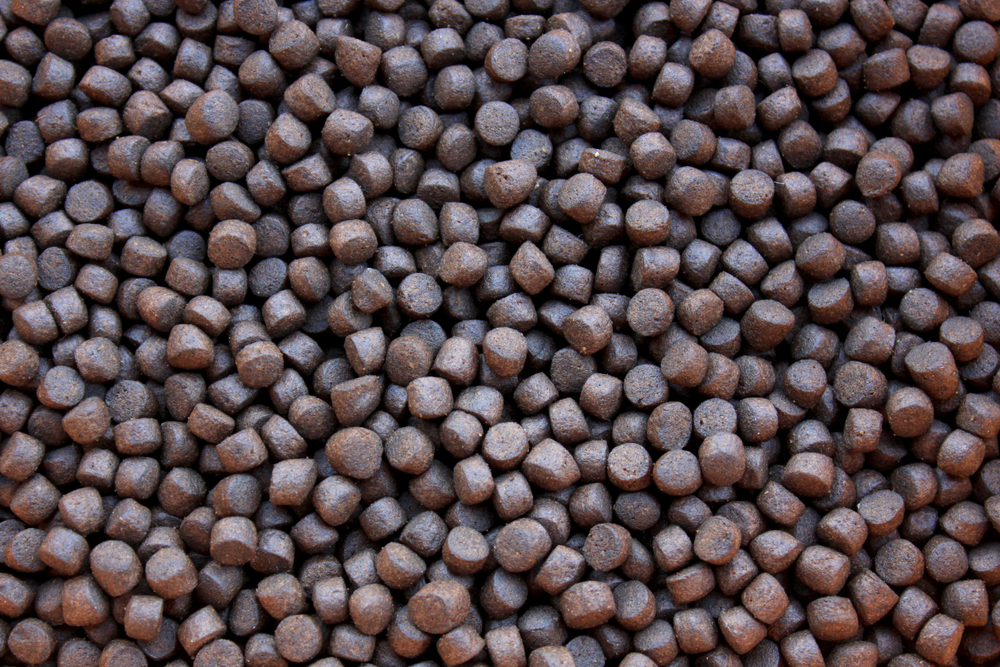
Making Aquafeed
Find innovative aquafeed equipment and connect directly with world-leading technology suppliers
Aquaculture feed is used when rearing marine livestock such as fish, shellfish, and algae. Quality nutrition is needed for healthy growth and reproduction and feed usually consists of fats, carbohydrates, protein, vitamins, and minerals. Extruded aquaculture feed floats on the water surface and pressure-pelleted feed will sink to the bottom.
Technology picks for aquafeed
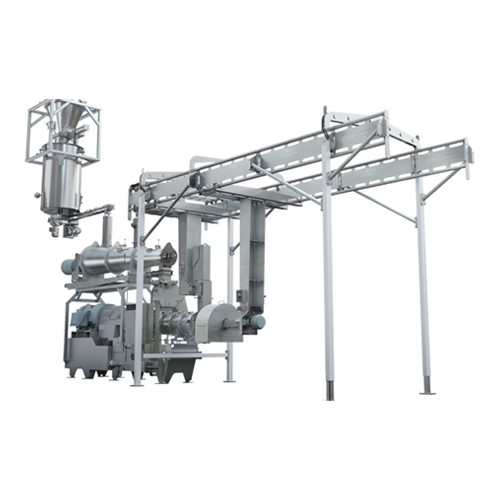
Conical twin screw extruder for pet food and aquatic feed
Precision-engineered for high-speed extrusion and drying proce...
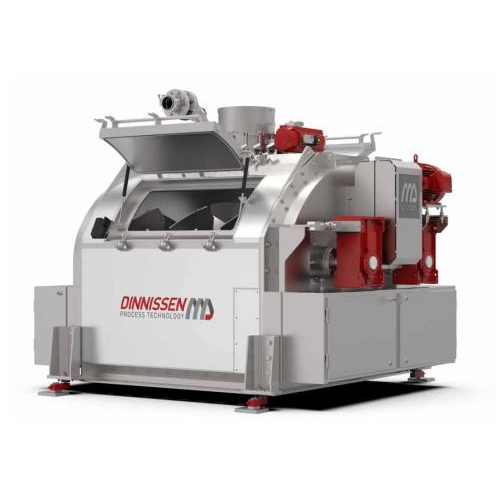
Advanced vacuum coating system for pet food and feed
Achieve uniform saturation in pellets and granules with precise liqu...
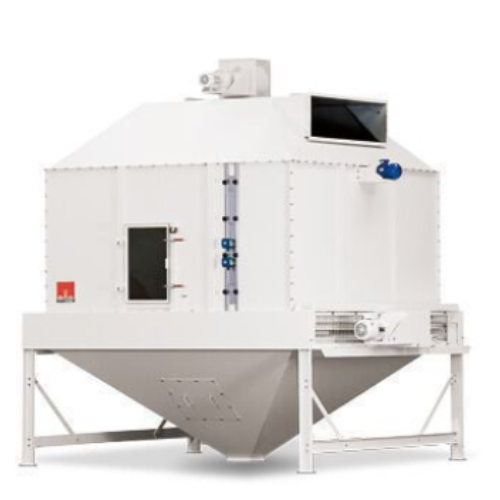
Counterflow dryer for pet food and fish feed
Optimize moisture control and enhance feed quality with efficient drying, cru...
Stories about aquafeed
Select your aquafeed process
Tell us about your production challenge
Apart from floating and sinking feed, pellet size and protein content are key parameters. Pellets should be large enough to be quickly found and still swallowed easily. Different species require different diets representing the plant-based or carnivorous diets in the wild. The required protein level in aquafeed differs per species, fish size and age, and breeding environment.
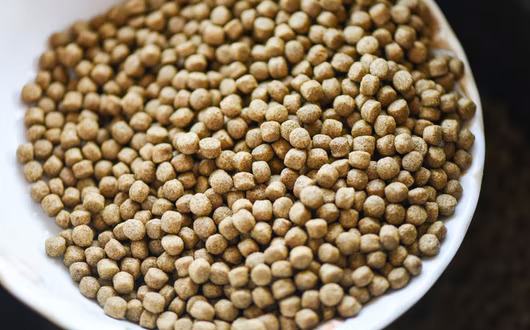
Protein shortage and overfishing
Aquafeed still relies very much on fish meal and fish oil made out of the by-catch of fisheries, which due to the growing worldwide protein shortage actually enhances overfishing. Insects, plant-based ingredients, and aquaculture by-products are therefore seen as promising more sustainable sources to help create the 37.7 million tons of aquafeed required by 2025.
Commercial fish feed manufacturers process dry ingredients for long-term storage and transport. Farms that manufacture feed themselves can more easily make wet feed and use local raw materials. Often feed is supplemented with certain additives such as mold inhibitors, pellet binders, grain conditioners, anti-stress agents, or for example immunostimulants as an alternative to antibiotics.
Technology for packing and processing aquafeed
As for every production plant, the technology used to make aqua feed will differ greatly depending on available resources and raw materials as well as the end product and quantity.
Generally speaking, the process is as follows: If required wet materials such as fish scraps are cut into smaller pieces and course dry materials like grains need to be milled first before blending. This premix or dough can then be shaped into the desired form by for example a pellet press or extrusion cooker and will be dried afterward. Starches and proteins are key in the formulation because they form a large part of the diet and alter properties when exposed to heat influencing for example solubility and digestibility.
Pasteurization or heat is essential for longer shelf life and is preferably stored in a cool and dry place. Silos systems should be easy to clean and provide easy accurate dosing into desired bagging systems or bulk containers for further use.
Which aquafeed technology do you need?
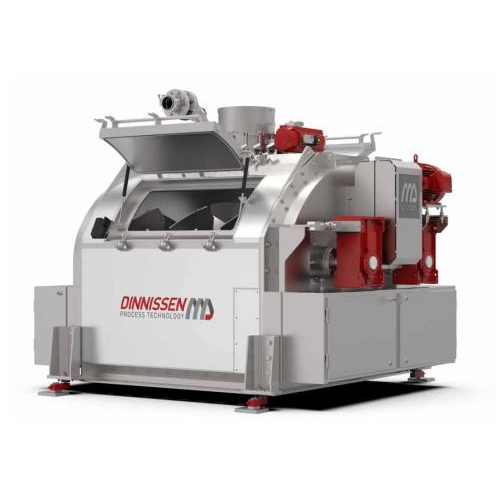
Advanced vacuum coating system for pet food and feed
Achieve uniform saturation in pellets and granules with precise liqu...
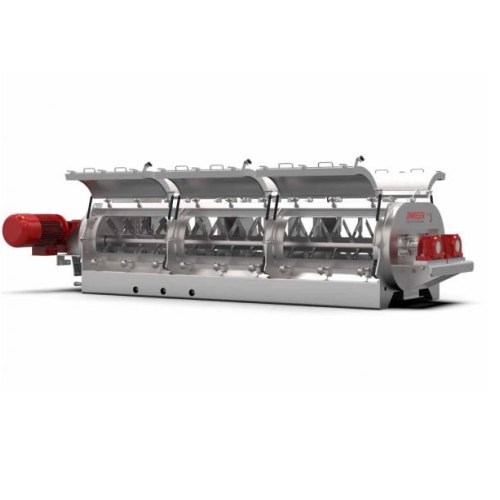
Industrial mixer for moisture conditioning
Ensure precise moisture levels and homogeneous mixtures for complex extrusion p...

Big bag conditioning system for compact materials
Struggling with clumped materials during unloading? This system expertl...
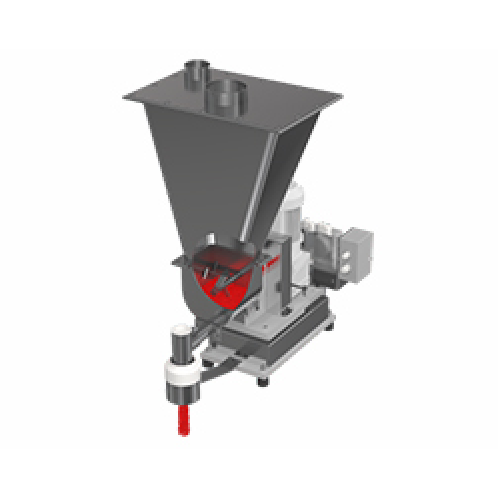
Single screw loss-in-weight feeder for powders and pellets
Ensure precise dosing and mixing in continuous automated oper...
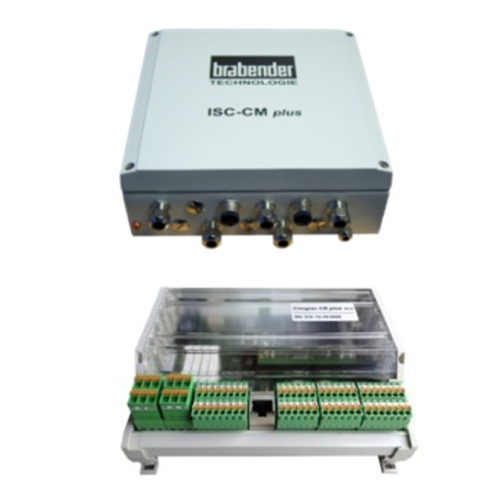
Feeder controller for gravimetric feeders
Optimize your dosing precision and monitoring accuracy with a versatile feeder c...
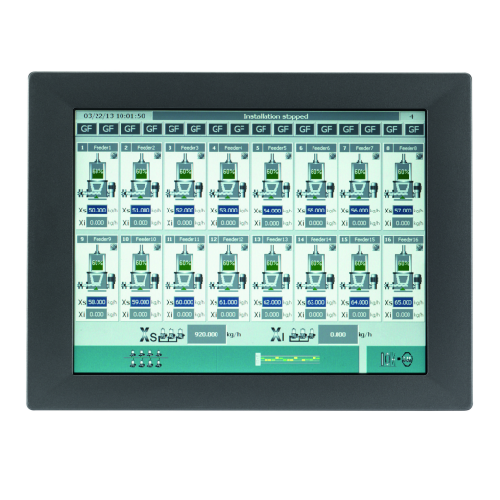
Gravimetric feeder operator interface
Efficiently manage up to 16 gravimetric feeders with a user-friendly interface, enabl...
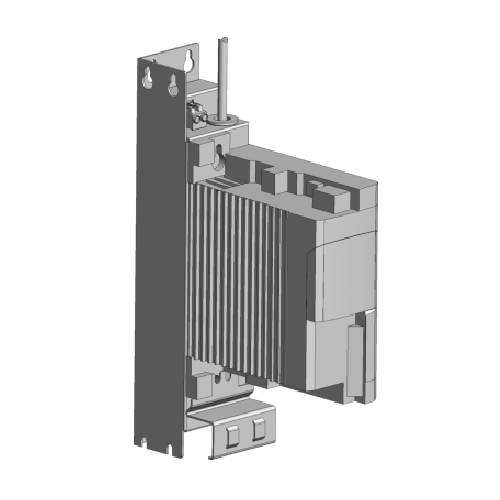
Speed controller for feeders
Ensure precise material flow by integrating this speed controller, ideal for managing both volu...
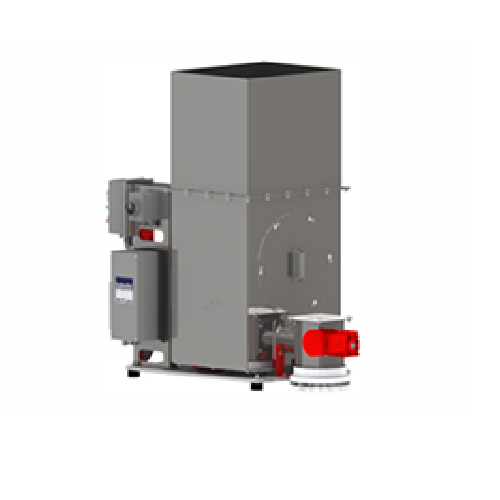
Loss-in-weight feeder for long and uneven fibers
Optimize feeding precision for challenging materials like long and uneven...
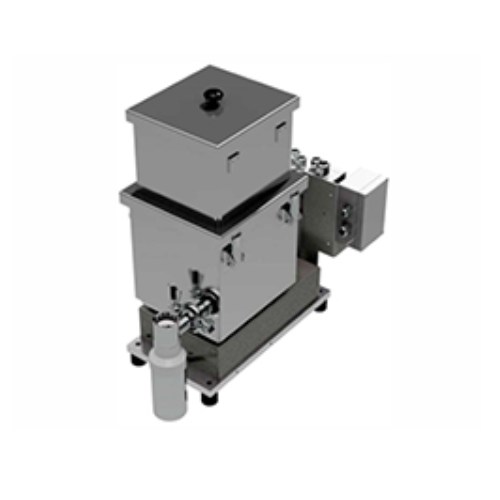
Batch feeder for bulk solids processing
Achieve precise batch dosing with this advanced feeder, designed to handle a variet...
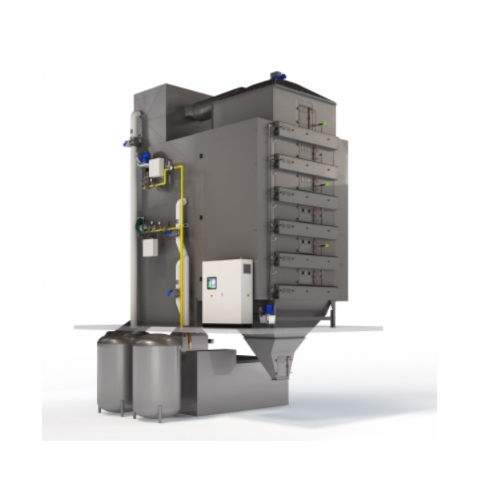
Industrial heat pump dryer
The drying of extruded products is highly energy-demanding in traditional belt dryers that use ga...
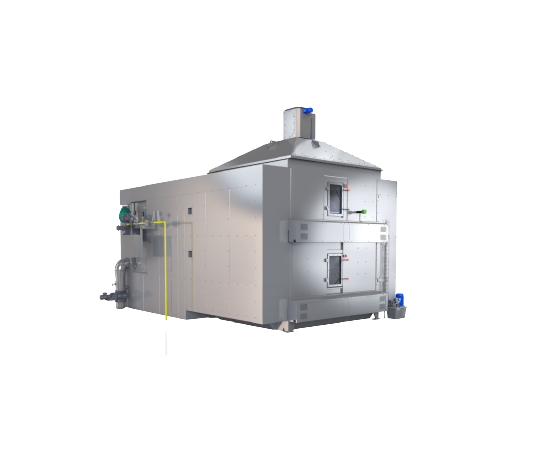
Continuous dryer machine
Traditional drying methods in the pet food, aquafeed, and extruded food industry can be the most ene...
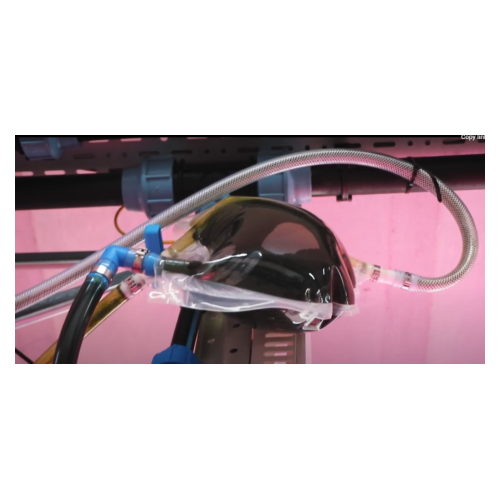
Indoor microalgae cultivation technology
Enhance sustainability and productivity in microalgae cultivation with a vertical ...
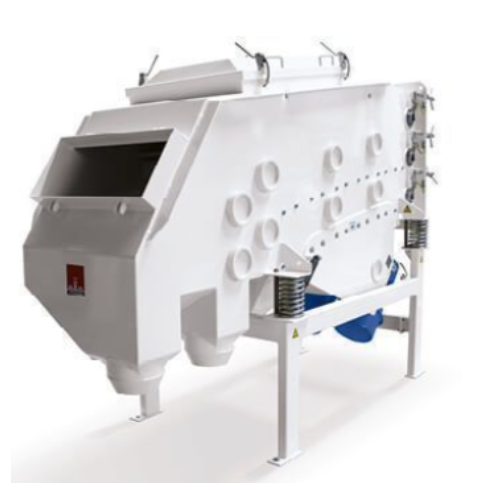
Industrial vibrating sieves for pellets and fine particles
Optimize feed quality and material flow in your production li...
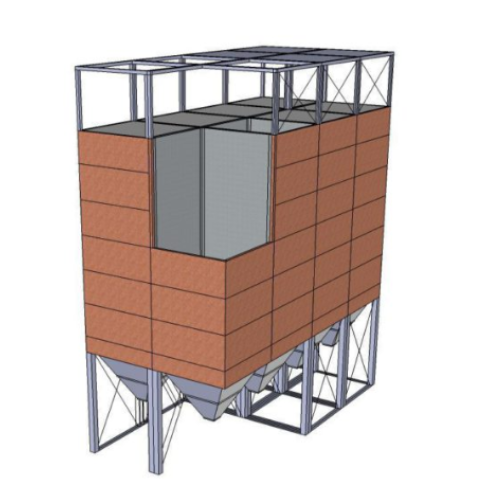
Square silo for bulk goods storage
Maximize your storage efficiency by 25% with square silos, uniquely designed for effecti...
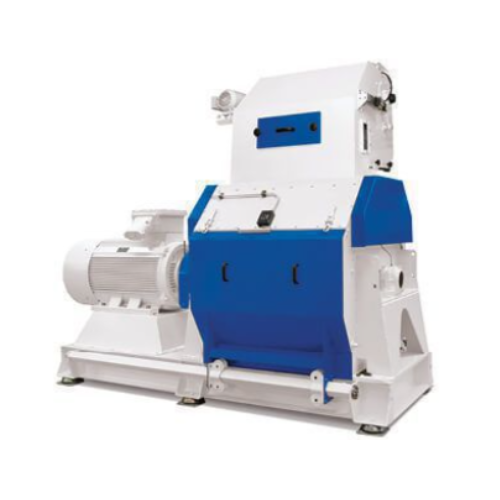
Hammer mills for high-efficiency grinding in feed production
Optimize your feed production with high-efficiency grinding...
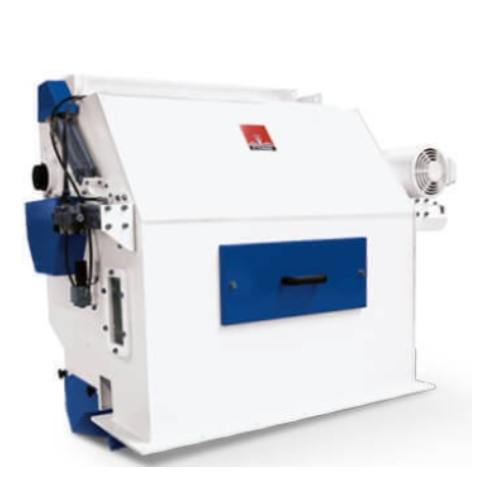
Roll feeders for consistent hammer mill supply
Ensure precise and controlled feedstock delivery to your hammer mill, effec...
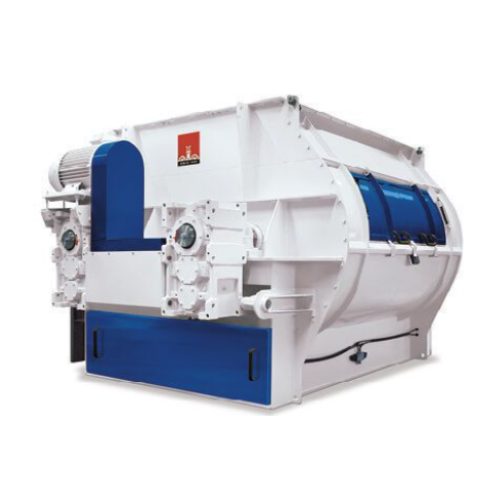
Double shaft paddle mixers for industrial powders and granulates
Achieve precise mixing and homogenization of dry powder...
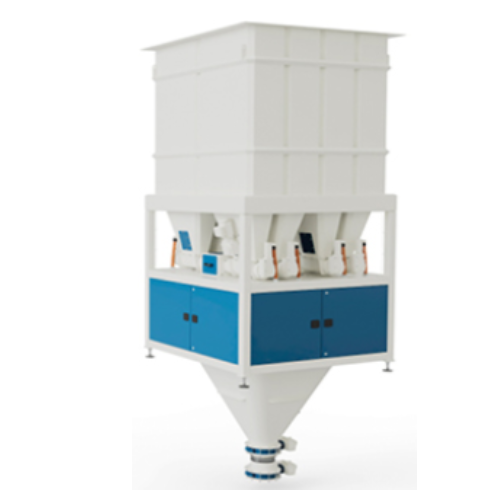
High accuracy micro dosing system
When handling diverse ingredients, precise dosing is crucial to ensuring consistent produ...
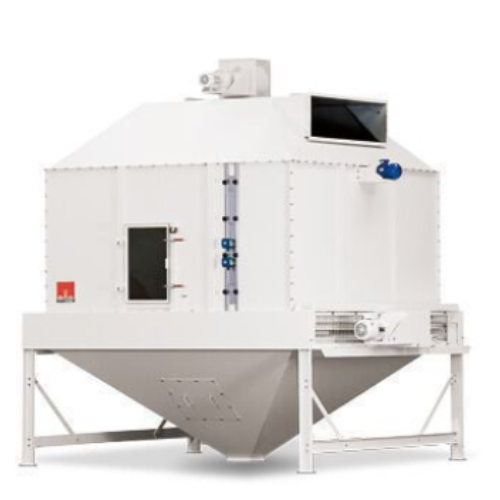
Counterflow dryer for pet food and fish feed
Optimize moisture control and enhance feed quality with efficient drying, cru...
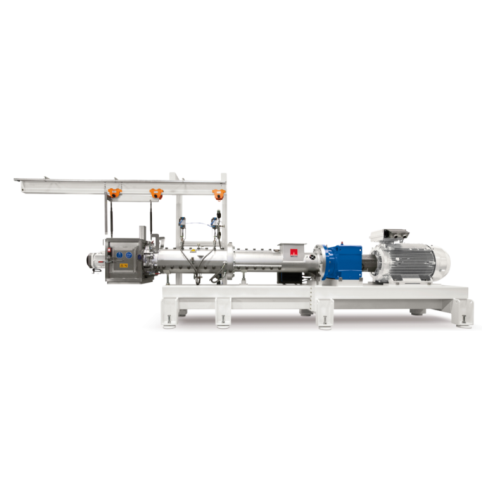
Extruders for animal feed production
Optimize nutritional value and ensure efficient processing of animal and aqua feeds wi...
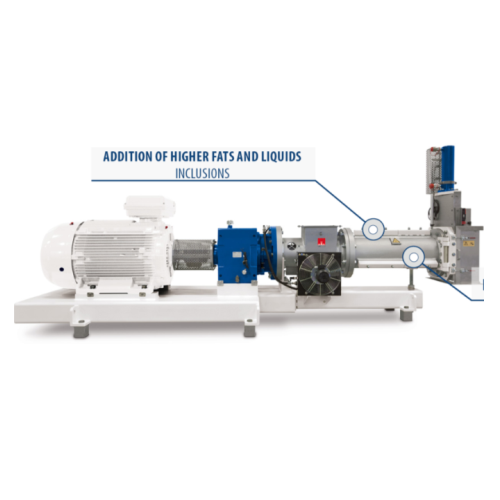
Feed expander for improved pellet mill output
Enhance your feed quality and production efficiency with a robust expander d...
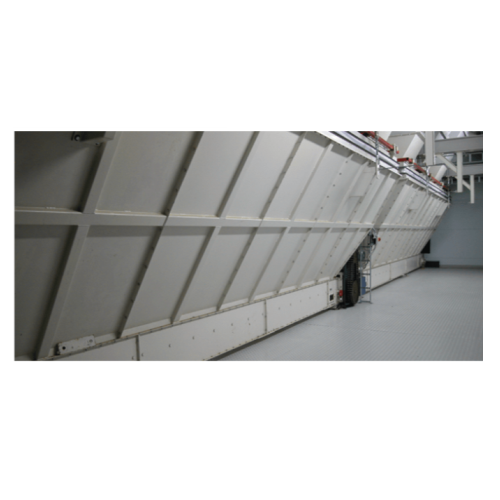
Batch weighers for large-volume powder and granulate weighing
Ensure precise ingredient dosing and streamline your produ...
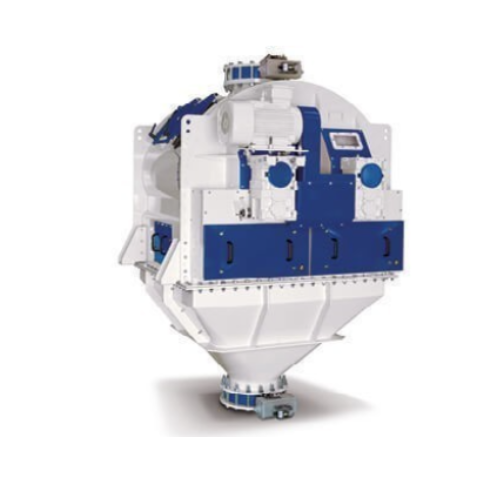
Vacuum coaters for high liquid addition in feed production
Enhance your feed production with precision liquid coating, s...
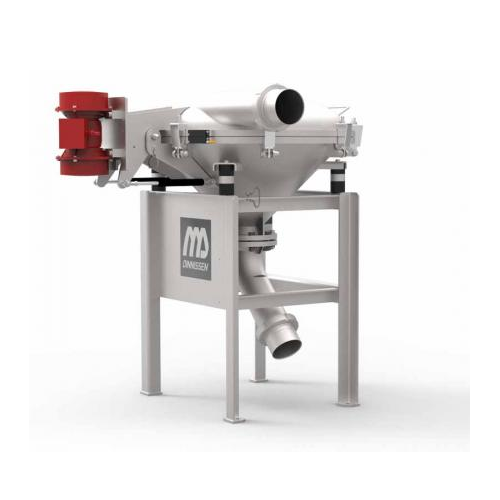
Industrial vibrating sifters for granular material separation
Achieve precise particle separation and ensure product pur...
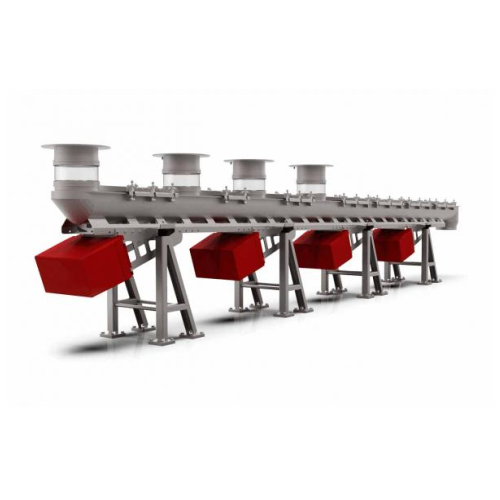
Vibration transport system for hygienic conveying of bulk goods
Optimize your production line with efficient and hygieni...
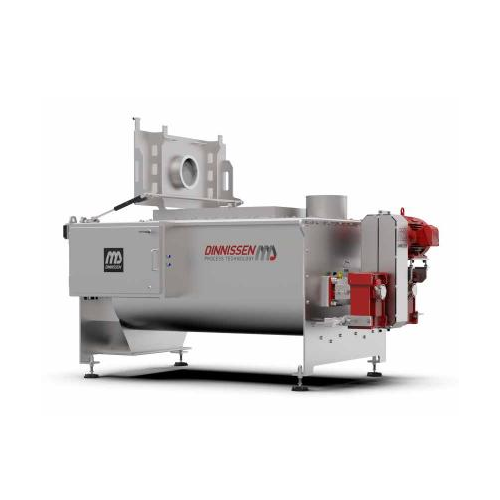
Continuous mixer for industrial powders and liquids
Achieve precise and efficient mixing of solids and liquids with minim...
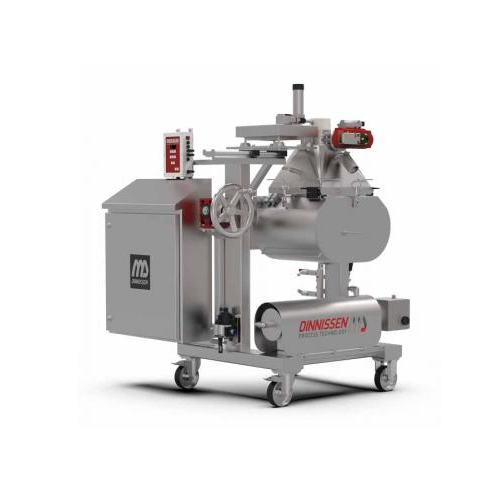
R&d mixer for small batch experimentation
Perfect your mixing techniques swiftly with precision-controlled small batch exp...
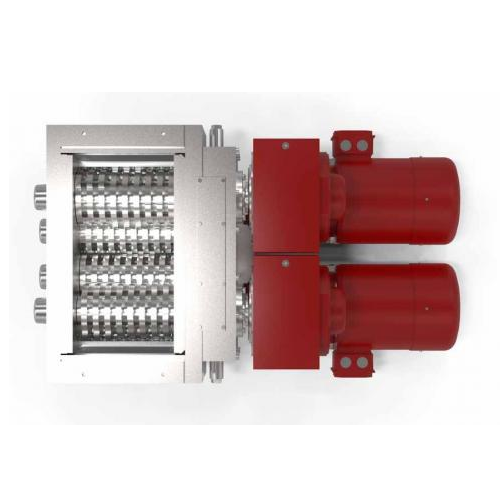
Industrial roller mill for grain size reduction
Achieve precise grain size reduction with minimal heat generation and opti...
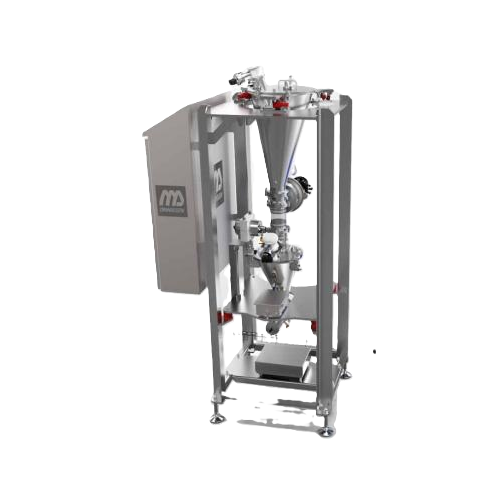
Micro dosing system for precise powder weighing
Achieve unparalleled dosing accuracy in your production line with a system...
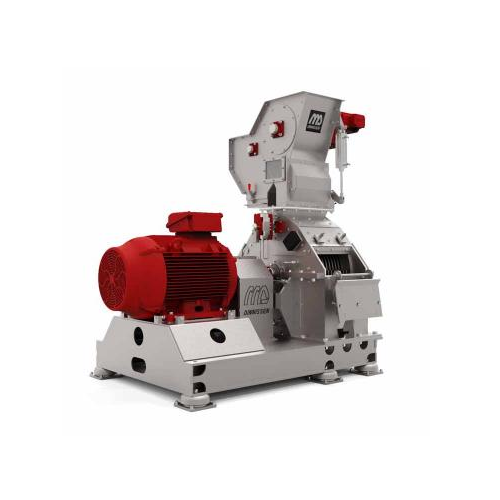
Industrial hammer mill for grinding and sifting
Ensure precise particle size reduction and consistent product quality with...
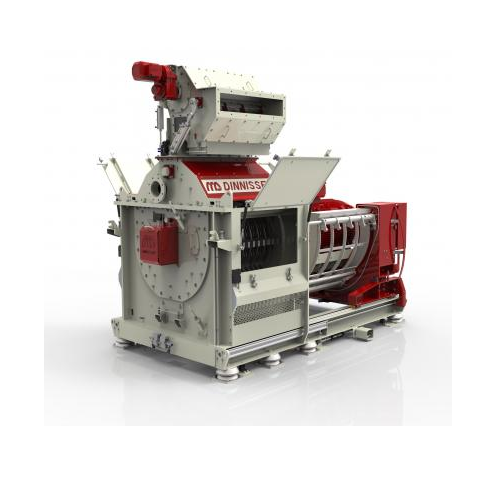
Fast screen exchange grinding solution for medium-hard products
Maximize your milling efficiency with a solution that al...
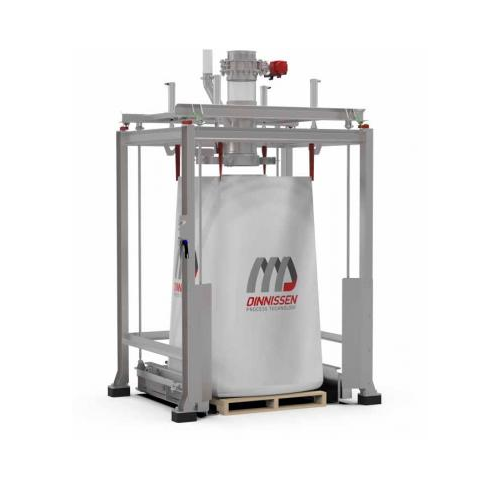
Calibratable big bag filling station for dust-free operations
Ensure precise, dust-free filling of bulk bags with ergono...
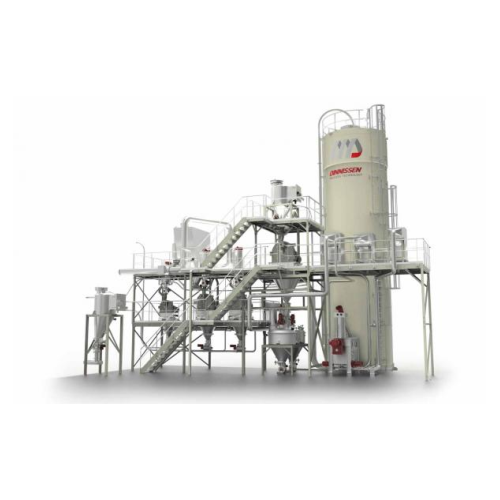
Centrifugal mill for fine grinding in industrial processes
Achieve exceptional fineness without overheating your materia...

Bag-in-box filling system for packaging efficiency
Streamline your packaging process by integrating filling and boxing in...
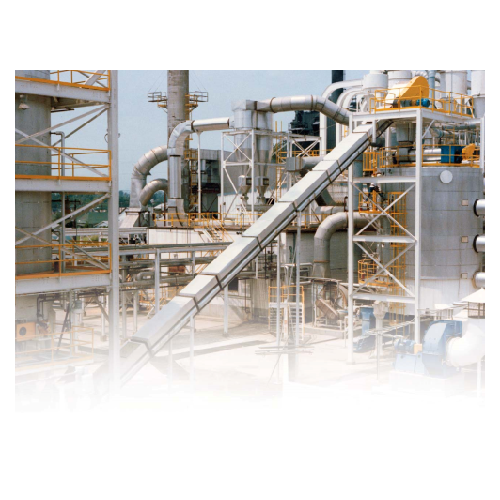
Efficient desolventization and toasting solution for oilseeds
Optimize solvent removal and toasting in your oilseed proc...
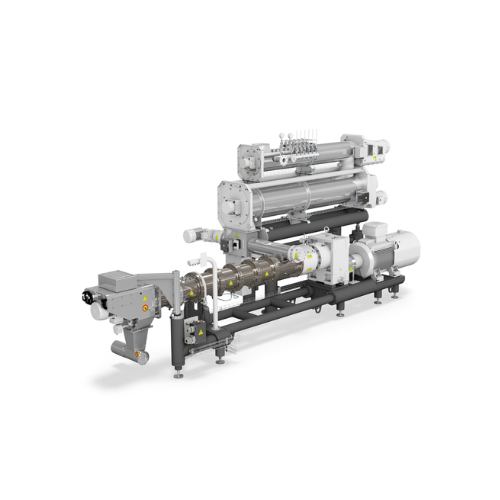
Single-screw extruder for pet food and aqua feed
For producers aiming to diversify their offerings, this single-screw extr...
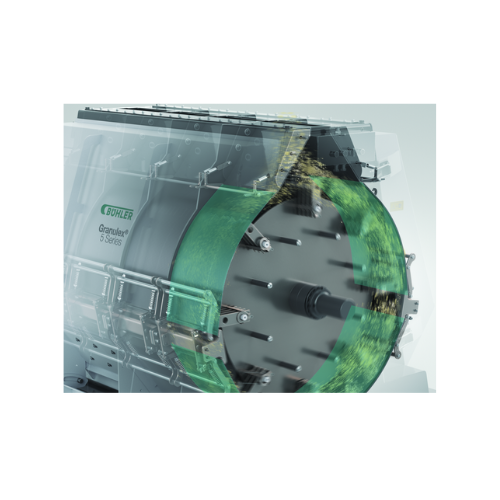
Horizontal hammer mill for grain processing
Optimize your grinding processes with our horizontal hammer mill, designed to ...
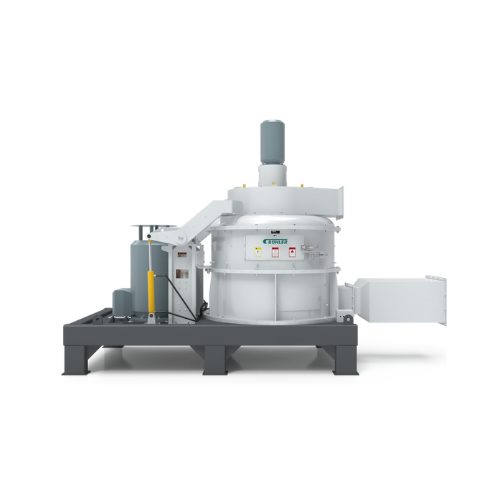
High-efficiency pulverizer for ultra-fine applications
Optimize your production of animal and aqua feed with this high-sp...
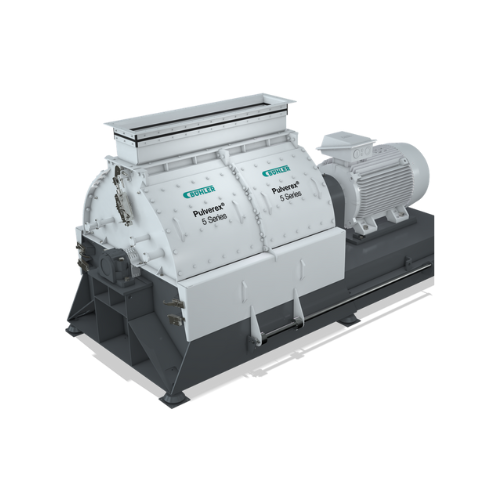
Pulverizer for fine grinding applications
Achieve optimal particle size distribution and enhance throughput with this adva...
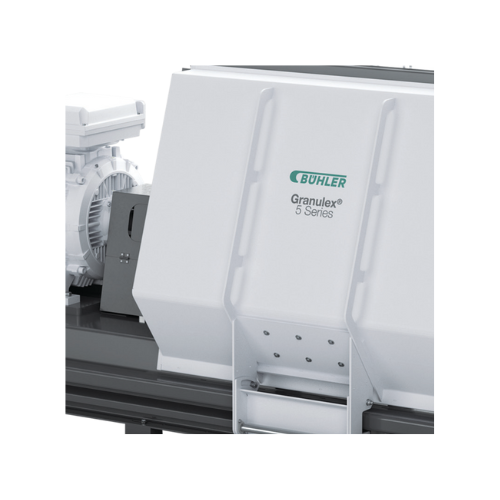
High-throughput hammer mill for animal feed production
Ideal for high-throughput operations, this hammer mill ensures pre...

Ultra-fine pulverizer for aqua feed and pet food
Achieve precise granulation with high efficiency for your feed and food p...
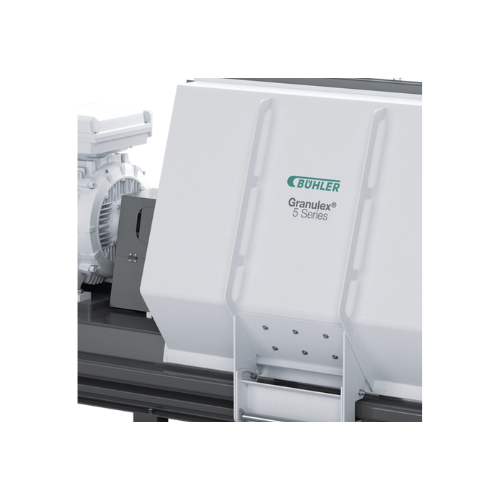
Hammer mill for animal feed grinding
Achieve precise granulation with high throughput and energy efficiency, while reducing...
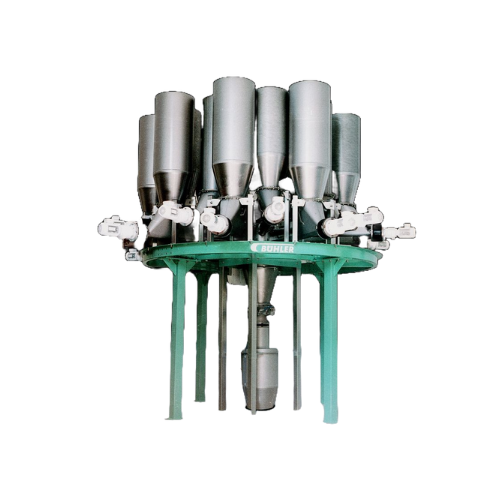
Micro-dosing system for animal feed additives
Achieve precise and consistent feed formulation with high-precision micro-do...
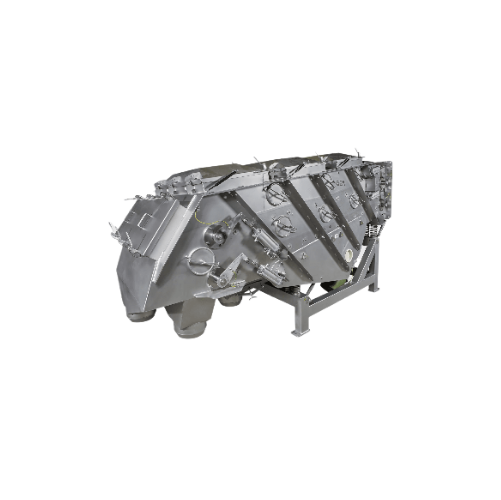
Sifter for pet food, fish feed, and animal feed
Achieve precise particle separation and enhance feed quality with this vib...
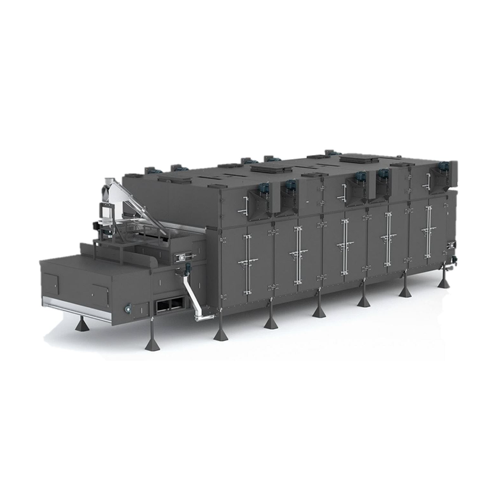
High capacity horizontal dryers and coolers for industrial applications
Achieve consistent moisture levels and uniformi...
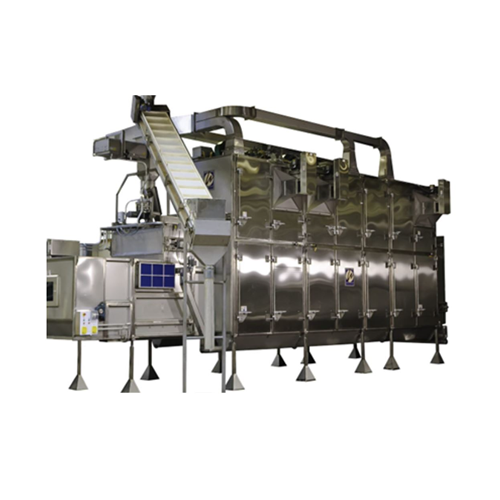
Sanitary dryers for textured vegetable proteins
Optimize drying and sanitation for textured vegetable proteins and pet foo...
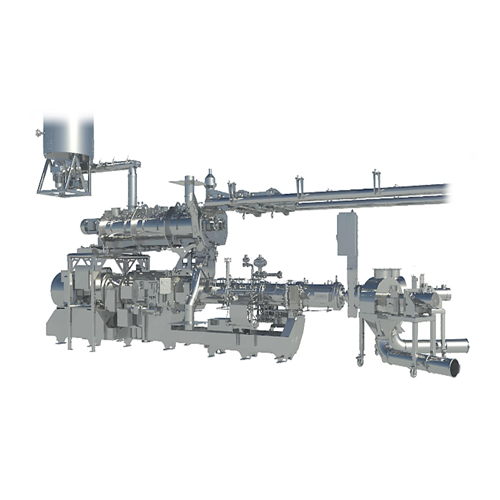
Extruder for aquatic feed production
Efficiently produce a wide range of aquatic and pet feed with precise control over pel...
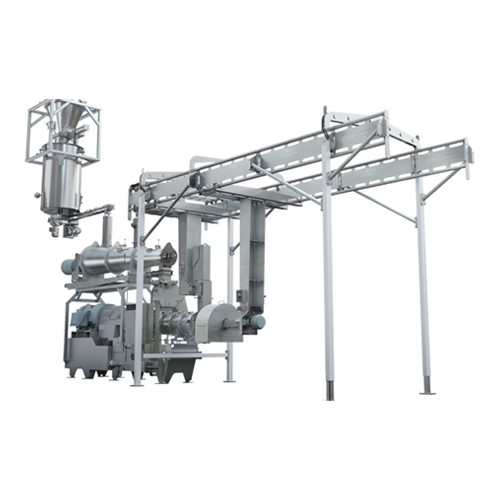
Conical twin screw extruder for pet food and aquatic feed
Precision-engineered for high-speed extrusion and drying proce...
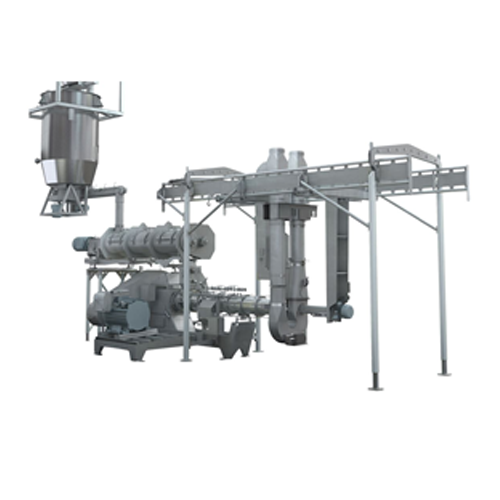
Single screw extruder for pet food and aquatic feed
Maximize production capacity and optimize product quality with advanc...
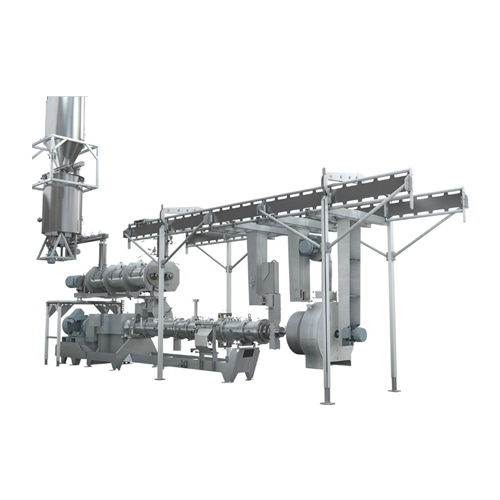
Twin screw extruder for pet and aquatic feed
Achieve exceptional cooking precision with our twin screw extruder, designed ...
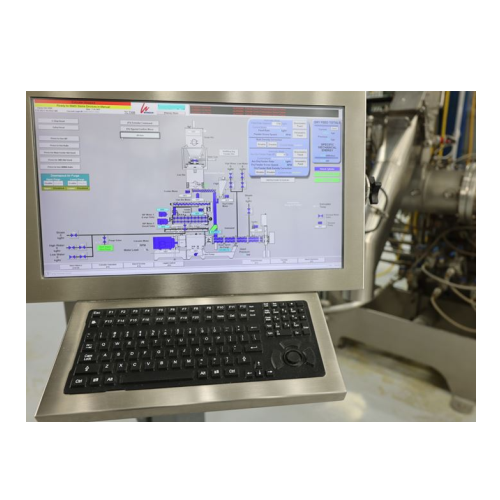
Automated process management system for industrial extrusion
Optimize your production line with precise control and moni...
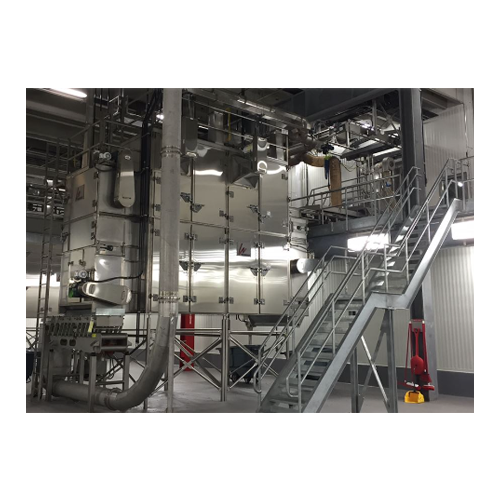
Convection roaster for pet food and delicate food products
Achieve optimal texture and moisture control in delicate food...
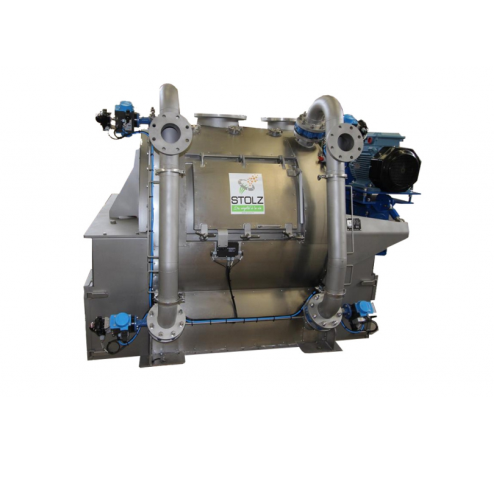
Vacuum coater for petfood and livestock feed
Enhance nutritional value and product quality with precision liquid incorpora...
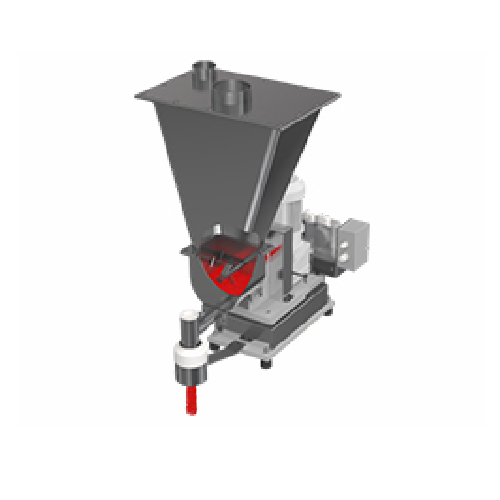
Single screw batch feeder with stirring agitator for powders and pellets
Ensure precise ingredient control and consiste...
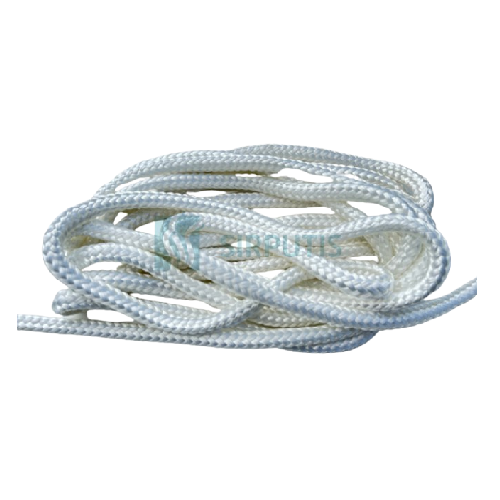
Seaweed substrate ropes for cultivation
Enhance seaweed cultivation efficiency by providing an optimal growth substrate tha...
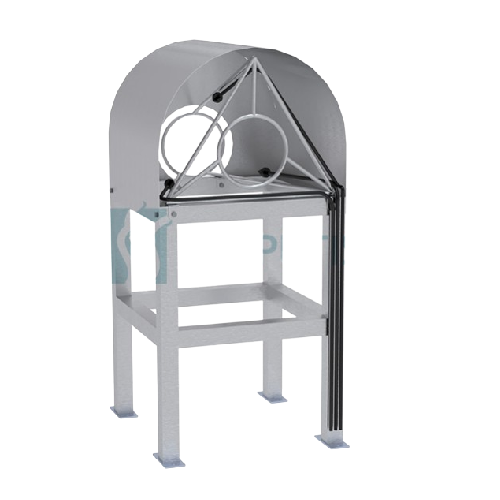
Seaweed substrate rope washer
Optimize your seaweed cultivation workflow with a solution designed to efficiently clean subst...
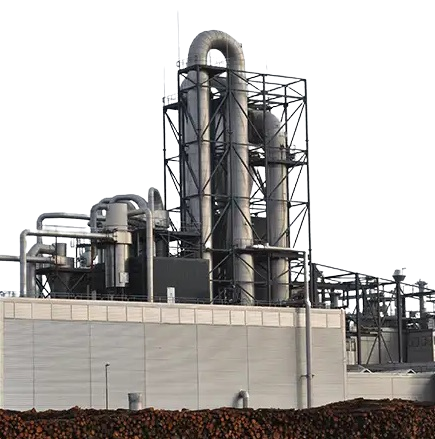
Energy efficient steam dryer for feed products
Traditional drying technologies with low investment cost, such as hot air d...
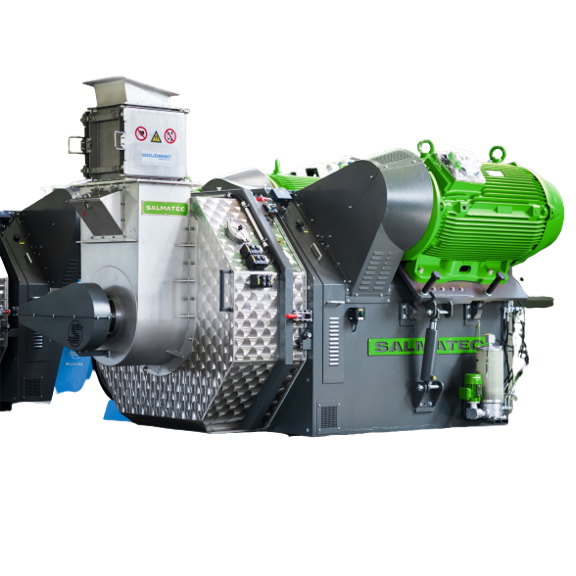
Complete pellet line
Large industries are shifting towards more environment-friendly technology, such as recycling wastes and...
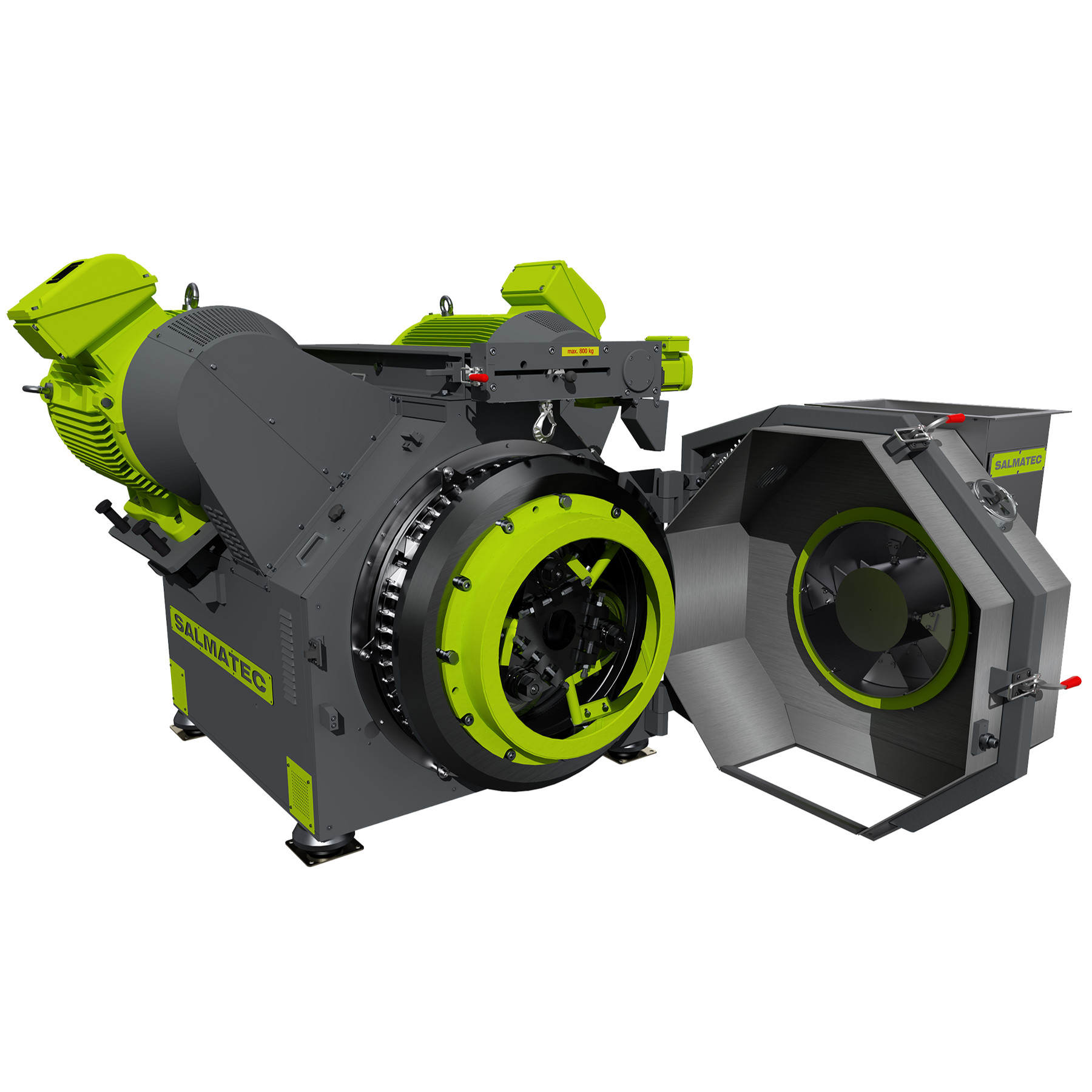
Industrial pellet mill
At the industrial level, the application areas of pellets range widely in fields such as feeds, biomas...
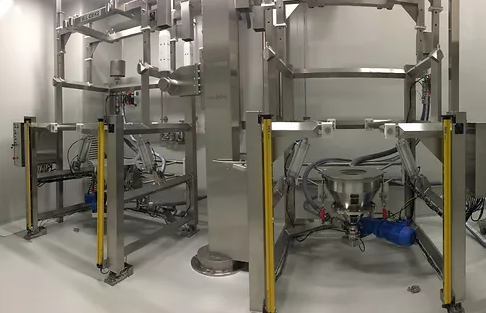
Big bag discharger
Big bags offer suitable material handling for powder products from pharma and food ingredients to bulk and...
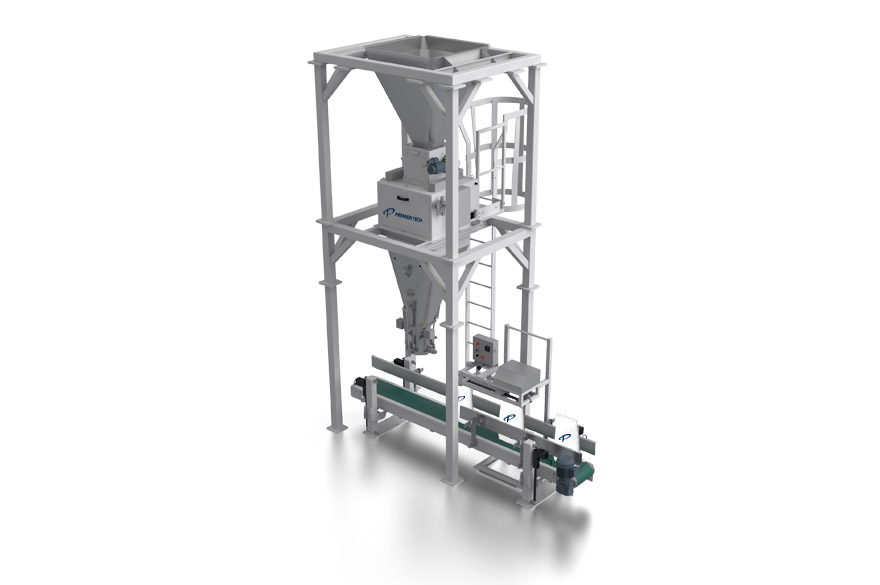
Manual bagger with net weigher
If you are looking for a weigher that is manually controlled for bagging, here it is. It has ...
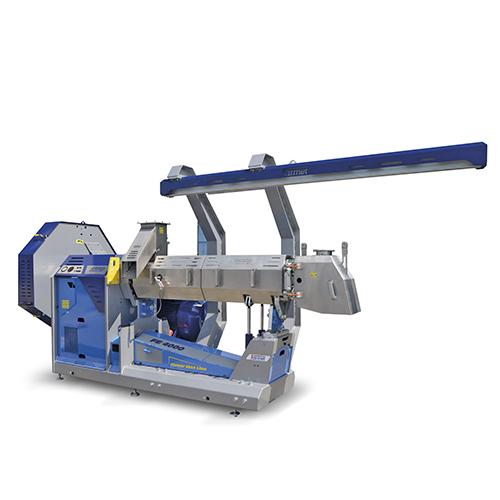
Organic soybean feed extruder
Soybeans are an essential ingredient in the creation of protein-rich animal feed. To achieve h...
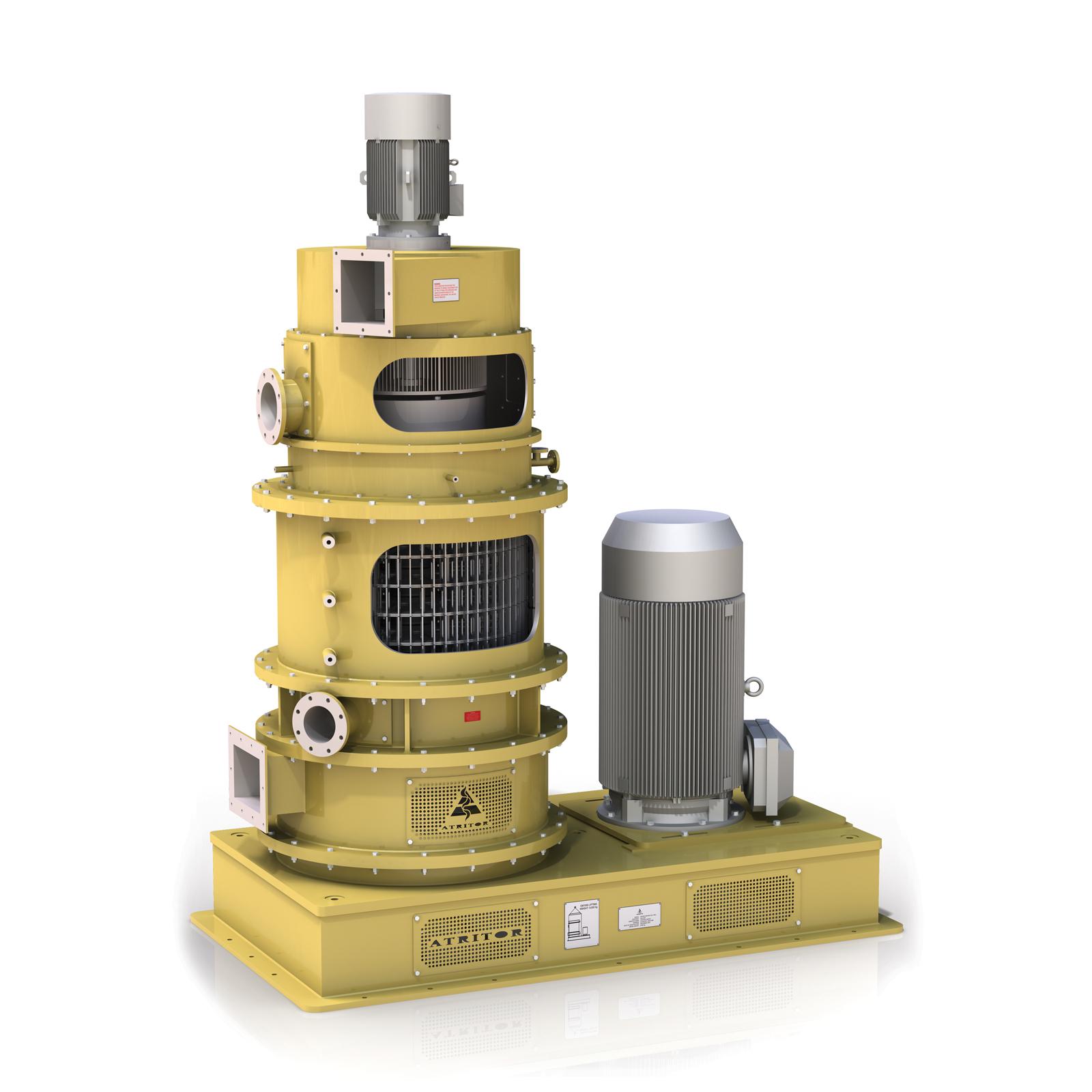
Milling and drying machine for fine powders
When you need to produce ultra-fine powders, the milling and drying process em...
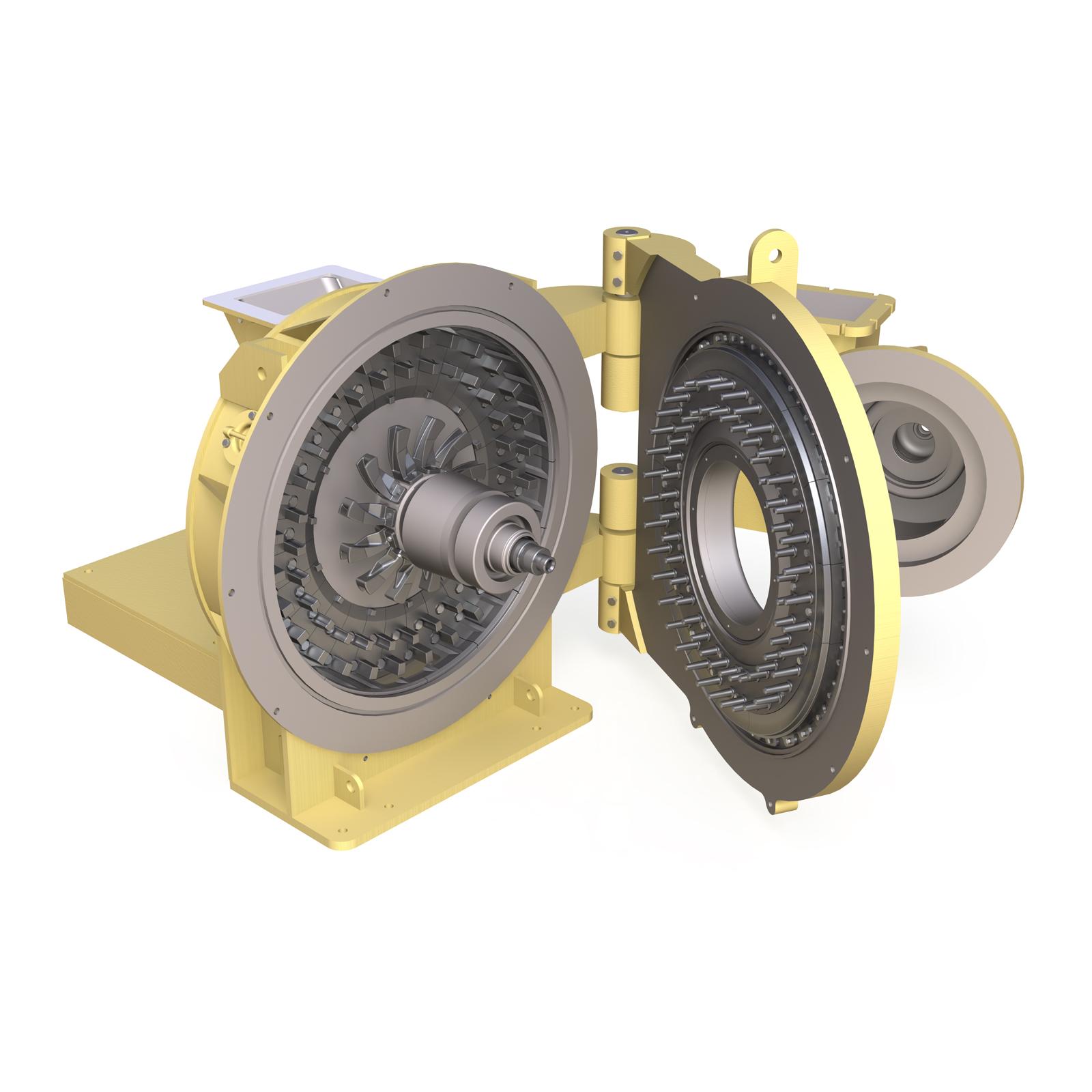
Flash drying grinder for powders
Drying and grinding can be an important feature when trying to process products such as raw...
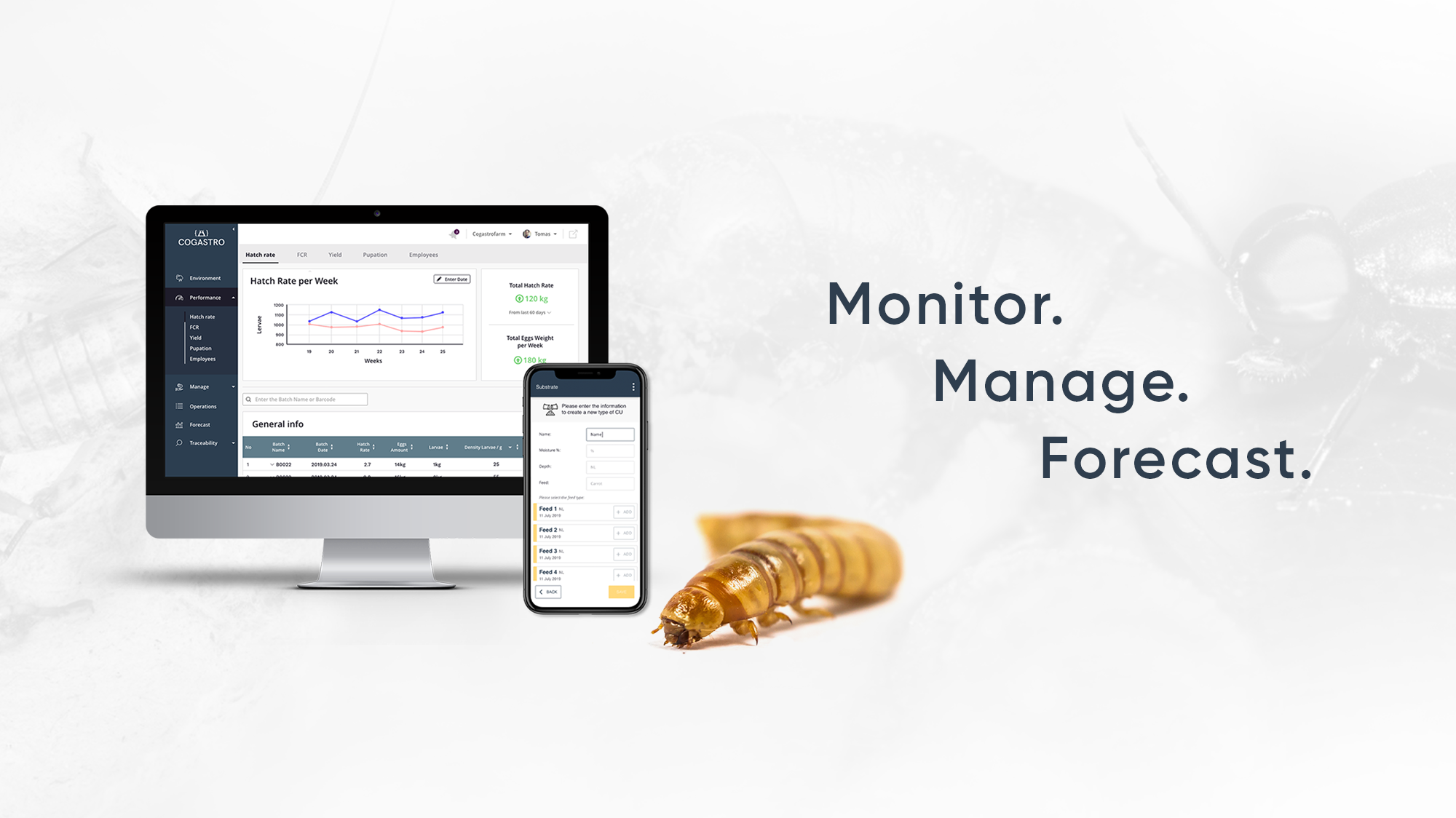
Insect farming software
No two insect farms are the same and so, each facility requires a modern and tailored solution to ope...

Macro ingredient dosing system
Traditional dosing systems do not have a very long operational life and are hard and expensiv...
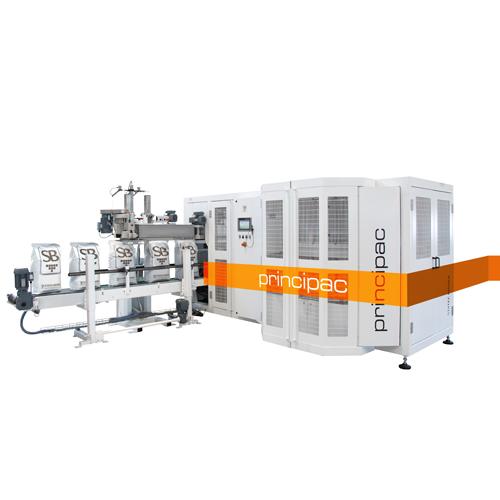
Open mouth bagging machine
If you are a manufacturer of fertilizers, bulk chemicals, sugar, seeds, or any grains it is likel...

Open mouth bag filling machine for powders
The packaging of powdery products such as flour can be challenging as it is cru...
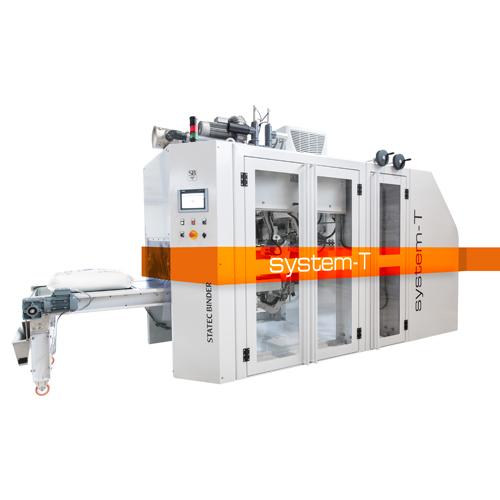
Form fill seal bagging machine
If you are in industries such as petrochemicals, fertilizers, animal feed, food, etc, you mus...
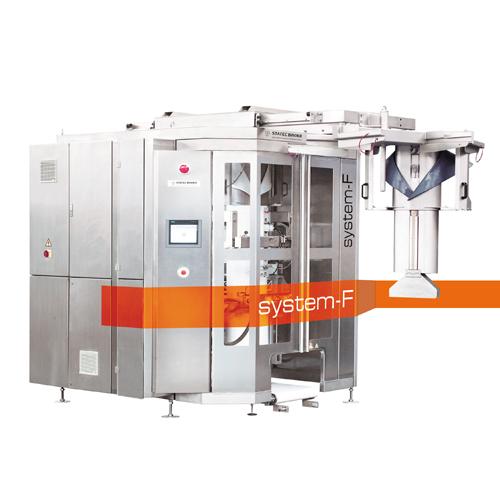
Vertical form fill seal machine
There is an increasing demand for a range of different package sizes of the same product. If...
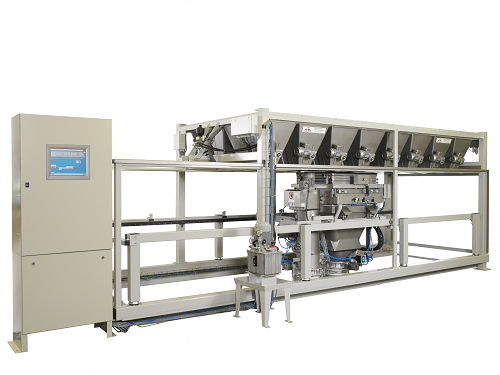
Micro powder dosing system
Micro dosing of powders and small components can be a major obstruction in the production process...
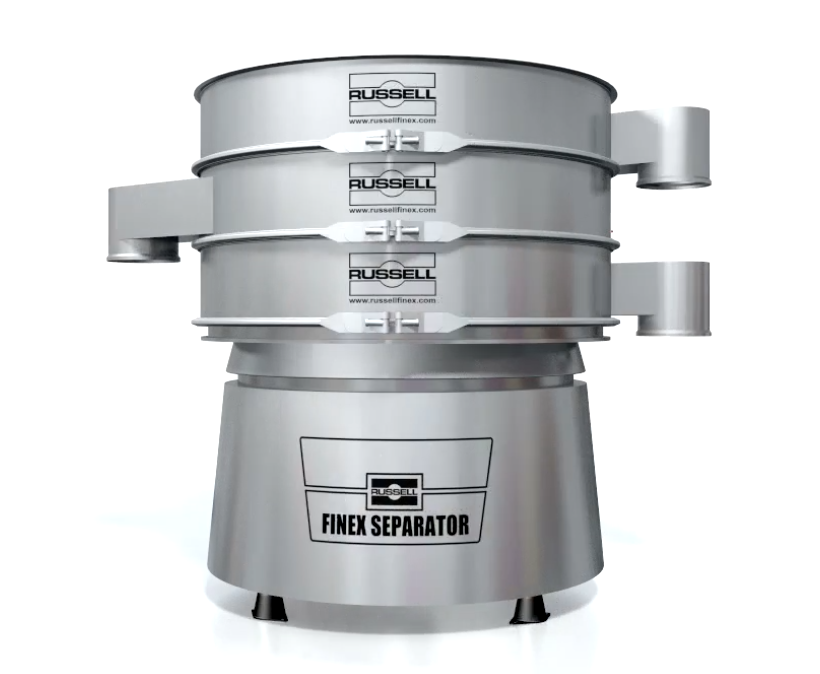
High capacity grading sieve
An industrial vibratory separator machine is multi-purpose, able to carry out a variety of diffe...
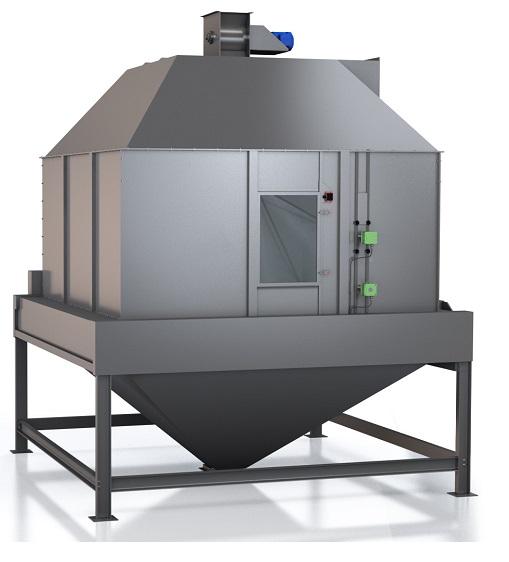
Continuous pellet cooler
Cooling is a very important and critical process for feed hygiene and pellet durability index. Pelle...
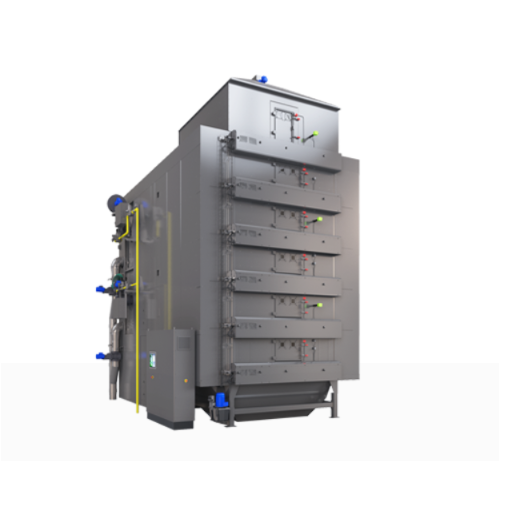
Recirculating batch dryer
Drying can be the most energy and time-consuming process in the food industry. This can have an ef...
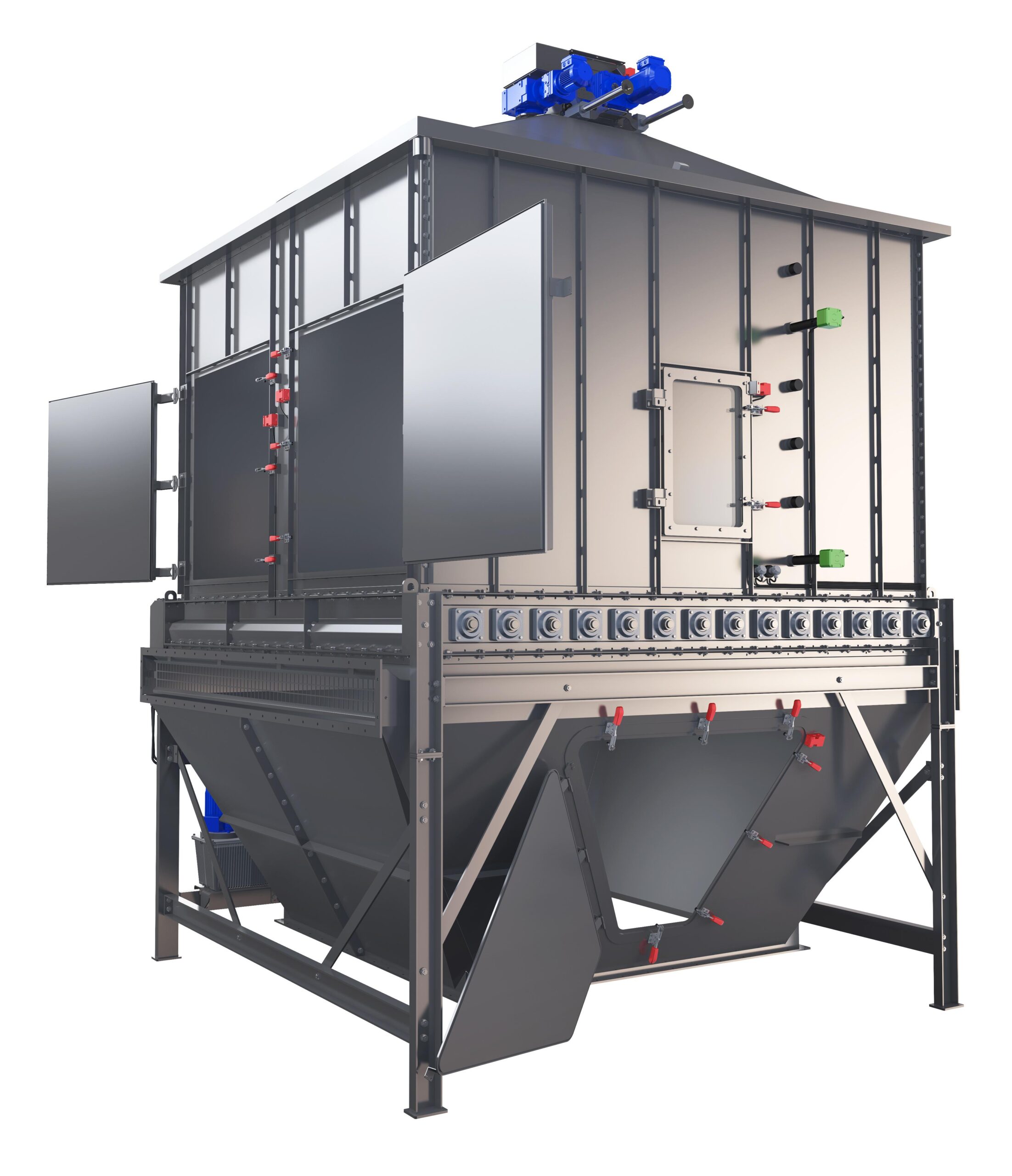
Counterflow pellet cooler
Food and feed industries require the highest standards of hygiene and sanitation. This entails fre...
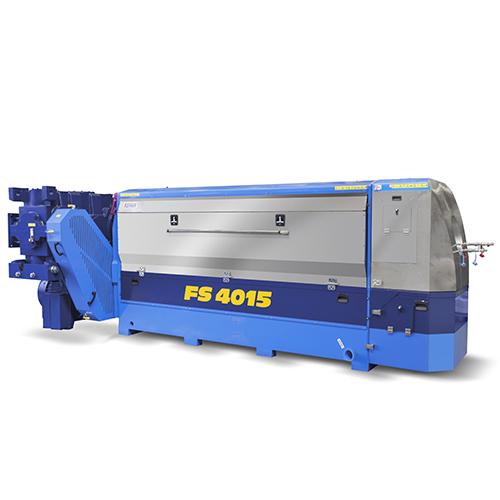
Organic soybean oil press
In traditional soybean oil production, chemical solvents such as hexane are used to facilitate liq...
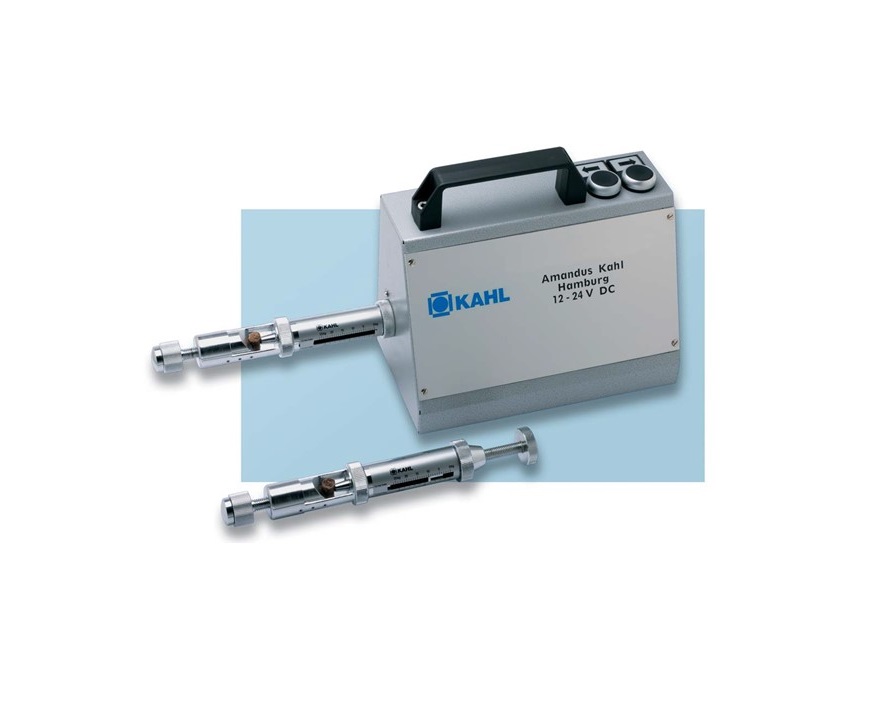
Pellet hardness tester
Control the quality of your pelletizing processes using a pellet hardness tester. Pellet hardness is o...
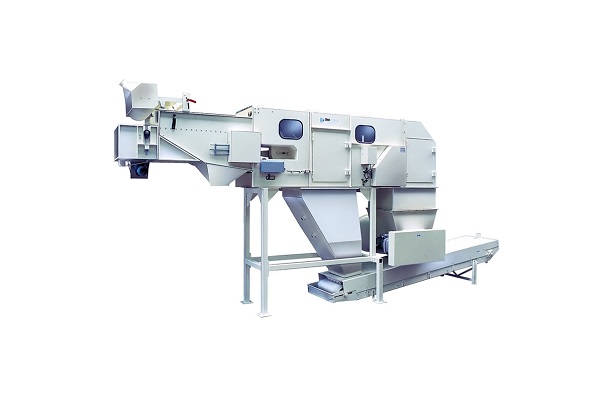
Automatic bag slitter
Unacceptably high dust levels can be generated whilst manual emptying and handling of bags, also produc...
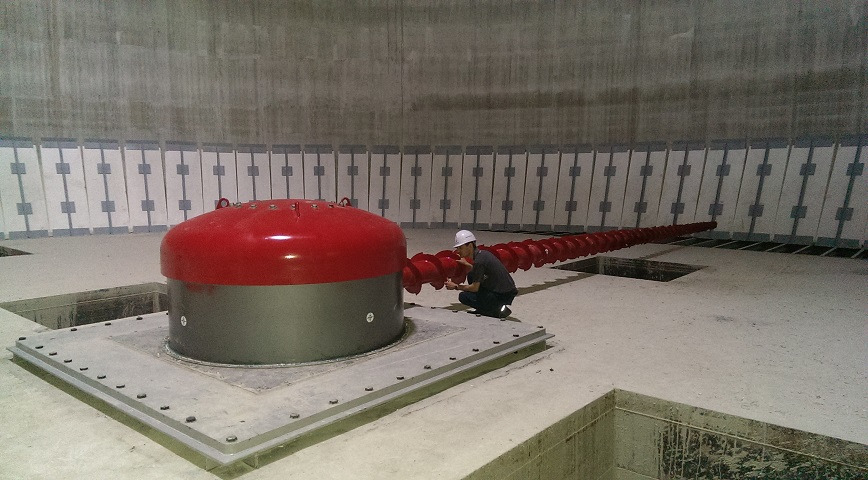
Silo extraction system
Materials without natural flowing properties are difficult to unload, even with the assistance of grav...
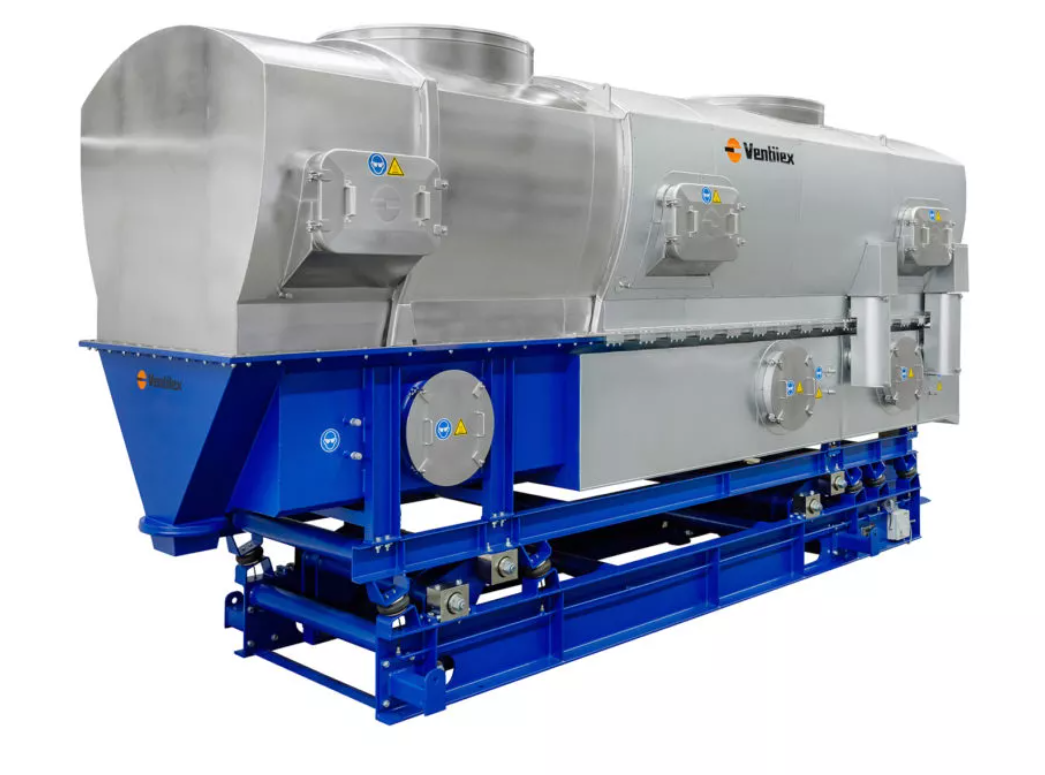
Continuous fluid bed dryer
In a Fluid Bed, a product or solid is made fluid by an upward moving flow of gas. The mechanical ...
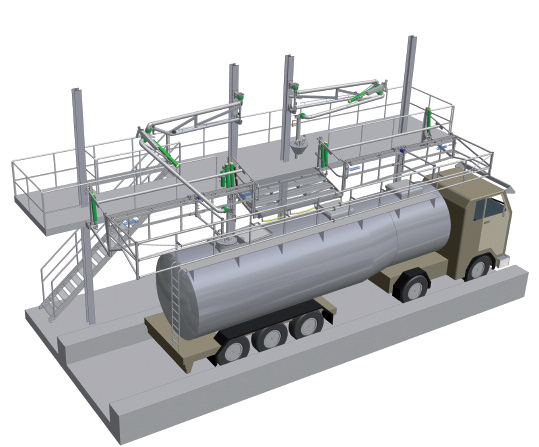
Folding stairs and safety cages
To ensure the safety of operator while working between a loading platform and road or rail t...
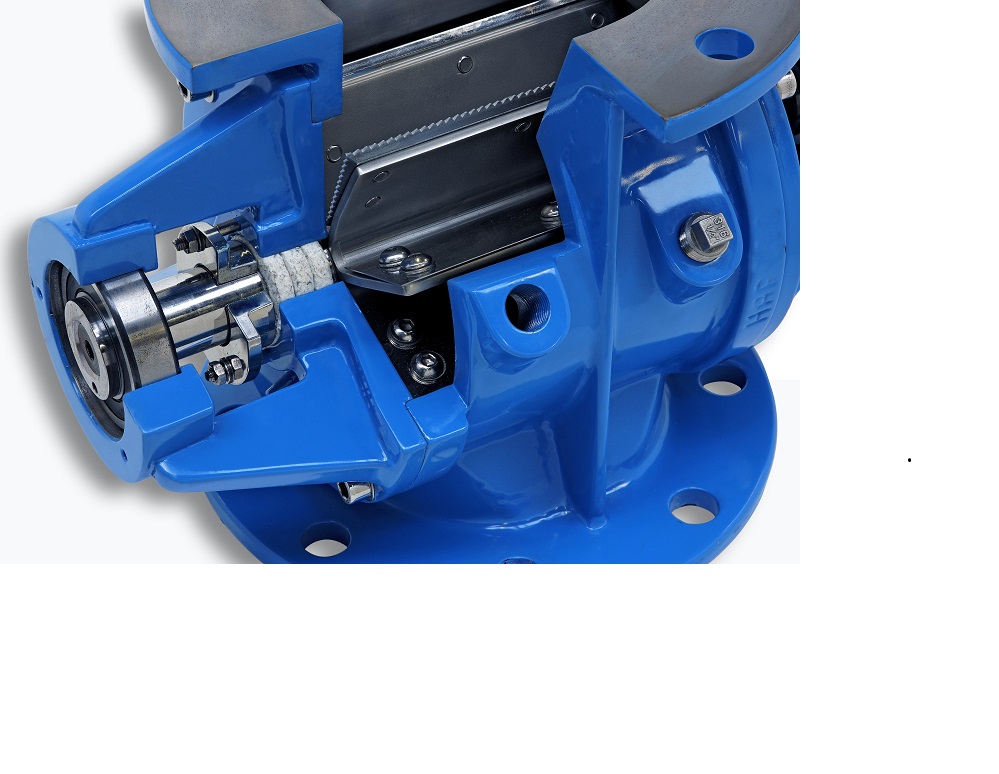
Heavy duty rotary valve
Handling powdered and granulated materials in pneumatic conveying systems requires consistent, safe v...
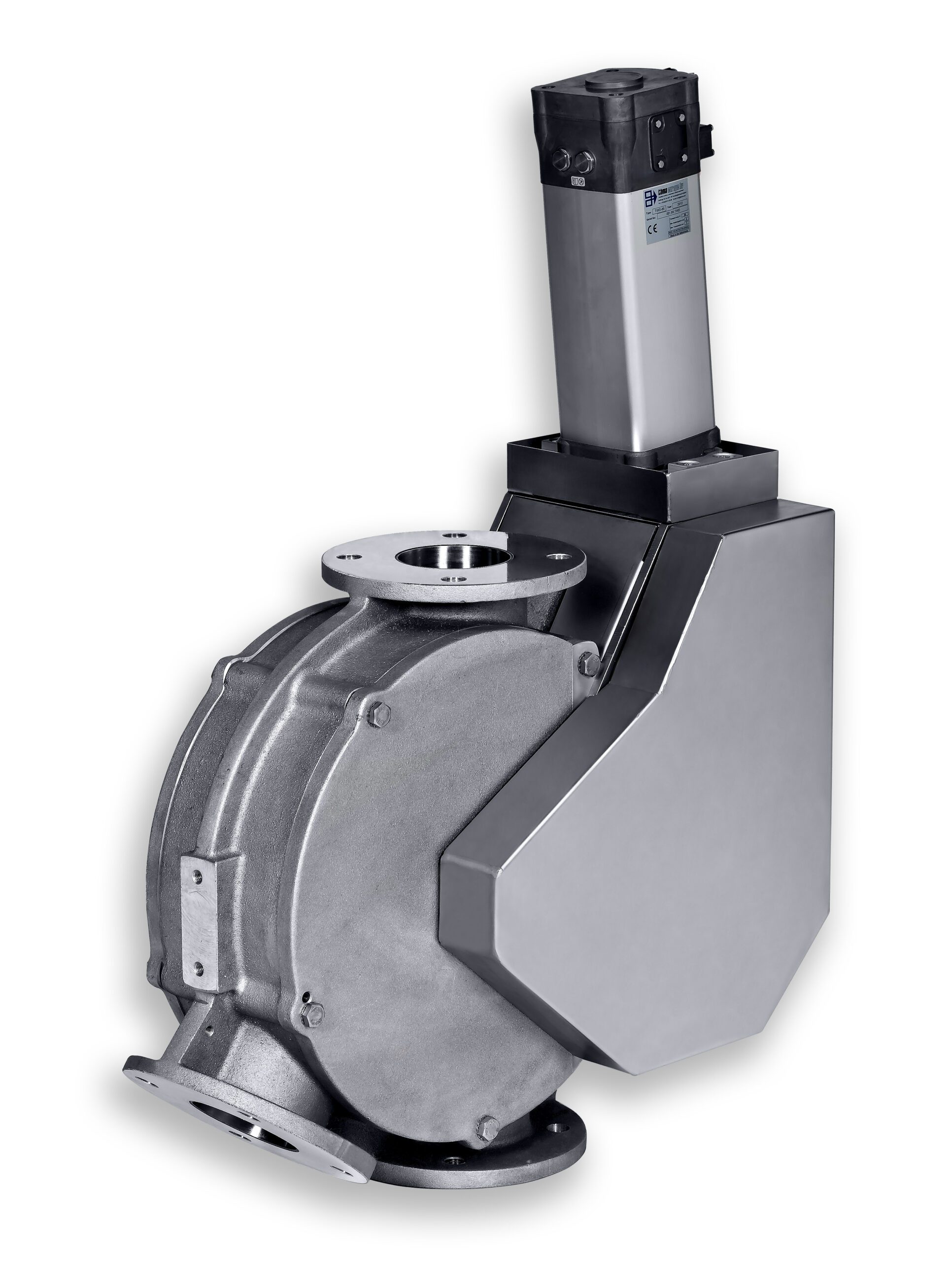
Dual channel plug diverter valve
Short switching times are often required when diverting or combining powder or granular sol...
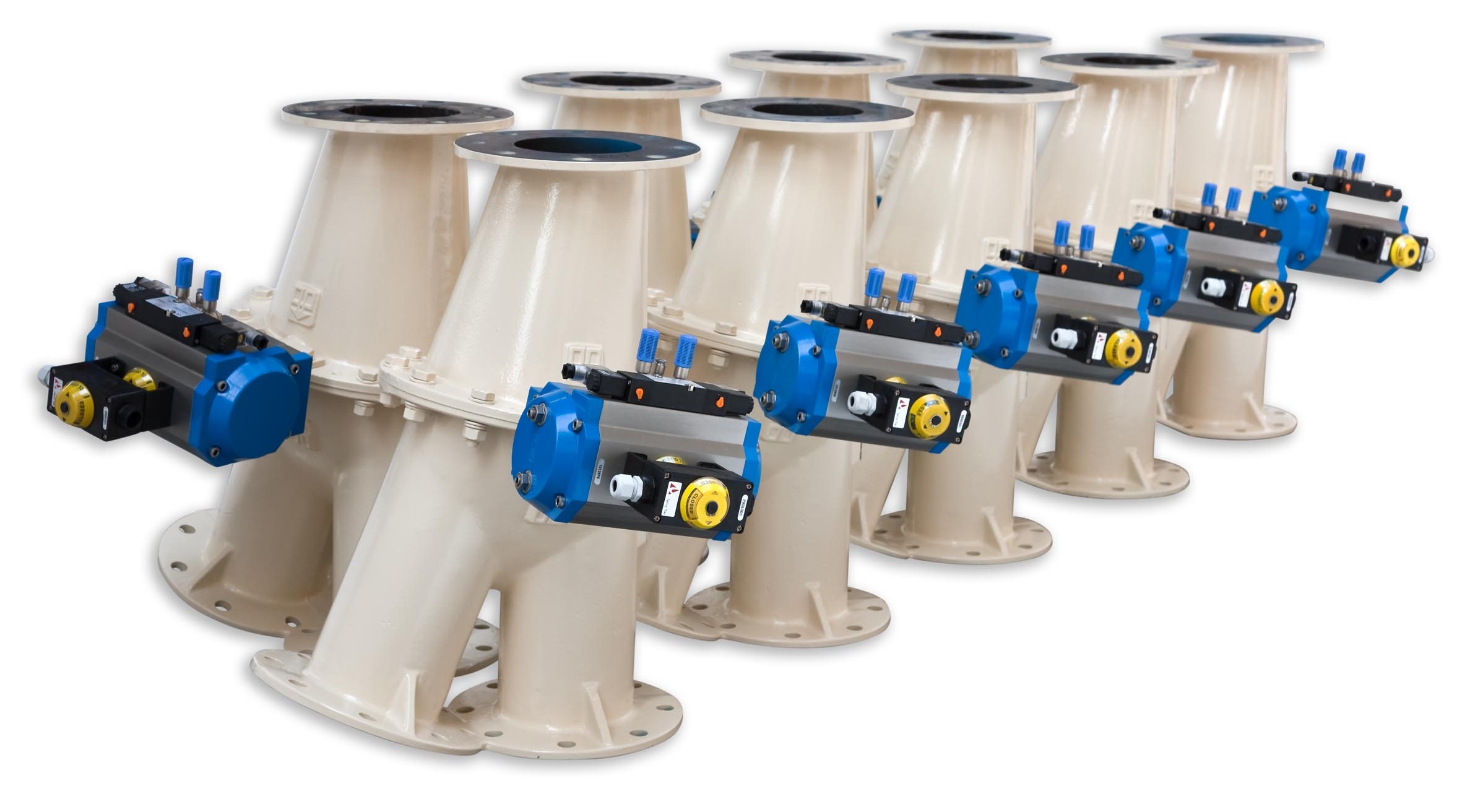
Two-way flap type diverter valve
Routing powder, pellets or granules from a product source to two receiving points must be d...
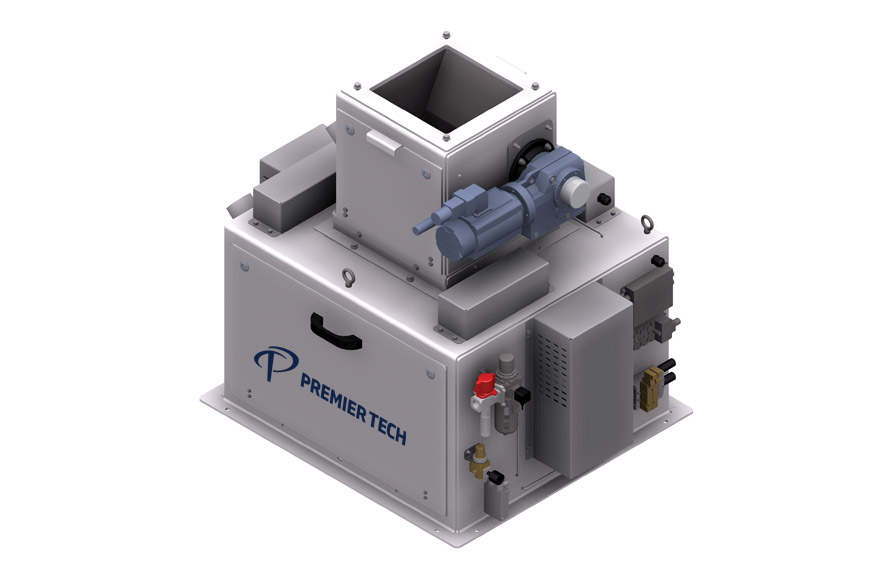
Electronic net weigher for high-capacity baggers
Electronic net weigher raises the industry’s standards to a higher level ...
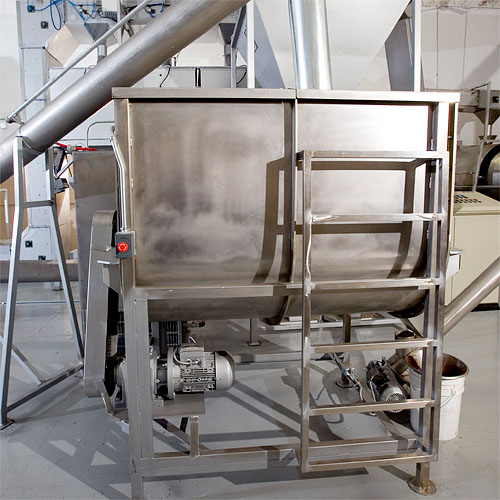
Basic mixer for granular foods
Straightforward blending solution for mixtures of beans, nuts, berries & powdered foods, ...
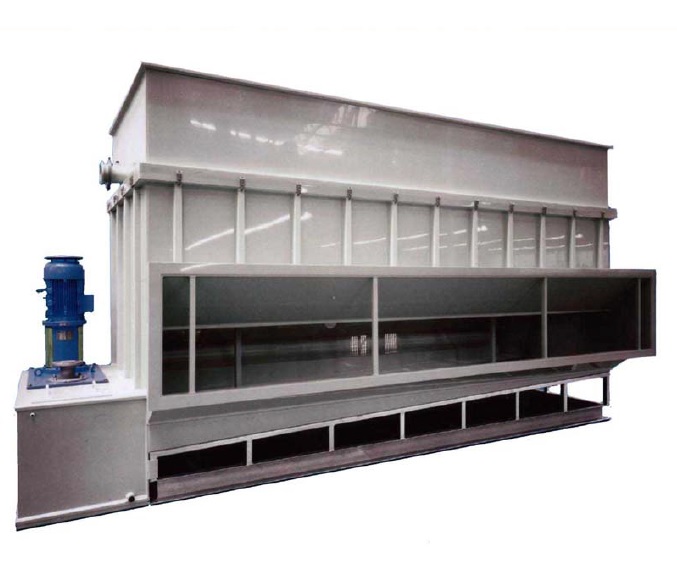
Air dehumidifier for bulk products
When your product or process is sensitive to humidity, using an air dehumidifier may res...

Manual bagger with gross weigher
This is a manual bagging set with an electronic gross weighing system to meet international...
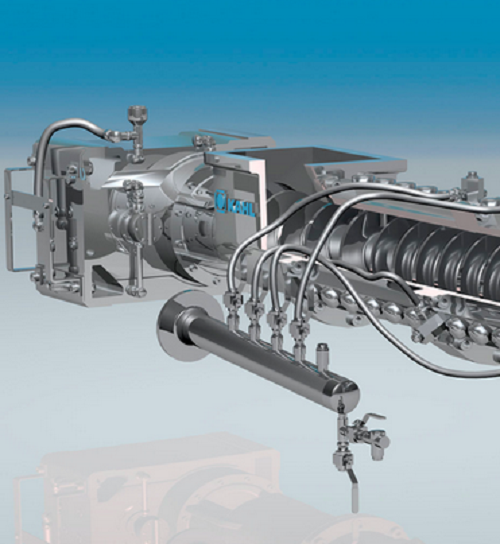
Extruder with annular gap expander
Products can be extruded with various shapes and characteristics by controlling the nozz...
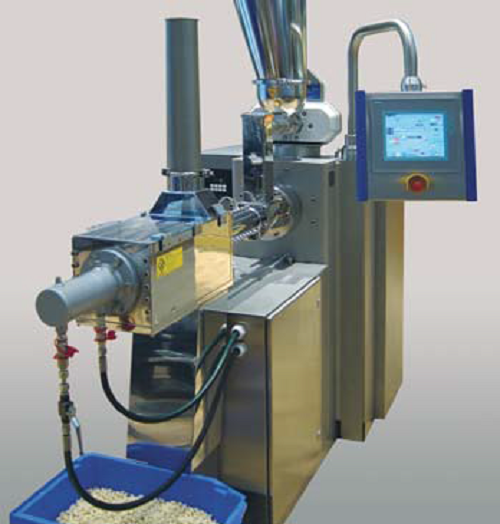
Laboratory extruder
Products can be extruded with a variety of shapes and characteristics by controlling the nozzle geometry ...
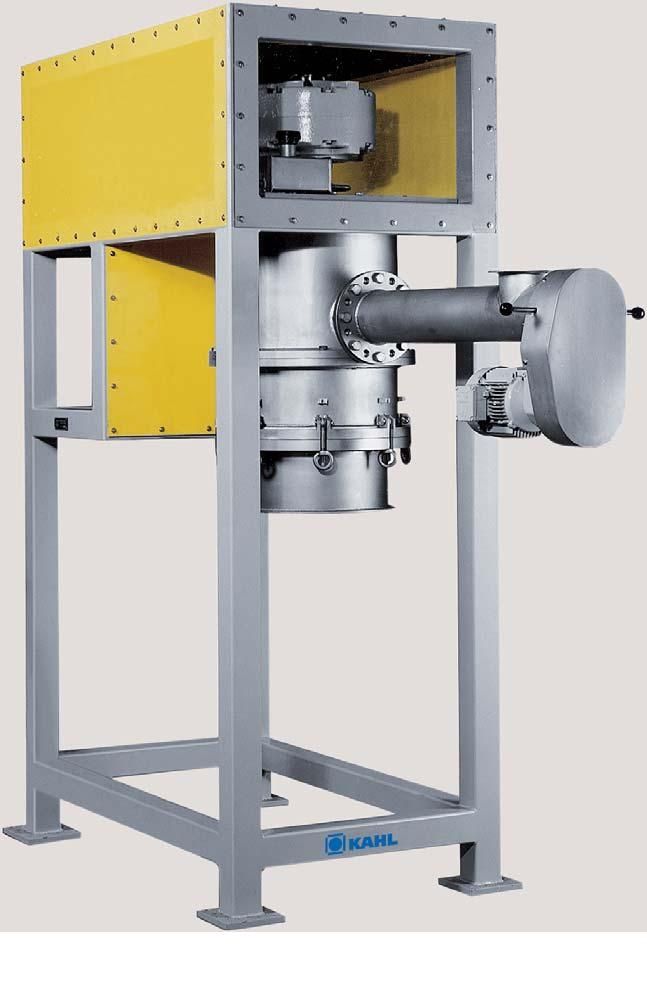
Pelleting press with overhead drive
Production of certain pelletized products requires working with output products of a pa...
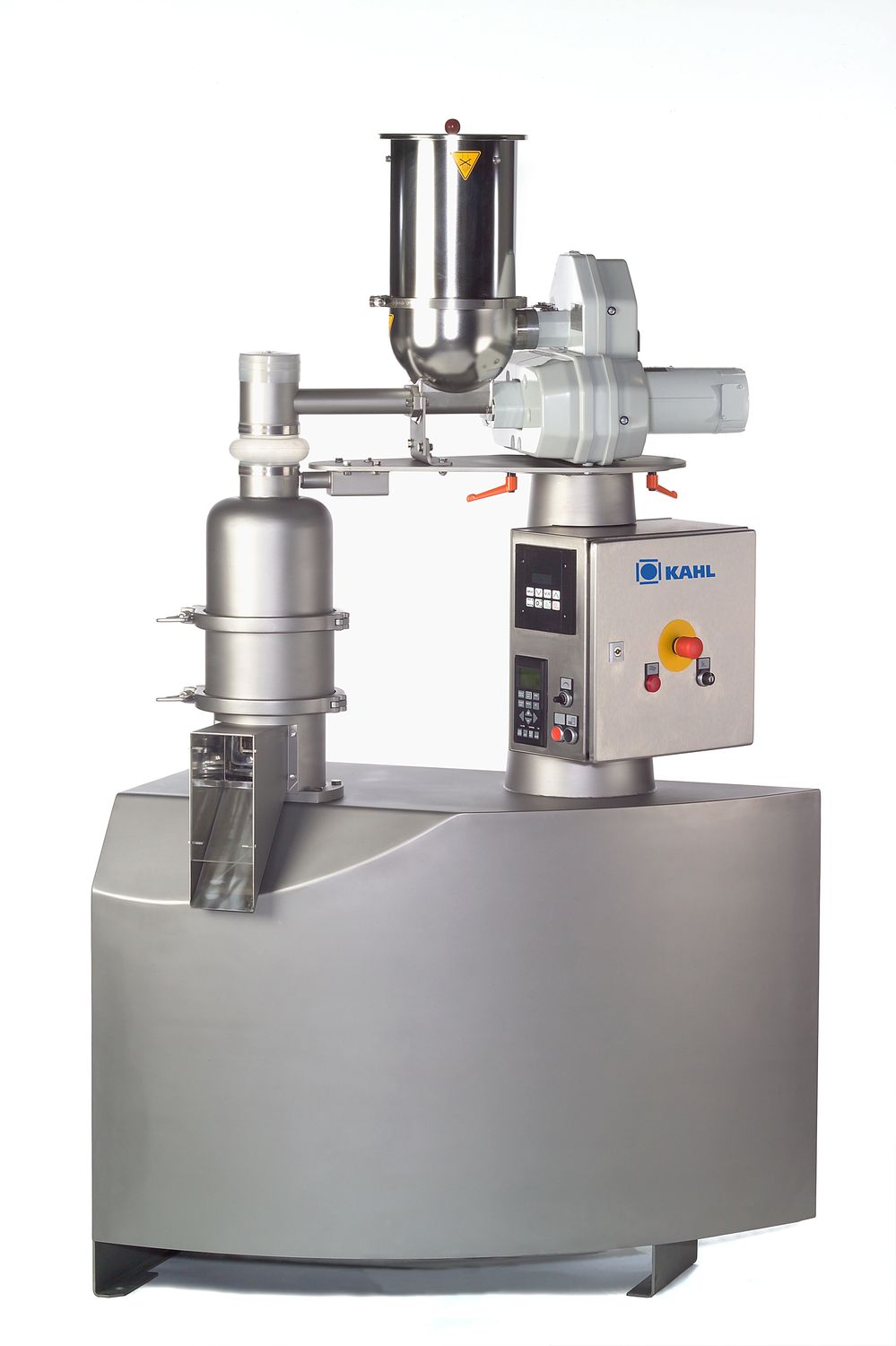
Hygienic pelleting press
The production of pelletized or granularized food products requires hygienic presses designed for hi...
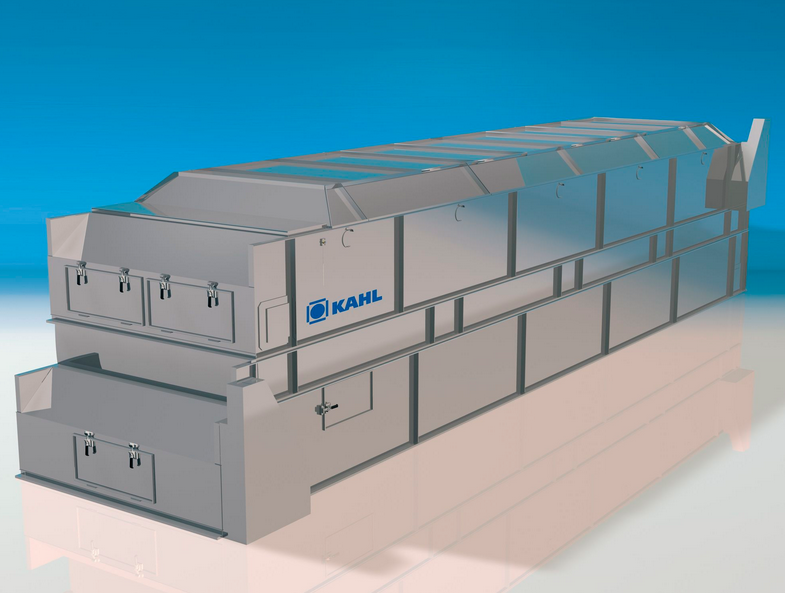
Belt dryer/cooler for pellets and granules
Many industries that process materials in pellet, powder, or crumble form need ...
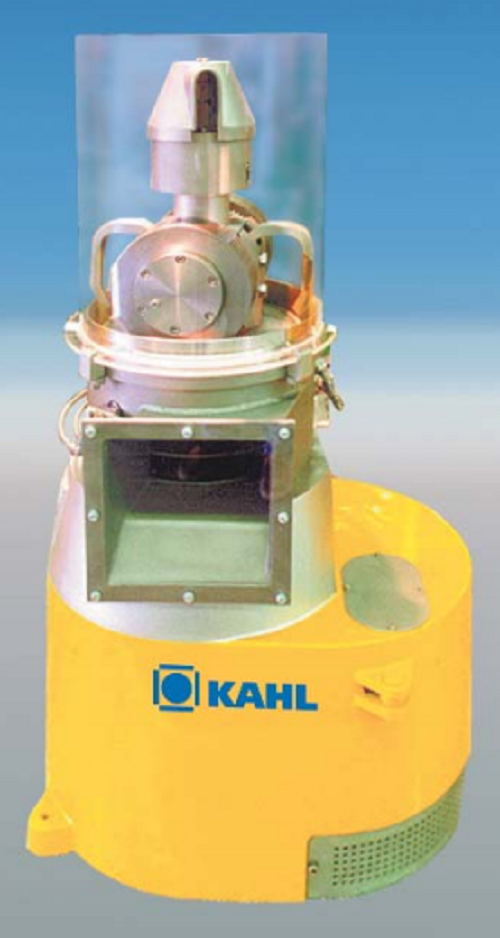
Small scale pelleting press
Many industries require reliable pelletizing equipment with smaller scale production capacities....