Industrial Drying Equipment
Find innovative drying equipment and connect directly with world-leading technology suppliers
Industrial drying machines are designed to remove moisture from your product. But the drying process must cater to variations in the state of matter and molecular structure of the input material. Industrial dryer technology exploits the modes of heat transfer (convection, conduction, radiation, evaporative cooling) to control the moisture content.
Innovative drying solutions
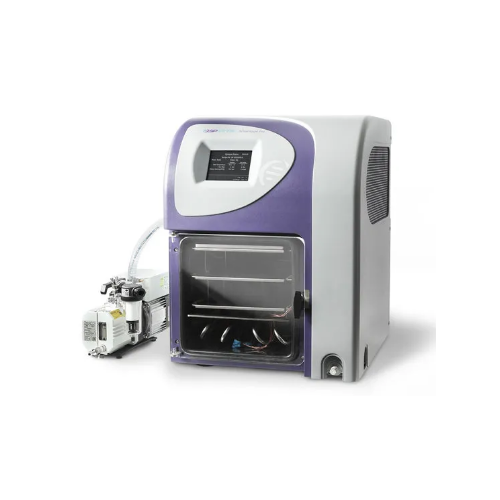
Benchtop freeze dryer for laboratory and small production use
Optimize your lab’s efficiency by adding precise, space-sa...
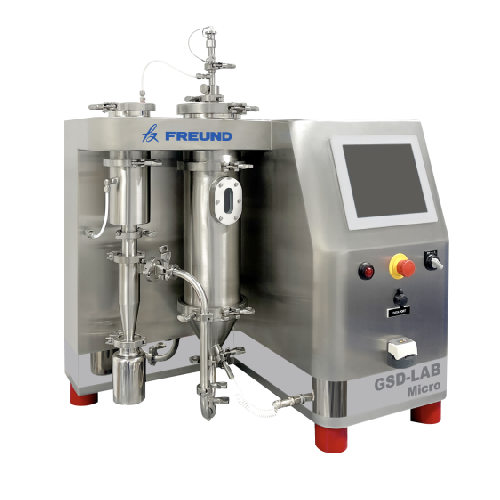
Benchtop spray dryer for drug discovery
Optimize your formulation development with a compact spray dryer that streamlines t...
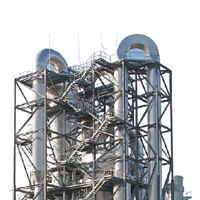
Exergy pressurized superheated steam dryer
Traditional dryers and heat transfer systems, like belt-, drum- or bed dryers a...
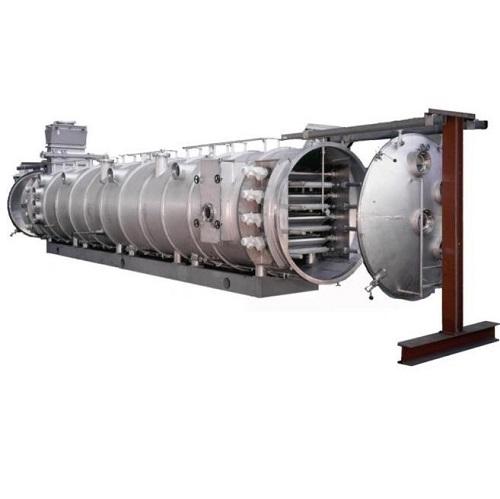
Vacuum belt dryer for fruit, vegetable and herbal extracts
Organic volatile compounds from fruits, vegetables and herbs ...
Use indirect drying systems for gentle heating
Industrial drying machines apply either direct or indirect heating. The former category transfers the temperature to the materials and includes processing equipment like drying cabinets or fluid bed dryers.
Indirect drying solutions heat a fluid that, in turn, heats the drying chamber. This technology is often engineered for batch processing and is designed to avoid atmospheric exposure. Infrared and microwave solutions are both indirect drying systems.
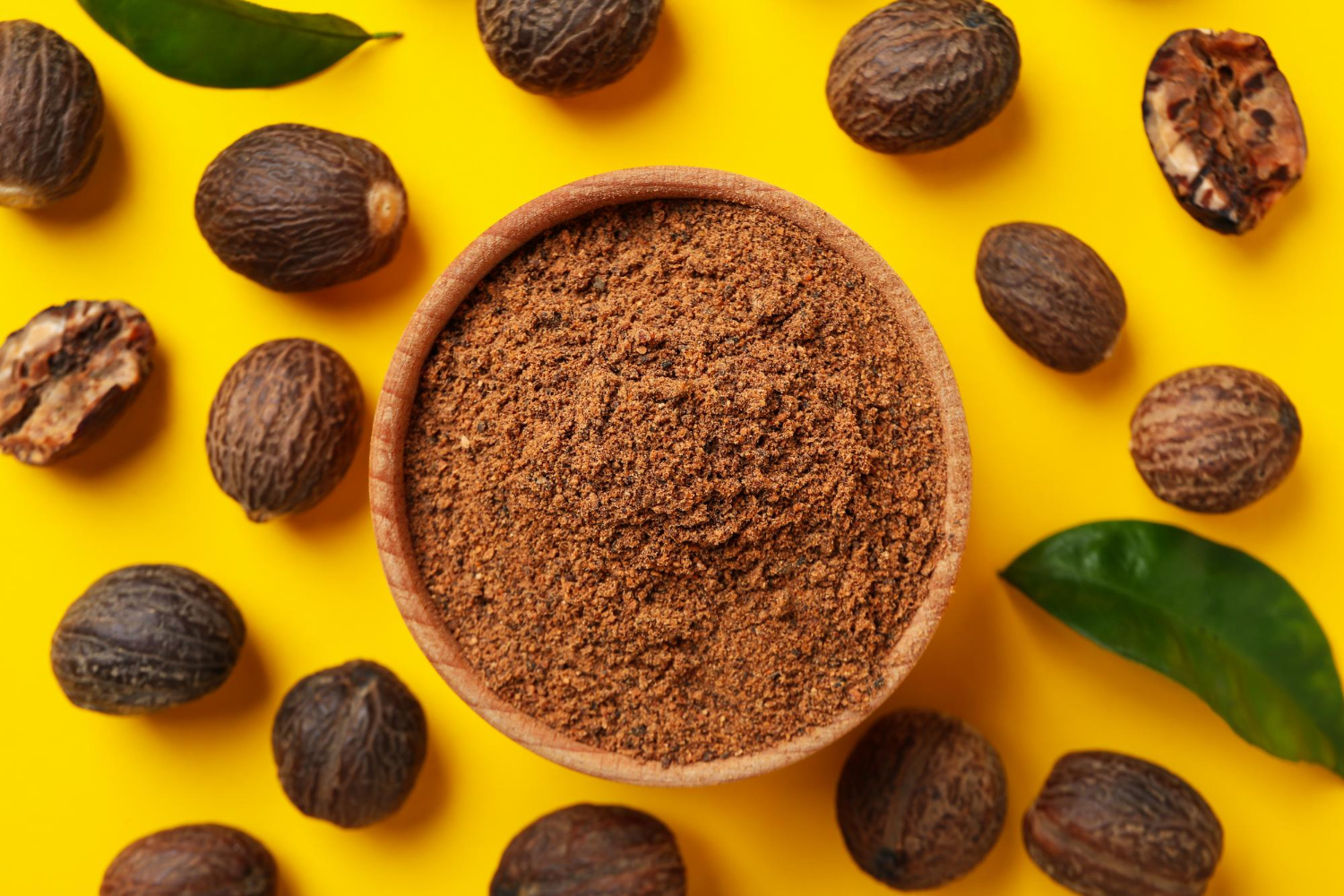
Industrial drying machines by convection are ideal for slurries and insoluble substances
Convection drying is essential for products that need to maintain texture, like milk powder or fruit powders. One of the primary methods for achieving convection is spray drying. The technique atomizes liquids into droplets and subjects them to evaporation, turning them into powdered solids.
Spray drying combines short residence with continuous processing, making it suitable for slurries, emulsions, and fluids.
Evaporate moisture from wet granules with fluidized bed dryers
Drying wet powders such as feed ingredients or ceramics present a unique challenge. The individual particles are coated by humidity, resulting in high moisture levels. But the materials cannot withstand aggressive heating methods.
Fluid bed dryers engineer a solution by blowing hot air through a perforated plate underneath the material. When the wet solids make contact with the airflow, the liquids are vaporized, leaving the particles in a dry state.

Dehumidification systems apply low temperatures to heat sensitive materials
Industrial dehumidifiers reduce the relative humidity in the stainless steel drum, gradually drying the materials inside. Solutions use a compressor or desiccant to lead humid air out of the chamber.
The low-temperature drying system is ideal for sensitive materials with a low tolerance for environmental changes like chemical powders. Dehumidifiers do not entirely eliminate the moisture from the drying objects, making them a safer choice for wet granulates for applications such as pharmaceutical tablets and seed pelleting.
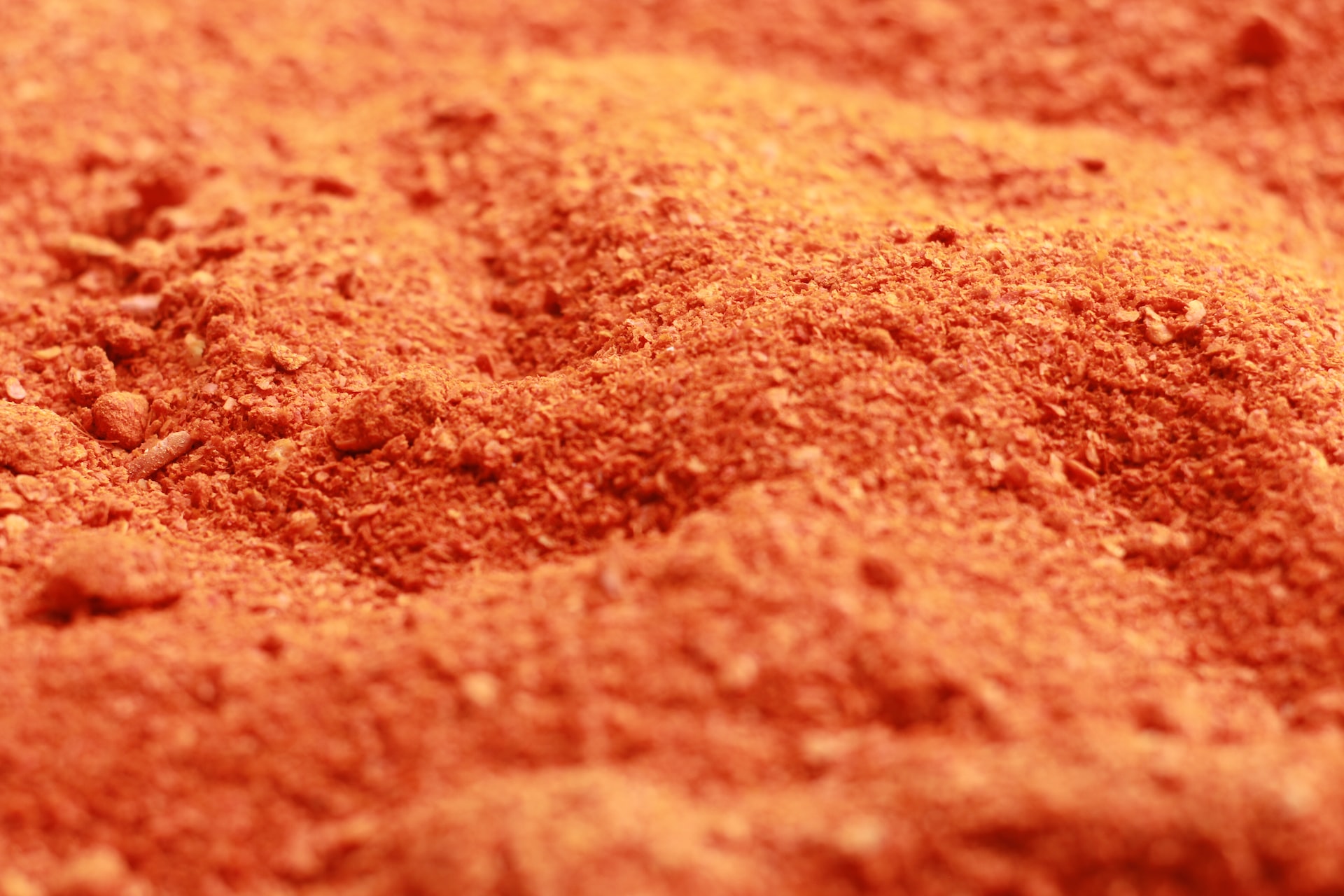
Sorption dehumidifiers strip ambiance air of excess water molecules
Another type of industrial dehumidifier within the processing industry extracts environmental moisture at the production site. Humidity control is particularly important where powders are handled as moisture negatively affects the flowability of materials. But excess humidity can also impact the properties of sensitive materials like flower extracts or dough-based products or soft-gel capsules.
Sorption dehumidifiers lead the ambiance air through a rotor coated with a desiccant, for example silica gel. The coating adsorbs the water molecules, allowing the dry air to circulate back into the environment.
Skip the liquefaction of ice crystals with lyophilization techniques
Some materials, such as ingredients for biopharmaceuticals or primary bakery products, are delivered frozen. But treating them with heat risks altering their properties as ice crystals melt into liquid.
Freeze-dryers bypass that phase to keep the materials intact and dry. This technology is based on the sublimation principle, where a solid turns directly into vapor without first turning into a liquid. Lyophilization occurs when the material is placed under a deep vacuum and subjected to heat energy, transforming the ice into gas.
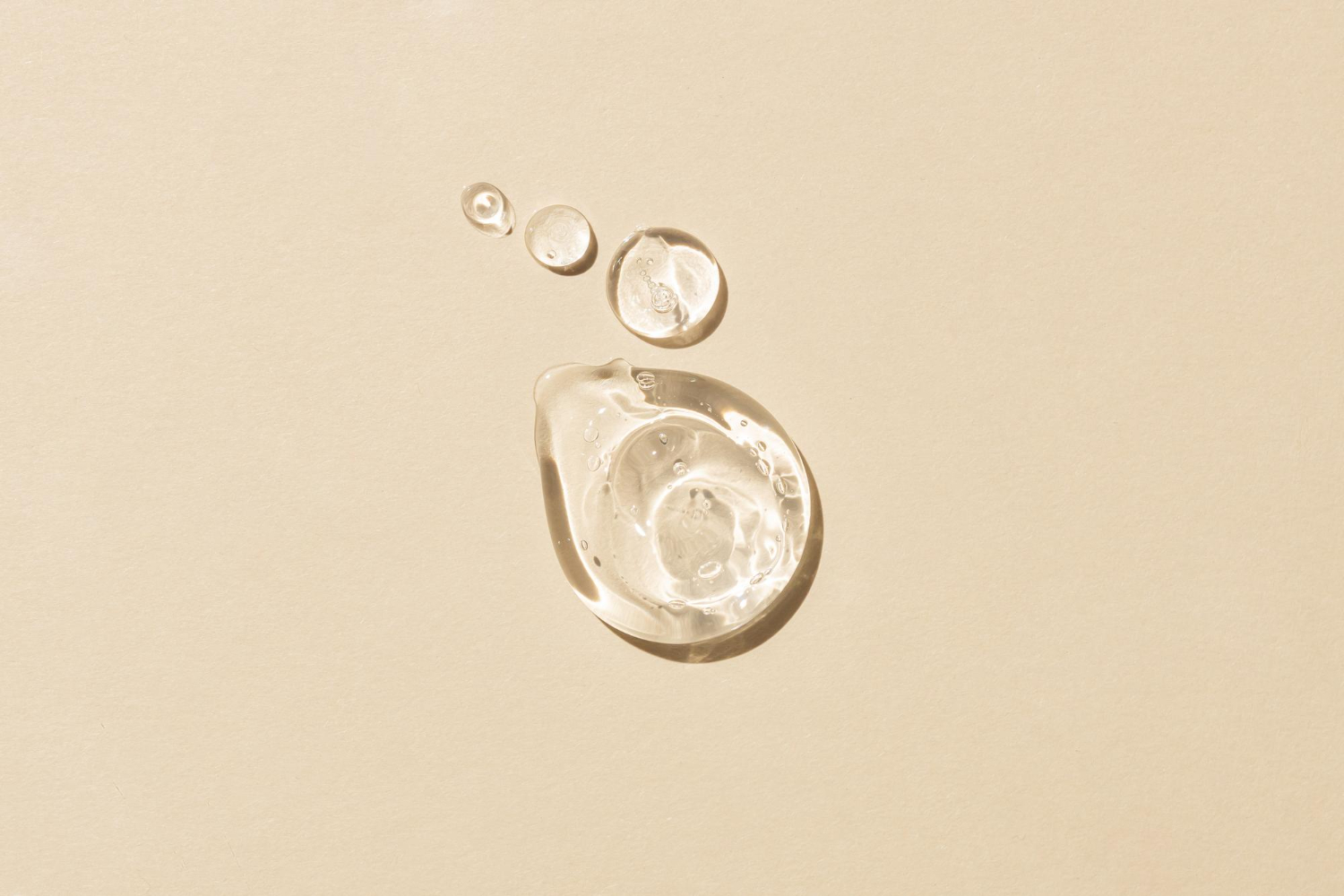
Free up trapped moisture with vacuum-chamber Industrial drying machines
Hygroscopic substances like glycerin or methanol used for biofuel products are difficult to dry with heat transfer. The molecules trap water that is difficult to release without compromising the material.
Vacuum drying equipment forces moisture out by dropping the pressure below the atmospheric pressure within the chamber. The outward flow of air leaving the system causes the water content to vaporize and escape the material.
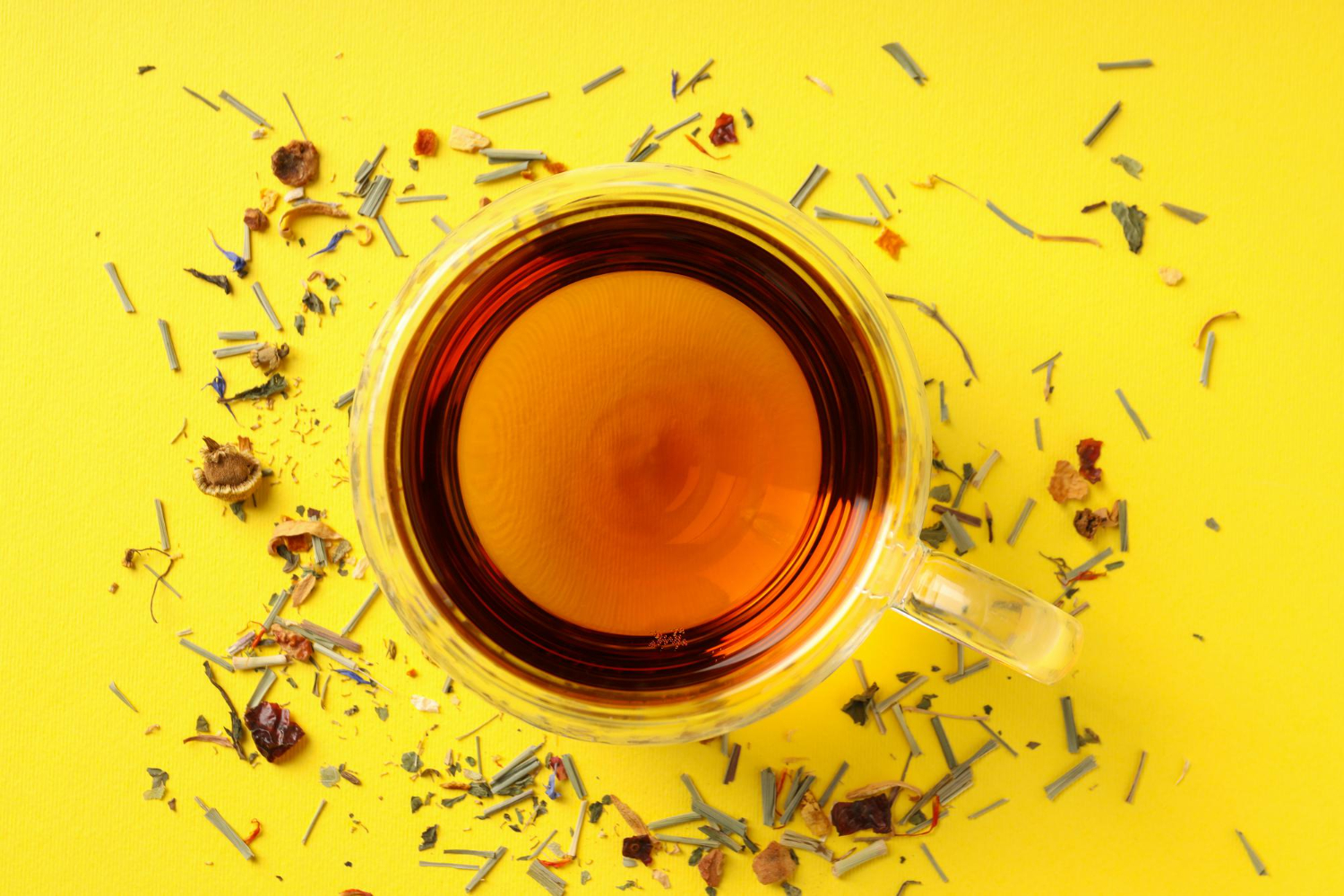
Drying cabinets are best suited for batch processing
Industrial dryers using conductive heat such as drying cabinets are better suited to batch processing. Industrial drying cabinets apply low-temperature heating for more extended periods.
Typically, this drying method is used not only to remove moisture from materials but to alter their compounds, too. So the technique is ideal for drying fresh produce like herbs or meats to make dried oregano or biltong.
Radiation drying systems exploit long wavelengths to create an indirect heating
Radiation drying systems apply long wavelengths in the electromagnetic spectrum to heat and dehumidify material indirectly. In contrast, infrared heaters radiate absorbed water molecules to create a low-energy drying environment. The technique is optimal if you manufacture materials that require a short drying process, like water-based ink or active pharmaceutical ingredients. On the other hand, Microwave drying is an alternative radiation solution. The technology relies on the vibration of water molecules to generate energy, creating mild drying conditions for delicate products such as berries or flower extracts.
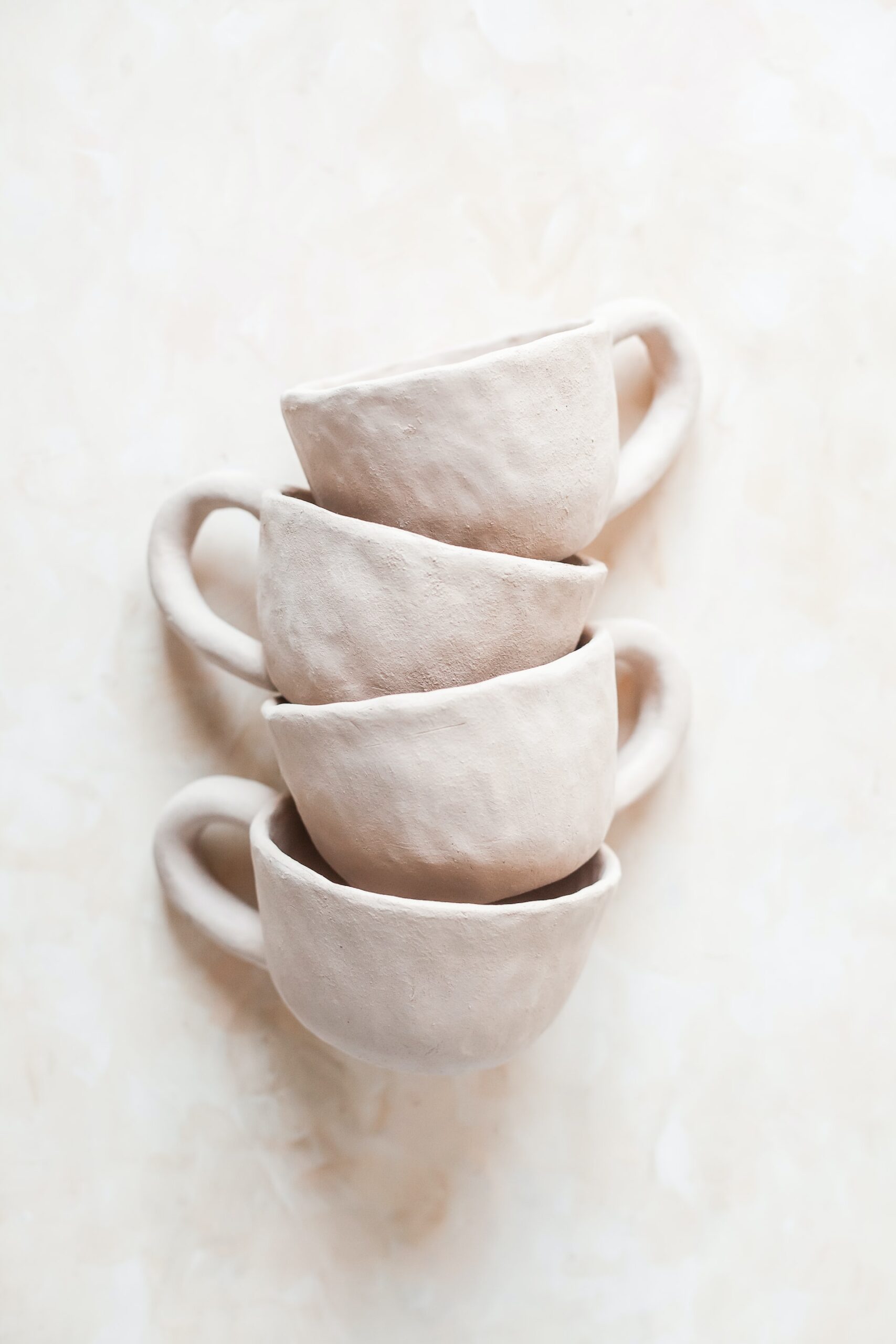
Reduce power consumption with energy-efficient industrial drying machines
One of the challenges of industrial drying equipment is power efficiency. The machine capacity and drying capability determine energy consumption, but other factors can improve effectiveness.
An electric heating element transfers a higher energy rate than burners or gas heaters. Efficiency is also impacted by the blower design. An open loop system uses a single blower for drying and air regeneration, causing losses in temperature. Closed loop drying equipment solves this inefficiency by adopting separate blowers for dry and moist air.
What are you making?
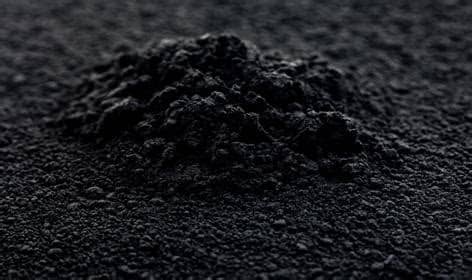
Activated carbon
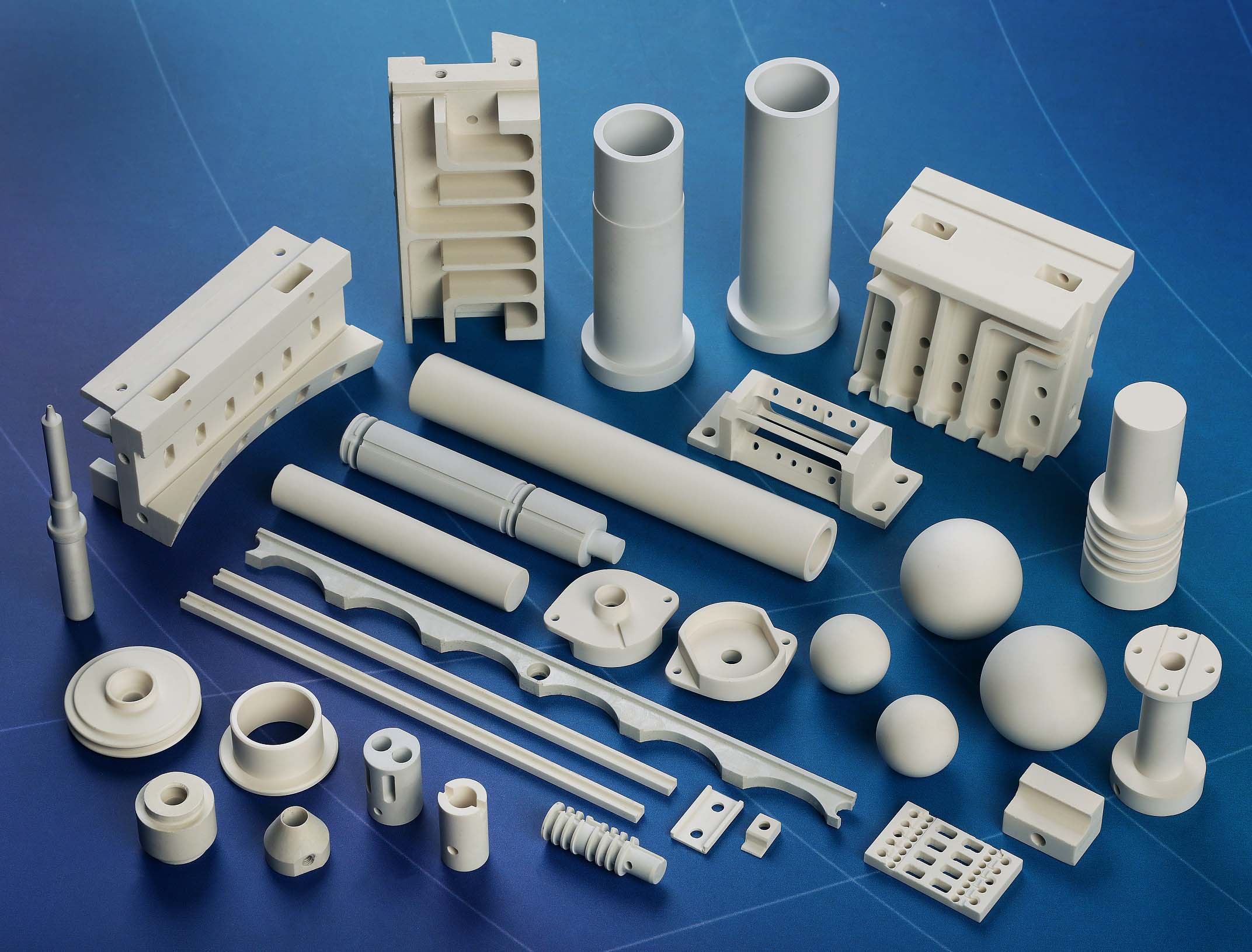
Advanced ceramics
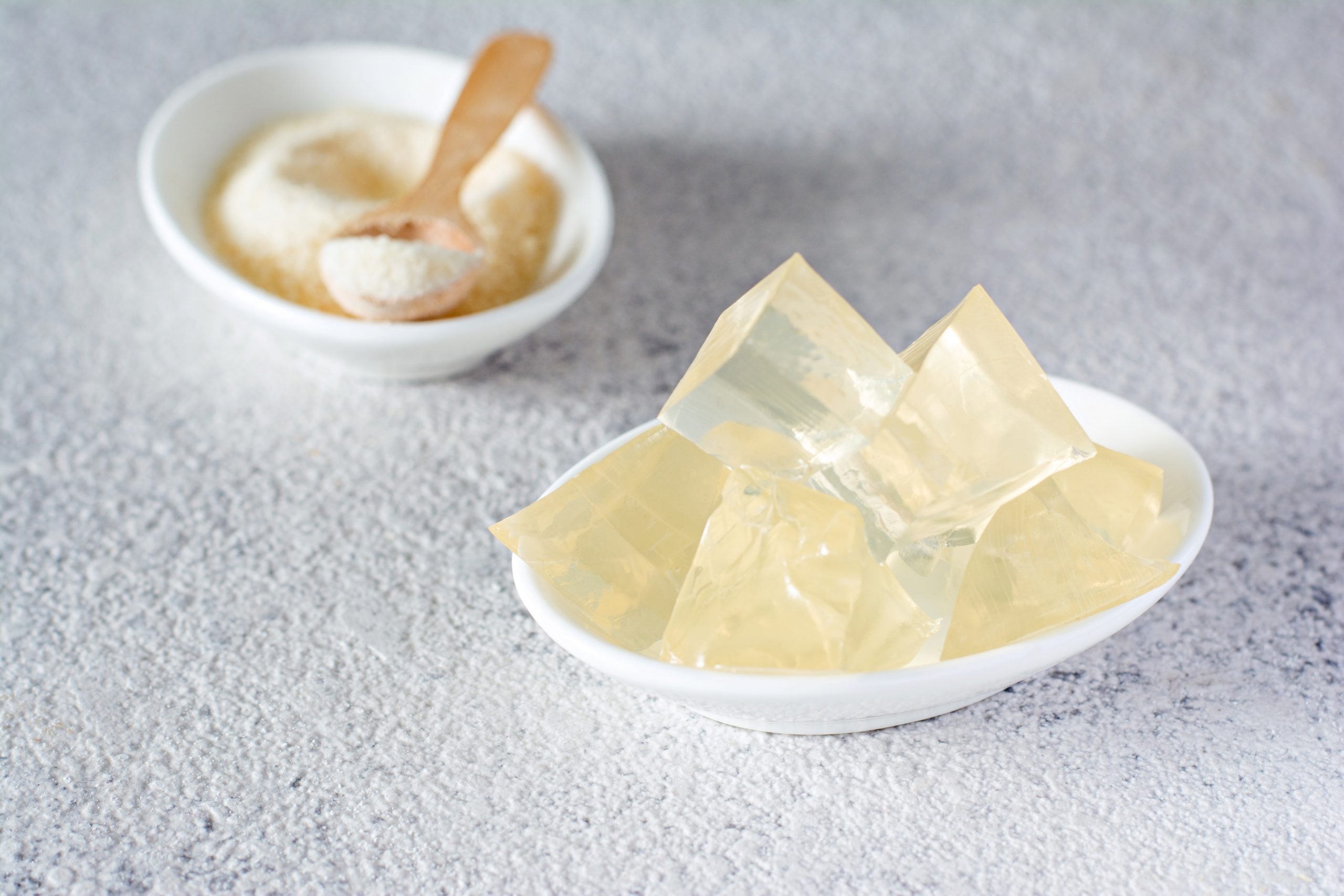
Agar-agar
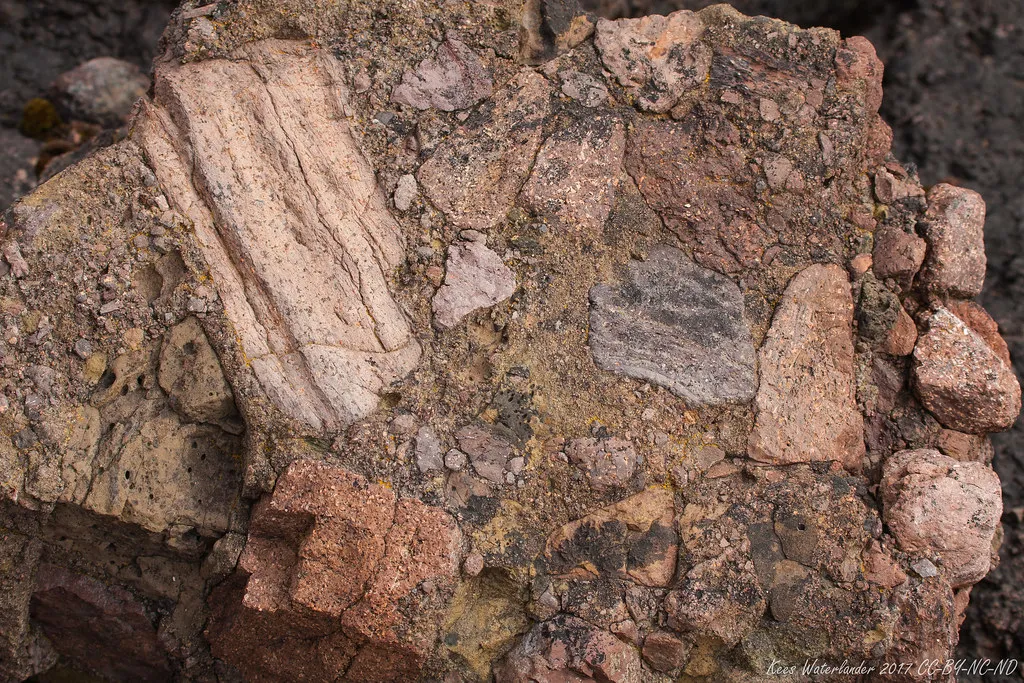
Agglomerates
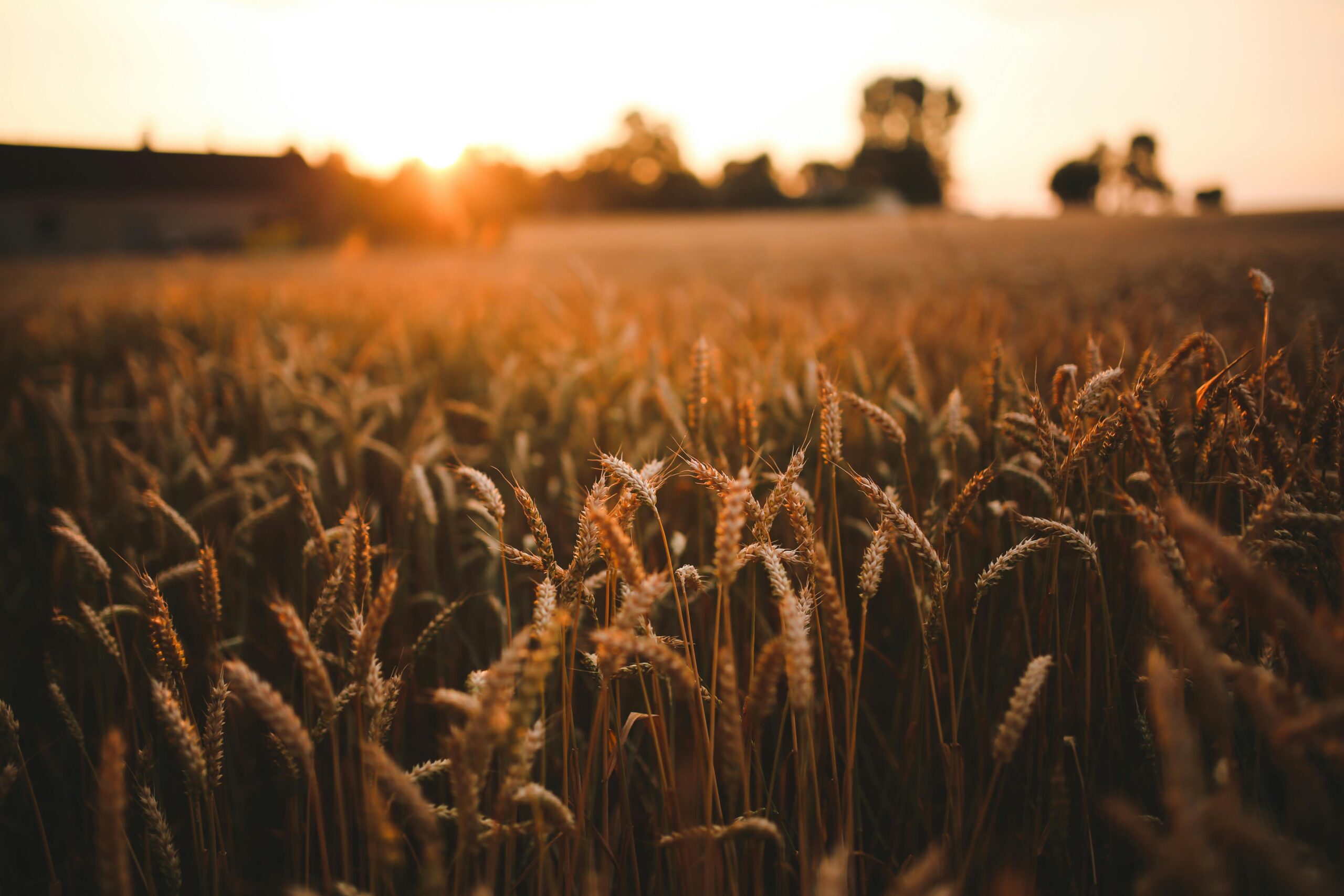
Agricultural by-products
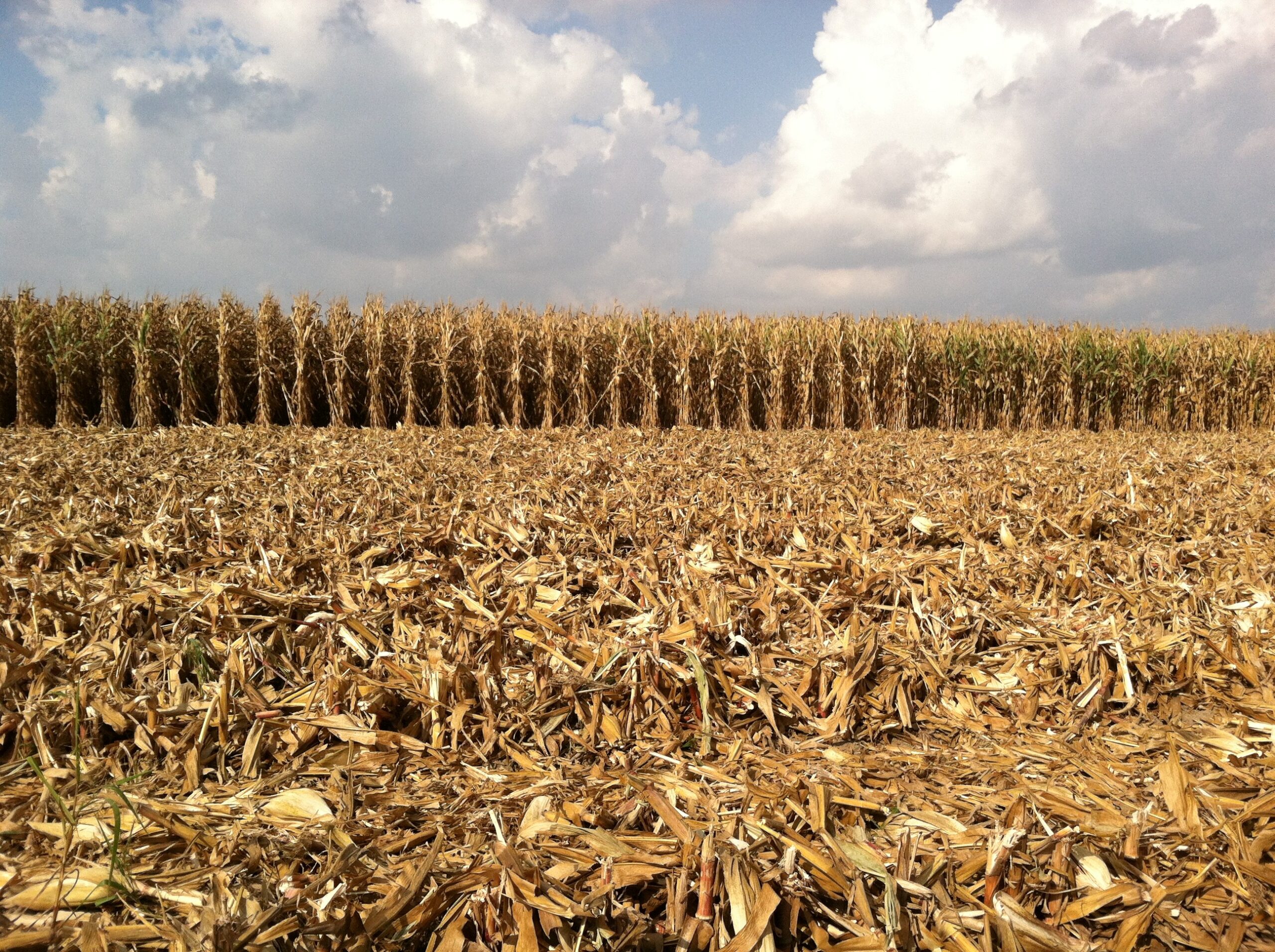
Agricultural residues
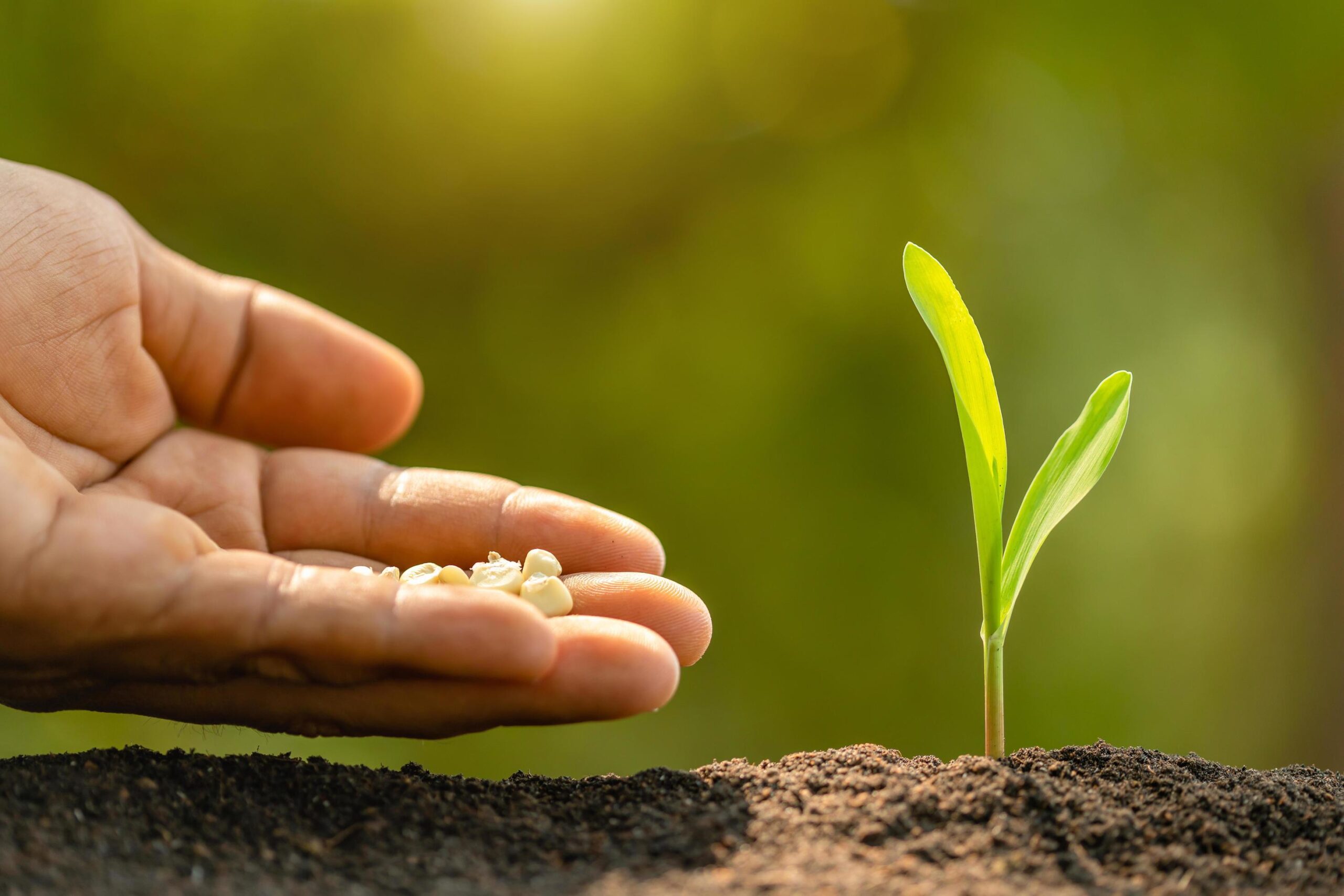
Agricultural seeds
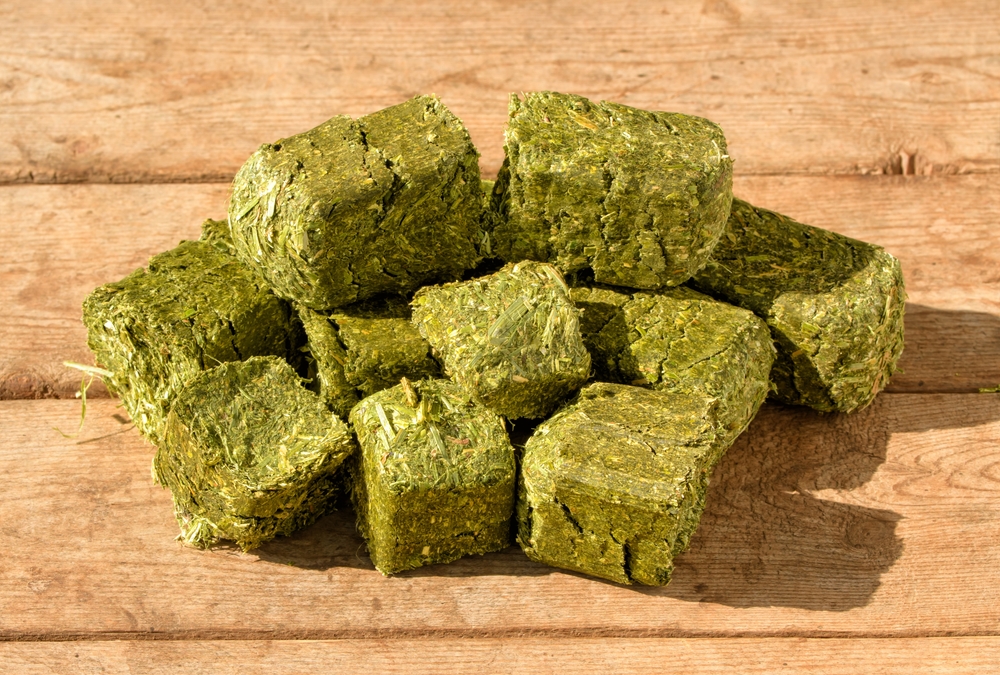
Alfalfa meal
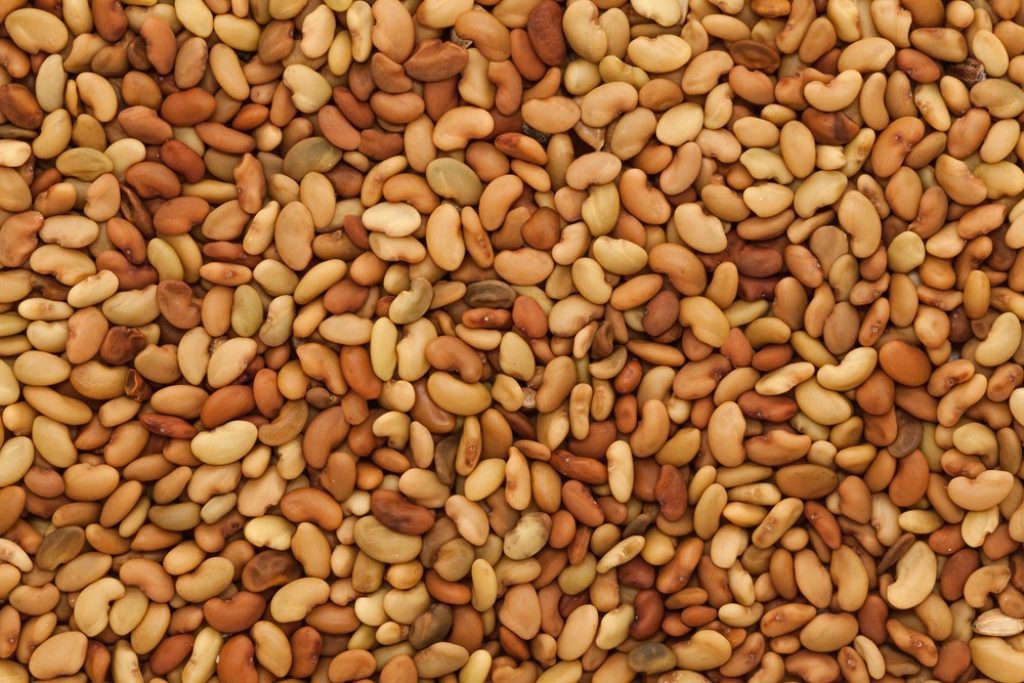
Alfalfa seeds
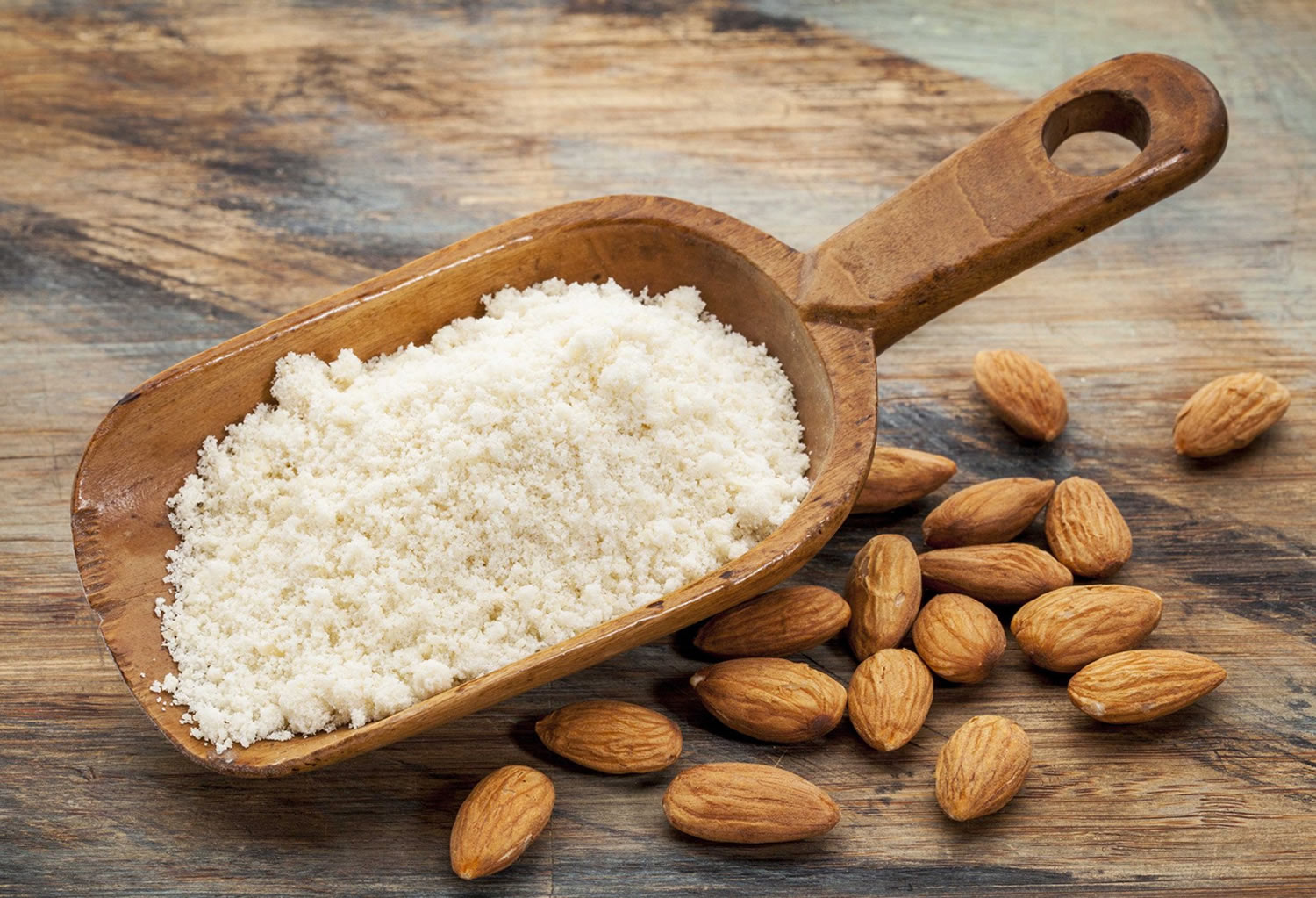
Almond flour
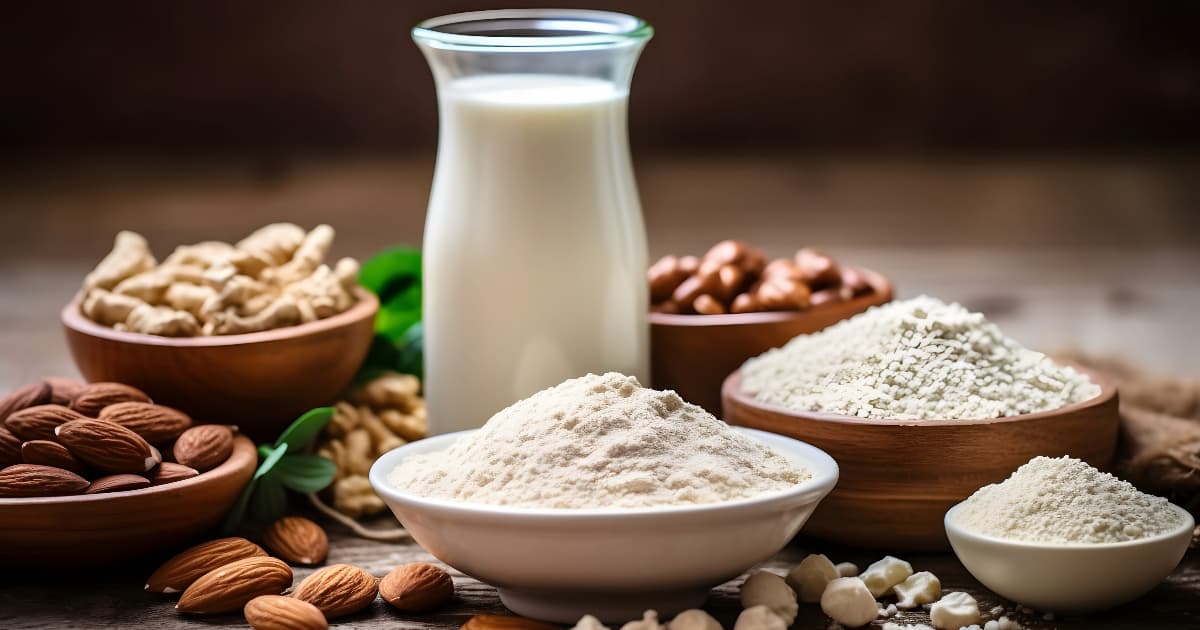
Almond milk powder
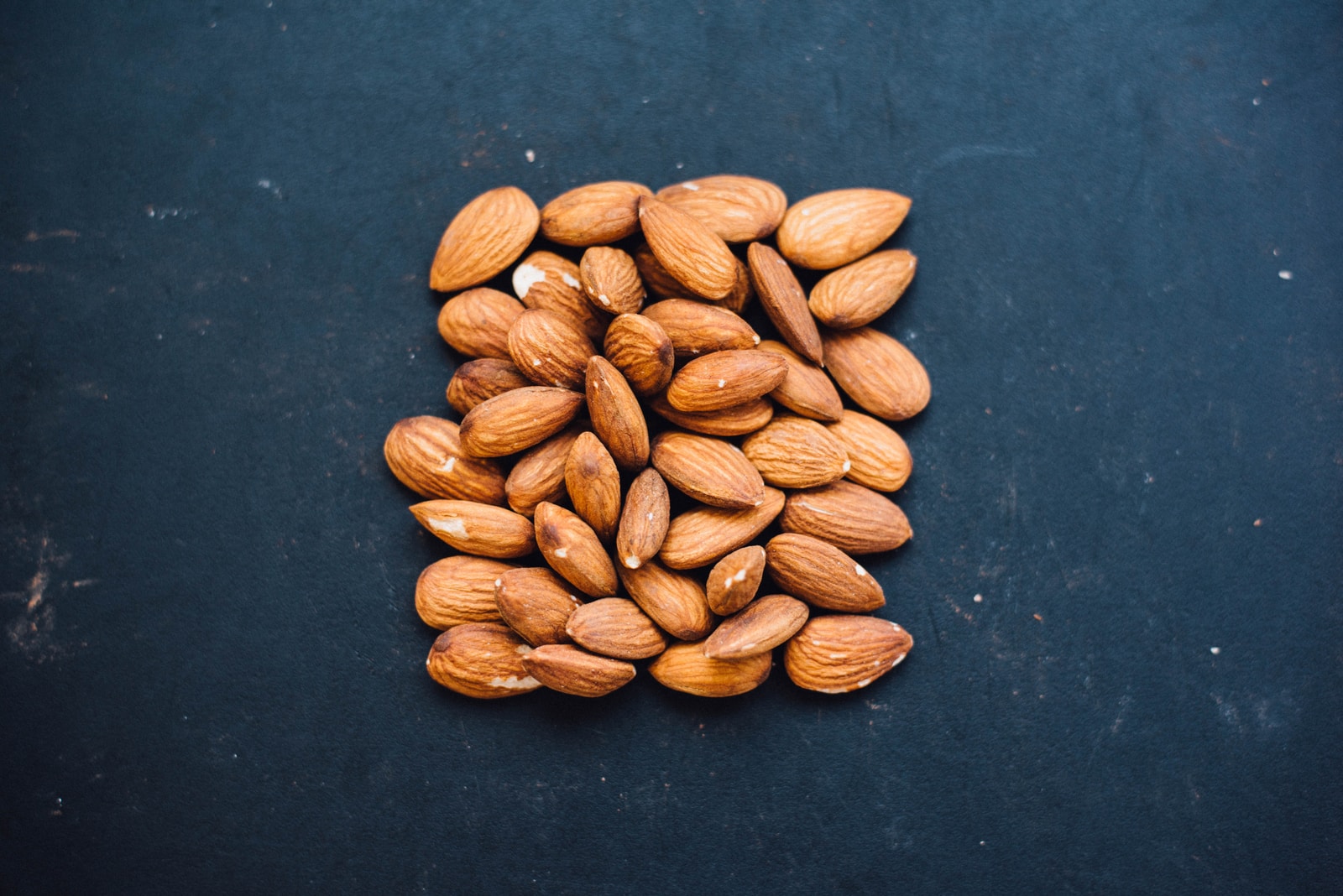
Almonds
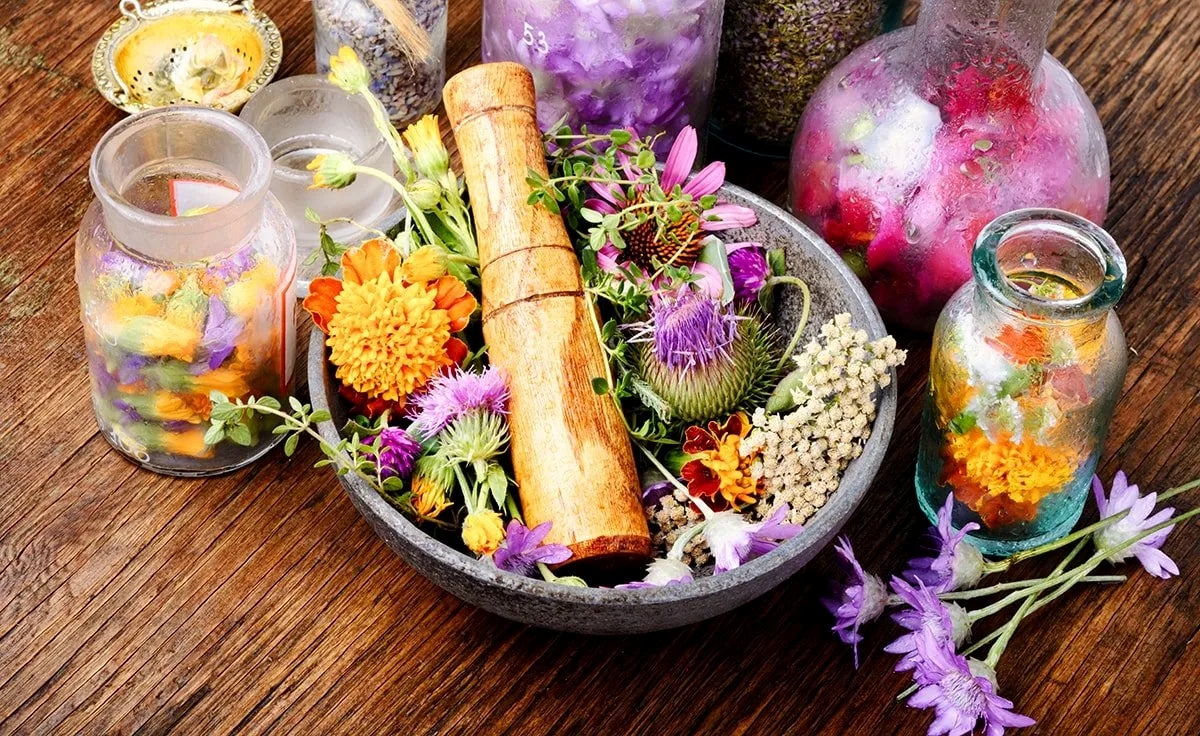
Alternative medicine
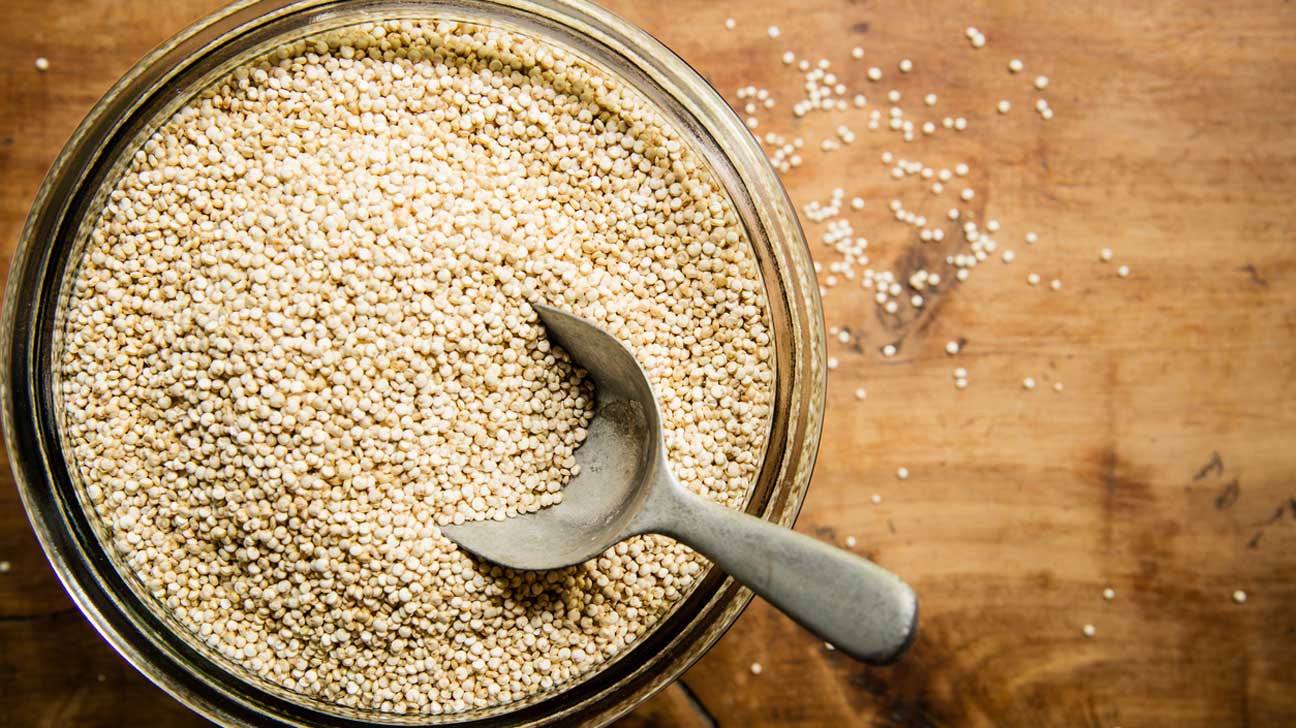
Alternative proteins
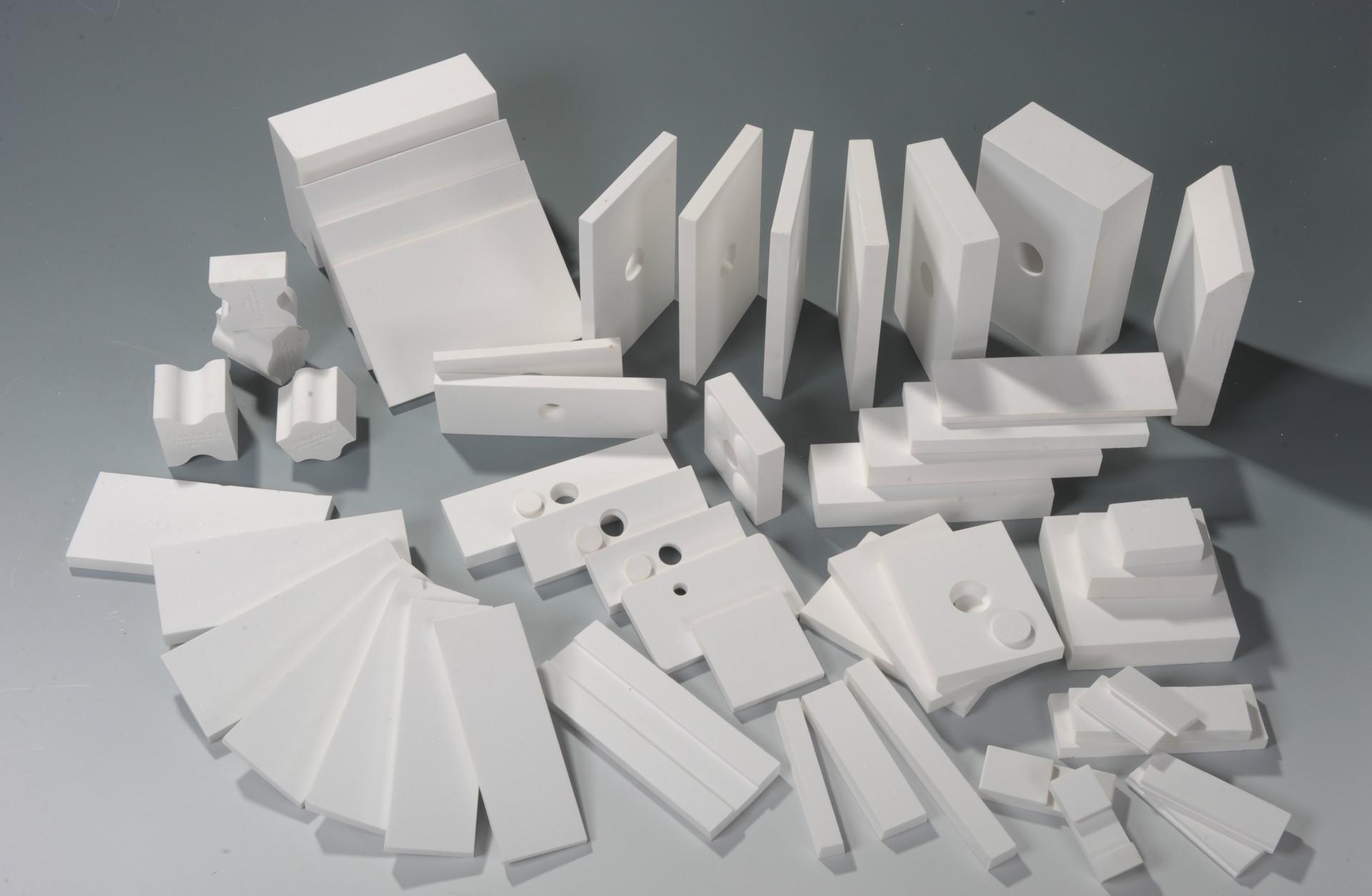
Alumina ceramics
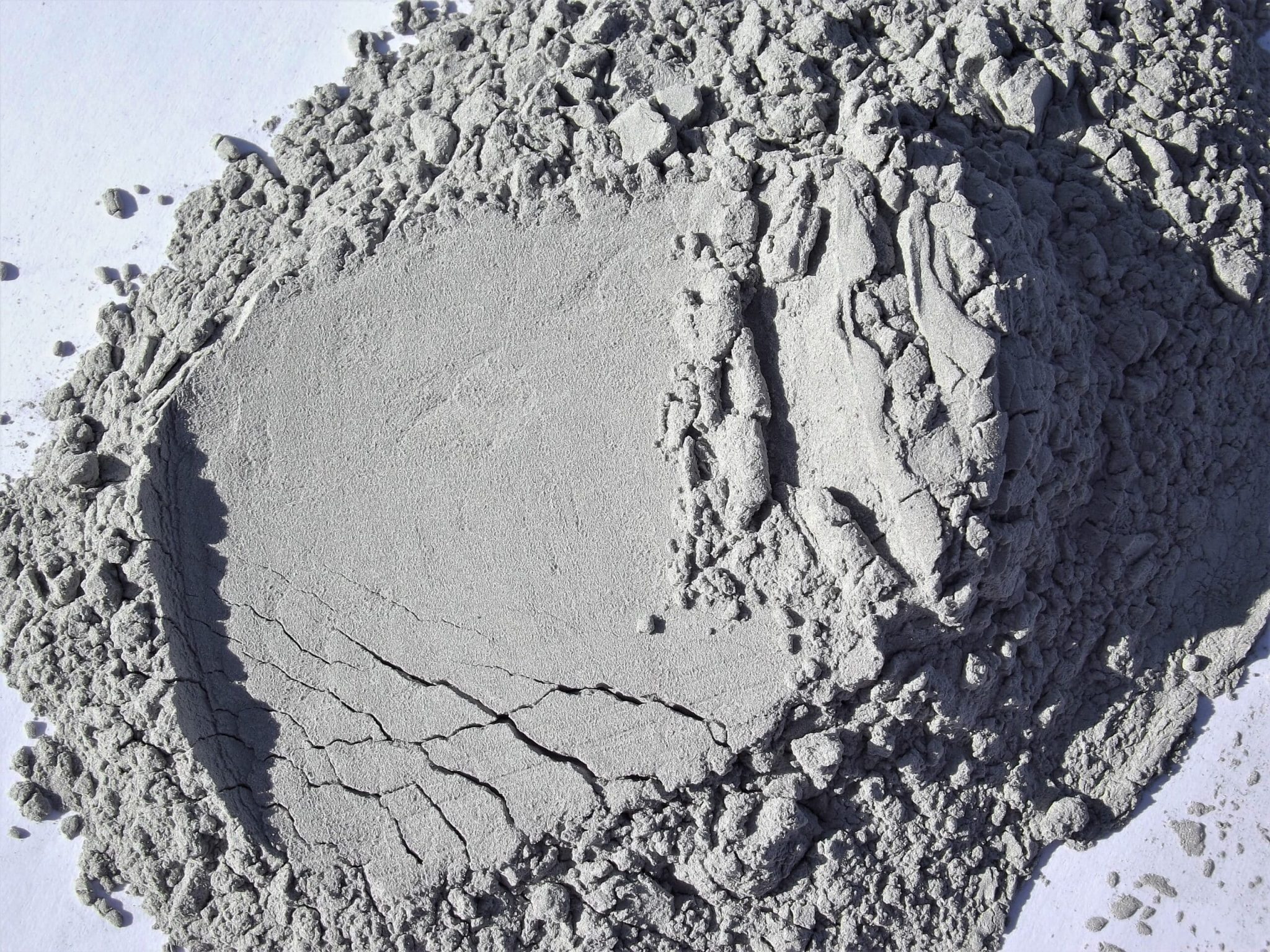
Aluminum powder
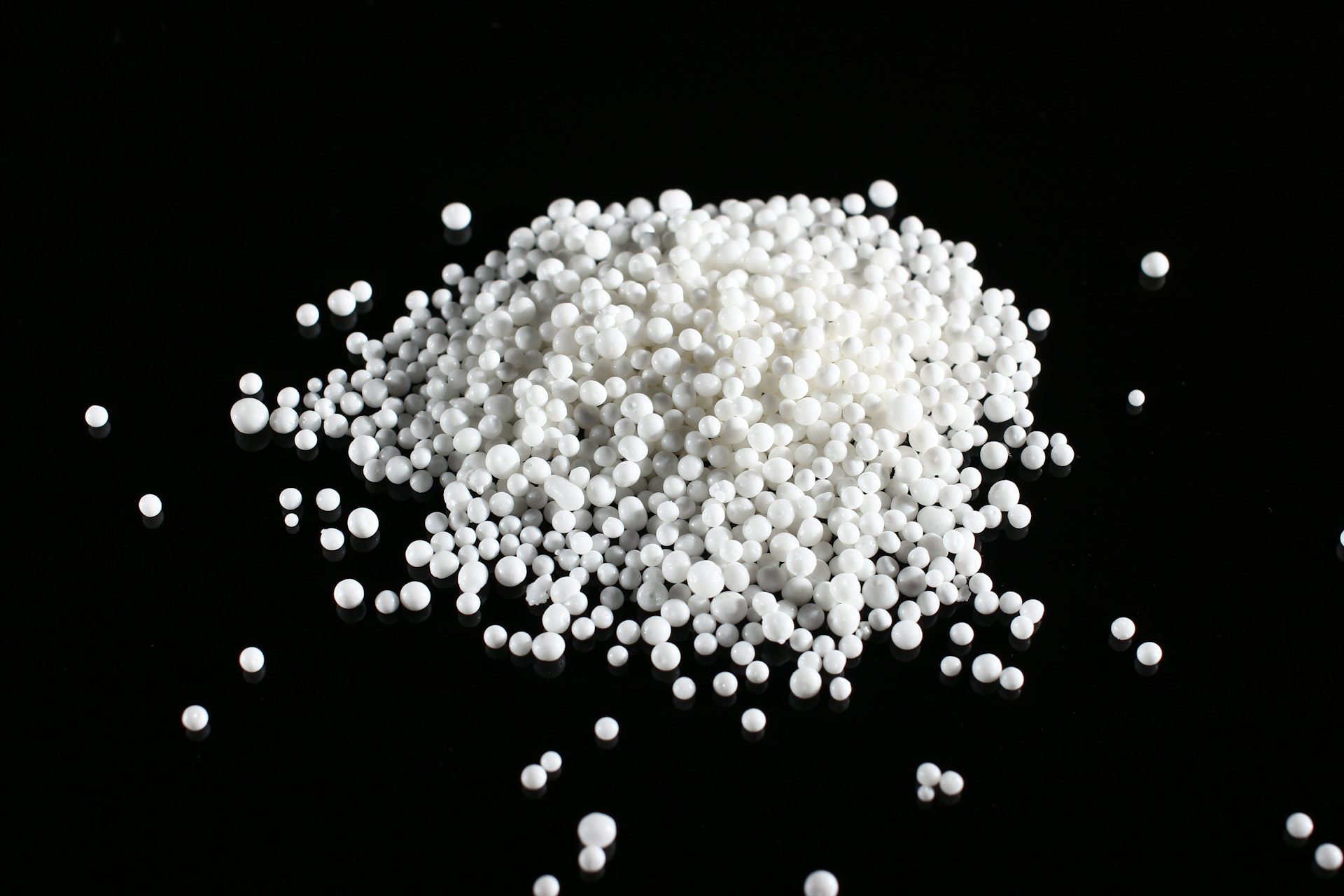
Ammonium nitrate
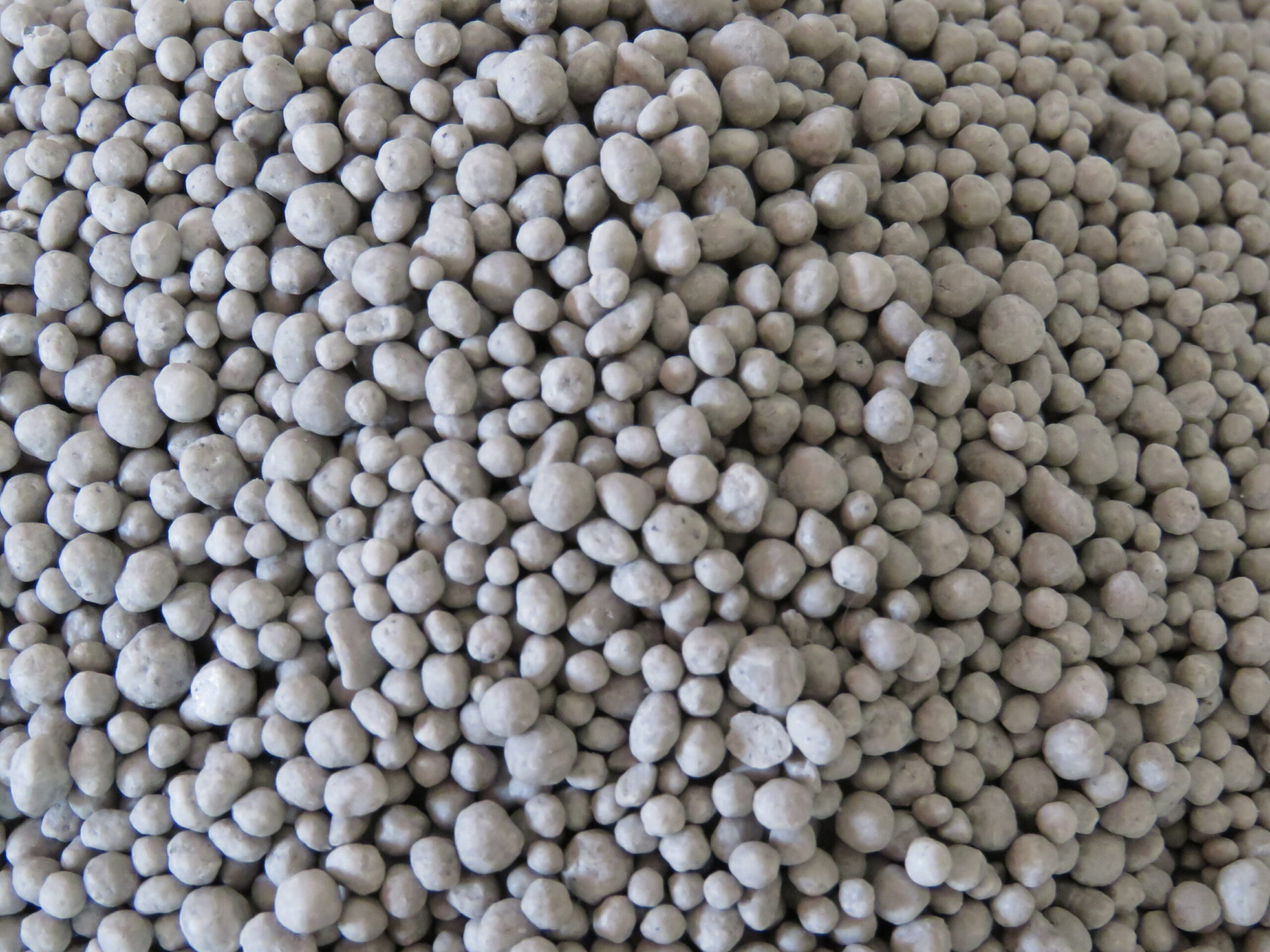
Ammonium nitrate fertilizer

Ammonium sulfate
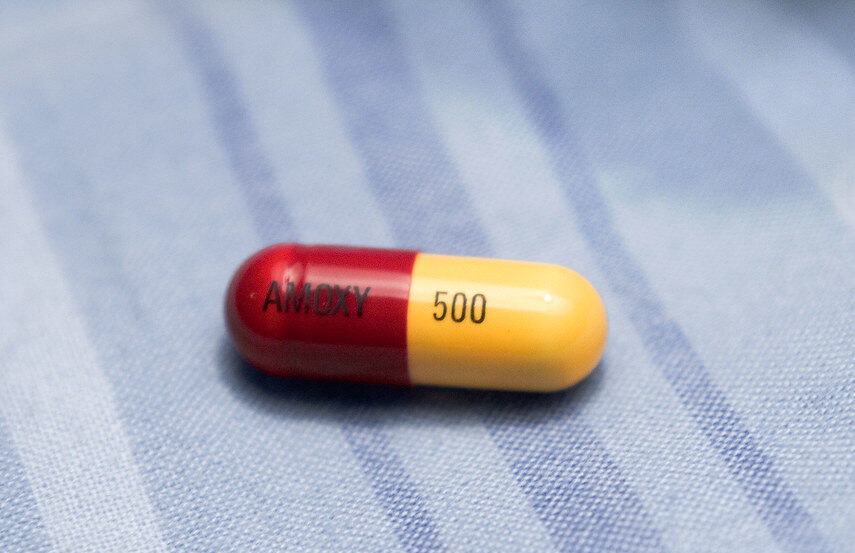
Amoxicillin capsules
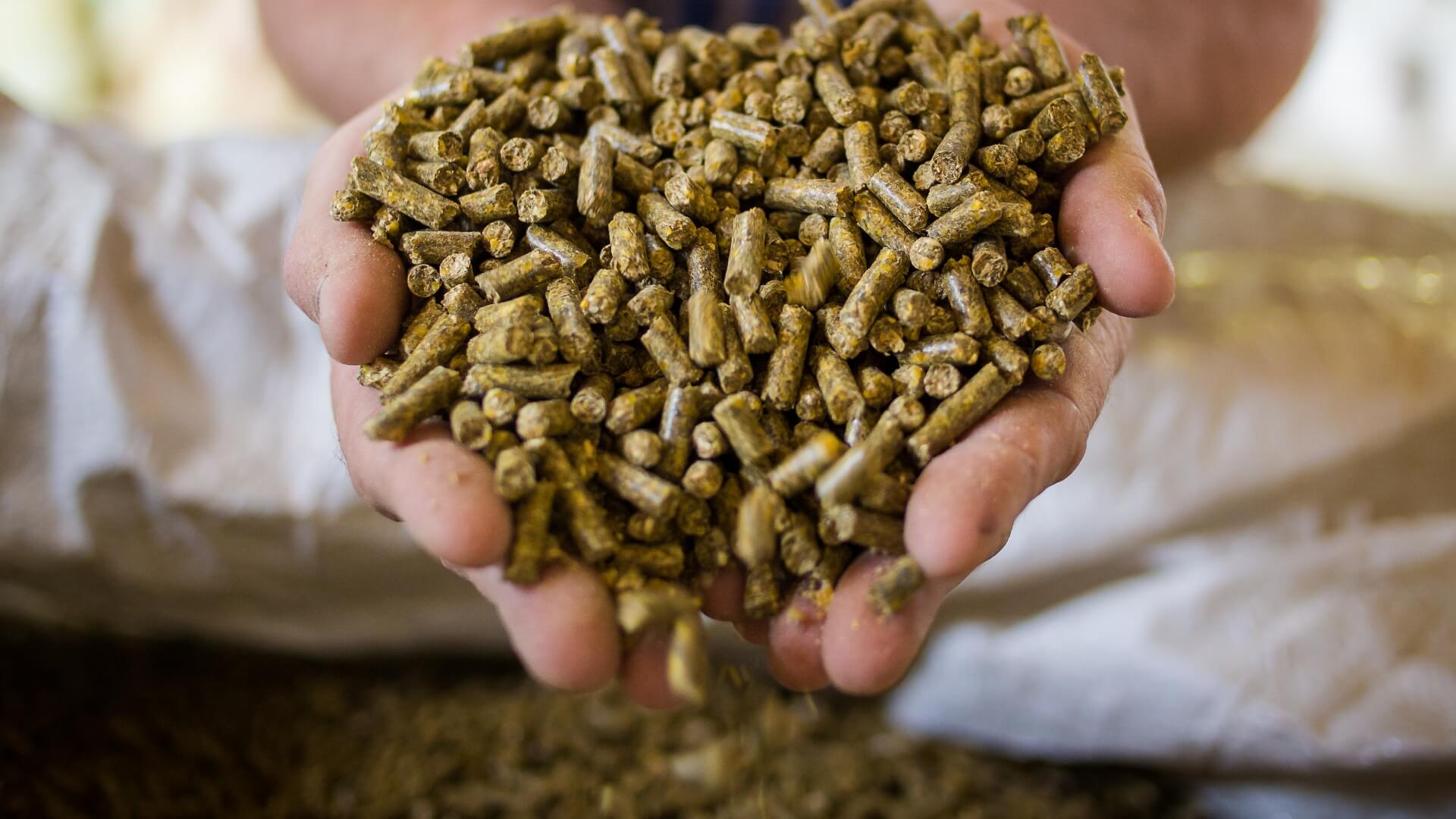
Animal feed
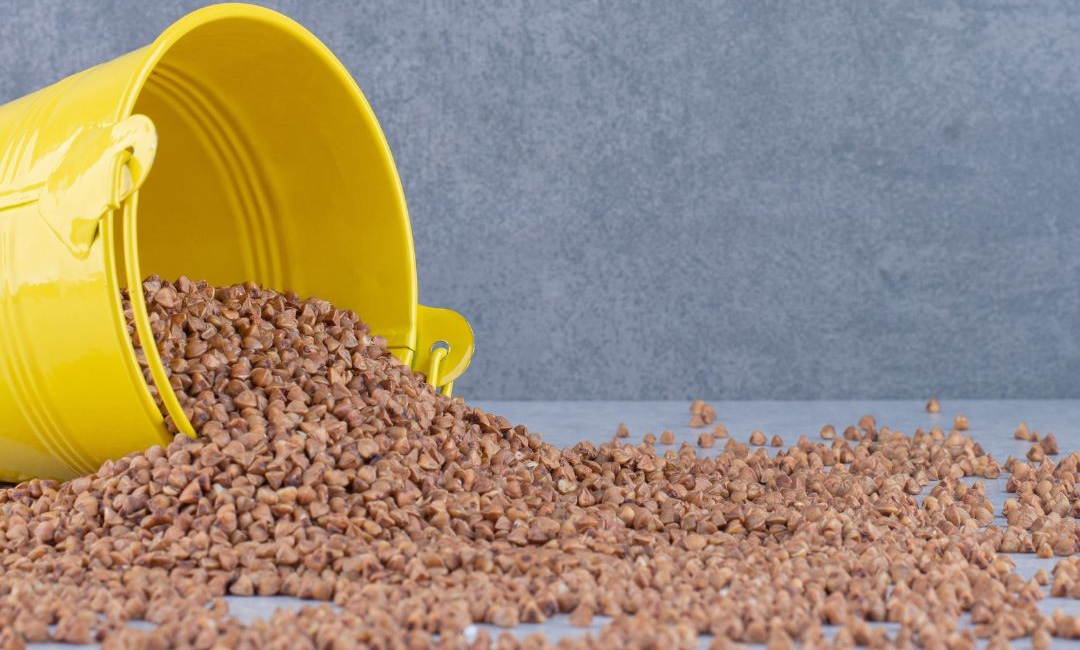
Animal feed additives
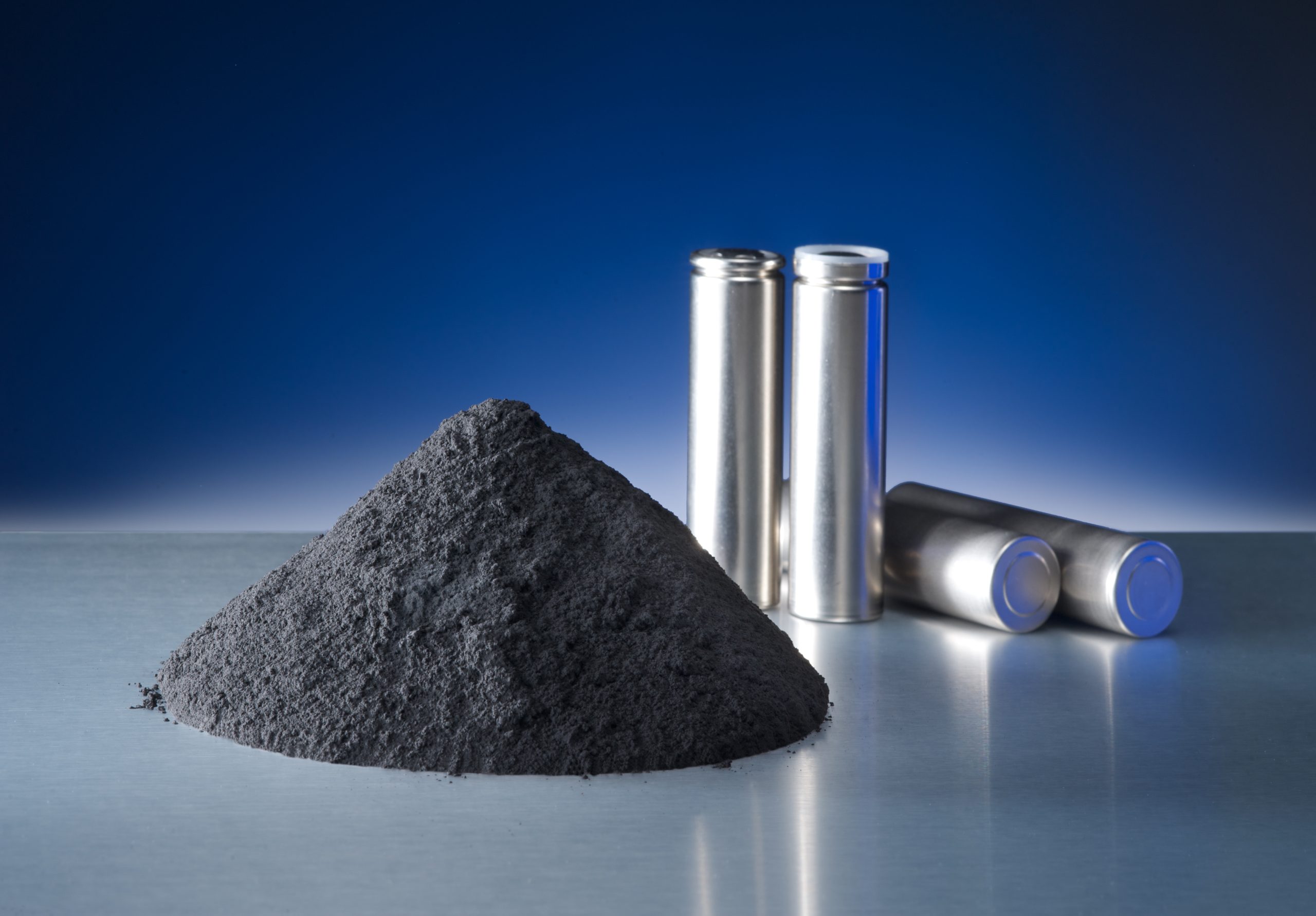
Anode and cathode materials
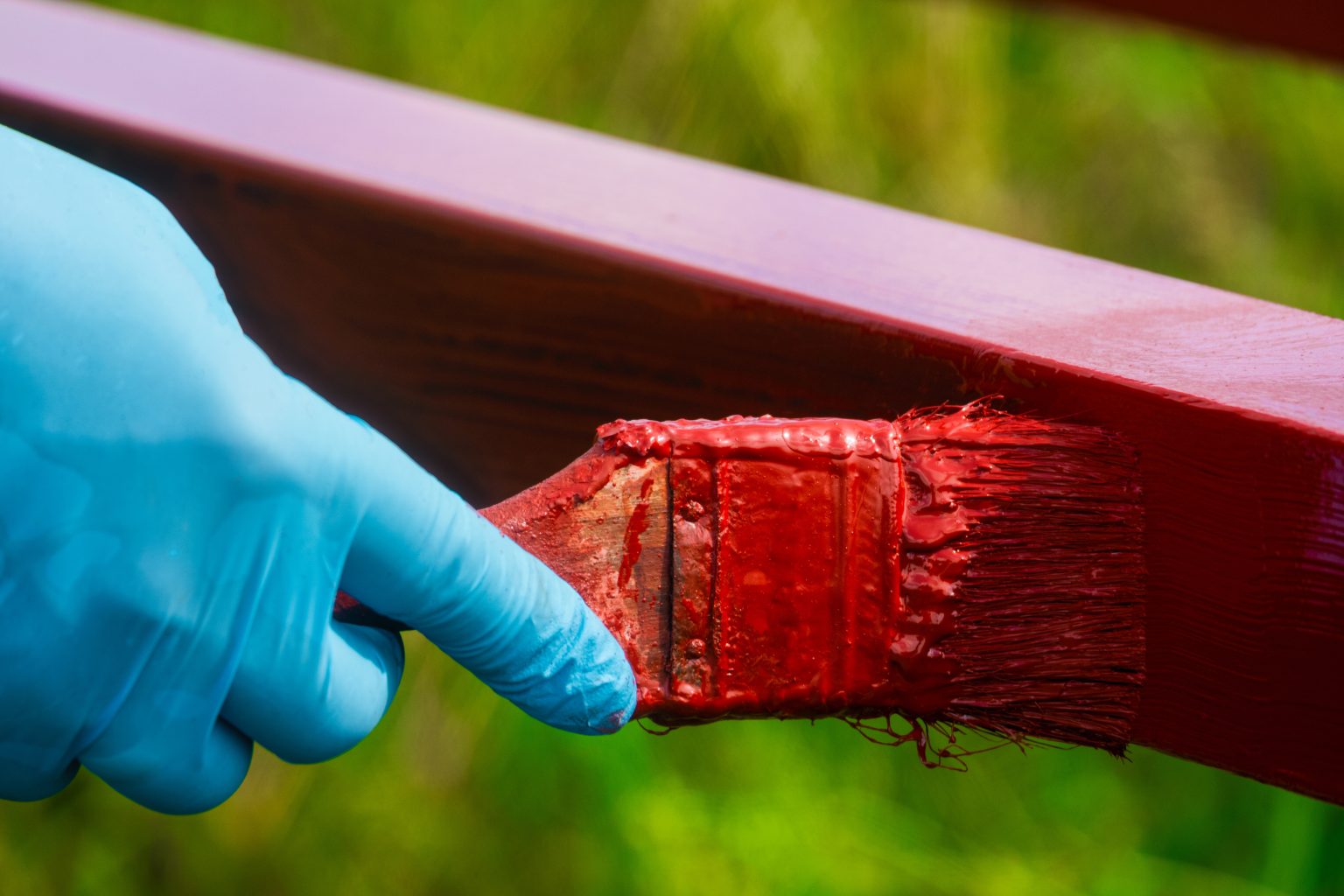
Anti-corrosion coatings
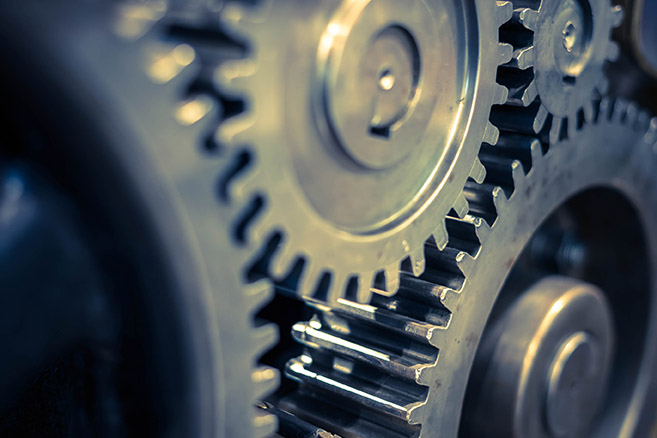
Anti-friction coatings

Antibiotic powders
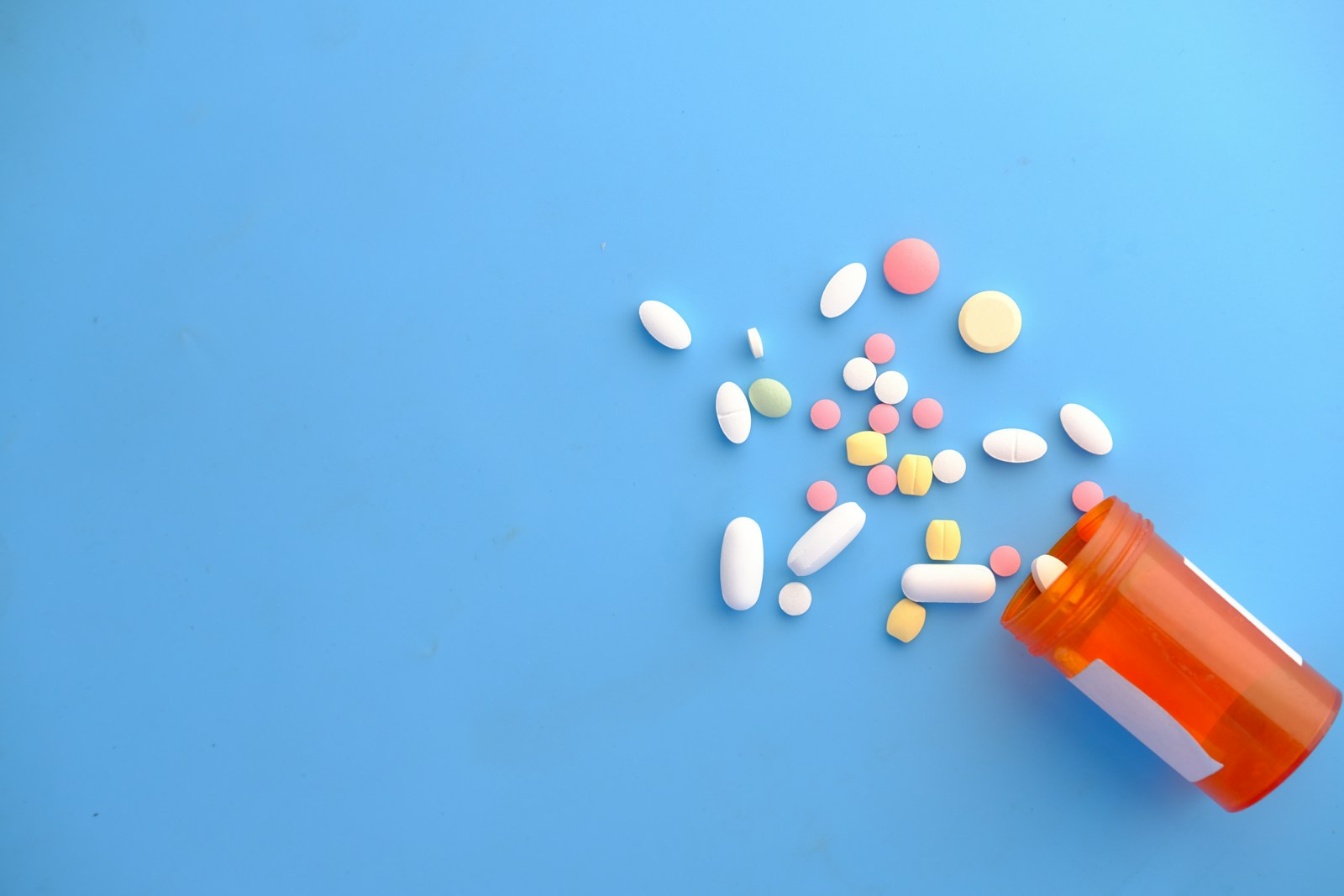
Antibiotic tablets
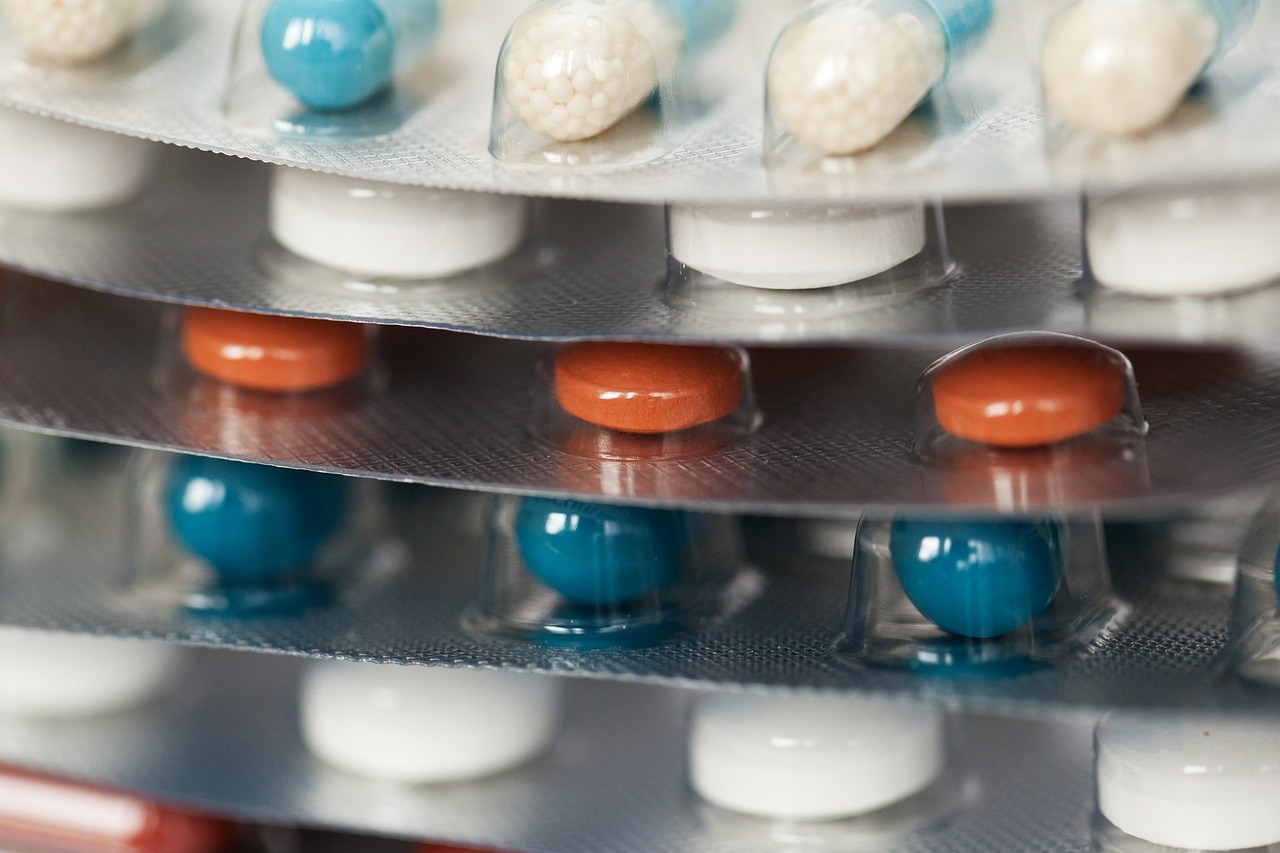
Antibiotics
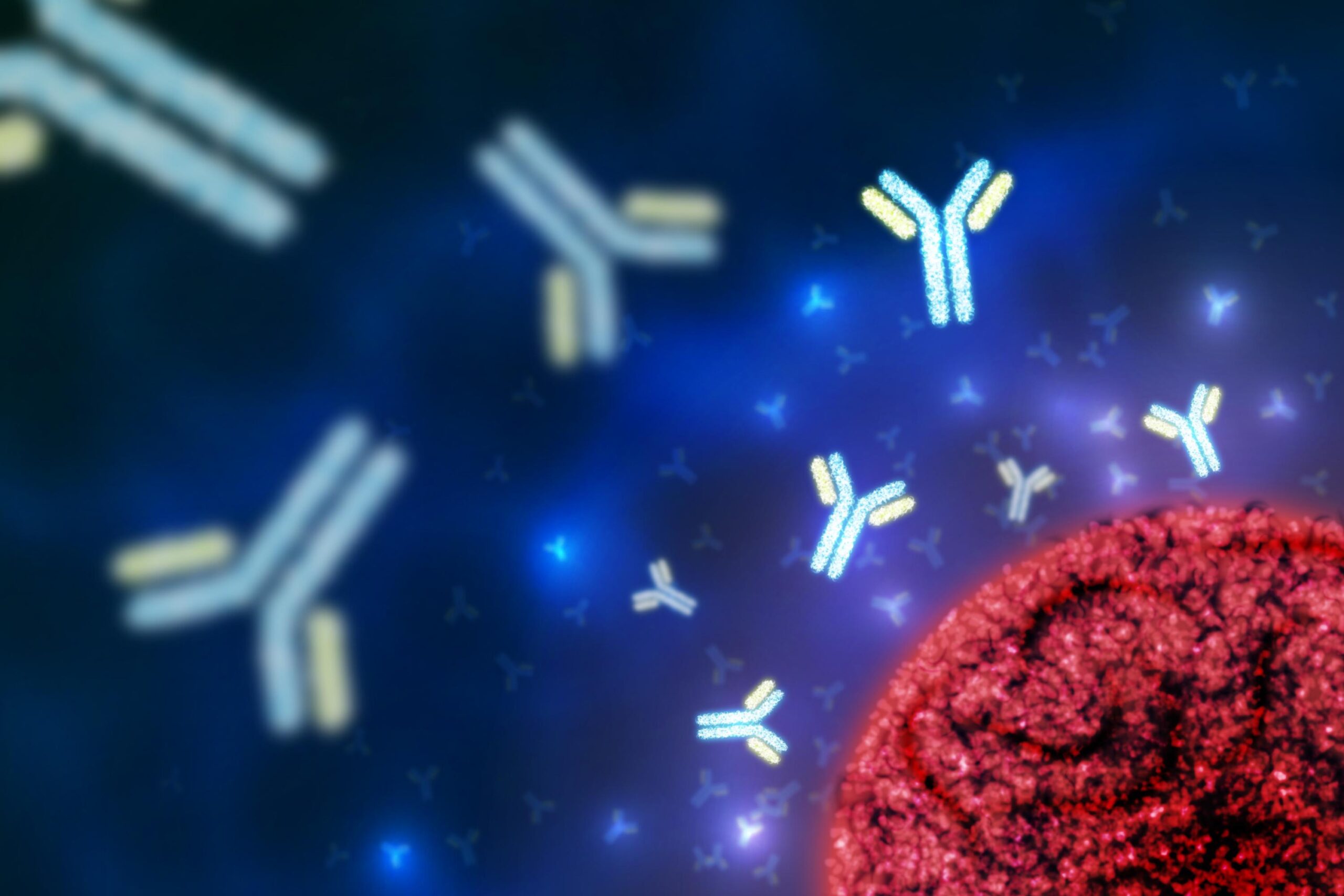
Antibodies
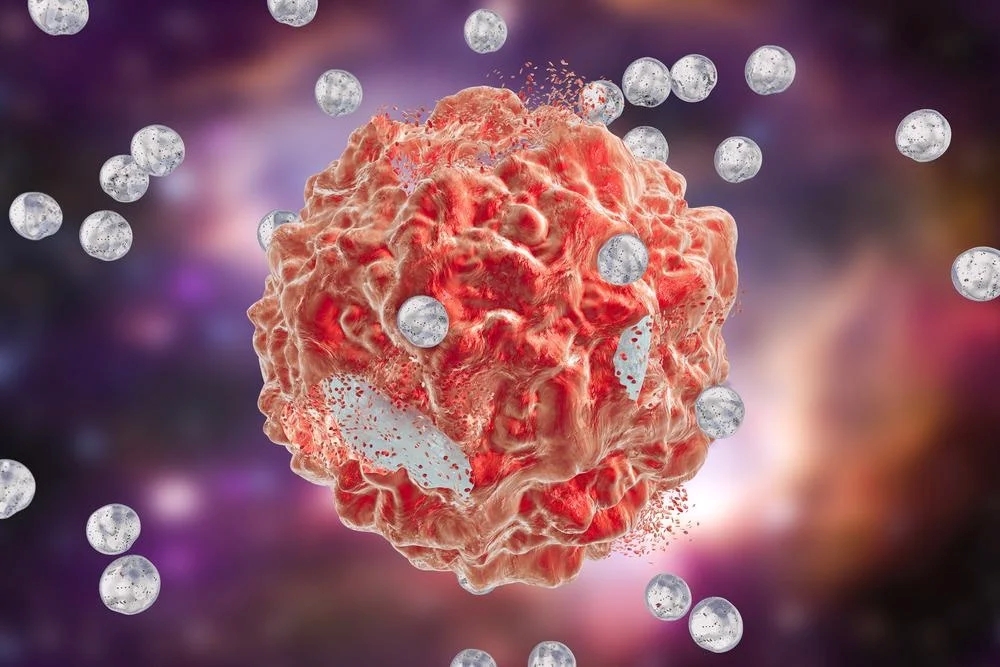
Anticancer drugs
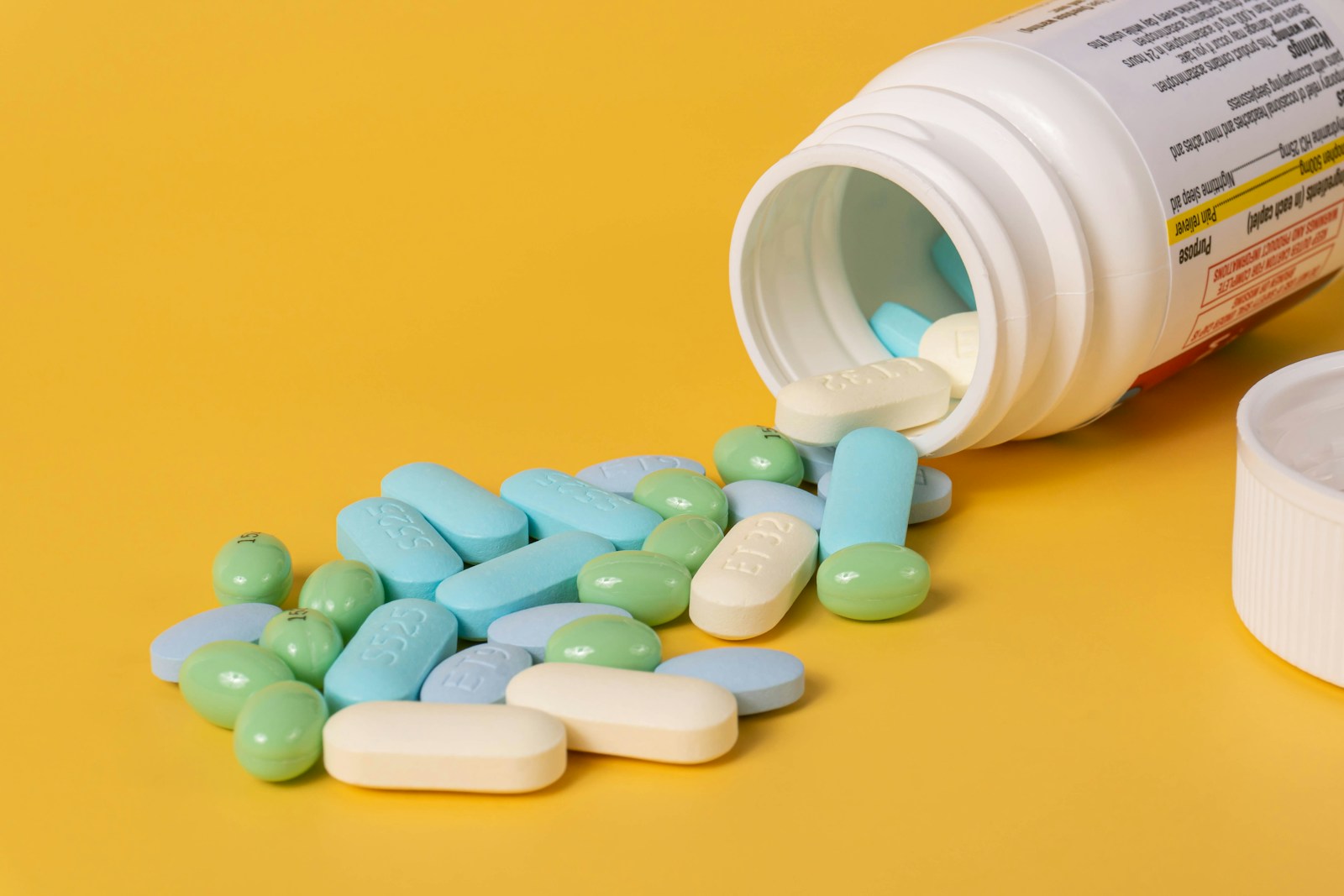
Antihistamine tablets
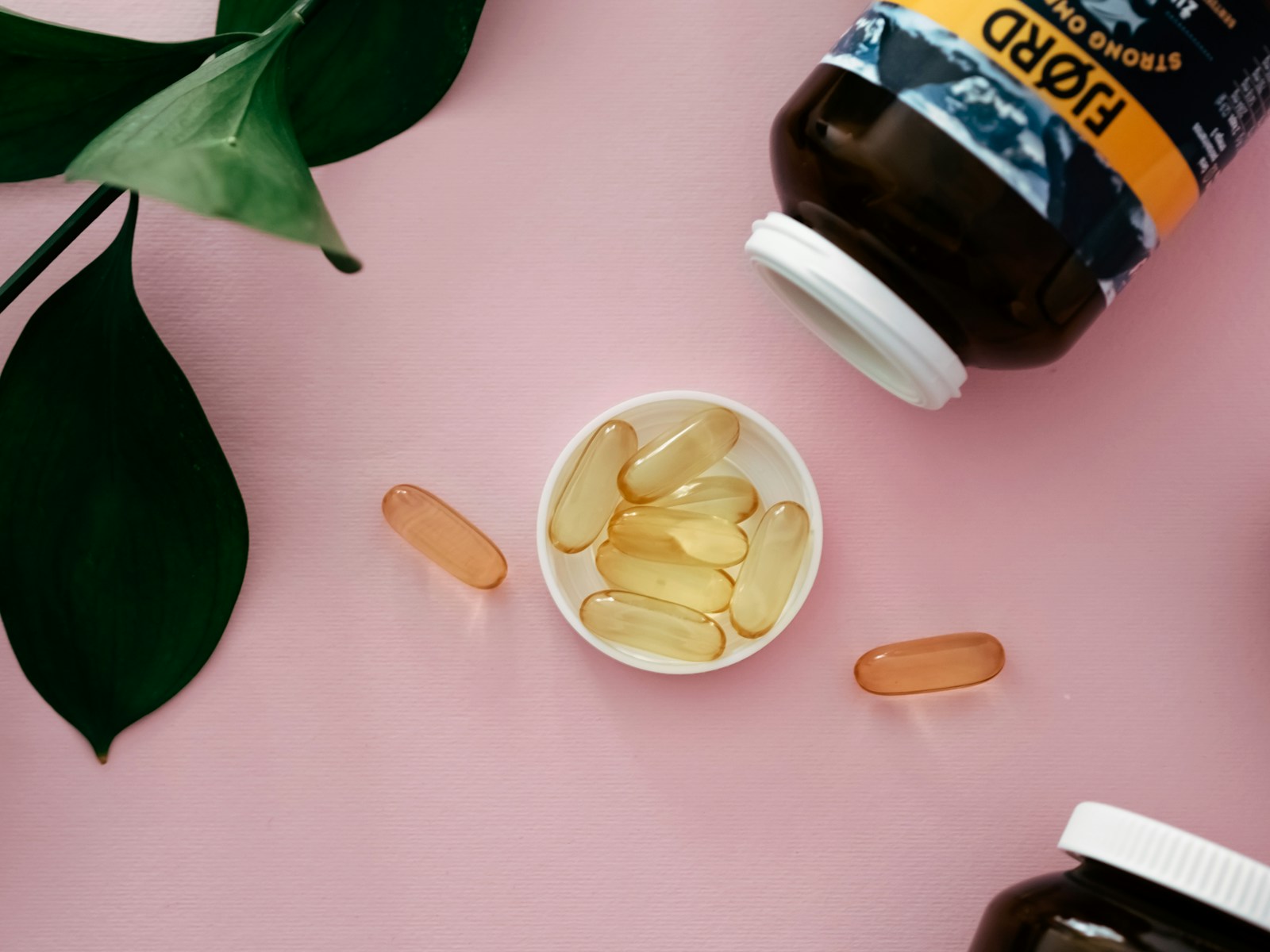
Antioxidant supplements
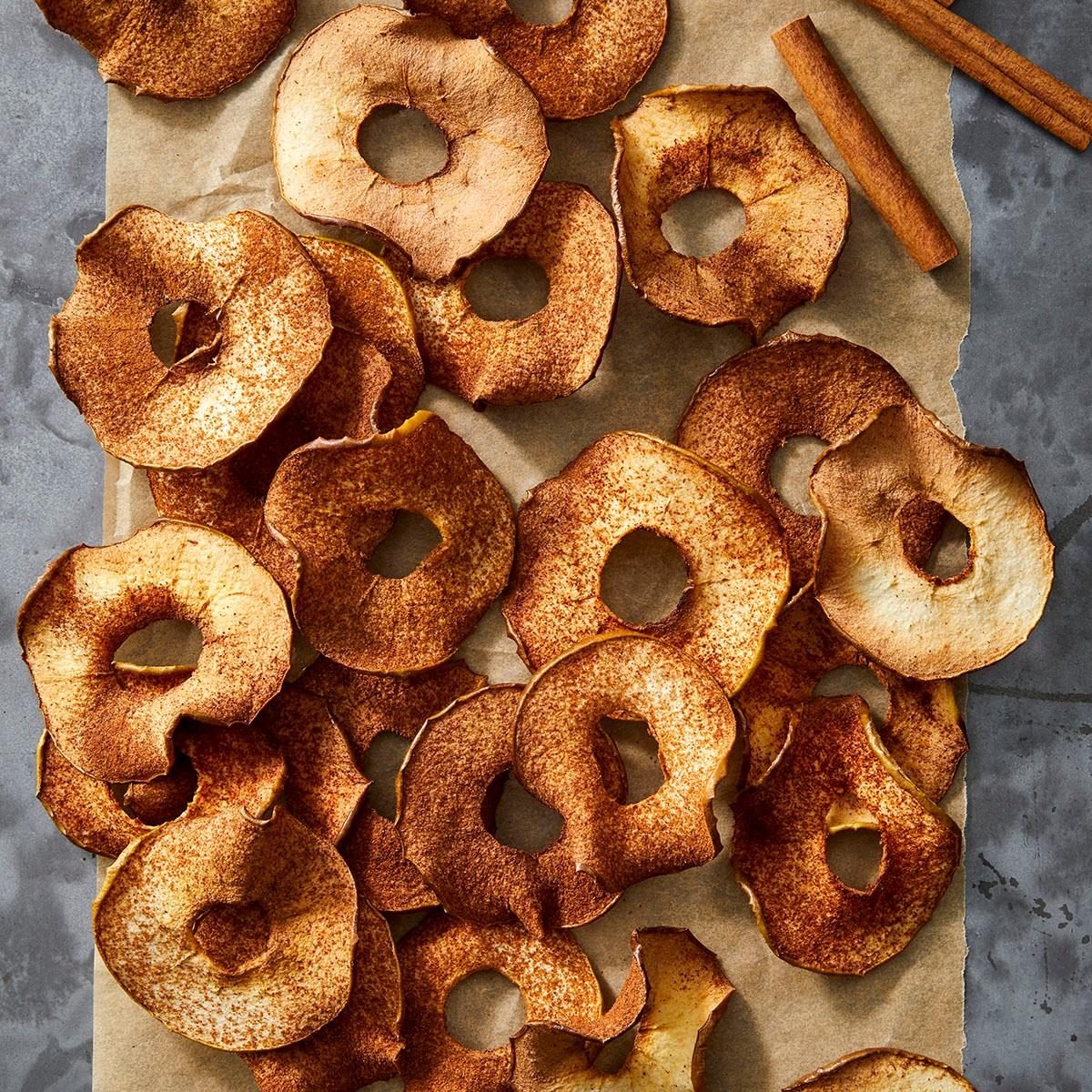
Apple chips
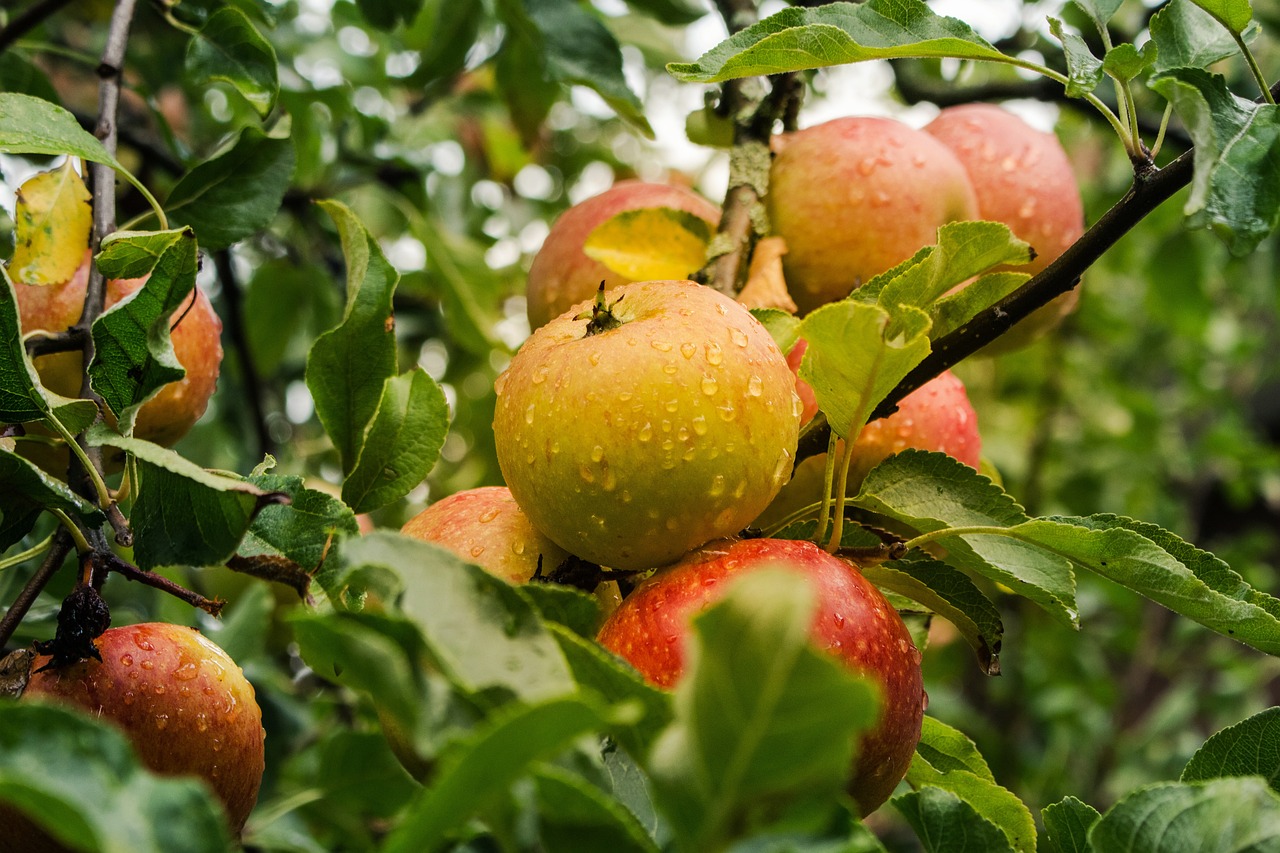
Apples
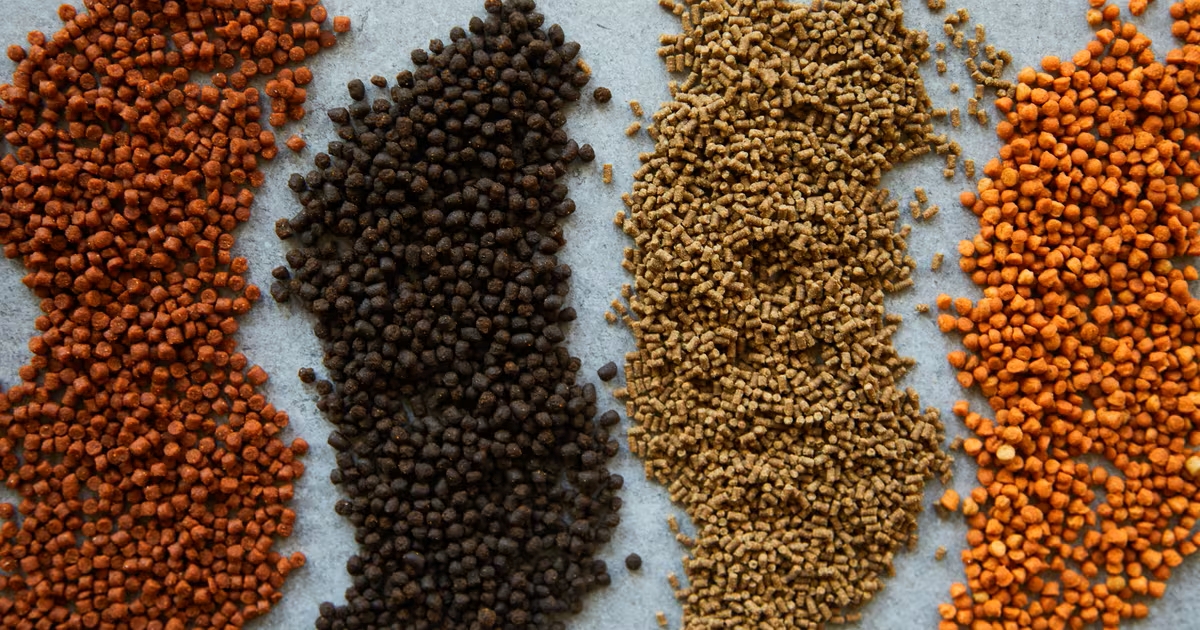
Aquafeed
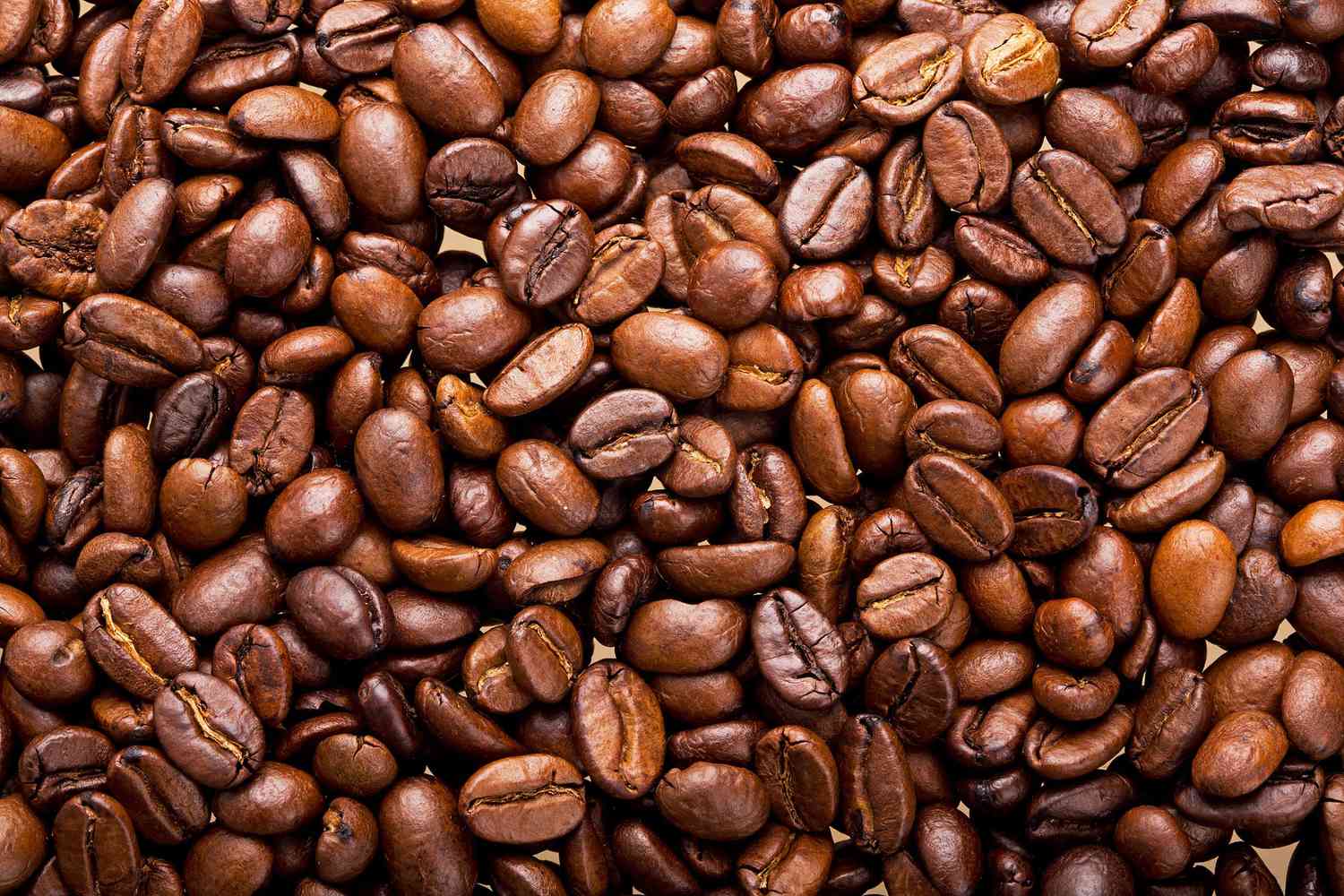
Arabica coffee beans
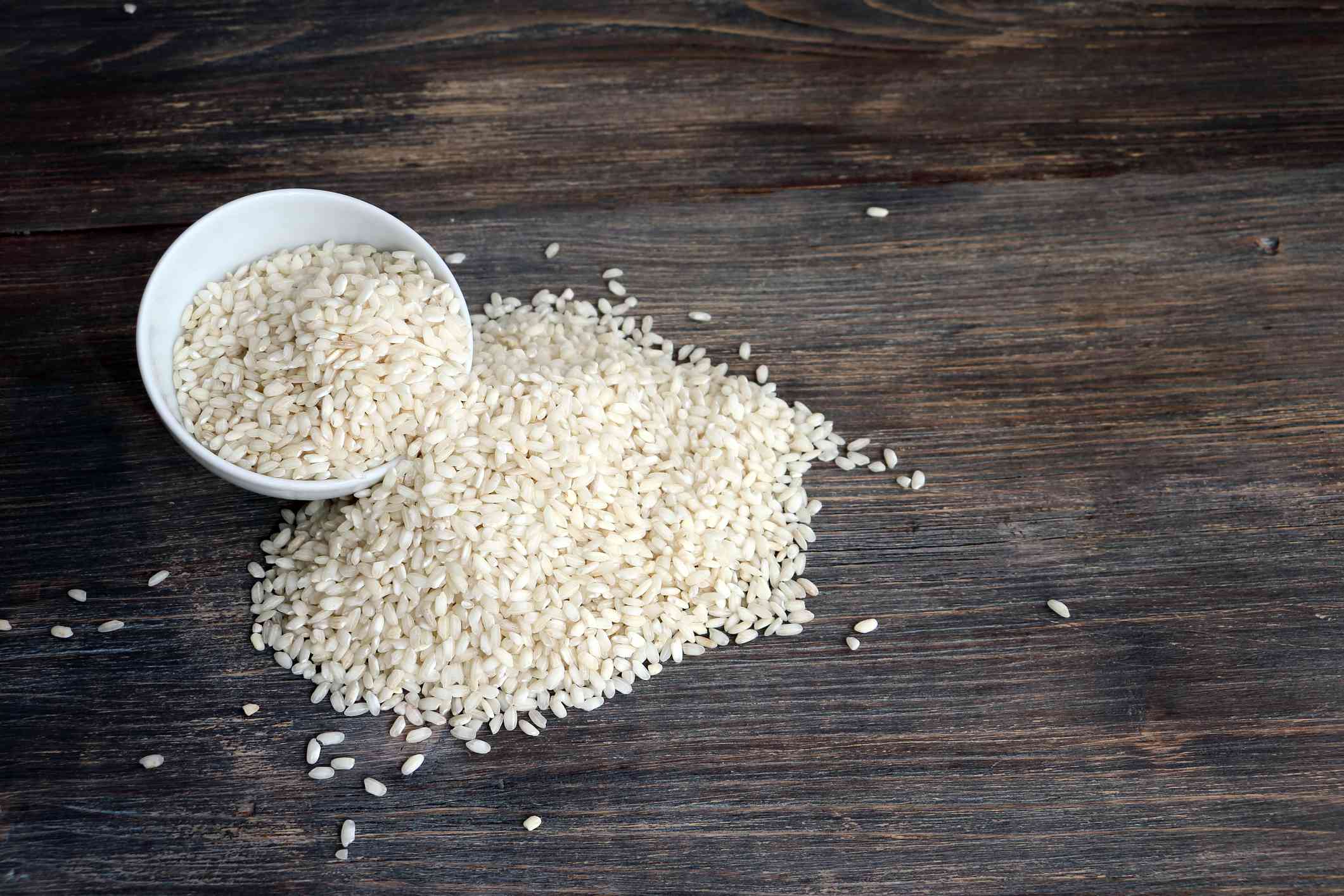
Arborio rice
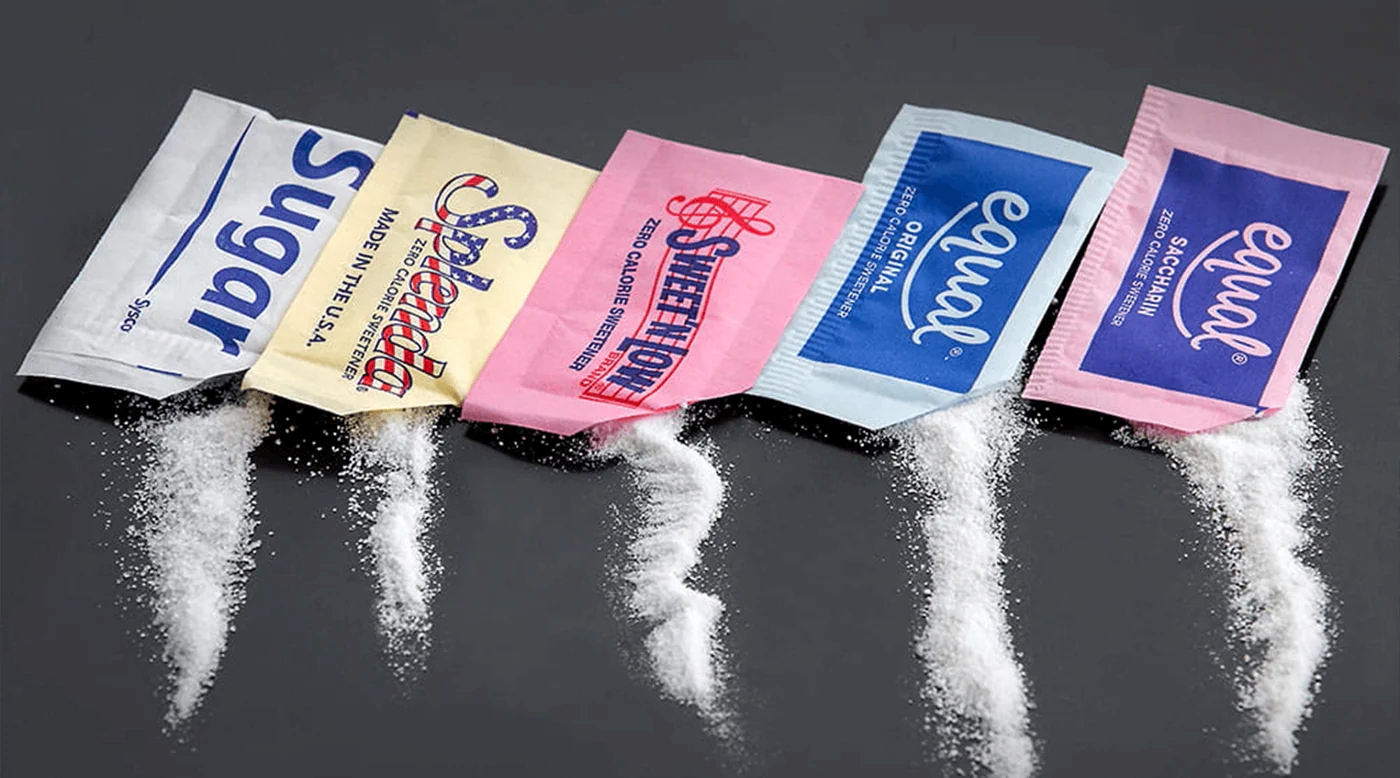
Artificial sweeteners
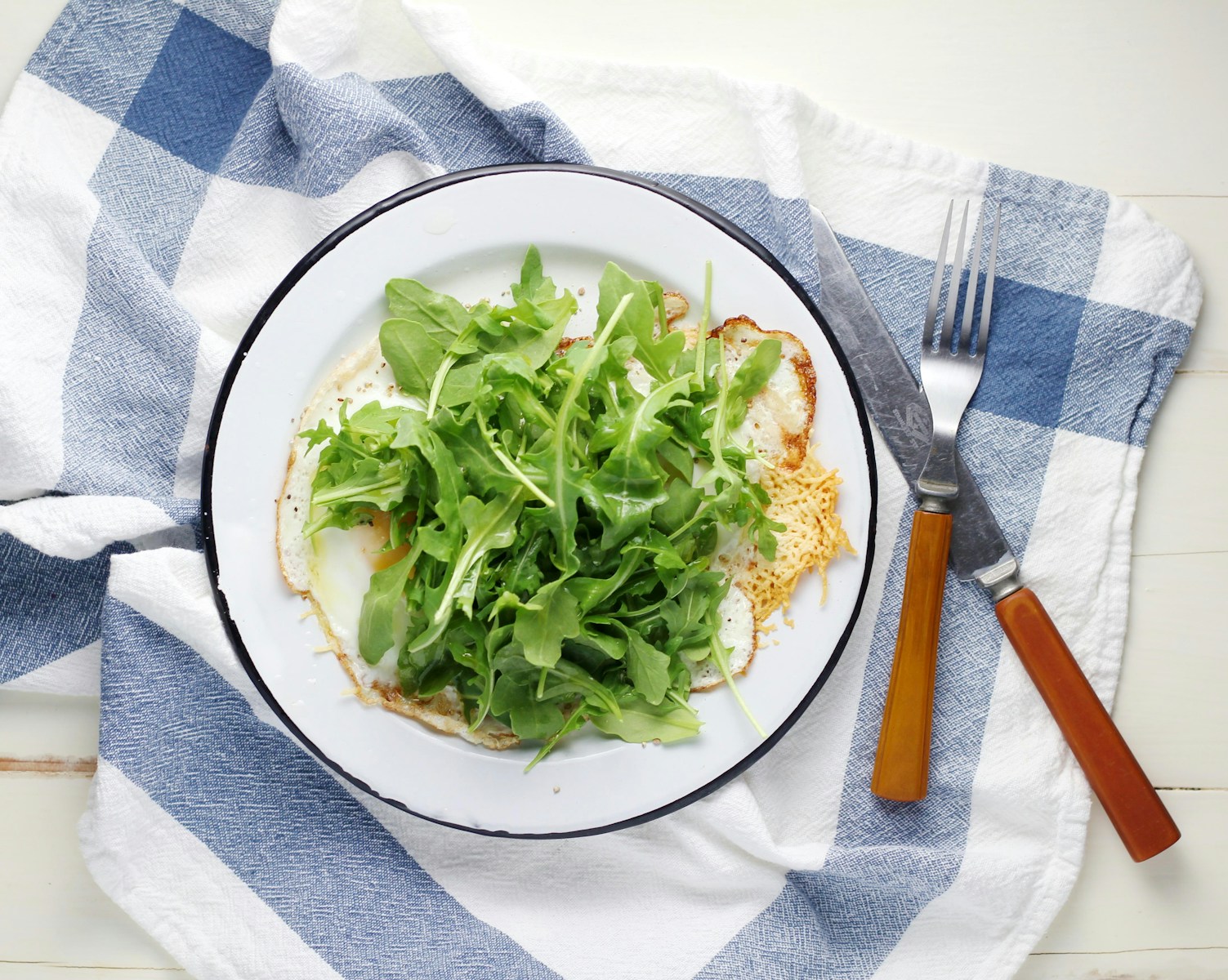
Arugula
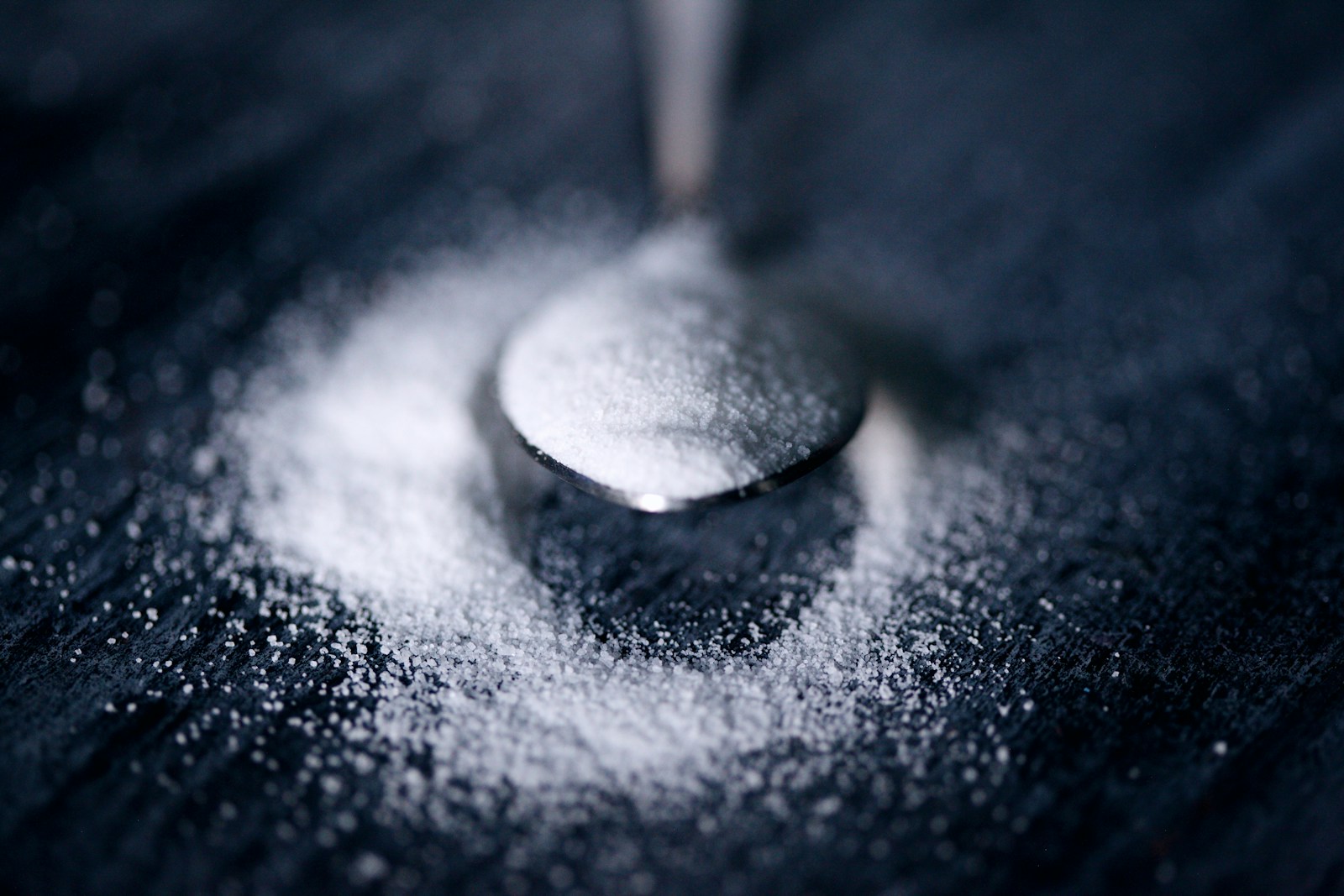
Aspartame
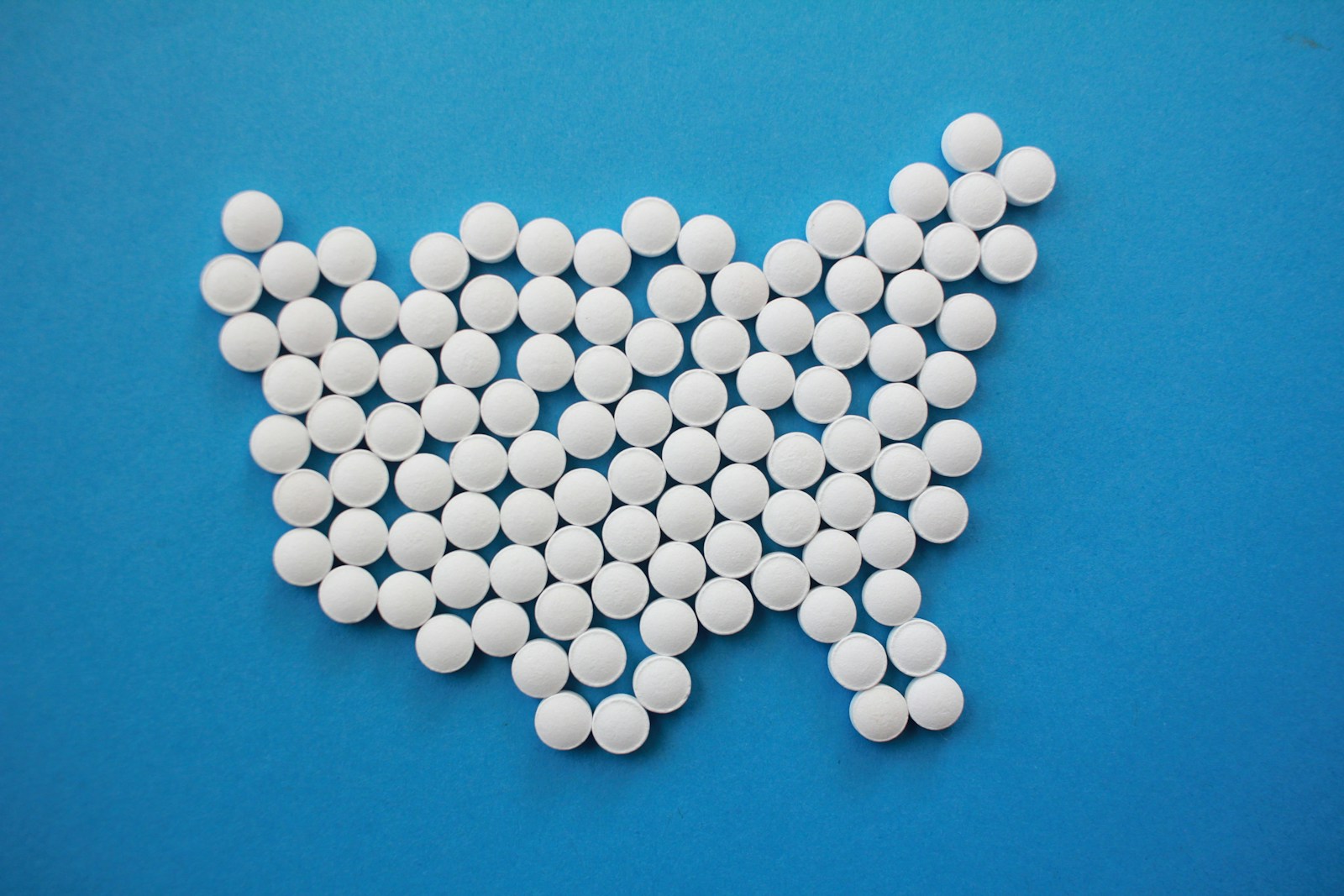
Aspirin
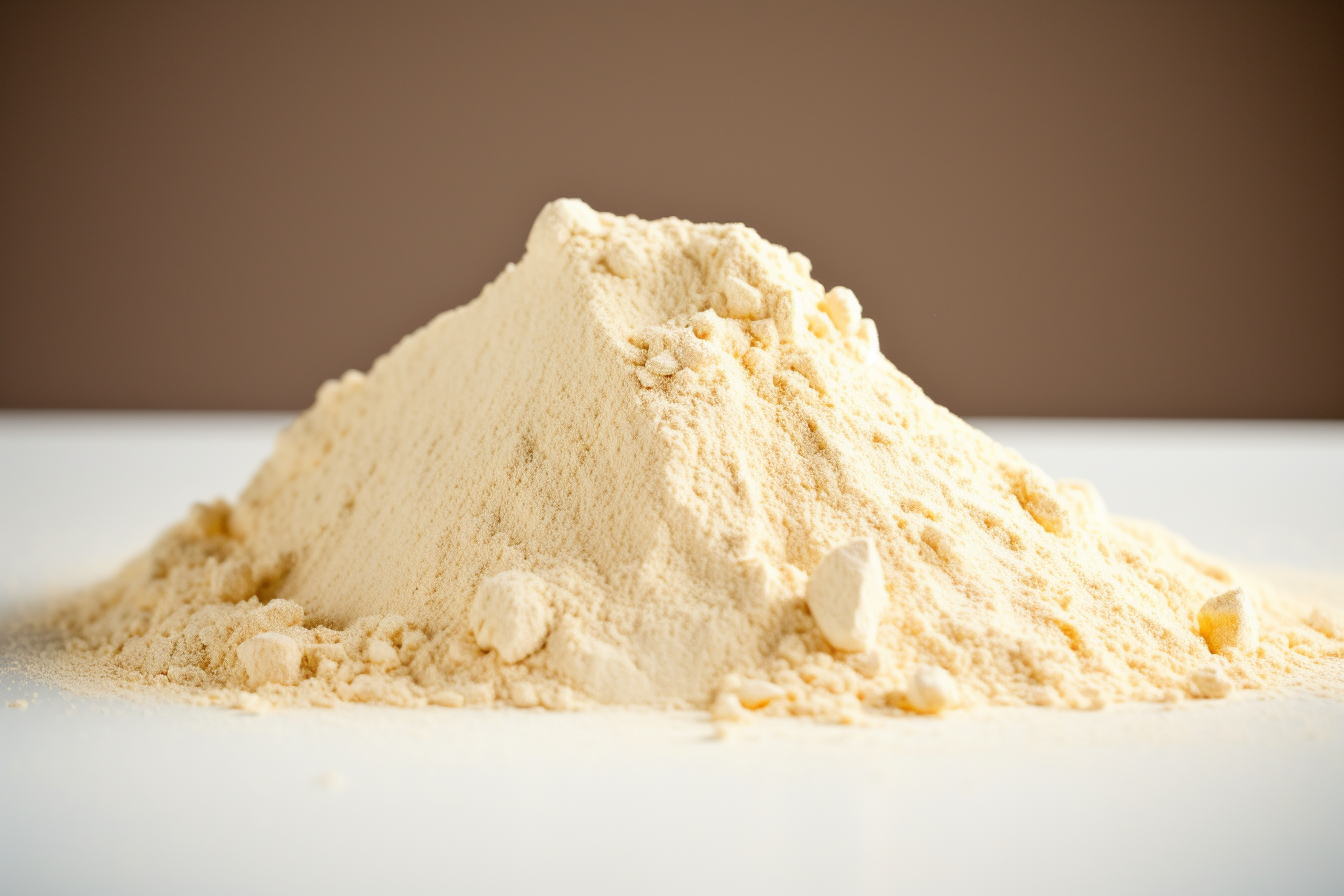
Automotive catalysts
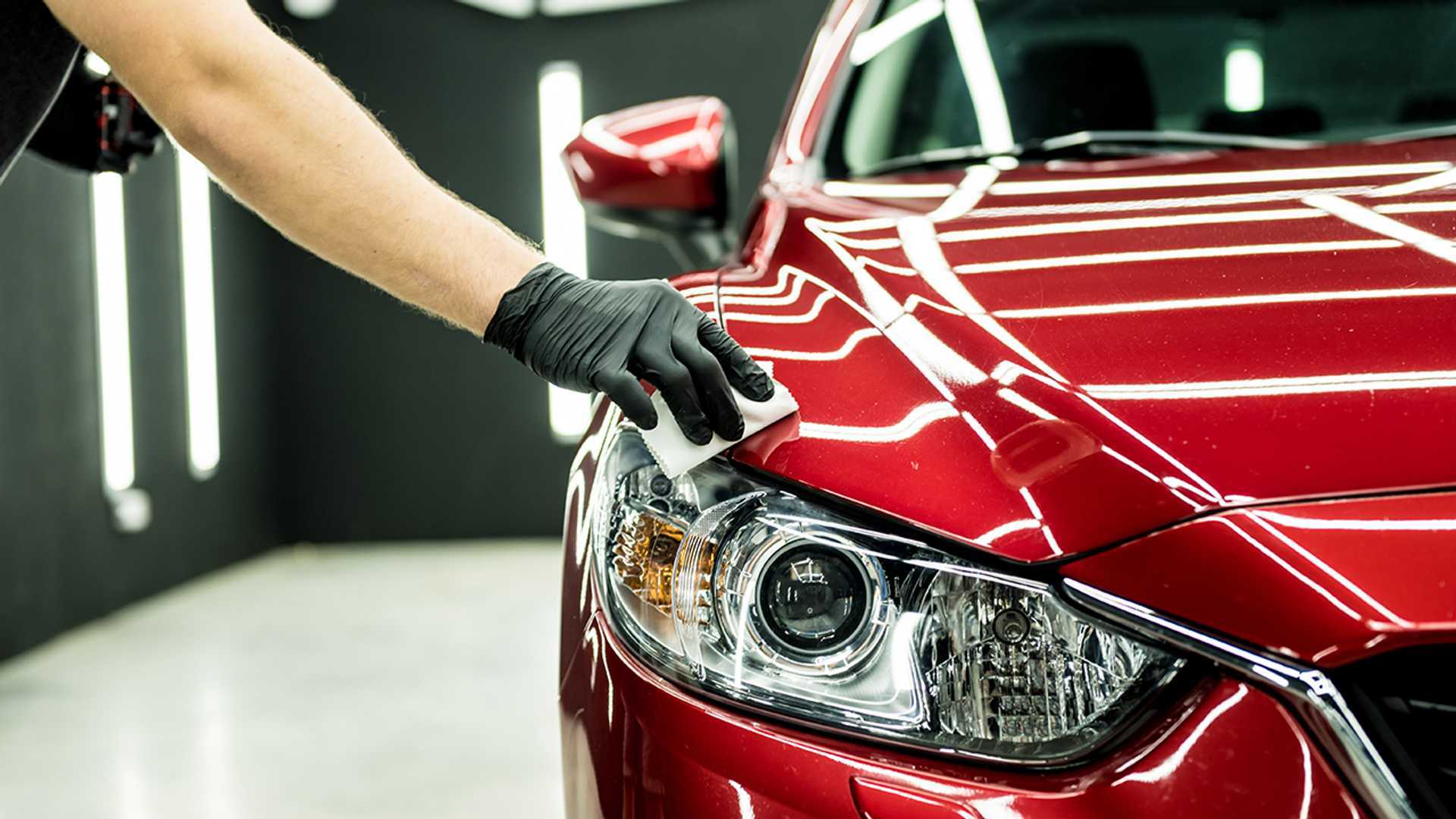
Automotive coatings
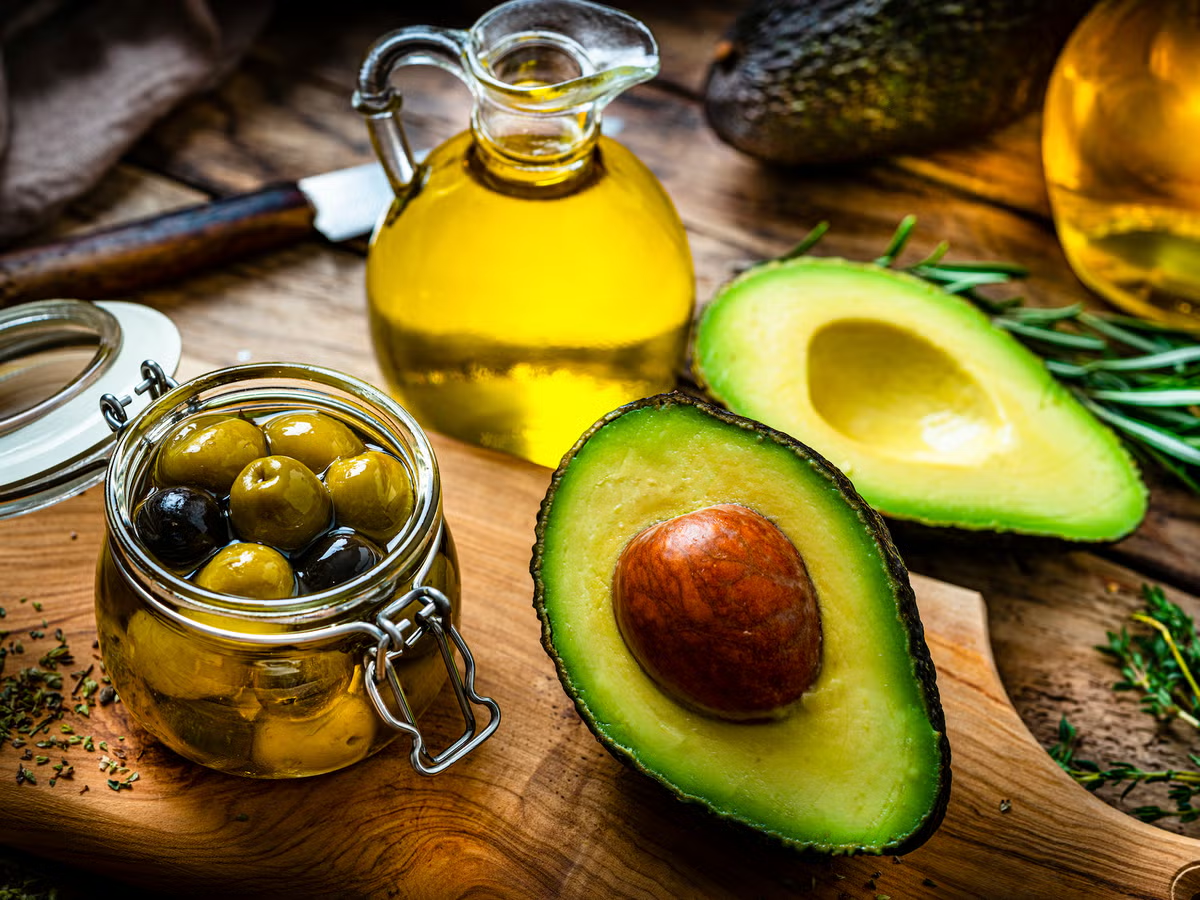
Avocado oil
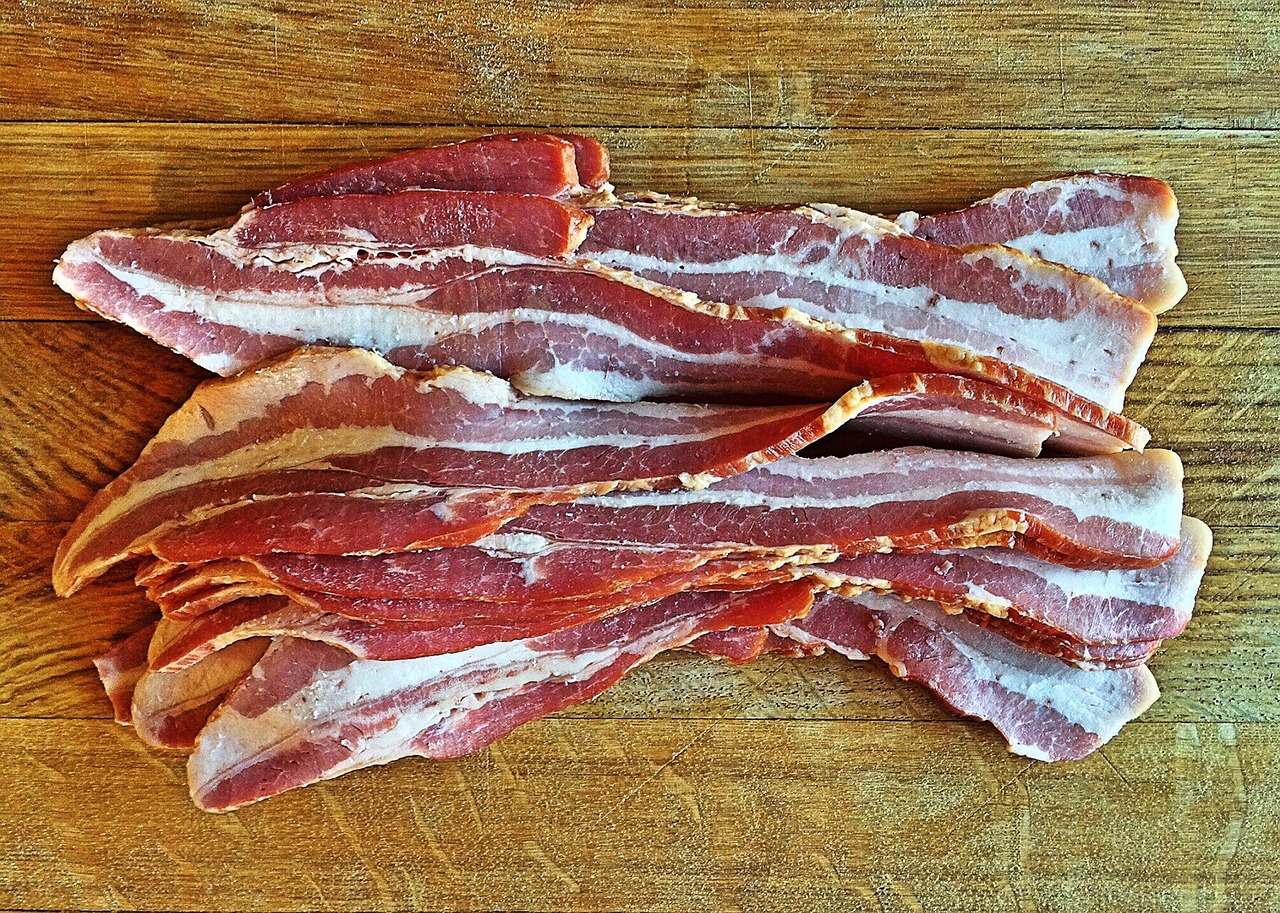
Bacon
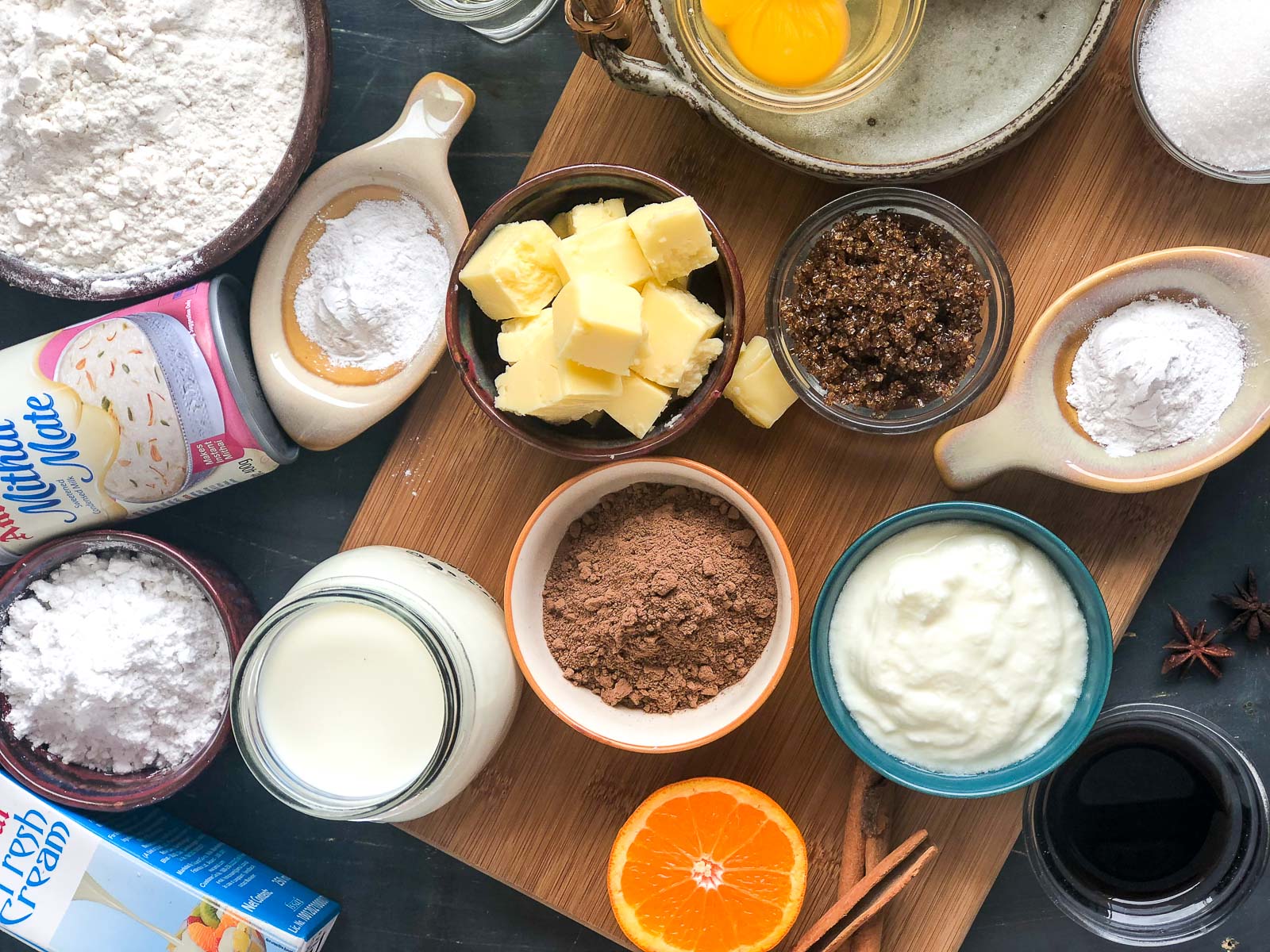
Bakery ingredients
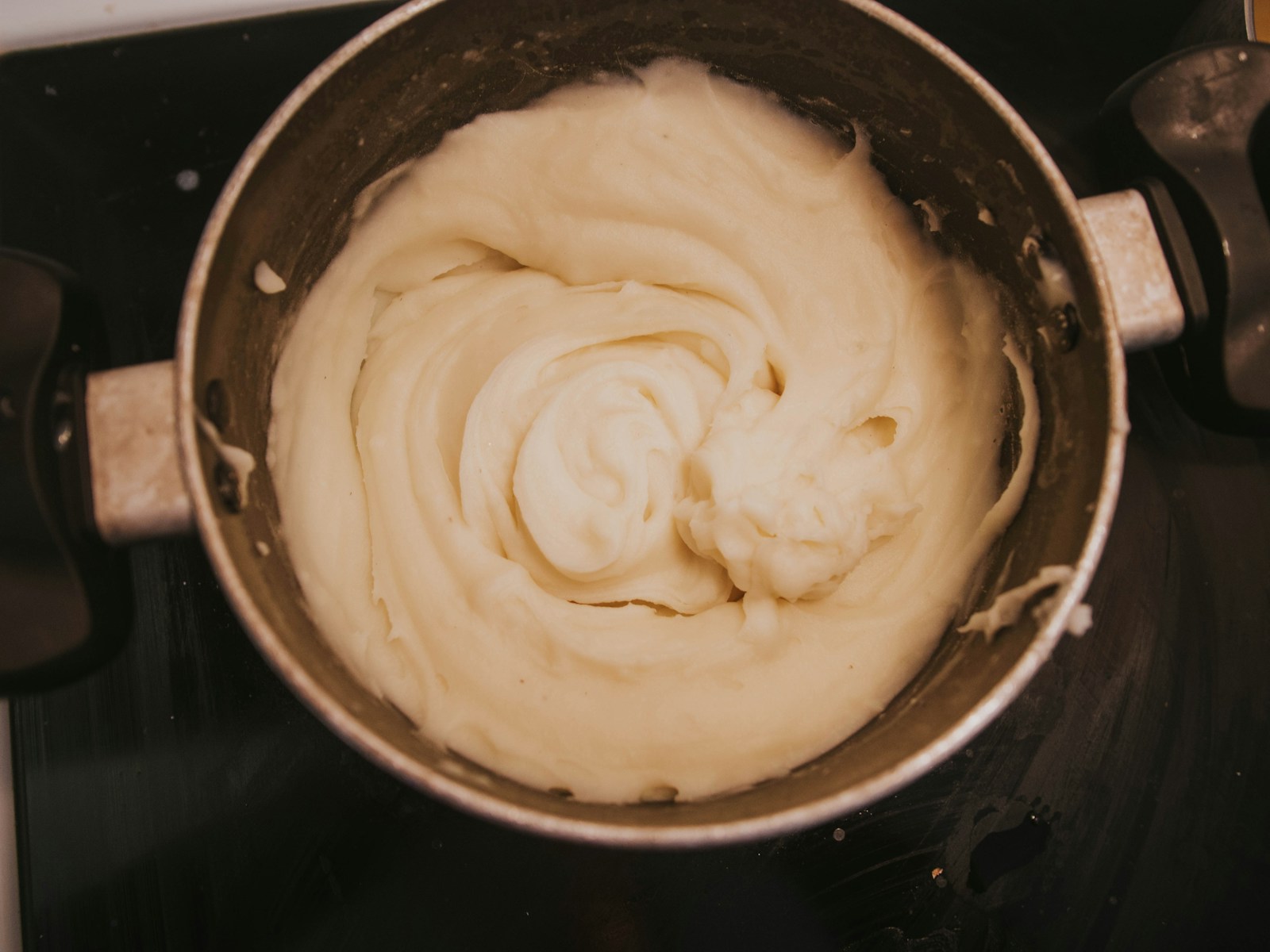
Bakery mixes
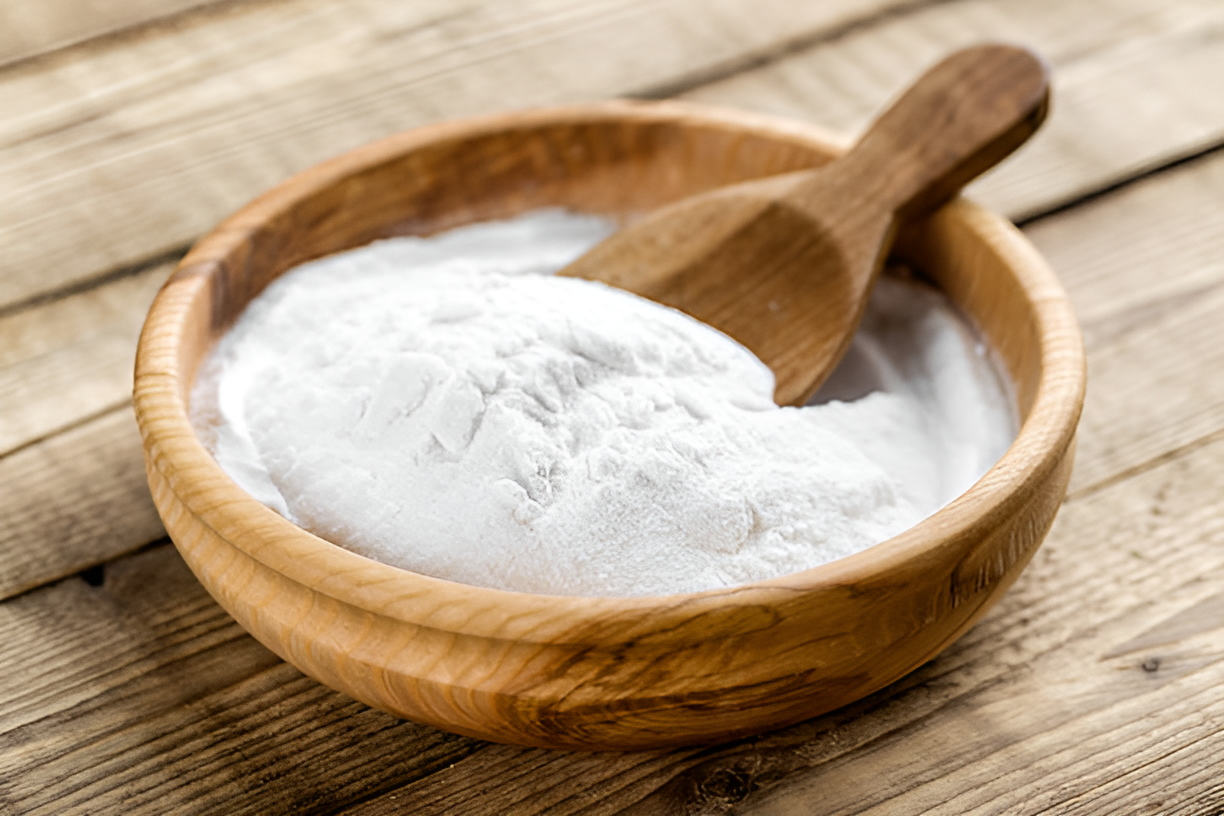
Baking soda
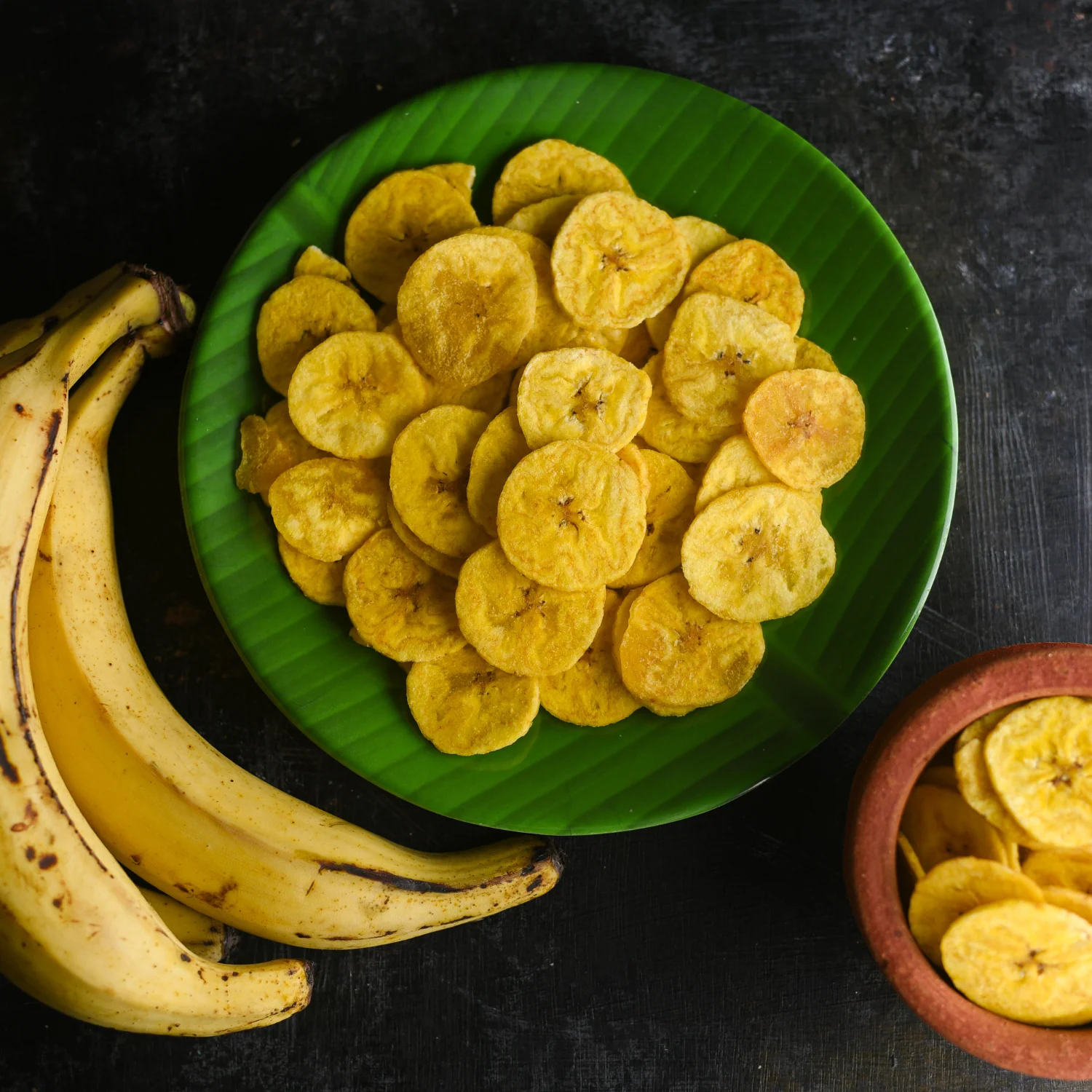
Banana chips
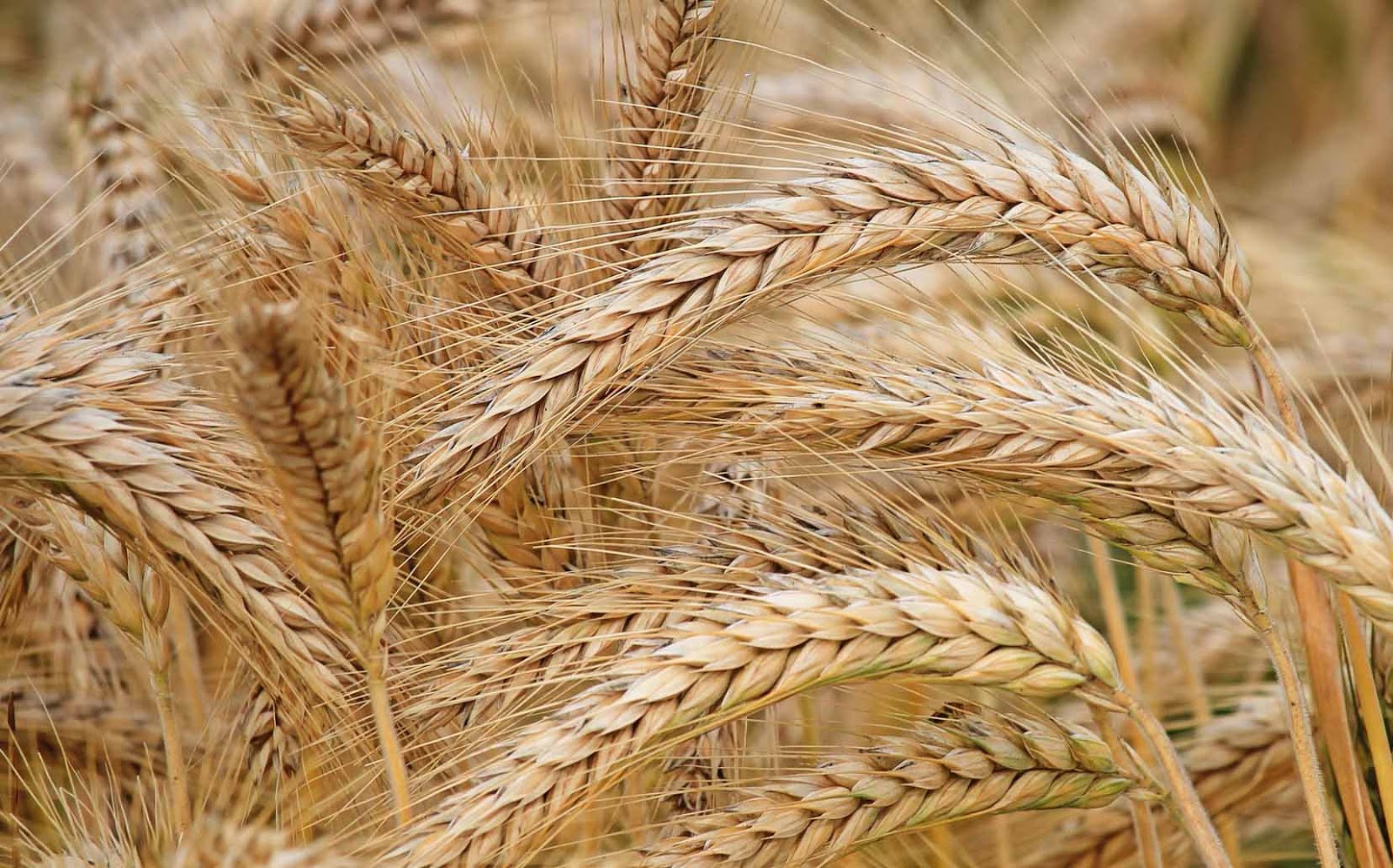
Barley

Barley flakes
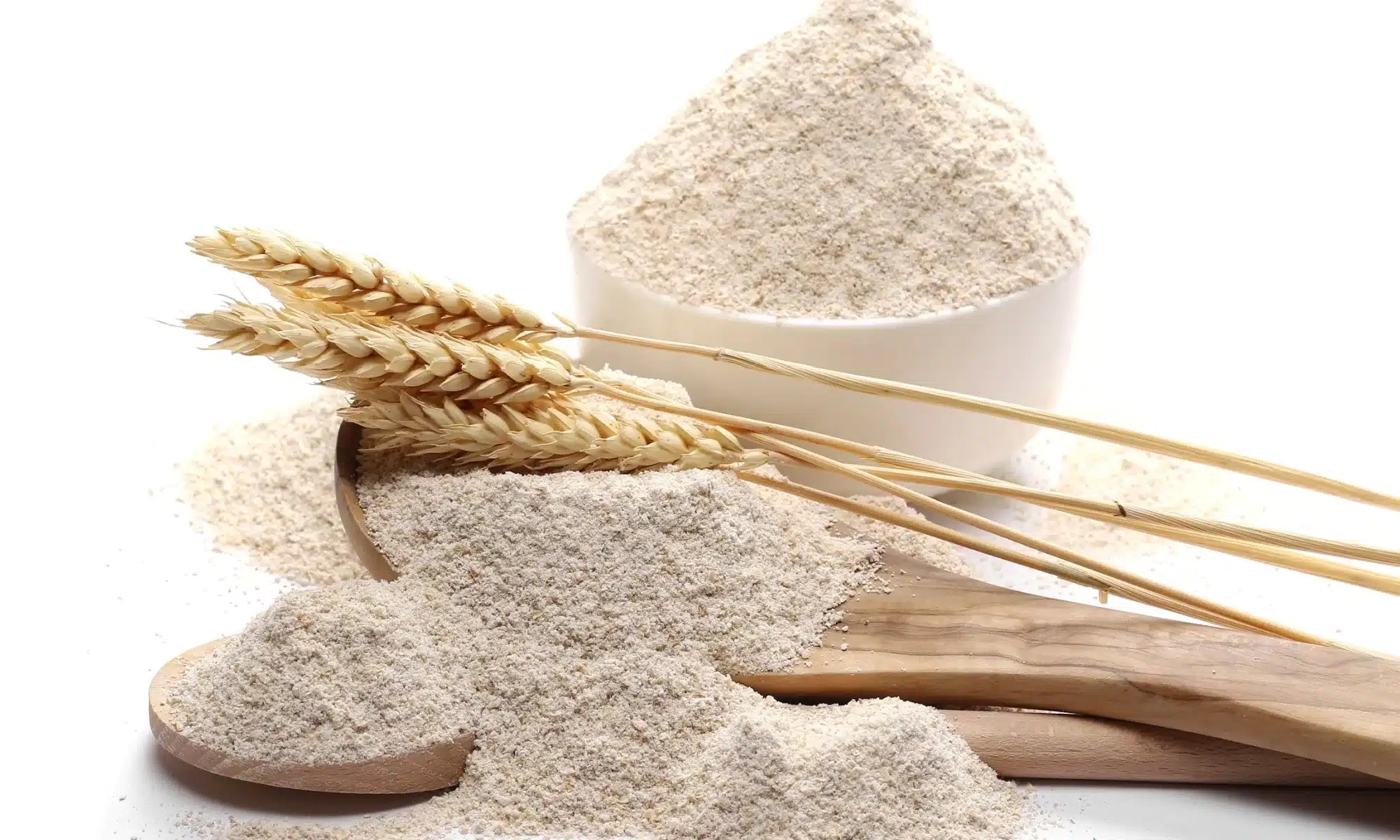
Barley flour
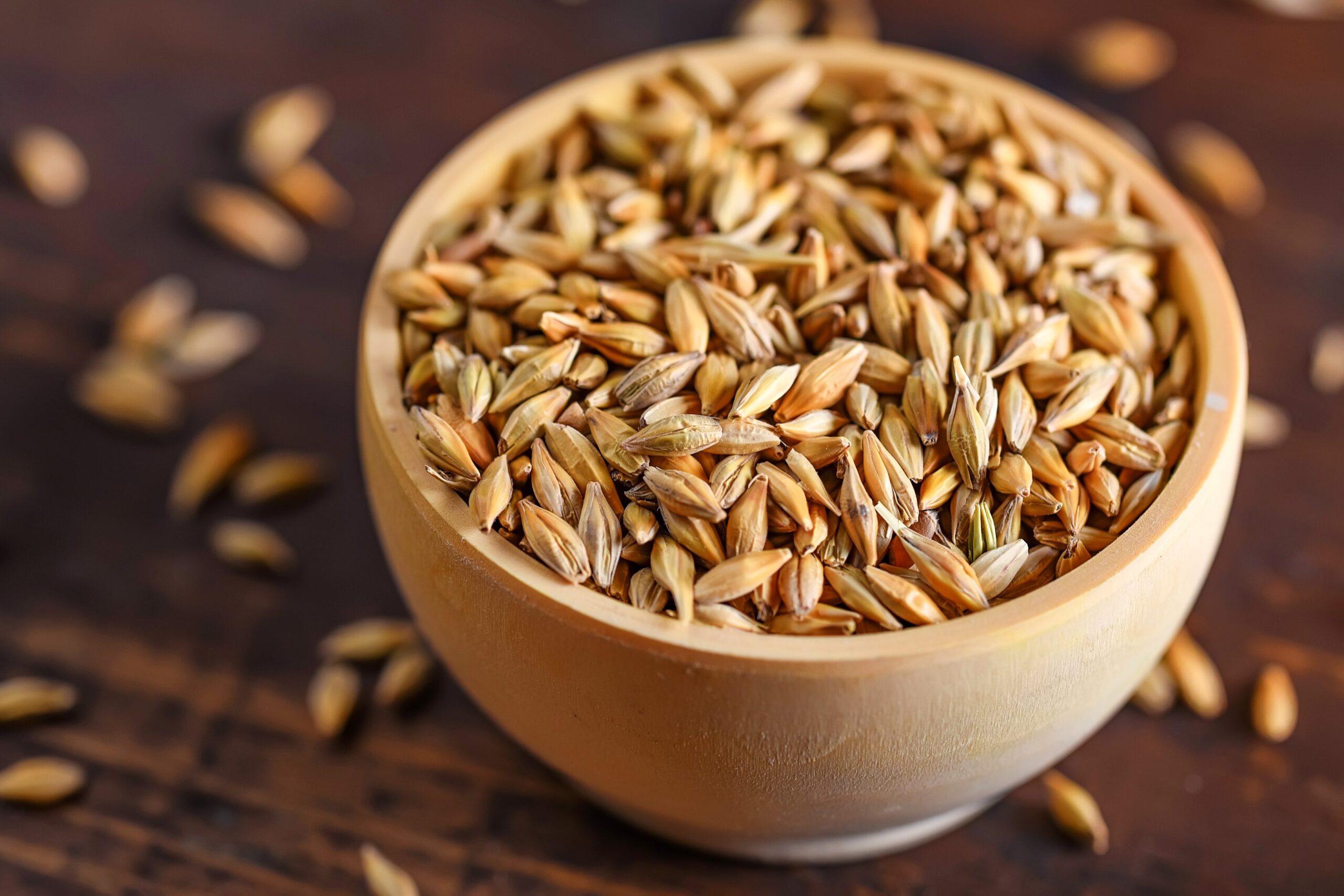
Barley malt
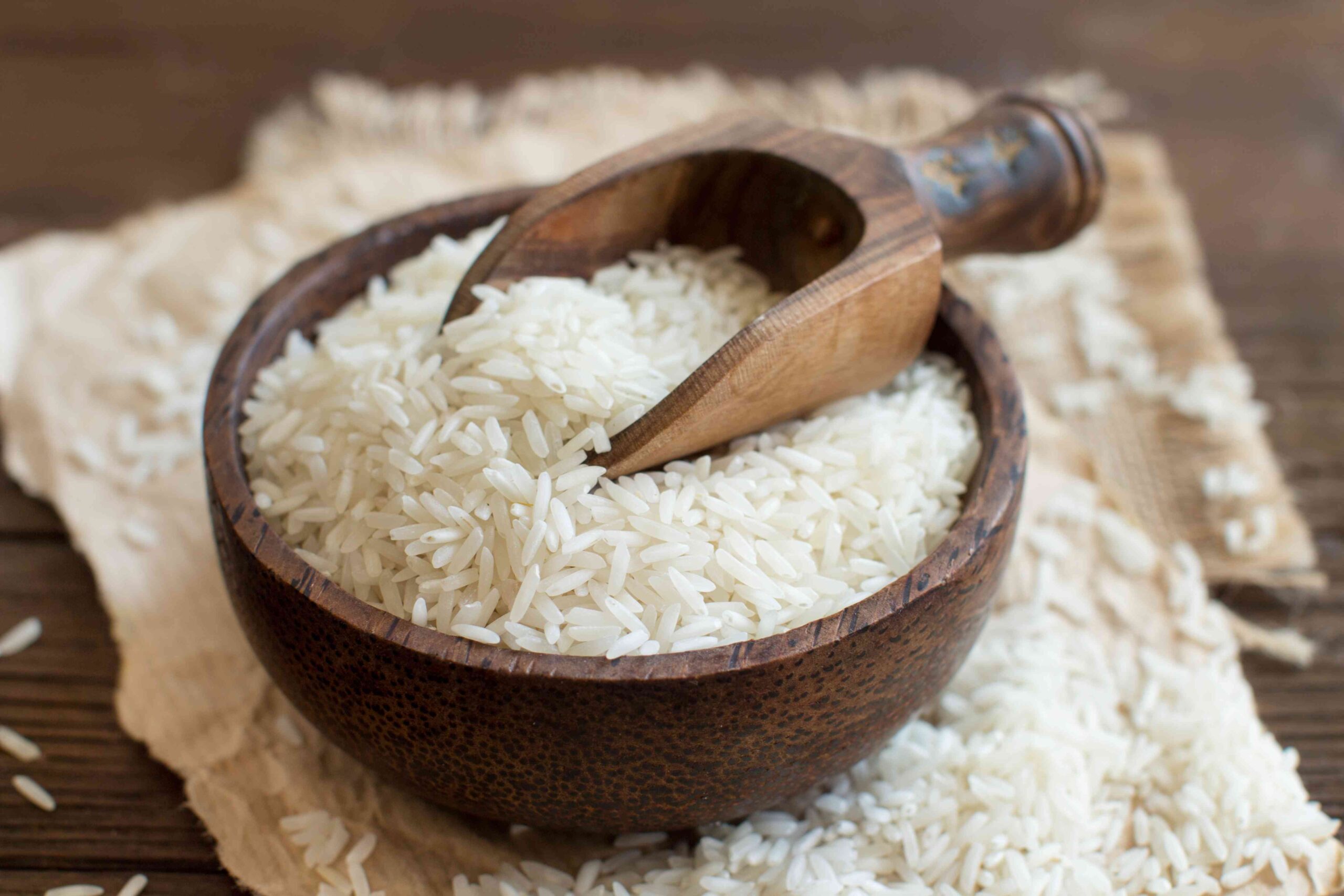
Basmati rice
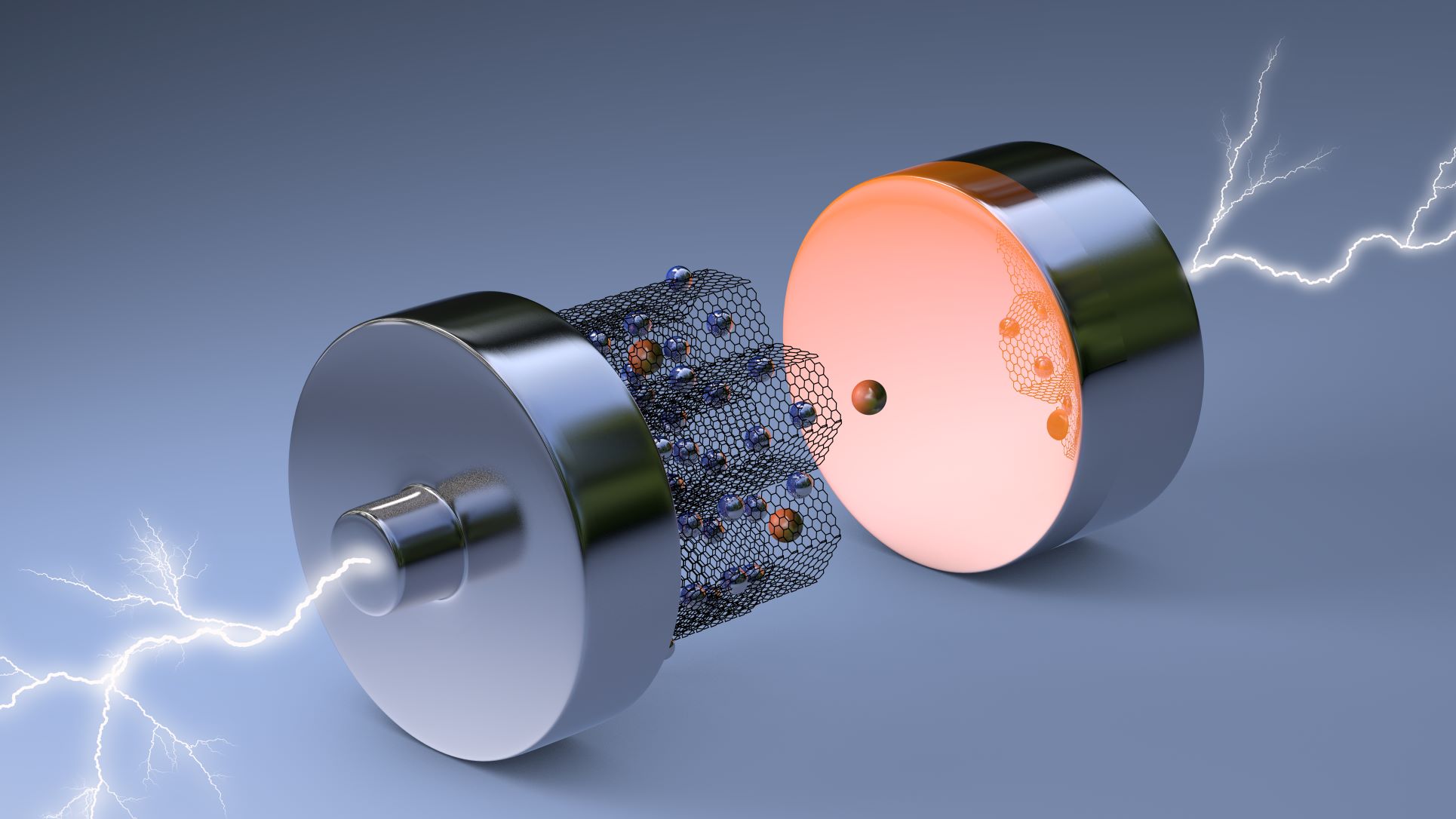
Battery electrodes
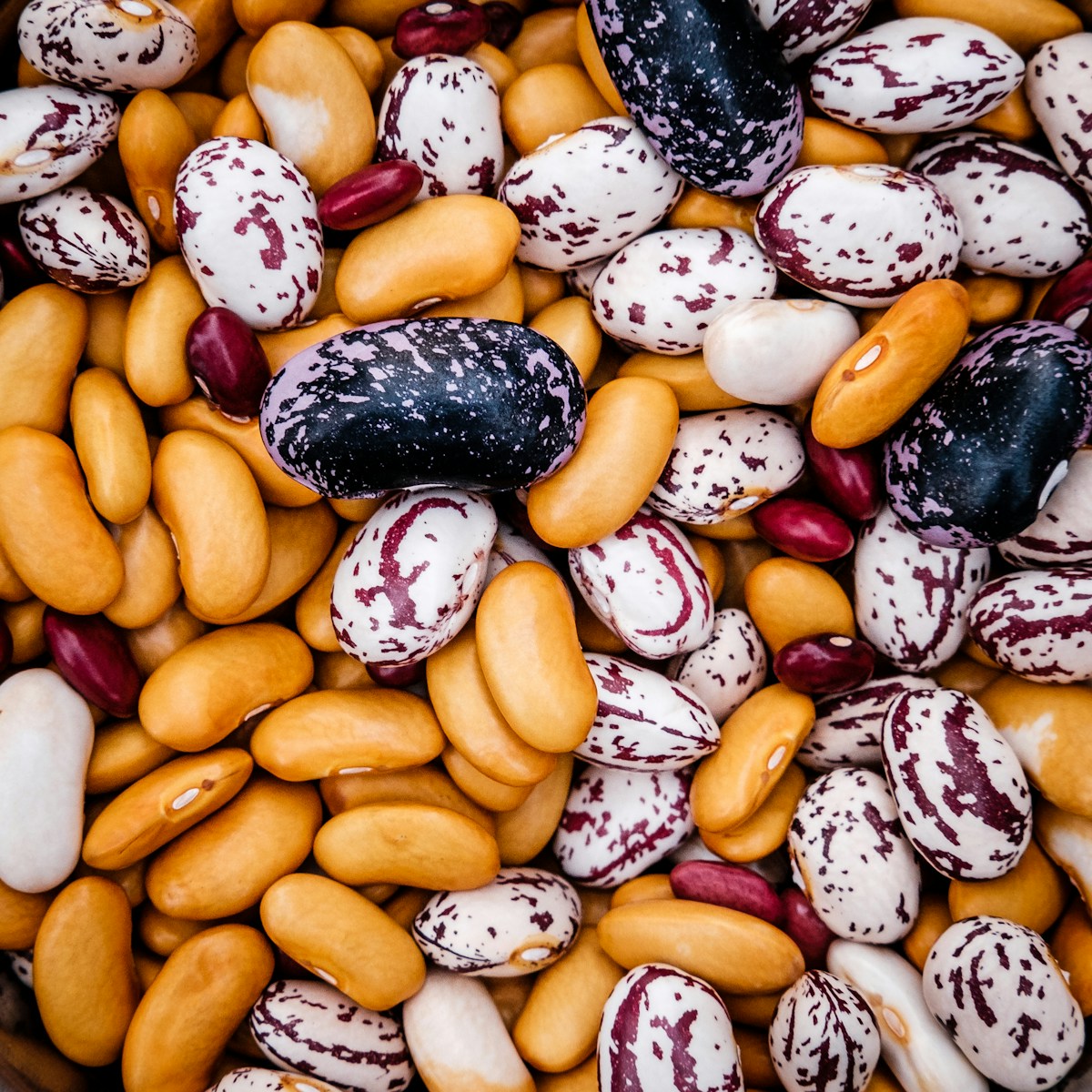
Beans
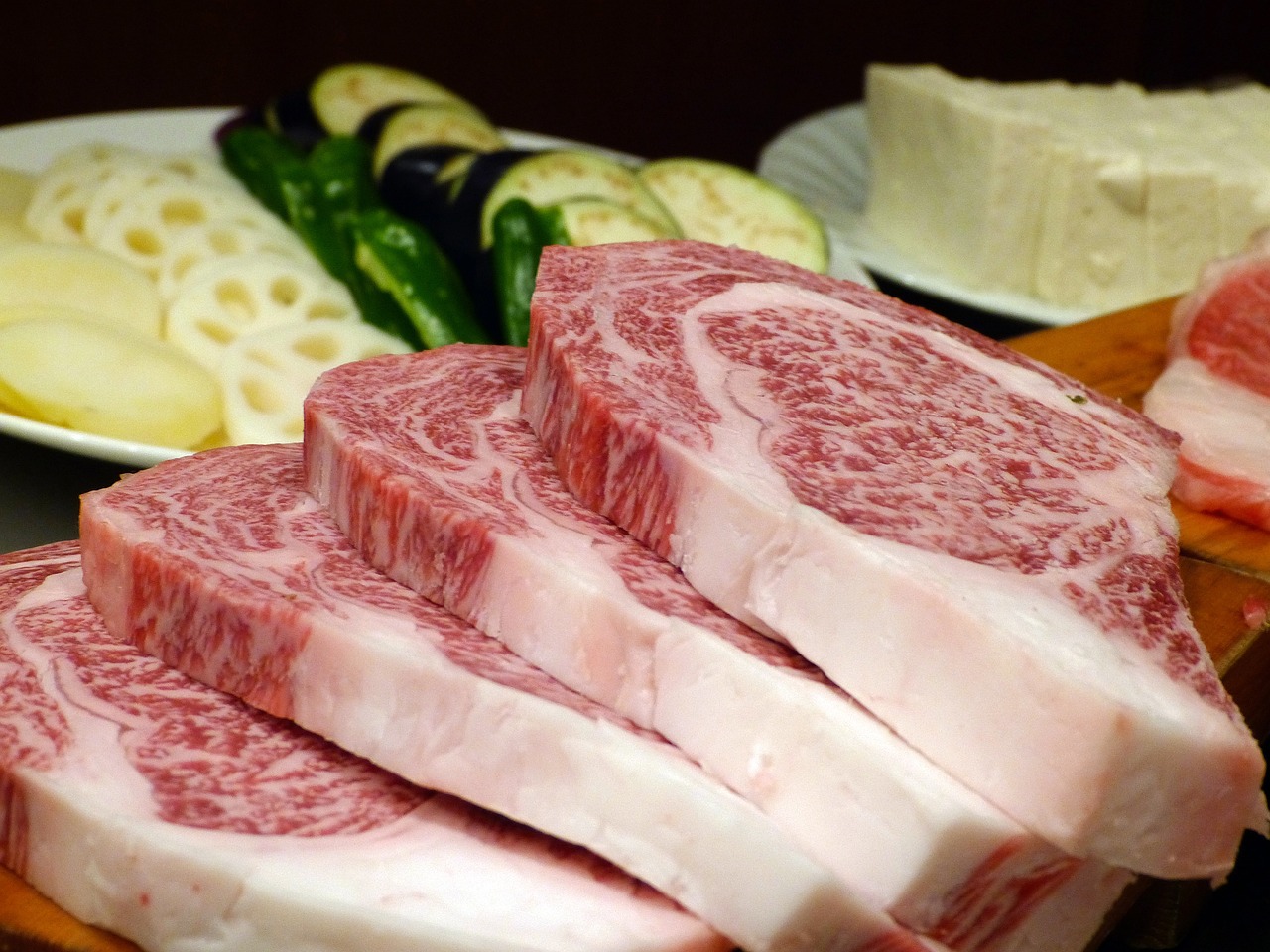
Beef
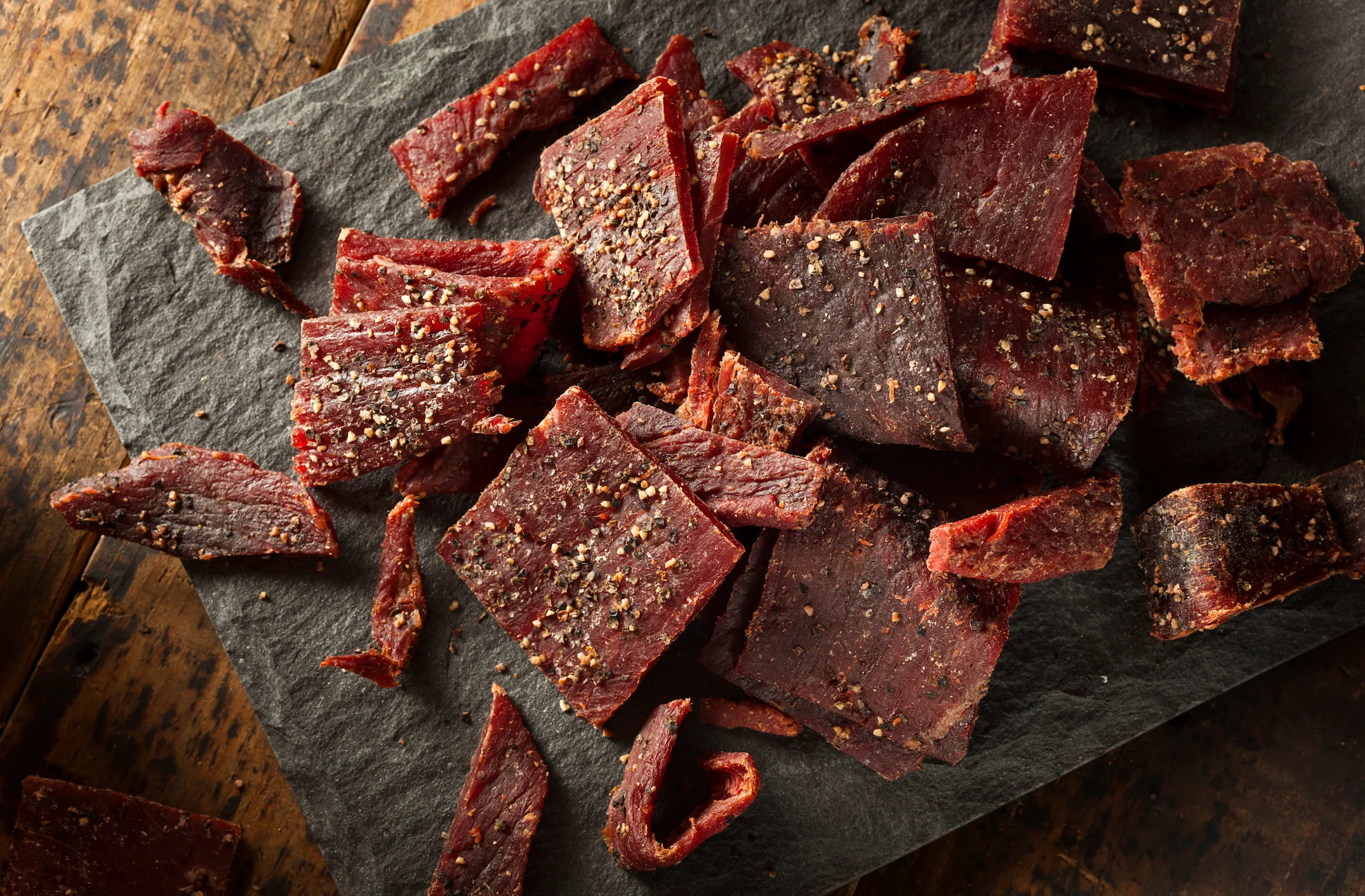
Beef jerky
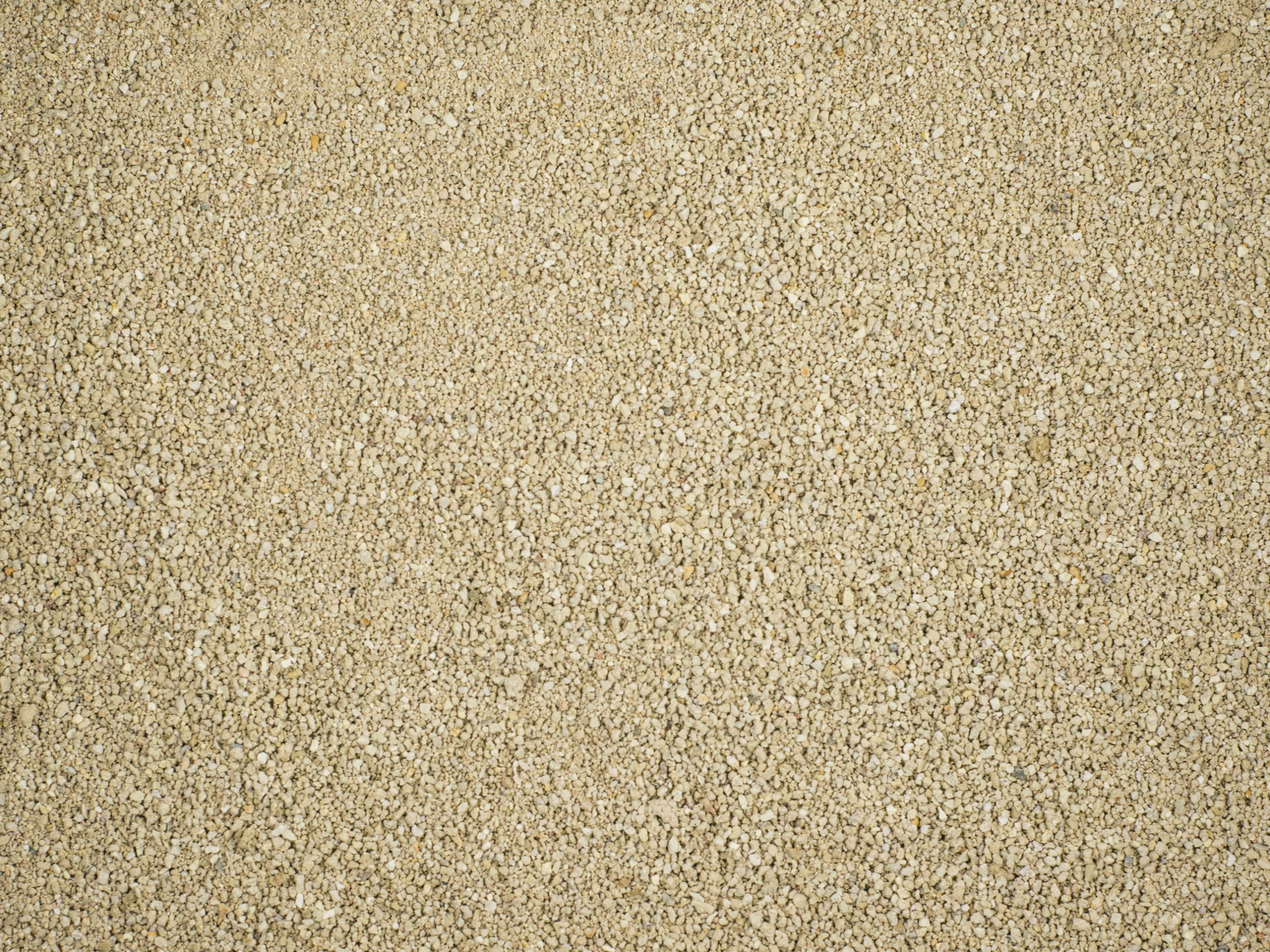
Bentonite
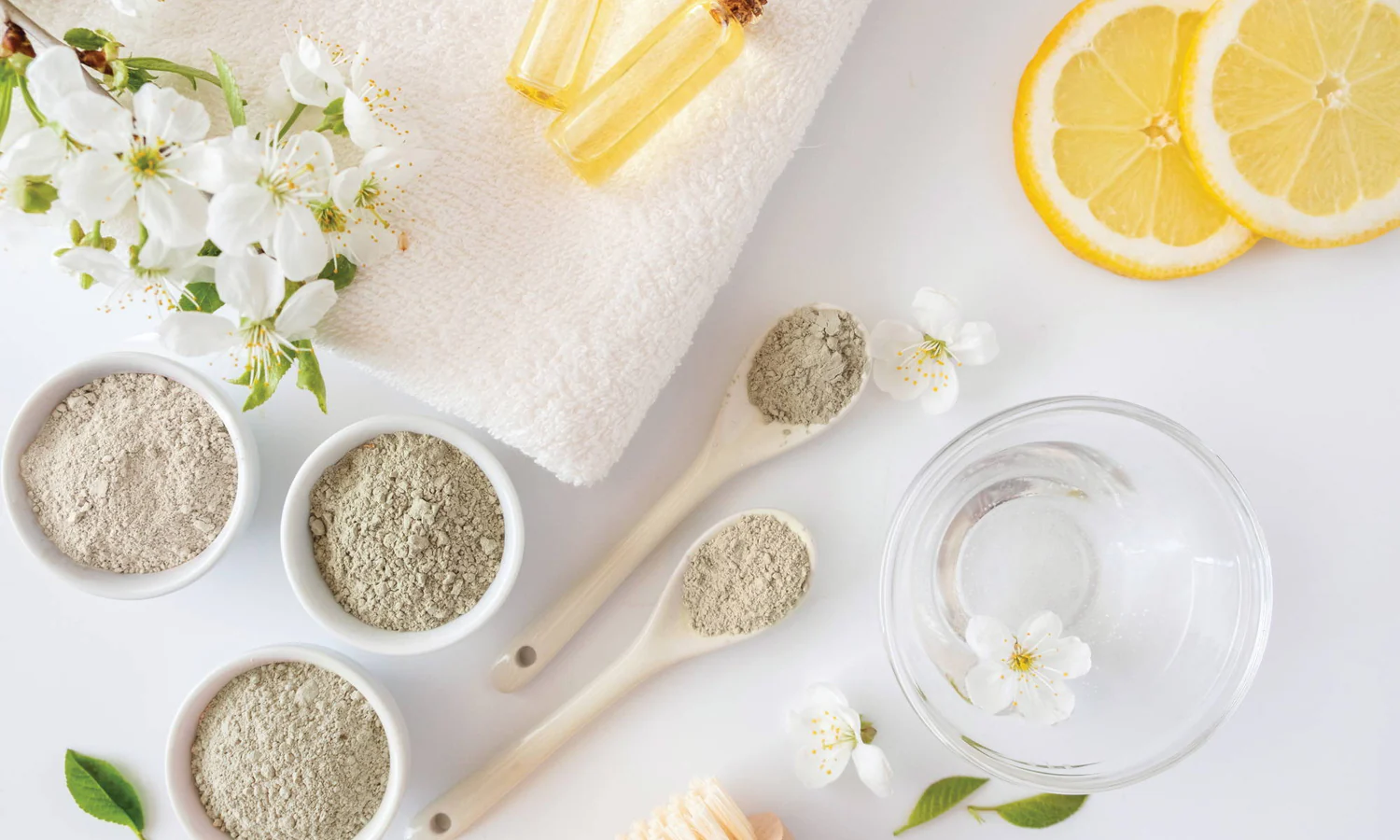
Bentonite clay
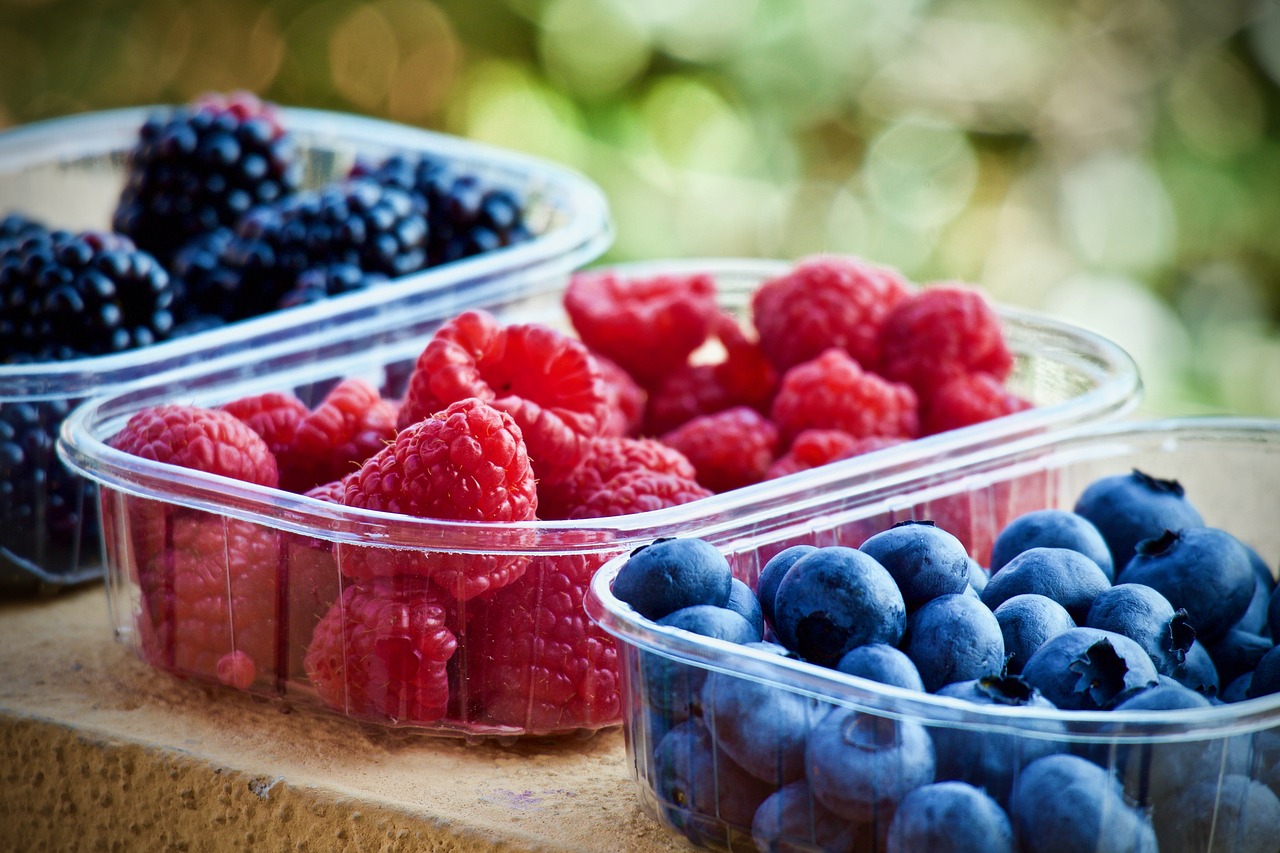
Berries
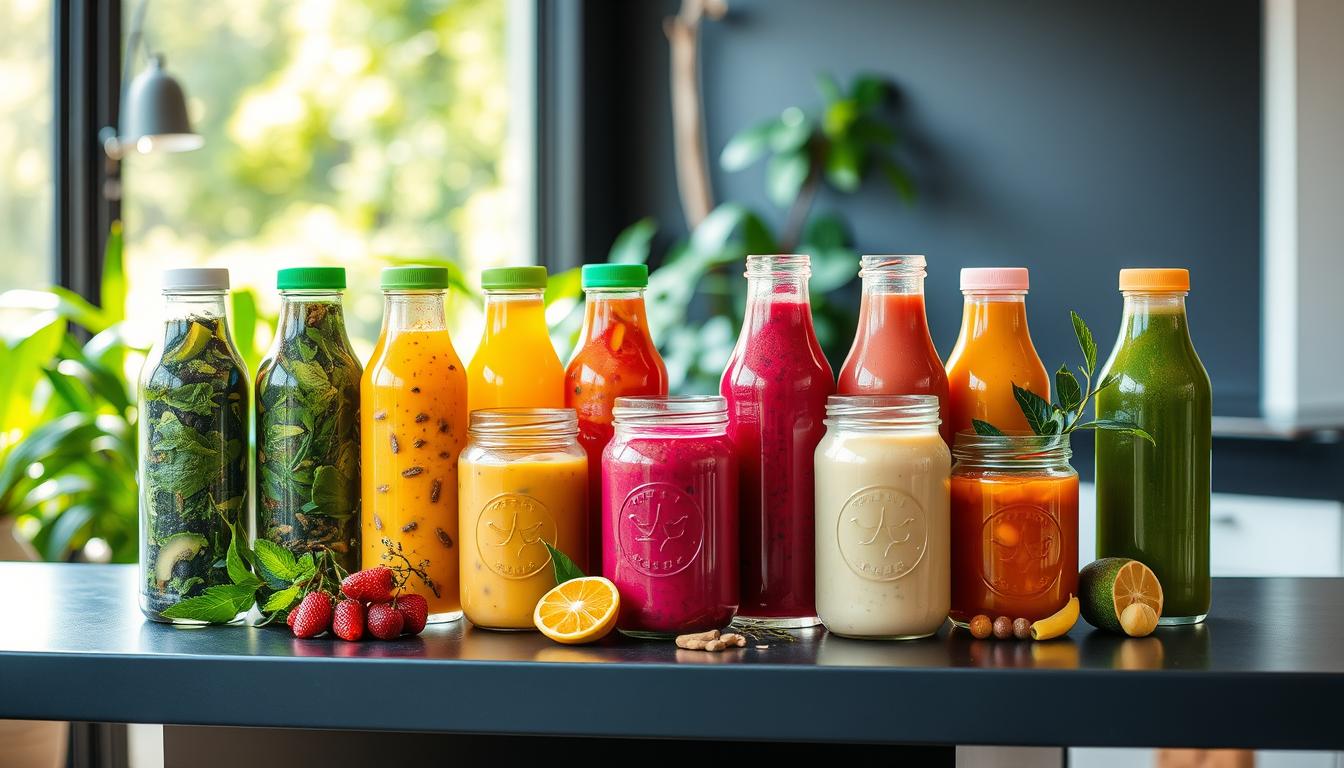
Beverage ingredients
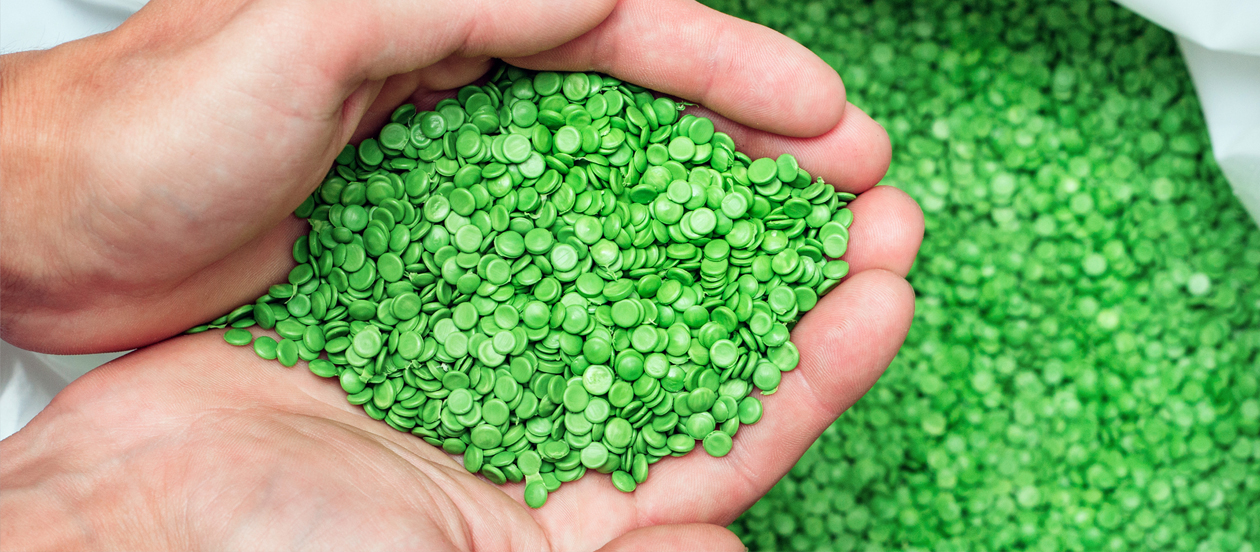
Bioplastics
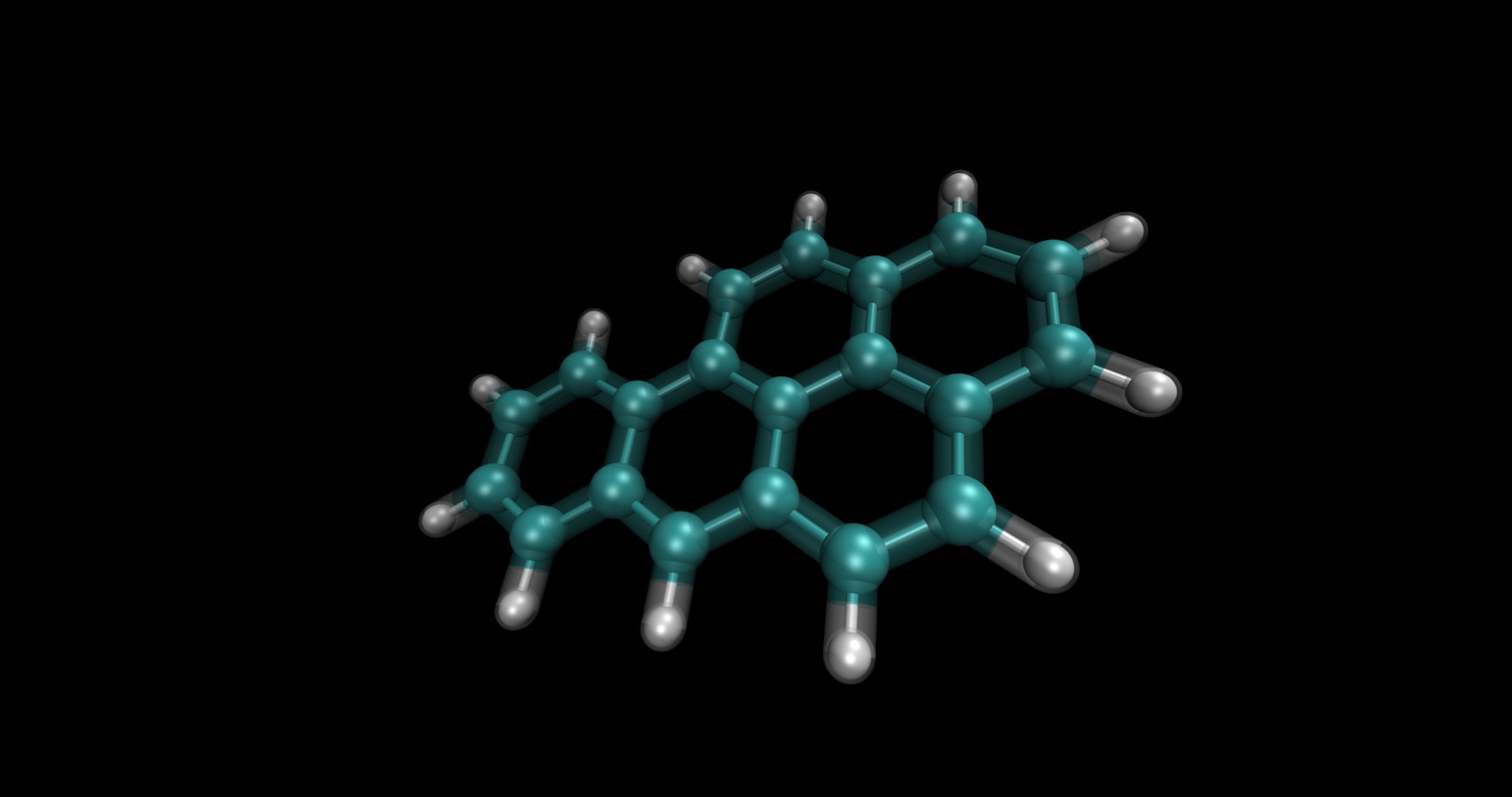
Bioactive compounds
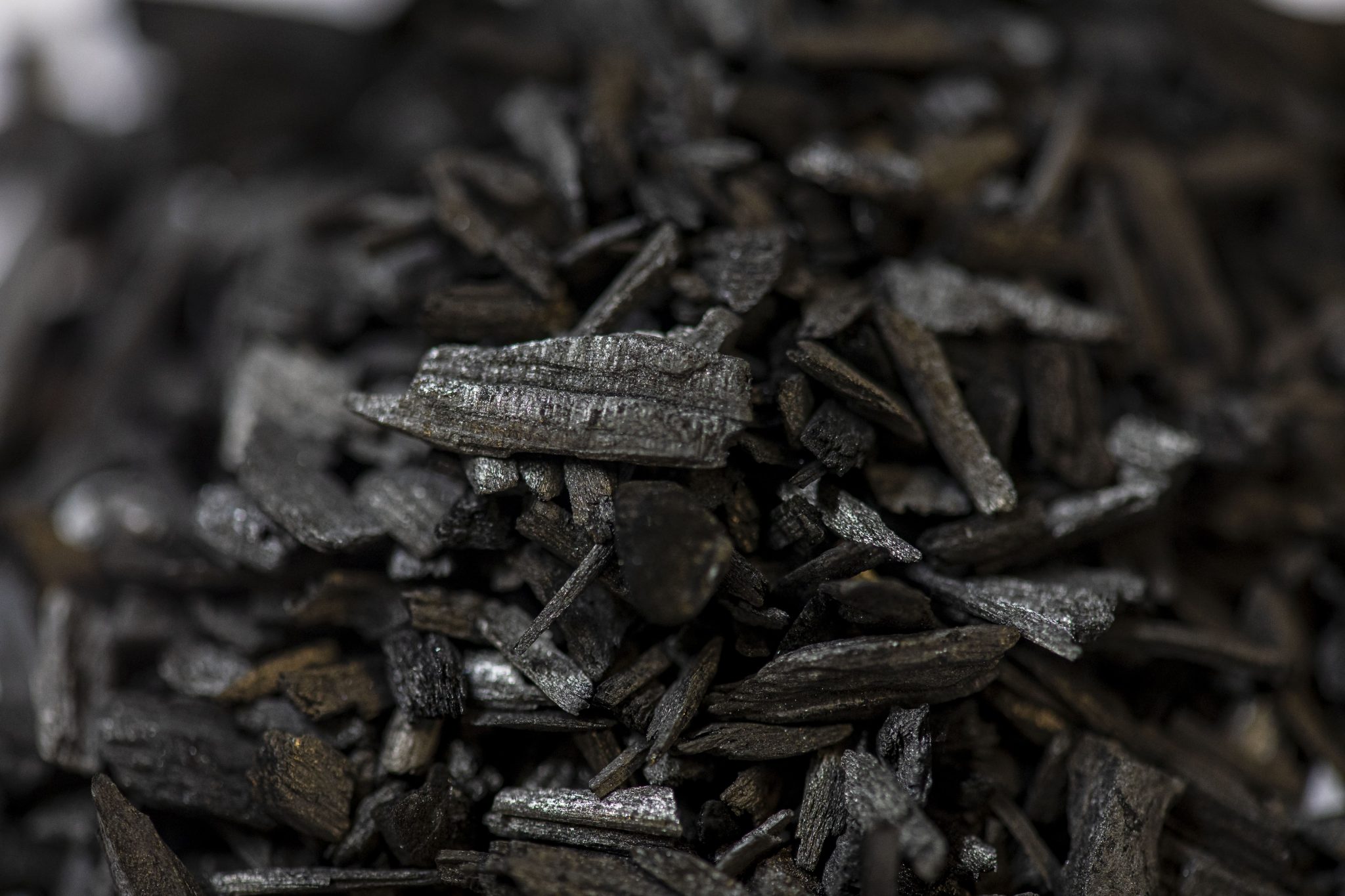
Biochar
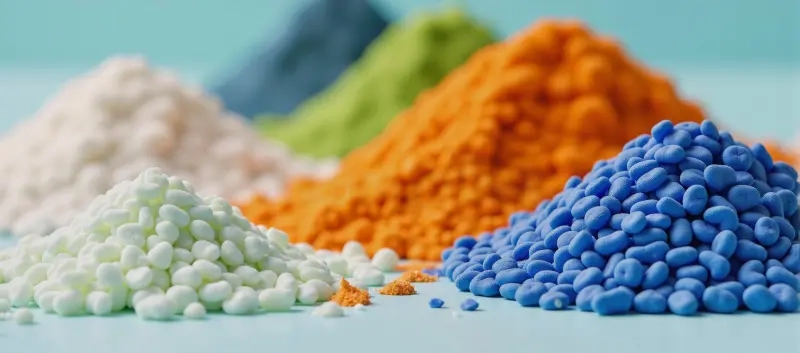
Biodegradable polymers
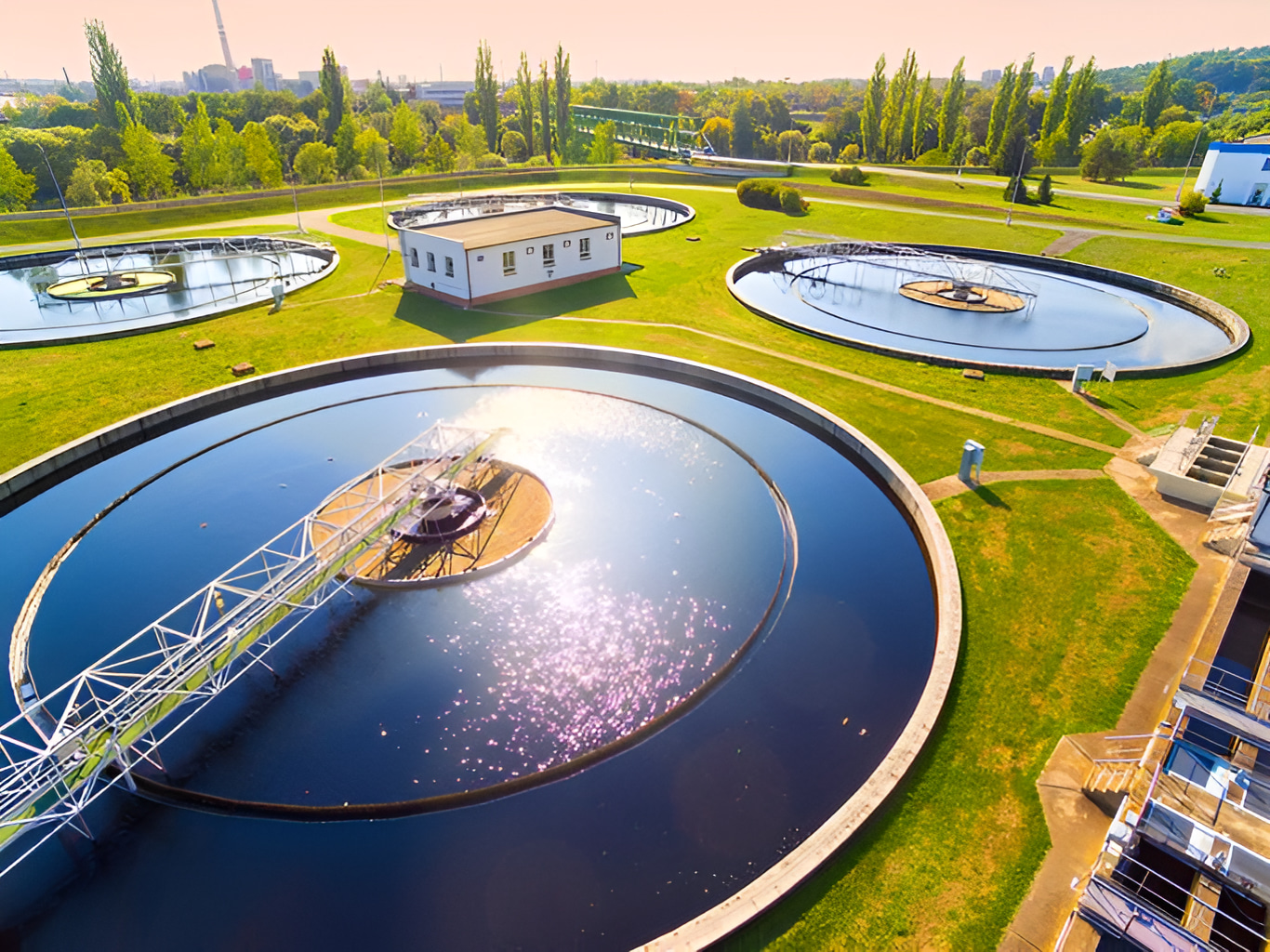
Bioenergy
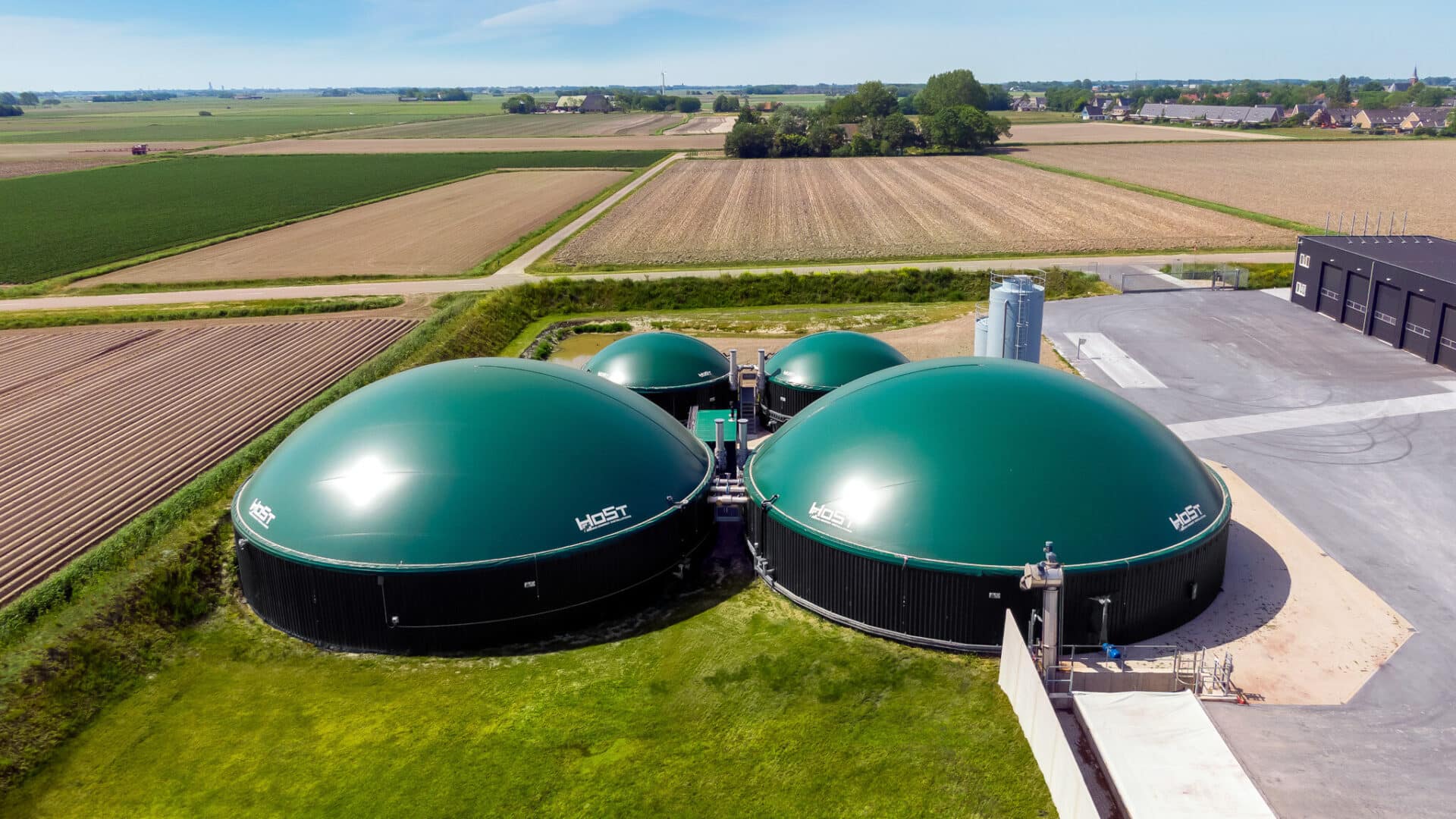
Biogas digestate
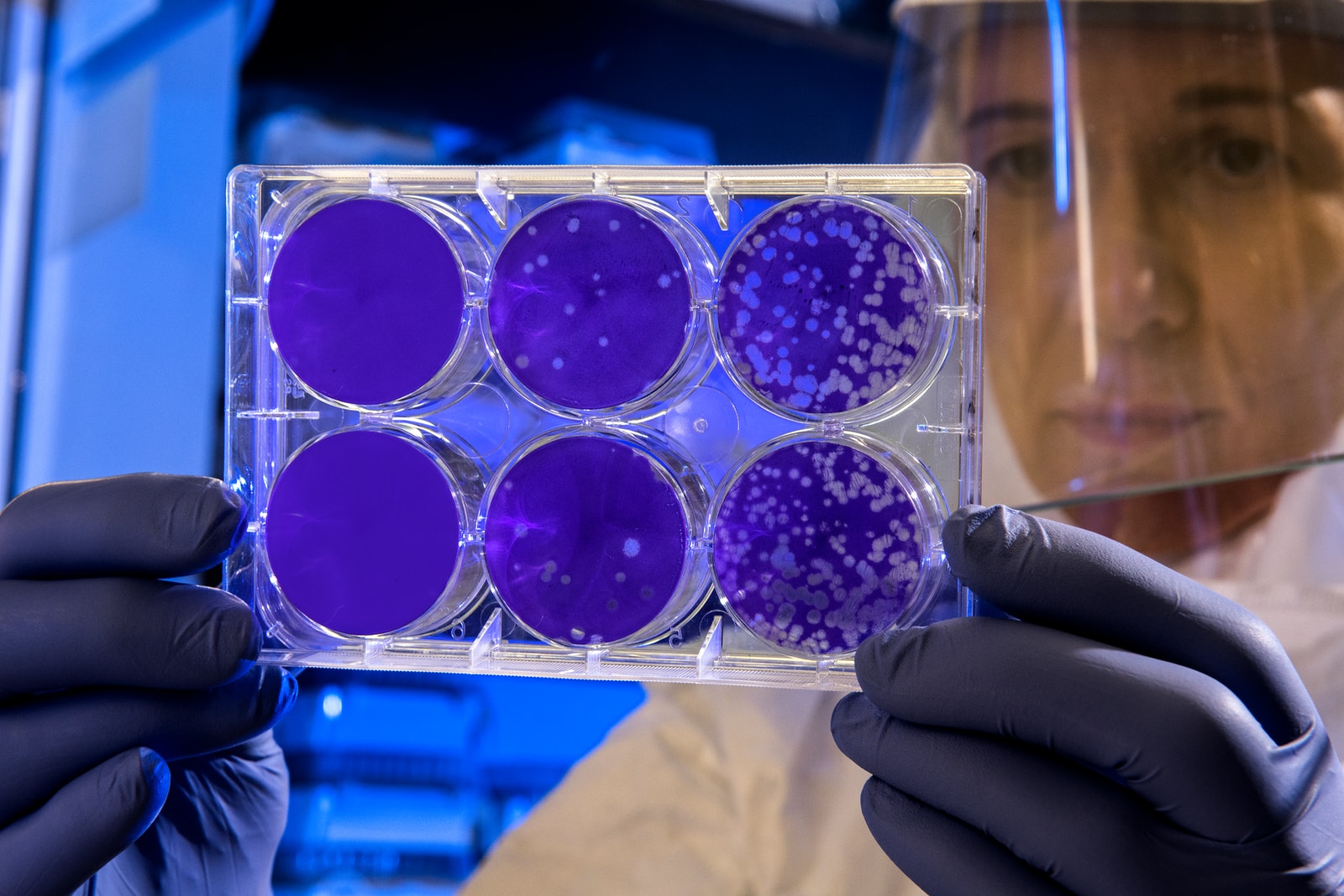
Biologics
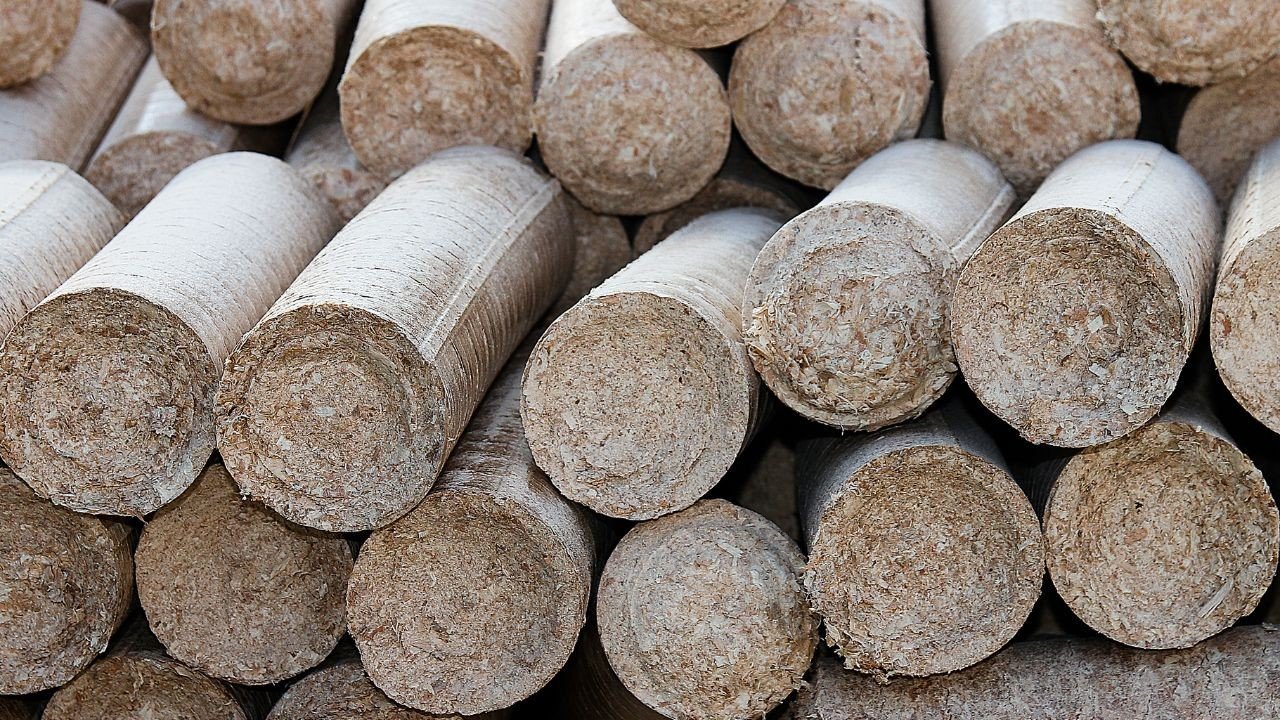
Biomass briquettes
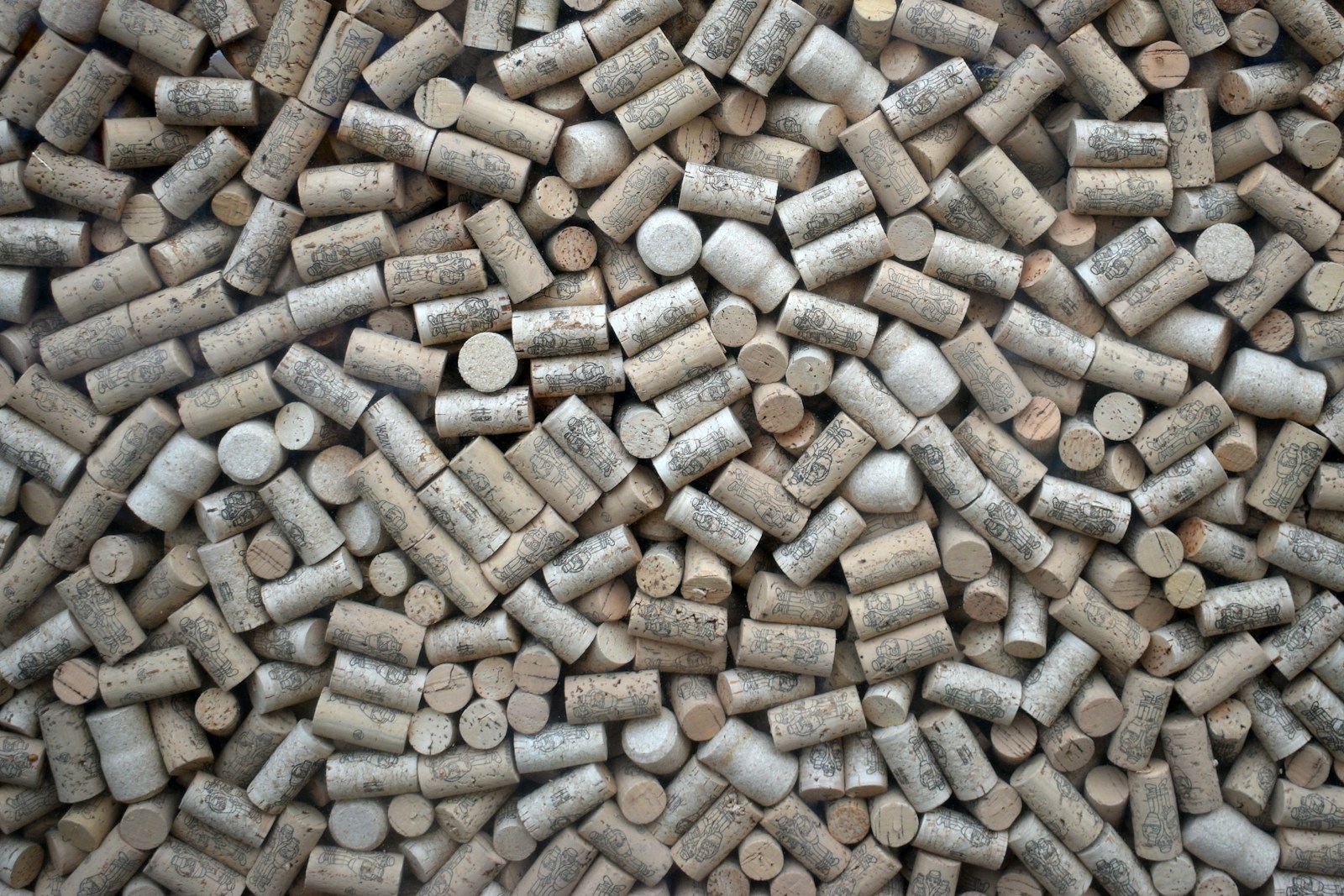
Biomass pellets
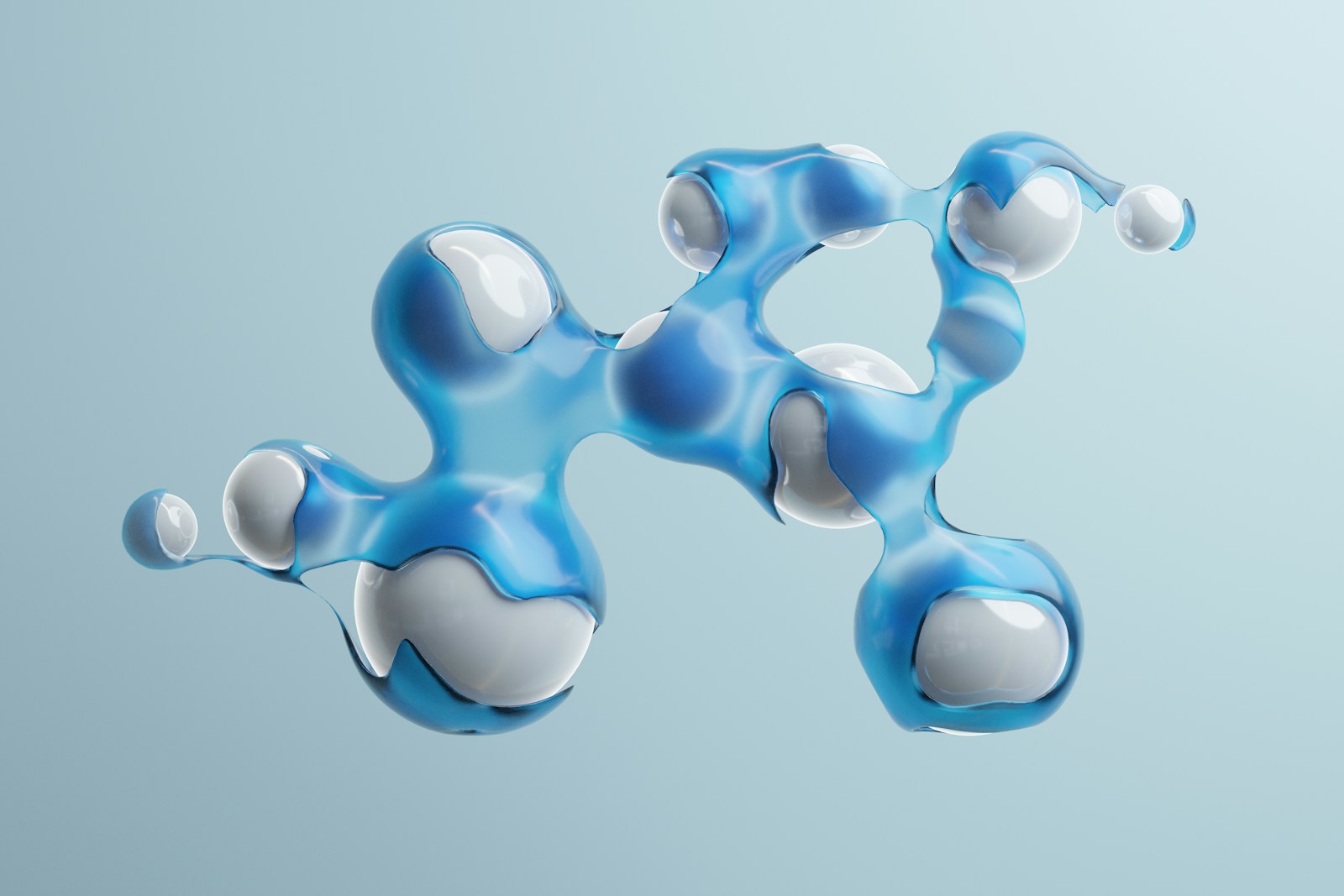
Biopolymers
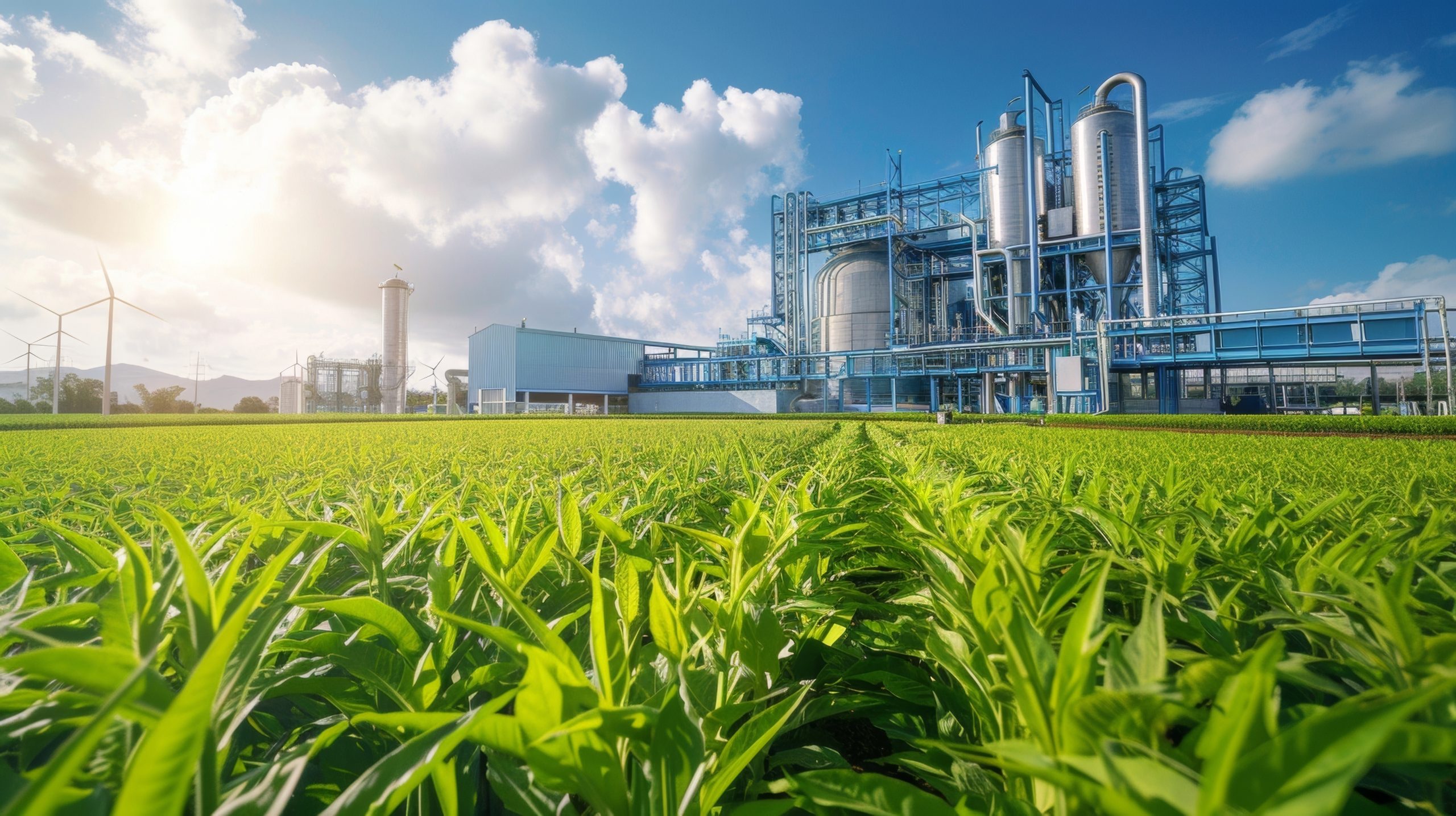
Biorefinery
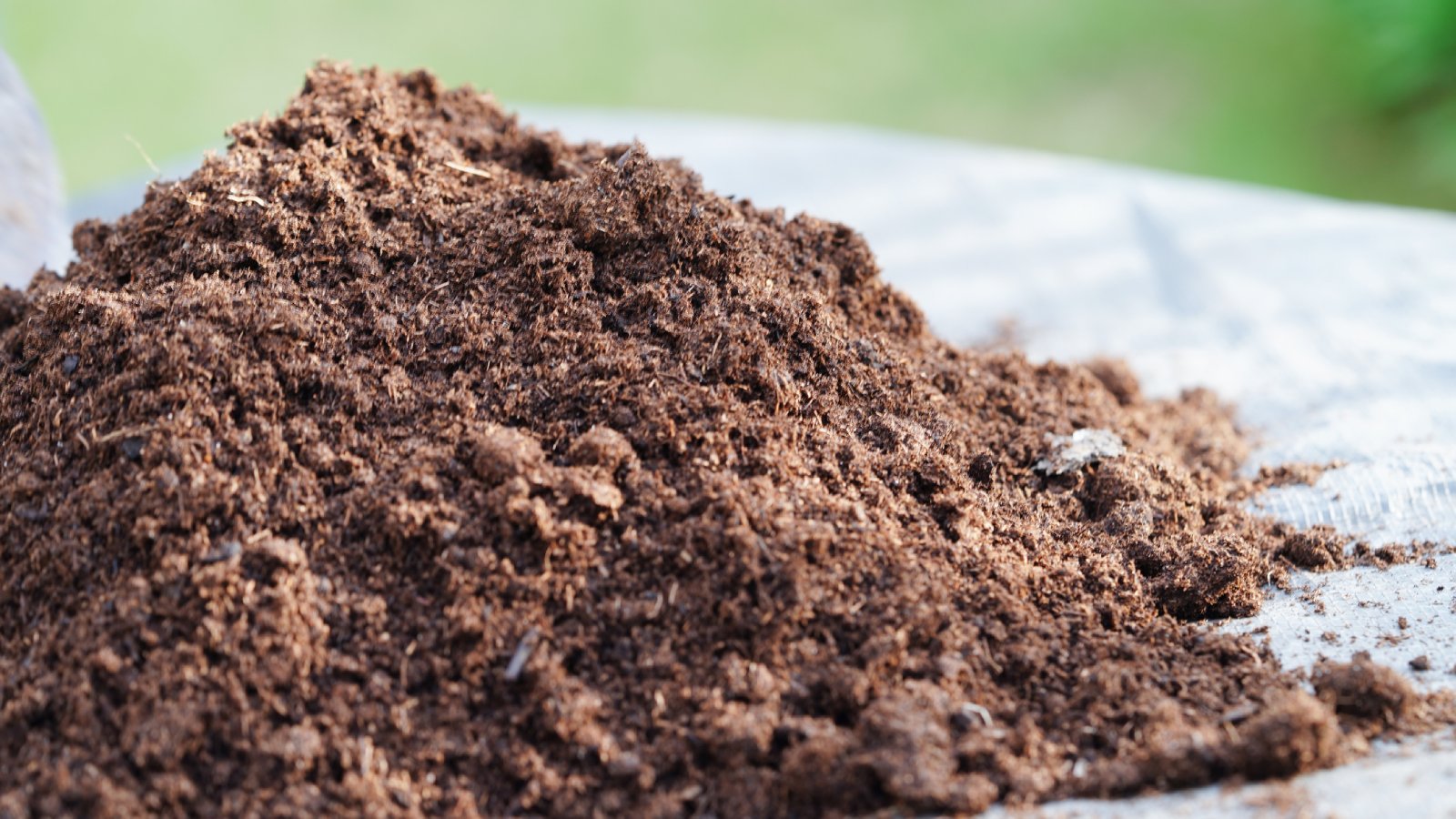
Biosolids
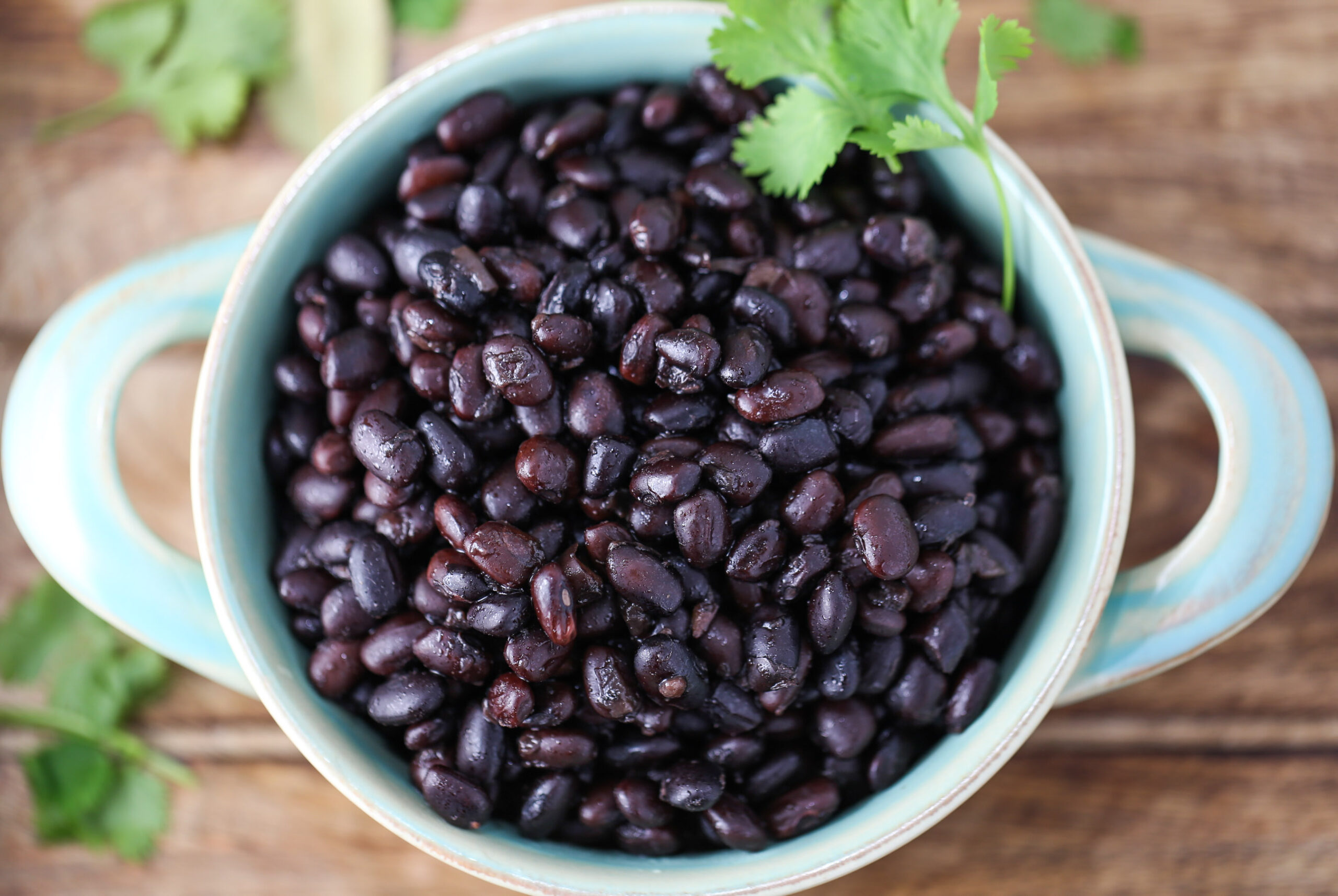
Black beans
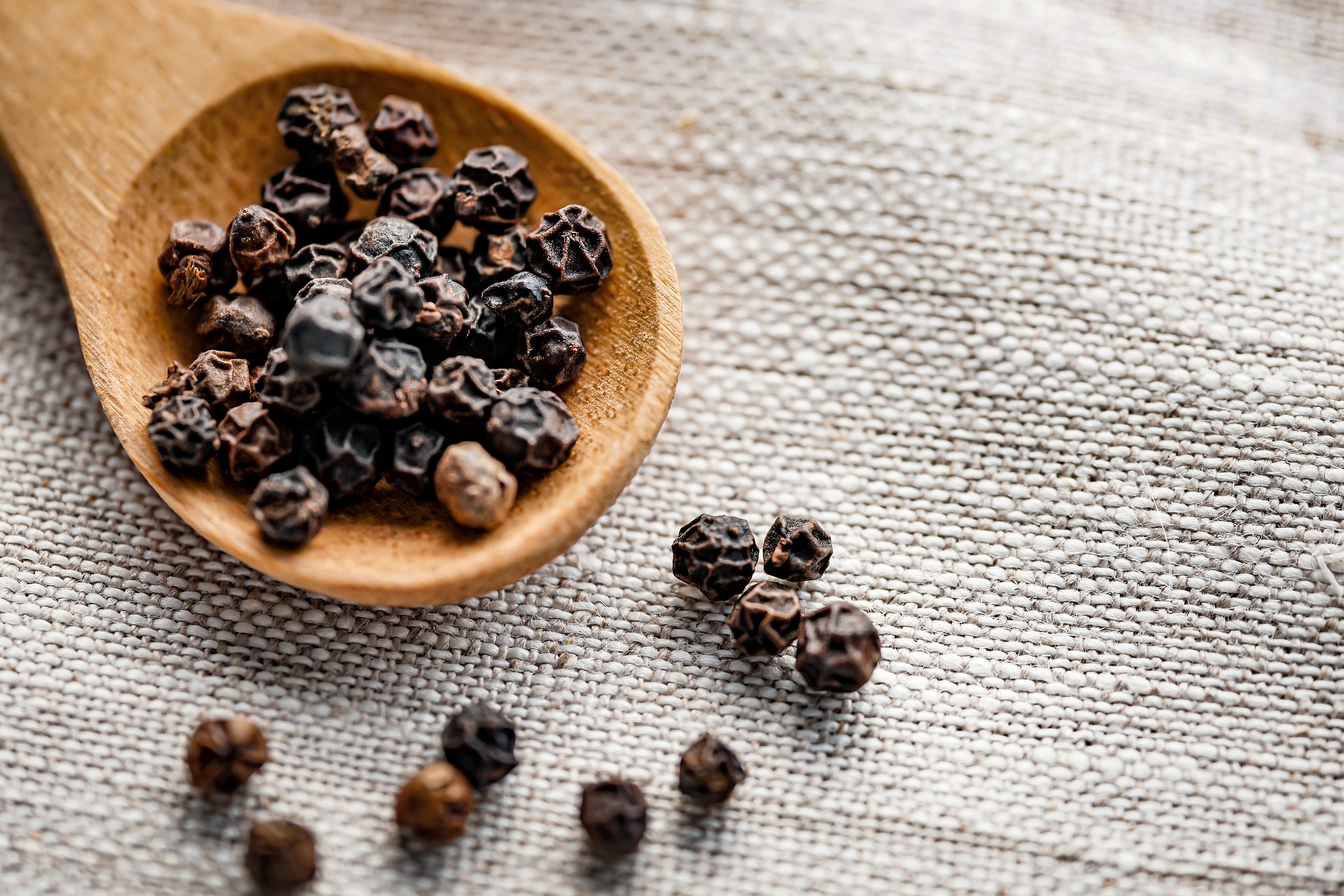
Black pepper
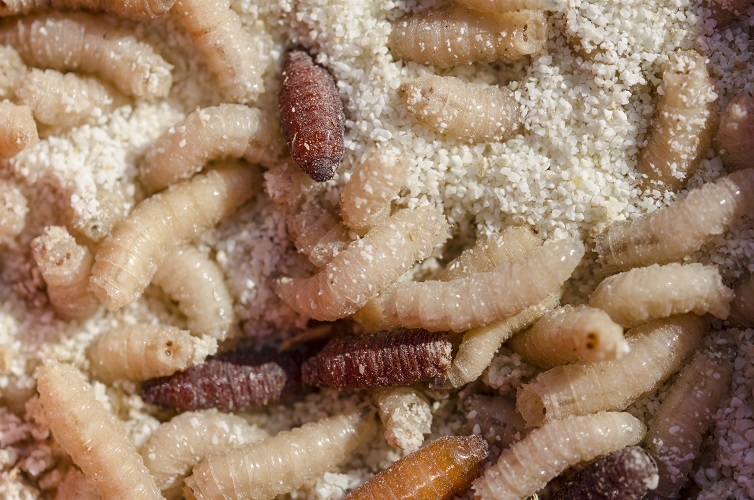
Black soldier fly protein
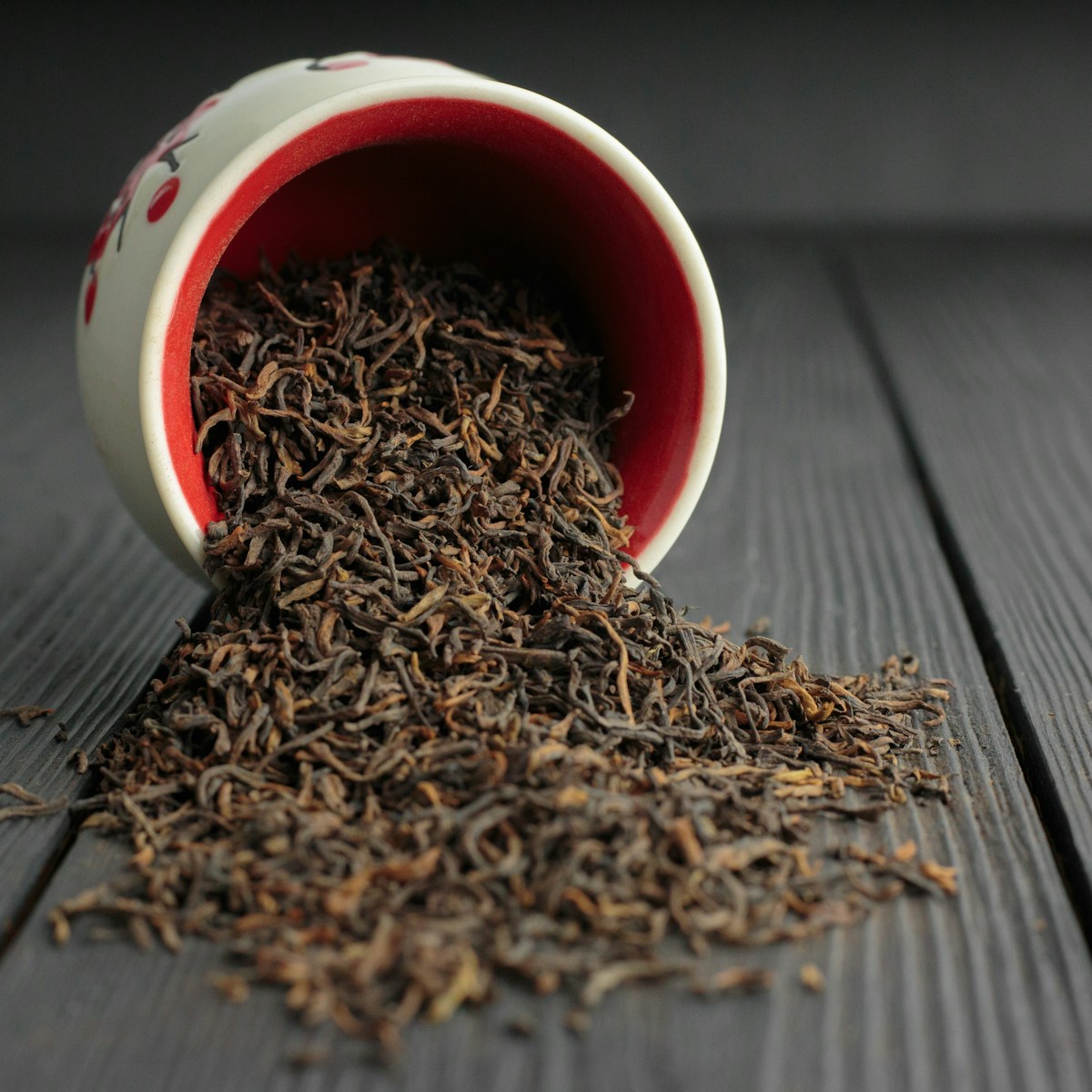
Black tea
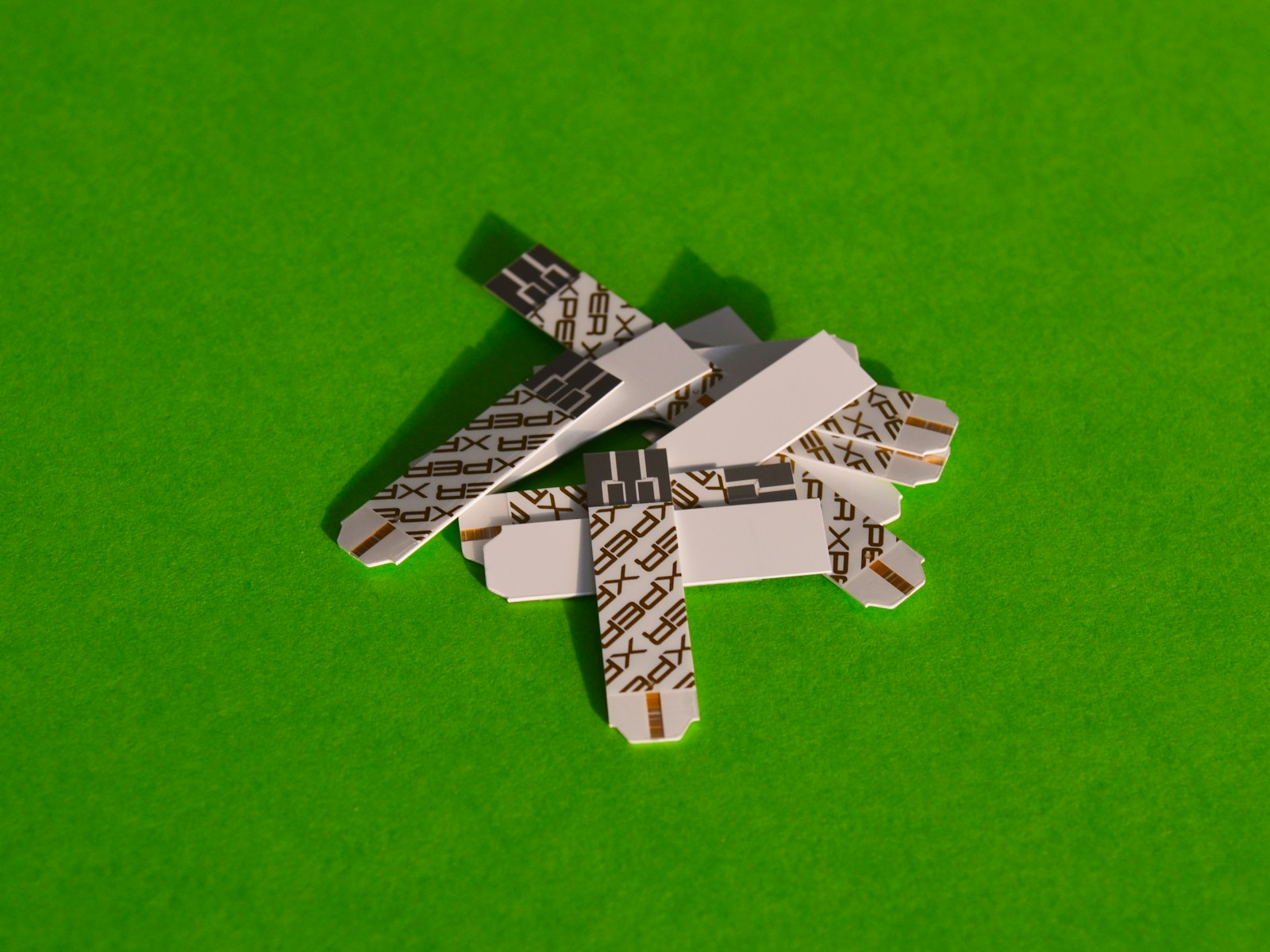
Blood glucose test strips
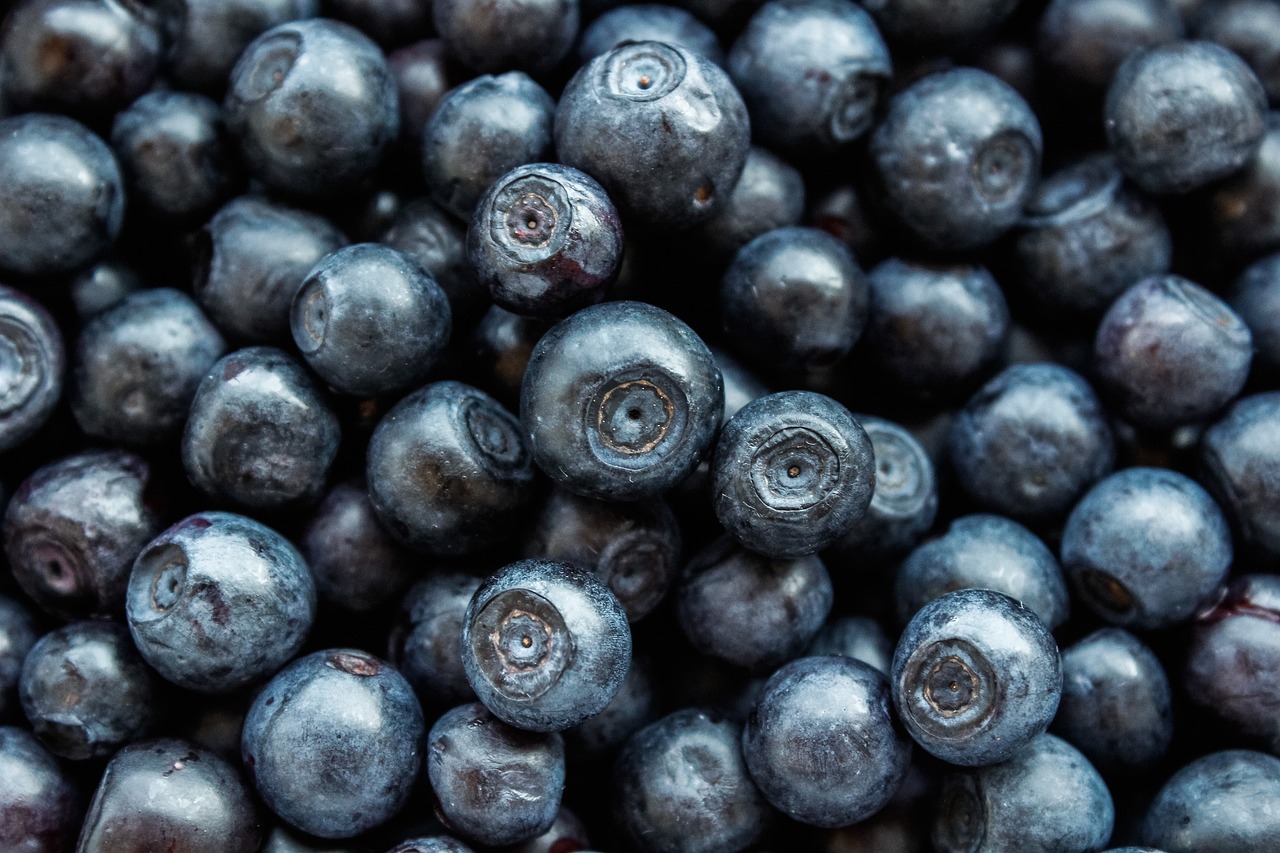
Blueberries
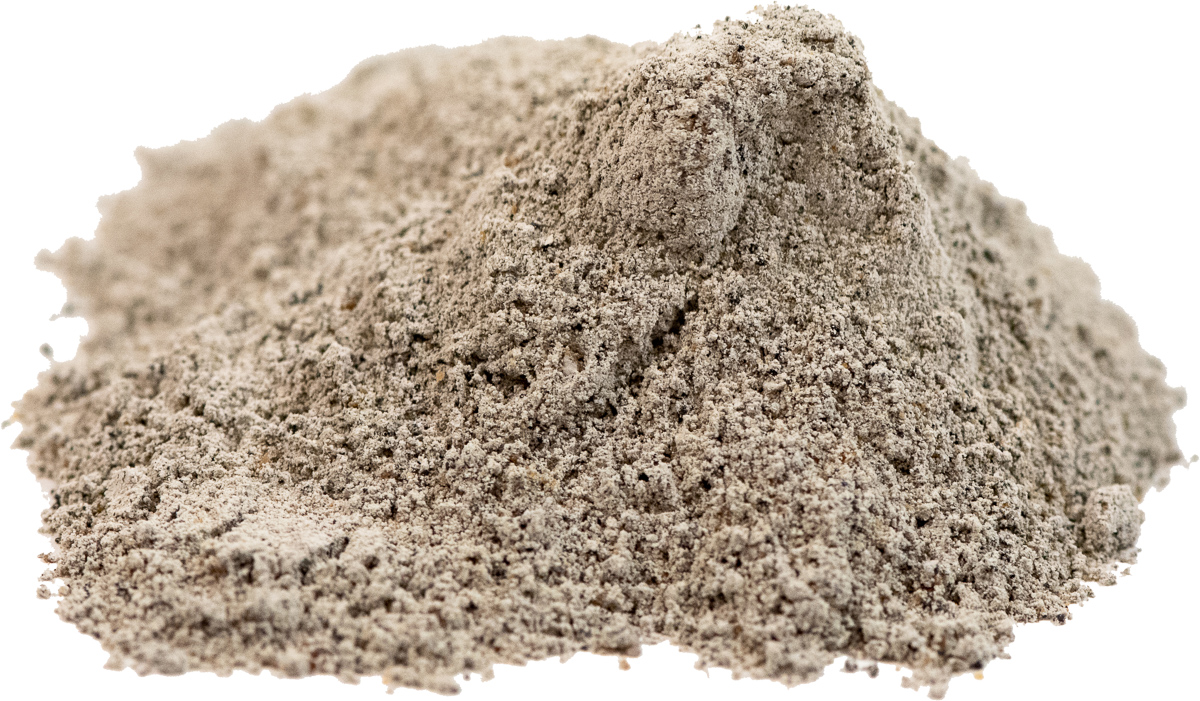
Bone meal

Botanical extracts
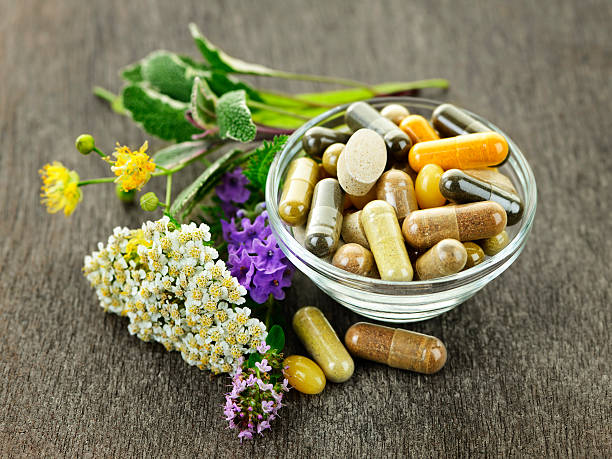
Botanical medicine
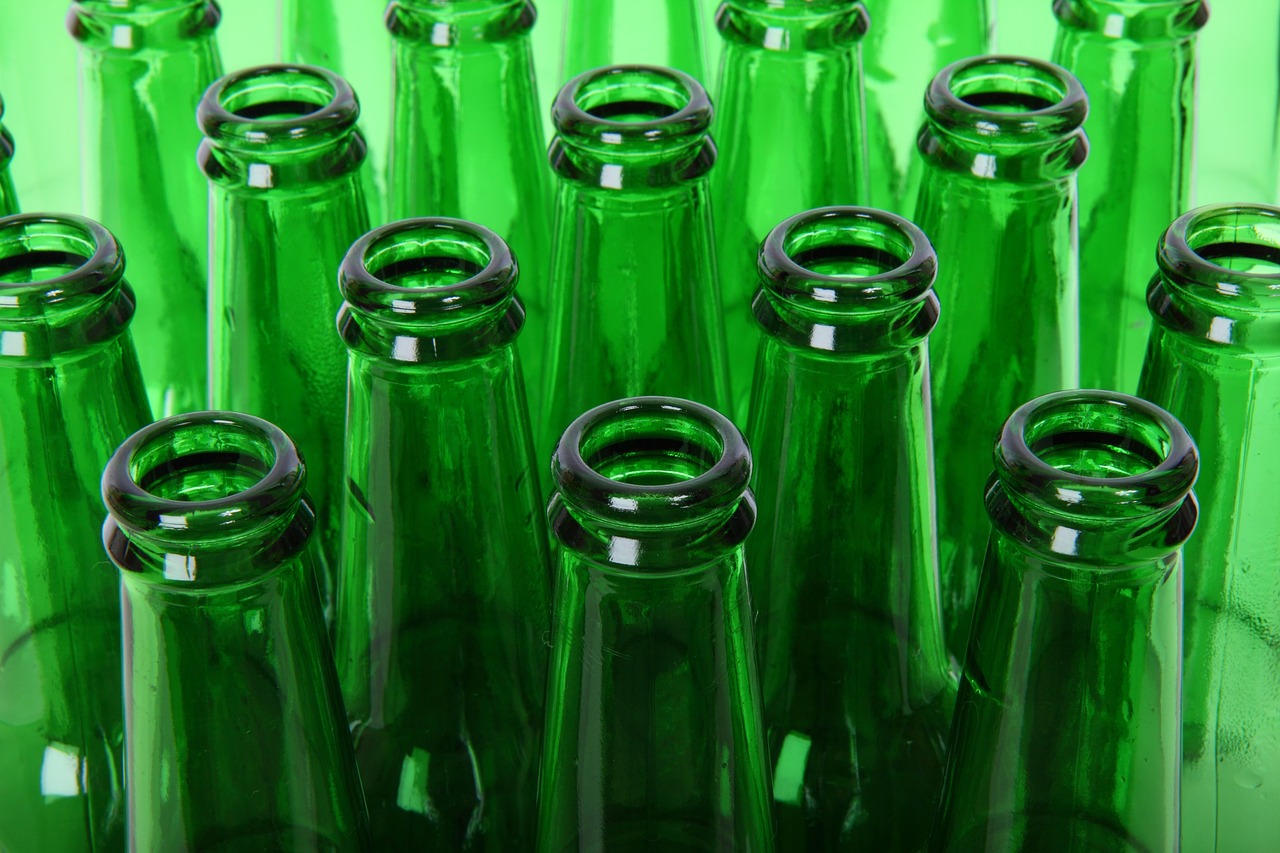
Bottles
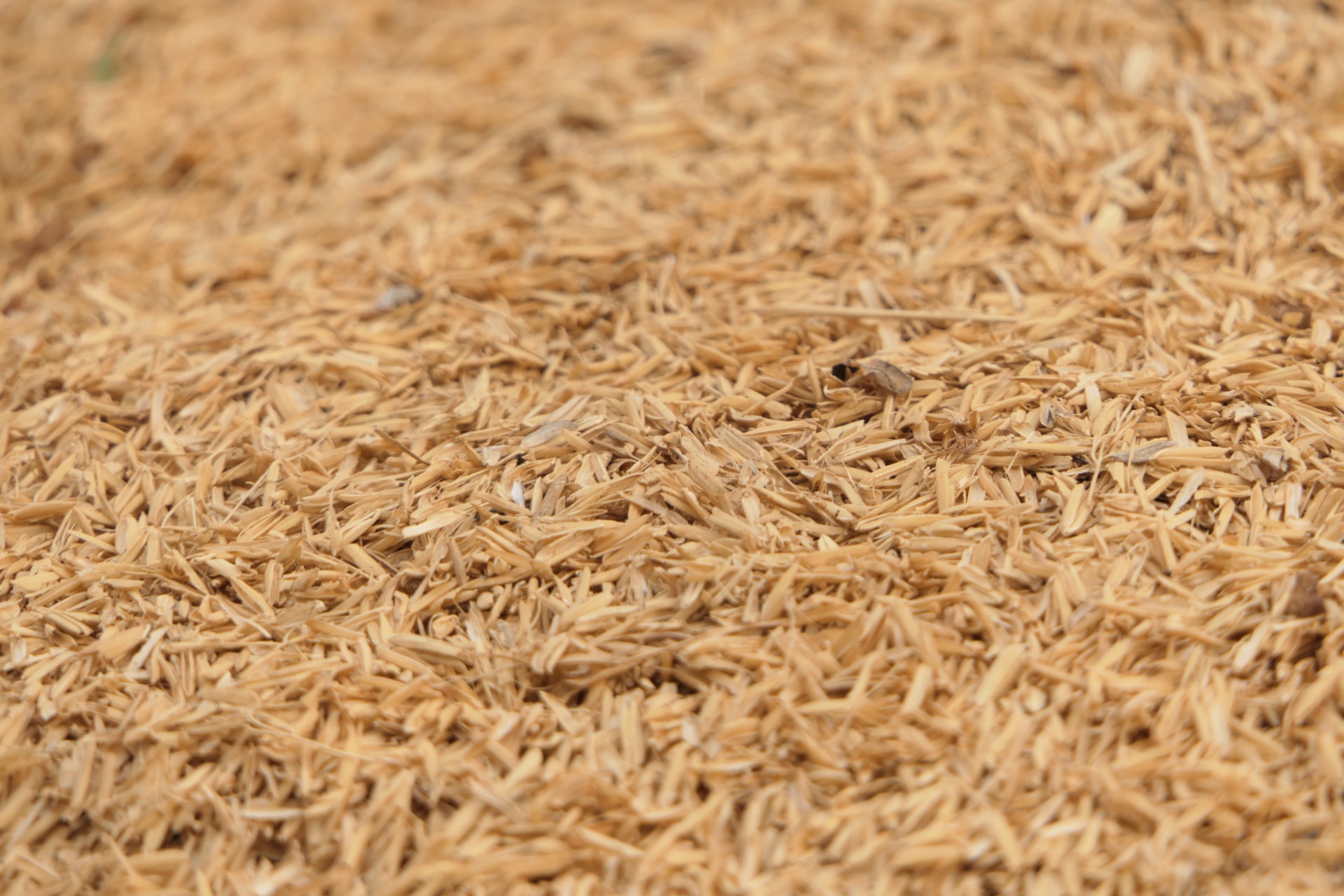
Bran
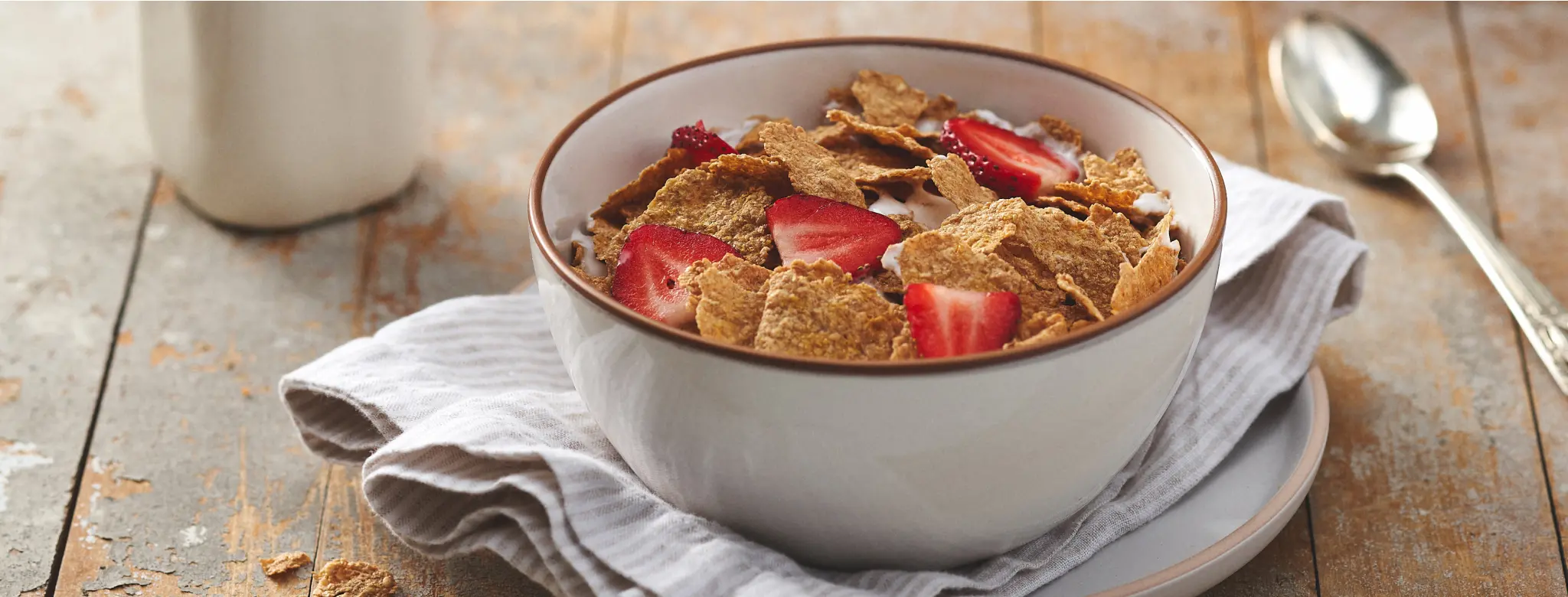
Bran flakes

Breadcrumbs
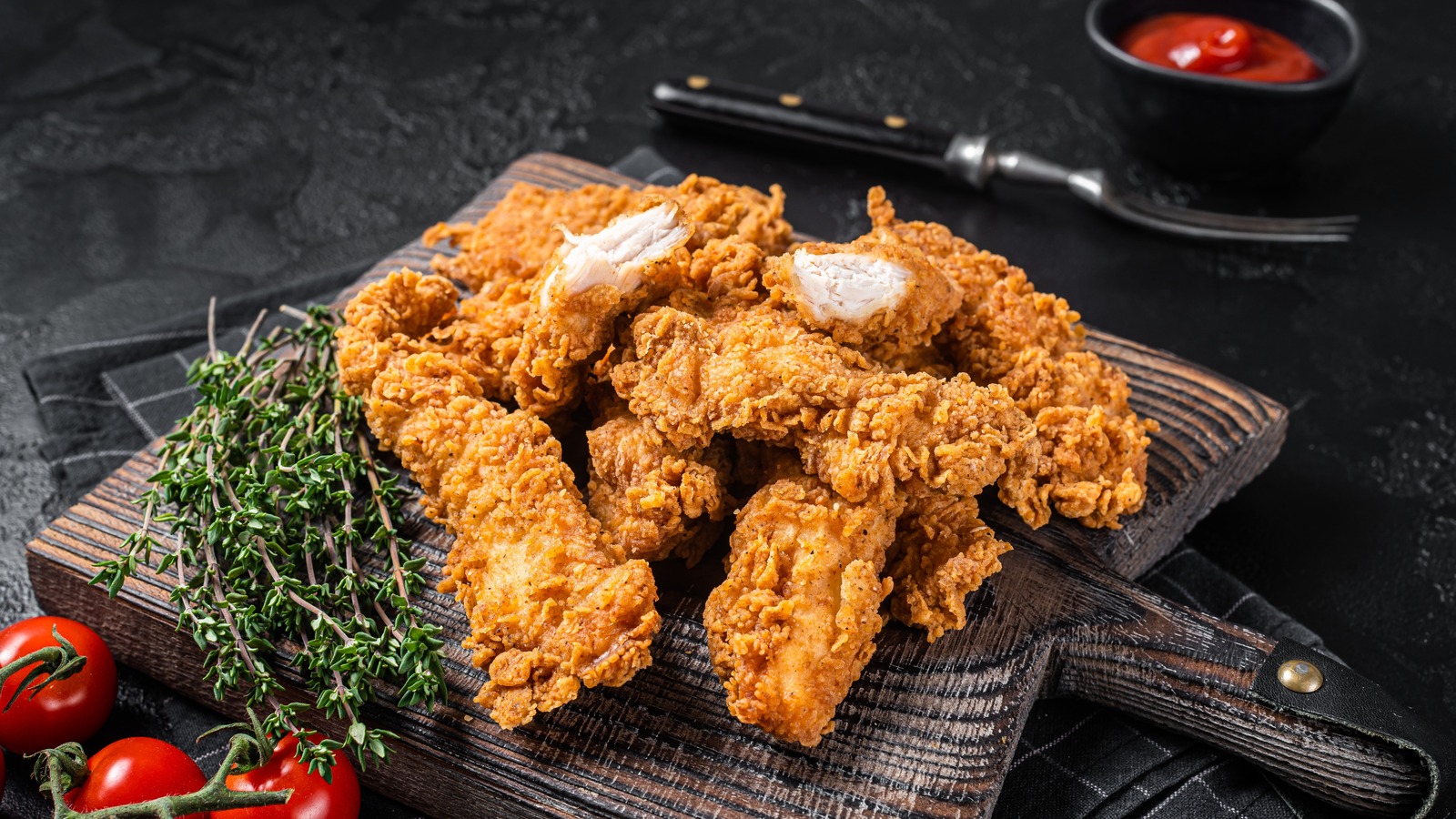
Breadings
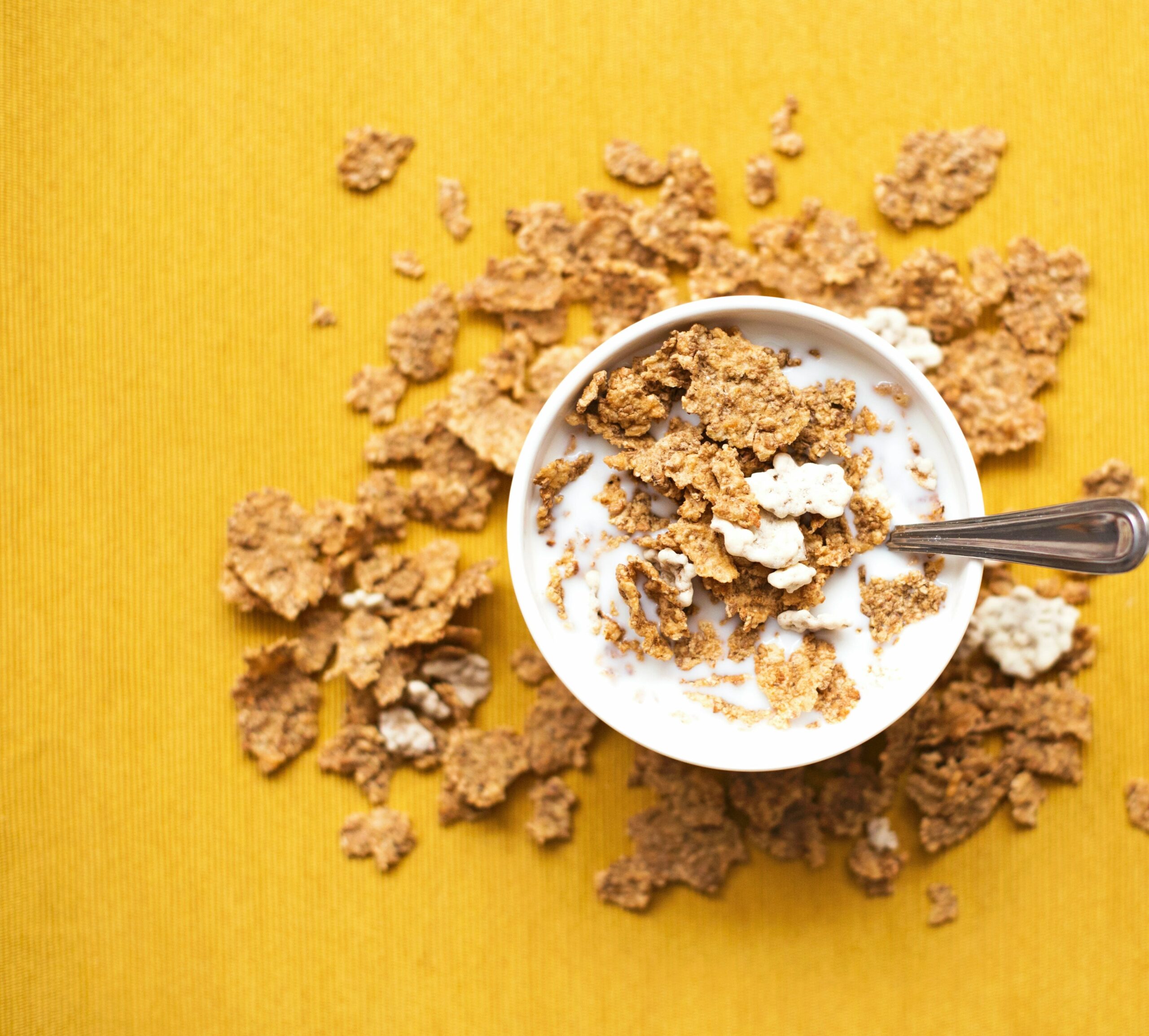
Breakfast cereals
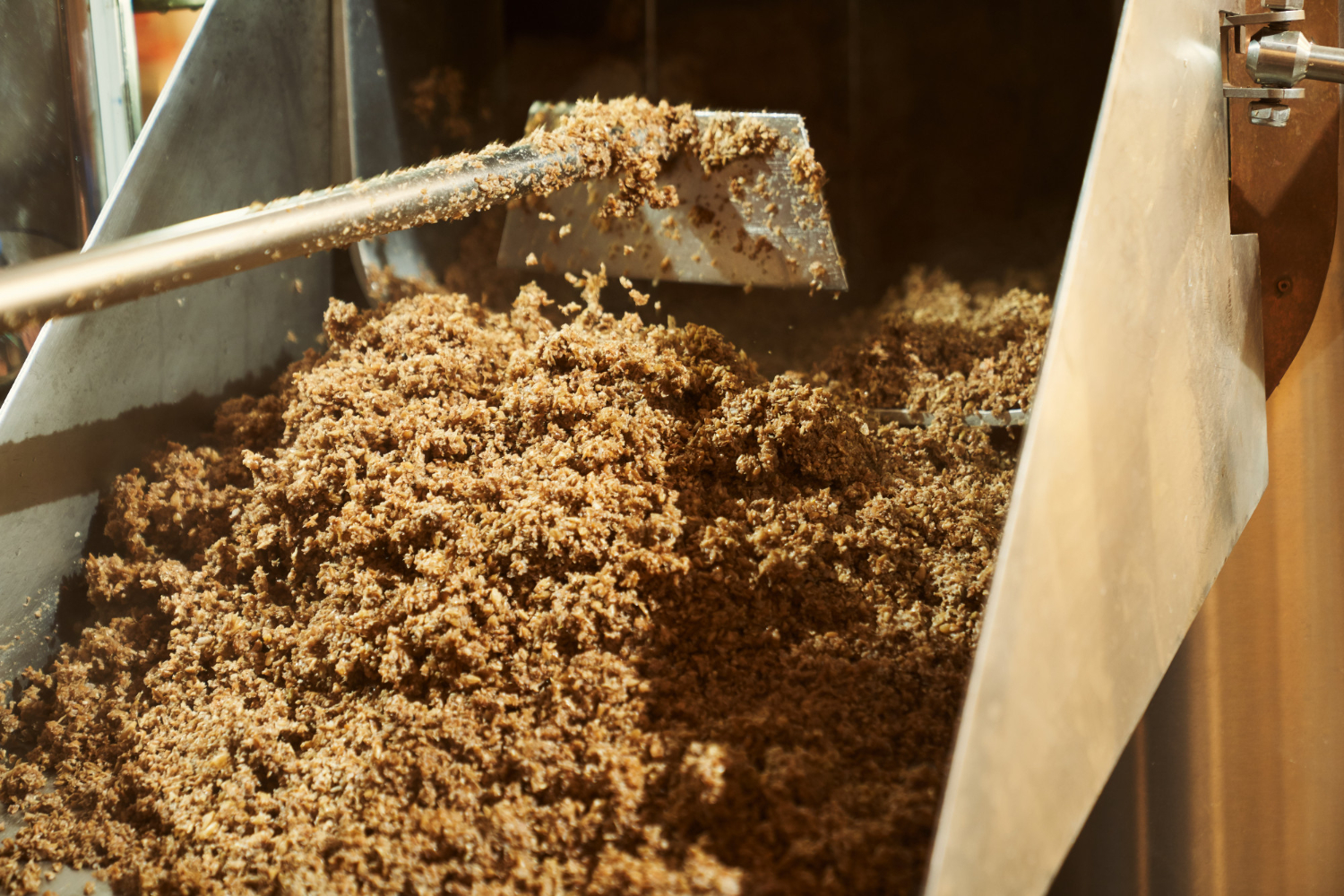
Brewers grain
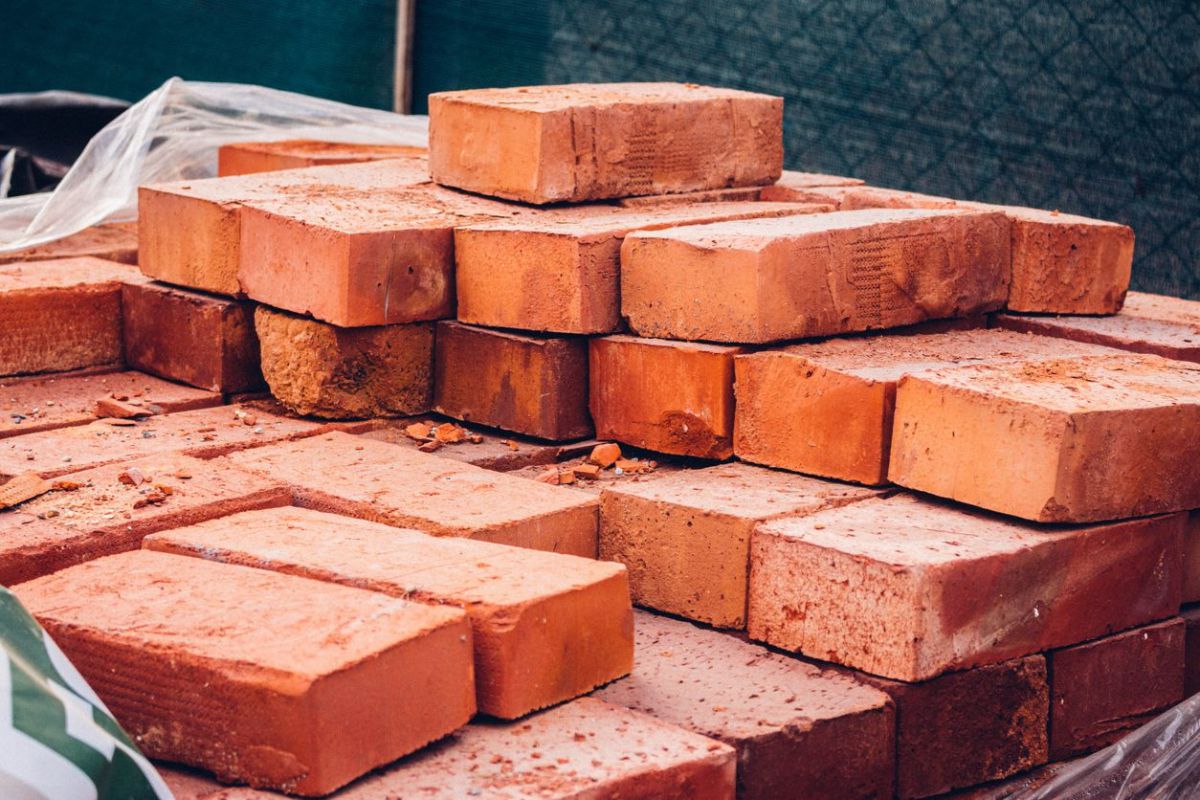
Brick
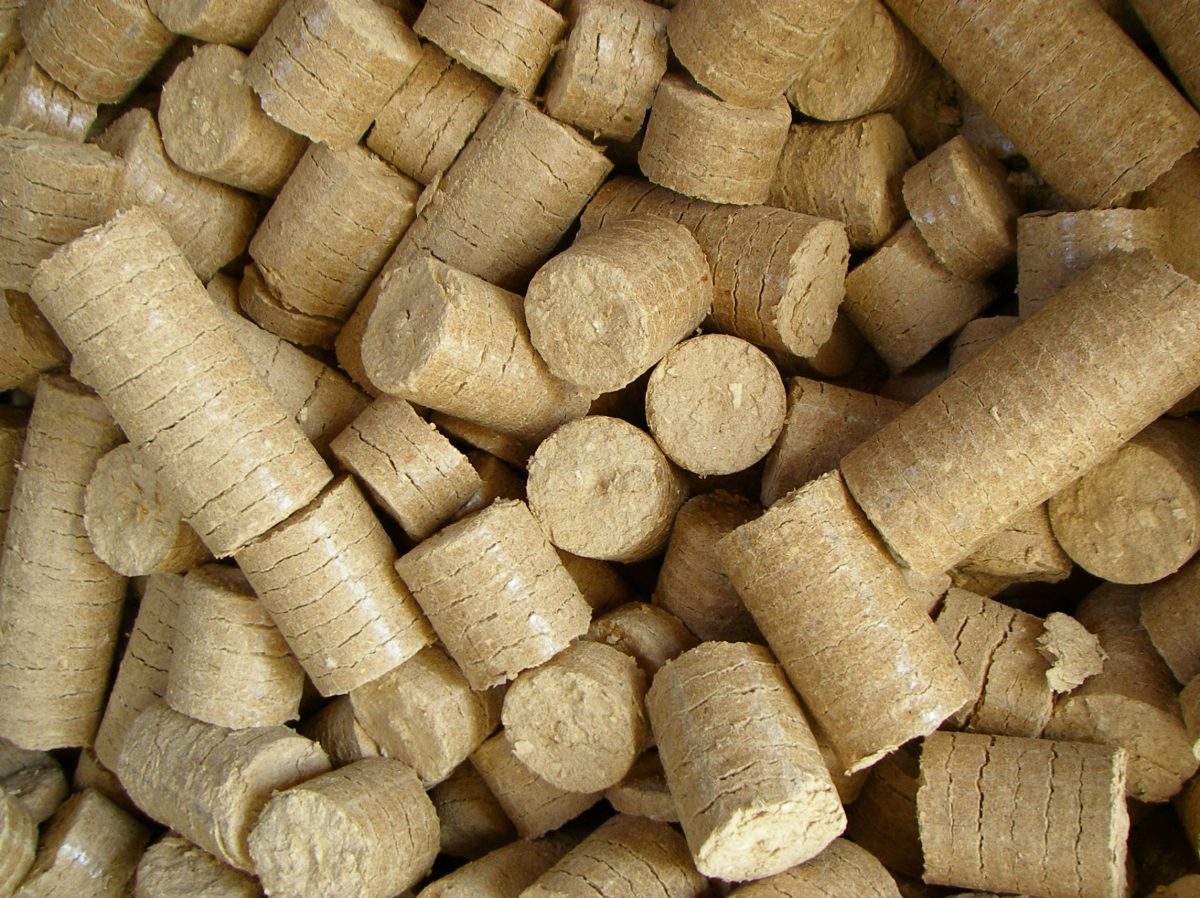
Briquettes
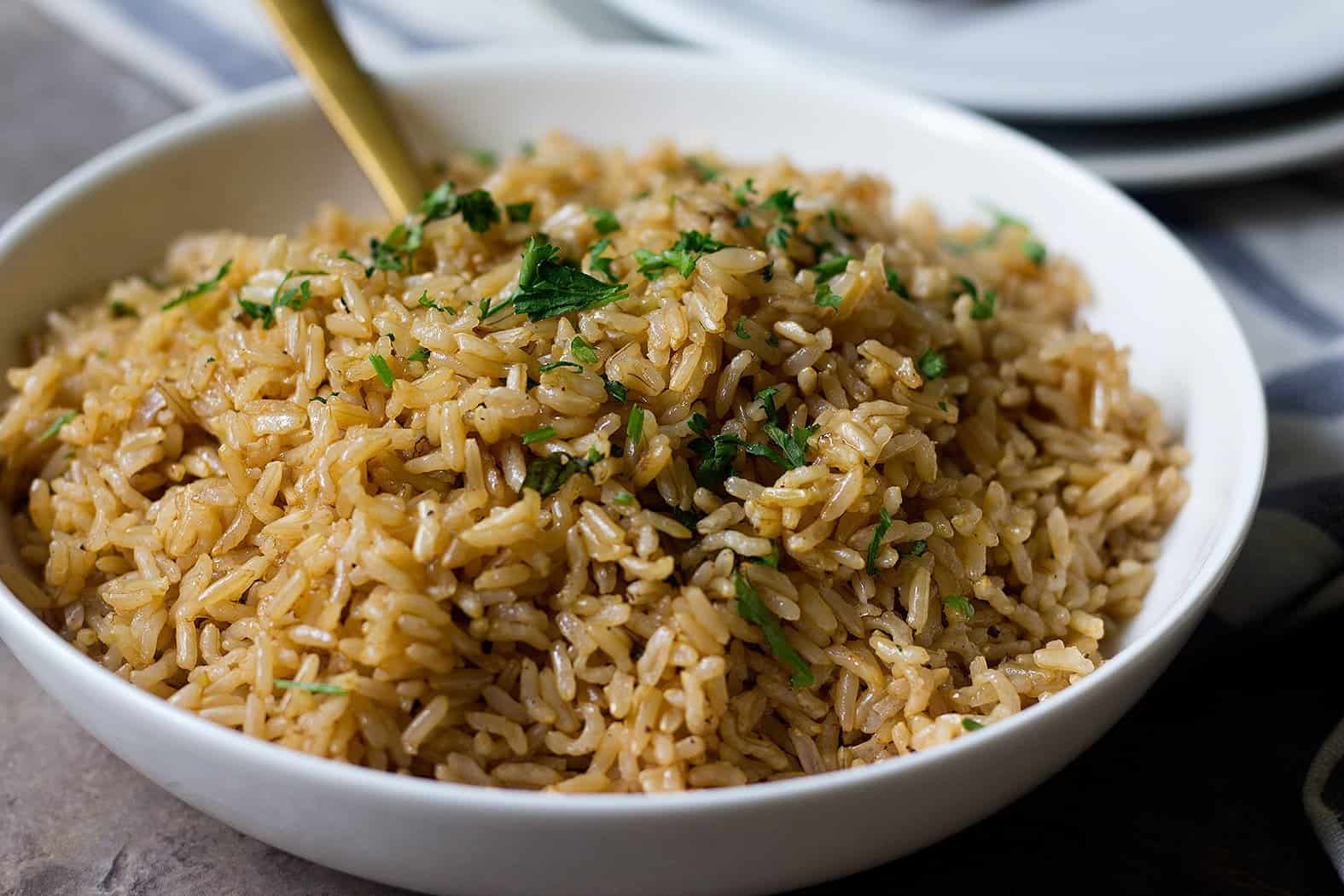
Brown rice
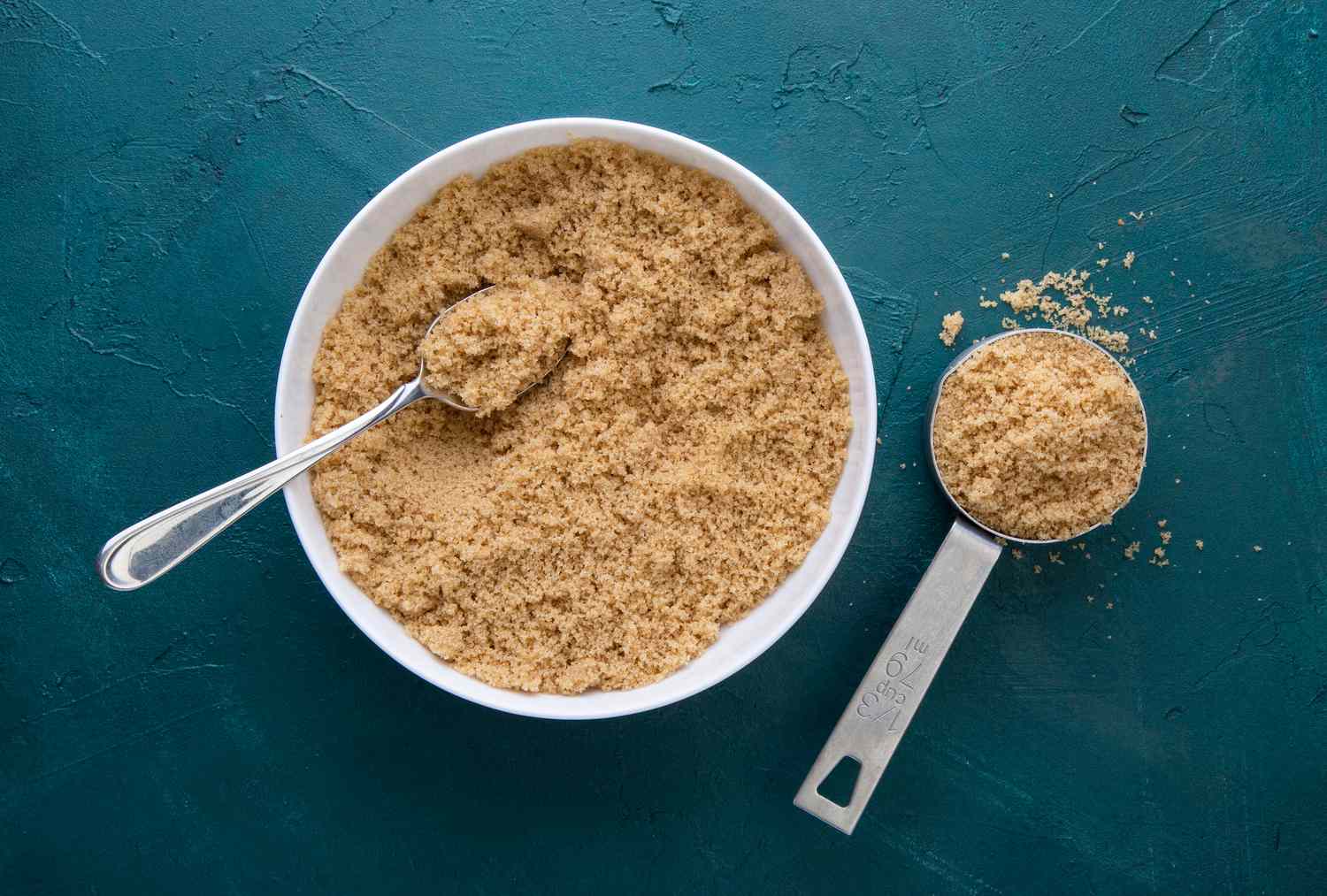
Brown sugar
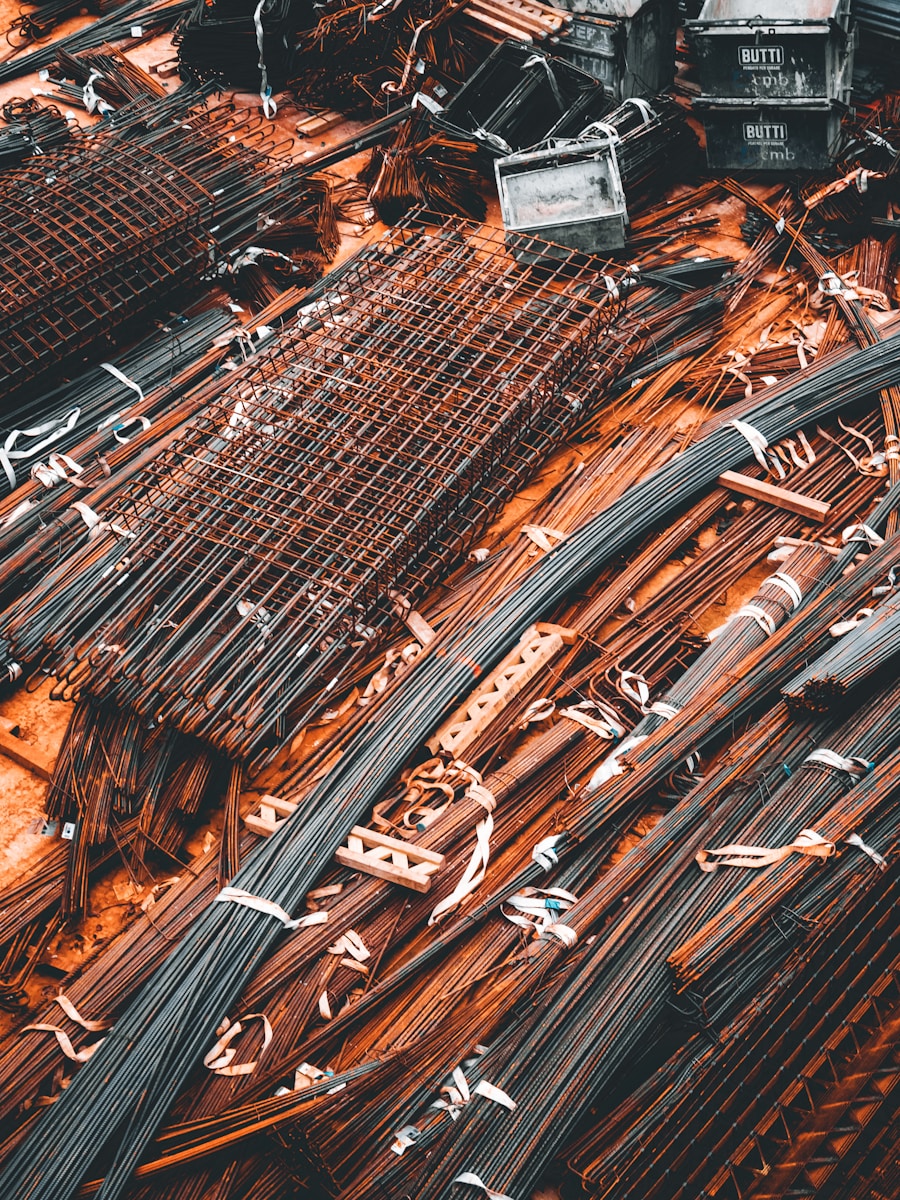
Building materials
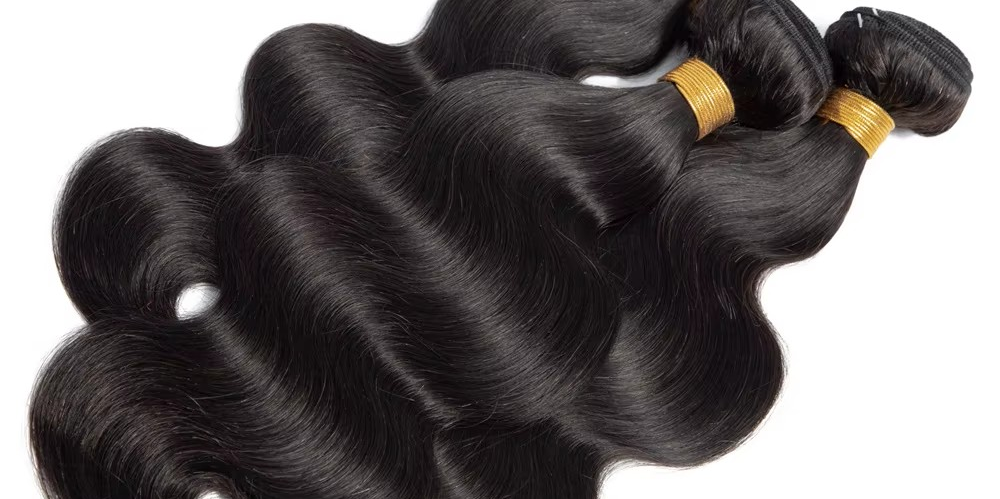
Bundles
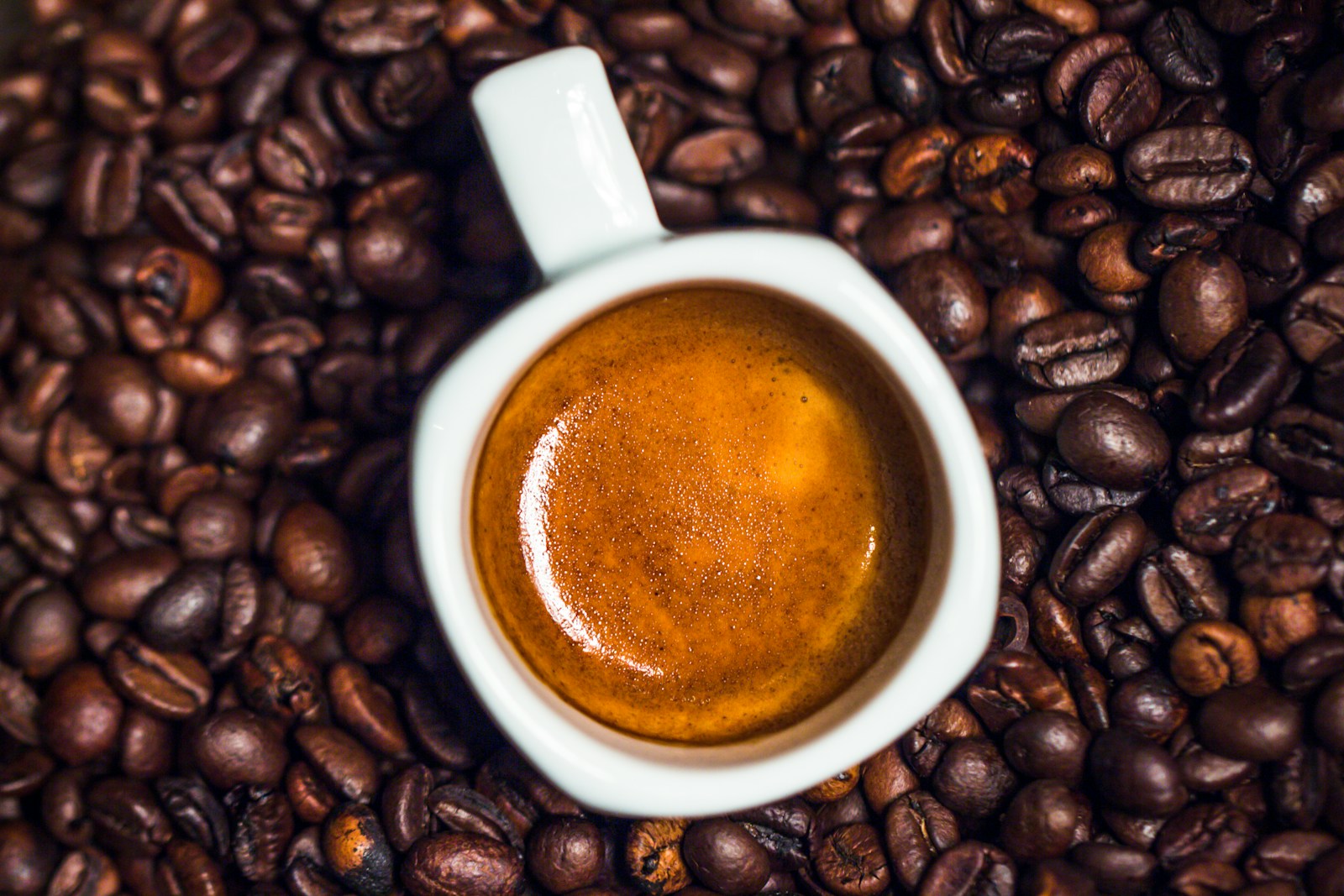
Caffeine
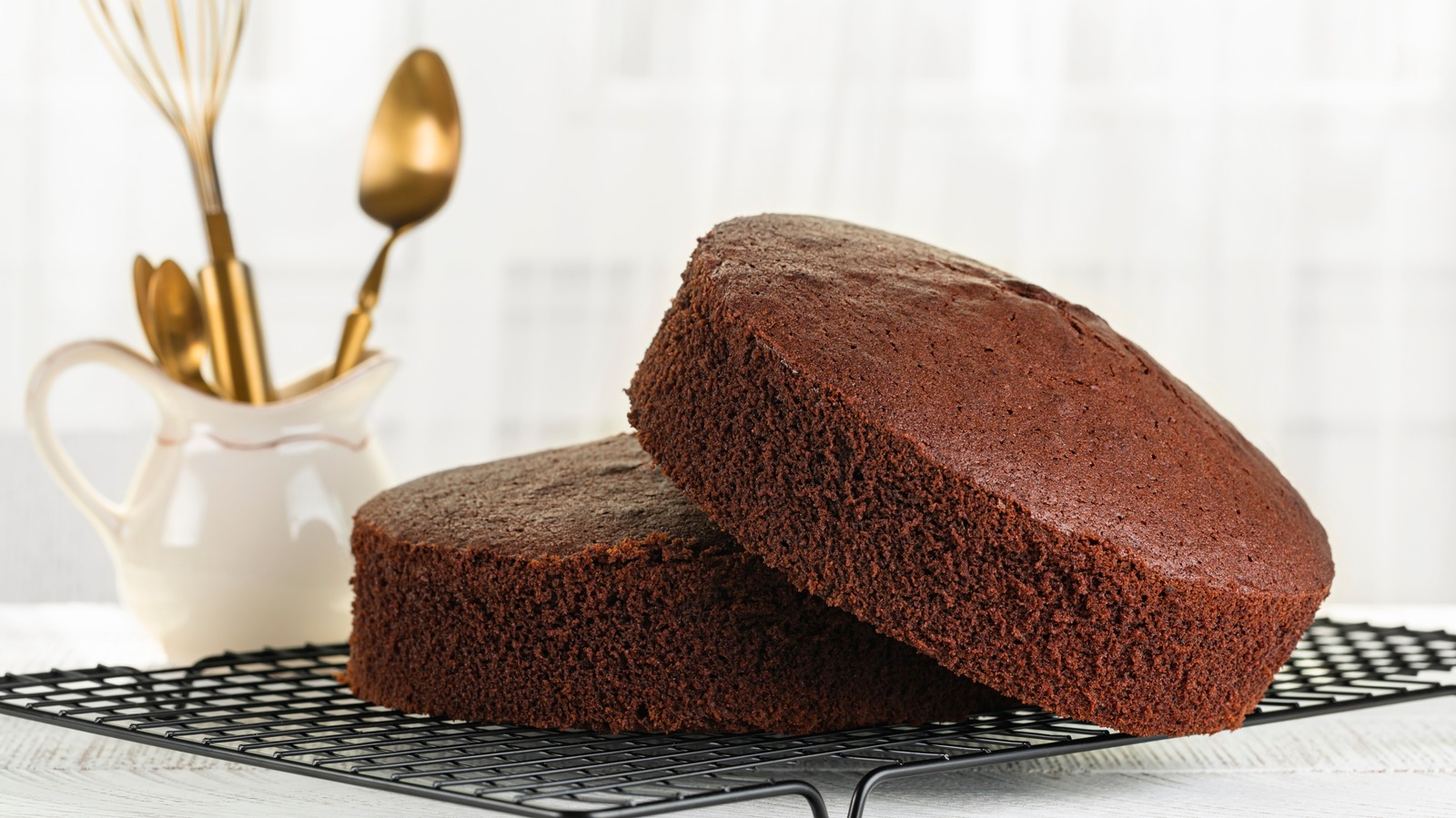
Cake mixes
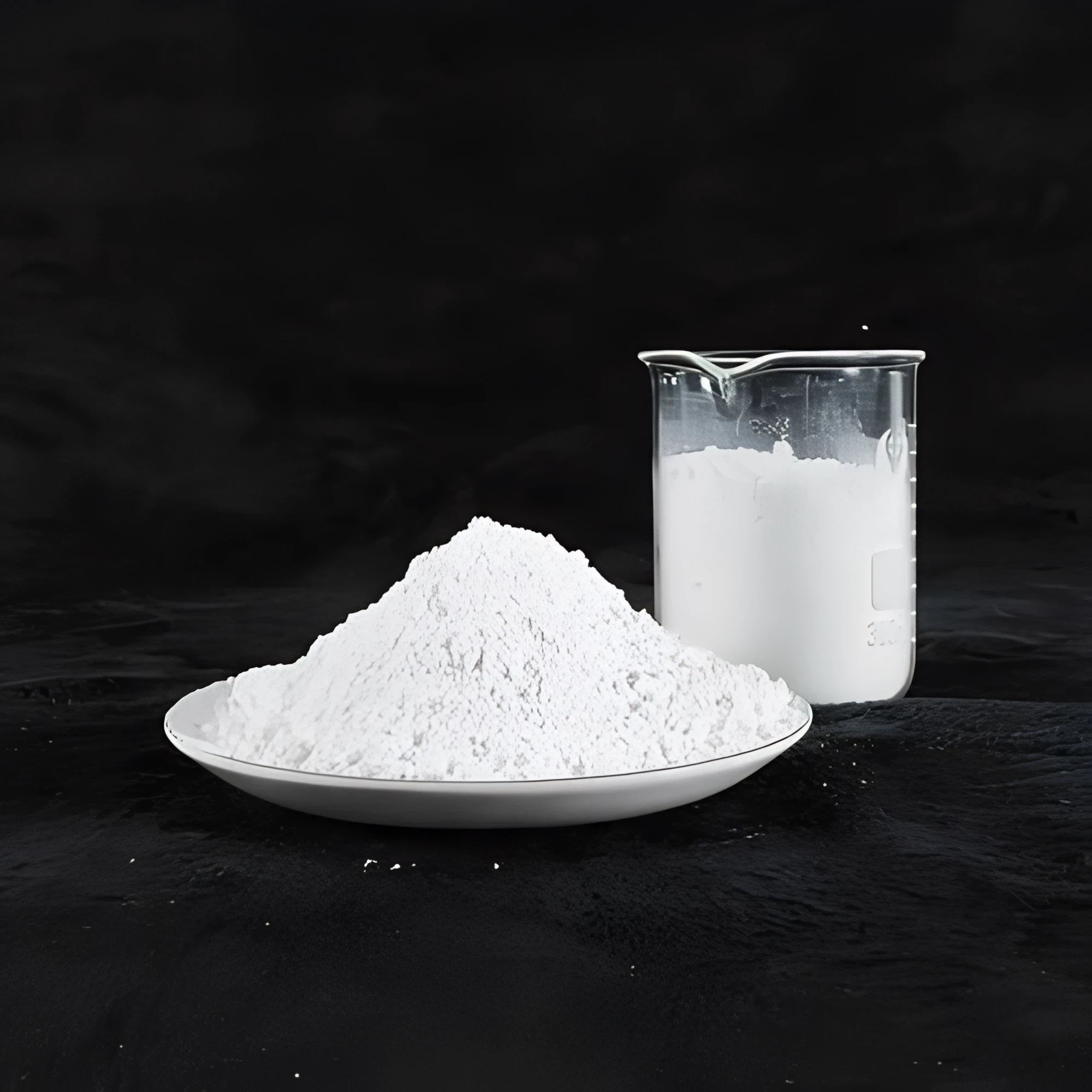
Calcium carbonate (gcc)
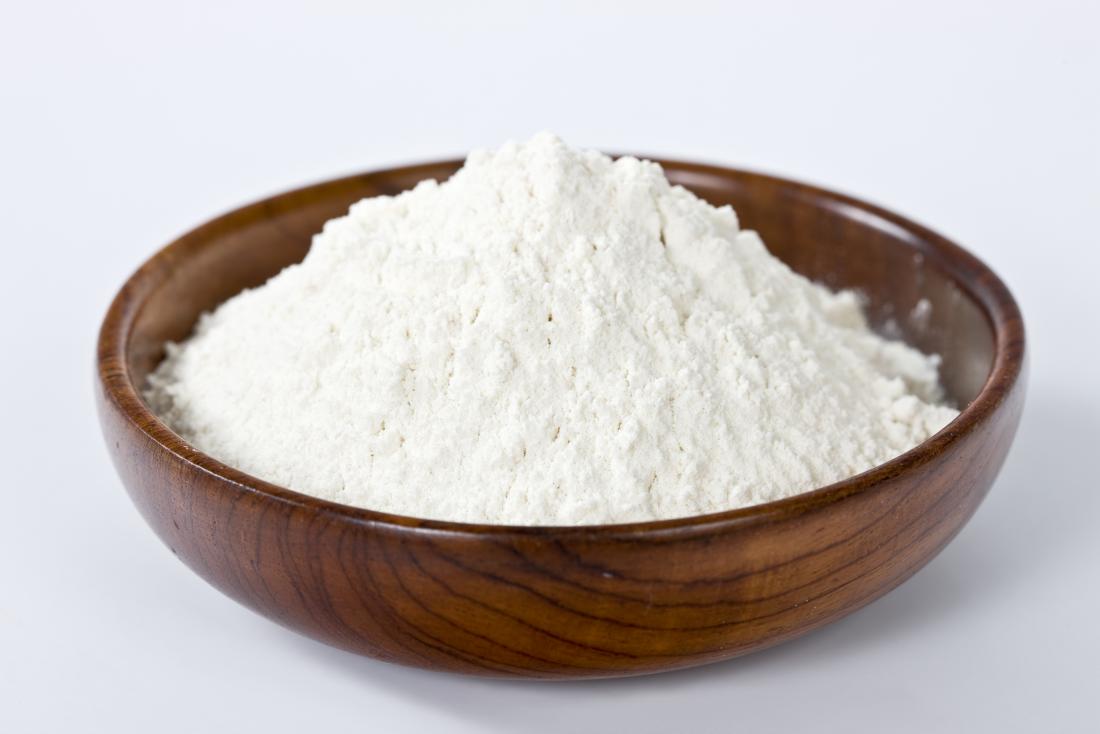
Calcium phosphate

Calcium supplements
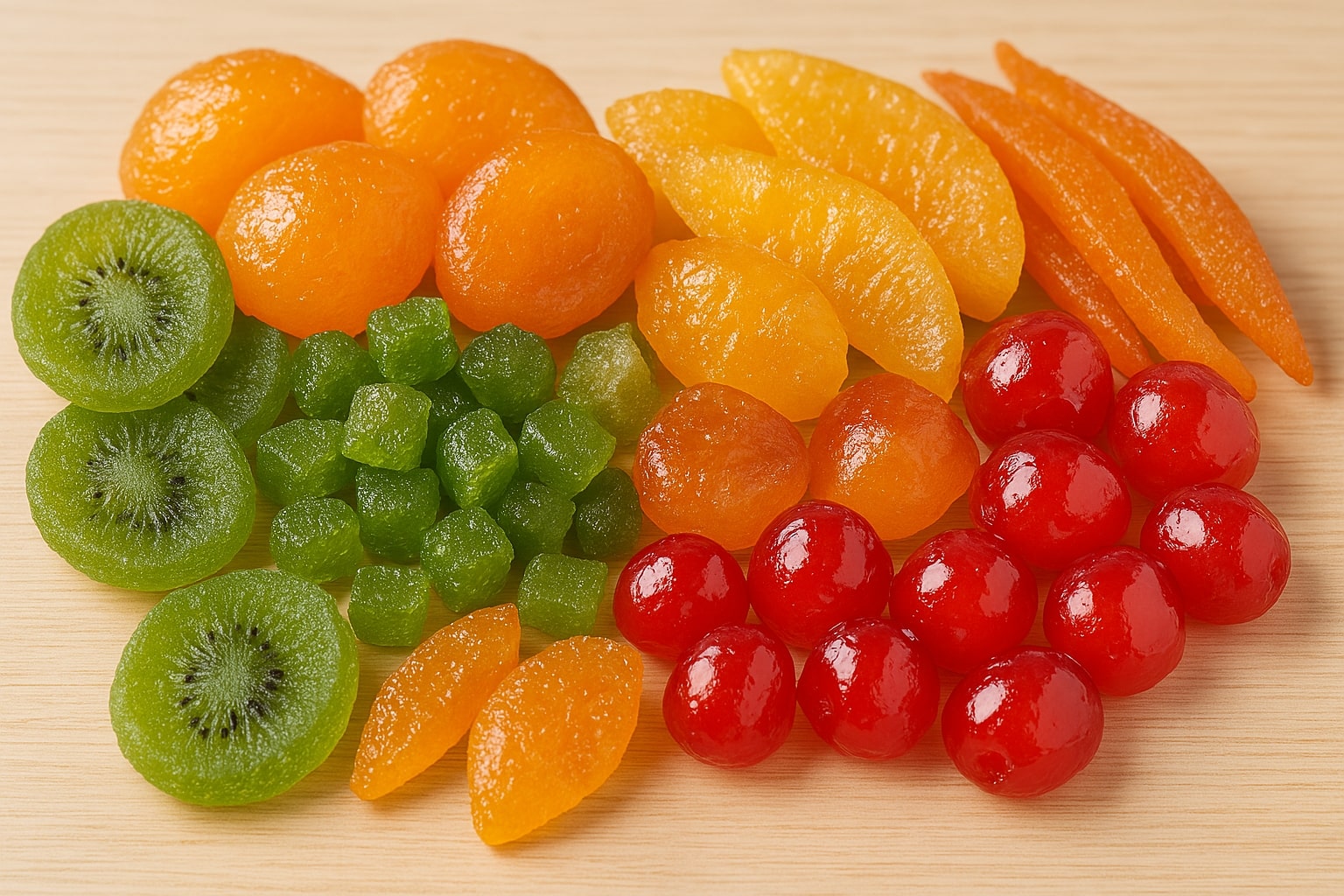
Candied fruits
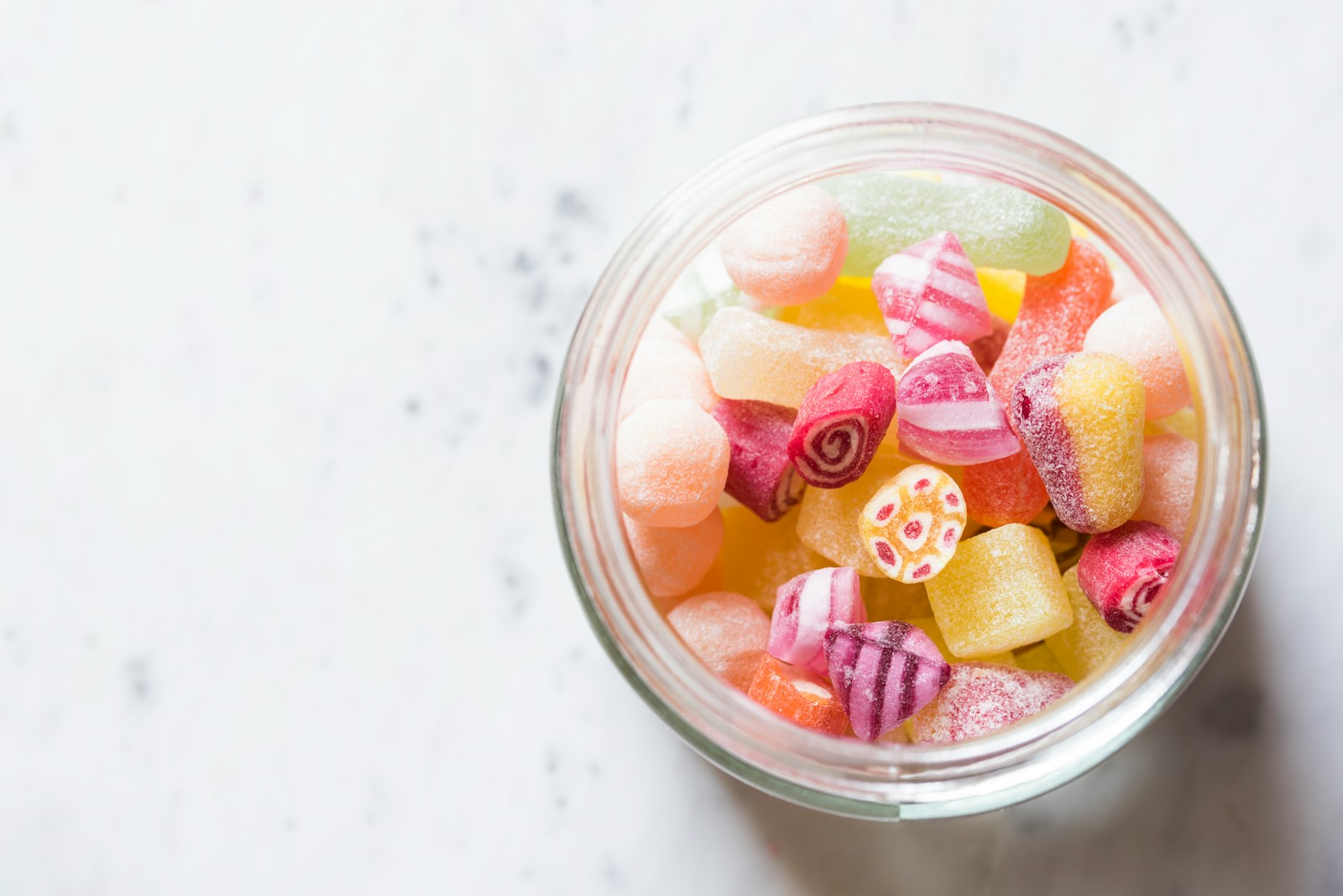
Candy coatings
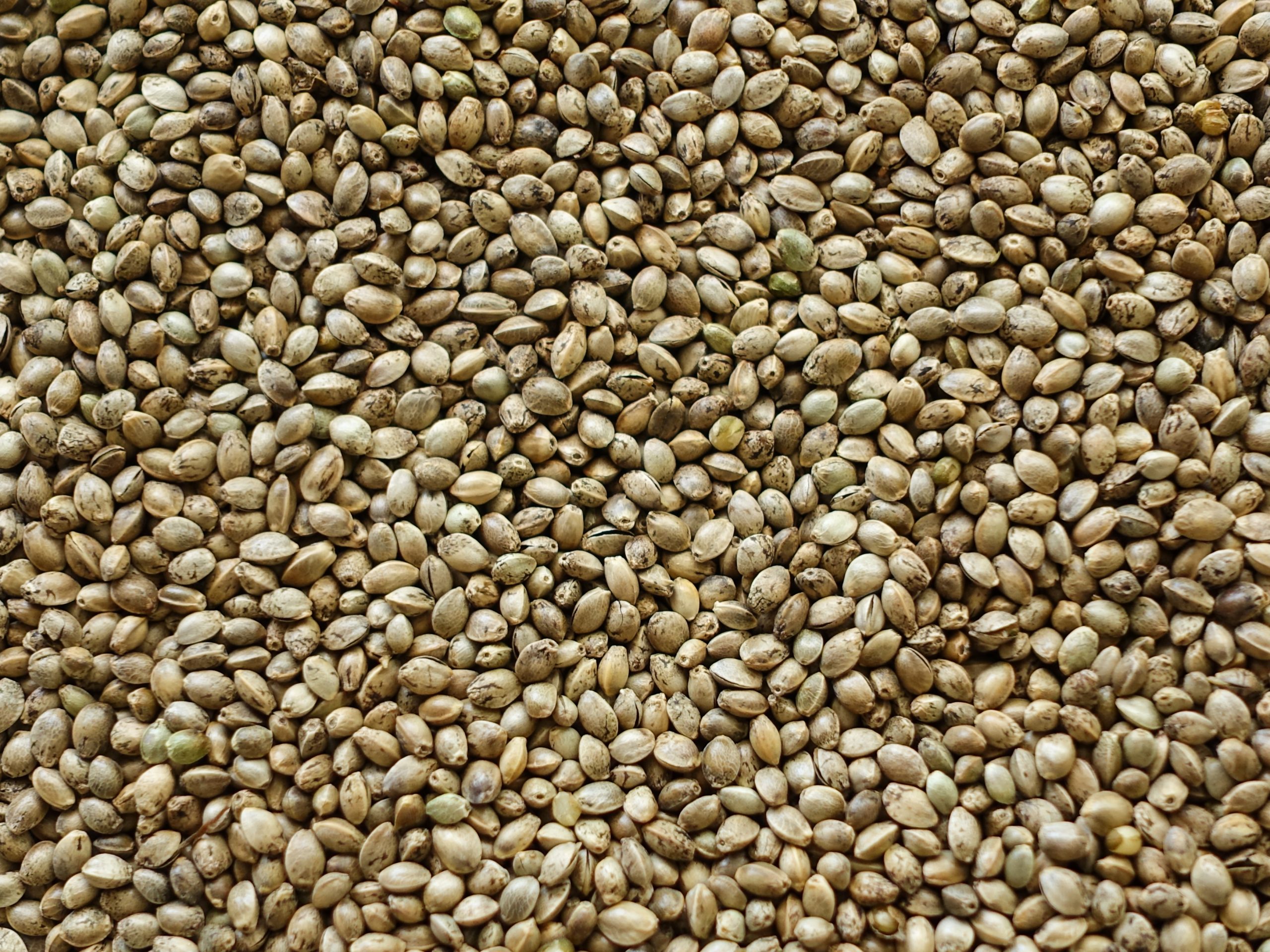
Cannabis seeds
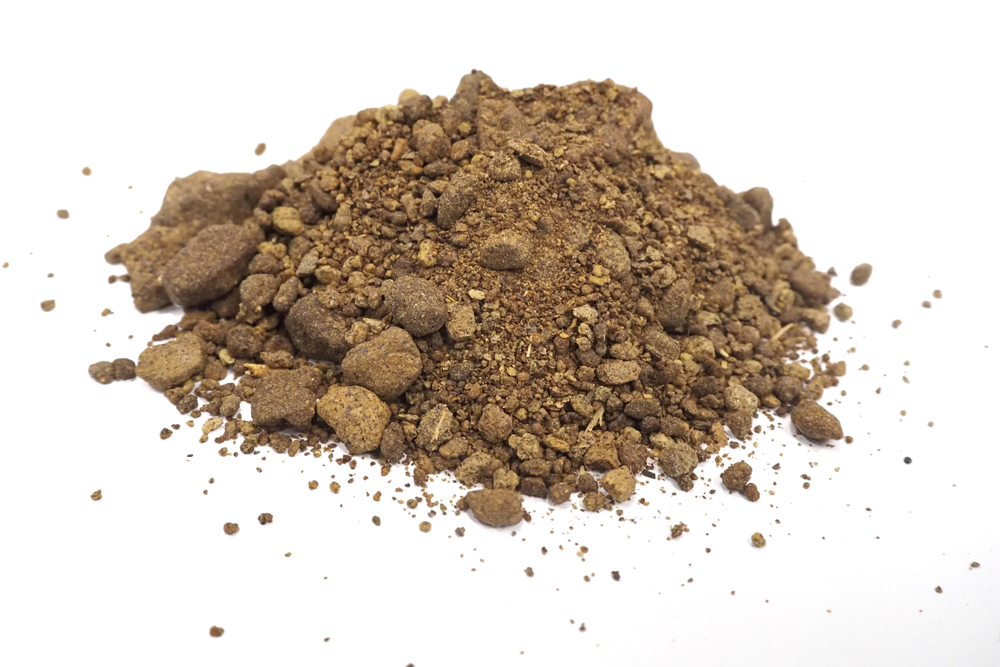
Canola meal
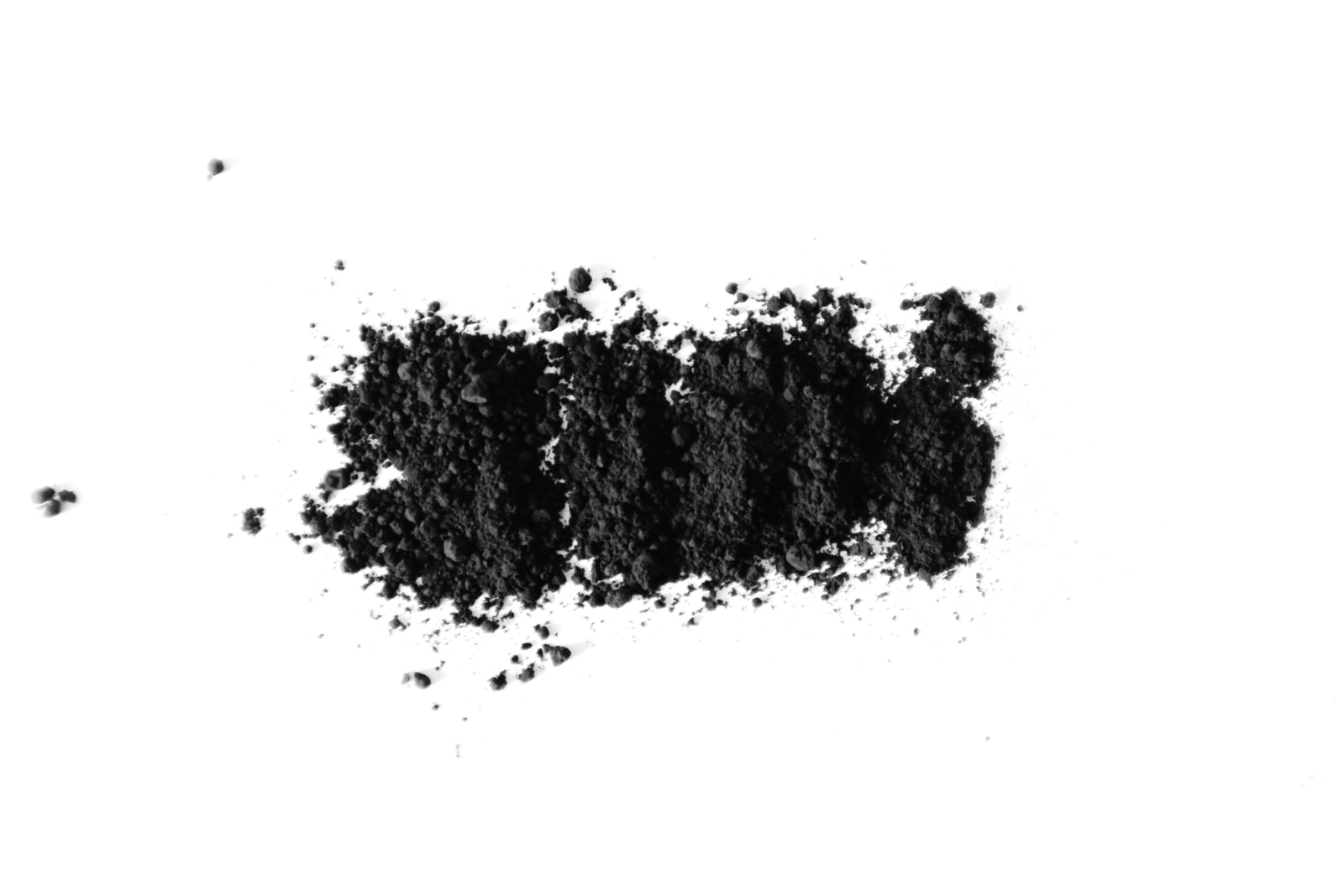
Carbon black
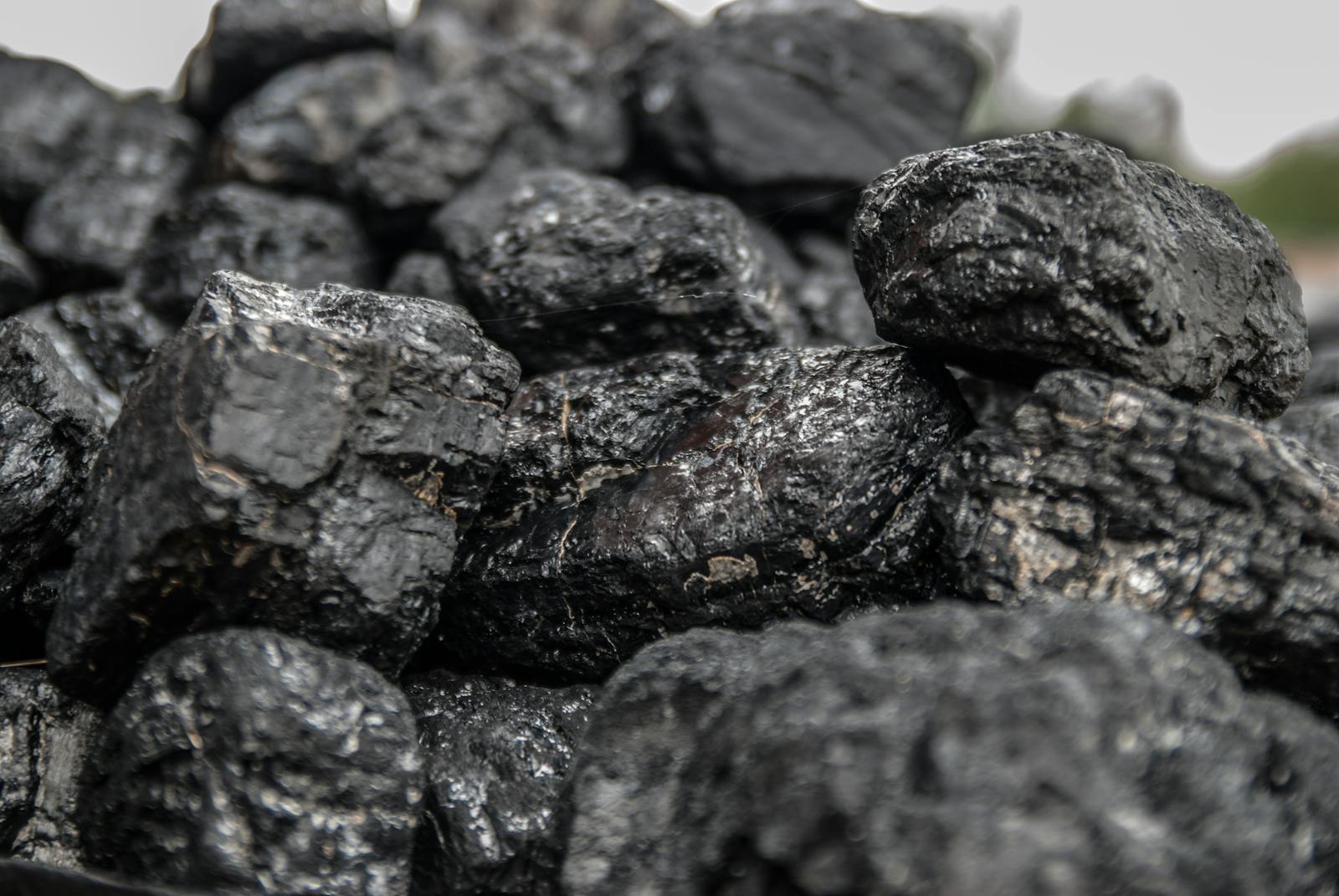
Carbon materials
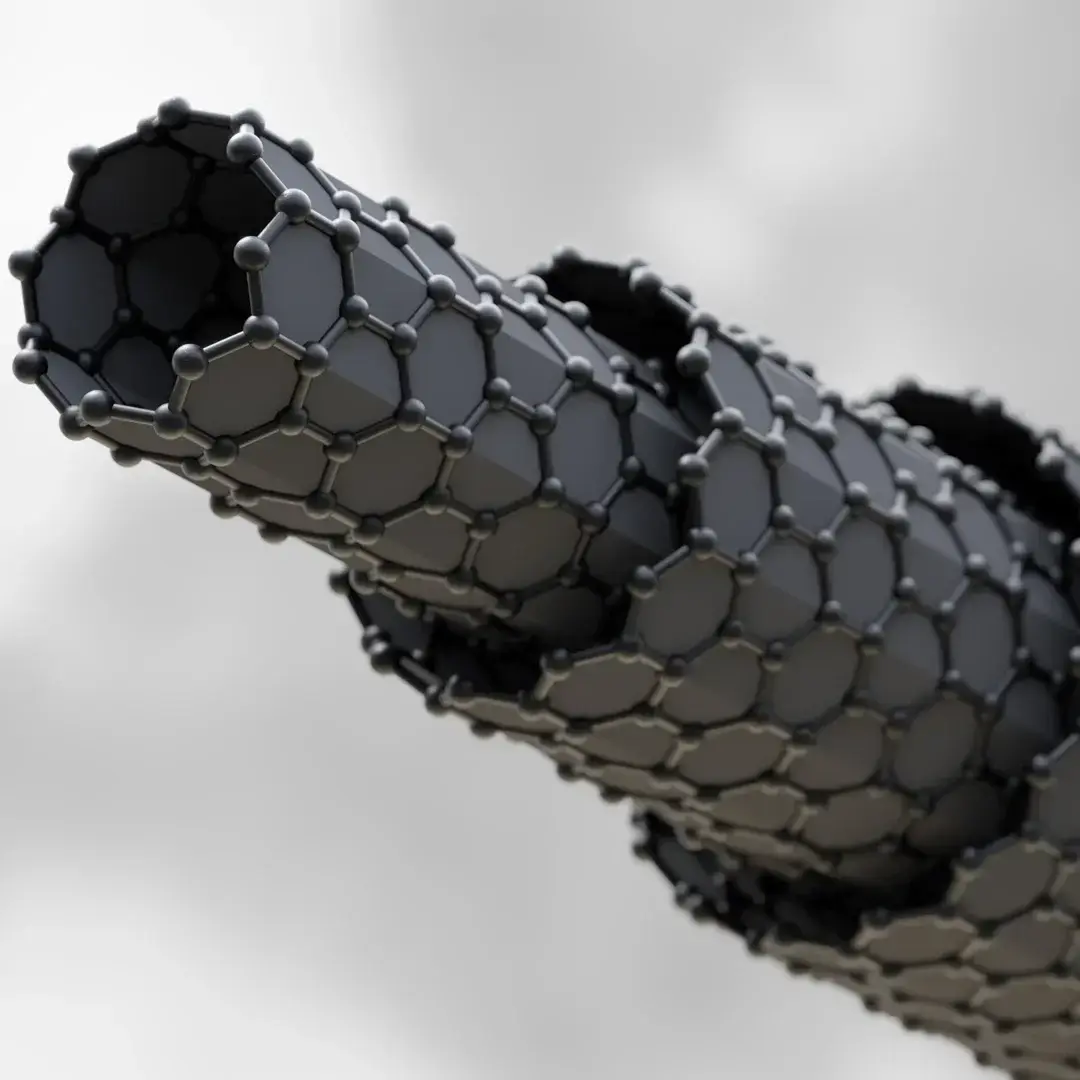
Carbon nanotubes
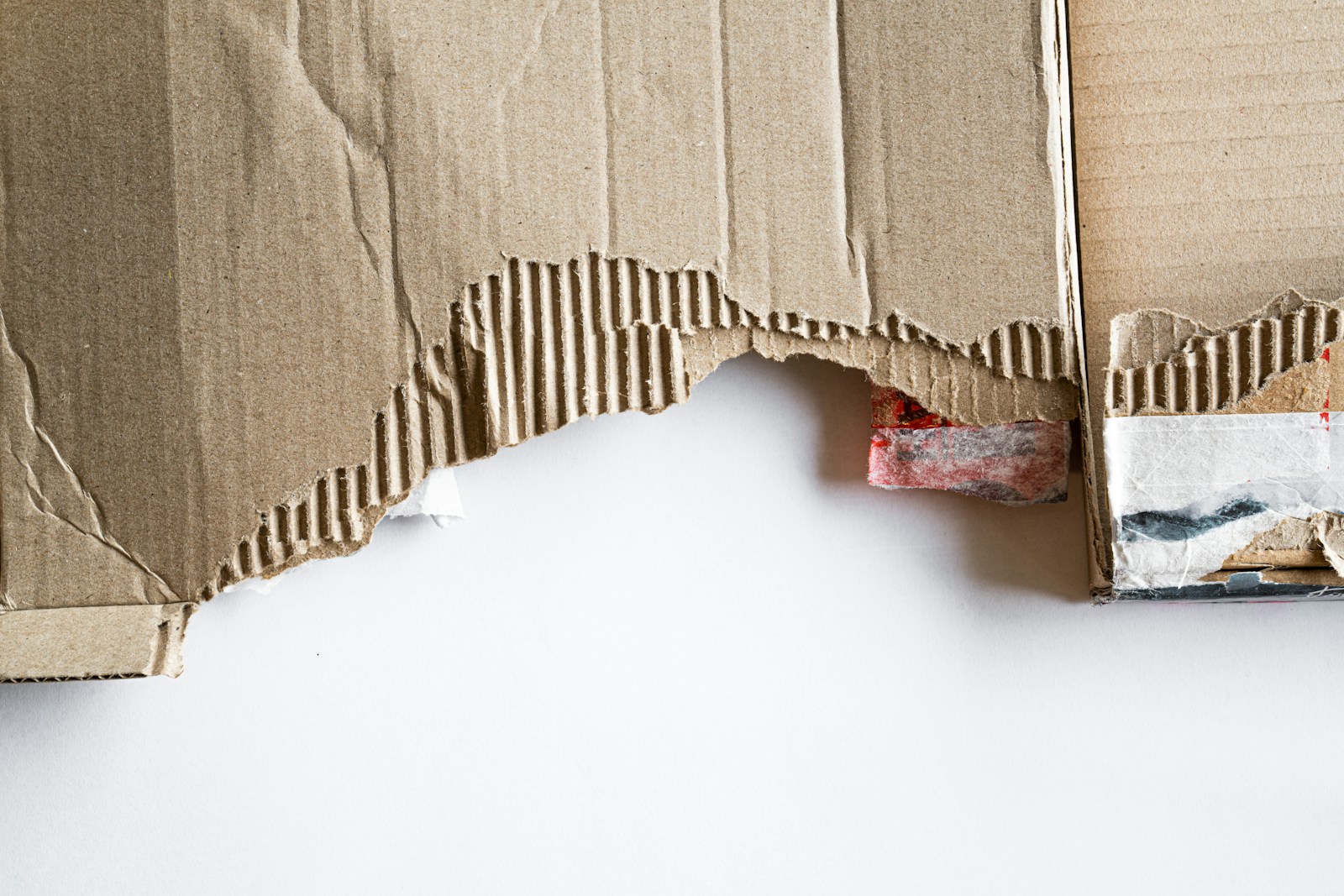
Cardboard
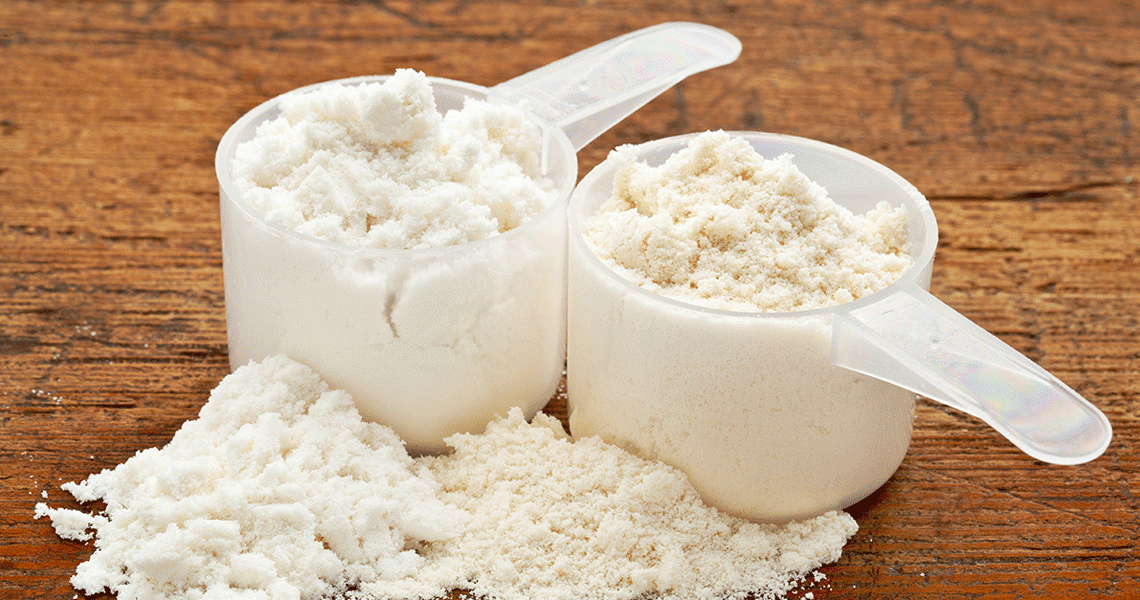
Casein
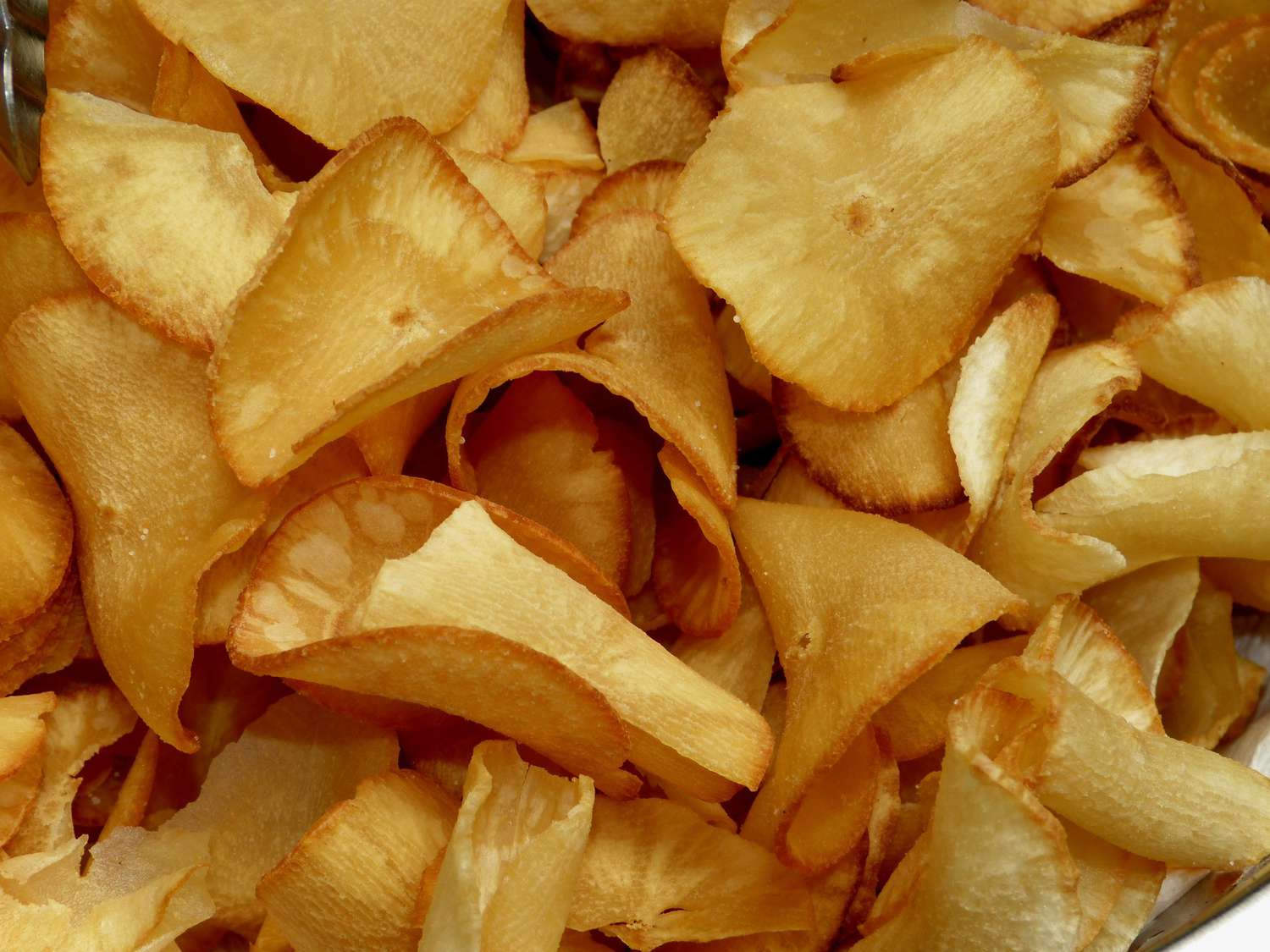
Cassava chips
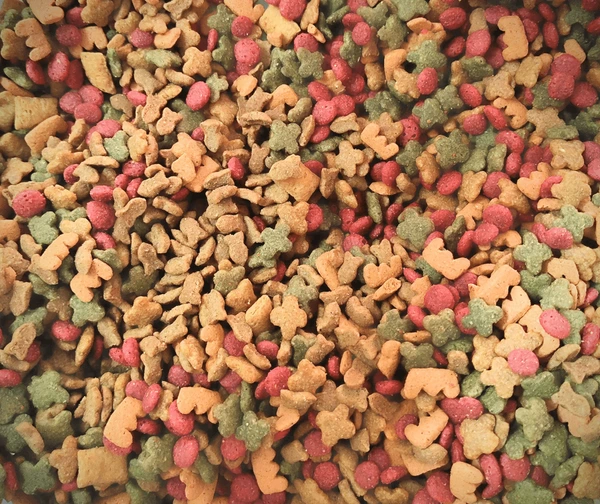
Cat biscuits
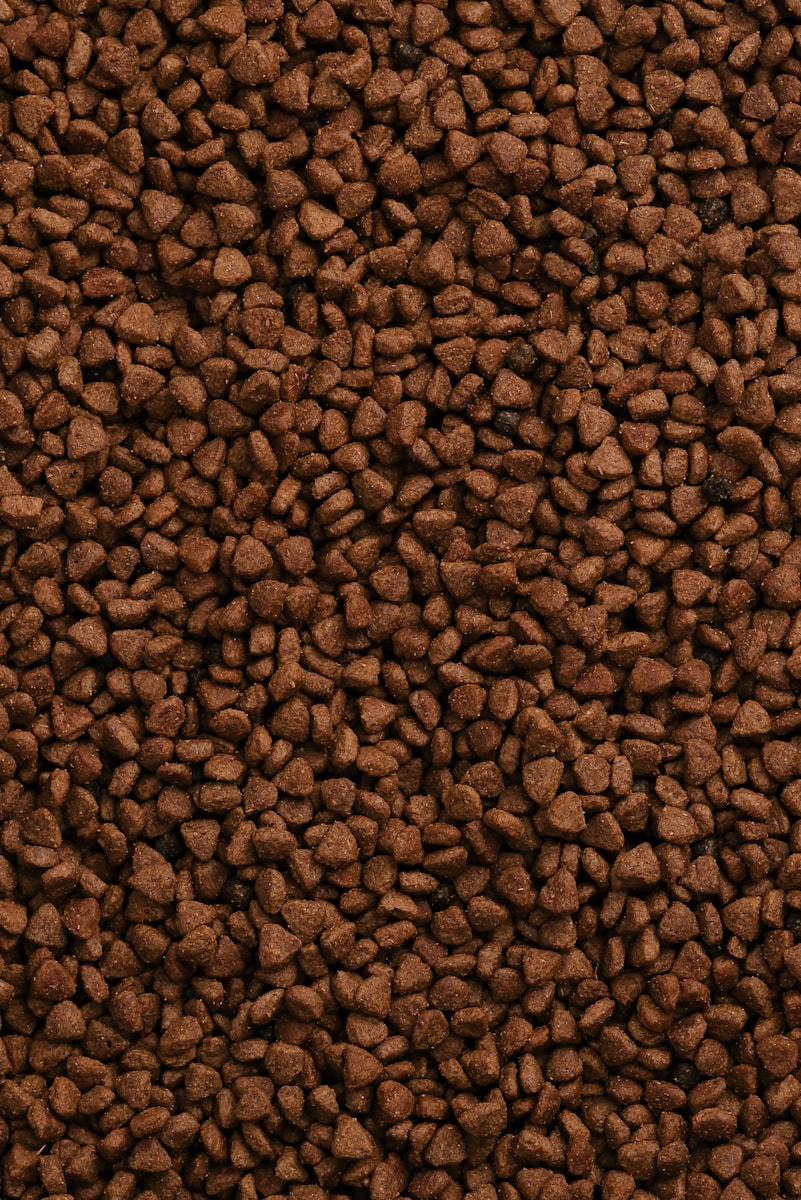
Cat kibble
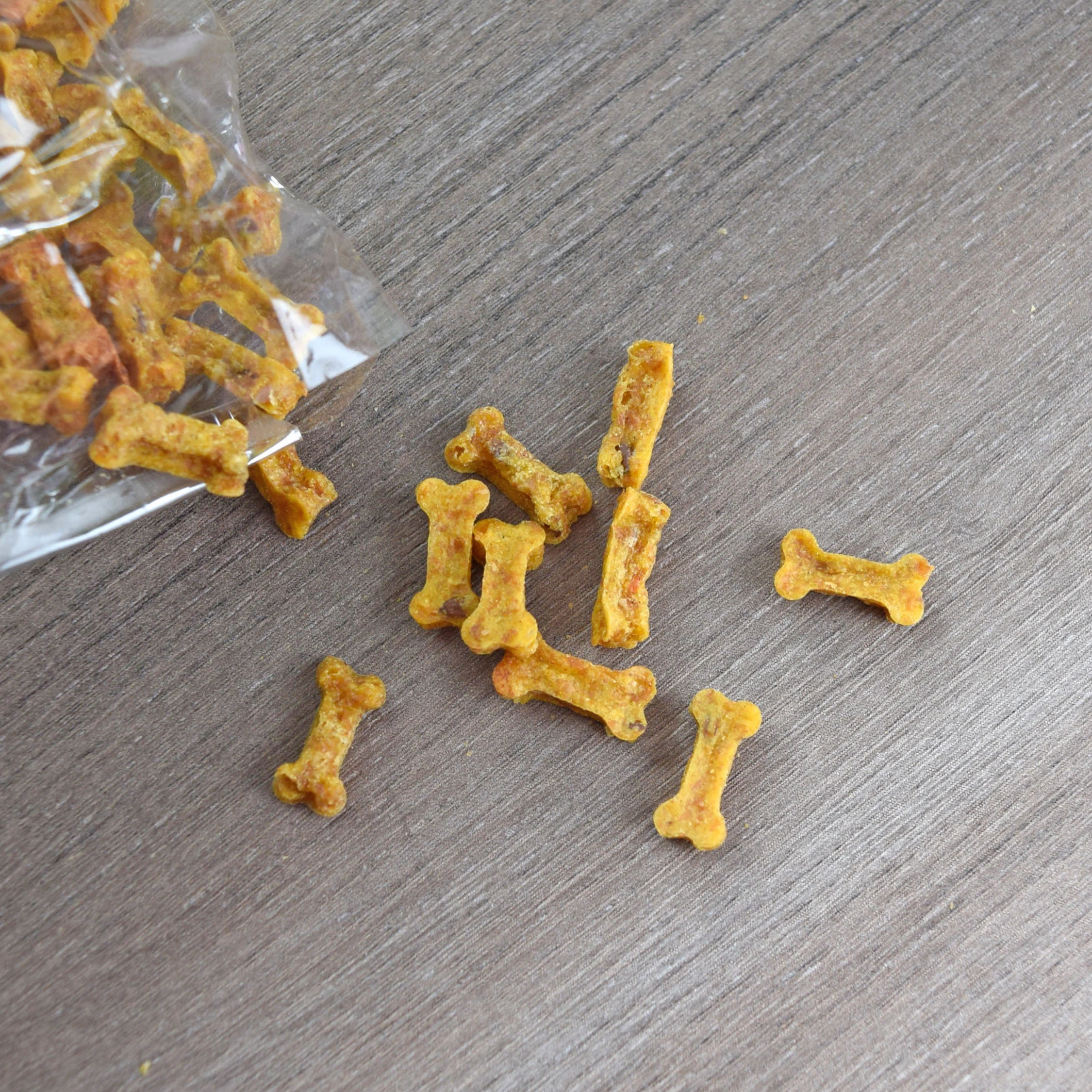
Cat treats
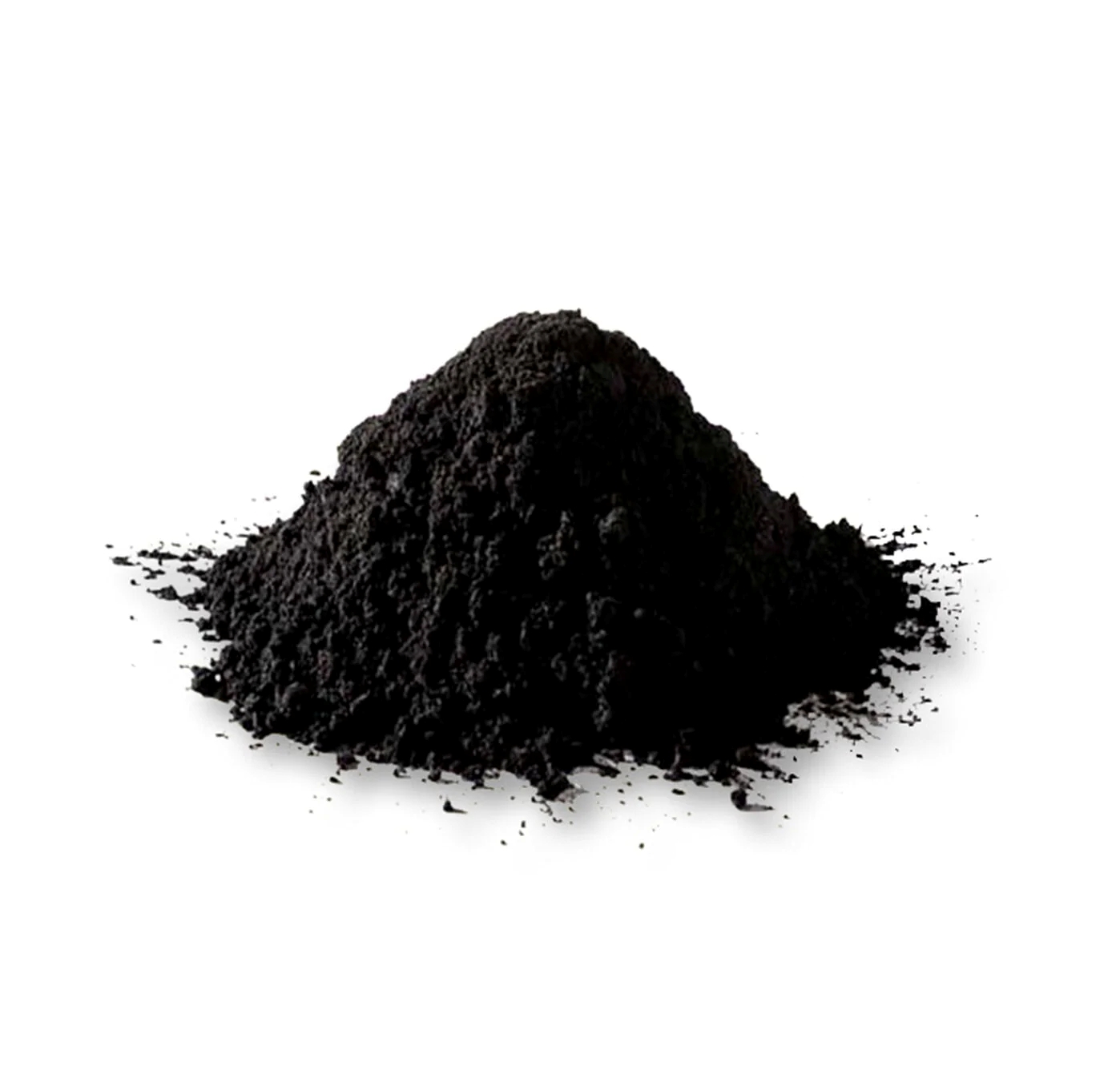
Catalyst powders
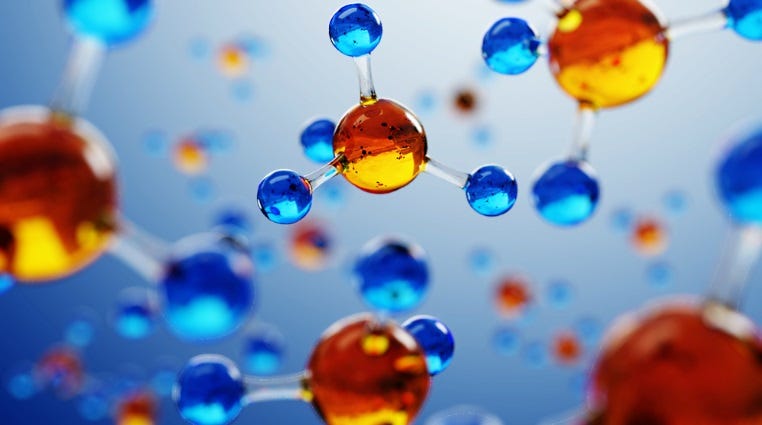
Catalysts
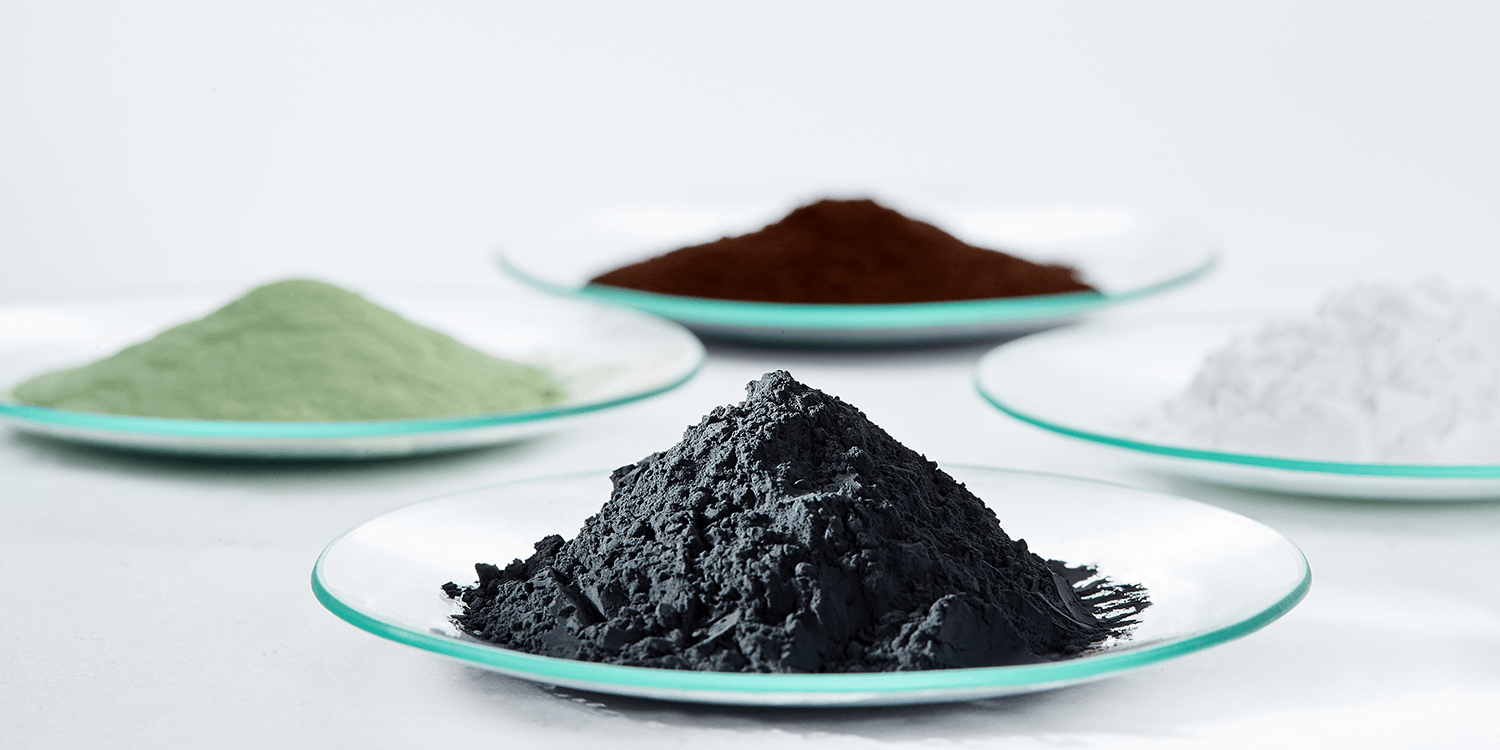
Cathode materials
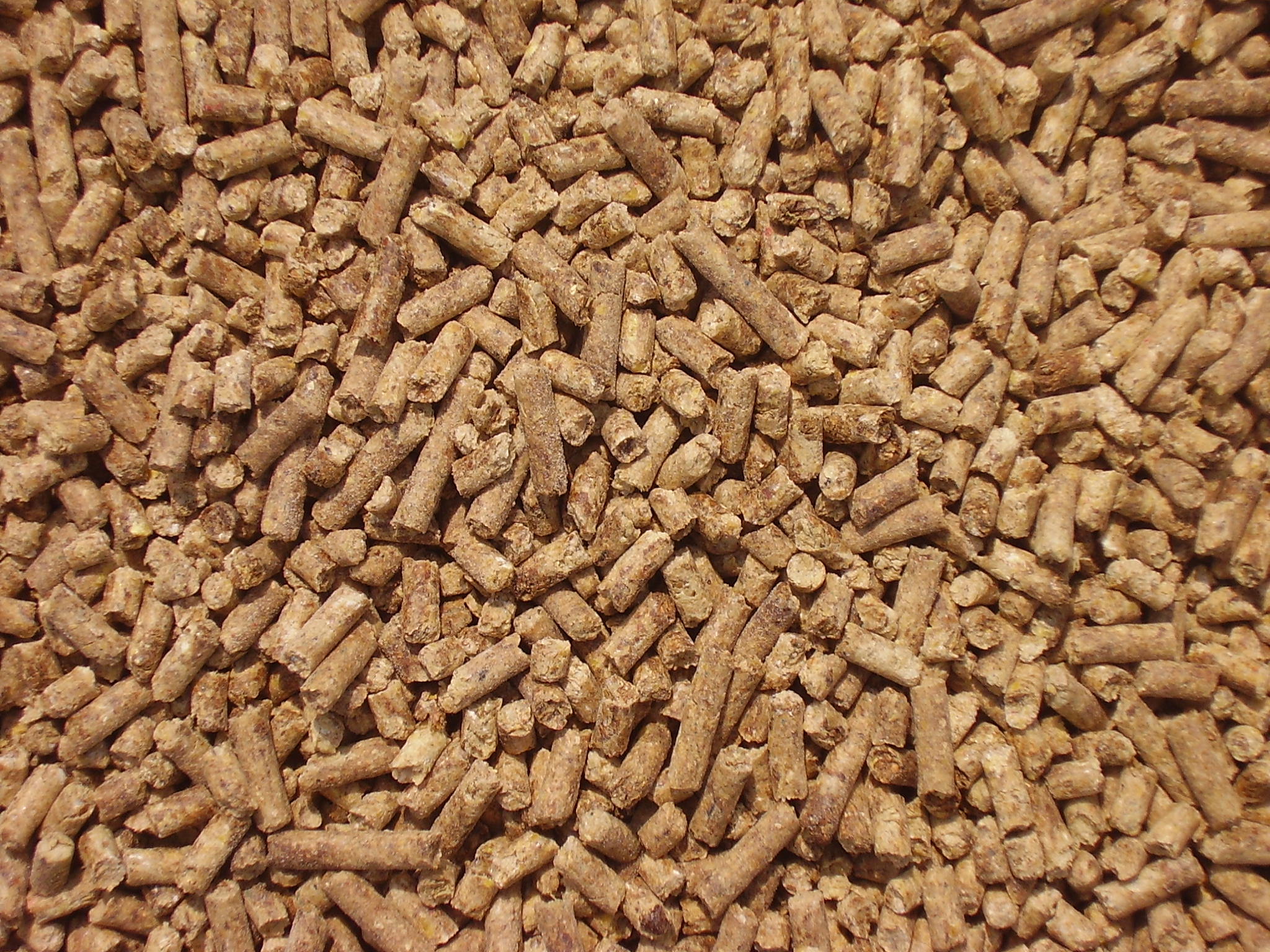
Cattle feed
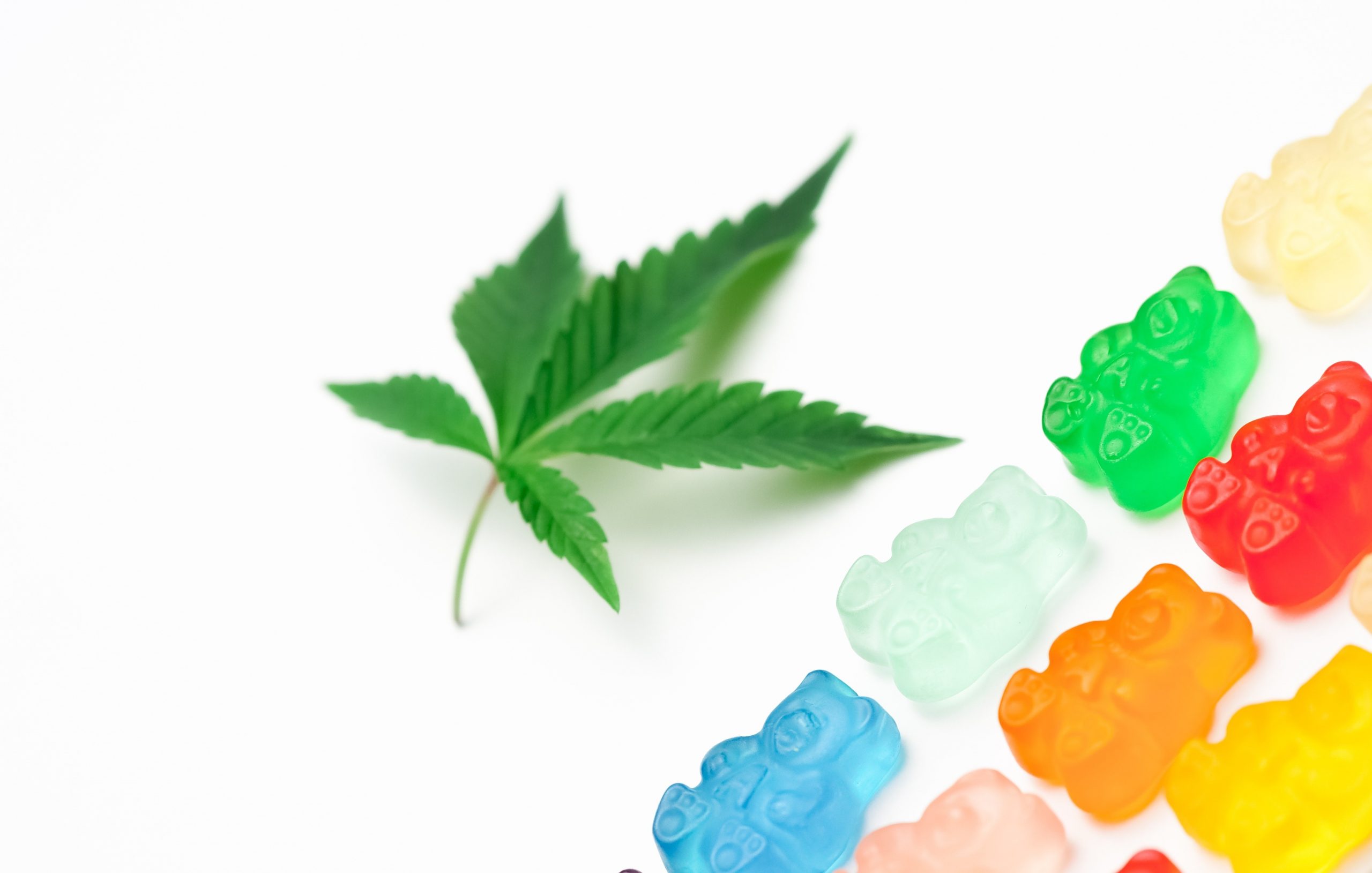
CBD gummies
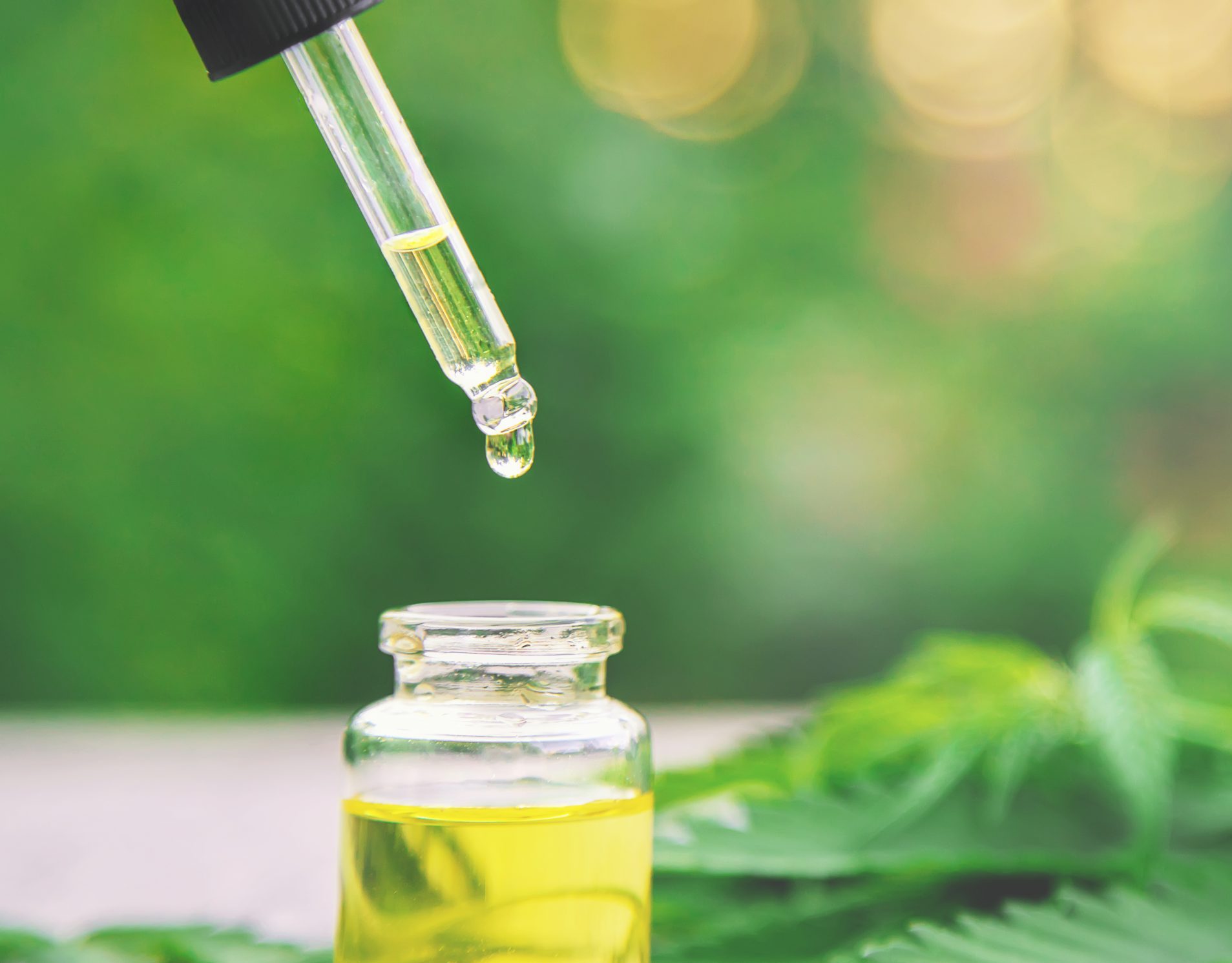
CBD oil
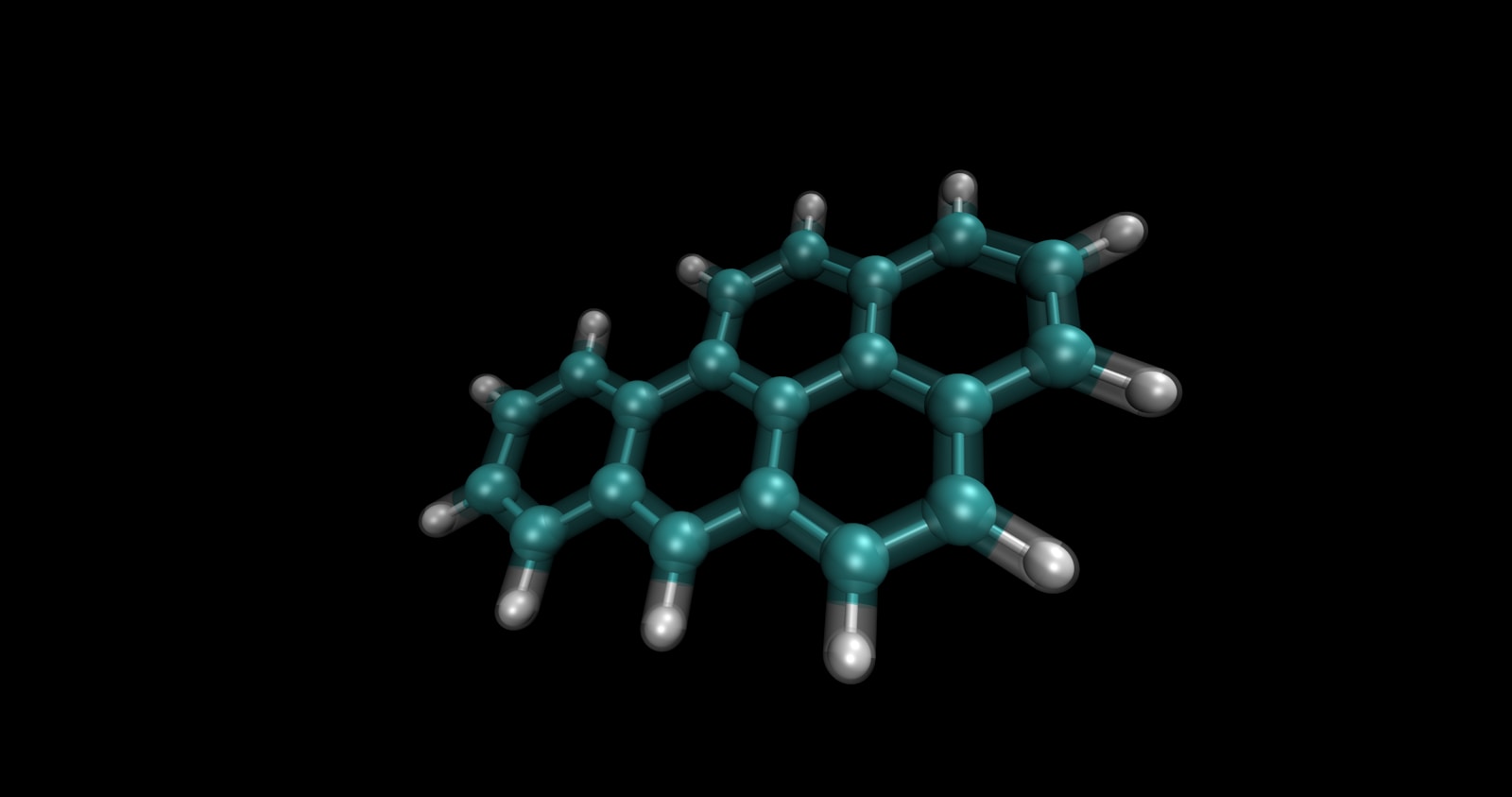
Cellulose
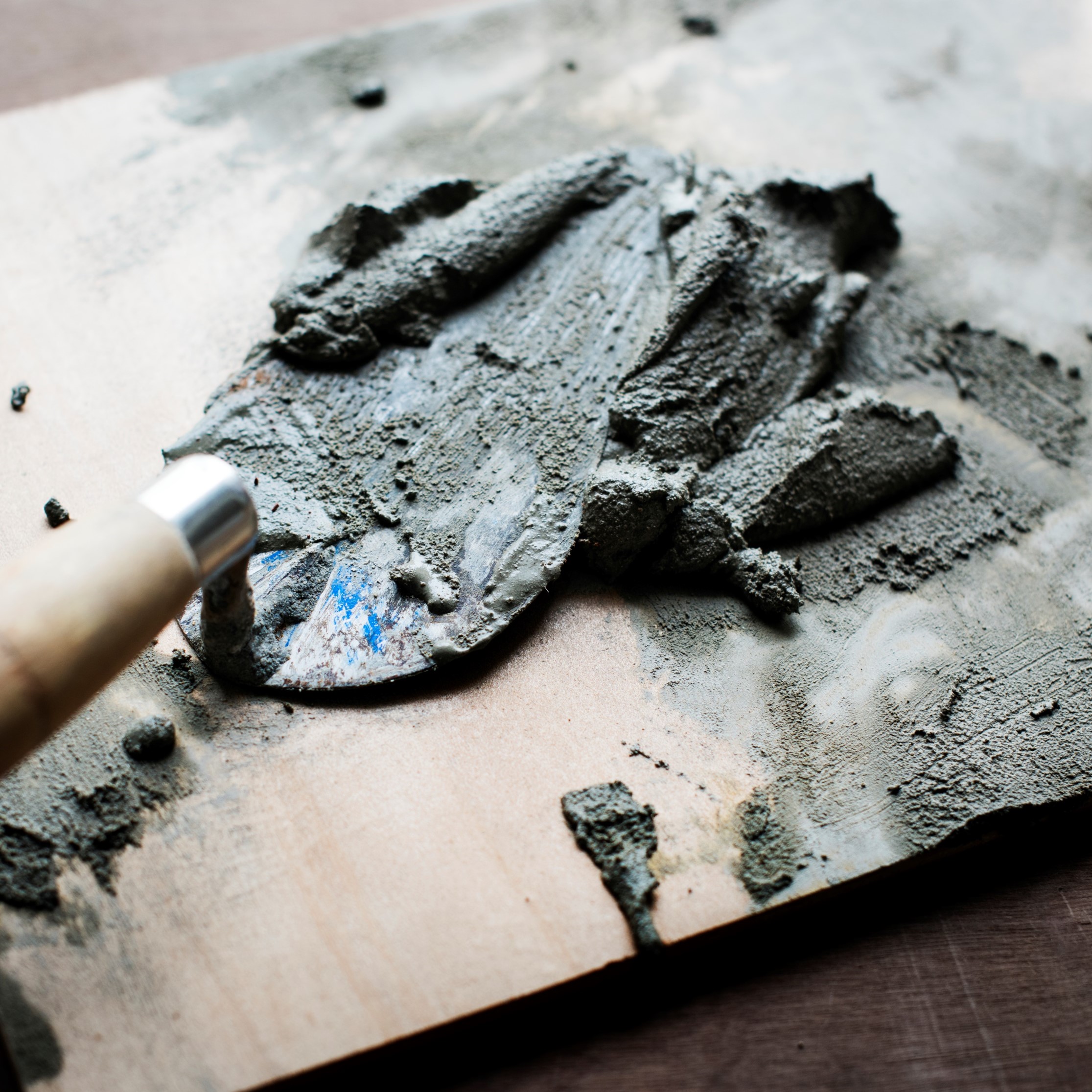
Cement
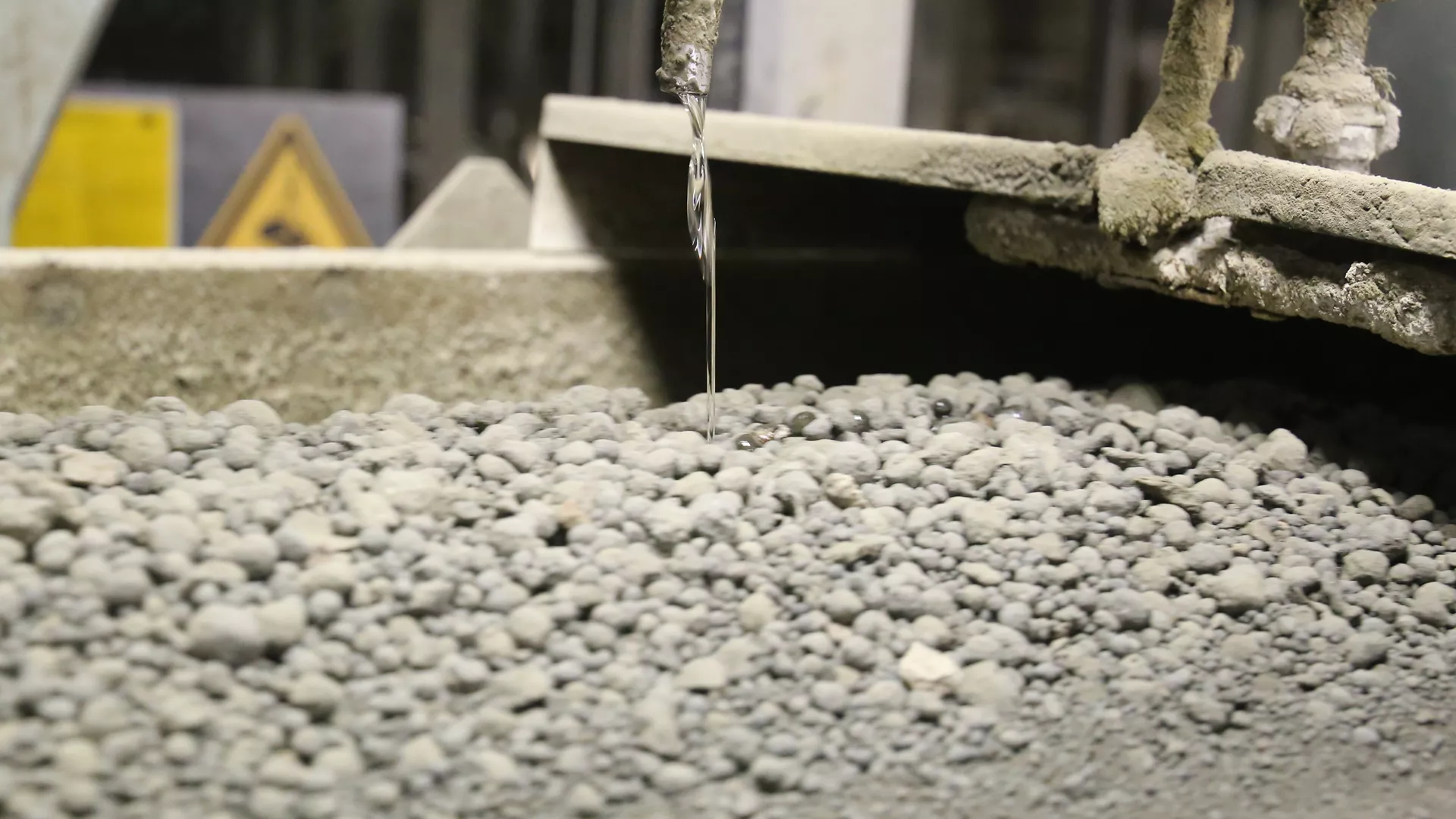
Cement additives

Ceramic glazes
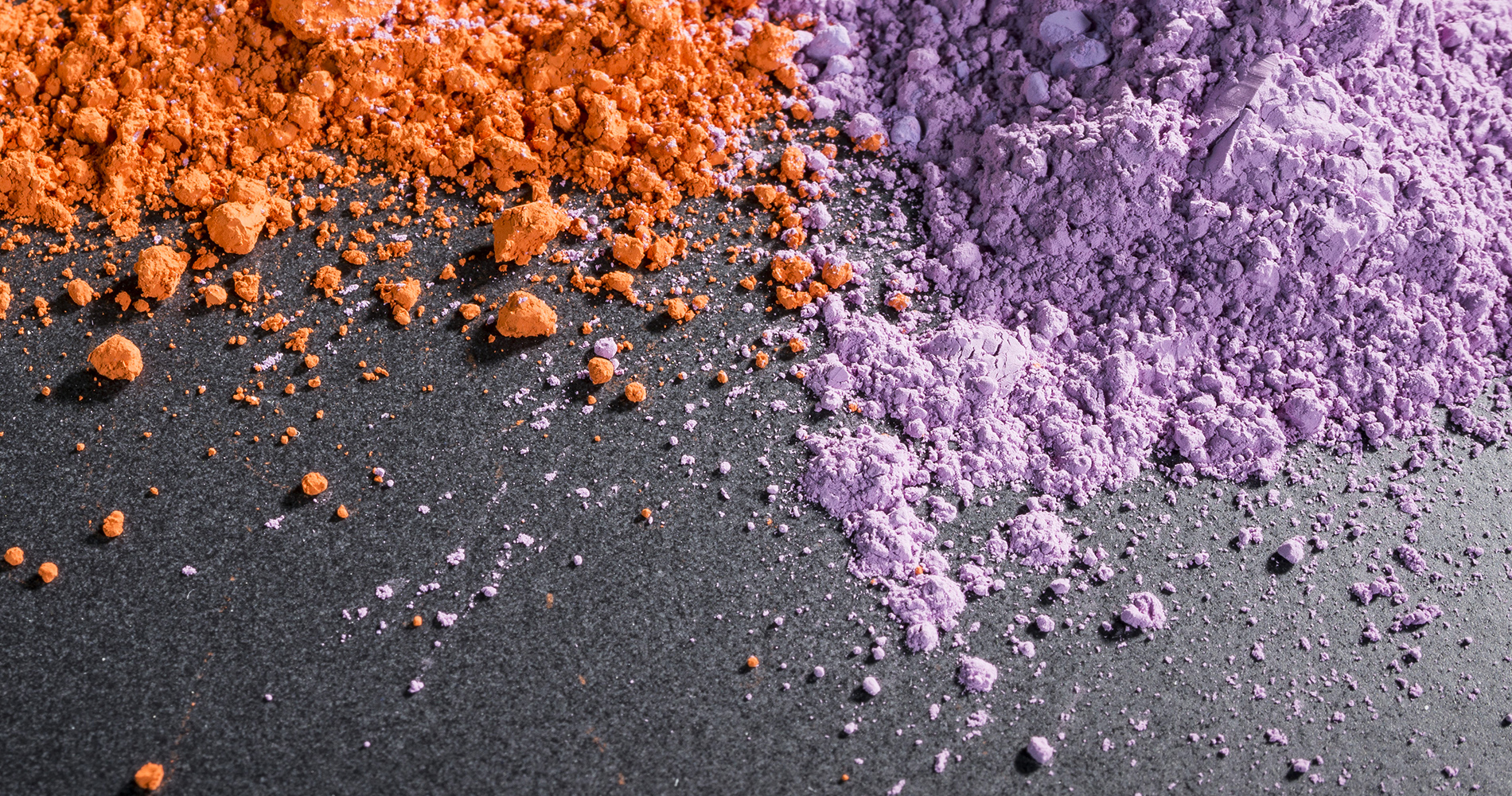
Ceramic pigments
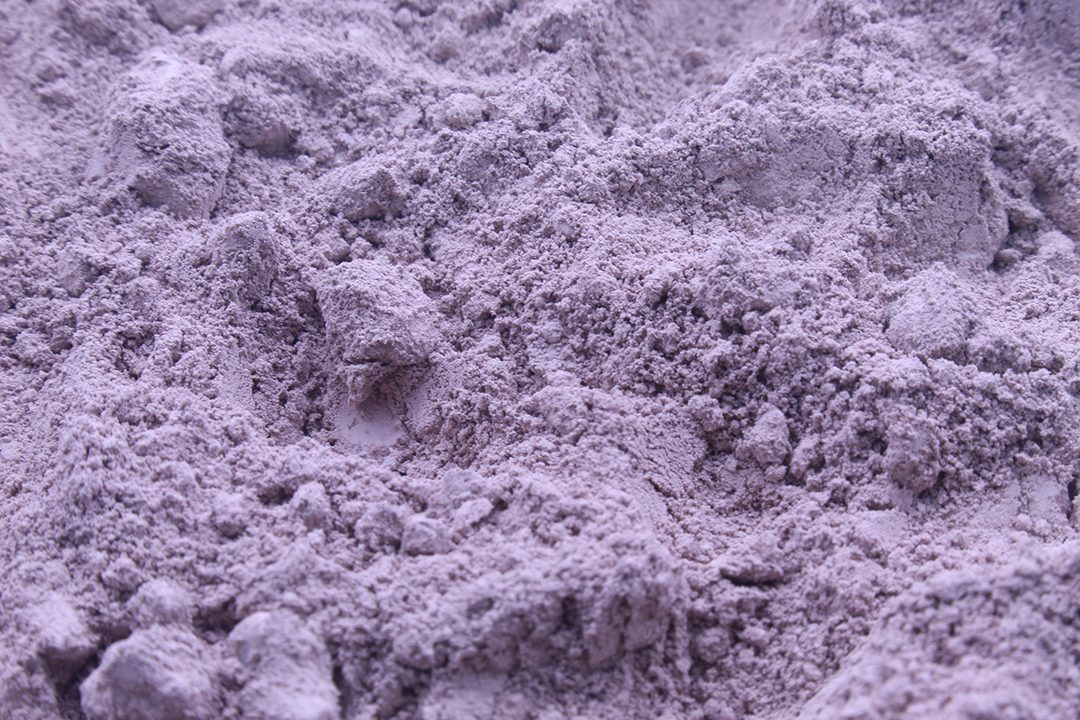
Ceramic powders

Cereal grains
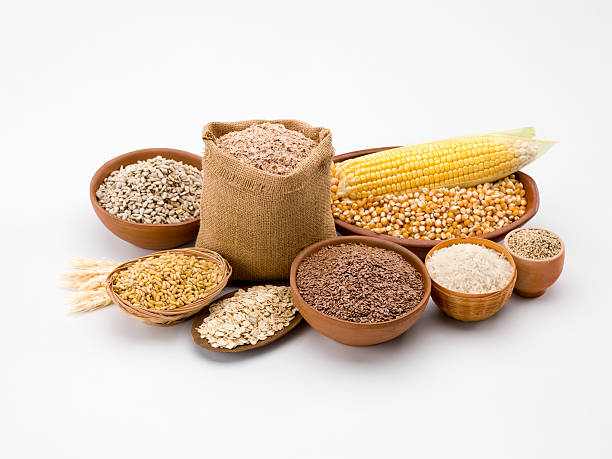
Cereals
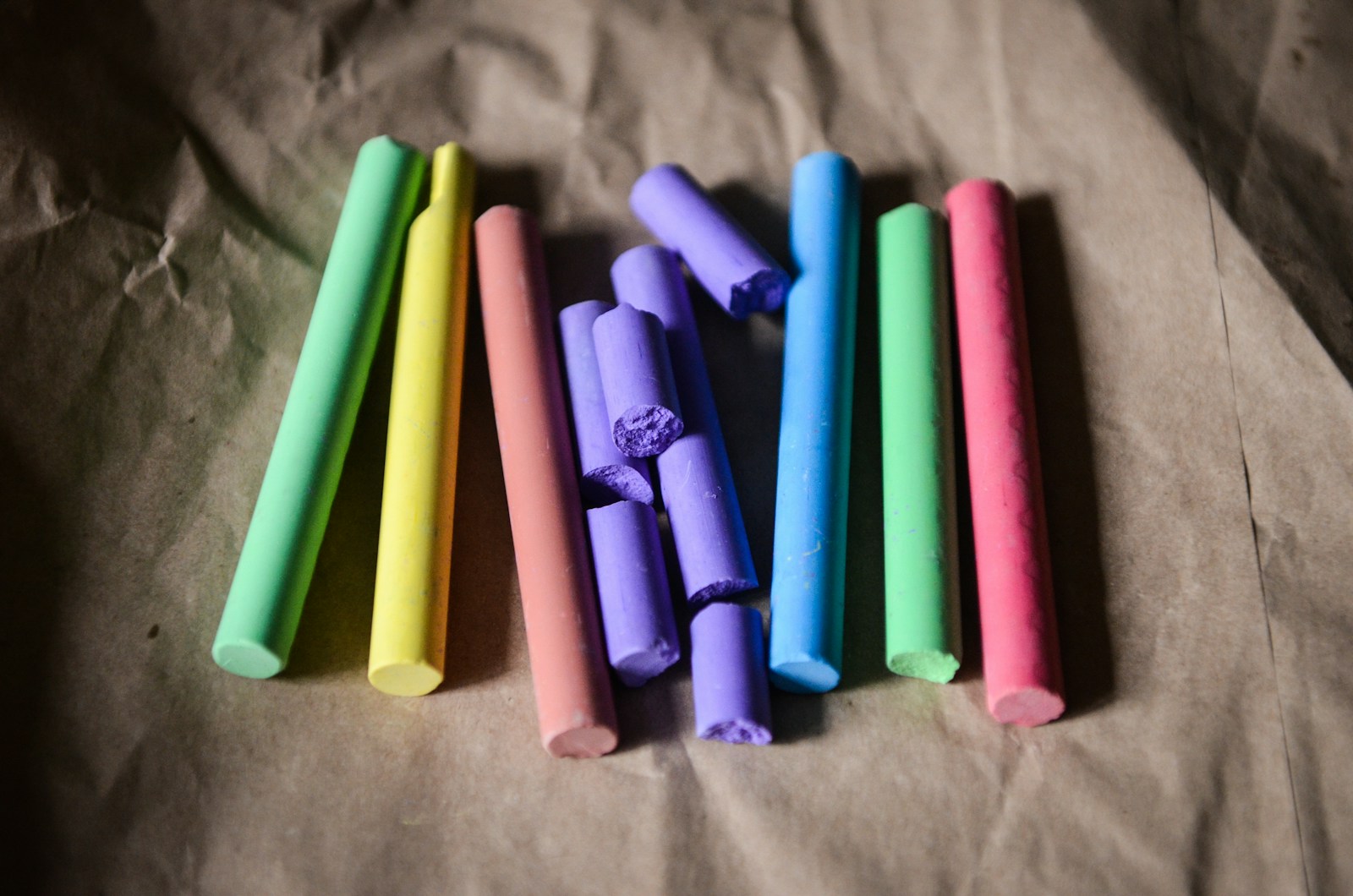
Chalk
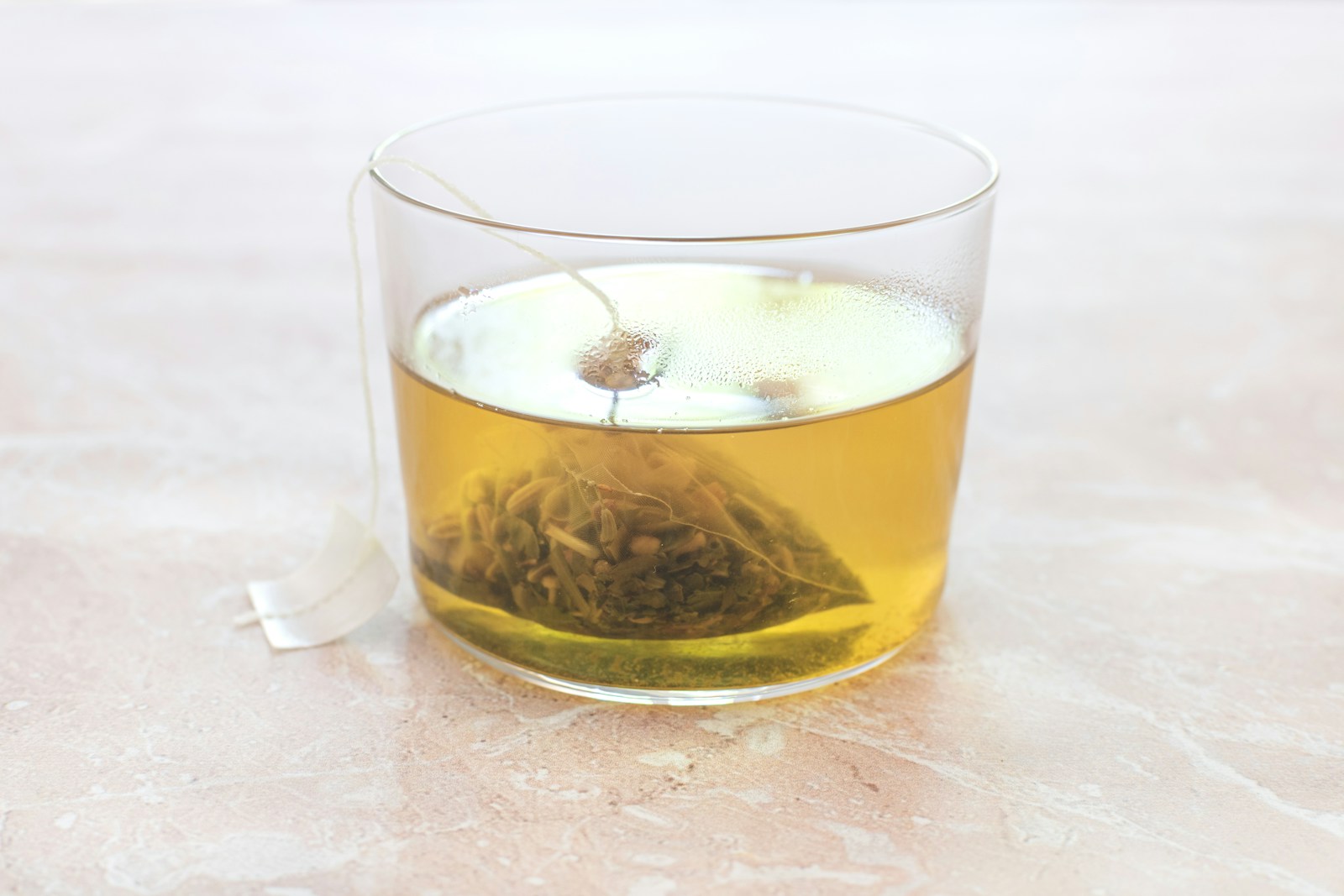
Chamomile tea bags
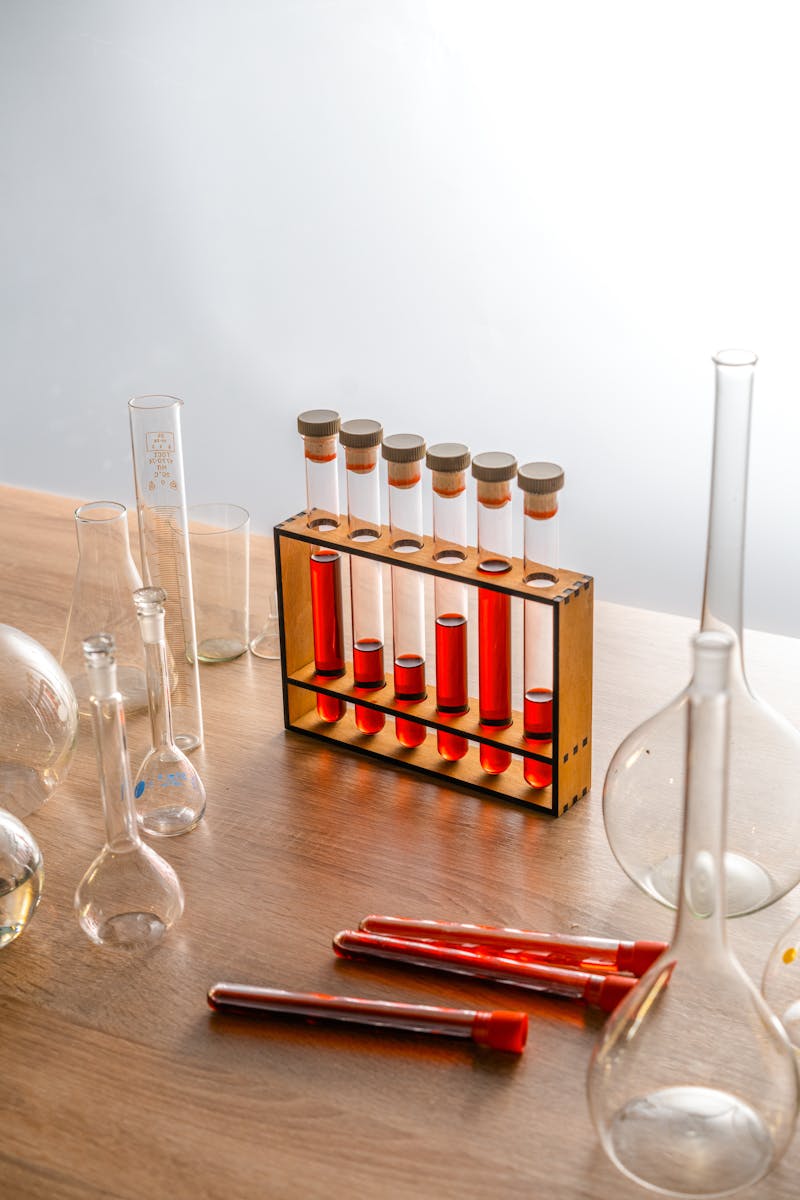
Chemical additives
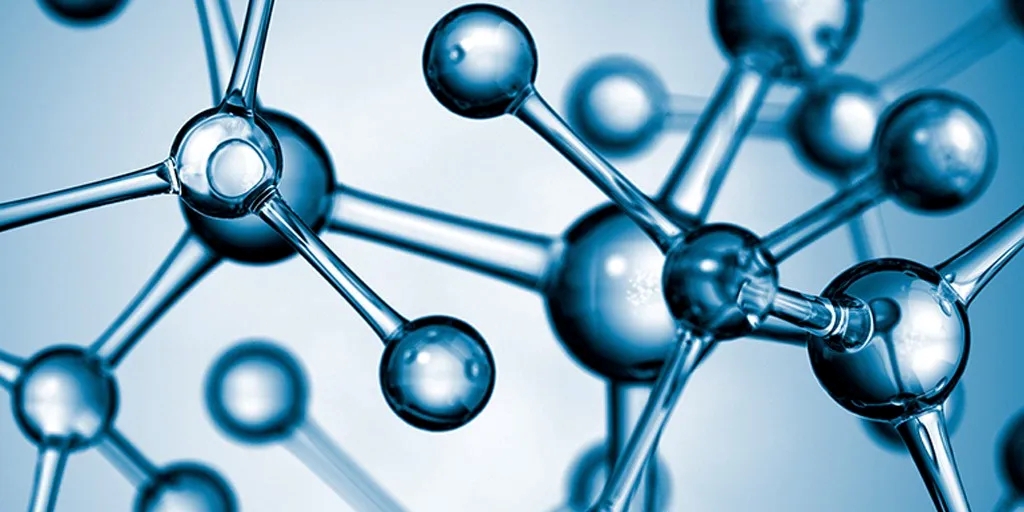
Chemical catalysts
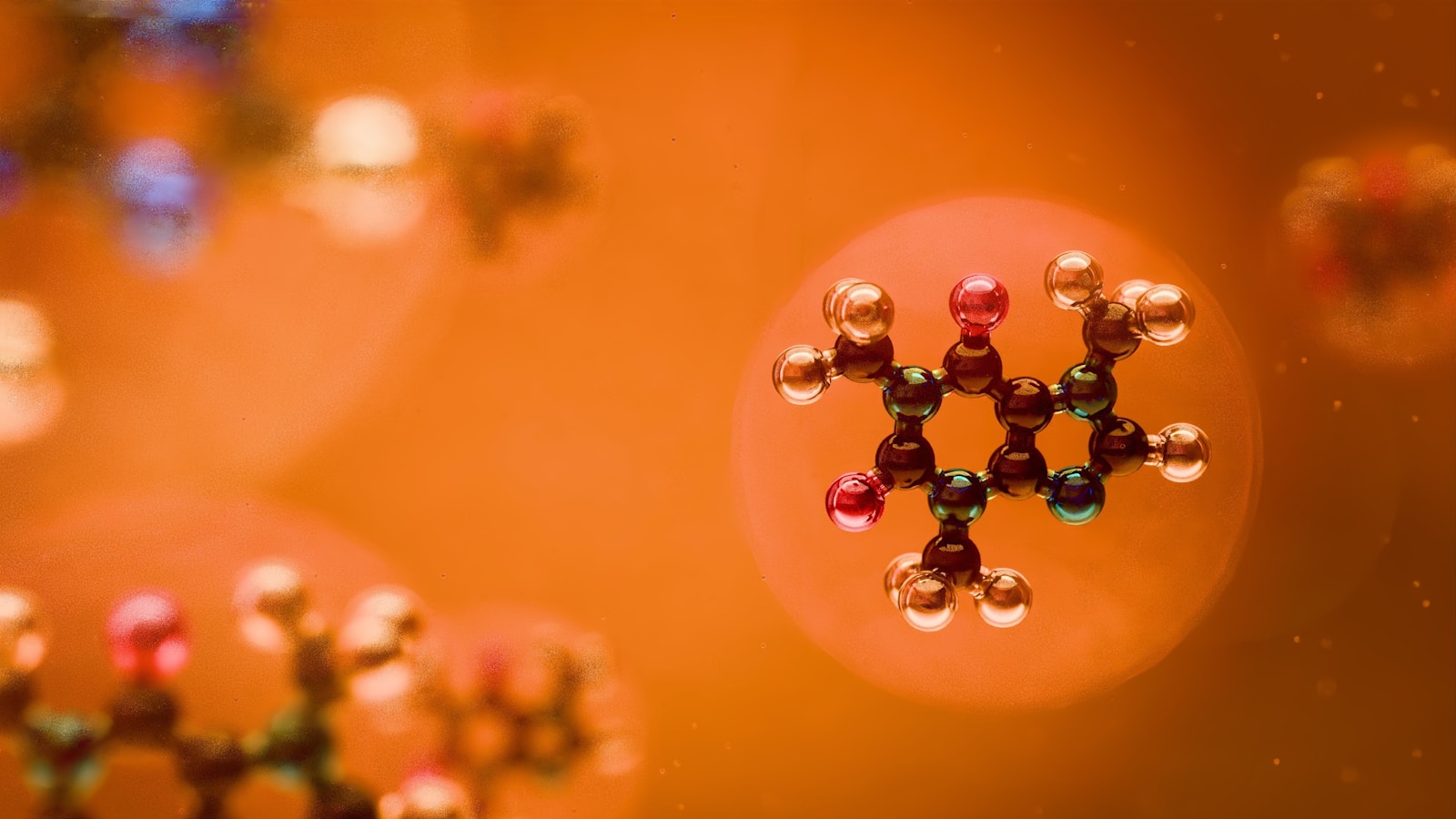
Chemical compounds
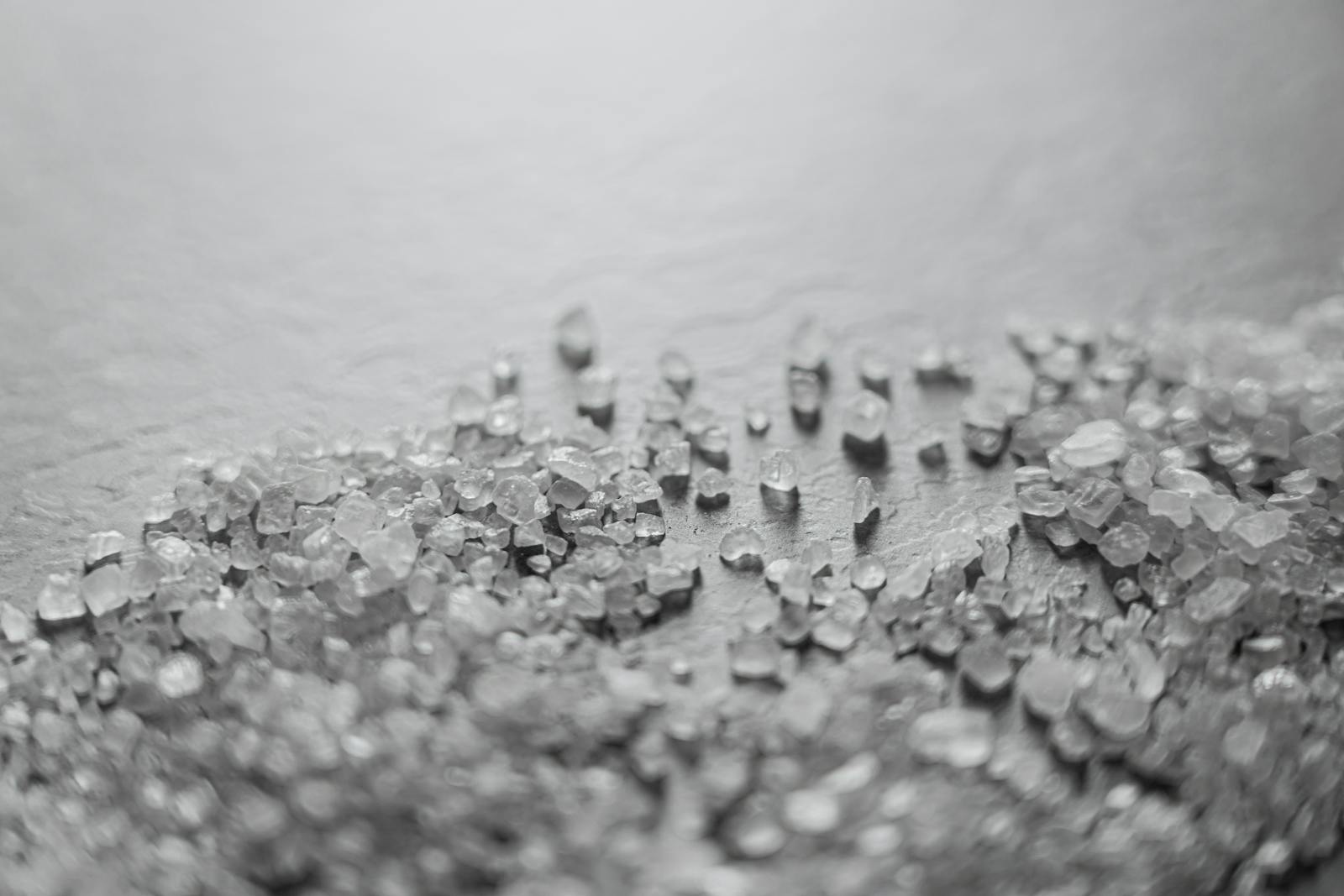
Chemical granules
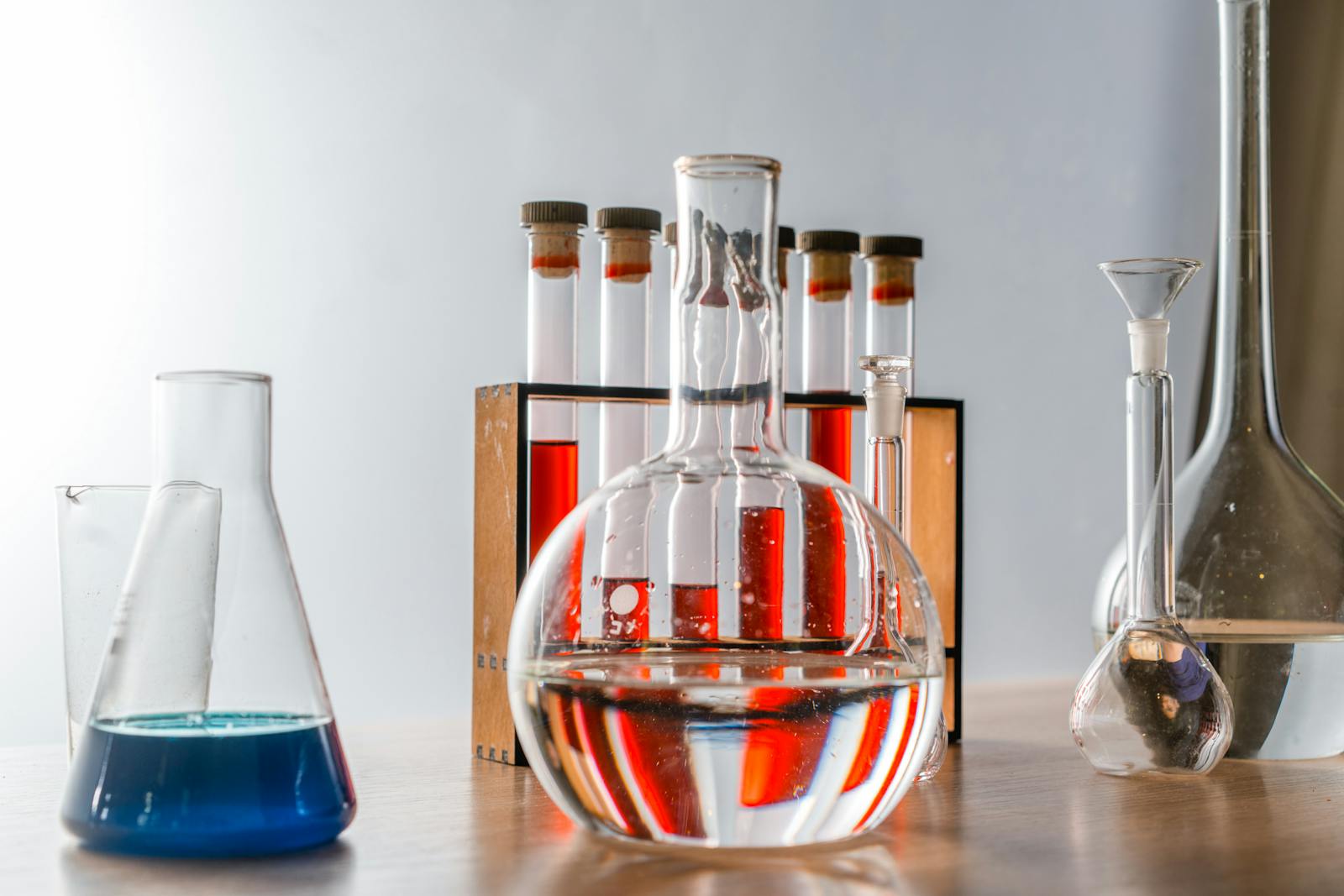
Chemical intermediates
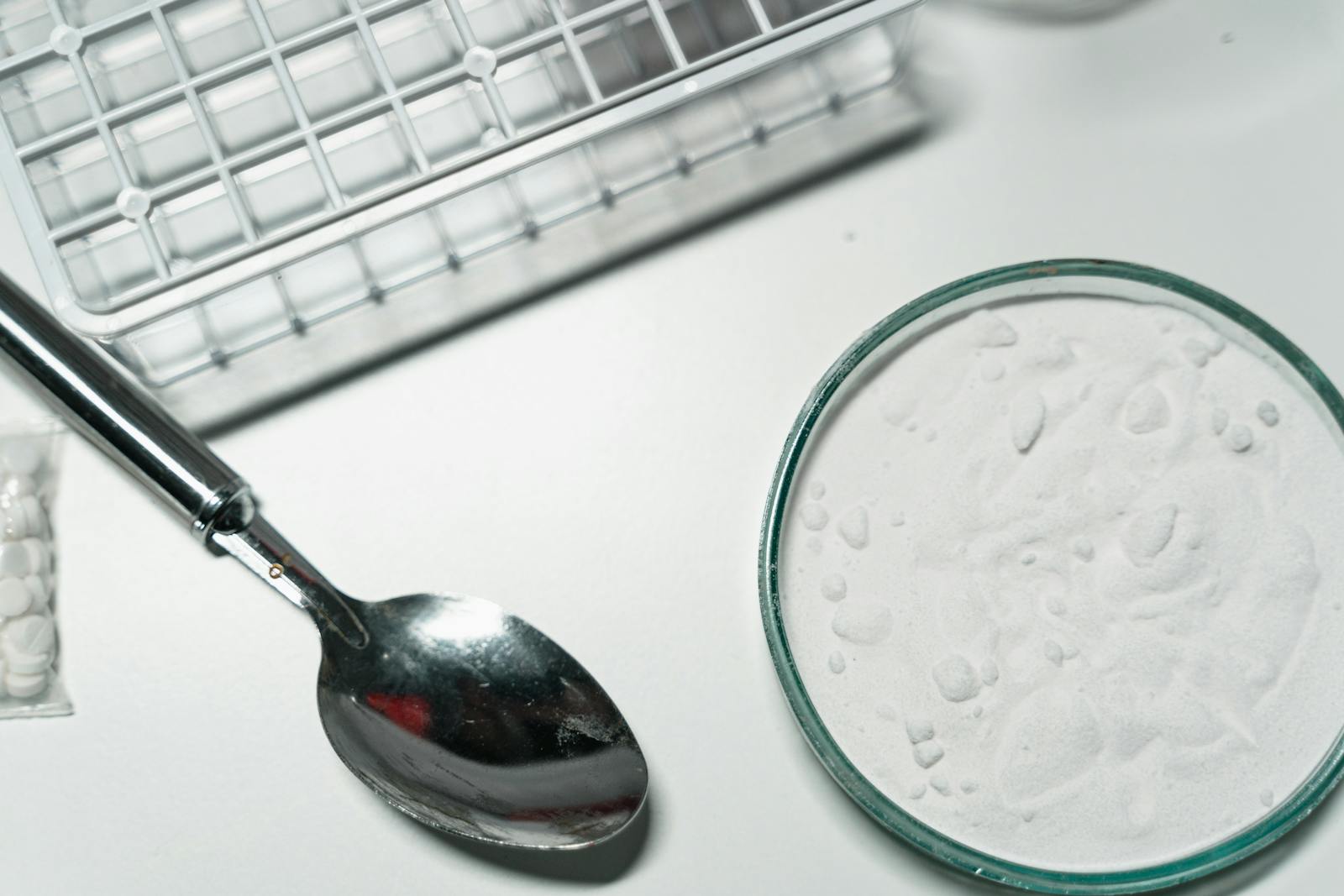
Chemical powders
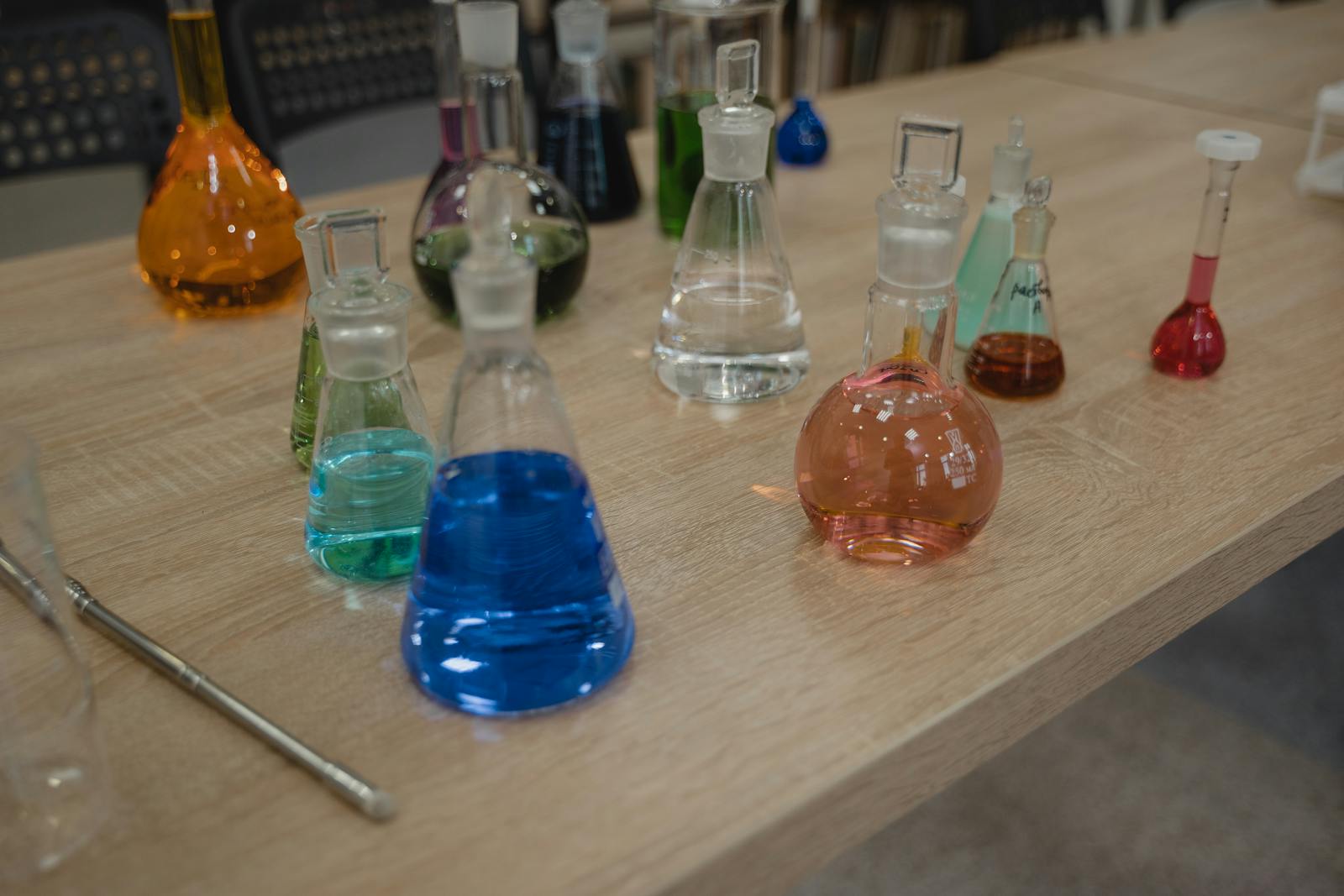
Chemical solvents
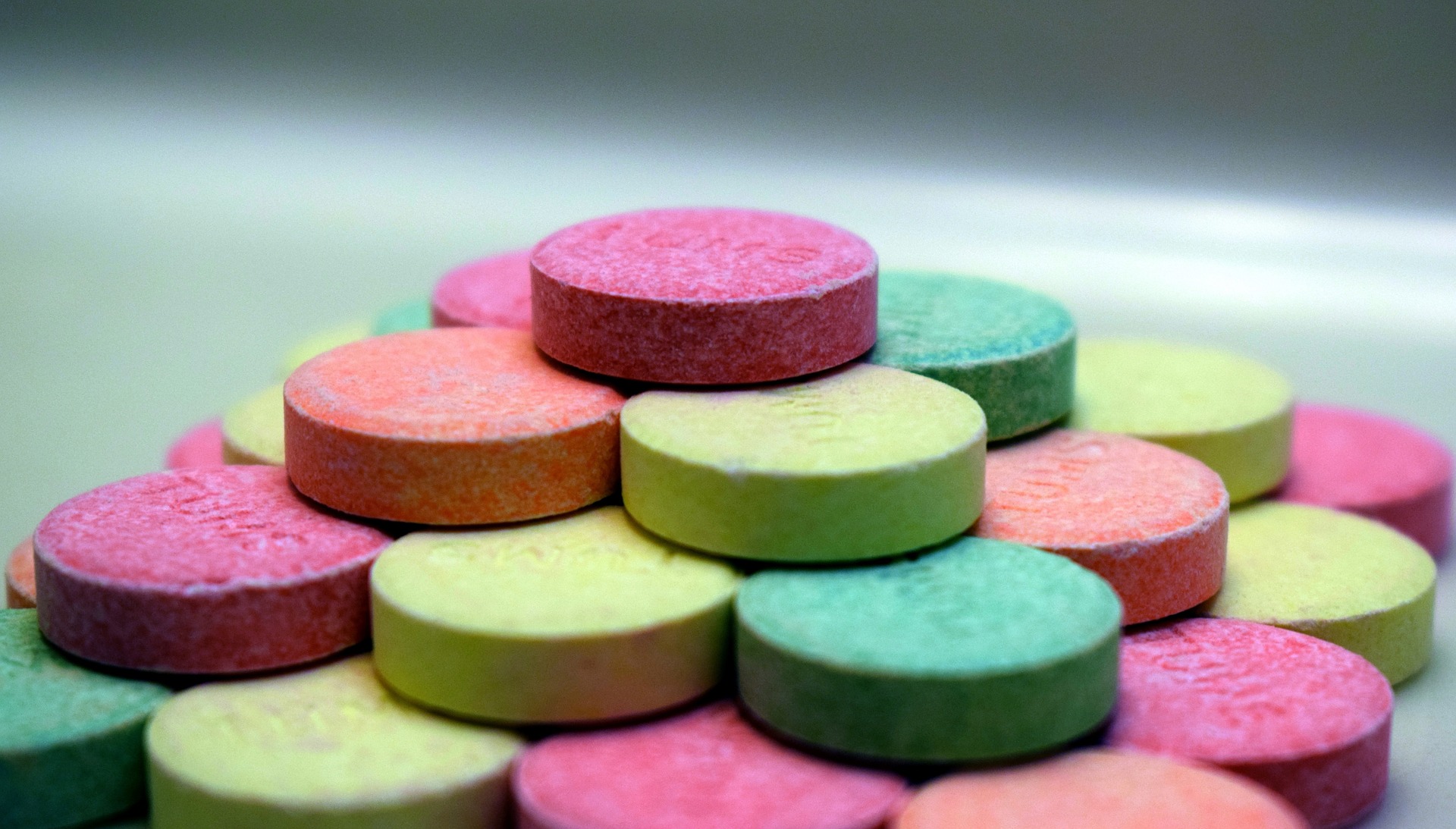
Chewable tablets
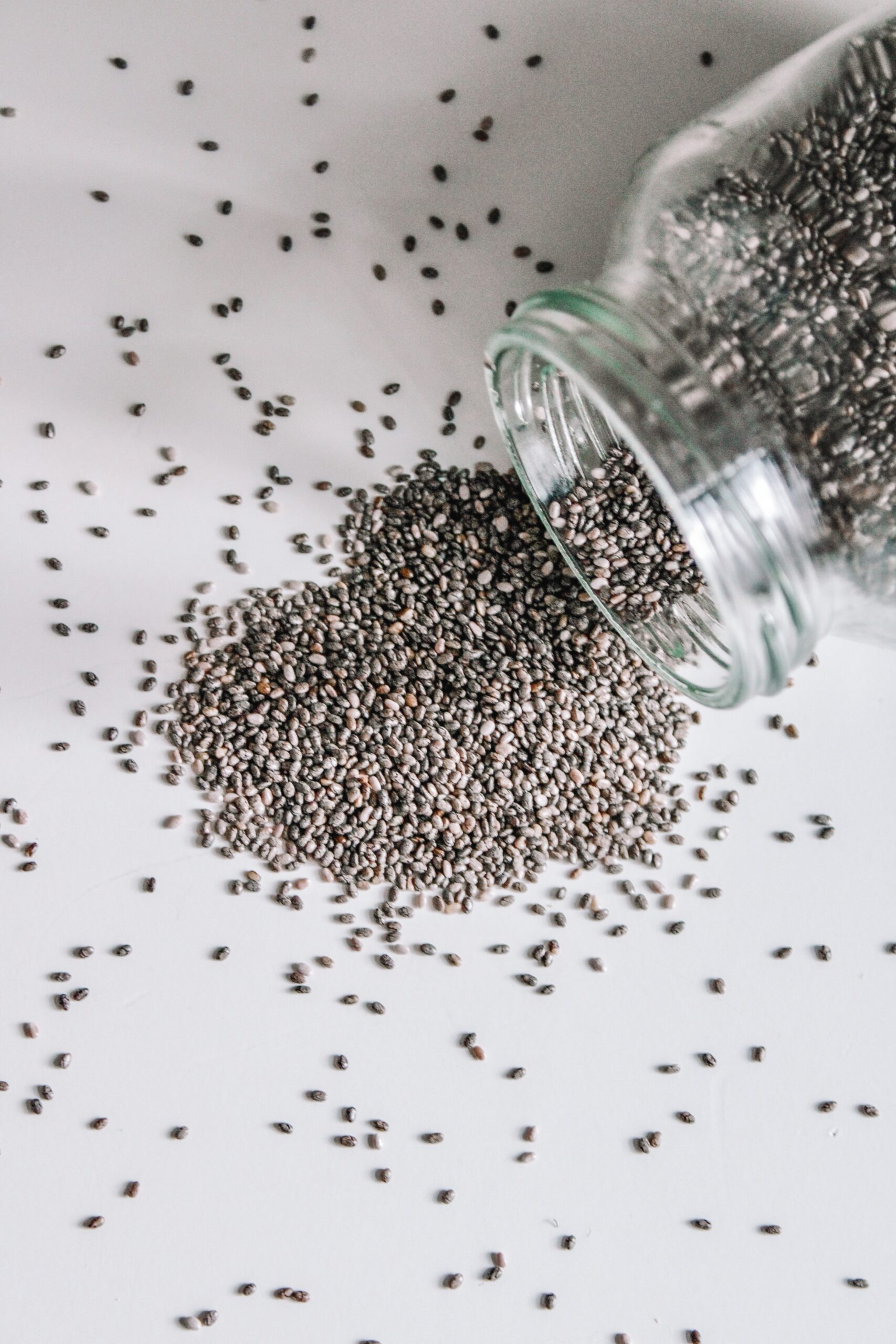
Chia seeds
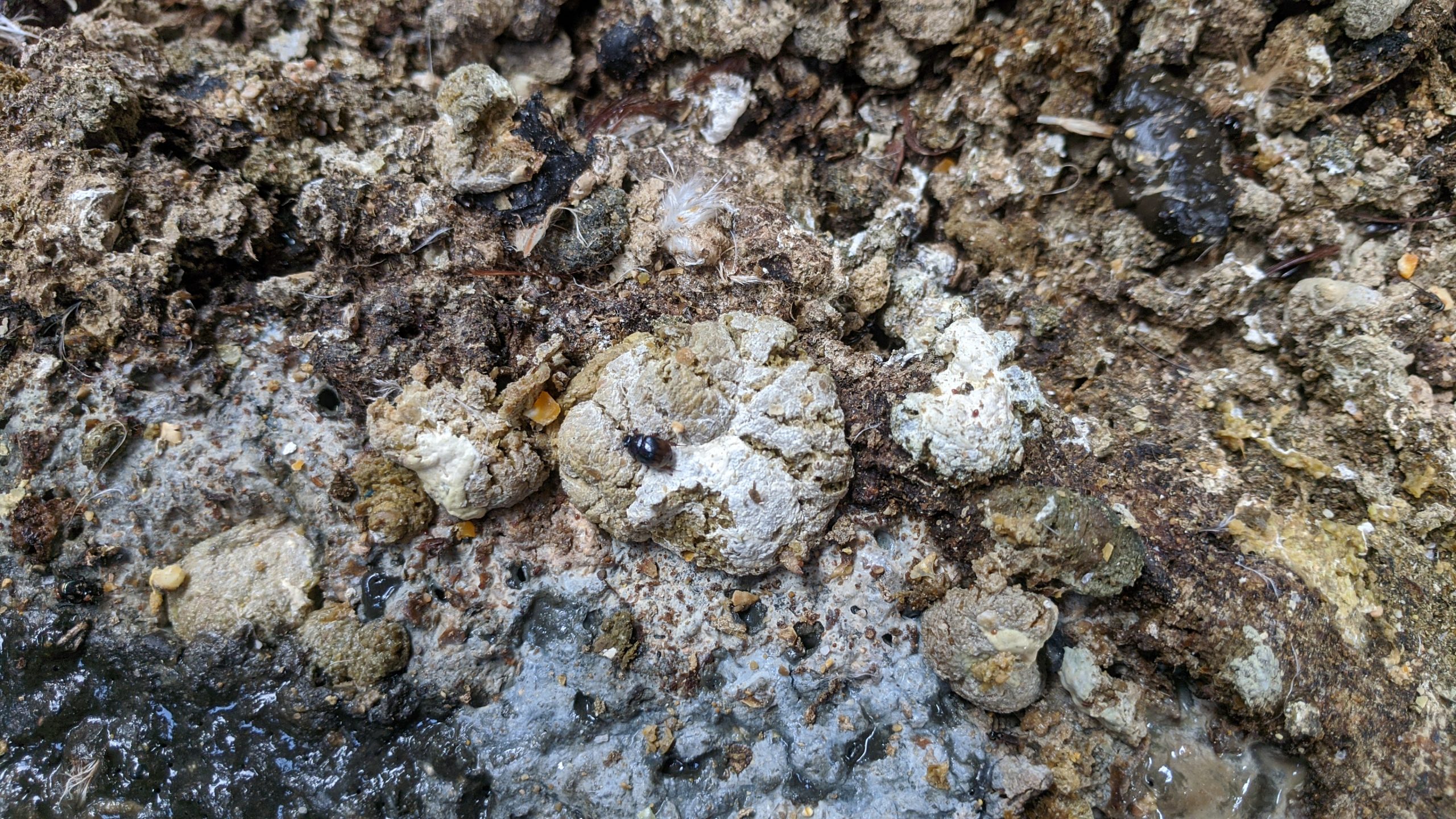
Chicken manure
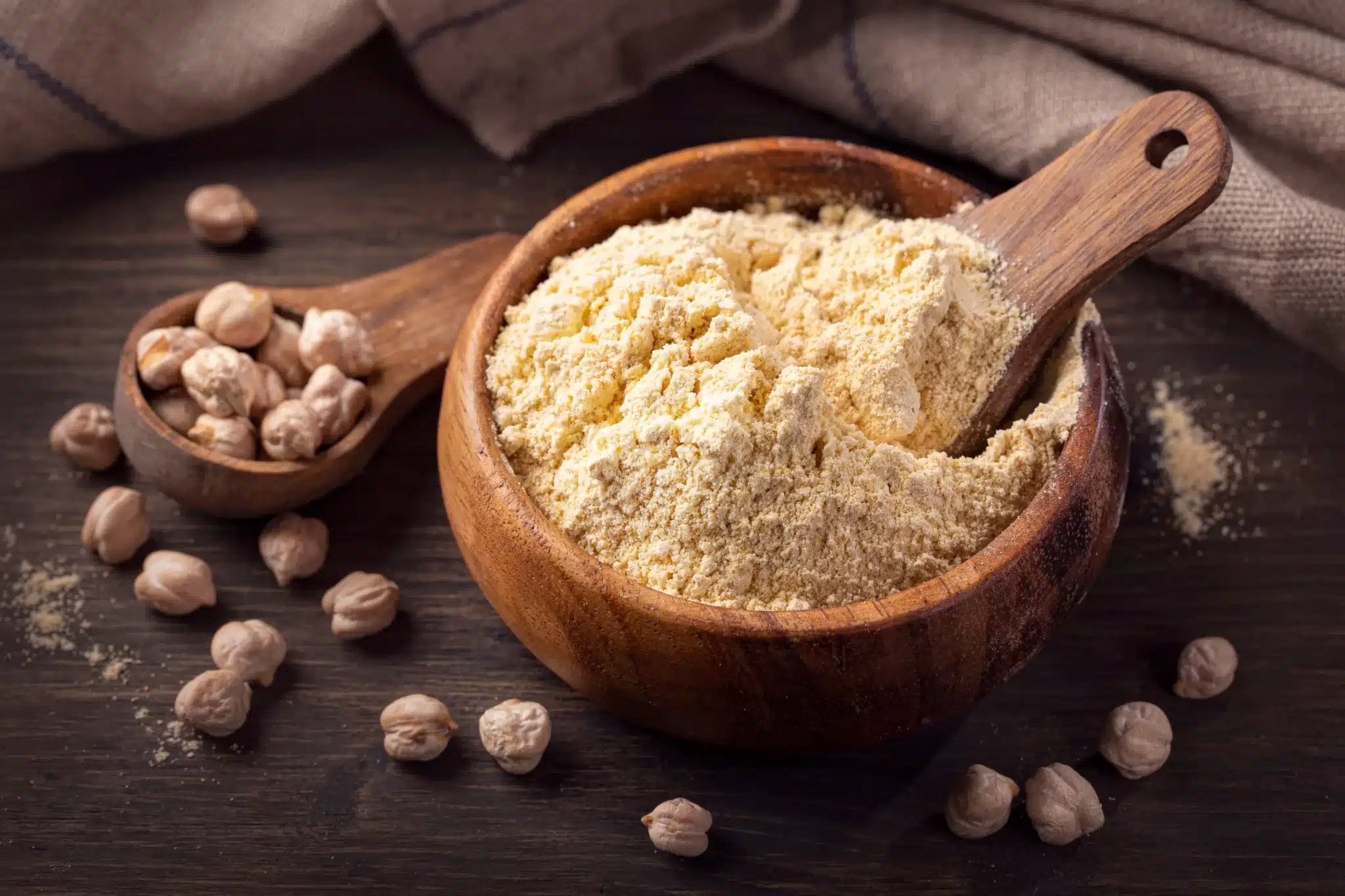
Chickpea flour
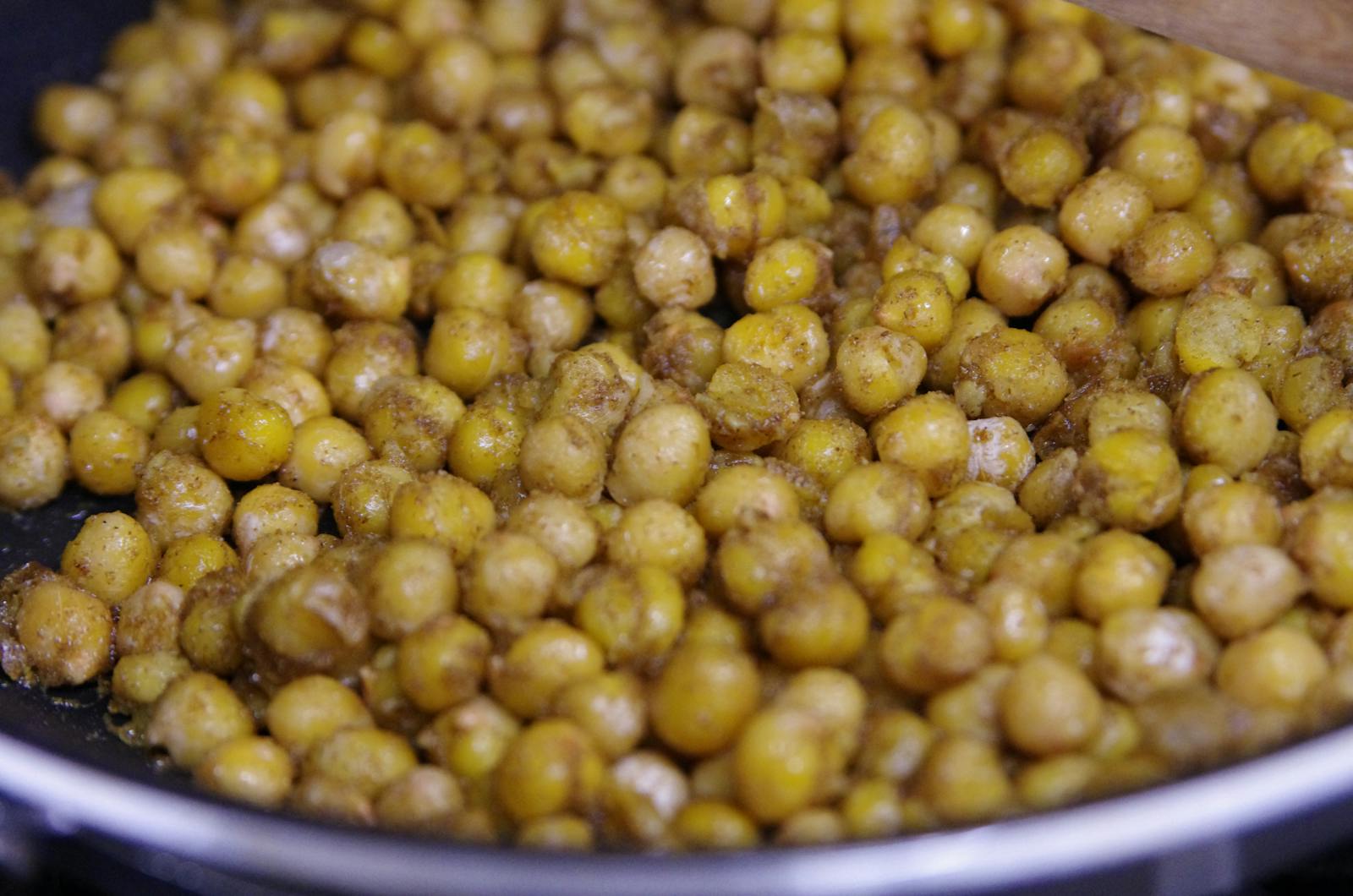
Chickpeas
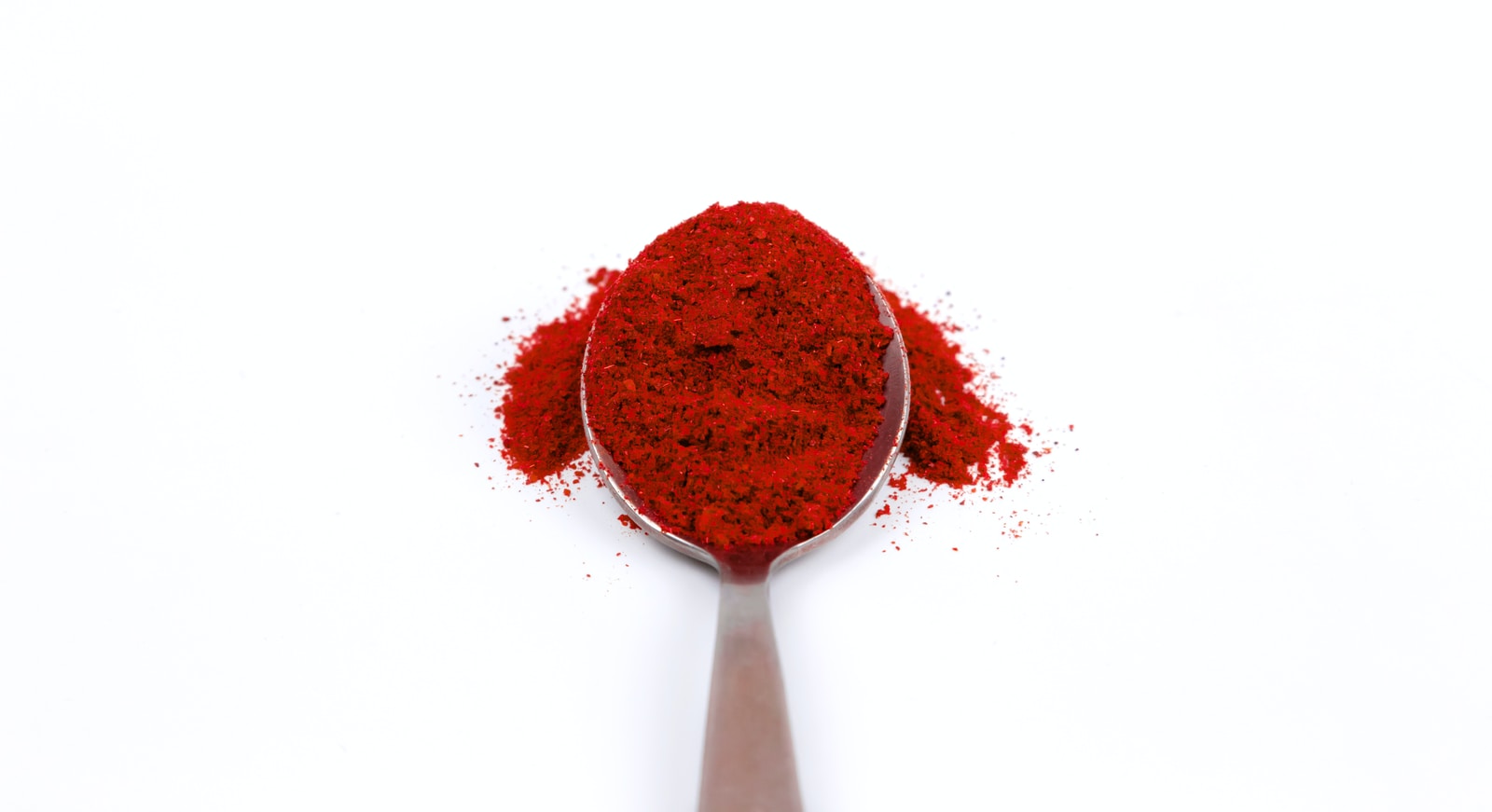
Chili powder
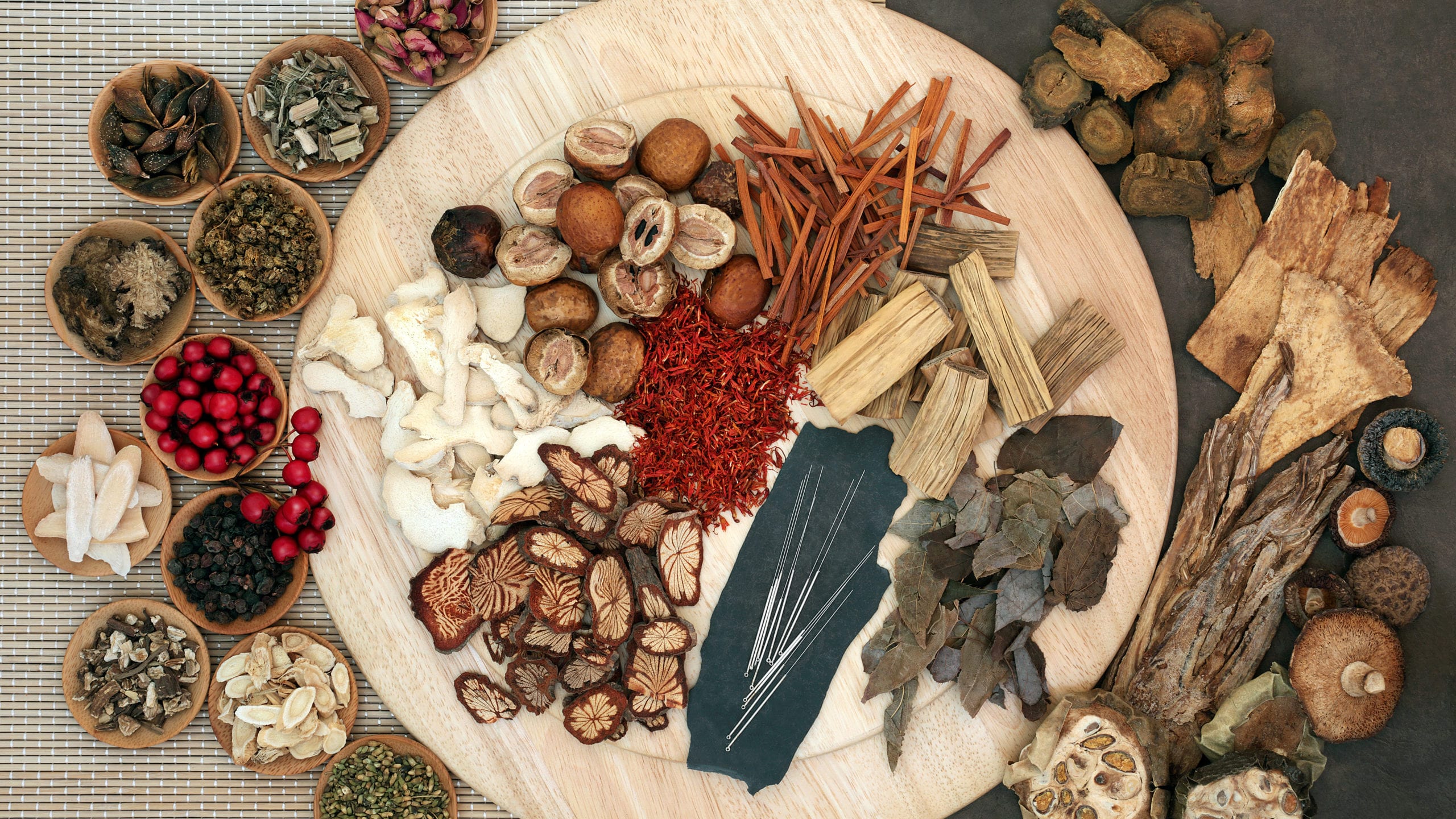
Chinese traditional medicine
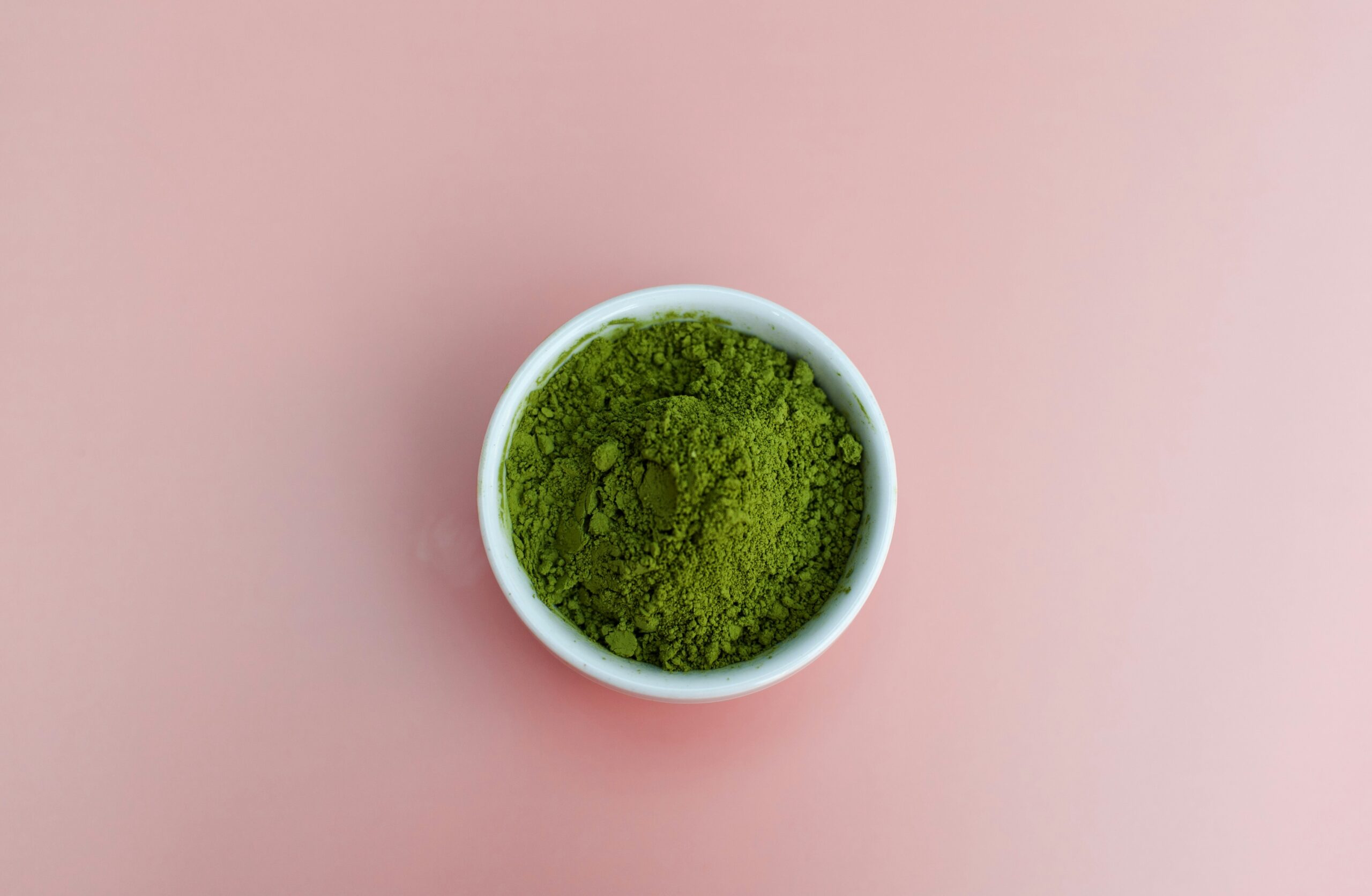
Chlorella powder
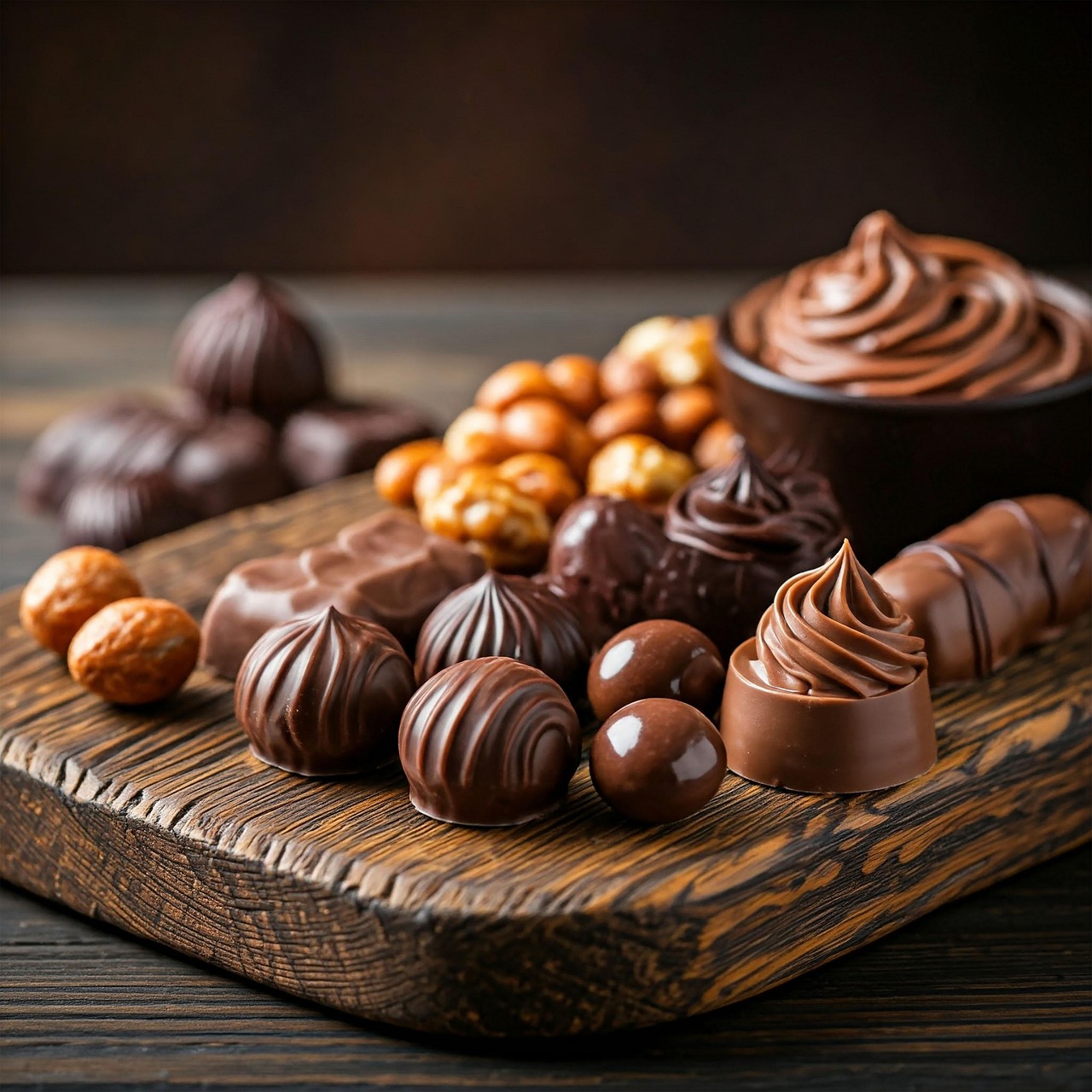
Chocolate dragees

Cinnamon powder
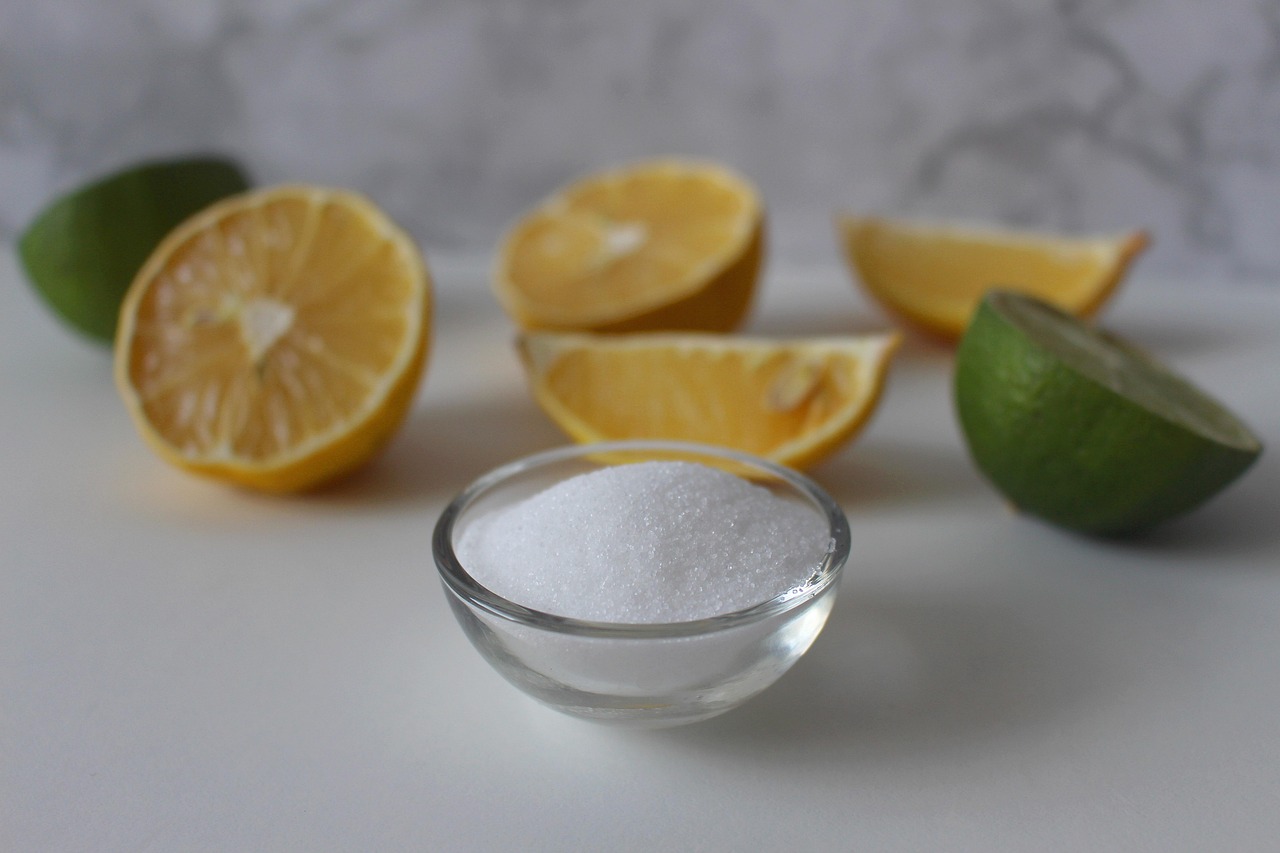
Citric acid
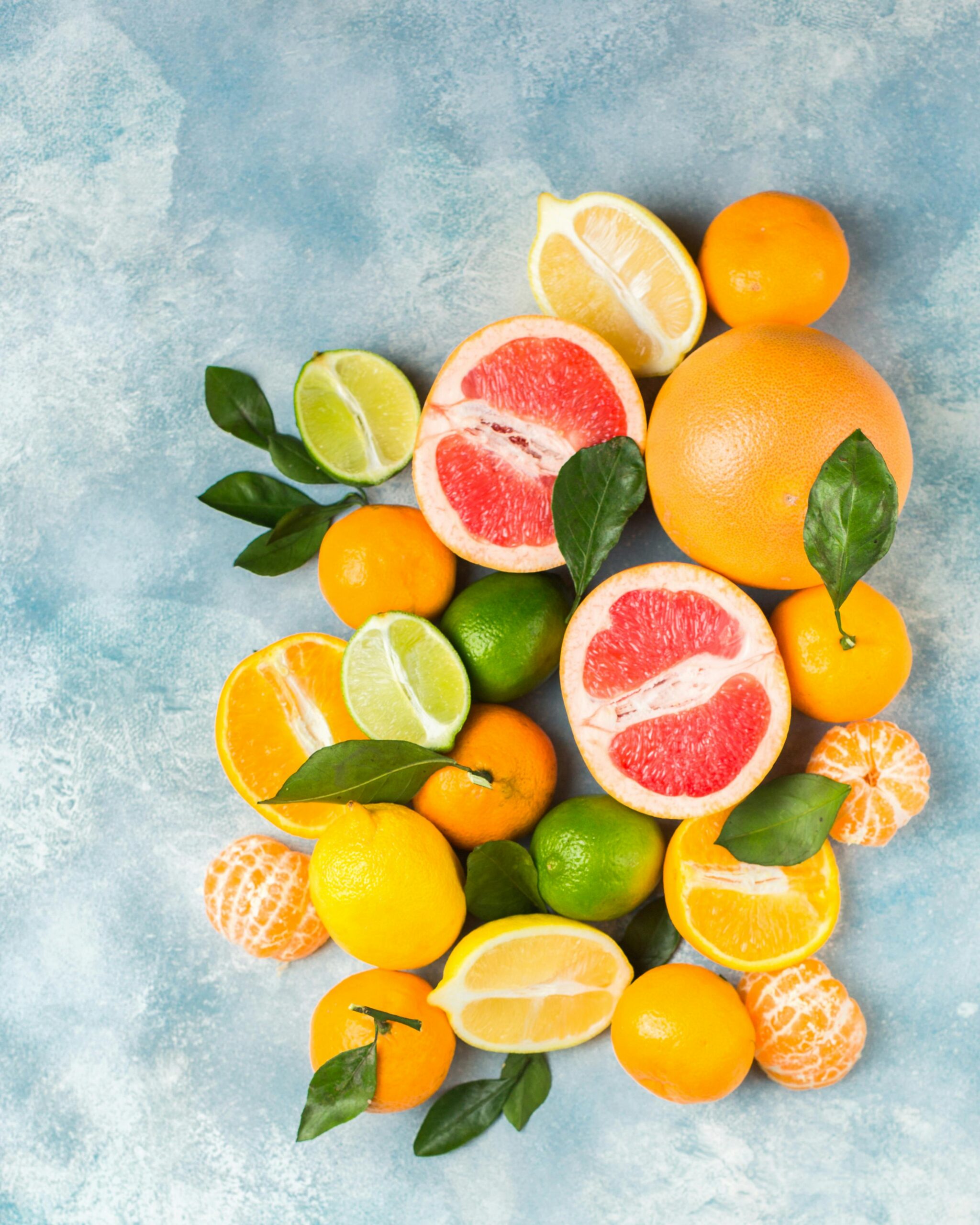
Citrus Fruit
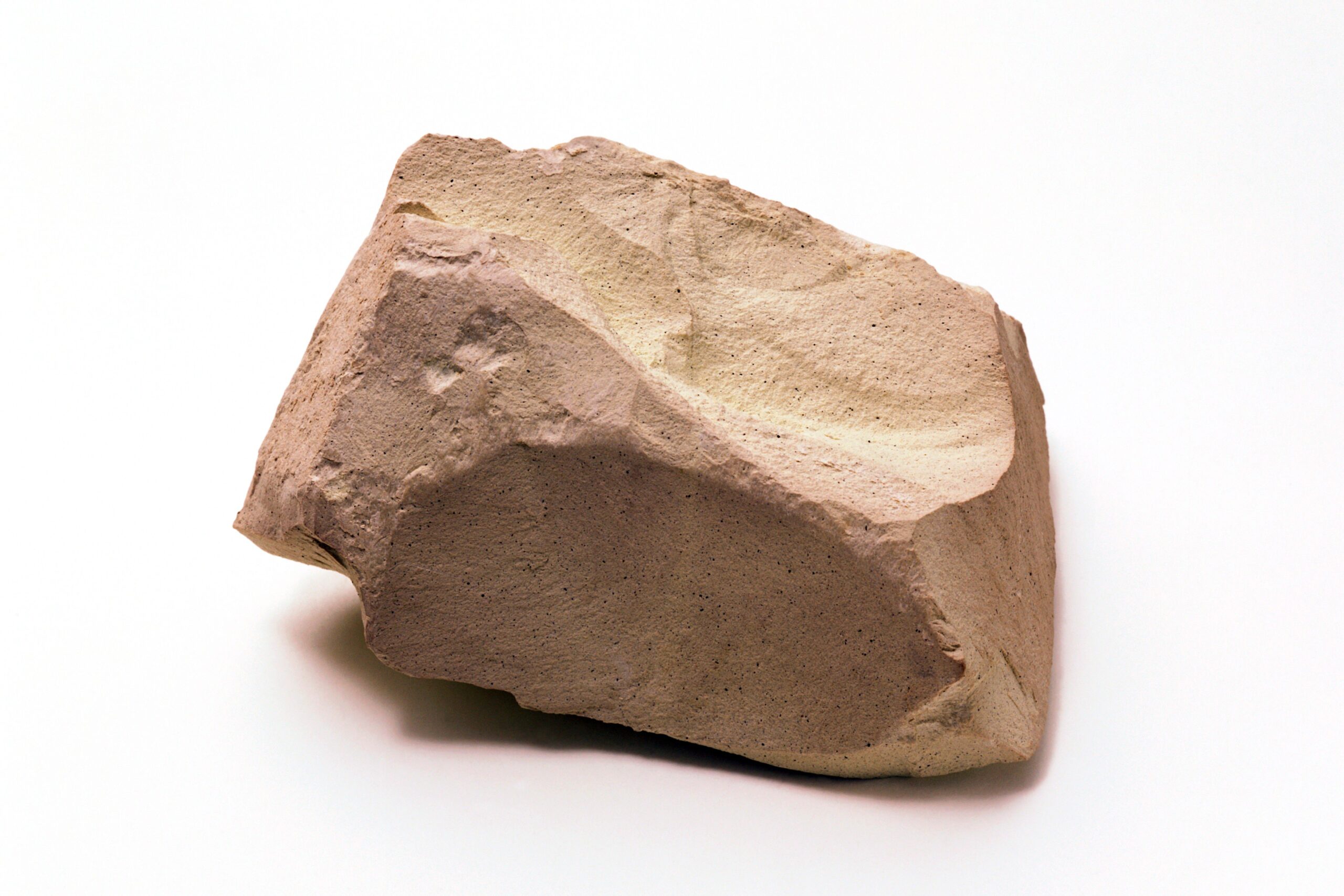
Clay
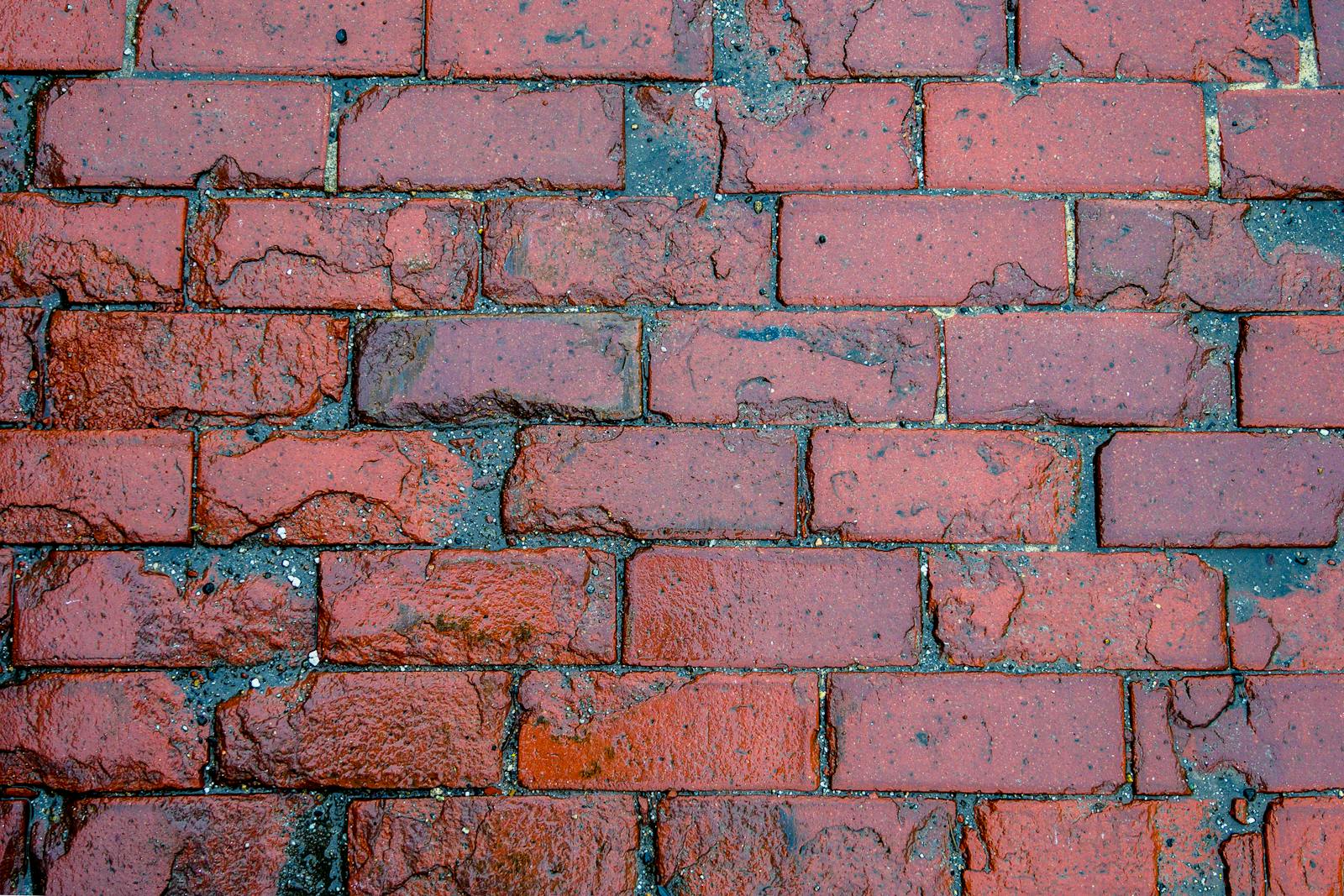
Clay bricks
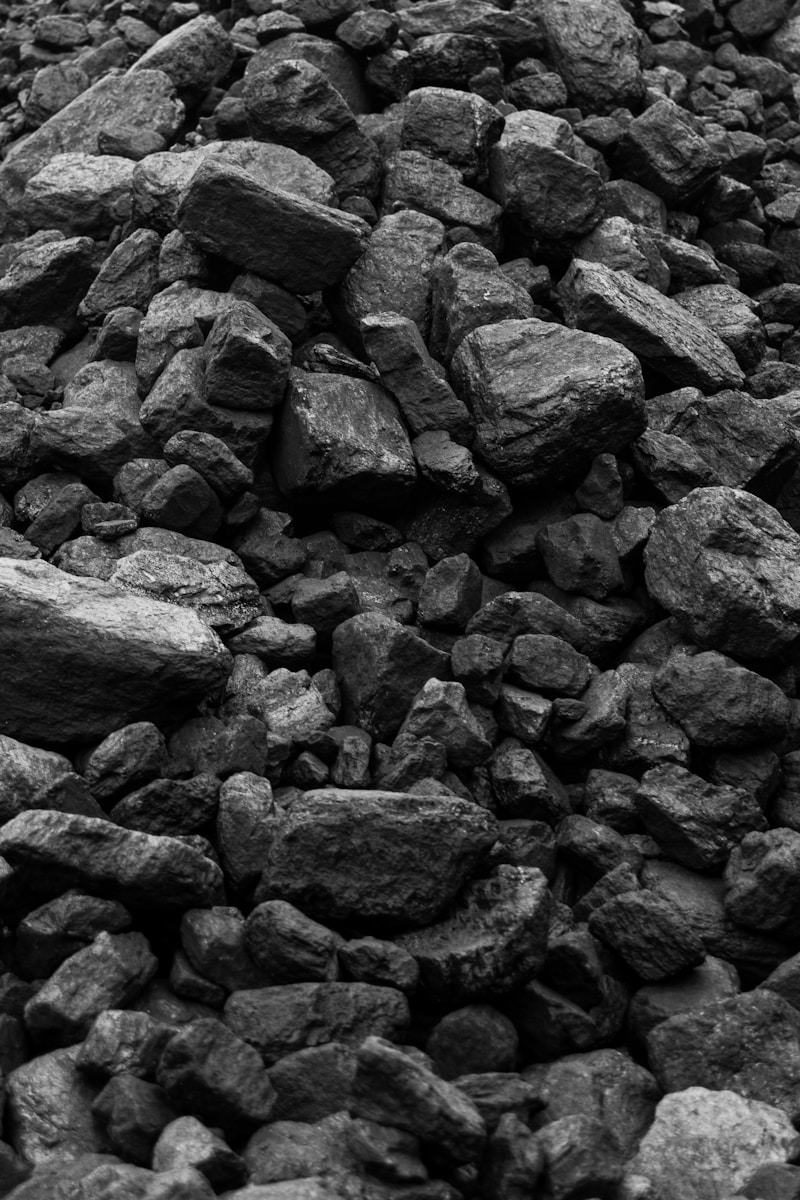
Coal
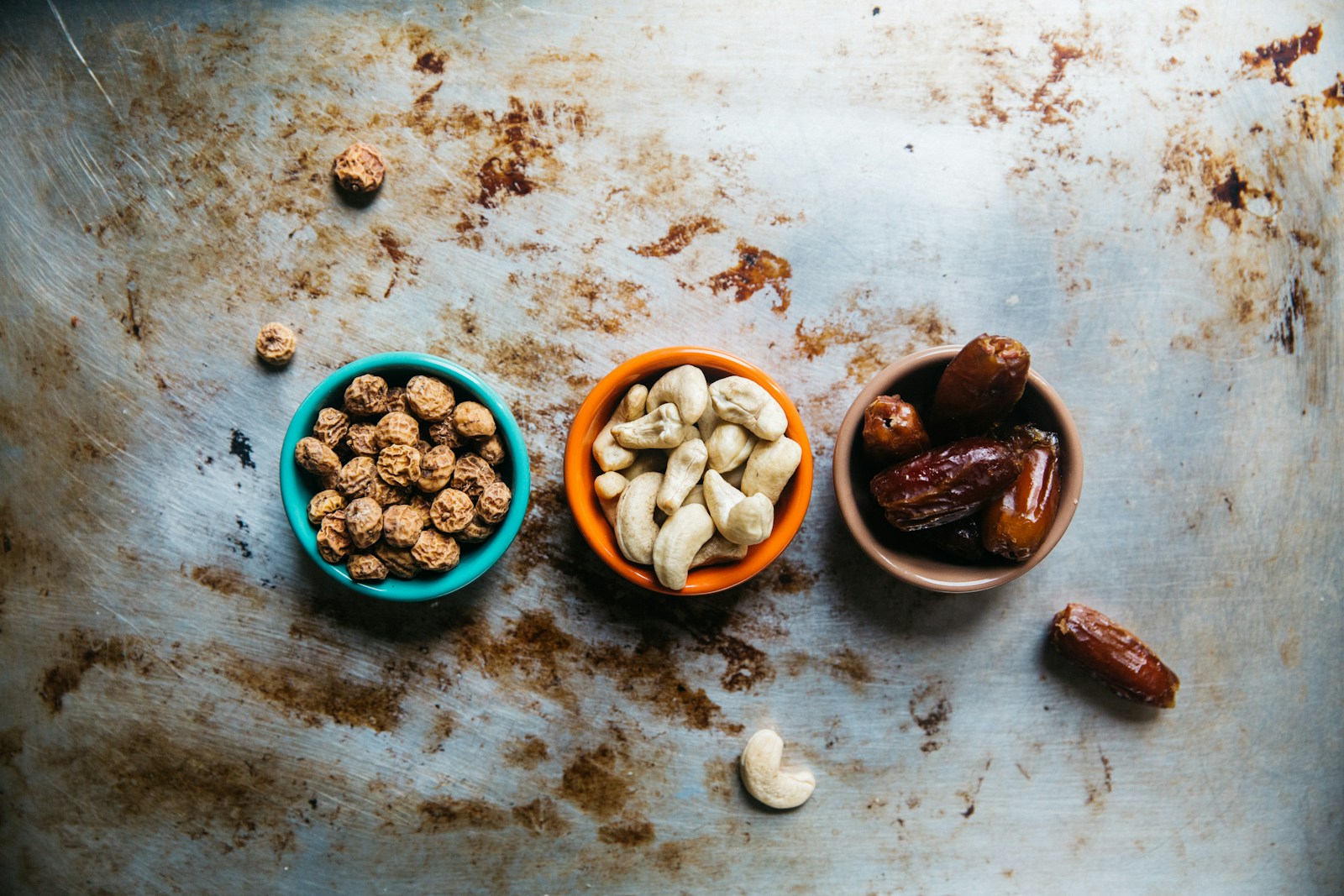
Coated nuts
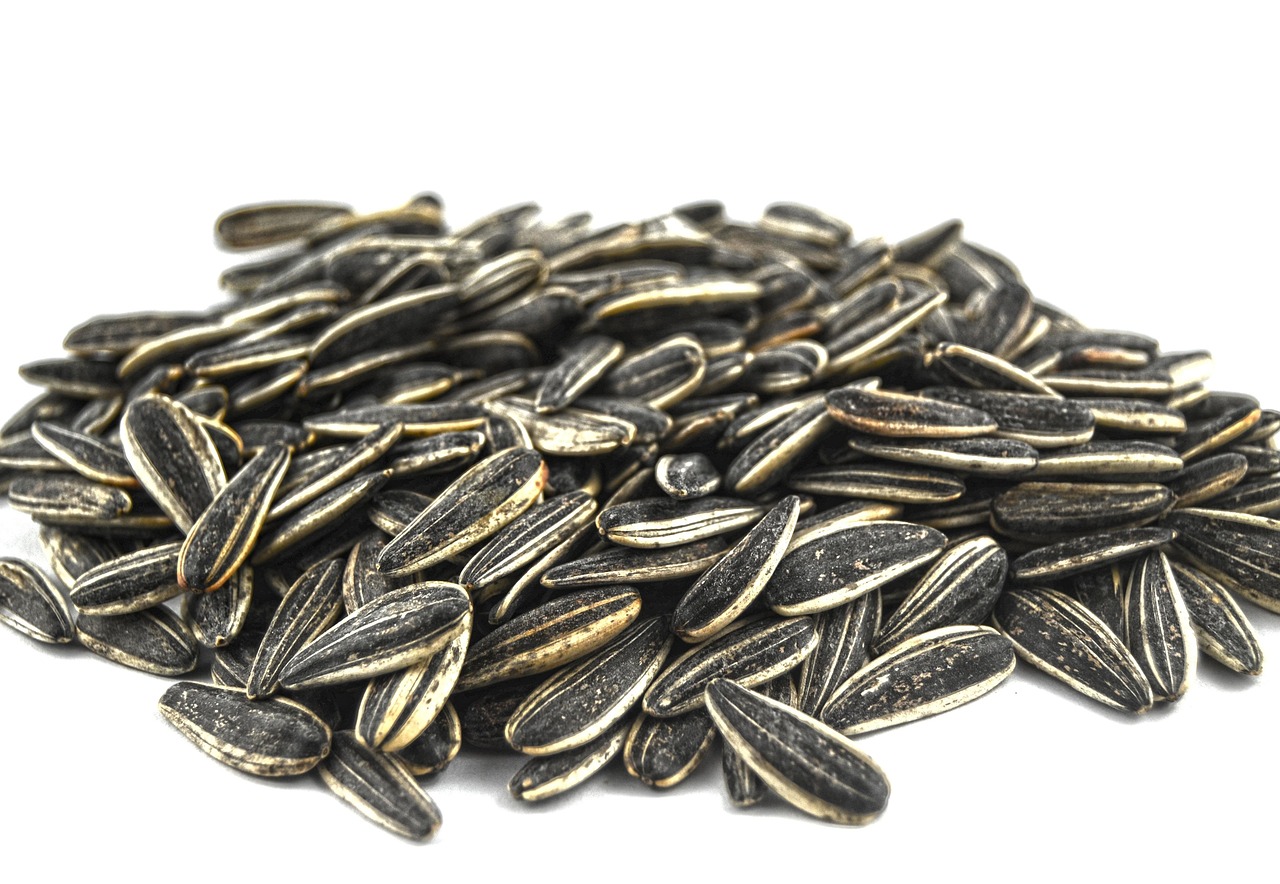
Coated seeds
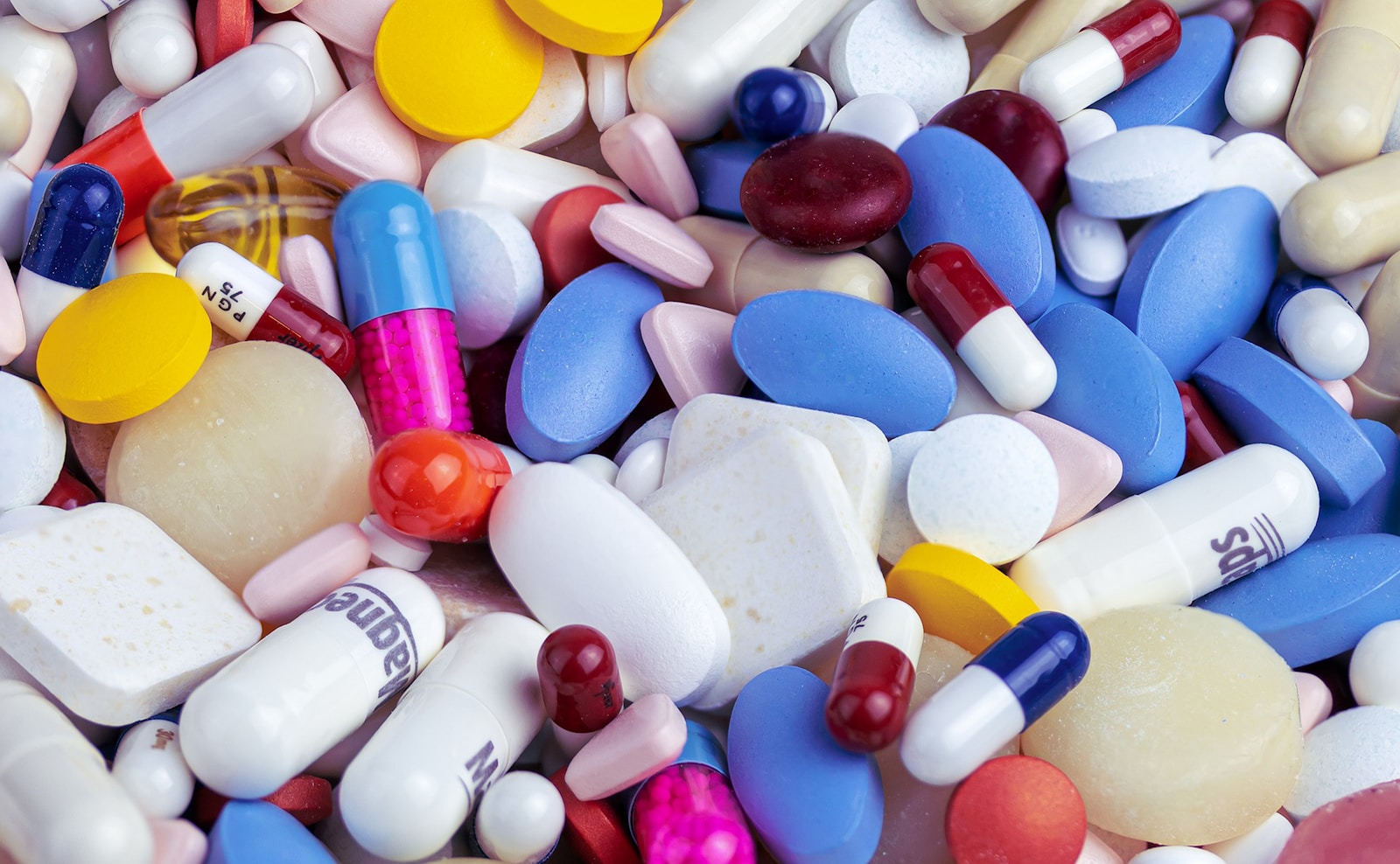
Coated tablets
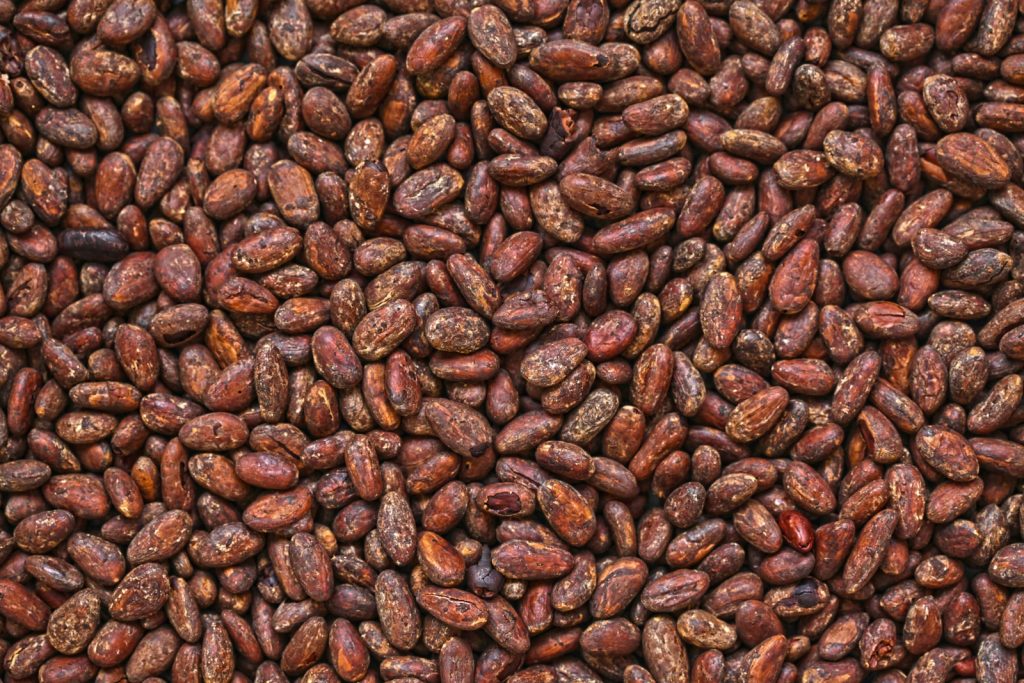
Cocoa beans
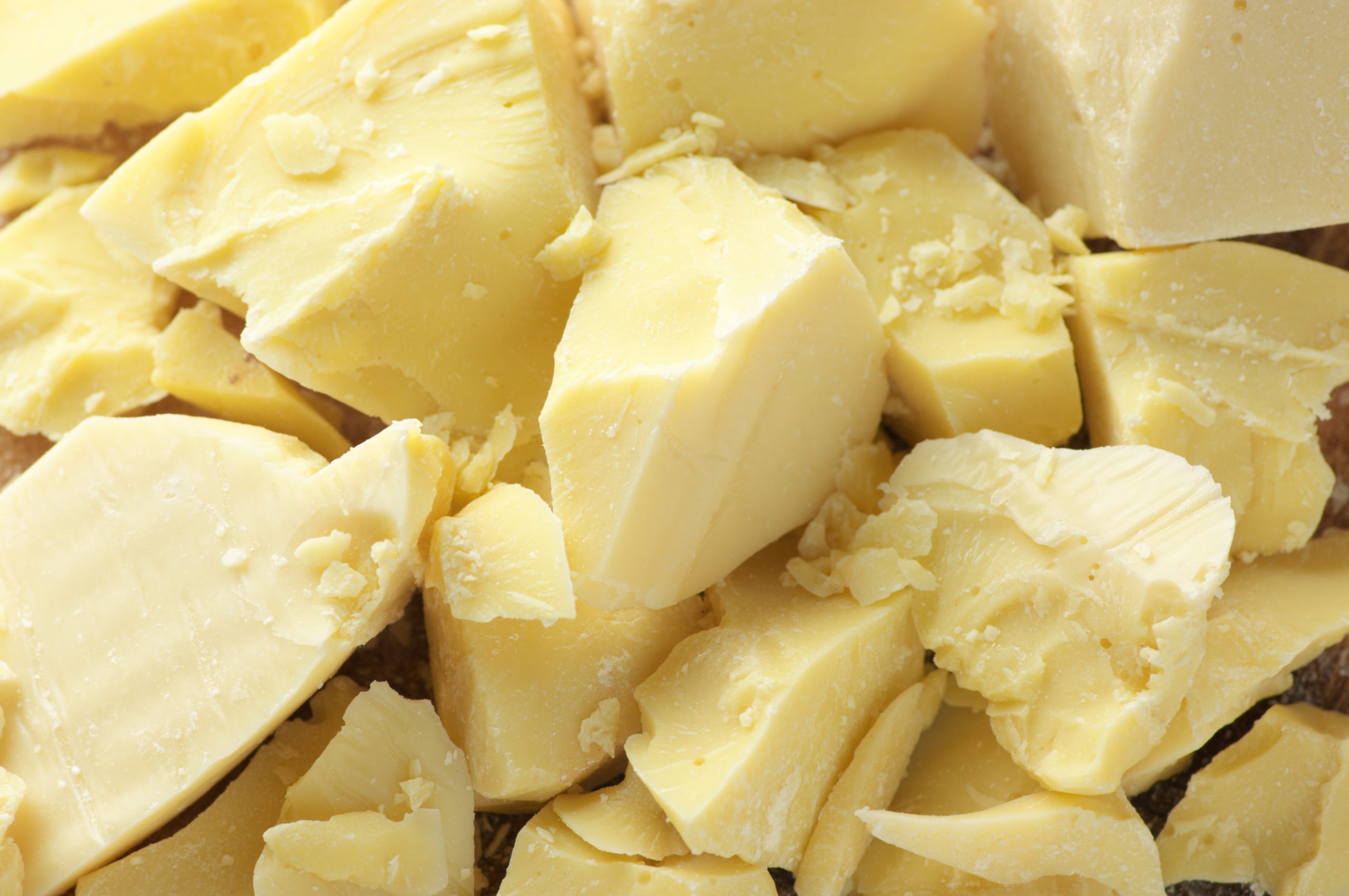
Cocoa butter
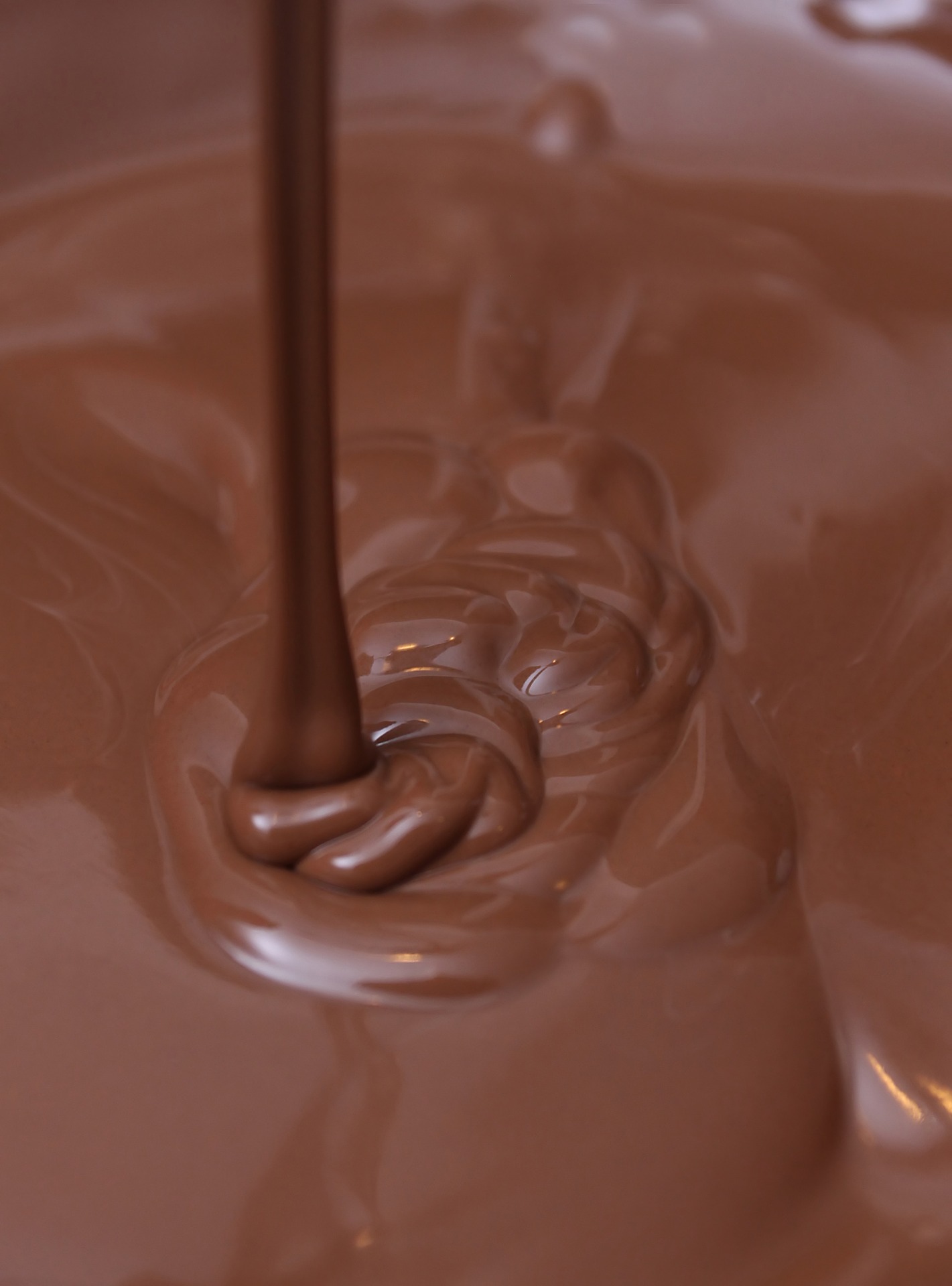
Cocoa liquor
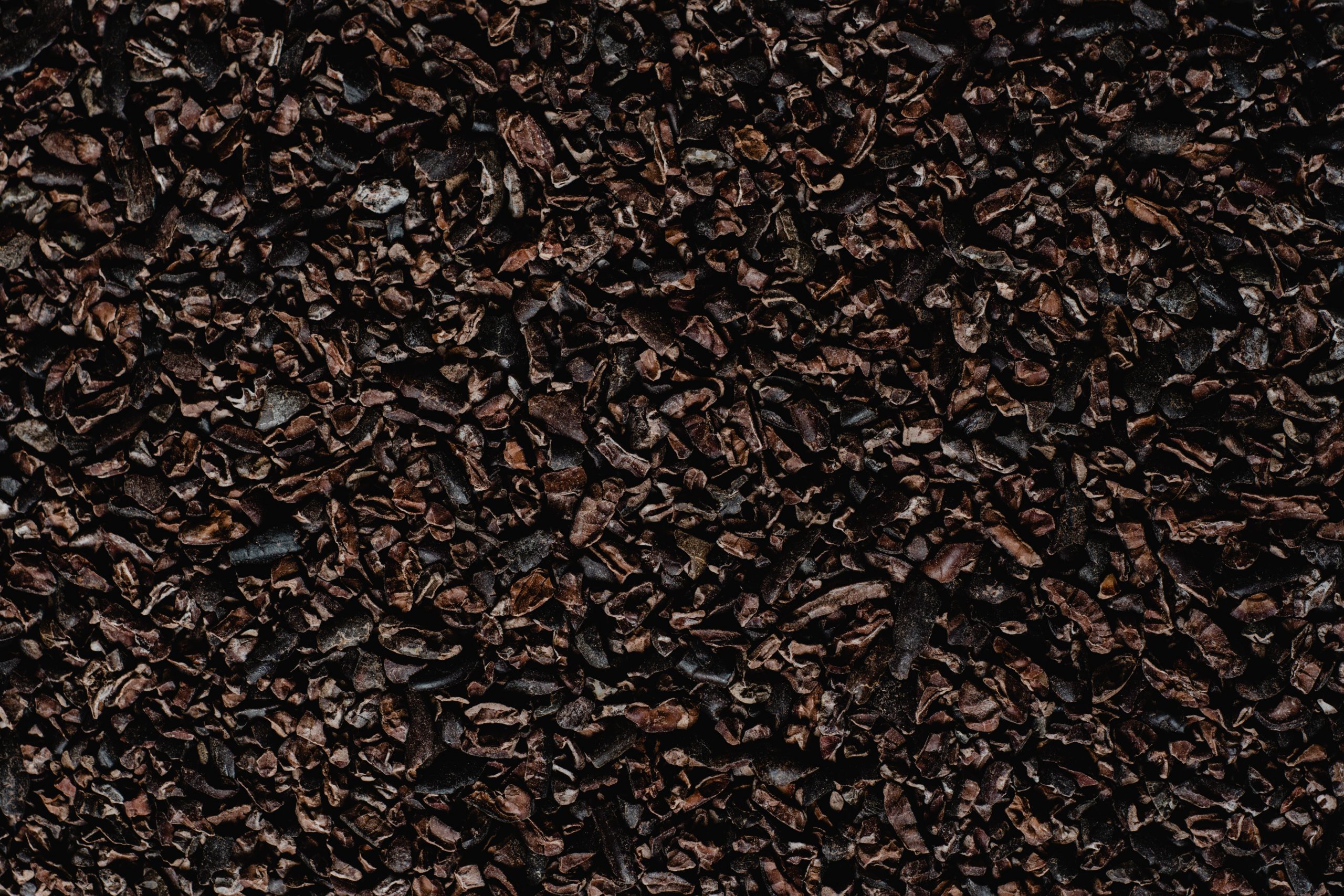
Cocoa nibs
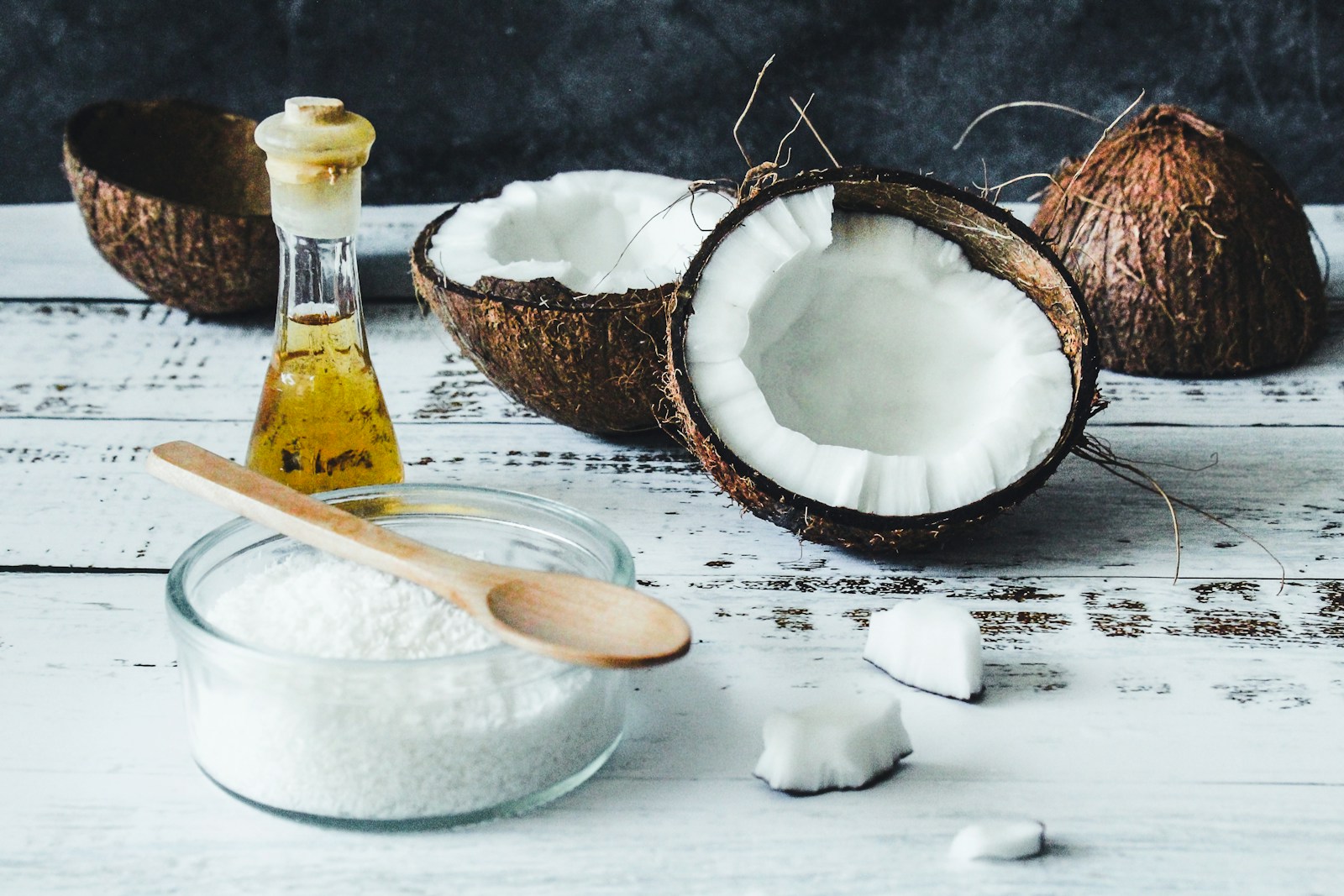
Coconut oil
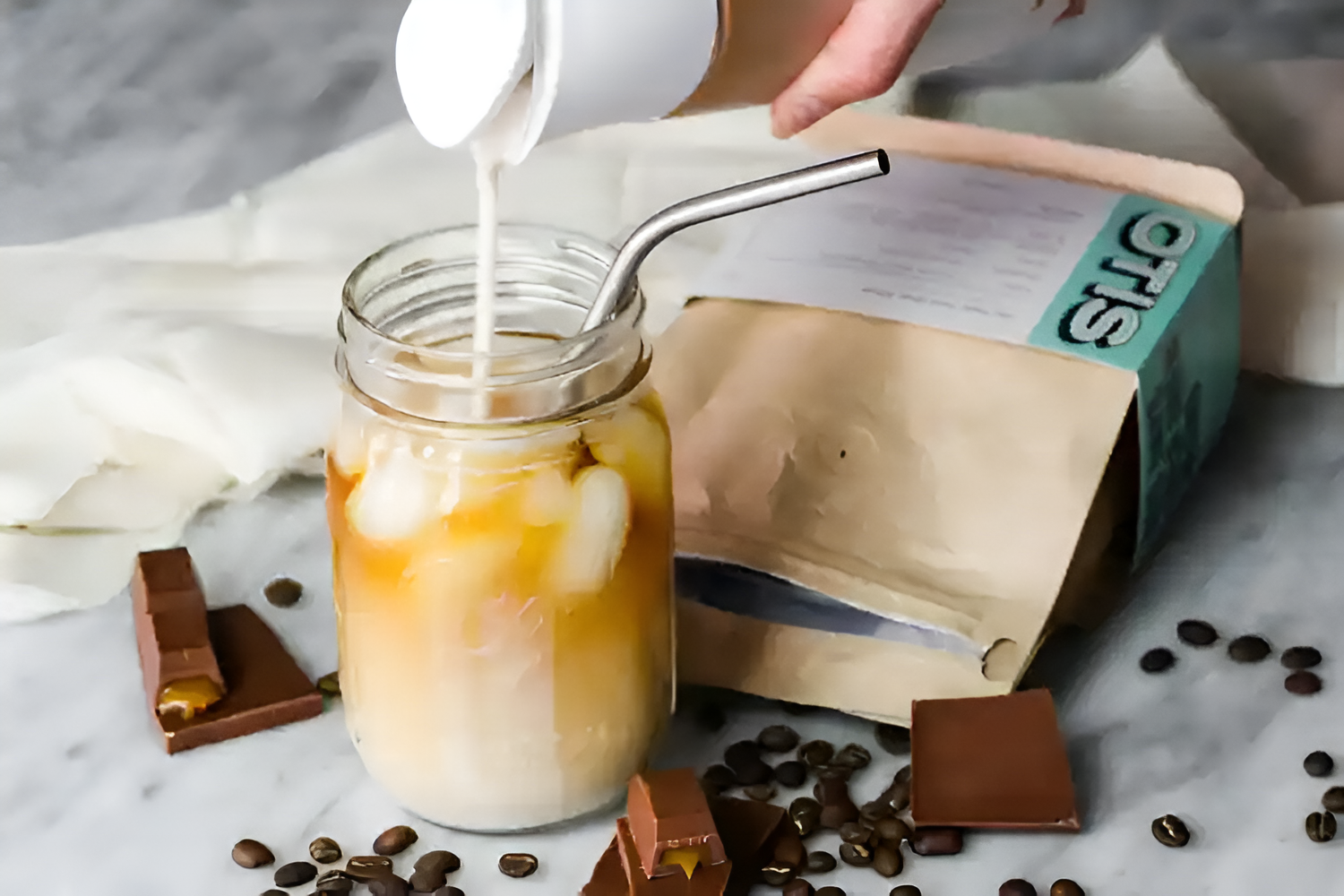
Coffee creamer
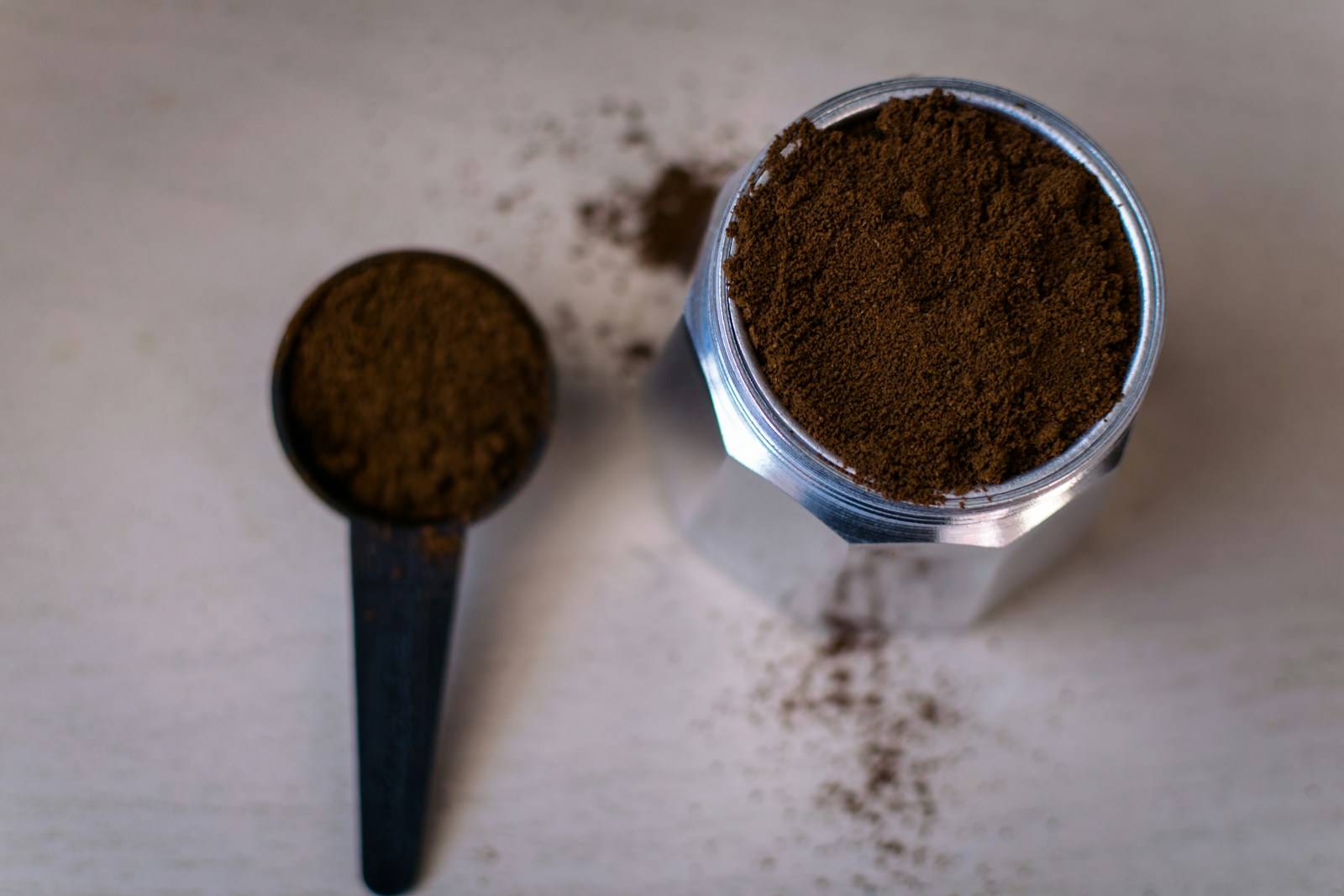
Coffee powder
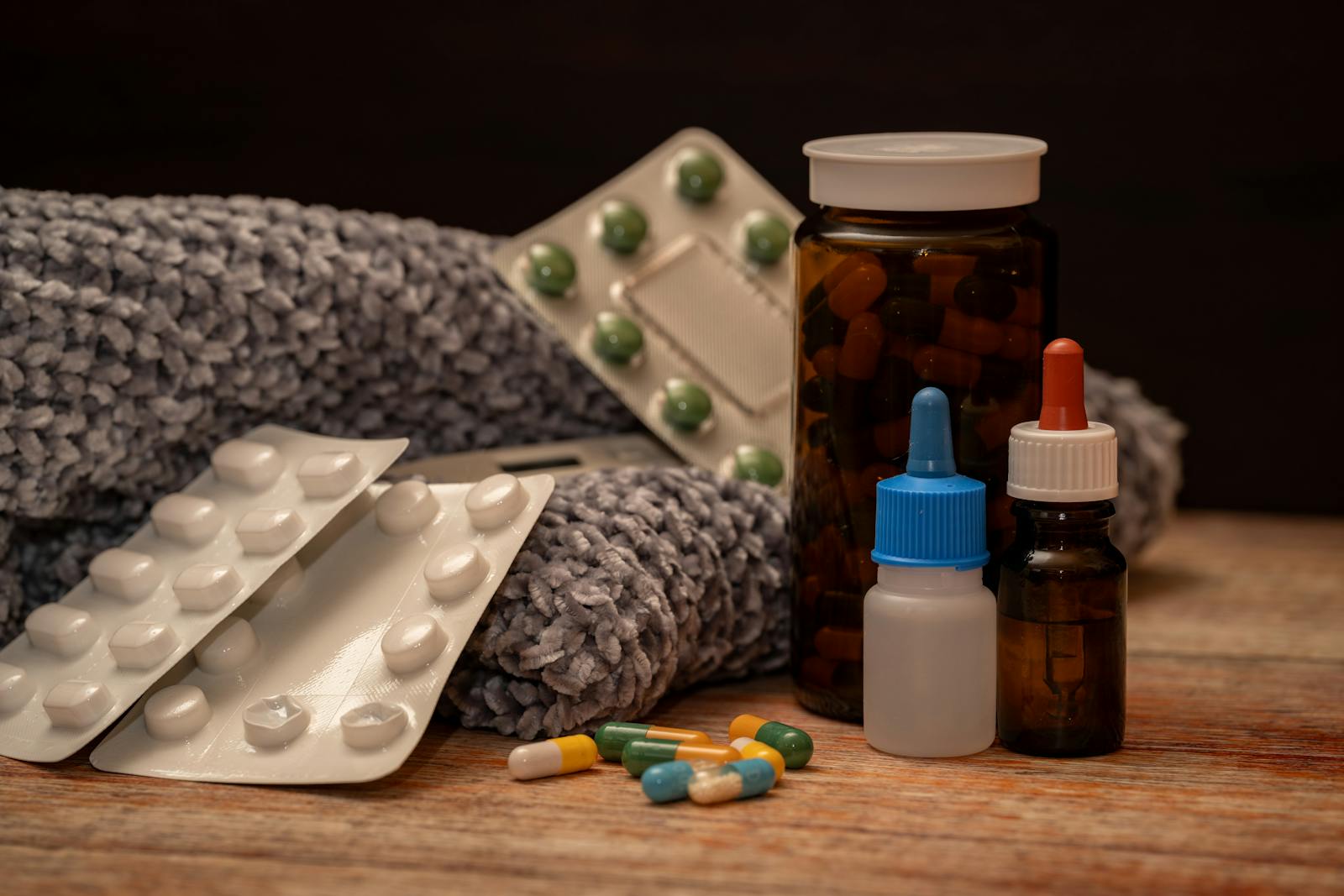
Cold and flu tablets
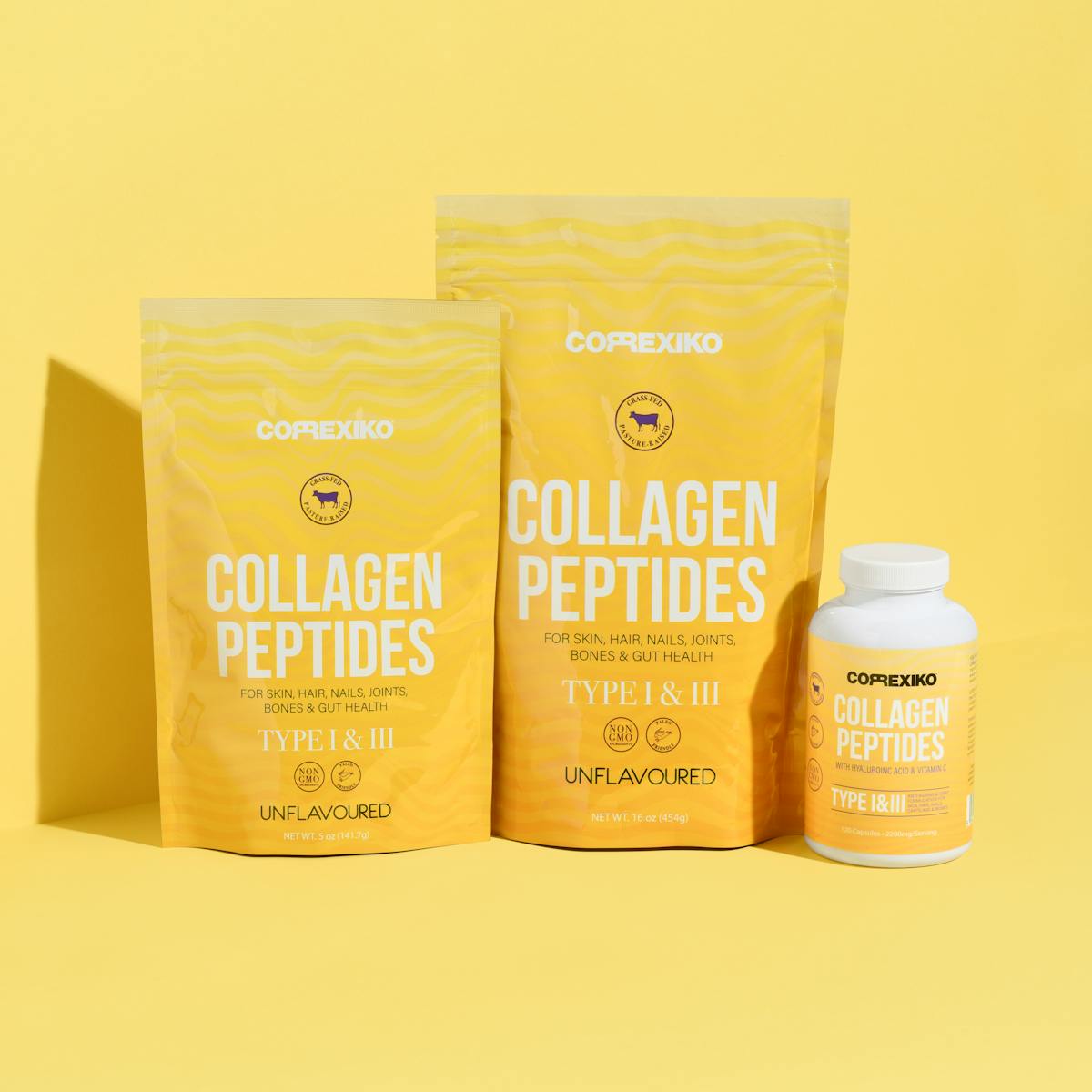
Collagen peptides
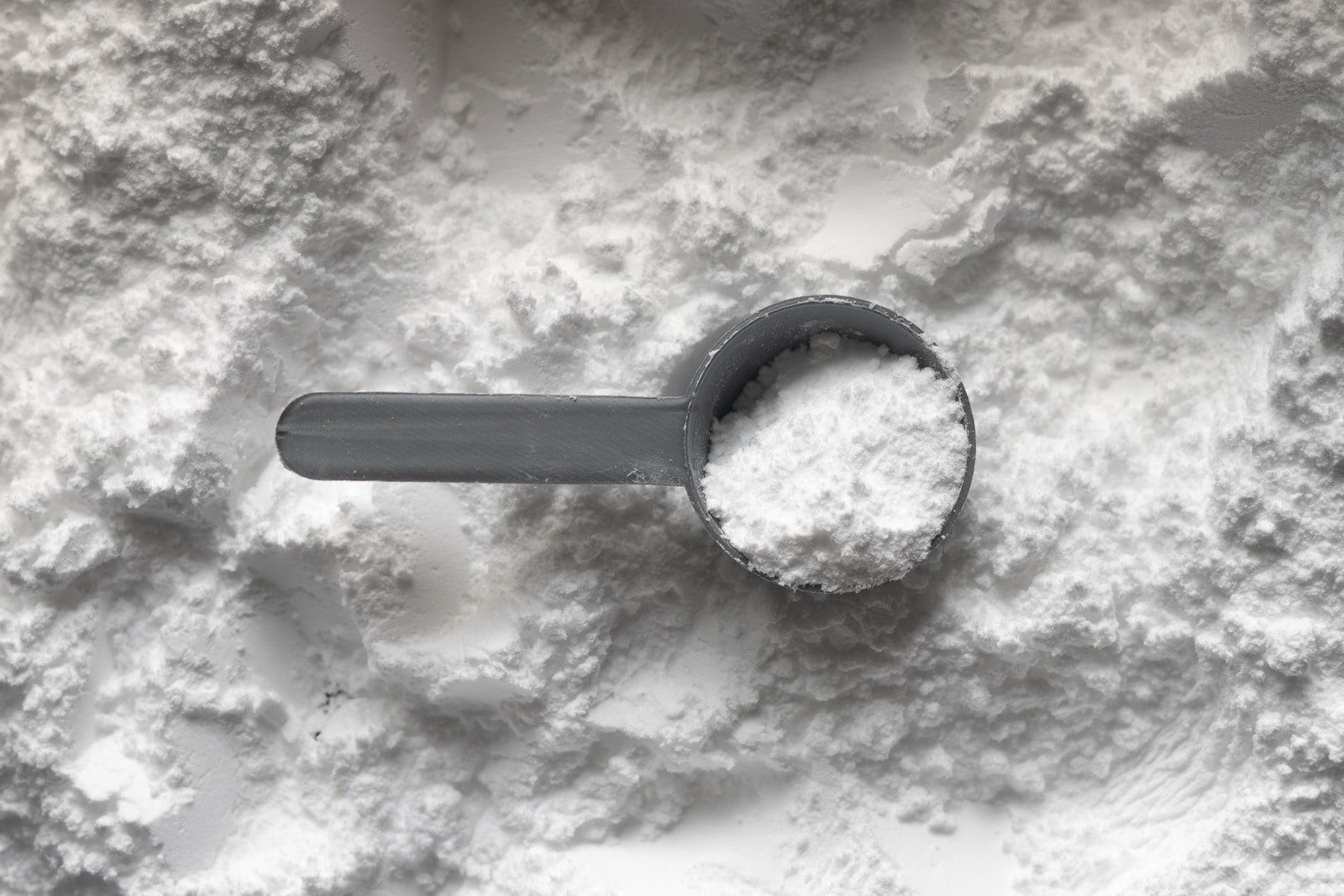
Collagen powder
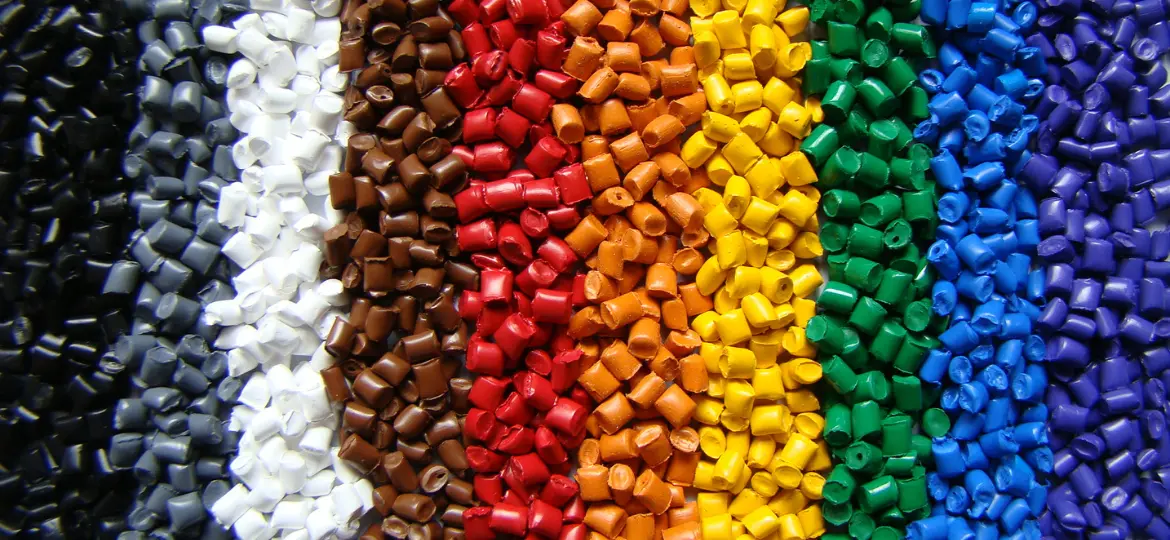
Color masterbatches
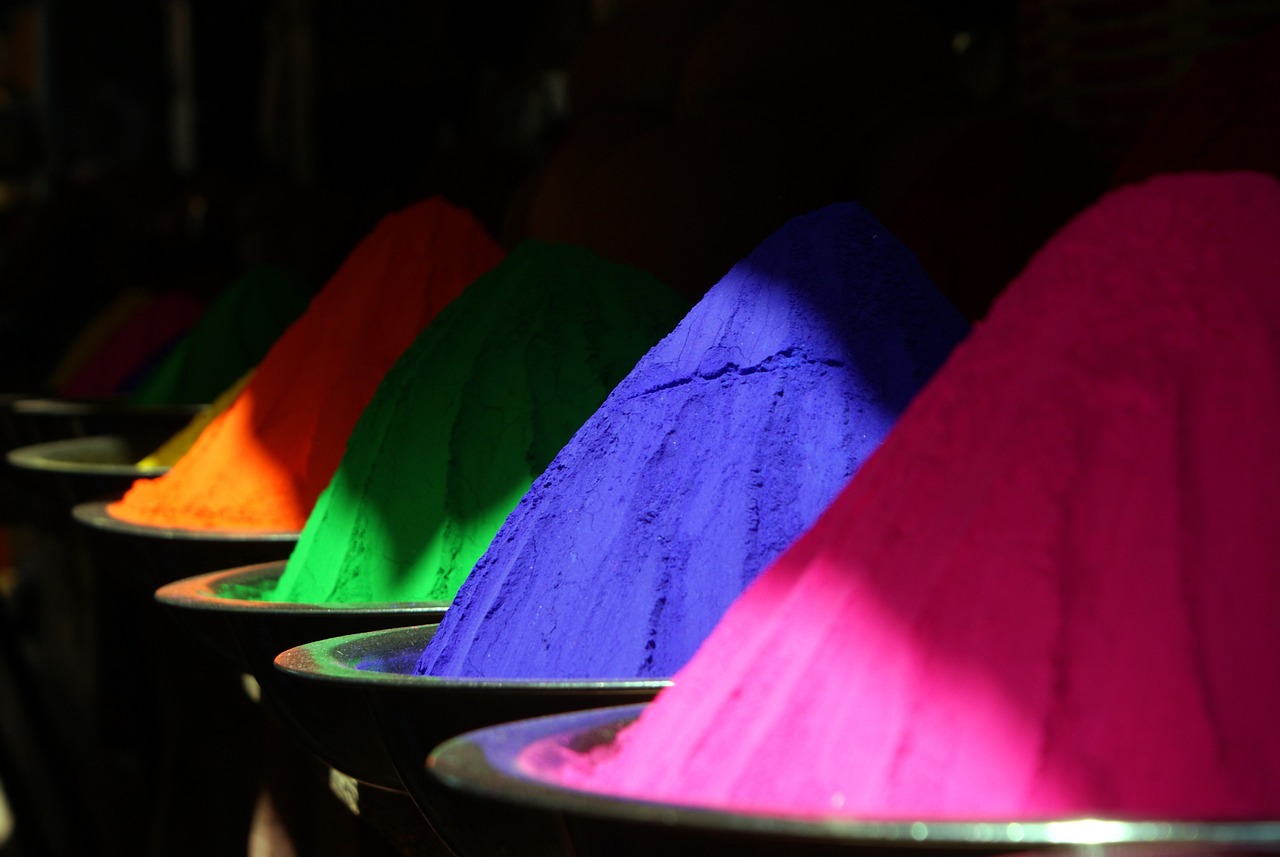
Colorants
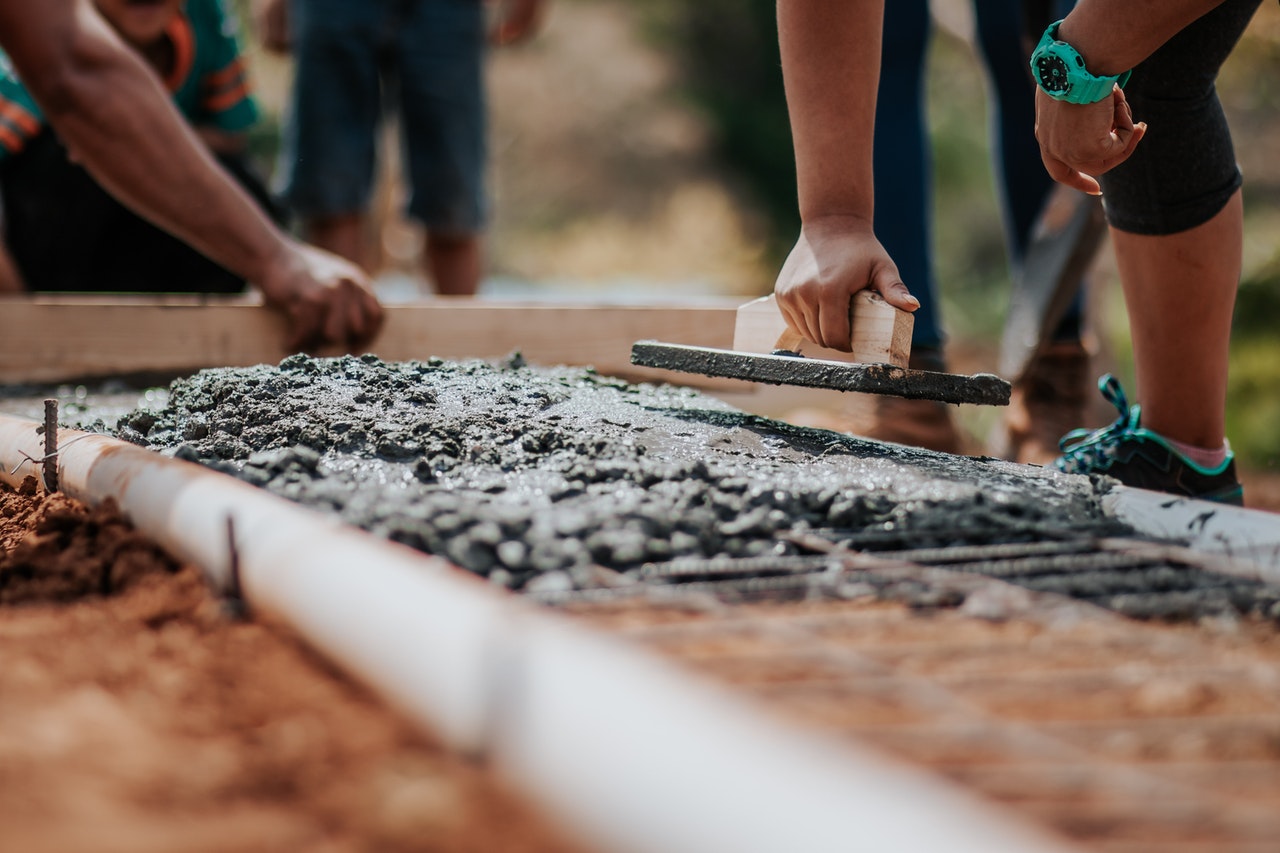
Concrete additives
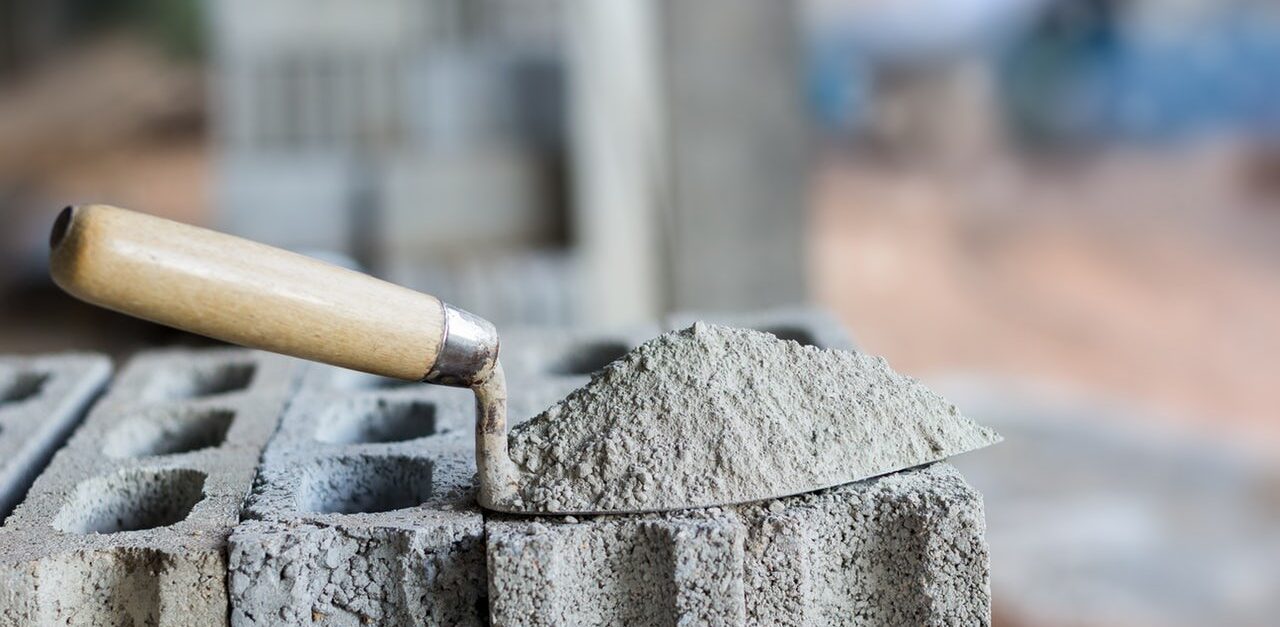
Concrete admixtures
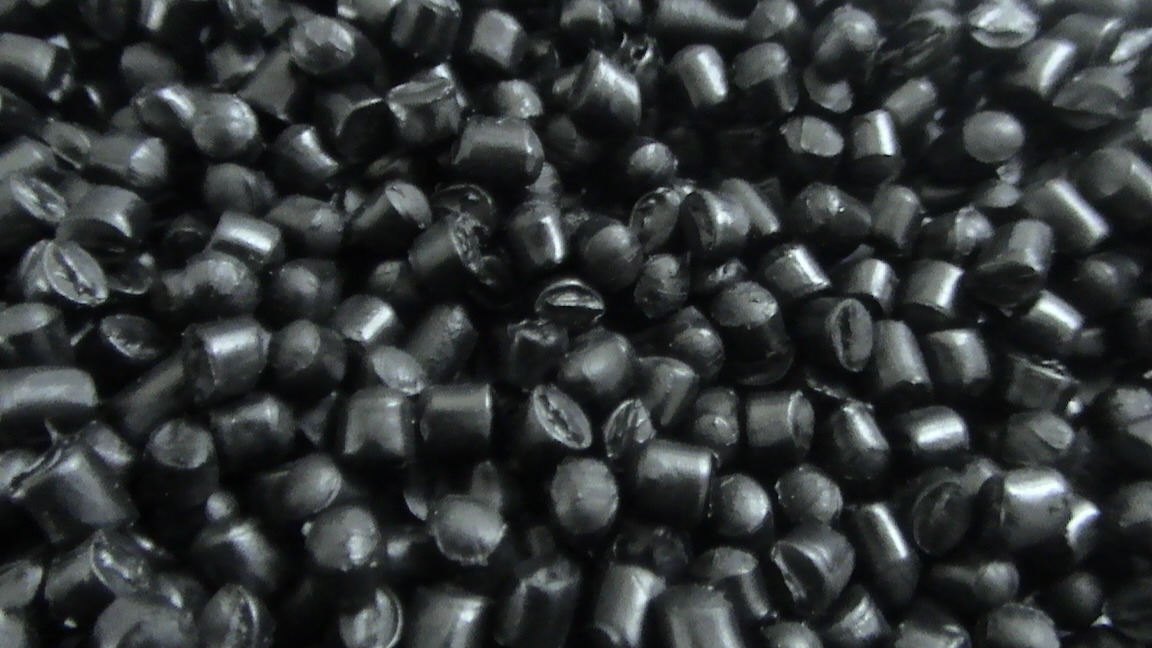
Conductive additives
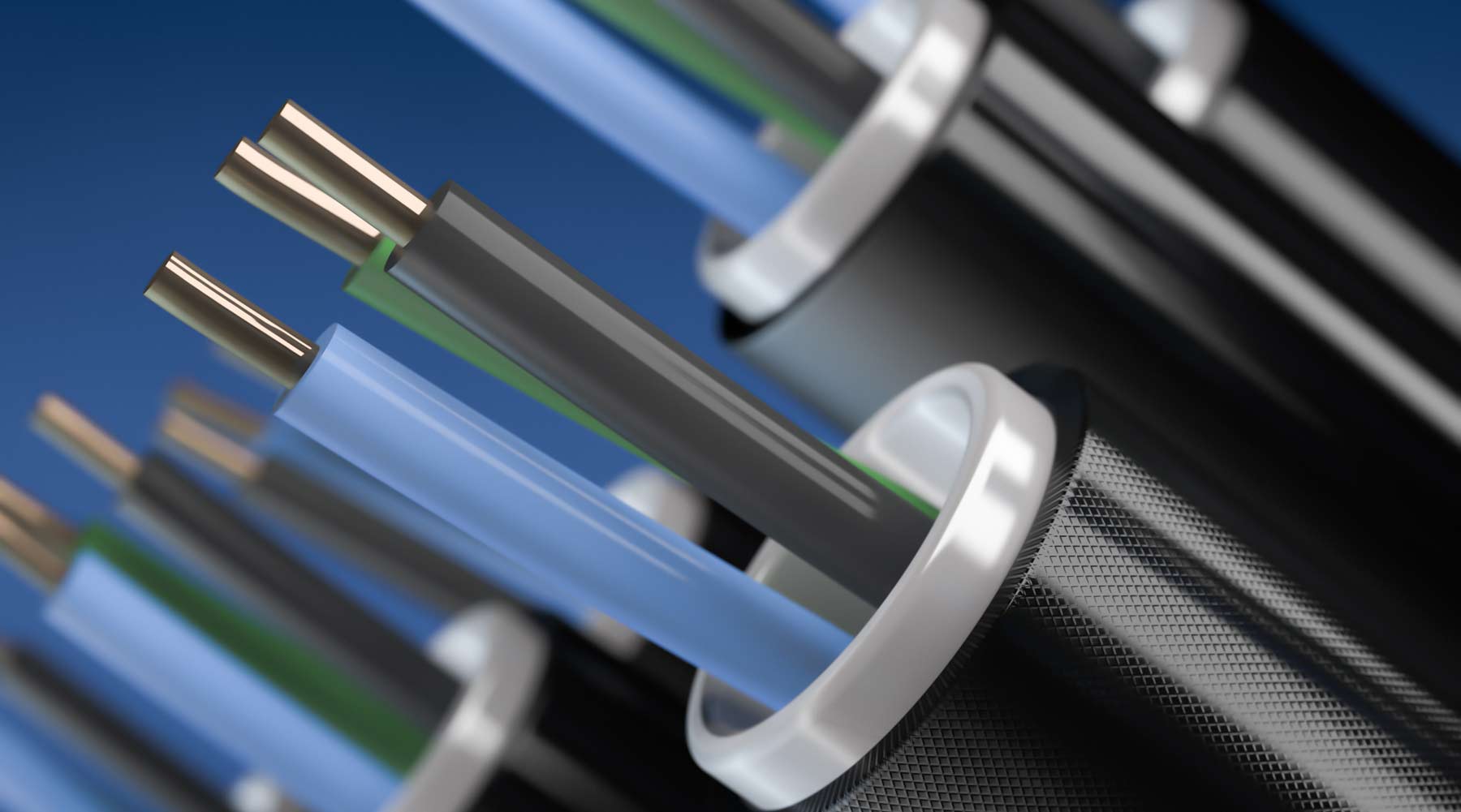
Conductive coatings
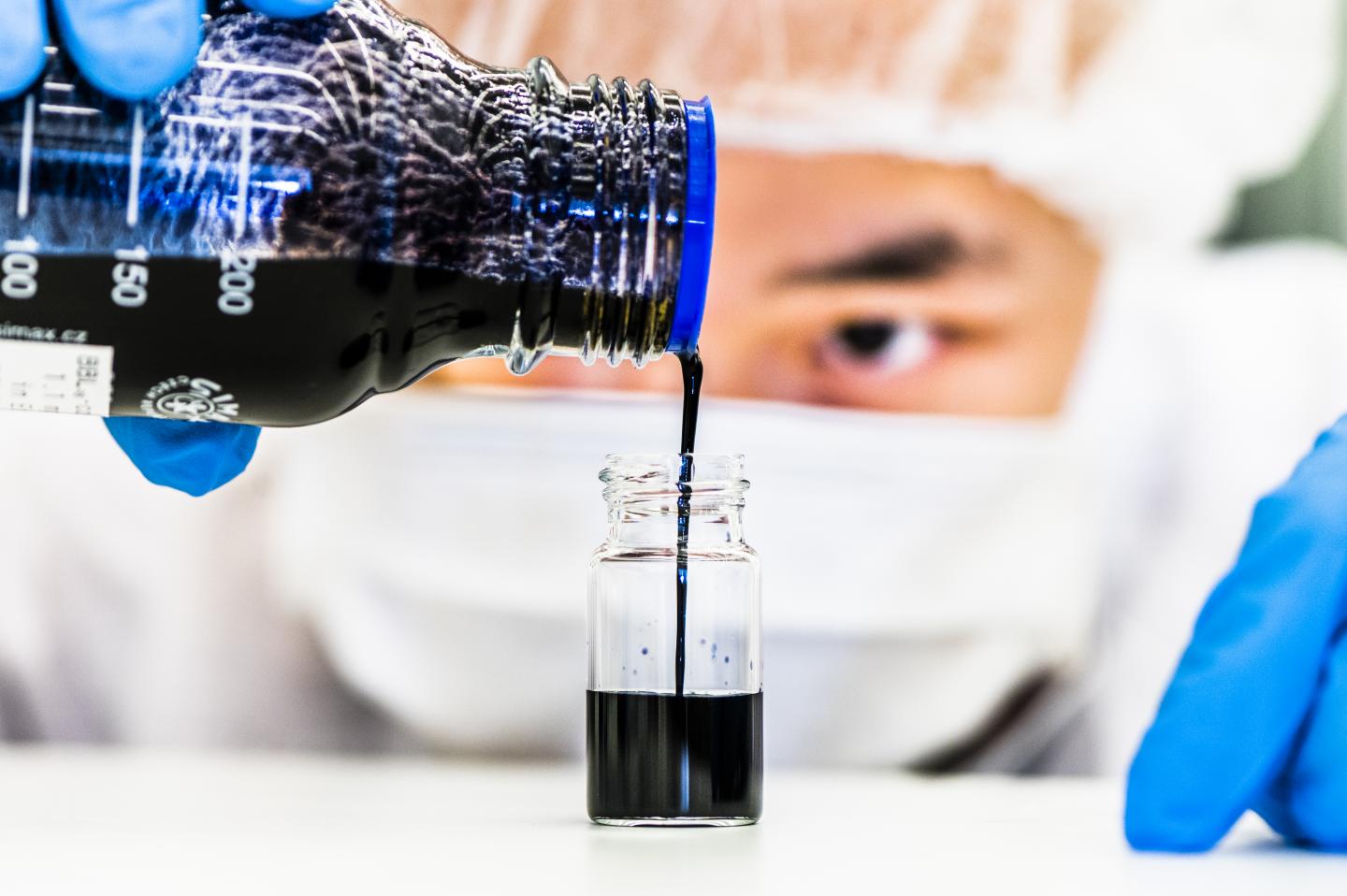
Conductive inks
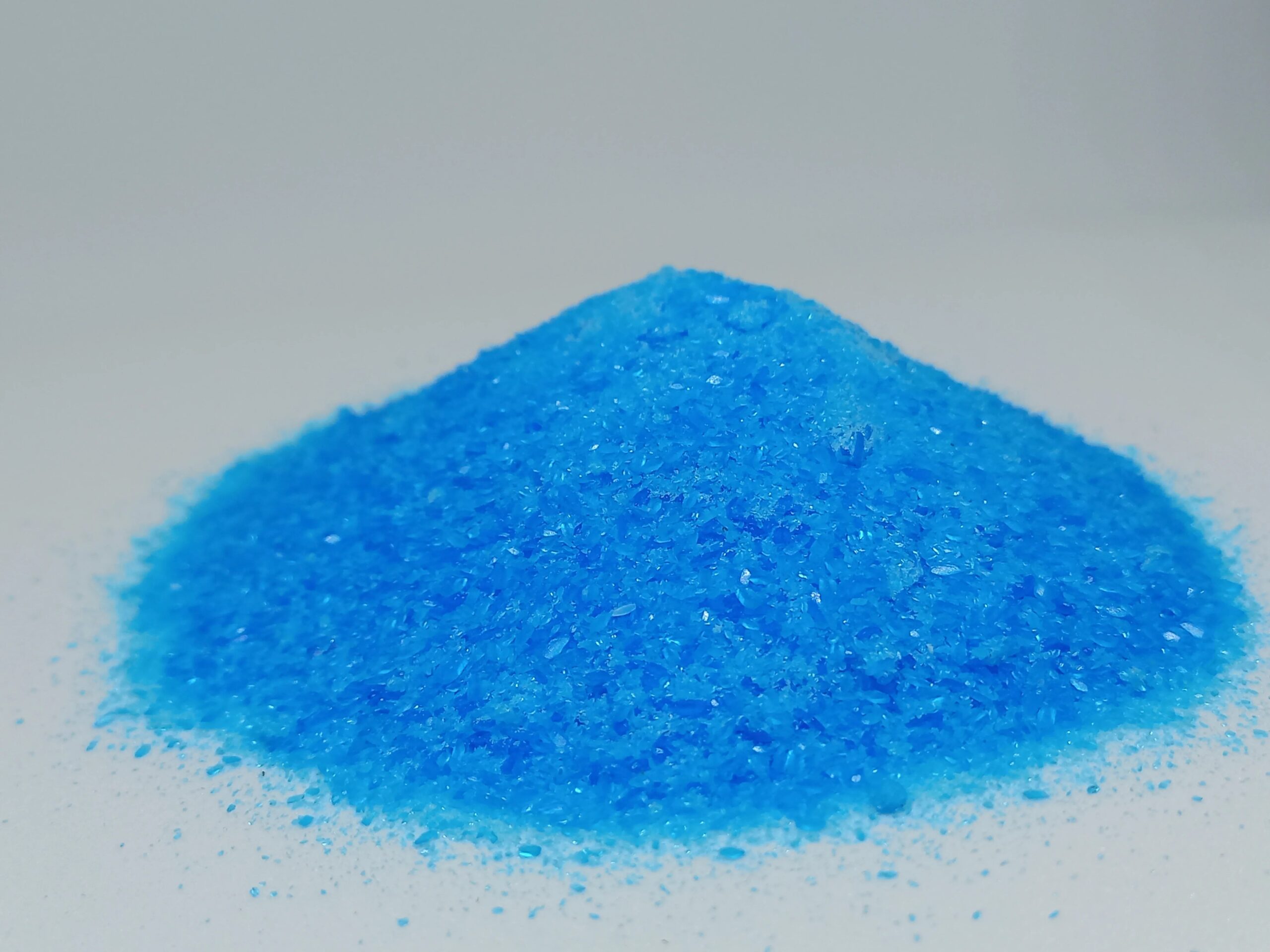
Copper sulfate
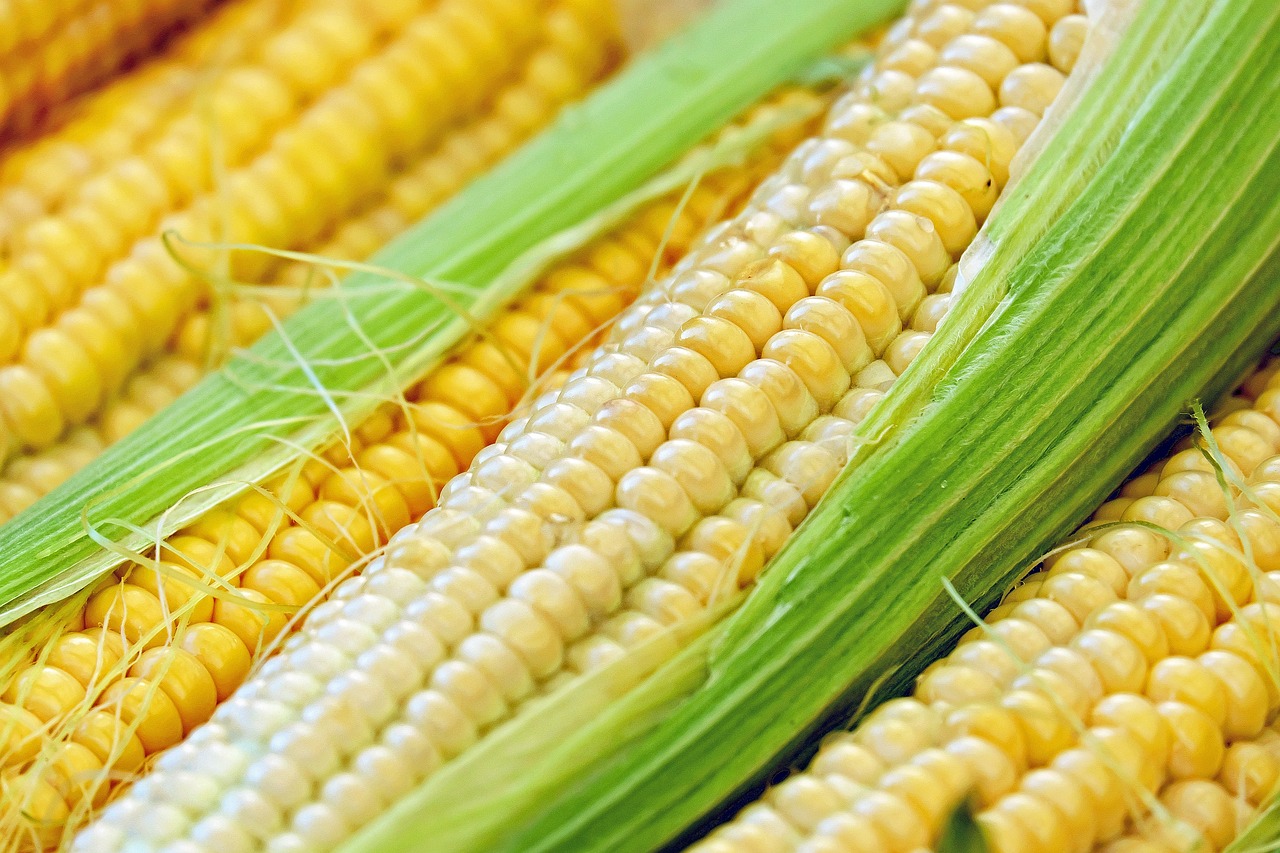
Corn
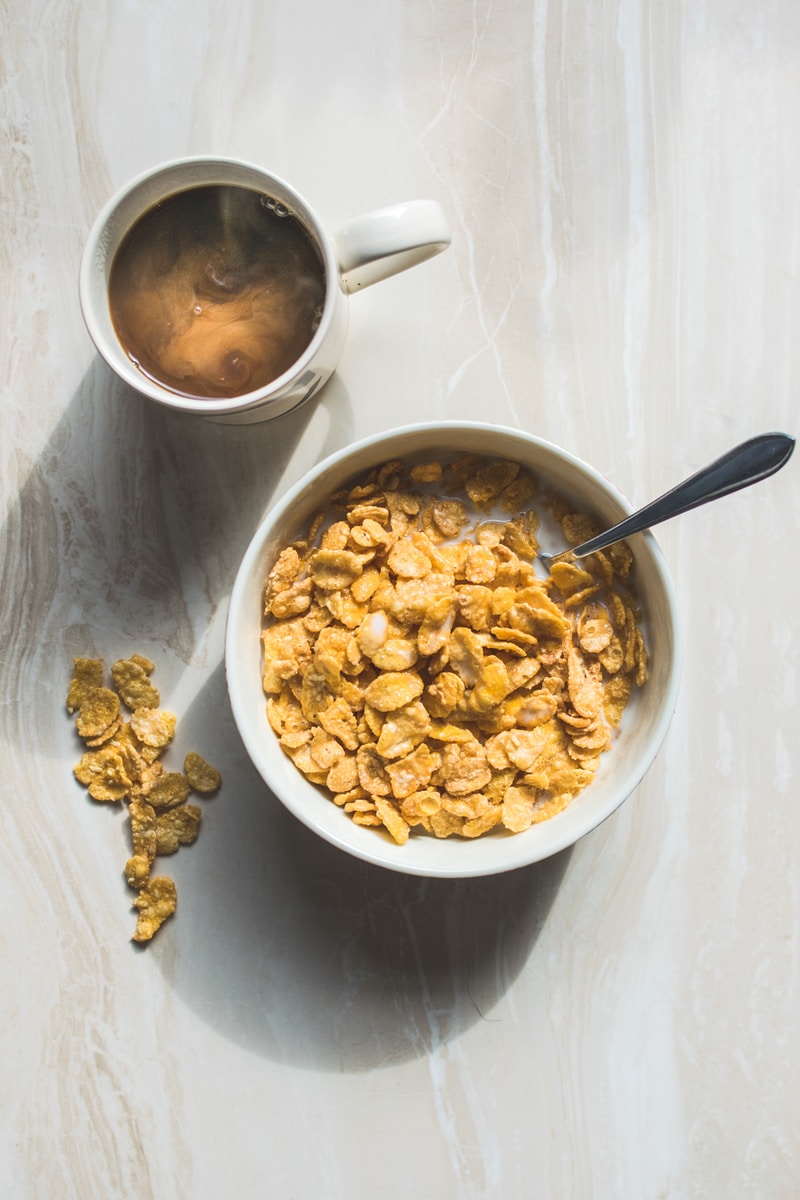
Corn flakes
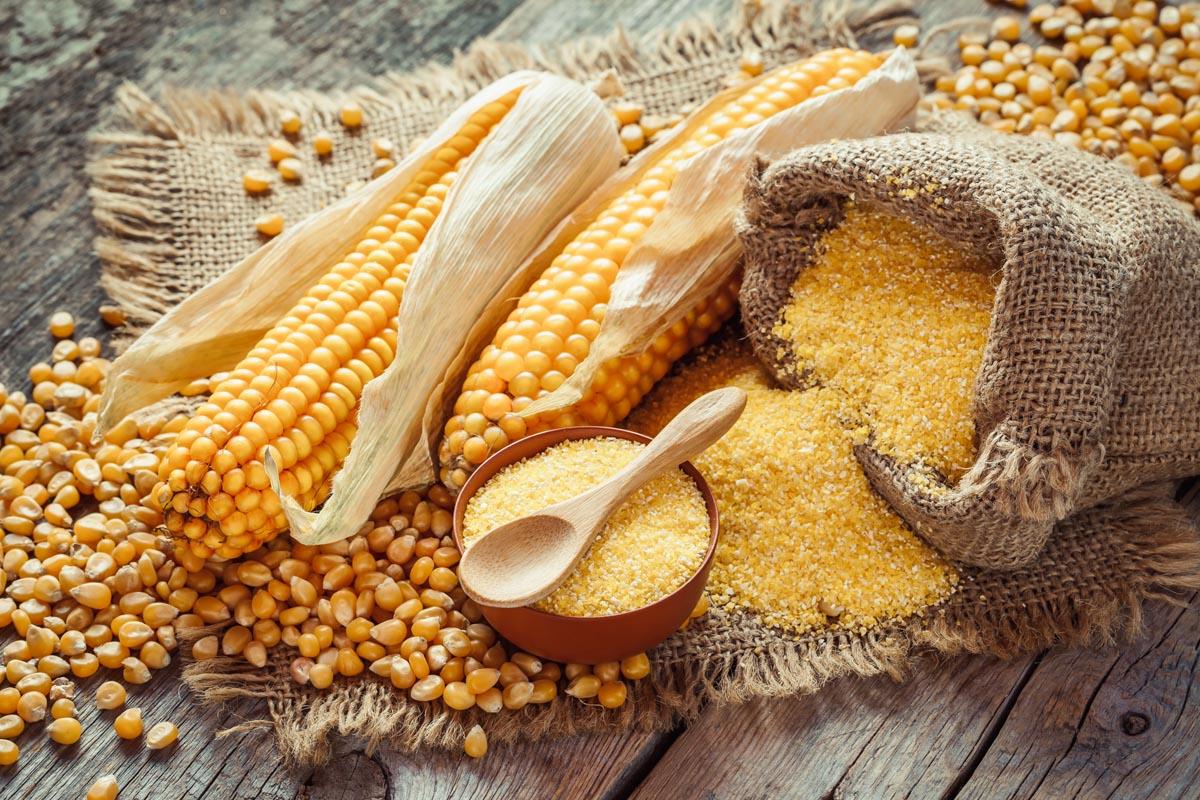
Corn gluten meal

Corn grits

Corn seeds
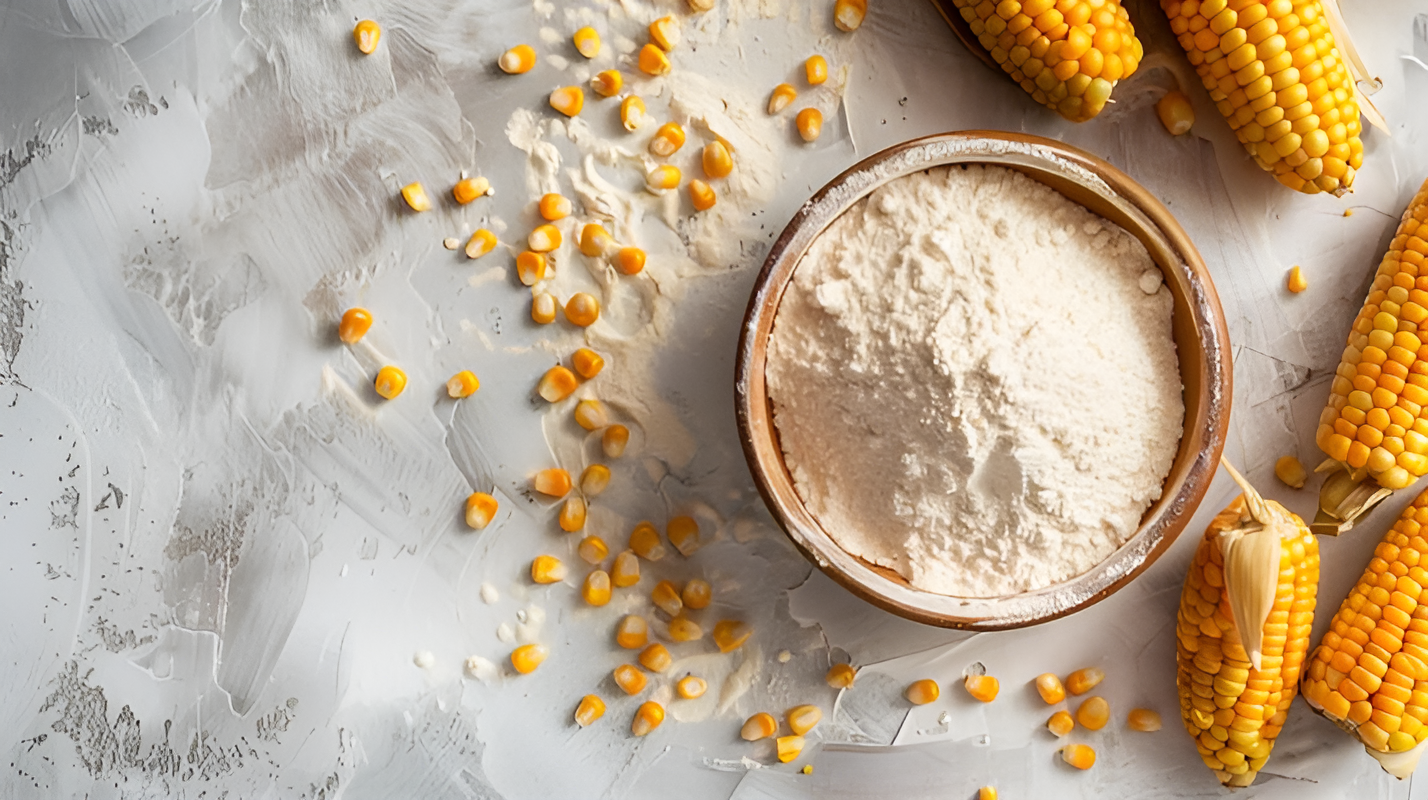
Cornstarch
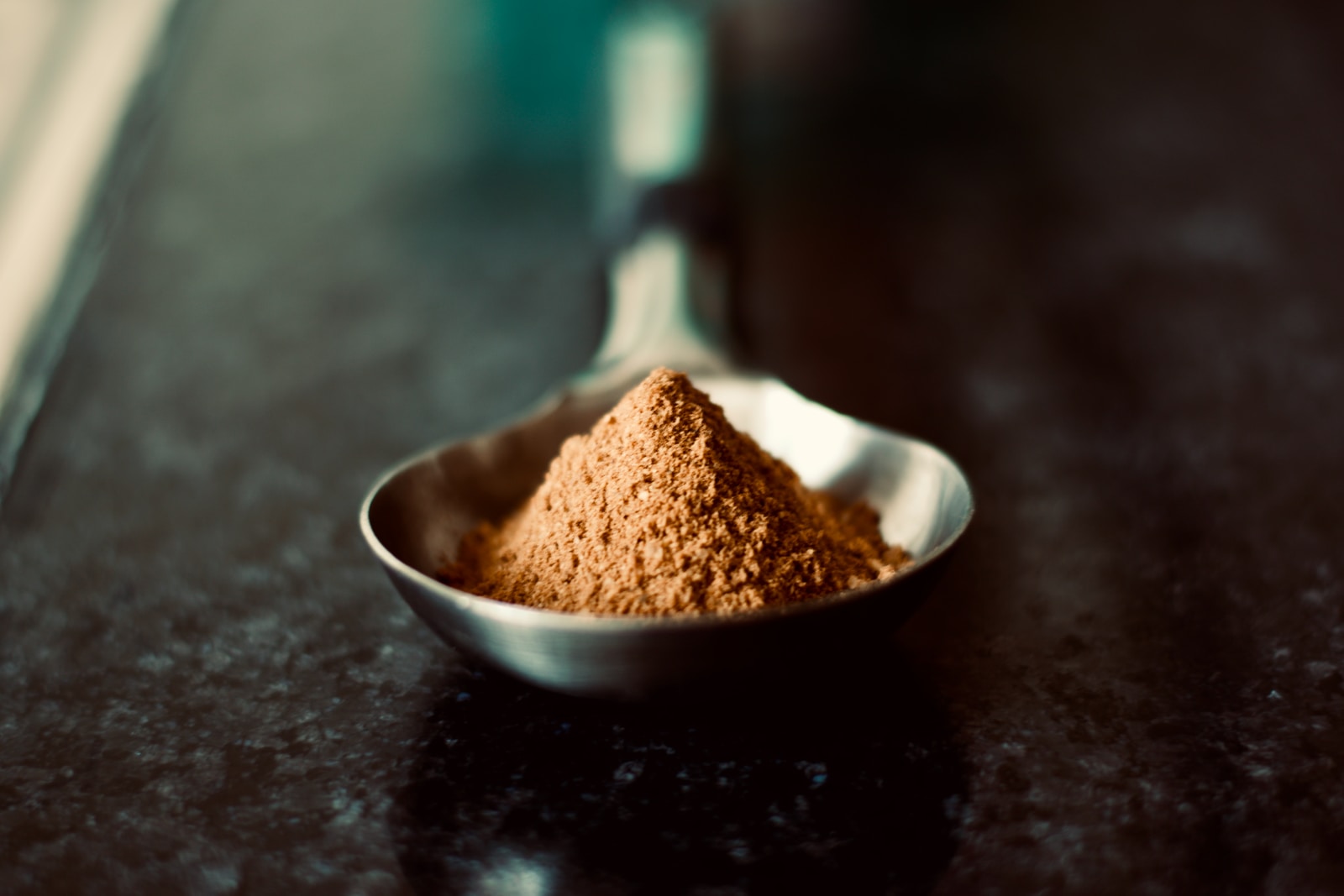
Cottonseed meal
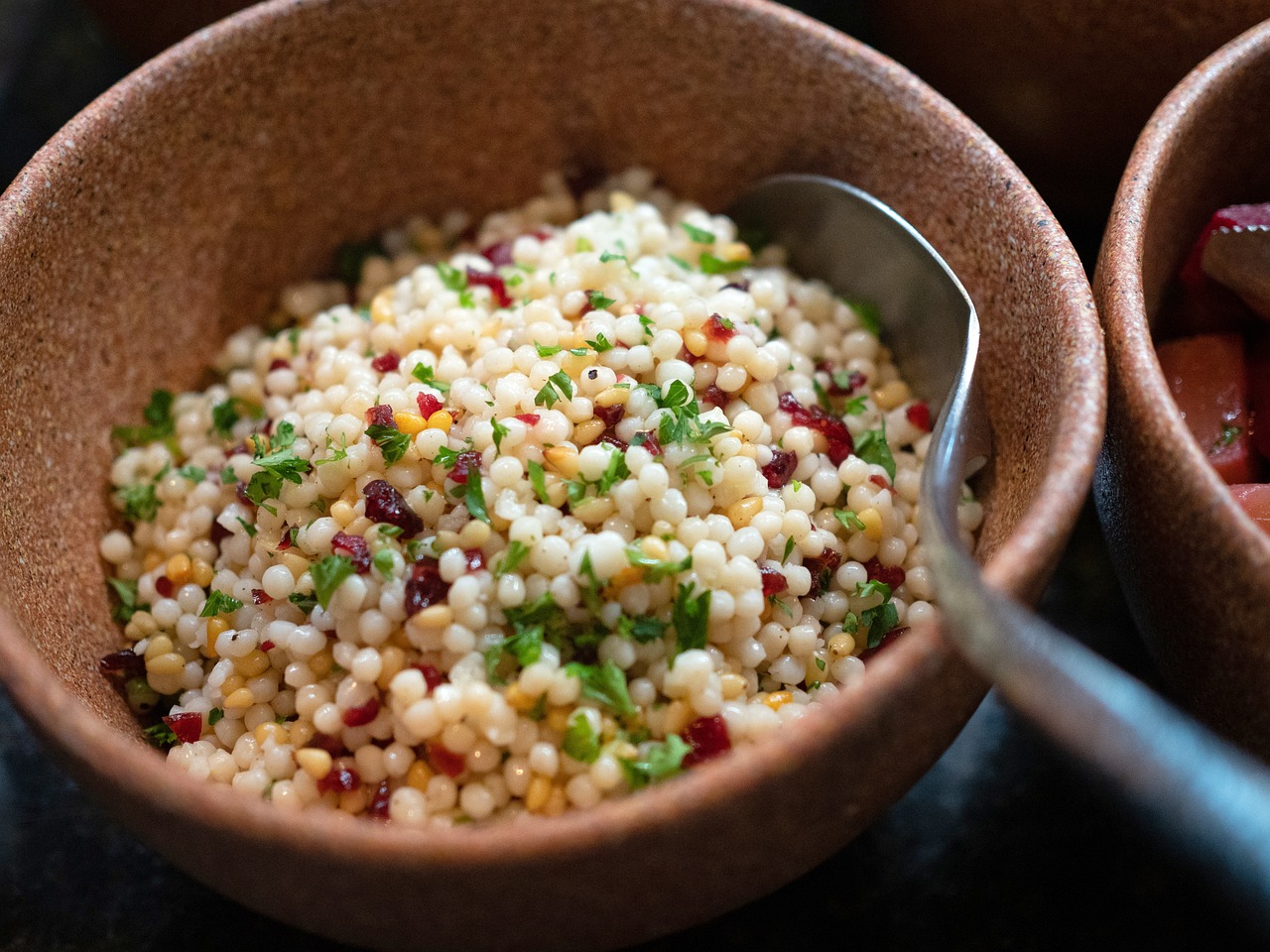
Couscous
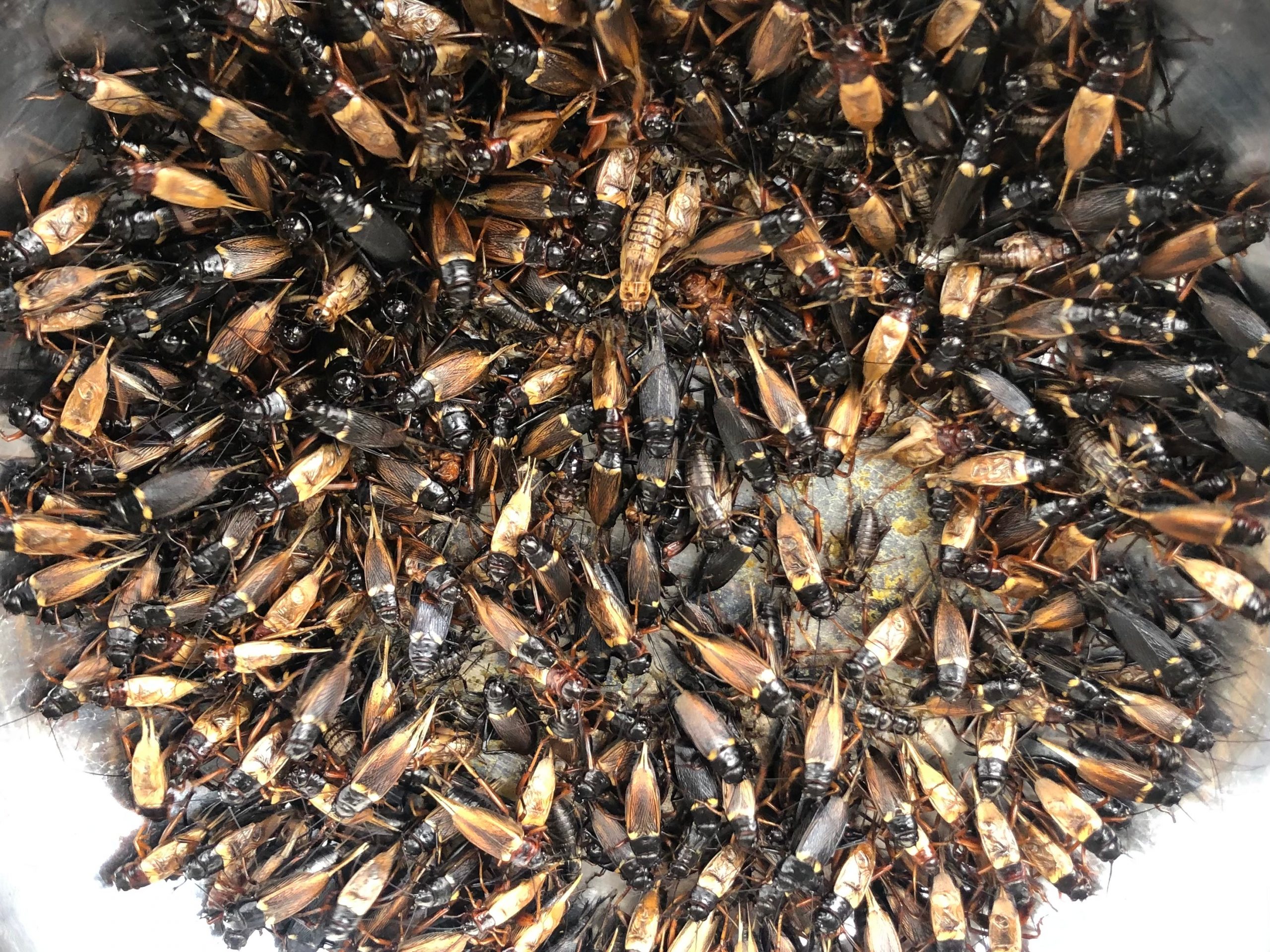
Cricket protein
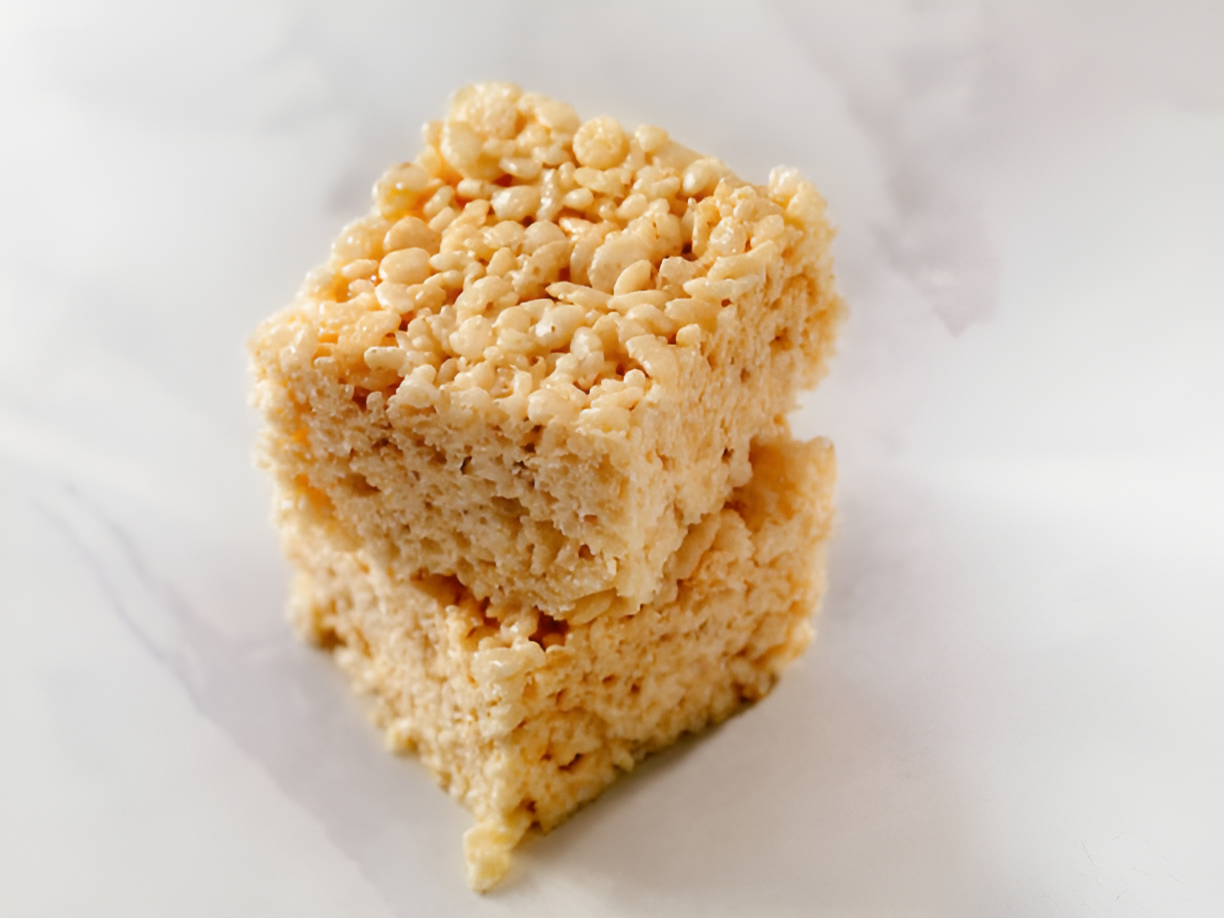
Crispies
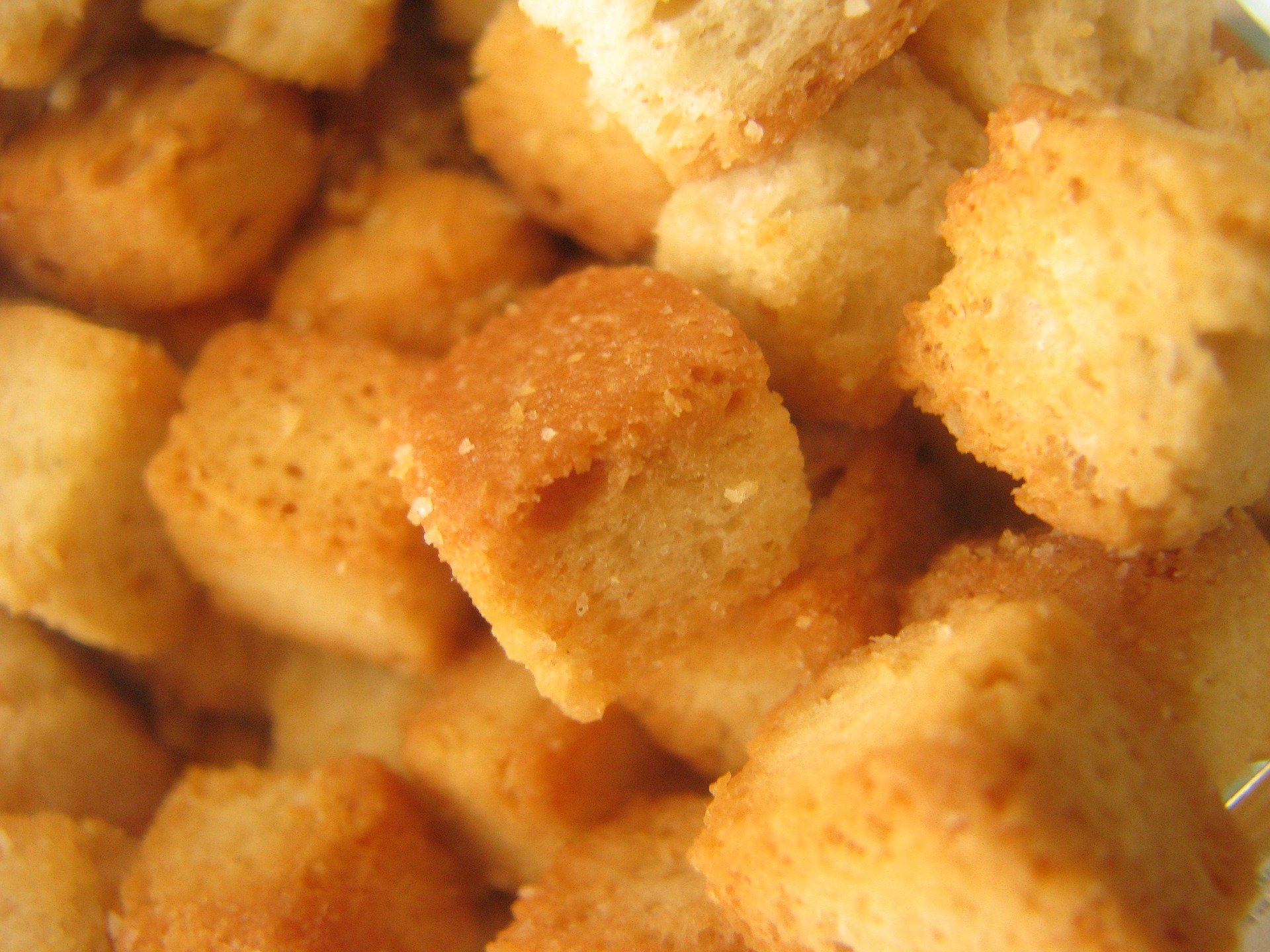
Croutons
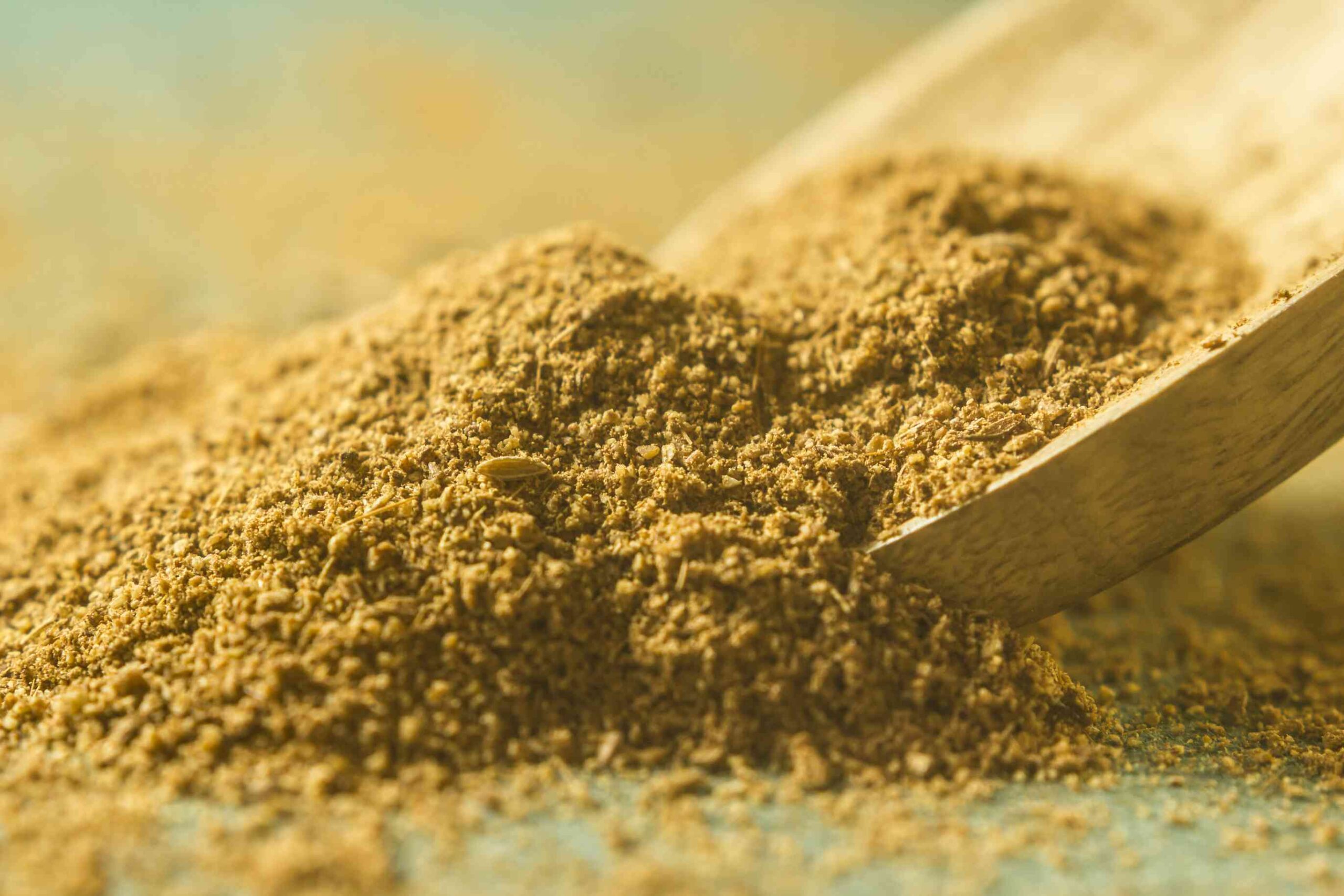
Cumin powder
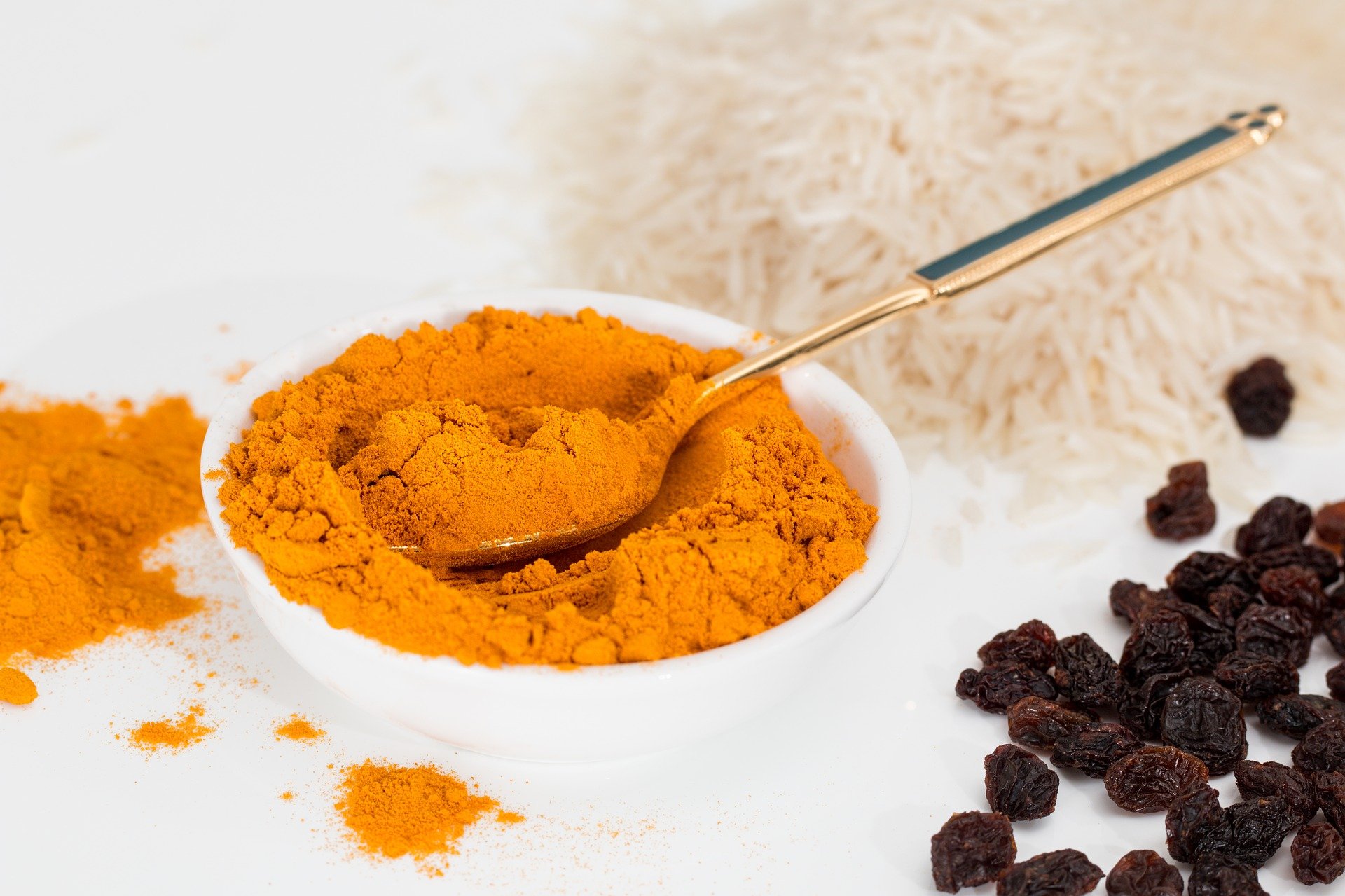
Curry powder
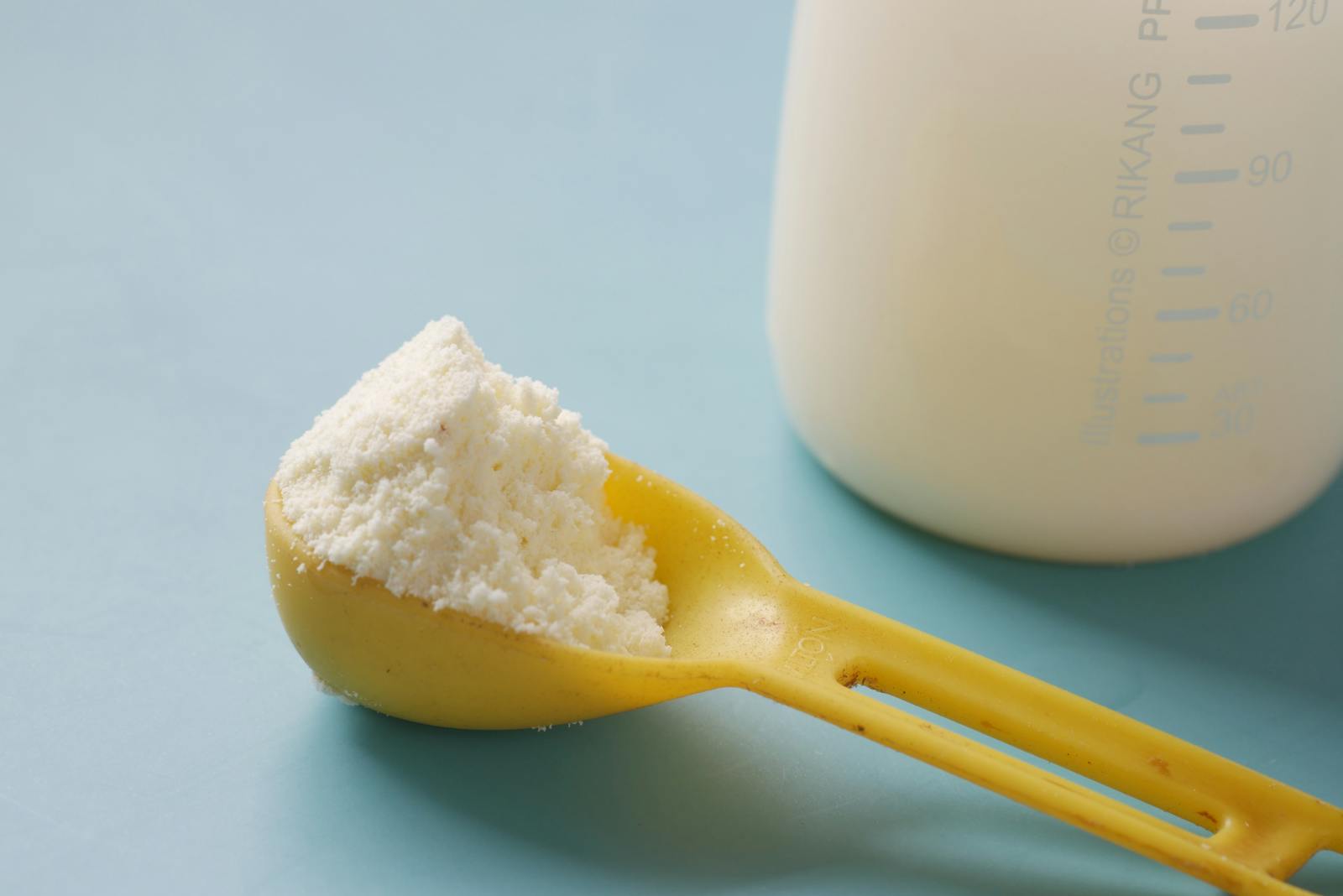
Dairy powder
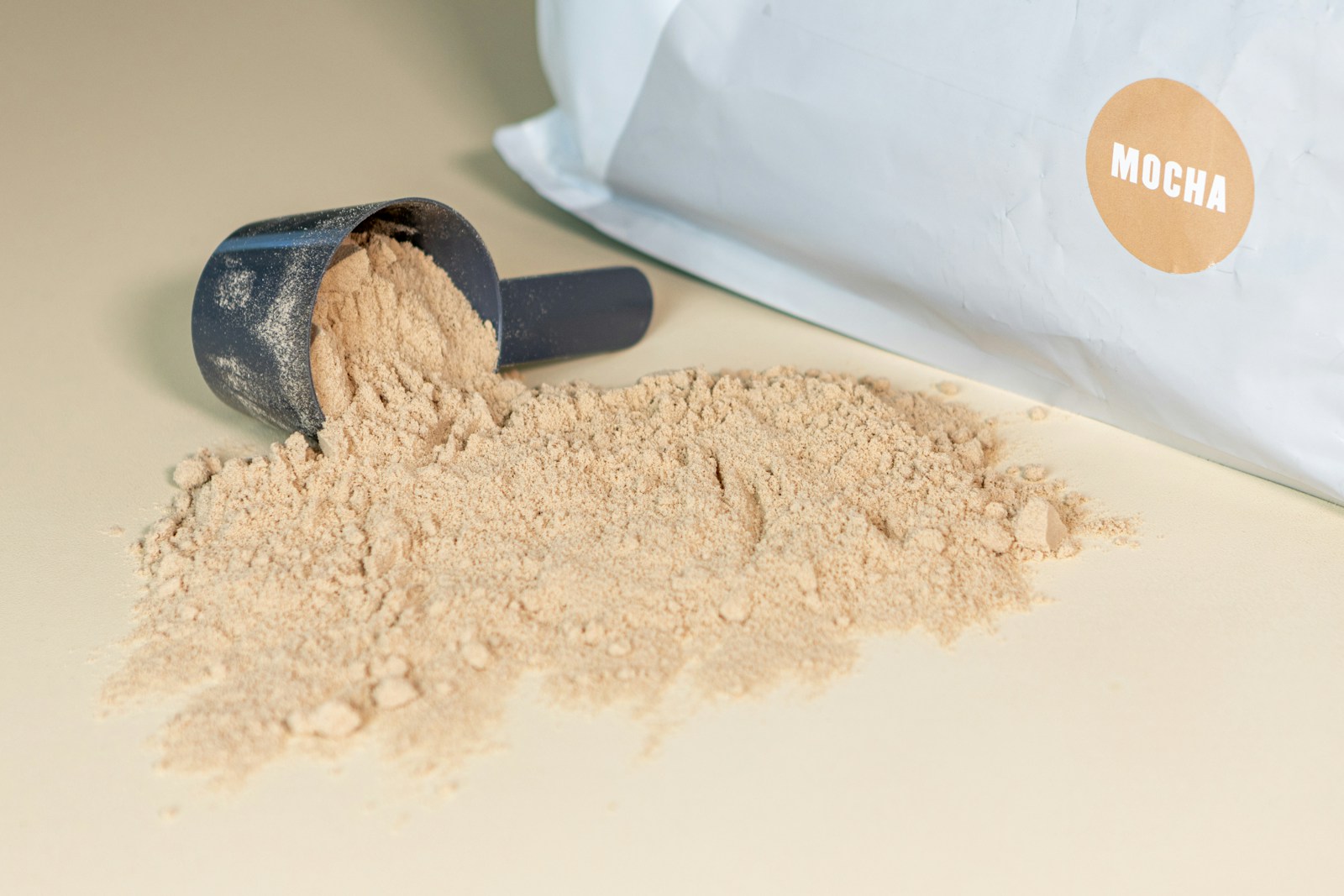
Dairy protein supplements
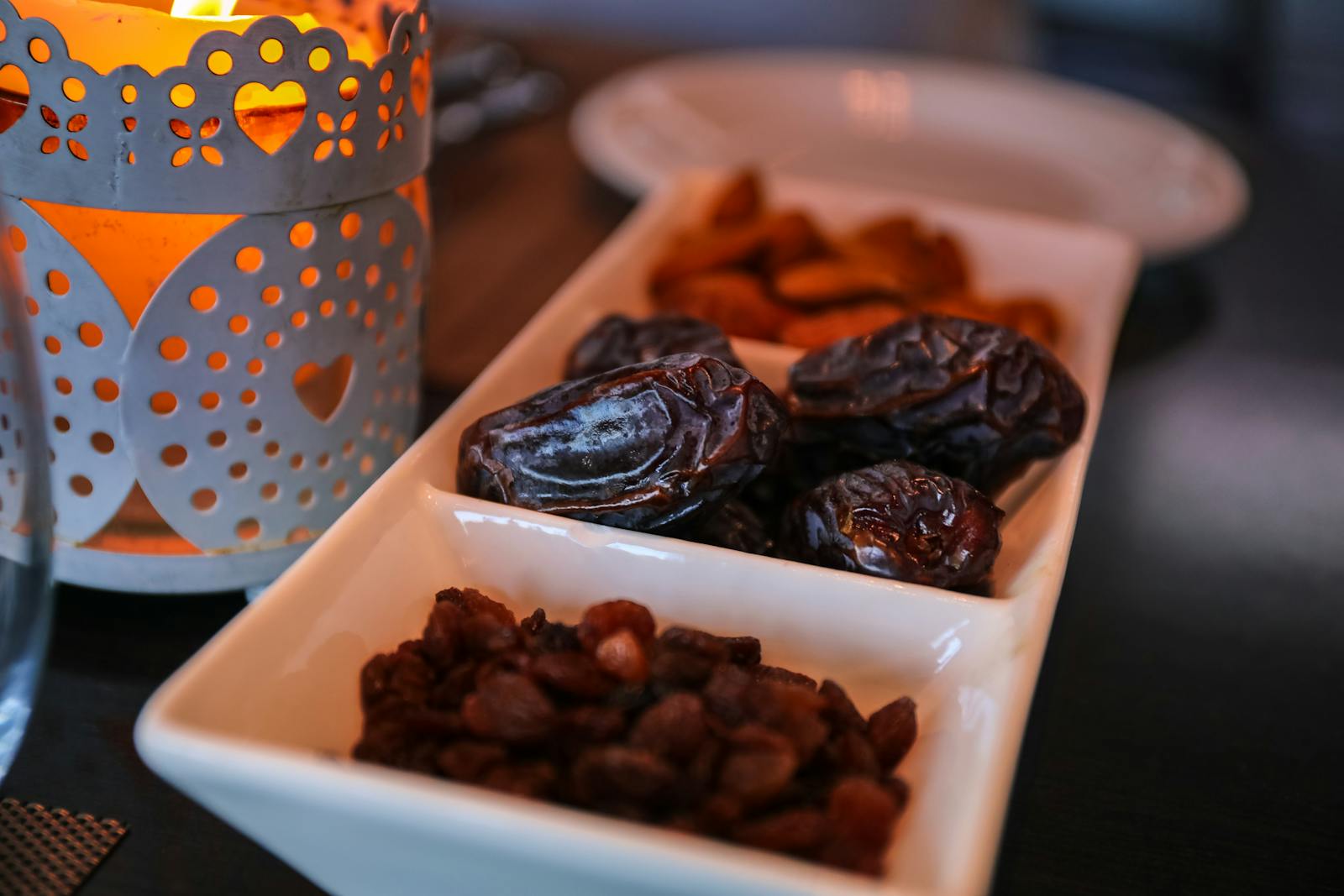
Dates
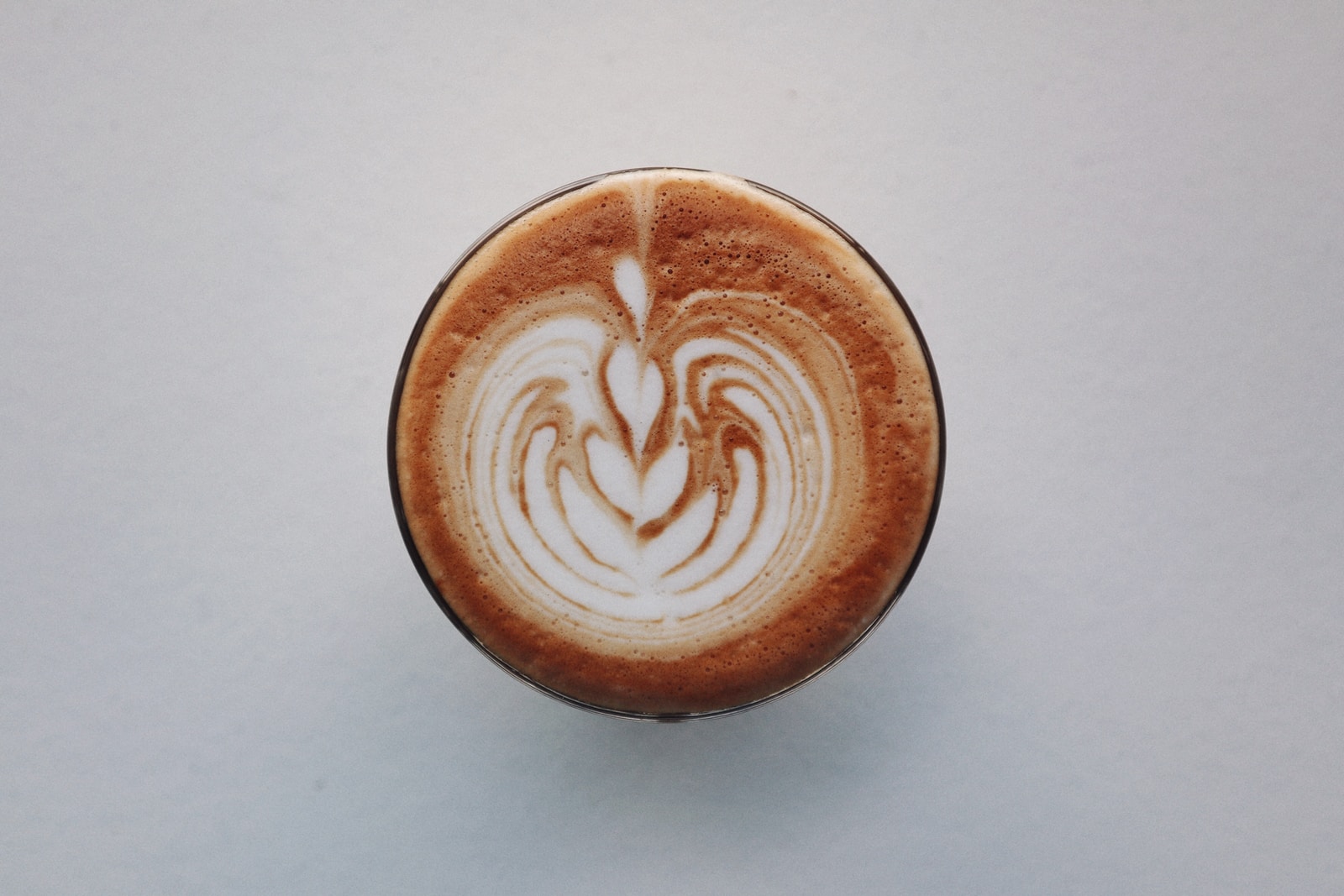
Decaffeinated coffee
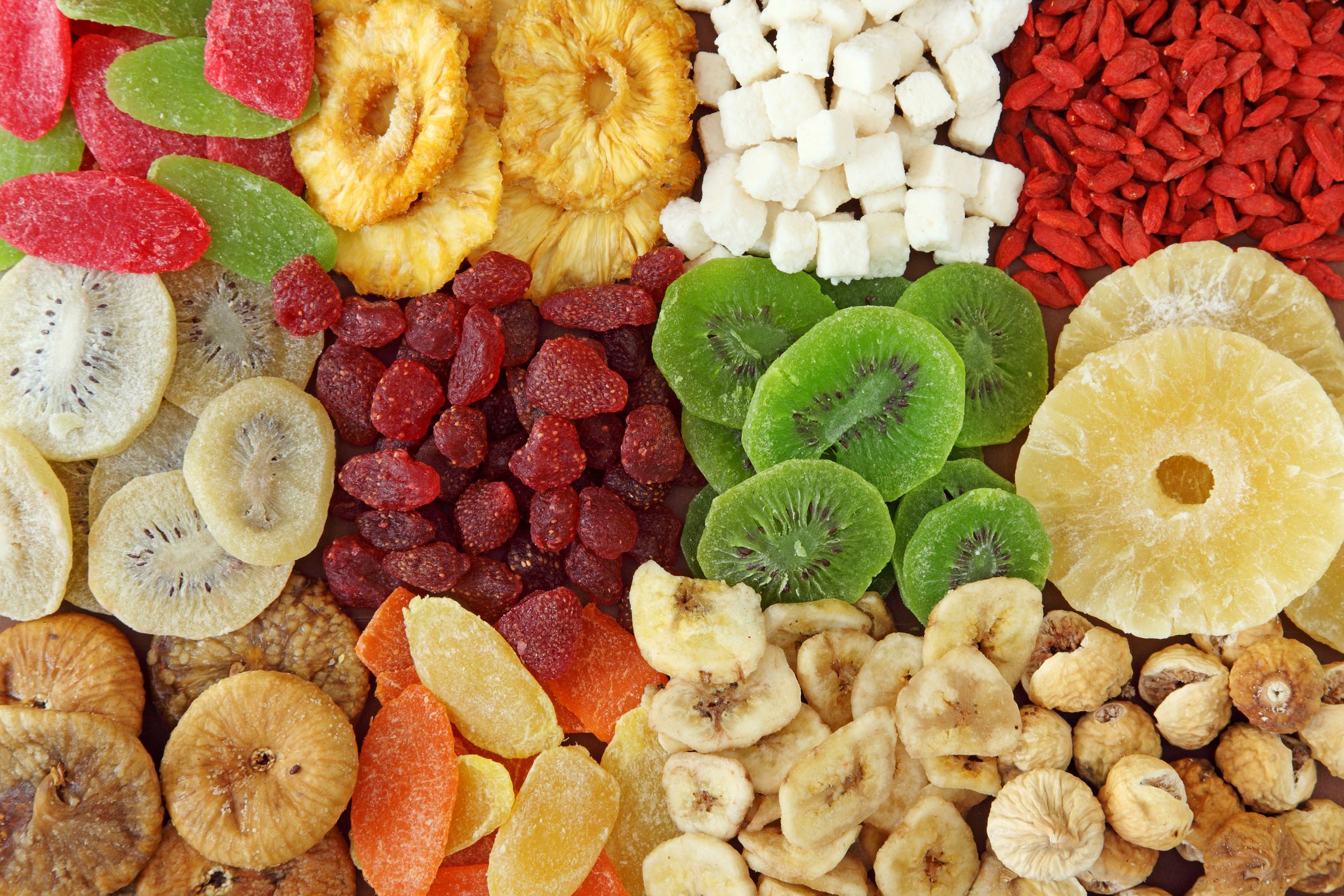
Dehydrated fruits
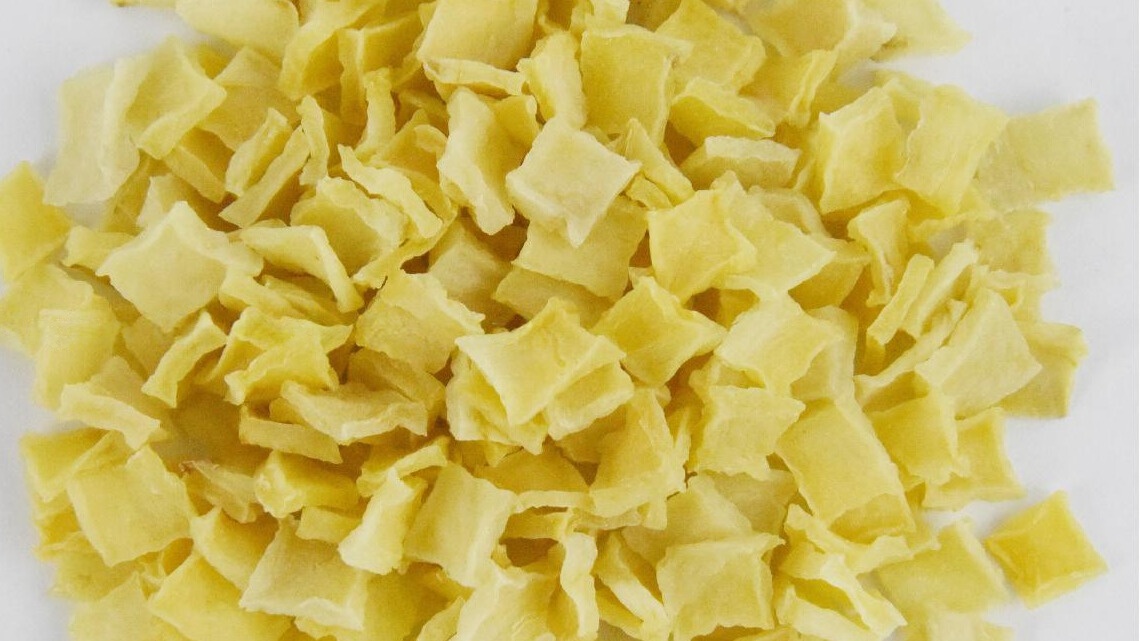
Dehydrated potato flakes
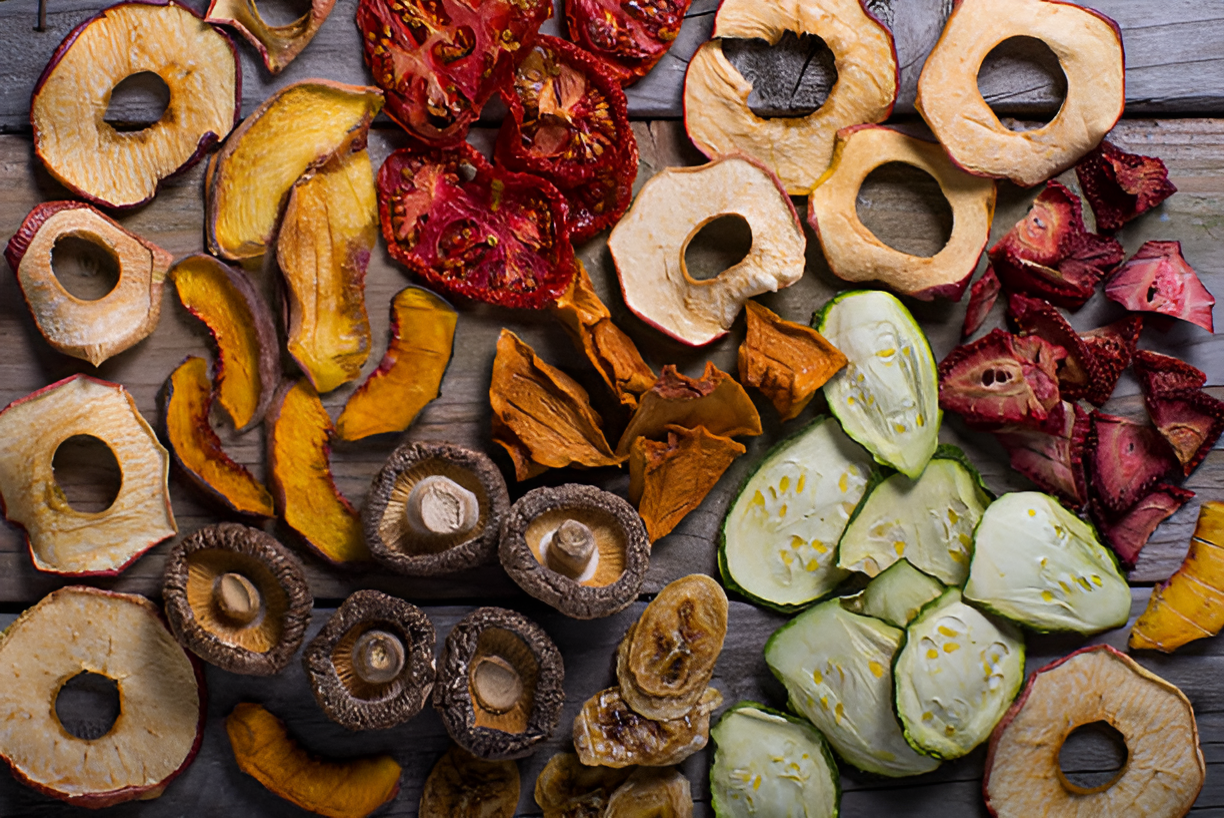
Dehydrated vegetables
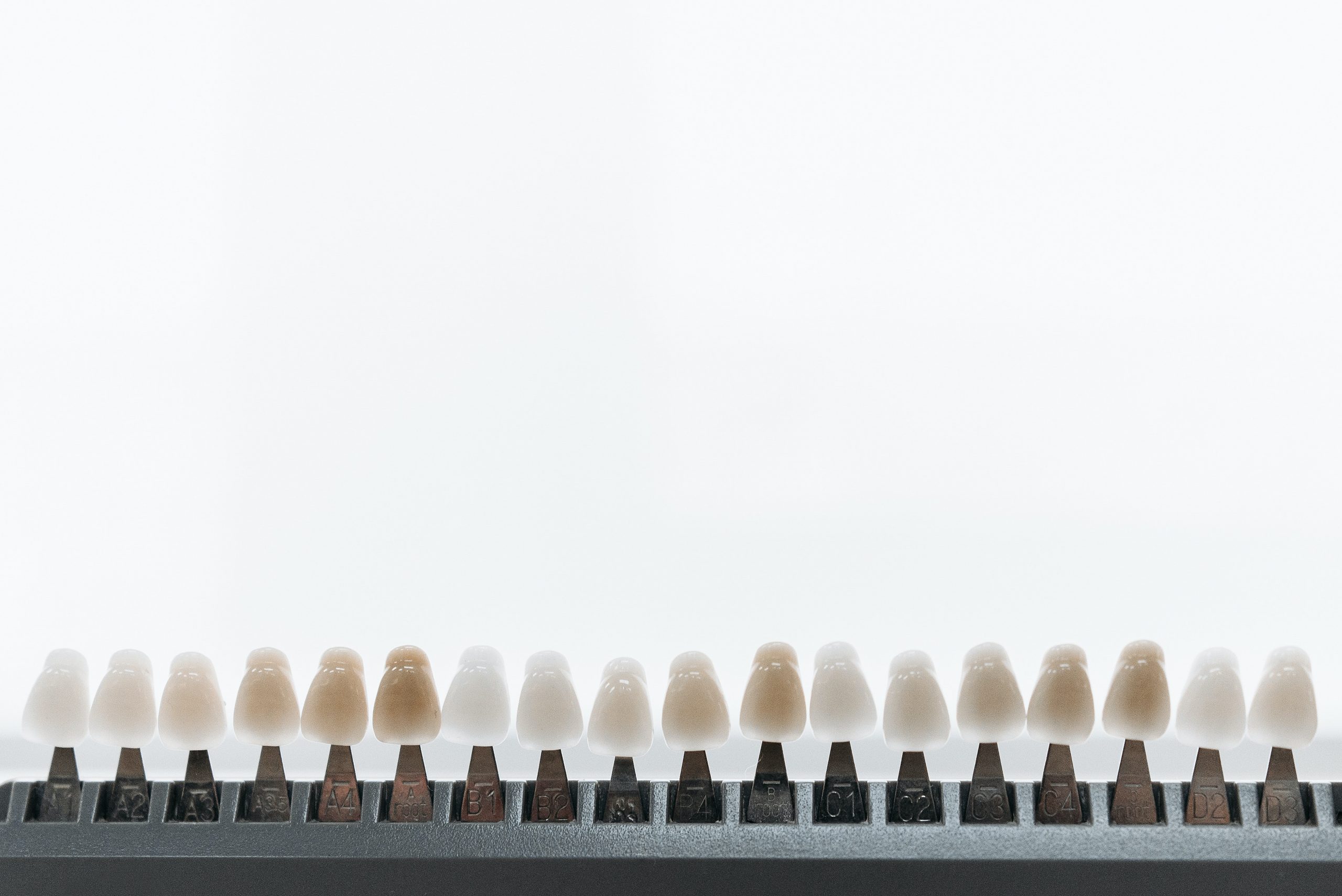
Dental implants
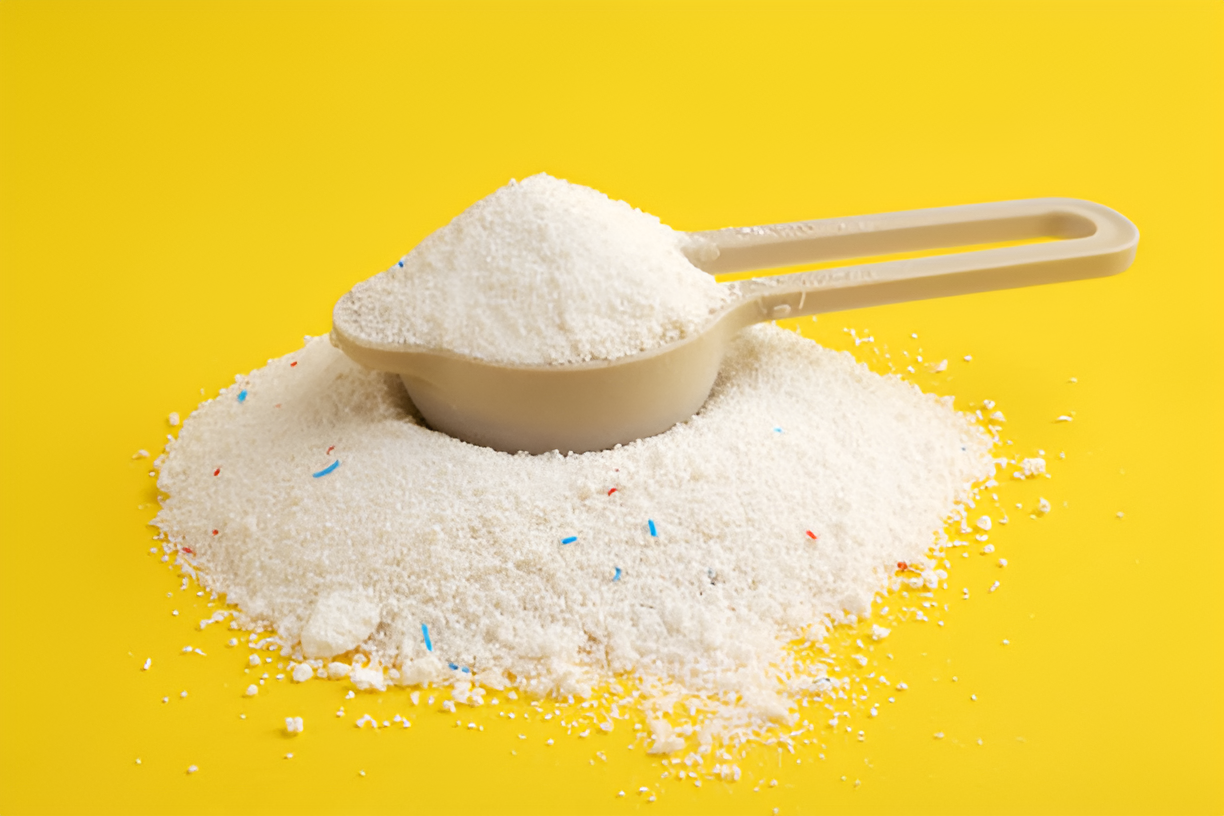
Detergent powder
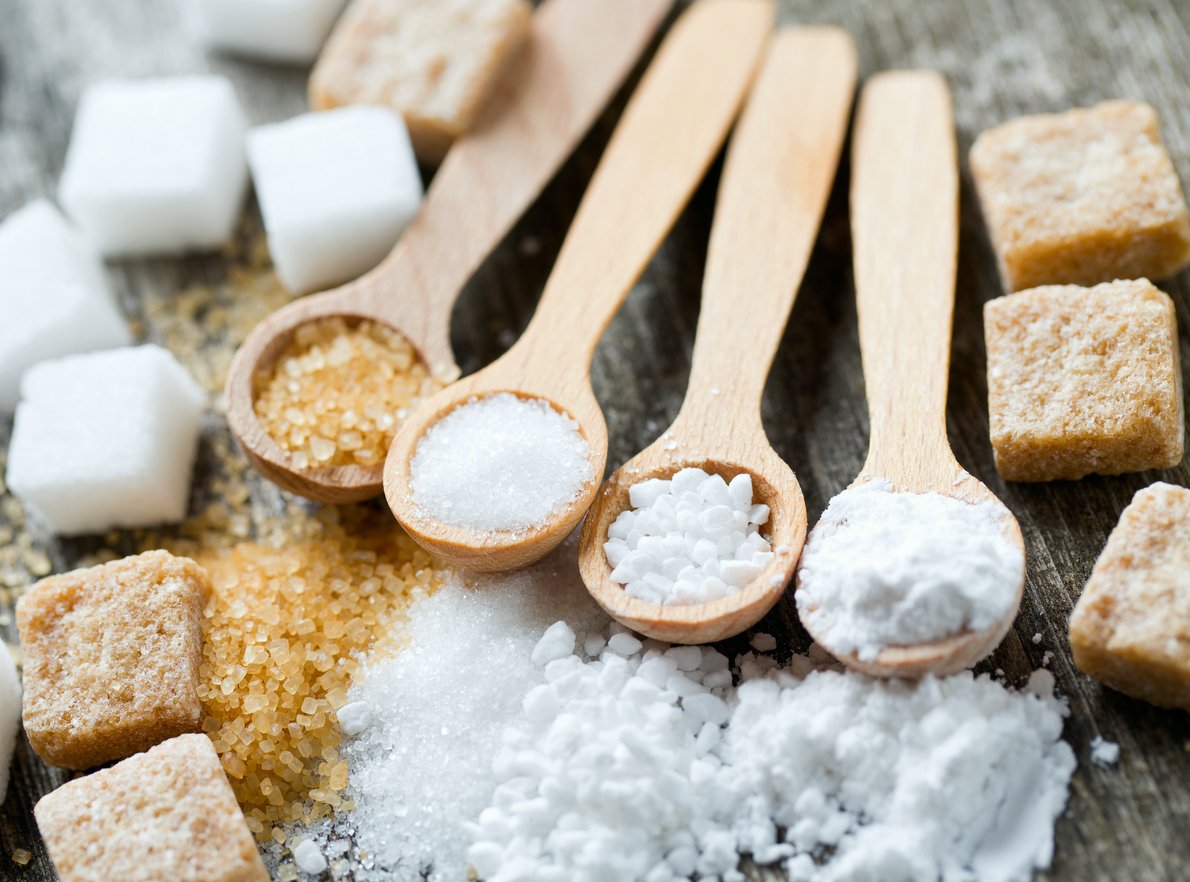
Dextrose
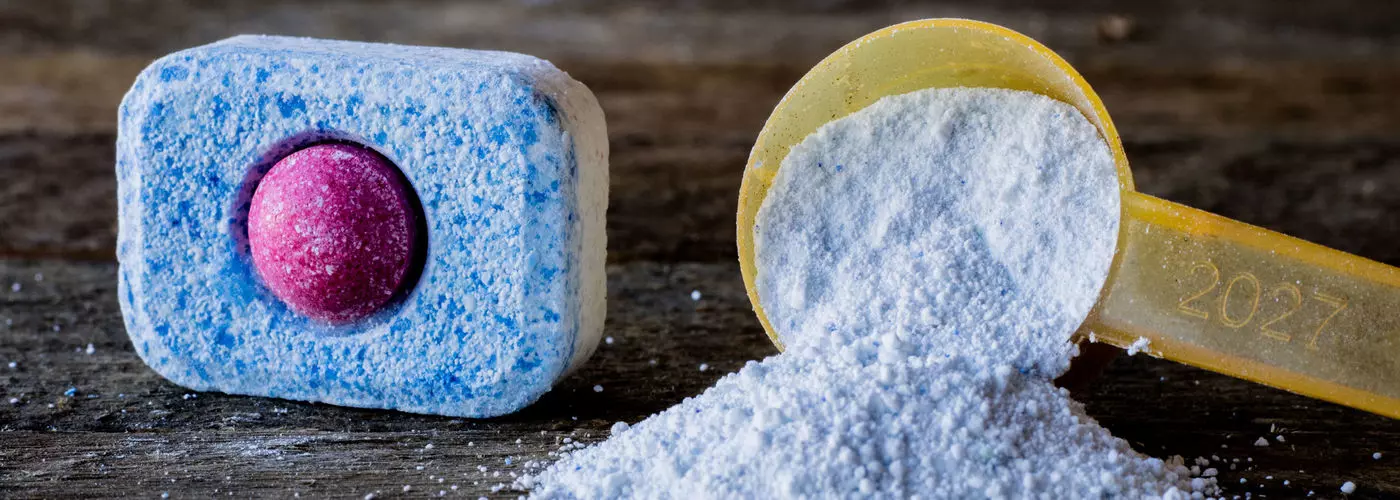
Dishwashing powder
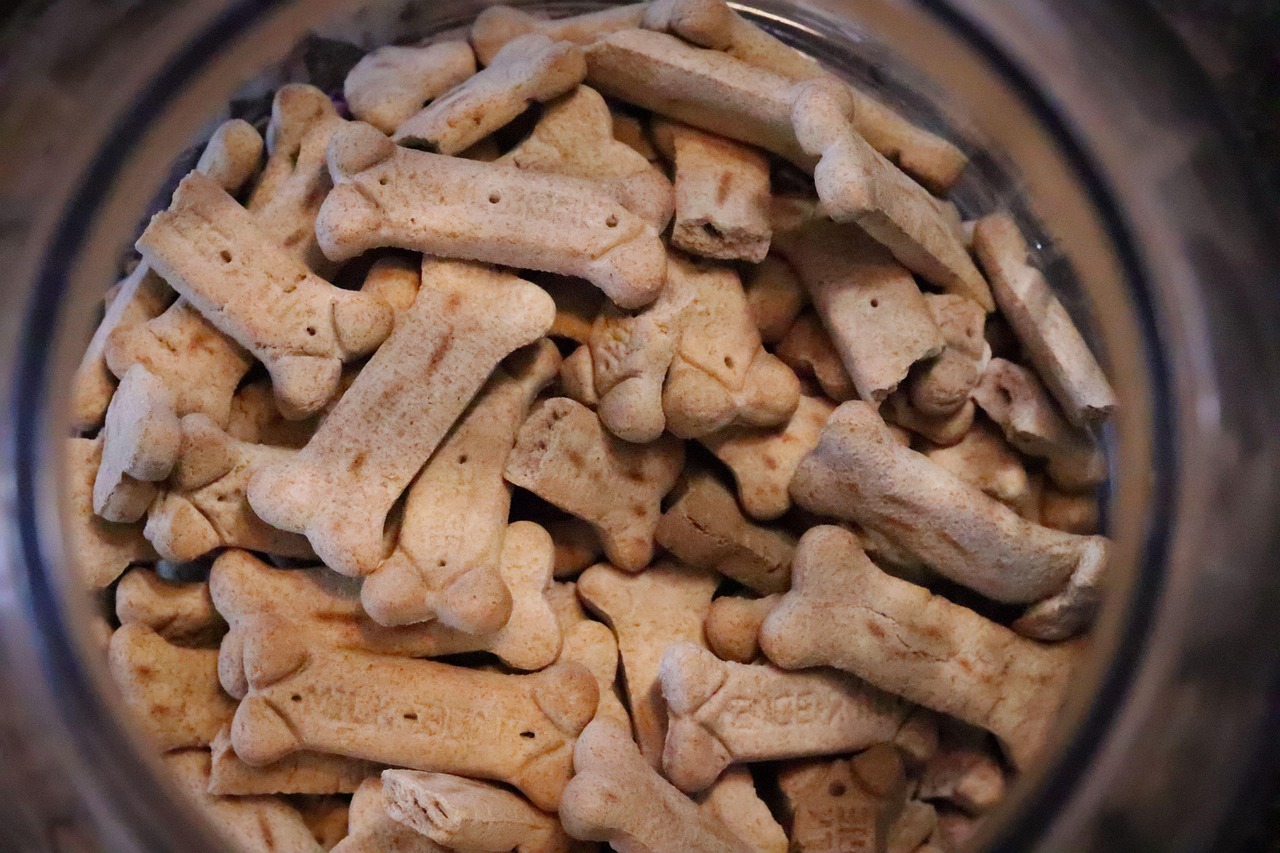
Dog biscuits
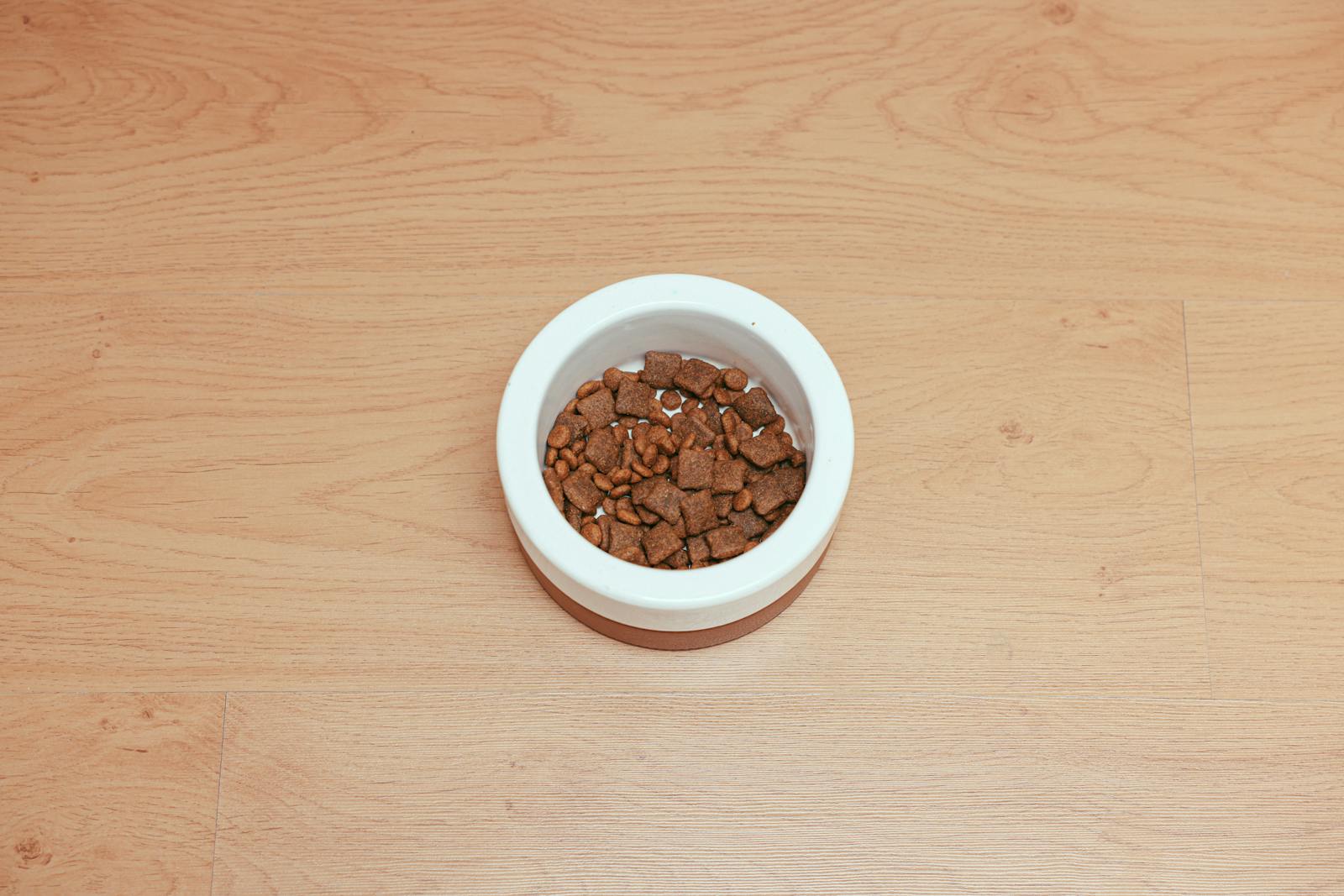
Dog food
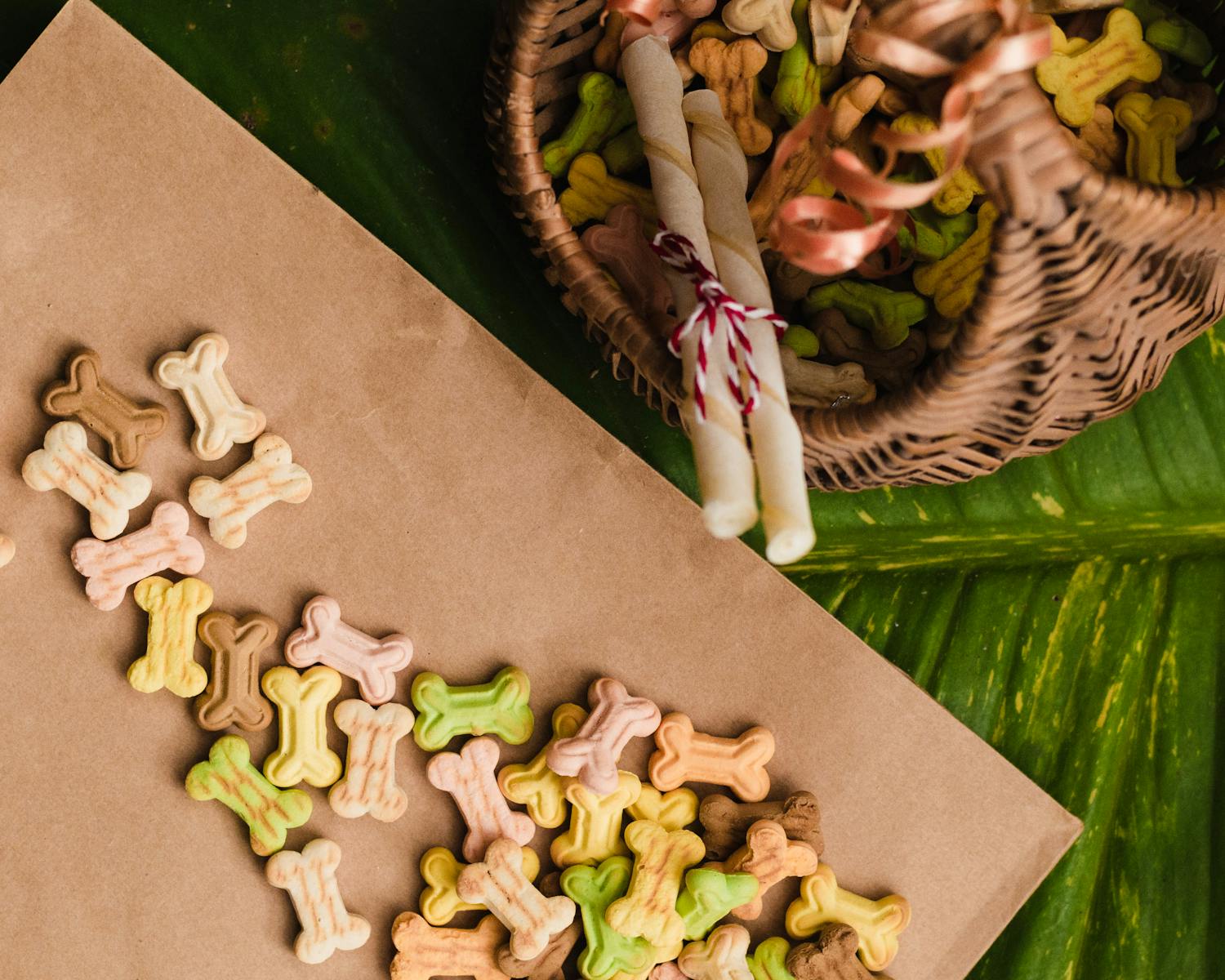
Dog treats
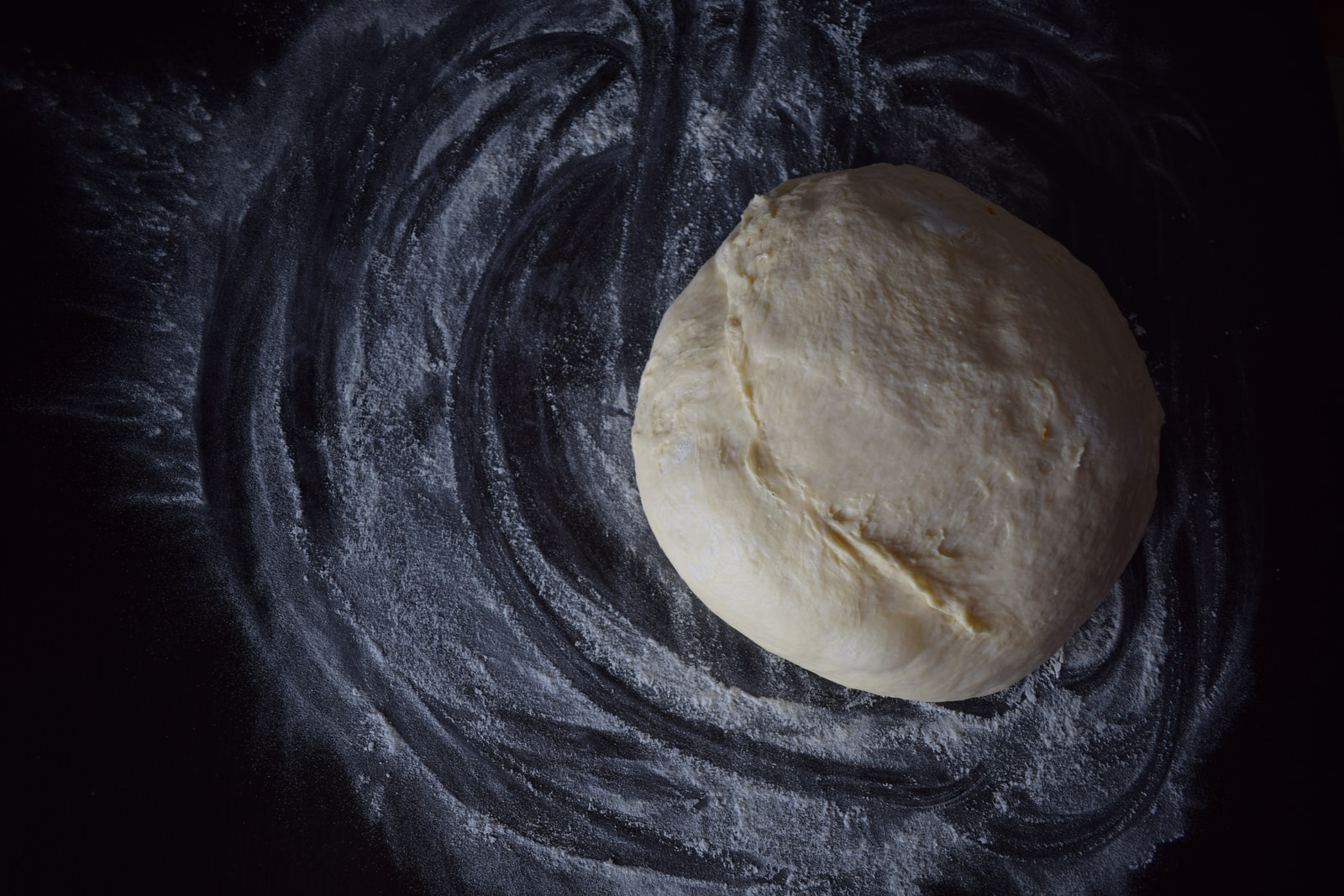
Dough
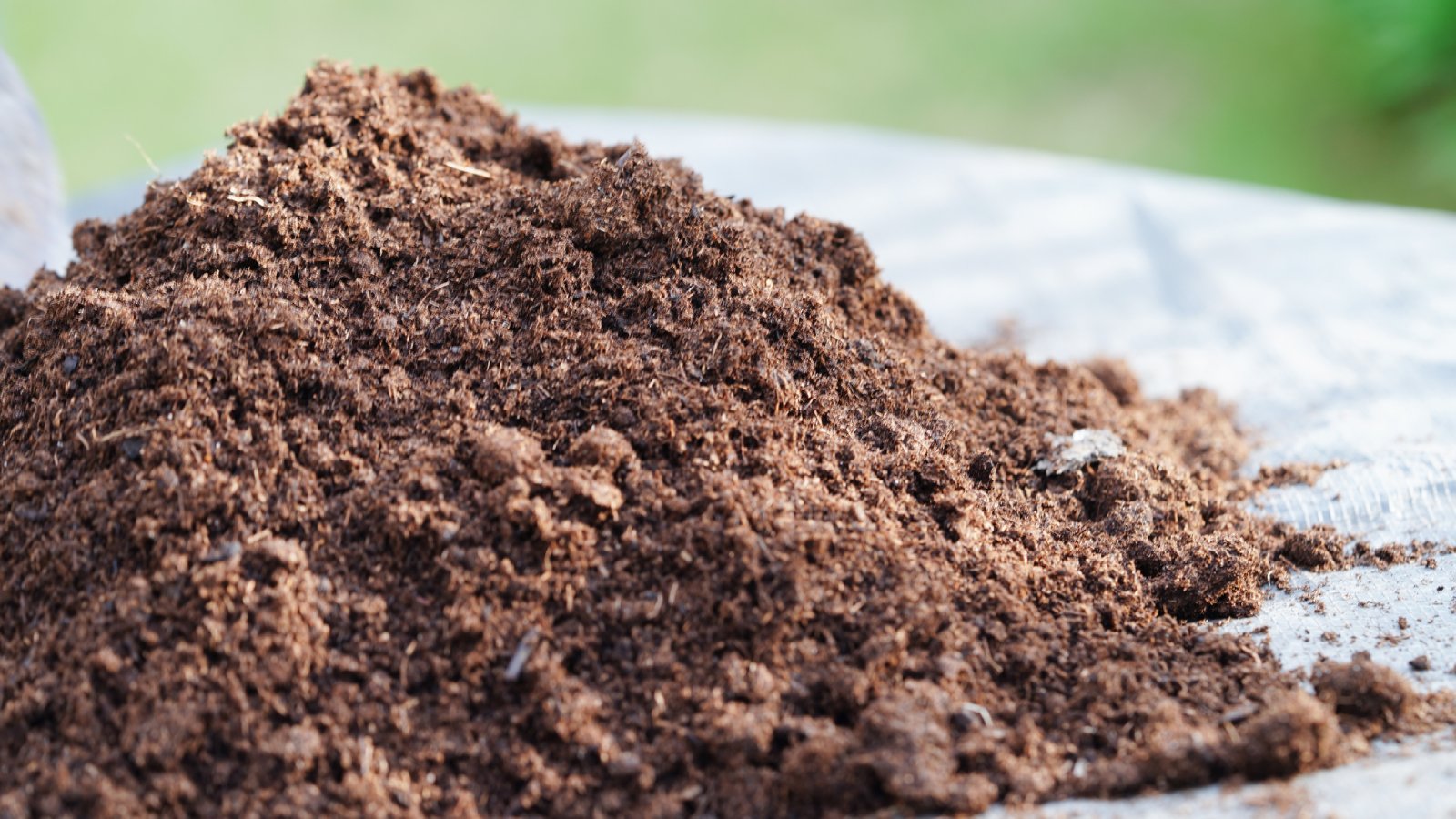
Dried biosolids
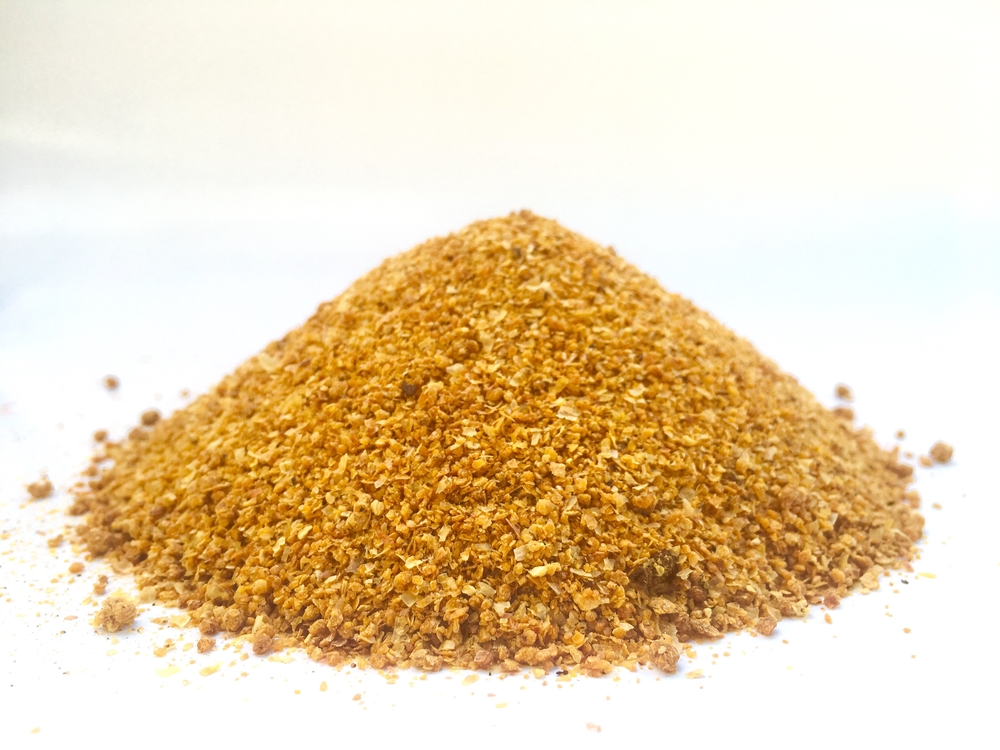
Dried distillers grains (DDGS)
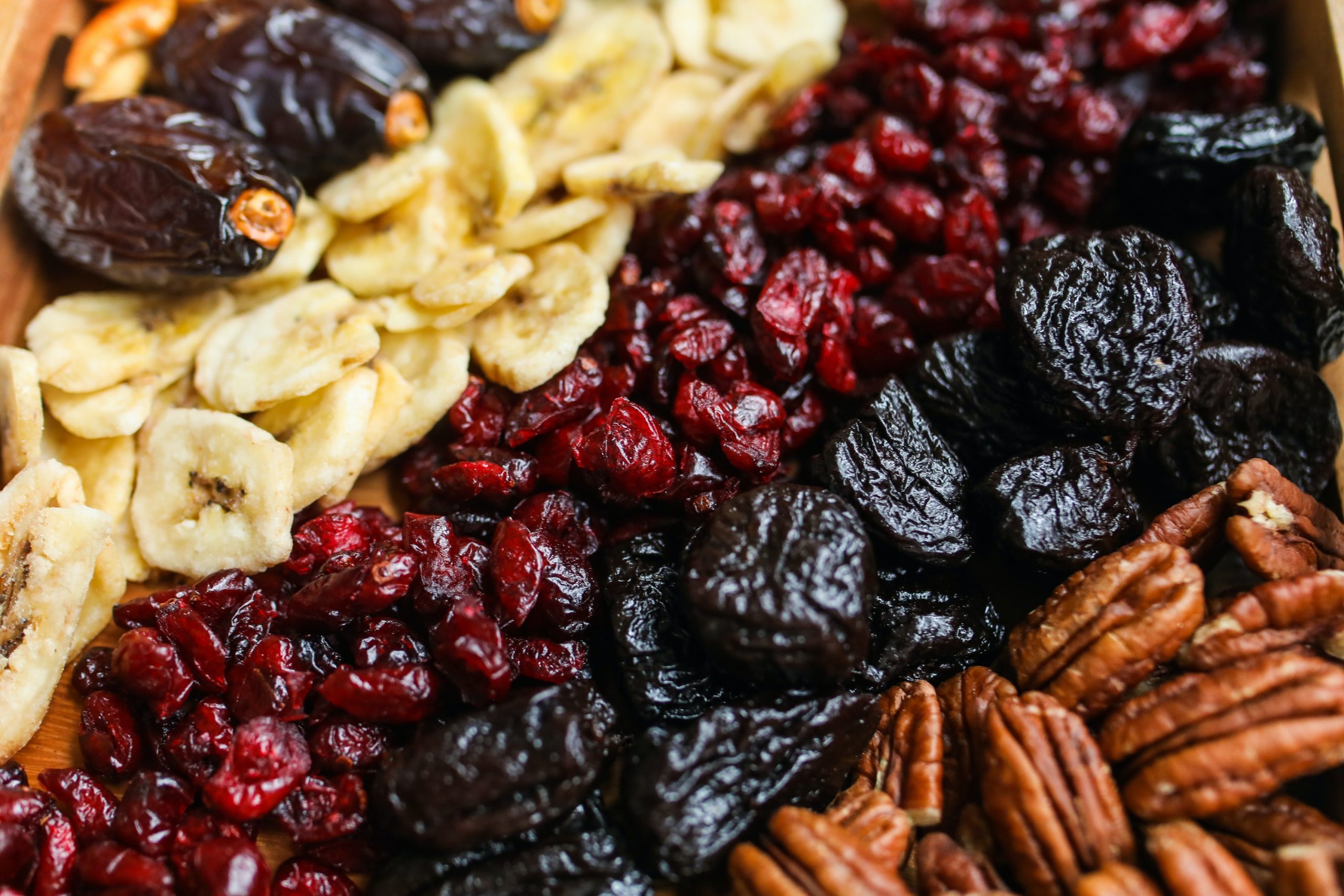
Dried fruit
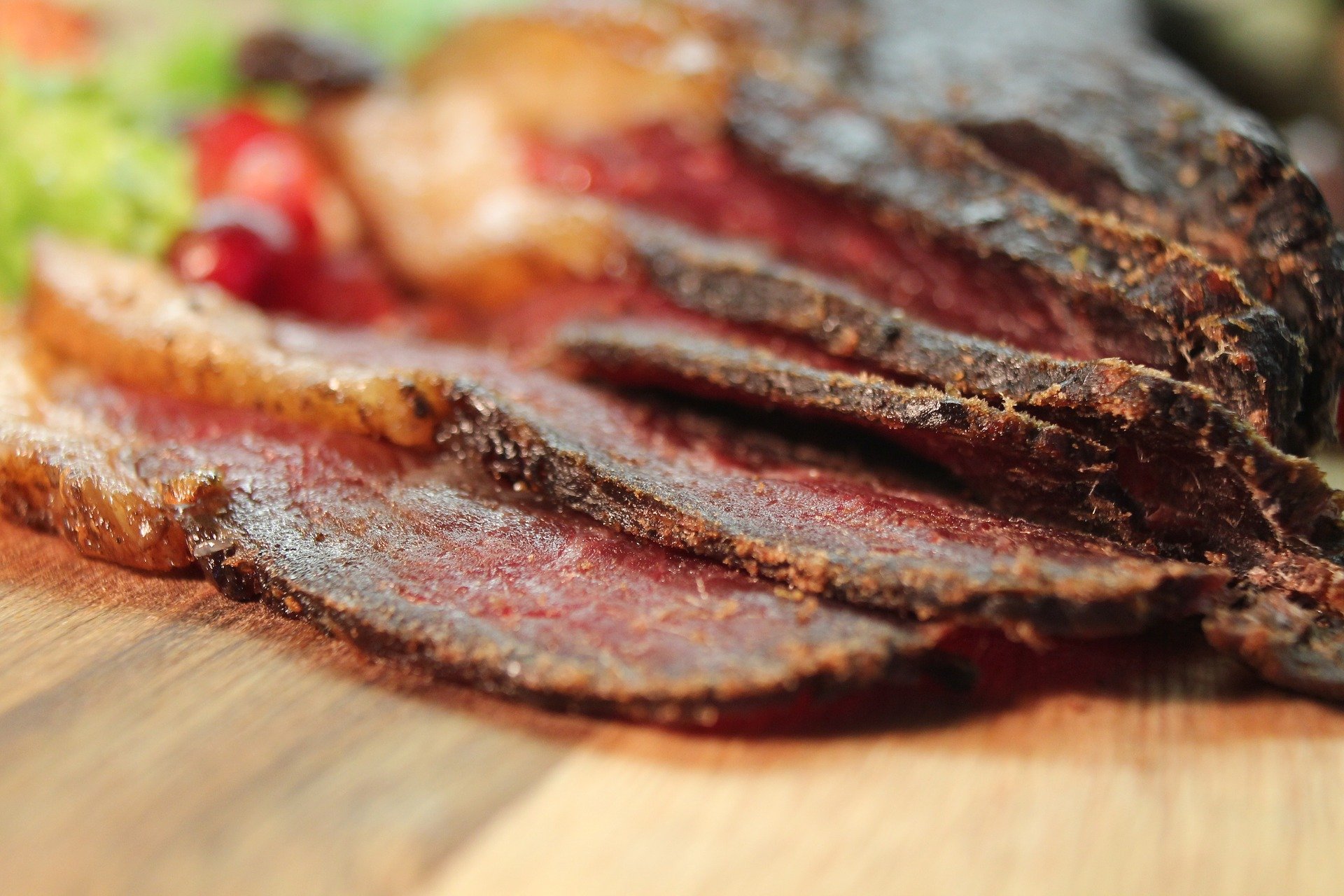
Dried meat
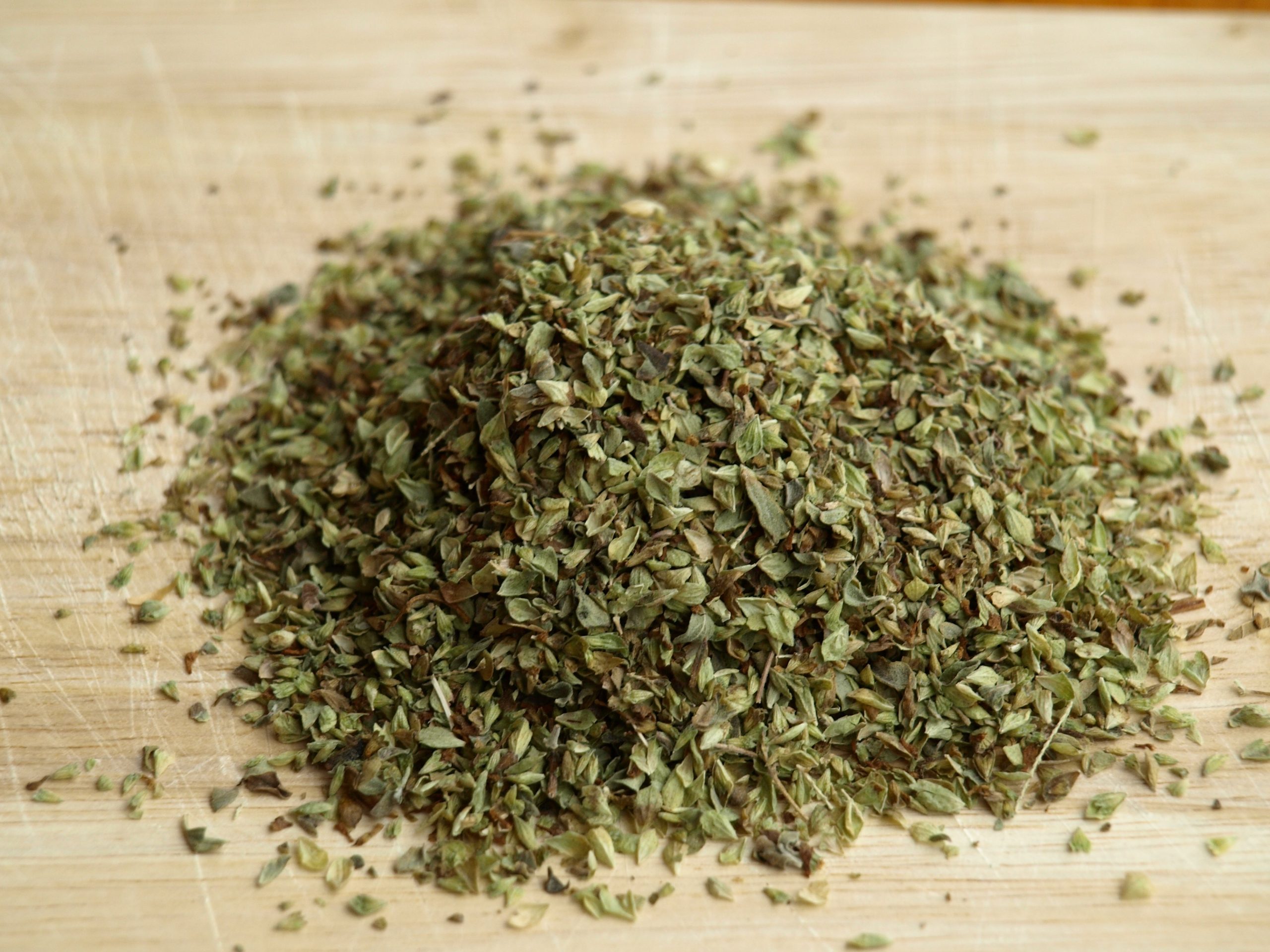
Dried oregano
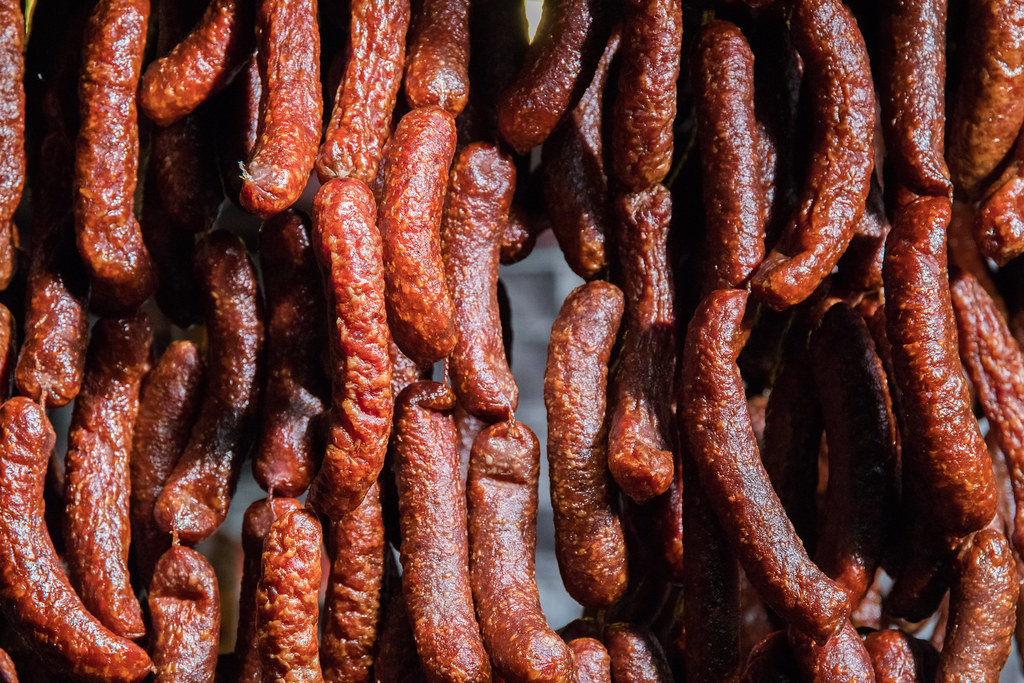
Dried sausage
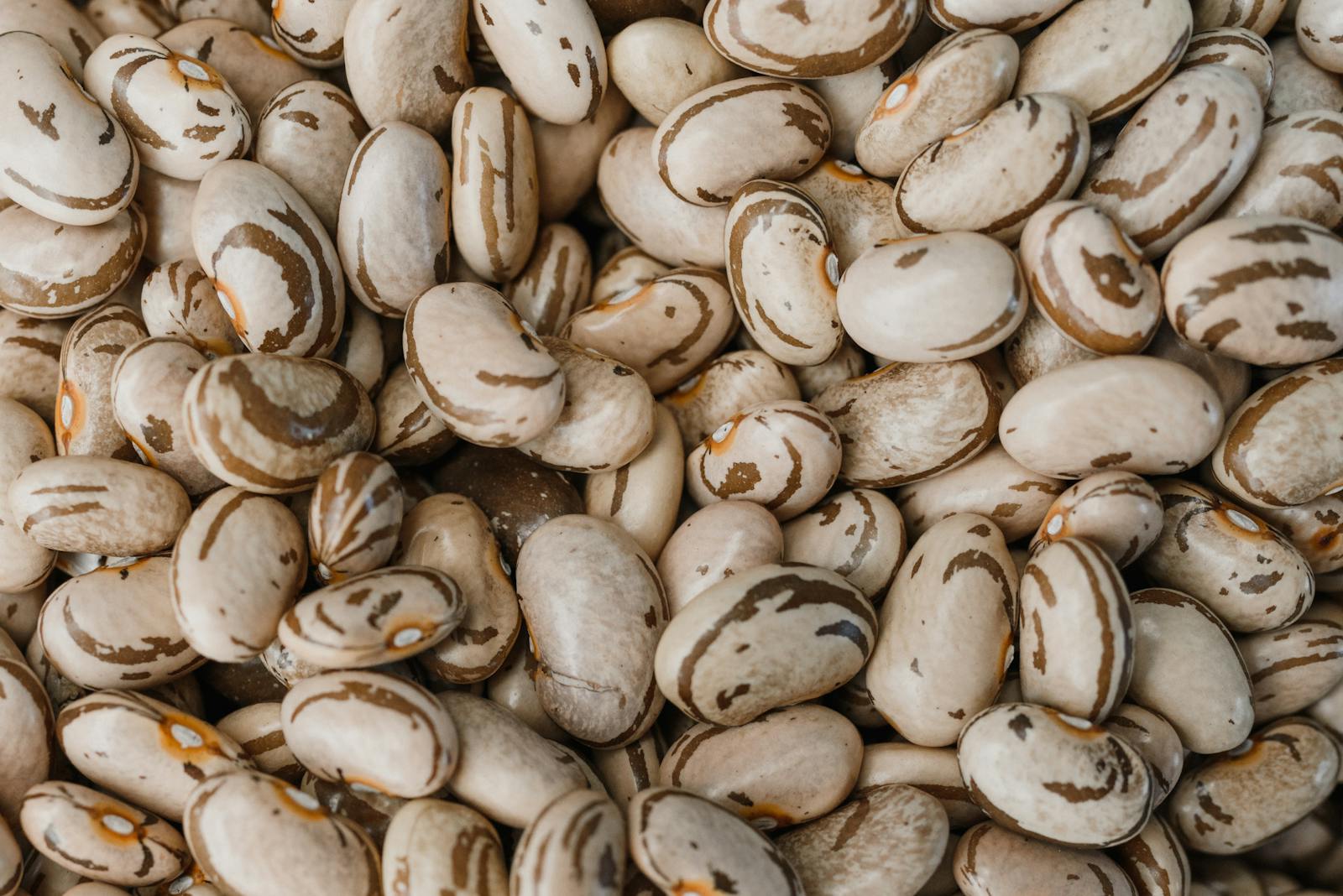
Dry beans
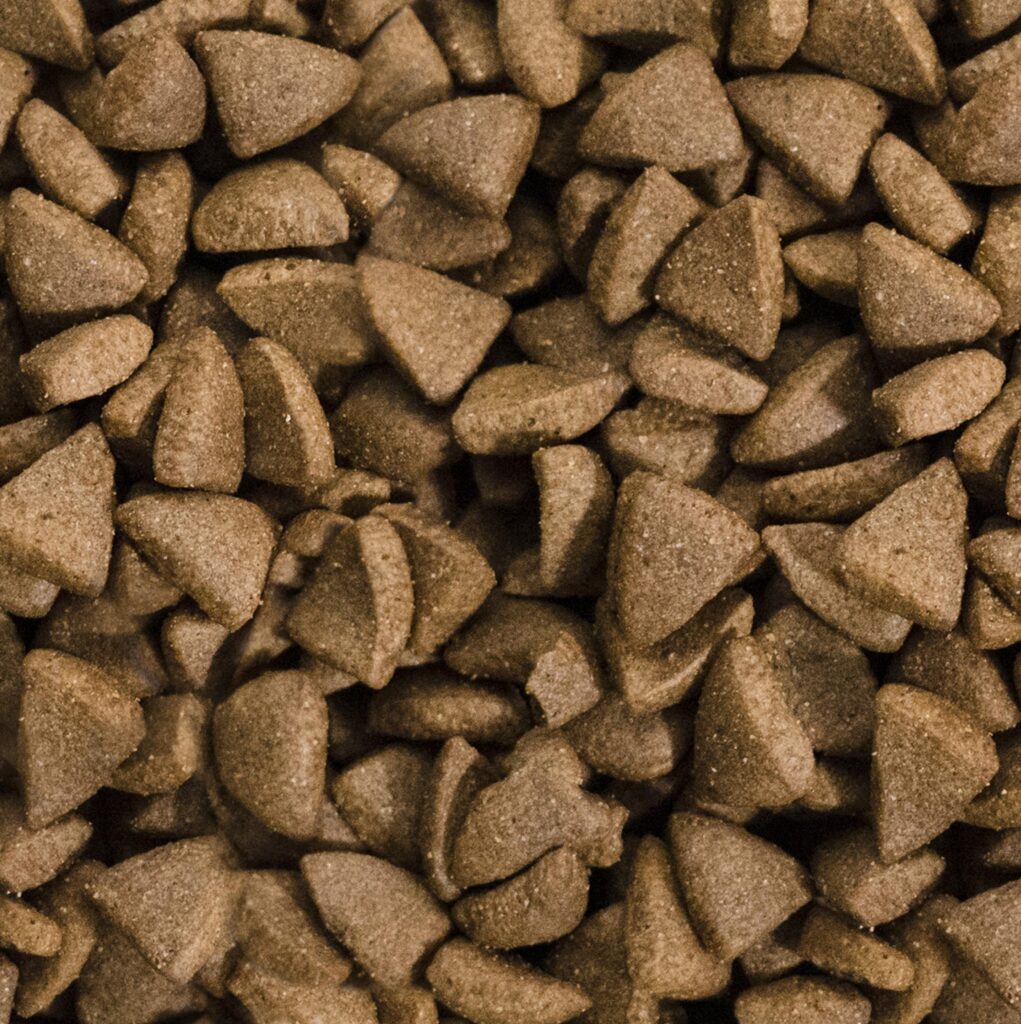
Dry pet food

Dry powders
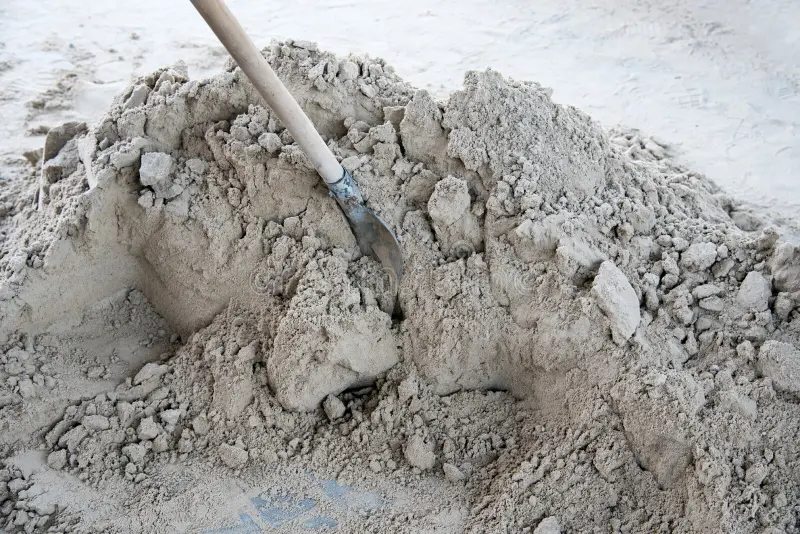
Drymix building materials
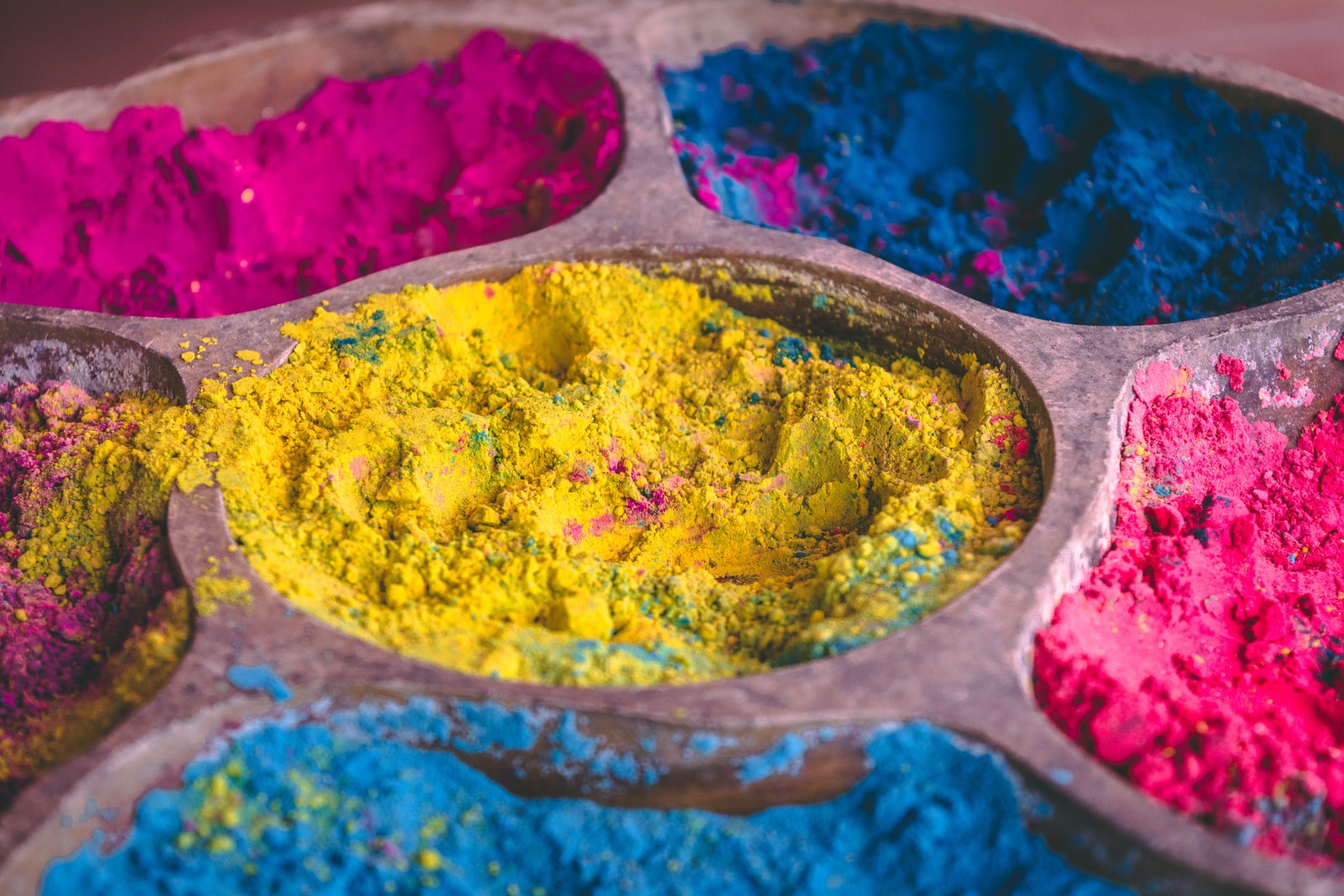
Dyes
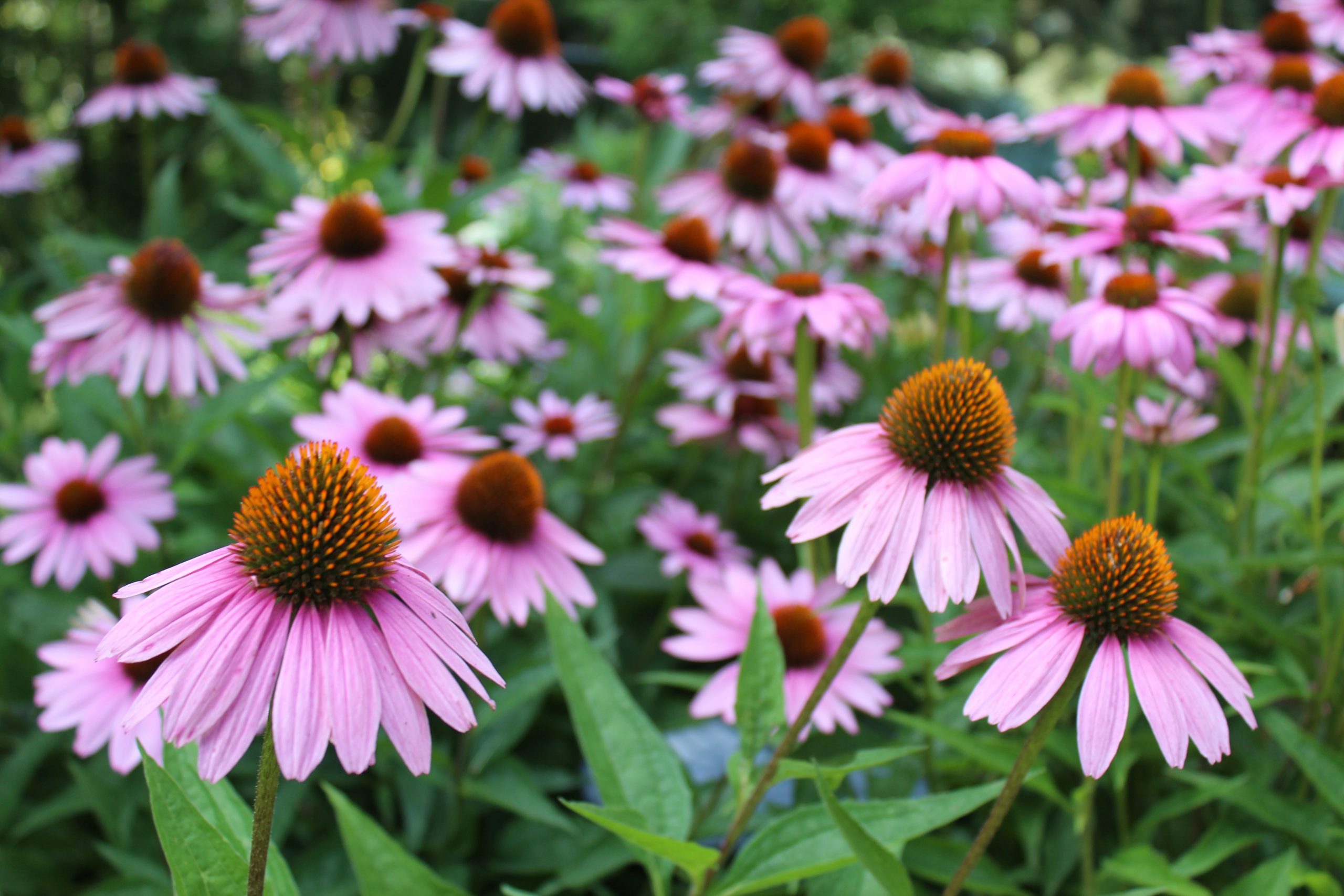
Echinacea extract
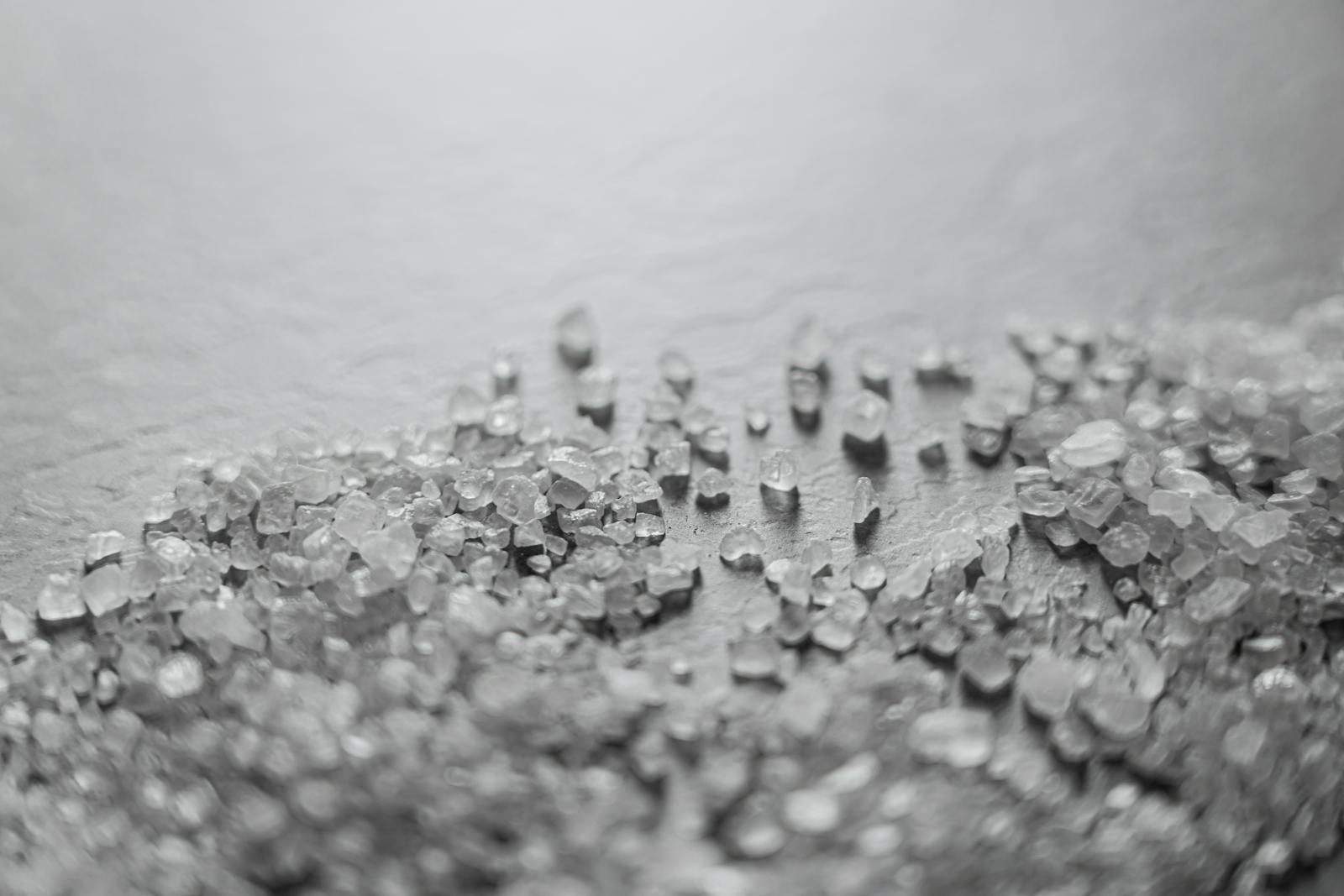
Effervescent granules
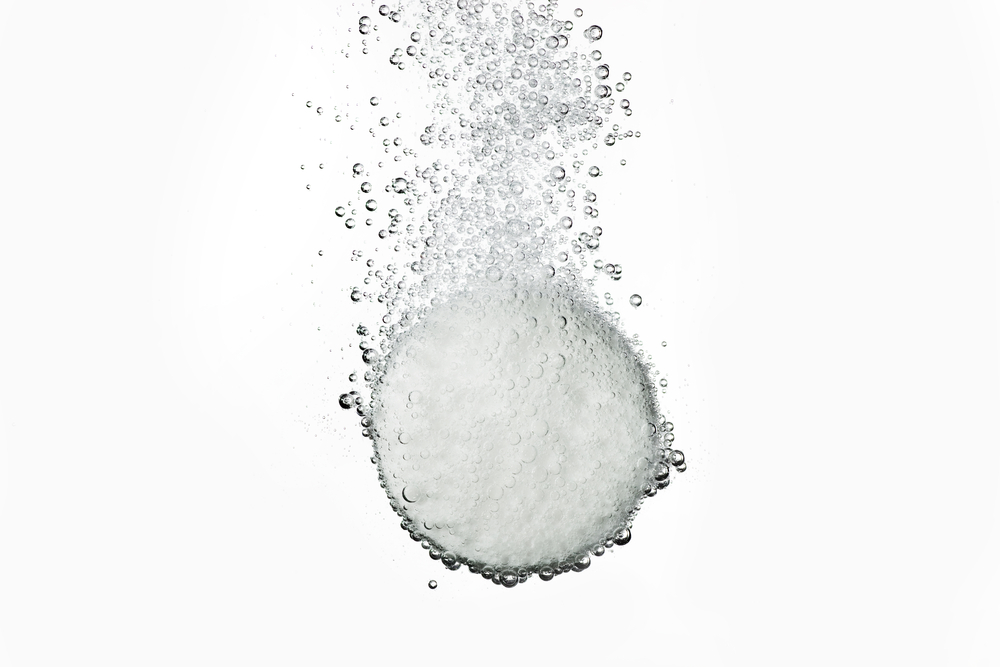
Effervescent tablets
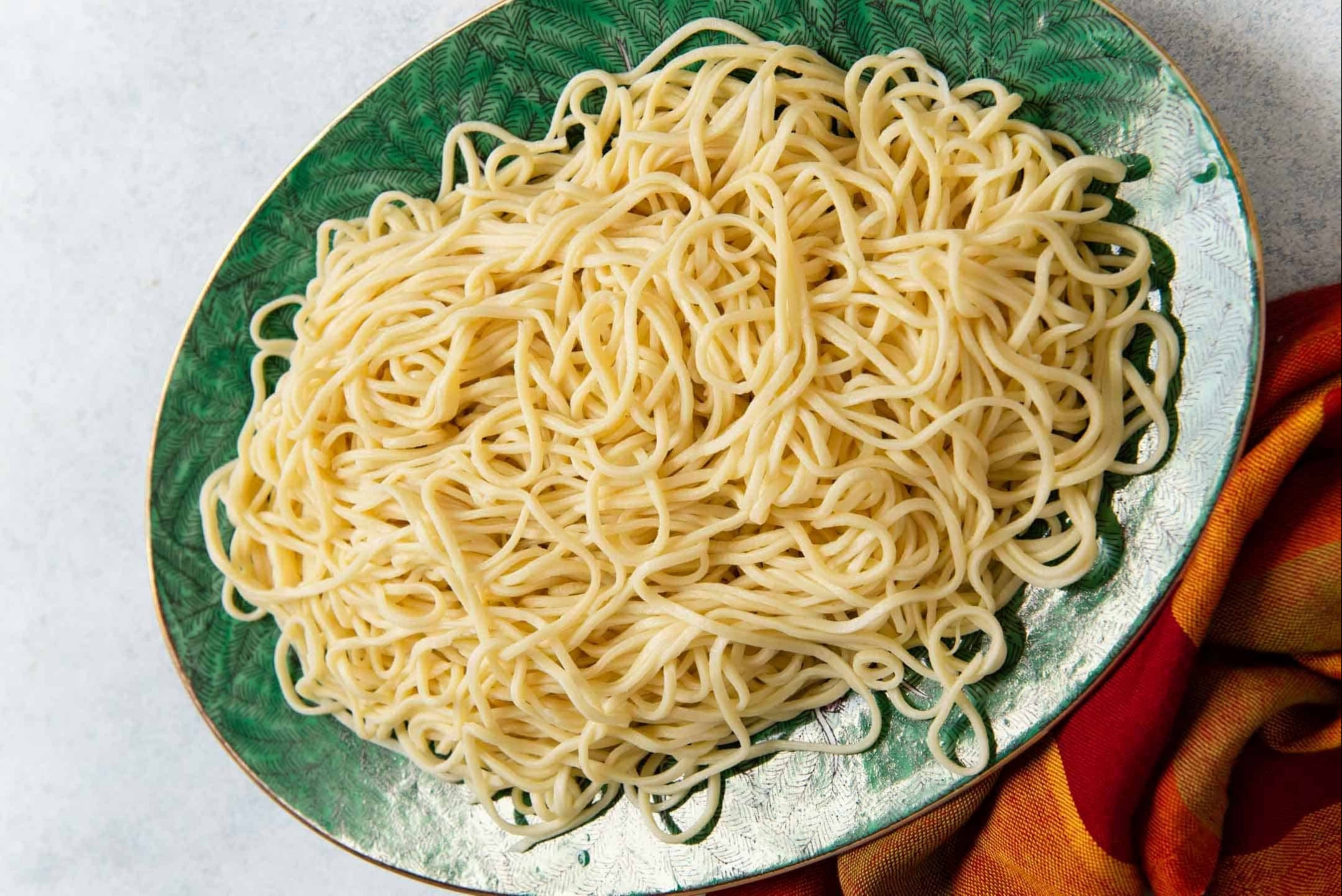
Egg noodles

Elderberry extract
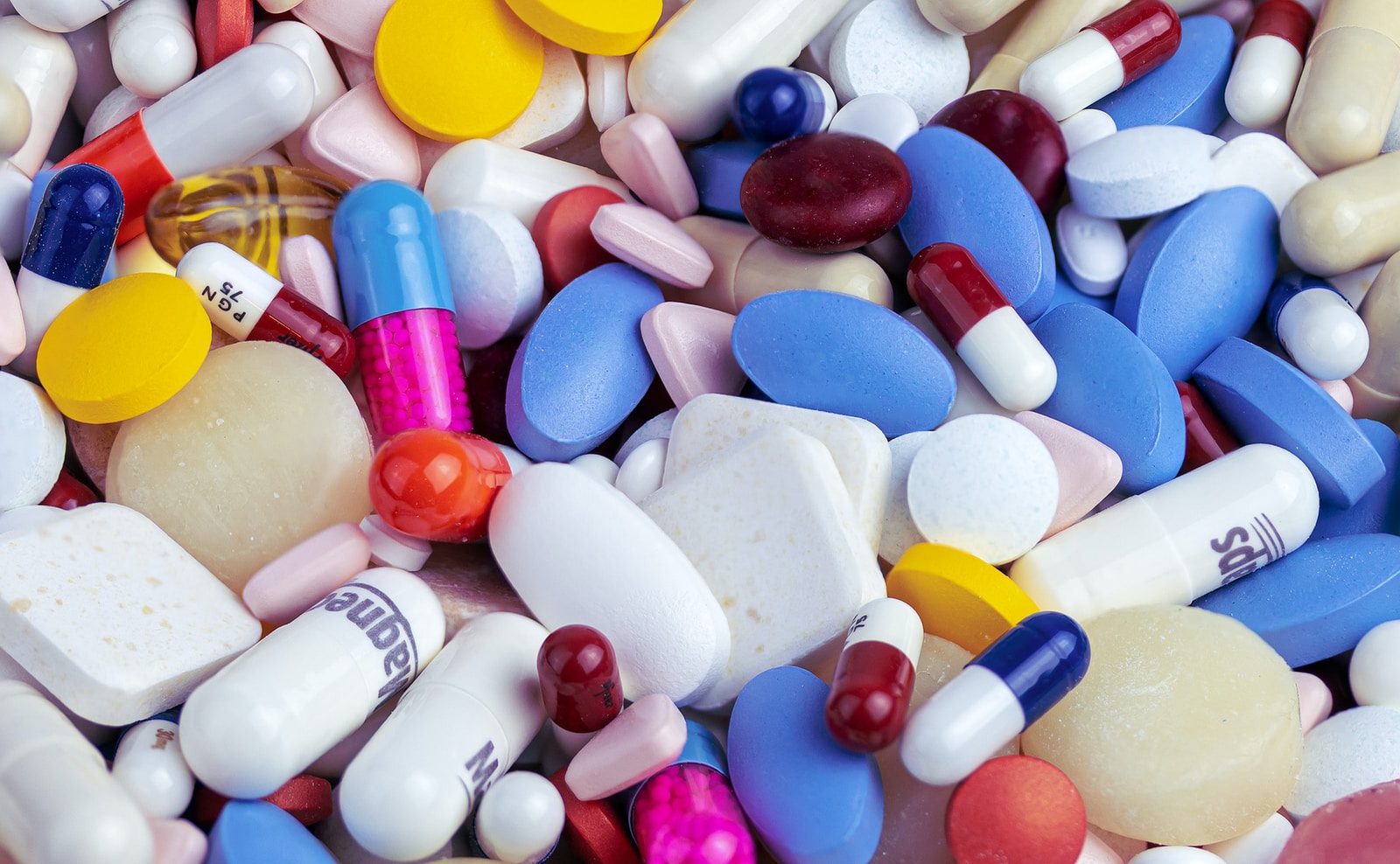
Enteric Coated Tablets
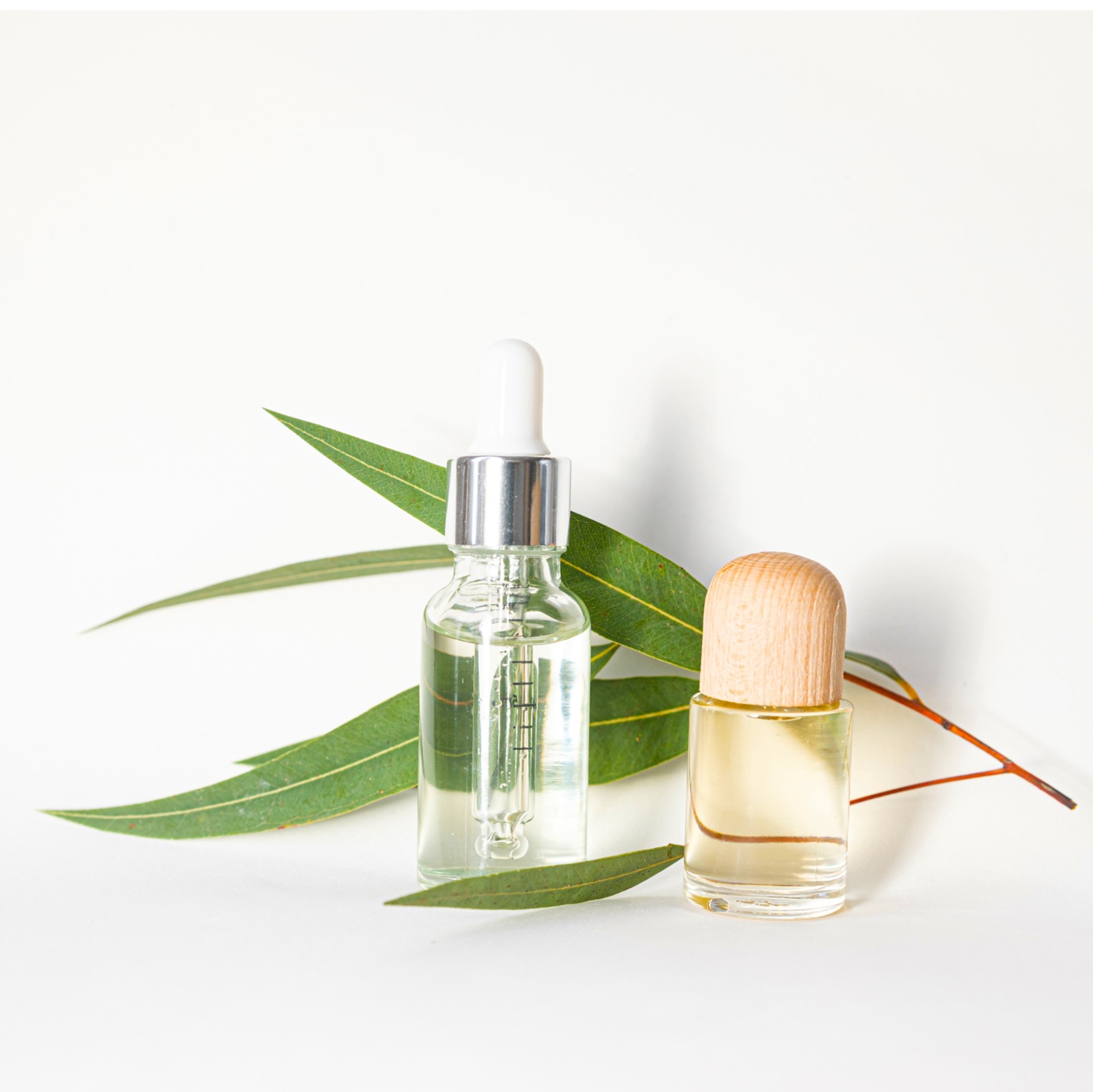
Eucalyptus oil
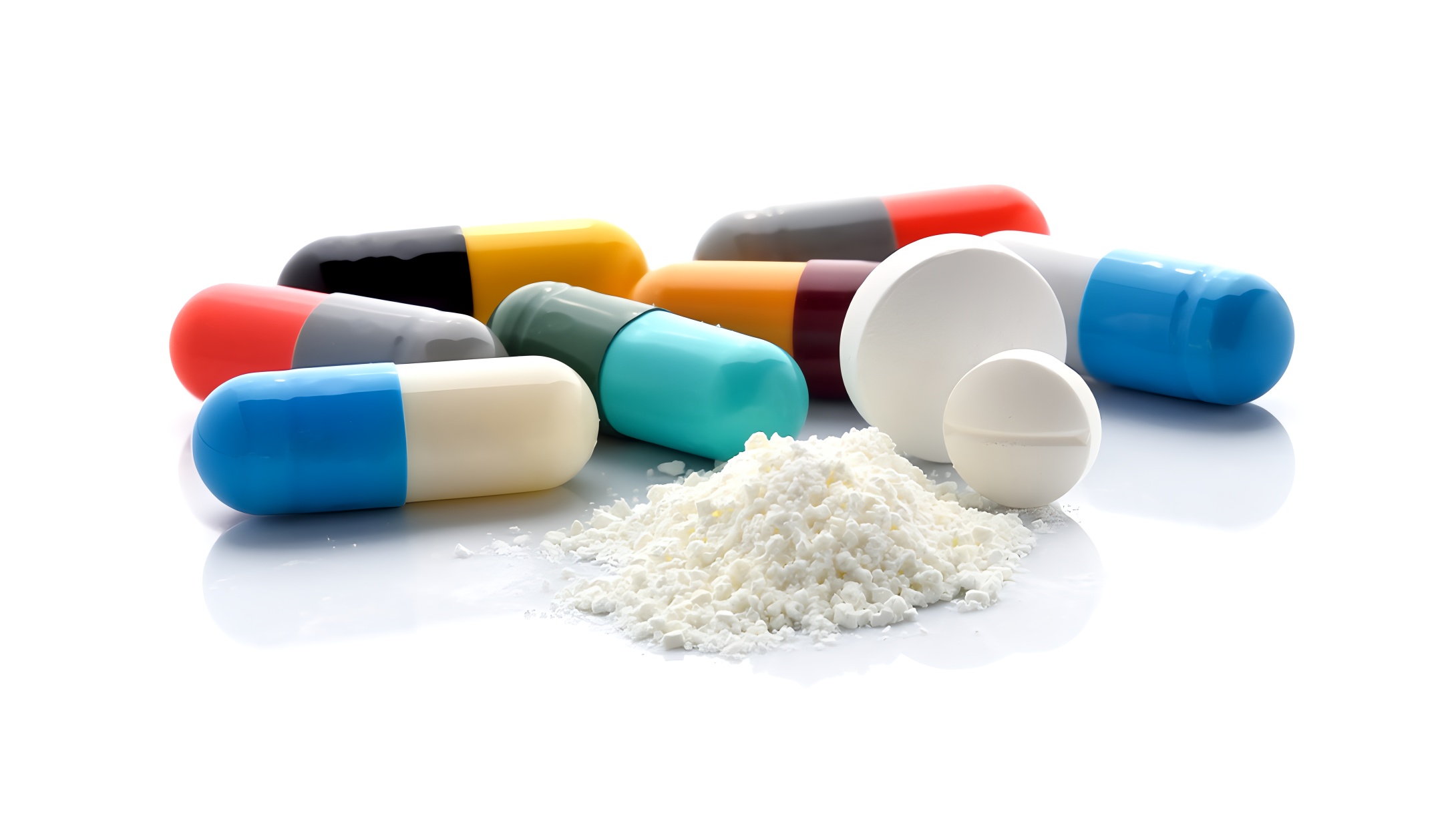
Excipients
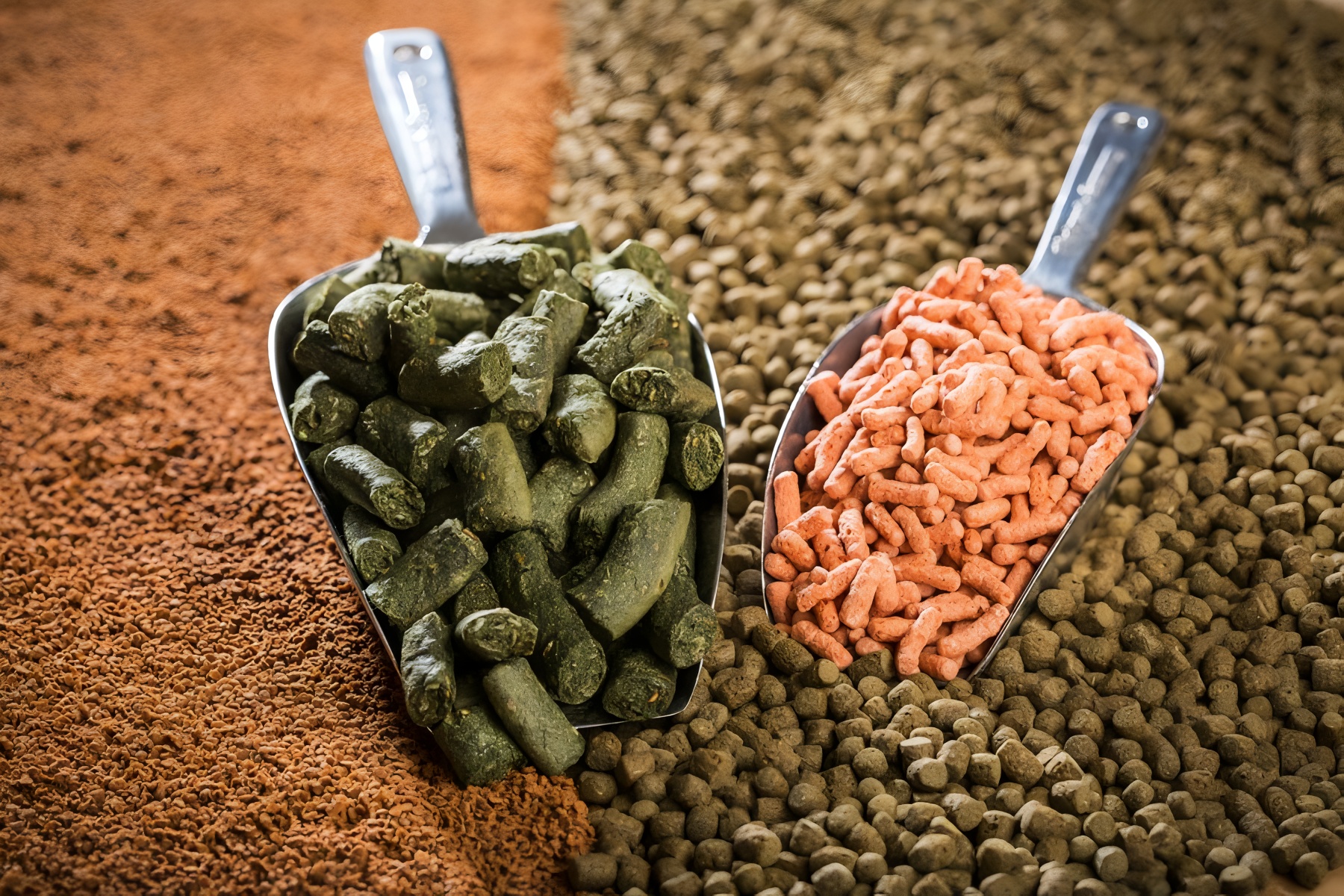
Extrudates
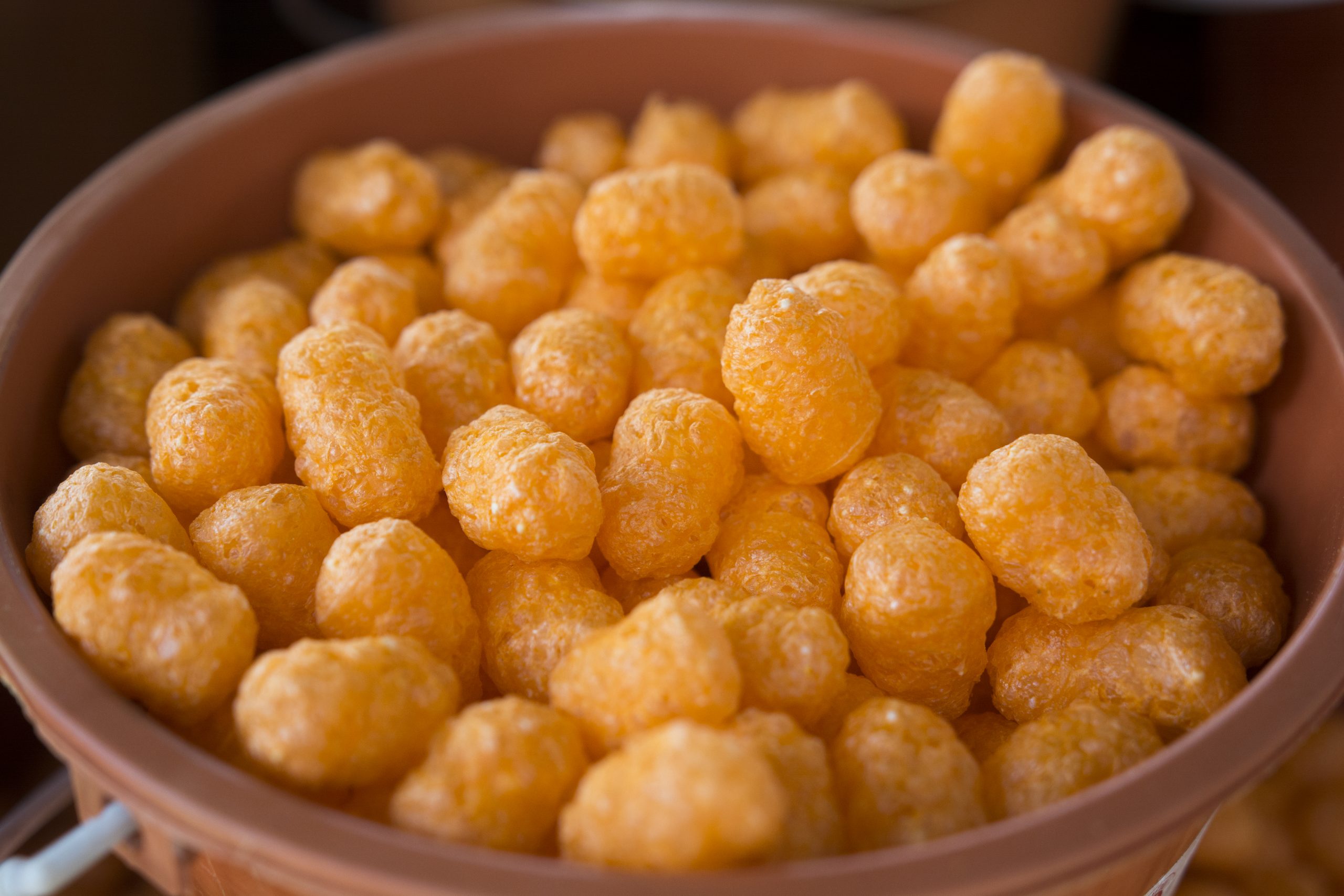
Extruded aquafeed
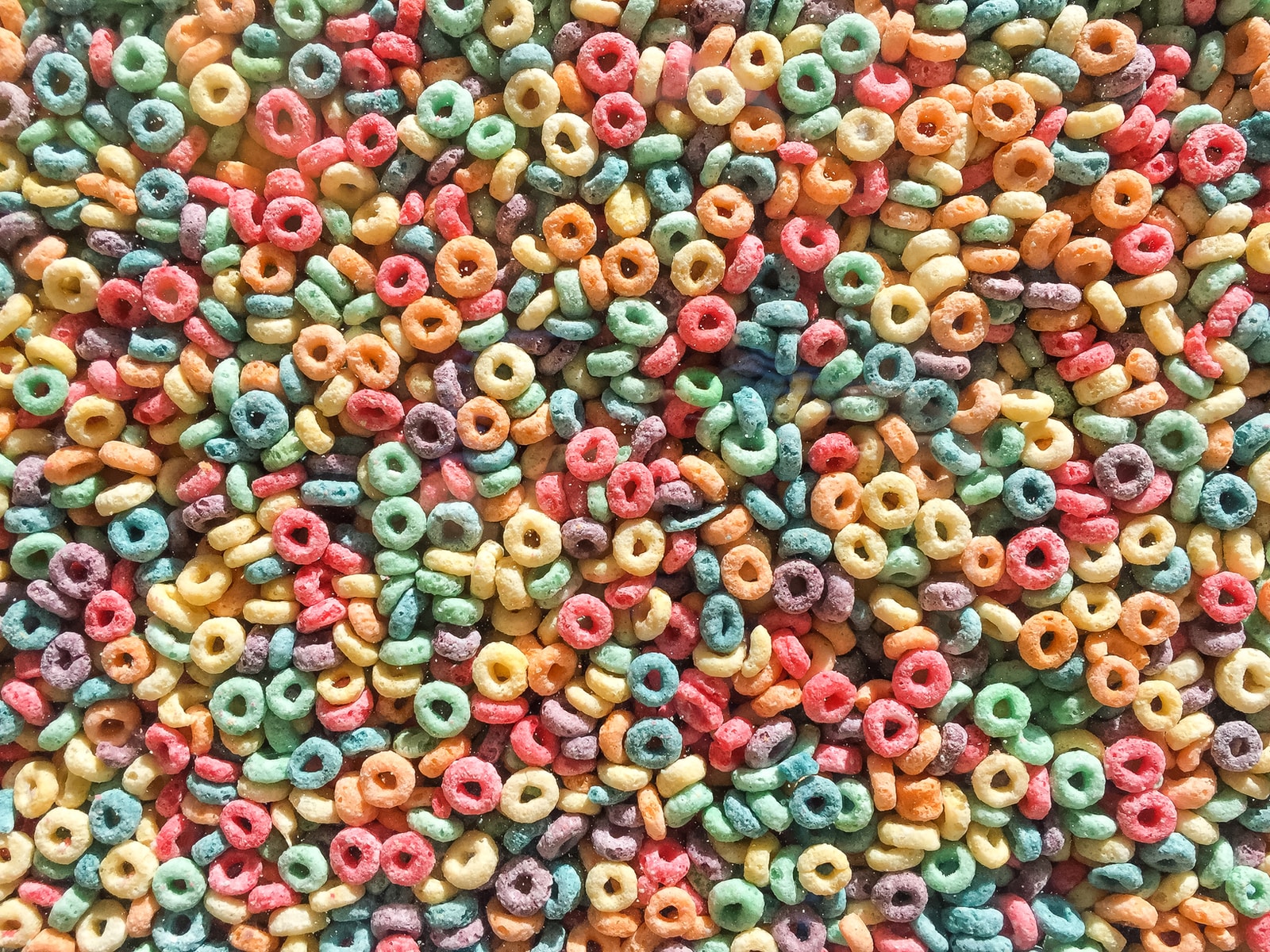
Extruded cereal
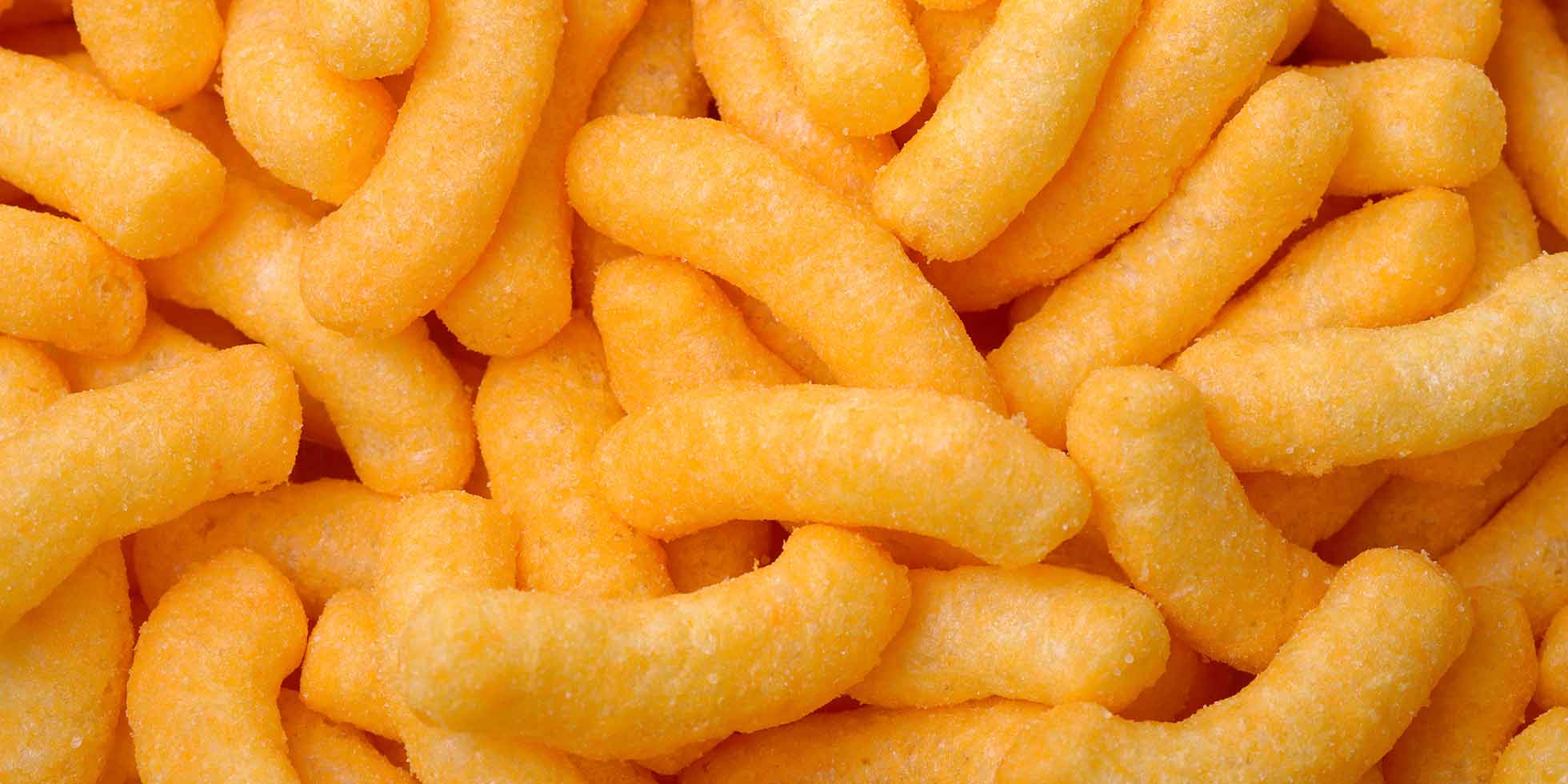
Extruded snacks
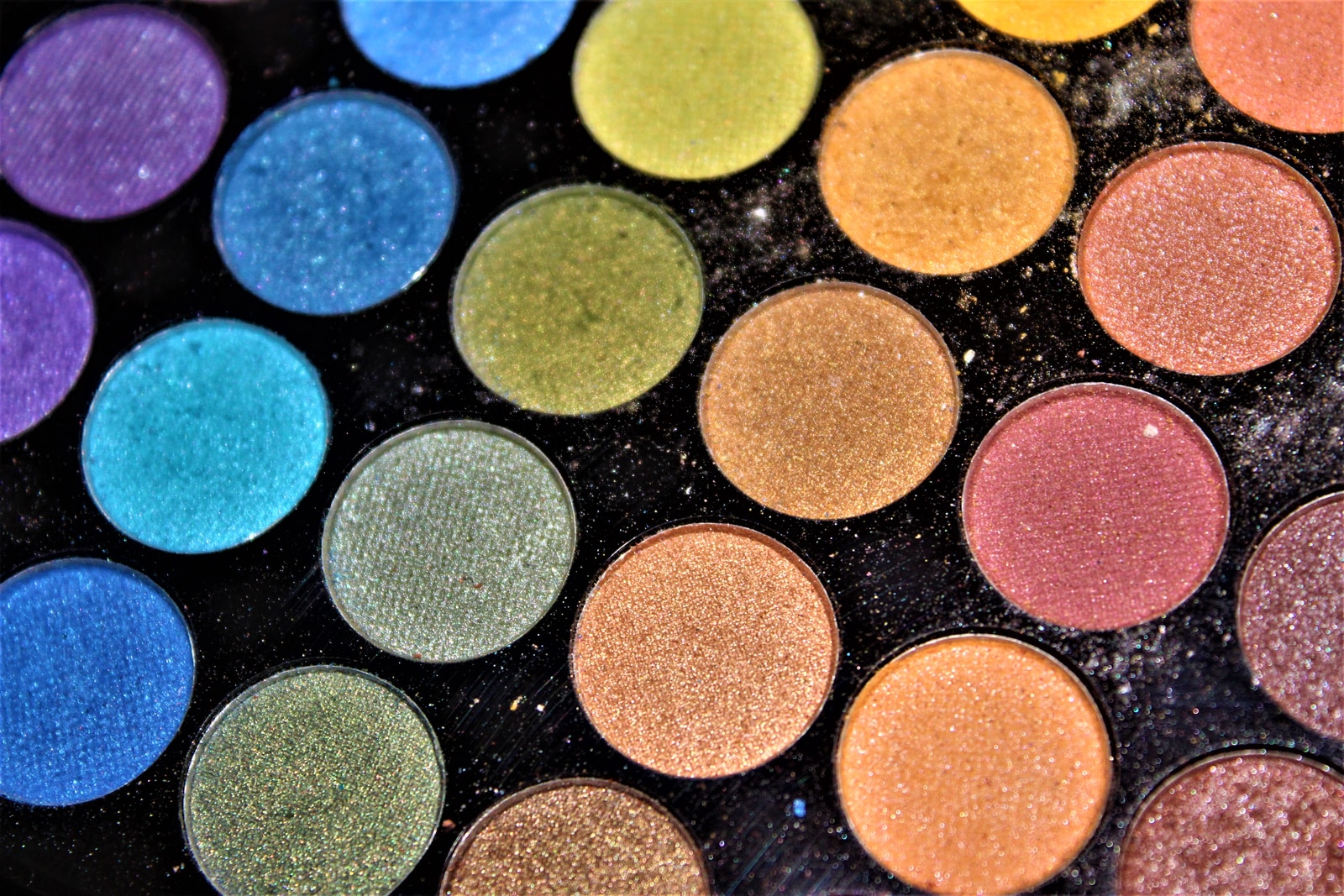
Eyeshadow
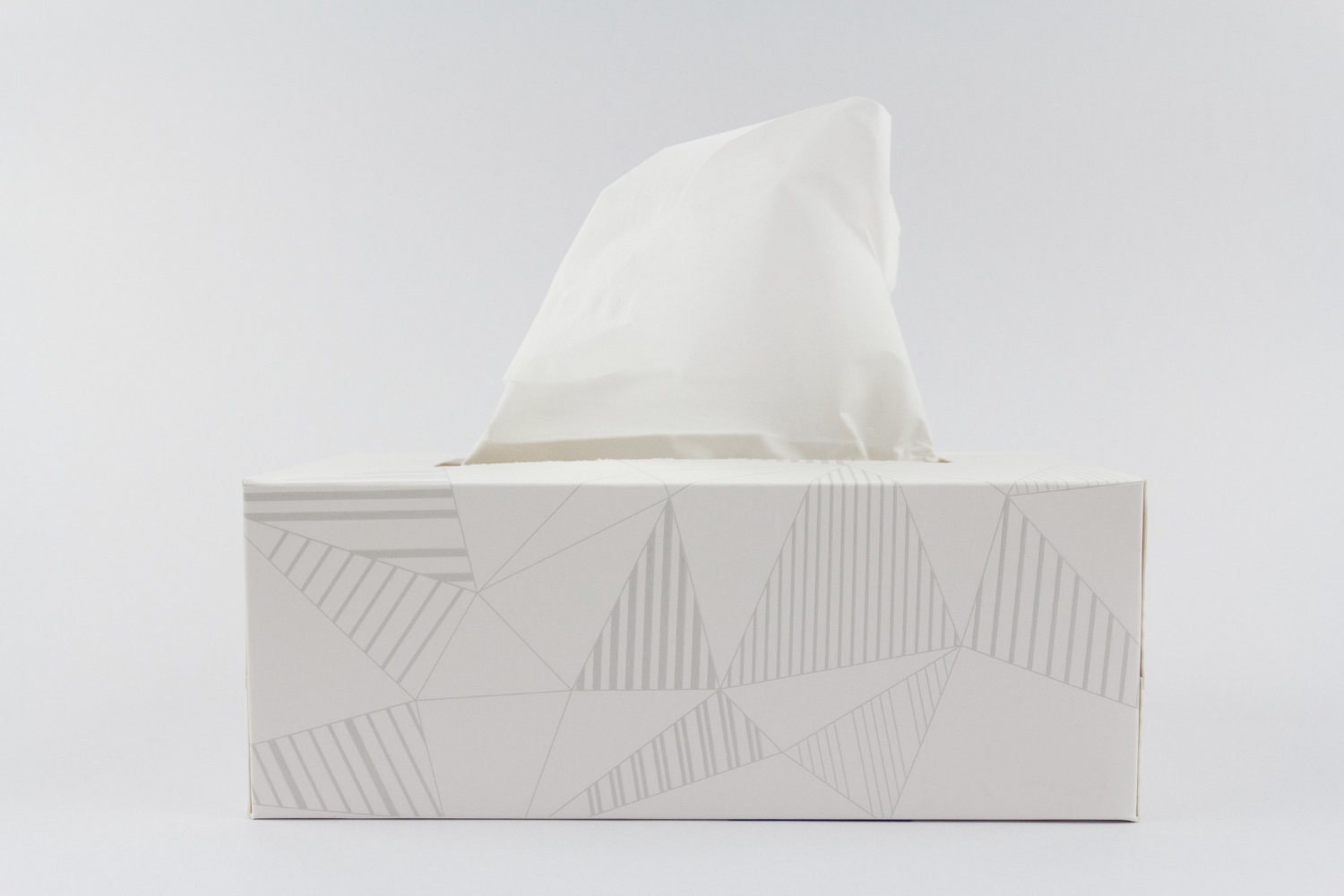
Facial Tissues
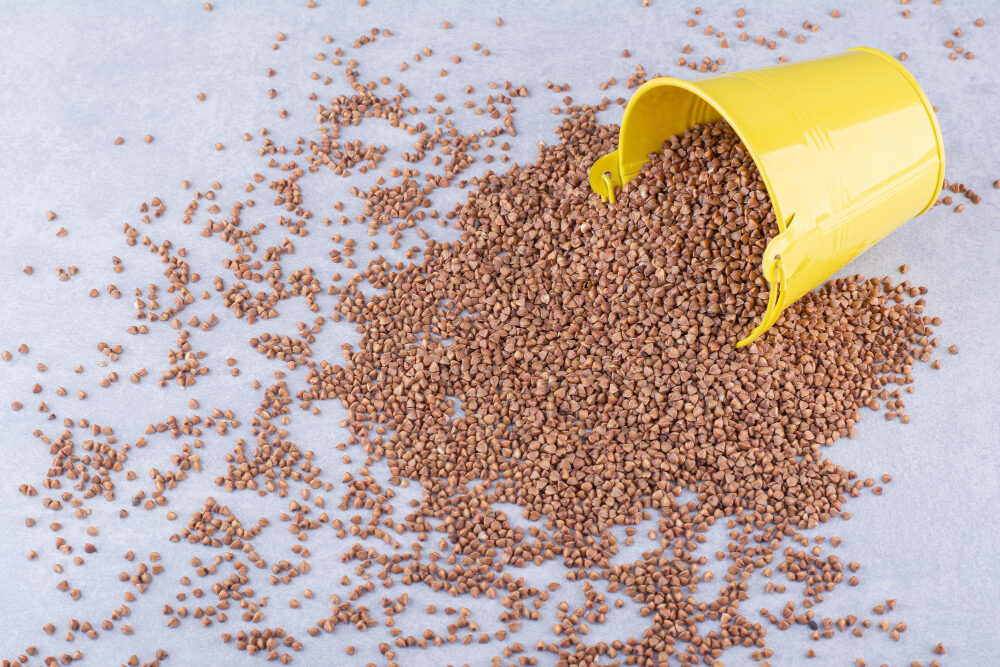
Feed additives
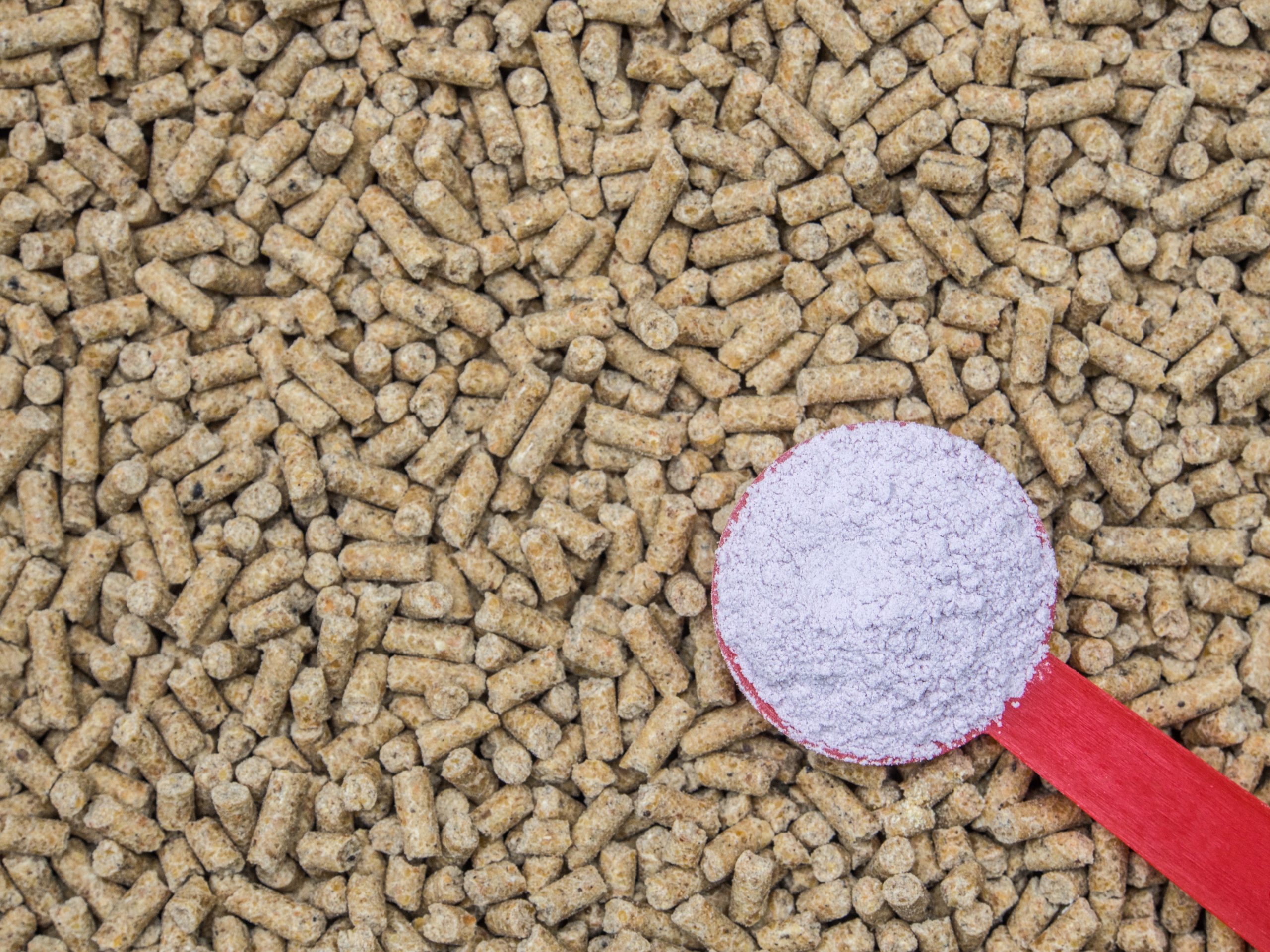
Feed concentrates

Fertilizer pellets
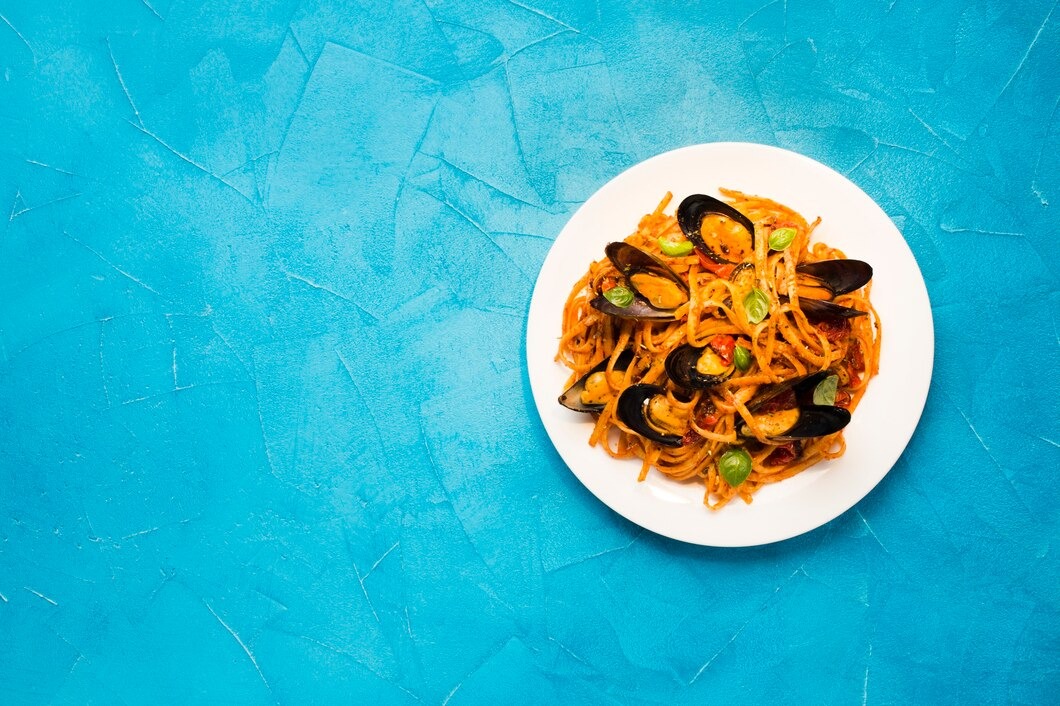
Fettuccine
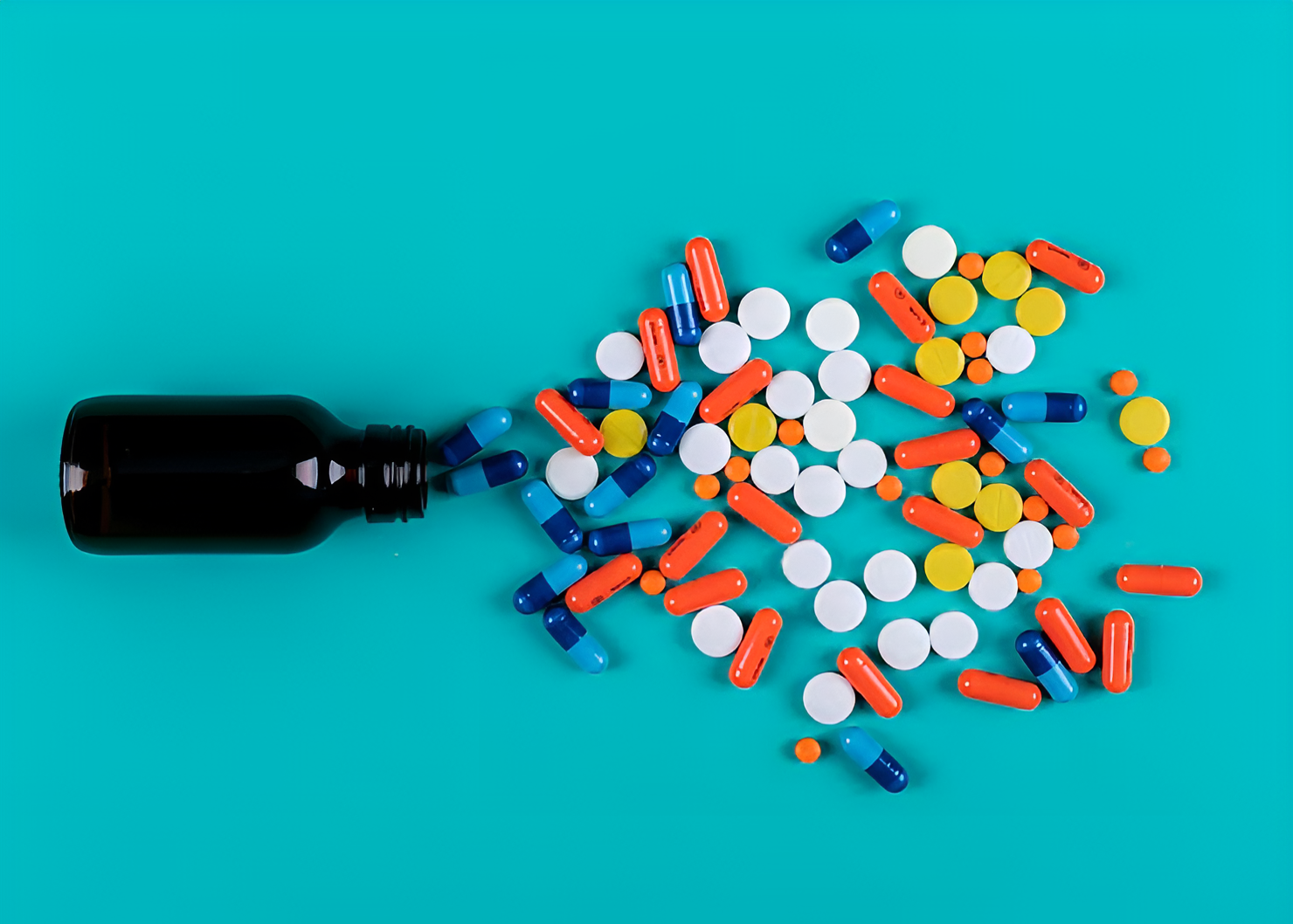
Film-coated tablets
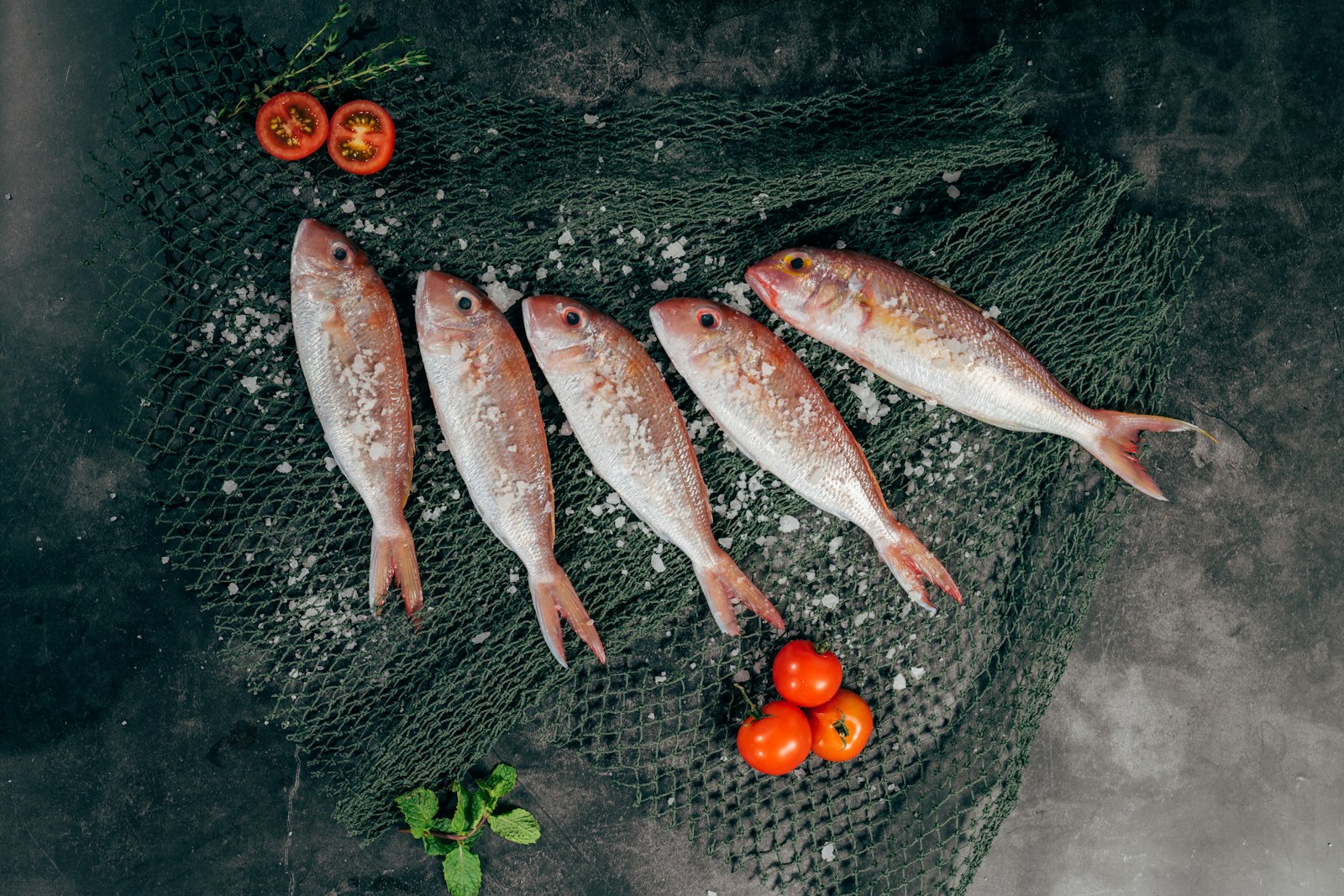
Fish by-products

Fish feed
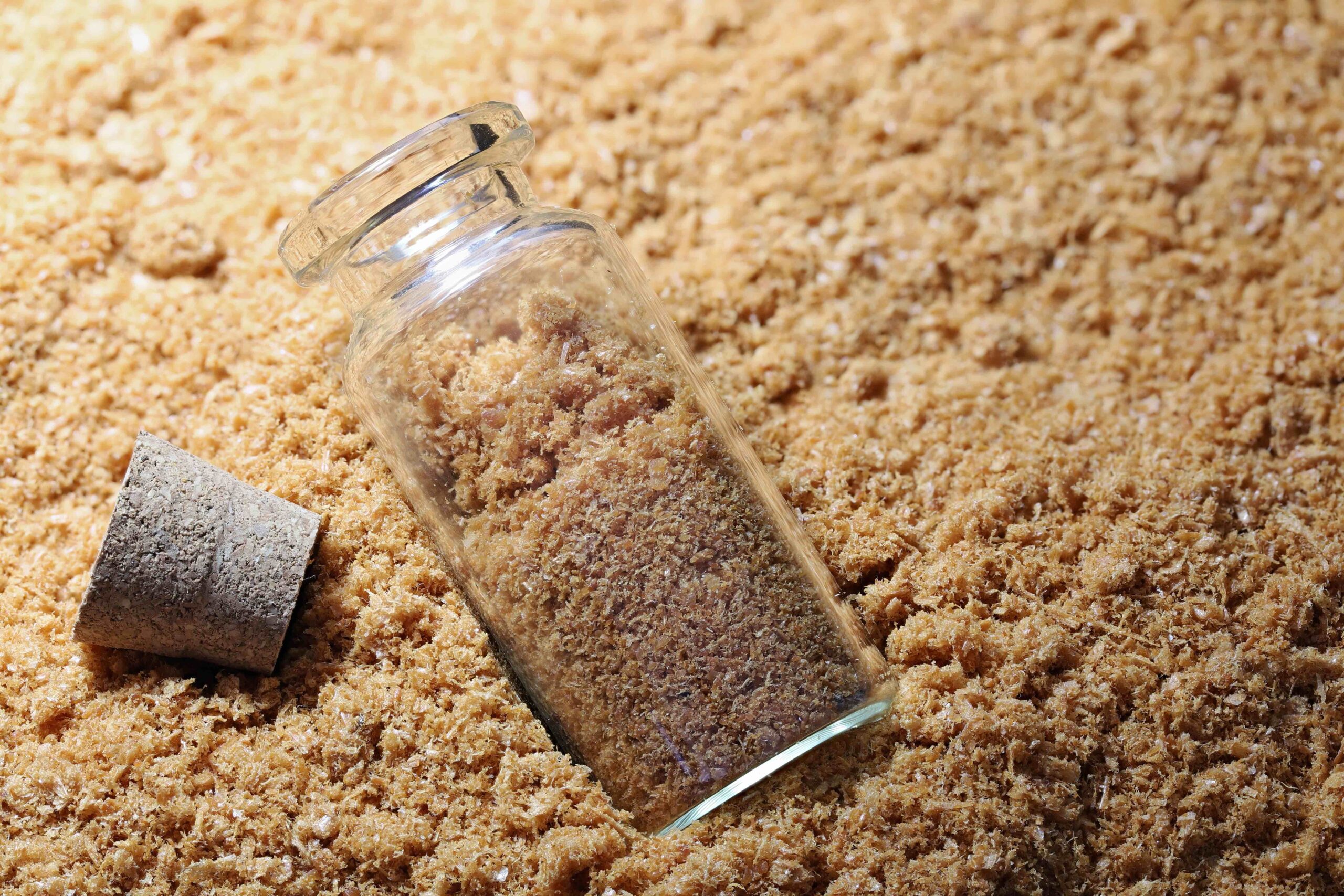
Fishmeal
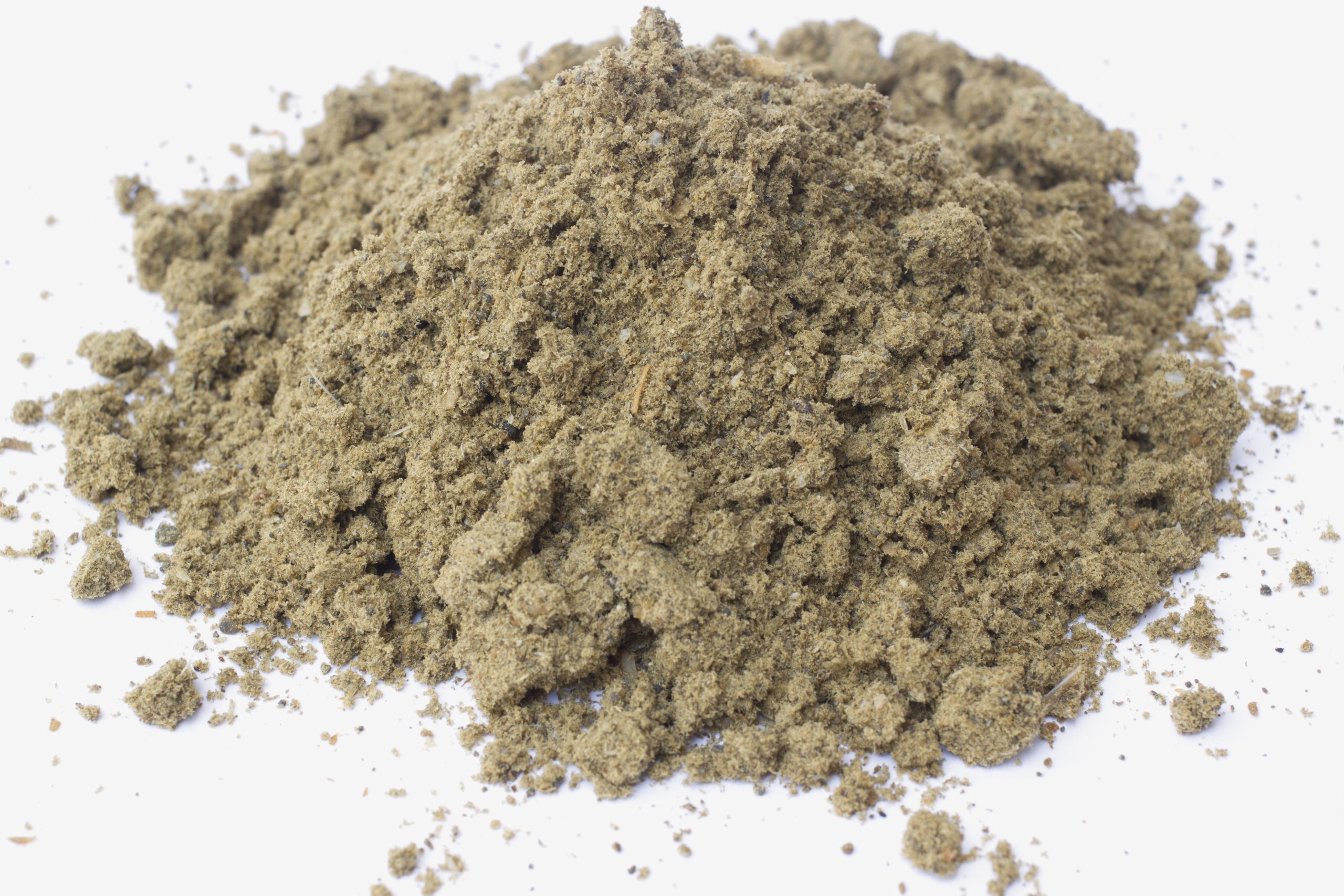
Fishmeal powder
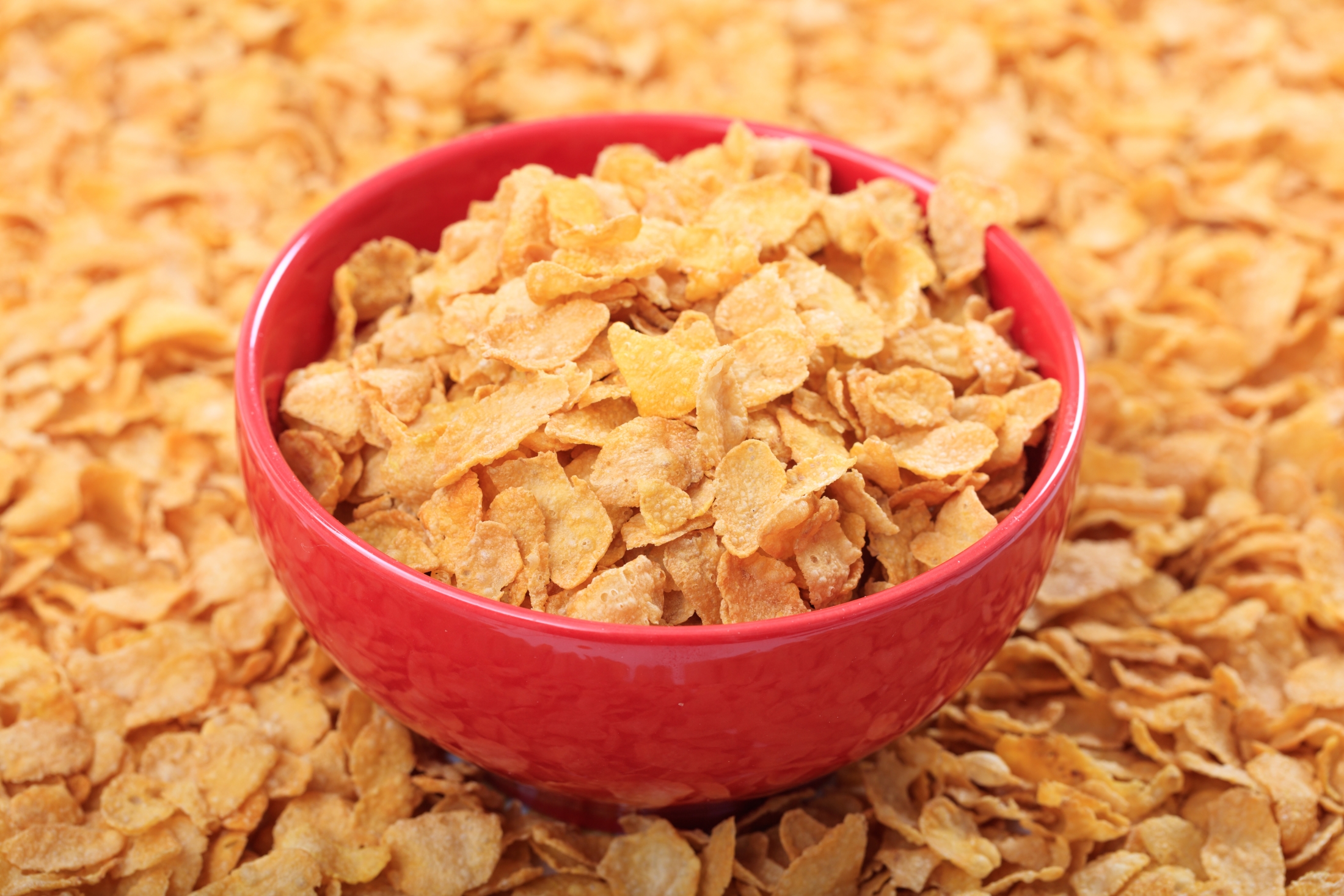
Flakes
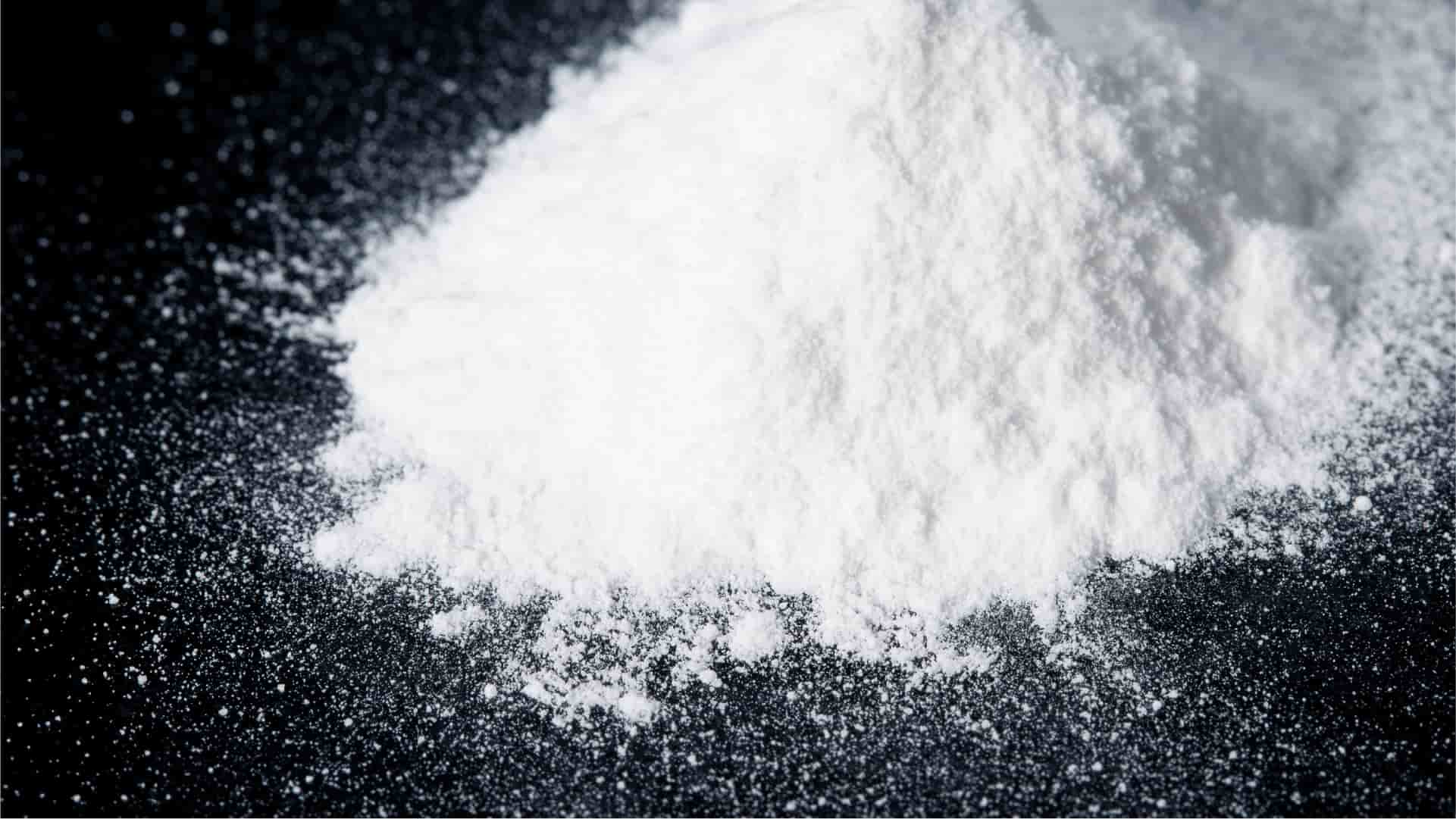
Flame retardants
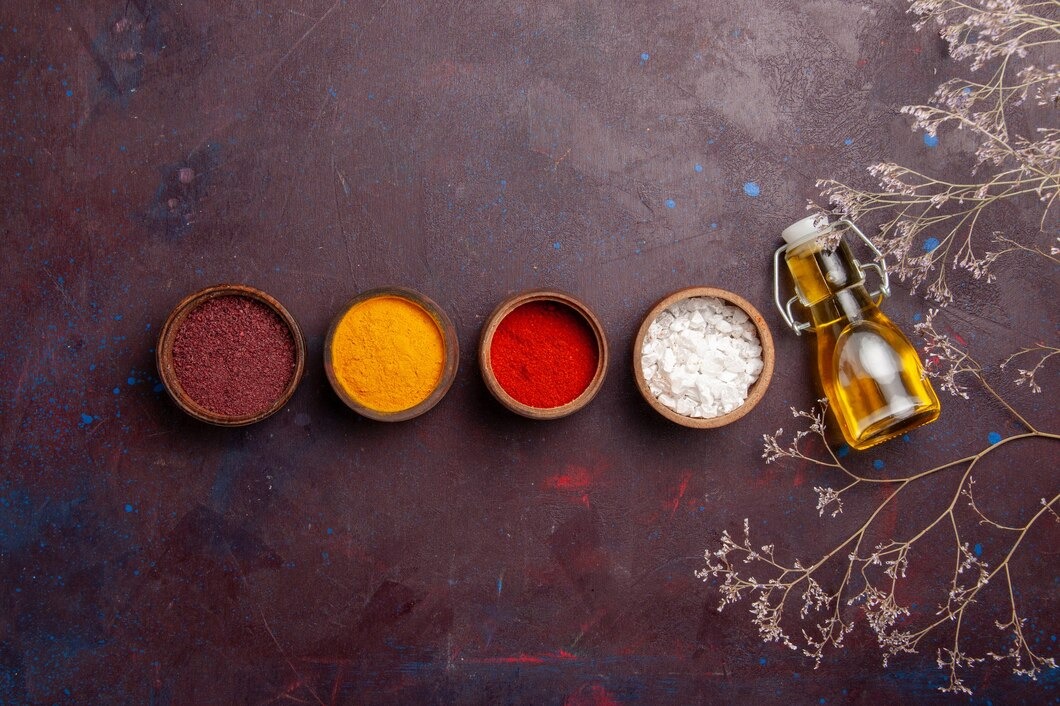
Flavor enhancers
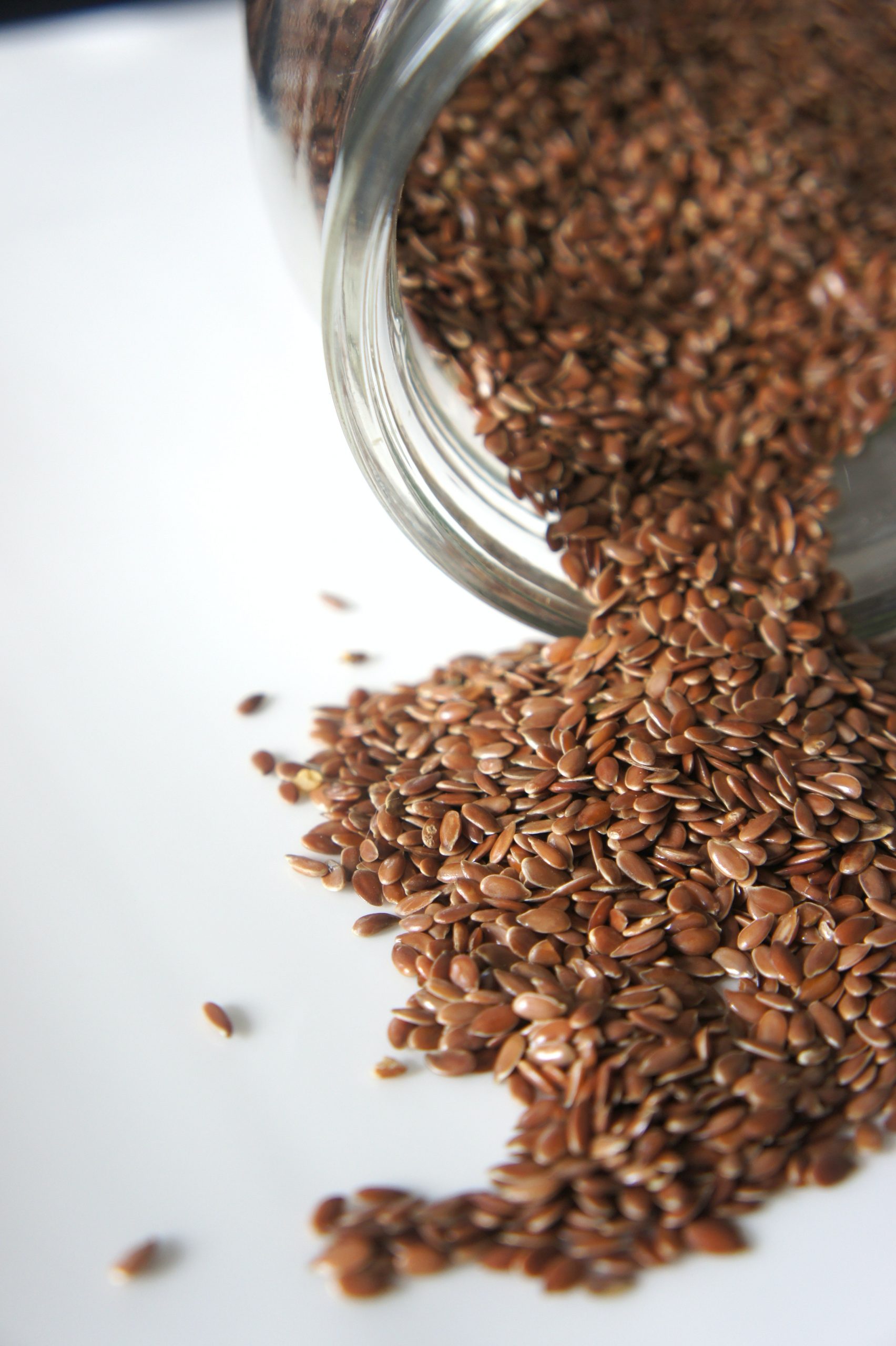
Flax seeds

Floating pellets
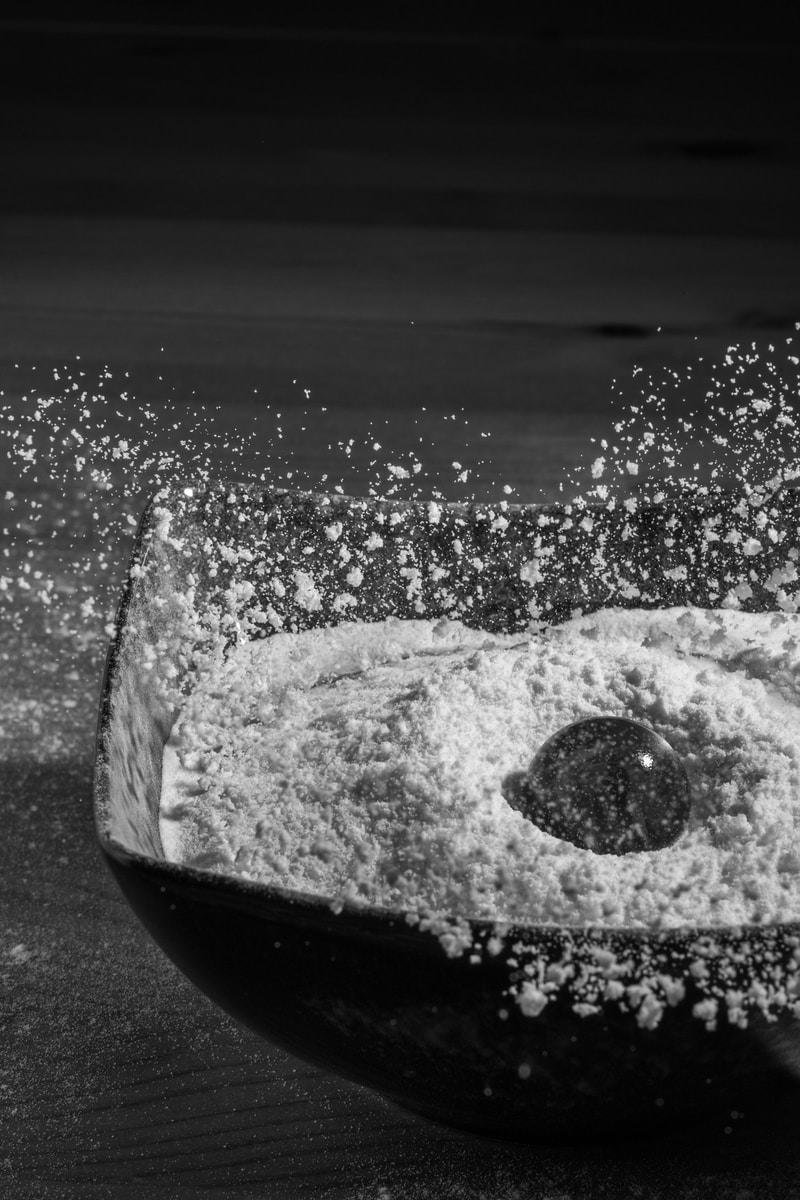
Flour
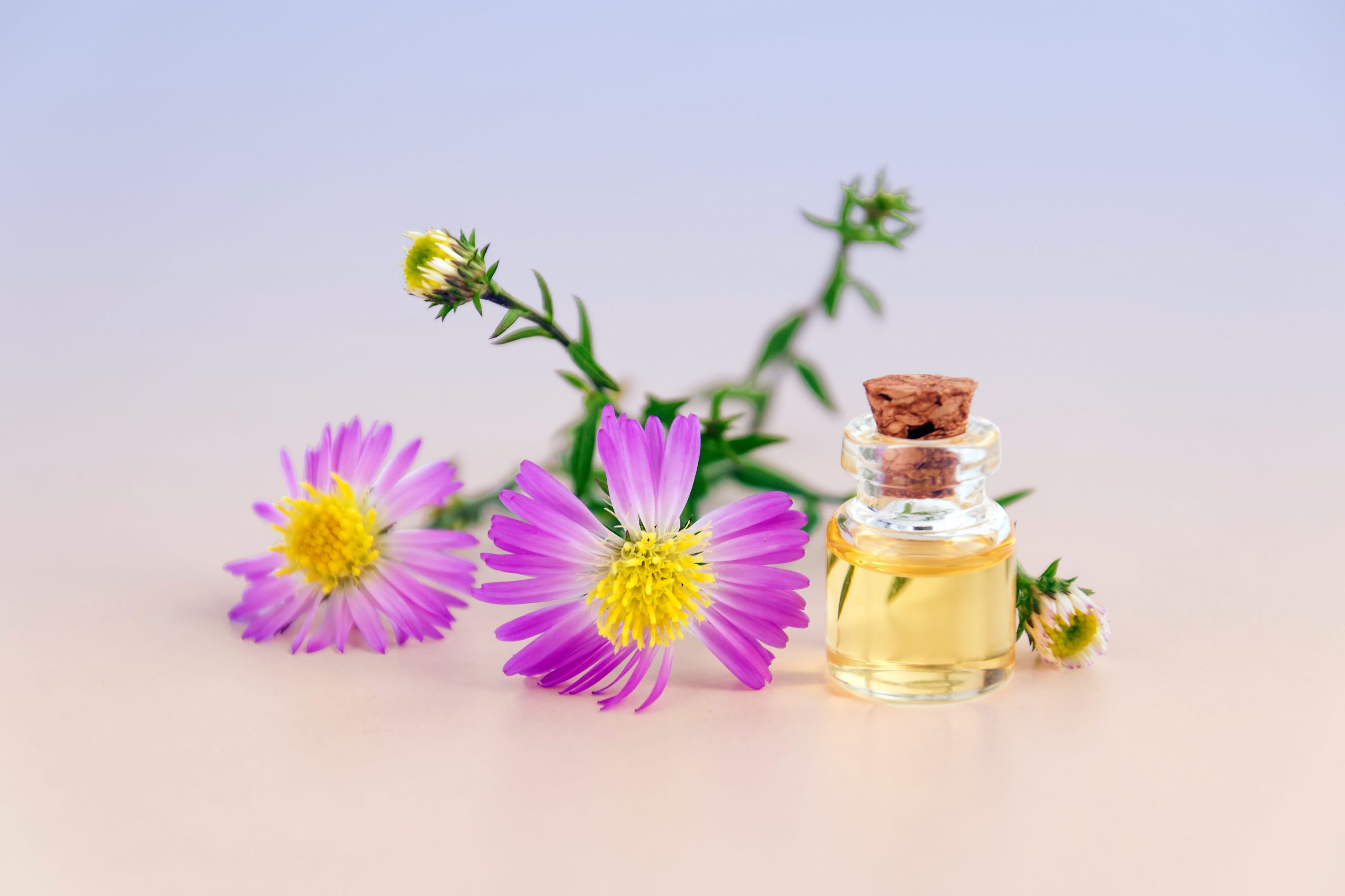
Flower extract
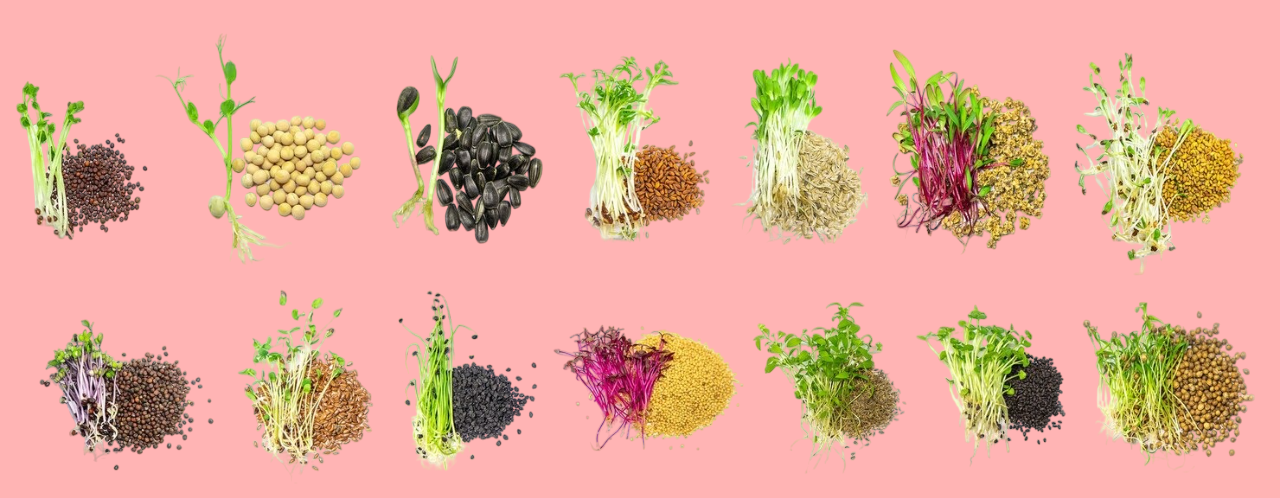
Flower seeds
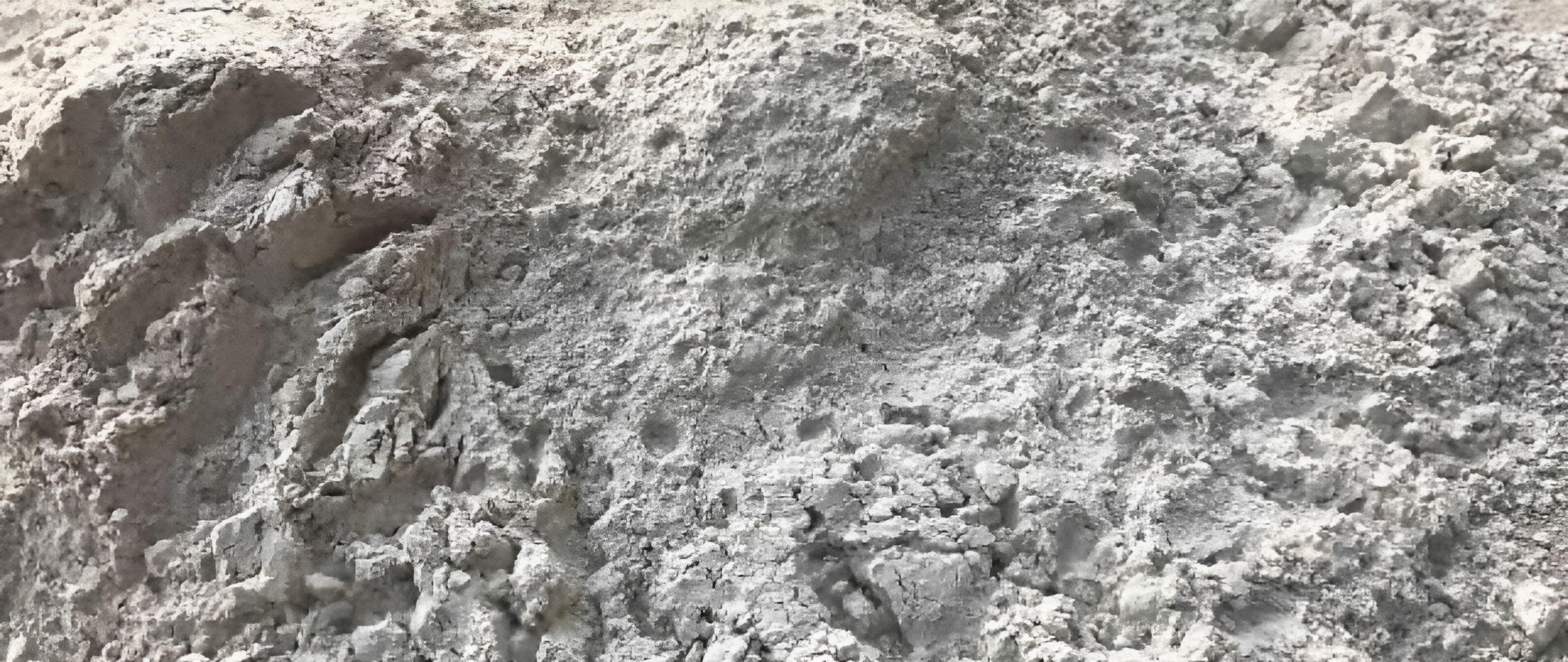
Fly ash
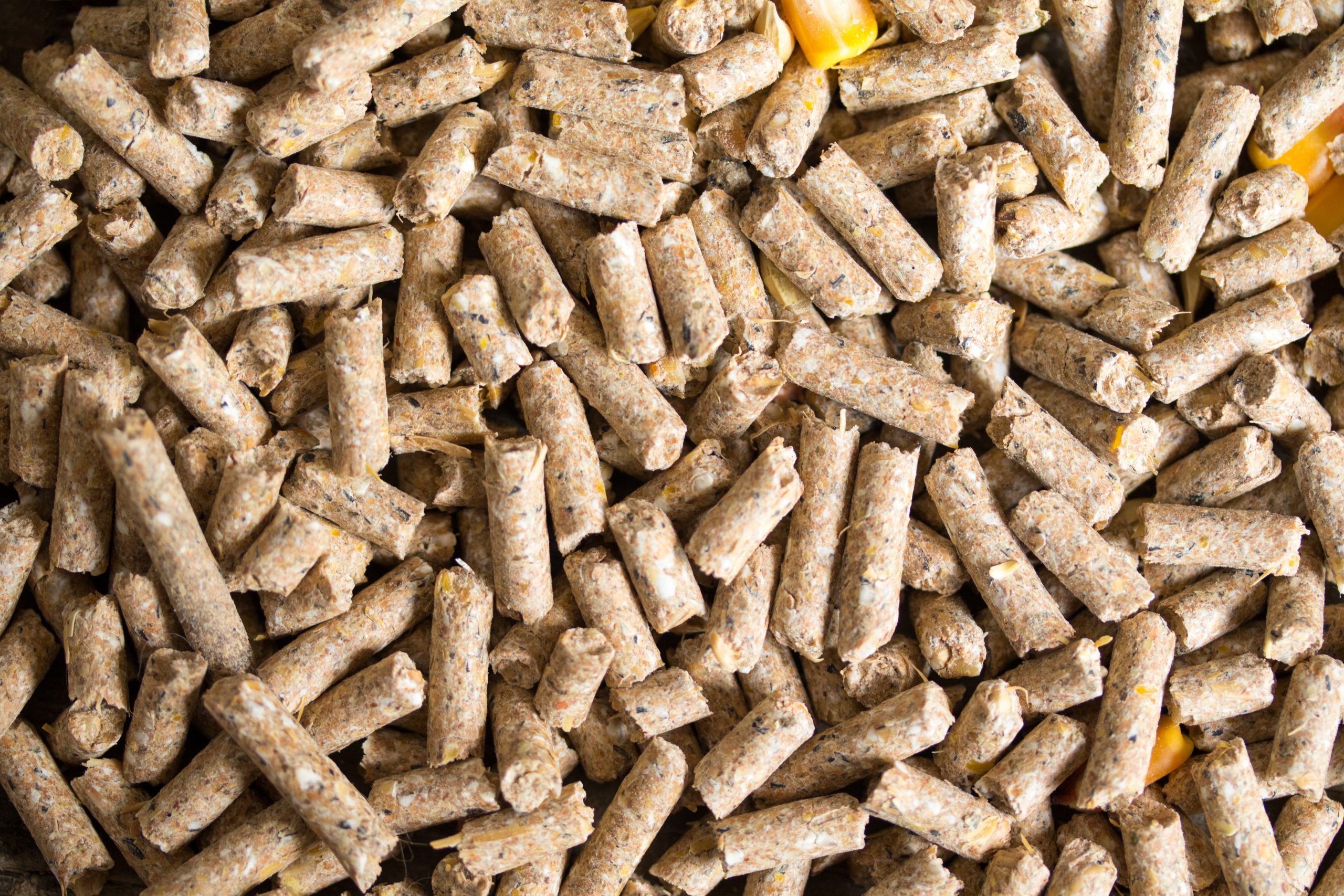
Fodder
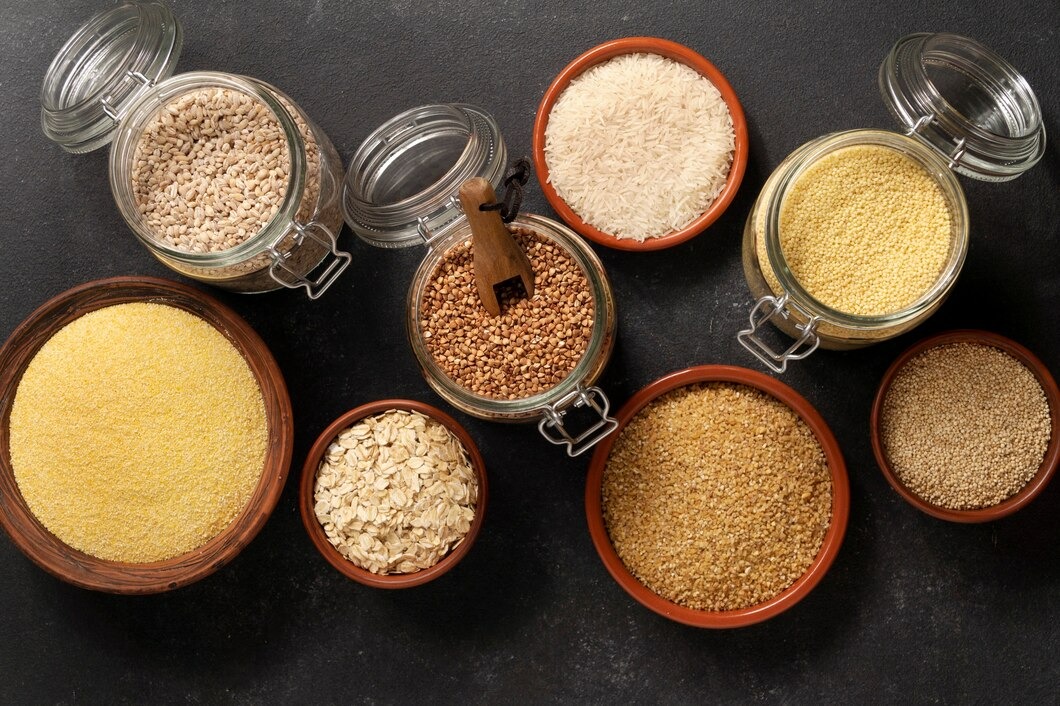
Food additives

Food colorants
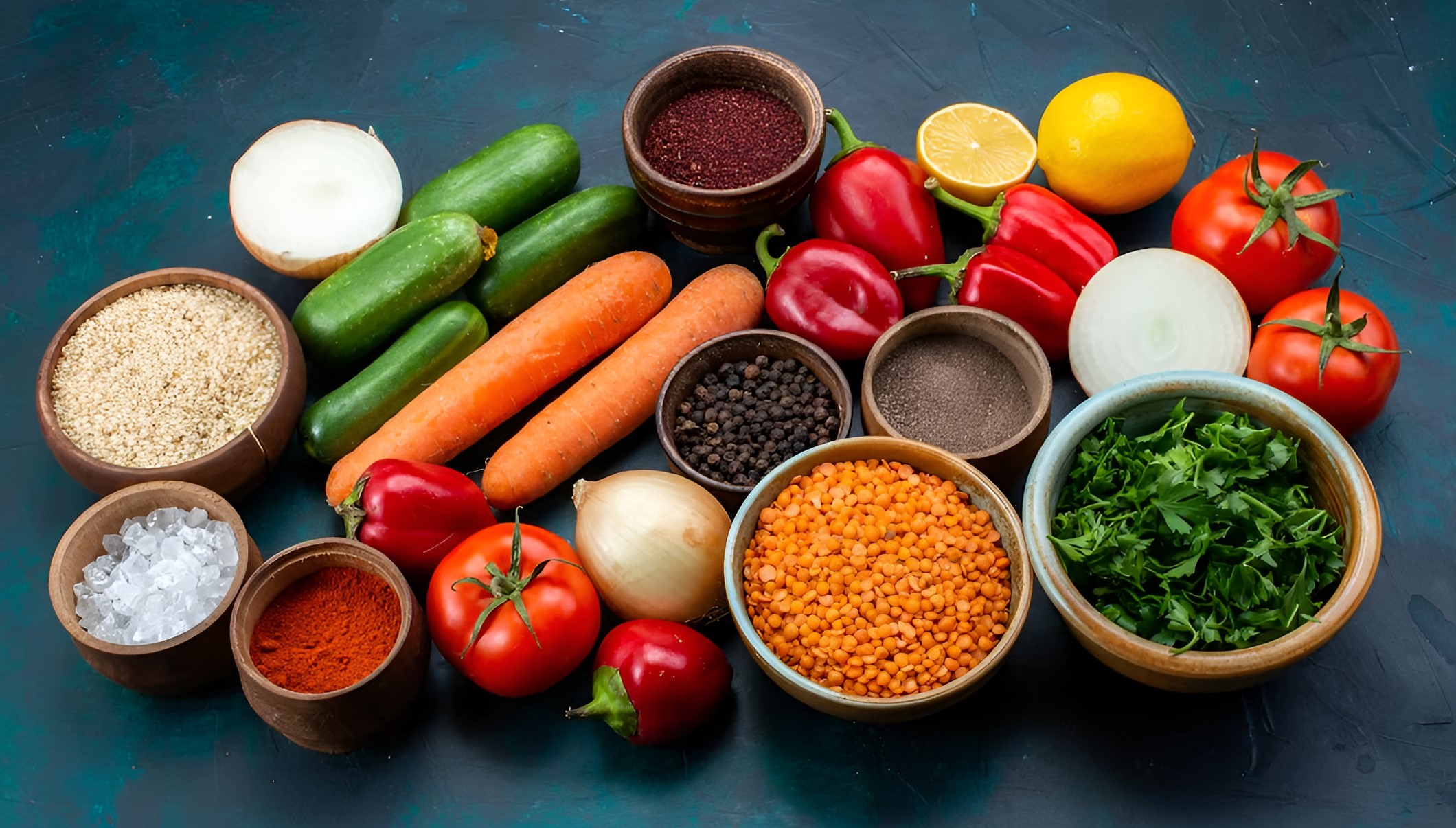
Food ingredients
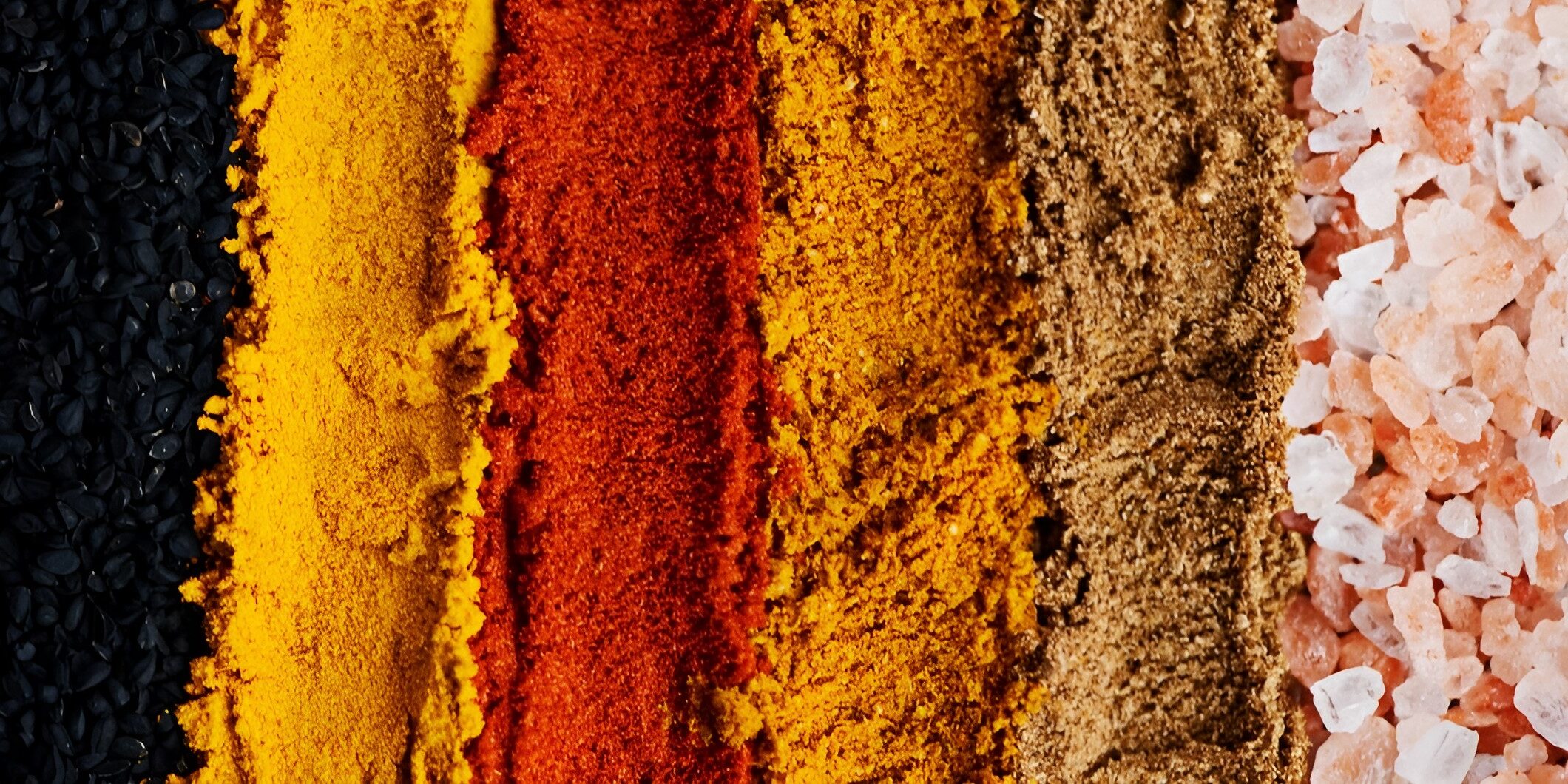
Food powders
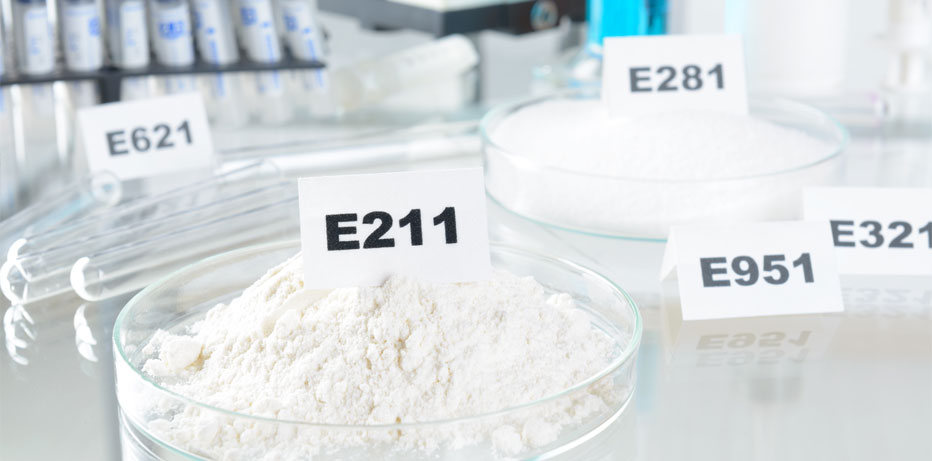
Food preservatives
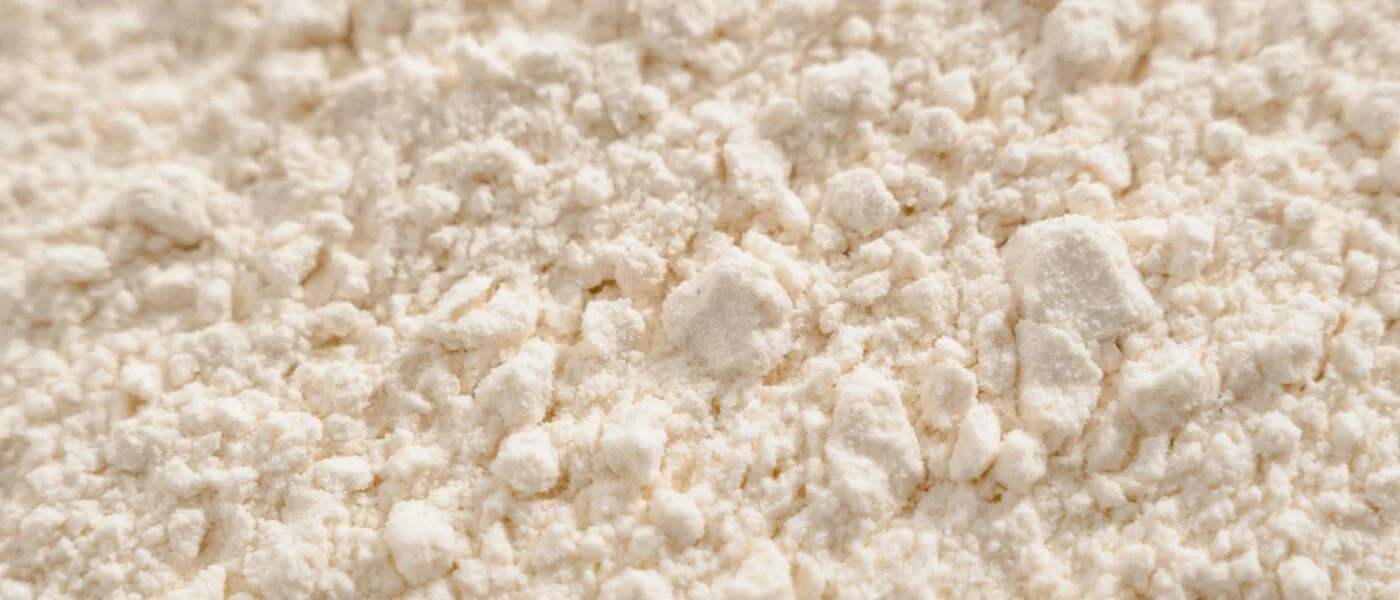
Free-flowing powders
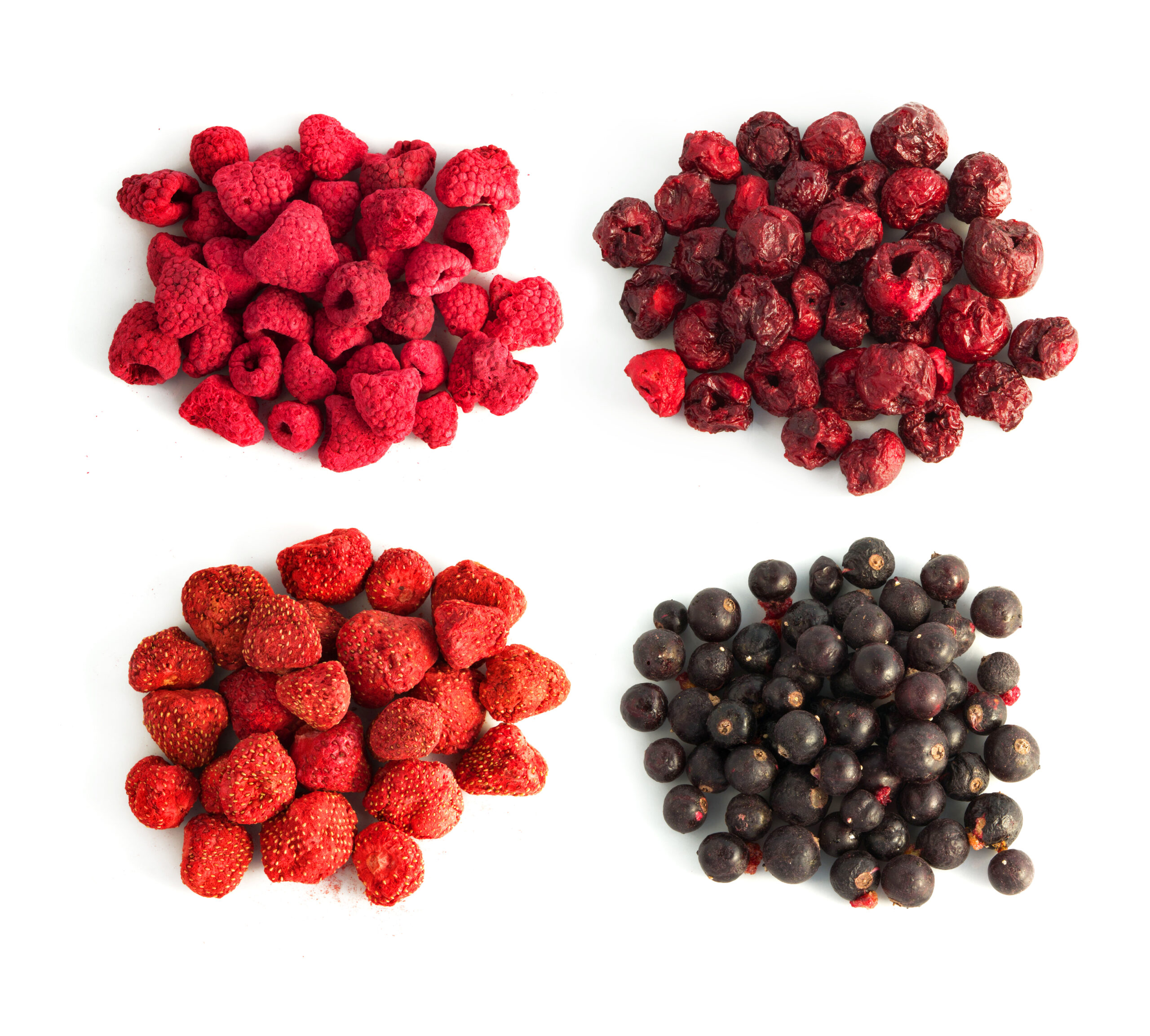
Freeze dried berries
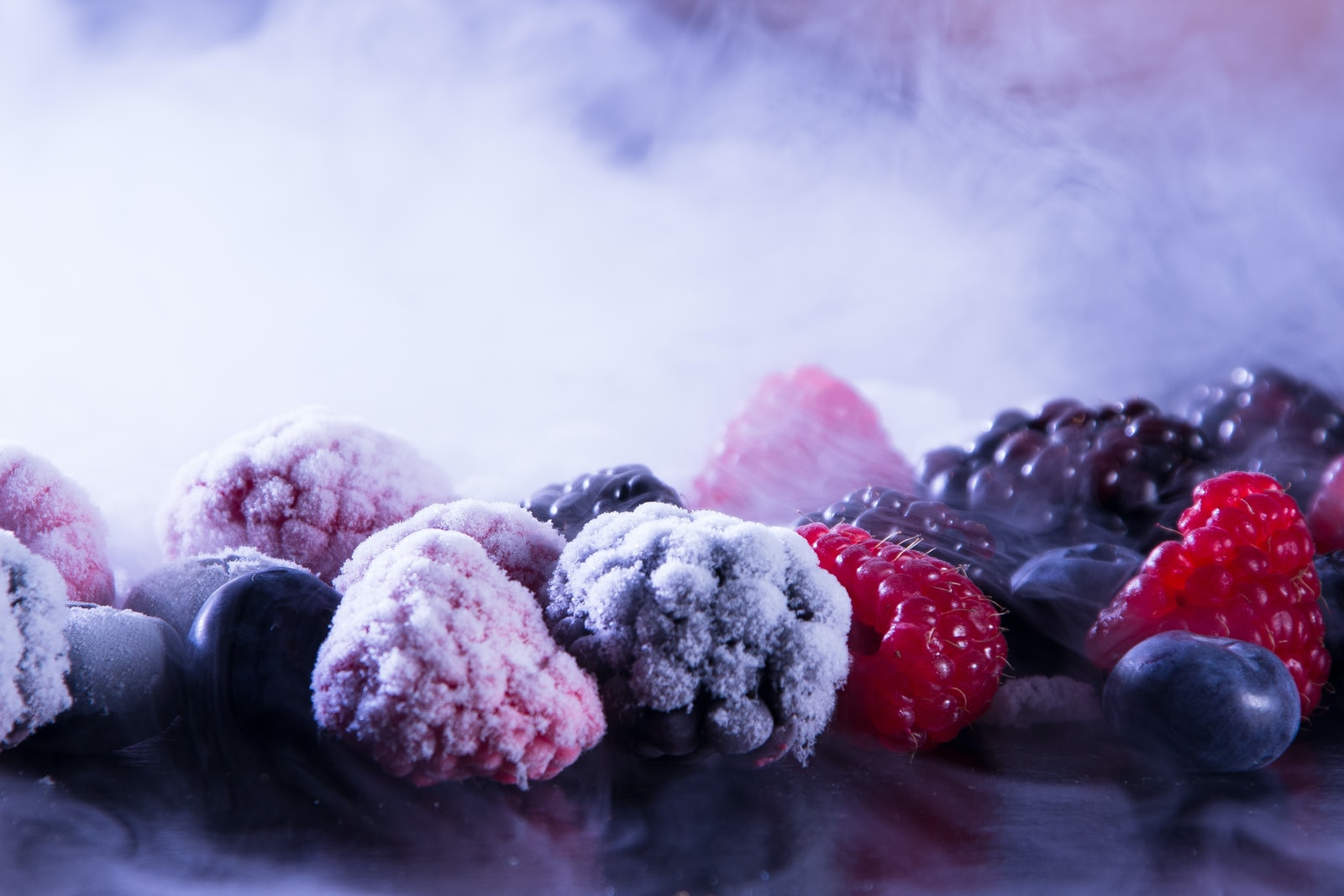
Frozen fruit
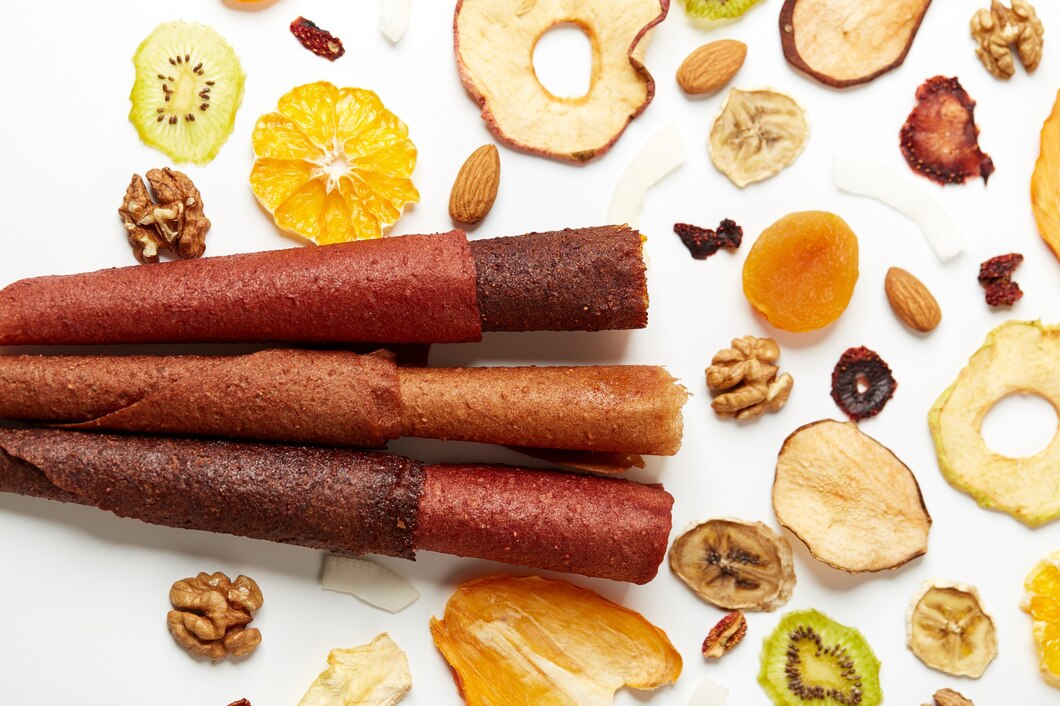
Fruit leather
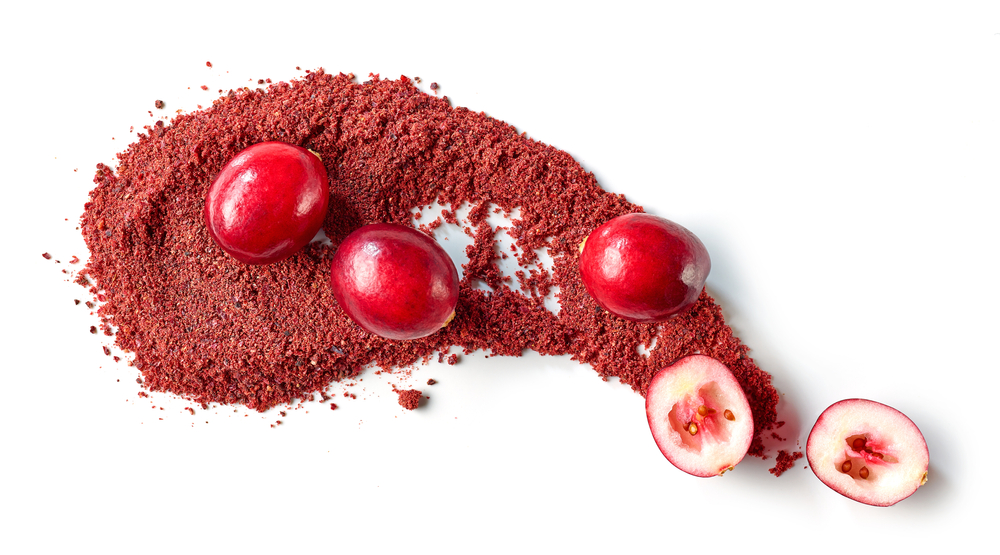
Fruit powder
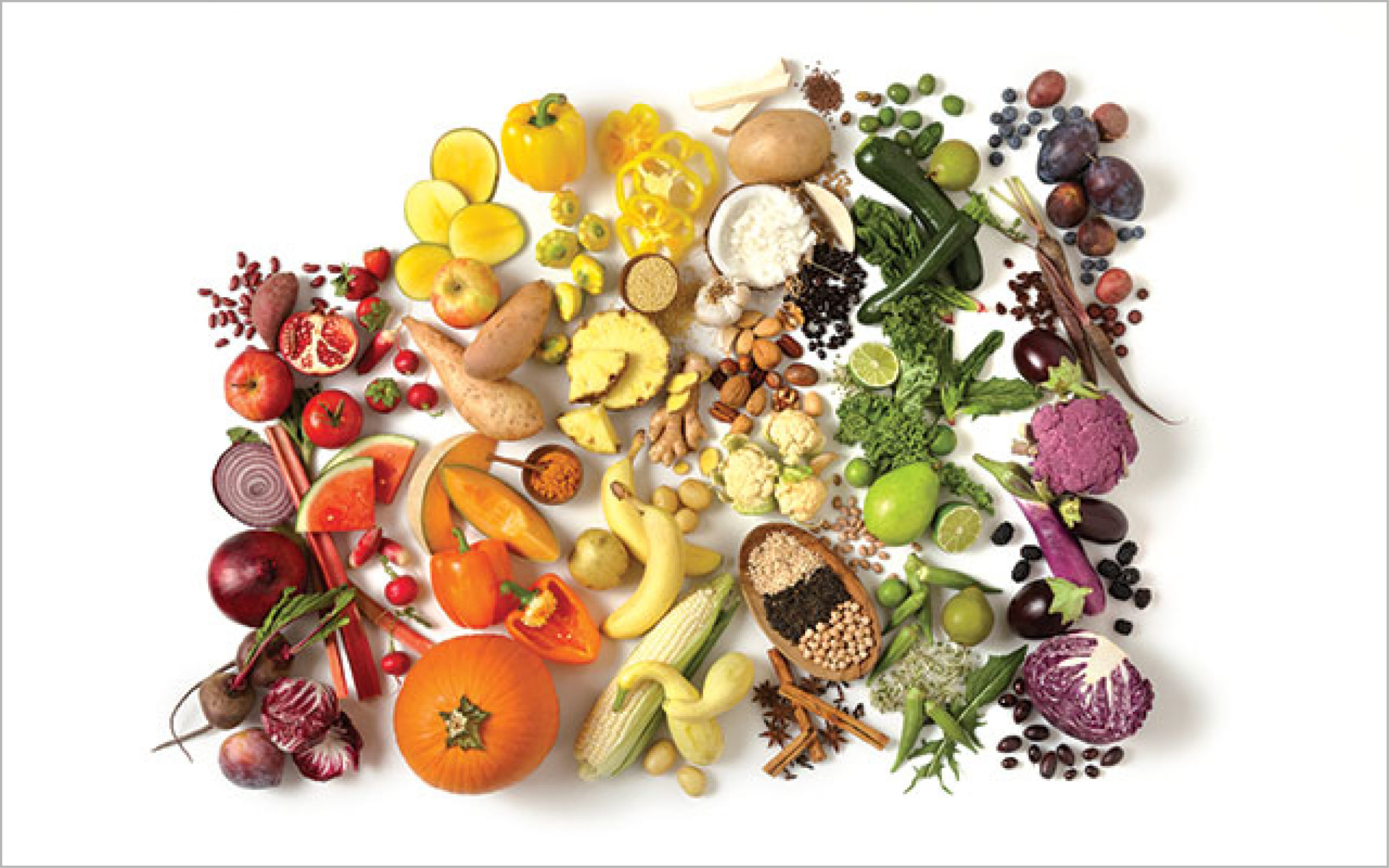
Functional foods
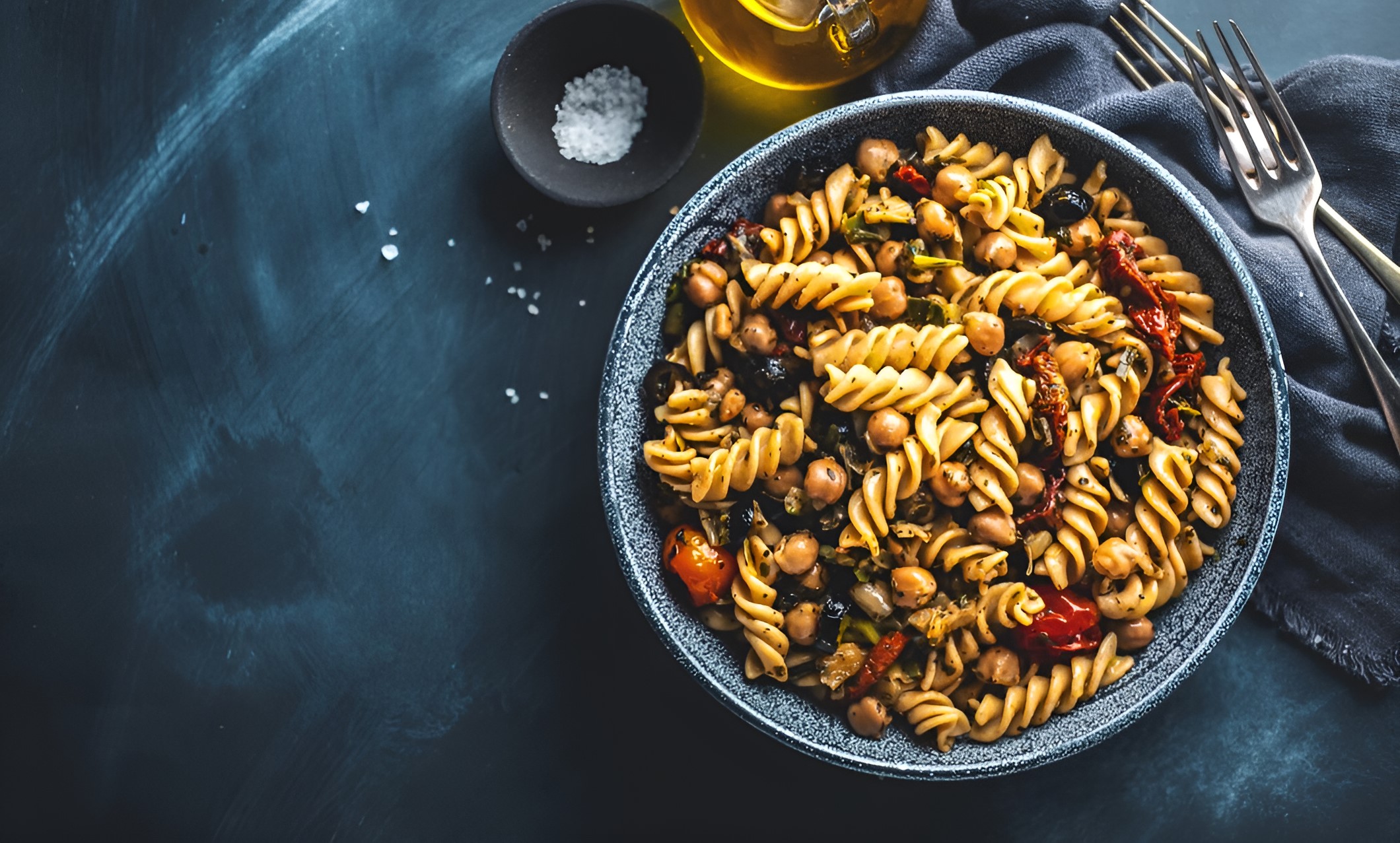
Fusilli pasta
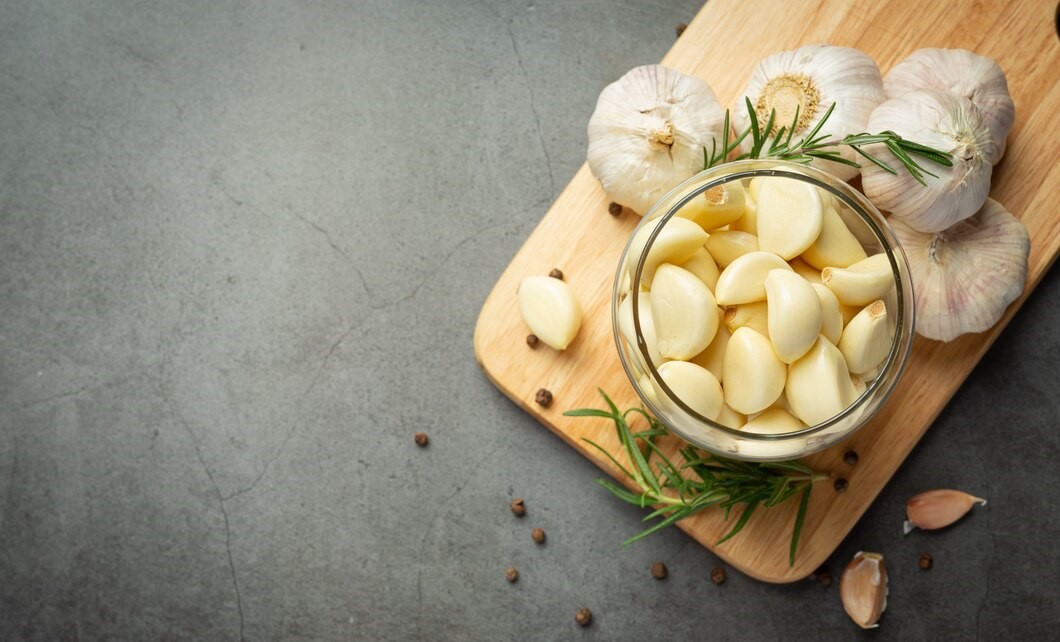
Garlic
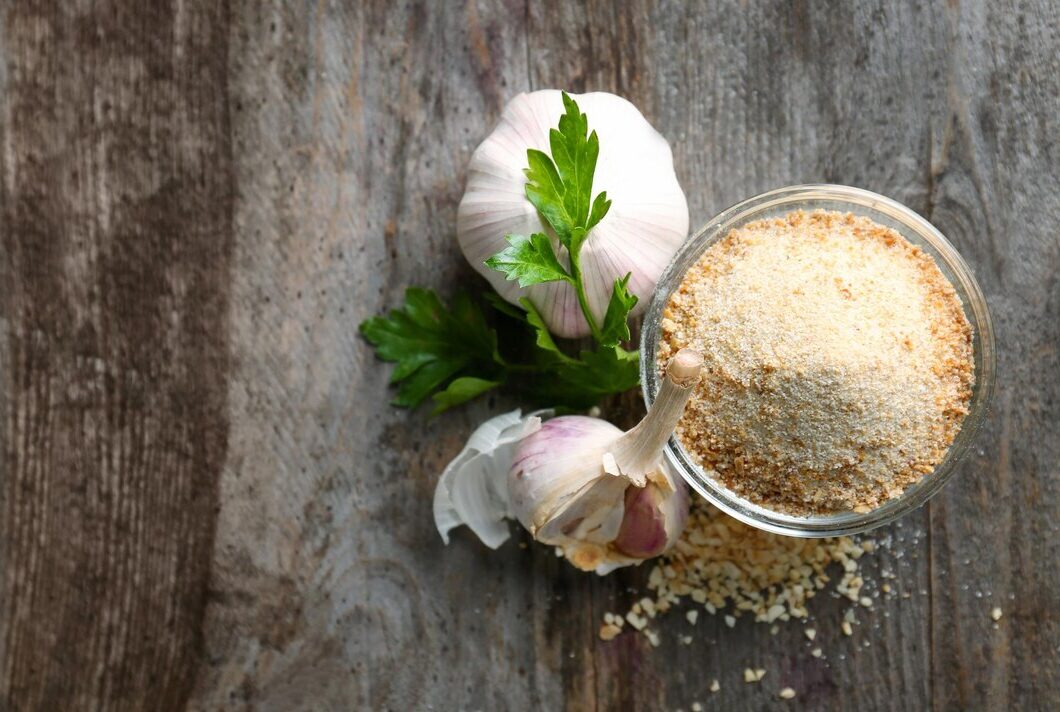
Garlic powder
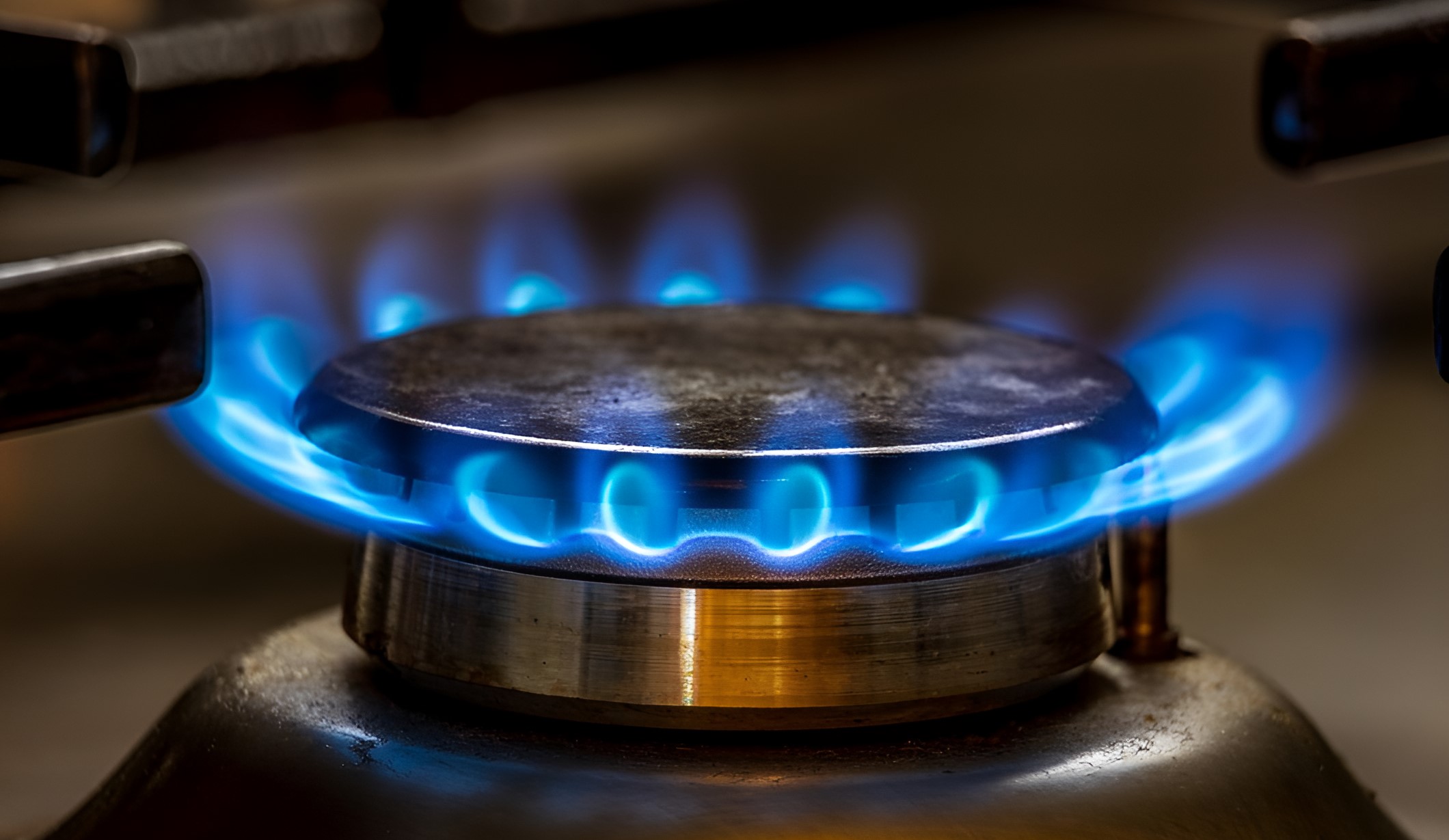
Gas

Gelatin capsules
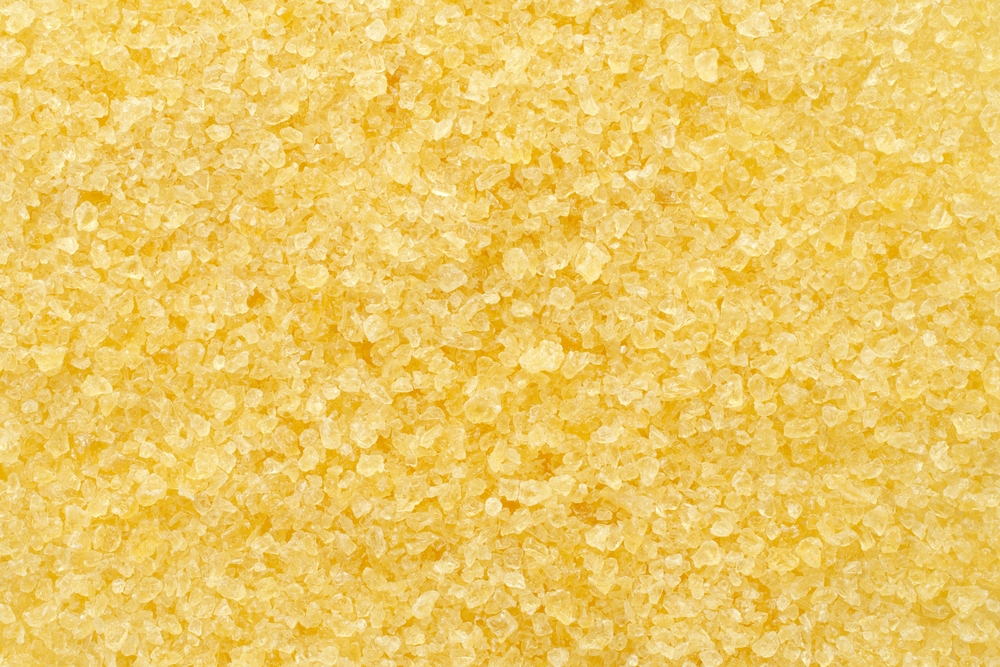
Gelatin powder
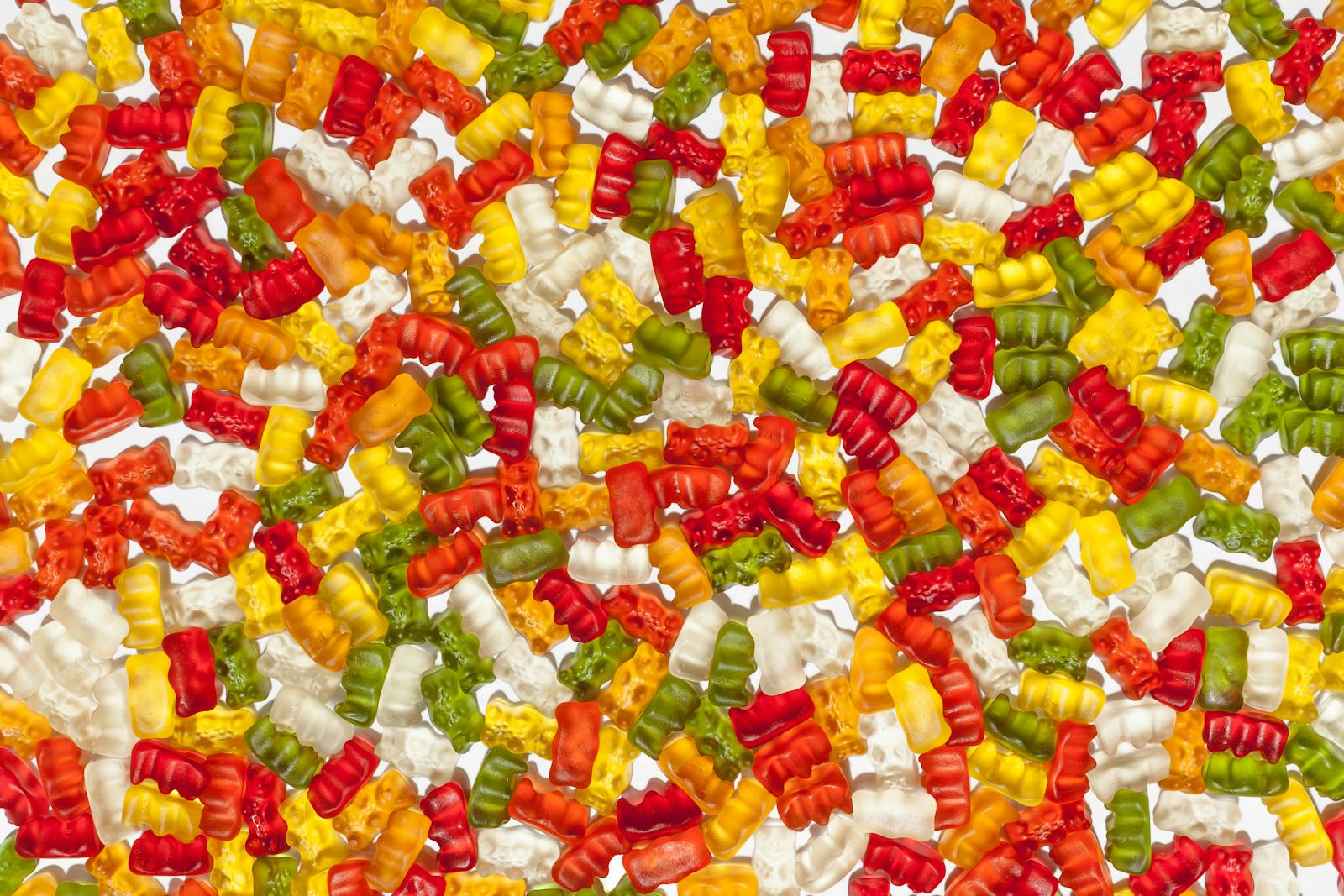
Gelatine
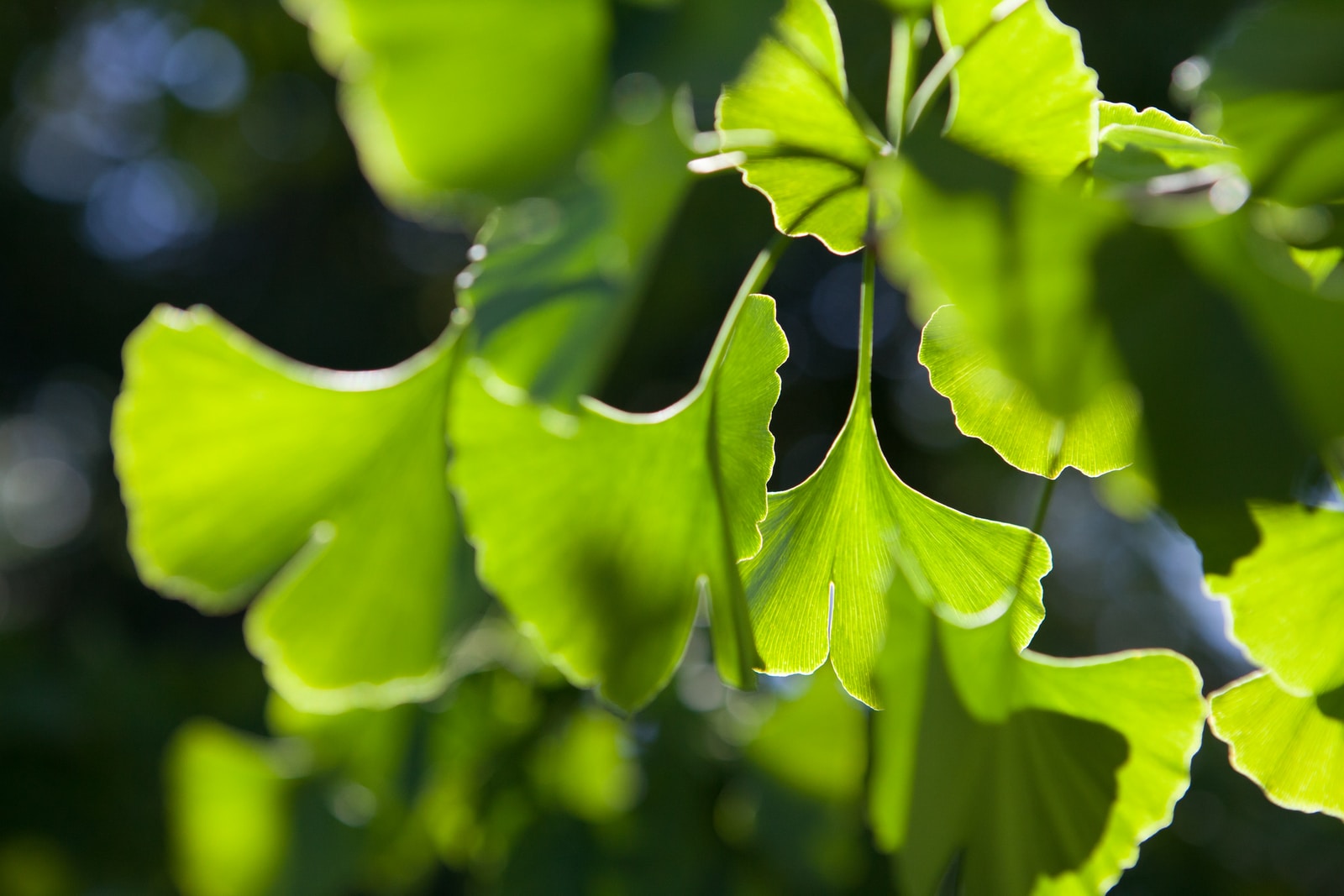
Ginkgo extract
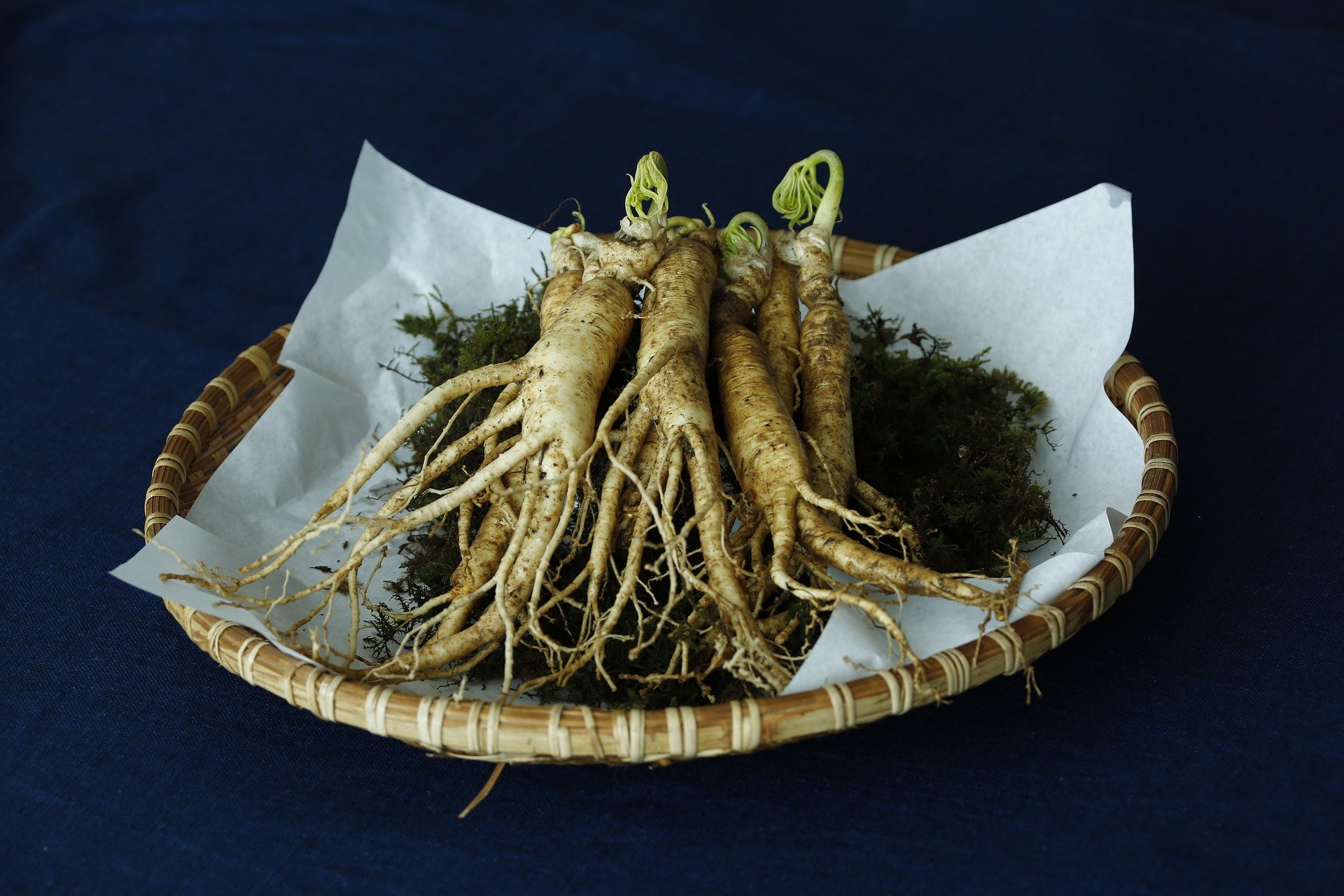
Ginseng extract
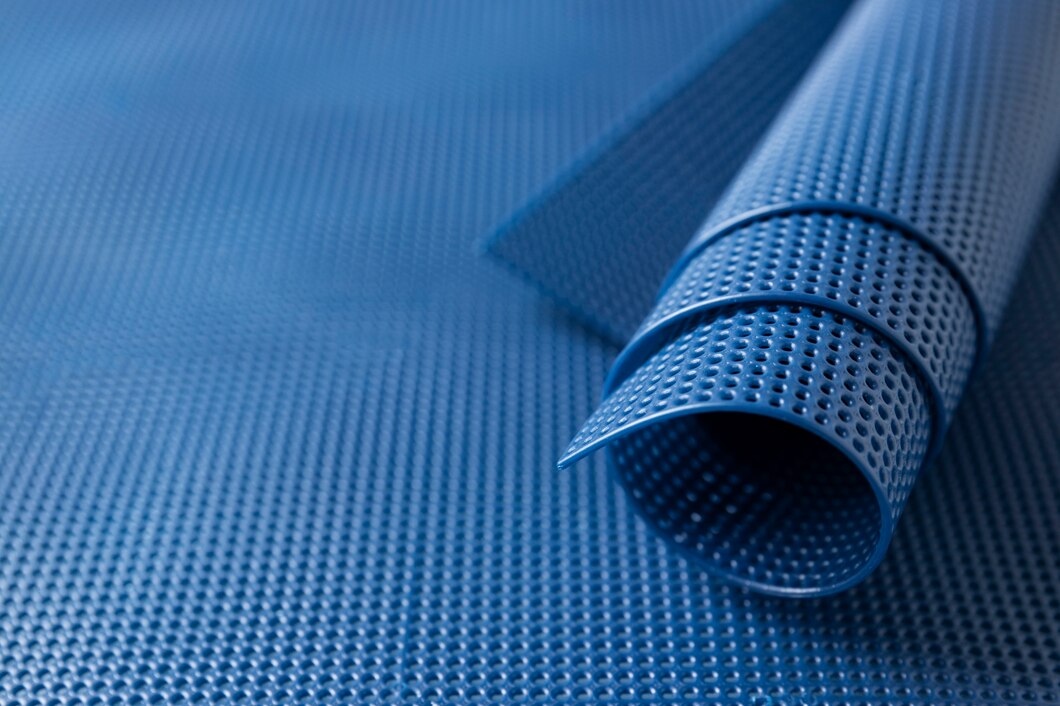
Glass fibers
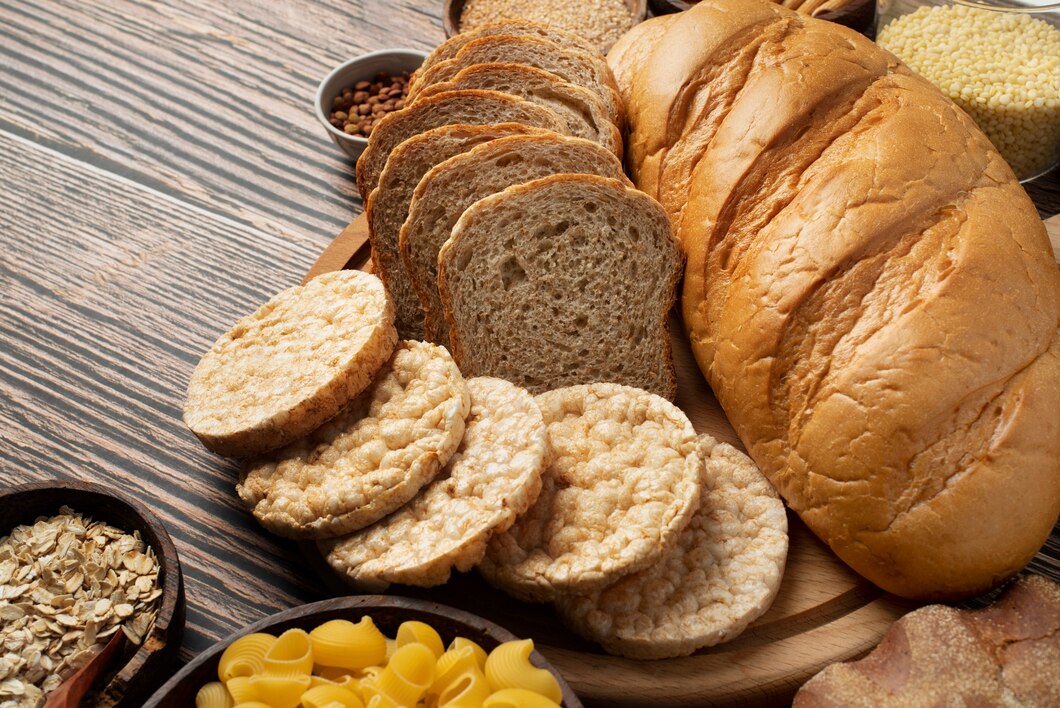
Gluten
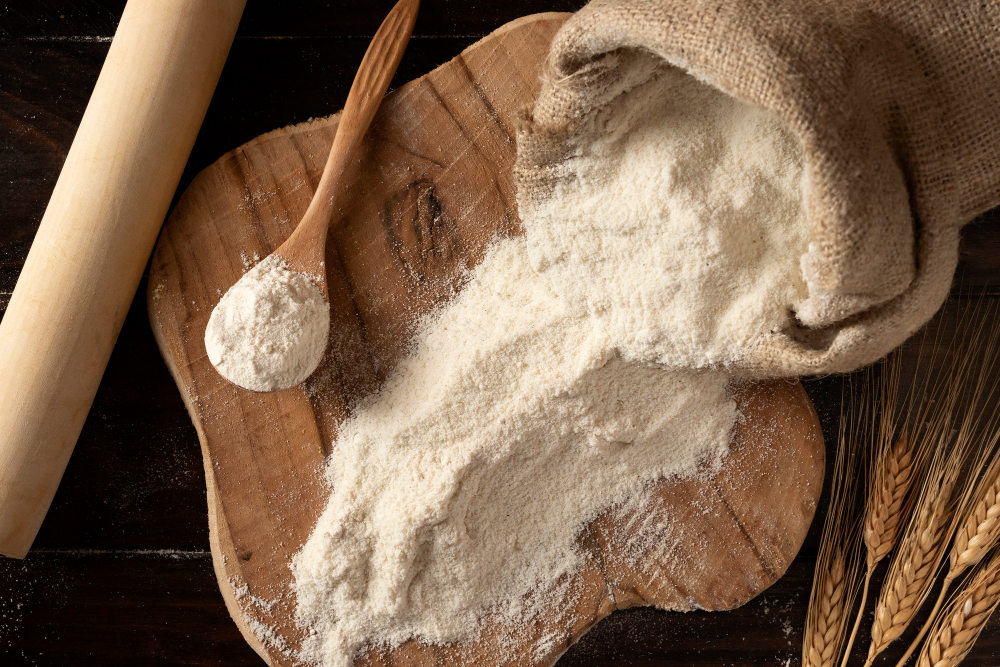
Gluten-free flour
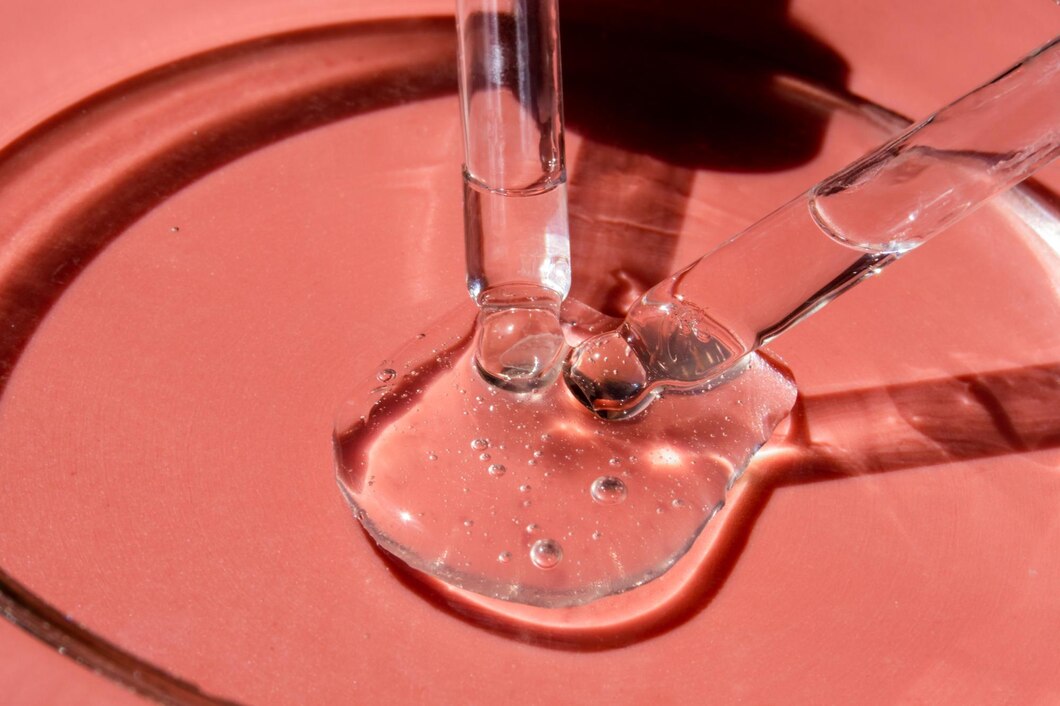
Glycerol
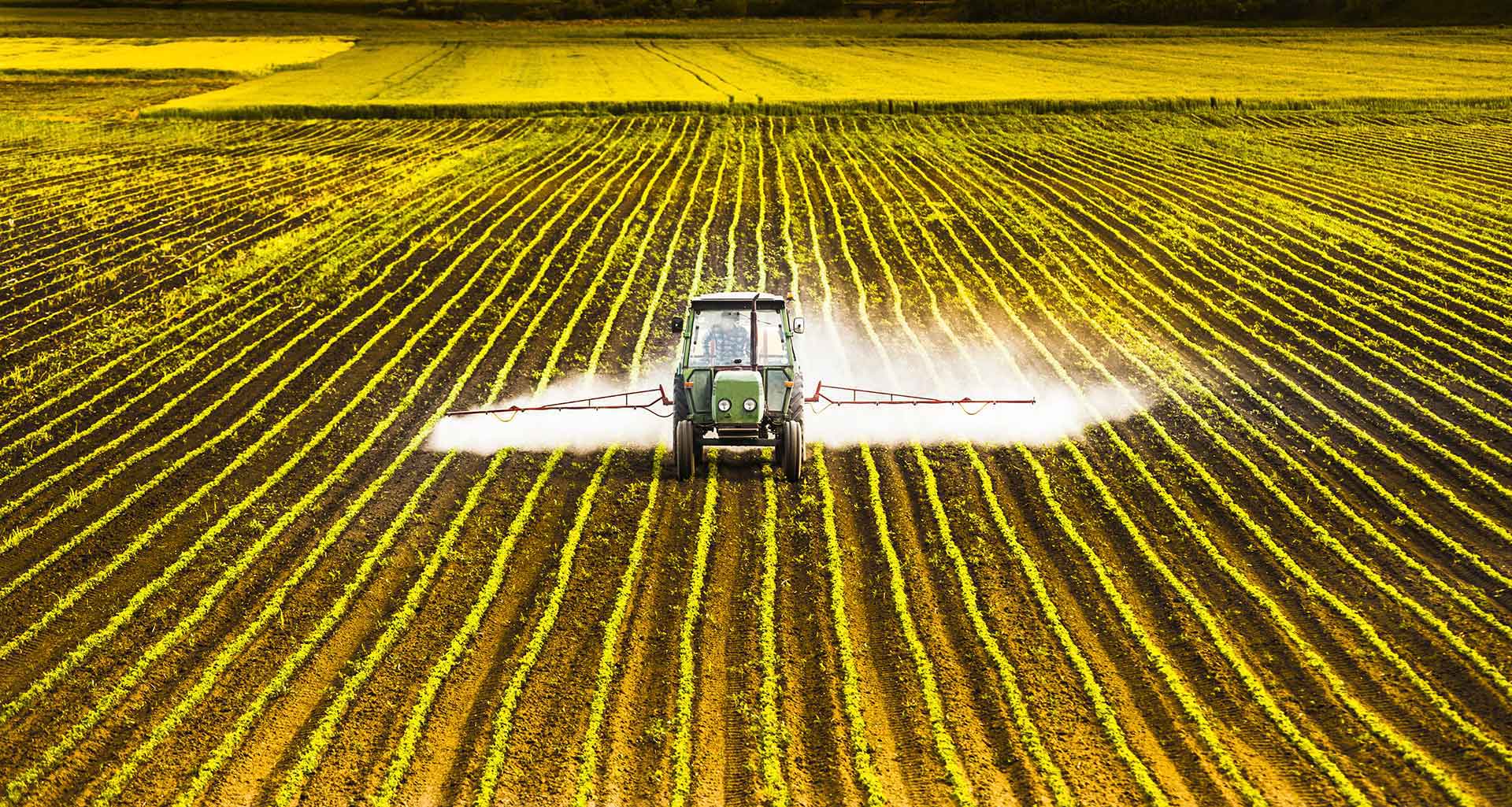
Glyphosate
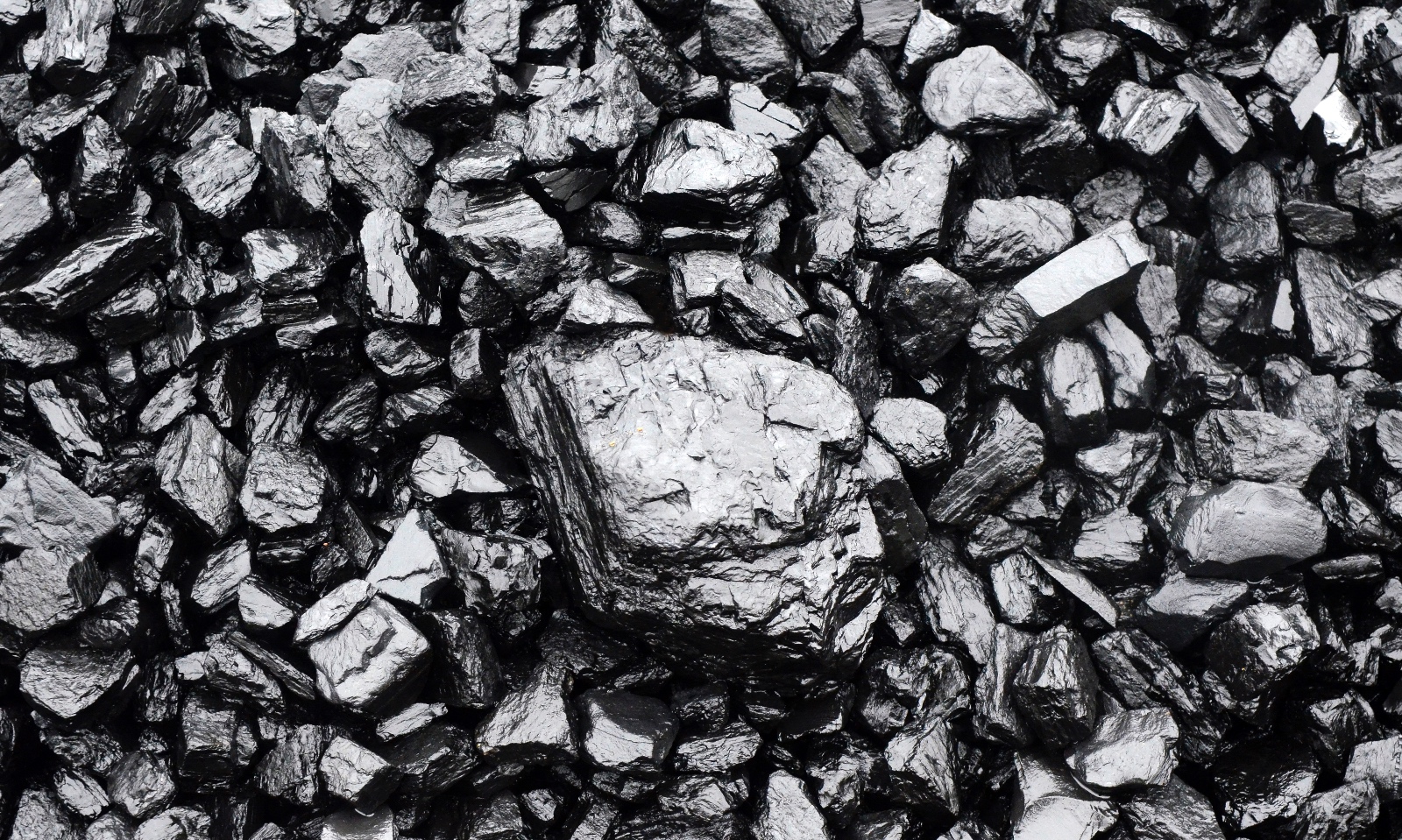
Graphite
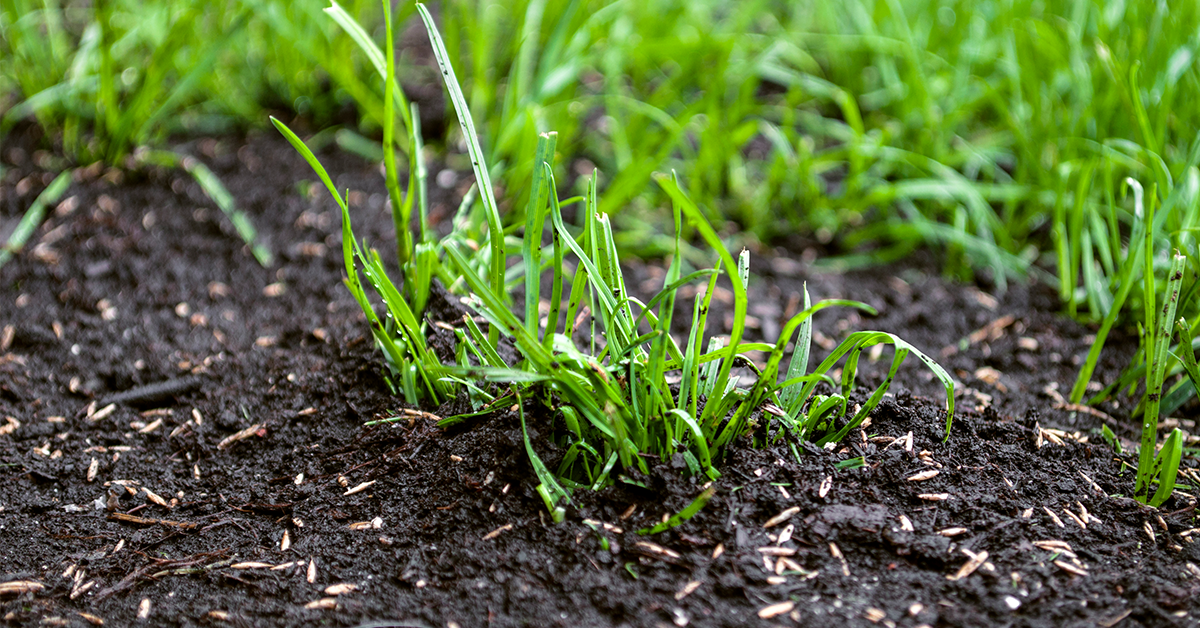
Grass seeds
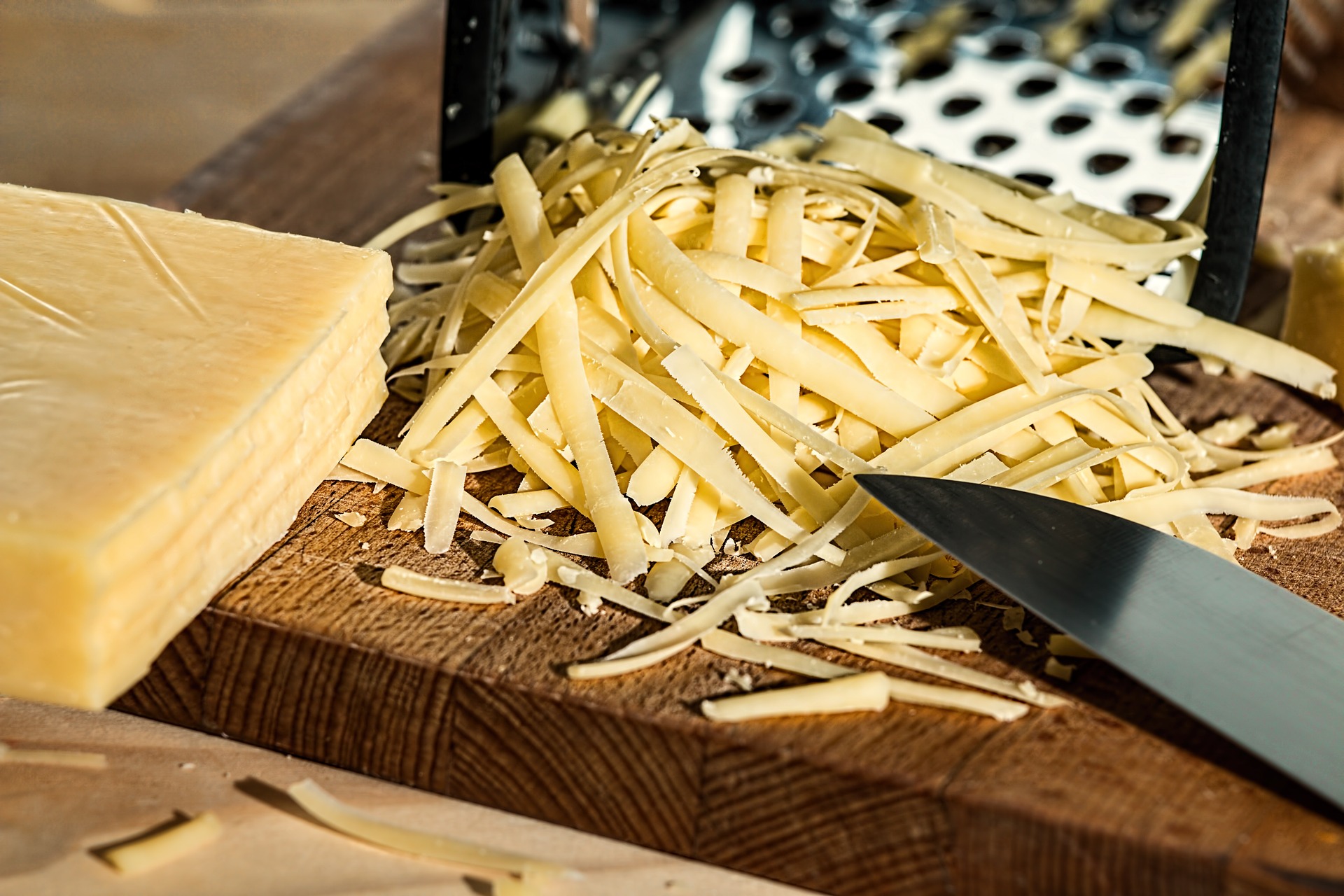
Grated cheese
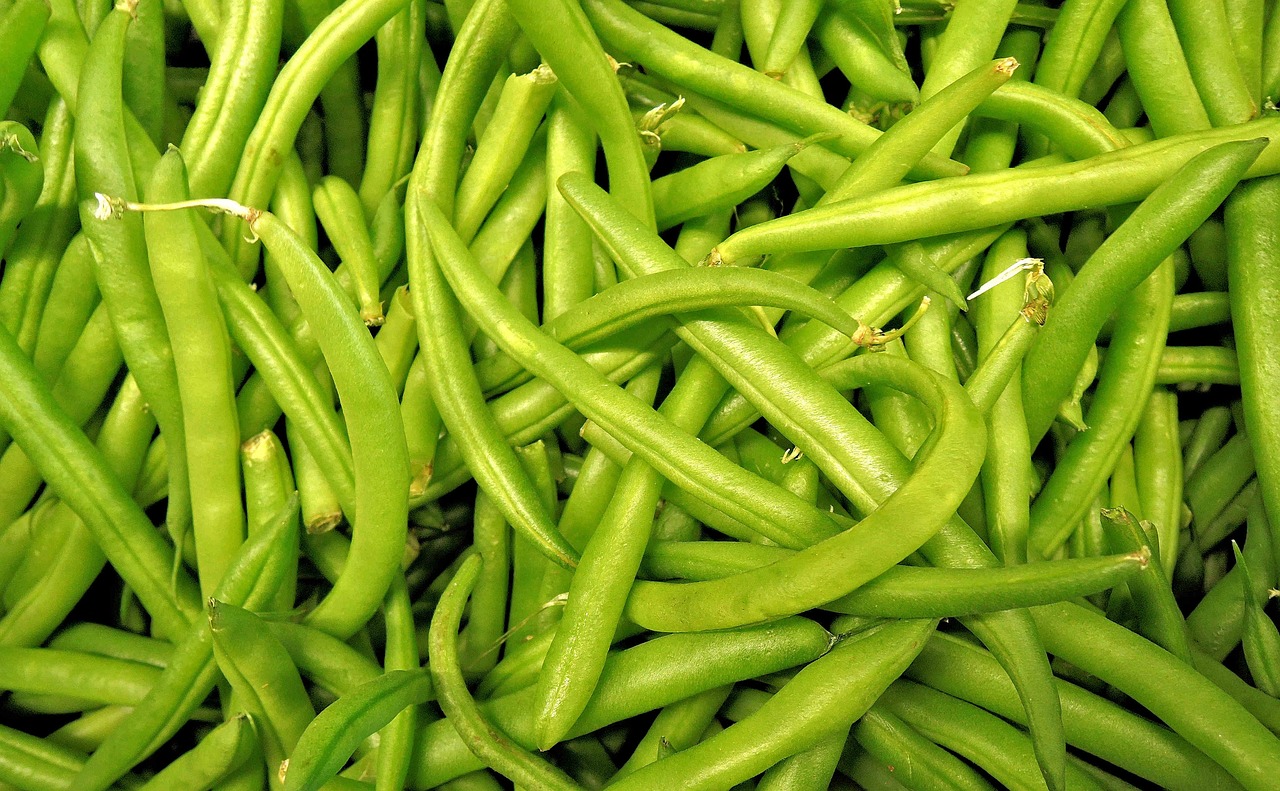
Green beans
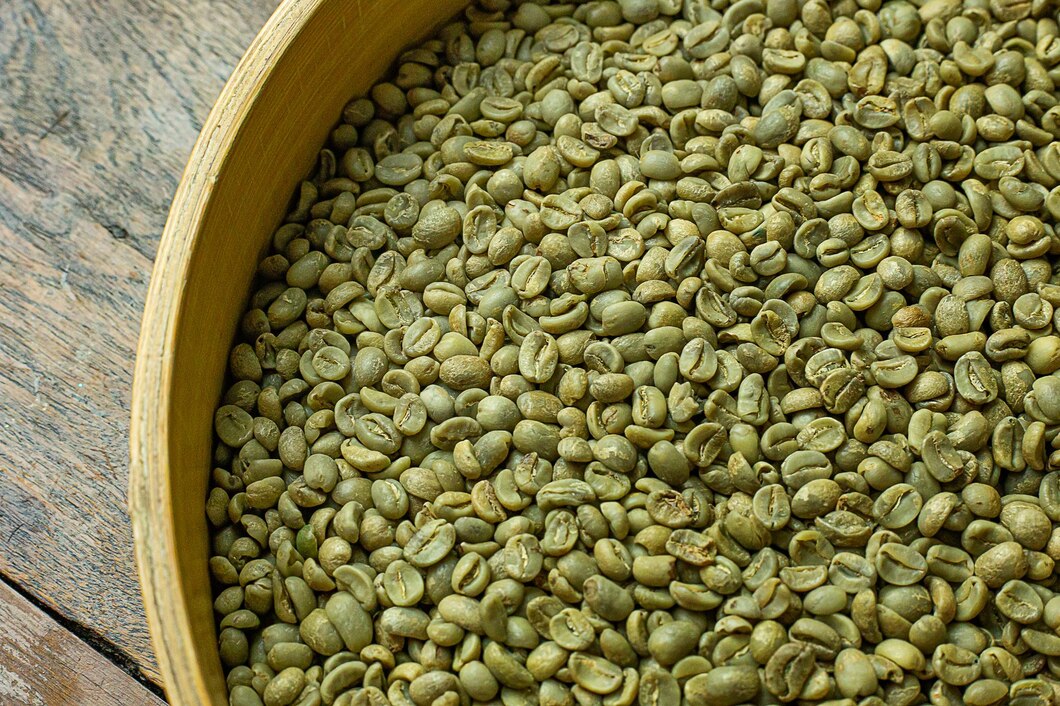
Green coffee beans
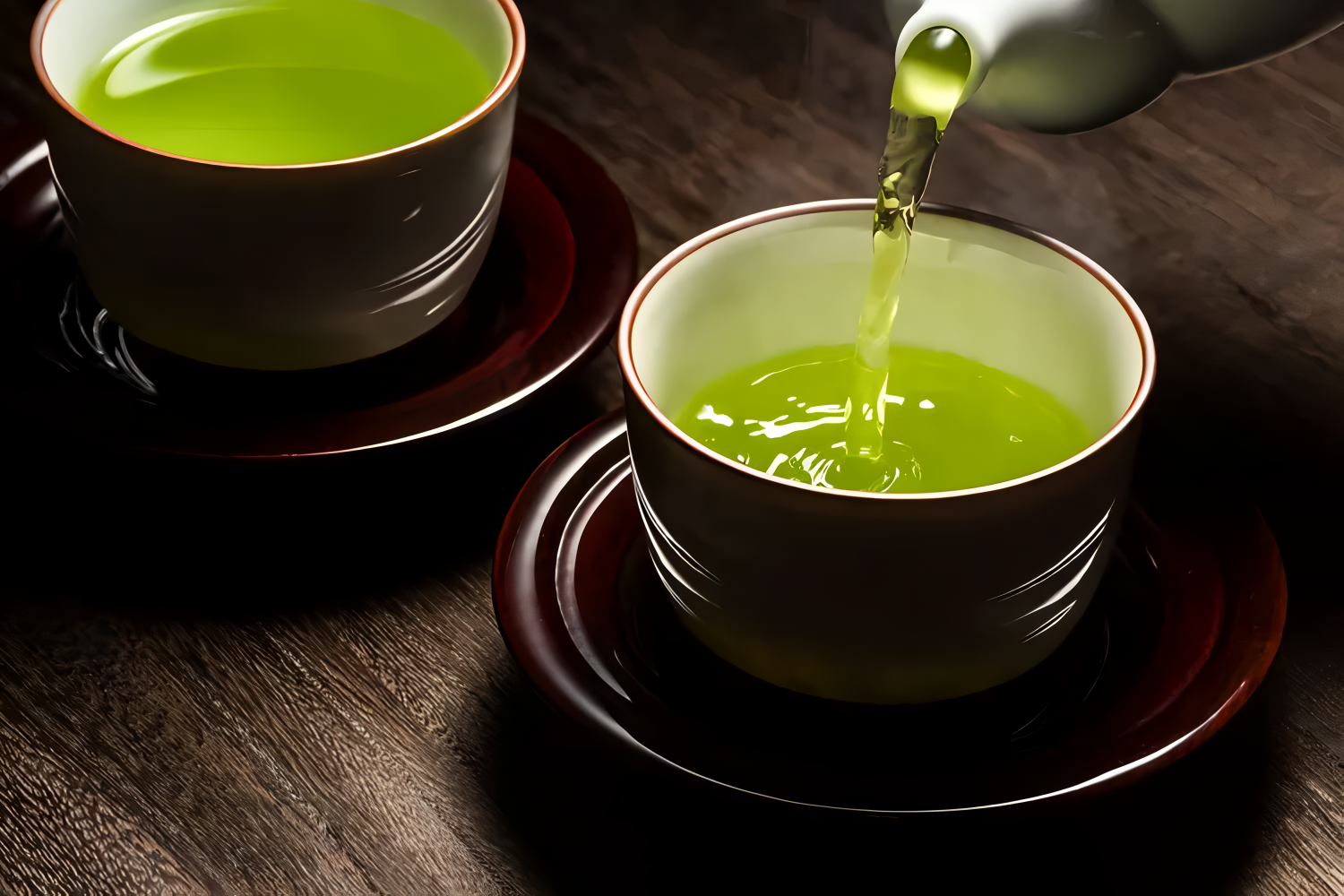
Green tea
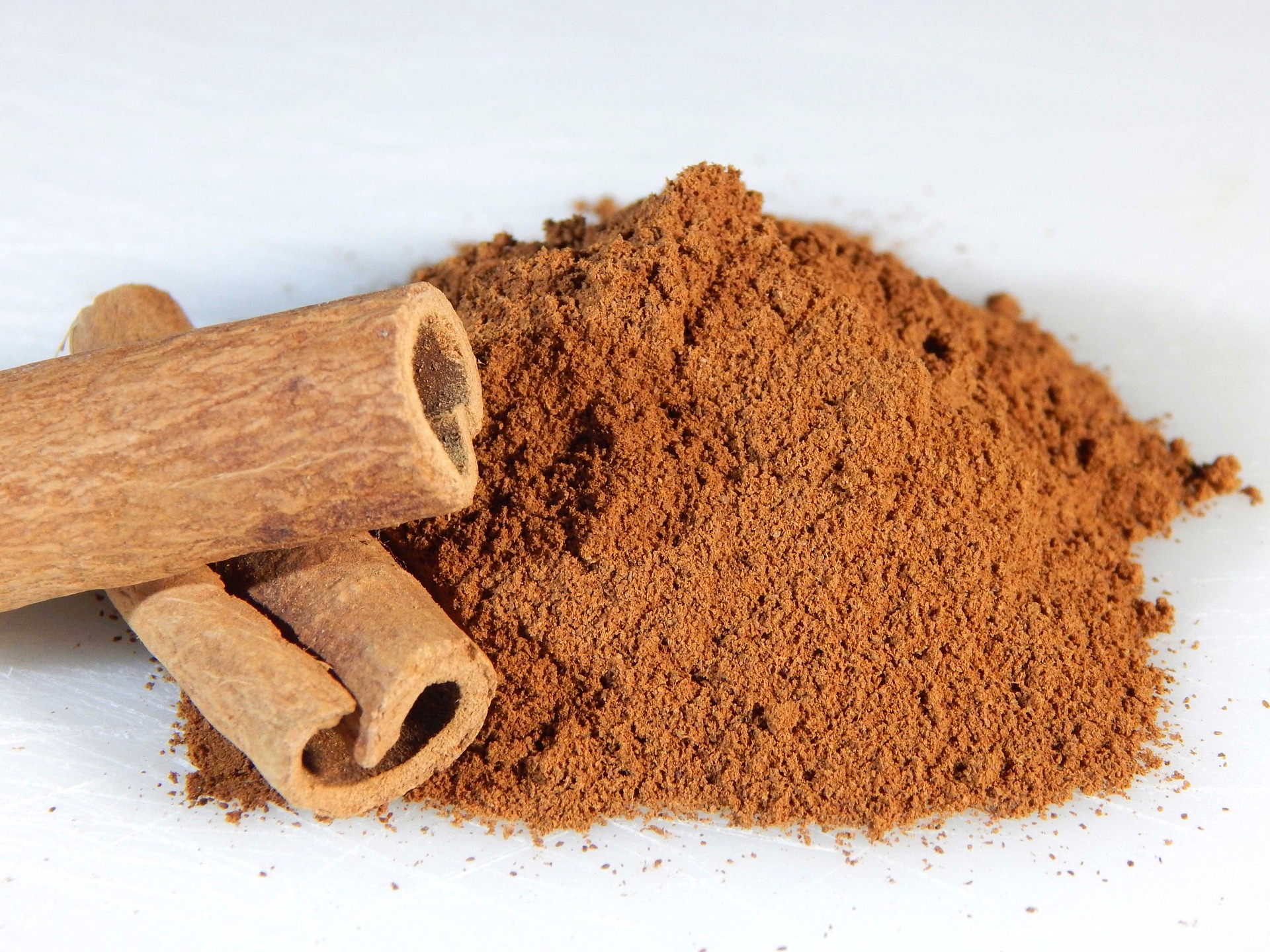
Ground cinnamon
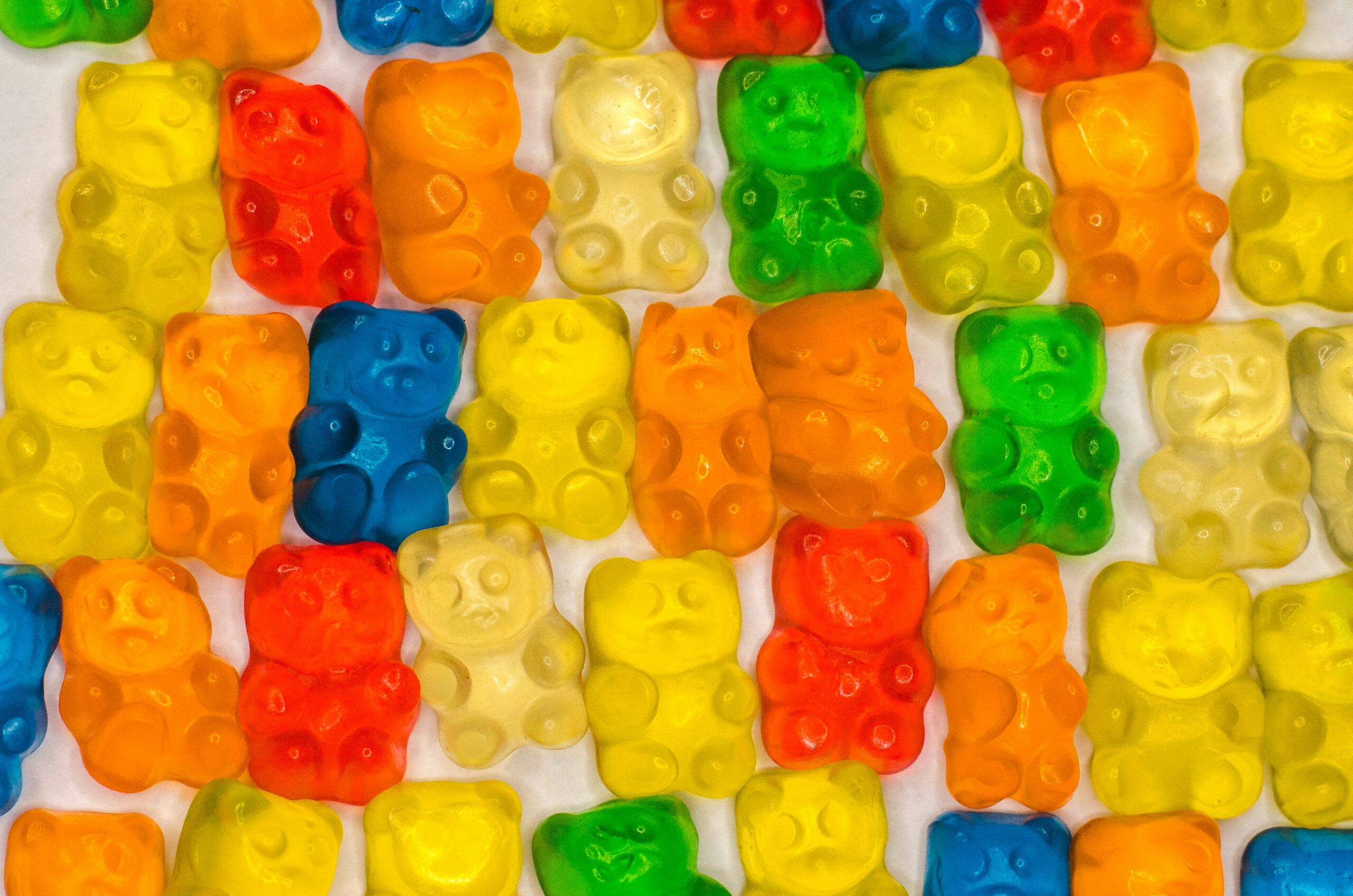
Gummy Bears
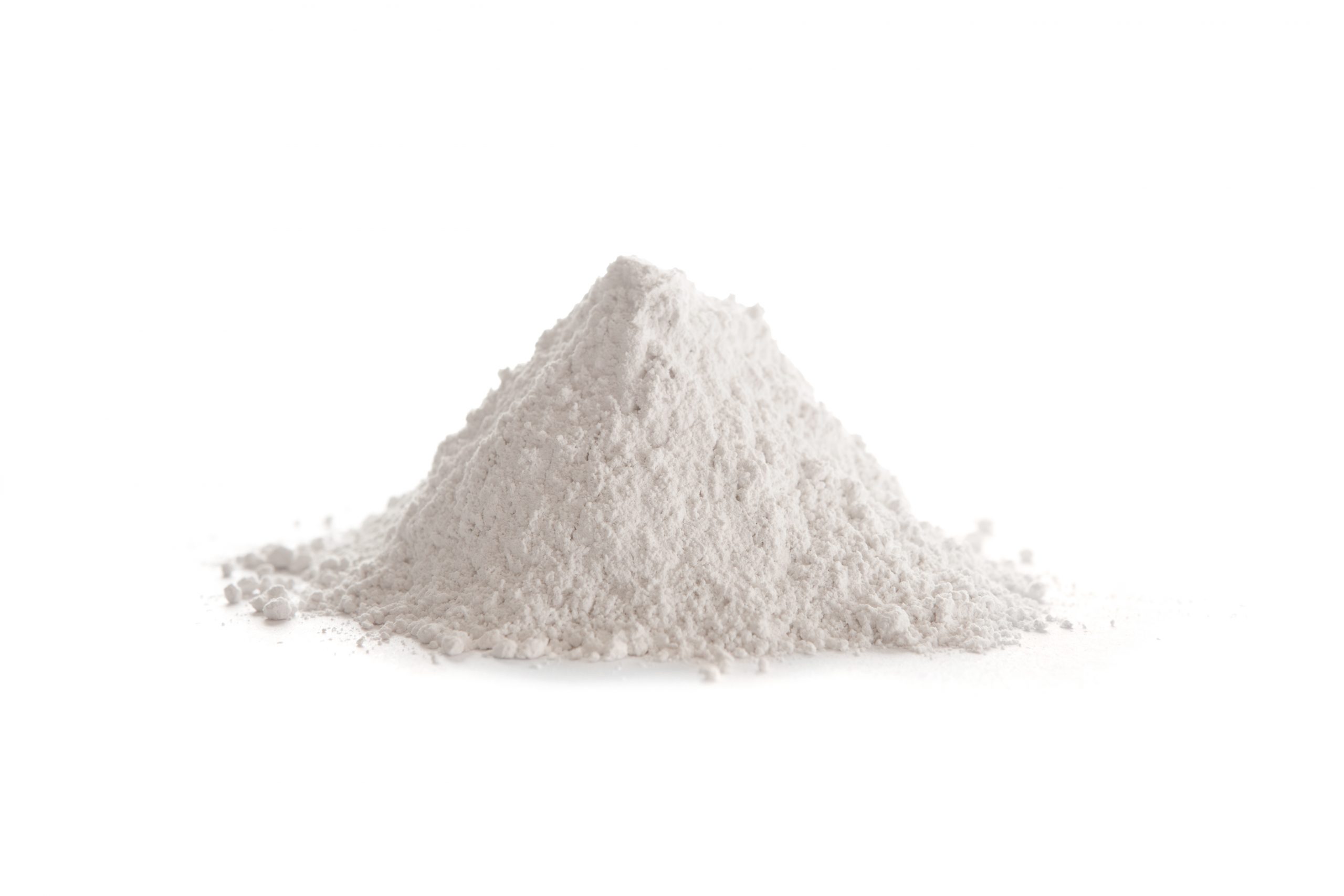
Gypsum
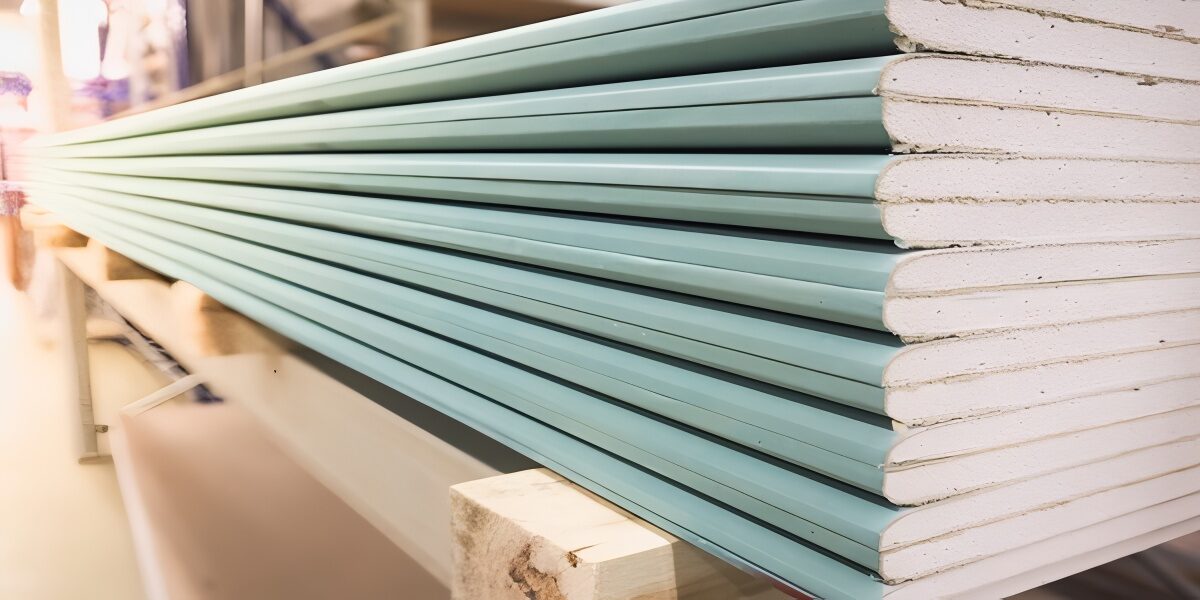
Gypsum board
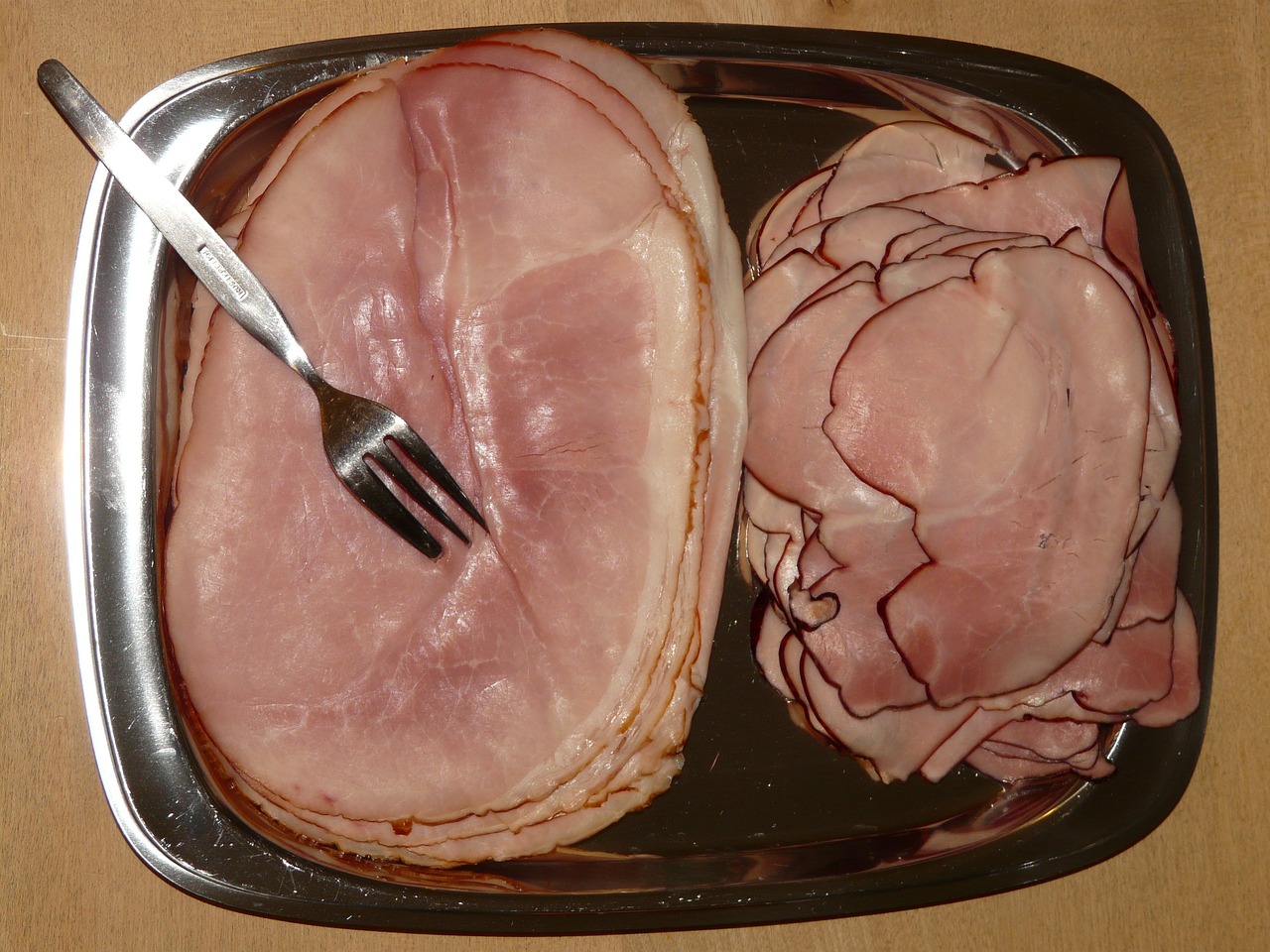
Ham
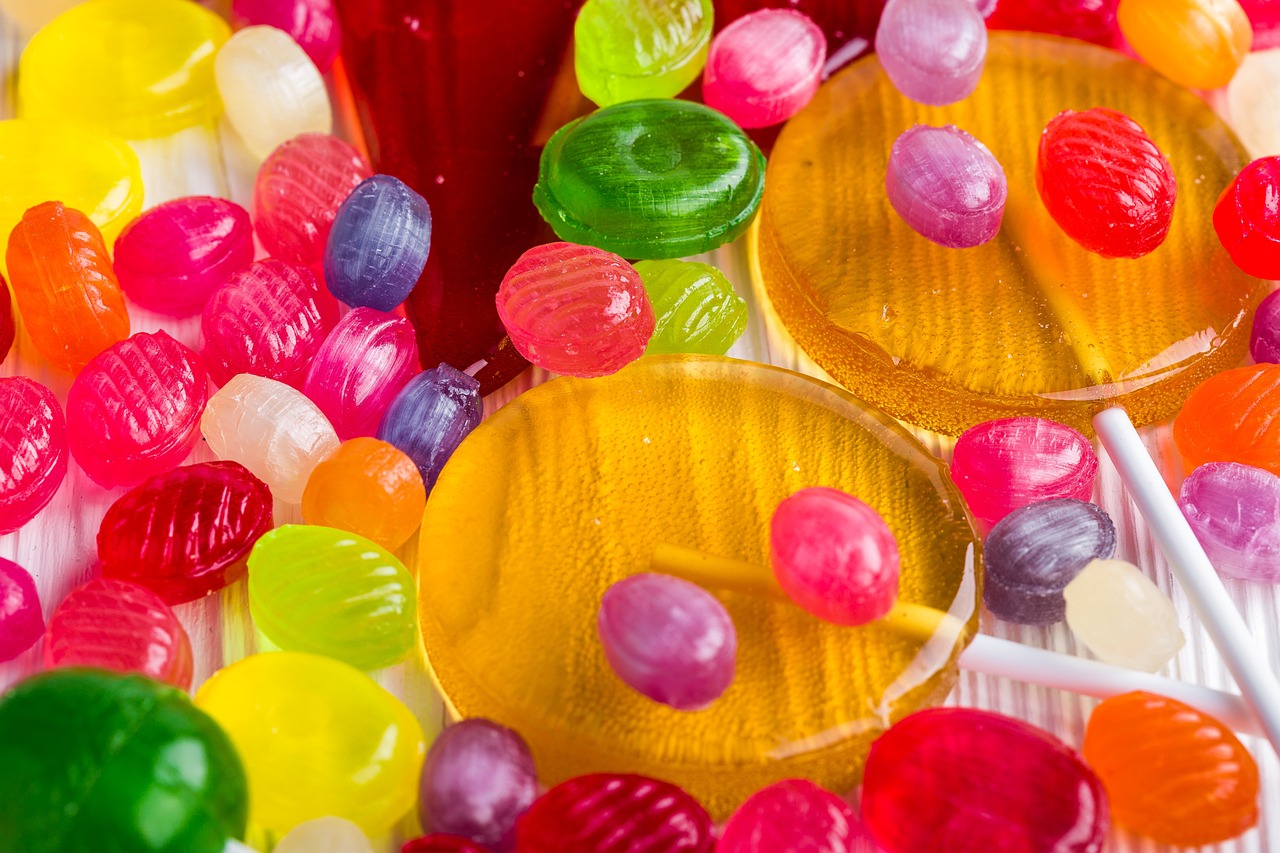
Hard Candy
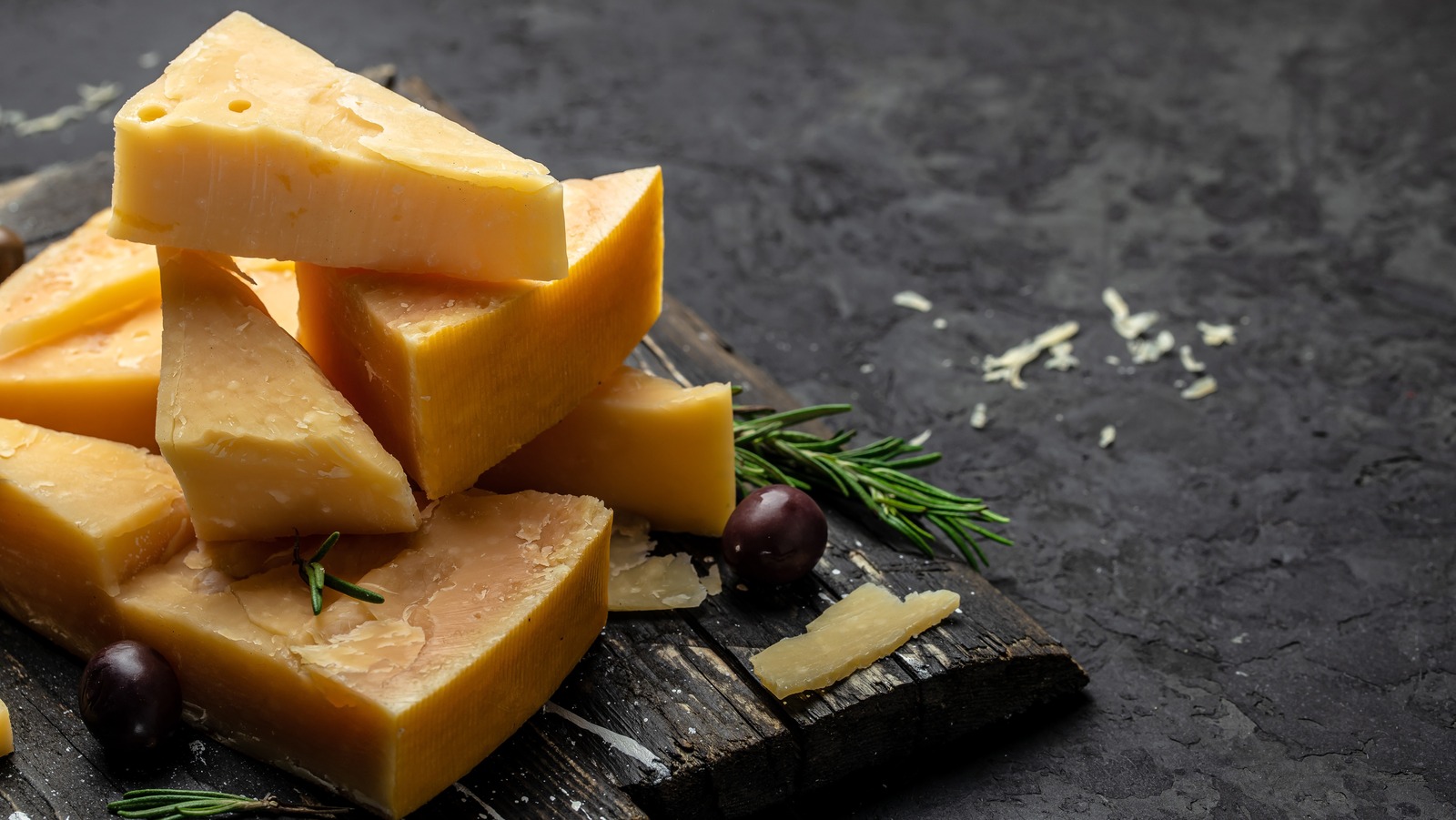
Hard cheese
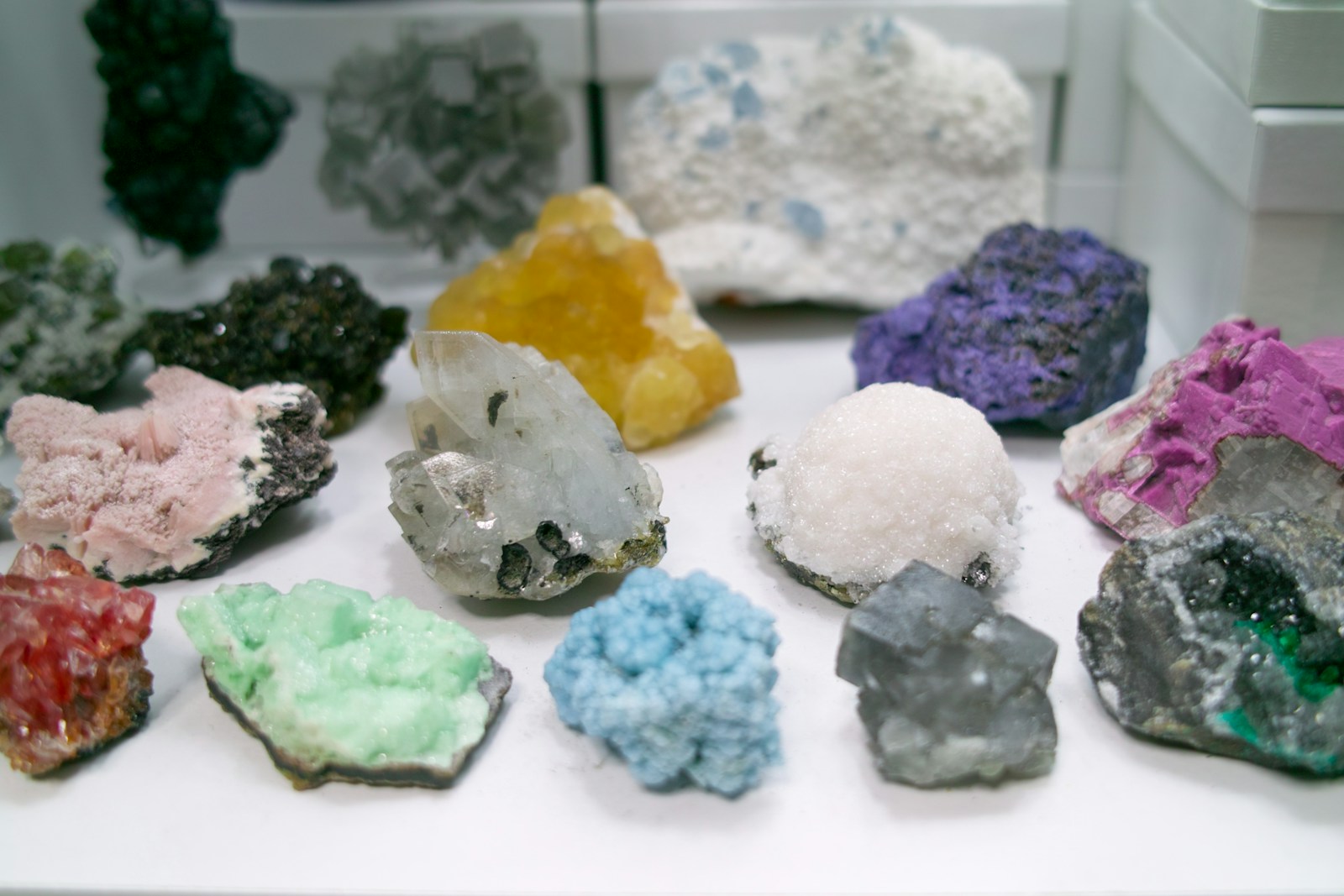
Hard minerals

Hazelnuts
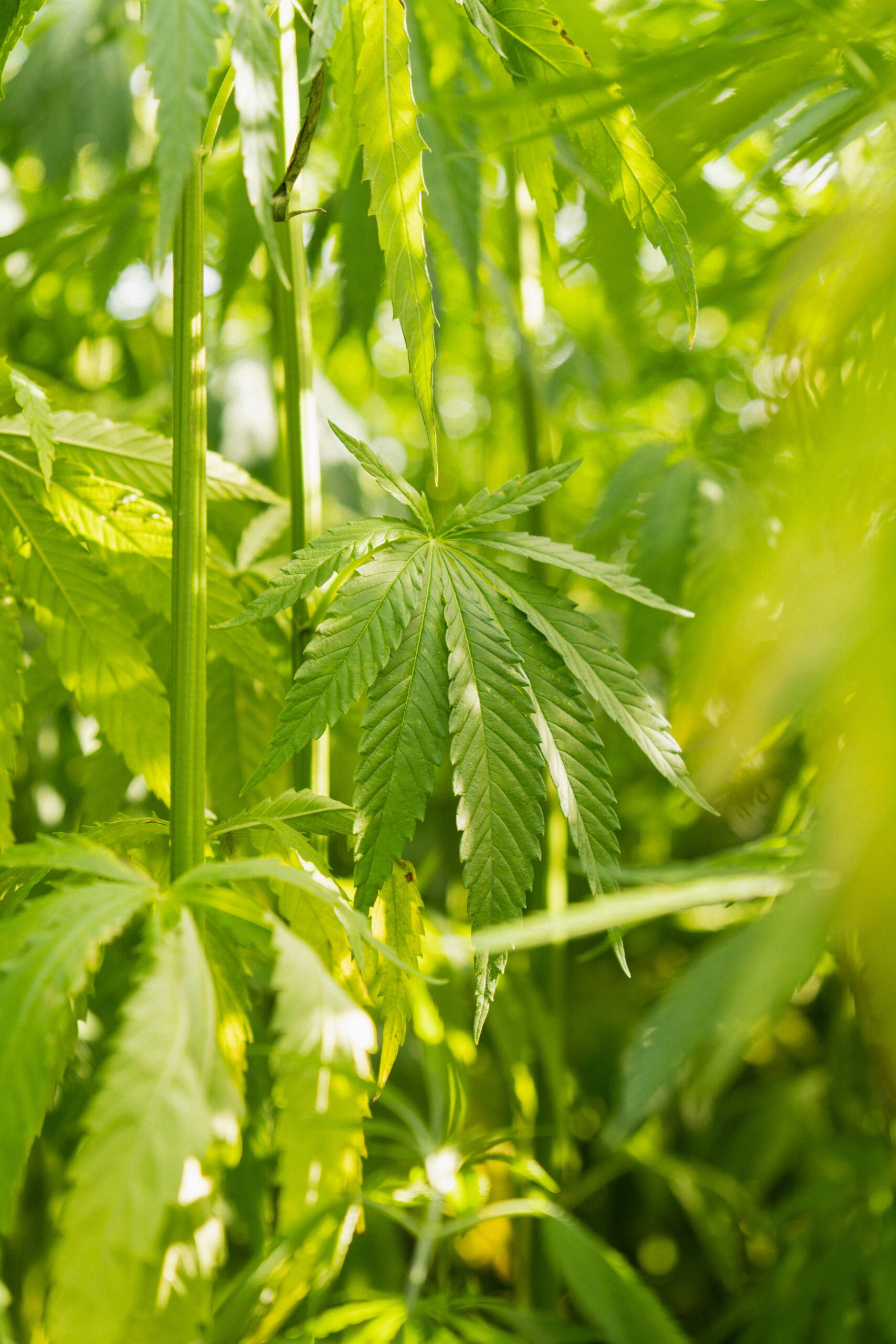
Hemp
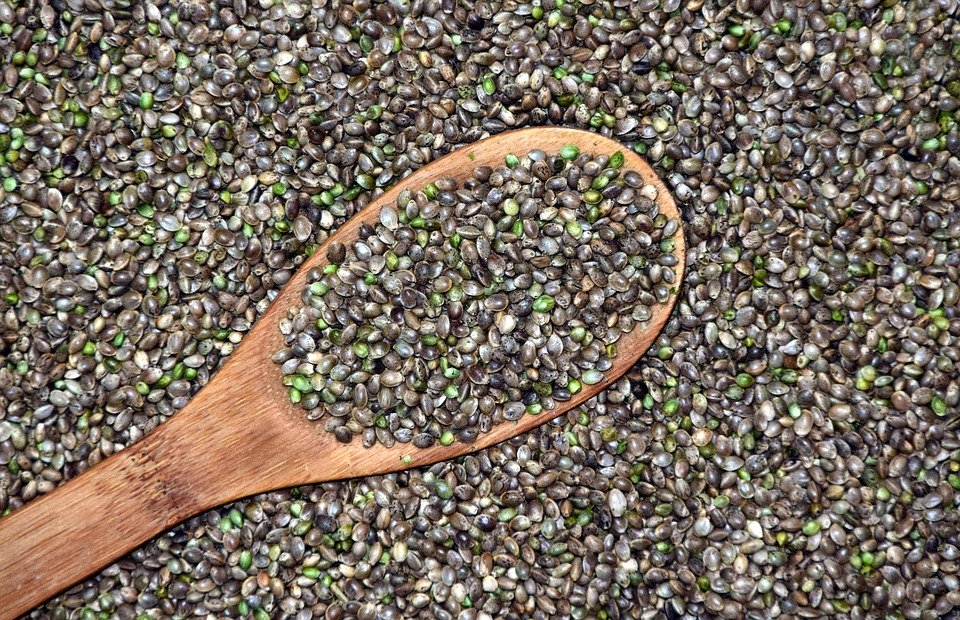
Hemp seeds
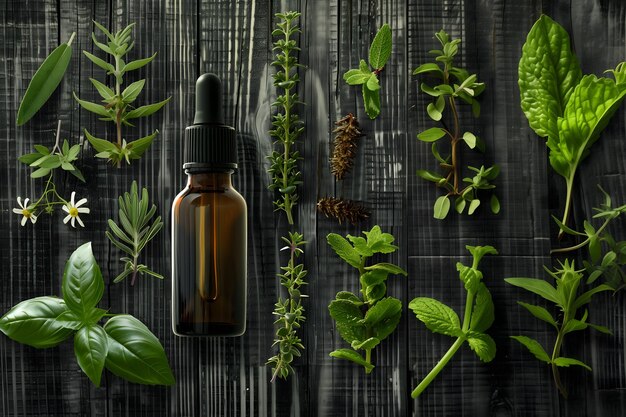
Herbal Extracts
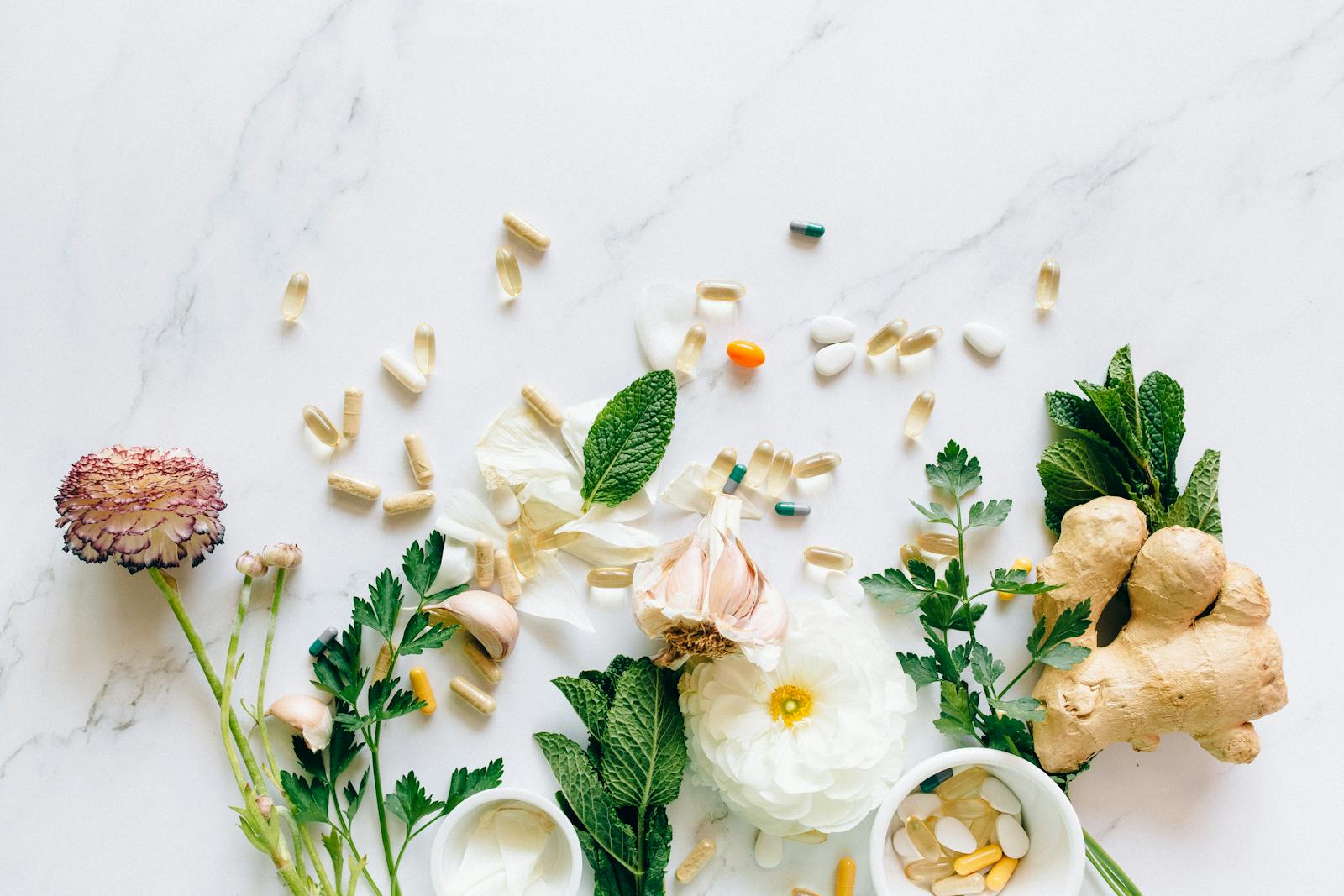
Herbal medicines
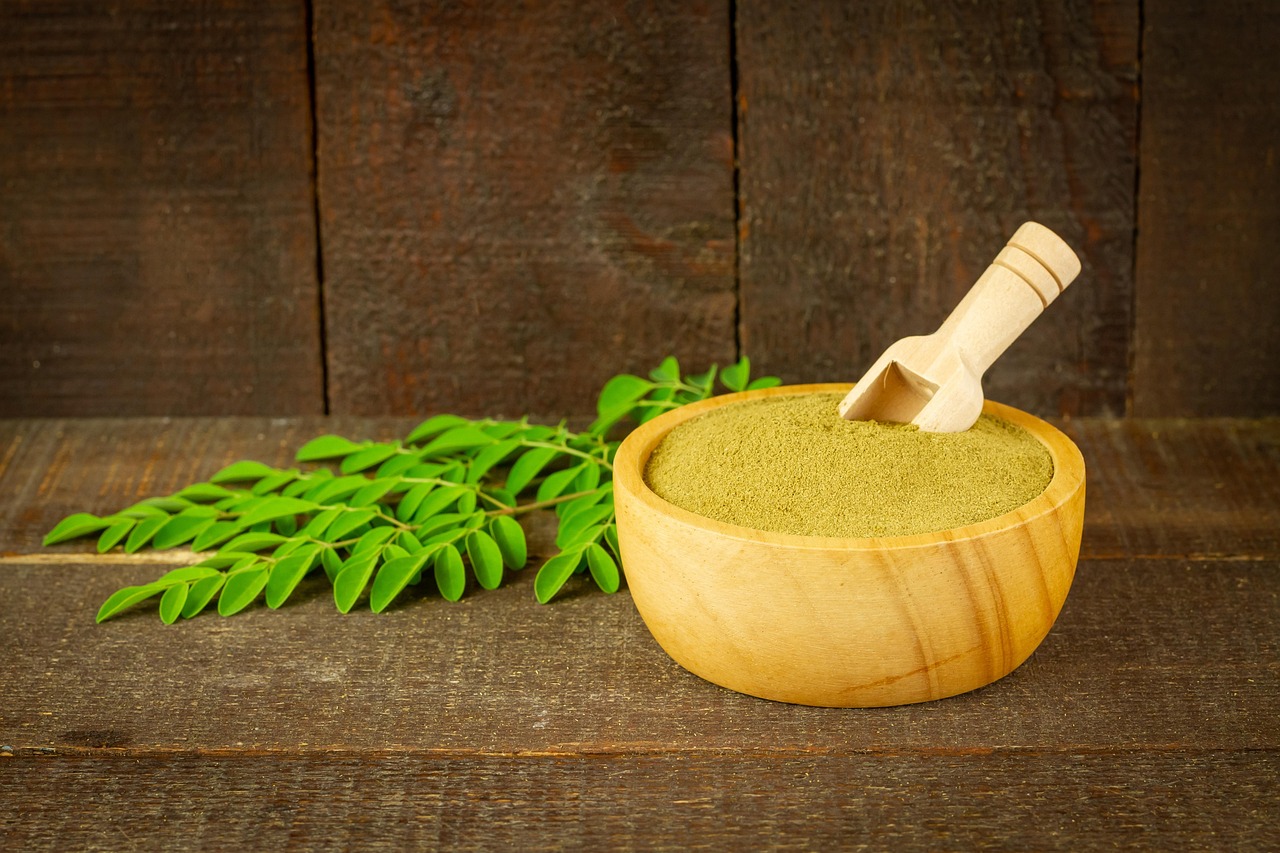
Herbal supplements
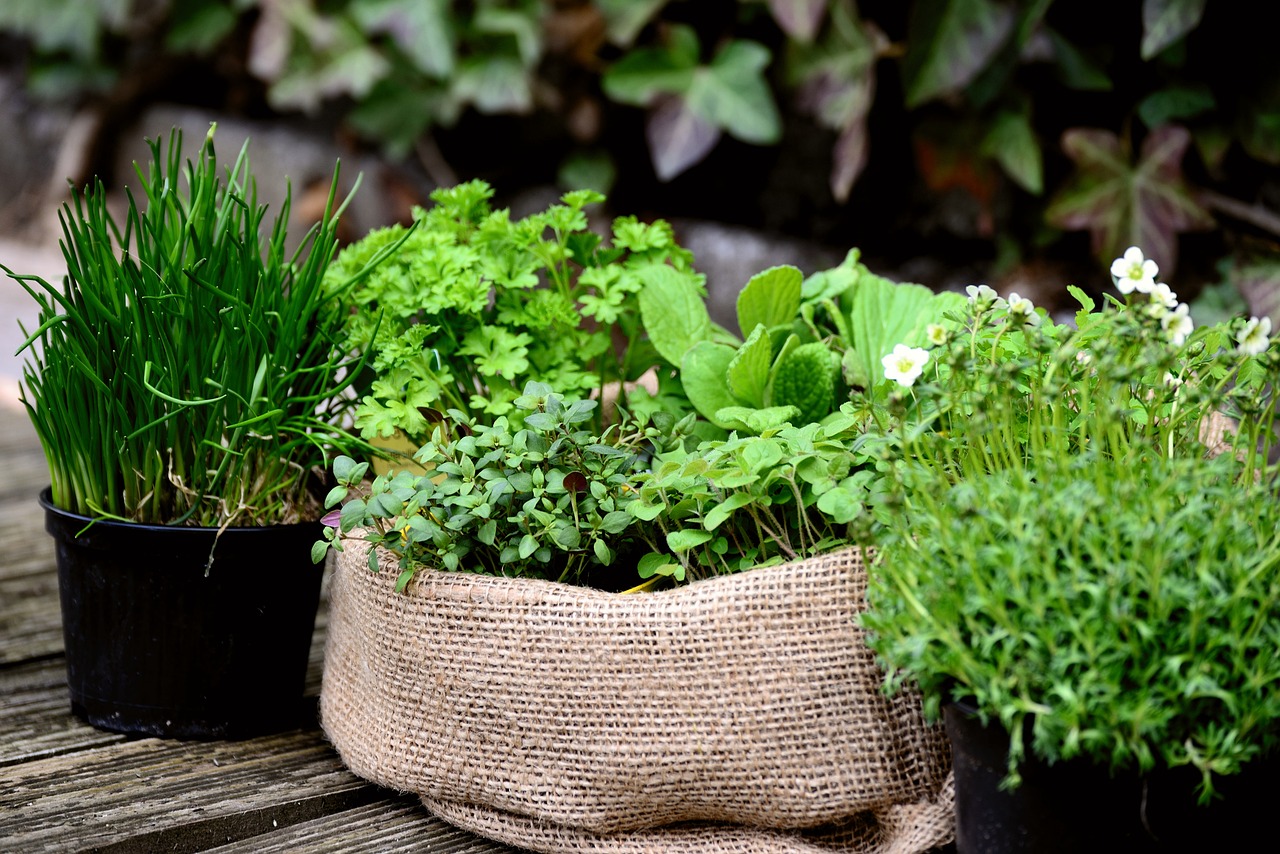
Herbs
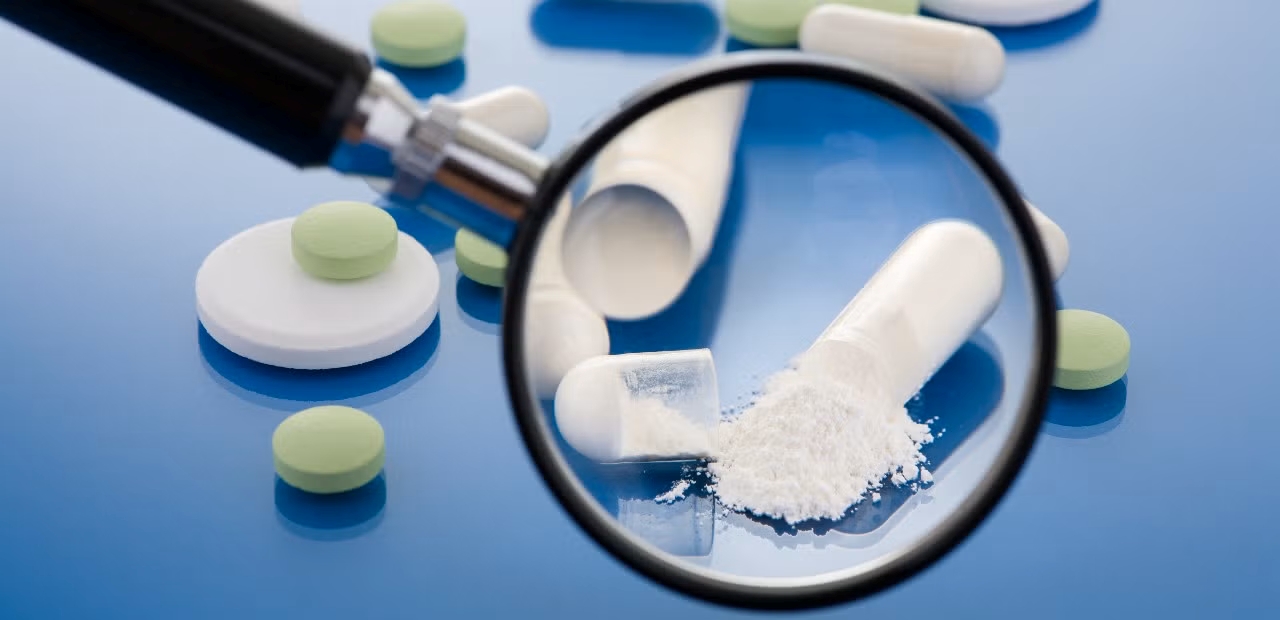
High-potency active pharmaceutical ingredients (hpapis)
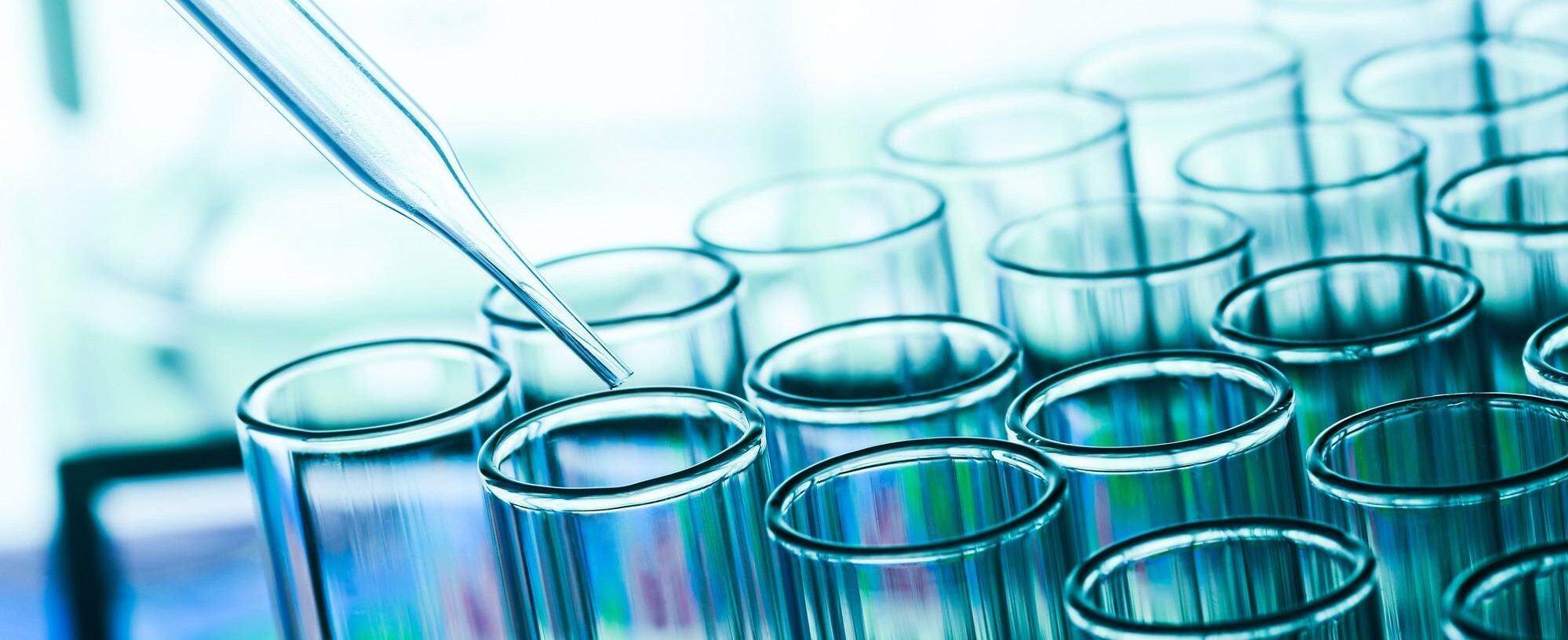
Highly Active Pharmaceutical Ingredients
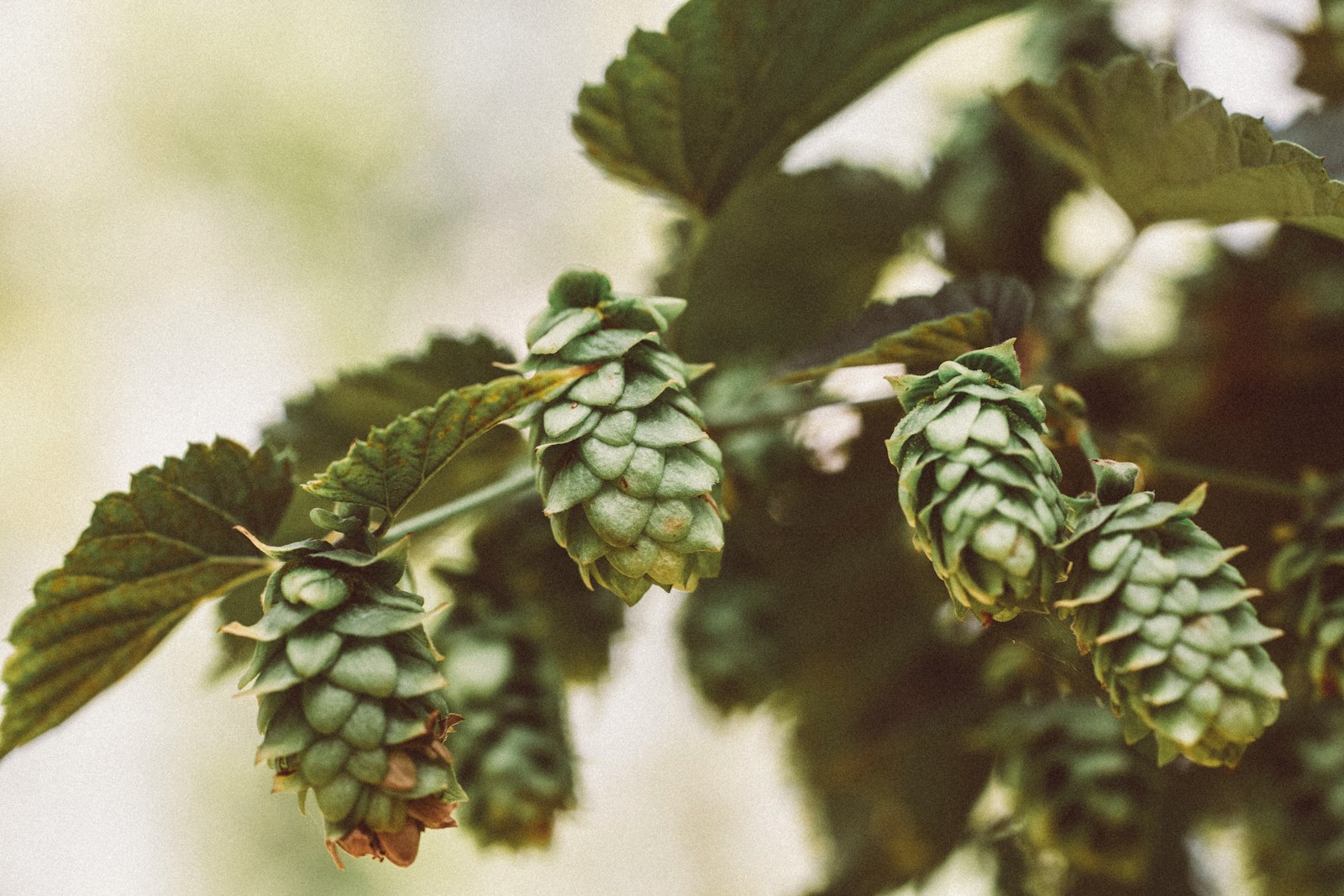
Hops
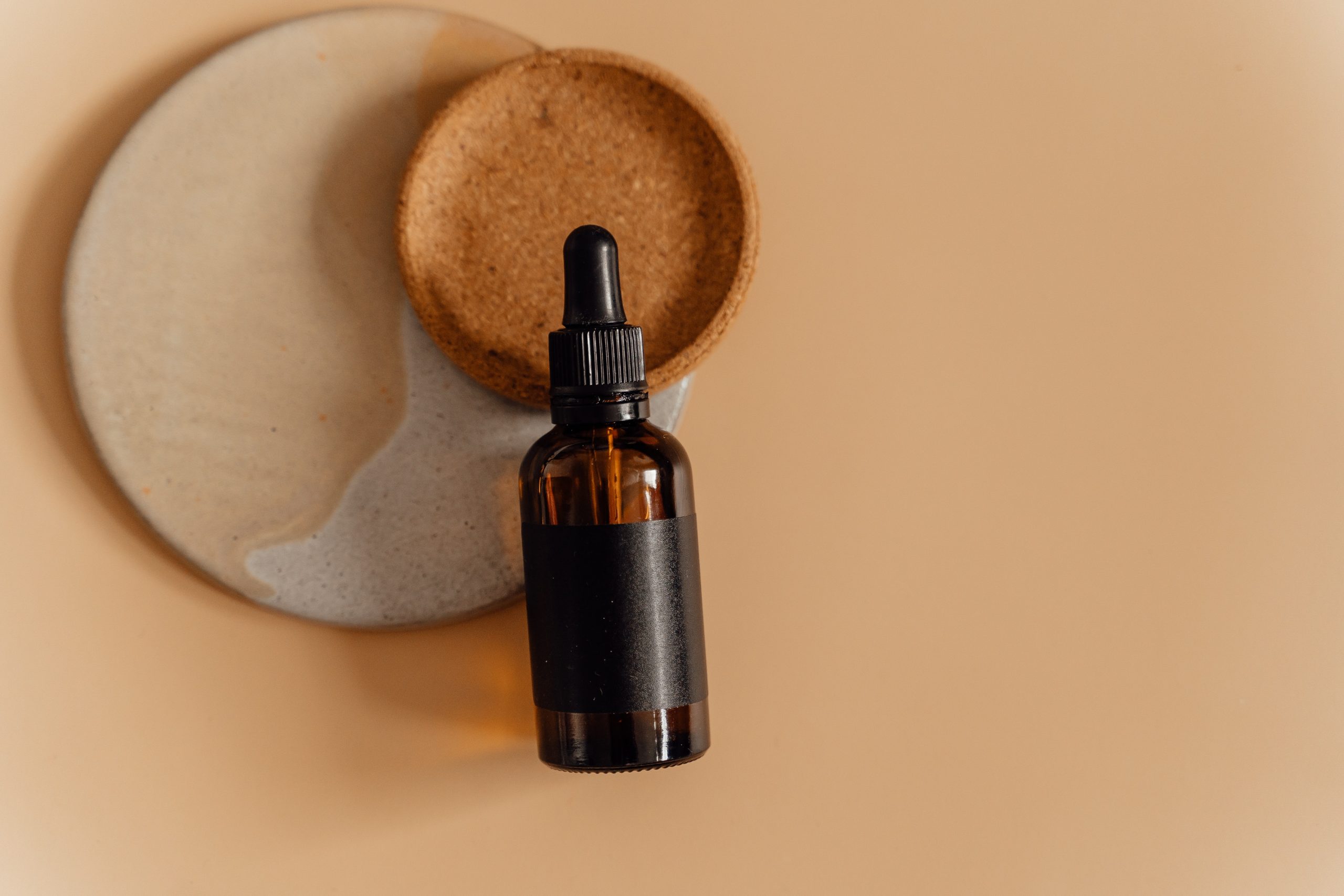
Hyaluronic acid

Hydrated lime
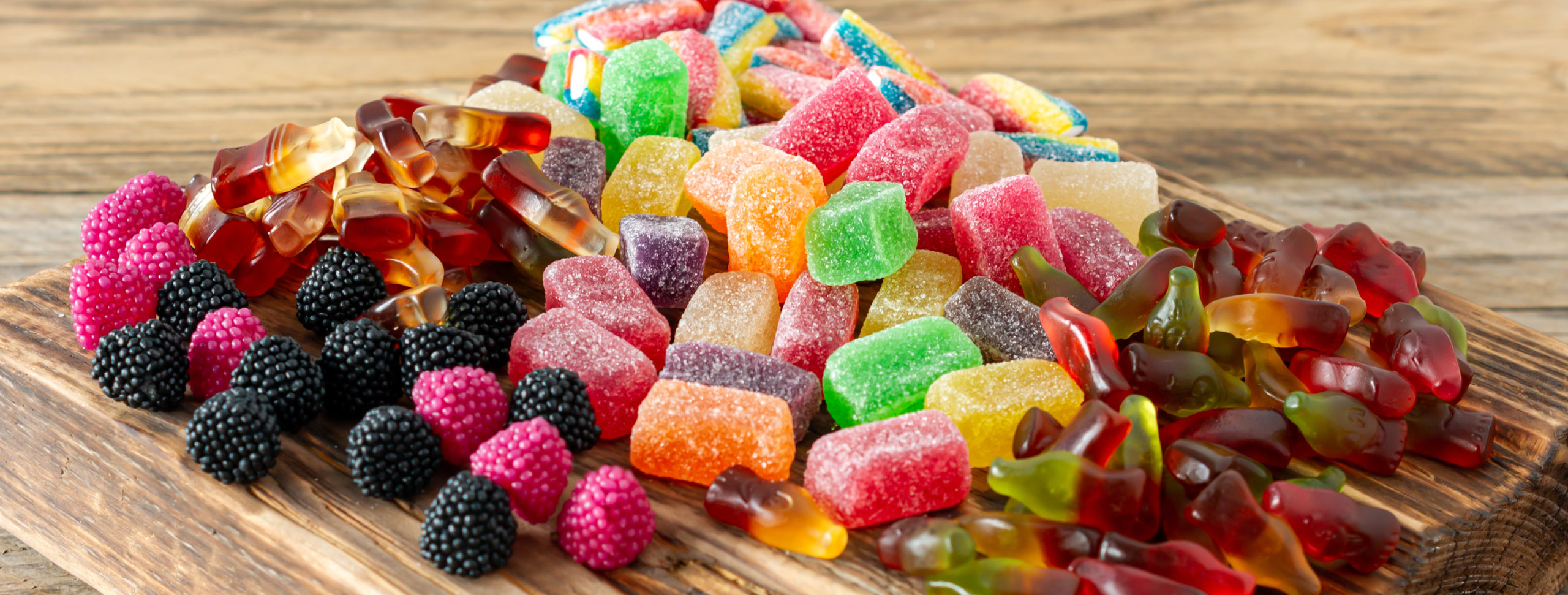
Hydrocolloids
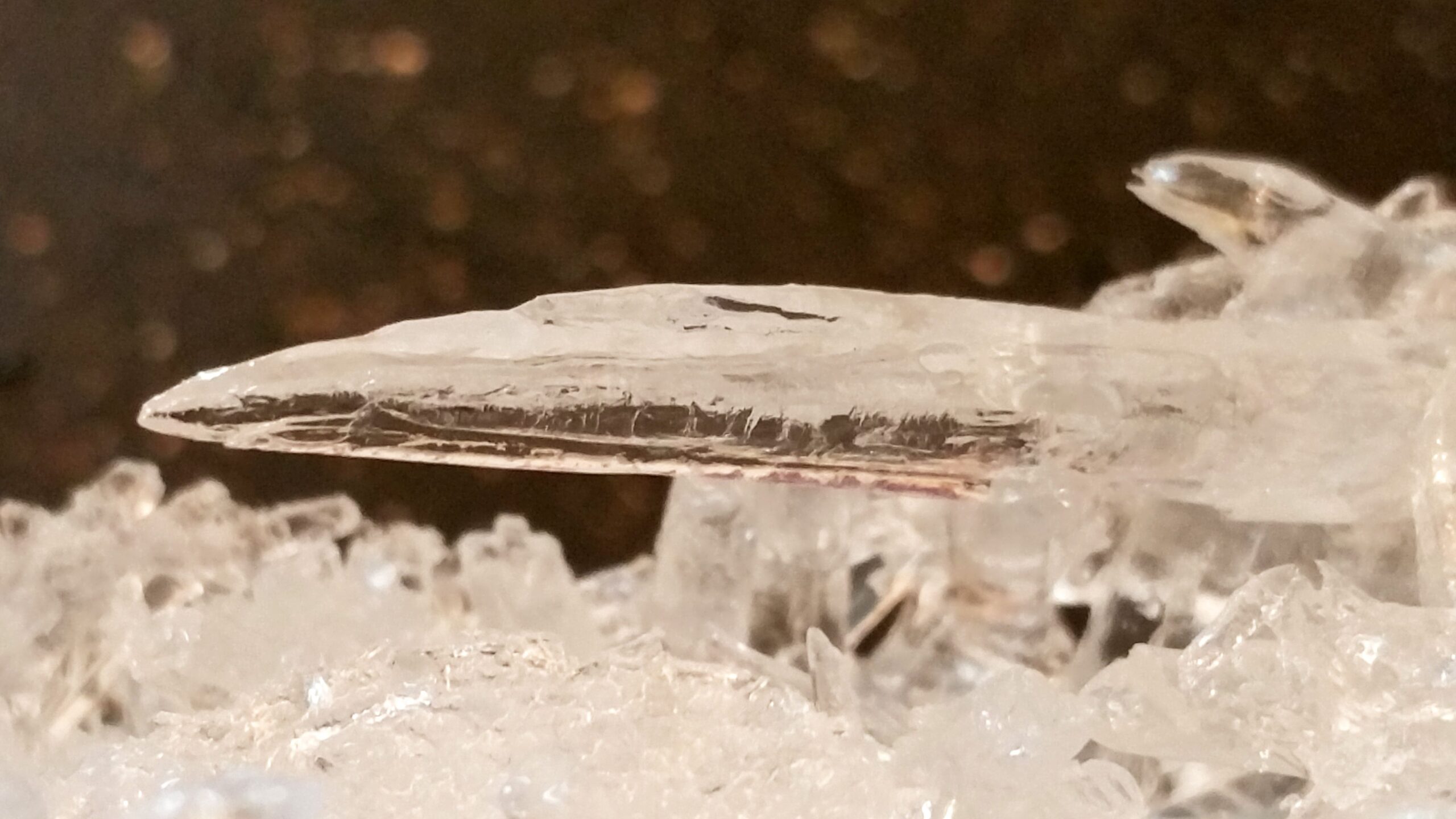
Hygroscopic products
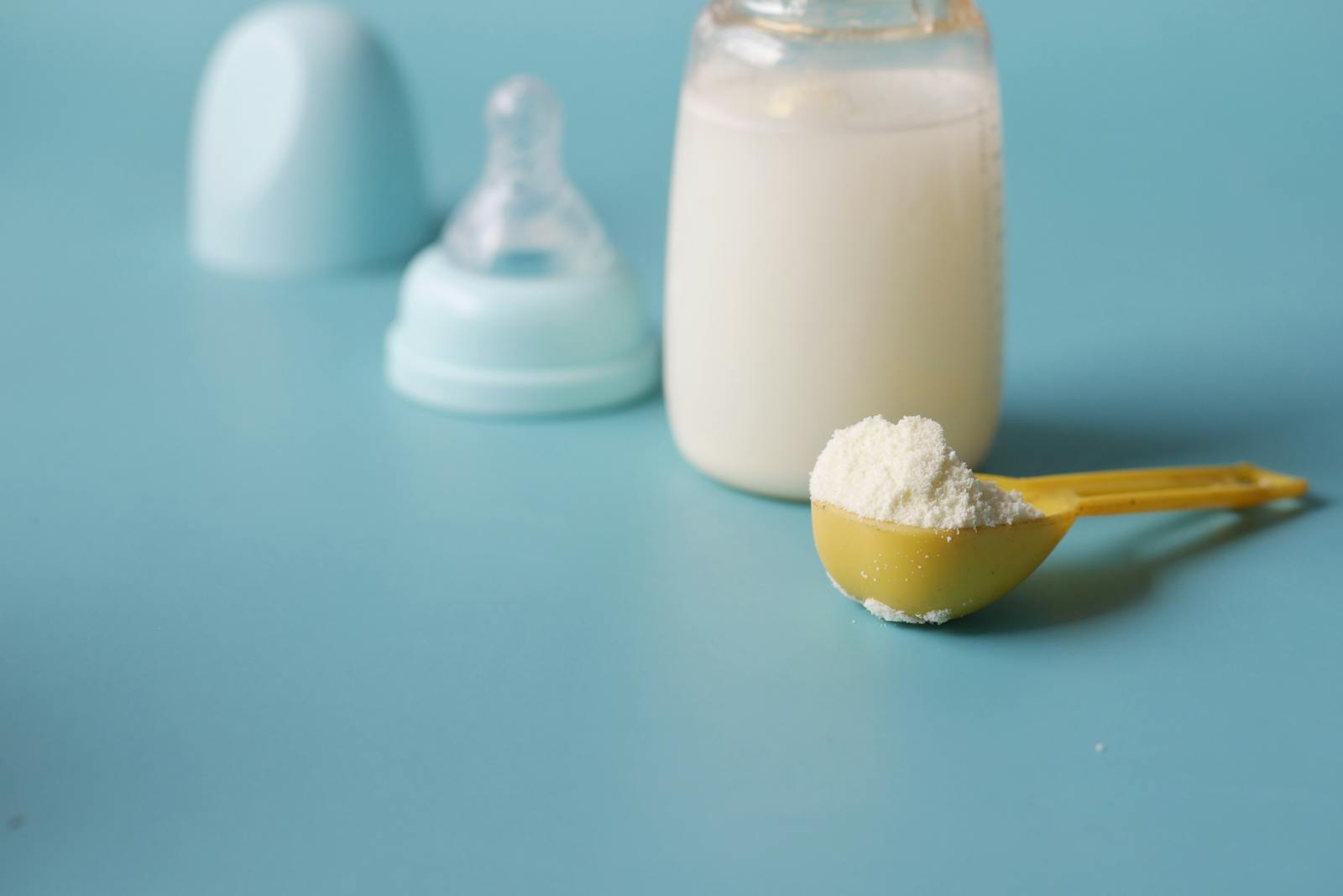
Infant formula
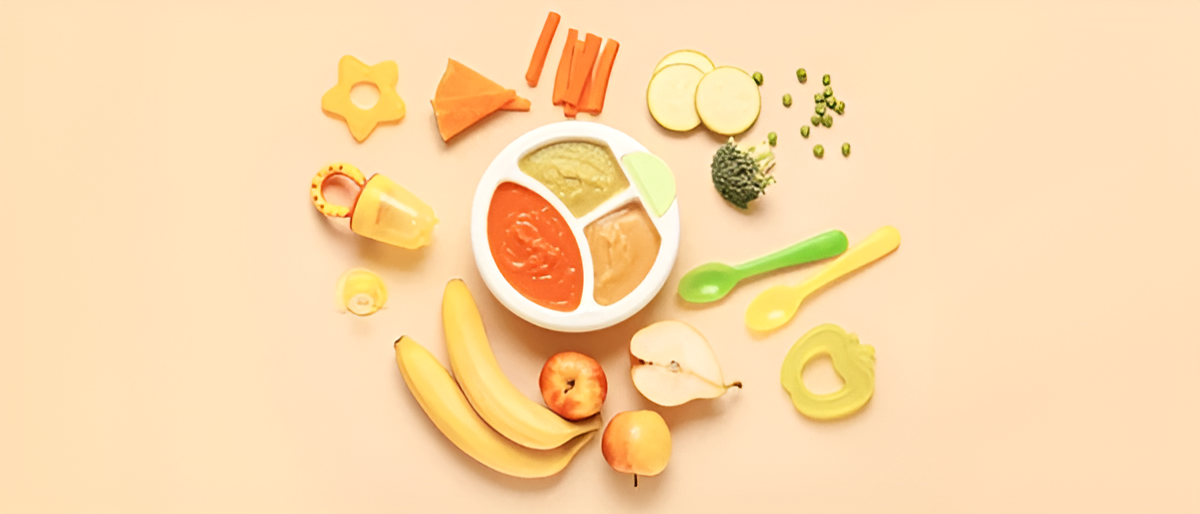
Infant nutrition
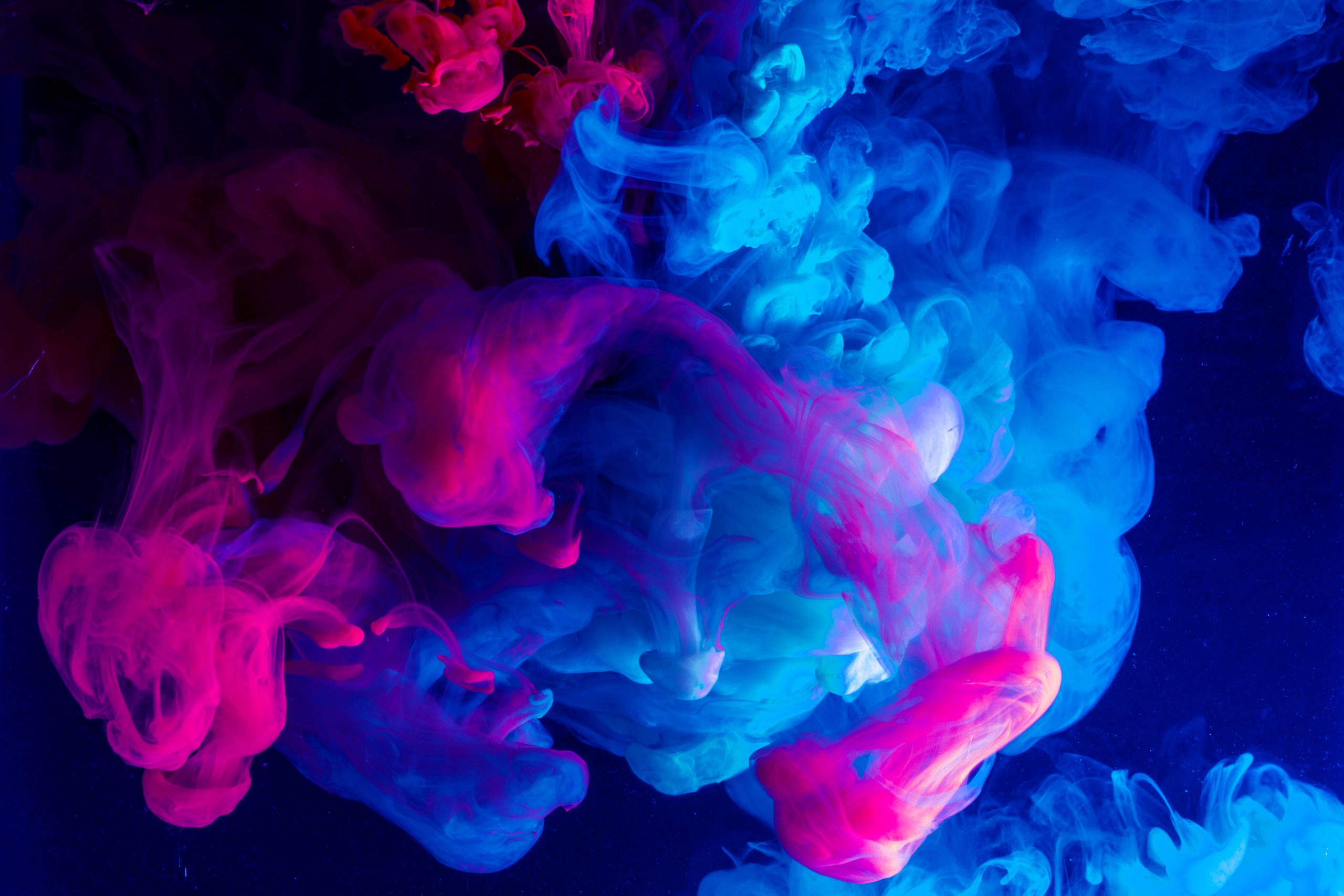
Ink
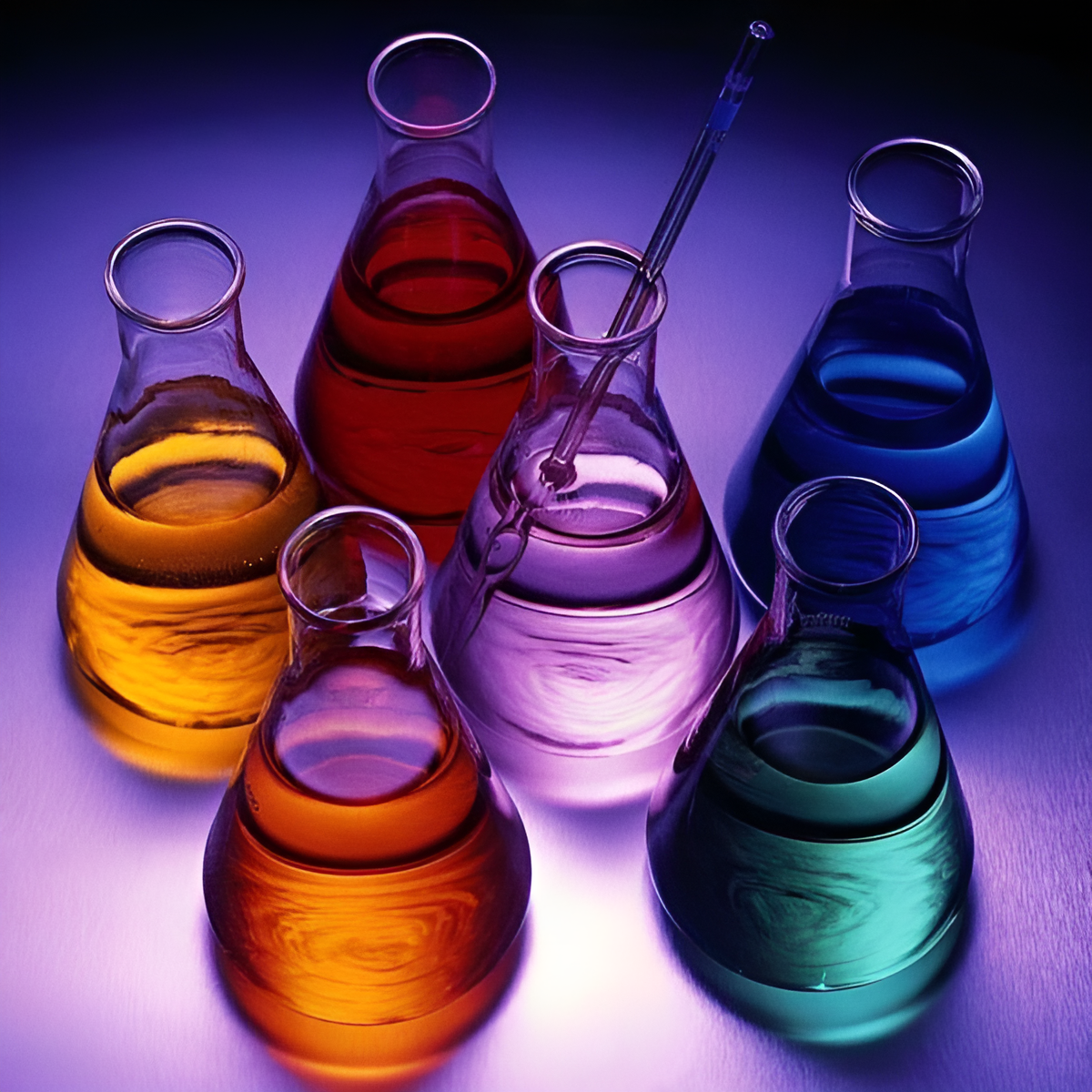
Inorganic chemicals
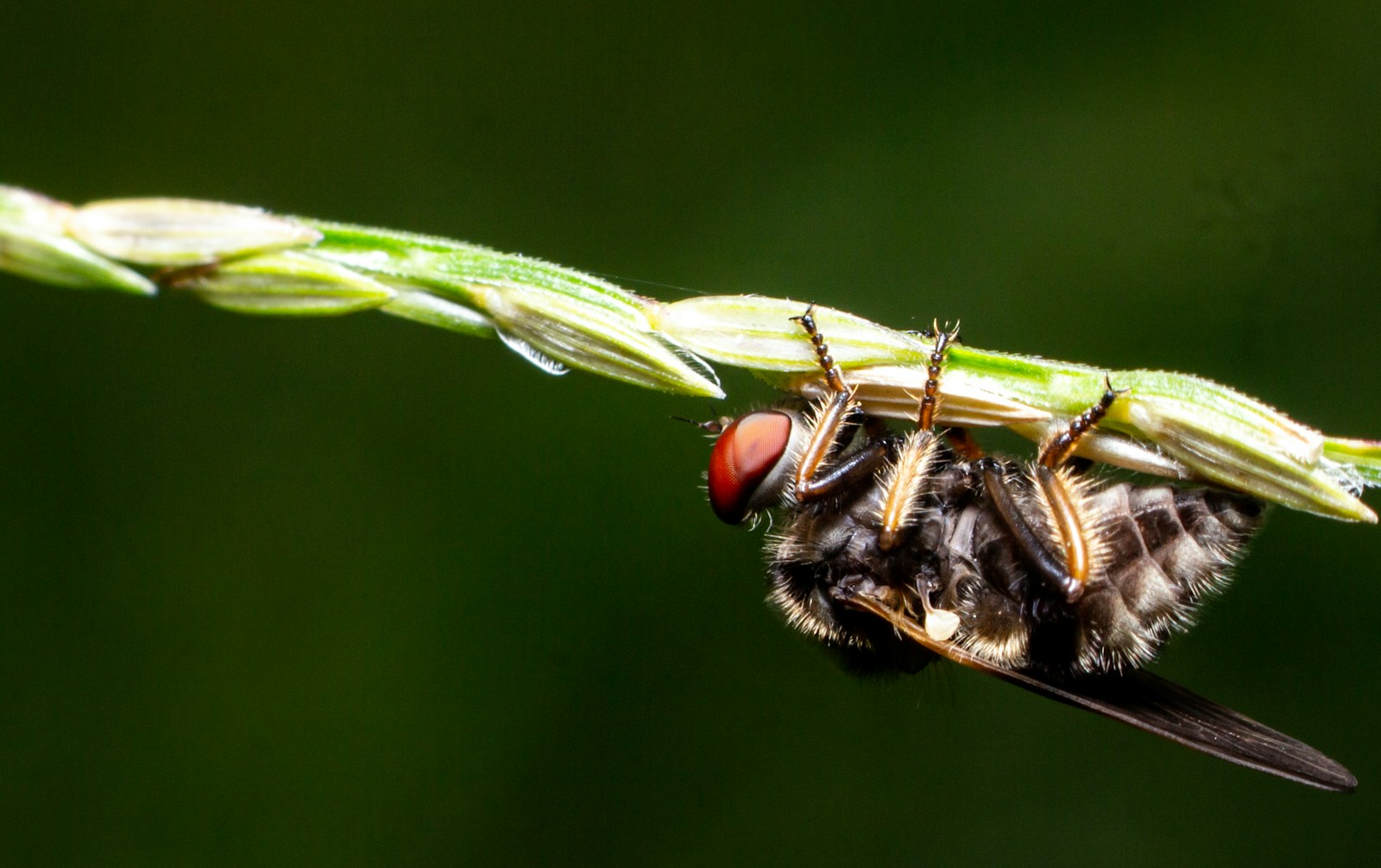
Insect technology
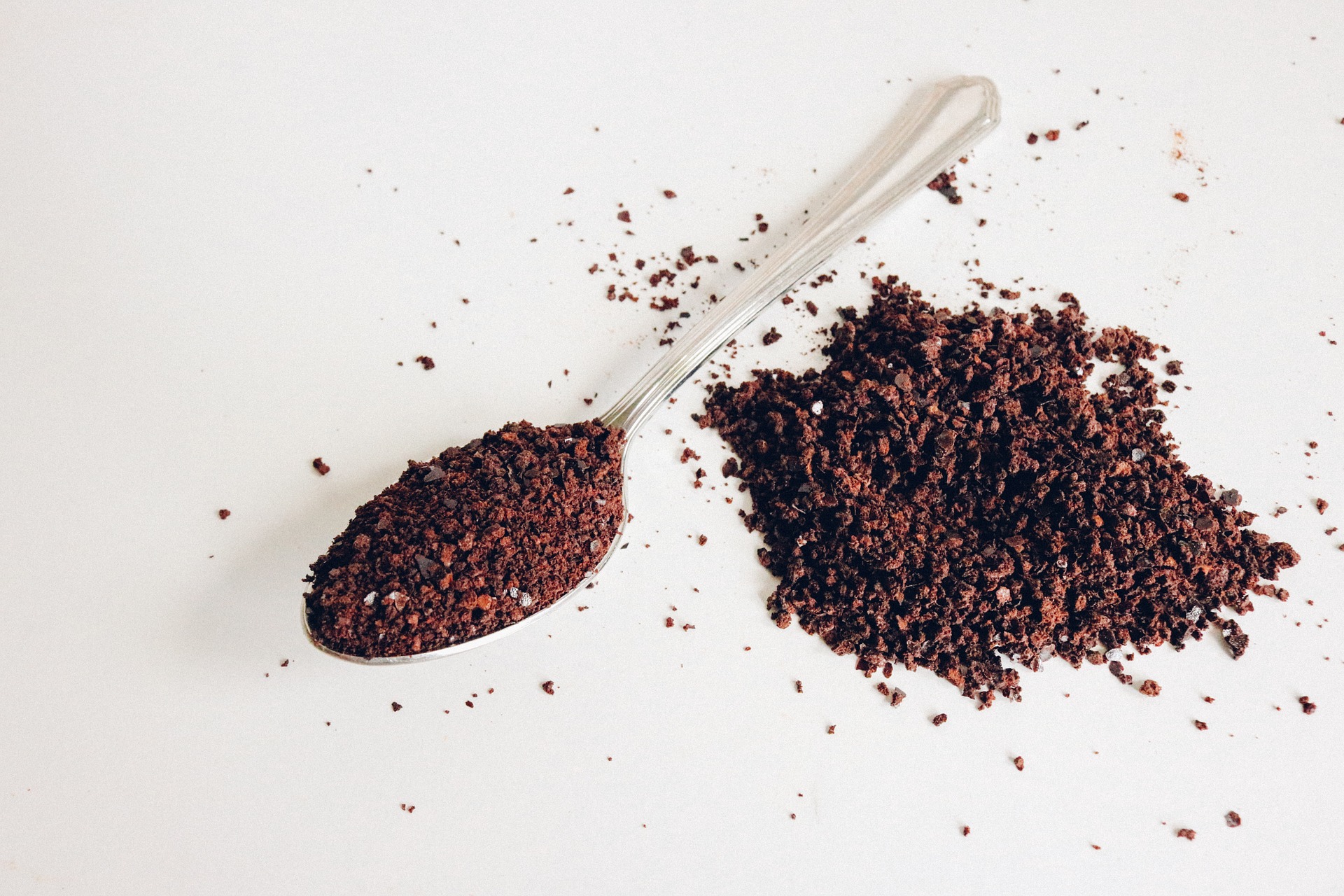
Instant coffee
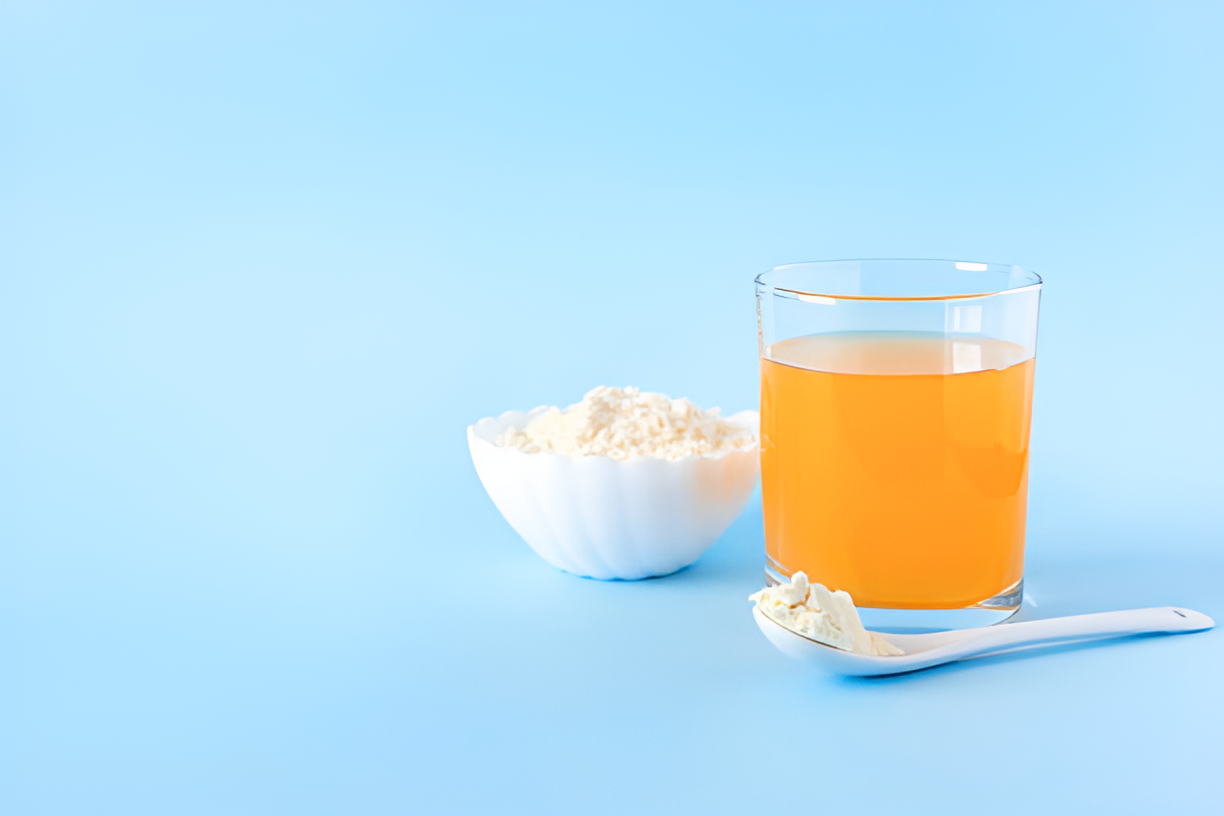
Instant drink powders
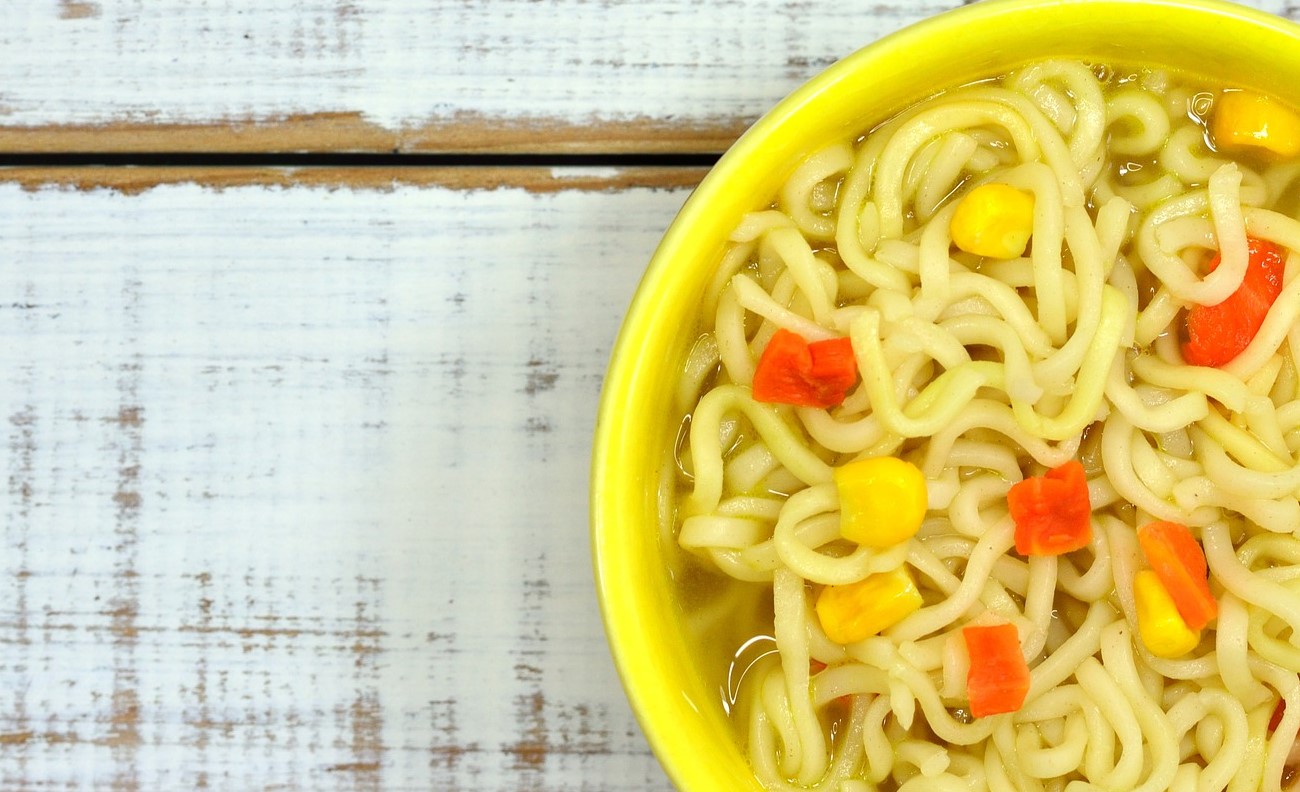
Instant soup
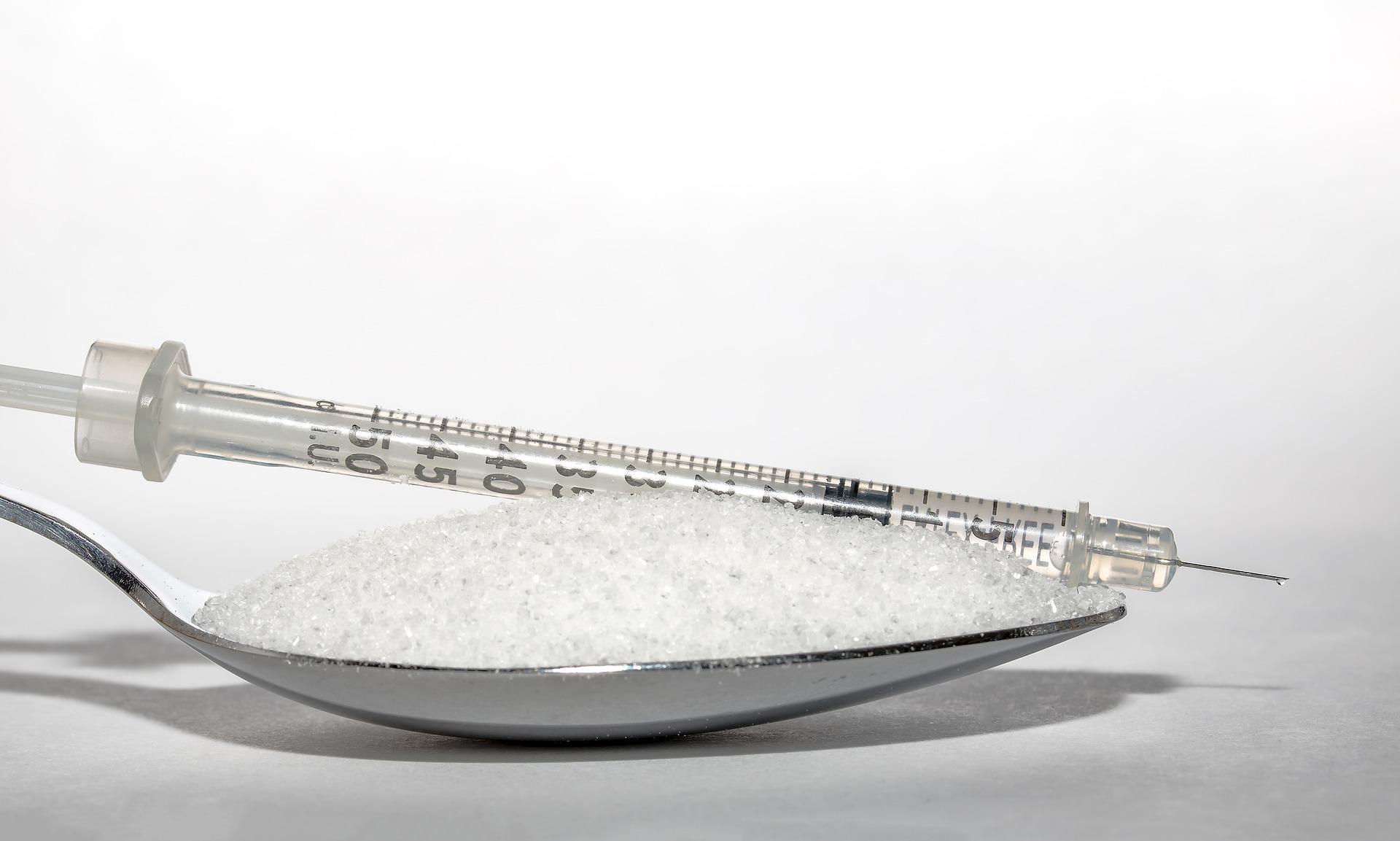
Insulin

Intermediates
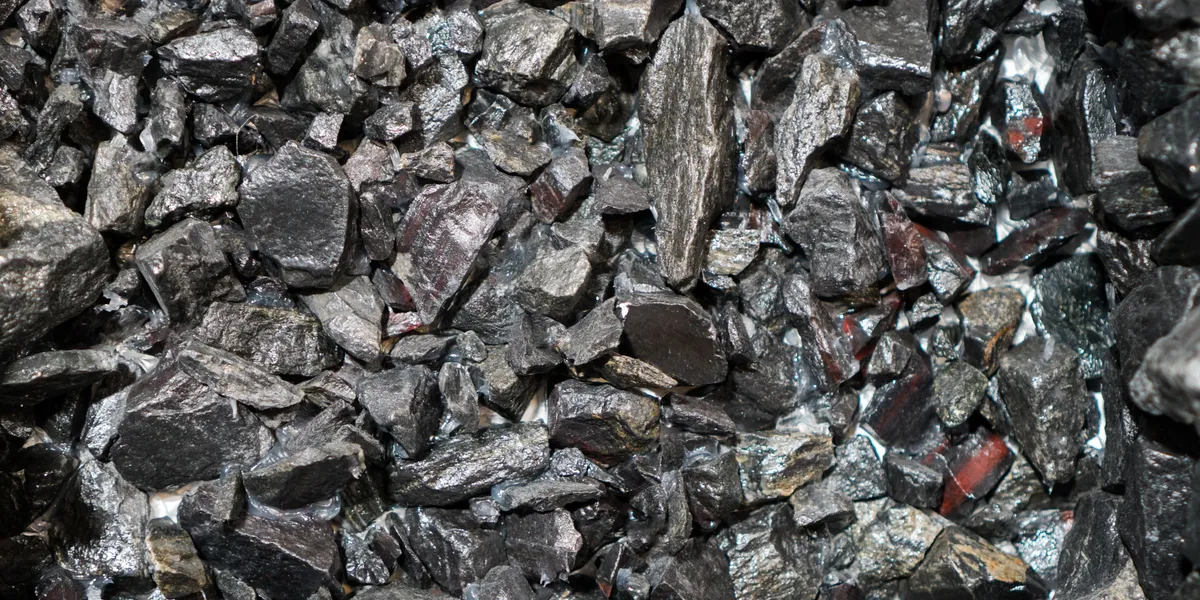
Iron ore concentrate
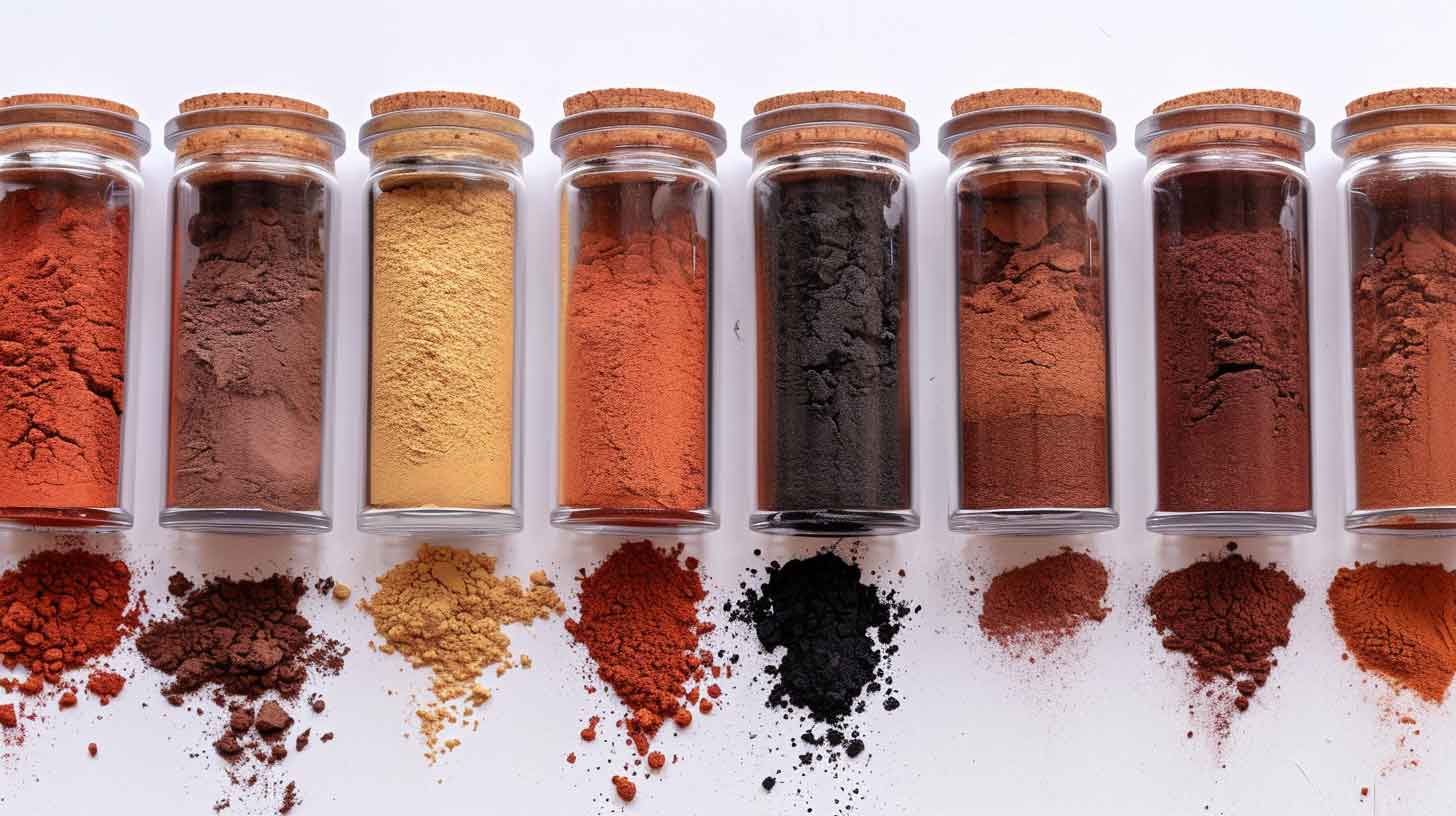
Iron oxide pigments
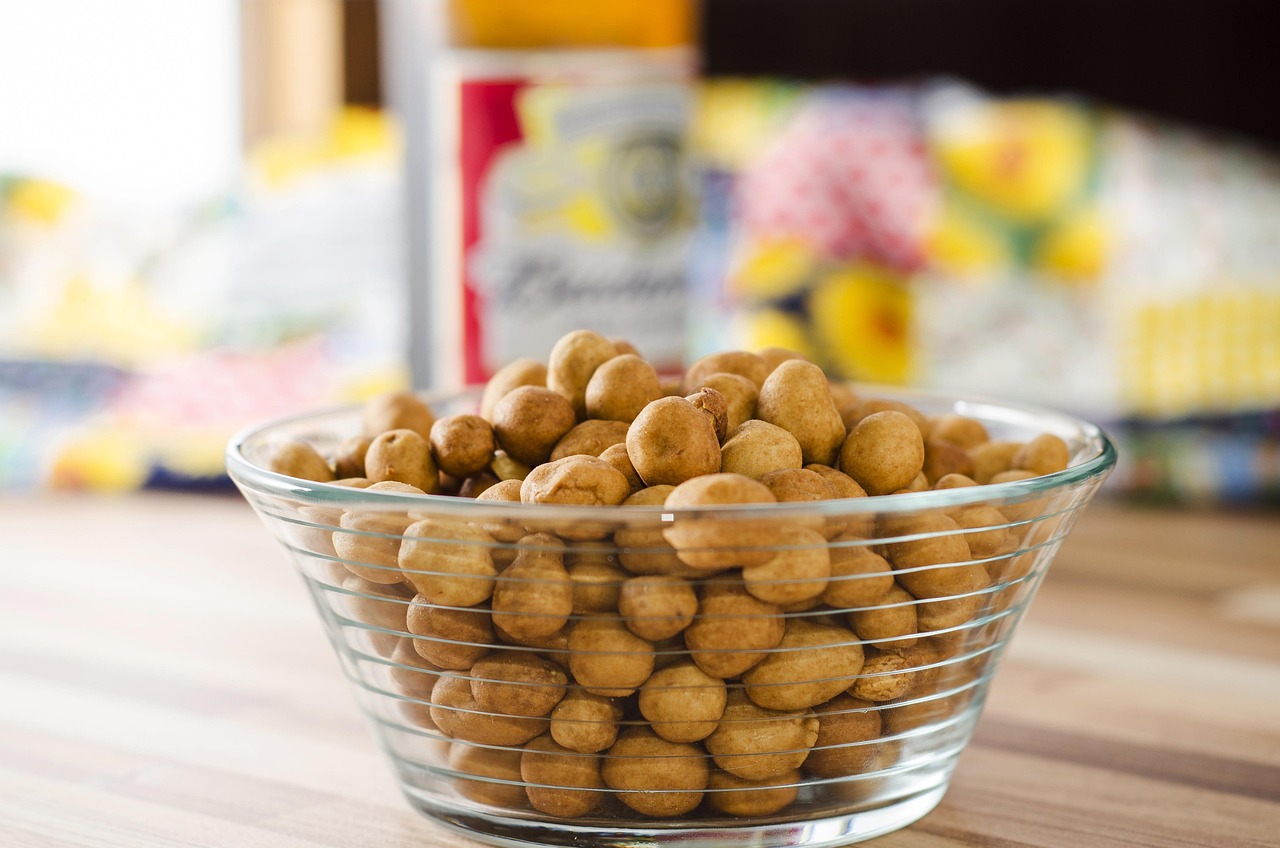
Japanese peanuts
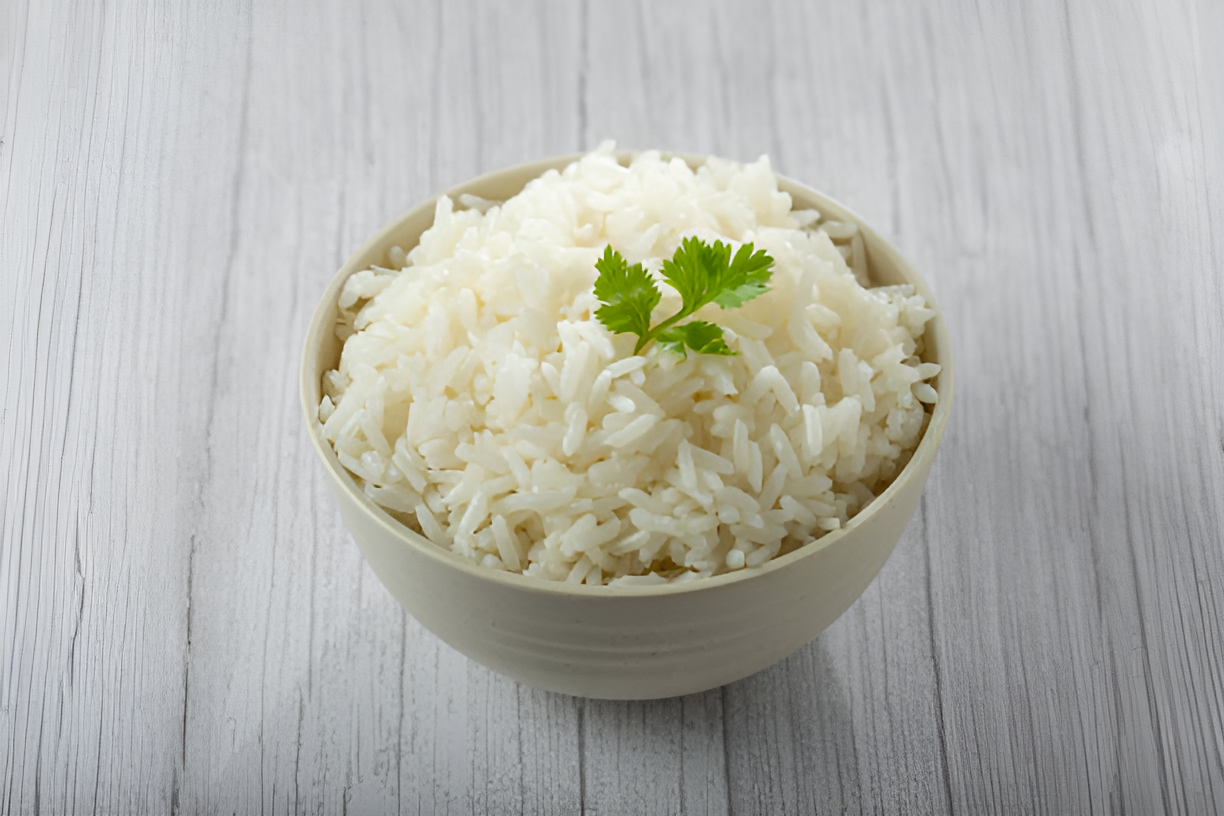
Jasmine rice
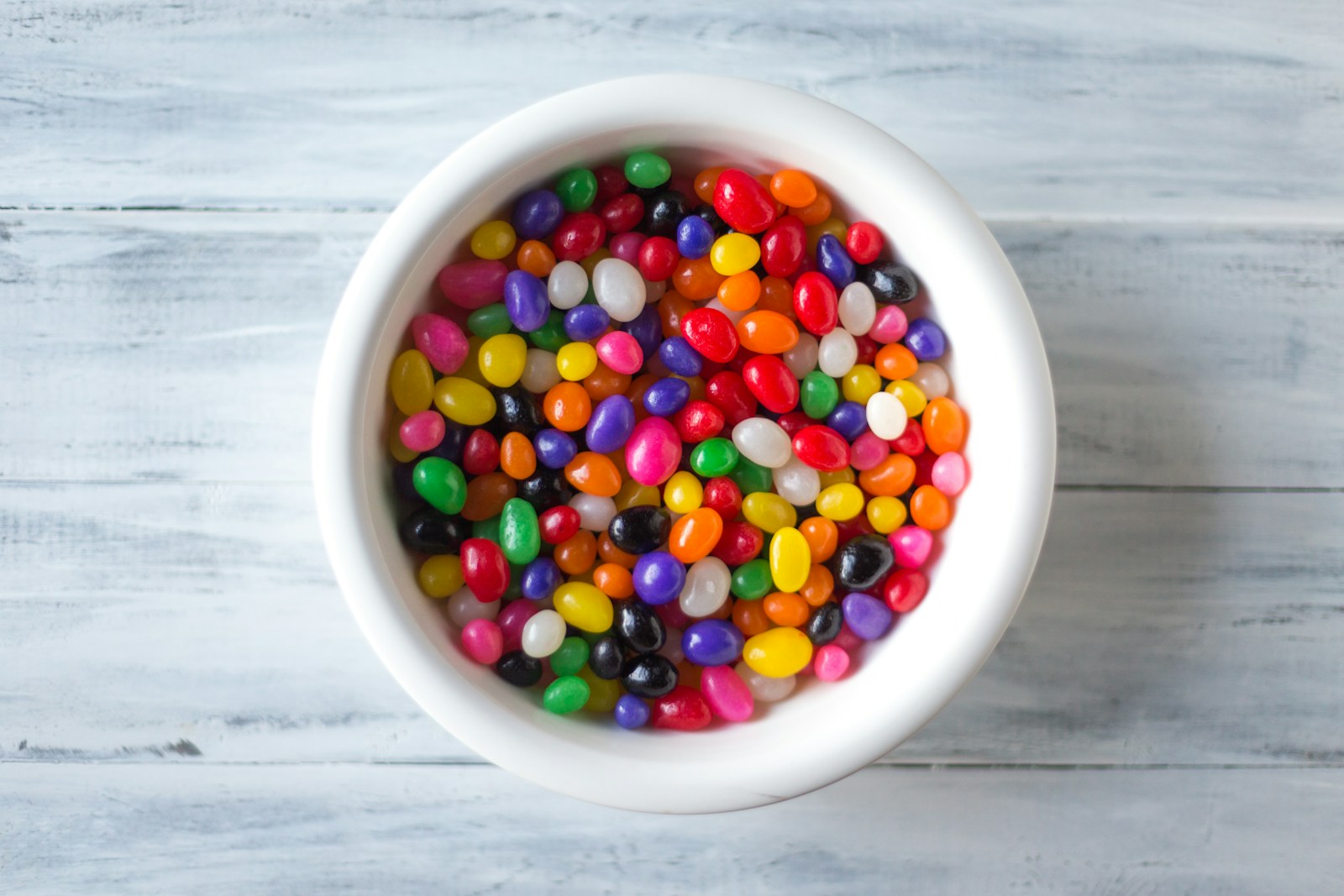
Jelly beans
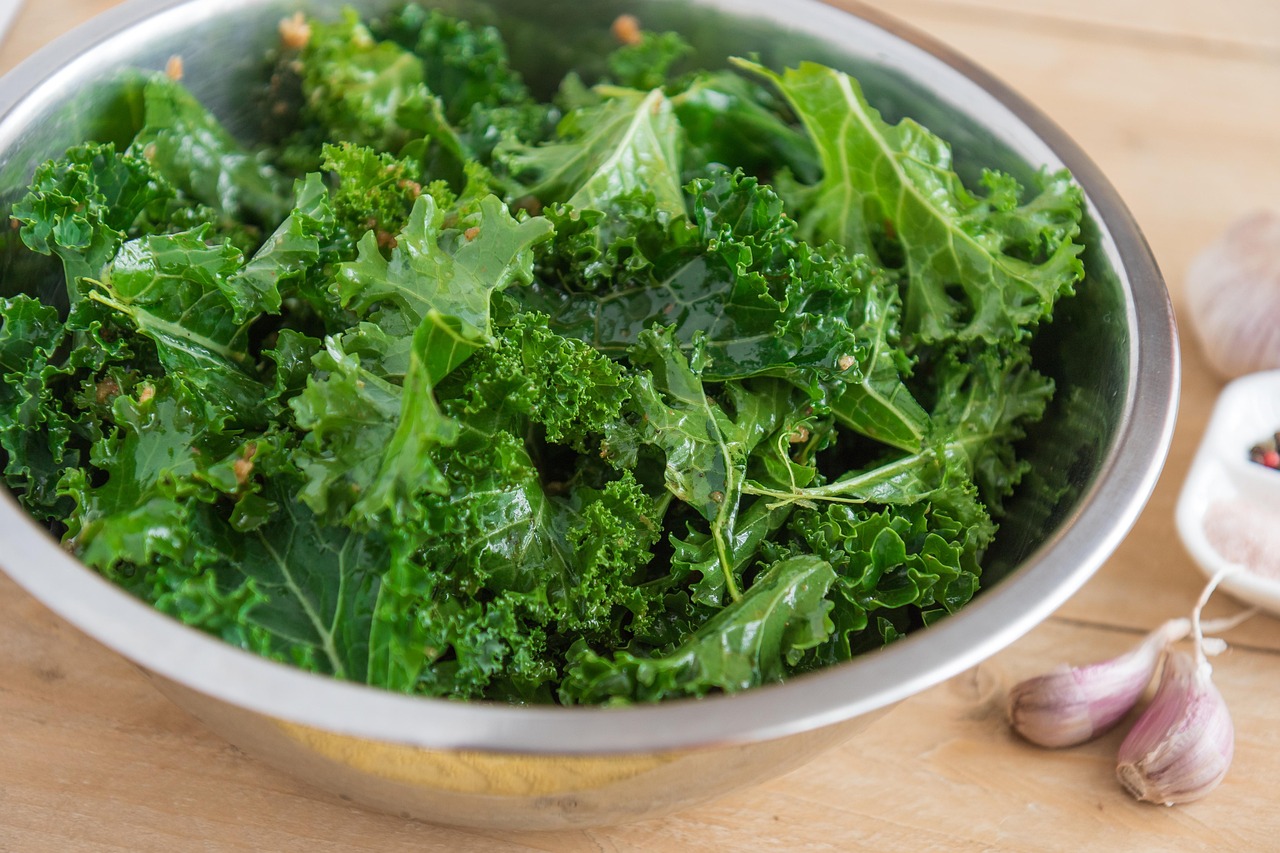
Kale
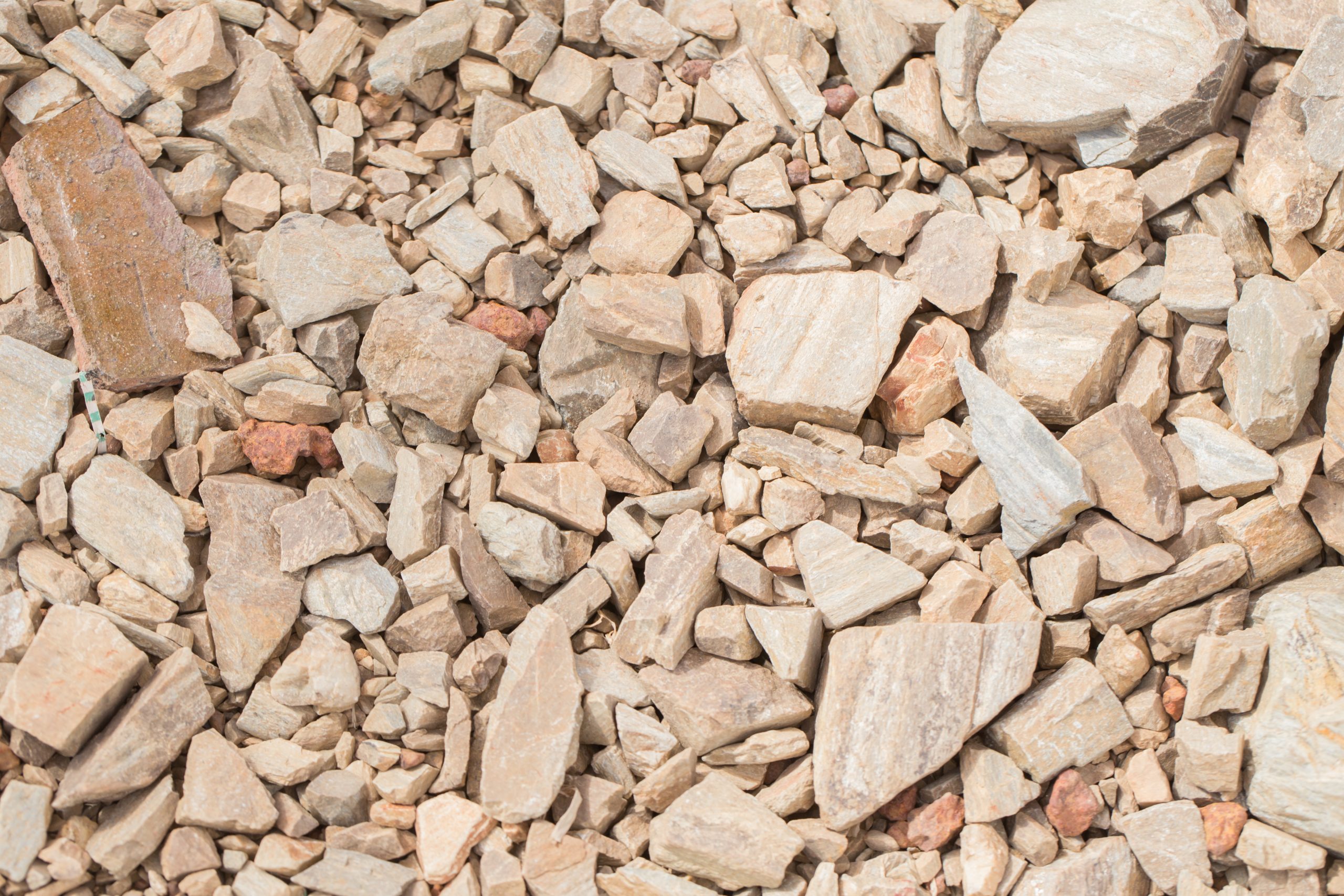
Kaolin
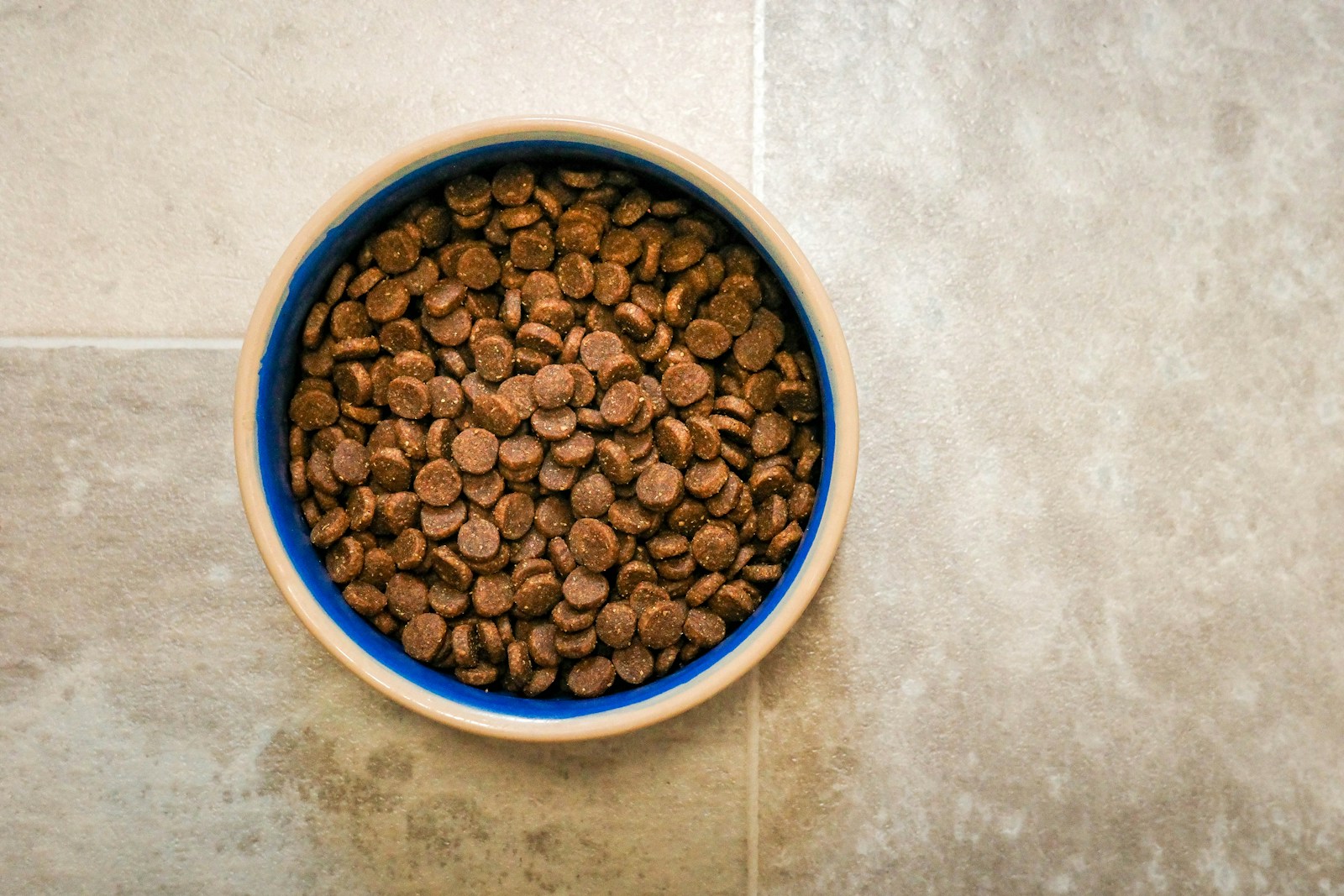
Kibble
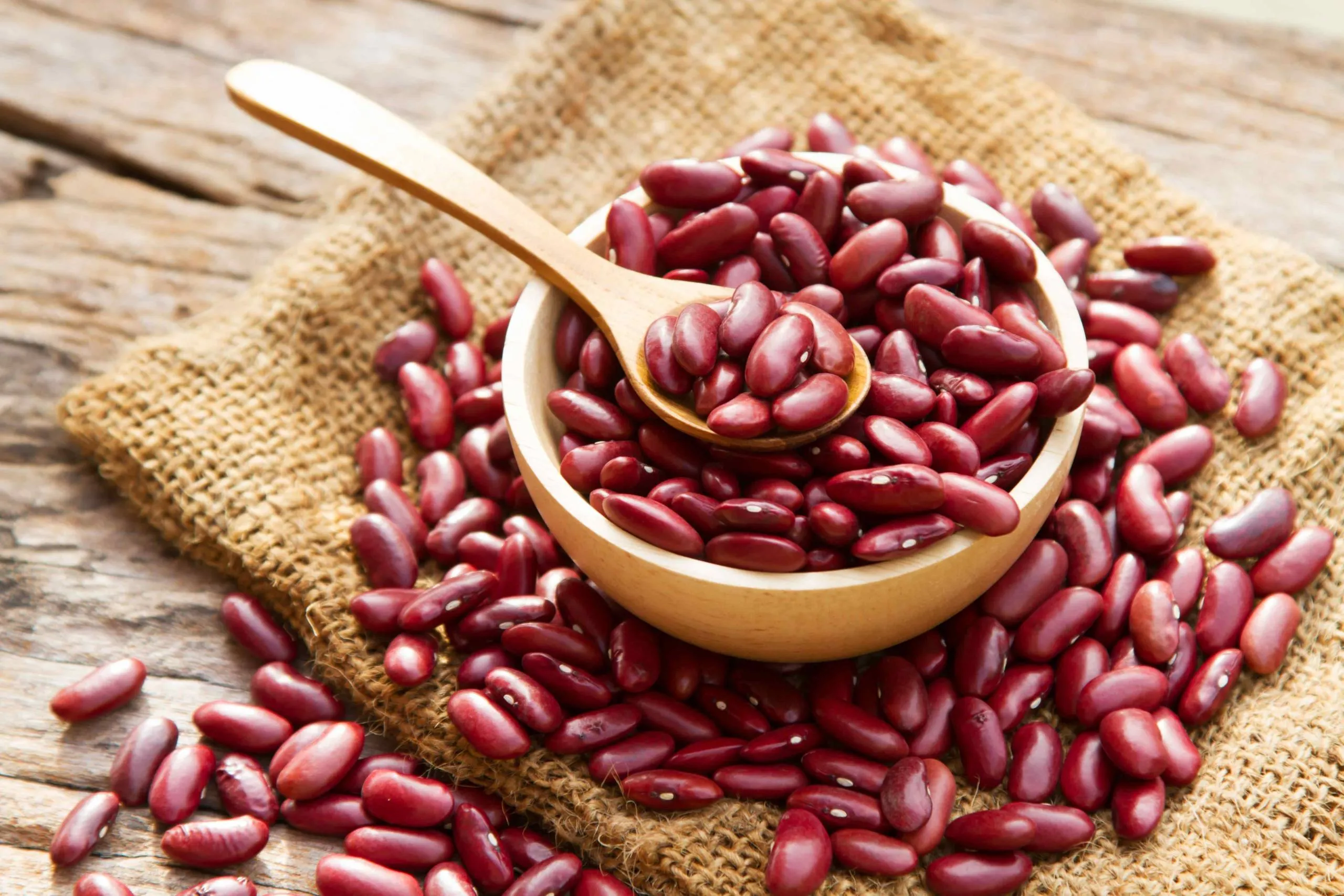
Kidney beans
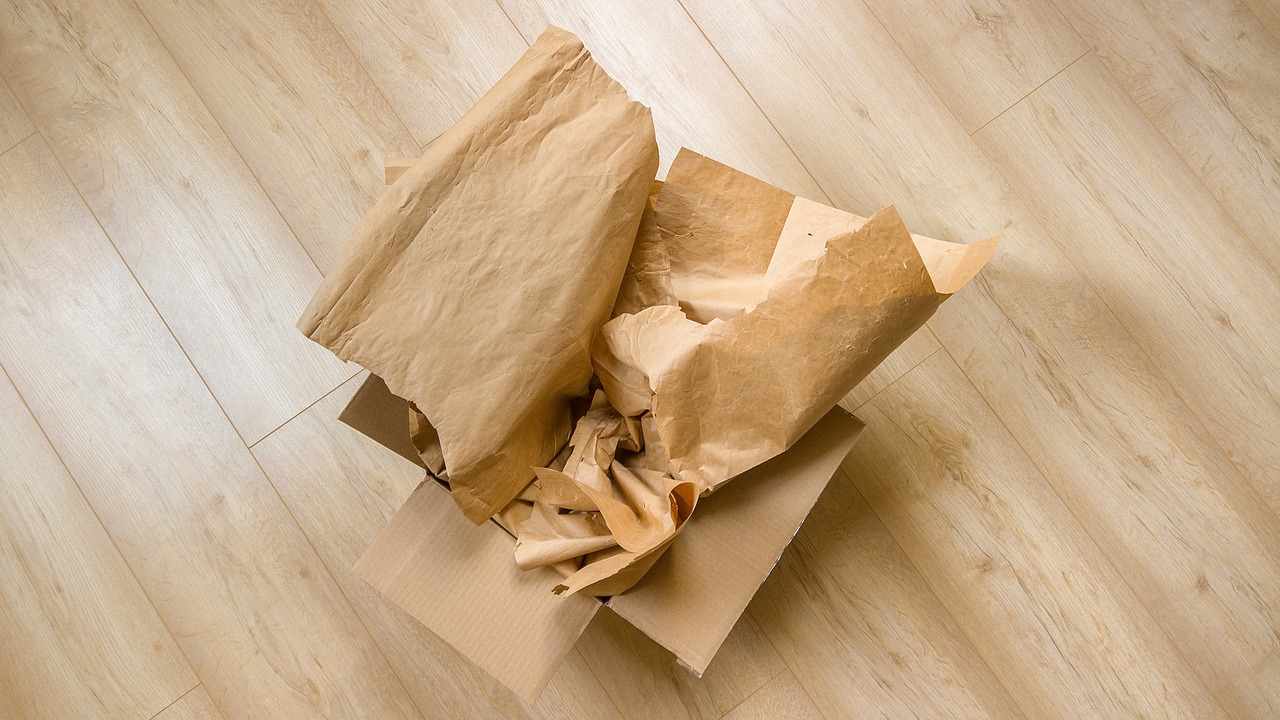
Kraft paper
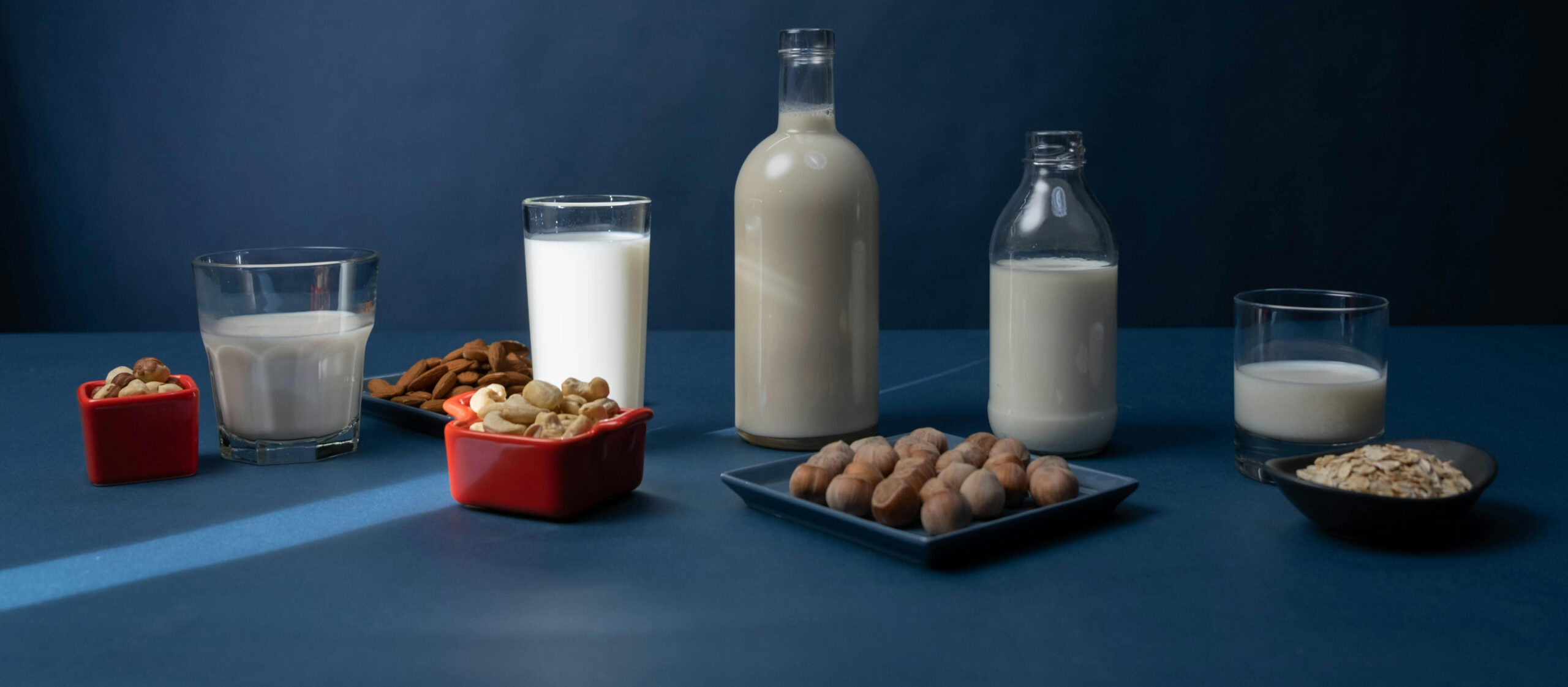
Lactose

Latex
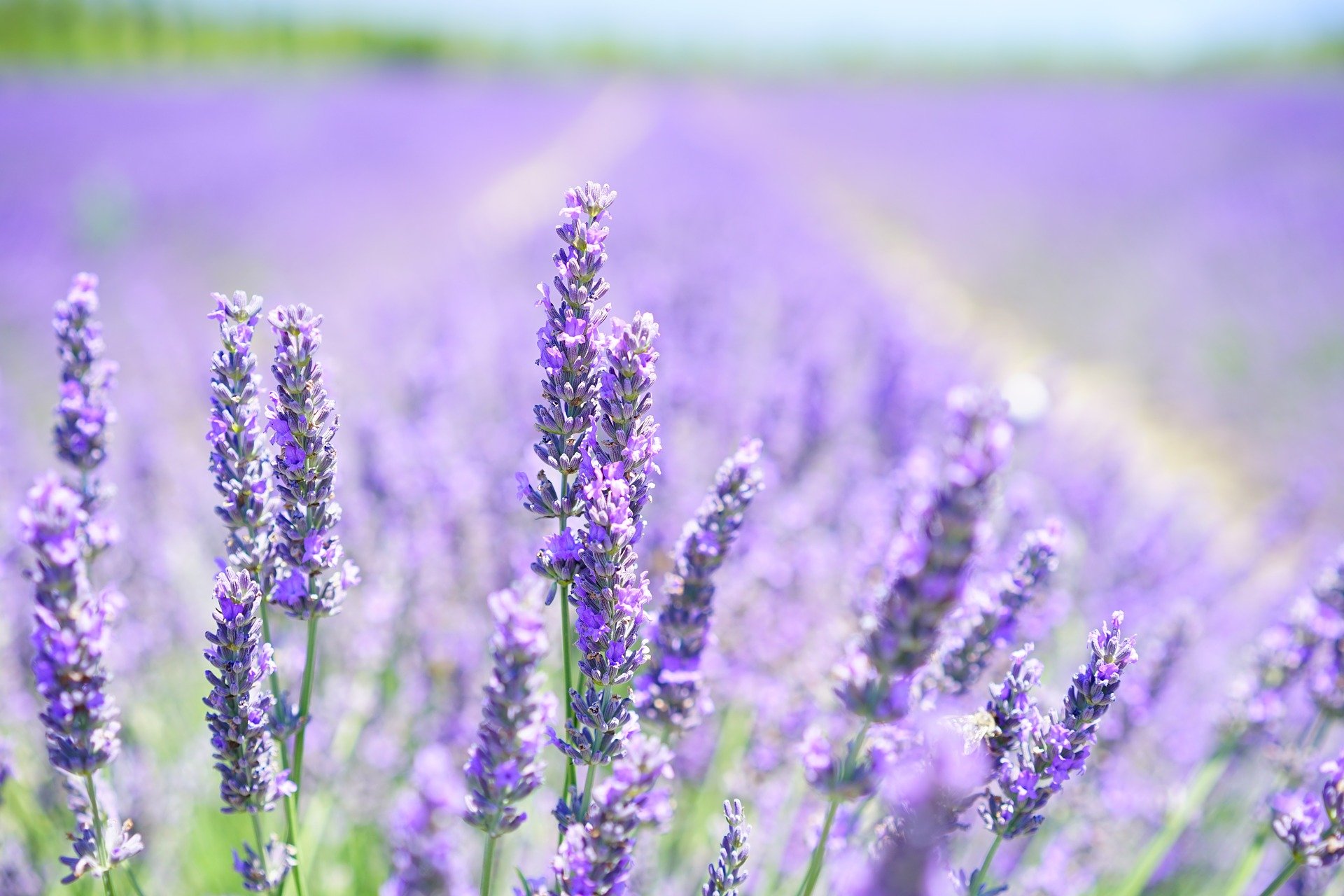
Lavender oil
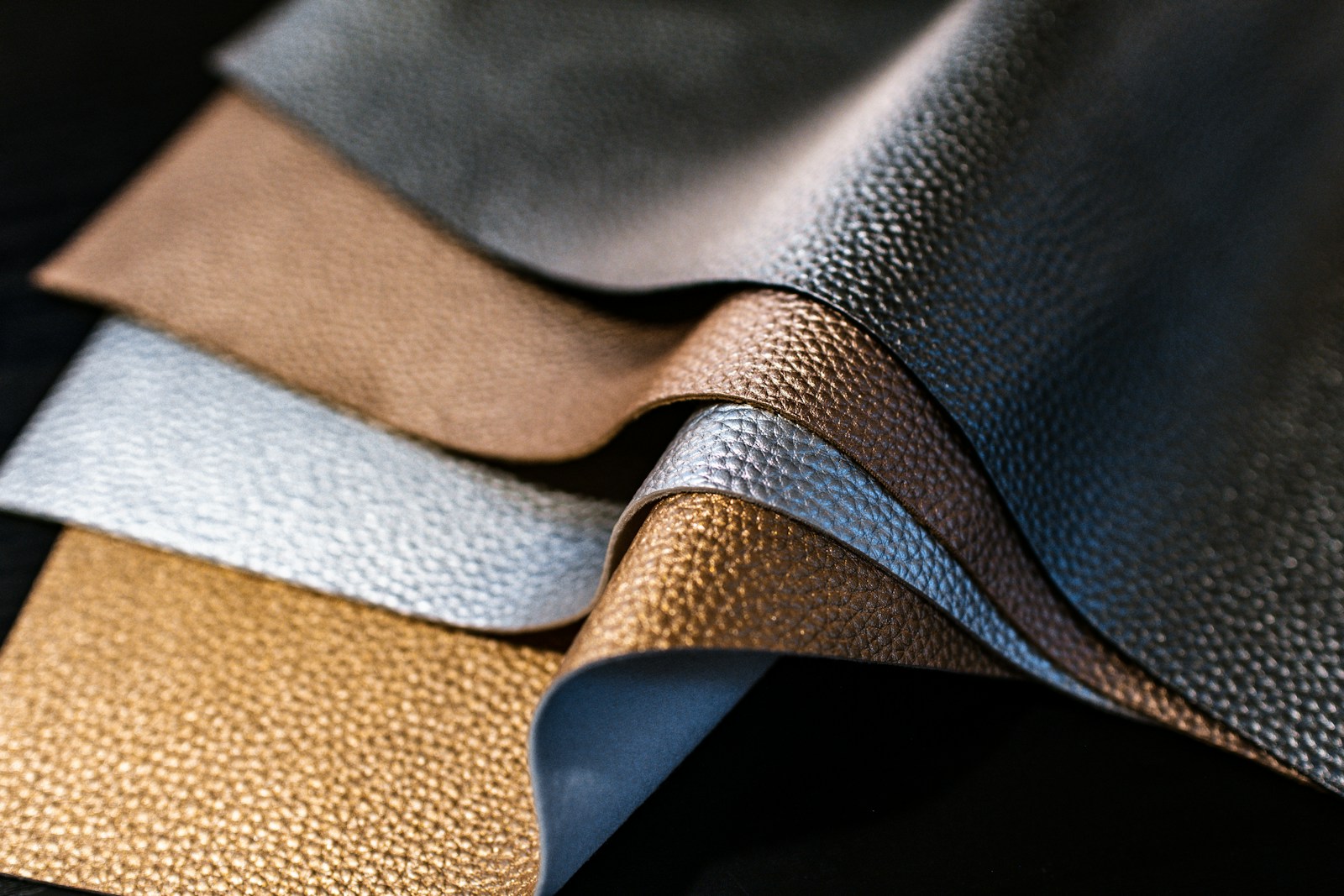
Leather
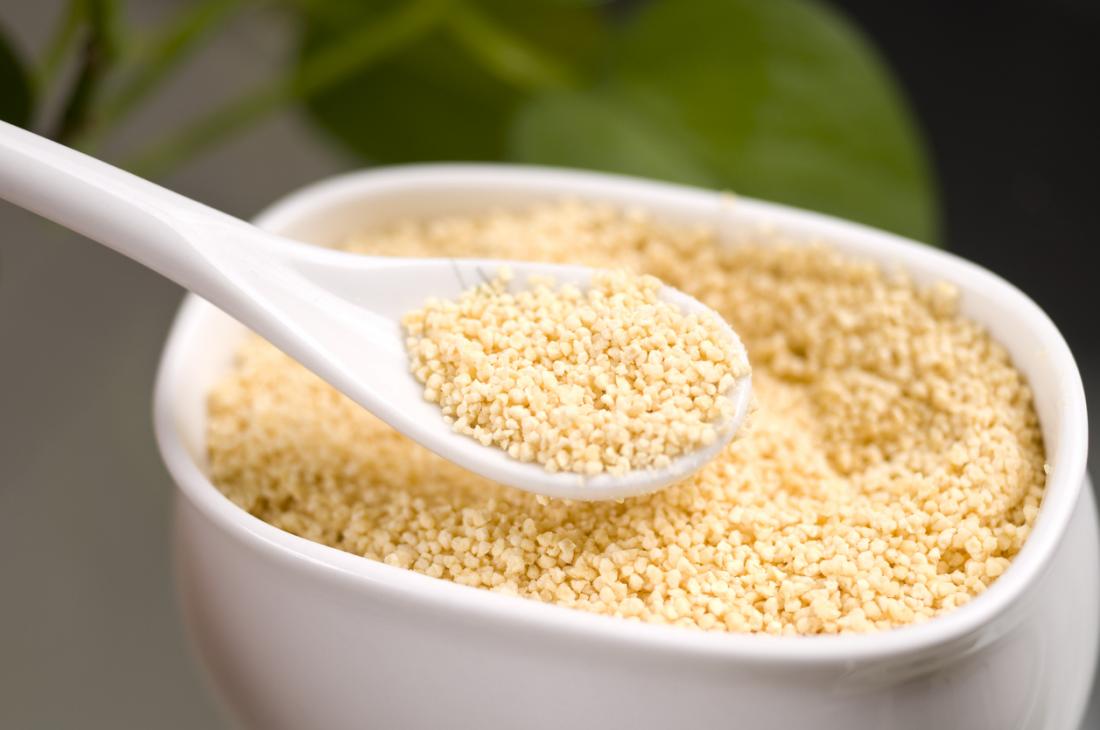
Lecithin
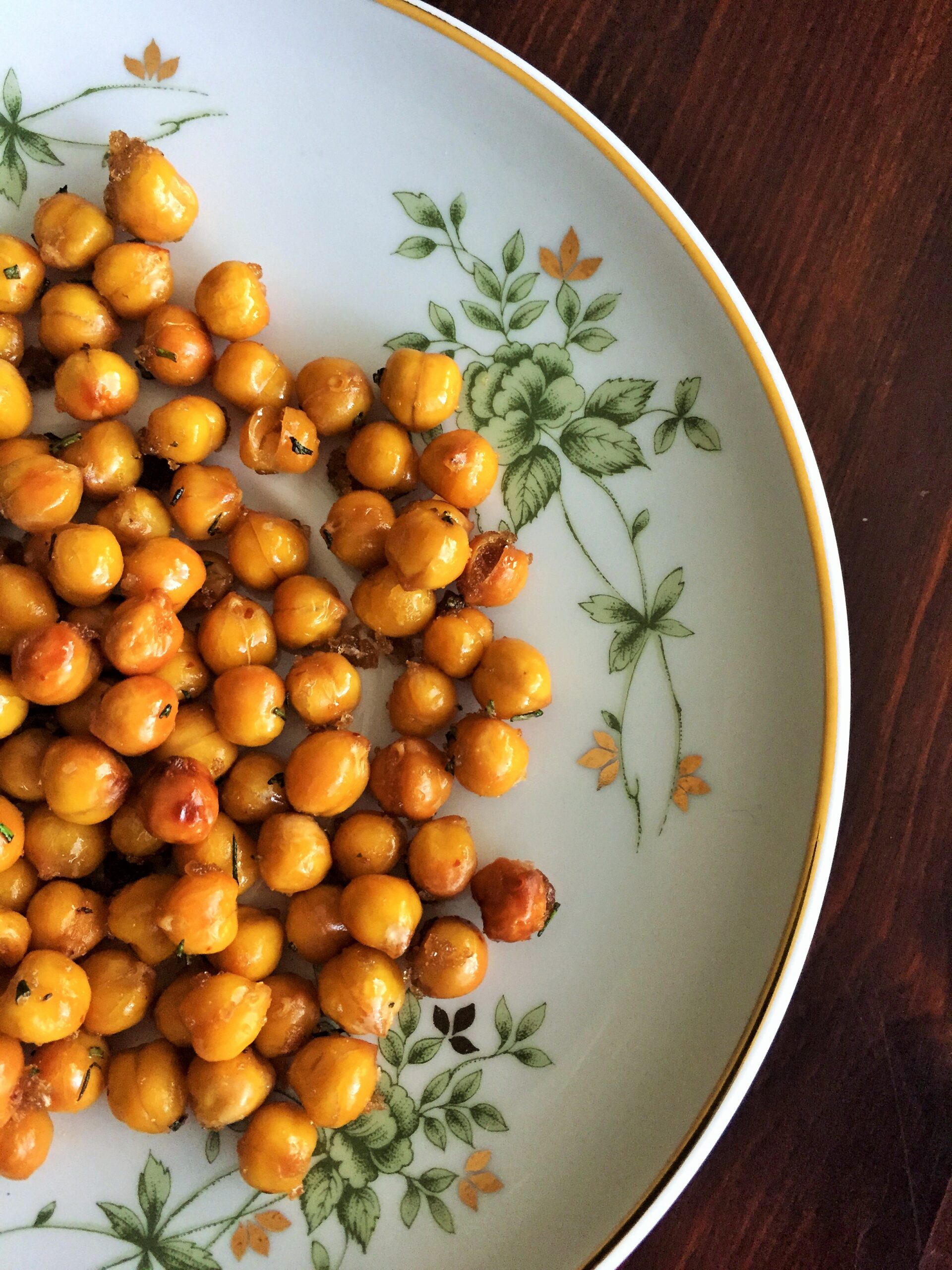
Legume snacks
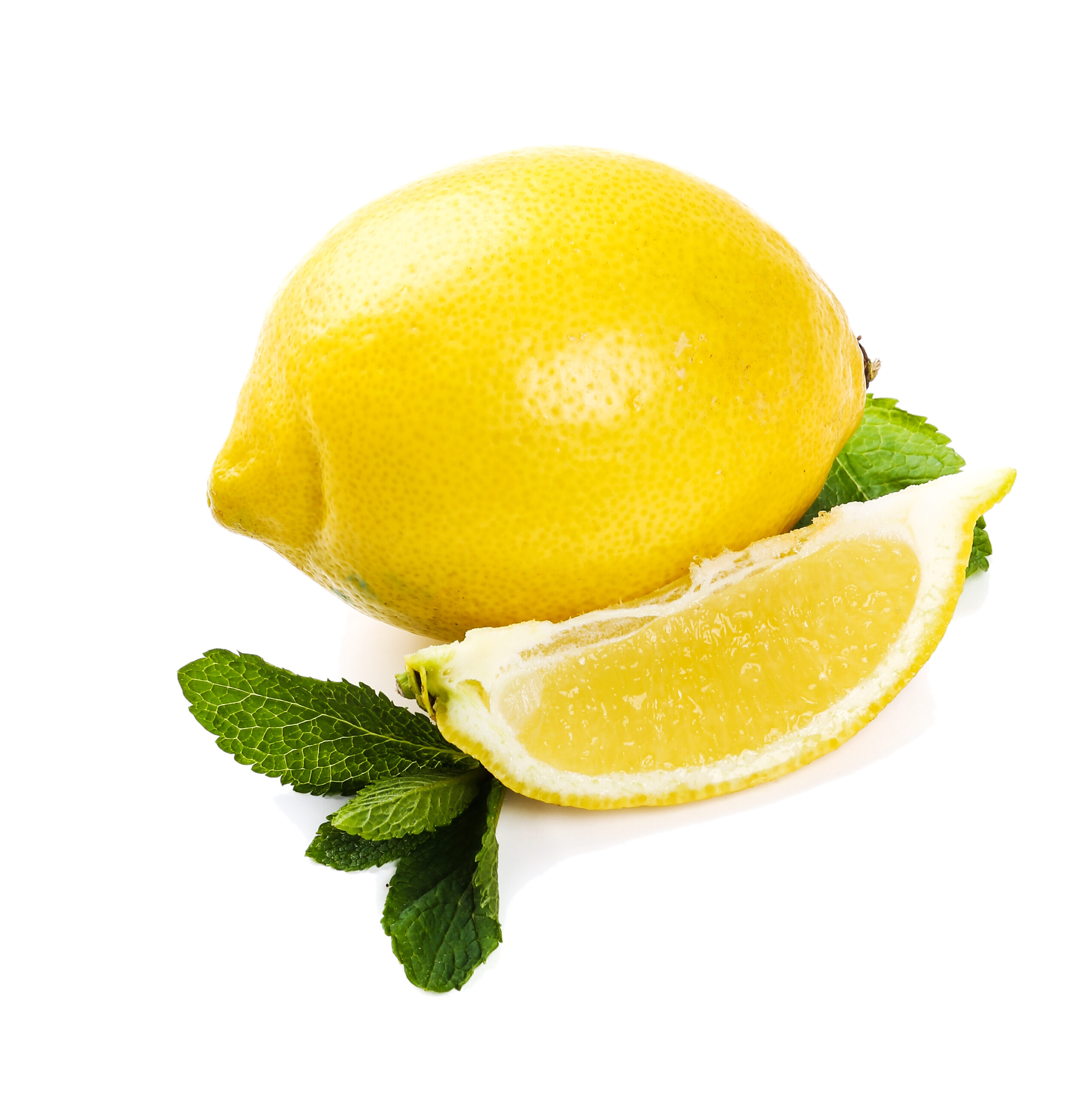
Lemons
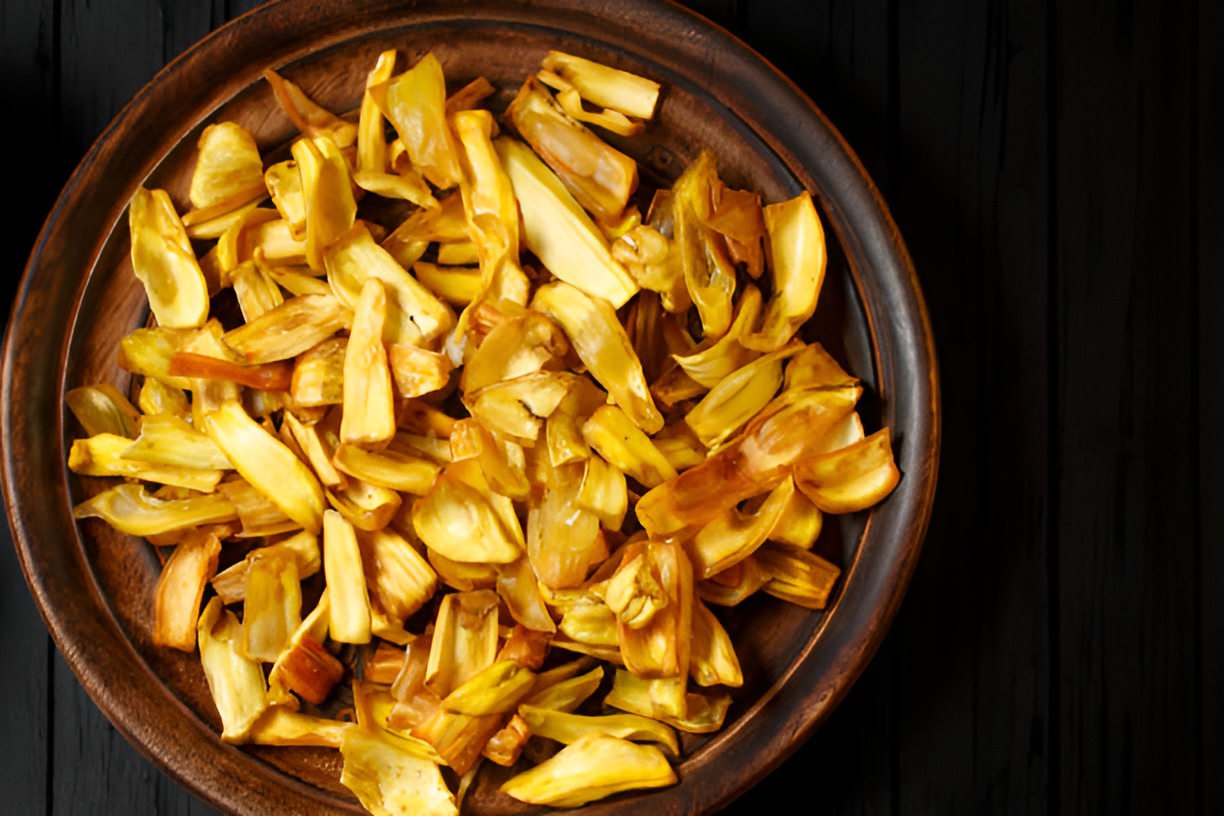
Lentil chips
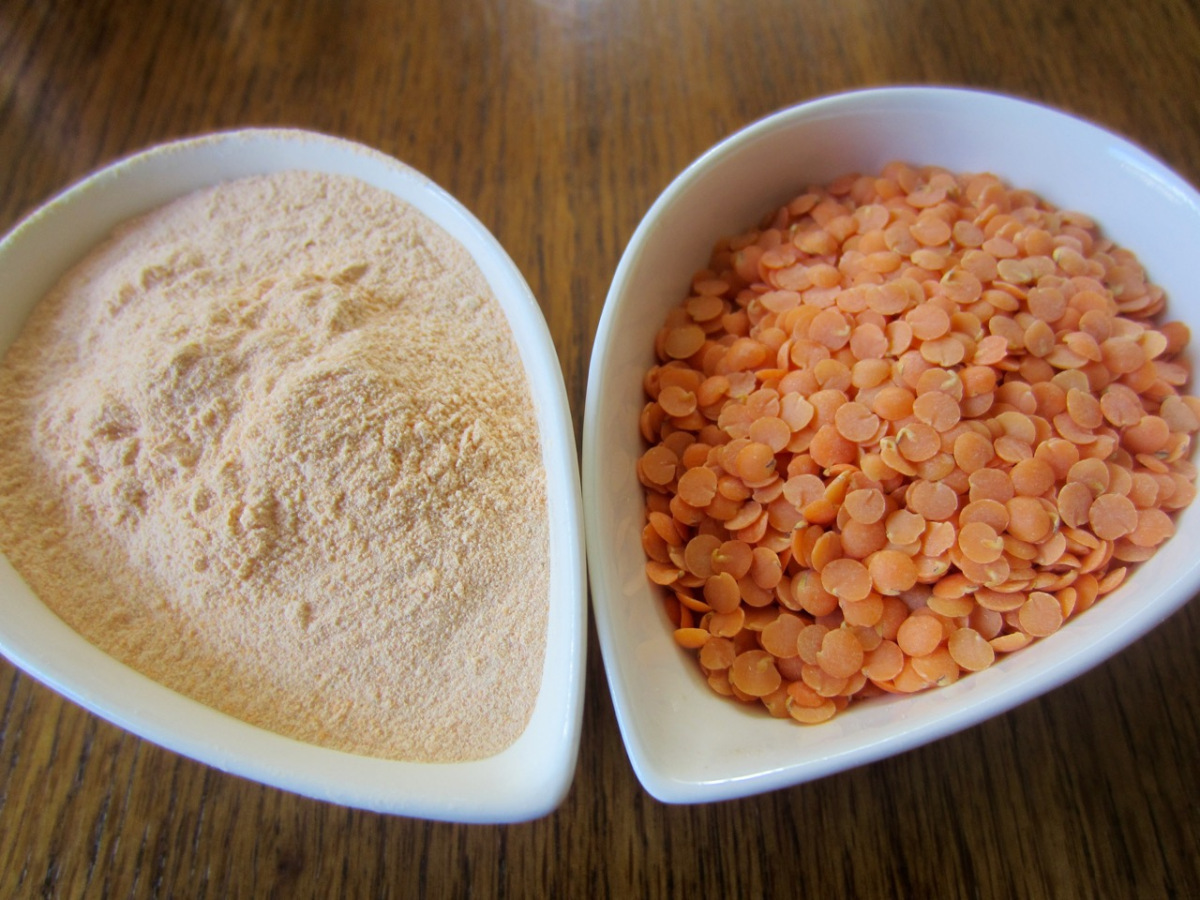
Lentil flour
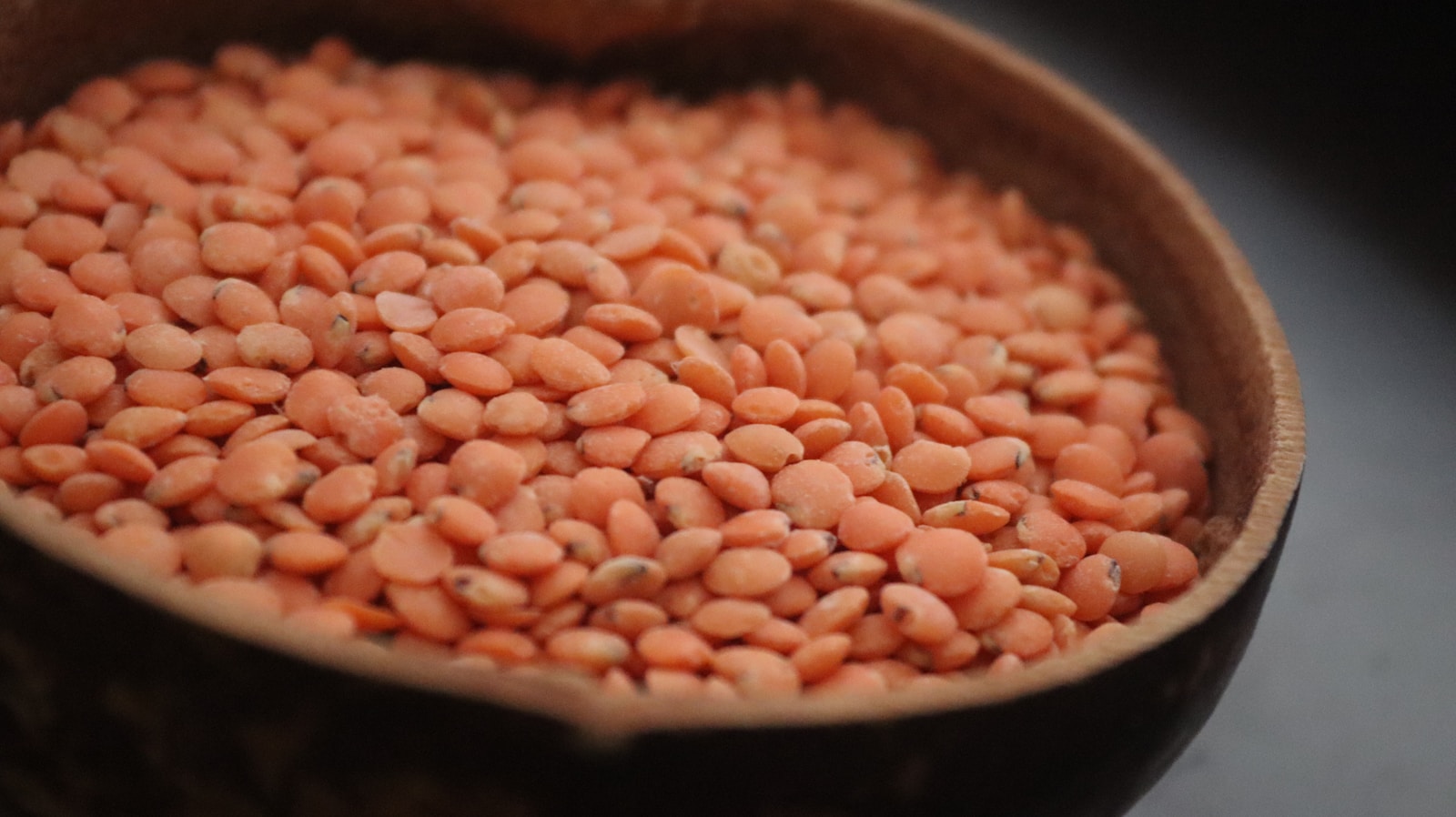
Lentils
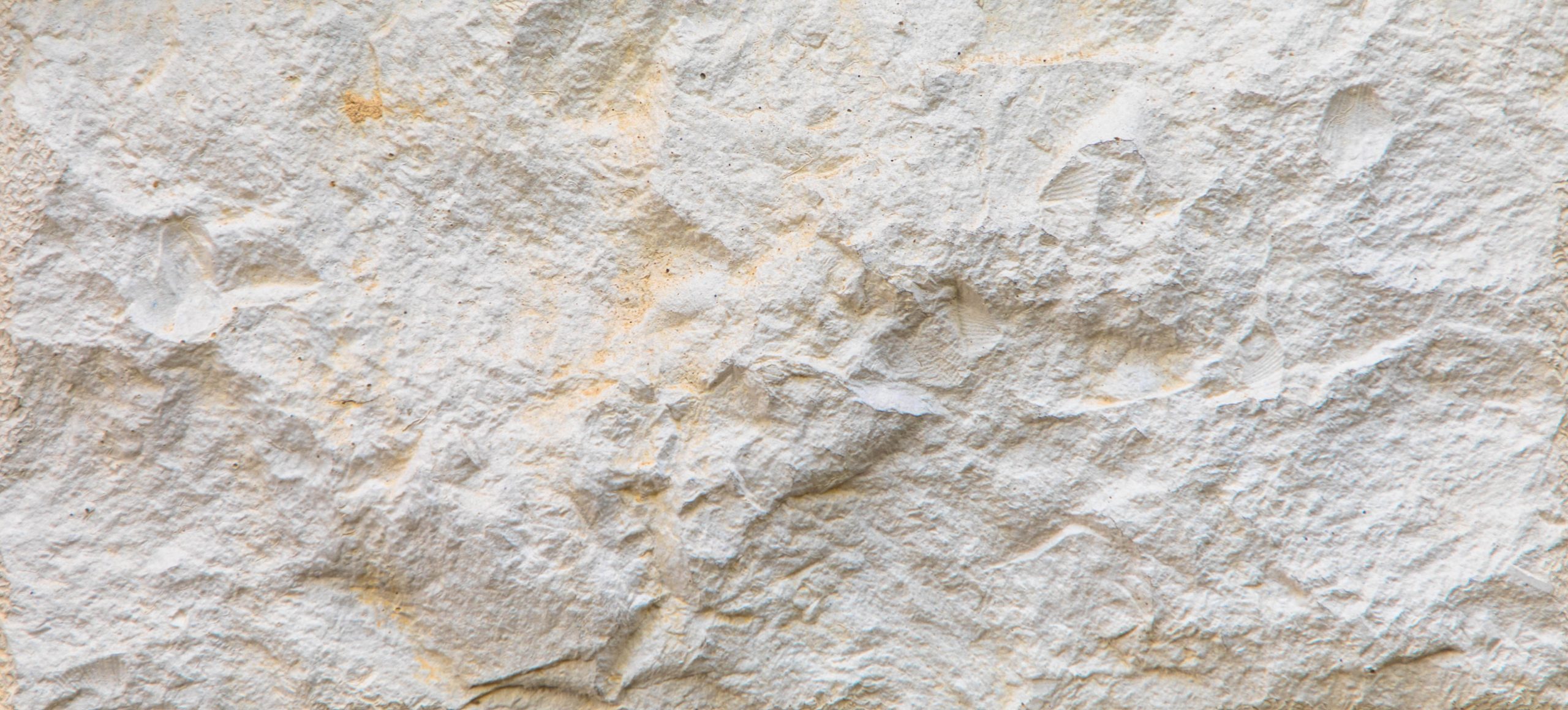
Limestone
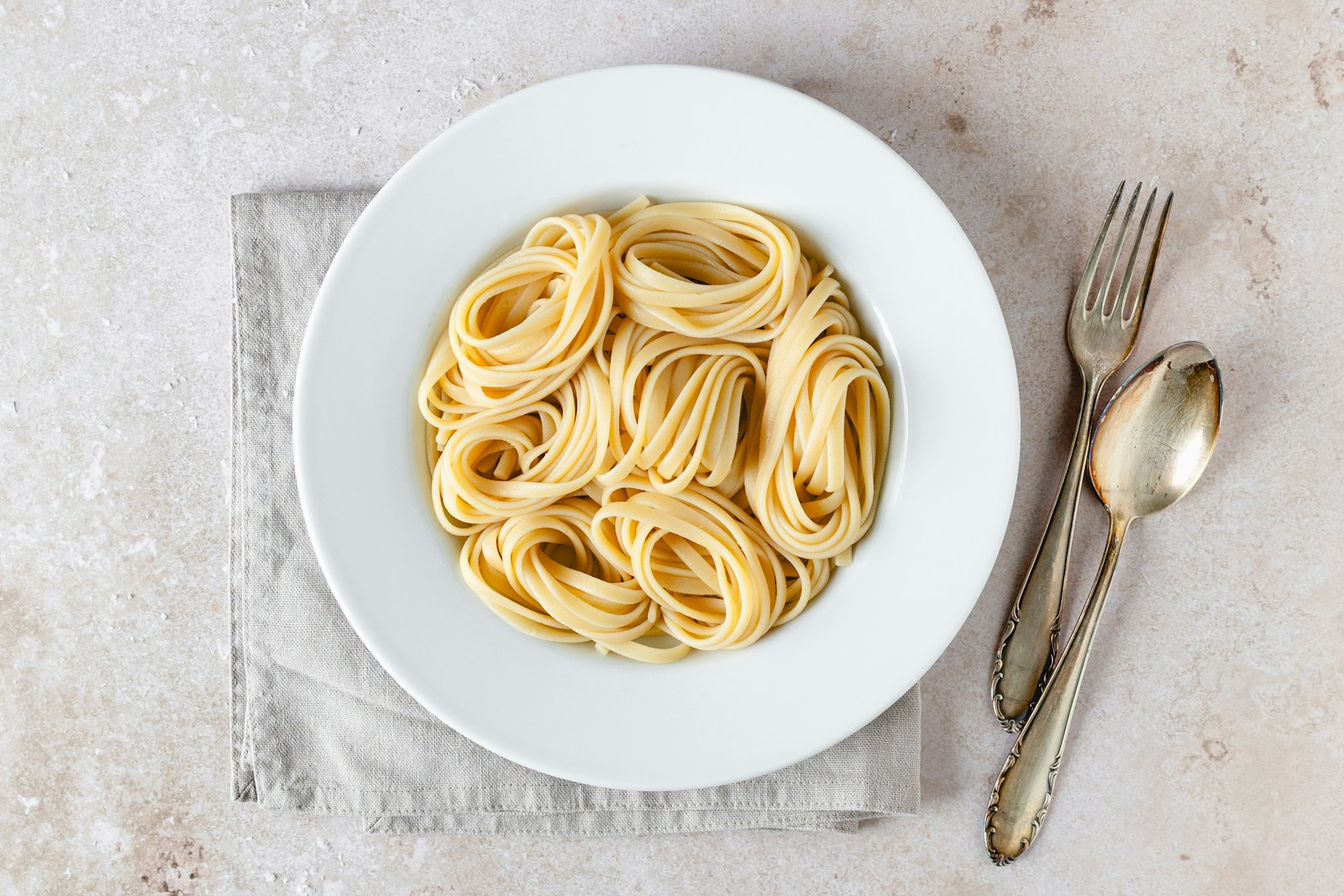
Linguine
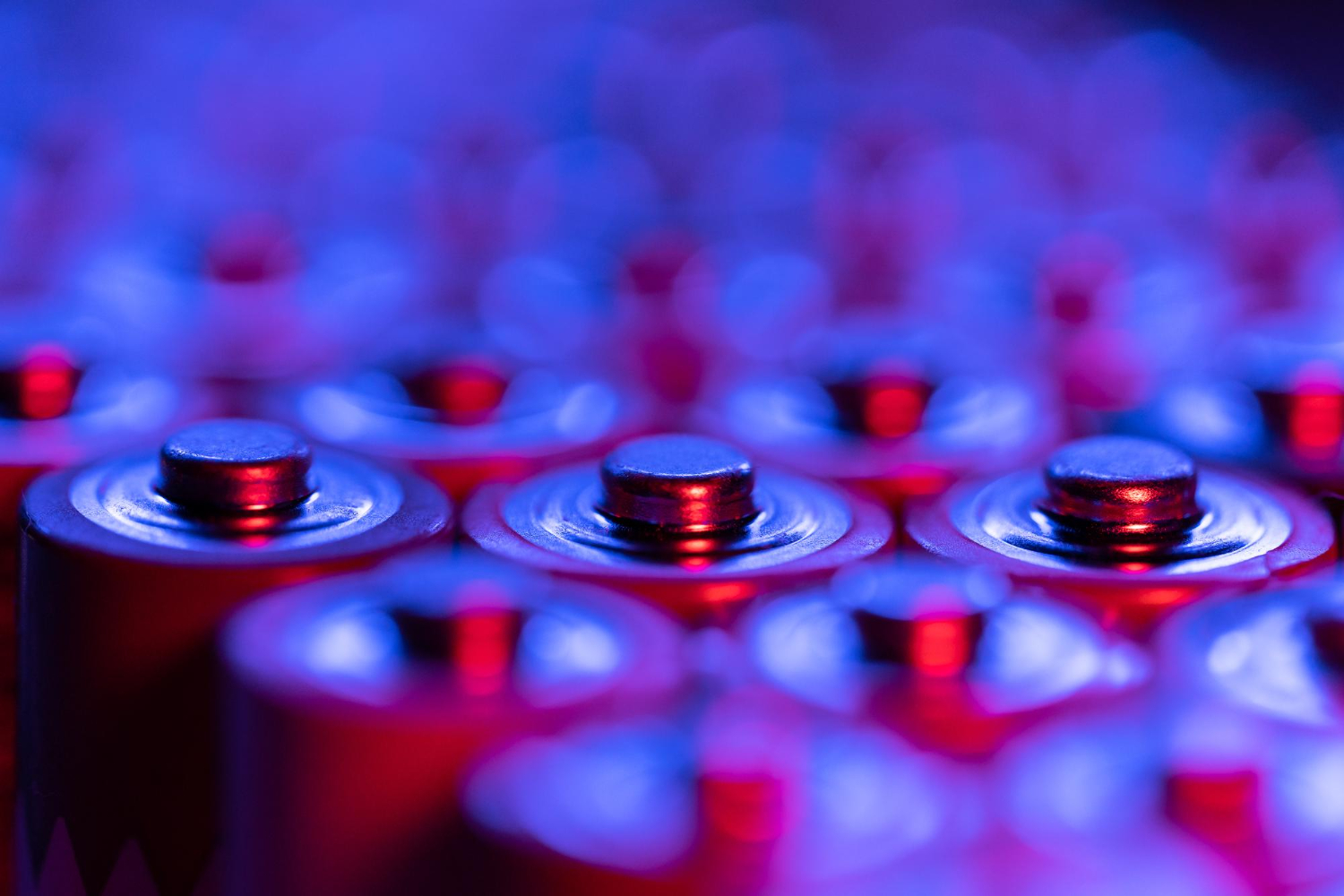
Lithium-ion batteries
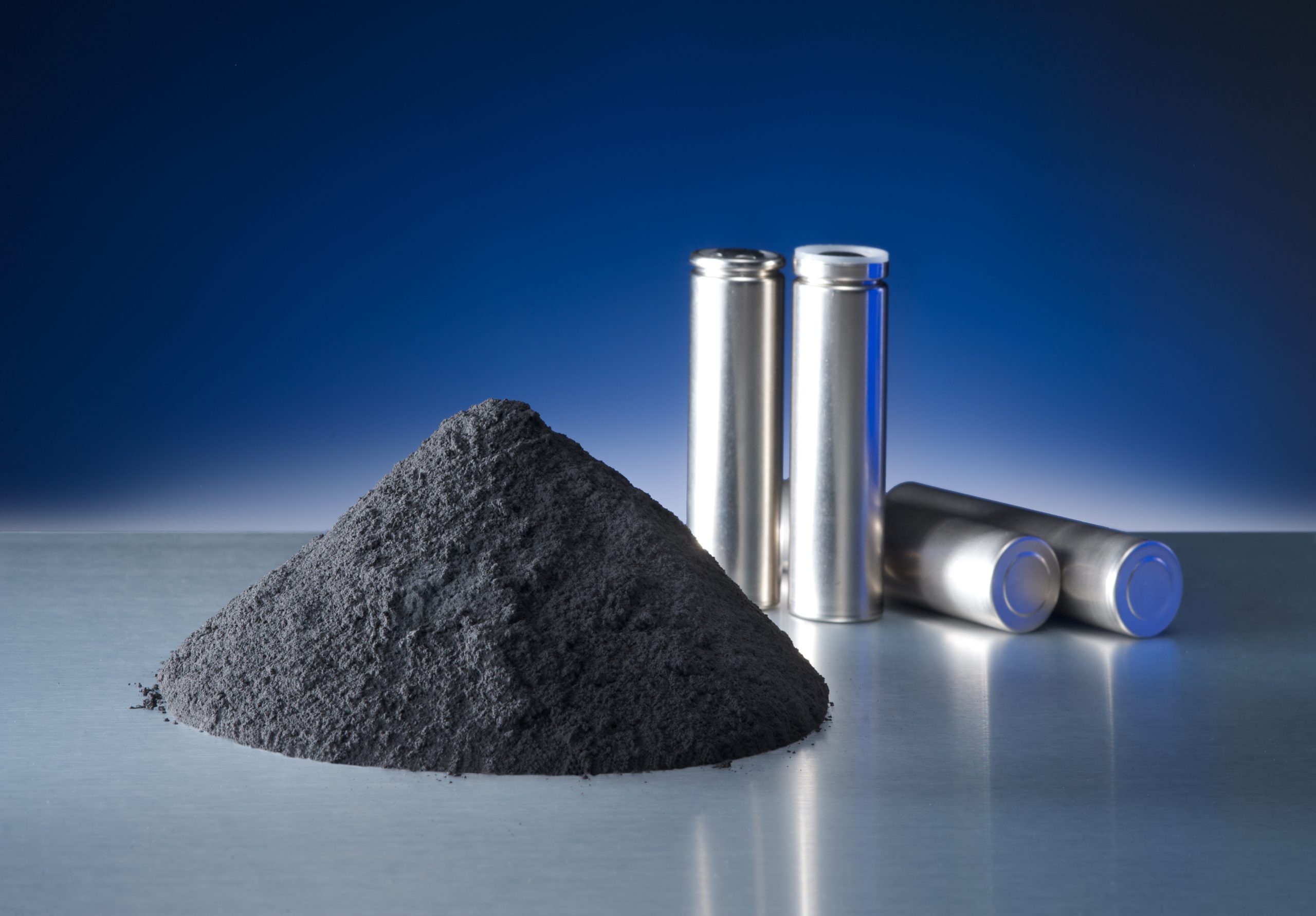
Lithium-ion battery anodes
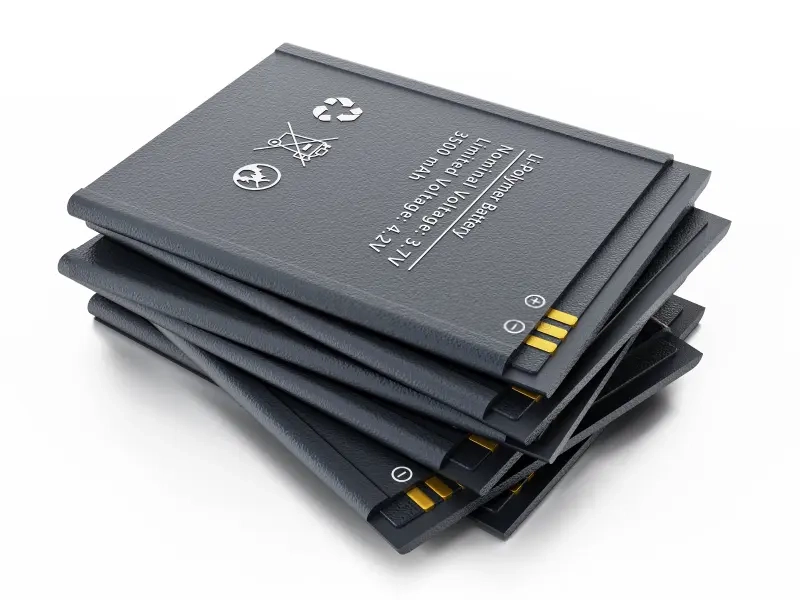
Lithium-ion battery cathodes
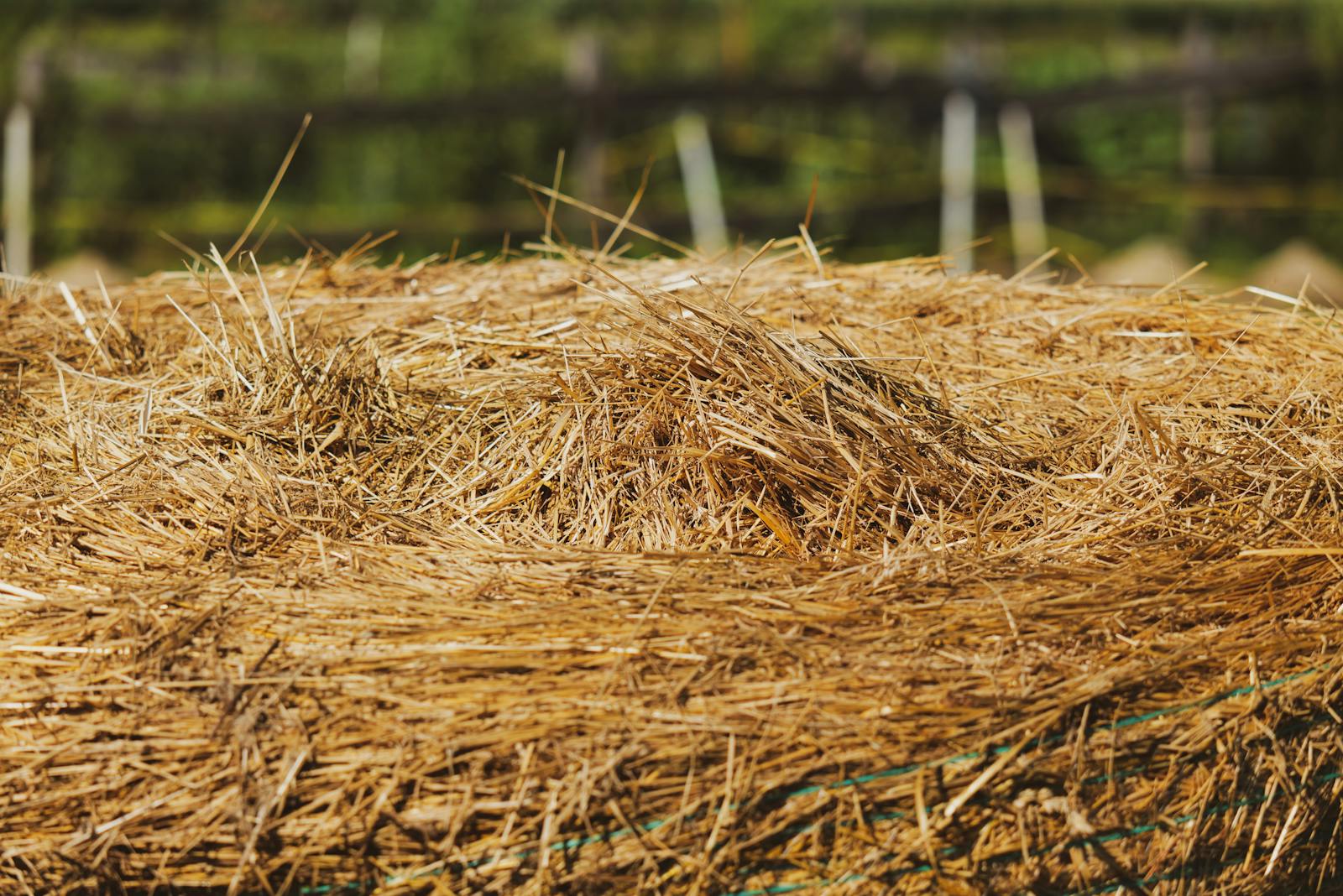
Livestock feed

Livestock manure
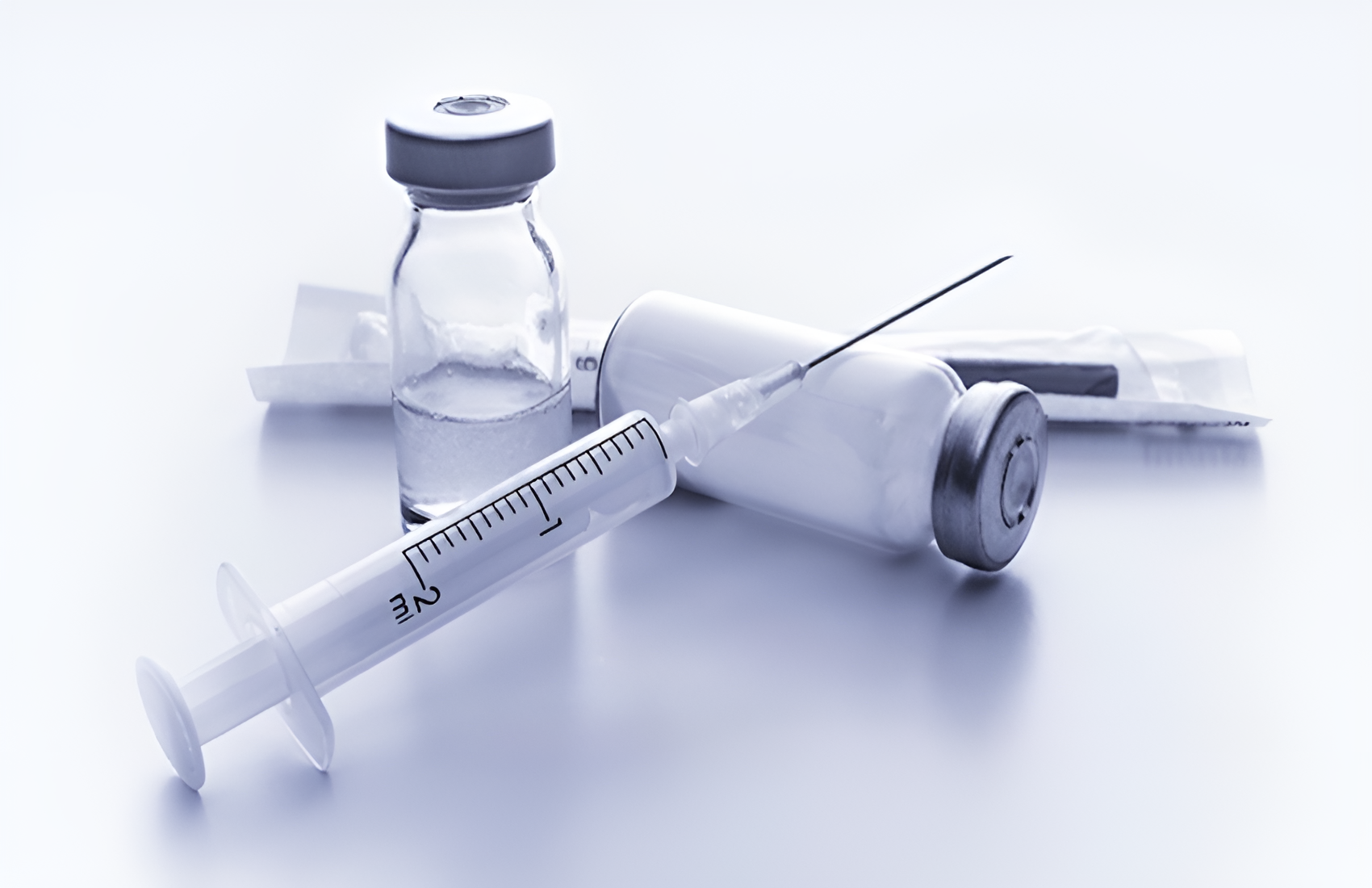
Lyophilized drugs
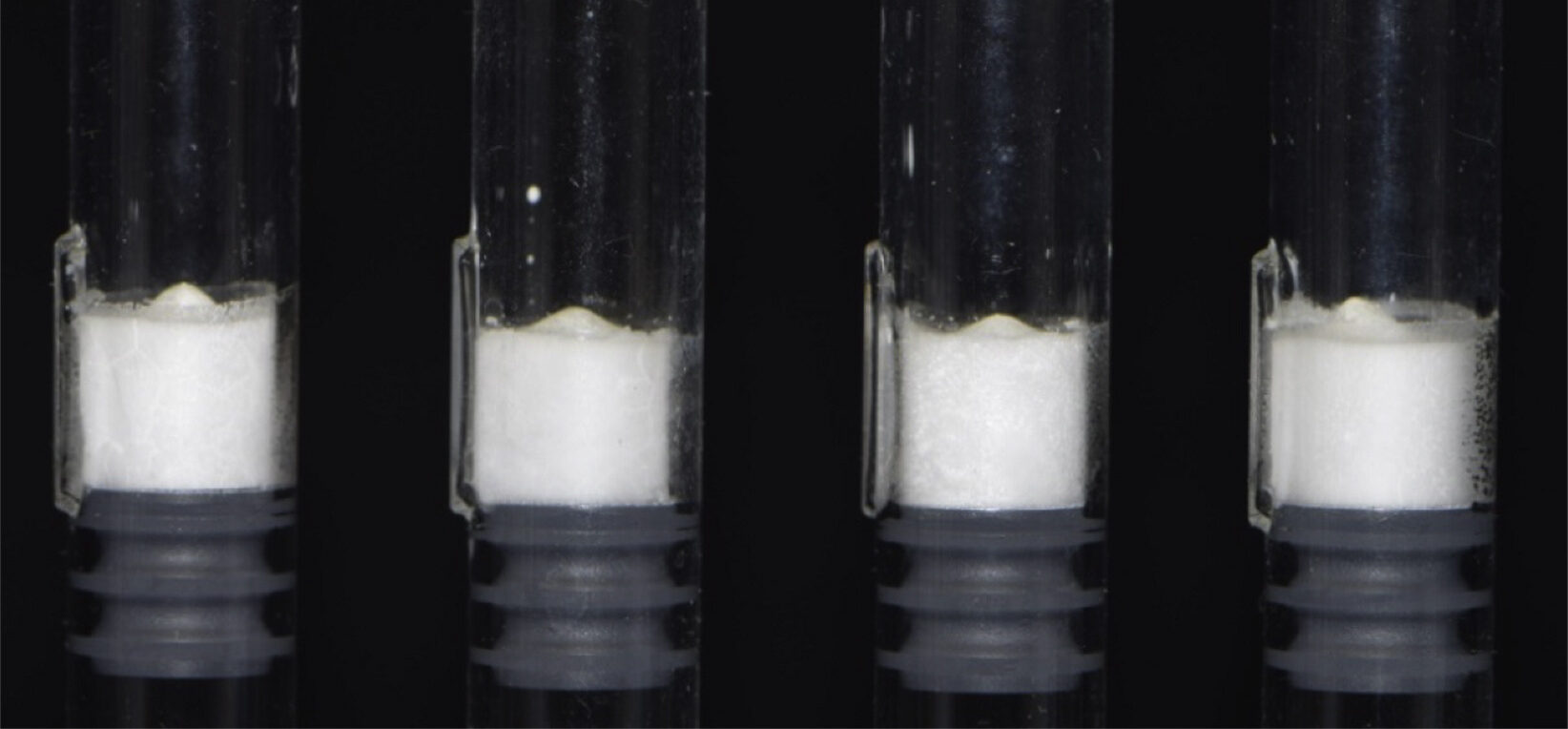
Lyophilized enzymes

Macaroni
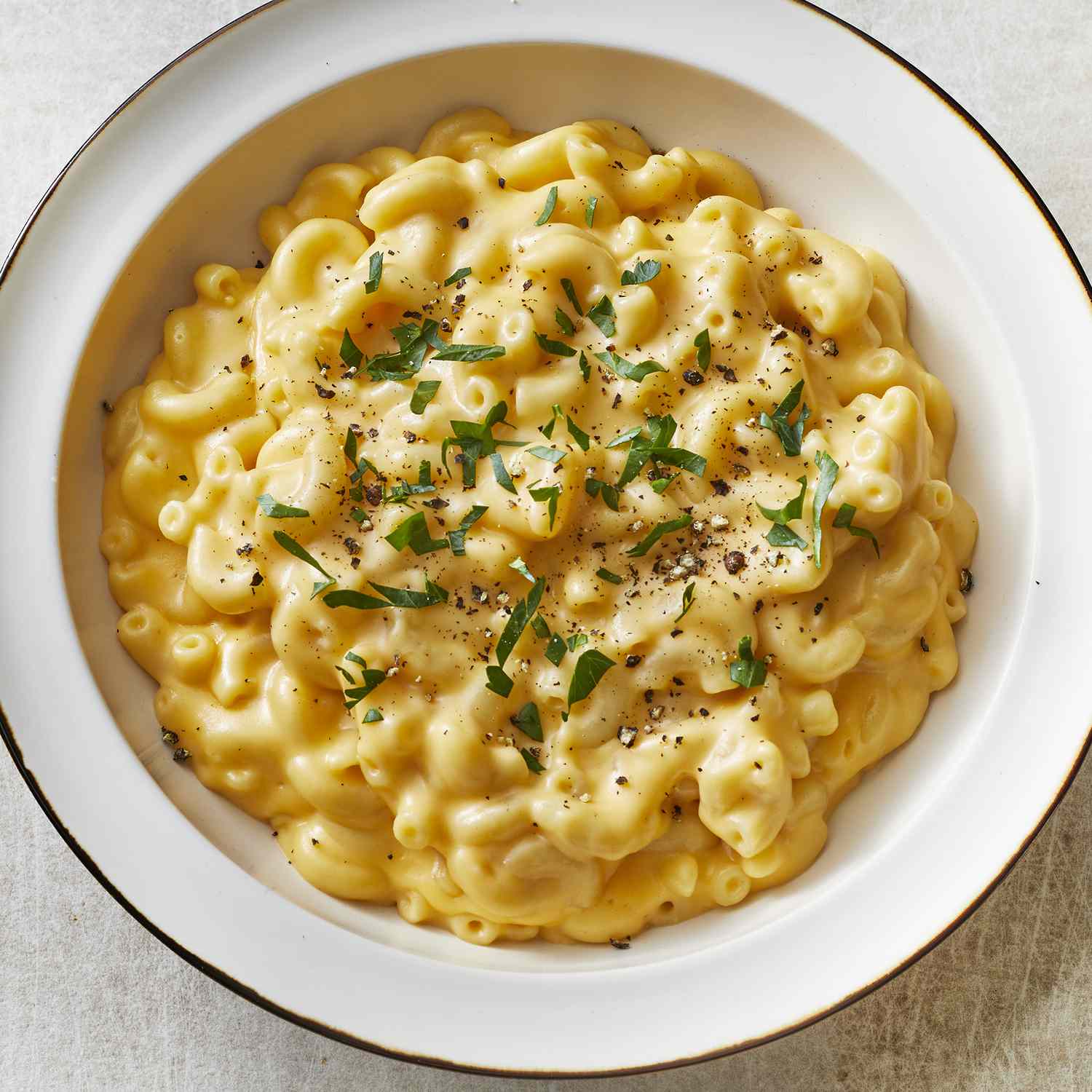
Macaroni and cheese
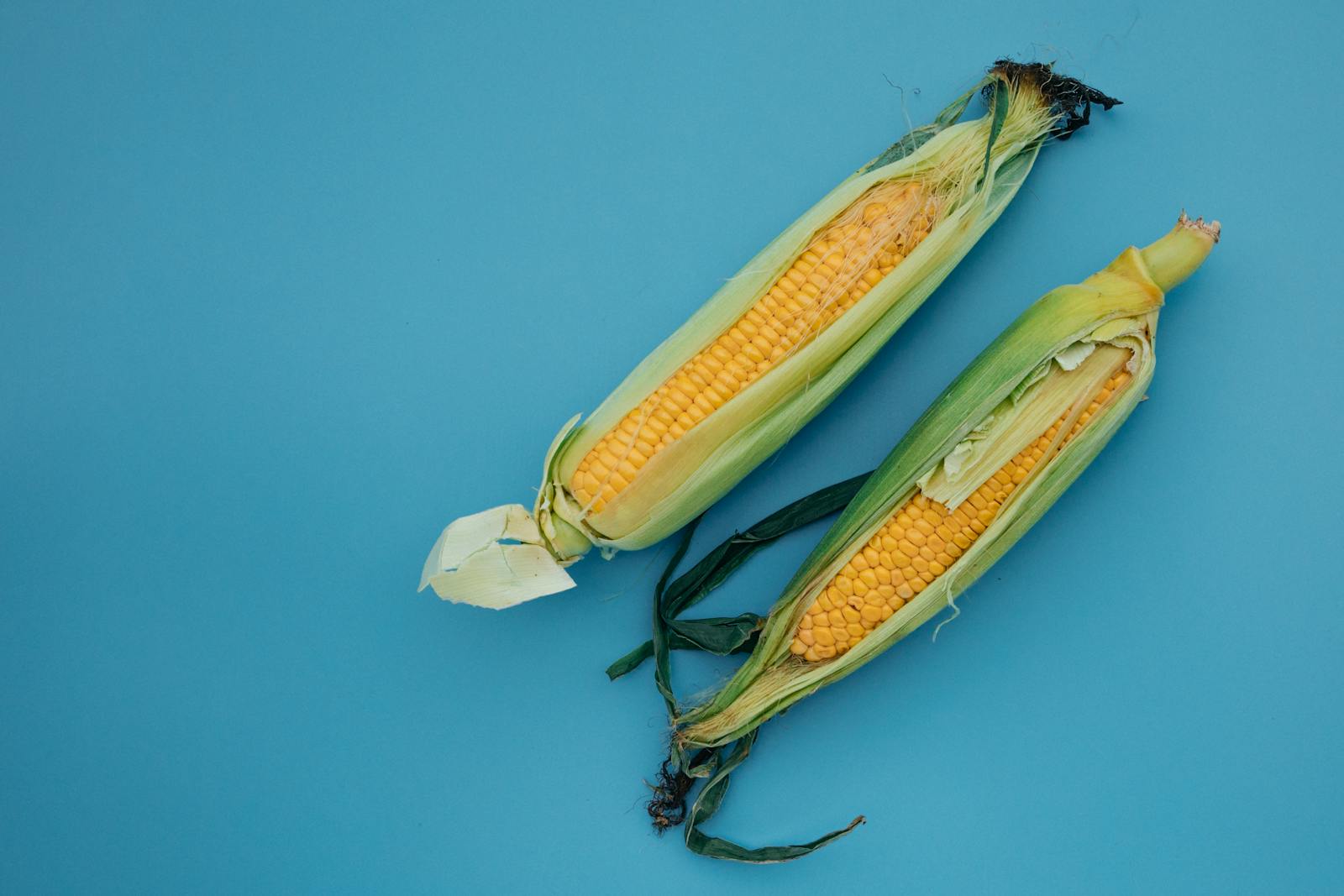
Maize
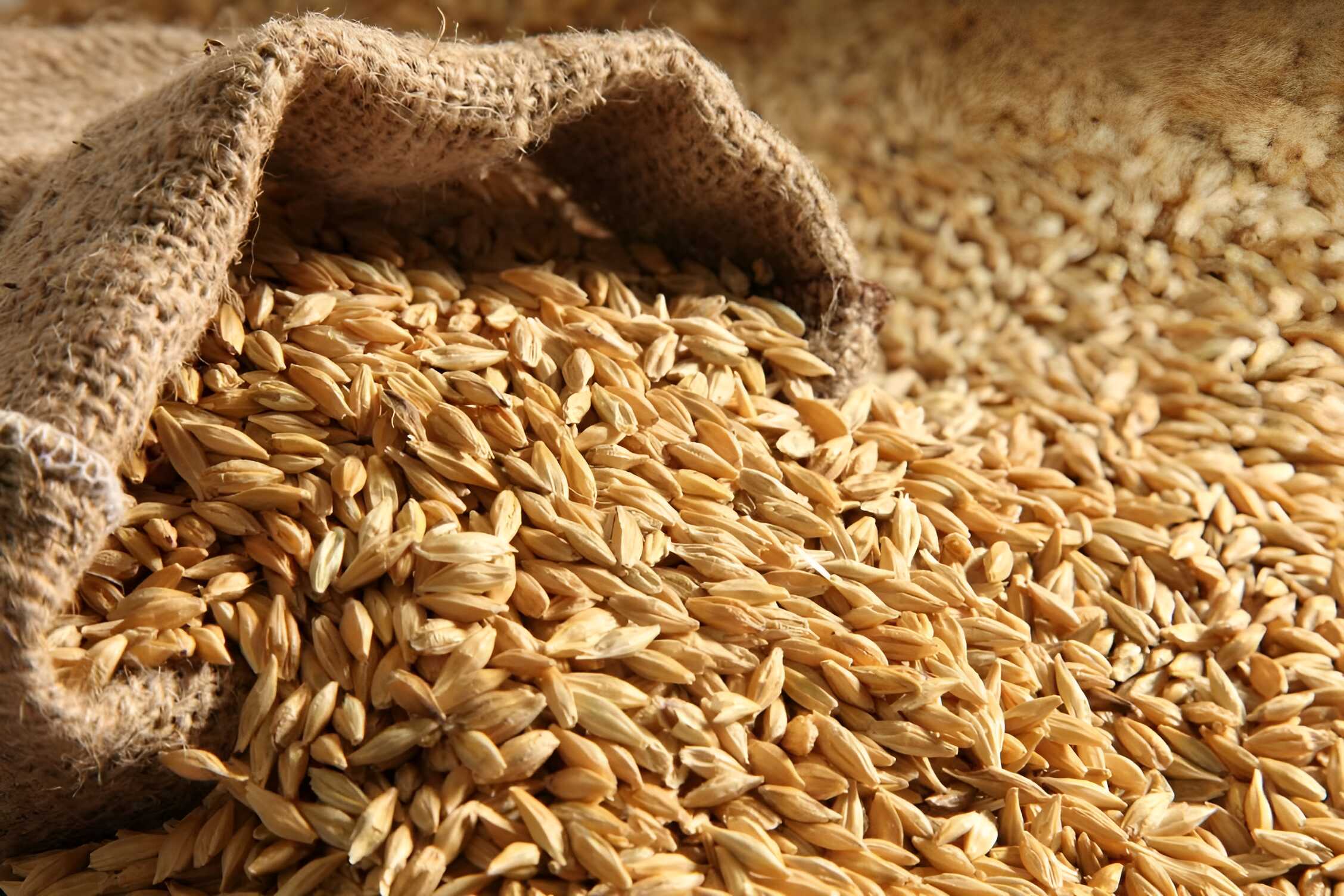
Malt
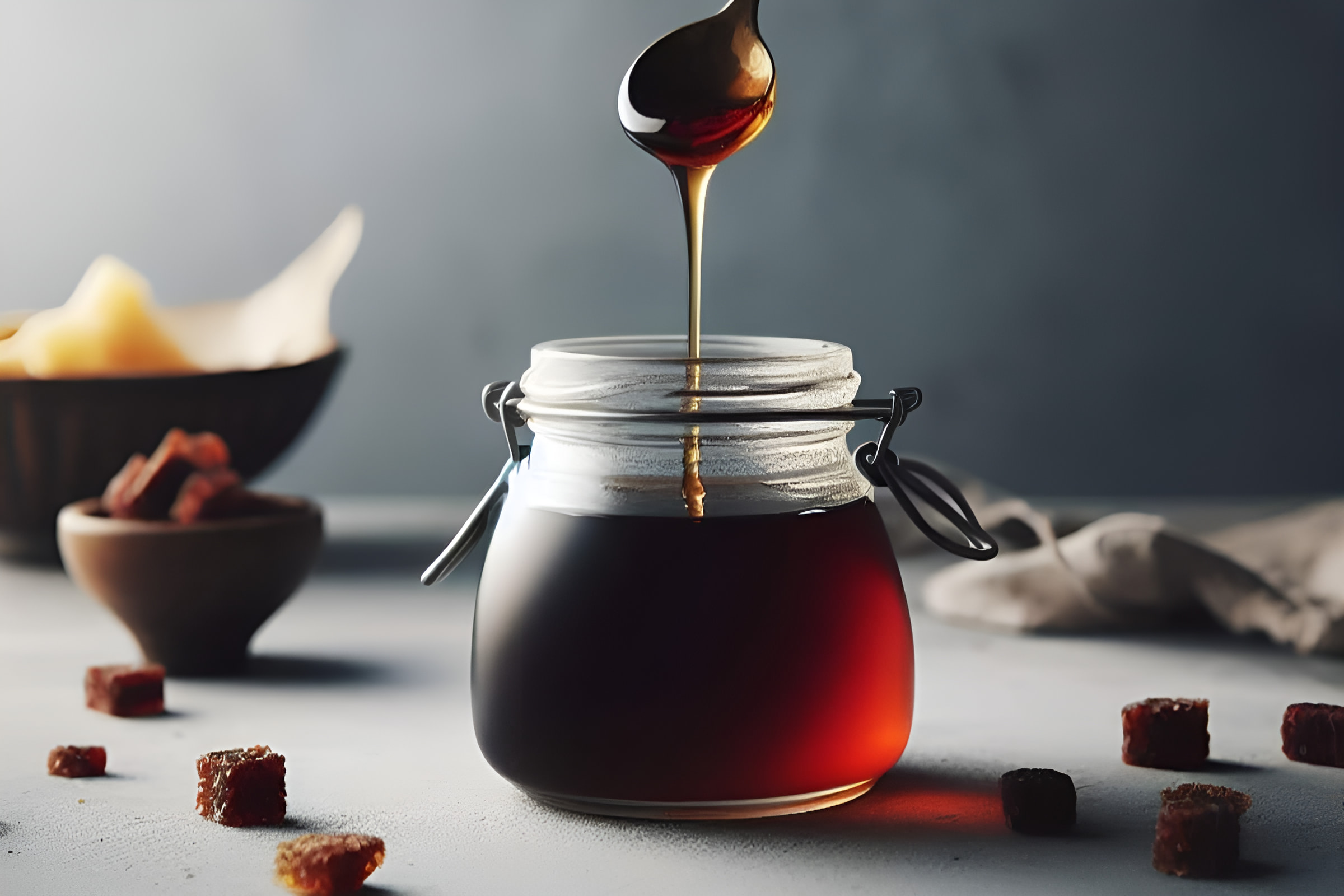
Malt extract
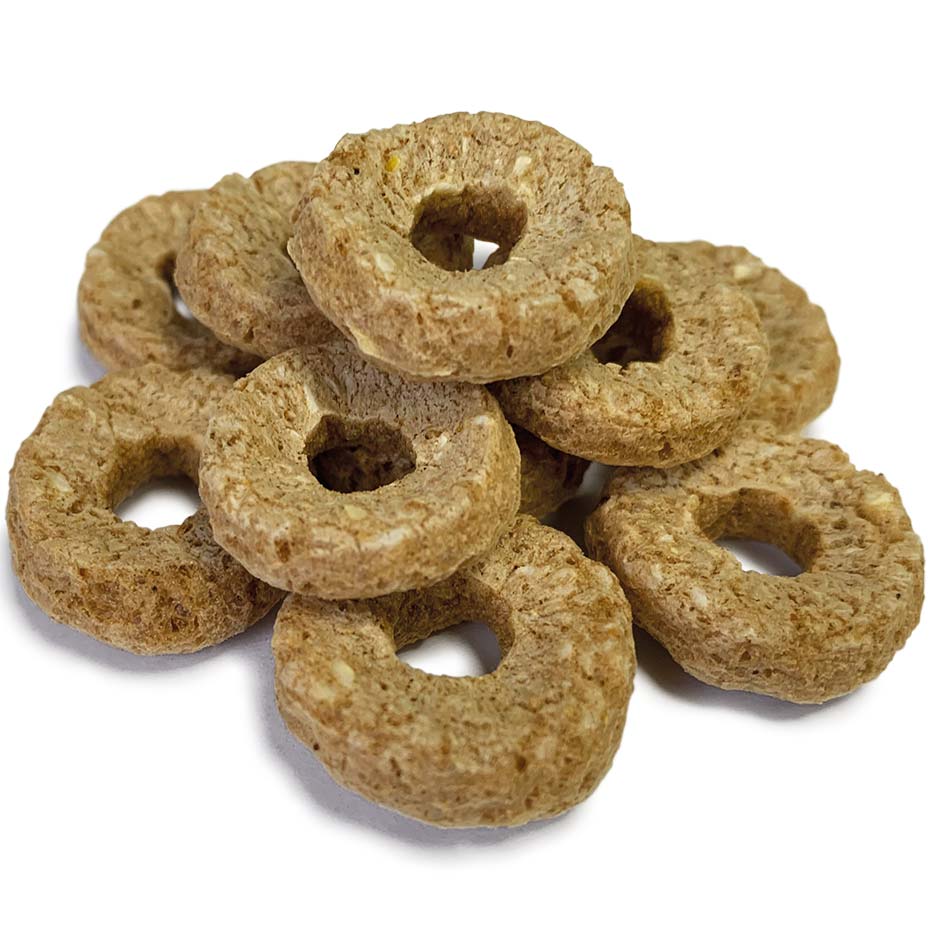
Malt rings
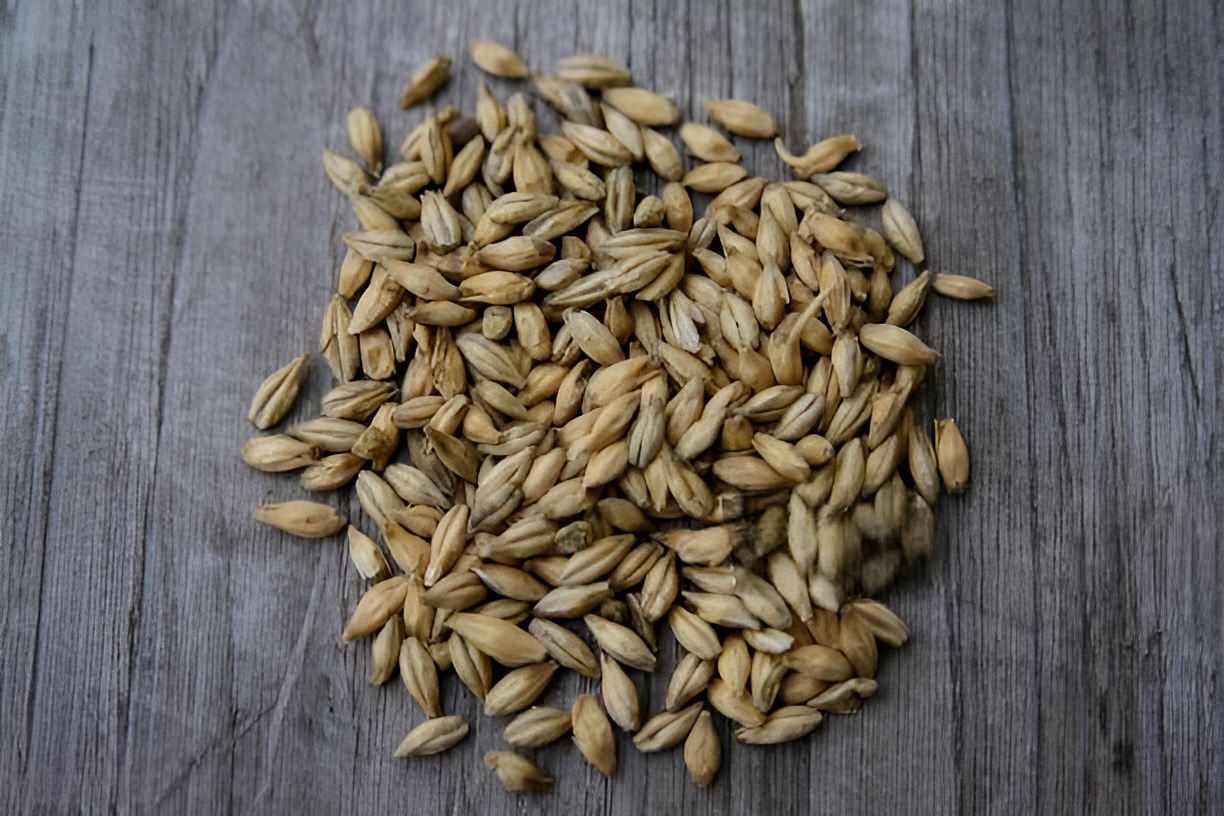
Malted barley
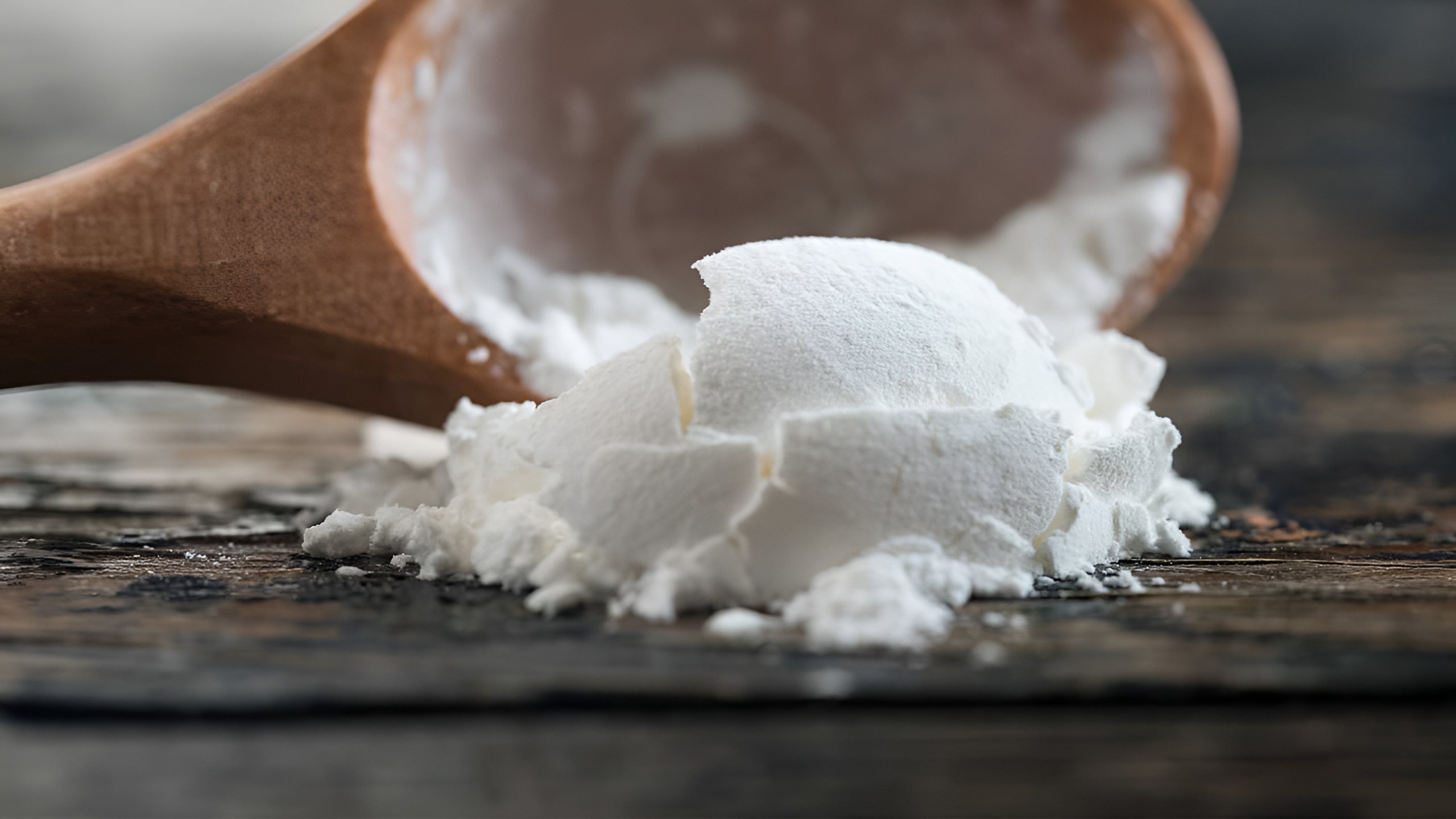
Maltodextrin
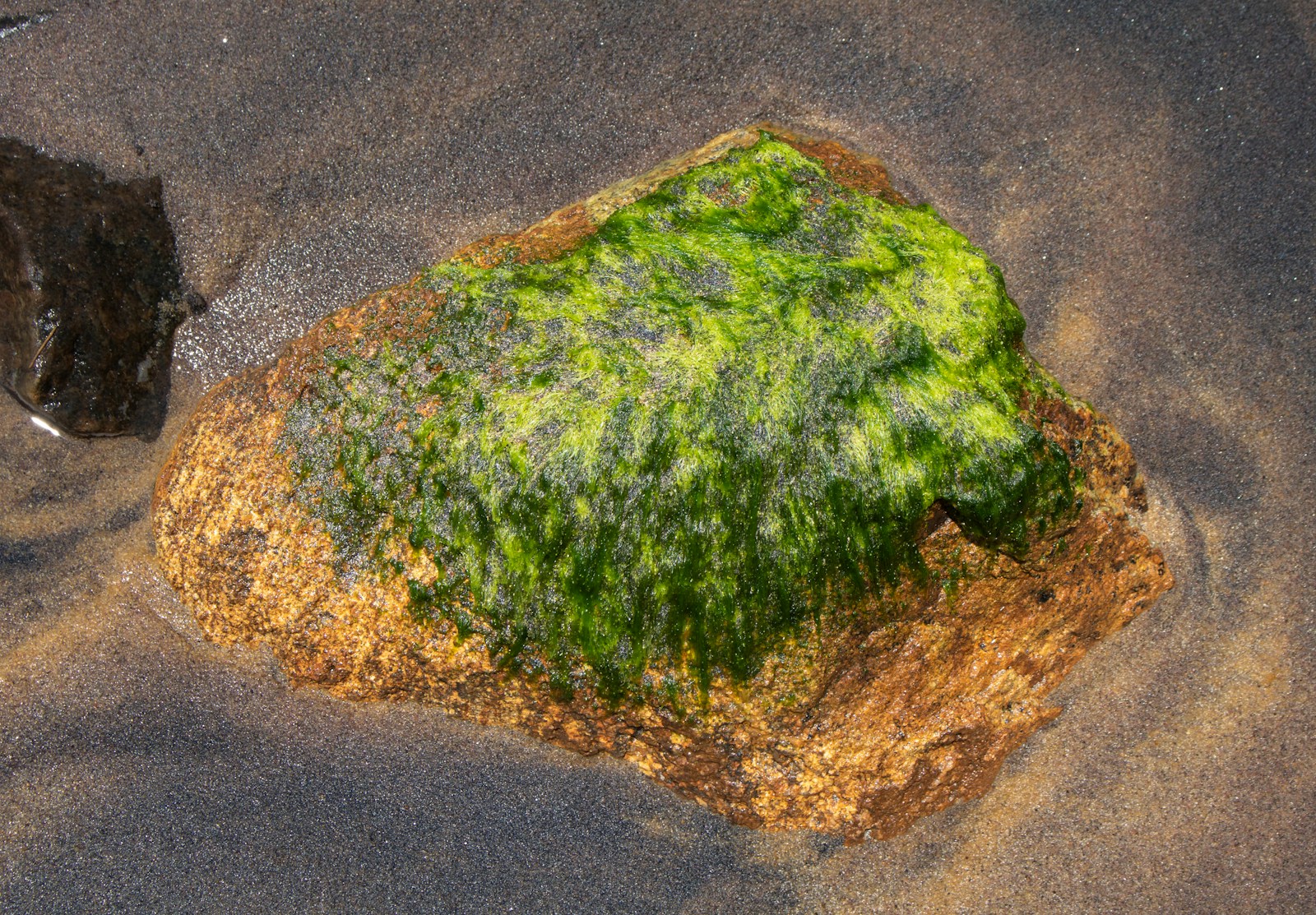
Marine algae
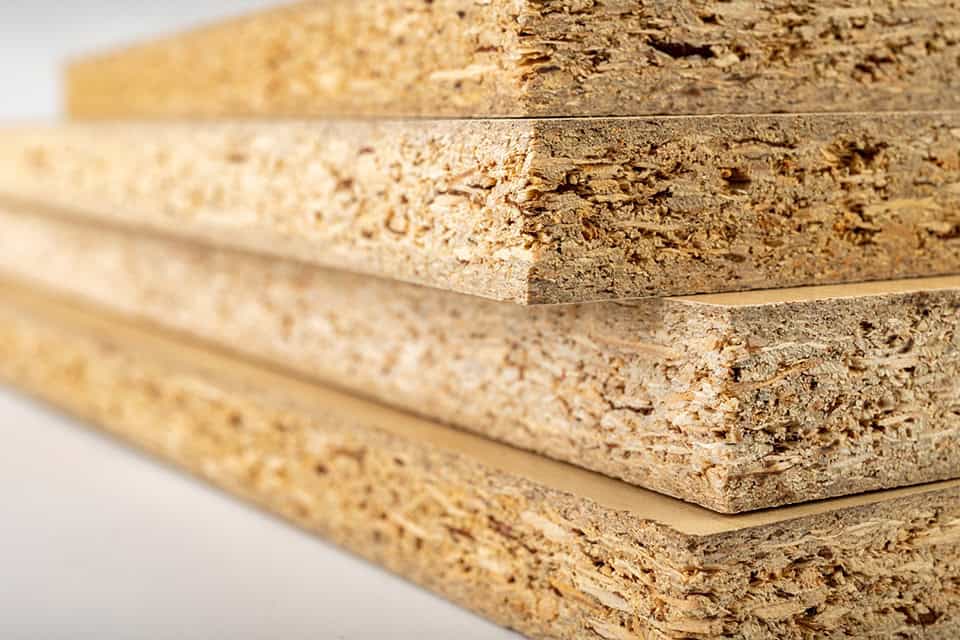
Mdf boards
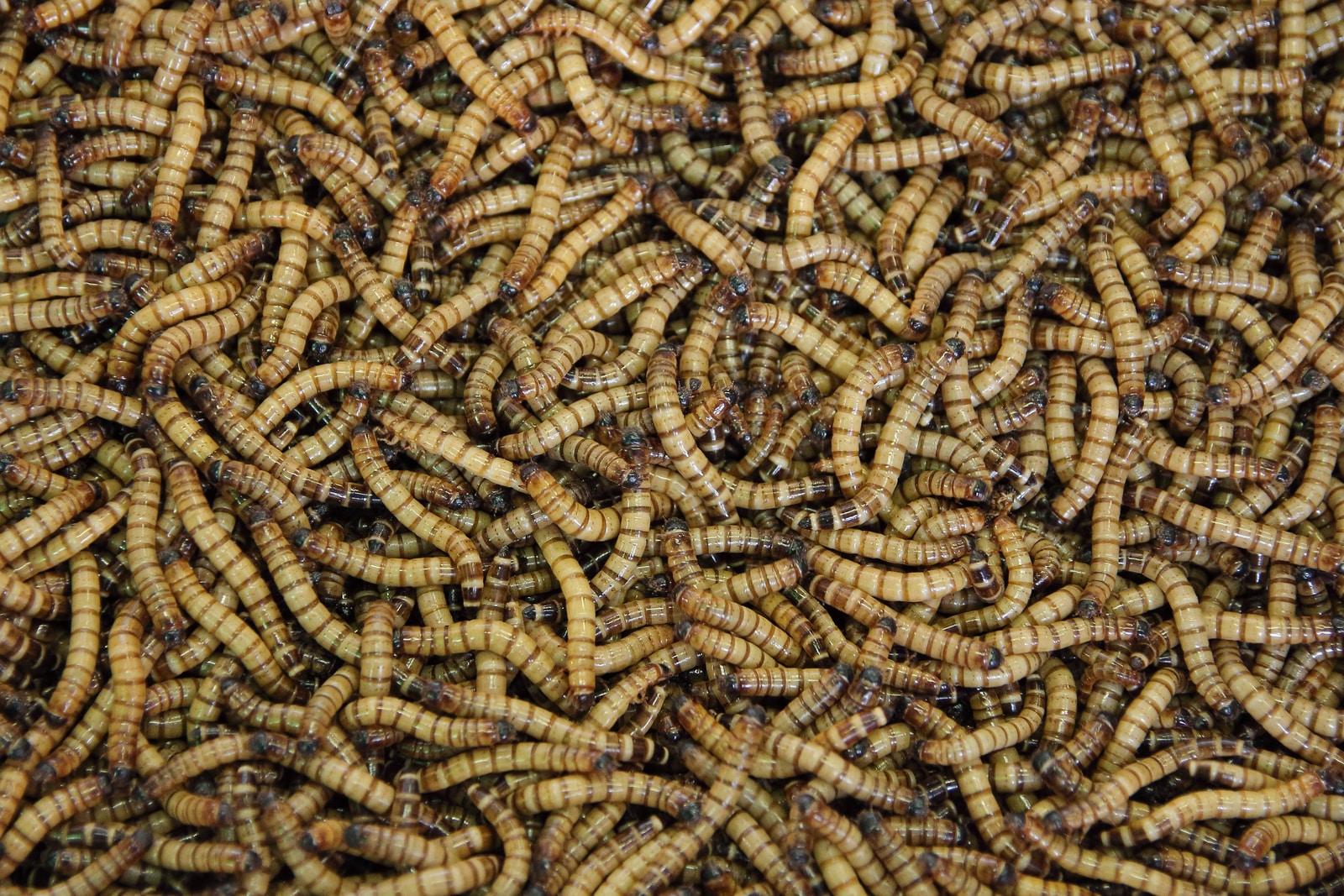
Mealworm protein
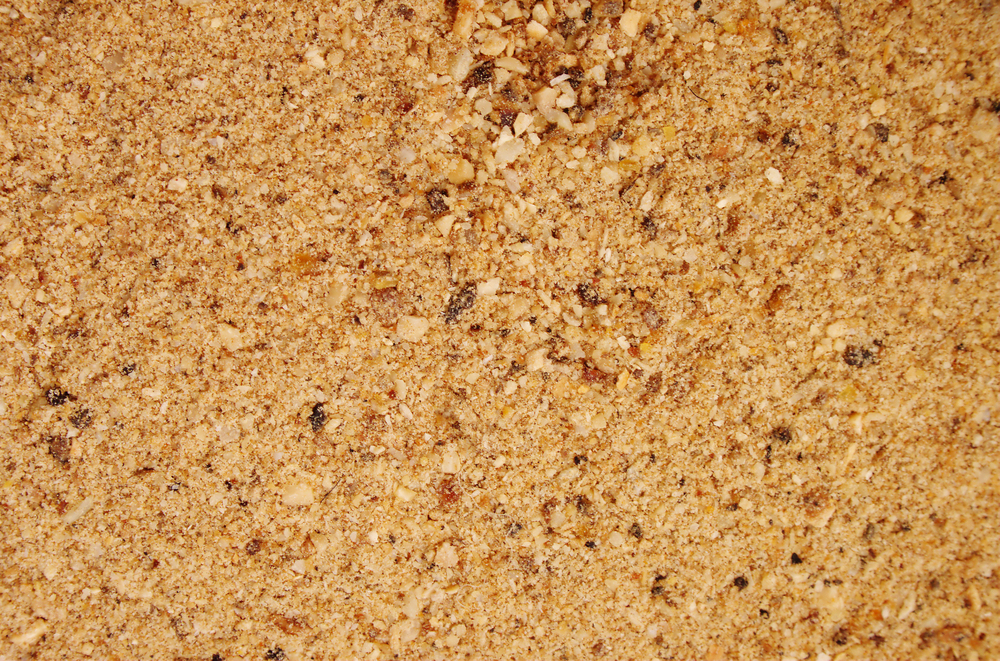
Meat and bone meal
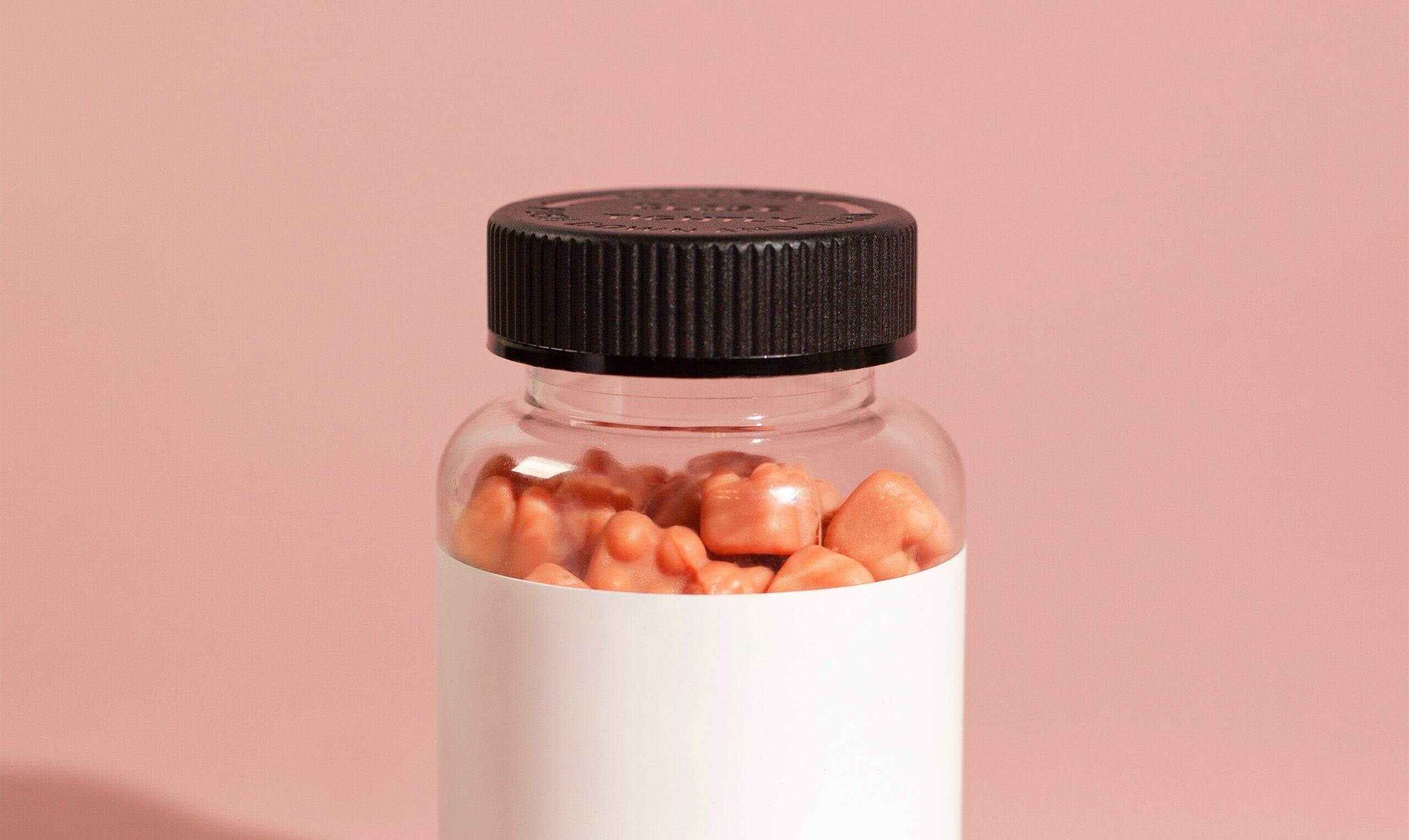
Medical gummies
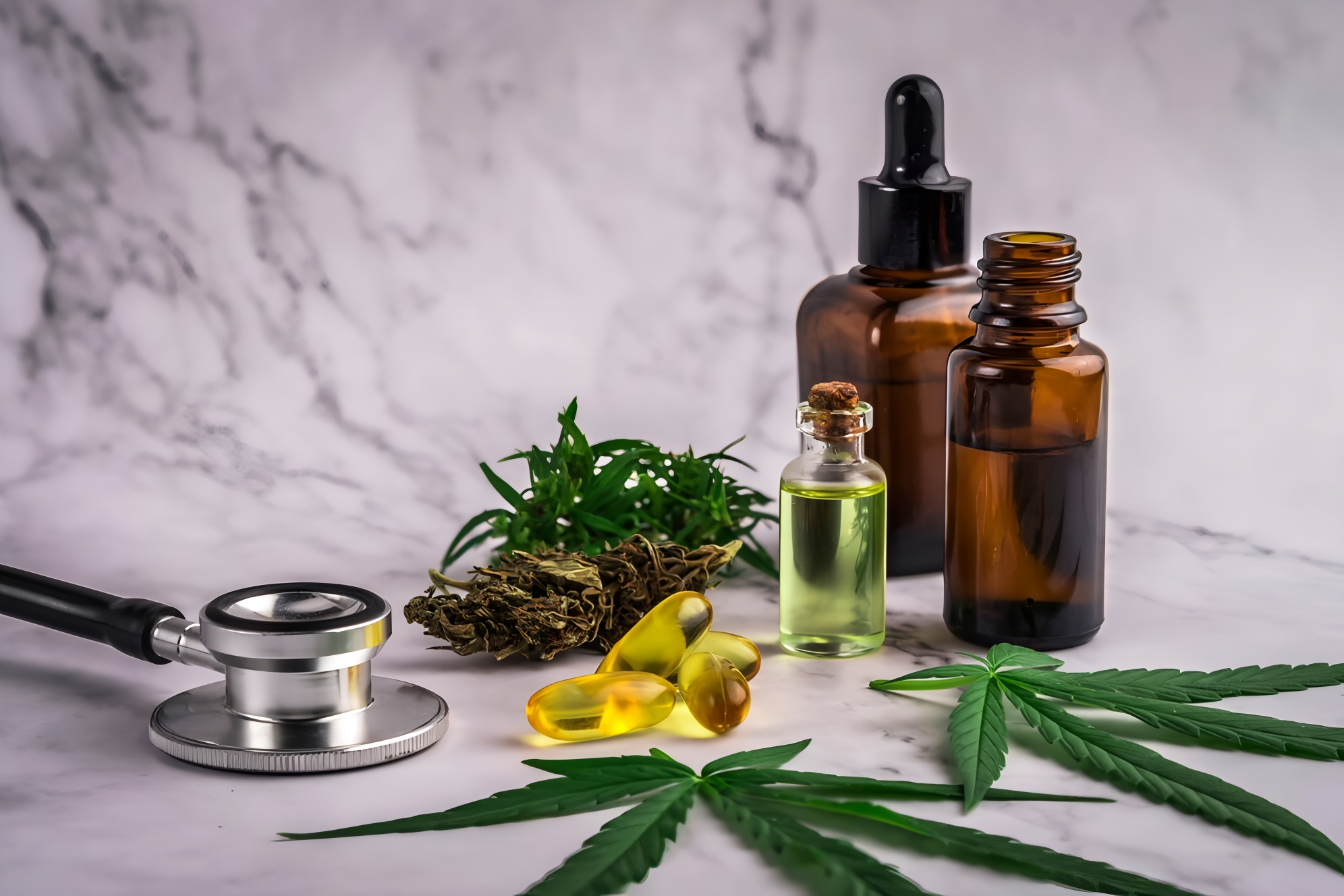
Medicinal cannabis
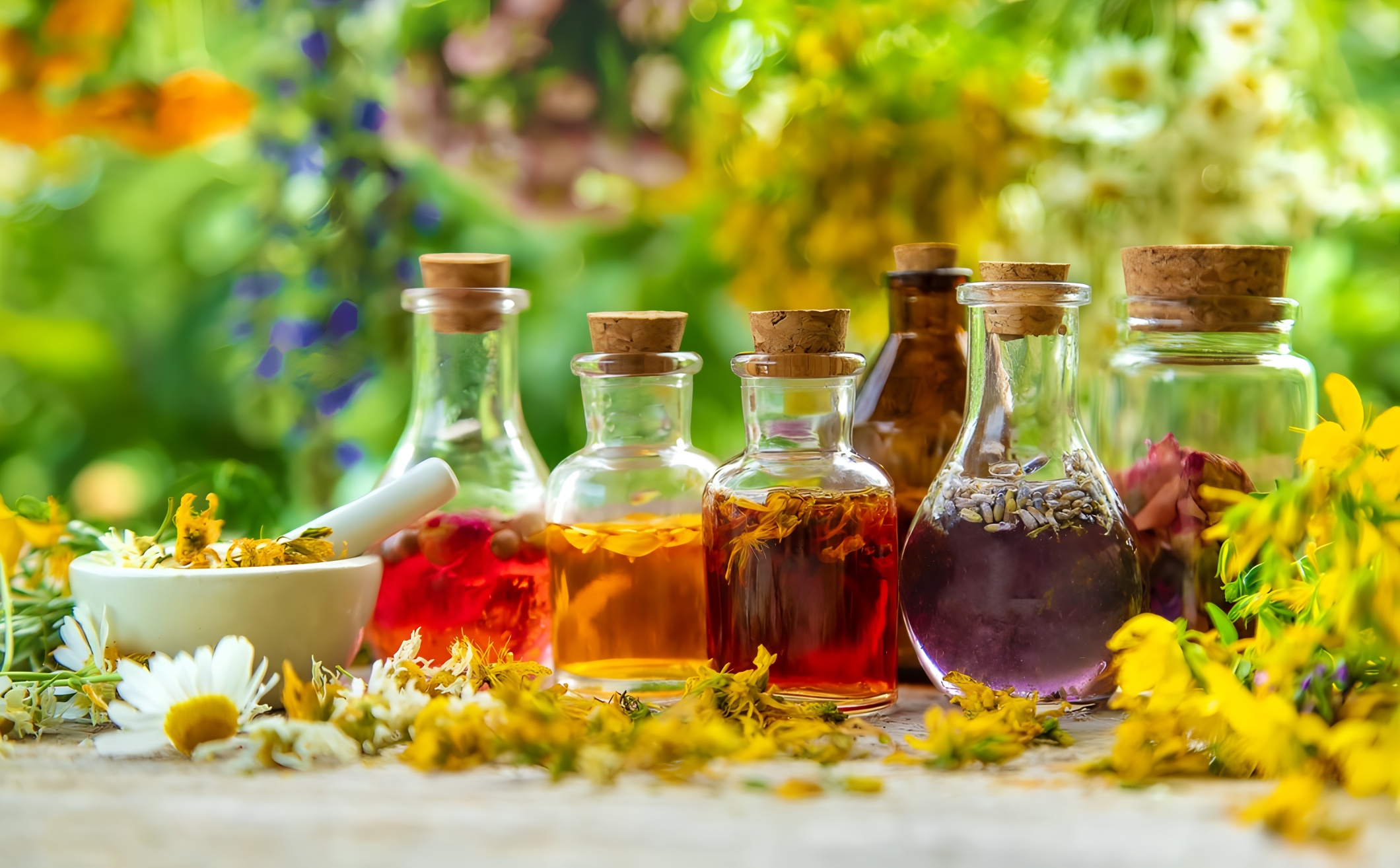
Medicinal herbs
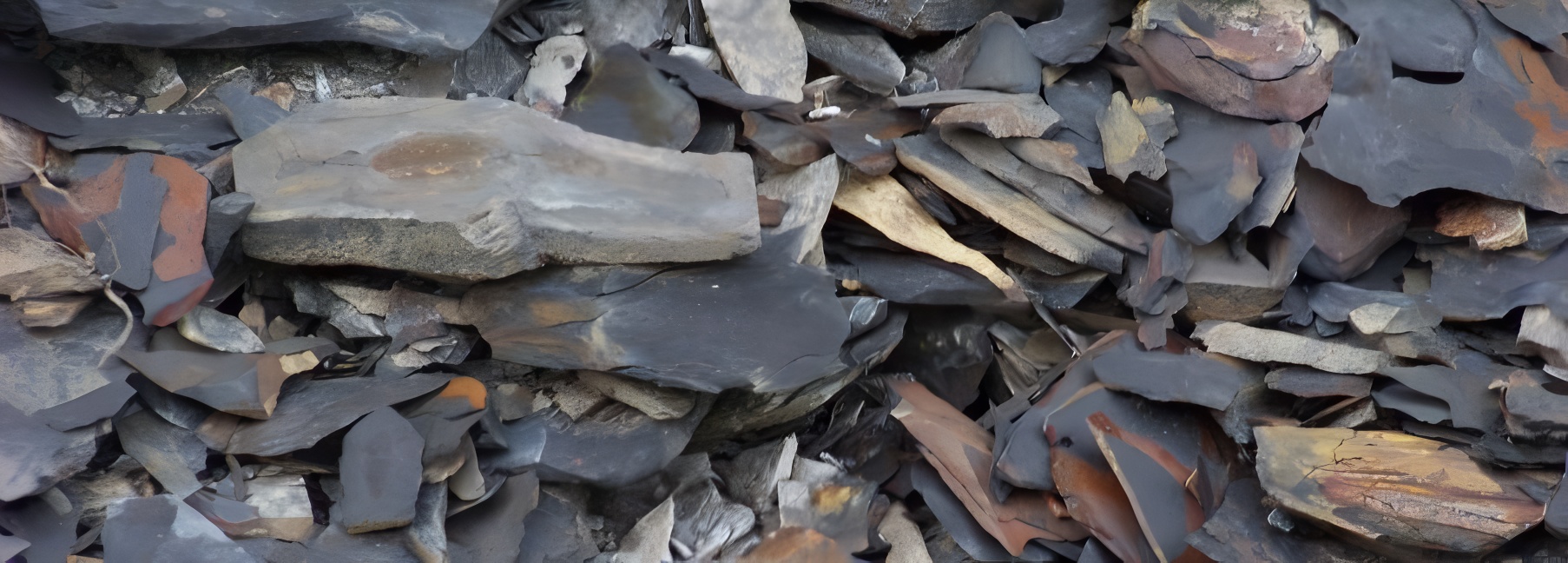
Metal ores
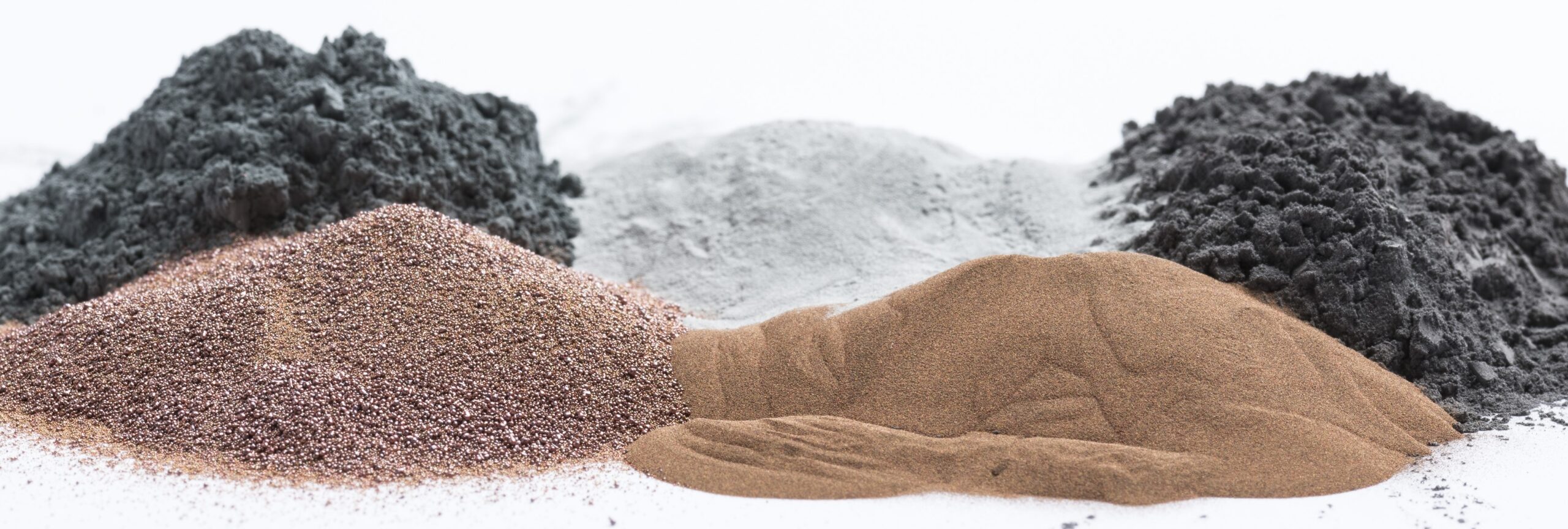
Metal powders
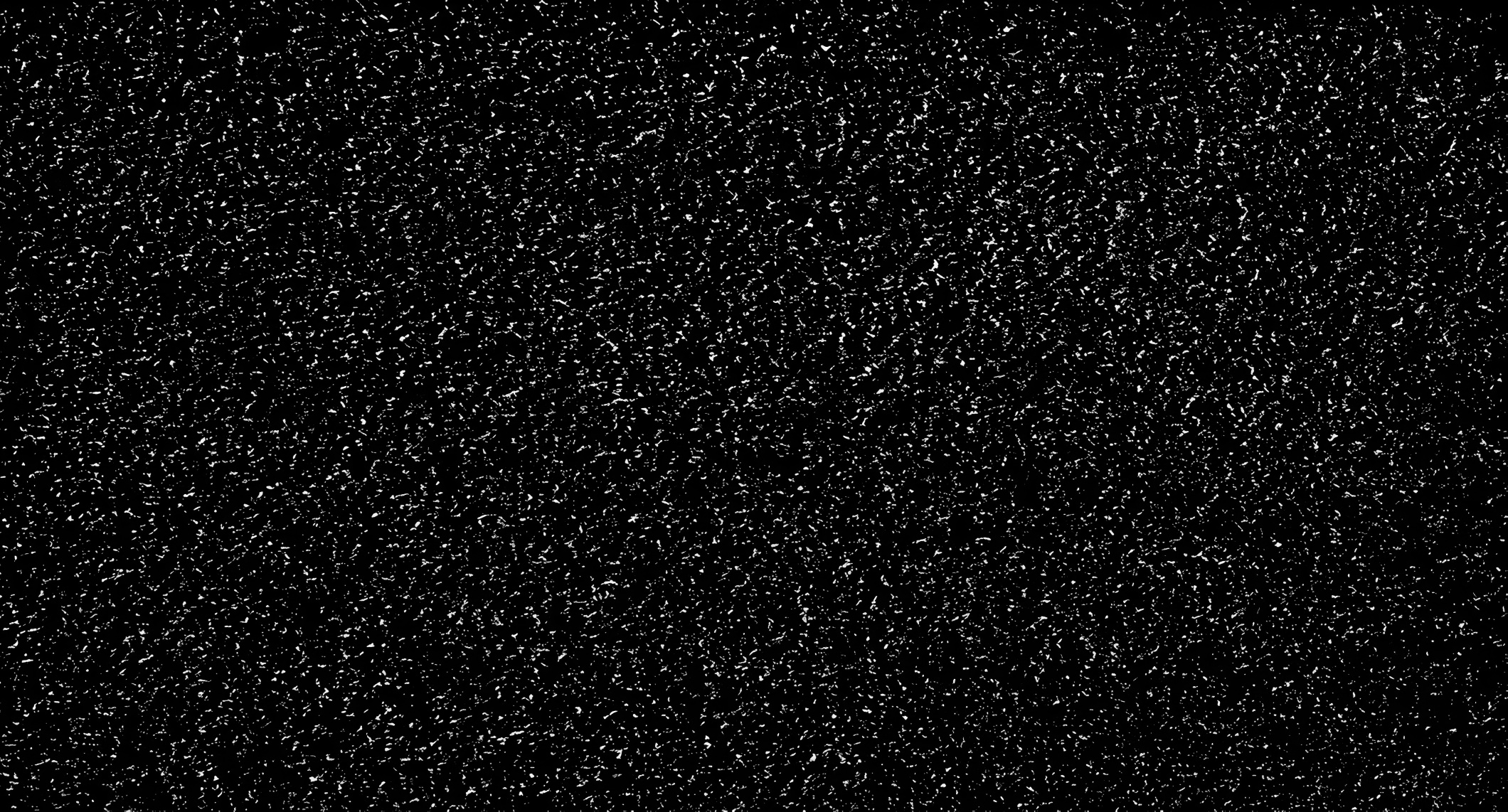
Metal salts
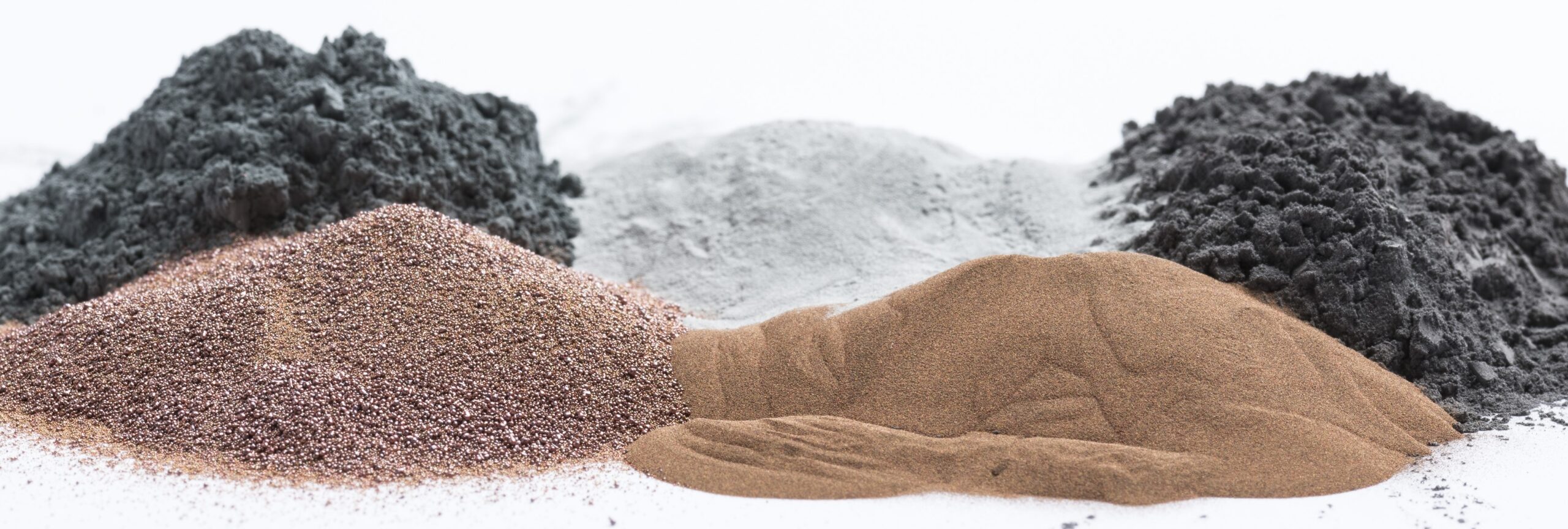
Metallic powders
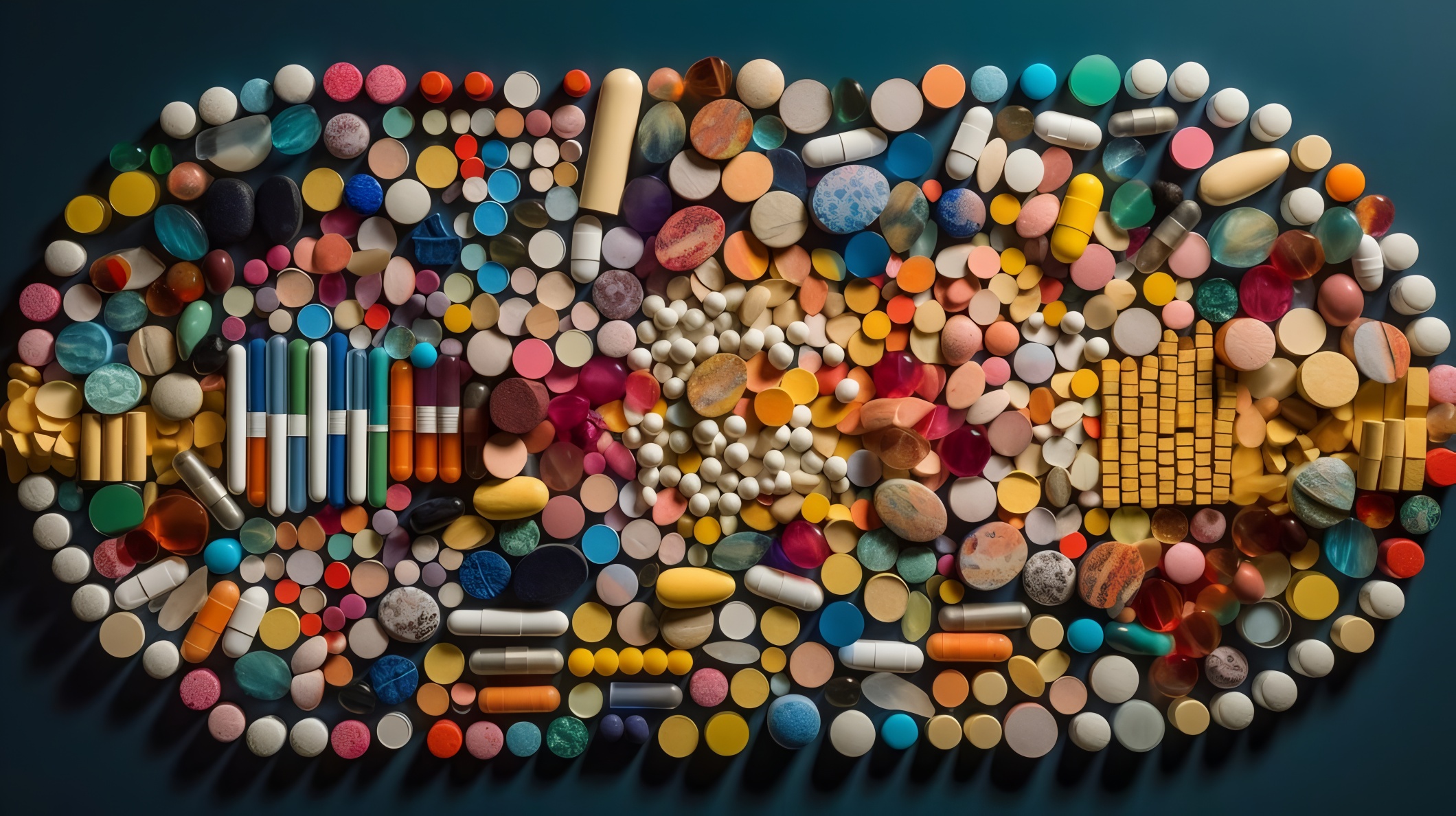
Micro-tablets

Microcrispies
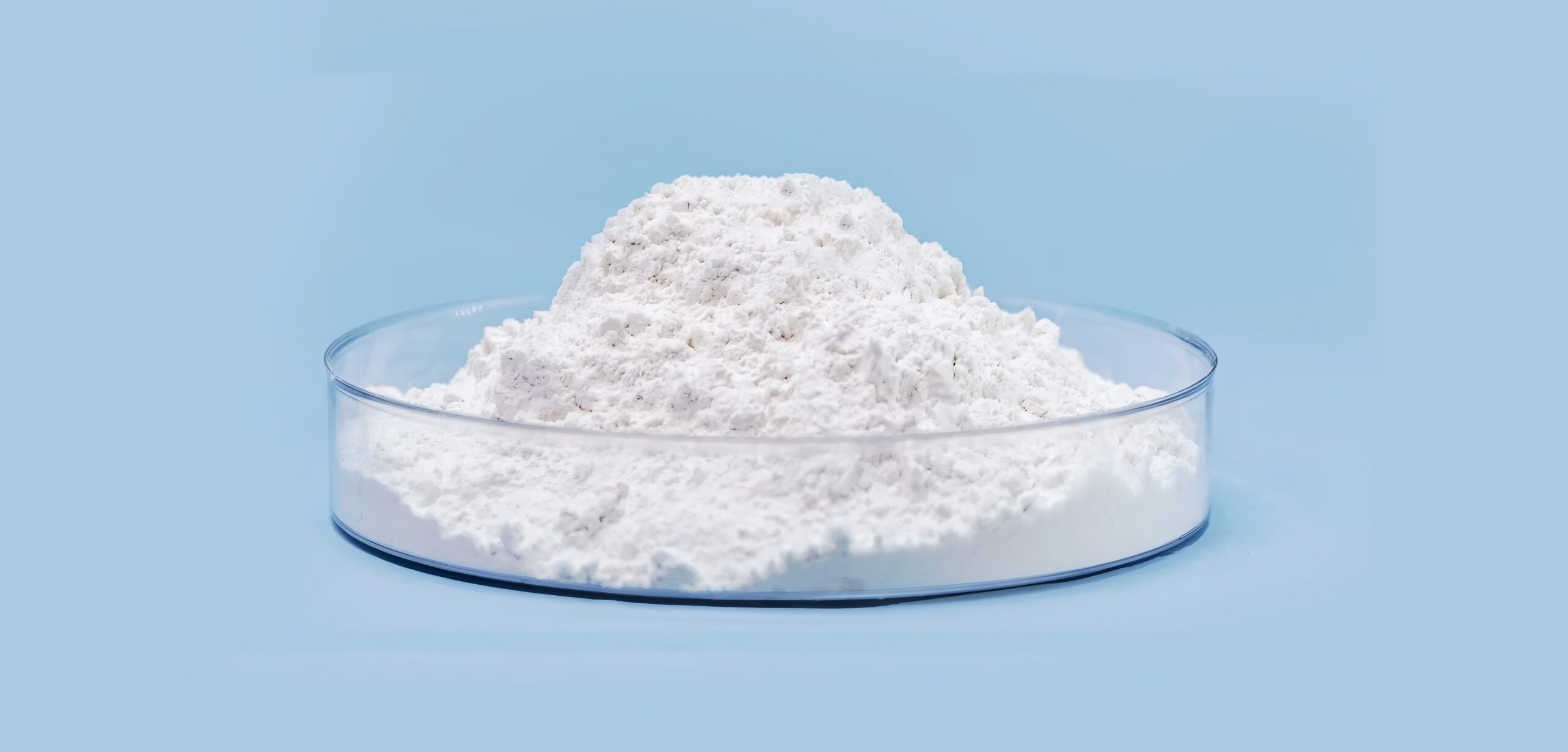
Microcrystalline cellulose
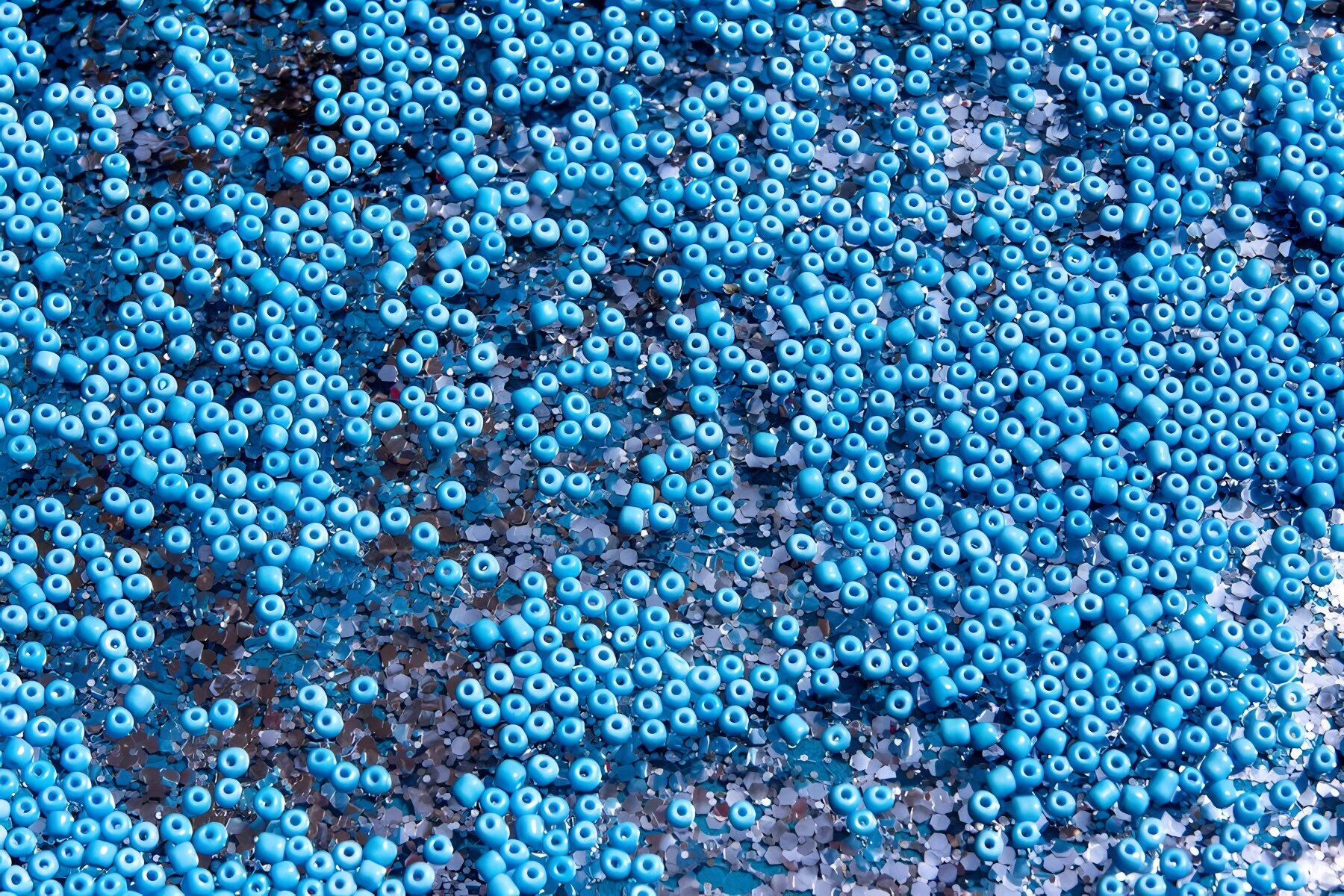
Microspheres
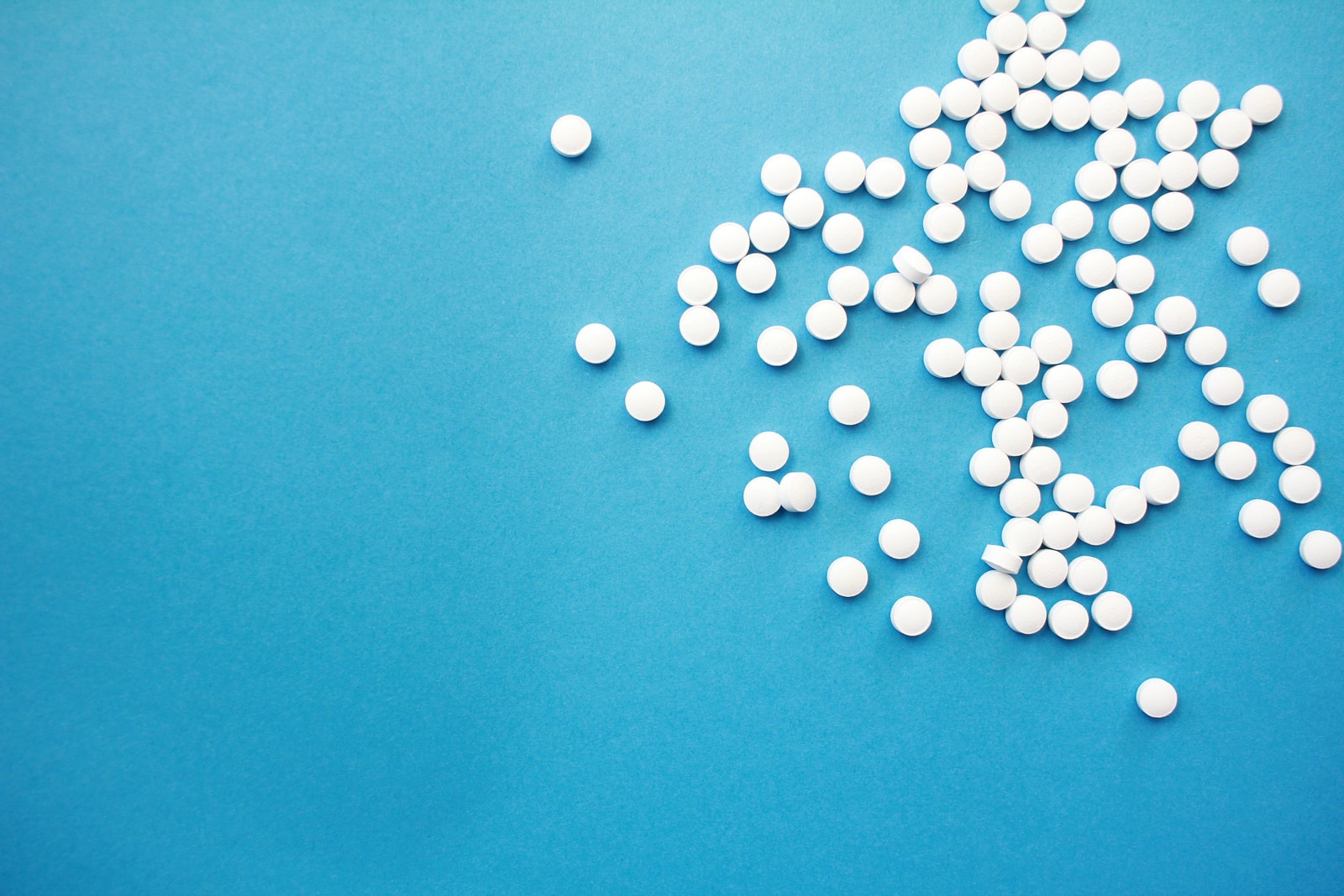
Microtablets
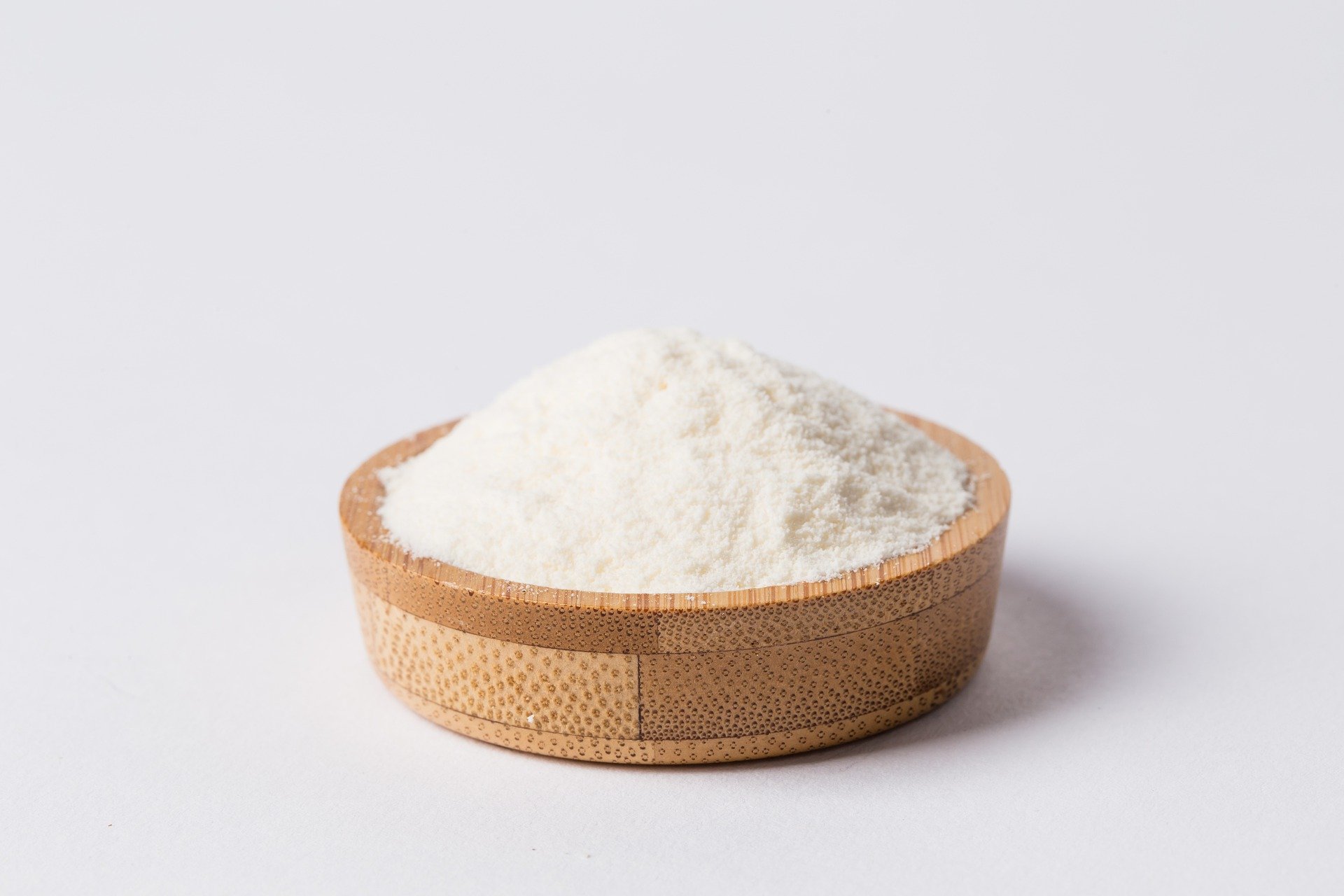
Milk powder
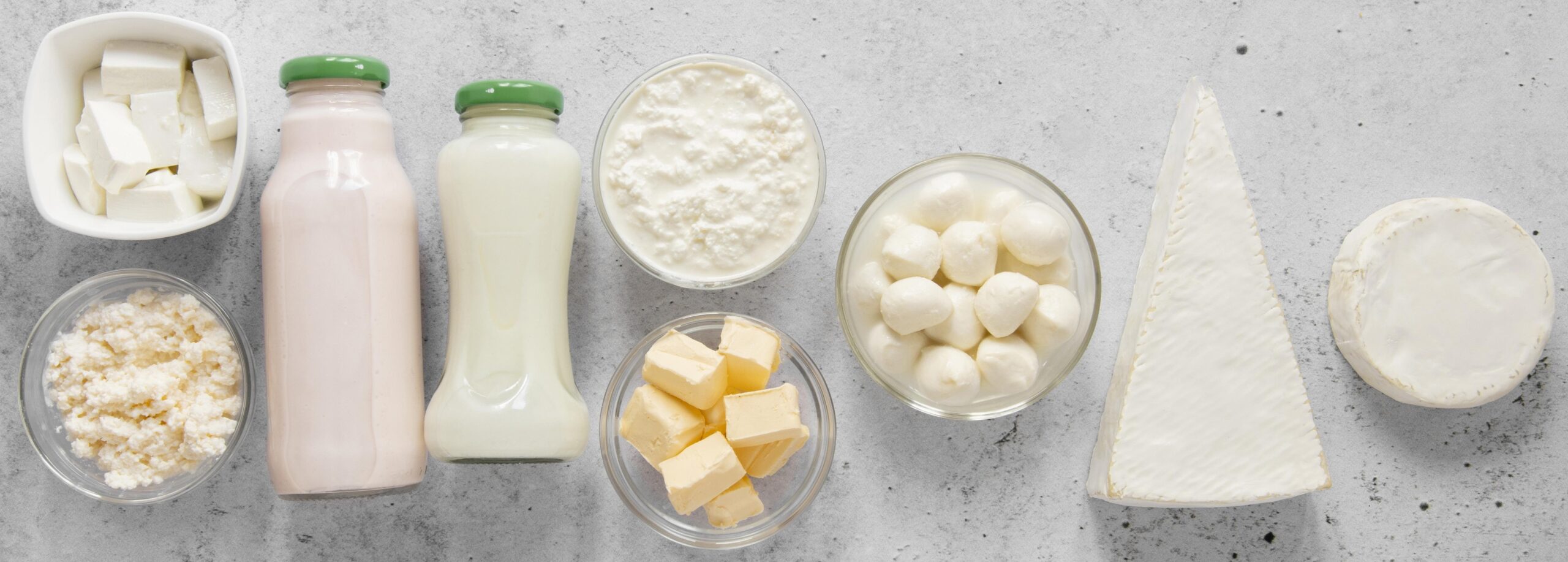
Milk protein isolate

Mineral fillers
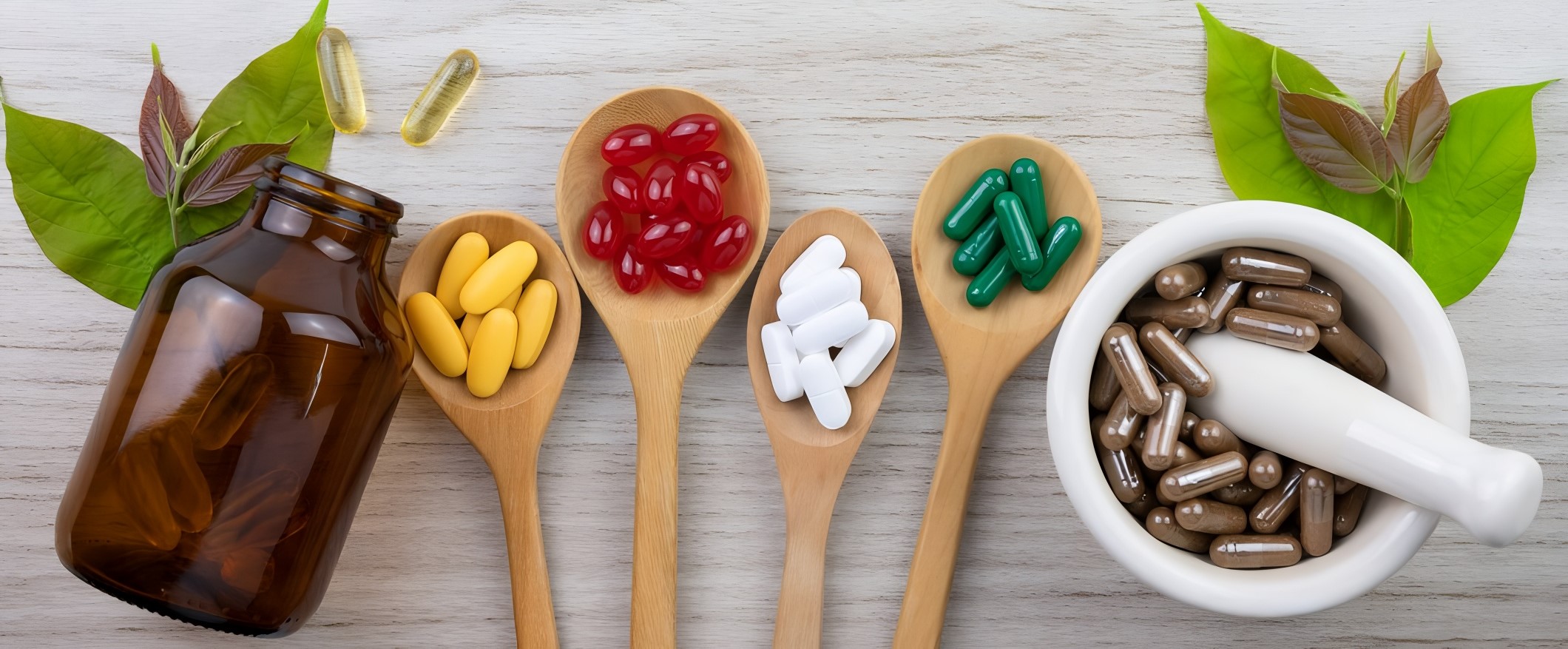
Mineral supplements
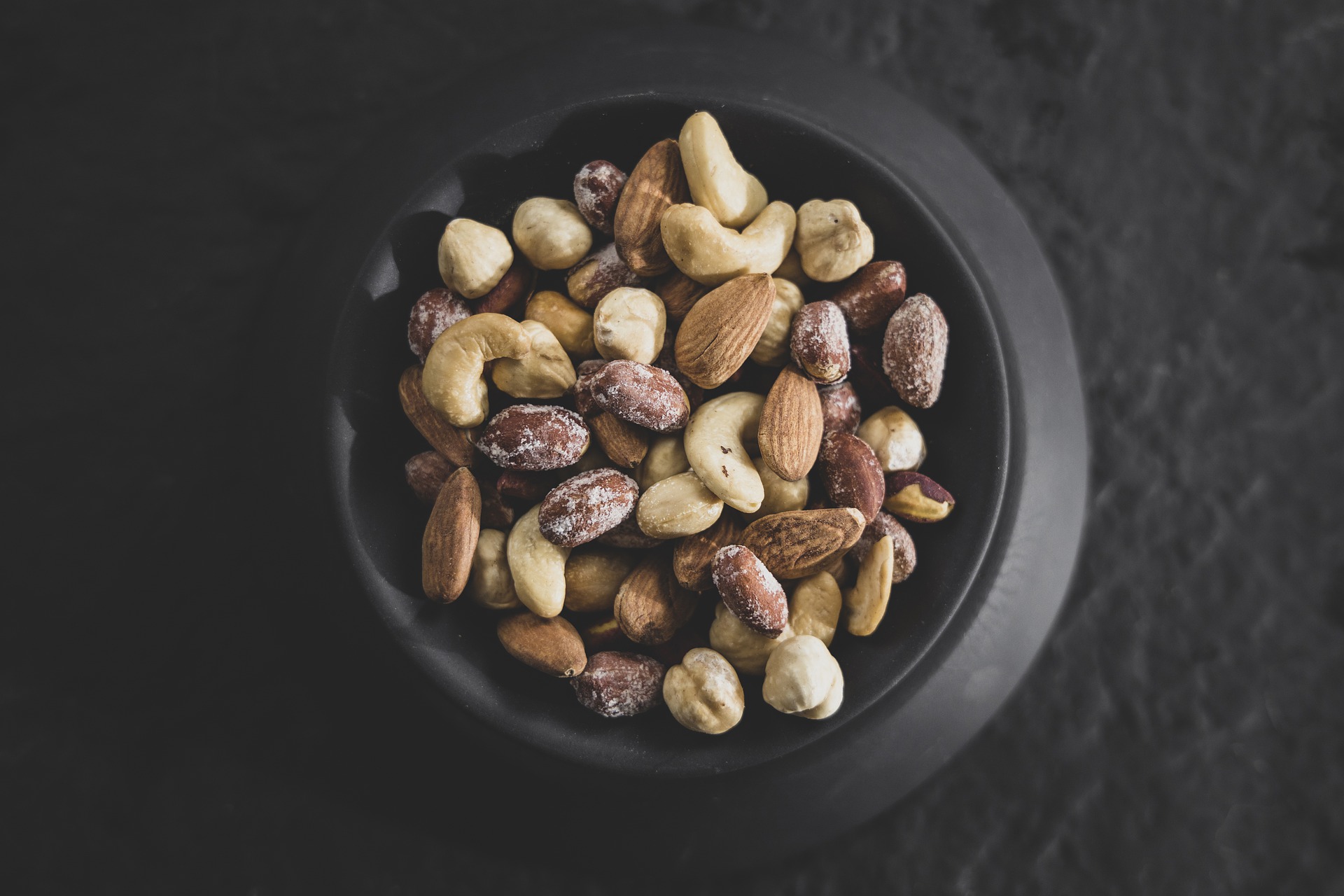
Mixed nuts
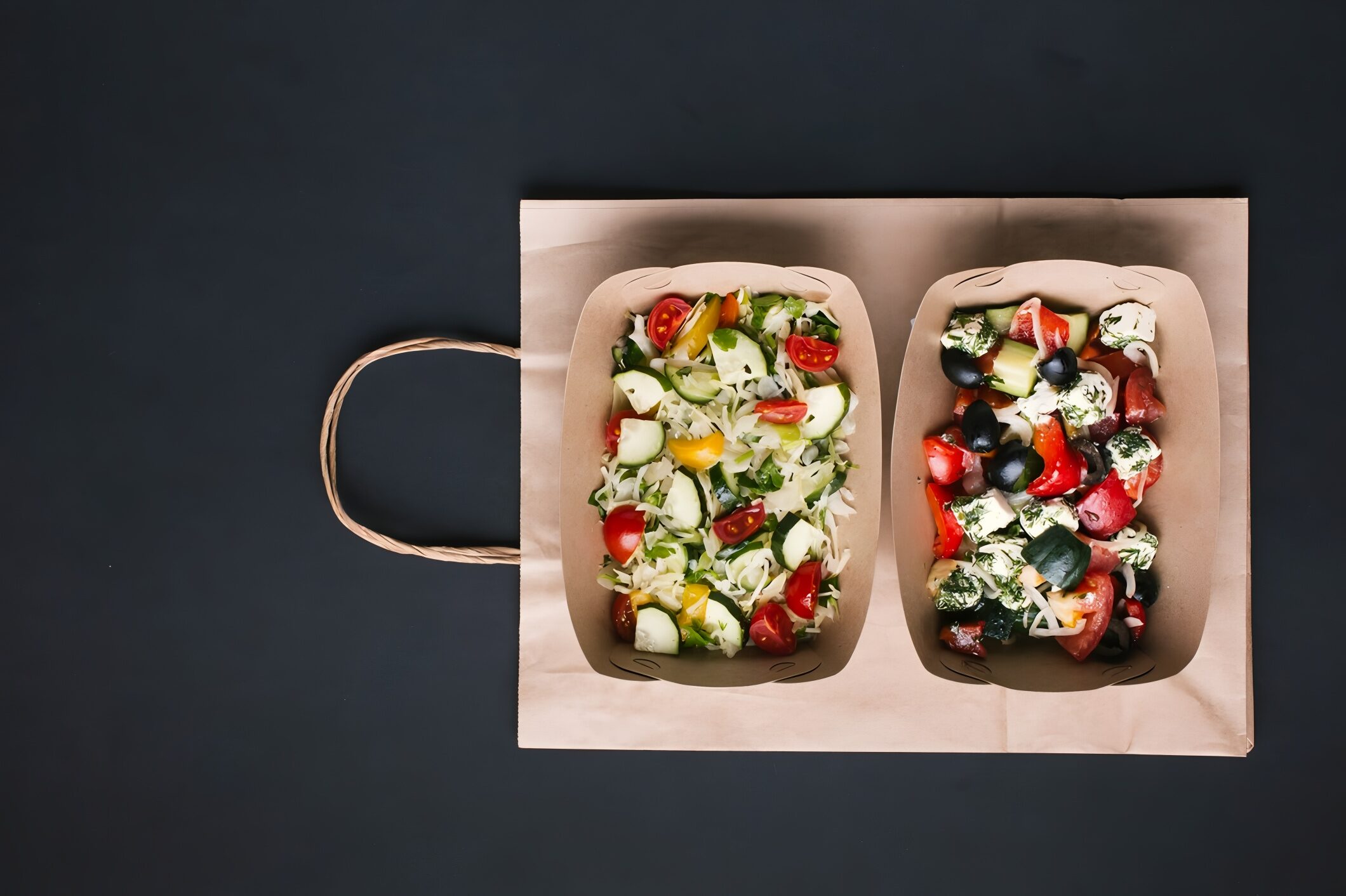
Mixed salad bags
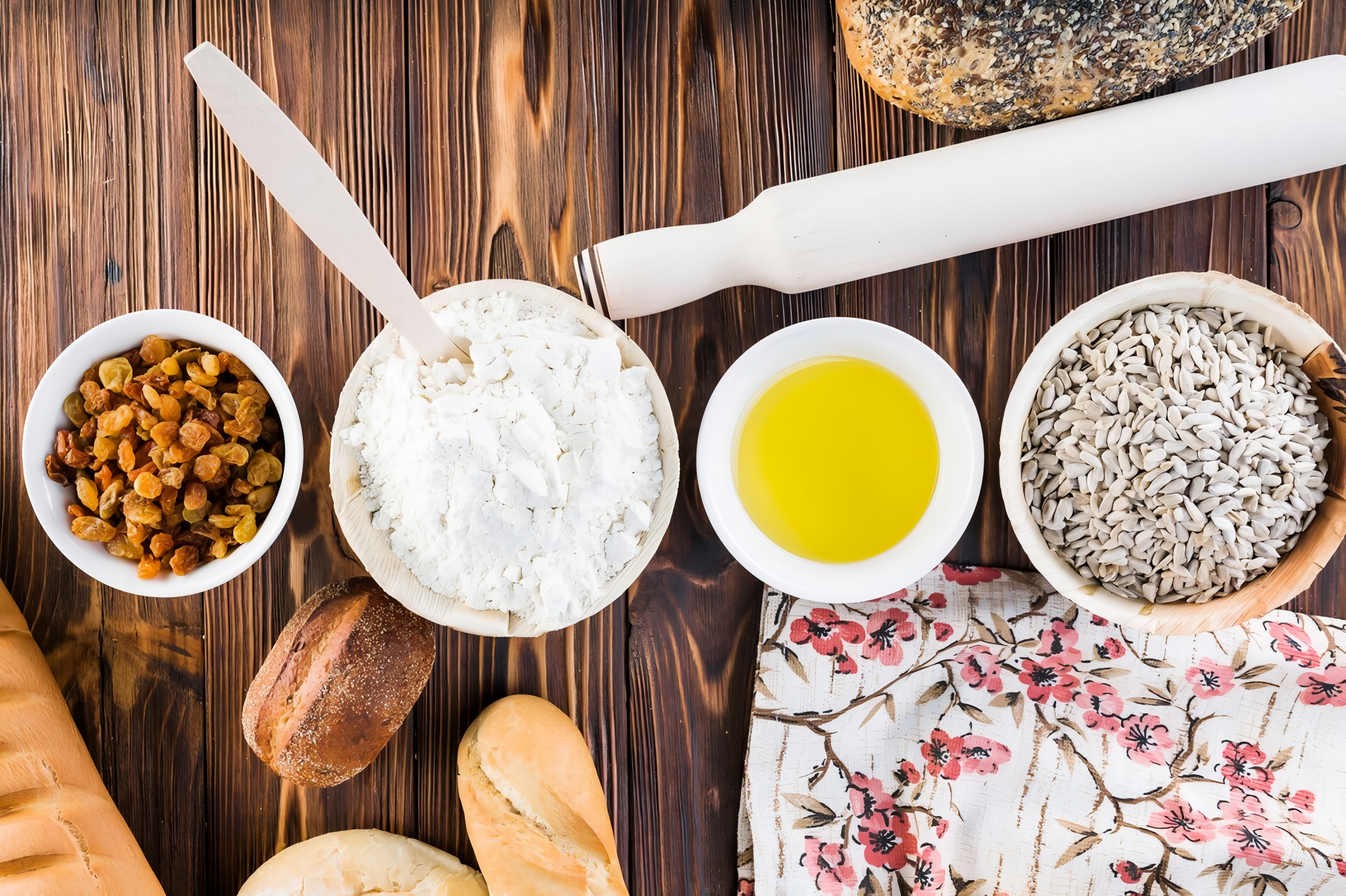
Modified starches
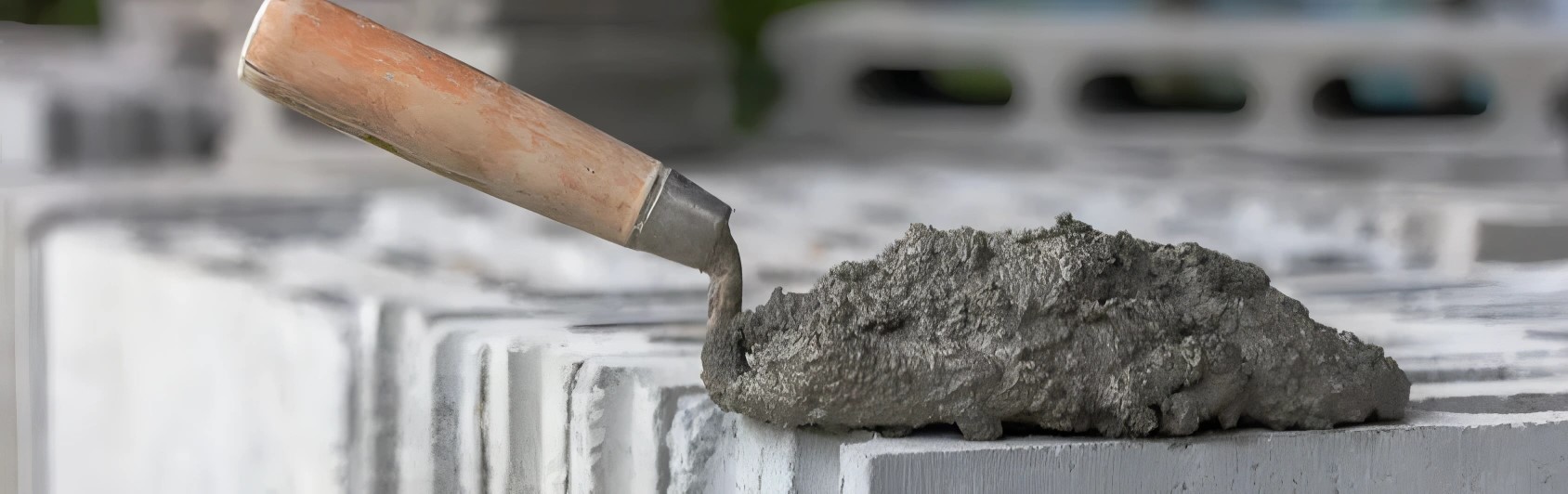
Mortar mix

Muesli
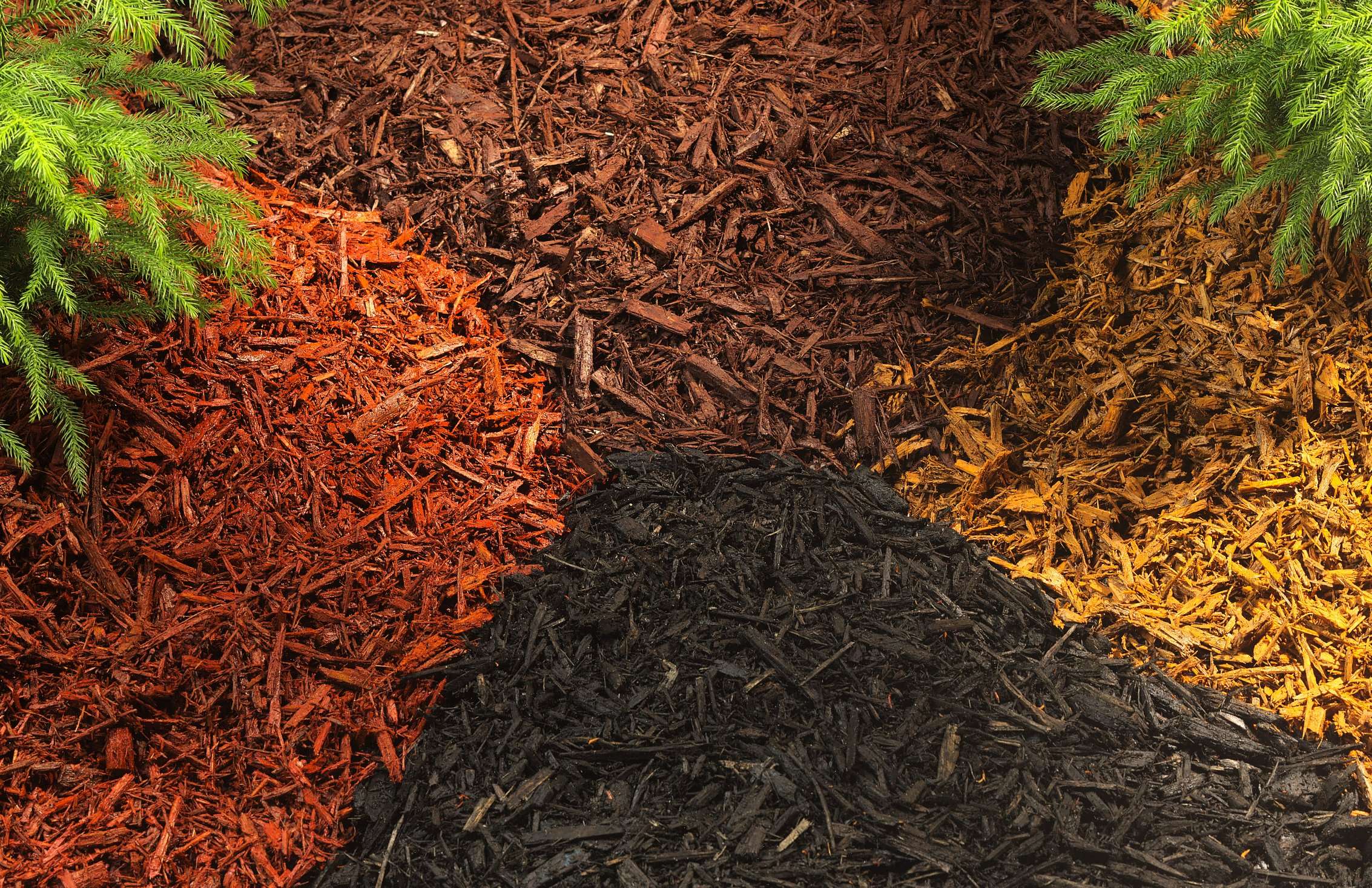
Mulch
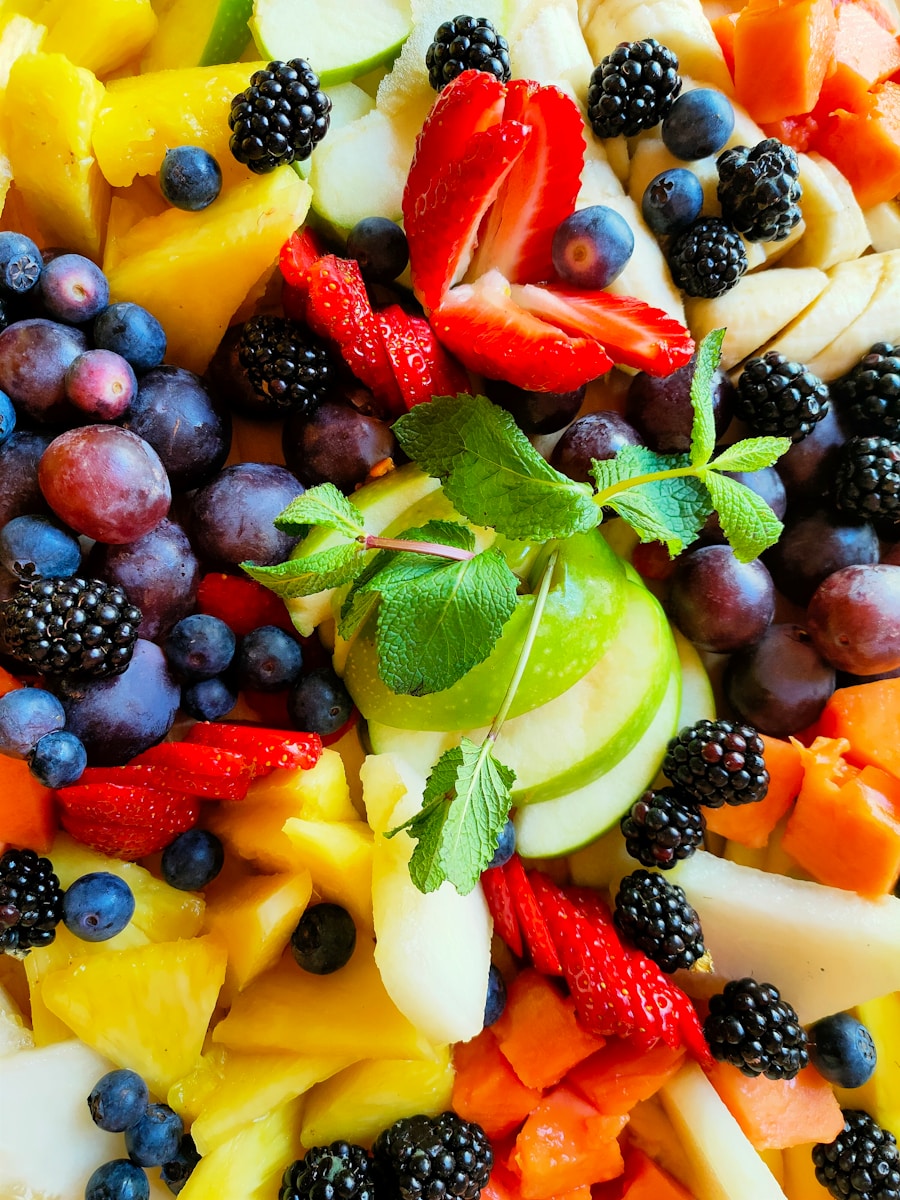
Multi-fruit solutions
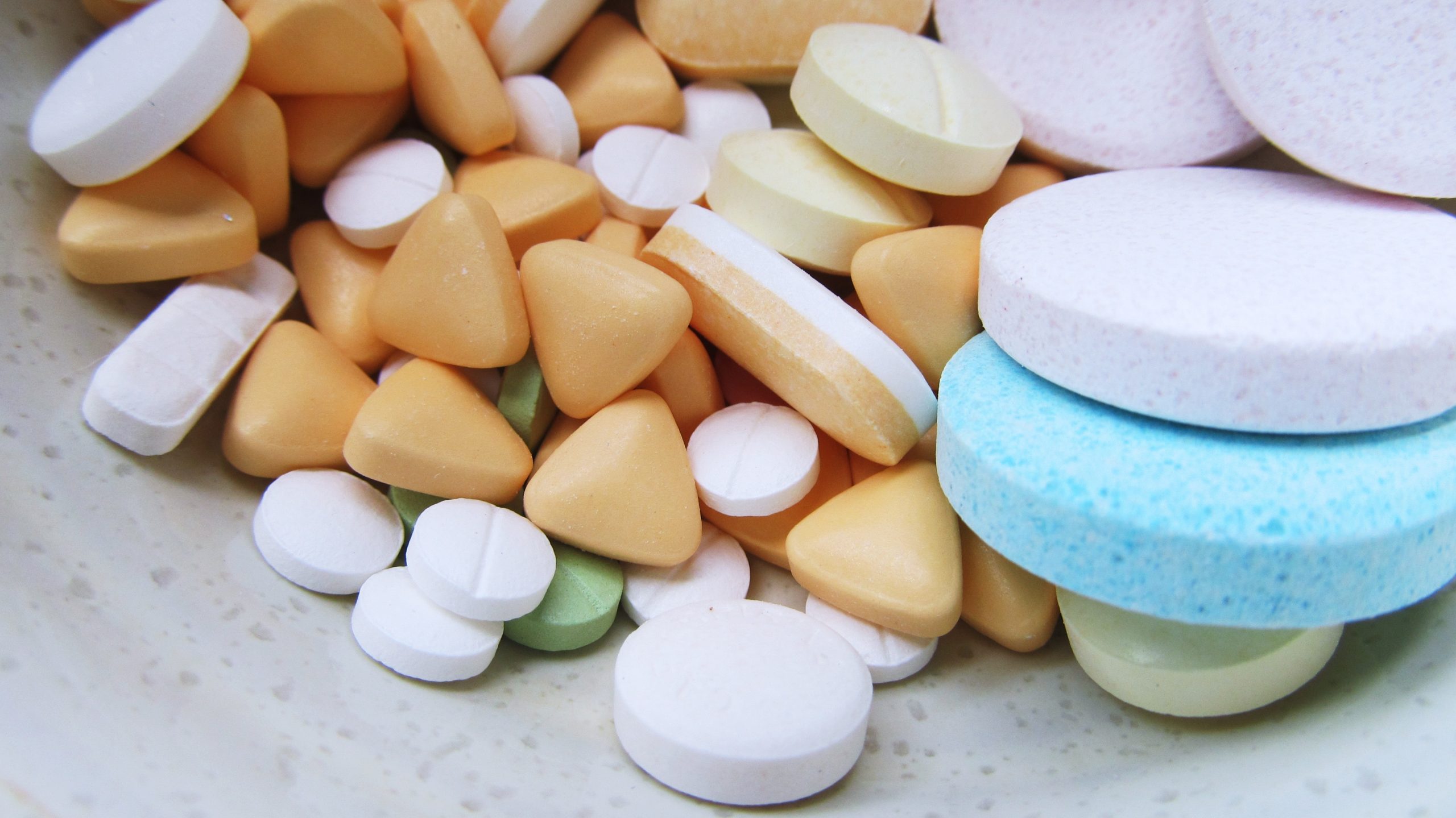
Multi-layer tablets
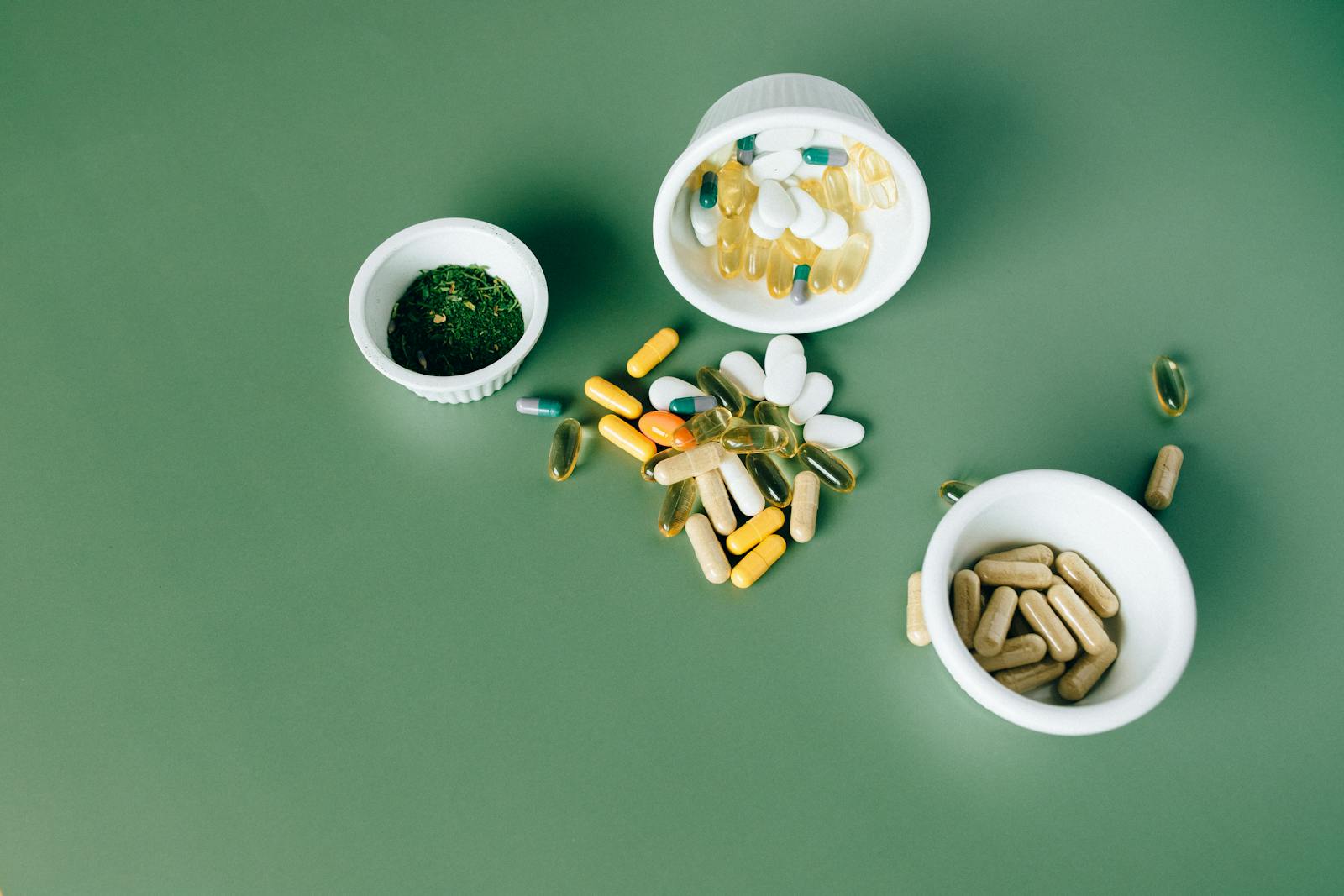
Multivitamin supplements

Mushrooms
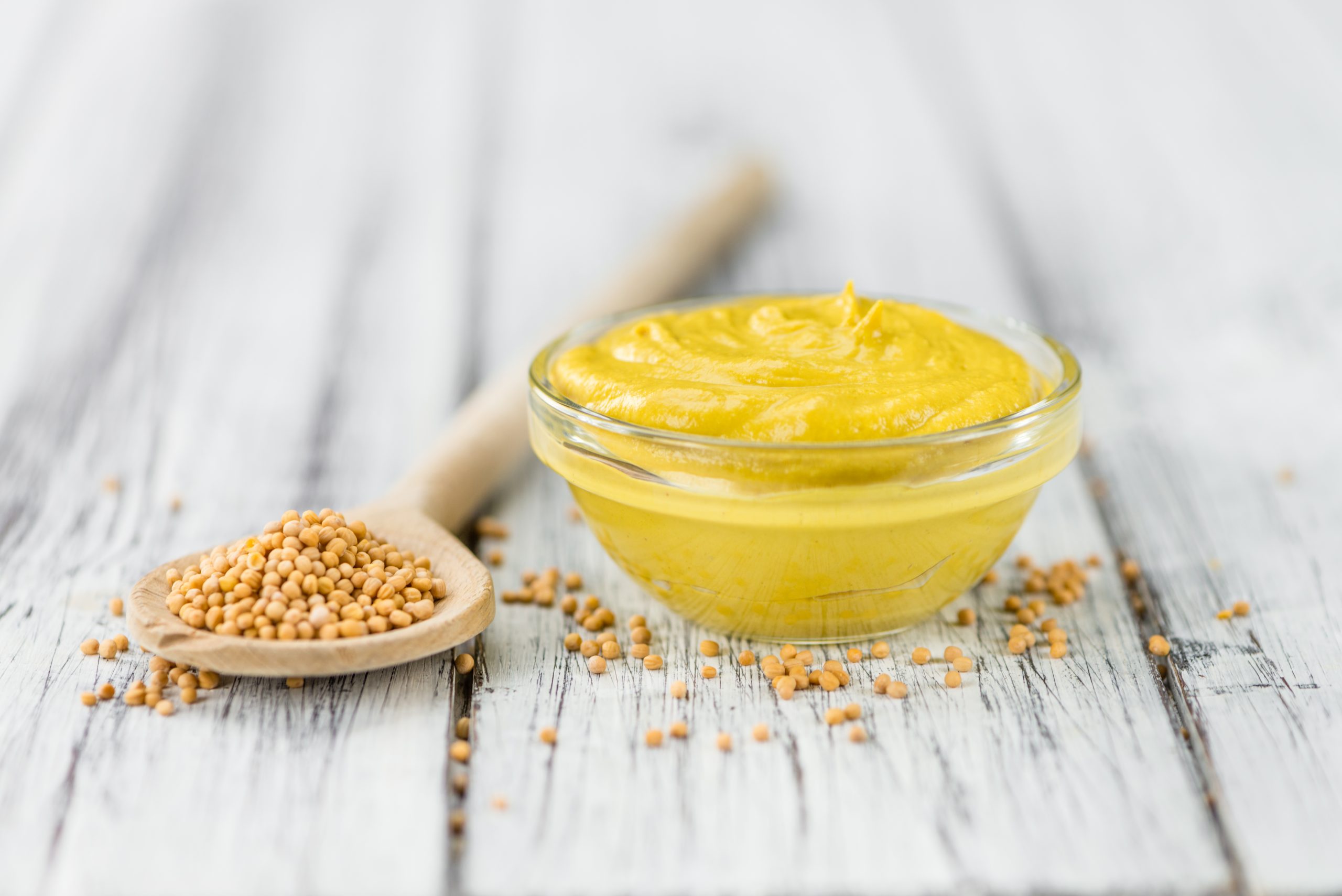
Mustard
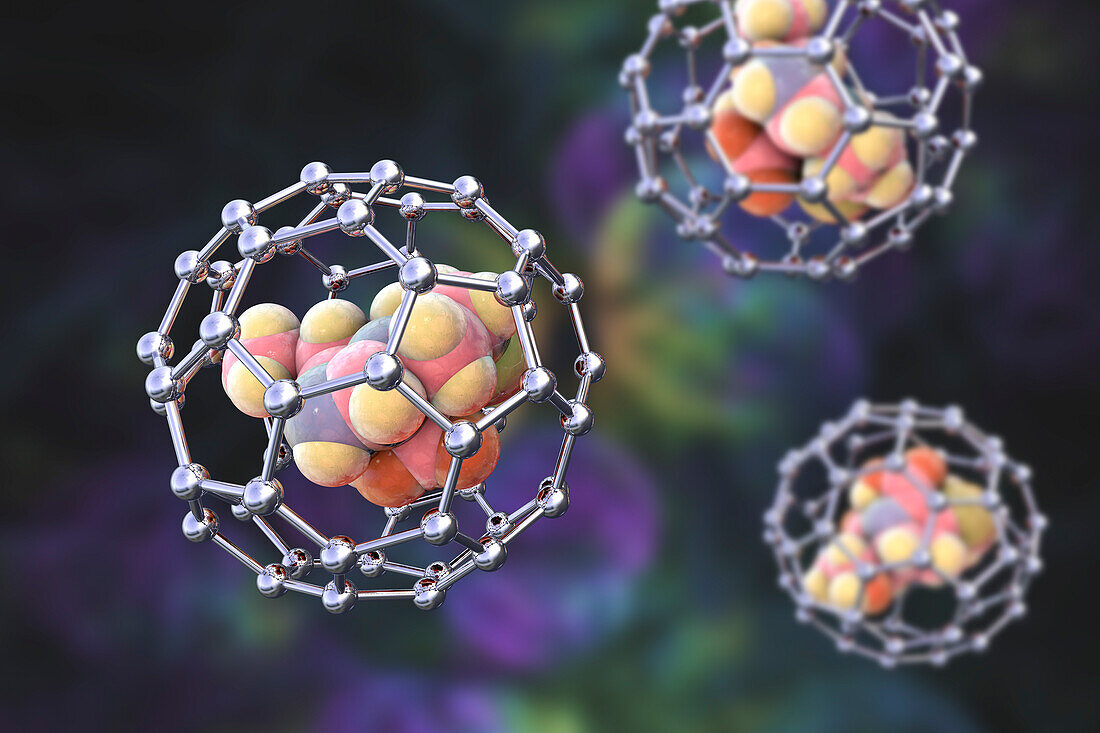
Nanoparticles
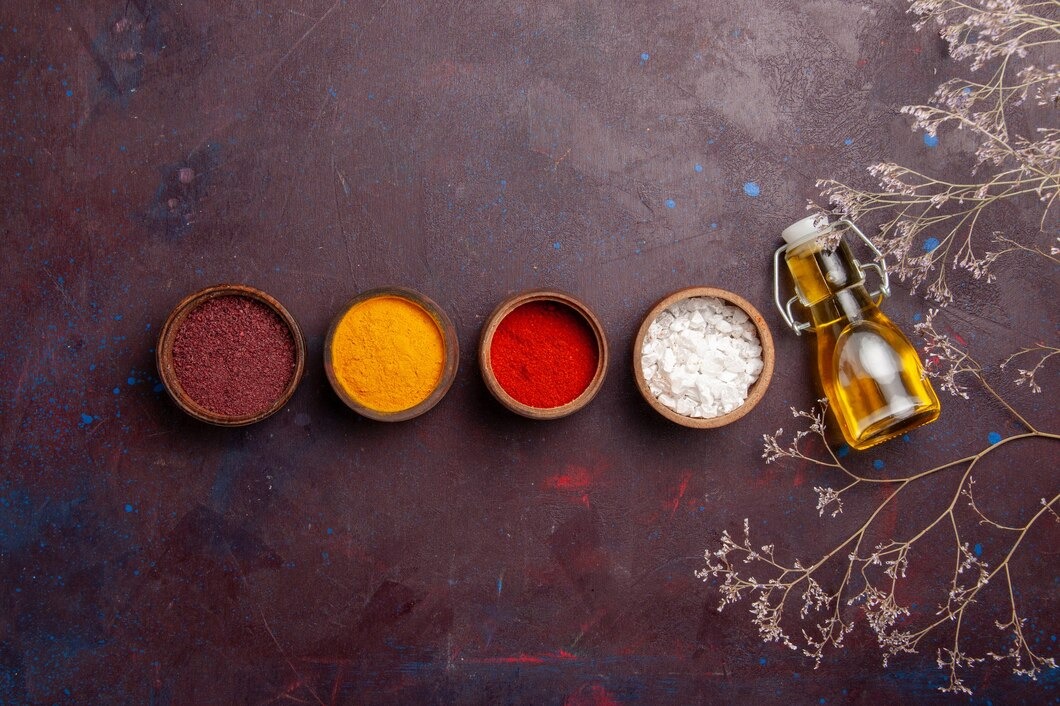
Natural food colorants
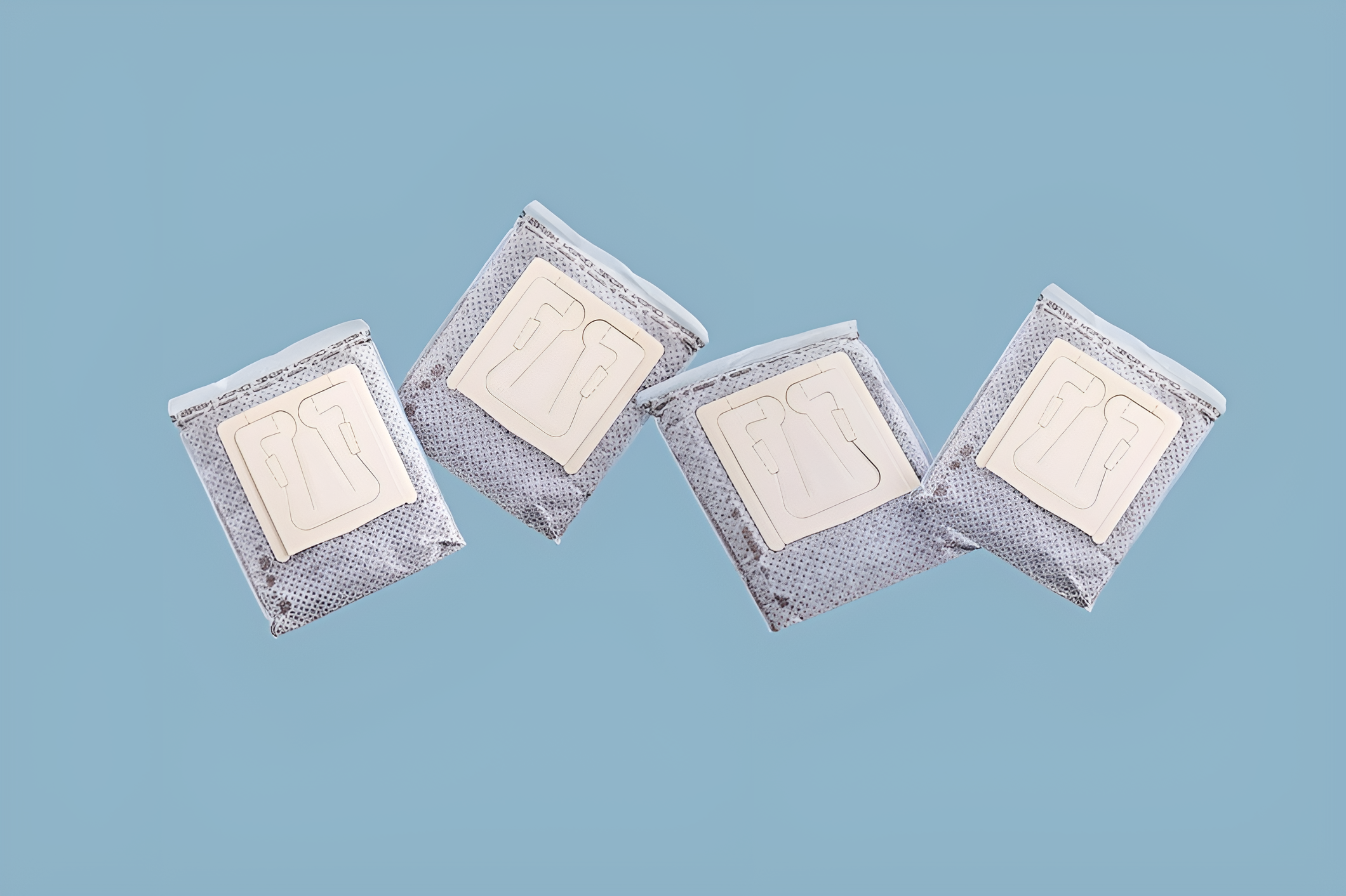
Nicotine patches
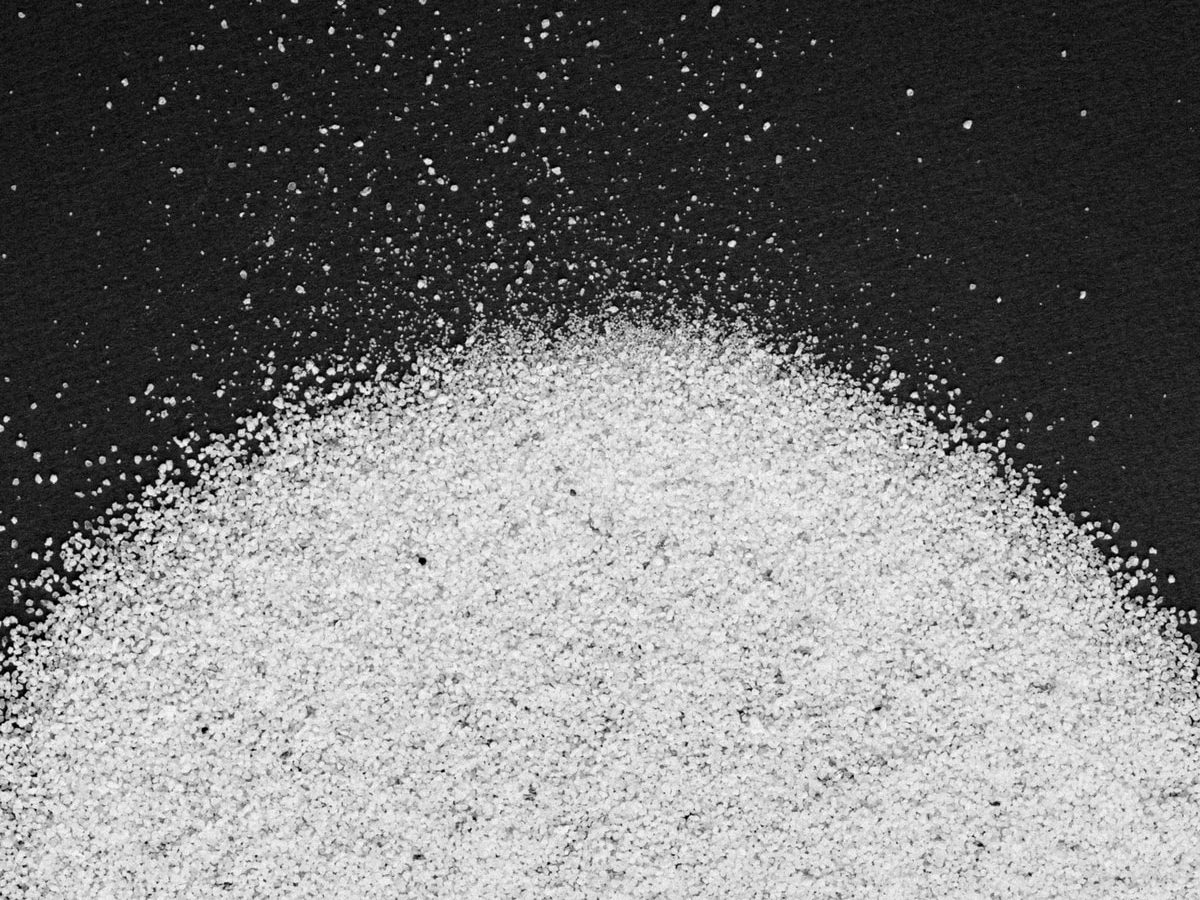
Nitrogen fertilizer
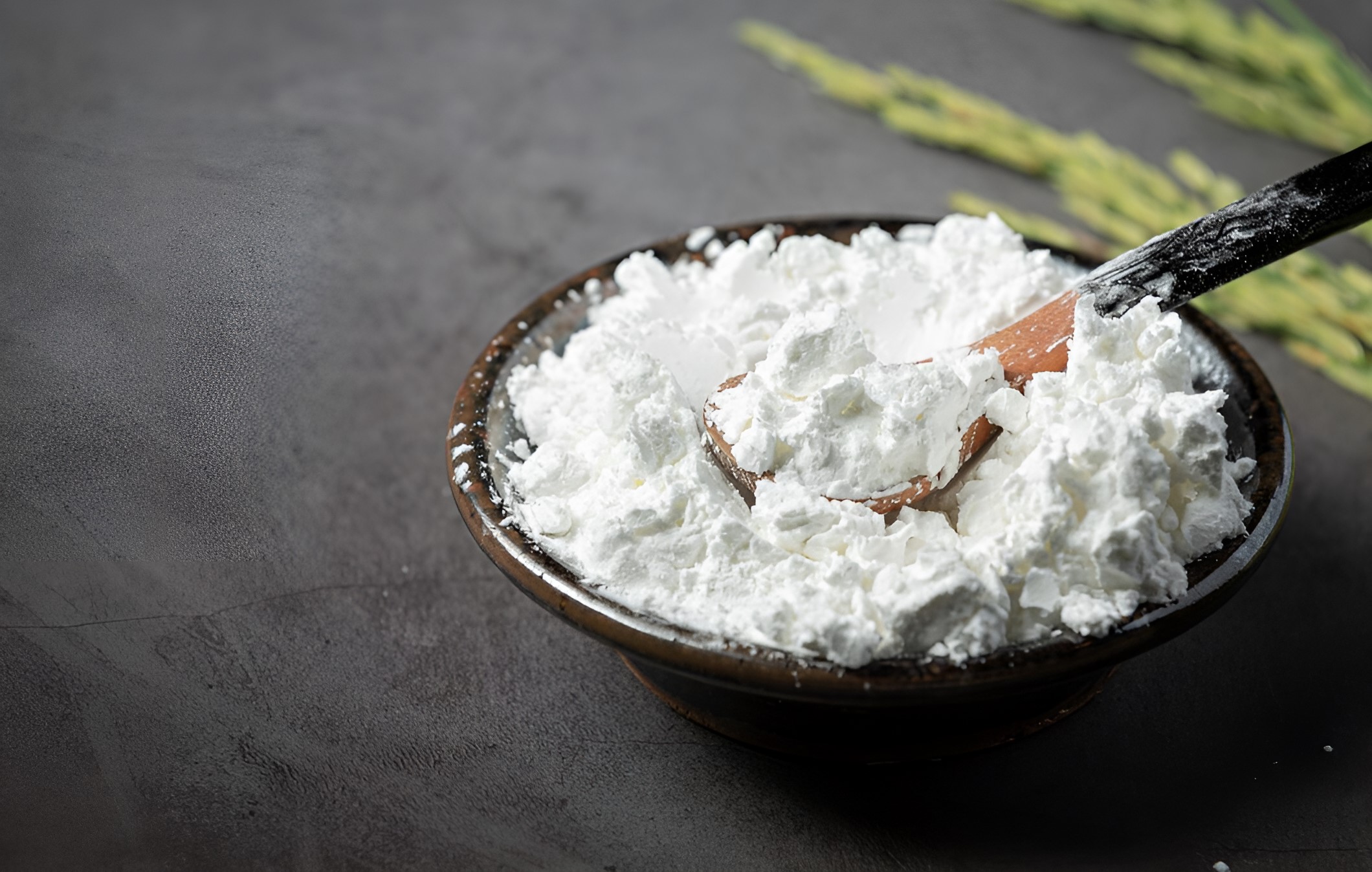
Non-dairy creamer
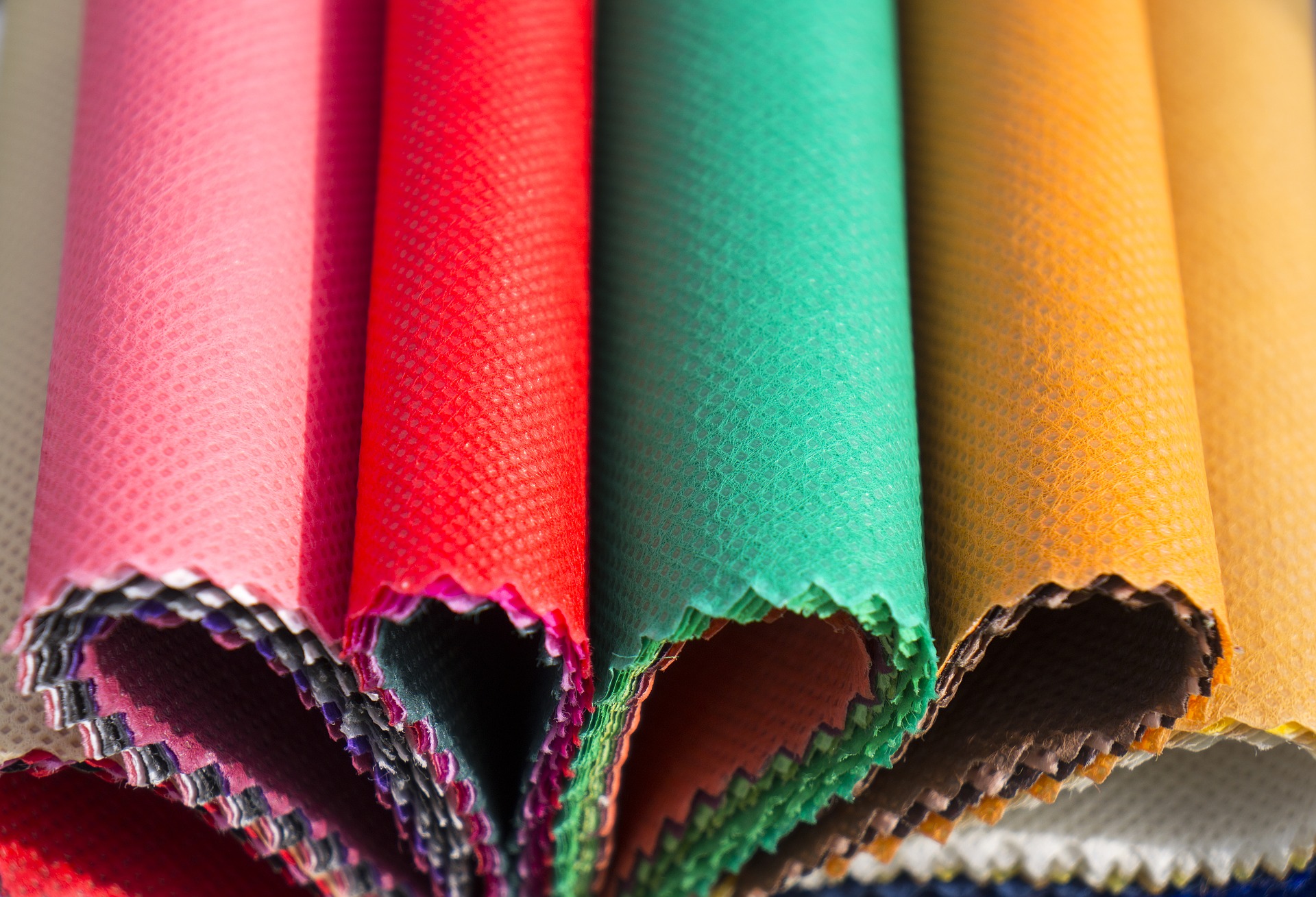
Nonwovens
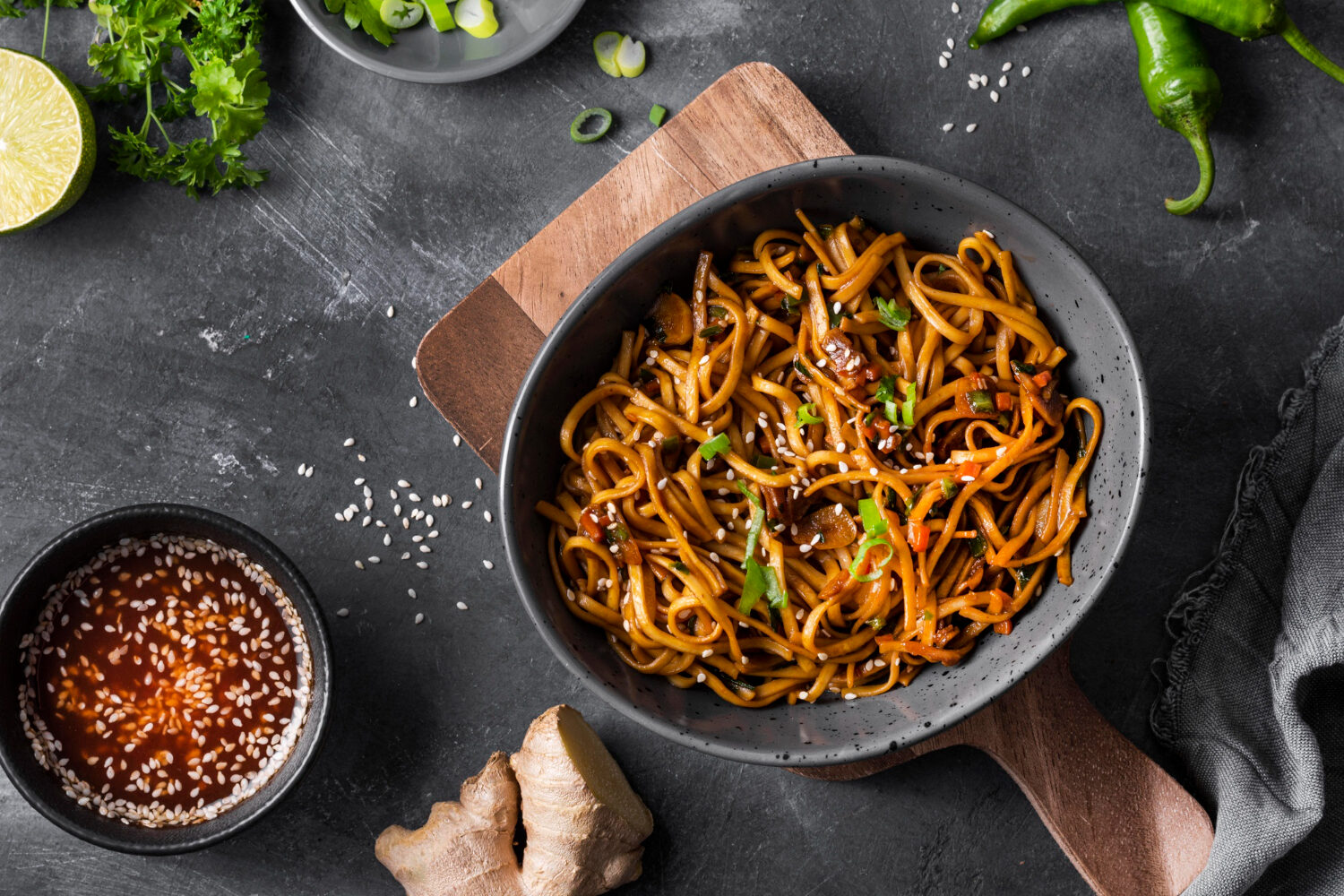
Noodles
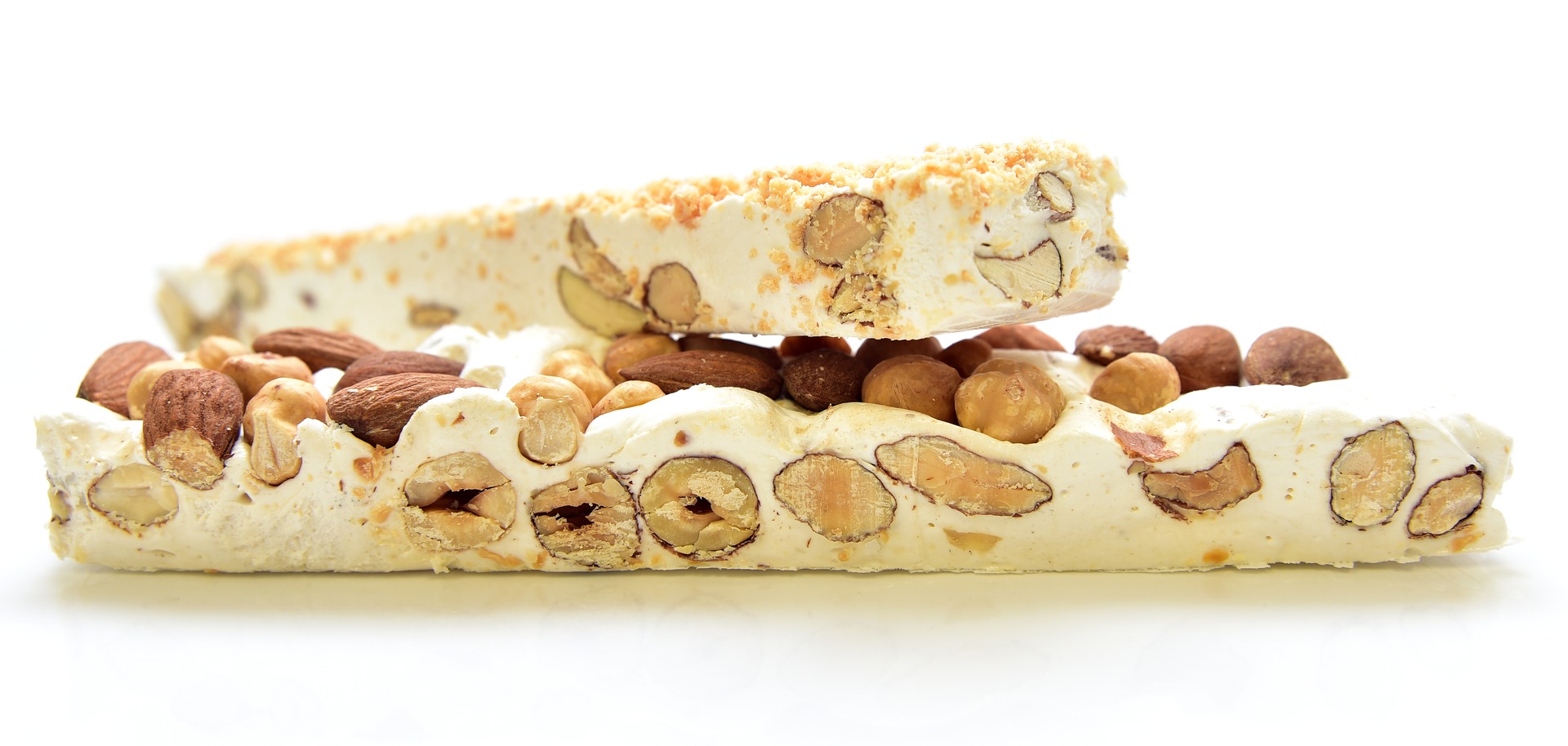
Nougat
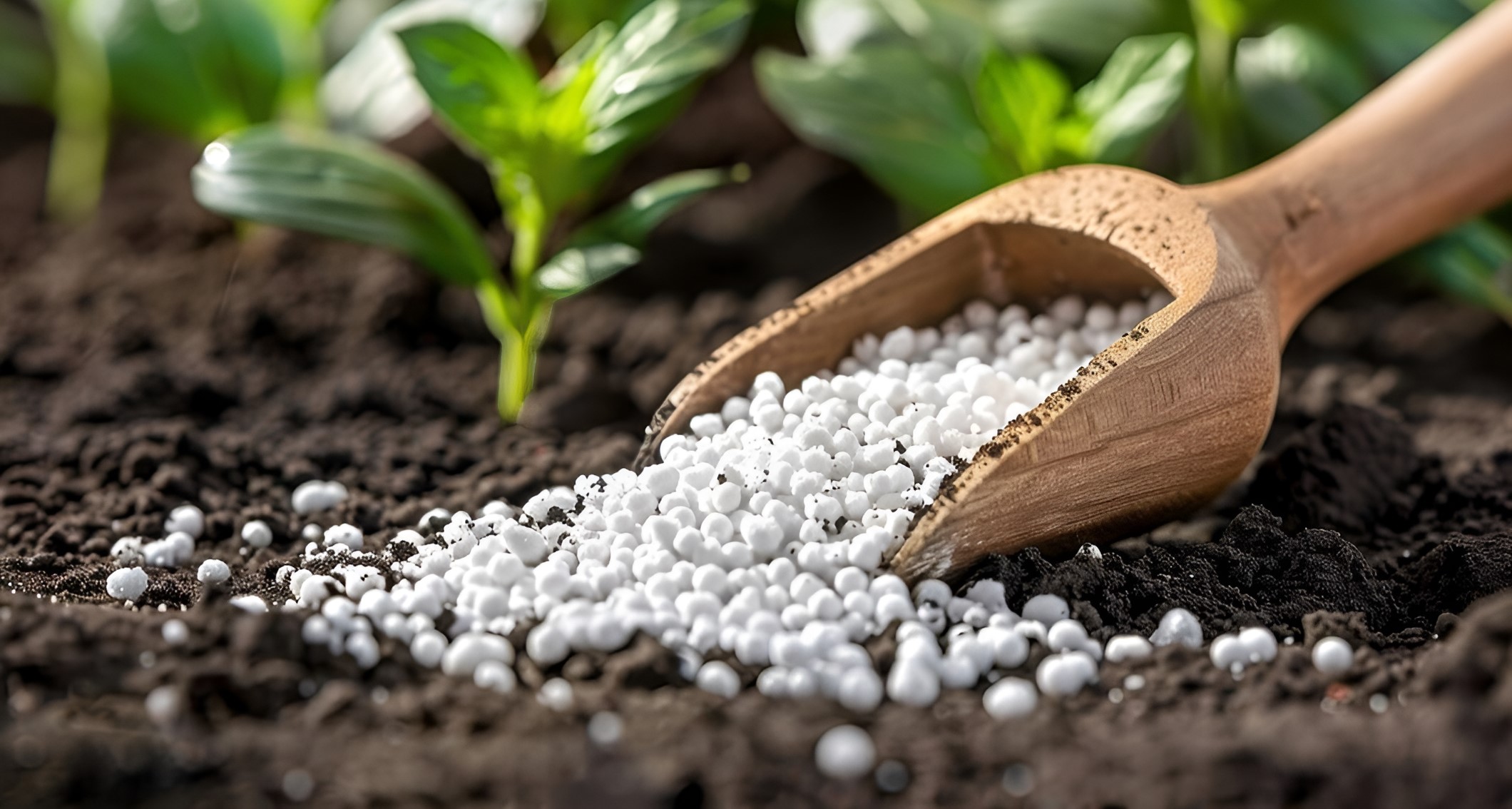
Npk fertilizers
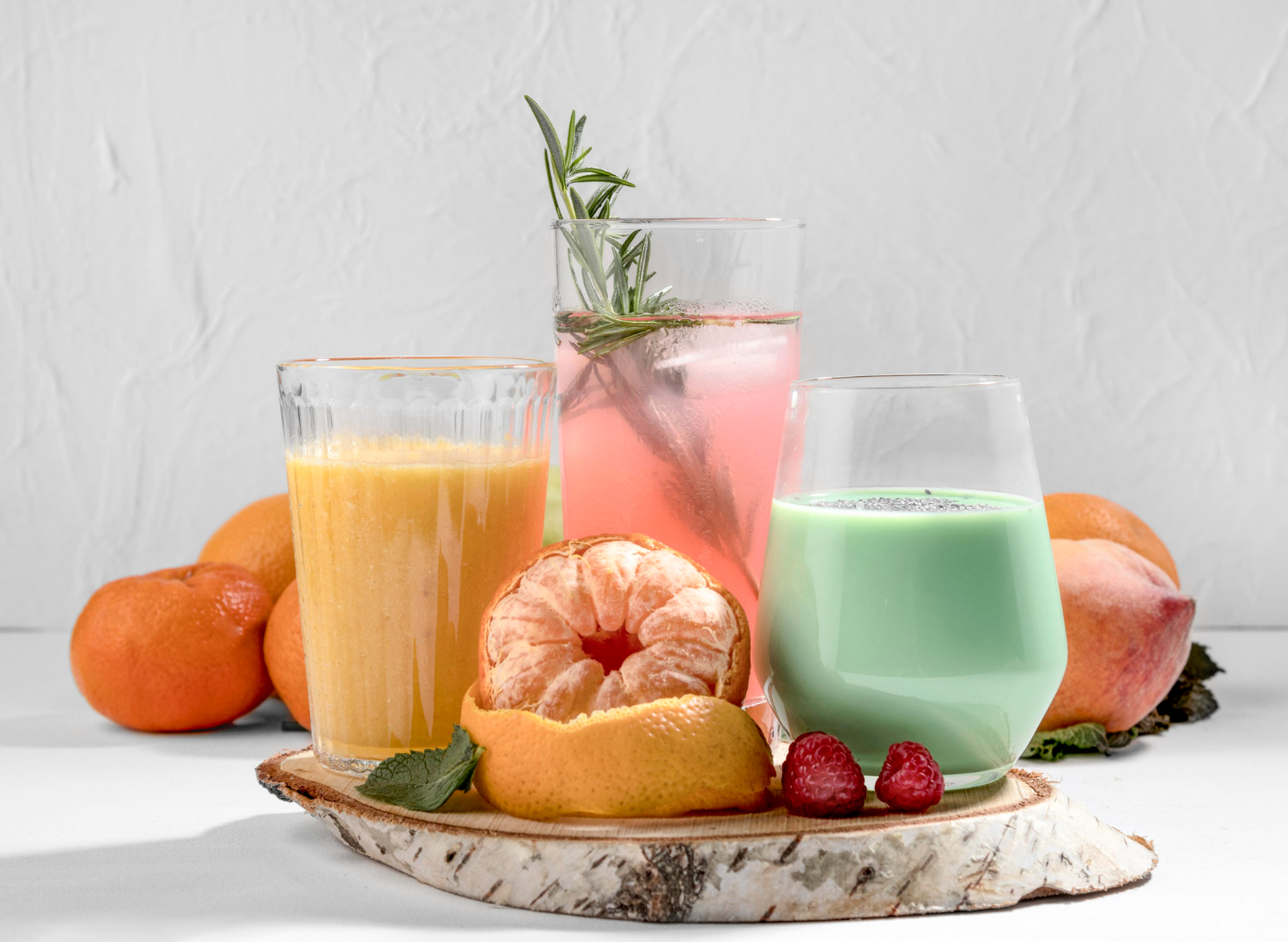
Nutritional drinks
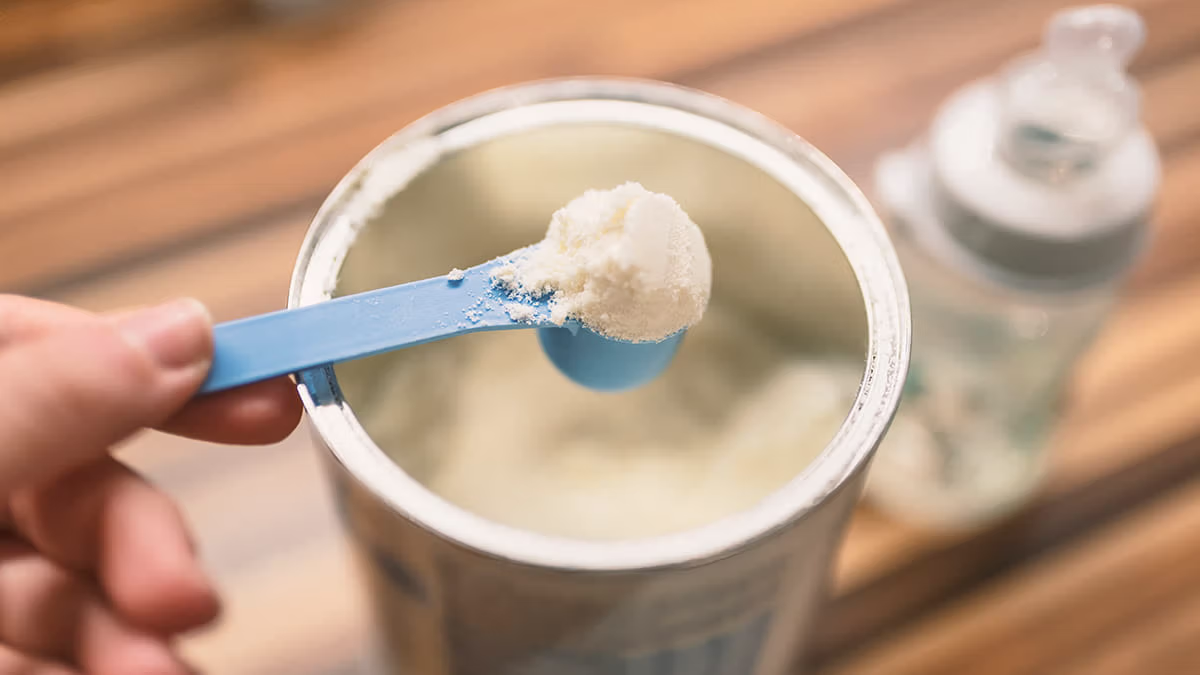
Nutritional formula
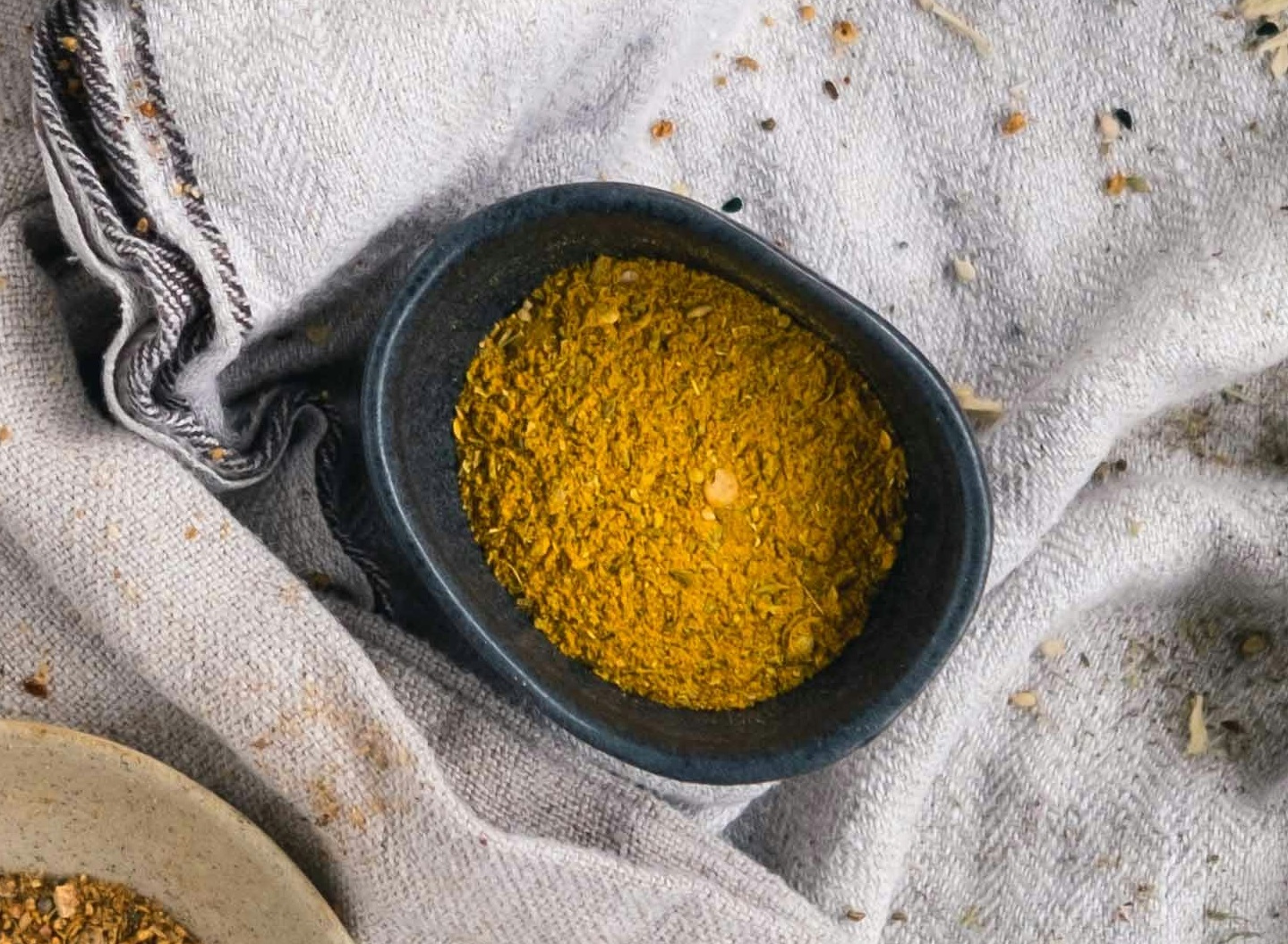
Nutritional yeast
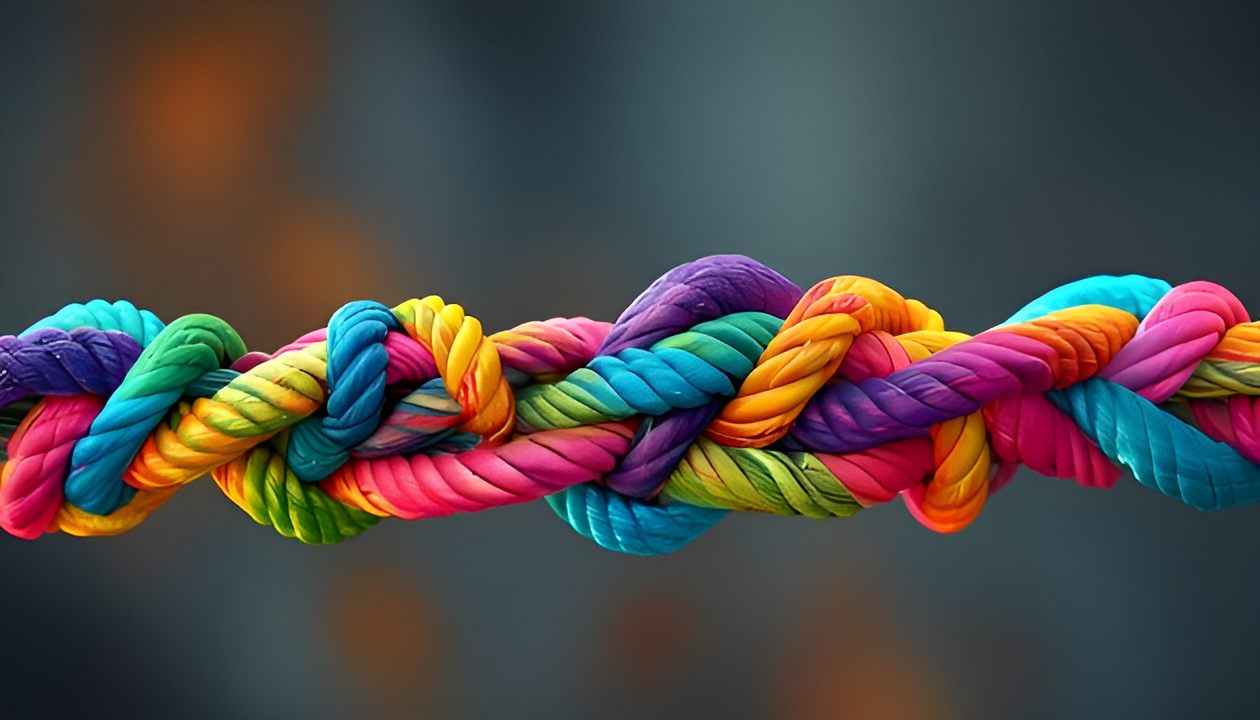
Nylon fibers
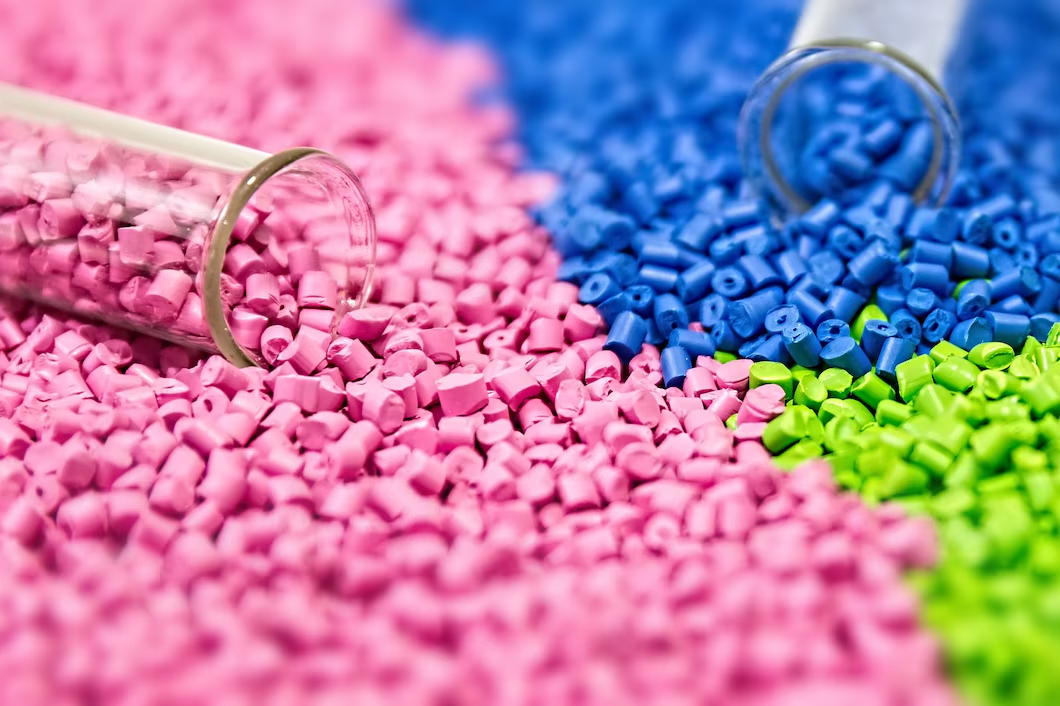
Nylon pellets
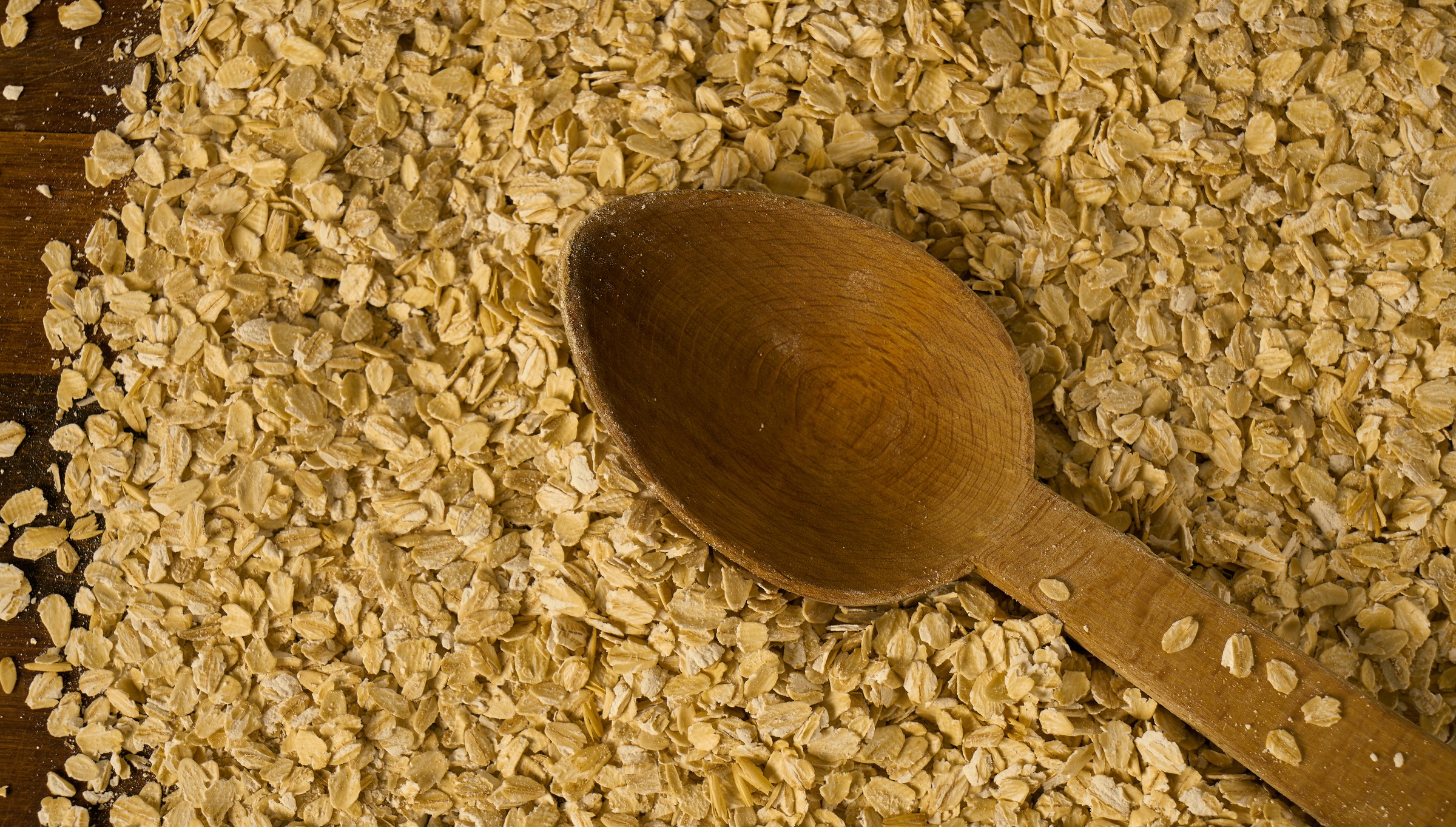
Oat bran
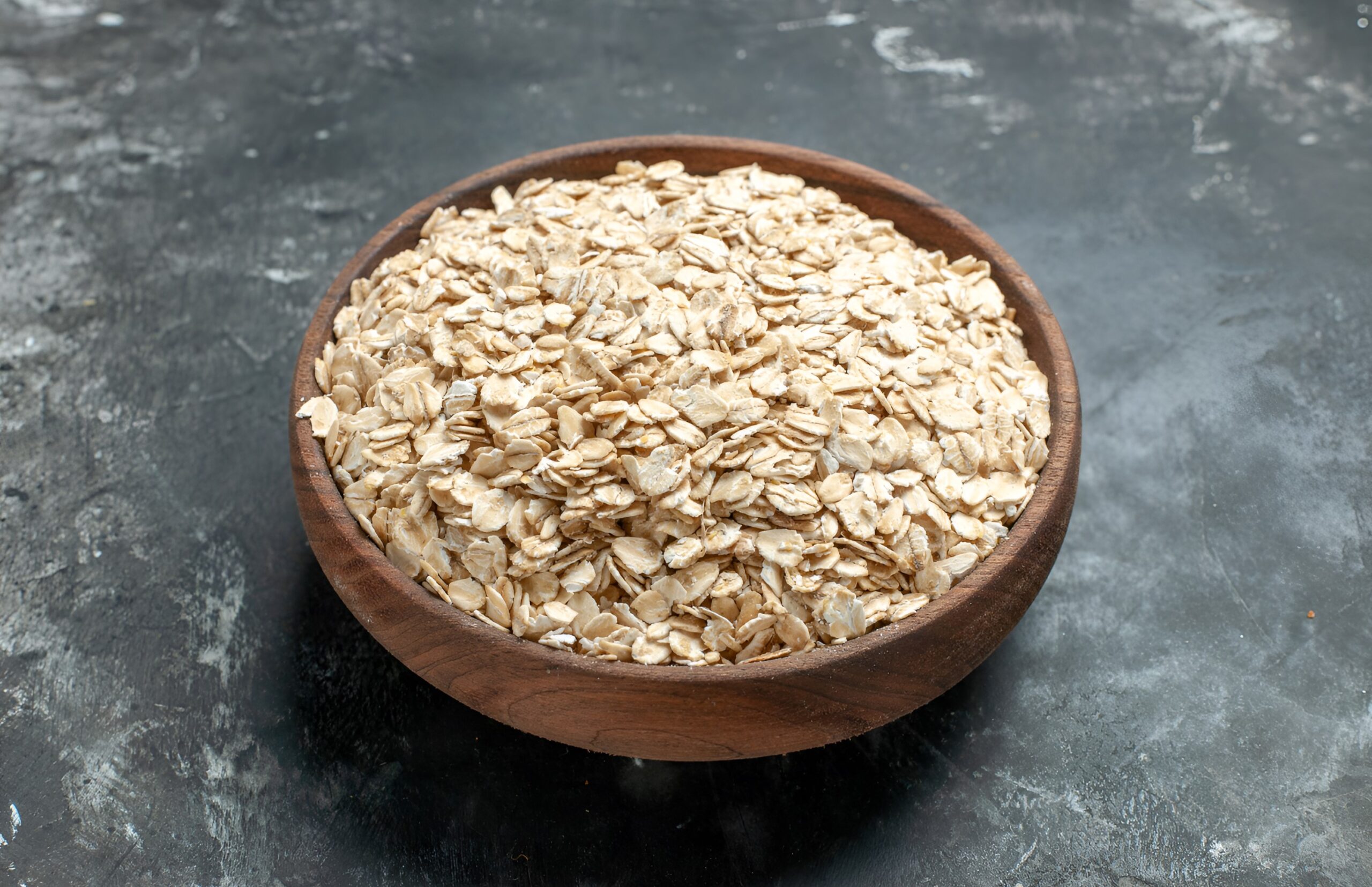
Oat flakes
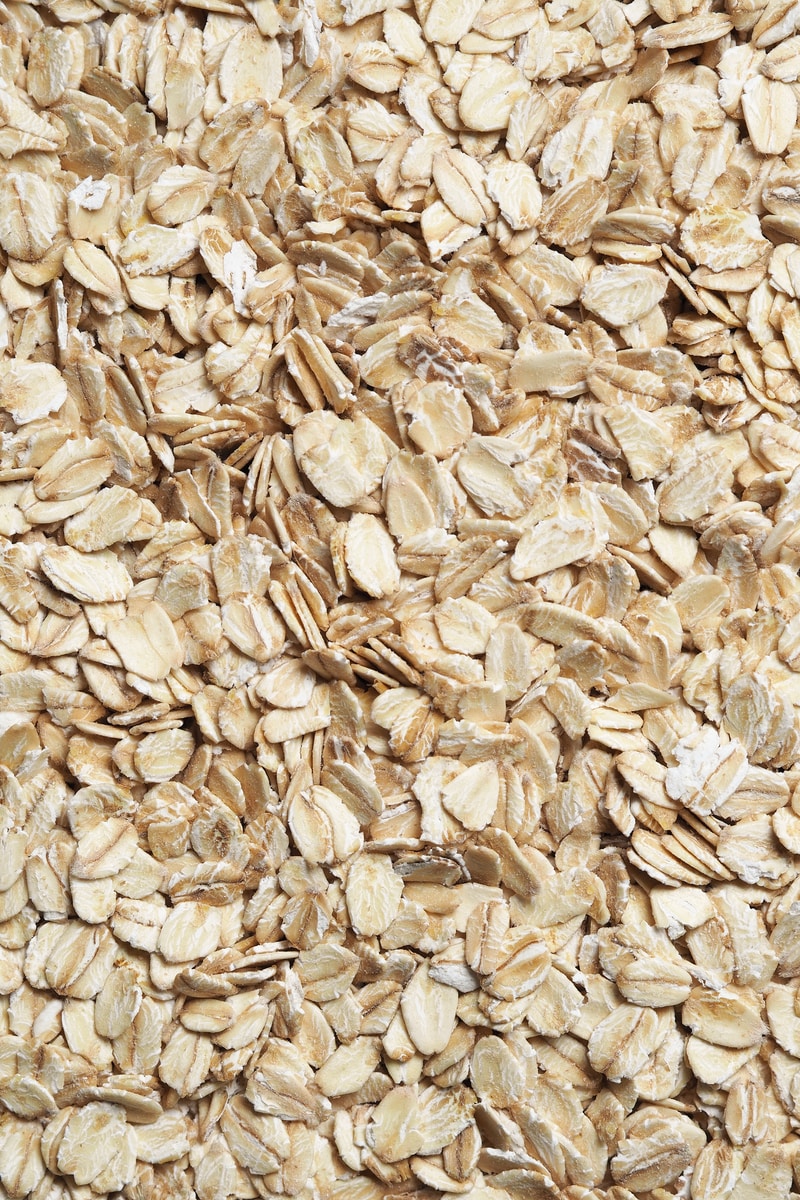
Oatmeal
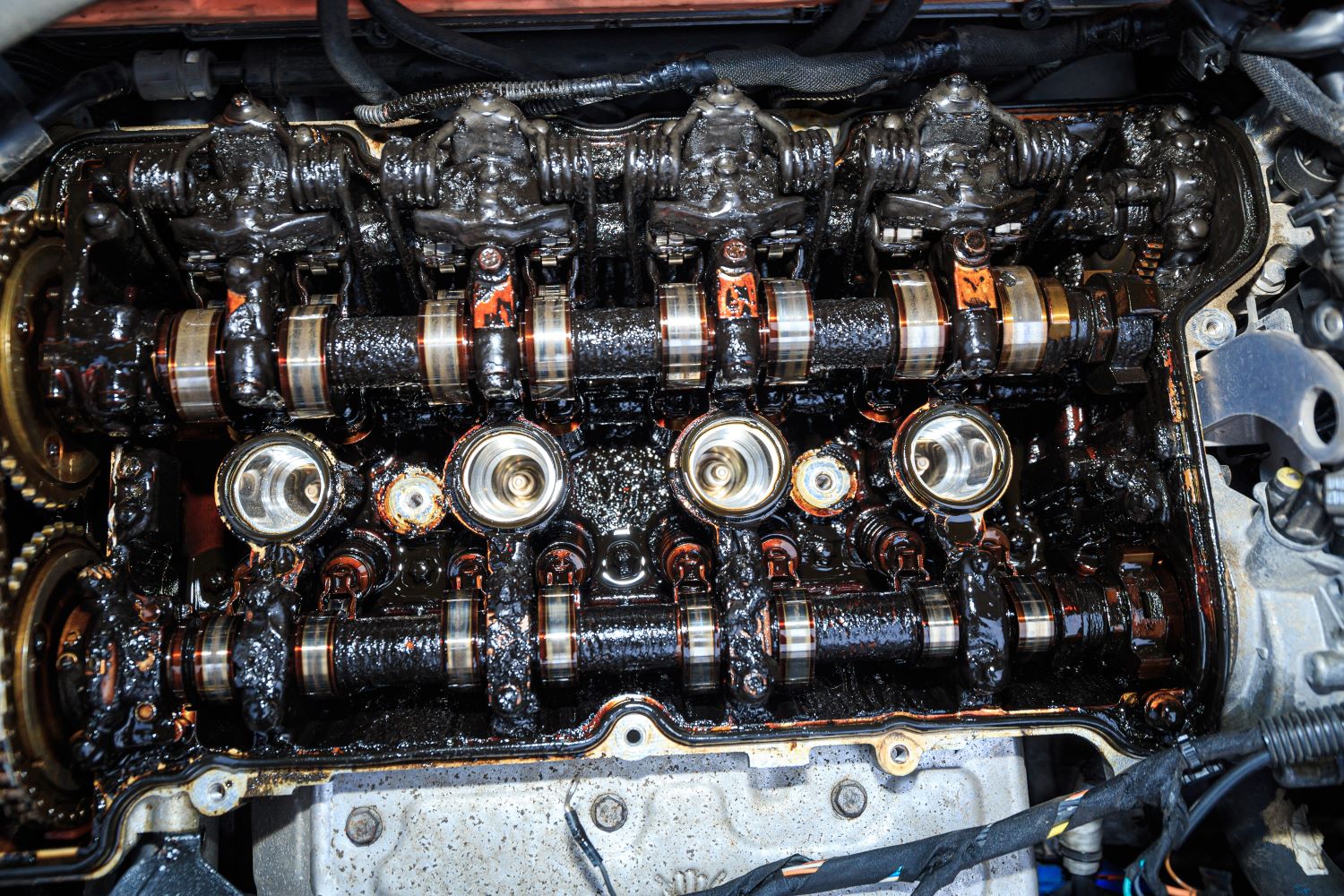
Oil sludge
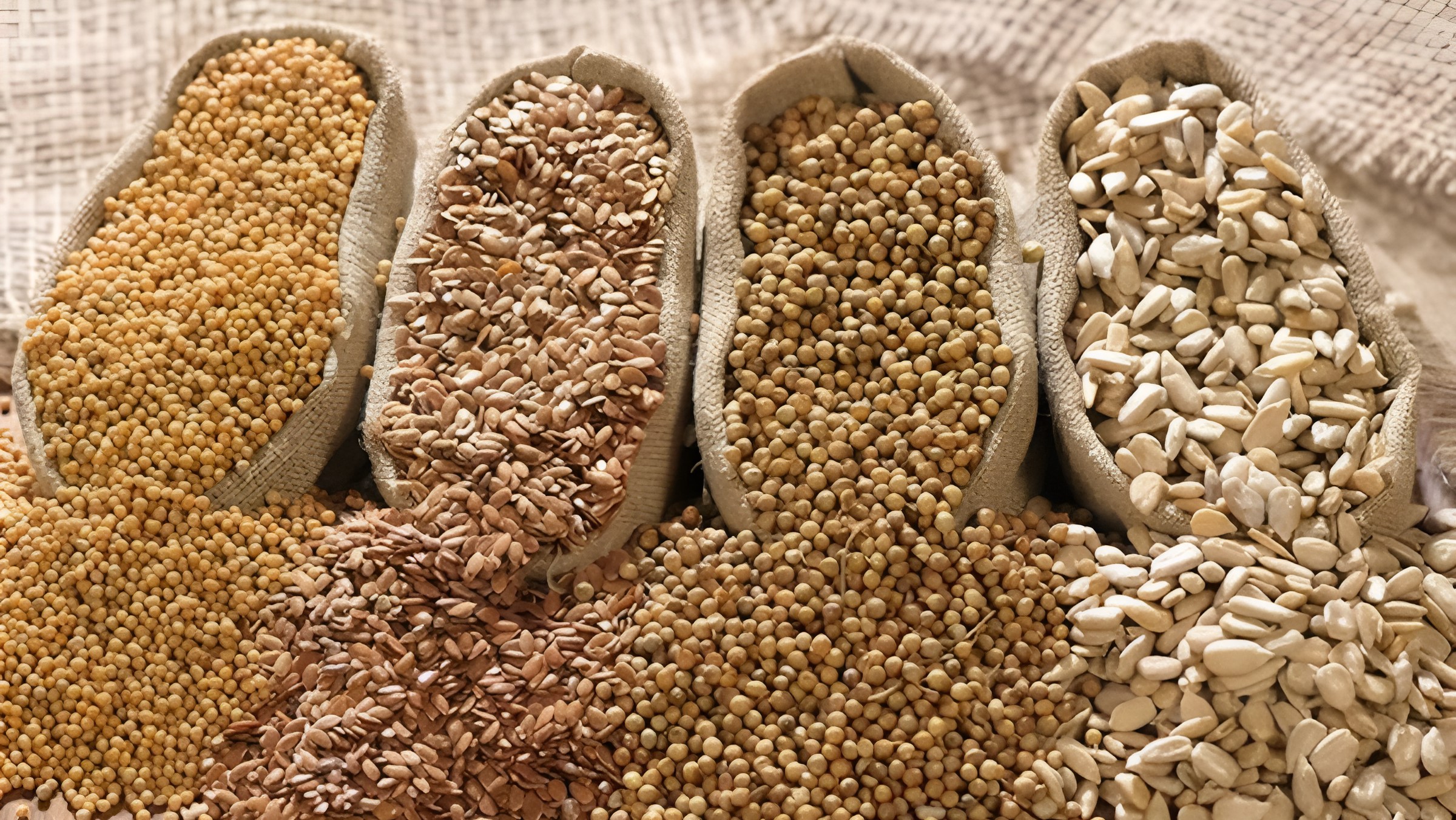
Oilseeds

Omega-3 capsules
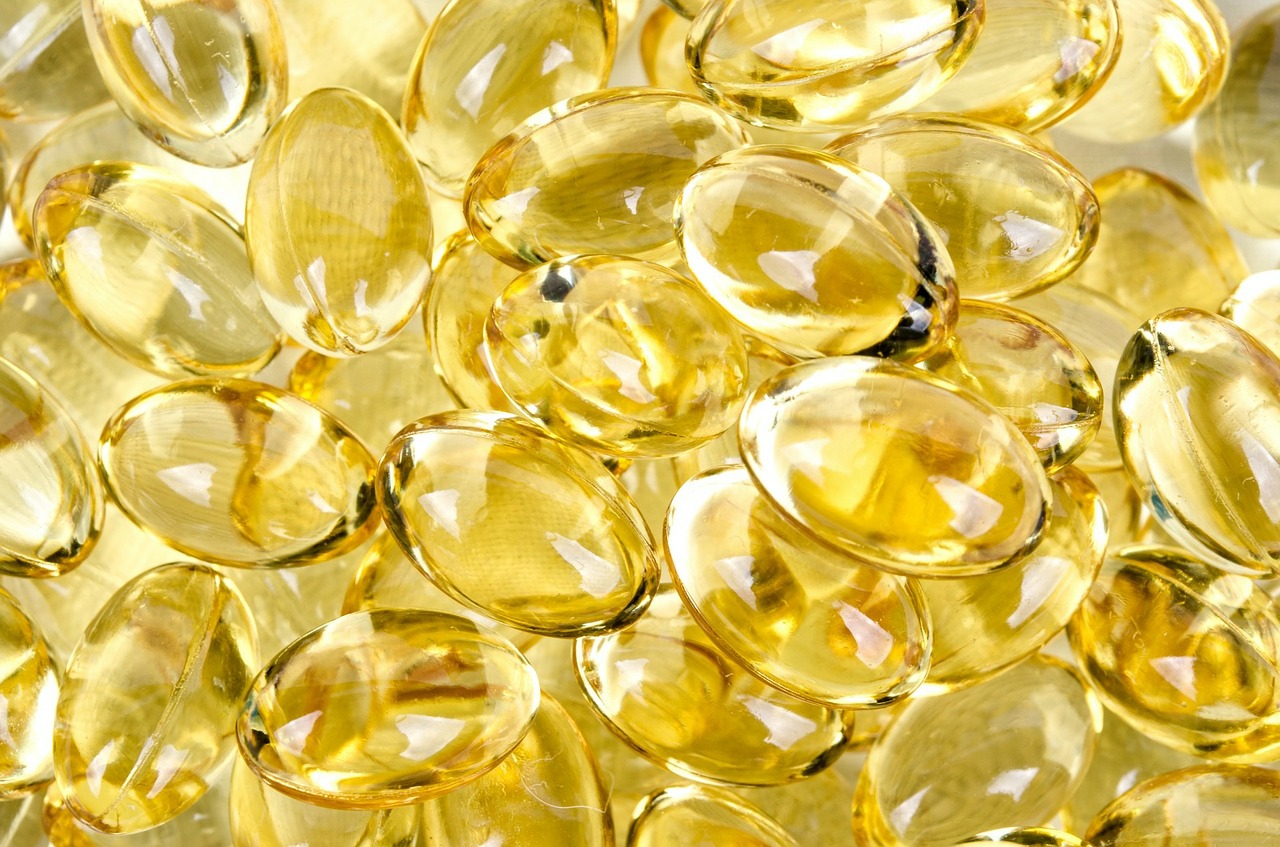
Omega 3 oil
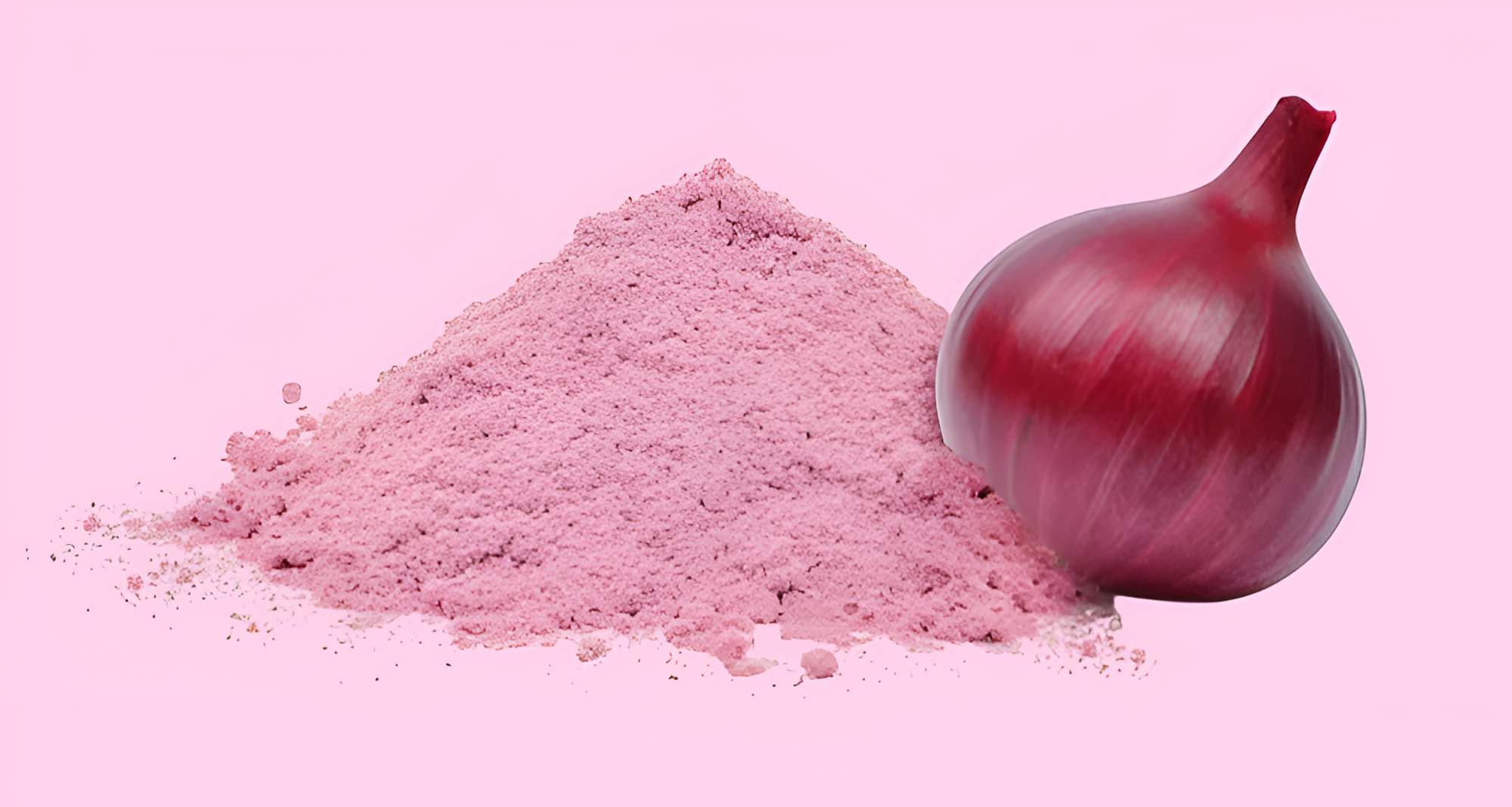
Onion powder

Oral solid dosage forms
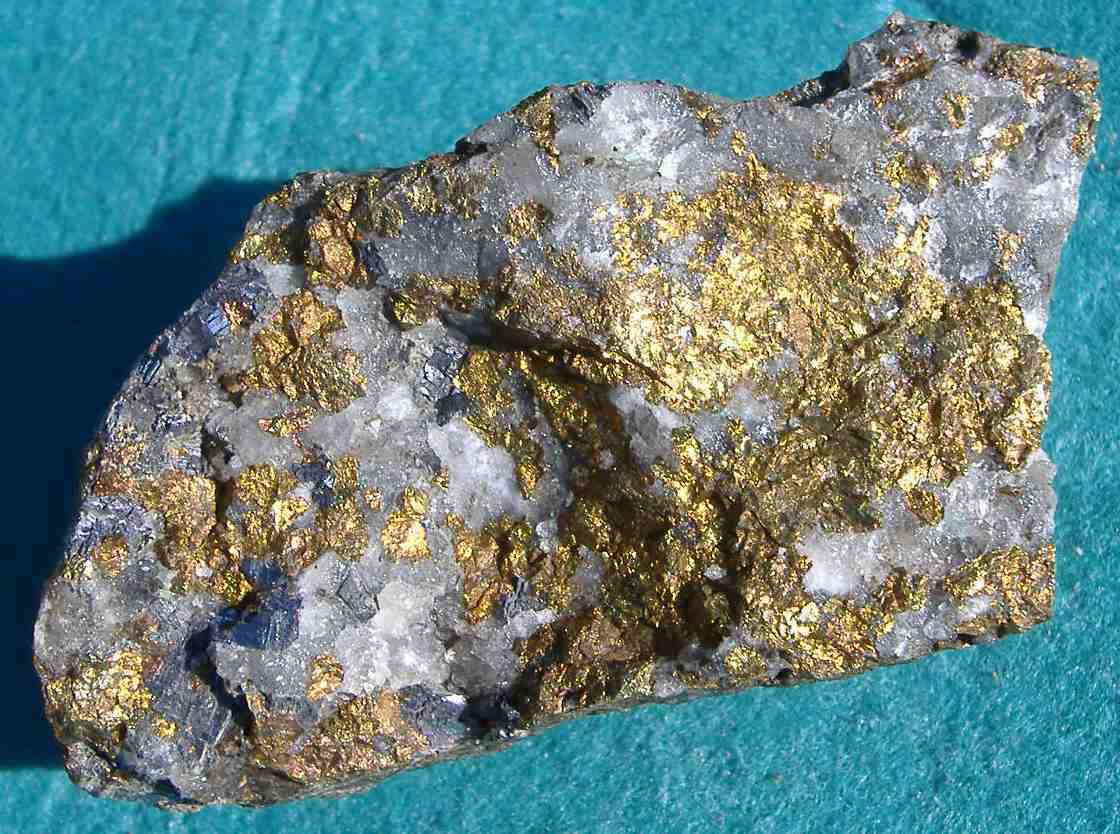
Ores
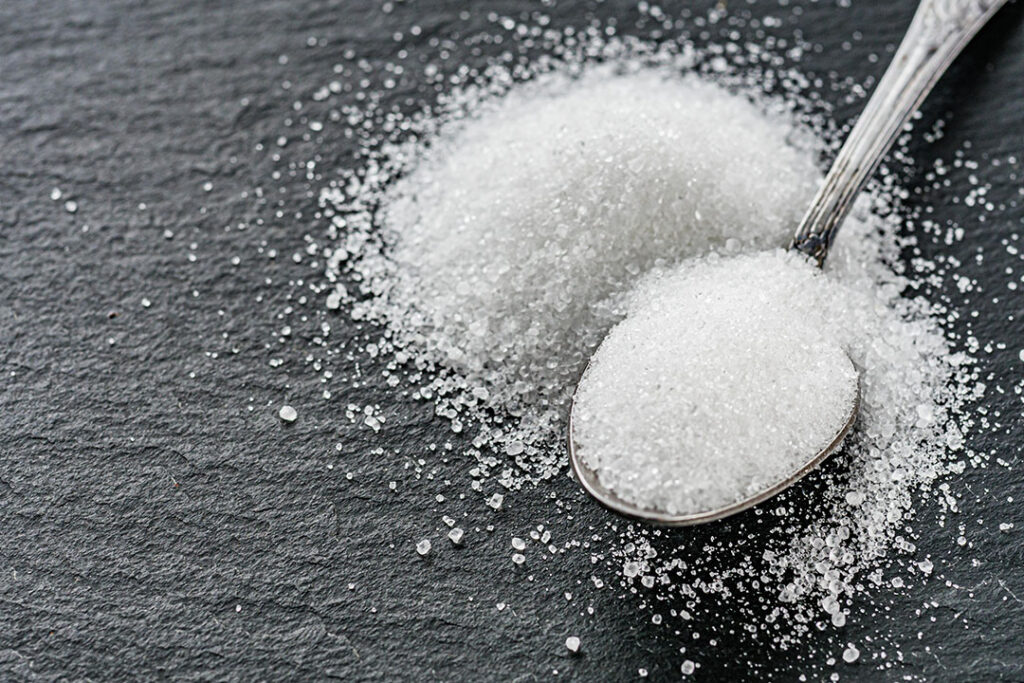
Organic acids
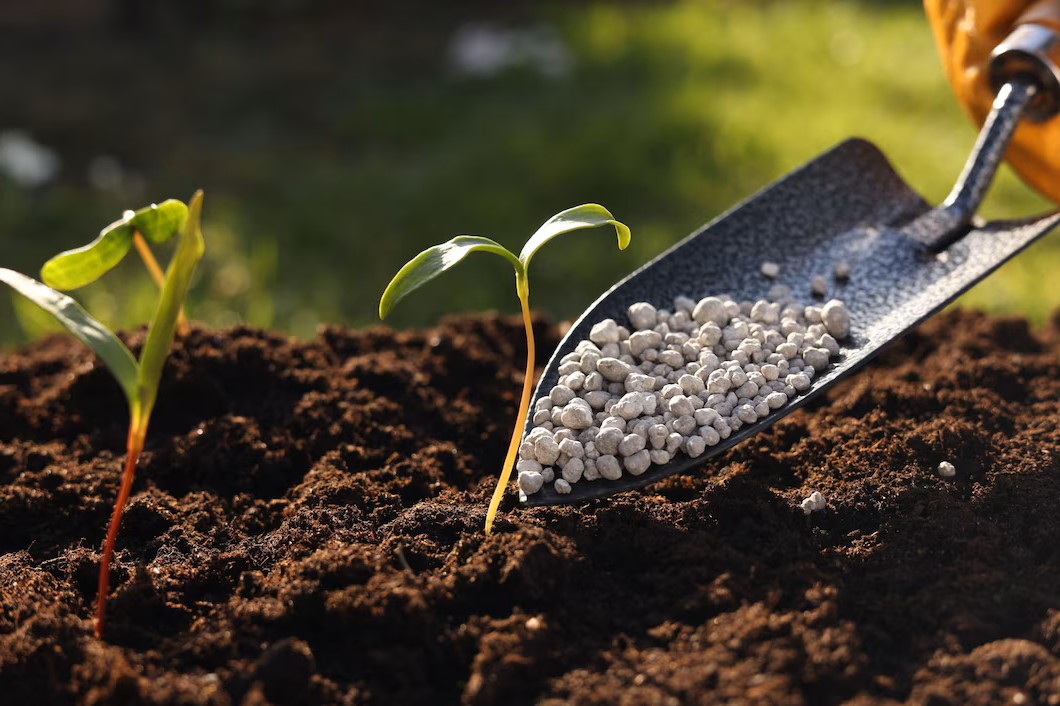
Organic fertilizer

Organic pigments
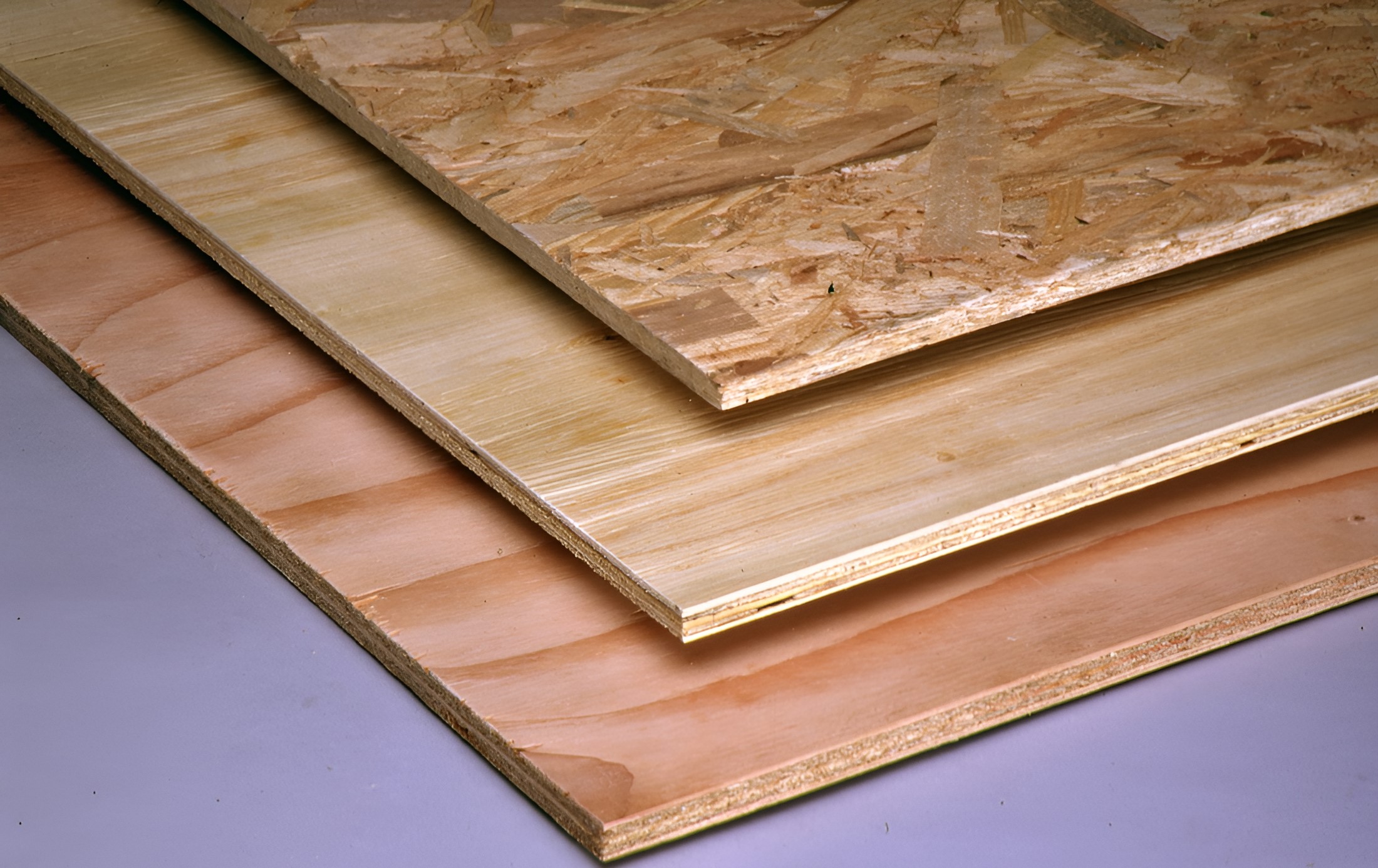
Osb boards
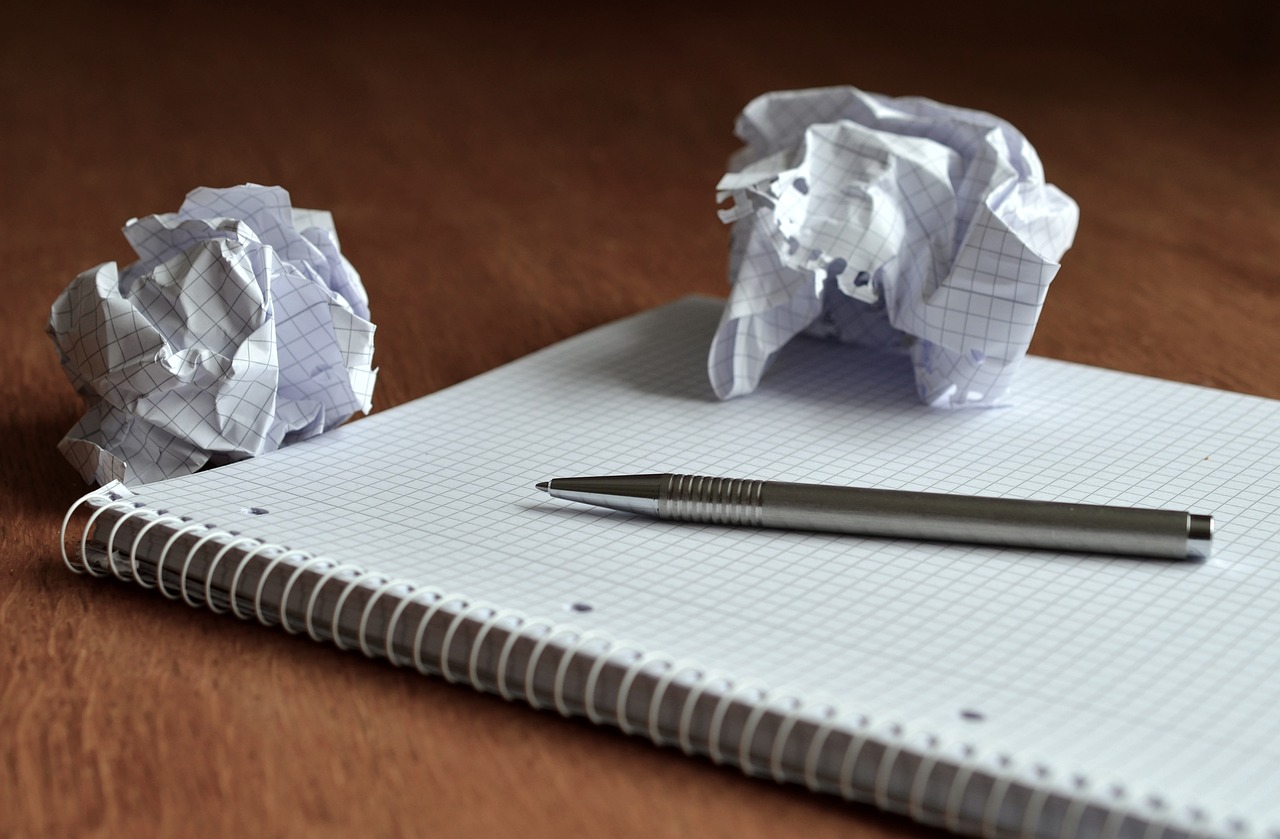
Paper
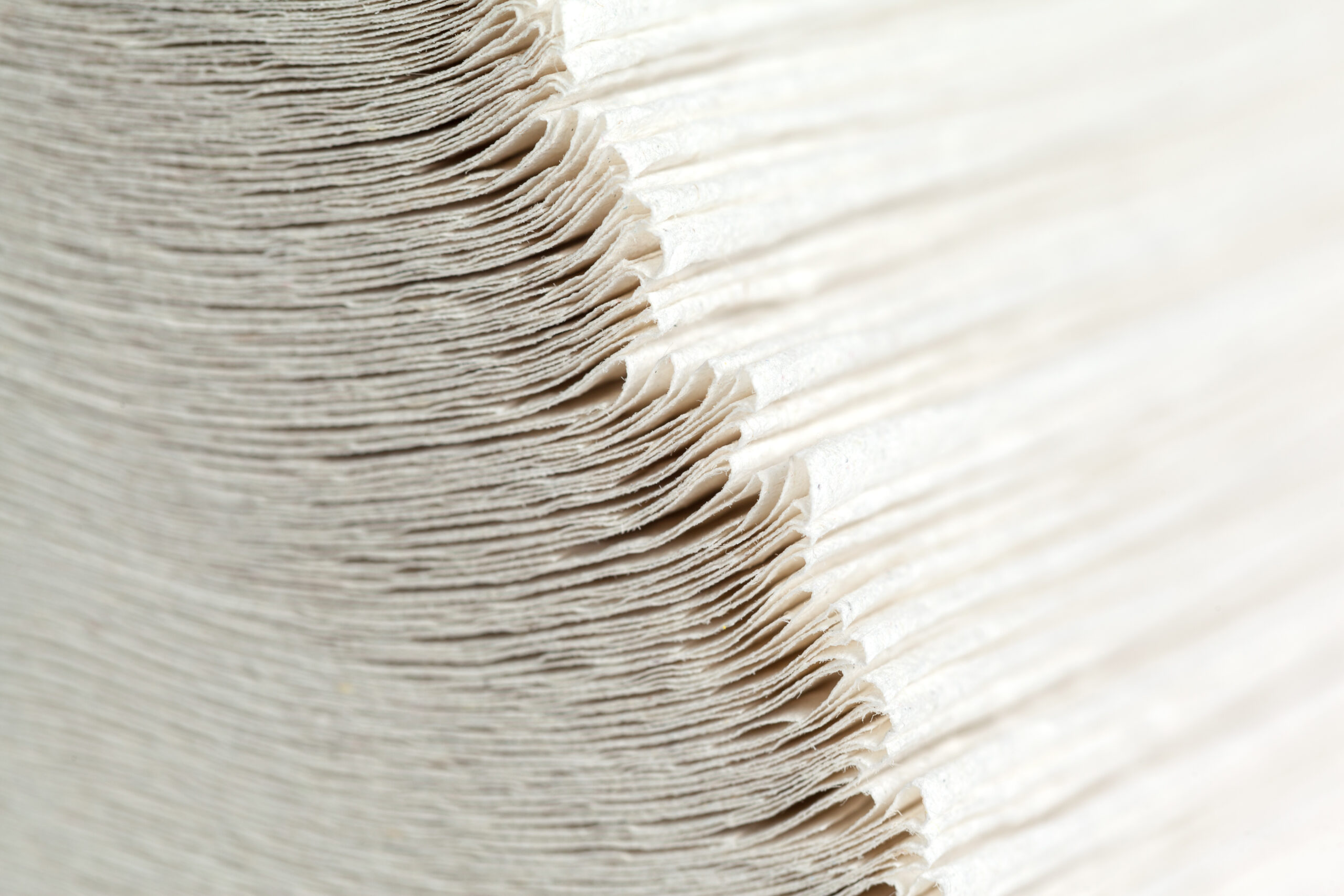
Paper pulp

Paper towels
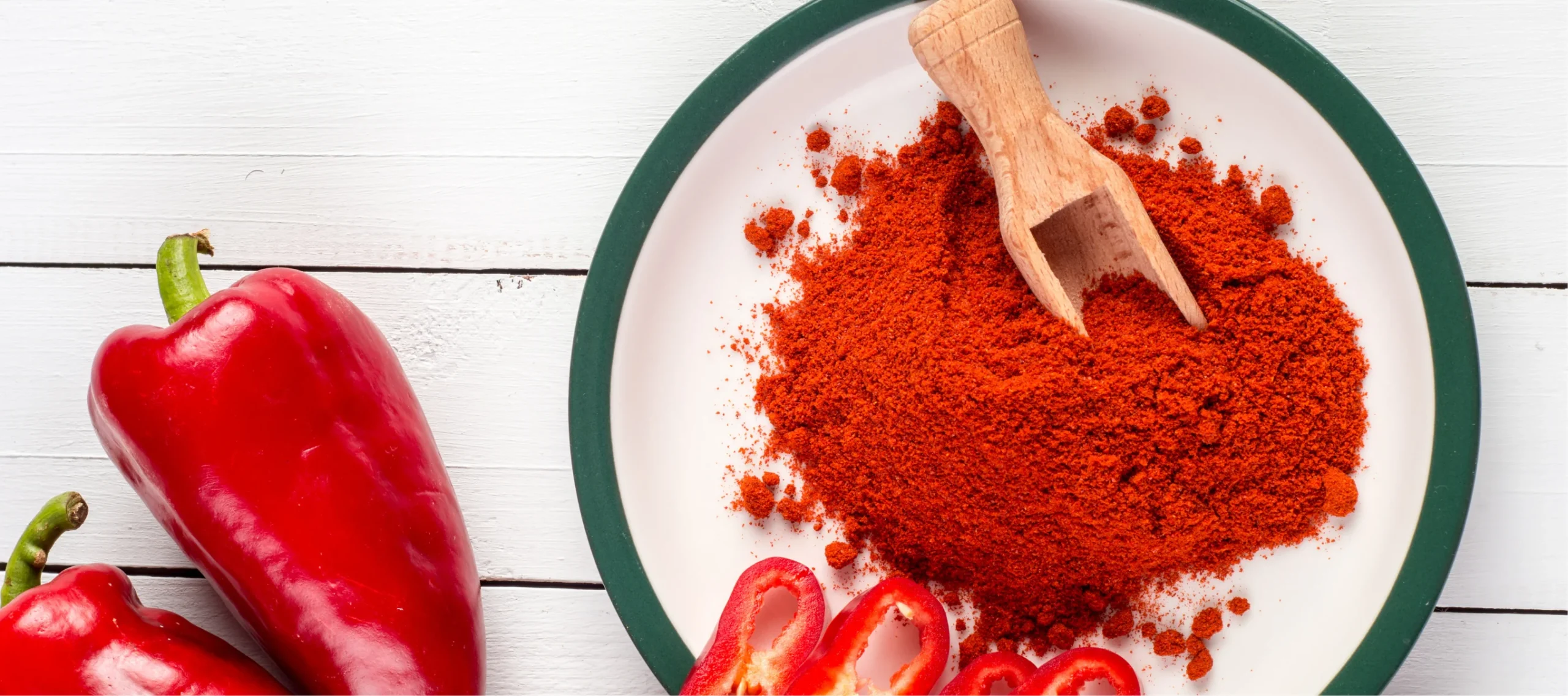
Paprika
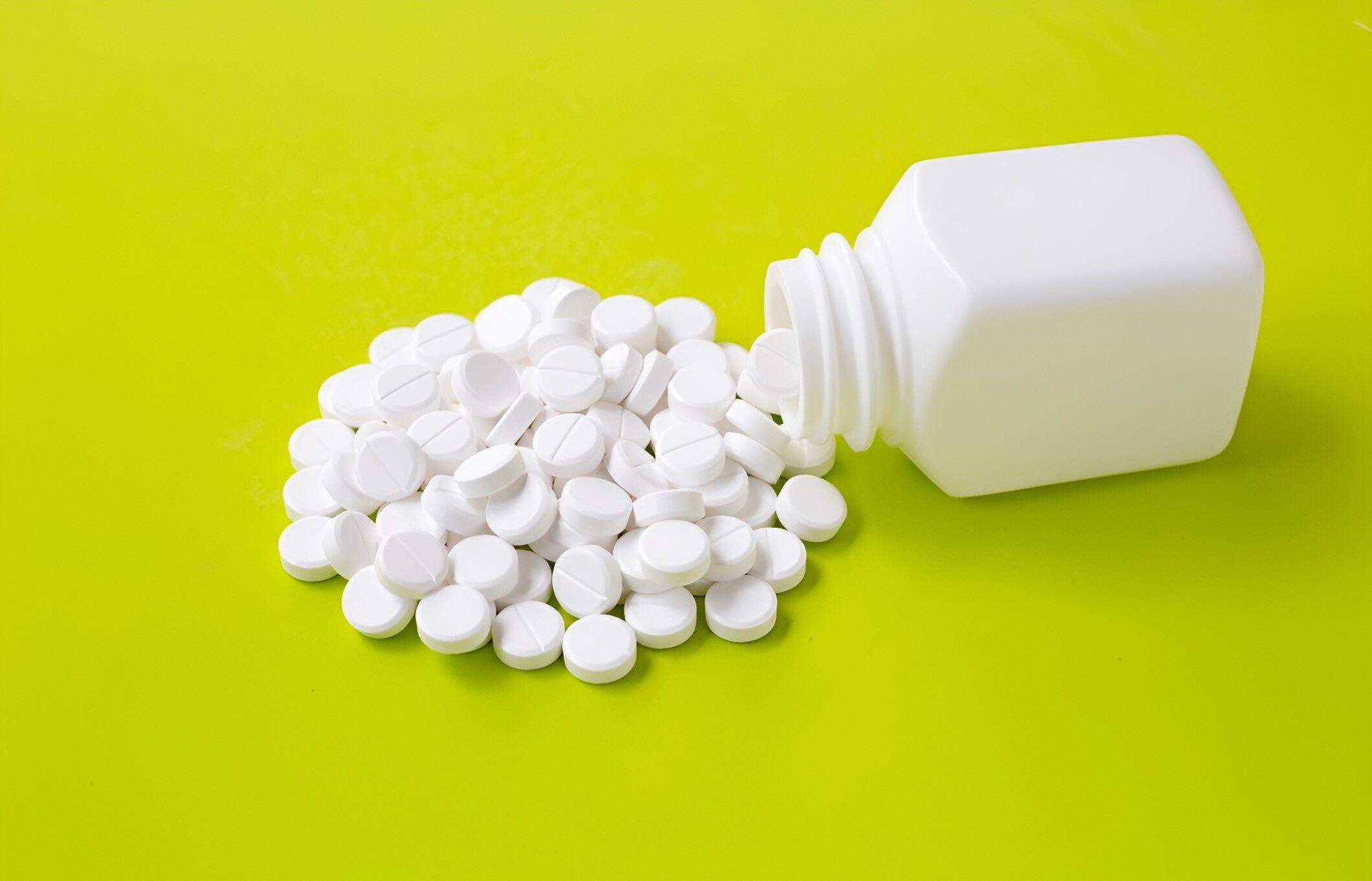
Paracetamol
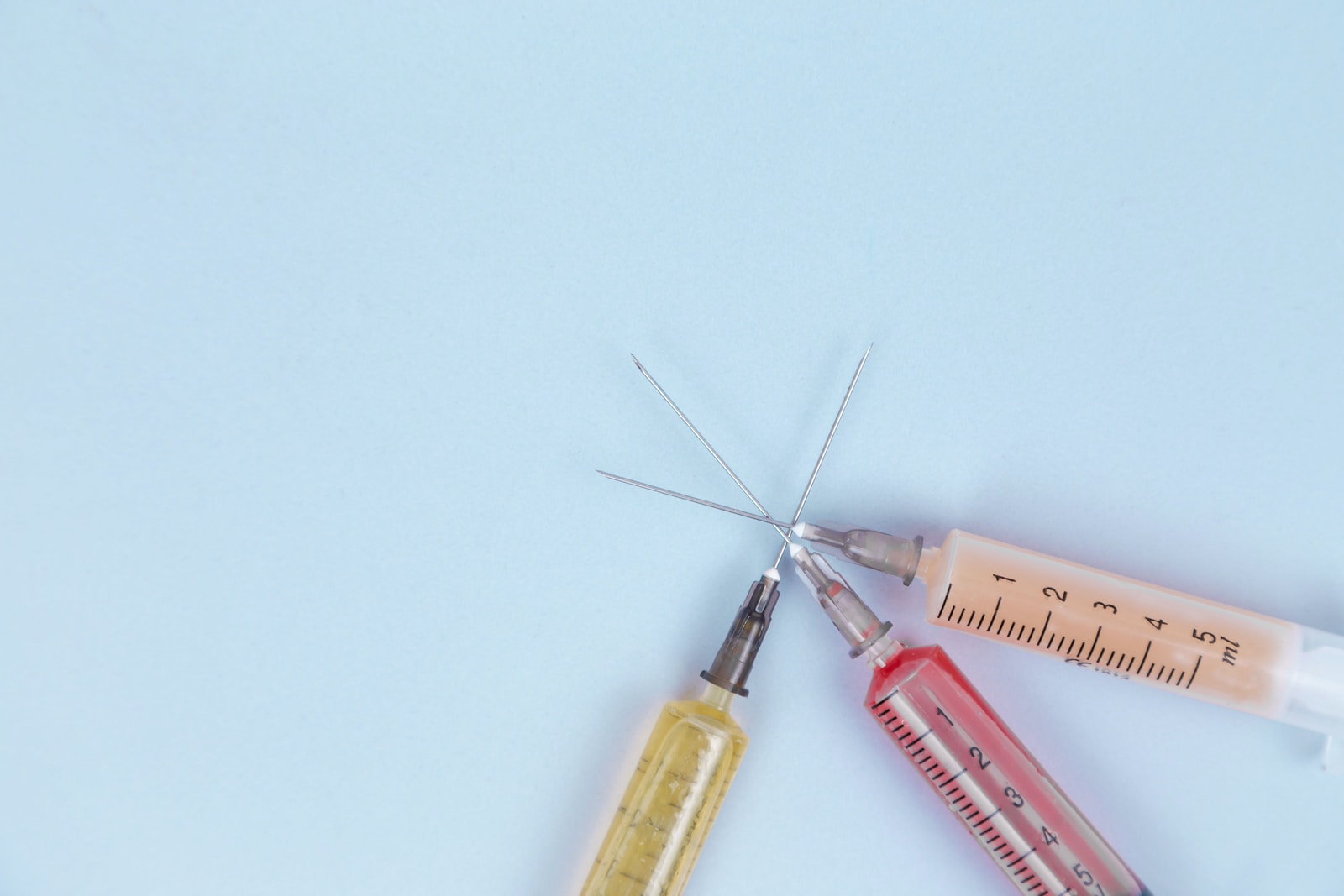
Parenterals
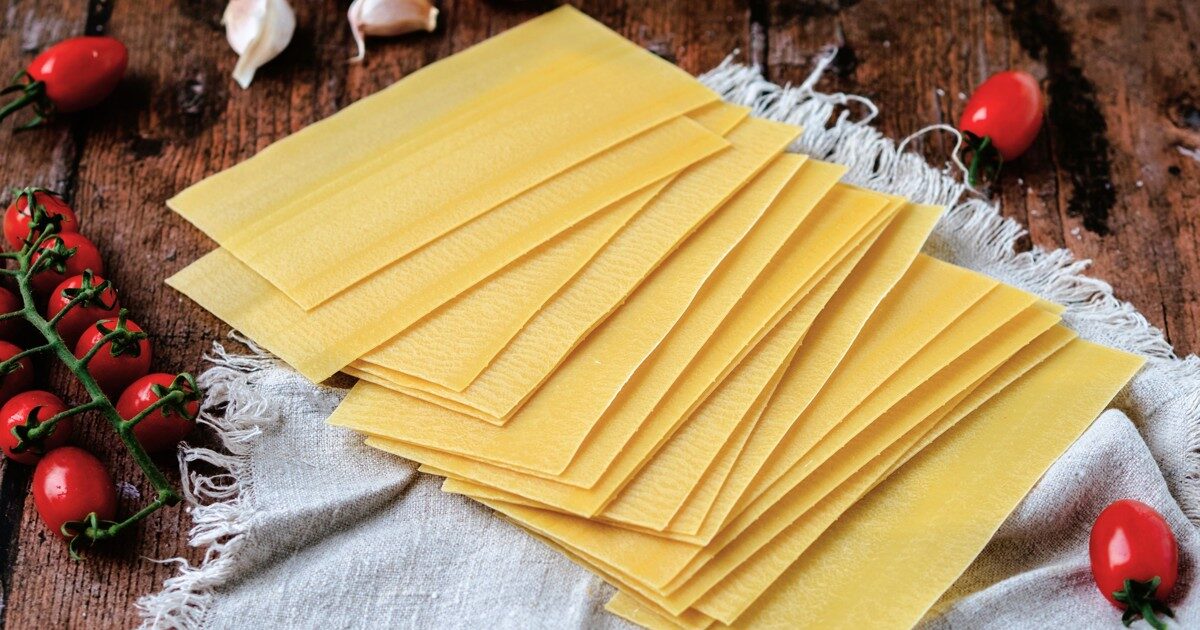
Pasta sheets

Pea protein isolate
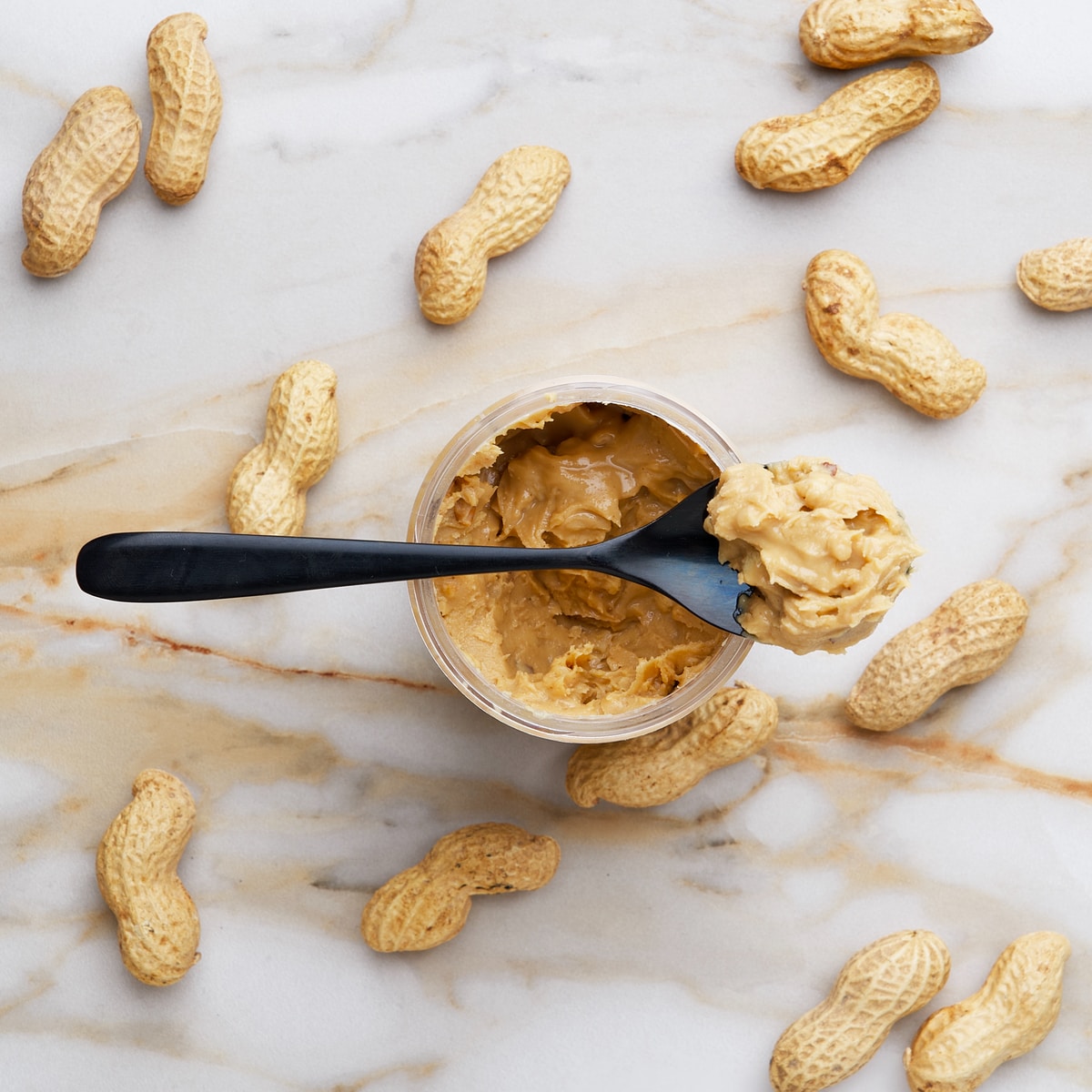
Peanut butter
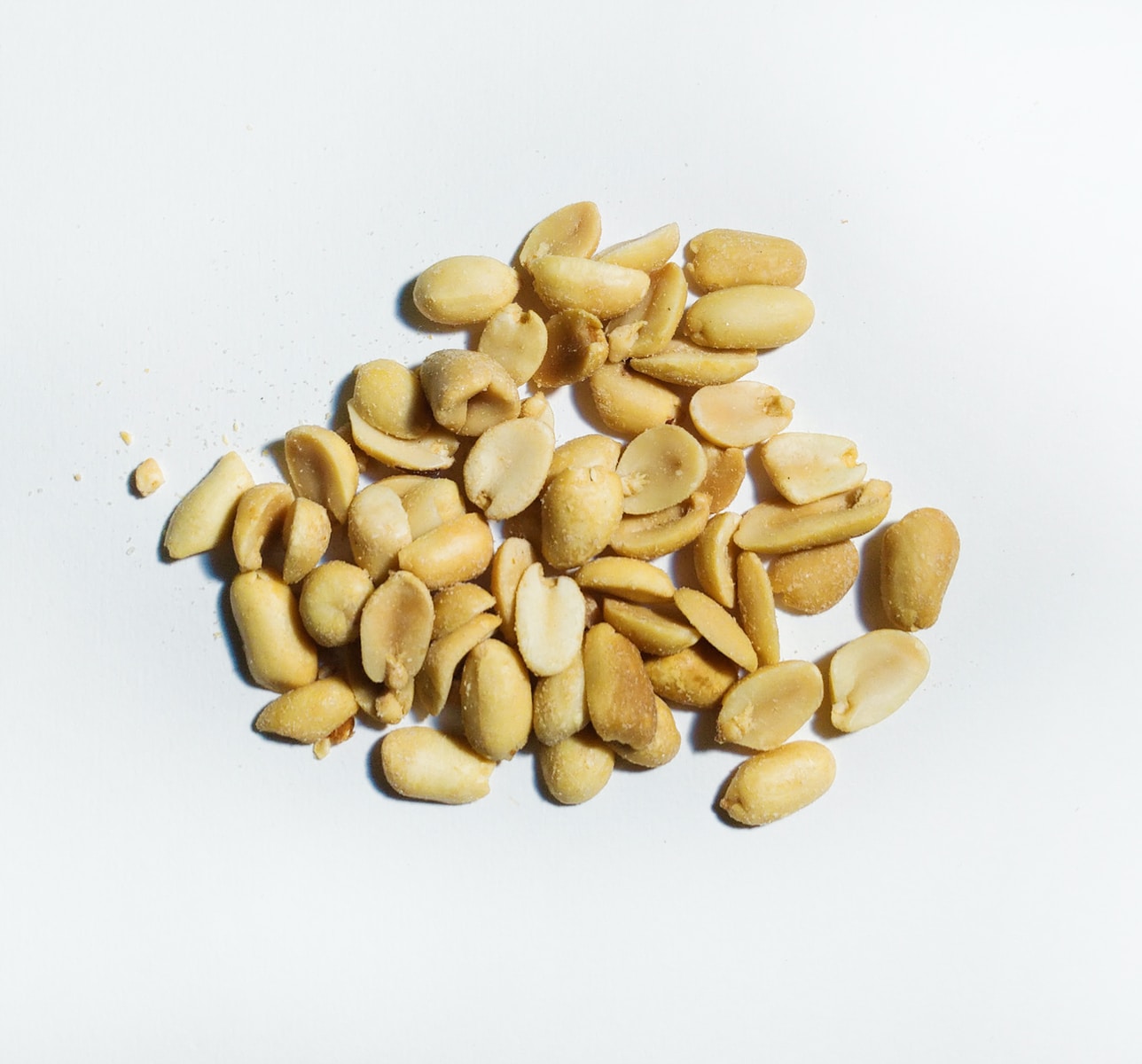
Peanuts
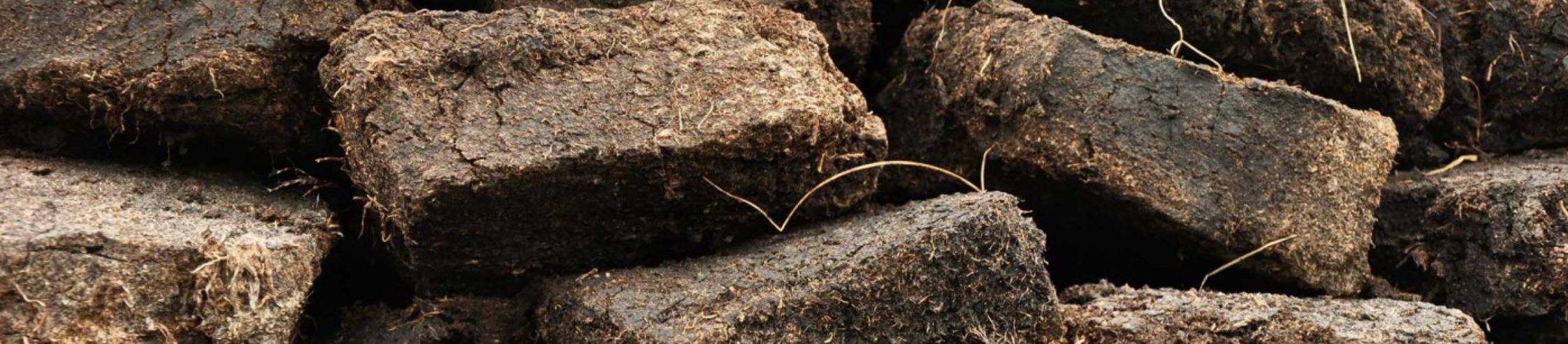
Peat
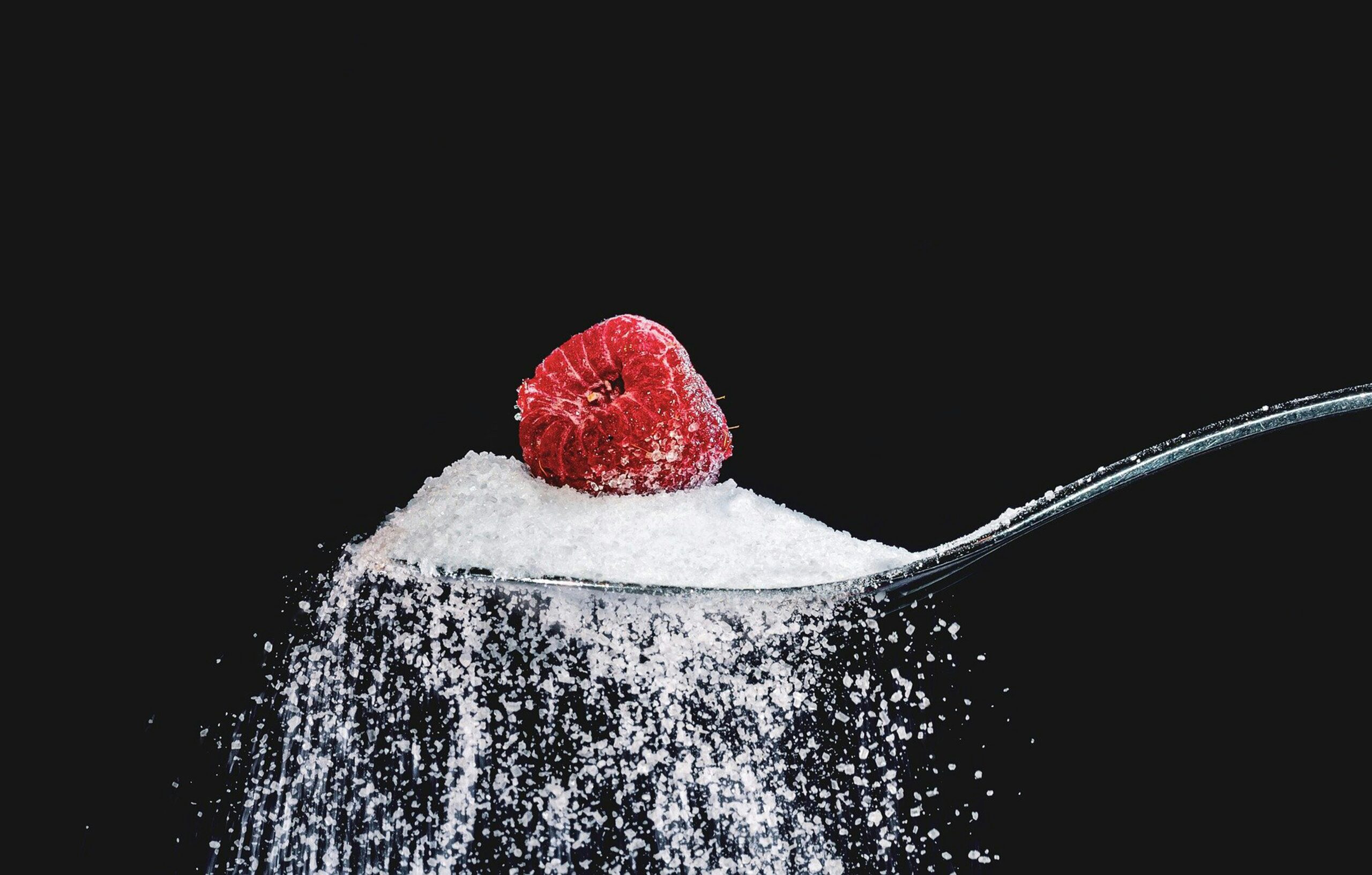
Pectin
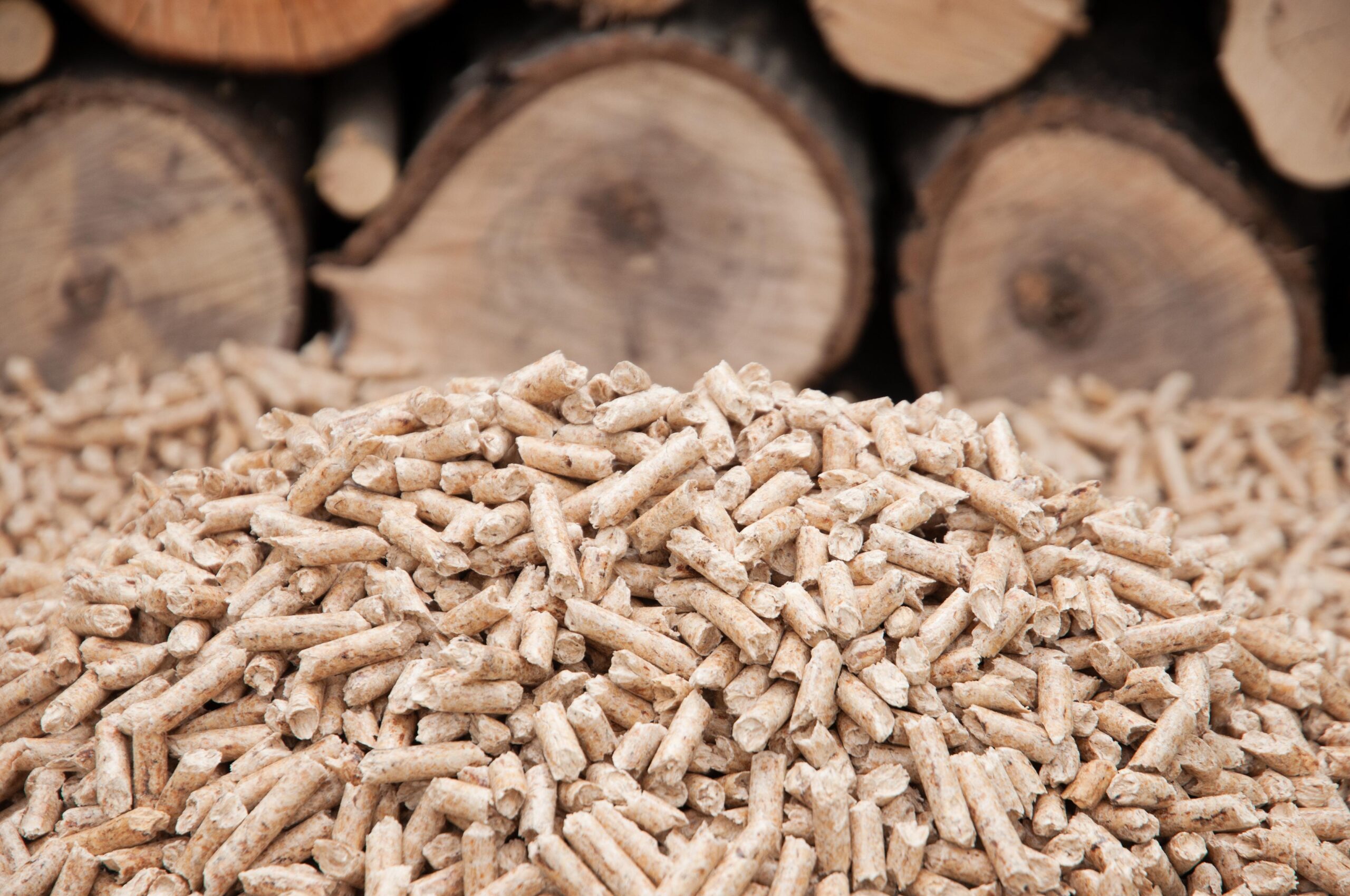
Pellet fuel
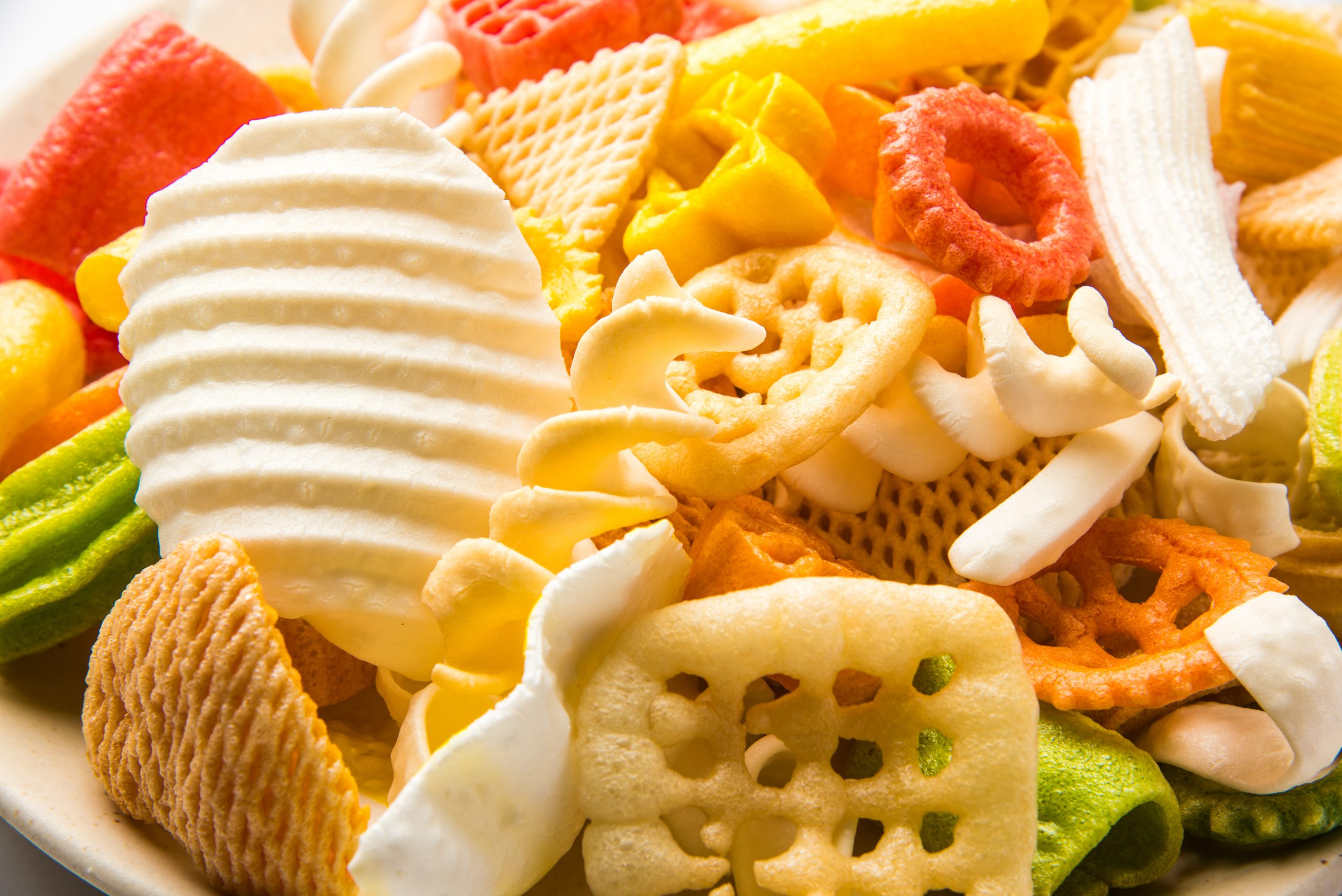
Pellet snacks
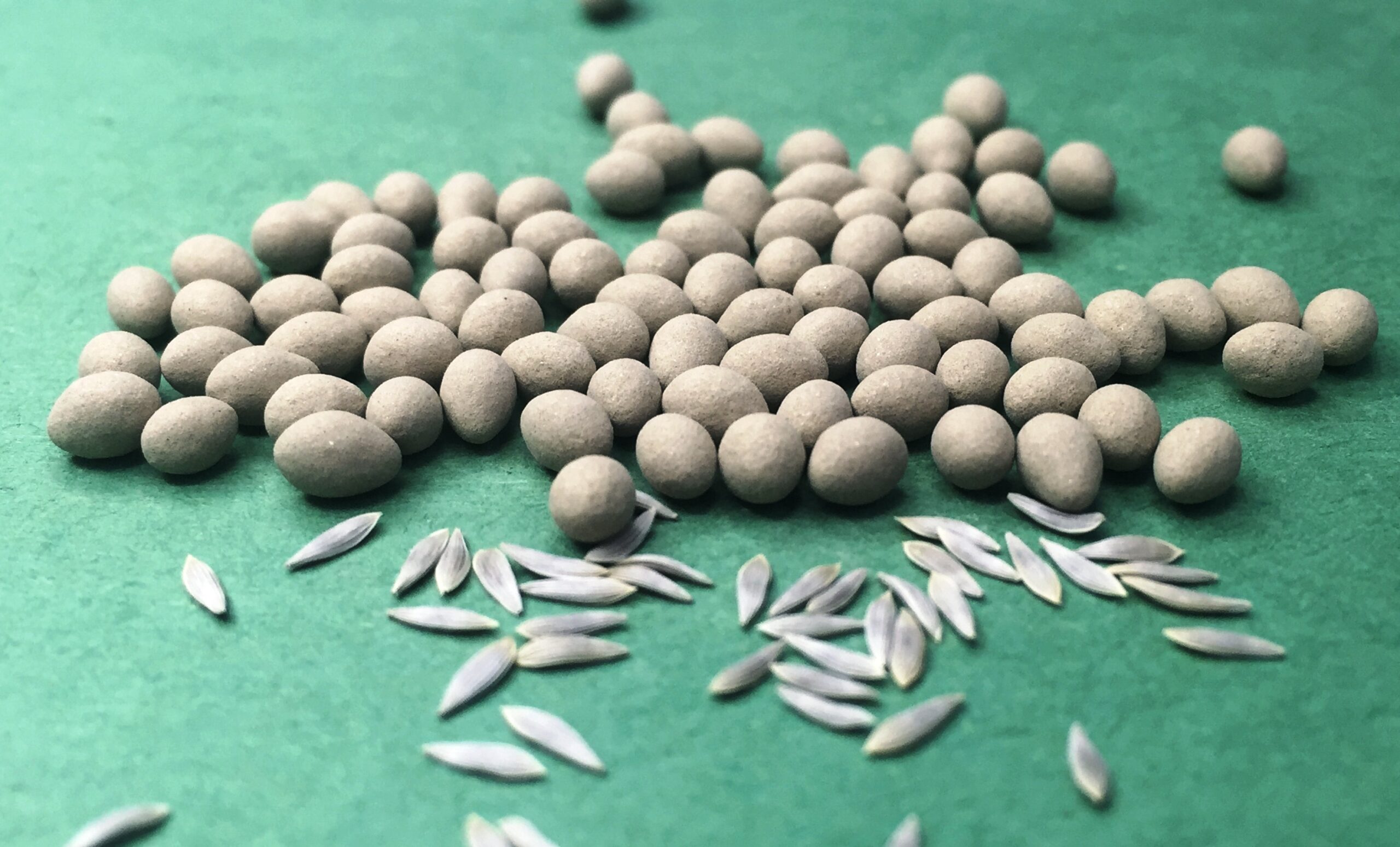
Pelleted seeds
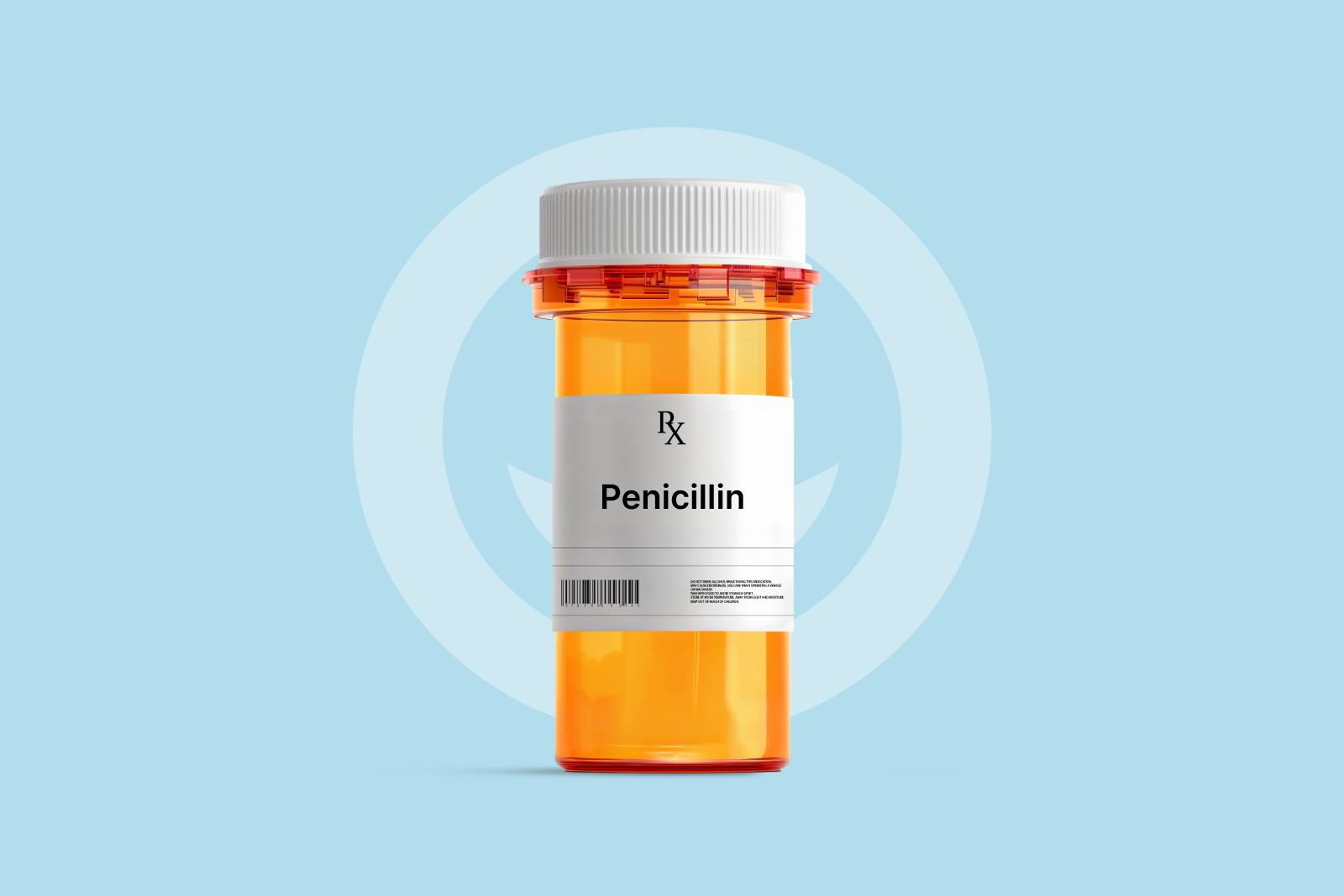
Penicillin
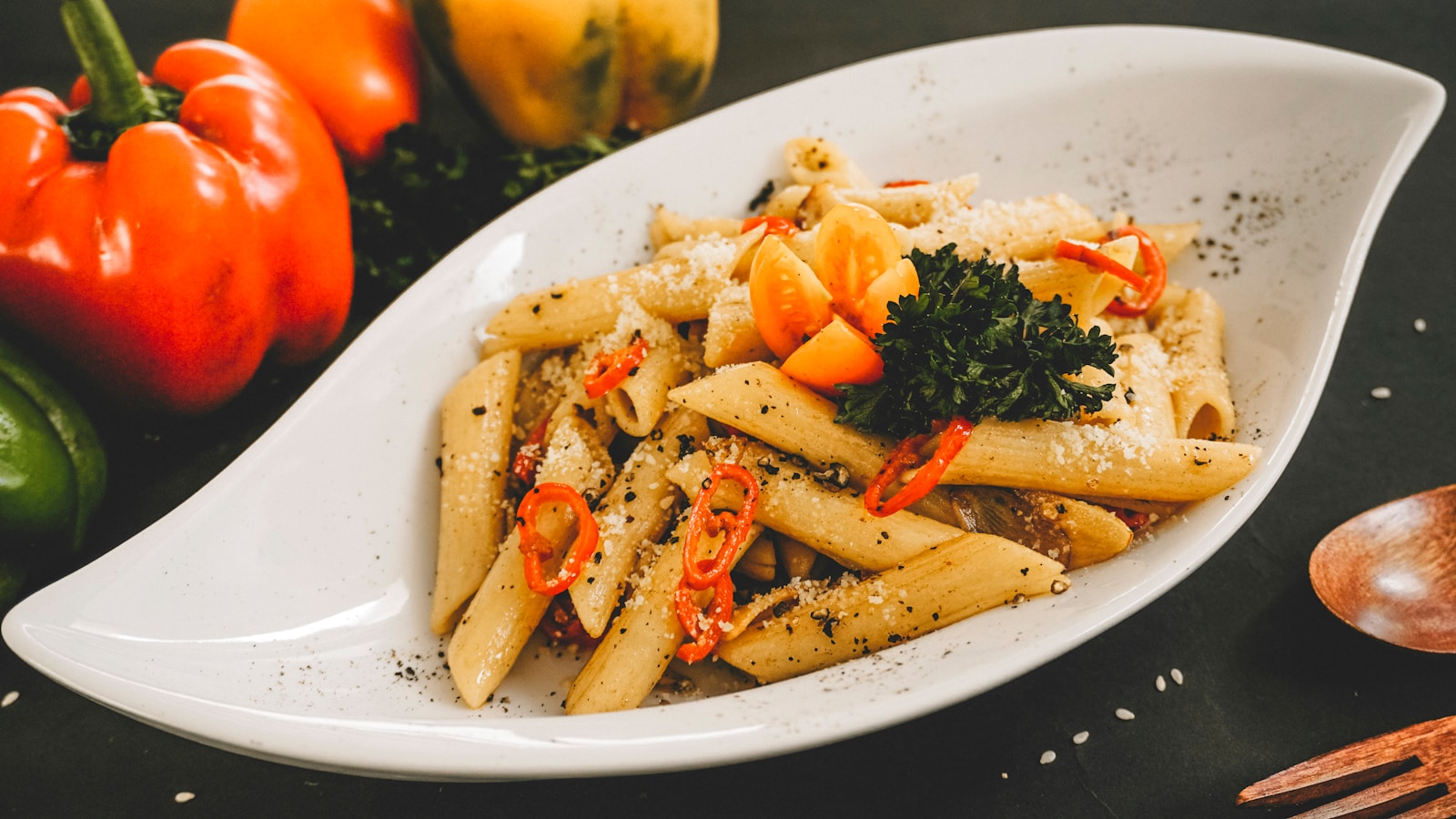
Penne pasta
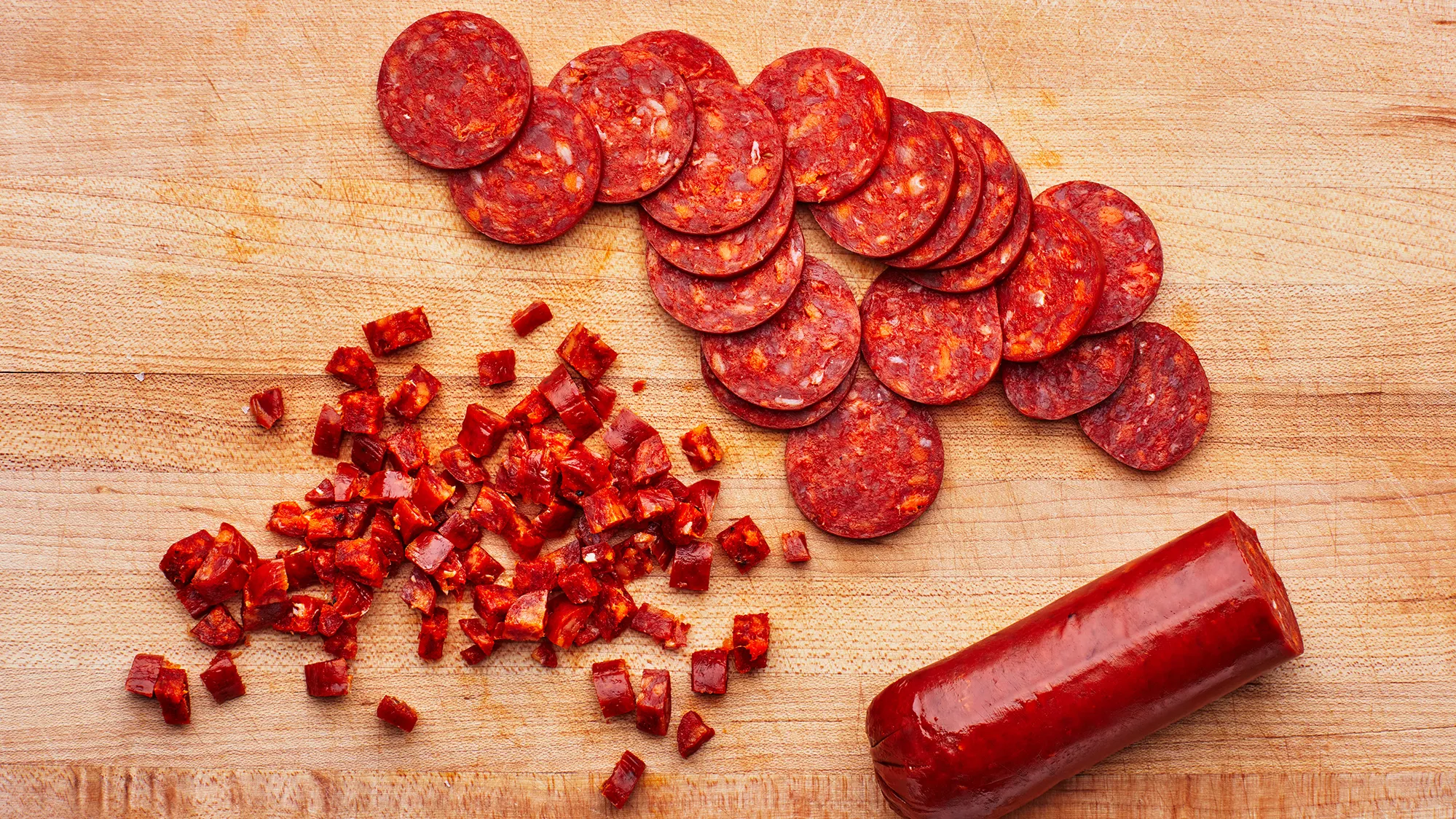
Pepperoni
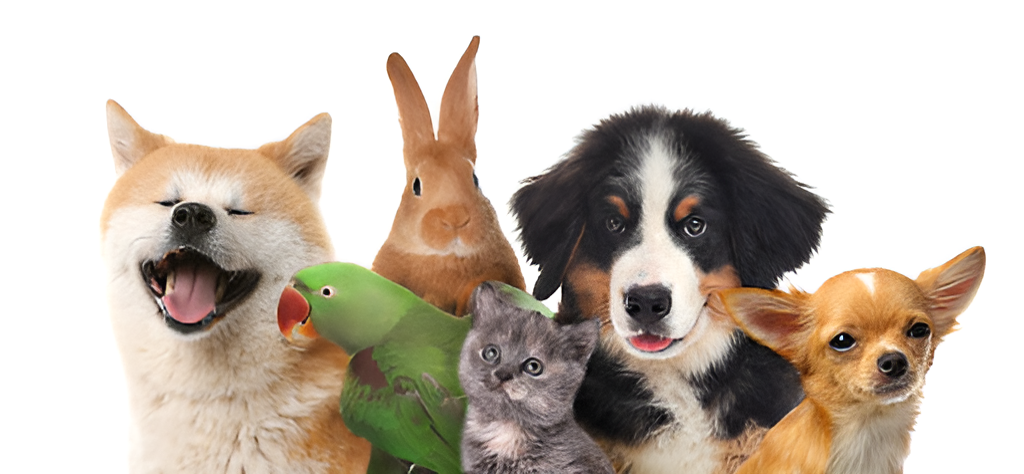
Pet care
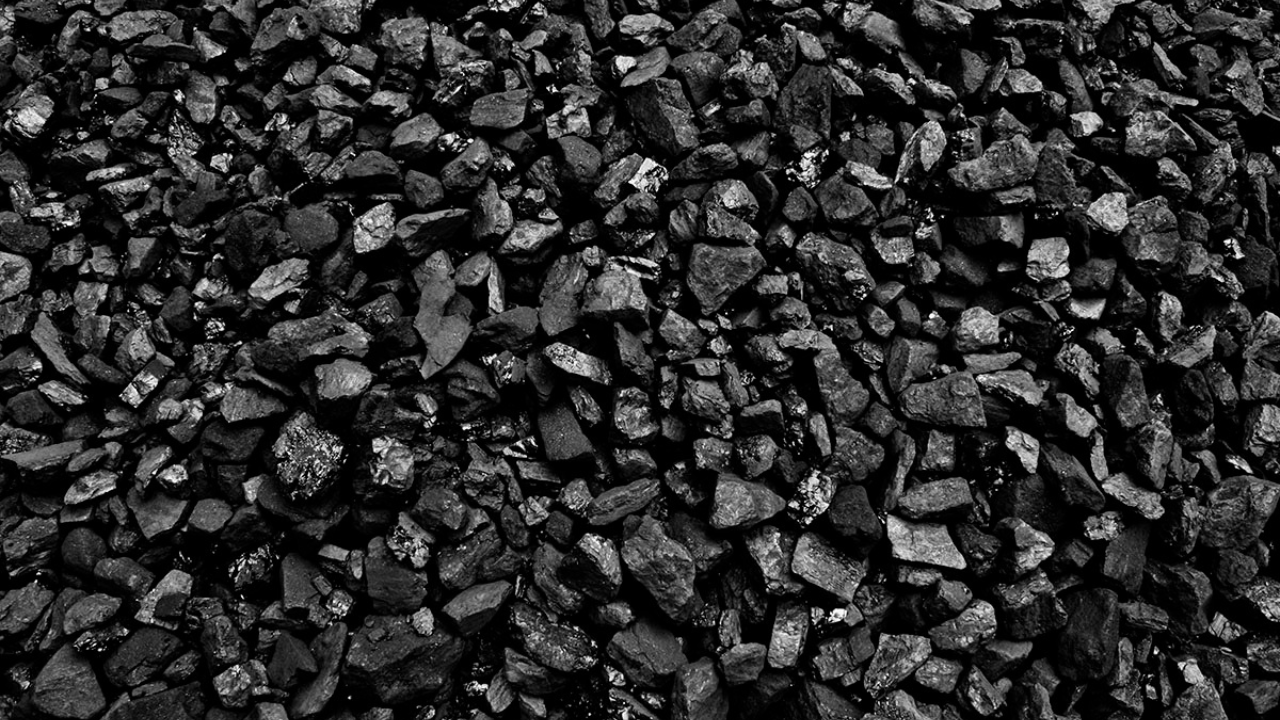
Petroleum coke
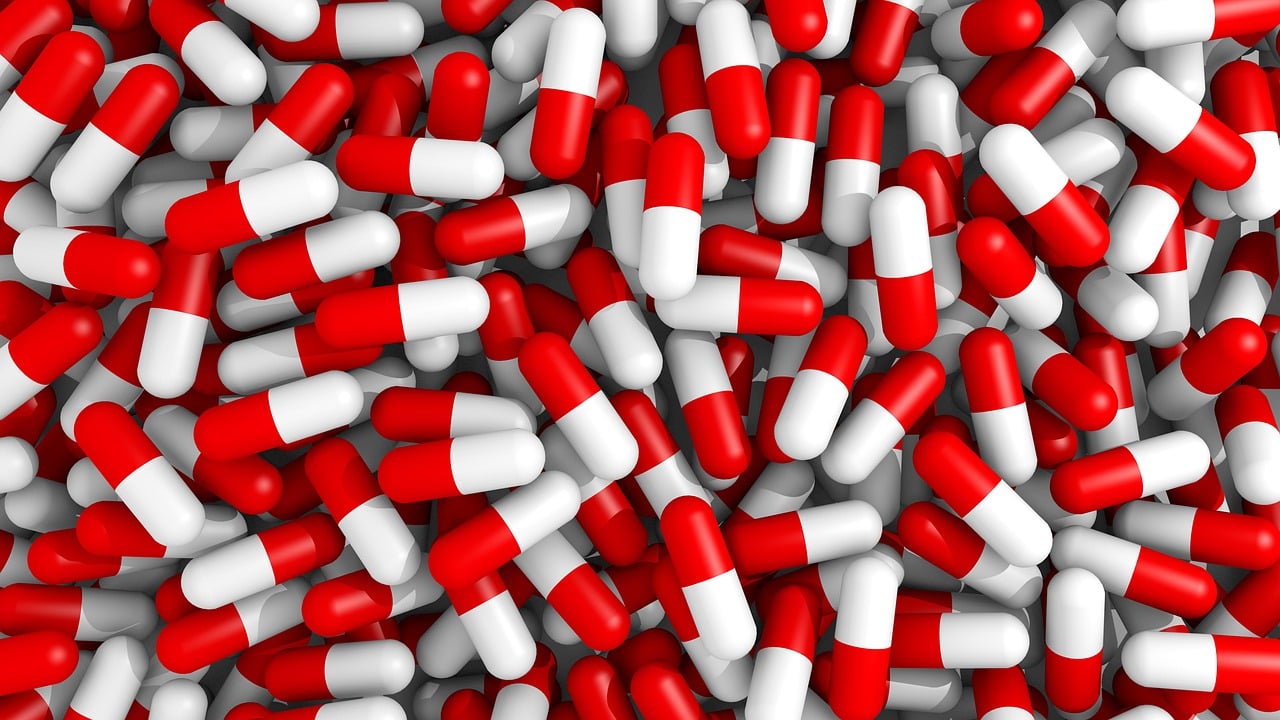
Pharmaceutical capsules
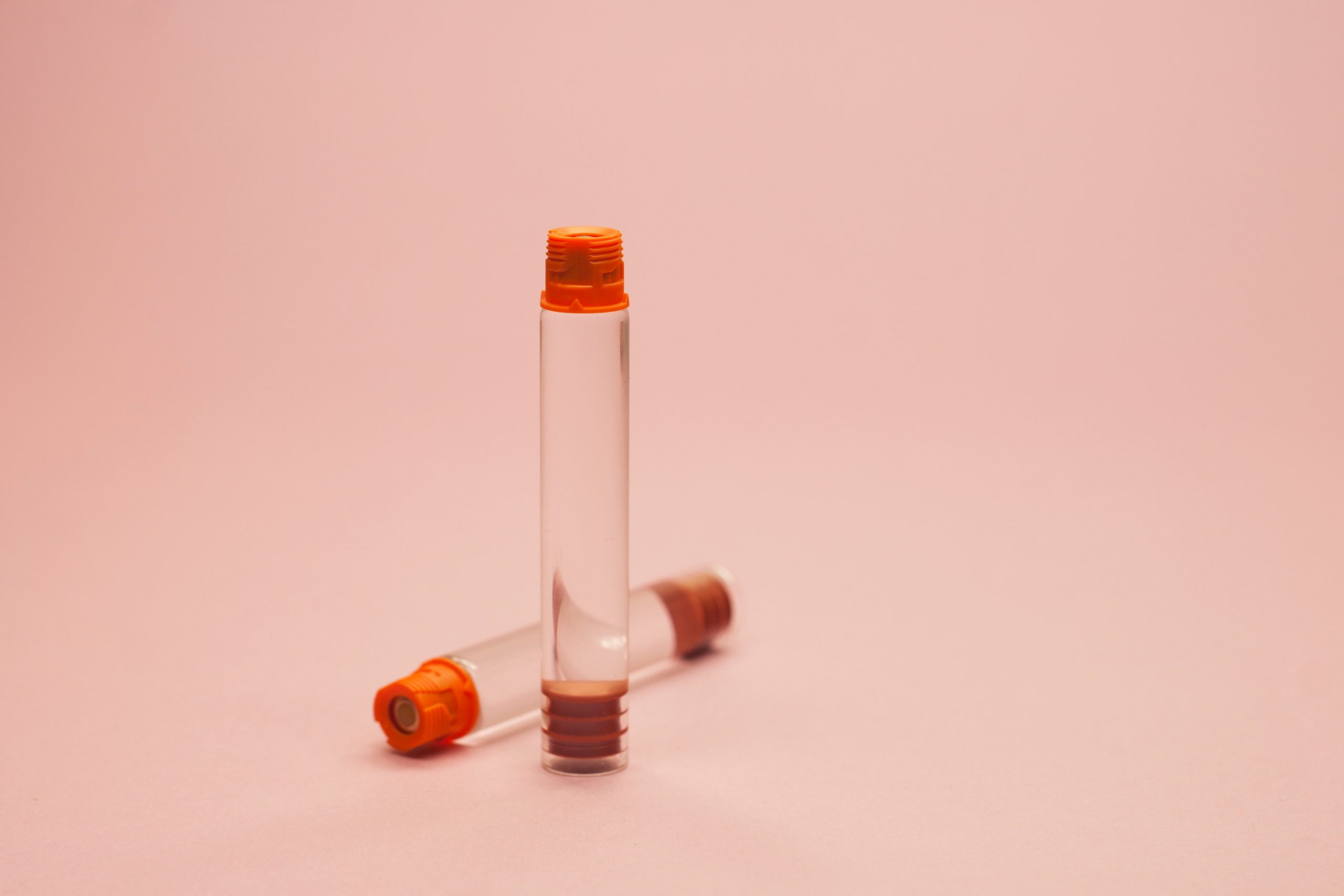
Pharmaceutical cartridges
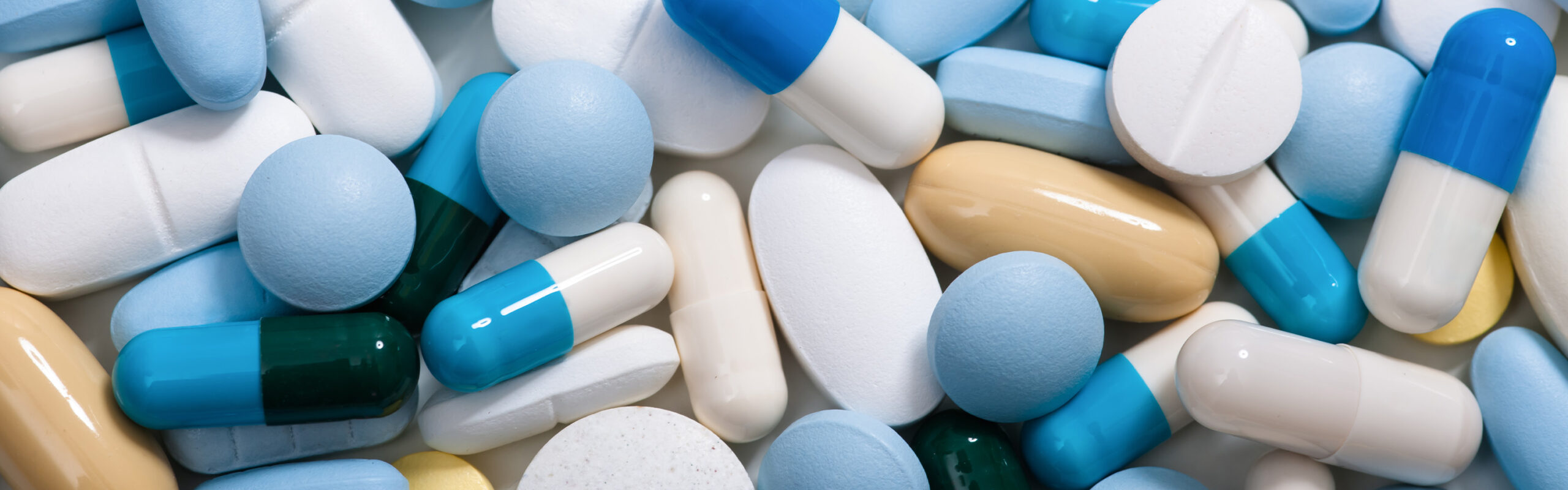
Pharmaceutical excipients
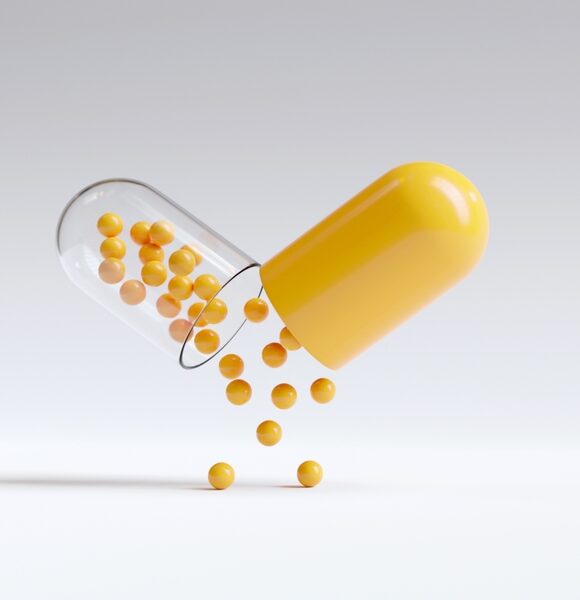
Pharmaceutical granules
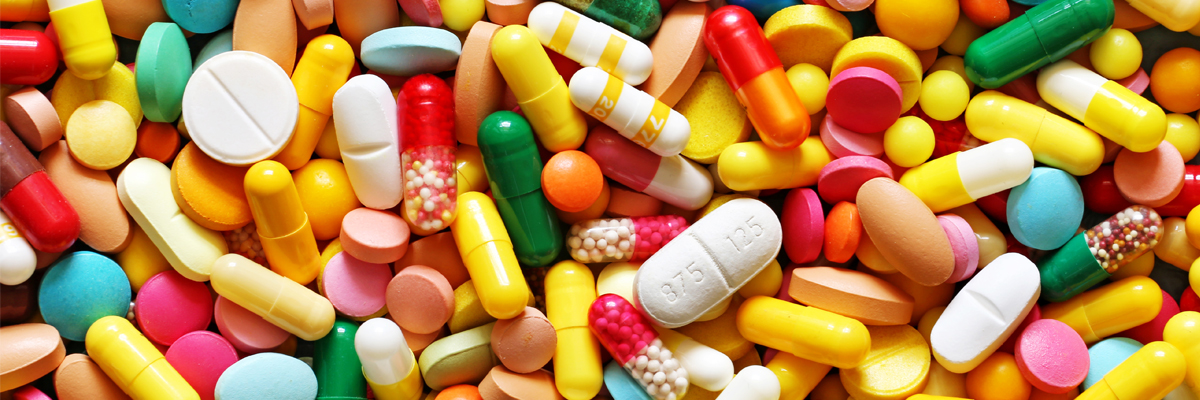
Pharmaceutical intermediates
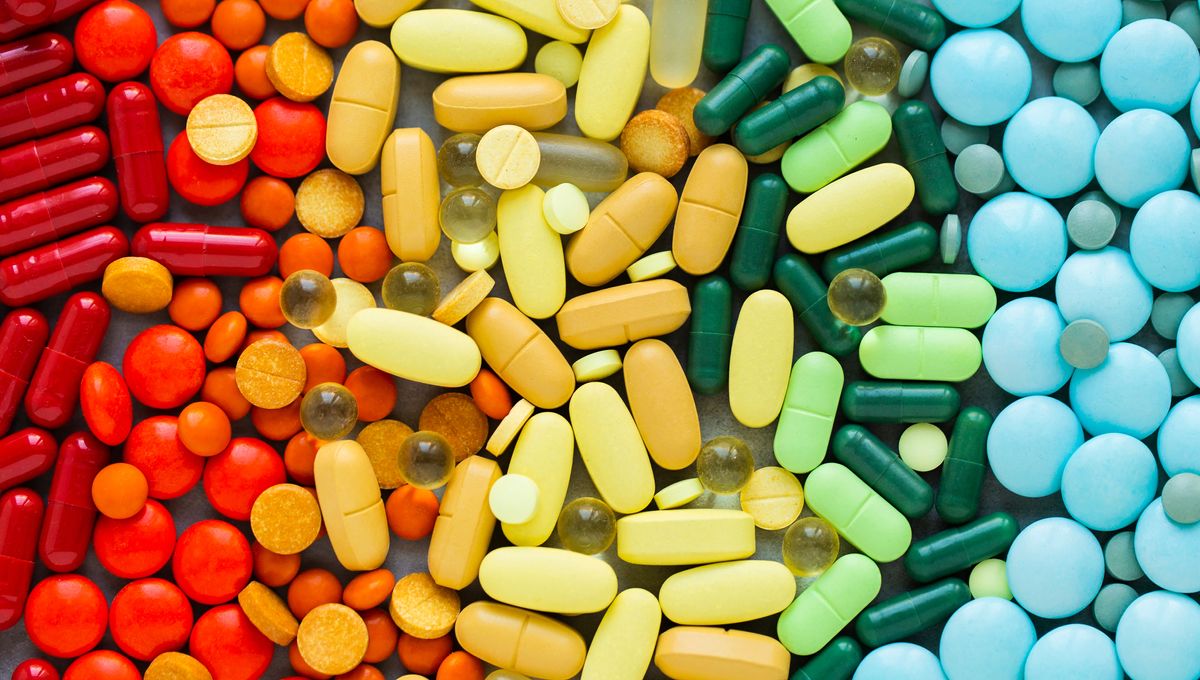
Pharmaceutical pills
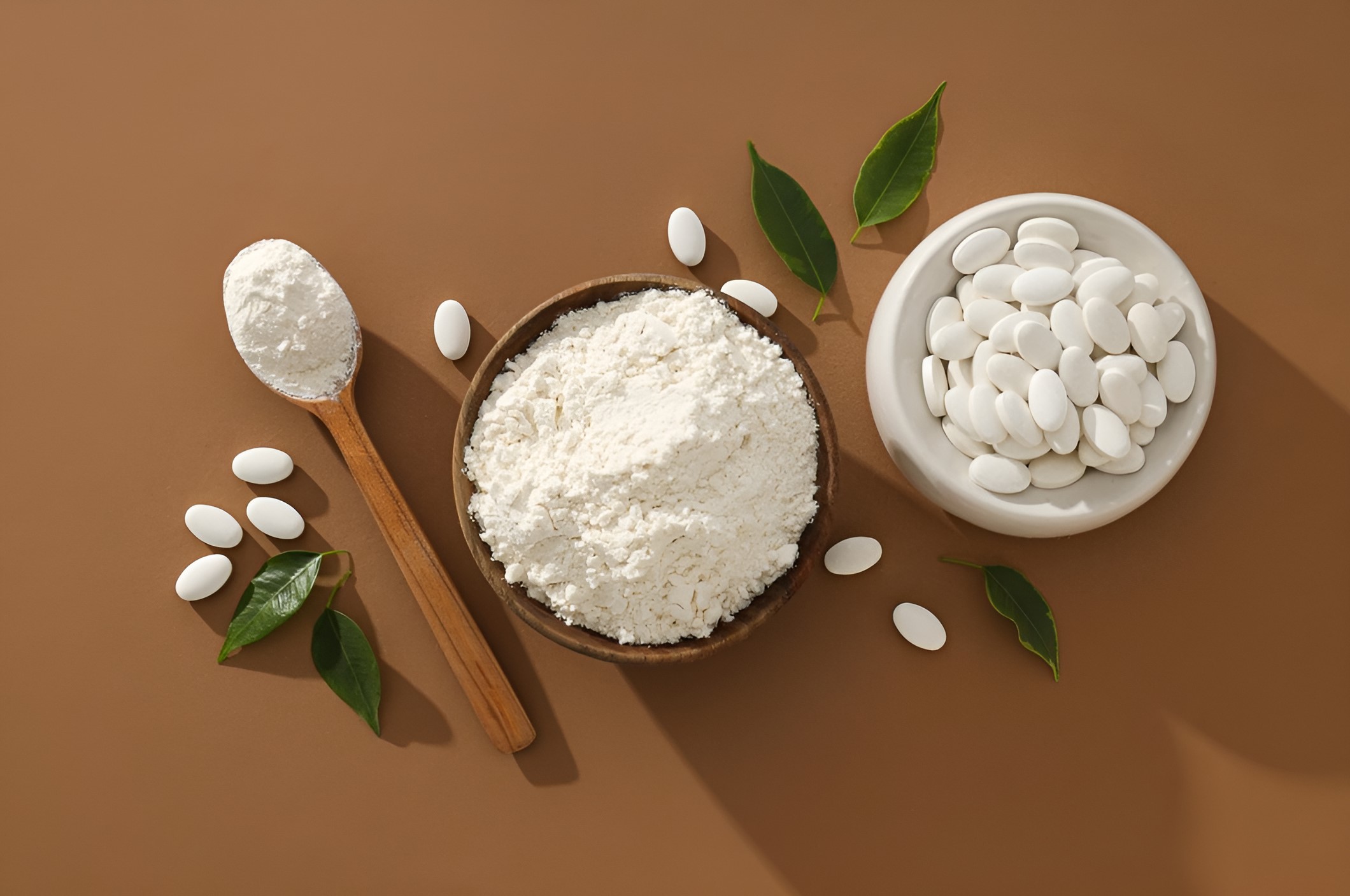
Pharmaceutical powders
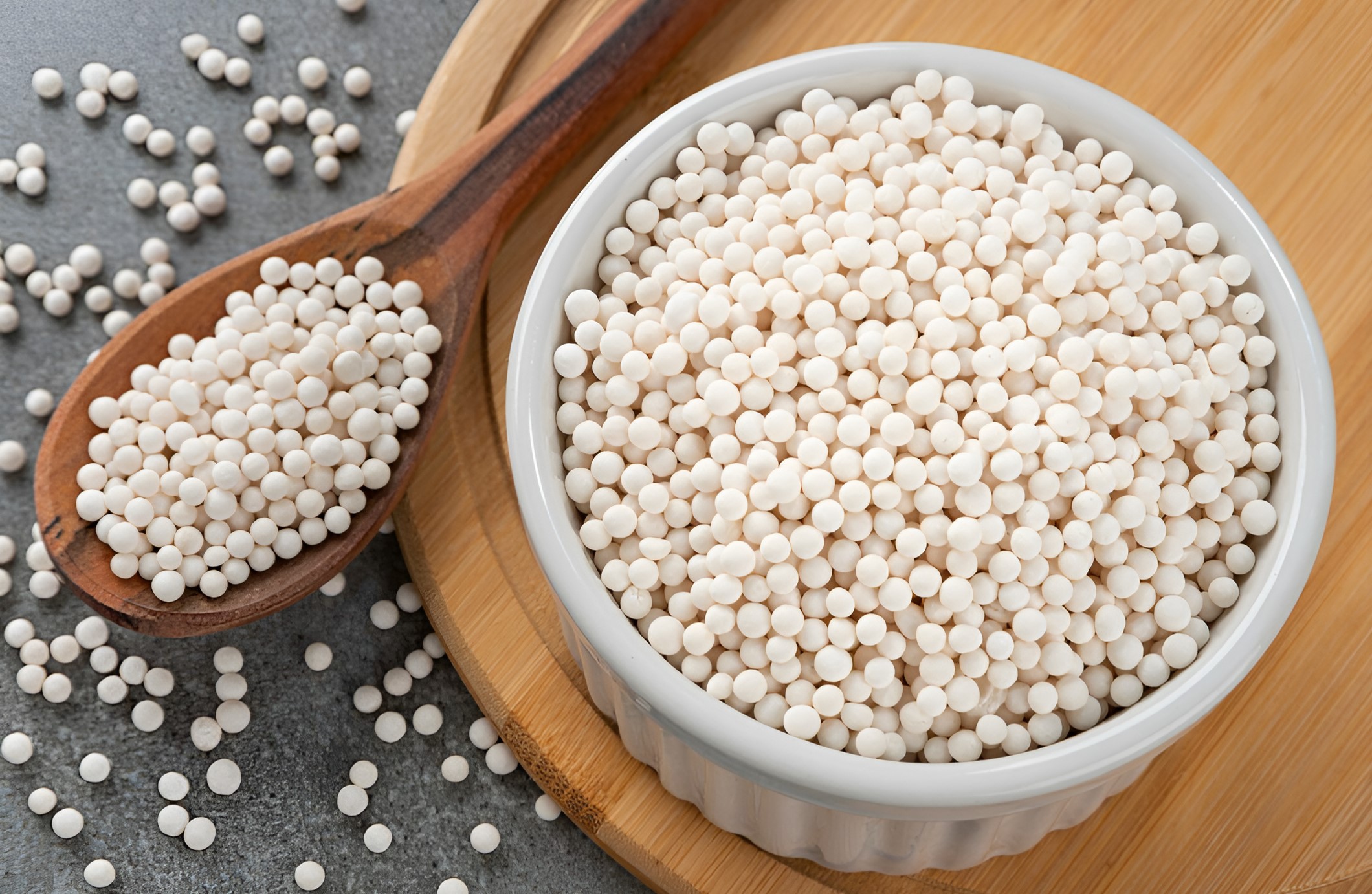
Phosphates
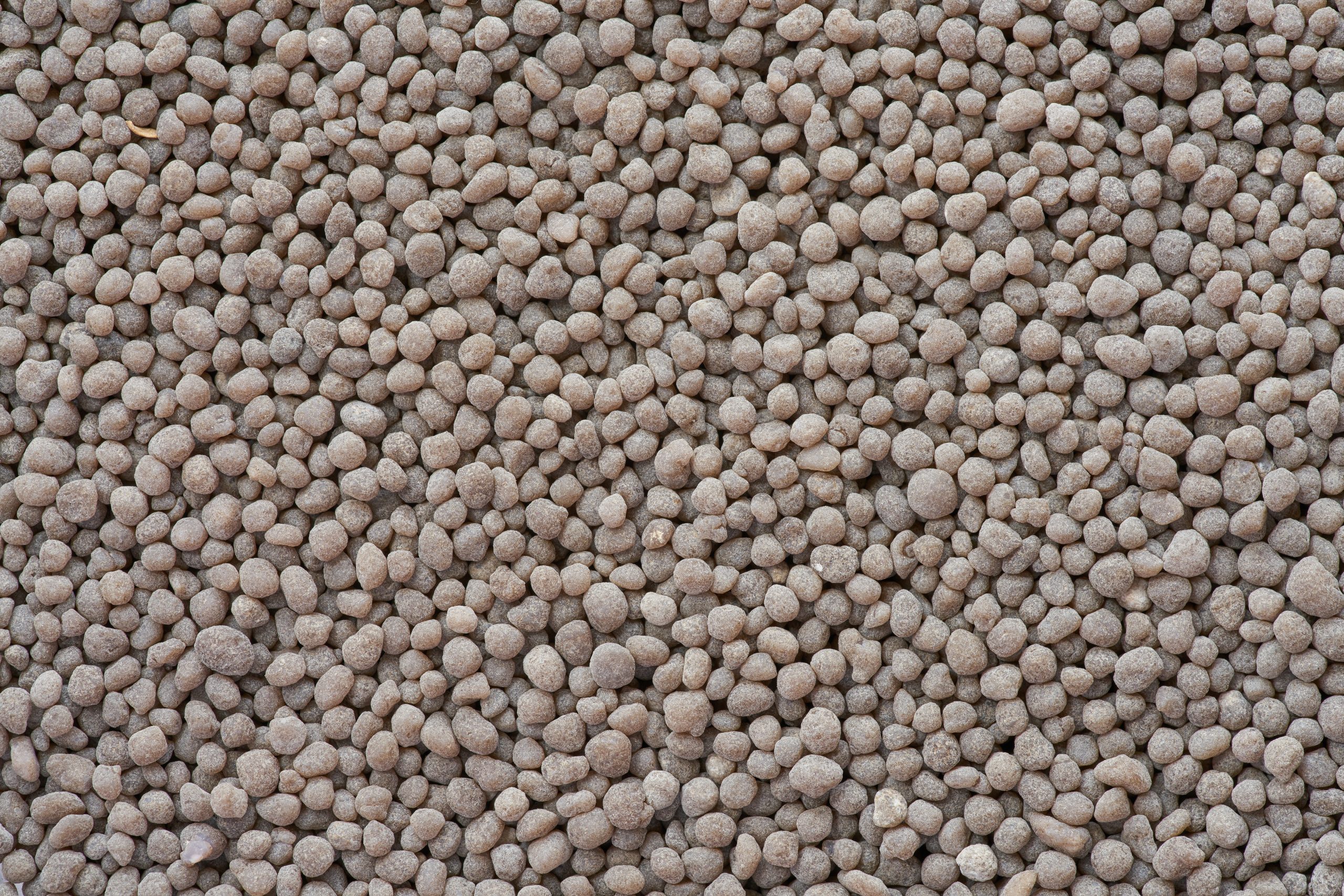
Phosphorus fertilizer
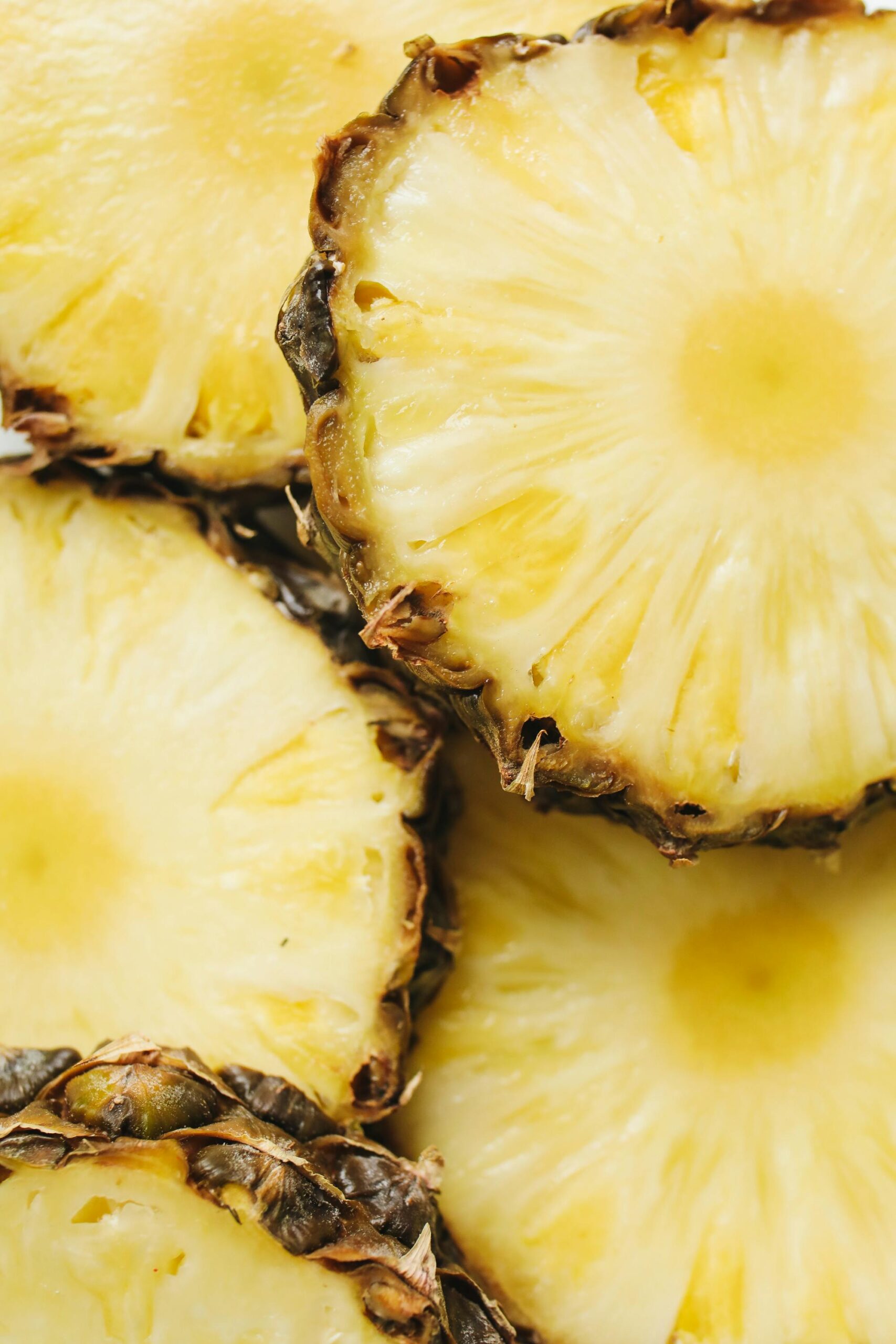
Pineapples

Frozen pizza
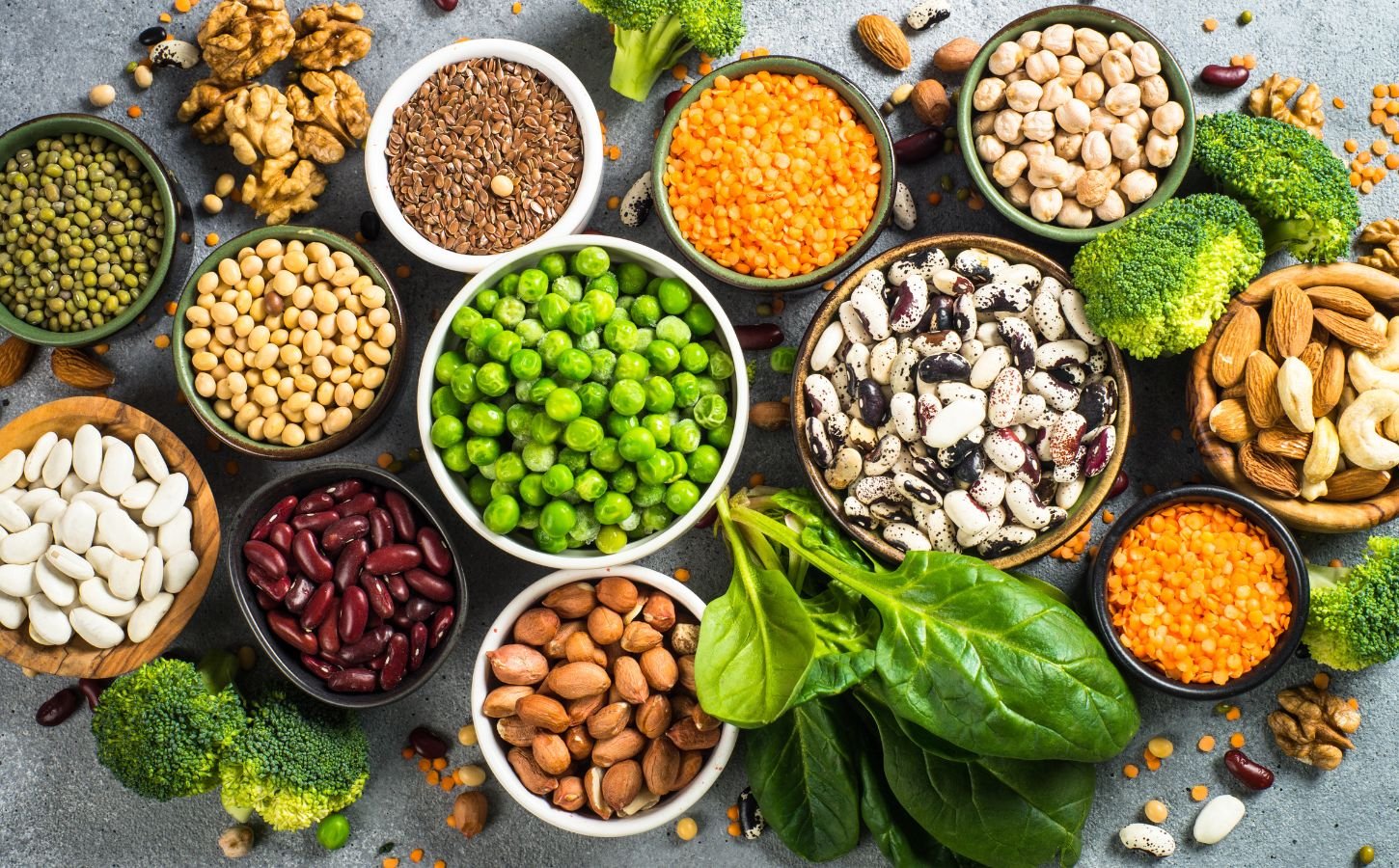
Plant-based protein
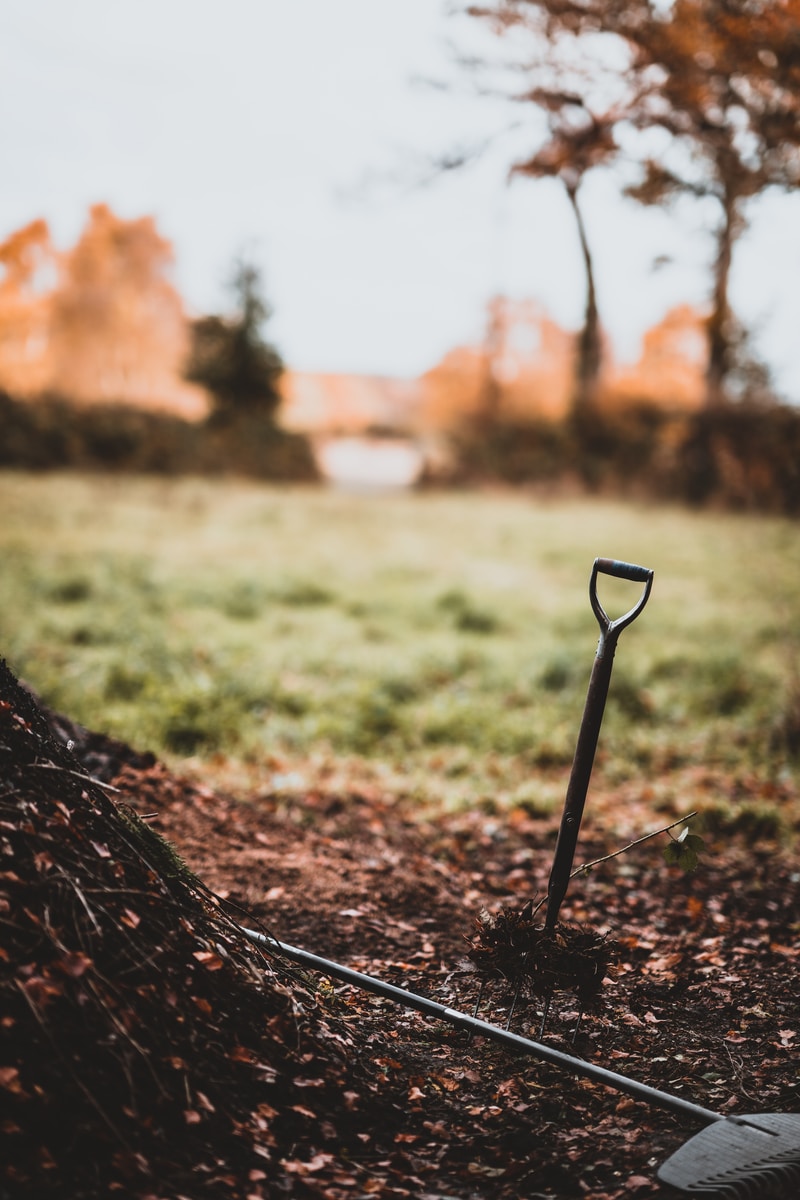
Plant waste
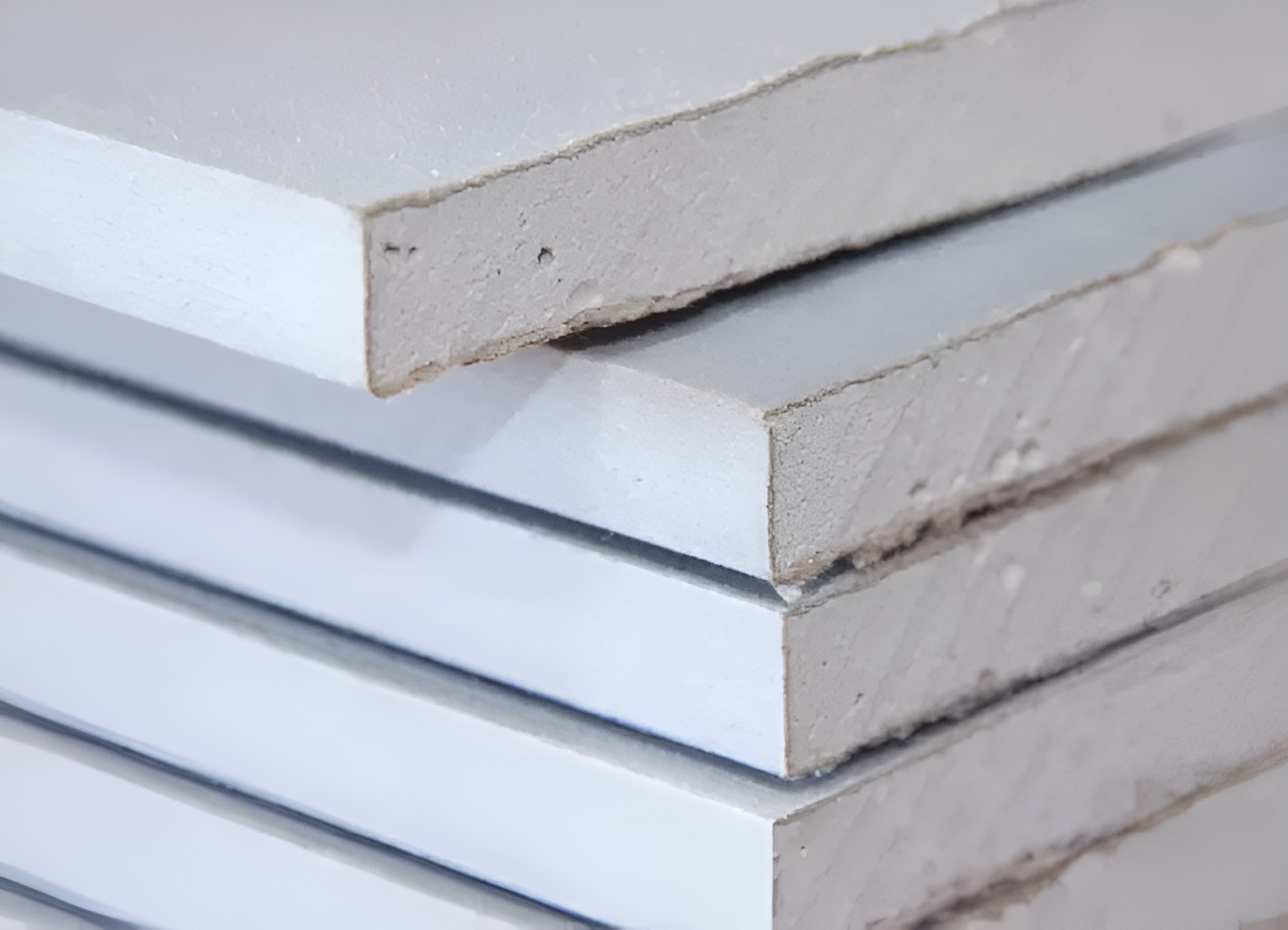
Plasterboard
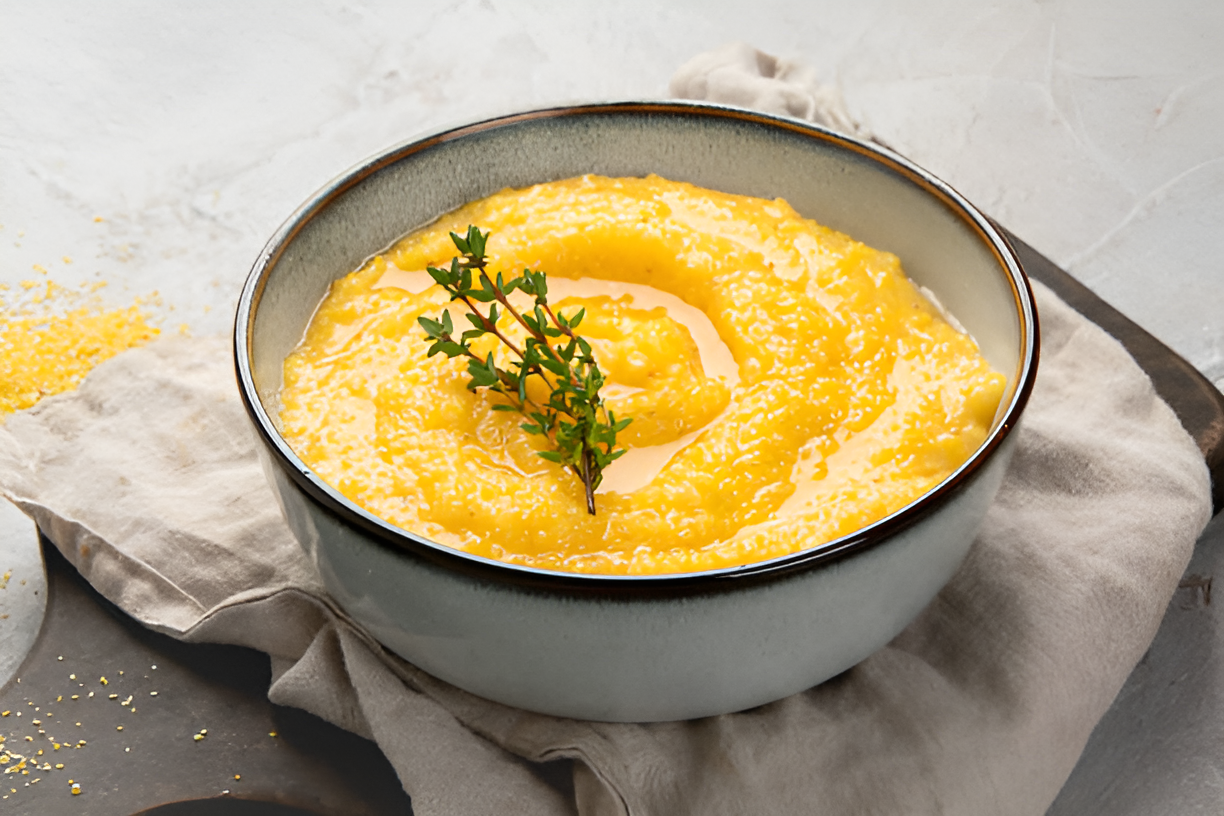
Polenta
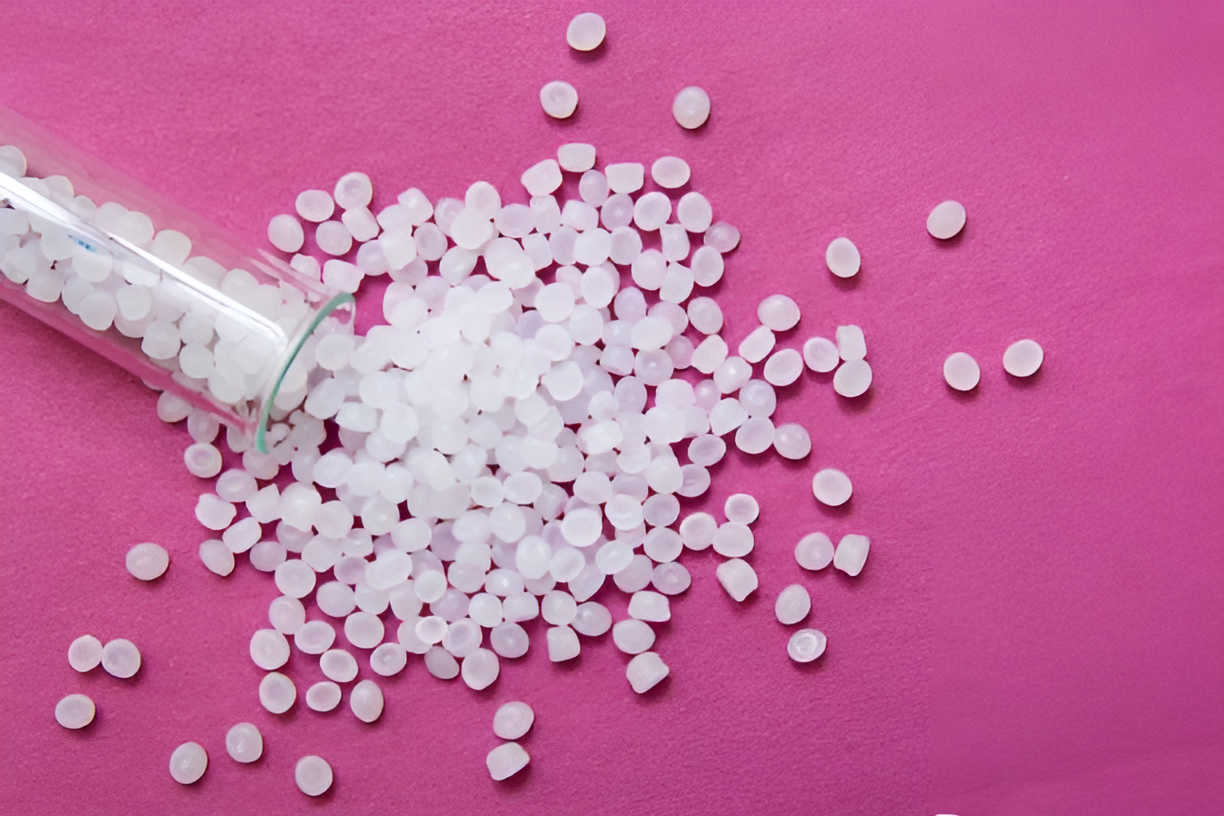
Polyethylene granules
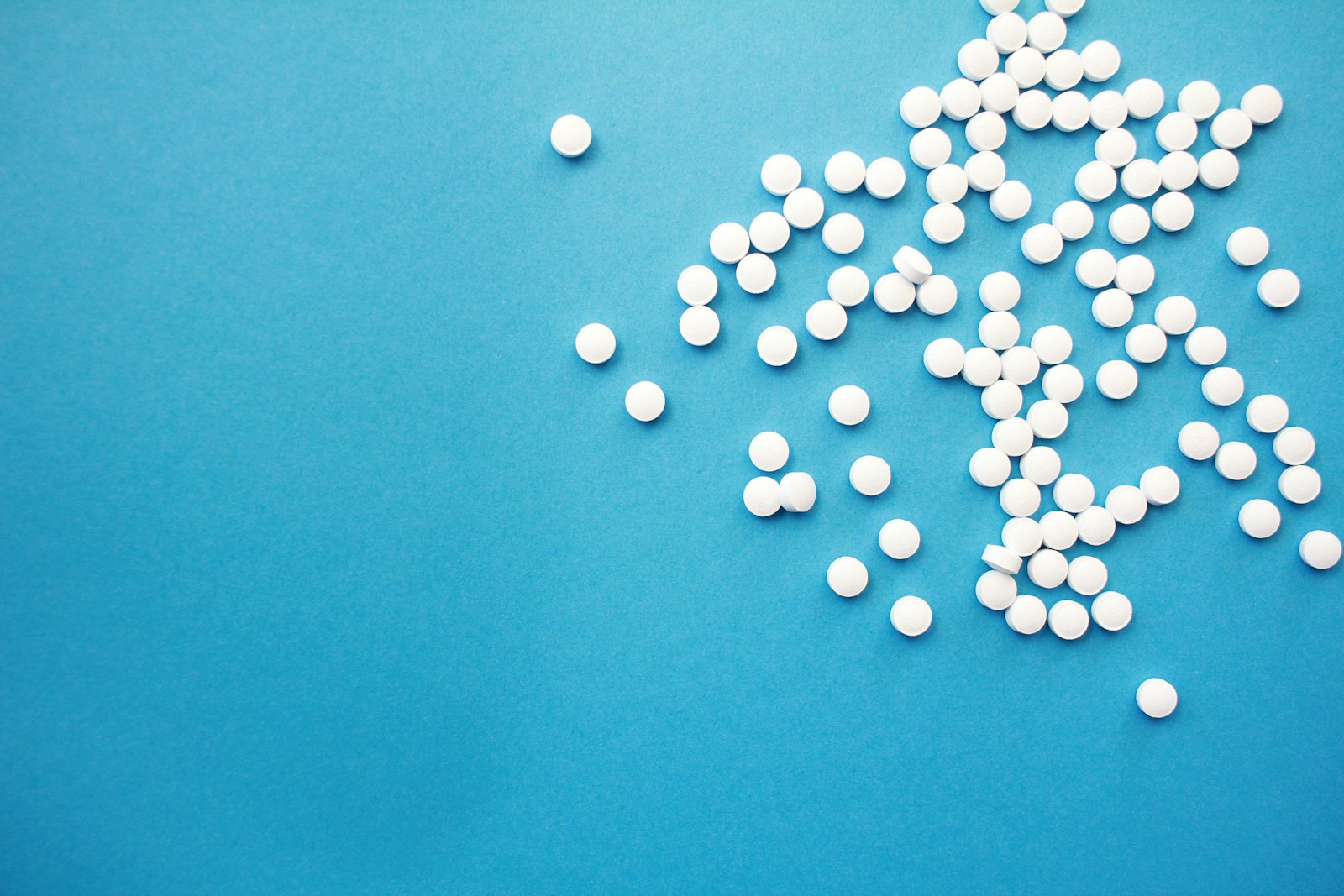
Polyethylene pellets
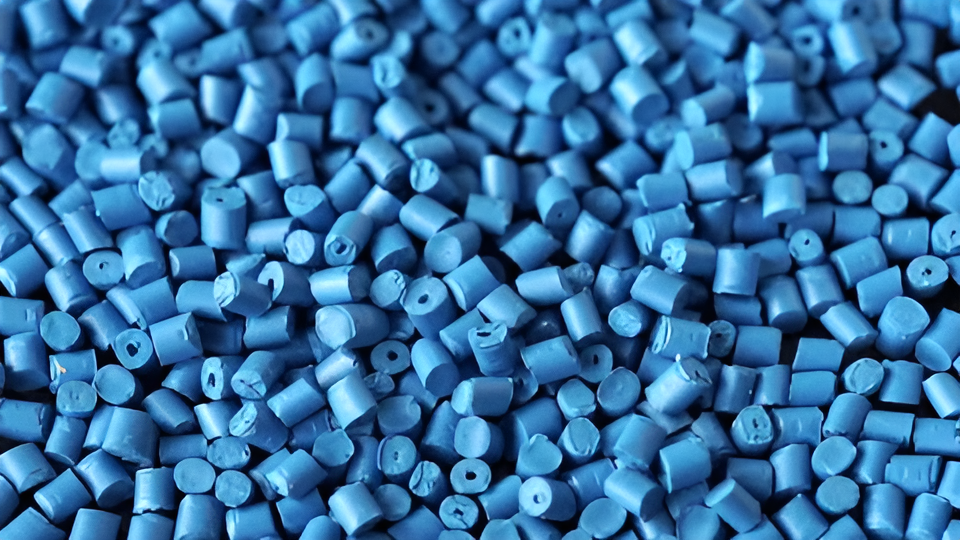
Polymer granules
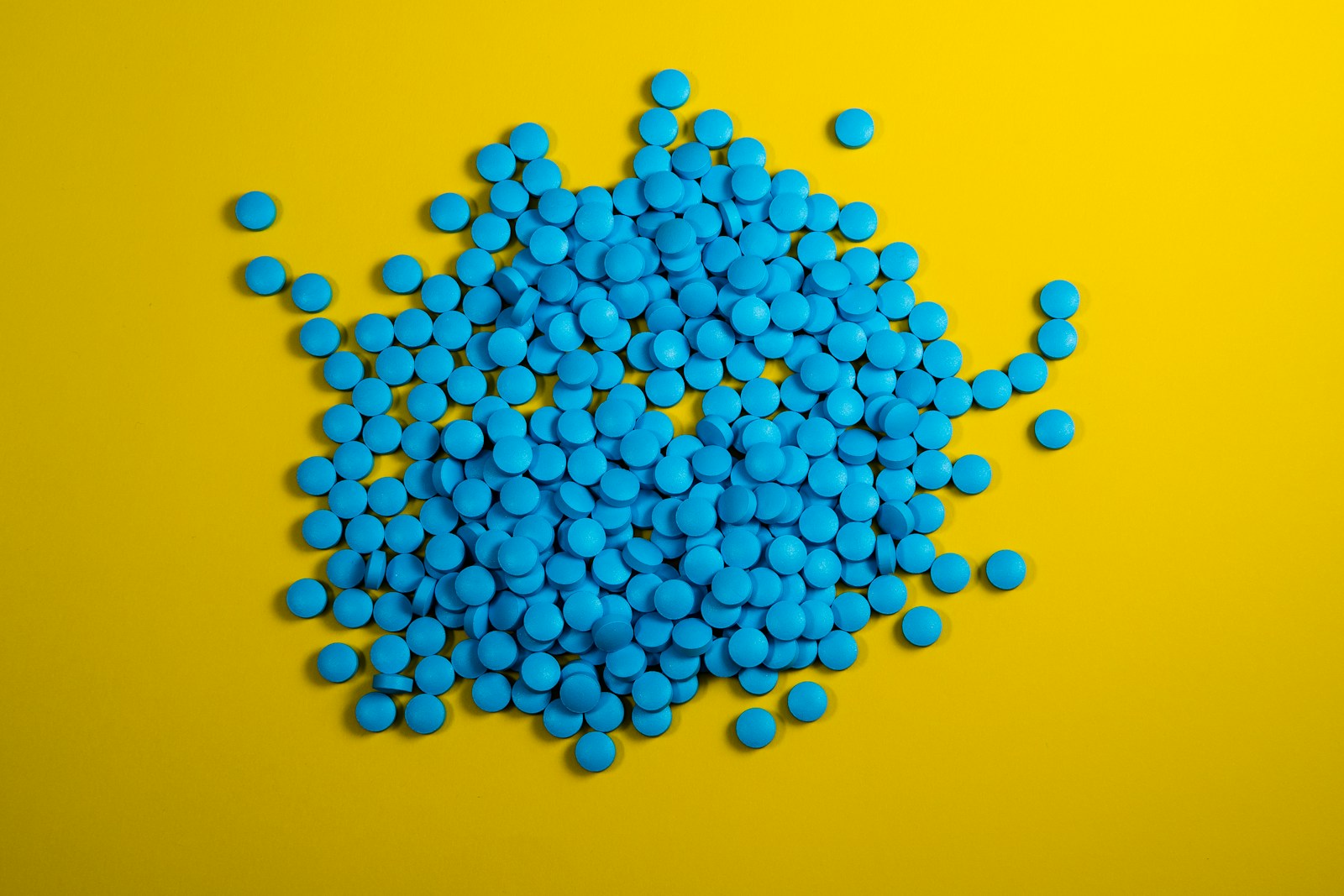
Polymer pellets
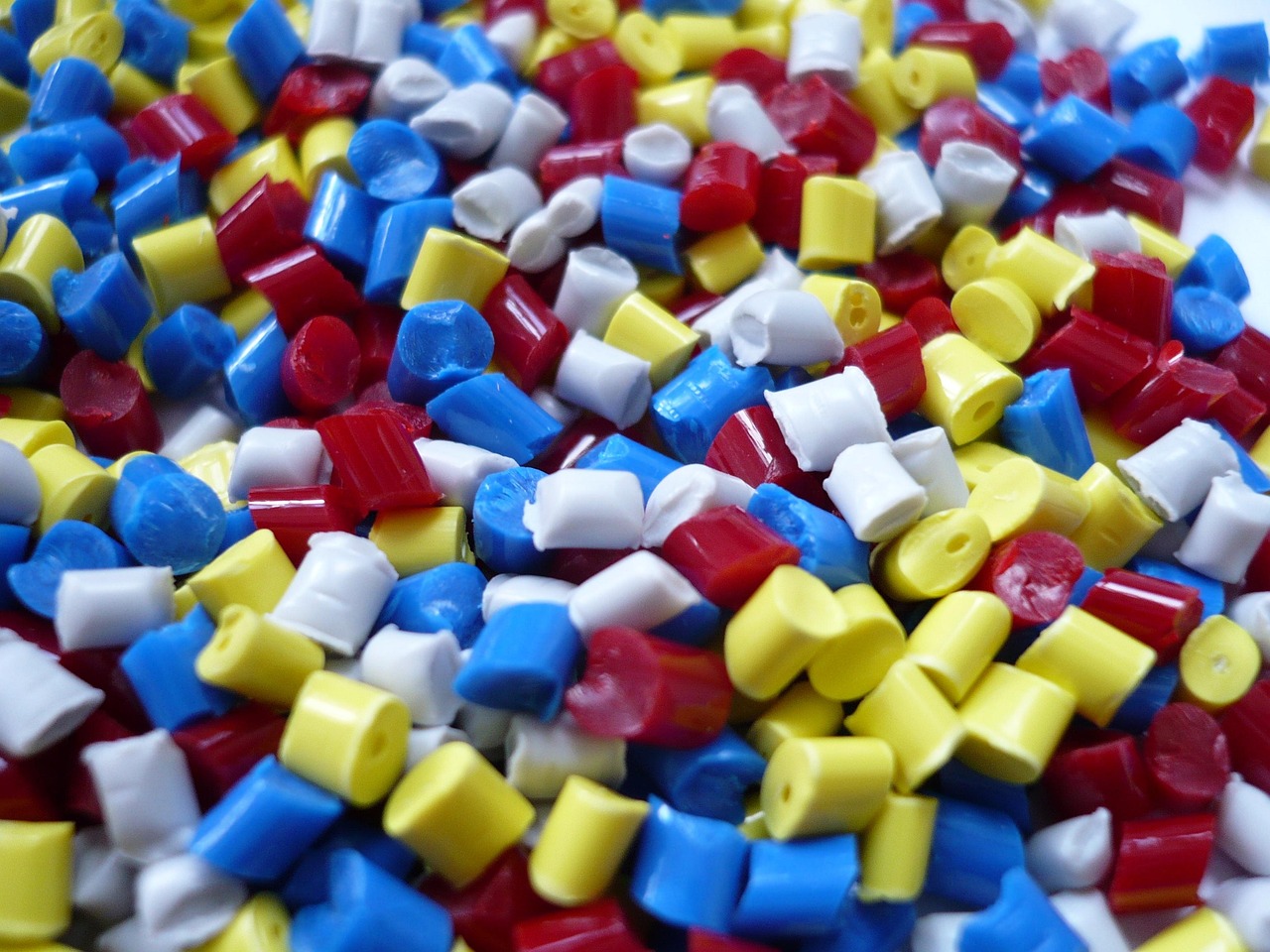
Polymer resins
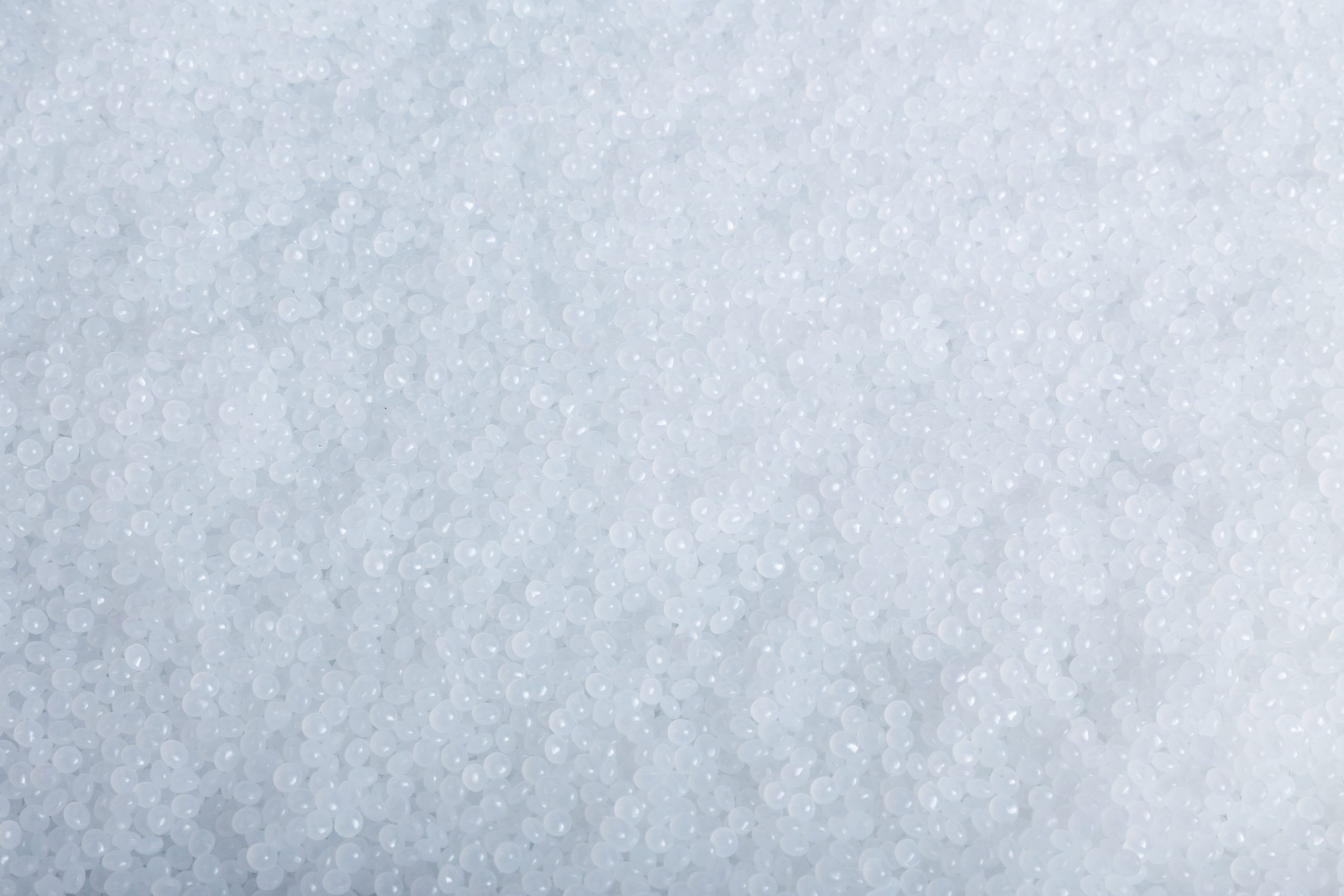
Polymers
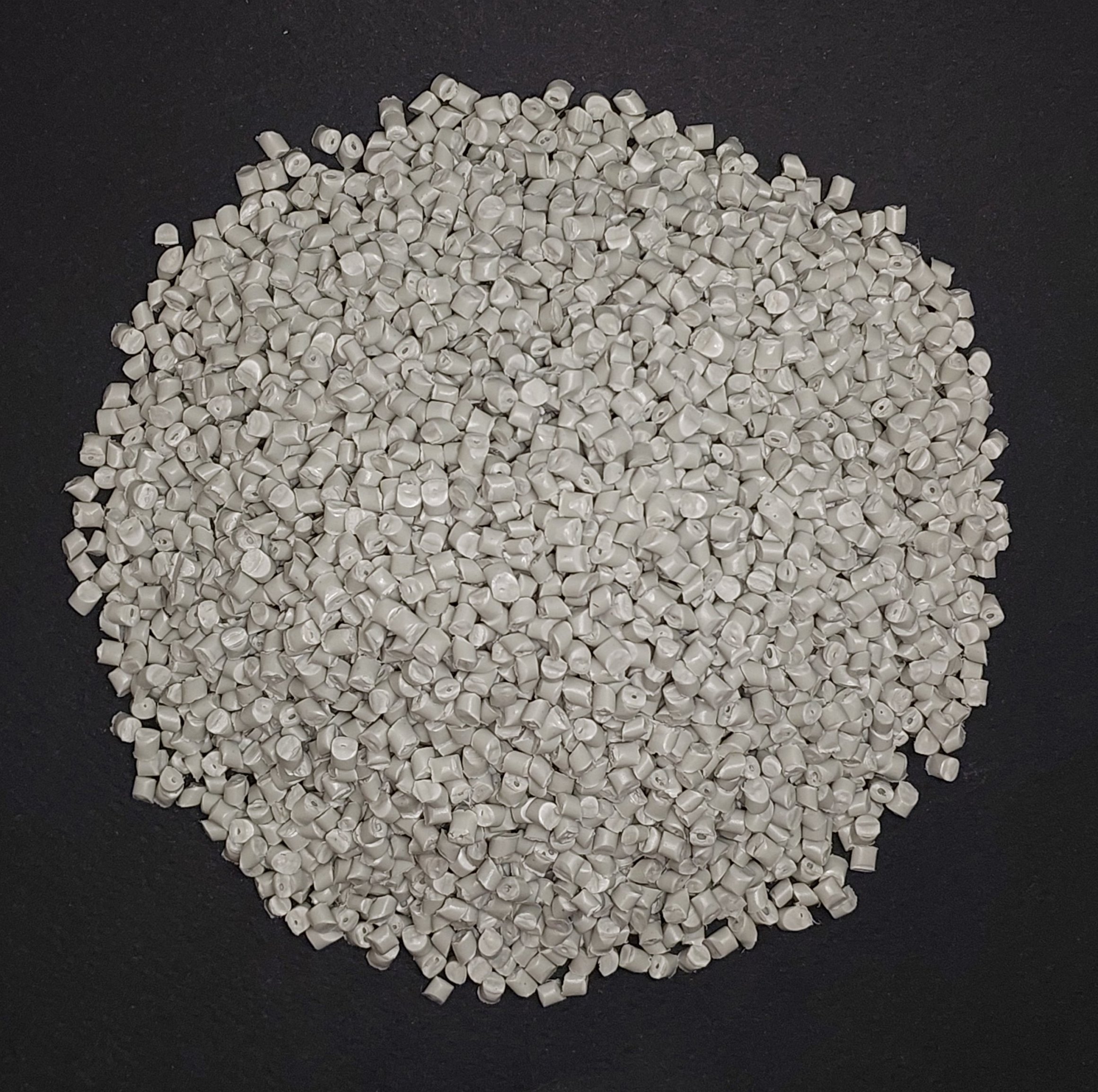
Polypropylene granules
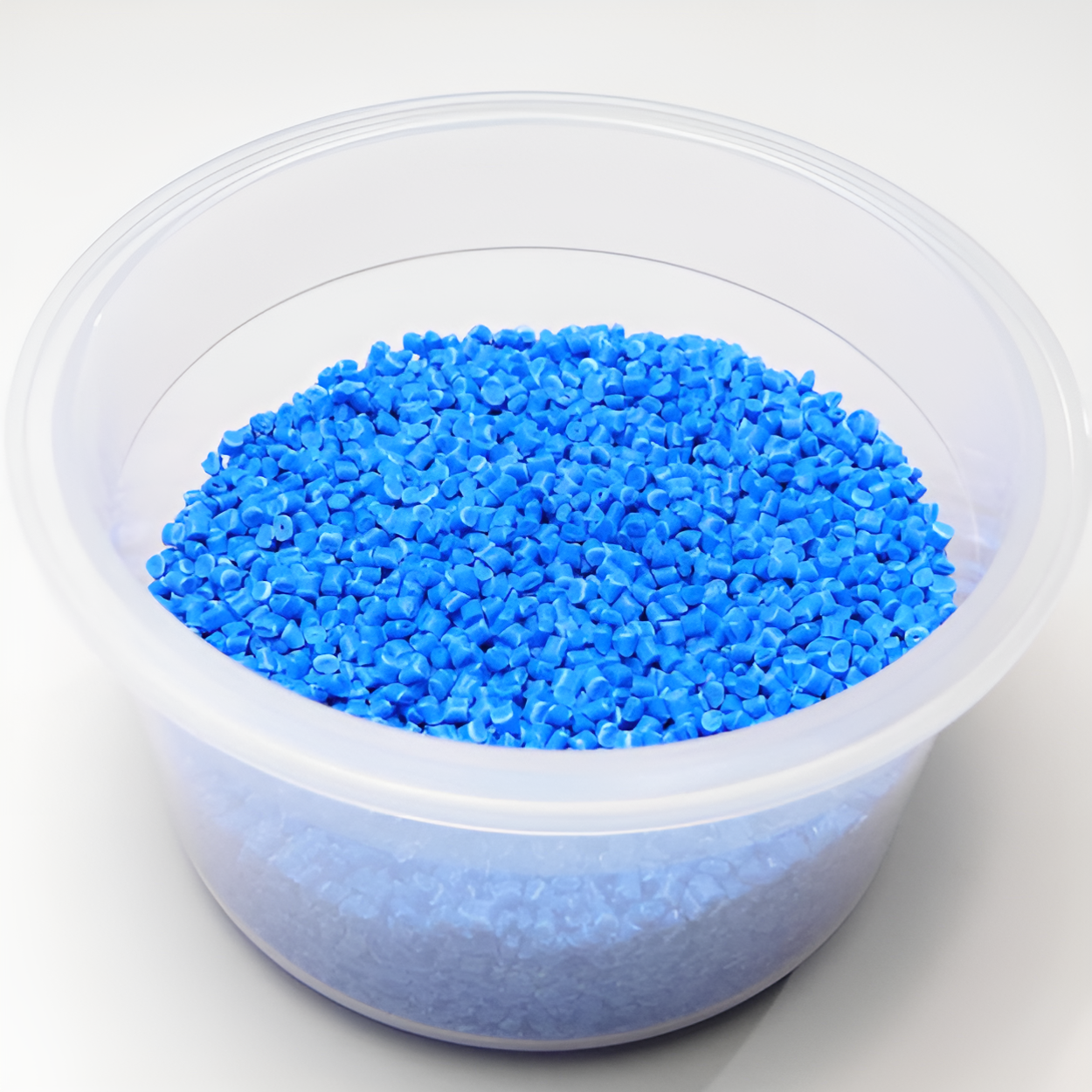
Polypropylene pellets
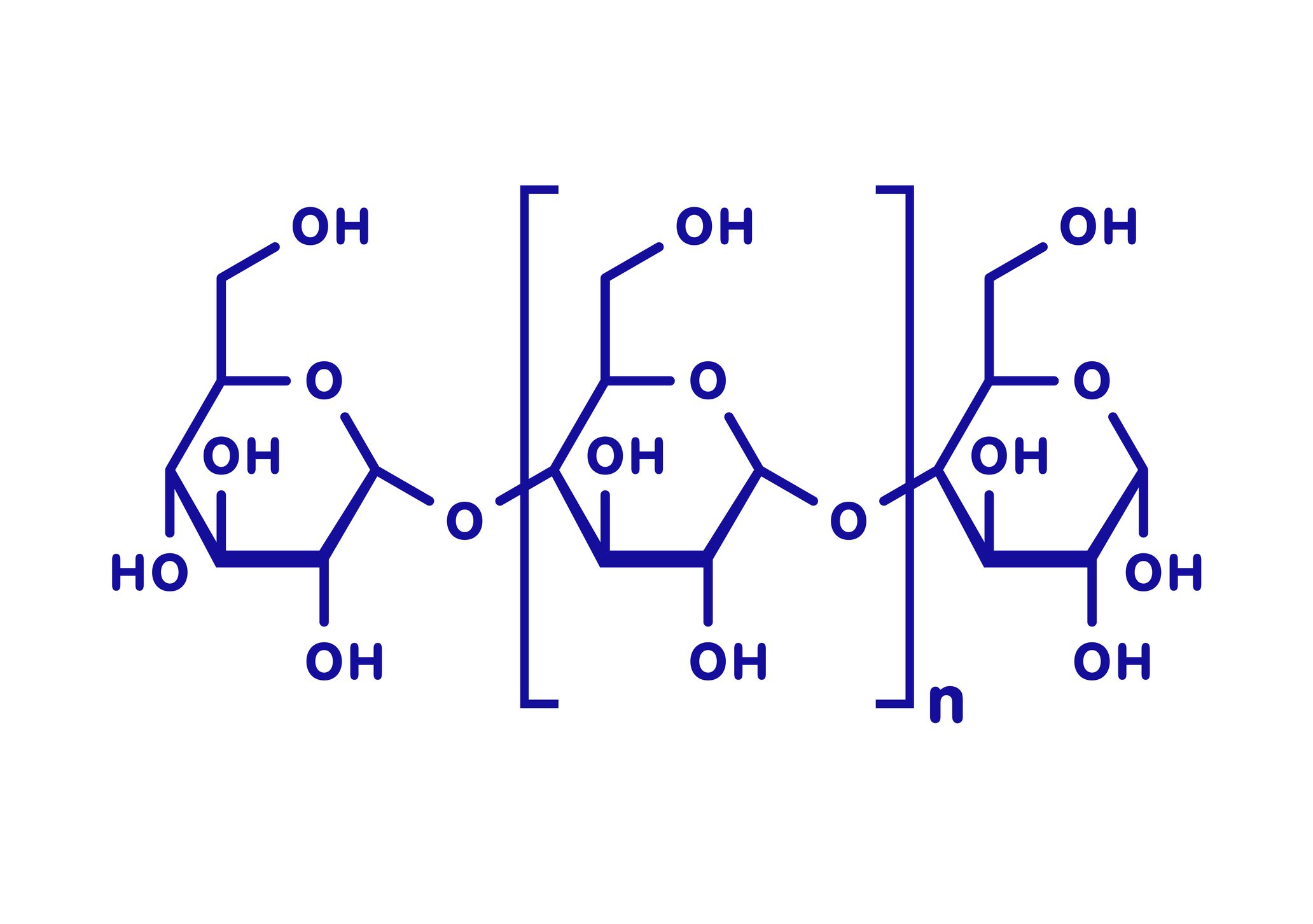
Polysaccharides
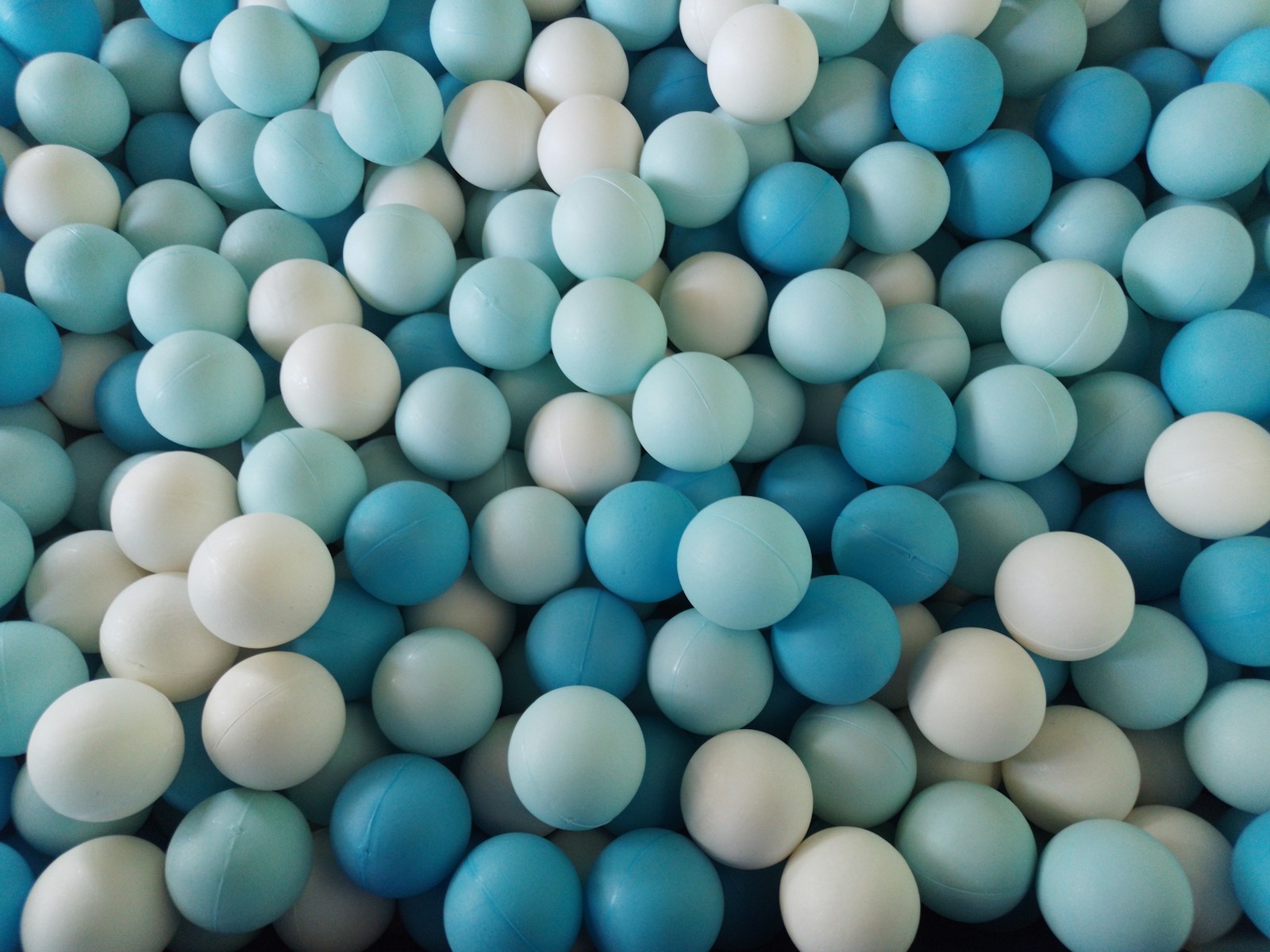
Polystyrene beads
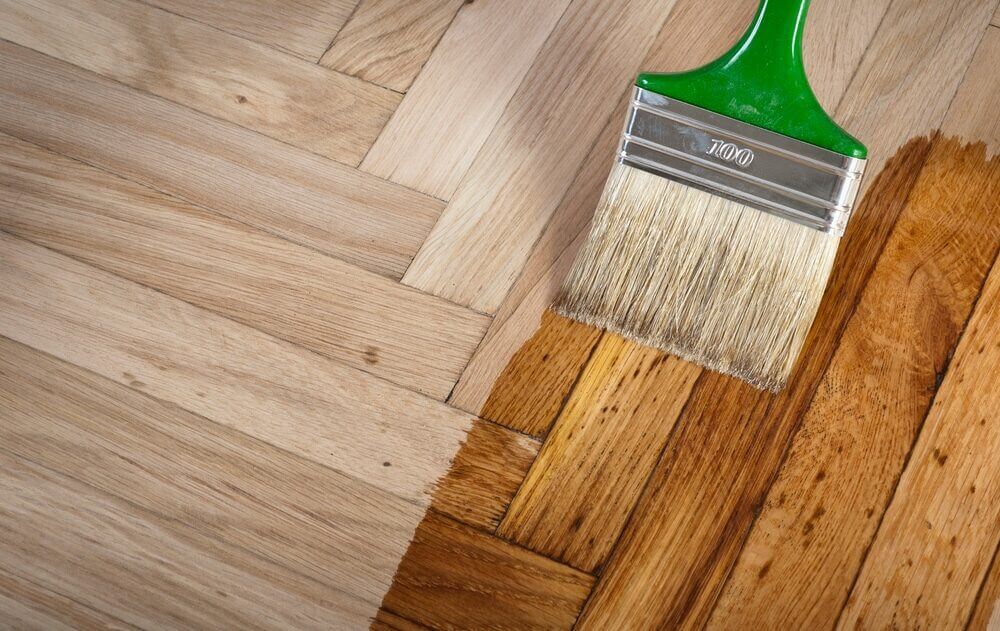
Polyurethane varnish
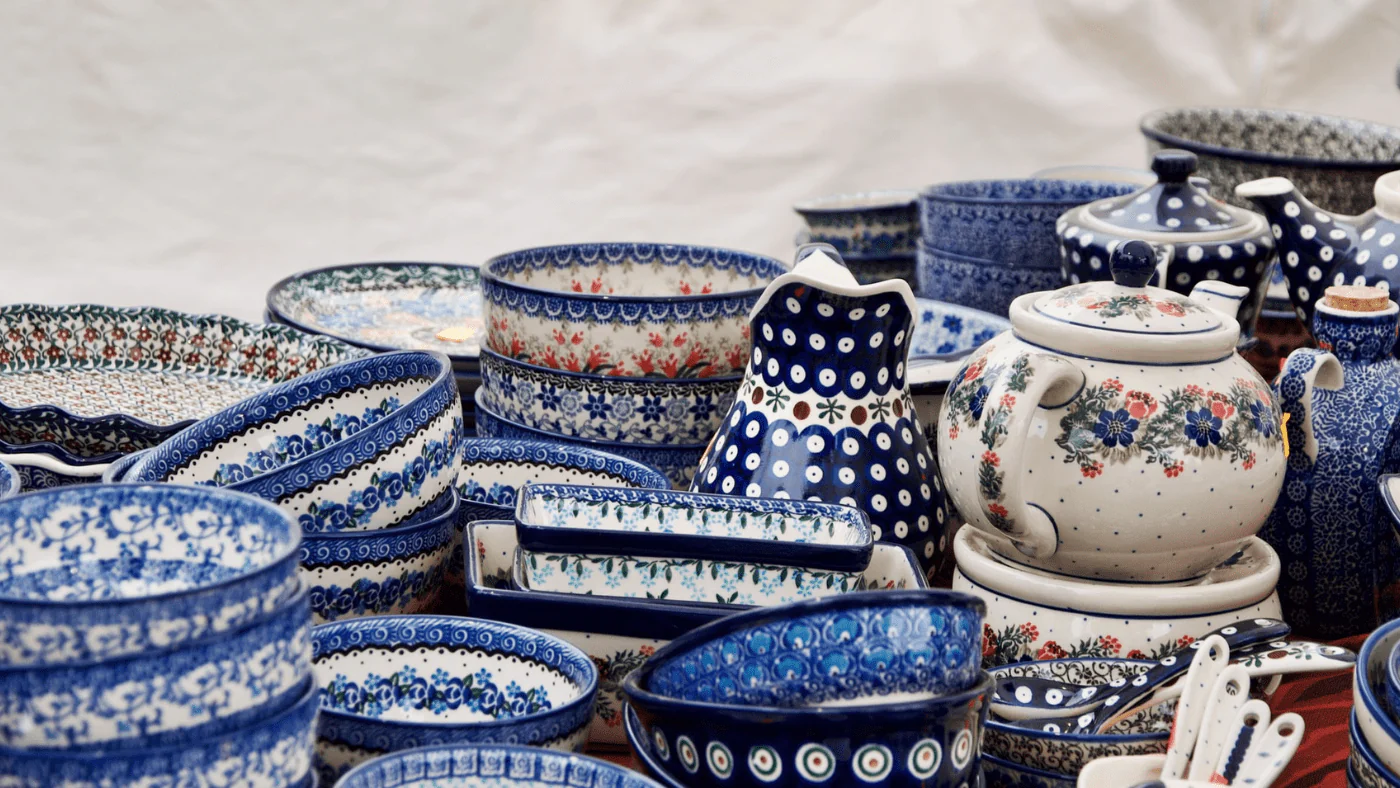
Porcelain
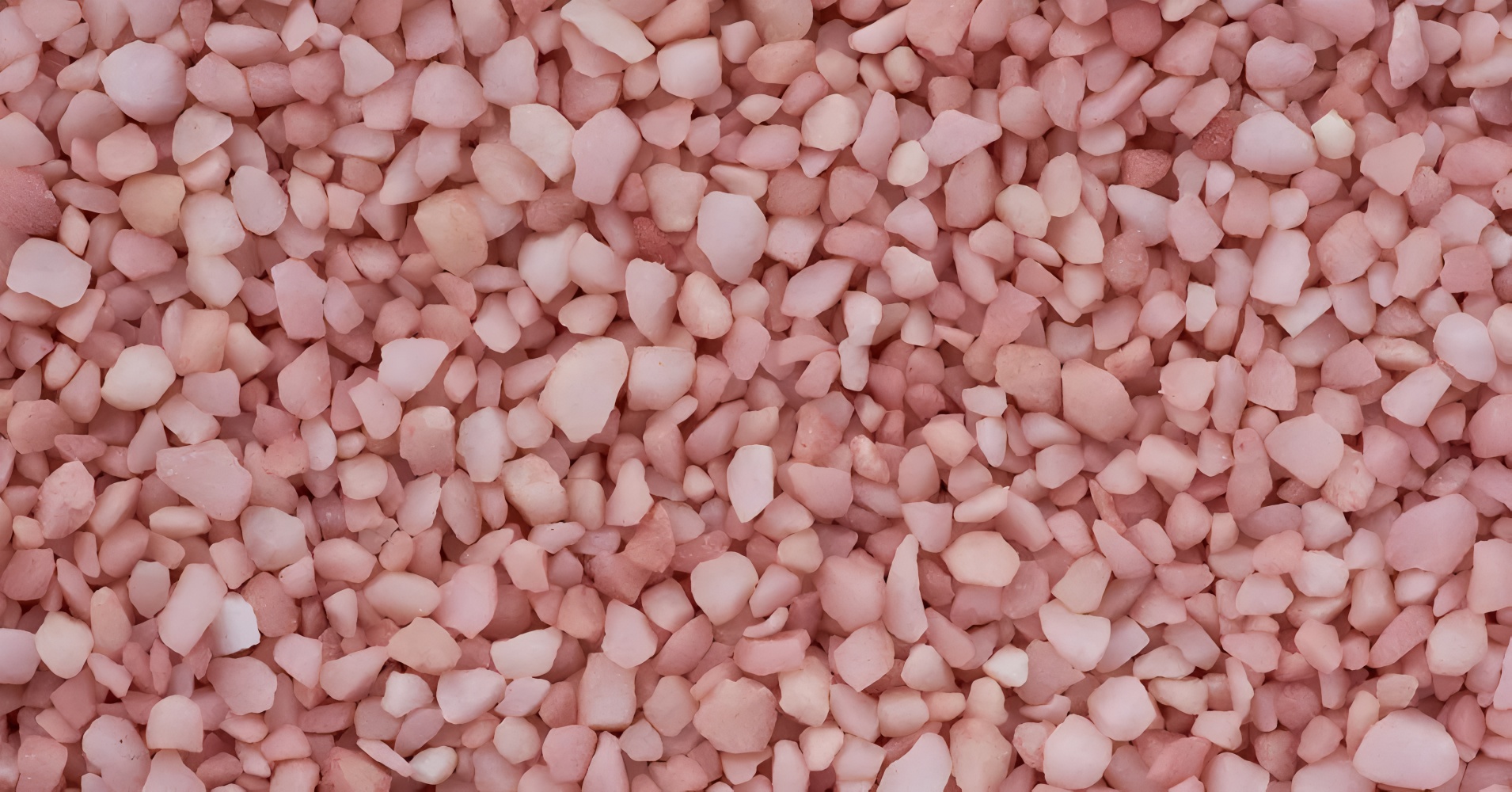
Potash
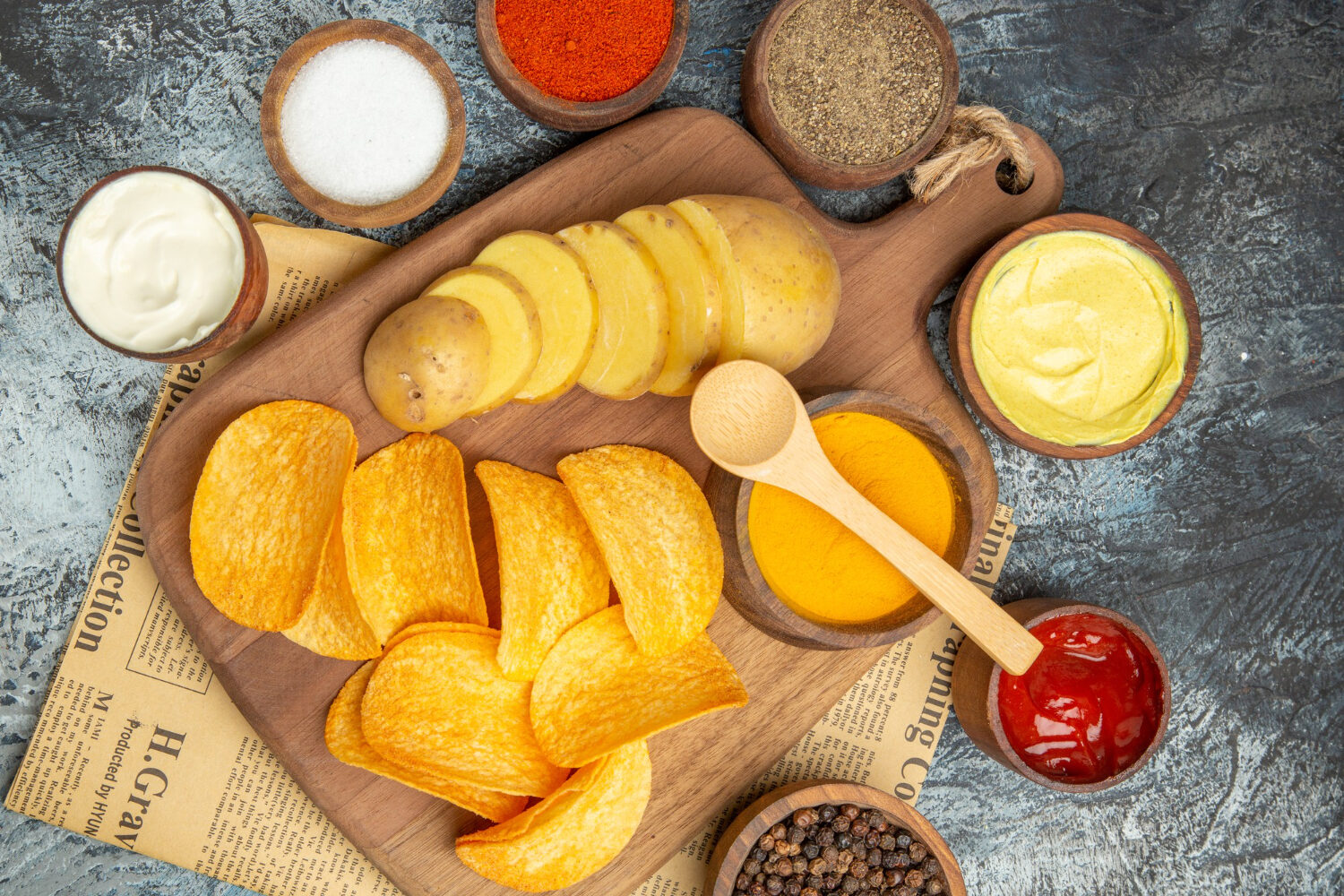
Potato co-products
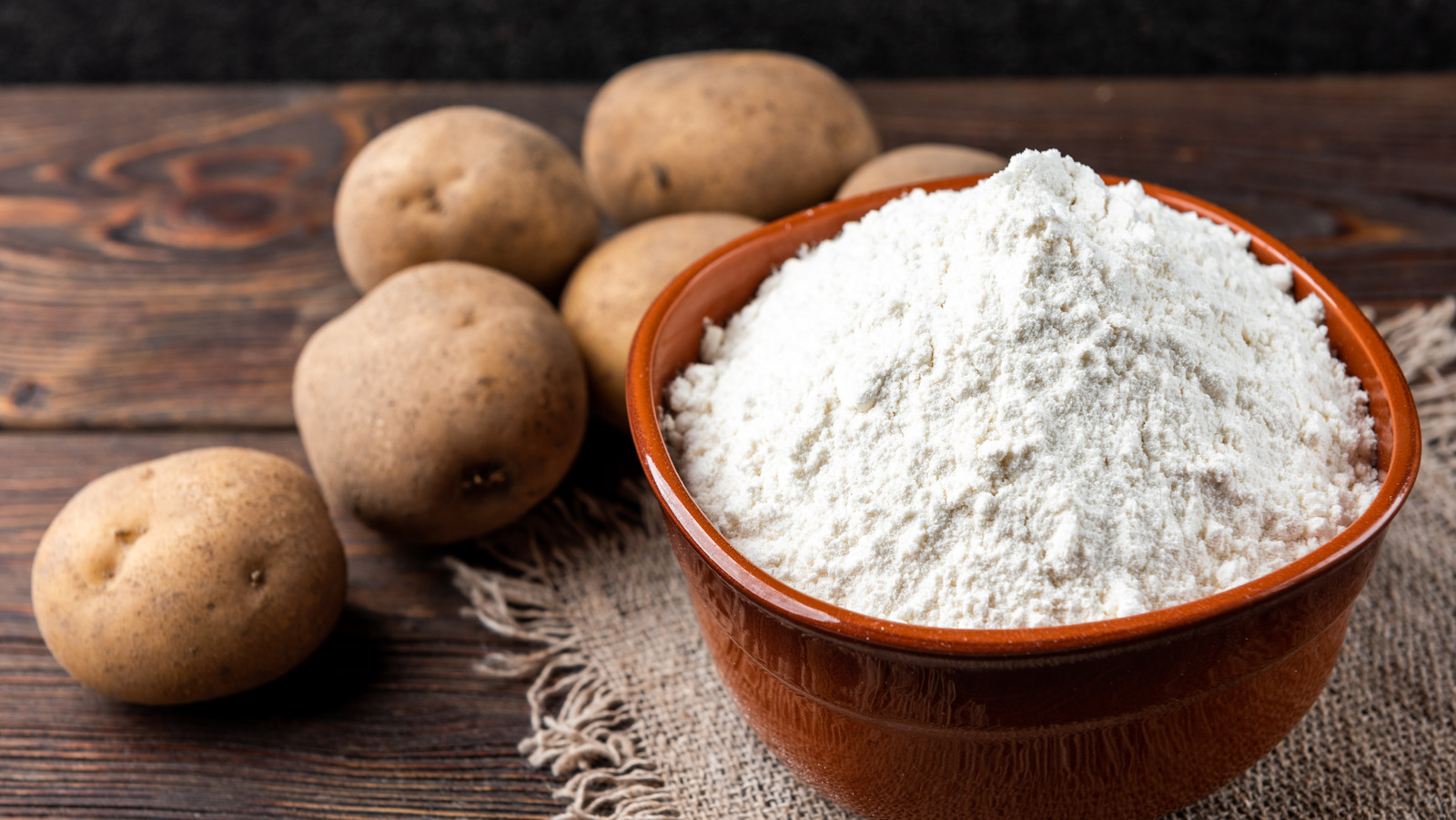
Potato starch
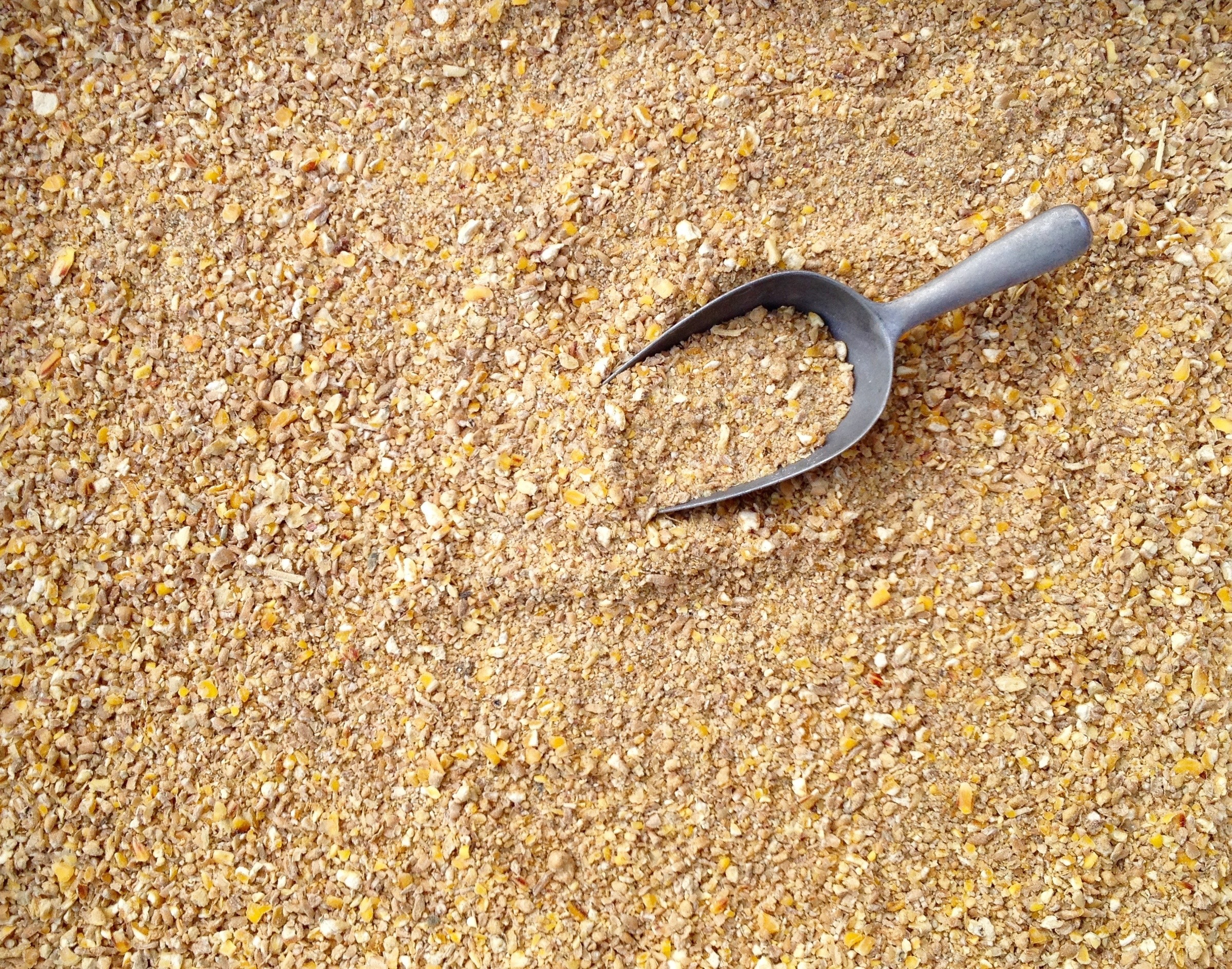
Poultry feed
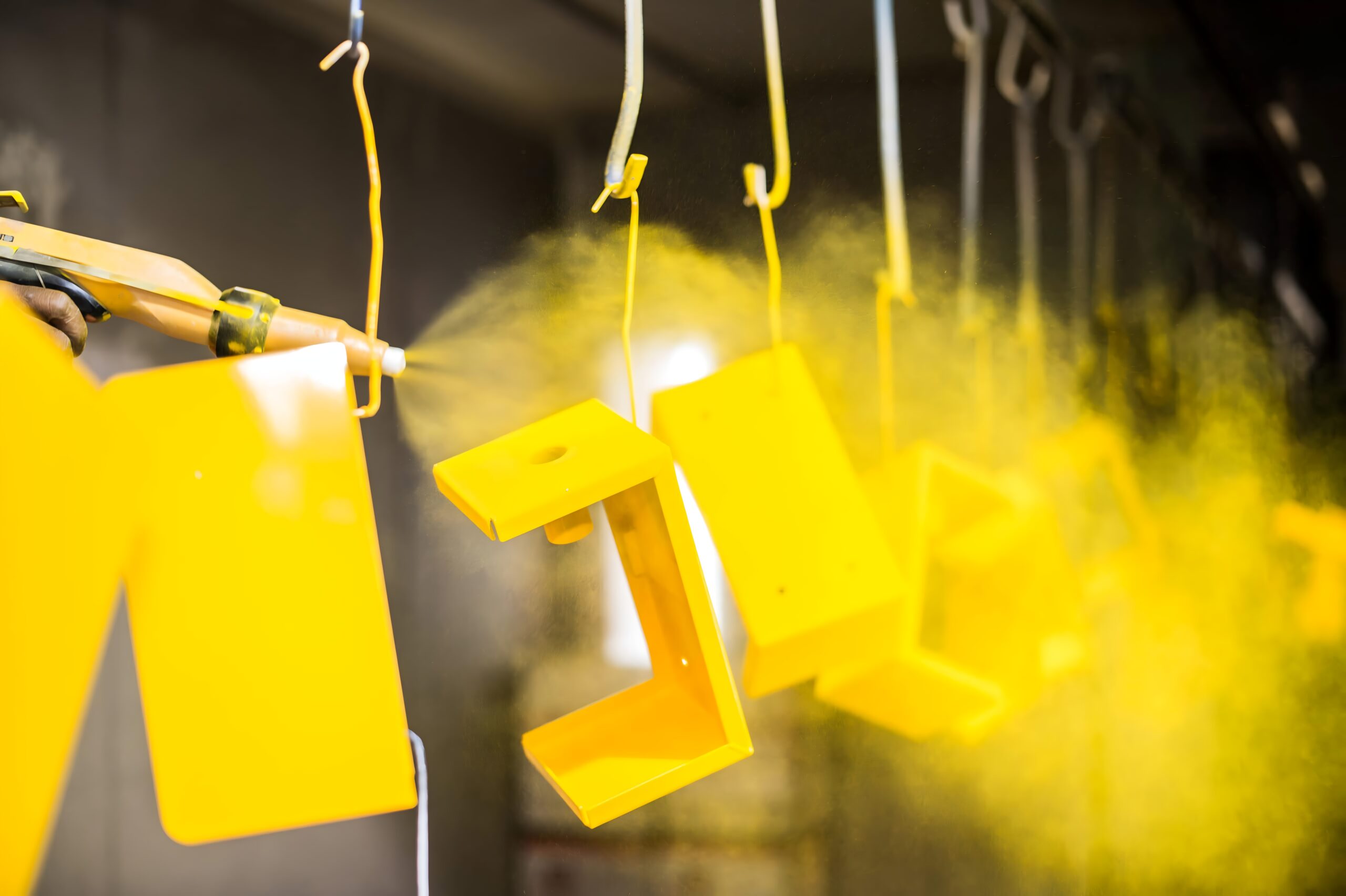
Powder coating
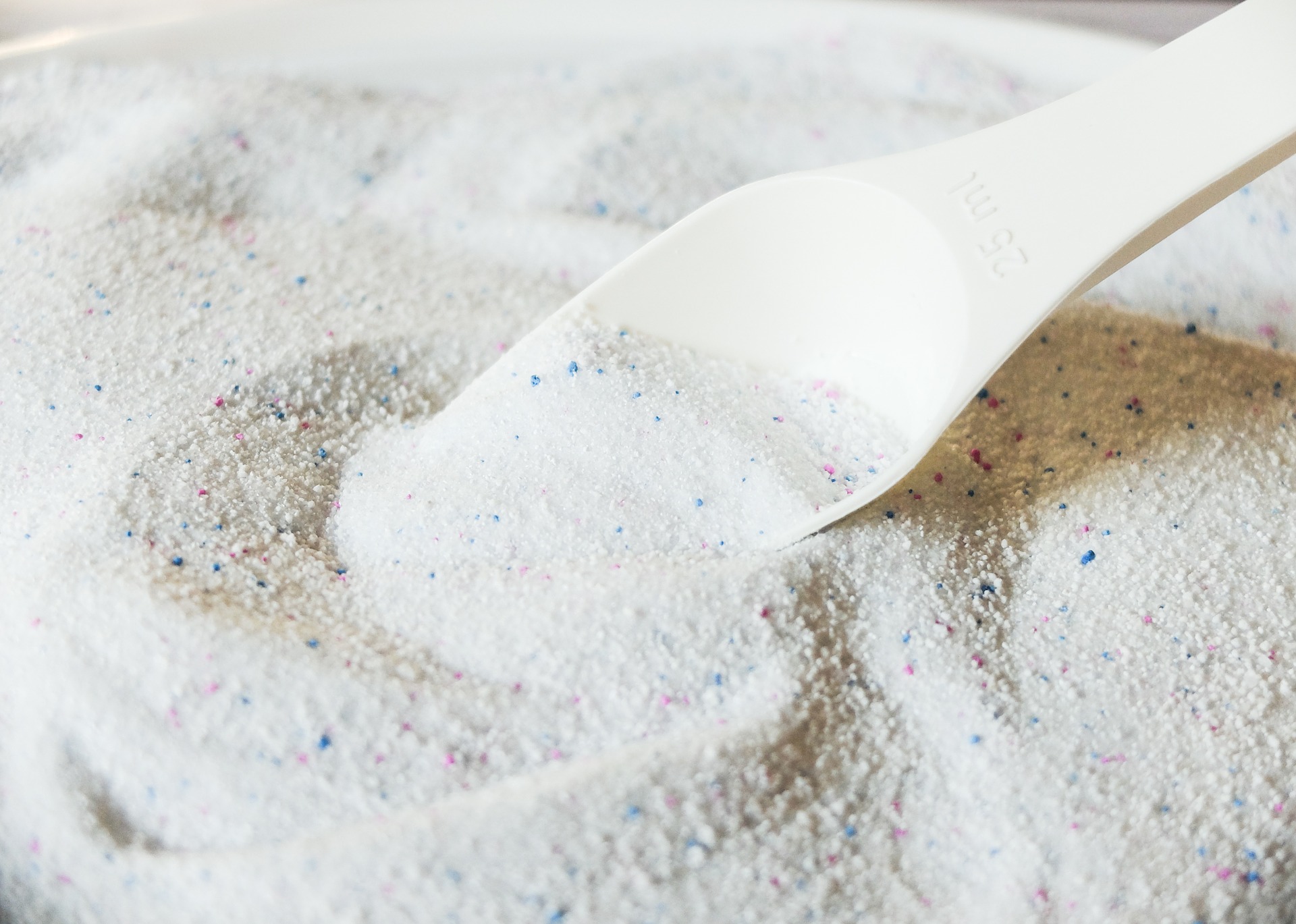
Powder detergent
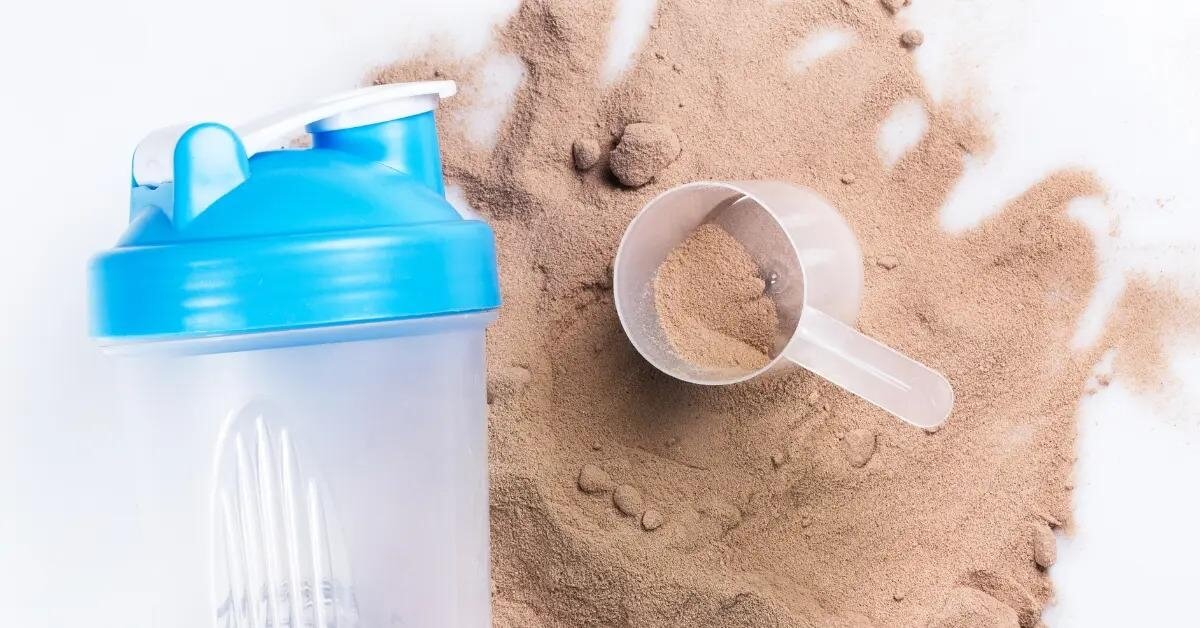
Powdered drink mixes
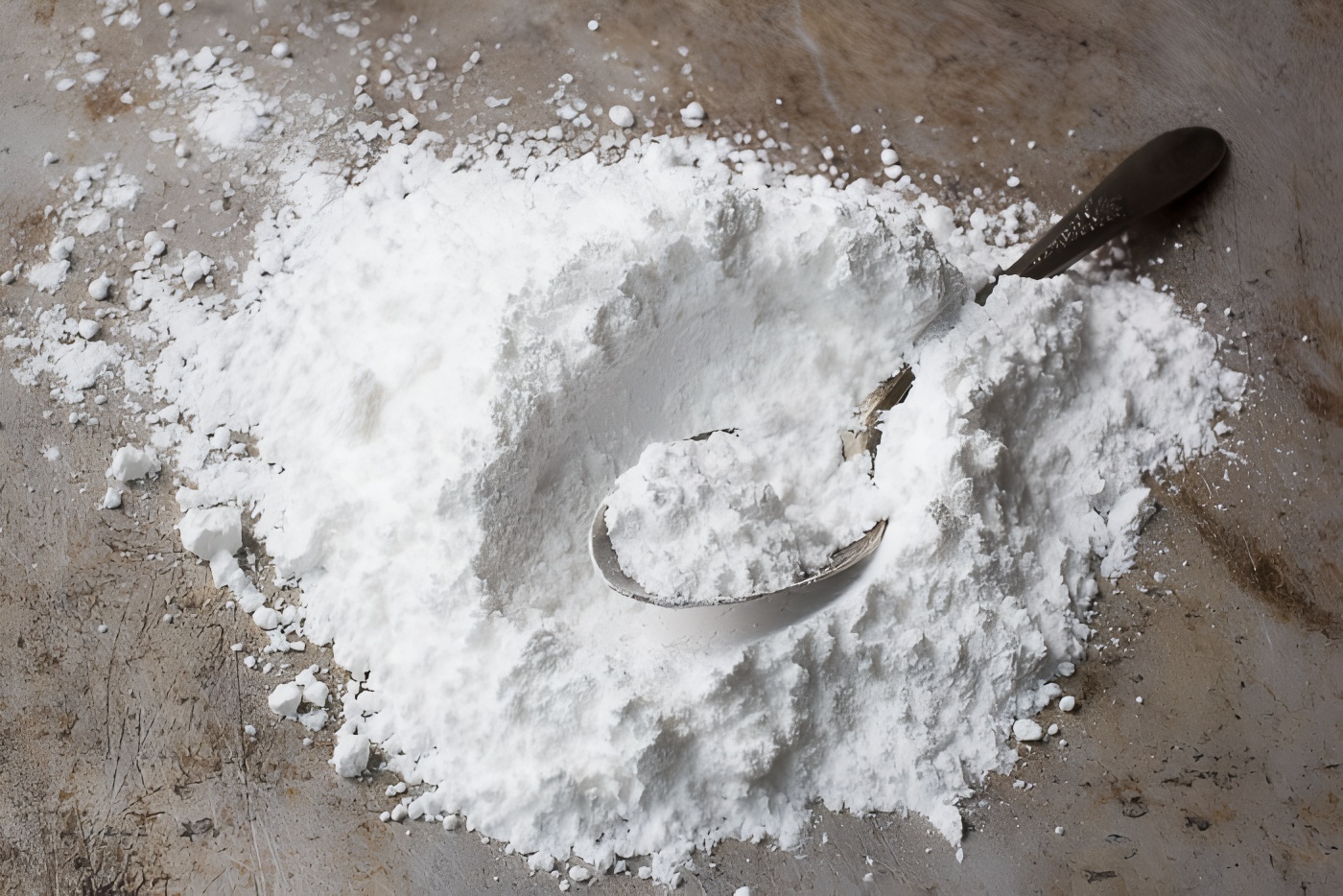
Powdered sugar

Pre-packaged meals
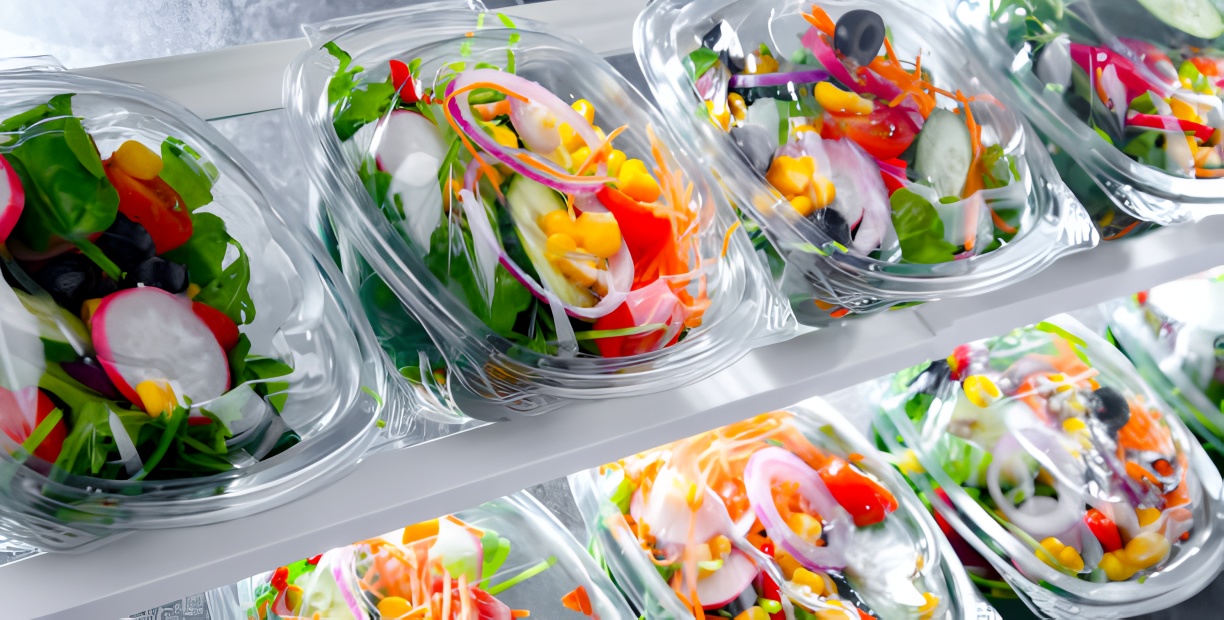
Pre-packaged salads
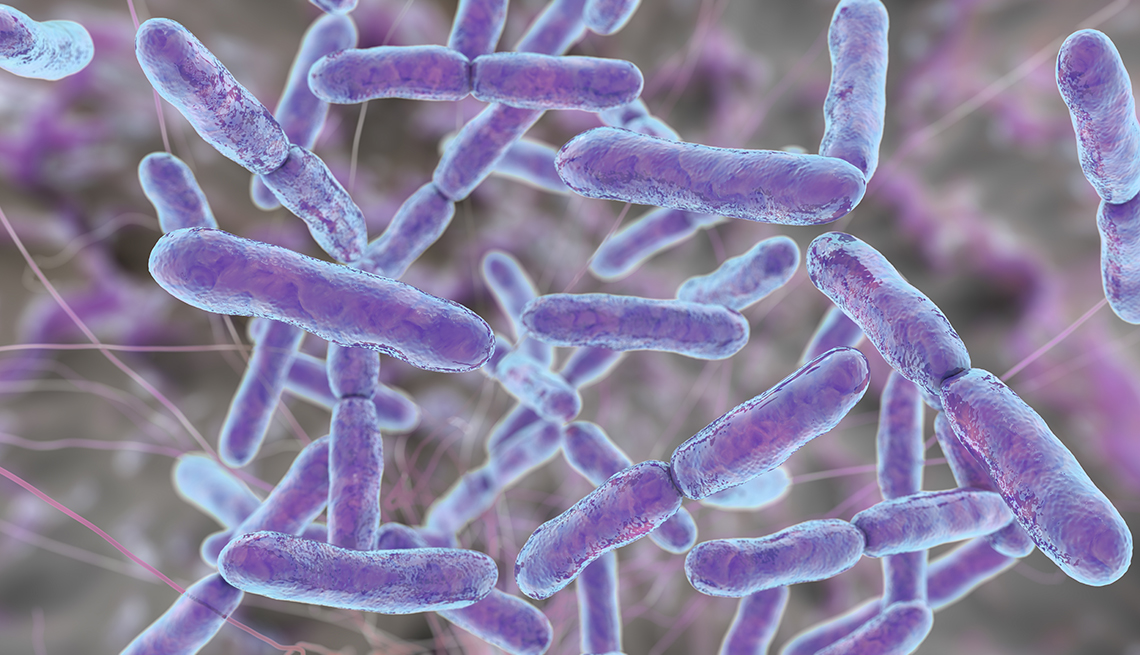
Probiotic cultures
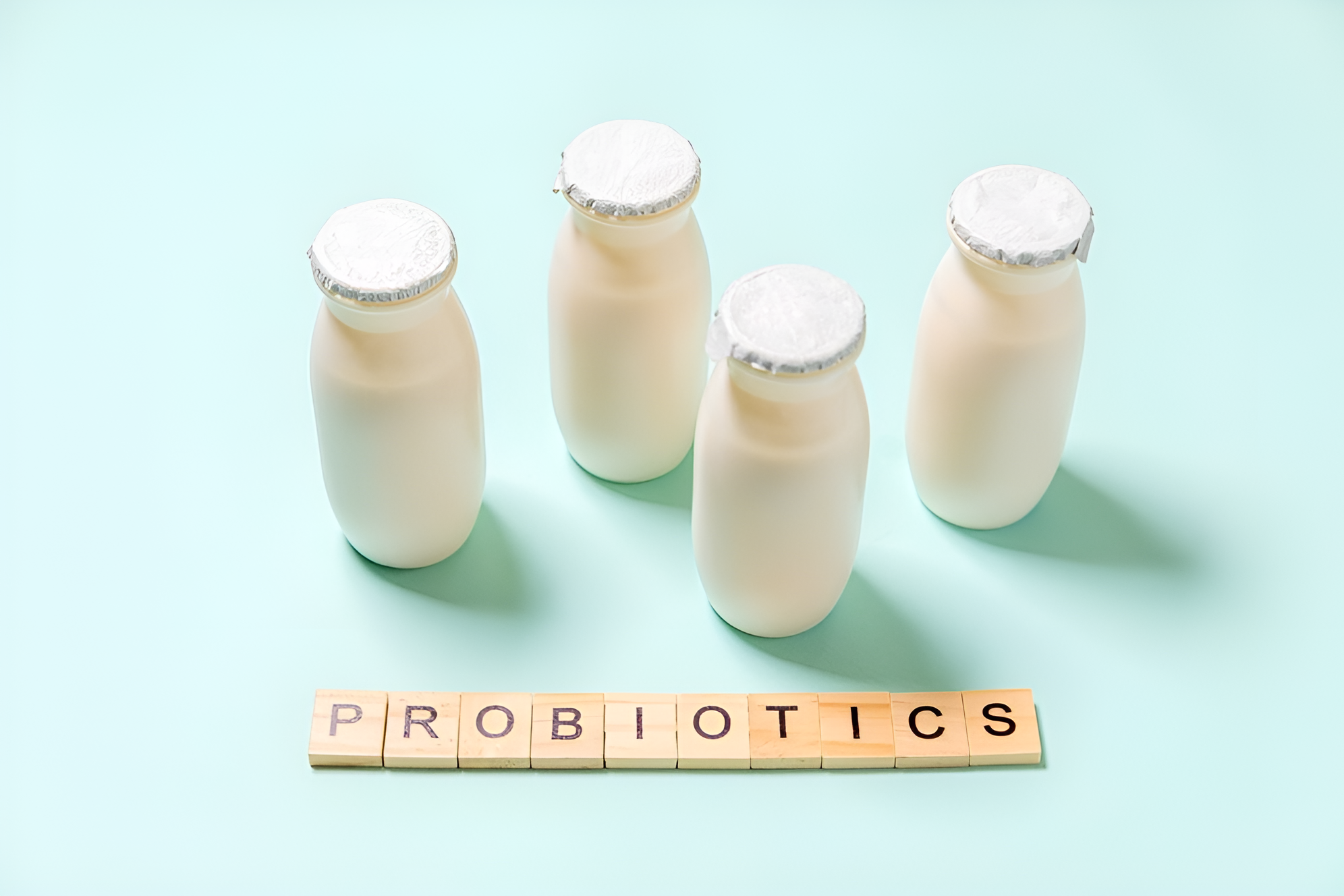
Probiotic drinks
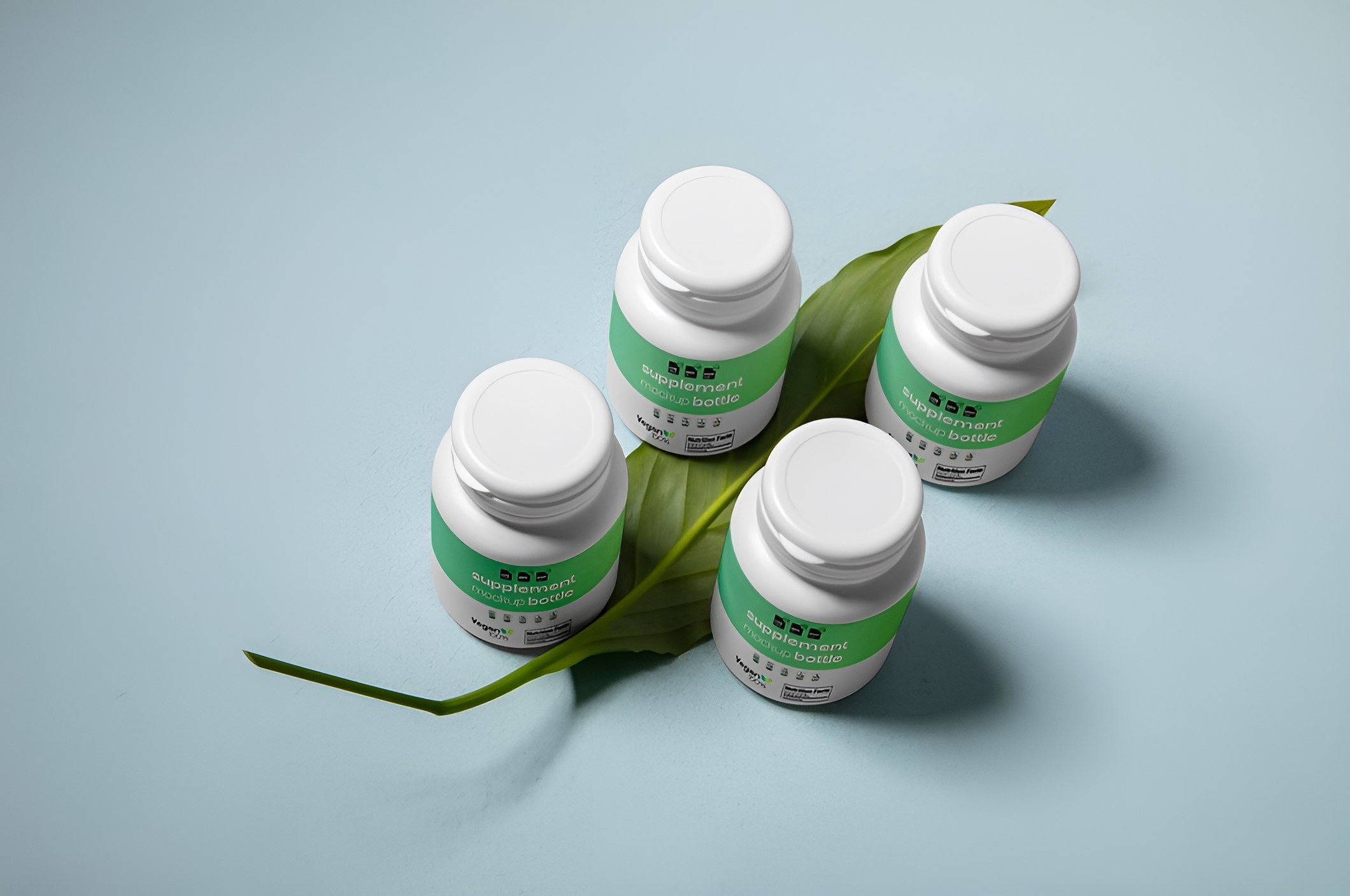
Probiotic supplements
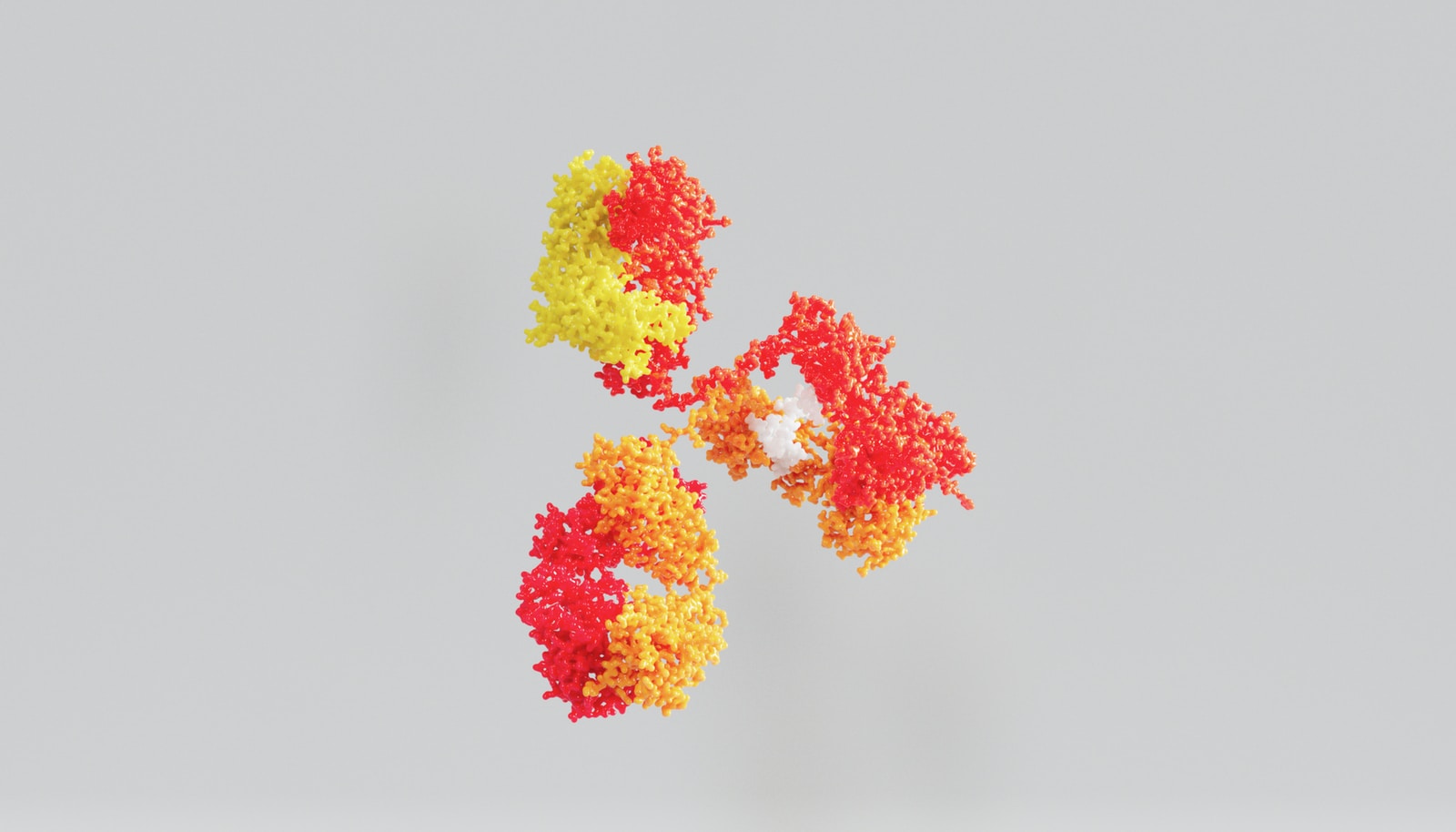
Probiotics

Processed animal by-products
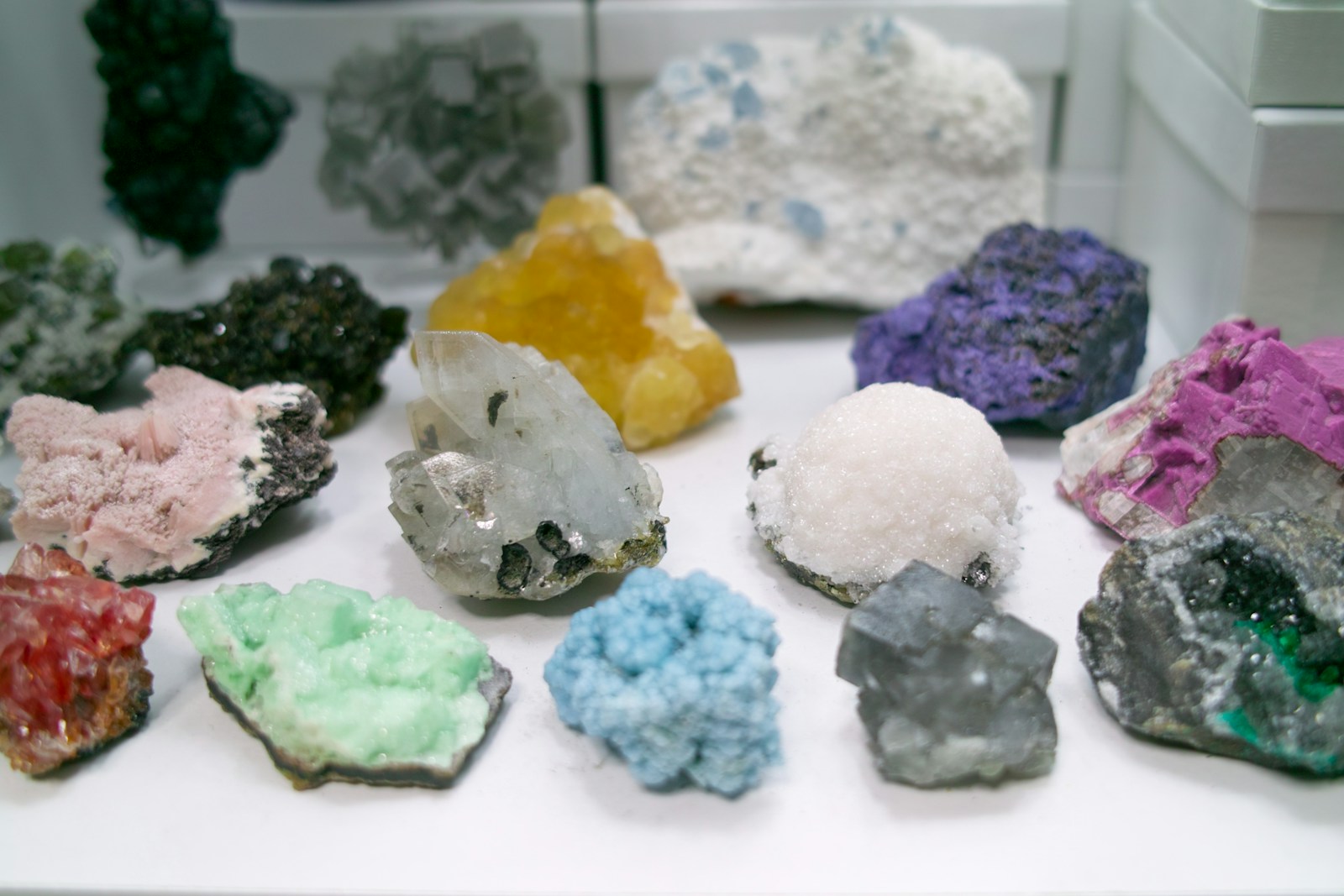
Processed minerals
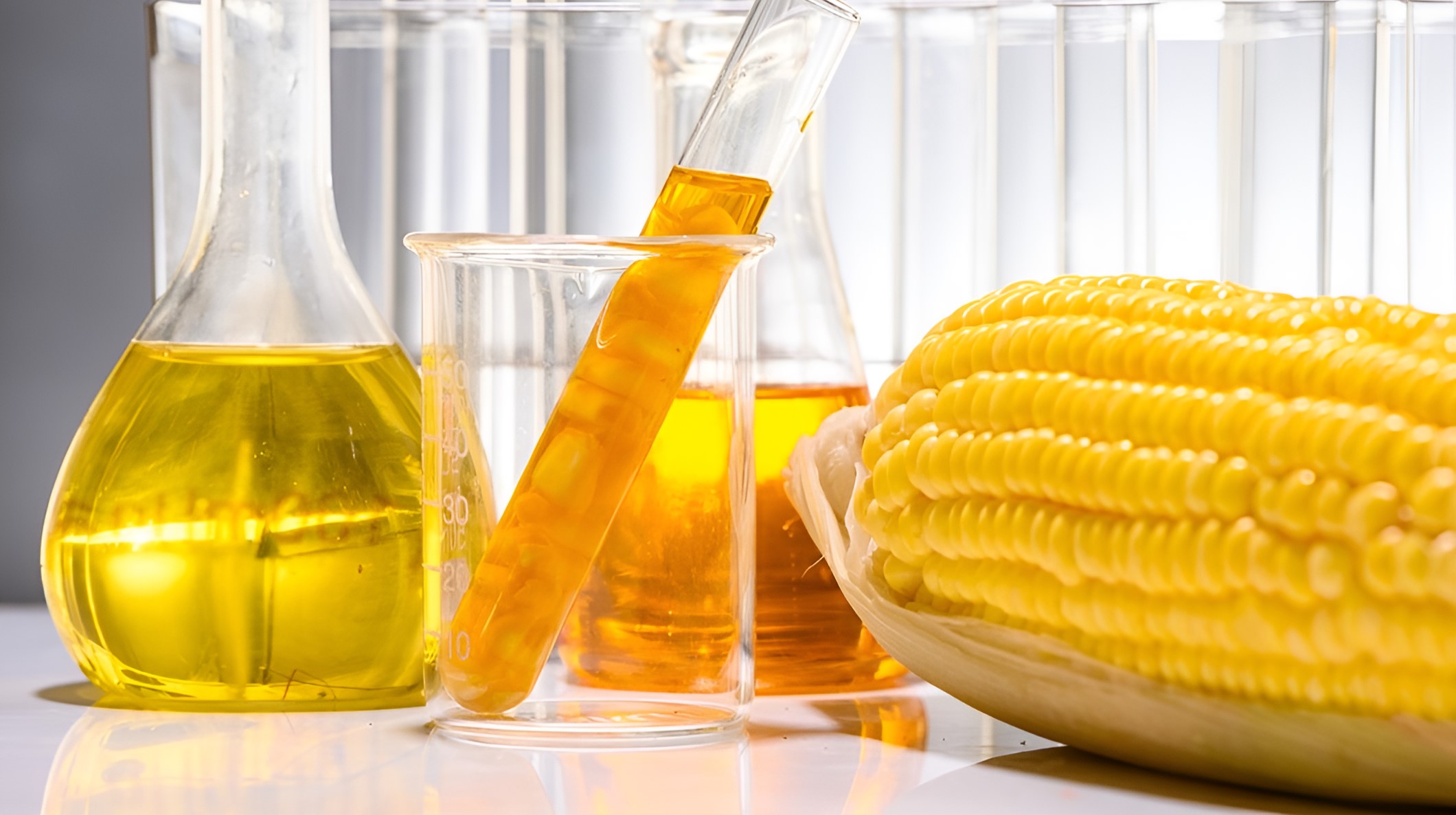
Propylene
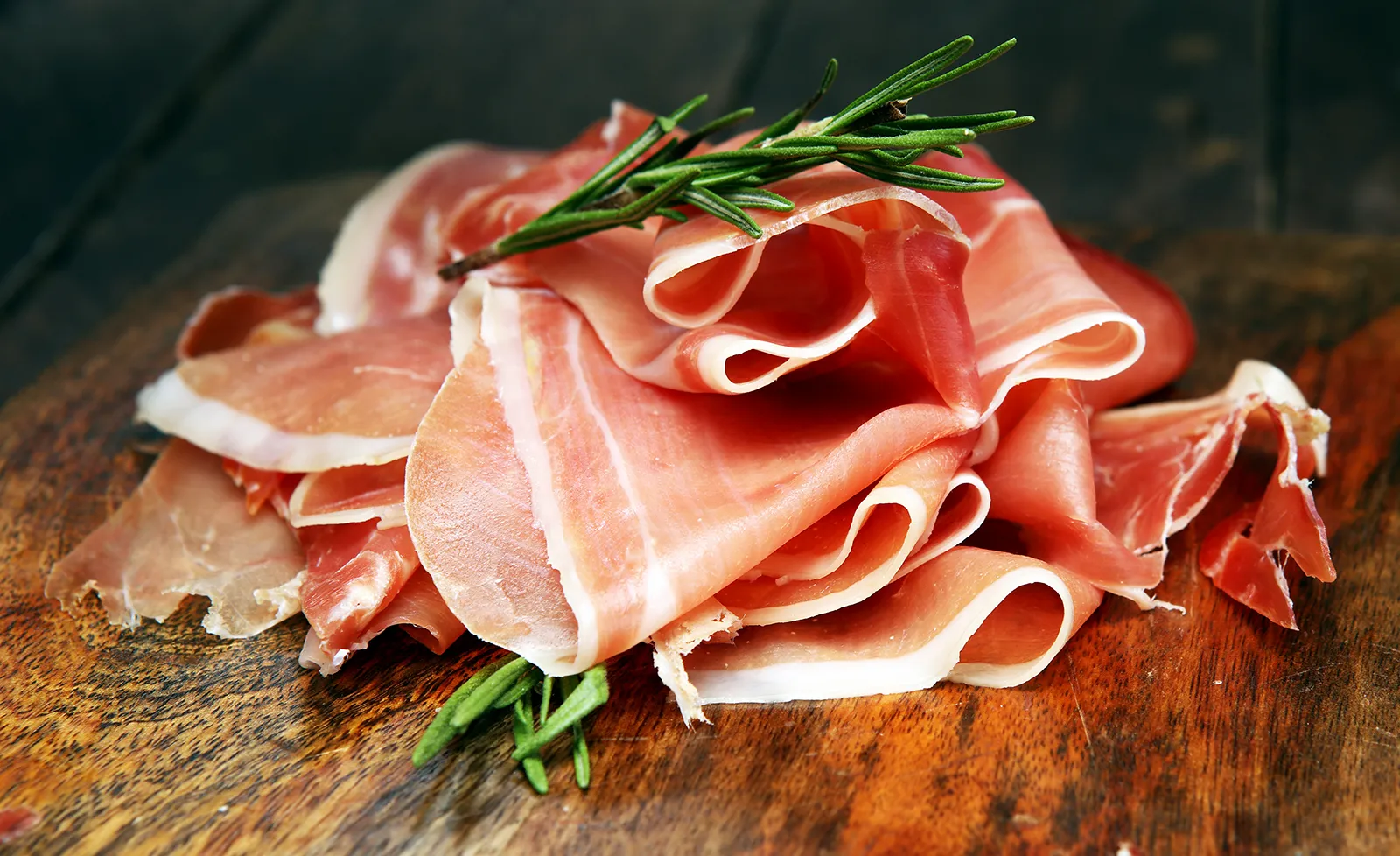
Prosciutto
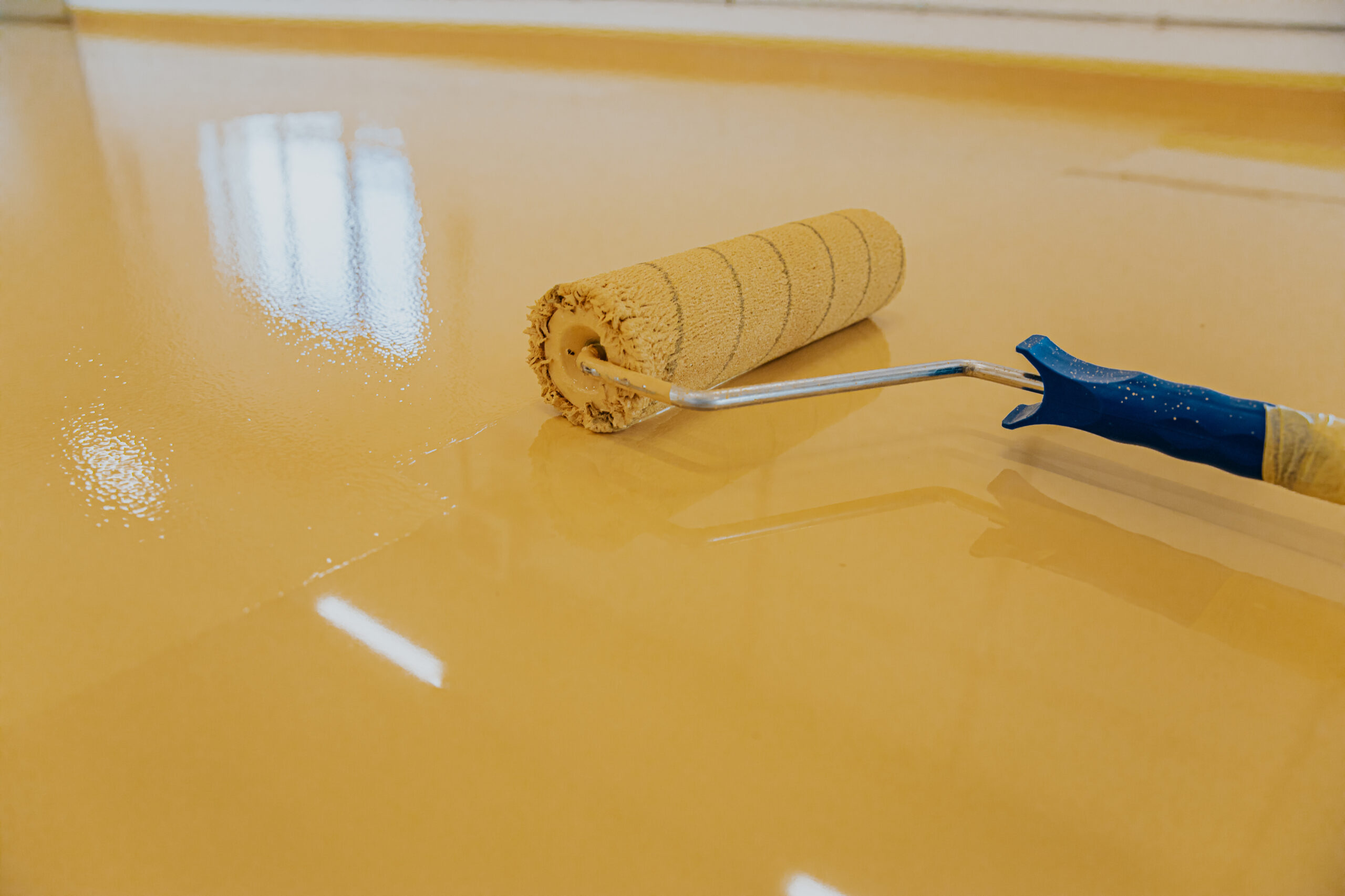
Protective coatings
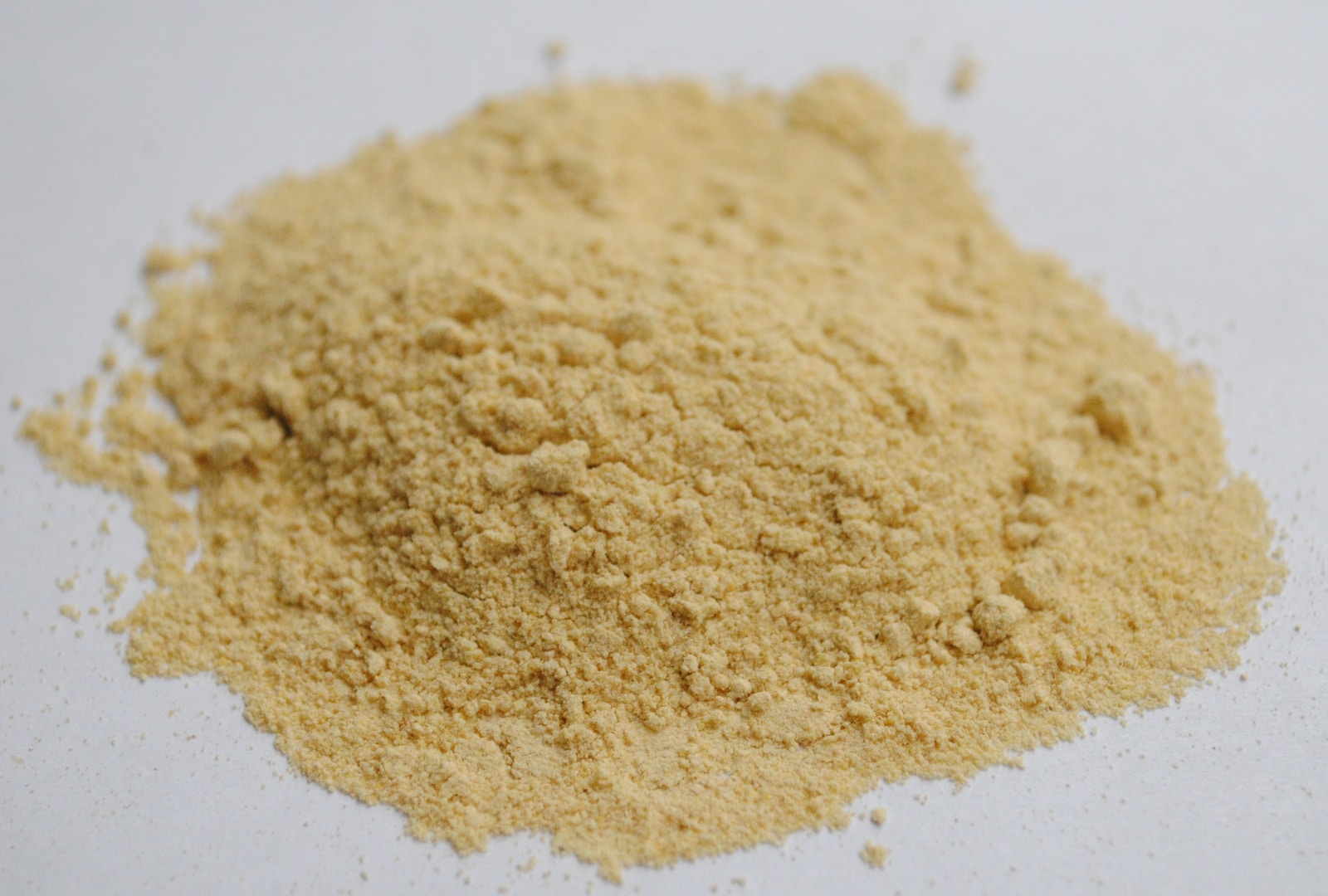
Protein powder
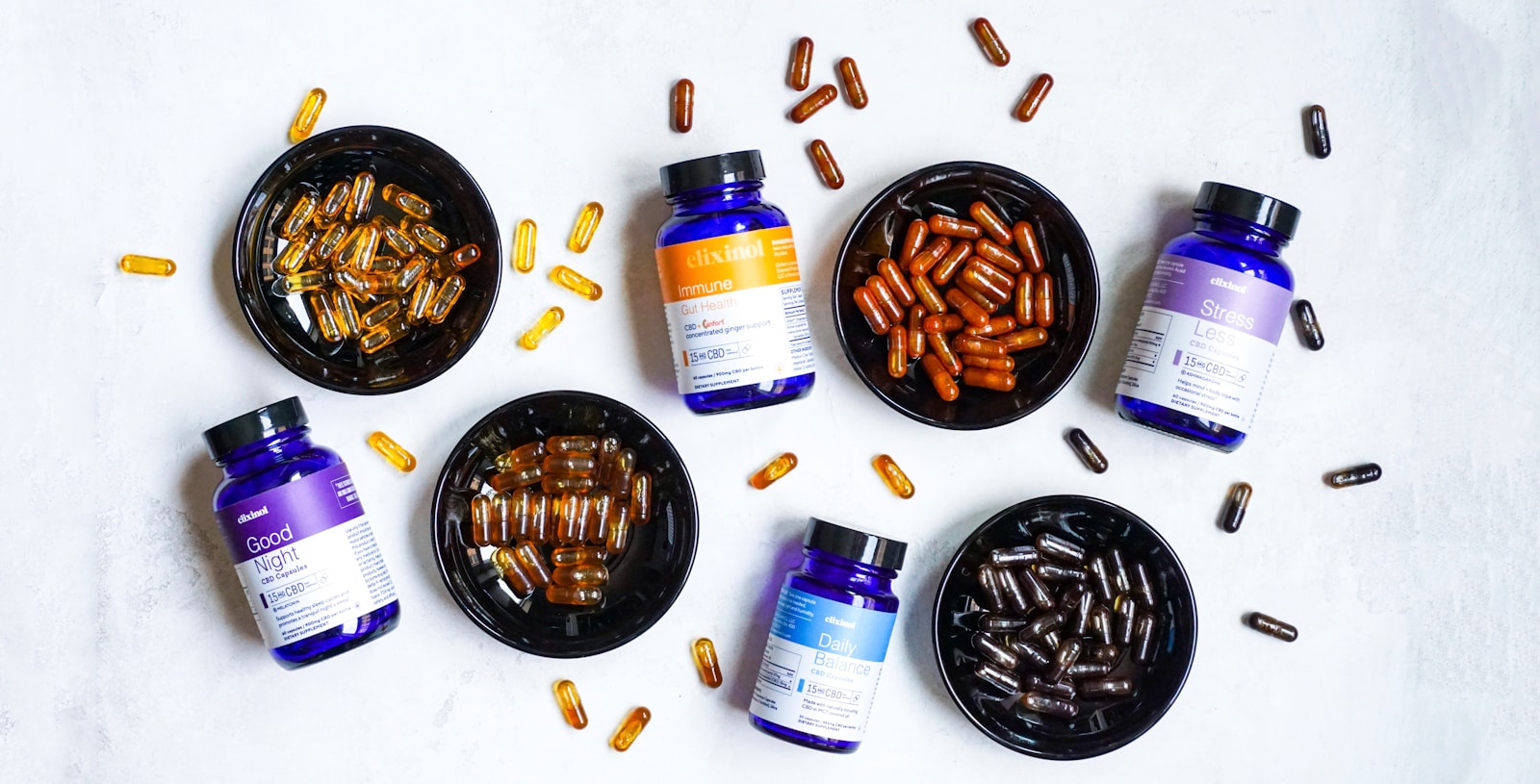
Protein supplements
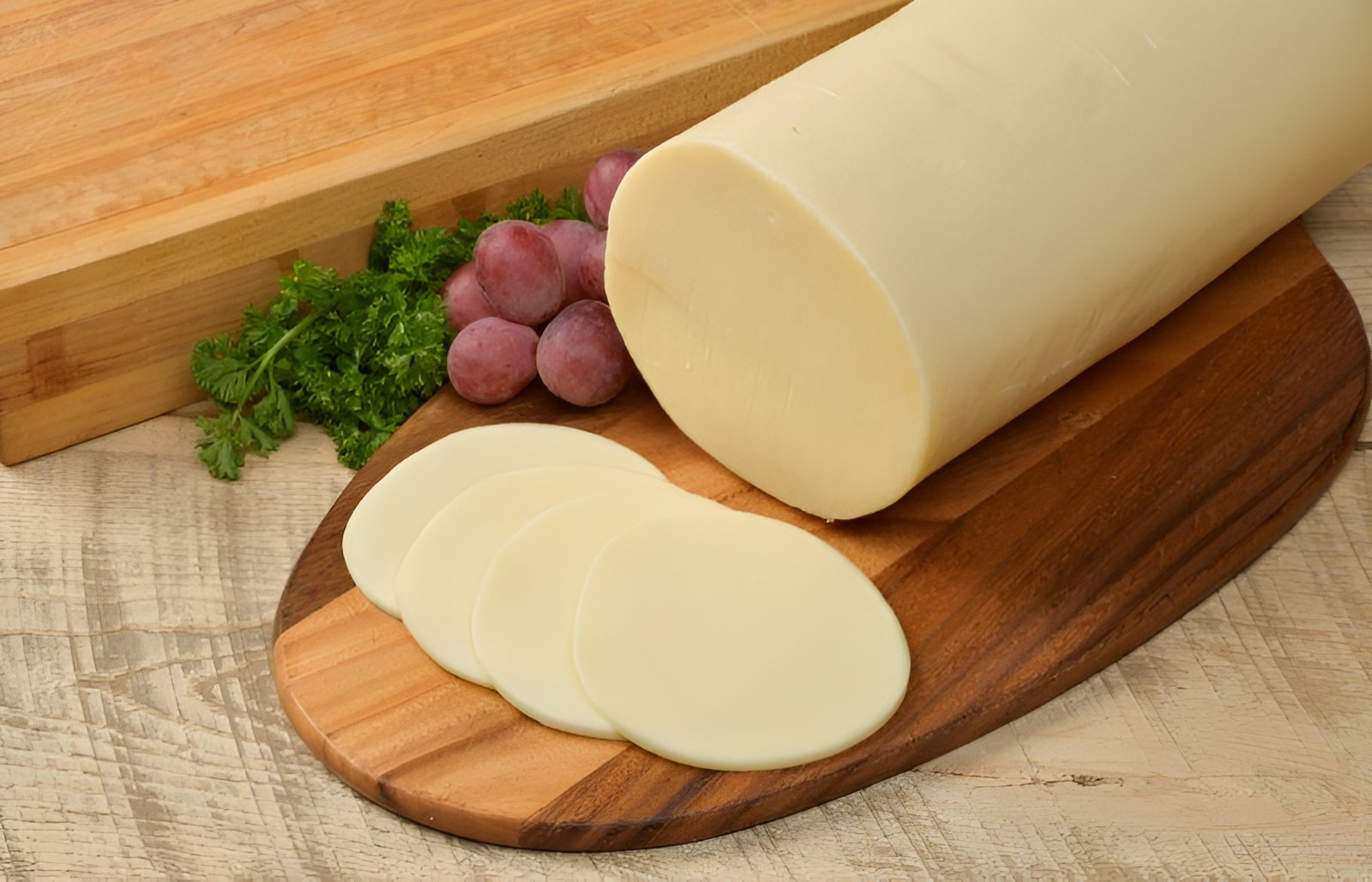
Provolone
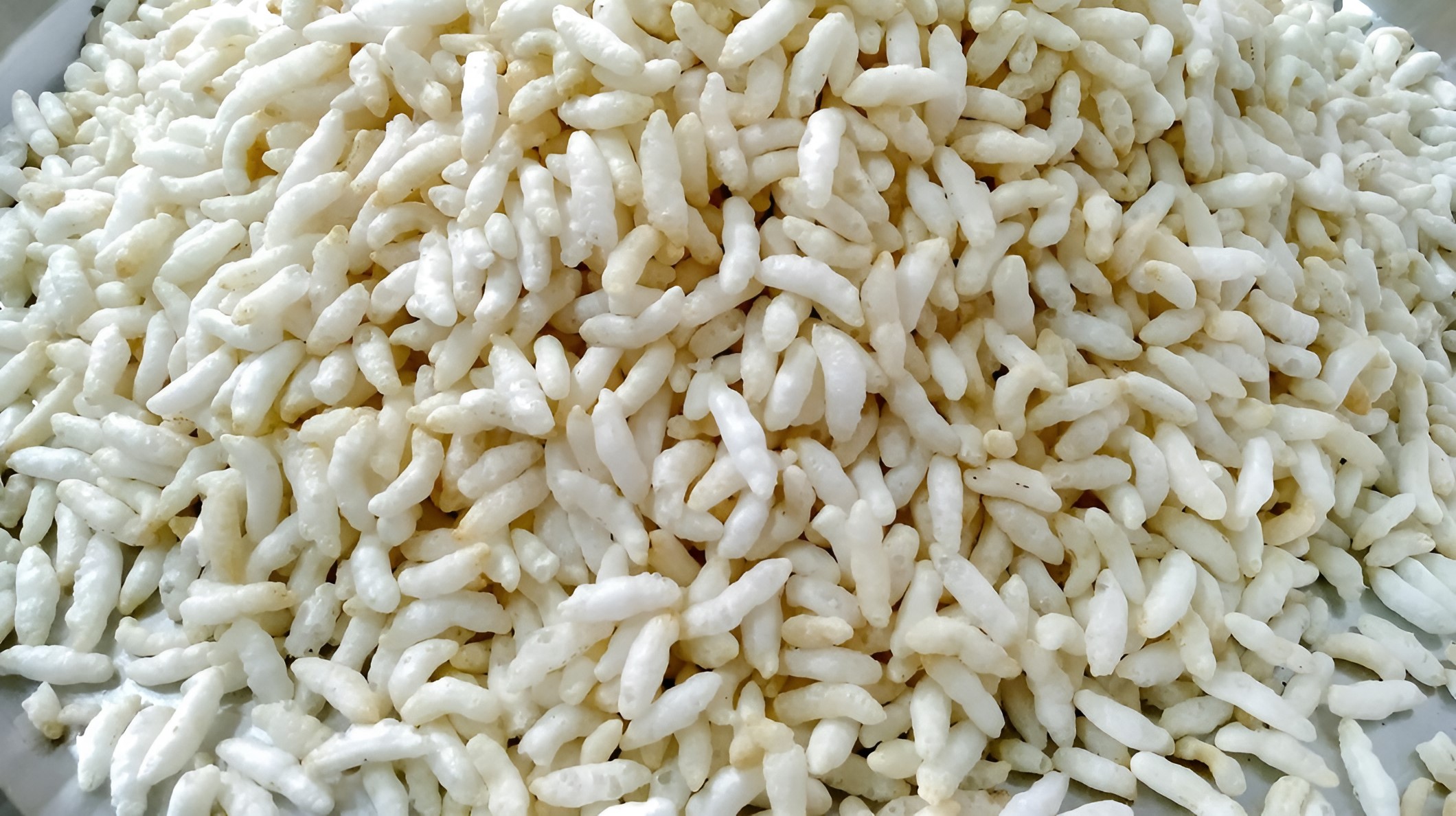
Puffed rice
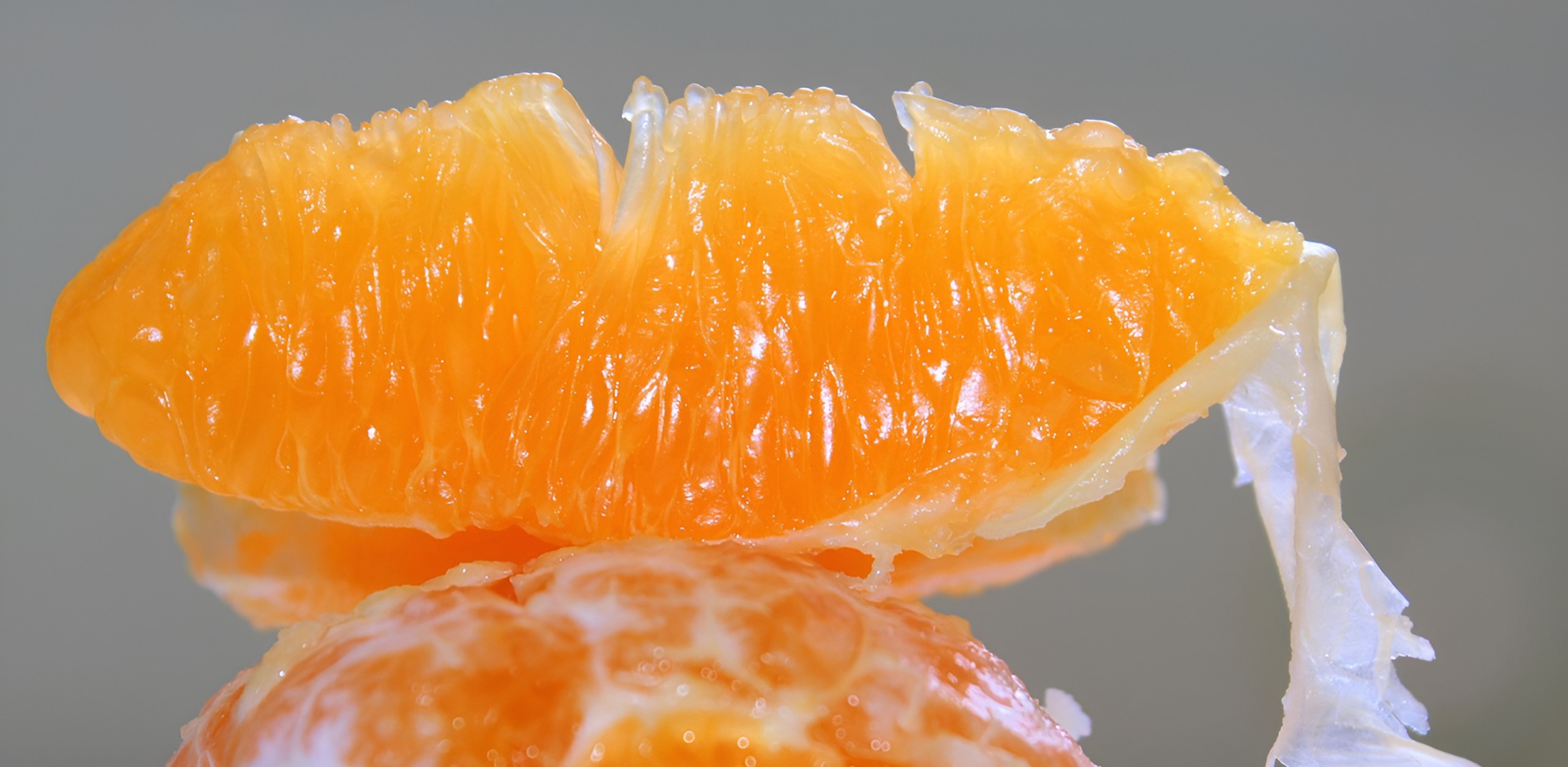
Pulp
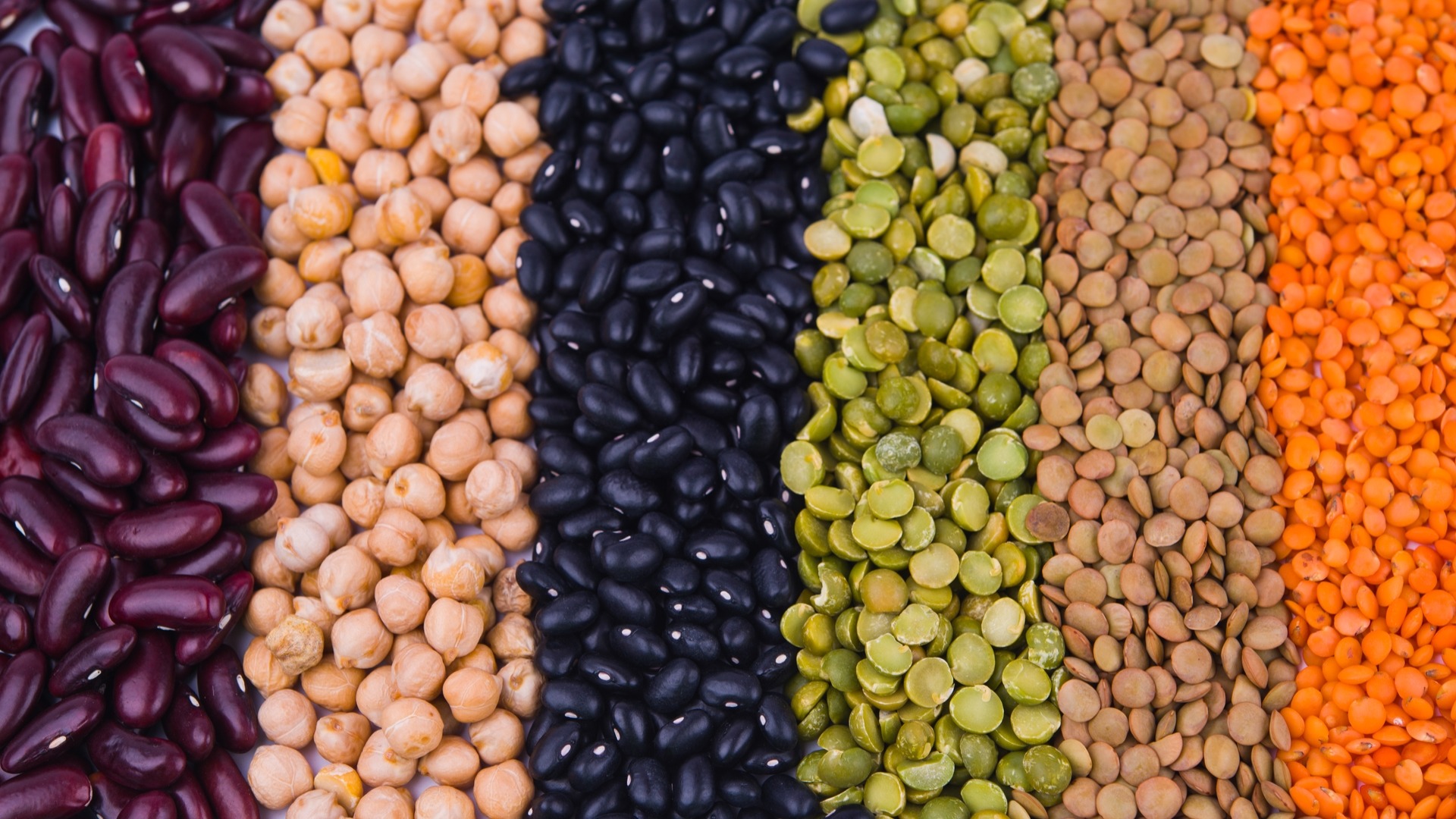
Pulses
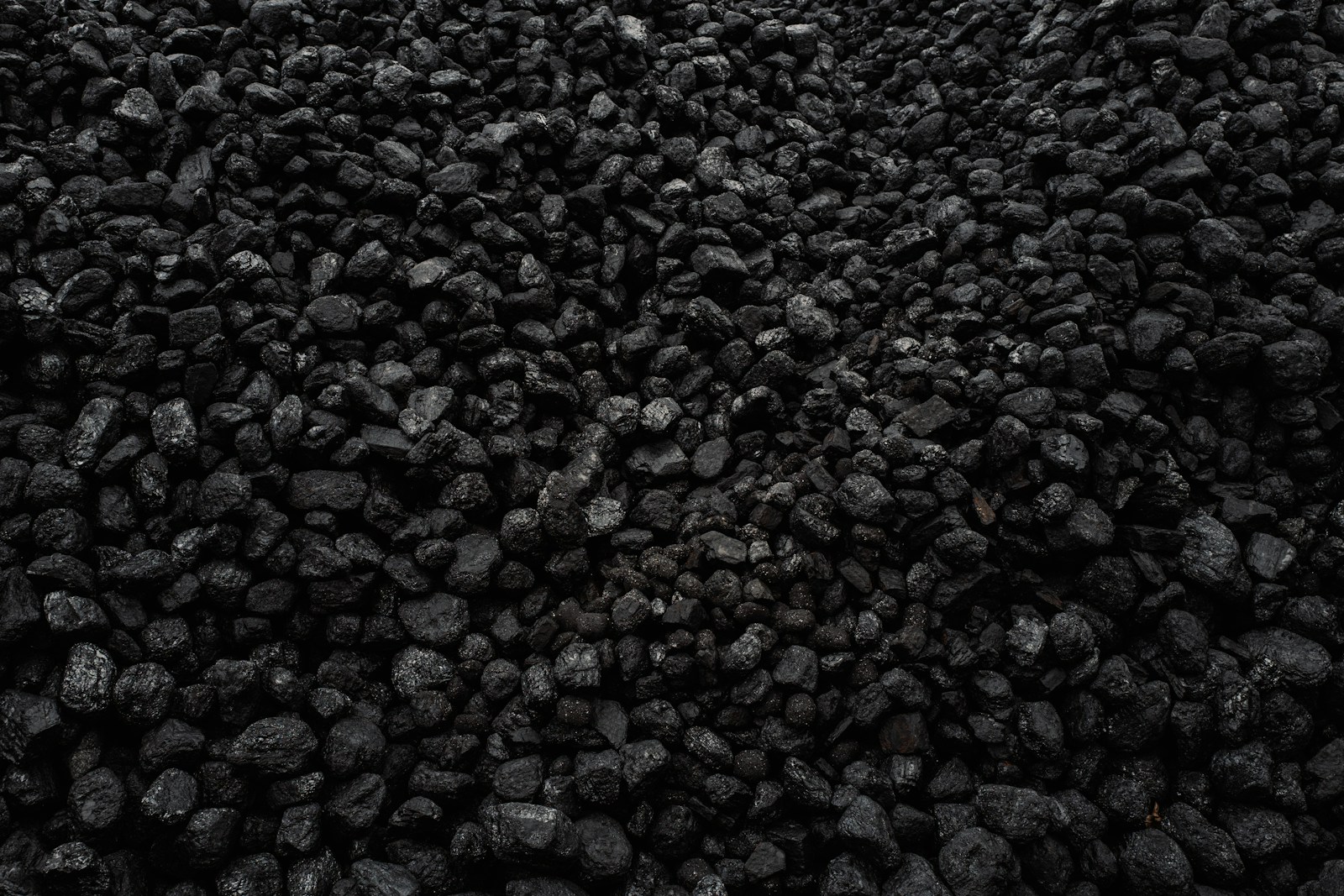
Pulverized coal
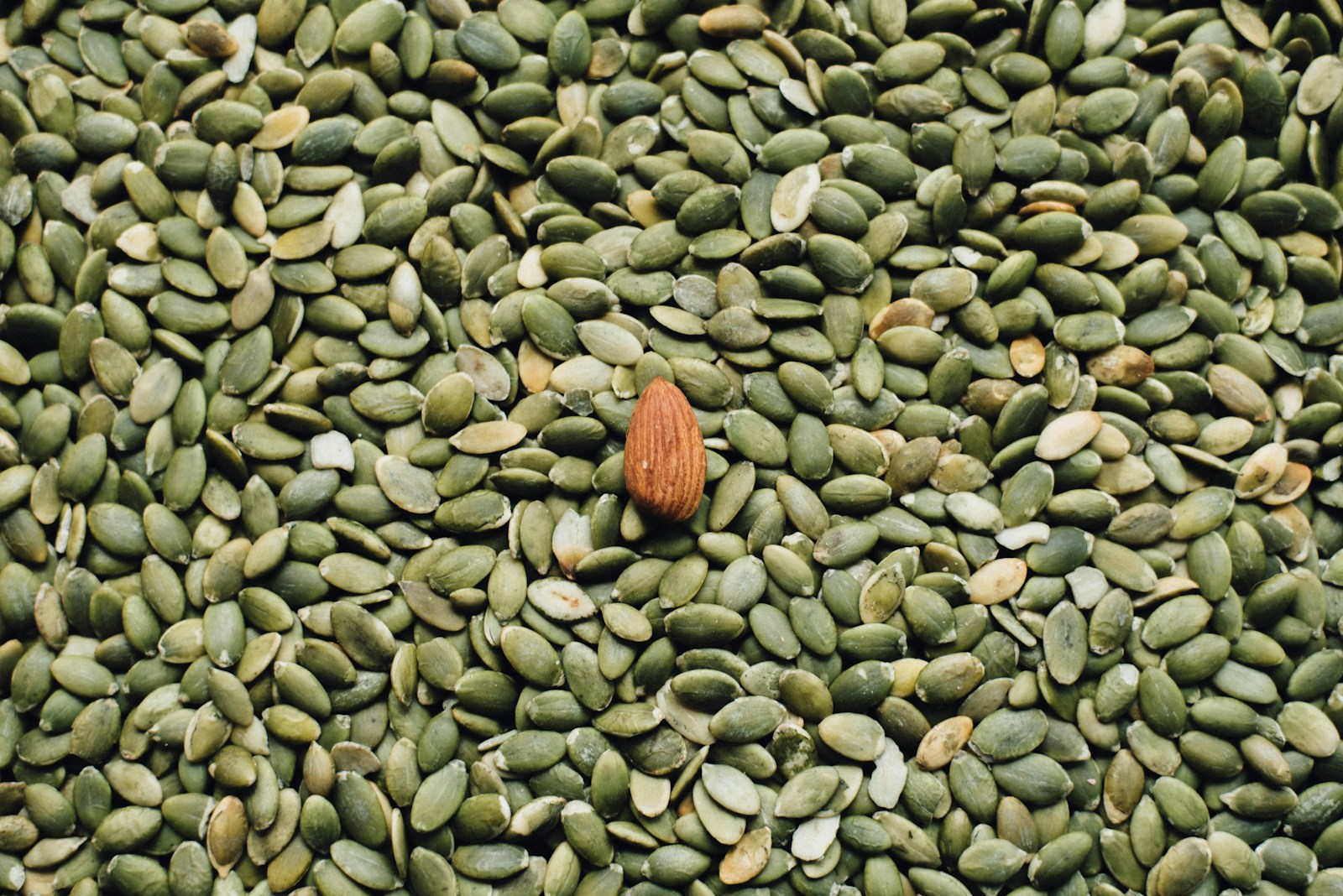
Pumpkin seeds
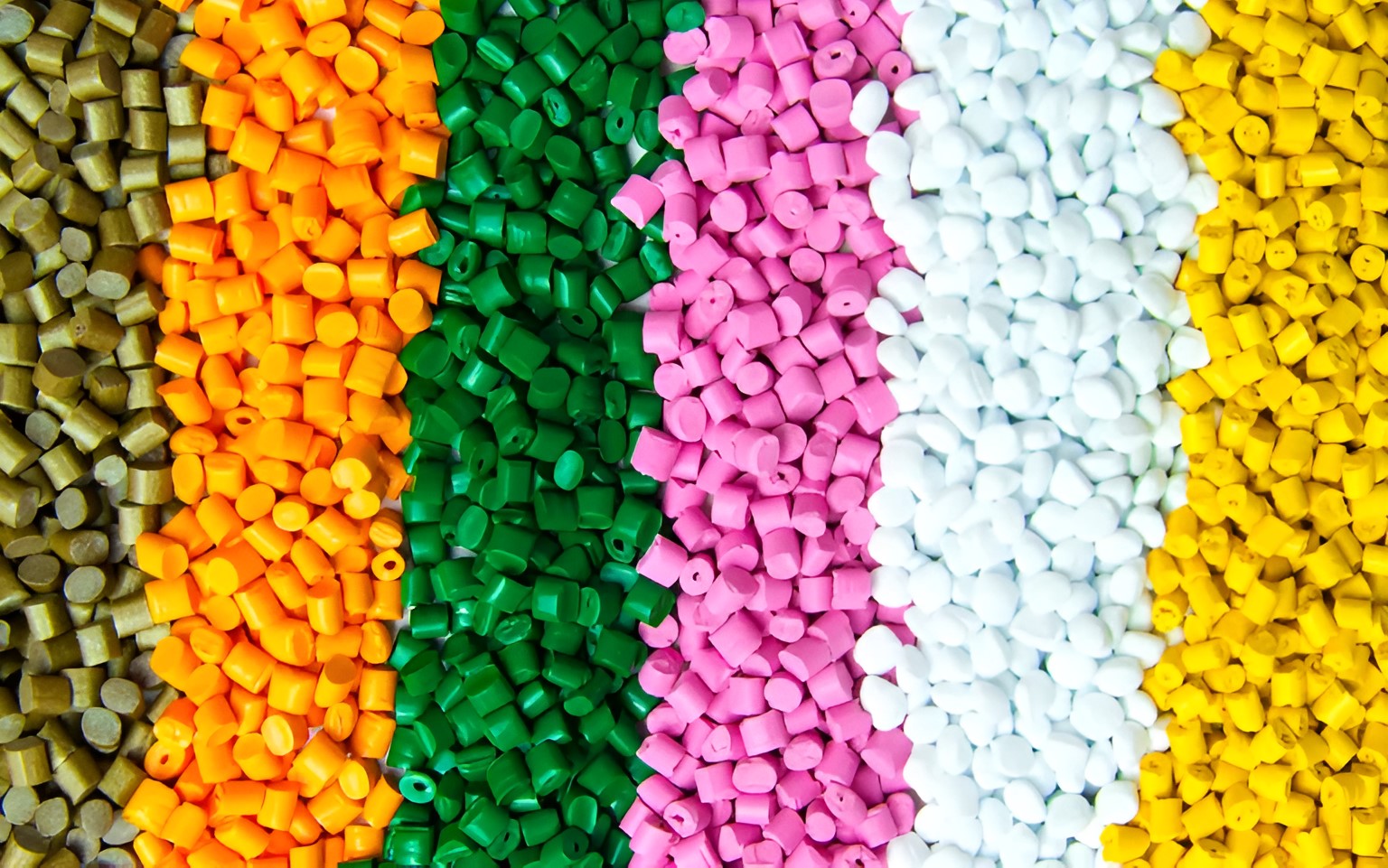
Pvc pellets
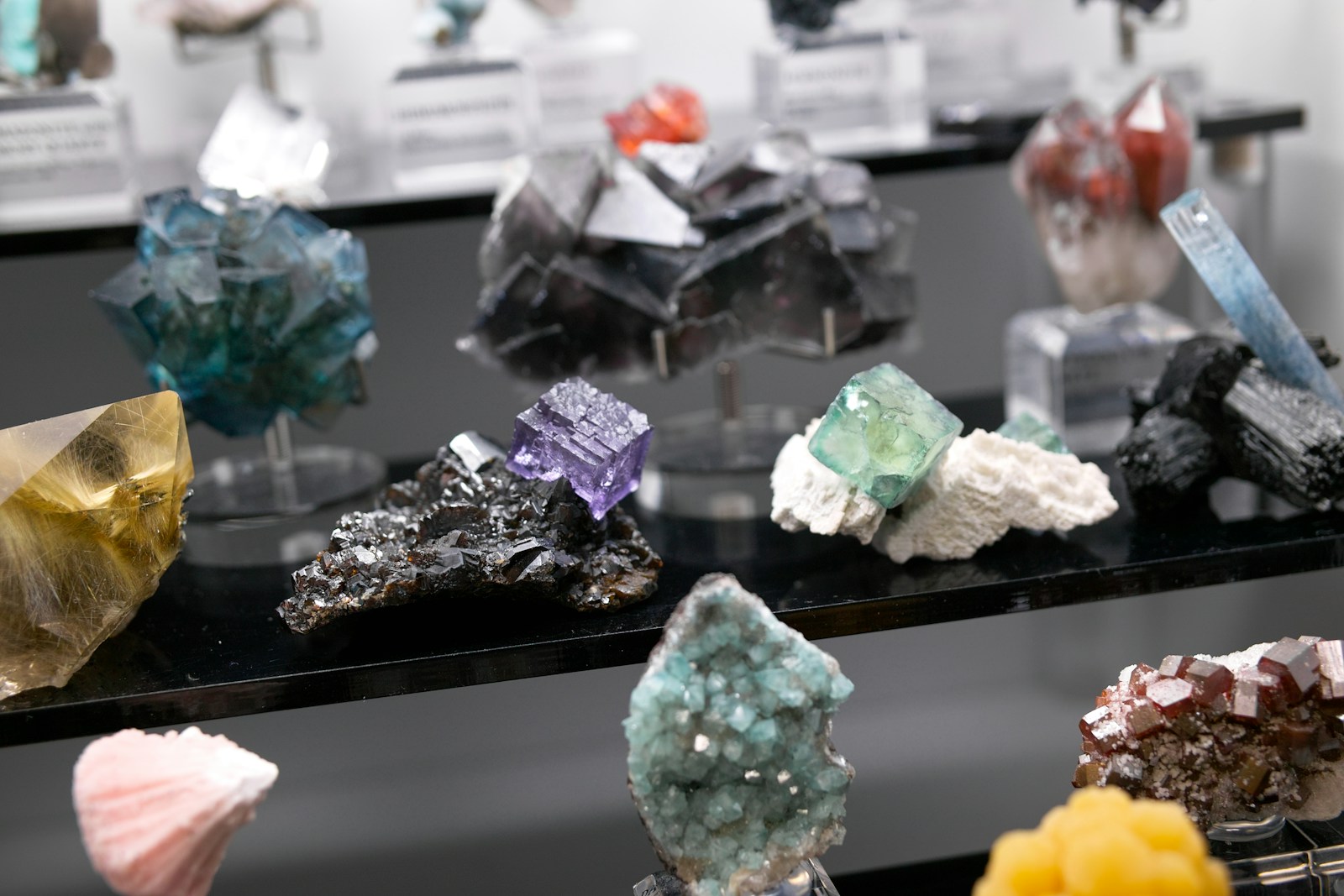
Quartz
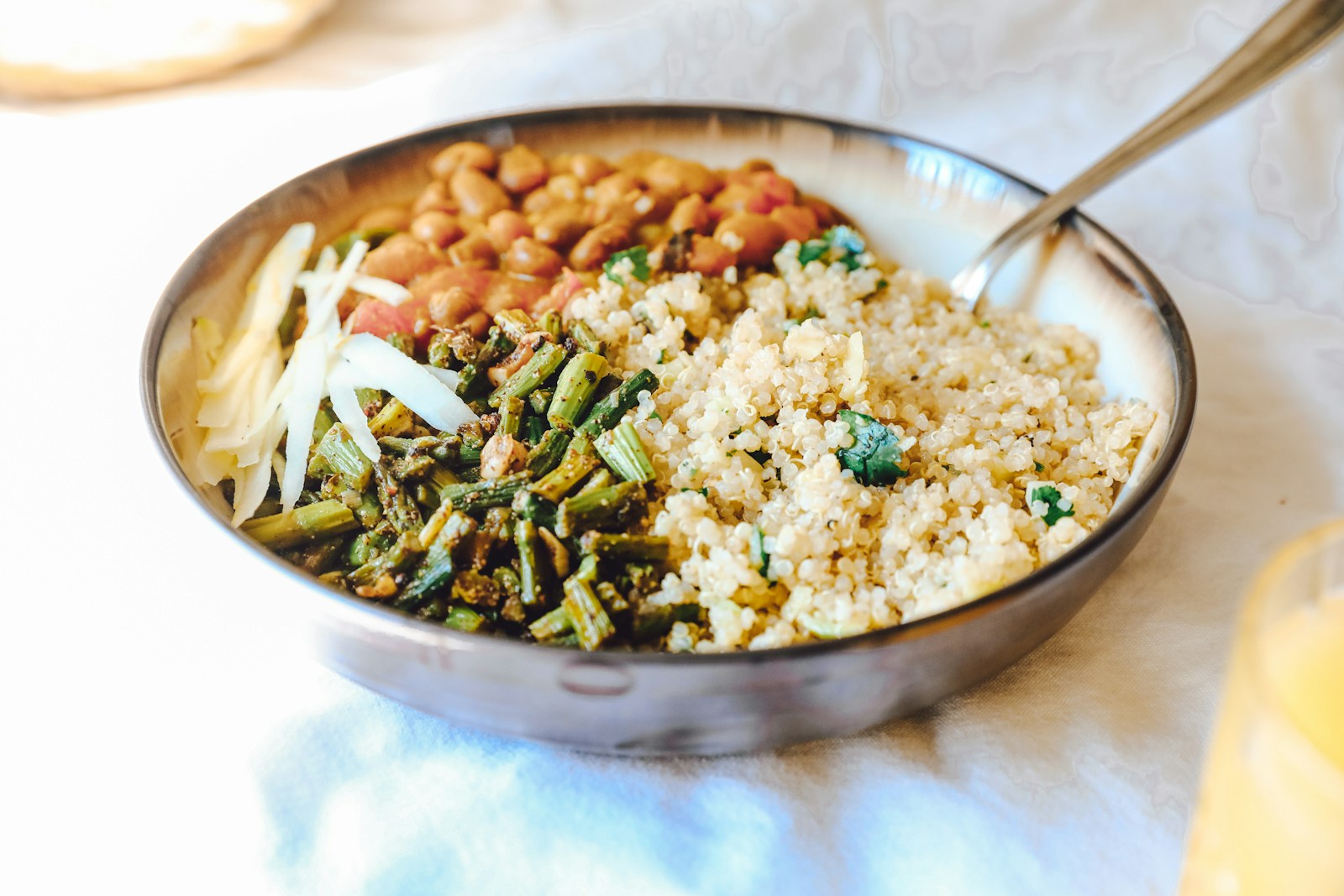
Quinoa
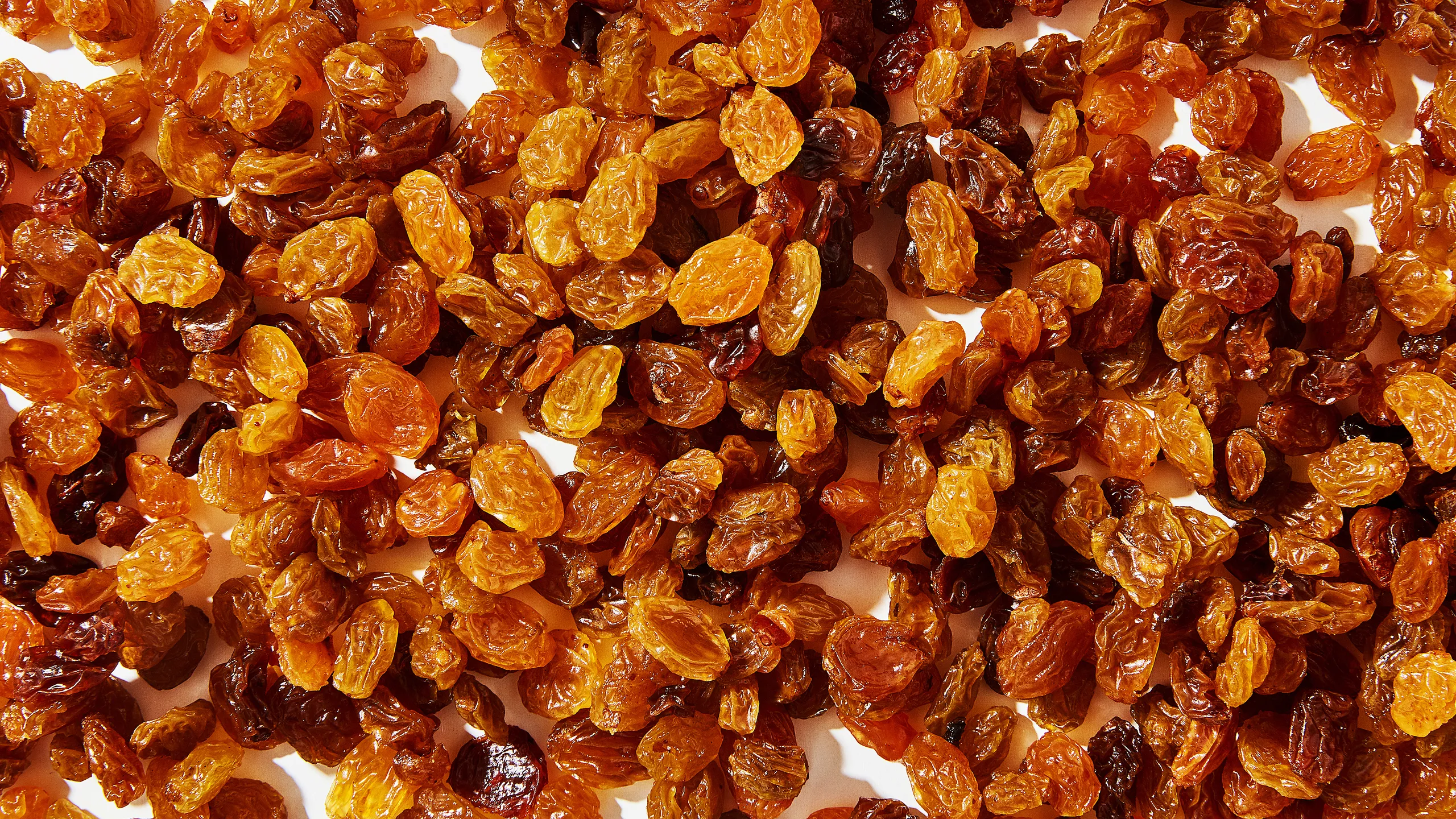
Raisins
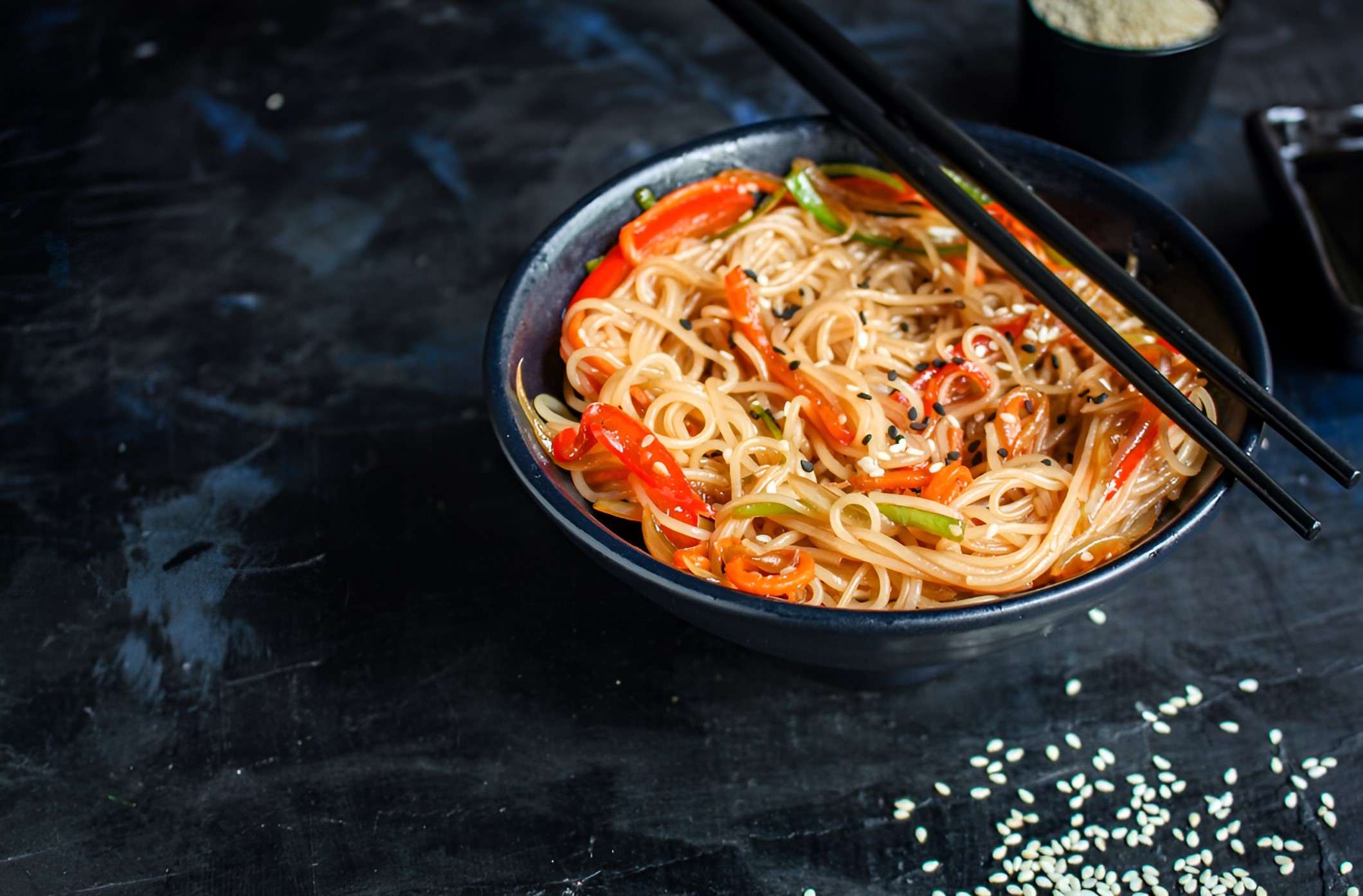
Ramen noodles

Recycled glass cullet
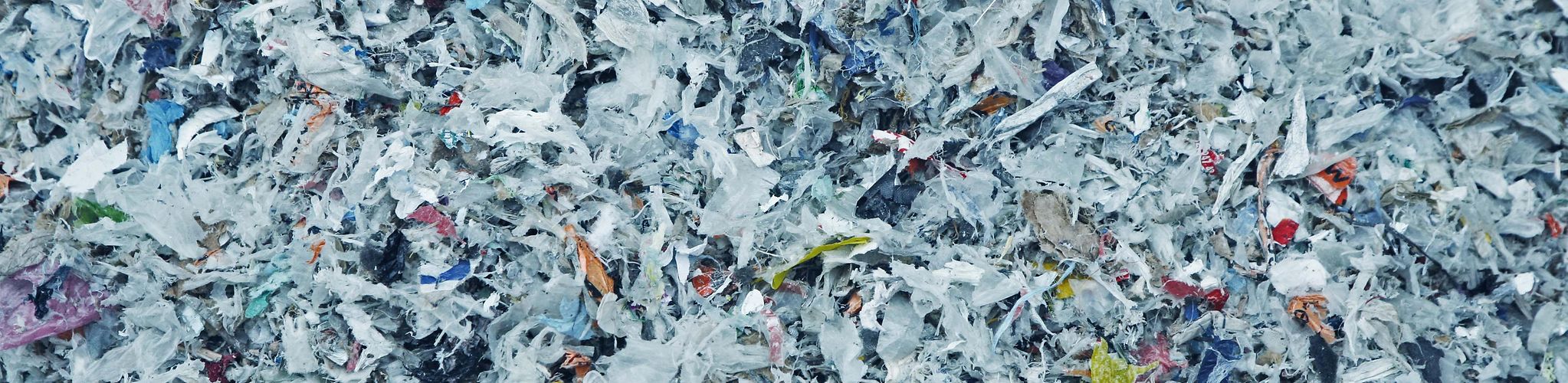
Recycled paper
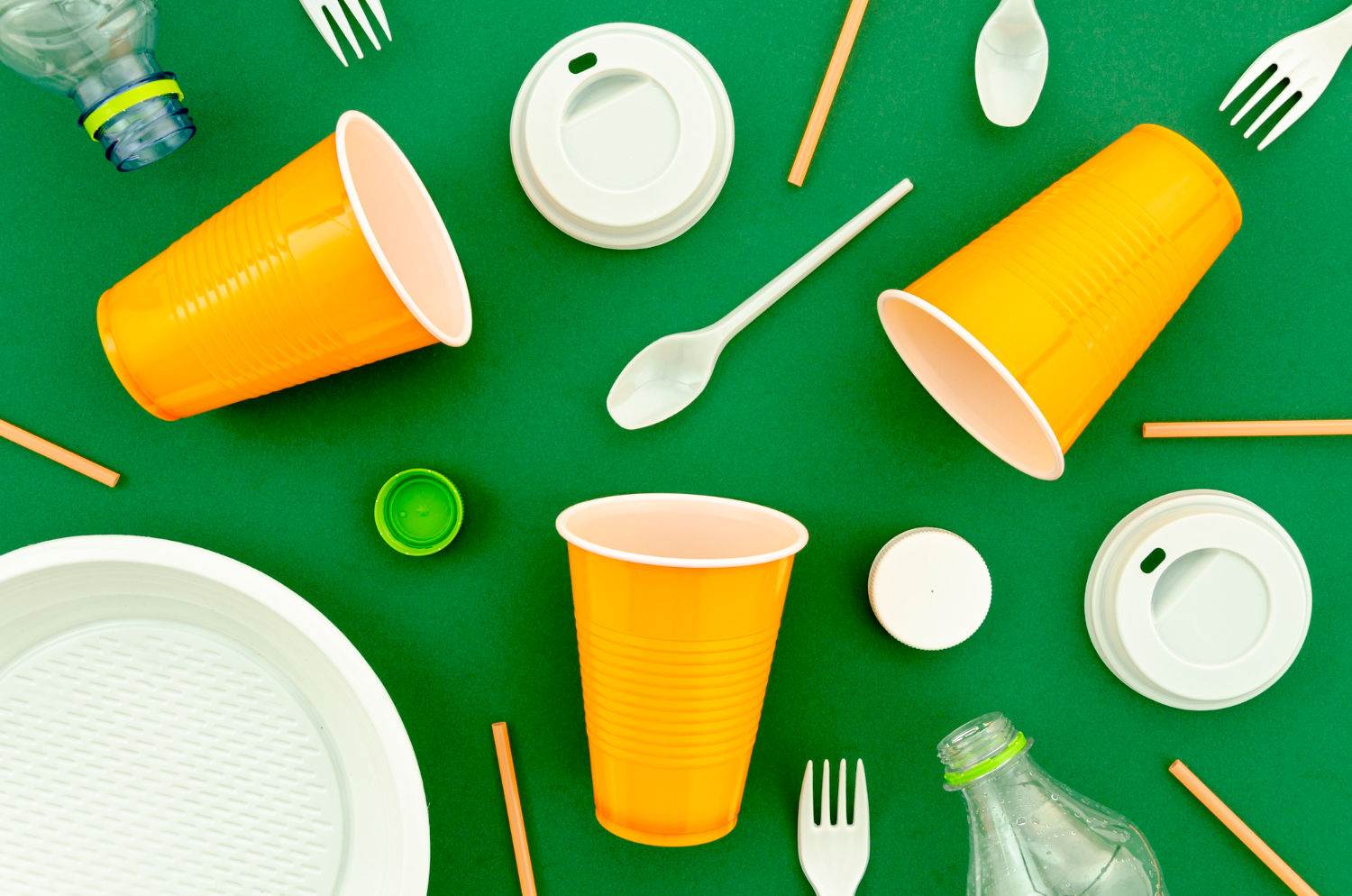
Recycled plastic
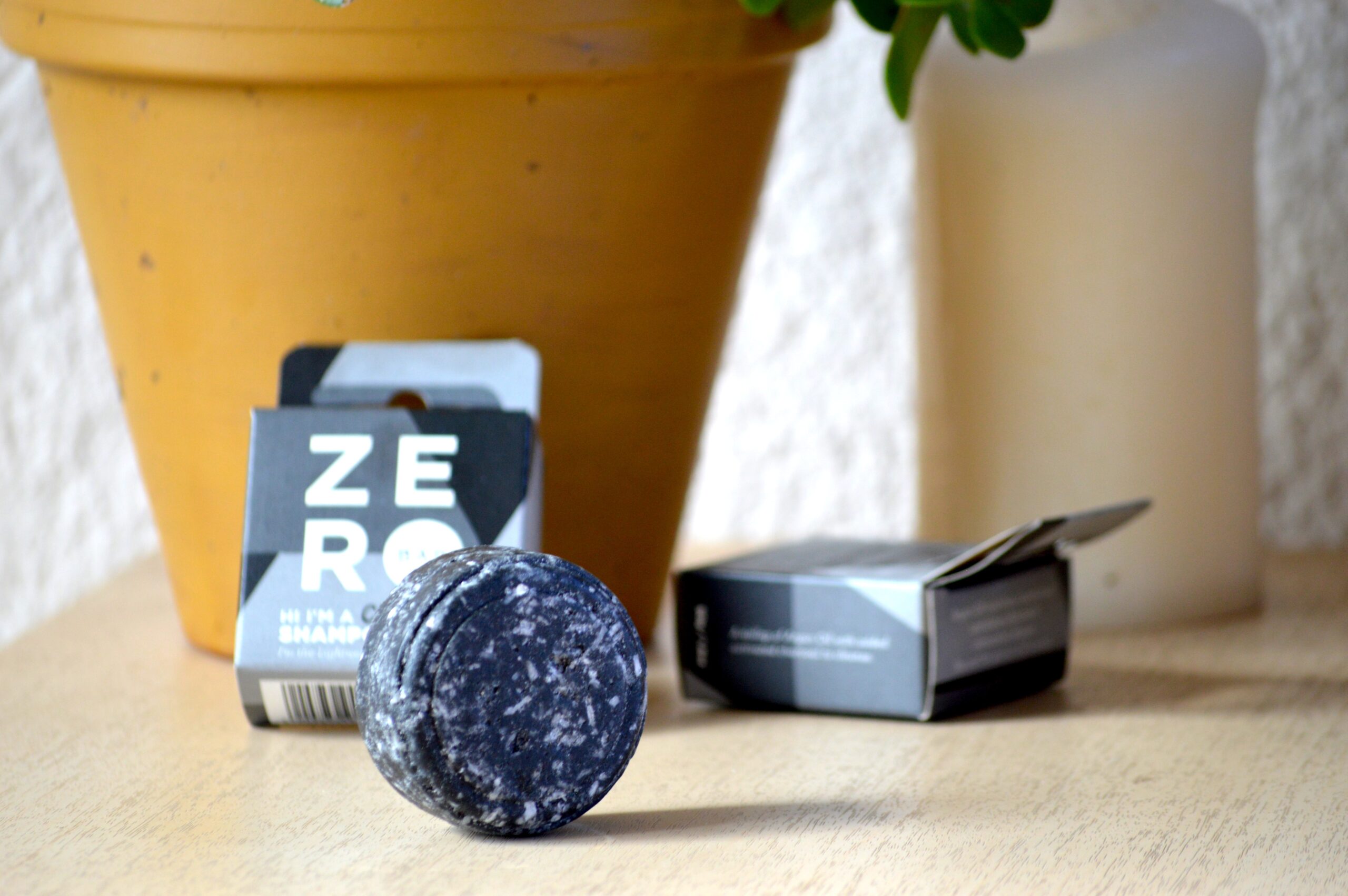
Refill tablets
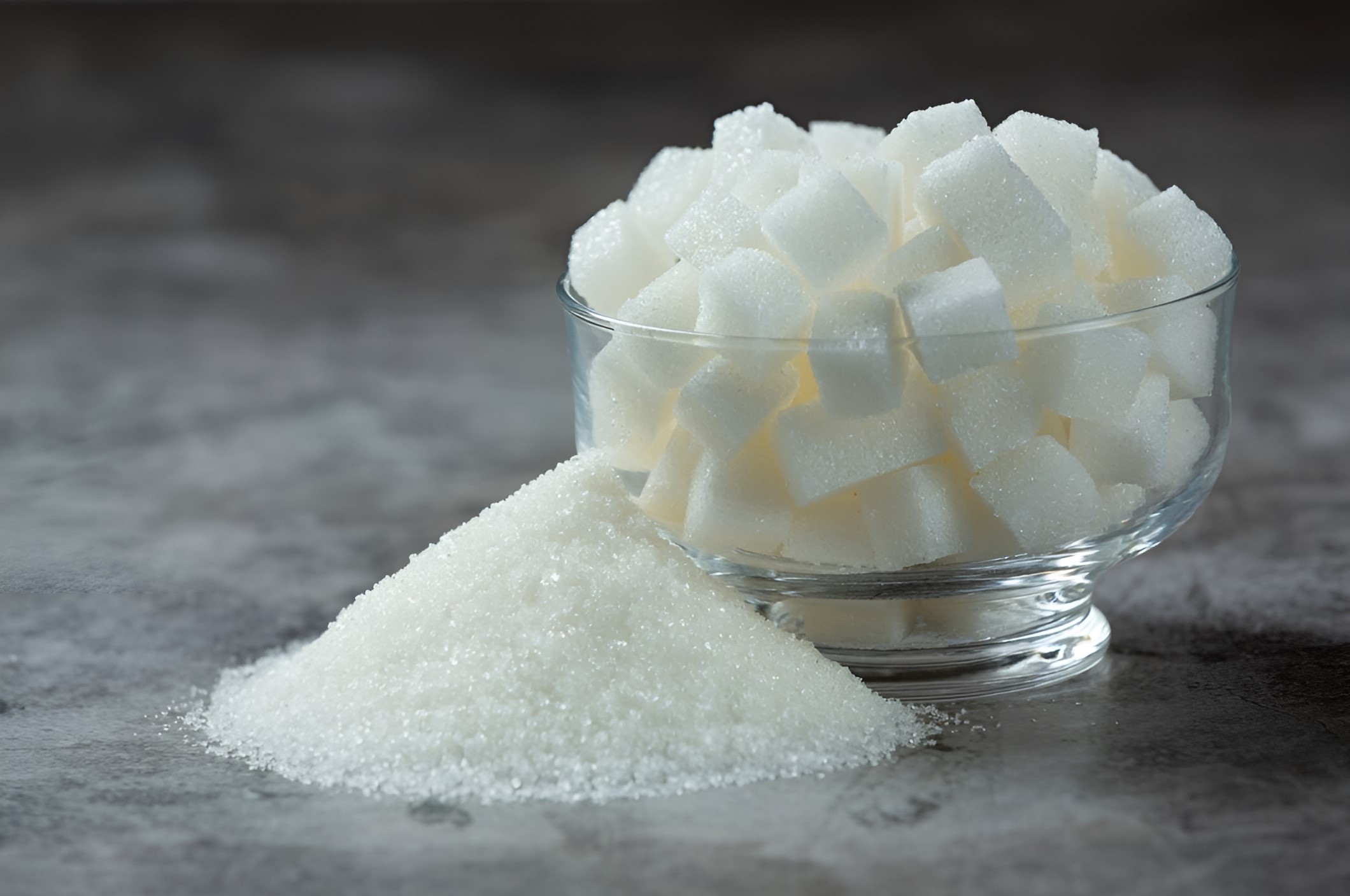
Refined sugar
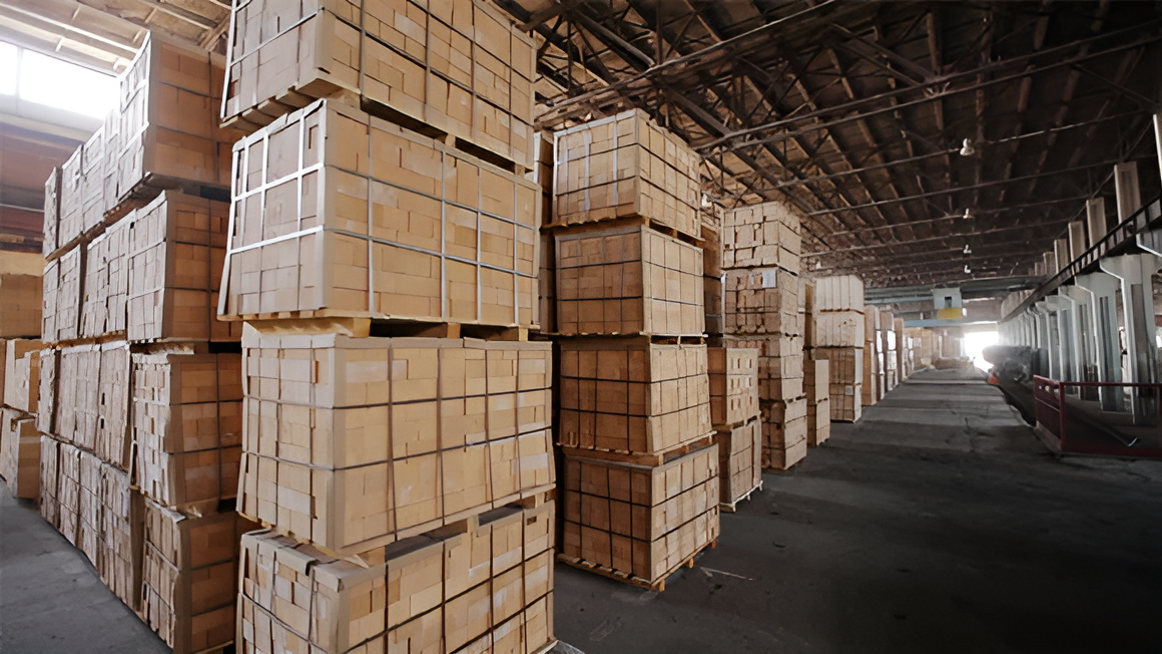
Refractory products
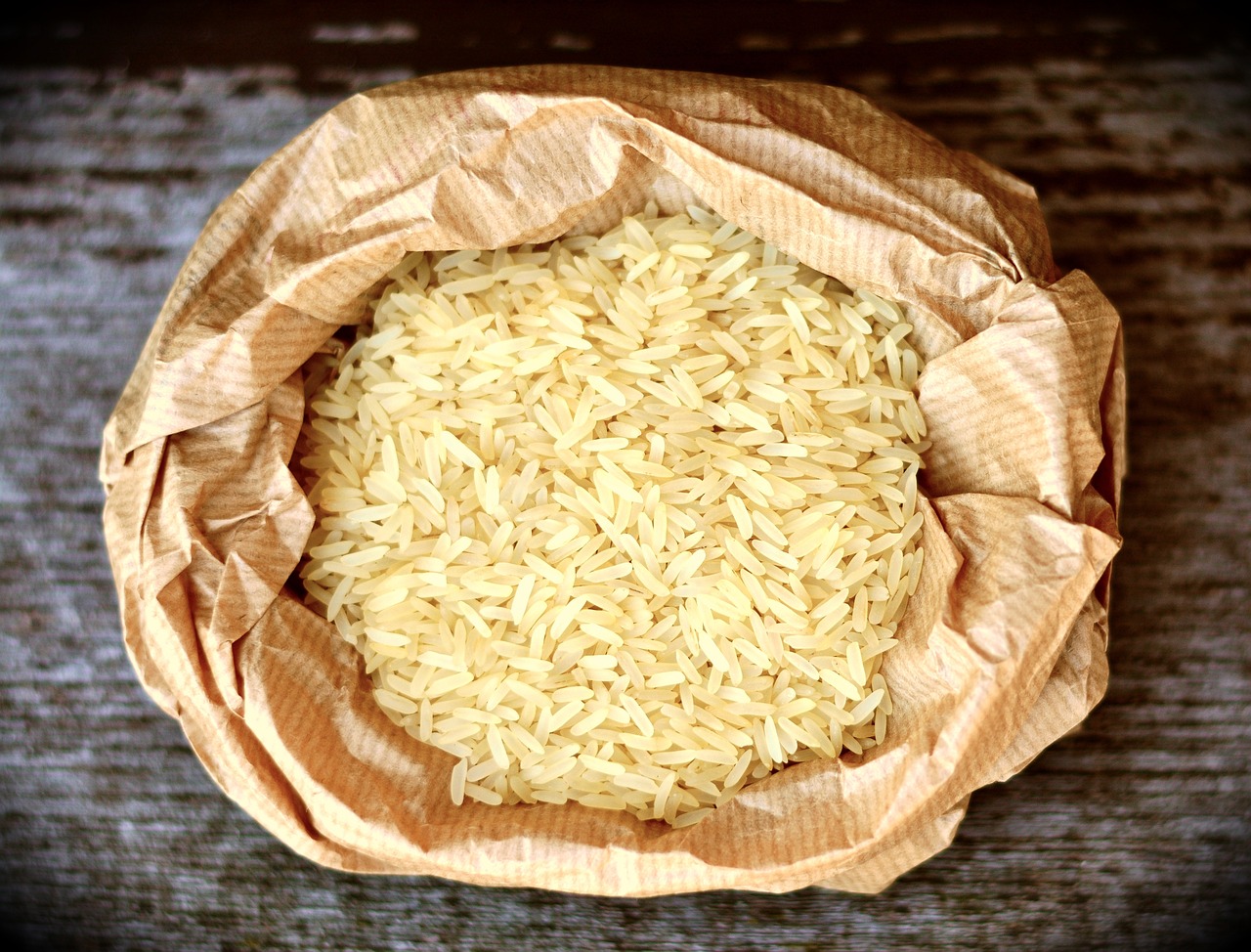
Rice
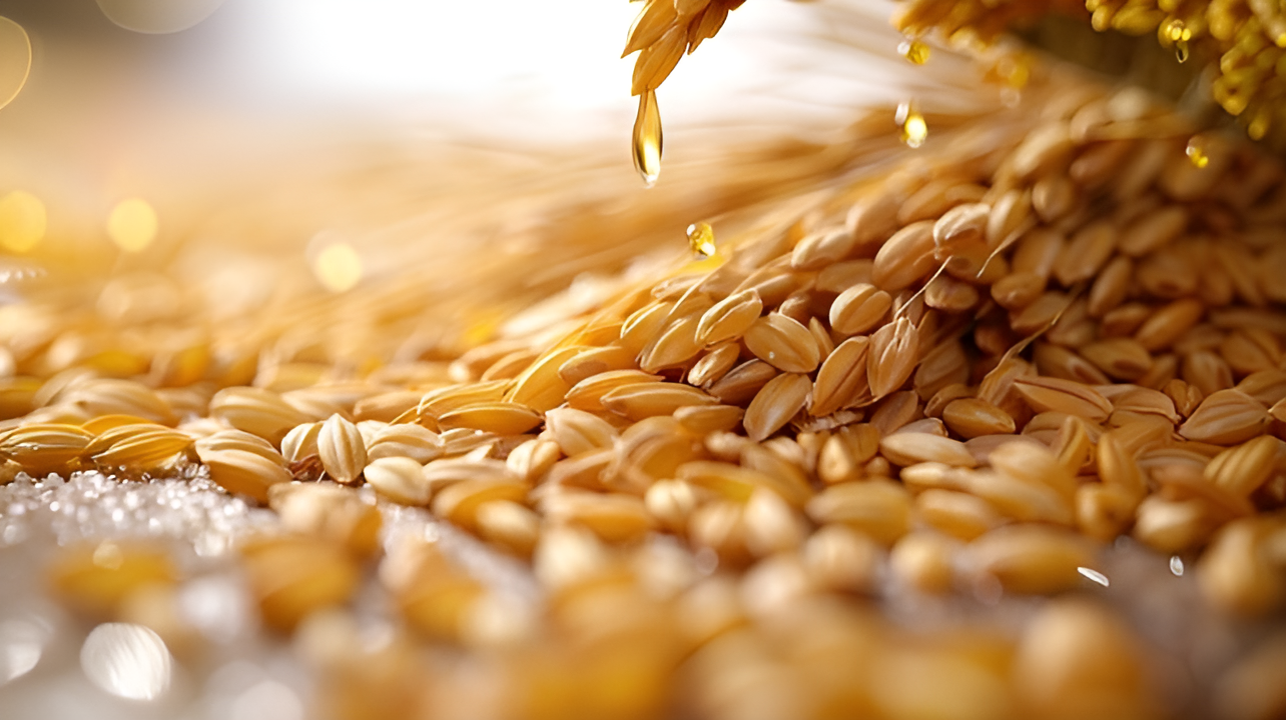
Rice bran
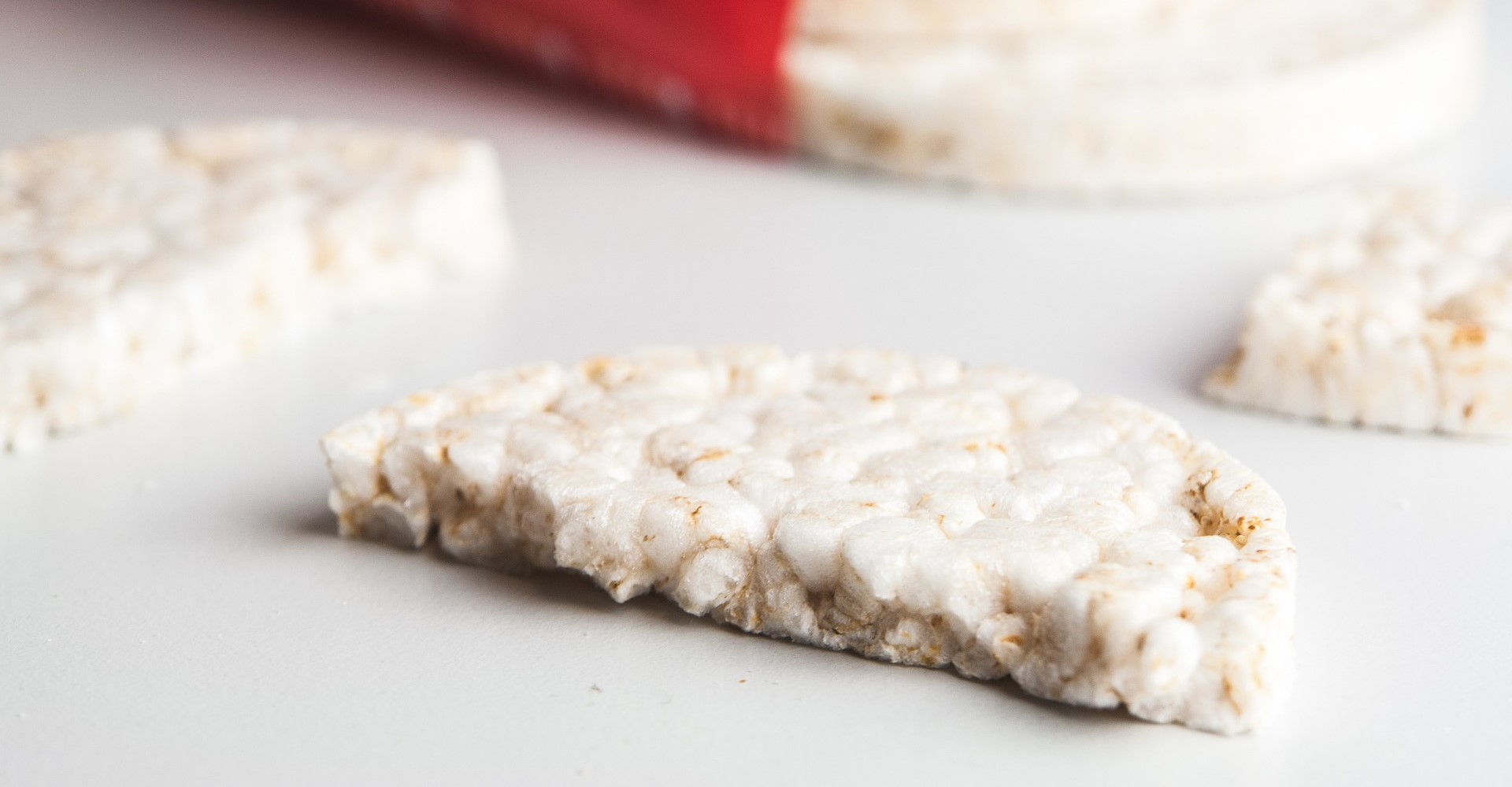
Rice cakes
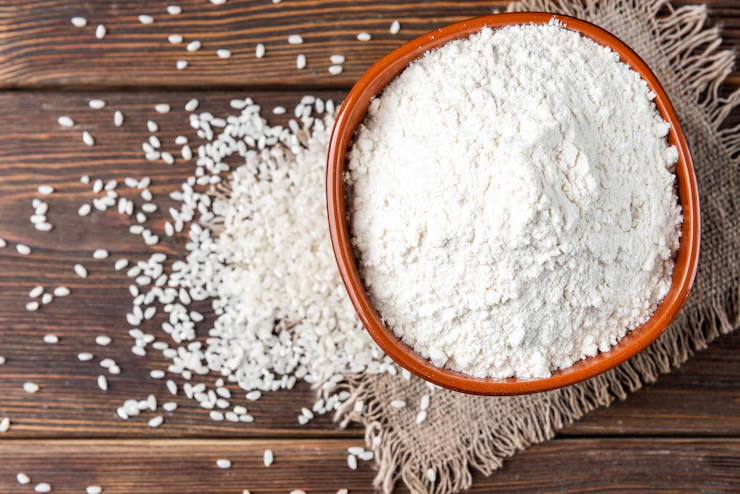
Rice flour
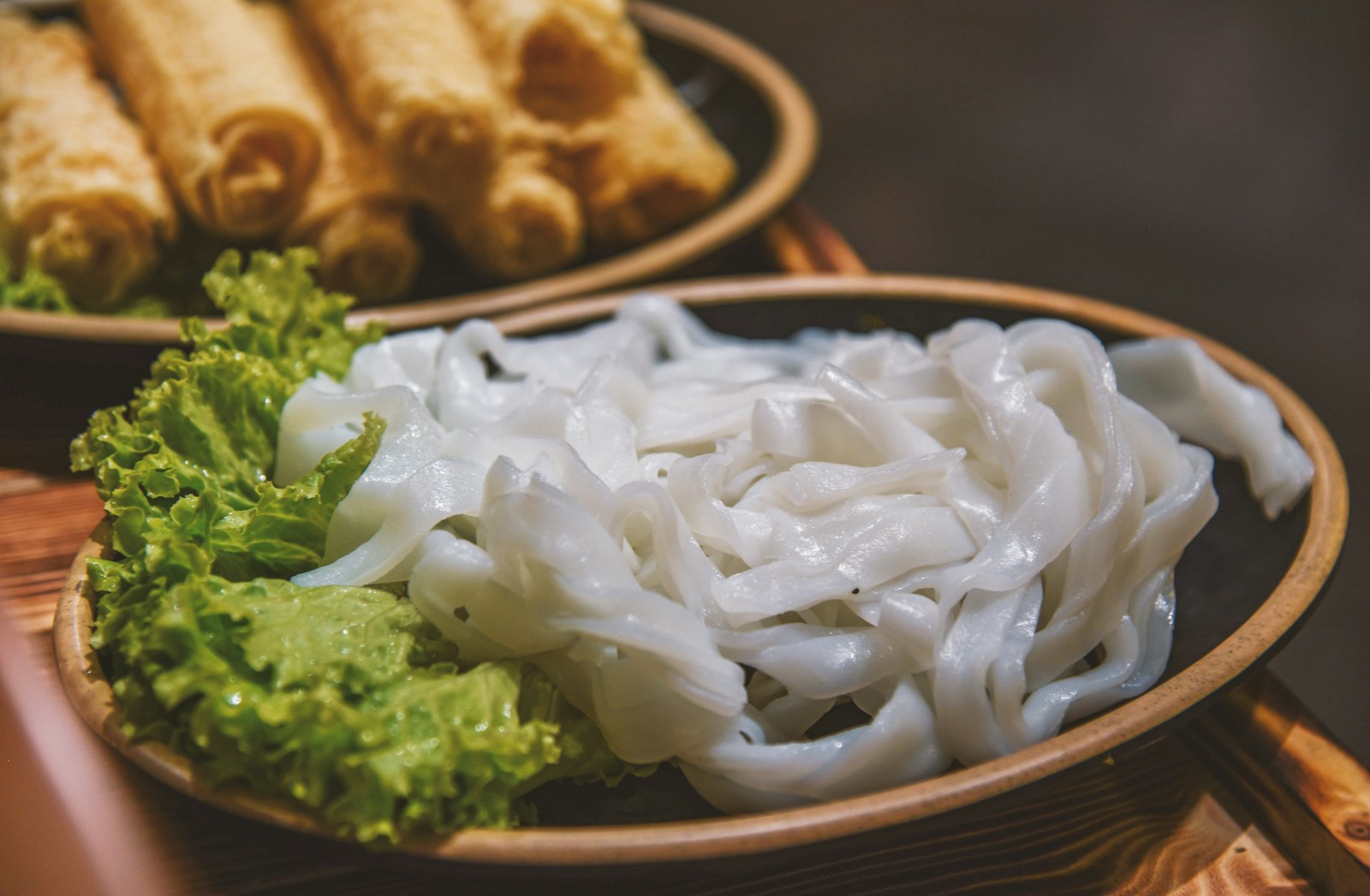
Rice noodles
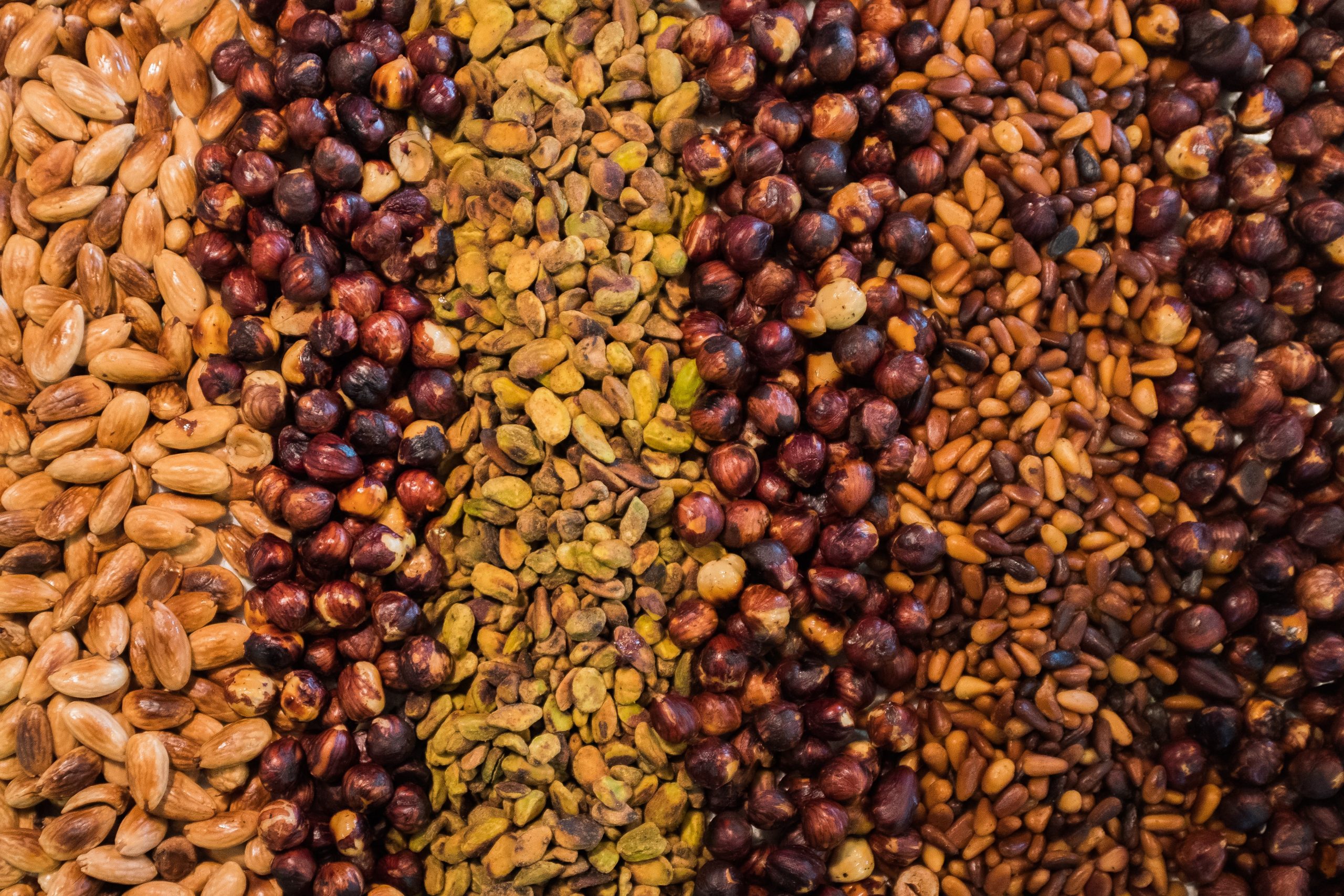
Roasted nuts
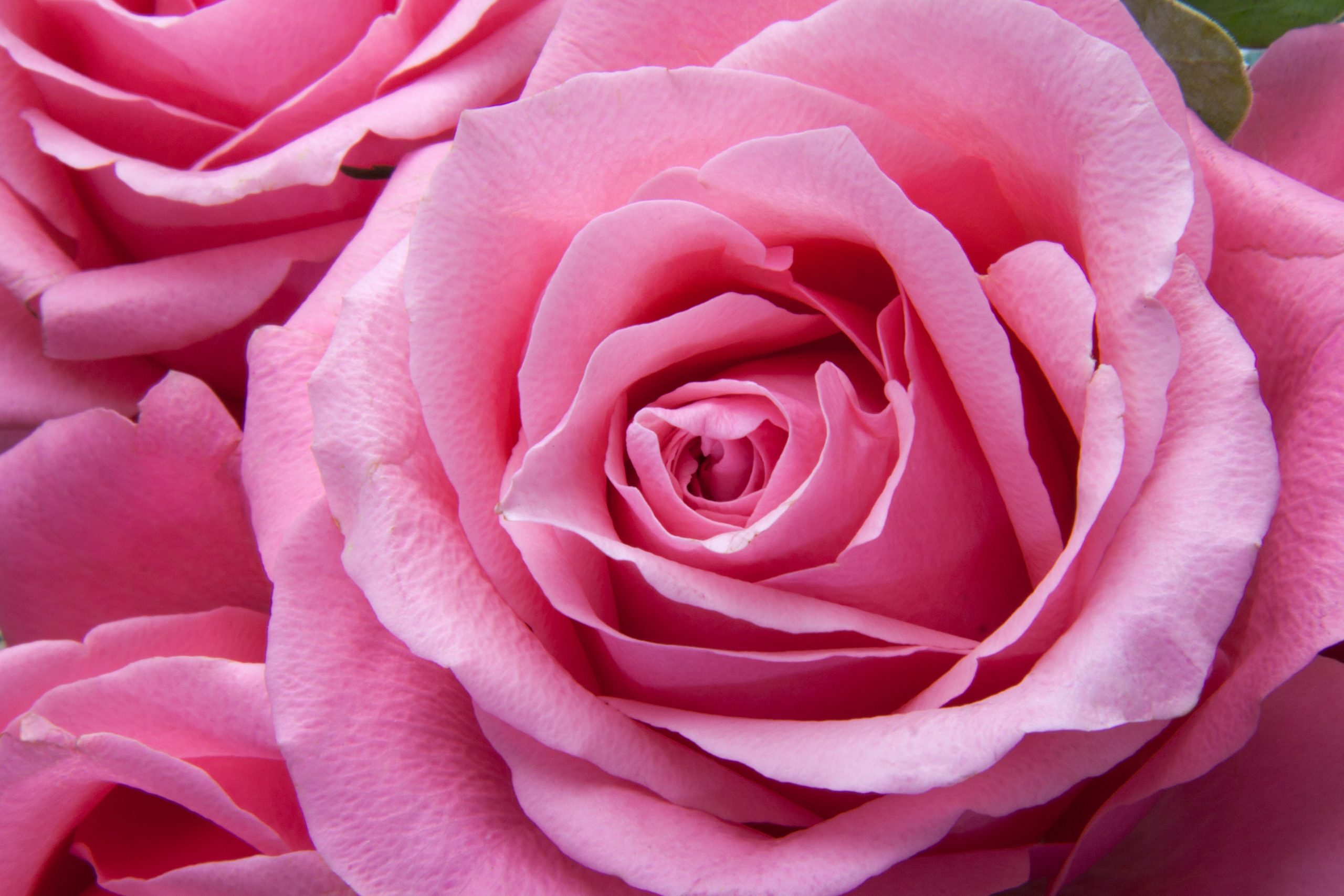
Rose oil
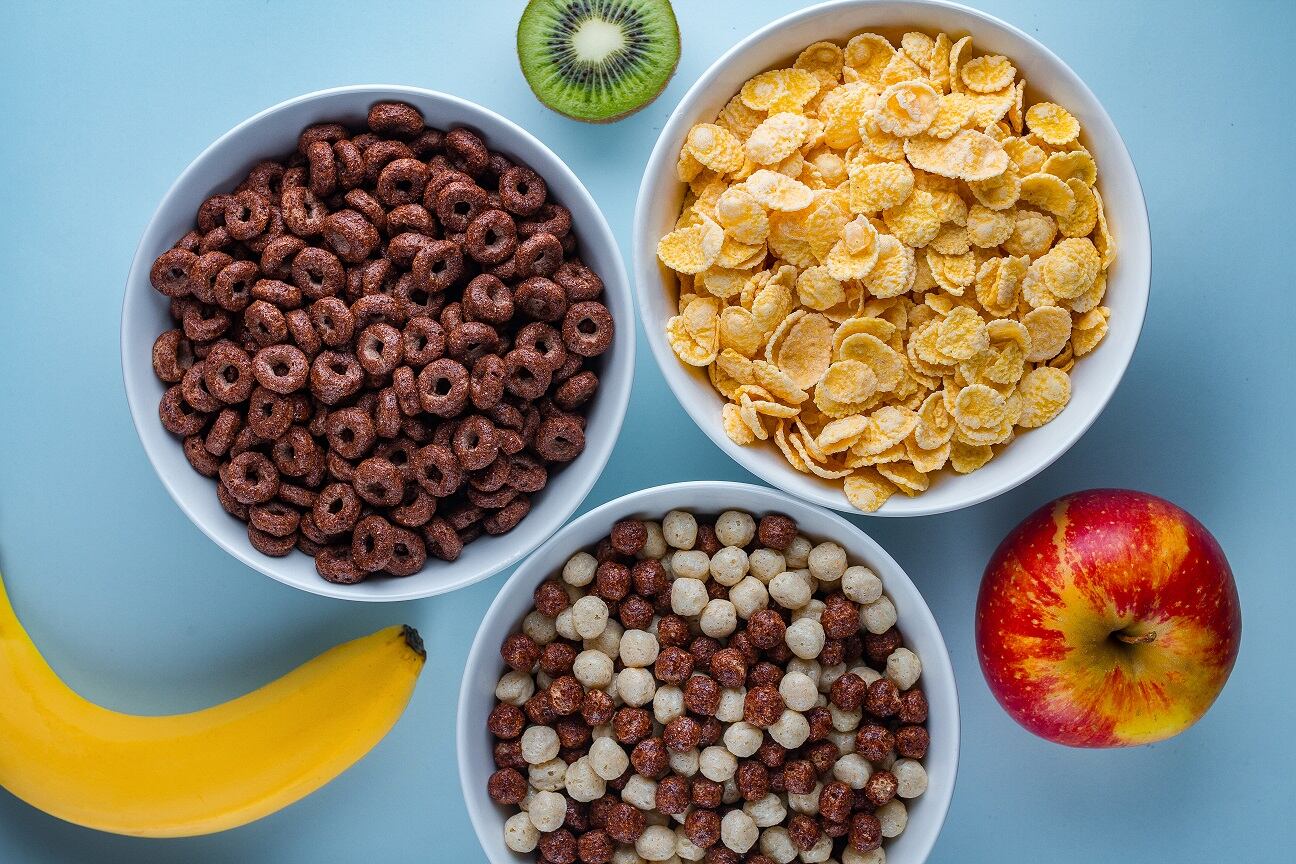
Rte cereals

Rye
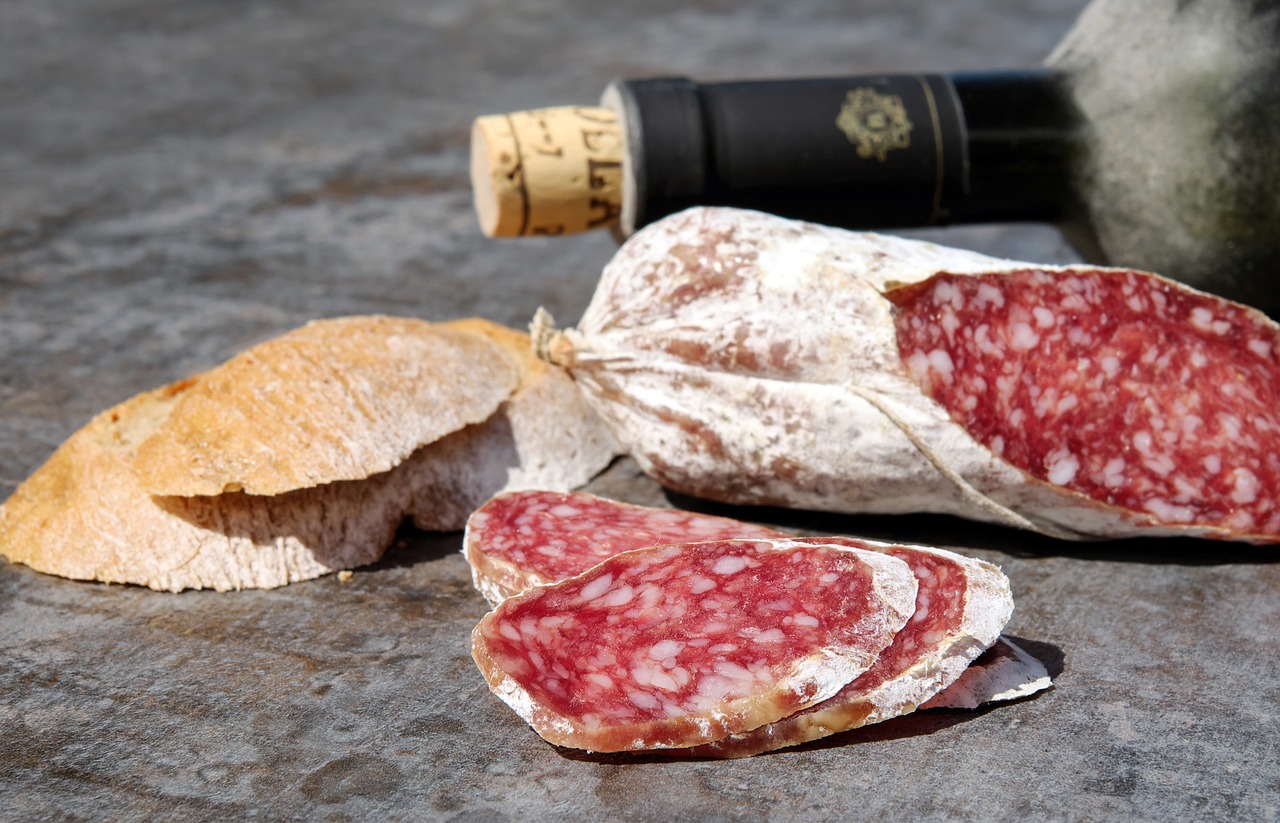
Salami
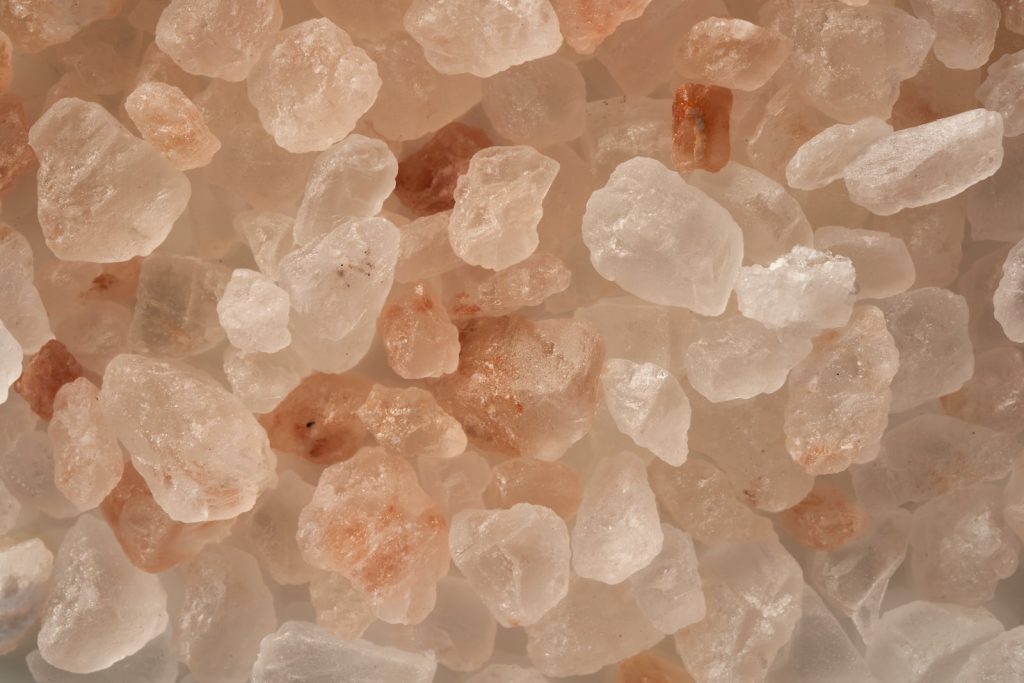
Salt
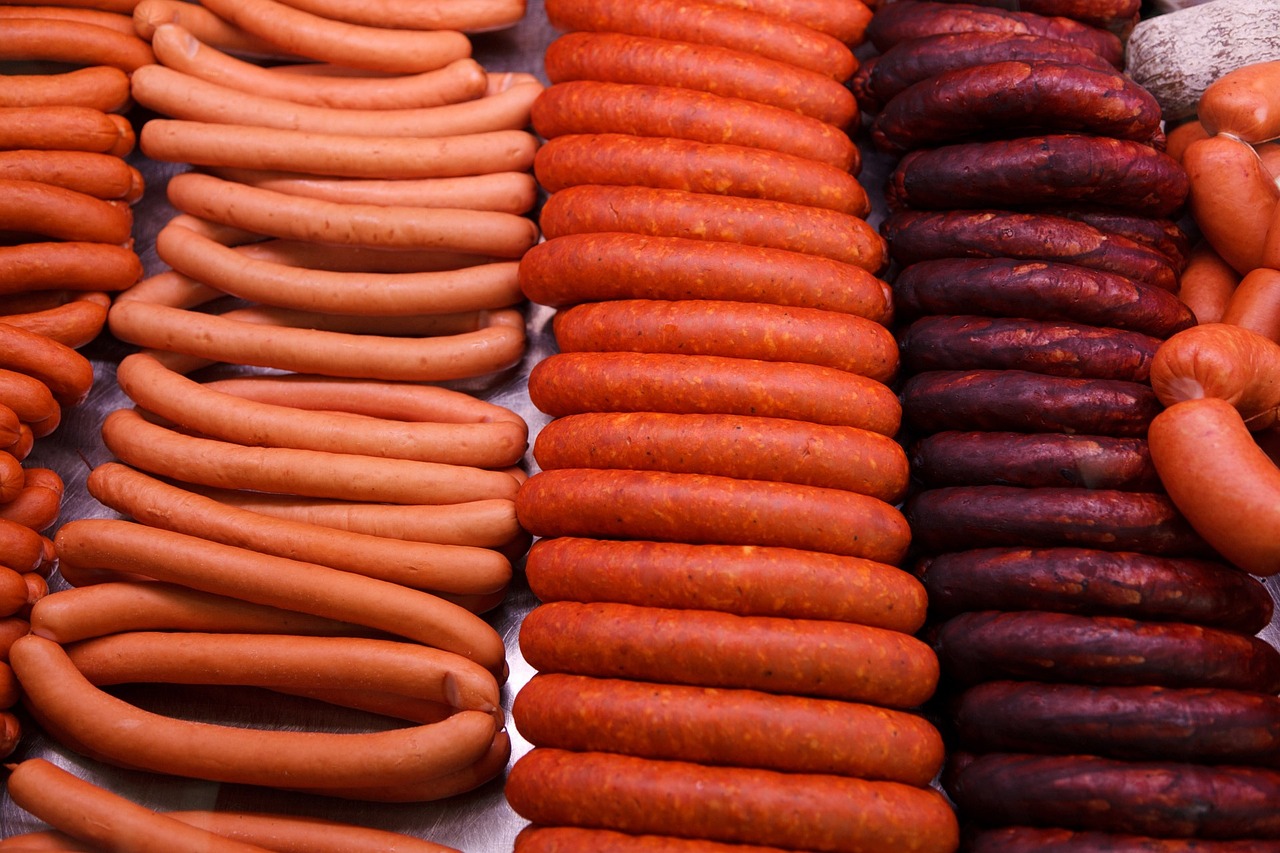
Sausages
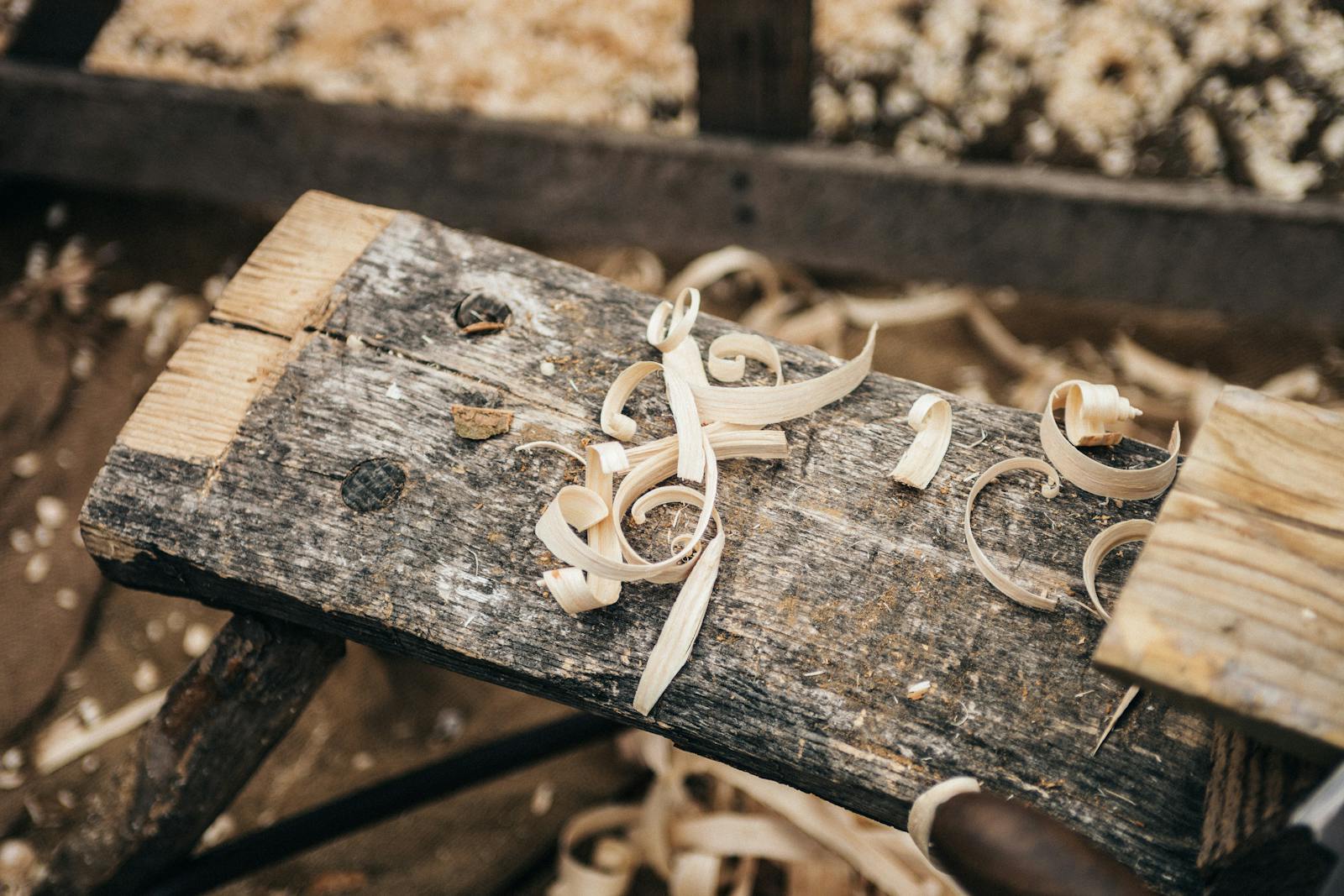
Sawdust
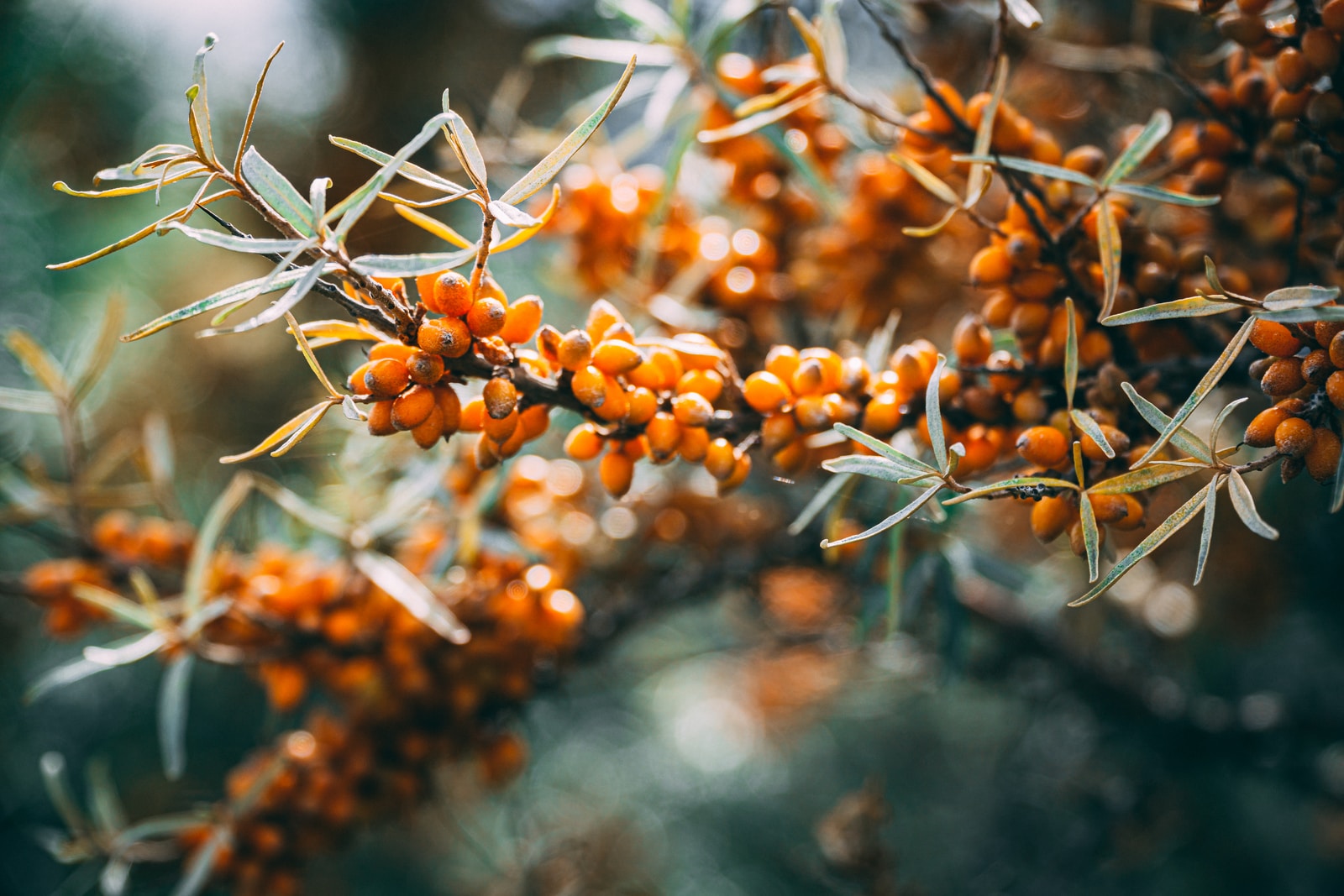
Sea buckthorn oil
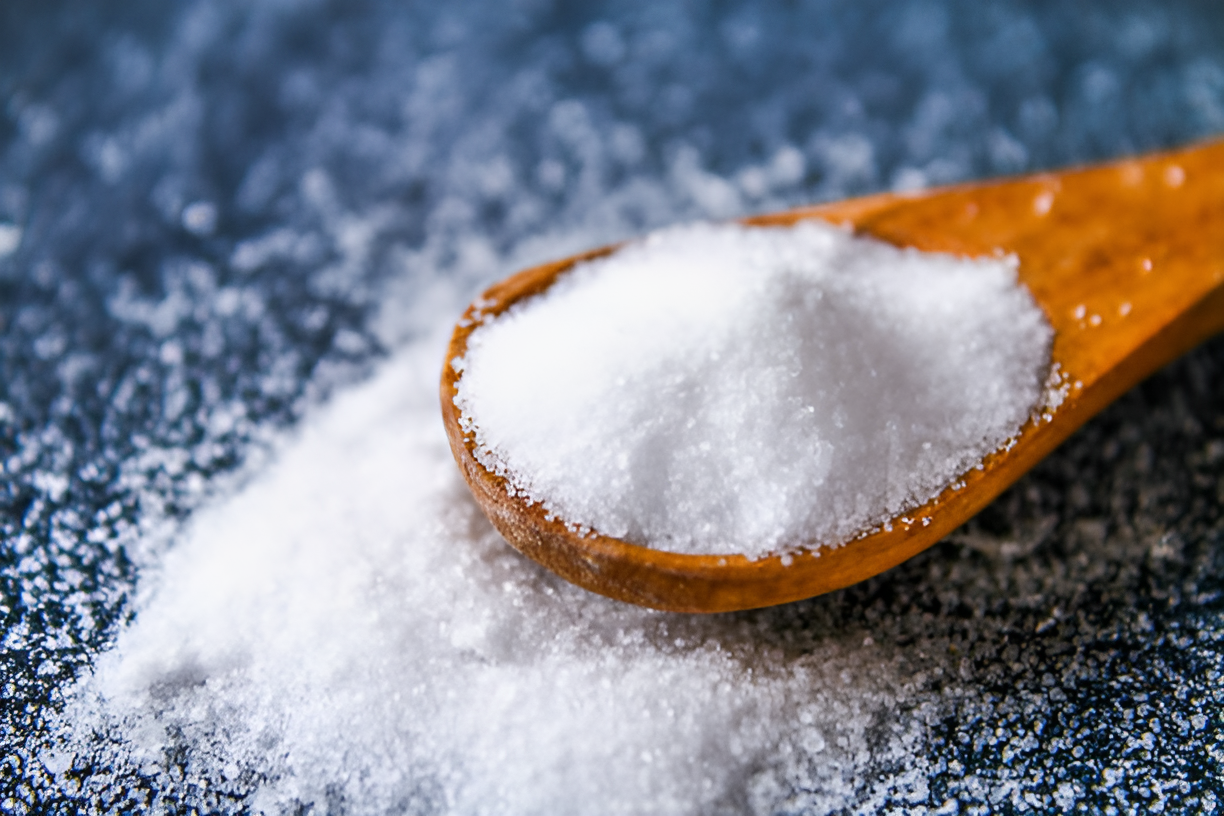
Sea salt
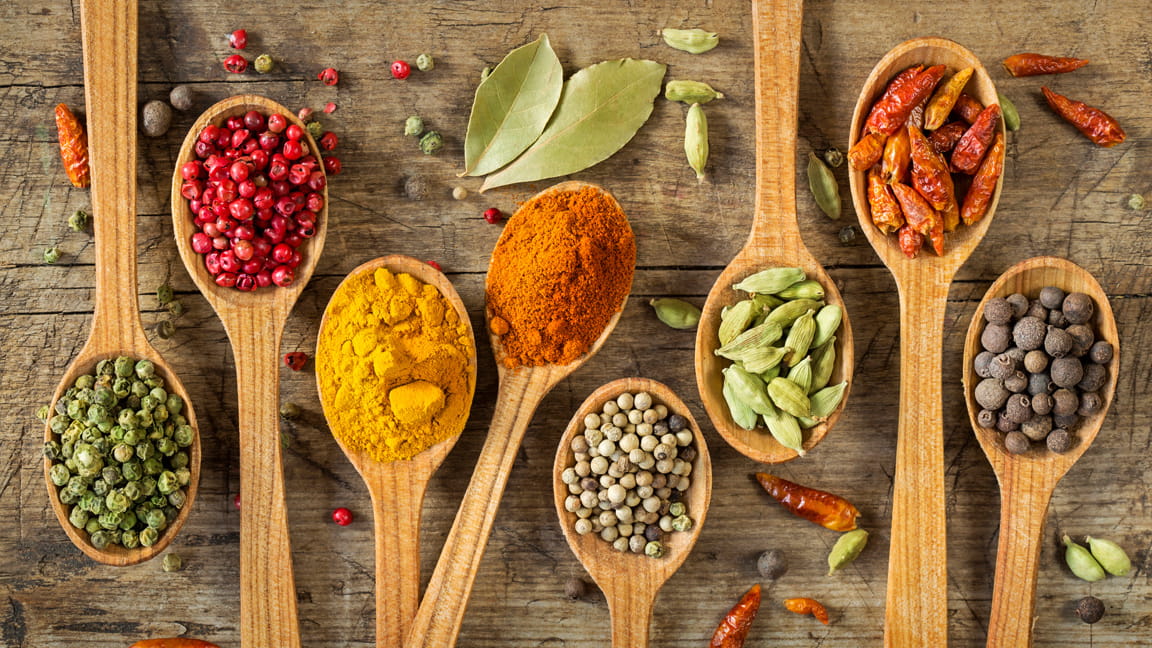
Seasonings
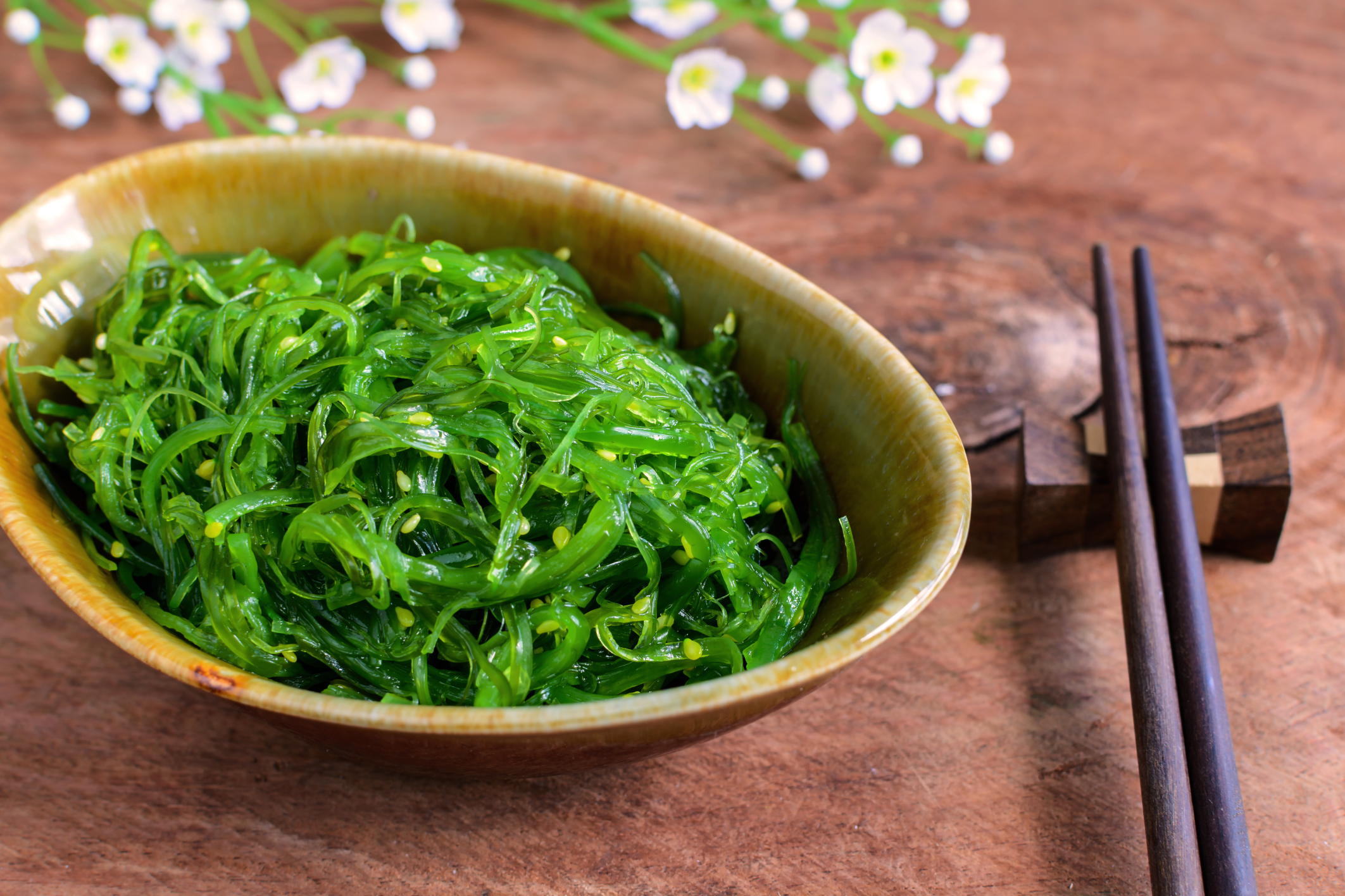
Seaweed
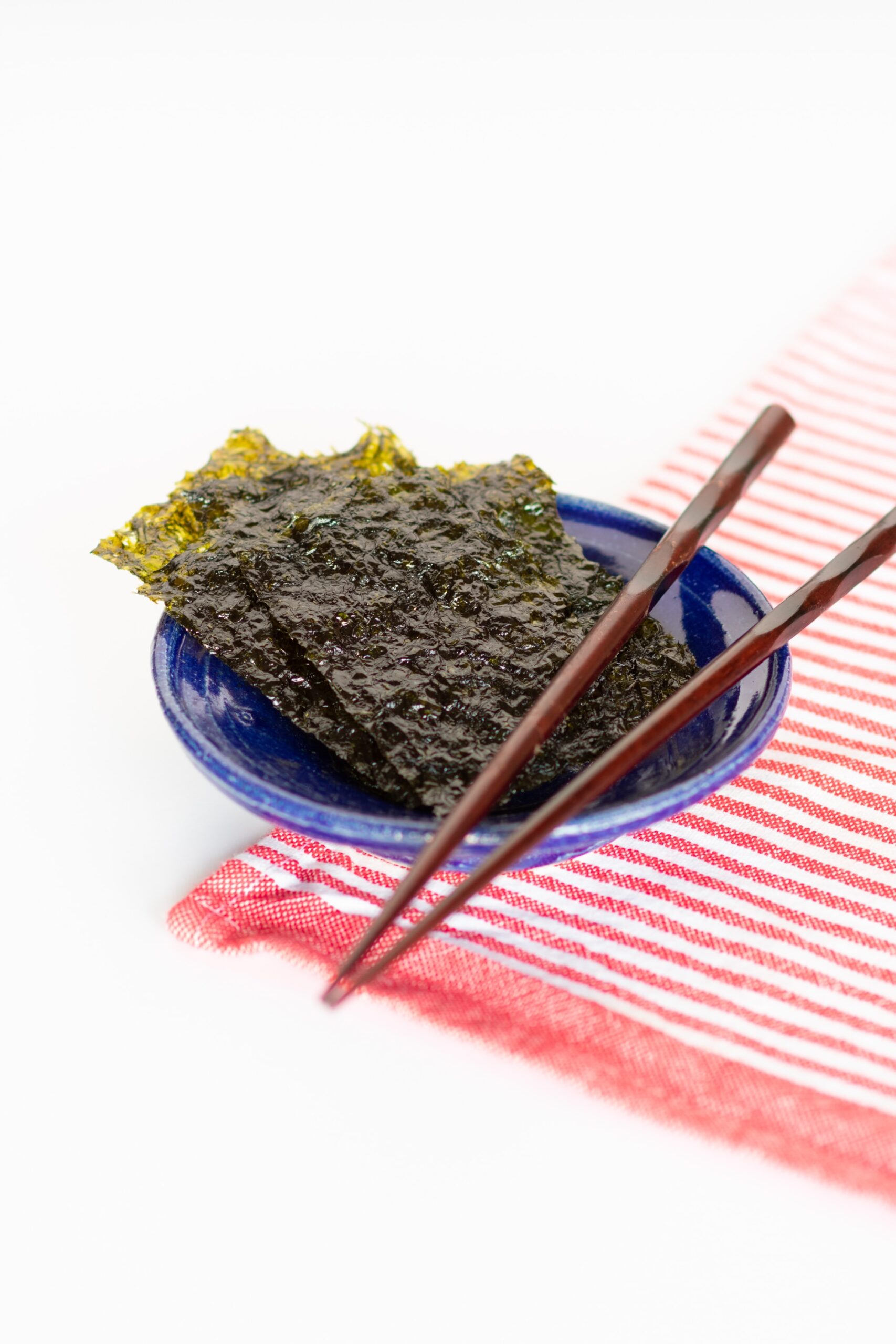
Seaweed snacks
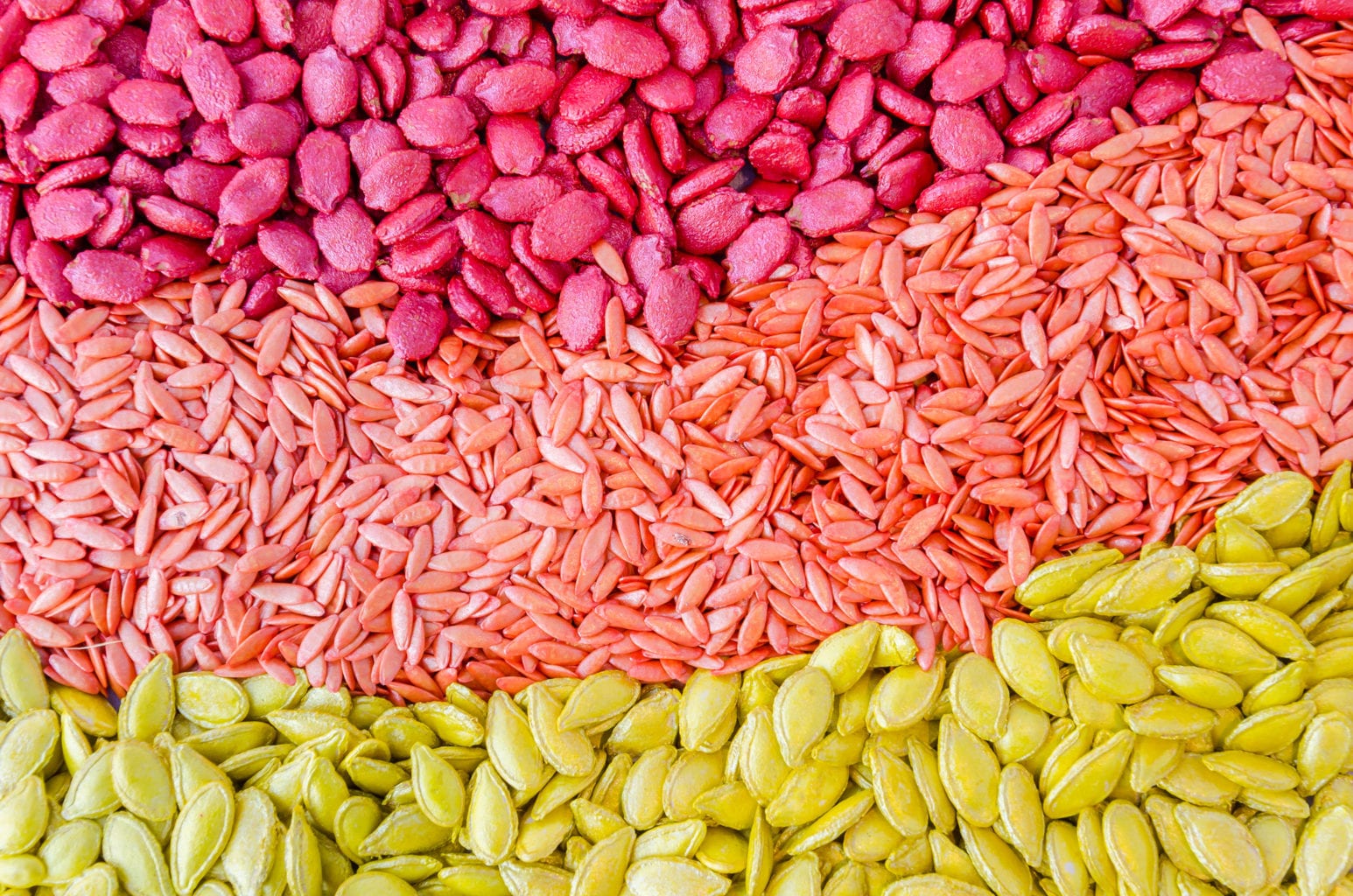
Seed coatings
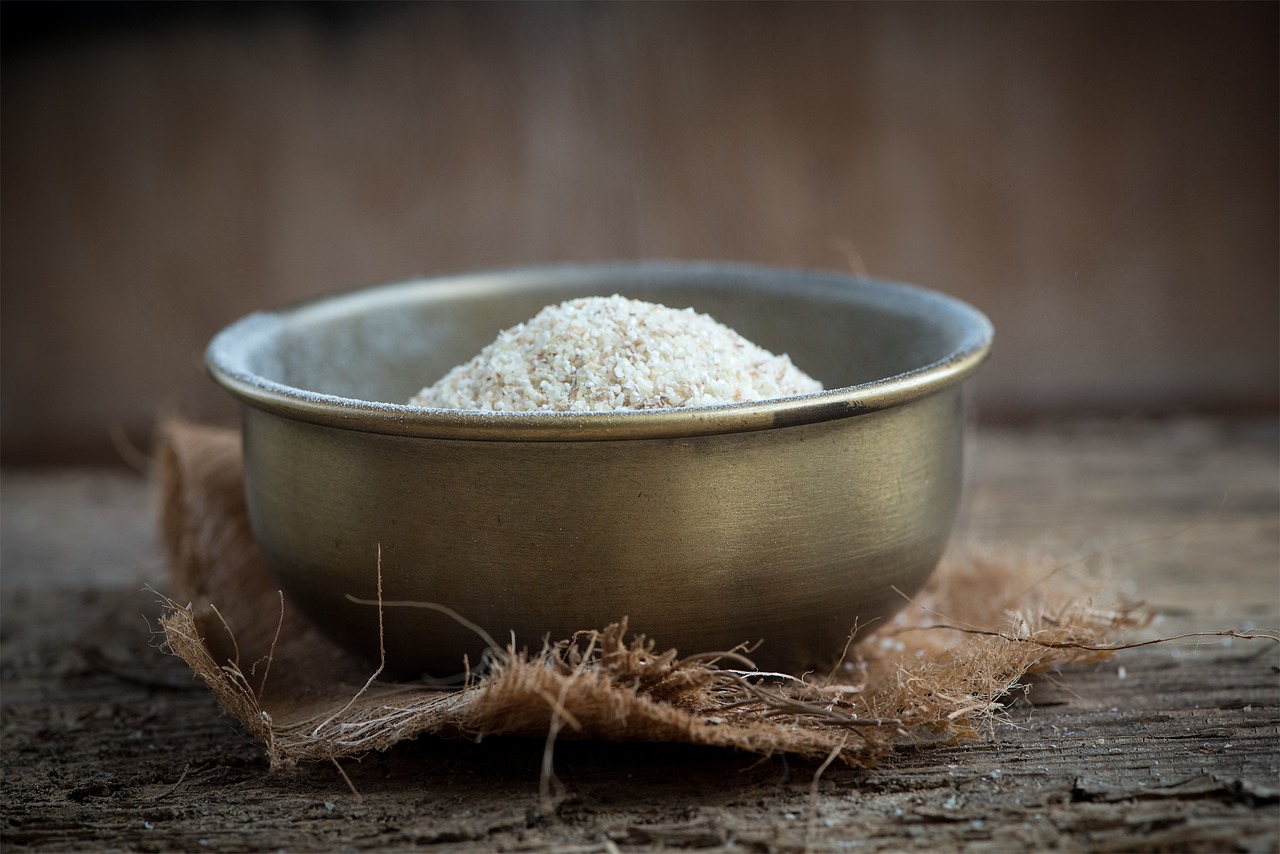
Semolina
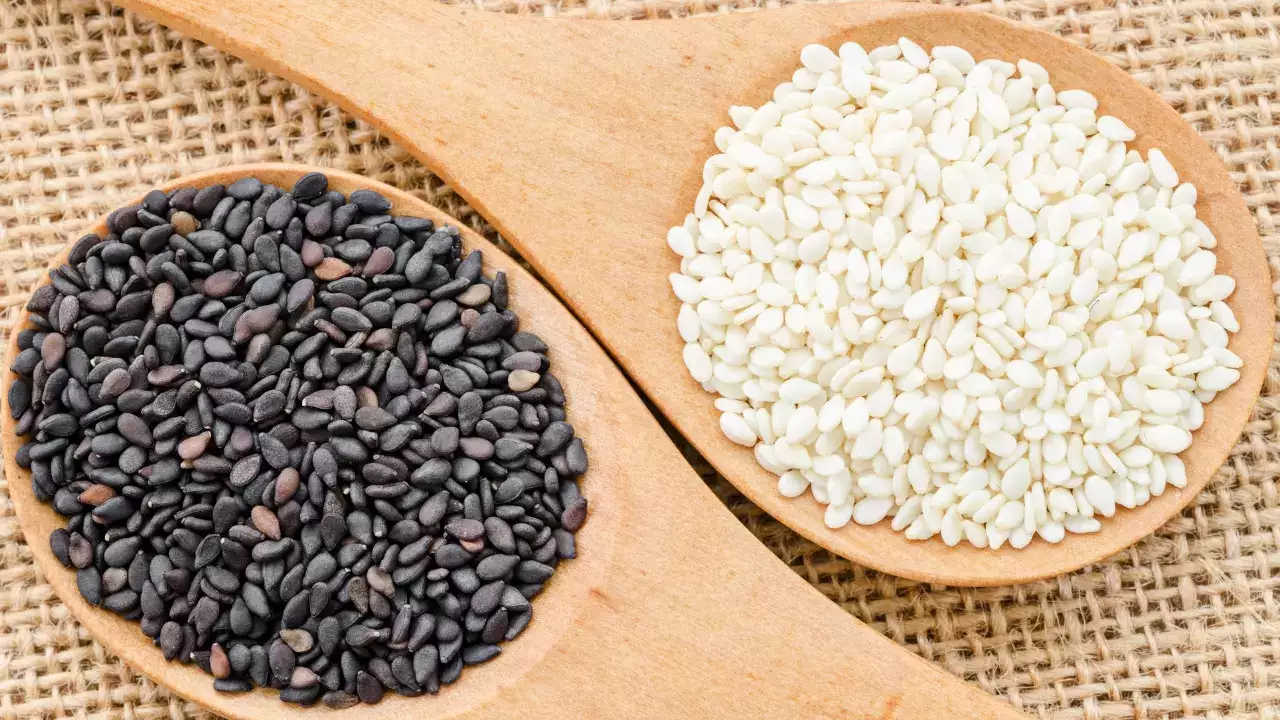
Sesame seeds
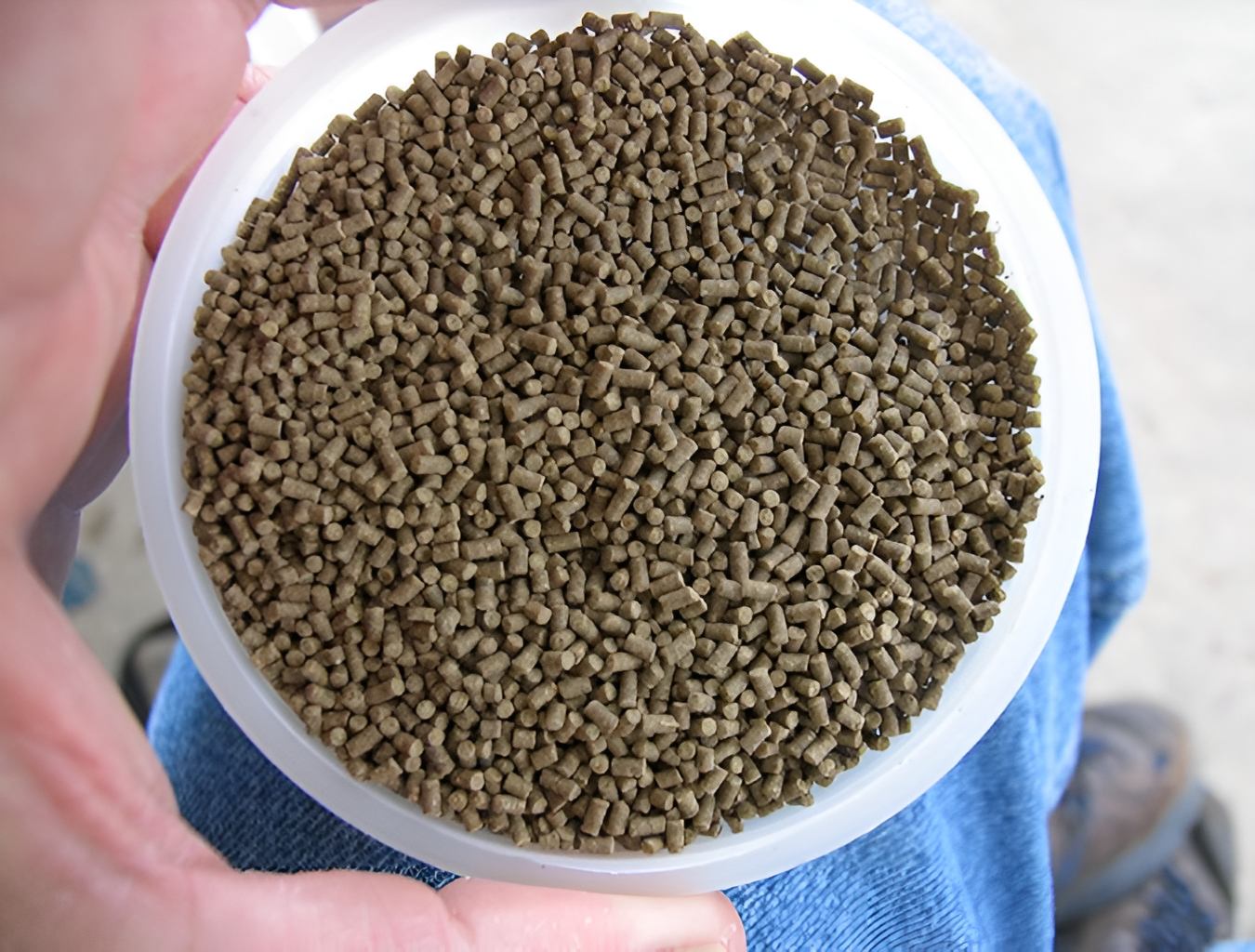
Shrimp feed
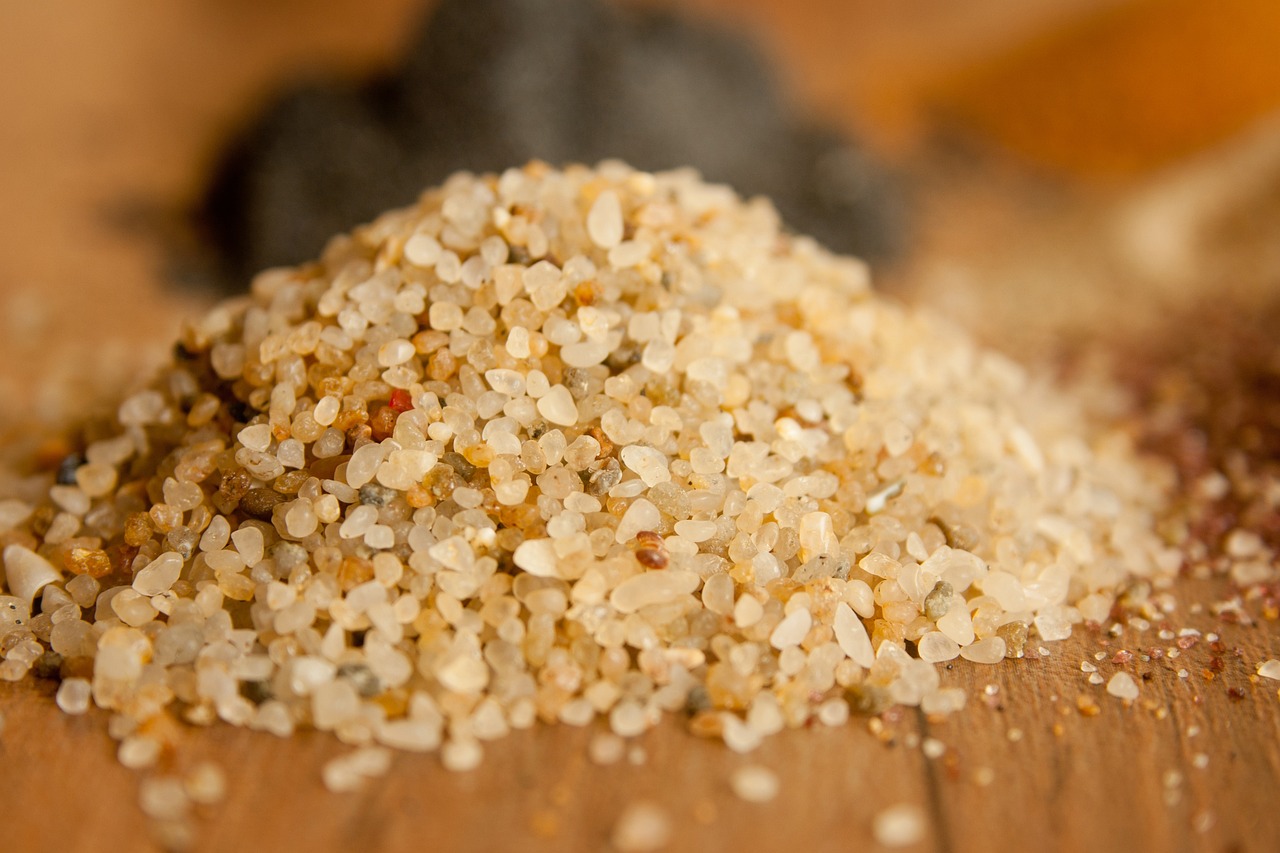
Silica
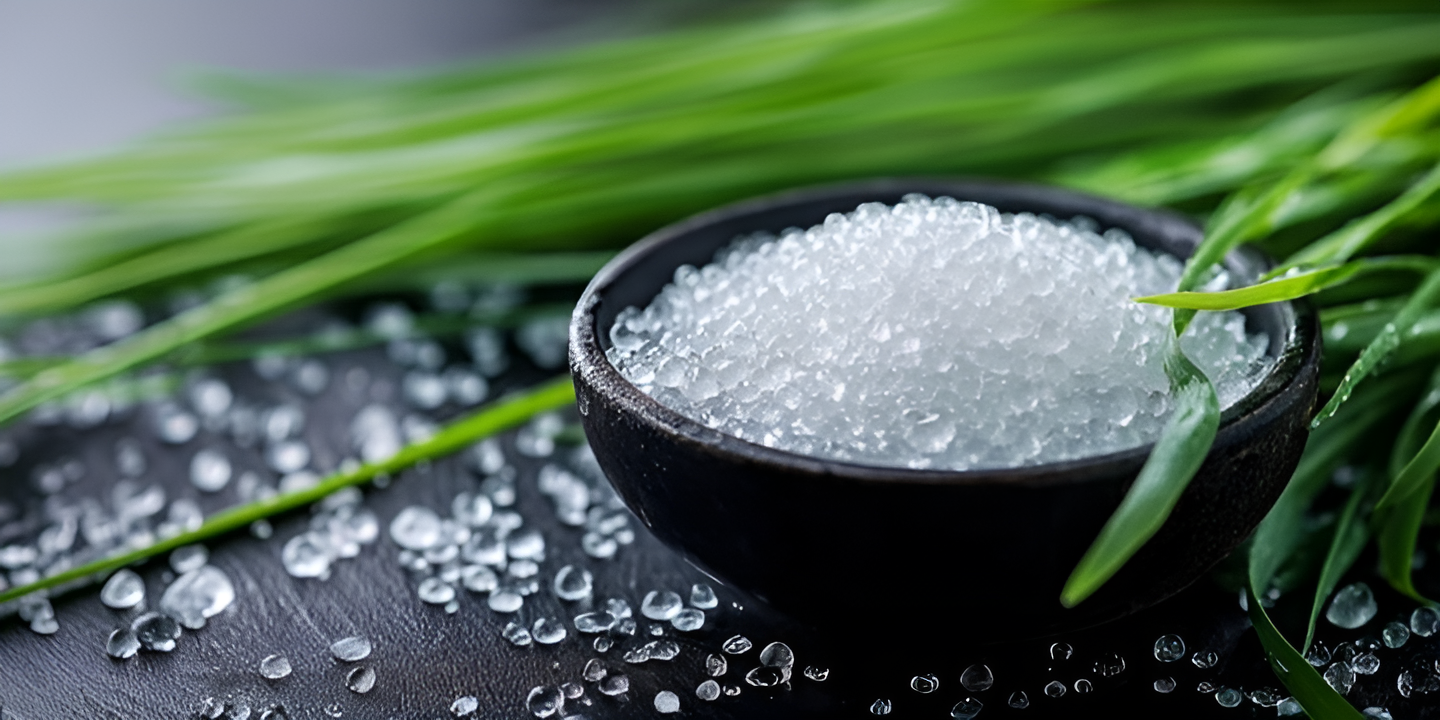
Silica gel
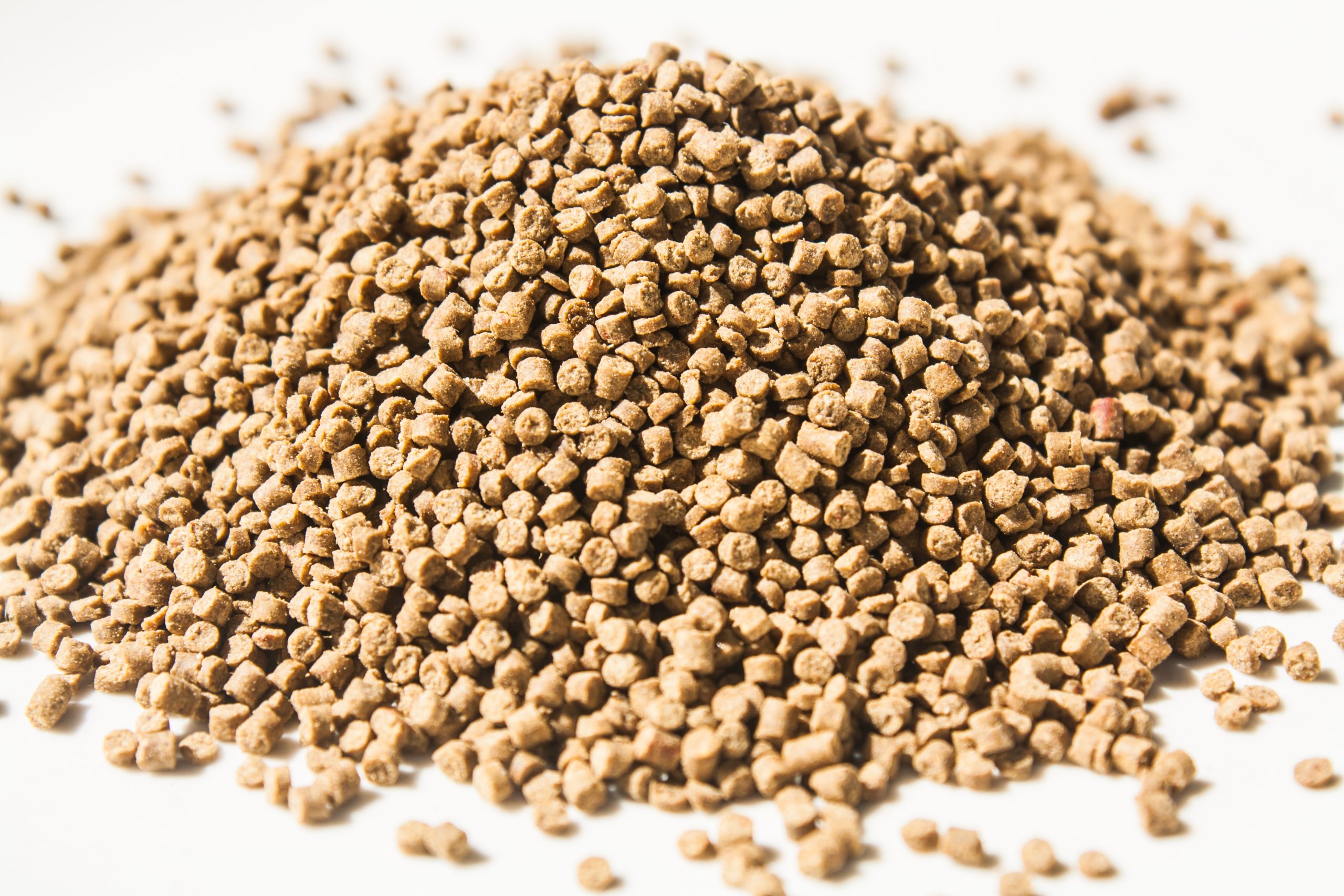
Sinking pellets
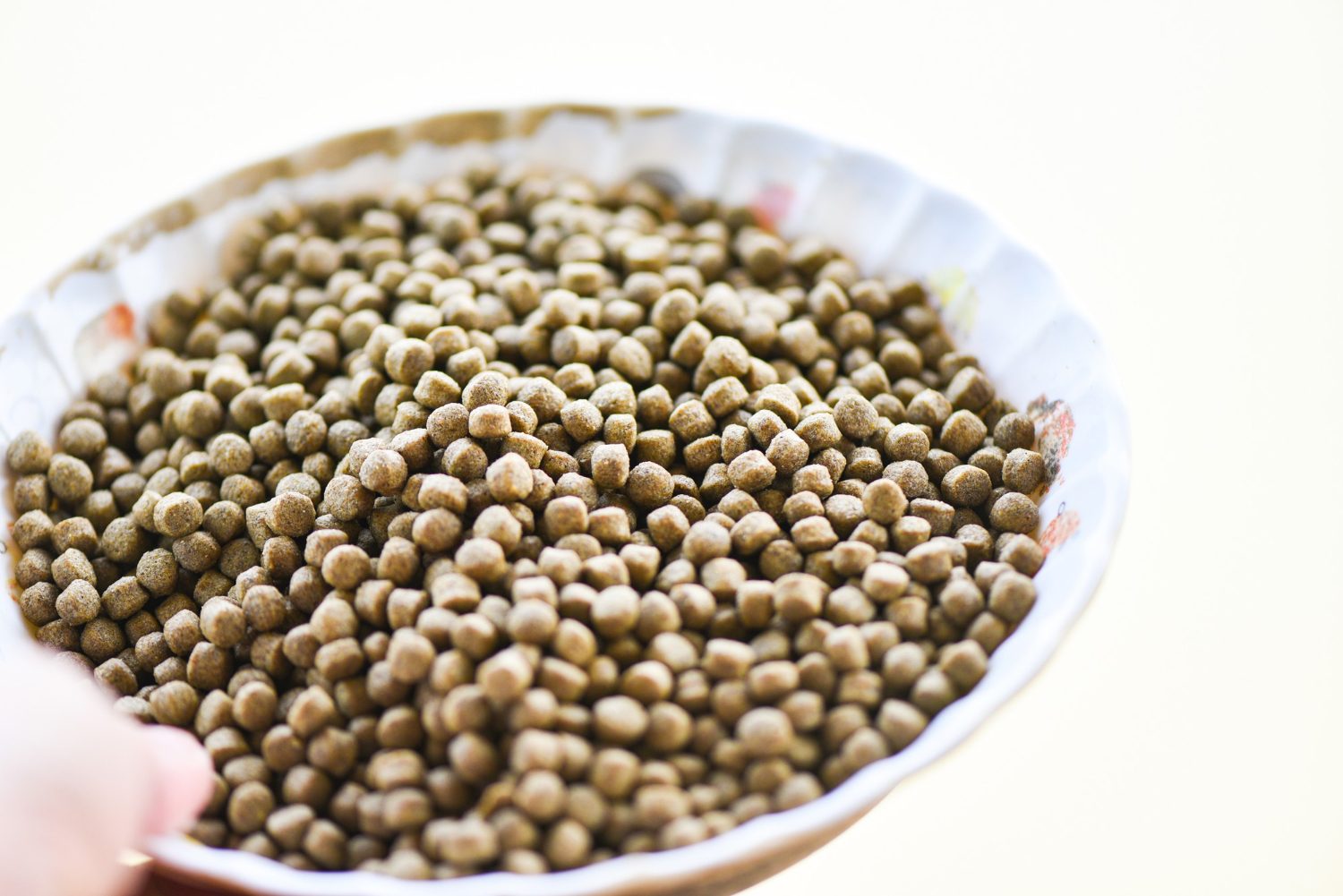
Slow sinking pellets
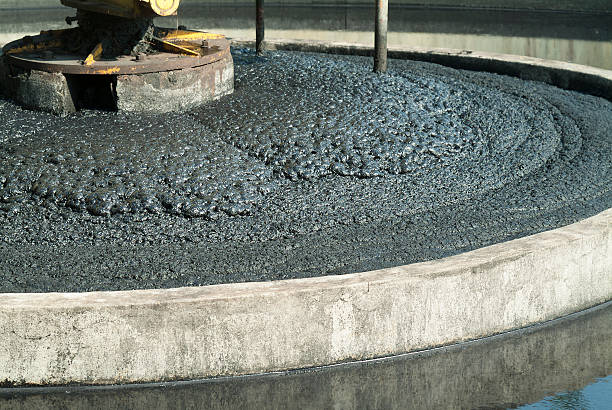
Sludge
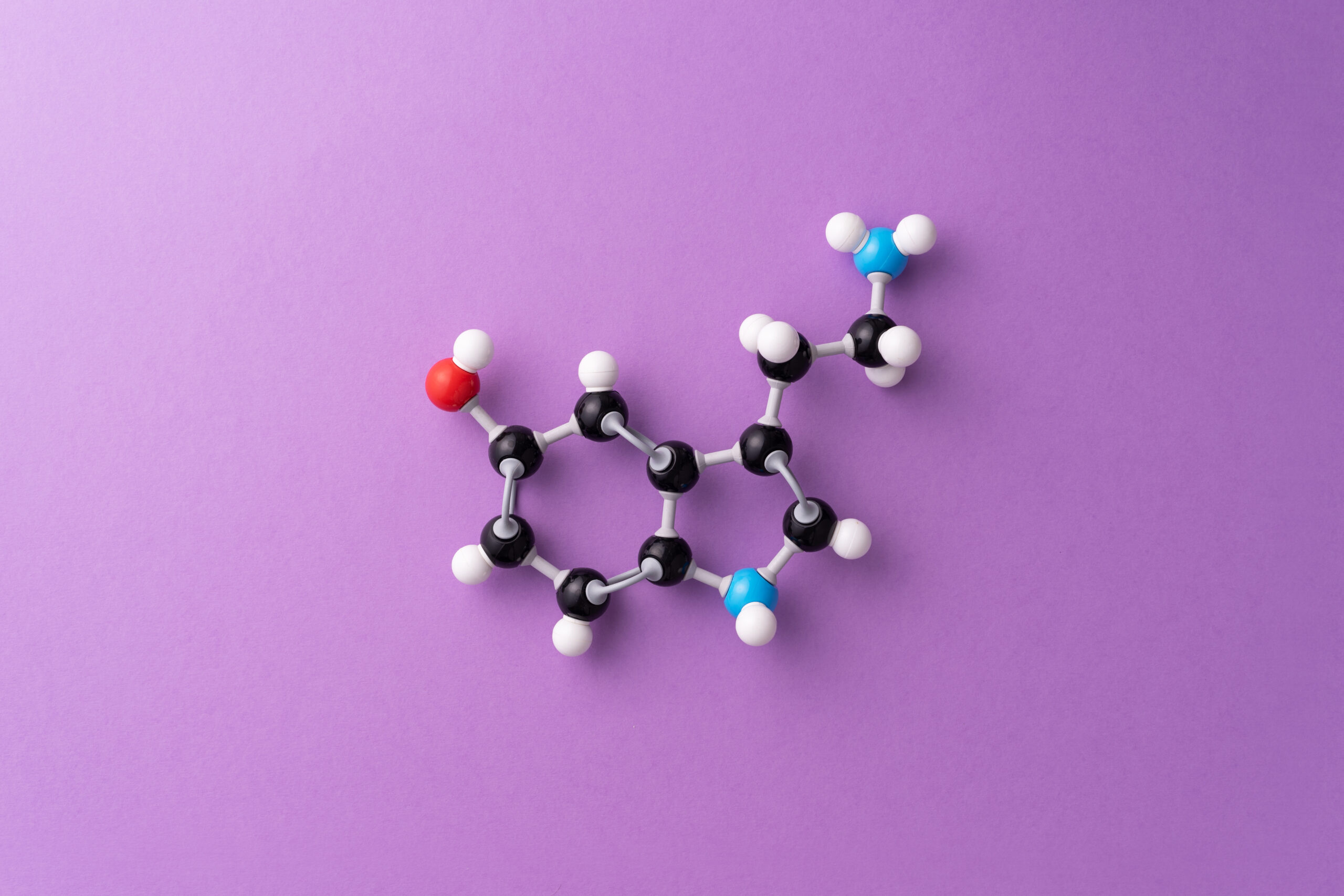
Small molecule drugs
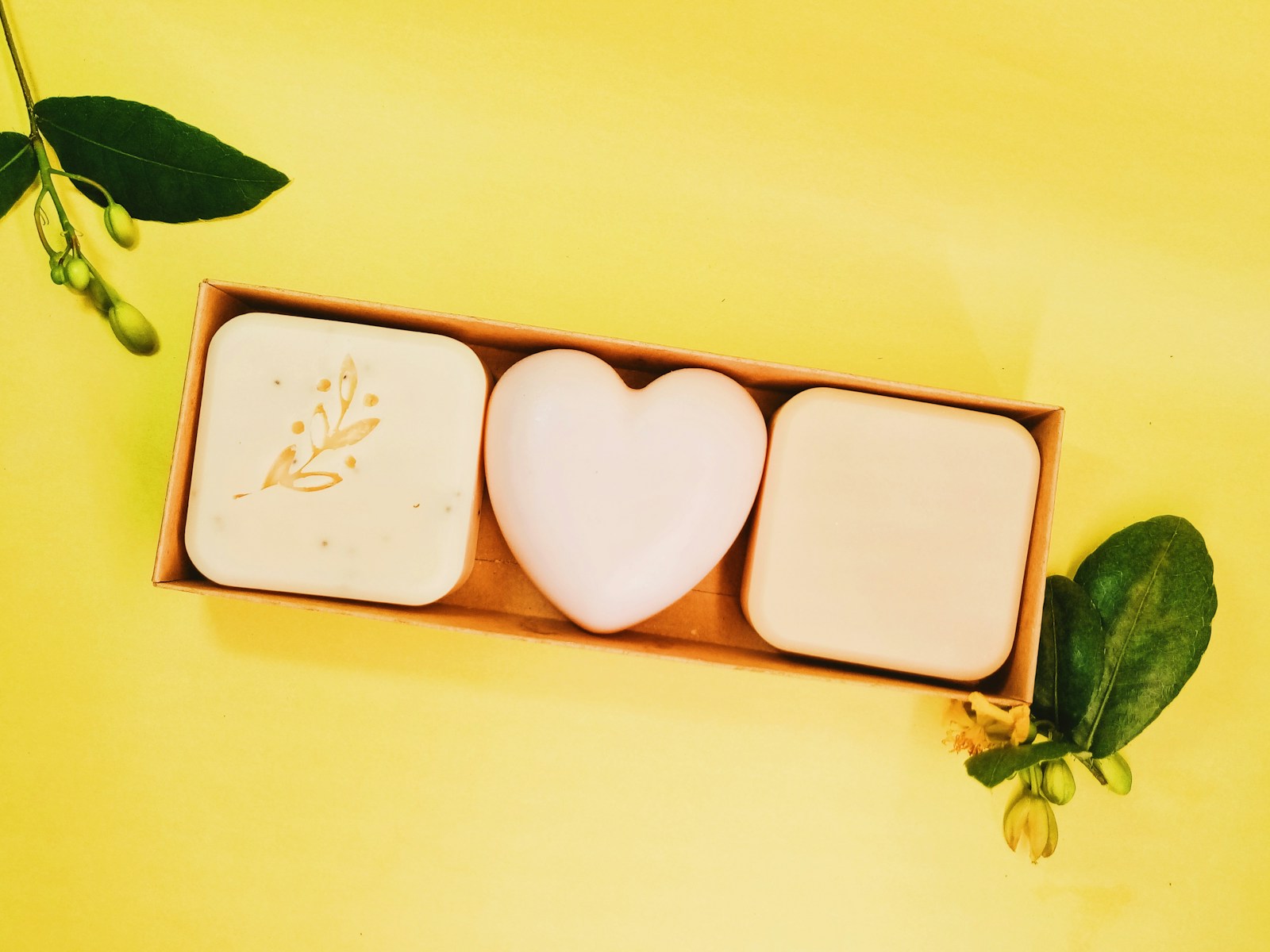
Soap
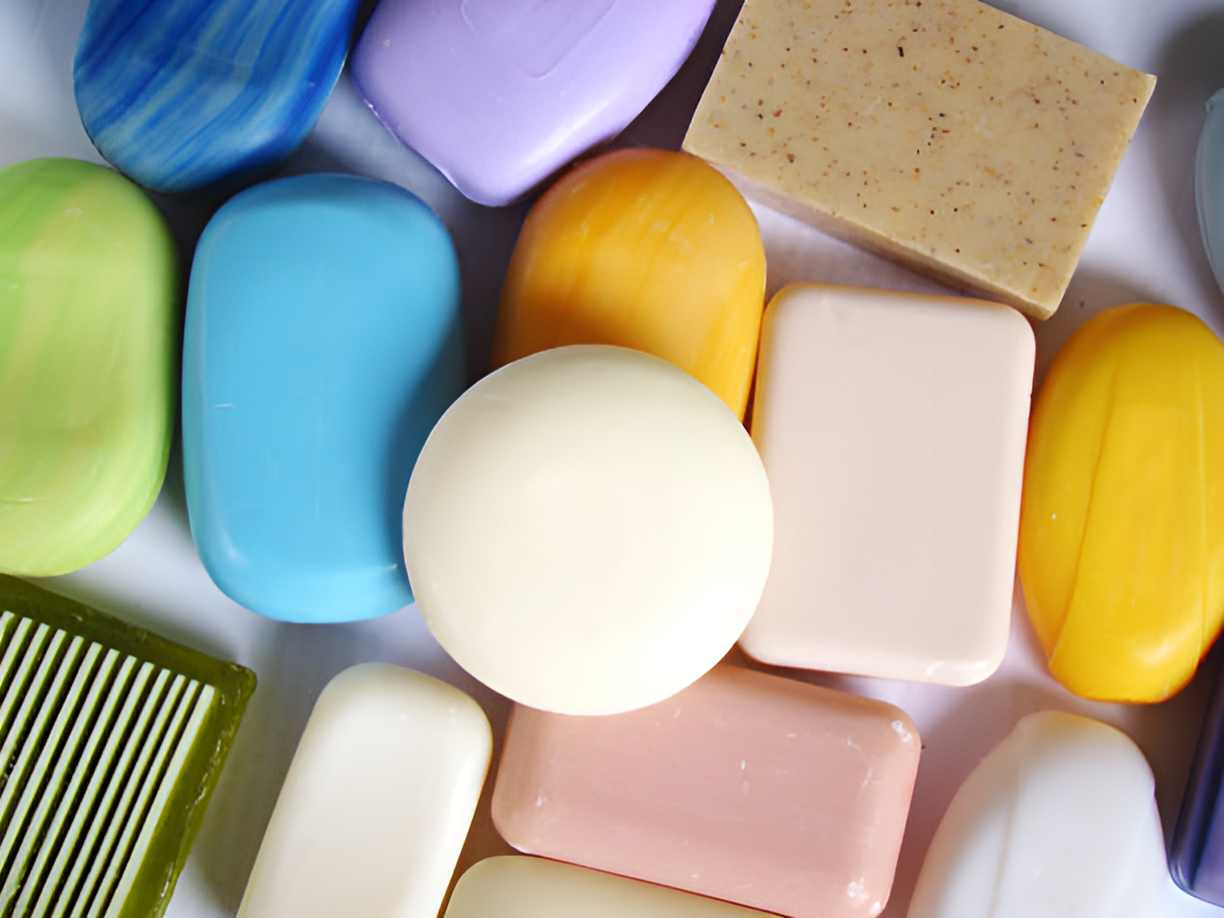
Soap bars
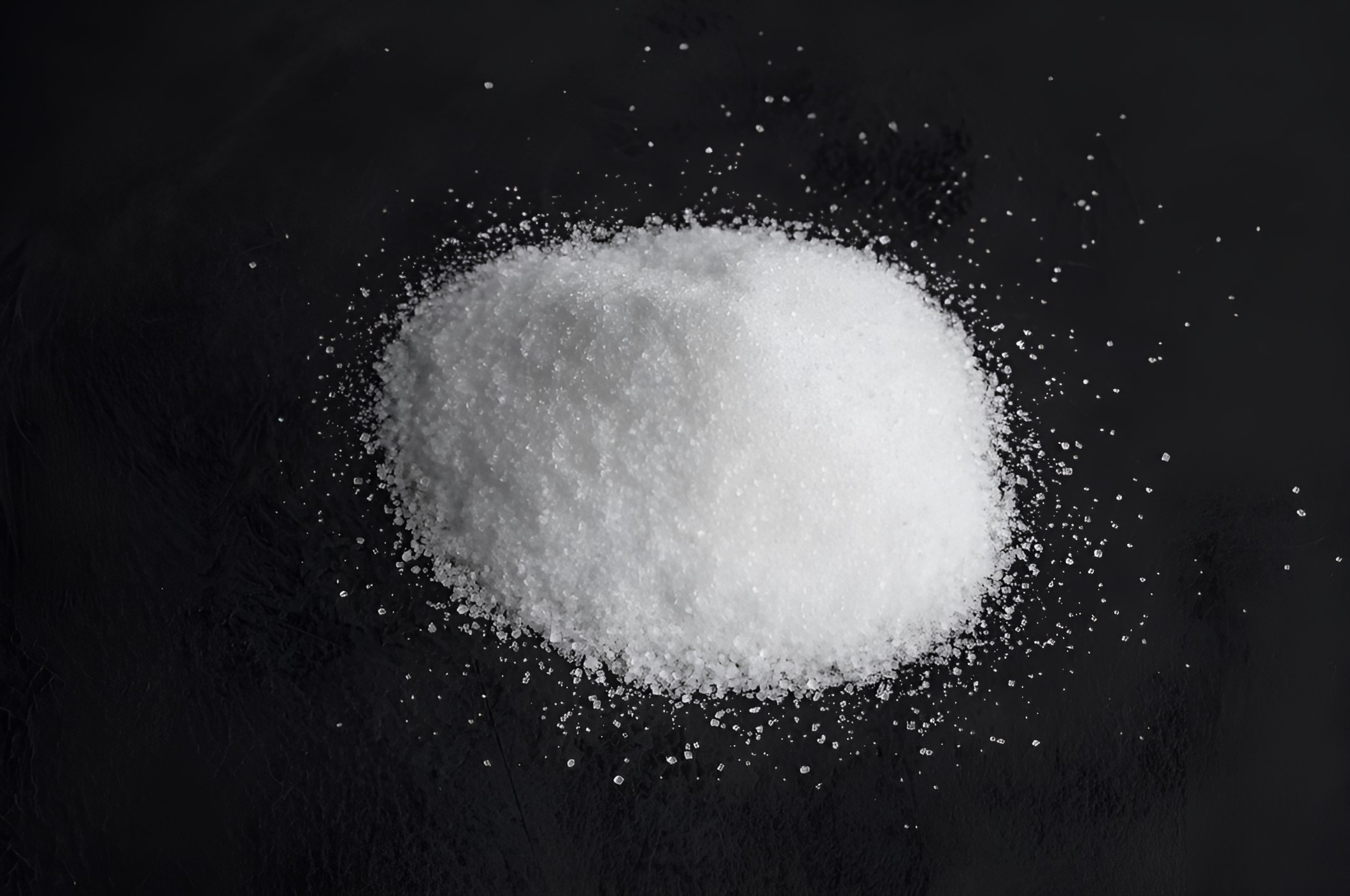
Sodium carbonate

Sodium chloride
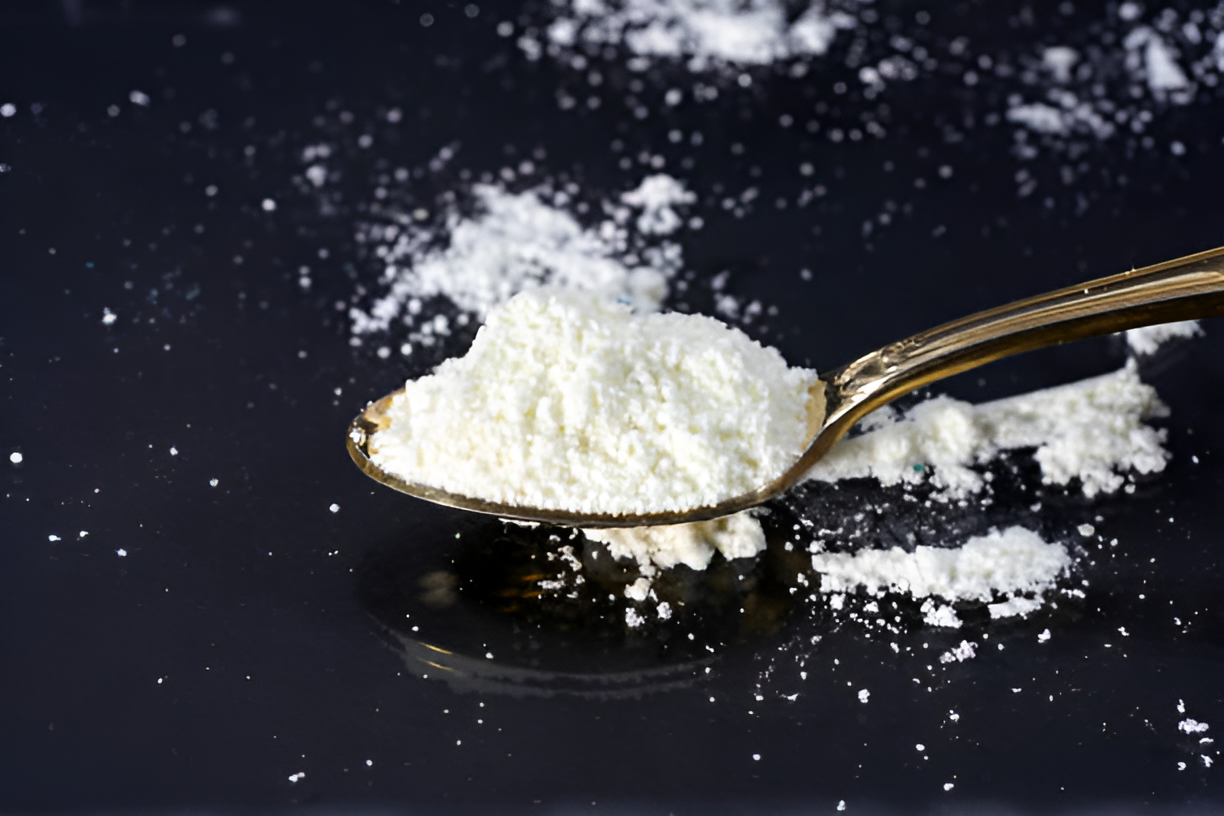
Sodium sulfate
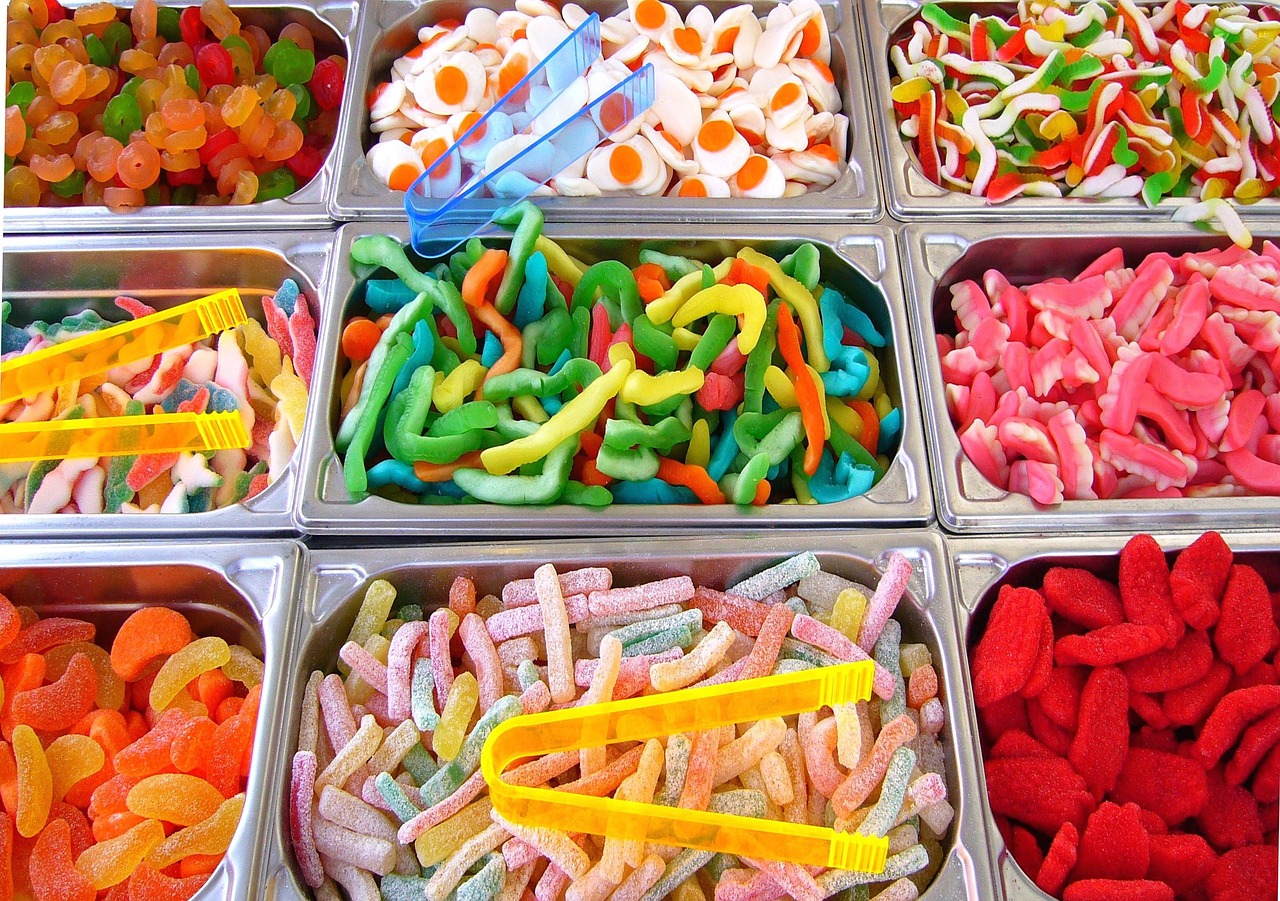
Soft Candy
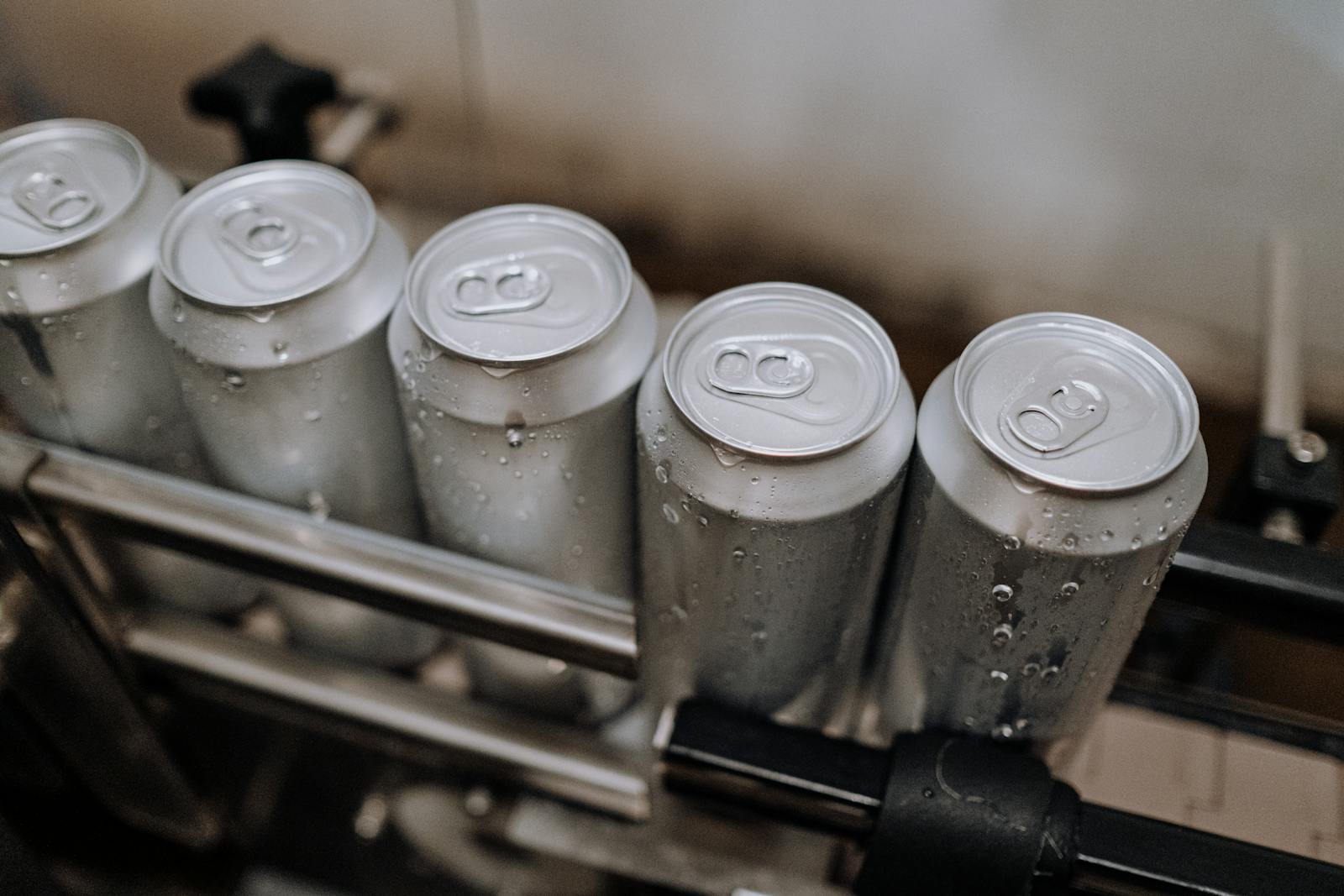
Soft drink cans
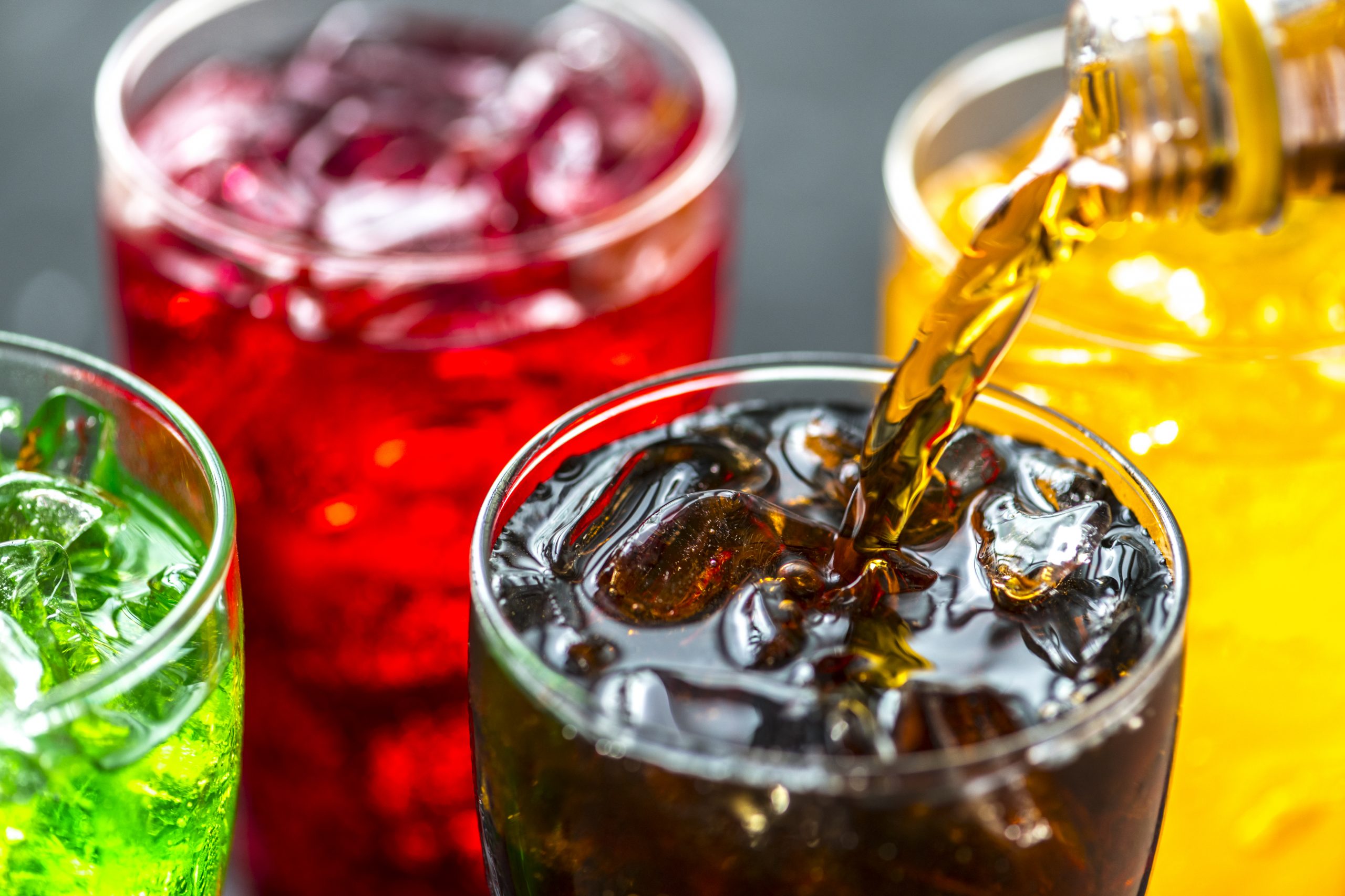
Soft drinks
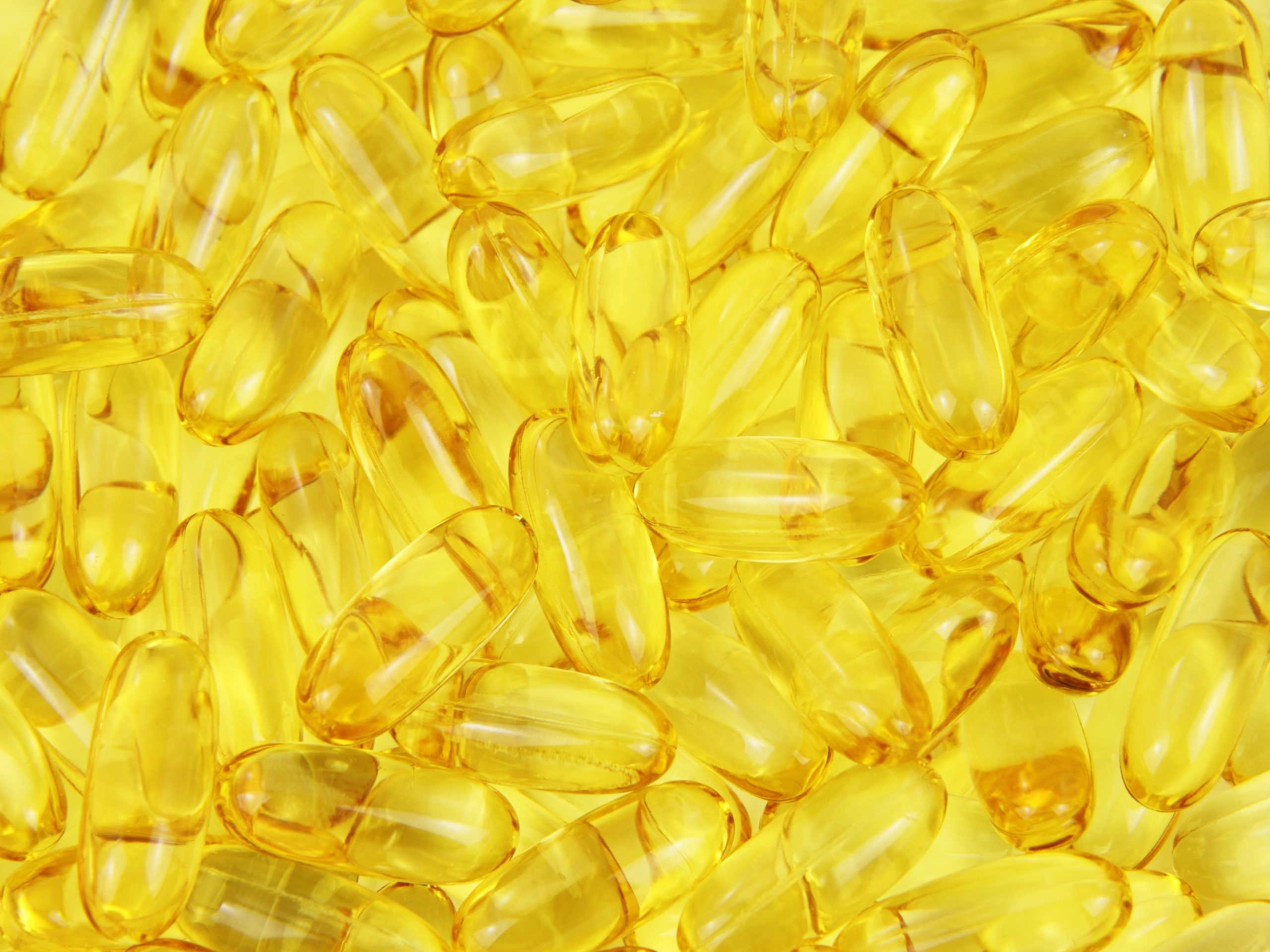
Softgel capsules
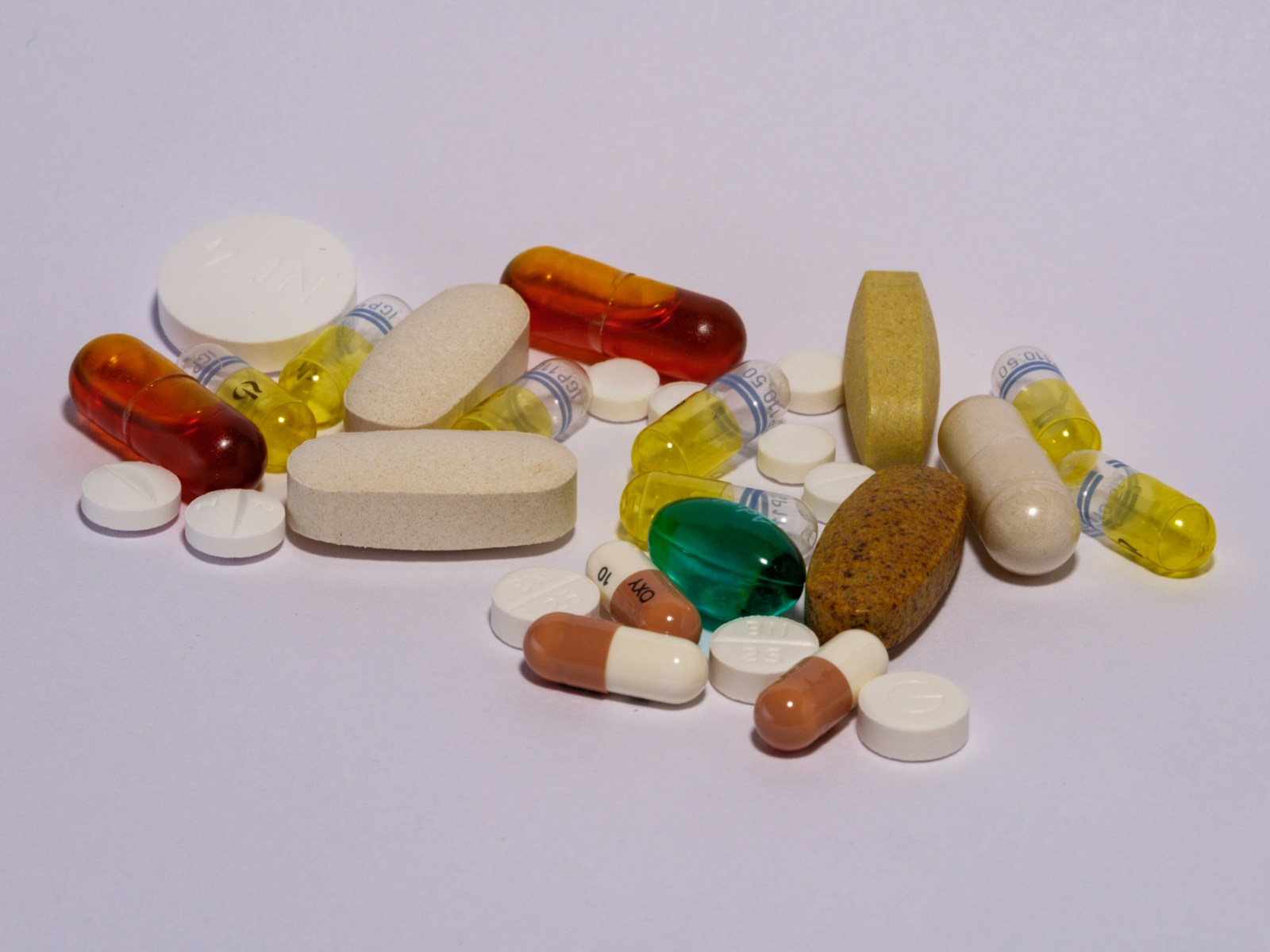
Solid dosage forms
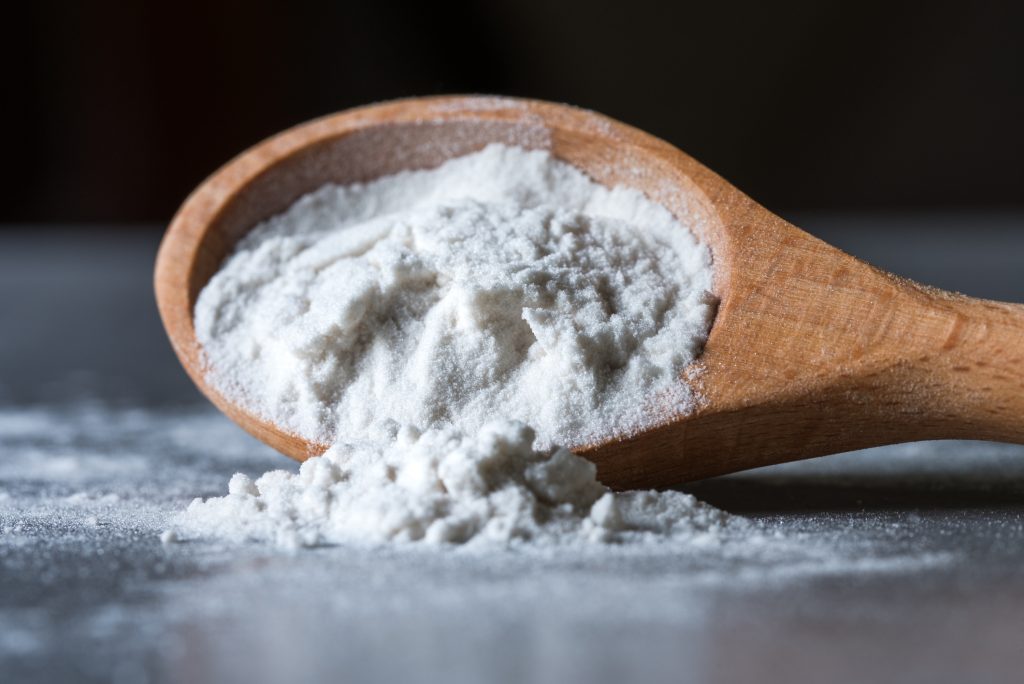
Solids
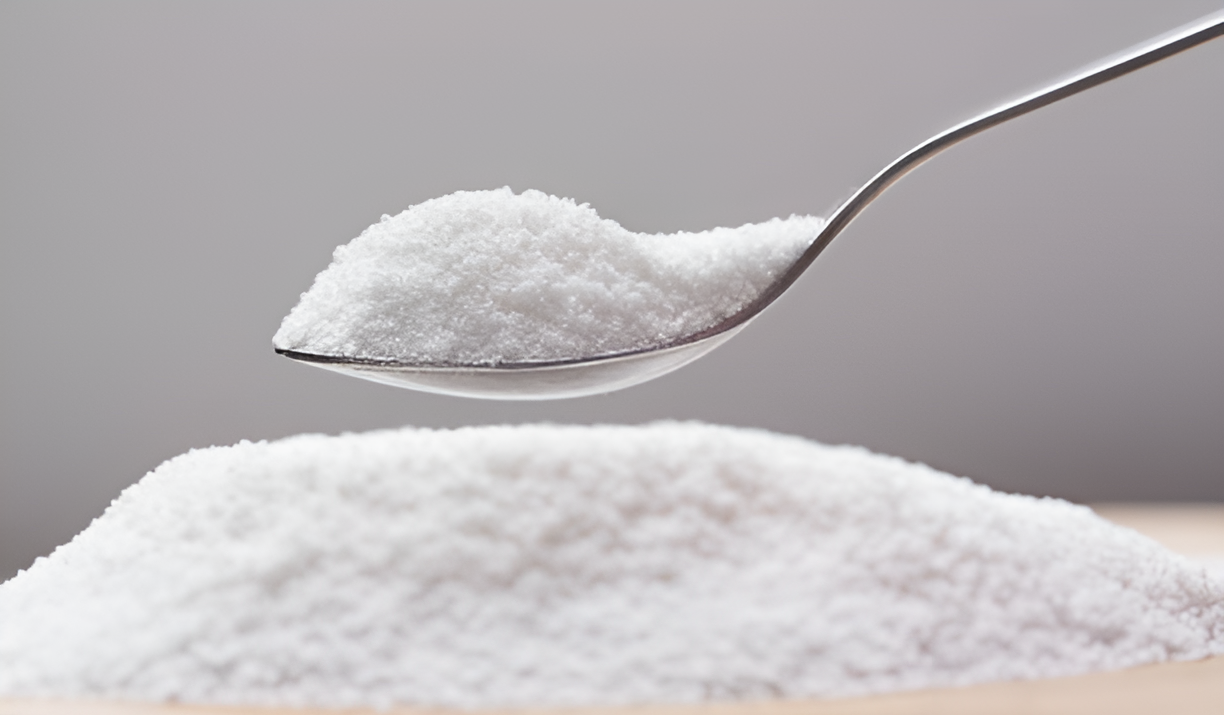
Sorbitol
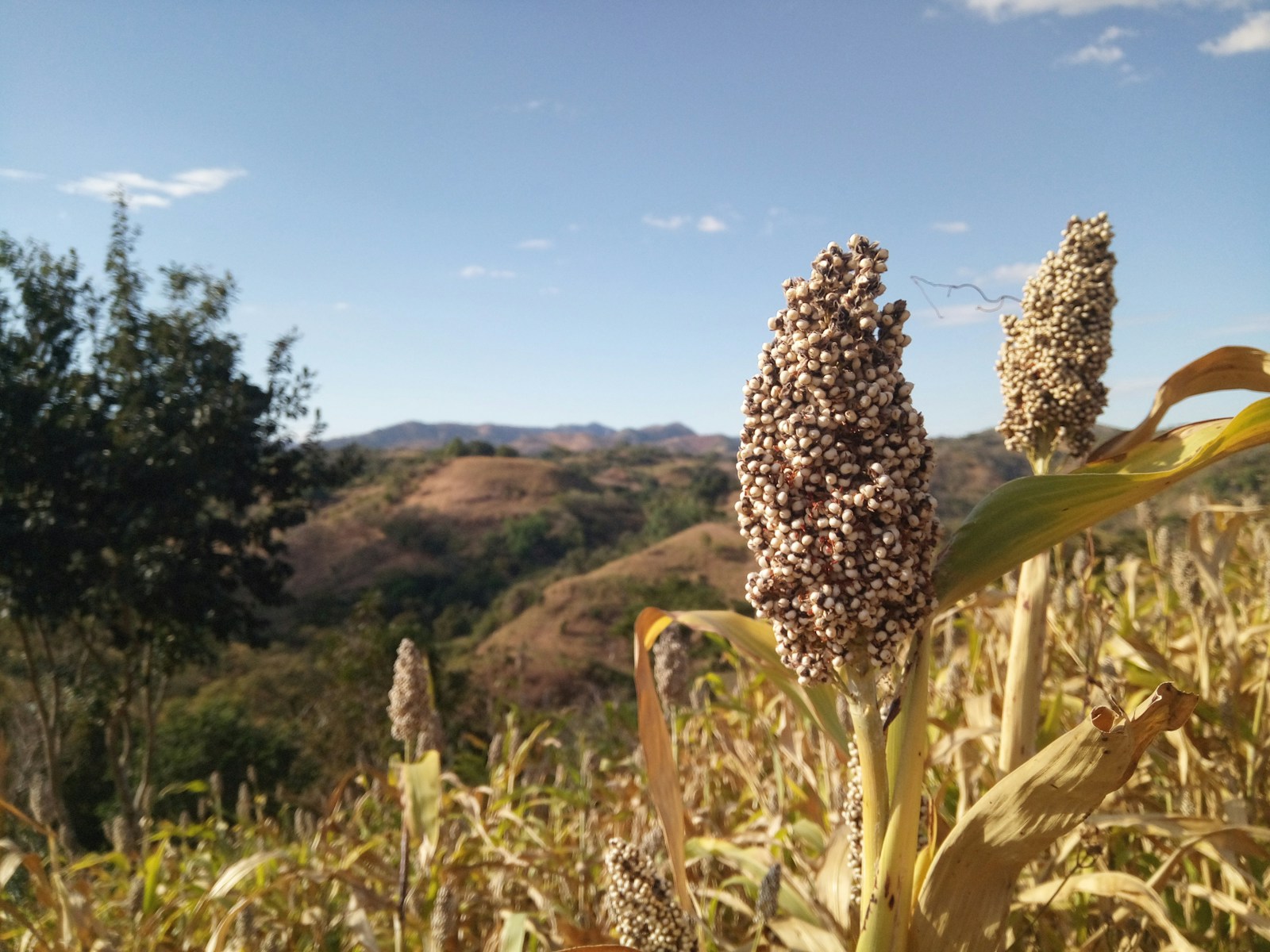
Sorghum
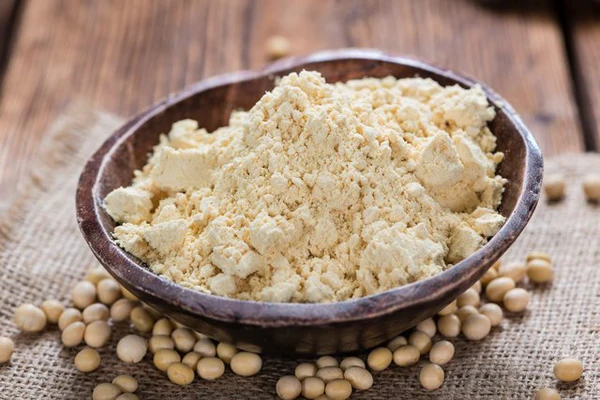
Soy flour
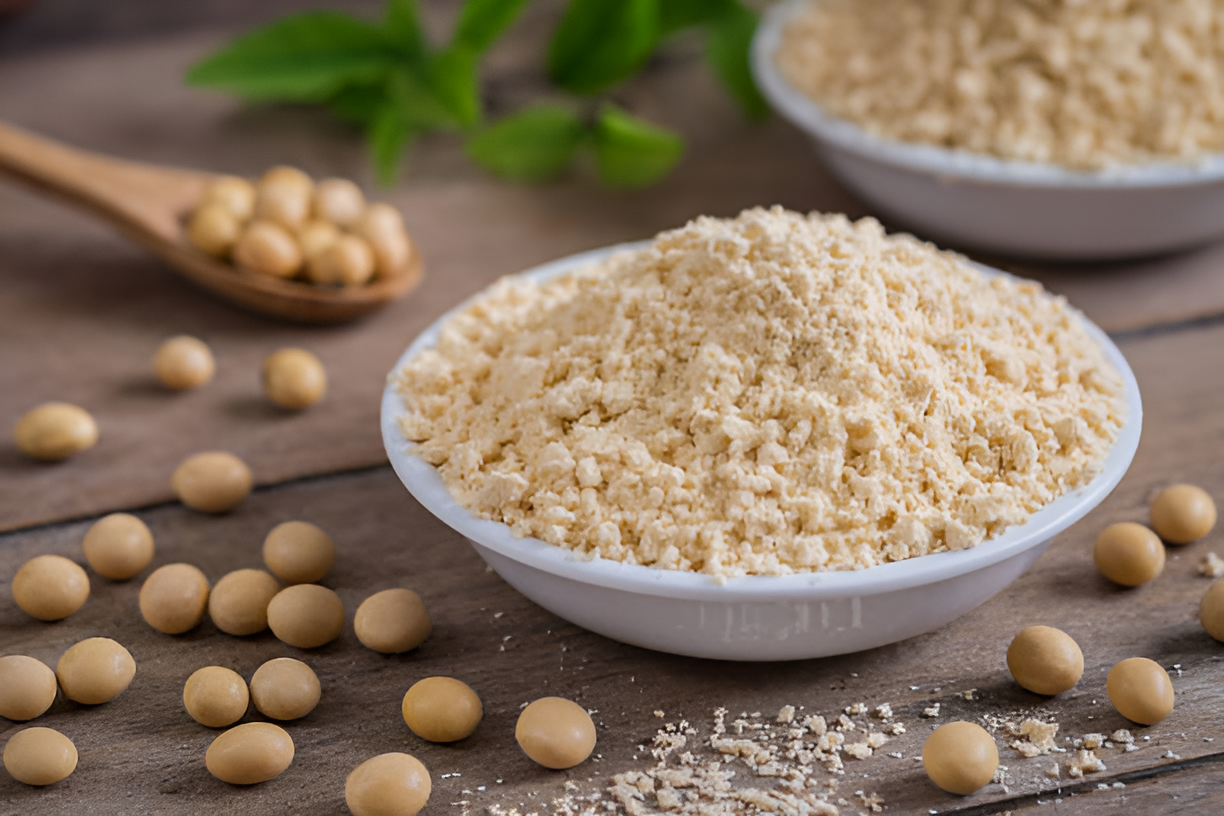
Soy protein isolate
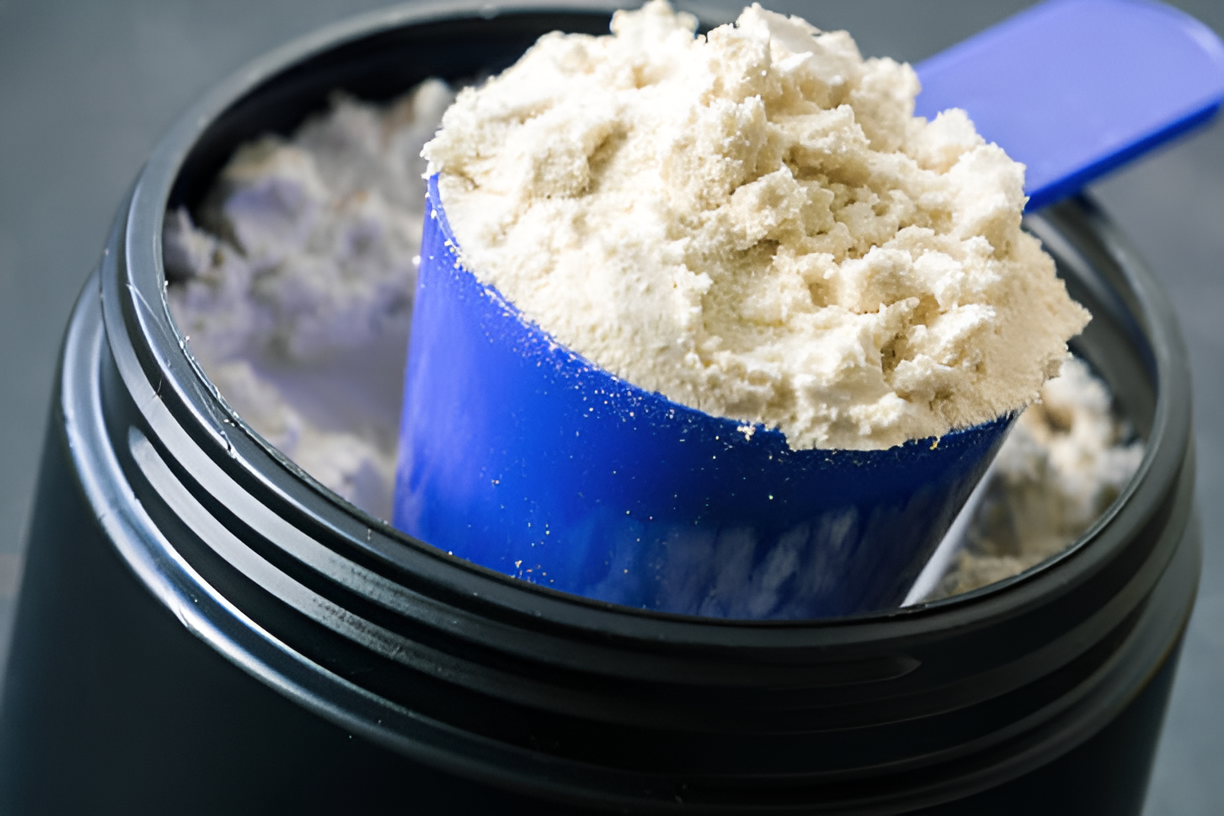
Soy protein powder
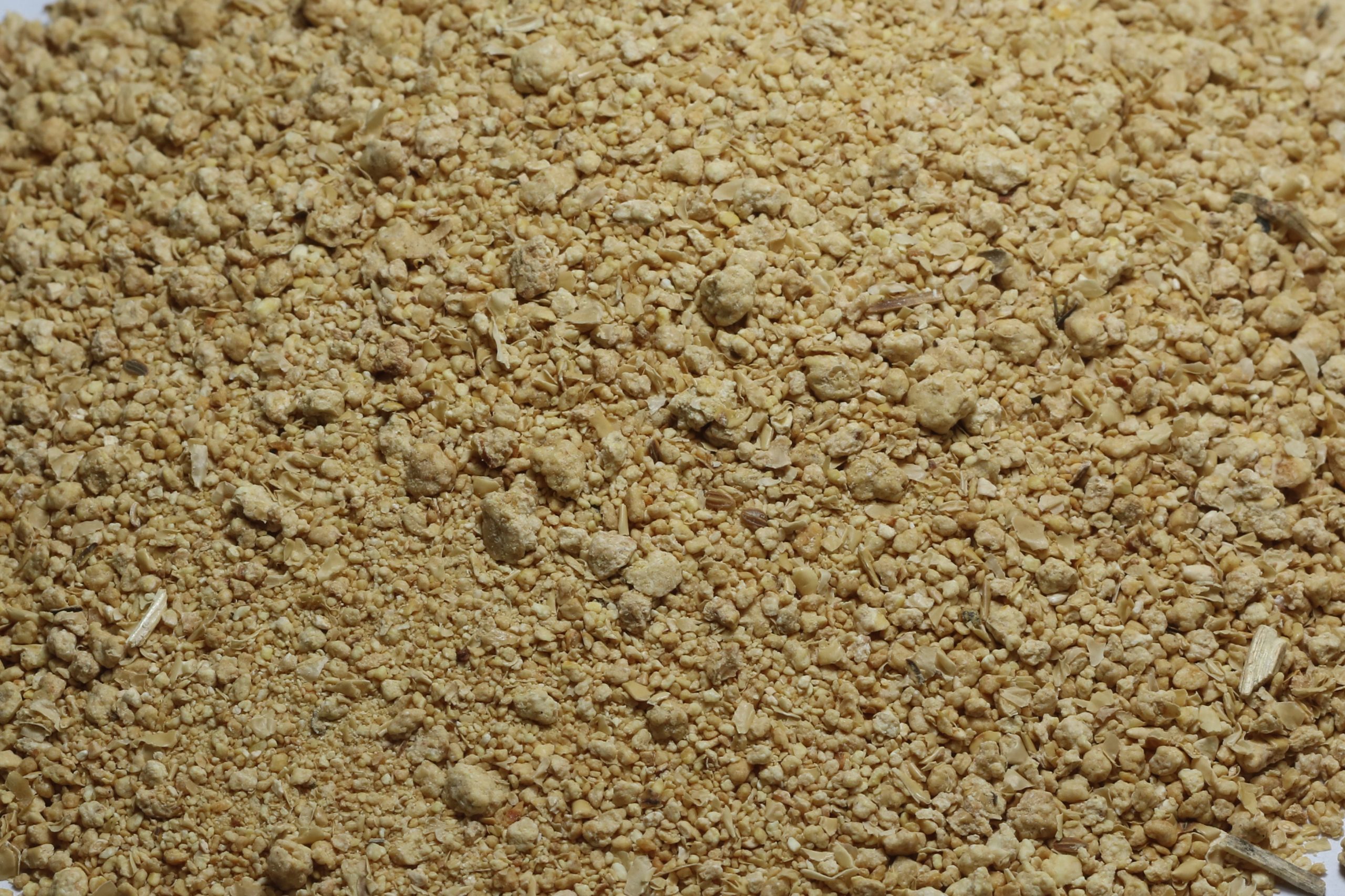
Soybean meal

Soybeans
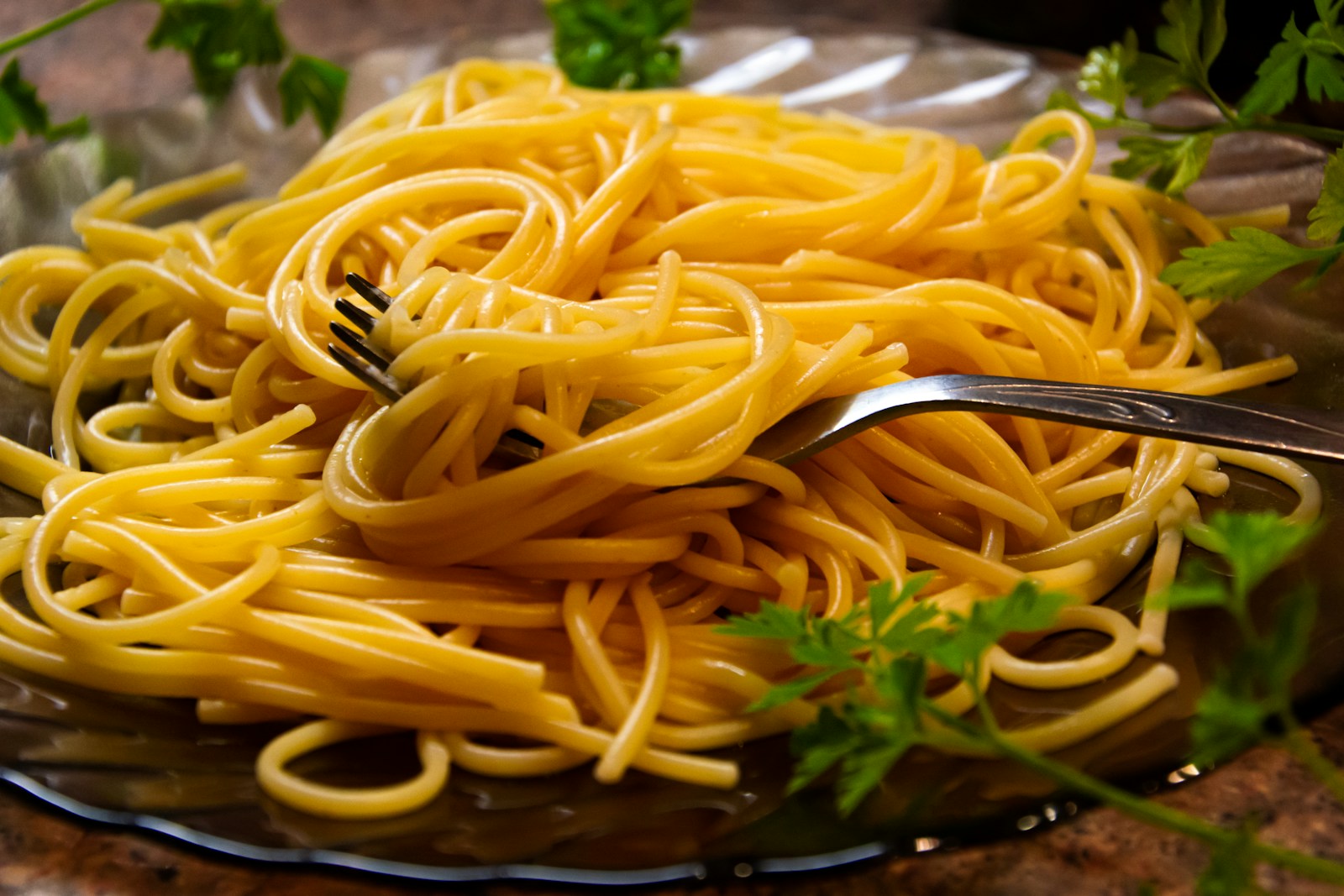
Spaghetti
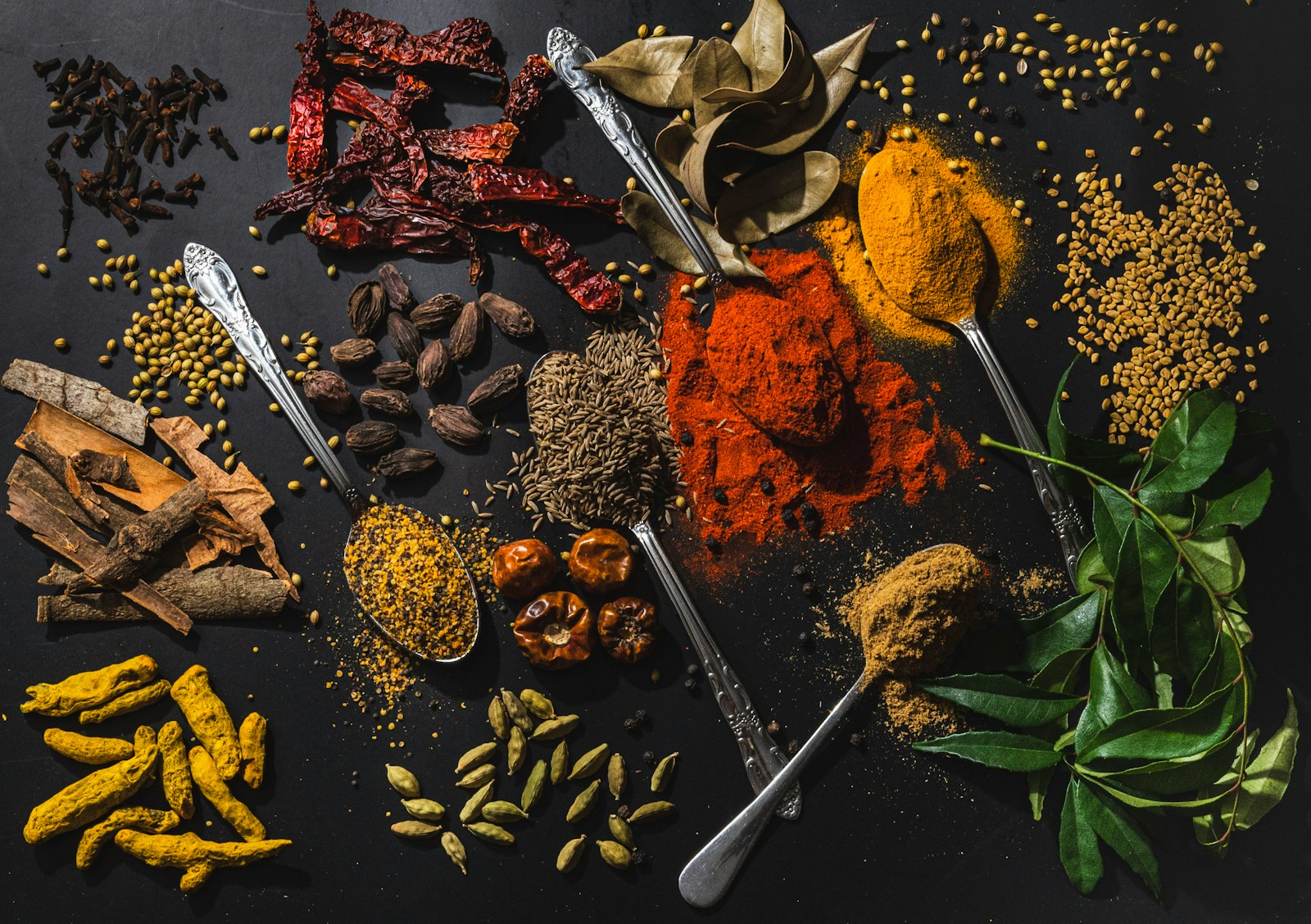
Spice blends
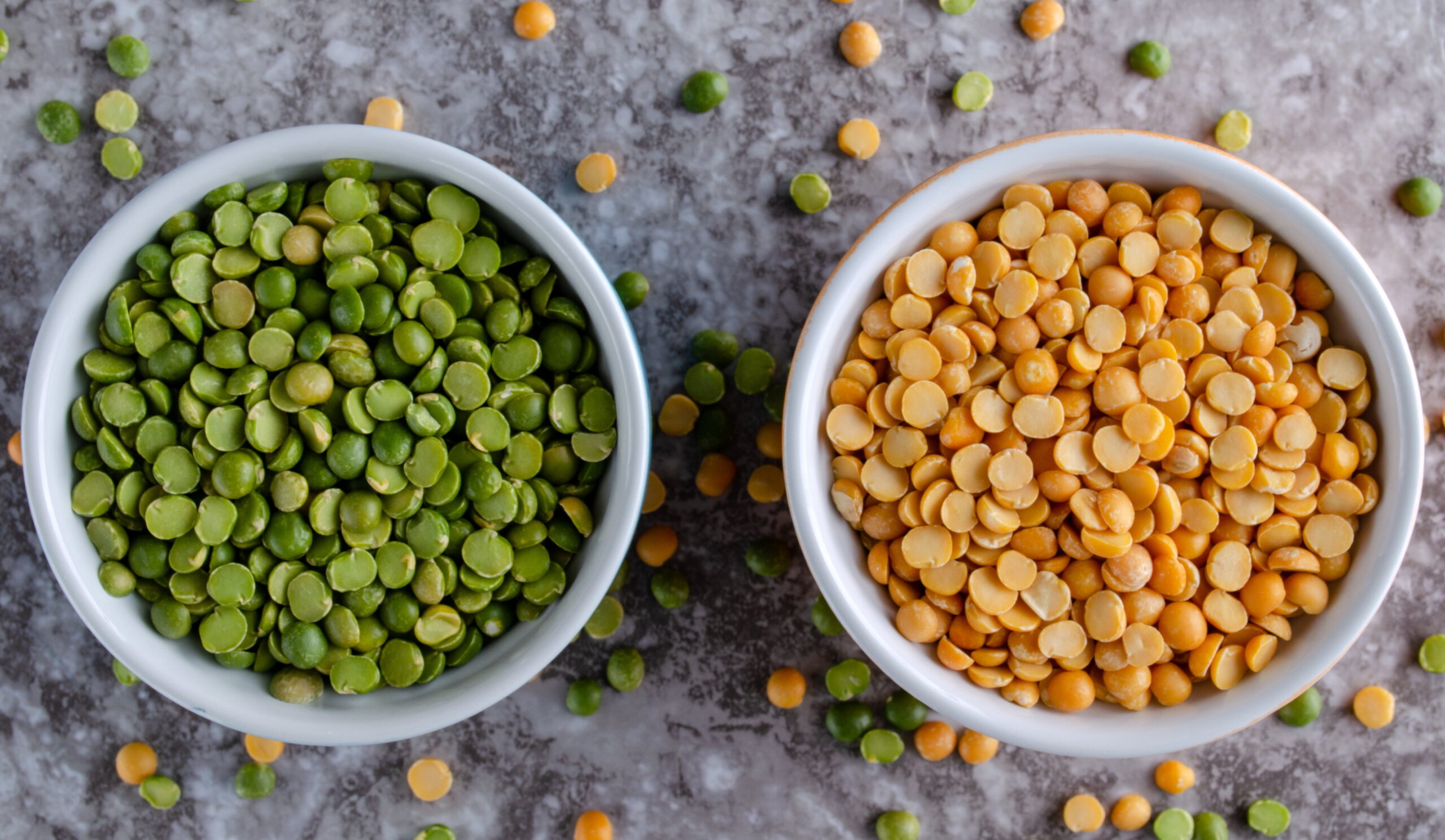
Split peas
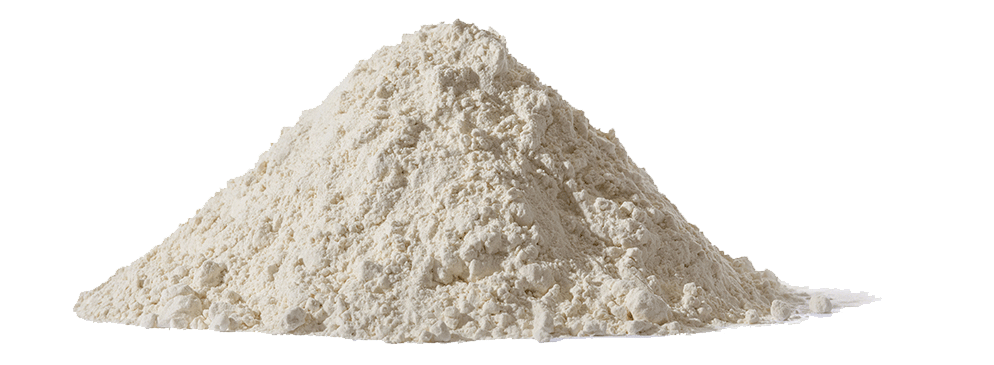
Starch
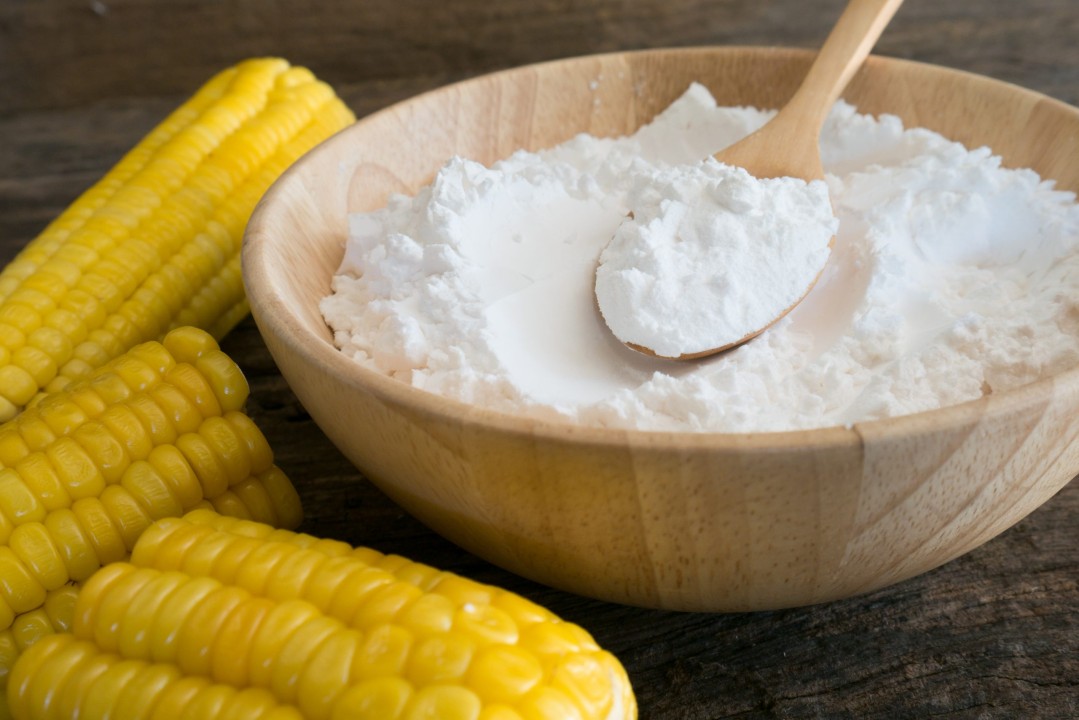
Starch derivatives
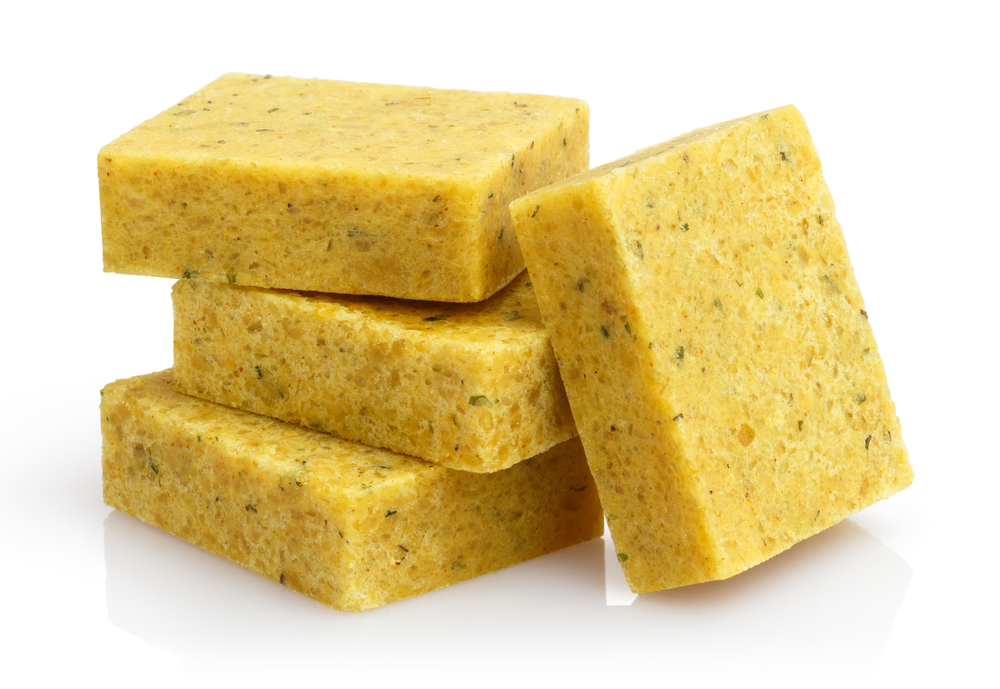
Stock cubes
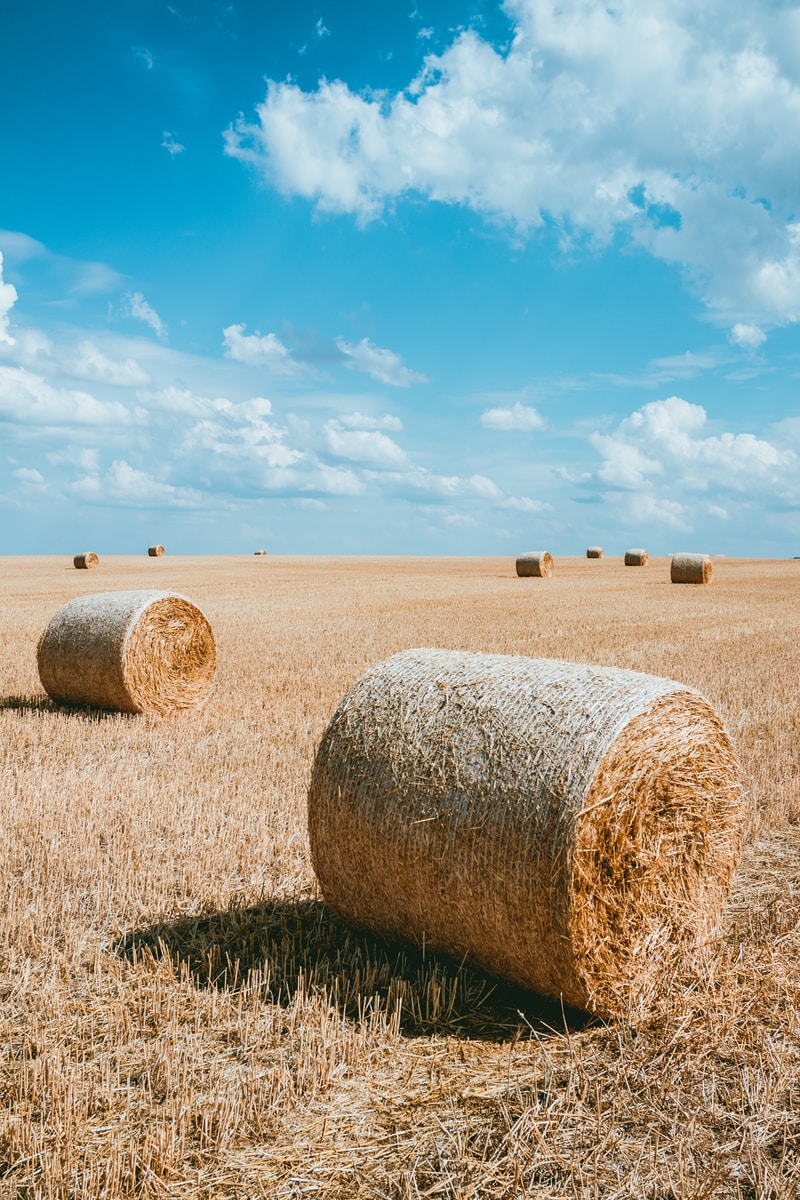
Straw
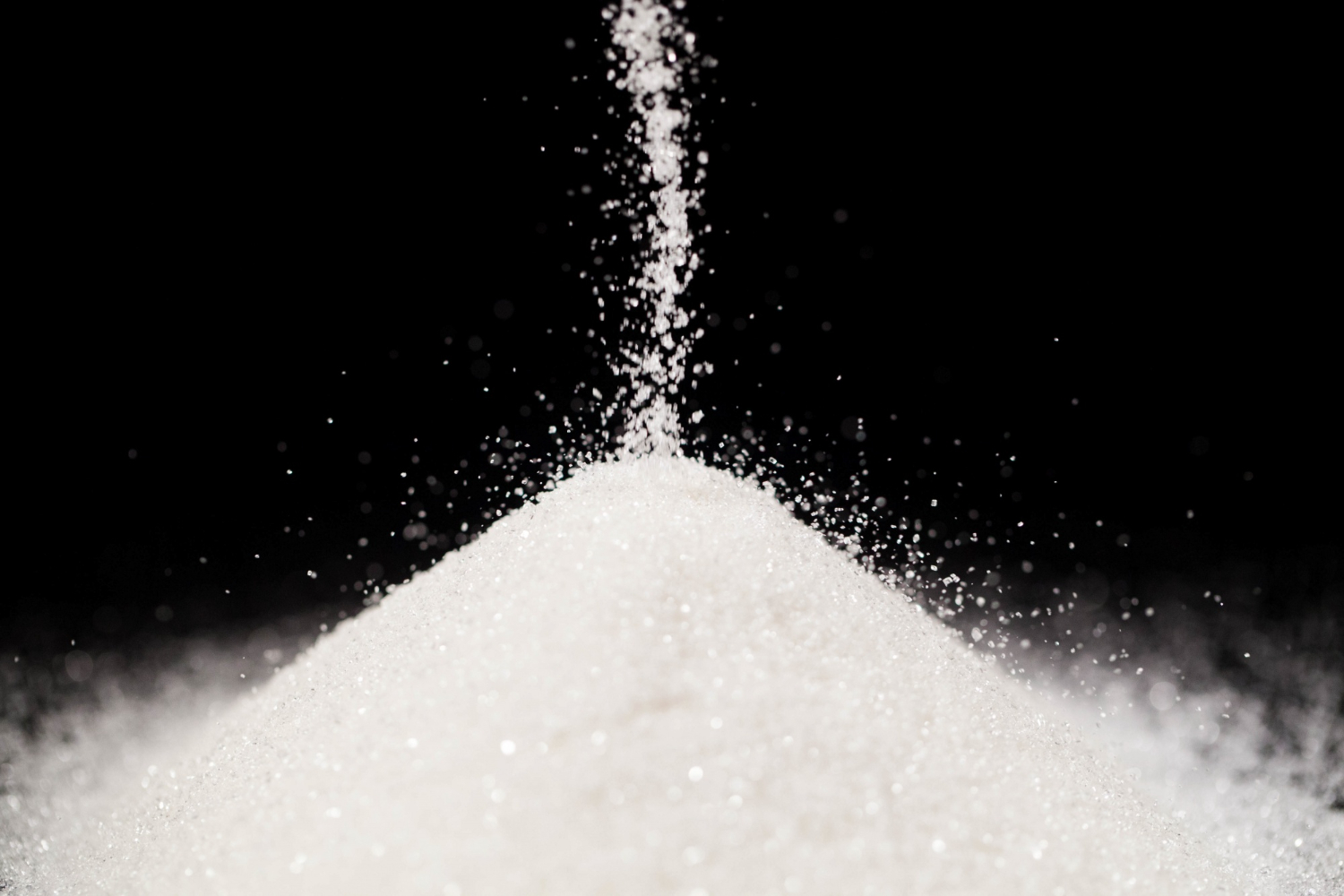
Sugar
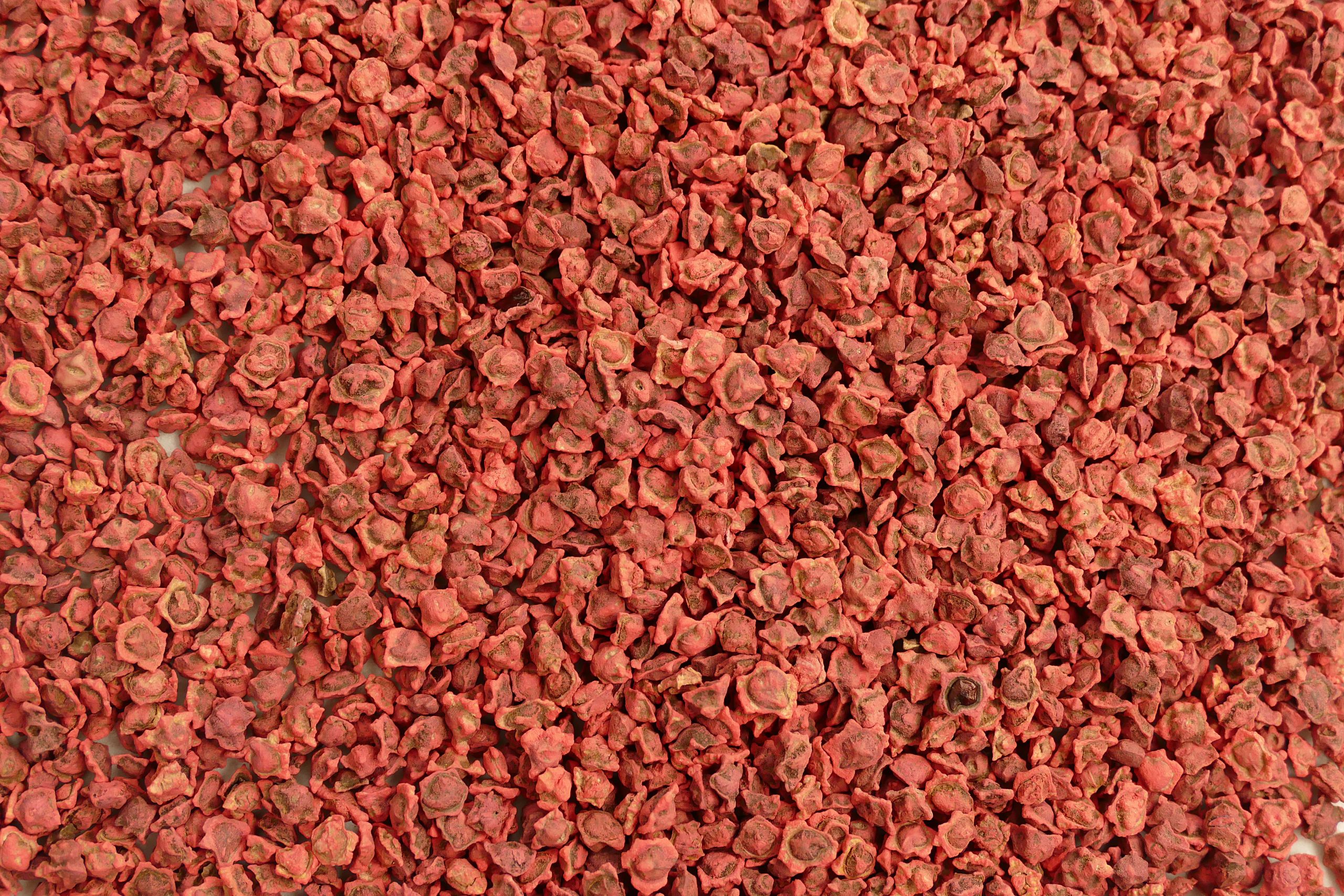
Sugar beet seeds
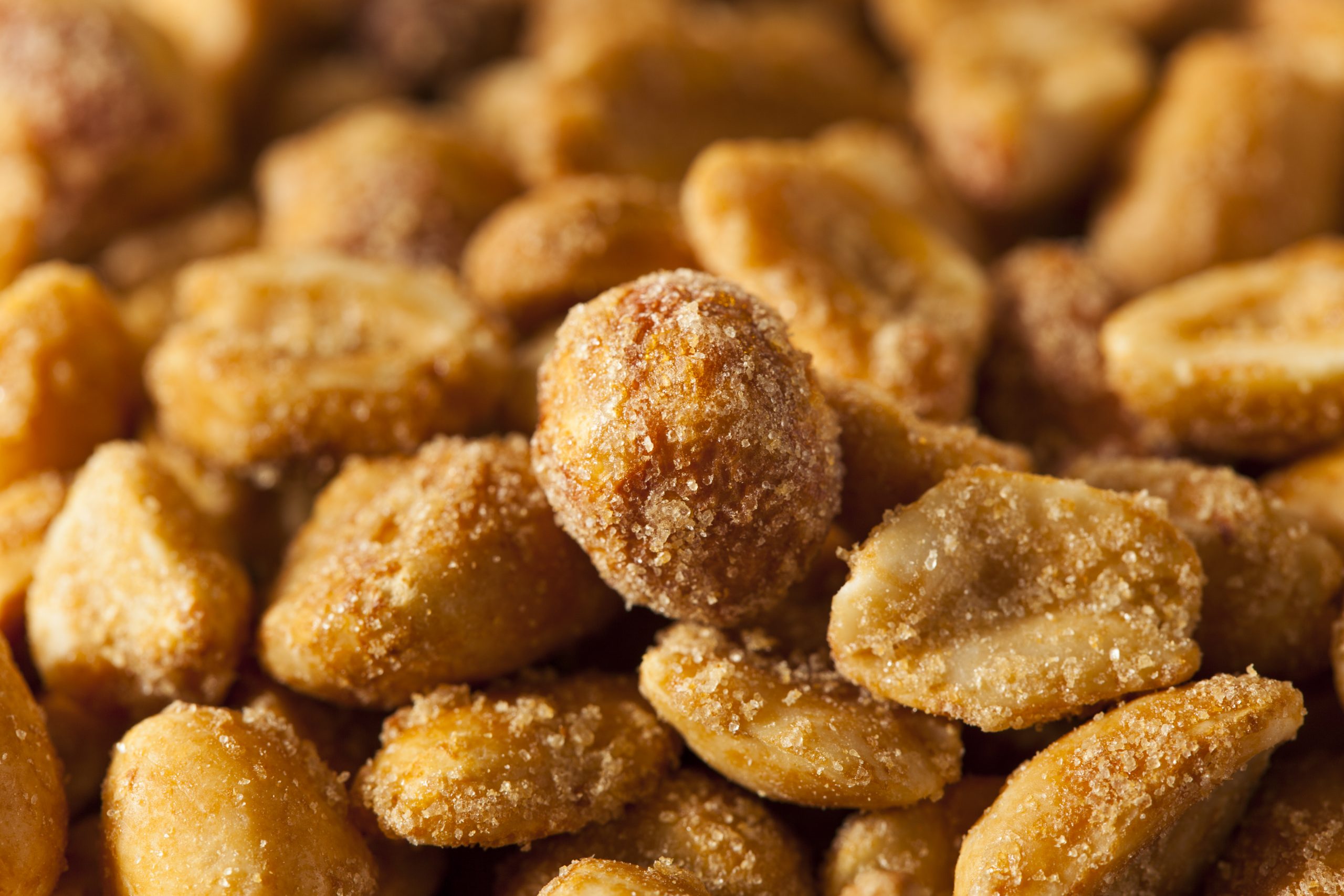
Sugar coated nuts
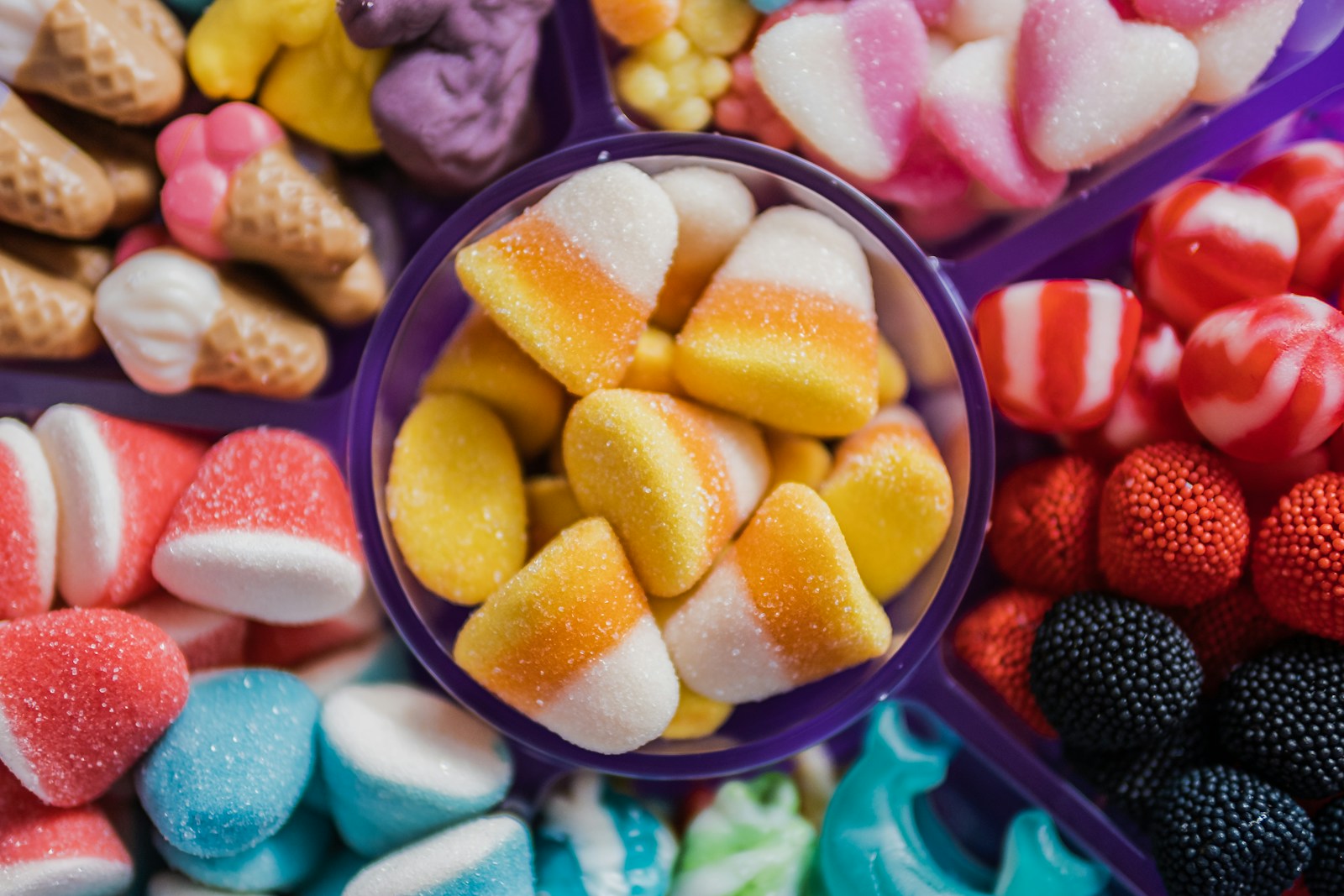
Sugar-coated sweets
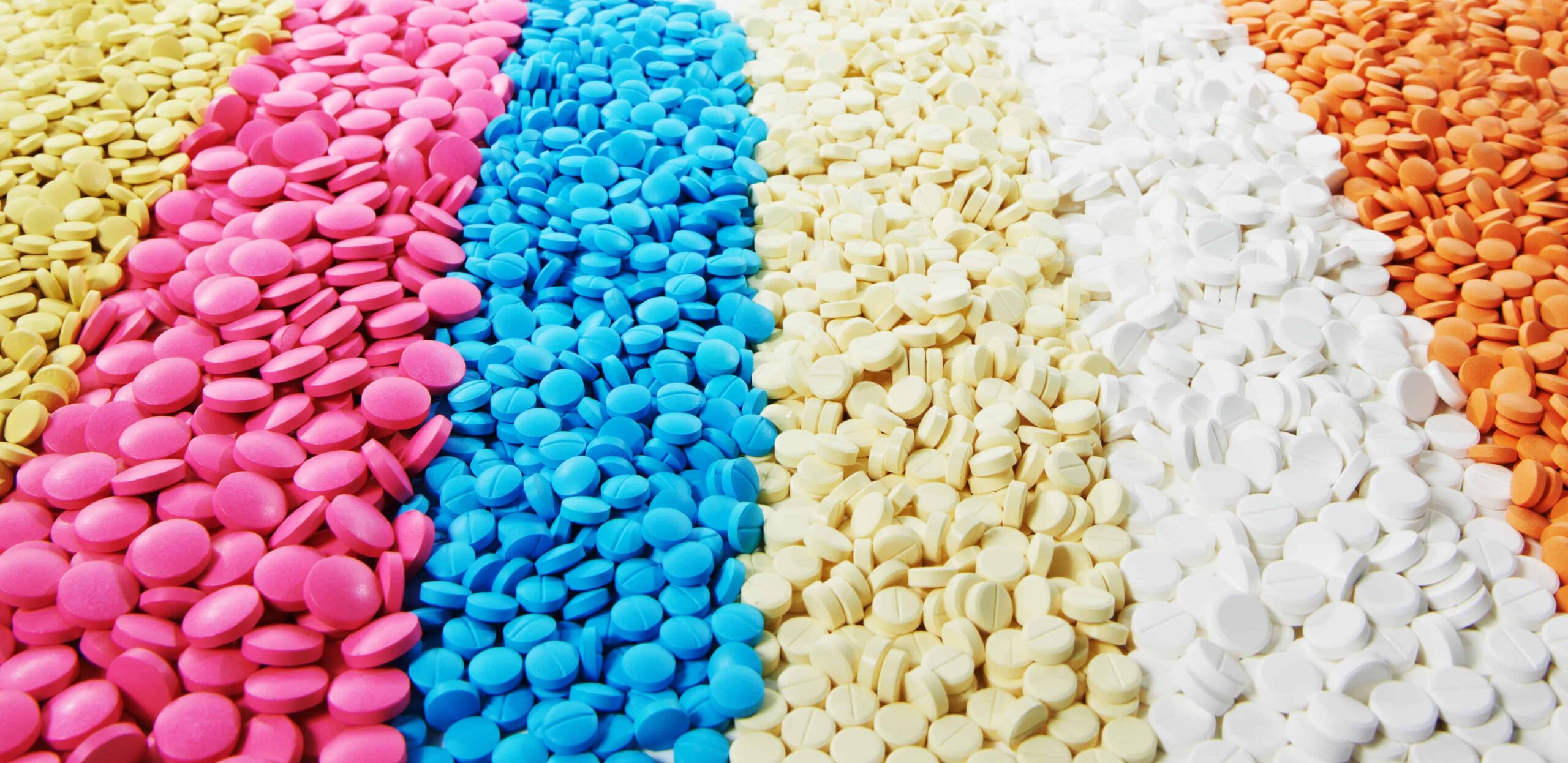
Sugar-coated tablets
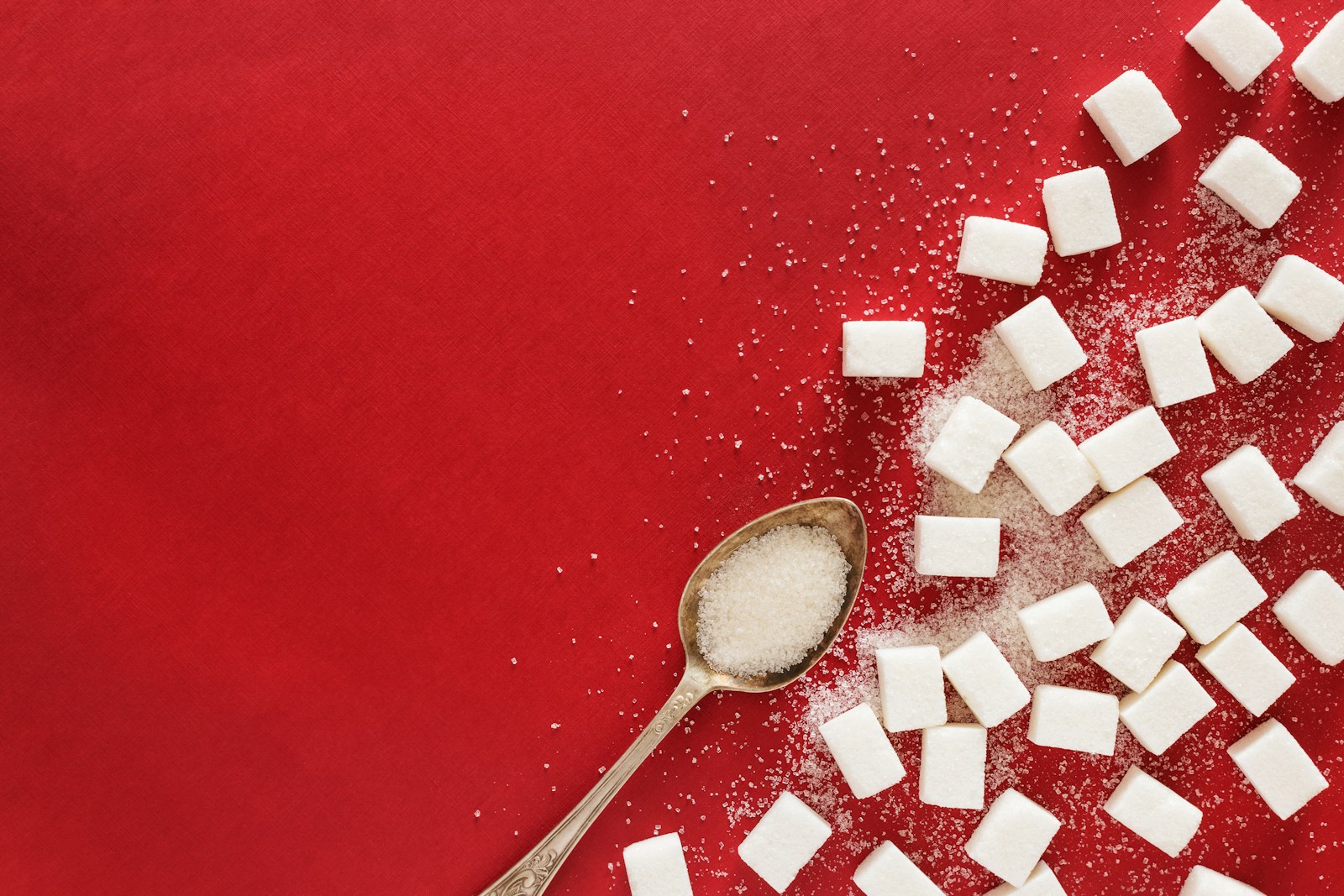
Sugar crystals
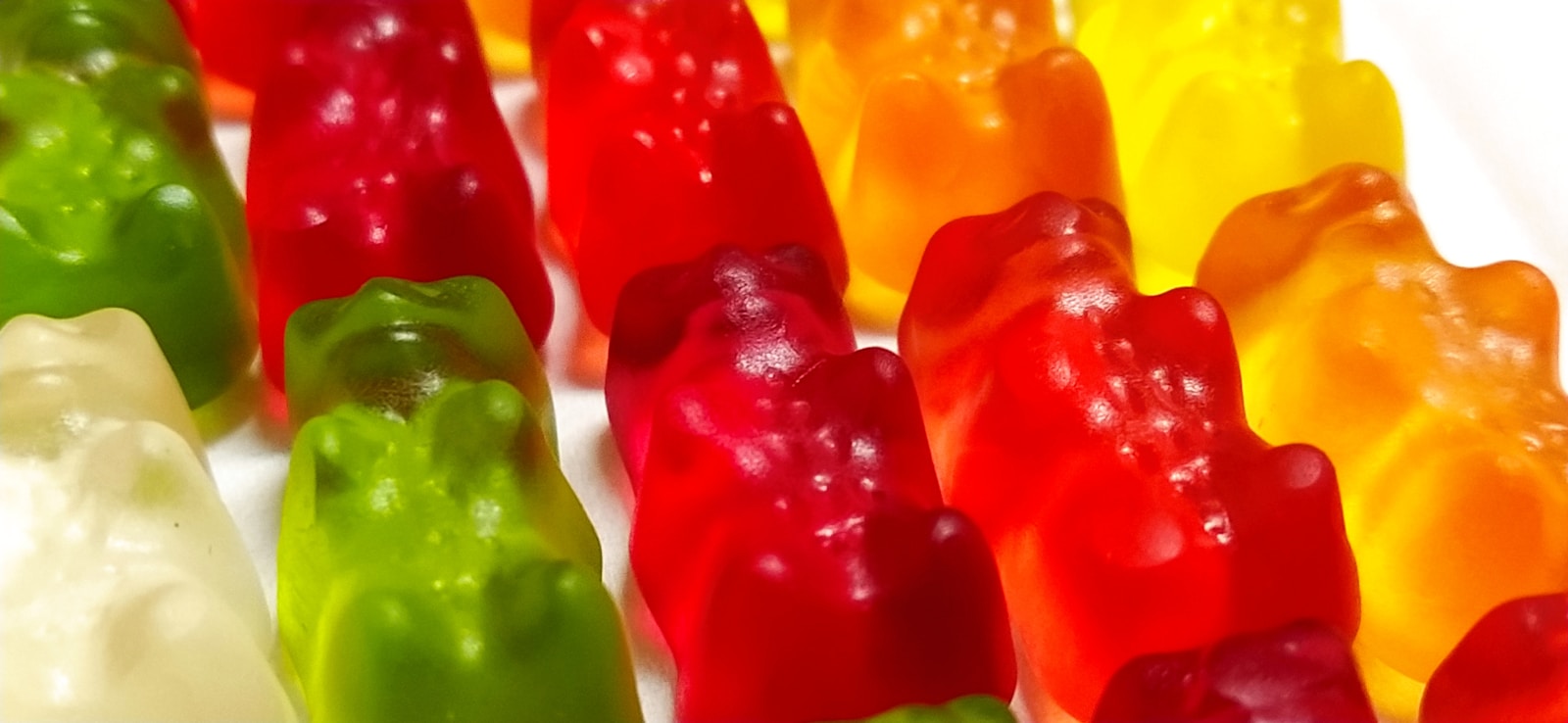
Sugar-free gummies

Sugar substitutes
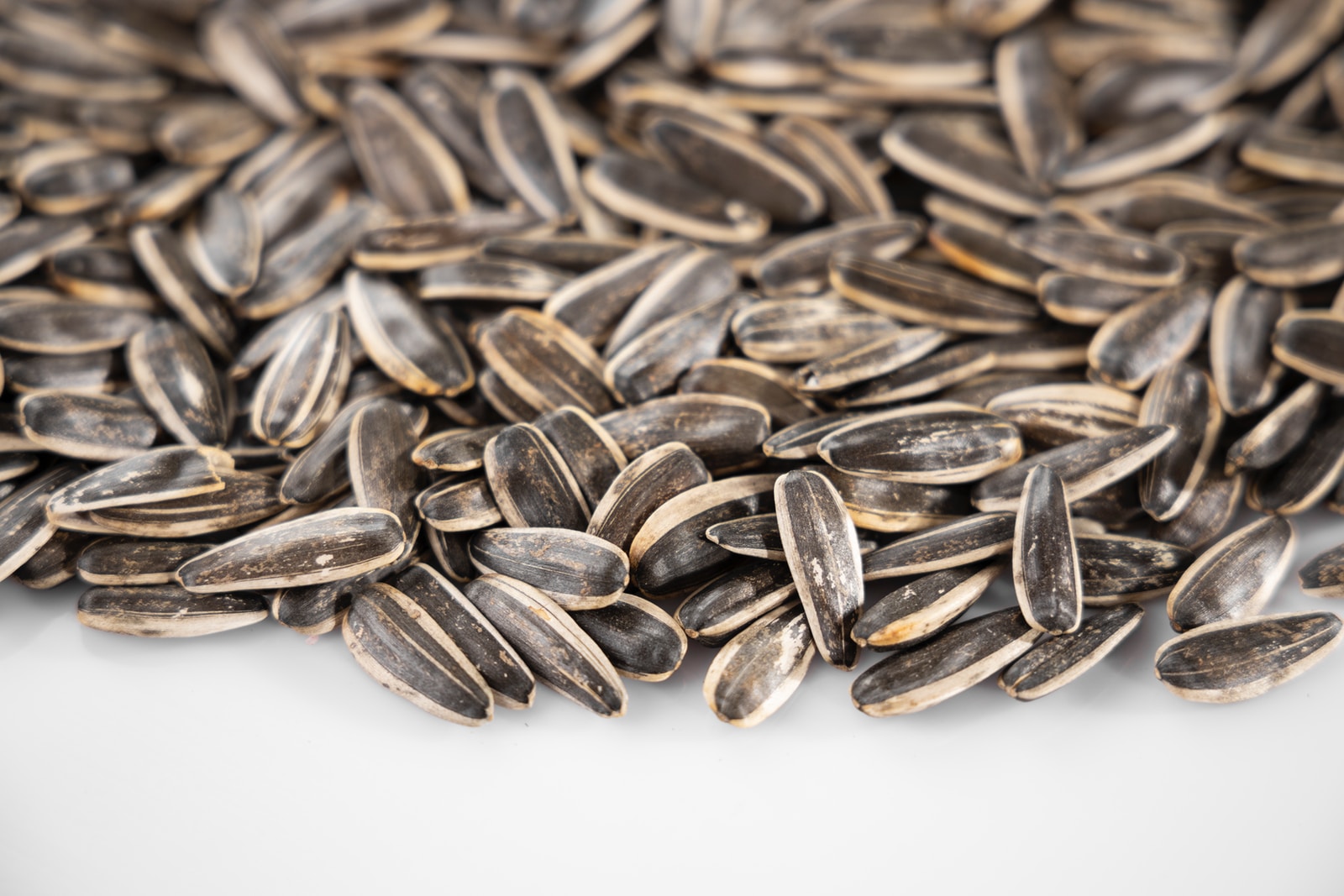
Sunflower seeds
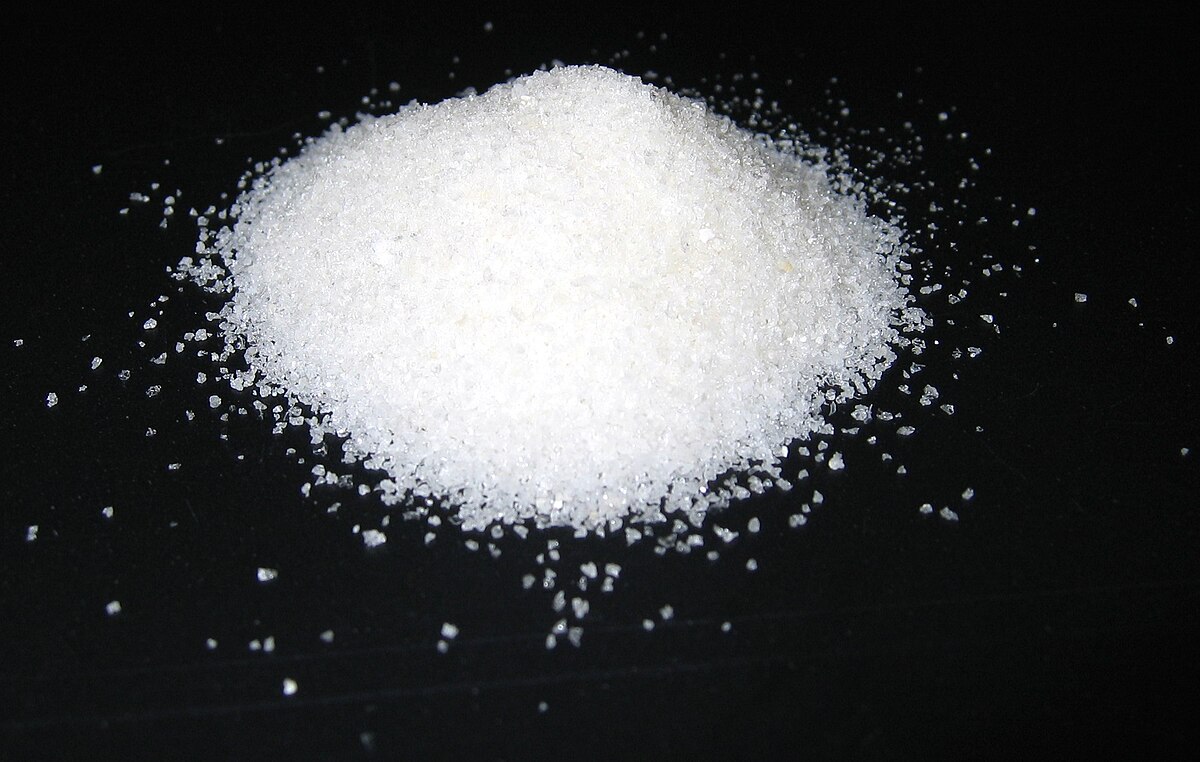
Superabsorbents

Surface coating

Surgical gloves
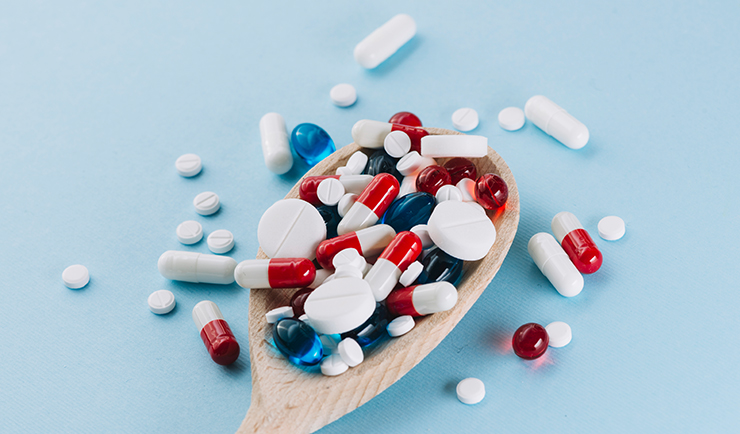
Sustained-release capsules

Sustained-release tablets
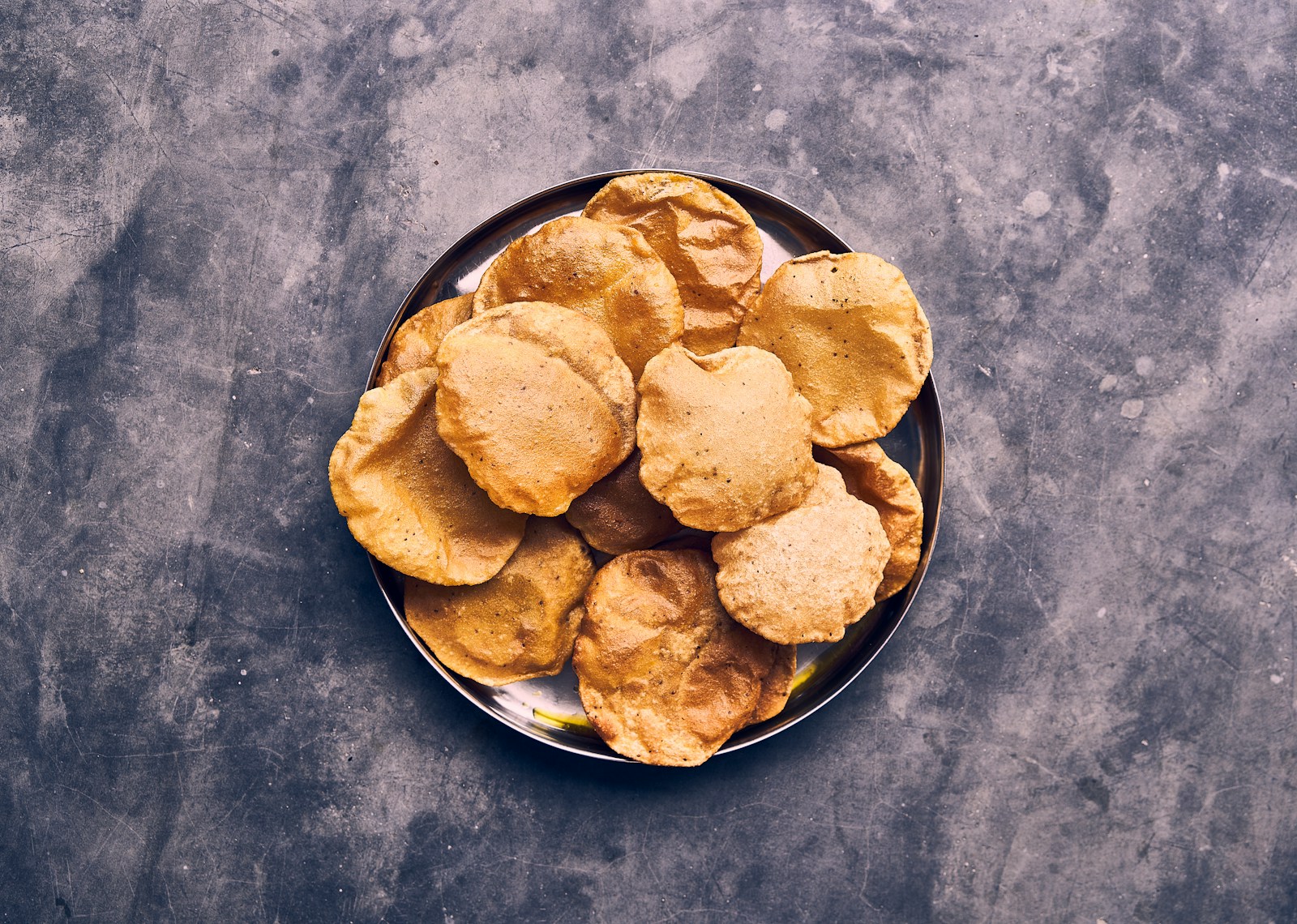
Sweet potato chips
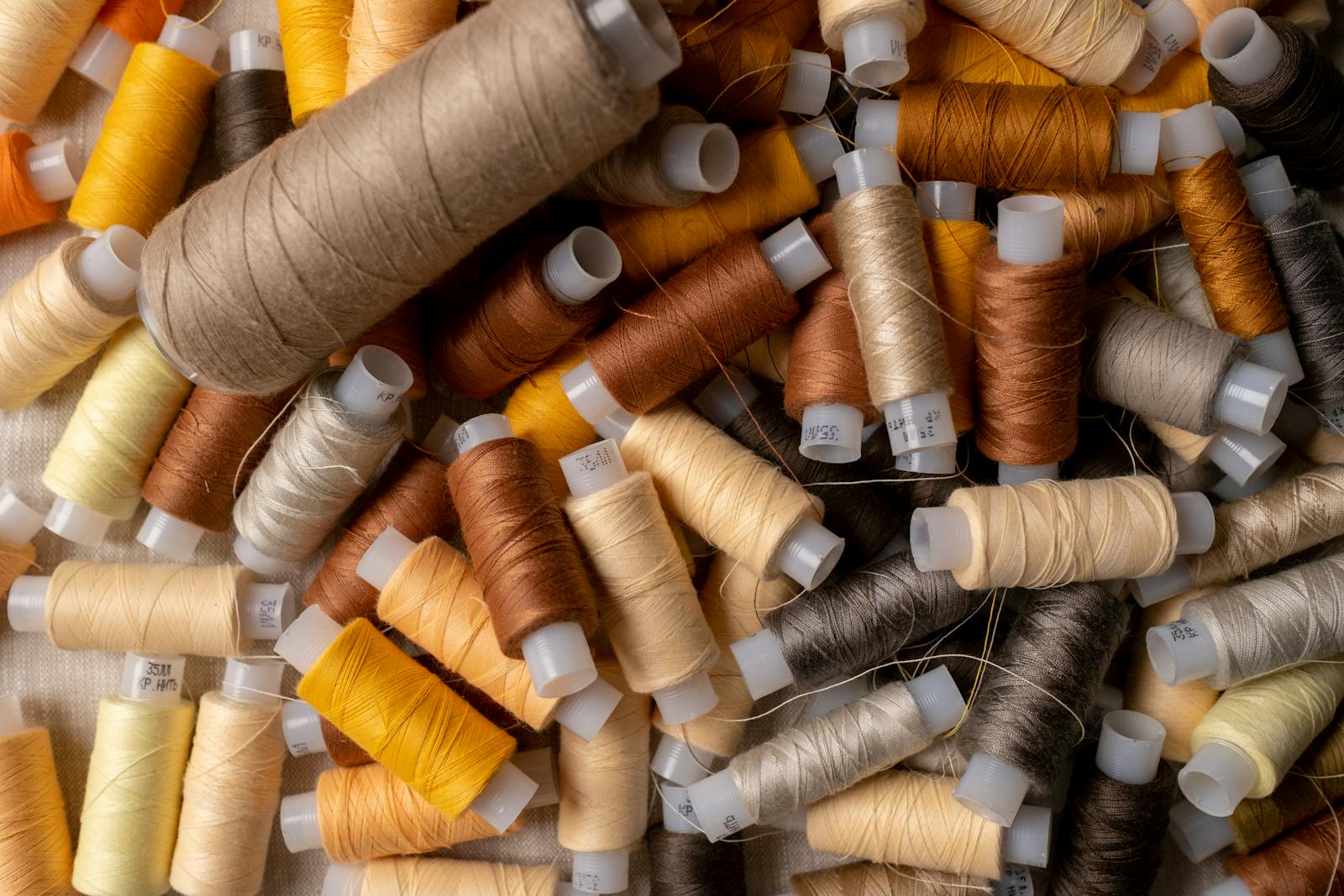
Synthetic fibers
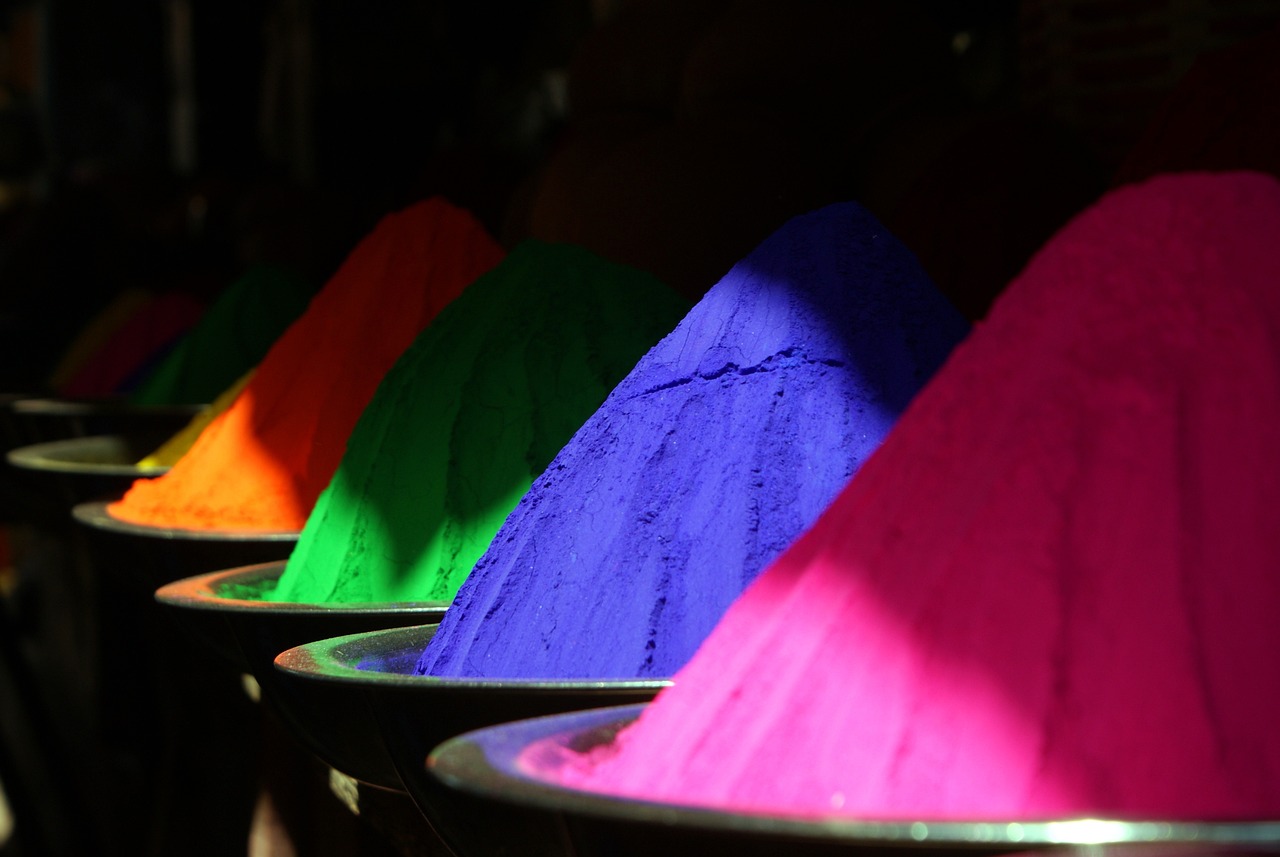
Synthetic pigments
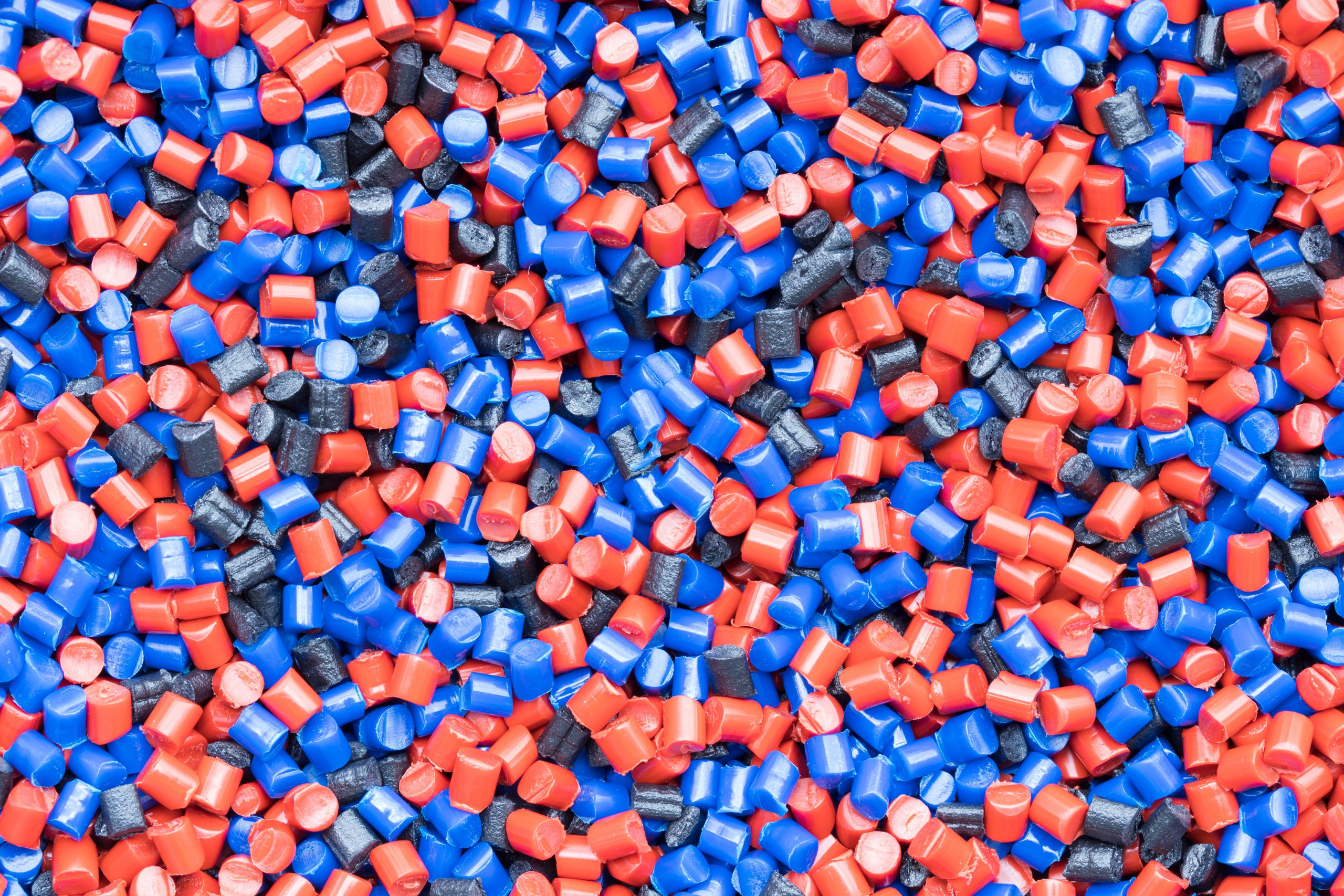
Synthetic resin
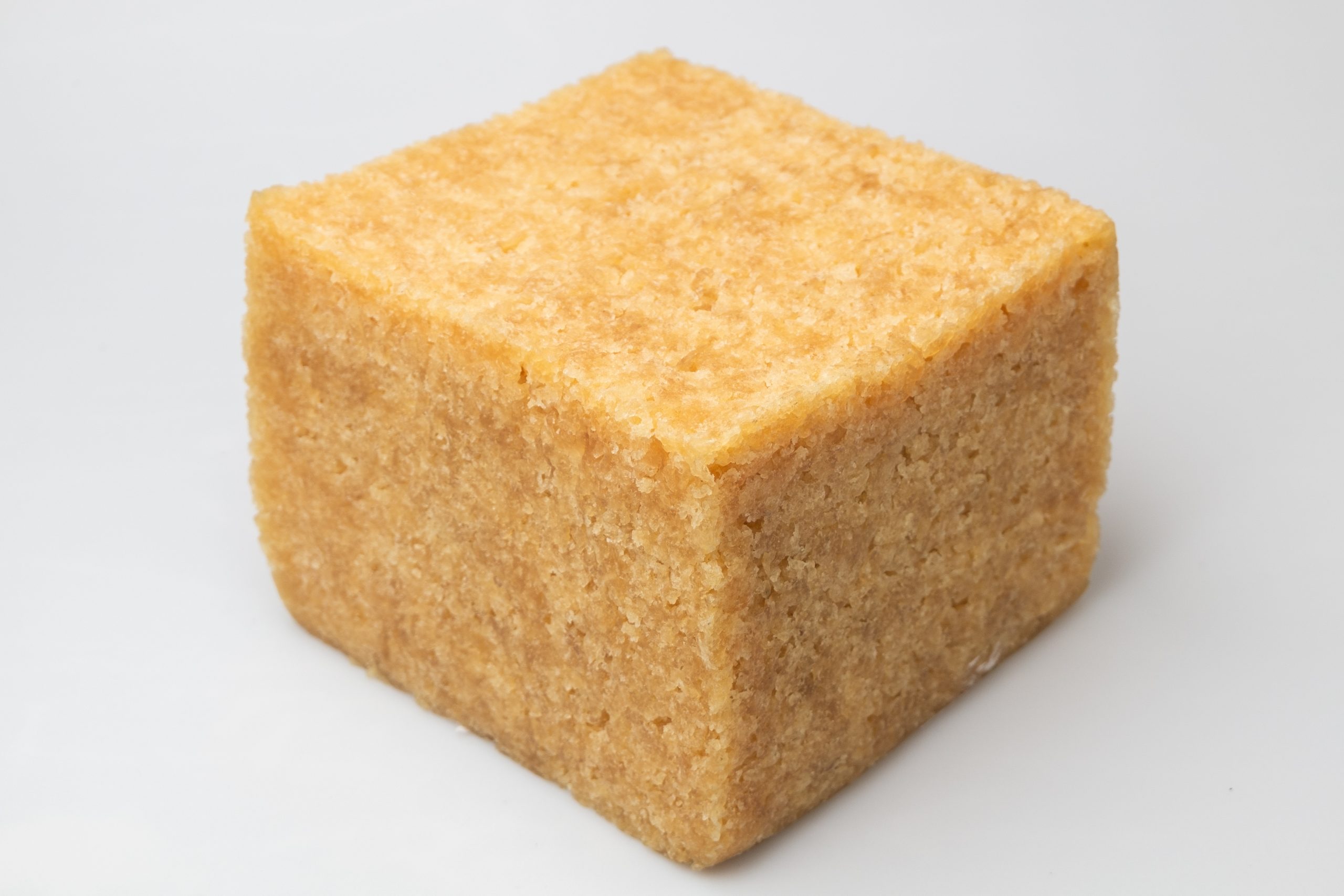
Synthetic rubber
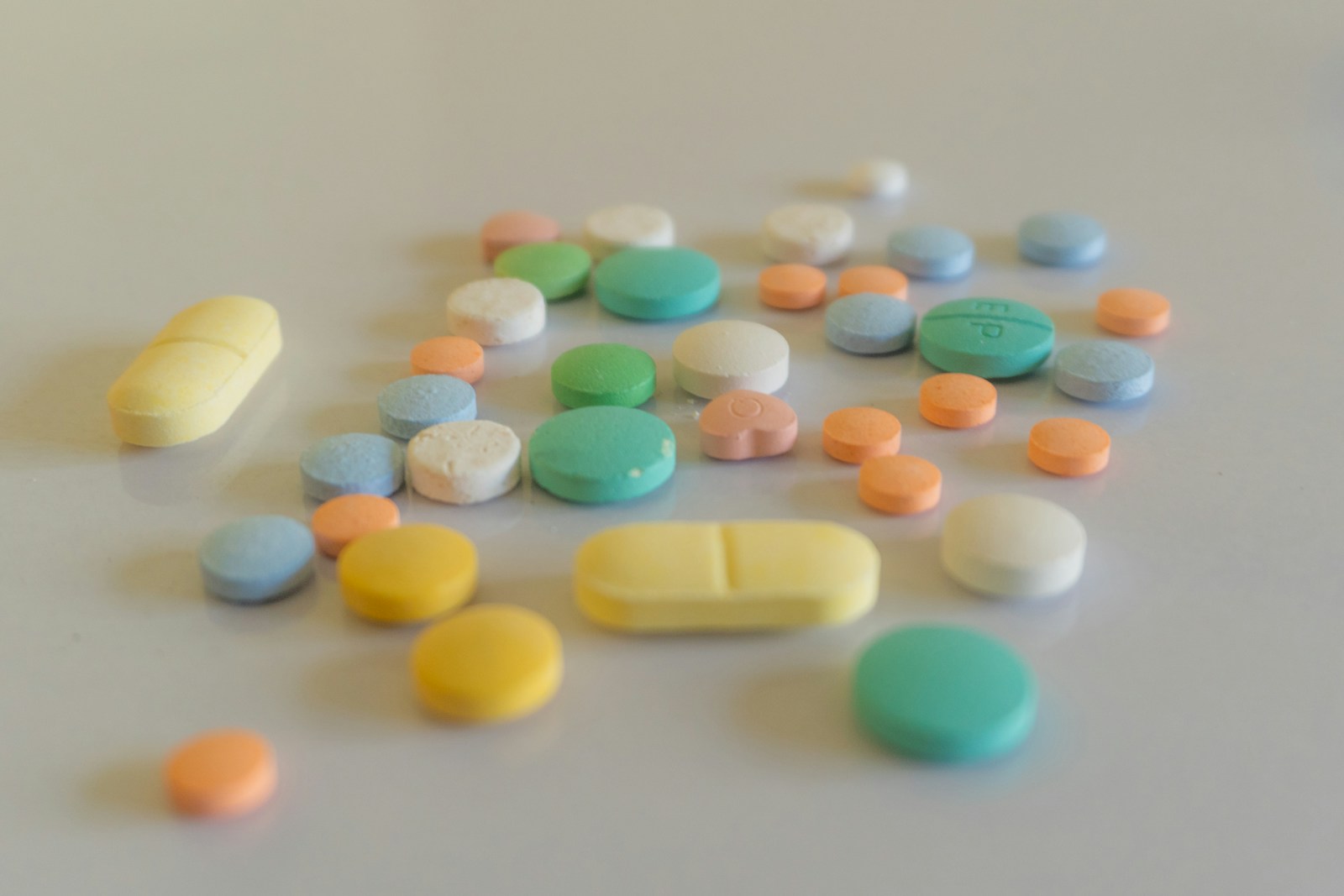
Tablet coatings
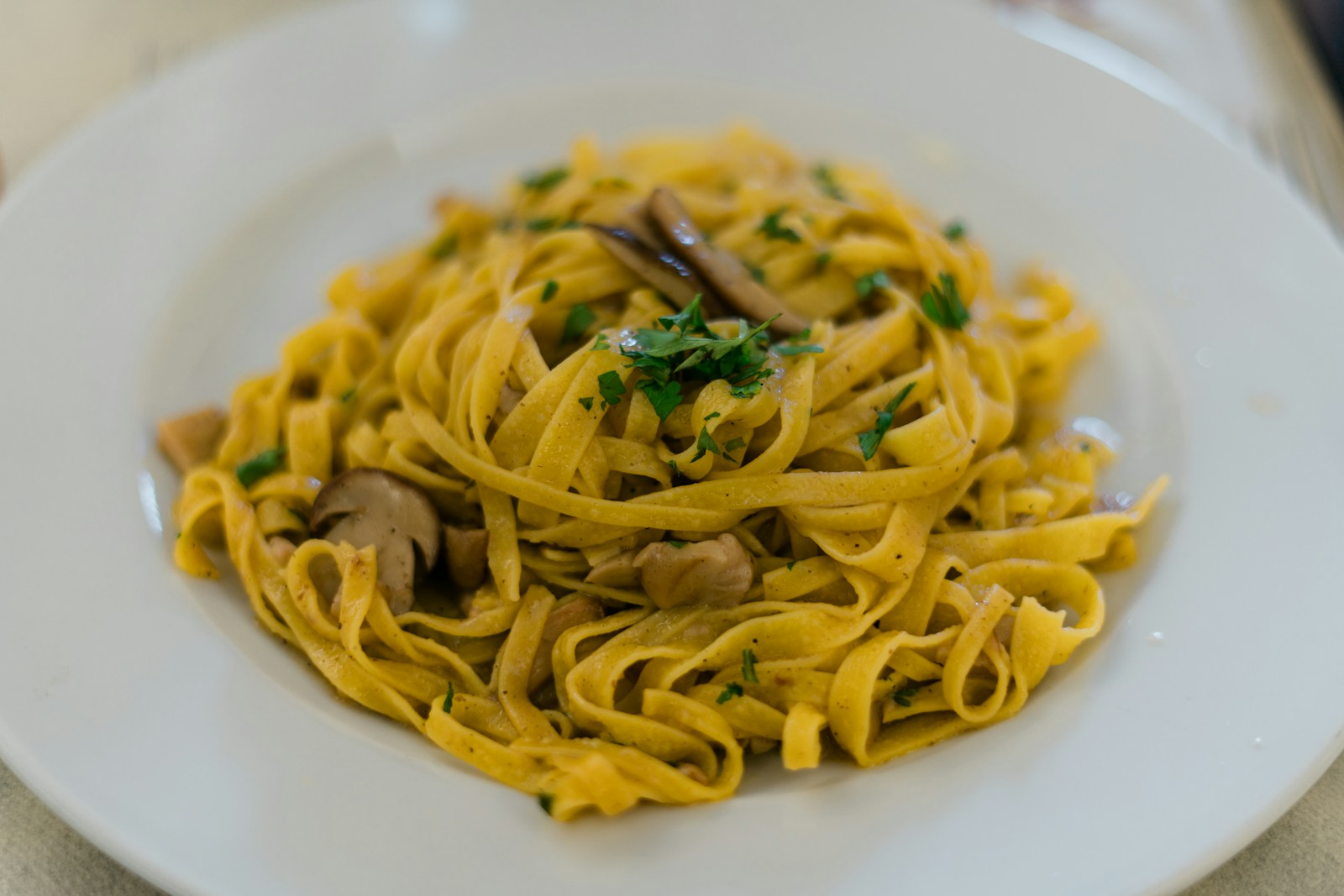
Tagliatelle
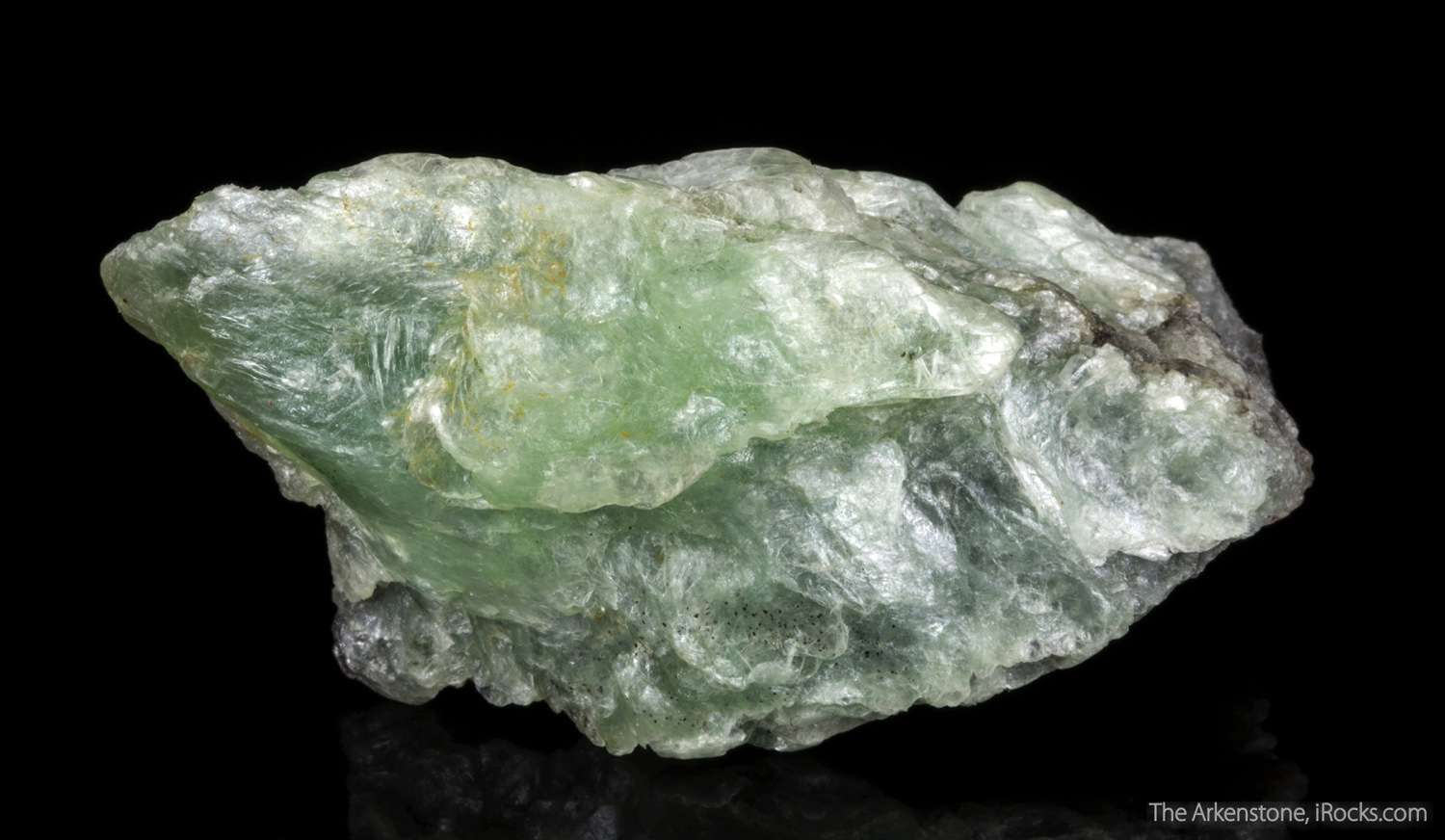
Talc
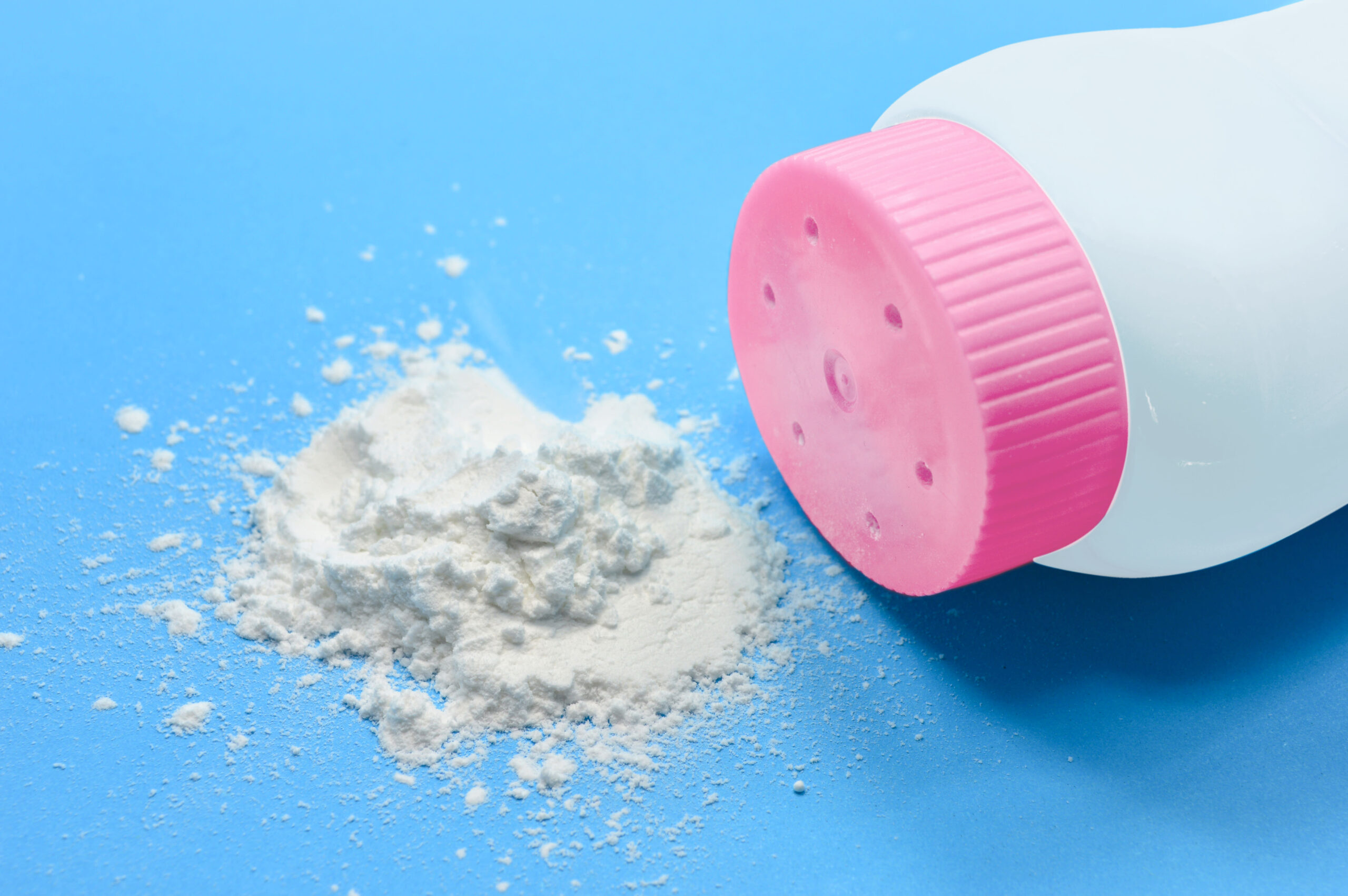
Talc powder

Tapioca pearls
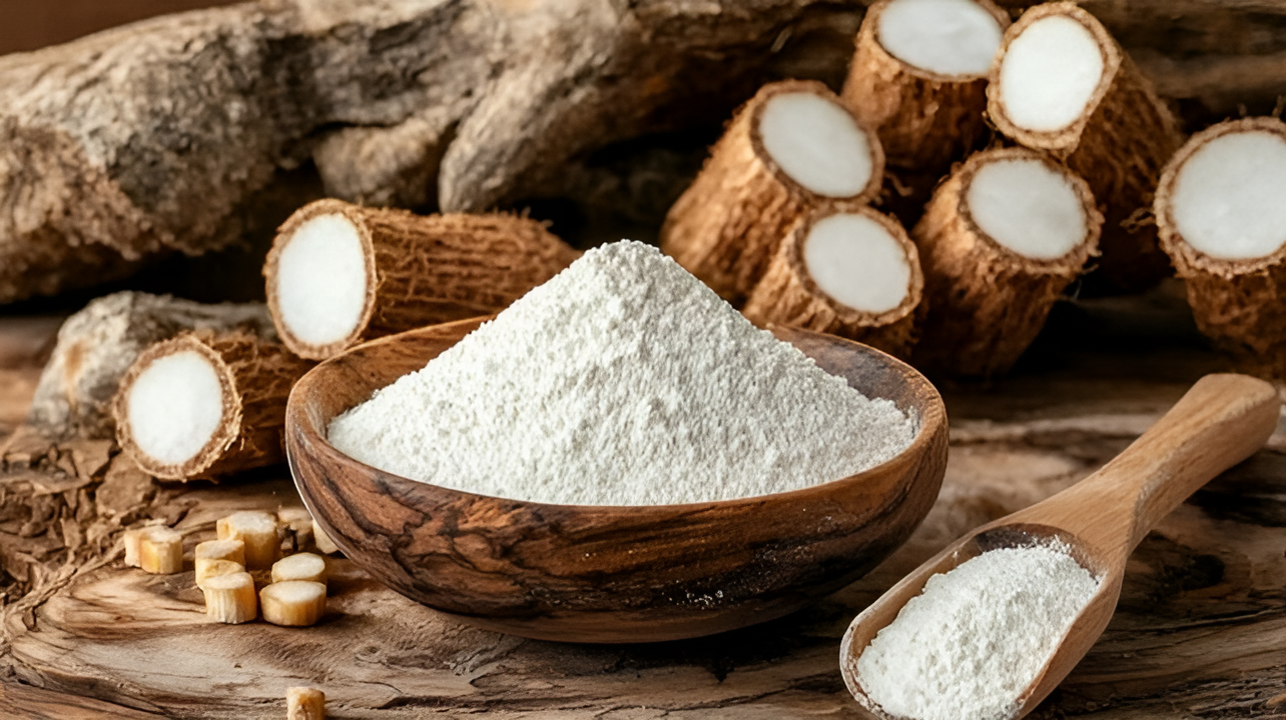
Tapioca starch
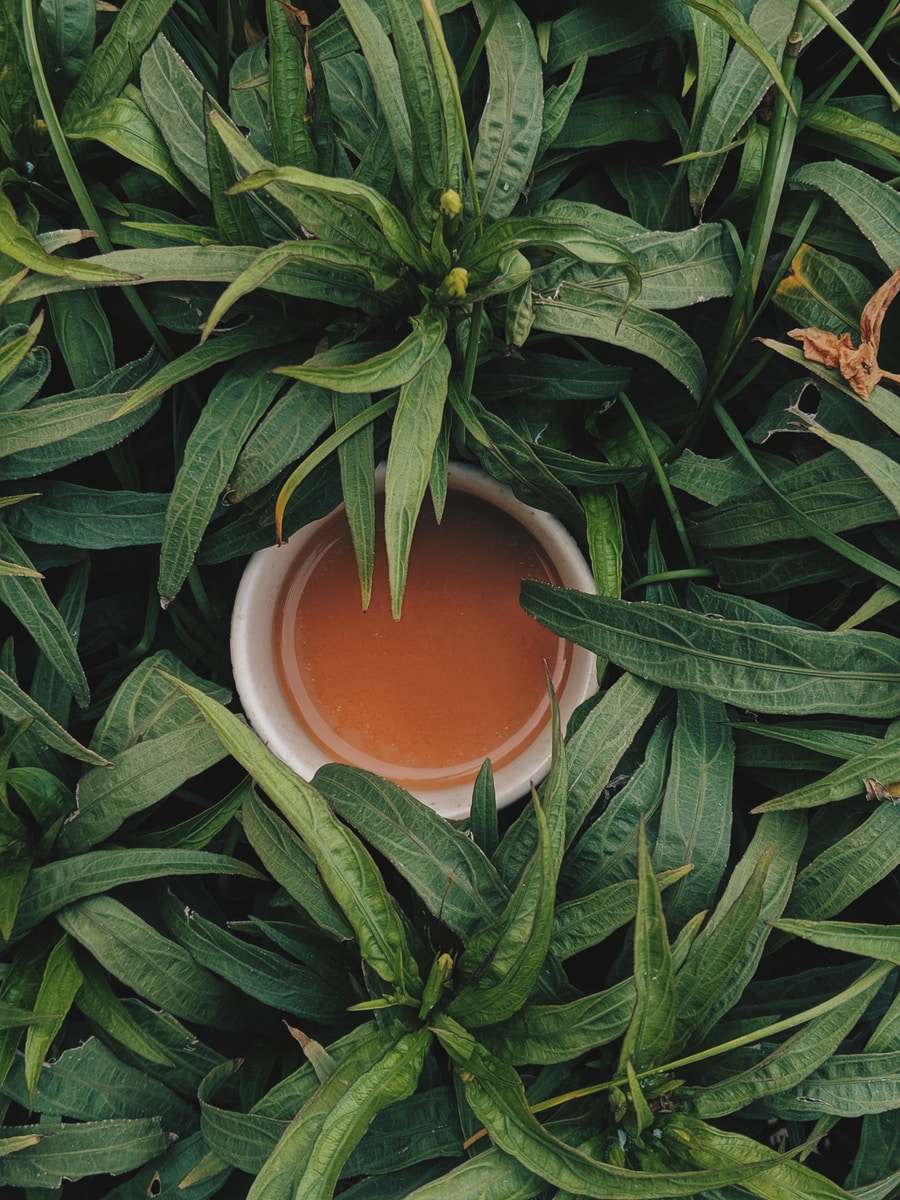
Tea
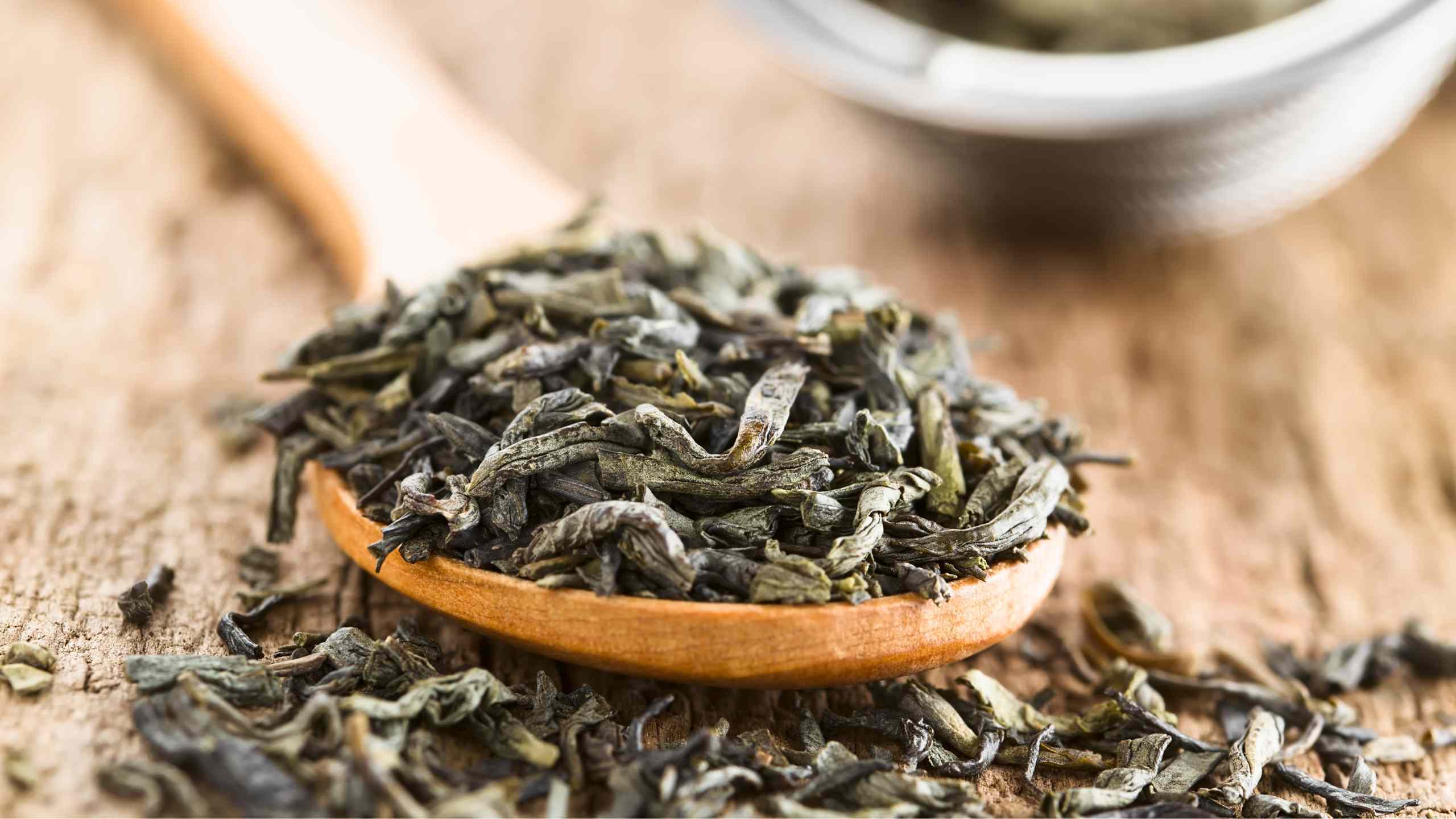
Tea extracts
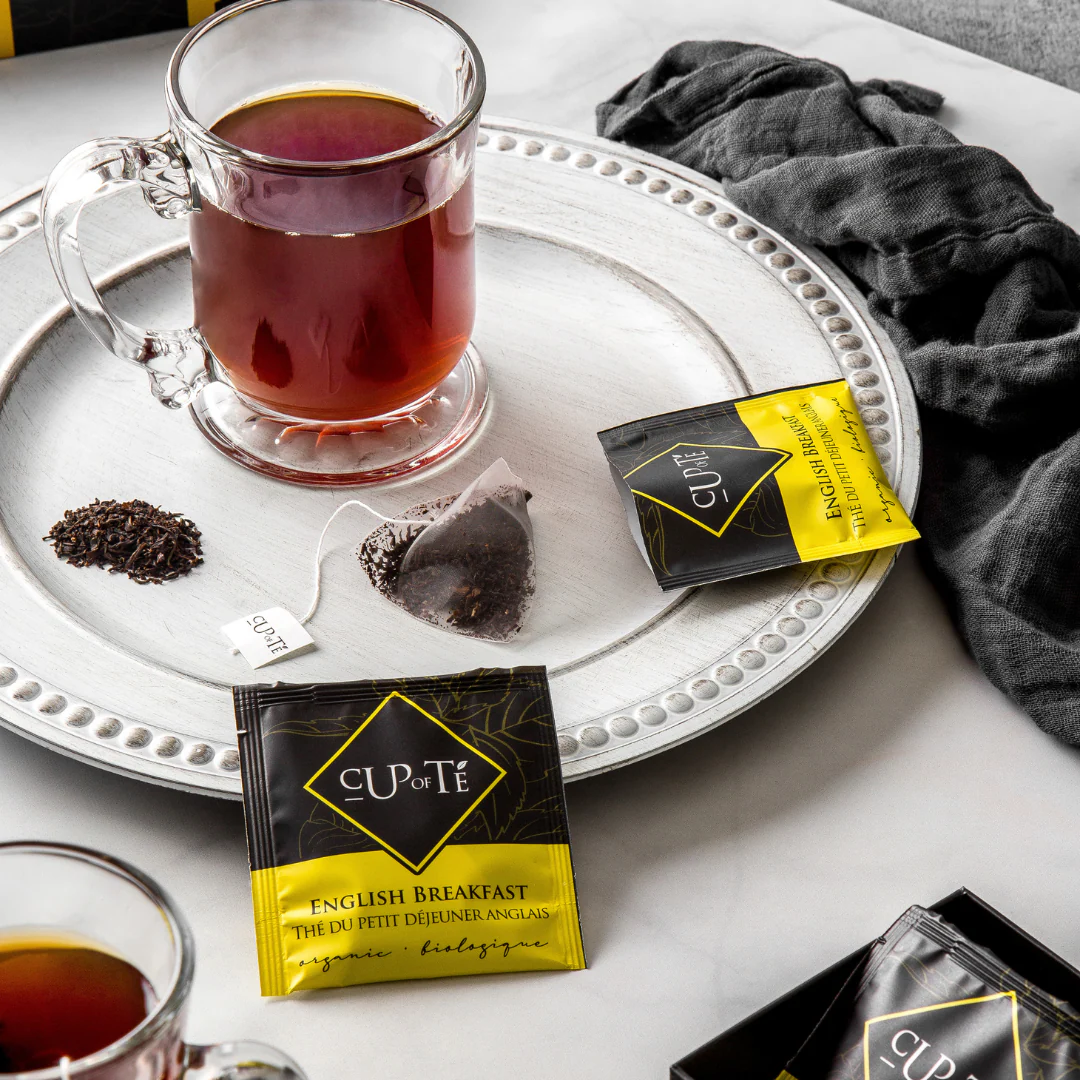
Tea sachets
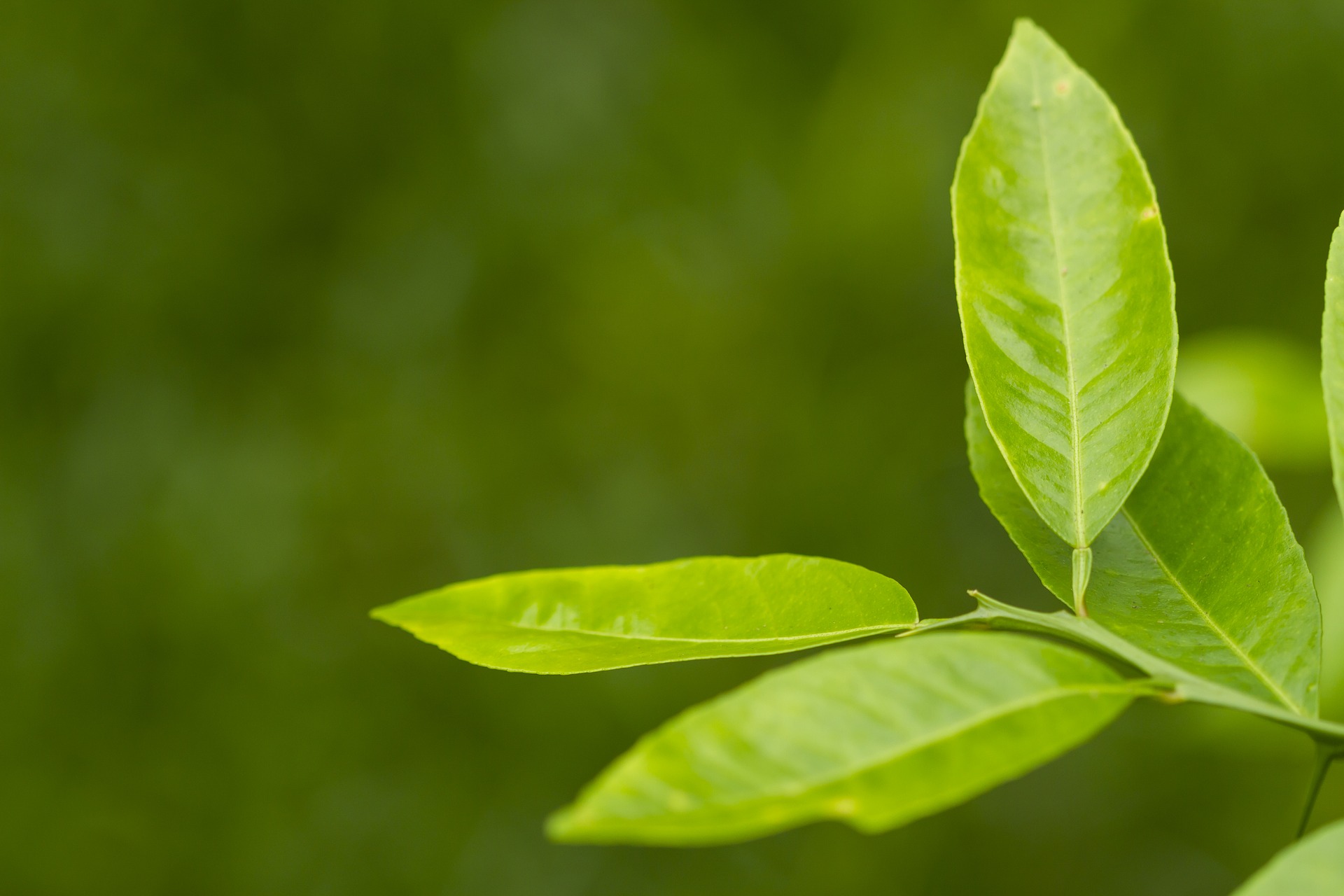
Tea tree oil
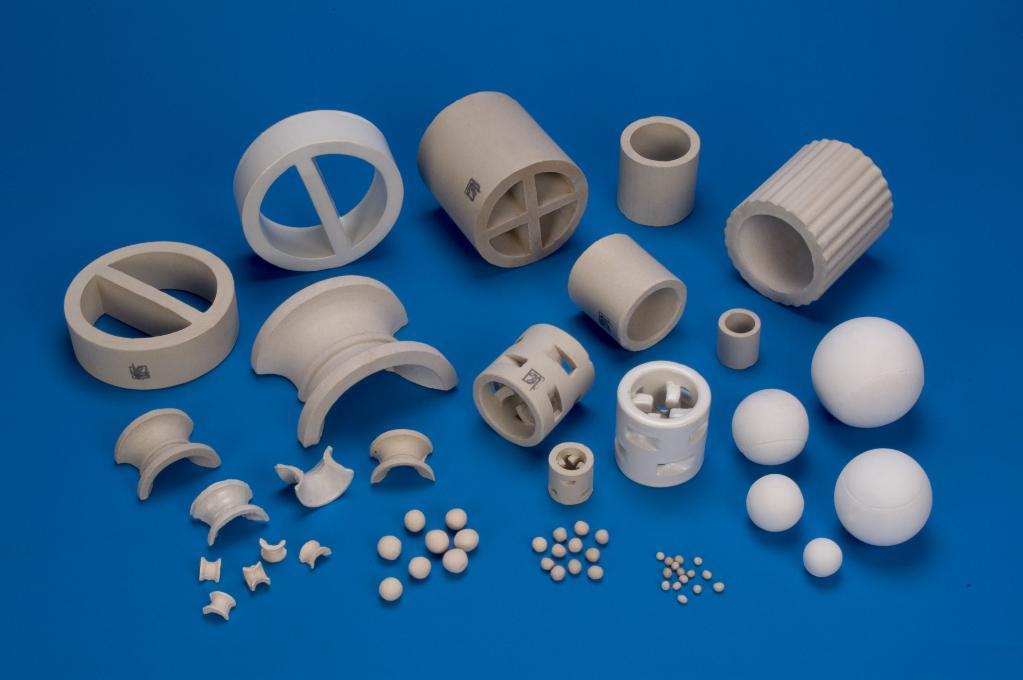
Technical ceramic
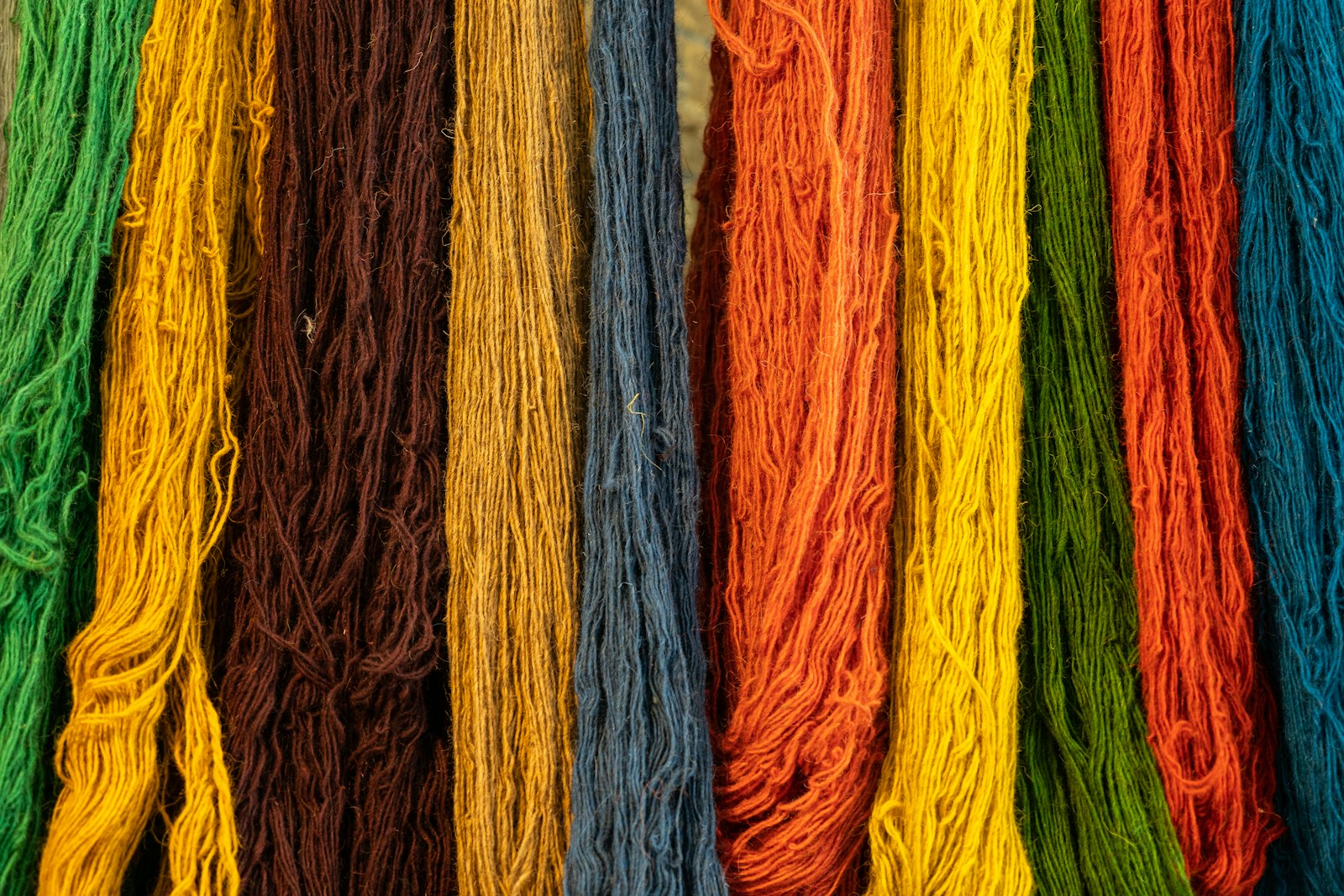
Textile fibers
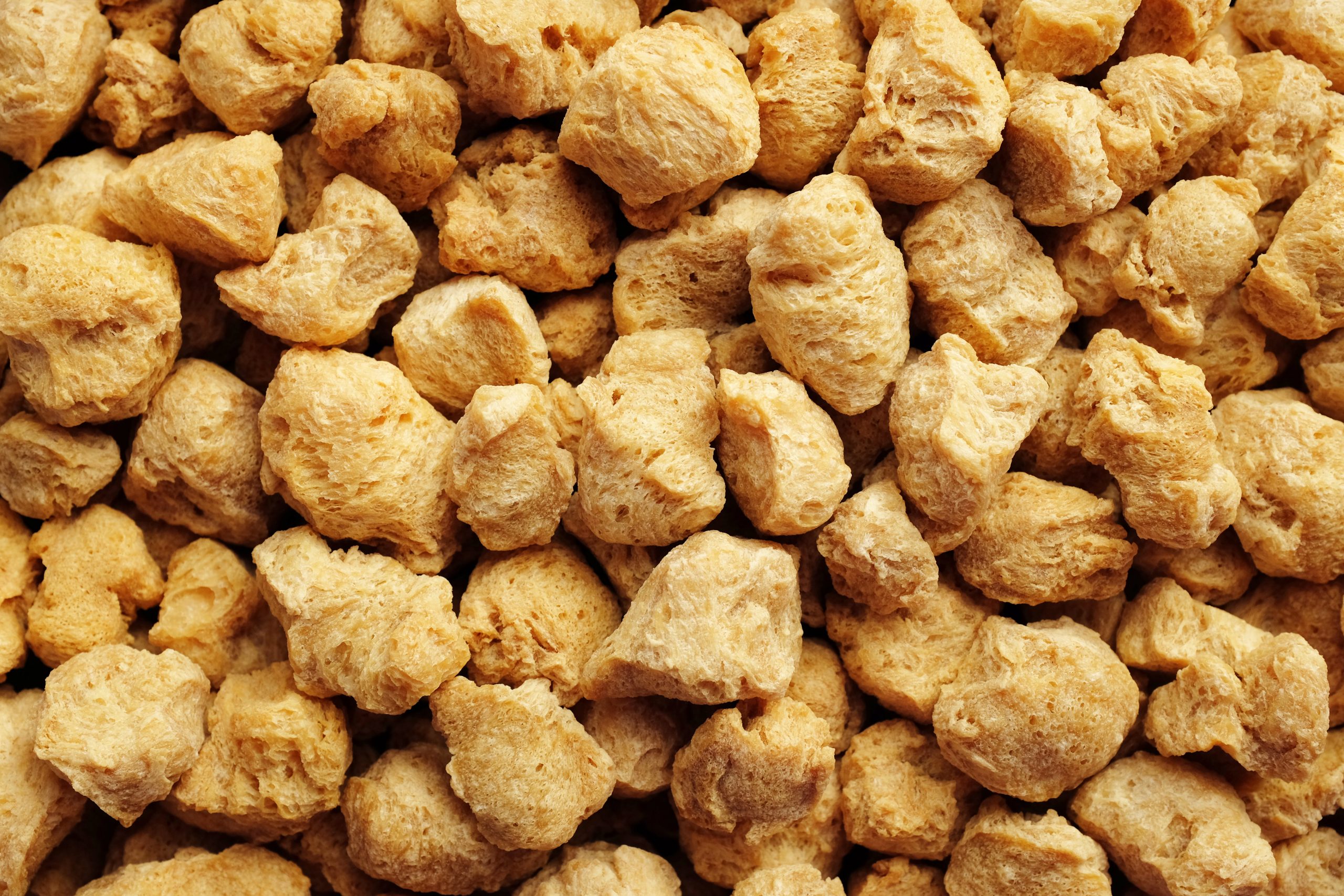
Textured Vegetable Protein
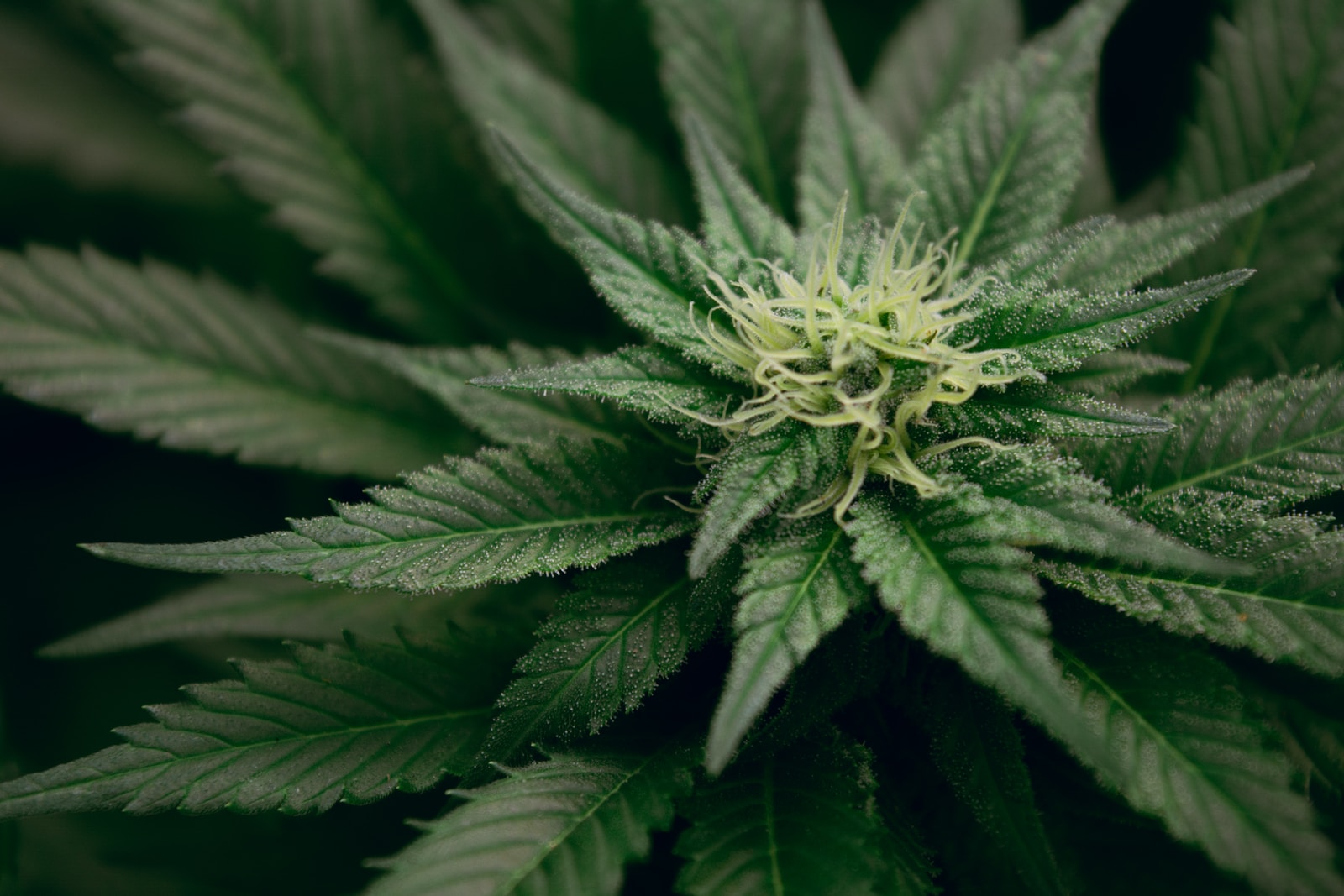
THC
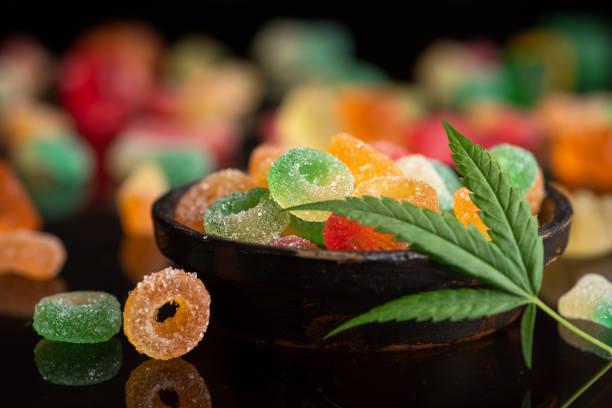
Thc gummies
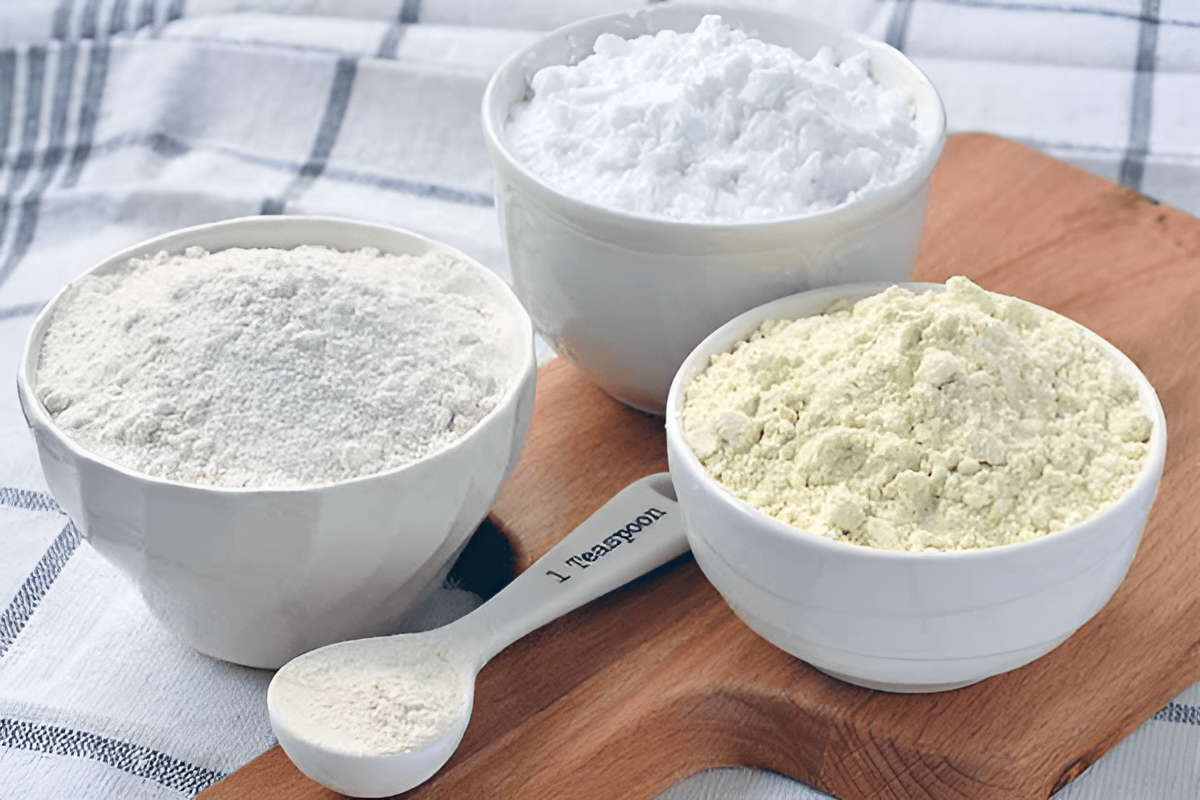
Thickening agents
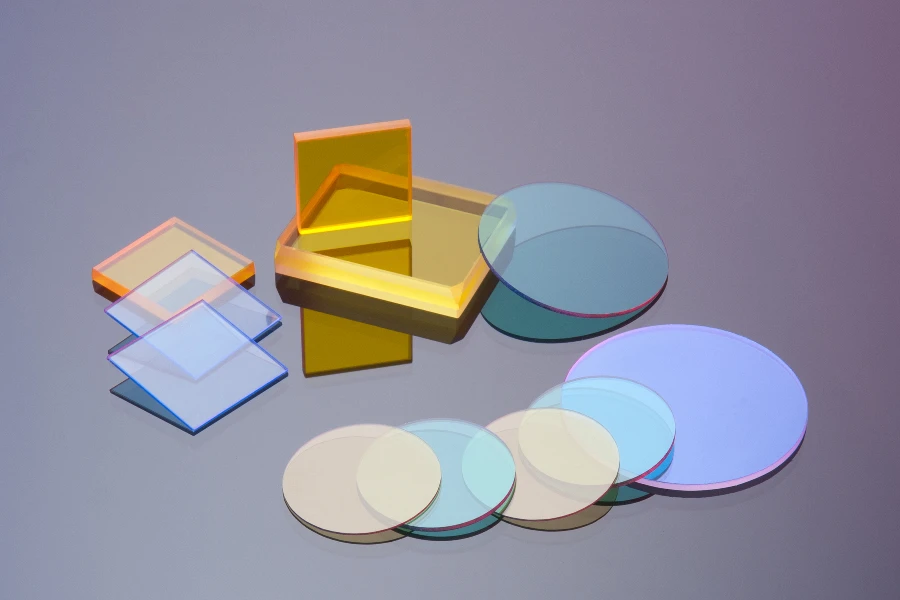
Thin film coatings
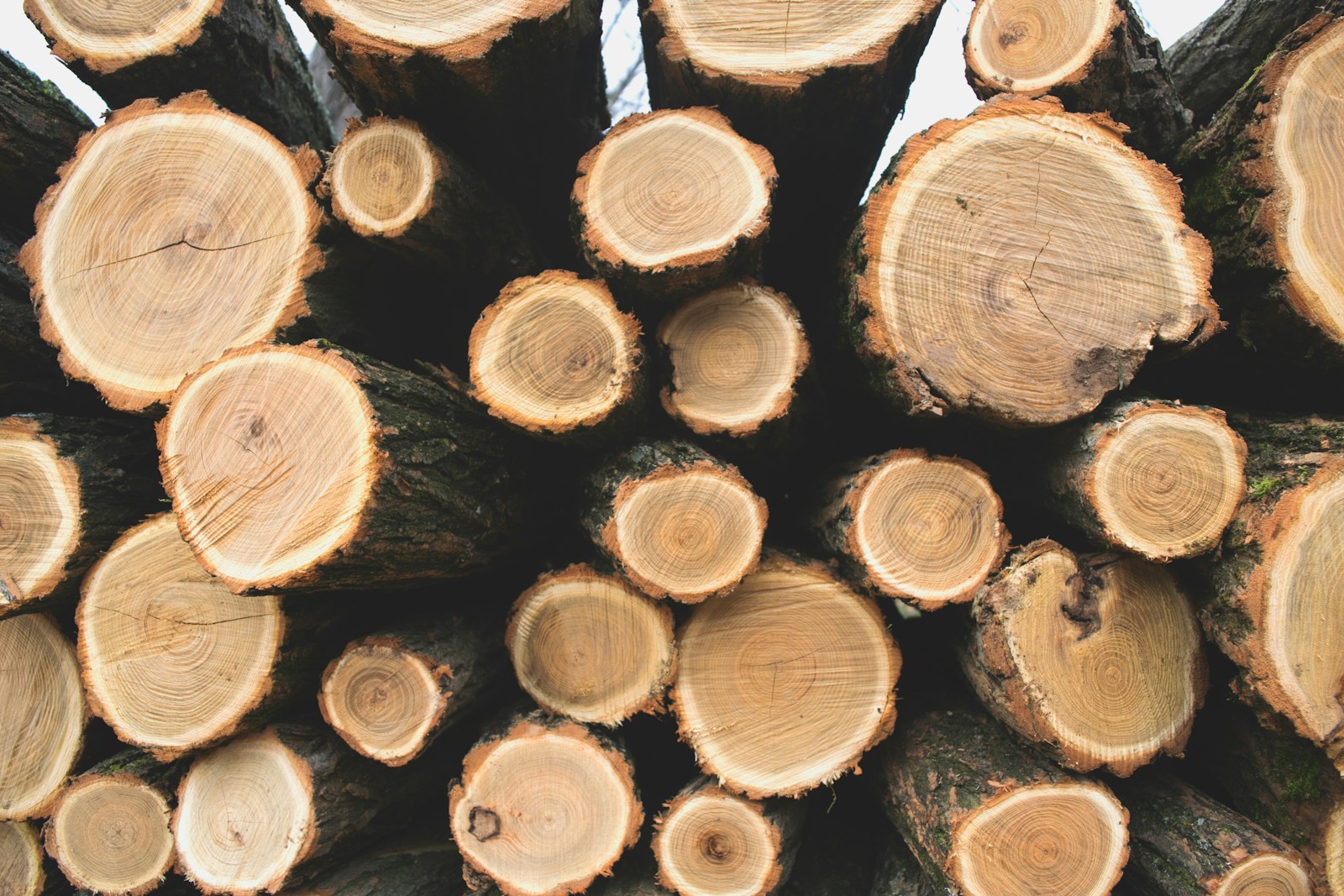
Timber
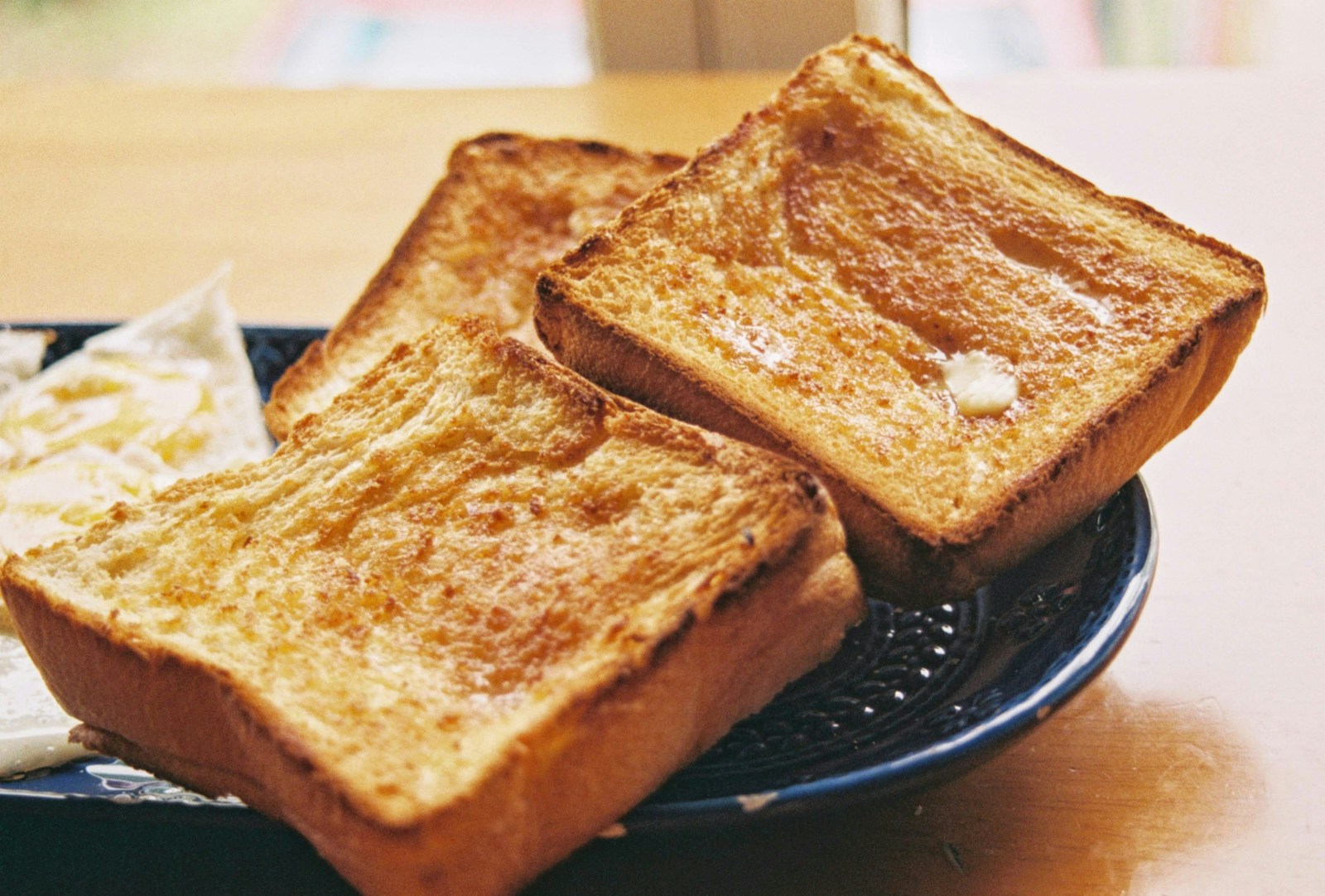
Toast
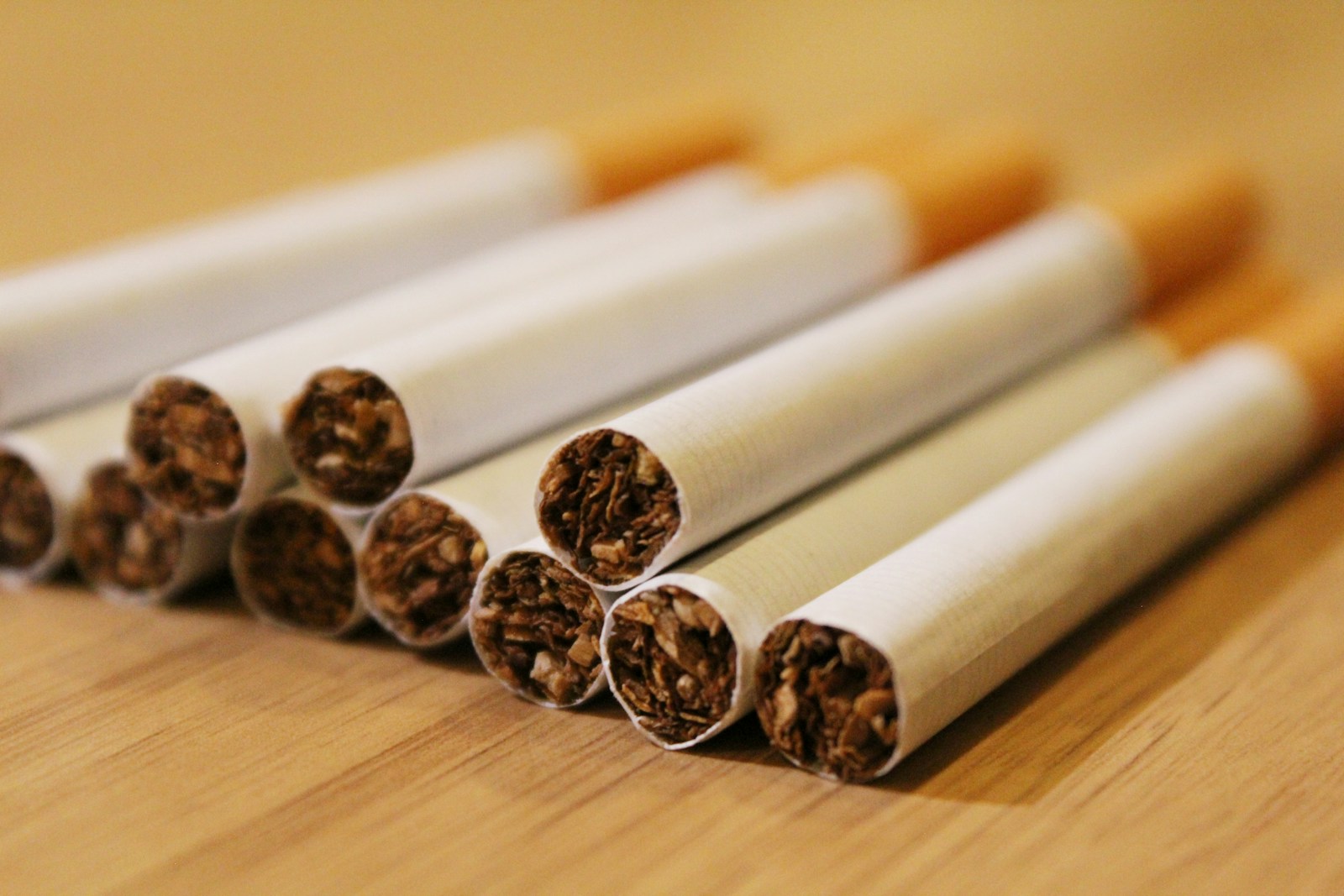
Tobacco

Tomato seeds
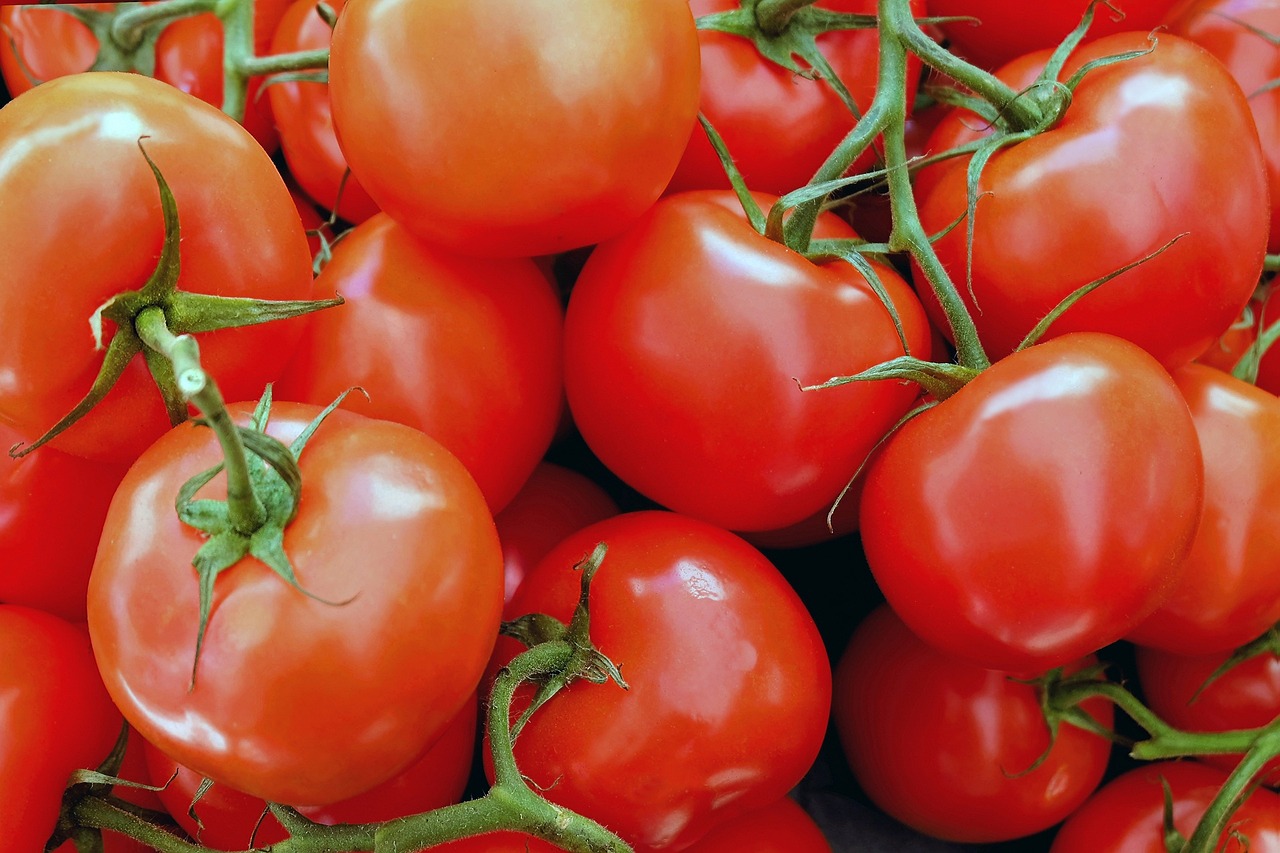
Tomatoes
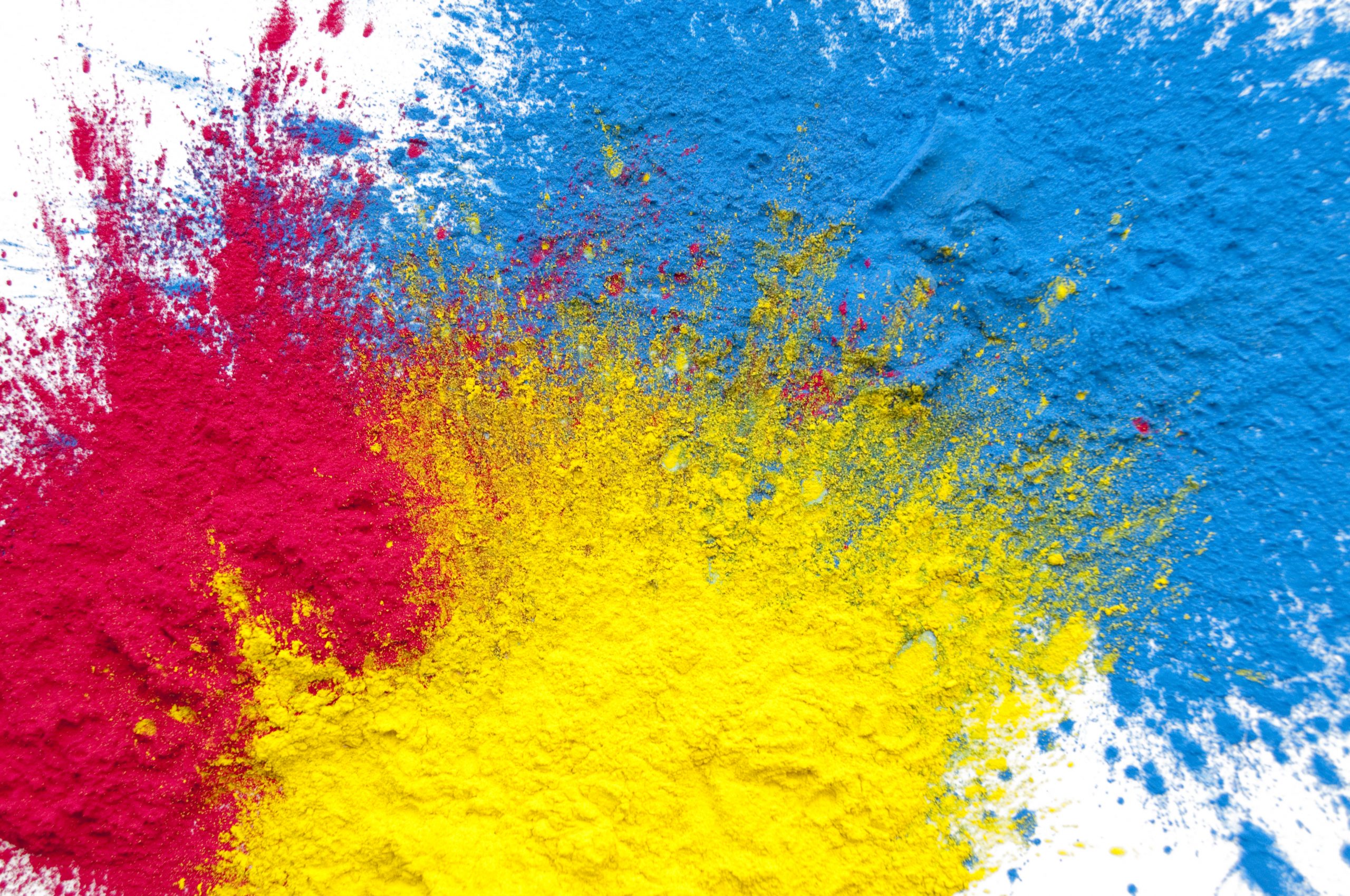
Toner
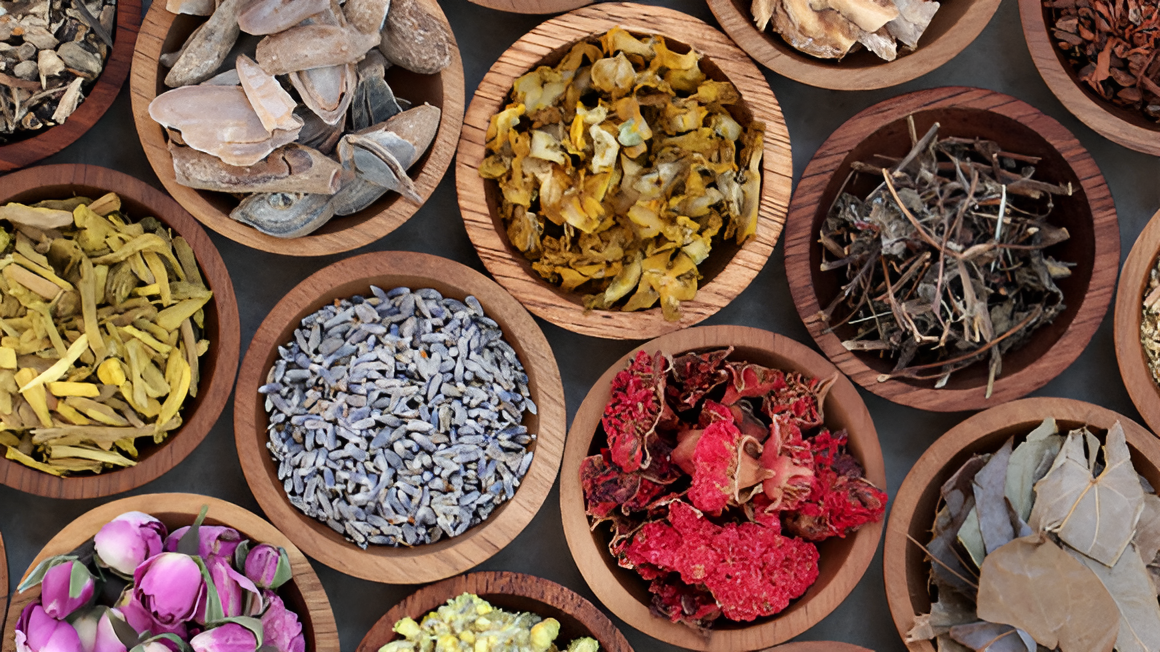
Traditional chinese medicine
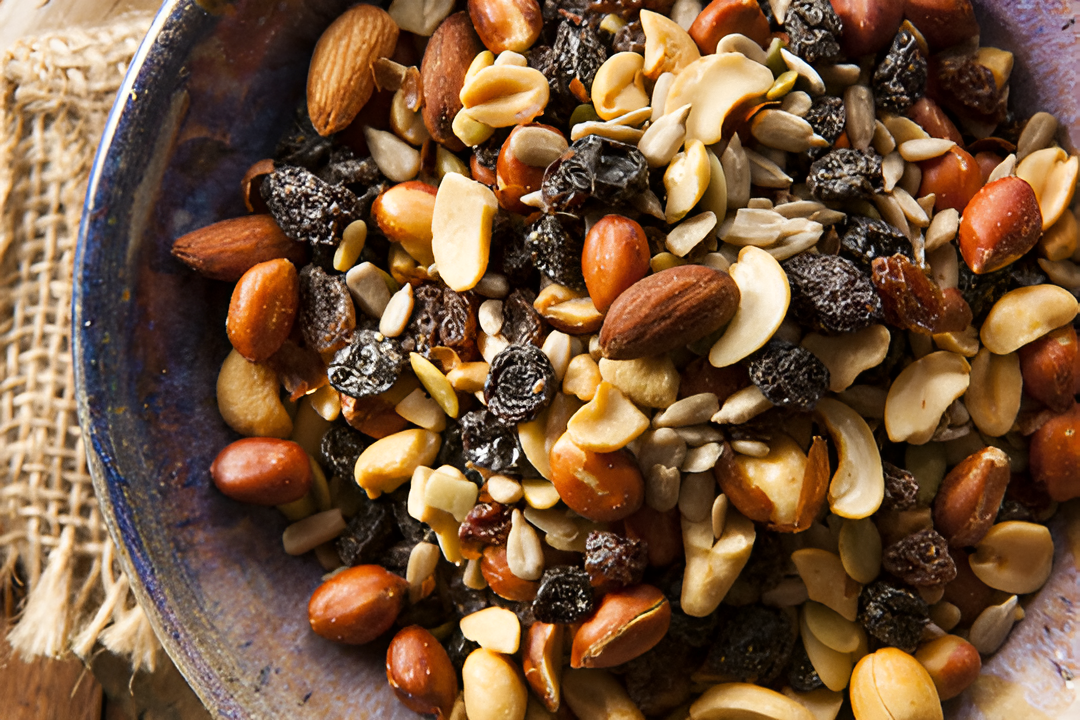
Trail mix
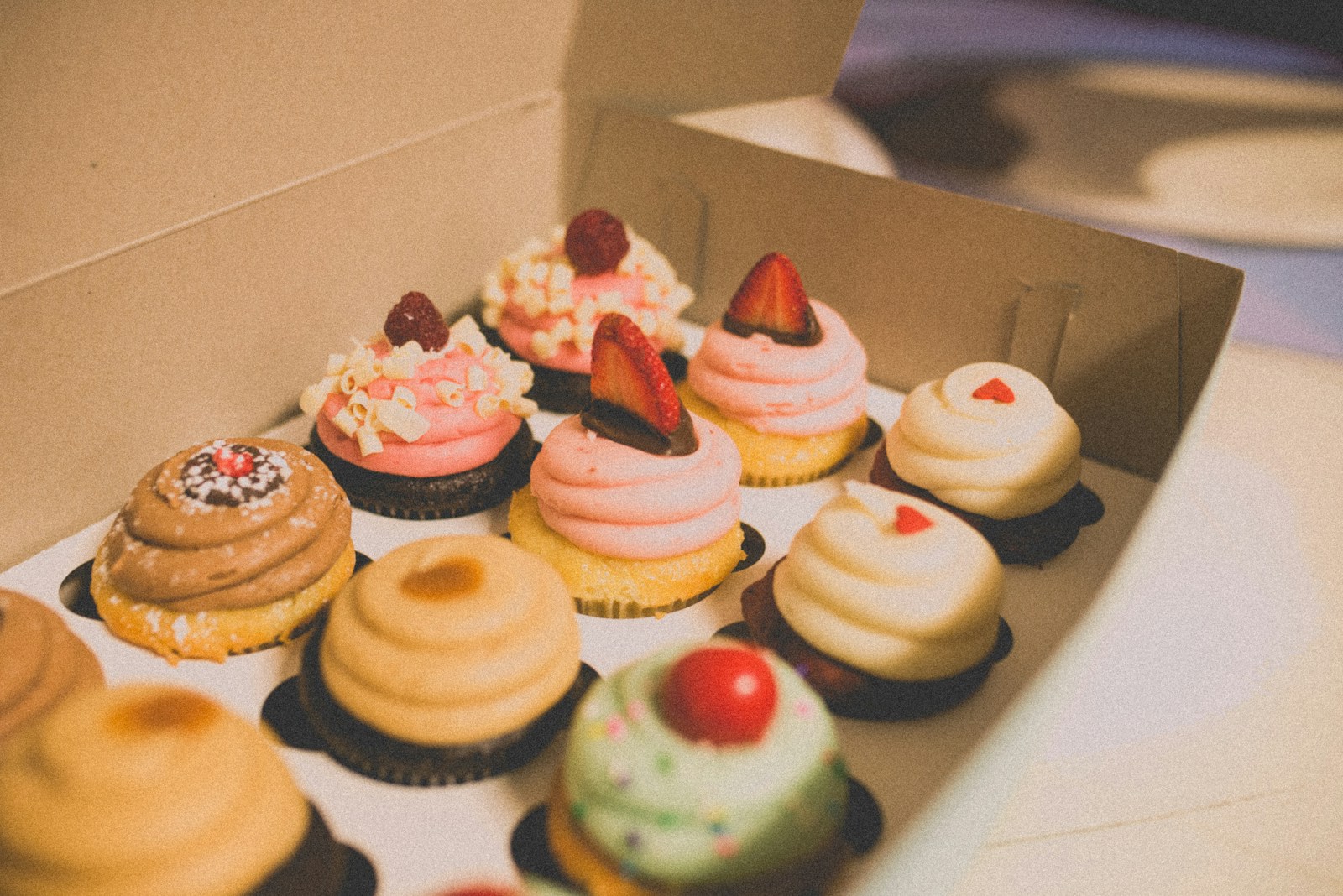
Treats
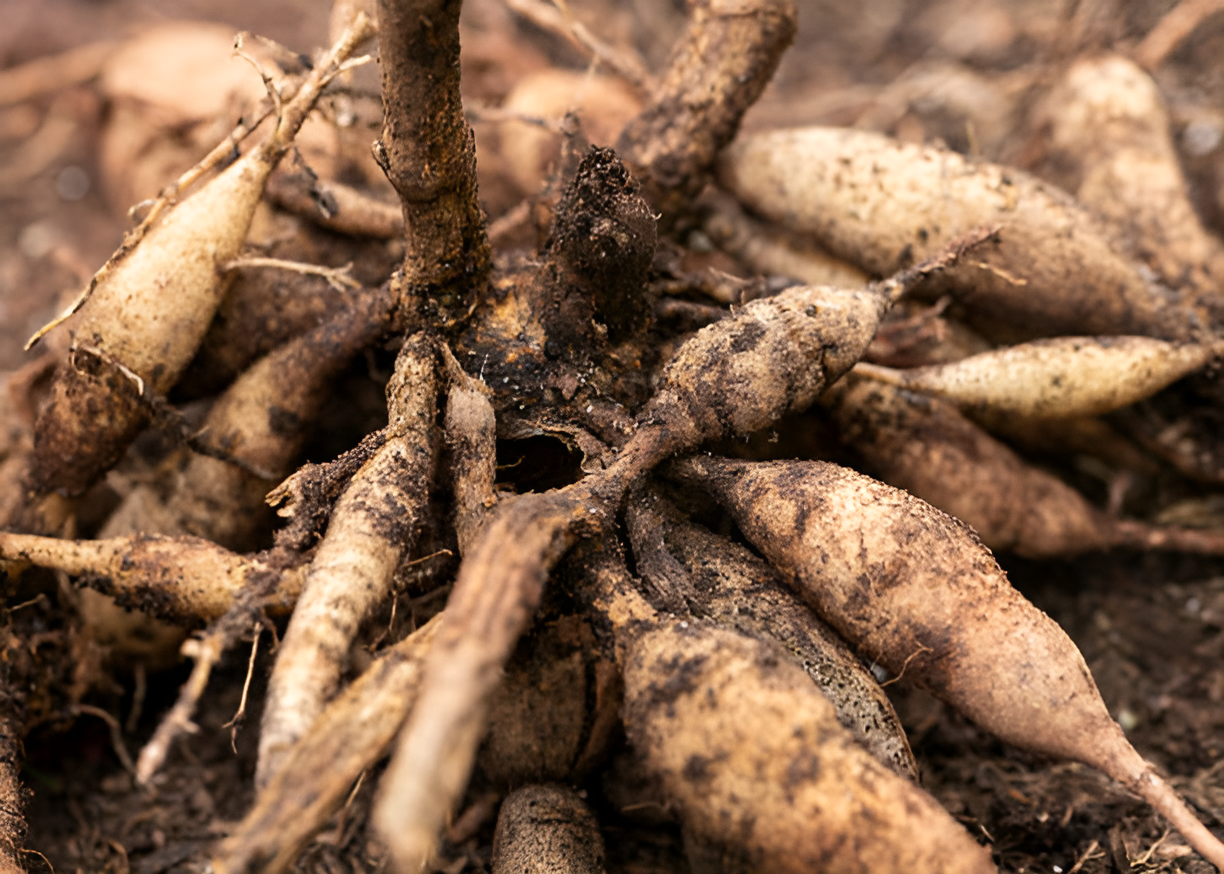
Tubers

Uncoated tablets
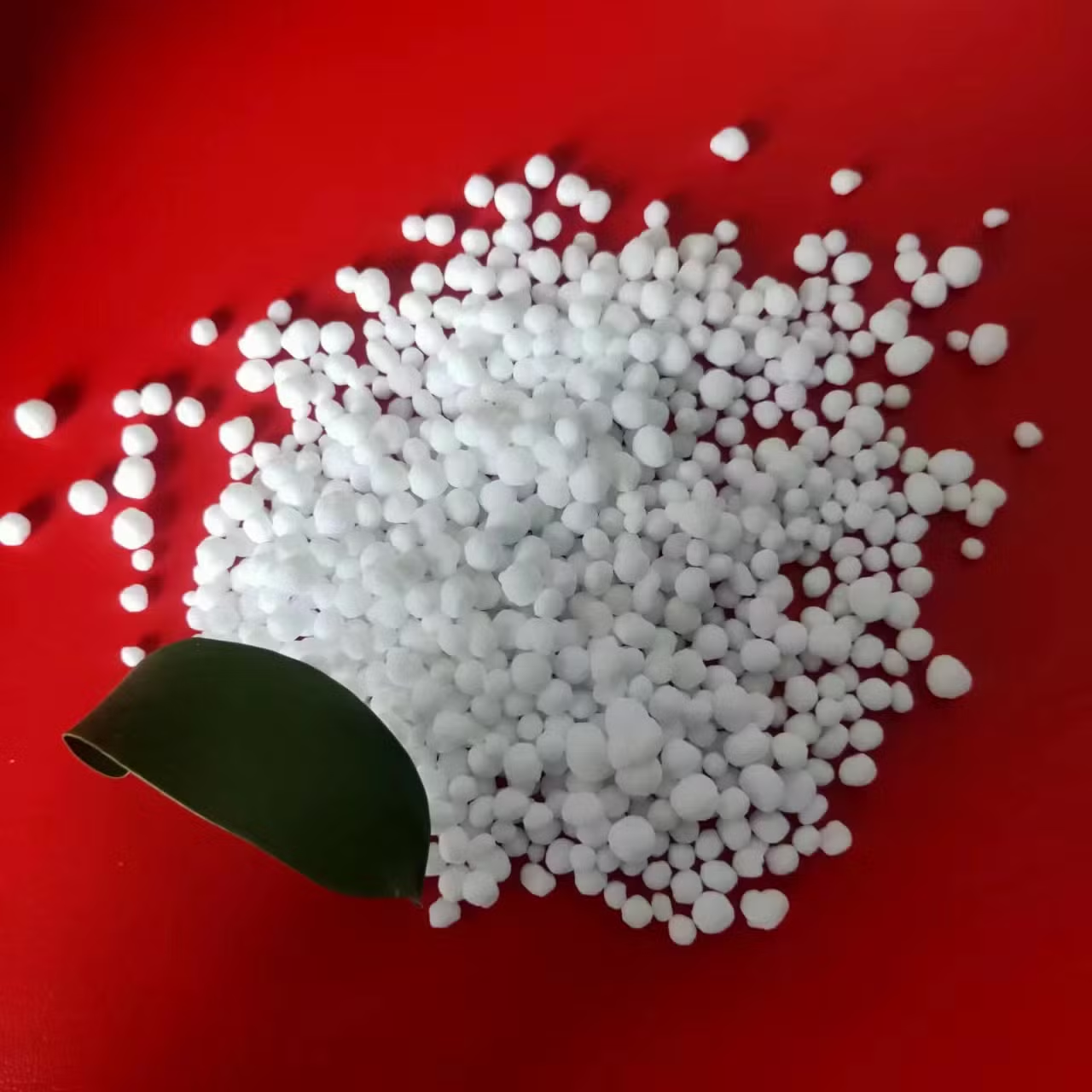
Urea
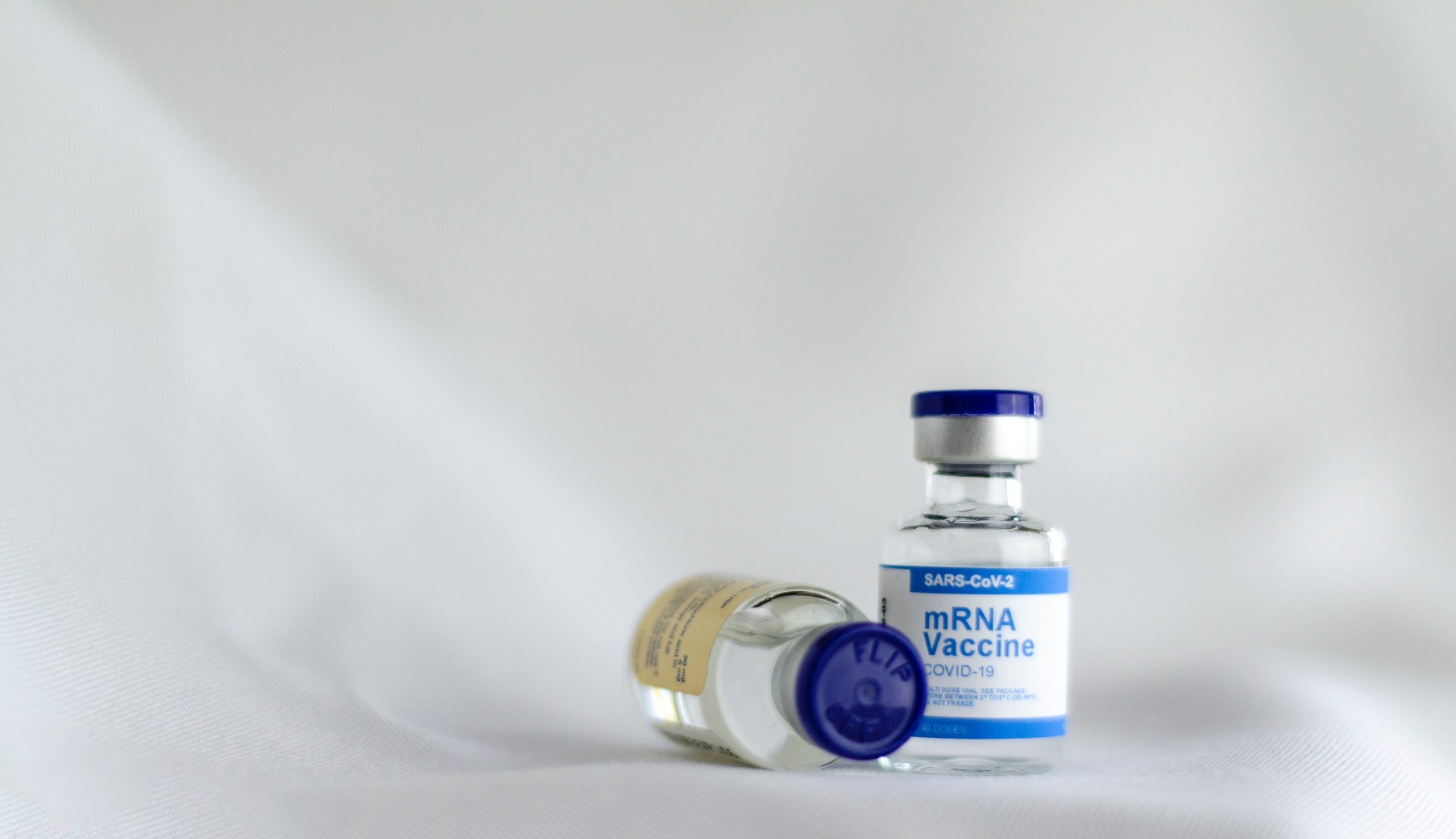
Vaccines
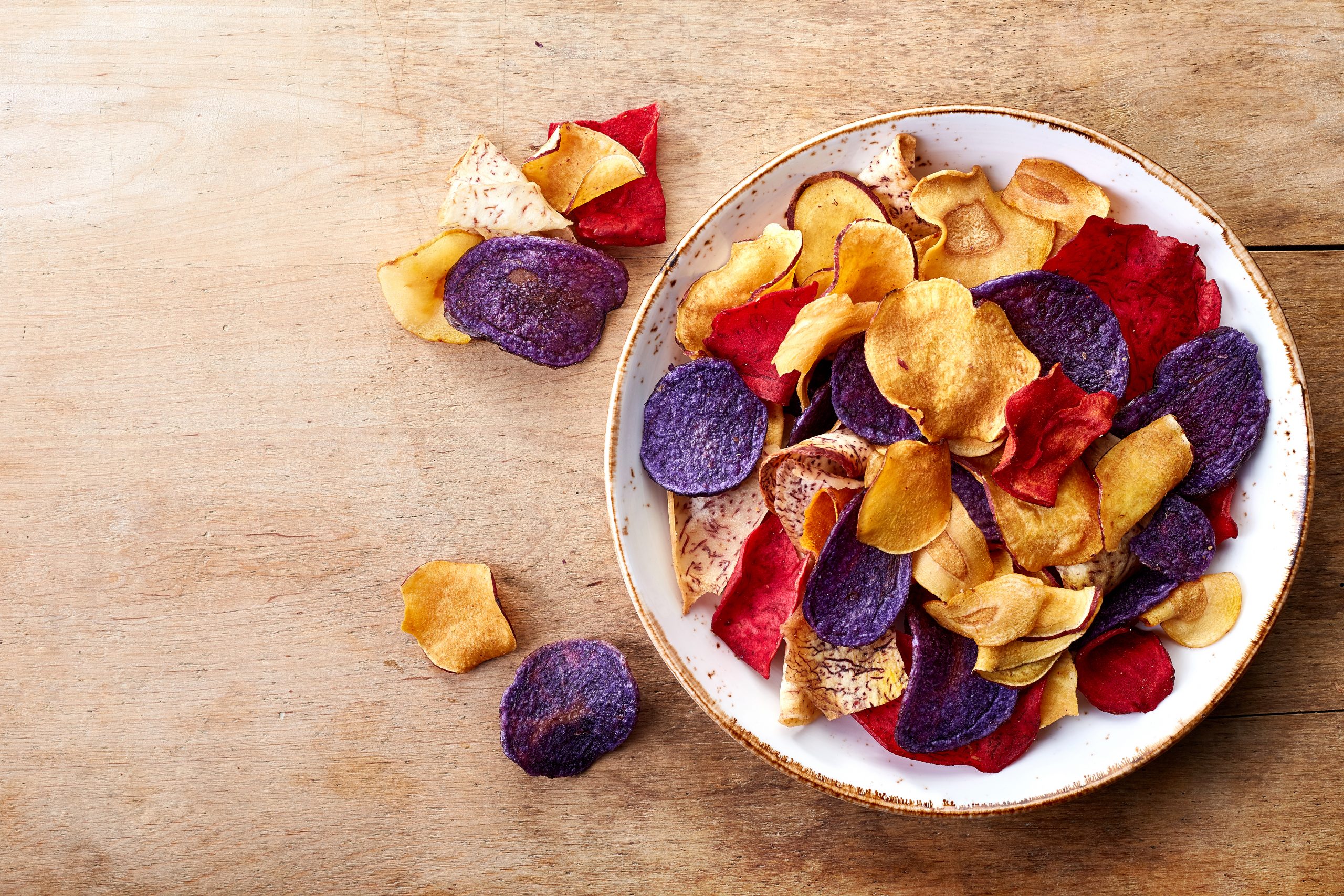
Vegetable chips
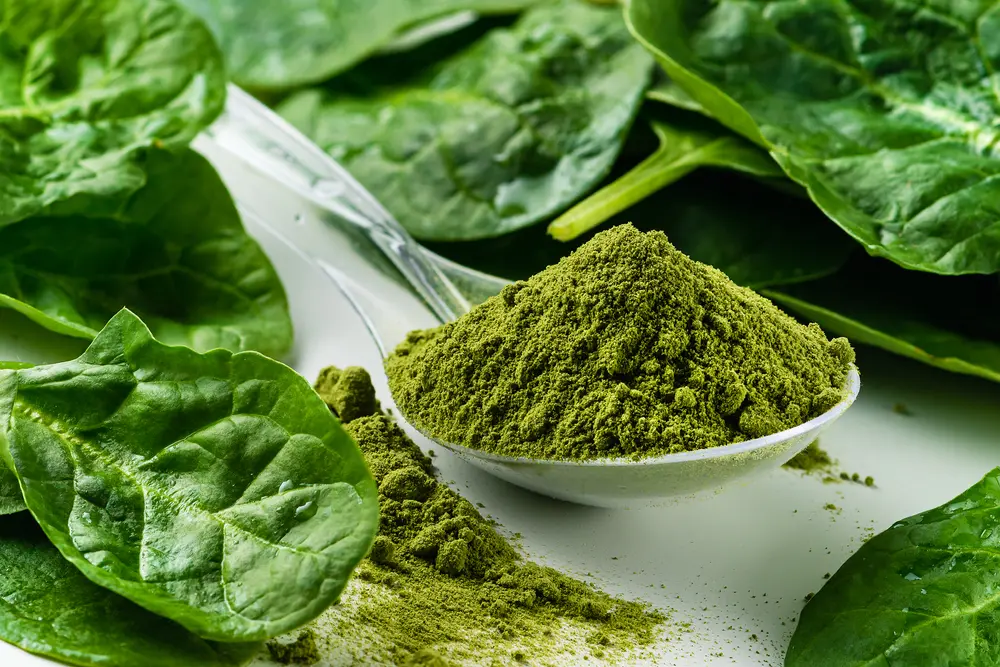
Vegetable powder
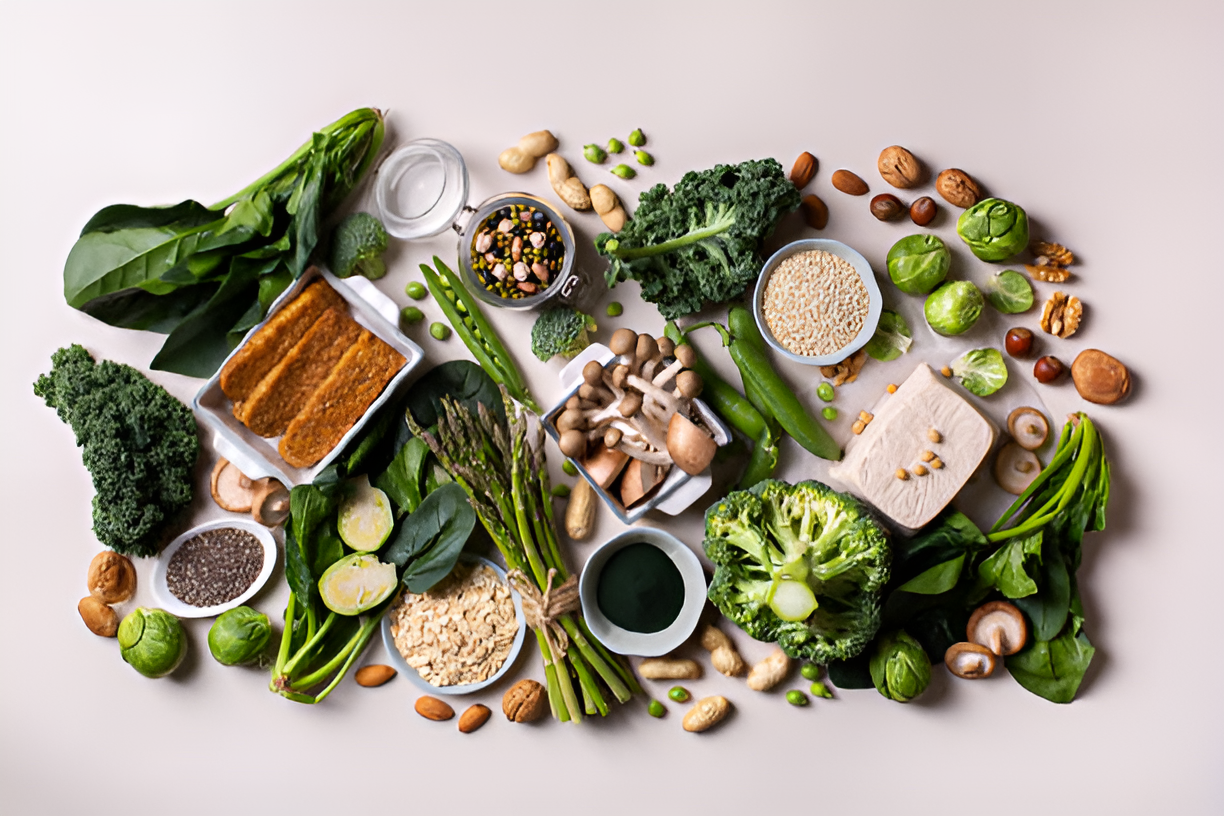
Vegetable proteins
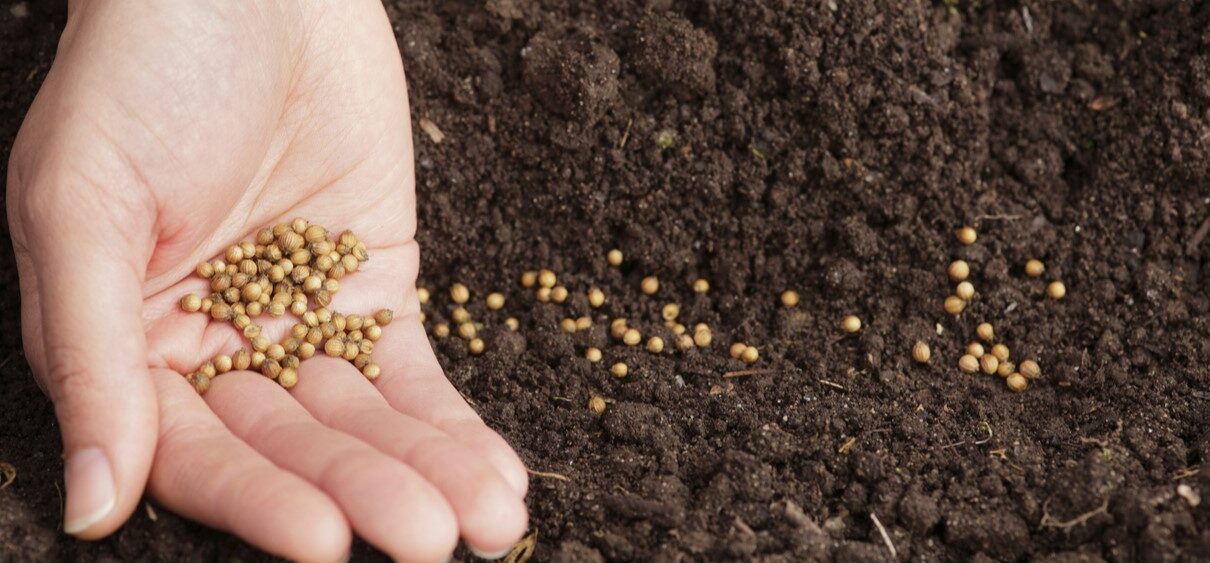
Vegetable seeds
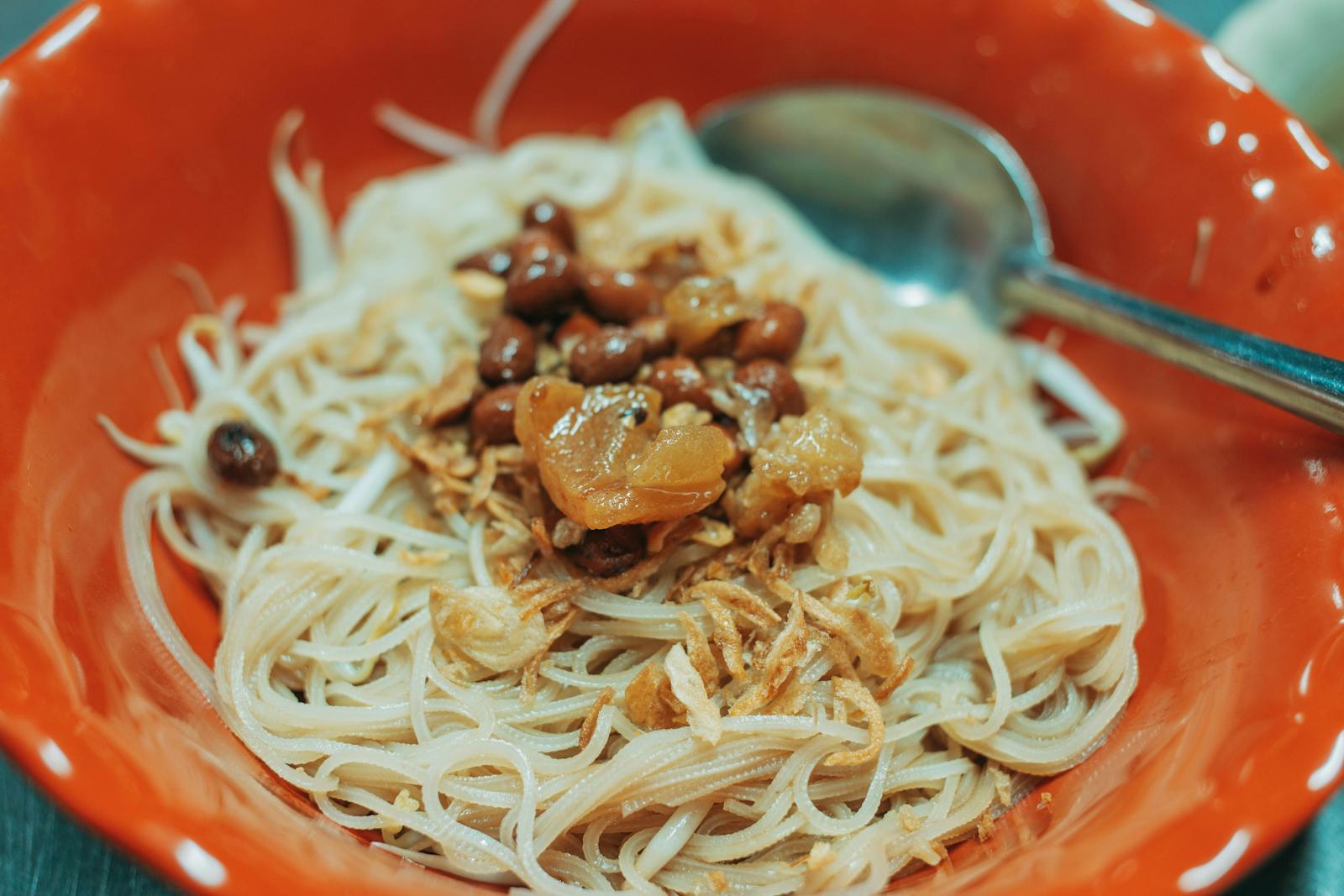
Vermicelli
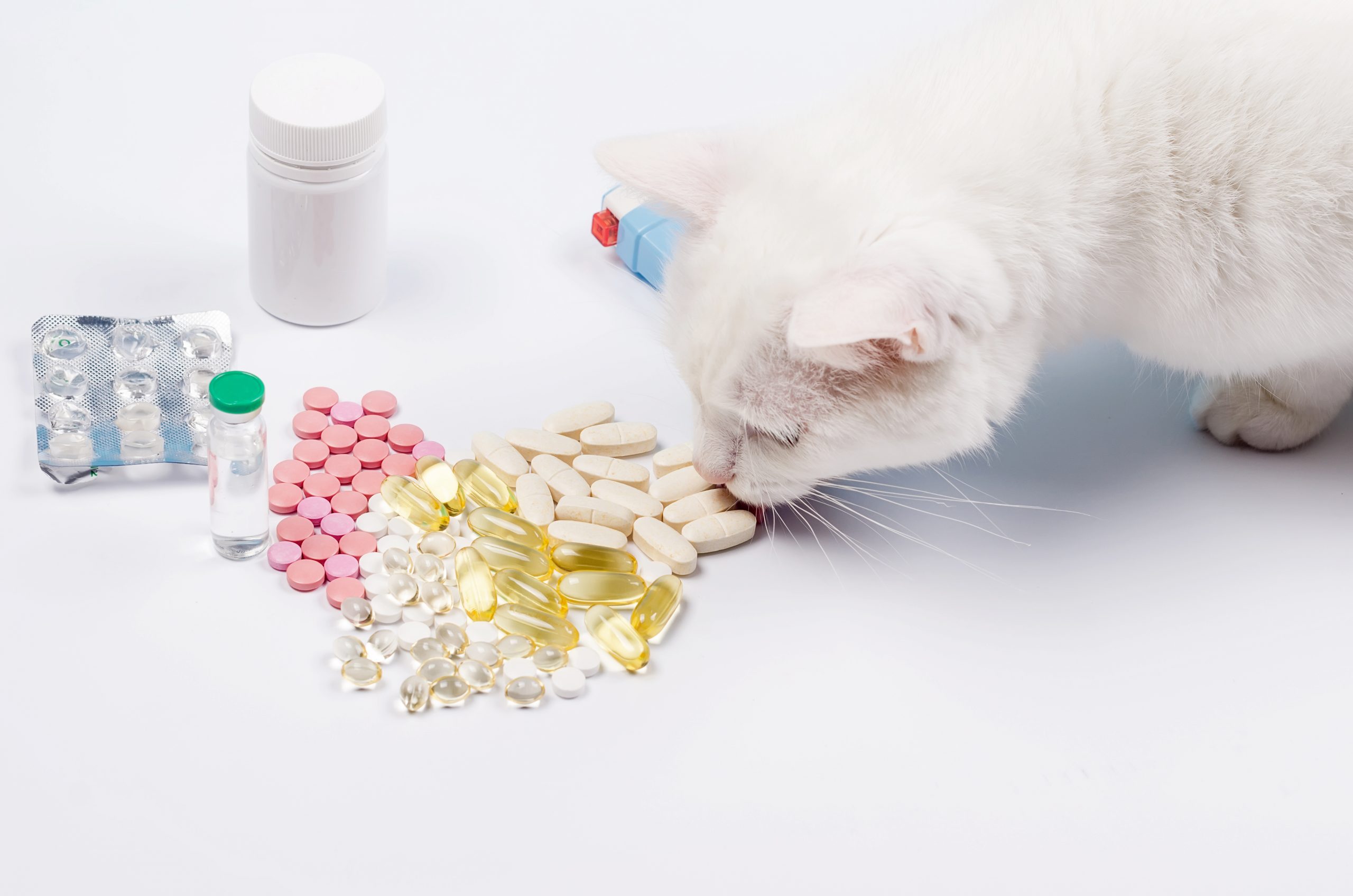
Veterinary tablets
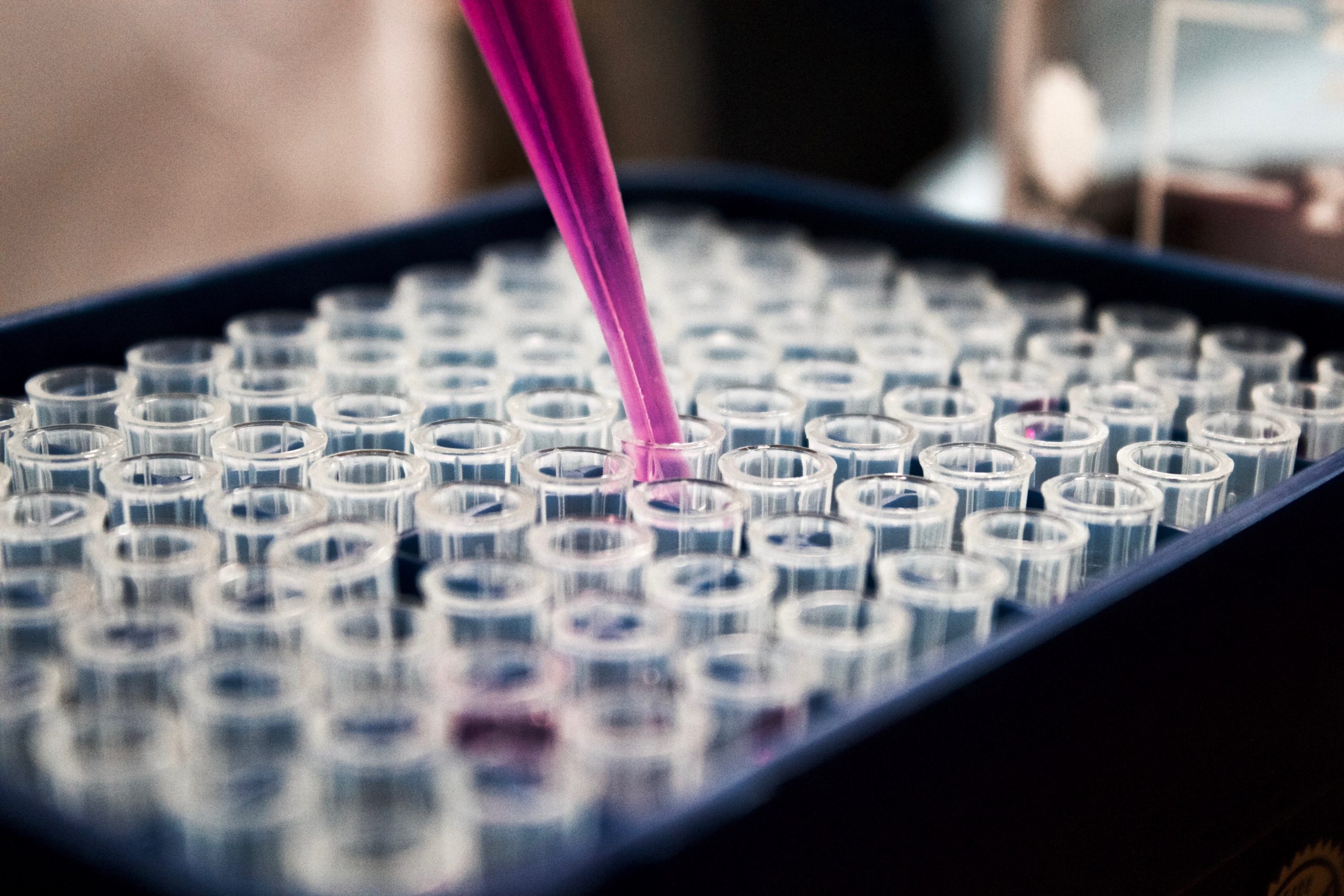
Vials
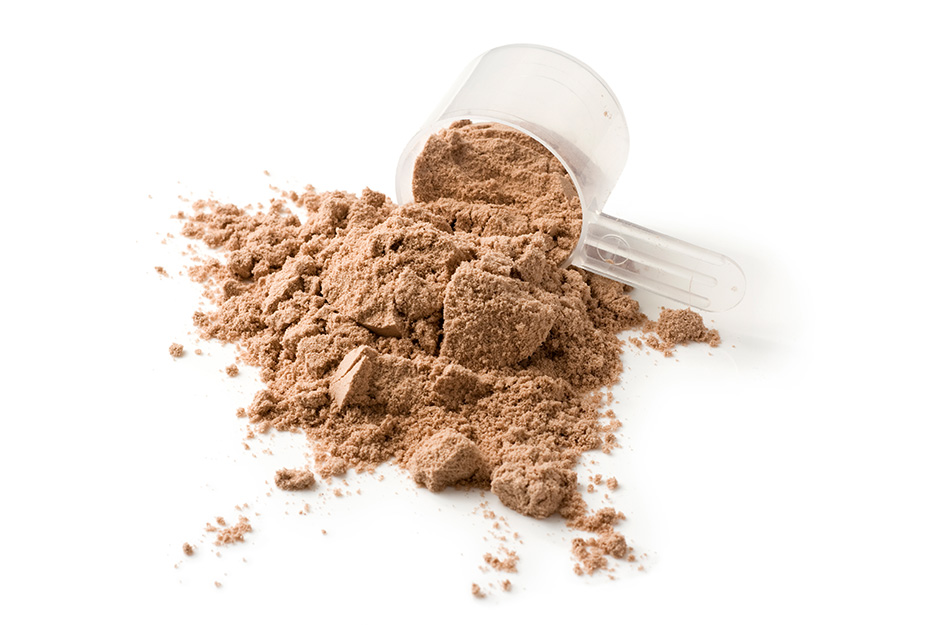
Vitamin premixes
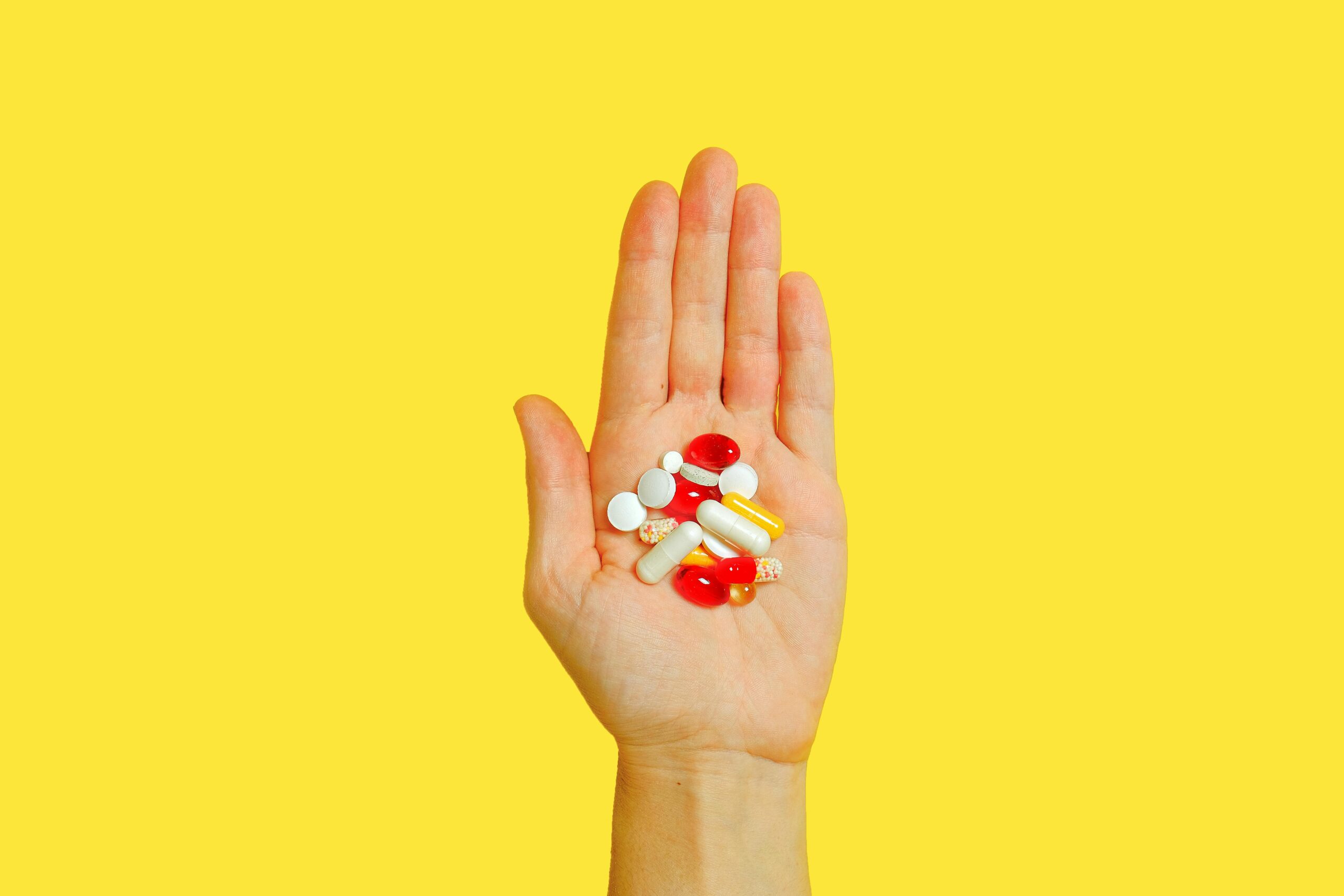
Vitamins
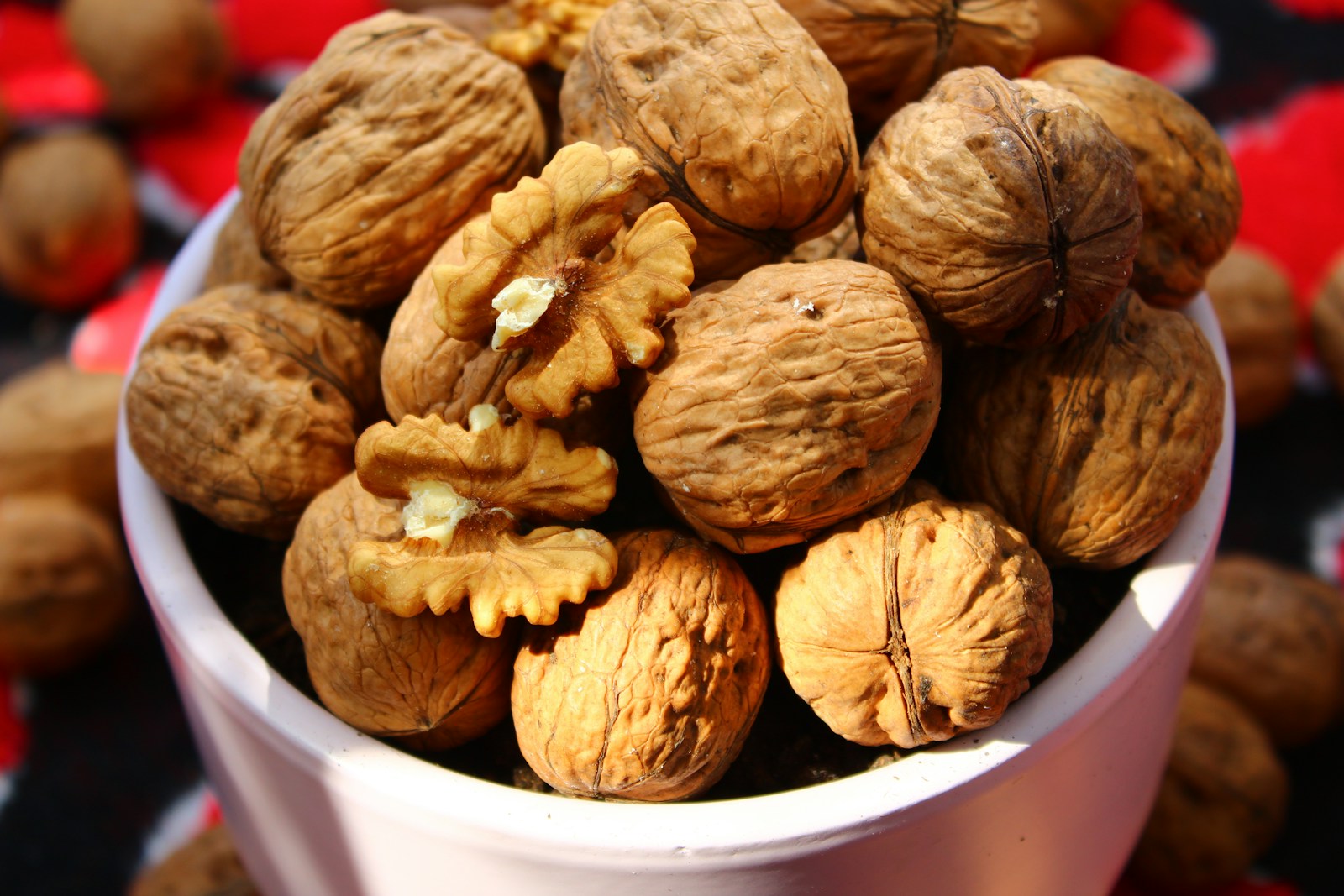
Walnuts
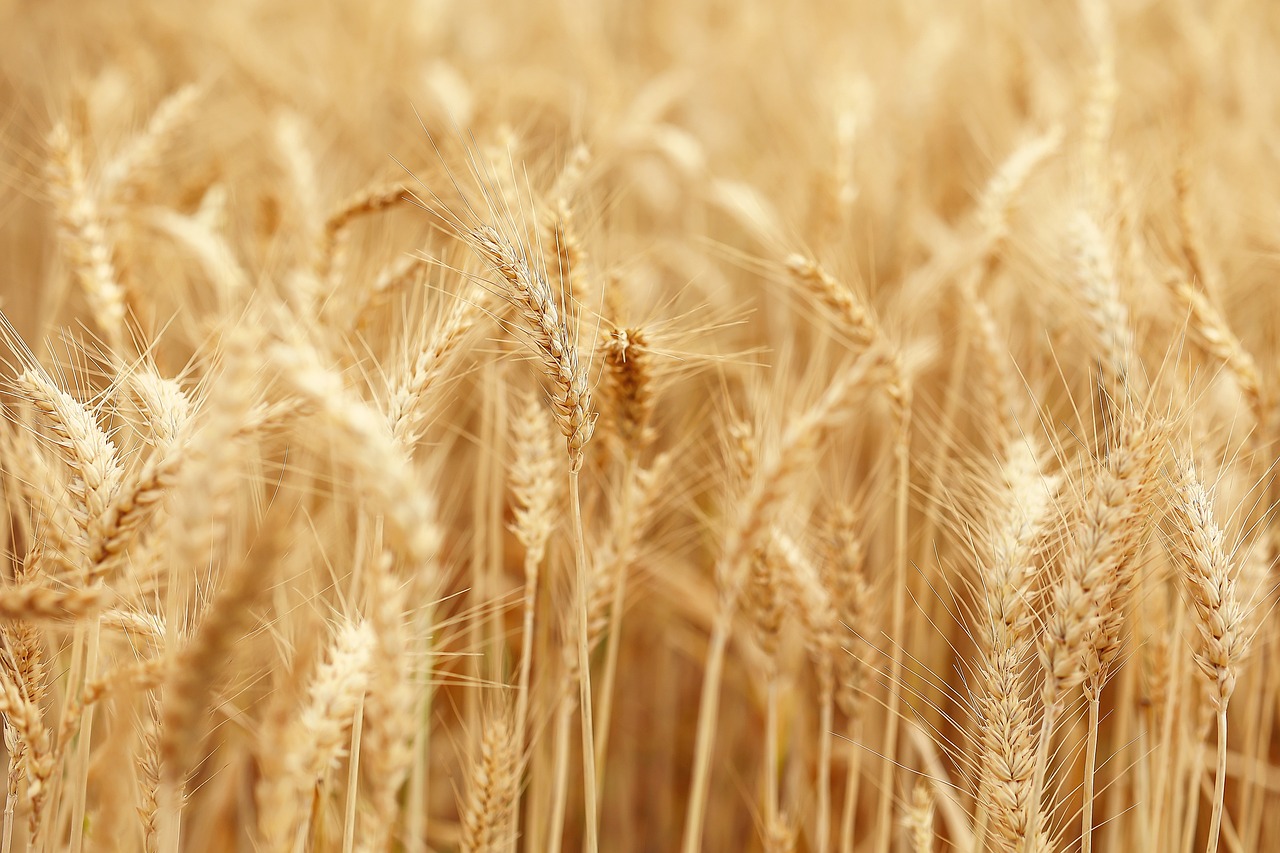
Wheat
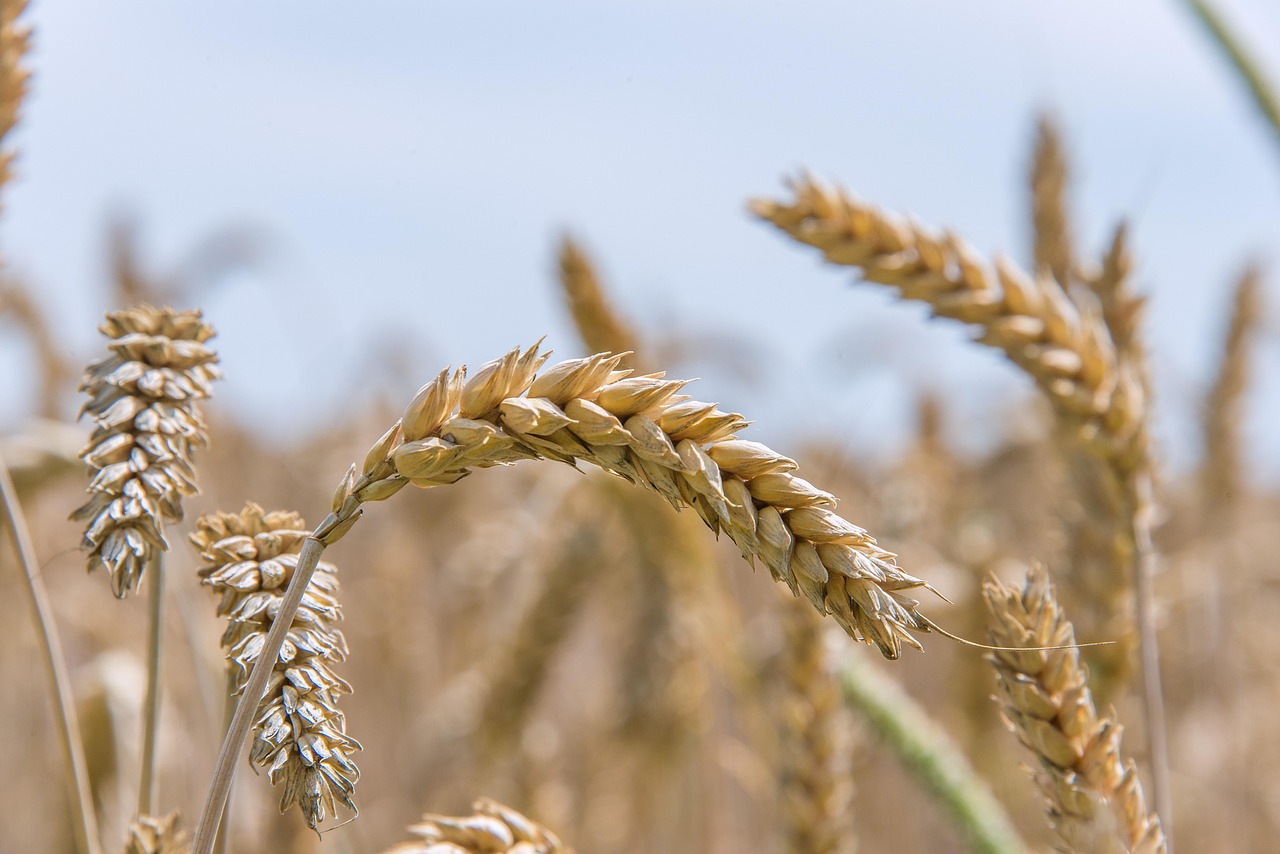
Wheat grains
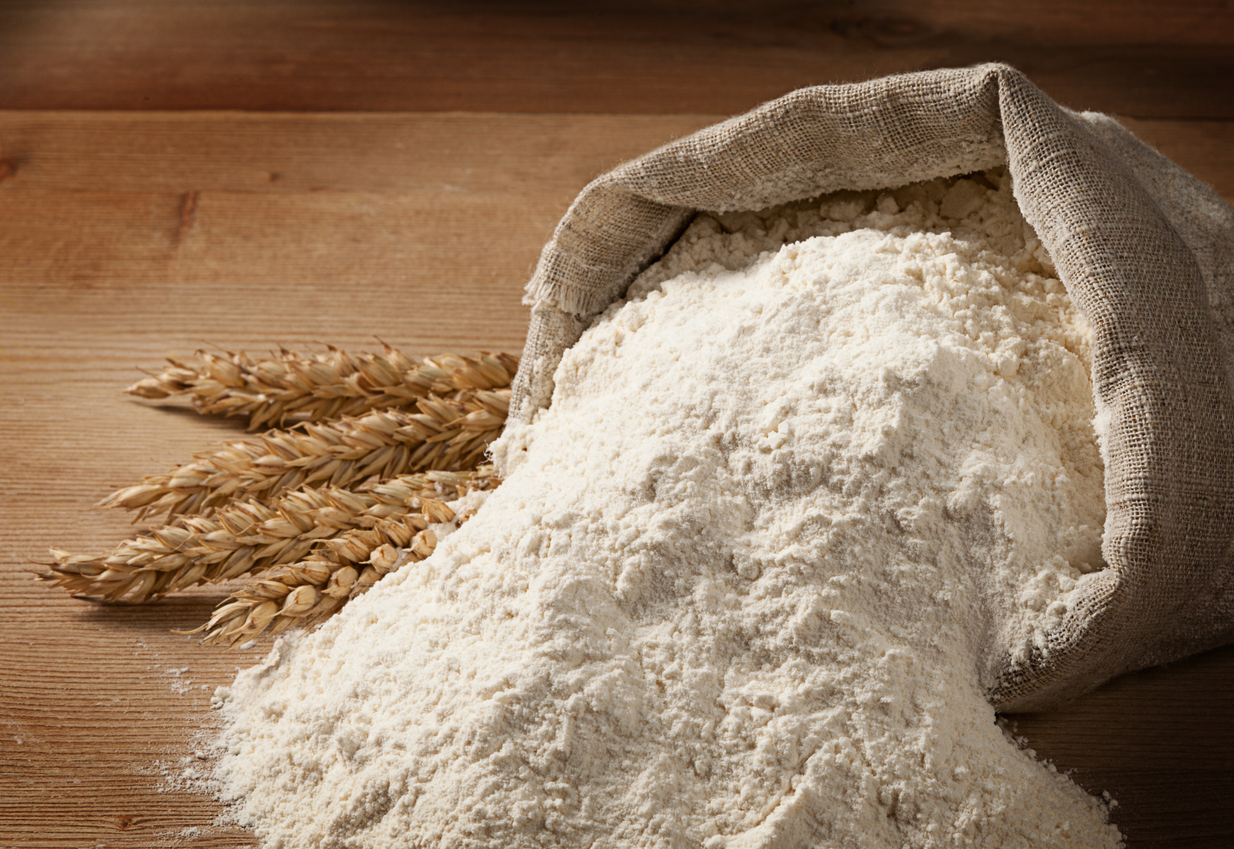
Wheat starch
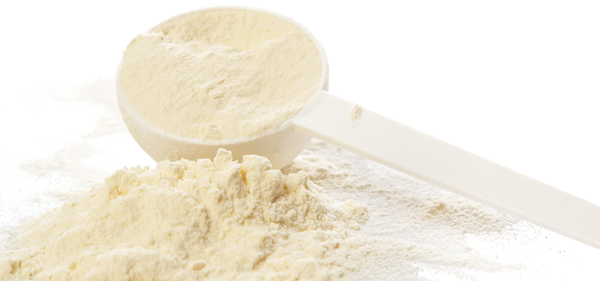
Whey protein
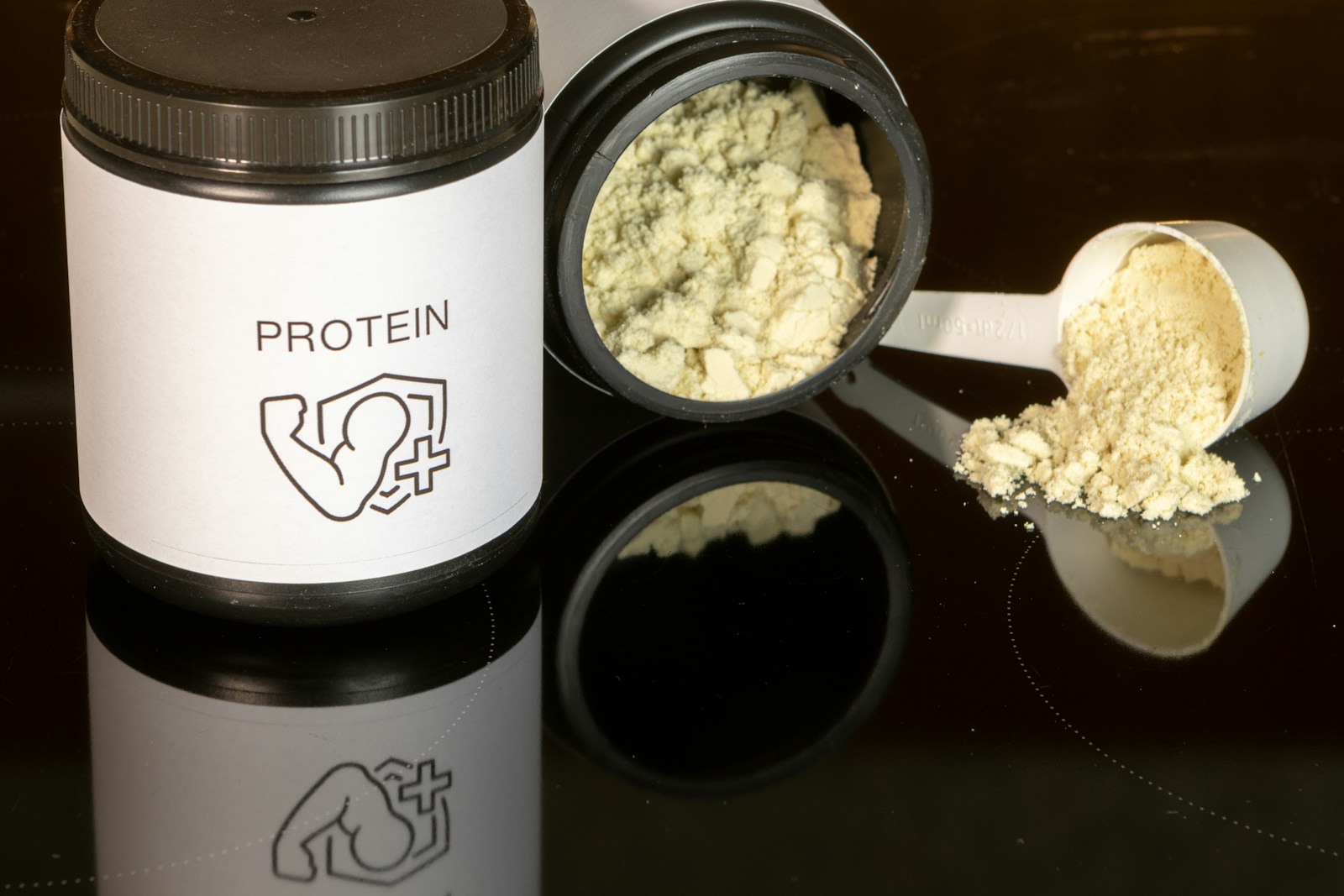
Whey protein isolate
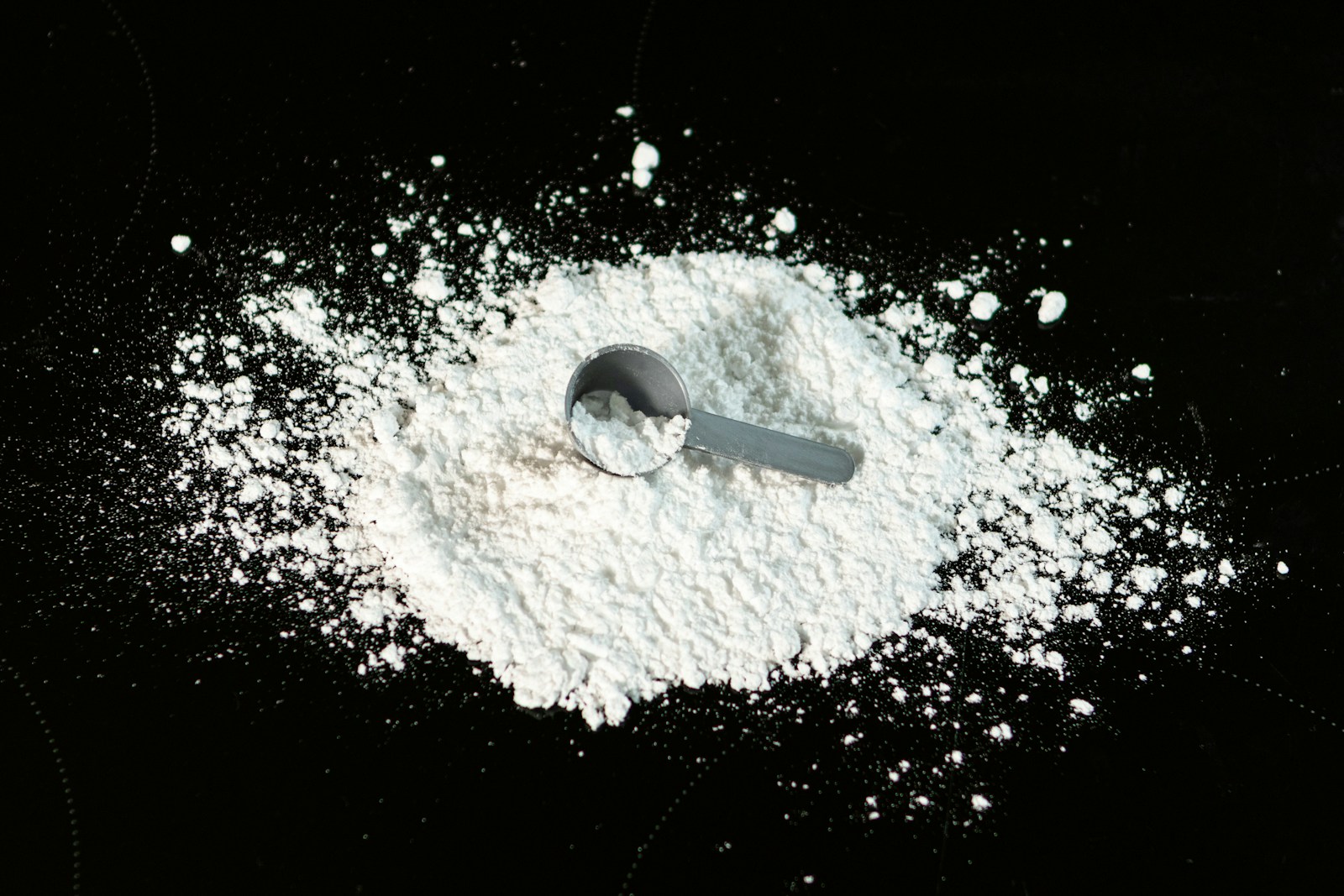
Whey protein powder
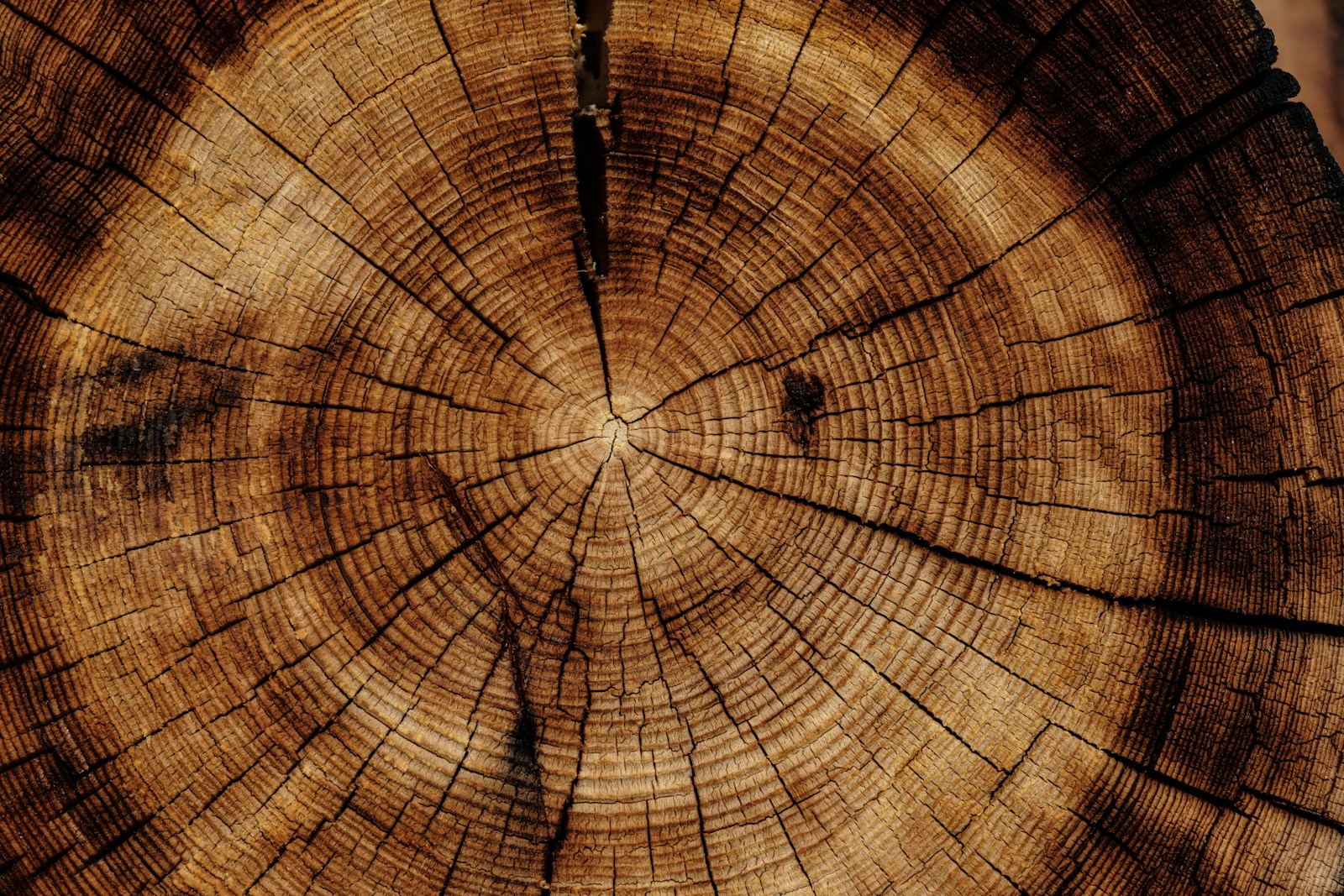
Wood
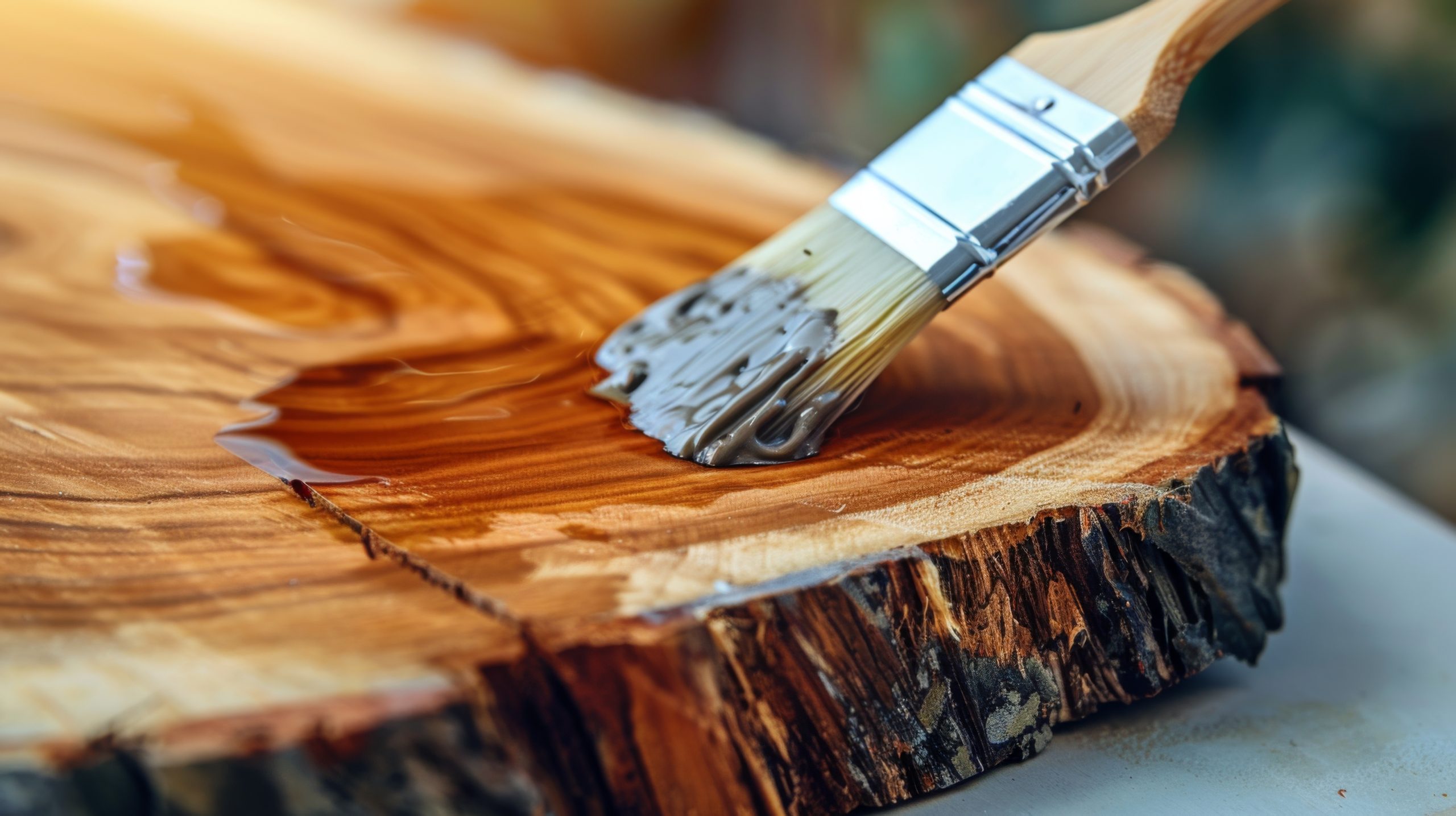
Wood coatings
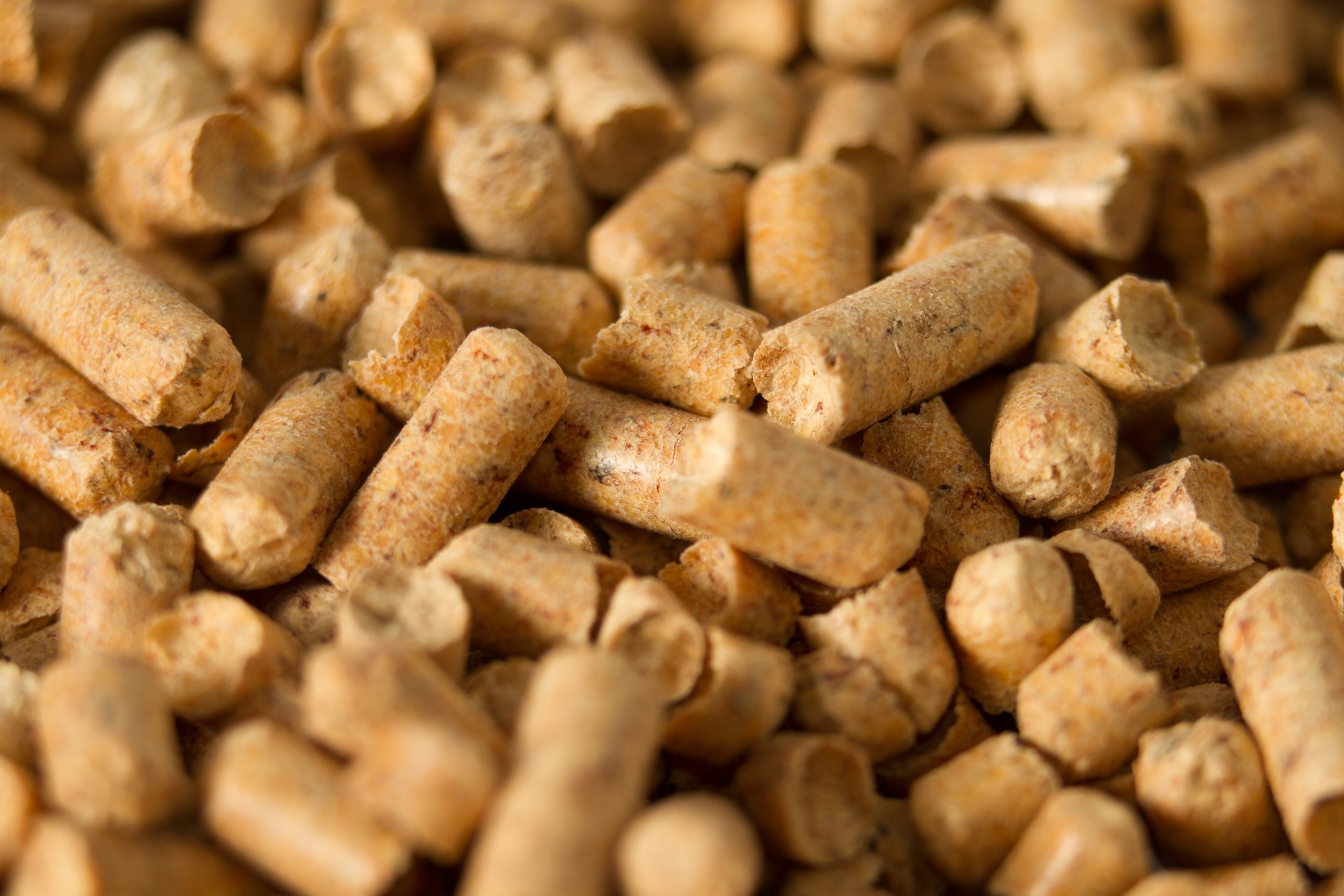
Wood pellets
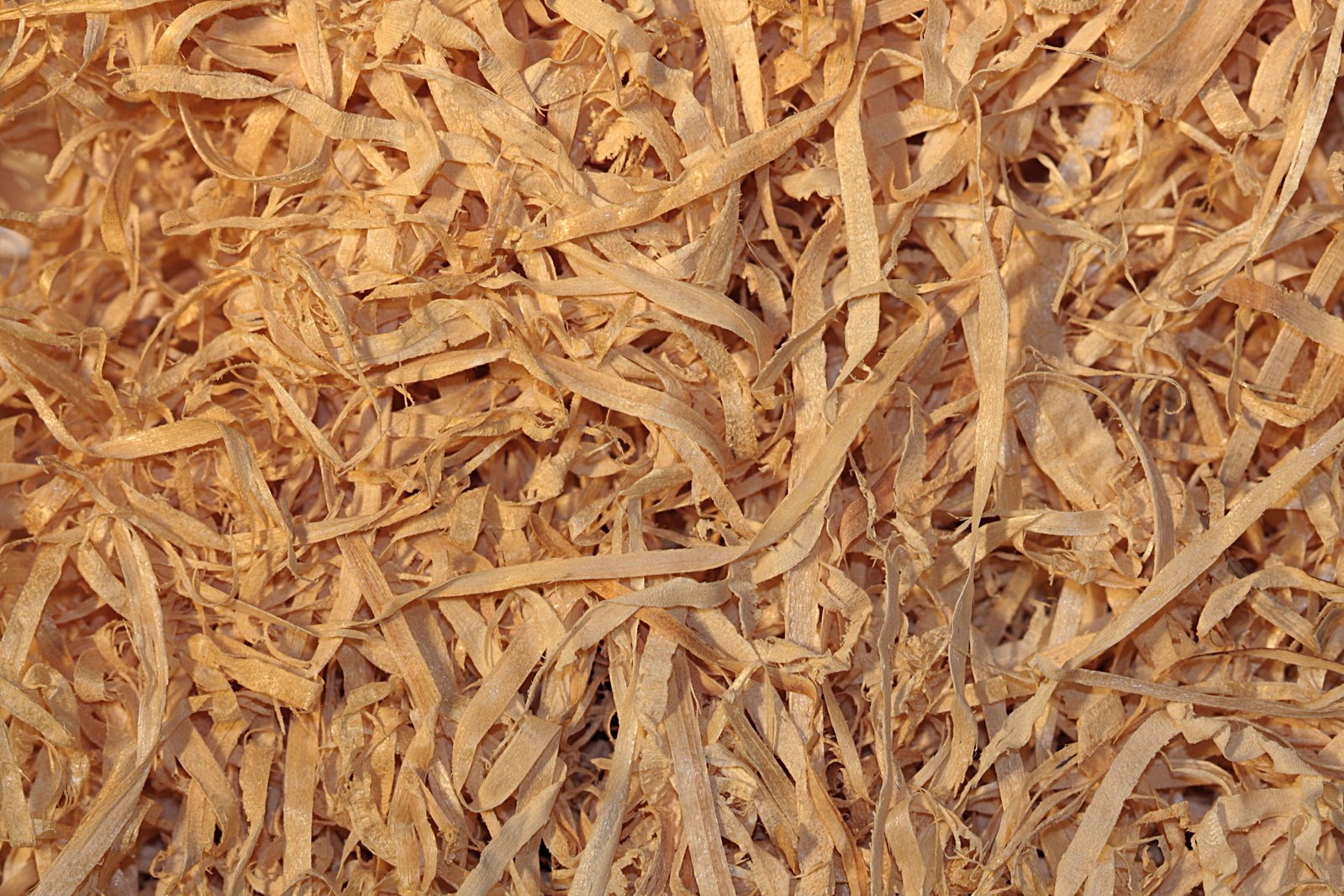
Wood pulp
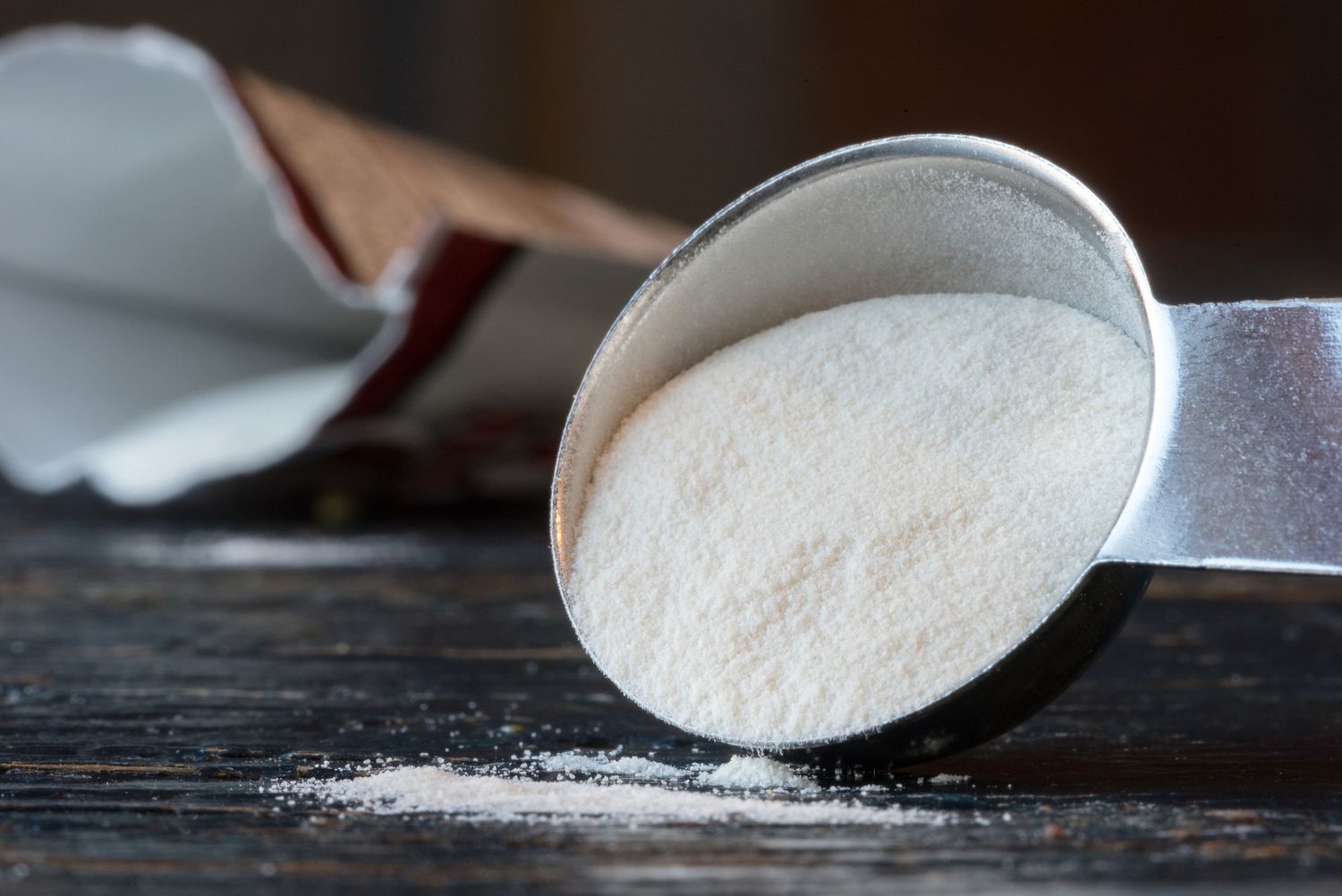
Xanthan gum
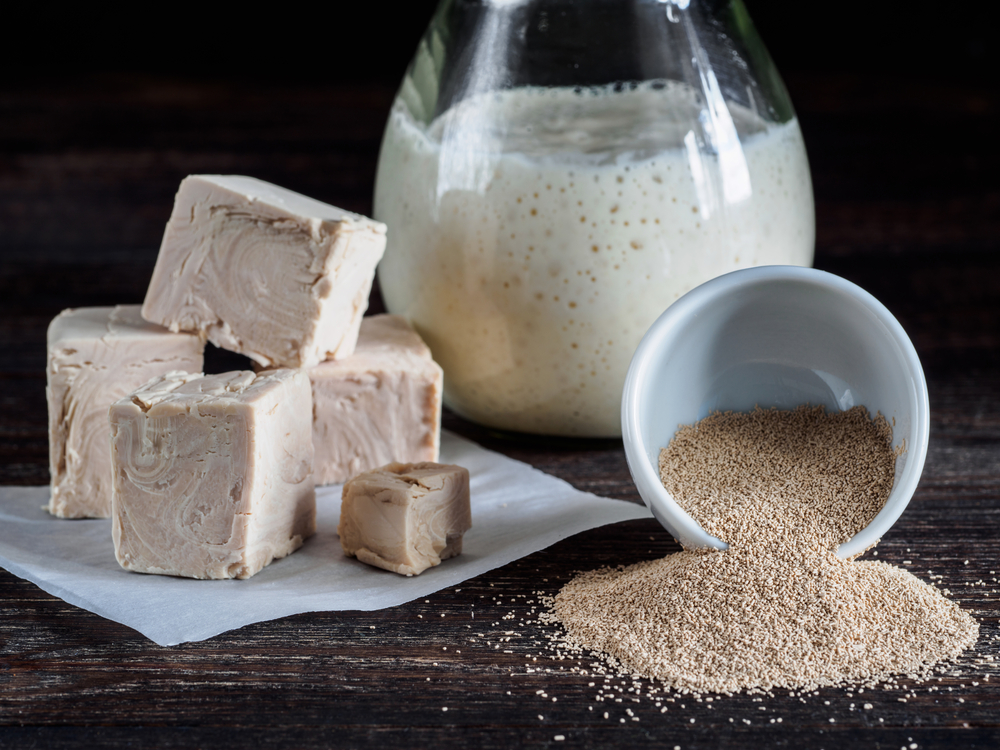
Yeast
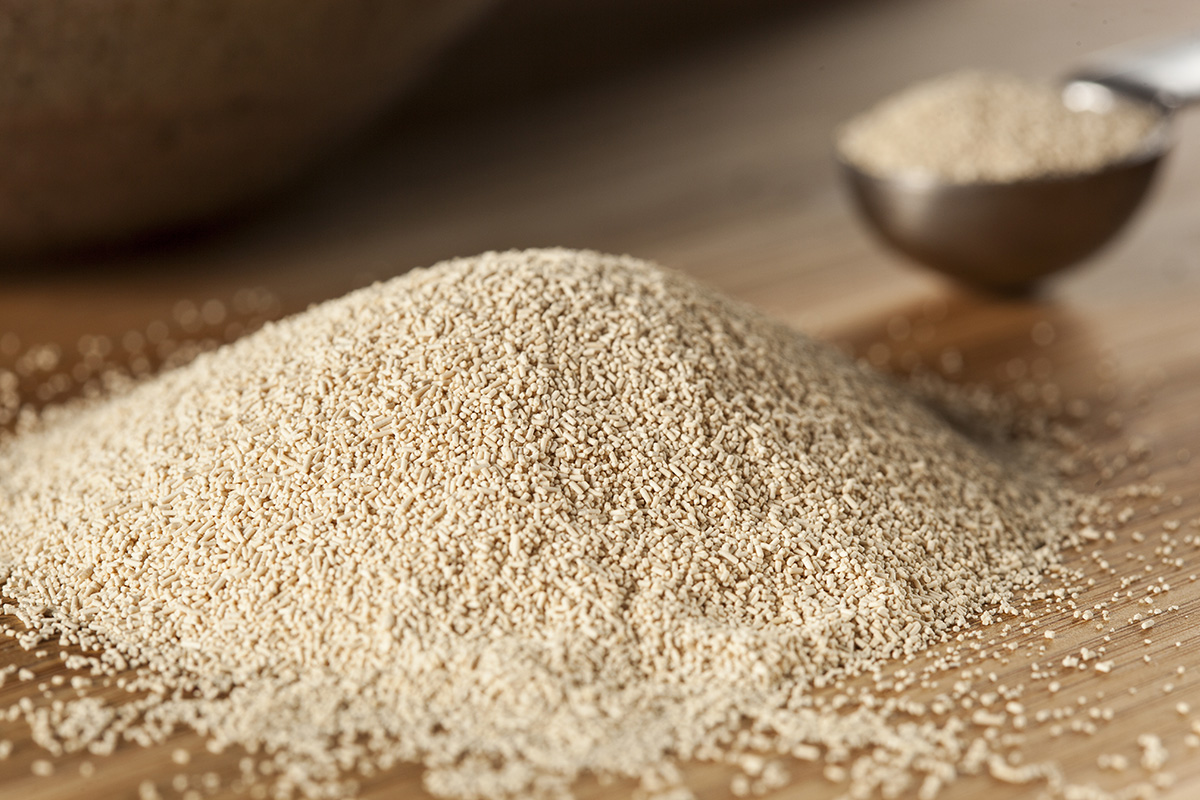
Yeast extract
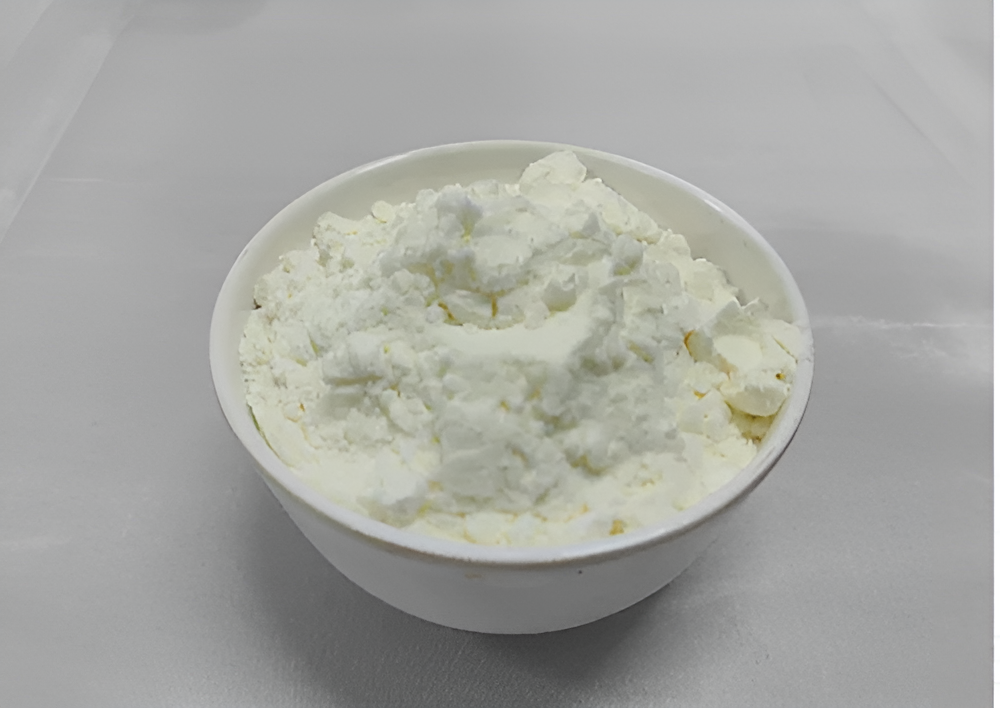
Yogurt powder
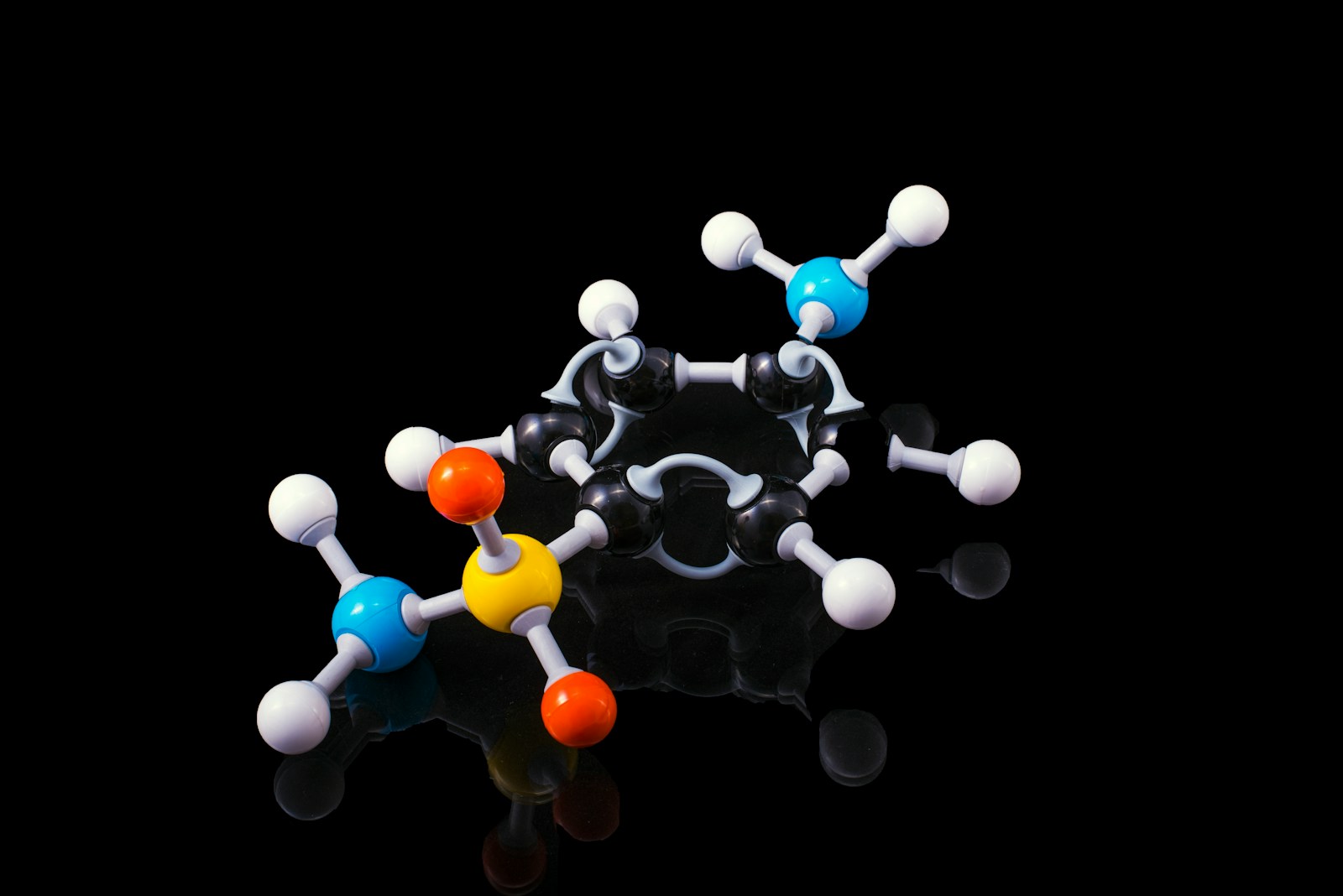
Zeolite catalysts
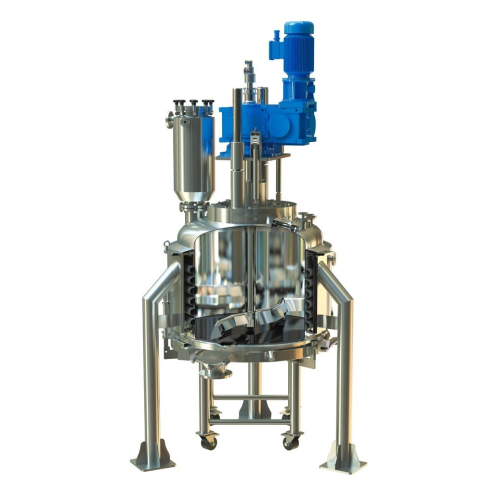
Agitated nutsche filter dryers
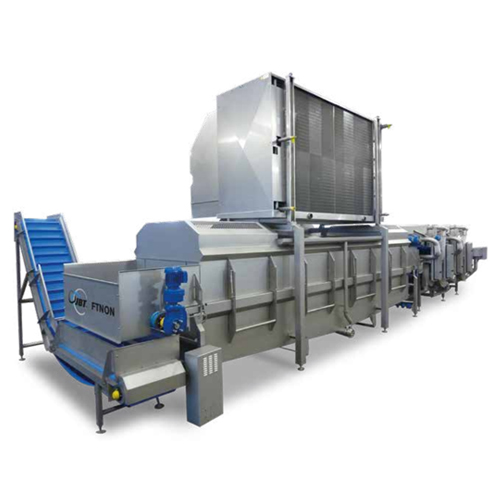
Air dryers
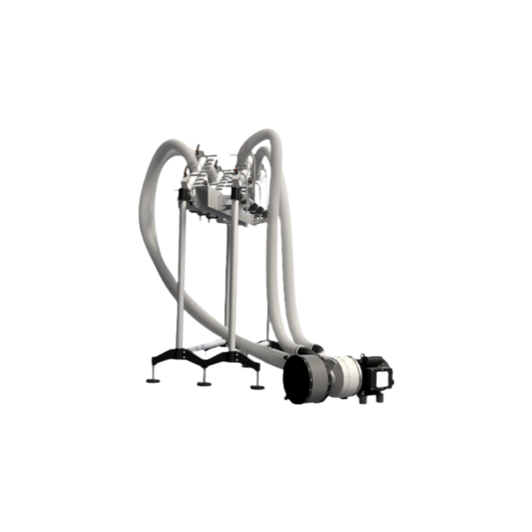
Air knife dryers
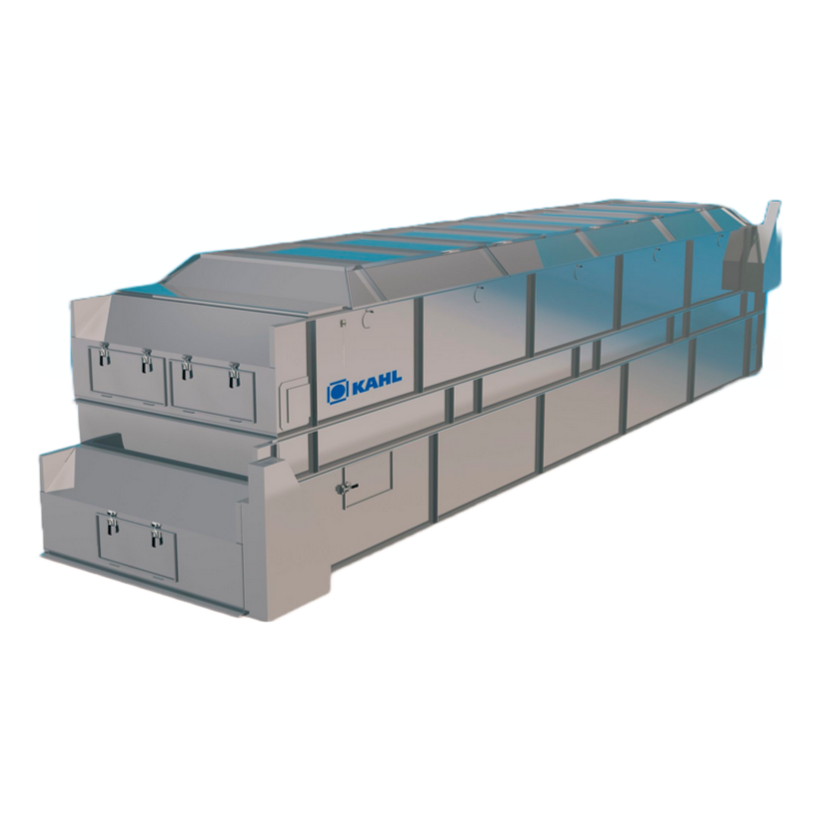
Belt dryers
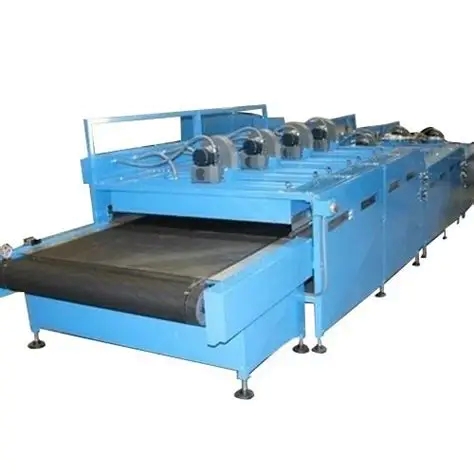
Box dryers
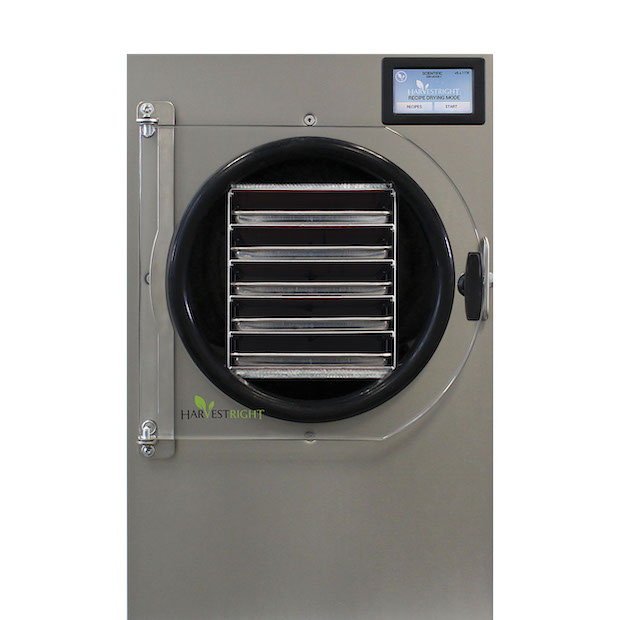
Cannabis freeze dryers
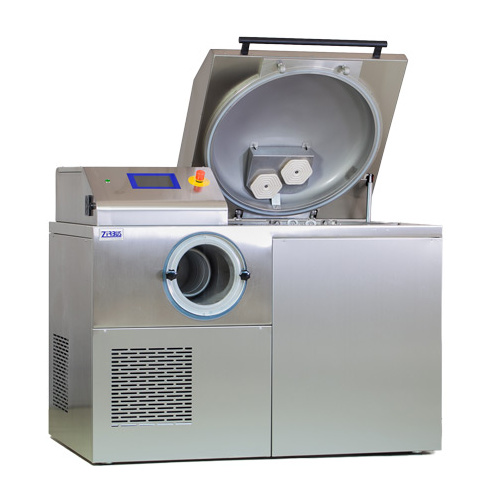
Centrifugal dryers
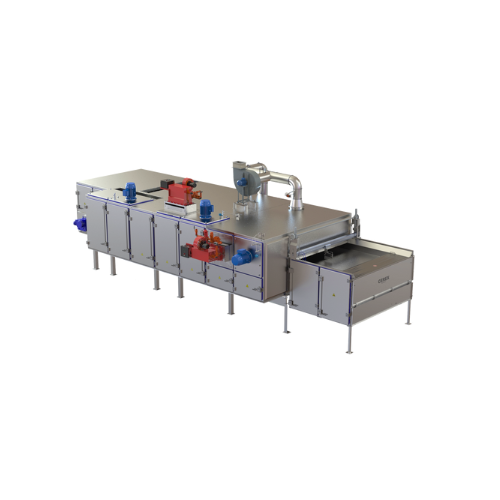
Coating dryers
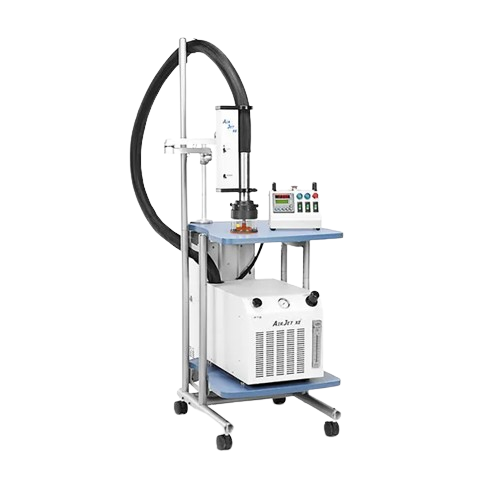
Compressed air dryers
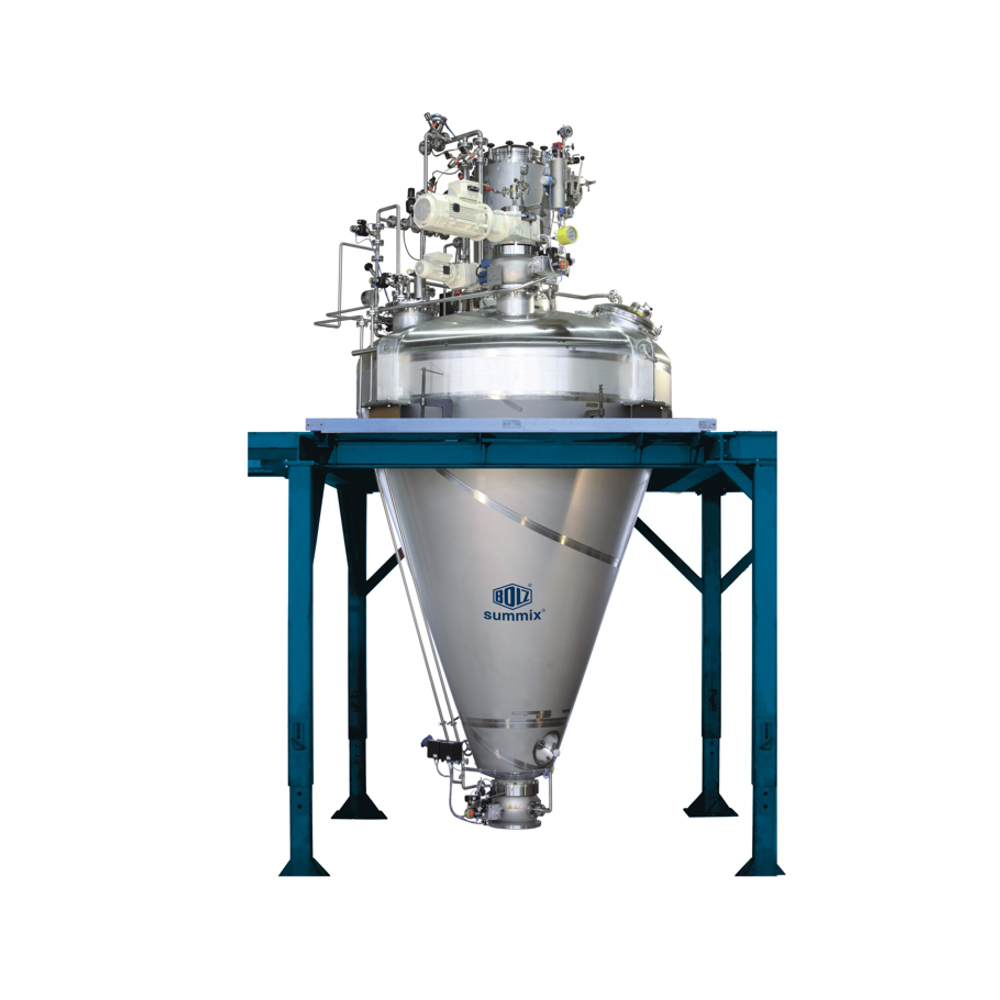
Conical screw dryers
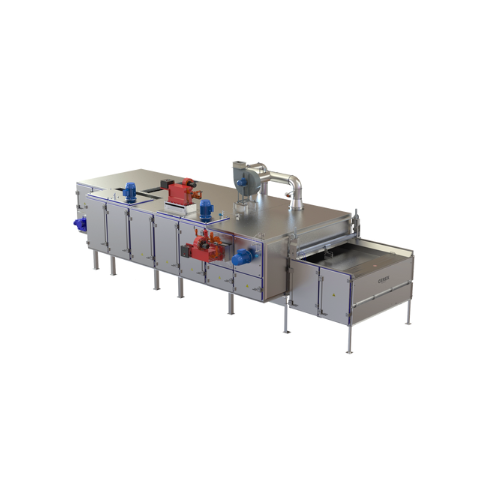
Conveyor dryers
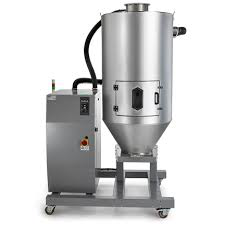
Desiccant wheel dryers
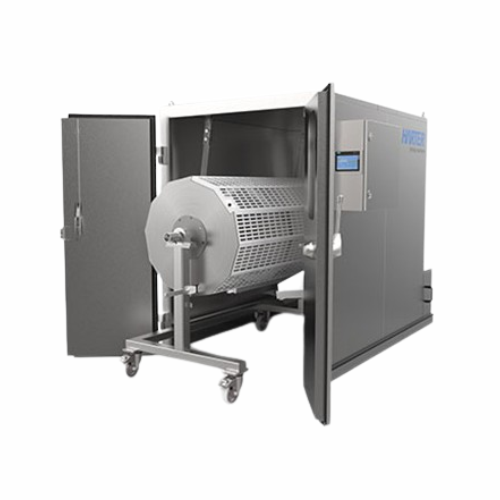
Drum dryers
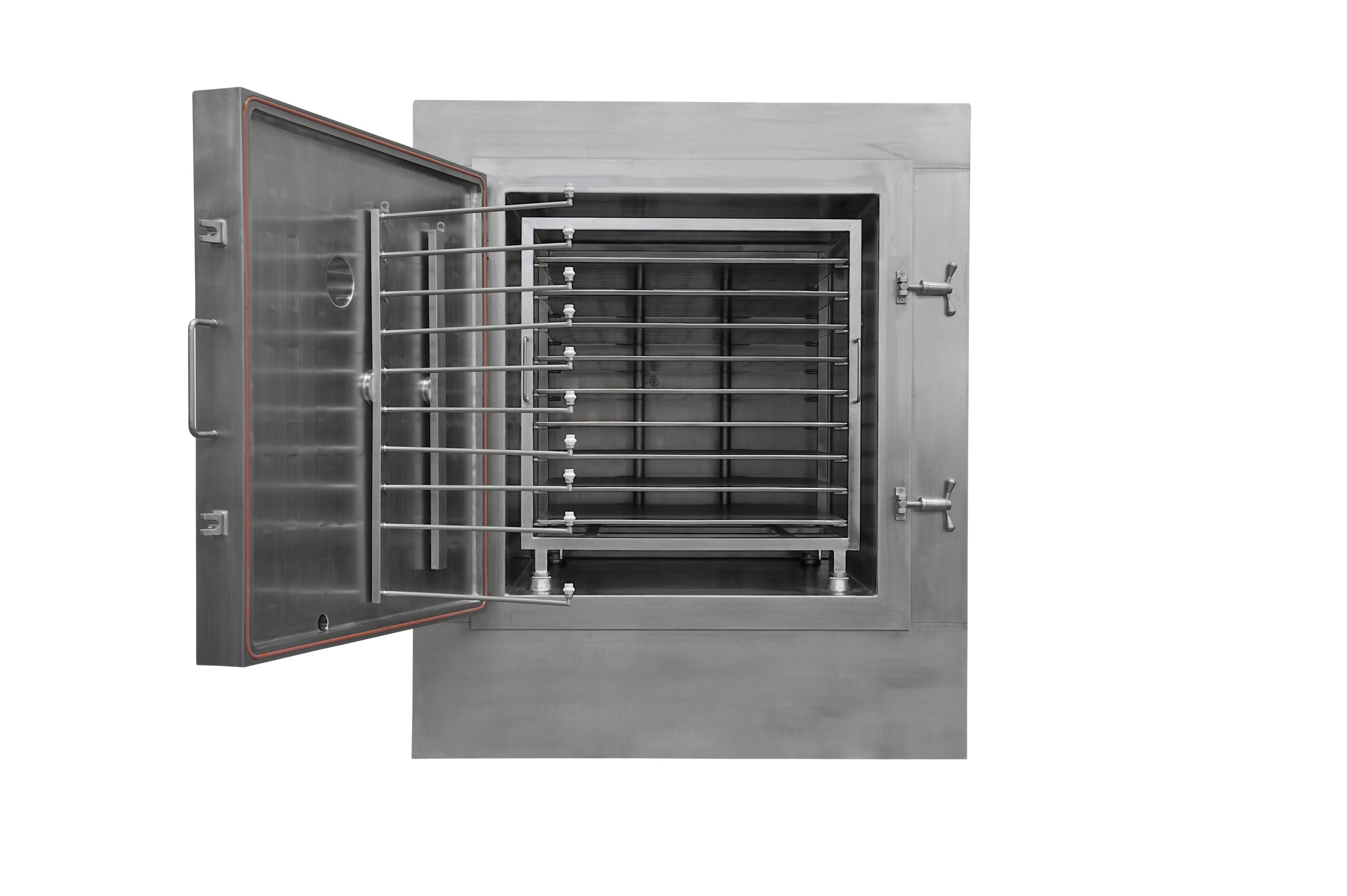
Drying Cabinets
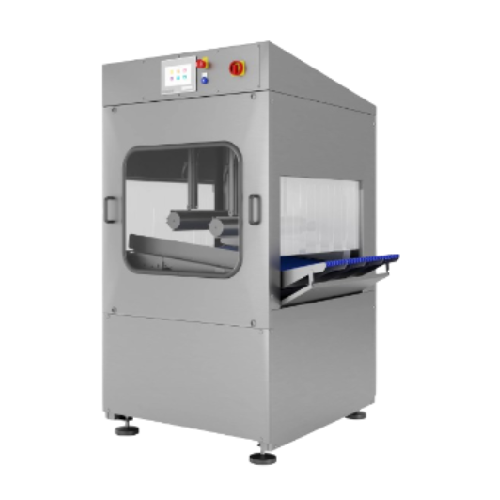
Drying tunnels
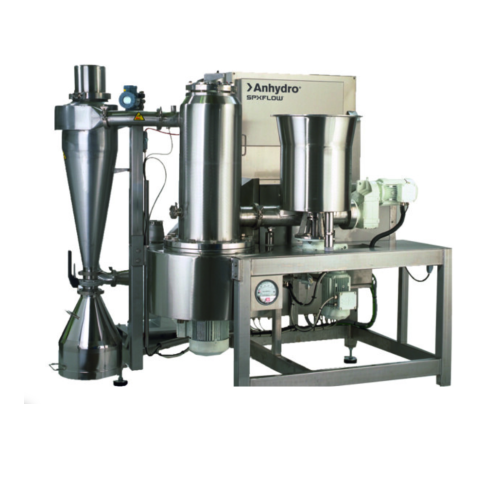
Flash dryers
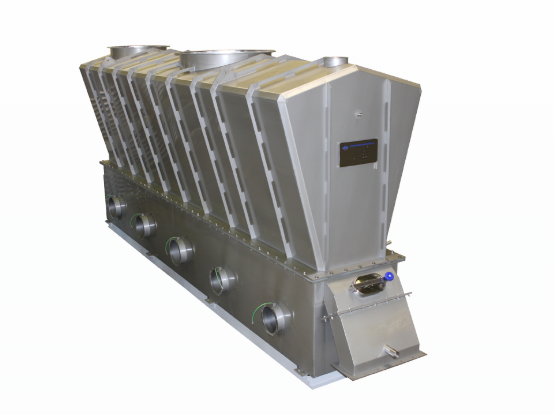
Fluid bed dryers
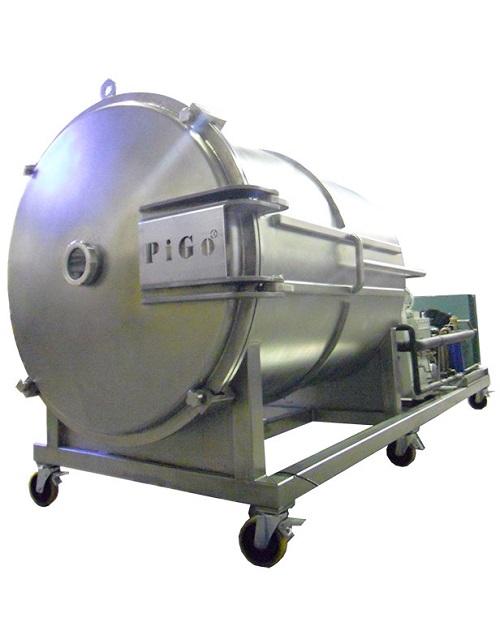
Freeze dryers
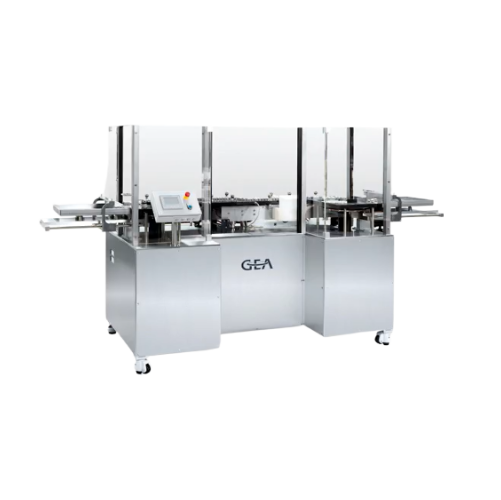
Gmp freeze dryers
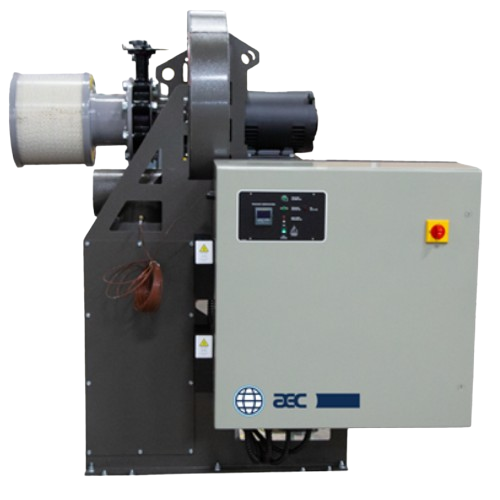
Hot air dryers
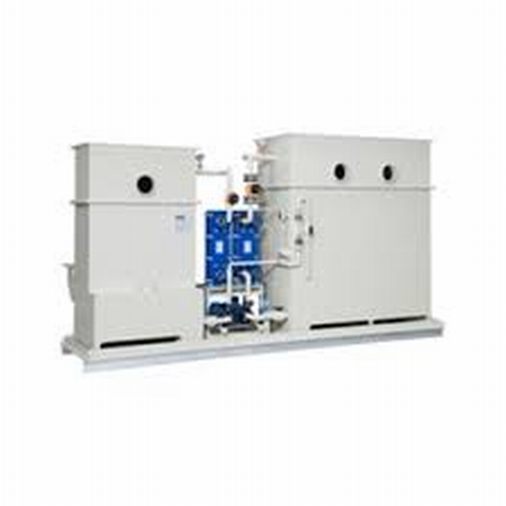
Humidity Control systems
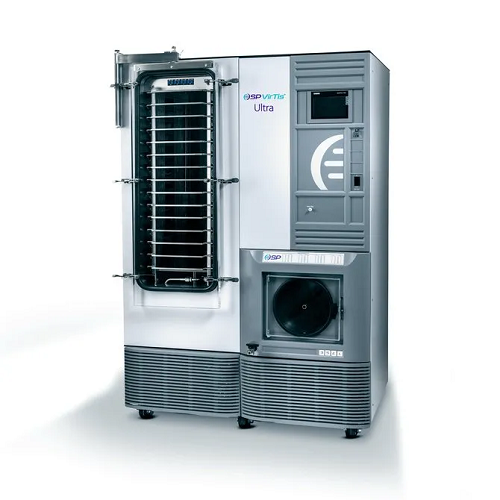
Laboratory dryers
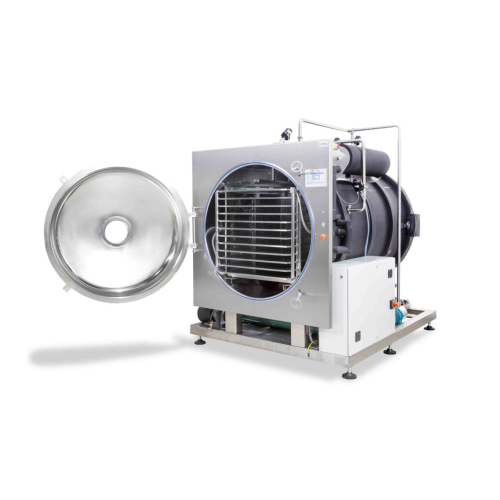
Laboratory freeze dryers
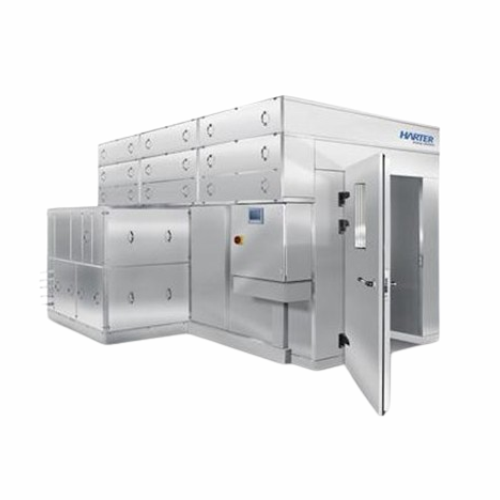
Layer dryers
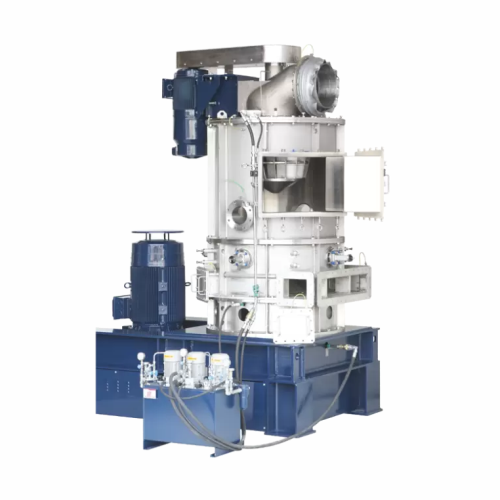
Milling flash dryers
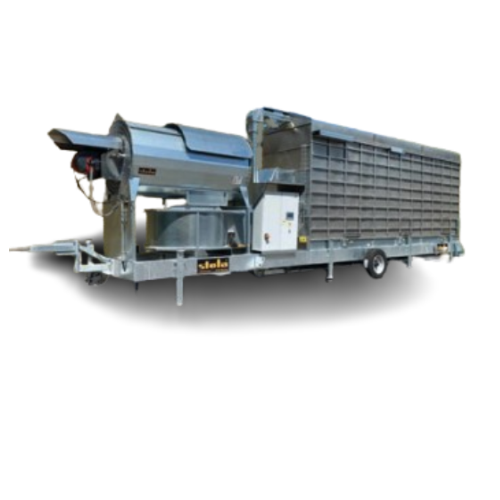
Mobile agricultural dryers
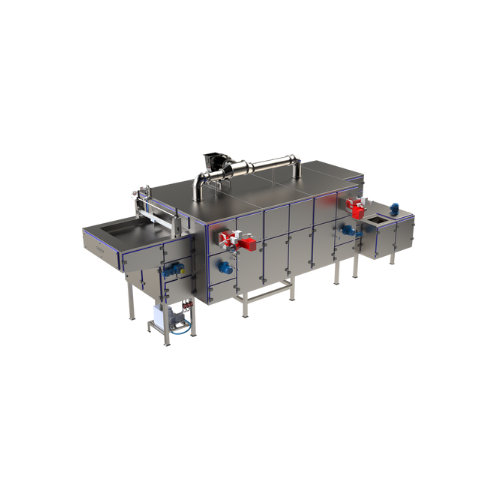
Multi tier dryers
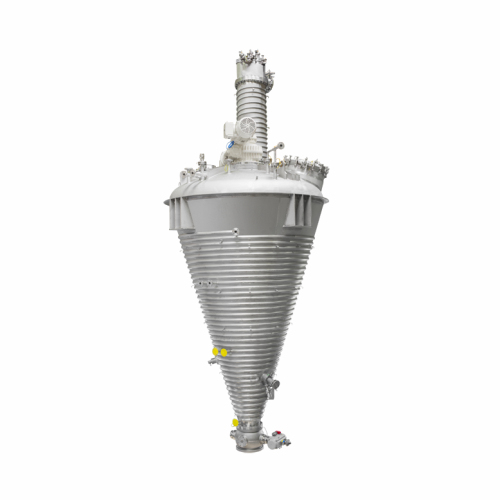
Paddle dryers
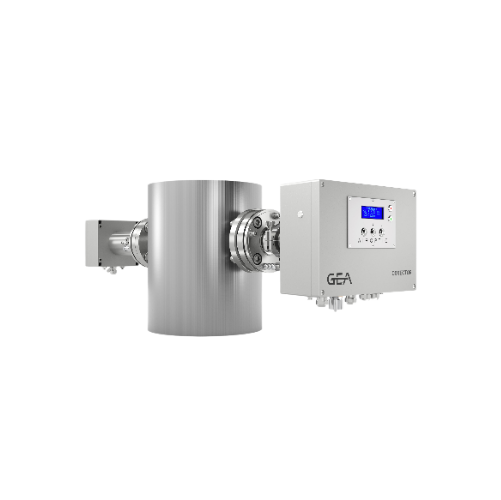
Ring dryers
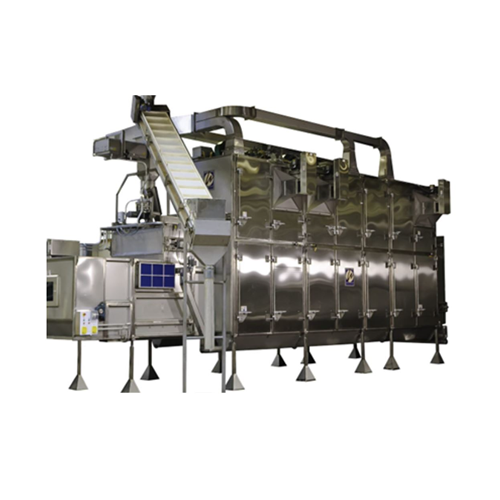
Sanitary dryers
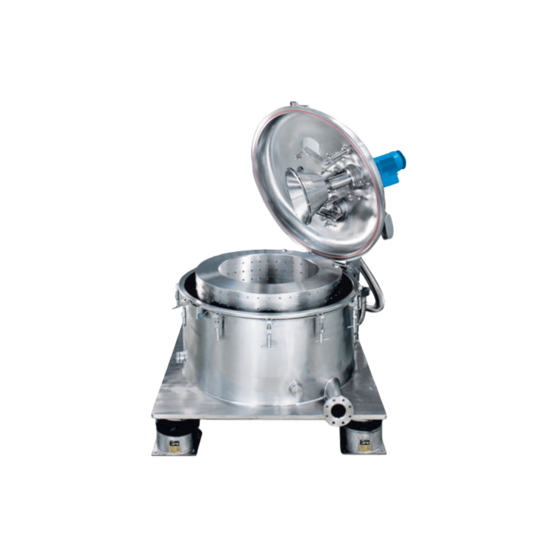
Scraper Centrifuges
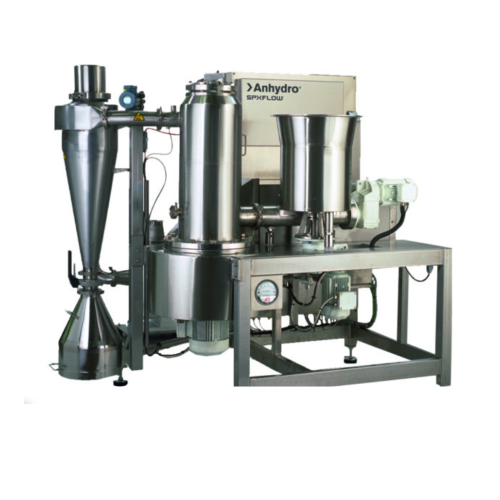
Spin flash dryers
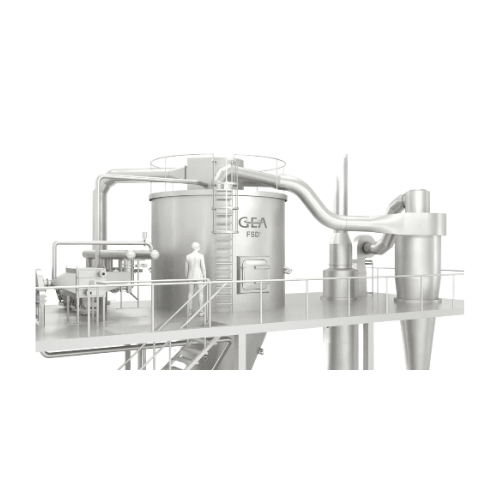
Spray Dryers
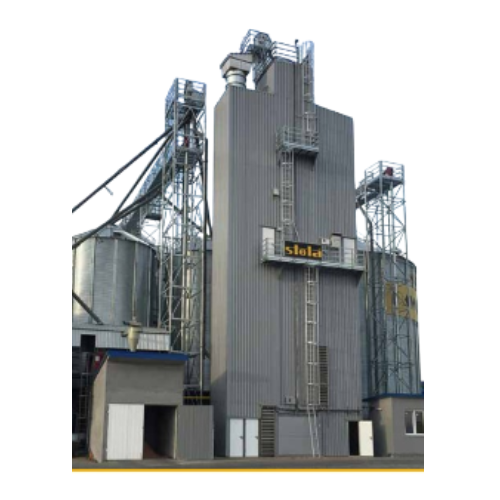
Stationary drying systems
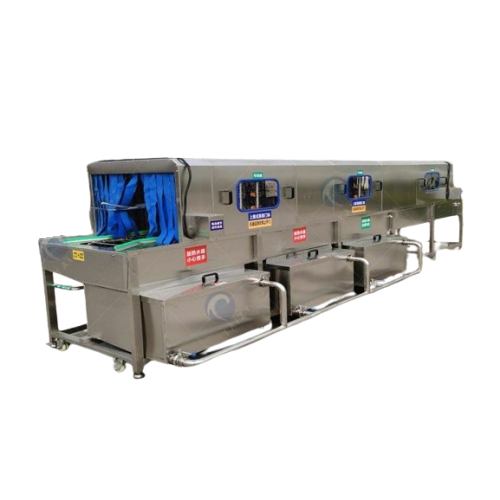
Tray dryers
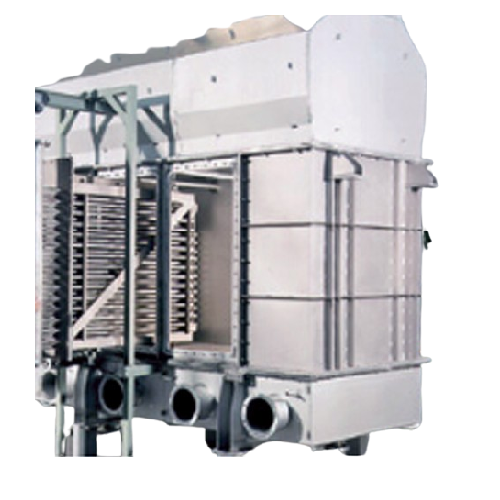
Tube bundle dryers
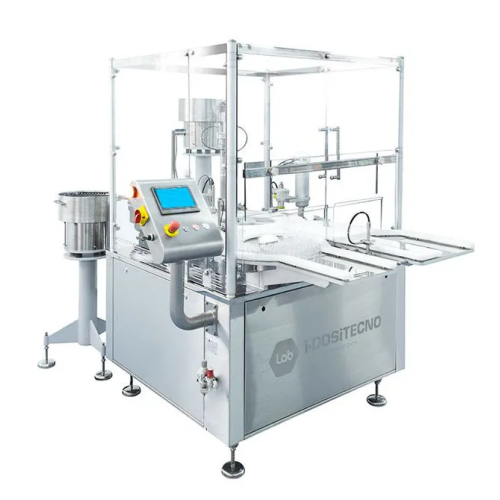
Tunnel dryers
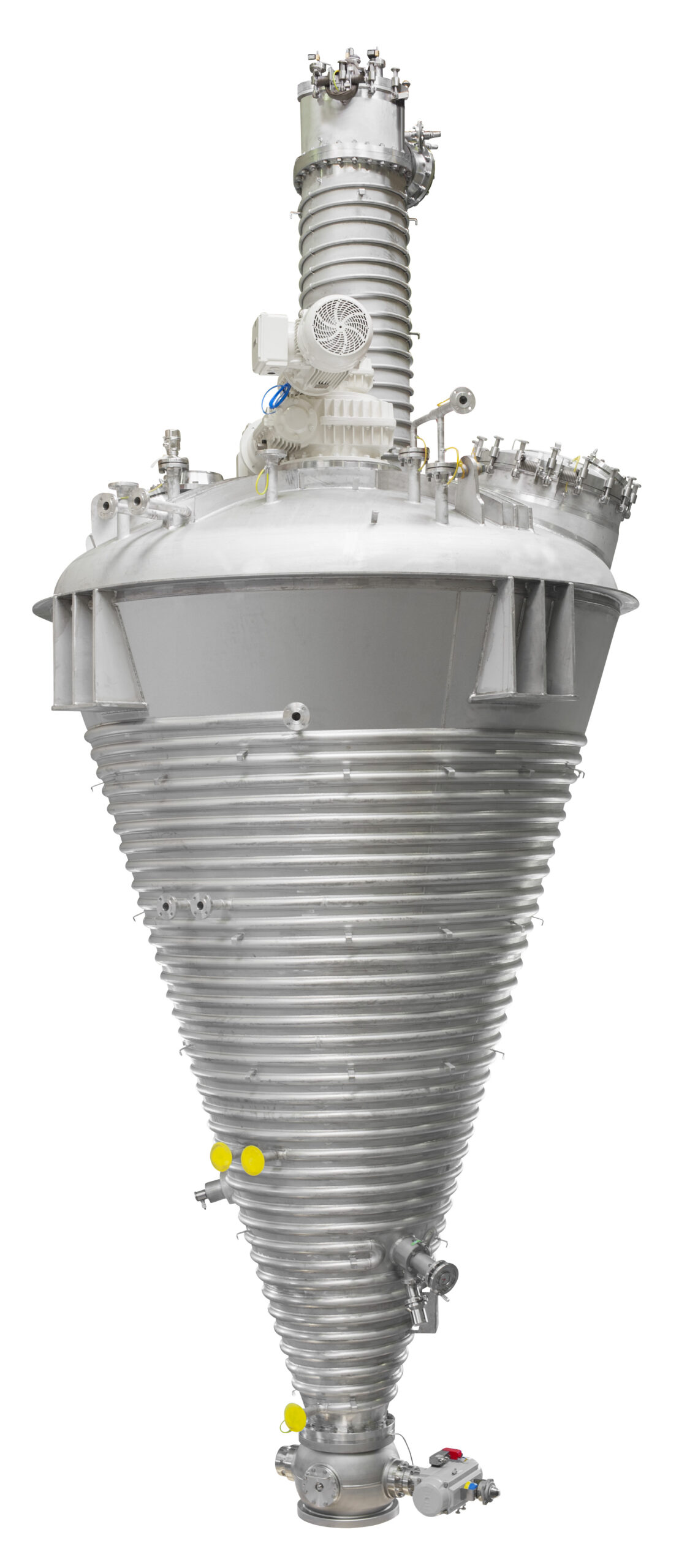
Vacuum dryers
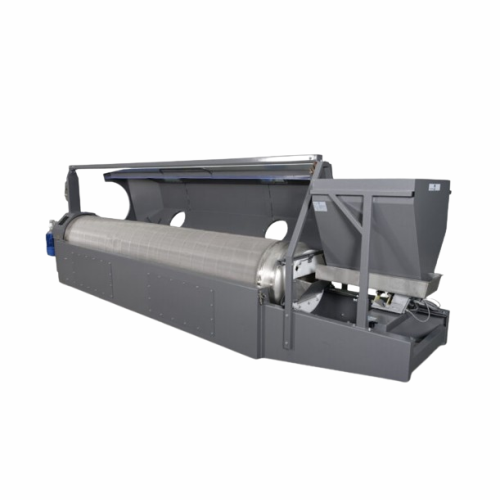
Vibrating fluid bed dryers
Which drying technology do you need?
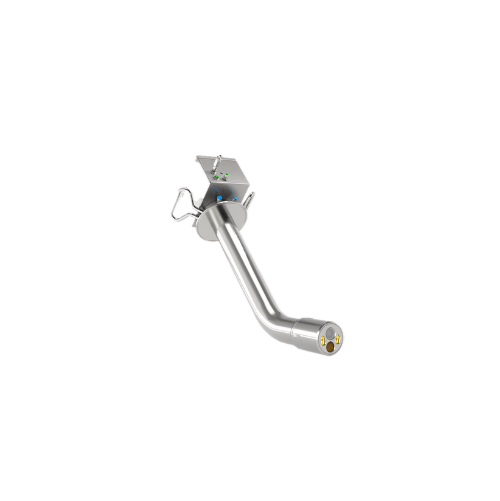
Dual camera system for spray dryer monitoring
Enhance safety and operational efficiency in your drying process by combinin...
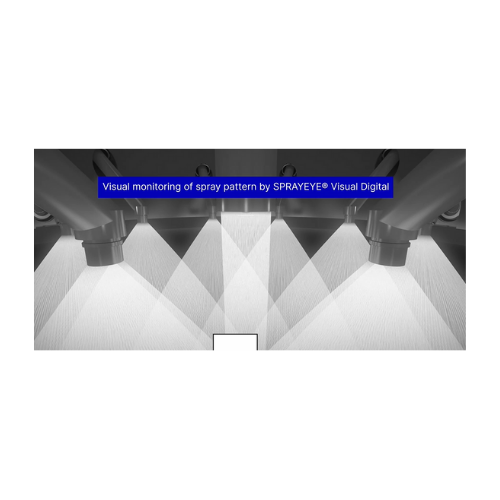
Spray dryer performance optimization system
Achieve unparalleled spray drying efficiency with real-time monitoring and con...
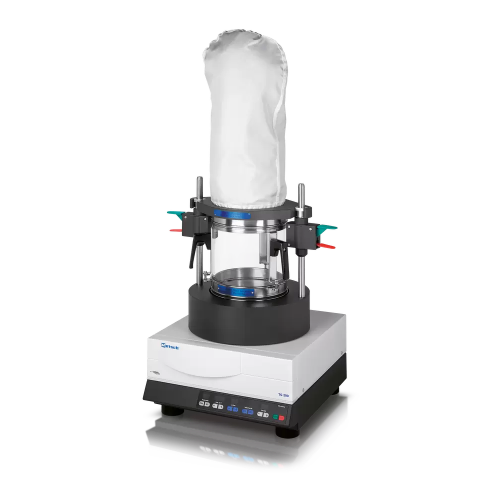
Fluid bed dryer for bulk material laboratory drying
Efficiently dry and mix organic and inorganic materials with precise ...
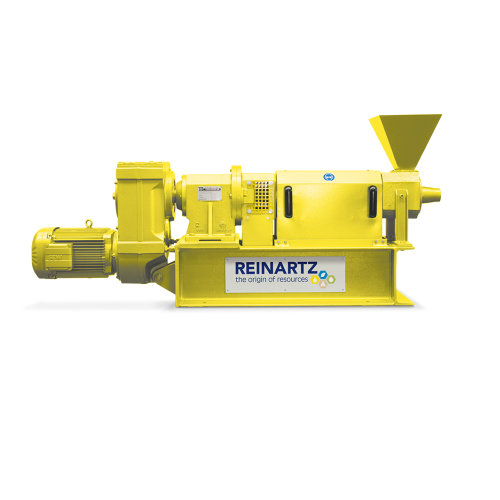
Efficient biomass screw dryers
Optimize biomass processing with screw drying technology that efficiently reduces moisture co...
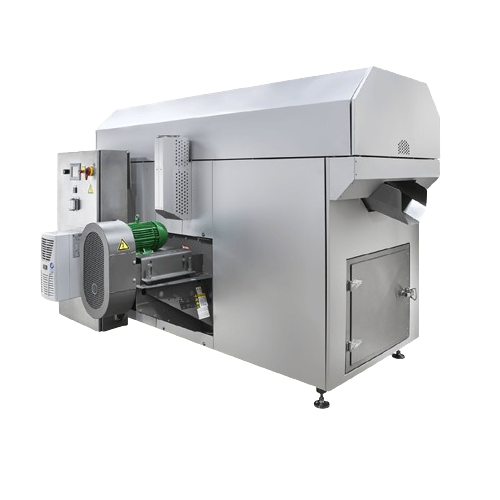
Industrial tumble dryer for moisture control in snack production
Ensure precise moisture reduction and optimal air circu...
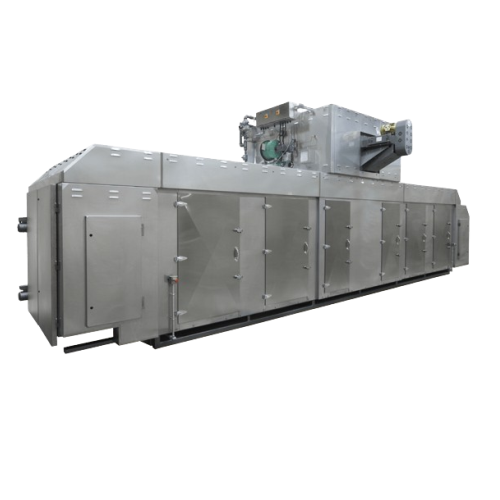
Industrial multi-pass dryer for bakery products
Ensure consistent moisture reduction and quality enhancement in your baker...
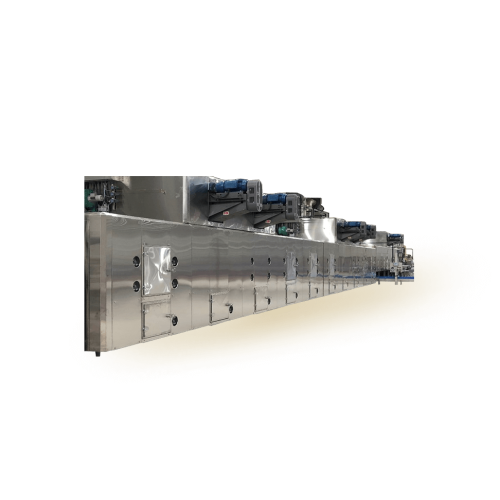
Convection oven with integrated dryer for large scale baking
Optimize your baking process with a convection oven that ef...
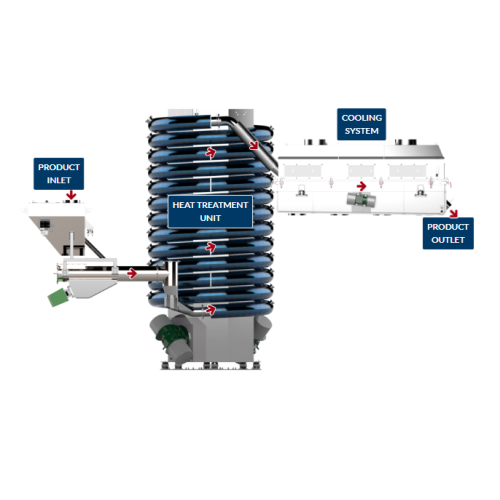
Industrial continuous heat treatment for dry ingredients
Optimize your production line with a continuous system that ensu...
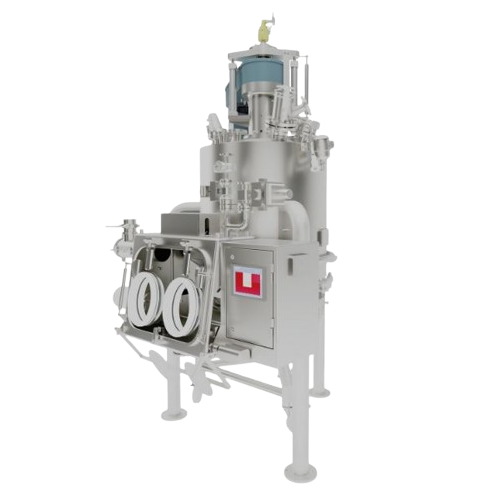
Agitated nutsche filter dryers for chemical synthesis
Enhance your production efficiency by integrating a system that com...
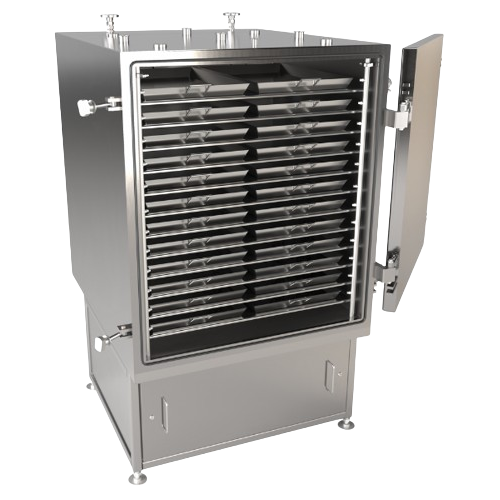
Vacuum tray dryer for pharmaceutical applications
Optimize drying of heat-sensitive compounds while maintaining product i...

Laboratory nutsche filter dryer for solid-liquid separation
Optimize your lab processes with a versatile benchtop filter...
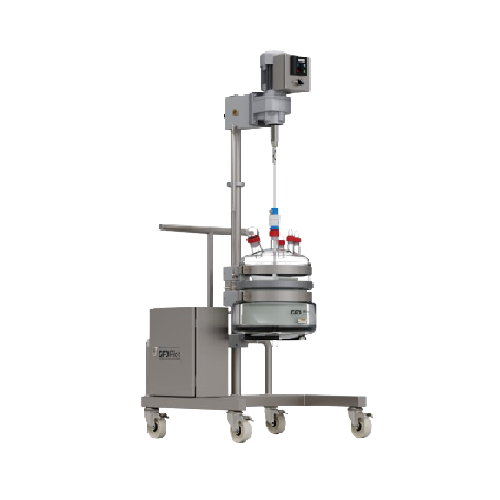
Pilot scale nutsche filter dryer for solid-liquid separation
Achieve maximum product recovery and consistent quality wit...
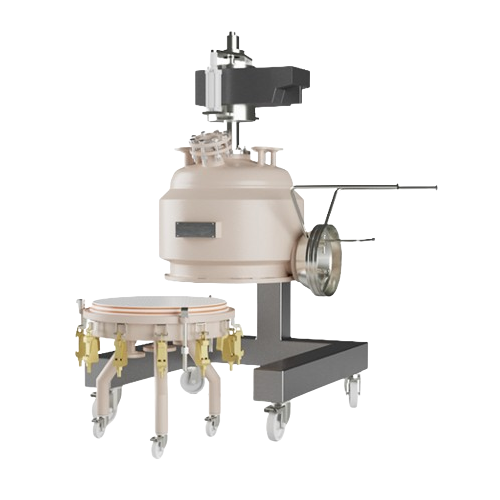
Nutsche filter dryer system for small scale batches
Efficiently tackle filtration and drying challenges with a compact, m...
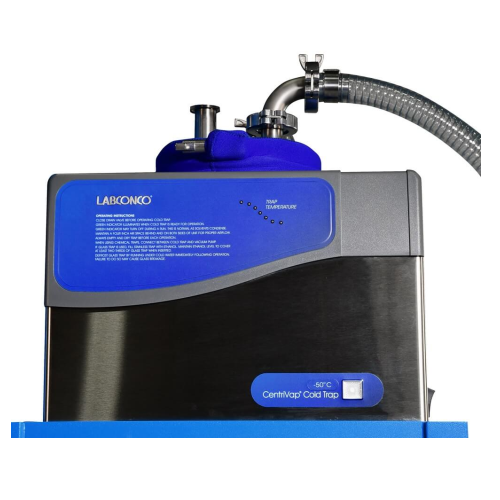
Vacuum cold trap for efficient purging and drying
Optimize your laboratory’s efficiency by integrating high-perform...
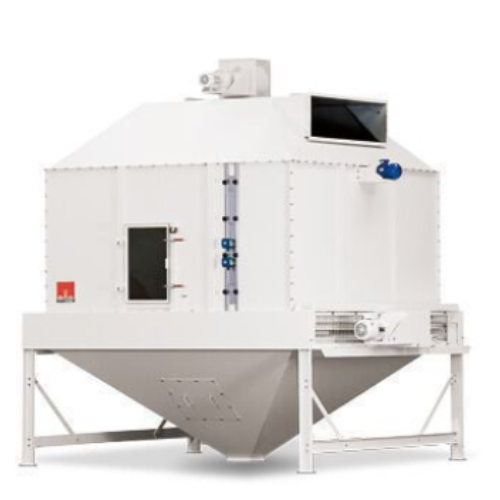
Counterflow dryer for pet food and fish feed
Optimize moisture control and enhance feed quality with efficient drying, cru...
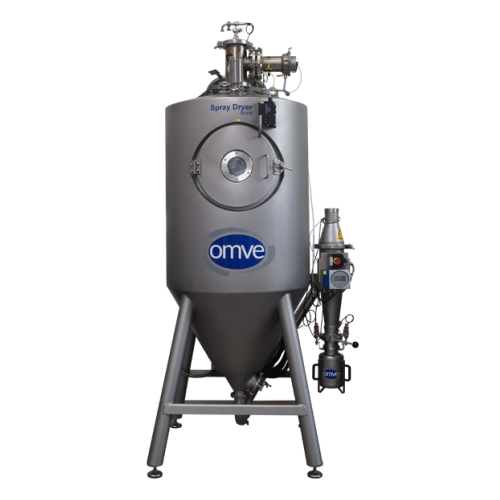
Pilot scale spray dryer for product development
Achieve precise moisture levels and product consistency in development env...
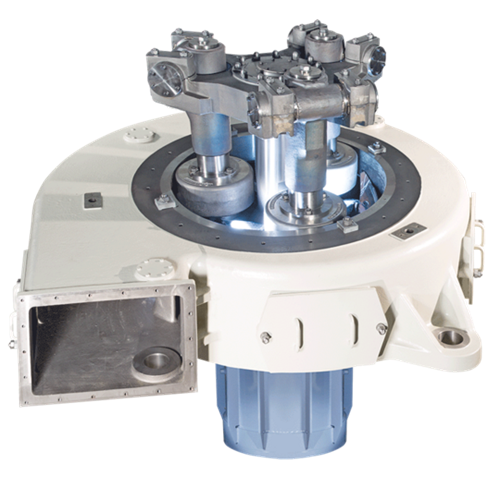
Pendulum mill for fine grinding and drying
Achieve efficient and precise grinding for soft to medium-hard materials while ...
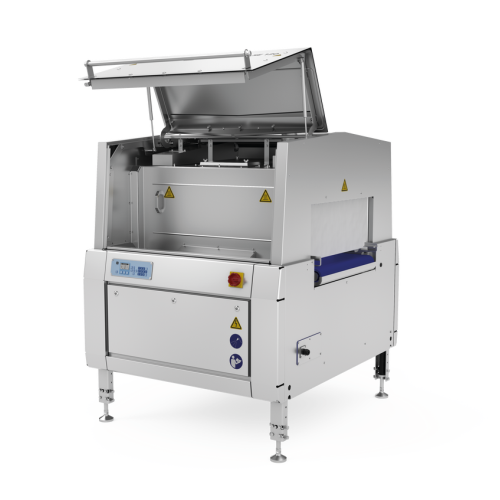
Industrial shrink and drying units for food products
Ensure optimal product integrity and extended shelf life by seamless...
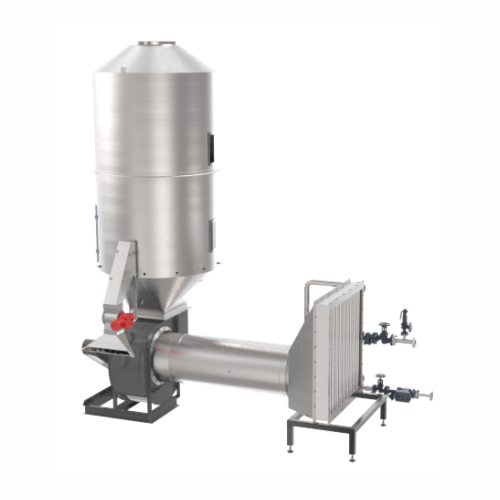
Sesame seed dryer
Optimize your sesame processing with efficient moisture removal, ensuring desired quality and consistency f...
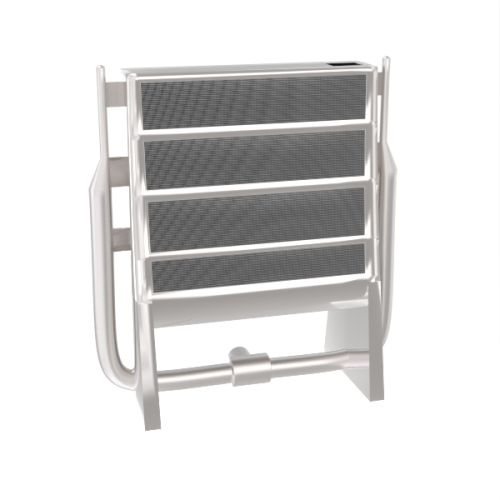
Vertical nut dryer
Achieve precise moisture control for nuts with a vertical dryer that optimizes space and adapts seamlessly...
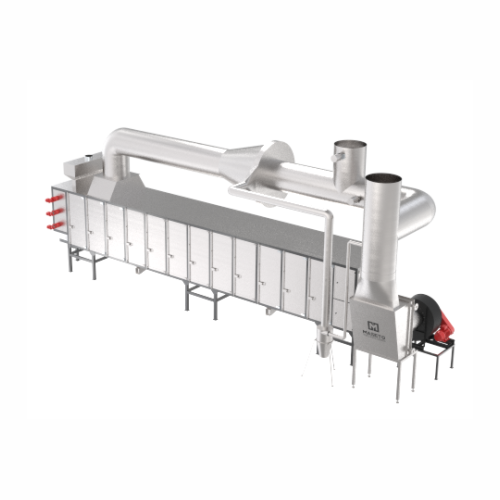
Horizontal tray dryer for moisture removal
Ensure consistent product quality in nut and olive processing by efficiently re...

External washing and drying system for ampoules and vials
Optimize your aseptic processing by seamlessly integrating a c...
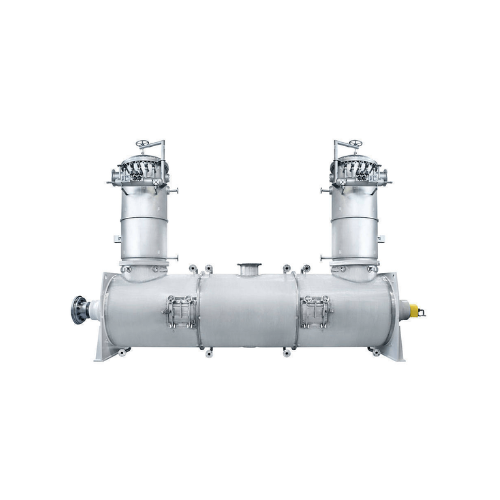
Vacuum paddle dryer for chemical and pharmaceutical applications
Achieve precise moisture control and efficient drying i...
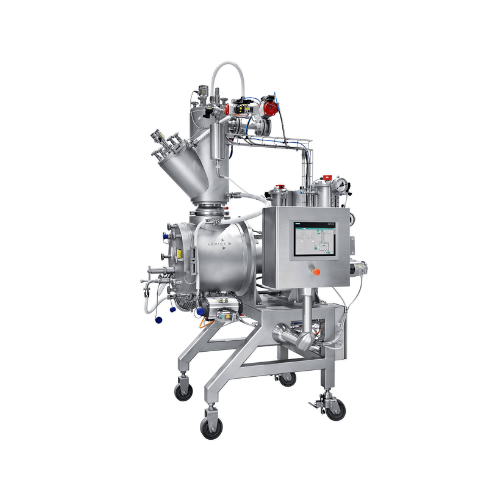
Vacuum paddle dryer for laboratory use
Achieve precise temperature and moisture control in your batches with this vacuum sh...
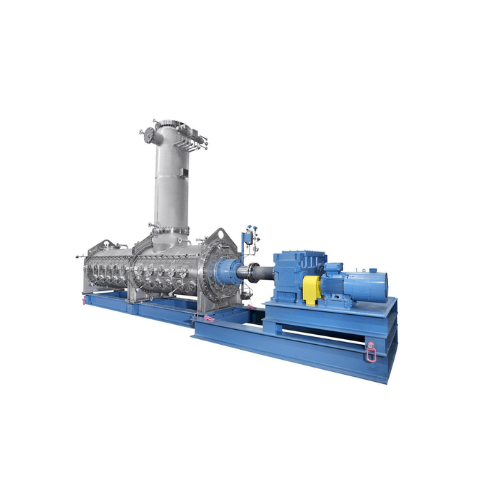
Continuous granulation dryer for chemical and polysaccharide applications
Enhance your production with precise drying ...
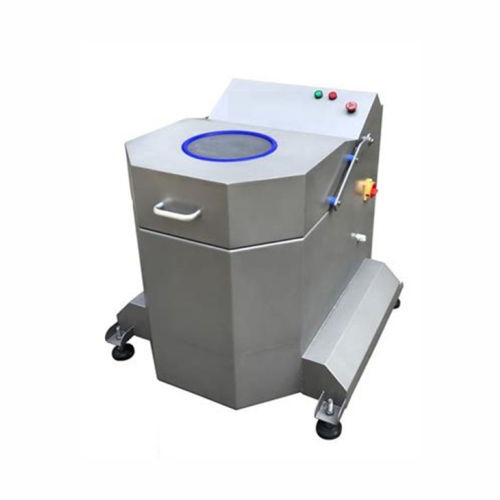
Vegetable and salad spin dryer
Optimize your vegetable and fruit processing with precision dehydration that maintains textur...
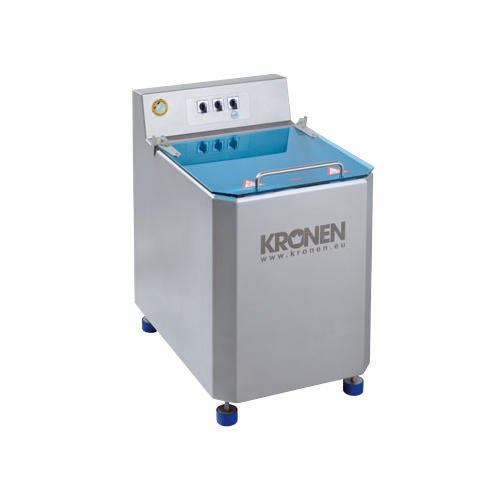
Industrial vegetable and lettuce spin-dryer
Achieve consistent, gentle drying for a wide range of food products with seven...
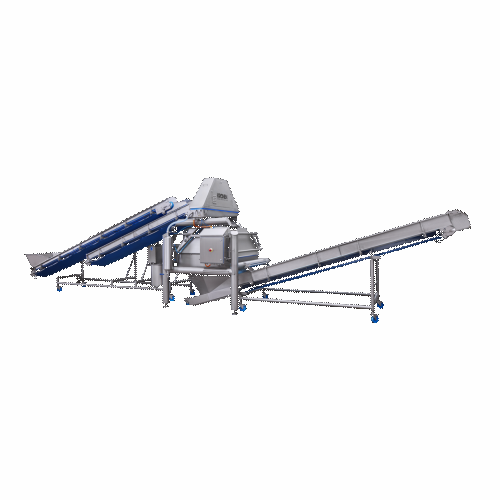
Centrifugal drying system for lettuce and vegetables
Enhance your production line’s efficiency with this high-capac...
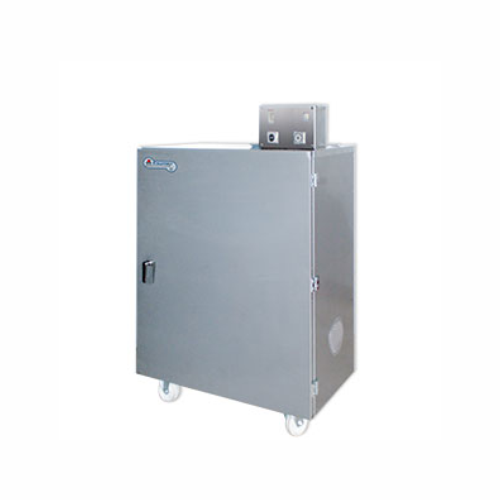
Industrial fruit drying cabinet
Efficiently transform fresh produce into long-lasting, nutrient-dense snacks with precise dr...
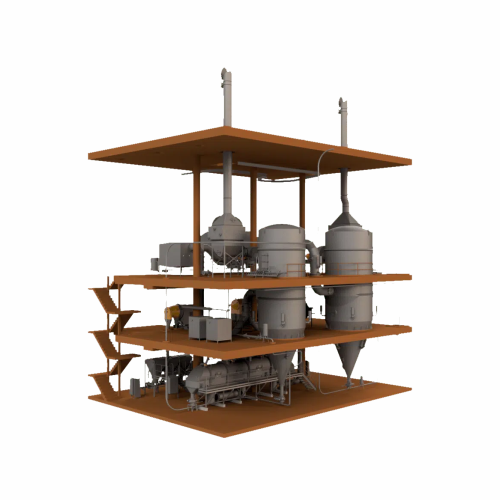
Lactose drying system for high-quality edible powder
Achieve precise and cost-effective lactose transformation into high-...
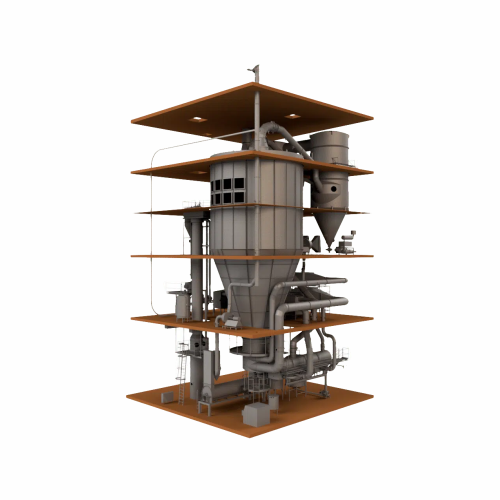
Permeate drying system for dairy applications
Optimize your dairy production with efficient permeate drying, delivering hi...
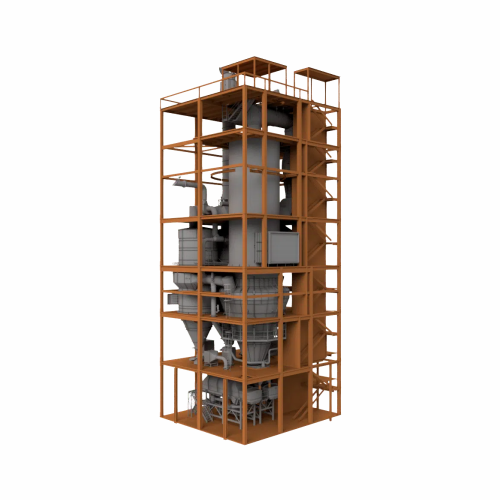
Milk drying system
Optimize your dairy production by efficiently transforming liquid inputs into high-quality, dry powders, e...
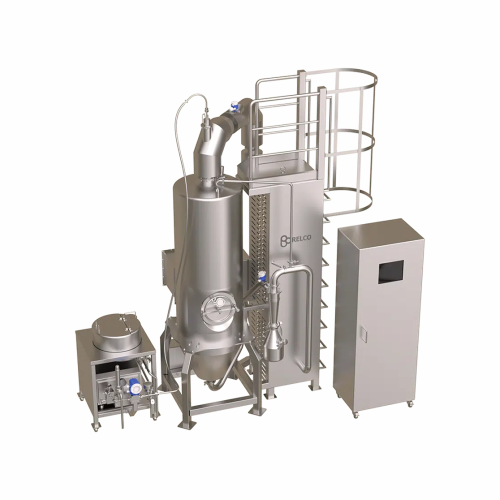
Pilot spray dryer for high-value proteins and nutraceuticals
Optimize powder development with precise pilot-scale spray ...
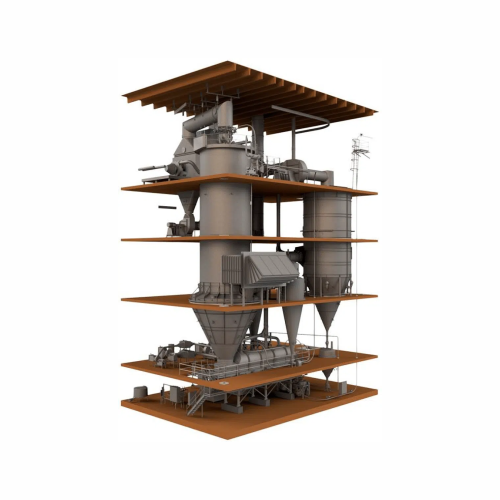
Protein drying system for dairy products
Optimize your dairy production with a customizable drying system designed for effi...
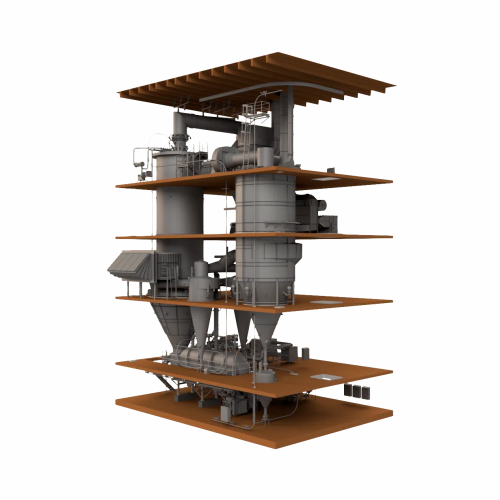
Tall form bustle dryer for dairy and food products
Experience efficient drying and precise moisture control with this inn...
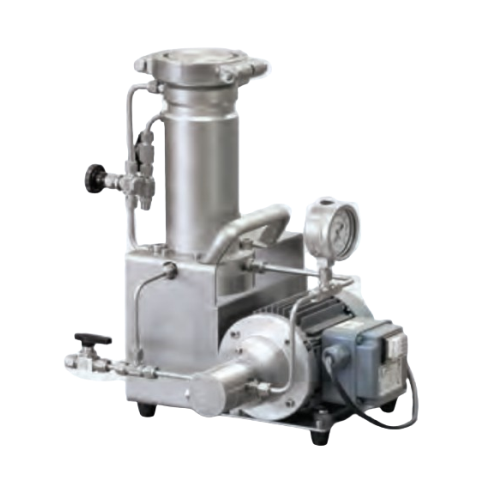
Timing belt drying system for whey and permeate powders
Ensure high-quality production of free-flowing and non-caking whe...
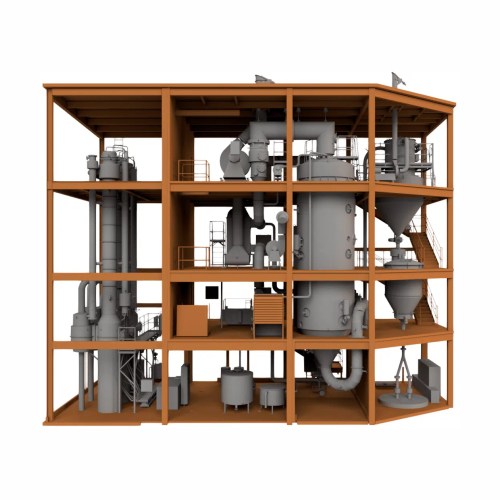
Compact drying solution for regular skim and Wpc powders
Streamline your drying process with a compact solution that effi...
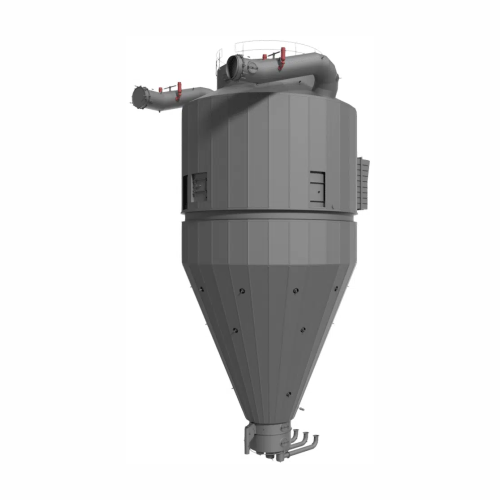
Wide body dryer for dairy and food products
Achieve precise moisture control and optimal powder agglomeration for dairy an...
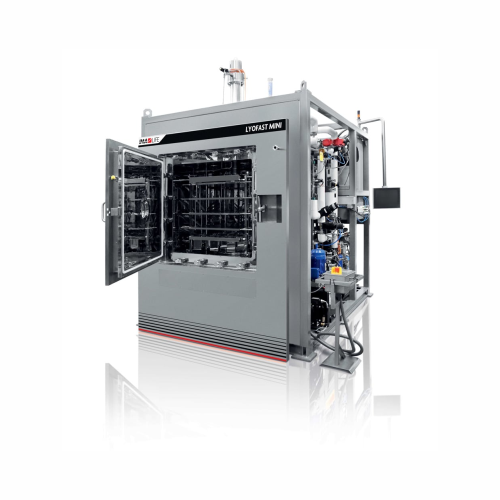
Pilot freeze dryer for pharmaceutical applications
Optimally bridge laboratory development and full-scale production with...
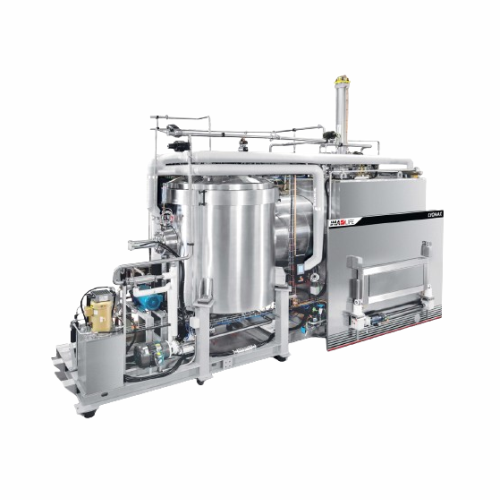
Industrial GMP freeze dryer
Optimize the lyophilization of sensitive pharmaceutical compounds with a machine designed for pr...
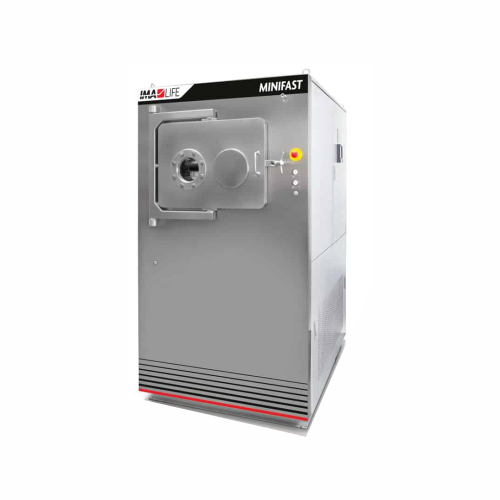
Pilot freeze dryer for r&d and small batch production
Optimize your freeze-drying process for pilot and laboratory applic...
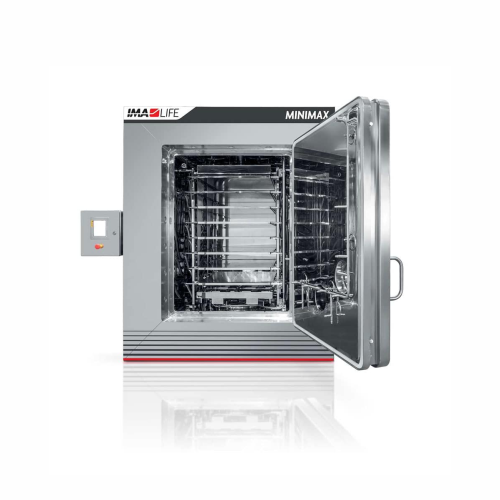
Small-scale freeze dryer for pharmaceutical applications
Optimize small-batch and pilot-scale lyophilization with advance...

Refrigeration system for freeze drying
Achieve ultra low-temperature cooling for freeze drying, ensuring environmental comp...
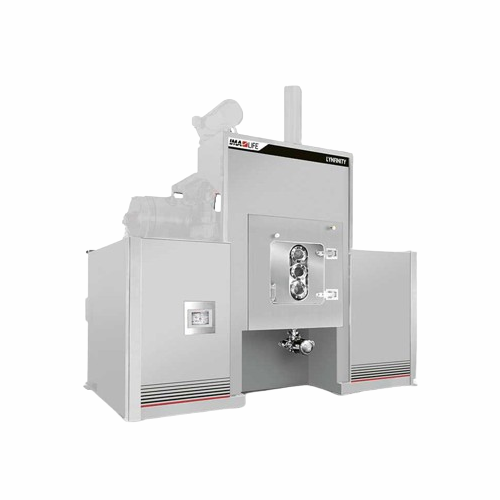
Continuous aseptic spray-freeze-drying system
Achieve higher sterility and improved product uniformity with a continuous a...
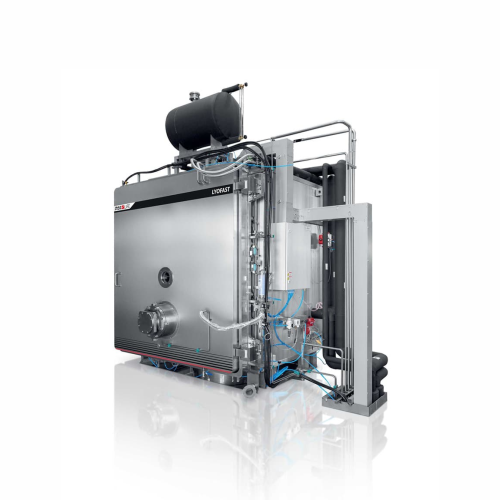
Industrial freeze dryer for biopharmaceuticals
Ensure the stability and longevity of your sensitive biopharmaceuticals thr...
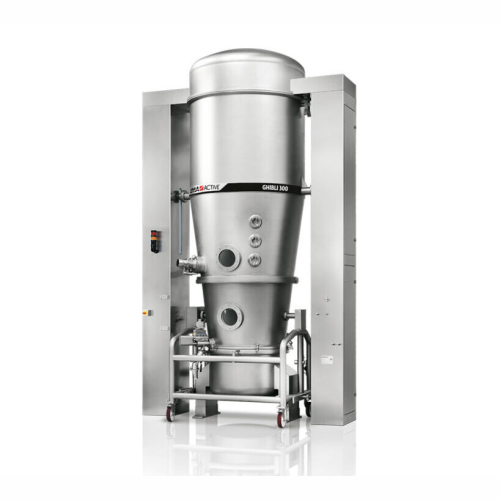
Fluid bed processor for pharmaceutical granulation and drying
Achieve precise drying, granulation, and coating of pharma...
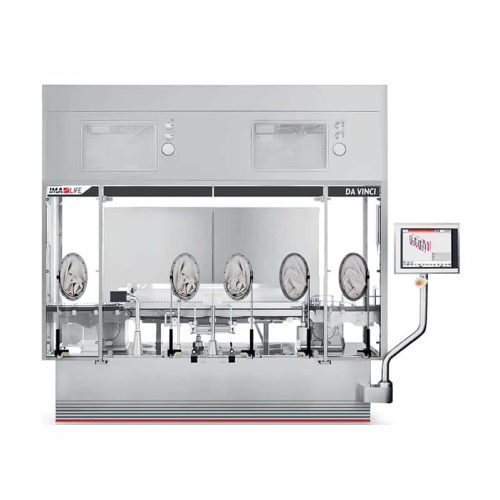
Wireless vial loading and unloading system for freeze-dryers
Enhance aseptic processing with this stand-alone, wireless ...
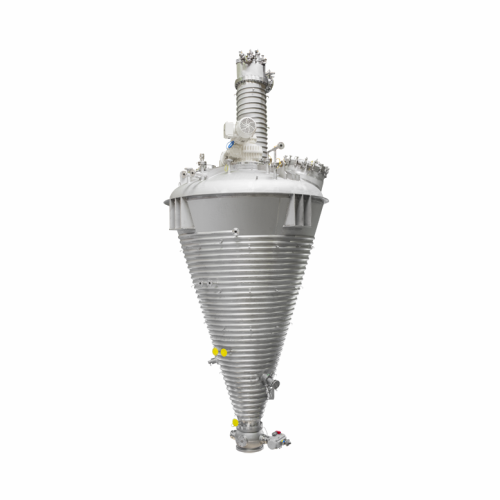
Vacuum dryers for powders and bulk solids
Achieve precise drying and mixing of sensitive materials with advanced vacuum te...
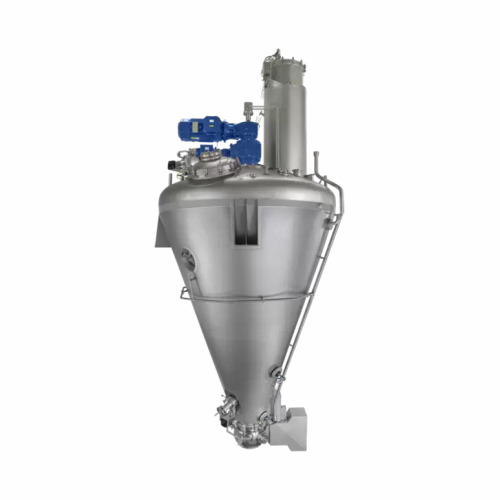
Vacuum dryer for powders and granules
Achieve precise moisture control for sensitive materials with a versatile vacuum dryi...
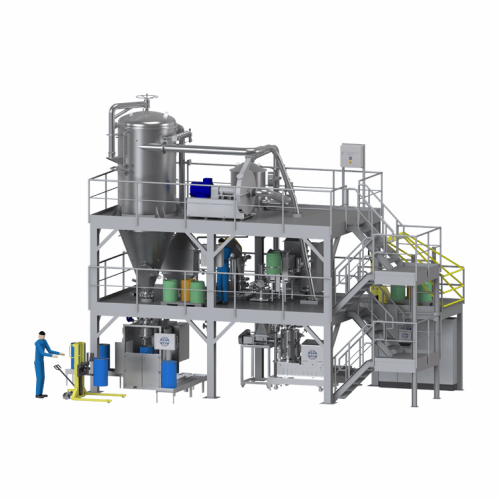
Drying systems for powders and bulk solids
Enhance your production line with precise control of moisture content in powder...
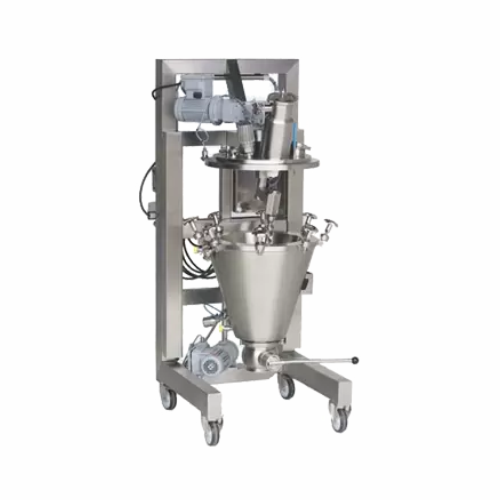
Laboratory vacuum dryer for heat-sensitive materials
Optimize moisture control in heat-sensitive materials with precise a...
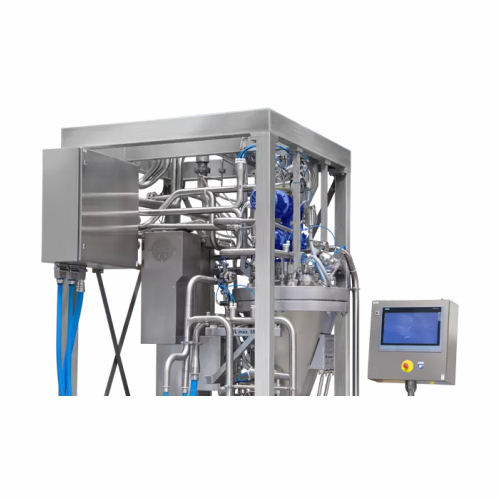
Pharmaceutical freeze dryer
Achieve contamination-free, high-quality pharmaceutical powders through an innovative freeze-dry...
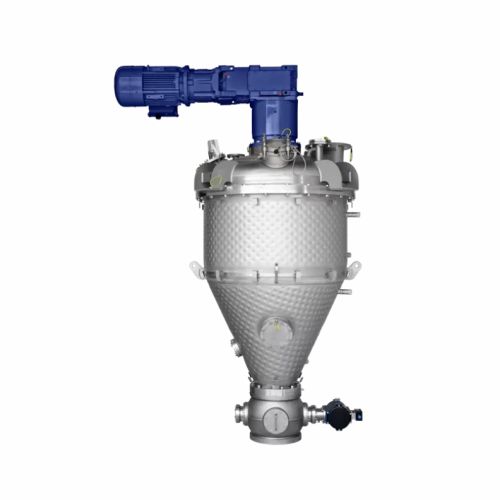
Conical paddle vacuum dryer for powders and granules
Achieve efficient drying of sensitive materials with this versatile ...
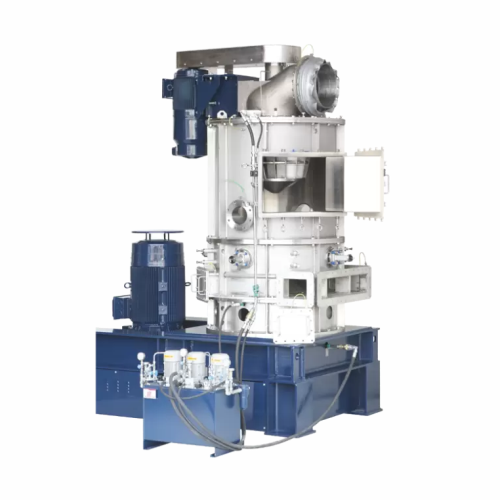
Ultra-fine powder flash drying system
Achieve rapid moisture removal and particle refinement with this integrated system, d...
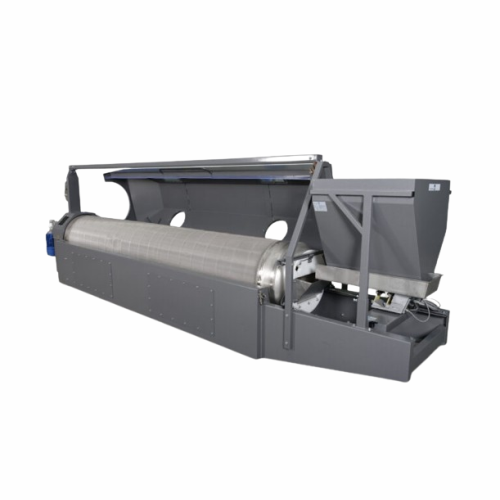
Continuous fluid bed drying system for seed coating
Elevate your seed coating operations with a continuous fluid bed dryi...
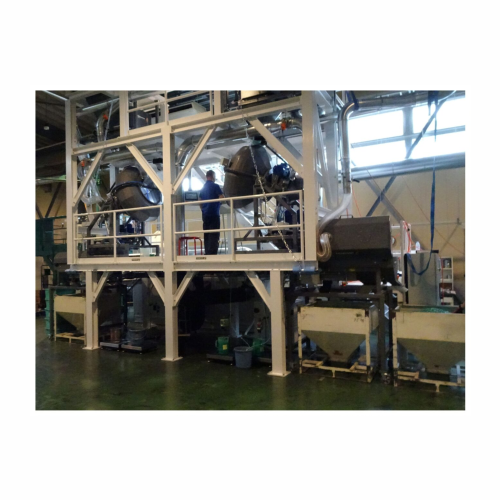
Integrated coater and dryer for fragile seeds
When you need to gently coat fragile seeds like cucumber, melon, and beans, ...
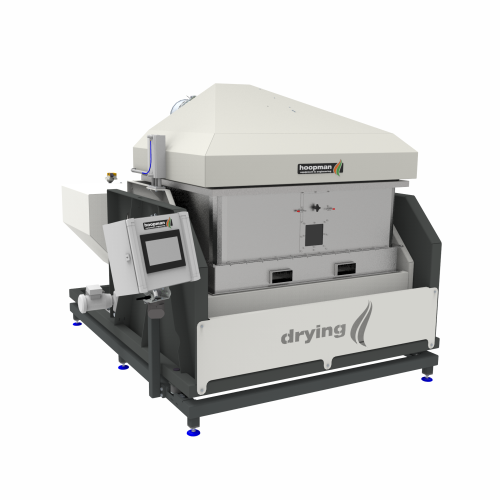
Seed drying system for large volume coated seeds
Achieve precise moisture control in your seed processing operations with ...
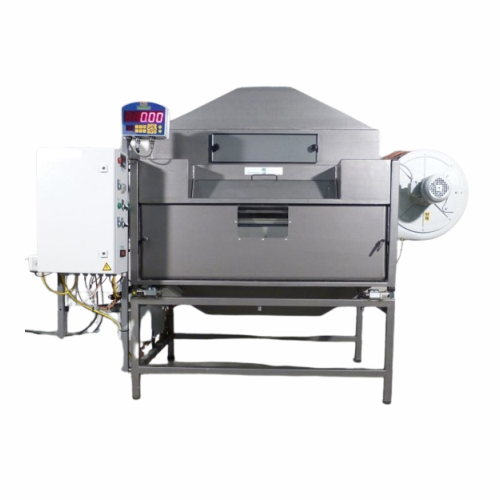
Batch drying system for pelleted products
Achieve precise moisture control and rapid drying for encrusted and pelleted see...
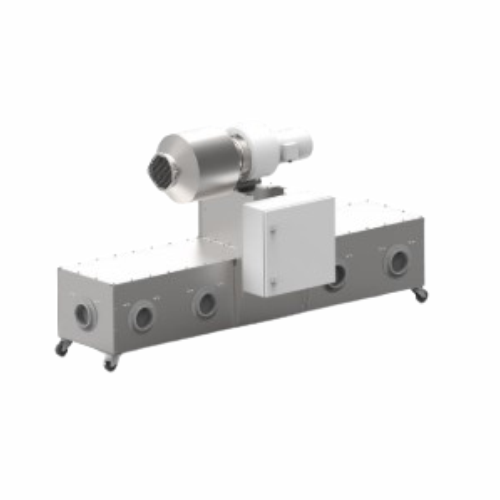
Cart drying system for non-threshed corn and seeds
Simplify your seed drying process with a flexible system designed for ...
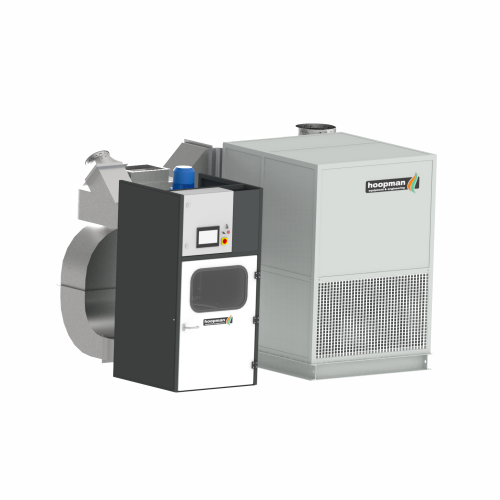
Fluid bed drying system for seed pellets
Achieve precise moisture control and optimal seed conditioning with this fluid bed...
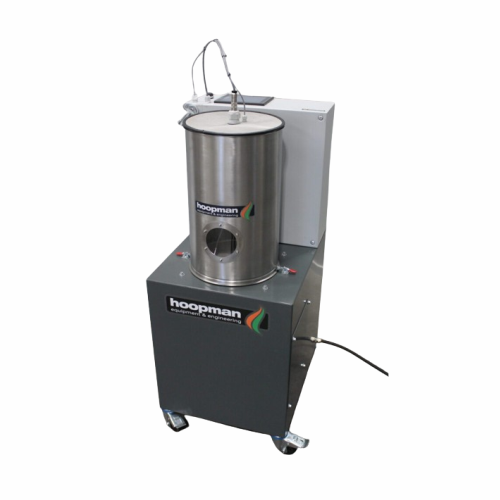
Fluid bed lab dryer for small seed lots
Efficiently dry and condition small seed lots with precise temperature control, ens...
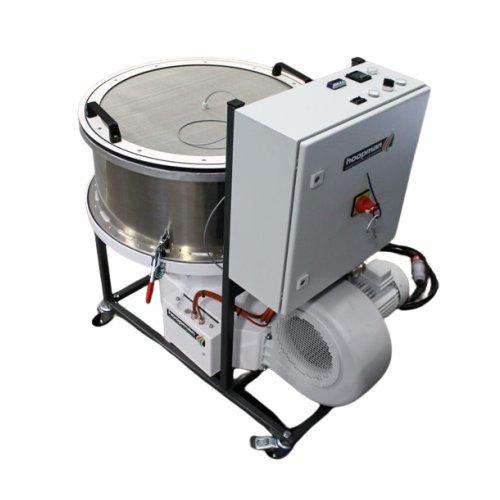
Mobile fluid bed dryer for small seed lots
Dry your small seed lots efficiently and flexibly with a mobile fluid bed dryer...
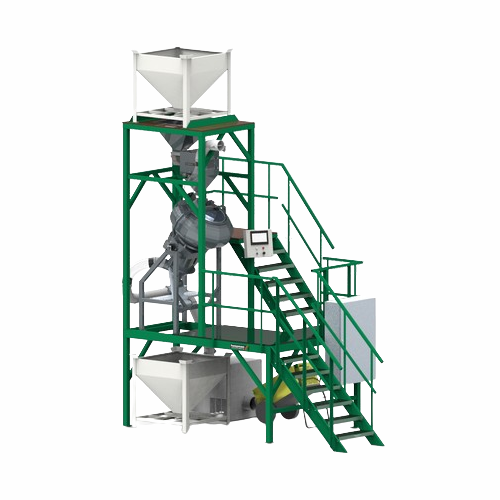
Integrated coater/dryer for seed treatment
Optimize seed coating and drying with a streamlined process that preserves seed...
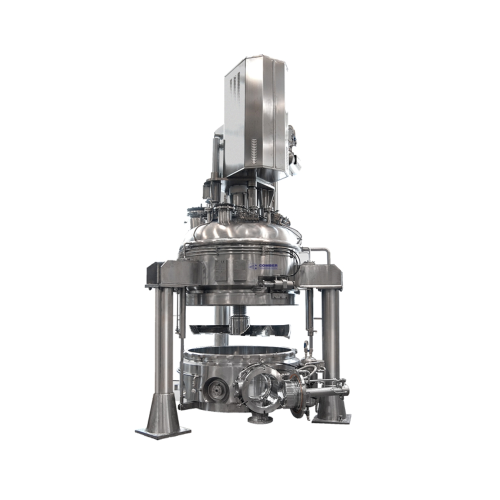
Vacuum pan dryer for heat-sensitive pasty products
When dealing with highly viscous, heat-sensitive products, efficient m...
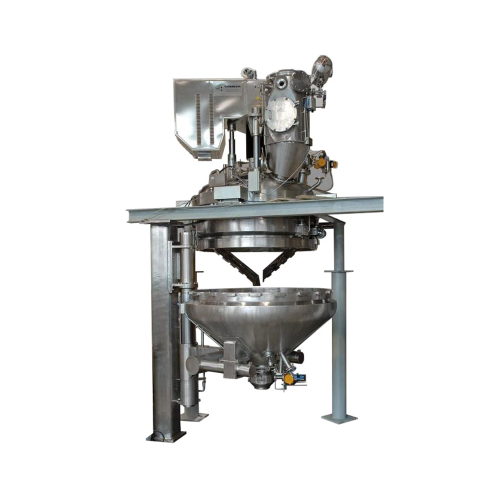
Vertical vacuum dryer for heat sensitive products
Achieve optimal drying and mixing for your heat-sensitive and shear-sen...
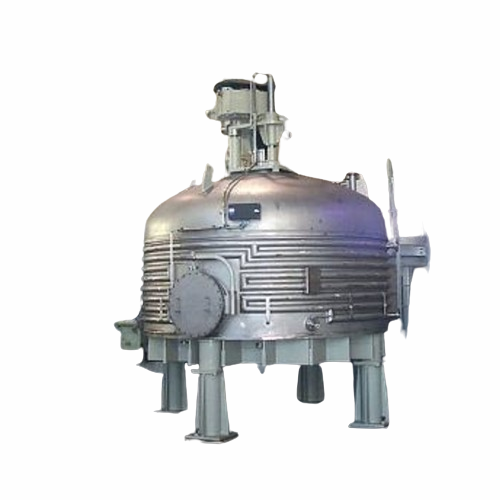
Chemical filter dryer for fine chemical production
When processing chemical intermediates, precise filtration and drying ...
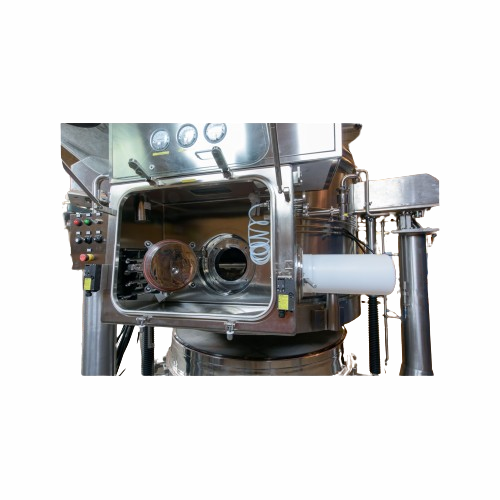
Filter dryer with containment system for hazardous materials
Ensure operator safety and product integrity during hazardo...
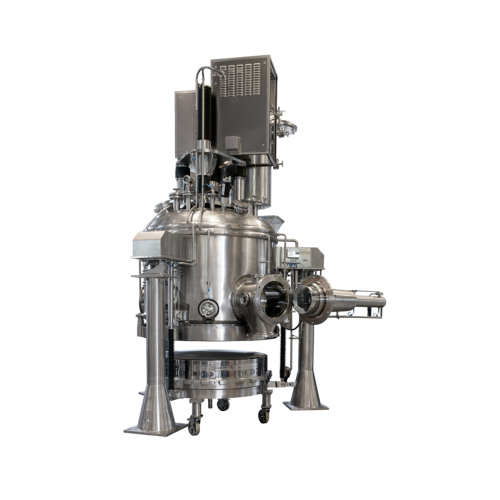
Pharmaceutical filter dryer
Achieve precise moisture control and efficient drying of sensitive materials with this advanced ...
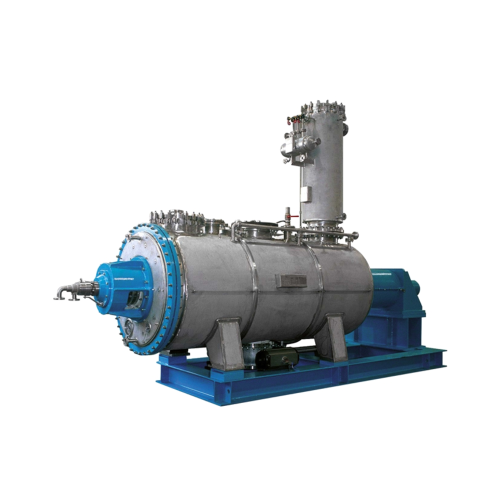
Horizontal vacuum paddle dryer for bulk production facilities
Achieve precise moisture control in powders with a versati...
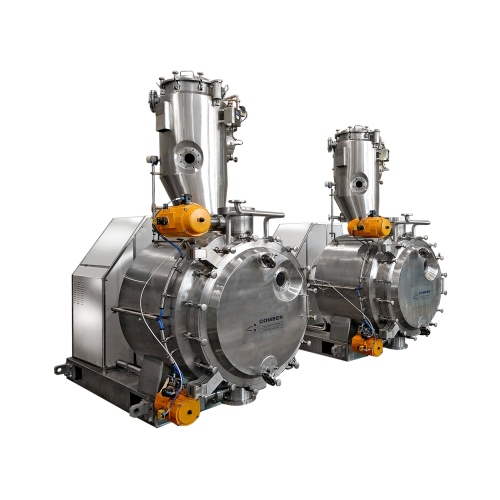
Horizontal vacuum paddle dryer for sensitive pharmaceutical ingredients
Achieve precise drying and mixing of sensitive ...
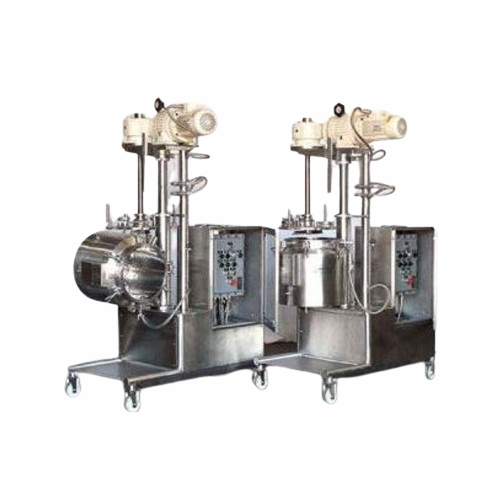
Pilot plant filter dryer for small scale production
Optimize filtration and drying processes in your pilot plant with a v...
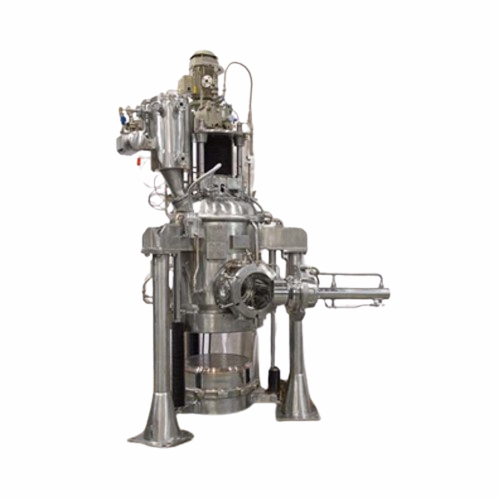
Pilot unit filter dryer for laboratory applications
Efficiently manage filtration and drying processes with precise tempe...
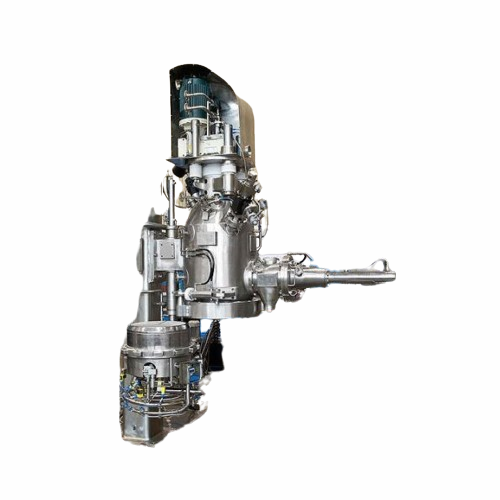
Sterilizable filter dryer for pharmaceutical applications
Ensure full sterility and efficient moisture removal in critic...

Conical screw vacuum dryer for hazardous and temperature-sensitive products
When you need precise moisture control for...
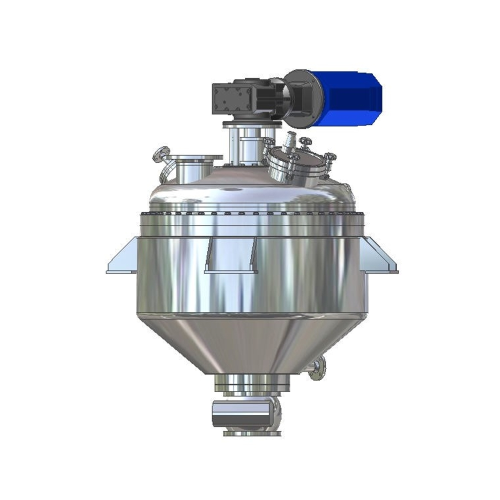
Vacuum drying solution for filter cake or viscous materials
When faced with the challenge of drying filter cake or trans...
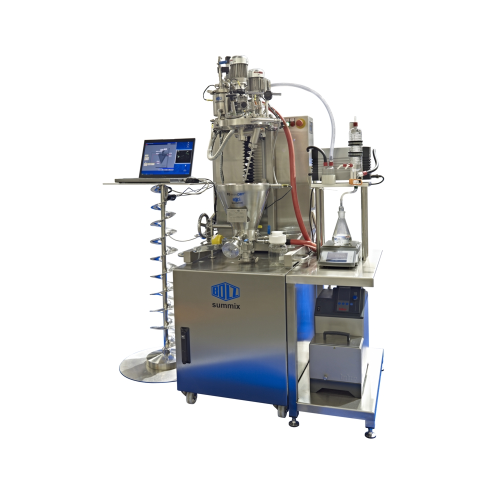
Laboratory system for drying and mixing processes
Enhance your R&D capabilities with precise drying and mixing contr...
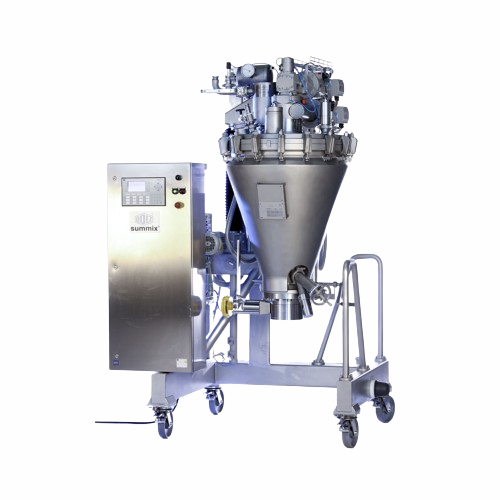
Pilot plant conical screw dryer
Optimize drying efficiency with this versatile pilot plant solution, ideal for simulating an...
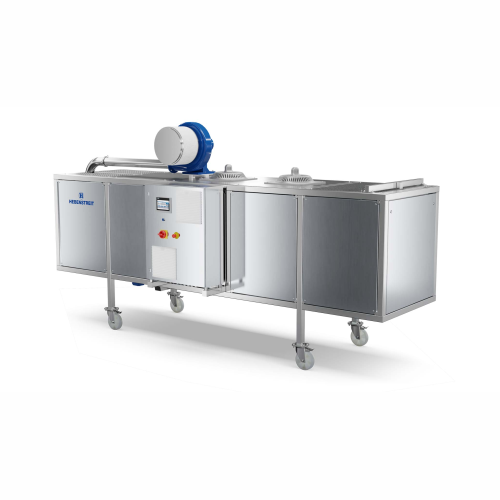
Industrial drum dryer for extruded snacks
For snack producers aiming to achieve precise moisture control, this rotating dr...
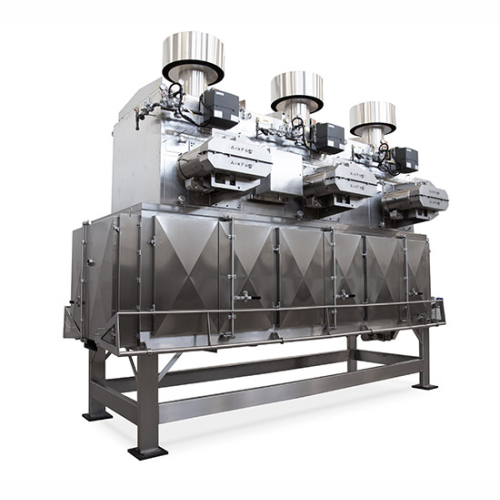
High volume rotary dryer roaster for continuous drying
Achieve uniform drying and roasting with a continuous, high-capaci...
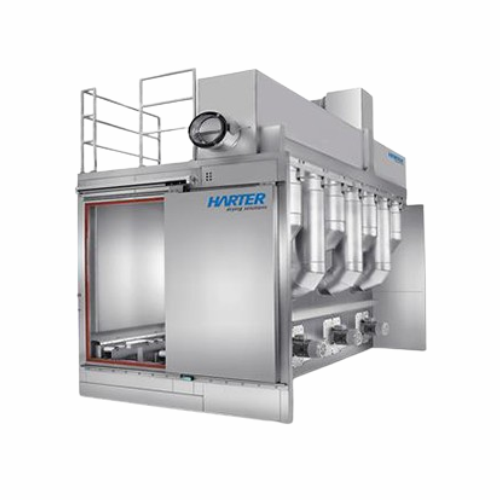
Industrial tunnel dryer
Optimize drying efficiency and maintain product quality with continuous tunnel drying, ideal for prec...
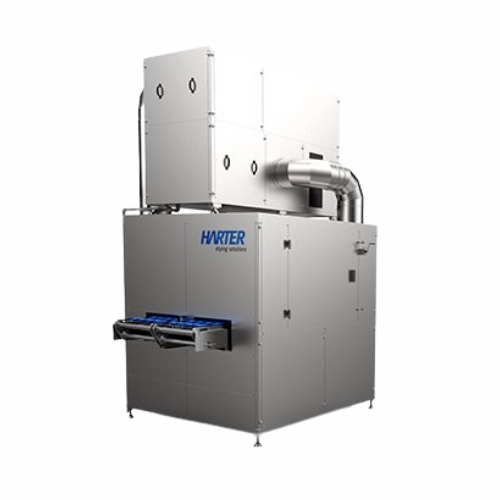
Large continuous tunnel dryer
Optimize your production with advanced drying and dehumidification technologies, ensuring prec...
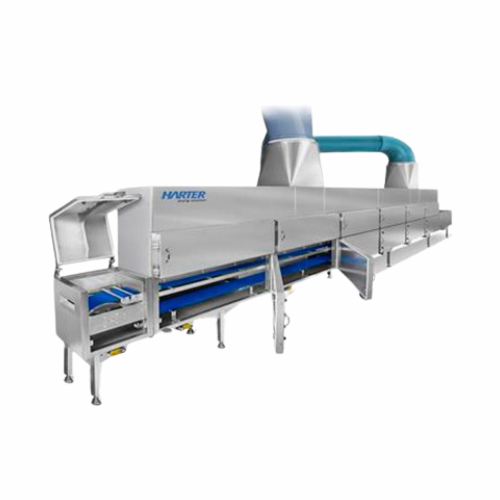
Continuous drying system for viscous substances
When handling viscous substances, ensure precise moisture control with con...
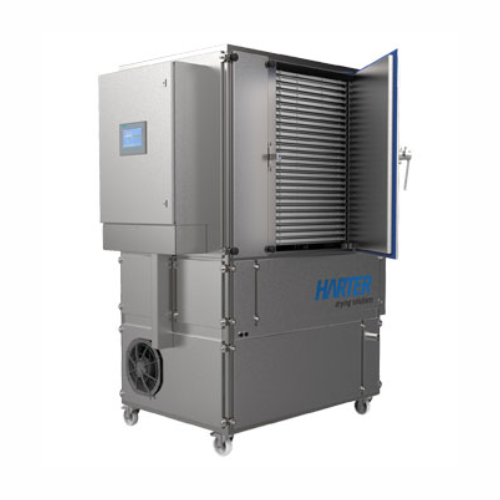
Pharmaceutical and laboratory product drying solution
Ensure precise moisture control for diverse products, from pharmace...
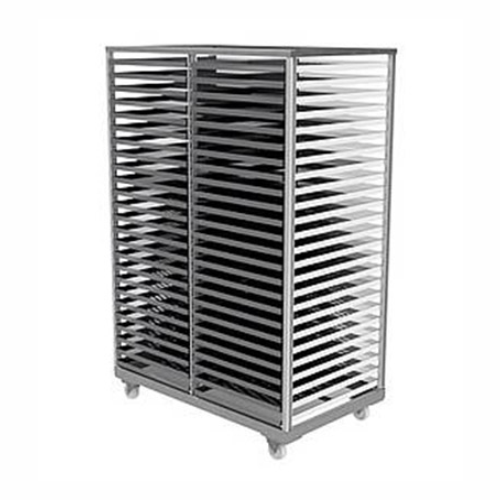
Pharmaceutical and med-tech drying solution
Achieve precise moisture control and adaptability across diverse products with...
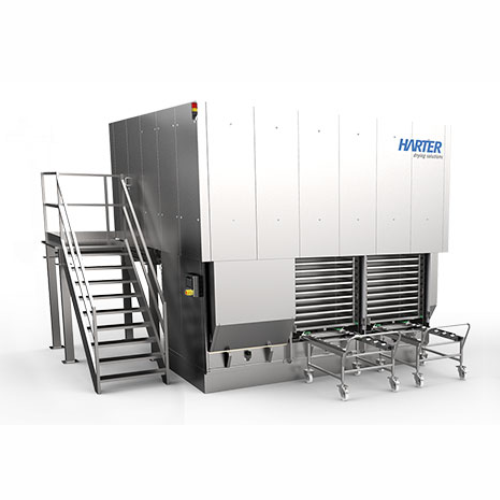
Batch-operated chamber dryer for surface drying
Enhance production efficiency with precise, low-temperature drying and coo...
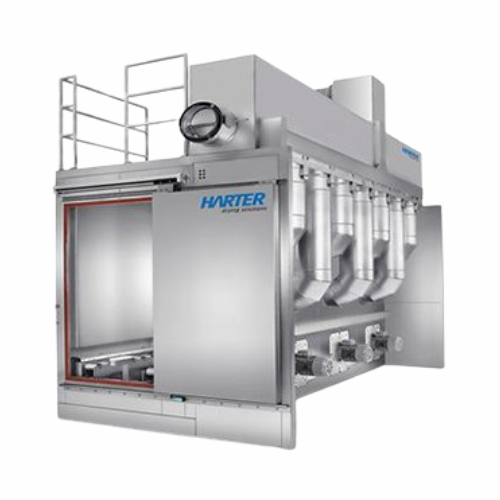
Continuous tunneling drying system for industrial applications
Streamline your drying process with precision-controlled ...
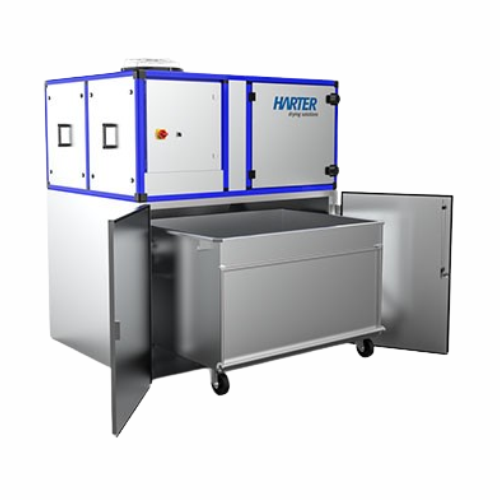
Industrial sludge drying solution
For facilities needing precise moisture removal, this compact solution ensures efficient ...
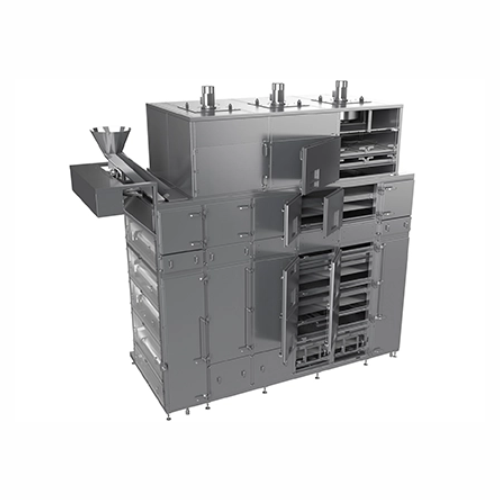
Continuous belt dryer for large-scale drying applications
Optimize your production with a continuous belt dryer, enginee...
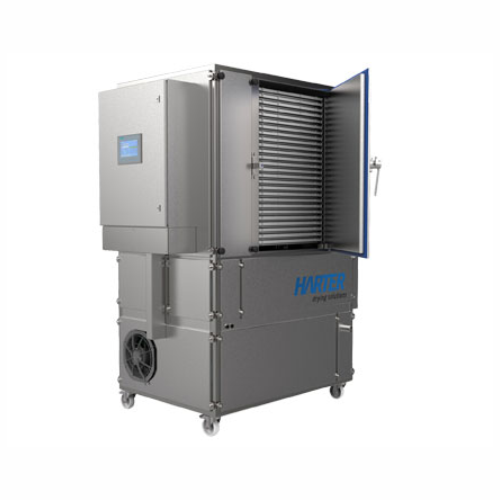
Compact dryer for product and process development
Optimize your testing and product development with a compact drying sol...
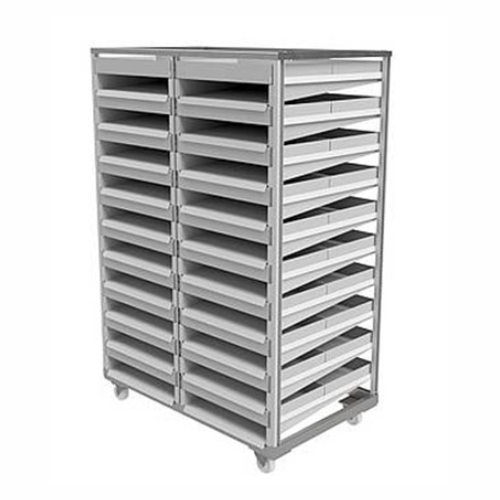
Flexible drying system for various industrial applications
Achieve precise moisture control across diverse materials wit...
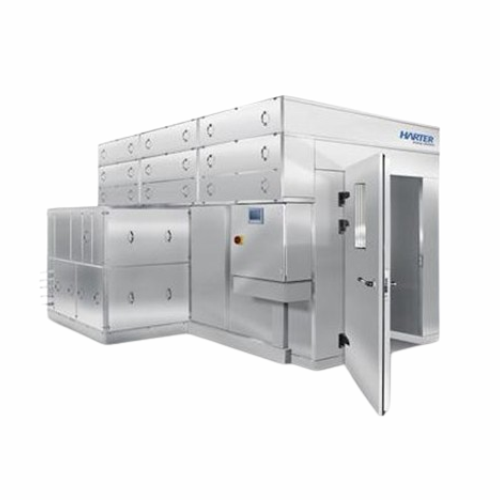
Batch drying solution for industrial applications
Achieve precise and gentle moisture control in diverse production proce...
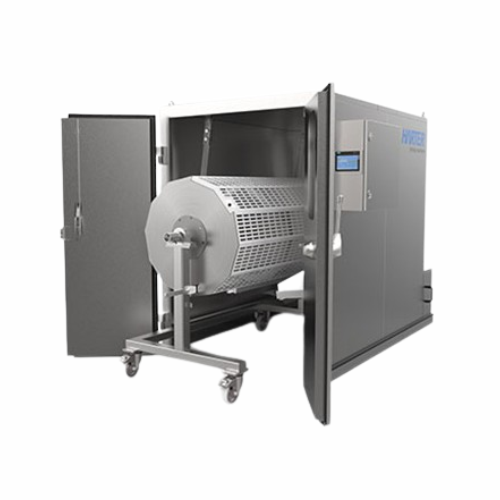
Drum dryer for animal feed
Achieve efficient and uniform drying for a variety of products, from nuts to medicinal cannabis, ...
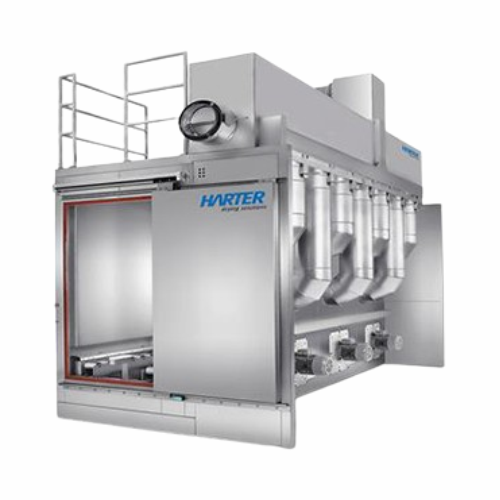
Continuous tunnel dryer for tray carts
Efficiently dry diverse products with precision temperature control, ensuring gentle...
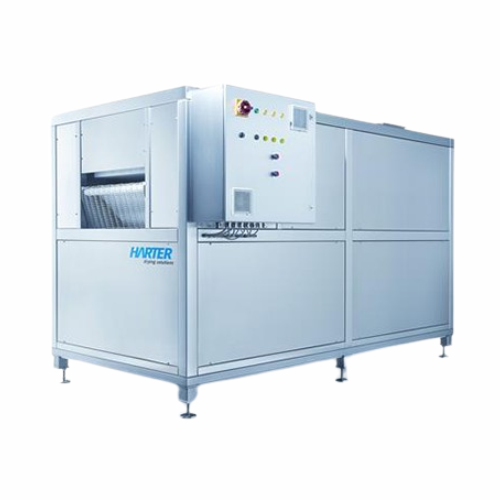
Continuous dryer for large production volumes
Achieve high-speed moisture removal with precision and minimal thermal impac...
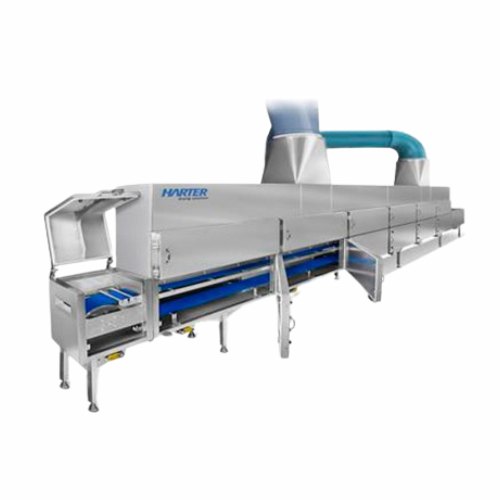
Continuous conveyor belt dryer for endless products
Optimize your continuous production line with a high-speed drying sol...
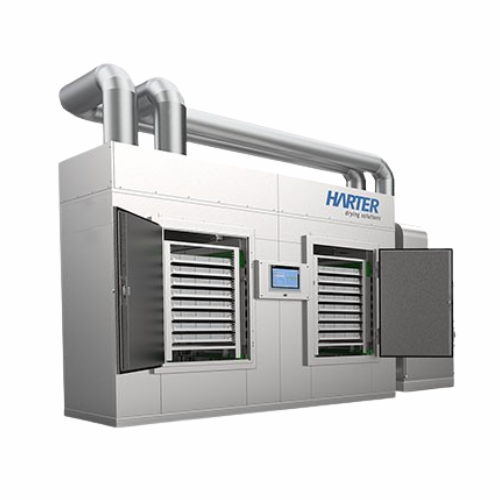
Batch drying solutions for industrial applications
Ensure precise moisture control across diverse materials with our vers...
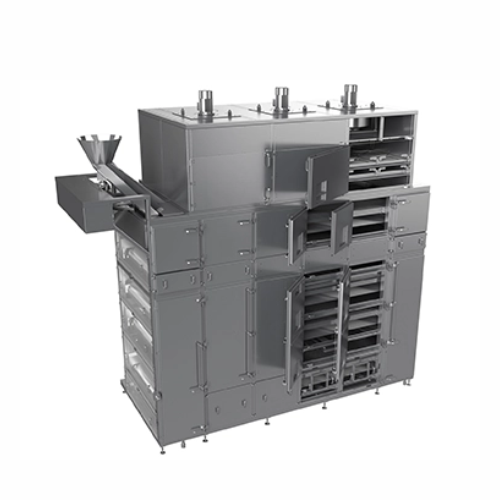
Continuous belt dryer for industrial production
For operations requiring precise moisture control, this continuous belt dr...

Compact food drying system
Achieve precise moisture control for product development and testing with this versatile compact ...
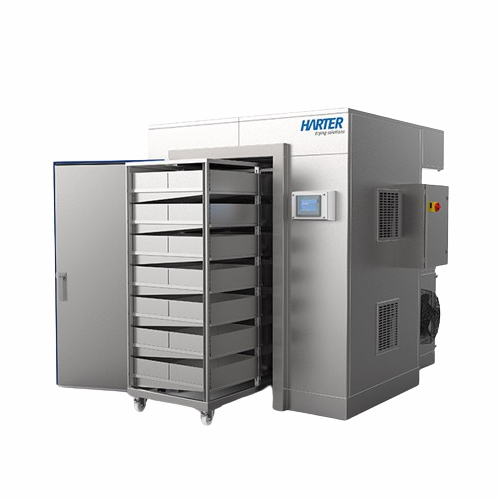
Food drying system for diverse products
Achieve precise moisture control and versatile drying for your diverse product line...
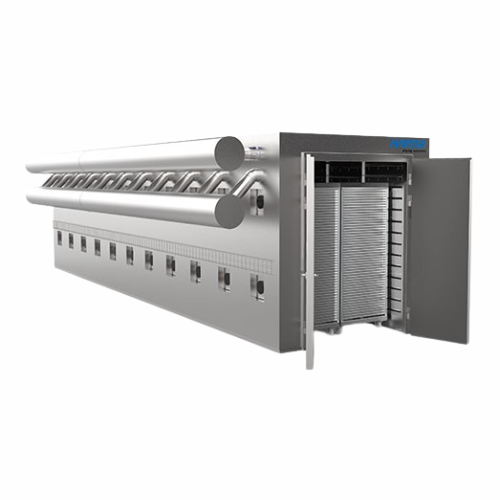
Batch drying system for food, pet feed, pharmaceuticals, and more
Optimize your drying needs with precision control for...
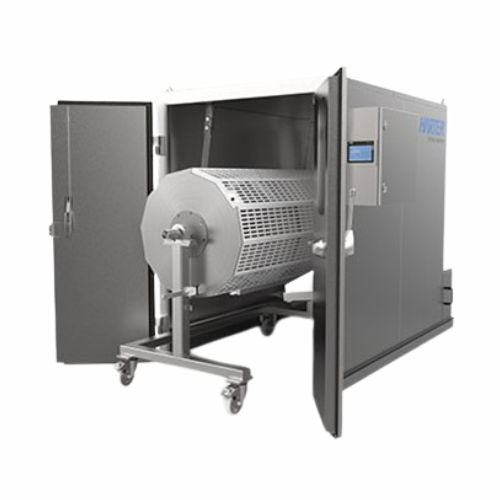
Rotary drum dryer for robust food products
Achieve uniform and gentle drying for sensitive and robust products alike with ...
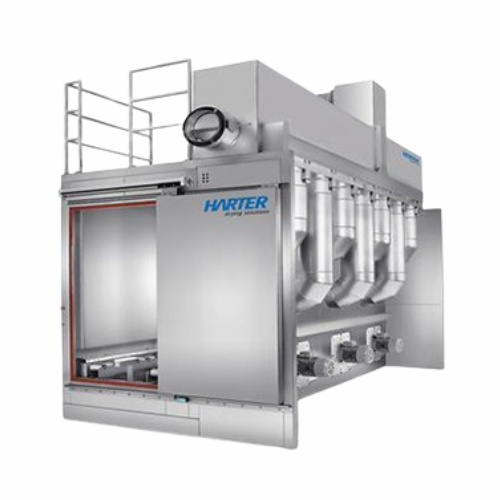
Continuous tunnel dryer for food products
Achieve precise moisture removal with adaptable drying technology, ensuring your...
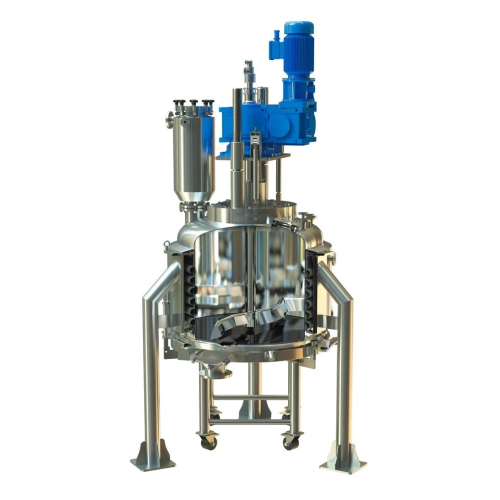
Nutsche filter dryer for pharmaceutical and chemical industries
Achieve precise filtration and efficient drying in one s...
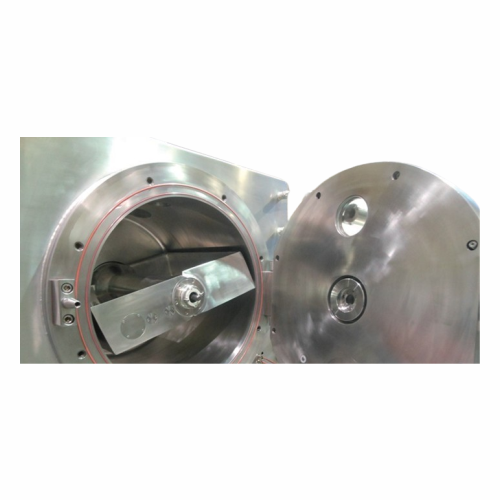
Rotary vacuum paddle dryer for pharmaceutical ingredients
Ensure precise moisture control and efficient drying for sensi...
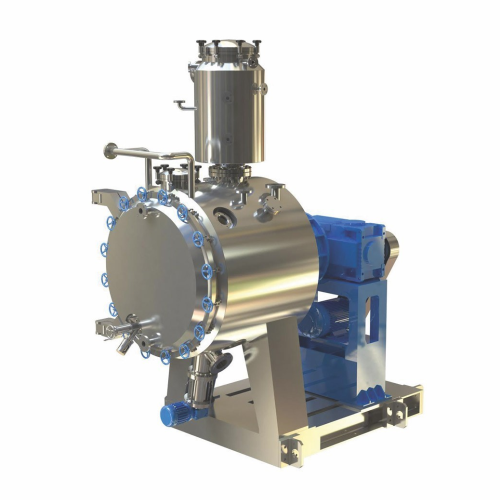
Vacuum paddle dryer for active pharmaceutical ingredients
For precise moisture control and contamination-free conditions...
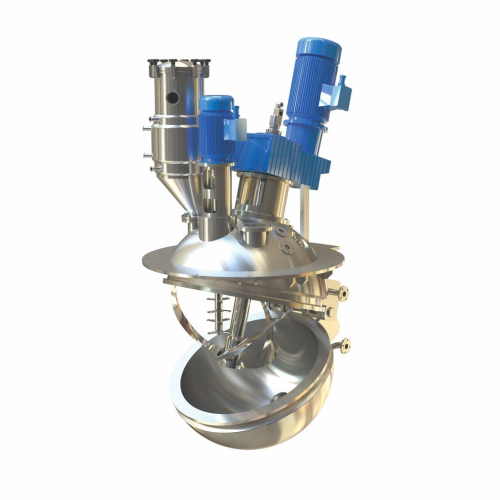
Spherical vacuum dryer for Apis and fine chemicals
Achieve precise moisture control and efficient drying for APIs and fin...
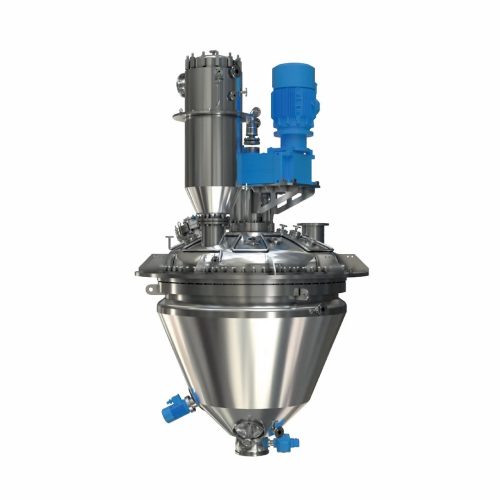
Vertical conical dryer for pharmaceutical ingredients
Optimize drying and mixing processes for high-value substances with...
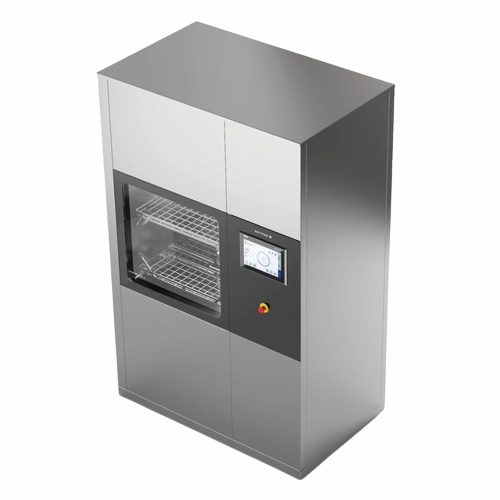
High-capacity cgmp washer/dryer for cleanrooms
Optimize your cleanroom operations with this compact washer/dryer, designed...
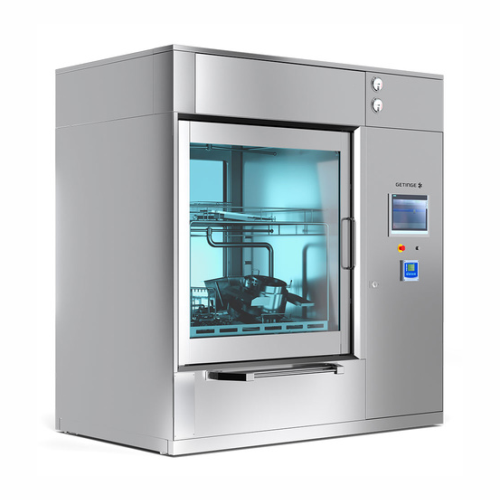
Cgmp washer/dryer for biopharmaceutical cleaning
Achieve optimal cleanliness with precise washing and drying for biopharma...
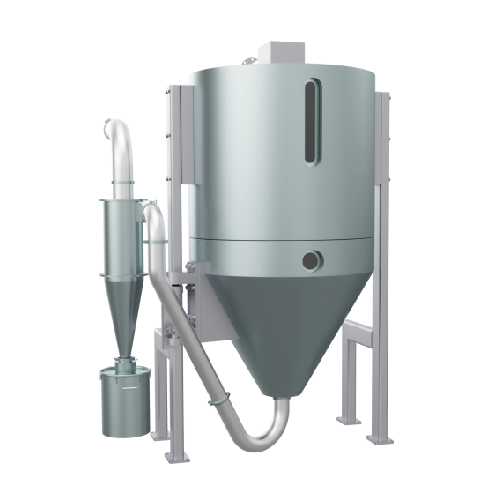
Commercial scale spray dryer for pharmaceutical materials
Optimize the drying of pharmaceutical and industrial materials...
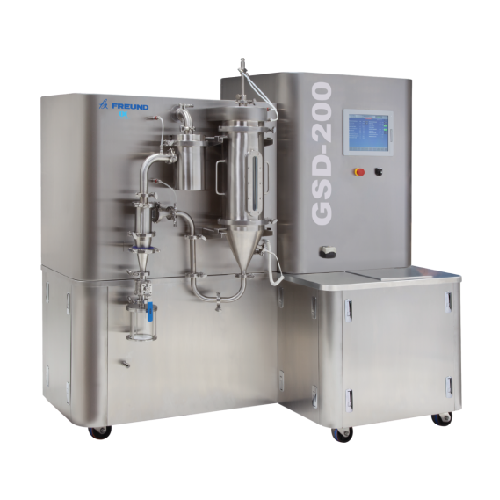
Laboratory spray dryer for sub-gram powder samples
Achieve precise control in developing fine chemical and pharmaceutical...

Pilot Gmp spray dryer system for small-scale manufacturing
For precise control in spray drying, streamline your small-sc...
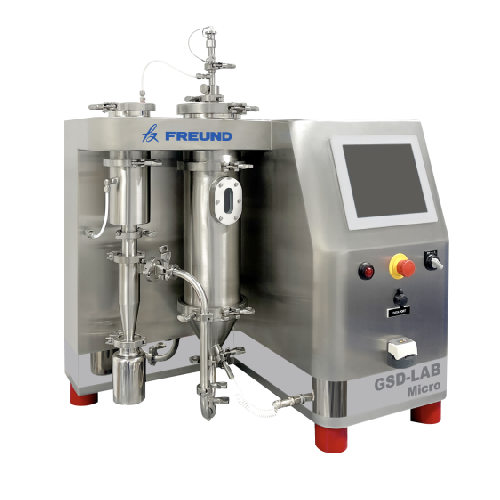
Benchtop spray dryer for drug discovery
Optimize your formulation development with a compact spray dryer that streamlines t...
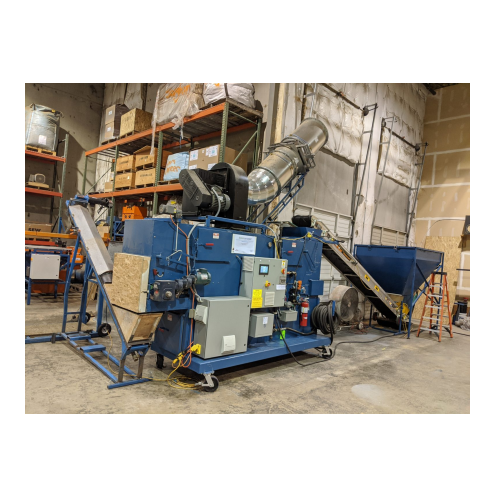
Downdraft conveyor dryer for industrial drying applications
Achieve consistent drying with reduced energy consumption us...
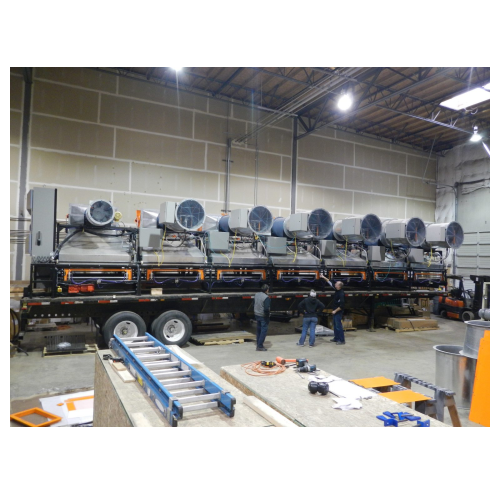
Downdraft dryer for biomass drying
Quickly reduce moisture content and energy consumption with a versatile dryer that reloc...

Advanced downdraft conveyor dryer for biomass feedstocks
Achieve precise moisture control and energy efficiency with adva...
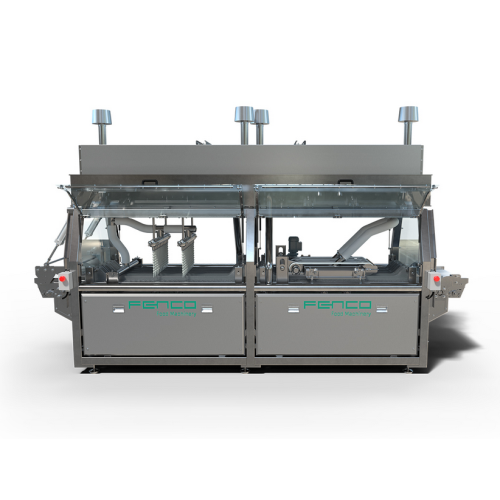
Efficient drying solution for food packaging pouches
Optimize your packaging line with precise moisture control, ensuring...
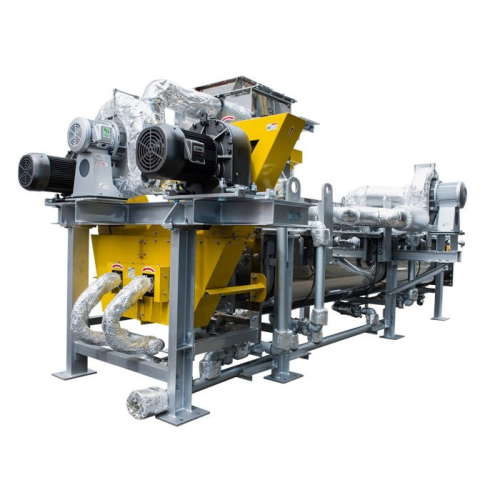
Sludge dryer for humid and pasty materials
Effortlessly manage pasty and sticky materials with a sludge dryer that ensures...
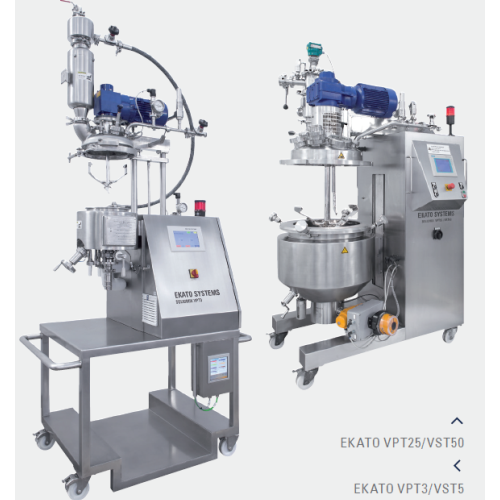
Laboratory mixer and dryer for solids
Enhance your laboratory capabilities with precision mixing and drying for small batch...
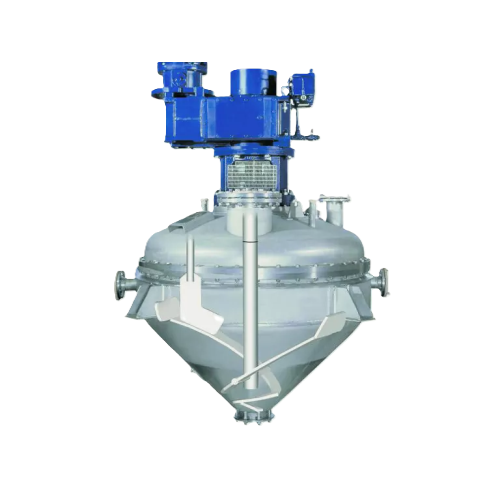
Vacuum dryer for free-flowing and pasty solids
Achieve precise drying and mixing with this vacuum dryer, optimizing heat t...
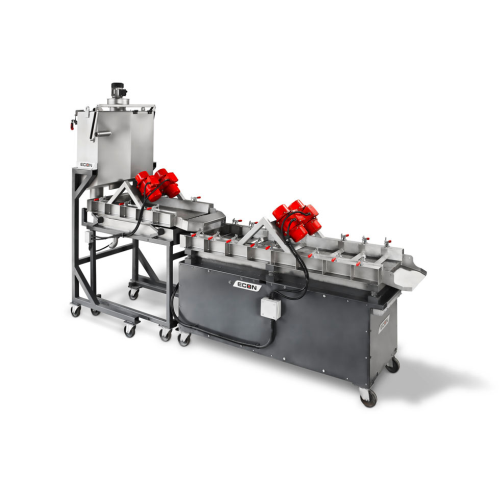
Vibration drying system for pellets
Achieve precise moisture control for pellets with high filler content, enhancing final ...
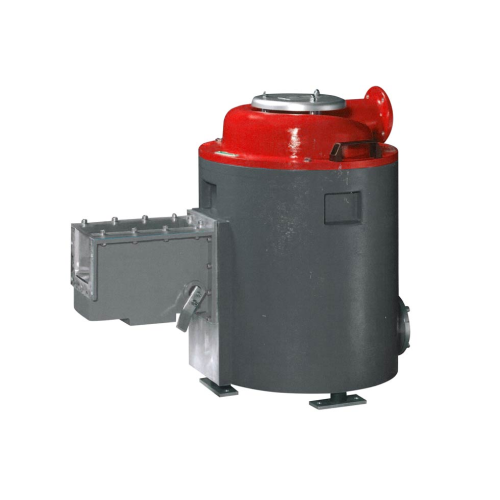
Pellet dryer for industrial recycling applications
Ensure precise moisture control for recycled plastic pellets and flake...
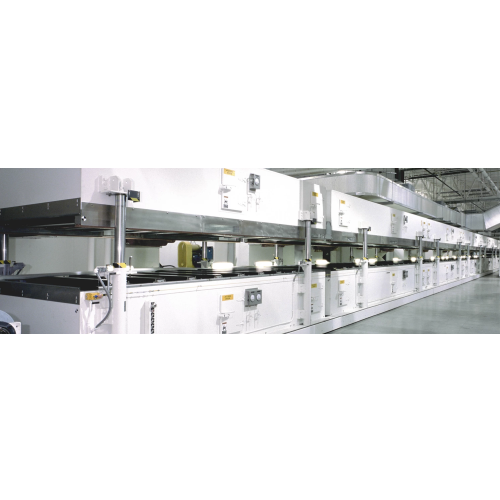
Non-contact drying system for flexible web materials
Achieve precise temperature control and uniform drying for ultra-thi...
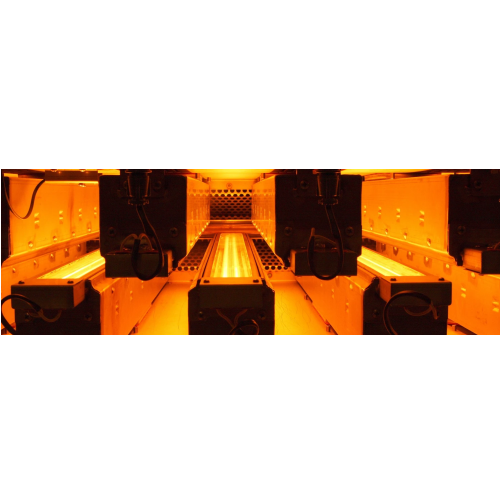
Infrared dryers and ovens for coating and substrate processing
Achieve precise drying and curing with customizable infra...
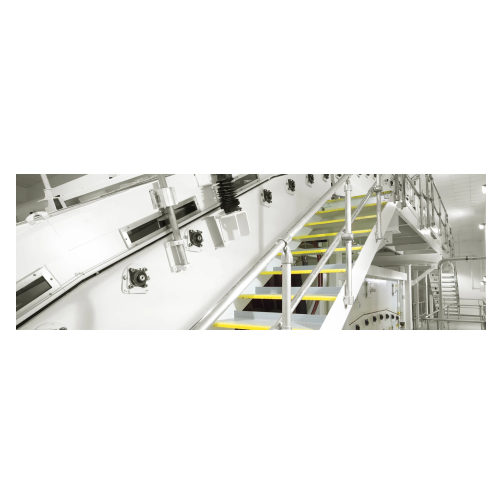
Roll support dryers for web transportation
Eliminate web curl issues and enhance drying precision for diverse materials wi...
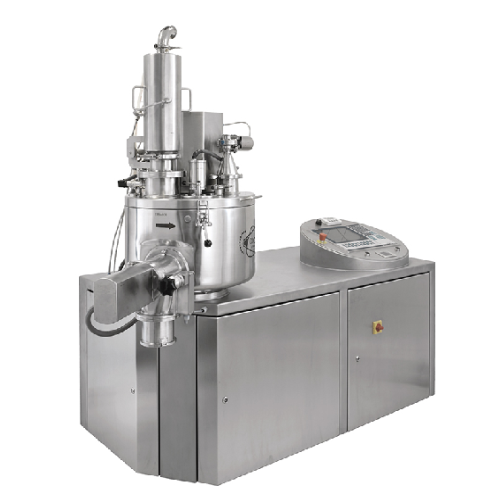
Pilot single-pot processor for granulation and drying
For efficient pilot production, streamline your mixing, granulating...

Single-pot processor for wet granulation and vacuum drying
Achieve efficient mixing, granulation, and swift vacuum dryin...
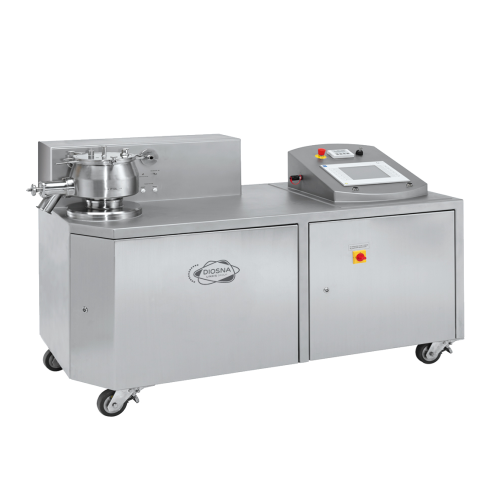
Laboratory unit for mixing, granulating, and vacuum drying
Achieve precise mixing, granulating, and drying in laboratory...
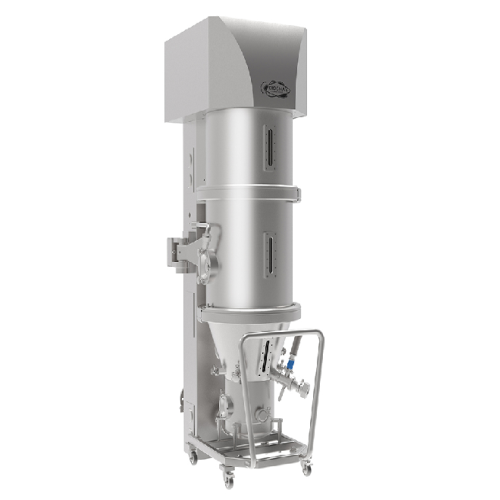
Fluid bed processor for granulating, drying, and coating in pilot scale
When scaling from laboratory to production, rel...
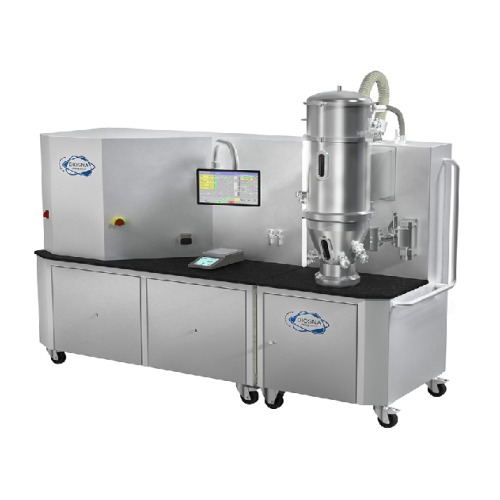
Laboratory fluid-bed dryer and tablet coater
Experience seamless transition from laboratory to production scale with a ver...
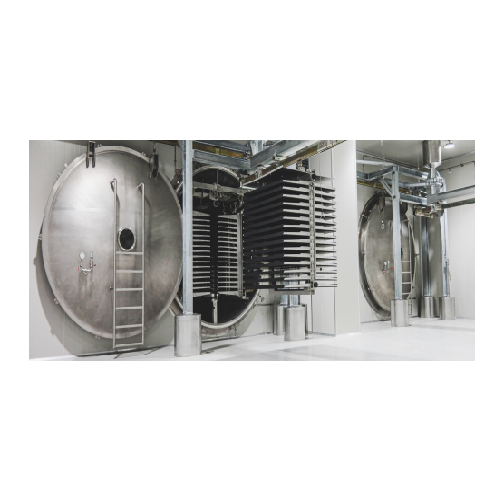
Vacuum and freeze drying plants for food and pharmaceuticals
Ensure high-quality, extended shelf-life products with inno...
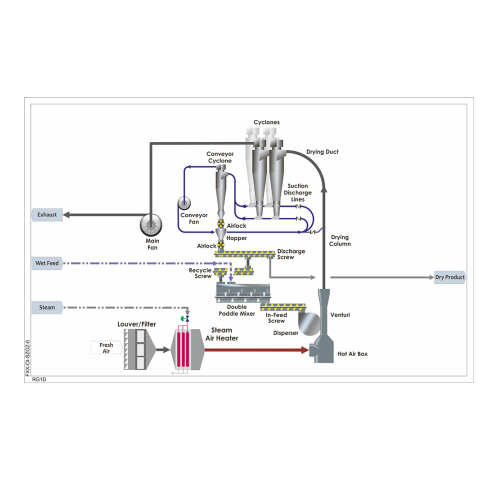
Corn starch drying solutions
Ensure precise moisture control and maintain product integrity in your corn starch processing w...
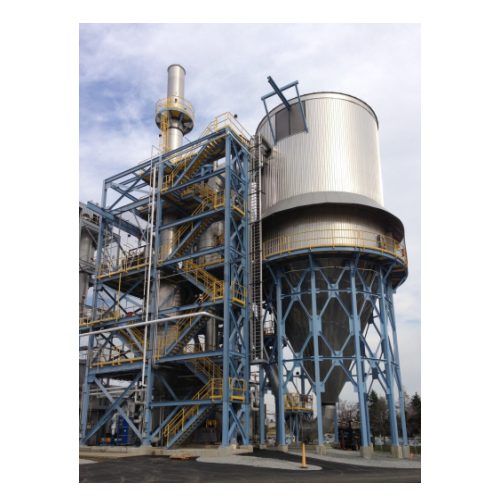
Spray dryers for lithium iron phosphate powder production
Optimize your lithium battery and electric vehicle production ...
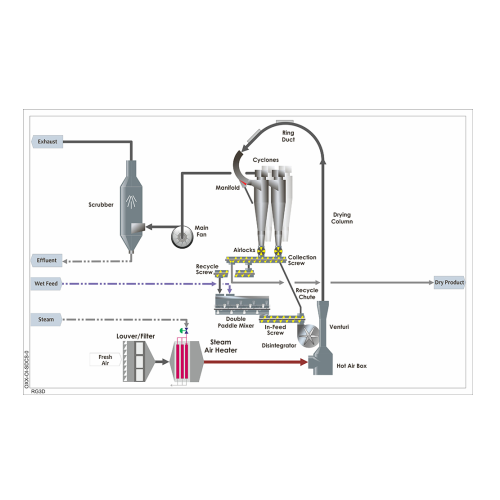
Pea fiber drying solutions for food or feed applications
Ensure top-tier product quality with precise drying of pea fiber...
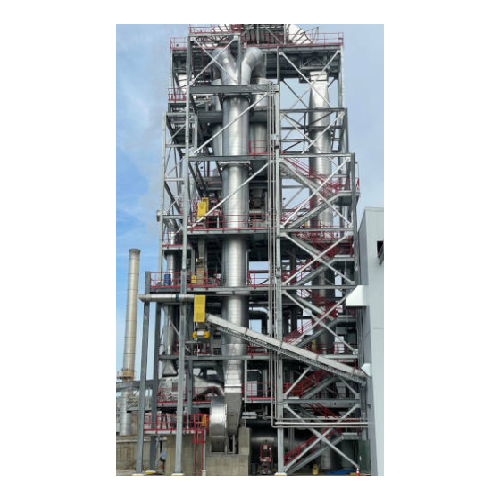
Industrial ring dryers for high-capacity drying applications
Maximize drying efficiency for diverse materials with ring ...
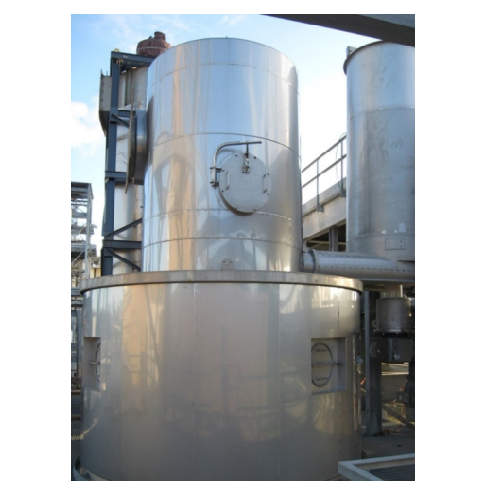
Industrial roto-flash dryer for chemical applications
Achieve uniform moisture and particle size in demanding drying proc...

Industrial rotary dryer for odor and emission control
For challenging drying applications with odor and emission concerns...
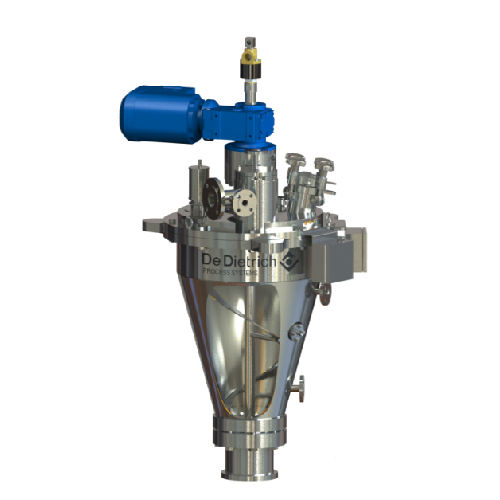
Vacuum drying for heat-sensitive products
Ensure moisture-sensitive formulations are dried efficiently without compromisin...
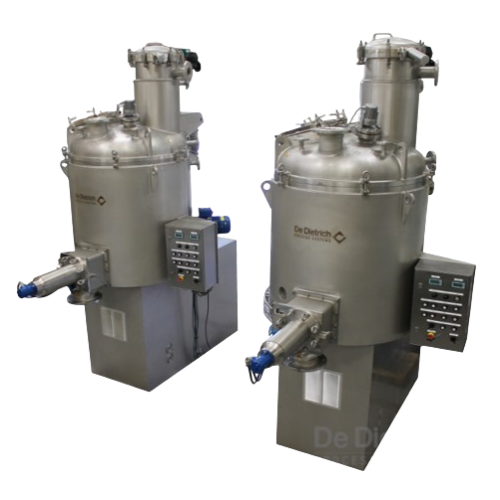
Industrial pan dryer for pharmaceuticals
For heat-sensitive powders and pastes requiring precise moisture levels, this pan ...
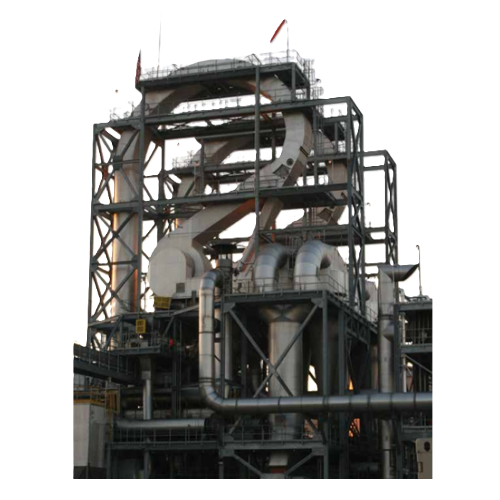
Flash dryer for surface moisture removal in powders
Optimize moisture removal in heat-sensitive materials with rapid, uni...
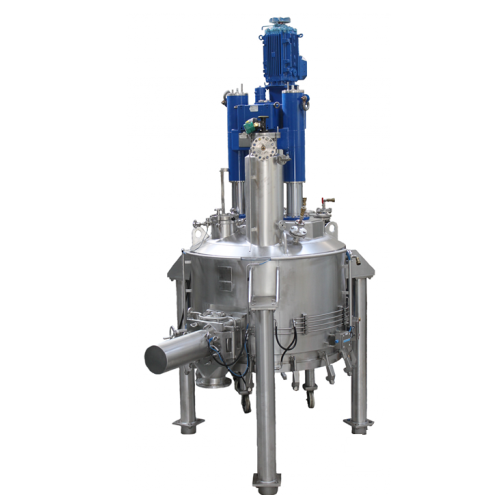
Agitated nutsche filter and filter-dryer for pharmaceuticals
Ensure precise filtration, washing, and drying of sensitive...
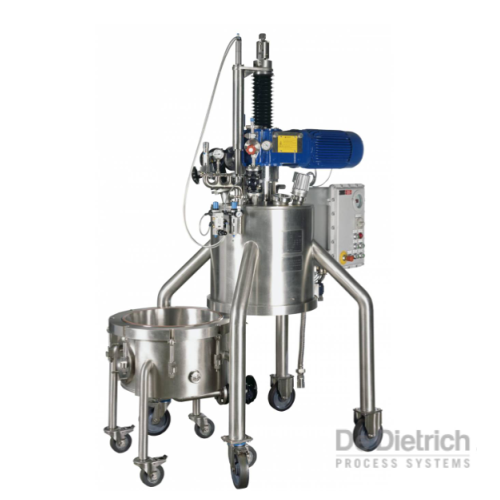
Pilot scale filter-dryer for pharmaceutical and chemical batches
Streamline small-batch production with a mobile filter-...
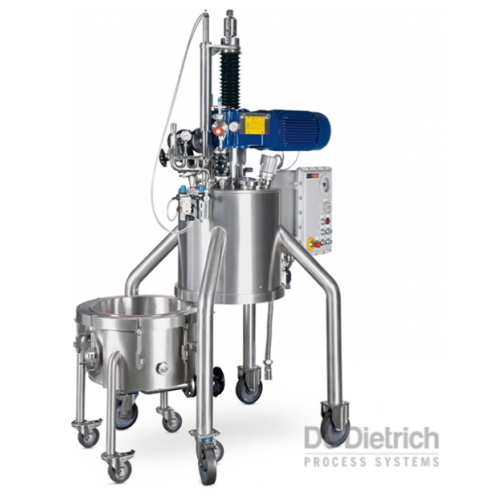
Microwave-enhanced filter dryer for chemical and pharmaceutical applications
Achieve rapid drying and efficient separa...
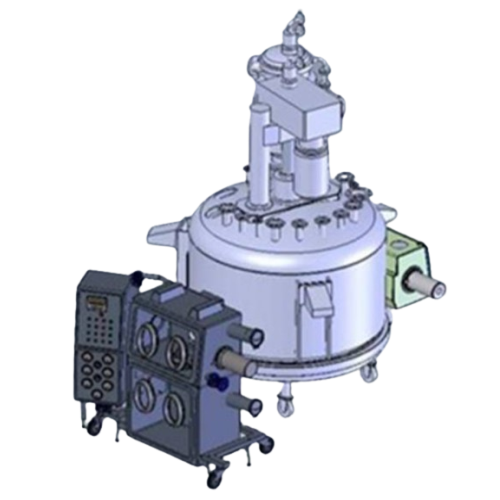
Industrial filter dryer for high potent Api production
Optimize your process of producing high-potency pharmaceuticals by...
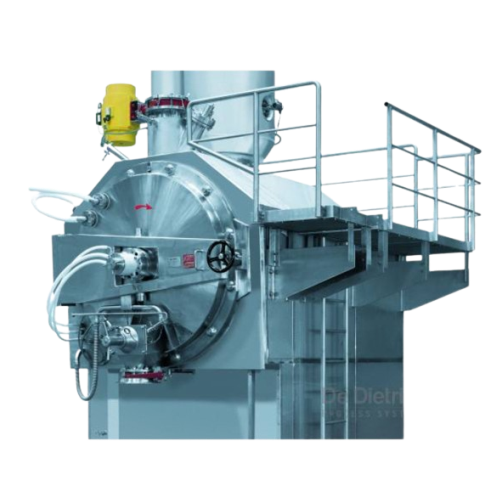
Universal dryer for herbal medicine production
Ensure optimal drying of plant-based pharmaceuticals, achieving precise moi...
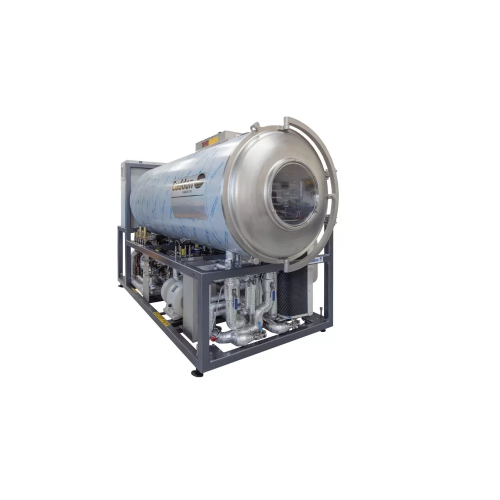
Freeze dryer for high sugar or acid content products
Achieve precise moisture control for challenging high sugar or acid ...
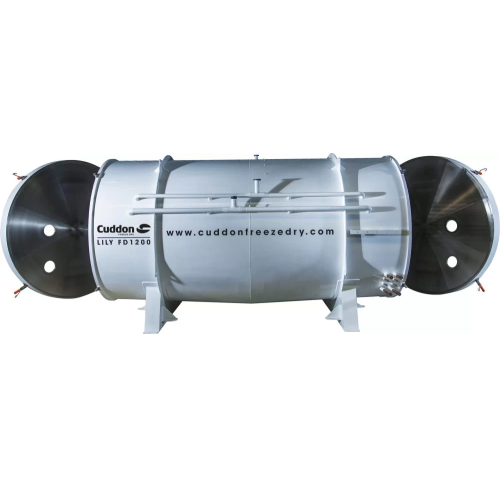
Industrial freeze dryer for large scale food processing
Optimize moisture removal for high-quality food preservation and ...
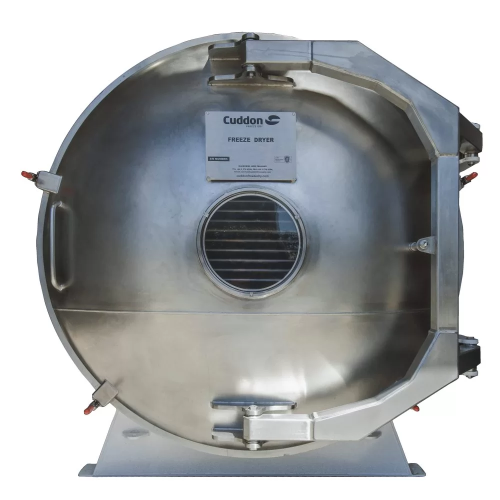
Industrial low temperature freeze dryer for high sugar or acid content products
For processing challenging high sugar ...
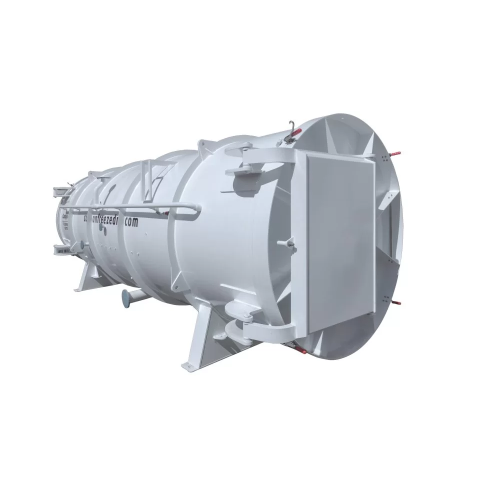
Large-scale industrial freeze dryer
Achieve precise moisture control and preserve product integrity with a large-scale free...
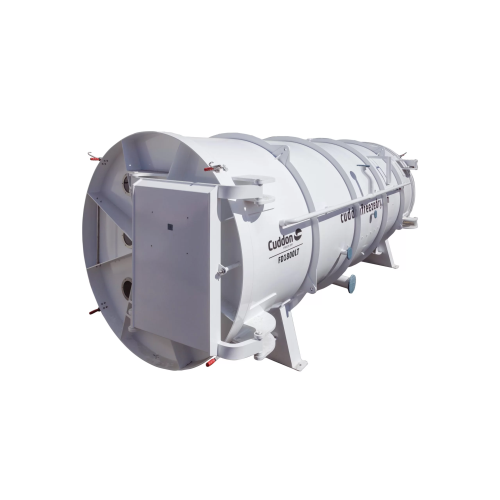
Low temperature freeze dryer for high sugar or acid content products
Perfect for producing freeze-dried goods from food...
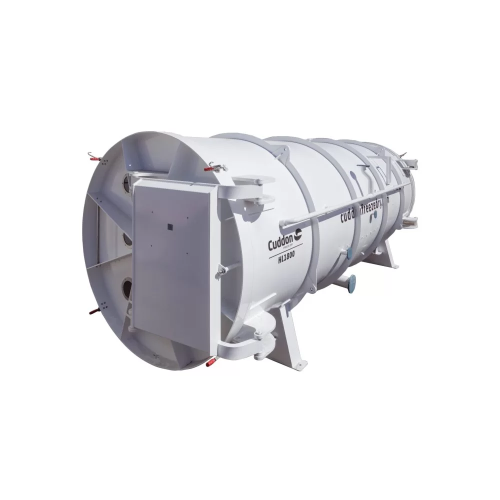
Cannabis freeze dryer for commercial use
Optimize moisture removal in cannabis products with precise control and high-speed...
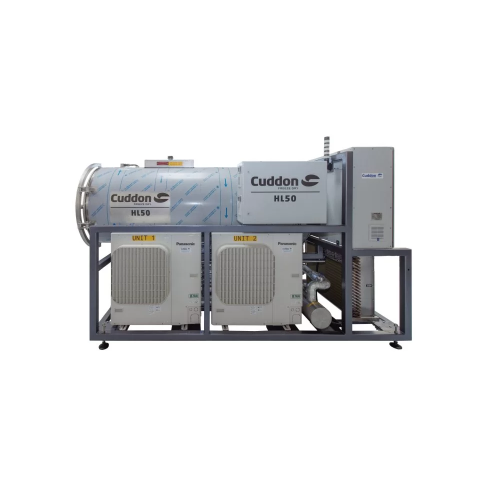
Cannabis freeze drying system
Optimize cannabis drying with precision-engineered freeze drying technology, designed to prese...

Commercial freeze dryer for cannabis products
Enhance your cannabis production with precise moisture control and achieve h...
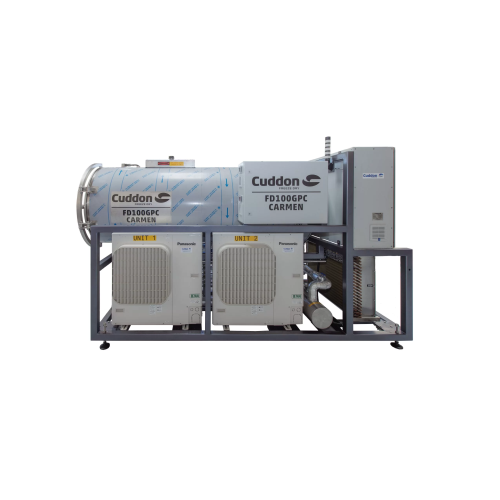
General purpose freeze dryer for small commercial batches
Maximize your production line’s flexibility with this ve...

Continuous vacuum dryer for protein products
Achieve precise moisture control and maintain product functionality with low-...
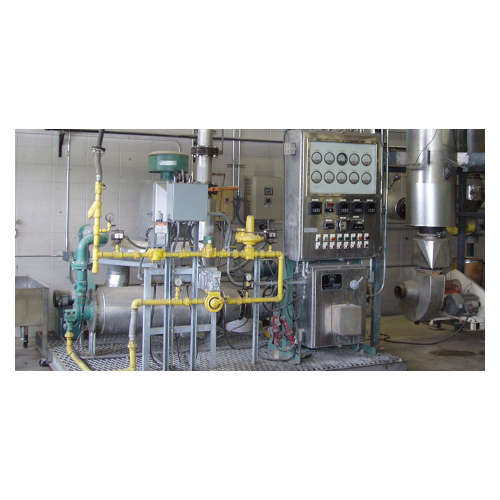
Vertical flash dryer for industrial drying applications
Optimize your production line with an energy-efficient vertical f...
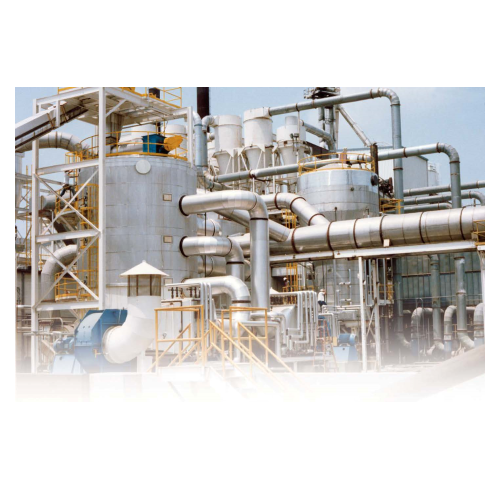
Efficient dryer-cooler for solvent-extracted meals
Optimize moisture control and energy efficiency in your production lin...
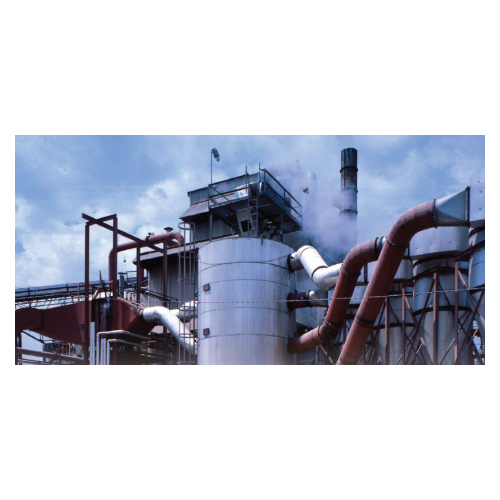
Dryer-cooler for solvent-extracted meal
Achieve optimal moisture and temperature control for solvent-extracted vegetable-oi...
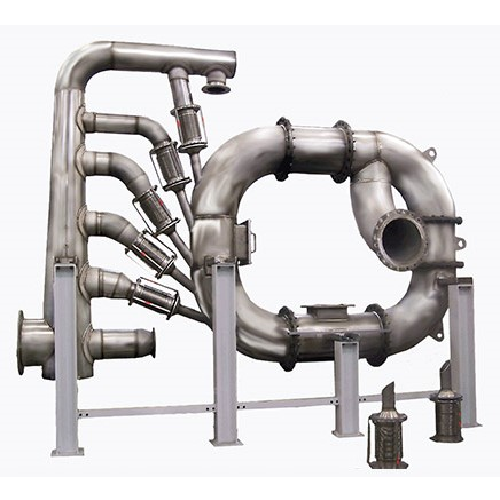
Milling flash dryer for fine powder processing
Achieve precise moisture control and prevent agglomeration in your processi...
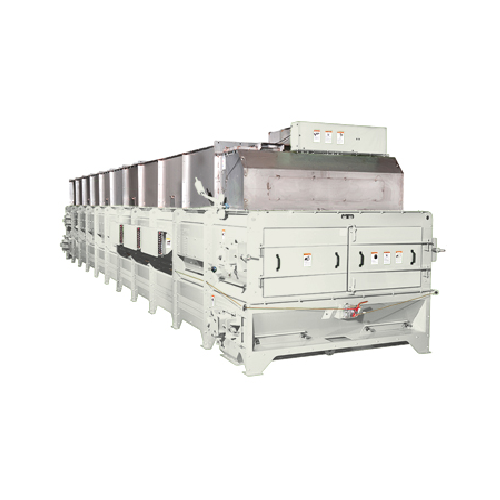
Heavy-duty horizontal dryer/cooler for pellets and meal
Optimize your production line with continuous high-speed drying a...
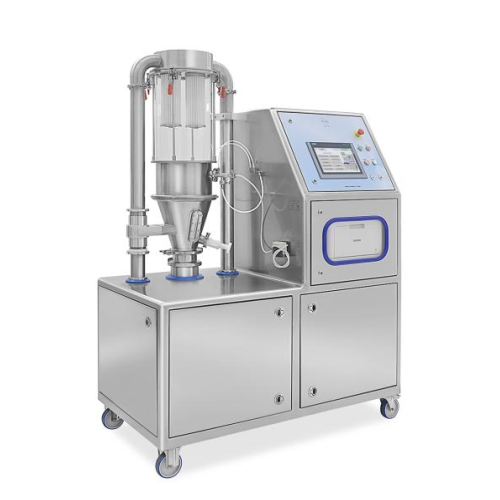
Laboratory fluid bed dryer for pharmaceutical granulation
Optimize your lab-scale drying and granulation processes with ...
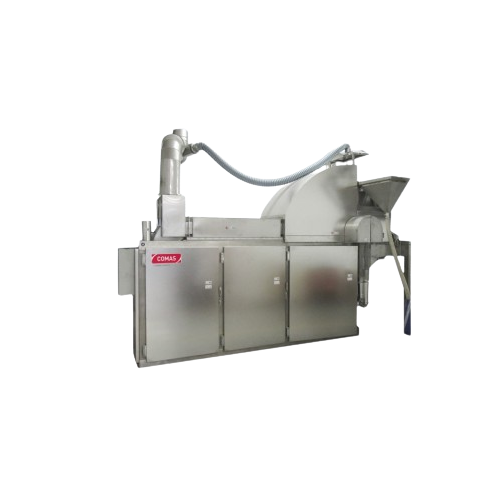
Drying solution for cosmetic slurries
Streamline the drying process of cosmetic slurries with precision control to achieve ...
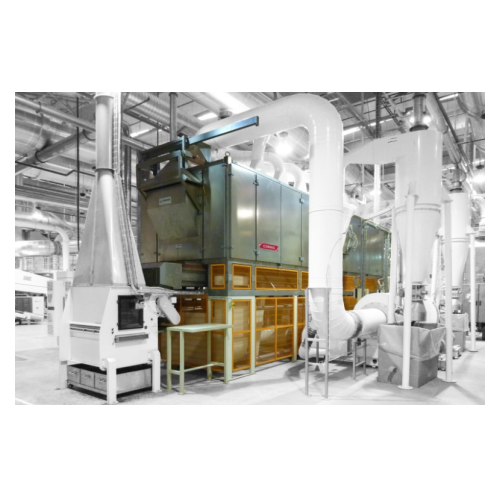
Cut stem air-vibro drying solution
Enhance your tobacco processing with precise drying that ensures optimal moisture contro...
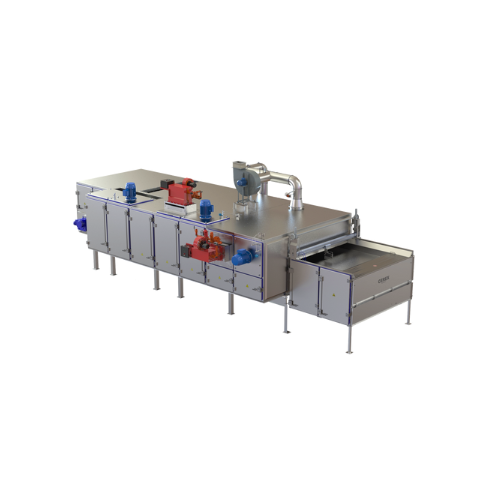
Coating dryers for breakfast cereal production
Achieve precise moisture control in coated cereal production with these mod...
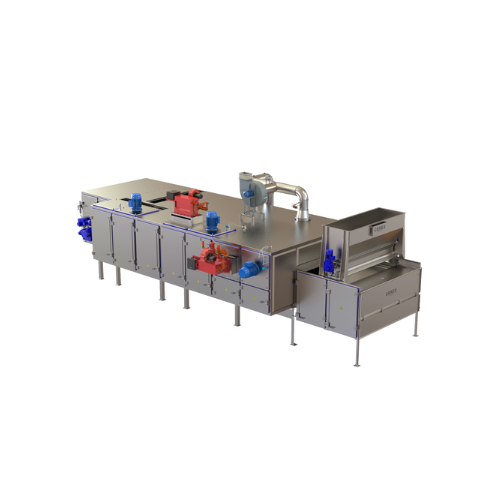
Granola drying solution
Optimize your granola production with modular drying technology that ensures precise moisture control...
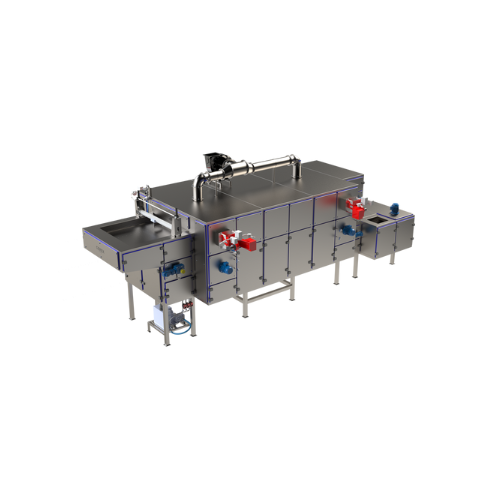
Multi-tier dryers for modern breakfast cereals
Optimize dry and cool cereal, nuts, and seed production with a compact modu...
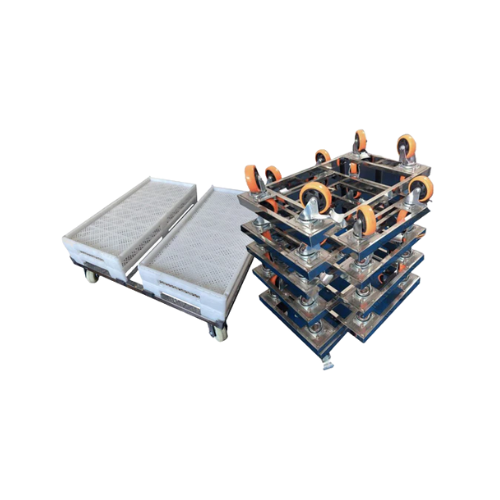
Drying trays for gummy candy production
Ensure proper drying and setting of your gummy candies and gelatin-based products w...
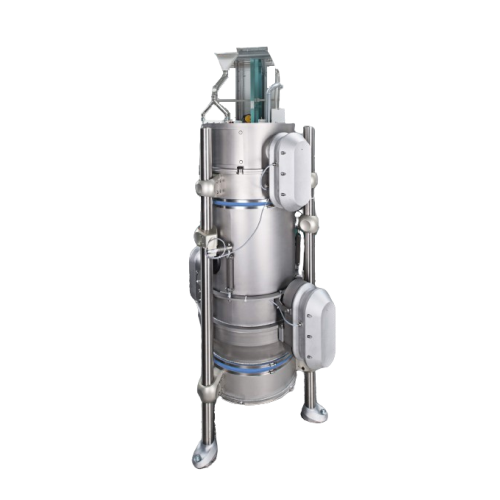
Advanced superheated steam drying solution
Harness the power of consistent drying technology to achieve optimal moisture c...
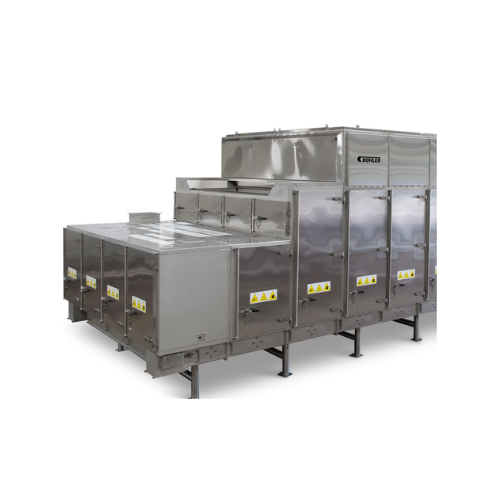
Multi-pass pet food dryer for consistent moisture content
Achieve precise moisture control and enhanced product quality ...
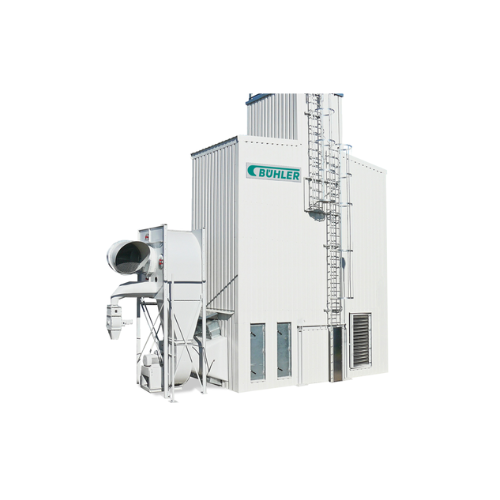
Continuous-flow dryer for grain and oilseeds
Streamline your grain and oilseed processes with efficient moisture eliminati...
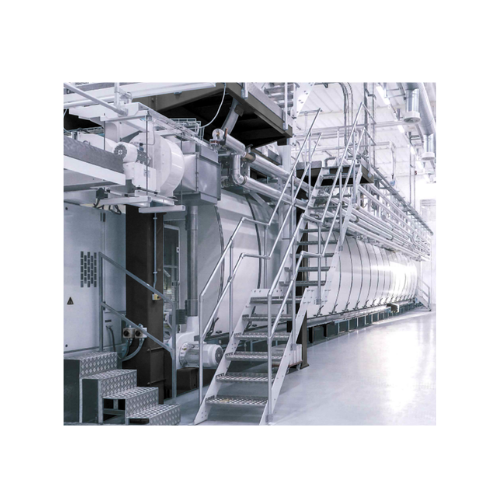
Long-goods pasta dryer
Achieve high-speed, energy-efficient drying for long-goods pasta while maintaining top product quality...
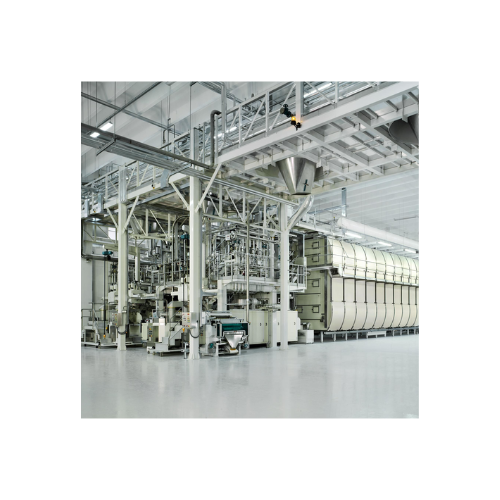
Short-goods pasta dryer for consistent and high-quality results
Ensure consistently high-quality pasta with customizable...
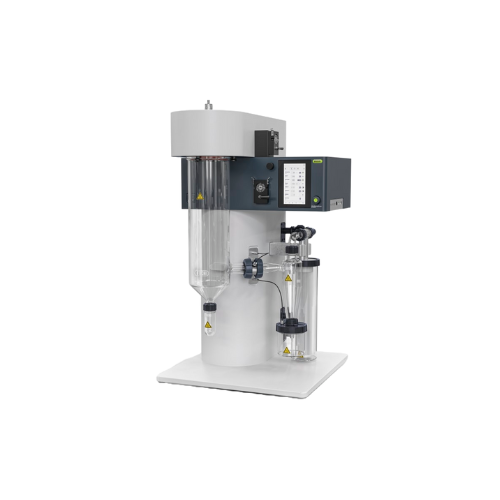
Laboratory spray dryer for organic solvent samples
Experience precise particle control and enhanced safety when convertin...
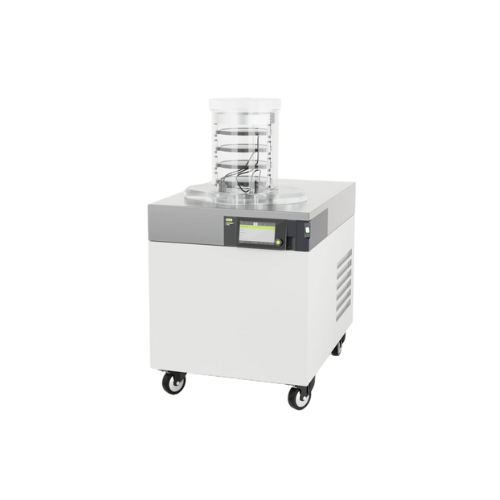
Laboratory freeze dryer for continuous sublimation
Achieve seamless continuous freeze drying with stable, reproducible pa...
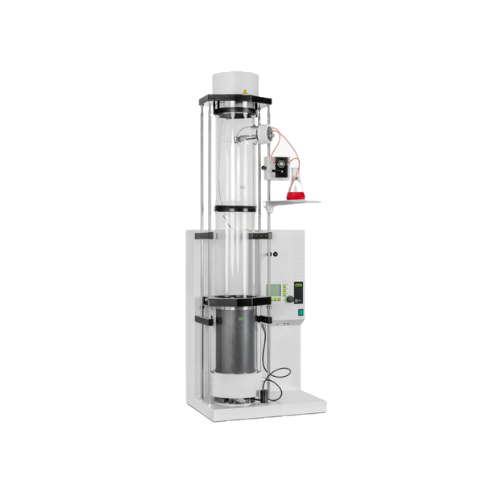
Nano spray drying system for pharmaceuticals and nanotechnology
Transform minuscule samples into submicron particles eff...
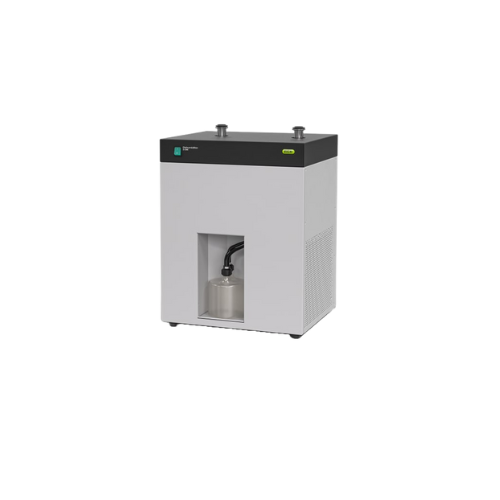
Industrial dehumidifier for continuous spray drying
Ensure stable spray drying conditions with precise humidity control, ...
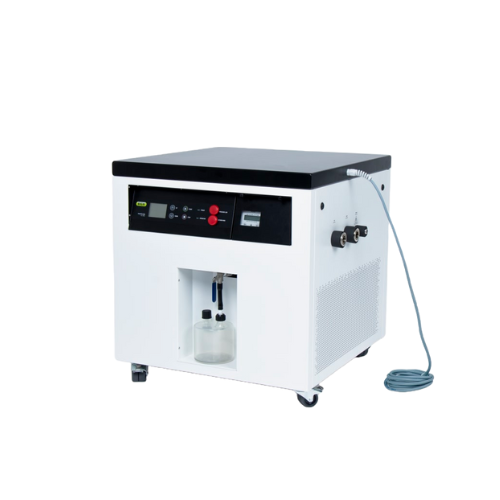
Inert loop for safe organic solvent spray drying
Ensure safe handling and efficient recovery of organic solvents in spray ...
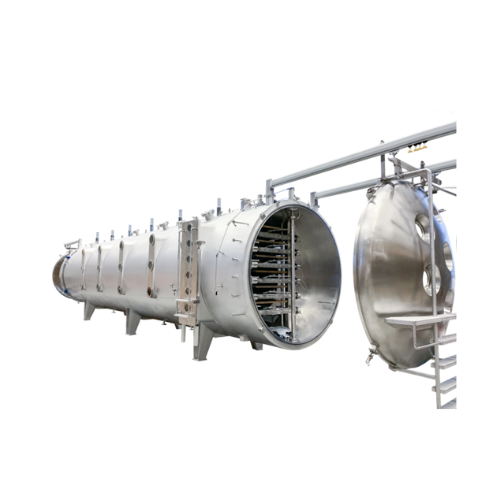
Continuous freeze drying solution for coffee and food pieces
Achieve optimal moisture removal in heat-sensitive products...
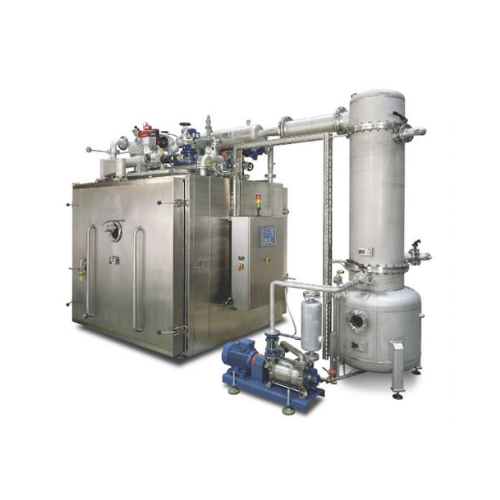
Vacuum dryer cabinet for heat-sensitive products
For manufacturers handling heat-sensitive products, achieving precise moi...
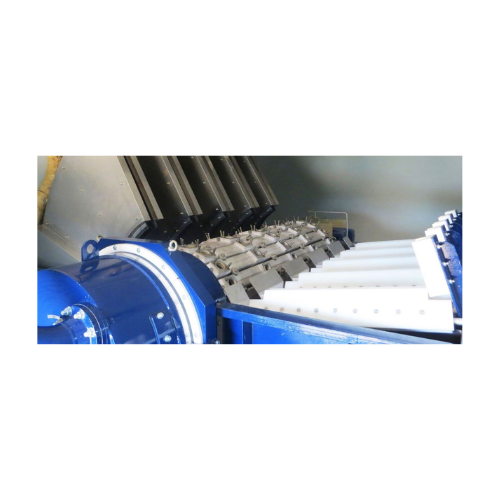
Disc filter for drying and filtering fine solids
Achieve unparalleled dryness and efficiency in fine solids processing wit...
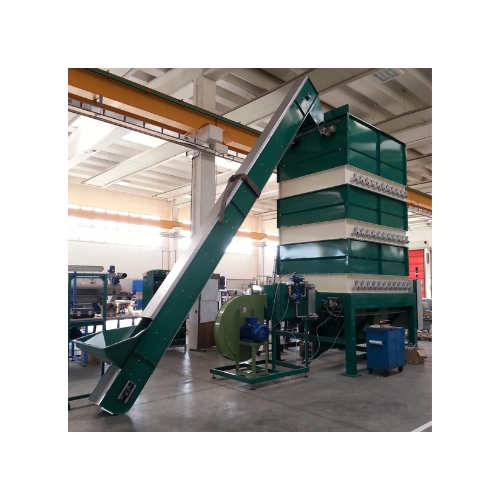
Vertical chestnuts dryer
Achieve optimal moisture removal for chestnuts with precise hot air cycling, perfect for converting ...
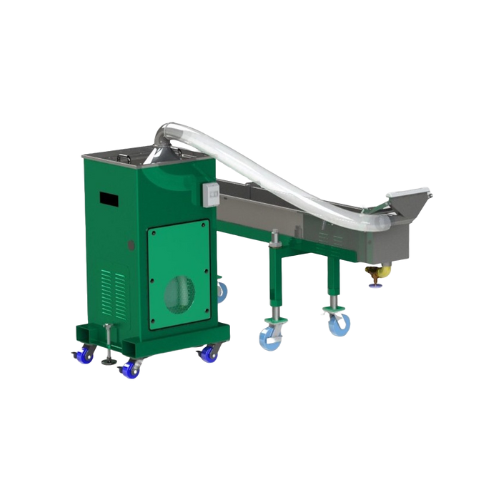
Advanced vacuum air dryer for pelletizing strands
Efficiently remove residual water from polymer strands with a vacuum ai...
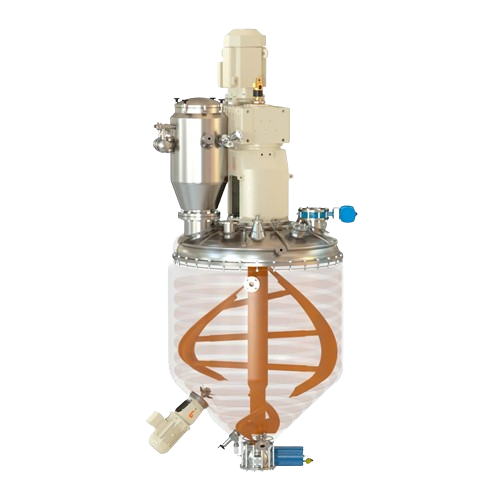
Vertical ribbon vacuum dryer for thermosensitive products
Achieve optimal drying of thermo-sensitive materials like powd...
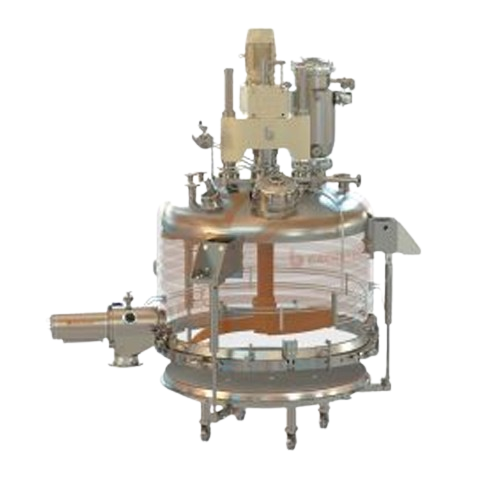
Agitated nutsche filter dryer for solid-liquid separation
Achieve high-purity solid-liquid separation with optimized thr...
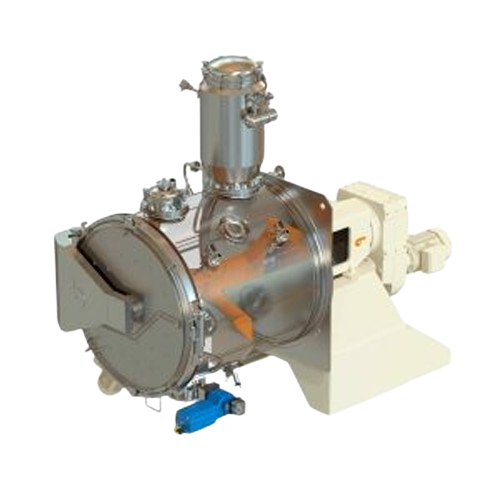
Sanitary horizontal paddle vacuum dryer
For sensitive product drying, ensuring short cycles and high thermal efficiency is ...
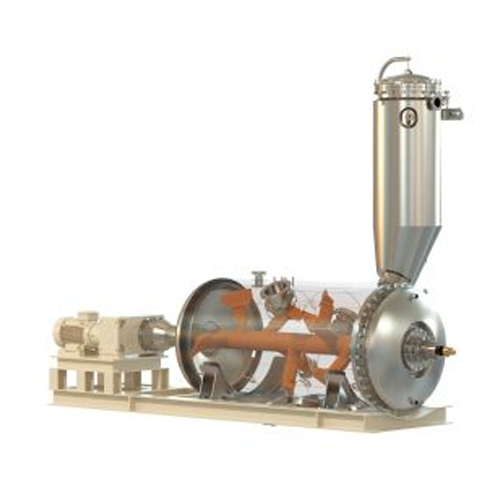
Horizontal vacuum paddle dryer for thermosensitive products
For high-viscosity products like active pharmaceuticals or p...
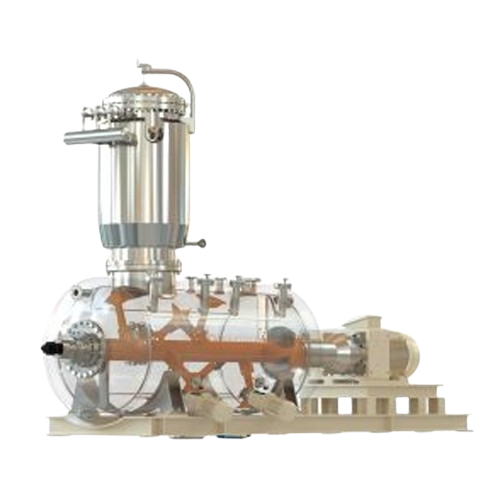
Horizontal vacuum paddle dryer for thermosensitive products
Achieve precise drying and mixing of high-viscosity, thermos...
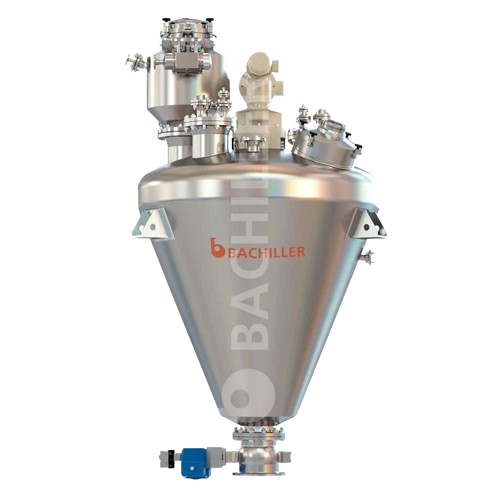
Vertical conical screw vacuum dryer
Achieve precise moisture control with ultra-vacuum batch drying, ideal for thermo-sensi...

Double cone vacuum dryer for thermosensitive products
For precise drying of heat-sensitive powders, this double cone vacu...
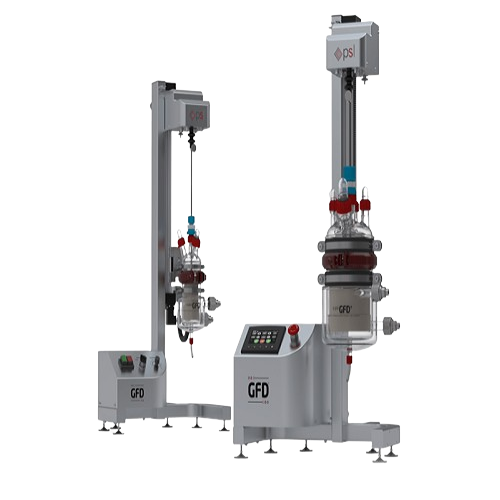
Automatable benchtop agitated nutsche filter-dryer
Effortlessly integrate seamless solid-liquid separation into your labo...
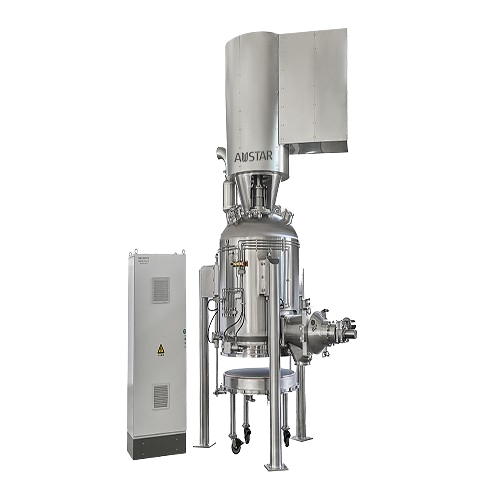
Nutsche filter-dryer for solid-liquid separation
Ensure precise moisture control and efficient solid-liquid separation for...
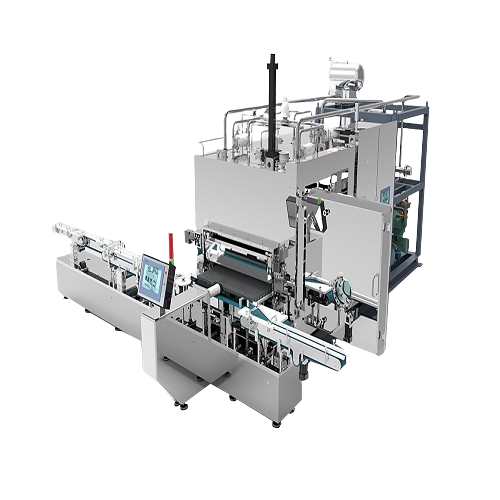
Commercial freeze dryer for pharmaceutical Api production
Ensure the stability and potency of your biopharmaceutical pro...
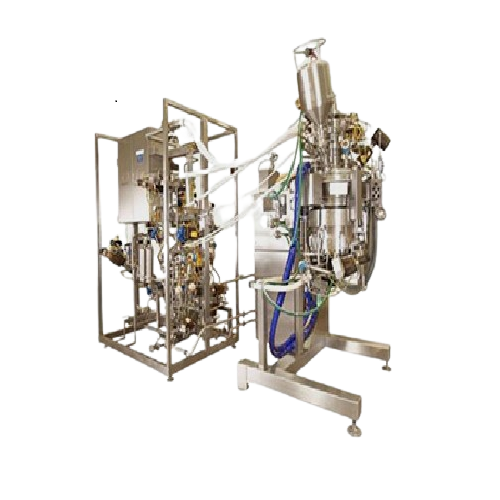
Microspheres process equipment for classification, washing, drying
Achieve high yield production of polymeric microsphe...
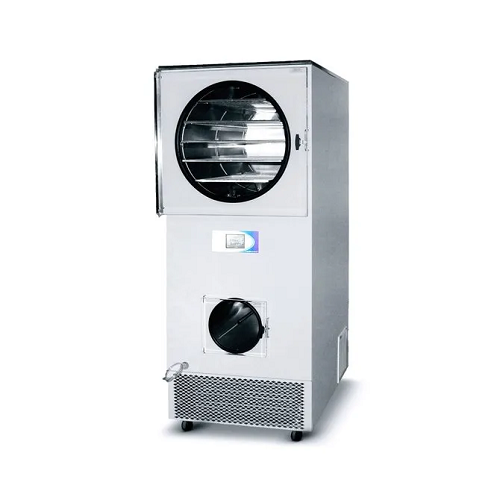
General purpose freeze dryer for archaeological and biological samples
Preserve and restore cultural and scientific tre...
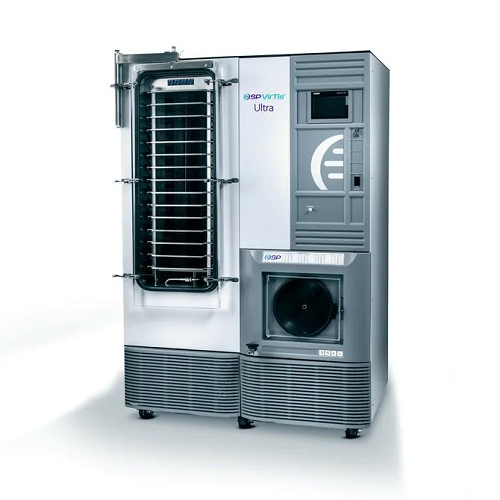
Pilot-production freeze dryers for diagnostic kits and tissue banking
Optimize your freeze-drying process with compact,...
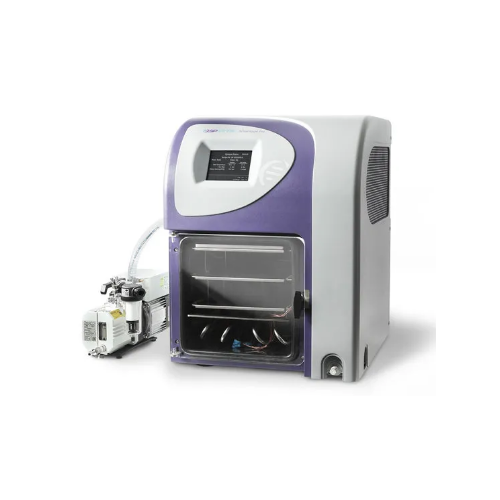
Benchtop freeze dryer for laboratory and small production use
Optimize your lab’s efficiency by adding precise, space-sa...
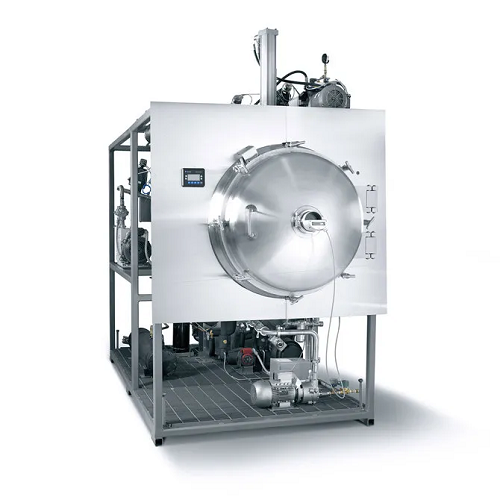
Customizable production freeze dryer for pharmaceuticals
Ensure precise moisture control and preservation with a versatil...
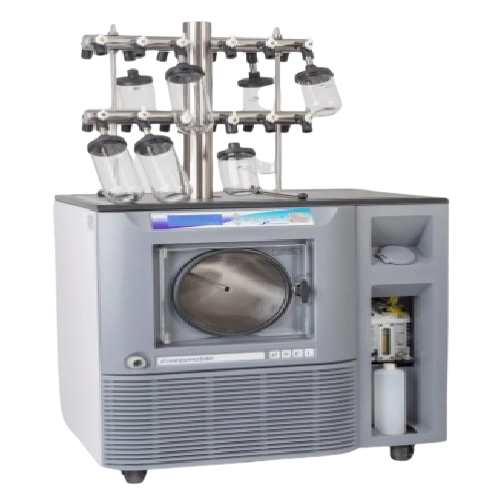
Laboratory freeze dryer for peptide production
Achieve precise moisture removal and stability with a versatile freeze-dryi...
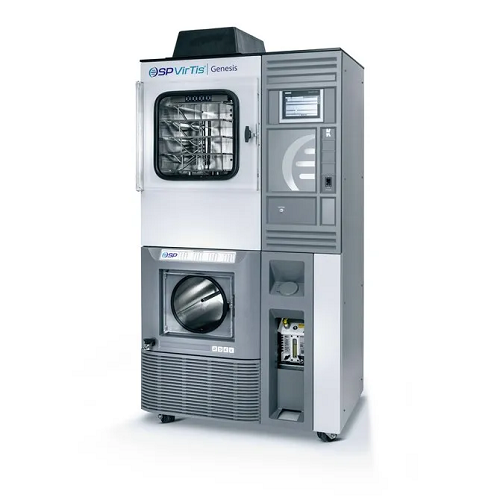
Pilot freeze dryer for research and small-scale production
Optimize moisture removal and sample preservation with this v...
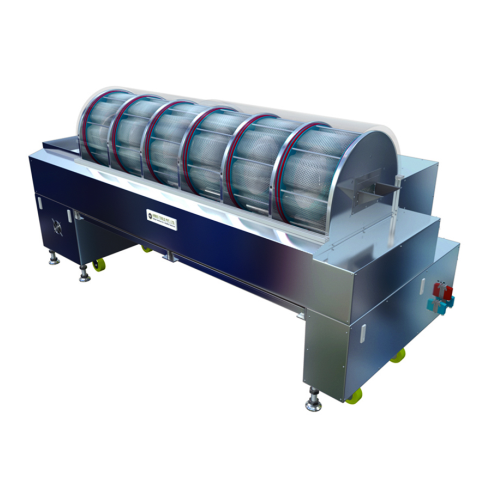
Softgel pre-dryer tumbler system
Ensure optimal shape and seam formation of softgel capsules with efficient oil removal, pav...
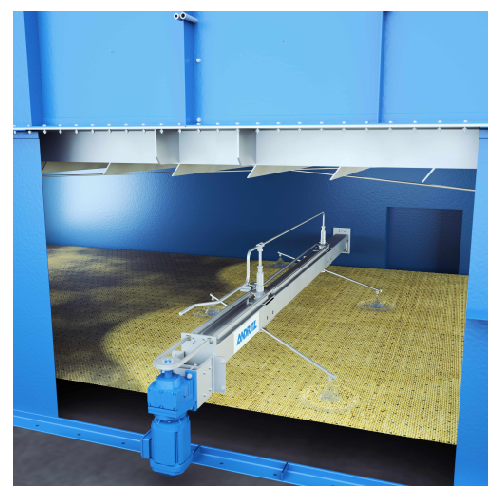
Belt dryer cleaning system
Maximize drying efficiency and product quality with an advanced belt-washing system designed to e...
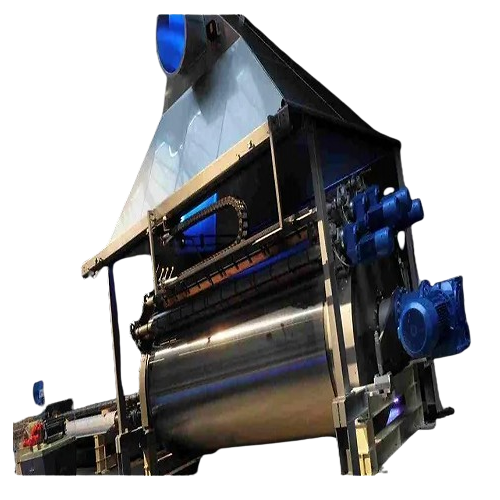
Contact drum dryer for industrial food and chemical processing
Optimize your drying process with a contact drum dryer th...
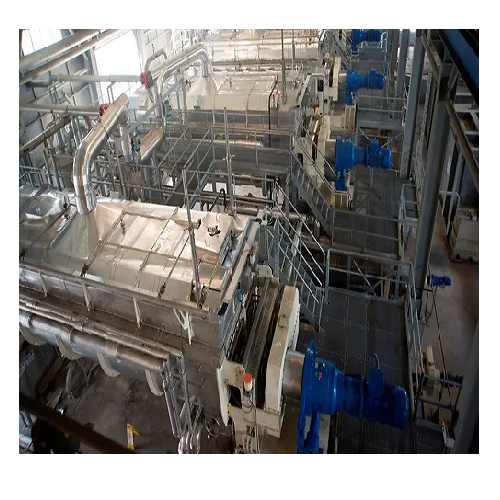
Paddle dryer for industrial sludge
Achieve consistent drying and pasteurization of complex materials with this advanced pad...
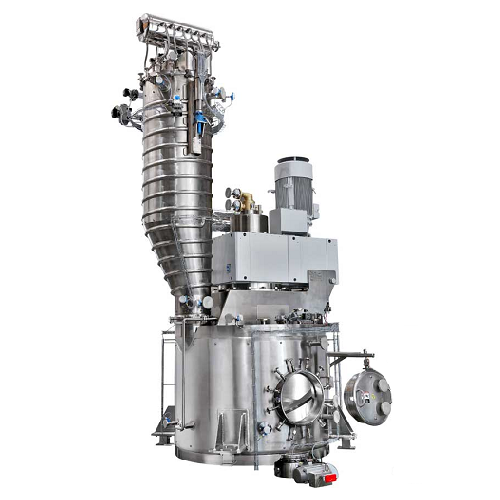
Vertical vacuum dryer and mixing reactor
Achieve precise control over drying and mixing processes with a versatile unit des...
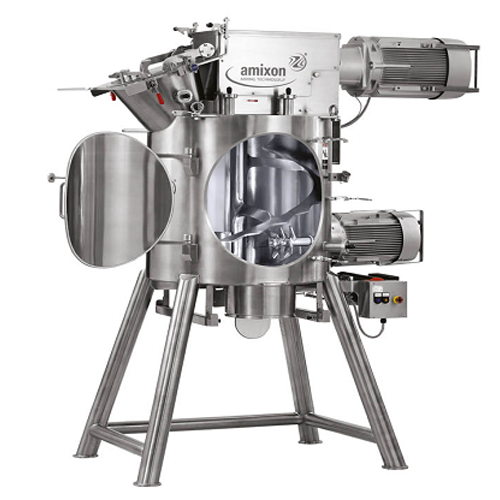
Vertical single-shaft mixer for dry, moist, and viscous materials
In industries requiring precise and thorough mixing o...
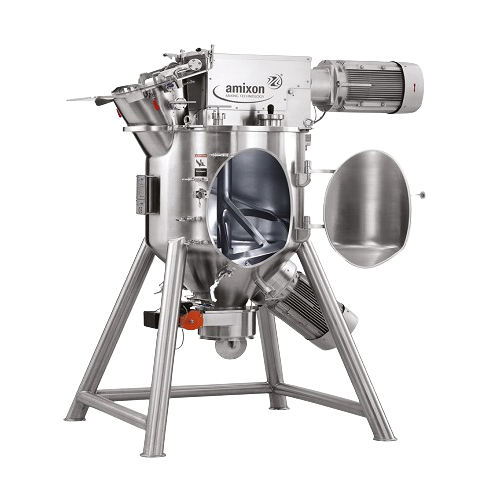
Conical mixer for dry, moist, and viscous materials
Achieve optimal mixing consistency and precision for diverse material...
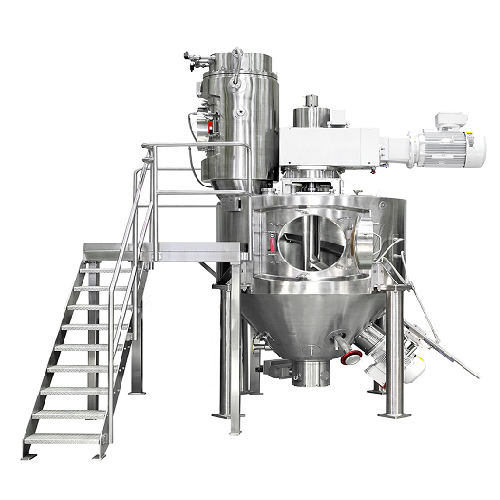
Conical vacuum dryer for viscous materials
Achieve precise drying and mixing of moist and viscous materials, ensuring cons...
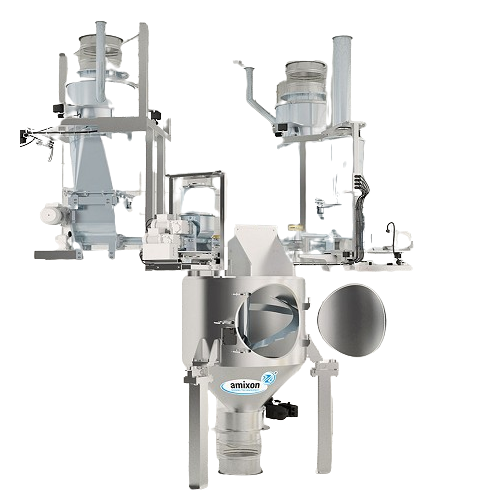
Continuous powder mixer for dry, moist and suspended goods
Achieve precise homogenization and deagglomeration with a con...
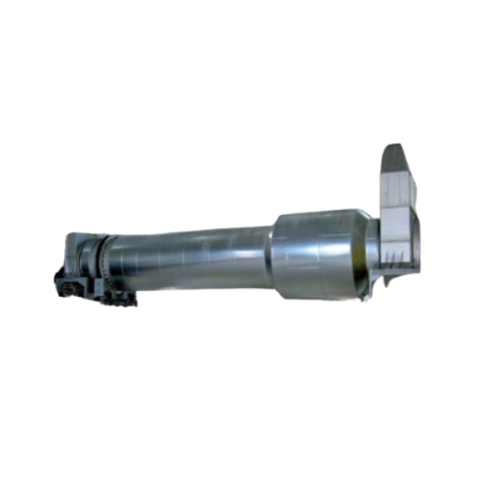
Indirect drying drums for solvent-based products
Optimize energy use and safety with our indirect drying drums, ideal for ...
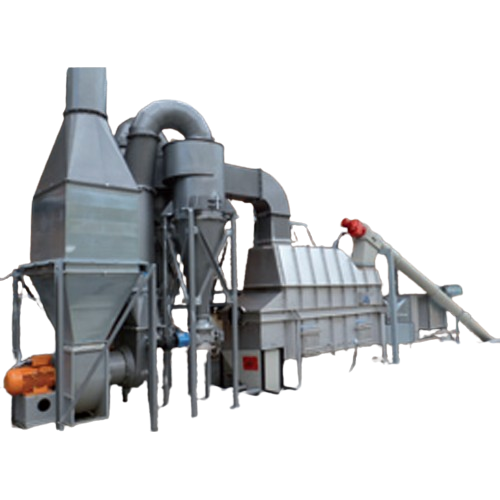
Biomass drying solution
Achieve efficient and gentle biomass drying with innovative heat exchange technology, ensuring optima...

Dryer for pigments and hydroxides
Achieve precision drying of complex suspensions and pastes into uniform powders, optimizi...
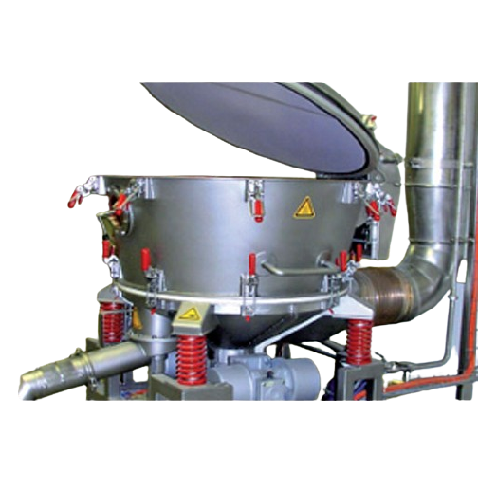
Vibration batch dryer for difficult solids
Ensure efficient drying of complex solids prone to sticking and shape irregular...

Industrial drum dryer for bulk solids
Optimize your production line with high-throughput drying for varied particle sizes, ...
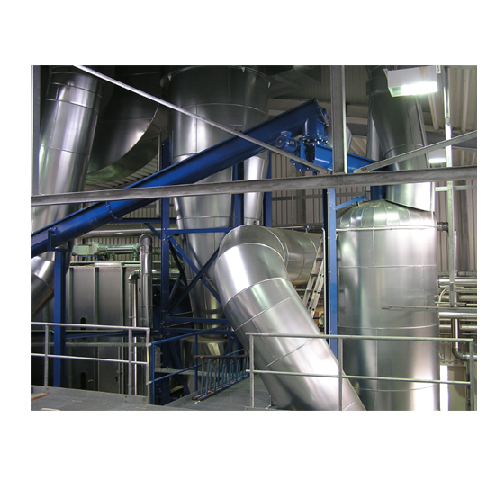
Flash dryer for high-moisture bulk materials
Tackle high-moisture challenges head-on with rapid drying solutions that effi...
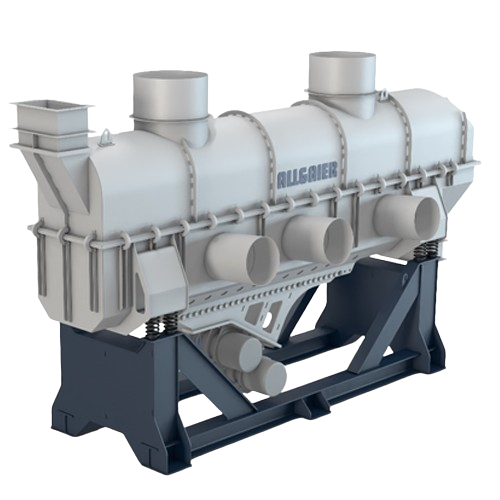
Fluidized bed dryer for industrial materials
Enhance product quality and energy efficiency with fluidized bed dryers, opti...
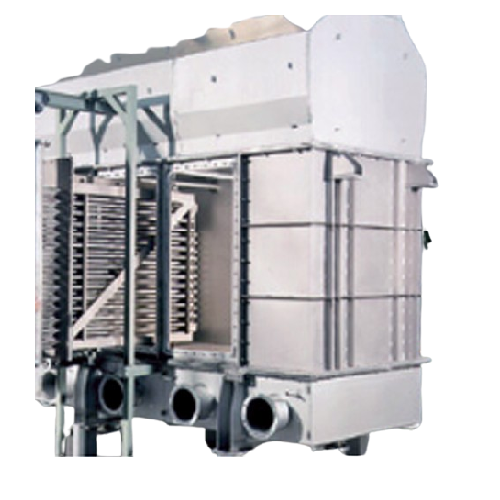
Fluidized bed dryers/coolers for bulk material processing
Achieve high-efficiency drying and cooling of bulk materials i...

Stainless steel drying hoppers for plastic processing
Optimize moisture control for thermoplastics with robust drying hop...
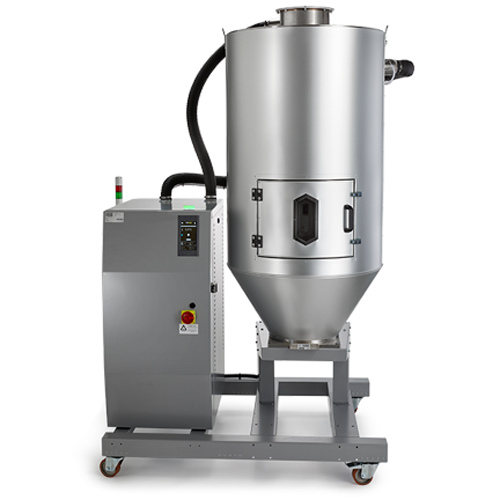
Desiccant wheel dryer for plastic processing
Optimize drying processes in plastic manufacturing with a system designed for...
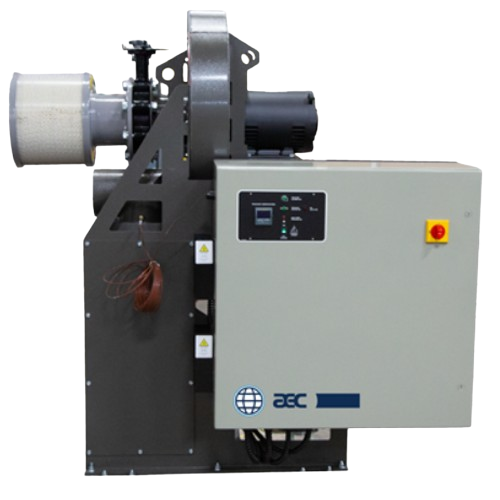
Hot air dryers for non-hygroscopic material
Ensure reliable material quality by effectively reducing moisture in non-hygro...
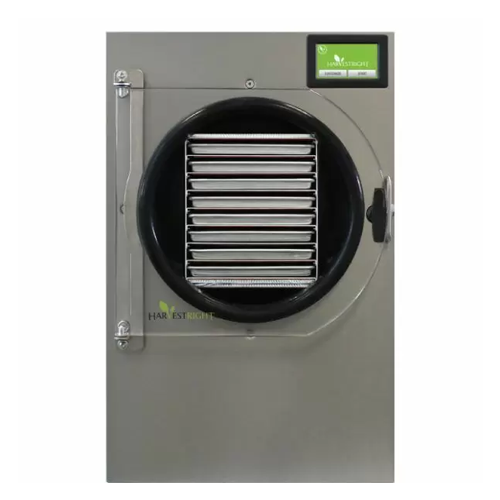
Pharmaceutical large freeze dryer with vacuum pump
Preserve the integrity and potency of sensitive compounds with precisi...
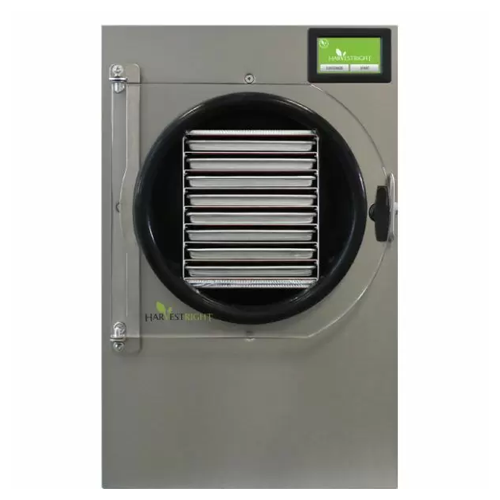
Pharmaceutical freeze dryer for medium scale production
Ensure optimal preservation of active ingredients through precise...
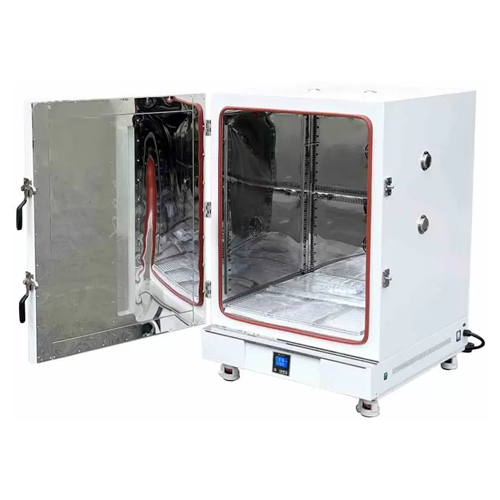
High-temperature forced convection oven for drying and sterilization
Achieve precise drying and sterilization for sensi...
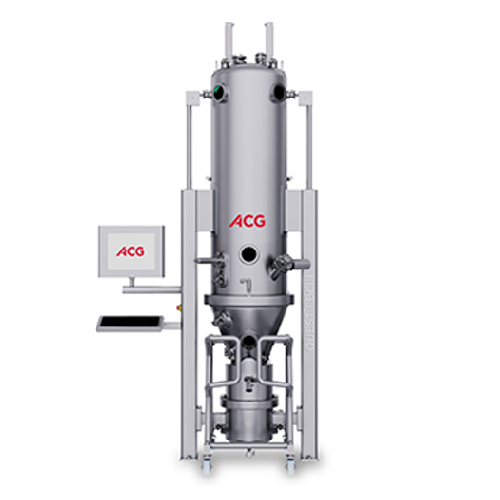
Intermediate-scale fluid bed system for drying and granulation
Achieve precise drying and granulation with this versatil...
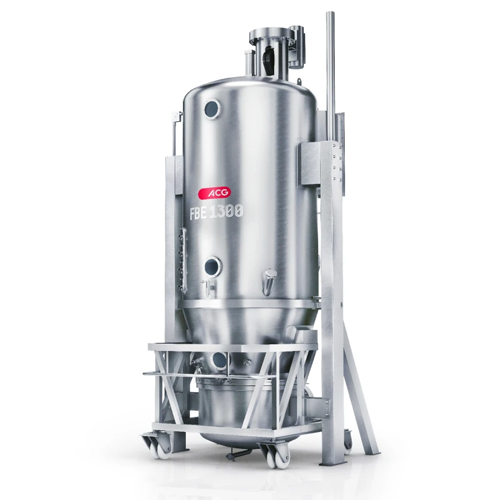
Fluid-bed drying and granulation system
Optimize your production line with high-speed batch processing for efficiently dryi...
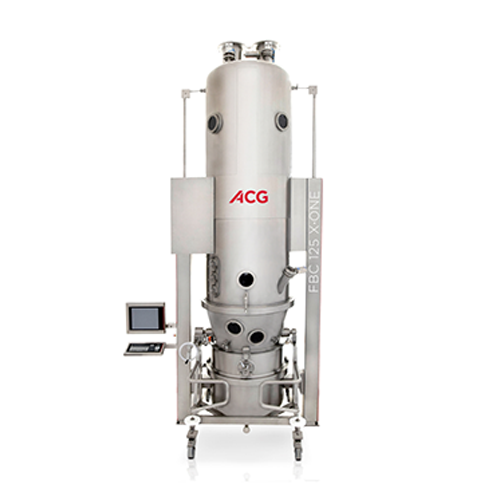
Fluid bed dryer with granulation and coating
Enhance your processing efficiency with a versatile system capable of combini...
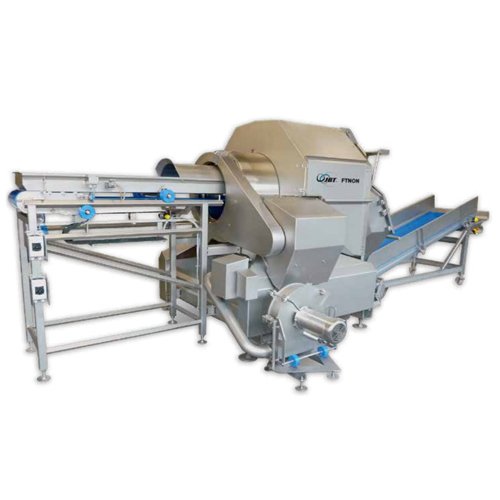
Centrifuge for drying fragile salads
Achieve consistent drying of delicate leafy greens with minimal damage, enhancing prod...
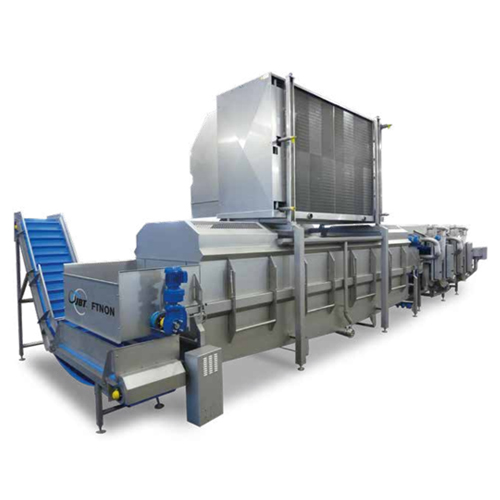
Air and suction dryers for fresh salads and vegetables
Ensure longer shelf life and optimal quality for your fresh produc...
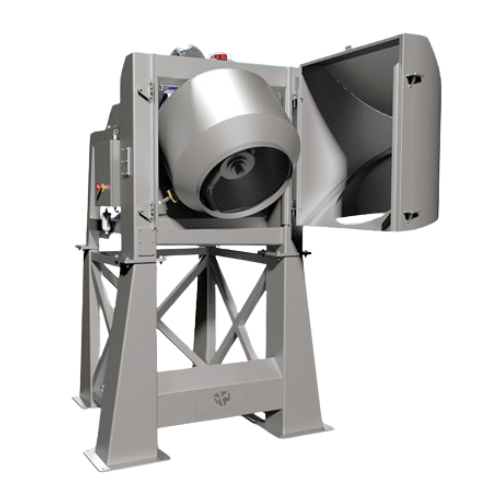
Centrifuge for drying fresh-cut vegetables
Enhance your production line with reliable surface water removal from fresh pro...
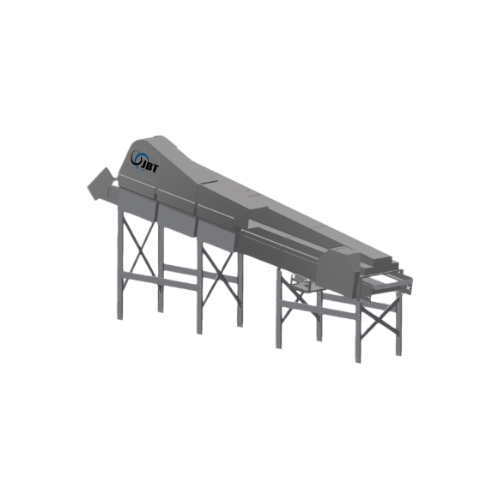
Single pass dryer for fresh produce
Optimize your fresh produce processing with a continuous drying solution that enhances ...
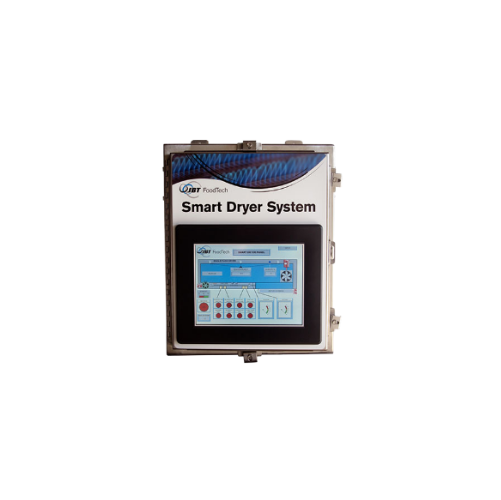
Smart dryer system for fresh produce
Optimize your fresh produce drying process while ensuring consistent quality and effic...
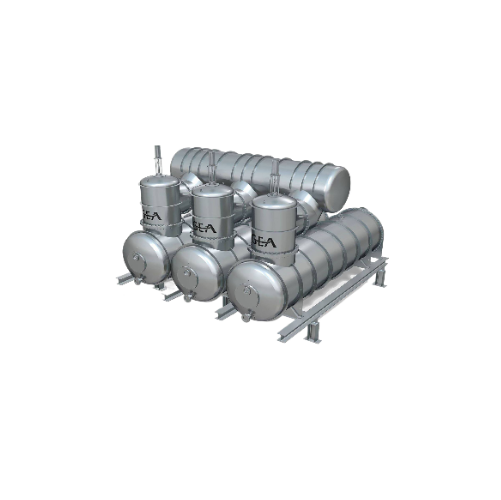
Dry condensing vacuum system for food industry
Optimize energy consumption and wastewater disposal in your production line...
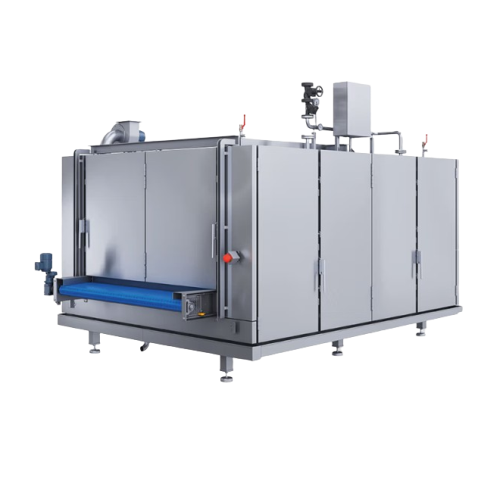
Industrial predryer for humidity reduction in food processing
Ensure optimal shelf life and prevent product sticking wit...
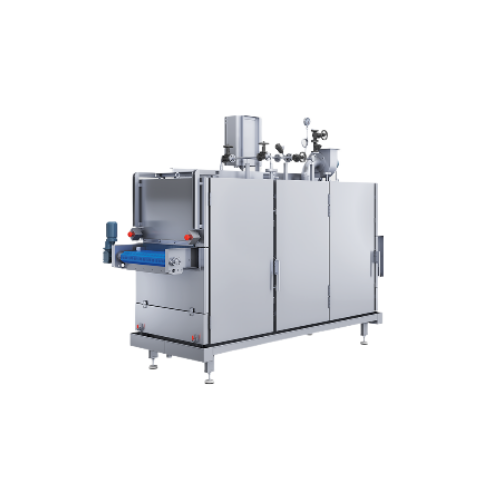
Surface drying system for pasta production
Ensure optimal surface drying of pasta and snacks post-pasteurization, preventi...
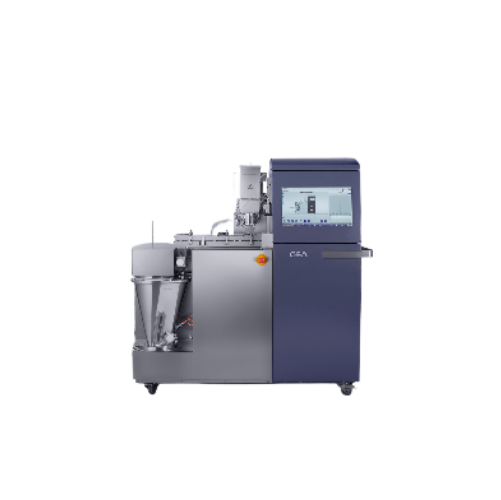
Continuous granulation and drying system for r&d
Develop precise pharmaceutical granules with this compact system, tailore...
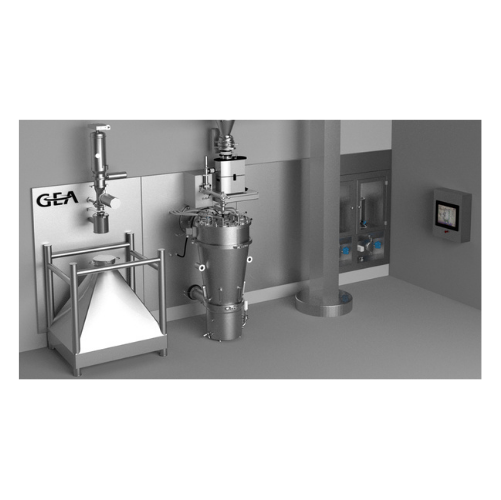
Continuous granulation and drying system for pharma production
Achieve precise control over granule quality with a conti...
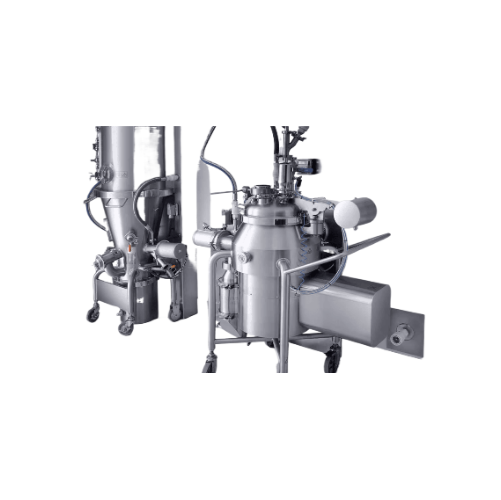
Integrated small-scale granulation and drying system
Ensure precise granule size and moisture control for enhanced tablet...
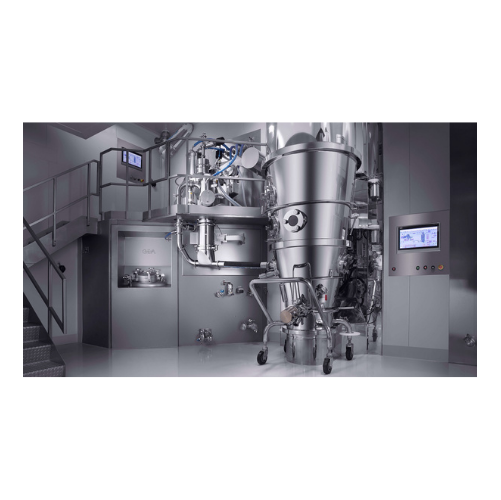
Integrated granulation and drying system for pharmaceuticals
Achieve seamless granulation and drying with our fully inte...
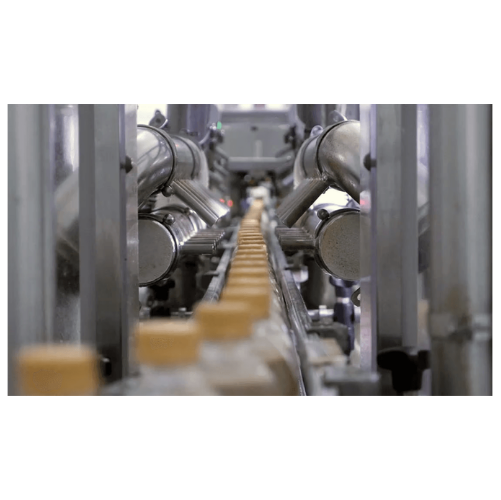
Container drying system for packaging lines
Ensure precise label applications by efficiently removing moisture from the su...
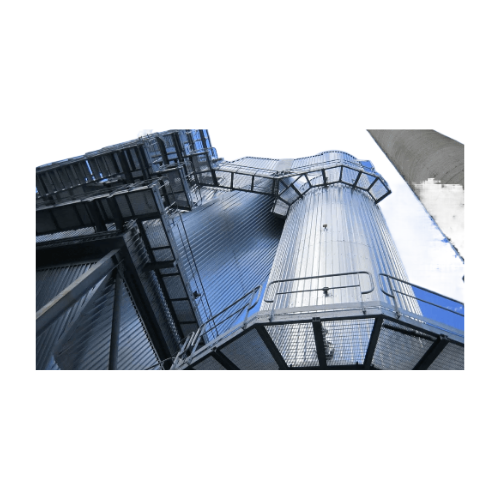
Dry sorption system for Sox removal
Optimize your emission control with a dry sorption system designed to efficiently remov...
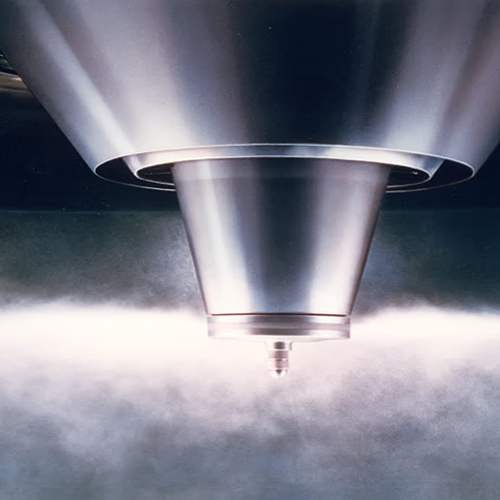
Spray dryer absorber for flue gas desulphurization
Efficiently transform gaseous pollutants into stable byproducts while ...
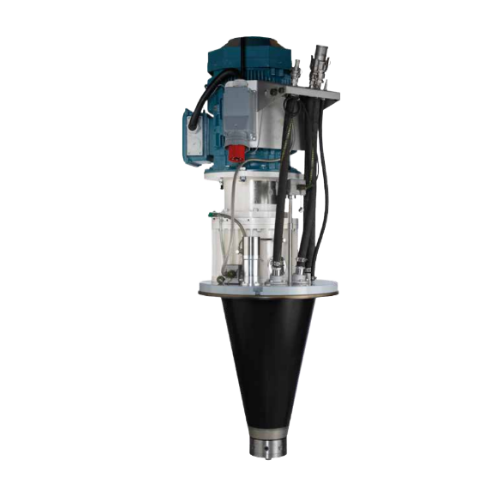
Spray drying evaporation for wastewater treatment
Achieve efficient zero liquid discharge with this spray drying evaporat...
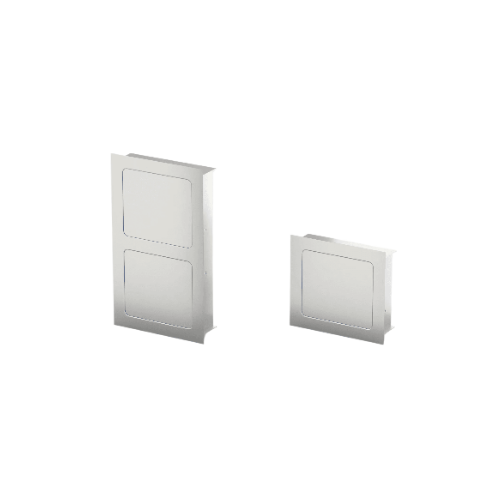
Explosion protection vents for spray dryers
Optimize safety and hygiene in your spray drying operations with advanced expl...
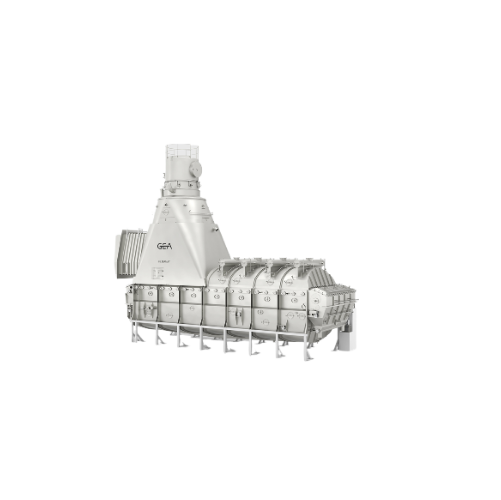
Spray drying solution for heat-sensitive products
Optimize the drying of heat-sensitive and challenging materials into hi...
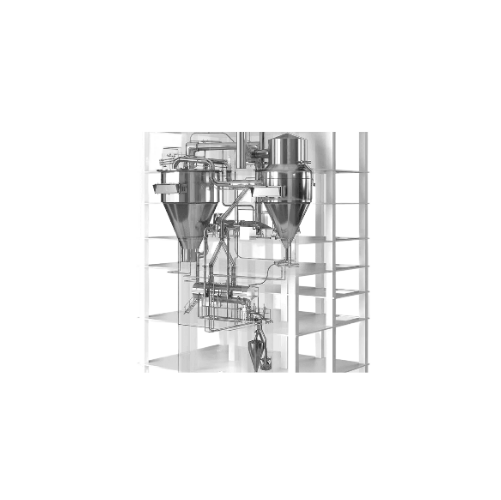
Spray dryer for agglomerated powders
Achieve uniform, coarse, and free-flowing agglomerated powders with precise drying and...
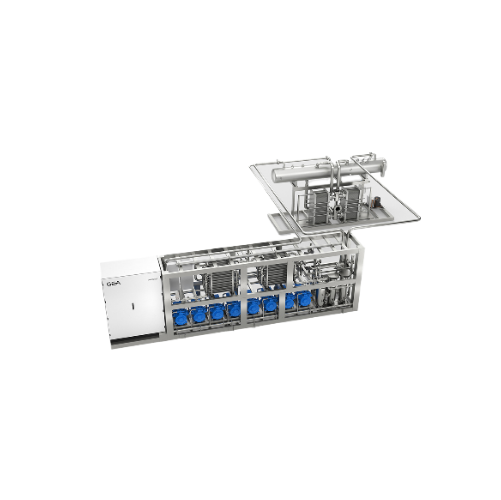
Heat pump solution for spray dryers
Enhance your spray drying efficiency and sustainability with an innovative heat pump sy...
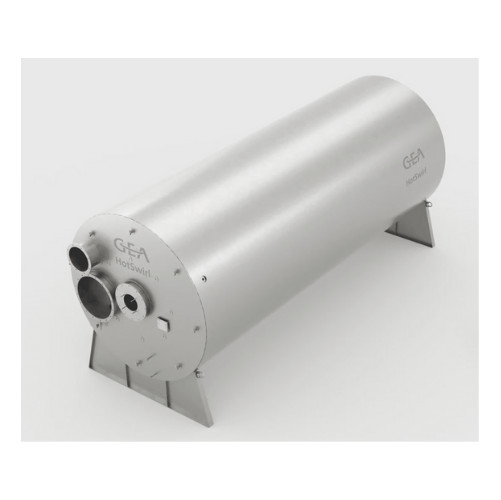
Industrial hot air system for spray dryers
Ensure consistent hot air delivery for critical drying processes, enhancing ene...
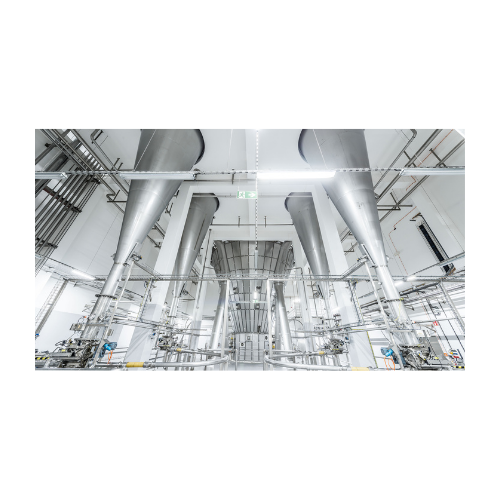
Spray dryer for nutritional and dairy powders
Achieve precise particle size and optimal drying of nutritional and dairy po...
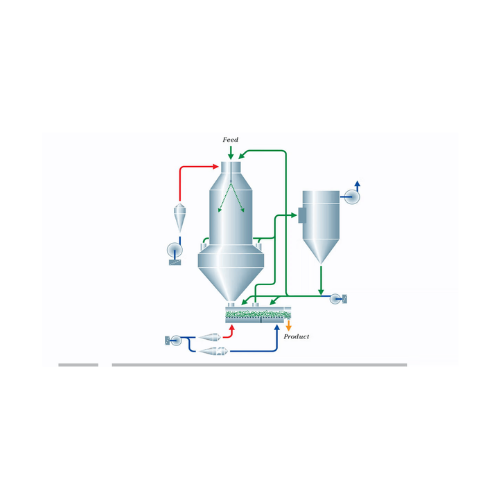
Spray drying solution for uniform powder production
Achieve seamless transformation of liquid feeds into uniform, free-fl...
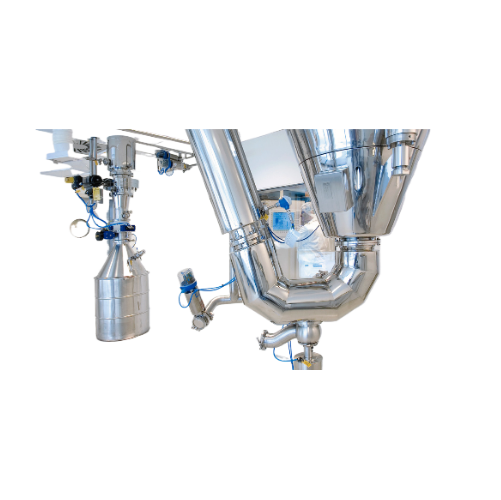
Pharmaceutical spray dryer
Unlock the potential of spray drying to enhance bioavailability, achieve controlled release, and ...

Lab-scale spray dryer for small volume powder samples
When developing new formulations, achieving consistent powder quali...
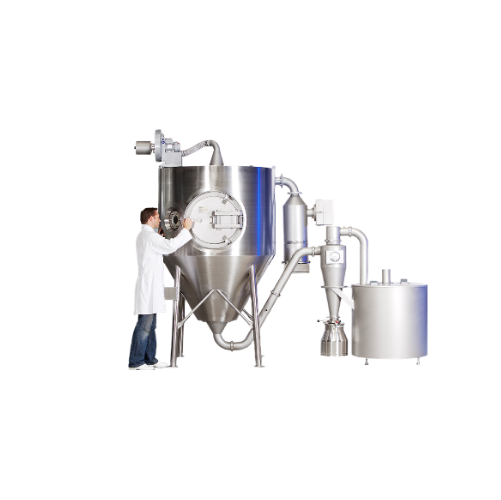
R&d spray drying solution for small batch production
Efficiently convert liquid solutions into precise, uniform powders f...
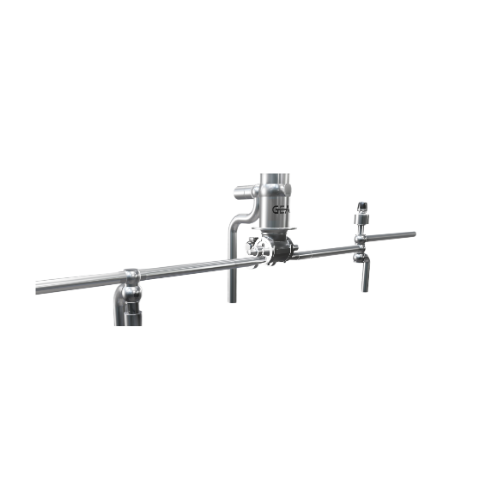
Automated fines return system for food and dairy spray dryers
Enhance your spray drying process by eliminating manual in...
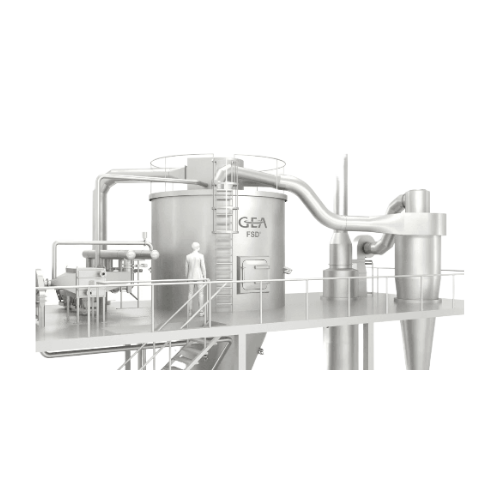
Spray dryers for ceramics and pharma products
Achieve consistent powder quality for heat-sensitive and sticky products wit...
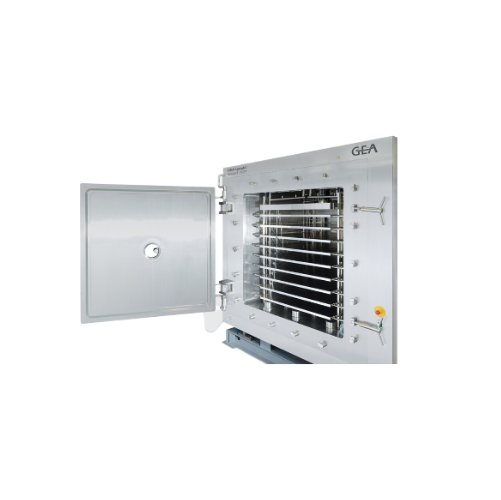
Pharmaceutical freeze dryer for large-scale production
Streamline your freeze-drying process with precision-engineered ly...
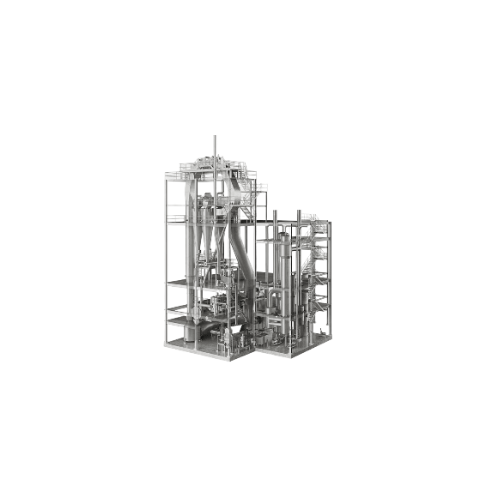
Feed-type ring dryer for industrial drying processes
Optimize your production with a versatile drying solution designed f...
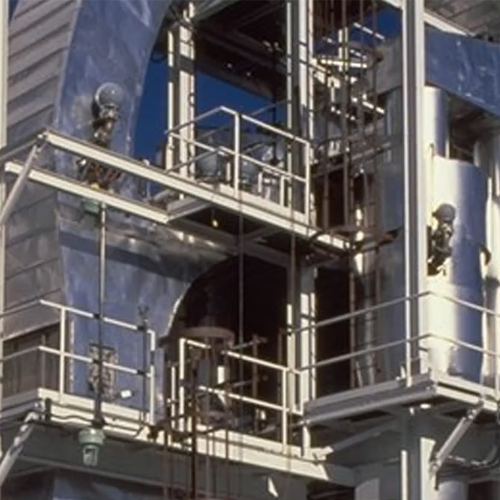
P-type ring dryer for thermally sensitive products
Optimize moisture control and prevent thermal degradation in your prod...
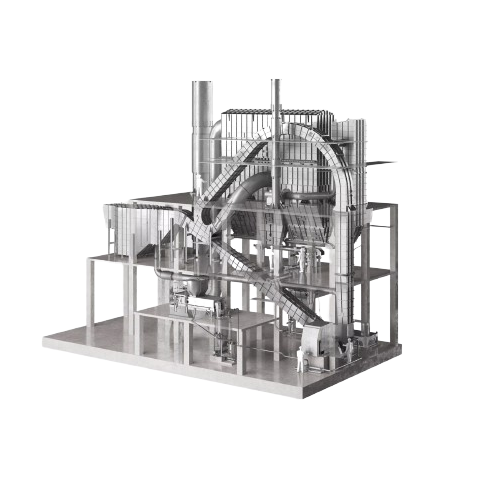
Industrial ring dryer for efficient particle processing
Control particle size and drying efficiency with precise recircul...

Industrial rotary dryer for high moisture content materials
Achieve consistent drying performance with industrial rotary...
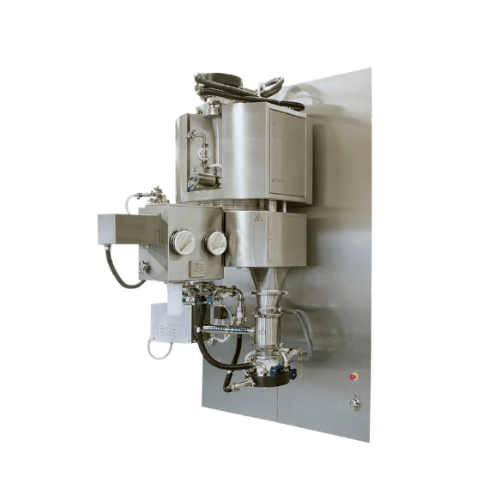
Single pot processor for granulation and drying
Streamline your pharmaceutical production with an integrated solution that...
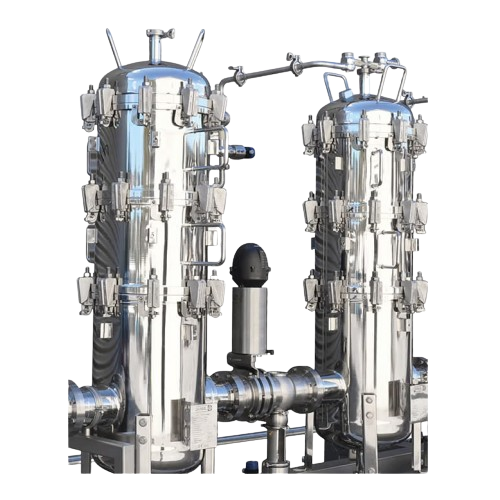
Aseptic spray dryer for pharmaceutical products
Optimize your sterile powder production with precise control over particle...
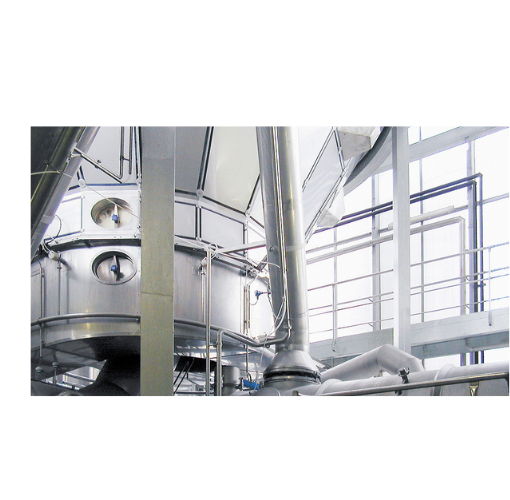
Spray dryer for whey and milk powders
Optimize your drying process for dense, agglomerated whey and milk powders with a spa...
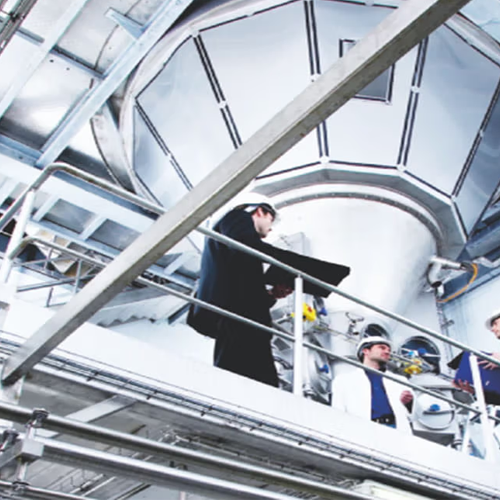
Conventional spray drying for chemical industry
Achieve optimal particle size uniformity in food powders with precision at...
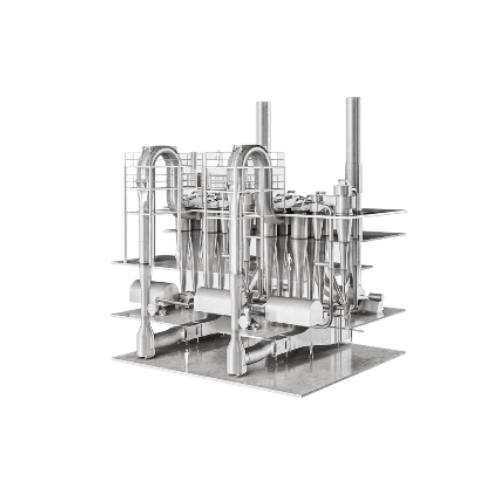
Flash dryer for industrial moisture removal
Optimize your production with rapid moisture removal, efficiently transforming...
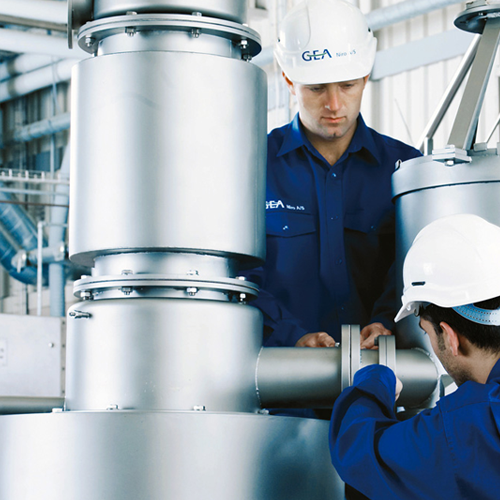
Swirl fluidizer for drying pastes and slurries
Optimize your production line with an efficient drying solution for homogen...
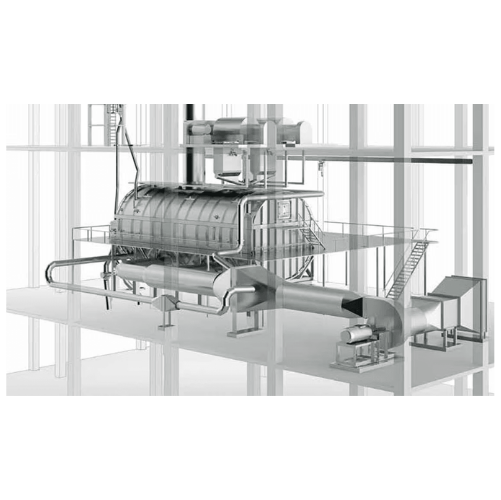
Fluid bed drying system for wet powder chemicals
Achieve efficient large-scale drying and cooling of wet powder chemicals ...
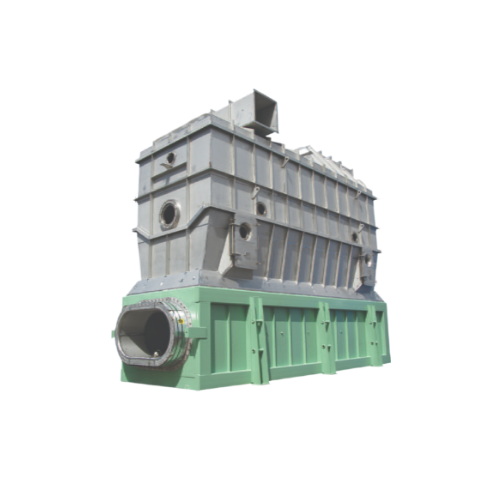
Static fluid bed dryer for powder and granular materials
Achieve optimal moisture control in powder and granular products...
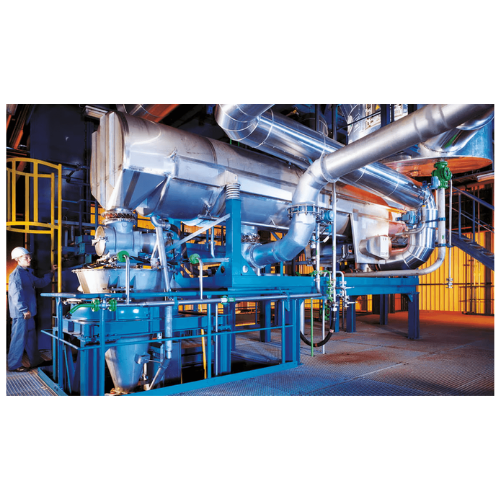
Vibrating fluid bed for final stage powder drying
Enhance powder processing precision with a vibrating fluid bed that ens...

Industrial freeze drying system for high-volume food products
Achieve precise moisture removal and preserve product qual...
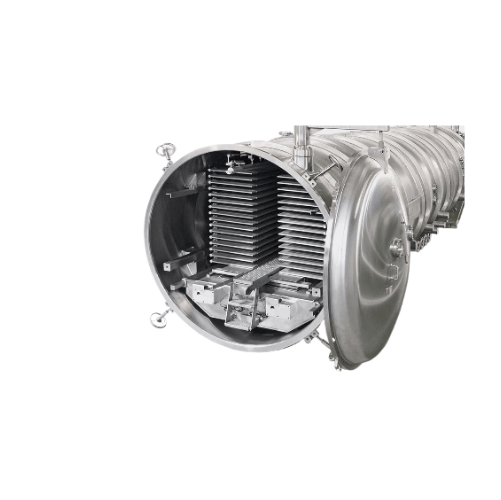
Batch freeze drying system for food and beverage preservation
Achieve precise and efficient preservation of your food an...
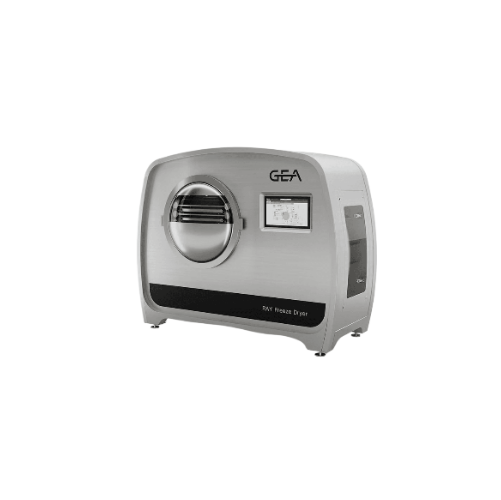
Pilot plant freeze dryer for sensitive products
Achieve precise moisture control and nutrient preservation in food and pha...
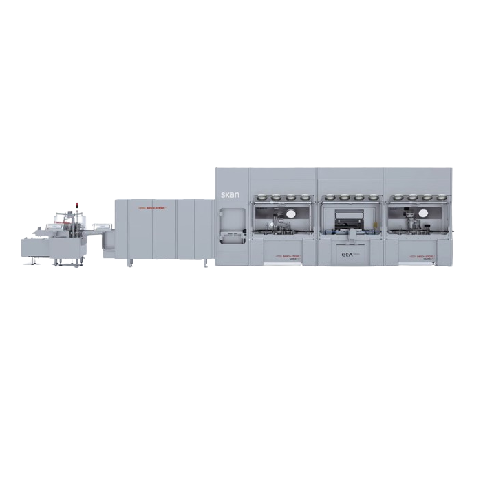
Freeze dryer for small-scale production
Optimize your production line with reliable lyophilization that ensures precise moi...
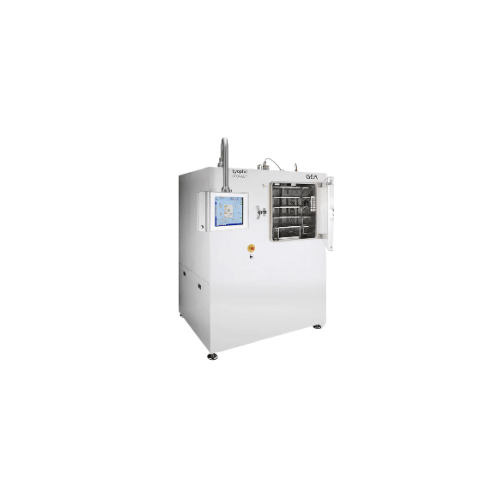
Small-scale pharmaceutical freeze dryer
Enhance precision in biopharmaceutical preparation with this versatile freeze dryer...
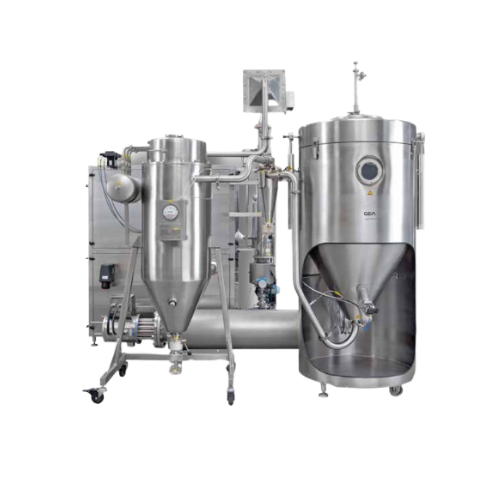
Spray dryer for food and dairy products
Achieve consistent drying for diverse powders and granulates with precision technol...
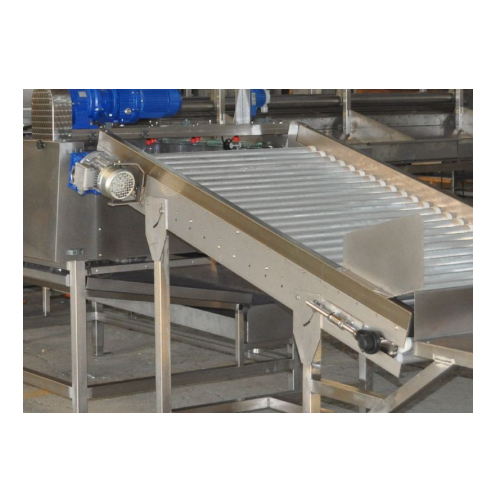
Industrial citrus fruit selection, washing, drying, and calibration line
Enhance your fruit processing efficiency with ...

Centrifugal dryer for efficient liquid product and solvent drying
Achieve precise solvent and liquid product drying wit...
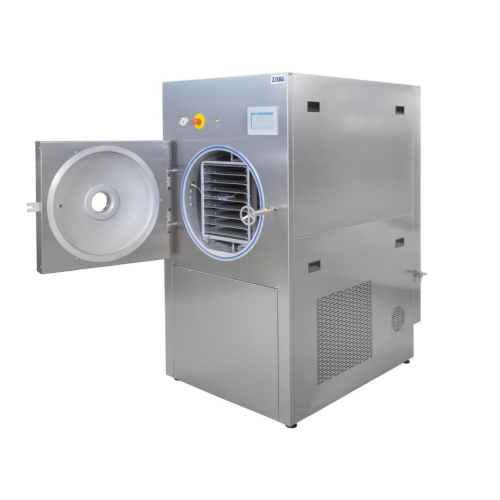
Food freeze dryer for bulk materials
Achieve efficient and uniform drying of fruits, herbs, and other materials with advanc...

Laboratory freeze dryer for small batch processing
Ensure precise moisture control and stability in sensitive samples wit...
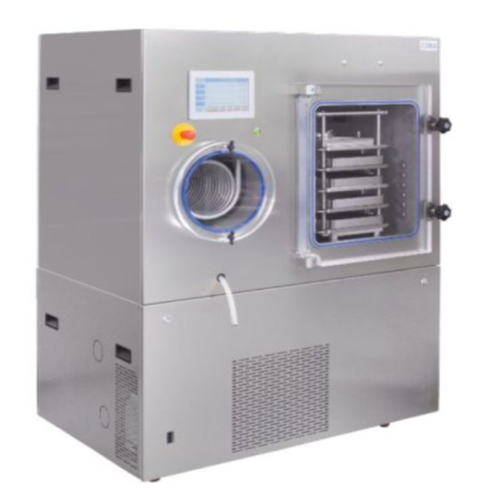
Pilot freeze dryers for research and development
Ensure precise dehydration of sensitive samples while maintaining structu...
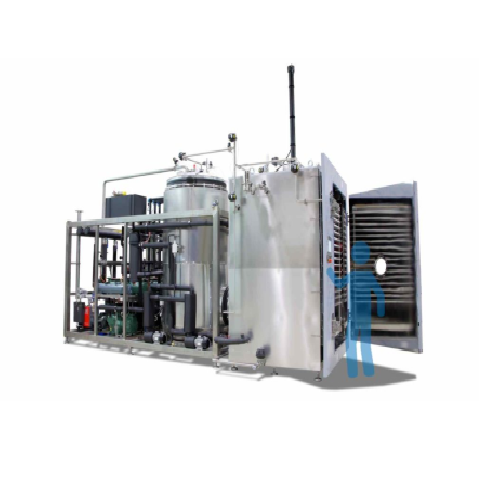
Freeze drying systems for pharmaceutical production
Optimize your production line with advanced freeze drying systems des...
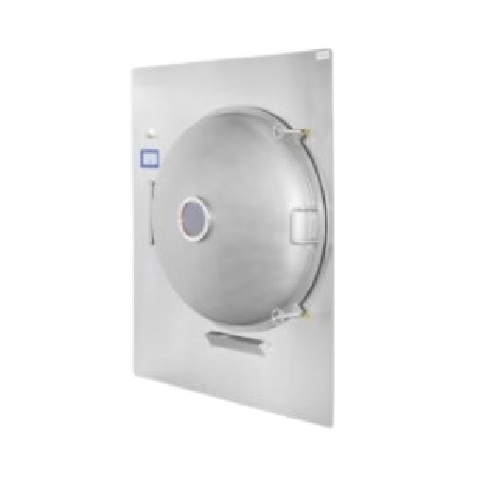
Laboratory vacuum drying system
Achieve precise moisture removal and maintain product integrity with advanced vacuum drying,...
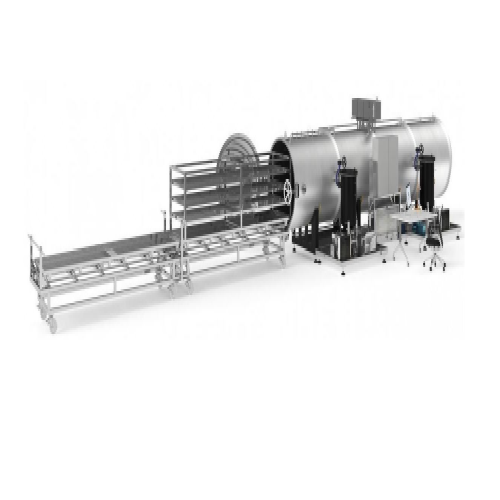
Freeze drying plants for archaeology and file rescue
Preserve and revive historical artifacts with precision freeze-dryin...
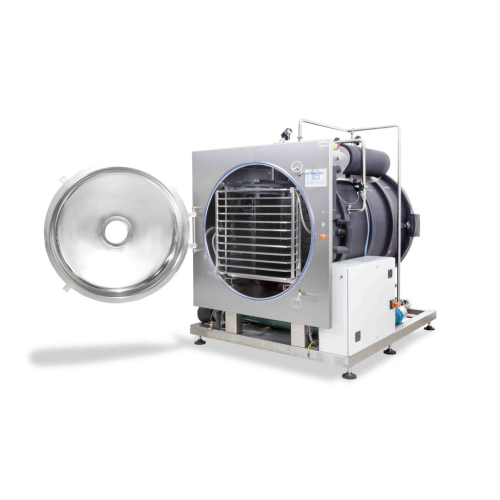
Single-chamber freeze dryer for liquid products
When precision drying of sensitive liquids is crucial, this single-chamber...
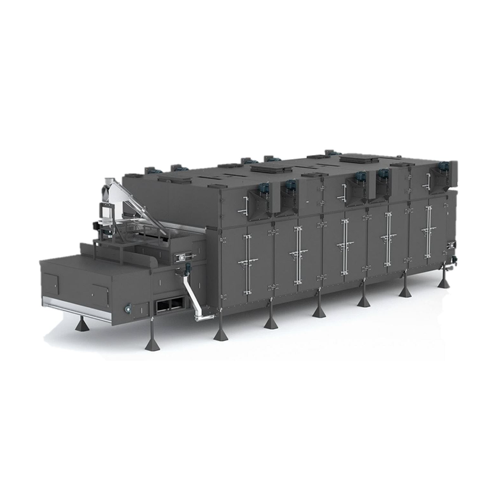
High capacity horizontal dryers and coolers for industrial applications
Achieve consistent moisture levels and uniformi...
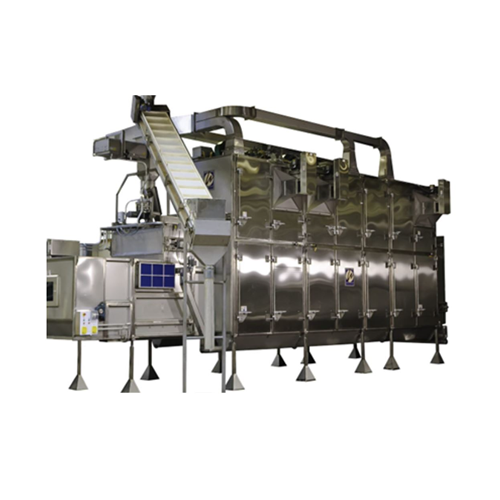
Sanitary dryers for textured vegetable proteins
Optimize drying and sanitation for textured vegetable proteins and pet foo...
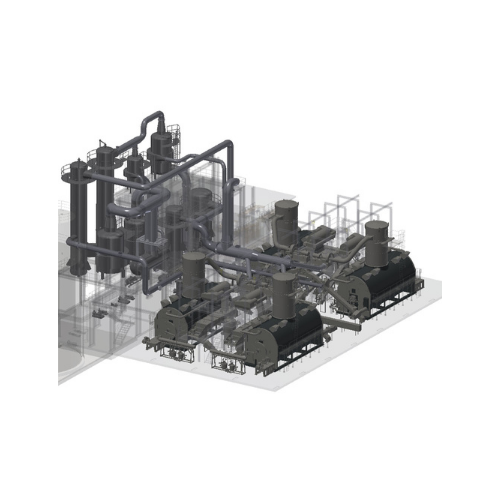
Drying systems for bioethanol production
Optimize your bioethanol production with advanced evaporation and drying equipment...
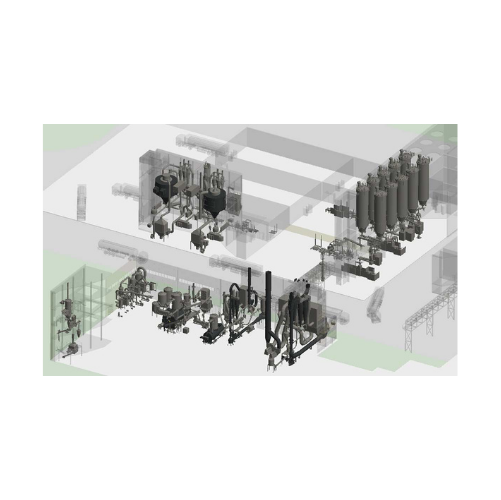
Corn wet milling plant drying systems
Optimize corn processing efficiency with integrated drying and dewatering systems des...
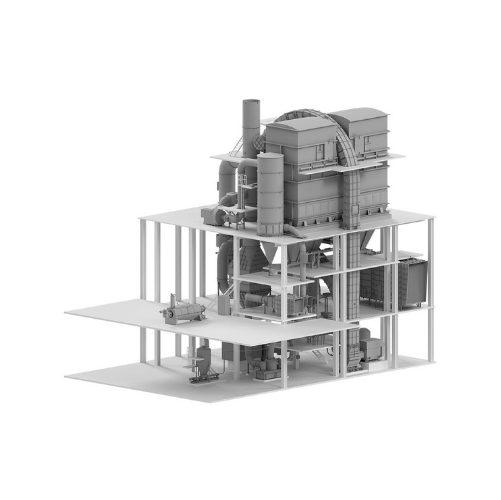
Flash dryer for corn starch
Reduce energy consumption and maintain product quality with efficient drying solutions designed ...
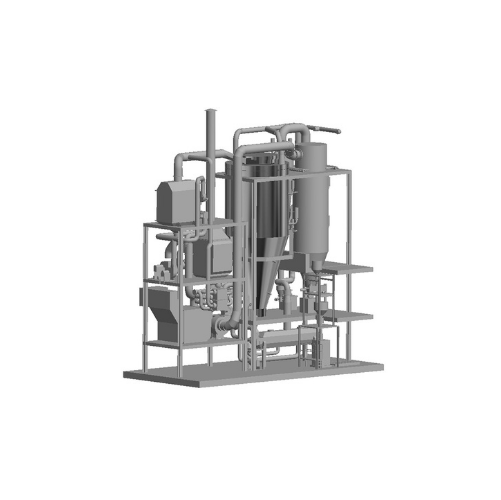
Spray drying system for heat sensitive products
For heat-sensitive products requiring precision drying, this spray drying ...
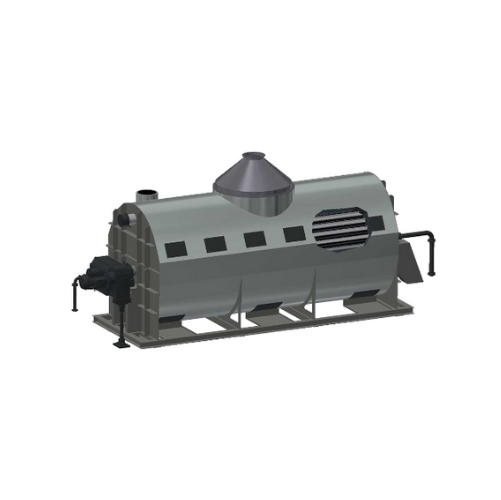
Steam heated tube bundle dryer
Efficiently achieve precise moisture control and gentle drying for diverse feedstocks with th...
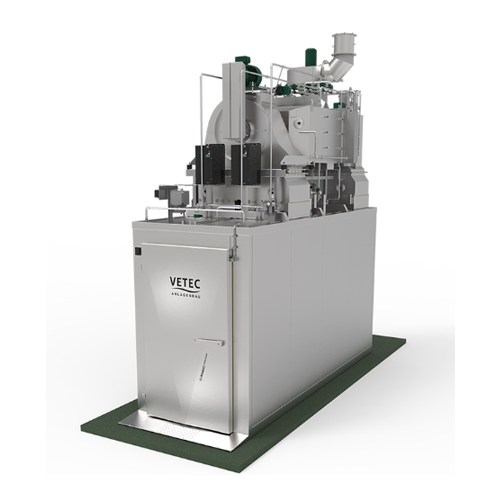
Drying and smoking solution for meat, fish, and cheese
Optimize your production with precise climate control, ensuring co...
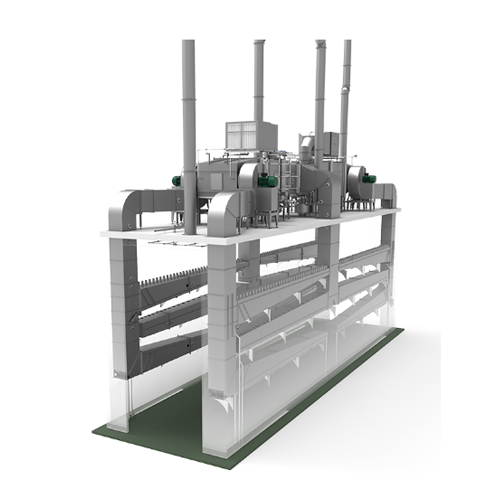
High-capacity industrial smoking and drying system
Maximize your production volume without expanding your facility footpr...
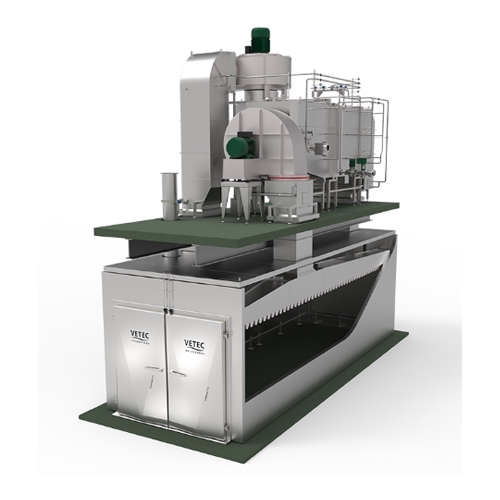
Advanced drying system for salami sticks
Achieve rapid drying and smoking of small-caliber products with up to 80% moisture...
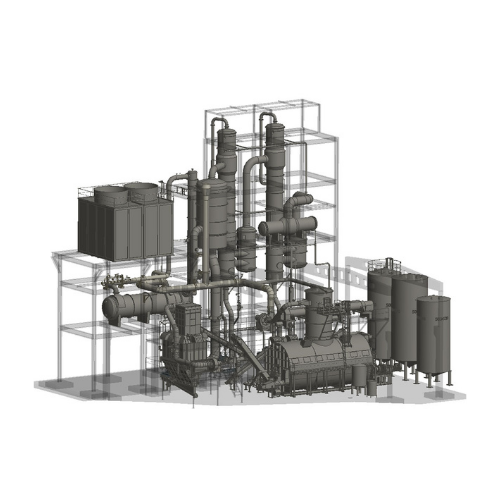
Drying systems for alcohol production
Enhance your spirits production with precise moisture control and nutrient retention,...

Horizontal air flow drying and smoking system for meat products
Achieve superior drying and smoking efficiency with hori...
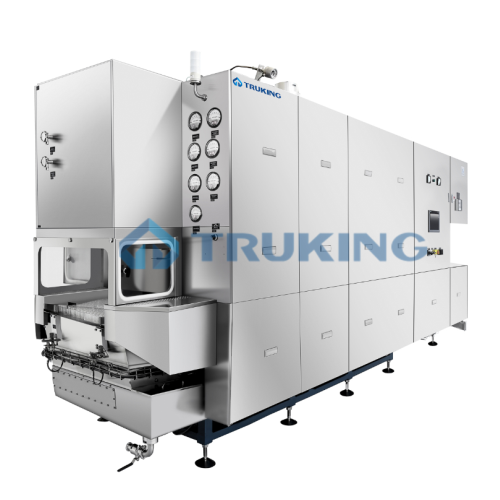
Sterilizing and drying tunnel for pharmaceutical vials
Ensure precise sterilization and depyrogenation of pharmaceutical ...
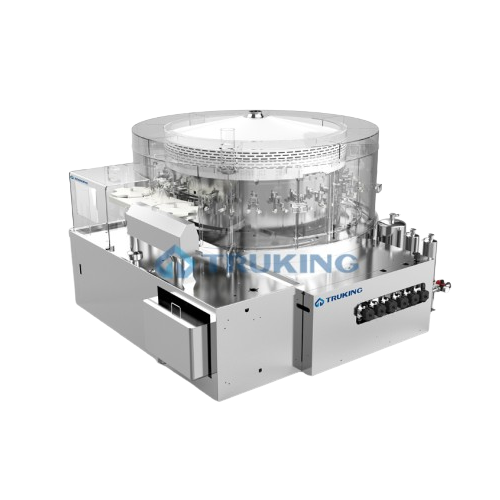
Industrial freeze dryer for pharmaceutical applications
Enhance your production line with precision cleaning solutions fo...
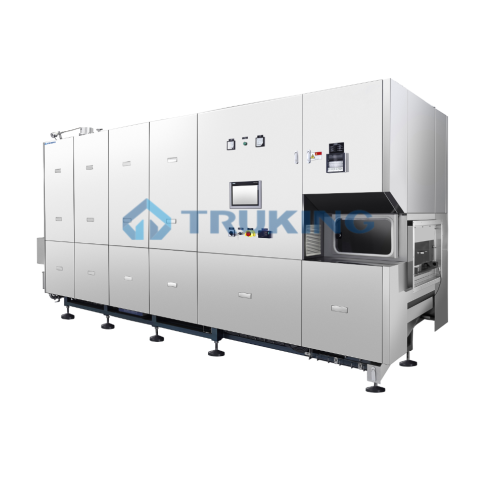
Sterilization and drying tunnel for glass bottles
Ensure aseptic integrity and regulatory compliance in injectable produc...
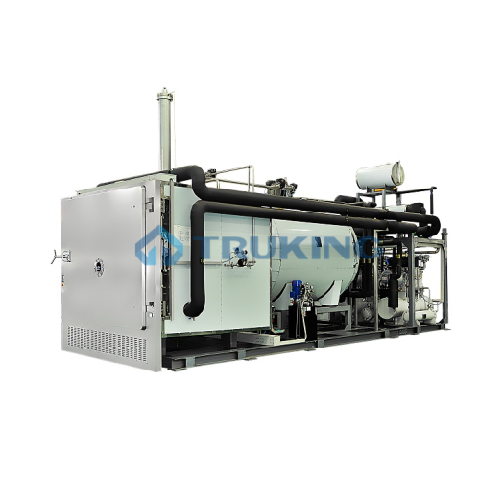
Industrial freeze dryer for pharma
Optimize moisture removal in lyophilized products with precise thermal conduction and ef...
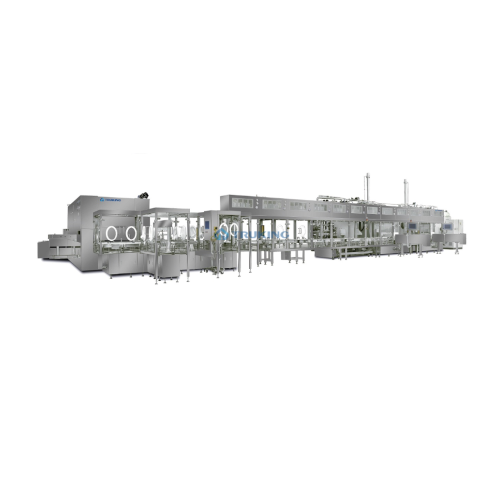
Auto loading & unloading system for freeze dryers
Efficiently manage vial handling in freeze-drying processes with automa...
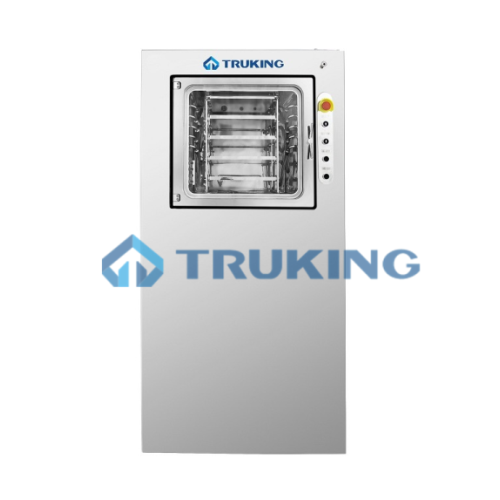
Laboratory freeze dryer for research and development
Optimize moisture removal with precision control during research and...
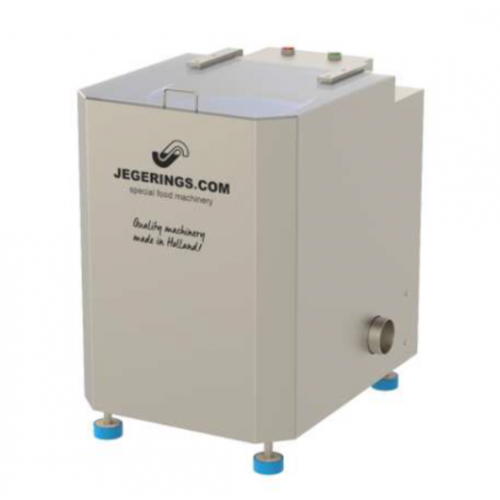
Centrifugal vegetable dryer for leafy and heavy vegetables
Efficiently remove excess water from leafy and heavy vegetabl...
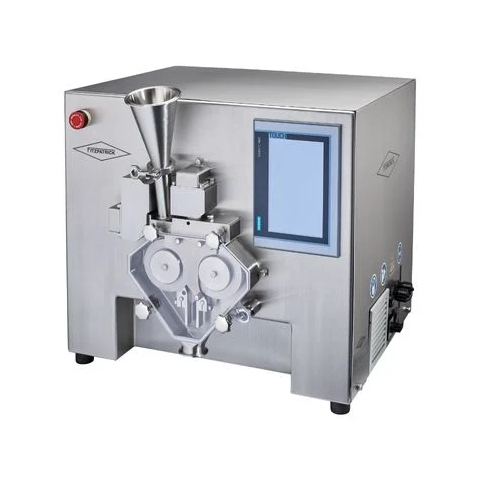
Lab scale roller compactor for dry granulation
Achieve seamless scale-up from lab development to full-scale production wit...
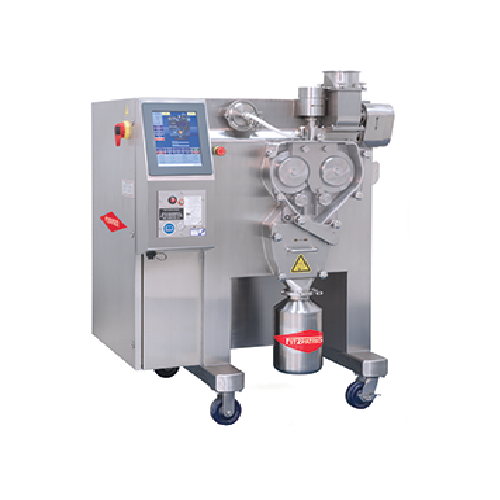
Roller compaction for dry granulation in pharmaceuticals
Ensure consistent granule size and density in your product line ...
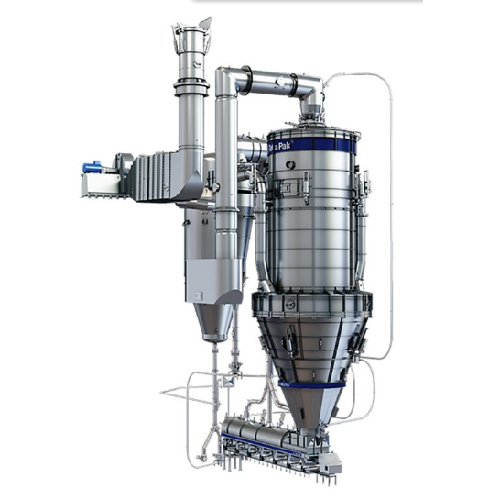
Spray dryer for heat-sensitive powders
Ensure high-quality drying of heat-sensitive powders, producing non-caking and non-h...
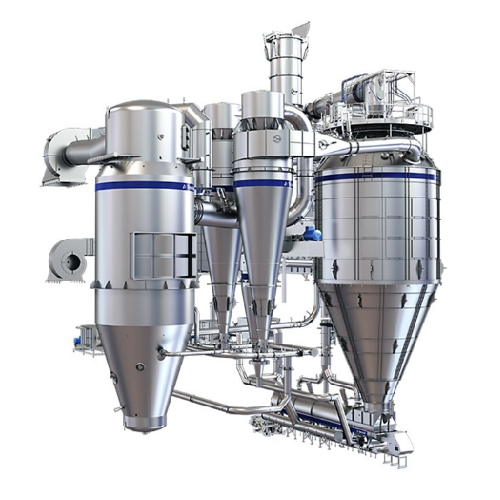
Spray drying system for nutritional powders
Enhance production efficiency and product quality with a versatile spray dryin...
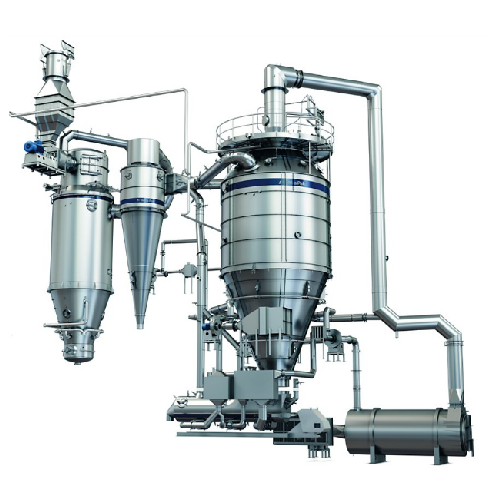
Versatile spray dryer for dairy and plant-based powders
Achieve precise moisture control and optimal powder functionality...
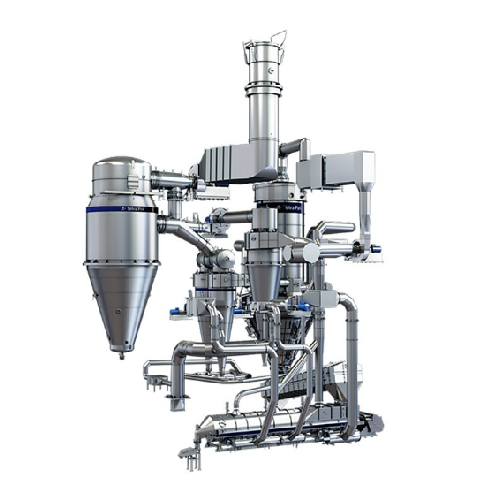
Permeate powder spray dryer
Optimize permeate powder production with continuous spray drying, ensuring premium, non-caking o...
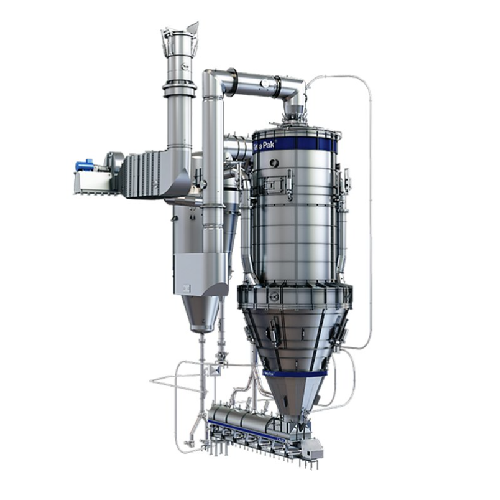
Spray dryer for heat-sensitive materials
Optimize your production line with a high-capacity spray dryer designed for precis...
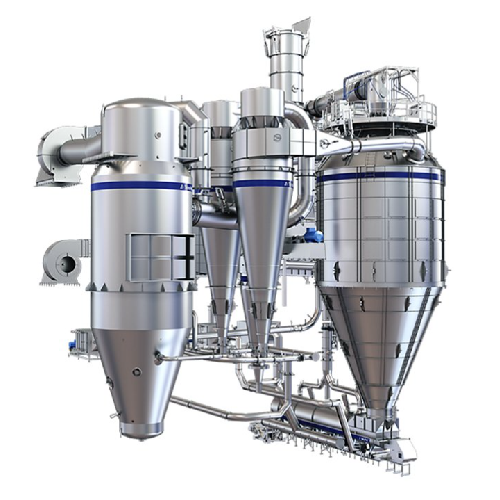
Spray dryer for nutritional powders
Ensure precise moisture control and enhance powder quality in nutritional products with...
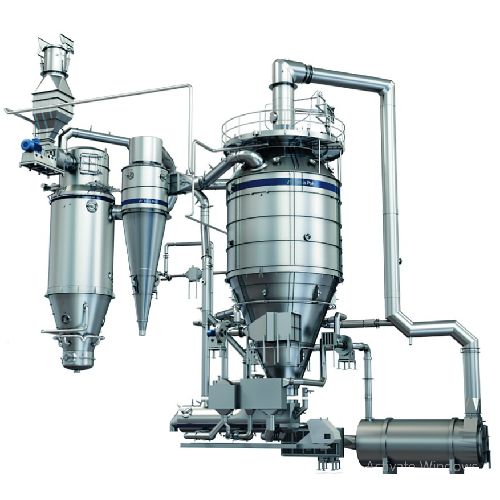
Spray dryer for dairy, whey, and plant-based powders
Achieve precise control over powder attributes with our versatile sp...

Continuous spray dryer for permeate powder
Efficiently transform liquid whey and milk into high-quality, non-caking, and n...
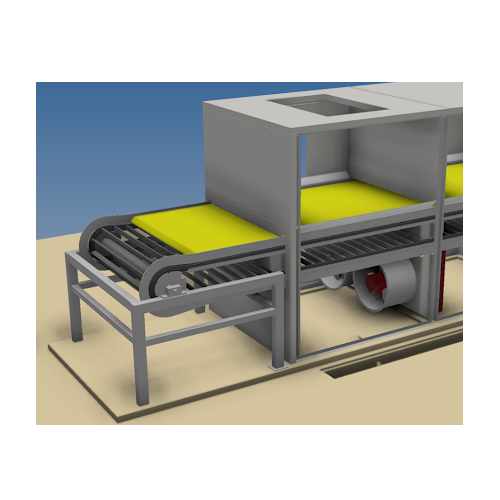
Belt dryer for large-scale continuous drying
Achieve precise moisture control and energy-efficient processing with this be...
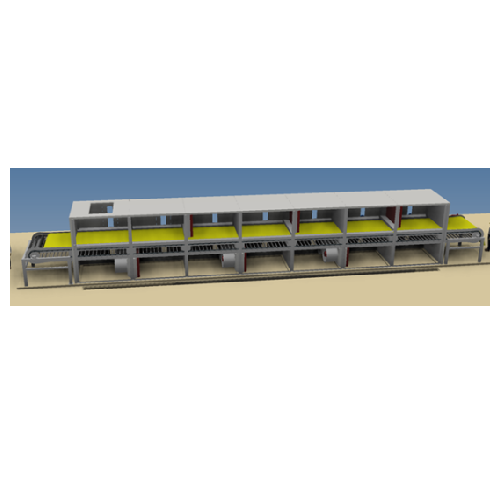
Belt dryers for gelatin processing
Efficiently transform liquid gelatin into high-quality solids with precise moisture cont...
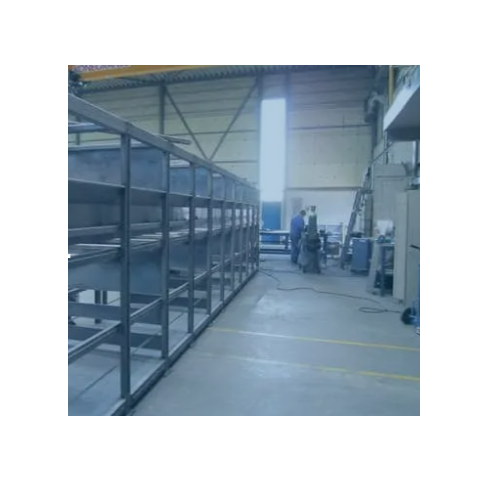
Continuous bulk fluid bed dryer
Achieve rapid and energy-efficient moisture removal across diverse materials with our advanc...
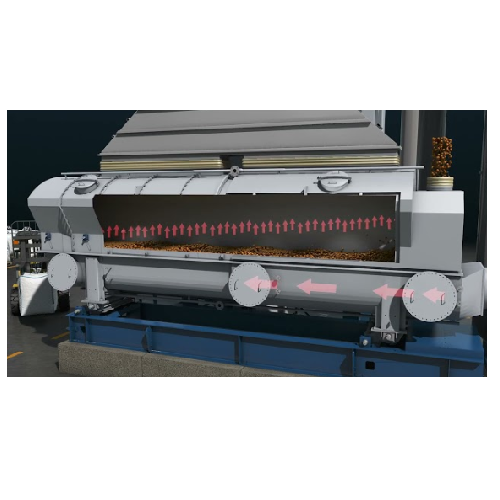
Continuous fluid bed dryers for various industrial applications
Achieve precise moisture control with fluid bed dryers, ...
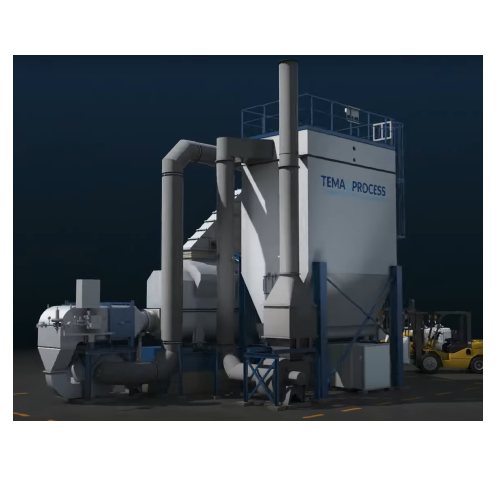
Continuous fluid bed dryer for powder and granules
Enhance your production line with precise moisture control and energy ...
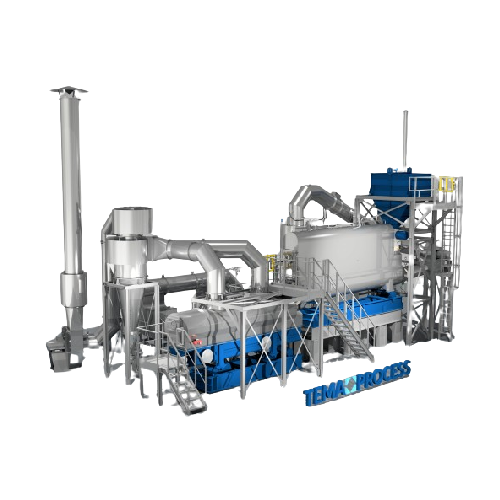
Vibrating fluid bed dryer for bulk materials
Ensure efficient moisture removal and thermal processing with this fluid bed ...
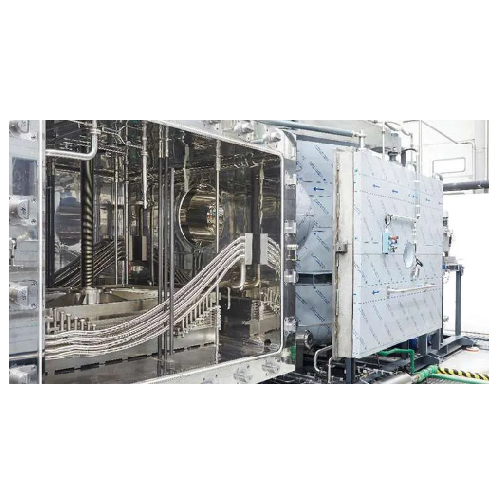
Cryogenic freeze dryer for biotherapy microbiotics
Achieve precise temperature control and efficient moisture removal in ...
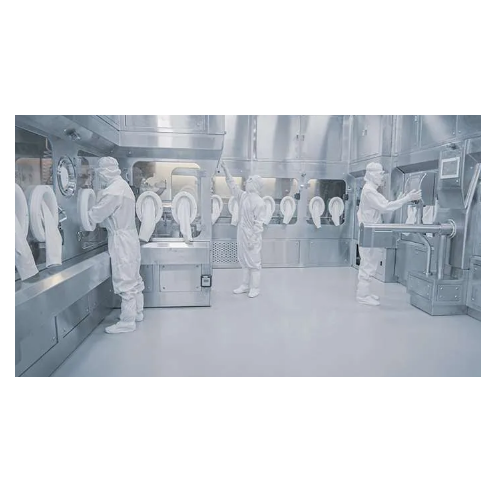
Vial filling line and freeze dryer system
For seamless drug production, integrate reliable vial filling with precision fre...
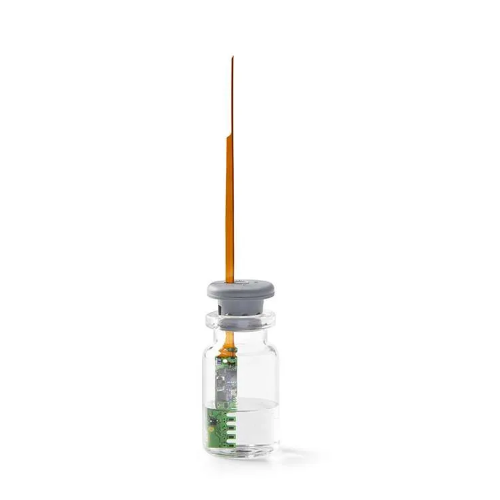
Gmp freeze dryer for small batch production
Optimize small-scale biopharmaceutical production with precise freeze-drying t...
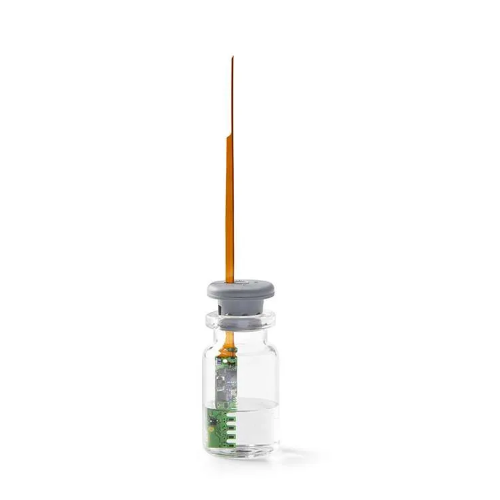
Sublimation front monitoring system for freeze drying
Ensure precise control over your freeze-drying process with real-ti...
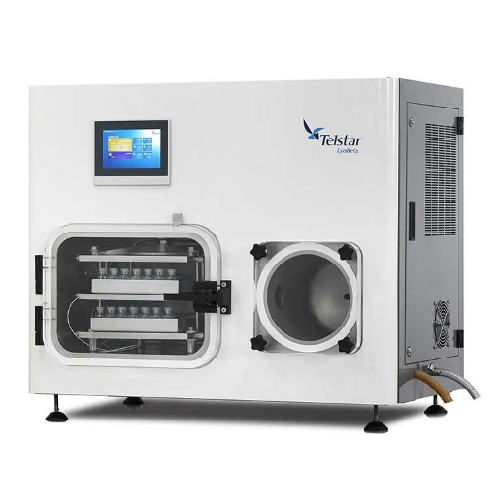
Freeze dryer for small batch scale-up in biotech and pharma
Optimize freeze-drying processes for small batches or high-v...
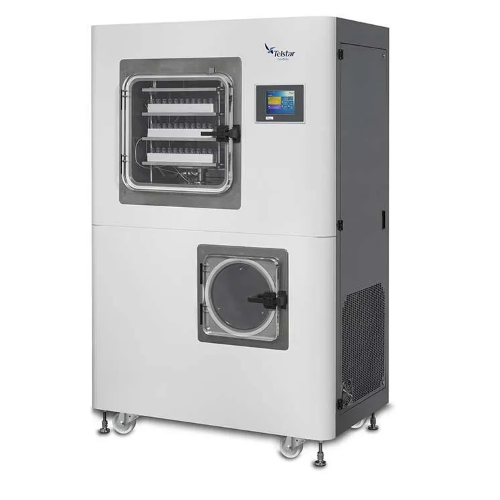
Research and scale-up freeze dryer for biological and pharmaceutical applications
Allows efficient scale-up of lyophi...
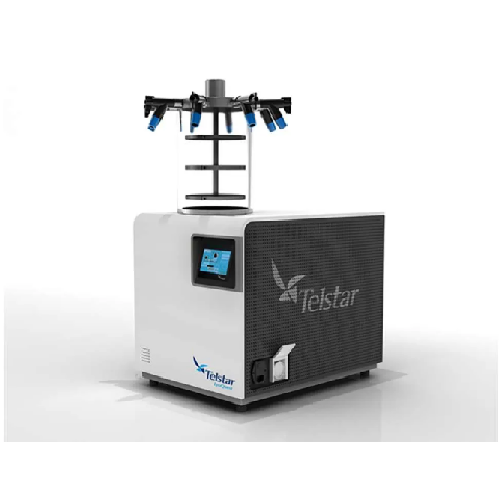
Basic research laboratory freeze dryer
Achieve unparalleled precision in lyophilization with a compact solution tailored fo...
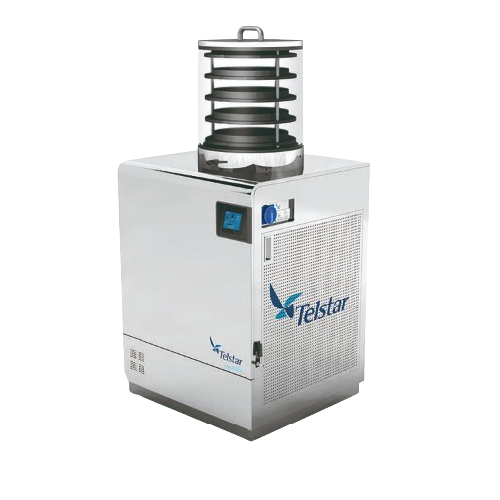
Basic research freeze dryer for biomedical applications
For laboratories seeking precise sample preservation, this bencht...
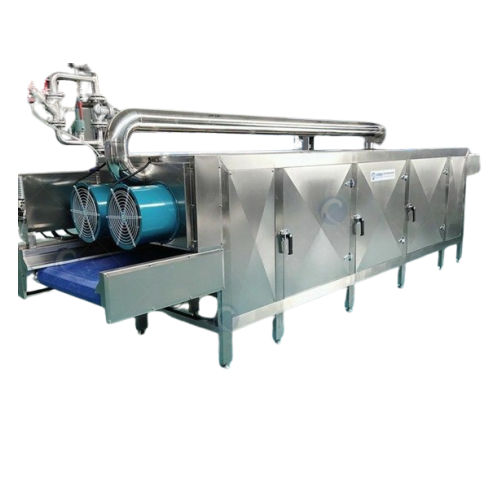
Continuous food washing and drying line for vacuum-packed products
Achieve optimal cleanliness and efficient moisture r...
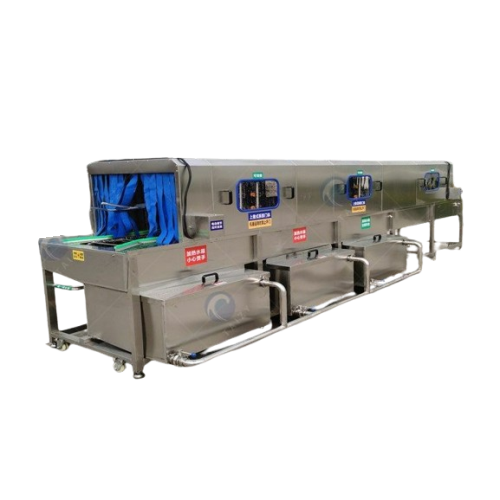
Integrated vegetable washing drying grading line
Effortlessly transform large volumes of freshly harvested produce into ma...
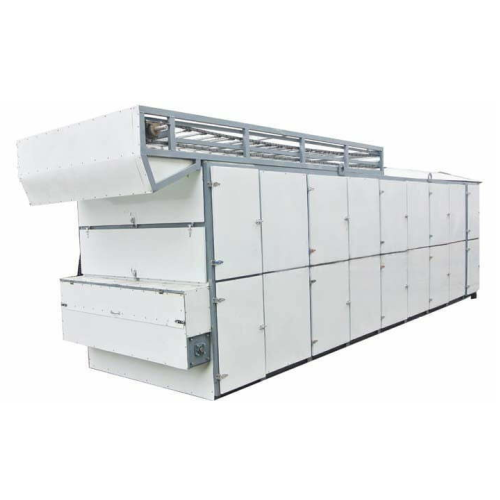
Mesh belt food dryer
Achieve uniform and efficient drying of diverse materials with the mesh belt food dryer, designed to max...
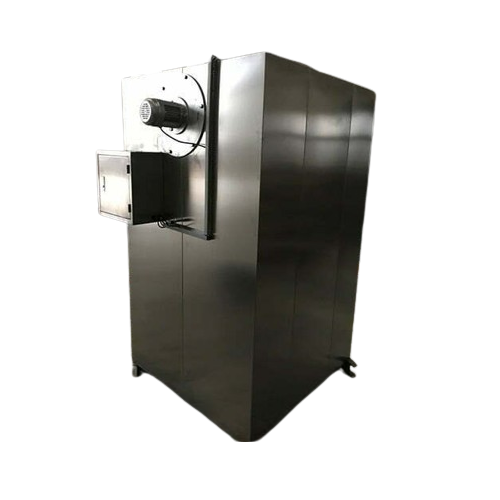
Industrial food drying oven
Achieve efficient dehydration and heat curing with precision control, ensuring uniform drying ac...
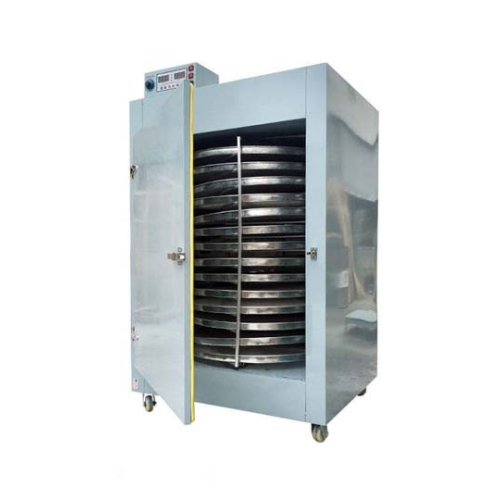
Fruit and vegetable drying equipment
Achieve optimal moisture control for your fruits, vegetables, and herbs with versatile...
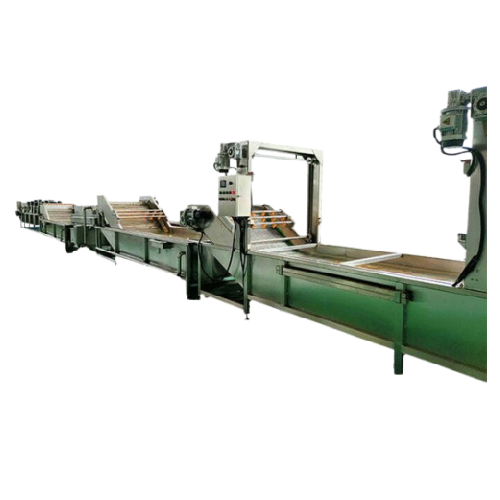
Date palm processing line for jujube cleaning and drying
Optimize your date and fruit production with our line that ensur...
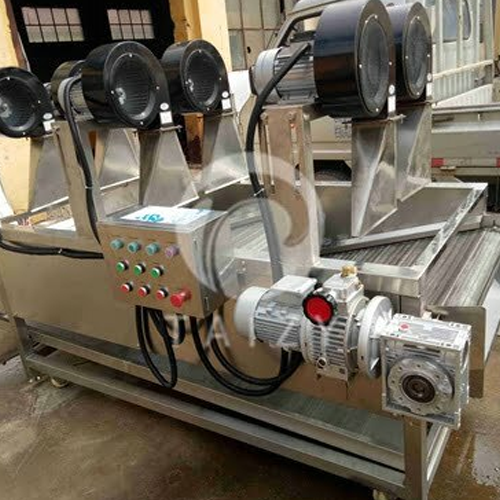
Air dryer for vegetables and fruits processing
Enhance your processing line with efficient moisture removal—perfect for ma...
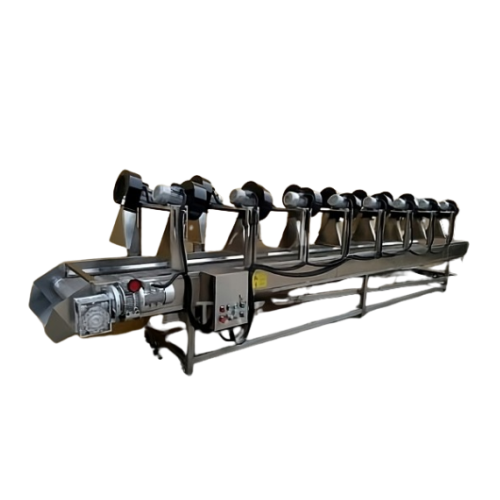
Vegetable and fruit air drying production line
Efficiently dry fruits, vegetables, and vacuum-packed goods while maintaini...
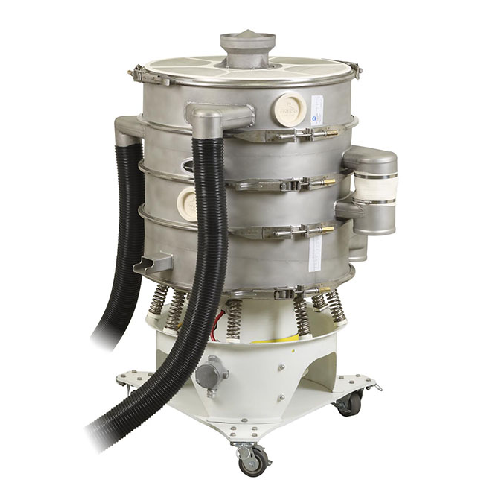
Drying and cooling classifier for plastic pellets
This solution enhances efficiency by combining drying, cooling, and cla...
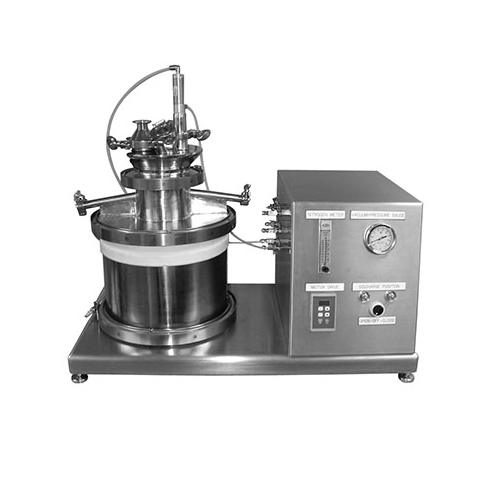
Pharmaceutical aseptic separator filter dryer
Achieve seamless filtration, washing, and vacuum drying in a single aseptic ...
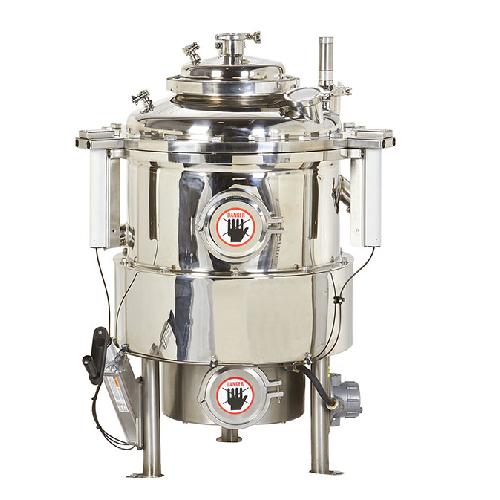
Pilot pharmaceutical aseptic separator and dryer
Achieve high-yield recovery of potent compounds with a separator that com...
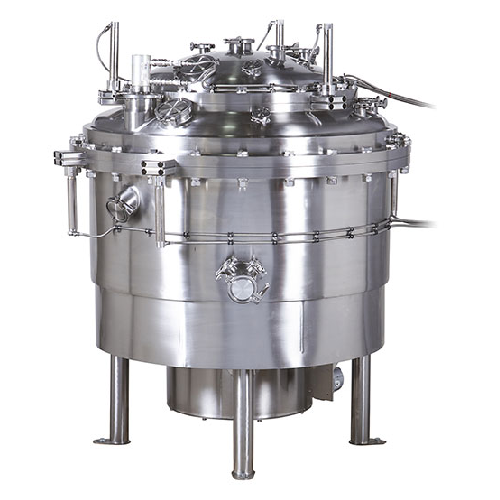
Pharmaceutical aseptic separator tumble dryer
Streamline moisture reduction with precision: this solution accelerates dryi...
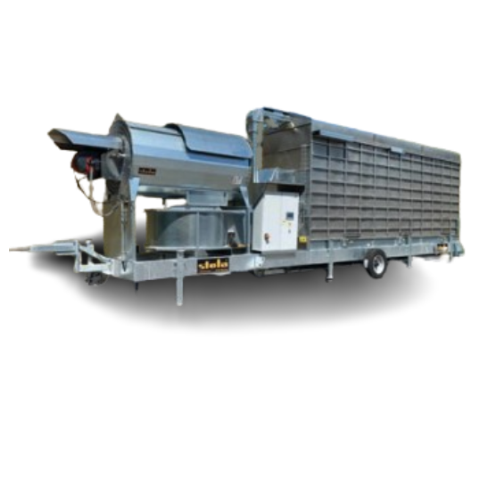
Mobile circulating dryer for agricultural products
Optimize your drying processes with a mobile circulating dryer, design...
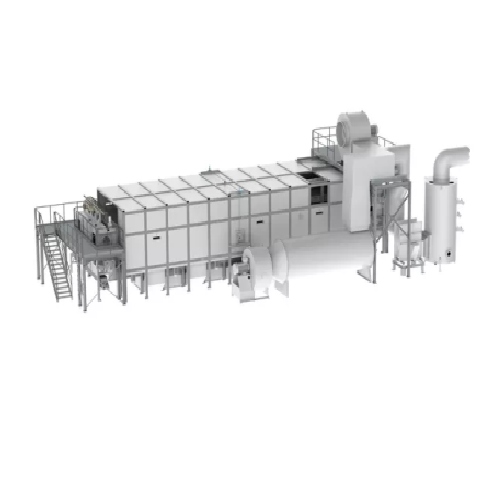
Slat conveyor dryer for industrial drying processes
Optimize your drying process with a robust slat conveyor system that ...
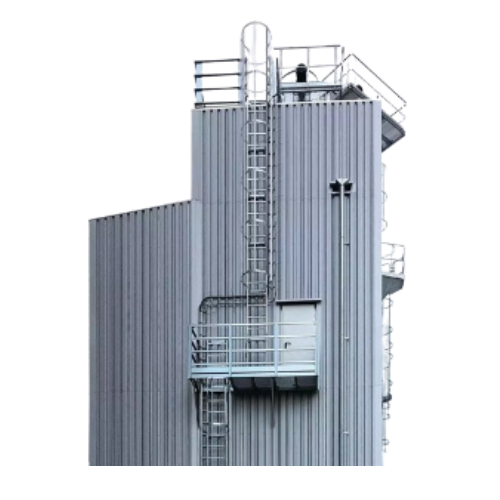
Stationary drying system for agricultural products
Optimize moisture control and energy efficiency in your drying process...
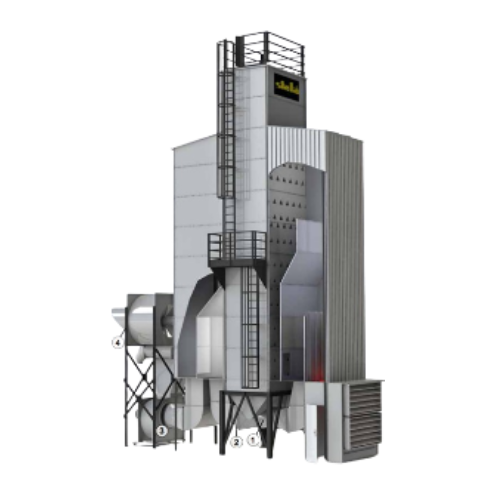
Stationary grain dryer with exhaust air system
Optimize your drying process with a system designed to handle diverse mater...
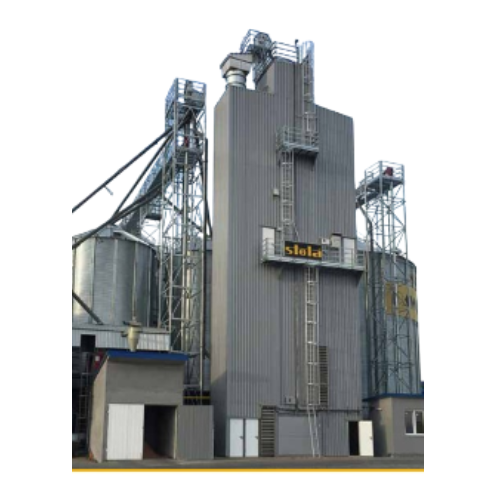
Grain dryer with air circulation system
Enhance efficiency and product quality with our versatile grain dryer, designed to ...
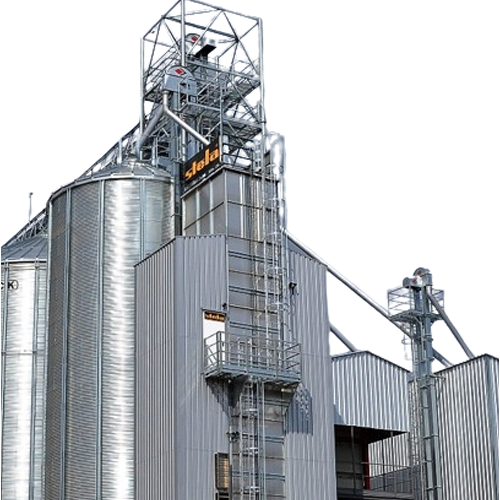
Stationary grain dryer with biturbo system
Optimize your drying processes with a system that efficiently manages air flow ...
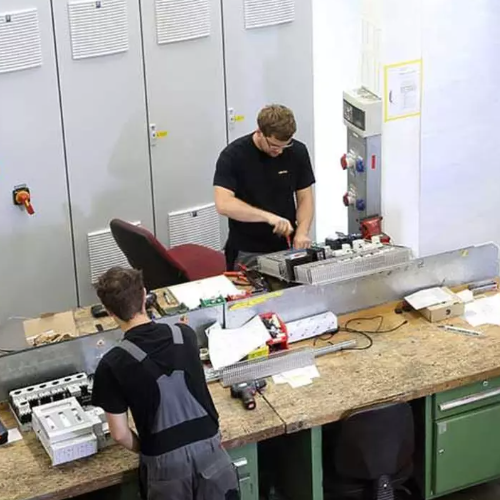
Low-emission belt drying systems for timber industry
Optimize moisture control and energy efficiency in drying processes ...
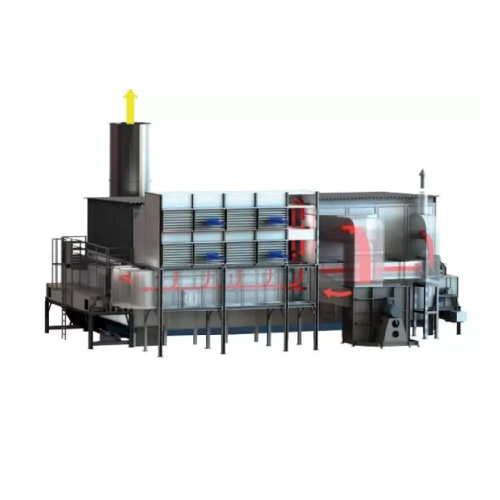
Belt dryer for timber industry
Optimize moisture removal and ensure consistent drying in your production line with advanced ...
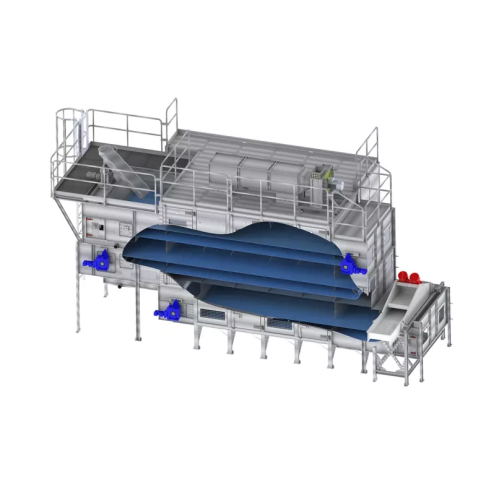
Layer dryer for food and pet food applications
Optimize drying efficiency with multi-layer technology that minimizes space...
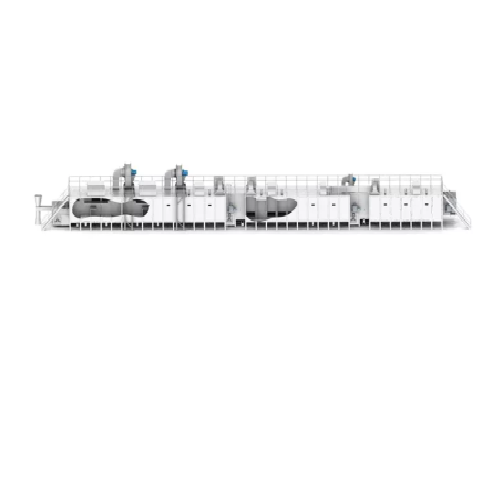
Belt dryer for food and pet food products
Optimize drying processes with customizable belt dryers, engineered to handle ro...
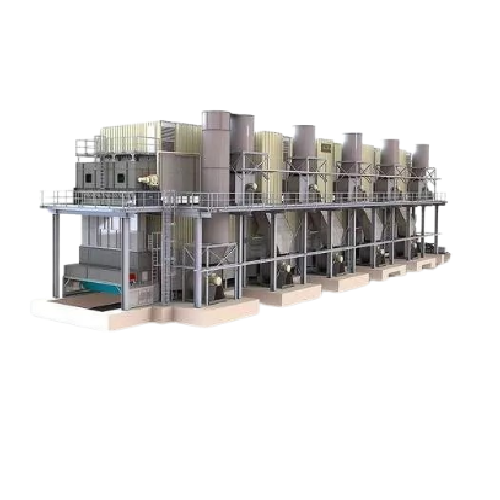
Belt dryer for sawdust
Optimize your drying process with advanced technology engineered for precise moisture reduction in div...
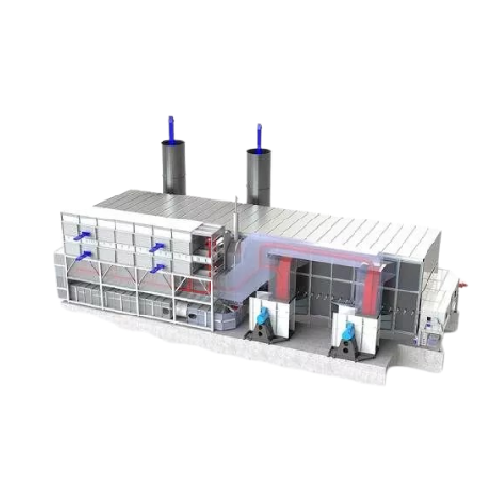
Low-emission belt dryer for timber industry
Achieve maximum drying efficiency and significant energy savings in your proce...
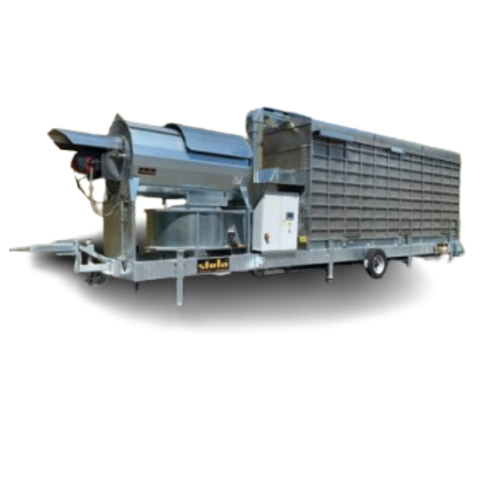
Hybrid dryer for agriculture and industrial applications
Achieve efficient moisture reduction in varied materials, from f...
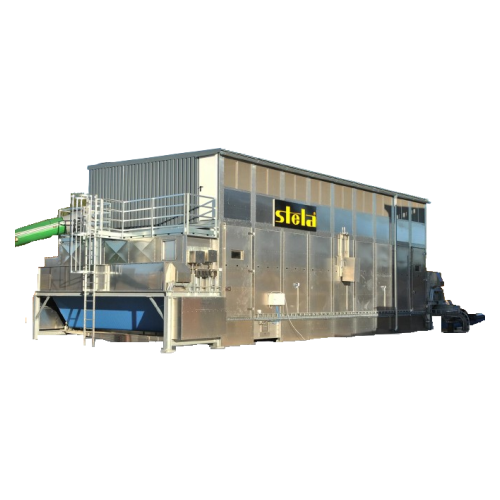
Mobile belt dryer for sawdust and biomass
Efficiently reduce moisture in a variety of materials, from sawdust to cereal sn...
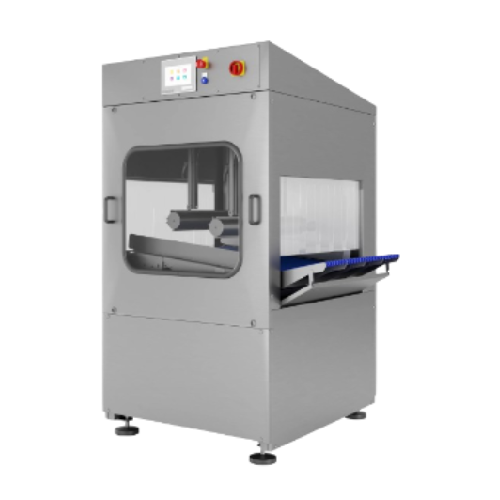
Stainless steel drying tunnel for packaging lines
Optimize your packaging line efficiency by ensuring products are thorou...
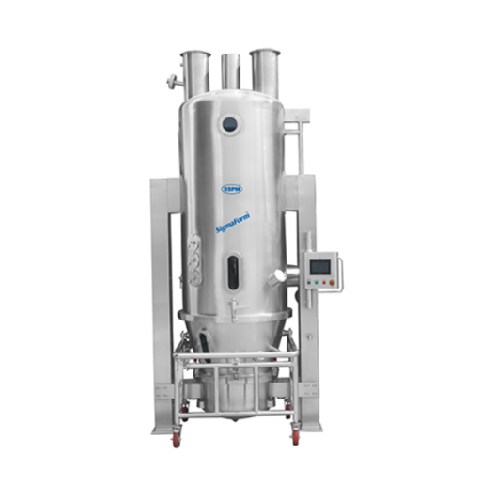
Fluid bed dryer for wet granulation in pharmaceutical industry
Streamline your production with fast, uniform drying and ...
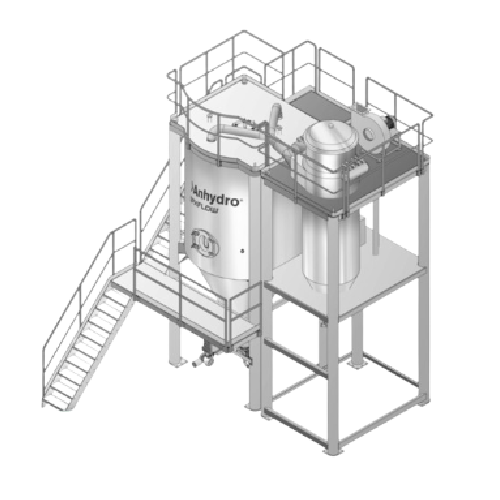
Small scale spray dryer for r&d and production
For precise moisture removal in small batches, this flexible spray drying s...
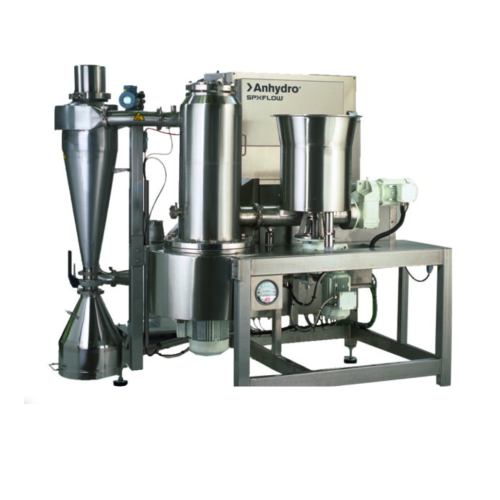
Small scale spin flash dryers for high-viscosity liquids
Optimize moisture control with cutting-edge spin flash dryers de...

Continuous drying for cohesive and non-cohesive pastes
Transform high-viscosity liquids and pastes into fine, flowable po...
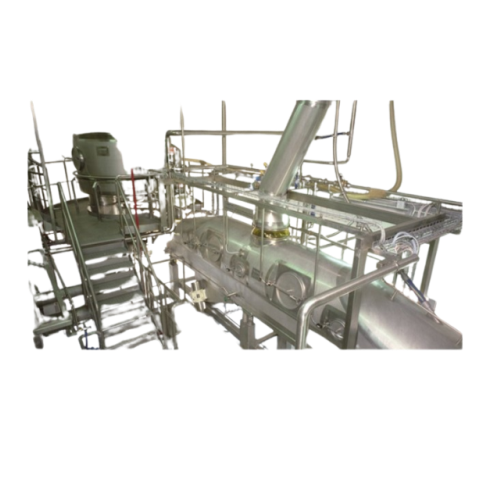
Spray bed dryer for agglomerated powder production
Efficiently transform liquid feedstock into consistent, dust-free powd...
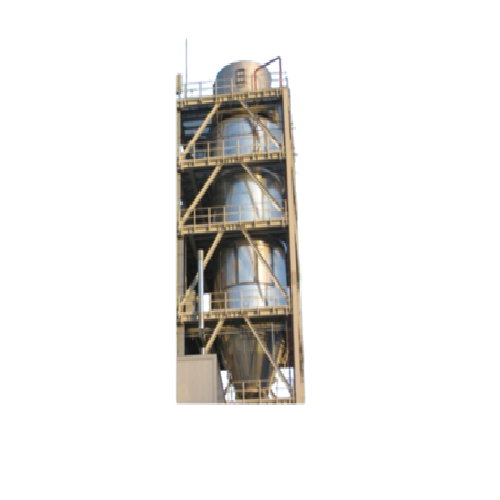
Tall form dryer for producing large non-agglomerated particles
Achieve precise particle size control and optimal moistur...
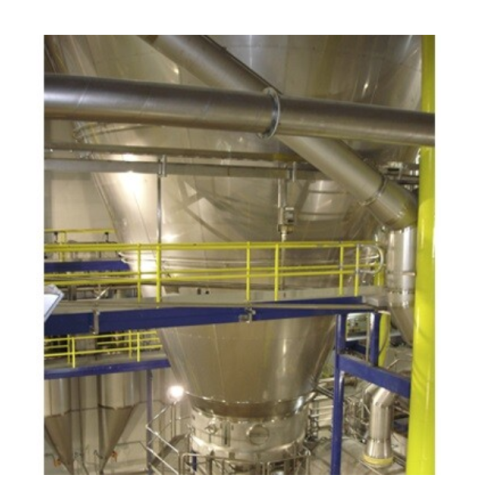
Spray dryers for producing free-flowing dustless powders
Achieve consistent product quality with customizable spray dryer...
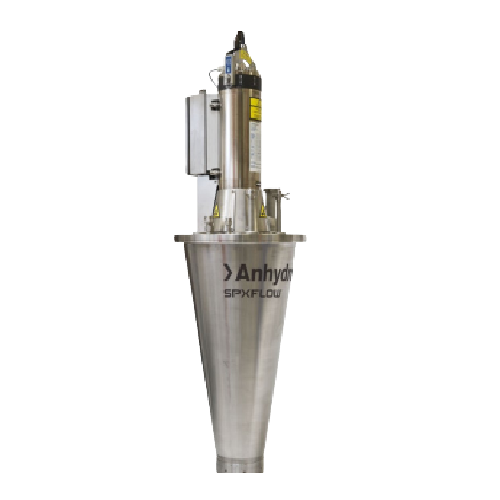
Centrifugal atomizer for precise spray drying
Achieve precise control over particle size and moisture content with centrif...
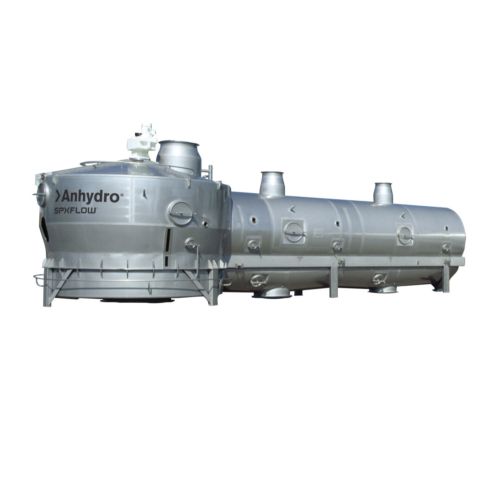
Industrial fluid bed dryers for powder processing
Enhance moisture control and uniformity in powder products with dynamic...

General purpose freeze dryer for bulk samples
Preserve delicate artifacts and specimens effectively with a versatile freez...
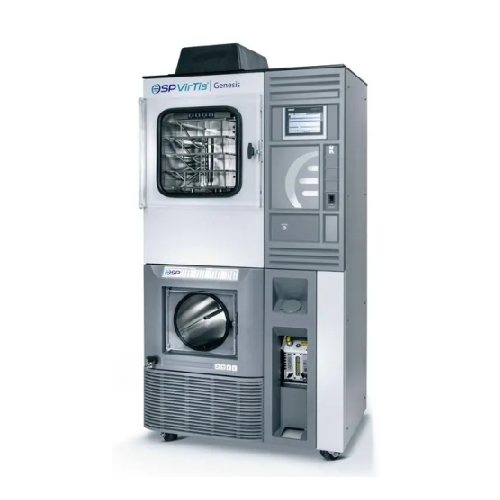
Pilot freeze dryer for laboratory and small-scale production
Achieve precise temperature and vacuum control for consiste...
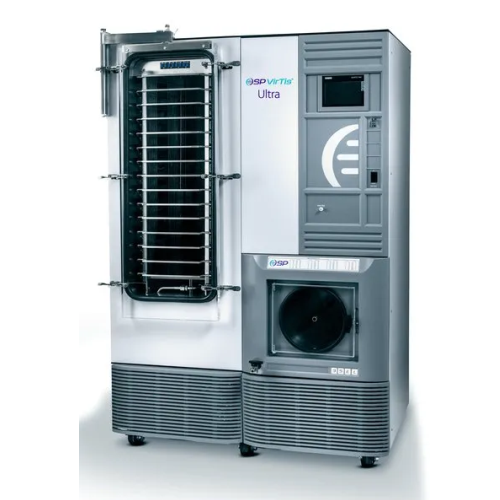
Pilot-production freeze dryer for diagnostic kits and Api
Optimize your lyophilization process with this versatile freez...
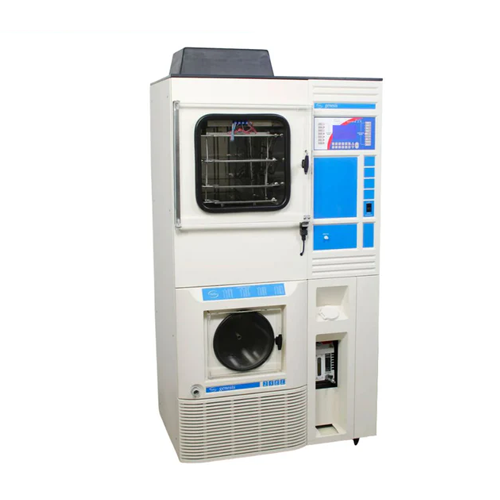
Optimized lyophilization with Smart freeze dryer technology
Streamline lyophilization cycle development with cutting-edg...
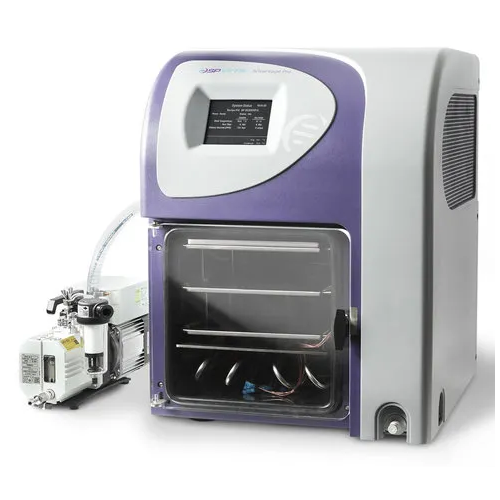
Benchtop freeze dryer for laboratory research
Streamline your lab’s freeze-drying processes with precision temperatu...
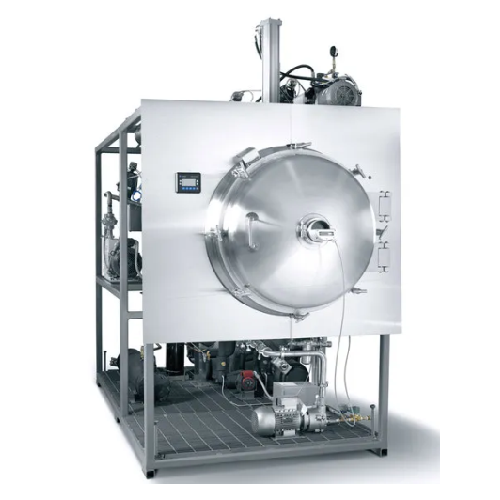
Production freeze dryer for pharmaceutical manufacturing
Achieve precise lyophilization for sensitive products with custo...
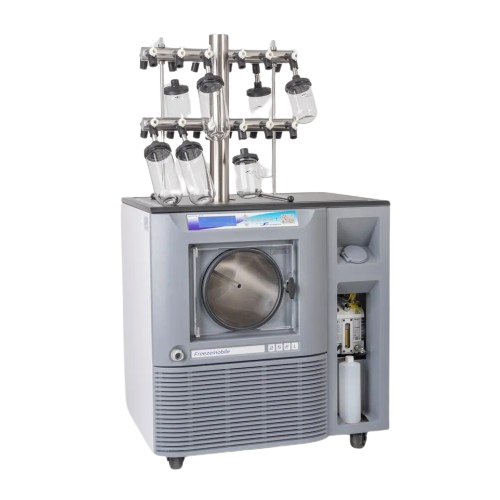
Laboratory freeze dryer
Achieve precise moisture control and enhanced product stability with this advanced freeze-drying solu...
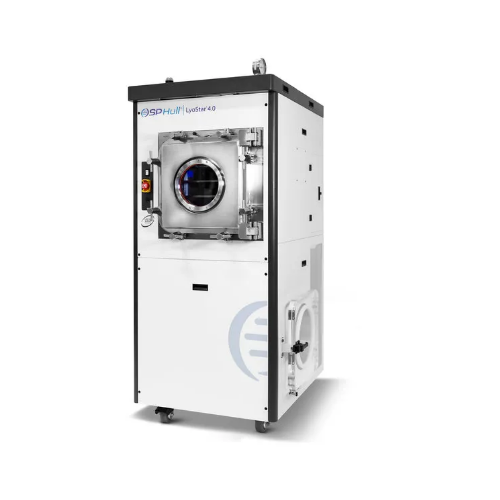
R&d and process development freeze dryer
Speed up your biologic development with precise lyophilization control, ensuring r...
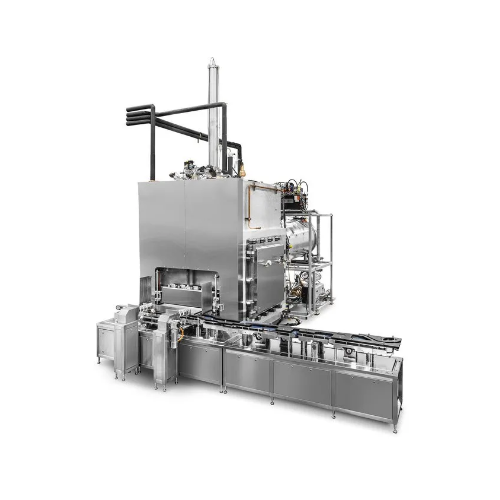
Freeze dryer loading and unloading systems for pharmaceutical processes
Optimize aseptic pharmaceutical processes with ...
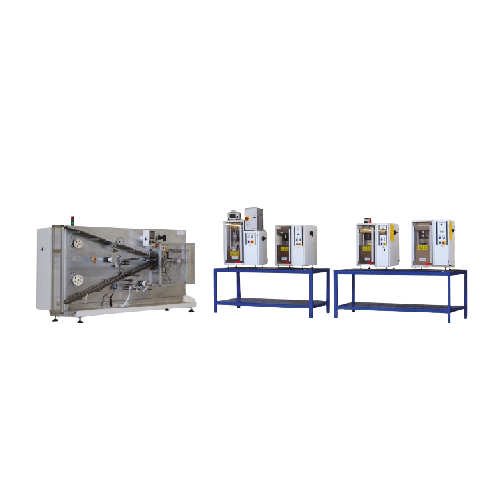
Industrial dry charge oven for battery manufacturing
Optimize your battery production with precision-engineered assembly ...
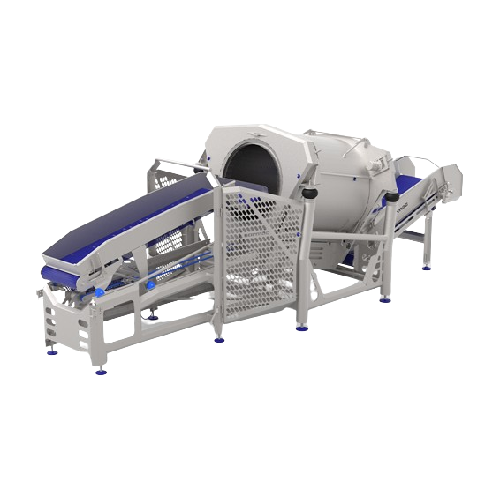
Centrifuge for drying leafy vegetables
Efficiently dry delicate leafy vegetables without product damage, ensuring optimal m...
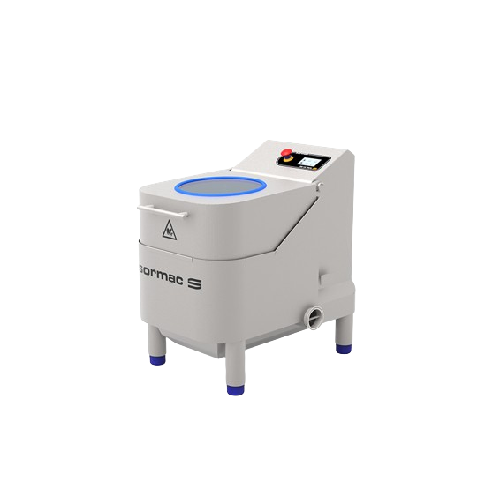
Centrifuge for drying delicate salad leaves and vegetables
Achieve precise moisture control for fresh salad leaves and d...
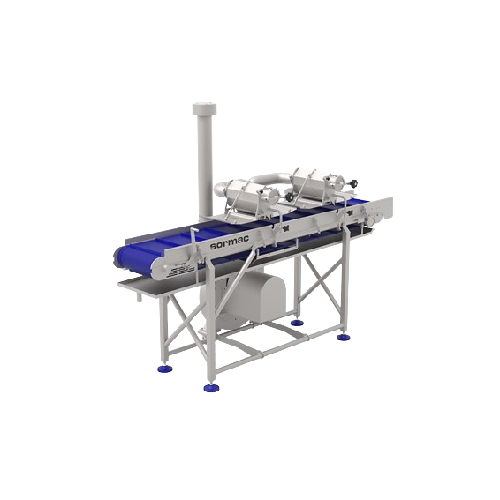
Drying conveyor for hard vegetables
Ensure optimal drying of hard vegetables with a seamless integration of air blowing sta...
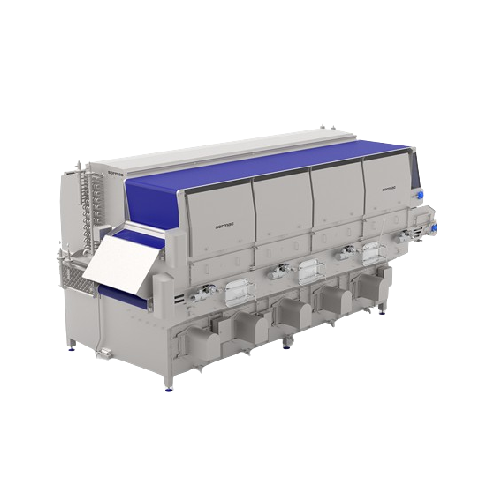
Air drying solution for leafy vegetables
Achieve optimal moisture reduction with precision air drying, ideal for maintainin...
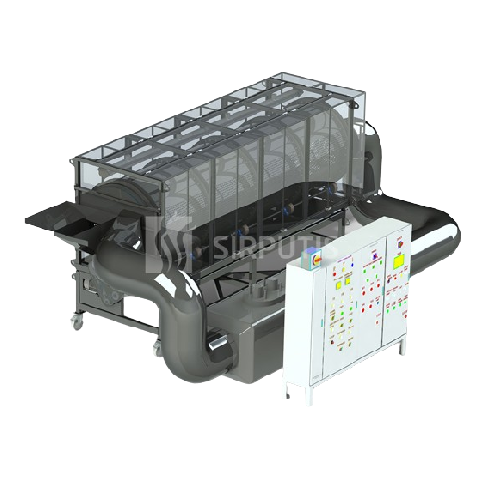
Industrial seaweed drum dryer
Optimize your seaweed and algae processing with an advanced drum drying solution that effectiv...
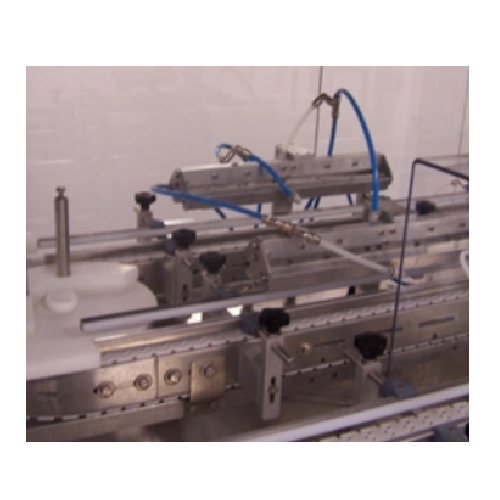
External washing and drying system for sealed vials
Ensure contamination-free packaging of liquid vials with this precise...
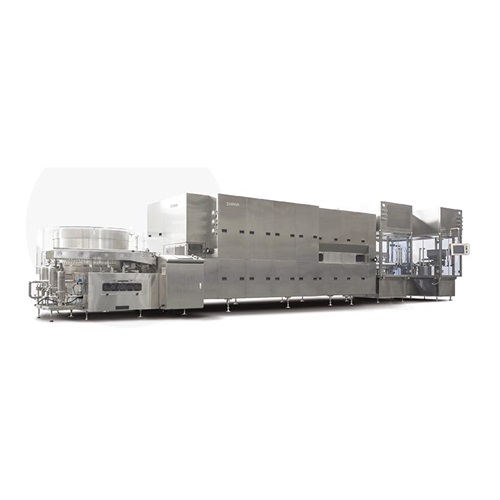
Vial washing drying filling sealing line for pharmaceutical production
Streamline your vial production with this integr...
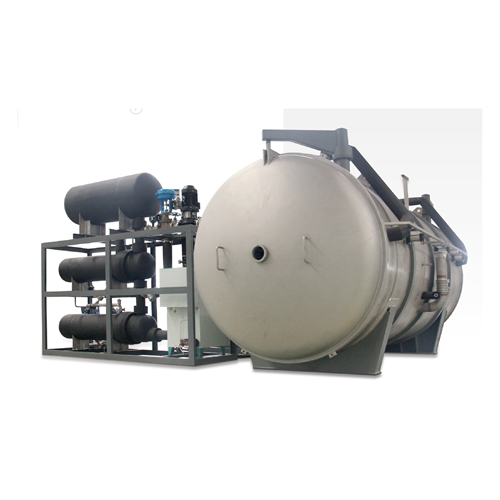
Food freeze dryer for large-scale production
Optimize your freeze-drying process with seamless integration of pre-freezing...
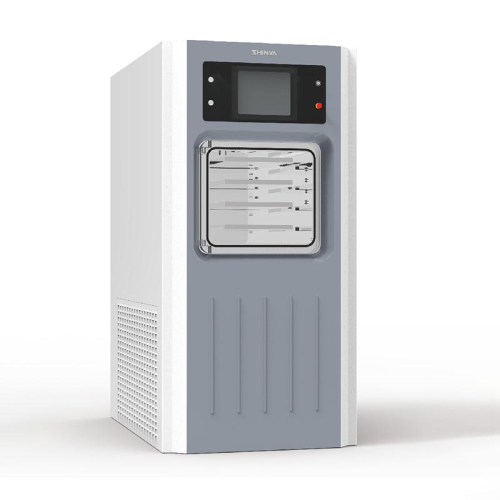
Laboratory freeze dryer for research and process amplification
Optimize freeze-drying processes with precision control, ...
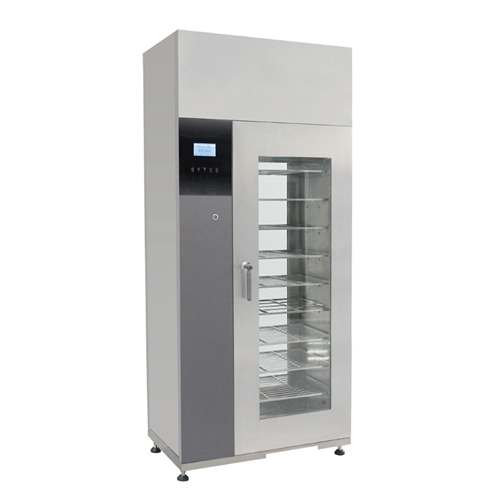
Medical drying cabinet for surgical instruments and glassware
Achieve optimal drying for precision instruments and glass...
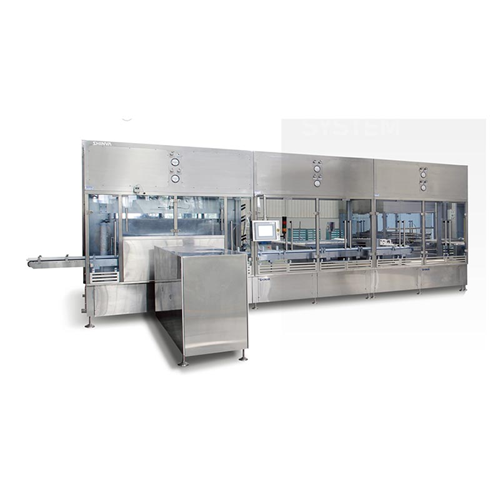
Automatic loading and unloading system for freeze-drying
Eliminate contamination risks and improve operational efficiency...

Efficient grinding and drying mill
Transform your production line with a versatile mill that simultaneously grinds, dries, ...
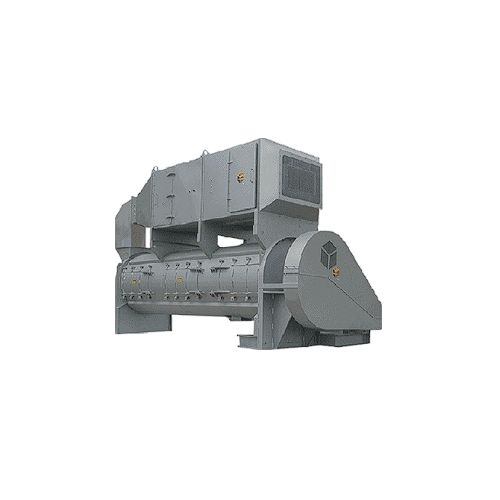
Pneumatic drying system for industrial slurries
Efficiently transform high-moisture slurries into dry solids in a single p...
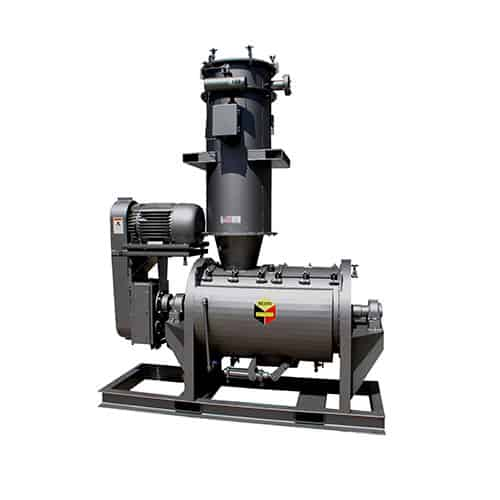
Industrial vacuum batch dryer for reducing moisture content
Achieve precise moisture control with a solution that handle...
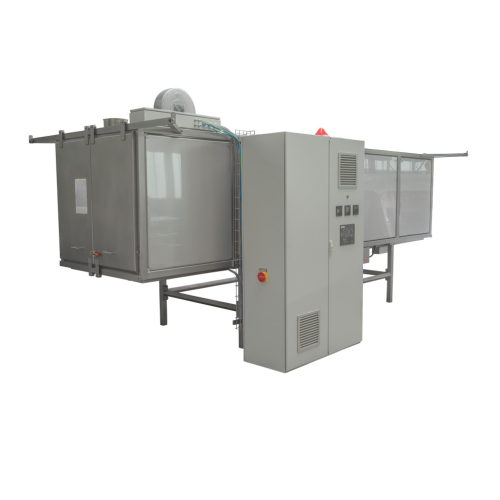
Infrared dryer for breakfast cereals
Optimize your snack production with precise moisture control, energy-efficient infrare...
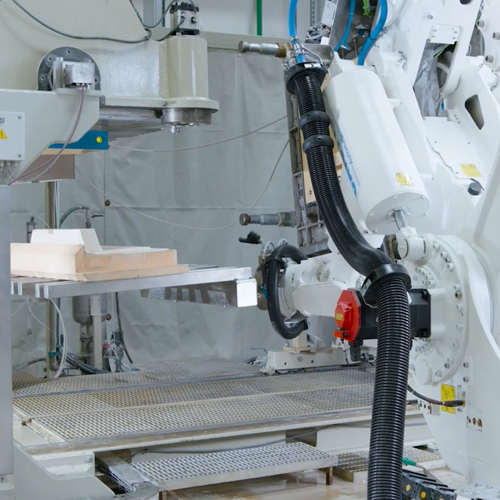
Ceramic sanitaryware casting and drying plants
Ensure top-quality ceramic sanitaryware production with comprehensive solut...
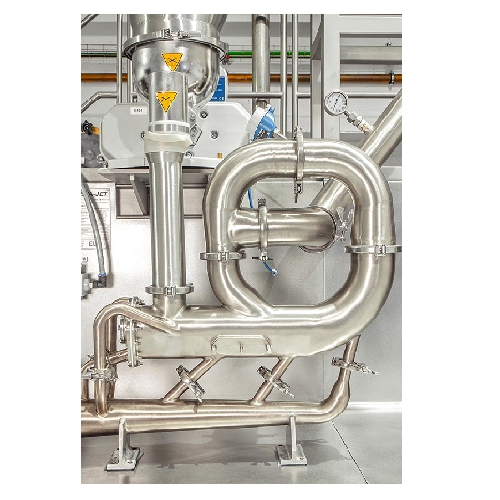
Continuous hot air conveying dryer for chemical and pharmaceutical industries
Ensure rapid moisture removal with high-...
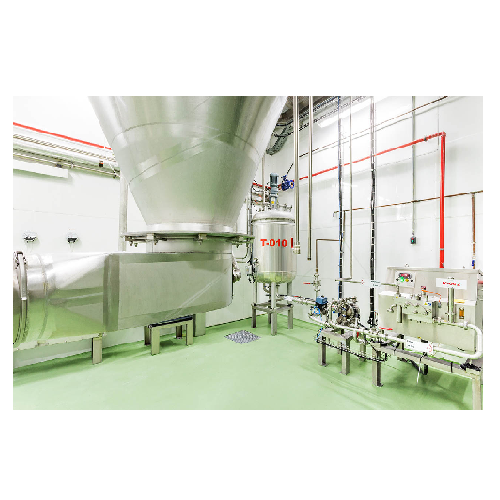
Continuous spray dryer for thermosensitive products
Ideal for processing thermosensitive slurries, this spray dryer ensur...
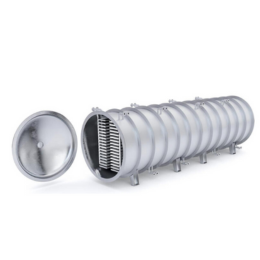
Semi-continuous freeze dryer with easy-loading
Freeze-drying is both a time- and energy-consuming process. In addition to ...
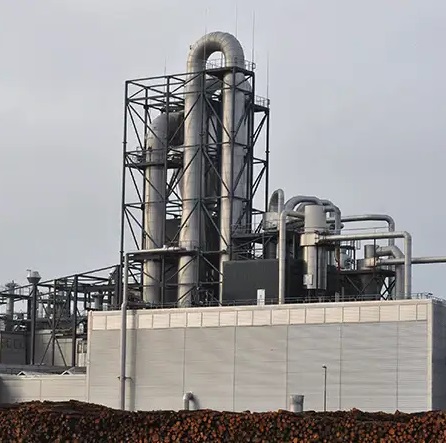
Energy saving vertical steam dryer for paper pulp
Apart from soil and water pollution with cholates, chlorine, and metal ...
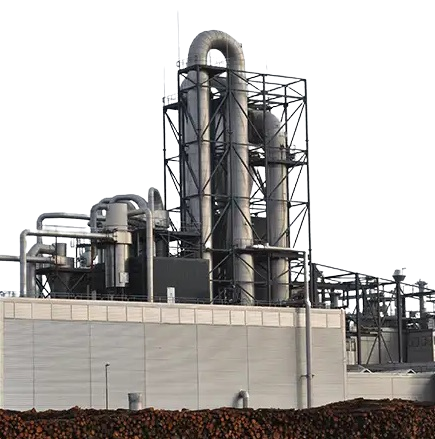
Energy efficient steam dryer for feed products
Traditional drying technologies with low investment cost, such as hot air d...
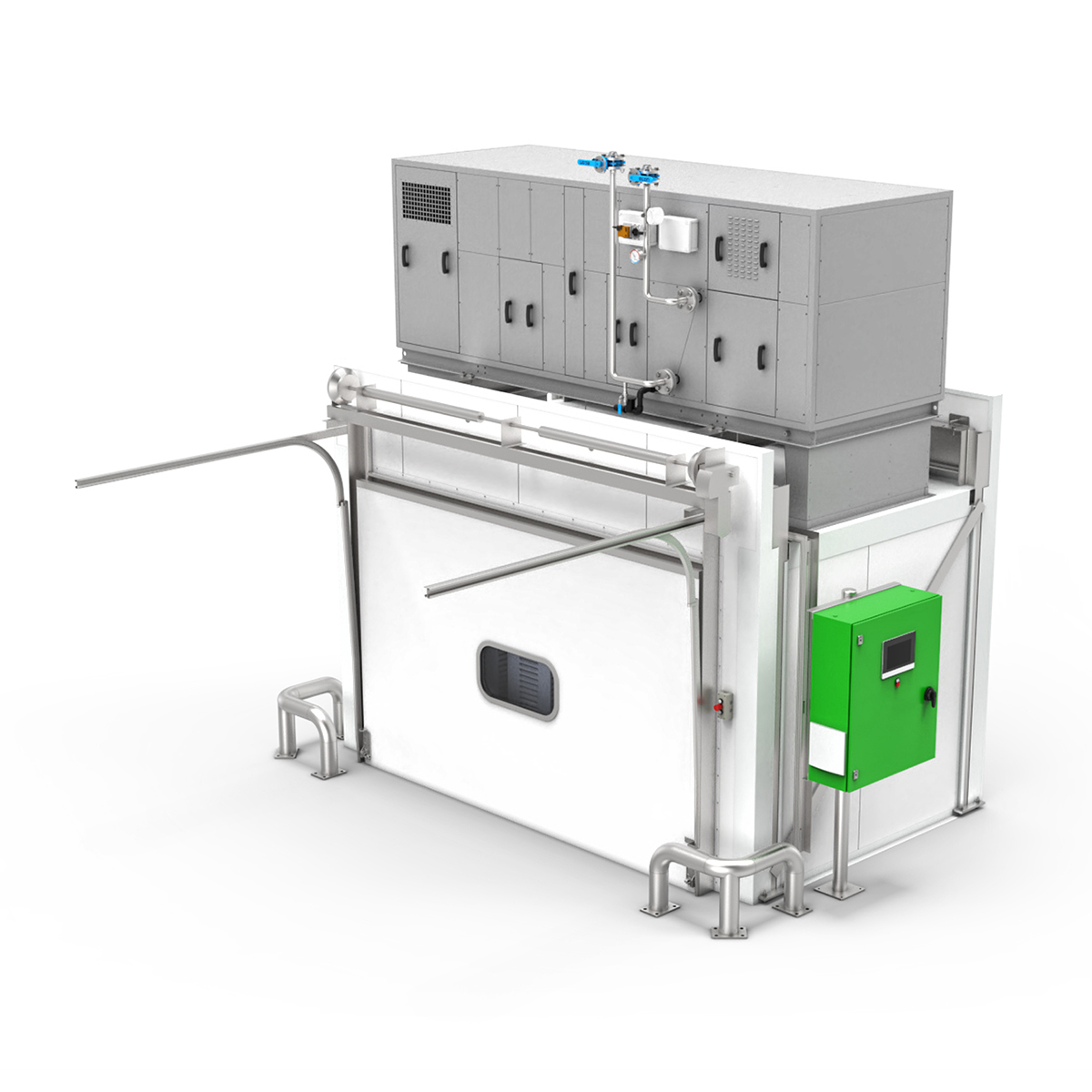
Entry-level conditioning system for drying nutraceutical gummies
The drying process demands specific environmental condi...
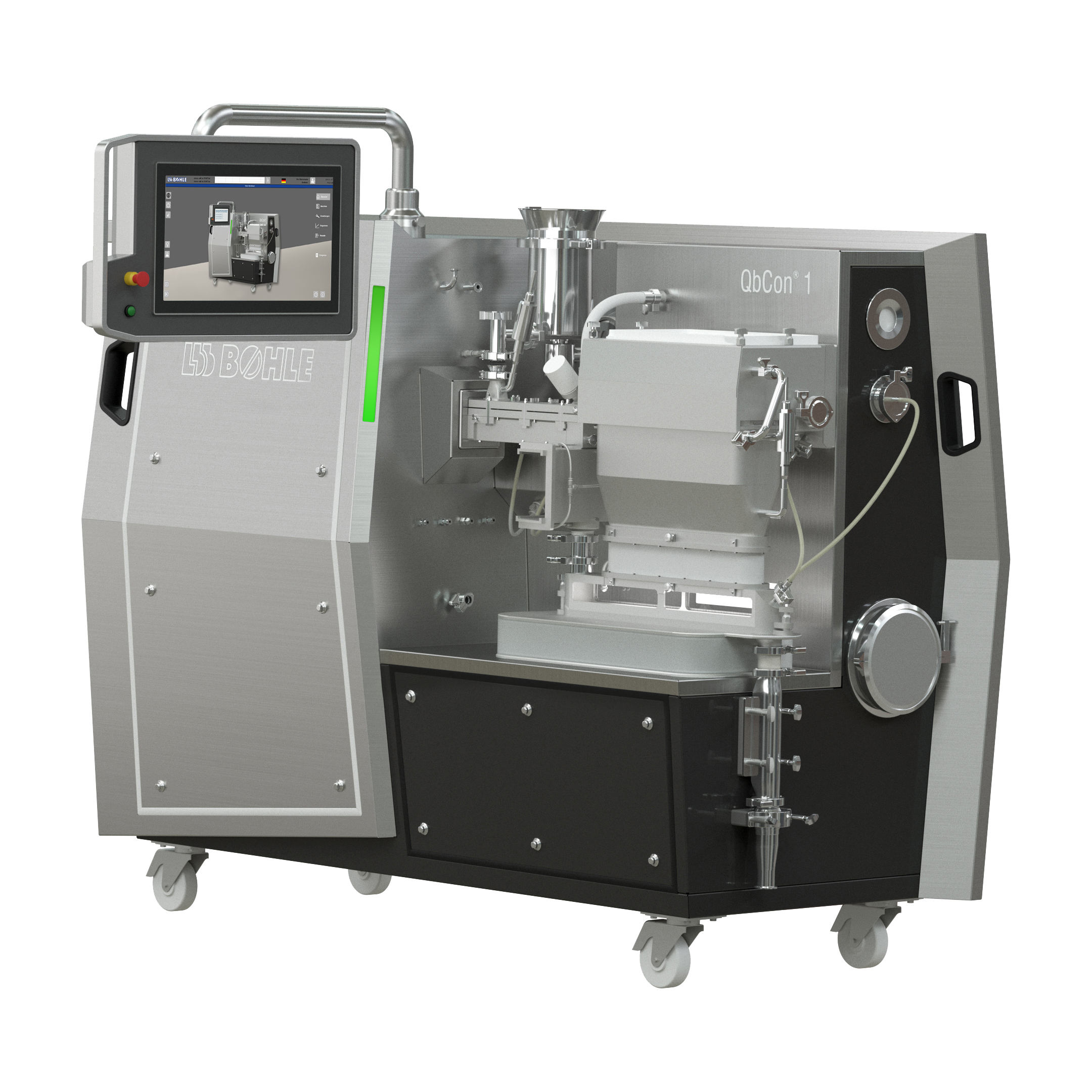
Continuous wet granulator and dryer for R&D
Pharmaceutical laboratories need compact equipment to handle and produce small...
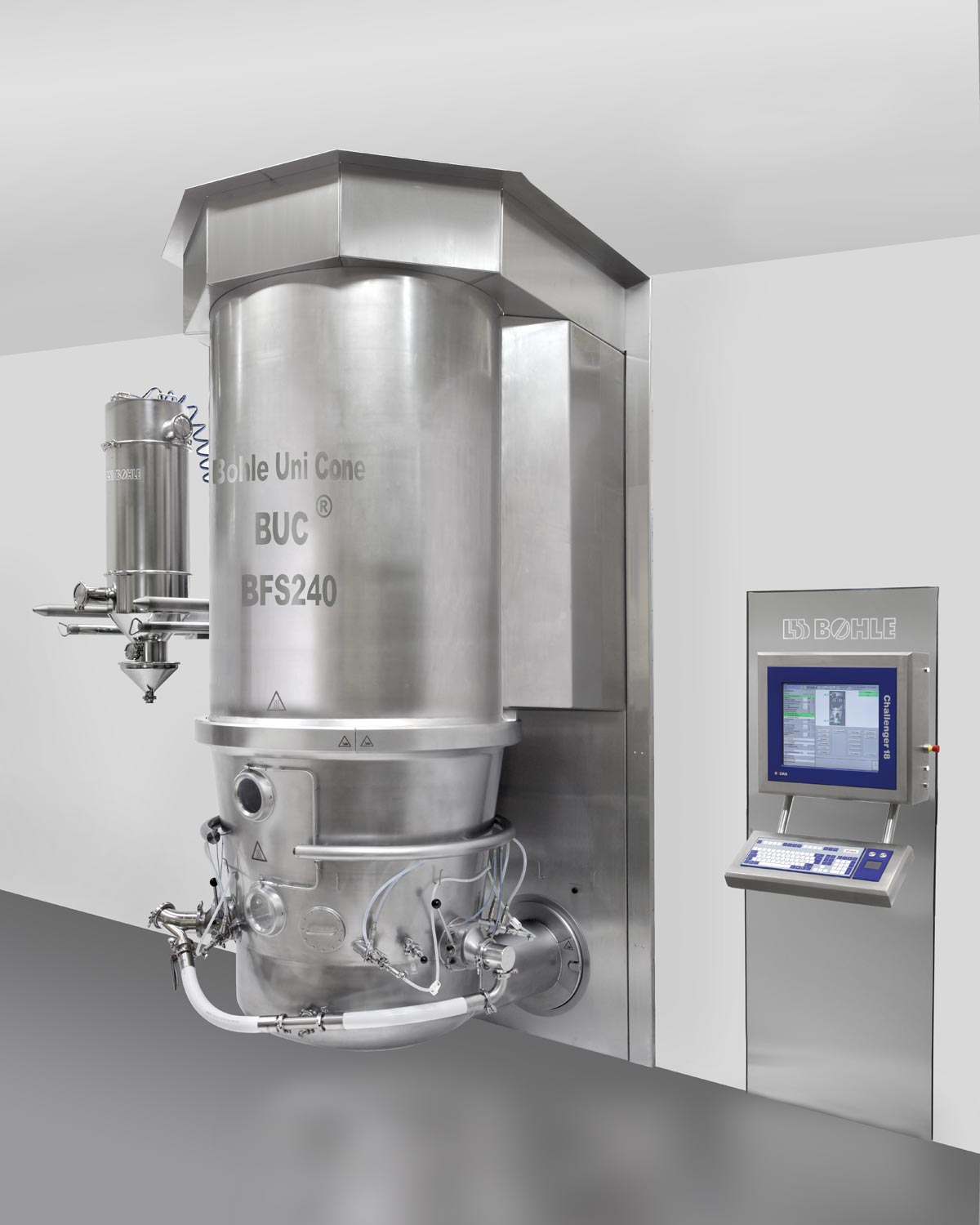
Fluidized bed system for the granulation and drying of pharmaceuticals
Pharmaceutical industries employ several process...
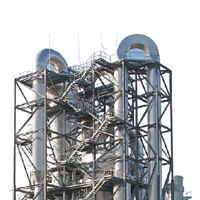
Exergy pressurized superheated steam dryer
Traditional dryers and heat transfer systems, like belt-, drum- or bed dryers a...
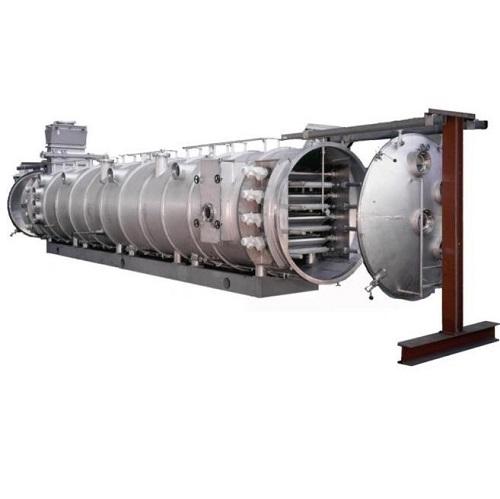
Vacuum belt dryer for fruit, vegetable and herbal extracts
Organic volatile compounds from fruits, vegetables and herbs ...
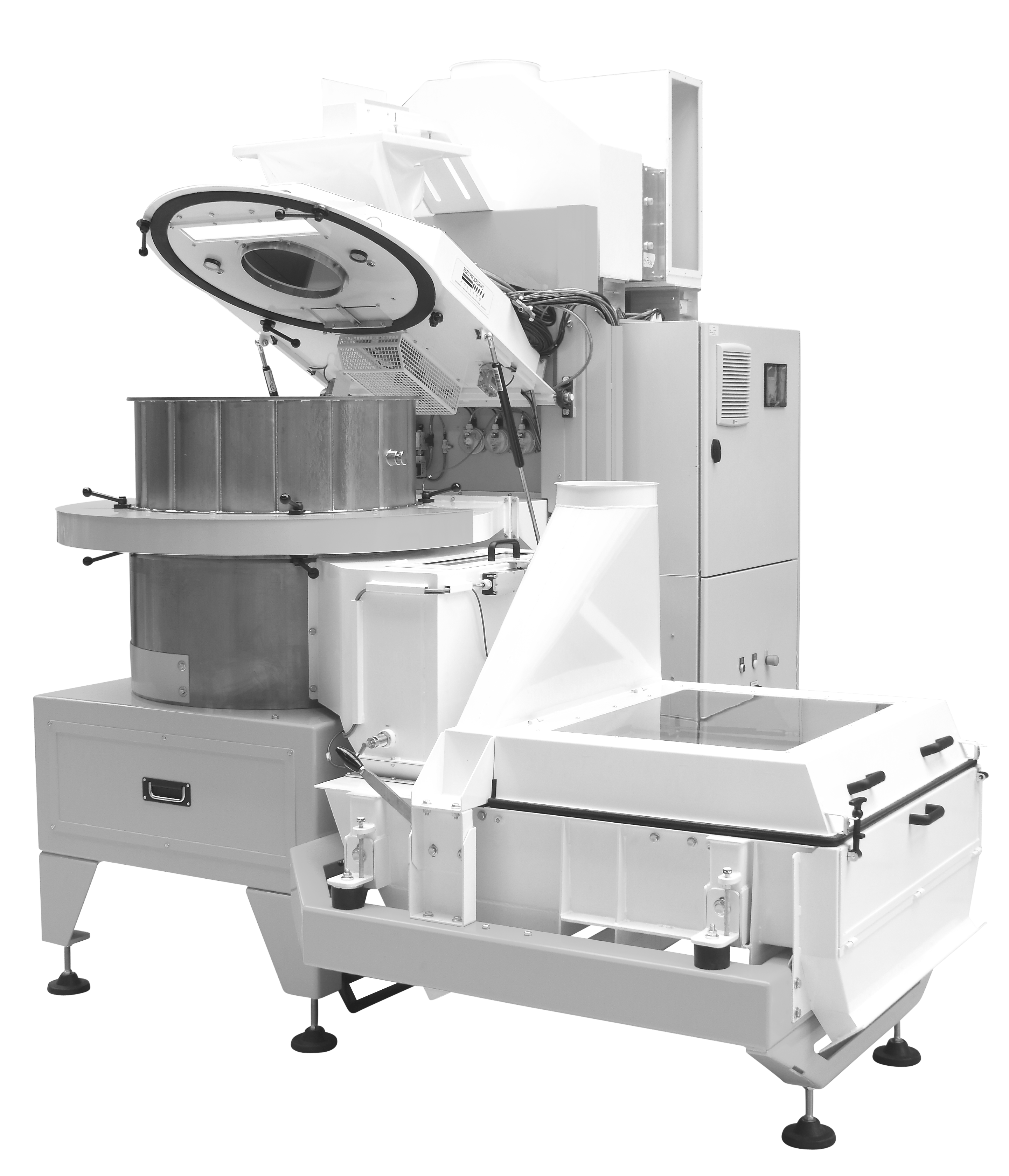
Rotary Seed Dryer Coater
Large-volume vegetable and field crop seeds manufacturers may prefer a fully automated coating and d...
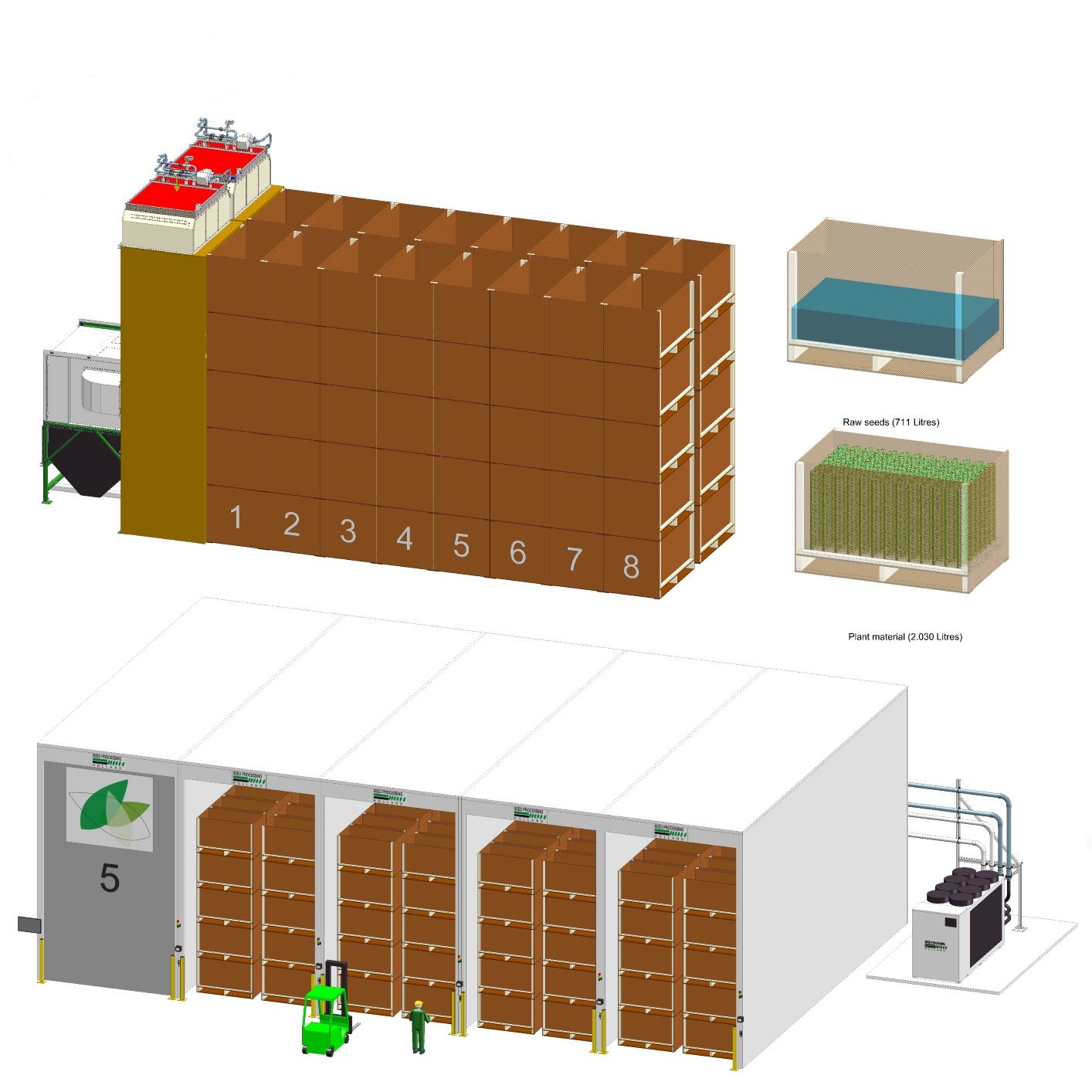
Conditioned Box Dryer
Seeds that are harvested are dried as part of their initial process of cleaning. Having huge quantities...
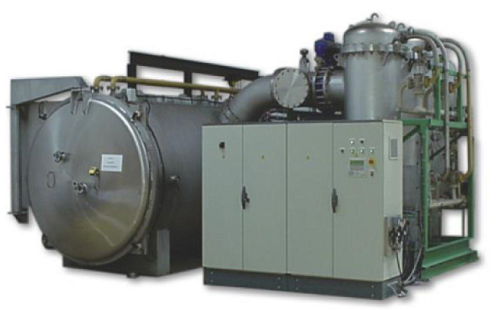
Freeze drying system for berries and fruit powders
Delicate fruits with high moisture levels, such as berries, risk losin...
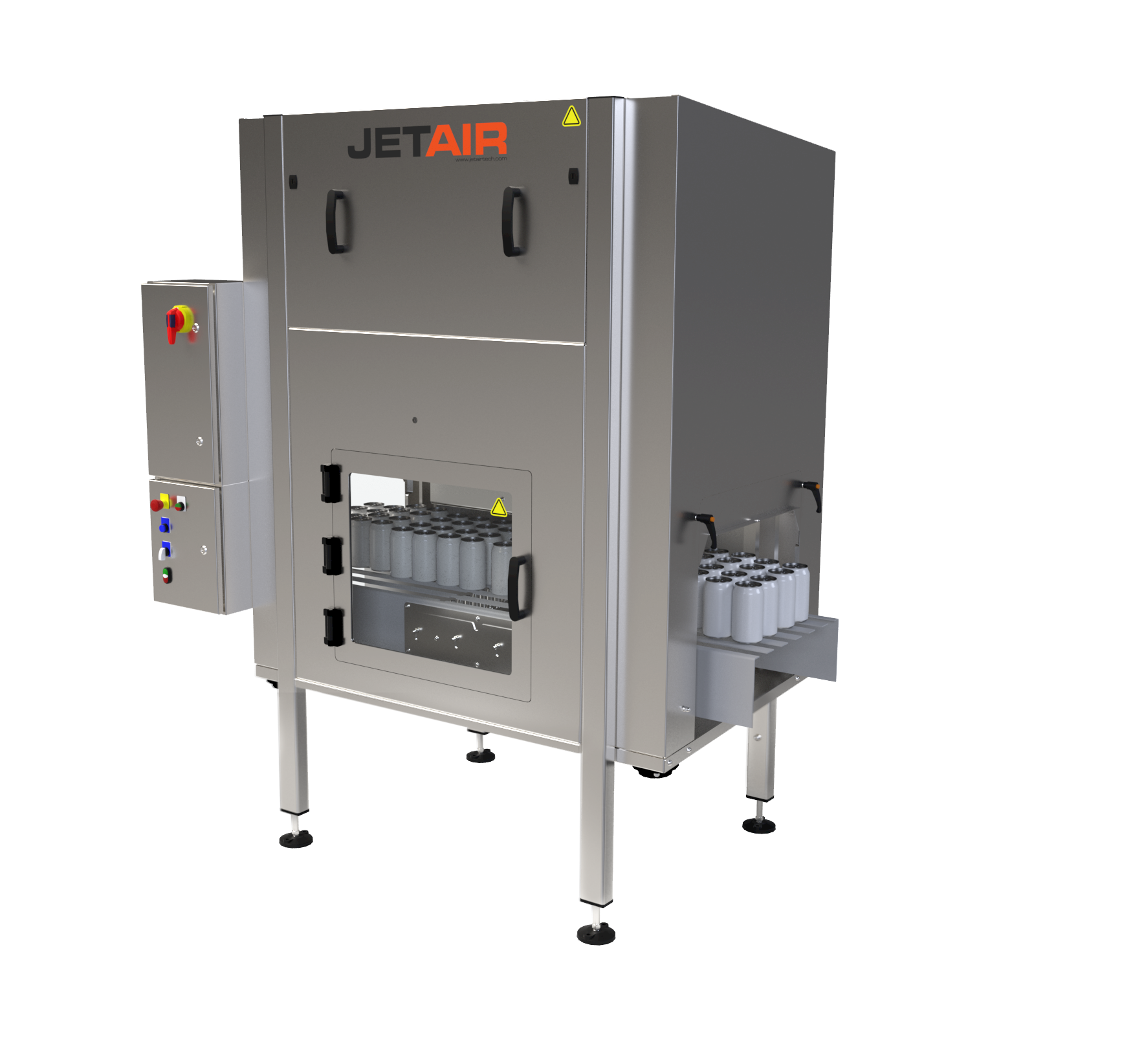
Mass flow air knife drying system for cans
For large-scale production of canned beverages, line throughput and efficiency ...
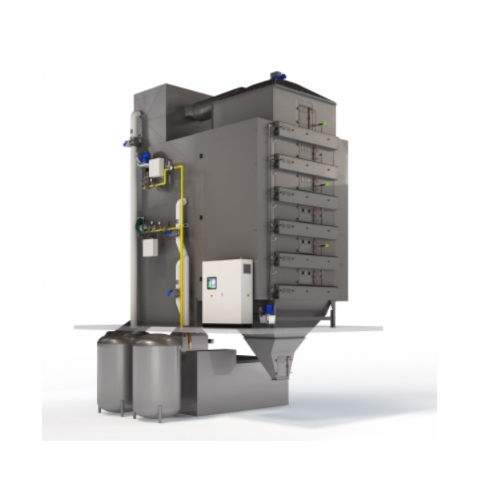
Industrial heat pump dryer
The drying of extruded products is highly energy-demanding in traditional belt dryers that use ga...
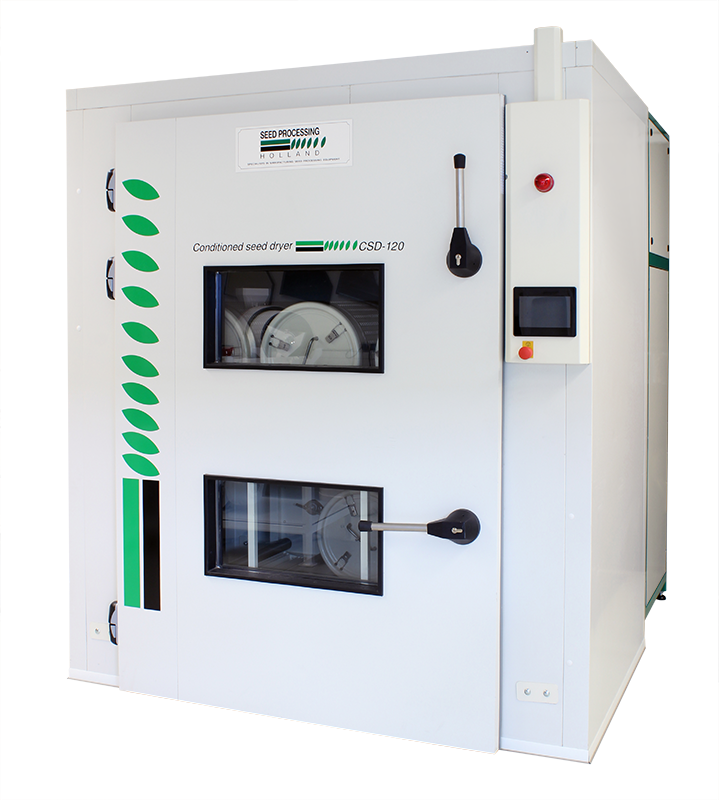
Conditioned seed drying machine
It’s essential to dry moist seeds before you process and store them. Seeds with too high or ...

Energy saving cabinet dryer for food
Traditional drying systems use a lot of energy and take a long time to dry the product...
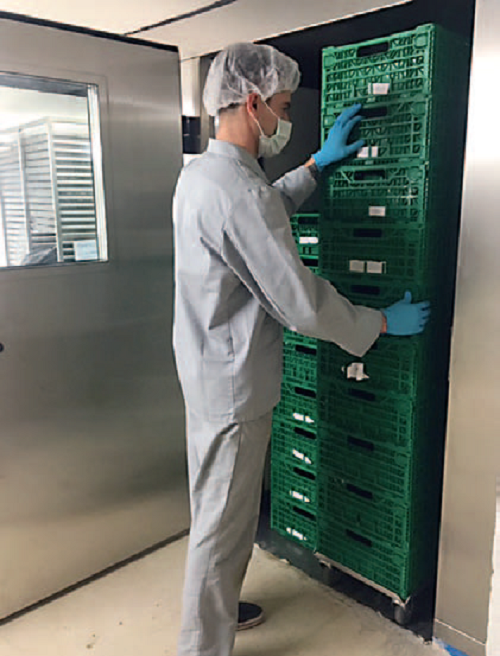
Cabinet dryer for cannabis
If you need careful drying for products like pharmaceutical-grade cannabis buds then traditional ...
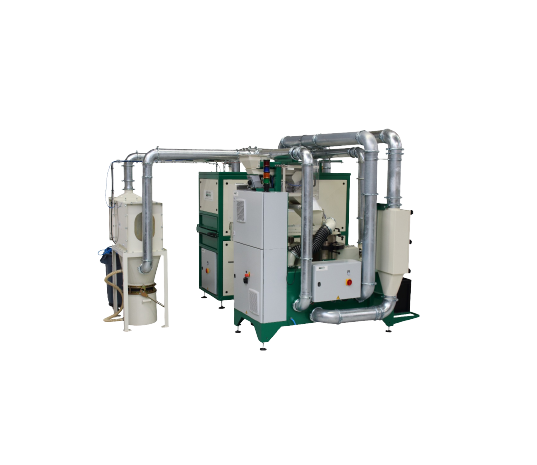
Seed Coating Machine With Integrated Dryer
Seed coating, also known as seed dressing, refers to the covering of seeds with...
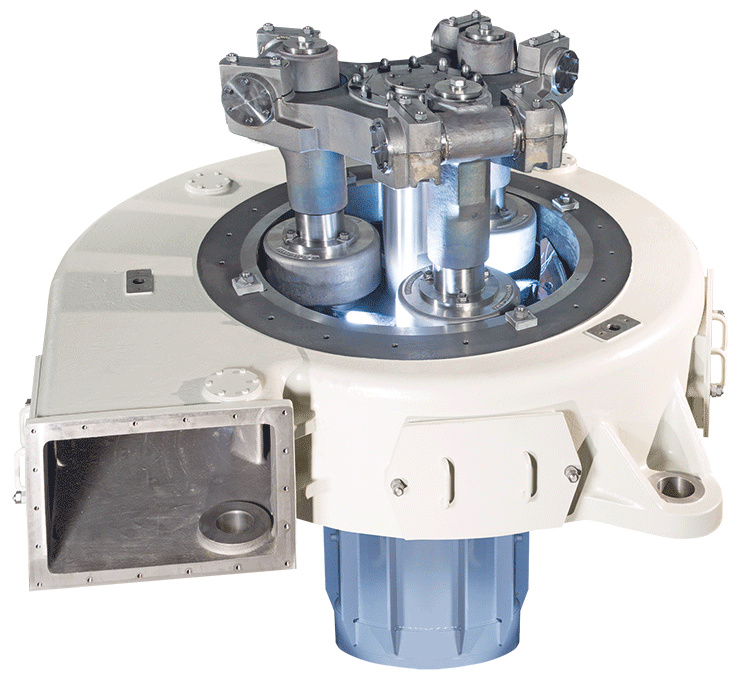
Grinding and drying of bentonite
After crushing and drying mined bentonite, this clay mineral is usually processed through a...
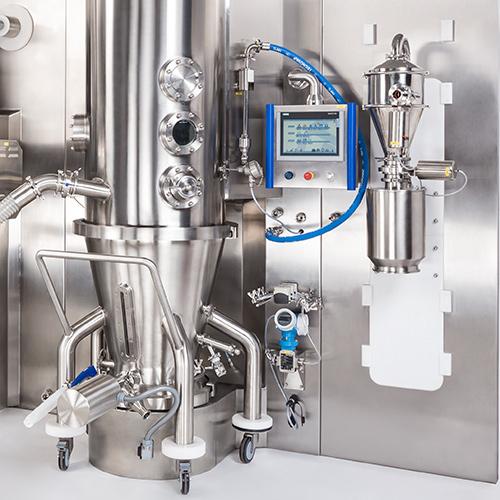
Fluid bed dryer for pharmaceutical solid dosage form
Fluid bed drying is a pharmaceutical process carried out to reduce t...
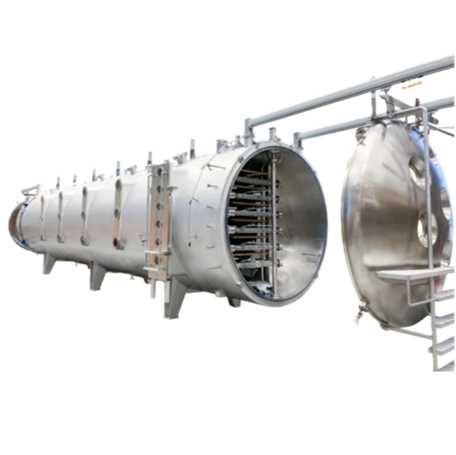
Vacuum belt dryer for instant drink powders
Extracting the essential acids and compounds from fruits and plants is a compl...
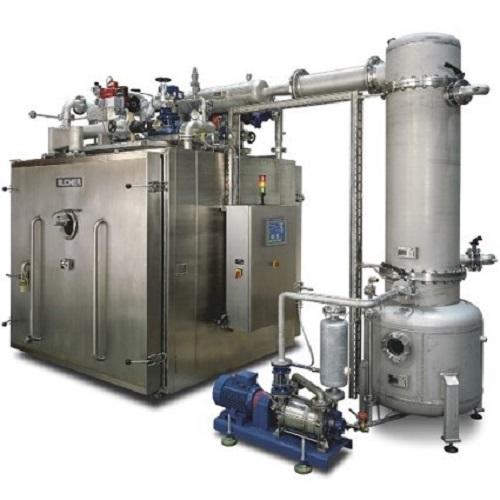
Vacuum cabinet dryer for plant extracts and functional foods
Plant extracts are vital to functional food preparations. B...
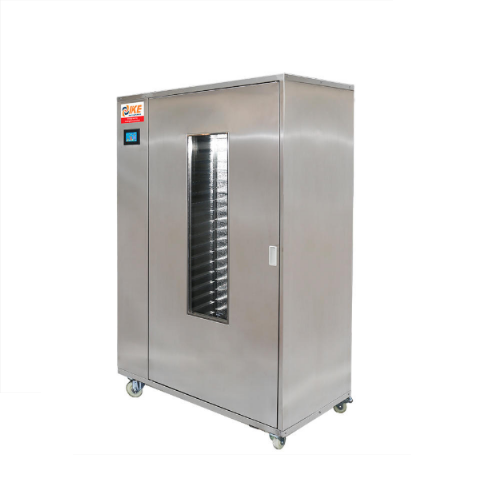
Industrial drying cabinet
The production of high-quality biltong and similar dried meat products can pose problems with main...
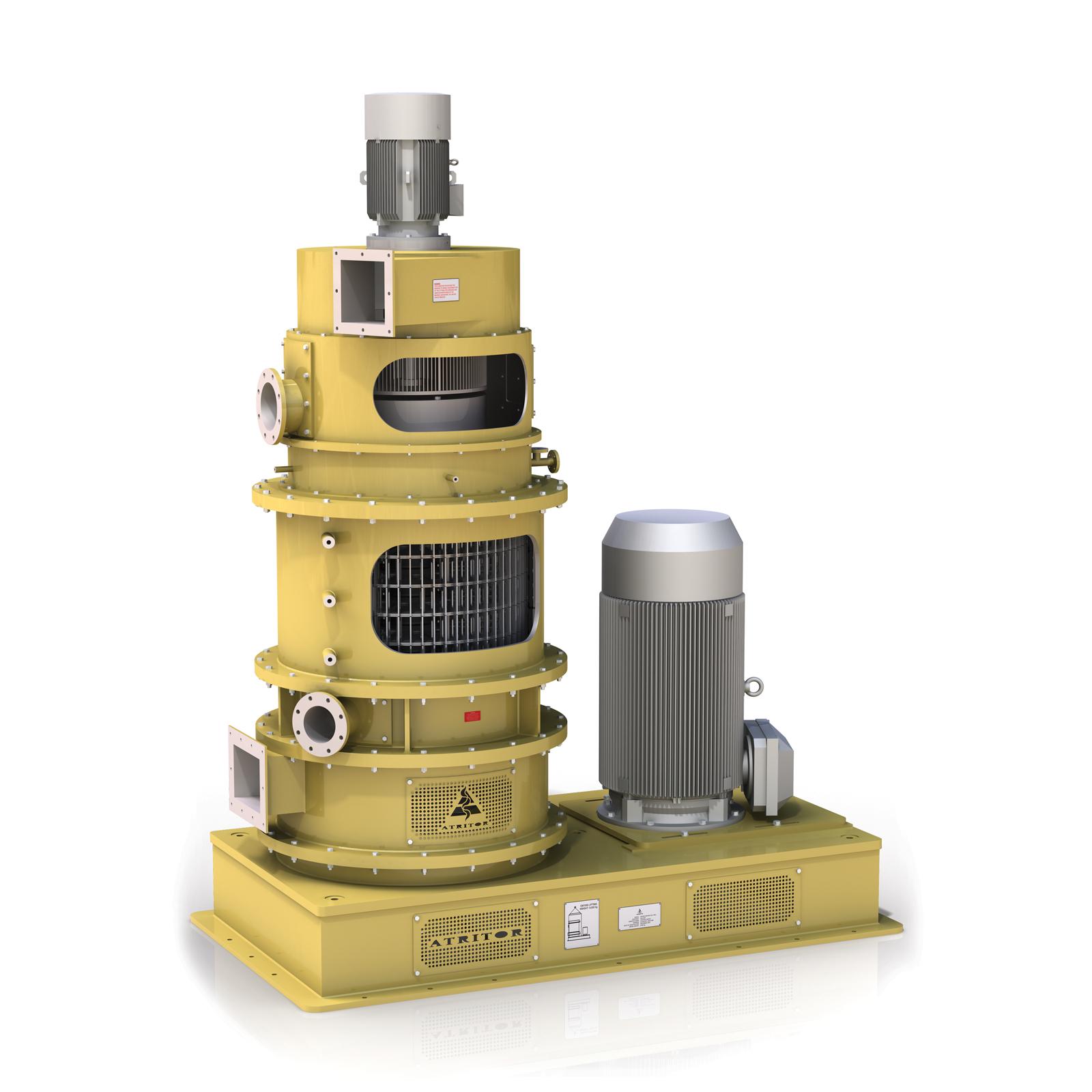
Milling and drying machine for fine powders
When you need to produce ultra-fine powders, the milling and drying process em...
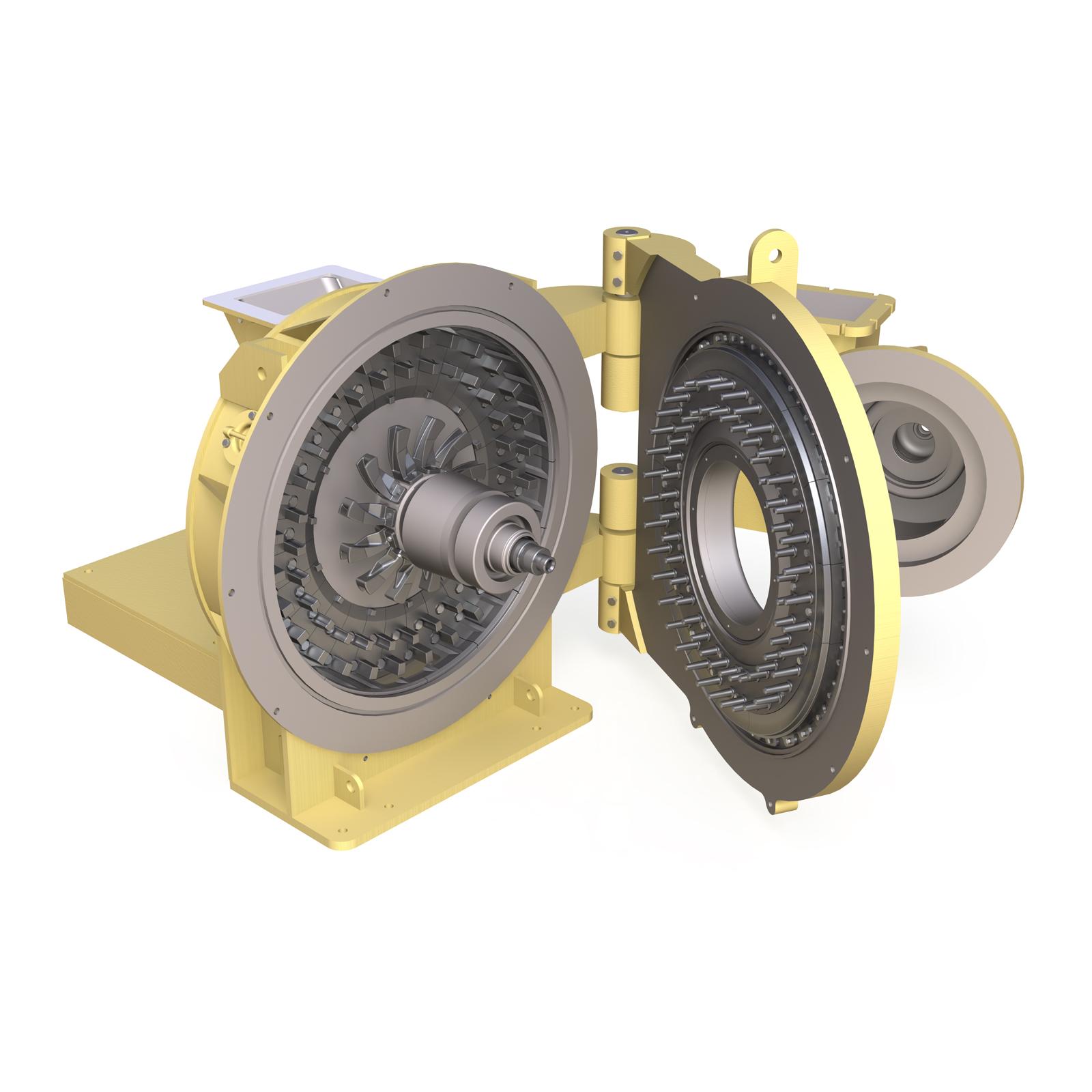
Flash drying grinder for powders
Drying and grinding can be an important feature when trying to process products such as raw...
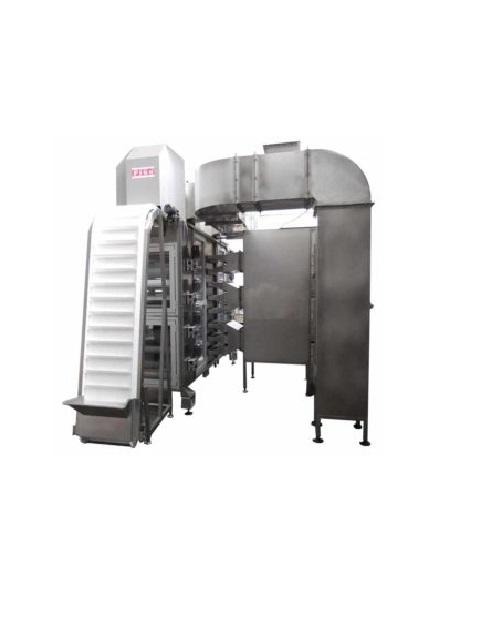
Industrial belt dryer for fruits and vegetables
The industrial belt dryer by Pigo is a simple yet super effective fruit an...
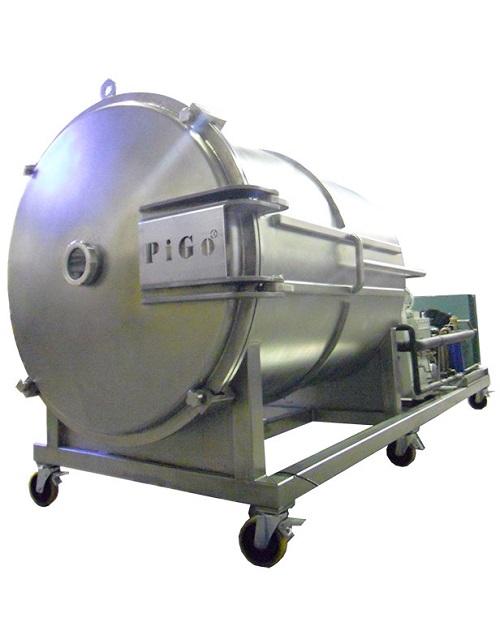
Industrial freeze-dryer for fruits
Freeze-drying is a complex and delicate process. If you are searching the market for a f...
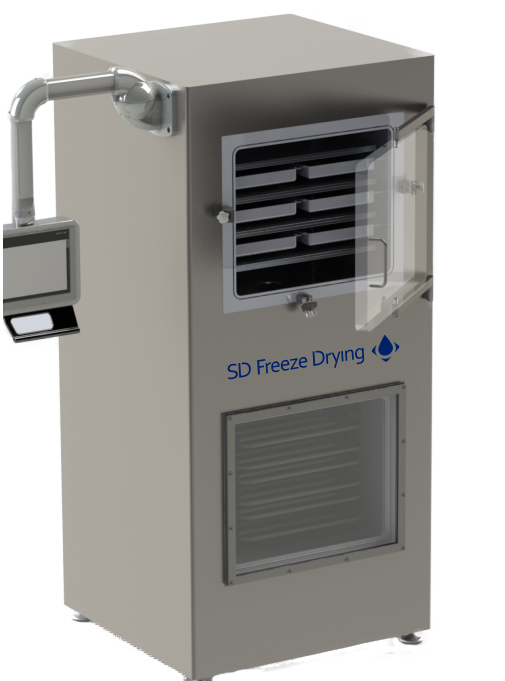
Pilot scale freeze dryer
Freeze drying is a complex and time-consuming drying process which requires maintaining the quality ...
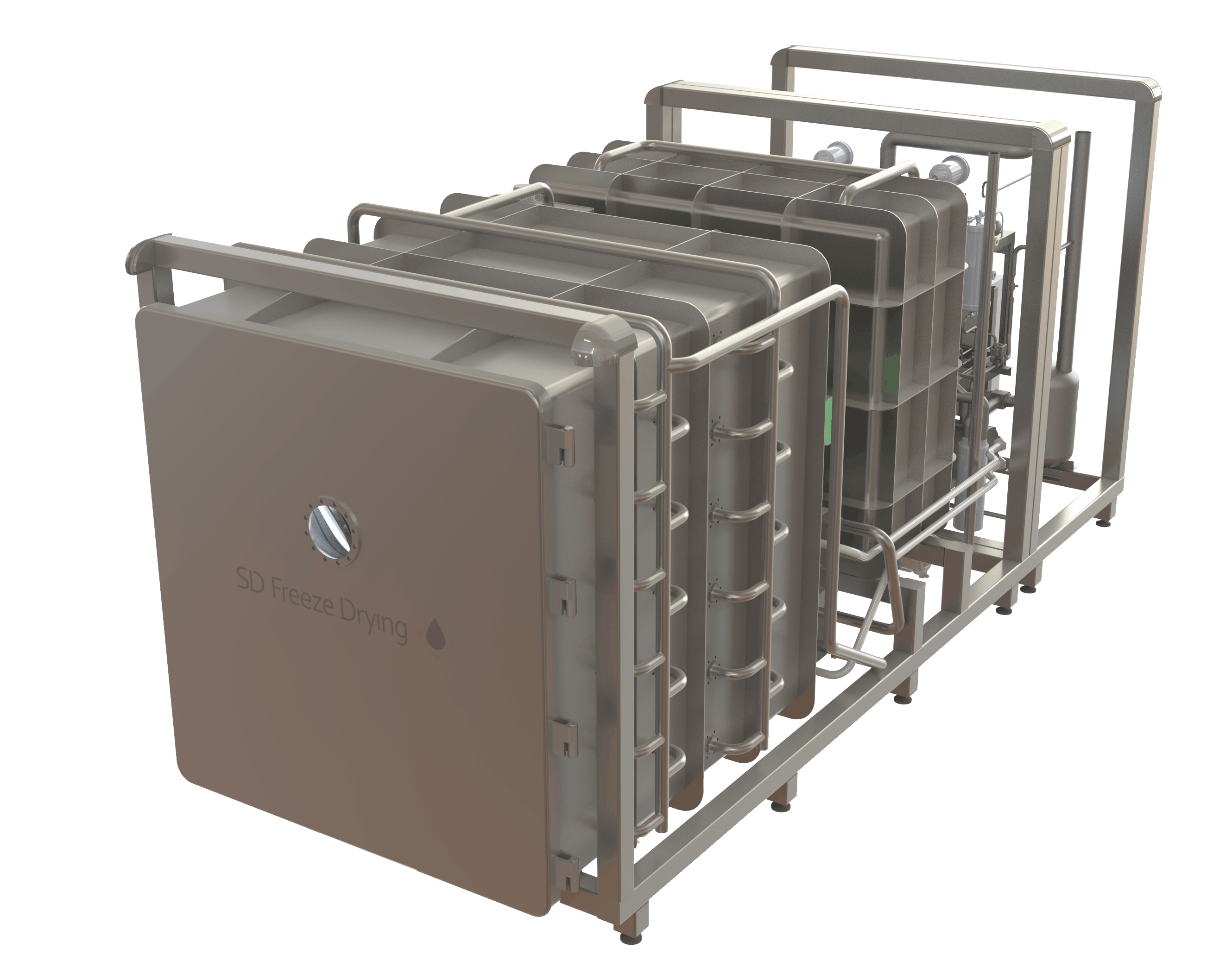
Industrial food freeze dryer
Nutraceuticals and dietary supplements can be highly sensitive and need to be protected against...

Automatic freeze drying system
Freeze drying can be an expensive and cumbersome process. When dealing with nutraceuticals it...
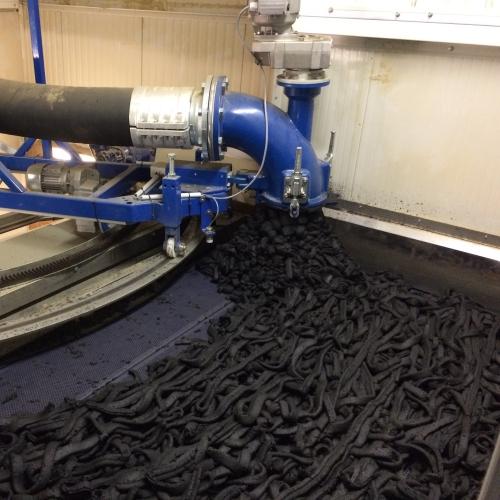
Belt dryer for sewage sludge
If your water treatment plant often facing difficulties with sewage sludge deposits, drying the...
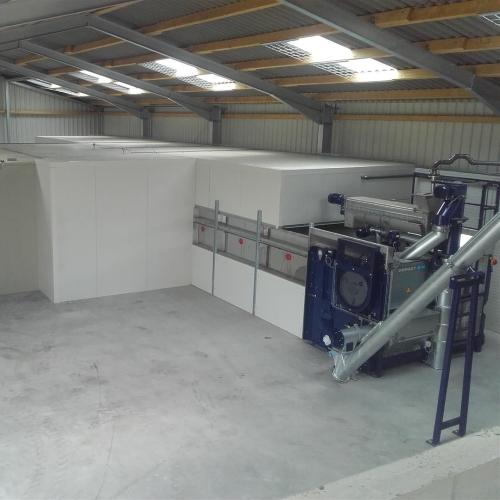
Belt dryer for digestate
The drying of poultry manure digestate requires careful and consistent moisture level control. A sus...
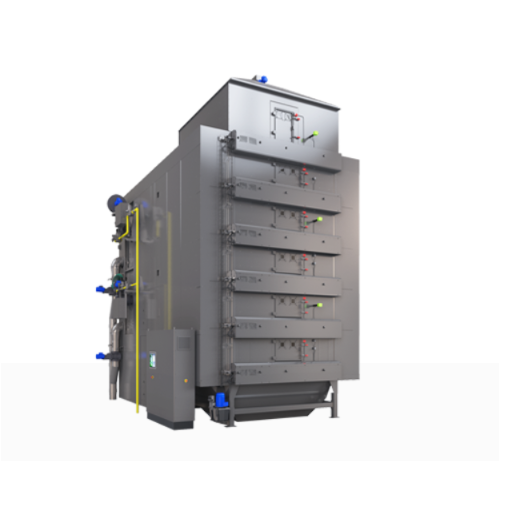
Recirculating batch dryer
Drying can be the most energy and time-consuming process in the food industry. This can have an ef...
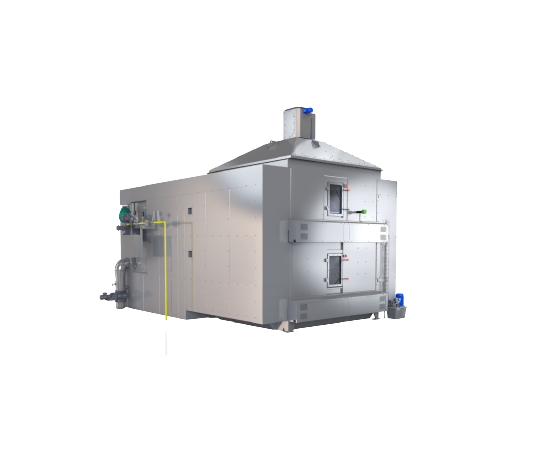
Continuous dryer machine
Traditional drying methods in the pet food, aquafeed, and extruded food industry can be the most ene...
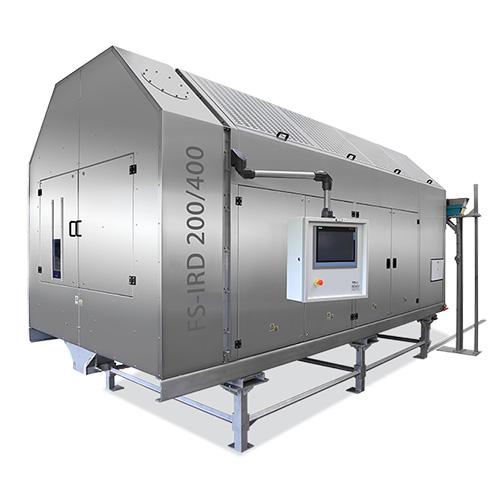
Infrared rotating drum dryer
Traditional drying methods are often slow and can actively damage ingredients, reducing the fin...
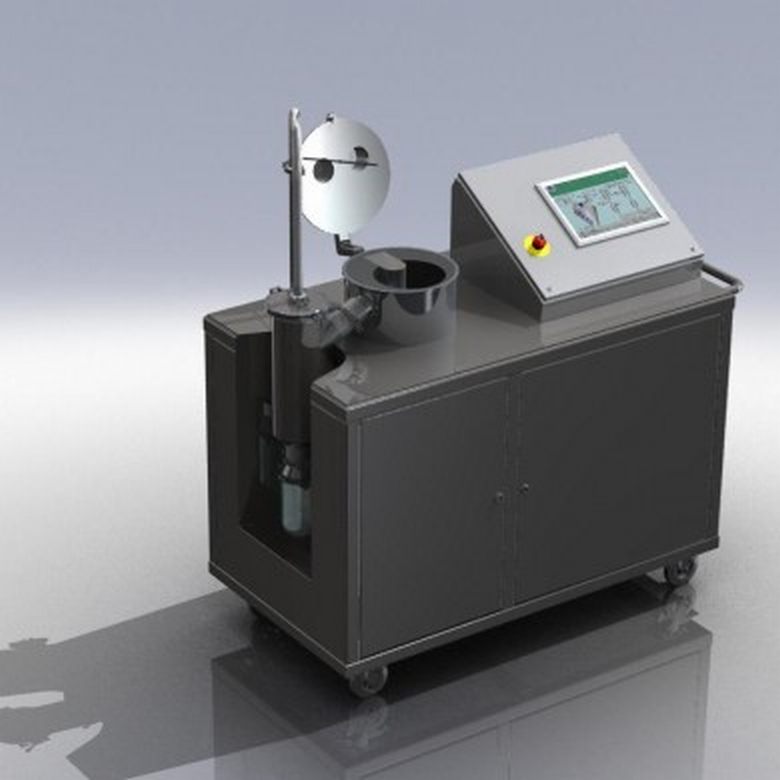
Laboratory scale active freeze dryer
The laboratory-scale active freeze-drying is used for dehydrating high-value products ...
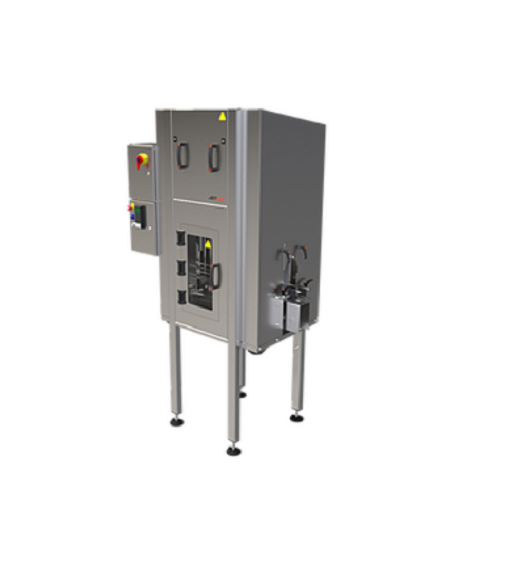
Air knife drying system for containers
In food or beverage production where a product is filled into jars, there is often r...
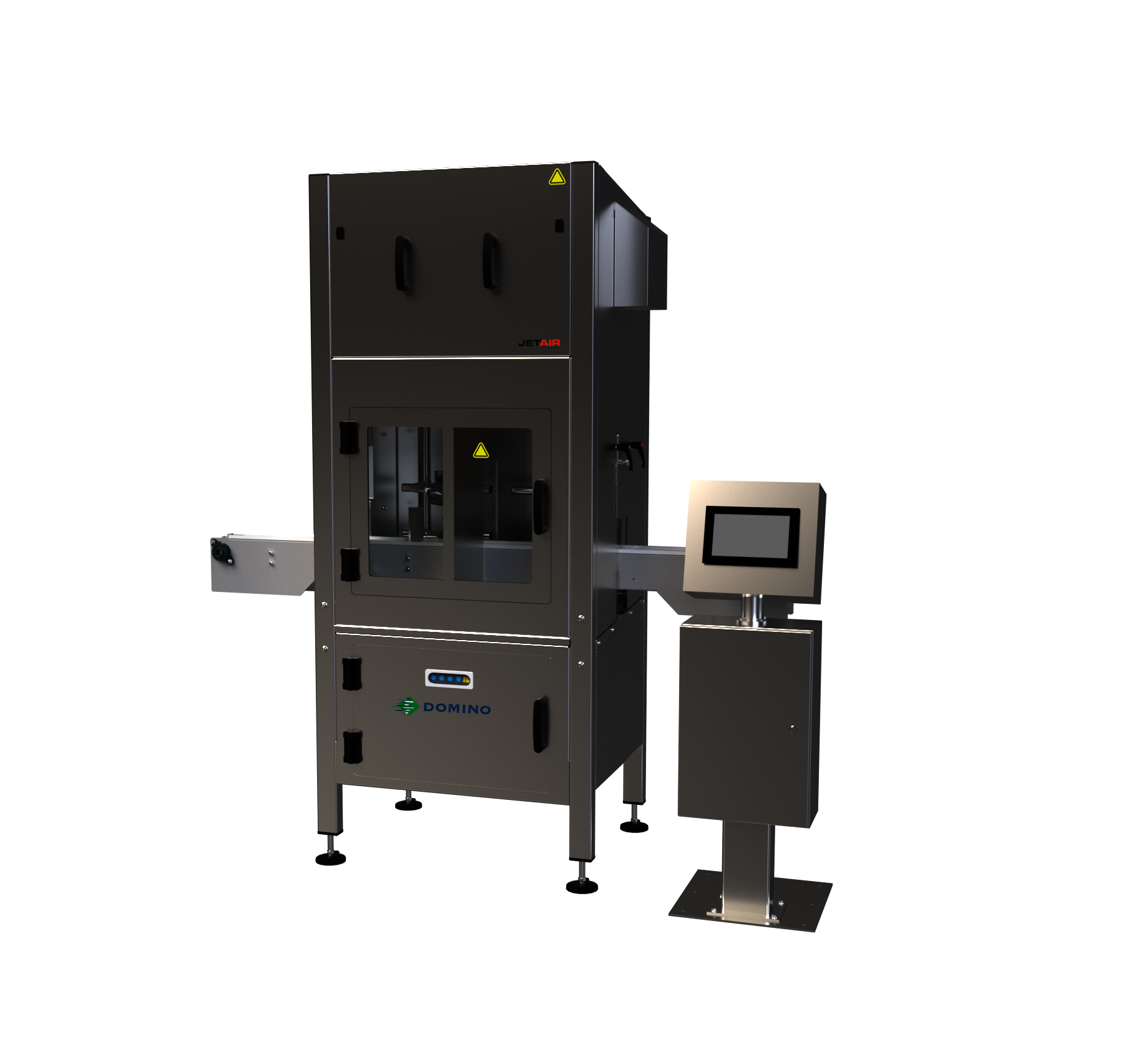
Code printer for cans with integrated drying system
Printing date and batch code information on canned consumer items req...
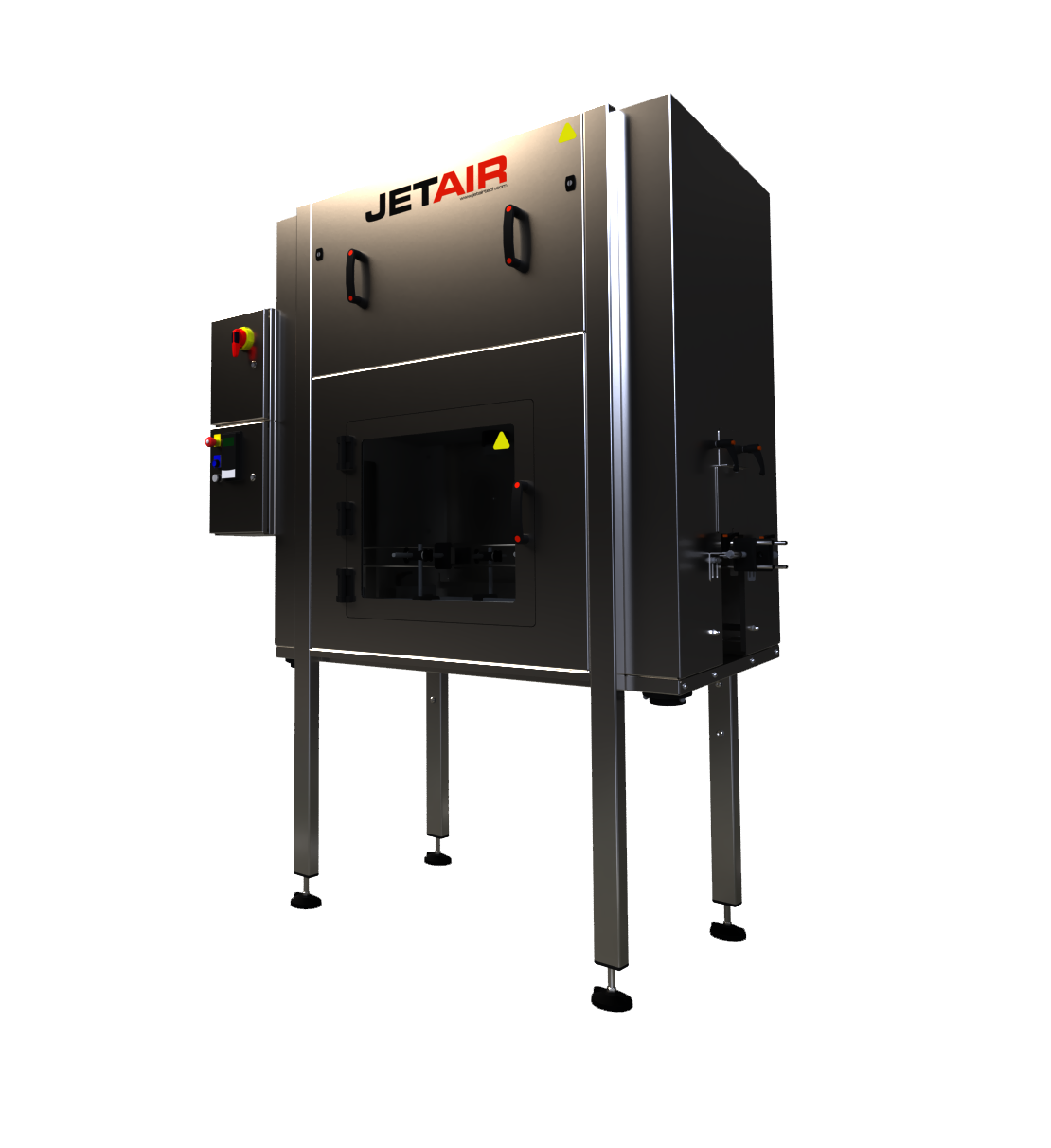
Air knife dryer for bottles
When filling glass bottles during beverage production, the cleaning and filling processes often ...
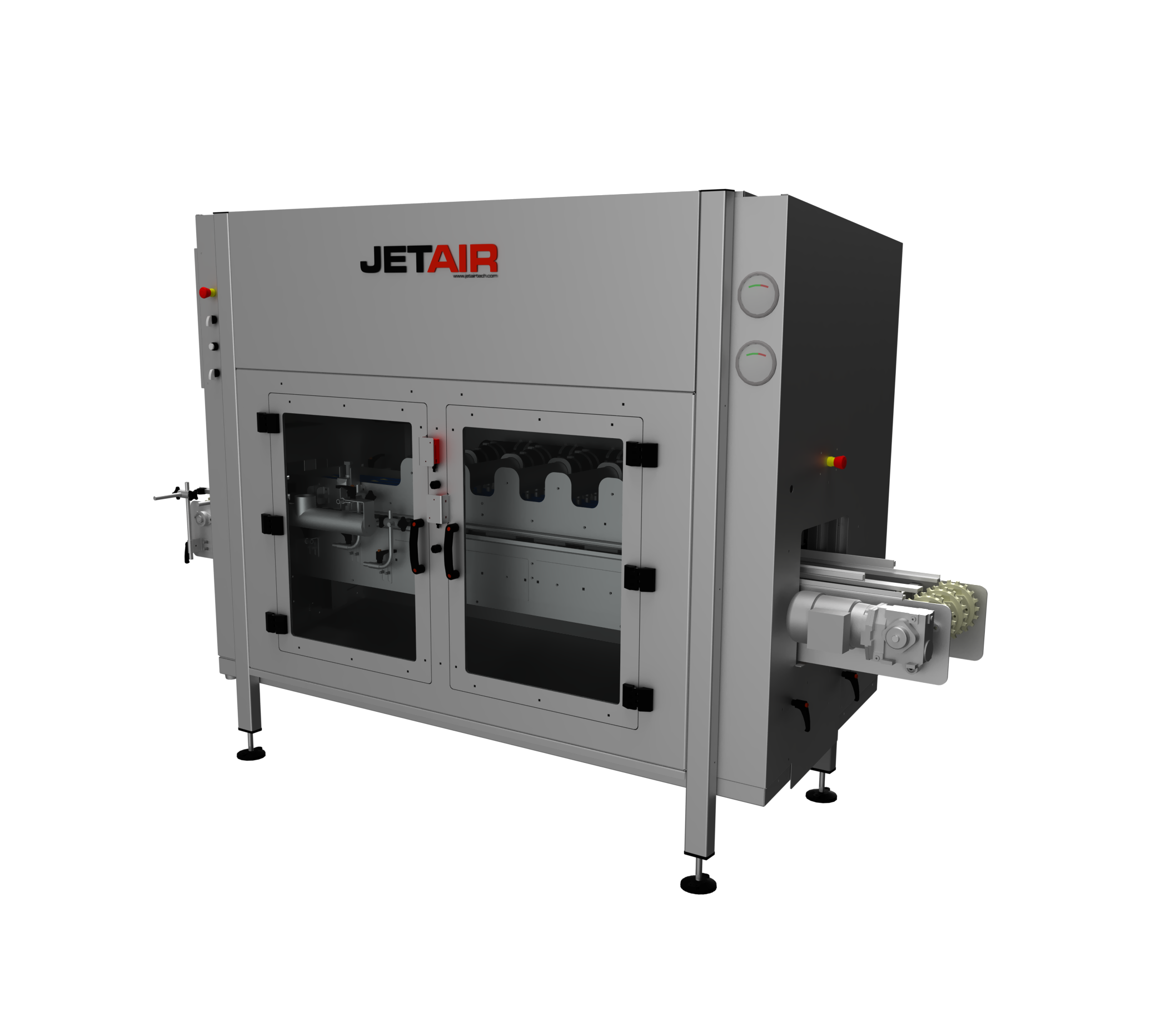
Air knife dryer for pouches
Flexible pouch packaging is a popular choice for many consumer food products. Before final print...
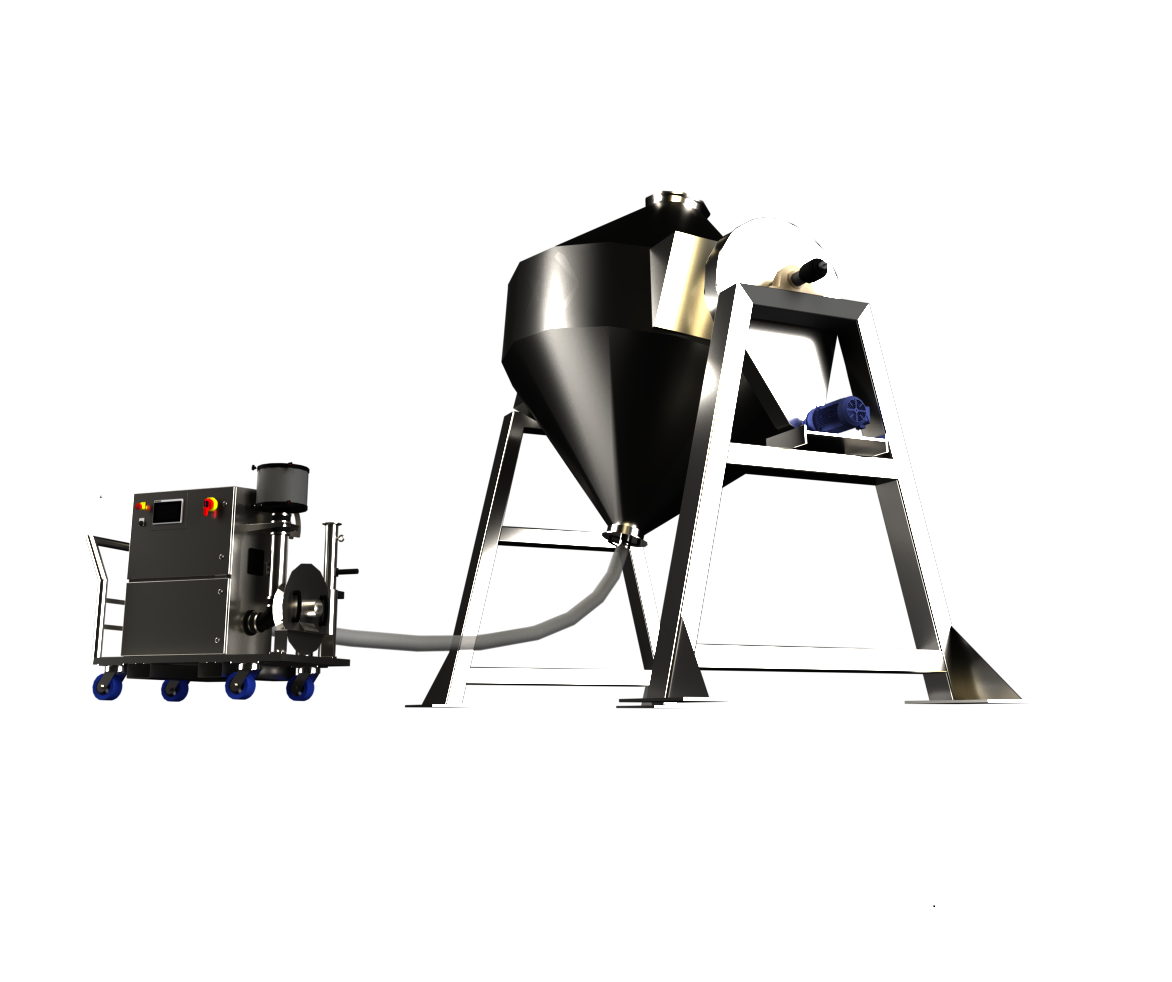
Mobile air knife dryer for tanks
Sanitizing and cleaning of large vessels such as storage tanks or blenders is a vital stage...
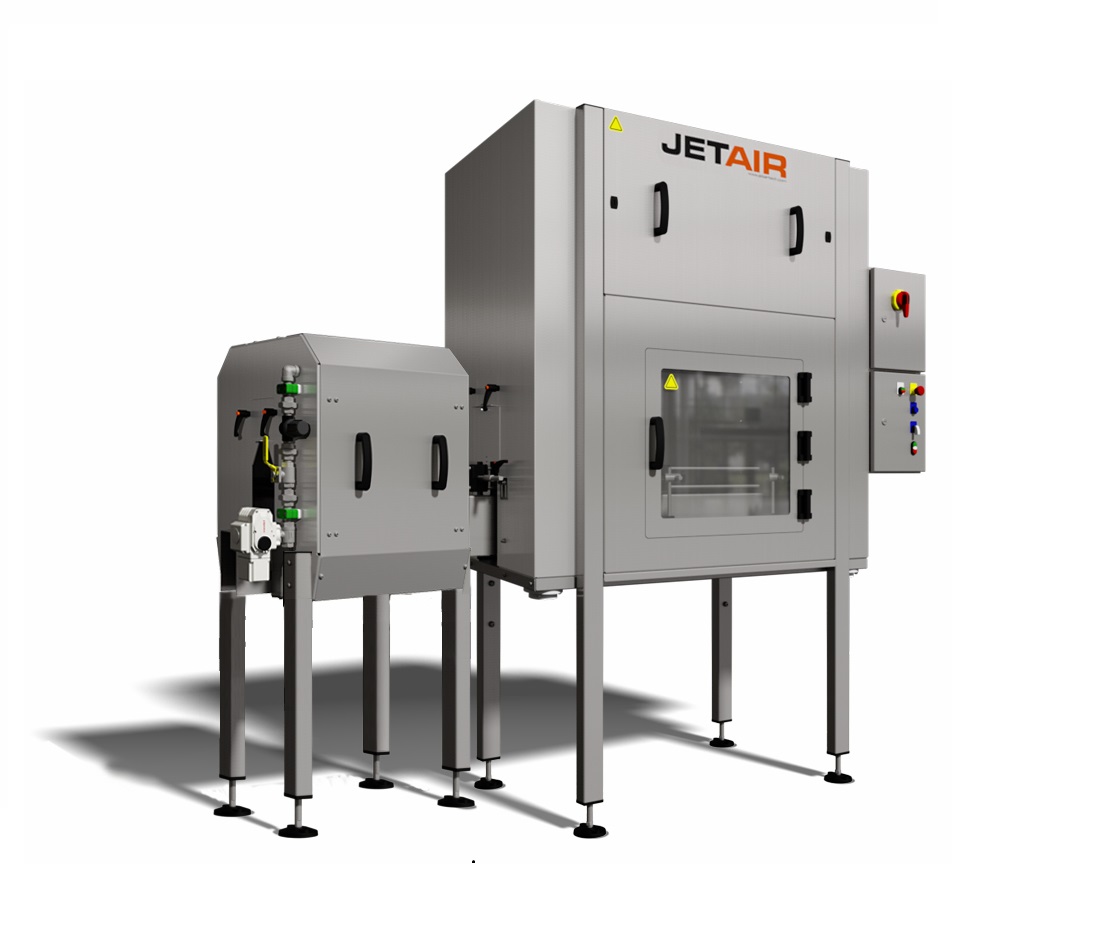
Rinsing and drying system for containers
The filling of containers used in a range of consumer-packaged goods often leads t...
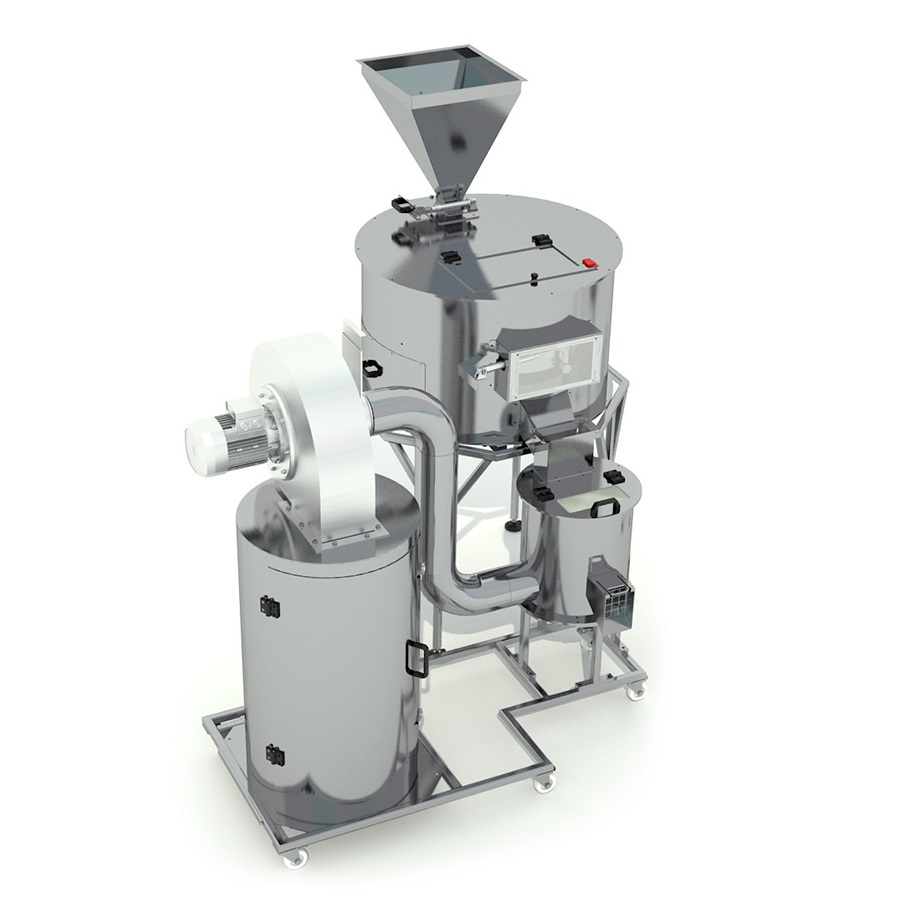
Entry-level infrared nut drying machine
For small scale production of cocoa beans and nuts, the use of traditional toasters...
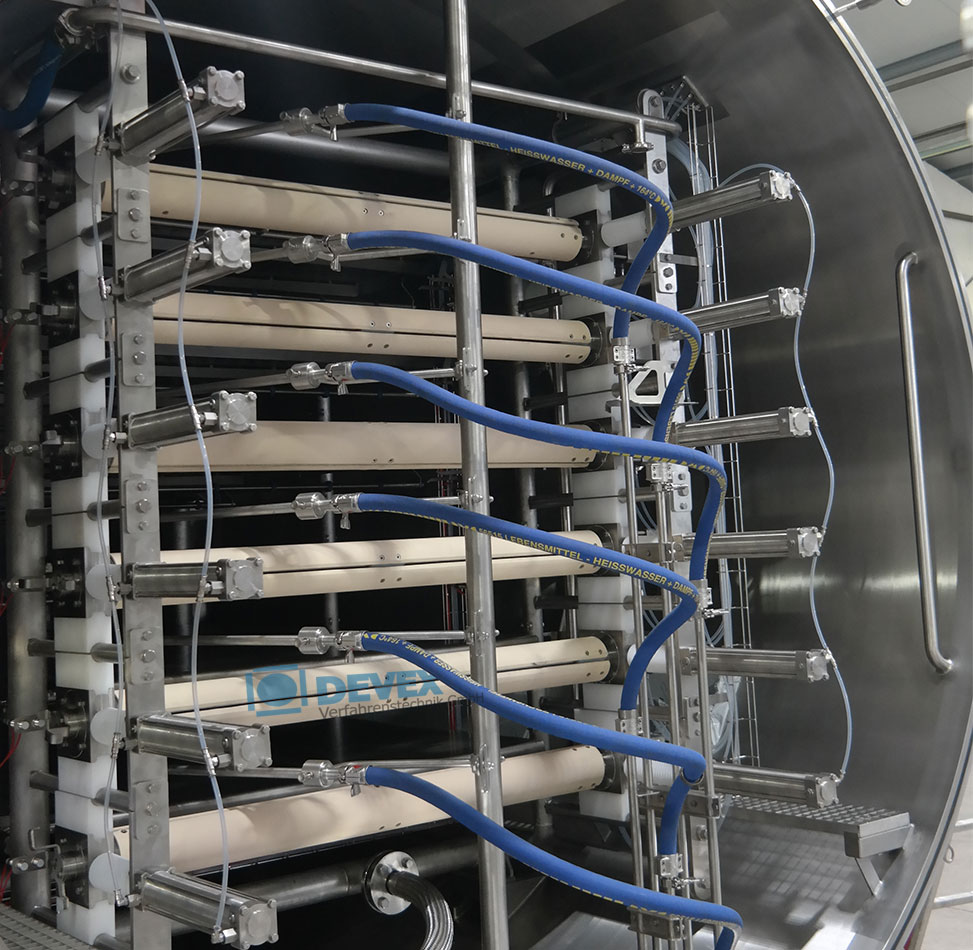
Continuous vacuum belt dryer
For gently drying liquid concentrates into granulates or powders, a vacuum drying solution is t...
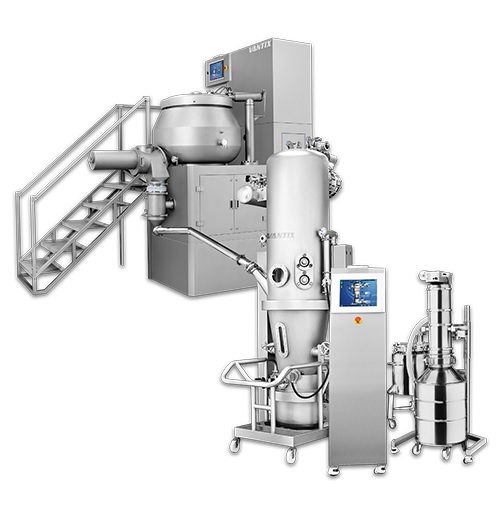
Granulation line of mixer and fluid bed dryer
A complete granulation line allows for the mixing and granulation of pharmac...
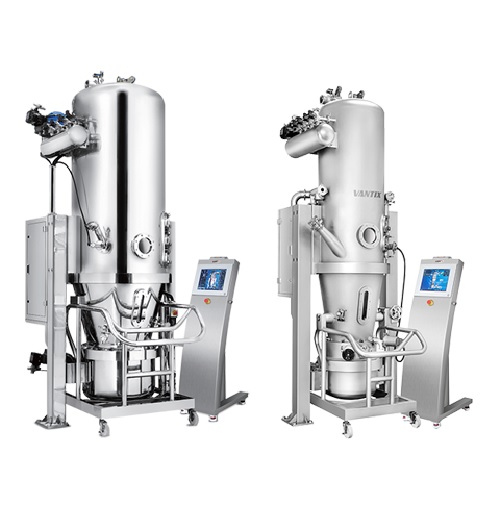
Fluid bed dryer for production scale
Fluidized bed drying (FBD) is a common process in the pharmaceutical industry for dryi...
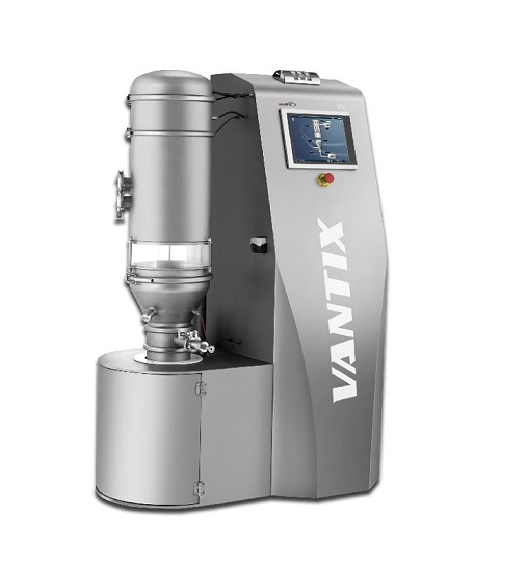
Fluid bed dryer for lab scale
Fluidised bed drying (FBD) is a common process in the pharmaceutical industry for drying compo...
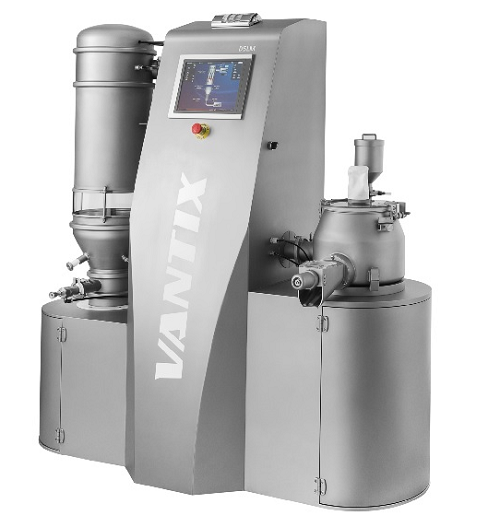
Fluid bed dryer and mixer for lab scale
Designed for pharmaceutical R&D, a lab-scale fluid bed dryer and mixer/granulat...
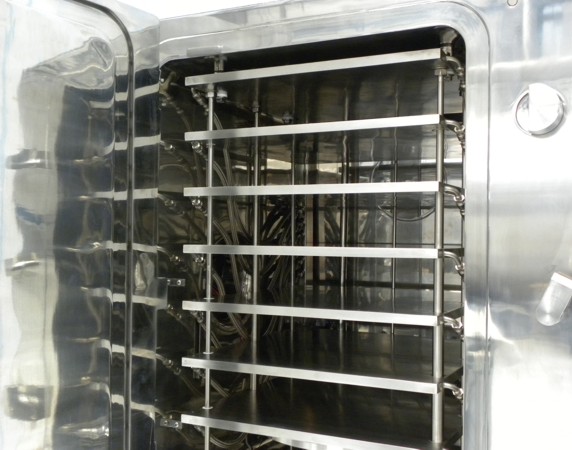
GMP laboratory freeze dryer
Freeze dryer designed for aseptic and small-scale production of high-value products.
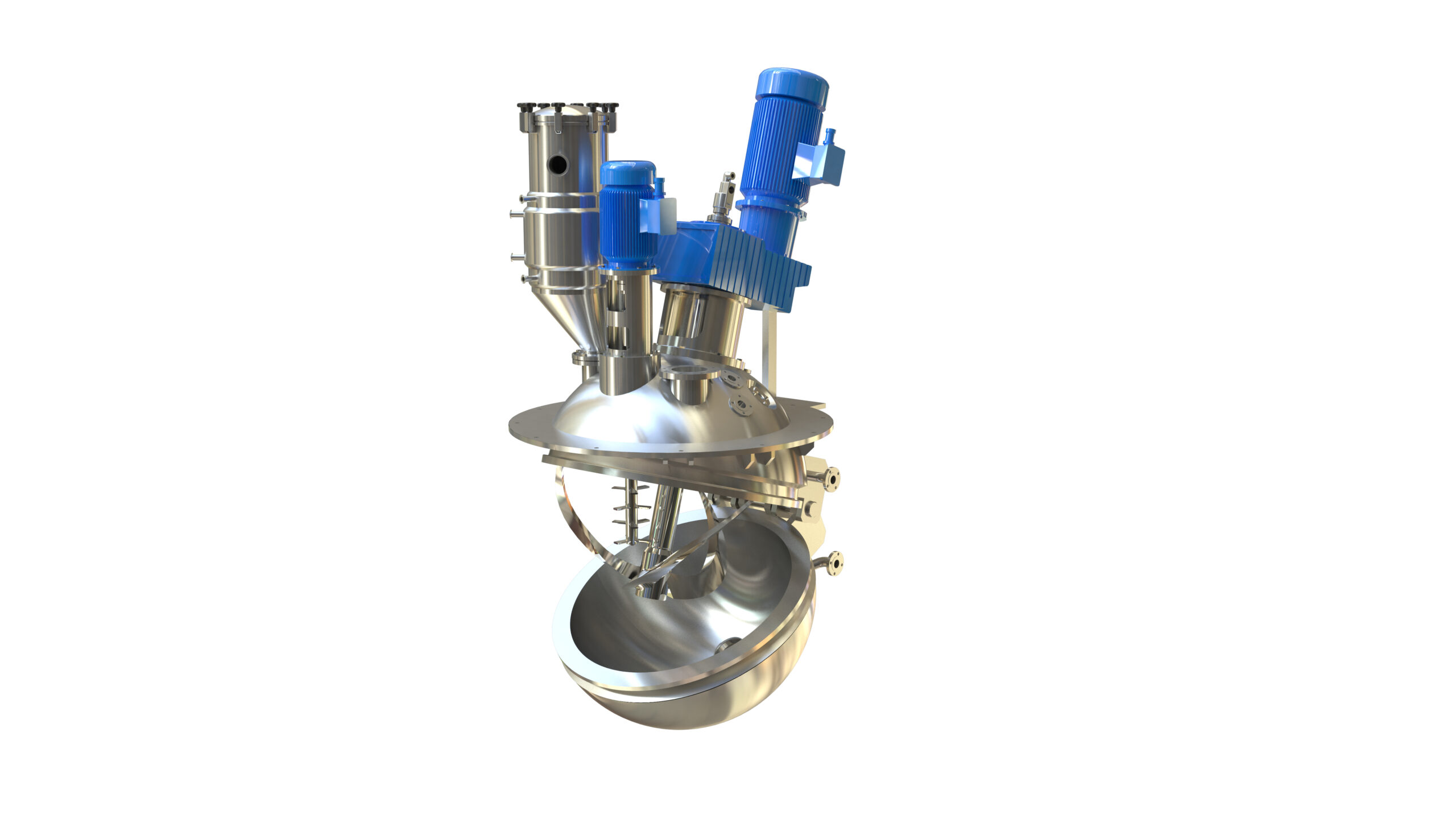
Spherical dryer
Drying vessels that are simple, reliable, and easy to maintain increases product quality and process efficienc...
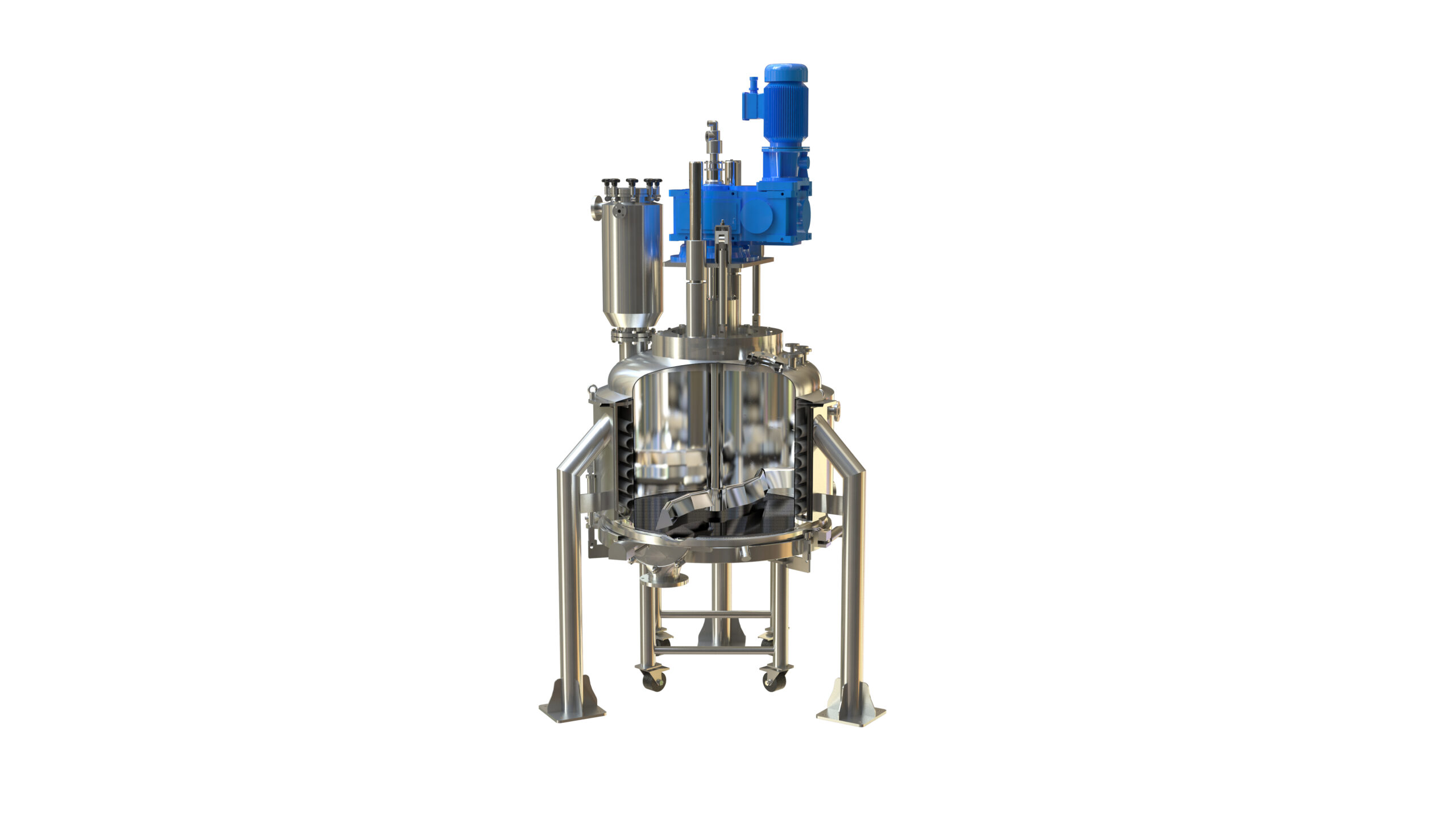
Filter dryer
The pharmaceutical and bioprocess industries need filtration processes of particularly high quality to ensure the...
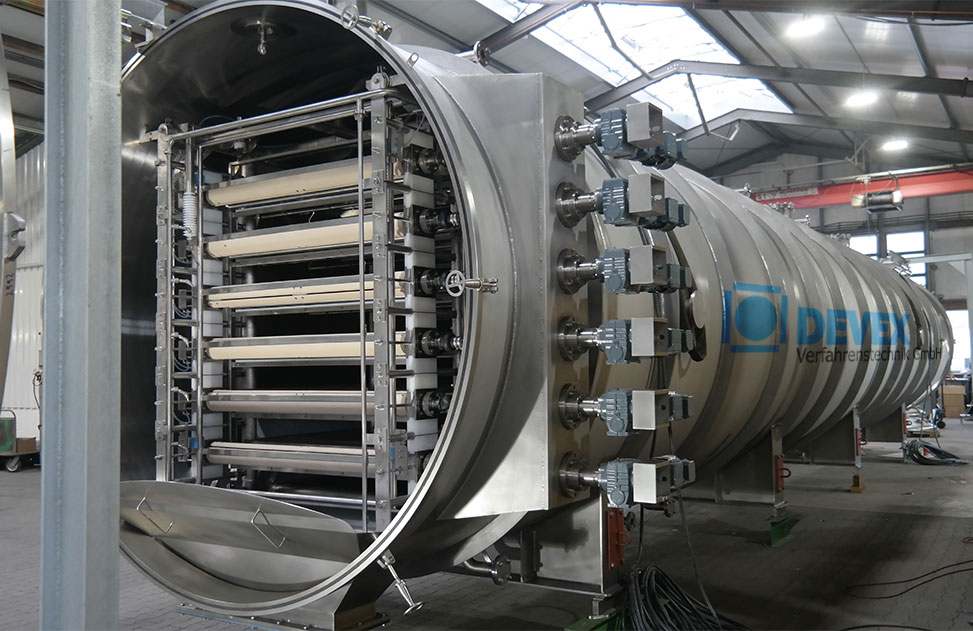
Continuous belt freeze dryer
Freeze drying is the most gentle and aroma protective method of drying, widely used in the coff...
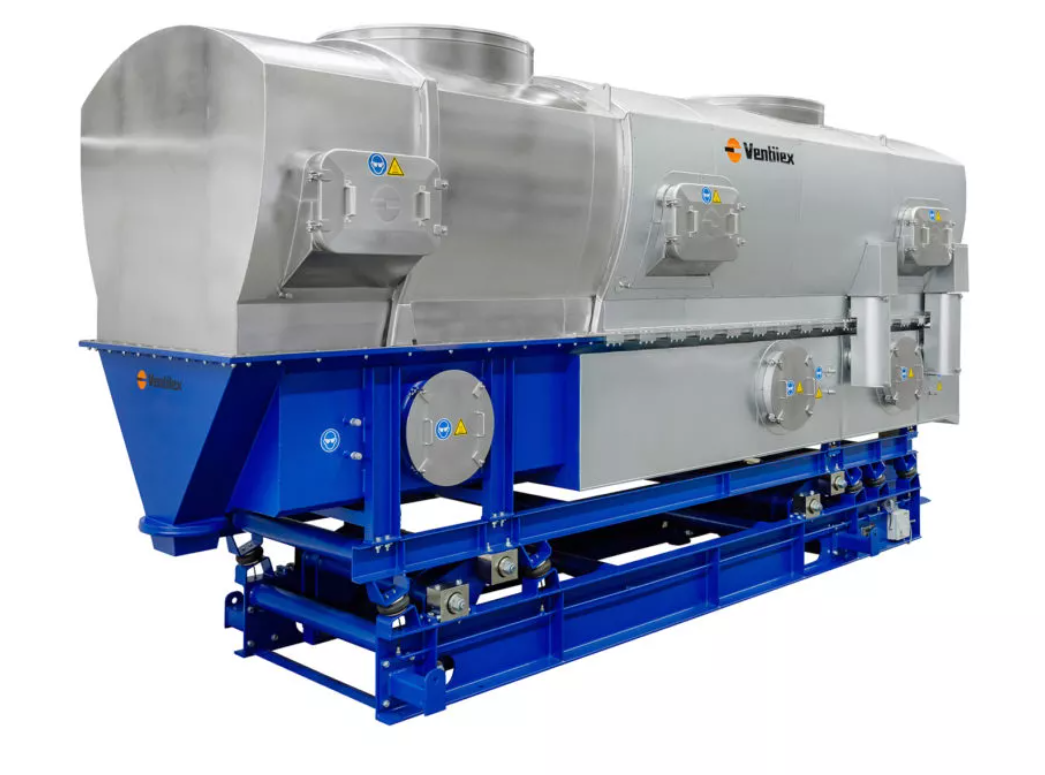
Continuous fluid bed dryer
In a Fluid Bed, a product or solid is made fluid by an upward moving flow of gas. The mechanical ...
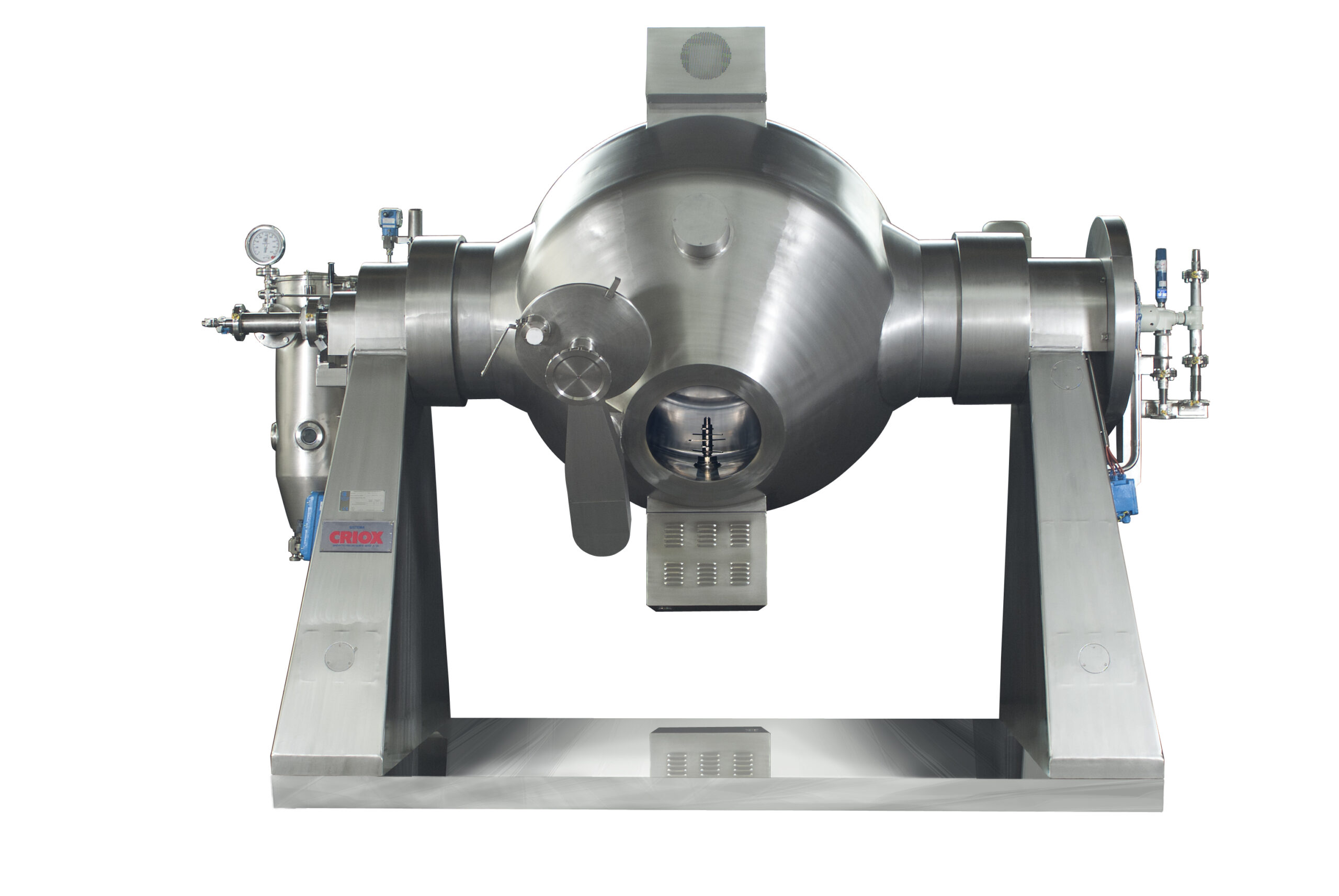
Rotary vacuum dryer
Powdered products tend to agglomerate during vacuum drying. This adds an additional step to the productio...
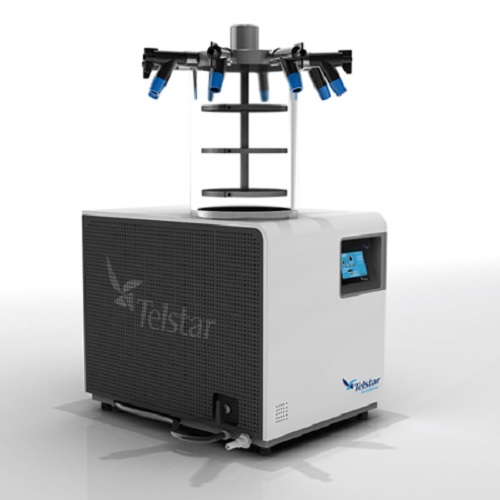
Multipurpose and R&D freeze dryer
A multipurpose unit in the research and development field. Some of the most common applic...
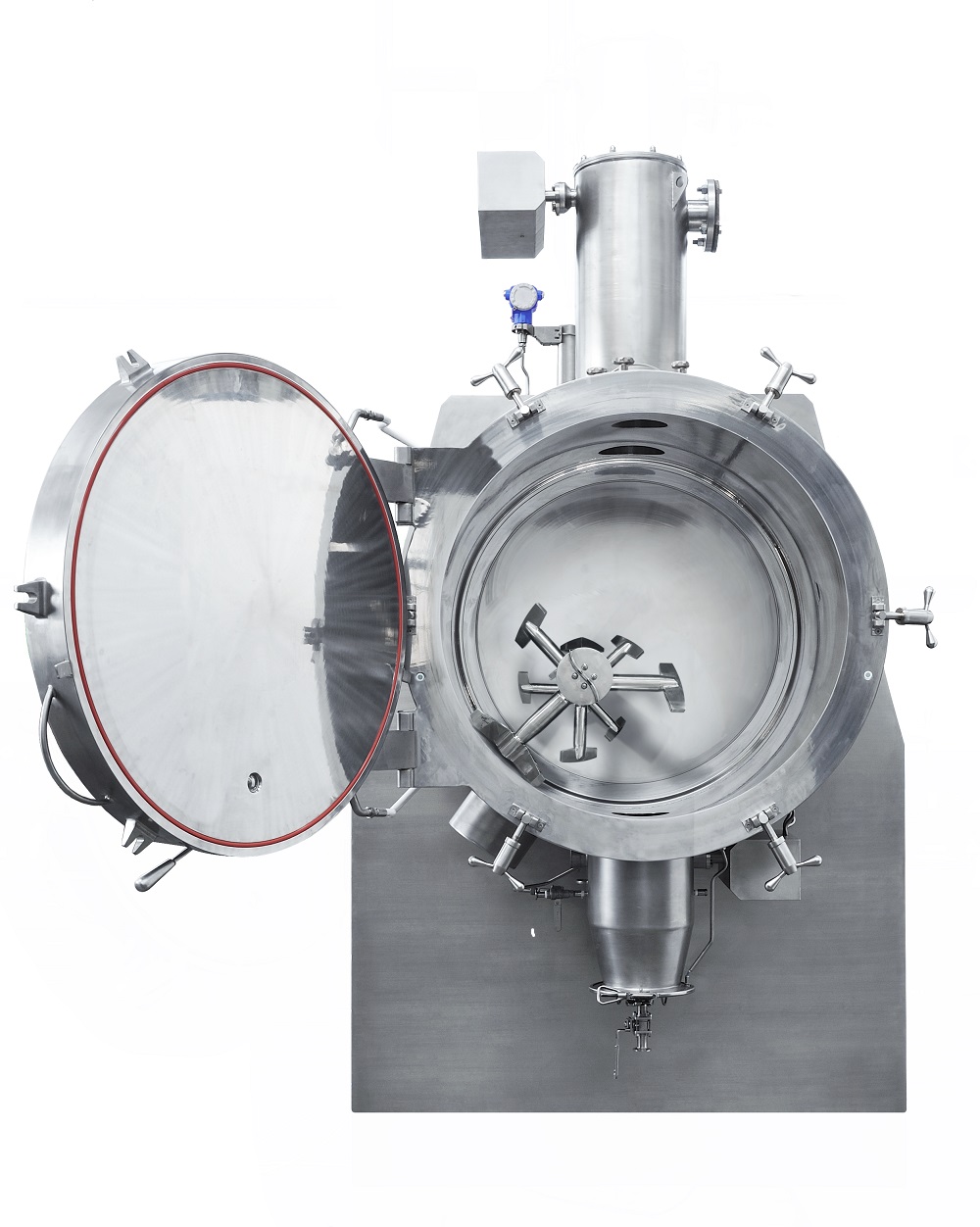
Horizontal vacuum dryer with eccentric agitator
Conventional dryers are inefficient and can lead to significant mechanical...
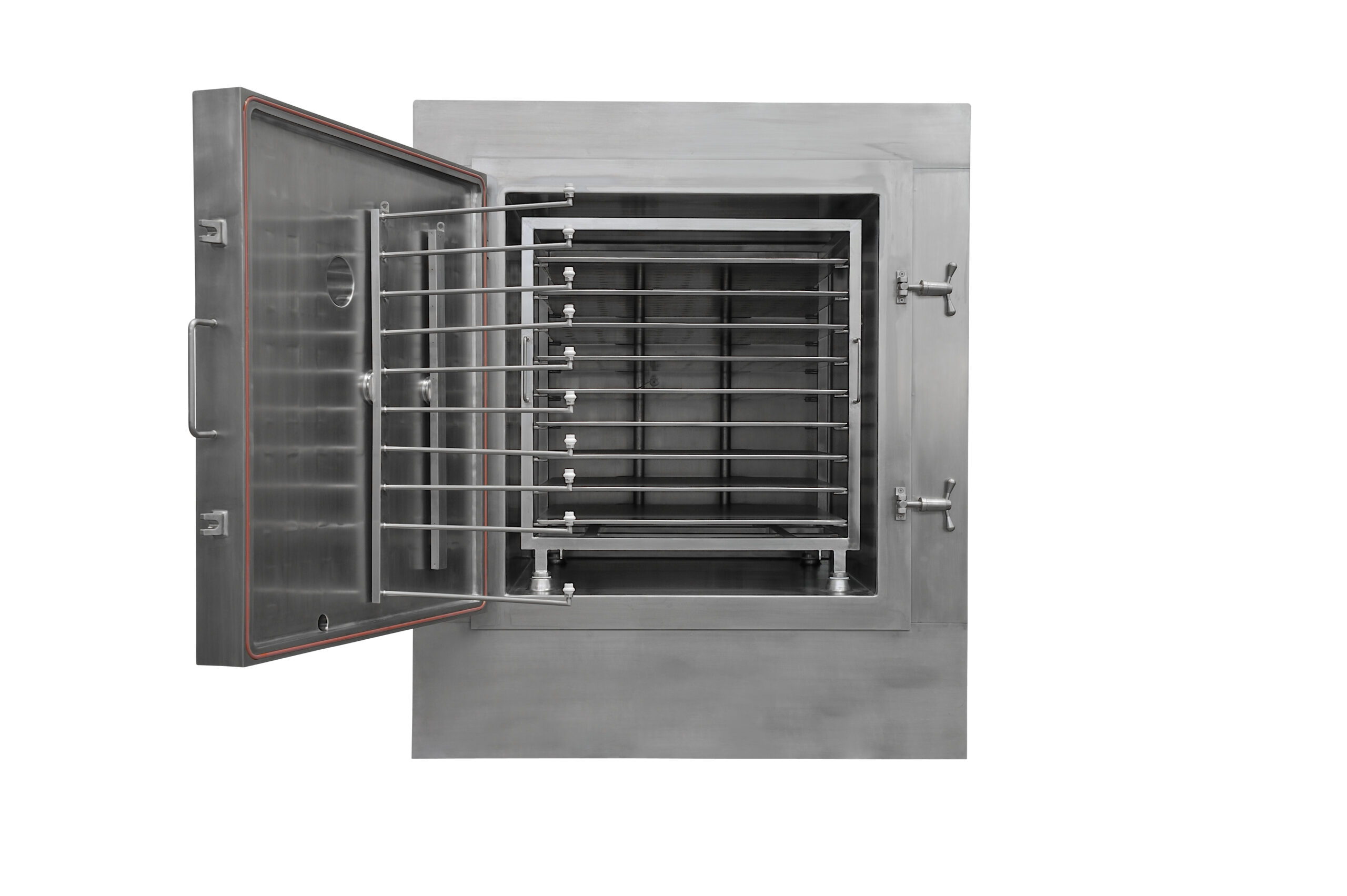
Vacuum tray dryer with clean-in-place system
Cabinet tray dryers can be difficult to clean, making their use difficult for...
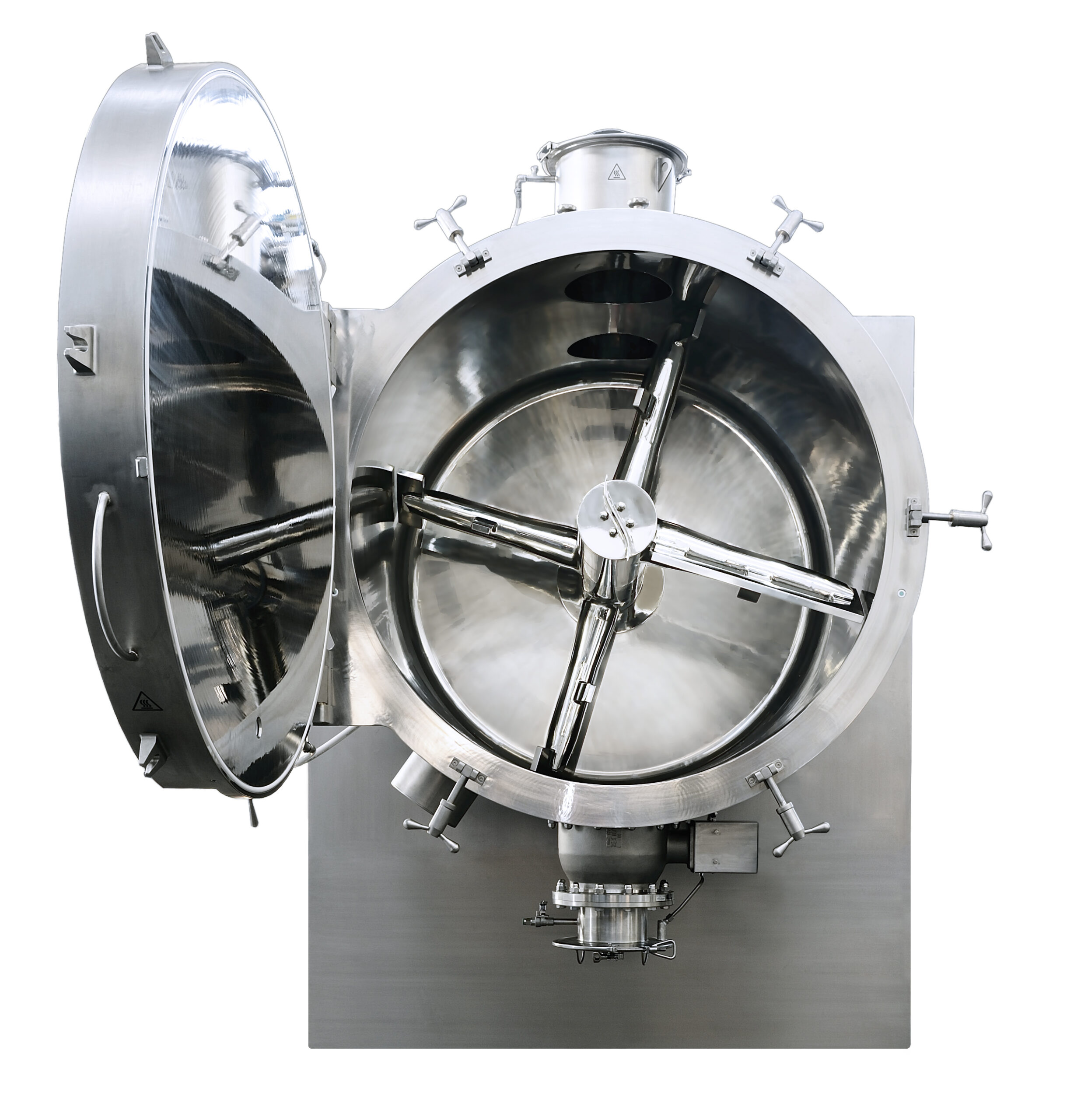
Horizontal paddle vacuum dryer
Agitated vacuum dryers can be difficult to clean which makes them unsuitable for multi-produc...
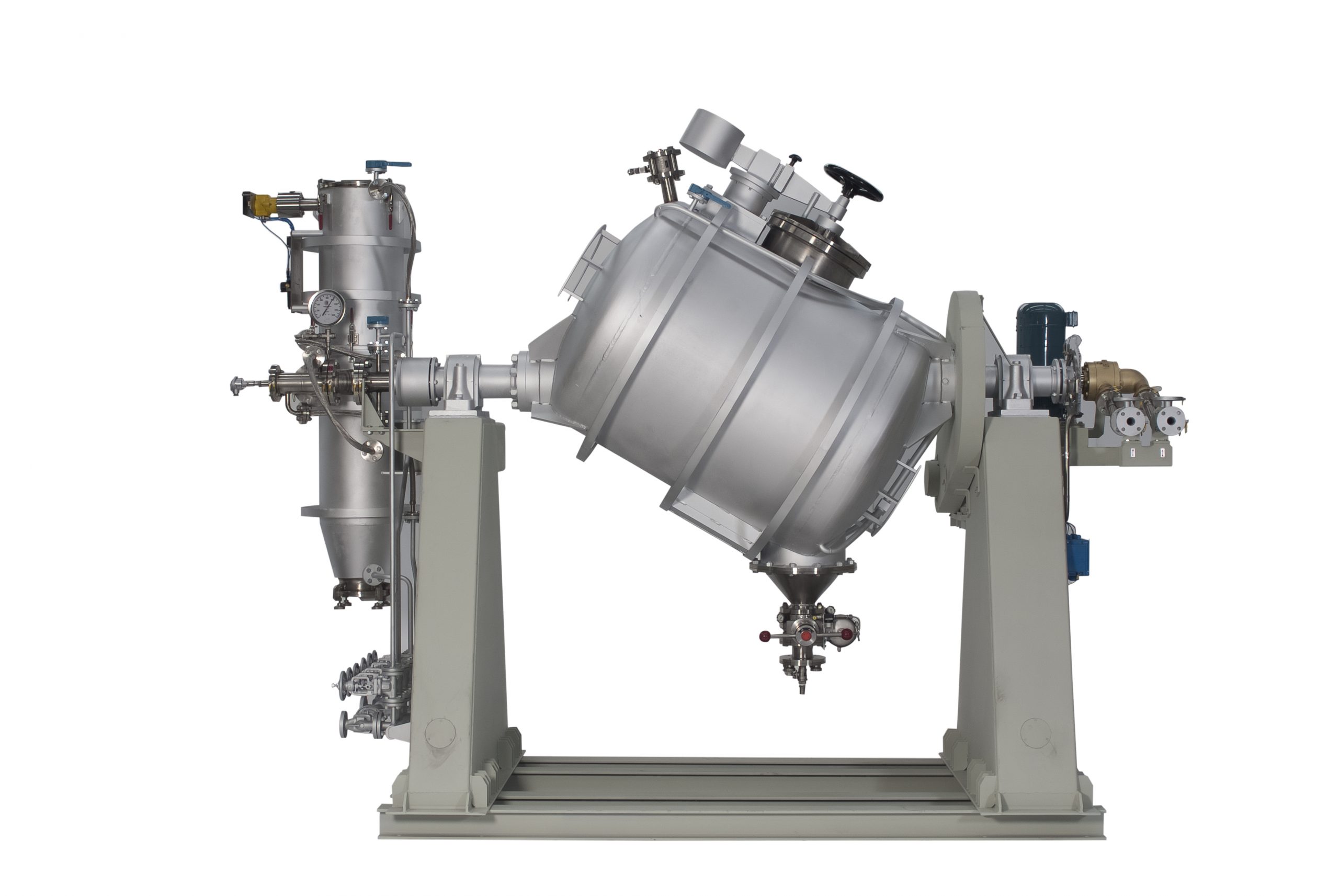
Tumble dryer for granulated plastics
Vacuum drying at high temperatures is important in the production of granulated plasti...
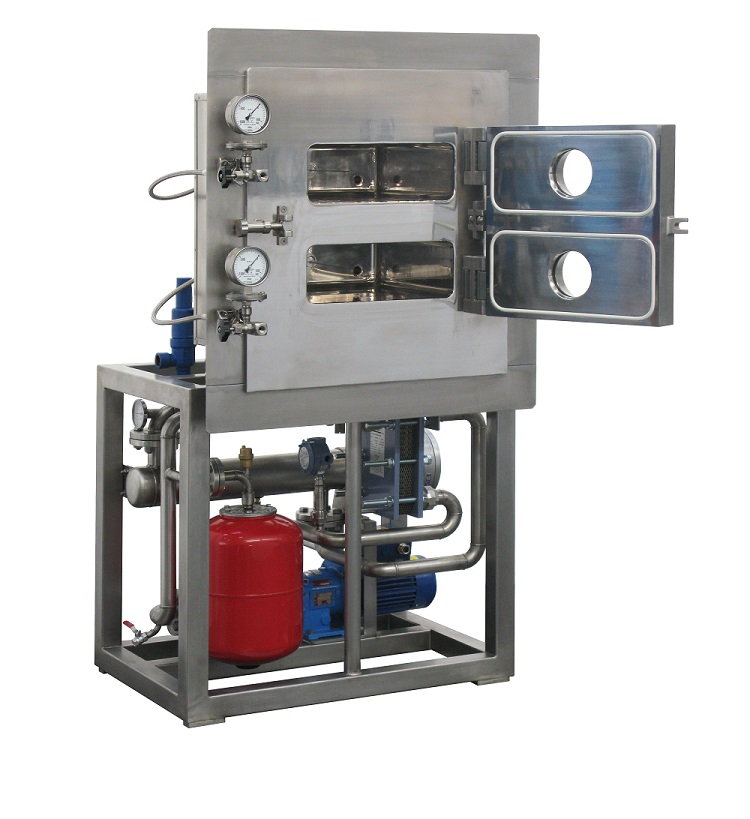
Laboratory-scale vacuum tray drying oven
Vacuum drying is used to remove moisture from sensitive materials. Drying small ba...
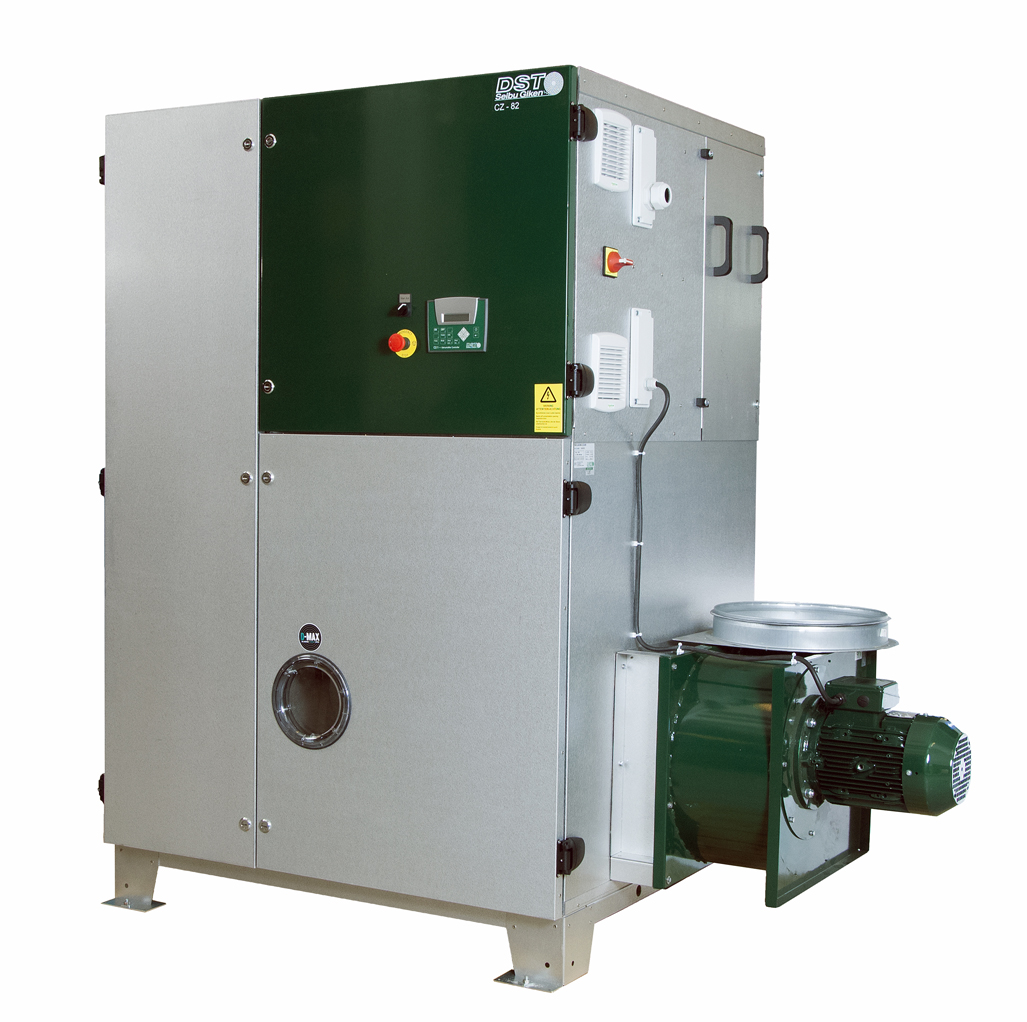
Sorption dehumidifier for deep drying
Humid ambient conditions such as those in tropical climates make dehumidification mor...
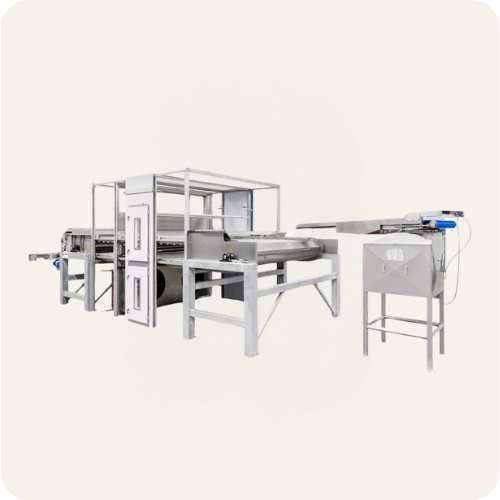
Hygienic belt dryer
A belt dryer typically applies the product through an infeed chamber onto a perforated horizontal belt, w...
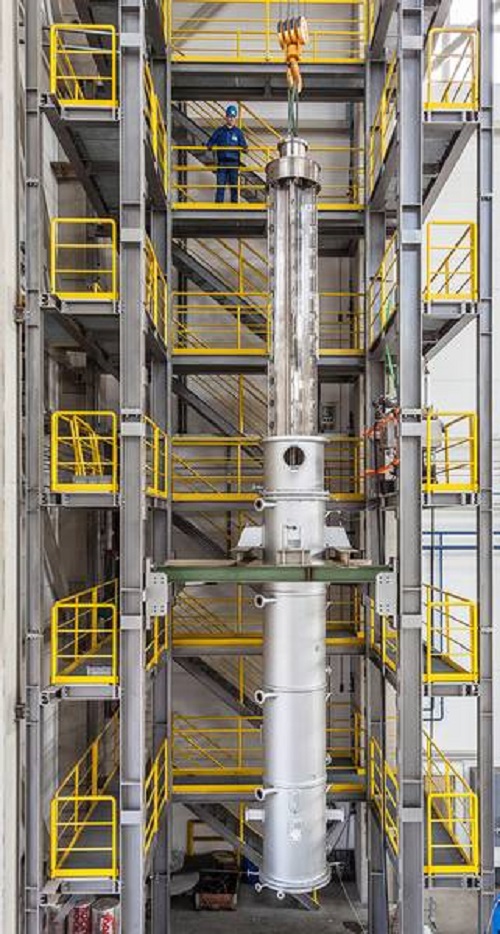
Thin film dryers
Dry dissolved or slurried crystallizing or amorphous products to a pourable powder.
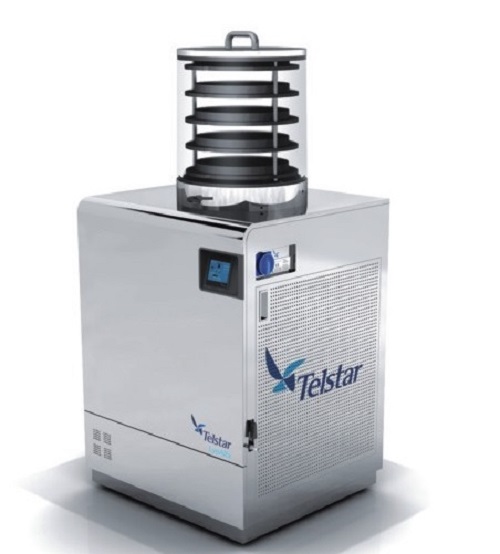
Compact laboratory freeze dryer
Particularly suitable for research centers requiring greater freeze drying capacity. Some of...
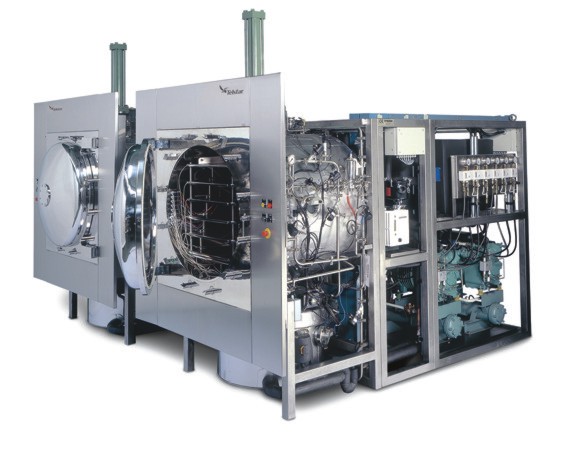
GMP freeze dryer
Designed to perform clinical trials, pilot, and small scale or large scale industrial drying processes, in ac...
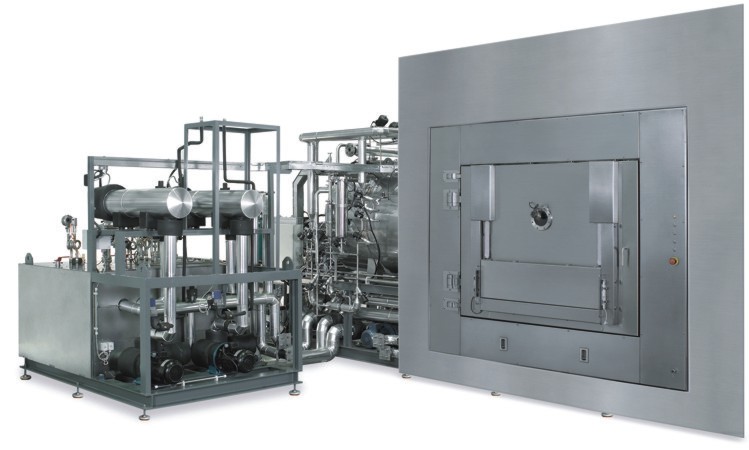
Custom engineered freeze dryer
For either bulk format or liquid in vials, ampoules or syringes, the Lyomega units are design...
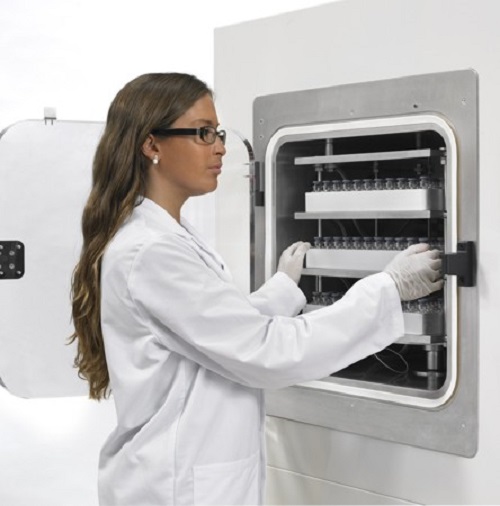
Pilot freeze dryer for scale up
Designed for biological, pharmaceutical and food products formulation and “scale up...

Belt dryer for wood
Processing of wood and biomass into pellets or other volume reduced products requires careful and consist...
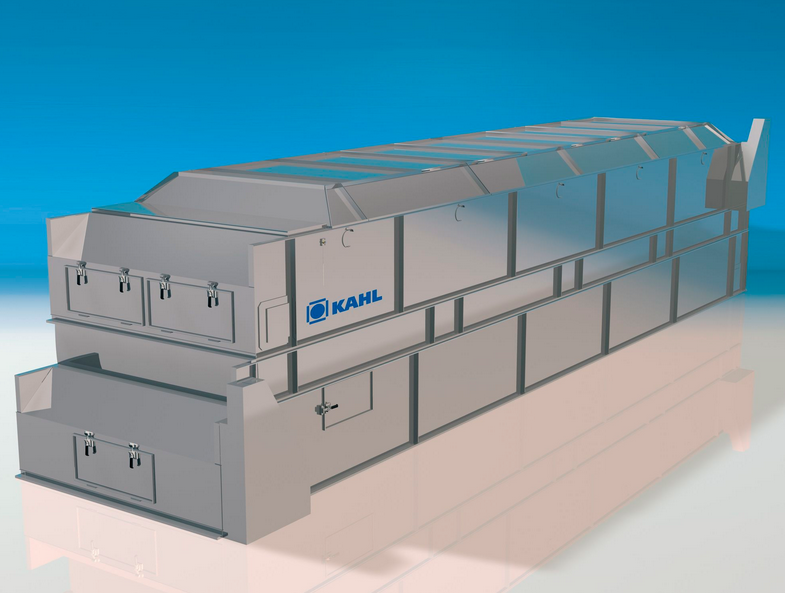
Belt dryer/cooler for pellets and granules
Many industries that process materials in pellet, powder, or crumble form need ...

Co2 recovery system for breweries
Unlock the full potential of fermentation by capturing and purifying CO2 for immediate re...
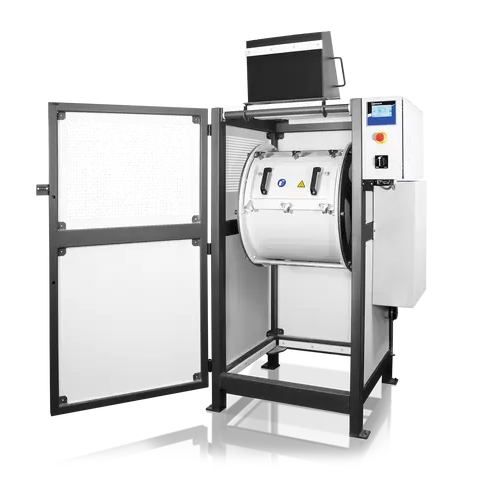
Drum mills for fine grinding of large volumes
Achieve consistent and precise pulverization of large sample volumes with dr...
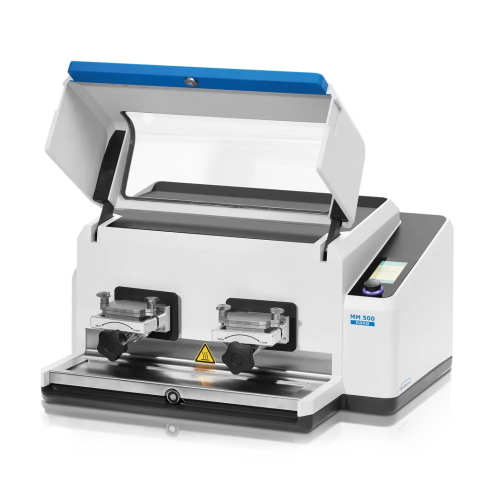
Ultrafine grinding solution for nanoparticles
Achieve ultrafine particle sizes with high-speed precision, ideal for labora...
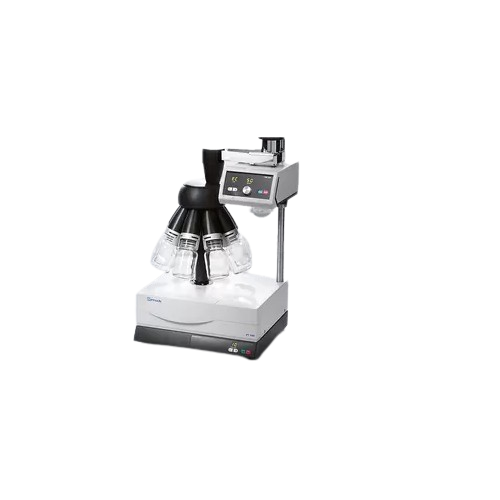
Sample dividing solutions for laboratory applications
Streamline your lab’s precision in sample preparation with so...
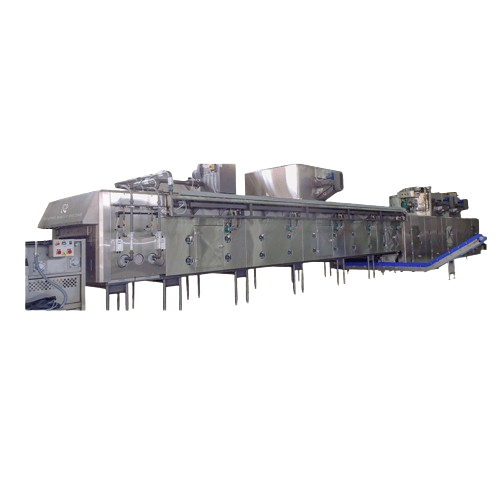
Smart bakery oven zone for flexible heating
Optimize your production with flexible heat transfer options that enhance cont...
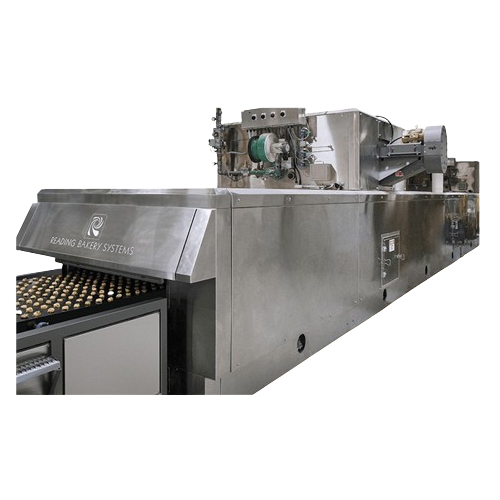
Emithermic zone for baking biscuits and cookies
Enhance your baking efficiency and precision with a flexible heat transfer...
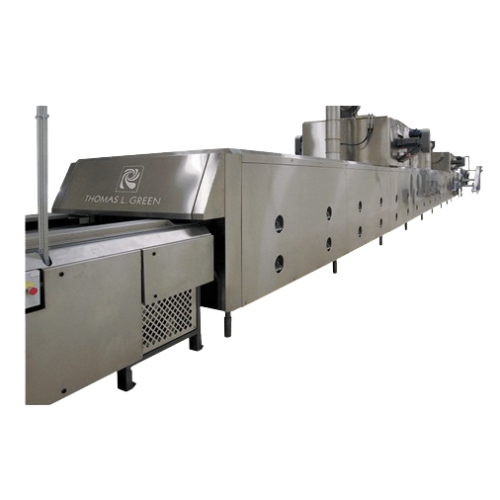
Emithermic Xe zone for baking biscuits and crackers
Achieve precise baking and drying for your bakery products with a sys...
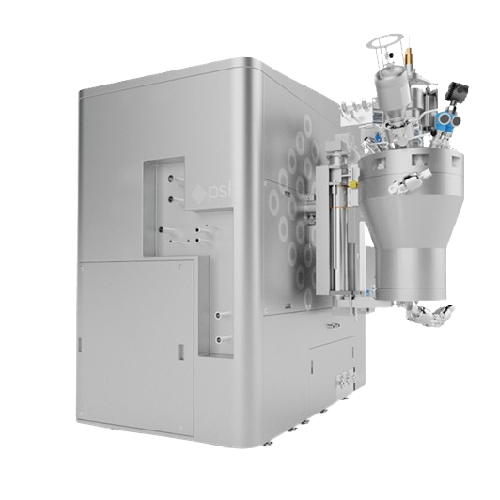
Microsphere refiner for aseptic drug manufacturing
Achieve precise control over microsphere drug formulations with this m...
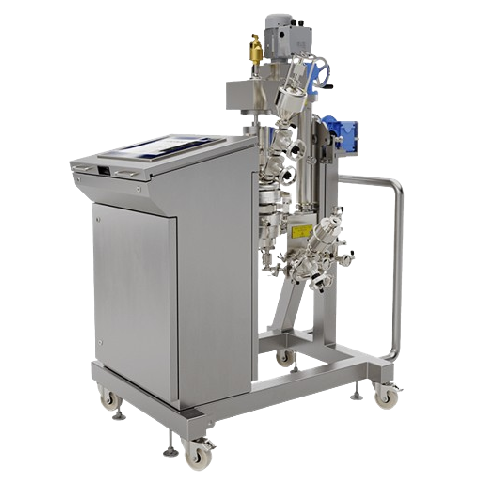
Microsphere process scale-up system for r&d
Enhance microsphere drug formulation with seamless scale-up capabilities, ensu...
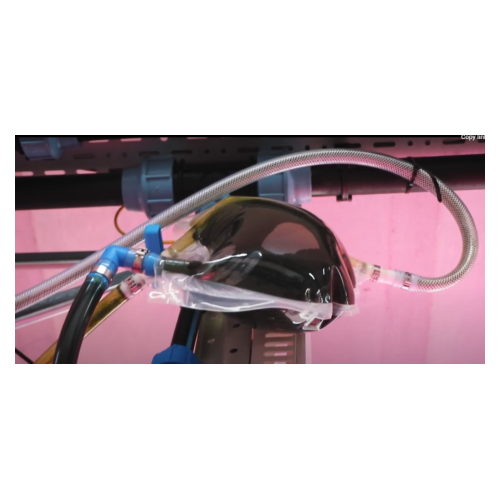
Indoor microalgae cultivation technology
Enhance sustainability and productivity in microalgae cultivation with a vertical ...
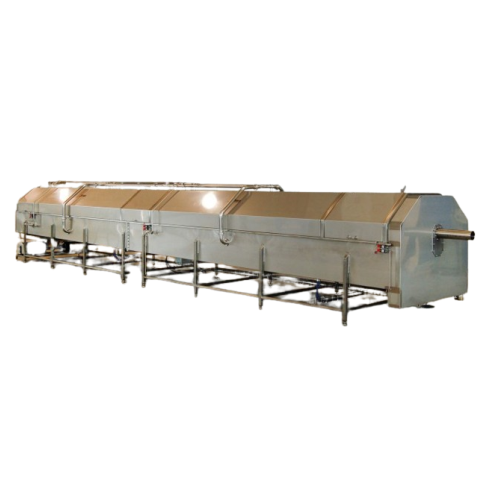
Mechanical ricotta drainage tunnels
Efficiently manage the draining, drying, and cooling of ricotta and curd with our advan...
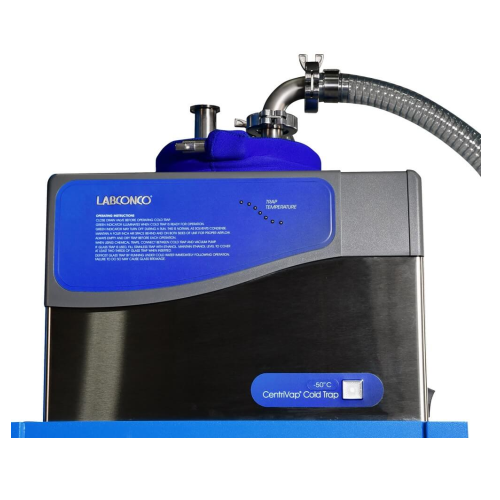
Vacuum cold trap for lab applications
Ensure efficient separation and purification in biopharmaceutical applications with t...
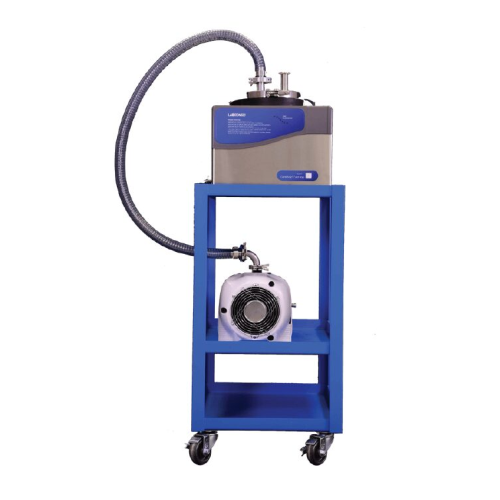
Laboratory vacuum cold trap for extract purification
Optimize your vacuum purging and drying applications with this advan...
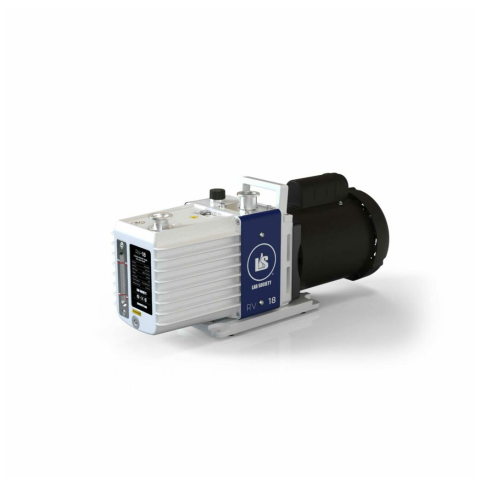
2-stage rotary vane vacuum pump for laboratory applications
Ensure reliable and efficient vacuum conditions for distilla...
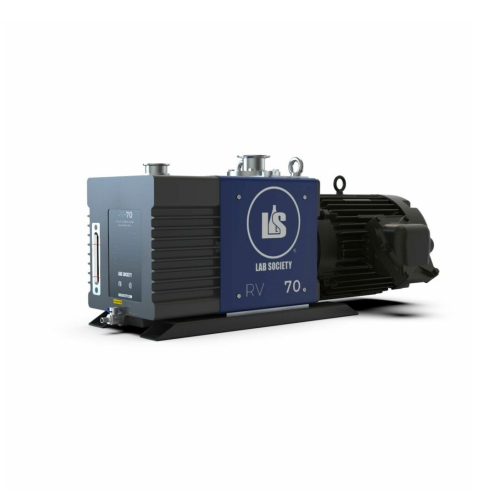
2-stage rotary vane vacuum pump for distillation processes
Achieve precise control and efficiency in distillation and fr...
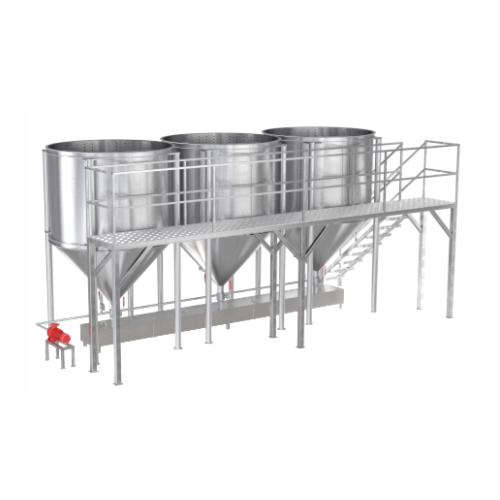
Sesame seed washing system
Eliminate the bitterness and impurities from sesame seeds efficiently, setting the stage for high...
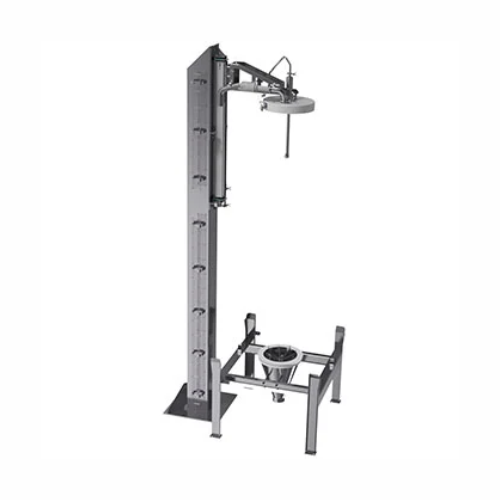
Ibc cleaning equipment for hygienic powder handling
Optimize cleaning efficiency and maintain hygiene standards with a ve...
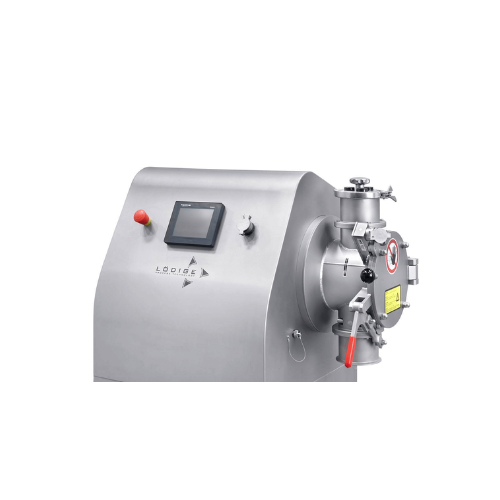
Laboratory ploughshare mixer for small-scale production
Achieve precise mixing and granulation for R&D and small-bat...
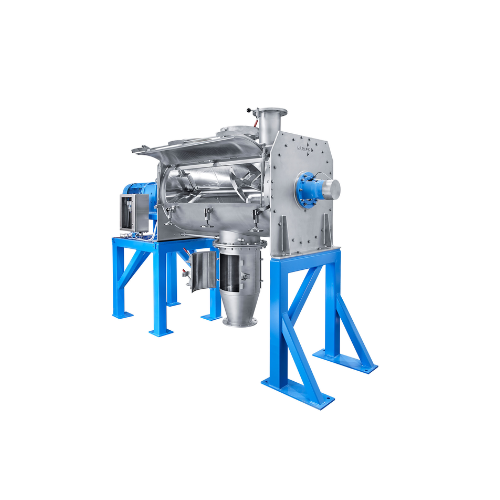
Ploughshare mixer for batch operation
Achieve superior mixing quality with a system designed for rapid batch operations. Ex...
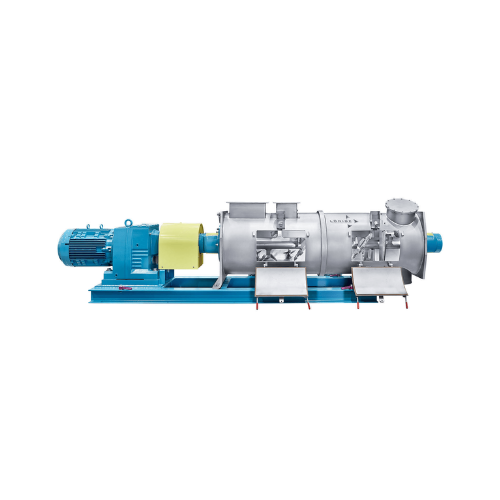
Continuous ploughshare mixer for diverse industrial applications
Enhance mixing efficiency and achieve precise particle ...
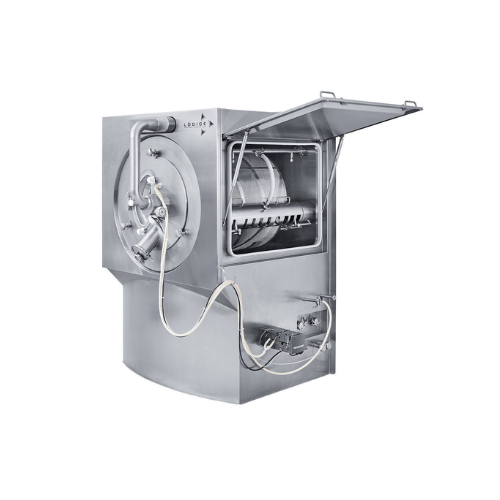
Tablet coater for pharmaceutical applications
Achieve uniform tablet coatings with exceptional efficiency and reduced proc...
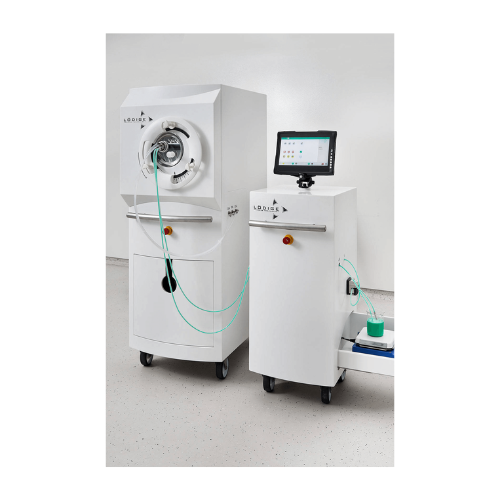
Laboratory tablet coater for pharmaceuticals
Achieve consistent and efficient coating of tablets with this innovative coat...
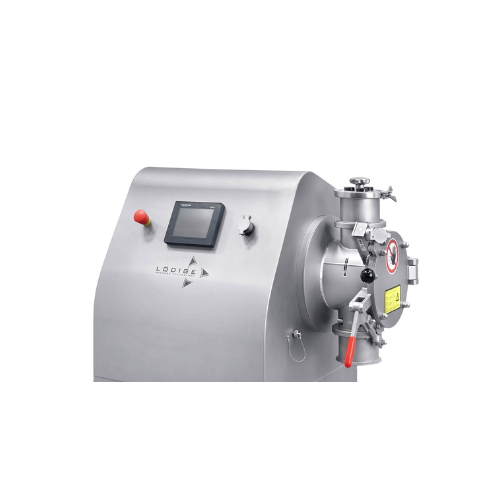
Laboratory mixer granulator
Achieve high-quality mixtures in R&D and small-batch production with versatile laboratory m...
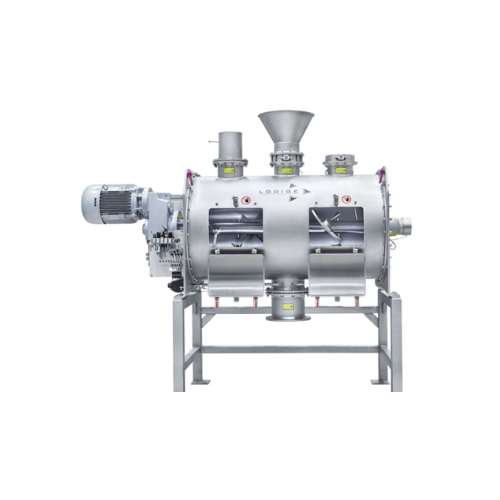
Batch mixer for powdery, granular, and fibrous materials
Achieve precise consistency and high batch reproducibility in yo...

Industrial food dehydrator for fruit and vegetables
Optimize your drying process with a high-temperature food dehydrator ...
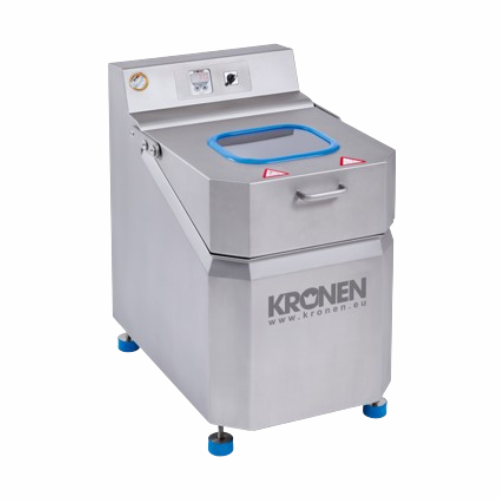
Industrial vegetable and lettuce spinner
Effortlessly achieve optimal drying and dewatering for salads, vegetables, and mor...
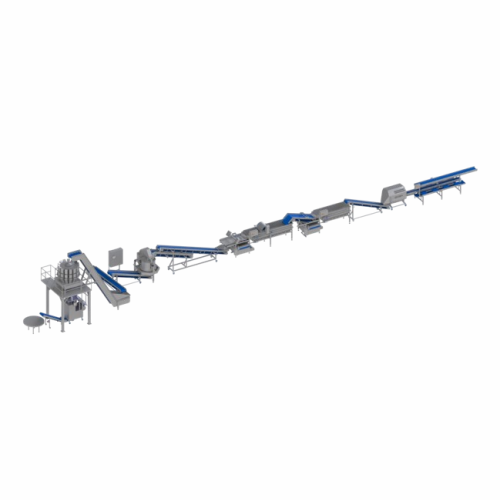
Lettuce processing and packaging line
Maximize throughput with seamless integration of trimming, cutting, washing, and pack...
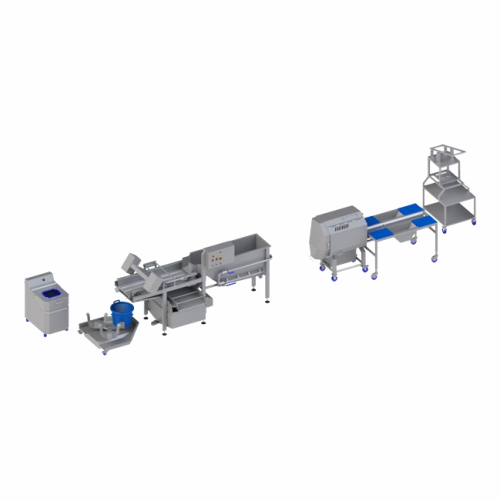
Processing line for lettuce, vegetables, and fruit
Enhance efficiency and product quality in your production line with a ...
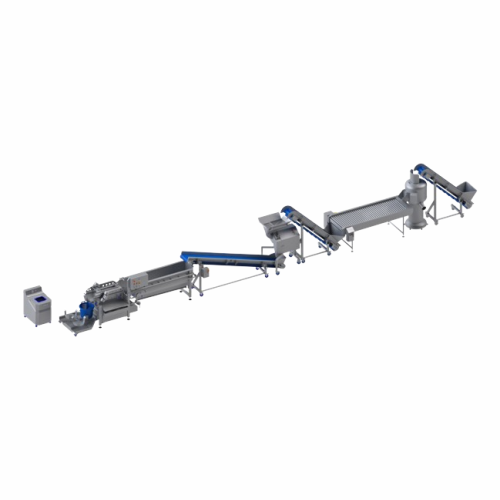
Potato processing line for tubers
For food processors seeking efficiency, this semi-automatic line streamlines peeling, cut...
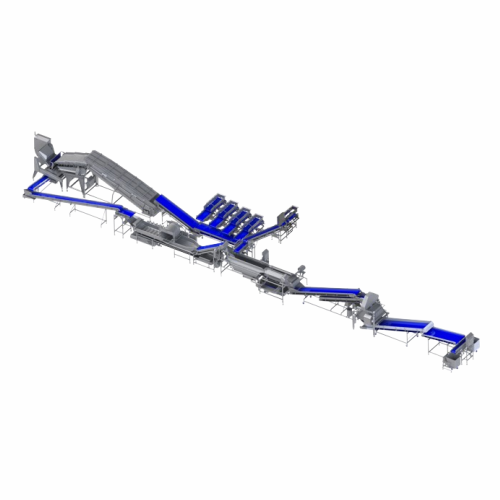
Automated processing line for lettuce and leafy vegetables
Optimize your salad and leafy greens processing with this ful...
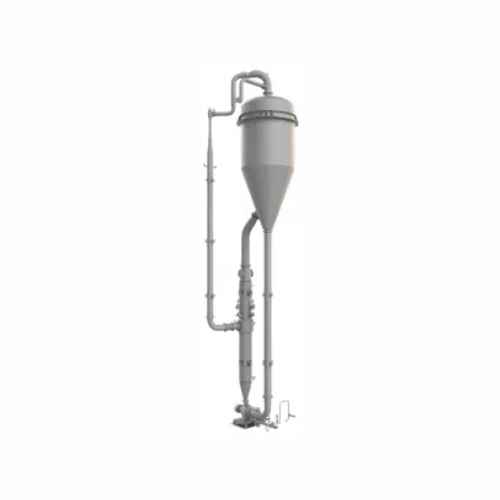
Lactose crystallizing evaporator
Optimize lactose yield and crystal size control in continuous processing, enhancing product...
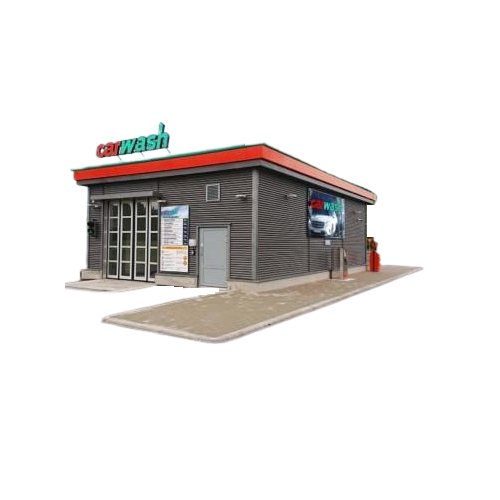
Modular car wash systems
Streamline vehicle cleaning with modular car wash systems, designed for efficiency in demanding envi...
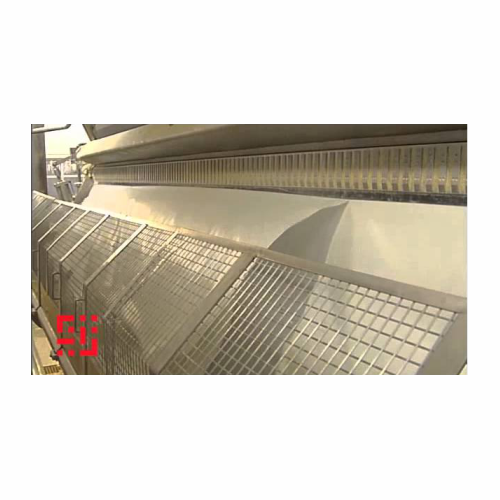
Industrial potato flake production line
Maximize yield and quality in potato processing by integrating advanced pre-cleanin...
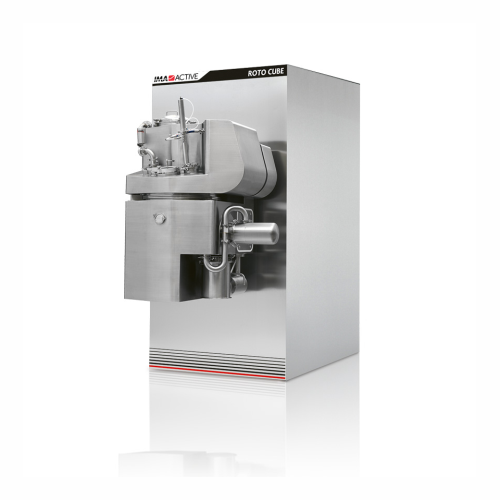
Single-pot granulation processor for pharmaceutical applications
For manufacturers needing precise granulation and dryin...
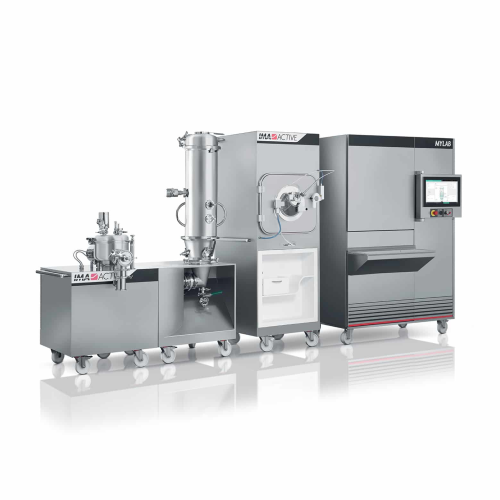
Fluid bed and coating system for small batch processing
Streamline your R&D process with a modular system that ensur...
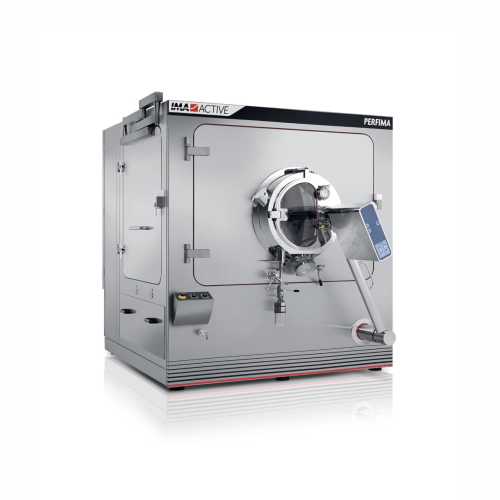
Industrial tablet coating solution
Achieve precise film and sugar coatings on a versatile range of tablet and pellet forms,...
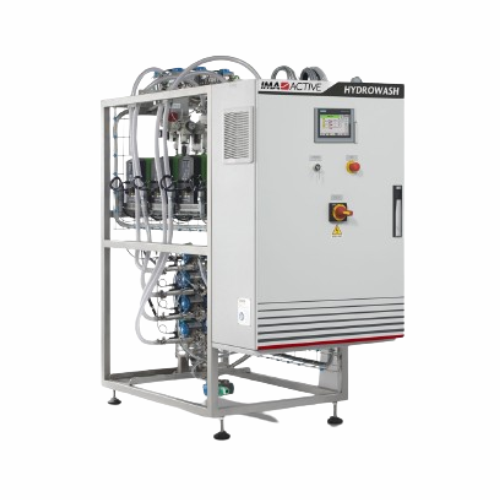
Industrial washing skid for pharmaceutical components
Ensure precise cleaning and drying of pharmaceutical components wit...
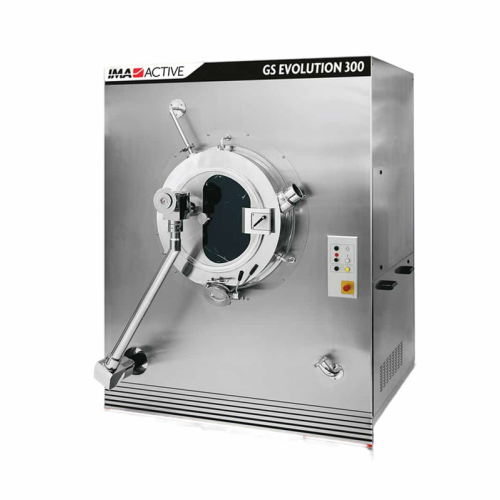
Tablet film and sugar coating pan
Achieve uniform coating while minimizing operator exposure to potent substances, ensuring...
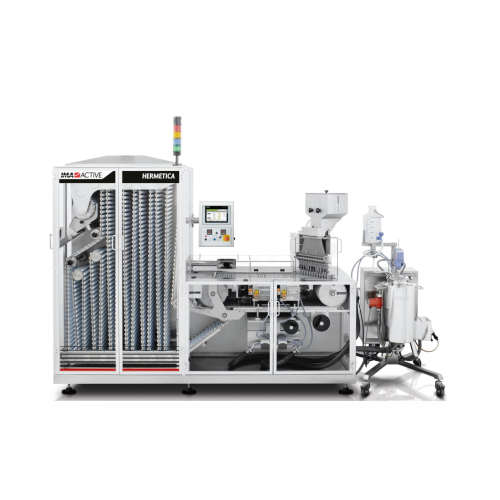
Capsule banding system for tamper-evident sealing
Ensure tamper-evident integrity for capsules by utilizing a precise ban...
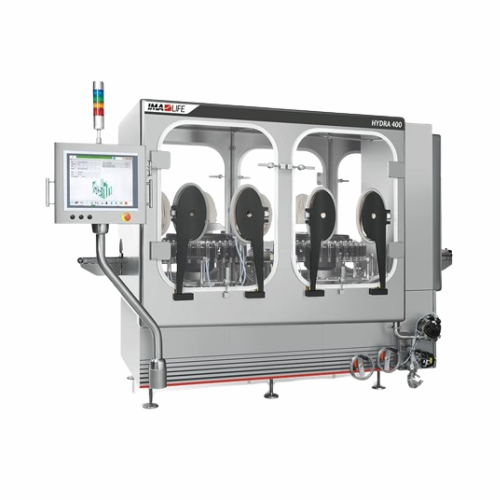
Vial external washer for cytotoxic product decontamination
Optimize the decontamination of pharmaceutical vials and cont...
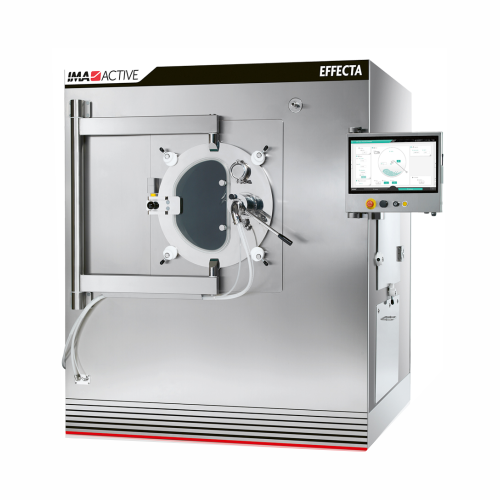
Tablet coating pan for pharmaceutical and nutraceutical industries
Enhance coating efficiency with a versatile solution...
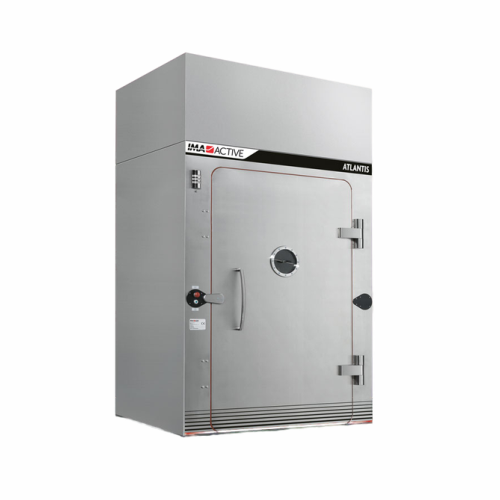
Pharmaceutical components washing station
Ensure optimal cleanliness with high-efficiency washing and drying of pharmaceut...
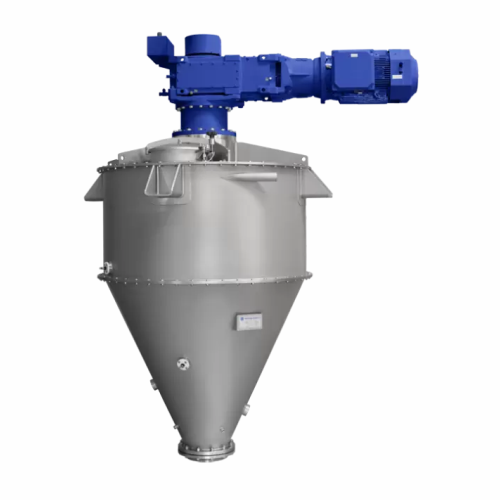
Conical paddle mixer for accurate powder blending
Achieve precise blending of fragile powders and liquids with a versatil...

Table roller mills for mineral raw material comminution
Achieve precise mineral raw material comminution and energy-effic...
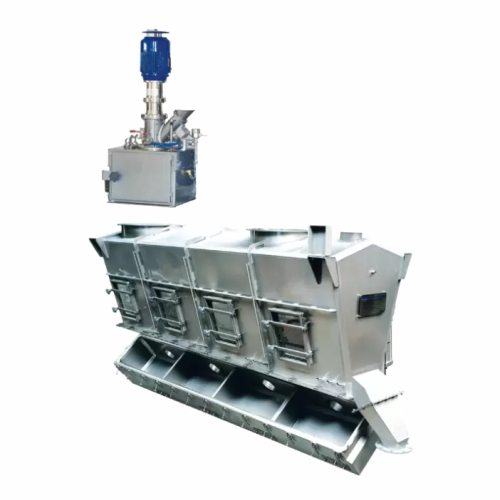
Continuous powder agglomeration system
Enhance product solubility and flowability while minimizing energy consumption with ...
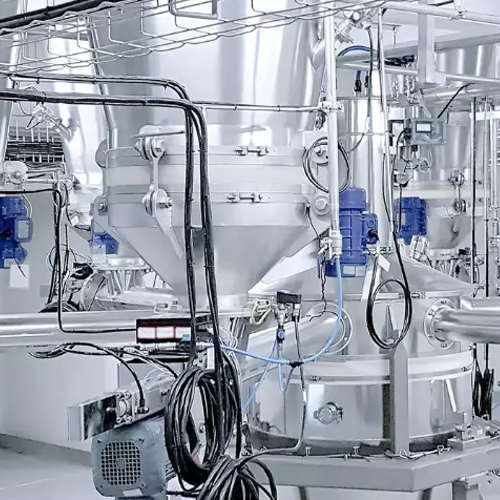
Conical screw mixer for powder blending
Achieve precise and homogeneous blending with the conical screw mixer, ensuring uni...
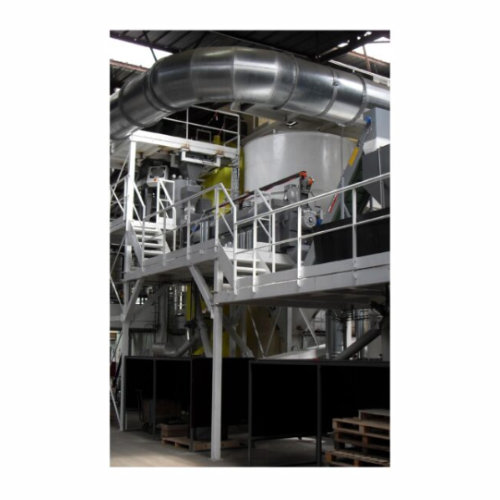
Grass and alfalfa encrusting line
Enhance seed performance with precise encrusting technology, ideal for agricultural seeds...
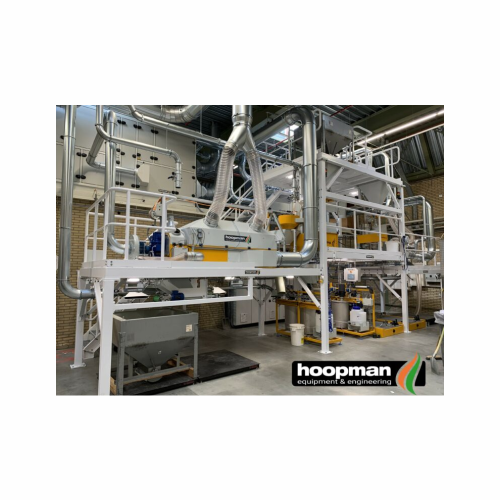
Organic seed coating lines
Achieve optimal seed coating with a natural, biodegradable solution that minimizes energy use and...
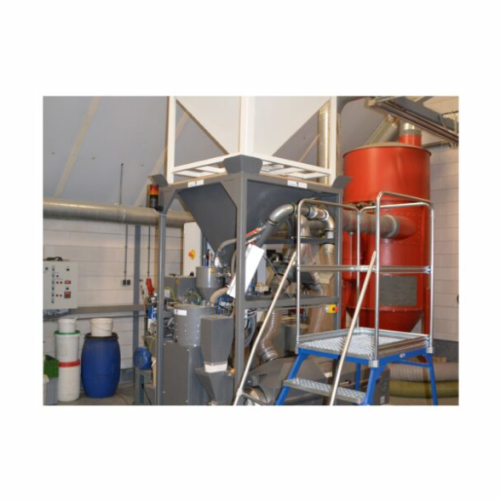
Compact seed coating system for small production
Efficiently scale your seed processing with a reliable system designed fo...

Mid-capacity film coating solution
Enhance your seed coating and biofuel pellet production with a customizable turn-key sol...
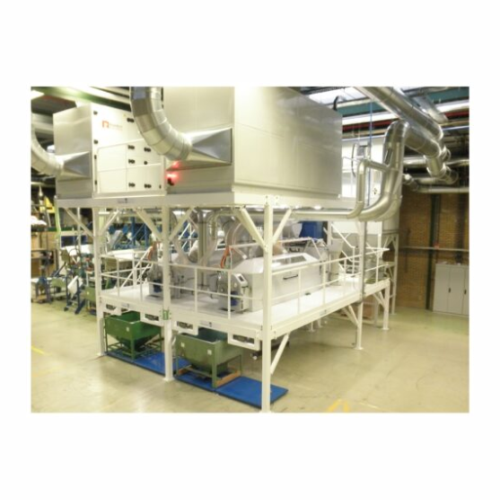
High-capacity filmcoating system for seed treatments
Optimize seed enhancement processes with a modular, high-throughput ...
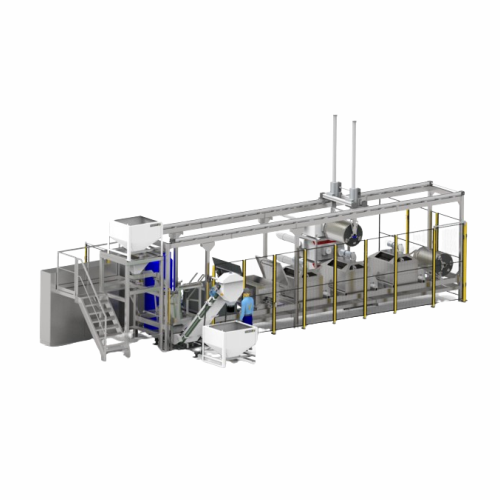
Liquid treatment system for seed processing
For seed processors seeking enhanced seed quality, this liquid treatment syste...
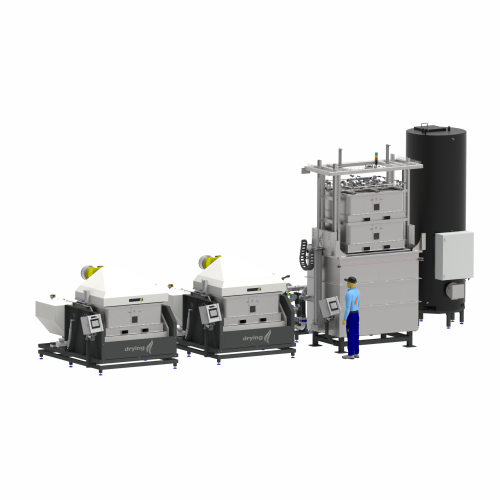
Flexible seed rinsing and treatment station
For seed producers needing precise, controlled treatment, this rinsing station...
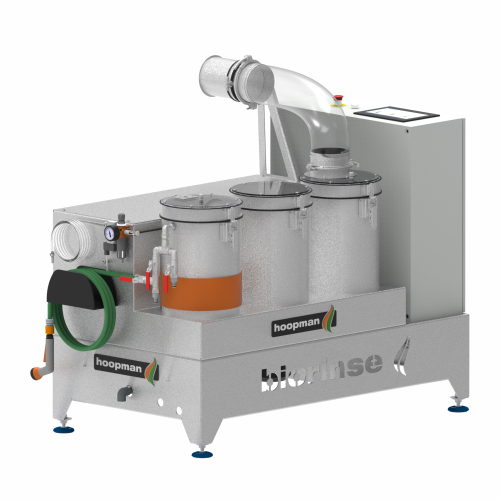
Seed disinfection and rinsing system
Optimize your seed processing by ensuring thorough disinfection and rinsing, maintaini...
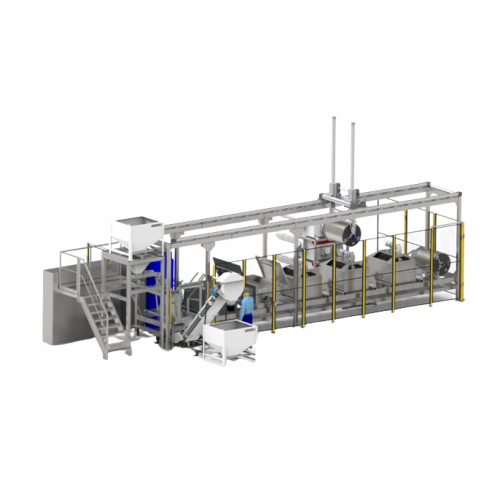
Modular system for liquid treatment protocols
Streamline your seed treatment process with a versatile system capable of ha...

Vacuum marinating and tumbling for laboratories and small enterprises
Streamline your meat processing operations with v...
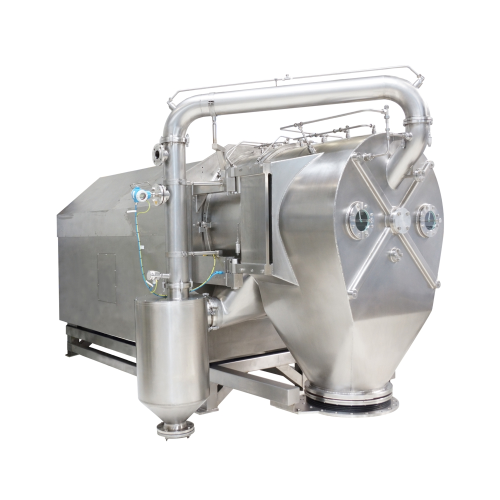
Inverting filter centrifuge for high-potent Api products
Achieve optimal separation and reduce residual moisture with pre...
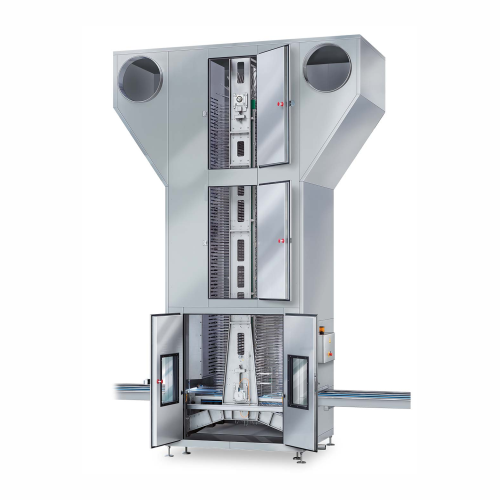
Wafer sandwich cooling systems
Efficiently setting cream fillings for clean cuts, this cooling system ensures your wafer san...
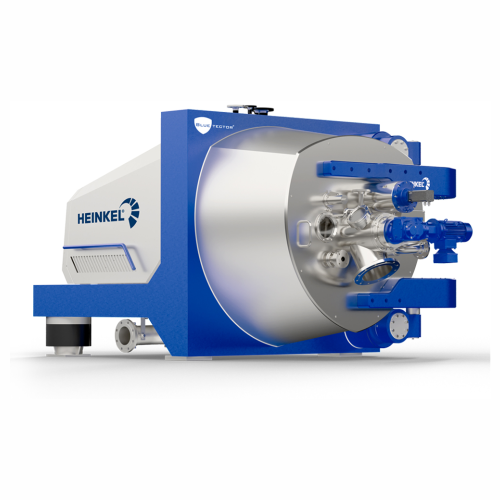
Horizontal peeler centrifuge for chemical applications
Achieve high-throughput product separation and purification with p...
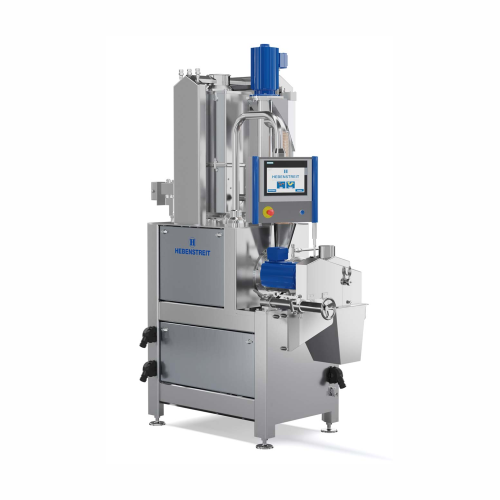
Single-screw cooking extruder for snack production
Optimize your snack production with a versatile extruder designed to h...
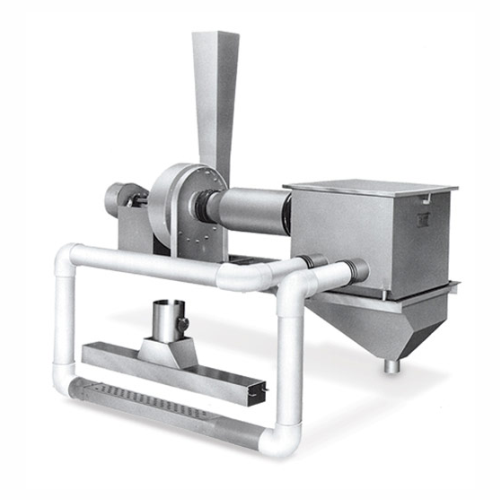
Industrial water removal system for food preparation
Enhance your production line with advanced surface water and starch ...
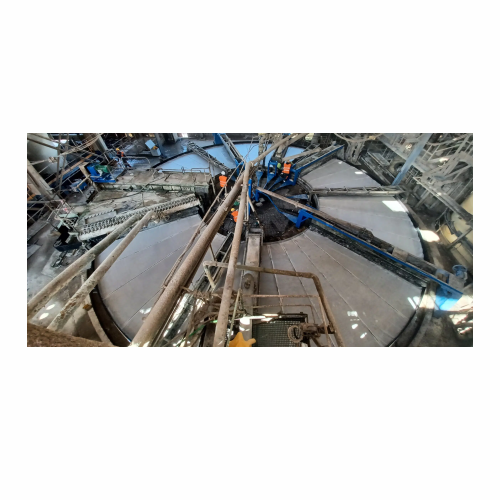
Vacuum table filters for liquid-solid separation
Optimize your liquid-solid separation with vacuum table filters, designed...
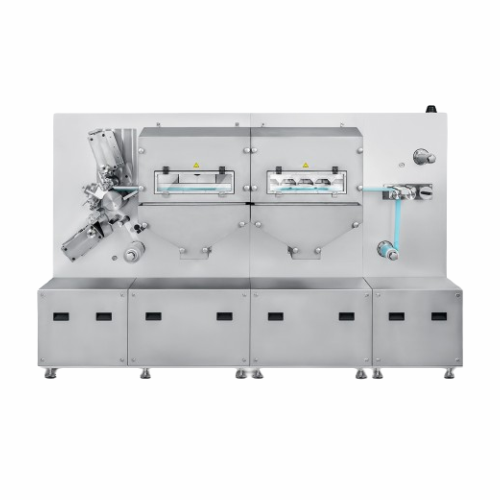
High-precision web material coating
Achieve precision coating with versatile solutions that ensure uniform application and ...
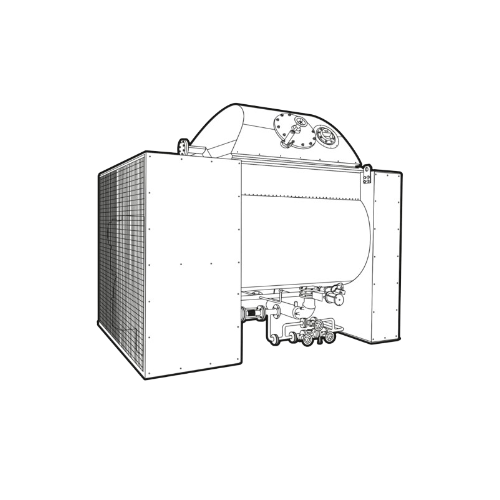
Cocoa sterilizing and alkalizing plant
Optimize cocoa product quality with a system engineered for precise sterilizing, alk...
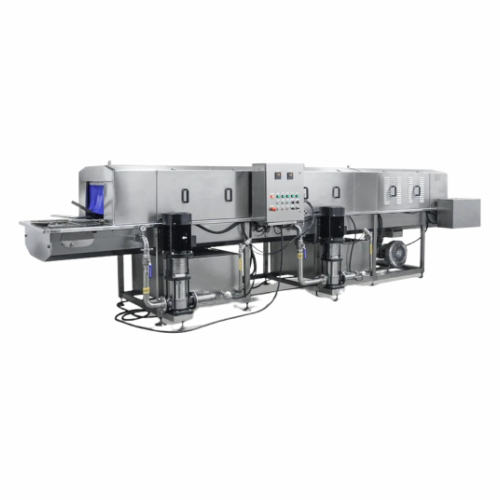
Automatic tray washer for gummy production cleanup
Eliminate gummy residue efficiently with high-pressure tray washing, e...
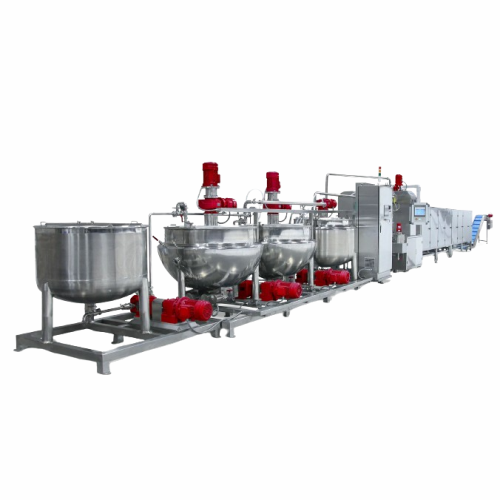
Automatic gummy manufacturing system
Efficiently streamline your candy production with a system capable of producing up to ...
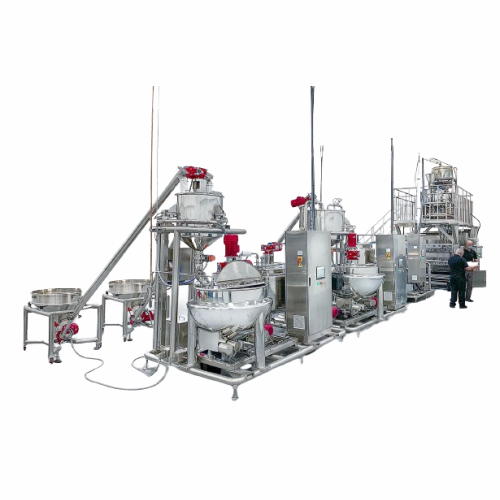
High-capacity gummy production system
Optimize your gummy production with a starchless system that deposits up to 240,000 g...
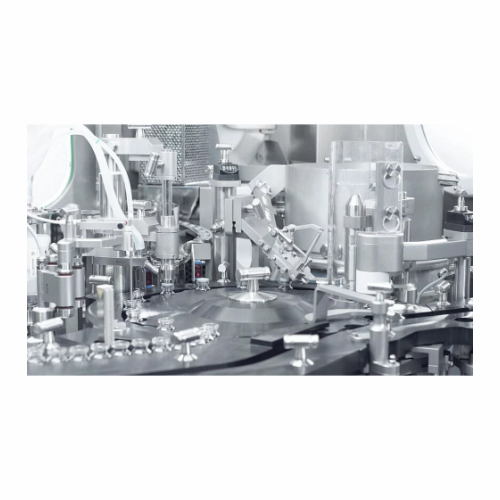
Vial filling for pharmaceuticals
Streamline your aseptic processing with vial filling machines that ensure sterile, precise,...
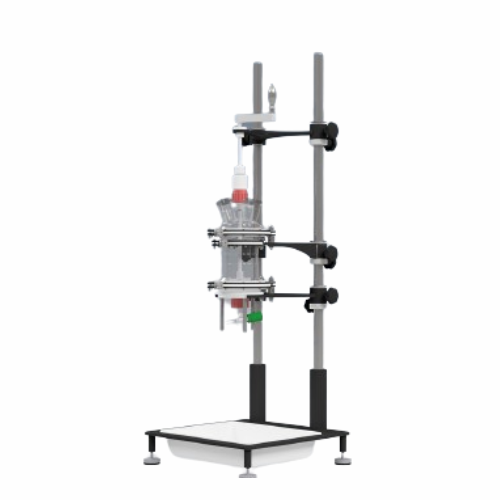
Lab nutsche filter for small scale filtration
Efficiently manage filtration and drying needs in fine chemical and pharmace...
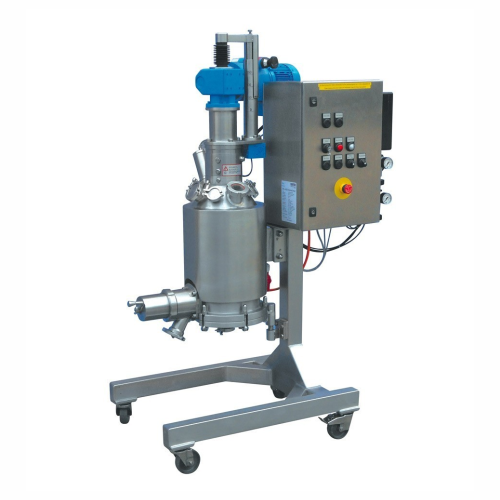
Chemical and pharmaceutical solid-liquid separation pilot plant
Optimize your pilot-scale production of pharmaceuticals ...
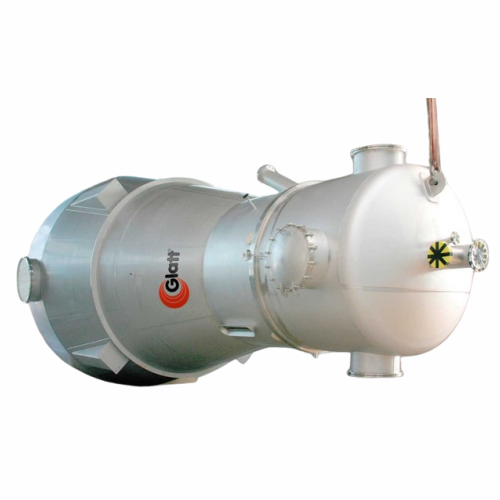
Fluid bed granulation system for food and chemical industries
Achieve efficient granulation and drying of liquids with c...
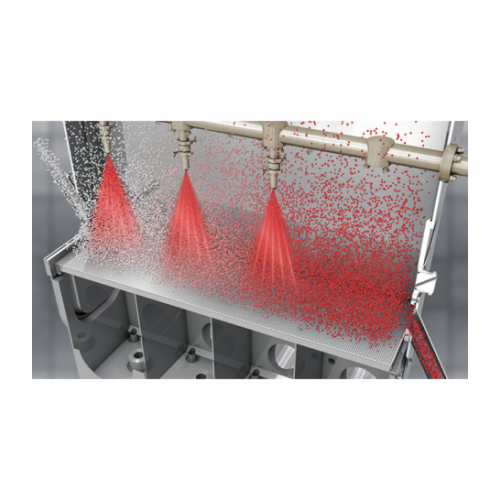
Fluid bed granulator for food and chemical industries
Ensure consistent particle size and moisture control in your produc...
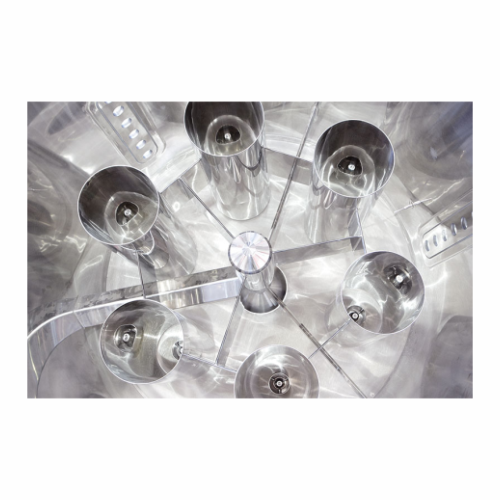
Fluid bed and spouted bed systems for granulation and coating
Optimize your production line with cutting-edge fluid bed ...
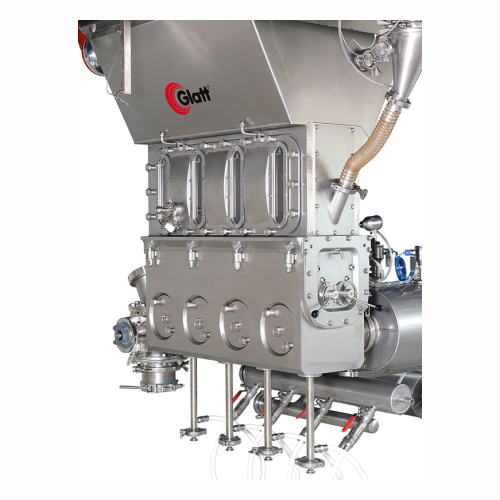
Spouted bed processing for food, feed, and fine chemicals
Tackle the challenge of processing temperature-sensitive and s...
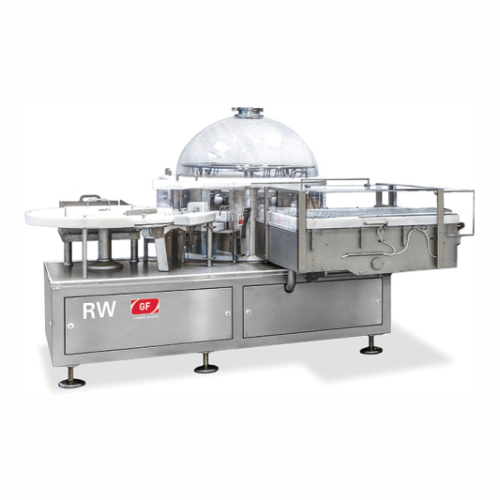
Rotary washer for pharmaceutical containers
Ensure optimal preparation of pharmaceutical containers with advanced rotary w...
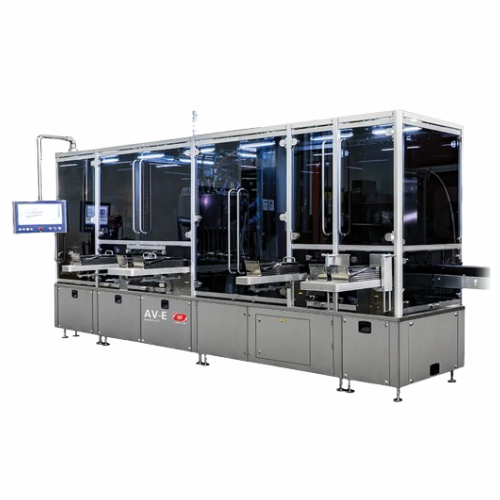
Optical inspection for ampoules, vials, cartridges, and syringes
Ensure product integrity and safety with this advanced ...
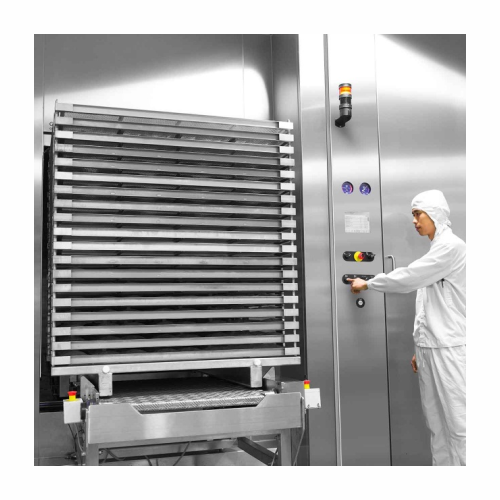
Pharmaceutical sterilization with steam/air mixture
Achieve sterile, dry, and ready-to-use pharmaceutical products with p...
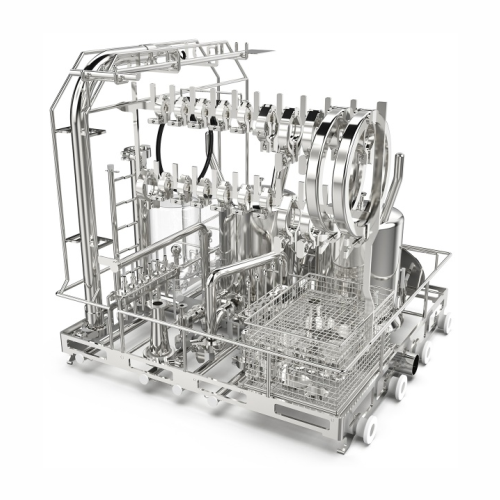
Loading solutions for Gmp washers
Ensure thorough cleaning and drying of biopharmaceutical components with modular loading ...
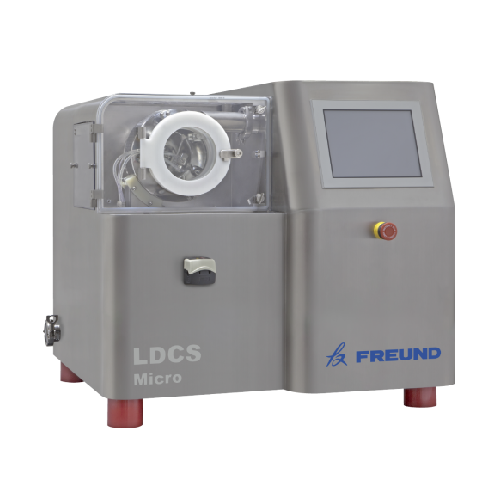
Laboratory film coating system for development and clinical batches
Achieve precision in tablet coating with a versatil...
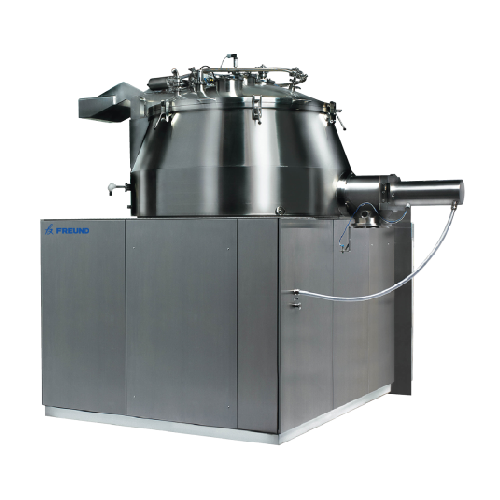
High shear granulation mixing system
Optimize your powder granulation process with a system designed for precise control ov...
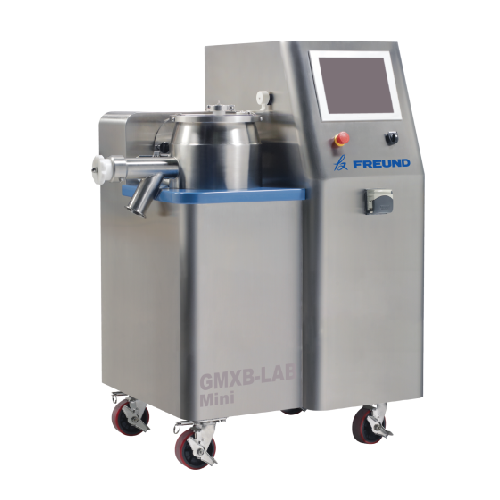
High shear granulator for wet granulation of powders
Achieve consistent granule density and size with a high shear granul...
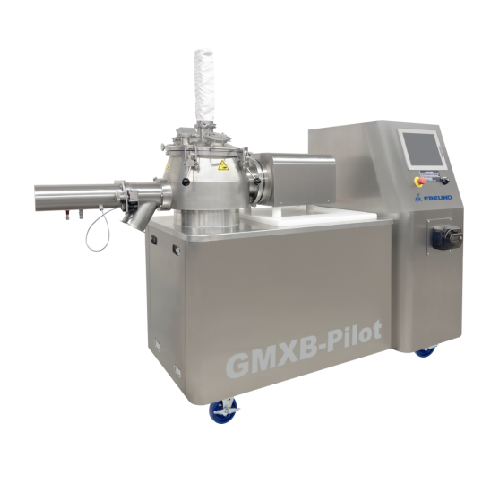
Pilot High shear granulator for wet granulation
Achieve consistent particle sizing and superior homogeneity in your powder...
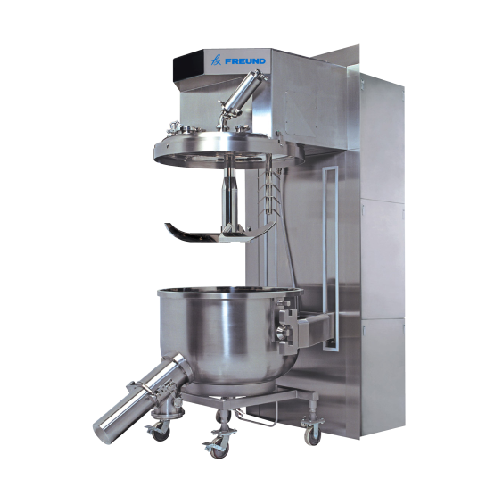
High shear wet granulation line
Achieve consistent and uniform granules with energy-efficient wet granulation designed to op...
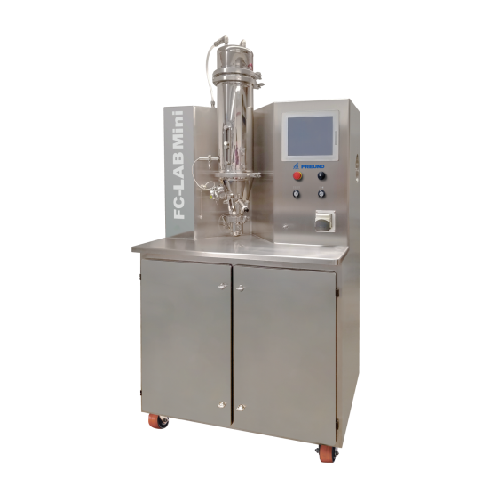
Laboratory fluid bed system for solvent processing
Optimize your laboratory scale operations with a versatile fluid bed s...
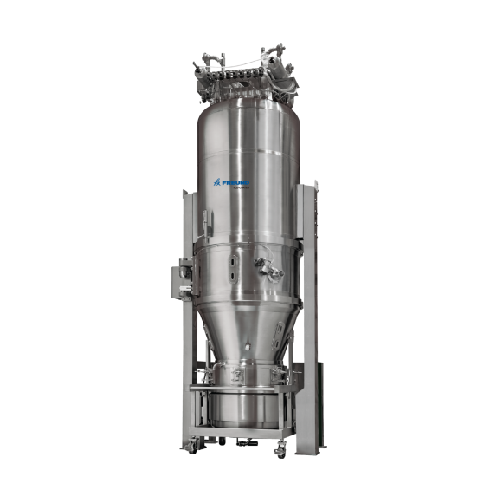
Fluid bed system for granulation and coating
Optimize your production with a multi-purpose fluid bed system designed for e...

Filter washing cabinet for industrial cartridge filters
Achieve hygienic standards with precision washing and drying of i...
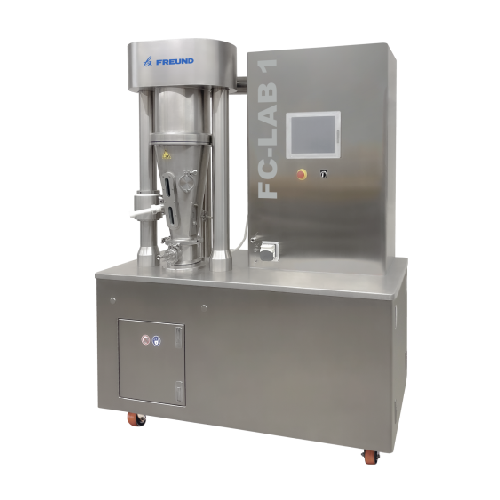
Laboratory scale fluid bed system for granulation and coating
For precise formulation and optimization, this fluid bed s...
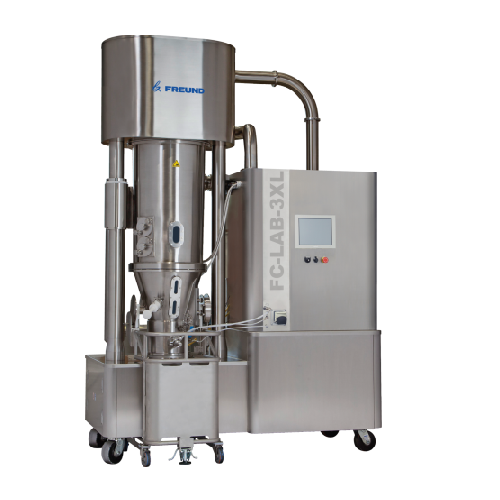
Laboratory fluid bed granulator and coater
For researchers and manufacturers requiring precise control in drying, granulat...
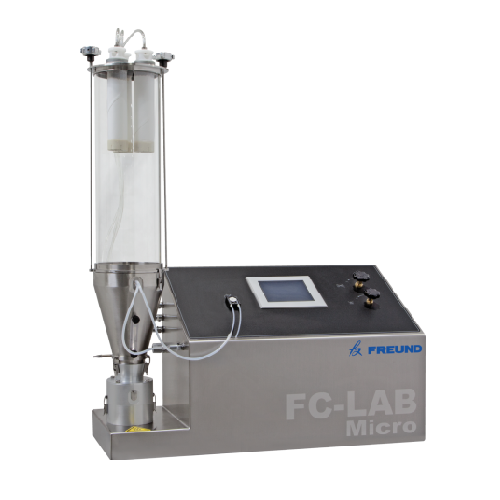
Development fluid bed system for feasibility studies
Explore precise granulation and coating capabilities for small batch...
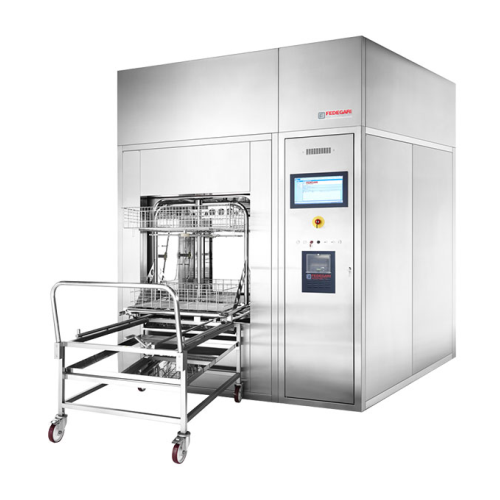
Industrial steam washer for pharmaceutical and food industry
For production lines requiring efficient and eco-friendly c...
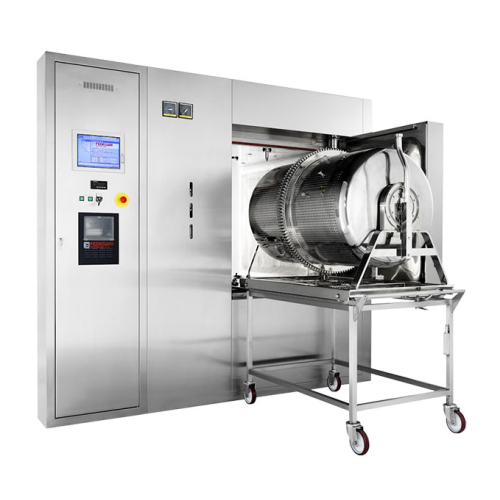
Elastomeric stopper sterilization system
Ensure sterilization and cleanliness of elastomeric vial stoppers with a system de...
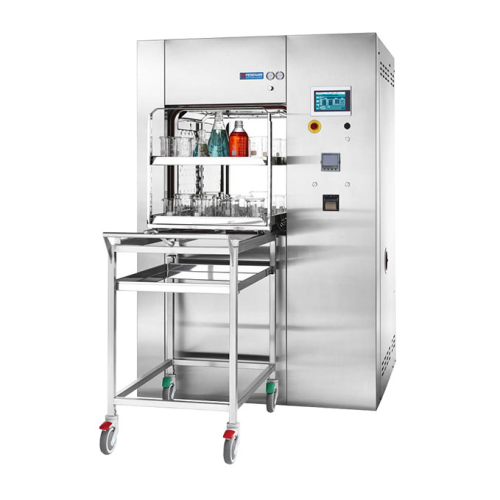
Laboratory sterilizer for microbiology and analytical labs
Designed for laboratories requiring versatile sterilization s...
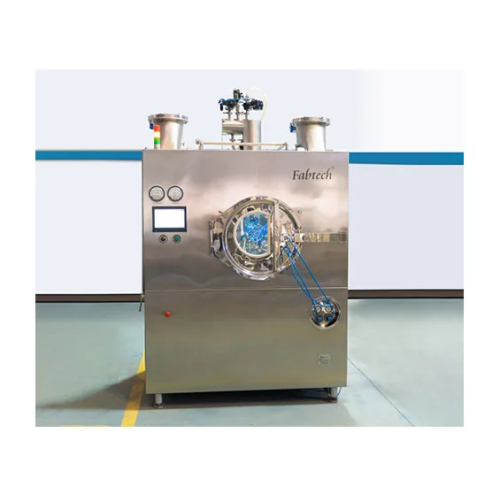
Tablet coating solution
Achieve precise tablet coating with uniformity and efficiency, tailored for diverse tablet types, ens...

Closed loop granulator for pharmaceutical production
Streamline your production with a fully automated closed-loop system...
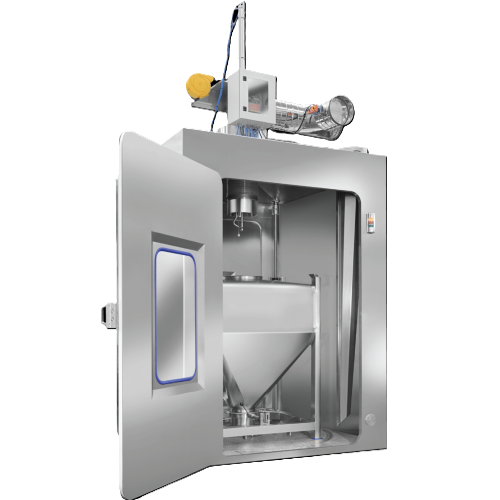
Internal and external bin washing cabinet
Streamline your sanitation process with automated bin cleaning that ensures thor...
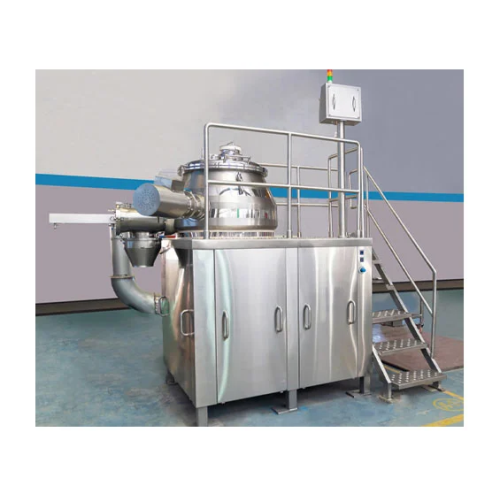
High shear mixer granulator for efficient wet granulation
Achieve consistent and precise granule formation with high she...
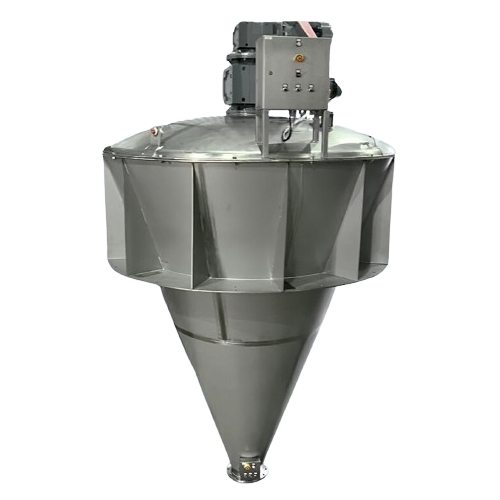
Conical powder mixer for uniform powder blending
Achieve consistent powder blending while preserving the integrity of deli...
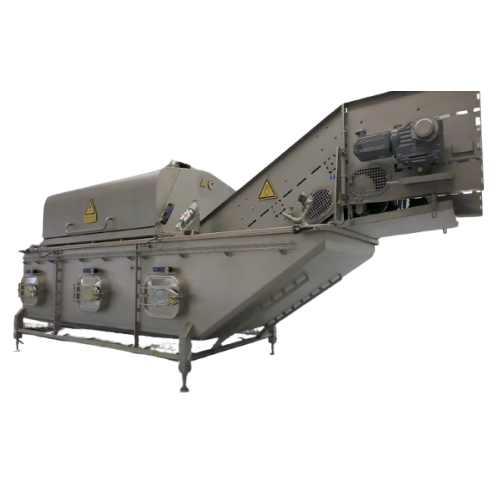
Pulsed electric field treatment for roots, tubers, and fruits
Enhance your production line with advanced pulsed electric...
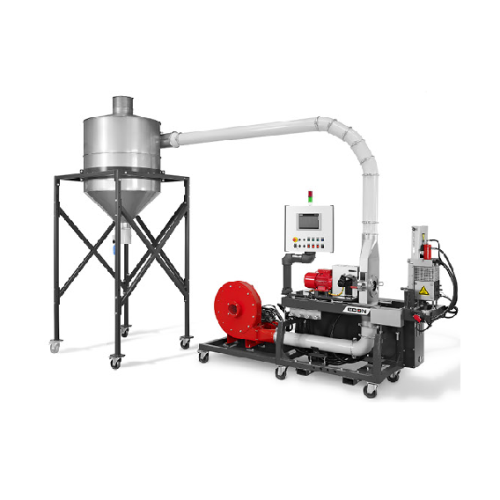
Air pelletizer for wood and natural fiber compounds
Optimize your pelletizing process with air-based cooling and conveyin...
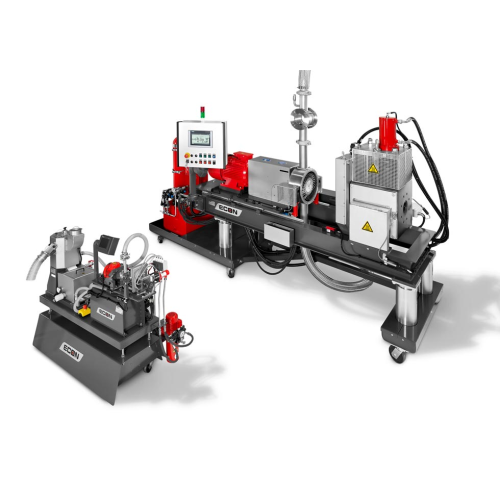
Underwater pelletizing system for thermoplastic materials
Optimize your thermoplastic pellet production with a reliable ...
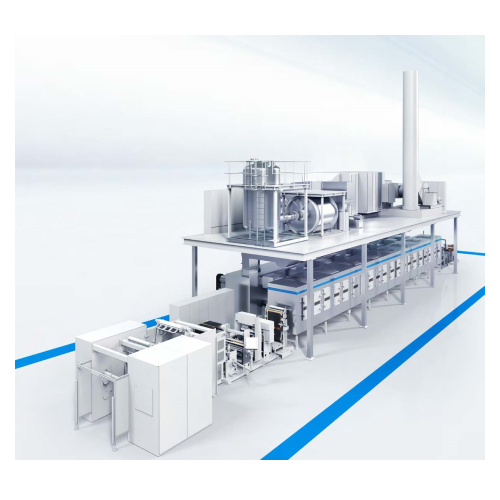
Electrode coating system for lithium-ion batteries
Achieve high-volume, precision electrode coating for lithium-ion batte...
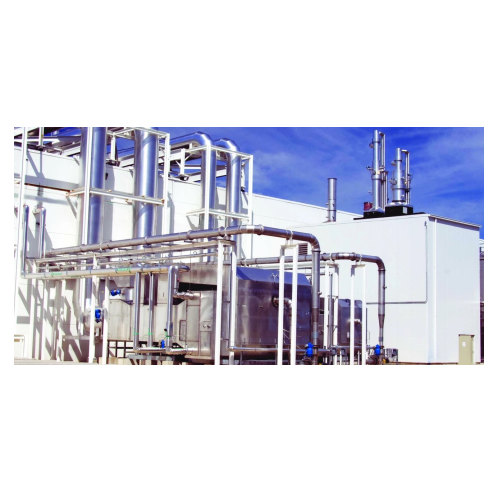
Solvent recovery systems for battery electrode manufacturing
Efficiently recover and purify solvents in battery electrod...
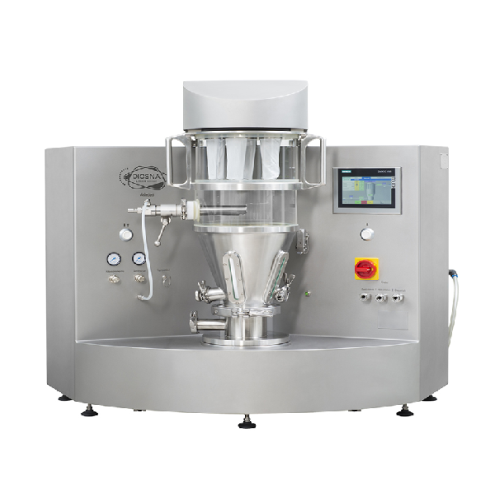
Laboratory granulator and coating system
Optimize your research with a versatile benchtop unit that combines fluid-bed proc...
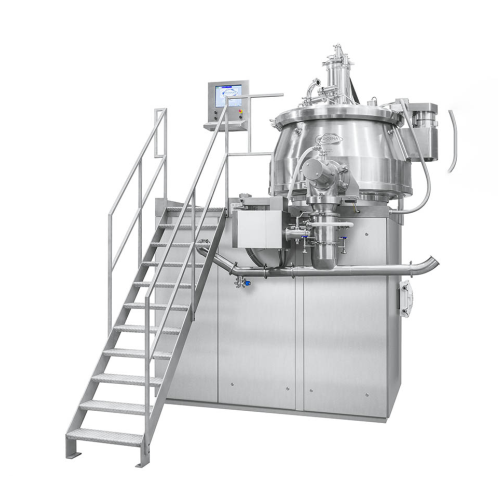
Granulation line for pharmaceutical manufacturing
Enhance your batch production with integrated mixer and fluid-bed techn...
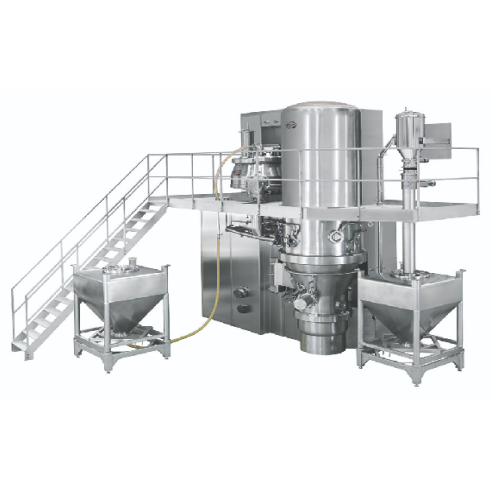
Pharmaceutical granulation line
Streamline your production with an integrated system that combines mixing, granulation, and ...
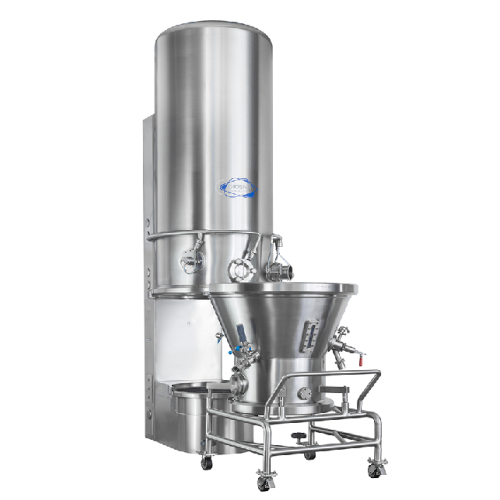
Fluid bed processor for large batch spray granulation
Optimize your production with precision granulation, drying, and co...
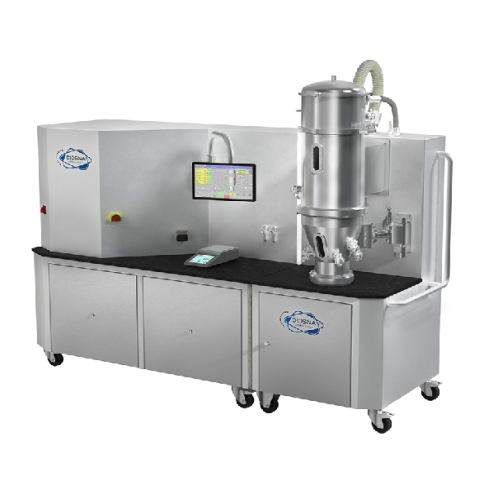
Midilab for efficient laboratory-scale product development
Streamline your laboratory and pilot-scale production process...
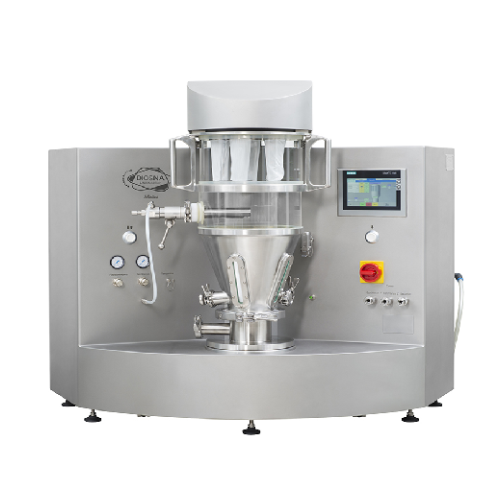
Laboratory coater and fluid bed processor
Optimize your research and development with a versatile benchtop unit that integ...
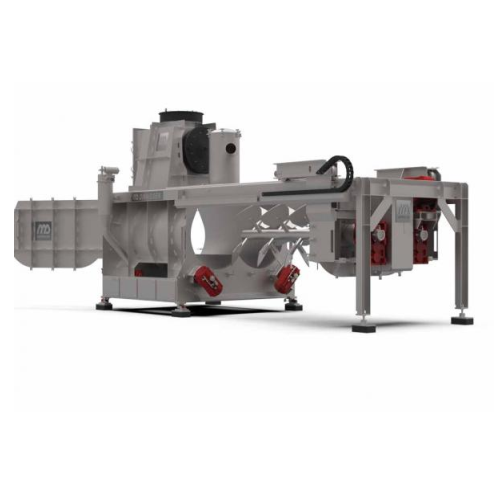
Industrial mixer for batch granules or grains
Achieve precise mixing with seamless integration of heating, sterilization, ...
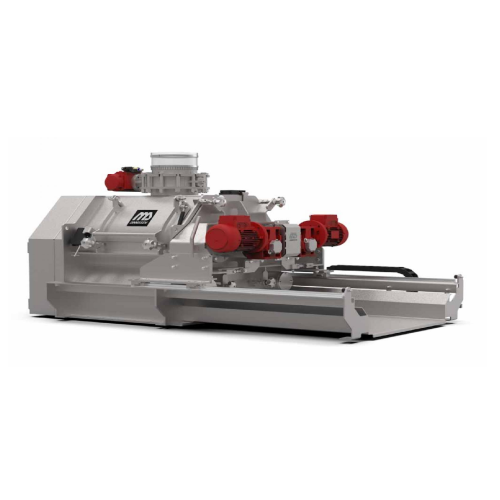
5-in-1 industrial mixer for food and chemical industries
Streamline your production with a multifunctional system that ef...
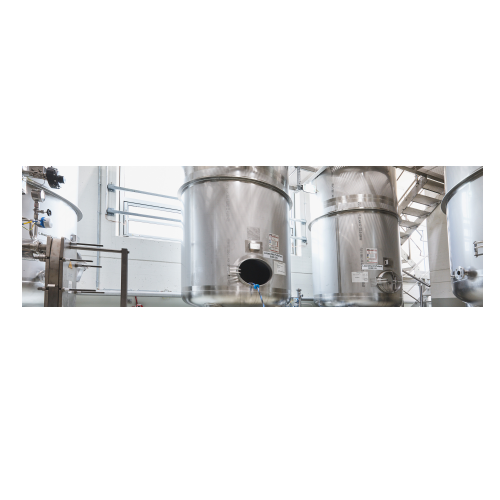
Thermal process plants for liquid treatment
Achieve precision thermal processing with systems designed to optimize the hea...
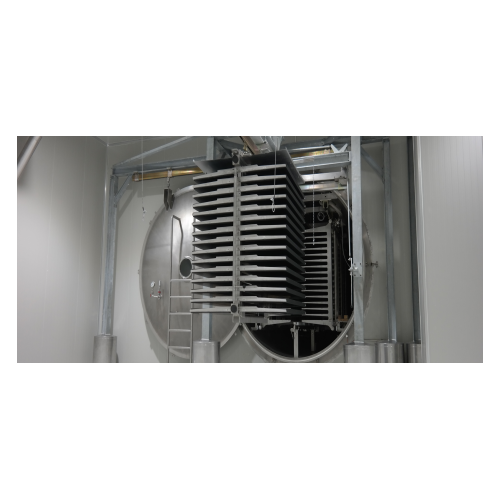
Processing plants for instant coffee production
Achieve optimal flavor retention and cost efficiency in instant coffee pro...
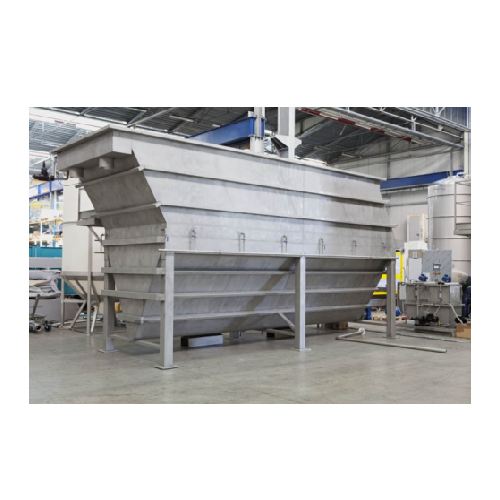
Chemical-physical treatment plants for water treatment
Optimize your water and wastewater treatment processes with system...
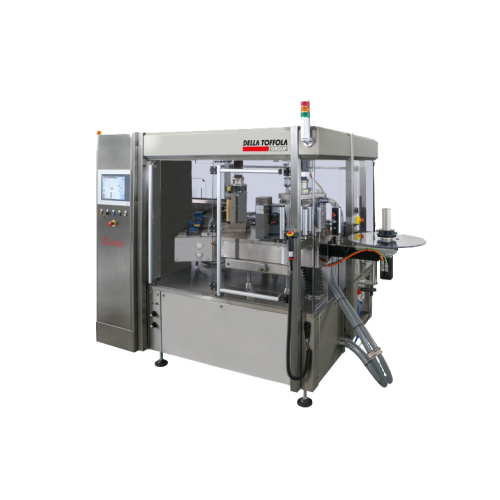
Roll linear labelling machines for bottling and packaging
Achieve precise and efficient labeling with roll linear labell...
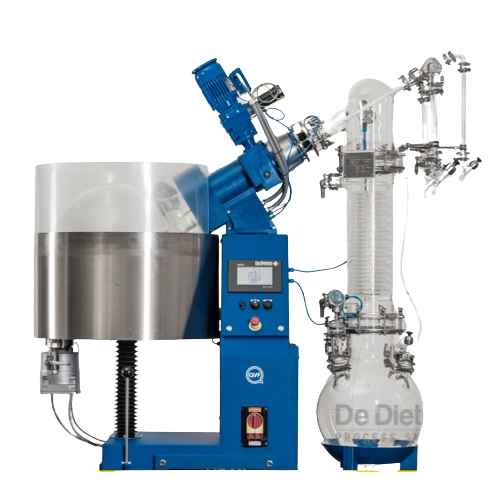
Rotary evaporator for solvent evaporation
Achieve precise solvent recovery and concentration control with this rotary evap...
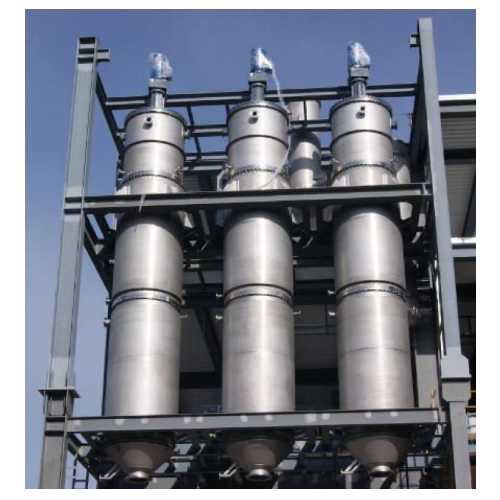
Thin film evaporator for temperature sensitive products
Need to purify temperature-sensitive compounds efficiently? Achie...
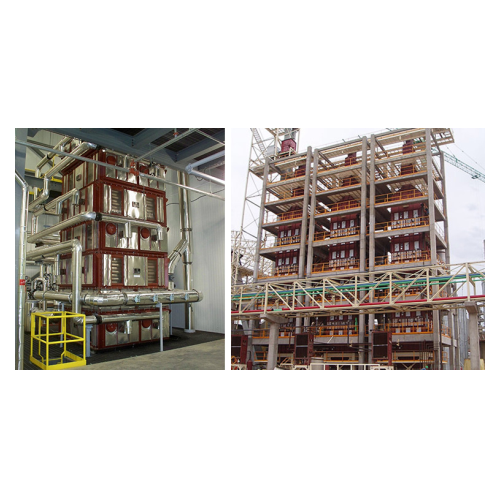
Vertical seed conditioning system for oil extraction
Ensure optimal oil yield and quality from oilseeds by employing a ve...
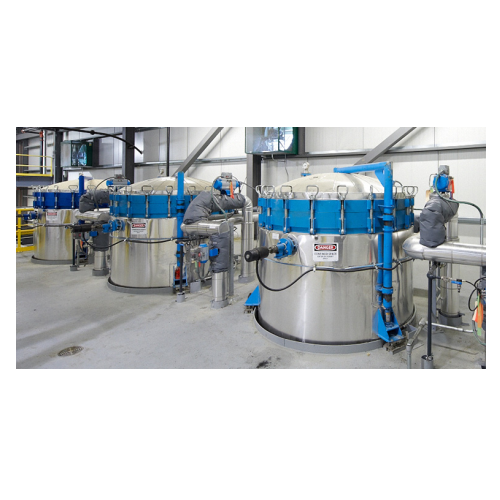
Industrial oil bleaching process
Optimize your oil purification process with advanced bleaching technology, significantly en...
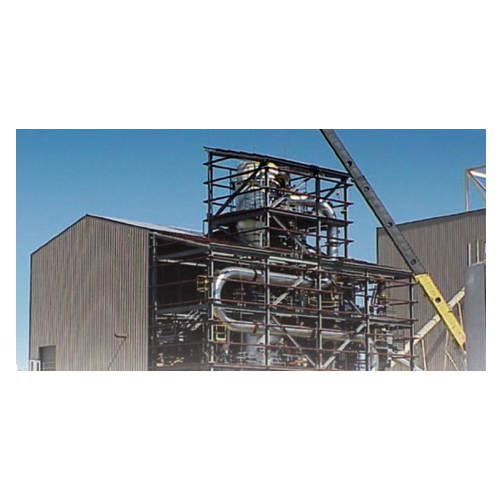
Flash desolventization system for oilseed processing
Achieve rapid desolventization with minimal heat exposure, preservin...
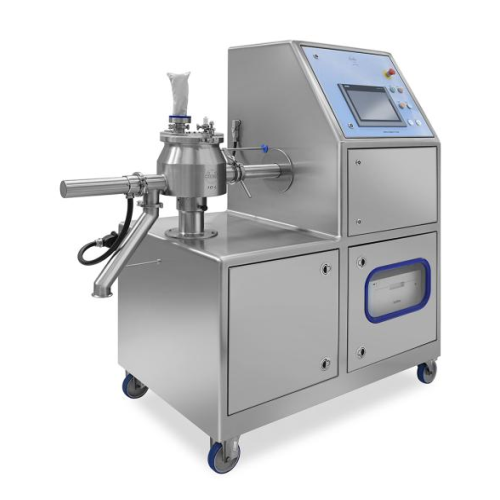
Laboratory high shear mixer for wet mixing and granulation
Optimize your mixing, granulation, and drying processes with ...
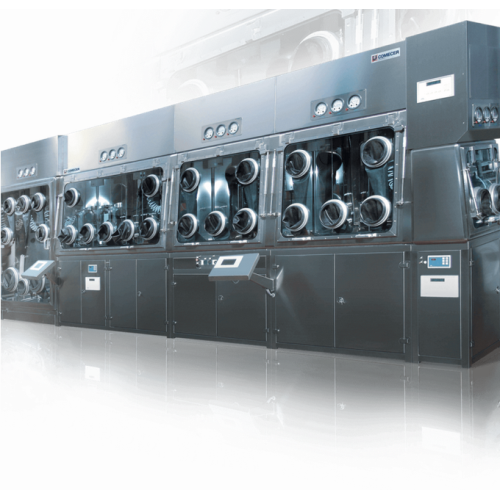
Six stage r&d isolator for safe material handling
Ensure optimal operator safety and material containment during complex ...
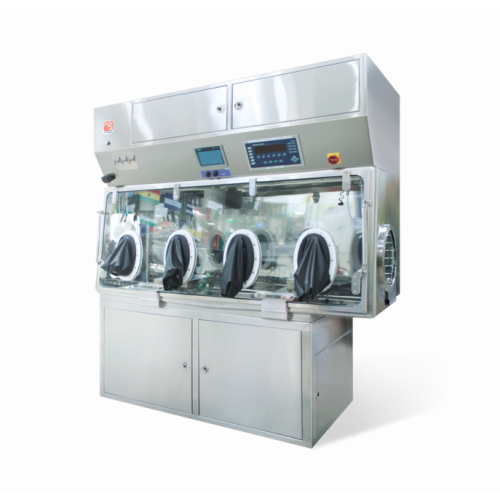
Production isolator for powder preparation and weighing
Ensure precise weighing and safe handling of pharmaceutical powde...
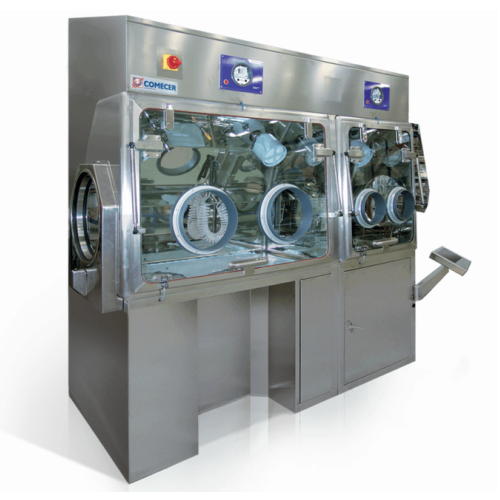
Isolator for weighing and dispensing of micronized substances
Ensure safe and precise handling of highly potent substanc...
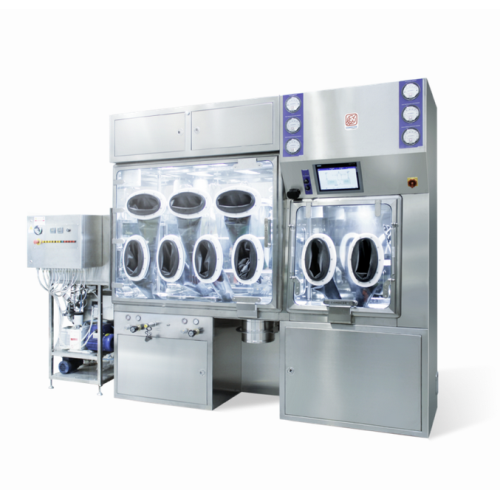
Custom r&d isolator for precise dispensing operations
When handling sensitive compounds, precision and operator safety ar...
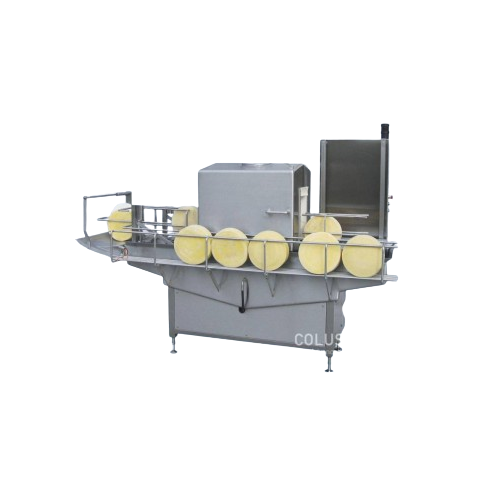
Automatic cheese washing system for dairy industry
Ensure your cheese production maintains optimal hygiene and efficiency...
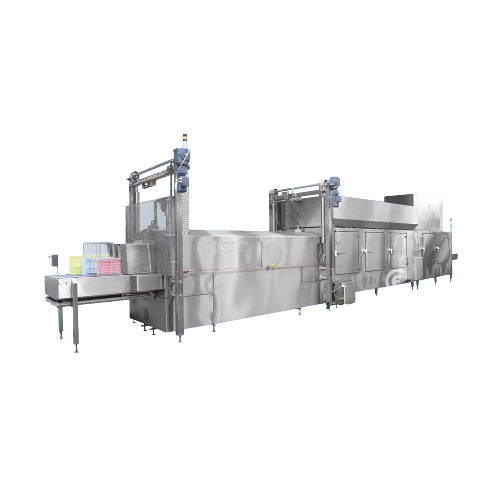
Chocolate mould washer
Ensure immaculate cleanliness and precise drying of chocolate moulds, enhancing production efficiency ...
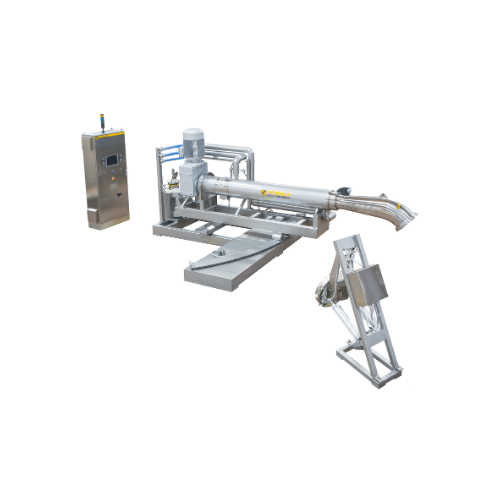
Oscillating heat exchanger for gelatin production
Ensure hygienic transfer in gelatin production with an innovative oscil...
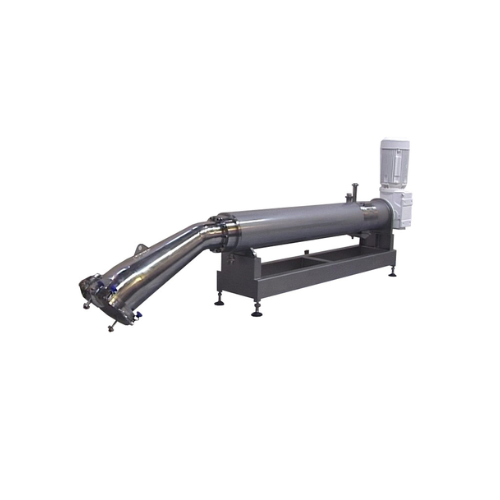
Scraped surface heat exchangers for gelatine processing
Effortlessly manage the cooling, gelling, and extrusion of gelati...
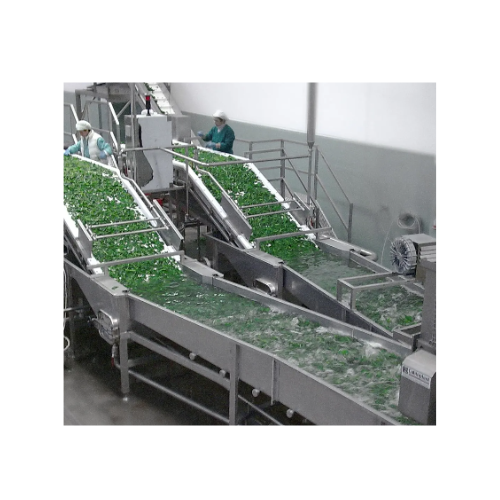
Leaf vegetable sorting and cooling system
Ensure optimal freshness and extended shelf life for leaf vegetables with precis...
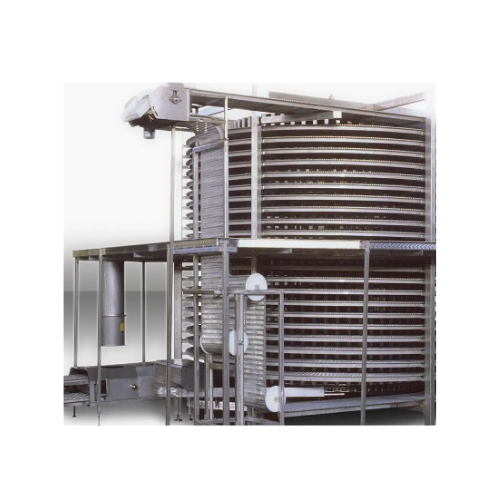
Industrial spiral freezing system
Optimize your food processing line with a reliable spiral system, designed to efficiently...
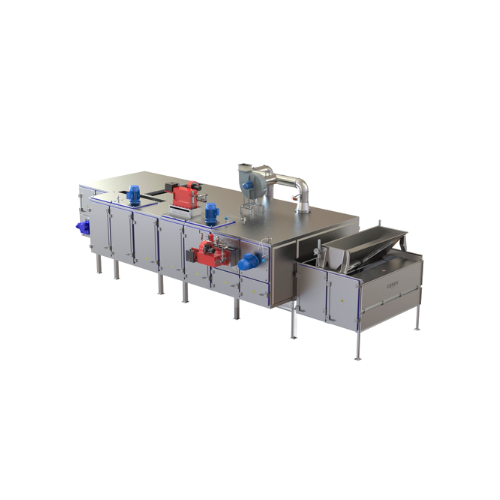
Nut and seed roaster for snack production
Ensure precise roasting and cooling of nuts and seeds while maintaining hygiene ...
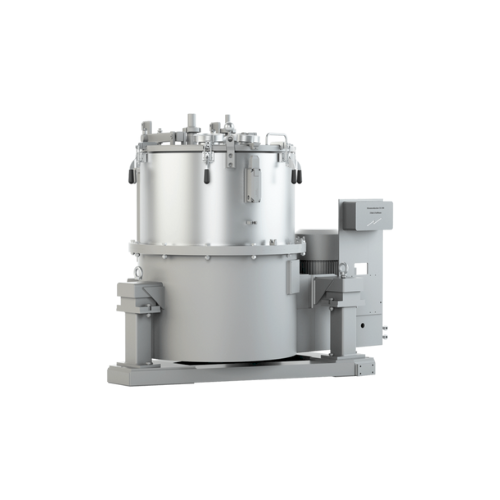
Industrial filter centrifuges for high solids content processing
Optimize processing of high-solid slurries with efficie...
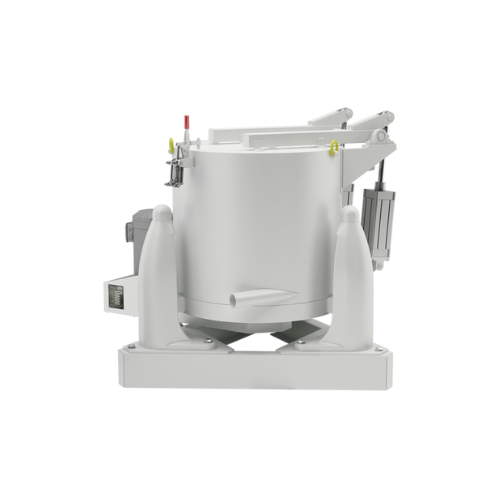
Batch centrifuge for de-oiling metal chips
Optimize your metalworking process with a centrifuge solution that handles de-o...
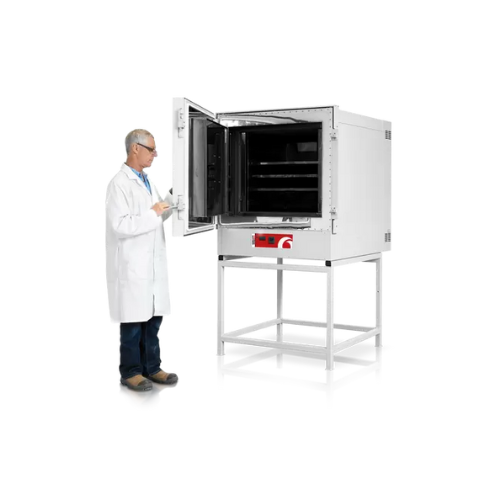
High temperature industrial oven for advanced heating processes
Achieve precise heat treatment for critical components, ...
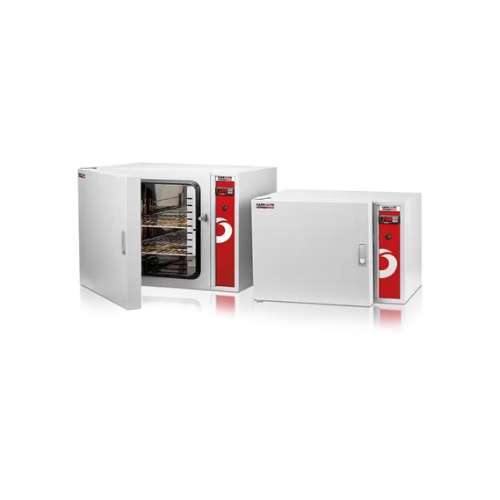
Laboratory oven for accurate thermal processing
Achieve precise thermal control for sensitive formulations, ensuring consi...
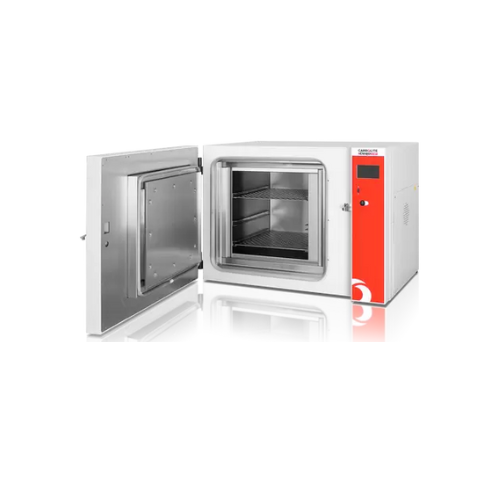
High temperature laboratory oven for precise heating
Achieve precise temperature control and uniformity essential for hea...
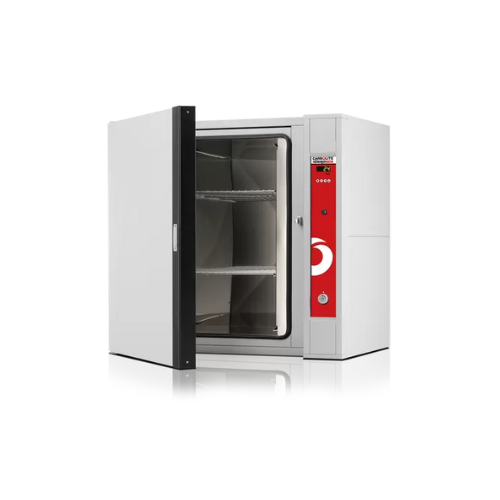
Fan convection laboratory oven for precise temperature control
Ensure uniform heating and rapid recovery in demanding la...
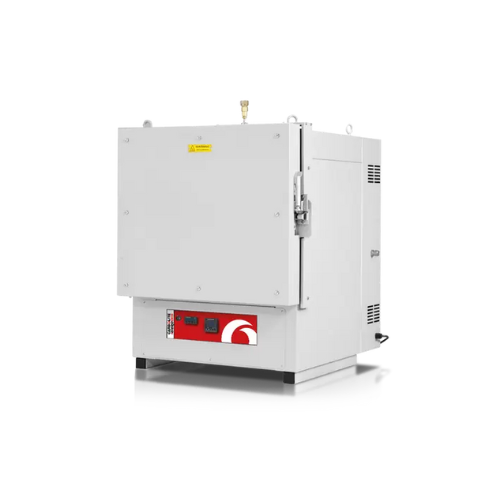
High temperature clean room ovens
Achieve precise environmental control for heating, drying, and sterilizing sensitive mate...
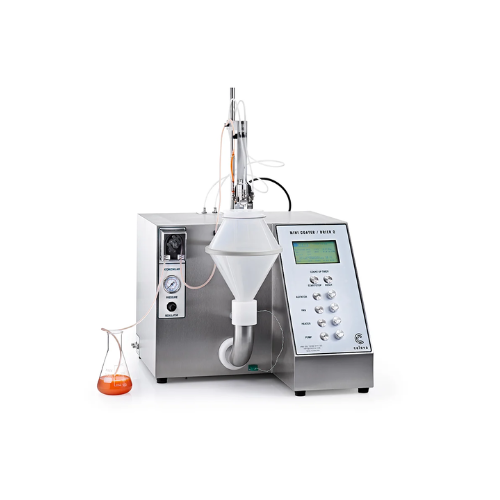
Small batch tablet and pellet coating solution
Optimize your small batch coating and drying processes with a versatile ben...
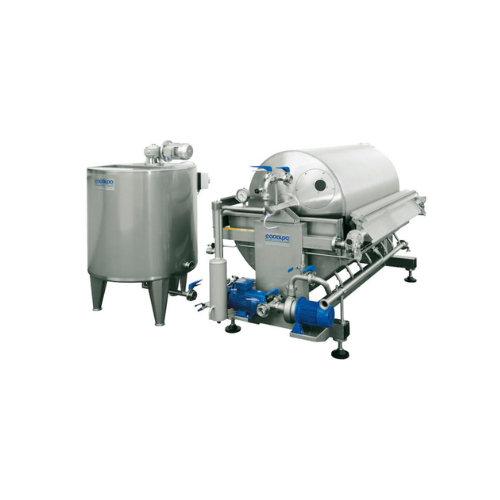
Rotary vacuum filter for wine filtration
Enhance your wine production with efficient filtration of grape must and wine lees...
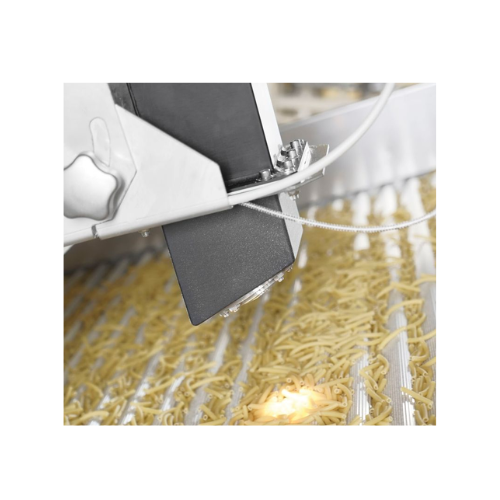
Digital process service for regulating water in dough preparation
Achieve consistent dough moisture levels with this di...
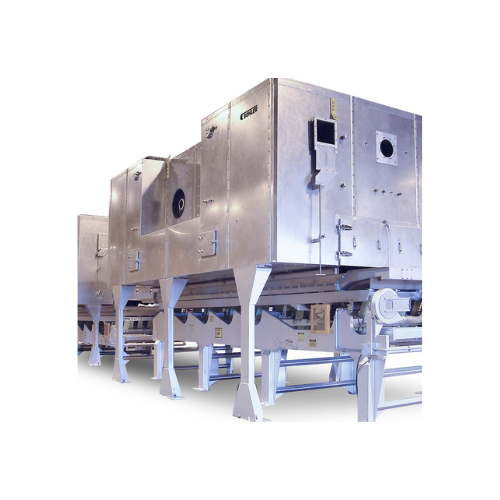
Fluid-bed toaster for cereal processing
Achieve precise control over texture and taste while reducing operating costs with ...
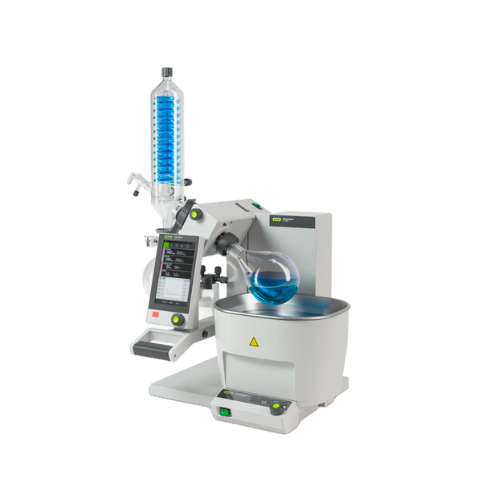
Rotary evaporation for laboratory applications
Achieve precise evaporation and concentration with modular, high-speed rota...
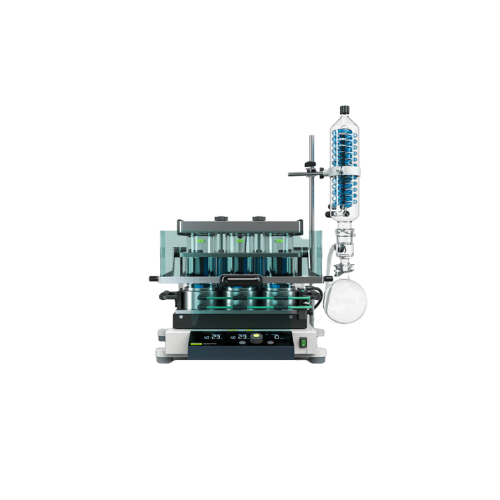
Parallel evaporation system for laboratory sample preparation
Achieve precise sample concentration and drying with autom...
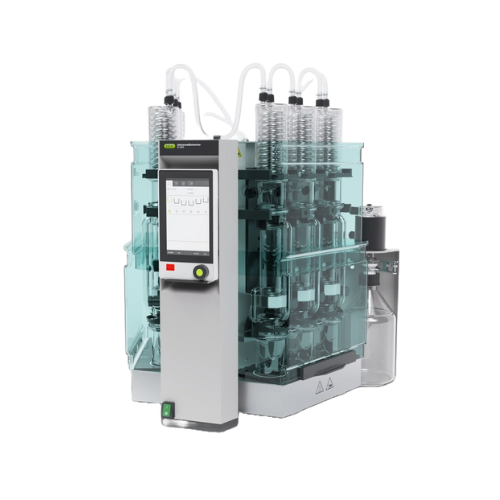
Multitasking extraction system
Effortlessly manage complex extractions with high-speed, reliable results, ensuring sample in...
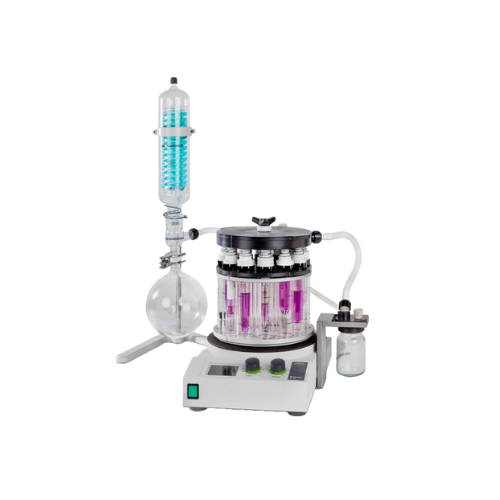
Parallel sample evaporator
Process multiple samples efficiently with precise control, ensuring quick evaporation and consist...
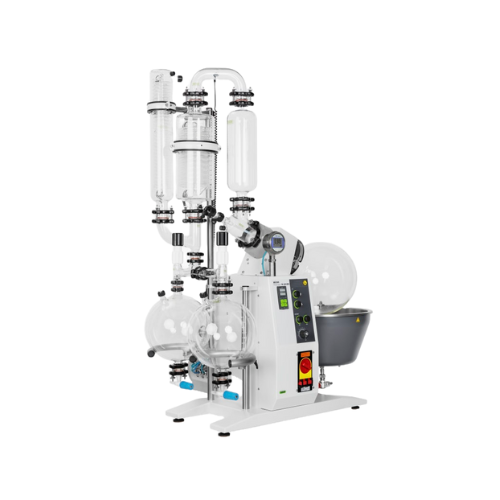
Industrial rotary evaporator for large-scale distillation
Ideal for scaling up laboratory processes, this robust rotary ...
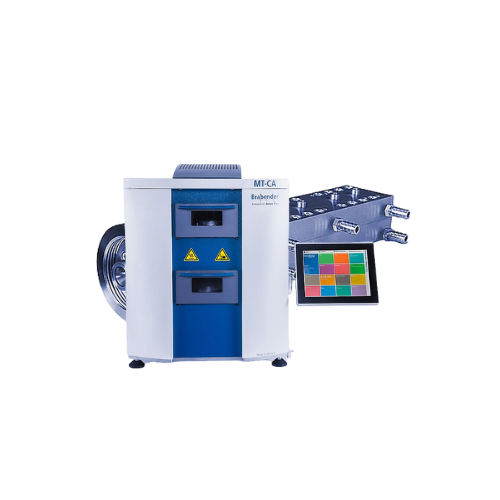
Moisture analyzer for flour and tobacco
Optimize your moisture measurement process with precision and speed, ensuring quali...
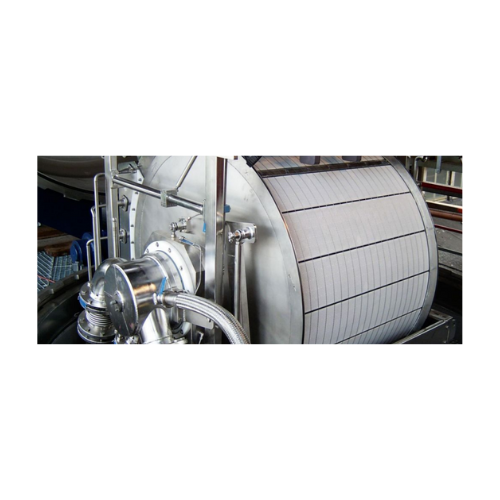
Pressure drum filter for fine-grained products
Achieve exceptional precision in fine particles processing with this pressu...
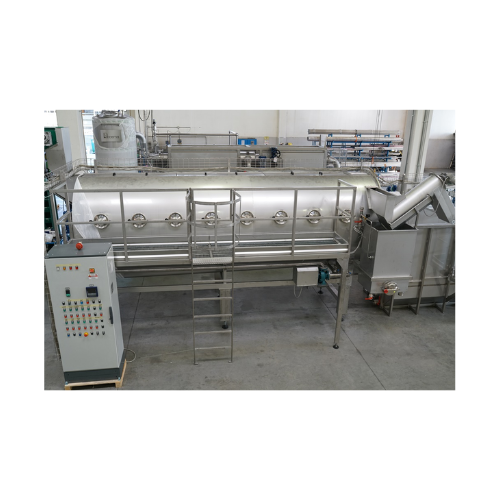
Chestnut sterilisation system for parasite control
Ensure pest-free chestnuts with precision-controlled hot water sterili...
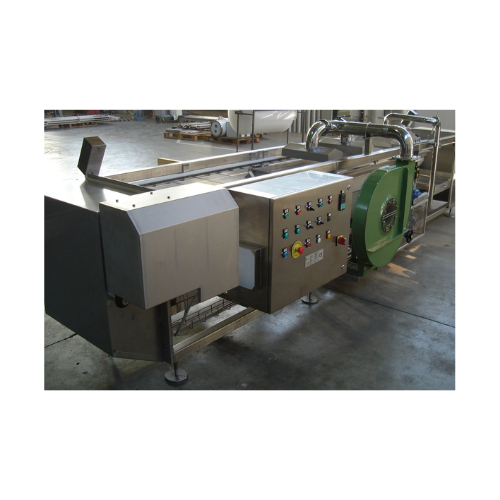
Chestnut glazing tunnel
Achieve perfectly glazed chestnuts every time with our linear glazing tunnels that ensure consistent ...
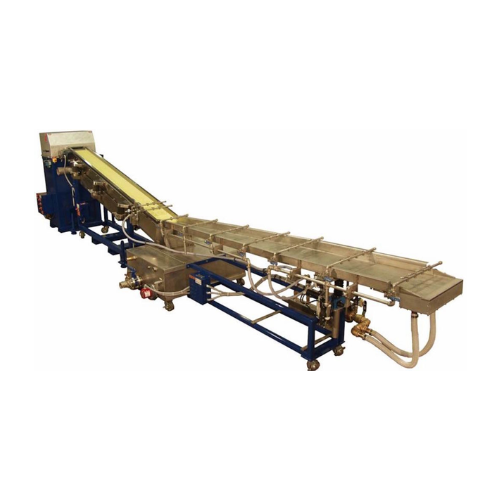
Automatic strand pelletizer for reinforced and filled polymers
Optimize your polymer production with precise pelletizing...
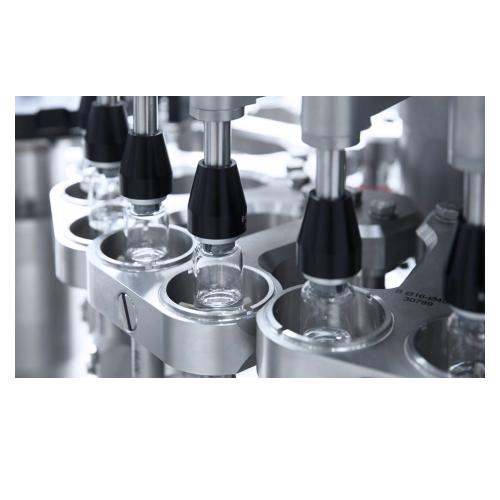
Container exterior cleaning for pharmaceutical applications
Achieve consistent cleanliness and dryness for your containe...
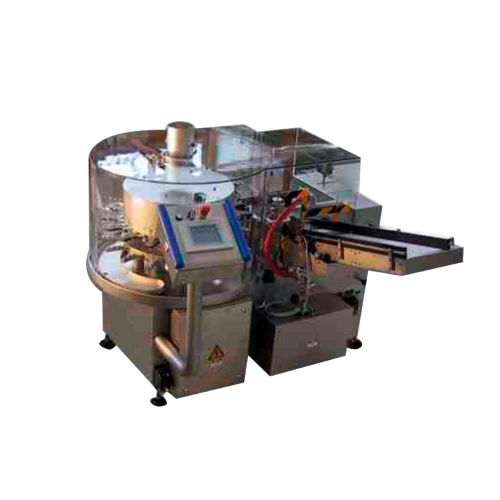
Automated washing system for vials, syringes, cartridges, and ampoules
Achieve sterile conditions with this high-speed ...
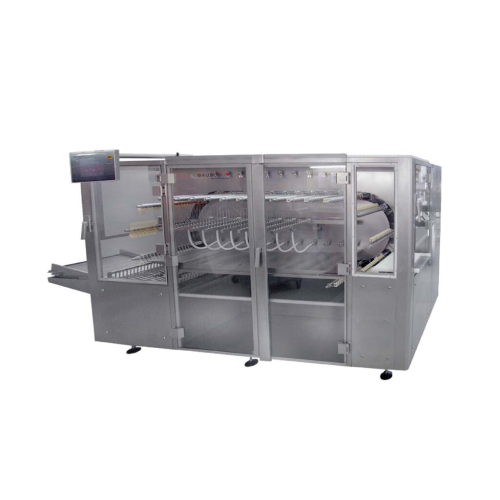
High-speed washing system for ampoules and vials
Ensure contamination-free ampoules and syringes with this advanced washin...
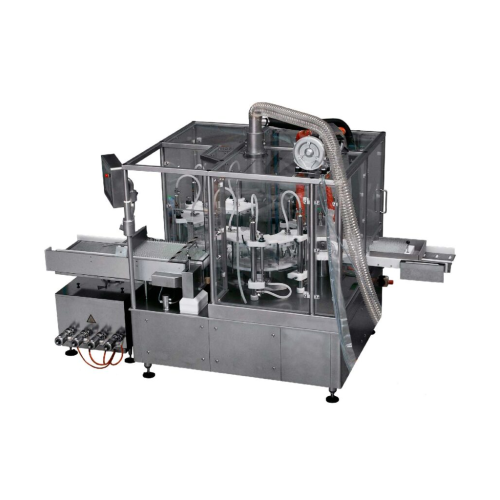
Automatic external washing system for ampoules and vials
Ensure optimal cleanliness of liquid medication containers with ...
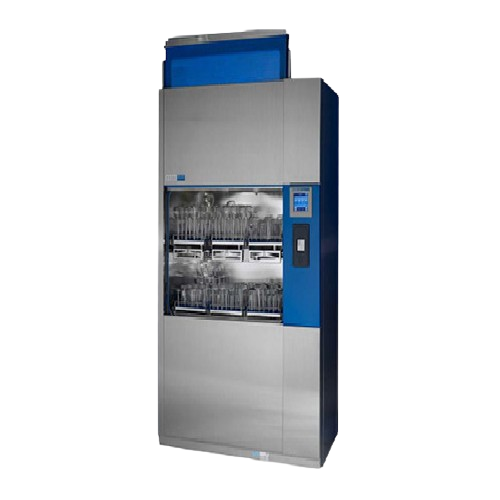
Laboratory instrument washer for scientific research and quality control
Achieve consistent results with thorough clean...
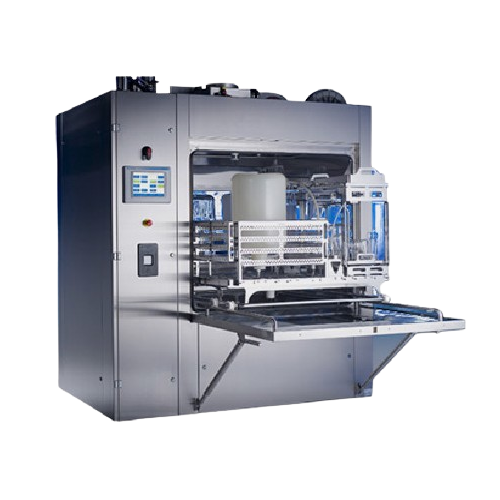
Gmp washer for pharmaceutical contamination control
Ensure verifiable cleaning and drying of critical components in bioph...
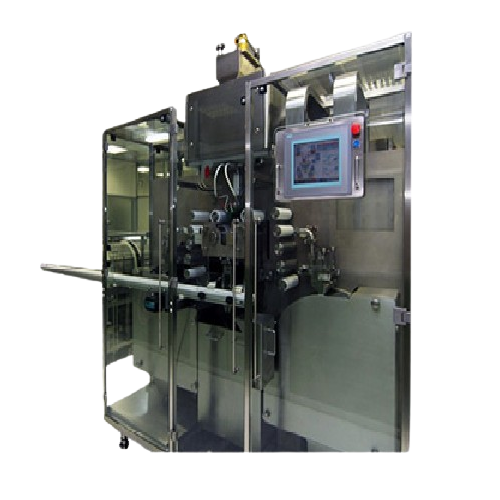
Soft gel encapsulation system
Efficiently produce high-quality soft gel capsules with precision encapsulation, rapid drying,...
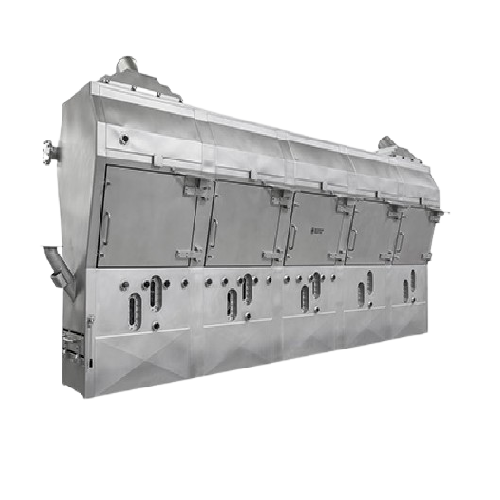
Continuous wet granulation equipment
Optimize your production line with continuous wet granulation, seamlessly transforming...
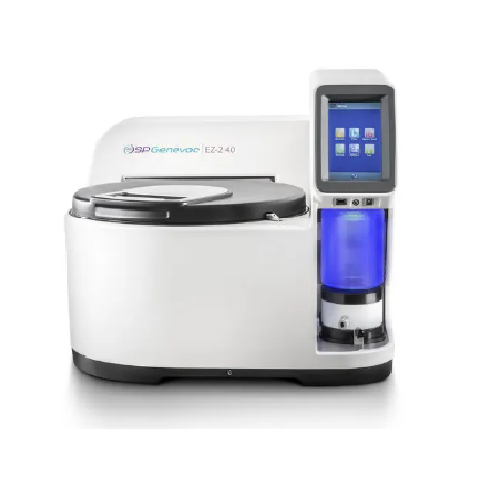
Centrifugal evaporator for medicinal chemistry
Achieve precise evaporation and crystallization with innovative anti-bumpin...

Pilot lyophilizers for pharmaceutical development
For precision freeze-drying in clinical trial production, these pilot l...
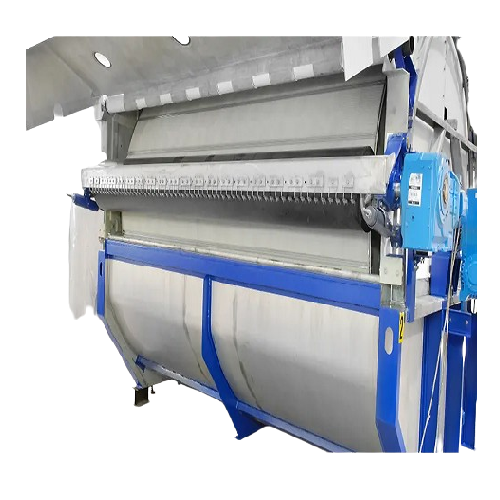
Vacuum drum filter for solid/liquid separation
Optimize your solid/liquid separation process with a versatile vacuum drum ...
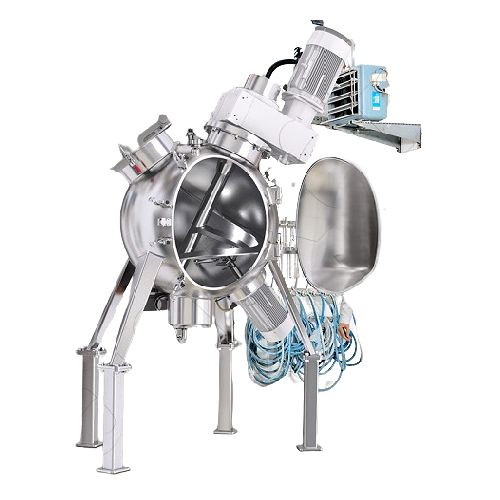
Spherical mixer for industrial mixing applications
Experience precise and efficient mixing with this hollow spherical mix...
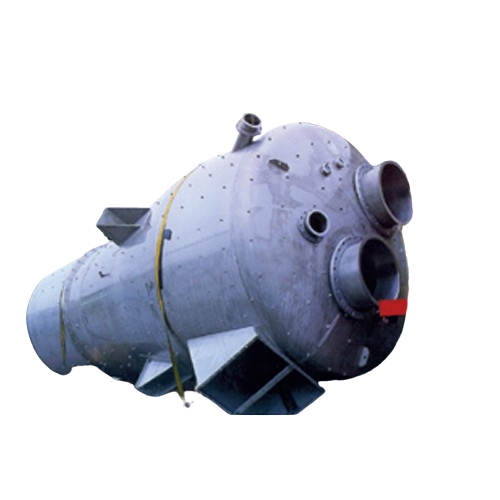
Fluidized bed spray granulators for liquid to solid conversion
Transform liquid suspensions into stable, dust-free granu...
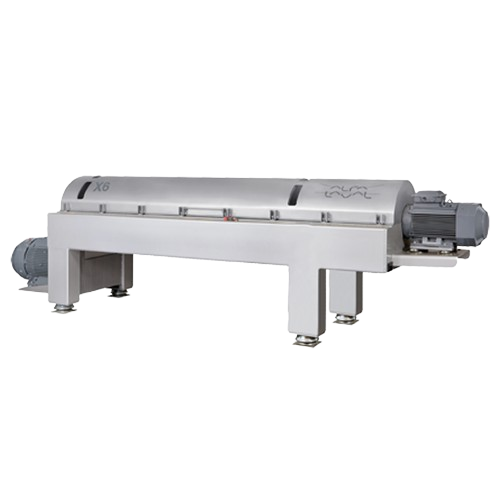
Decanter centrifuge for olive oil processing
Optimize olive oil production by achieving higher oil clarity and reduced wat...
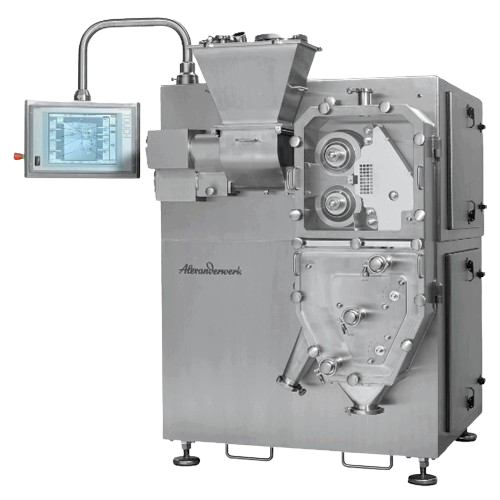
Pharmaceutical roller compaction solution
Optimize your pharmaceutical tablet production with precision granulation and co...
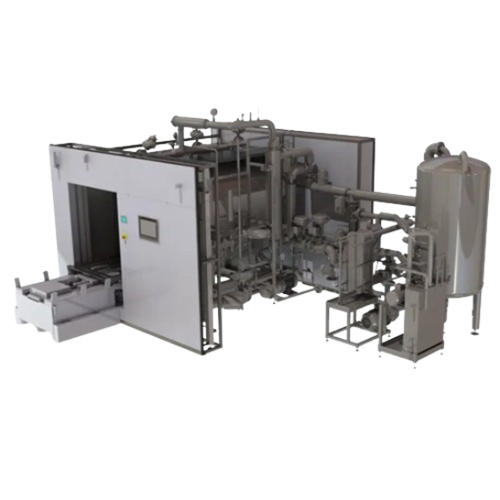
Superheated water sterilization autoclave for pharmaceutical applications
Ensure precise sterilization of sensitive li...
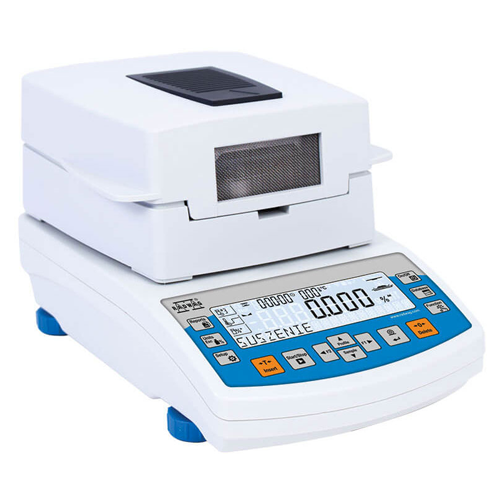
Moisture analyzer for laboratory samples
Accurate moisture analysis is crucial for ensuring product quality in pharmaceutic...
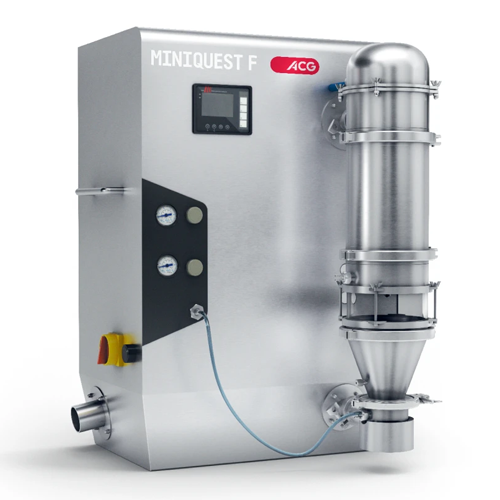
Tabletop granulation system for small batches
Enhance R&D capabilities with this innovative solution designed for gra...
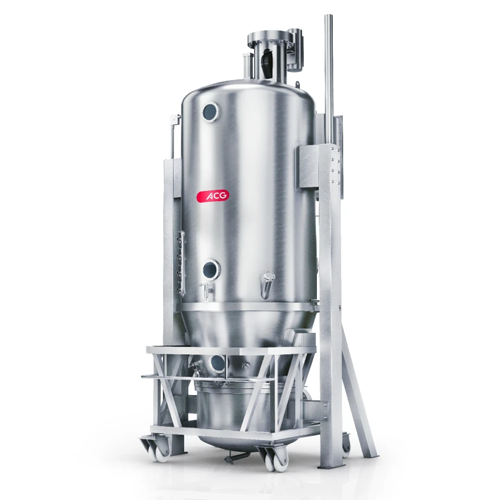
Advanced fluid bed for pharmaceutical granulation
Achieve precise granulation and drying for pharmaceutical powders with ...
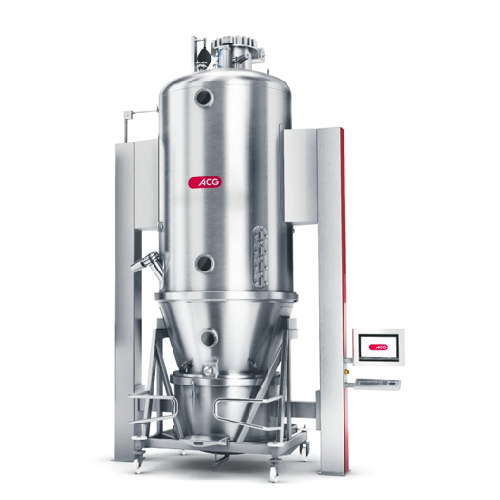
Fluid-bed granulator for top-spray applications
Need precise granulation and drying for sensitive materials? This fluid-be...
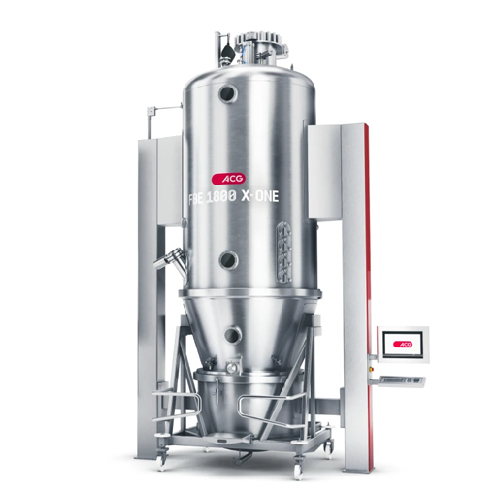
Fluid bed granulator for pharmaceutical applications
Optimize your granulation and drying processes with advanced fluid-b...
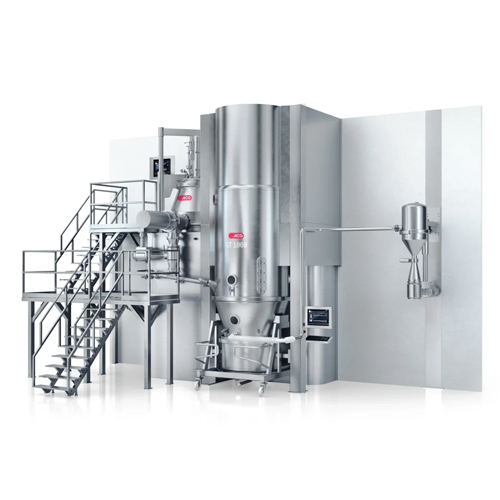
Integrated granulation train for pharmaceutical processes
Achieve precise granulation, uniform mixing, and efficient dry...
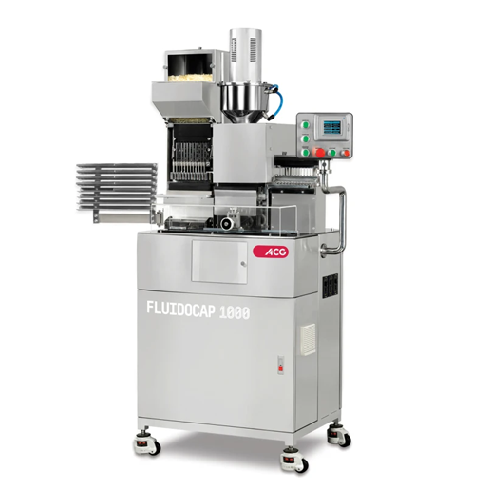
Liquid capsule filling for r&d and pilot-scale production
Optimize liquid capsule production with a compact machine that...
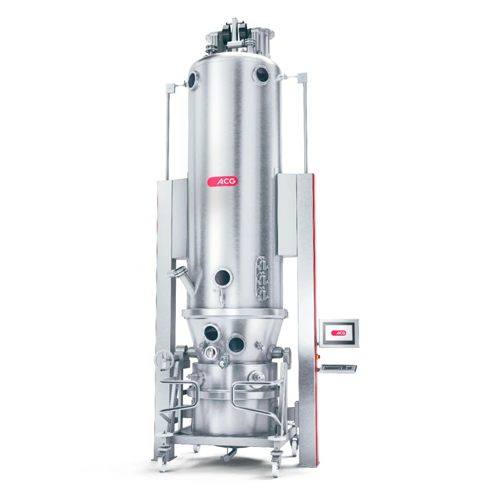
Fluid bed combo for granulation and coating
Achieve seamless granulation and coating with batch and high-speed operations,...
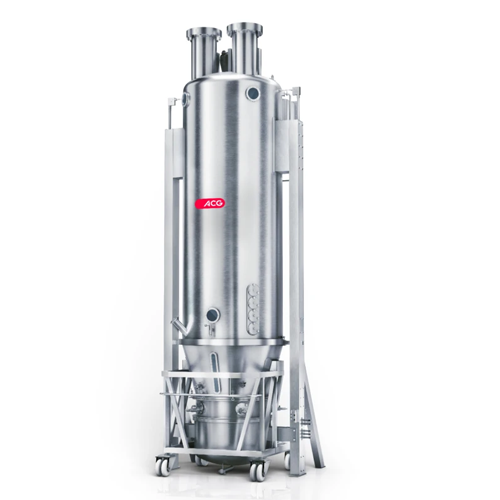
Fluid bed combo for top-spray granulation and wurster coating
Optimize your batch processing with a versatile system cap...
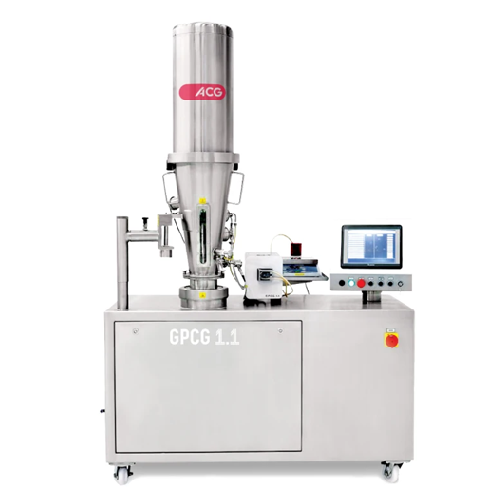
Fluid bed combo for granulation and coating
Streamline your manufacturing with a versatile fluid bed combo, integrating gr...
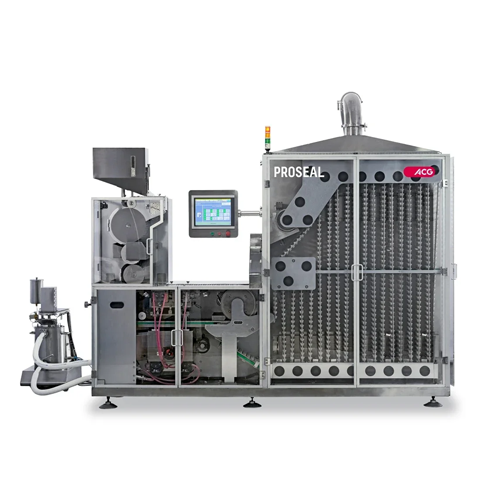
Capsule band sealer for liquid-filled hard capsules
Seamlessly seal liquid-filled hard capsules to enhance product integr...
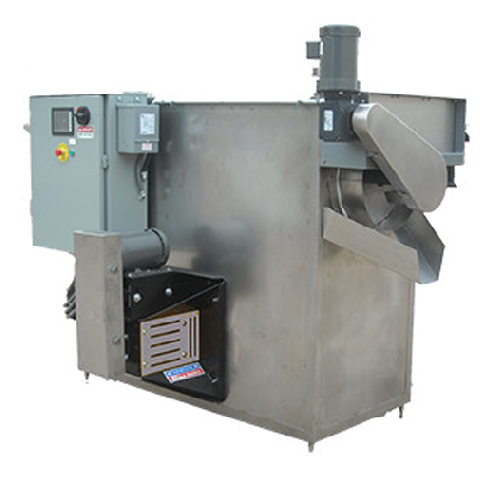
High capacity continuous puffer for popcorn
Optimize your snack production with advanced airflow and speed controls design...
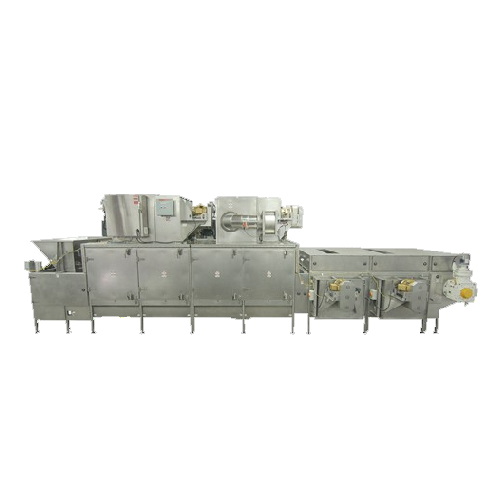
Continuous nut roaster for large-scale nut processing
Streamline your nut processing capabilities with a machine designed...
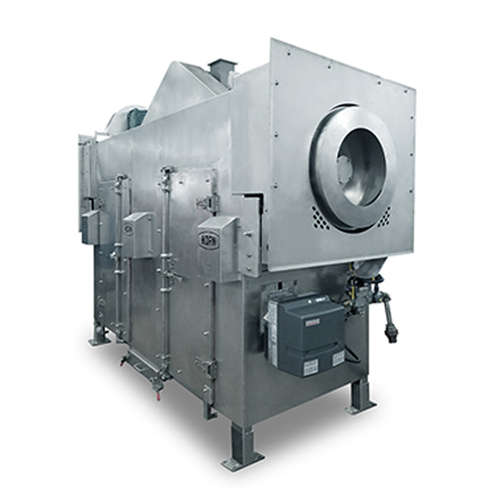
Modular rotary oven for snack food processing
Optimize flavor infusion and moisture control in snack production with a mod...
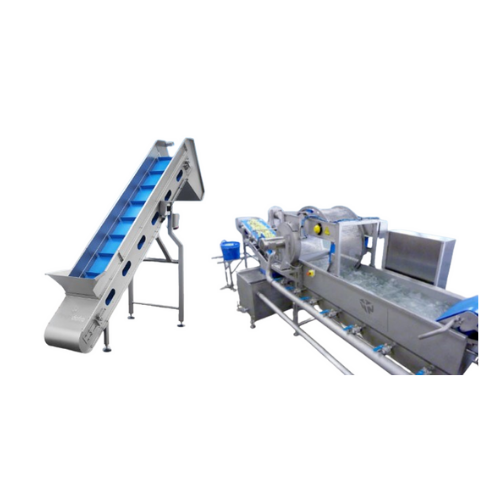
Salad processing line for fresh cut vegetables
Efficiently transform raw produce into market-ready salad mixes with stream...
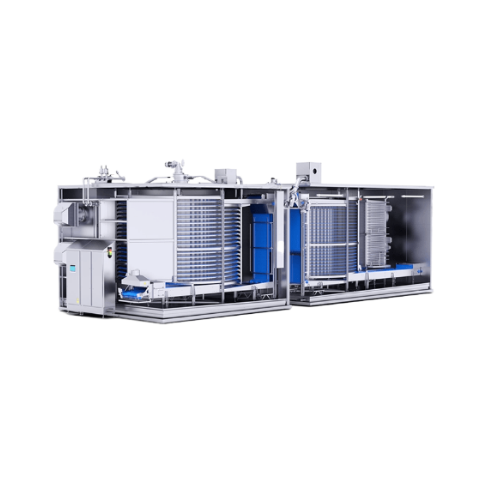
Spiral pasteurization system for packaged foods
Enhance product durability and quality with a compact spiral pasteurizatio...
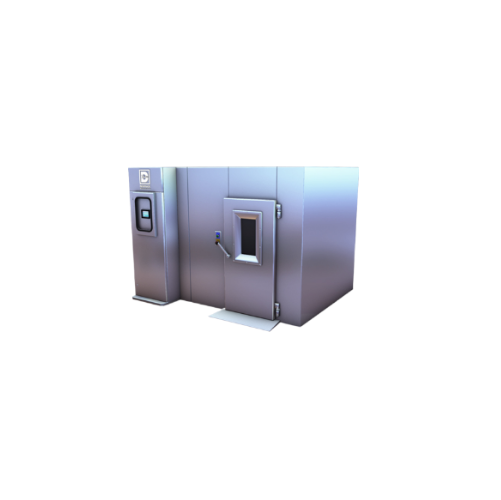
Multi-purpose batch cooker for meat, fish, and vegetables
Achieve consistent cooking and uniform results for diverse foo...
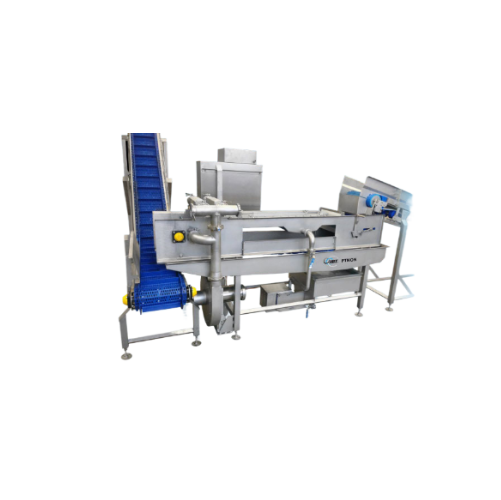
Fruit and vegetable shelf life extender
Extend the freshness and appeal of your produce with our innovative dipping solutio...
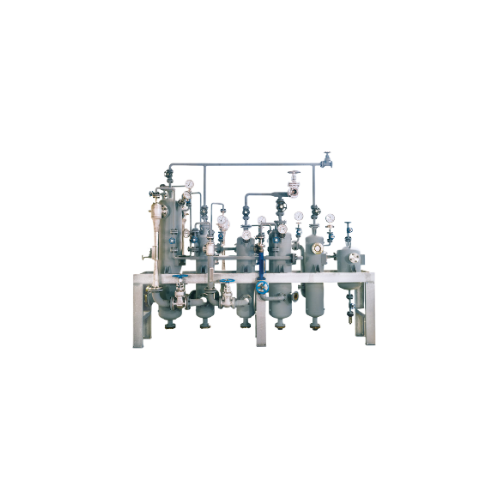
Multi-stage steam jet vacuum pumps for industrial applications
Achieve precise vacuum conditions for evaporation, distil...
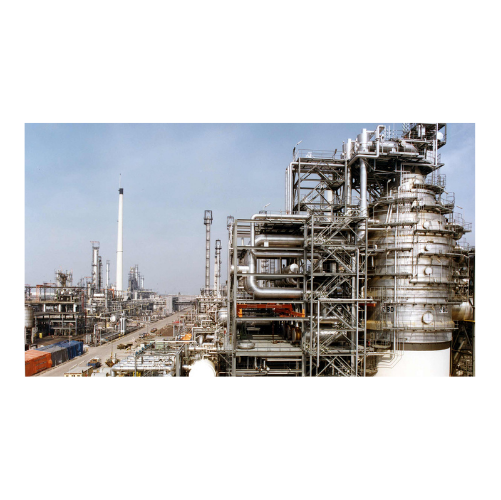
Combined steam jet and liquid ring vacuum pump systems
Optimize vacuum creation and maintenance in processes like distill...
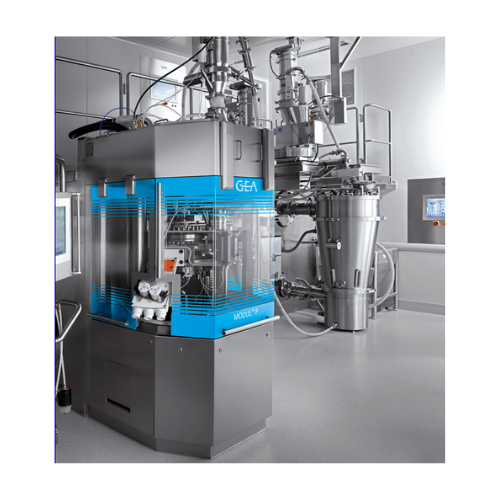
Continuous granulation and compression line for pharmaceuticals
Optimize your pharmaceutical production with a line that...
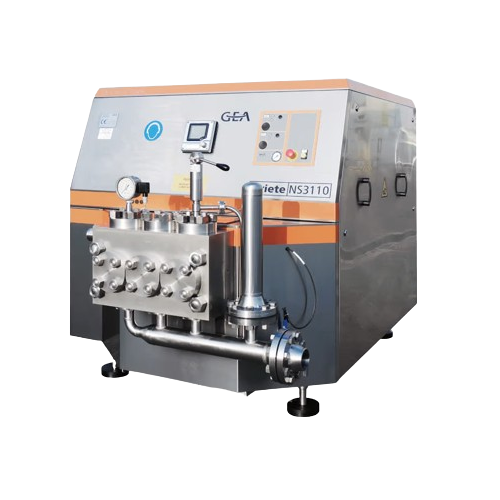
High pressure pumps for viscous fluid transfer
Optimize fluid transfer with high pressure pumps designed to handle viscous...
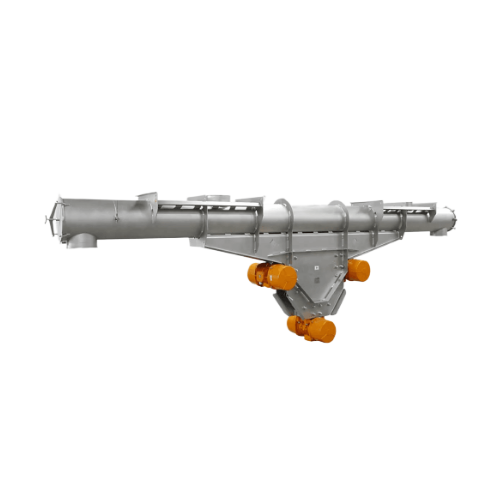
Vibrating conveyor for powder and granule handling
Effortlessly convey and process fragile products with precision, minim...
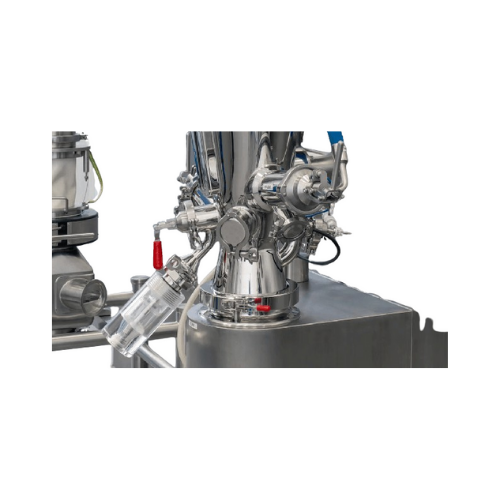
Contained powder sampling system
Ensure contamination-free sampling of active powders with fully contained system integratio...
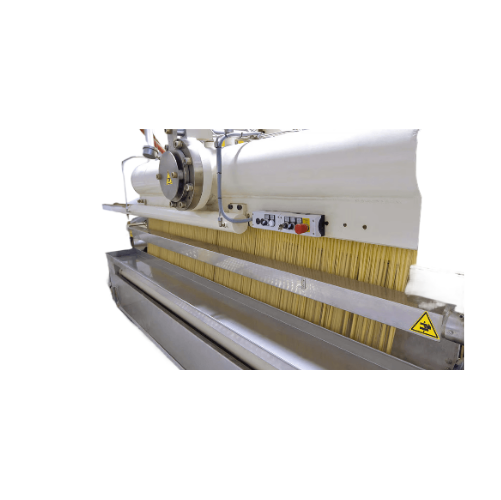
Long-cut pasta production line
Optimize your long-cut pasta production with a single-tier system designed for precise moistu...
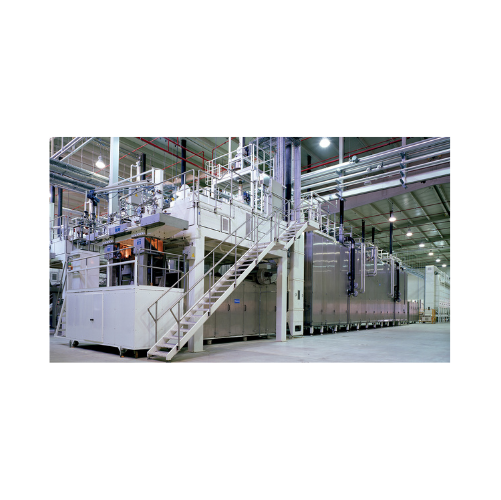
Short-cut pasta production line
Optimize your pasta production with a line engineered for efficient short-cut pasta shaping,...

Industrial Long-cut pasta production line
Achieve superior long pasta quality with energy reductions up to 30%, featuring ...
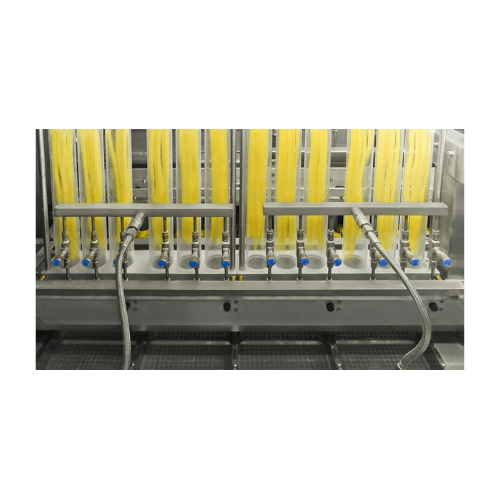
Nest-shaped pasta production line
Streamline your pasta production with a solution designed to retain the integrity of nest...
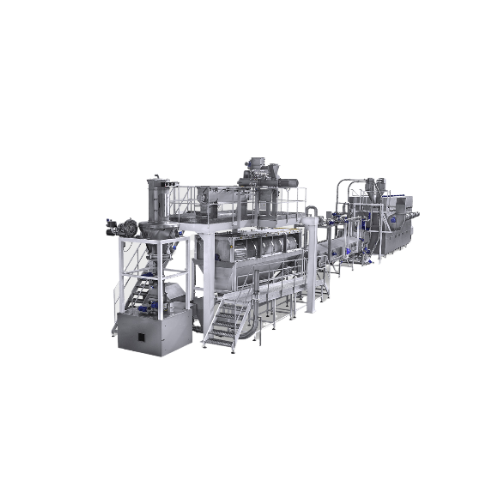
Couscous production line
Enhance your couscous production with a seamlessly integrated line that ensures precise granule sizi...
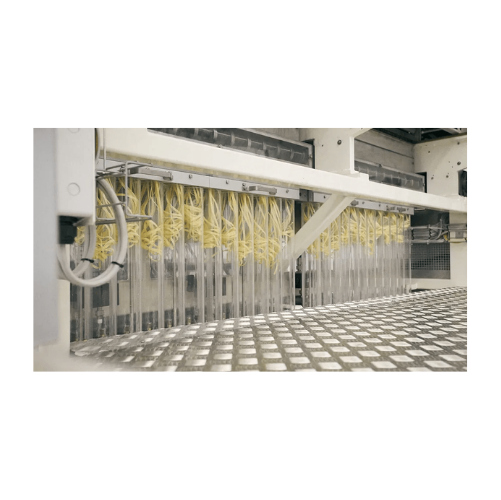
Nest-shaped short pasta production line
Optimize your pasta production with a streamlined process that enhances drying effi...
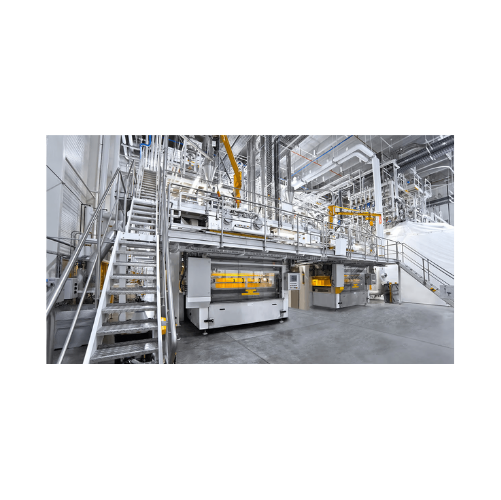
Long-cut multi tier pasta line
Optimize your pasta production with high-speed, multi-tier drying and precise compression, en...
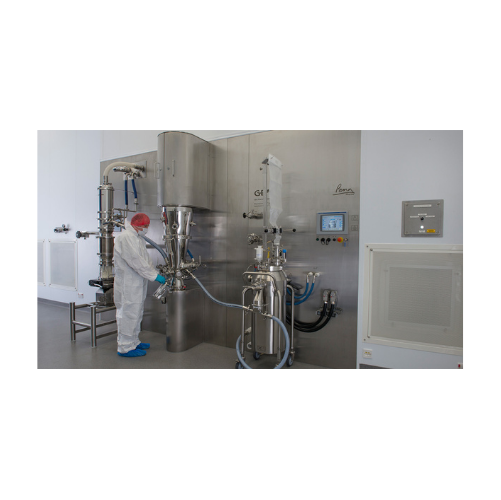
Pharmaceutical r&d granulation system
Optimize your pharmaceutical research with a versatile small-scale granulation system...
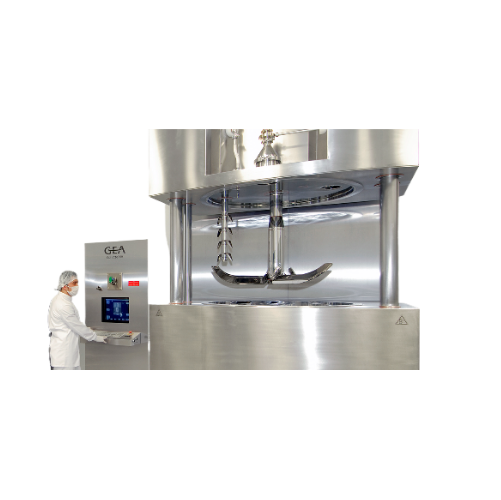
High shear granulator for pharmaceutical applications
Efficiently transform powders into uniform granules for consistent ...
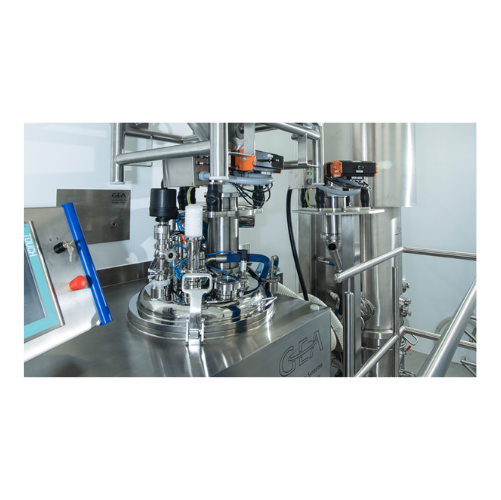
Pharmaceutical bottom-drive high shear granulator
Achieve optimal granule uniformity and precise control over moisture le...
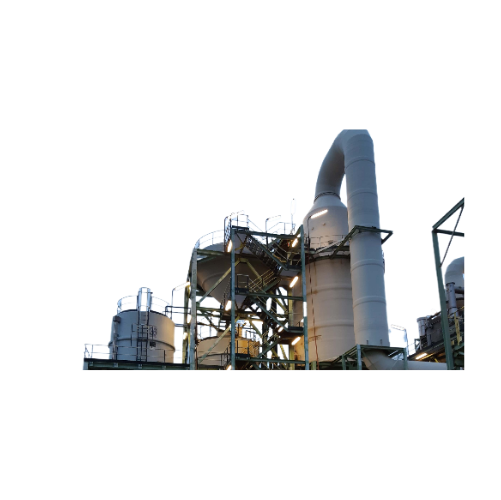
Heavy metal removal system for industrial flue gas
Effectively remove harmful heavy metals from industrial emissions whil...

Lecithin adding system for dairy powders
Enhance your spray drying process by seamlessly integrating lecithin to improve so...
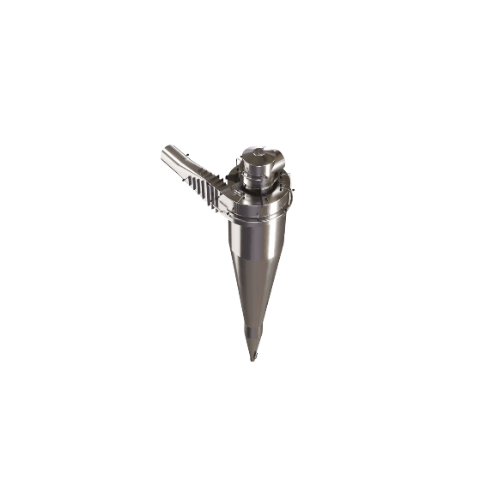
Powder separation cyclone for food and chemical industries
Optimize your powder production with advanced cyclone technol...

Process analytical technology for lyophilization
Ensure product integrity by detecting trace contaminants and optimizing l...
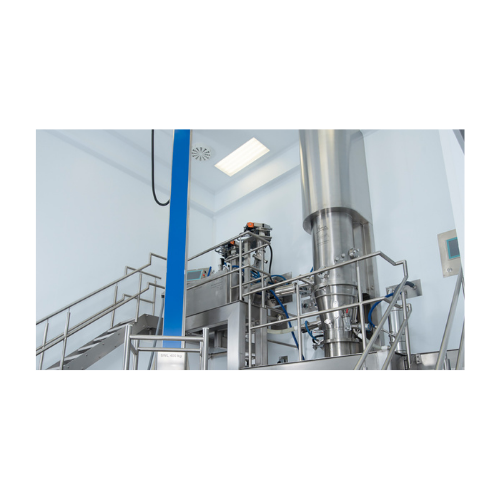
Fluid bed pellet coating solution
Achieve precise and uniform pellet coating with fluid bed technology for enhanced product...
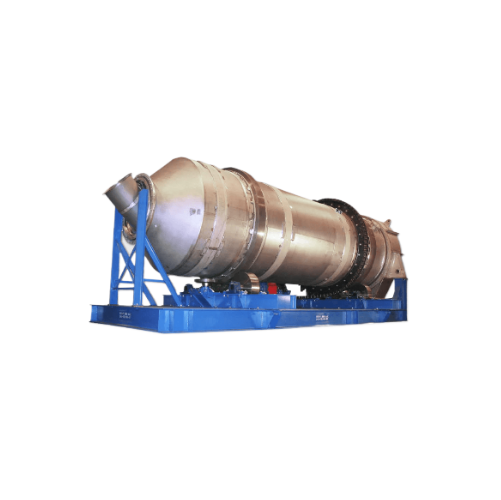
Potash conditioning system
Achieve optimal potash granule polishing and drying with precise control over moisture and glazin...
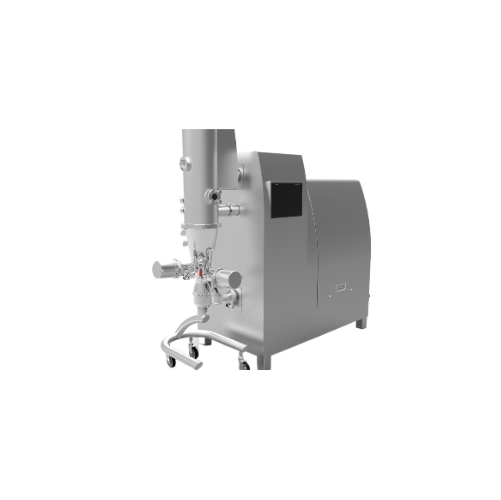
Pharmaceutical fluid bed processor for r&d
Optimize your pharmaceutical R&D with a versatile fluid bed processor desi...
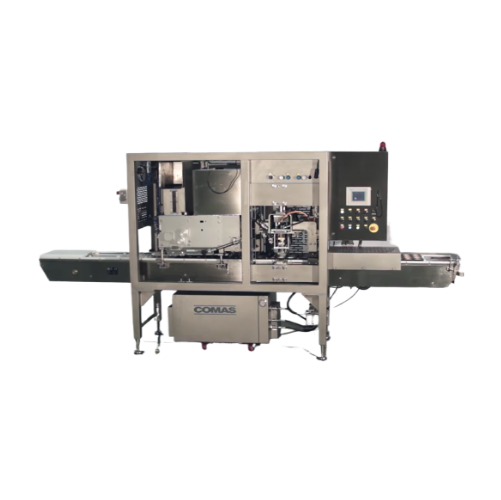
Aroma recovery system for instant coffee processing
Capture and enhance coffee aromas with a specialized system designed ...
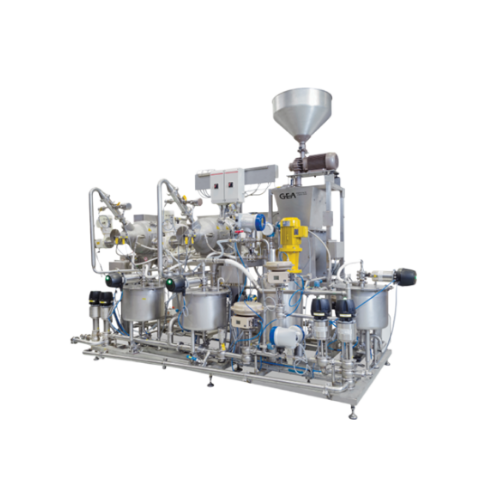
Wet grinding system for coffee flavor preservation
Achieve unparalleled coffee flavor and aroma by integrating a low-temp...
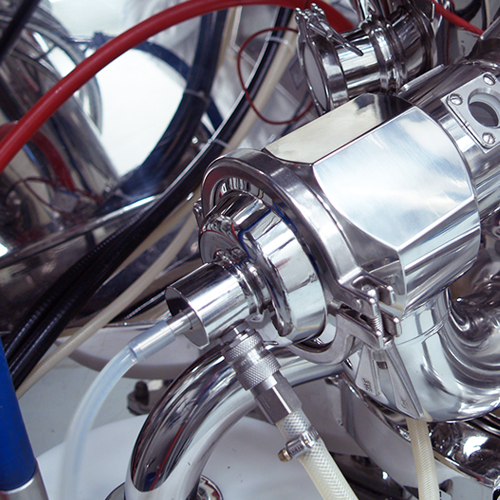
Flexstream fluid bed processor for pharmaceutical applications
Addressing the limitations of traditional fluid bed proce...
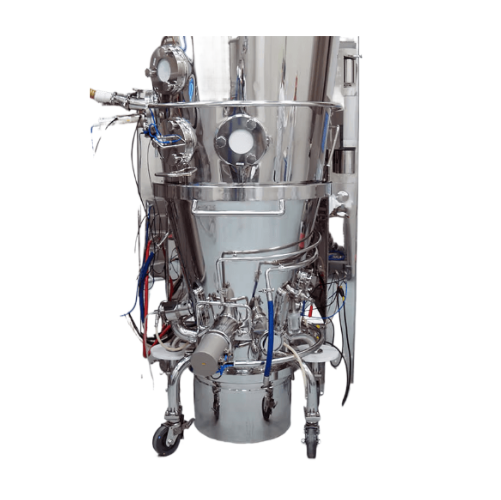
Fluid bed processing of pharmaceuticals
Enhance your pharmaceutical production with versatile fluid bed processors, enablin...
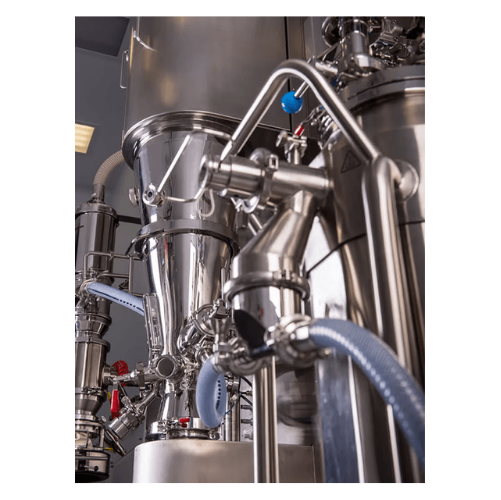
Pharmaceutical fluid bed r&d processing
Ensure precise formulation and consistency in pharmaceutical and nutraceutical tabl...
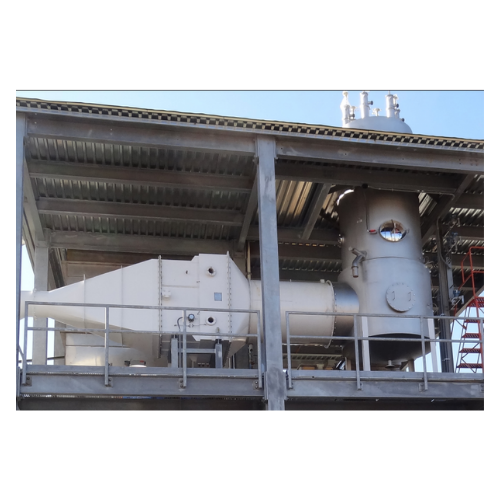
Dust-free granulation system for non-heat sensitive liquid feeds
Transform liquid feeds into dust-free, free-flowing gra...
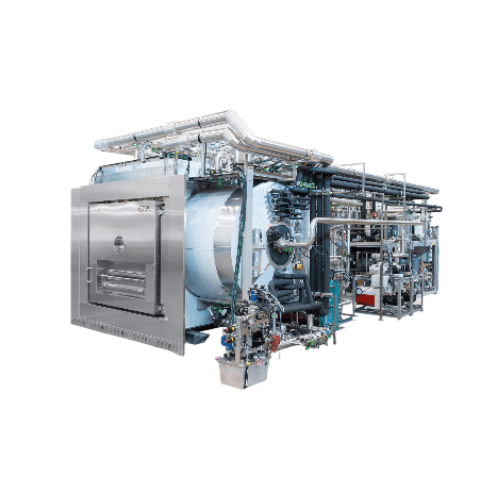
Pharmaceutical lyophilization for large-scale production
Ensure precision in pharmaceutical freeze drying with controlled...
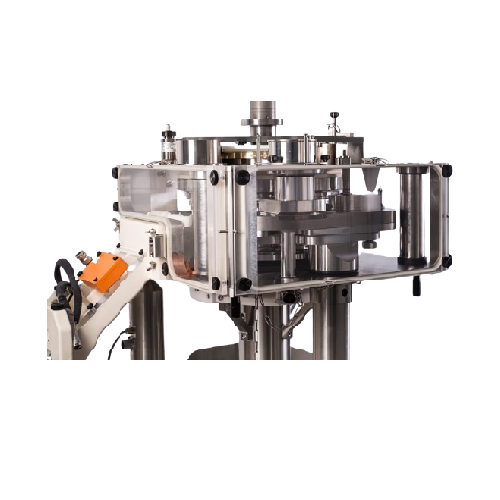
Wash-off-line system for pharmaceutical plants
Optimize your production with a versatile wash-off-line system, ensuring pr...
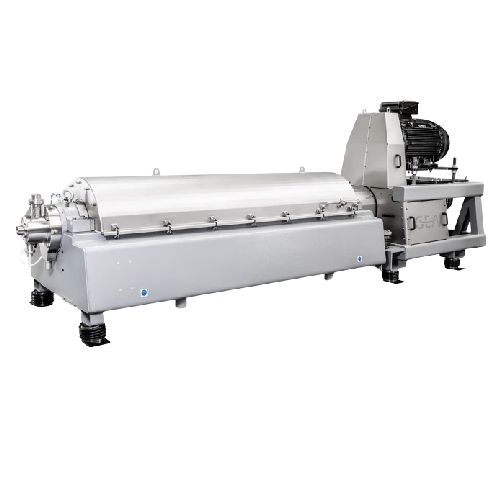
2-phase separating decanter for chemical and mineral processing
Ensure precise separation and optimal moisture control i...
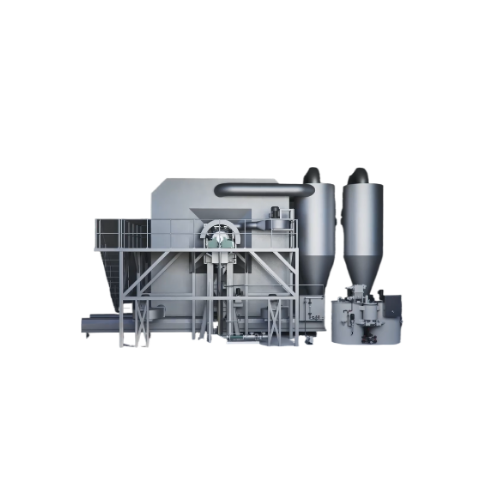
Biosolids granulator for waste treatment
Transform raw sludge into valuable granules with a solution that securely dries an...
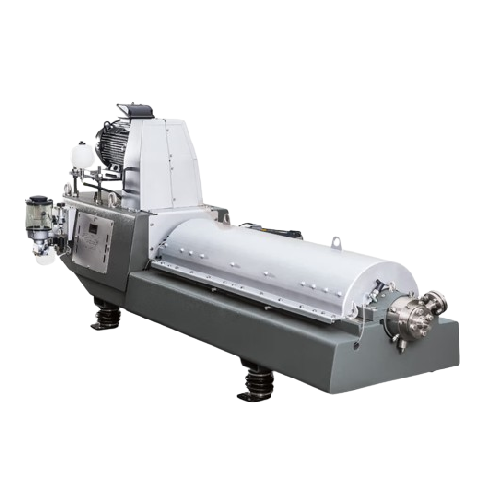
Decanter centrifuge for chemical and mineral processing
Optimize dewatering and clarification efficiencies in your proces...
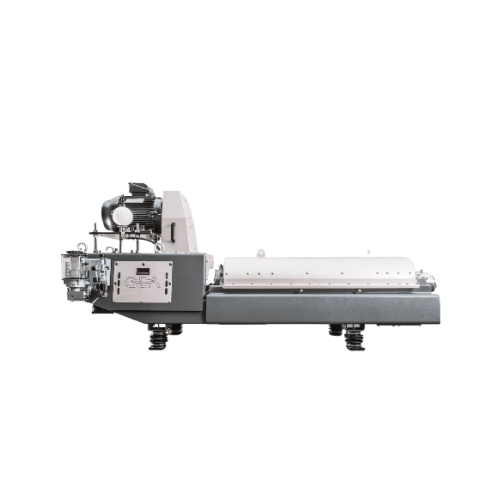
Chemical and mineral processing centrifuge
Optimize your chemical and mineral extraction processes with this high-performa...
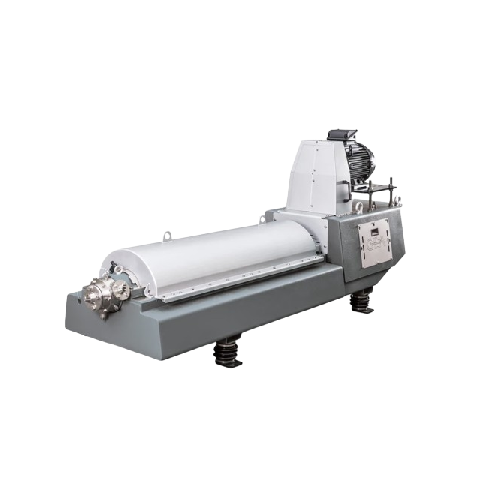
3-phase separating decanter for animal by-products
Enhance your recovery processes with a decanter centrifuge designed to...
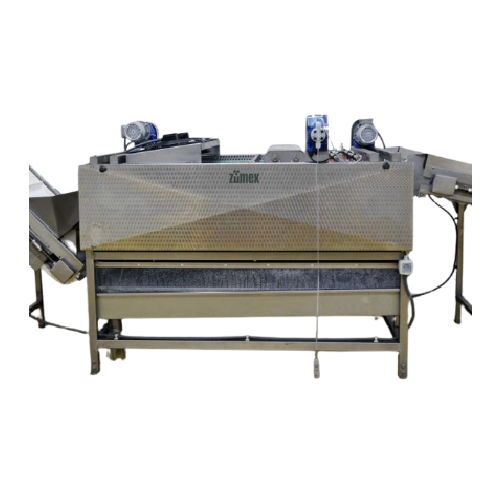
Industrial fruit washing and loading hopper system
Streamline your juice production by ensuring optimal fruit preparation...
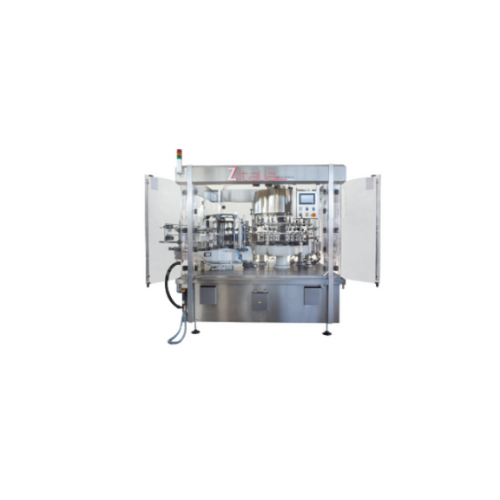
Stand-alone autoclaves with round chamber for laboratory and pharmaceutical use
Achieve seamless sterilization and pre...
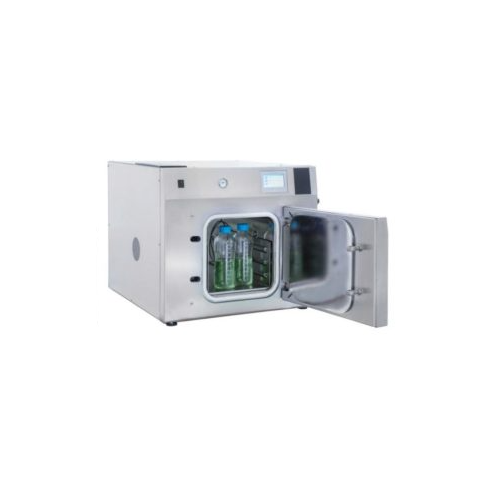
Table top autoclaves for laboratory use
Optimize sterilization efficiency in your laboratory with space-saving, high-capaci...
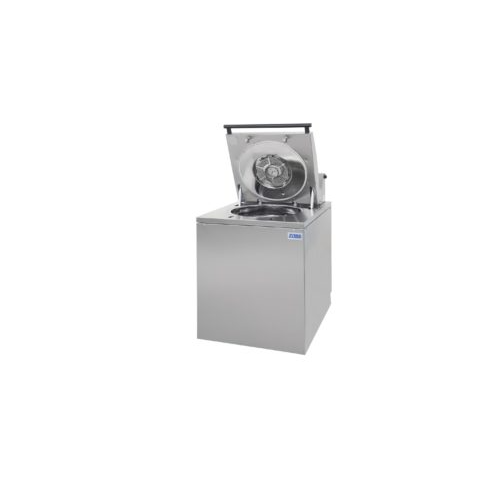
Vertical autoclaves for laboratory use
Optimize your lab’s sterilization and drying processes with versatile vertical...
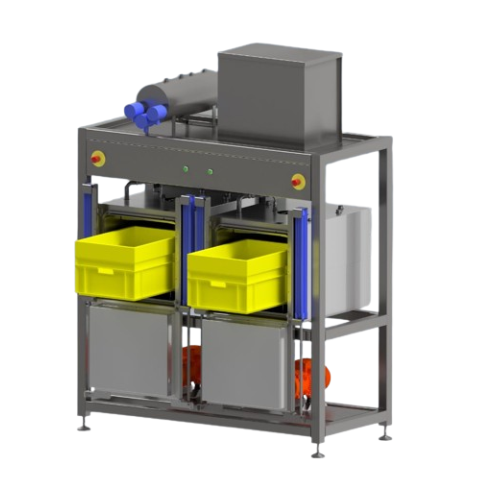
Steam conditioning plants for polyamide plastics
Enhance the durability and assembly readiness of polyamide components wit...
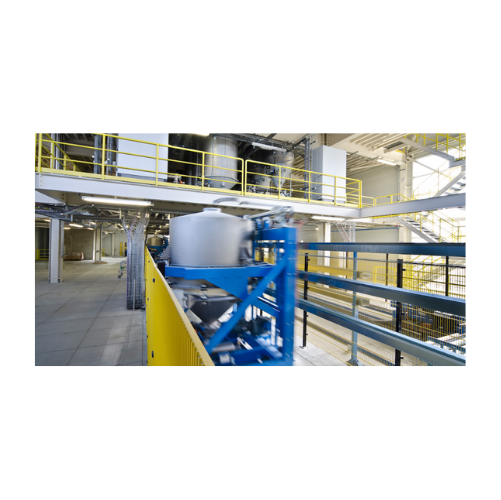
Plastic processing systems for high plant availability
Achieve unparalleled throughput and efficiency in your production ...
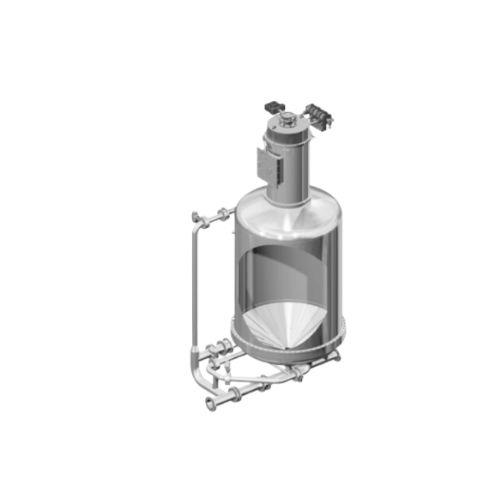
Pneumatic mixer for fluidizable bulk materials
Achieve uniform and gentle mixing of powdered ingredients with minimal effo...
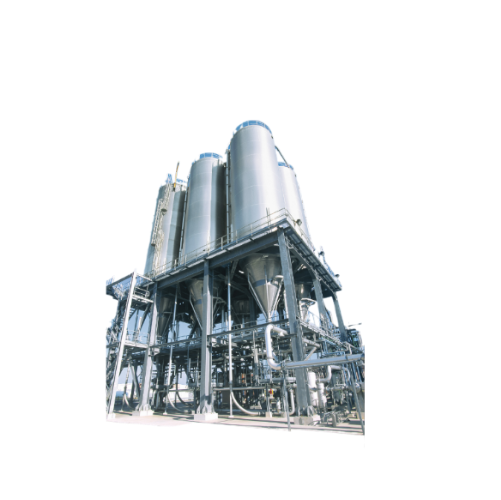
Advanced degassing and temperature control solution for process silos
Optimize your production line with precise contro...
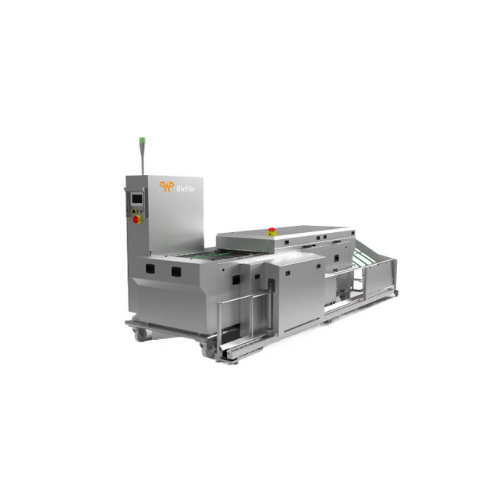
Industrial baking sheet cleaning system
Enhance hygiene and streamline operations with a system designed to clean, dry, and...
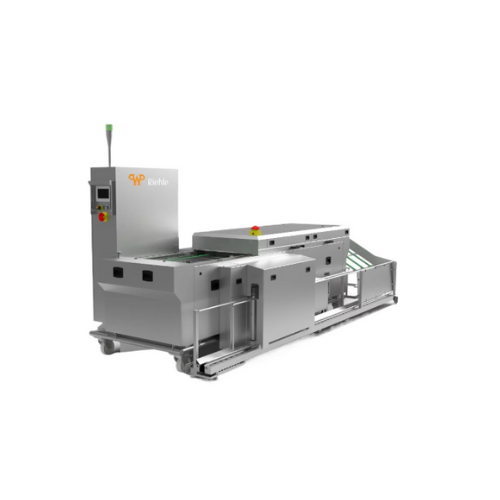
Tray cleaning system for bakery applications
Ensure the highest hygiene standards with a system that efficiently cleans an...
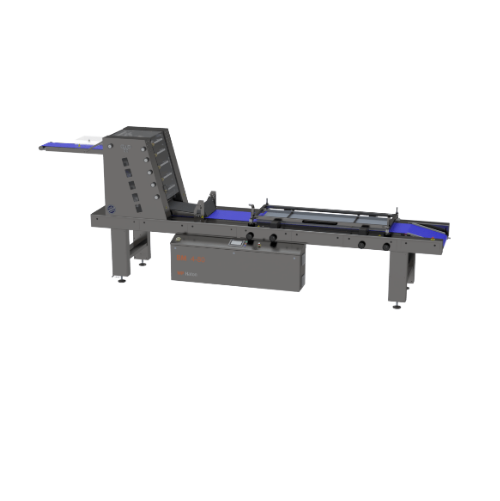
Industrial long moulder for high-capacity dough processing
Optimize your bakery production with a high-speed moulder tha...
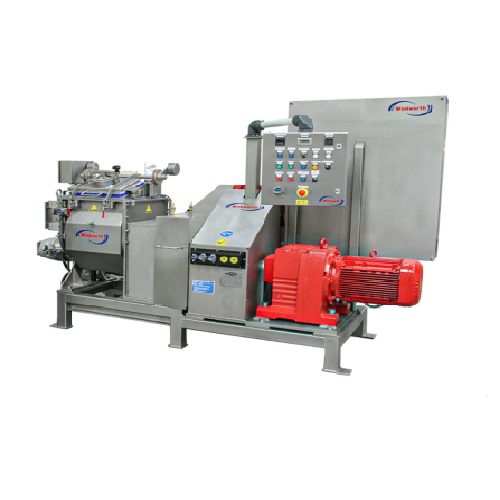
Industrial sigma mixer extruder for homogeneous mixing and extrusion
Achieve precise mixing and seamless extrusion of d...
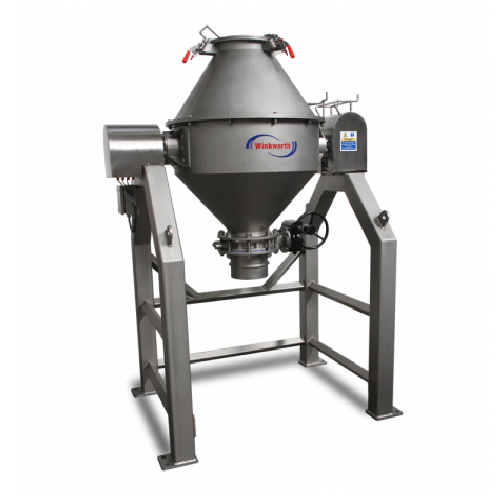
Double cone mixer for free-flowing material blending
Optimize your production with precision blending and gentle drying o...
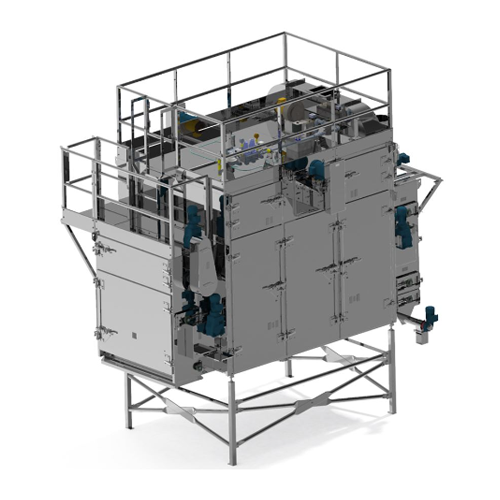
Light duty oven for snacks and light density foods
Maximize efficiency with precision-controlled drying and heating of sn...
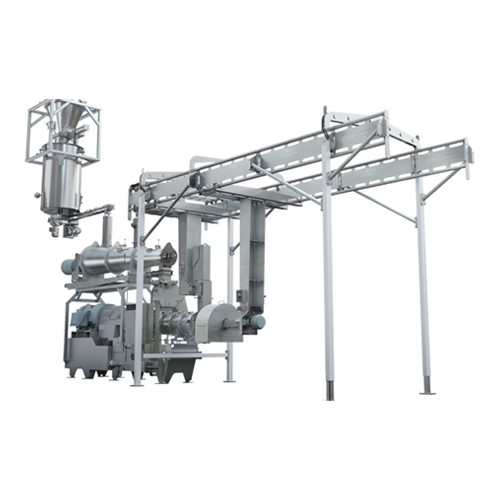
Conical twin screw extruder for pet food and aquatic feed
Precision-engineered for high-speed extrusion and drying proce...
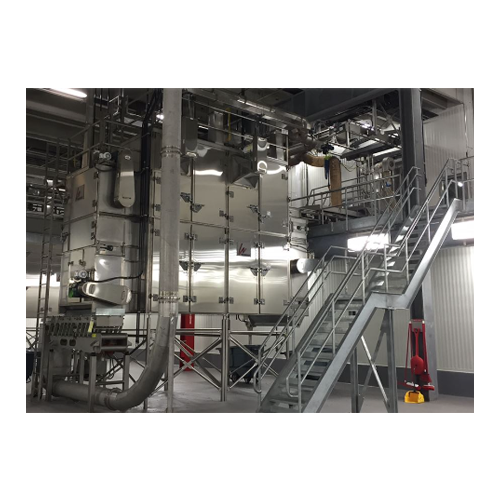
Convection roaster for pet food and delicate food products
Achieve optimal texture and moisture control in delicate food...
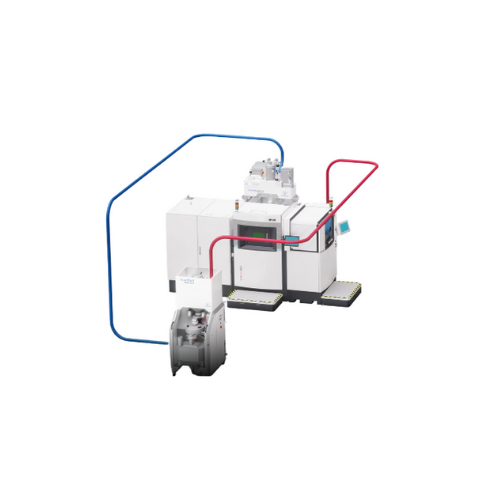
Closed powder handling loop for Eos metal Am printers
Effortlessly manage metal 3D printing powders with a solution that ...
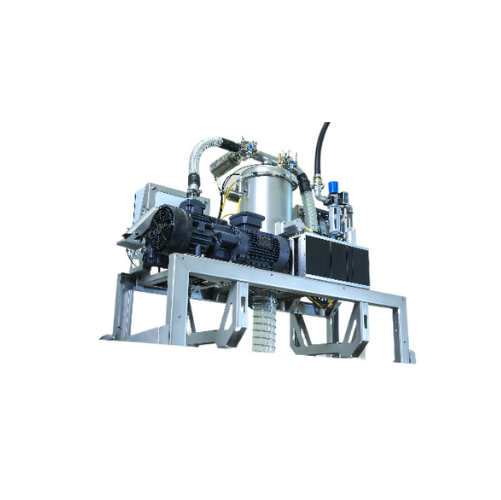
Automatic metal powder filling system for 3d printers
Ensure seamless operation of your 3D printing process with a system...
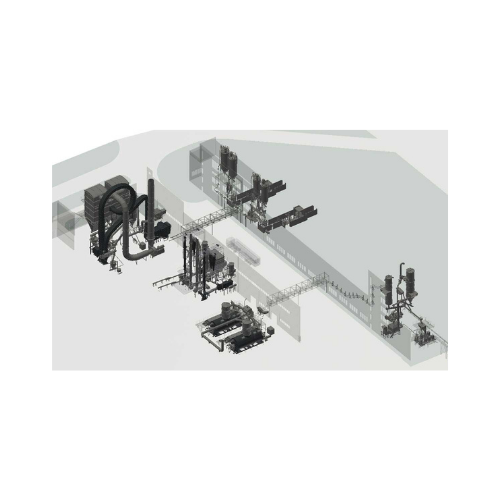
Wheat processing systems for industrial applications
Maximize efficiency in wheat processing with a system designed for p...
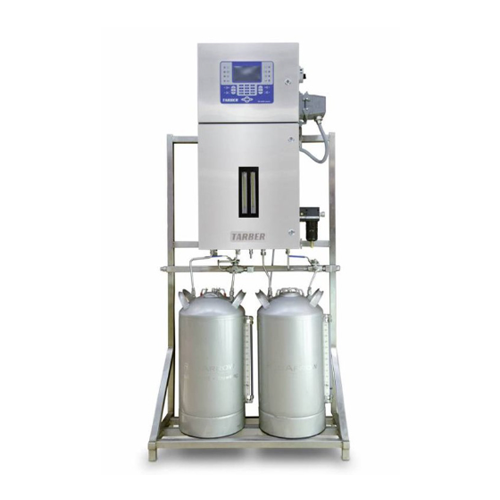
Liquid smoke system for meat and seafood processing
Achieve uniform smoking results across diverse products by employing ...

Thermal processing system for various meat products
Optimize your thermal processing with a versatile system that ensures...
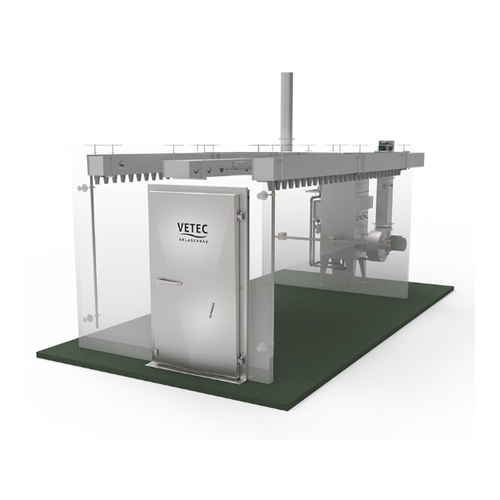
Air-conditioning curing for raw sausage production
Enhance your meat processing line with precise climate management for ...
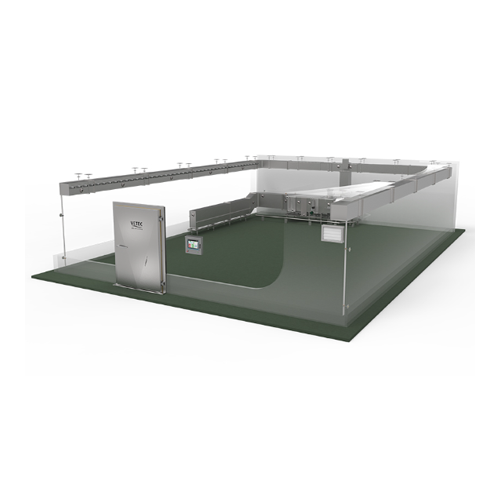
Air-conditioned storage chambers for post-curing
Ensure consistent product quality with precise humidity control, essentia...
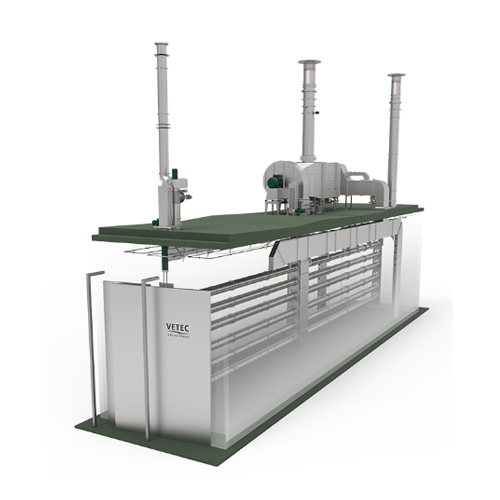
Cross-flow smoking and fermentation system for raw sausage
Enhance yield and ensure consistent quality in sausage and fi...

Brushing systems for agricultural produce
Enhance the precision and efficiency of fruit and vegetable processing with vers...
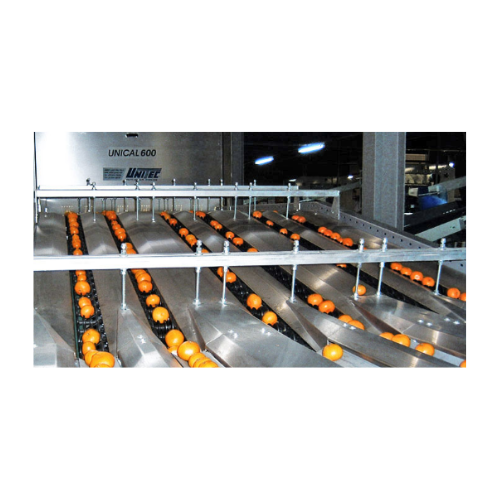
Mandarin and clementine processing sorting and grading system
Optimize your citrus operations with advanced processing s...
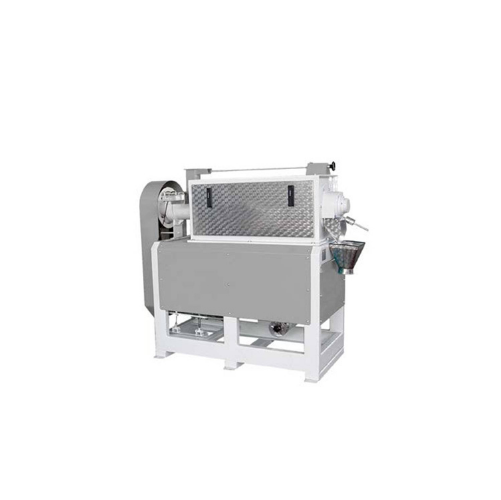
Water polisher for rice refinement
Enhance rice quality and shelf life by efficiently removing bran residues, minimizing ox...
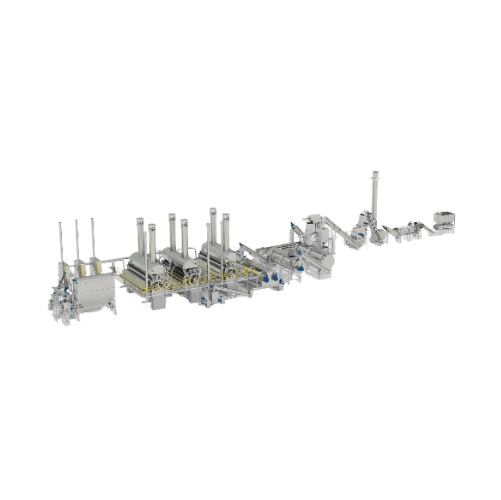
Turnkey potato flake processing line
Effortlessly transform raw potatoes into high-quality flakes with this integrated line...
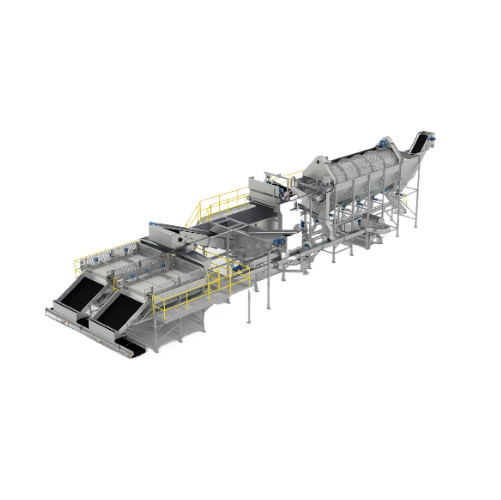
Industrial potato washing line
Optimize your potato processing with a versatile washing line that ensures thorough cleaning,...
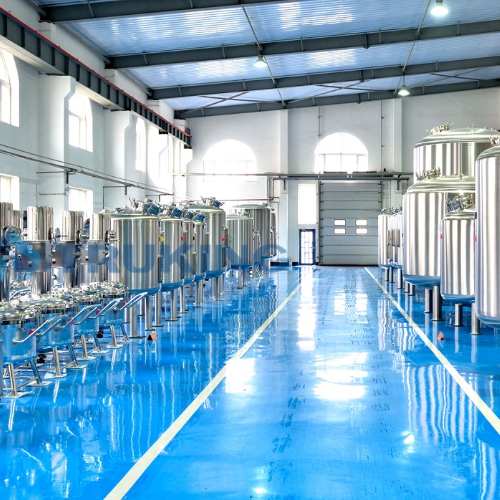
Stainless steel craft tanks for biopharmaceuticals
Ensure precise temperature control and customized capacity for your fo...

Robotic sterilization logistics system
Ensure seamless aseptic transfers across production stages with this robotic logisti...
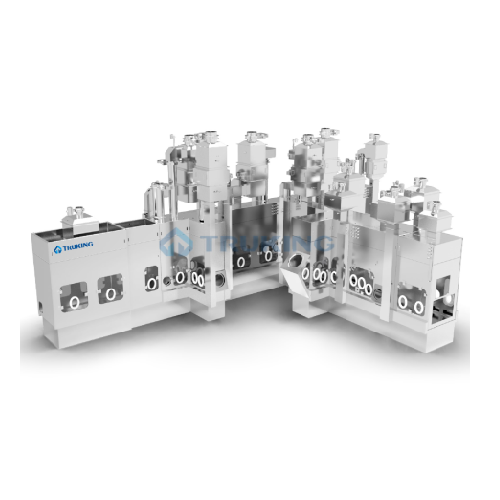
Pharmaceutical isolator system for aseptic production
Ensure aseptic conditions and operator safety with a robust isolati...
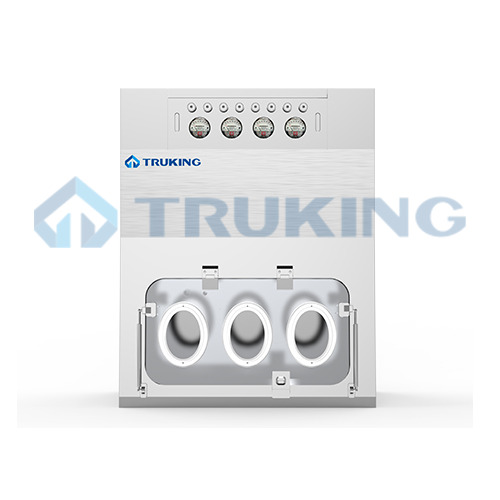
Feeding isolator for liquid preparation in pharmaceuticals
Ensure precise and contamination-free preparation of liquid p...
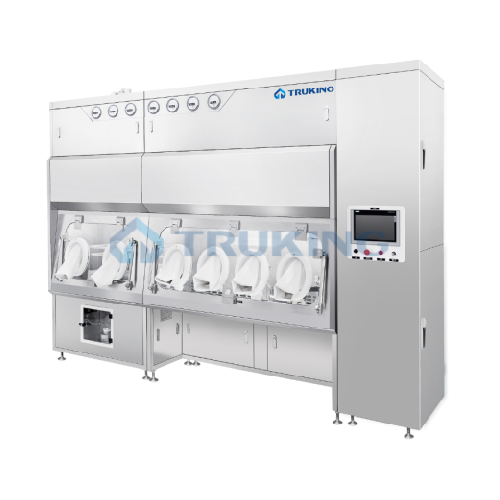
Sterility testing isolator for aseptic environment
Ensure precise sterility testing and prevent contamination with an iso...
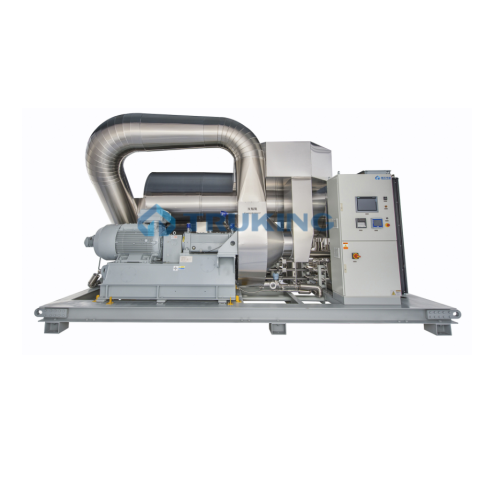
Hot press distilled water unit for pharmaceutical applications
Ensure superior water purity in pharmaceutical production...
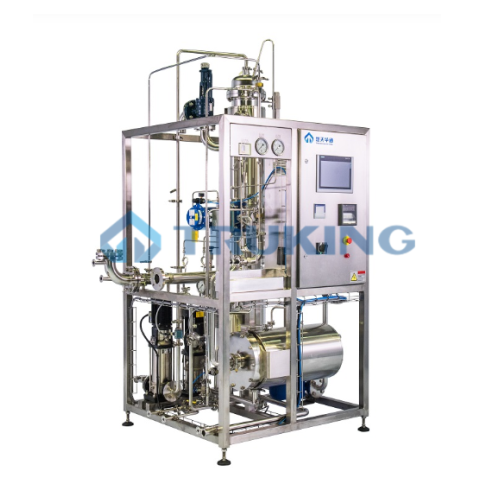
Pure steam generator for pharmaceutical and biotech industries
Ensure optimal steam quality and compliance with stringen...
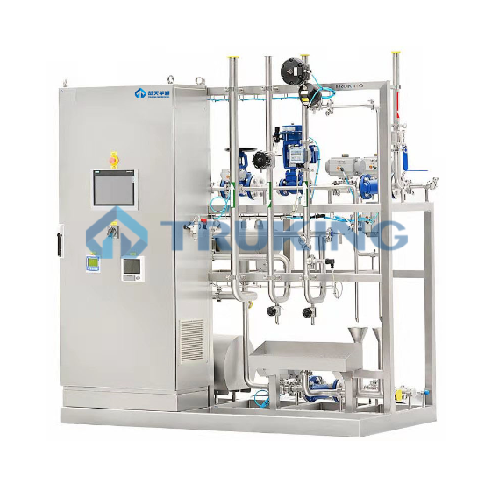
Pharmaceutical ultra pure water distribution system
Ensure stringent purity standards with a modular water distribution s...
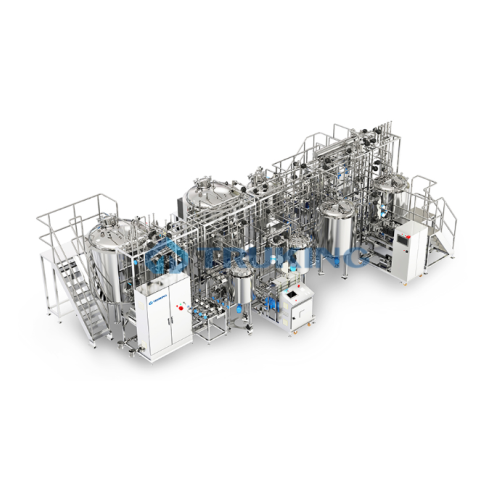
Complex preparation system for industrial microsphere production
Achieve precise particle size and uniform drug encapsul...
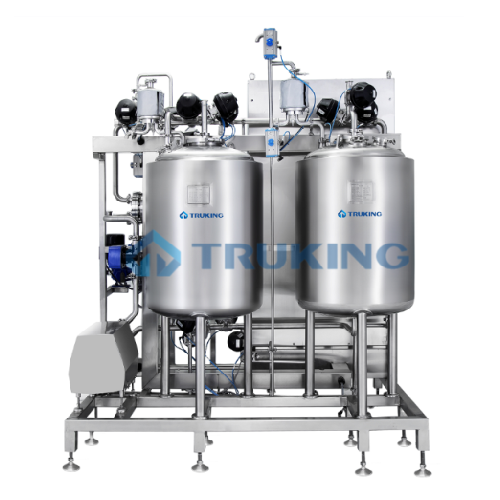
Comprehensive auxiliary system for online cleaning and temperature control
Ensure reliable and precise control in phar...
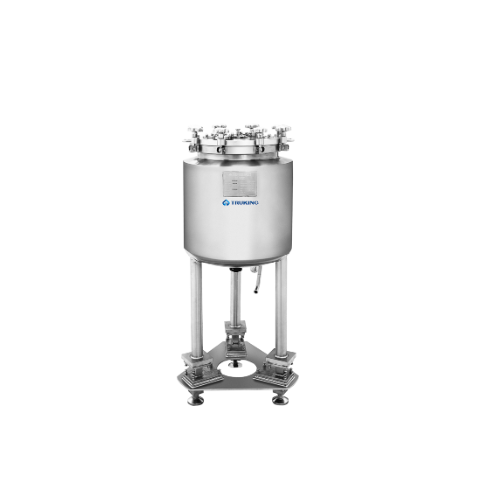
Sanitary vessels for pharmaceutical applications
Ensuring the highest standards of aseptic processing, these sanitary vess...
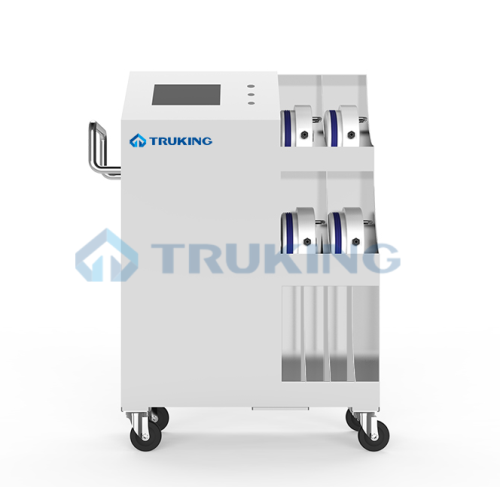
Isolator for sterility testing in pharmaceutical manufacturing
Ensure precise sterility testing with advanced isolators ...
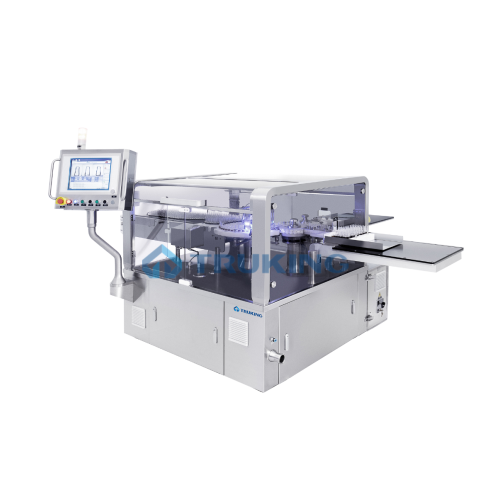
Automatic inspection system for sealing defects in ampoules
Ensure flawless ampoule sealing with a high-precision inspec...
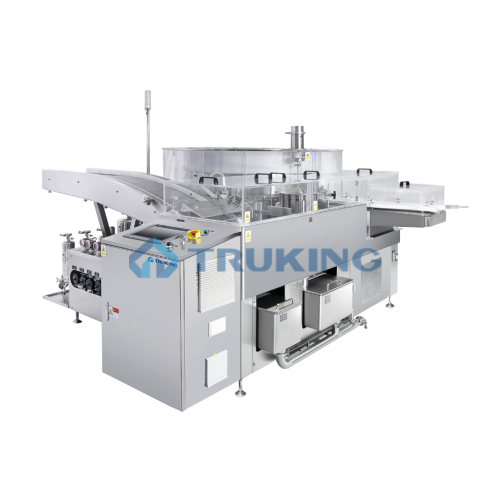
Vertical ultrasonic washing system for oral liquid bottles
Ensure optimal cleaning and sterilization with a compact vert...
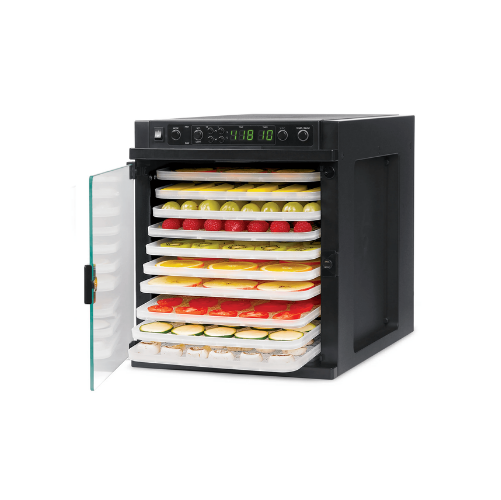
Compact food dehydrator with Bpa-free trays
Achieve precise dehydration with compact, kitchen-friendly equipment, perfect ...
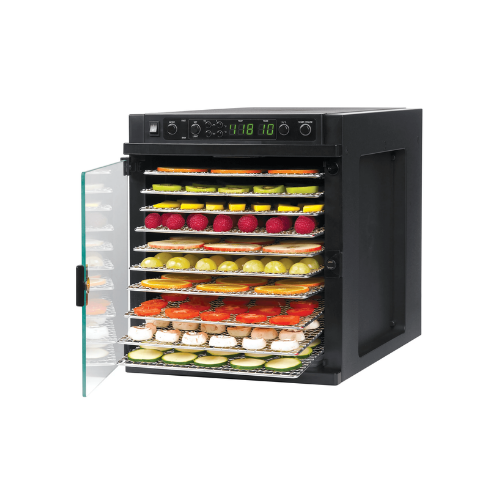
Compact food dehydrator for fruits and meats
Achieve precise dehydration of fruits, vegetables, and meats with a compact s...
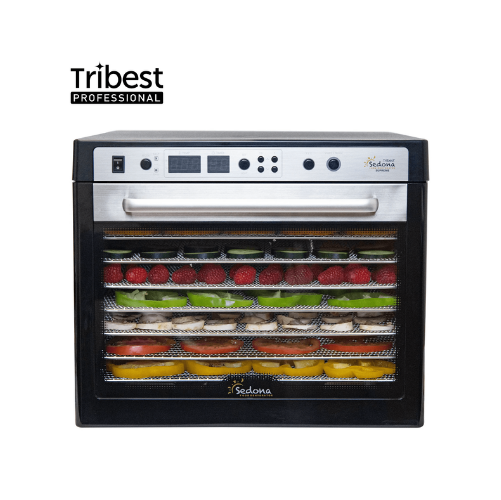
Large-capacity commercial food dehydrator
Achieve precise dehydration for a wide range of food items with unmatched consis...

Food dehydrator with Bpa-free trays
Effortlessly retain nutrients while creating a variety of dehydrated snacks using dual ...

Cabinet Food dehydrator
Achieve precise drying control with dual fan technology, ensuring even airflow and optimal nutrient p...
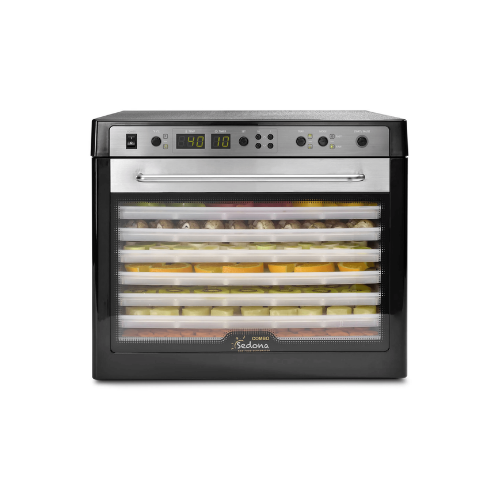
Food dehydrator with Bpa-free plastic trays
Achieve precise dehydration for fruits, vegetables, and snacks with advanced t...
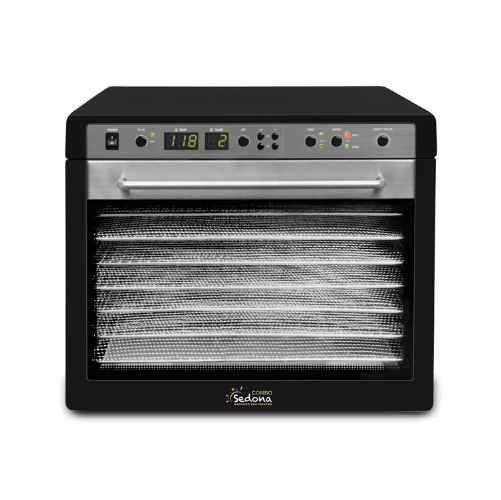
Food dehydrator with stainless steel trays
Achieve optimal dehydration with precise temperature control and efficient dual...
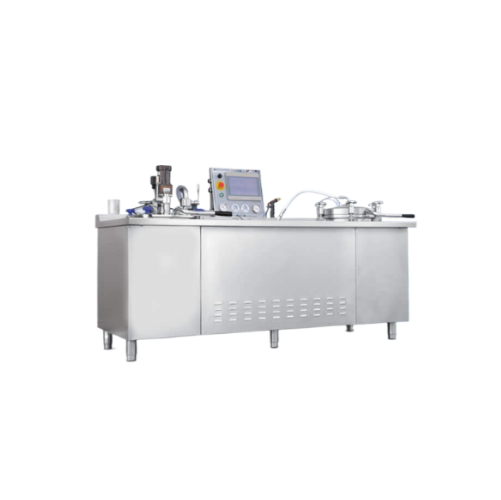
Low temperature food dehydration system for fruit and vegetables
Optimize your food processing with advanced low-tempera...
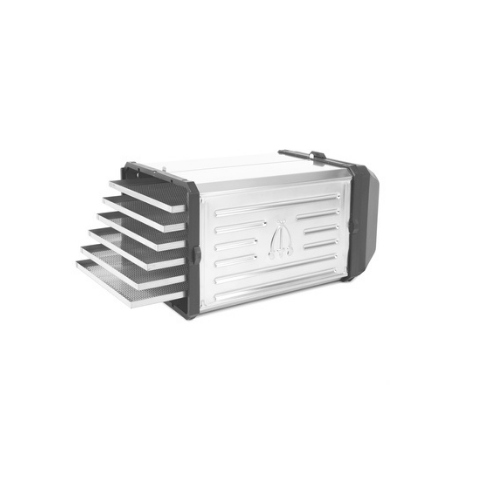
Professional food dehydrator for fruits and vegetables
Enhance your culinary creations with precise dehydration technolog...
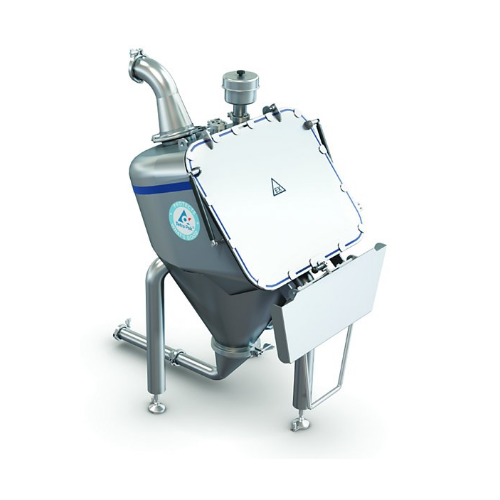
Bag tipping unit for Cip processes in powder handling
Ensure seamless powder handling and high hygiene standards in your ...
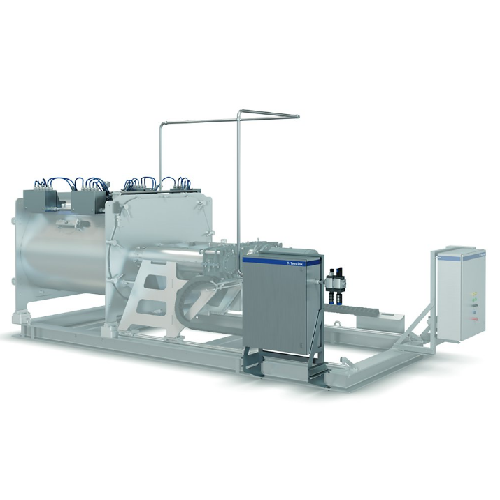
Air jet cleaning system for powder production
Eliminate water and chemical use while maximizing production efficiency with...
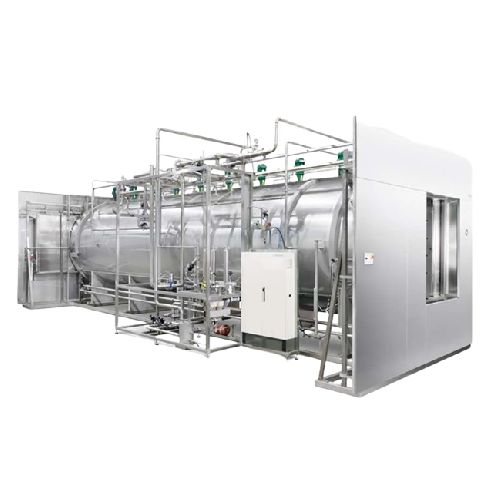
Steam & air mixture sterilizer for parenteral solutions
Achieve robust and effective sterilization for delicate pharmaceu...
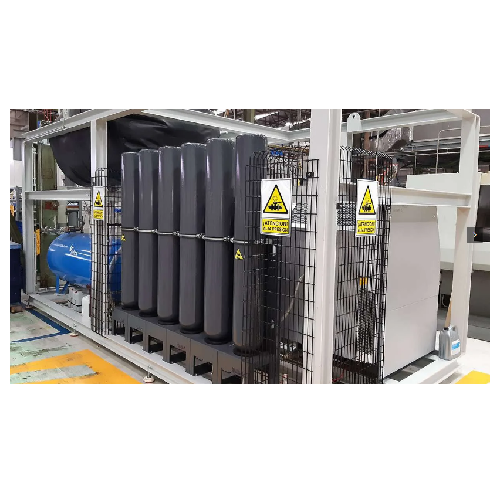
Helium recovery system for industrial applications
As helium costs rise and supply dwindles, efficiently recovering and p...
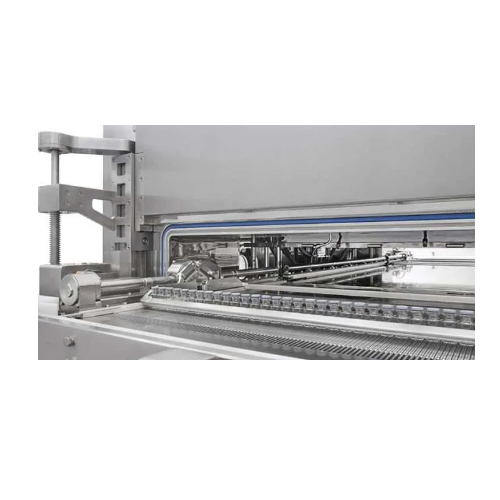
Sterile lyophilization for oncology pharmaceuticals
Optimize the sterility and stability of high-potency drugs with advan...
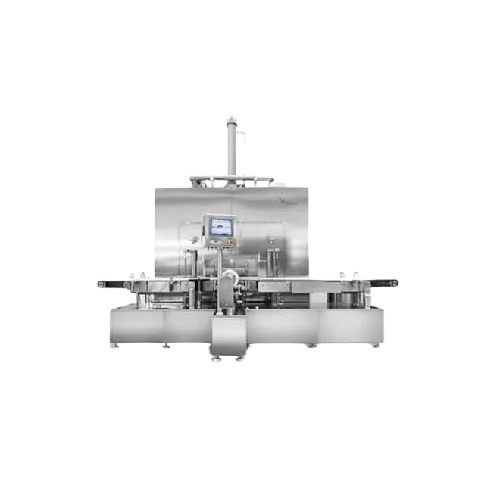
Sterile lyophilisation and filling line
Ensure aseptic conditions while freeze-drying biopharmaceuticals and high-potent dr...
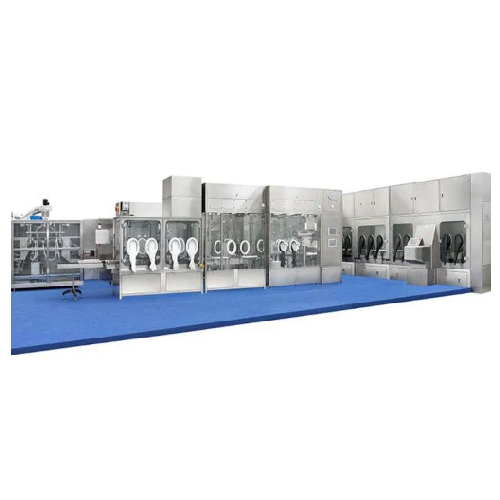
Lyophilization for live bacteria vaccine production
Ensure precise moisture control when freeze-drying live attenuated ba...
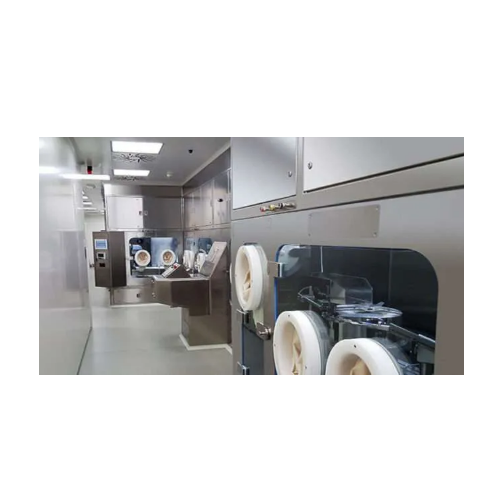
pharmaceutical lyophilised filling line
For high-precision production of moisture-sensitive drugs, this aseptic system ensu...
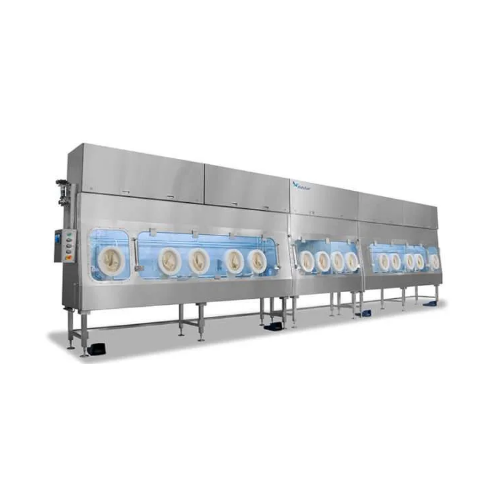
Two lyophiliser unloading isolators for hygroscopic products
Ensure precise moisture control and sterility for hygroscop...
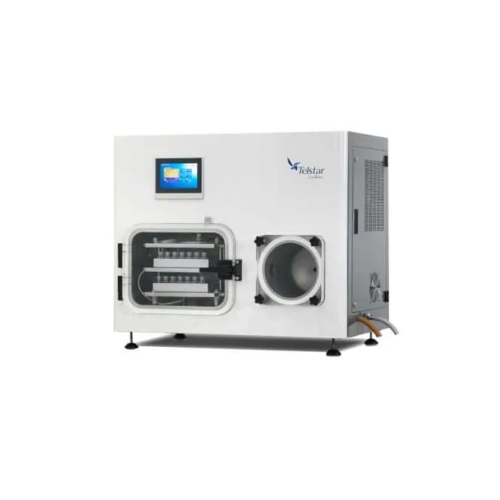
Peptide production lyophilizer for pharmaceutical and veterinary use
Optimize peptide stability and purity in your prod...
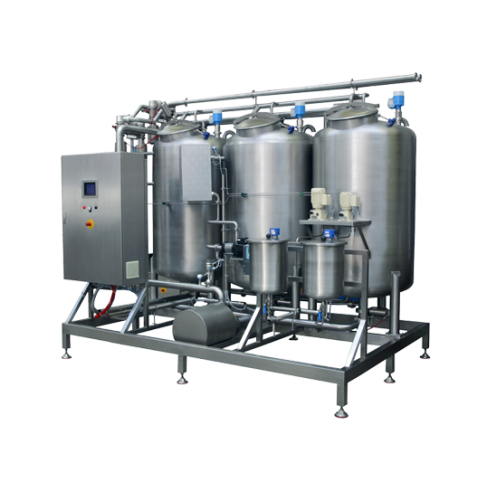
Automated cleaning in place system for bakery production lines
Ensure unmatched hygiene and operational efficiency in fo...
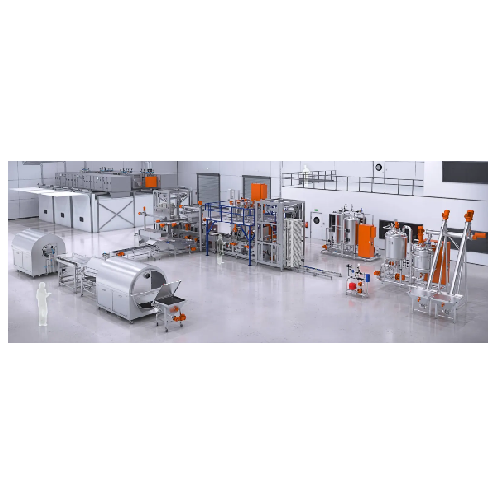
Automatic production line for gummies, jellies, and nutraceuticals
Optimize your production space with a compact line t...
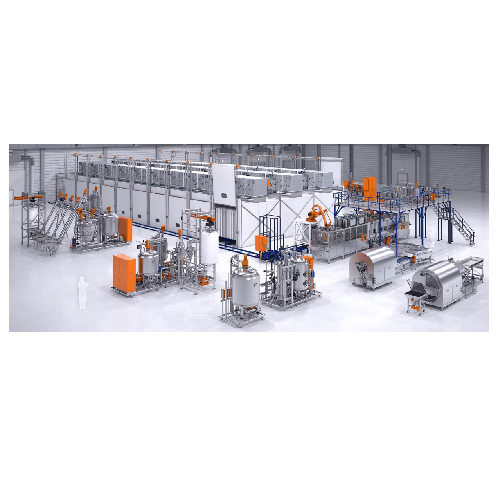
Robotic high capacity production line for gummies and jellies
Optimize your gummy and jelly production with a high-capac...
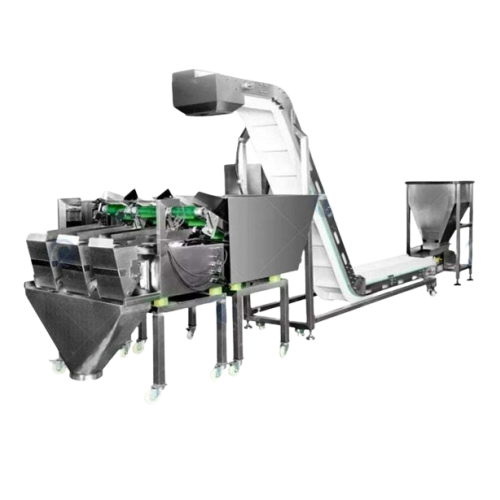
Vegetable salad production line for lettuce processing
Streamline your vegetable processing with an all-in-one solution d...
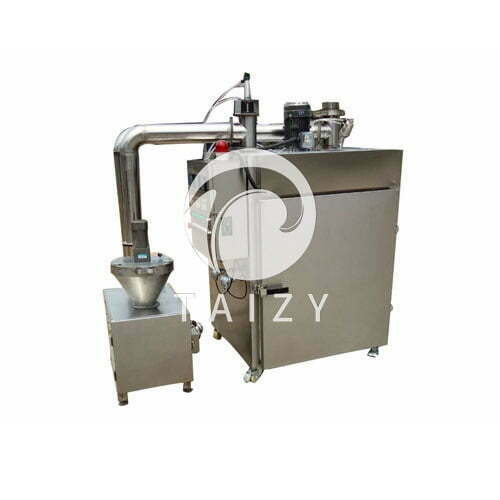
Industrial smoking chamber for smoked meat and fish products
Achieve consistent smoky flavors and enhanced textures in y...
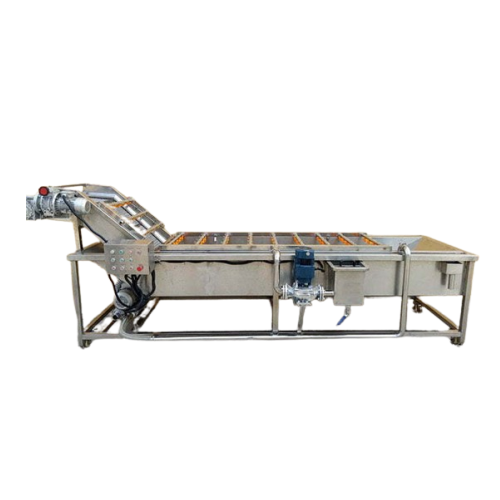
Industrial strawberry and blueberry washer
Ensure your soft fruits remain intact and impurity-free with this specialized w...
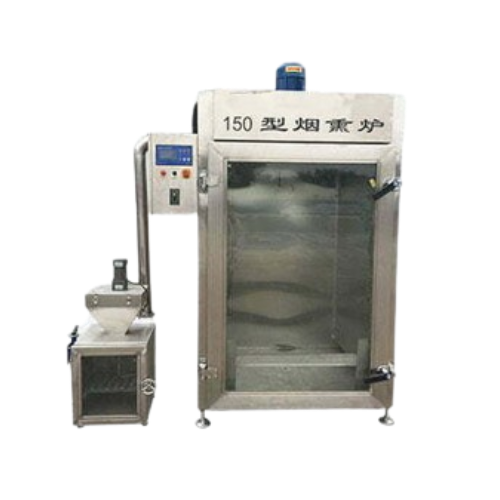
Industrial sausage smoking oven with easy operation
Streamline your meat processing with an advanced sausage smoking oven...
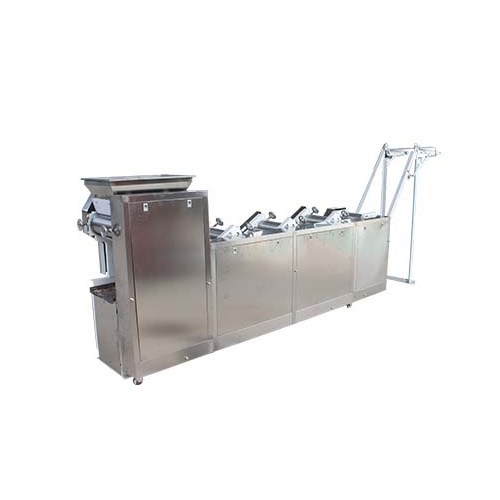
Automatic noodle maker for diverse noodle shapes
Streamline your noodle production with a machine that crafts a variety of...
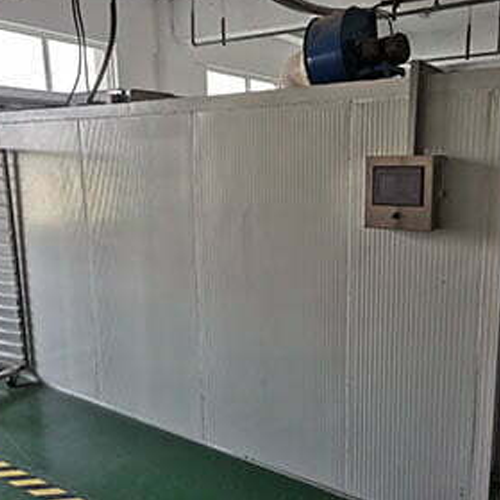
Commercial mango dehydrator
Optimize your fruit processing with a commercial mango dehydrator that ensures precise moisture ...
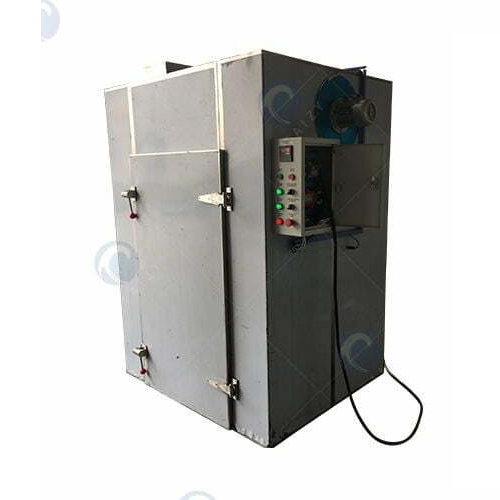
Ginger powder processing line
Optimize your spice production with comprehensive ginger powder processing, transforming fresh...
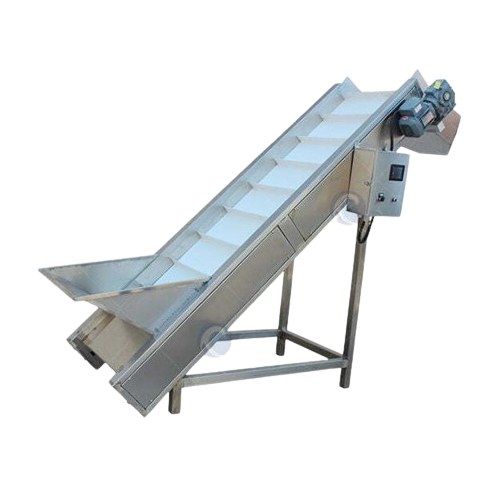
Complete fruit and vegetable washing plant
Optimize your production line with efficient fruit and vegetable washing, ensur...
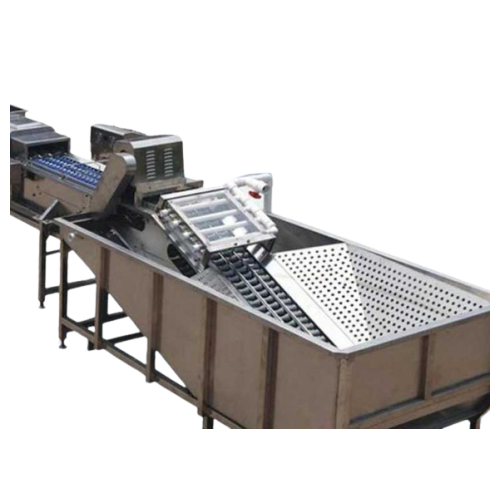
Automatic egg washing machine for chicken and duck eggs
Ensure hygiene and extend shelf life with this advanced egg washi...
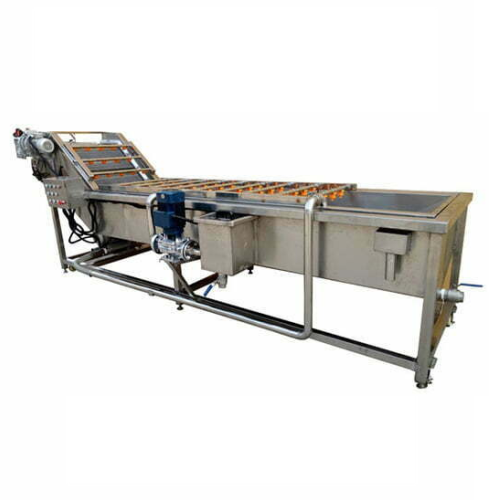
Chili pepper washing line for industrial processing
Efficiently streamline your pepper processing with a continuous washi...
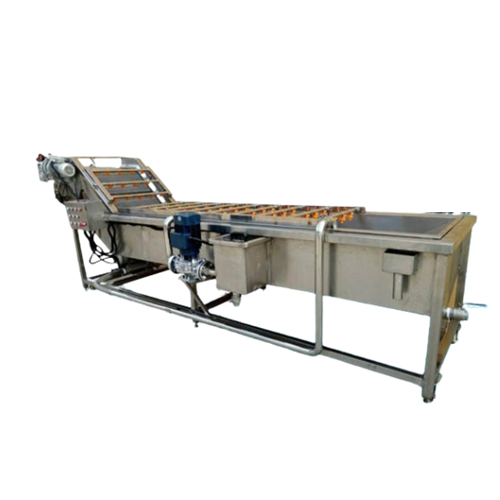
Bean sprout washing station for optimal cleanliness
Ensure your bean sprouts and leafy greens are impeccably clean and re...
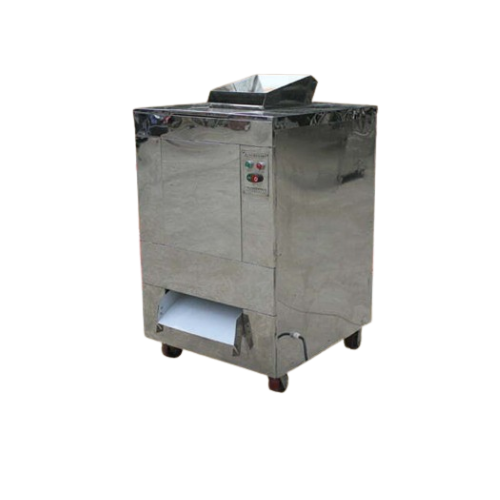
Boba tapioca pearl maker for bubble tea
Optimize your bubble tea production with precise control over tapioca pearl formati...
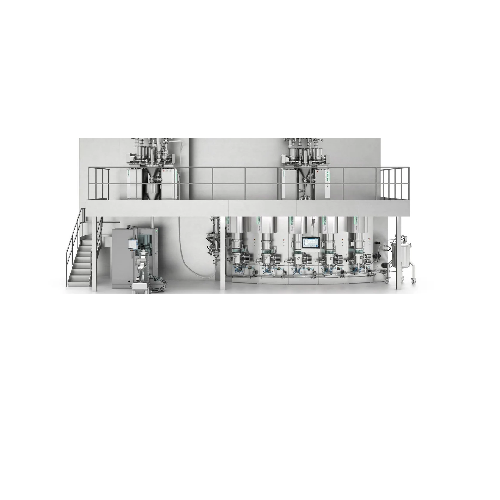
Continuous manufacturing for pharmaceuticals
Achieve precision in oral solid dosage production with seamless continuous pr...

Fluid bed processor for pharmaceutical granulation and coating
Achieve superior granulation and coating of pharmaceutica...
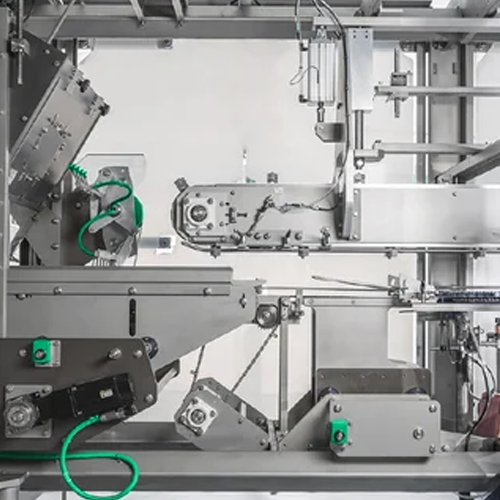
Nutraceutical products processing and packaging
Streamline your nutraceutical production with versatile equipment capable ...
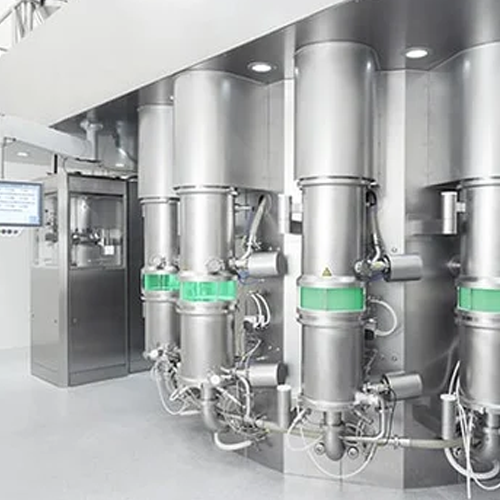
Pharma r&d equipment for solid dosage forms
Optimize your pharmaceutical production with cutting-edge equipment designed f...
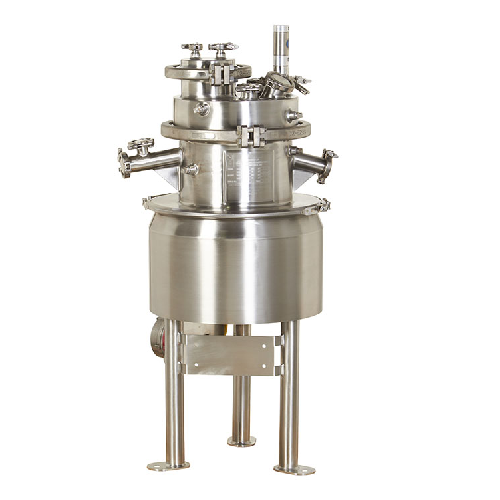
Lab Pharmaceutical aseptic separator
Achieve high-yield recovery and safe handling of potent pharmaceuticals with this asep...
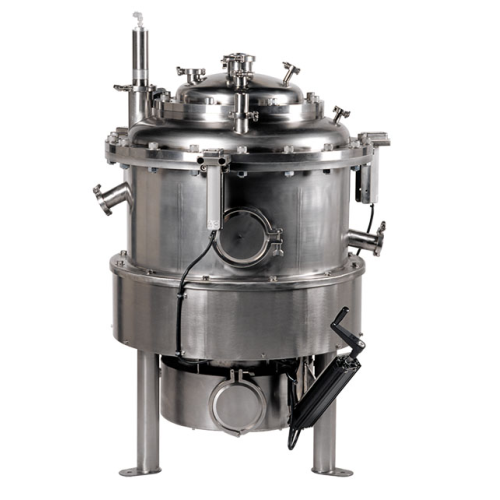
Pharmaceutical aseptic separation system
Achieve precise separation and efficient drying of pharmaceutical powders with an ...
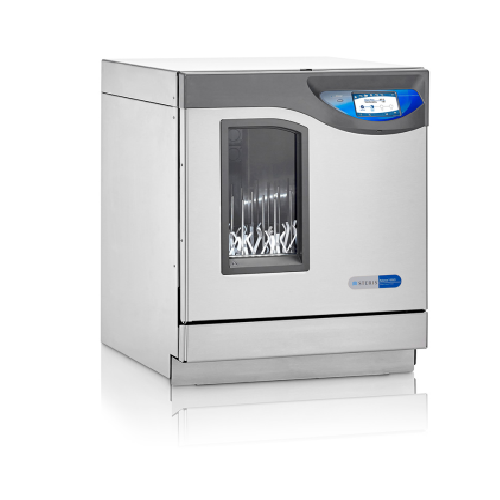
Laboratory glassware washer for research labs
Achieve unmatched cleaning and drying of laboratory glassware, ensuring prec...
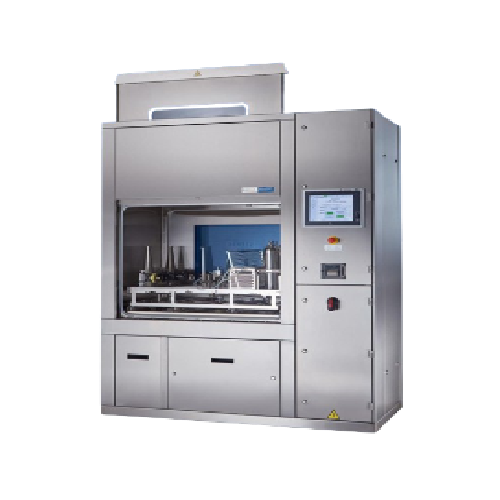
Pharmaceutical grade washer for biotechnology and pharmaceutical manufacturing
Efficiently clean and prepare your labo...
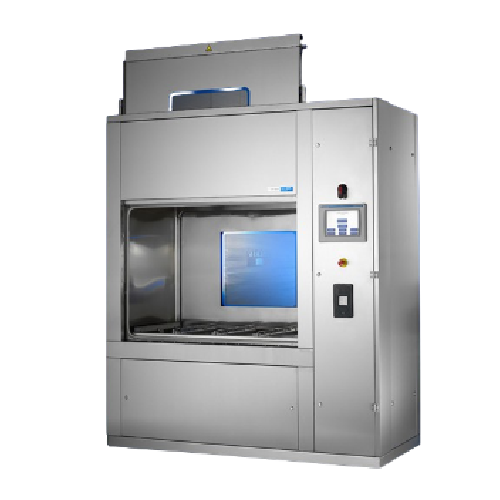
Pharmaceutical glassware and component washer
Optimize your cleaning processes with a high-capacity system that efficientl...
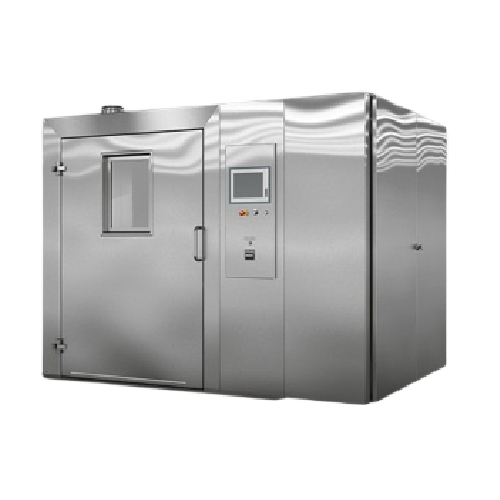
Pharmaceutical grade washer for large components
Ensure compliance and maximize productivity with a high-performance solut...

Saturated steam autoclave for pharmaceutical decontamination
Ensure precise decontamination and sterilization with a sol...
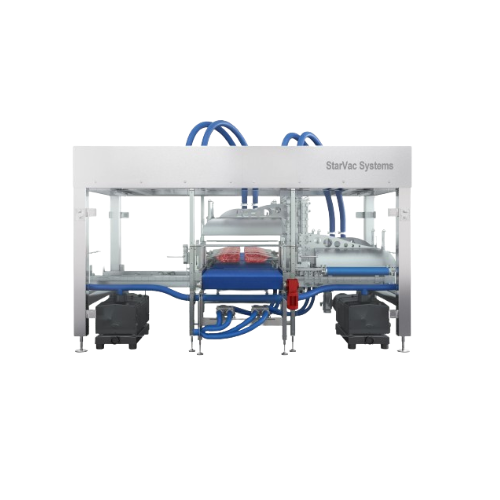
Industrial-scale vacuum packing for fresh meat and cheese
Optimize packaging operations with this machine designed for h...
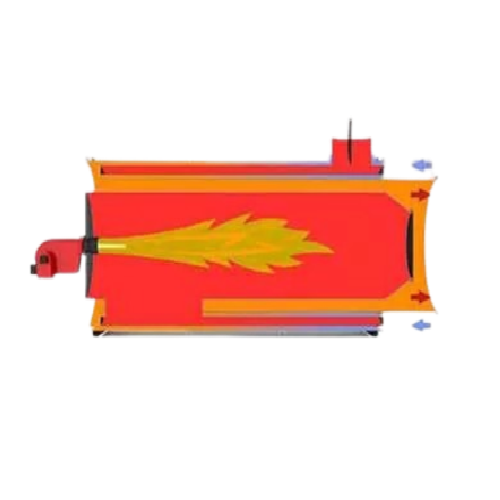
Industrial air heater for agriculture and industry
Optimize energy efficiency and maintain high air quality in your produ...
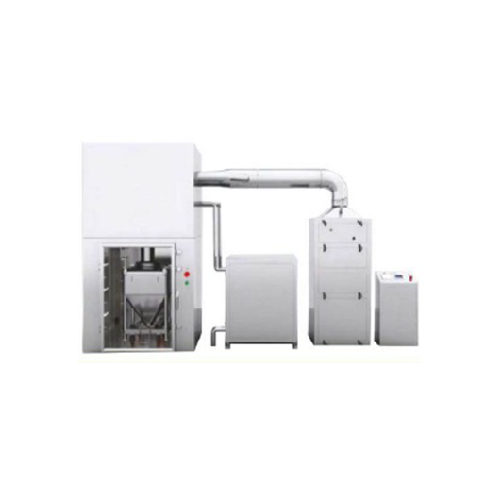
Bin washing station for pharmaceutical applications
Achieve reliable sanitation and enhanced efficiency with this tailore...
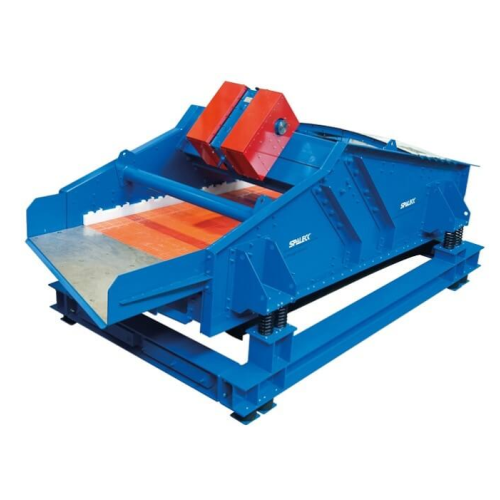
Dewatering screens for industrial applications
Efficiently transforming wet material into dry, manageable outputs, these d...

Industrial smoking chamber for meat processing
Achieve consistent, high-quality smoking for diverse foods with this chambe...
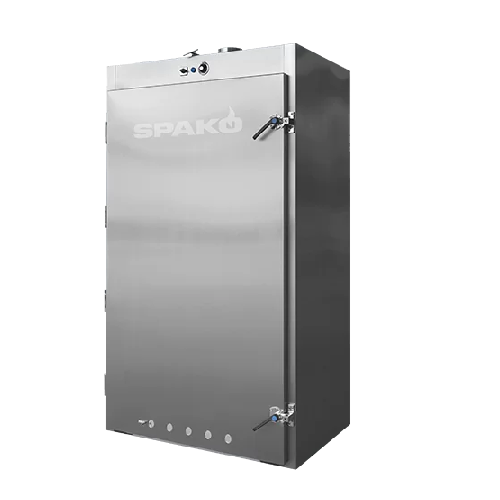
Smoking chamber for meat processing
Enhance your food products’ flavor profile with precise smoking, coloring, and dr...
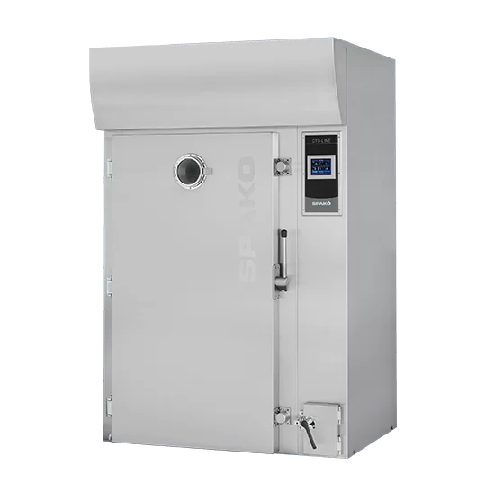
Combination chamber for meat processing
Optimize your food production with a multi-process chamber designed to seamlessly i...
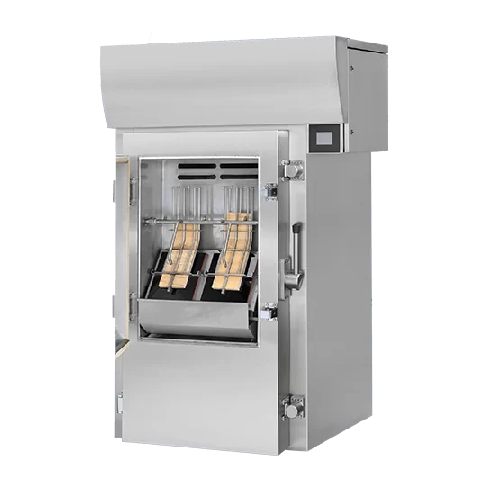
Combination chamber for smoking, cooking, and baking
Optimize your food processing with a versatile chamber that efficien...

Centrifugal evaporators for medicinal chemistry
Streamline your solvent evaporation and drying processes with this solutio...
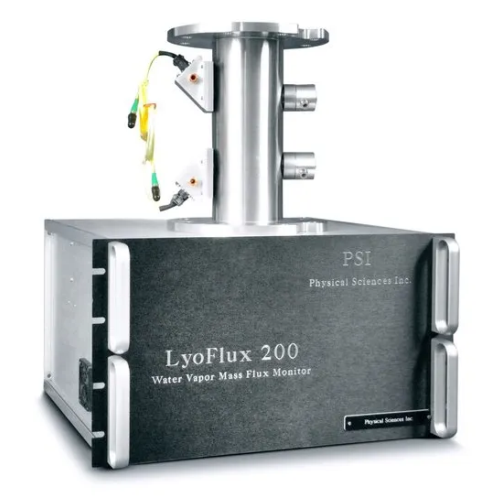
Lyophilization process optimization sensors
Achieve precise real-time monitoring of water vapor during freeze-drying, stre...
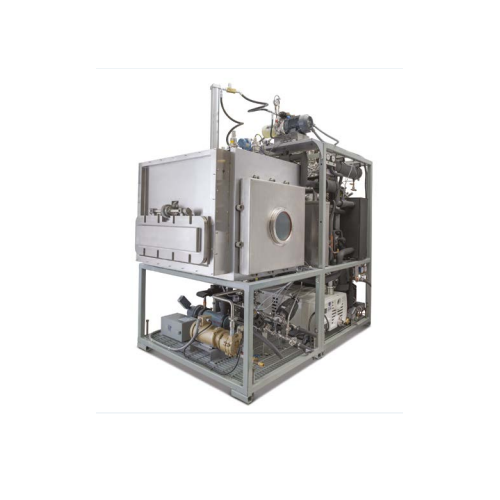
Controlled lyophilization nucleation system for drug development
Achieve consistent freeze-drying outcomes with precise ...
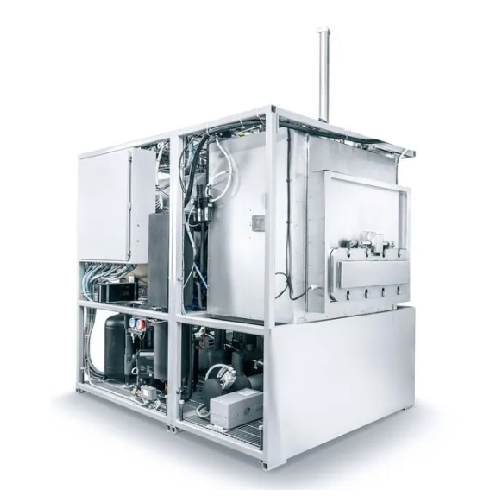
Pilot lyophilizers for therapeutic proteins and clinical trials
Optimize your freeze-drying process with advanced lyophi...
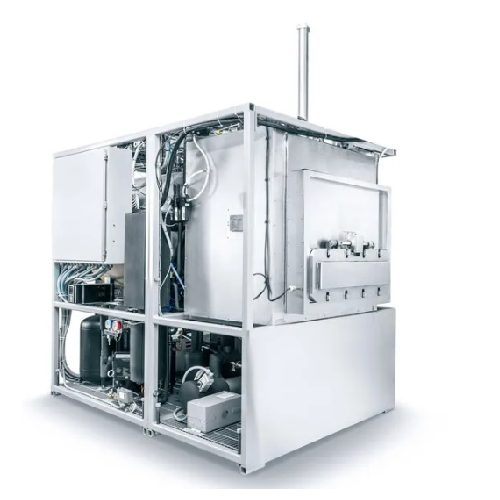
Production lyophilizer for pharmaceuticals
Ensure precise freeze-drying for high-value pharmaceuticals with cutting-edge t...
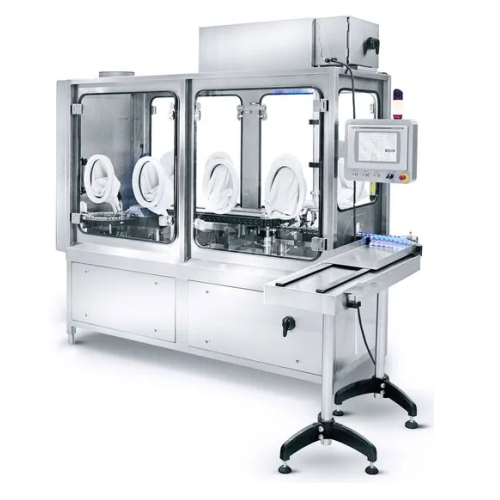
External vial washer for pharmaceutical industry
Ensure complete decontamination of vial exteriors with precision washing ...
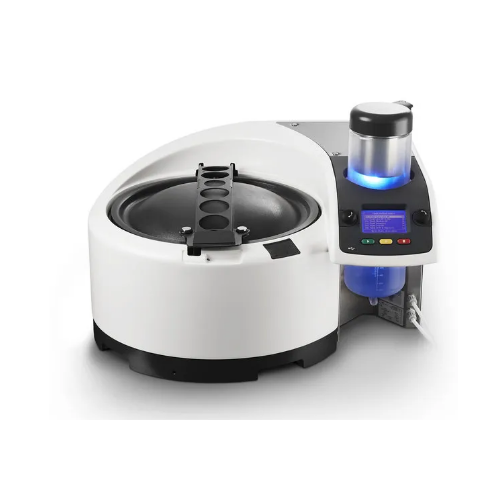
Benchtop evaporator for parallel chemistry and environmental testing
Enhance lab efficiency with a compact evaporator t...
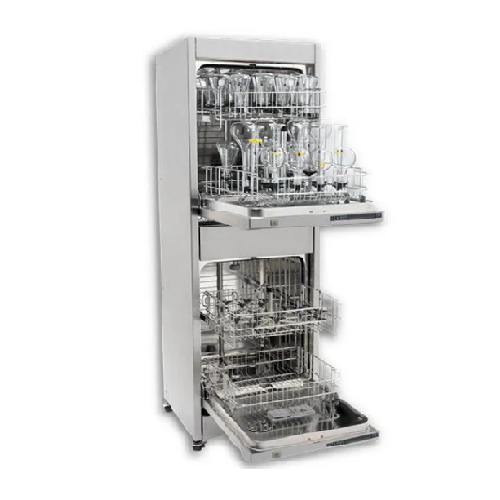
Vertical glassware washer for laboratory use
Maximize lab space with a compact washer featuring dual independent chambers ...
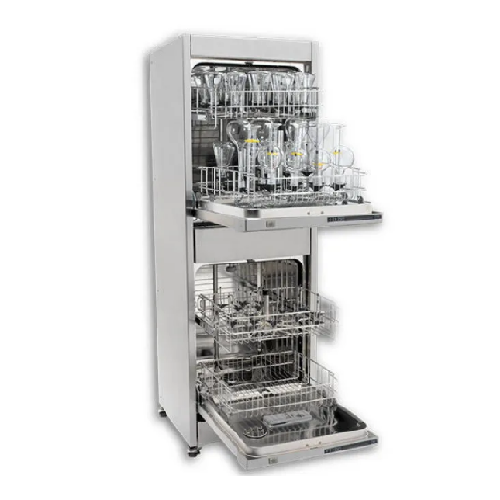
Vertical space-saving glassware washer
Maximize lab efficiency with a space-saving washer that ensures thorough cleaning an...
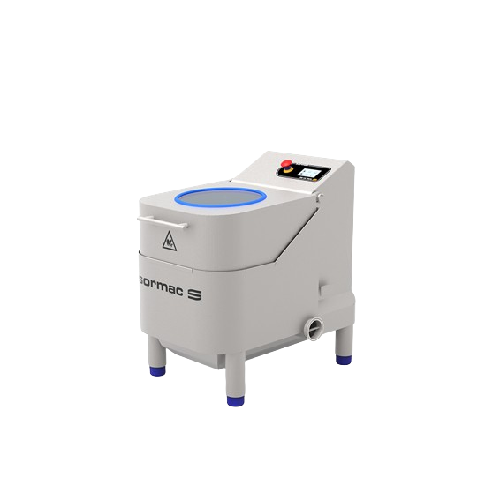
Centrifuge for removing water from leafy vegetables
Eliminate excess water from leafy vegetables efficiently, ensuring op...
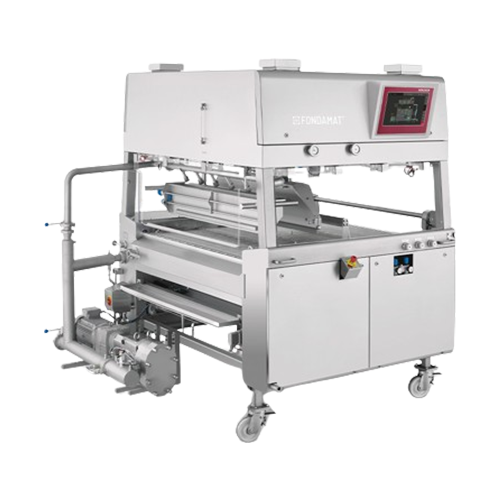
Sugar and fondant coating solution
Achieve precise, multi-color or single coat applications with thin, uniform layers, seam...
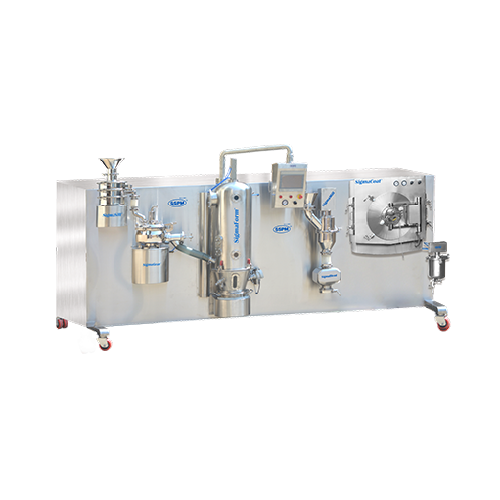
Compact wet granulation r&d system
Ensure precise formulation of pharmaceutical powders with a scalable, lab-friendly syste...
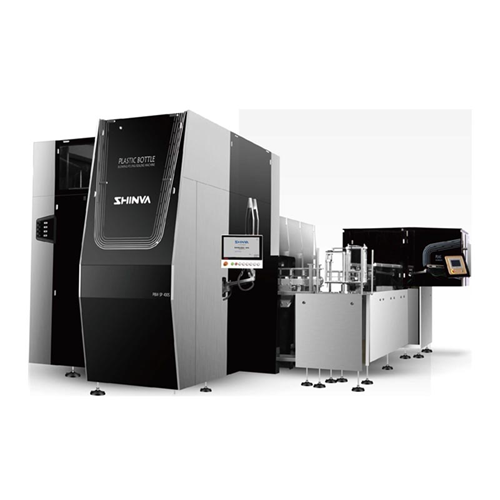
Reciprocating plastic bottle blow-fill-seal system
Achieve seamless integration of bottle forming, filling, and sealing w...
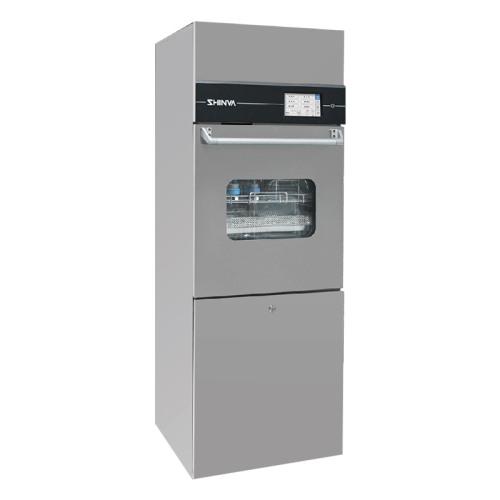
Automatic washer-disinfector for surgical and dental instruments
Ensure optimal hygiene and performance in medical instr...
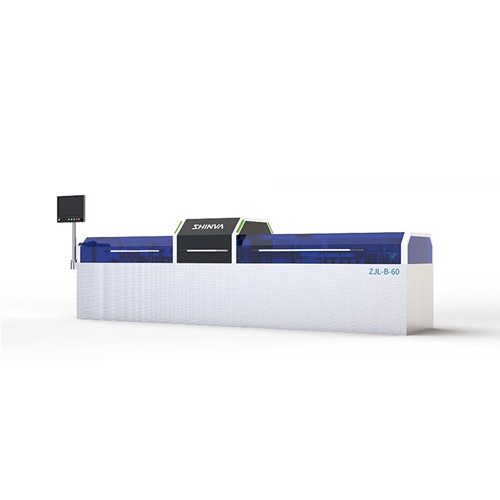
Plastic bottle Bfs leak detection solution for small volume injections
Ensure sealed integrity with precision leak dete...
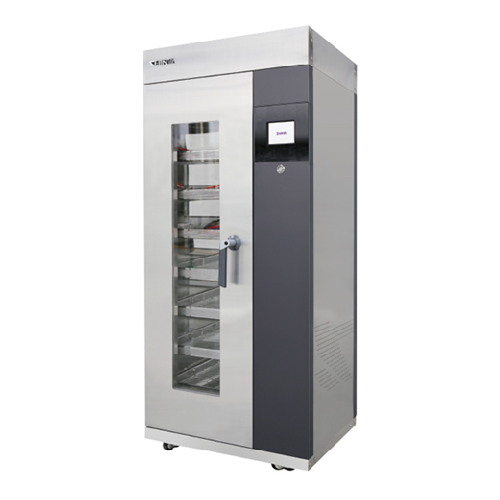
Hot air plate type storage cabinet for endoscopes
Optimize the drying and storage of endoscopes with this advanced cabine...
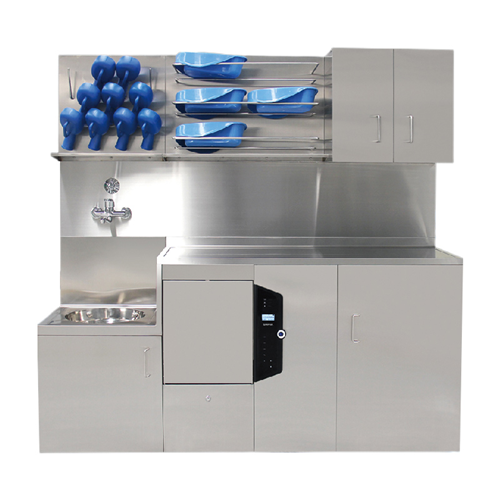
Quick ward washing-disinfection solution for hospitals
Streamline infection control in healthcare facilities with a compr...
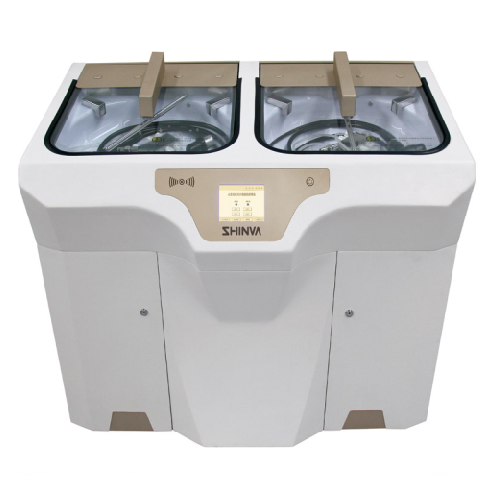
Automatic flexible endoscope washer-disinfector
Ensure thorough sanitization of flexible endoscopes with a solution that m...
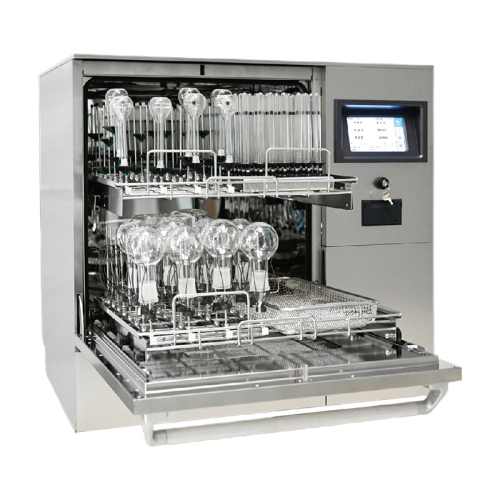
Laboratory washer disinfector for glass, ceramic, metal, and plastic utensils
Achieve thorough cleaning and disinfecti...
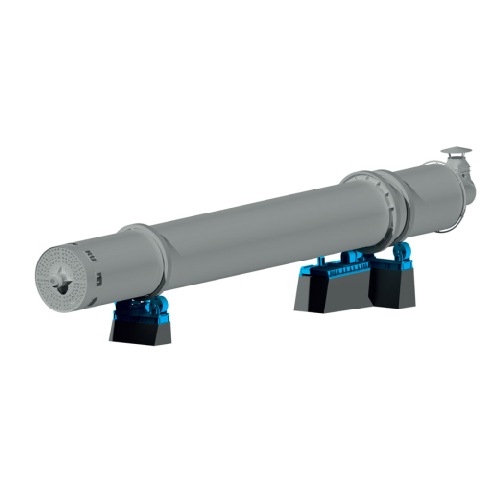
Seed conditioning system for edible oil processing
Optimize your oilseed processing with efficient moisture reduction and...

Coal pulverization grinding mill
Maximize efficiency in pulverizing coal with continuous operation and low maintenance, idea...
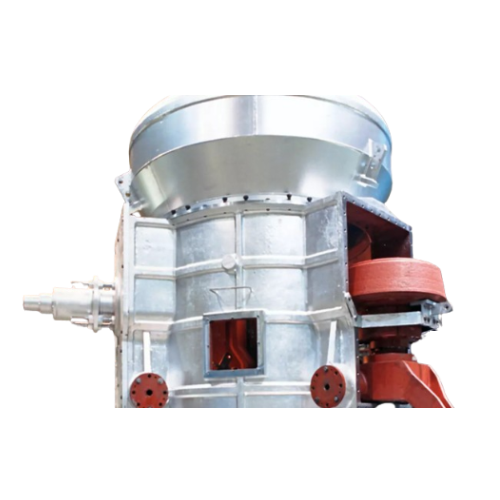
Pulverizing mill for coal processing
Achieve efficient fuel preparation with precision pulverization for consistent energy ...
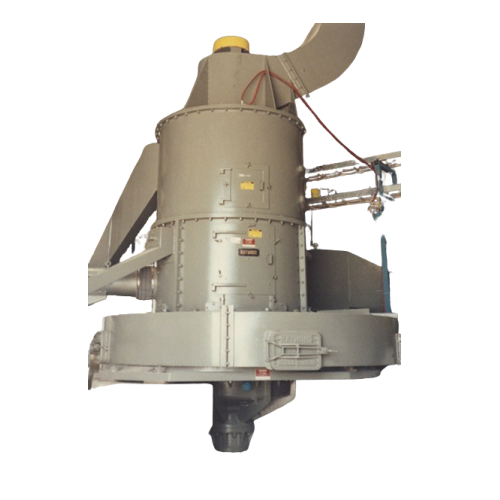
Vertical ring-roll mill for pulverizing minerals
Achieve precise particle size control and efficient material processing w...
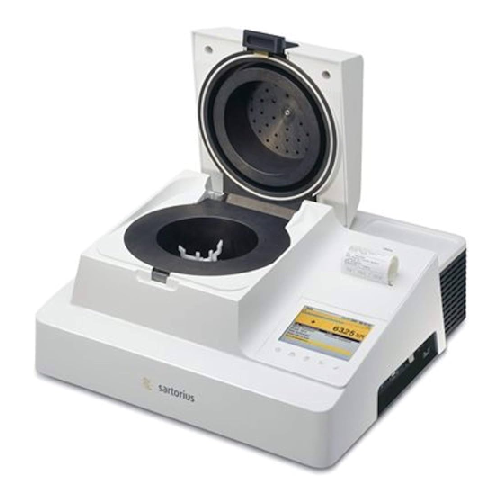
High-speed moisture analyzer for liquid and pasty samples
Ensure precise moisture analysis with rapid microwave drying, ...
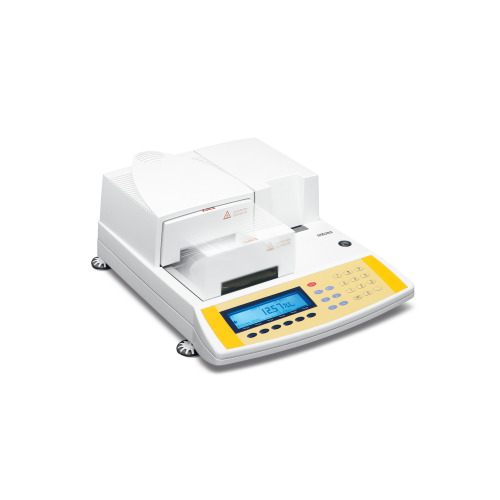
High-accuracy moisture analyzer for lab weighing
Achieve precise and reproducible moisture content determination for diver...
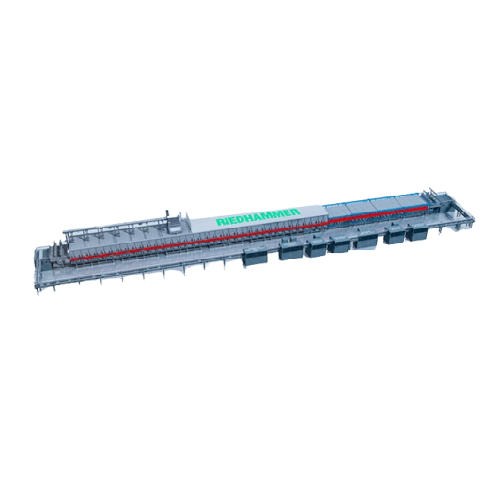
Lithium-ion battery powder processing solution
Optimize your lithium-ion battery manufacturing with advanced powder treatm...
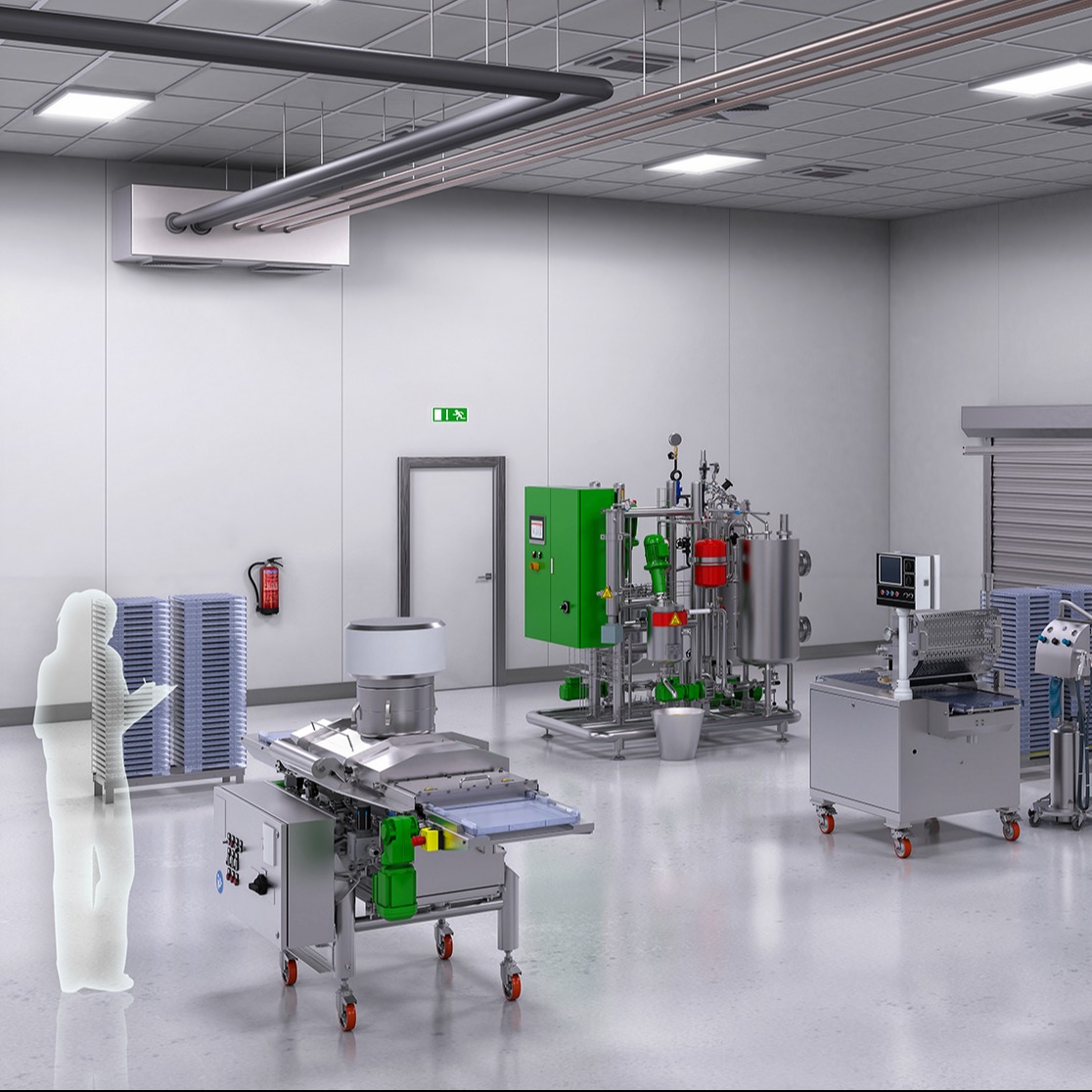
Start-up production line for CBD gummy production
High-value products like CBD gummies demand precision equipment such as...
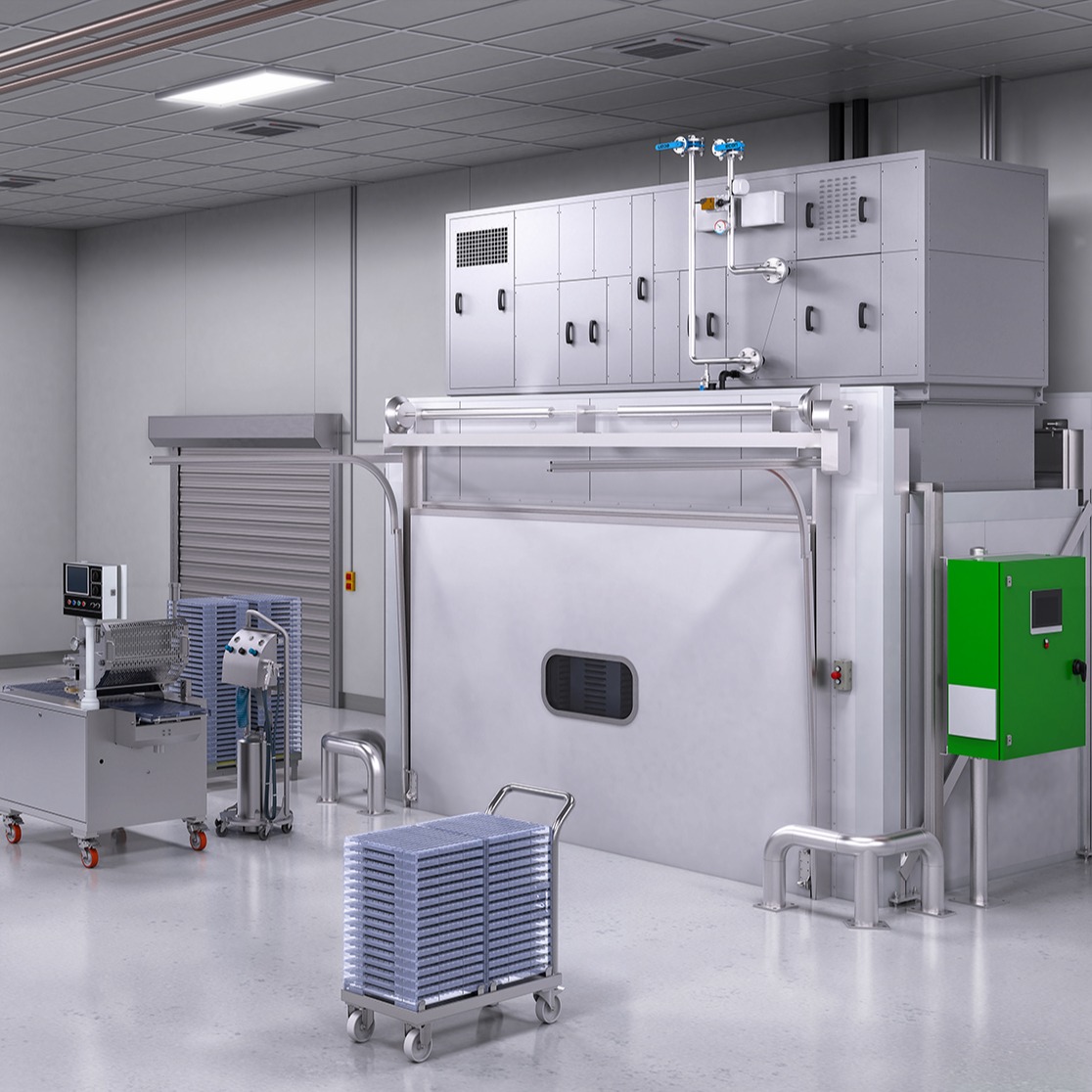
Lab scale production line for nutraceutical gummy production
By gradually investing in the individual parts, a productio...
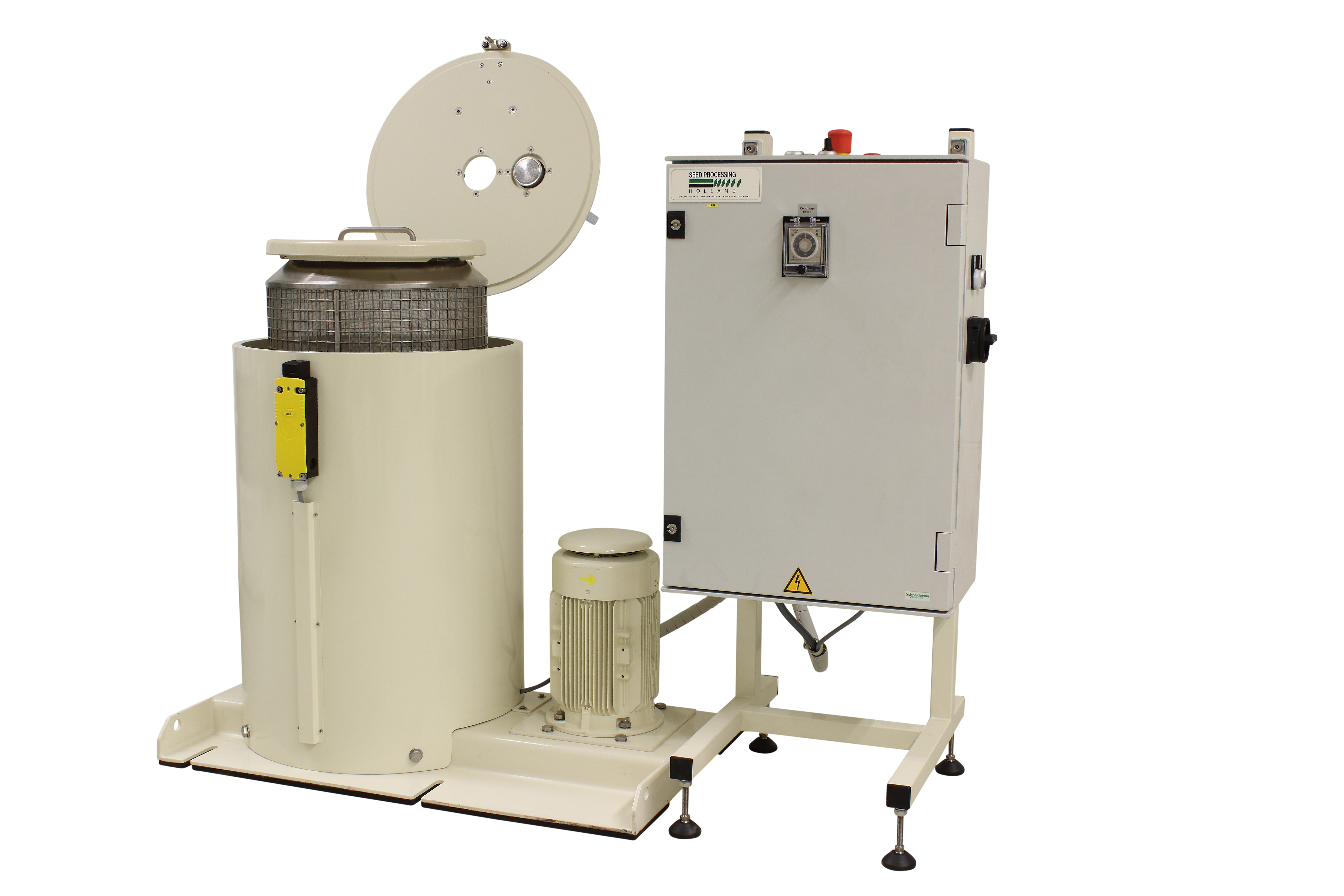
Seed Centrifuge Small
When drying extracted, disinfected, or primed seeds, the process can be very long, as they have high wa...
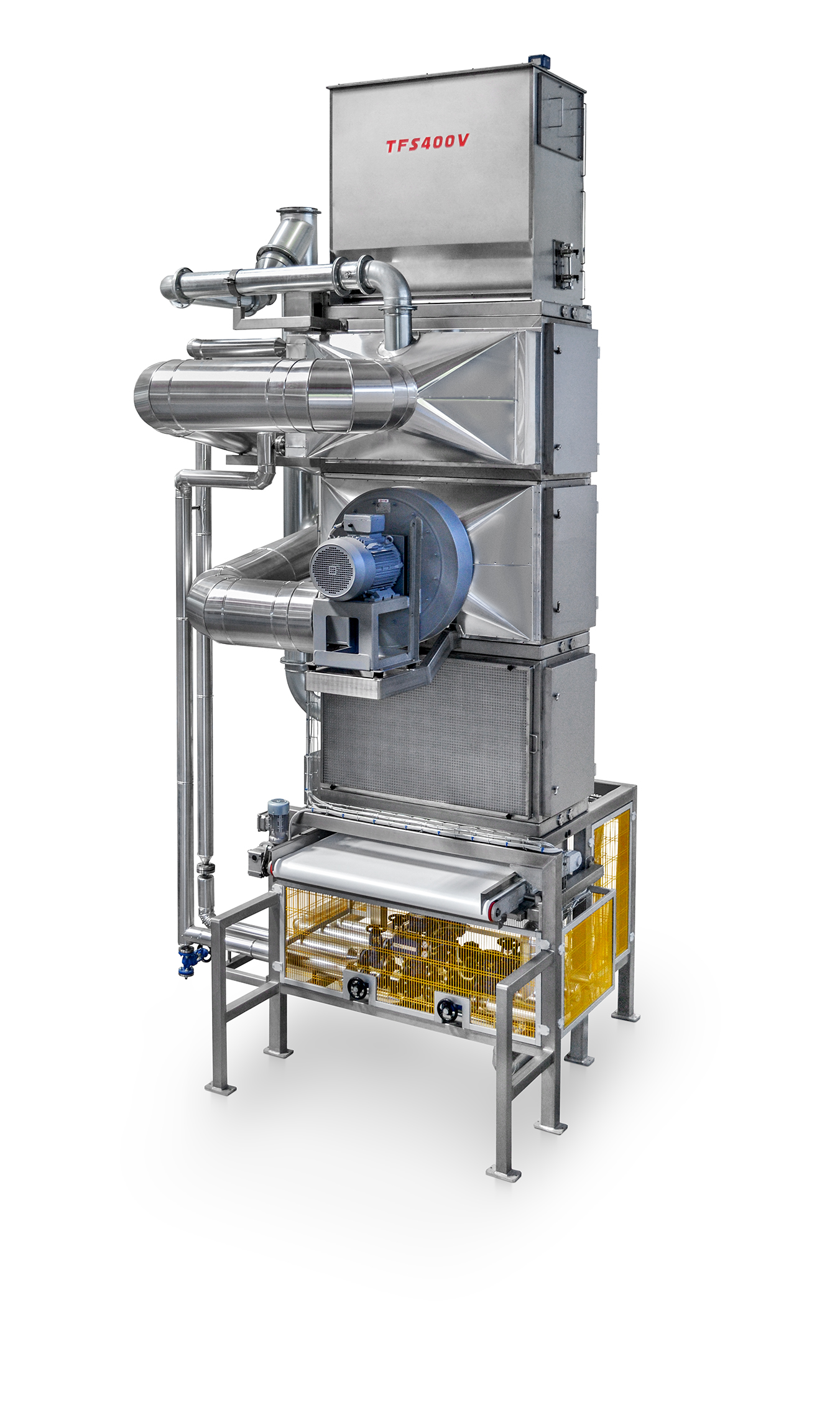
Industrial Nut Roaster
Moisture considerably depletes the shelf life of nut products. At the same time, however, manufacturer...
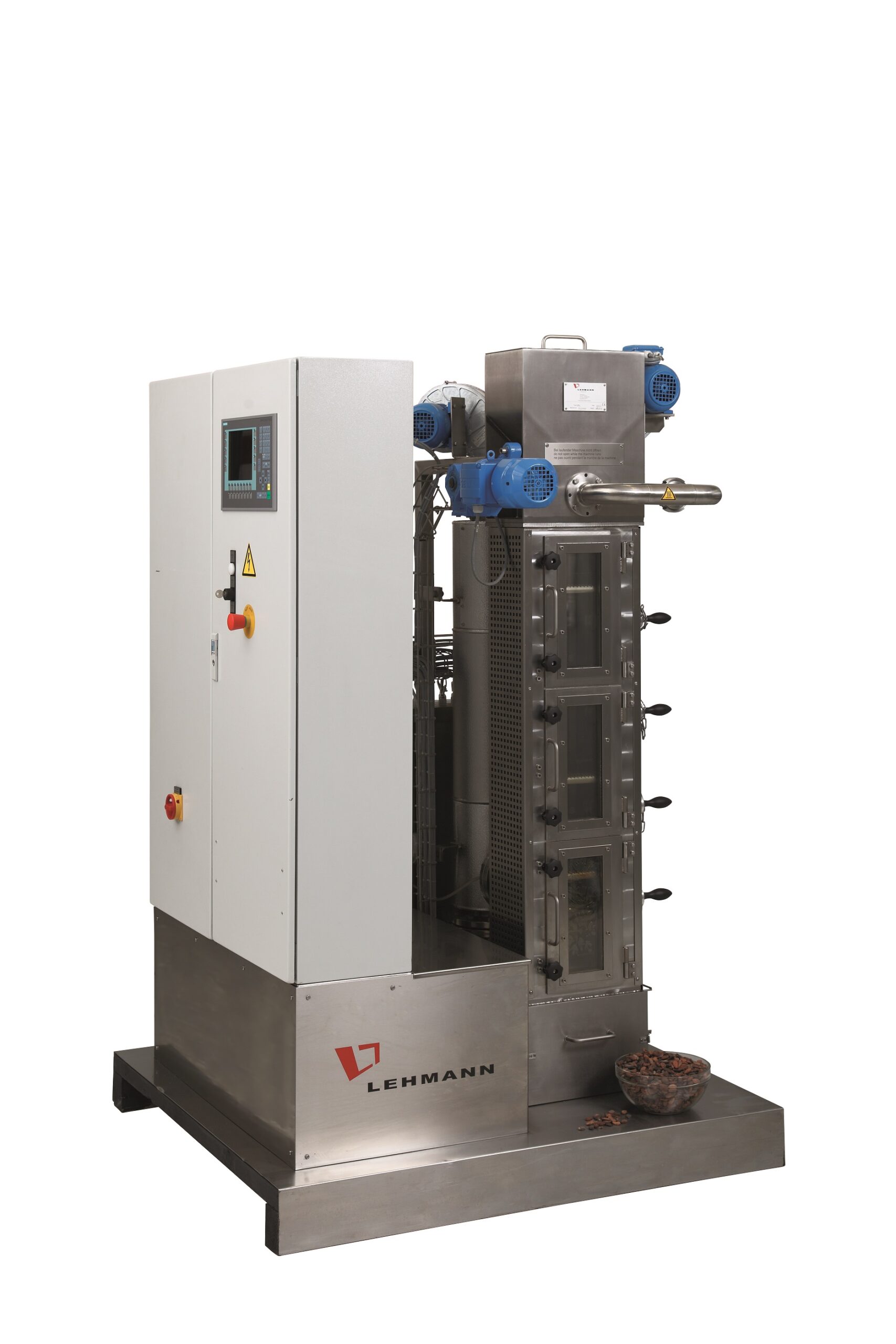
Continuous cocoa bean roasting line
When you are processing chocolate, after the conditioning and fermenting of cocoa, the ...

Industrial high shear mixer granulator for drug formation
It is rather difficult to successfully produce a pharmaceutica...
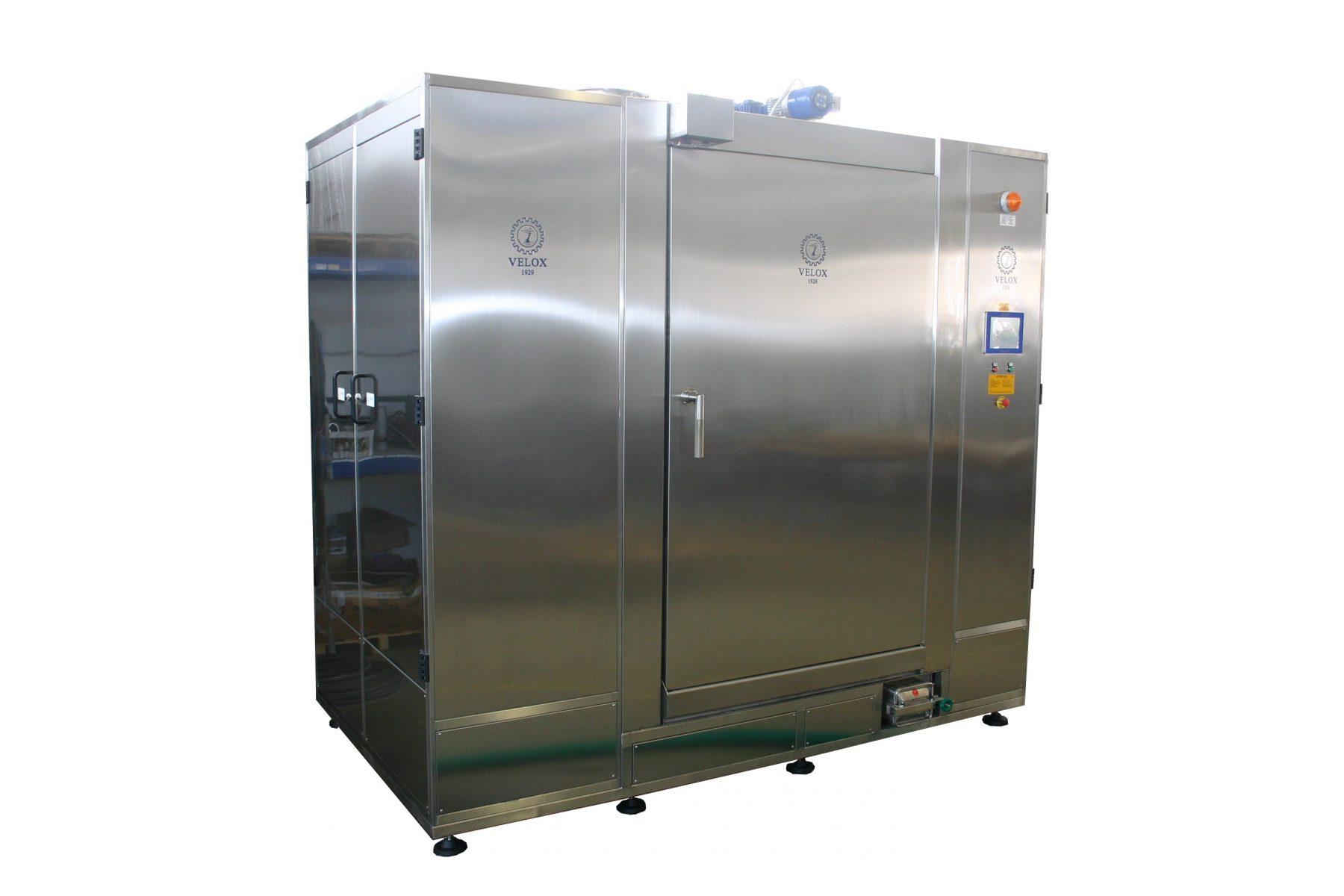
Washing cabinet for trolleys
Food manufacturing facilities, bakeries, or restaurants are ridden with efficiency-related issu...
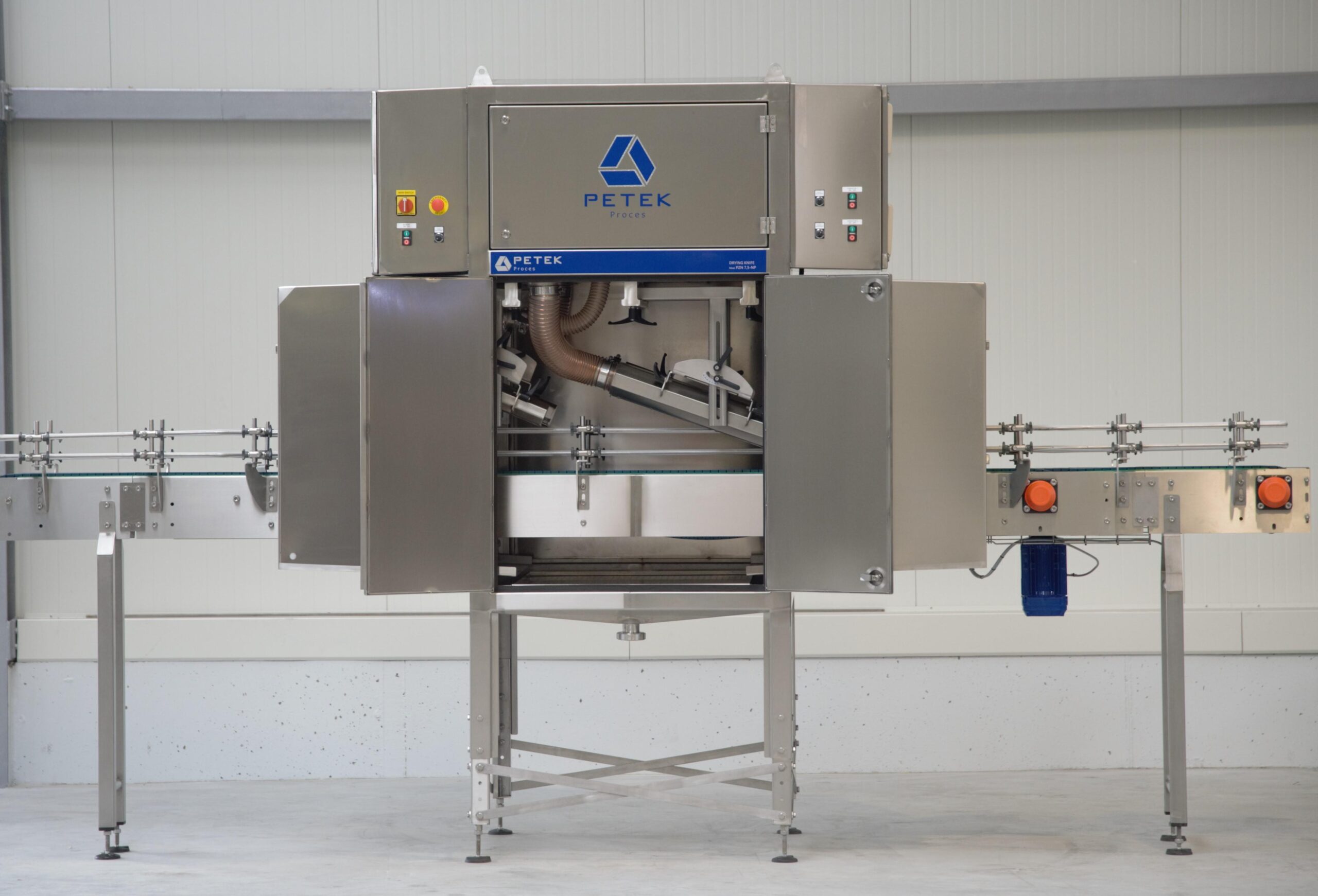
Air knife system for bottling lines
Wet containers are unacceptable and can be problematic in the food and beverage industr...

Evaporator for manure fertilizer
Traditionally, liquid manure processing can lose some important nutrients. An efficient ful...

Pelleting line for manure fertilizer
Manure fertilizer needs to be made marketable by making them visually attractive, with...
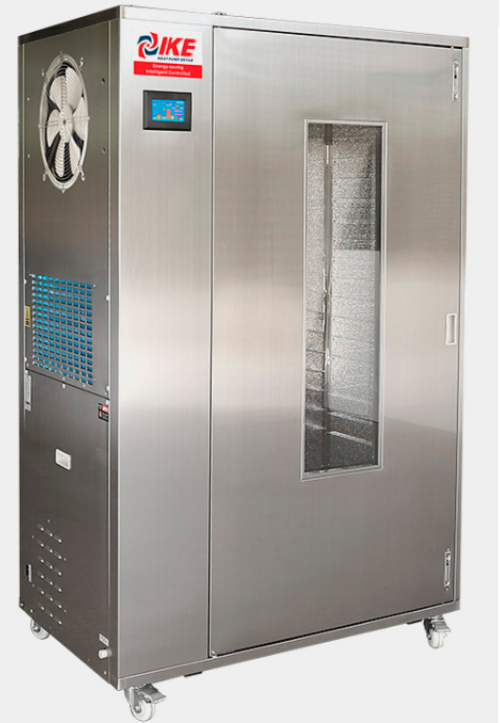
Industrial dehydration machine
Dried fruits are popular both as food in themselves and as ingredients. Traditional drying te...
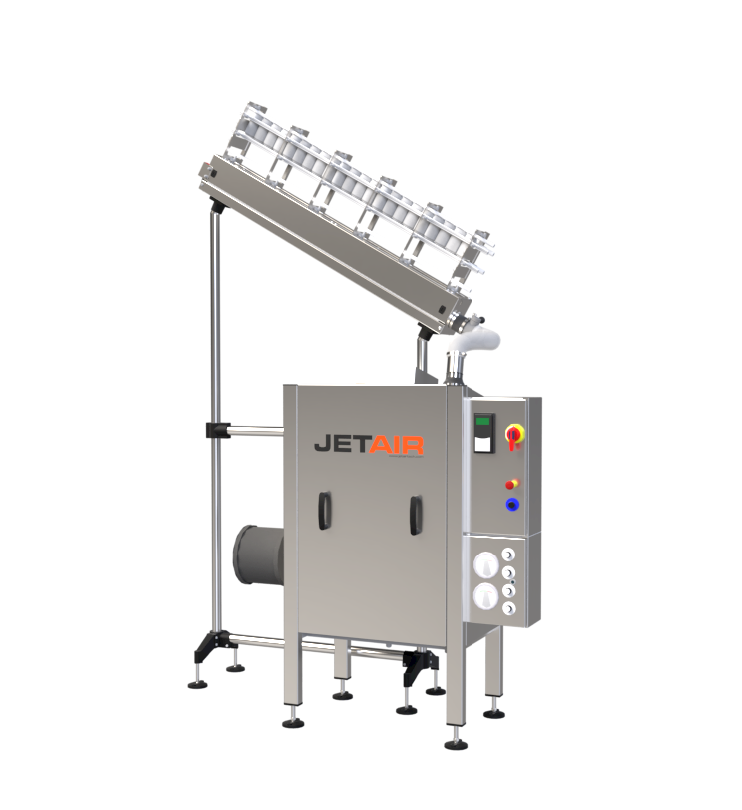
Air rinsing system for containers
Traditional water rinsing solutions for containers used in the food and pharmaceutical se...
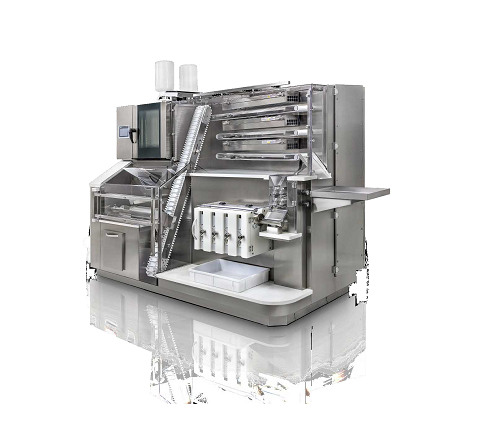
Small scale cocoa beans processing machine
For the highest quality chocolate production, complete control of the entire pr...
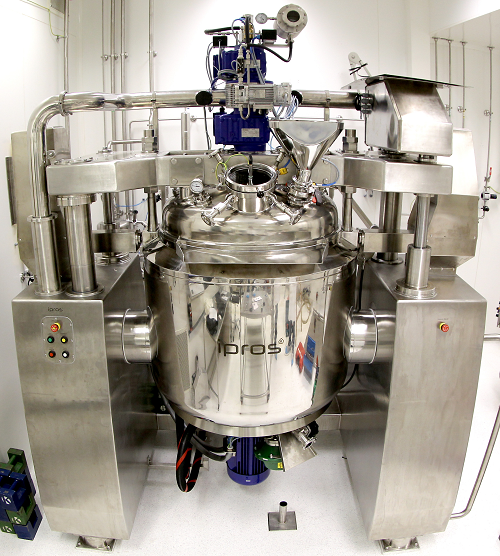
Homogenizer for creams
Homogenization (or pharmaceutical micronization) is the process of reducing particle sizes, and is a v...
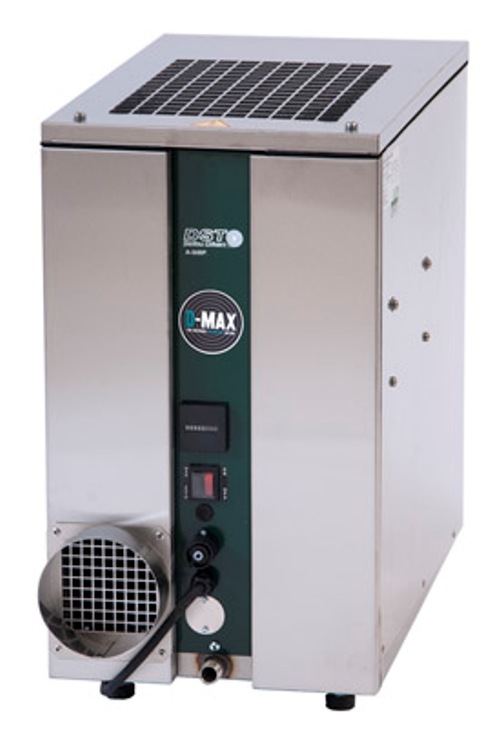
Sorption dehumidifier with air-chilled condenser
It is not always possible to duct out the wet air from a dehumidifier ser...
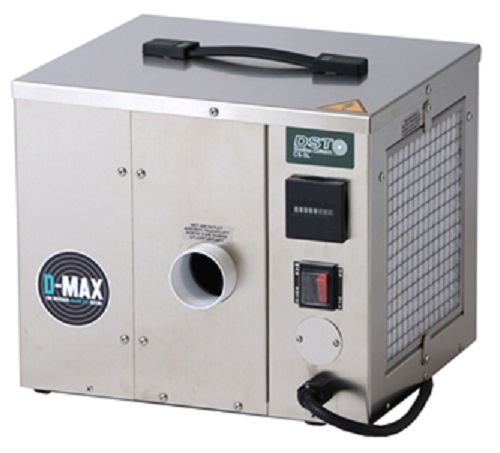
Small portable dehumidifier
Water damaged areas require dehumidification to limit the damage and prepare the area for restor...
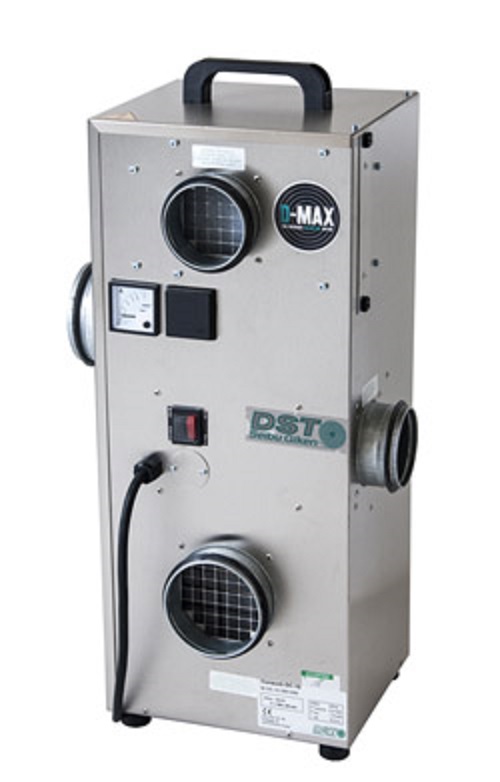
Sorption dehumidifier for large temperature differences
Small, humid areas can be difficult to dehumidify in humid ambien...
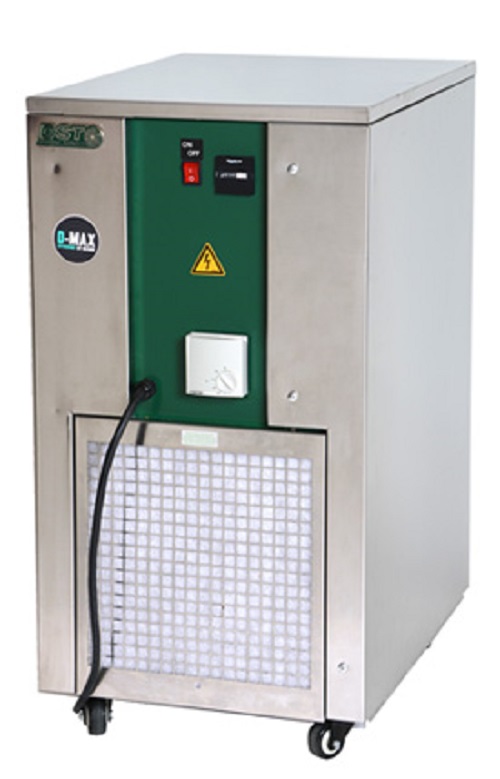
Dehumidifier for difficult wet airflows
Sealed rooms can be challenging to dehumidify with ordinary dehumidifiers. The wet ...
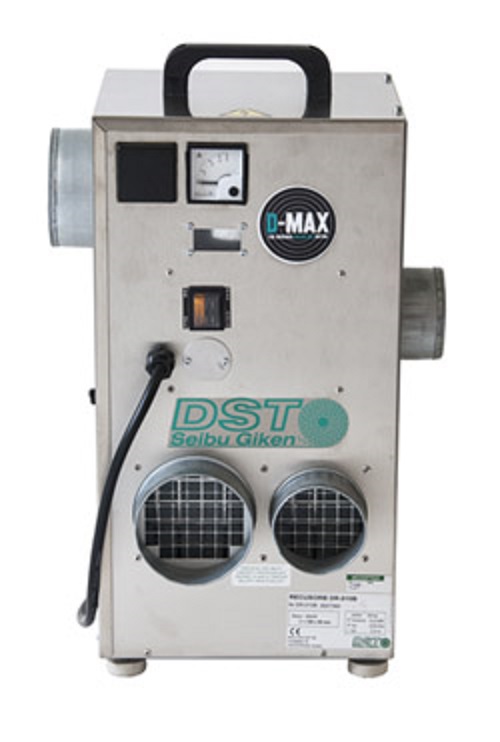
Sorption dehumidifier for overpressured rooms
Small humid spaces, used for processing or storage, often need a simple dehu...
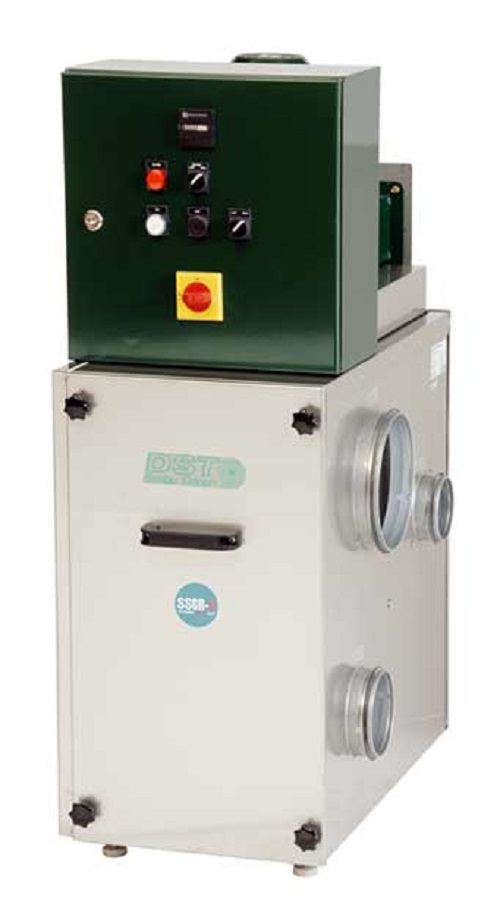
Heat recycling sorption dehumidifier
Facilities that handle large amounts of water can become very humid. High humidity may...
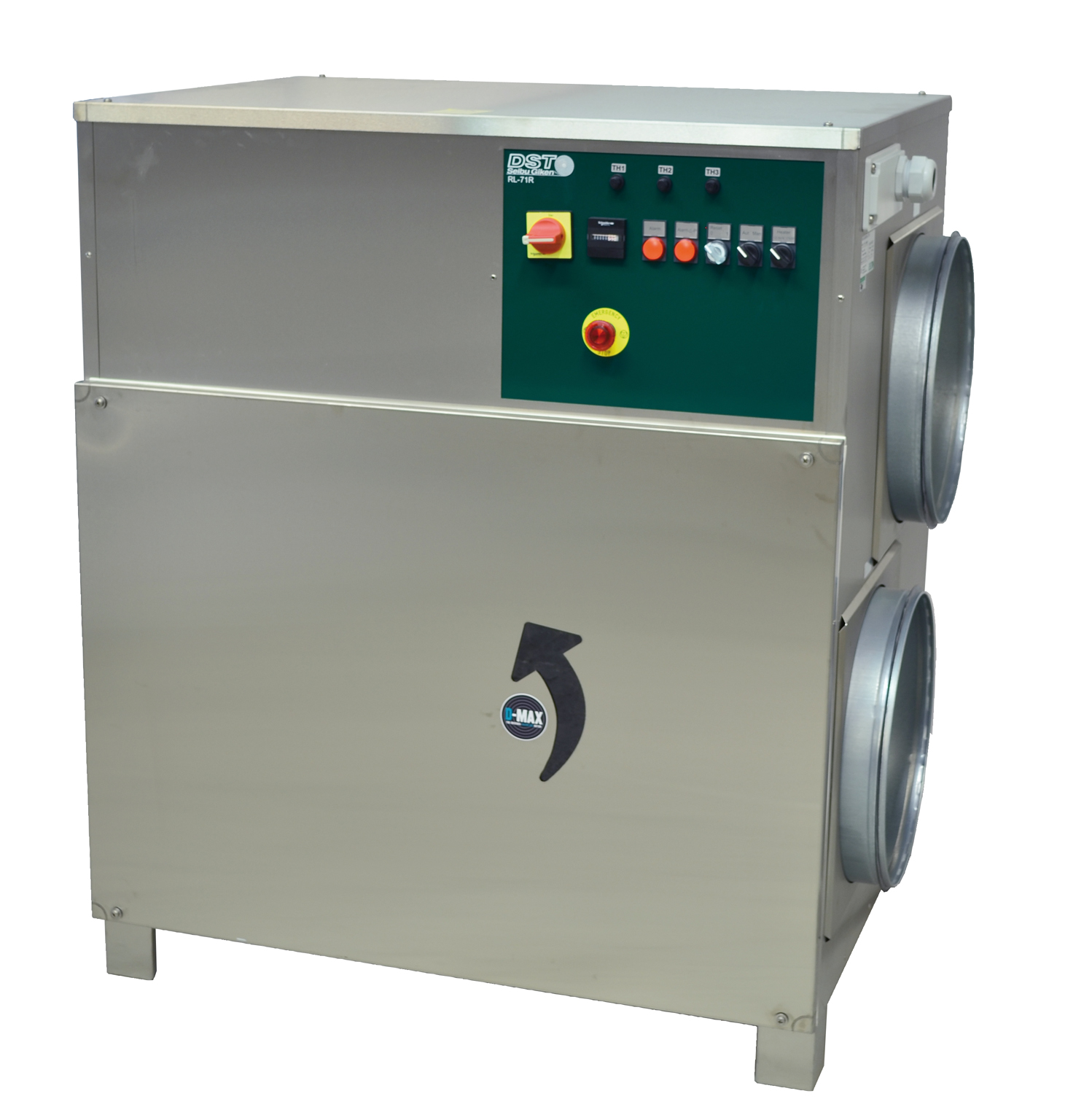
Industrial desiccant dehumidifier
Dehumidification of medium sized manufacturing and processing facilities can be a dauntin...
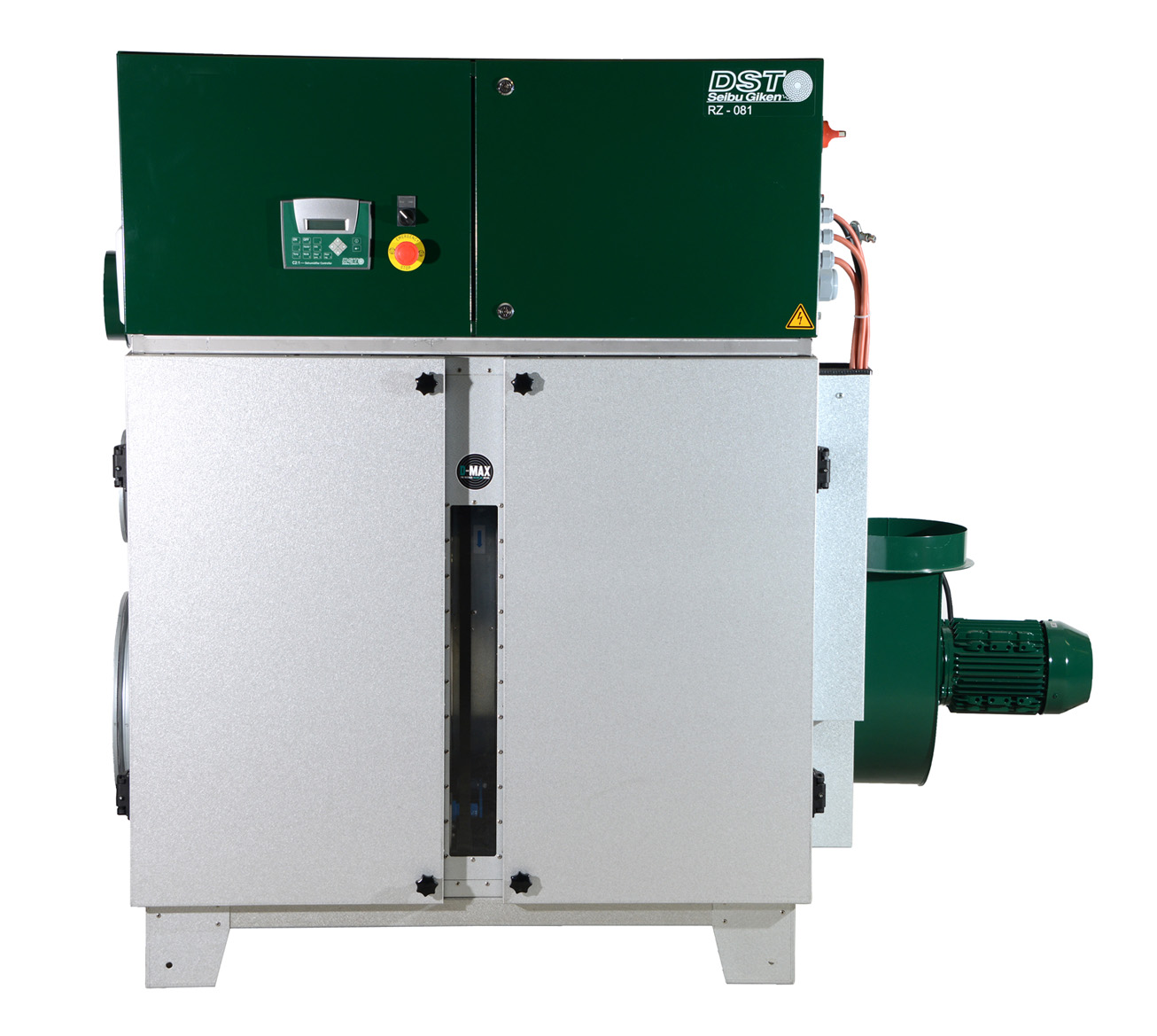
Large scale desiccant dehumidifier
Moisture sensitive processing and storage facilities need low humidity environments to s...
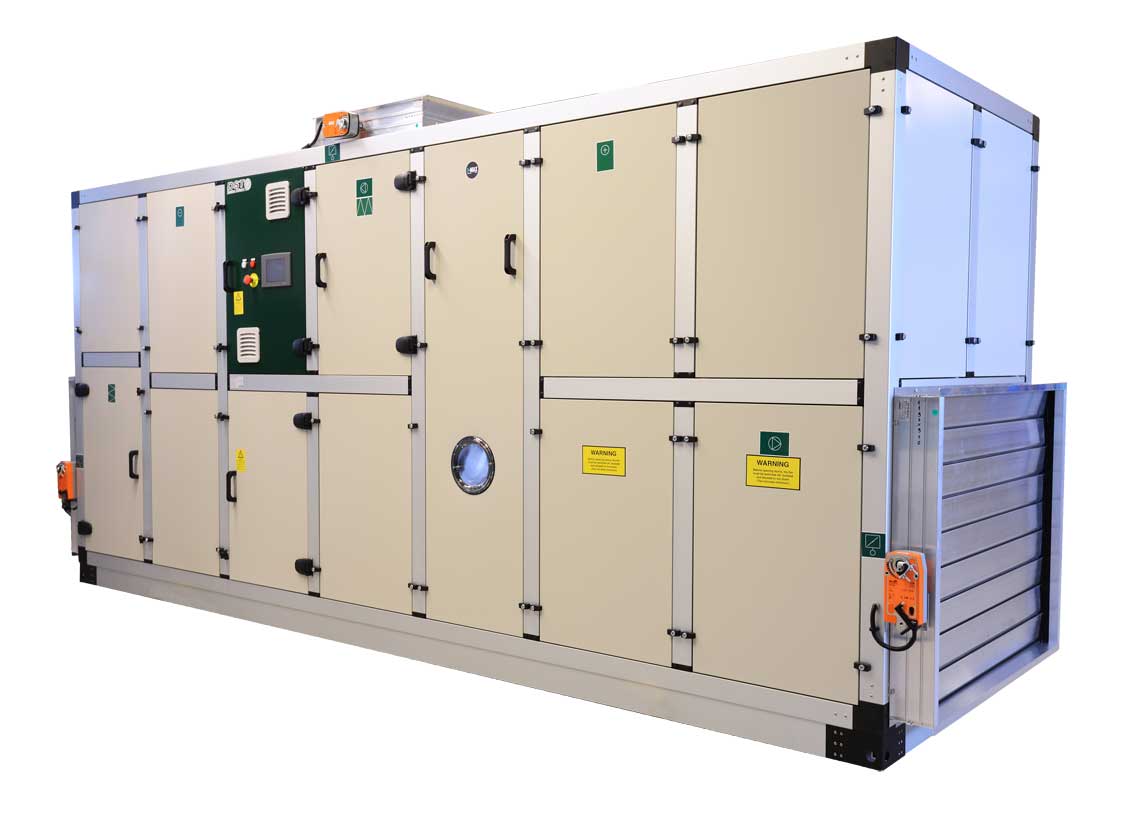
Customizable dehumidifier
Dehumidification needs can vary significantly from one project to another. Dehumidifiers with a fi...
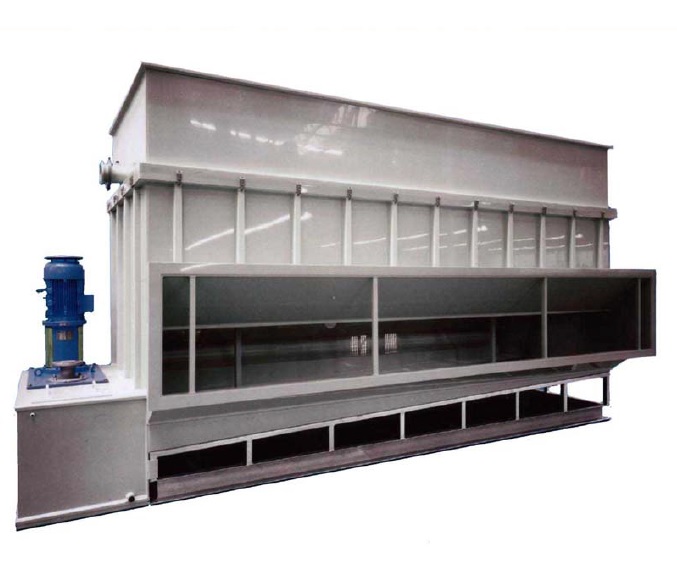
Air dehumidifier for bulk products
When your product or process is sensitive to humidity, using an air dehumidifier may res...
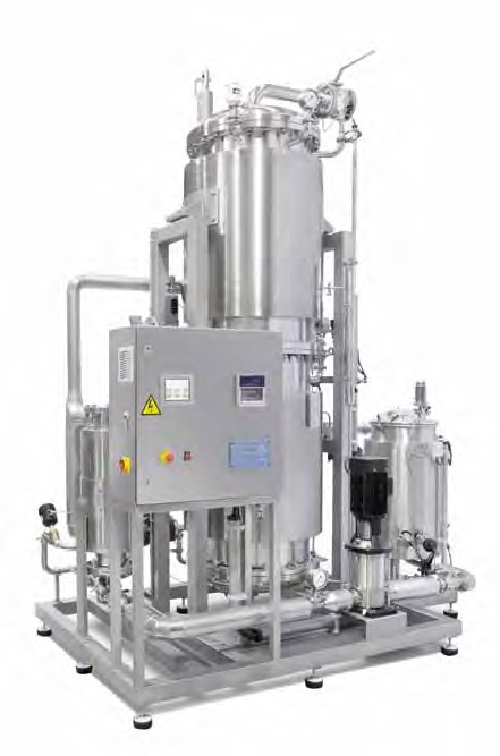
Electrical pure steam generator
Pure steam is defined as the steam which when condensed becomes WFI quality water in accorda...
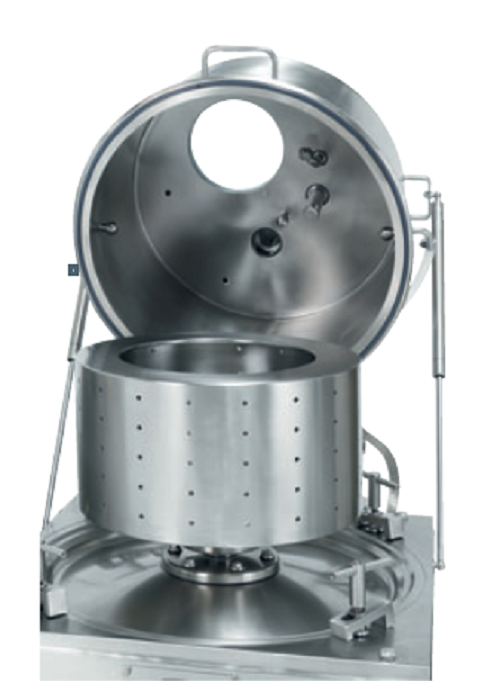
Isolator centrifuge
For transferring highly active pharmaceutical ingredients (HAPI) without contamination from the isolator ...
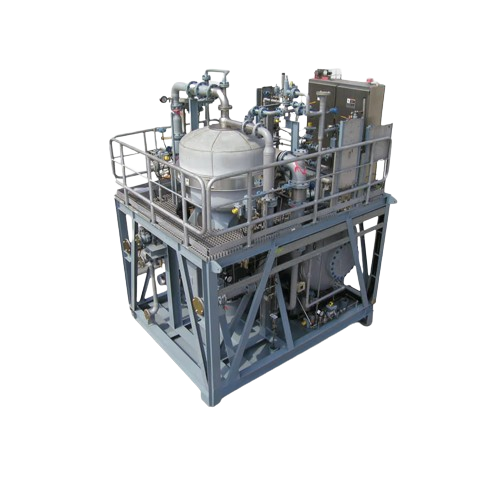
Nozzle separator for heavy crude oil dehydration
Achieve efficient dehydration of heavy crude oils with precision-engineer...
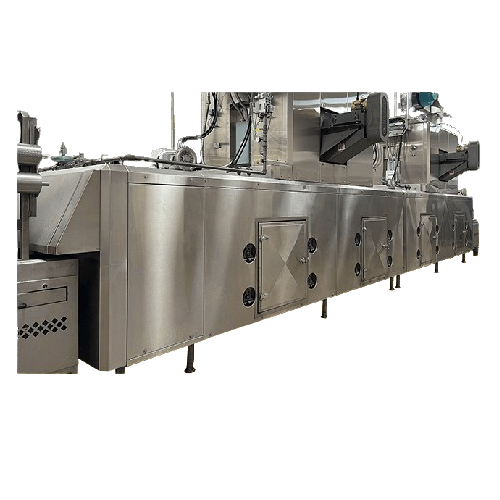
Electric oven zones for snack and cookie baking
Optimize your baking line with electric oven zones designed to eliminate e...
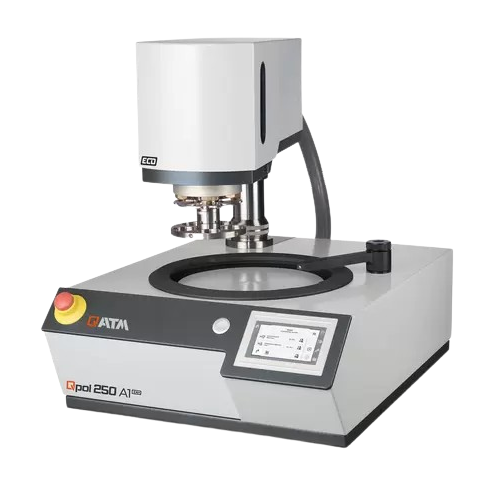
Metallographic grinder and polisher for sample preparation
Optimize your metallographic sample preparation with precisio...
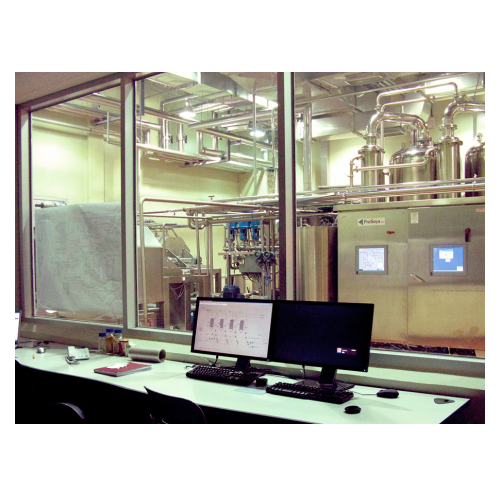
Soya protein isolate production line
Ensure the highest protein purity with this comprehensive production line designed to ...

Dairy alternative production technology
Transform your production line with efficient dairy-alternative technology, enablin...
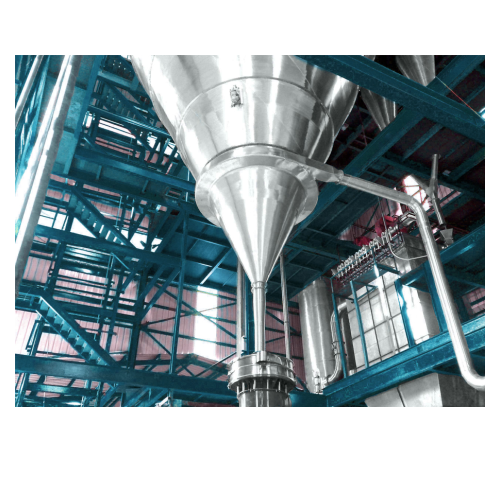
Milk powder processing plant
Achieve precise powder formulations with our state-of-the-art milk powder processing plant, ide...
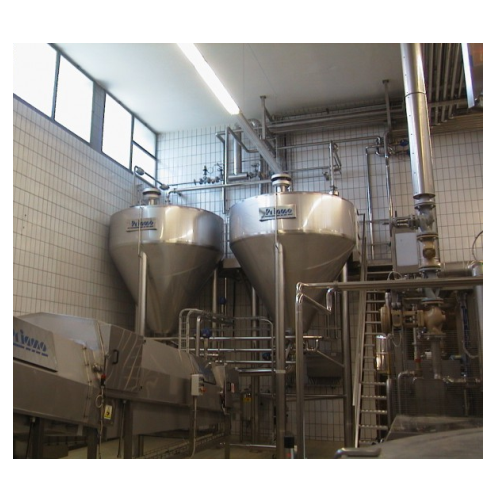
Ricotta cheese flocculation tank
Optimize your ricotta production with an efficient flocculation tank designed to maximize y...
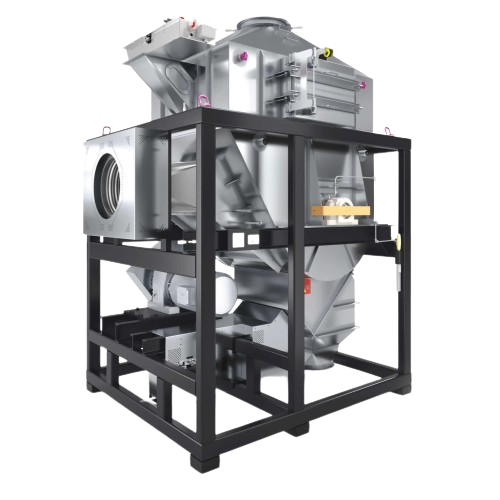
Green coffee preheating system
Optimize your coffee roasting process by utilizing waste heat for preheating, reducing energy...
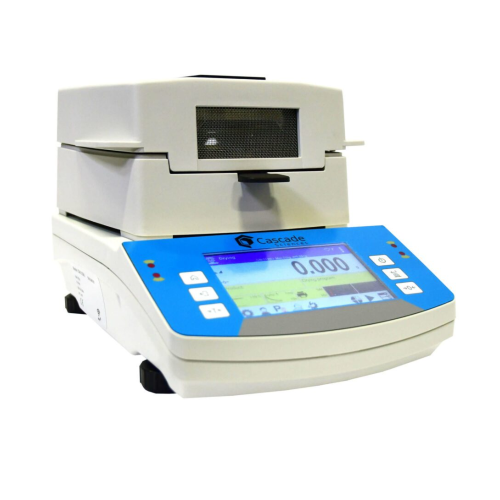
Moisture analyzer for precise and reliable measurements
Ensure precise moisture control in high-value products like lyoph...
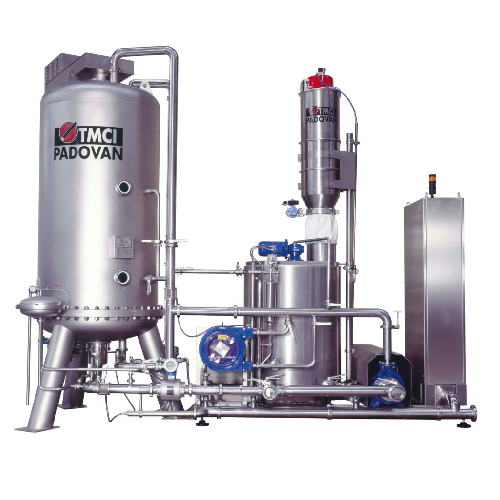
Ped tested filtration system for sparkling wines
Ensure consistent carbonation and clarity in your sparkling beverages wit...
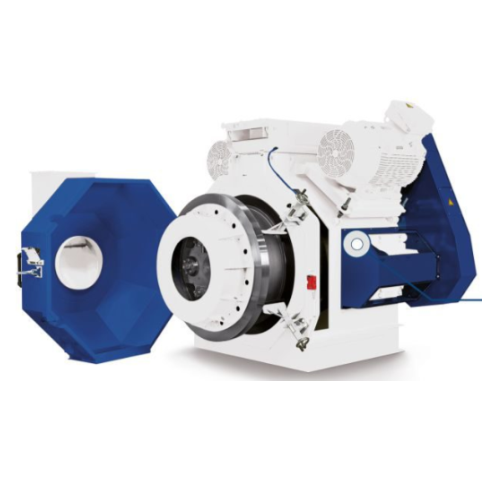
Pellet mill for animal feed production
Optimize your feed production with a robust pellet mill designed to enhance the dura...
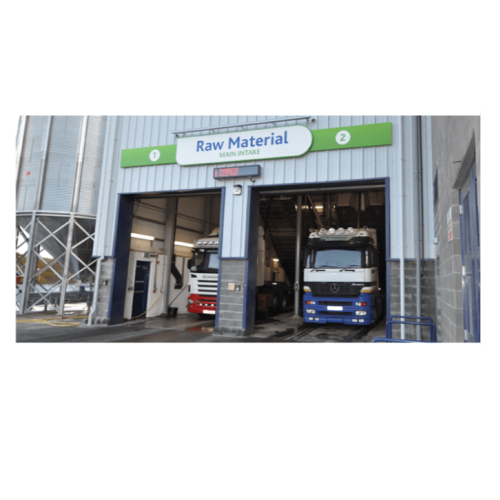
Product intake solutions for feed processing
Optimize your feed production with efficient material intake systems, ensurin...

Small-scale scraped surface heat exchanger for high-viscosity products
For R&D teams tackling complex formulations...
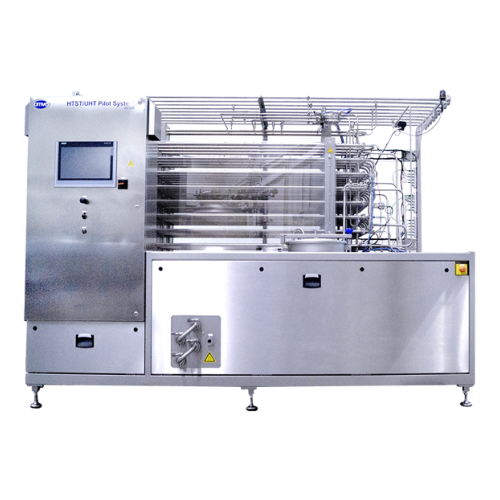
Uht/htst aseptic processor for pilot plants
Achieve precise heat treatment and aseptic processing with flexible pilot syst...
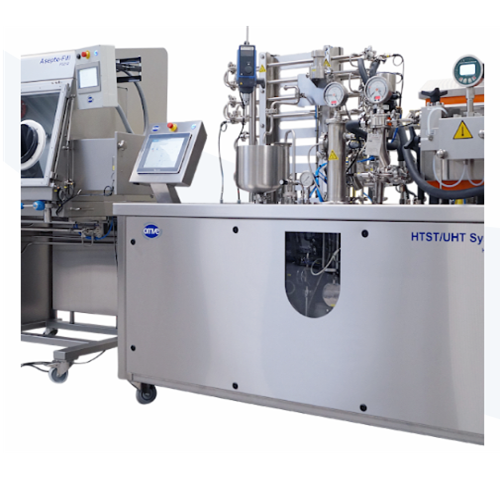
Customized process plants for plant-based beverages
Efficiently scale your production of plant-based beverages with modul...
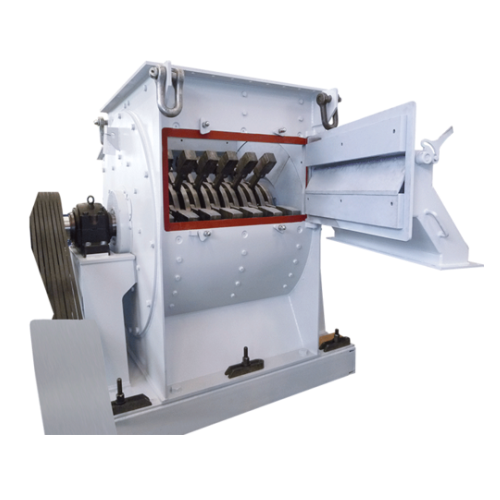
Industrial hammer mill for mineral processing
Optimize your material processing with an advanced hammer mill designed to e...
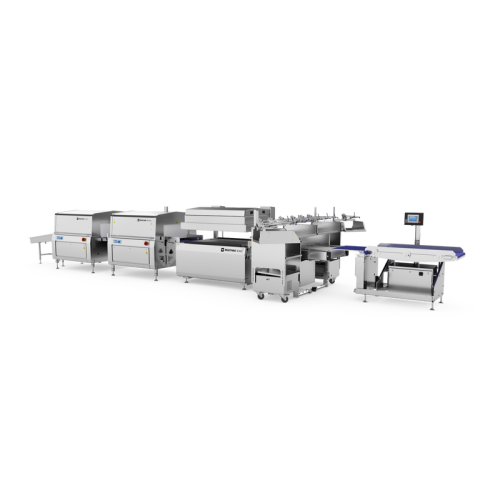
Vacuum packaging chamber for industrial products
Achieve consistent sealing precision and extended shelf life for diverse ...

Hygienic mixer for batch operation
Achieve consistent and precise mix quality across diverse powders and granules with this...
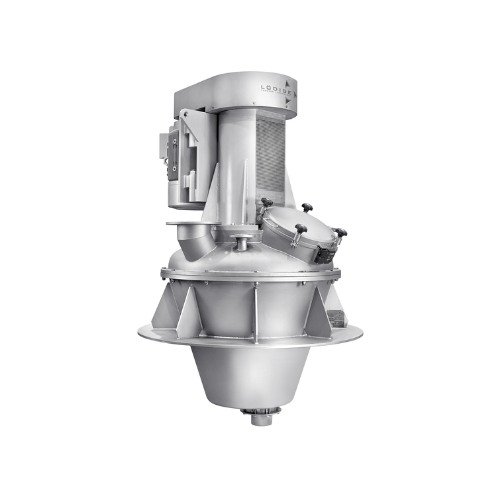
Wet mixer for viscous and paste-like products
Achieve high-quality mixing of medium to highly viscous products with precis...
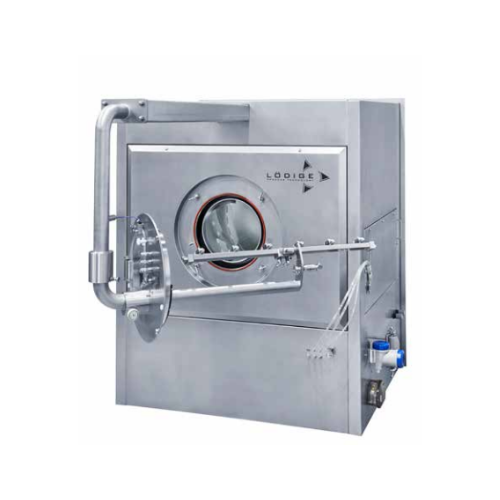
Film coater for Otc and food supplements
Achieve optimal film coating for tablets and capsules with precision-engineered so...
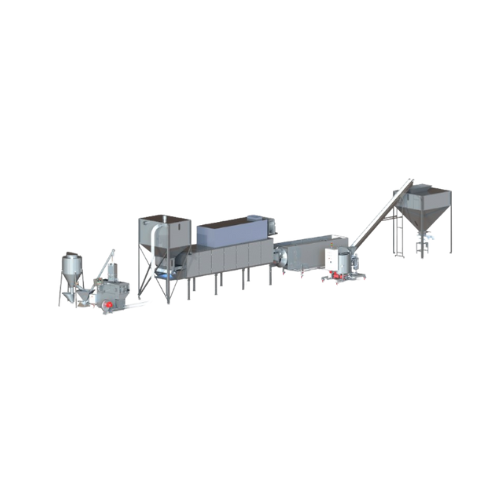
Single-screw high shear extruder
Optimize your snack production with precise control over raw material transformation, from ...
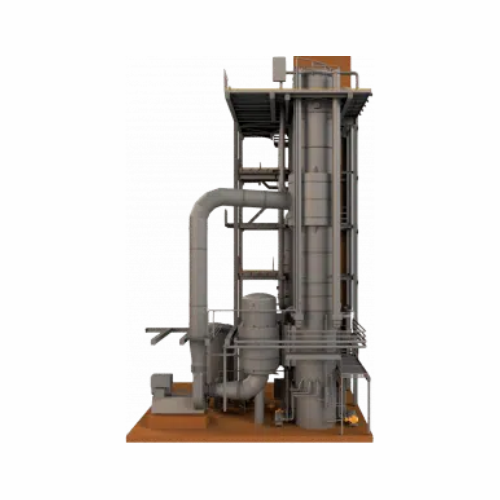
Milk product evaporator for high solids concentration
Efficiently concentrate milk products to high solids, optimizing pr...

High-concentration dairy evaporator
Achieve high solids concentrations with enhanced efficiency by integrating this evapora...
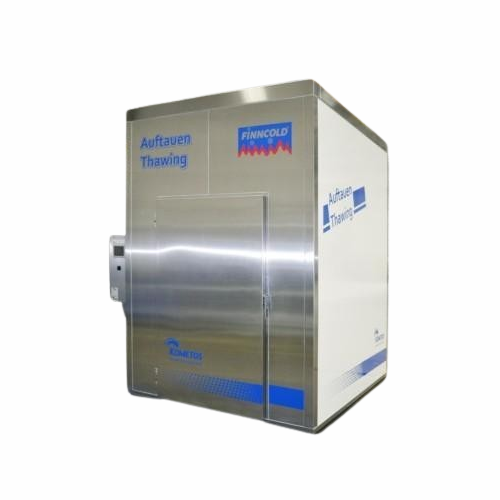
Industrial thawing systems for meat products
Optimize your food production line with advanced thawing systems designed to ...
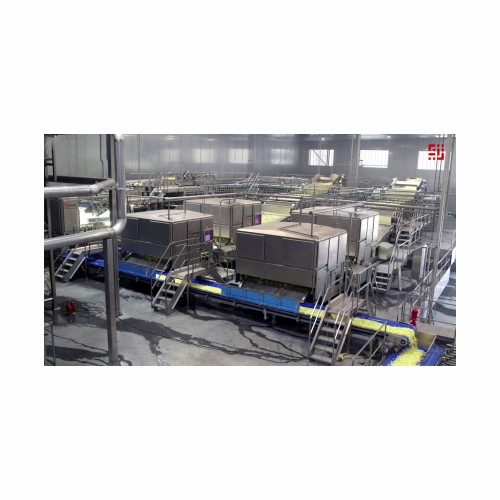
French fry and coated french fry processing line
Optimize every potato’s potential from pre-cleaning to frying with ...
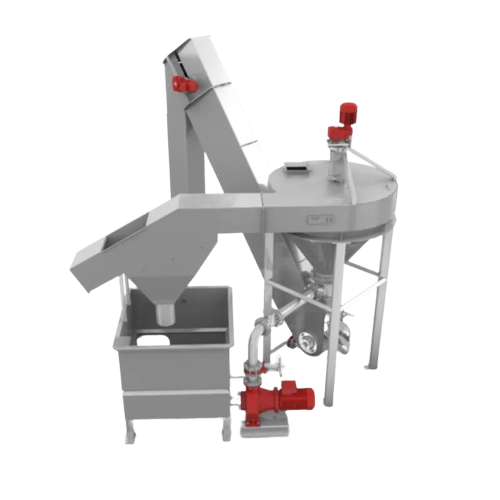
Hash brown production line for formed potato products
Optimize potato processing with this advanced production line, tran...
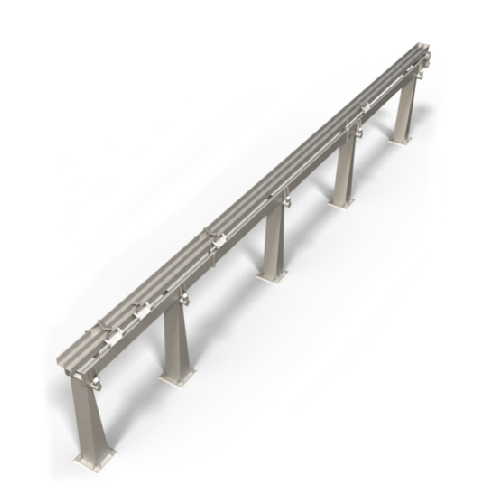
Collection conveyors for food processing
Optimize your production line by efficiently collecting and conveying solid produc...
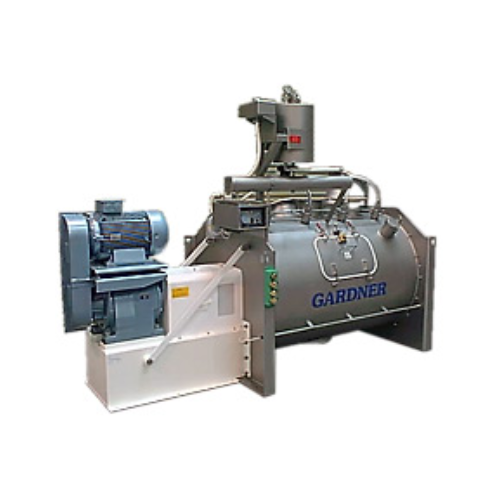
High shear plough mixer for powders, granules, and pastes
Achieve rapid and efficient blending with high shear mixers de...
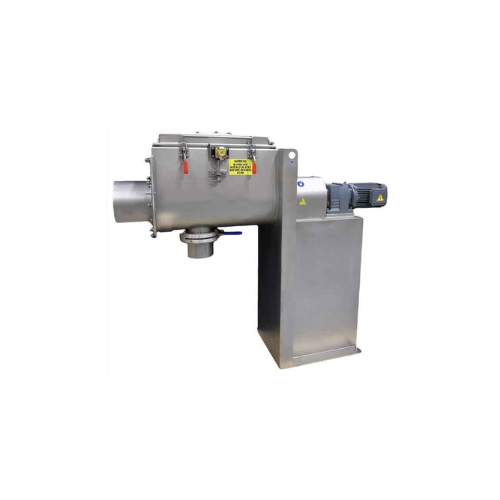
Homogenous blending solution for powders and granules
Achieve precise, homogenous blending of challenging materials like ...
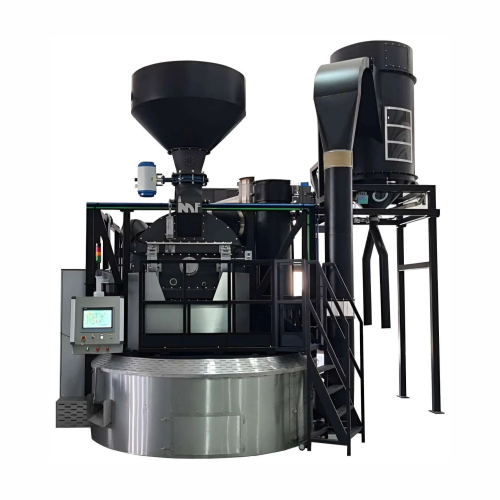
Industrial coffee roaster 480kg batch capacity
Optimize your coffee production with precision roasting for up to 480 kg pe...
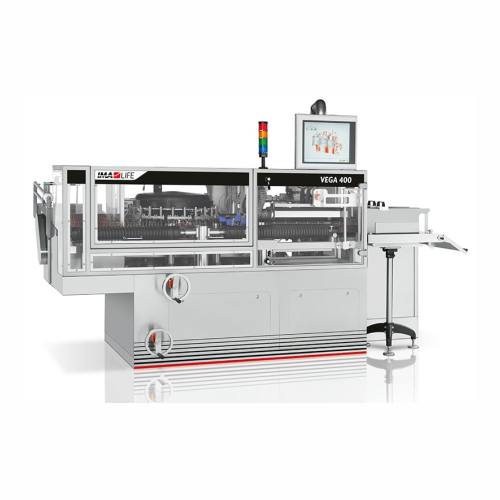
Ampoule external washer for decontamination
Ensure contamination-free glass containers with a high-speed solution designed...
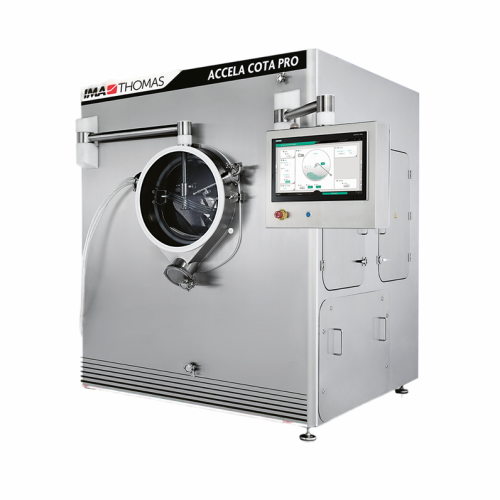
Automated coating pan for pharmaceutical tablets
Enhance your tablet production with a fully automated system that ensures...
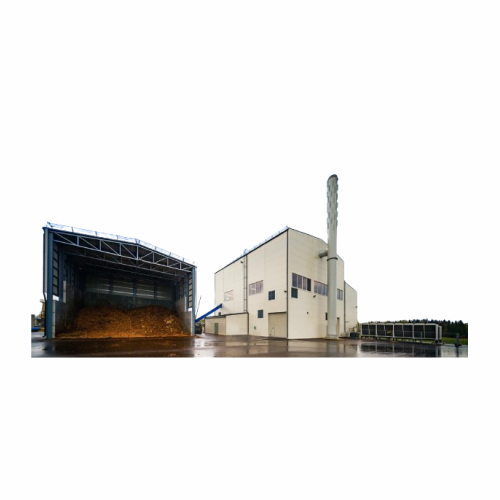
Industrial water tube steam boilers
Optimize energy efficiency and reduce fossil fuel reliance with high-performance steam ...
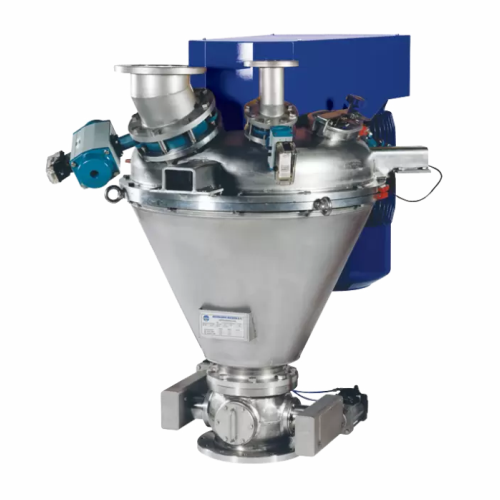
High shear impact mixer for agglomeration and dispersion
Achieve precise homogeneity and efficient agglomeration with a h...
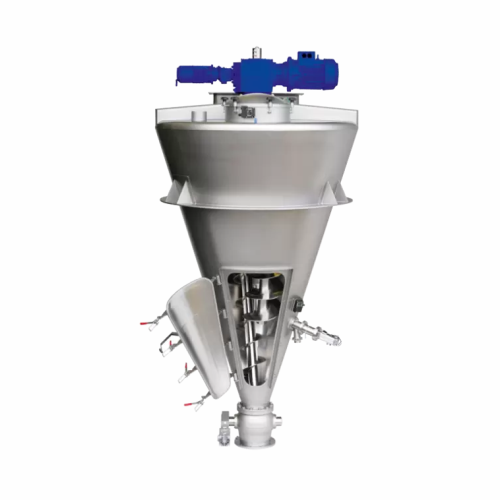
Batch mixer for segregative, free-flowing powders and pastes
Achieve precise and gentle batch mixing for delicate produc...
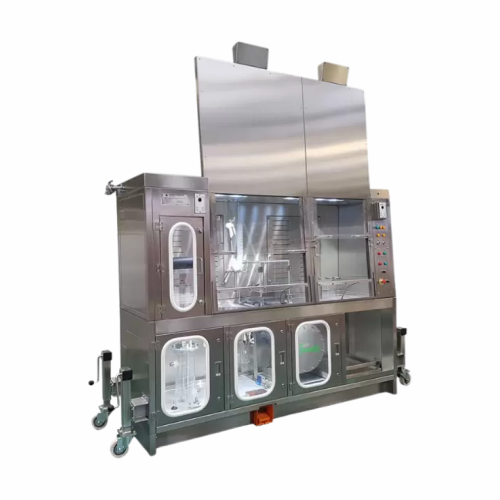
Containment solutions for hazardous material processing
Ensure safe and efficient processing of hazardous materials with ...
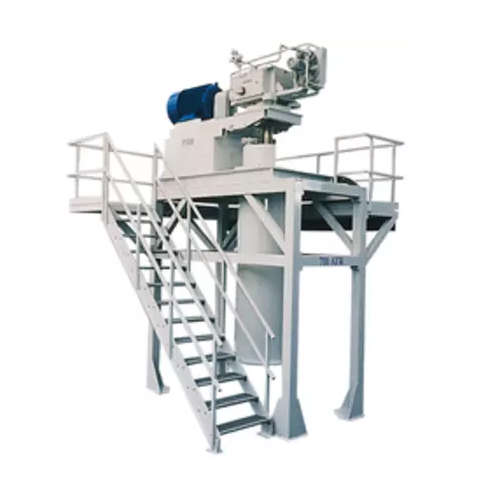
Ultra-fine grinding with ball mills and agitated media mills
Achieve precision in ultra-fine grinding for demanding mate...
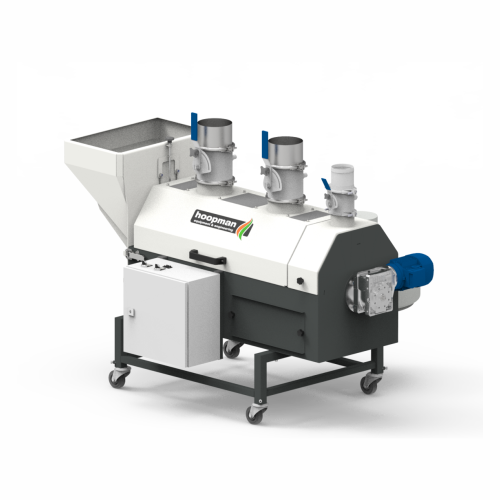
Lab conditioner for de-dusting and curing film-coated seeds
Efficiently de-dust and cure your film-coated seeds with thi...
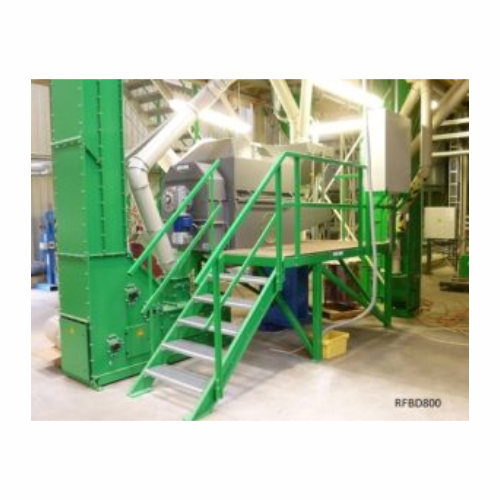
High capacity seed dedusting and conditioning system
Achieve optimal seed quality with a high-capacity system that seamle...
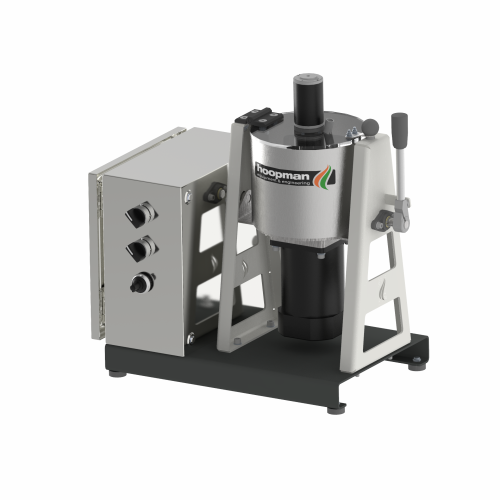
Rotary seed coating system
Enhance seed coating precision with high-capacity rotary systems, minimizing damage and boosting ...
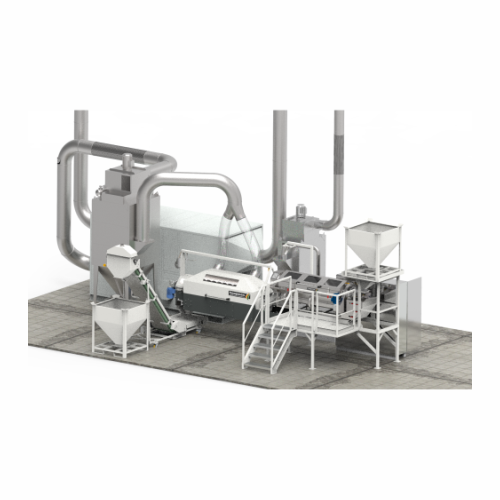
Steam-based seed disinfection system
Eliminate seed-borne pathogens with a steam-based technology that preserves germinatio...
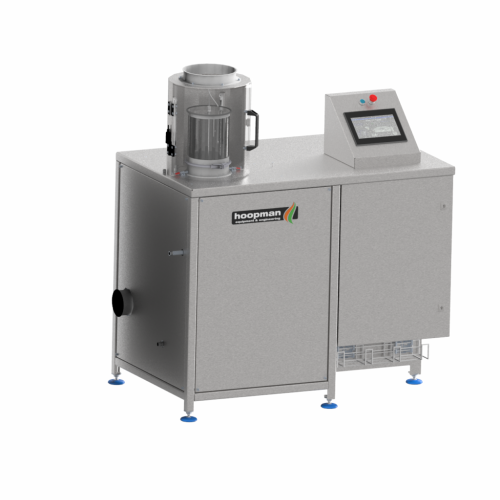
Seed disinfection system for small seed lots
Streamline seed treatment with a powerful system capable of developing steam ...
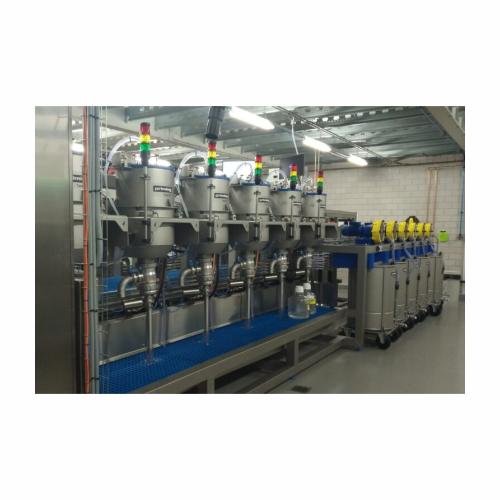
Liquid matrix priming unit
Ensure seed vitality and improve germination rates with advanced liquid matrix priming, designed ...
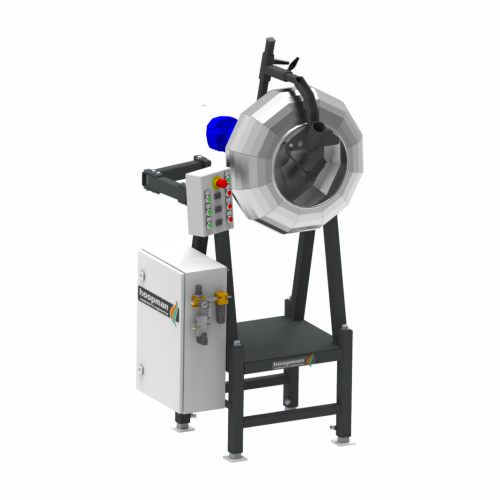
Pelleting equipment for precision seed treatment
Achieve consistent and precise coating of seeds with exceptional control ...
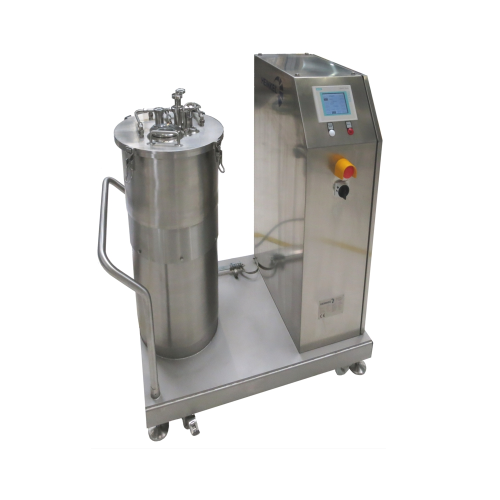
Vertical pilot plant centrifuge for pharmaceutical applications
Ensure precise separation and optimal scaling in your la...
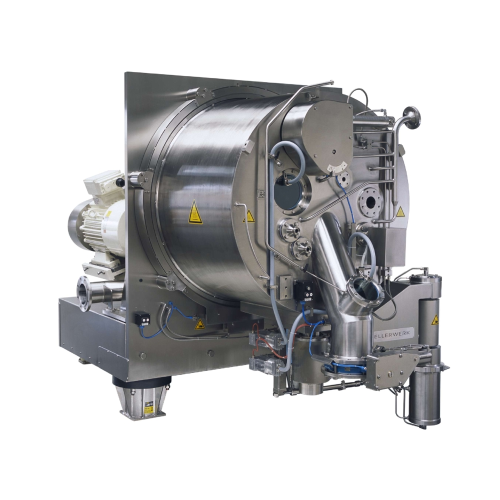
Pharmaceutical horizontal peeler centrifuge
Optimize product consistency and purity with precise separation and filtration...
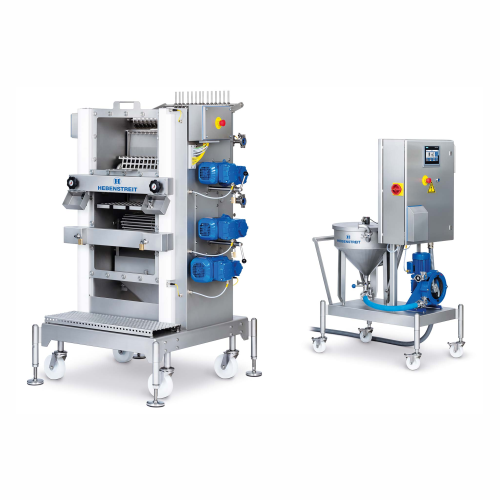
Continuous extruded snack dyeing system
Enhance the aesthetics of your extruded snacks with precise and continuous dyeing, ...
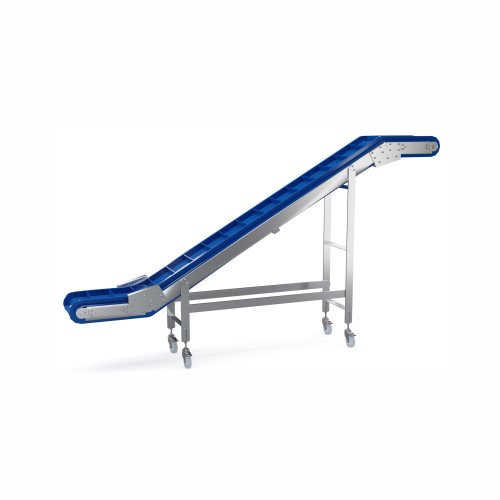
Conveyor systems for snack production
Streamline your snack production with advanced conveyor systems designed for seamless...
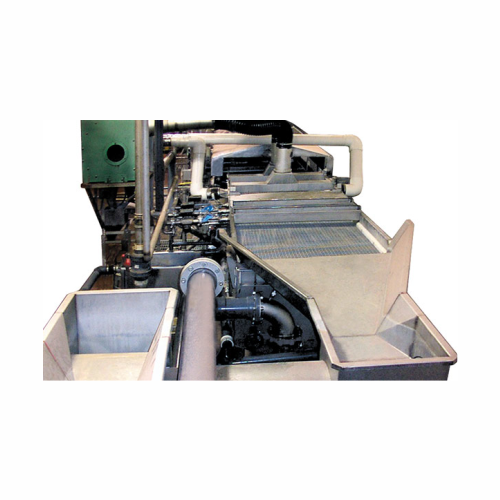
Potato slice washer for surface starch and fines removal
Ensure optimal cleaning and dewatering of potato slices while si...
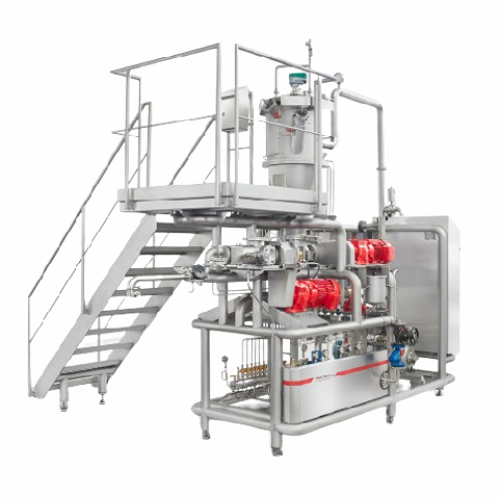
Integrated process system for hard caramel production
Optimize your candy production with a fully integrated system desig...
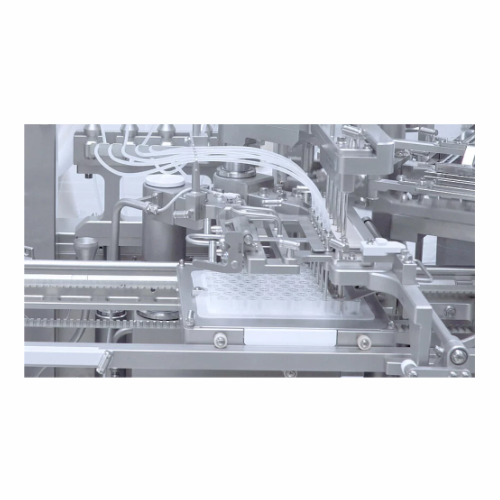
Aseptic syringe filling solution for Rtu containers
Streamline your pharmaceutical liquid filling operations with precise...
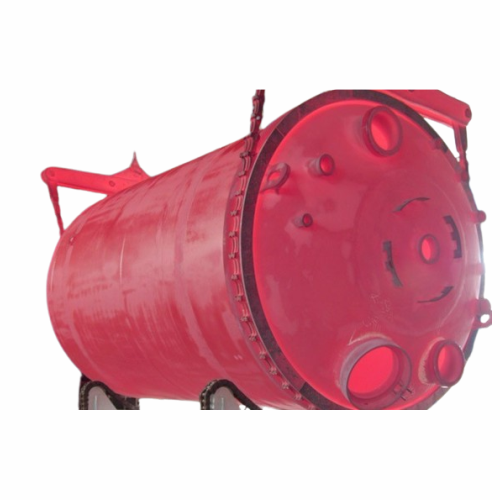
Din standard glass-lined reactors
Streamline your chemical reactions with these DIN standard glass-lined reactors, designed...
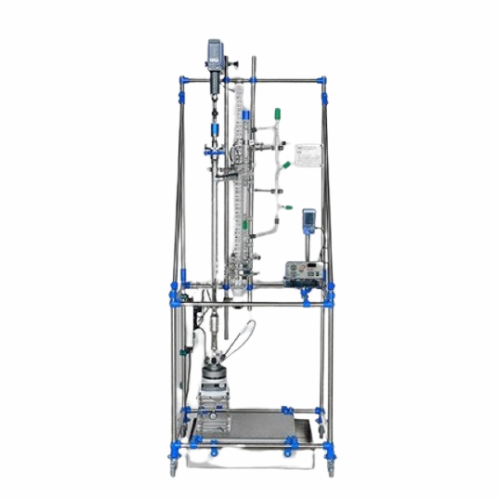
Industrial continuous distillation system
Enhance product purity and efficiency with a robust continuous distillation syst...

Wiped film evaporator for high boiling point materials
For challenging separations of high boiling, viscous, or heat-sens...
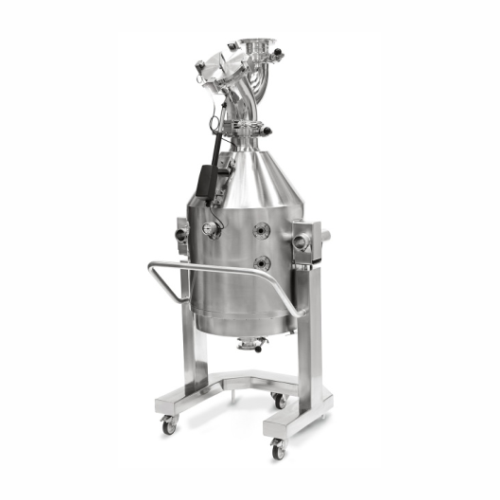
Sterile closure processing system for pharmaceutical production
Ensure your pharmaceutical closures remain sterile and i...
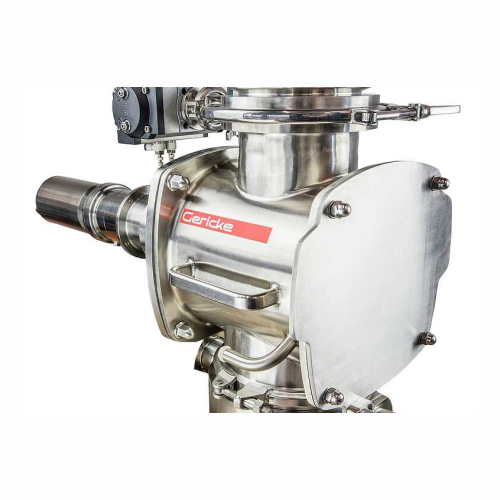
Mini batch blender for pharmaceutical solids
Achieve precise mixing homogeneity with the mini batch blender, perfect for l...
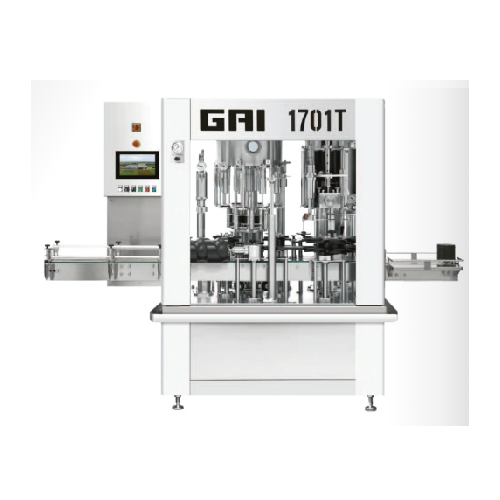
Complete bottling lines for beverage industries
Optimize your bottling process with high-speed, precision-engineered lines...
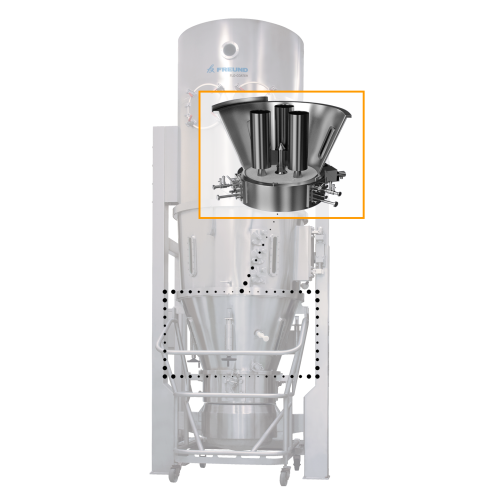
Wurster coating system for fine powders and pellets
Achieve precision coating for multiparticulate cores and mini-tablets...
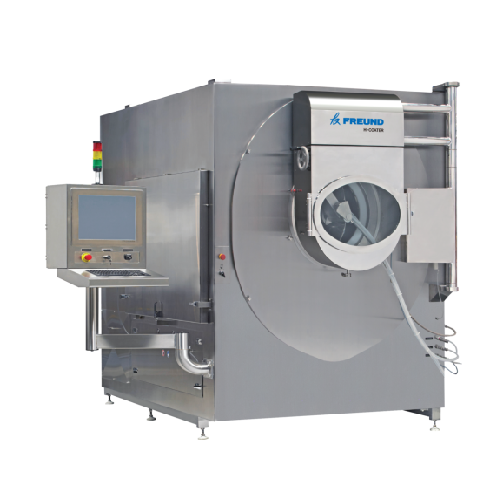
Tablet coater for precision pan coating
Achieve precise coating control for pharmaceuticals and nutraceuticals, accommodati...

Integrated plenum tablet coater
Achieve consistent and high-quality coatings on tablets with advanced airflow management, ef...
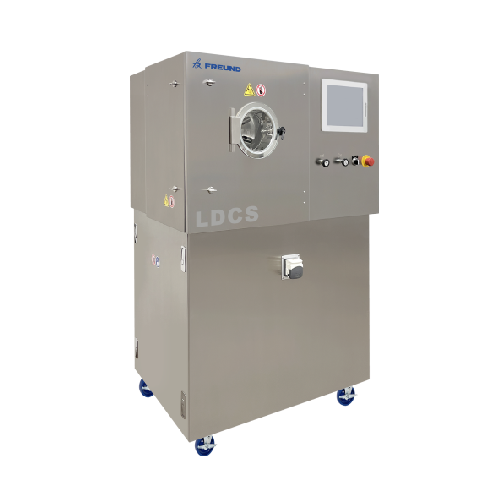
Tablet coating system for laboratory development
Optimize your tablet formulation development with a versatile coating sys...
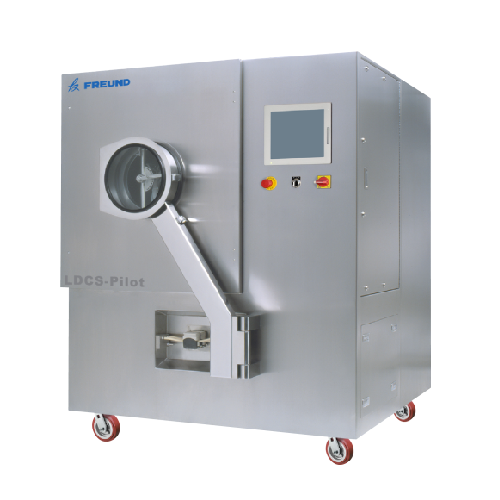
Laboratory and pilot scale pan coater
Maximize coating efficiency in tablet production with this advanced pan coater, offer...

Laboratory development coating system for tablet coating
Efficiently manage small-scale batch coating with versatile, ful...
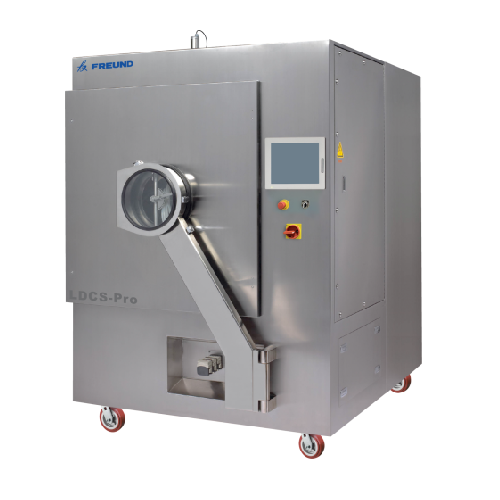
Portable pan coater for pilot scale tablet coating
Achieve uniform tablet coating with interchangeable pans and anti-mark...
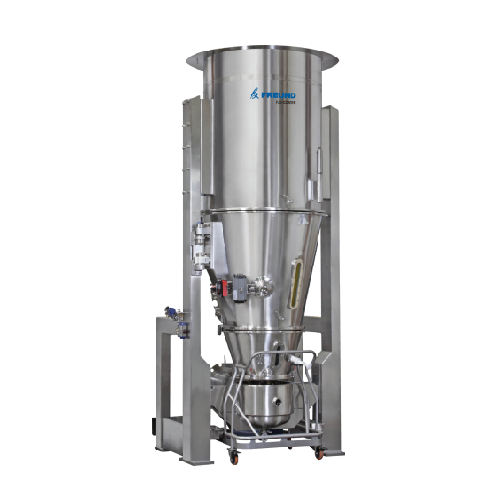
Fluid bed granulator for industrial granulation
Optimize your production efficiency with versatile fluid bed granulation, ...
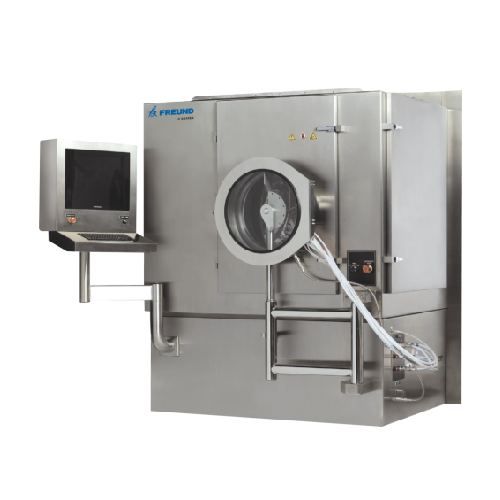
Tablet coating system for aqueous, solvent, and sugar films
Achieve precision coating with flexible application capabili...
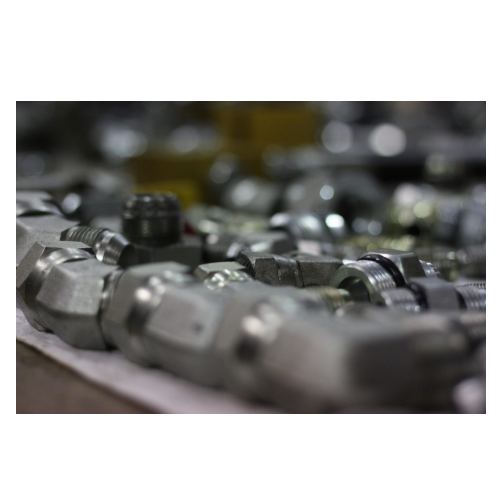
Replacement parts for rotary shear systems
Optimize your biomass processing with durable rotary shear systems, ensuring ef...
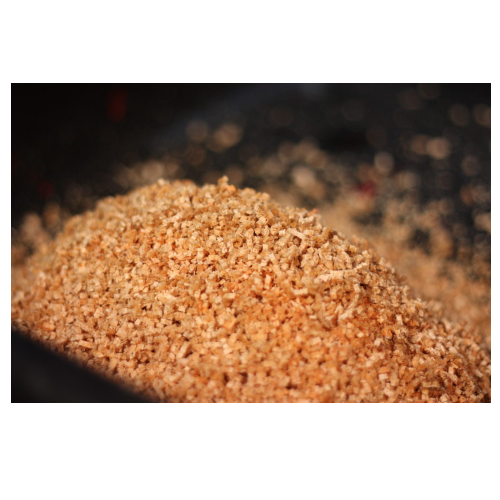
Precision feedstocks for biomass energy production
Optimize your biomass conversion with precision-sized feedstocks desig...
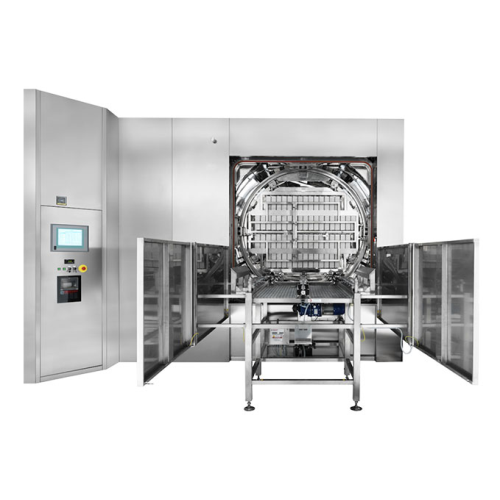
Superheated water sterilizer for large volume parenterals
When sterilizing large volumes of liquid products, achieving p...
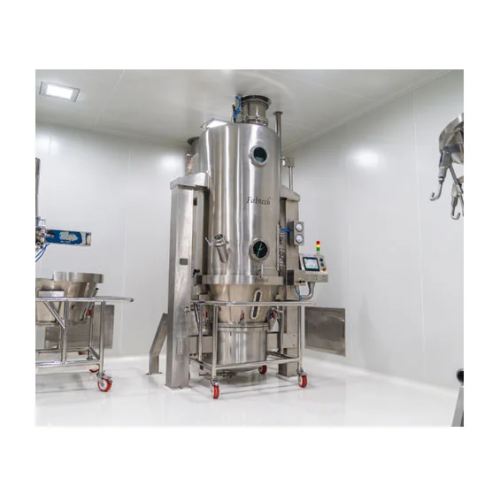
Fluid bed processor for granulation and coating
Fluid bed processors offer efficient granulation and coating, streamlining...
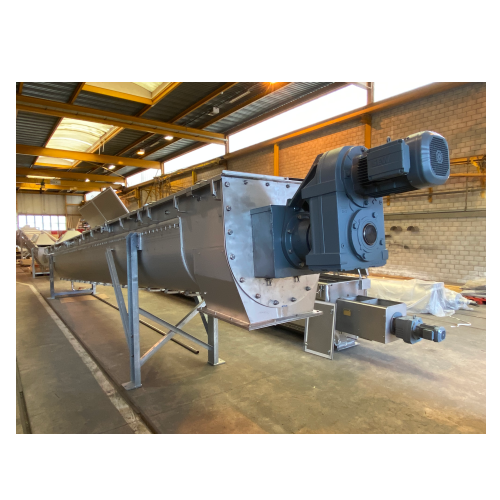
Screw heat exchanger for efficient thermal processing
Optimize your heating and cooling processes with this robust double...
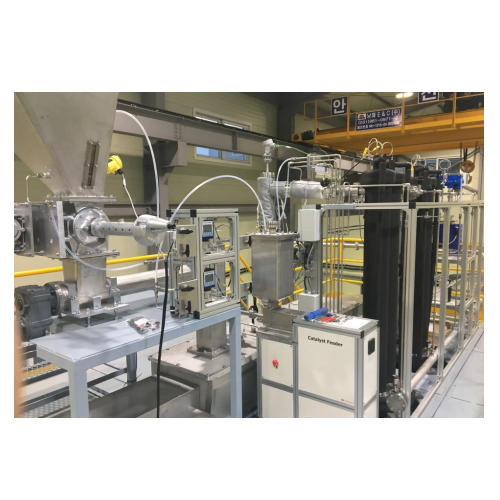
Pyrolysis for biomass conversion
Transform diverse waste materials into valuable bio-commodities and energy through advanced...
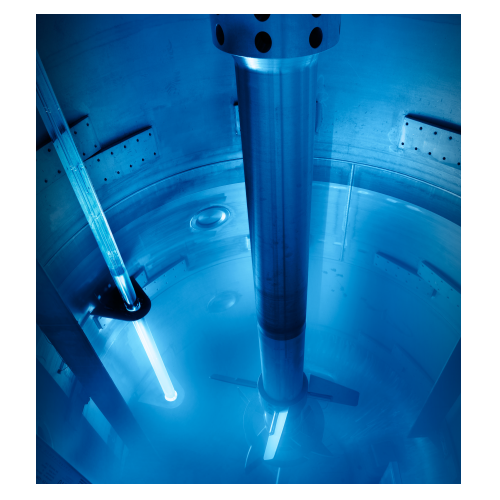
Industrial photochemical reactors for multiphase reactions
Optimize multiphase chemical reactions with light-activated p...
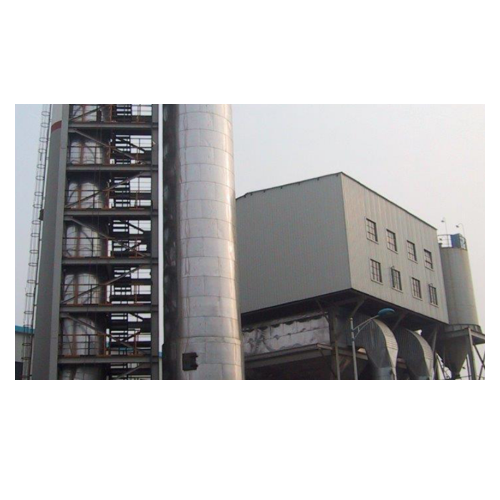
Evaporative gas cooling system for industrial gases
Optimize exhaust gas management with precision cooling and conditioni...
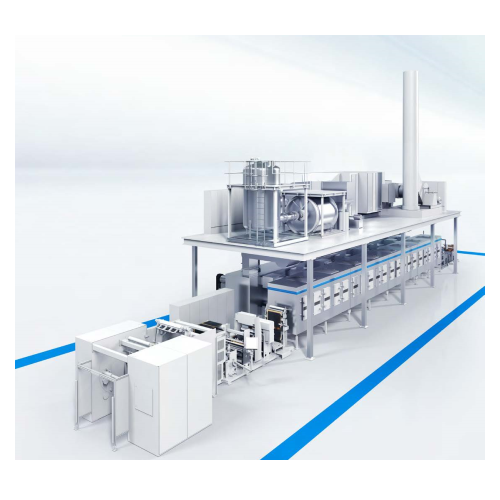
Battery electrode coating line
Optimize your battery production with a comprehensive coating line that enhances throughput a...
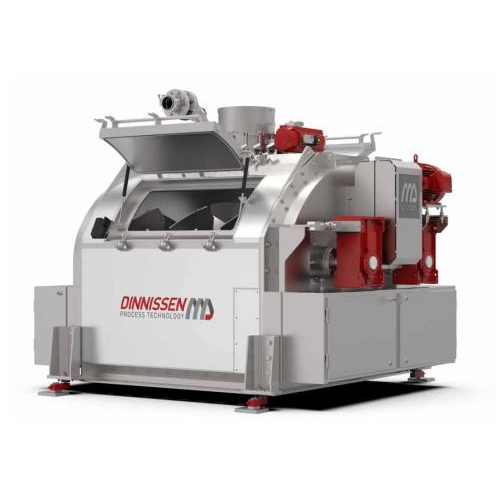
Advanced vacuum coating system for pet food and feed
Achieve uniform saturation in pellets and granules with precise liqu...
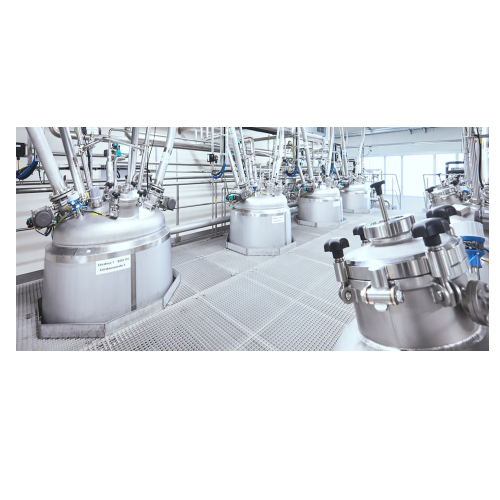
Extraction plant for natural essences and active ingredients
Optimize your extraction processes with a versatile system ...
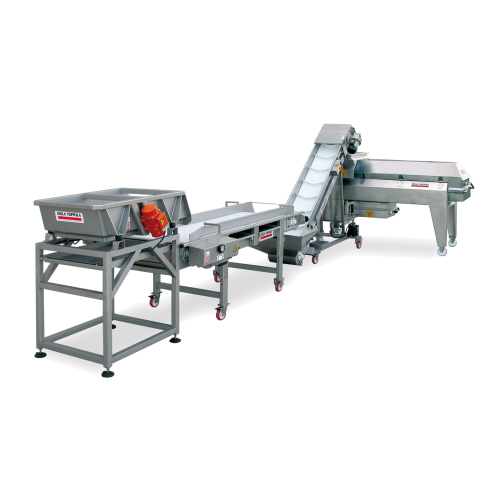
Grape sorting and washing lines
Optimize grape processing with efficient sorting and washing lines that streamline the prepa...
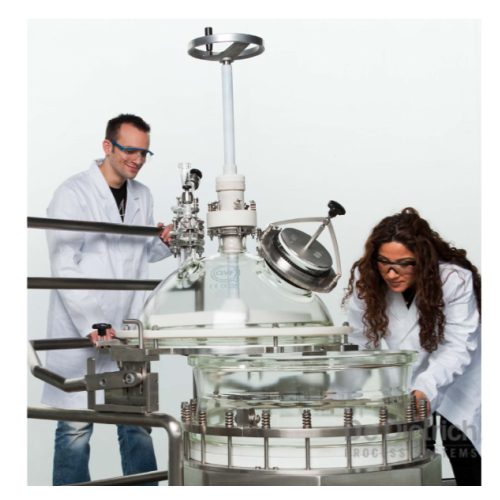
Glass nutsche filter for fine chemical and pharmaceutical filtration
For precise separation and filtration in R&D ...
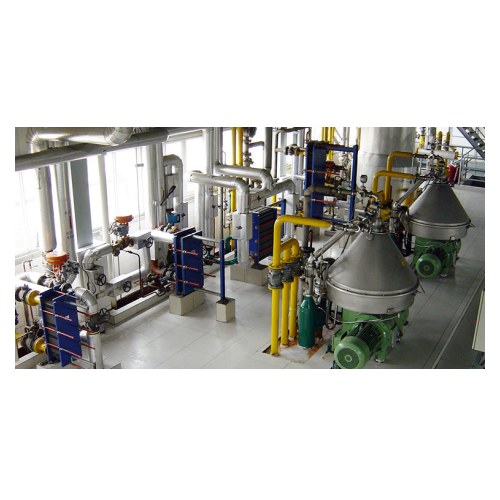
Oil and fat refining system
Ensure high-quality oil and fat production by efficiently removing contaminants such as phosphat...
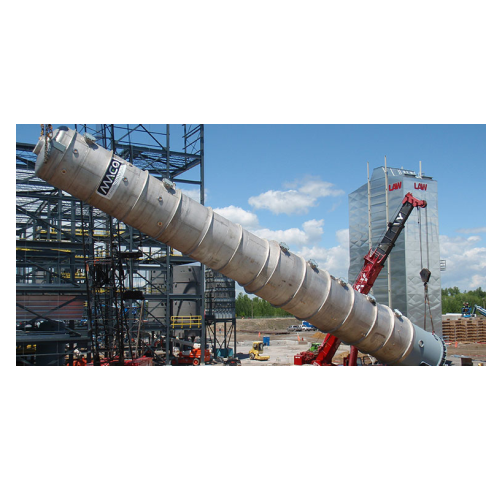
Continuous deodorizing for oils and fats
Achieve optimal purity and flavor in oils and fats with advanced continuous deodor...
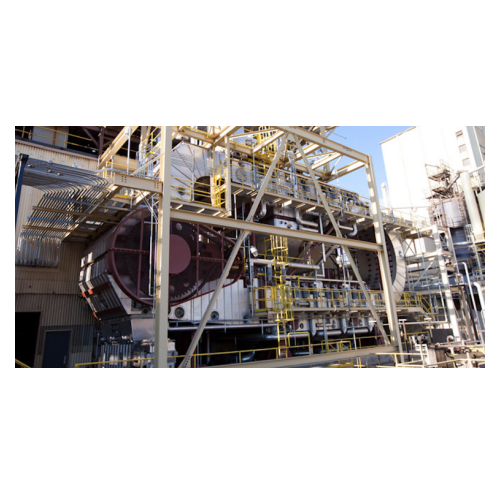
Percolation extractor for high-volume vegetable protein extraction
Optimize extraction efficiency across diverse materi...
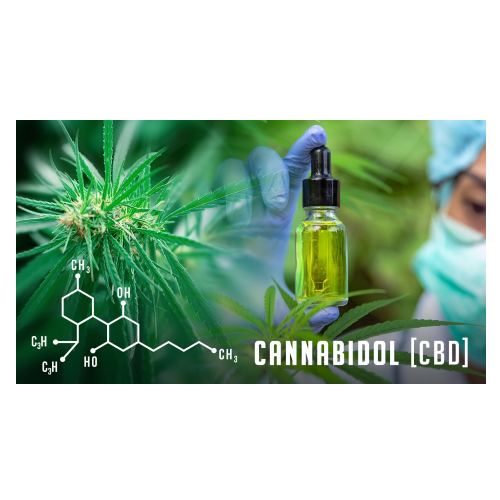
Hemp Cbd oil extraction system
Achieve maximum CBD oil recovery while maintaining product purity with scalable extraction ca...
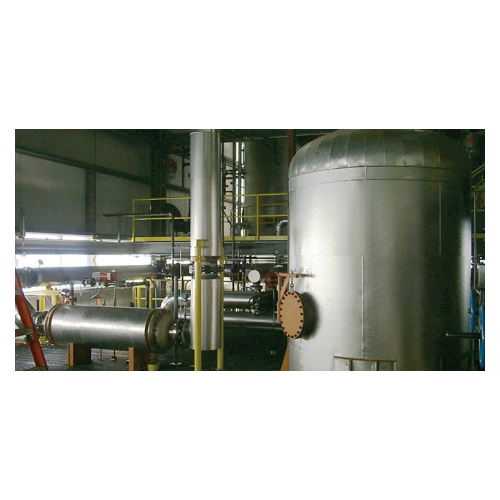
Zero effluent discharge system for solvent extraction plants
Eliminate wastewater in your solvent extraction process whi...
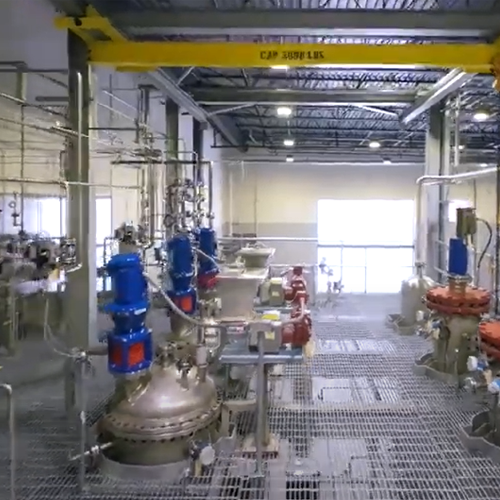
Renewable diesel pretreatment system
Extend hydrotreater catalyst life and boost plant uptime by optimizing feedstock purit...
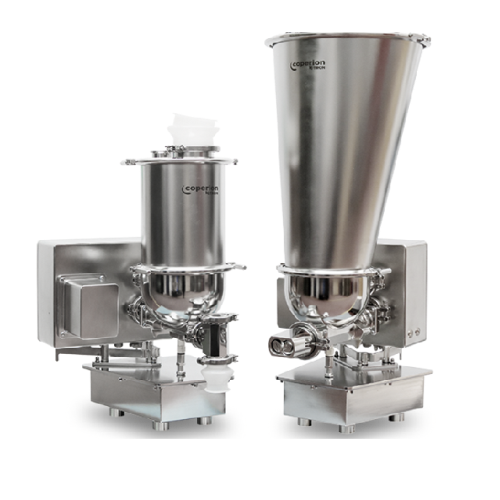
Pharmaceutical design feeders for precise ingredient handling
Achieve precise ingredient handling and seamless integrati...
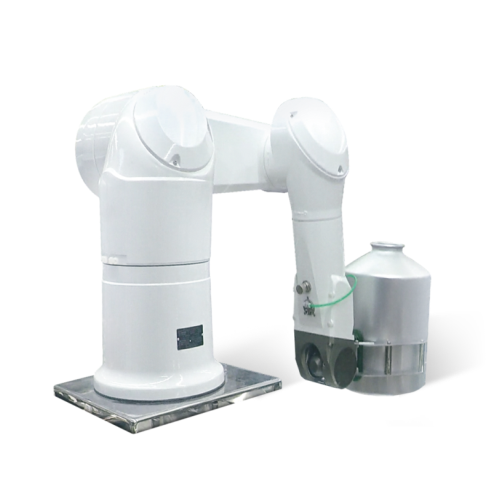
Tipping and filling line for bulk Api powder production
Ensure precise and aseptic handling of pharmaceutical powders wit...
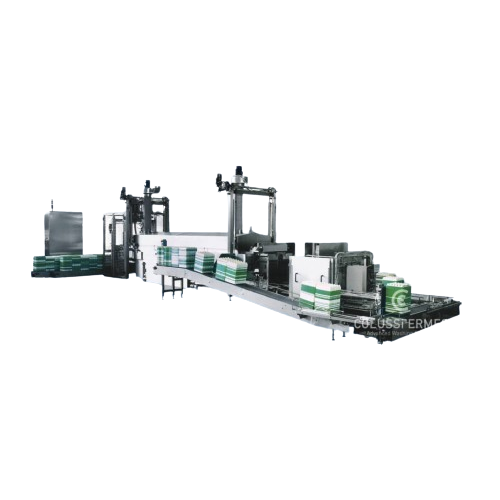
Industrial egg tray washer
Ensure immaculate cleanliness and hygiene of egg trays while boosting efficiency with an advanced...
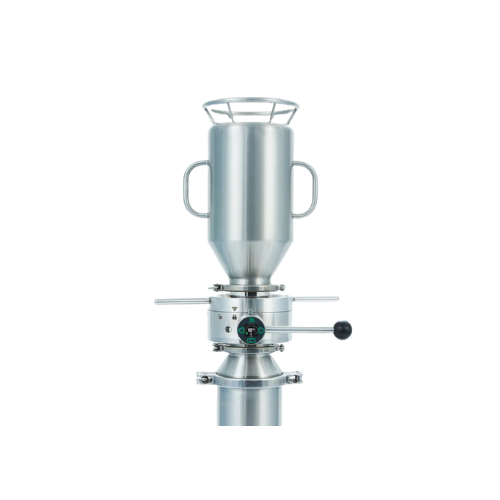
High containment powder transfer valve
Ensure high containment for potent powders in your production line, reducing contami...
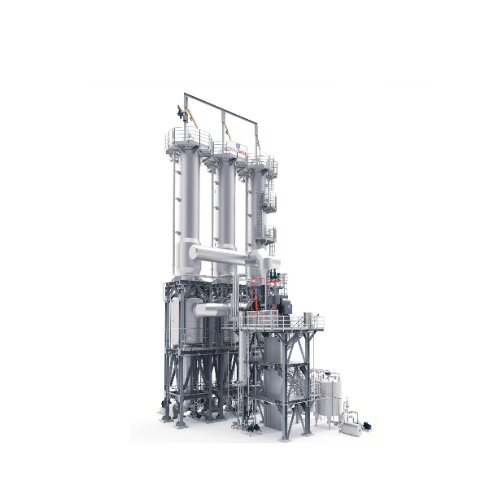
Energy efficient tomato evaporator
Achieve up to 98% steam savings in your evaporation process while ensuring minimal CO2 e...
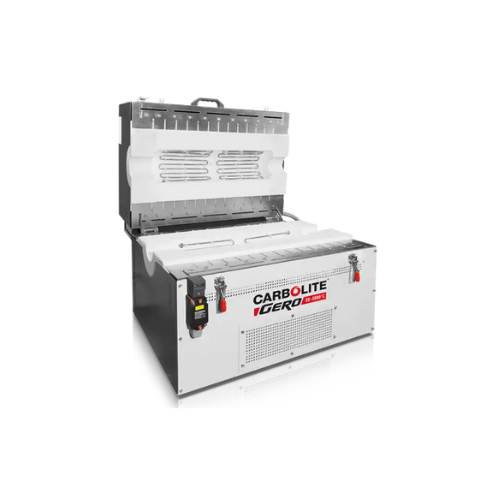
Split tube furnace for high-temperature applications
Enhance your thermal processing operations with a split tube furnace...
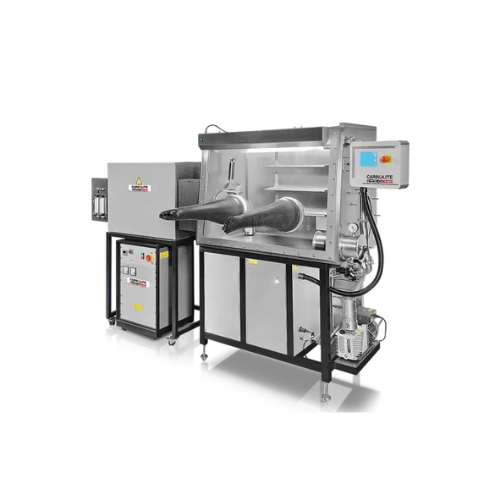
Glove box furnace for high-temperature applications
Optimize your high-temperature heat treatment and containment process...
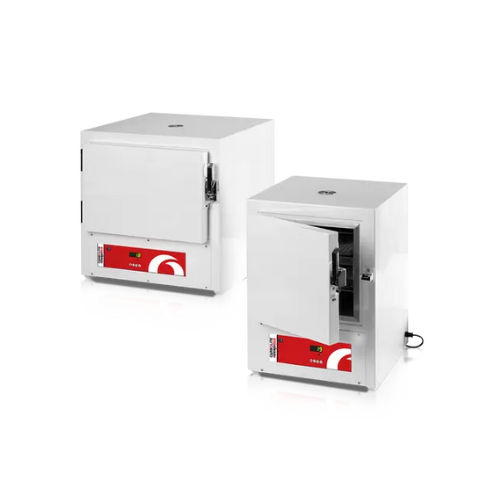
Clean room oven for class 100 environments
Achieve precise temperature control and maintain particle integrity in critical...
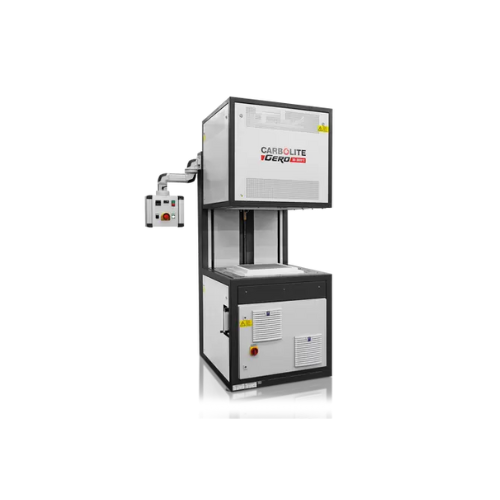
Top hat industrial furnace for high-temperature applications
Achieve precise high-temperature processing with this advan...
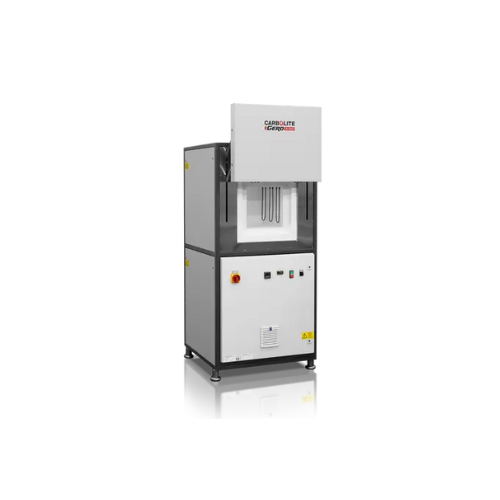
High temperature chamber furnace for sintering ceramics
Achieve precise thermal consistency for high-temperature applicat...
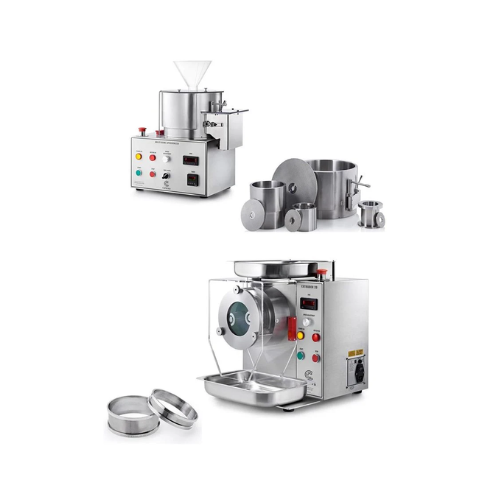
Flexible spheronization kit for wet granulation pellets
Achieve precise pellet and granule formation with a versatile ben...
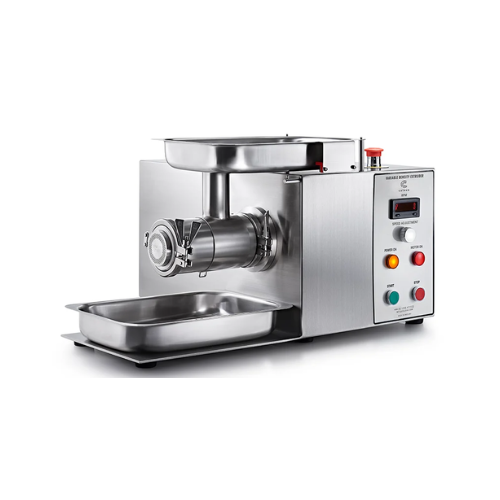
Variable density pellets extruder and spheronizer
Develop diverse pellet densities for enhanced drug formulation with pre...
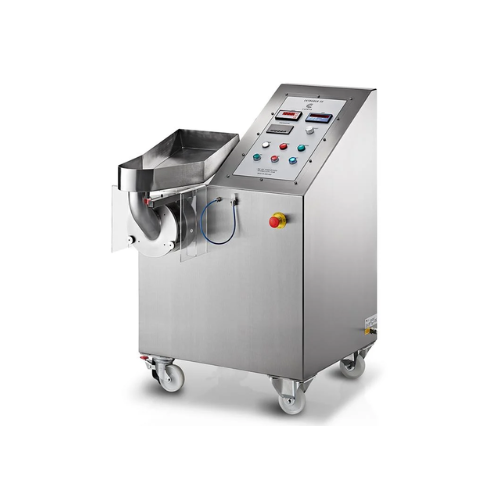
Spheroid extruder spheronizer 50kg per hour
Efficiently handle product development and contract manufacturing with a versa...
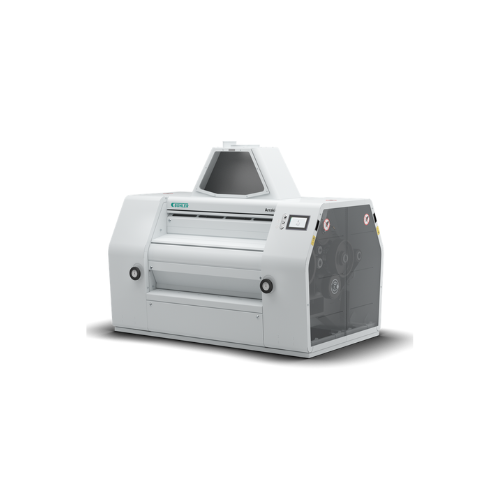
Four-roller and eight-roller mill for wheat and grain grinding
Optimize your grinding operations with this versatile rol...
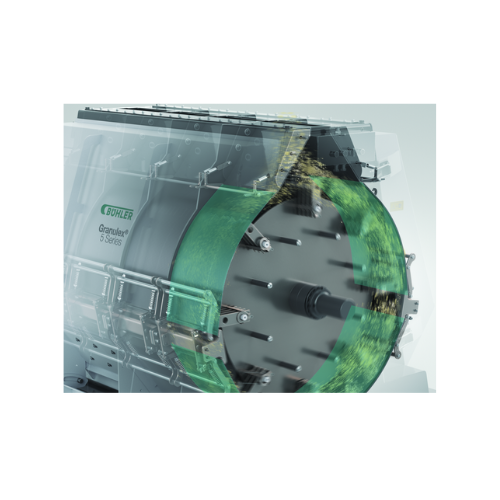
Horizontal hammer mill for grain processing
Optimize your grinding processes with our horizontal hammer mill, designed to ...
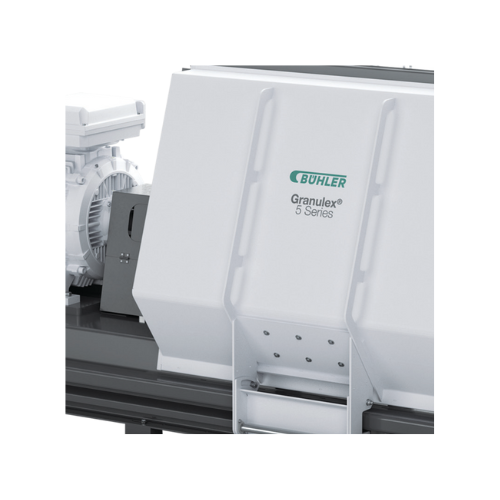
High-throughput hammer mill for animal feed production
Ideal for high-throughput operations, this hammer mill ensures pre...

Hydrothermal kiln for oats and sorghum
Optimize your grain production with advanced enzyme inactivation and hydrothermal tr...
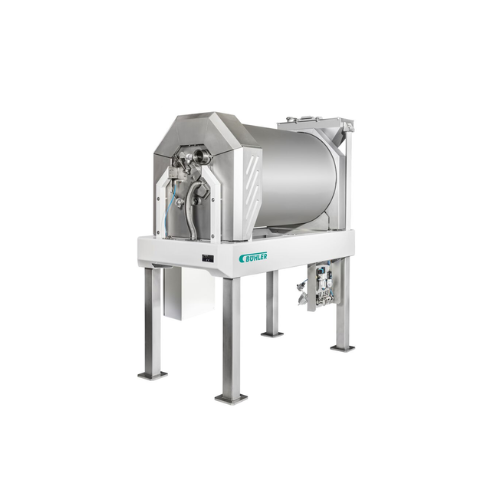
Infrared pre-treatment for cocoa beans
Achieve optimal cocoa nib separation and consistent moisture control while preventin...
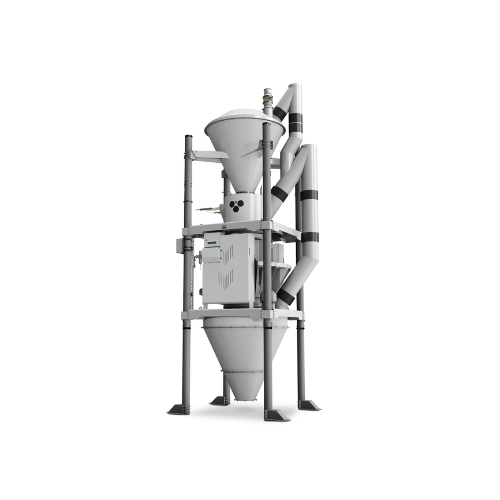
Fully automatic batch scale for powdery and granular products
Achieve precise and repeatable dosing for powdery and gran...
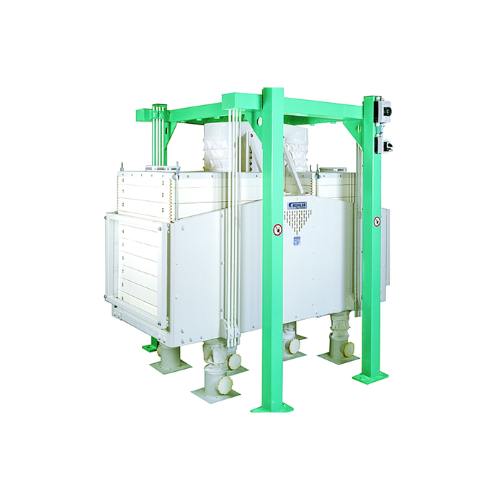
Rice sifter for optimal rice processing
Achieve precise rice classification and quality enhancement with this compact sifti...
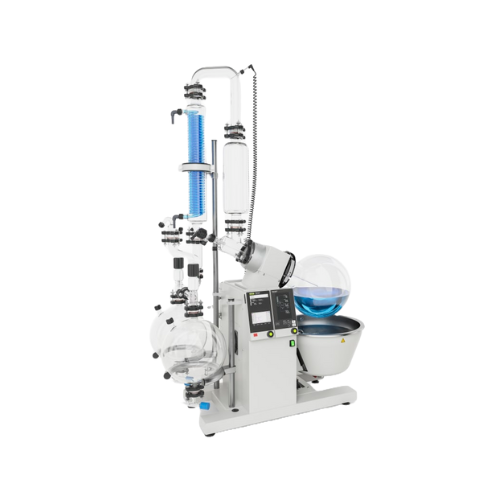
Industrial rotary evaporator for distillation
Optimize your distillation efficiency with a solution designed for precise c...
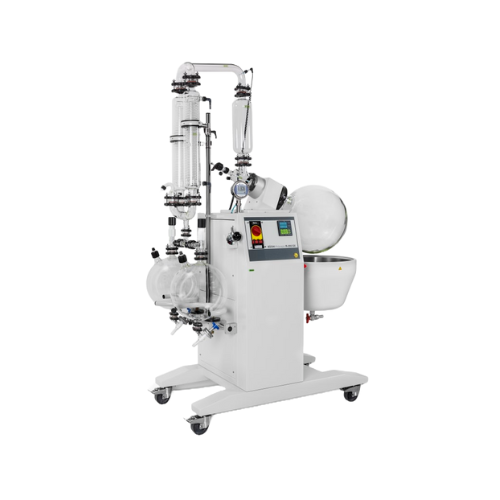
Rotary evaporator for large-scale industrial distillation
Achieve precise separation and concentration with a rotary eva...
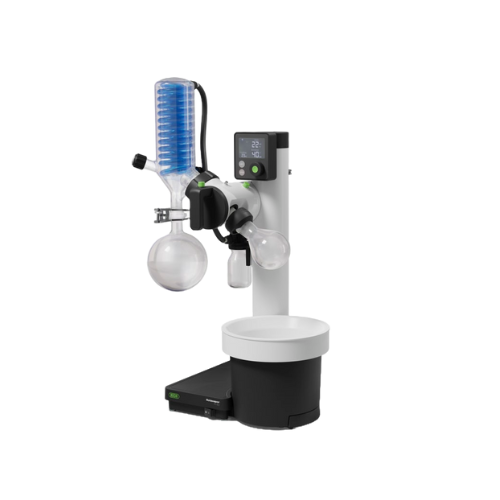
Compact rotary evaporator for laboratory distillation
Achieve efficient solvent removal and sample concentration with thi...
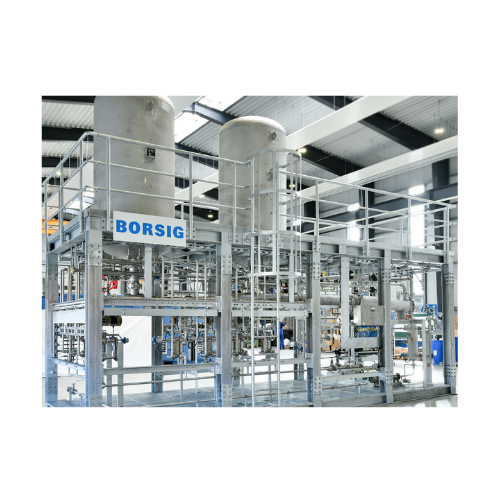
Pervaporation membrane for solvent dehydration
Efficiently separate and dehydrate solvents at molecular levels, ensuring p...
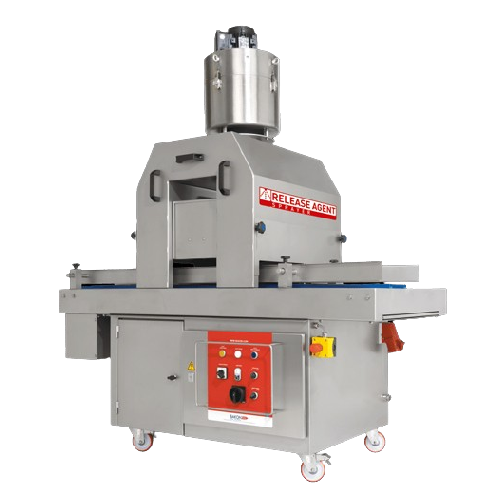
Release agent sprayer for baking trays and moulds
Achieve perfect results in baking by ensuring efficient and uniform gre...
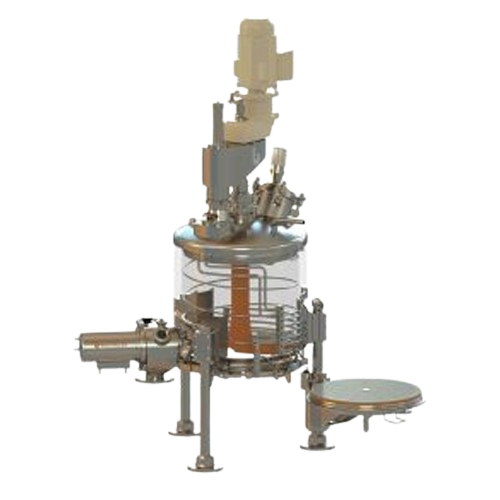
Agitated nutsche filter for solid-liquid separation
Ensure high-purity solid-liquid separation with minimized contaminati...
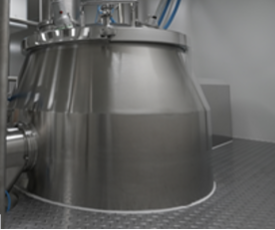
Continuous wet granulation equipment
Achieve optimal particle size and uniformity in pharmaceutical production with our con...
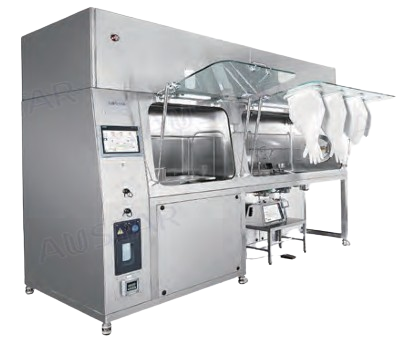
Sterilisable isolator workstation for aseptic containment
Ensure precise contamination control and sterile conditions du...
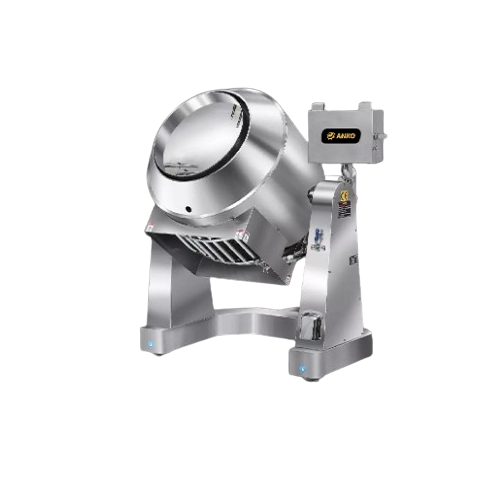
Industrial stir fryer for food production
Maximize cooking efficiency with a multi-function stir fryer that excels in cont...
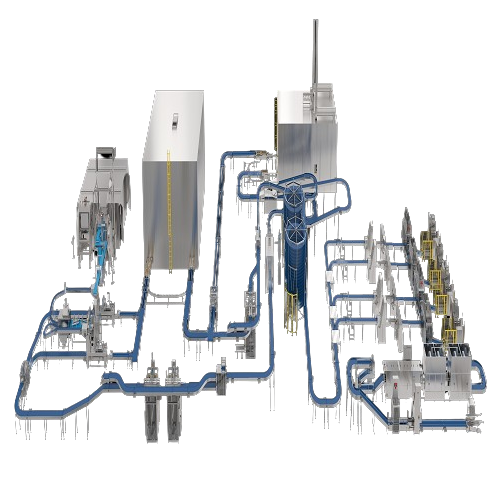
Soft bread production system
Optimize your bakery operations by integrating a high-speed system for producing a wide variety...
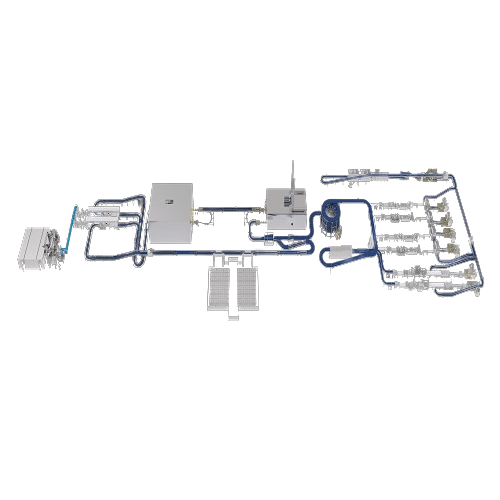
High-speed bun and roll production system
Optimize your bakery’s output with this high-speed system designed to stre...

Automated sheeting and laminating solution for filled snack bread production
Enhance your bakery line’s efficien...
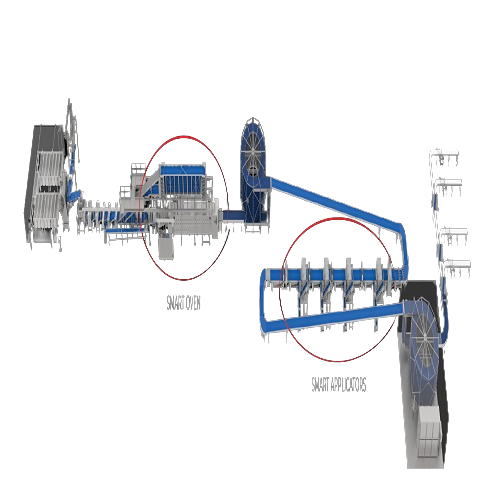
Ai solutions for pizza production in bakeries
Bring unparalleled precision and efficiency to your bakery with intelligent ...
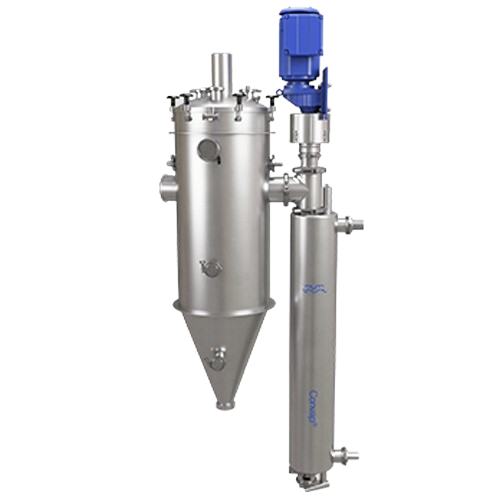
Scraped surface evaporator for high-viscosity materials
Efficiently concentrate high-viscosity and hard-to-handle materia...
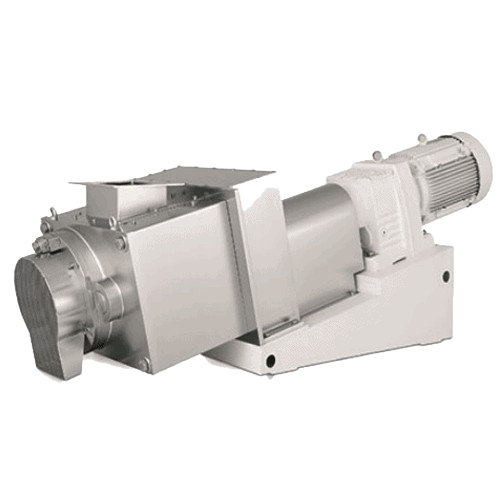
Moist granulation system for pharmaceutical and chemical industries
Transform powdered materials into uniform granules ...
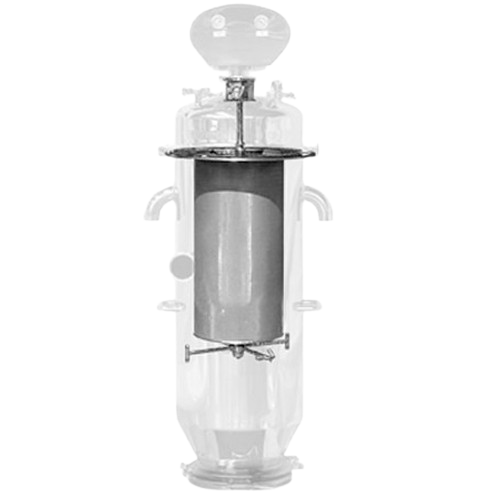
Vacuum transfer system with integrated cleaning
Ensure sterile powder handling and contamination-free production with vacu...
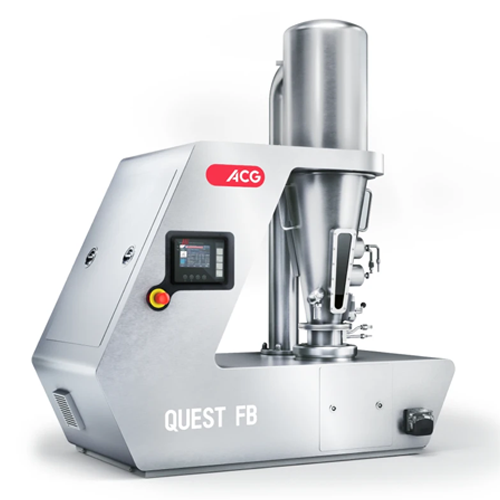
Versatile fluid bed combo for granulation and coating
Optimize lab-scale R&D with an adaptable fluid bed system, sea...
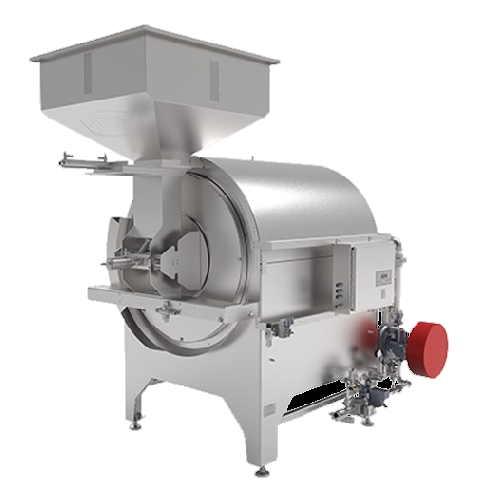
Batch roaster for nut processing
Achieve precise roasting and flavor development with batch roasters that offer customizable...
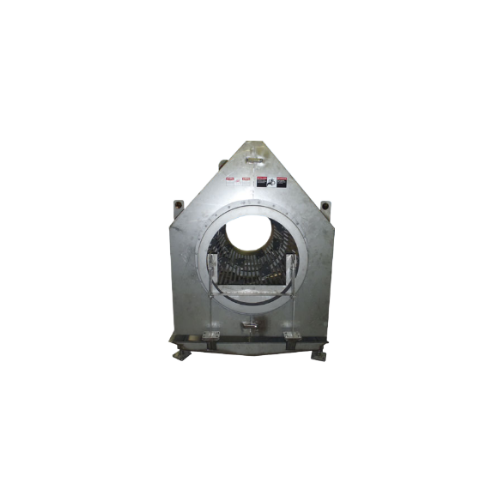
Bird tumbler for water removal in poultry processing
Optimize your poultry processing line with advanced water removal te...
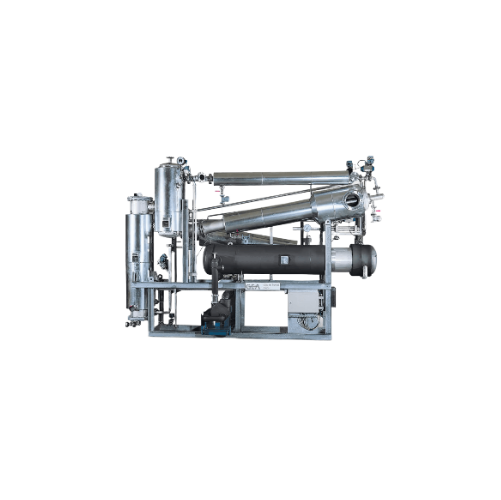
Product driven steam jet vacuum systems for polyester and nylon production
Optimize your vacuum processes with product...
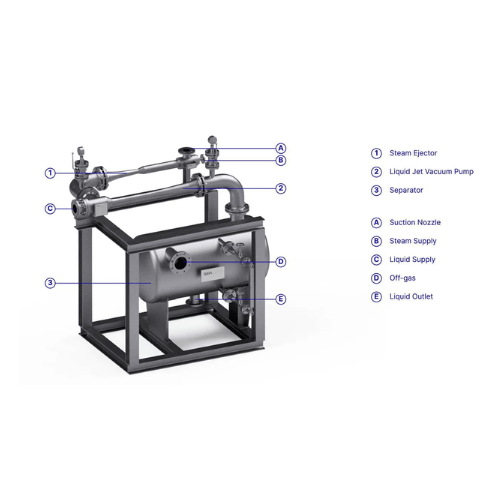
Steam jet liquid ejector vacuum system for chemical applications
Achieve reliable vacuum under challenging conditions wi...
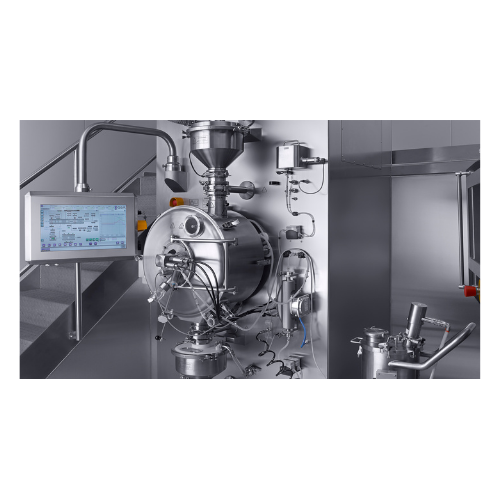
Pharmaceutical tablet coating system
Achieve precise and efficient coating of pharmaceutical tablets to enhance product sta...
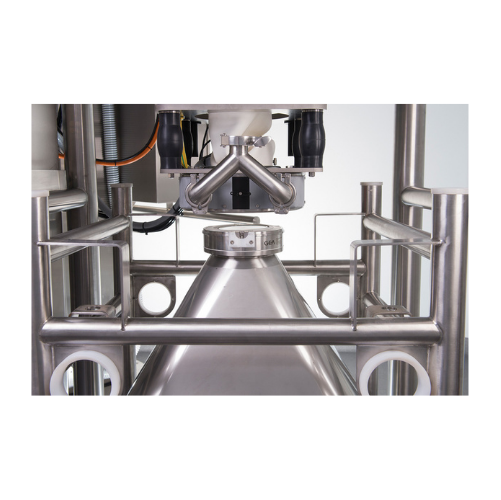
Pharmaceutical intermediate bulk containers (ibc)
Streamline pharmaceutical production with precise containment and trans...
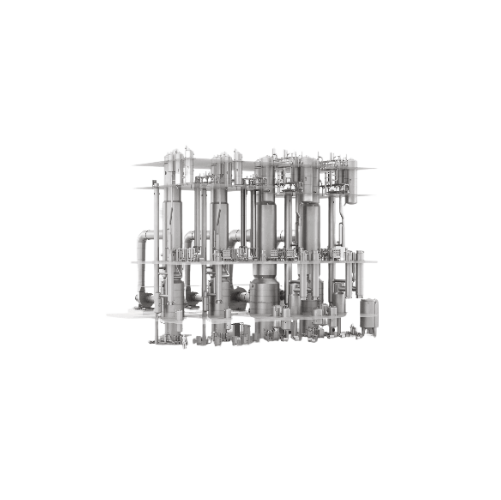
Dairy evaporator for nutritional formula
Enhance your dairy processing by optimizing energy efficiency and product quality ...
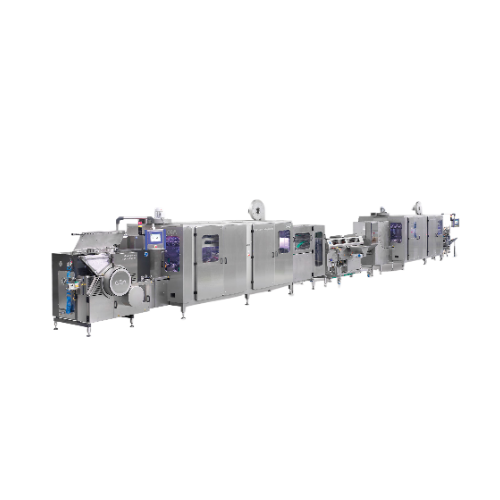
Coated lollipop production line
Transform your confectionery line with a solution that forms, cools, and coats 3D lollipops ...
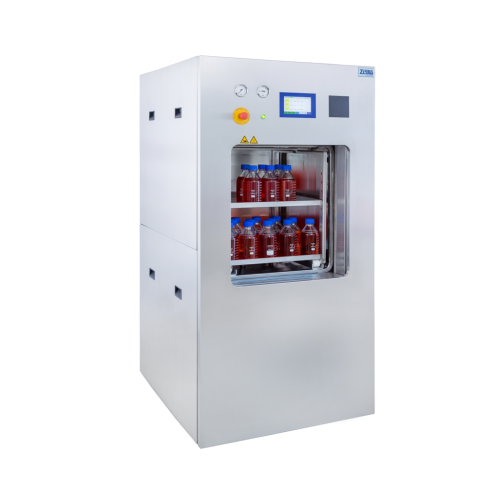
Autoclaves for laboratory and production with square chamber
Optimize your laboratory space with compact autoclaves that...
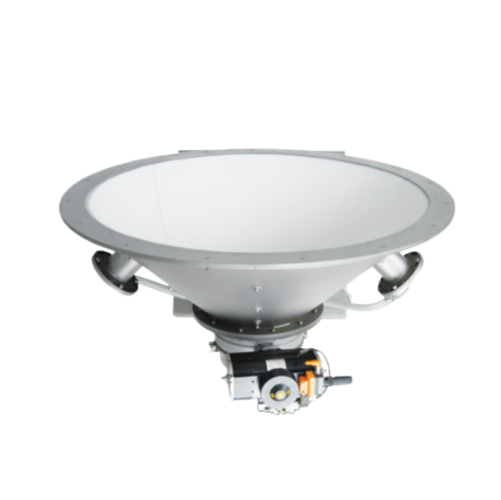
Fluidizing bed for bulk material discharge
Optimize your material flow with a fluidizing bed designed for seamless dischar...
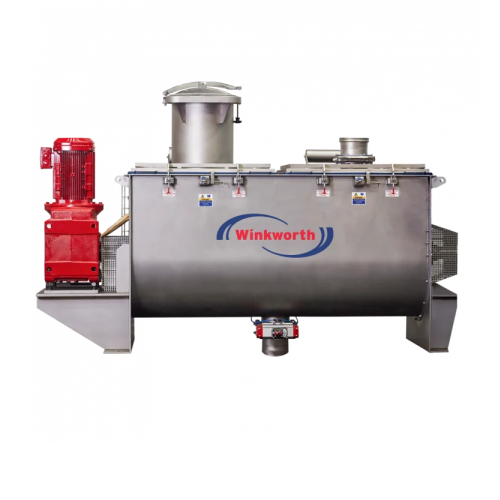
Efficient ribbon mixers for precise powder blending
Achieve consistent and uniform blending with this advanced U-Trough m...
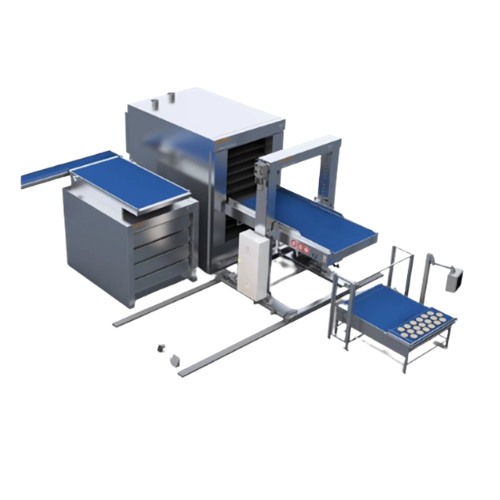
Industrial vacuum cooling system for bakeries
Achieve rapid cooling of oven-hot baked goods with minimal moisture loss, en...
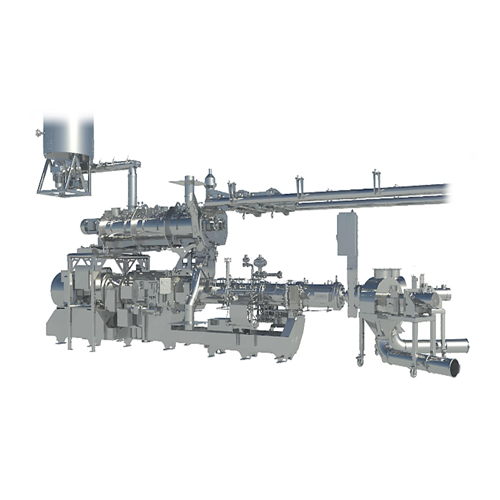
Extruder for aquatic feed production
Efficiently produce a wide range of aquatic and pet feed with precise control over pel...
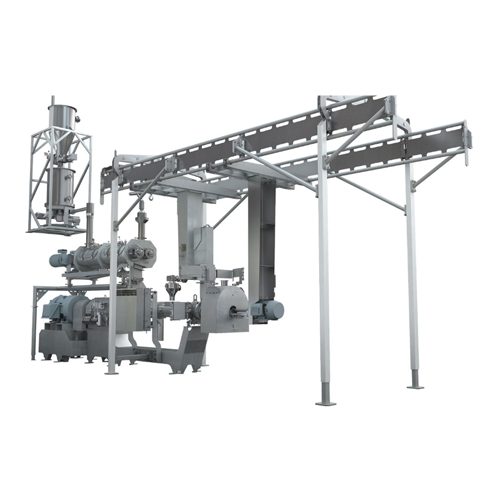
High-sme extruder for structured meat analogs
Enhance production versatility with precise extrusion control, accommodating...
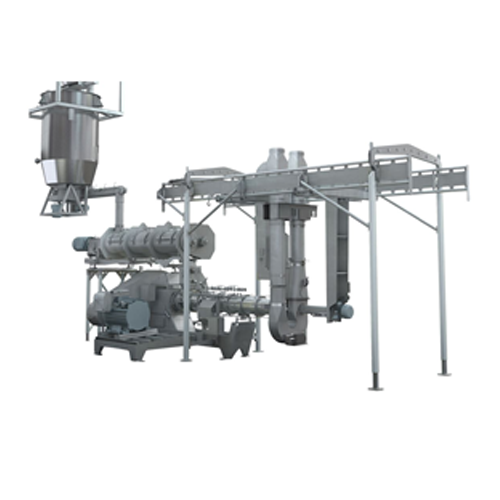
Single screw extruder for pet food and aquatic feed
Maximize production capacity and optimize product quality with advanc...
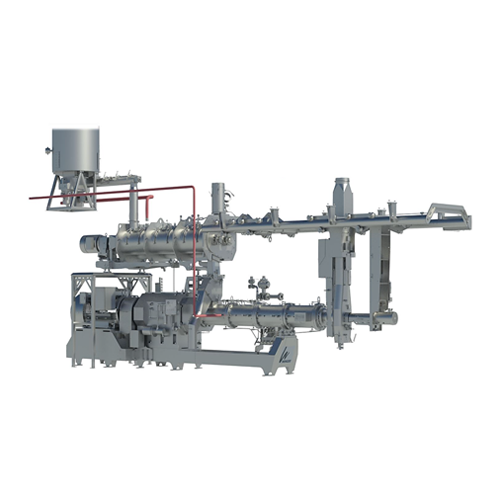
Extruder for high-volume pet food production
Maximize production efficiency with an advanced extrusion system designed for...
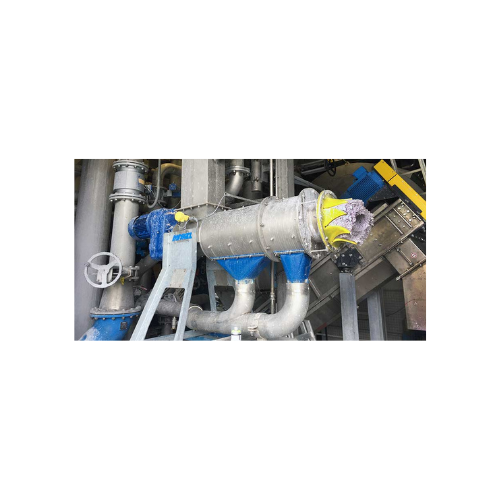
Pulp and paper horizontal screw press separator
Optimize your pulp recycling and manure treatment with high-efficiency sol...
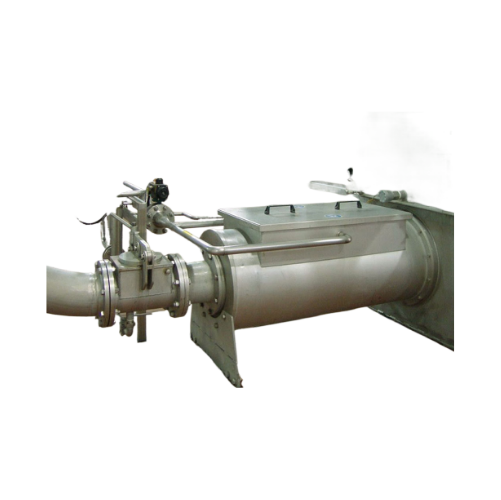
Wet spent grains pre-dewatering system
Optimize your brewery operations with a dewatering system that efficiently reduces m...
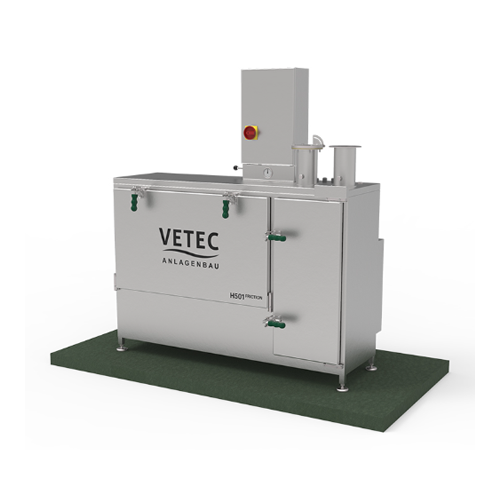
Friction smoke generator for hot smoking and climatic maturing
Optimize your production with a friction smoke generator ...
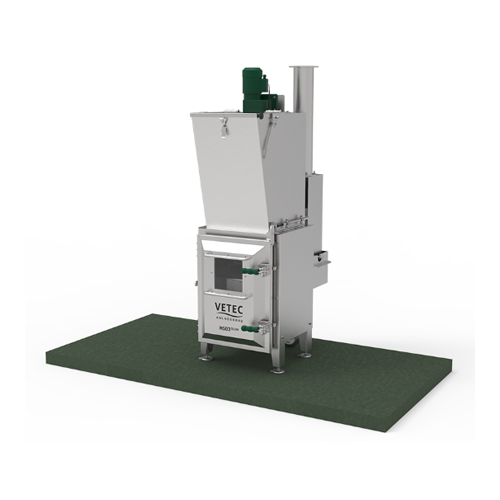
Closed glow smoke generator for hot smoking installations
Enhance your smoking process with efficient energy use and sea...
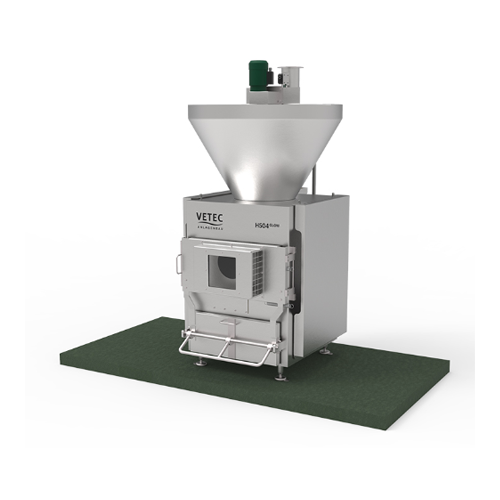
Glowing smoke generator for hot smoking installations
Enhance your production line with dense, aromatic smoke that ensure...
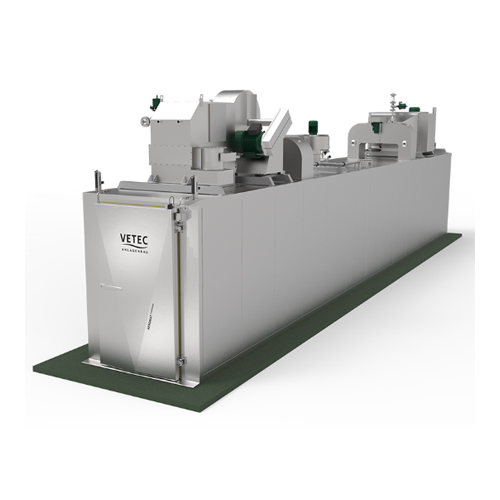
Advanced processing unit for meat and fish products
Transition seamlessly from hot to cold processing with a system that ...
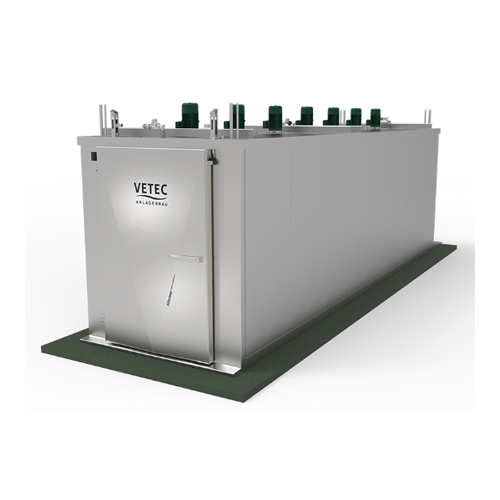
Industrial food cooling system
Achieve precise core temperatures and optimized shelf life with rapid cooling for diverse foo...
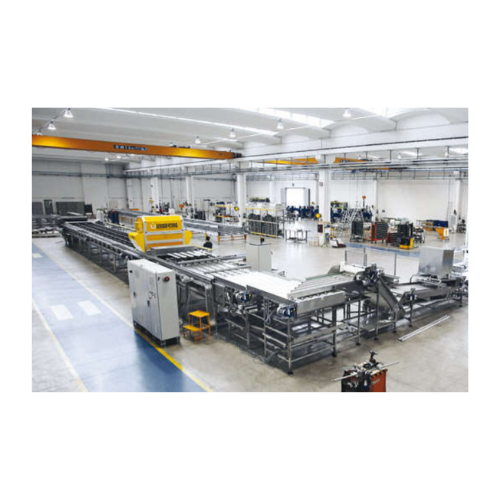
Avocado sorting and processing systems
Ensure consistent quality and maximize yield in your avocado production with precisi...
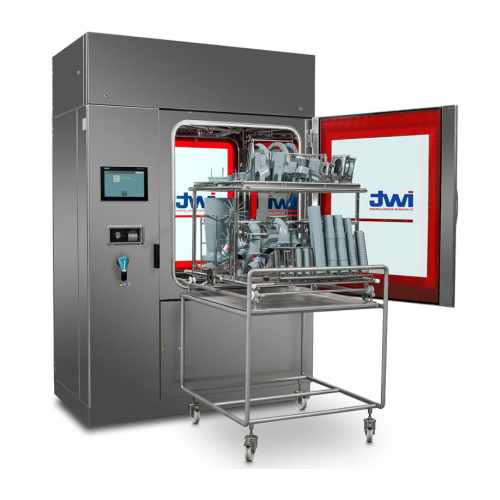
Gmp contact part washers for pharmaceutical industry
Ensure product integrity and hygiene with specialized washing system...
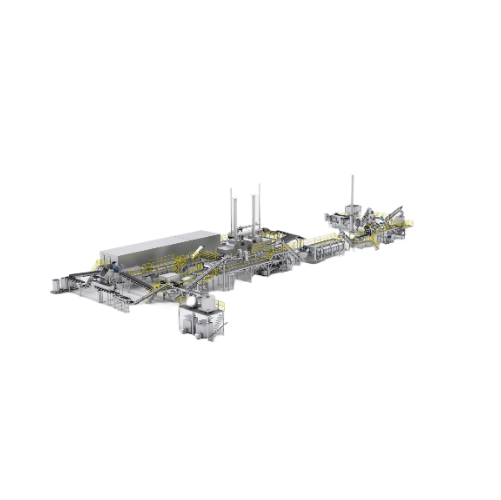
French fry production line
Optimize your French fry production with a seamless line that ensures precise cutting, consistent...
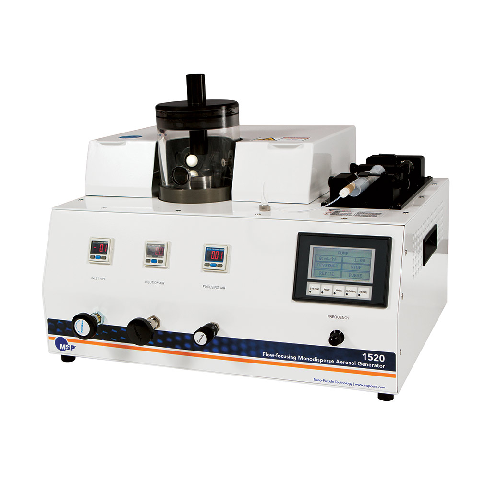
Flow focusing monodisperse aerosol generator
Achieve precise particle sizing with a generator that creates highly monodisp...
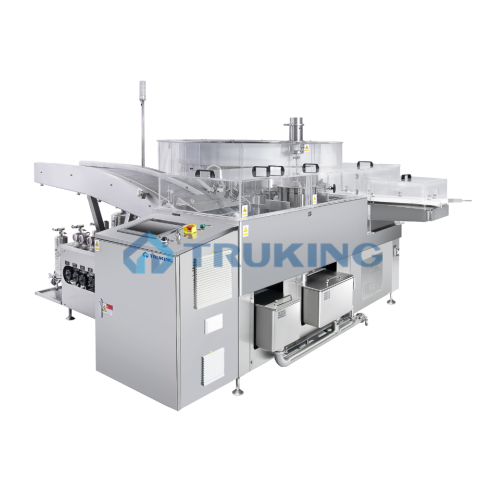
Vertical ultrasonic washing for pharmaceutical containers
Ensure immaculate cleanliness and sterilization of pharmaceuti...
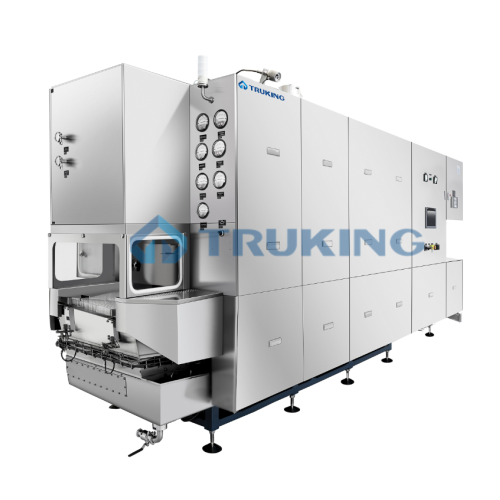
Sterilizing and depyrogenization tunnel for ampoules
Ensure sterile and pyrogen-free ampoules with precision control in d...
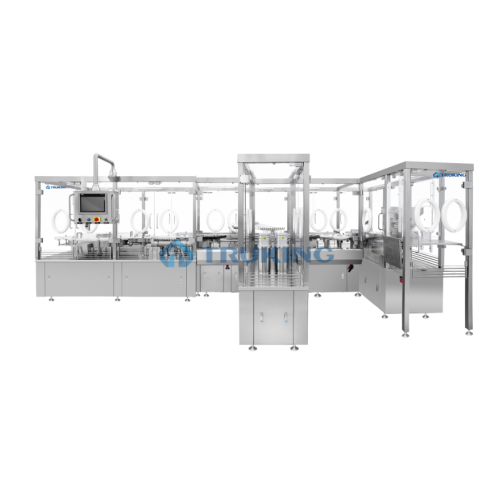
Vial filling and stoppering system for aseptic production
Streamline aseptic production by integrating high-speed vial f...
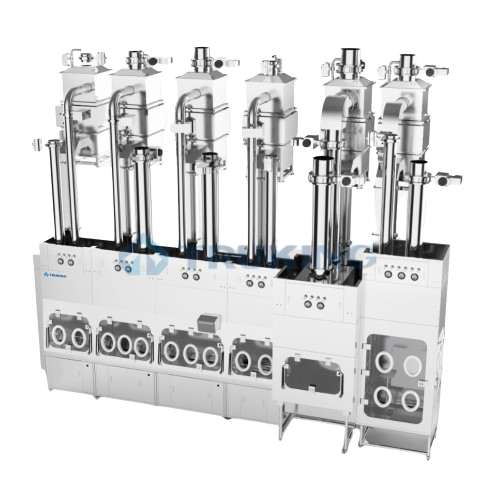
Active pharmaceutical ingredient isolation system
Ensure the aseptic production of pharmaceuticals while protecting perso...
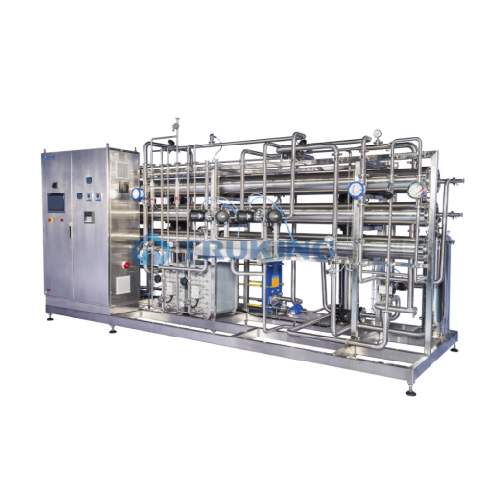
Ultra-pure water preparation system for pharmaceutical industry
Ensure your pharmaceutical production line meets stringe...
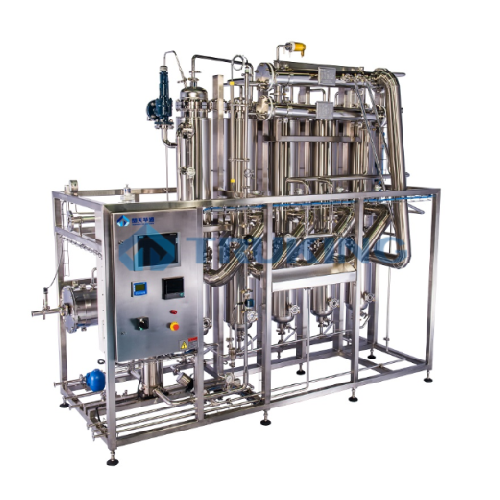
Multi-effect water distillator for pharmaceutical applications
Ensure your production line meets stringent regulatory st...
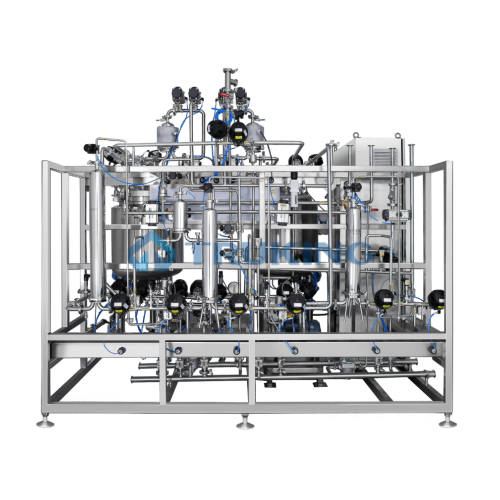
Pharmaceutical preparation system
Achieve seamless integration in pharmaceutical processes with a preparation system that o...
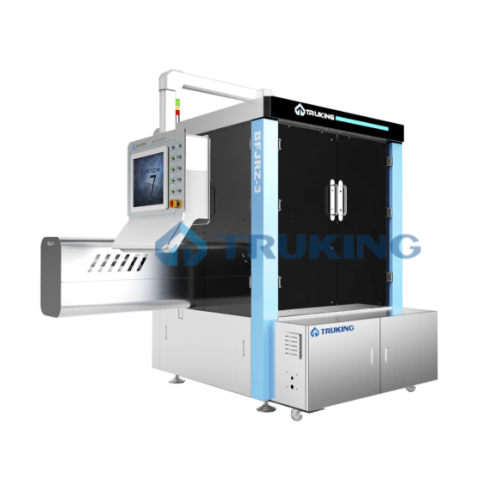
X-ray inspection for pharmaceutical vials
Ensure product purity by detecting contaminants in pharmaceutical vials with adv...
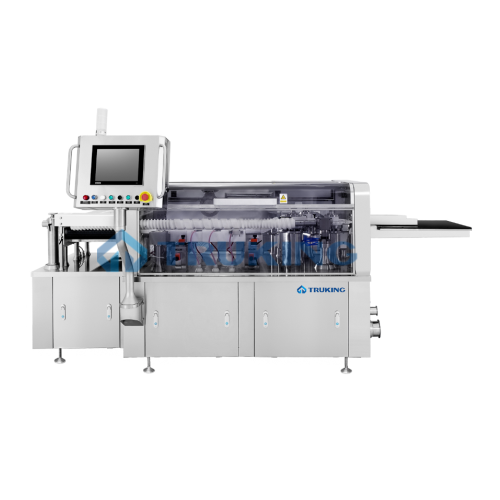
Automatic leak detection system for pharmaceutical containers
Ensure the integrity of pharmaceutical containers with pre...
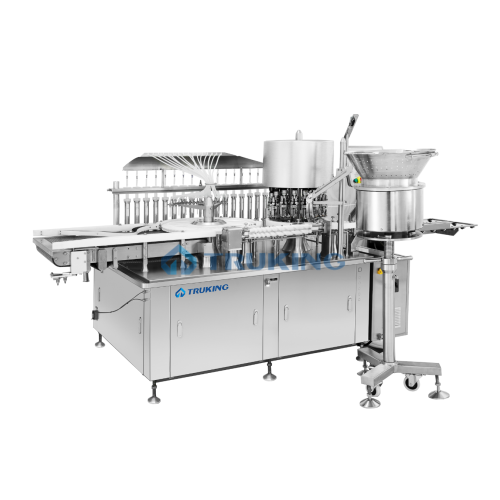
Oral liquid bottle filling & capping system
Streamline your liquid manufacturing processes with precise filling and secure...
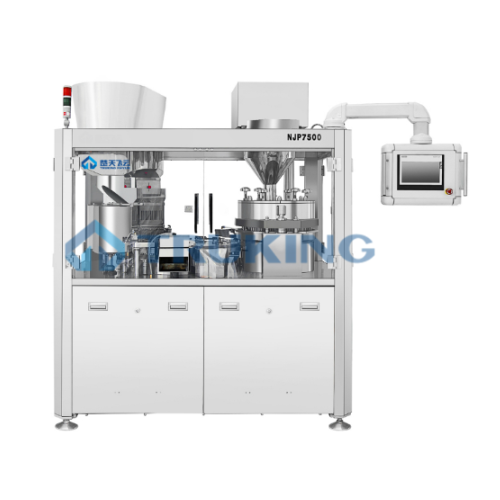
Fully automatic hard capsule filling machine
Enhance pharmaceutical production with precise capsule filling, ensuring opti...
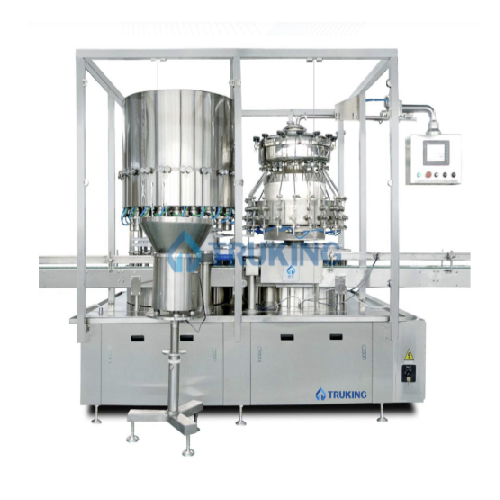
Gravity rotary filling for large infusion bottles
Ensure precise filling and secure stoppering of large infusion bottles ...

High capacity automatic blister packaging system
Streamline your production line with a high-speed blister packaging syste...
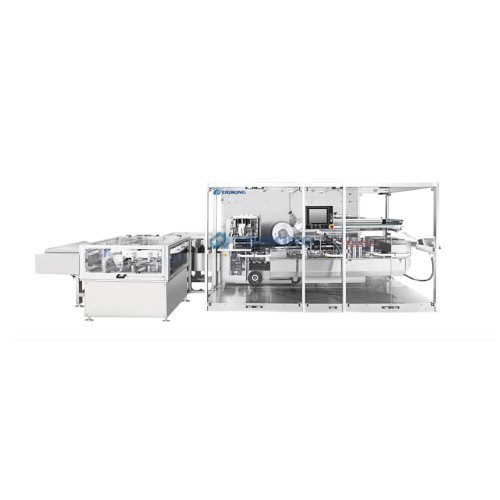
Secondary packaging cartoner for ampoules and vials
Optimize your aseptic production with efficient high-capacity carton ...
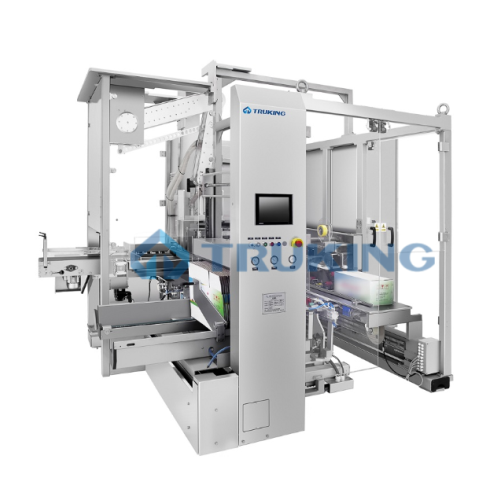
Automatic case packer for pharmaceutical industry
Optimize your packaging process with a versatile case packer designed t...
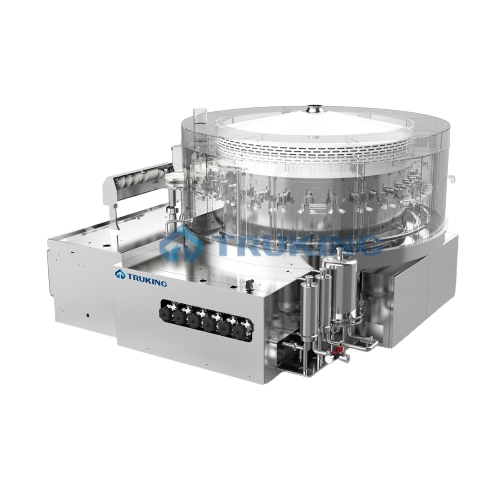
Ultrasonic pre-washing system for large infusion glass bottles
Optimize your cleaning process with an ultrasonic pre-was...
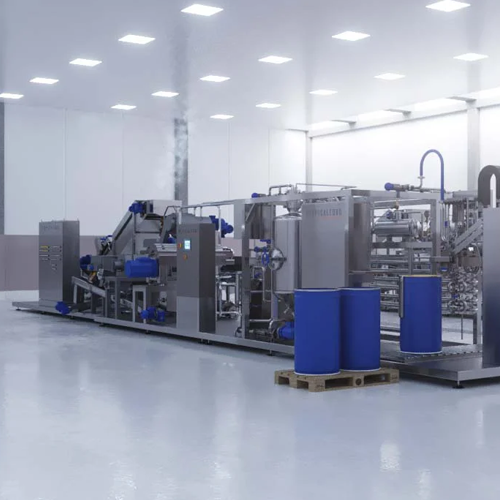
Multifruit processing line for wholemeal pulps and juices
Optimize your fruit processing capabilities with a skid-based ...
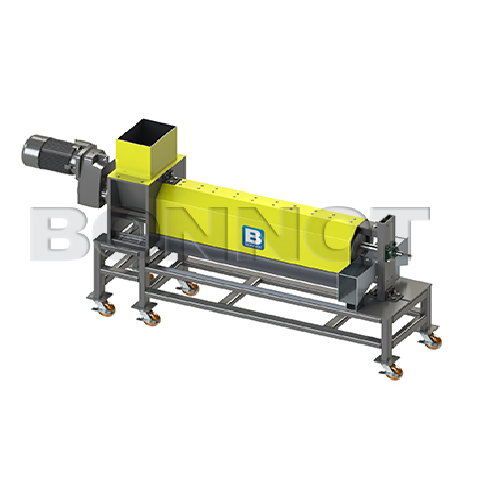
Dewatering solution for spent grain
Achieve efficient moisture reduction in spent grains with this continuous mechanical sc...
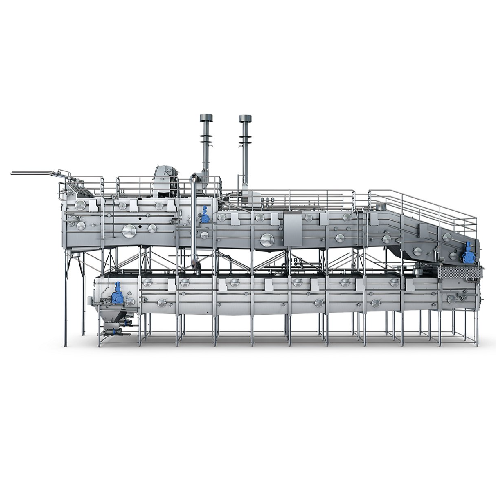
Draining matting solution for granular or matted curd cheese
Optimize your cheese production with a continuous, automate...
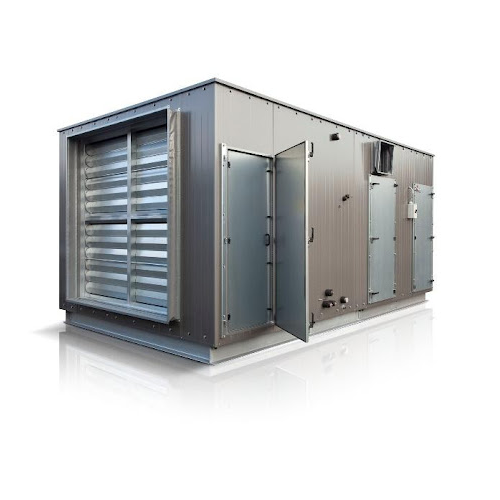
Ventilation and dehumidification for meat processing plants
Achieve precise humidity and condensation control in meat pr...
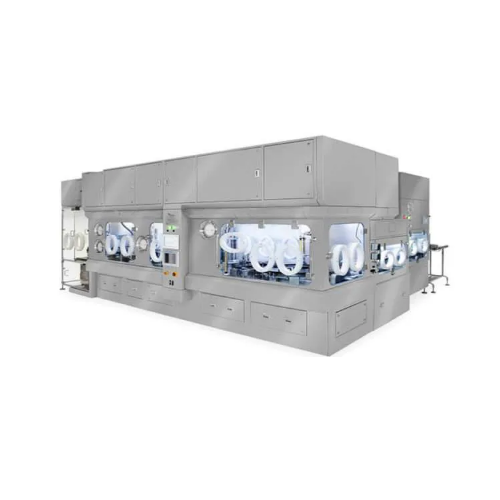
Sterile lyophilized filling line
Ensure sterility and precision in filling pharmaceuticals with advanced isolator lines desi...
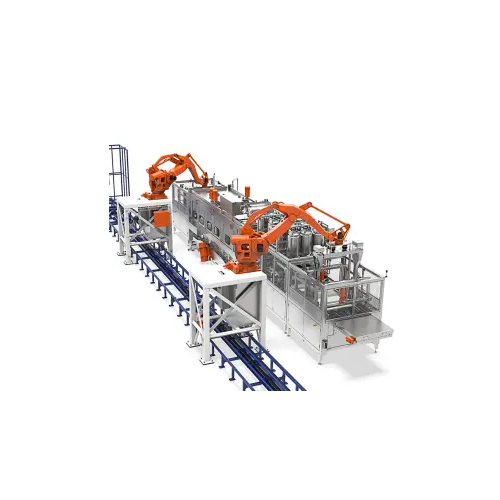
Industrial gummy and jelly production line
Optimize your gummy and jelly production with a system that streamlines operati...
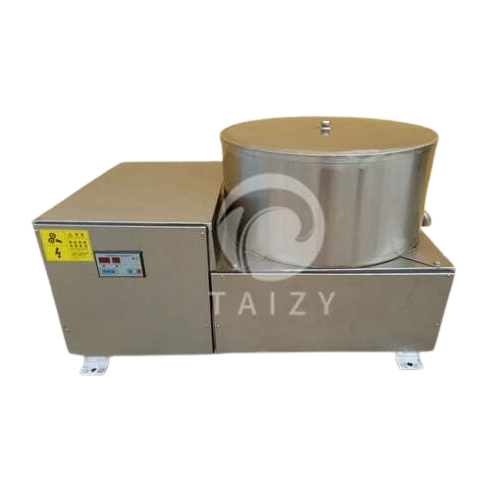
Small vegetable food dehydrator
Efficiently remove moisture from your fruits and vegetables with this centrifugal dehydrator...
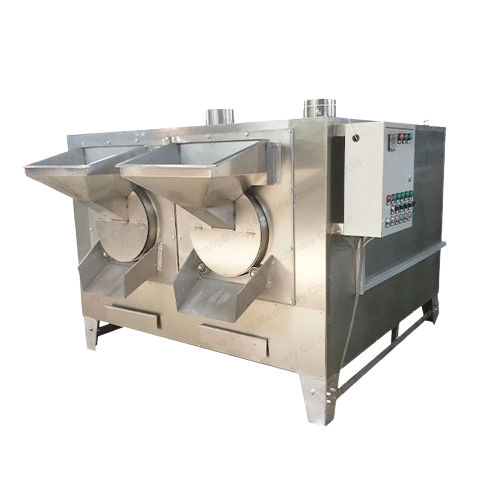
Peanut roaster for various nuts
Elevate your nut processing with efficient roasting solutions that enhance flavor, texture, ...
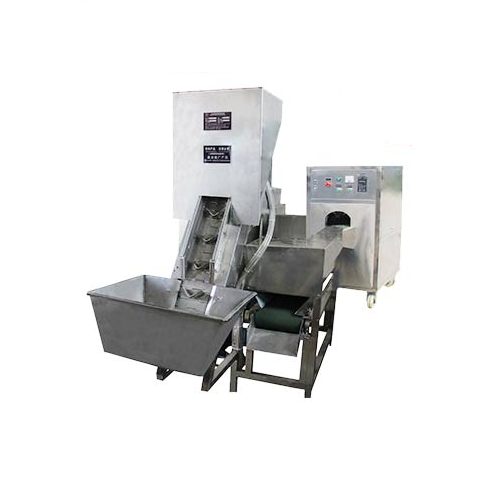
Industrial onion peeling solution
Optimize your onion processing with precision peeling and cutting, reducing waste and enh...
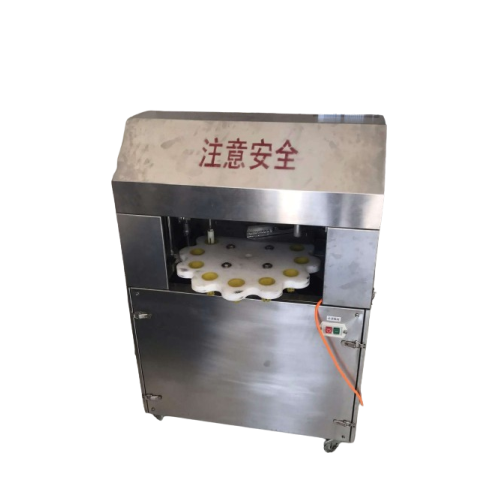
Jujube pitting and nut removing solution
Streamline your fruit processing with this efficient solution designed to remove p...
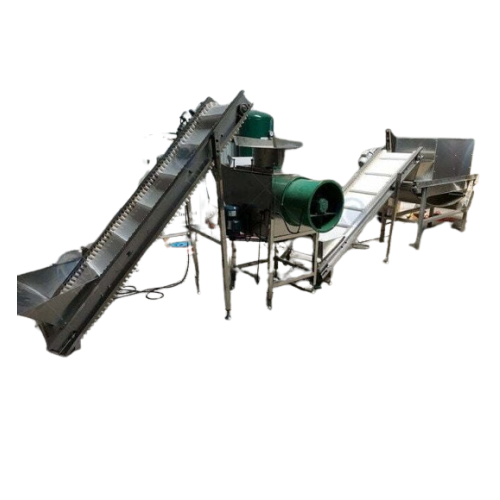
Garlic splitting and peeling line
Streamline garlic processing with this high-speed line designed to efficiently split, pee...
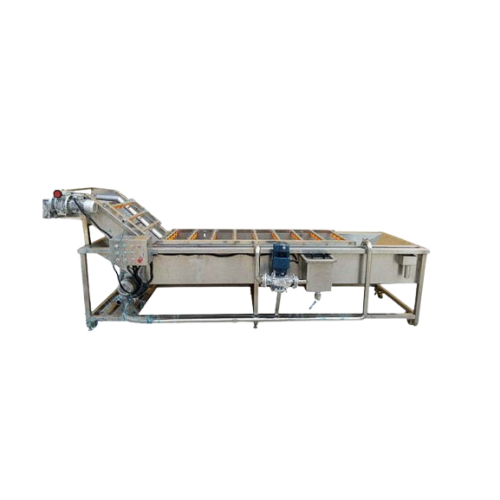
Bubble type fruit and vegetable washer
Ensure your produce is impeccably clean and damage-free with our bubble-type washing...
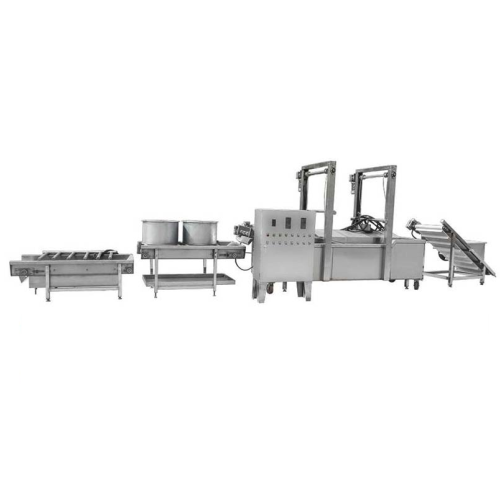
Fried food production line
Achieve consistent quality in fried snacks with this integrated production line, streamlining pro...
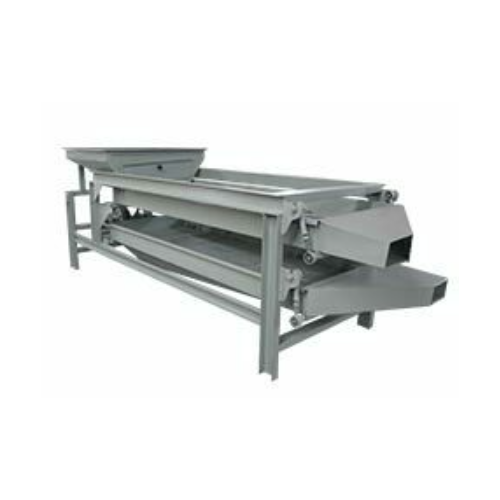
Small scale cashew nut processing plant
Optimize your nut processing with our comprehensive cashew line, designed to stream...
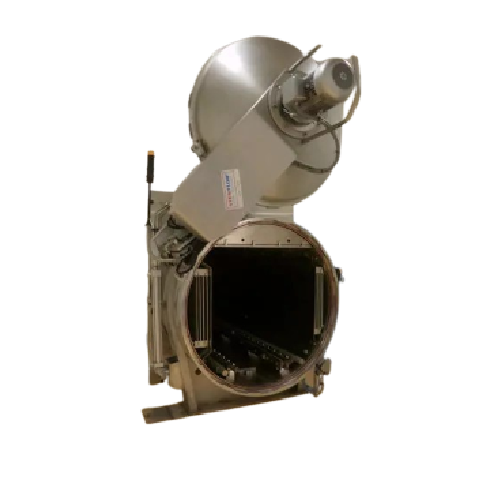
Steam air autoclave for pharmaceutical industry
Ensure precise sterilization of sensitive pharmaceutical products while ma...
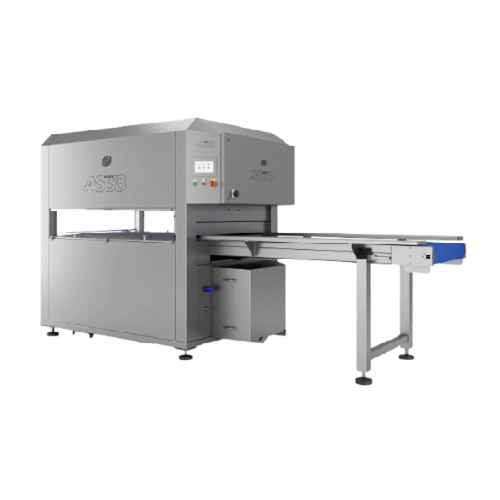
Automatic belt chamber vacuum packing for meat and cheese
Achieve seamless integration into your packaging line with a m...
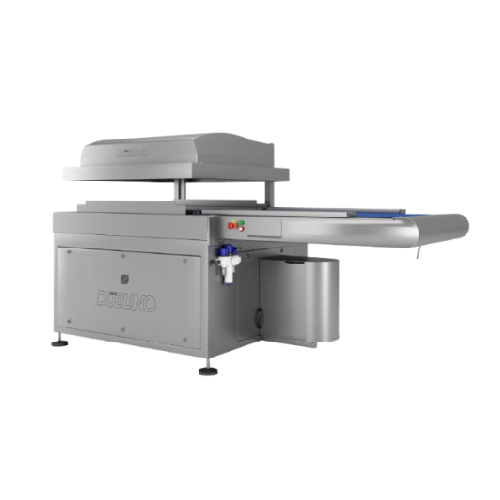
Mid-size belt-chamber vacuum packaging for smallgoods and seafoods
Optimize your packaging line with efficient mid-spee...
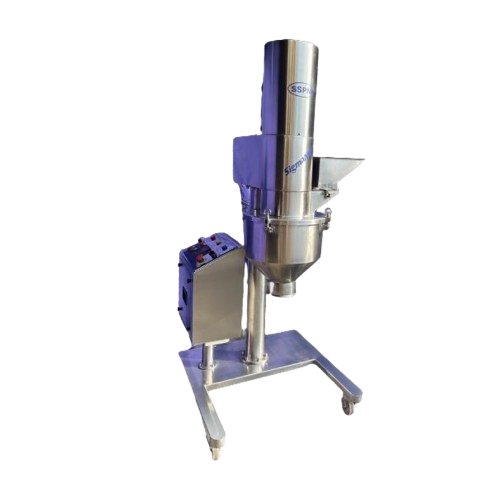
Wet granulation system for pharmaceutical tablets
Optimize your tablet production with precise particle size reduction an...
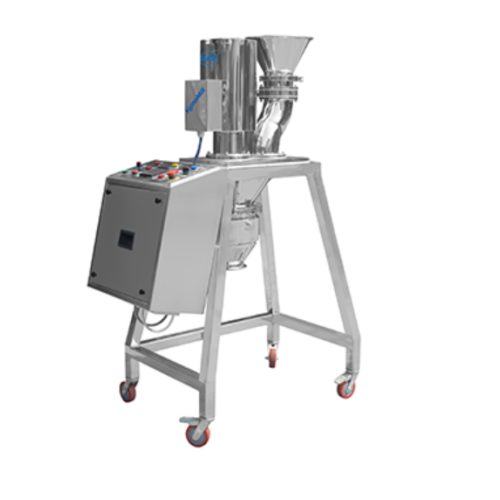
Wet granulation co mill for pharmaceutical formulations
Optimize your manufacturing process with precise particle size re...
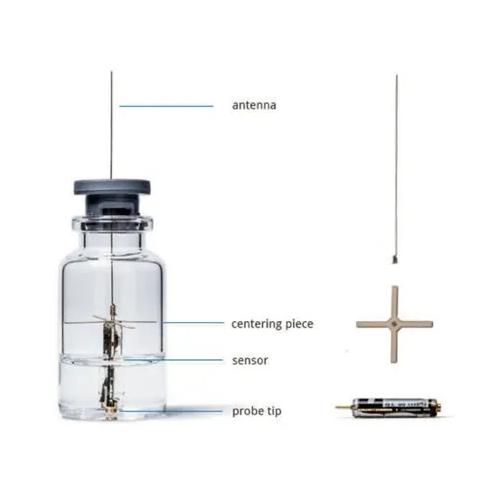
Wireless temperature sensors for lyophilization
Enhance your lyophilization workflow with precise, real-time temperature m...
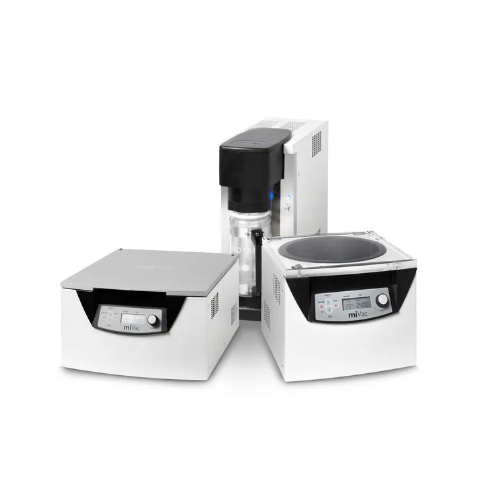
Centrifugal evaporator for solvent evaporation
Achieve precise solvent removal with a versatile system designed for effici...
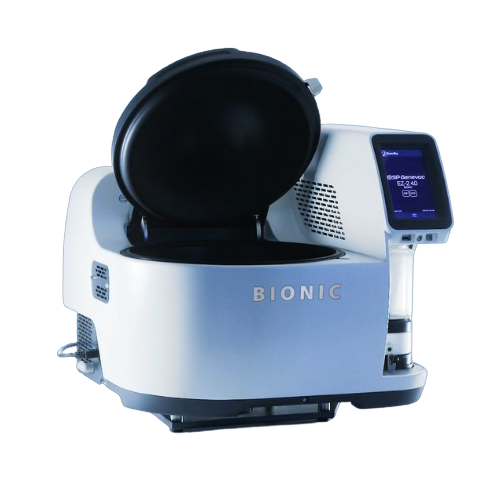
Glassware washer for laboratory use
Achieve precision cleaning of varied laboratory glassware with minimal contamination ri...
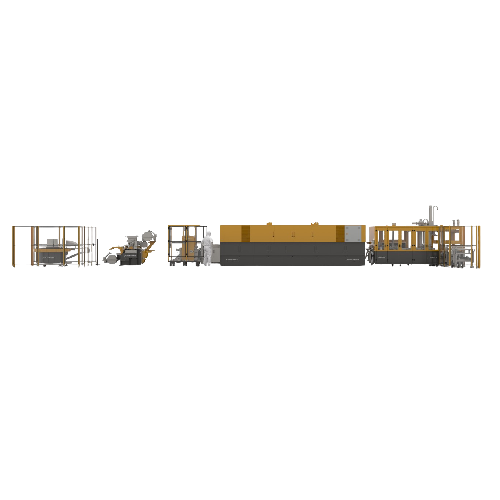
Pasting line for e-bike plates
Ideal for ensuring precision and consistency, this pasting line enhances the efficiency of ba...
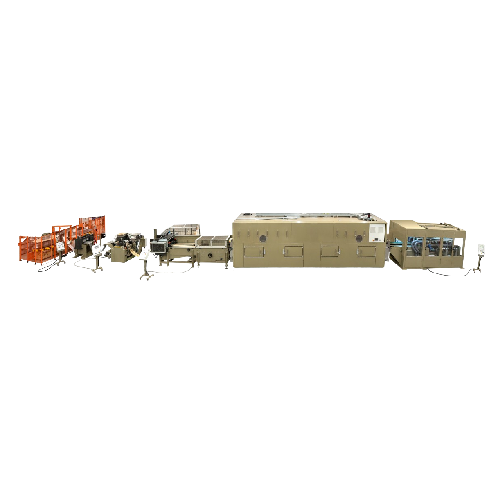
Pasting line for high-thickness plates
Optimize your battery production with precision control using a pasting line designe...
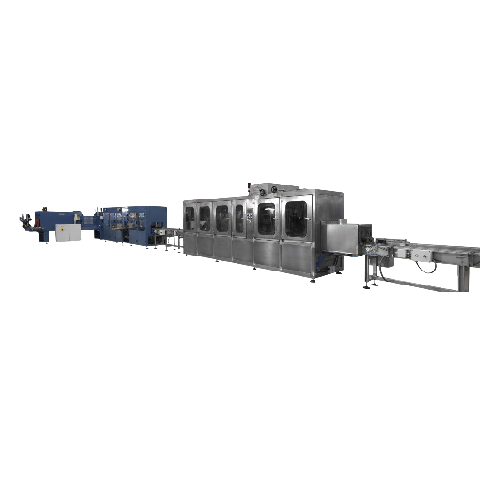
Battery plate finishing line for lead-acid batteries
Ensure your lead-acid battery plates achieve optimal thickness and u...
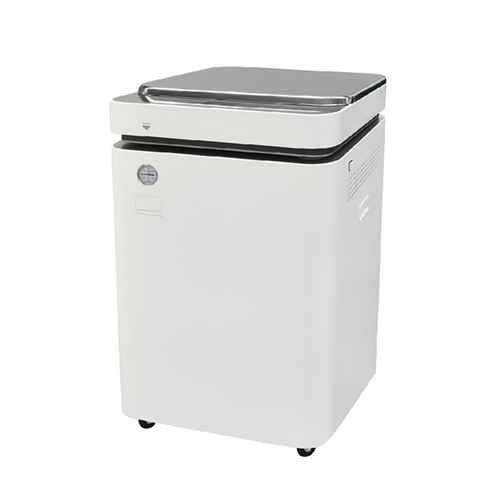
Laboratory series steam sterilizers
Ensure the sterility of your labware and culture media with reliable steam-based steril...
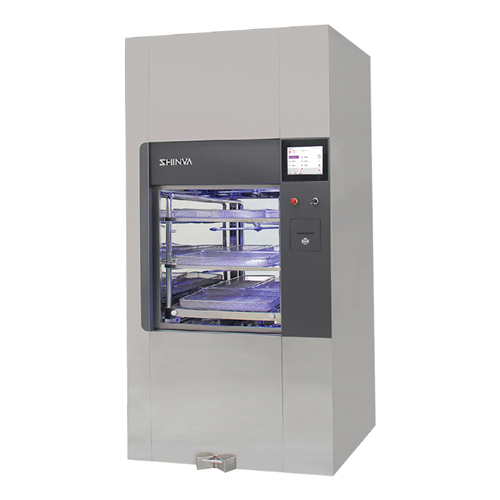
Washer-disinfector for surgical instruments
Ensure thorough cleaning and disinfection of medical and surgical instruments ...
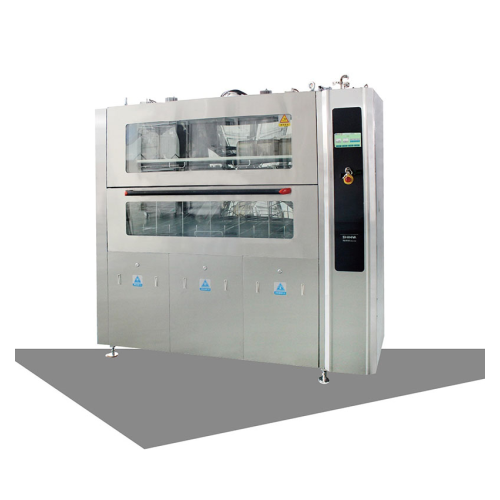
Laboratory cage box cleaning system
Ensure fast and thorough cleaning of cage boxes and accessories with a versatile high-p...
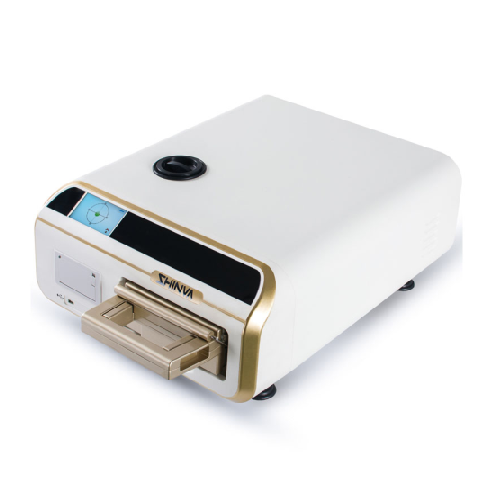
Cassette autoclave for sterilization in medical settings
Ensure the reliable sterilization of medical and laboratory inst...
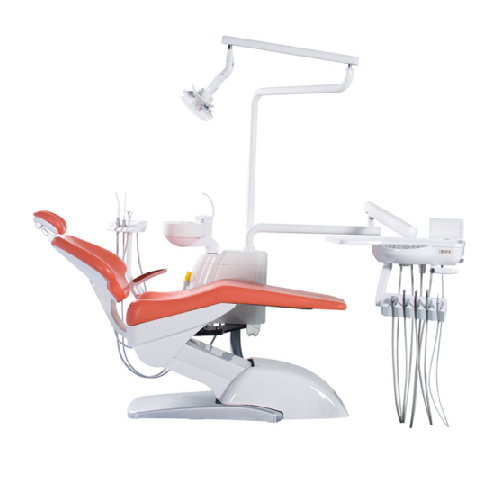
Dental equipment sterilizer
Ensure complete infection control and safety with advanced sterilization and cleaning capabiliti...
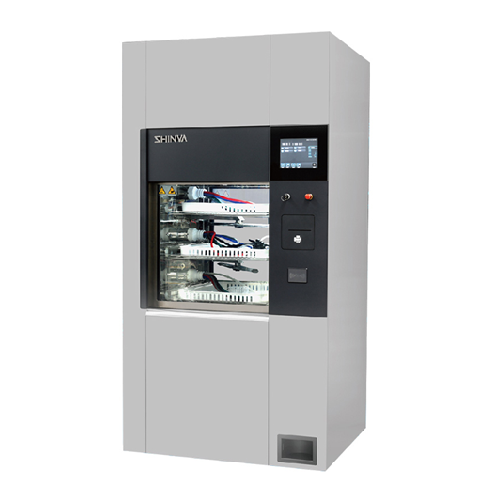
Flexible endoscope washer-disinfector
Ensure precise cleaning and disinfection of complex medical instruments with a washer...
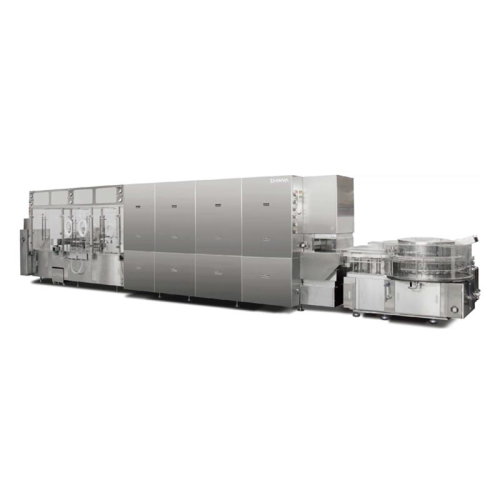
Ampoule washing, filling, and sealing line
Streamline your ampoule production with an integrated washing, filling, and sea...
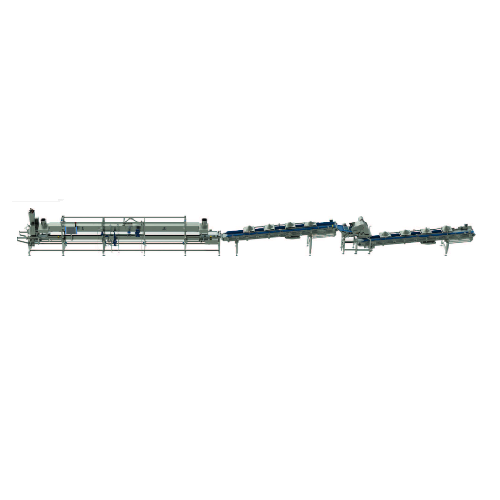
Pet food production line
Enhance your pet food production with a seamless, efficient system that emulsifies, extrudes, and pa...
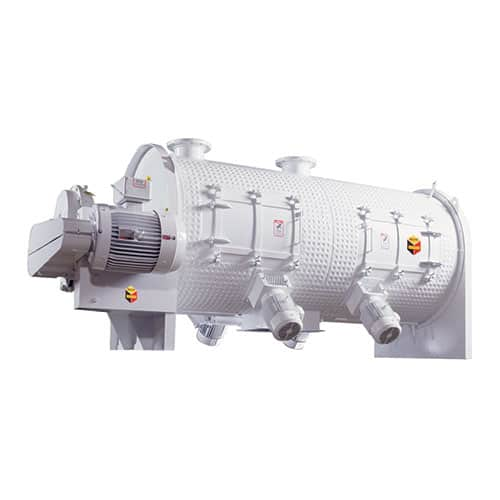
Industrial plow mixer for efficient solid and liquid mixing
Experience unparalleled mixing precision with high-speed plo...

Mechanical air separator for uniform fineness
Achieve precise material separation and de-dusting with our air separator, e...
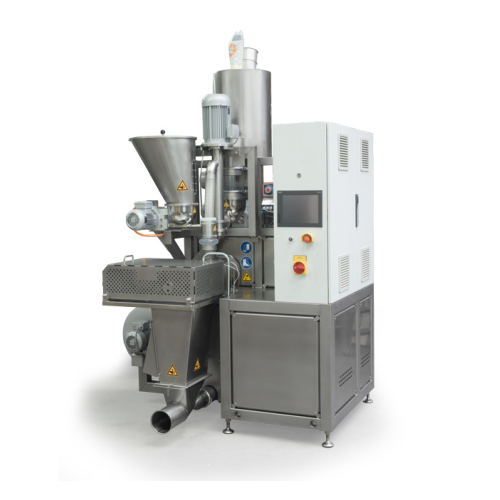
Food product extruder for low to high capacity production
Optimize your snack production with versatile extruders that e...
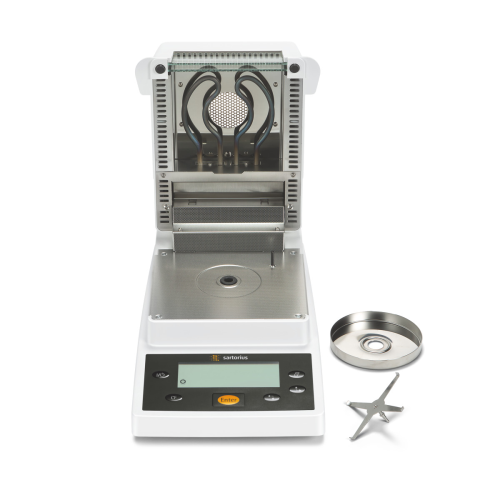
Infrared moisture analyzer for lab and production use
Achieve precise and reliable moisture analysis with minimal time an...
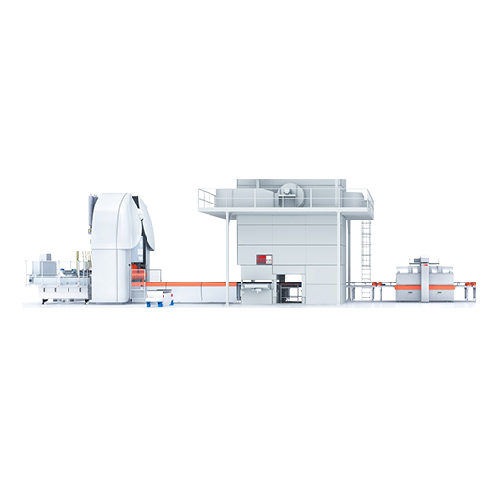
Advanced ceramic tile production line
Elevate your ceramic tile production with an all-encompassing solution that seamlessl...
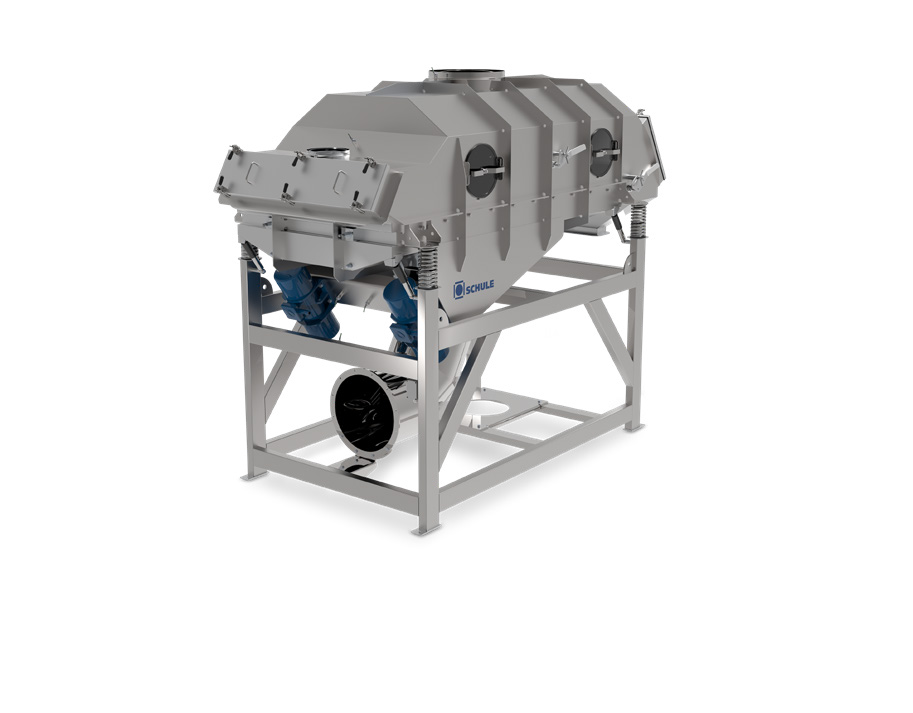
Fluidized bed drier/cooler for grains
Processed grains absorb moisture throughout the production line. Lowering that water ...
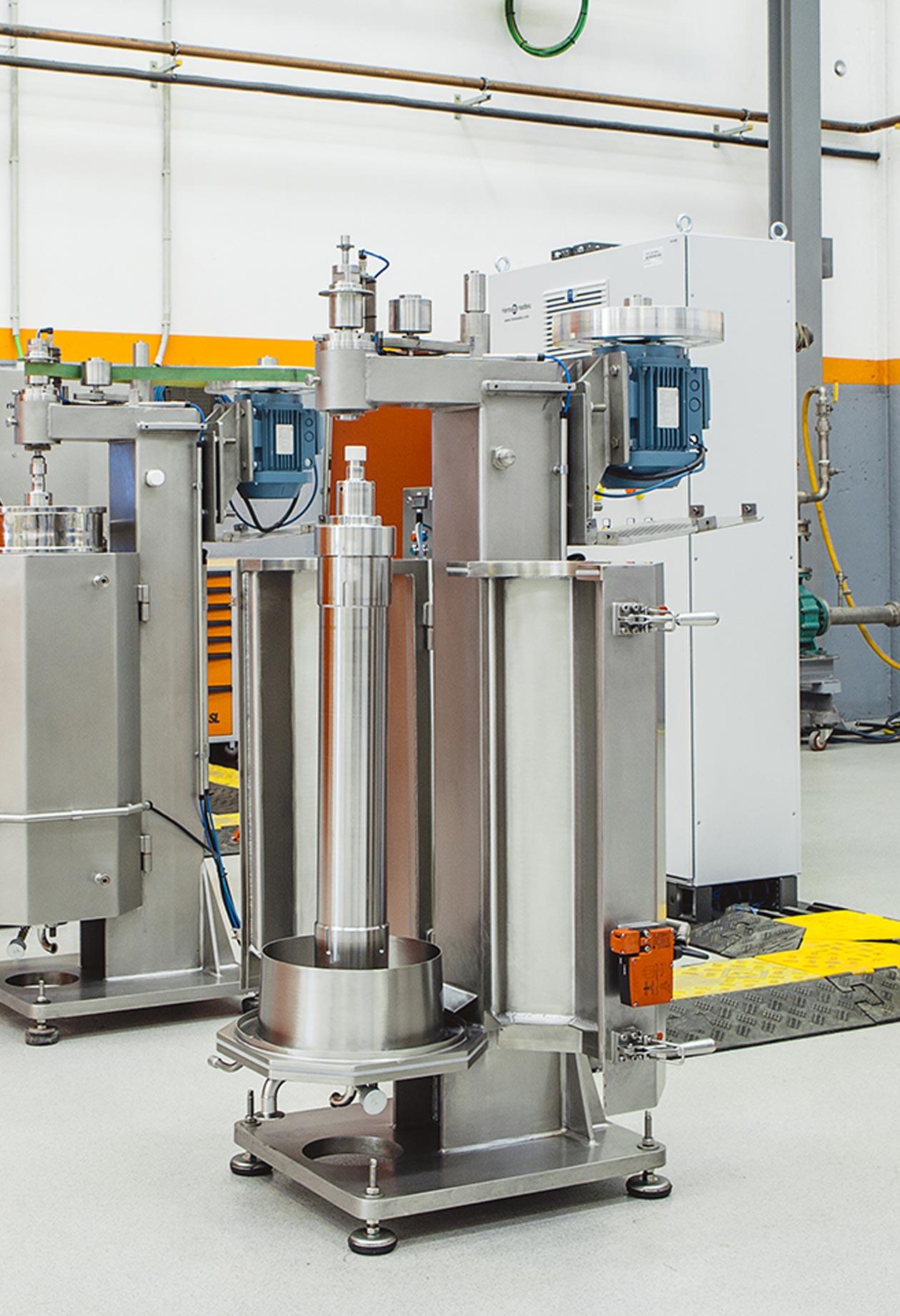
Water oil separation centrifuge
Some industries, such as petrochemical, generate large volumes of oily wastewater due to the...
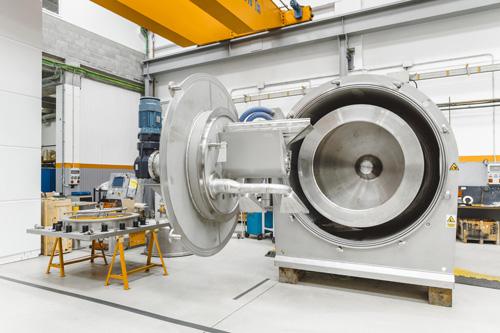
Automatic centrifuge for cannabis
Centrifugation is an effective method for producing cannabis extracts. The extraction pro...
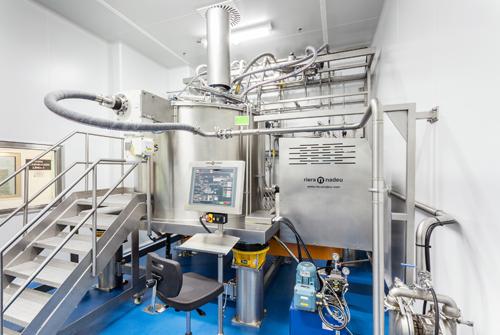
Automatic centrifuge for lithium carbonate
The battery industry requires high purity components. To obtain more than 99.5%...
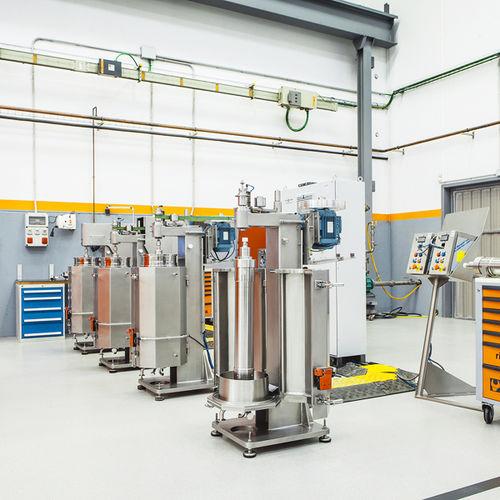
Blood plasma centrifuge
Efficiently separating blood cells from plasma is key in the accuracy of diagnostic tests, as cellula...
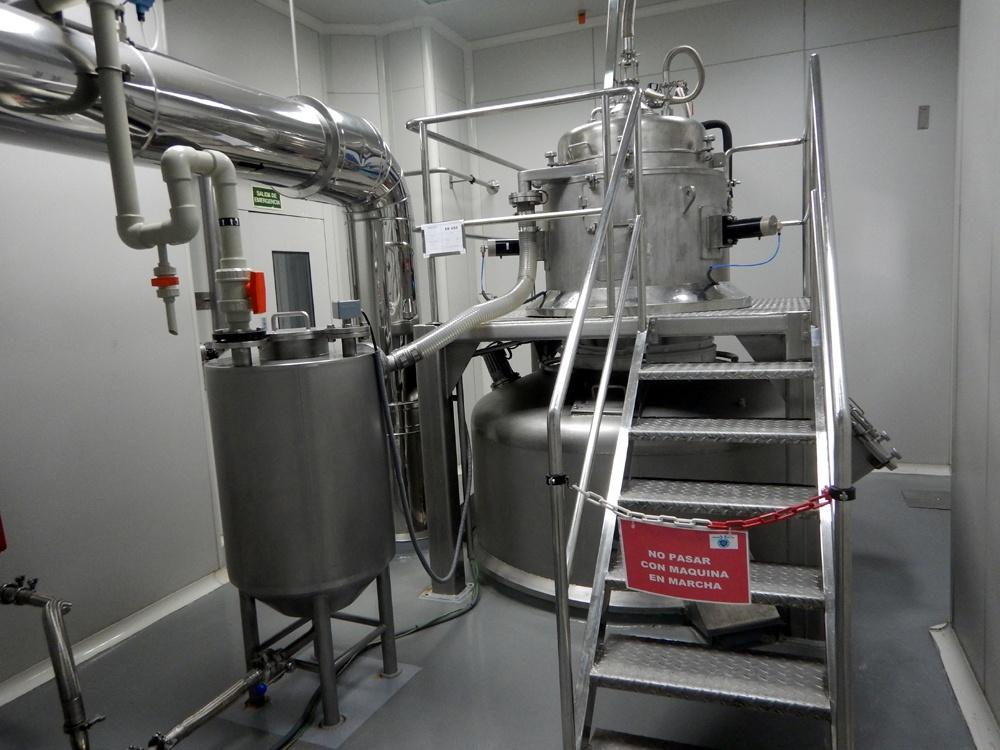
Continuous centrifuge for lithium hydroxide
Lithium hydroxide, a lithium compound used in making lithium batteries, is ind...
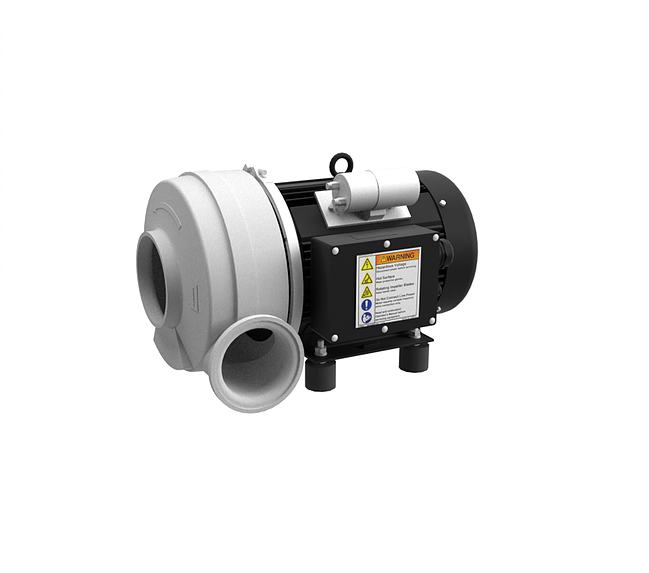
Blow off system for containers
Packaging powders into plastic or glass containers often leaves a residue that needs to be re...
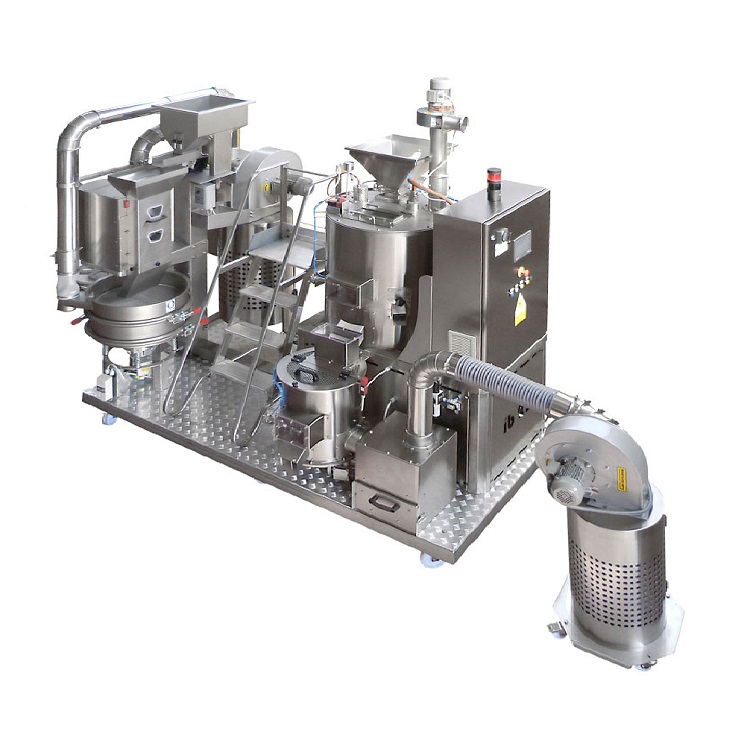
R&D roaster for cocoa beans
When designing a new chocolate line or experimenting with new ingredients for existing processes...
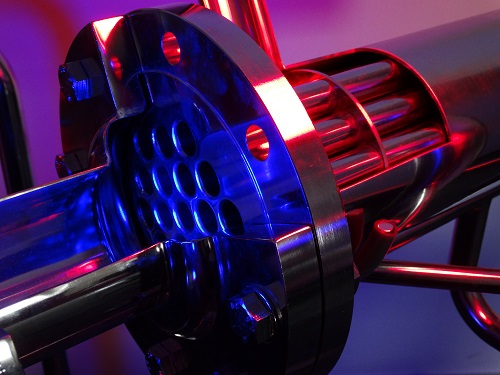
Shell and tube heat exchanger
Heating, cooling and tempering are important processes in the production of many products acro...
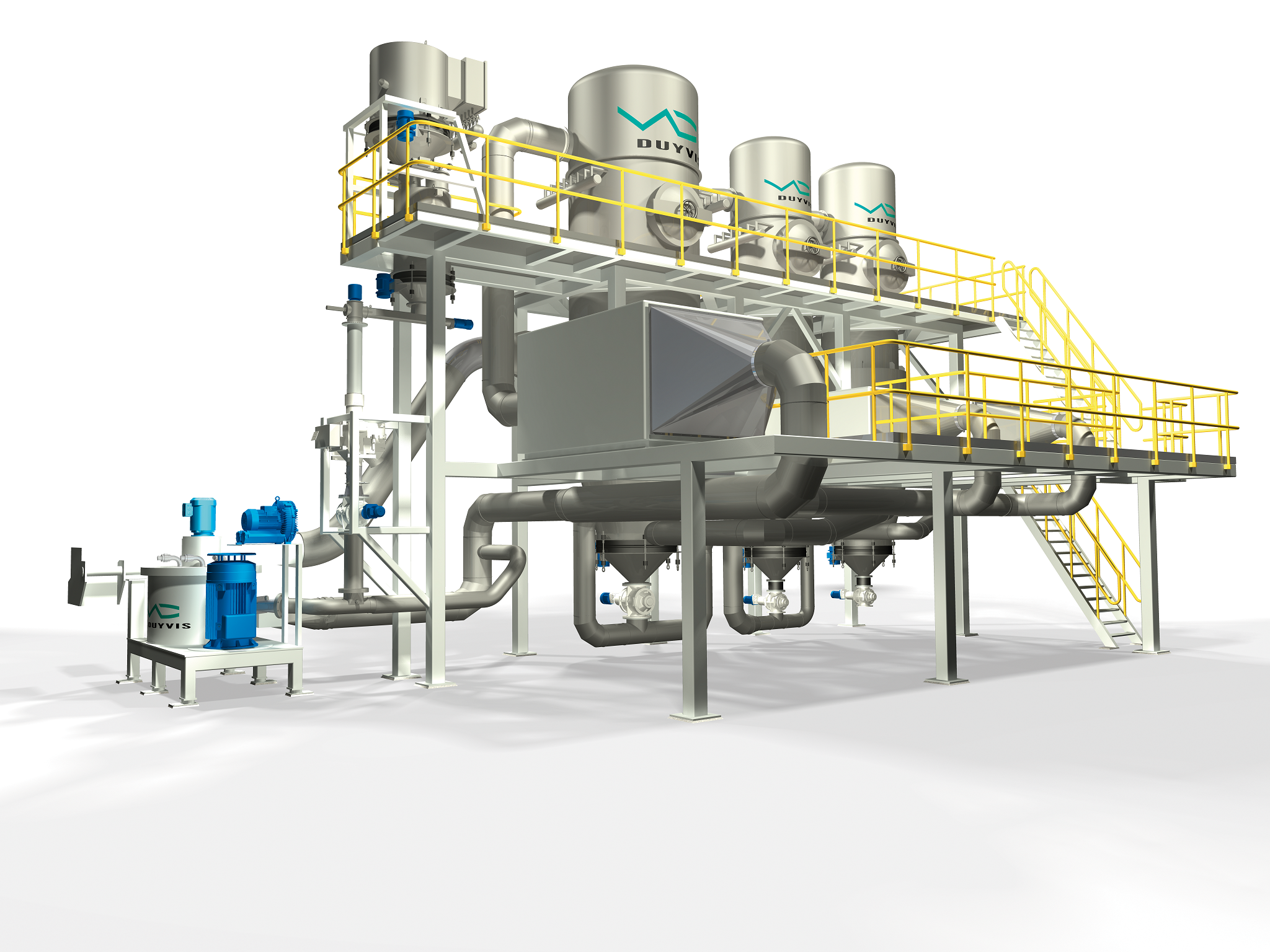
Cocoa powder processing line
Cocoa beans are first fermented, dried, roasted, and separated from their skins to obtain a coc...
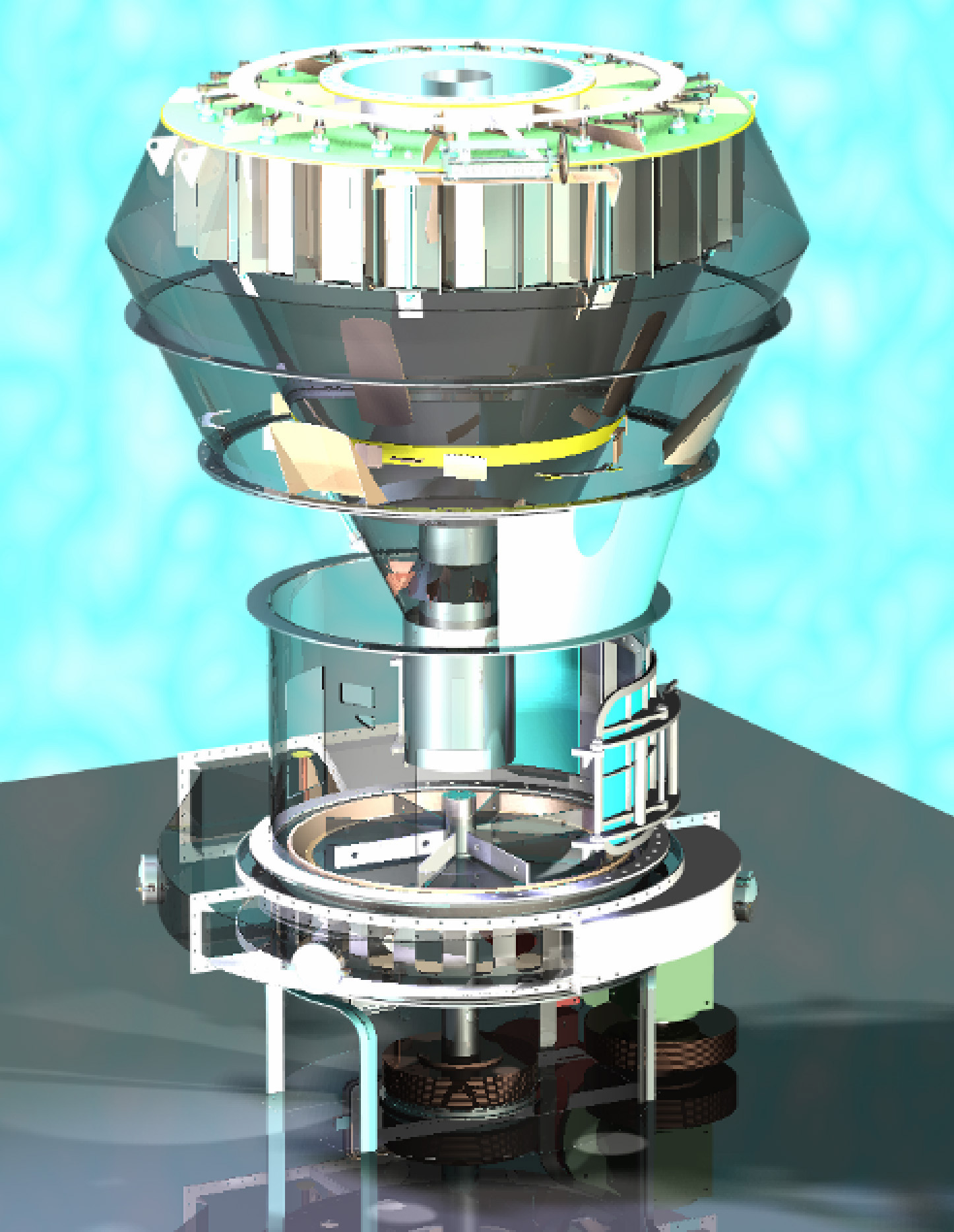
Horizontal impact calciner
Quality of synthetic gypsum and stucco products is highly influenced by the quality of the calcin...
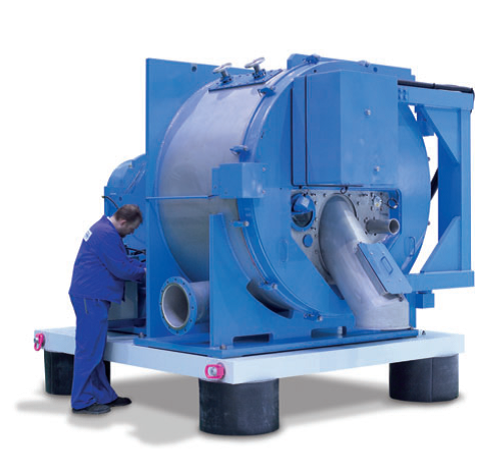
Horizontal chemical scraper centrifuge
For slurries difficult to discharge, a scraper can improve process reliability, effi...
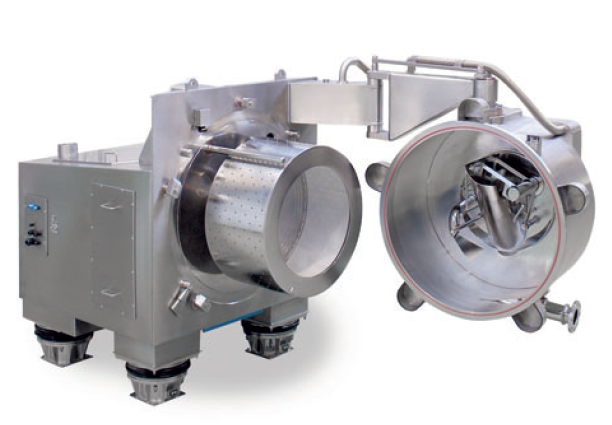
Horizontal pharmaceutical scraper centrifuge
For slurries difficult to discharge, a scraper can improve process reliabilit...
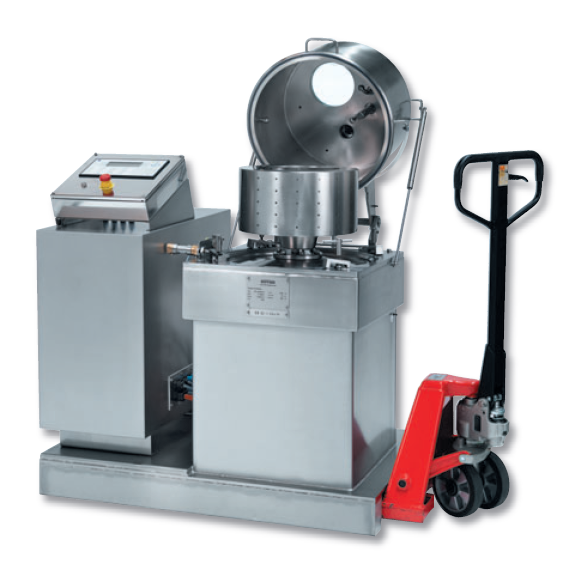
Mobile pilot plant centrifuge
The system is perfectly suited for pilot plants as well as small-quantity productions in the f...
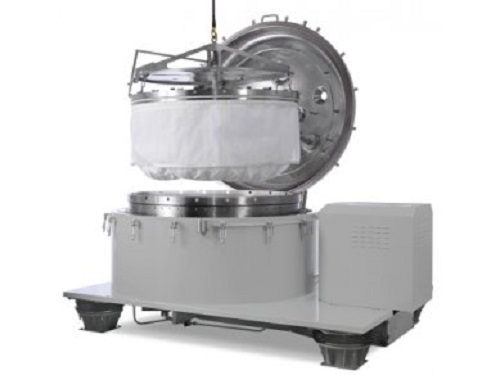
Vertical top discharge centrifuge
Discharge solids vertically upward through manual action, optionally using a filter bag o...
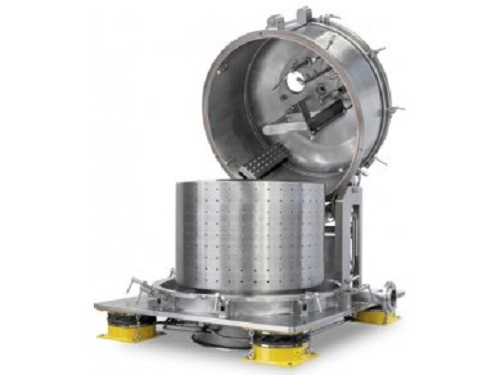
Vertical peeler centrifuge
A vertical peeler centrifuge is used to separate solids, usually to separate fine particles from ...
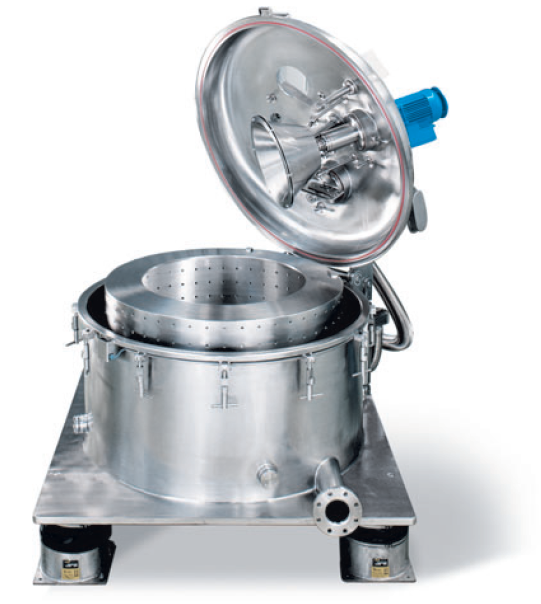
Vertical scraper centrifuges
Vertical Bottom discharge Centrifuges work discontinuously, discharging the solids to the botto...
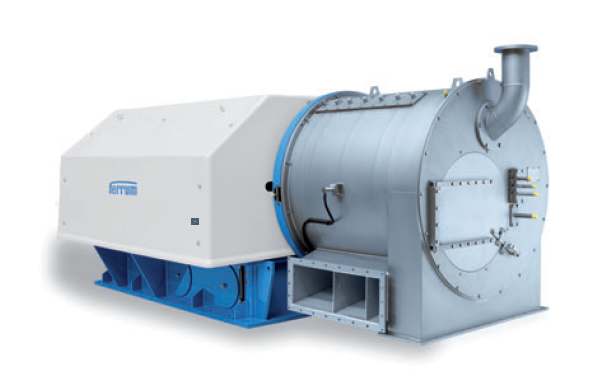
Pusher centrifuge
Pusher centrifuges are continuously operating filter centrifuges and can have several basket stages dependi...
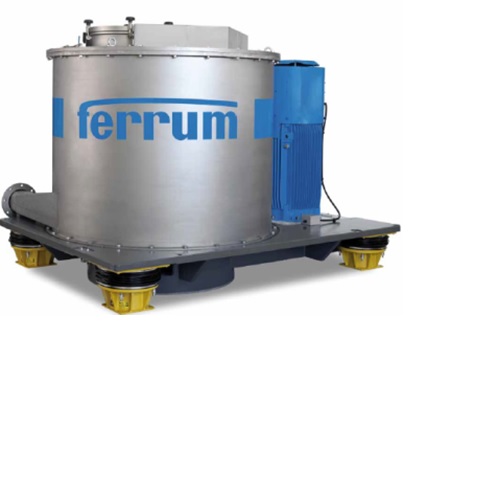
Gypsum centrifuge
Especially designed for flue gas desulphurization, applications in coal fired power plants and waste incine...
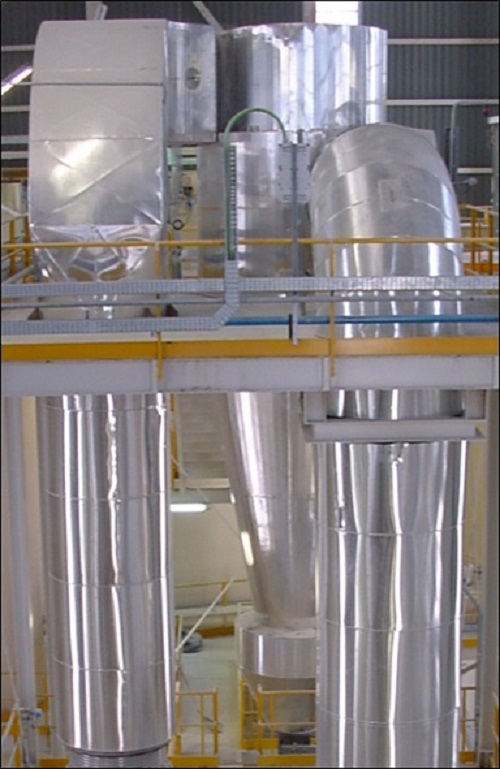
Flash calciner
Quality of gypsum plaster products is highly influenced by the quality of the calcining process employed in pro...