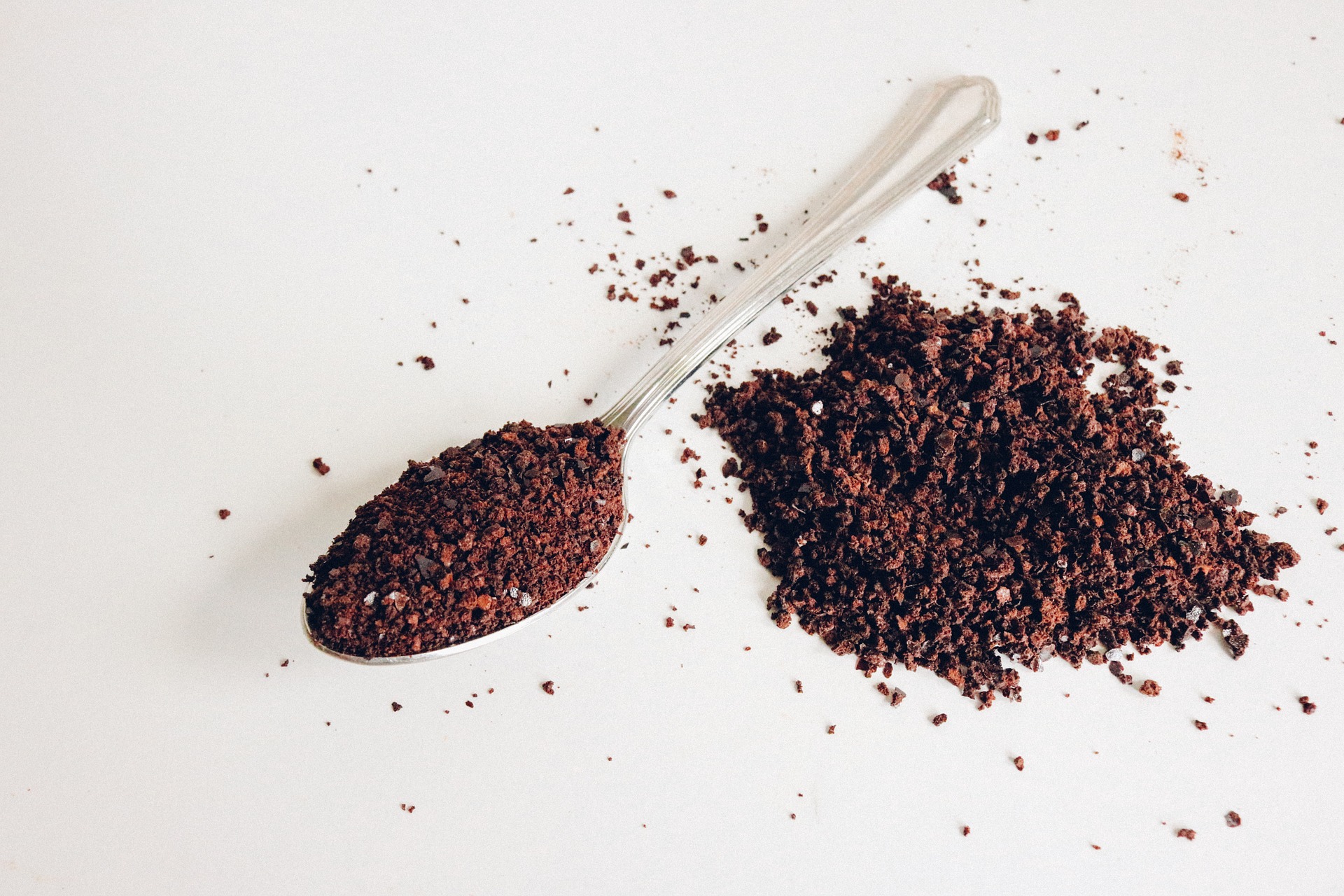
Making Instant Coffee
Find innovative production technology for making instant coffee and connect directly with world-leading specialists
Do you know that the famous classical music composer and pianist Ludwig van Beethoven insisted on drinking a cup of coffee made from exactly 60 pieces of coffee beans? Currently, around 50% of the world’s green coffee beans undergo processing through instant coffee manufacturing equipment to produce instant coffee. The process requires roasting, grinding, brewing, and heating to obtain the extract; the coffee extract will either go through a spray drying process or a freeze-drying process.
Stories about instant coffee
Select your instant coffee process
Tell us about your production challenge
Let’s start: roast and grind your coffee beans…
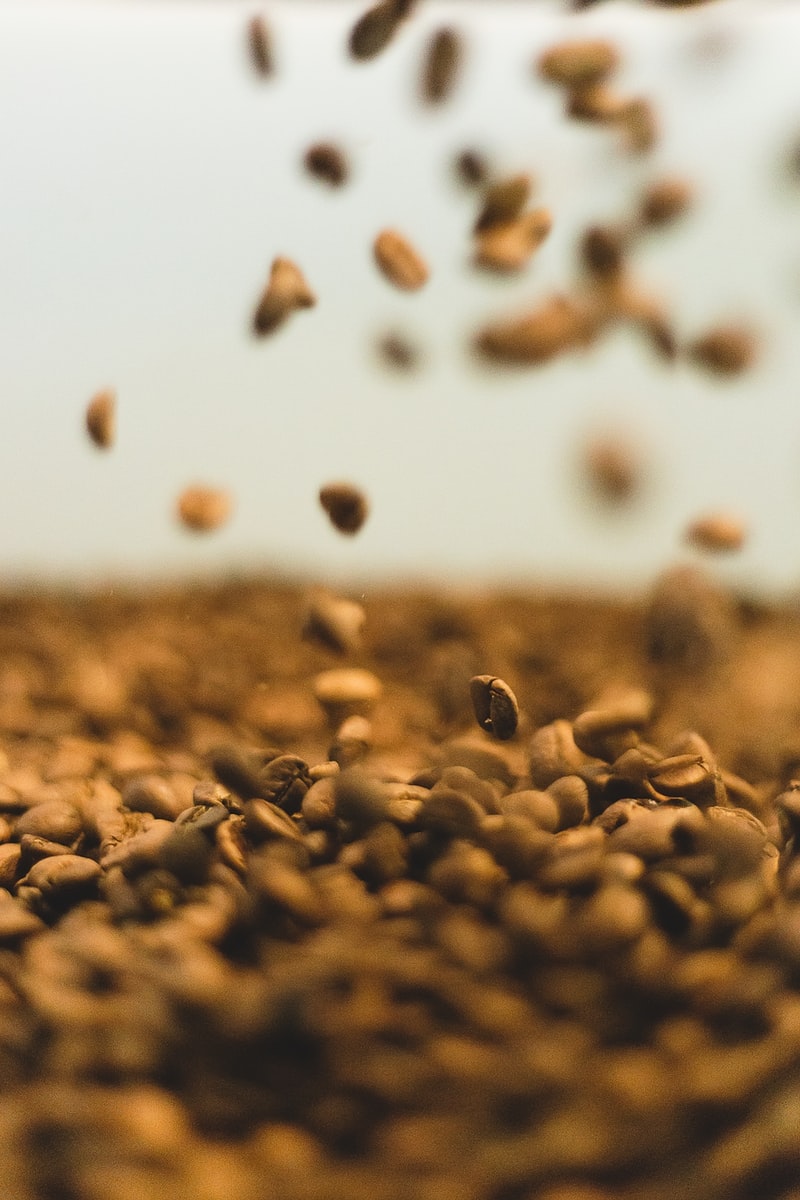
The instant coffee production process starts with cleaning and sieving the green coffee beans to remove dirt and unwanted debris. Then, they are loaded up in large ovens for roasting at a temperature of 200°C while being constantly stirred to ensure even roasting without burning. The roasting step takes only 10 minutes – just the time for the beans to turn brown. Before grinding them into powder using an industrial grinder, they are cooled rapidly down to 40 °C. While grinding the beans, a large amount of their aroma is released into the air.
… then brew powder, and condense extracts using instant coffee manufacturing equipment
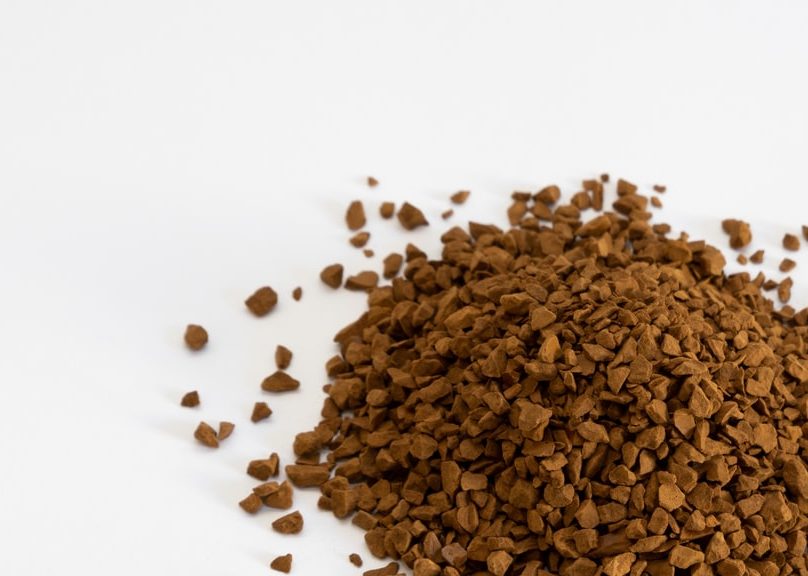
To minimize the loss, nitrogen gas is pumped through the ground coffee to collect the aromas and store them in a tank. The aroma will be added later in the production. The coffee powder goes to the pressure vessel, where water and steam are applied to make brewed coffee. Then, the brewed coffee is heated in the evaporator at 70 °C until it is condensed by 50% into an extract. This extract will undergo either a spray drying or freeze-drying process to obtain instant coffee. Both methods remove moisture and turn our coffee extract into instant coffee.
Instant coffee production: the freeze-drying method
Freeze-drying is the most common process used to remove moisture from coffee extracts. This process minimizes the chances of altering the flavor and aroma. The process involves freezing the coffee extracts to turn them into solid slabs. We are talking about ice age temperatures, around -40 °C or lower. The slabs are broken down into granules and loaded into trays for vacuum heating. The process removes the remaining moisture from the granules by applying heat at 60 °C under pressure in a strong vacuum.
This is called the sublimation process, where solid crystals turn to vapor without passing through a liquid phase. The aromas collected and stored in the tank are sprayed over the granules as they pass through giant sacks before they are prepared for packaging.
Instant coffee production: The spray-drying method
Another method used for drying coffee extract is the spray-drying process. The process involves atomizing or spraying the liquid coffee extract into tiny droplets. At the same time, a high-velocity stream of hot air at more than 500 °C quickly vaporizes the moisture leaving instant coffee powder.
This method can quickly dry the coffee extract into powder but may lose part of its flavor and aroma due to high temperature and pressure during the drying process. In terms of operating cost, this method is cheaper to operate compared to the freeze-drying method.
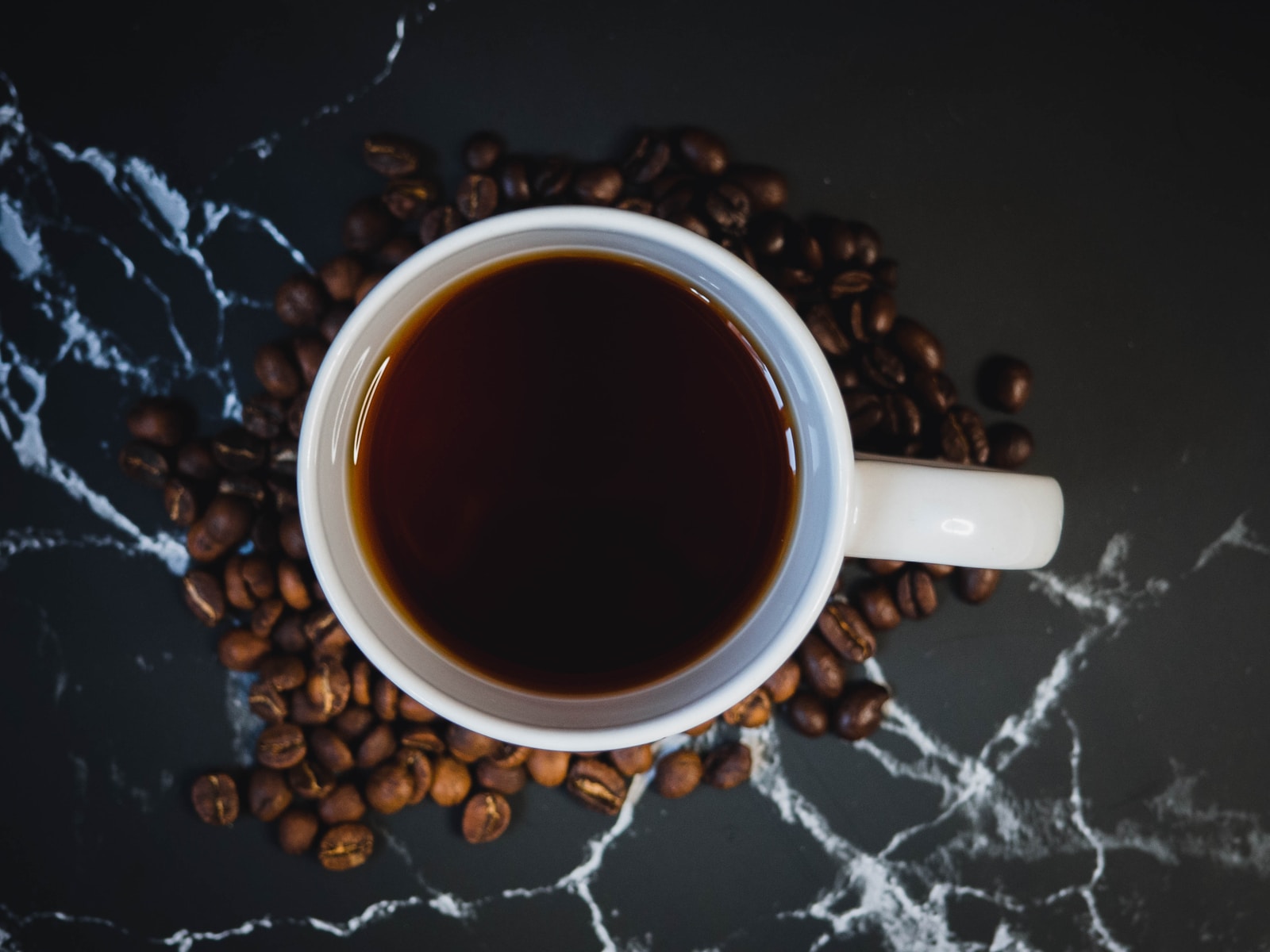
Producing energy from byproducts of instant coffee
Producers utilize most of the byproducts to minimize waste. For instant coffee producers, the main byproduct is spent coffee grounds which can be a versatile source of green energy. The coffee grounds can produce the same amount of energy as coal when burned. Spent coffee grounds can also be processed to extract more oil to be used as biodiesel, while the byproduct after oil extraction can be used as fertilizer or formed into briquettes or pellets to be burned into boilers as biofuel. Making coffee waste into usable energy is much more sustainable and environment-friendly for producers.
Processing steps involved in instant coffee making
Which instant coffee technology do you need?
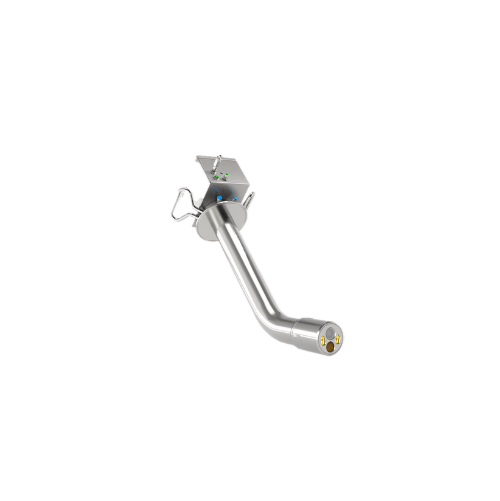
Dual camera system for spray dryer monitoring
Enhance safety and operational efficiency in your drying process by combinin...
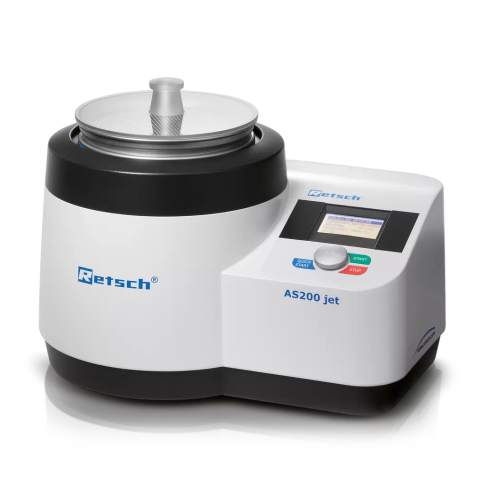
Air jet sieving system for powdered materials
Optimize particle distribution with precision air jet sieving, designed to e...
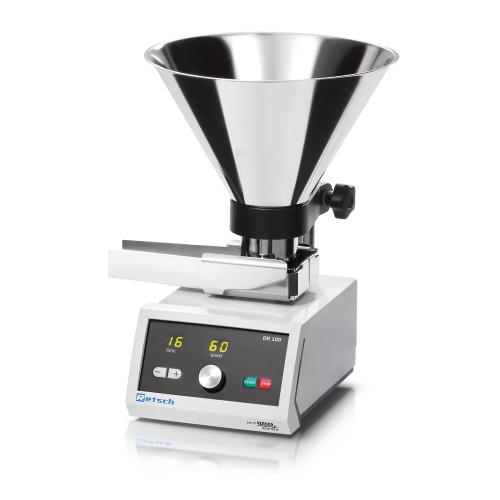
Vibratory feeder for bulk materials and fine powders
Ensure consistent material flow and precise feeding for optimized pr...
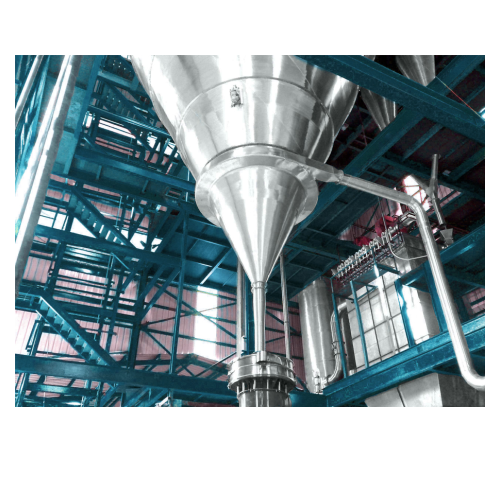
Milk powder processing plant
Achieve precise powder formulations with our state-of-the-art milk powder processing plant, ide...

Industrial coffee roaster for large scale production
Enhance your coffee’s aroma and flavor profile with an industr...
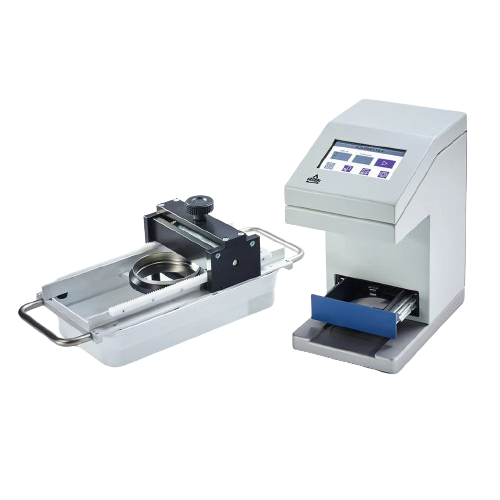
Color measurement tool for ground coffee
Ensure accurate coffee color measurement with a reflection-based system, vital for...
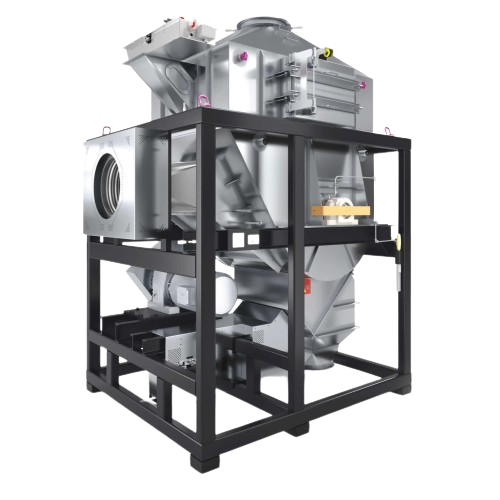
Green coffee preheating system
Optimize your coffee roasting process by utilizing waste heat for preheating, reducing energy...
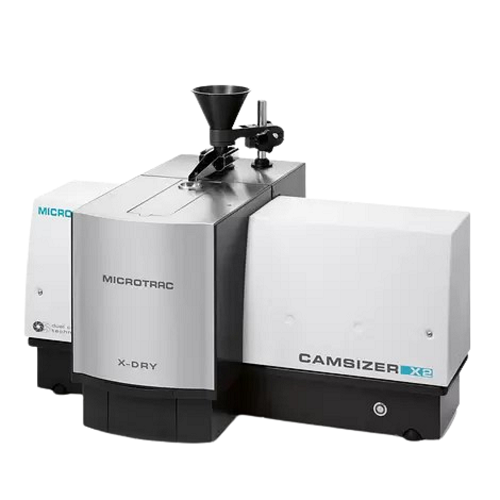
Particle size and shape analyzer
Achieve precise particle size and shape analysis from 0.8 μm to 8 mm with exceptional speed...
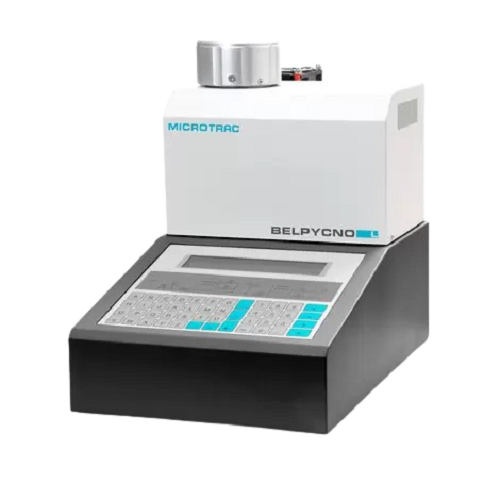
Gas pycnometer for precise density determination
Achieve accurate and reliable density measurements for a diverse range of...
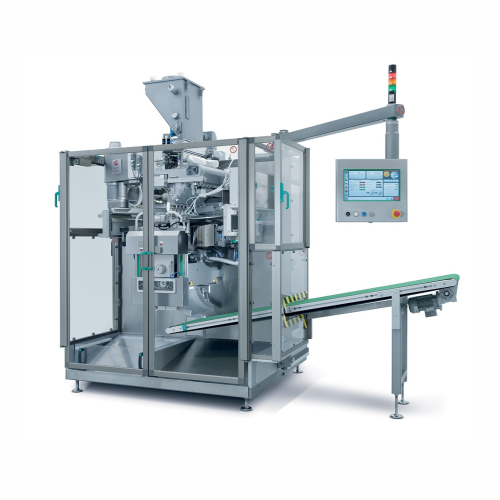
Sachet filling and closing system
Optimize your production line with a versatile solution designed to fill, seal, and count...
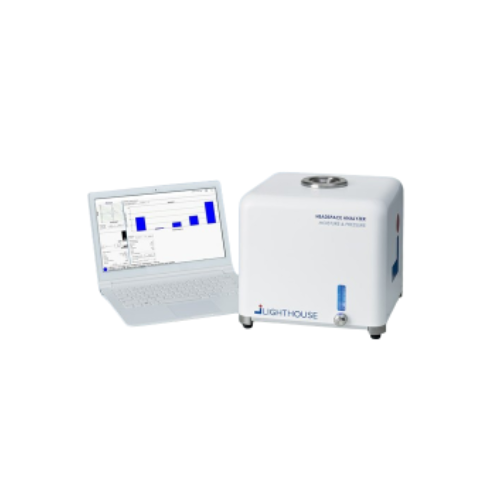
Moisture and pressure headspace analysis for sealed parenteral containers
Ensure accurate moisture and pressure assess...
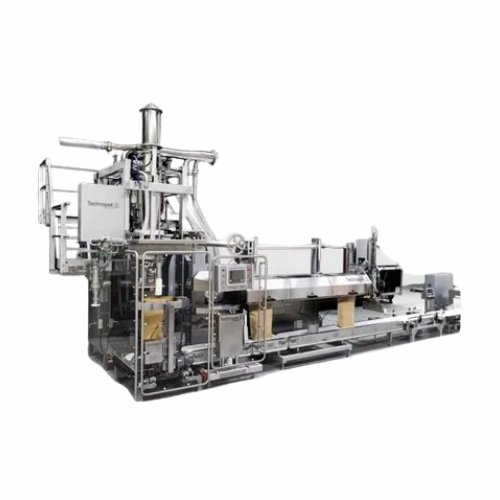
25kg automatic dry powder packaging system
Optimize your packaging line efficiency with precise, high-speed handling for 2...
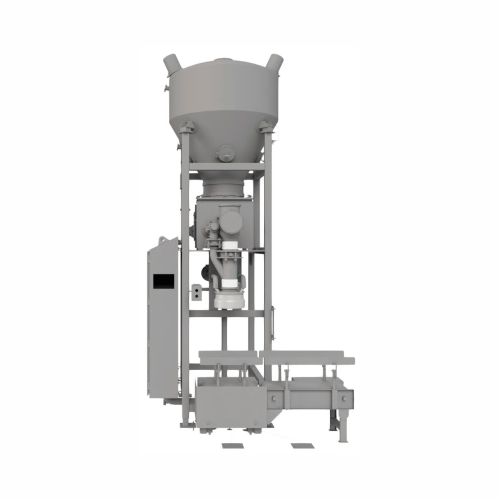
25kg powder packaging system for sanitary applications
Achieve high accuracy and hygiene in powder packaging with a syste...
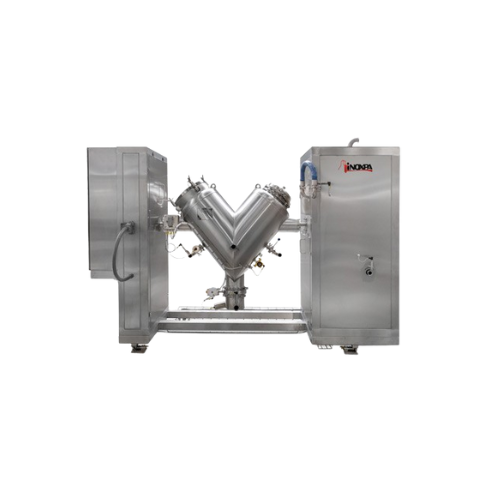
Industrial v-type solids blender for homogeneous mixture
Achieve precise blending of diverse powders and solids using the...
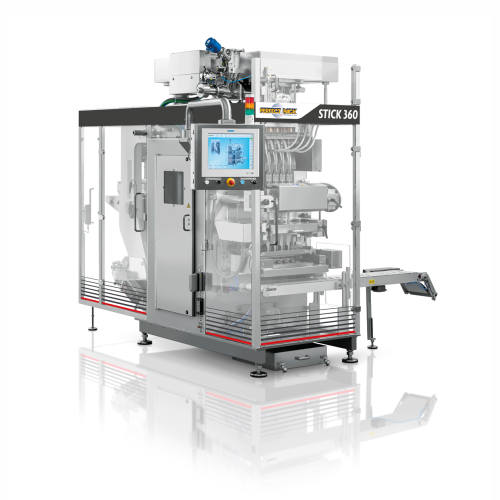
Vertical intermittent motion stick packaging
Experience seamless packing for diverse products, from powders to dense paste...
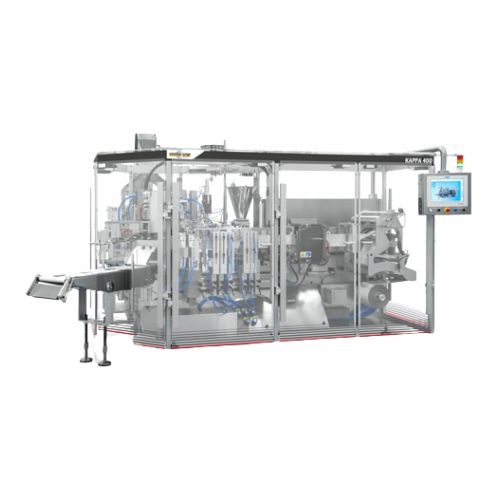
Horizontal intermittent motion sachet packaging solution
Optimize your packaging operations with a versatile sachet solut...
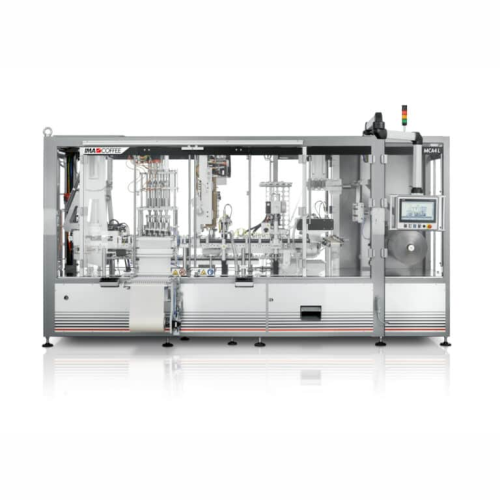
Capsule filling and sealing system for coffee
Optimize your capsule production with a system designed to enhance precision...
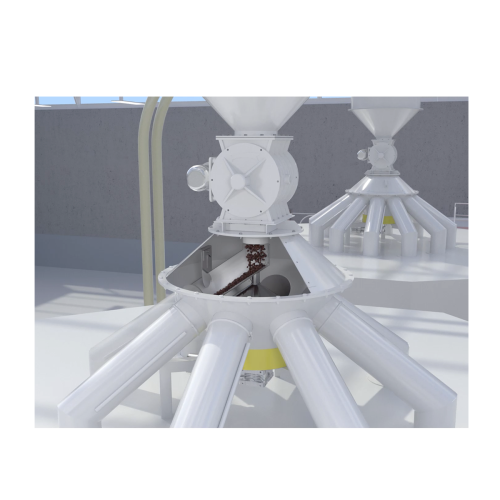
Roasted coffee handling and conveying system
Ensure the gentle handling of roasted coffee with versatile conveying solutio...
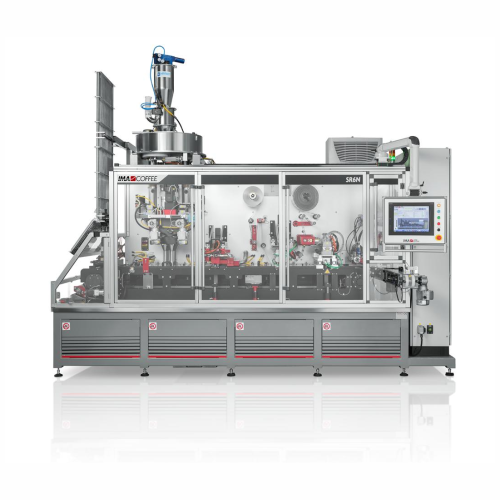
Capsule filling and sealing system for coffee products
Optimizing the precision of coffee and tea capsule production, thi...

Rotary doypack packaging system for various materials
Enhance your packaging line with versatile doypack machines designe...
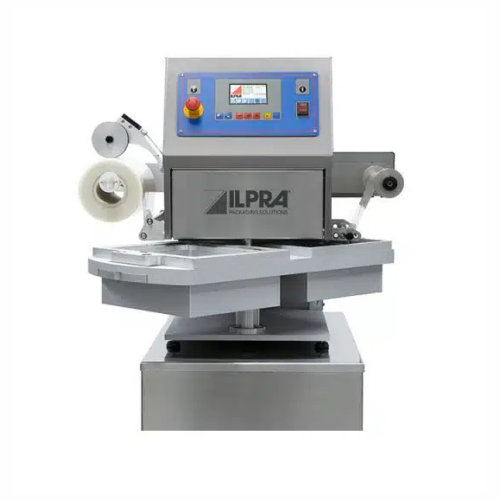
Traysealer for modified atmosphere packaging - food products
Optimize your packaging line with this semi-automatic trays...
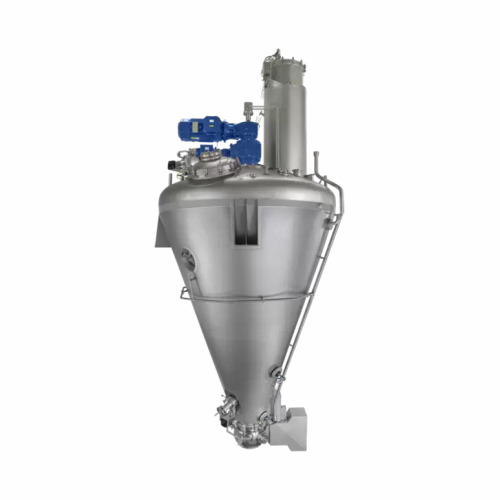
Vacuum dryer for powders and granules
Achieve precise moisture control for sensitive materials with a versatile vacuum dryi...
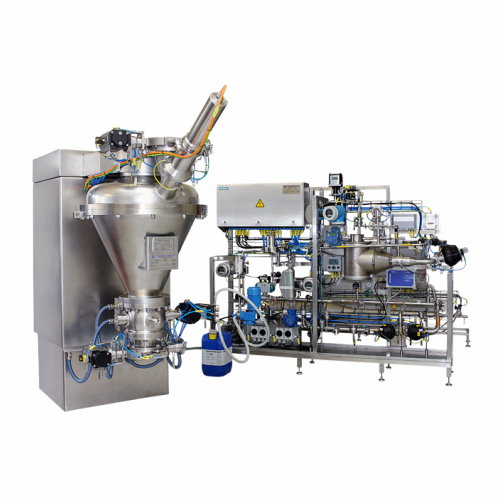
Cip/sip cleaning for solids processing systems
Ensure seamless transitions and maintain hygienic production environments w...
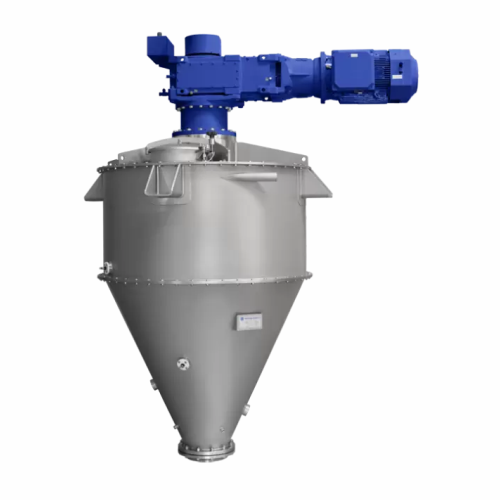
Conical paddle mixer for accurate powder blending
Achieve precise blending of fragile powders and liquids with a versatil...
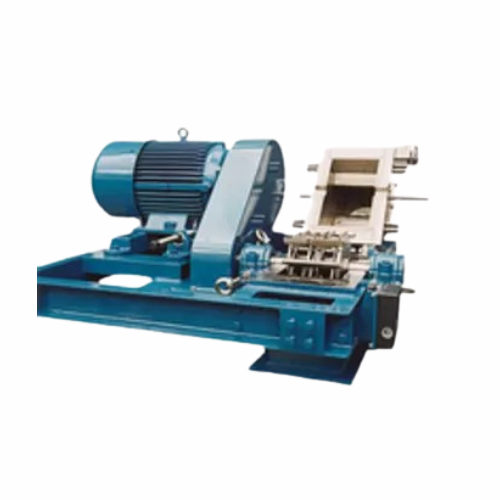
High-speed pulverizer for carbon black production
Achieve consistent particle size and optimal homogenization with high-s...
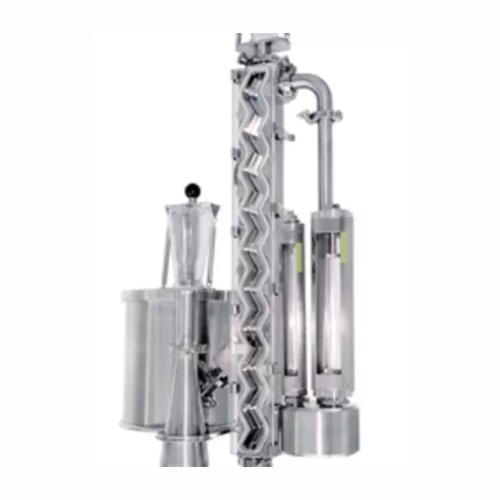
Gravity classifier for precise particle separation
Achieve sharp separations in particle processing with minimal maintena...
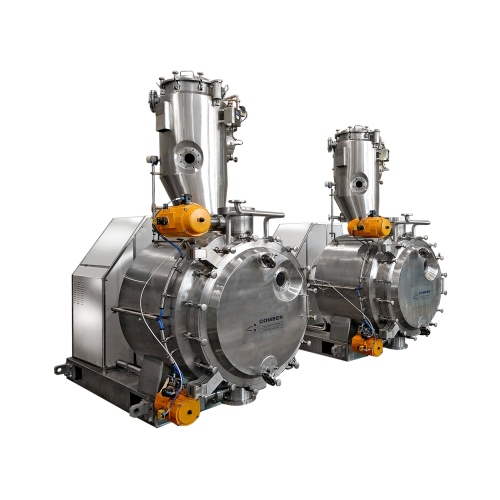
Horizontal vacuum paddle dryer for sensitive pharmaceutical ingredients
Achieve precise drying and mixing of sensitive ...
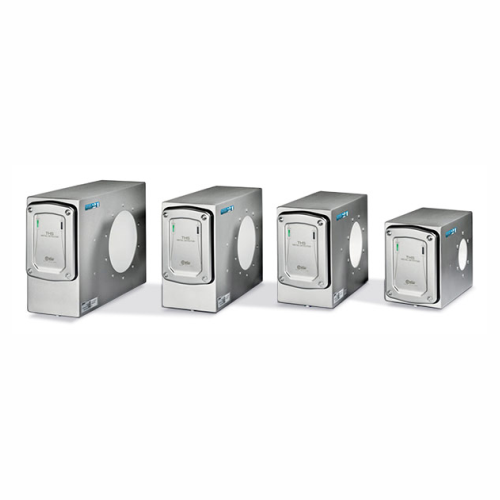
Industrial metal detector for gravity feed applications
Ensure the purity of your products by detecting and removing both...
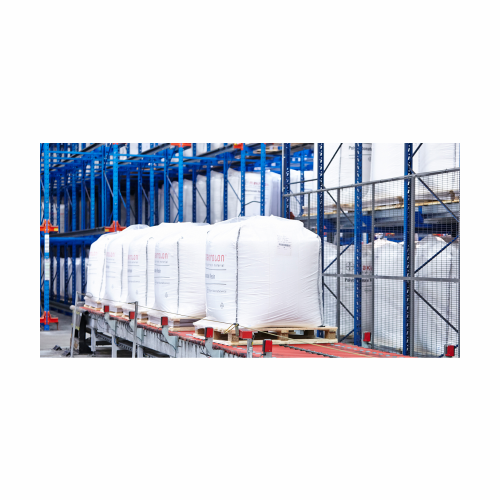
Stationary entry packaging system for valve bags
Optimize your packaging workflow with a high-speed, modular filling syste...

Pre-breaker for initial material size reduction
Efficiently prepare your bulk materials for further processing by swiftly ...
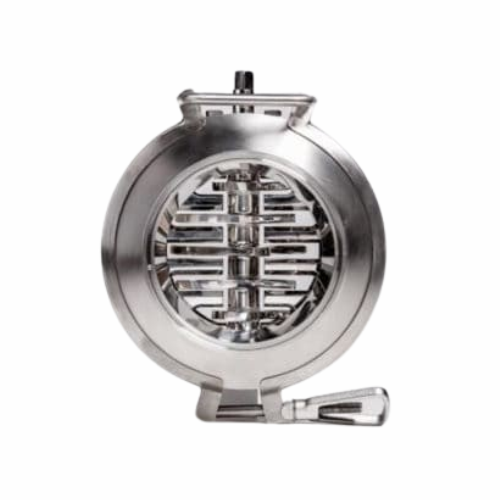
Rotary crushing valve for lump breaking
When handling bulk solids, effective pre-breaking and sizing are crucial to ensure ...
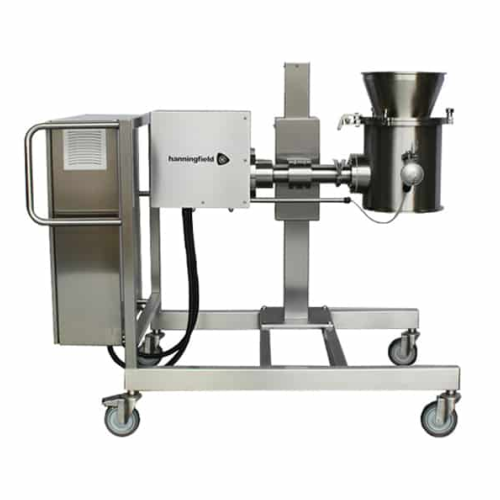
Conical mills for size reduction in pharmaceutical production
Achieve precise particle size control with an innovative m...
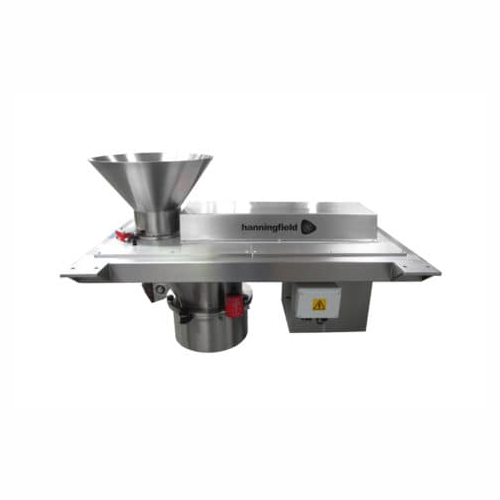
Over-driven conical mills for precise particle size reduction
Achieve consistent particle size reduction with minimal he...
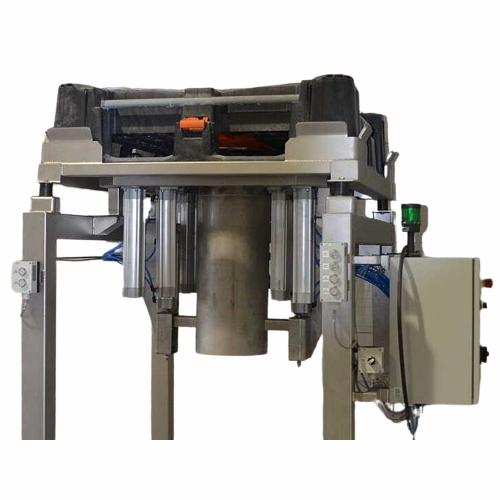
Big bag pallet unloader for bulk products
Efficient and reliable solution for unloading and transporting powders and bulk ...
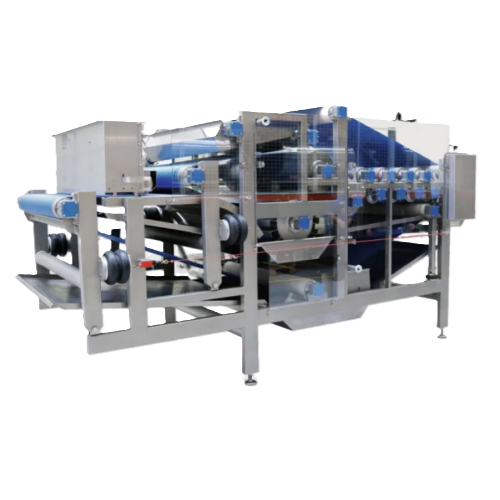
Industrial belt press for fruit and vegetable processing
Optimize your juice yield and reduce drying costs in starch and ...
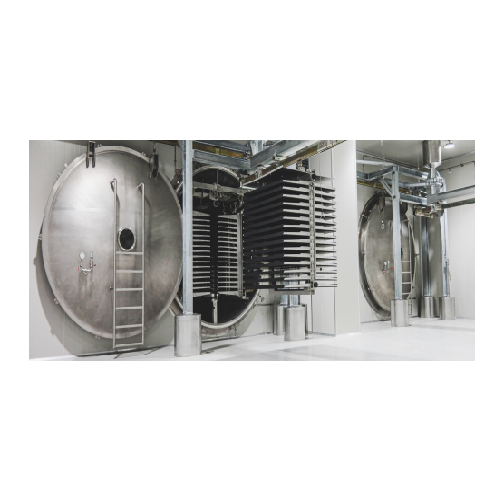
Vacuum and freeze drying plants for food and pharmaceuticals
Ensure high-quality, extended shelf-life products with inno...
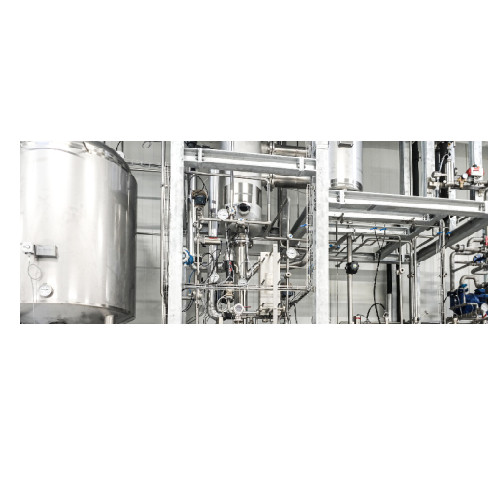
Evaporation plant for liquid mixtures
Achieve precise thermal separation of multi-component liquid mixtures, optimizing con...
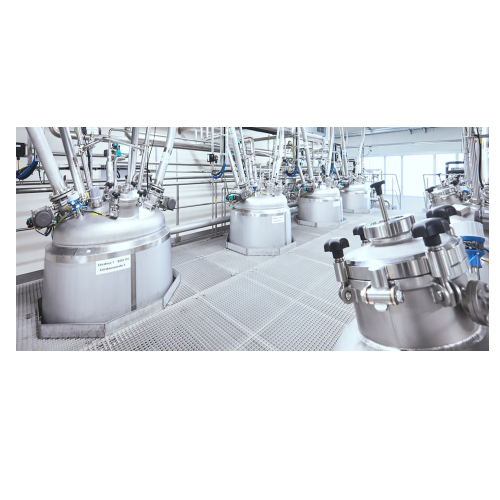
Extraction plant for natural essences and active ingredients
Optimize your extraction processes with a versatile system ...
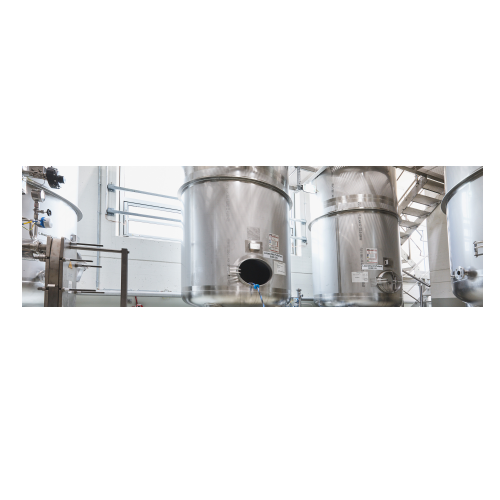
Thermal process plants for liquid treatment
Achieve precision thermal processing with systems designed to optimize the hea...
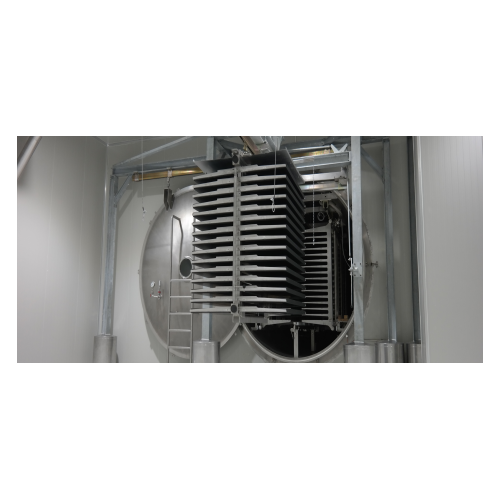
Processing plants for instant coffee production
Achieve optimal flavor retention and cost efficiency in instant coffee pro...
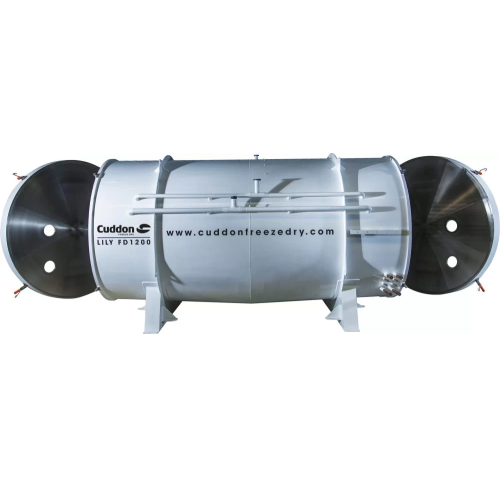
Industrial freeze dryer for large scale food processing
Optimize moisture removal for high-quality food preservation and ...
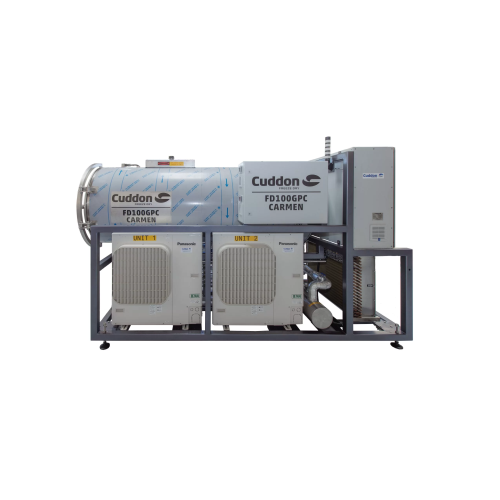
General purpose freeze dryer for small commercial batches
Maximize your production line’s flexibility with this ve...
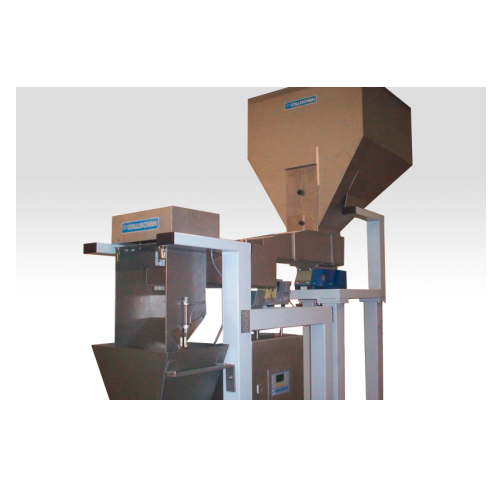
Weigh filler for bulk quantities 2-20kg
Optimizing your filling process with precision, this equipment handles bulk quantit...
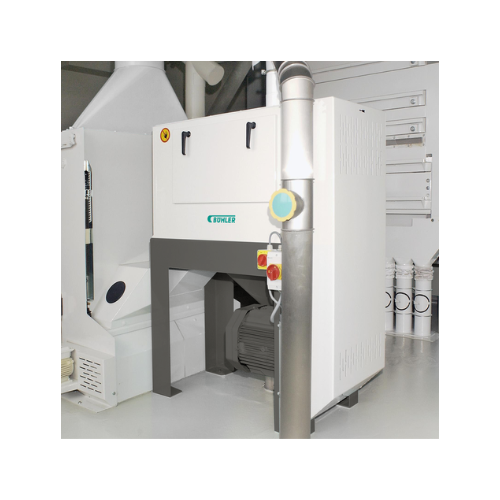
Grain scourer for wheat, durum, and rye
Enhance grain processing by efficiently removing impurities like dust, sand, and so...

Industrial coffee grinder for consistent particle sizes
Achieve precise, consistent coffee grinds essential for specializ...
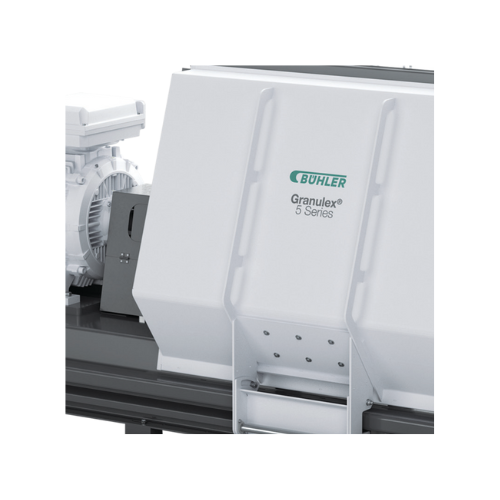
High-throughput hammer mill for animal feed production
Ideal for high-throughput operations, this hammer mill ensures pre...
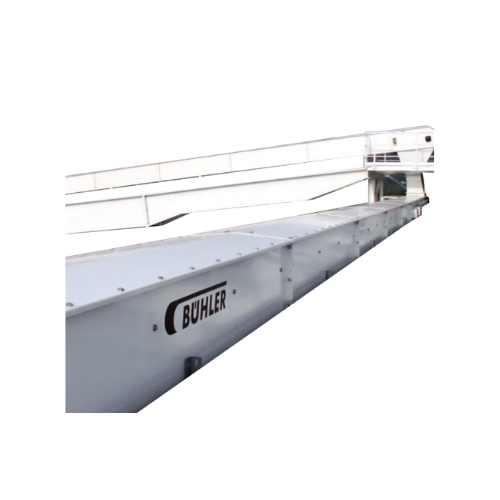
Heavy-duty trough chain conveyor for high throughput applications
Optimized for high-capacity operations, this robust c...

Control systems for wet grinding industry
Enhance precision and efficiency in your production line with advanced control s...
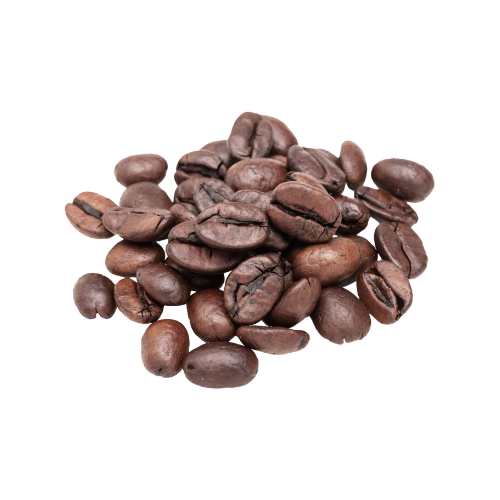
Coffee processing system for integrated coffee production
Enhance your coffee production with a versatile system that in...
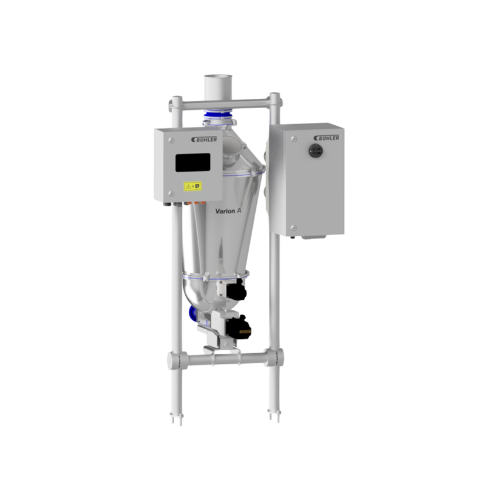
Batch scale for high accuracy weighing of powdery products
Achieve unparalleled precision in powder dosing with our batc...
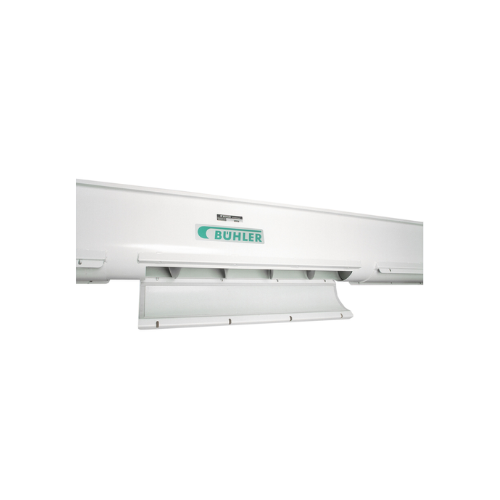
Trough screw conveyor for transporting grains
Efficiently transport and handle bulk materials like grains and flour with r...

Twin-screw extruder for breakfast cereal
Optimize your production with a robust twin-screw extruder that accommodates high ...

Ultra-fine pulverizer for aqua feed and pet food
Achieve precise granulation with high efficiency for your feed and food p...
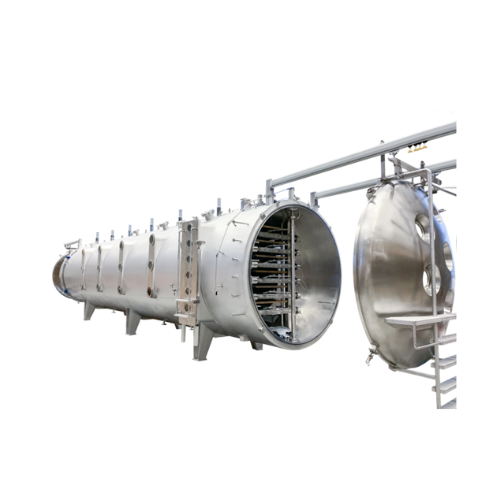
Continuous freeze drying solution for coffee and food pieces
Achieve optimal moisture removal in heat-sensitive products...
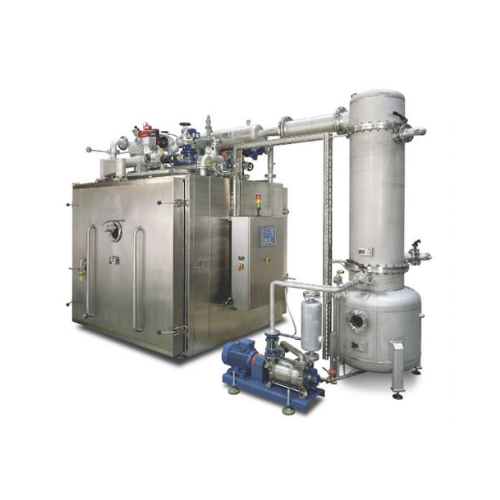
Vacuum dryer cabinet for heat-sensitive products
For manufacturers handling heat-sensitive products, achieving precise moi...
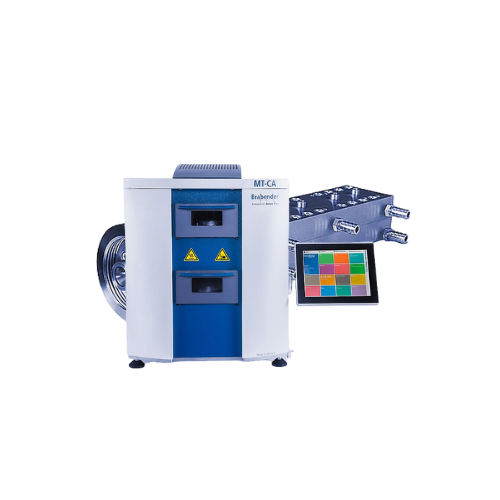
Moisture analyzer for flour and tobacco
Optimize your moisture measurement process with precision and speed, ensuring quali...
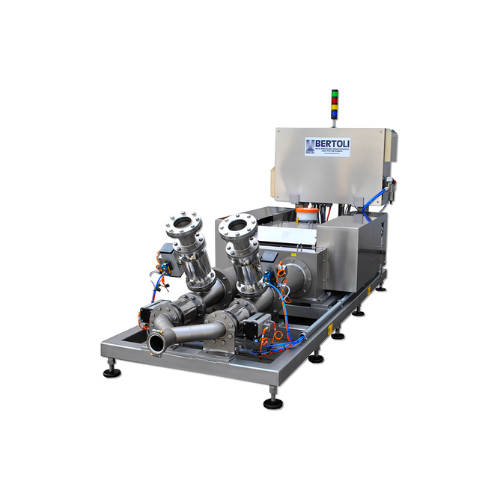
Industrial homogenizer for food and beverage applications
For manufacturers seeking consistent quality, this homogenizer...
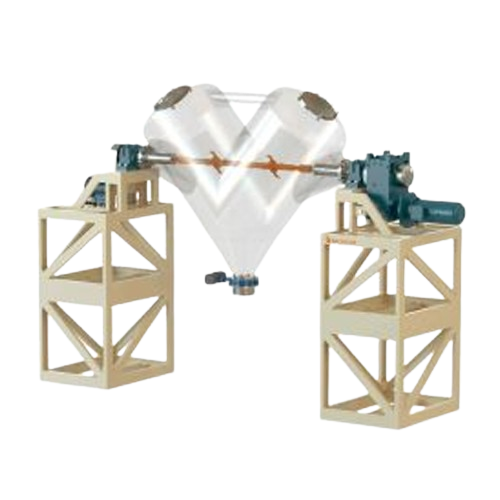
V shape mixer for solids and powders
Ideal for preserving the delicate structures of fragile materials, this mixer ensures ...
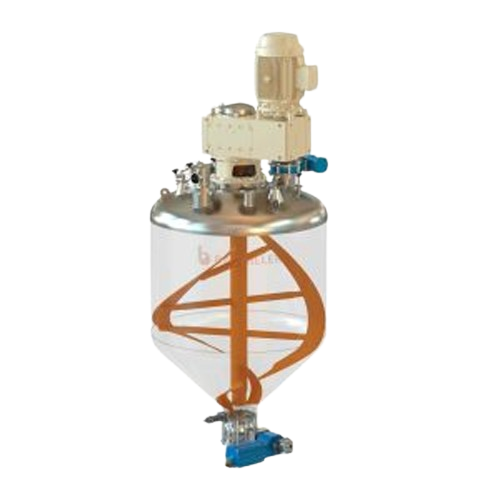
Vertical ribbon mixer for solids and powders
Achieve rapid, uniform mixing of powders and solids while preserving particle...
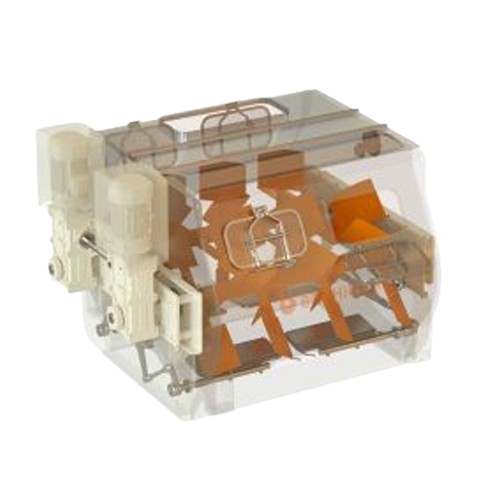
Double shaft paddle mixer for solids and powders
Achieve unparalleled mixing precision for fragile and diverse materials w...
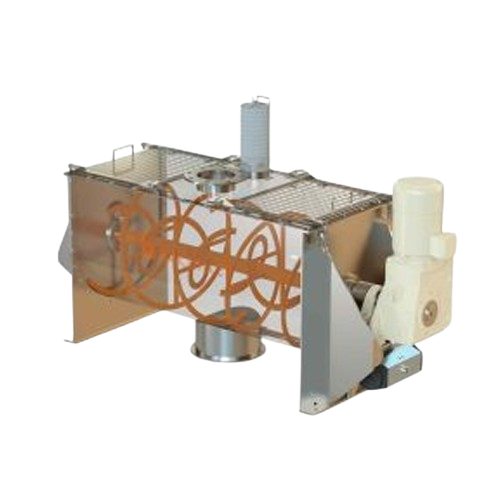
Horizontal ribbon blender for solids and powders
Efficiently achieve uniform blending of bulk solids and powders, ensuring...
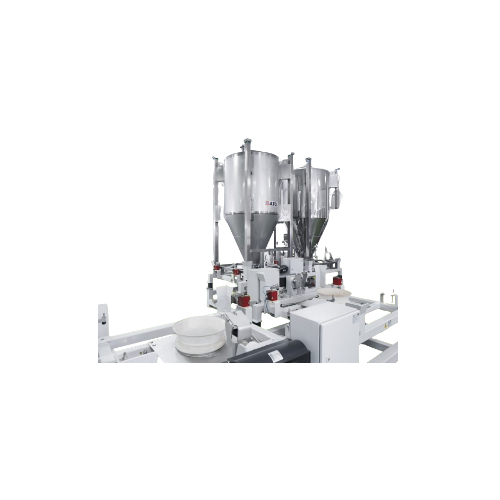
Dust-free docking collar for containers and bins
Achieve seamless, dust-free connections between containers and processing...
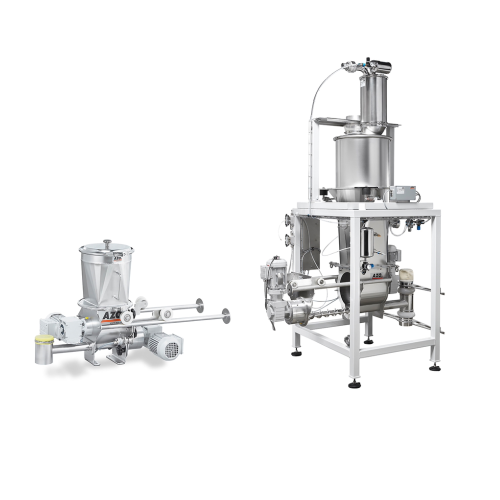
Accurate dosing for powder products
Ensure precise dosing and consistent flow of bulk powders in your production line to en...
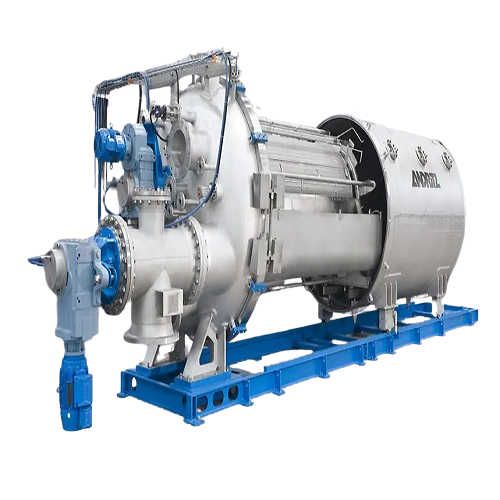
Pressure drum filter for ultra fine-grained products
When traditional filtration methods fall short, ensure ultra-fine pr...
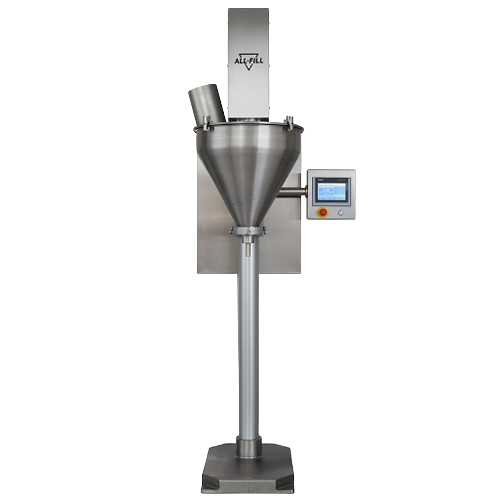
Volumetric filler for bags and rigid containers
Optimize precision filling of powders and granules with a versatile soluti...
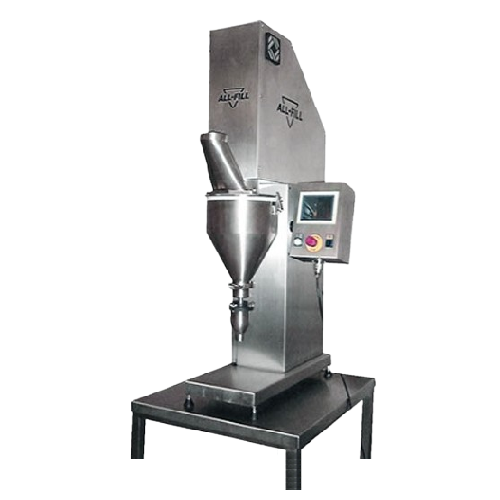
Miniature auger filler for precise powder filling
Achieve precision filling with a compact, bench-top auger solution desi...
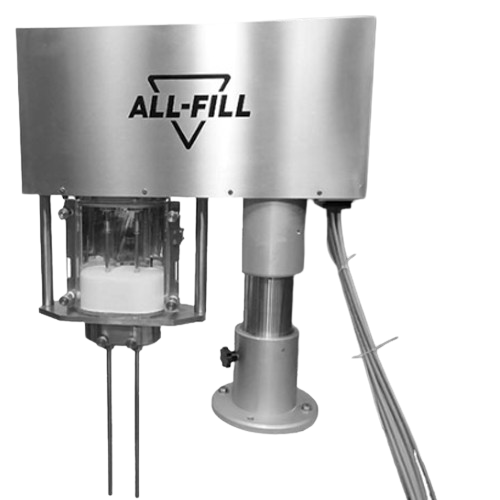
Multi-fill powder filling system
Achieve precise and consistent filling for your powdered and granulated products with a mod...
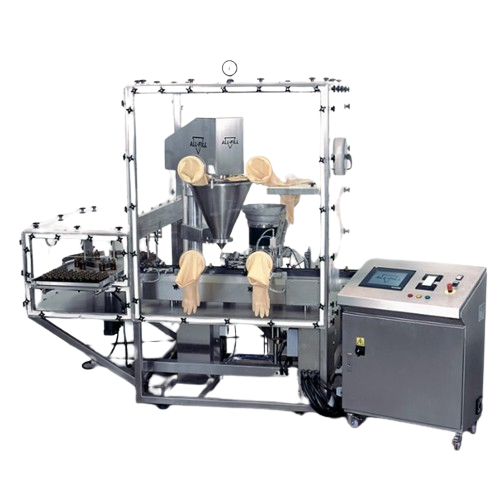
Special purpose auger filling systems for diverse industries
For manufacturers handling precise dosing, our advanced aug...

In-line filling system for various container sizes
Streamline your production with versatile in-line filling solutions th...
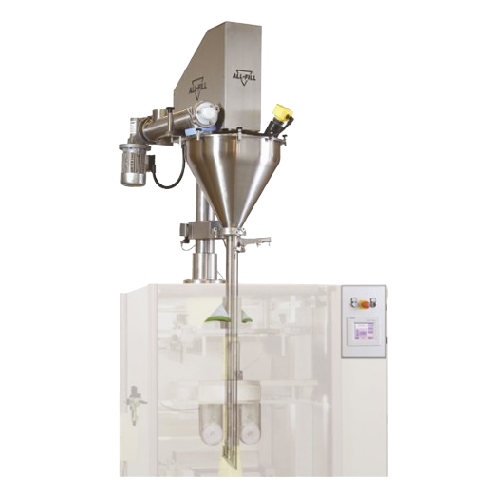
Vertical form fill seal filling system for auger applications
Effortlessly integrate precise powder and granule filling ...
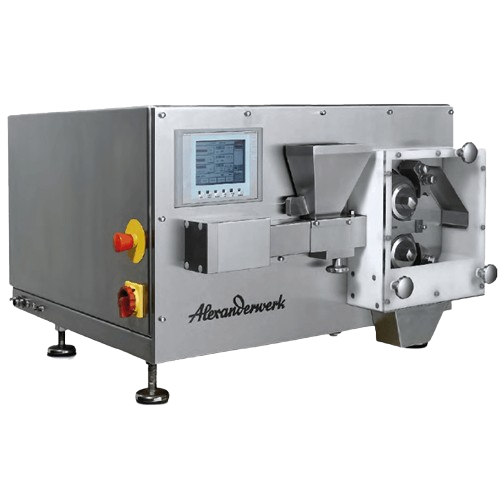
Dry granulation technology
Achieve precise control over particle size and density with our compacting and granulation soluti...
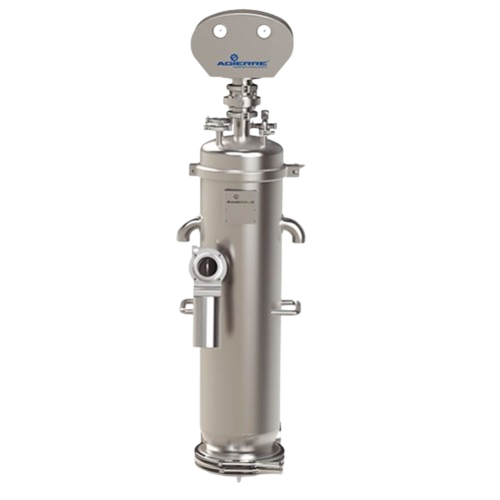
Vacuum conveyor for powder and granule transfer
Ensure efficient and contamination-free transfer of powders and granules w...
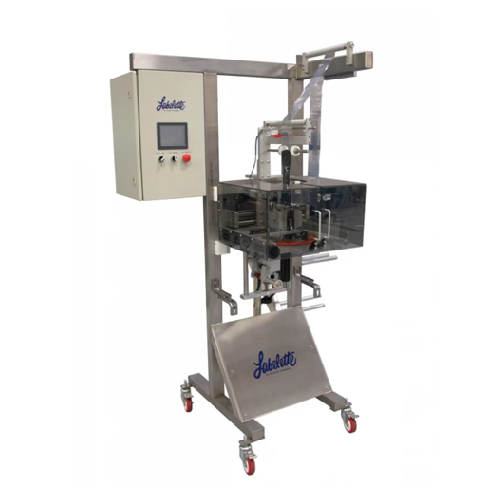
Full body sleeving systems for packaging applications
Achieve seamless, high-speed labeling precision for diverse contain...
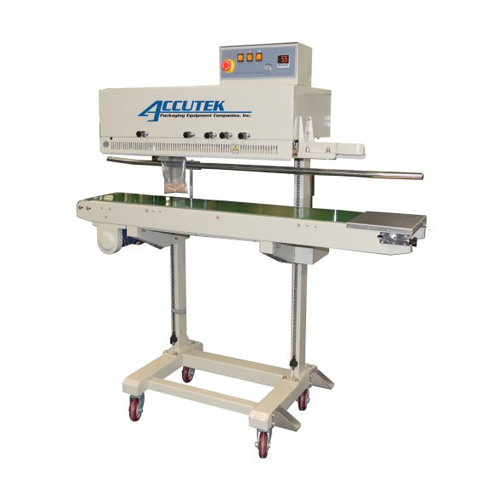
Heat sealer for thermoplastic bags
Ensure airtight seals on thermoplastic bags with precise temperature control and adjusta...
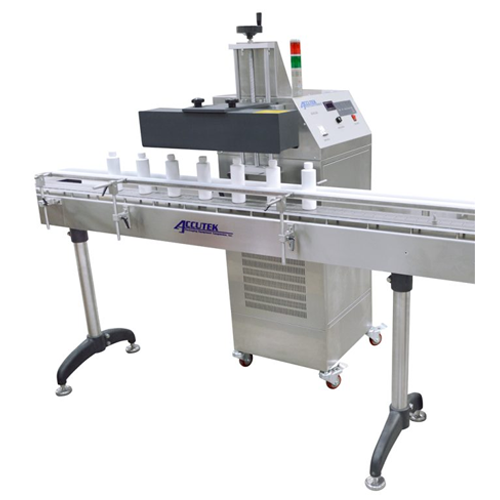
Automatic induction sealer for cap sealing
Achieve precise and reliable cap sealing with our advanced induction technology...
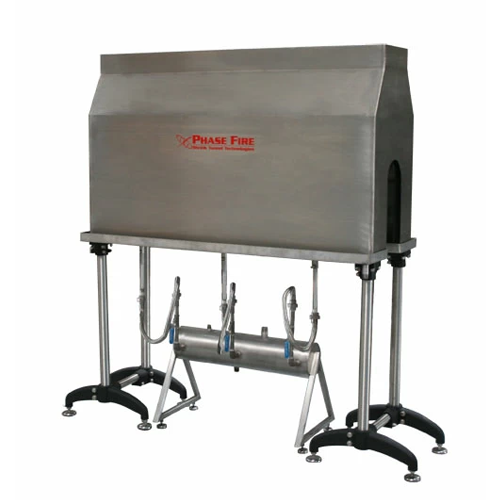
Steam shrink tunnels for versatile packaging
Enhance your packaging efficiency with this adaptable steam shrink tunnel, de...
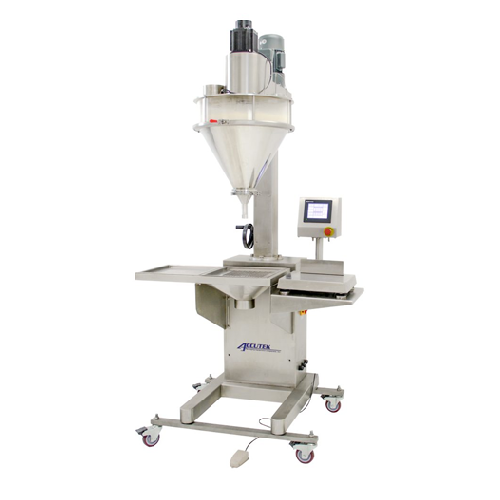
Powder filling machine for dry products
Achieve precision and consistency in filling dry powders and granules with a versat...
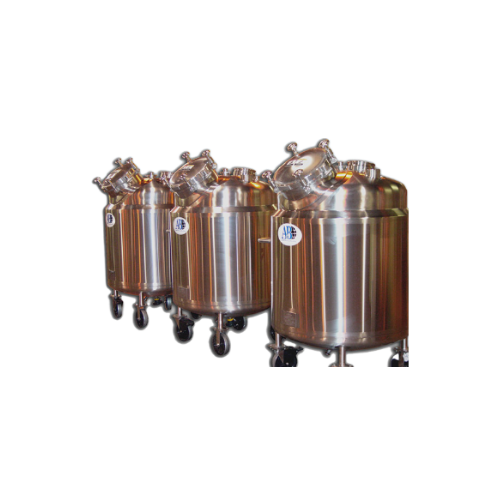
Industrial pressure vessels
Ensure product integrity and regulatory compliance with engineered-to-order pressure vessels, de...
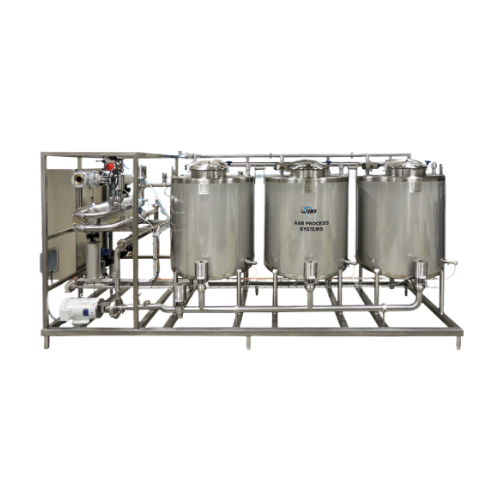
Clean-in-place system for diverse processing needs
Ensure the precision and consistency of your cleaning cycles with a ro...
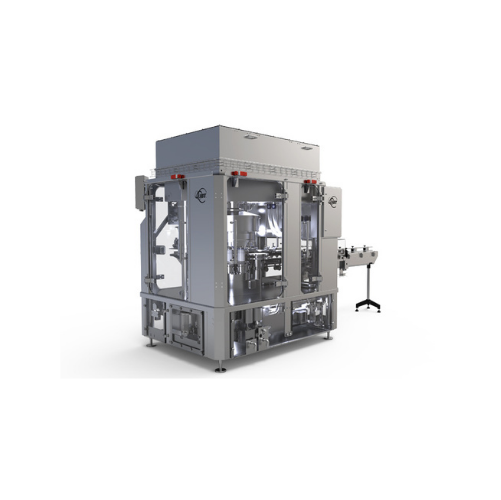
Powder can seamer for nutraceutical and beverage powders
Achieve precision and hygiene with this can seamer designed for ...
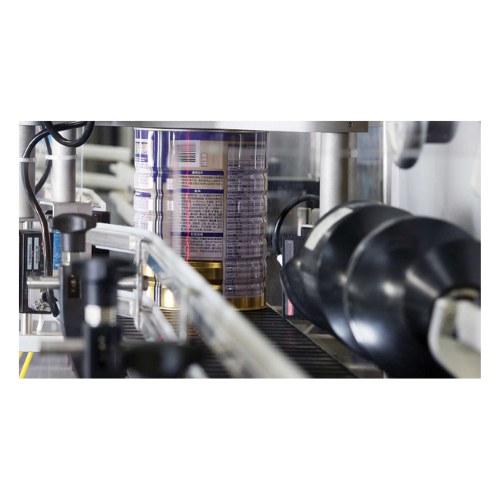
Barcode reading and verification system
Ensure every container has the correct product with a cutting-edge scanning system ...
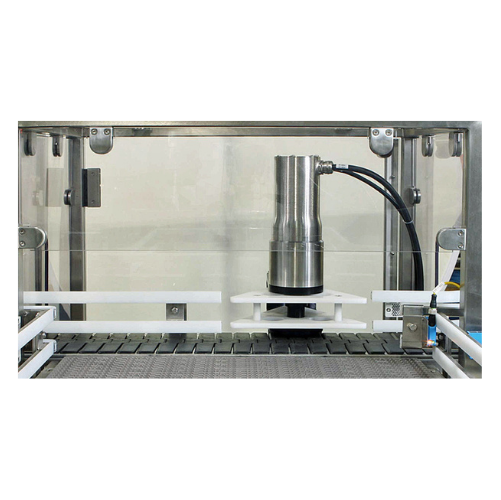
High-speed container reject system
Ensure product integrity by swiftly rejecting non-compliant containers at speeds up to 3...
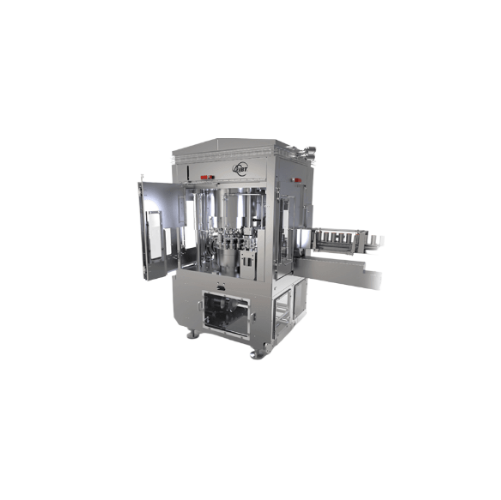
Can seamer for high-speed liquid applications
Ensure consistent seal integrity and maximize throughput with this advanced ...
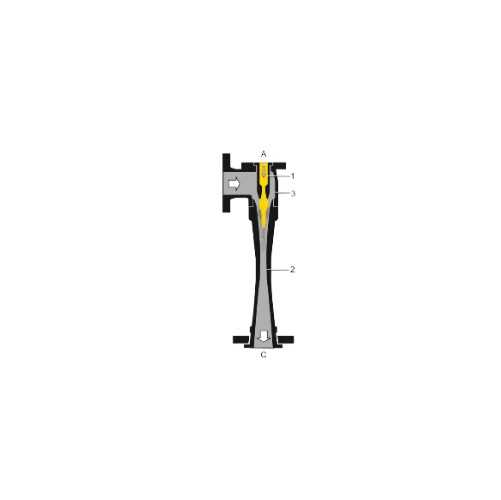
Industrial ejectors for reliable jet pump applications
Enhance process efficiency and reliability with industrial ejector...
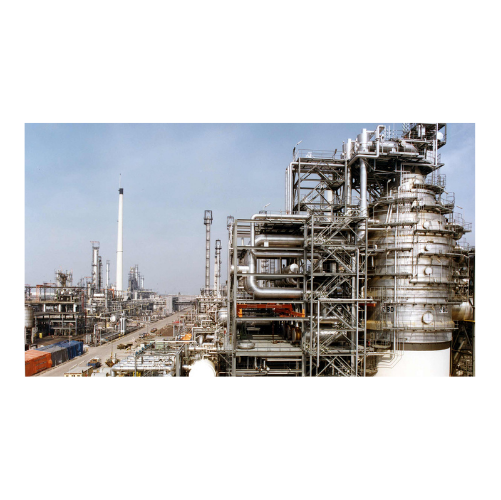
Combined steam jet and liquid ring vacuum pump systems
Optimize vacuum creation and maintenance in processes like distill...
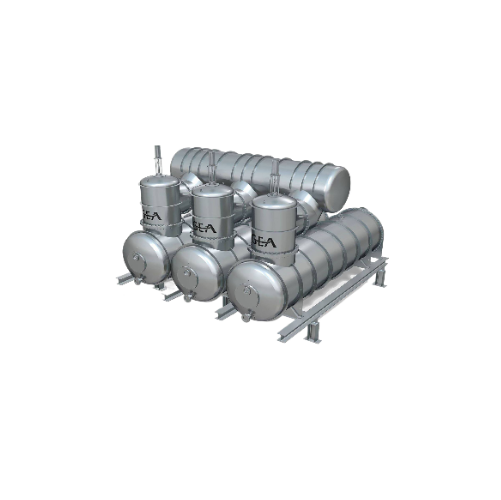
Dry condensing vacuum system for food industry
Optimize energy consumption and wastewater disposal in your production line...
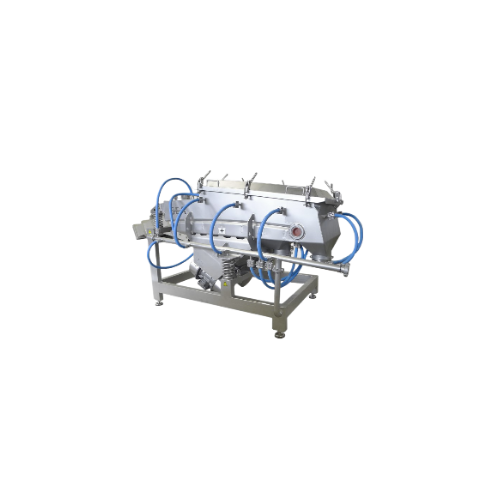
Industrial sifters for beverage processing
Optimize your beverage production with precisely engineered sifters that ensure...
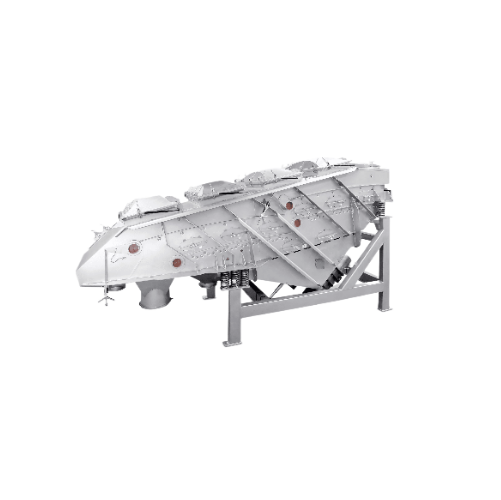
Vibrating sifter for chemical applications
Achieve precise particle separation with this vibrating sifter, ensuring optima...
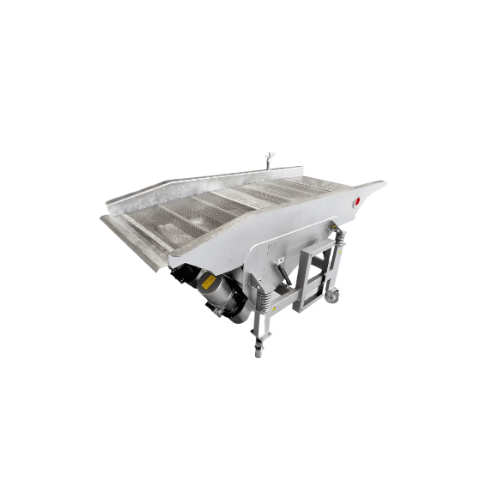
Food product sifter
Ensure precise separation with vibratory sifters designed for continuous operation, delivering gentle han...
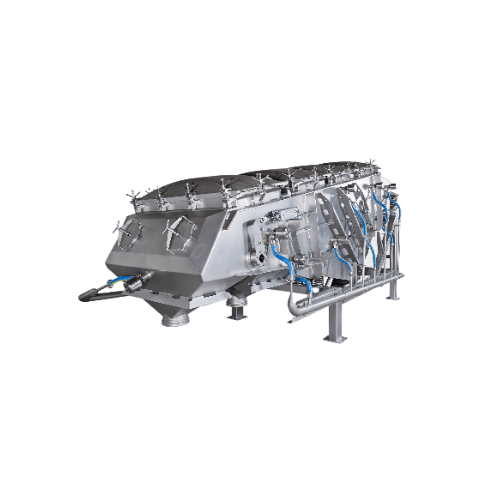
Industrial powder sifter with sanitary compliance
Optimize your powder processing with this versatile sifter, ensuring pr...
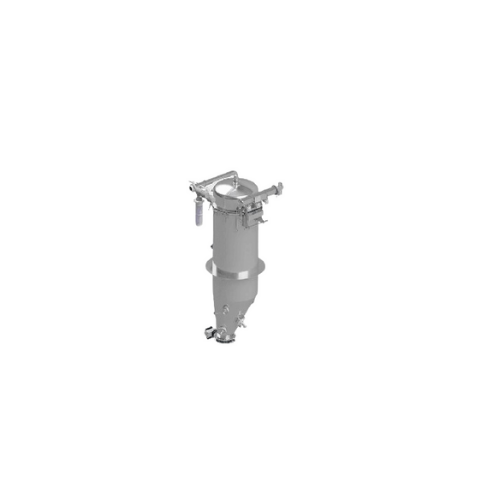
Dense phase vacuum conveying system for powder handling
Effortlessly transport delicate powders and fragile granules with...
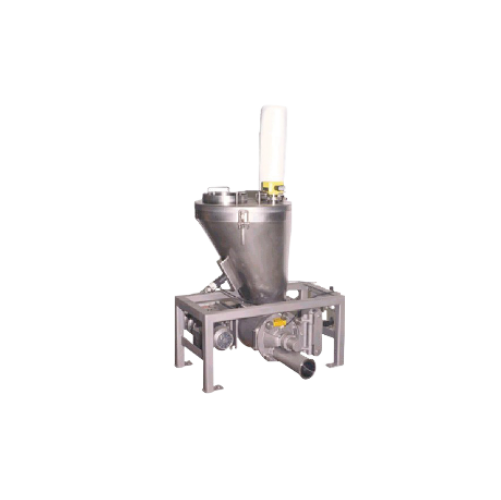
Lean phase pressure conveying for powder handling
Effortlessly transport and manage powdered materials with lean phase pr...
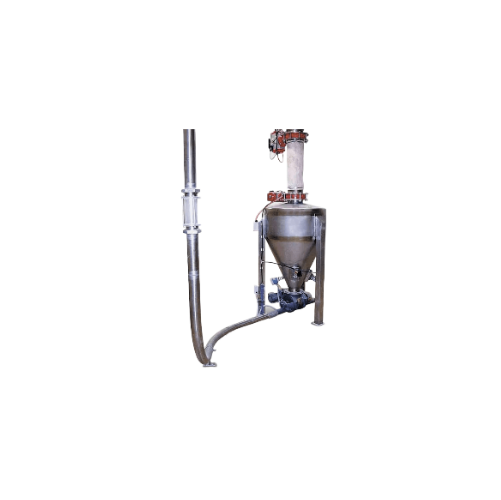
Lean phase vacuum conveying system for powder handling
Efficiently transport and separate powders and granules with preci...
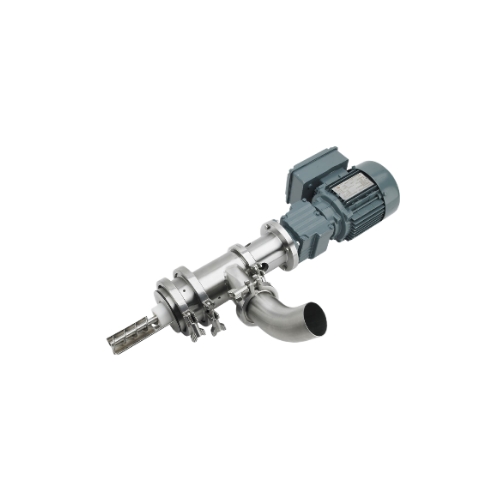
Auger powder sampler for industrial quality control
Ensure precise quality control by integrating an auger powder sampler...
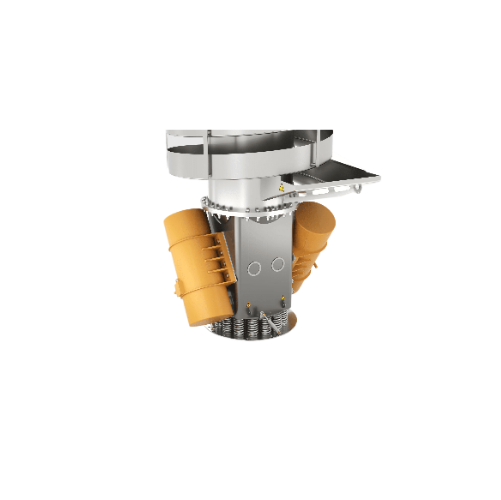
Vibratory spiral elevator for vertical transport
Achieve efficient vertical transport with precise temperature control, su...
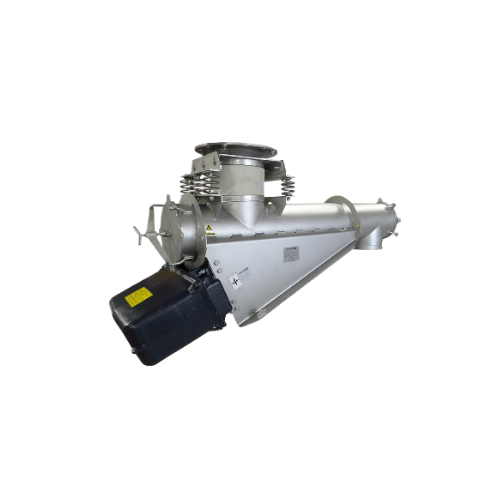
Vibrating feeder for food and pharmaceutical industries
Optimize your production line with precision dosing and gentle ma...
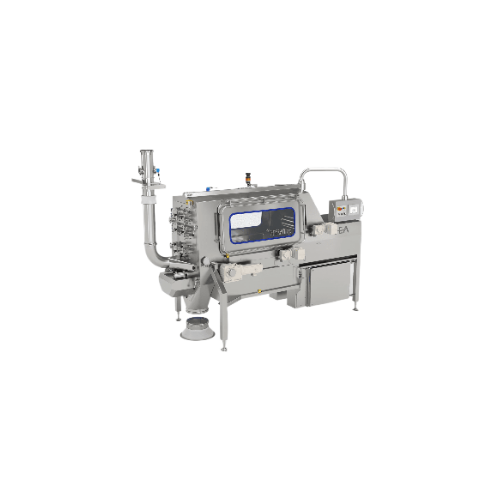
Automatic bag slitting and emptying for powders
Streamline your powder-processing operations by seamlessly integrating bag...
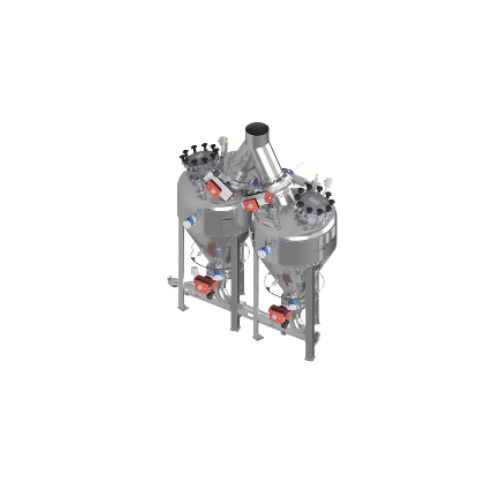
Dense phase pressure conveying system
Efficiently transport high-capacity powders across long distances with precision and ...
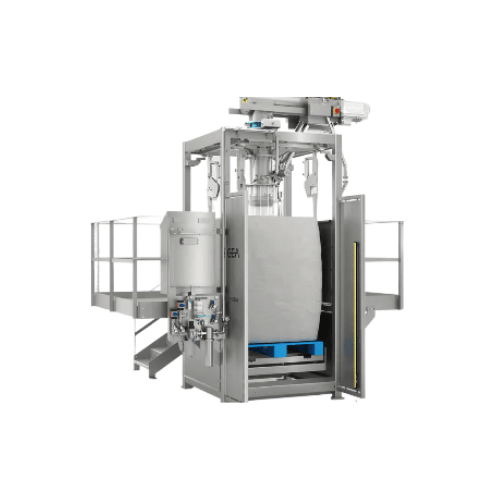
Low care bulk powder fillers
Optimize your production efficiency by accurately filling flexible bulk containers with dry pow...
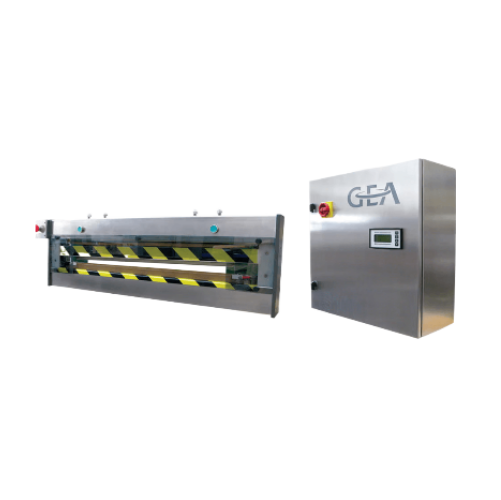
Plastic bag sealer for polyethylene bags
Achieve consistent hermetic sealing of polyethylene bags while preserving the inte...

Continuous leveler and sealer for powder packing
Enhance efficiency in powder packaging with a system that ensures precise...
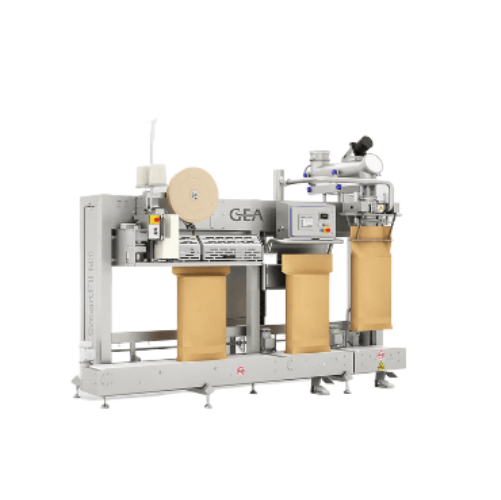
Semi-automatic powder filling system for food products
Achieve precise and flexible filling for food powders and granules...
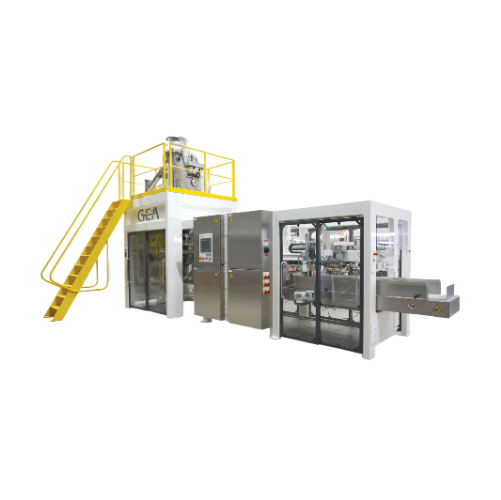
Automated powder bag filling system
Streamline your powder packaging operations with a fully integrated system that automat...
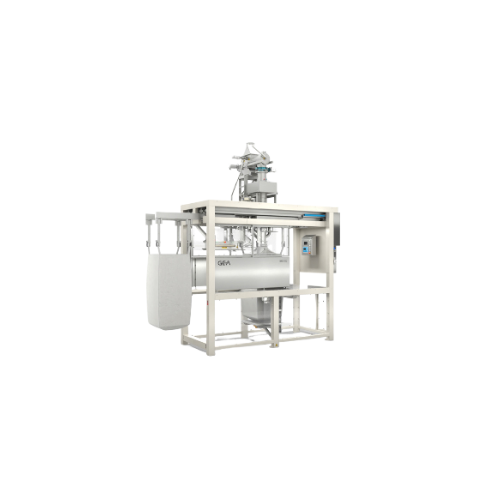
High care bulk powder fillers
Ensure hygienic packaging for your bulk powders with a system designed to enhance filling accu...
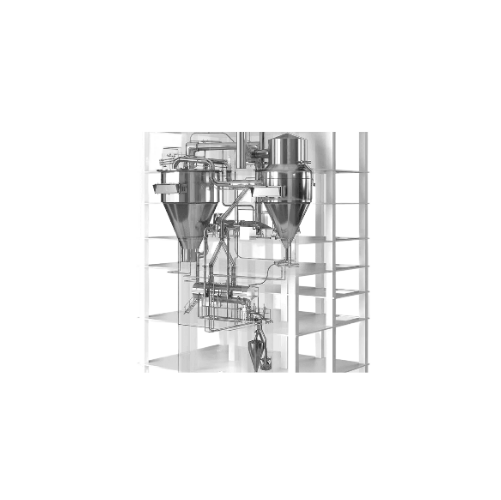
Spray dryer for agglomerated powders
Achieve uniform, coarse, and free-flowing agglomerated powders with precise drying and...
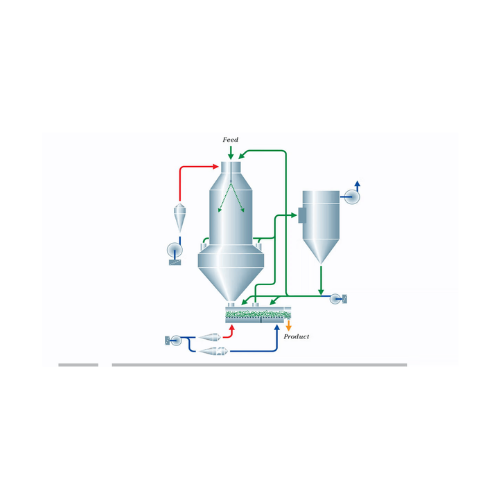
Spray drying solution for uniform powder production
Achieve seamless transformation of liquid feeds into uniform, free-fl...

Lab-scale spray dryer for small volume powder samples
When developing new formulations, achieving consistent powder quali...
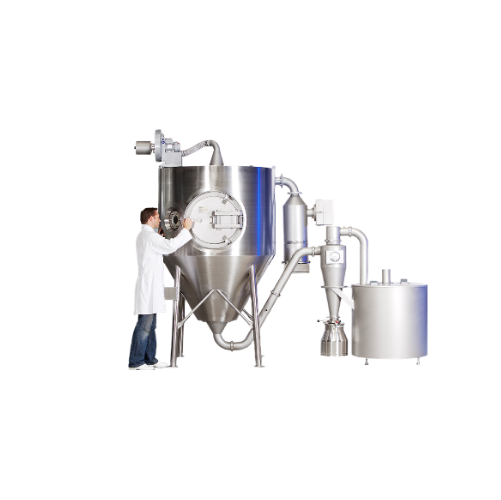
R&d spray drying solution for small batch production
Efficiently convert liquid solutions into precise, uniform powders f...
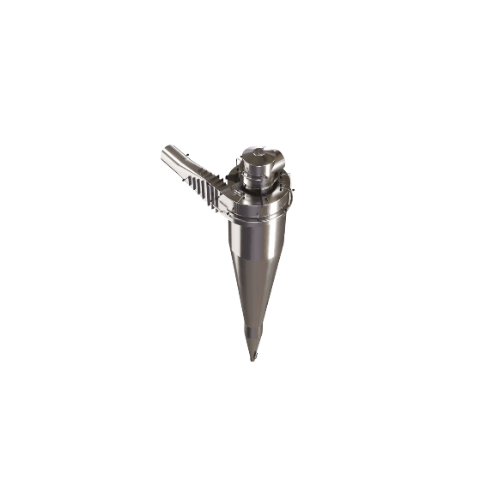
Powder separation cyclone for food and chemical industries
Optimize your powder production with advanced cyclone technol...
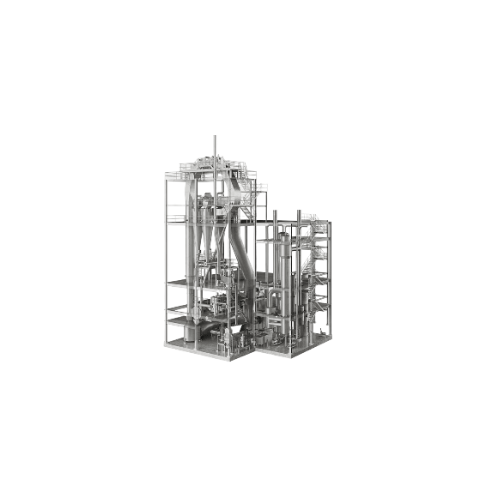
Feed-type ring dryer for industrial drying processes
Optimize your production with a versatile drying solution designed f...
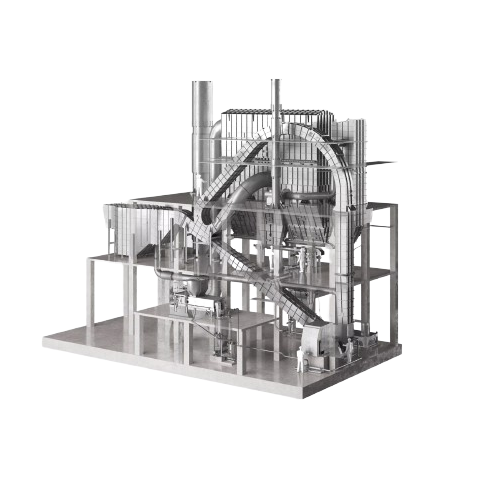
Industrial ring dryer for efficient particle processing
Control particle size and drying efficiency with precise recircul...
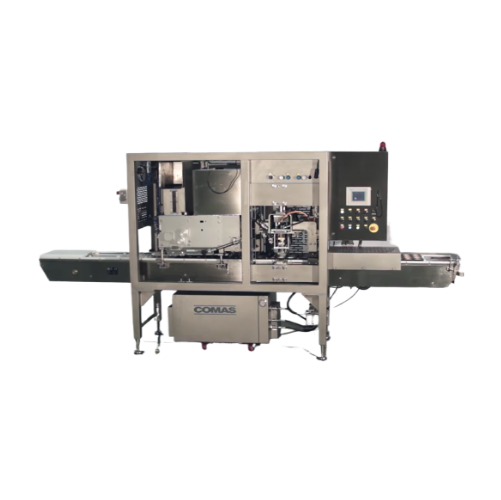
Aroma recovery system for instant coffee processing
Capture and enhance coffee aromas with a specialized system designed ...
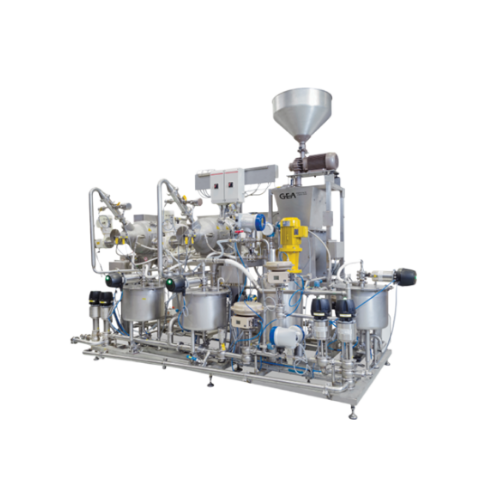
Wet grinding system for coffee flavor preservation
Achieve unparalleled coffee flavor and aroma by integrating a low-temp...
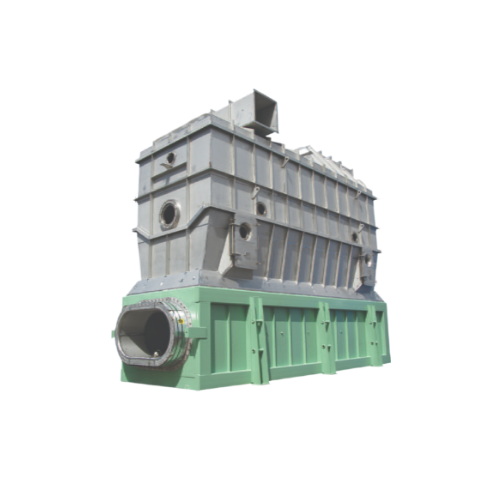
Static fluid bed dryer for powder and granular materials
Achieve optimal moisture control in powder and granular products...

Industrial freeze drying system for high-volume food products
Achieve precise moisture removal and preserve product qual...
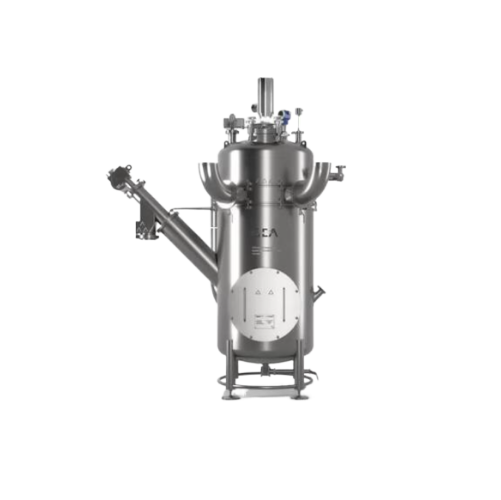
Liquid nitrogen freezer for sensitive food and fermentation ingredients
Achieve rapid, uniform freezing of sensitive fo...
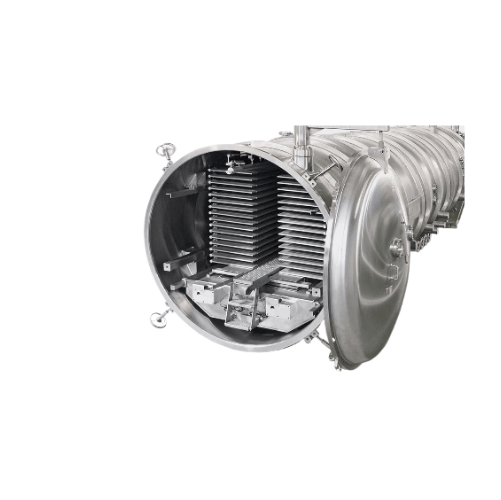
Batch freeze drying system for food and beverage preservation
Achieve precise and efficient preservation of your food an...
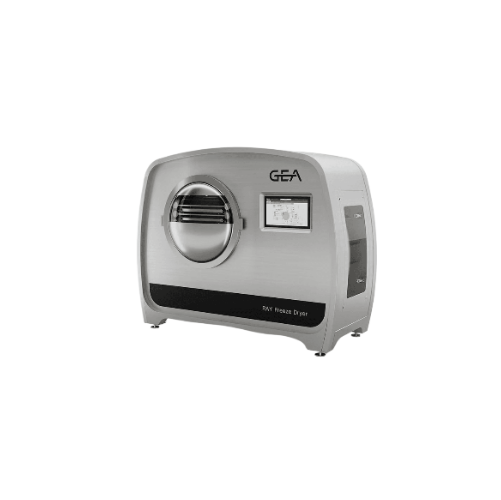
Pilot plant freeze dryer for sensitive products
Achieve precise moisture control and nutrient preservation in food and pha...
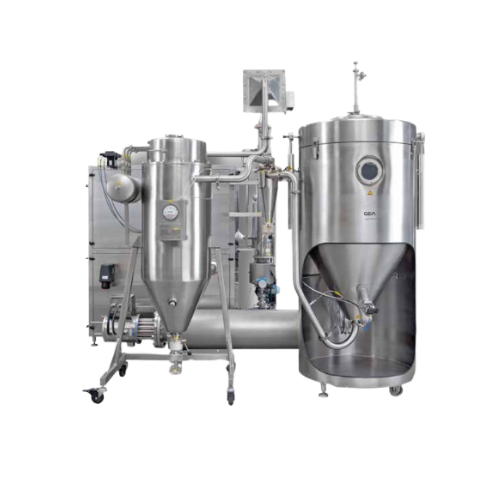
Spray dryer for food and dairy products
Achieve consistent drying for diverse powders and granulates with precision technol...

Industrial coffee extraction system for high yields
Maximize coffee yield and quality with precision-controlled extractio...
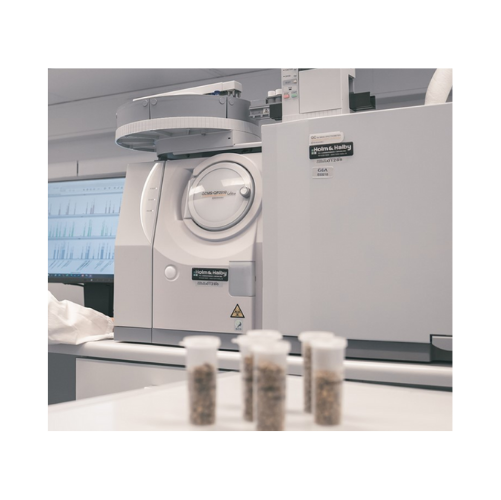
Aroma analysis for instant coffee processing
Improve flavor preservation by analyzing and optimizing aroma retention at ev...
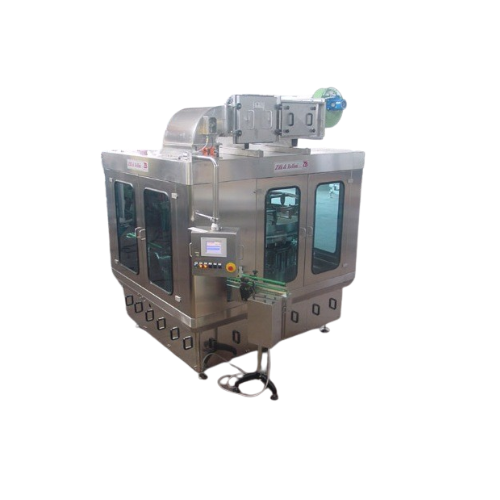
Industrial powder fillers for various containers
Optimize your packaging line with high-speed powder fillers that handle d...
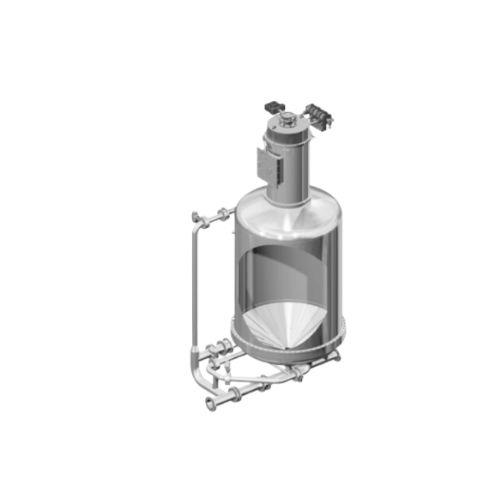
Pneumatic mixer for fluidizable bulk materials
Achieve uniform and gentle mixing of powdered ingredients with minimal effo...
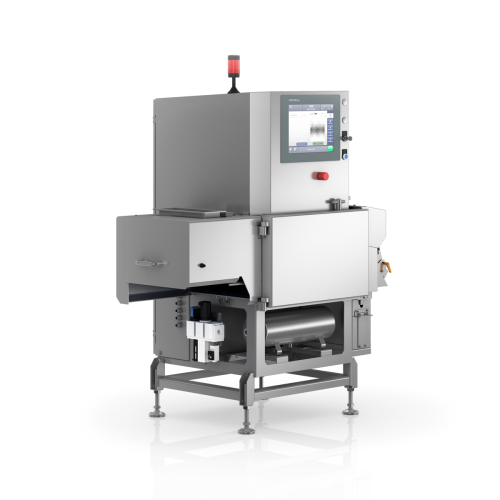
X-ray scanner for bulk material inspection
Ensure product safety and minimize downtime by intercepting foreign contaminant...
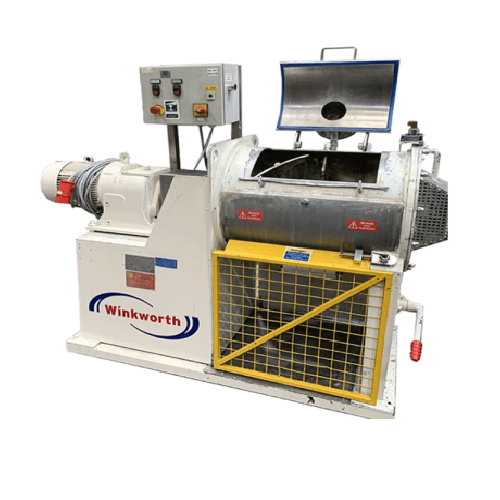
Industrial rapid turbulent mixer for homogeneous mixing
Achieve unparalleled homogeneity with rapid turbulent mixing, ess...
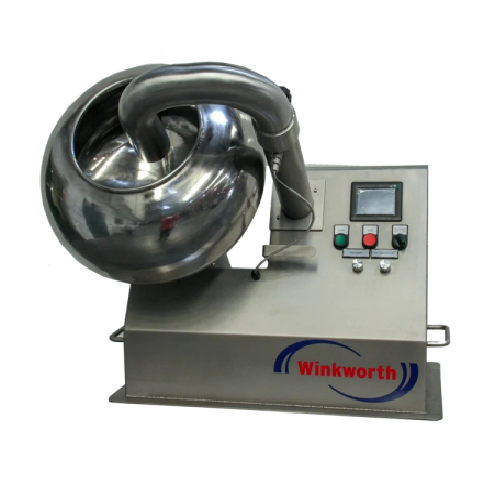
Industrial coating pan for food and pharmaceutical products
Optimize your production with precision mixing and coating, ...
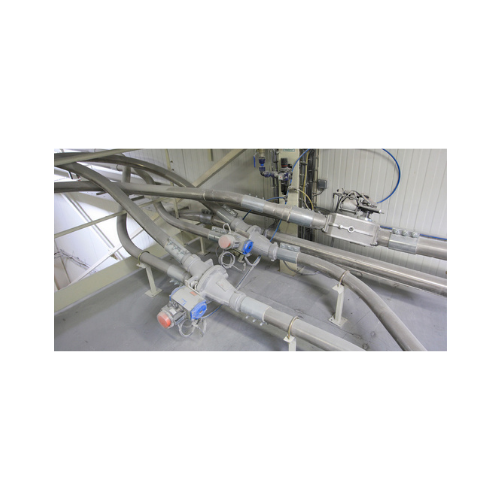
Flap diverter valves for pneumatic conveying
Streamline material flow in your pneumatic conveying system by effortlessly r...
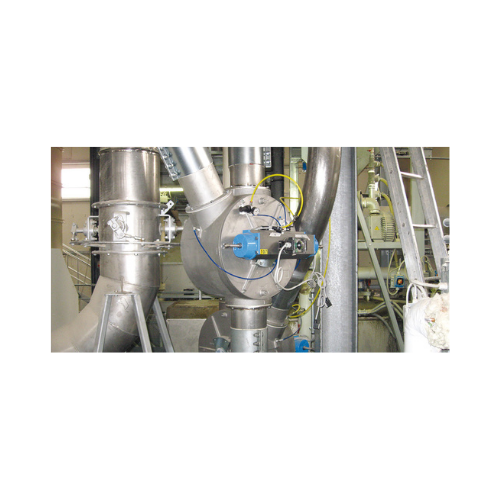
Drum-type diverter valves for pneumatic conveying
Optimize your pneumatic conveying system by effortlessly controlling th...
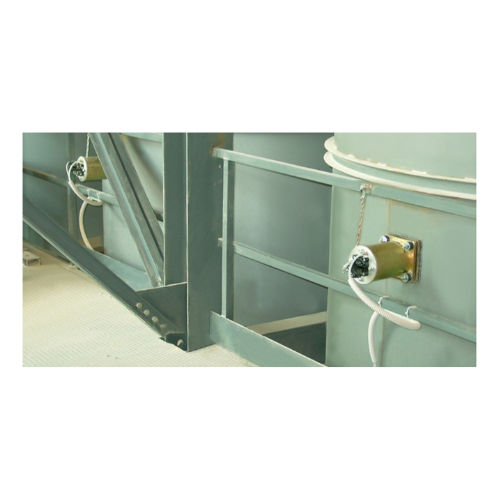
Air cannons for resolving bulk material flow issues
Solve bridging and rat-holing issues in bulk material storage with po...
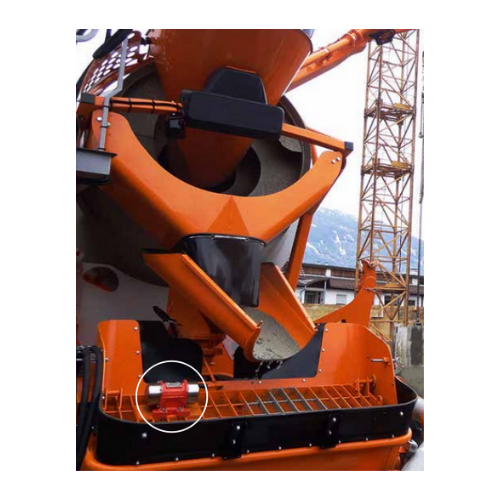
Continuous impact vibrator for aggregate reclaiming
Tackle material flow challenges head-on by preventing common issues l...
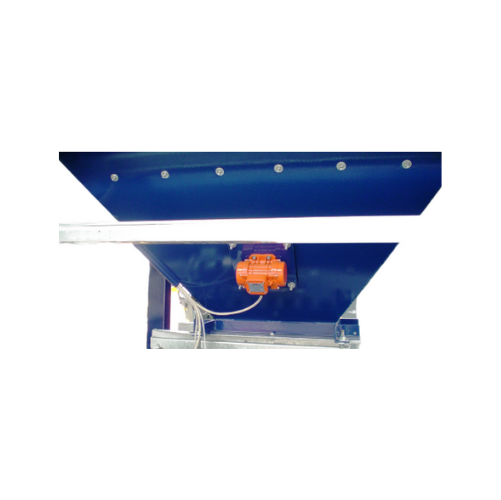
Industrial electric vibrator for bulk solids discharging
Enhance material flow efficiency and ensure consistent output ac...
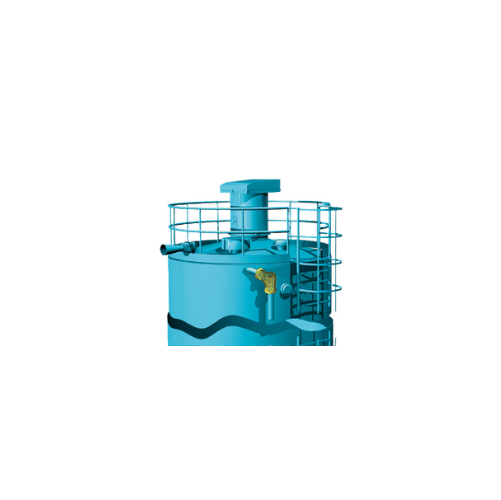
Silo overfilling safety system
Ensure safe silo filling with our system that prevents overfilling and excess pressurization,...
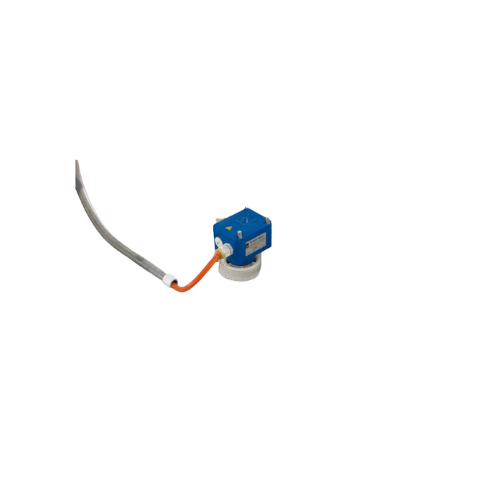
Bin level indicator for bulk solids
Ensure precise material level detection across your production processes, minimizing th...
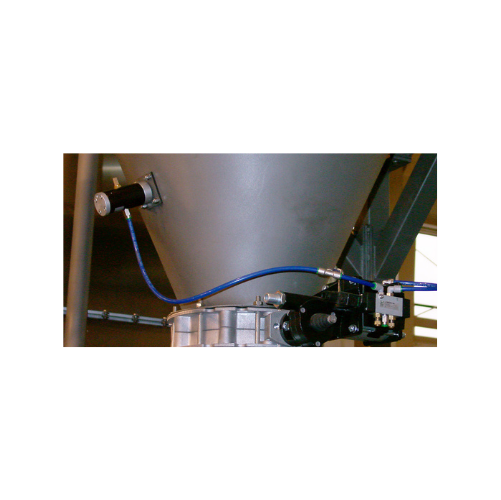
Pneumatic linear vibrators for bulk material flow
Prevent bridging and rat-holing in your production process with silent,...
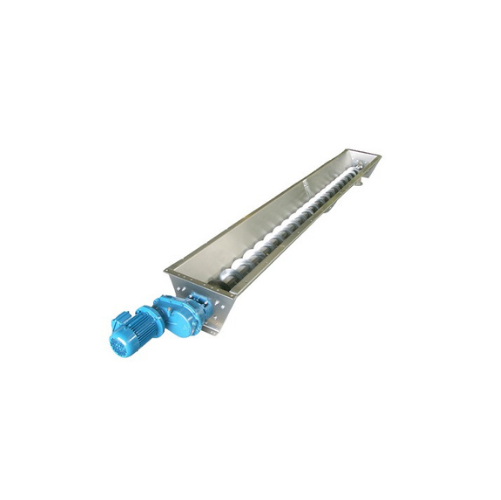
Stainless steel trough screw conveyor
Ideal for precise handling of powdery and granular materials, this solution ensures m...
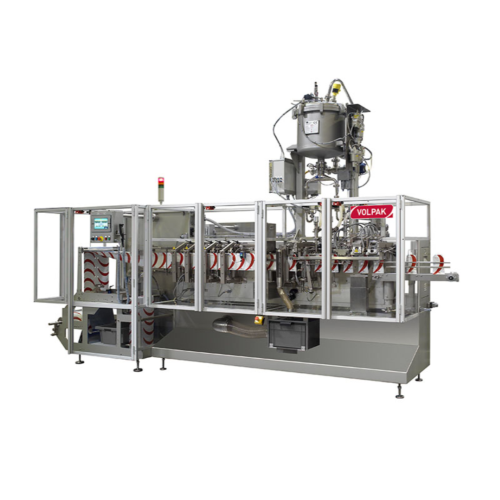
Stand-up pouch packaging for various products
For manufacturers seeking versatile packaging solutions, this machine delive...
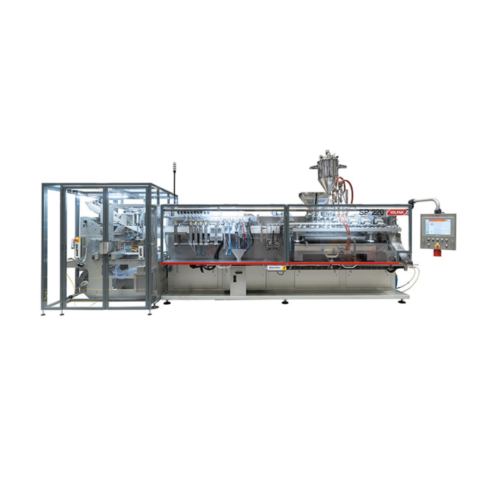
Stand-up pouch packaging for various industries
Elevate your packaging capabilities with a high-speed horizontal pouching ...
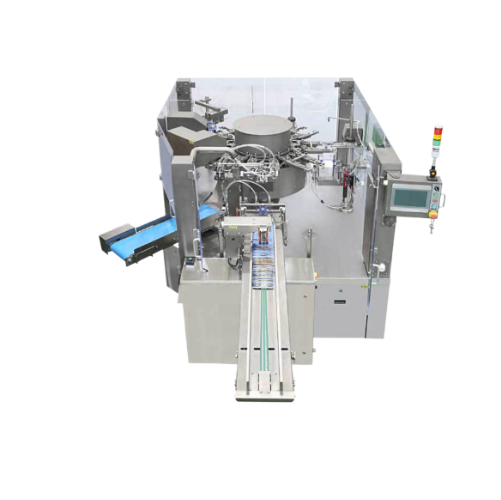
Rotary pouch packaging system for food and powder products
Streamline your packaging process with a rotary system that e...
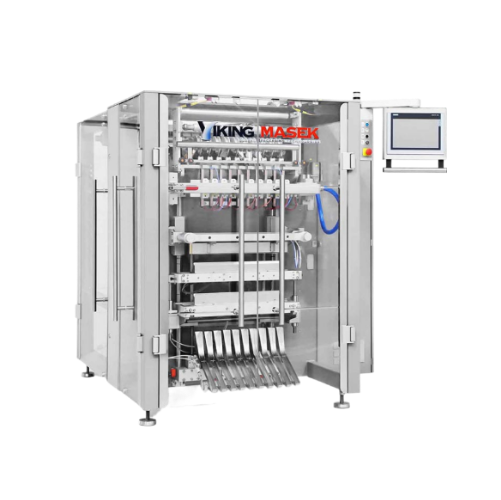
Stick pack packaging for powders and liquids
Streamline your packing process with high-speed, servo-driven stick pack mach...
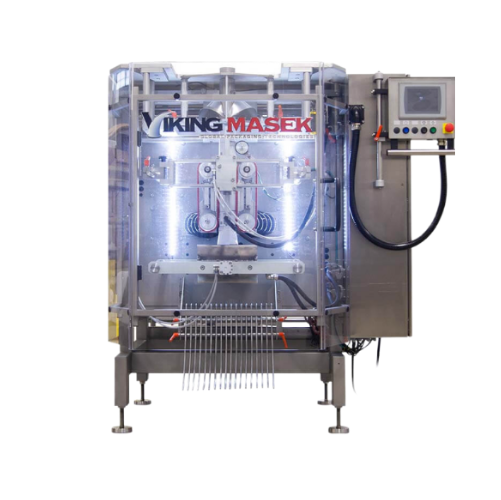
Vertical form fill seal for dusty and liquid products
Optimize your packaging line with a versatile solution designed to ...
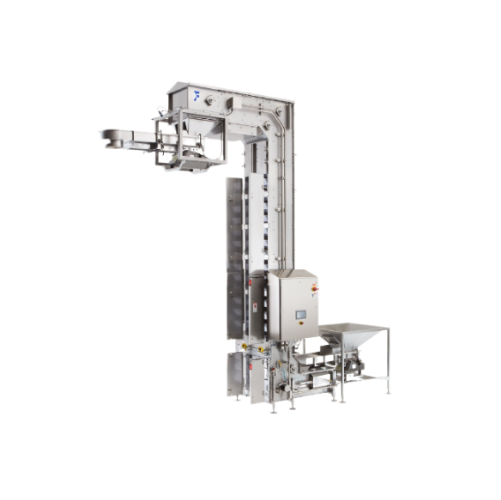
Automated infeed and outfeed systems for packaging lines
Streamline your production line by integrating reliable infeed a...
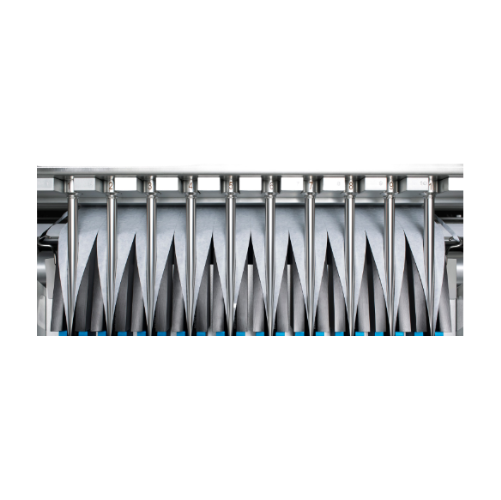
Stick pack packaging for pharmaceutical products
Enhance your production efficiency with compact stick pack solutions, off...
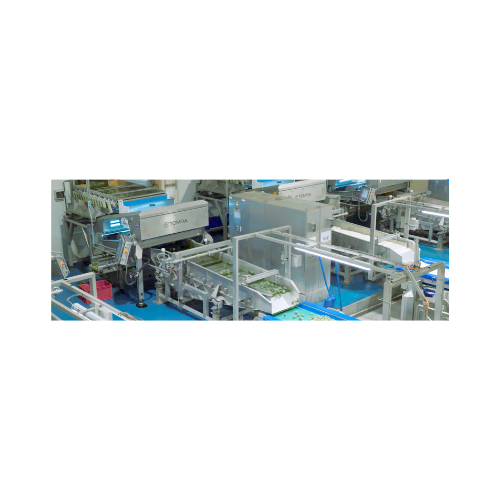
Blizzard sorter for Iqf fruits and vegetables
Optimize your frozen food production with a compact sorter that seamlessly r...
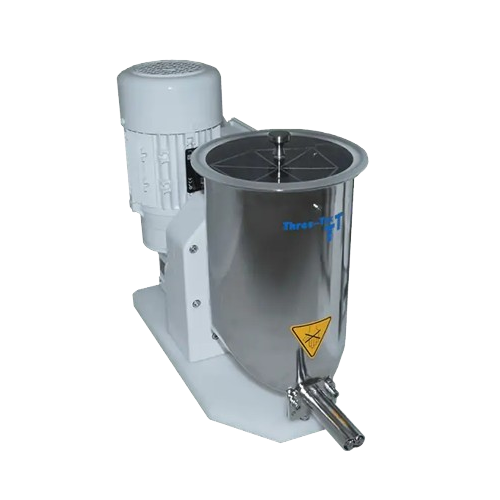
Twin screw feeder for dosing bulk solids
Ideal for precise bulk solids dosing, this twin screw feeder ensures consistent fl...
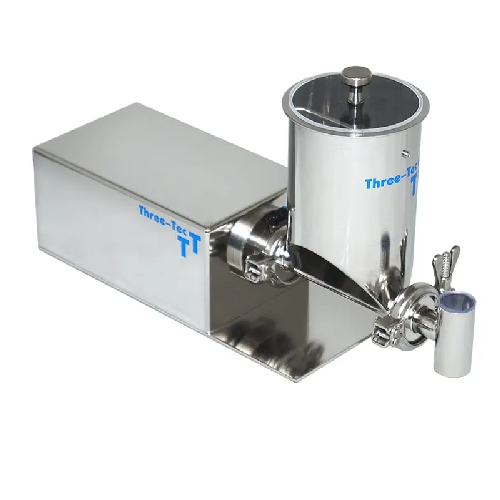
Volumetric single-screw feeder for fine dosing
Achieve precise and consistent dosing of fine powders and granules with a c...
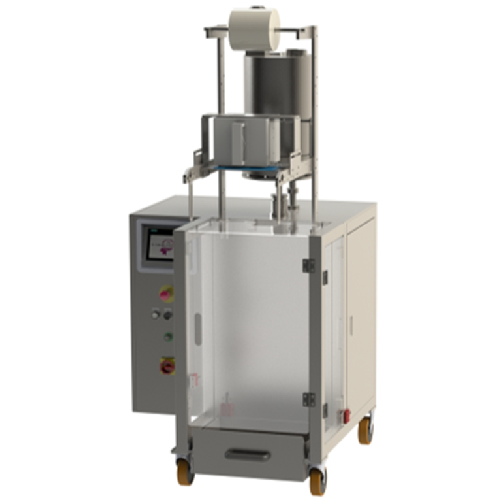
Granule filling sachet machine
Ideal for optimizing packing operations, this granule-filling sachet machine ensures precise ...
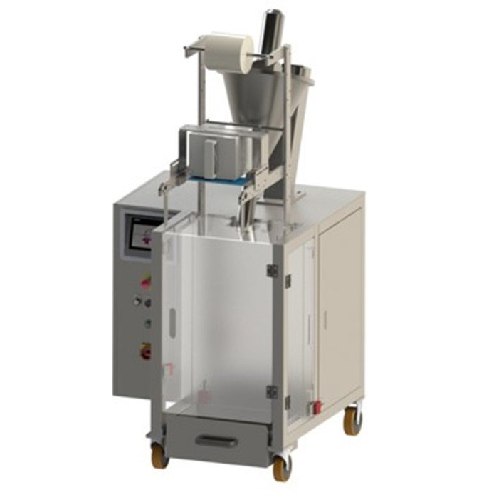
Sachet powder filling machine
Optimize your packaging line with this efficient solution for precise powder filling, ensuring...
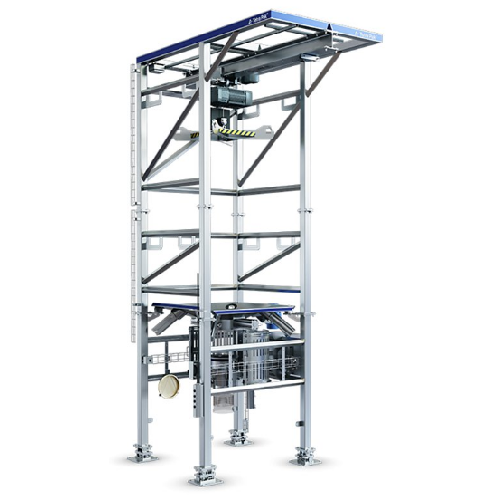
Big bag discharger for powder handling
Effortlessly discharge large bags of powdered ingredients with a modular, safe syste...
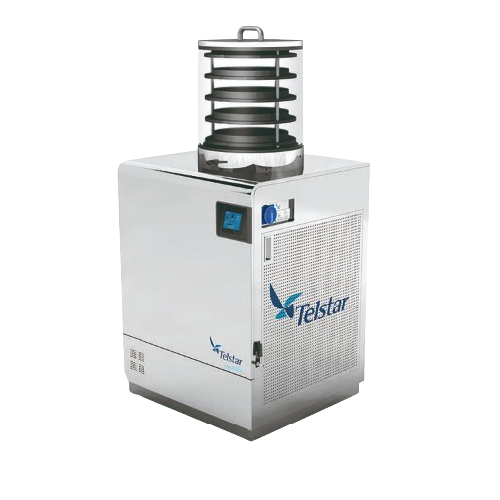
Basic research freeze dryer for biomedical applications
For laboratories seeking precise sample preservation, this bencht...
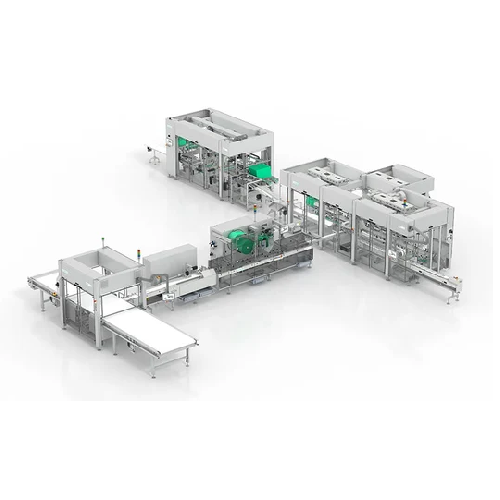
Horizontal flow wrapper for food packaging
Simplify your packaging process with our high-speed horizontal flow wrapper tha...
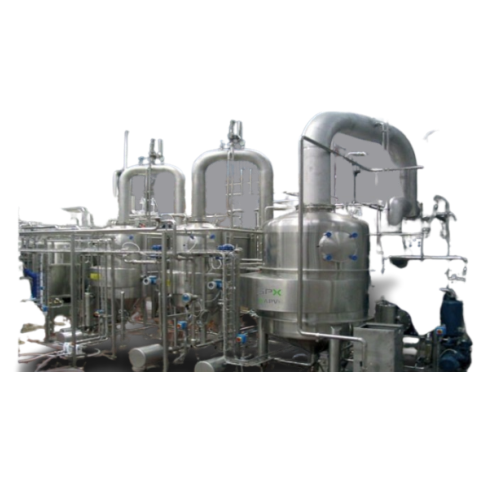
Rising/falling film plate evaporator for heat sensitive products
Efficiently concentrate heat-sensitive liquids with ris...
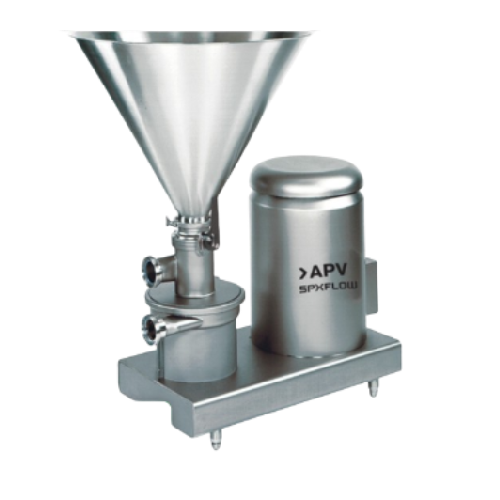
Batch powder mixer for circulatory dispersion
Optimize your batch production with a powder mixer designed for efficient di...
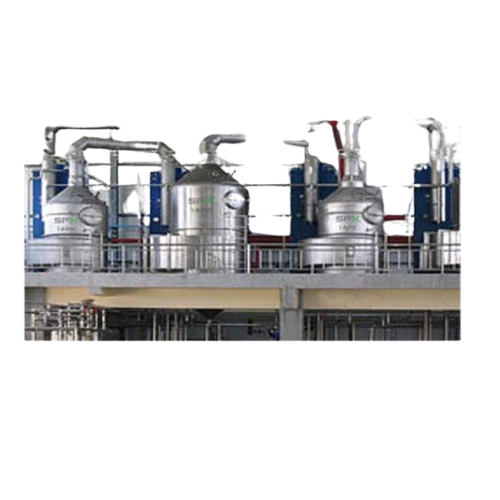
Falling film plate evaporators for fruit juice concentration
Achieve precise concentration of liquid products with minim...
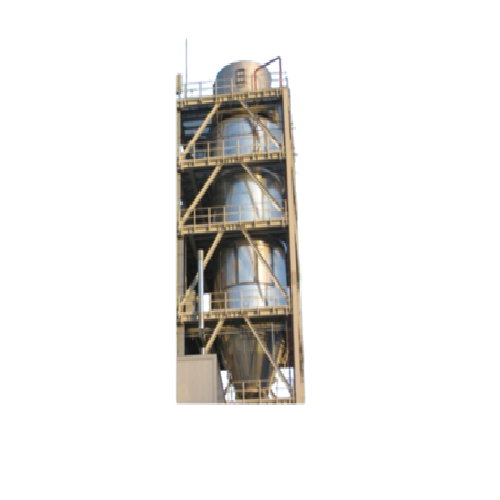
Tall form dryer for producing large non-agglomerated particles
Achieve precise particle size control and optimal moistur...
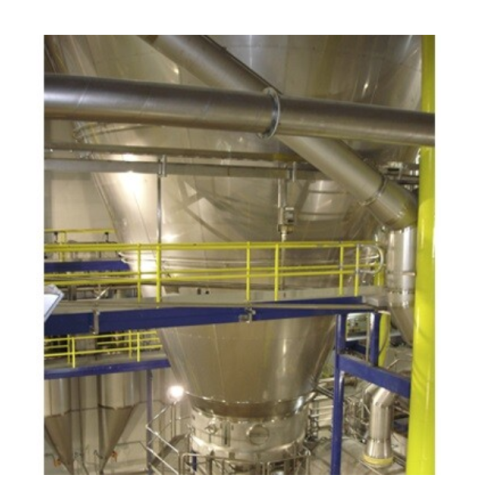
Spray dryers for producing free-flowing dustless powders
Achieve consistent product quality with customizable spray dryer...
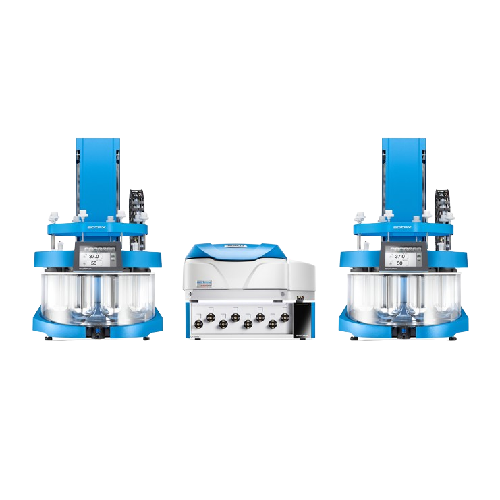
Real-time Uv-vis analysis for dissolution testing
Efficiently perform dual dissolution tests simultaneously, seamlessly i...
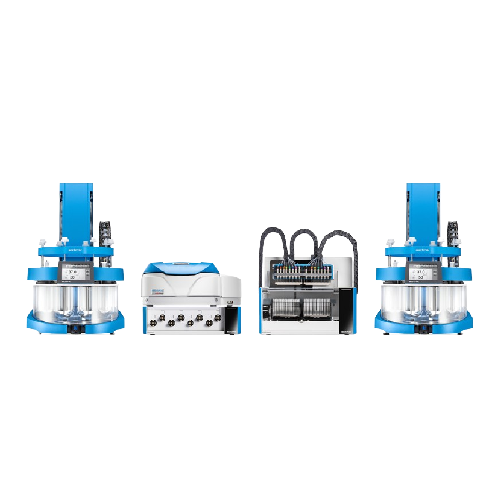
Automated dissolution testing system for 16 vessels
Maximize your laboratory throughput by conducting parallel dissolutio...
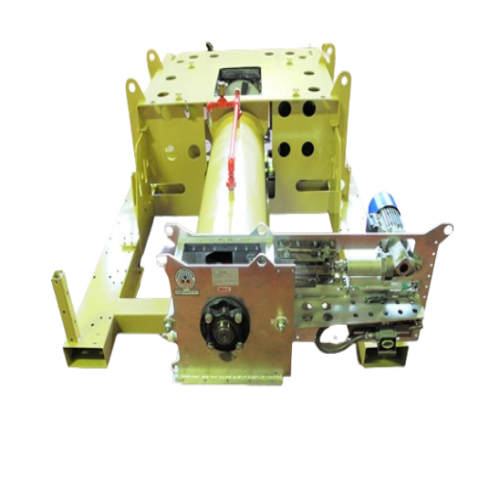
Dosing feeder for coffee production
Streamline your coffee production with precision control, ensuring consistent packing l...
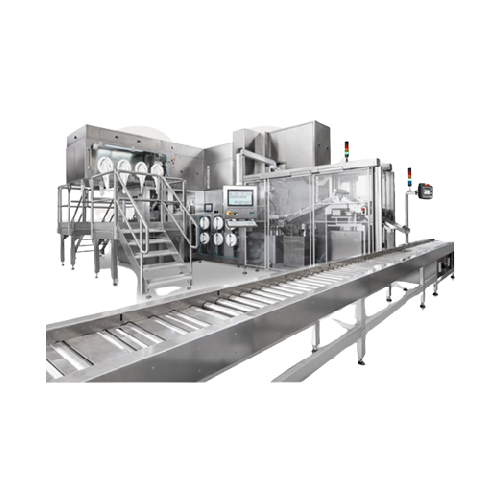
Filling solution for powders and liquids in diagnostics
Simplify precision filling of diverse products, from freeze-dried...
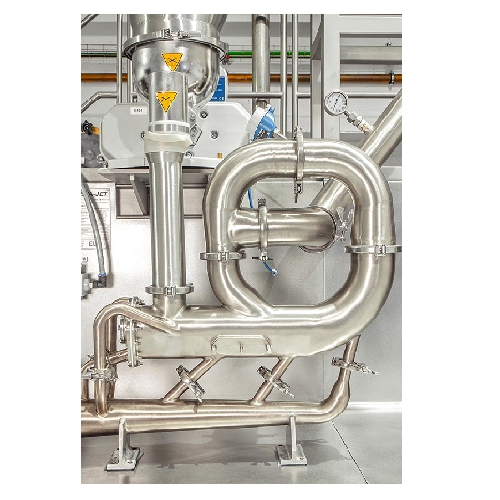
Continuous hot air conveying dryer for chemical and pharmaceutical industries
Ensure rapid moisture removal with high-...
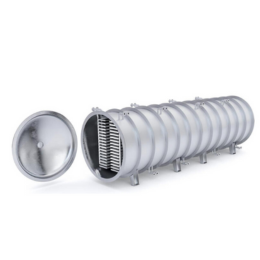
Semi-continuous freeze dryer with easy-loading
Freeze-drying is both a time- and energy-consuming process. In addition to ...
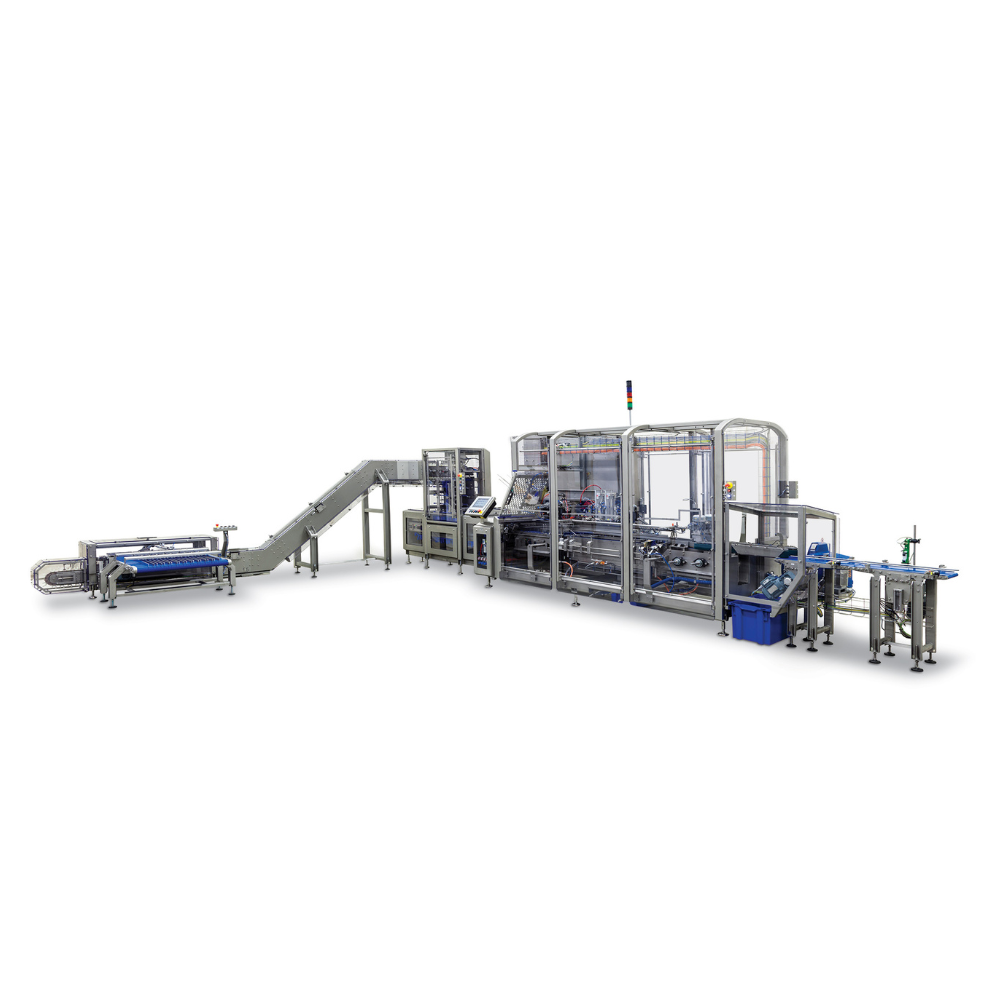
High-speed Cartoner For Single-Serve Products
Large-volume producers of single-serve packs, such as sugar sticks, instant ...
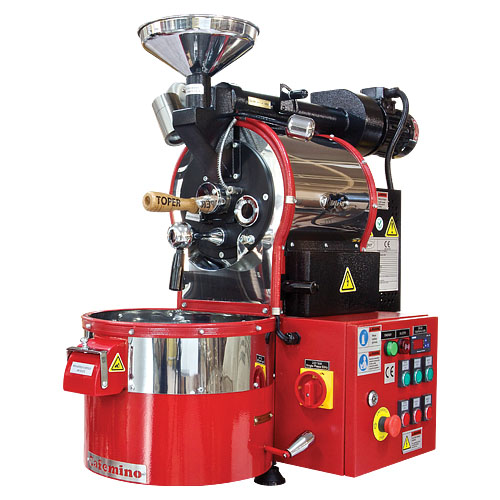
Electrical mini coffee roaster
If you are looking to gain full control of the roasting process, obtain 5 – 6 kg / hou...
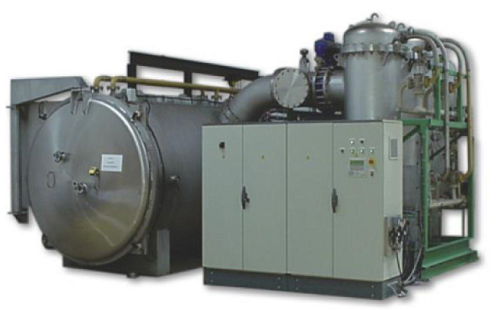
Freeze drying system for berries and fruit powders
Delicate fruits with high moisture levels, such as berries, risk losin...
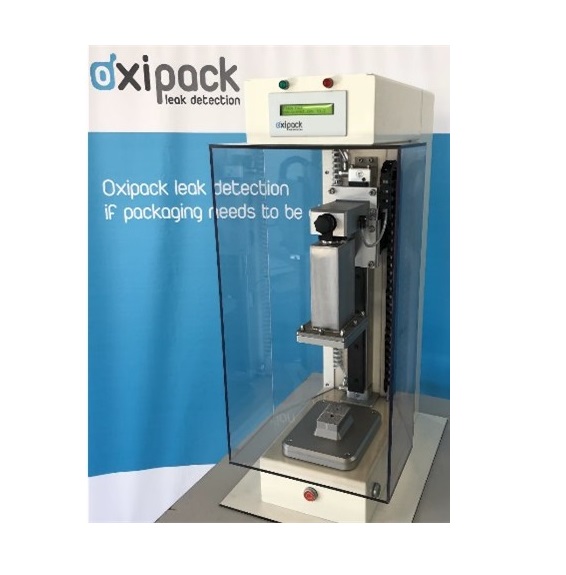
Leak tester for vacuum packaging
Roasted coffee beans, as well as grounded coffee, rapidly diminish in flavor. The oxyge...
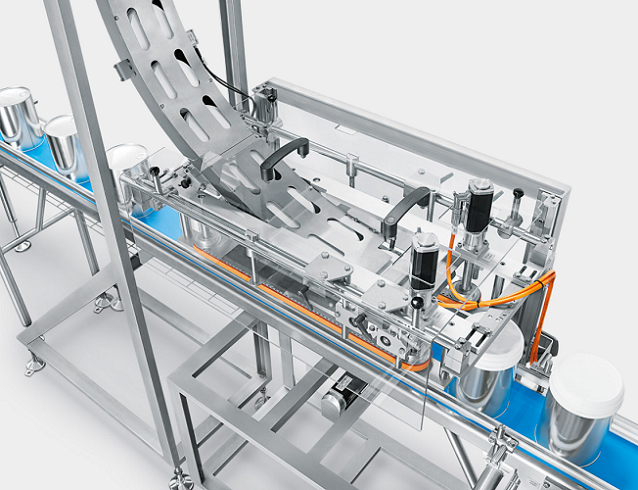
Capping machine for plastic lid oatmeal tins
Some products ask for a plastic reusable lid after the can has been sea...
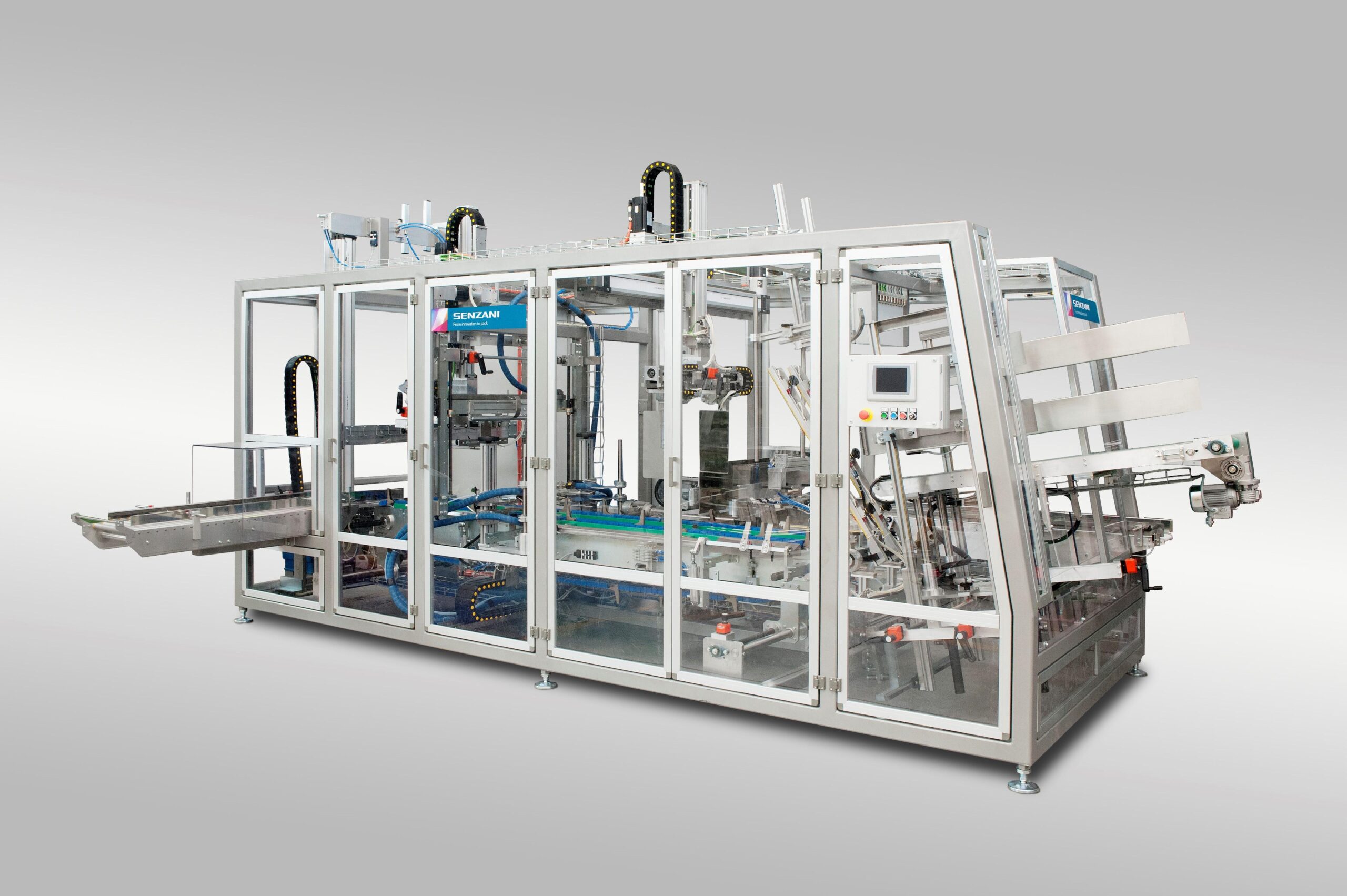
Wraparound case packer
Packaging companies need to pay attention to personalization in shape and design in addition to the at...
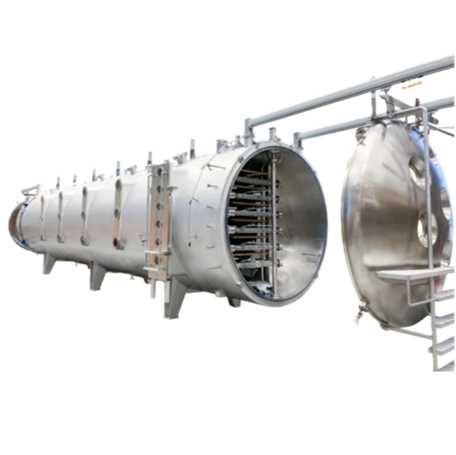
Vacuum belt dryer for instant drink powders
Extracting the essential acids and compounds from fruits and plants is a compl...
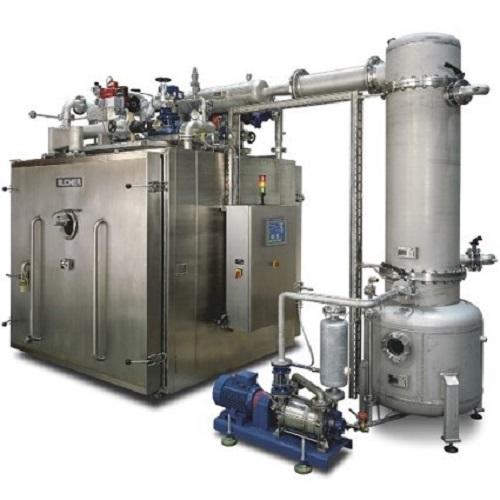
Vacuum cabinet dryer for plant extracts and functional foods
Plant extracts are vital to functional food preparations. B...
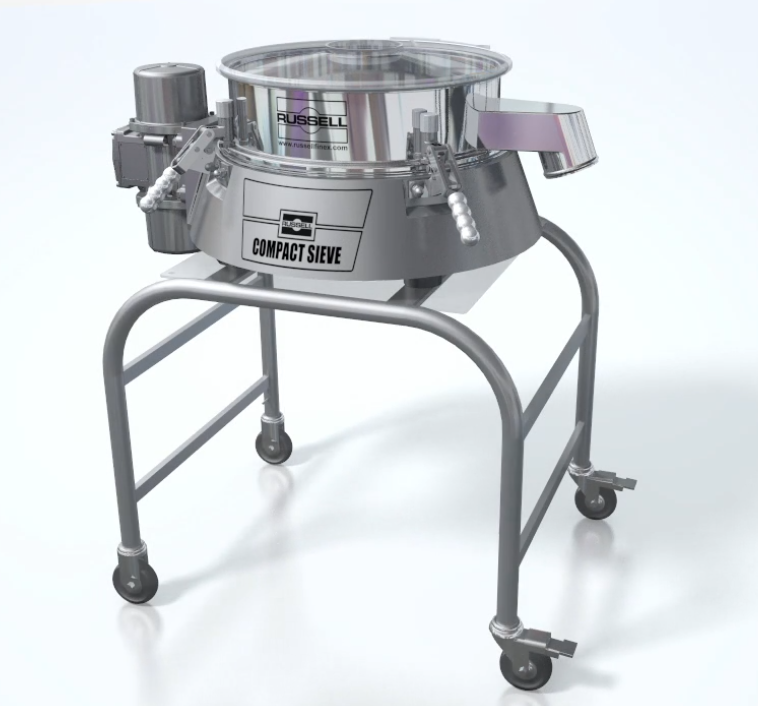
Vibrating screening machine for coffee
Coffee bean separation is one of the important steps during bulk coffee production. ...
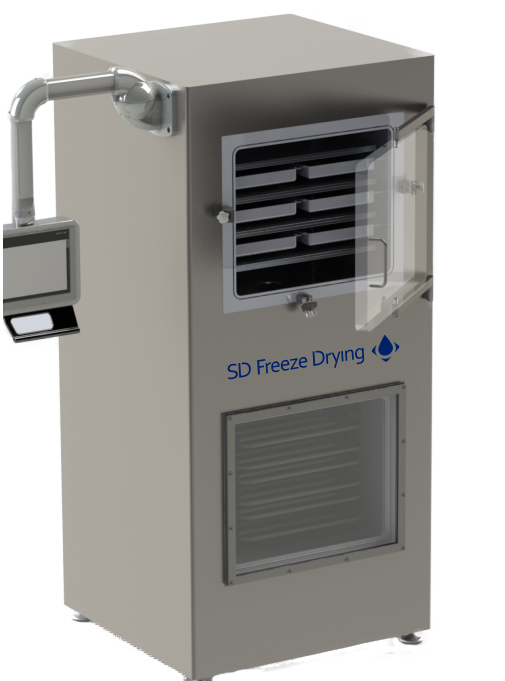
Pilot scale freeze dryer
Freeze drying is a complex and time-consuming drying process which requires maintaining the quality ...
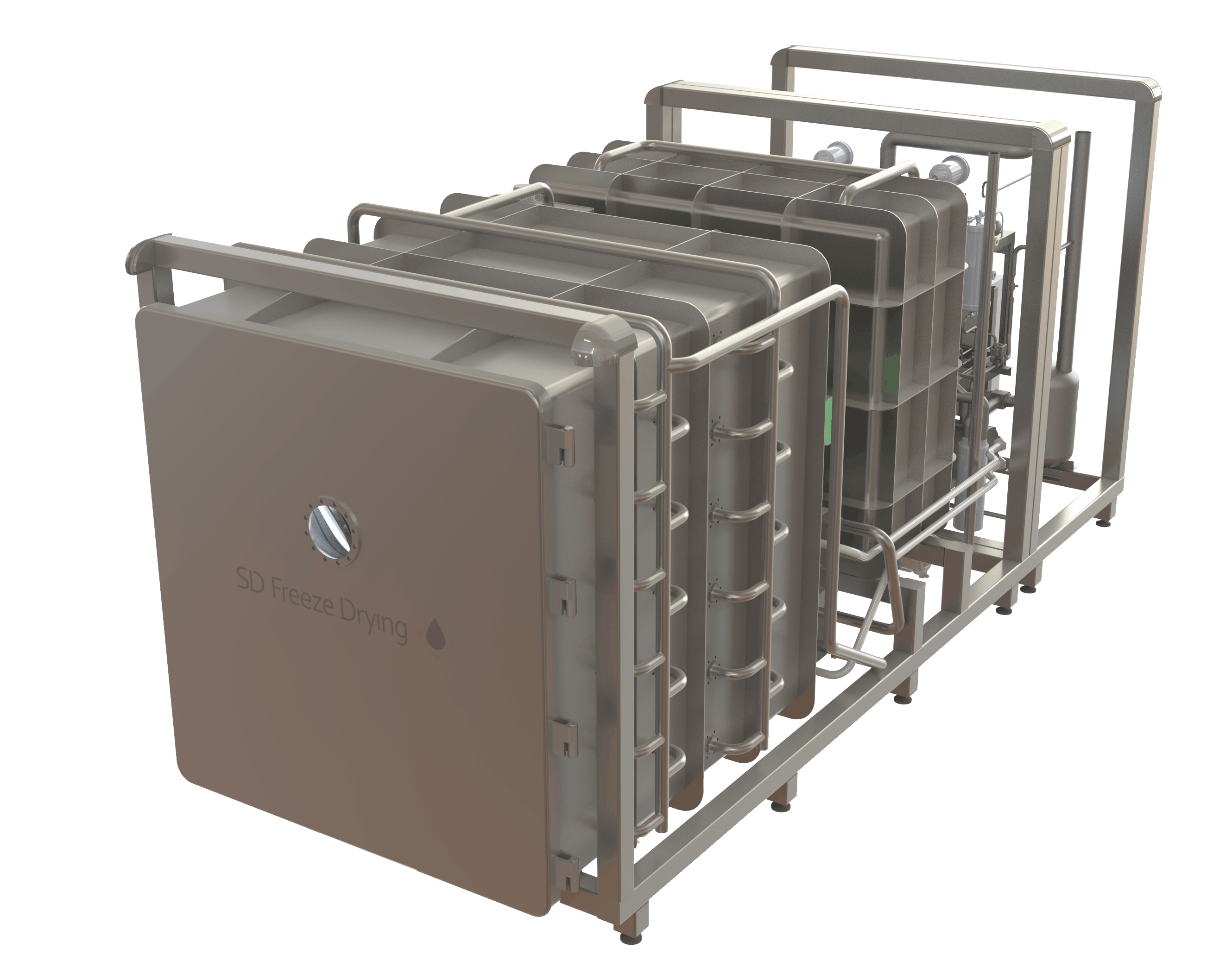
Industrial food freeze dryer
Nutraceuticals and dietary supplements can be highly sensitive and need to be protected against...

Automatic freeze drying system
Freeze drying can be an expensive and cumbersome process. When dealing with nutraceuticals it...
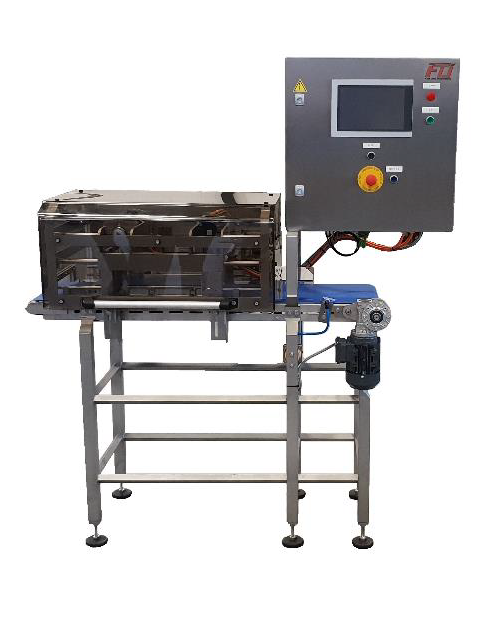
Entry-level high volume package seal tester
Manufactured food products need to be packed in gas-filled pouches to ensure t...

High-Speed Pouch Packaging Machine
For large scale production of powders and liquids in a wide range of industry sectors, a...
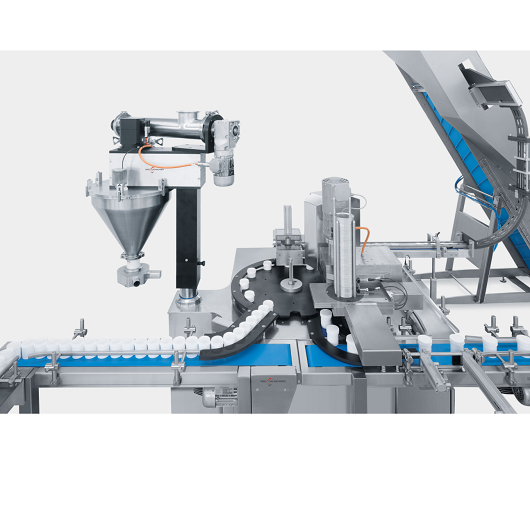
Can filling equipment
Having separate equipment for different process steps like filling and closing, can put a brake on grow...
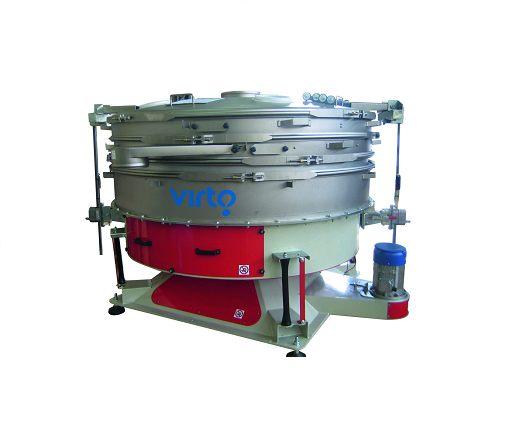
Tumbler sieve for classifying and dedusting granular materials
For the classification of delicate granular material, scr...

High volume particles separation sieve
For large scale production processes in the chemicals or food industries that requir...
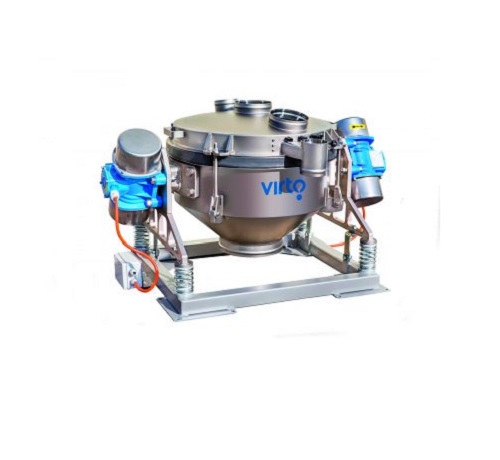
Multifrequency sieve for separation of difficult particles
Separating particles in difficult-to-process materials for pr...
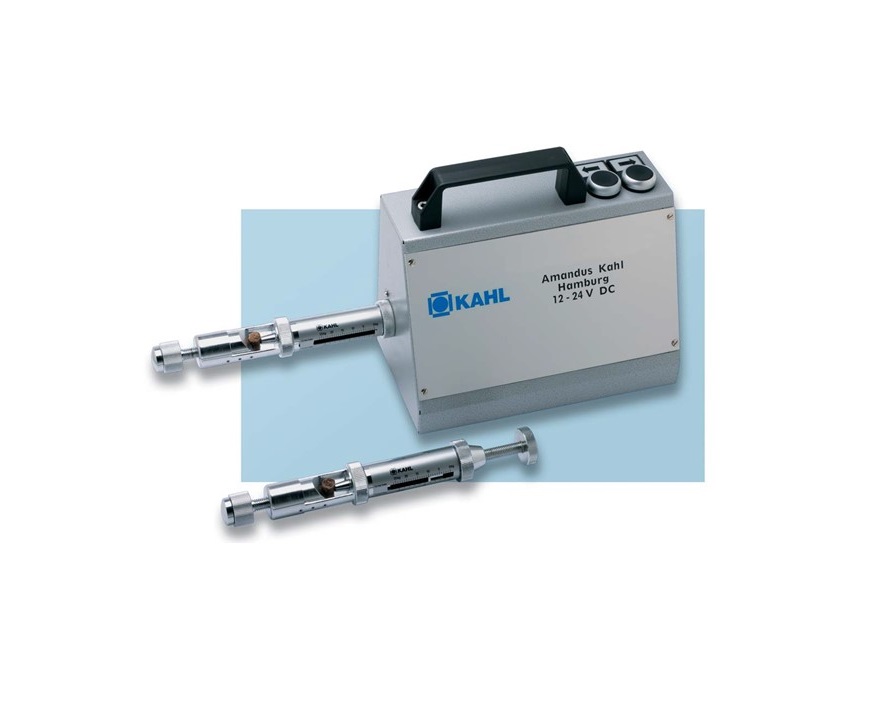
Pellet hardness tester
Control the quality of your pelletizing processes using a pellet hardness tester. Pellet hardness is o...
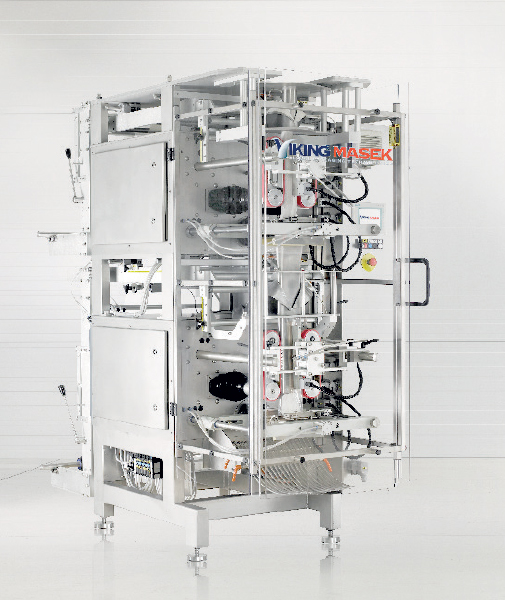
Bag-in-Bag machine
If you are looking for a compact packing machine that packs multiple smaller packs in one master bag; this...
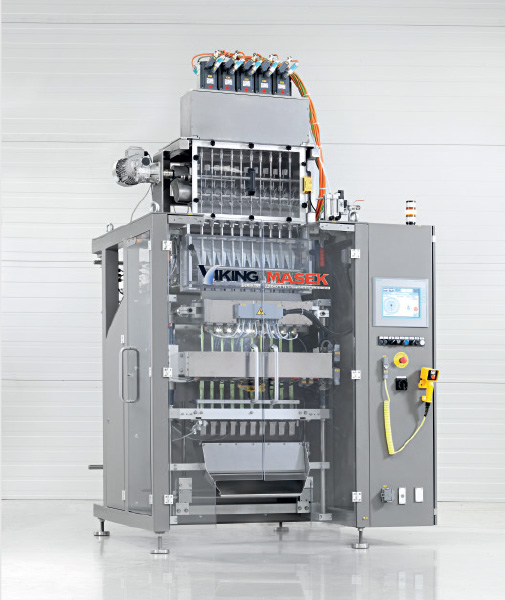
Stickpack Machine
If you are looking to pack your product into stick packs from 17 x 40 mm to 100 x 200 mm in size, you may b...
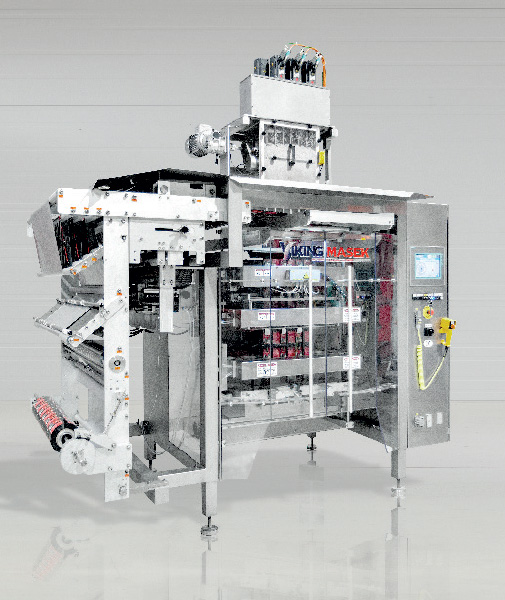
Sachet Machine
If you want to pack into eye-catching 4-side sealed sachets between 40×50 mm and 250×200 mm in size, ...
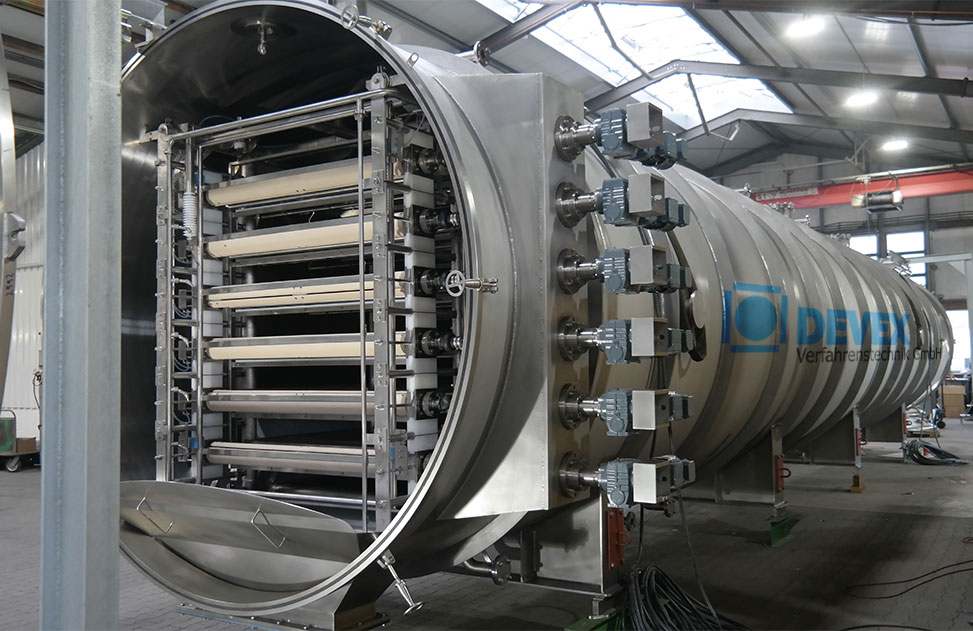
Continuous belt freeze dryer
Freeze drying is the most gentle and aroma protective method of drying, widely used in the coff...
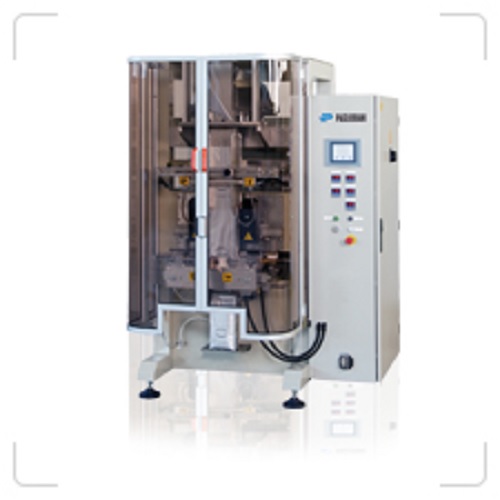
Packaging machine for sealed plastic bags from 250 g to 10 kg
Sealing small quantities of solids or liquids into plastic...
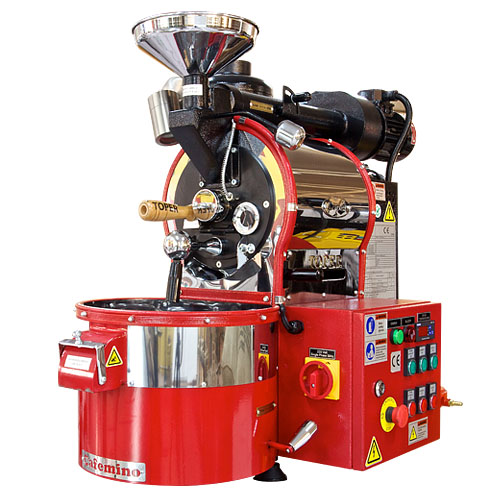
Gas heated mini coffee roaster
Choose traditional gas heating to take full control of the roasting process and obtain 5 R...
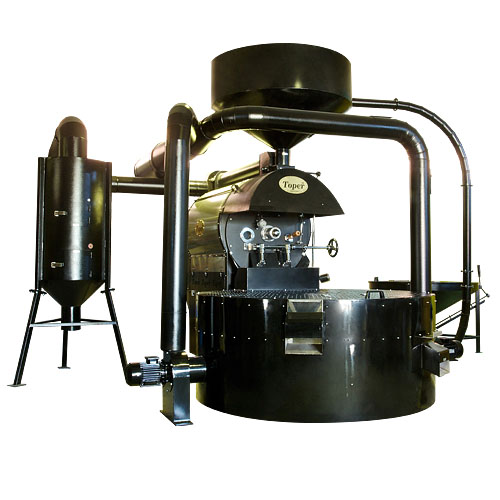
Industrial coffee roaster
Roast 120 – 3,000 kgs of coffee beans per hour with the latest industrial technologies integ...
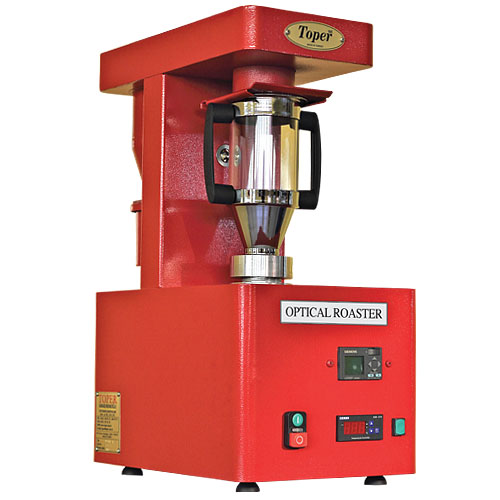
Optical coffee roaster
If you want to see or show all the roasting phases and reactions of the coffee beans, an optical coffe...
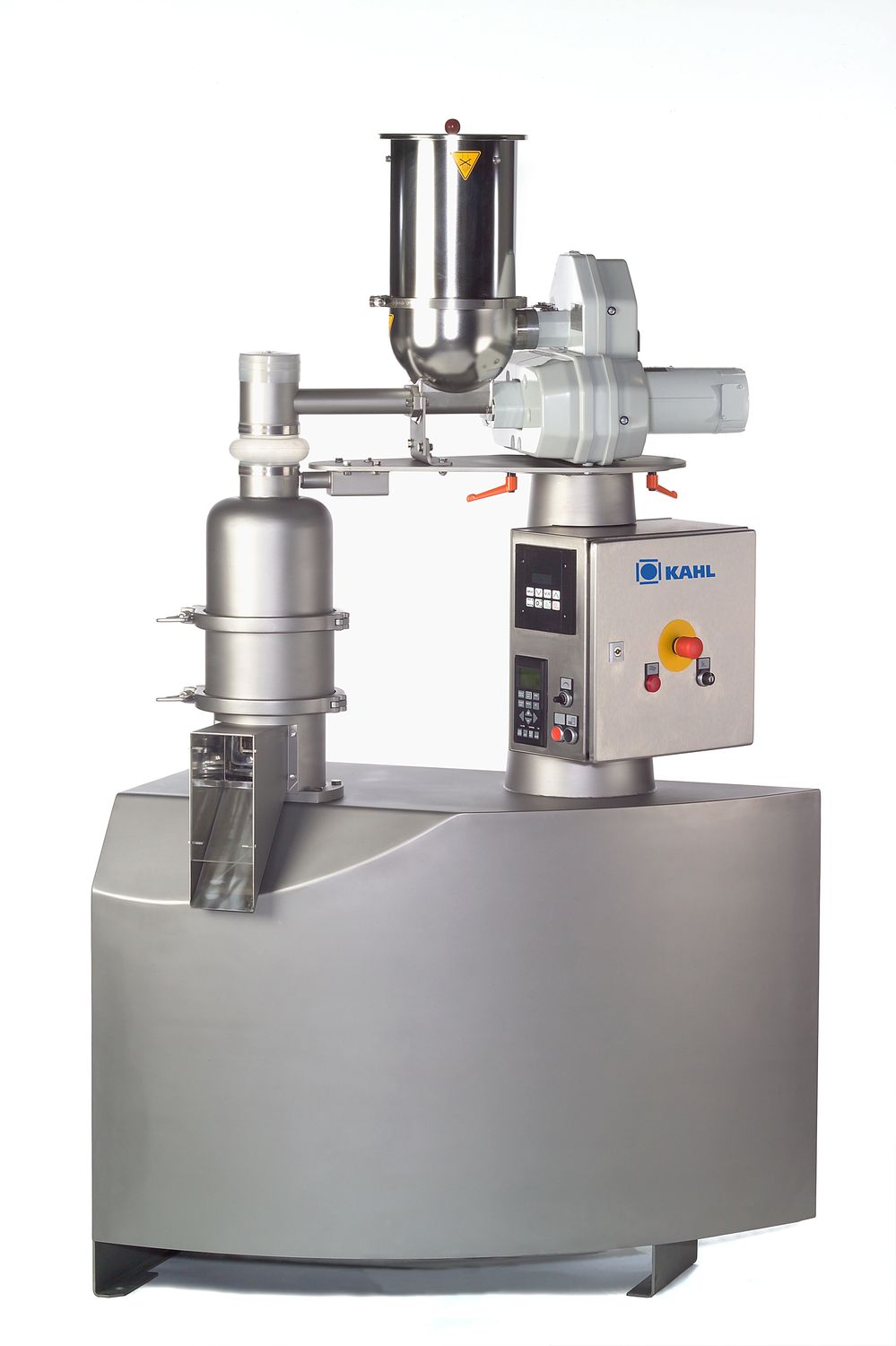
Hygienic pelleting press
The production of pelletized or granularized food products requires hygienic presses designed for hi...