Industrial Milling Equipment
Find innovative milling equipment and connect directly with world-leading technology suppliers
Milling machines are used to reduce the size of material by cutting, crushing, or grinding it. The choice of industrial milling equipment depends on the industry and the materials to work with. Besides, there is a significant difference between those aimed to remove layers from metal or other materials workpieces and those designed to reduce particle size for materials that come in bulk.
Innovative milling solutions
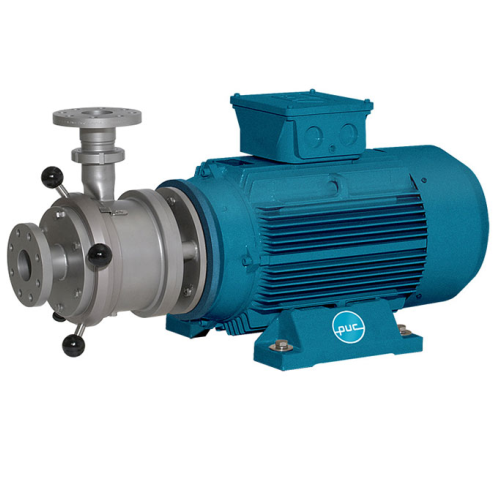
Colloid mill for emulsifying and wet milling applications
Achieve precise mixing and grinding with our colloid mill, des...
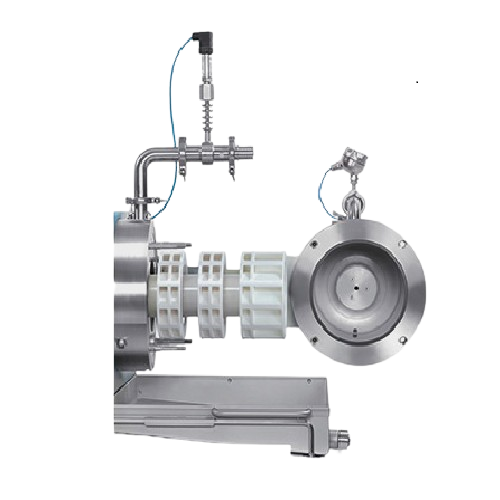
Bead mill for nano-preparation grinding
Achieve precise nano-processing and efficient wet grinding for pharmaceuticals and ...
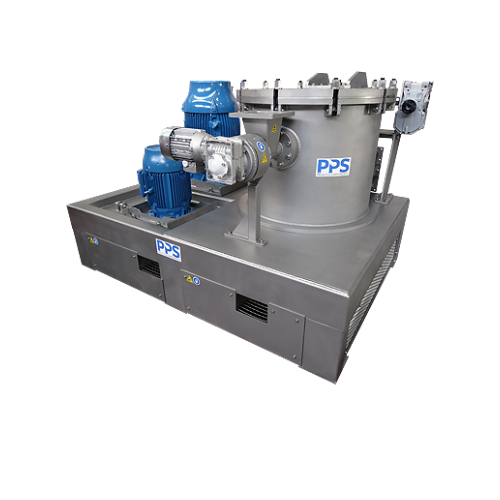
Air classifier mill for ultra-fine powder grinding
Optimize your milling operations with precision particle size control ...
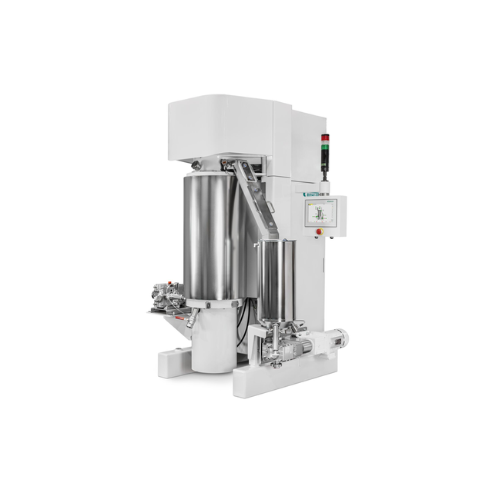
Ball mill for chocolate, cocoa, and nut products
Optimize your grinding processes and achieve perfect product consistency ...
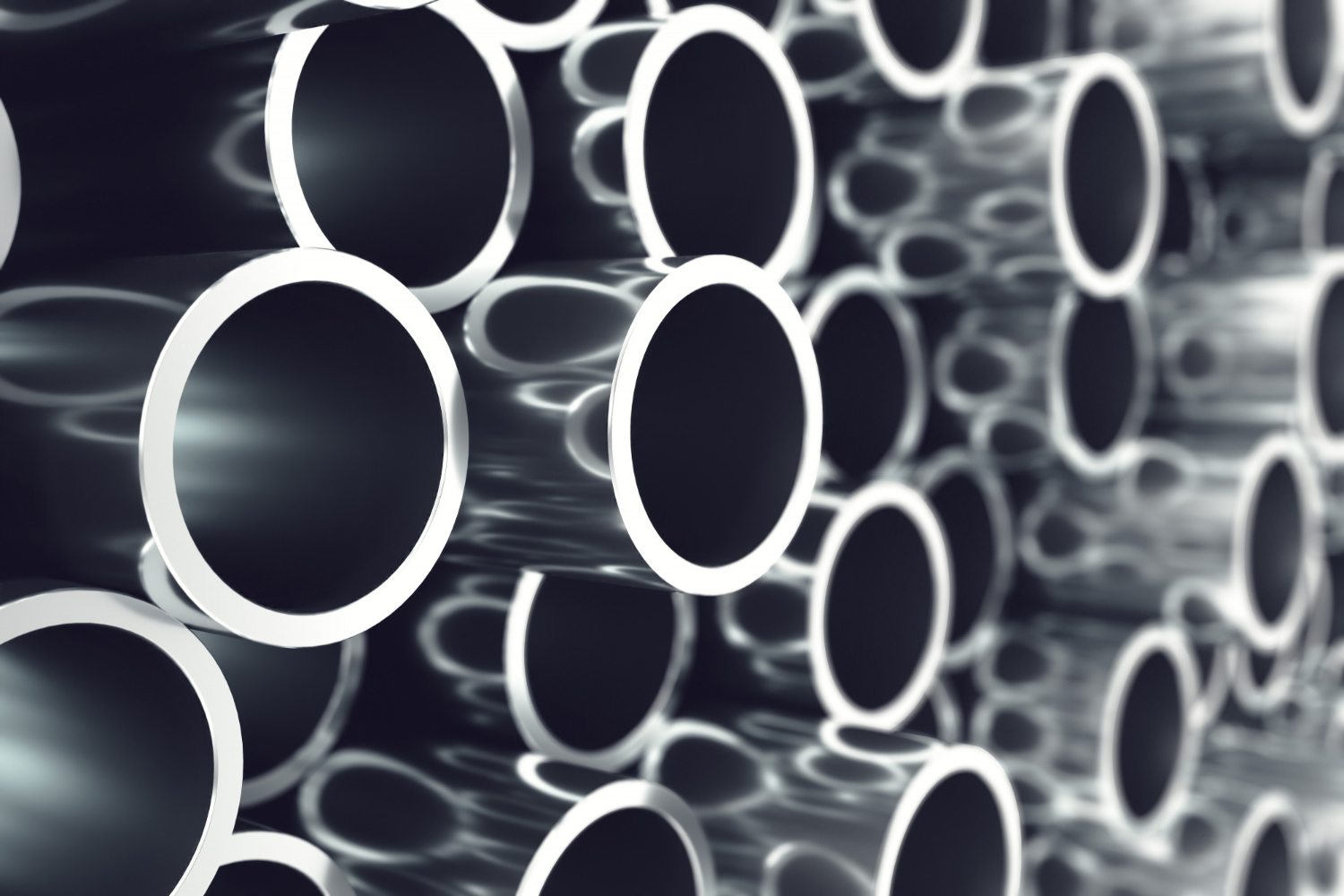
Two main types of milling equipment for the metal manufacturing industry
In metal works the mill equipment removes material from a metal piece by cutting or shaping it with rotating multi-point cutters. The orientation of the cutters is what makes these machines different. They can move in a horizontal or vertical axe, giving the name to horizontal milling and vertical milling machines, which are the main configuration of these machines. They are suited to precision work and can be manual, semiautomatic, or fully automatic by computerized numerical control (CNC).
With the milling equipment, you can make plane, two-dimensional and three-dimensional surfaces, for many industrial parts.
High-precision machines need cooling while working
These milling machines are very precise in their cuts and shapes, in addition, they give great surface finish thanks to the speed and other variables. The high speed of the cutting tool and the friction between the tool and the workpiece generate heat, being necessary to use a coolant throughout the entire process.
Nowadays the machining centers are full of CNC milling equipment that are more efficient, highly accurate, and safe to use. They are also great for special designs, dimensions, and materials, for micro machining as well as for large and heavy-duty operations. But you can still find manual and semiautomatic technology for low-complexity shapes.
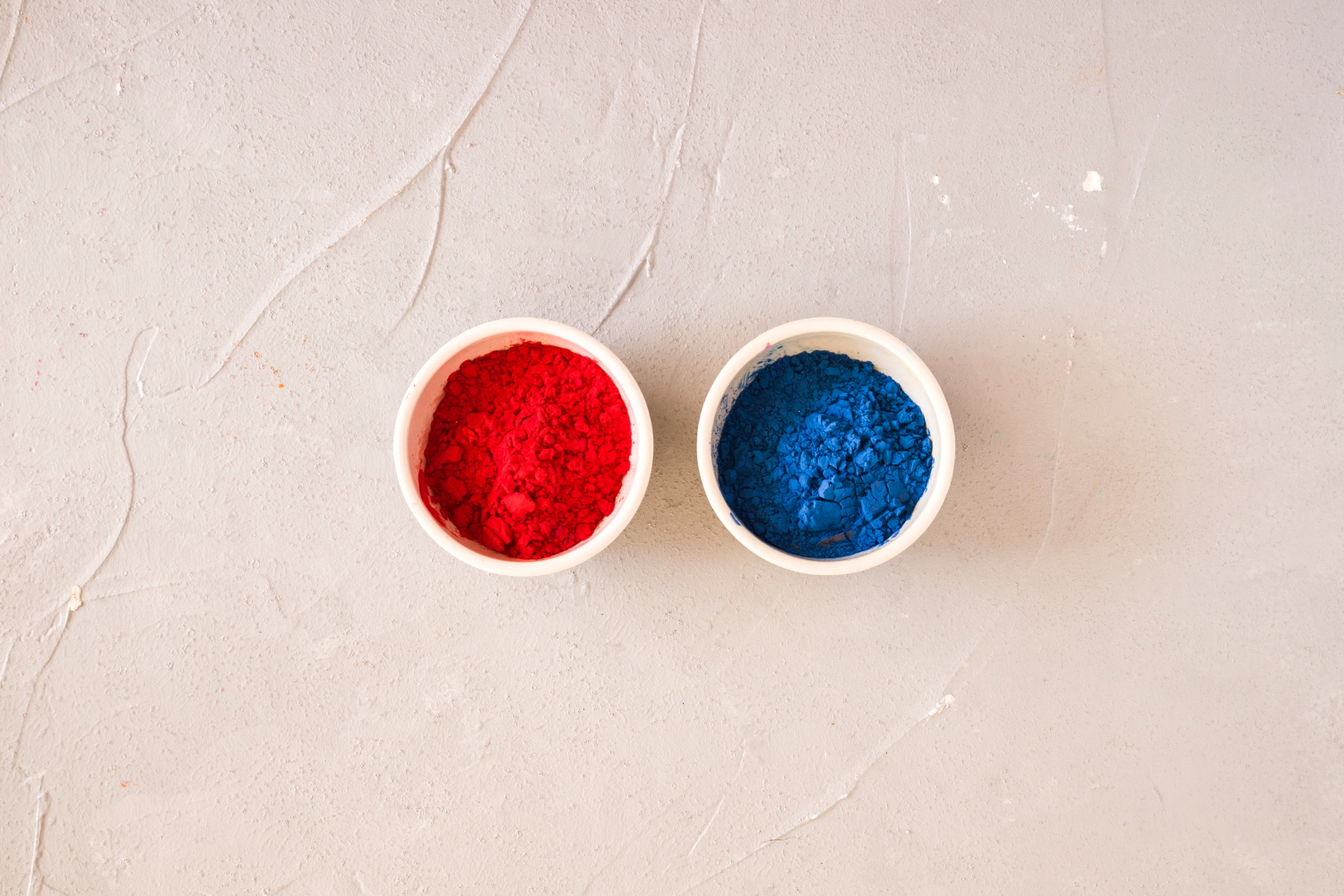
Milling equipment for crushing and grinding bulk material
The milling equipment used for bulk material is designed to crush or grind the different materials to reduce their size in smaller particles, even into powder. You can find milling machines for grains, minerals, wood, composites, and many other materials. Your selection of milling equipment depends on the type of materials you are going to process, and the desired particle size.
Industries such as feed, food, pharmaceuticals, and mining, use mainly hammer mills, roller mills, ball mills, agitated media mills, jet mills, and classifier mills in their processes.
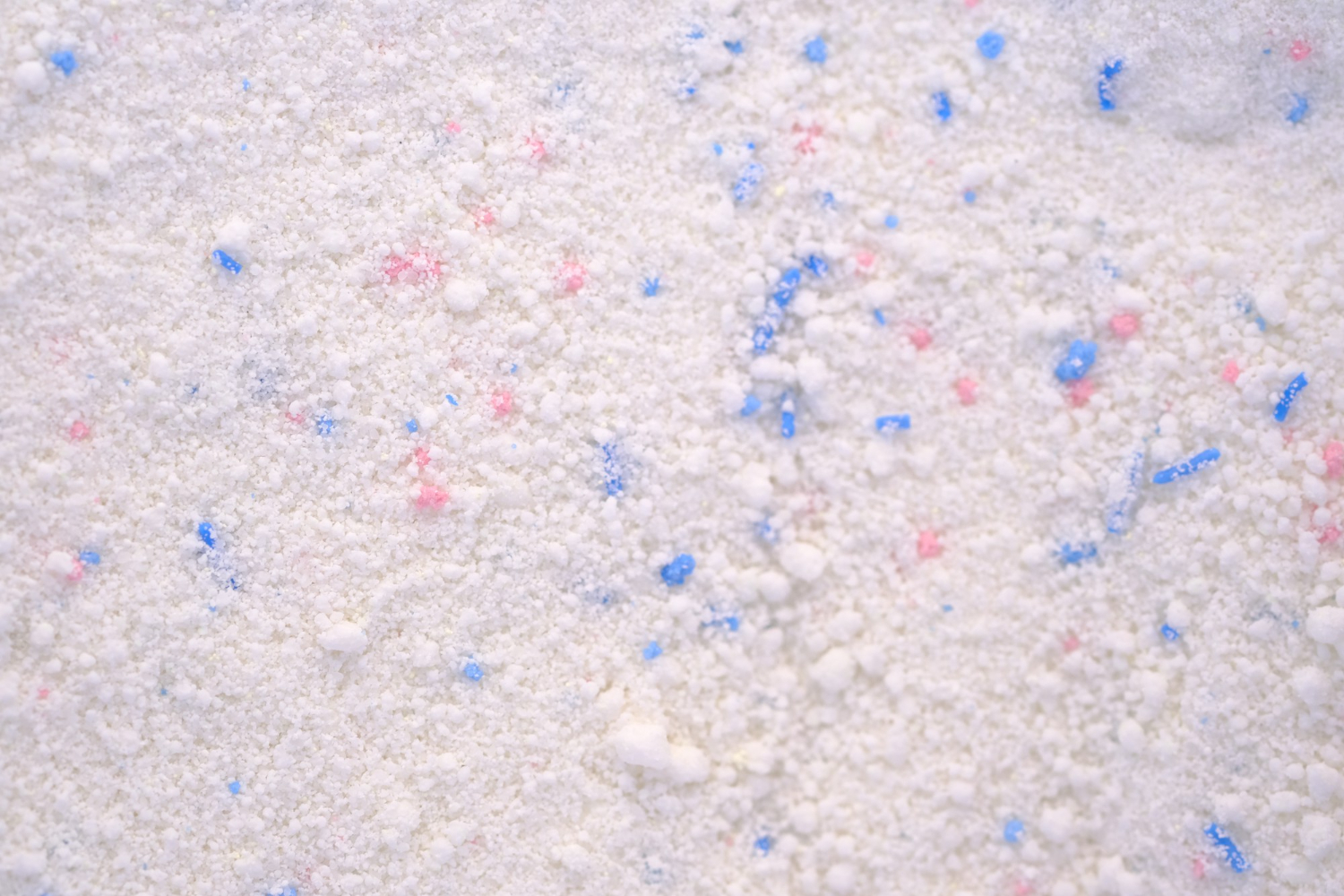
Temperature and speed are important variables to control in the hammer mill
A hammer mill has a horizontal rotor with a shaft that contains hammers, also called blades or knives. These are the elements that crush or grind the bulk material, that rotates with a speed that is settled according to the material that is being processed. This machine also contains a screen that filters the crushed material and ensures that only the particles with the desired size pass through.
The hammer mill needs to have sensors of speed and temperature to keep in good conditions the machine as well as the raw material, moreover to control the variables of the process. Choose a hammer mill with easy access to the chamber to do maintenance and reparations, furthermore replace the hammers frequently to guarantee their sharpness and good state.
This mill equipment is an important part of the process line of feed, food, chemicals, and cosmetics.
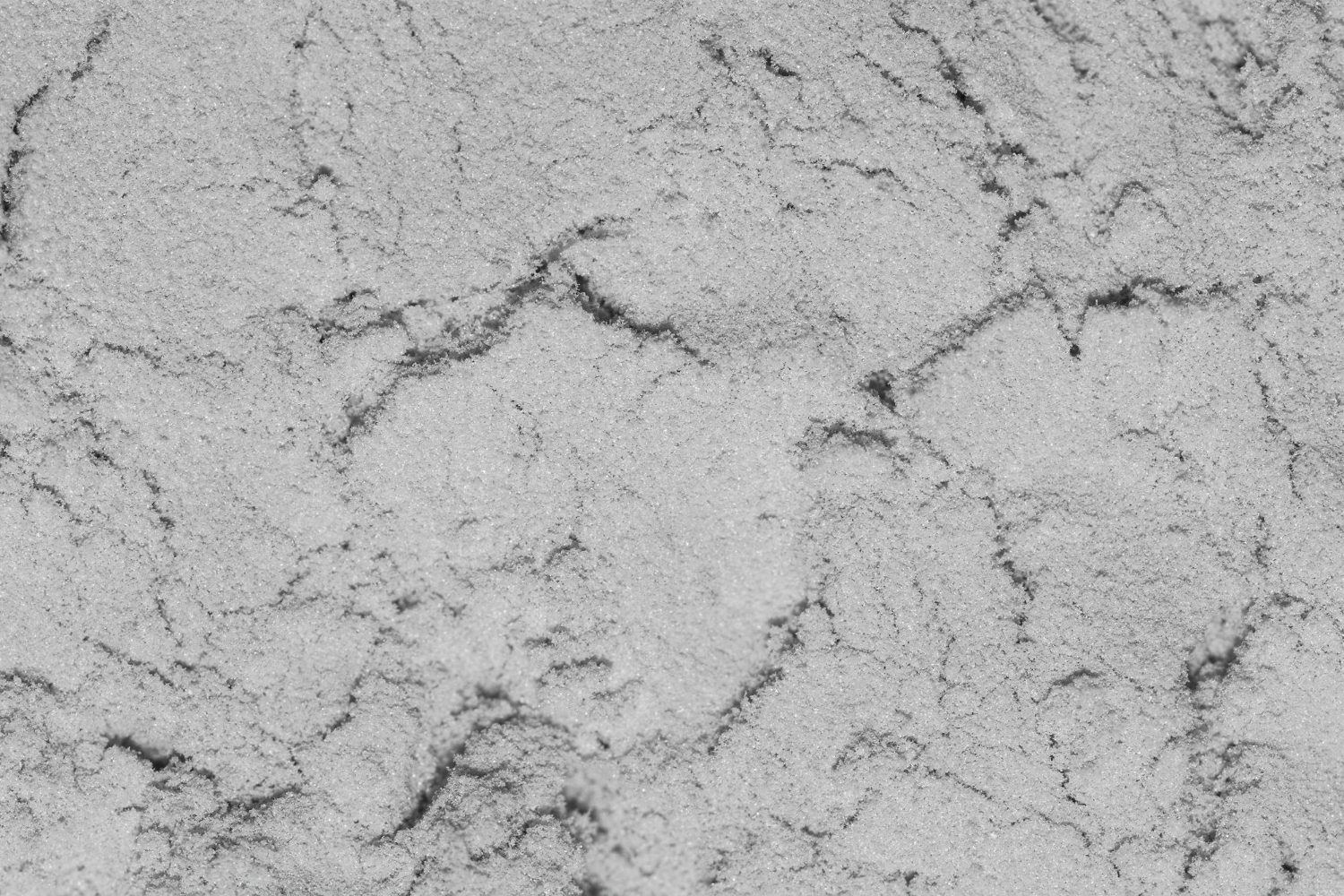
Roller mills need more maintenance but are great for large productions
A roller mill has one or more cylindrical rollers or wheels, that rotate to crush or grind the materials by friction. They can be horizontal or vertically oriented. The horizontal roller mills have rollers placed parallel in the horizontal axe, turning in opposite directions and at different speeds, generating pressure and tear between them and the material that passes through. The vertical roller mills have a spinning plate or grinding table with rollers placed in its perimeter, which exerts vertical pressure on the material over the plate.
The roller milling equipment is great to grind grains, cement, clay, rocks, and other minerals. Due to the tear and wear of the rollers, it is important to have regular maintenance and replacement of the rollers, especially if they process abrasive materials. Is also important to adjust the gap between the rollers according to the material and particle size you need.
Ball mills should have balls denser and bigger than the material being processed.
The ball mills have a rotating drum with balls inside that spin around hitting the material as they drop. The impact of the balls against the material reduces the size of the particles. Choose the characteristics of the balls according to the raw material to process, they need to have a bigger size and bigger density than the product being ground. The balls’ material needs to be compatible with the product to avoid contamination, corrosion, or cause an explosion.
This milling equipment is good for turning into powder dry or wet material such as coal, cement, rocks, minerals, ceramics, pigments, and some metals.
A classifier mill equipment is an impact mill that integrates a particle classifier
The classifier milling system is a mix of an impact mill and a particle classifier. The principle of this milling machine is to reduce the particle size and automatically take out of the grinding zone those particles that have a specific reduced size, the others will come back to the grinding zone until they have the right size. Most of the classifier mills use air to classify the particles.
The classifier milling equipment is commonly used in pharmaceuticals, cosmetics, powder coatings, pigments, and other areas that need fine particles.
What are you making?
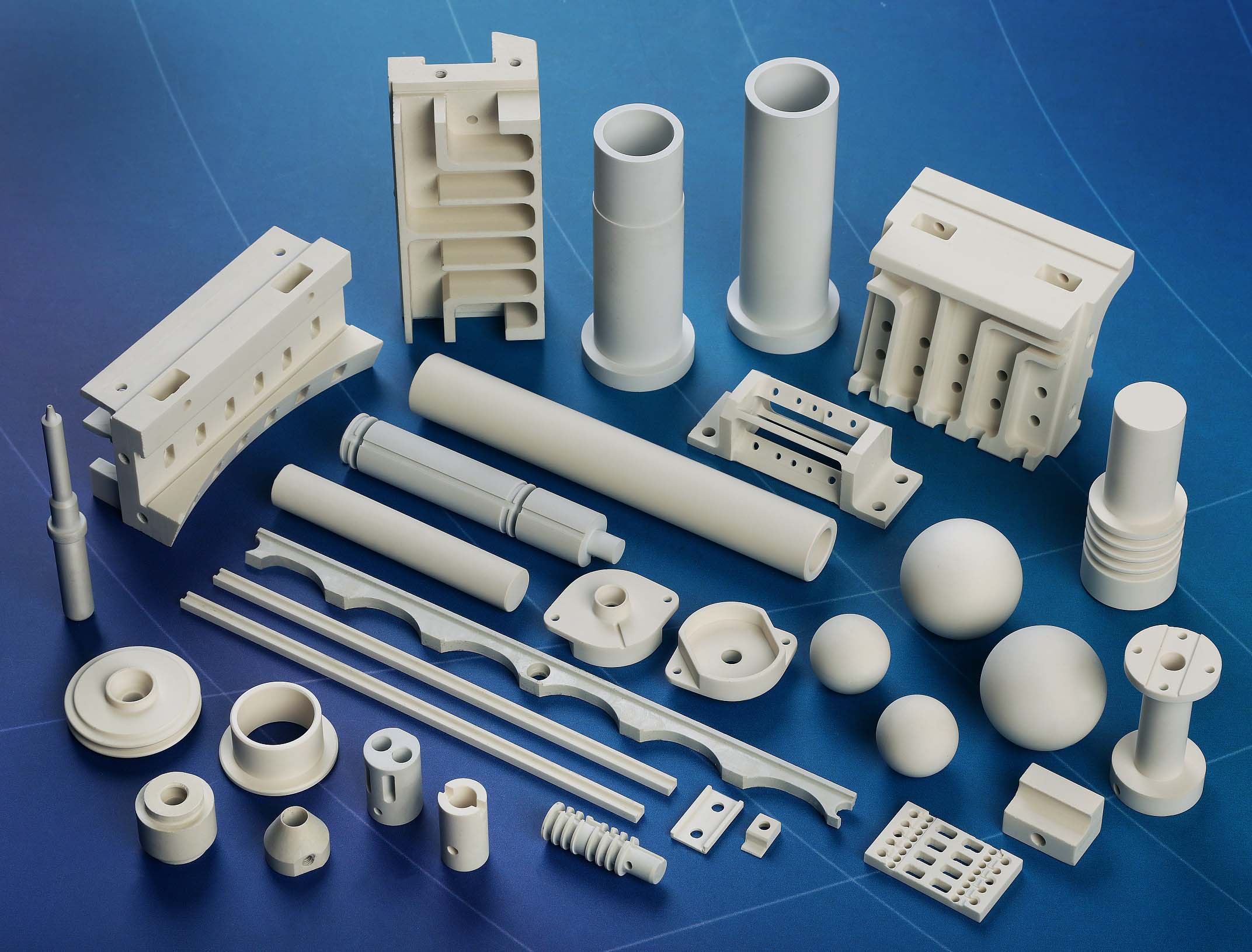
Advanced ceramics
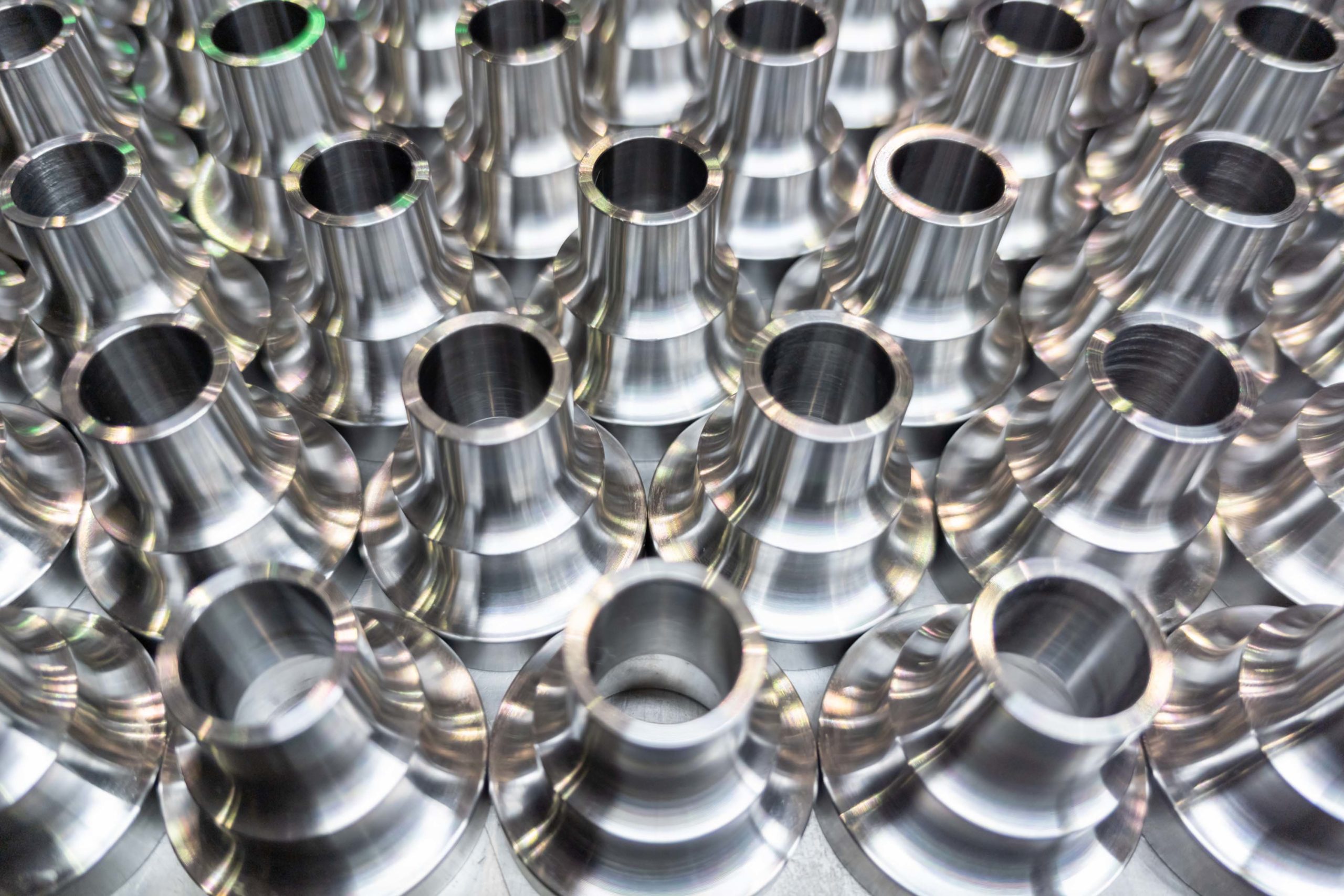
Aerospace components
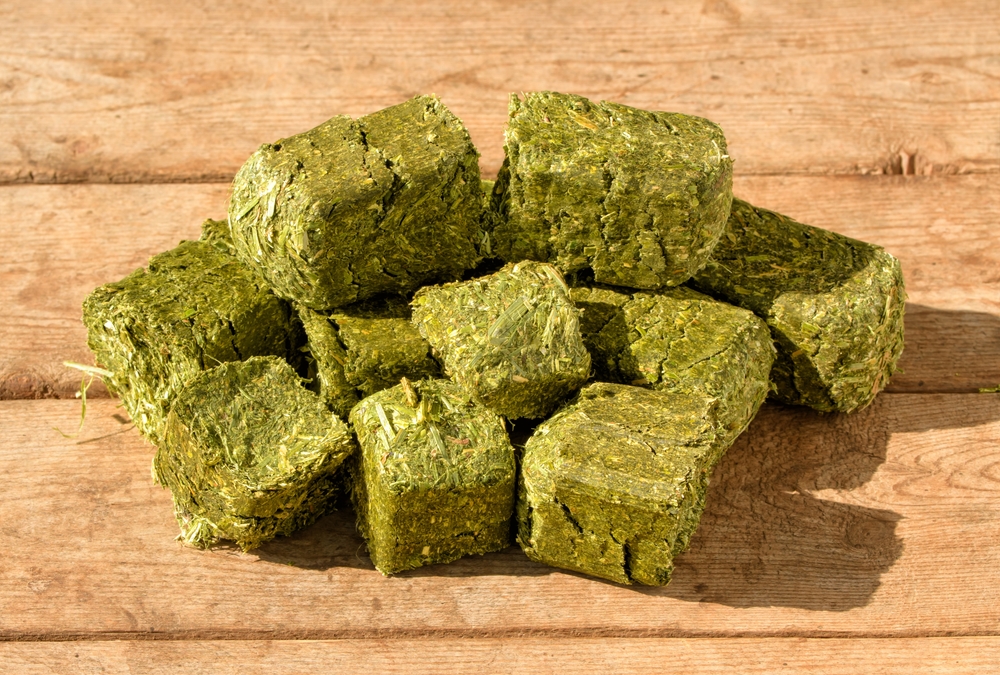
Alfalfa meal
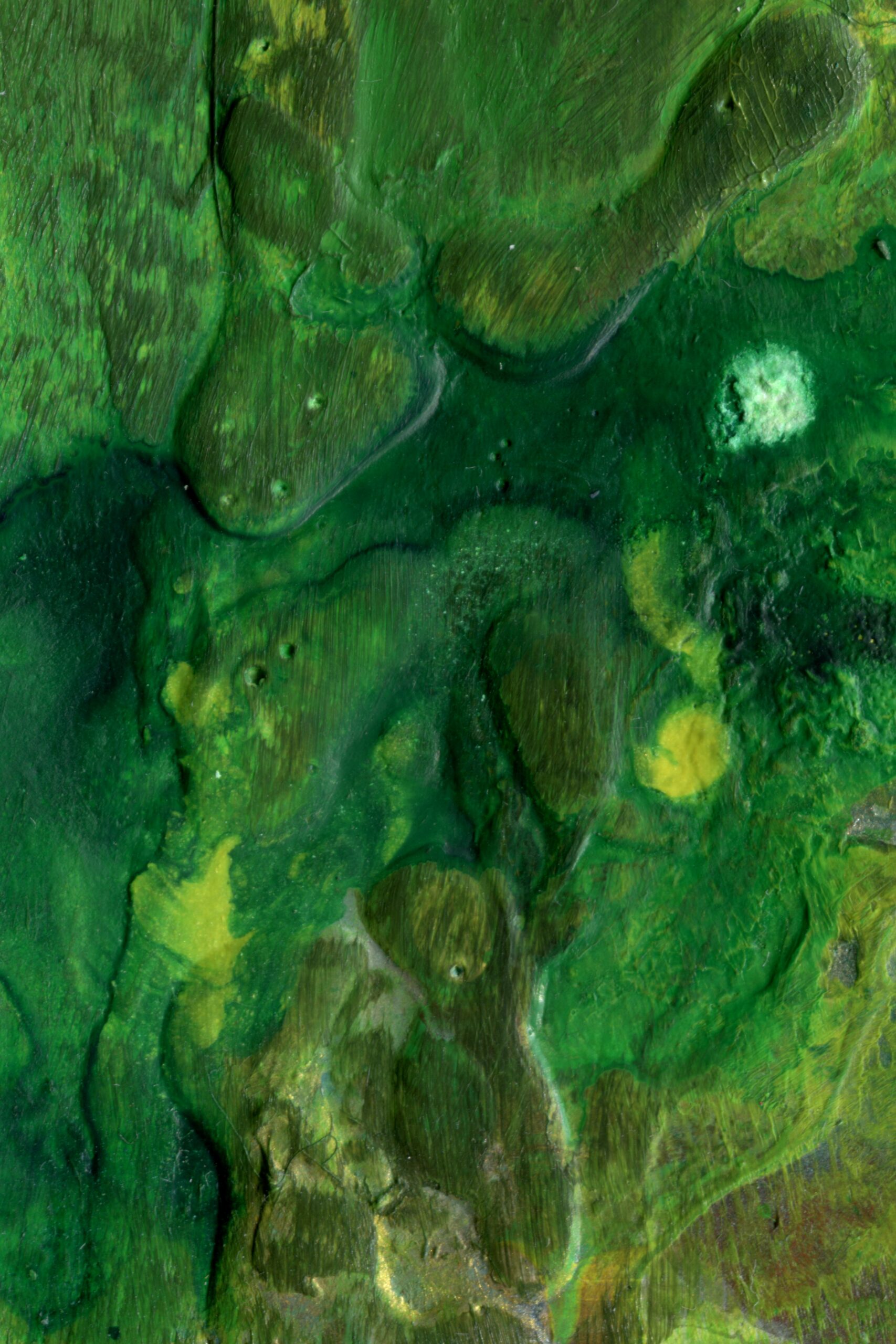
Algae
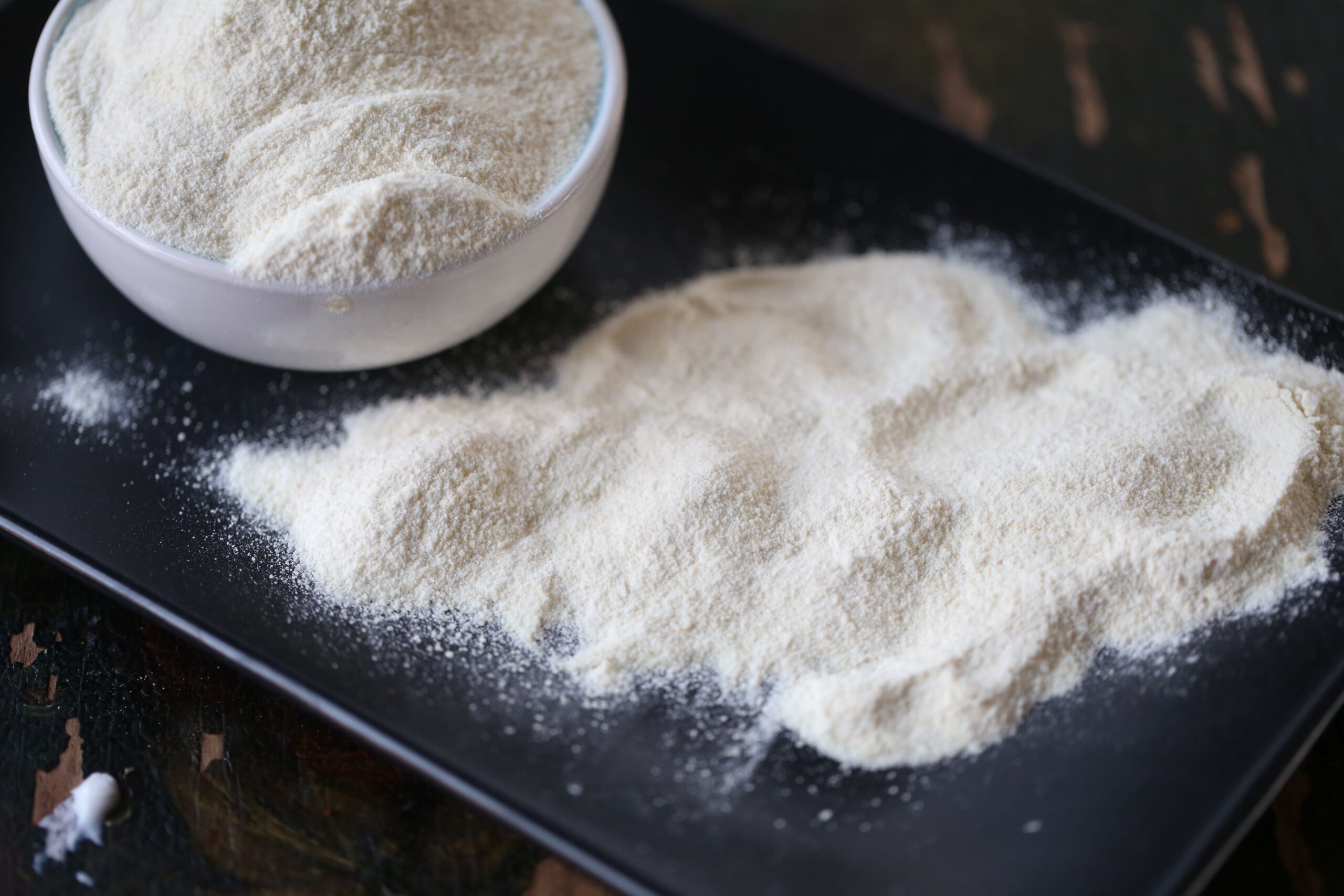
All-purpose flour
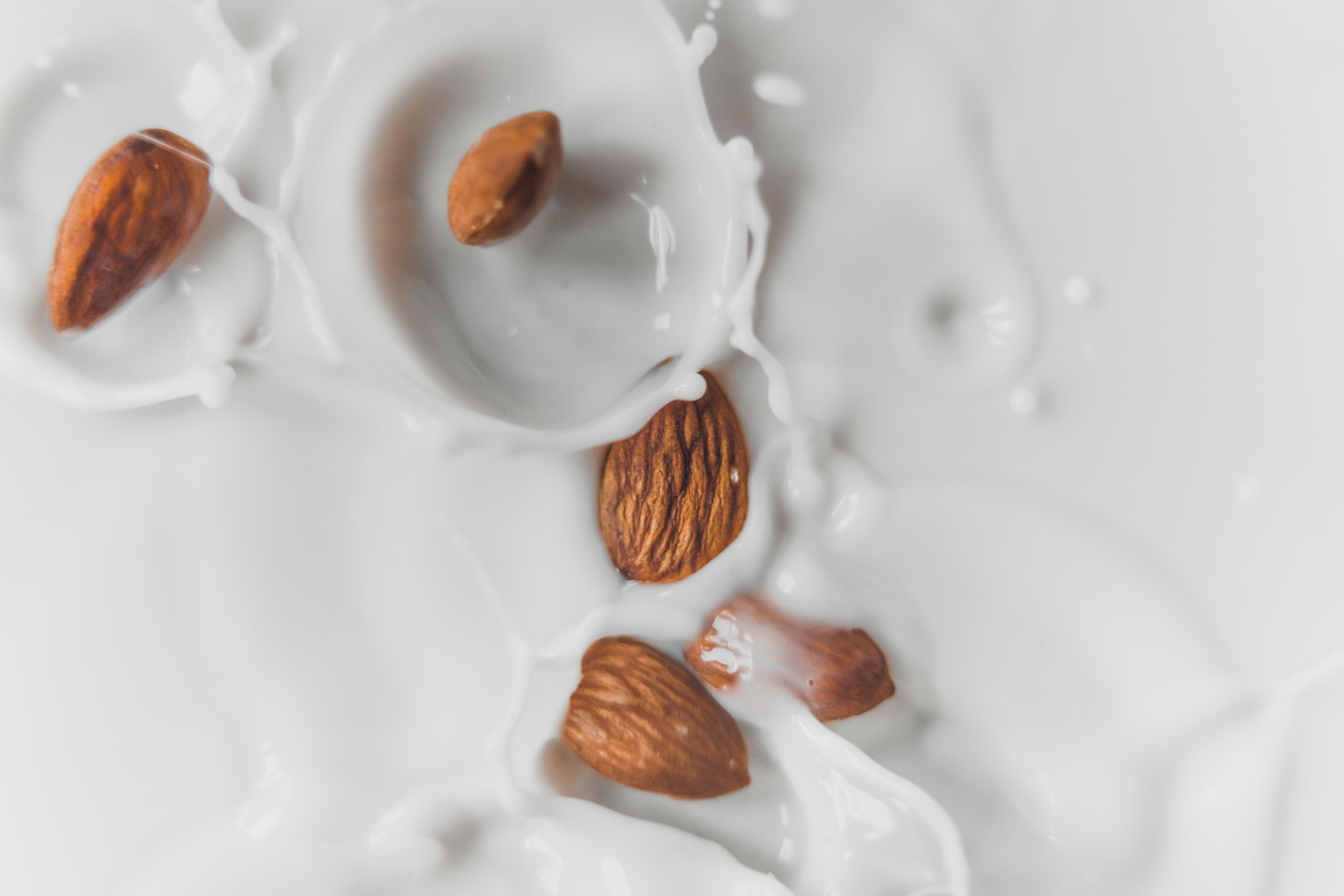
Almond milk
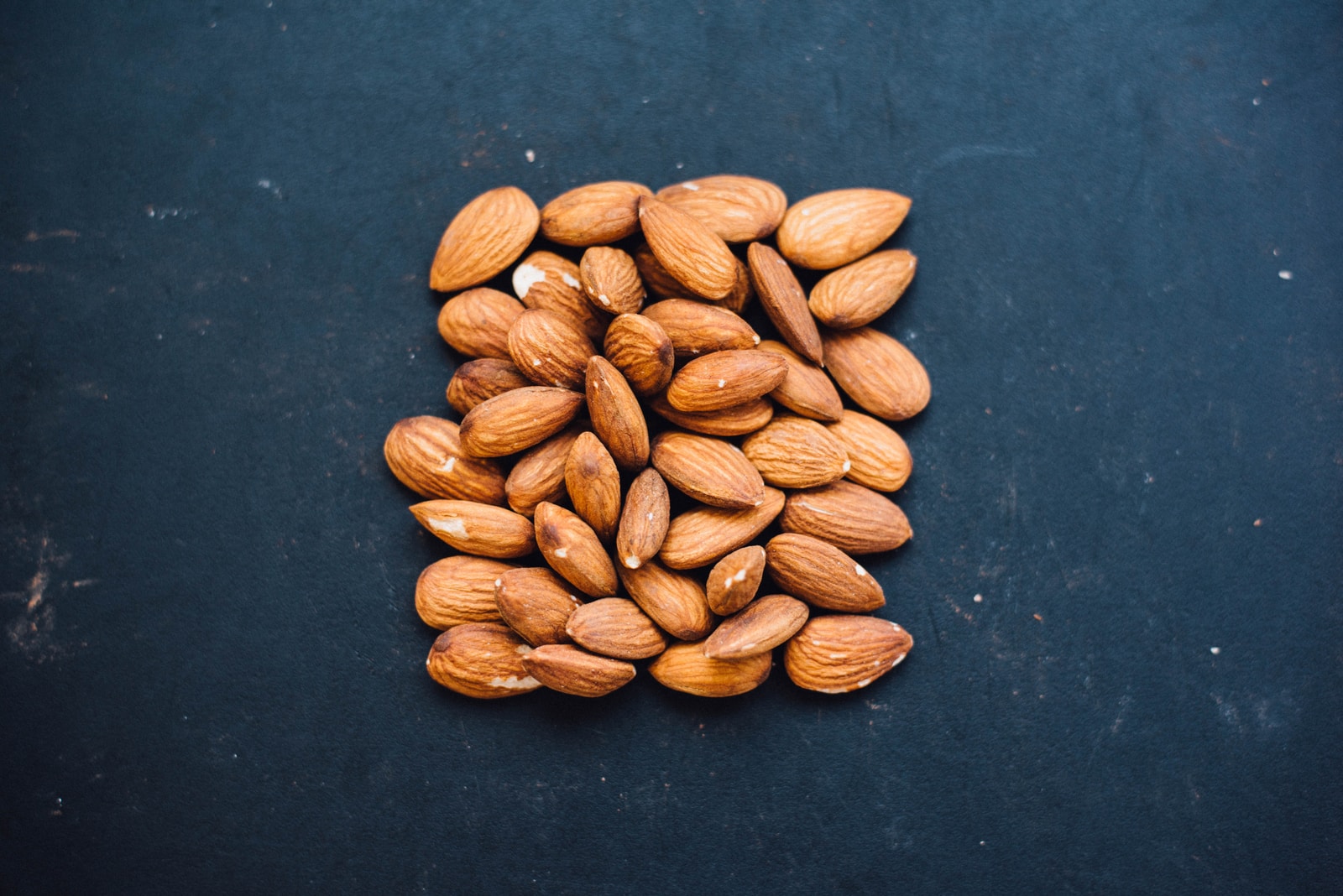
Almonds
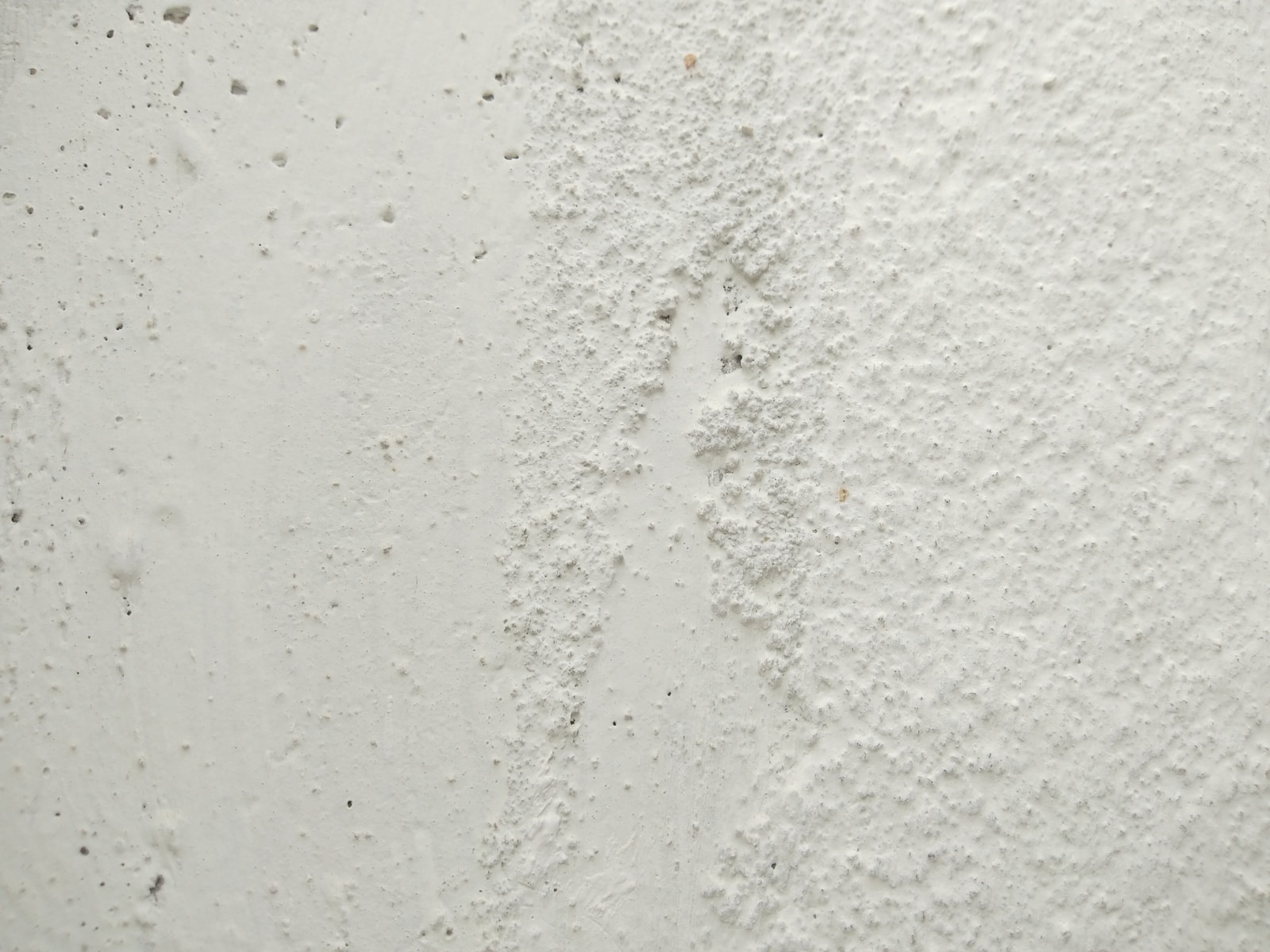
Aluminium oxide
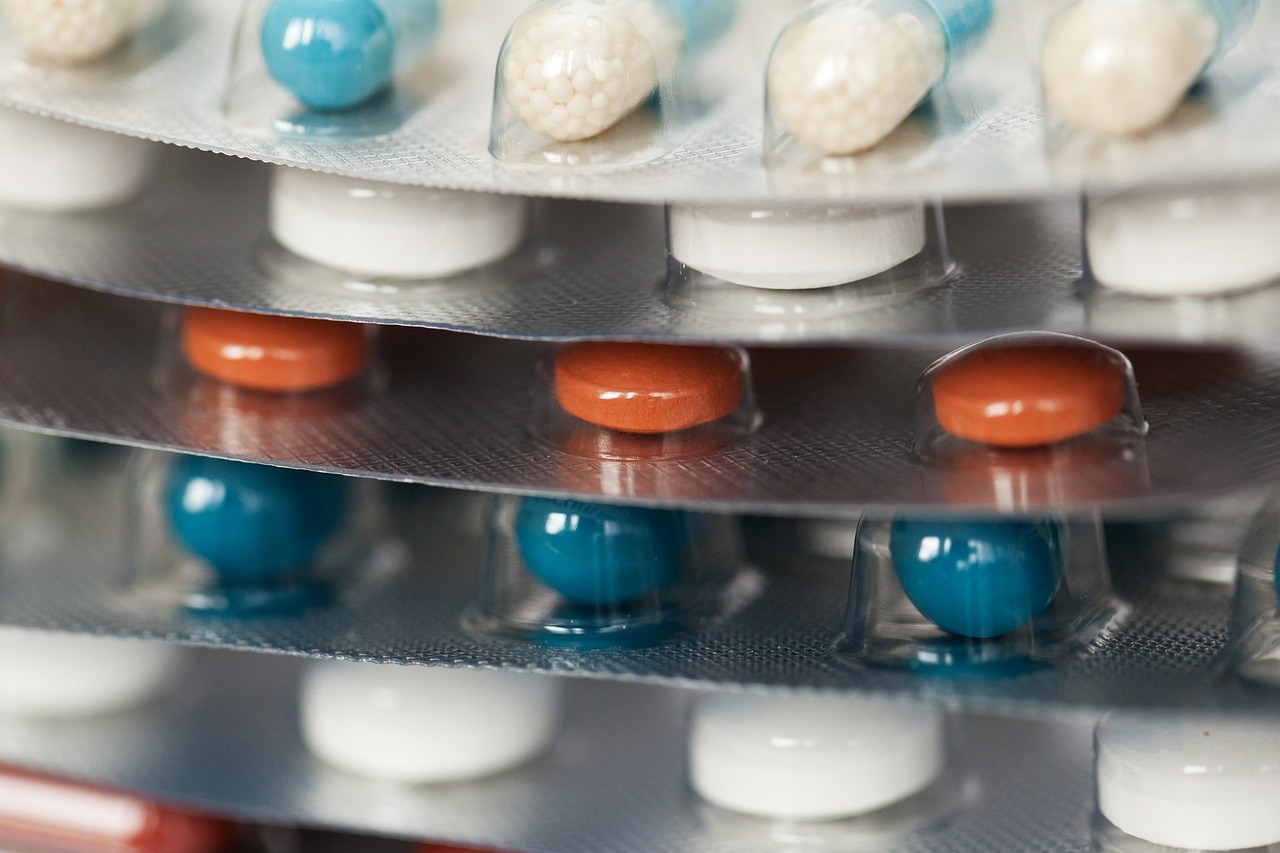
Antibiotics
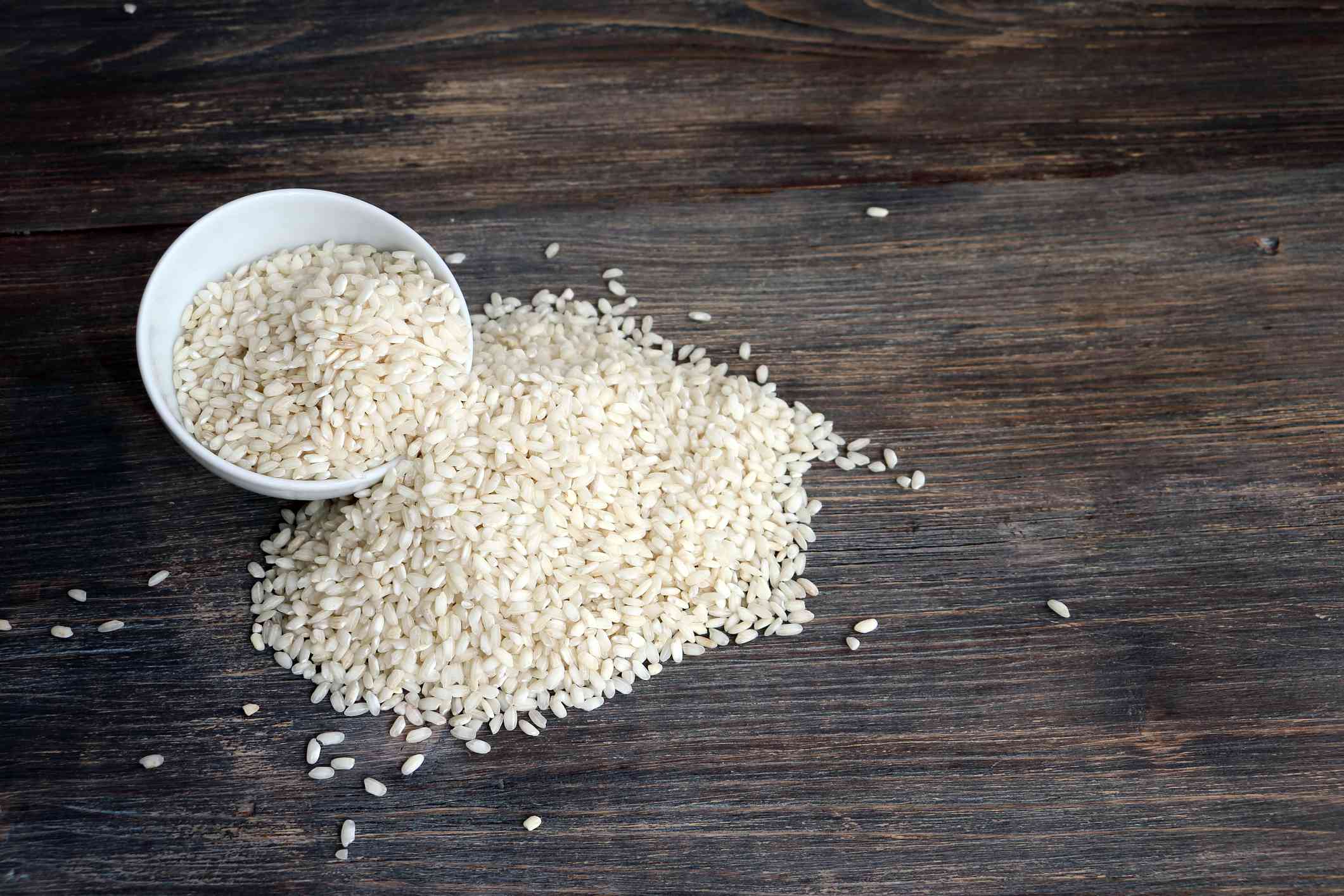
Arborio rice
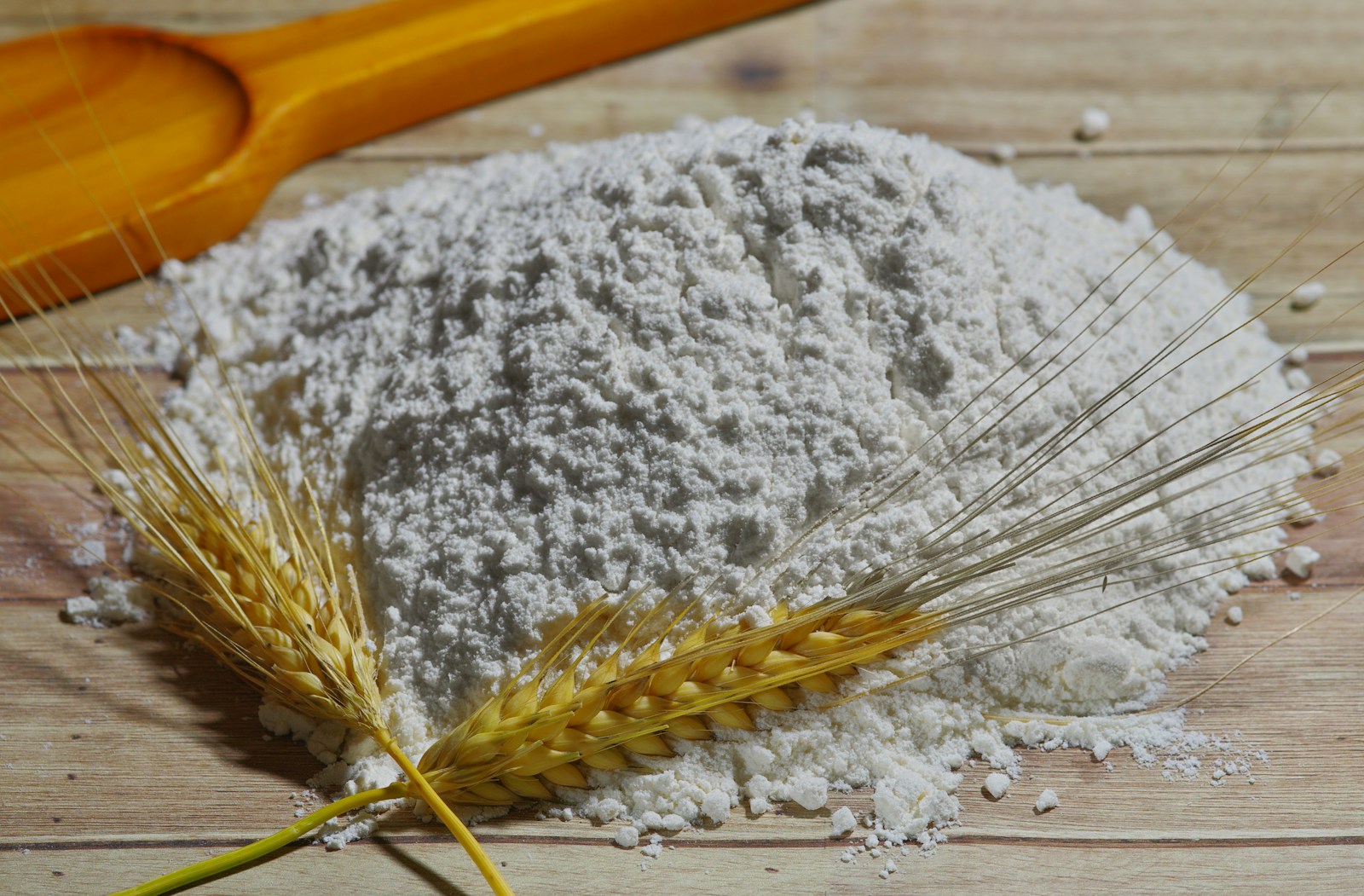
Bakery flour
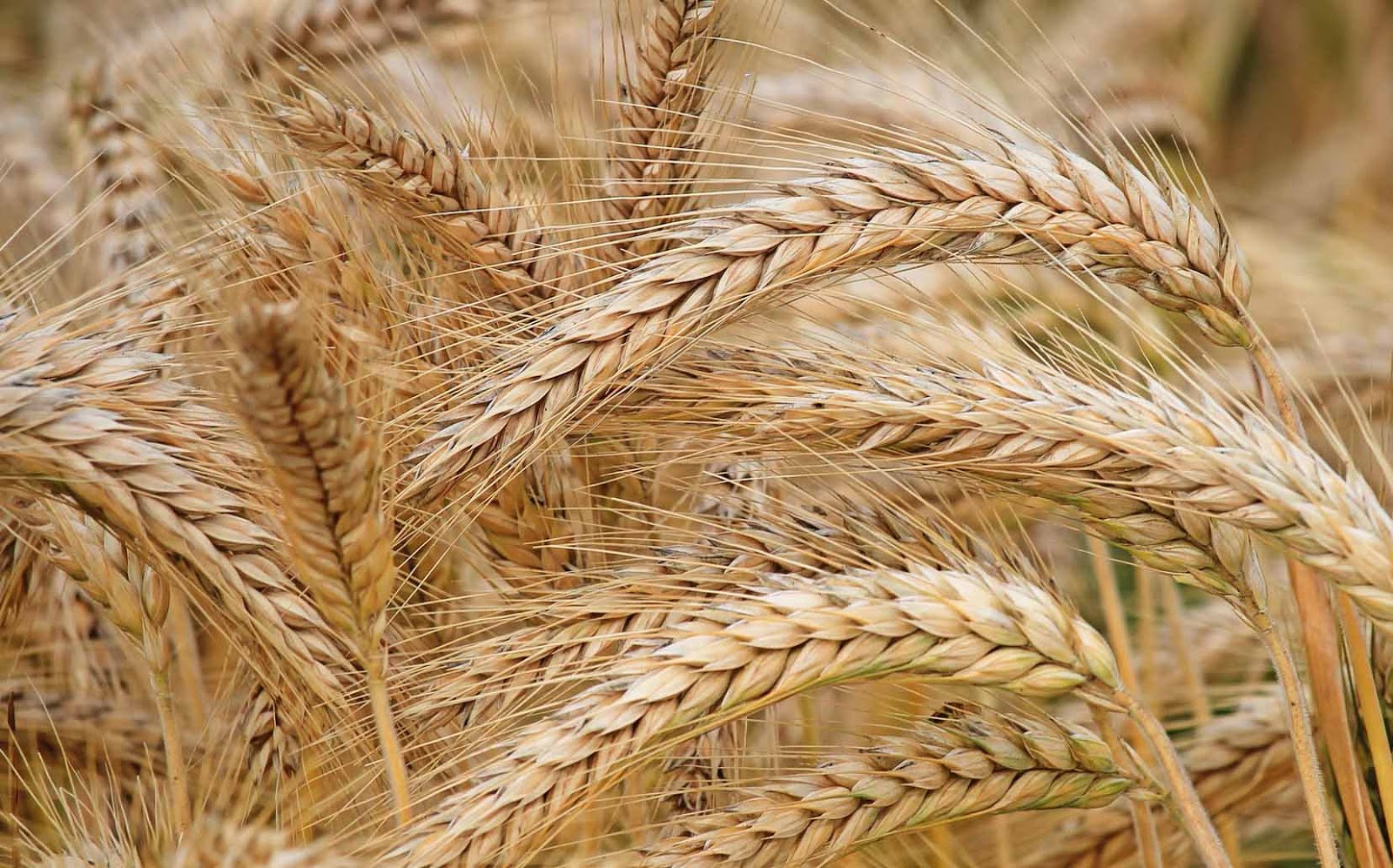
Barley
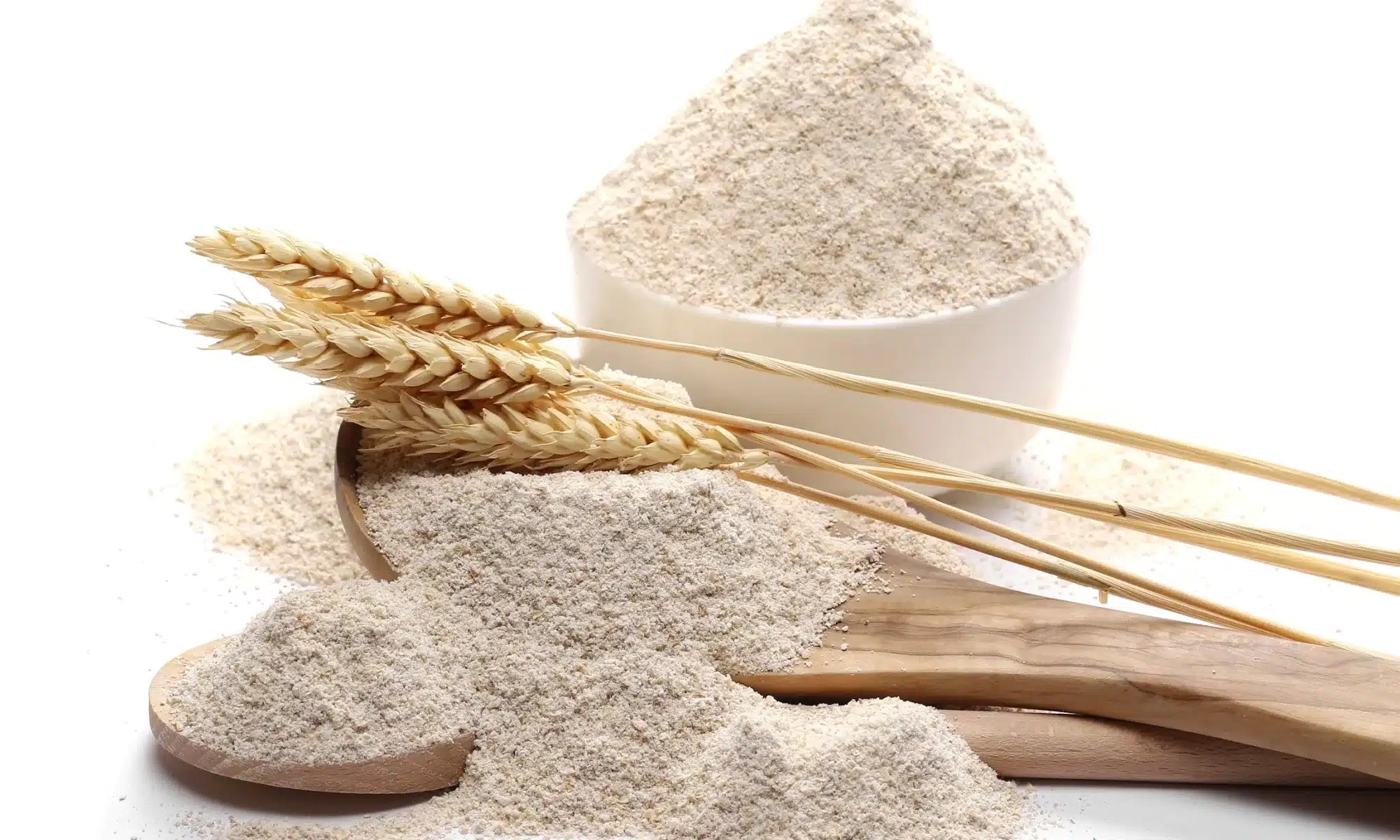
Barley flour
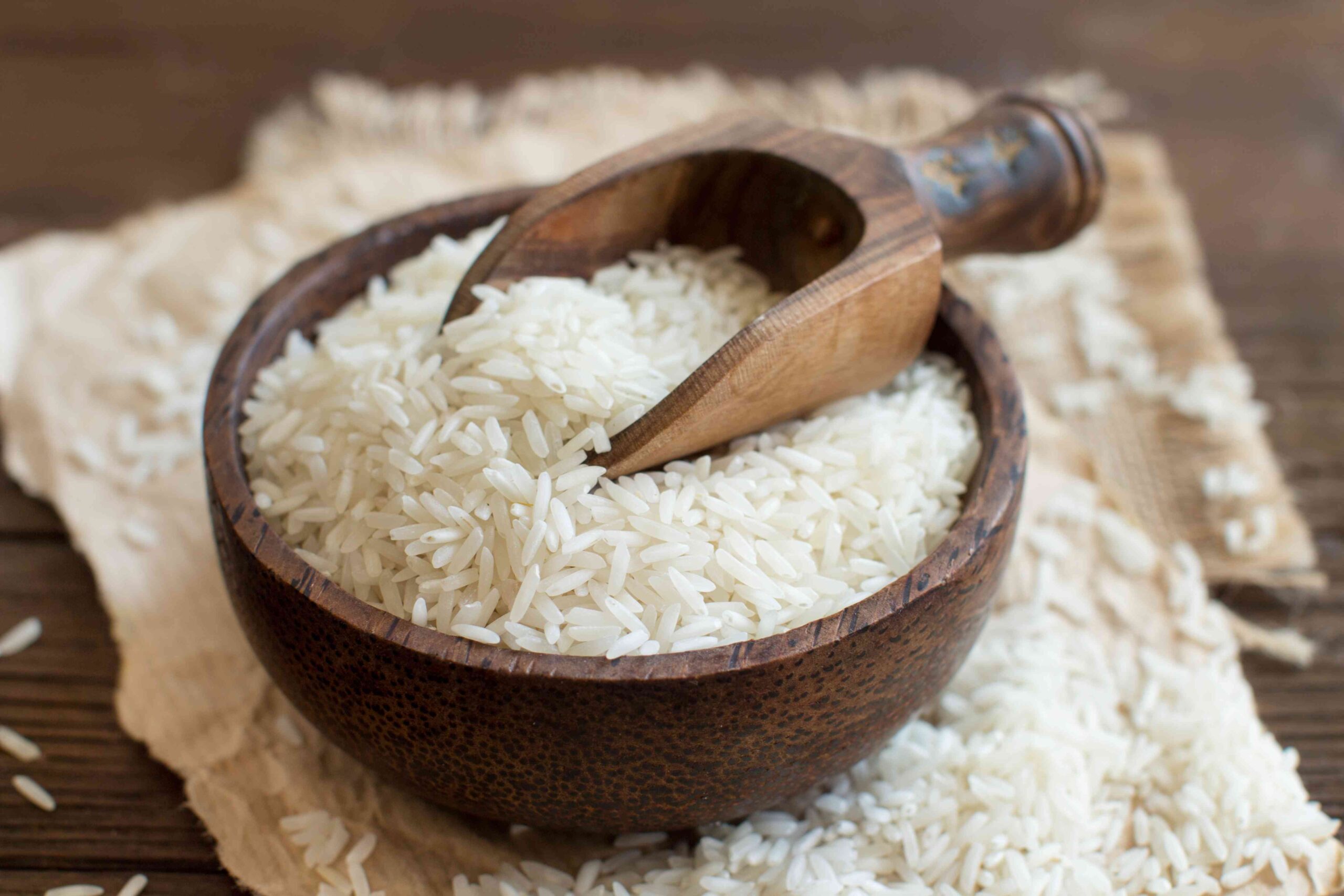
Basmati rice
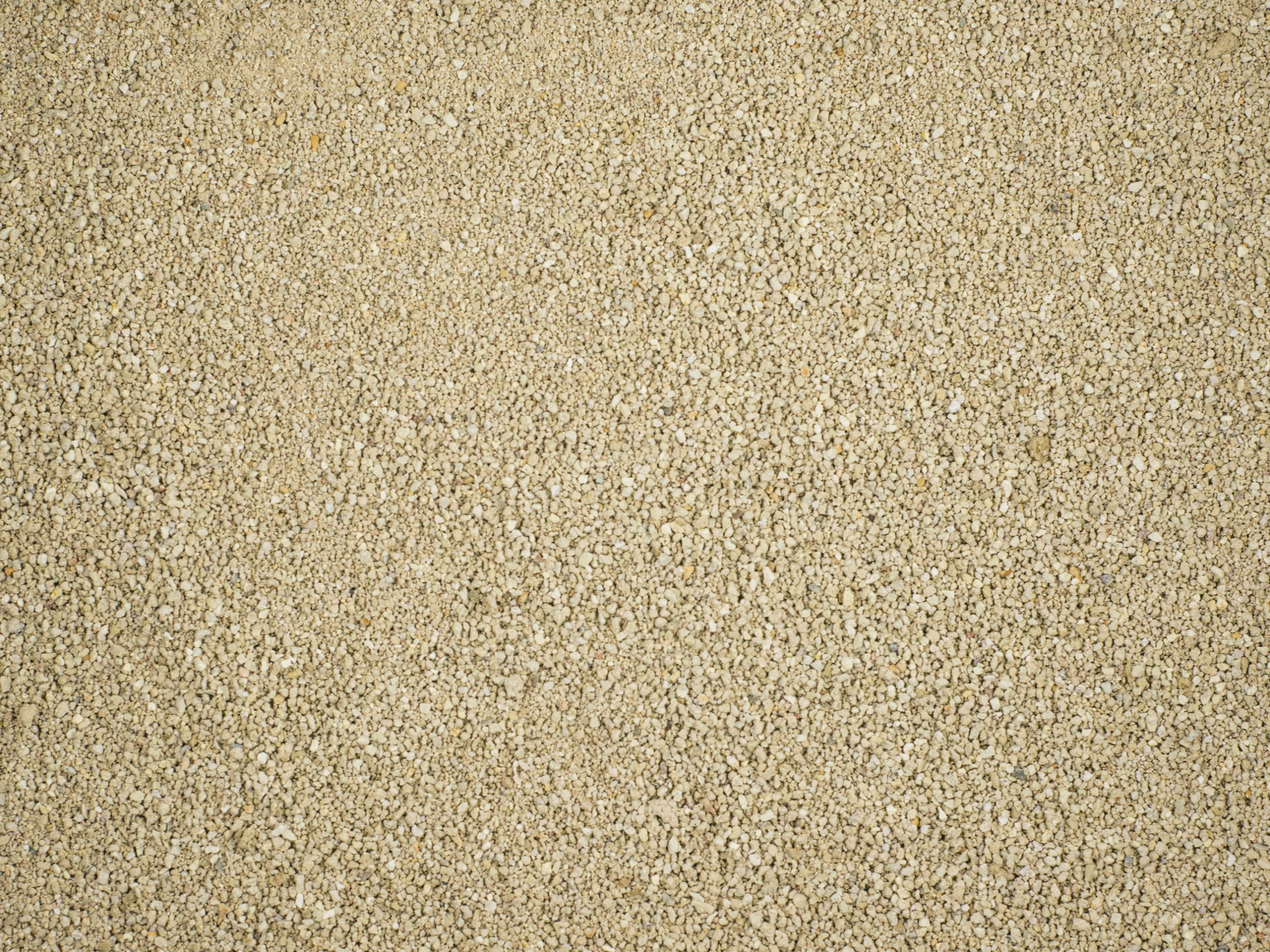
Bentonite
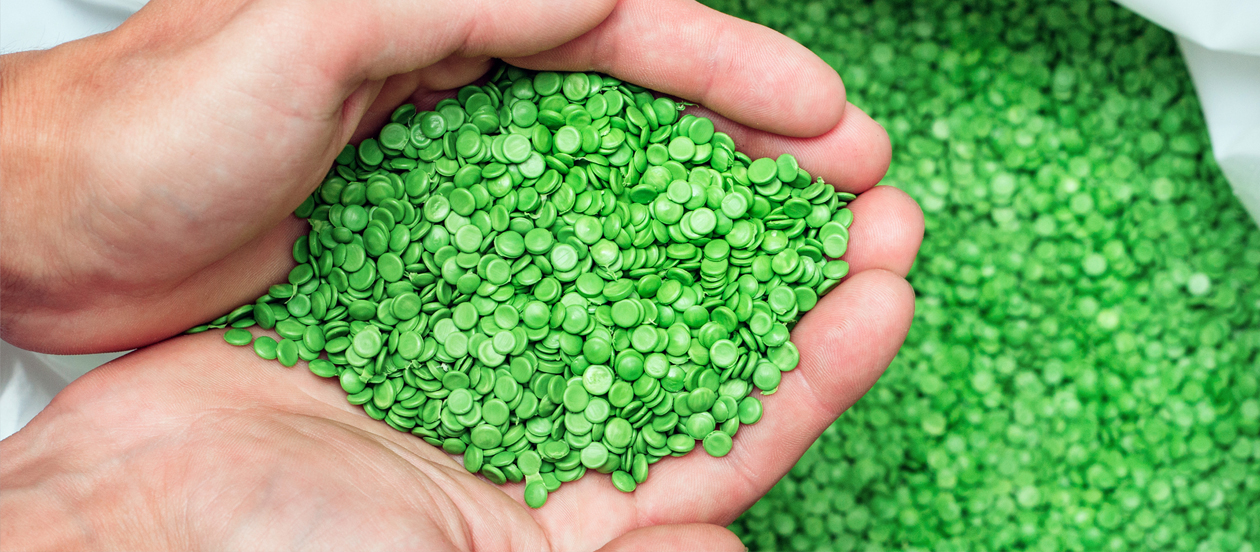
Bioplastics
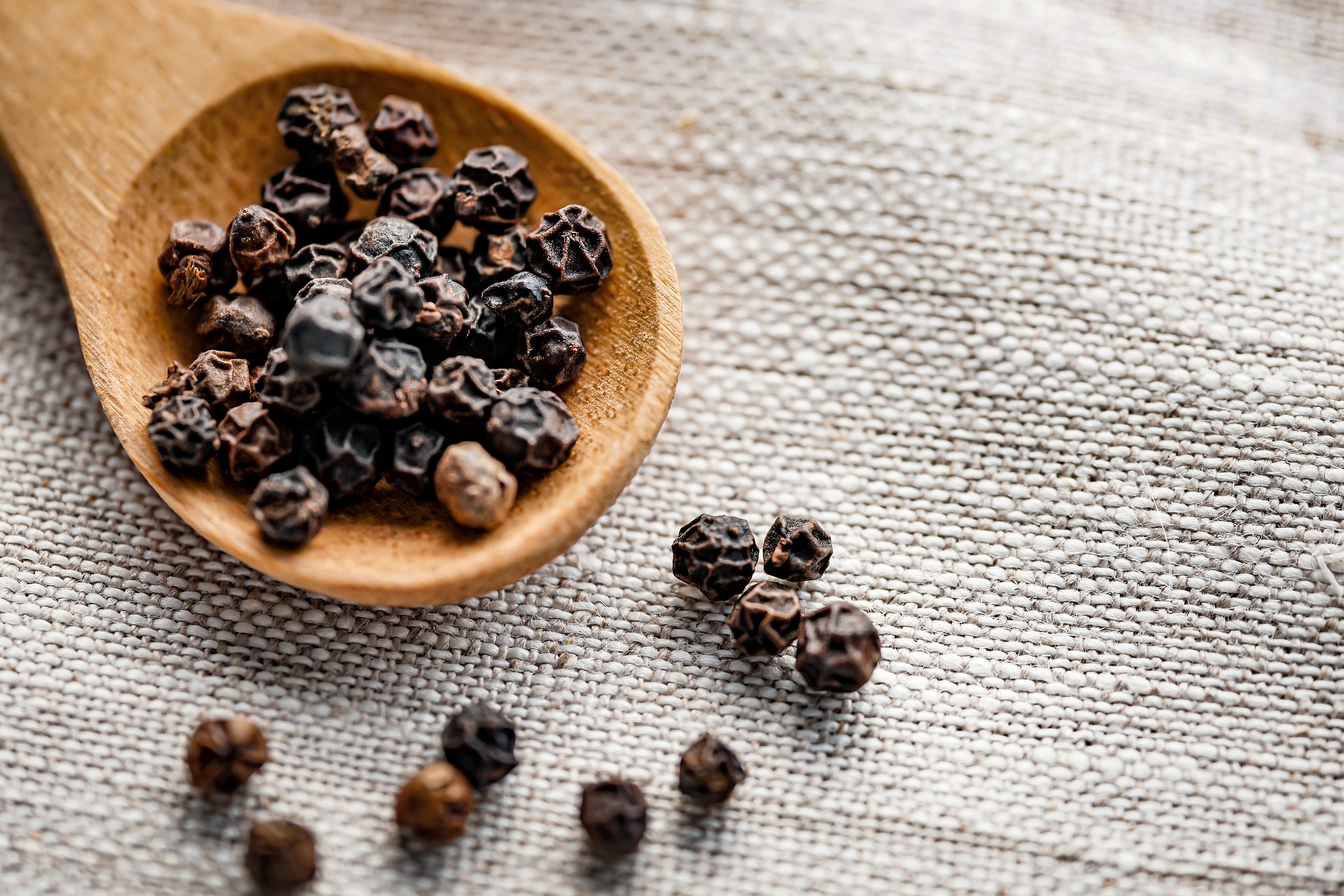
Black pepper
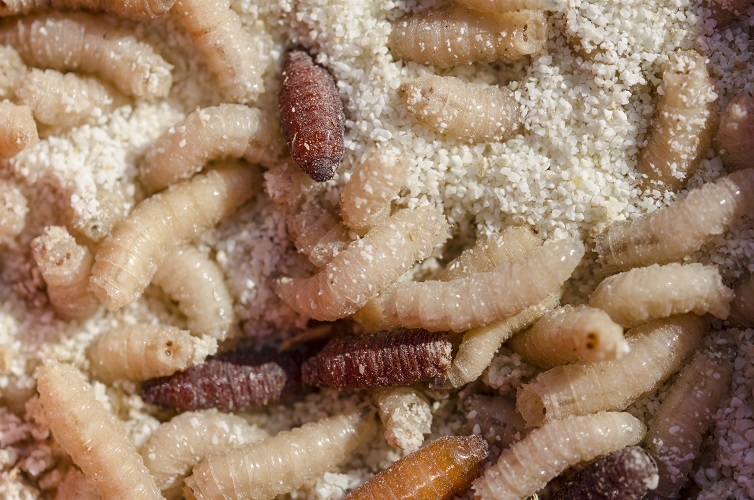
Black soldier fly protein
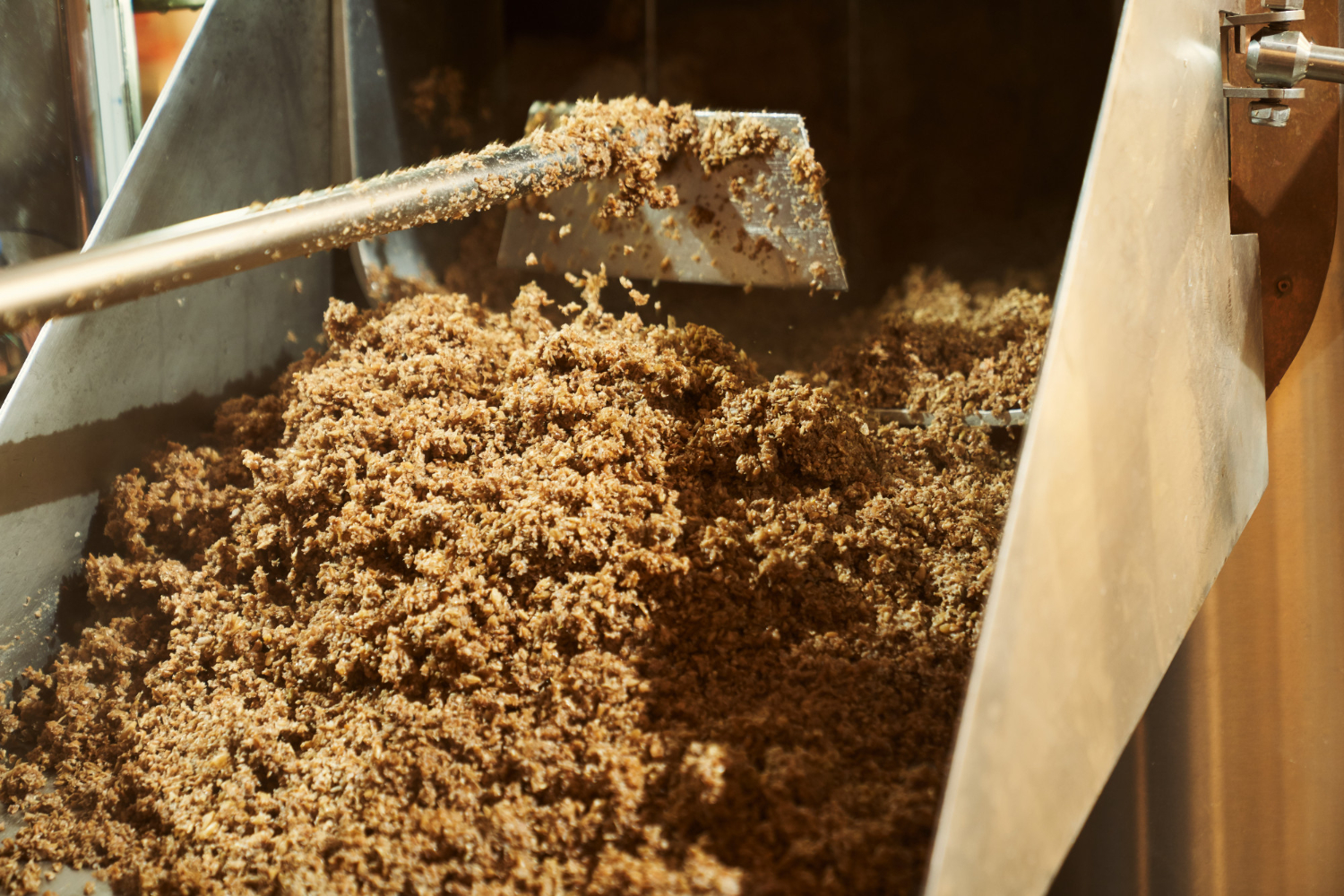
Brewers grain
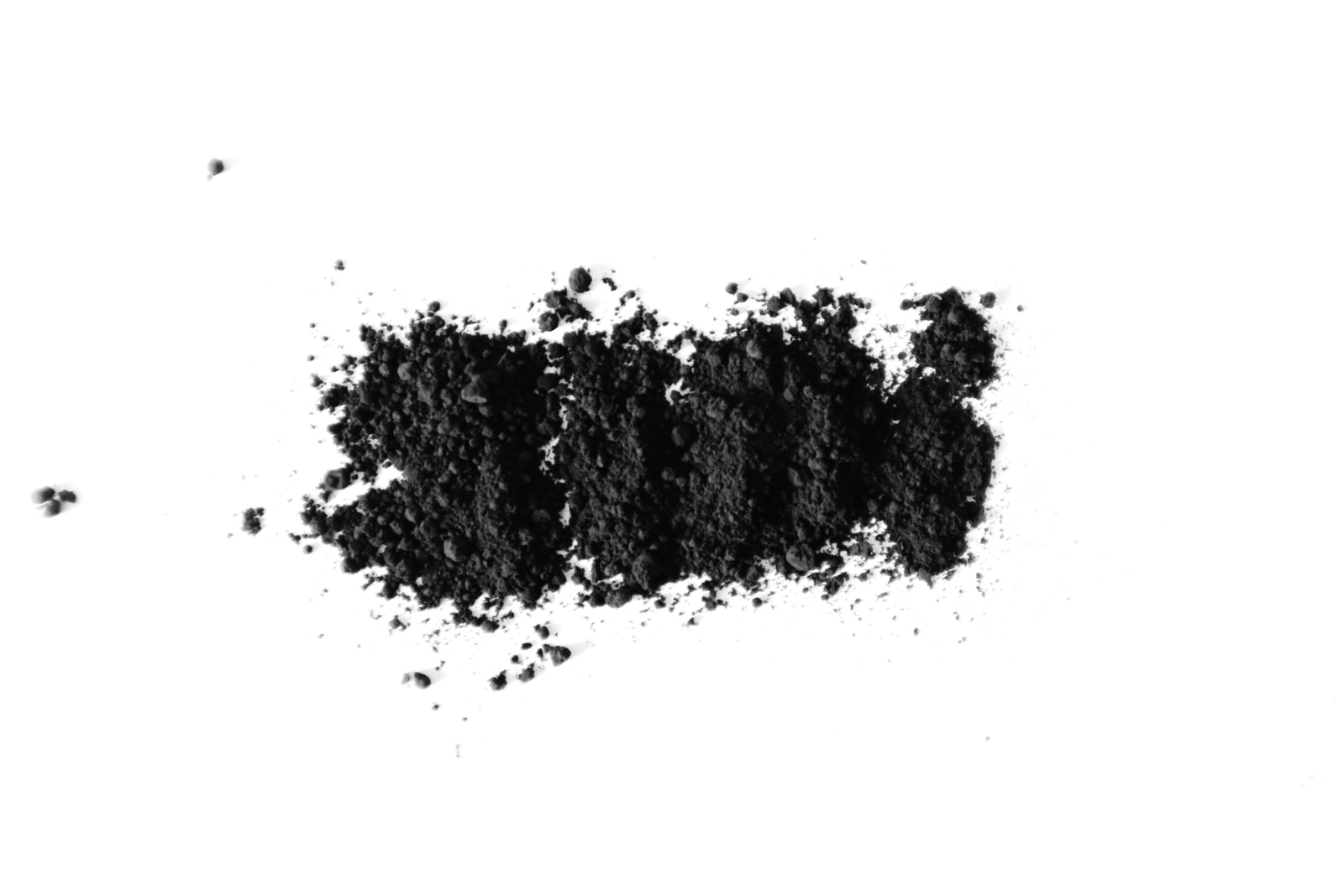
Carbon black
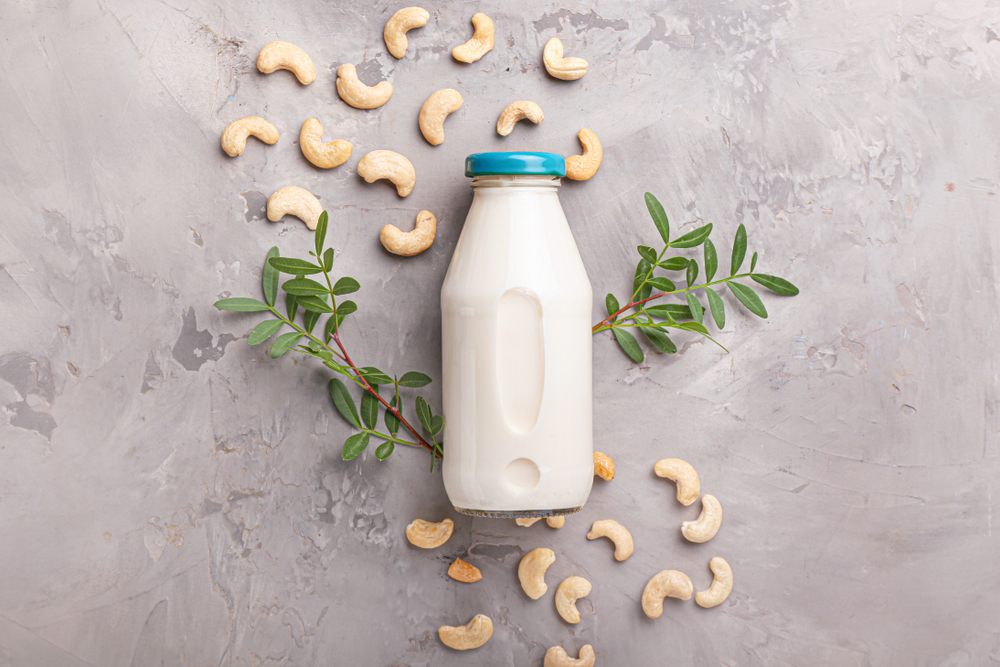
Cashew milk
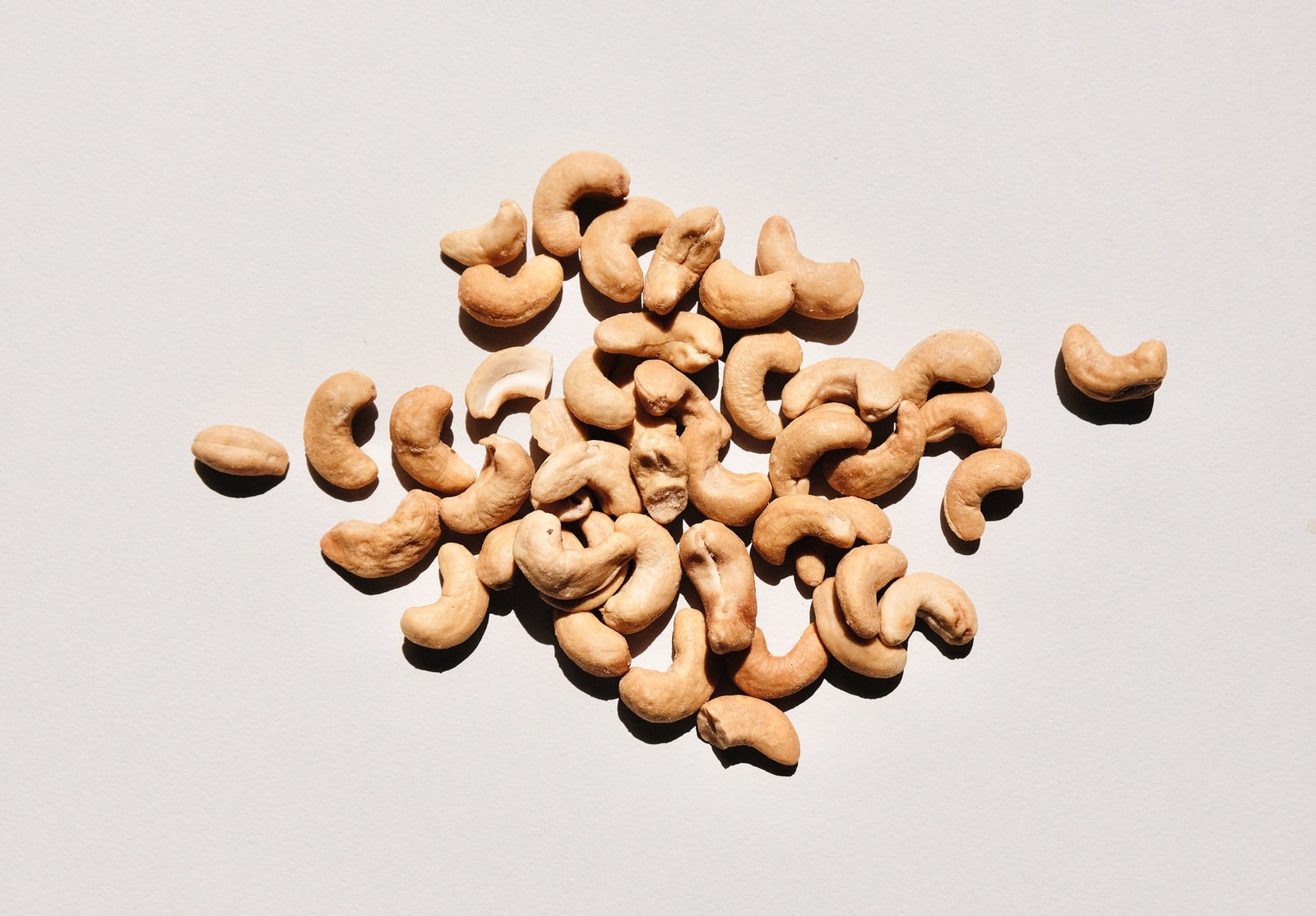
Cashews
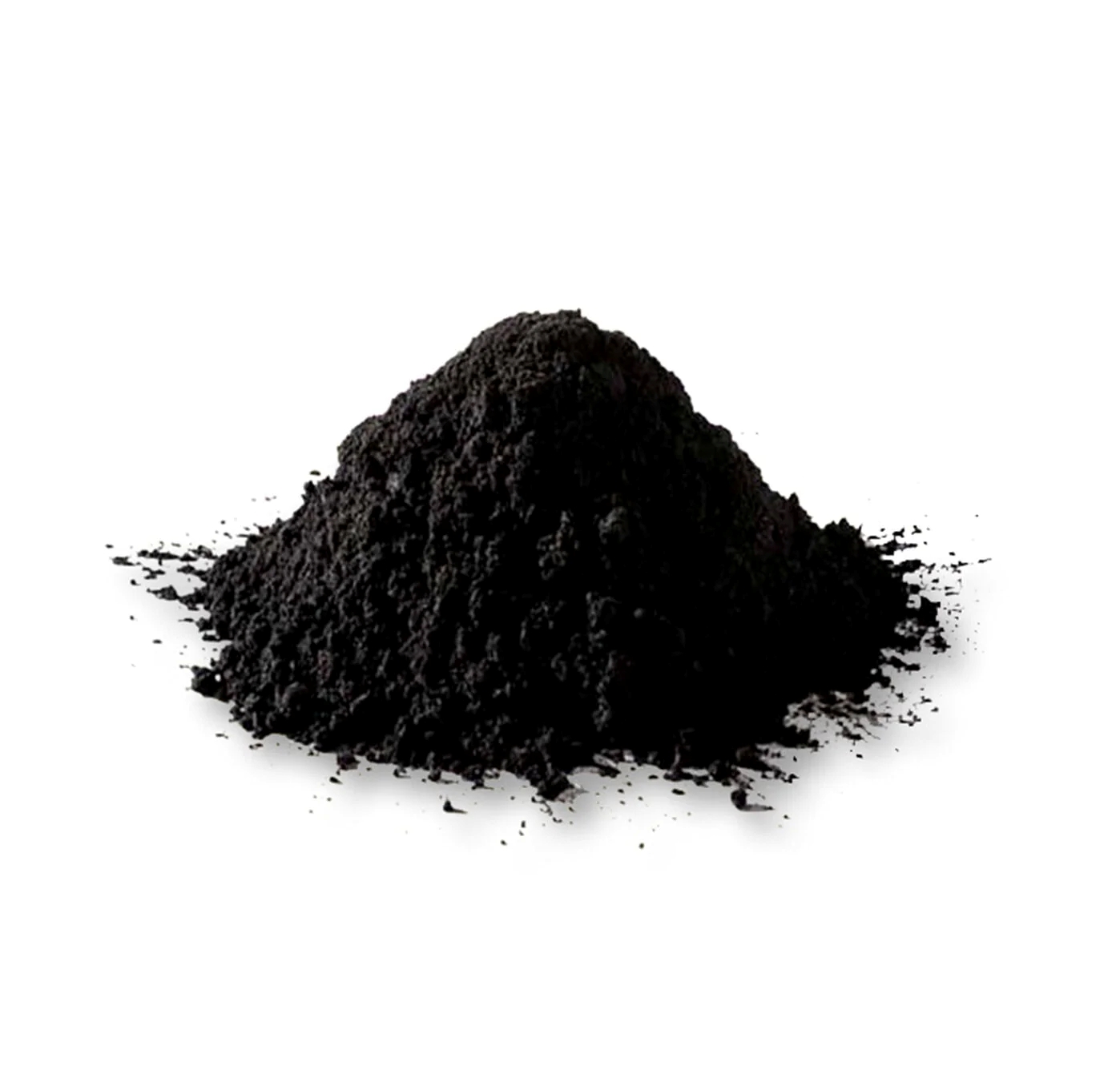
Catalyst powders
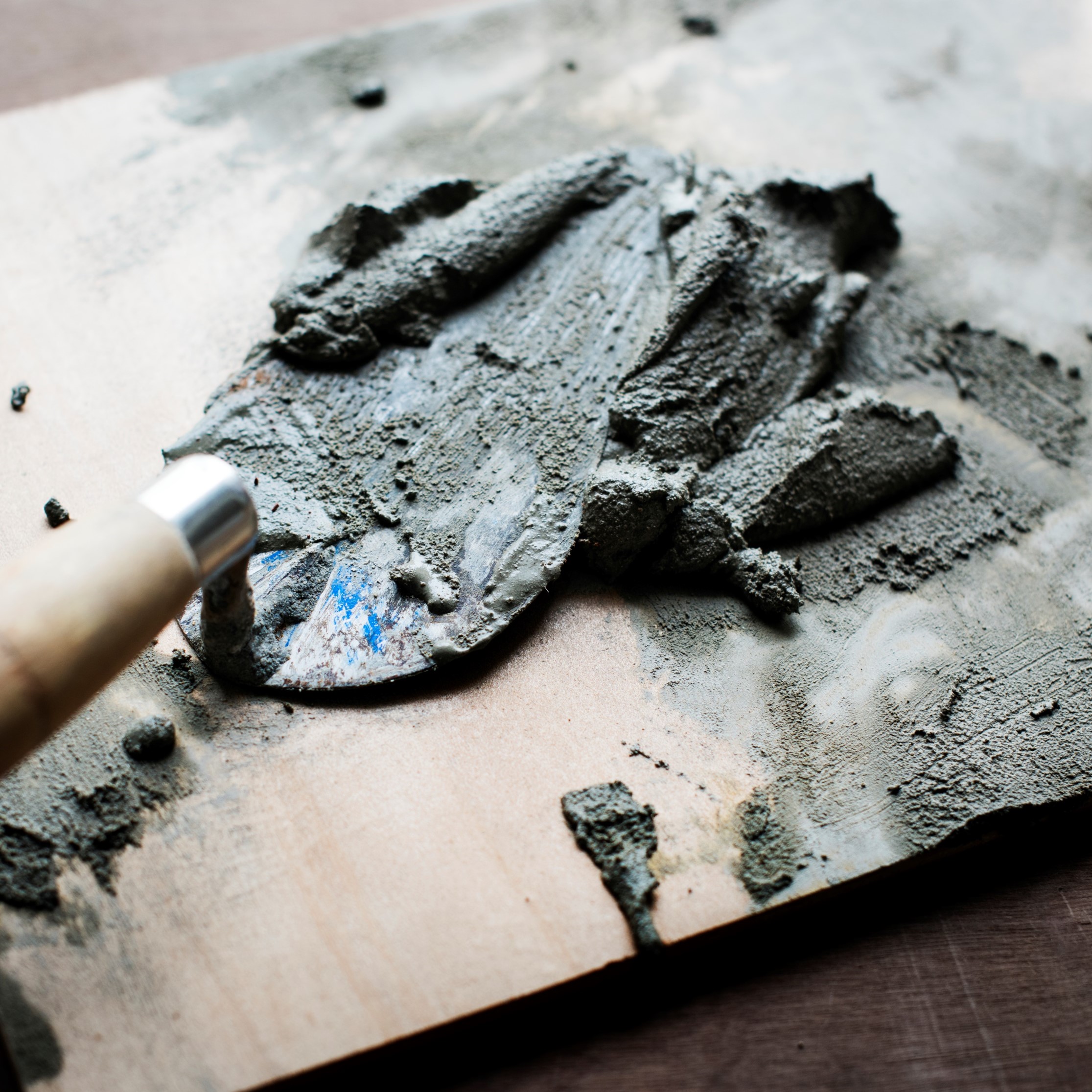
Cement
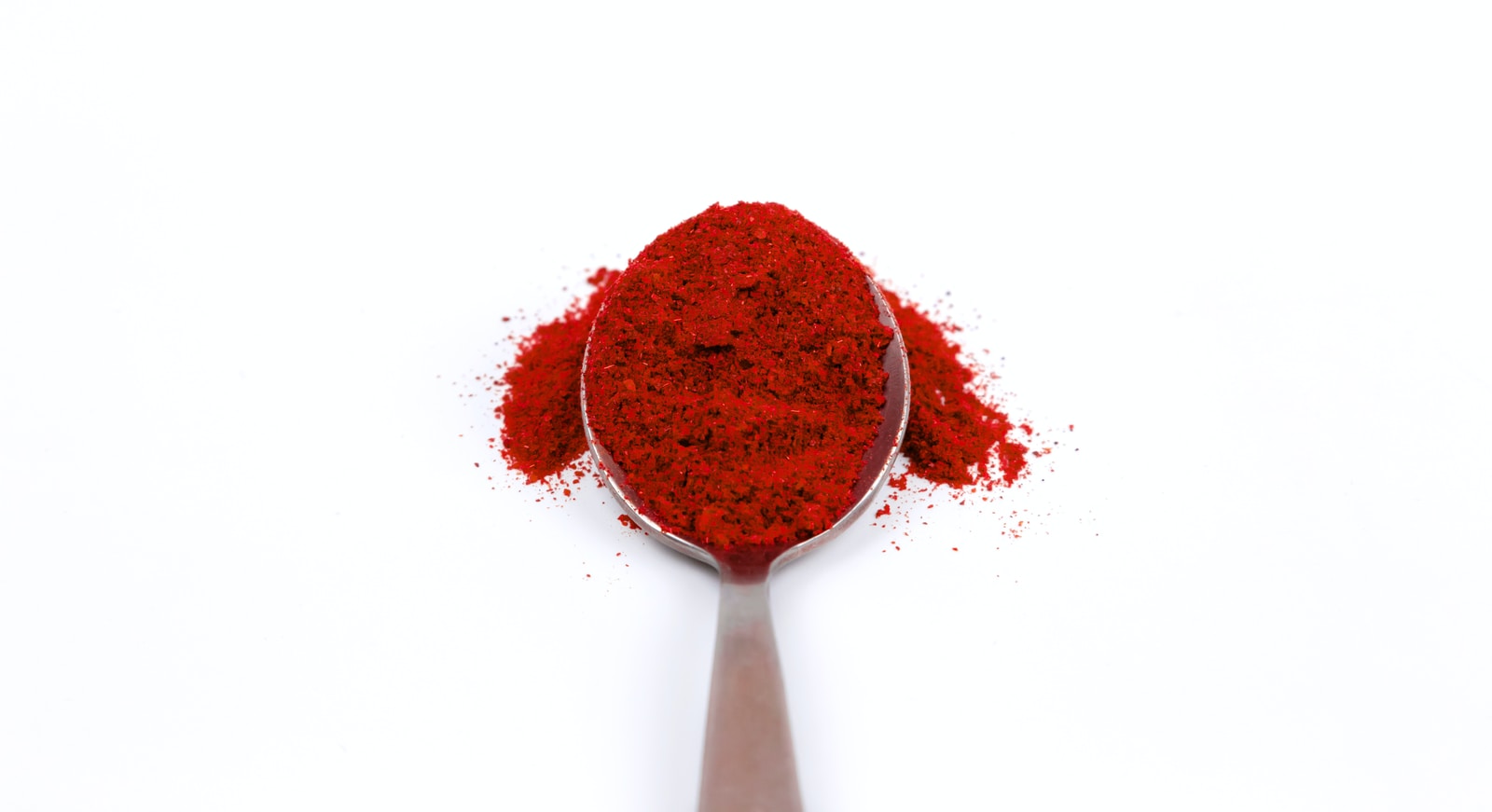
Chili powder
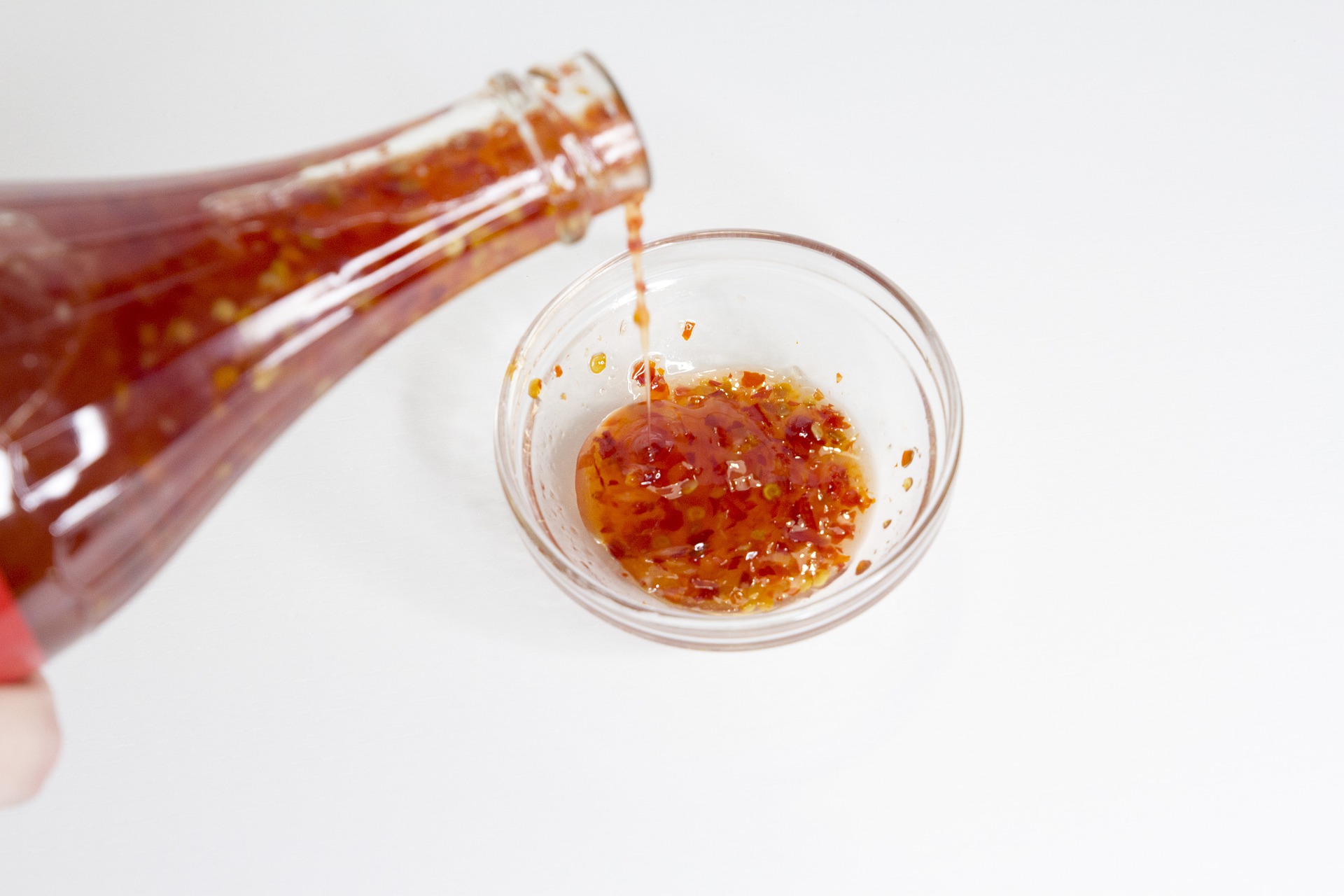
Chili sauce
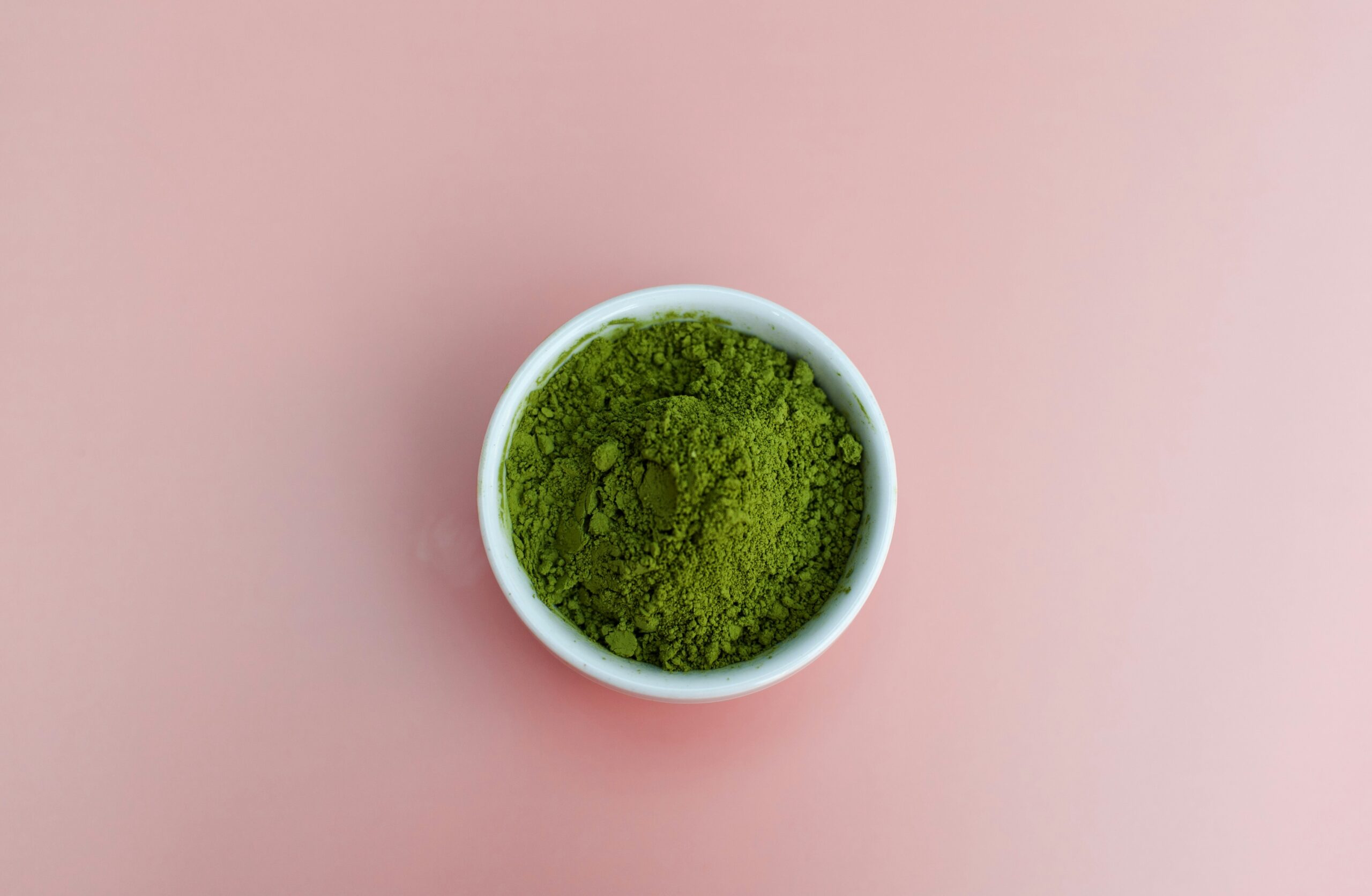
Chlorella powder
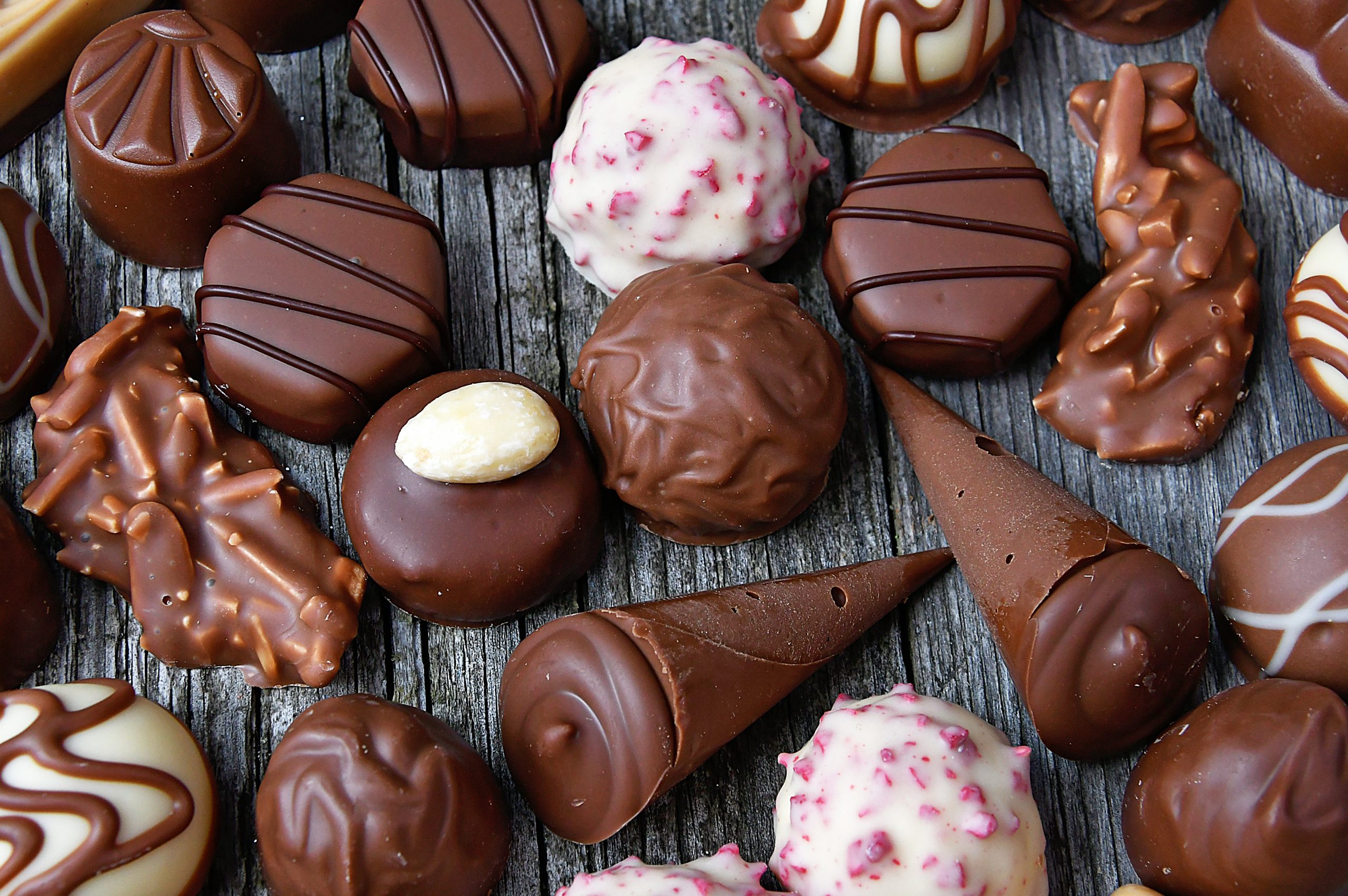
Chocolate coatings
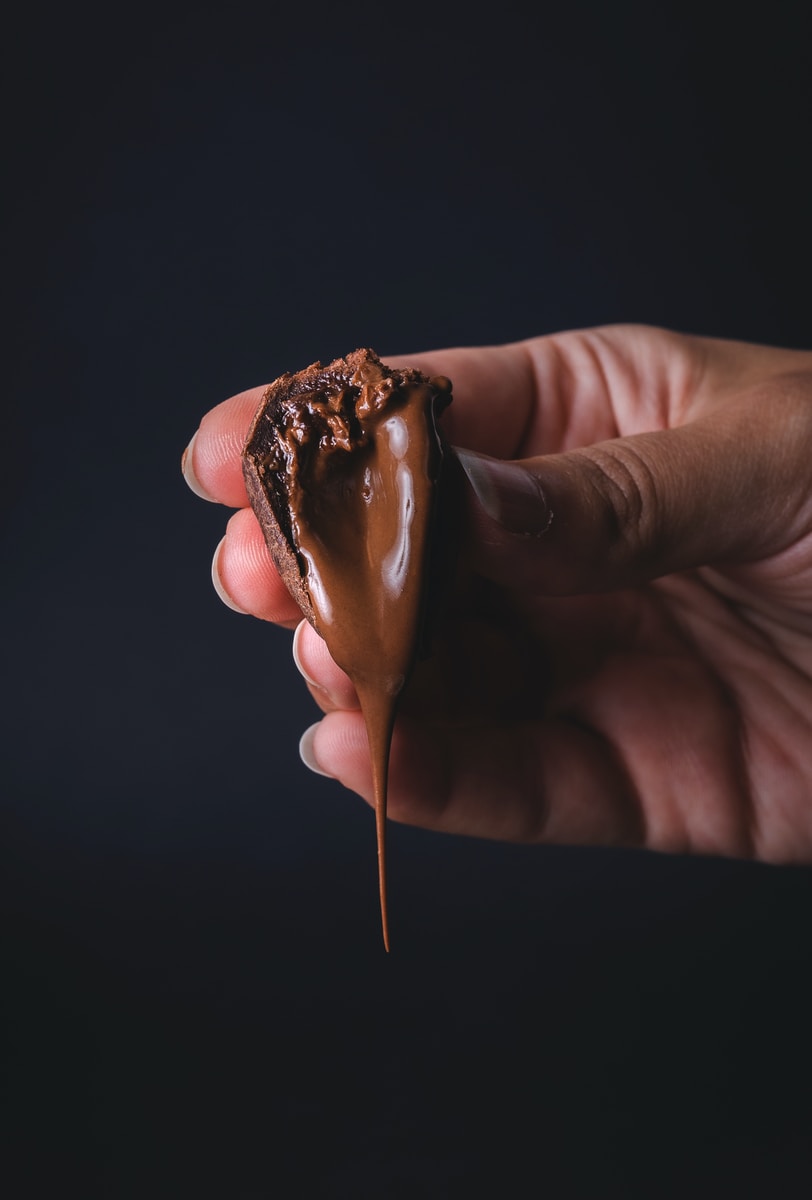
Chocolate fillings
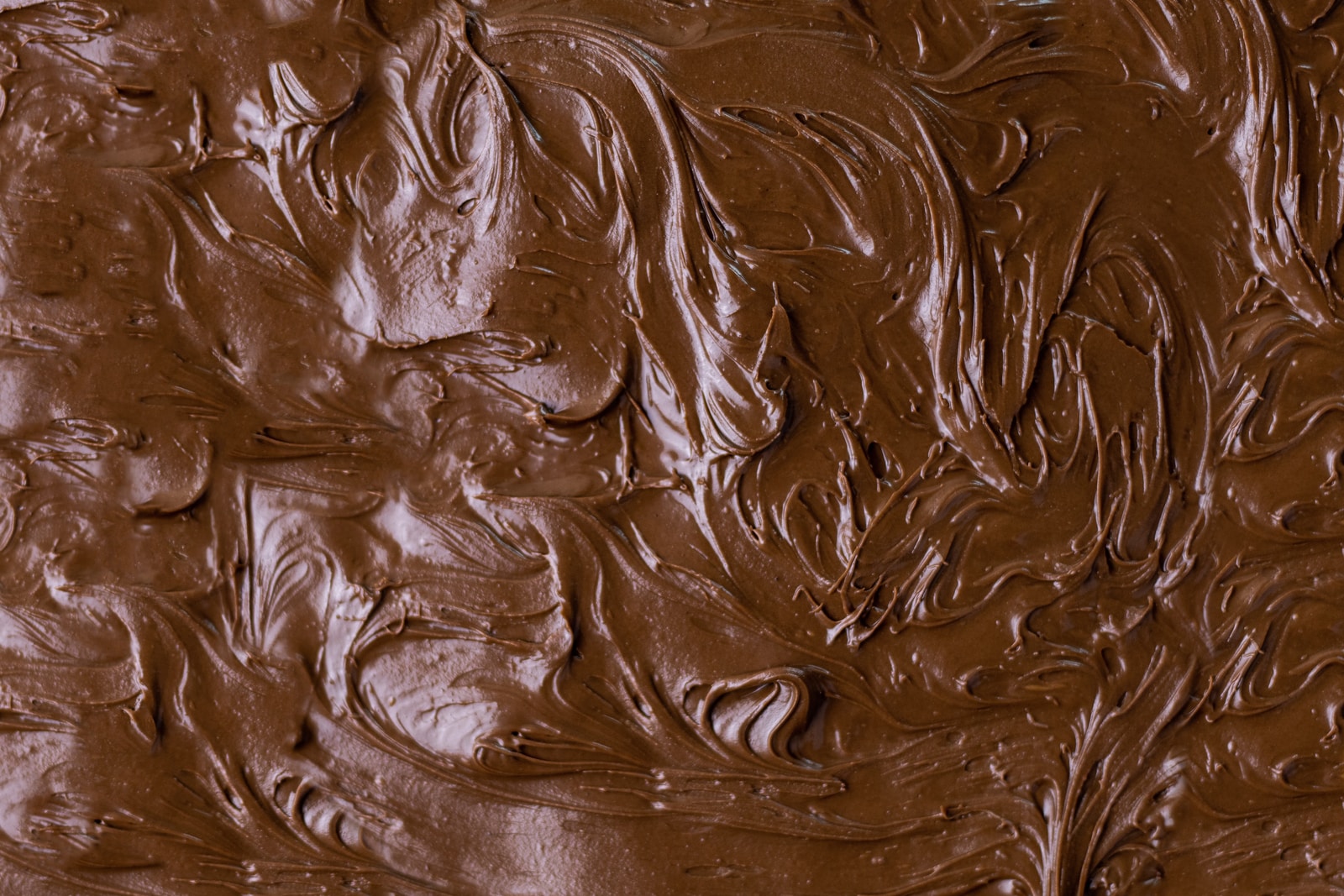
Chocolate spread
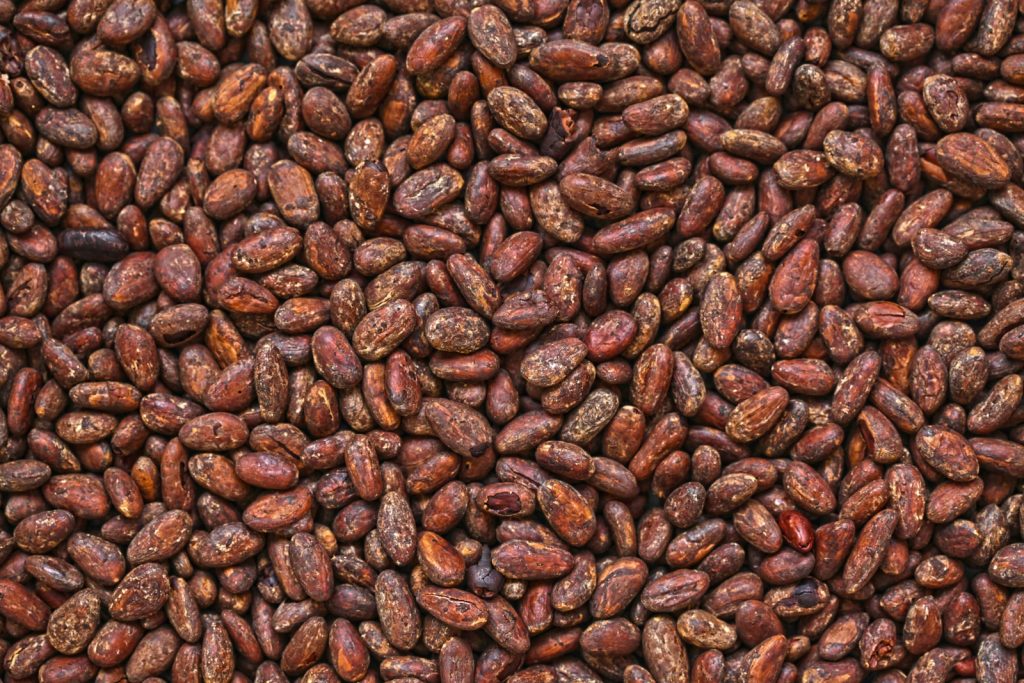
Cocoa beans
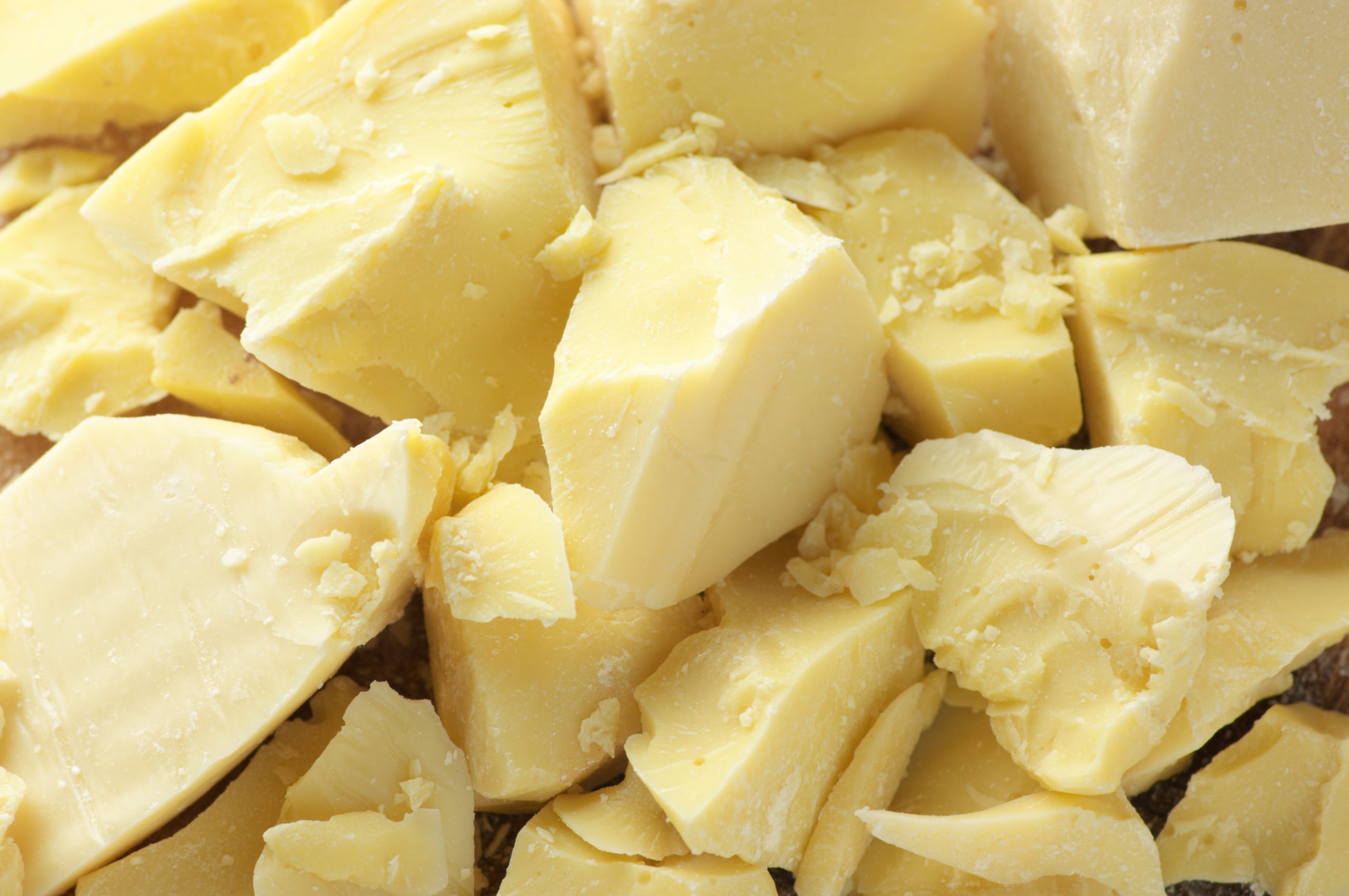
Cocoa butter
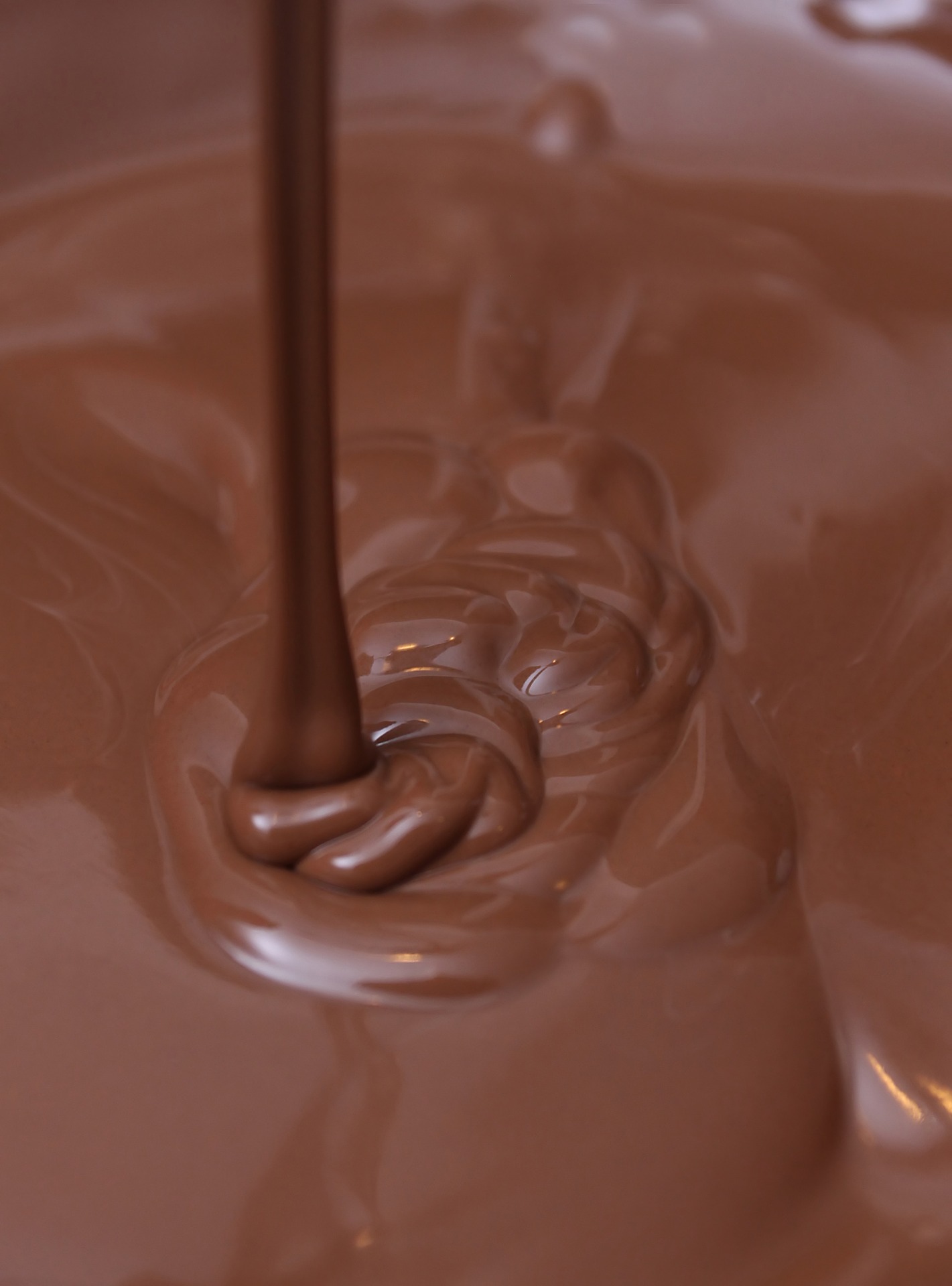
Cocoa liquor
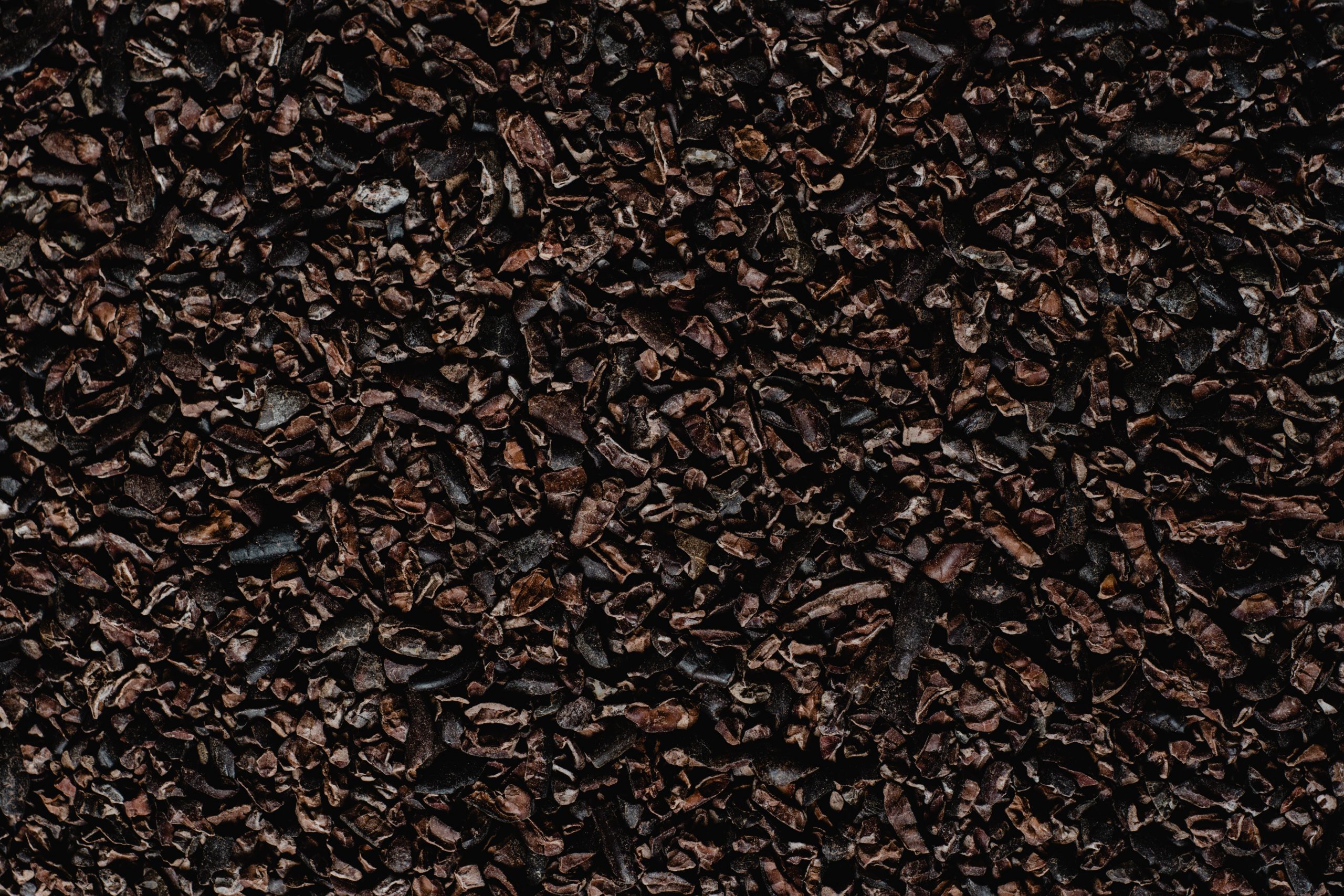
Cocoa nibs
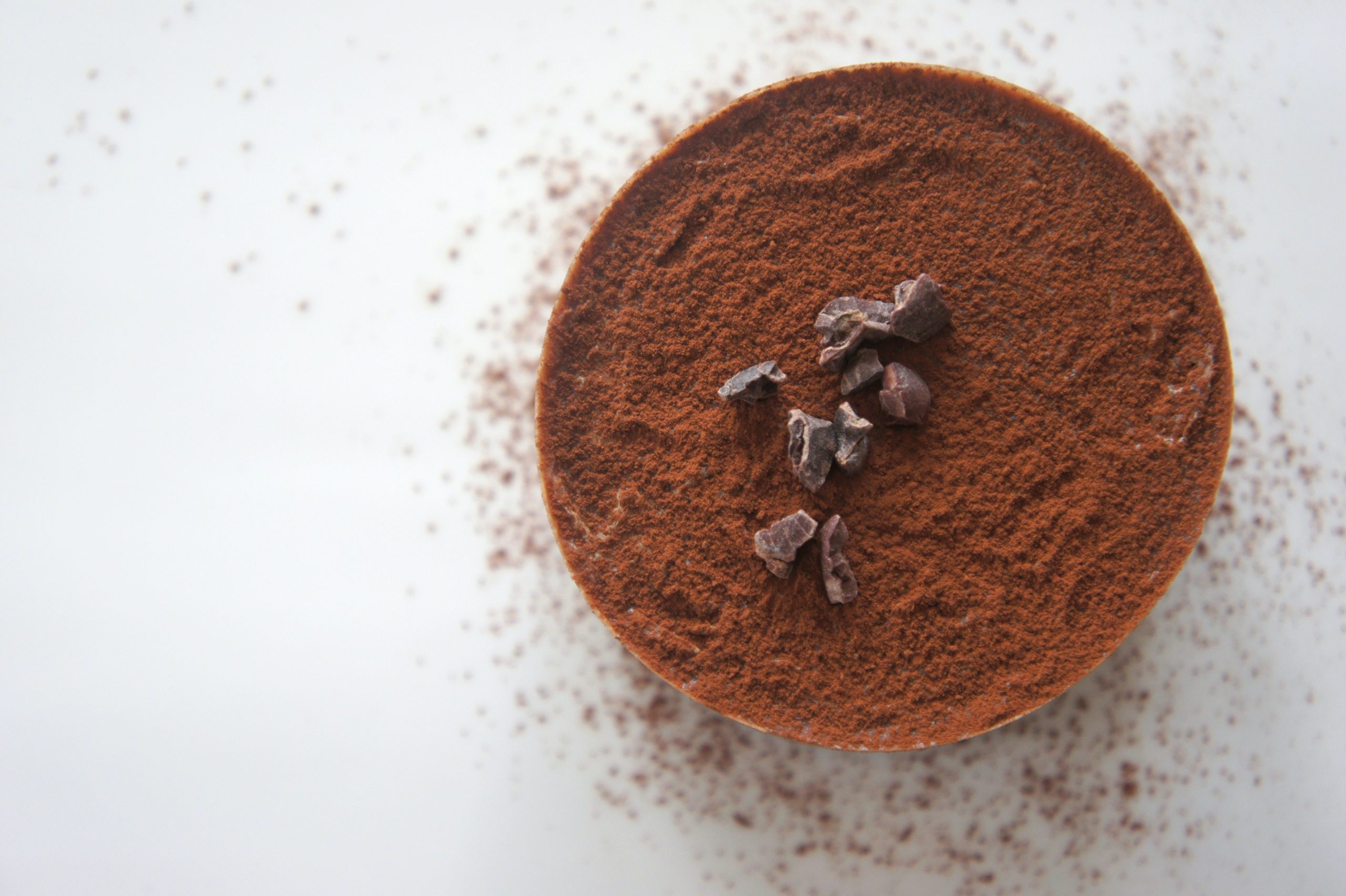
Cocoa powder
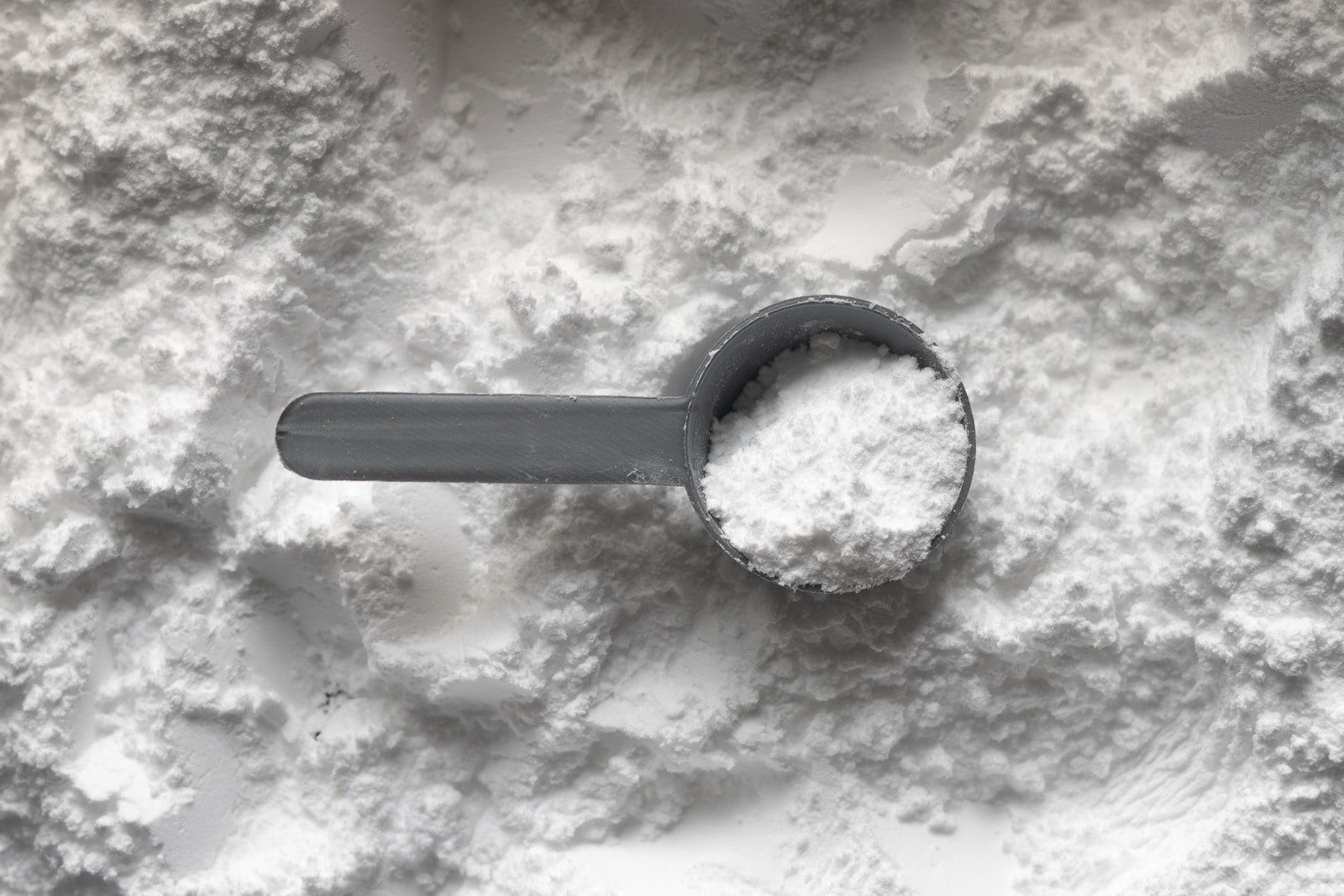
Collagen powder
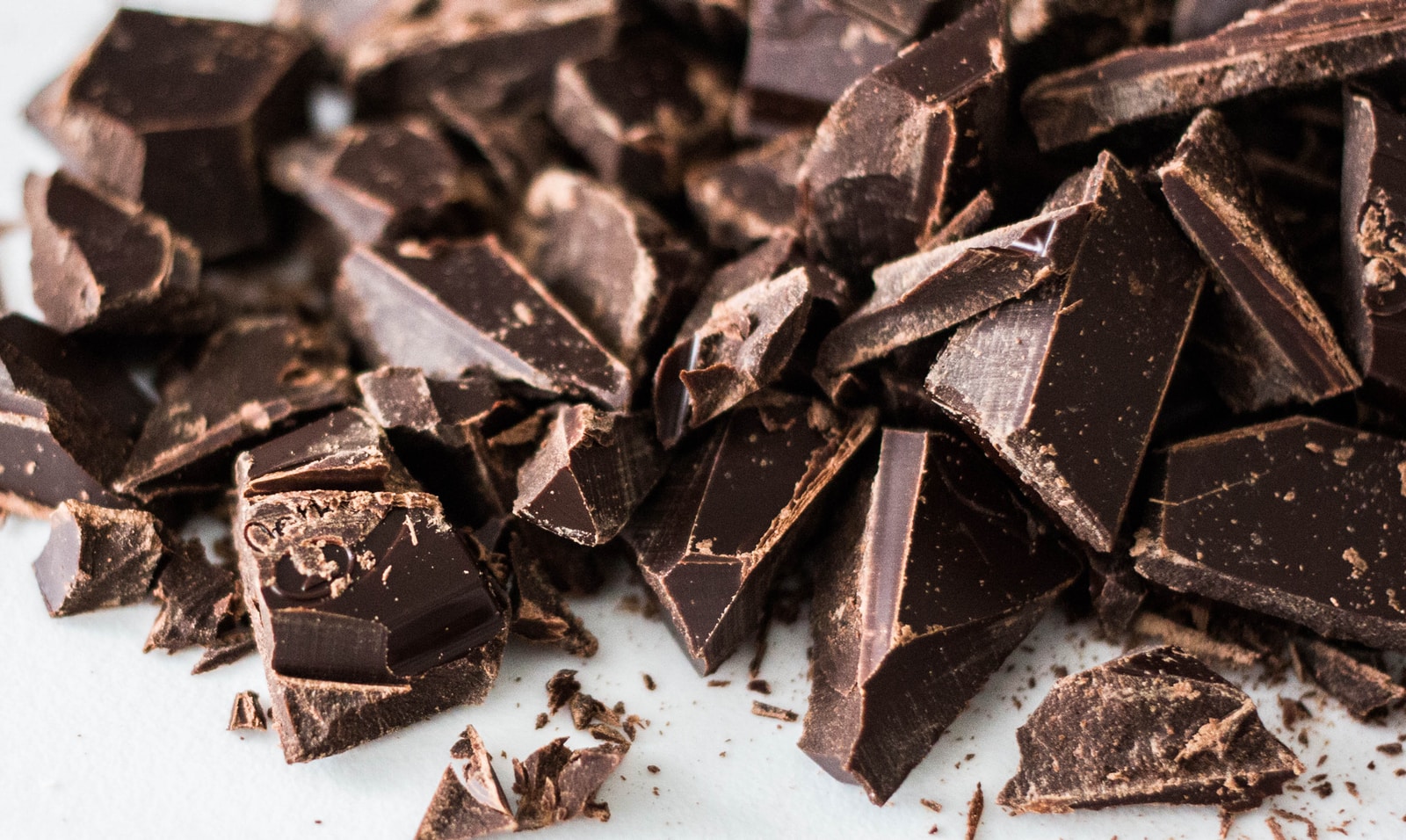
Compound chocolate
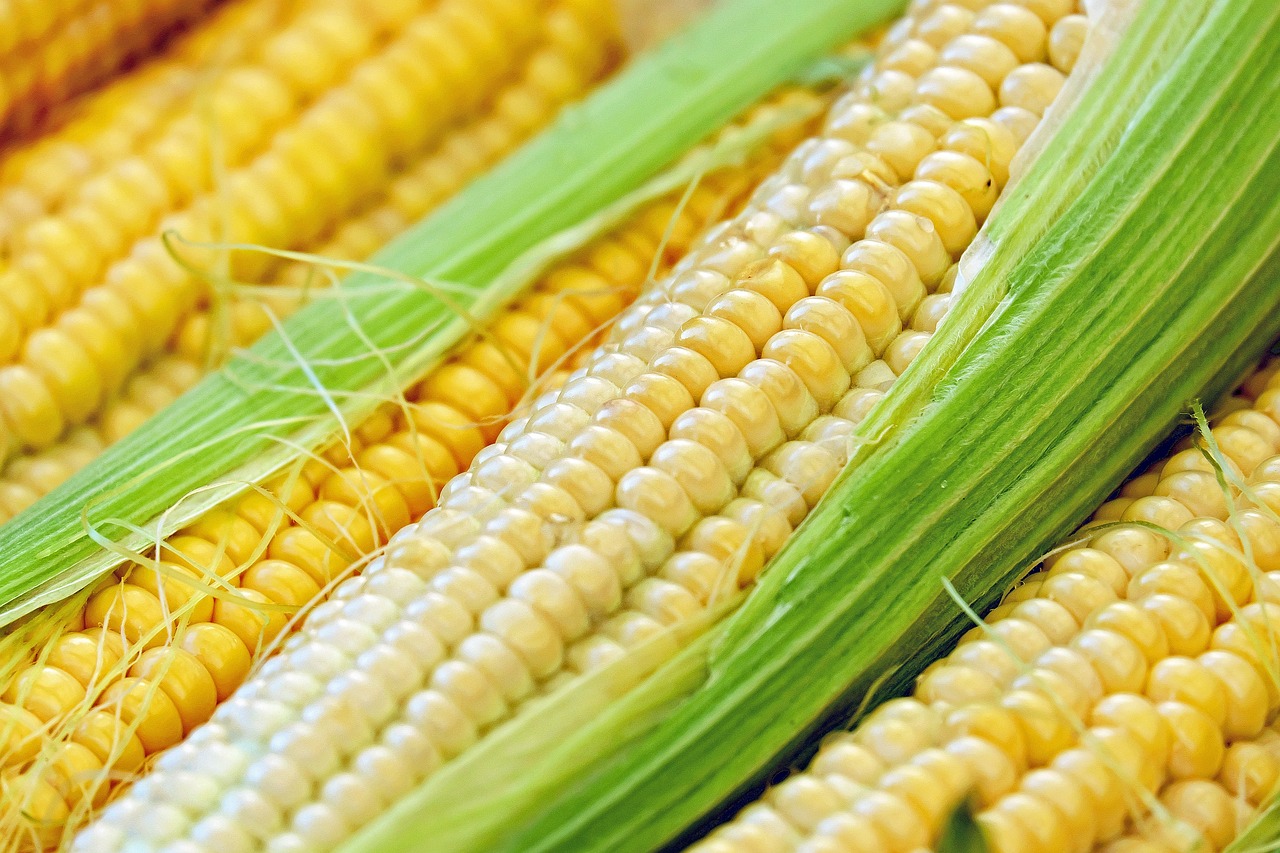
Corn
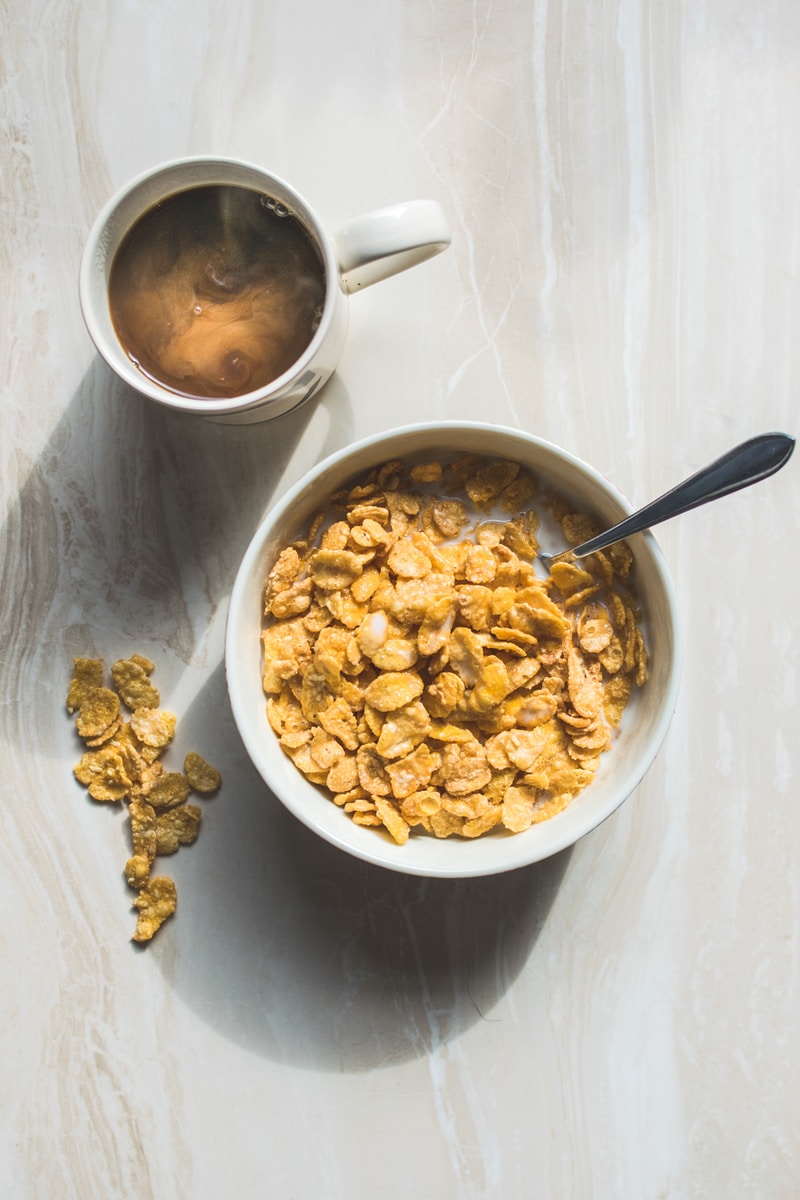
Corn flakes
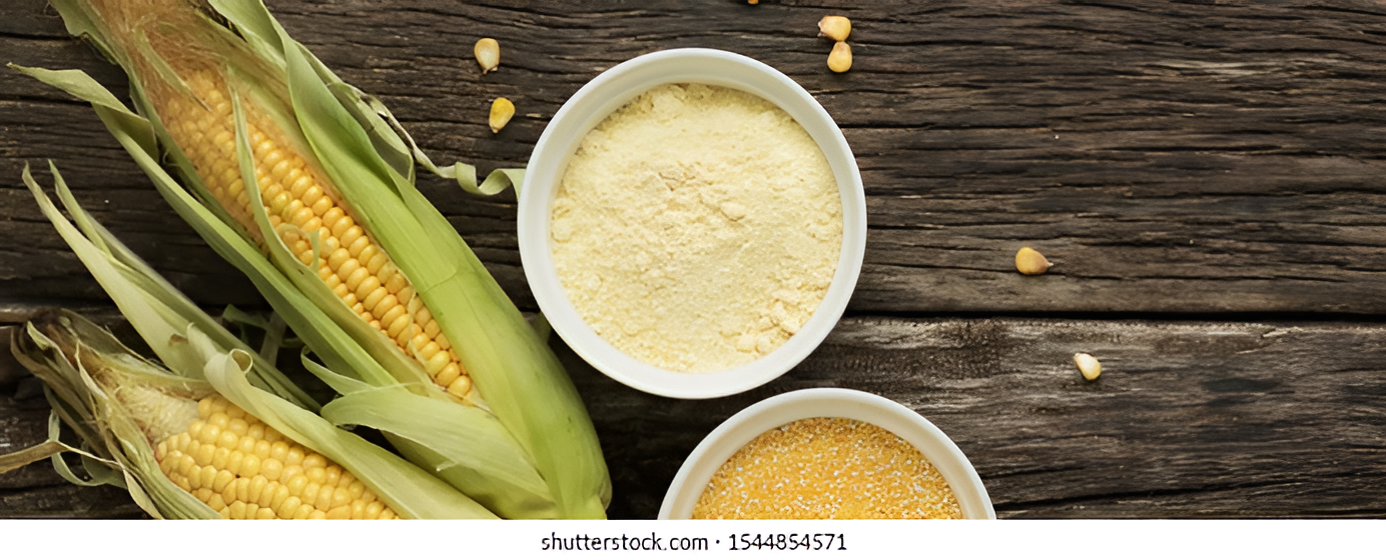
Corn flour

Corn grits
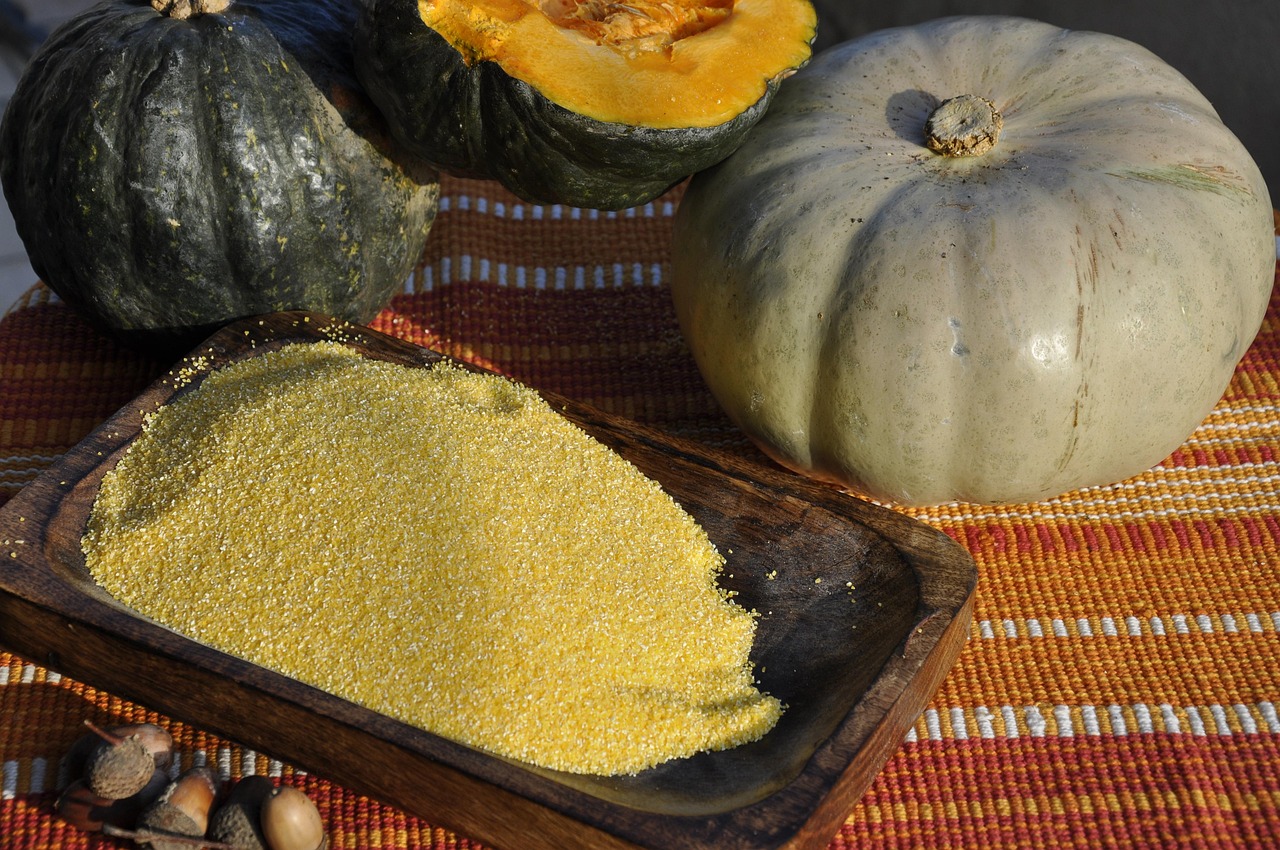
Cornmeal
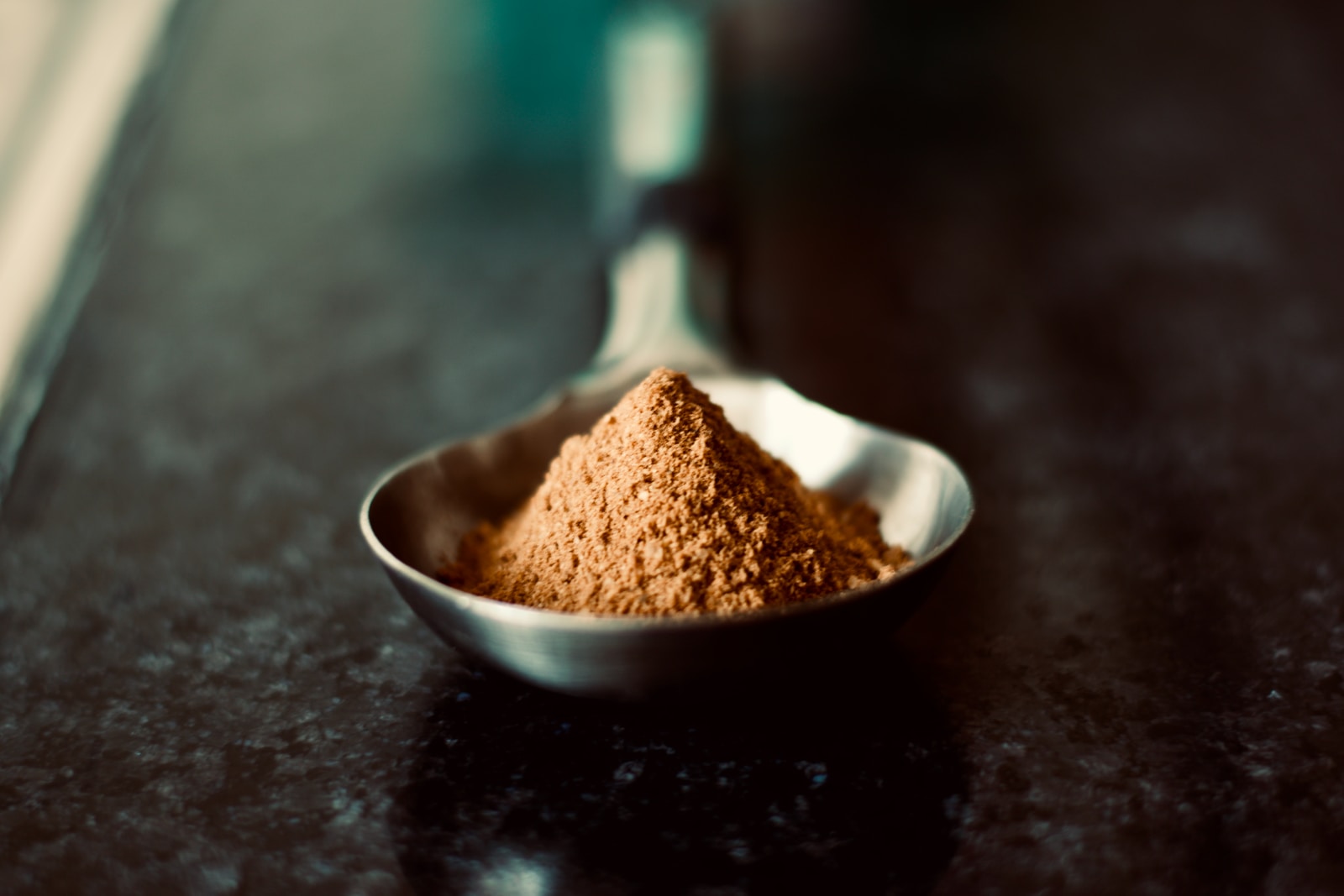
Cottonseed meal
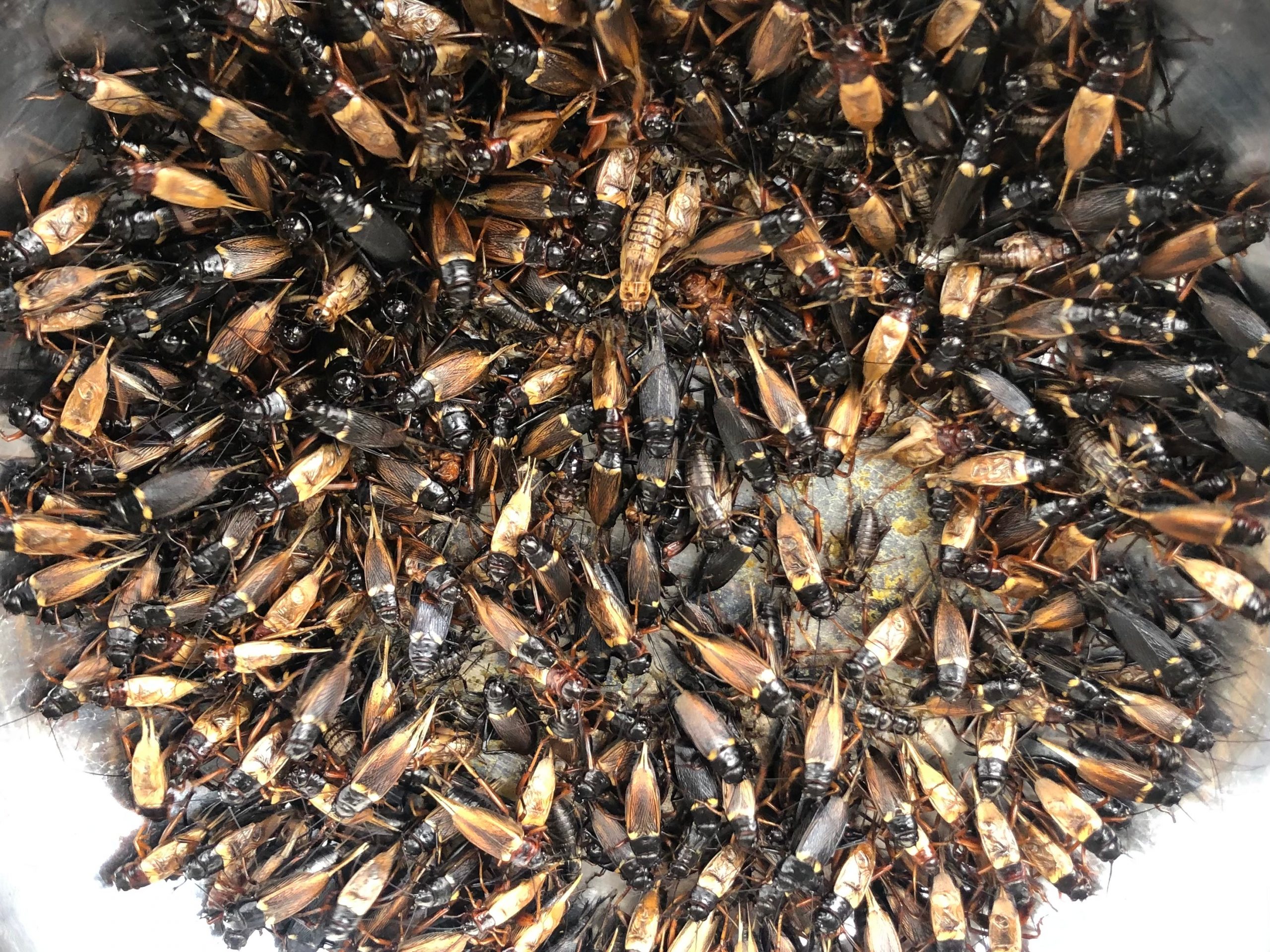
Cricket protein
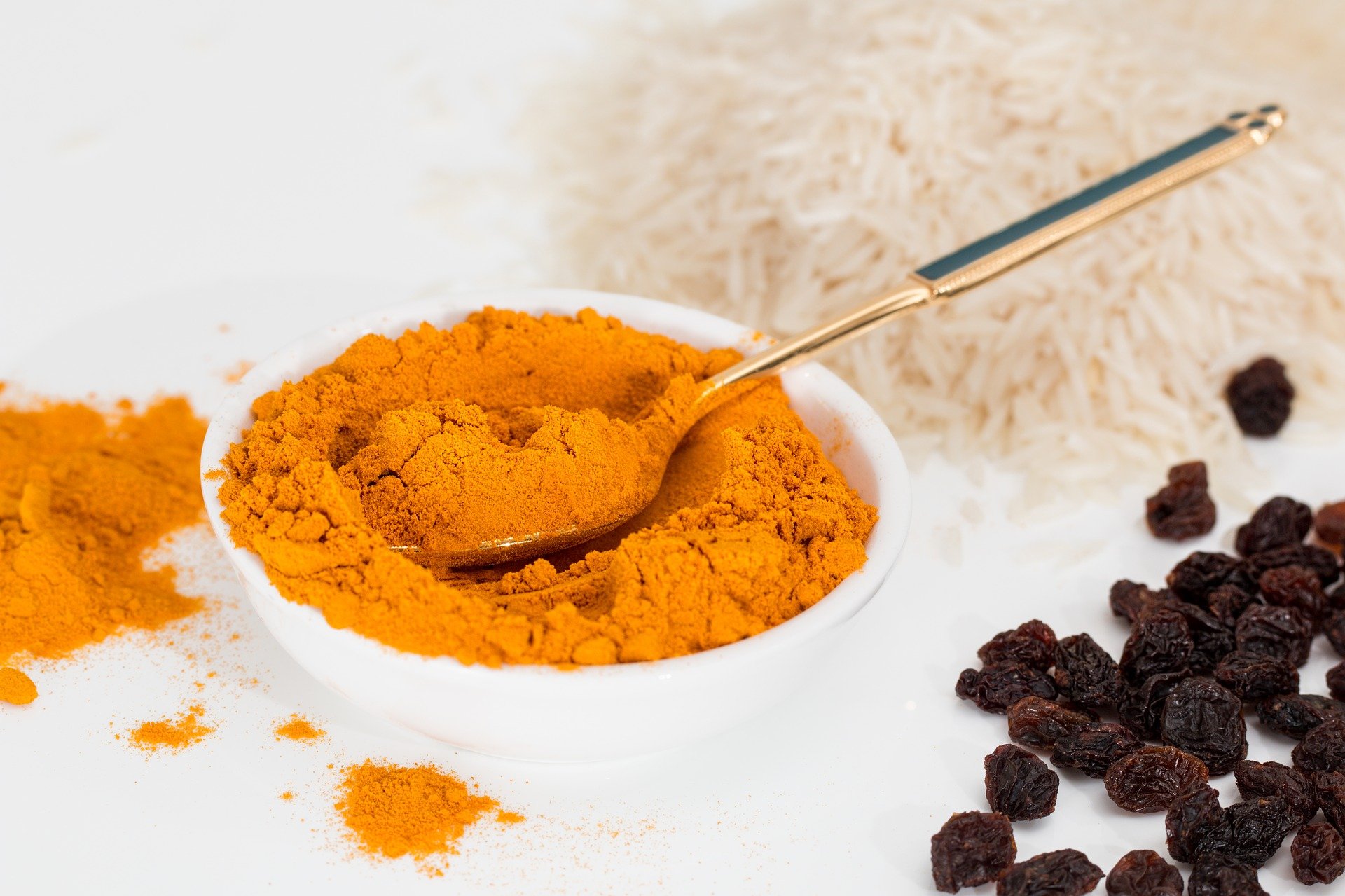
Curry powder
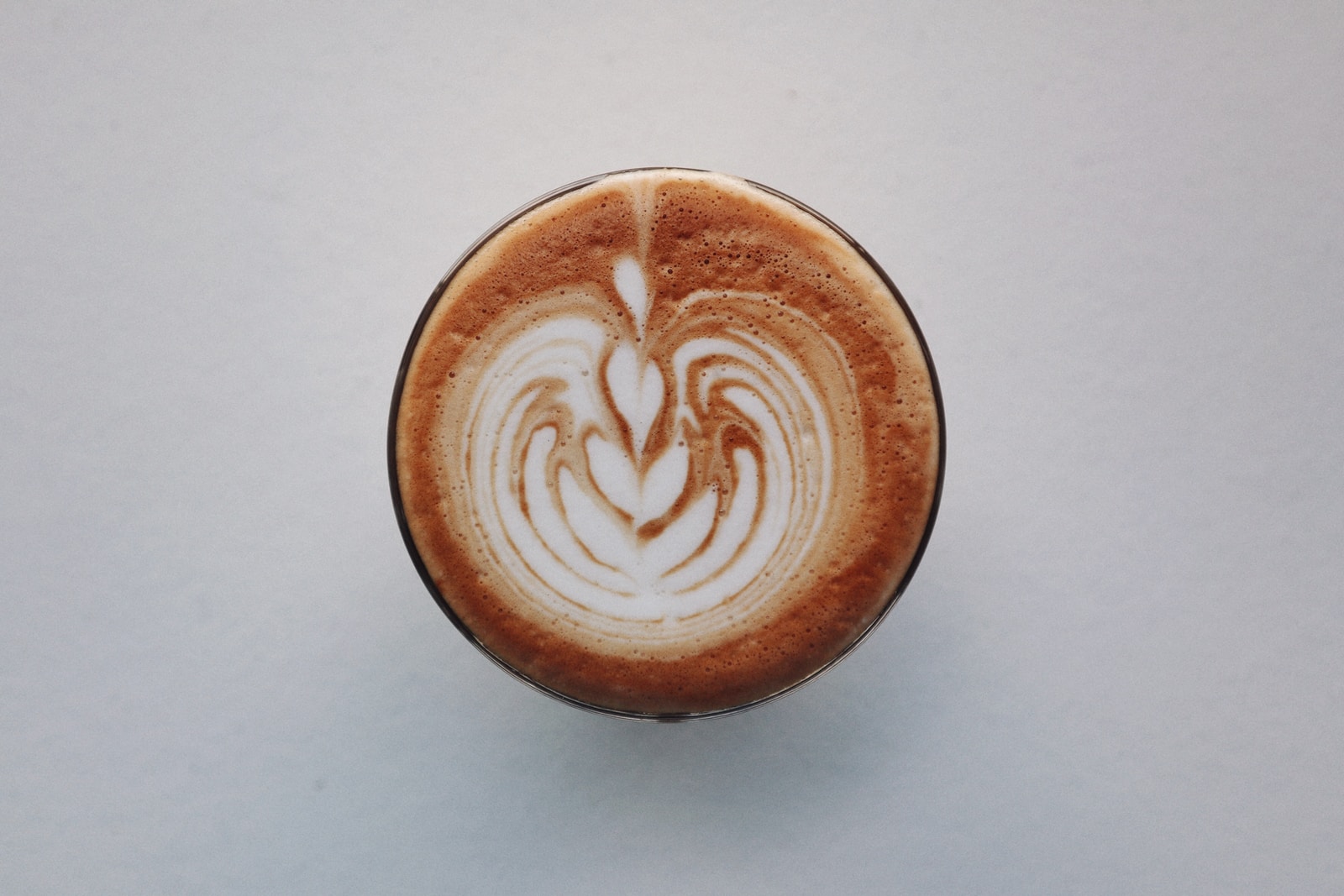
Decaffeinated coffee
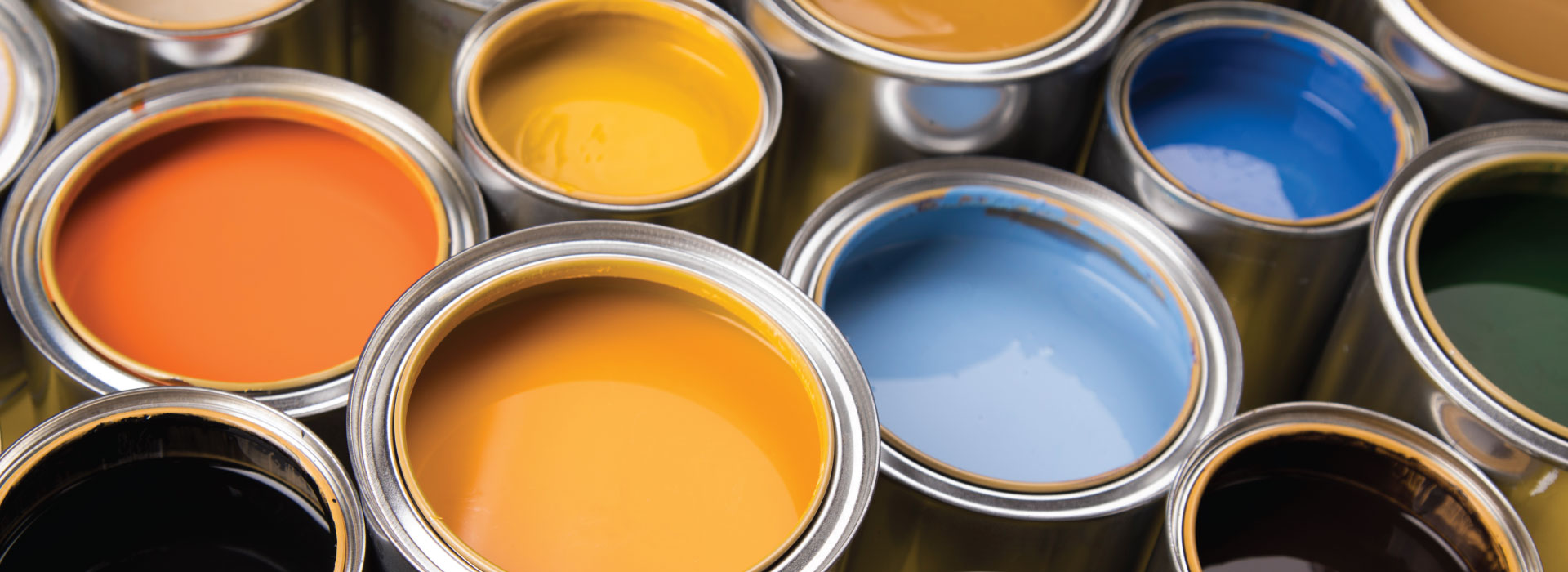
Dispersion paints
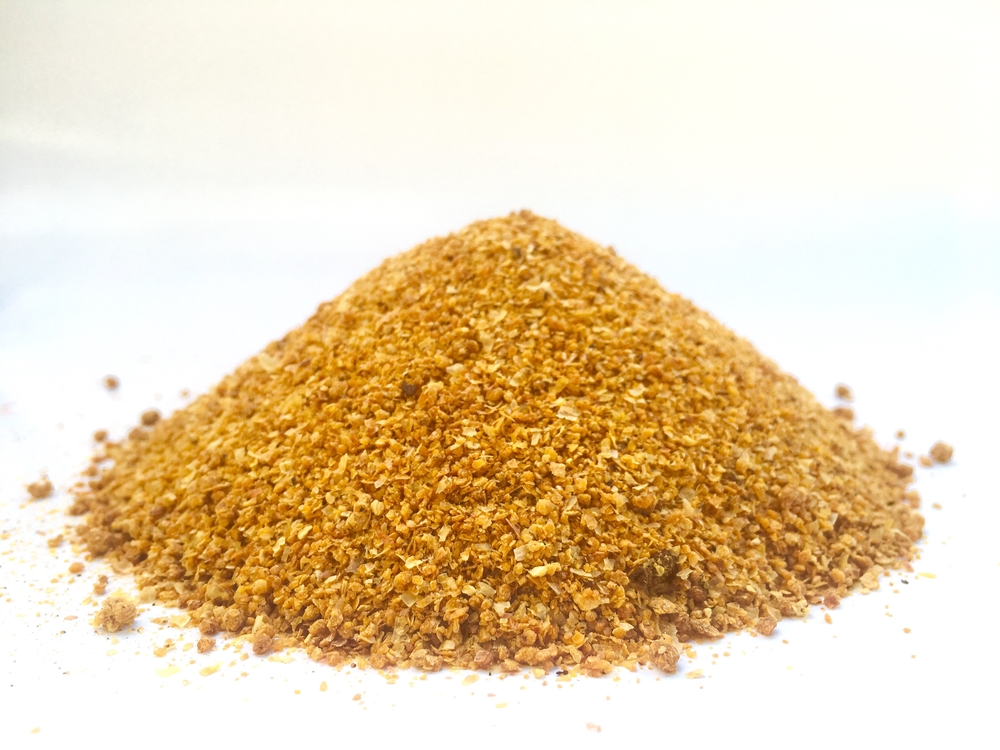
Dried distillers grains (DDGS)
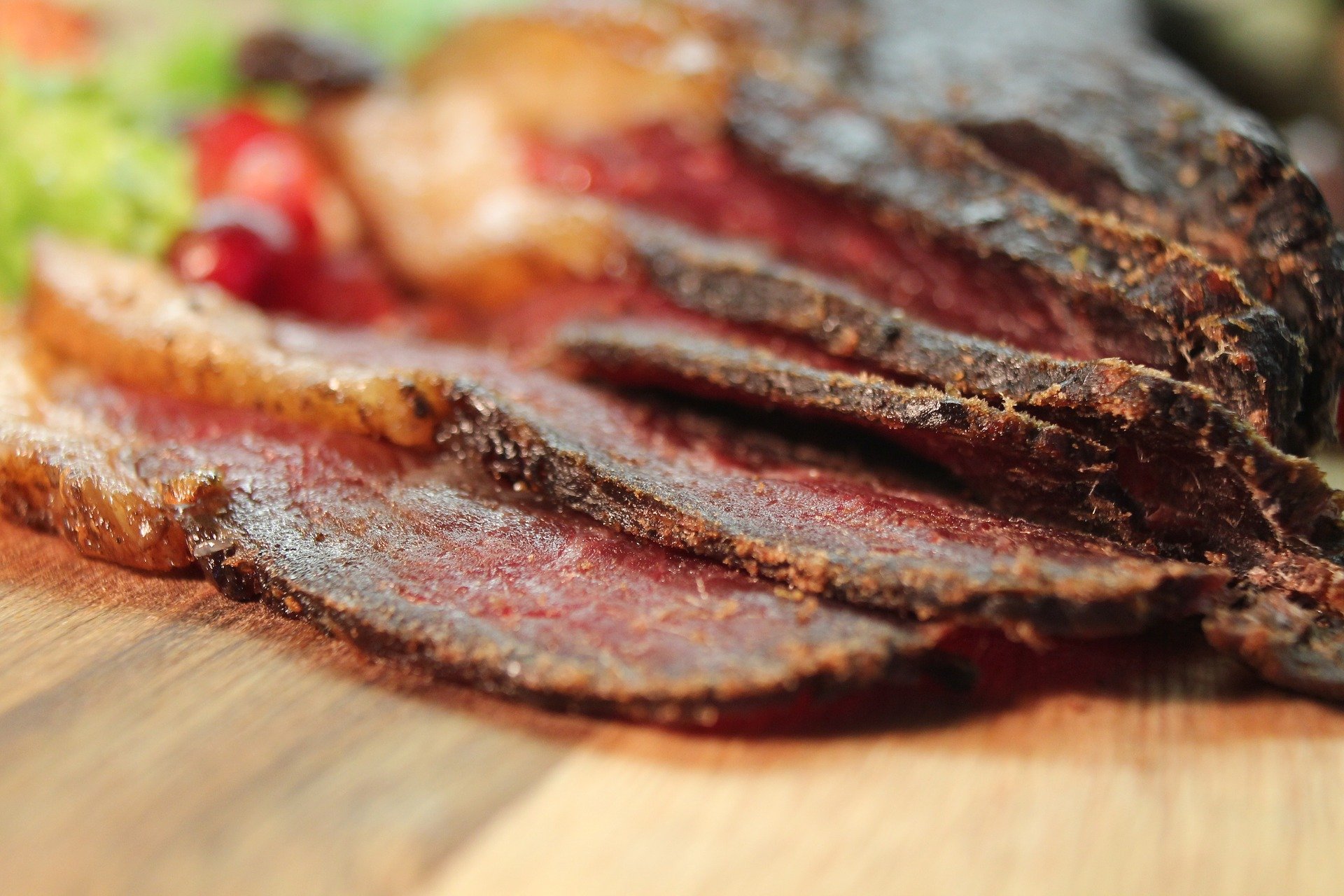
Dried meat
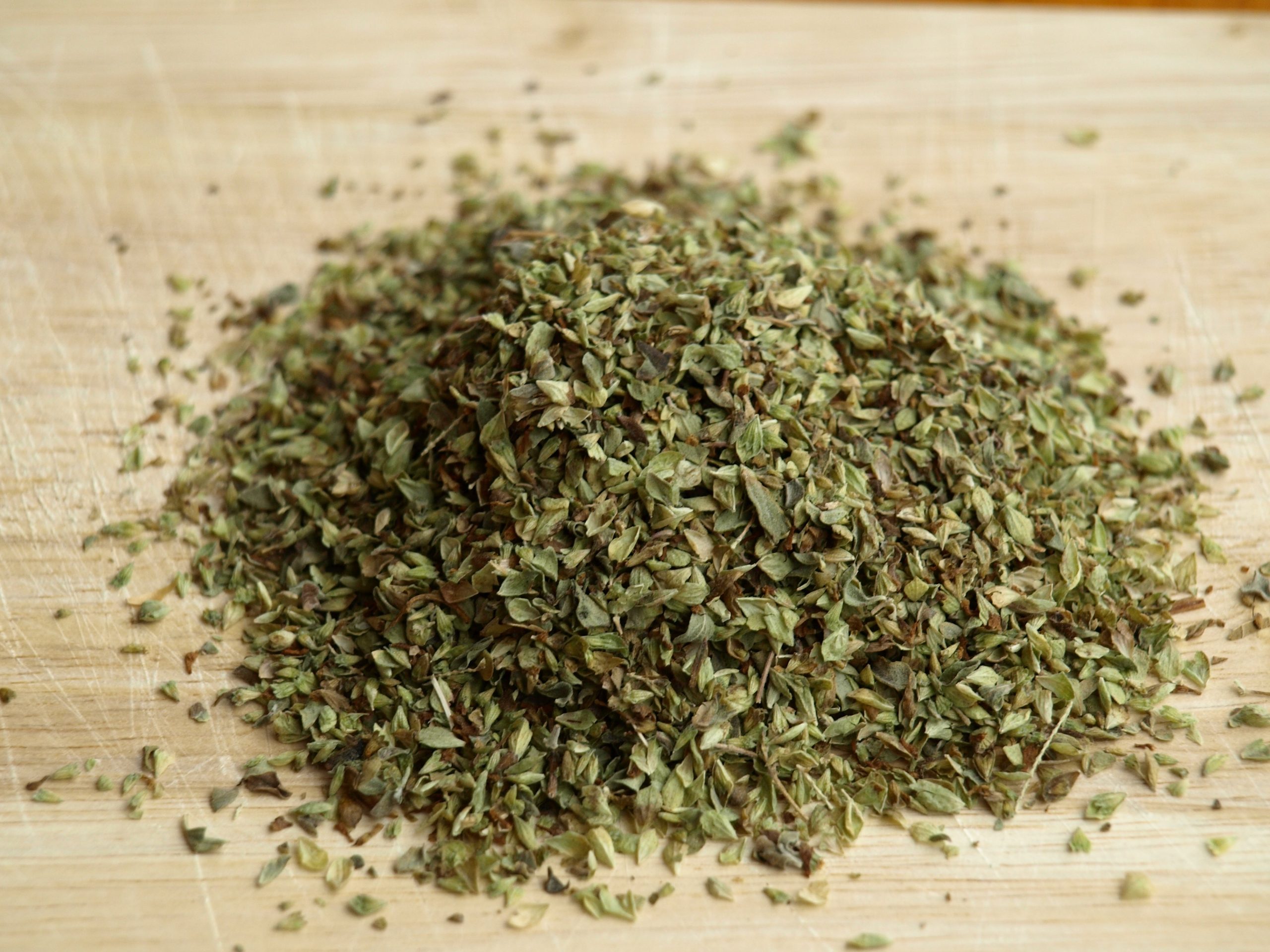
Dried oregano
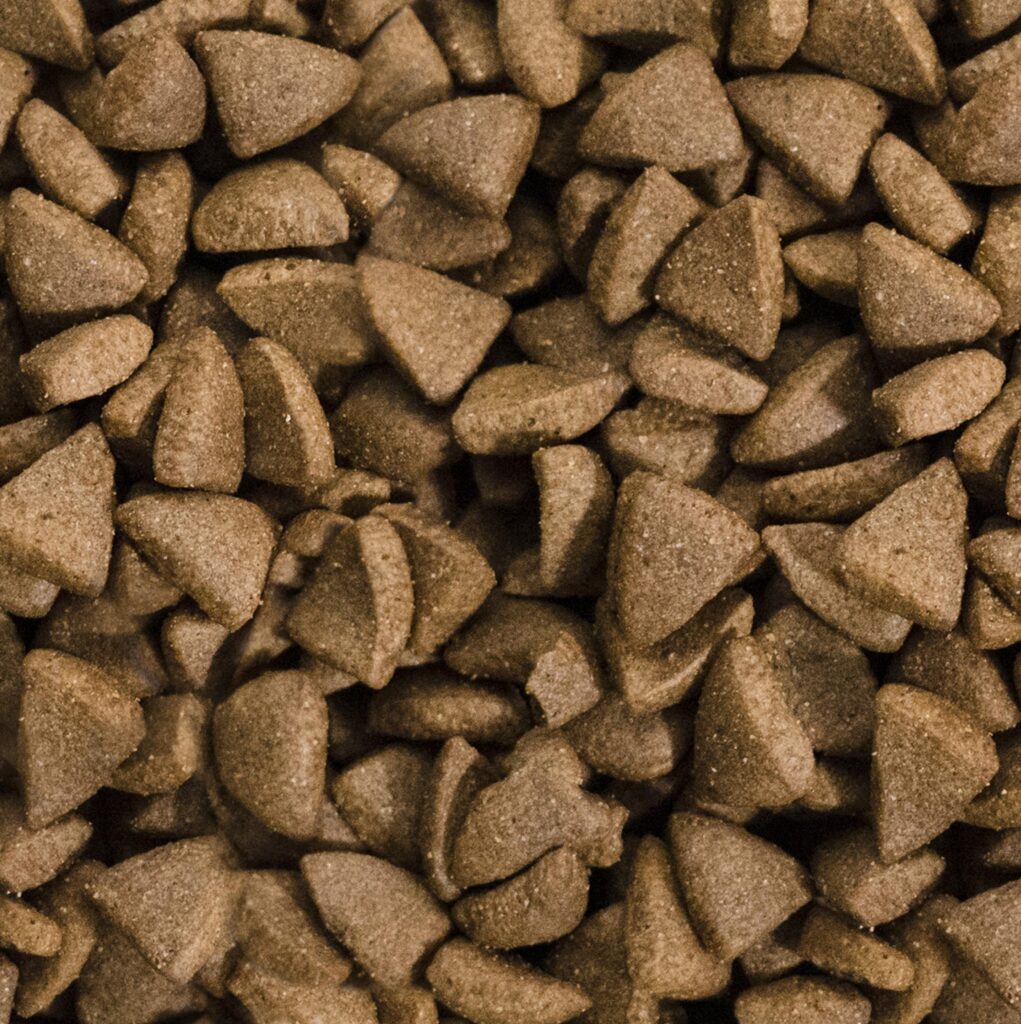
Dry pet food
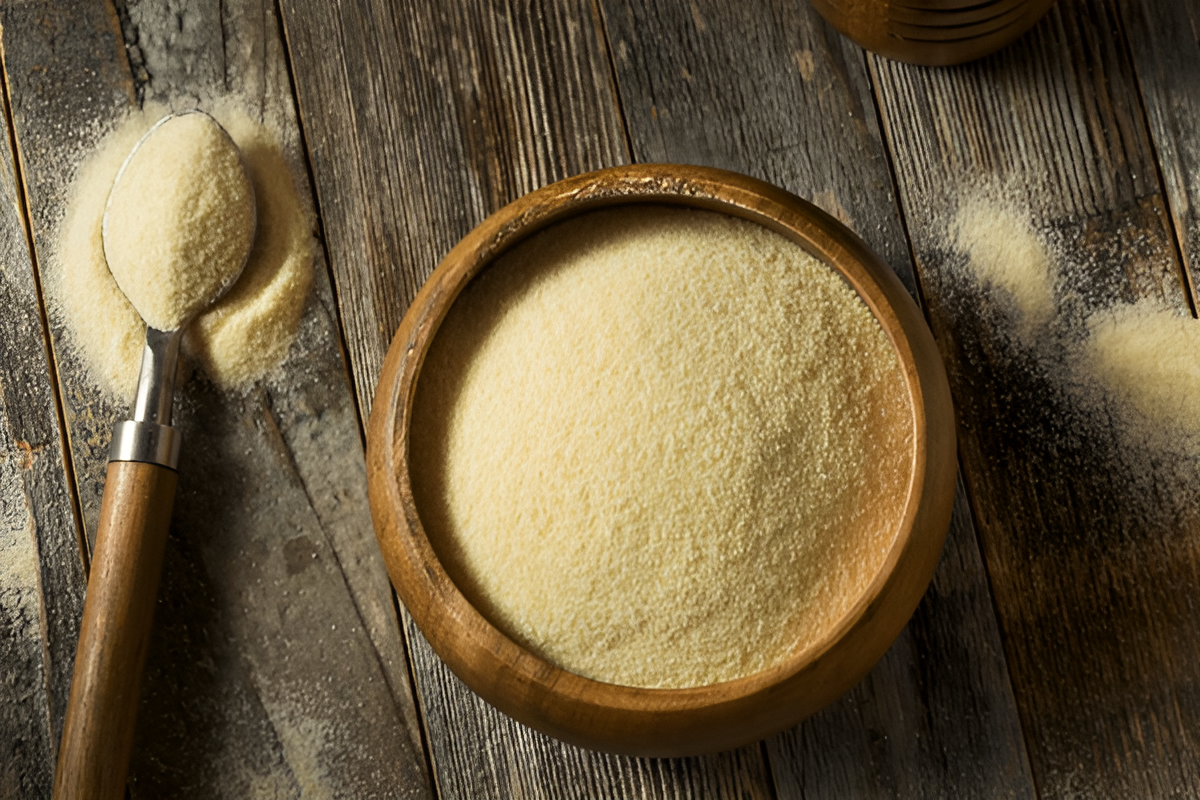
Durum wheat semolina
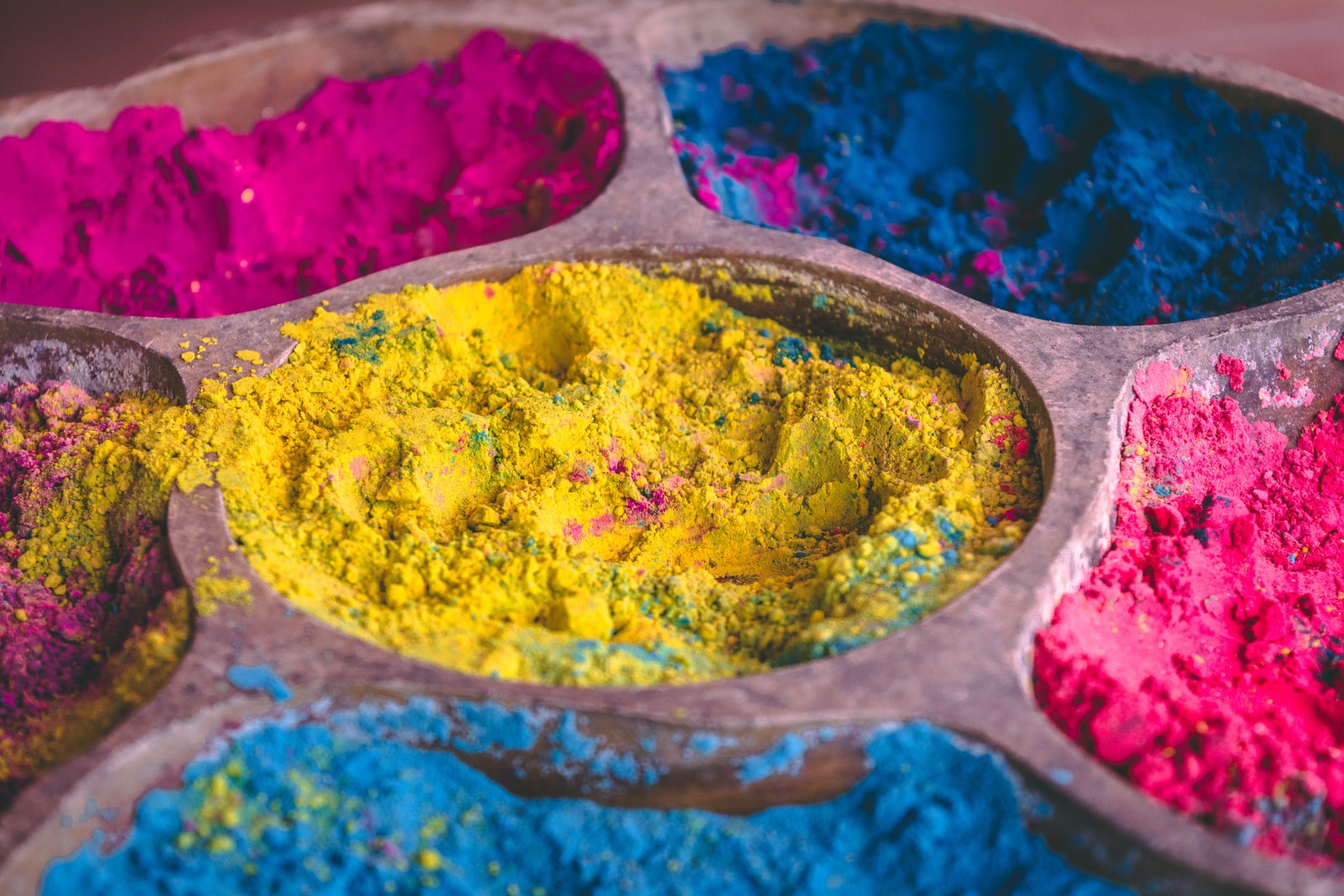
Dyes
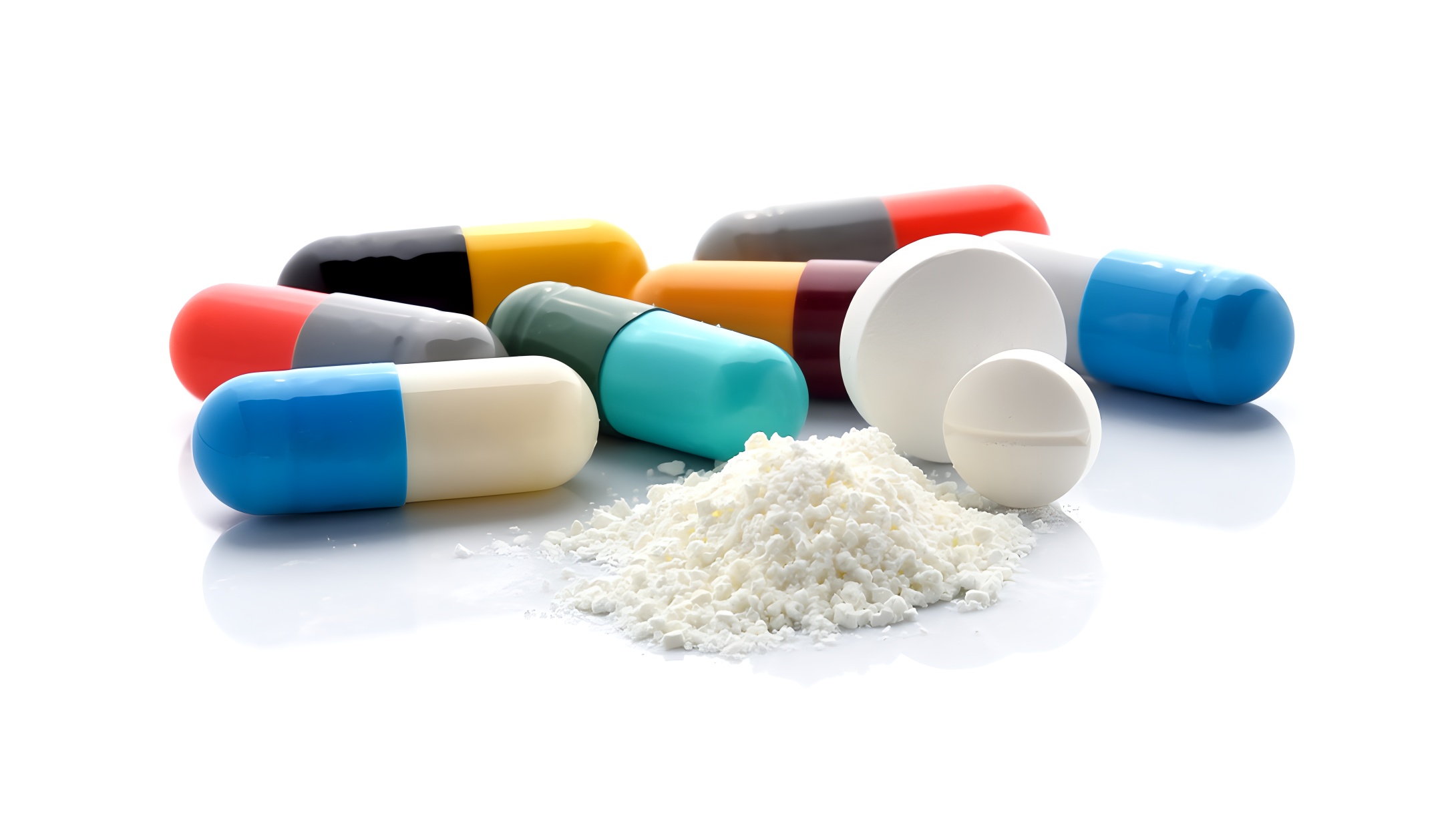
Excipients
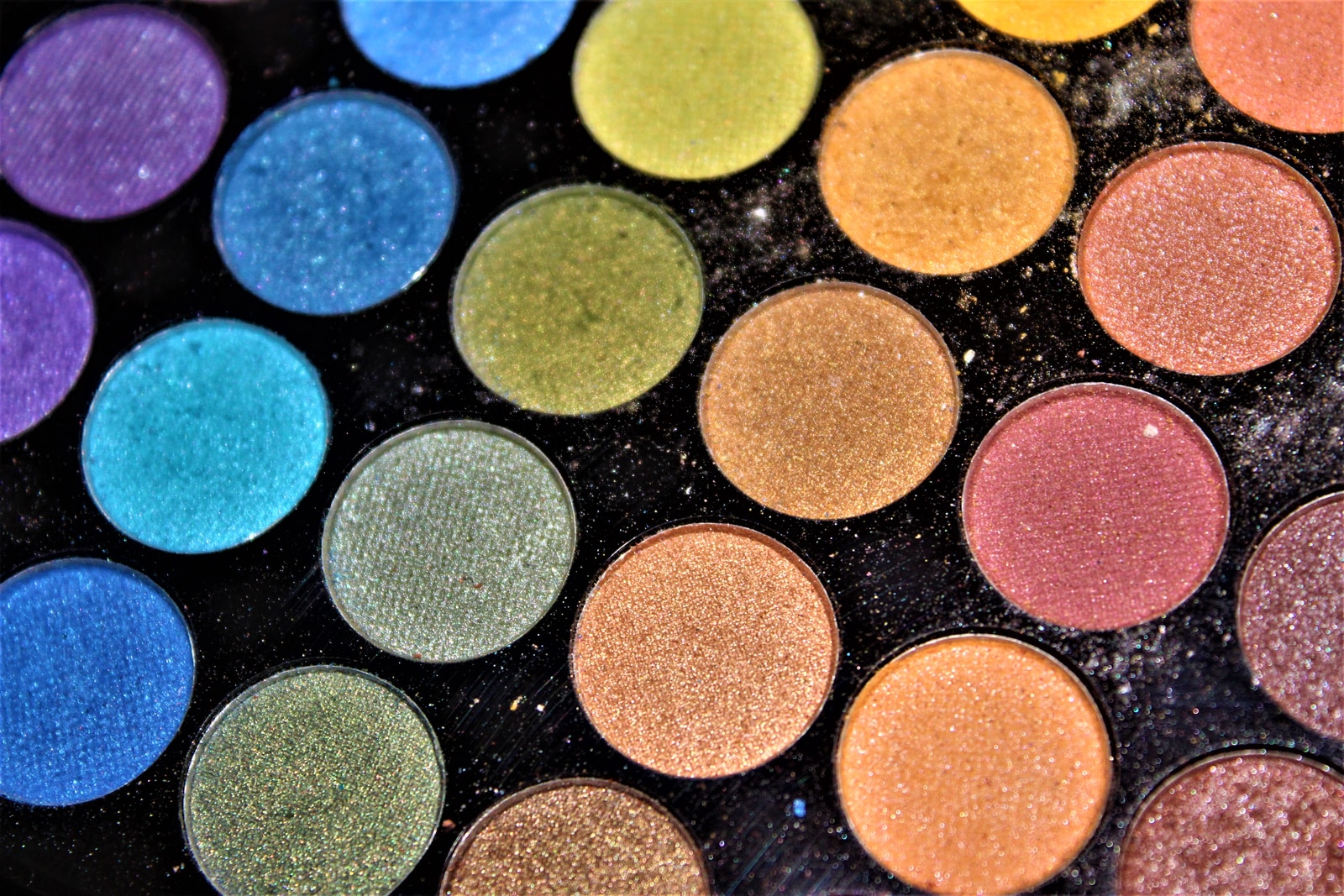
Eyeshadow
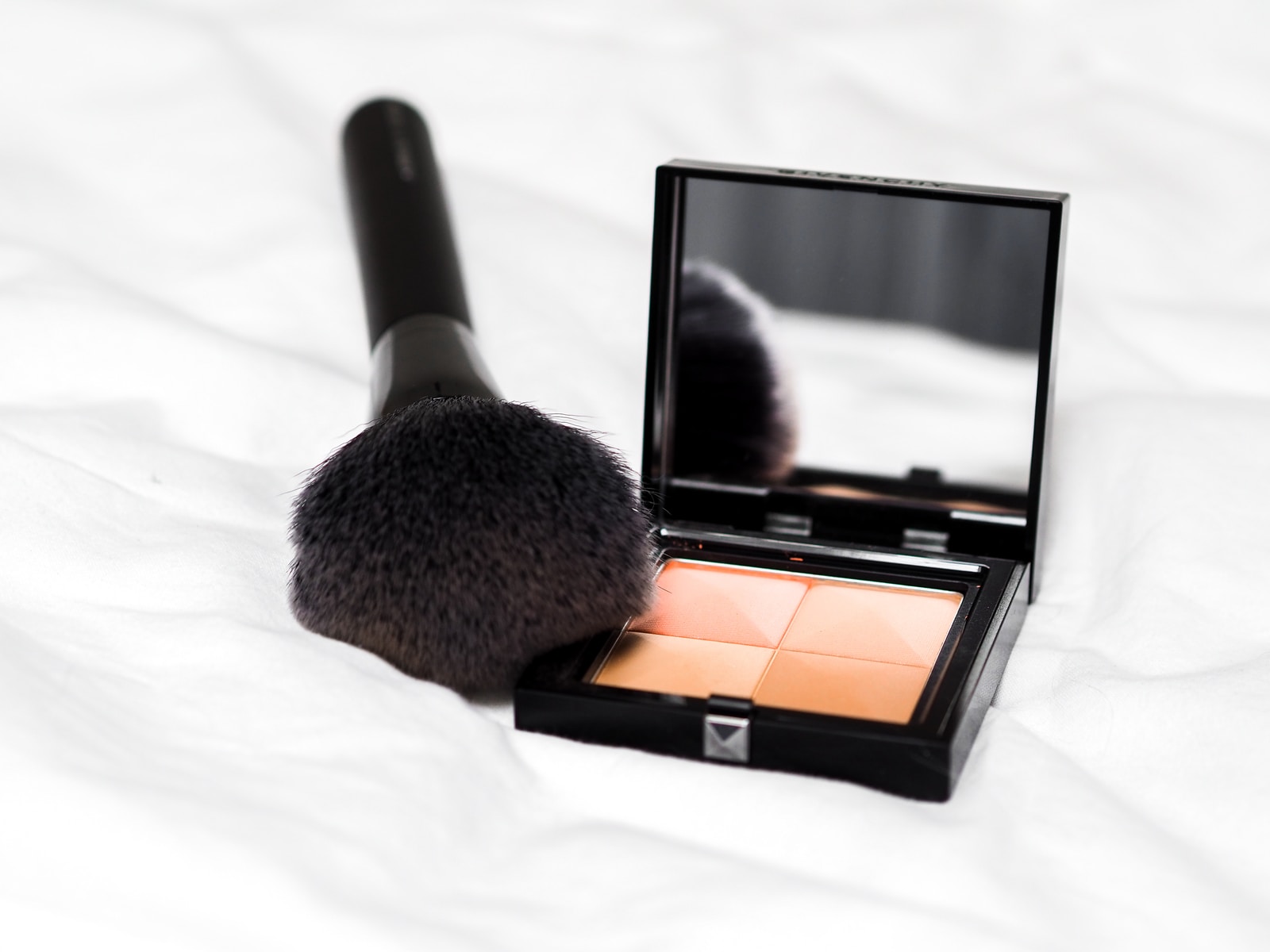
Face powder
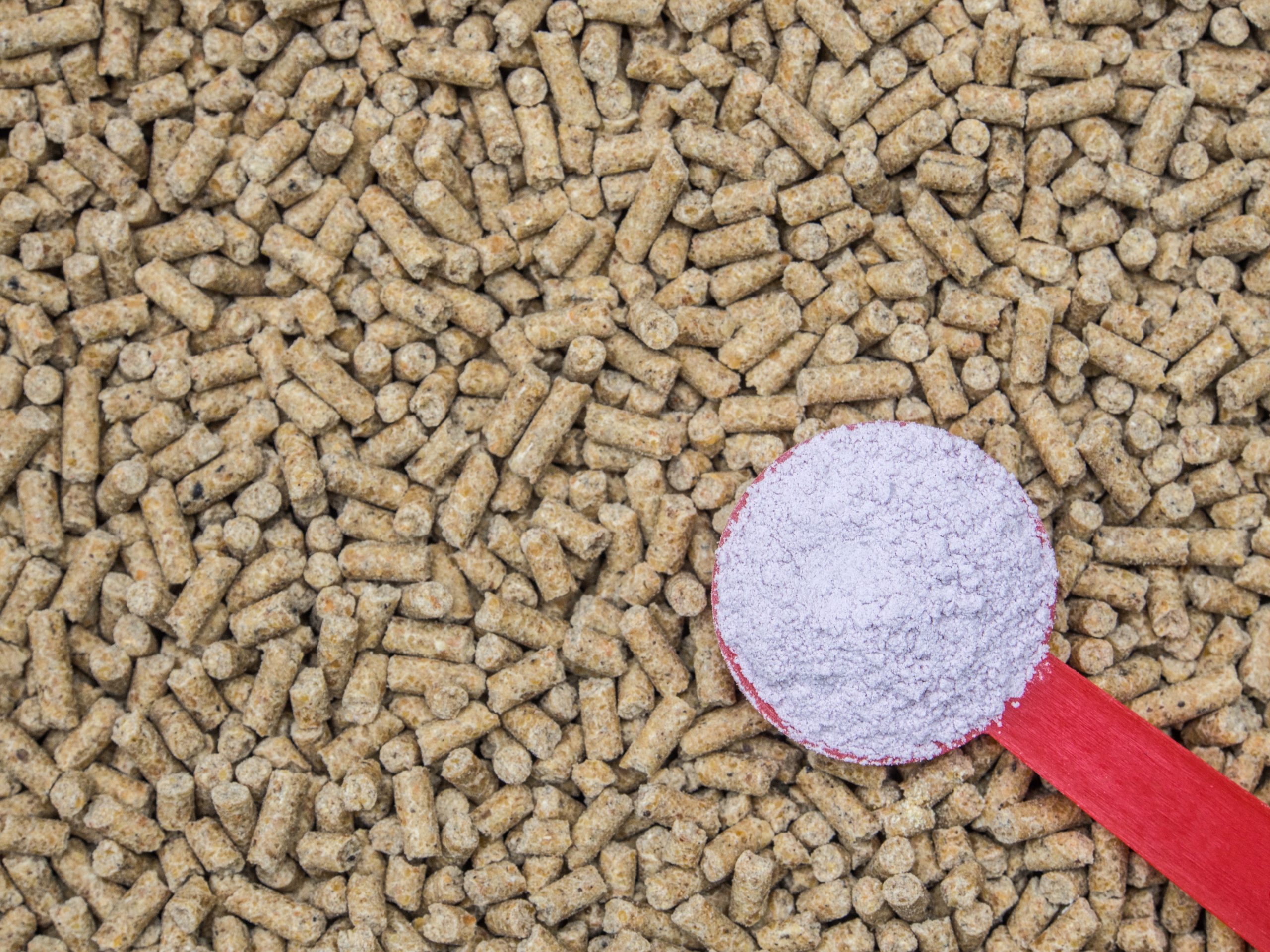
Feed concentrates
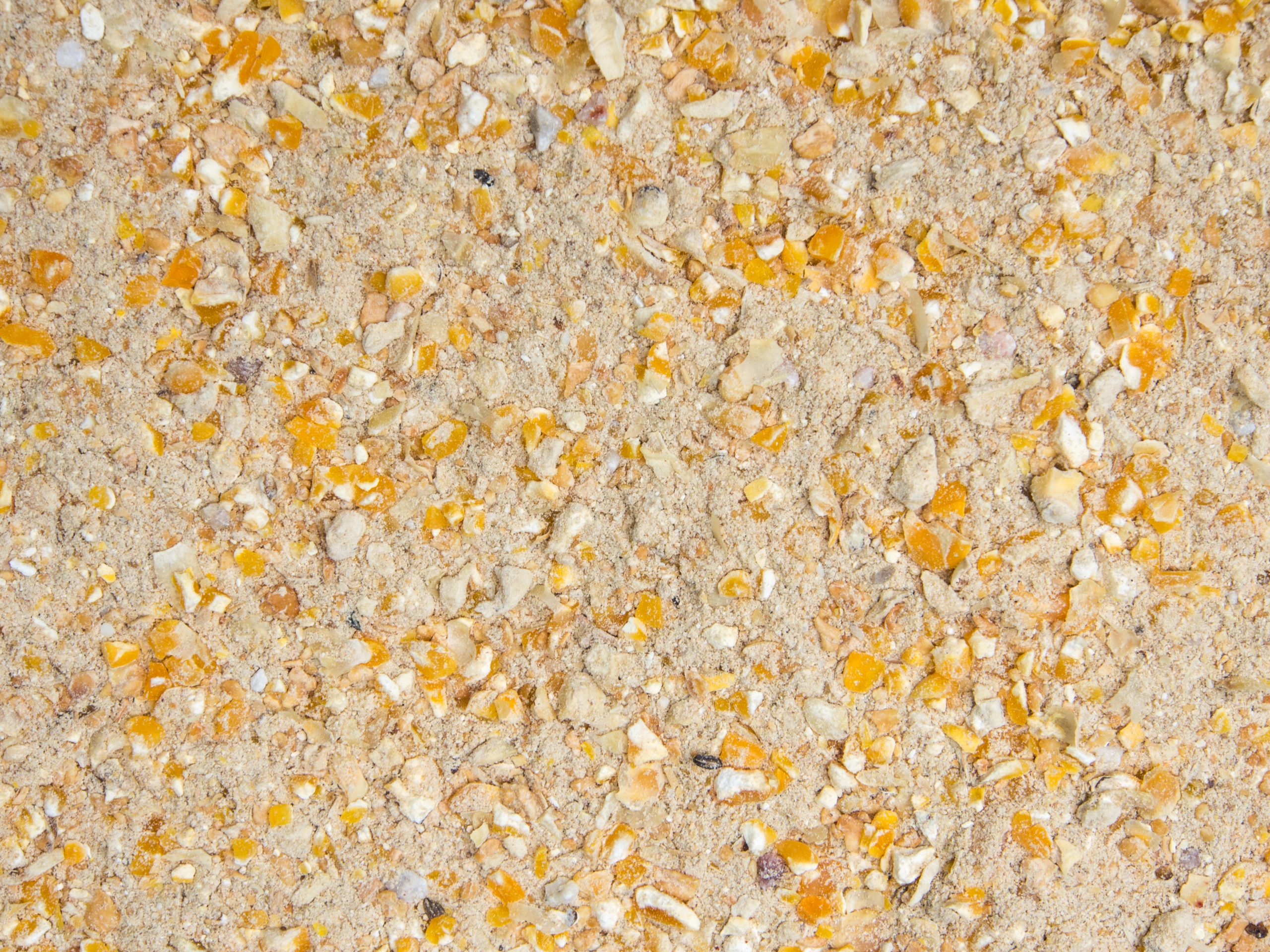
Feed premixes
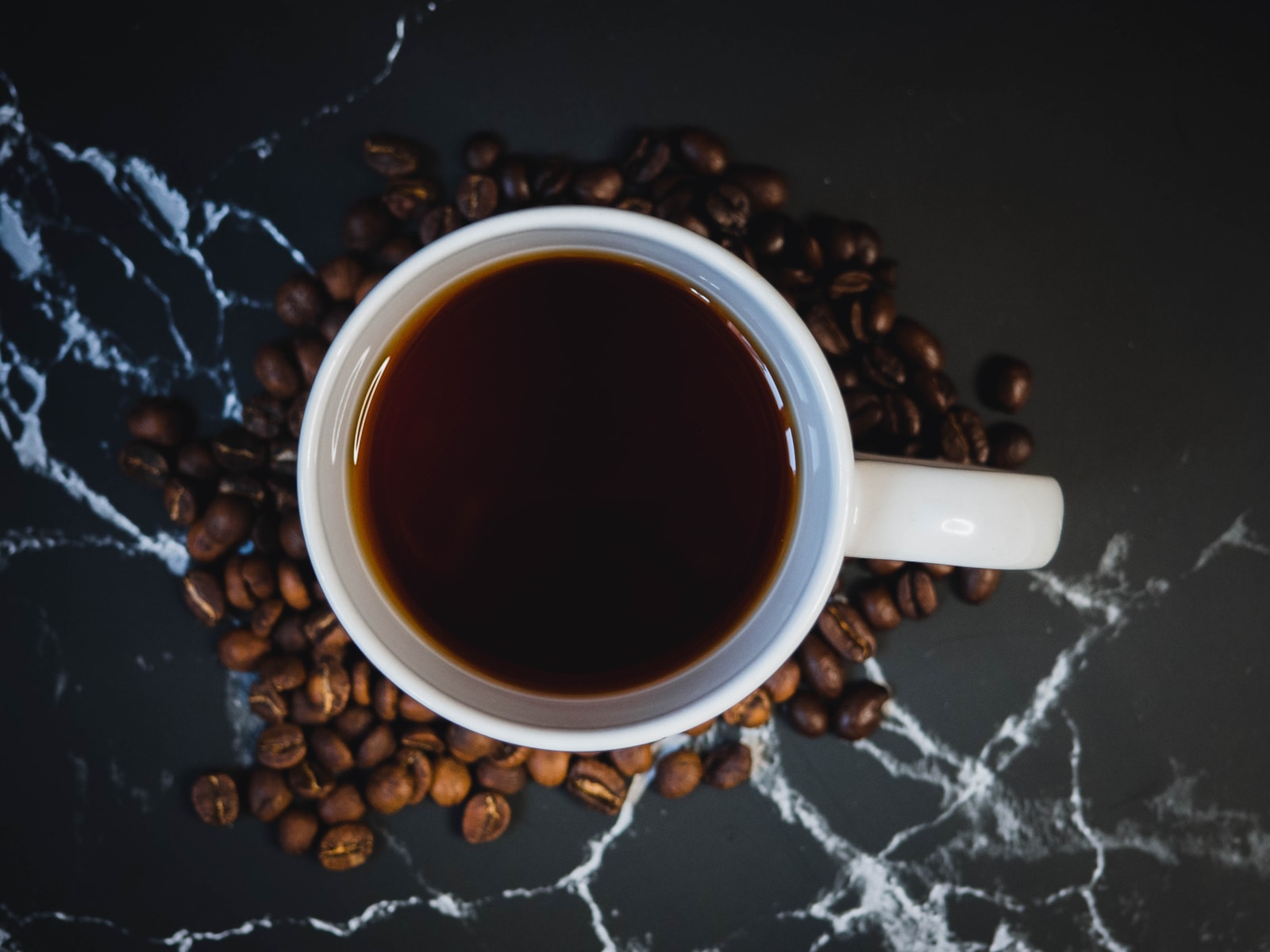
Filter coffee
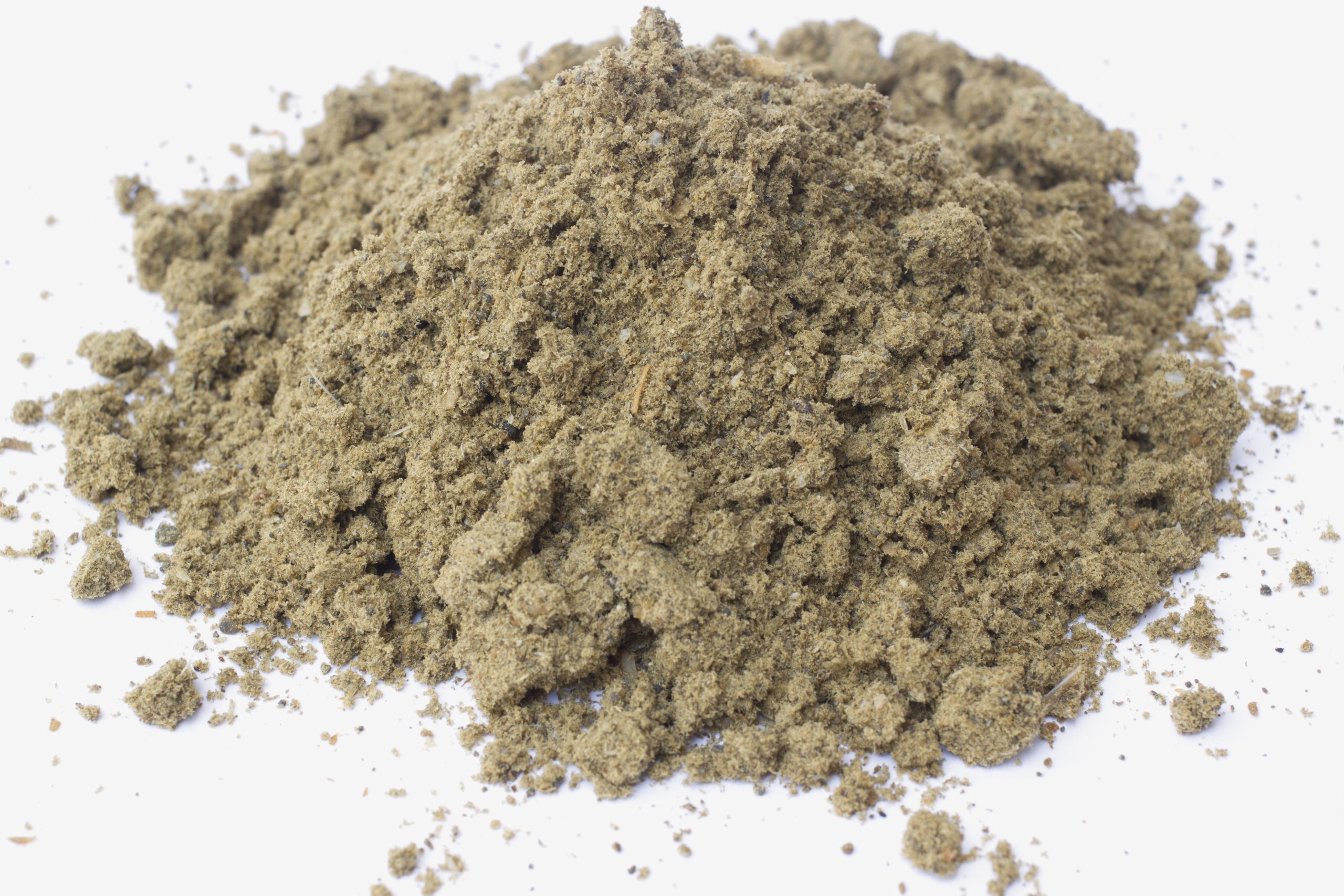
Fishmeal powder

Floating pellets
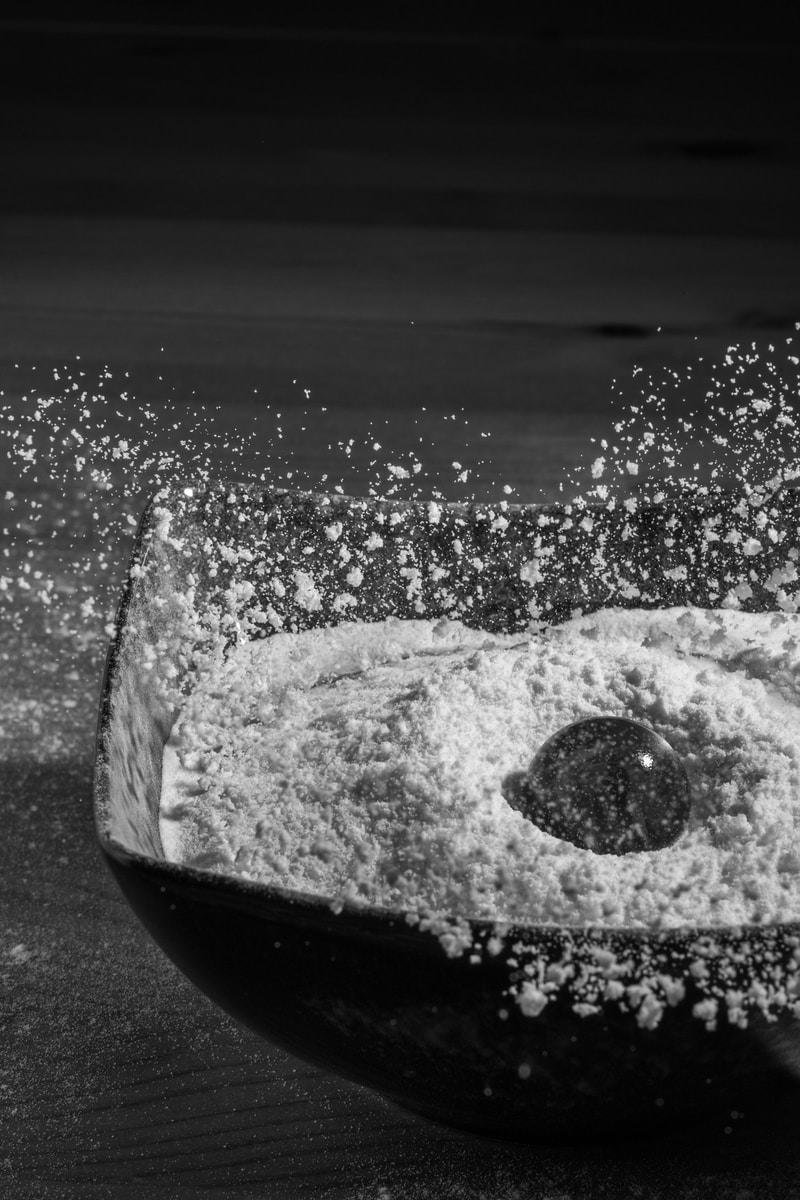
Flour
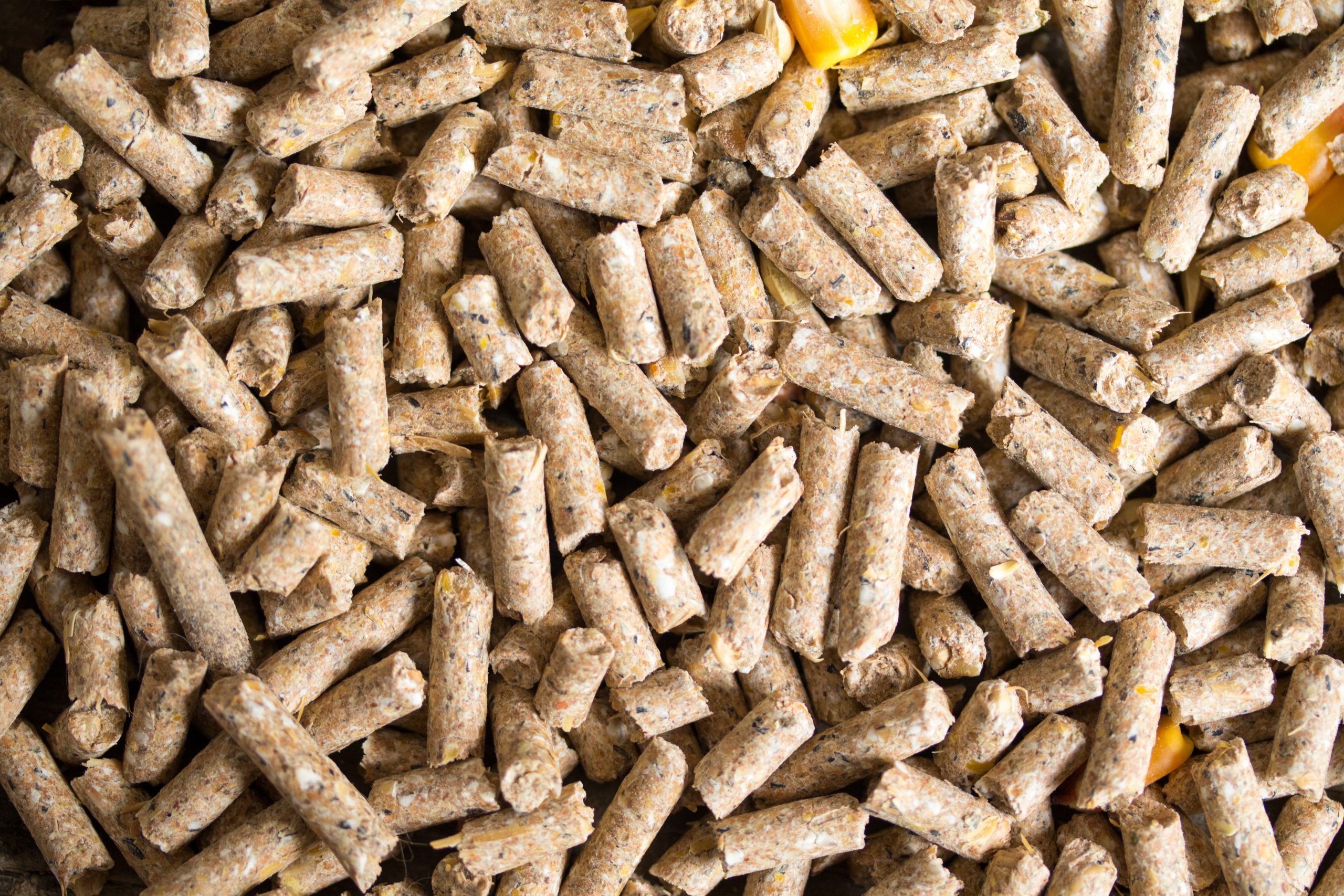
Fodder
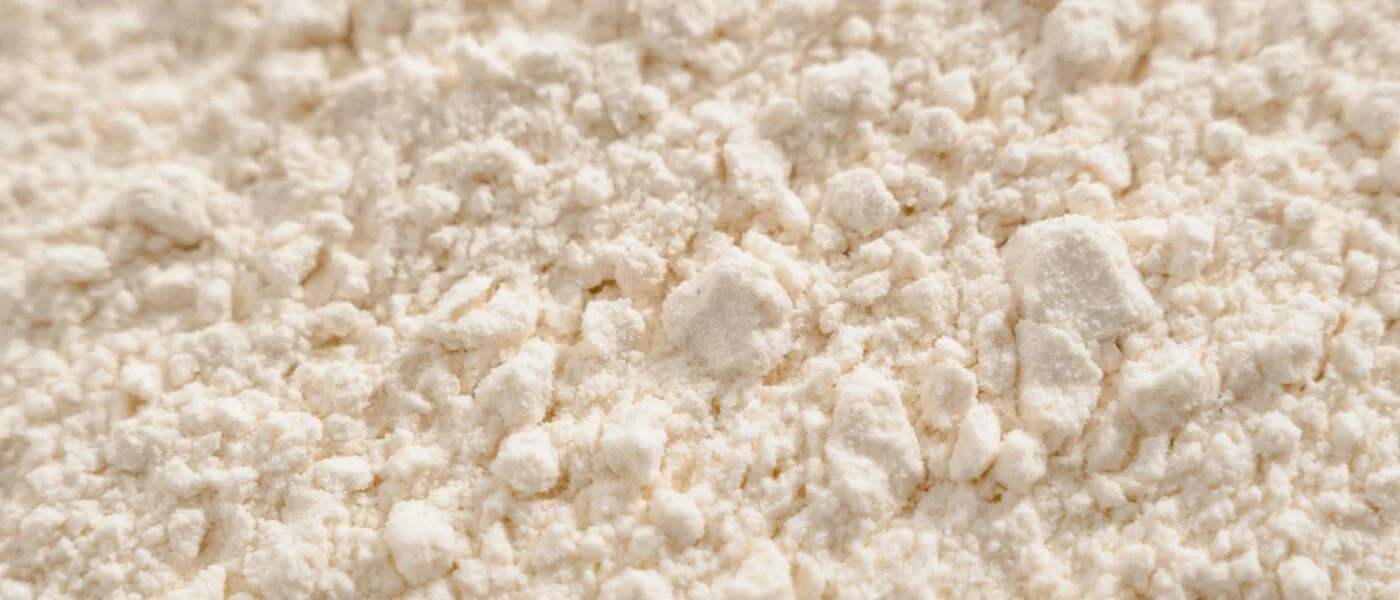
Free-flowing powders
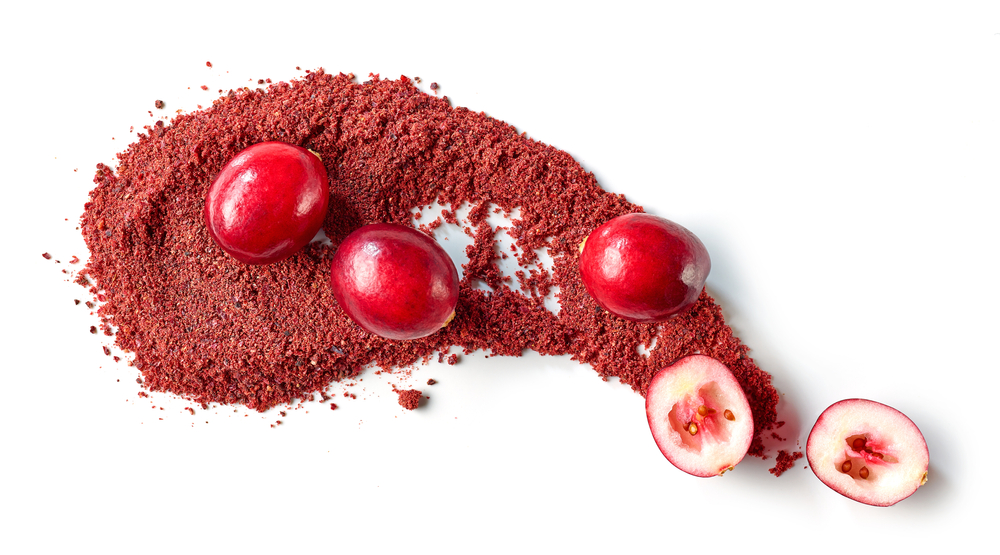
Fruit powder

Fruit puree
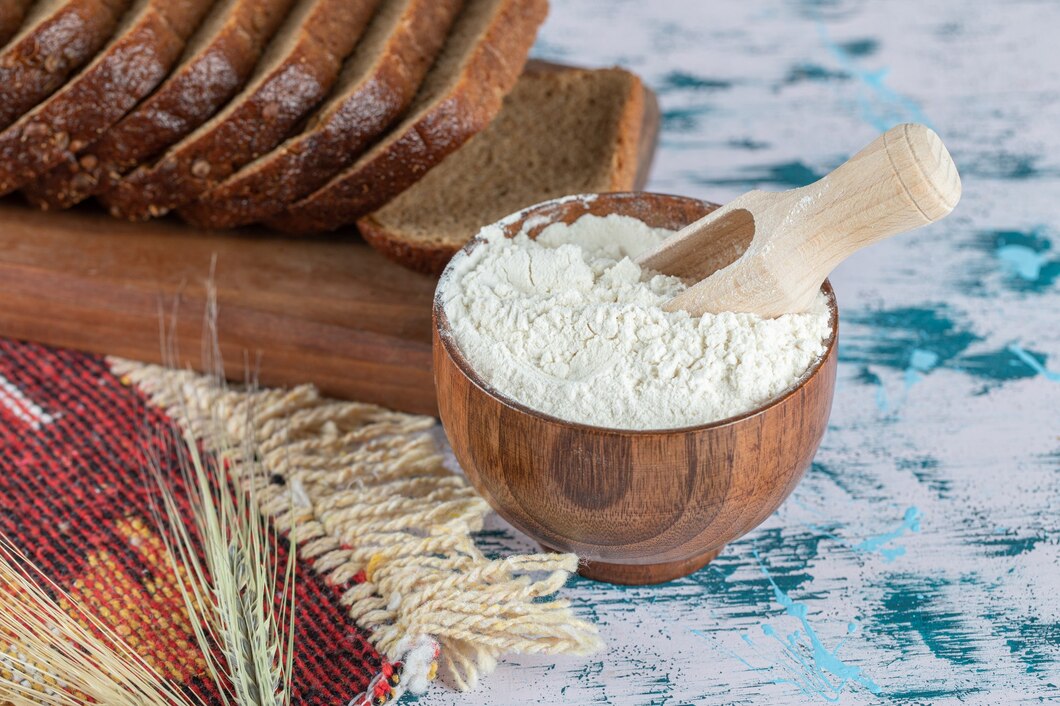
Functional flours
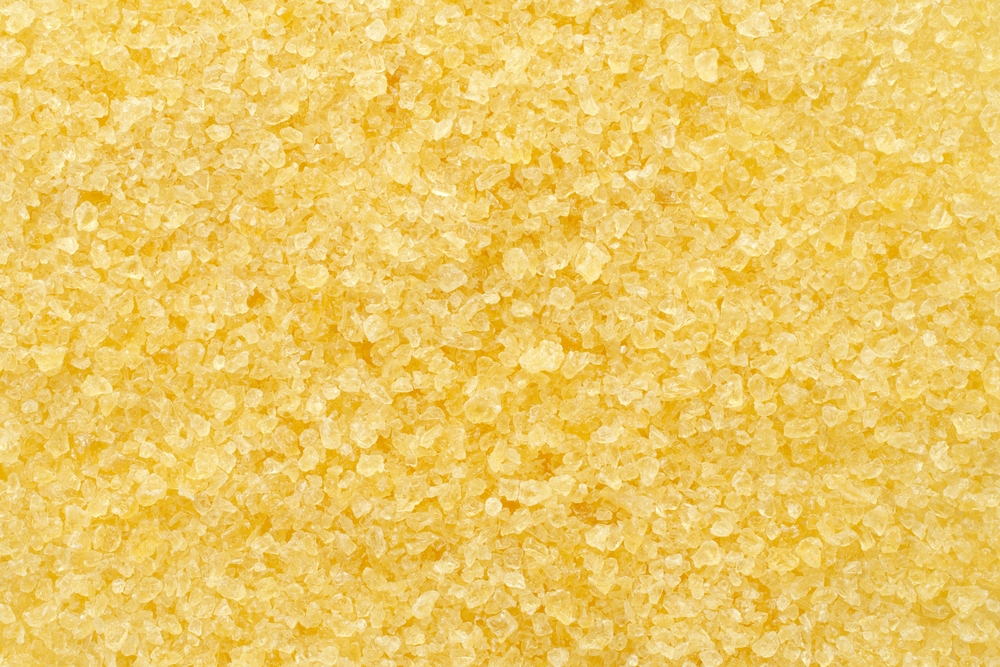
Gelatin powder
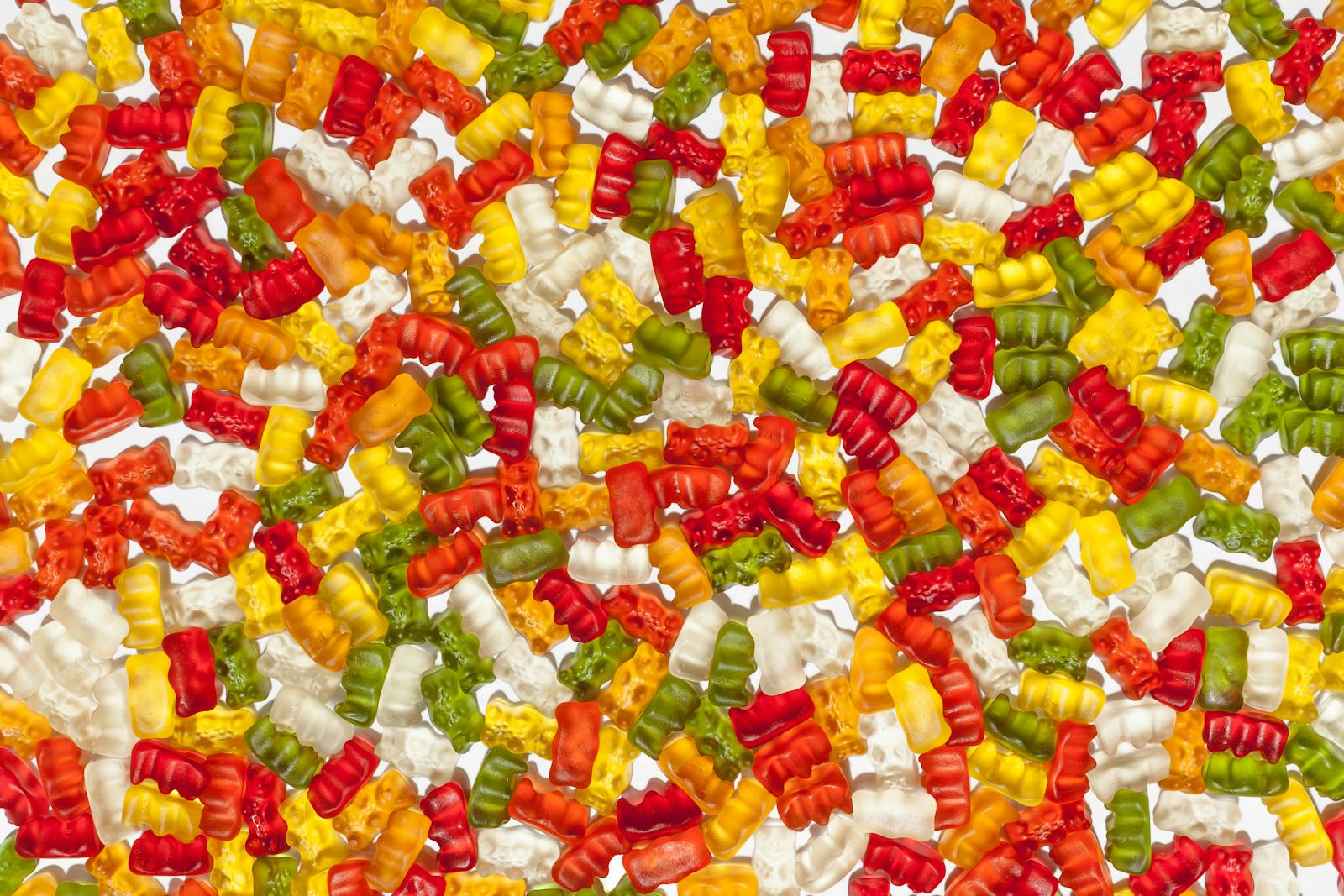
Gelatine
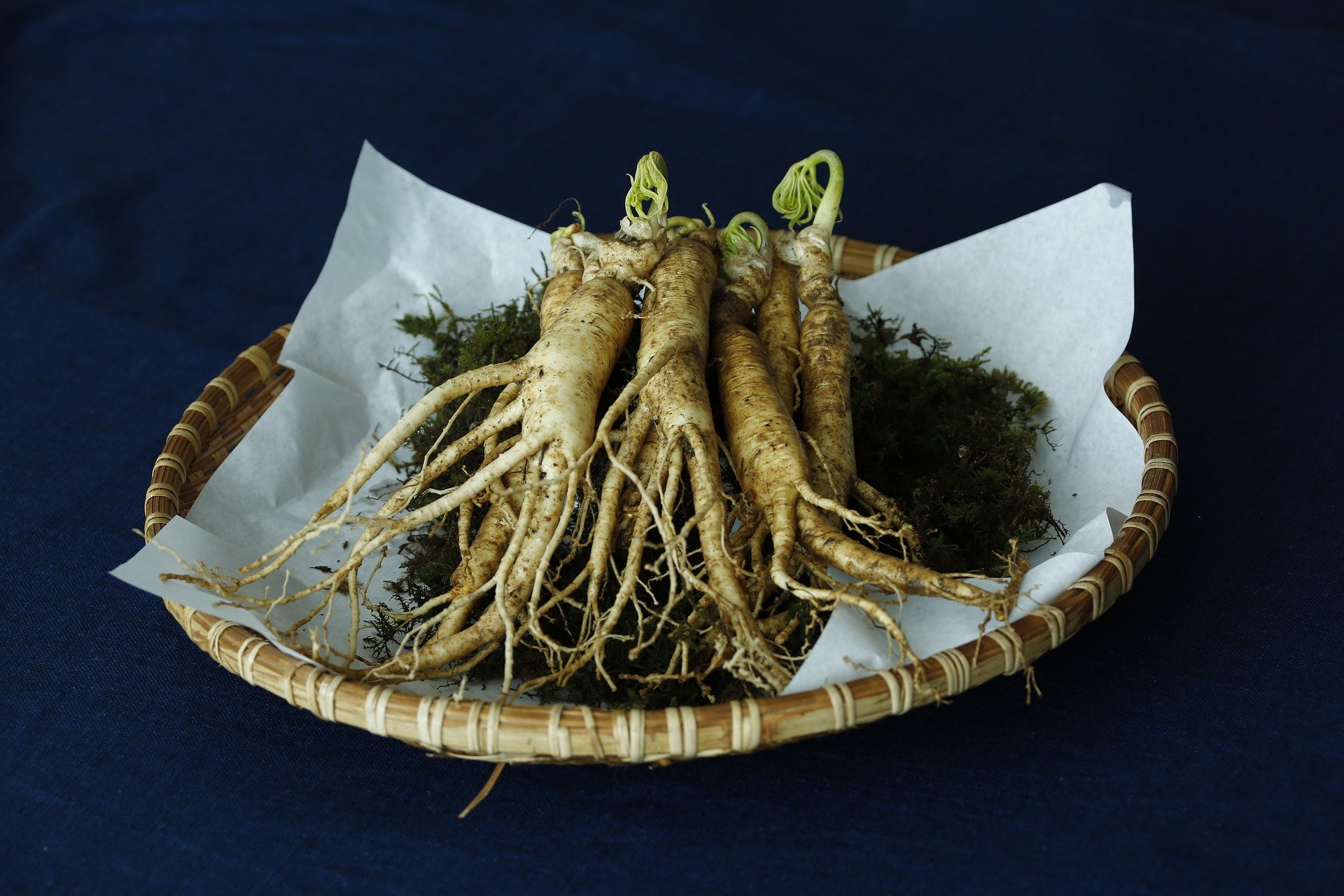
Ginseng extract
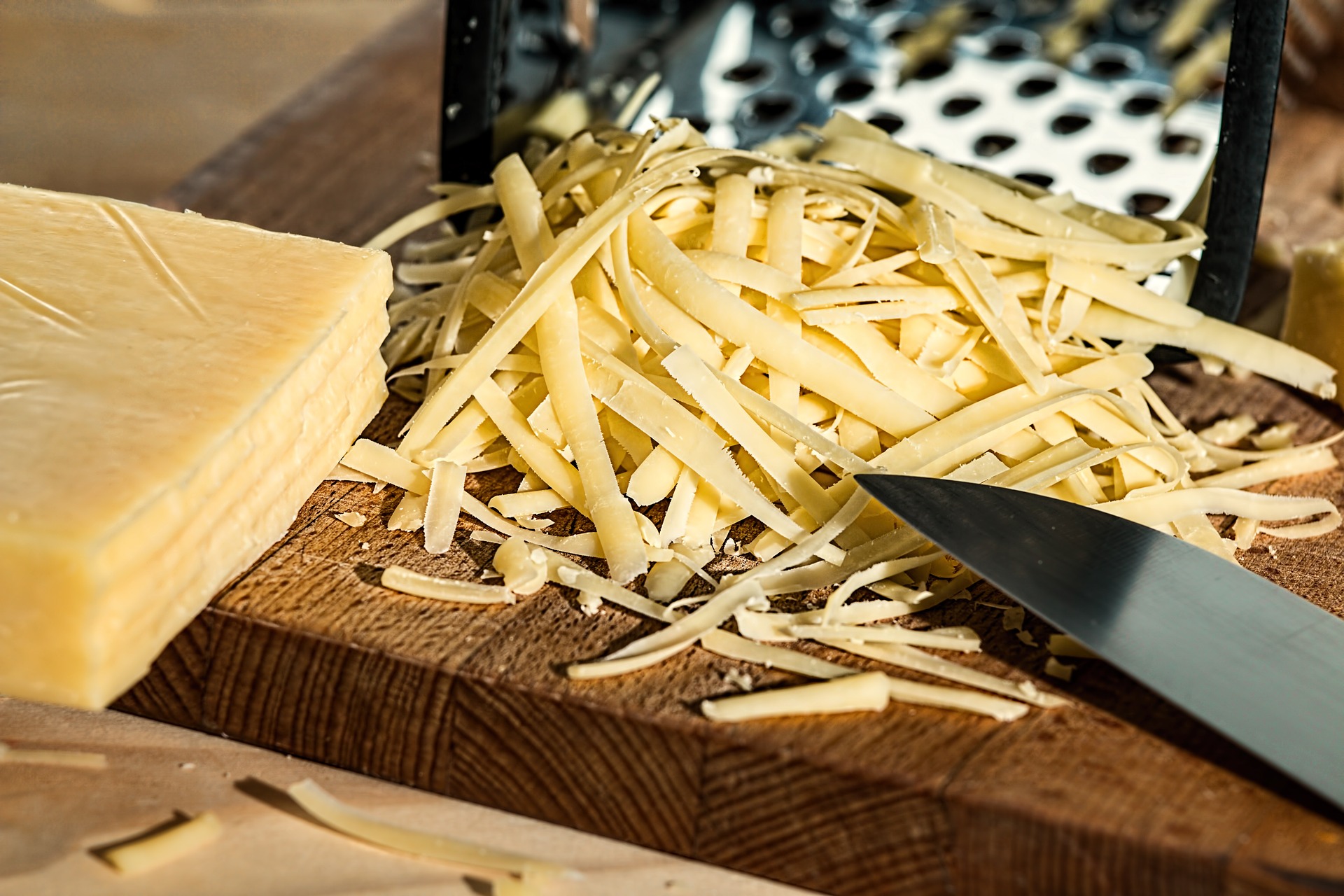
Grated cheese
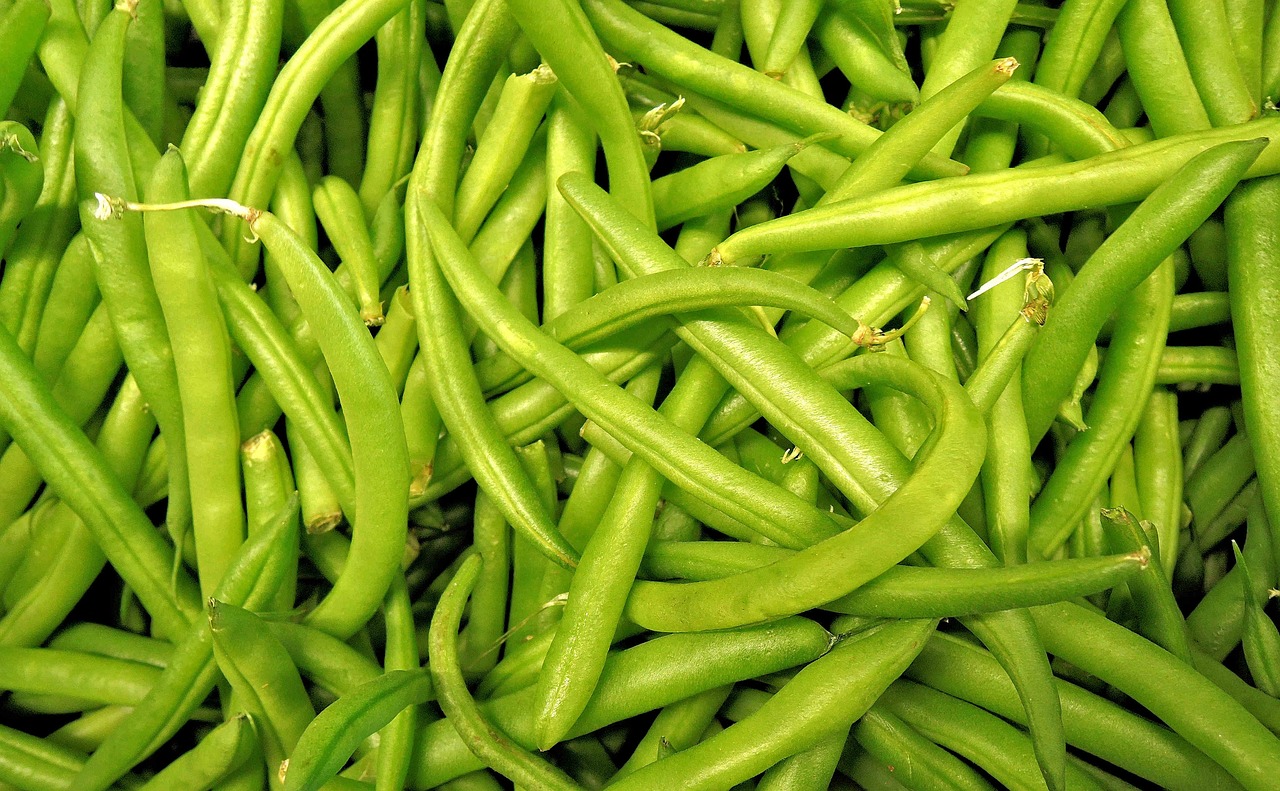
Green beans
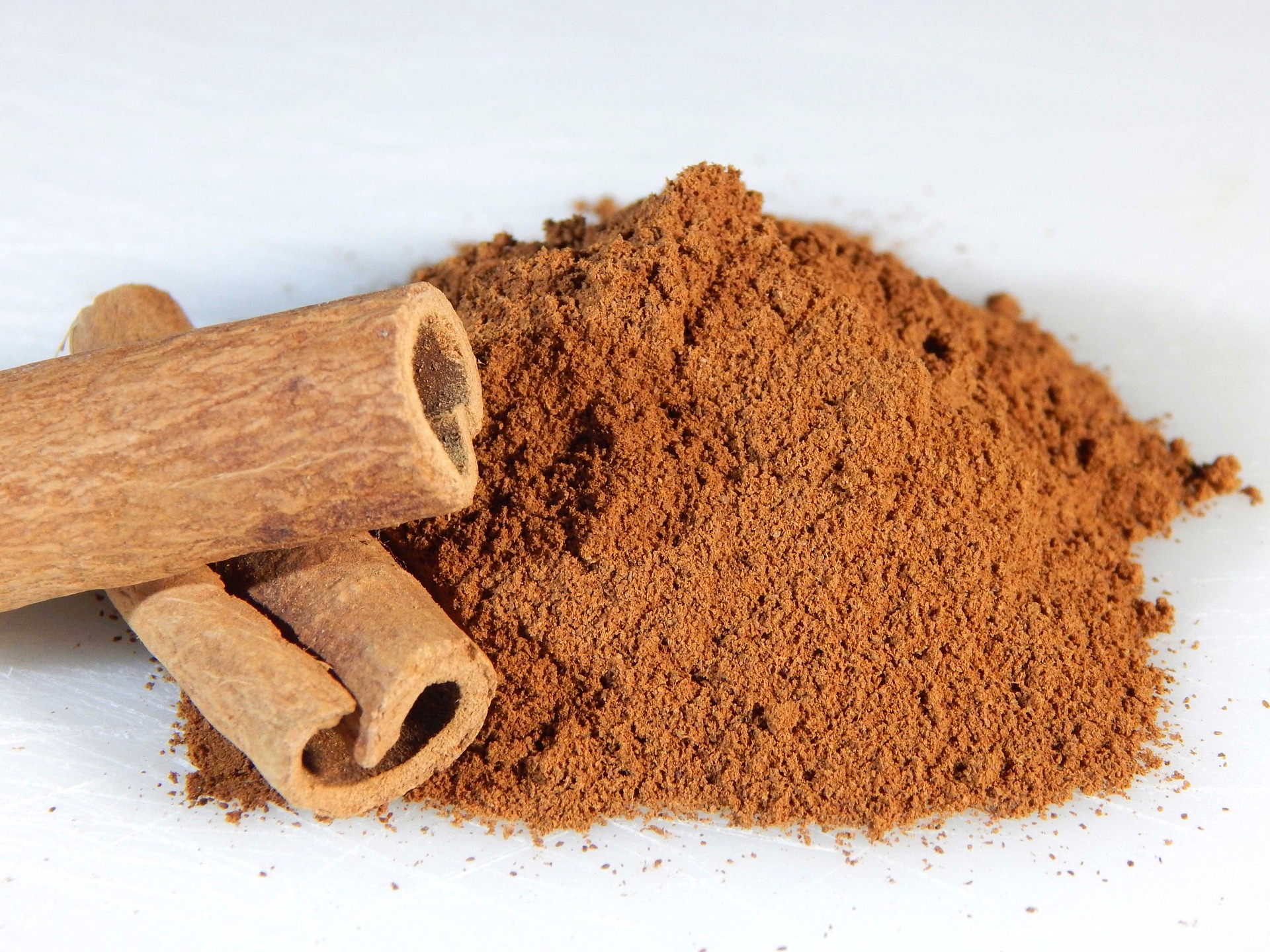
Ground cinnamon
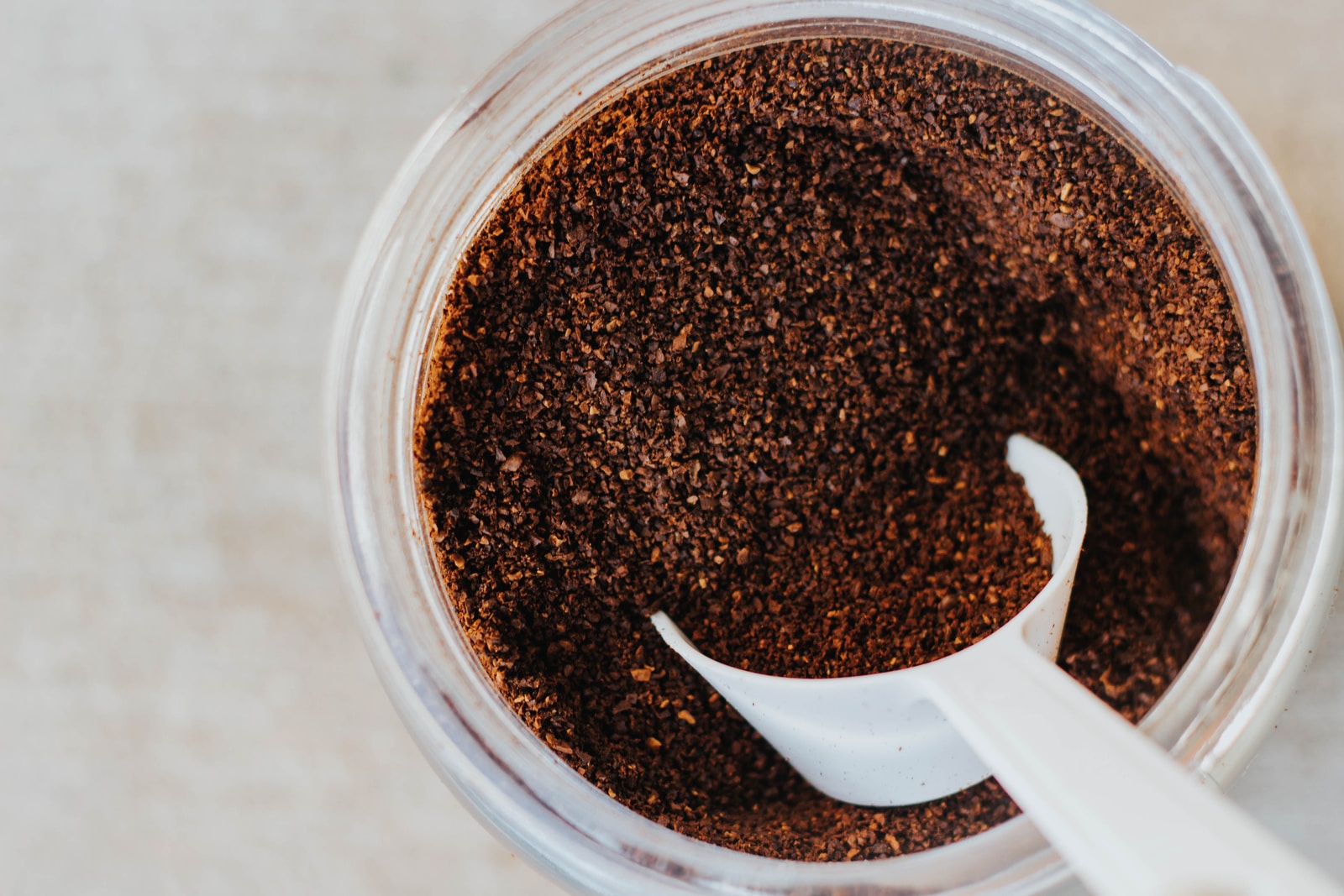
Ground coffee
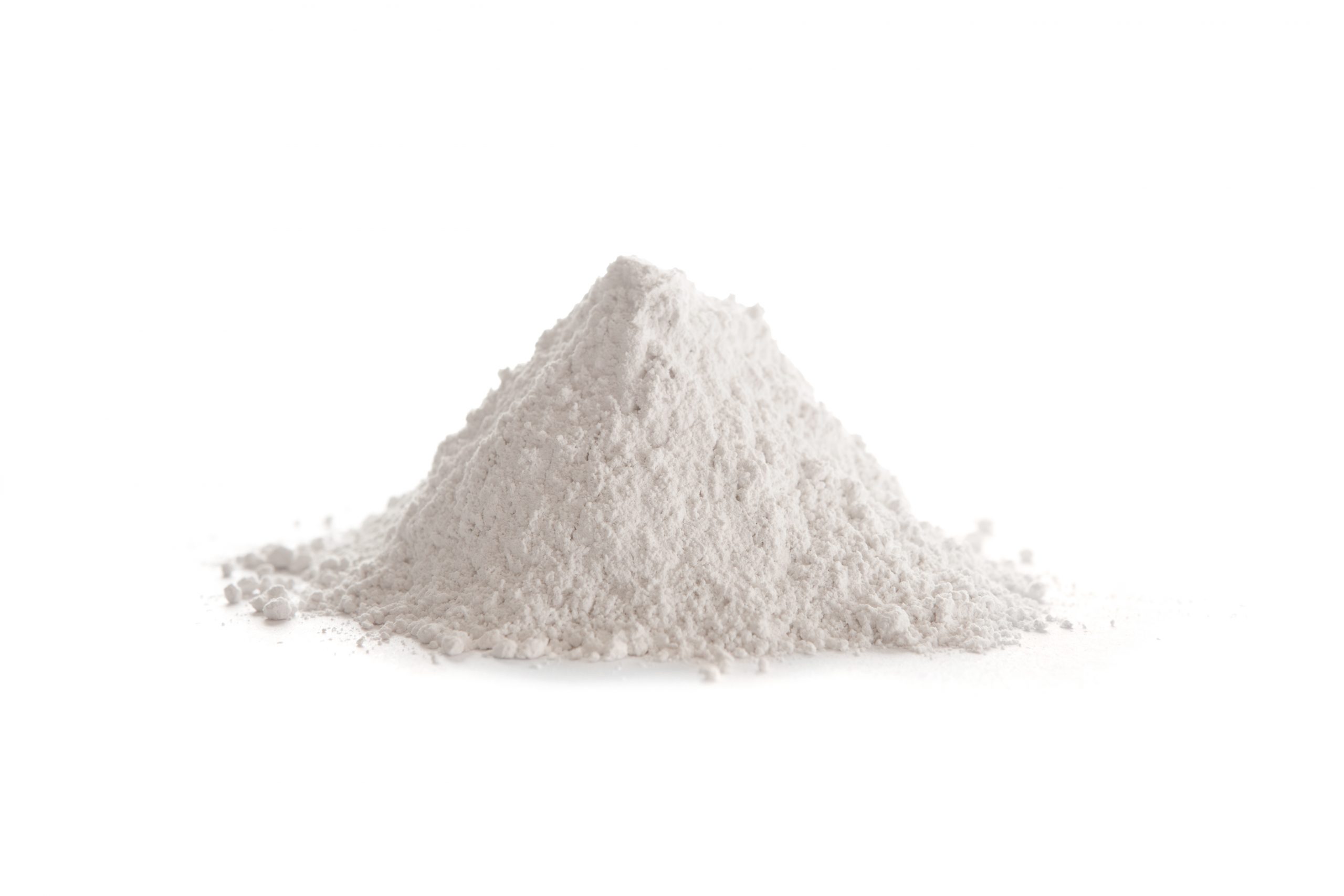
Gypsum
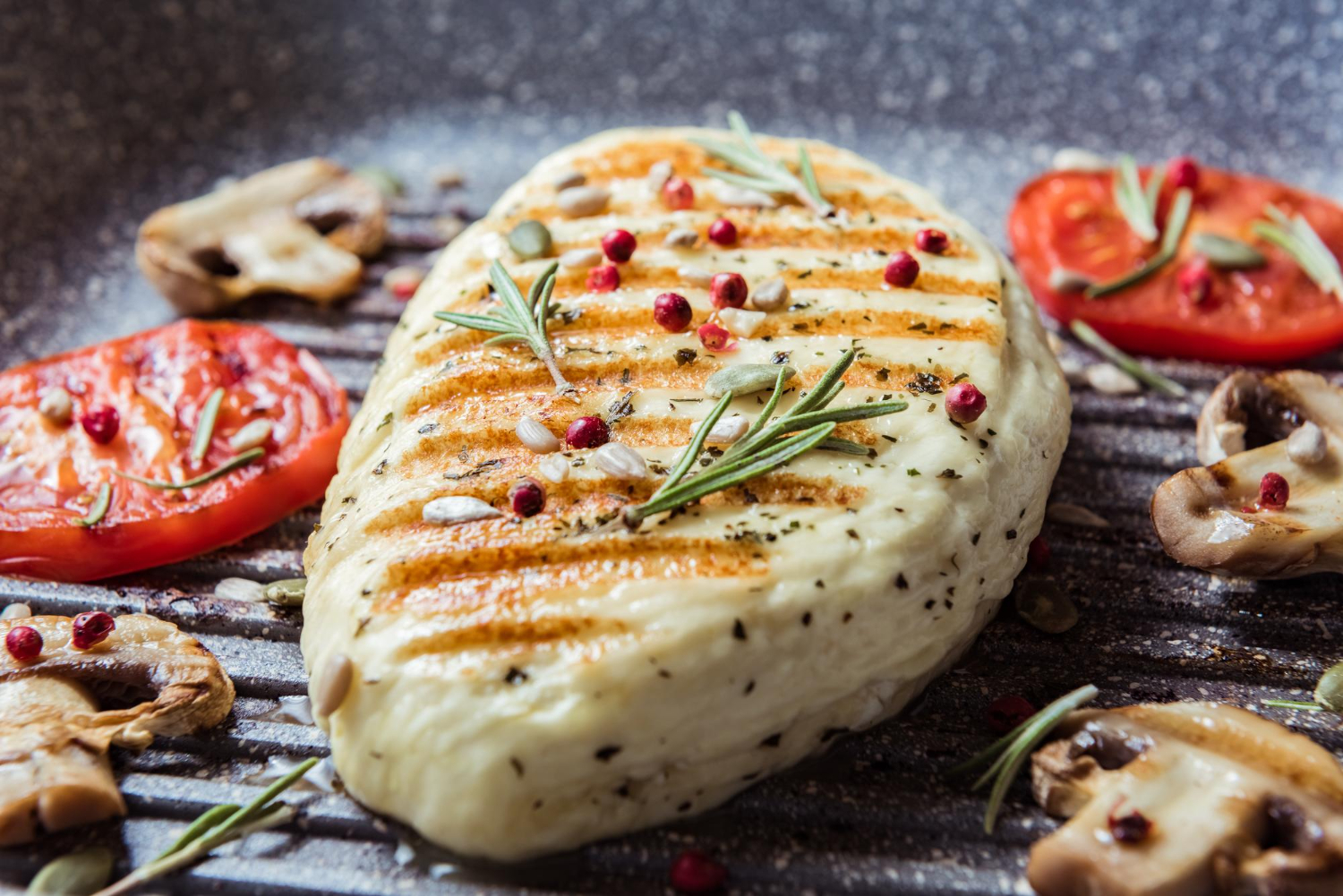
Halloumi

Hazelnuts
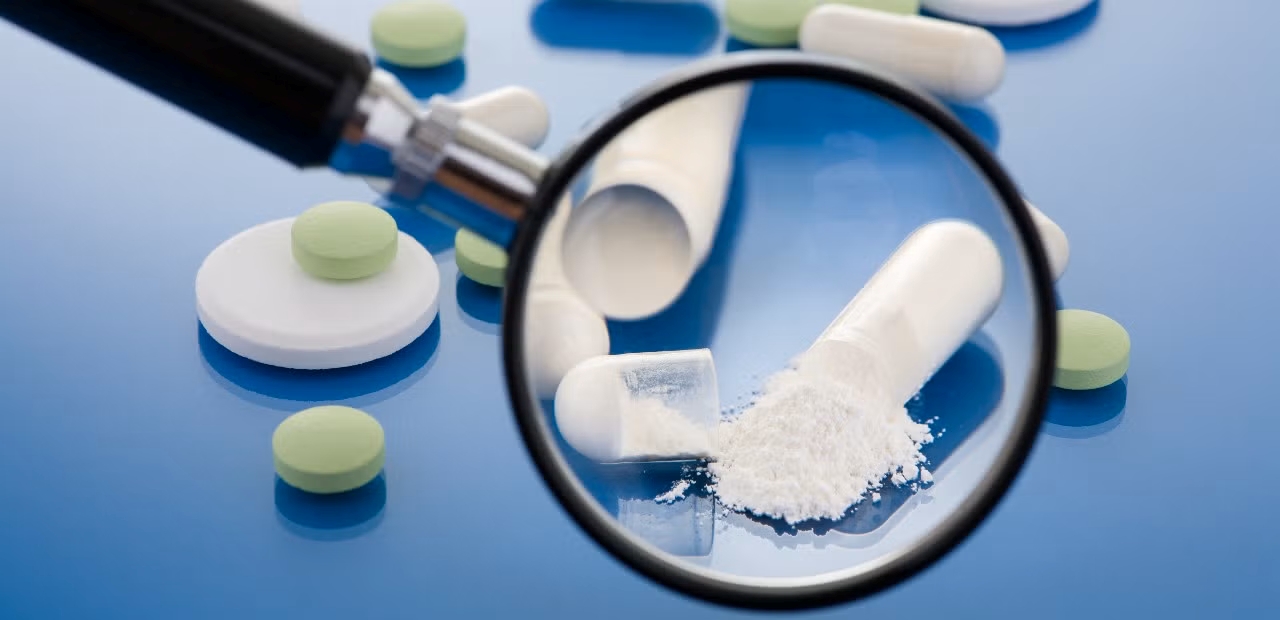
High-potency active pharmaceutical ingredients (hpapis)
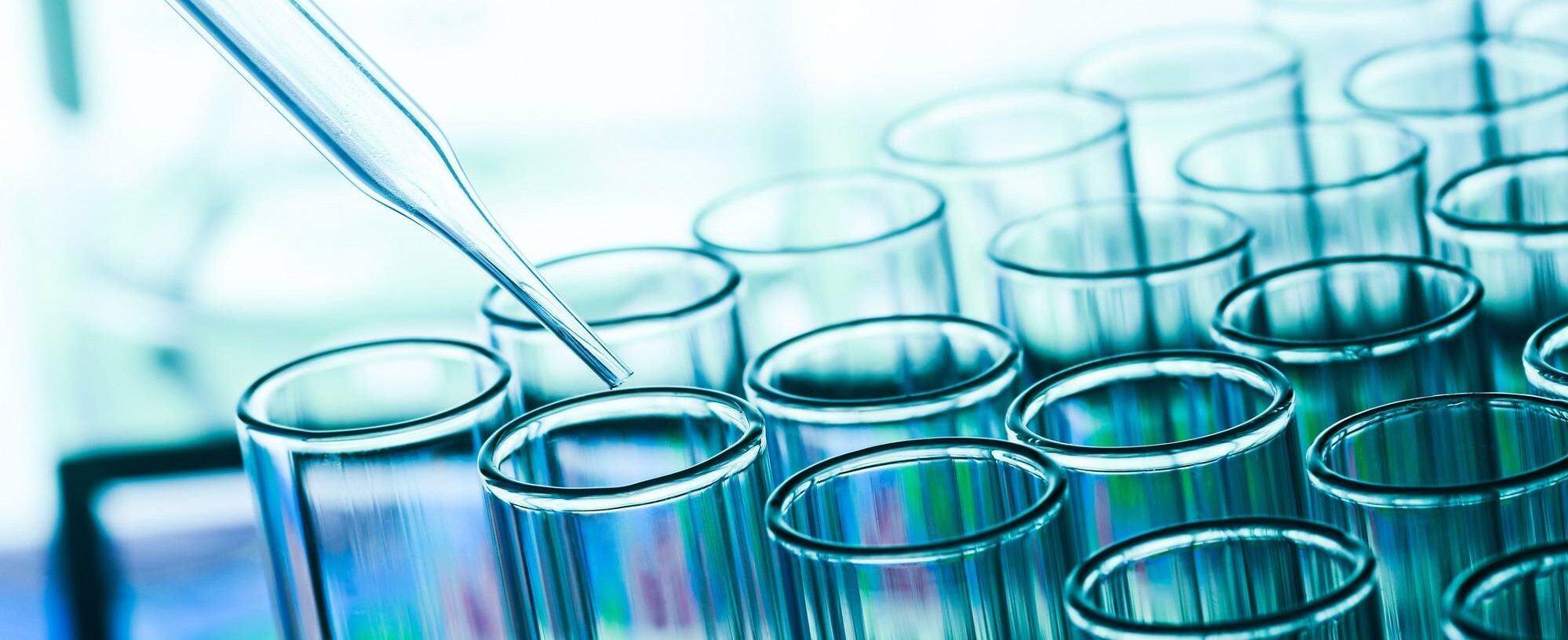
Highly Active Pharmaceutical Ingredients
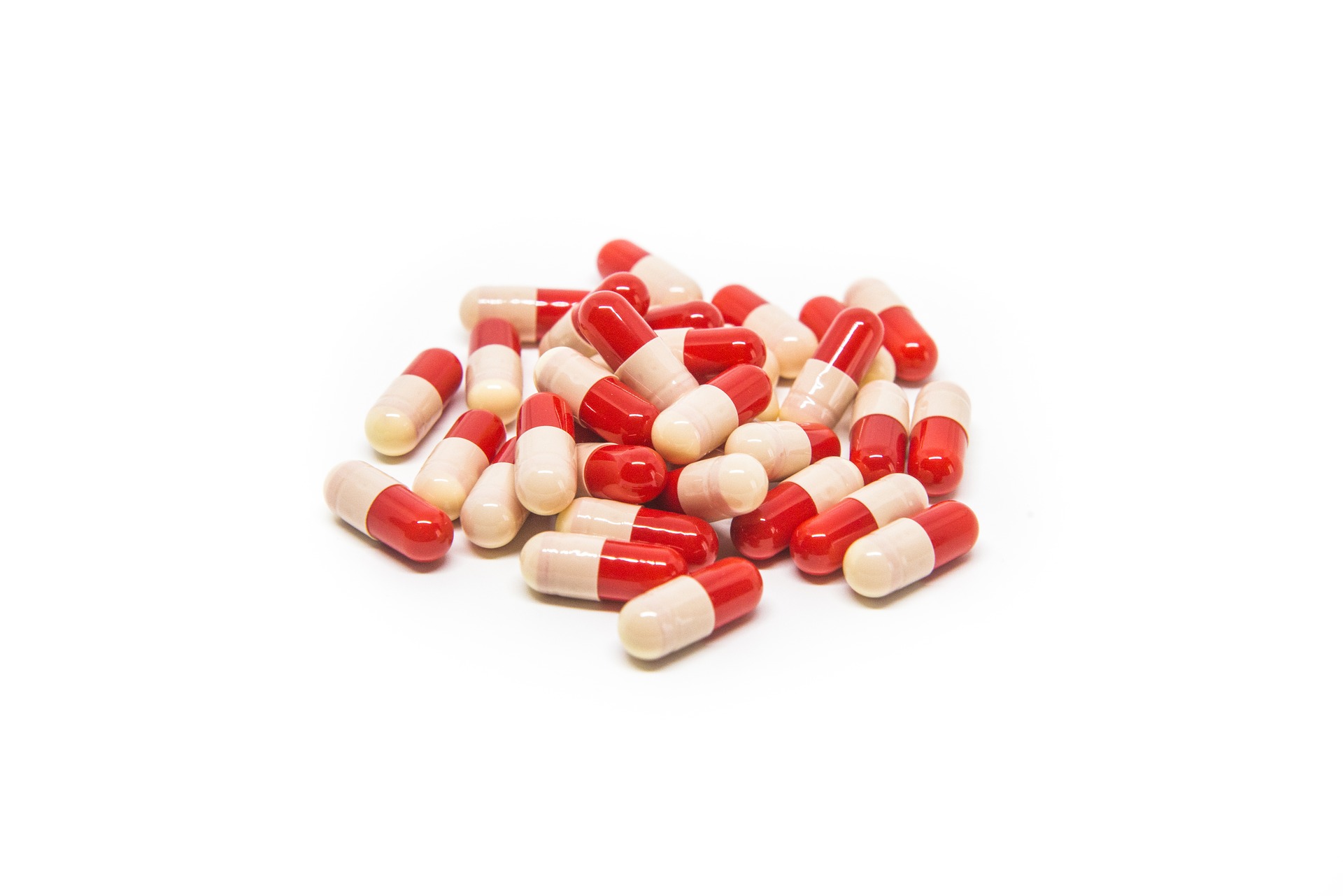
HPMC capsules
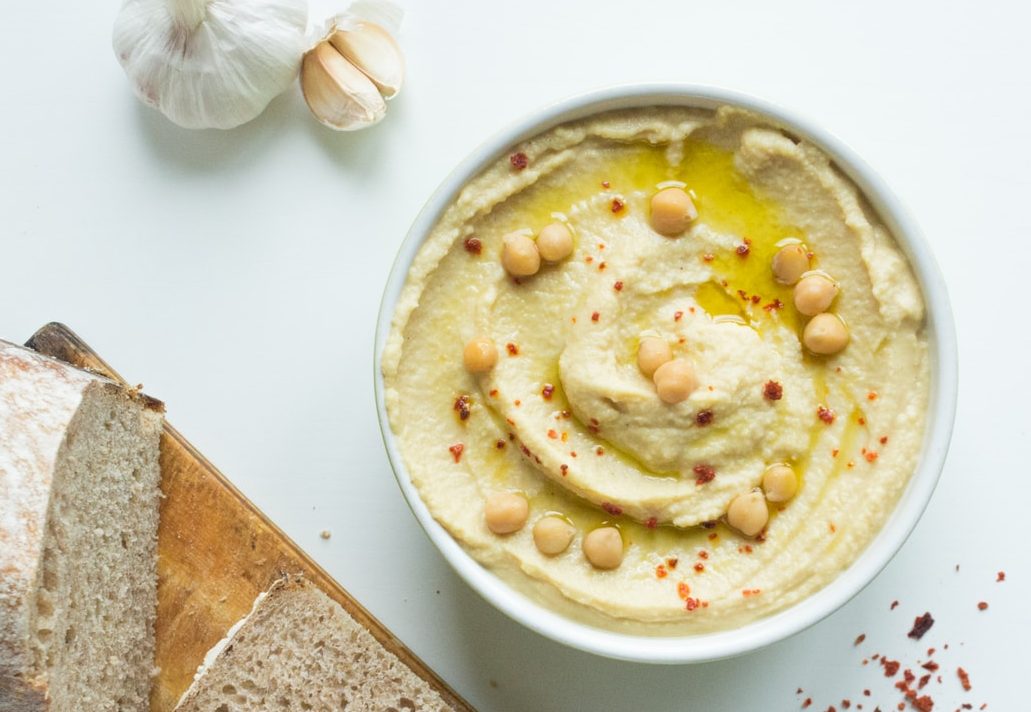
Hummus
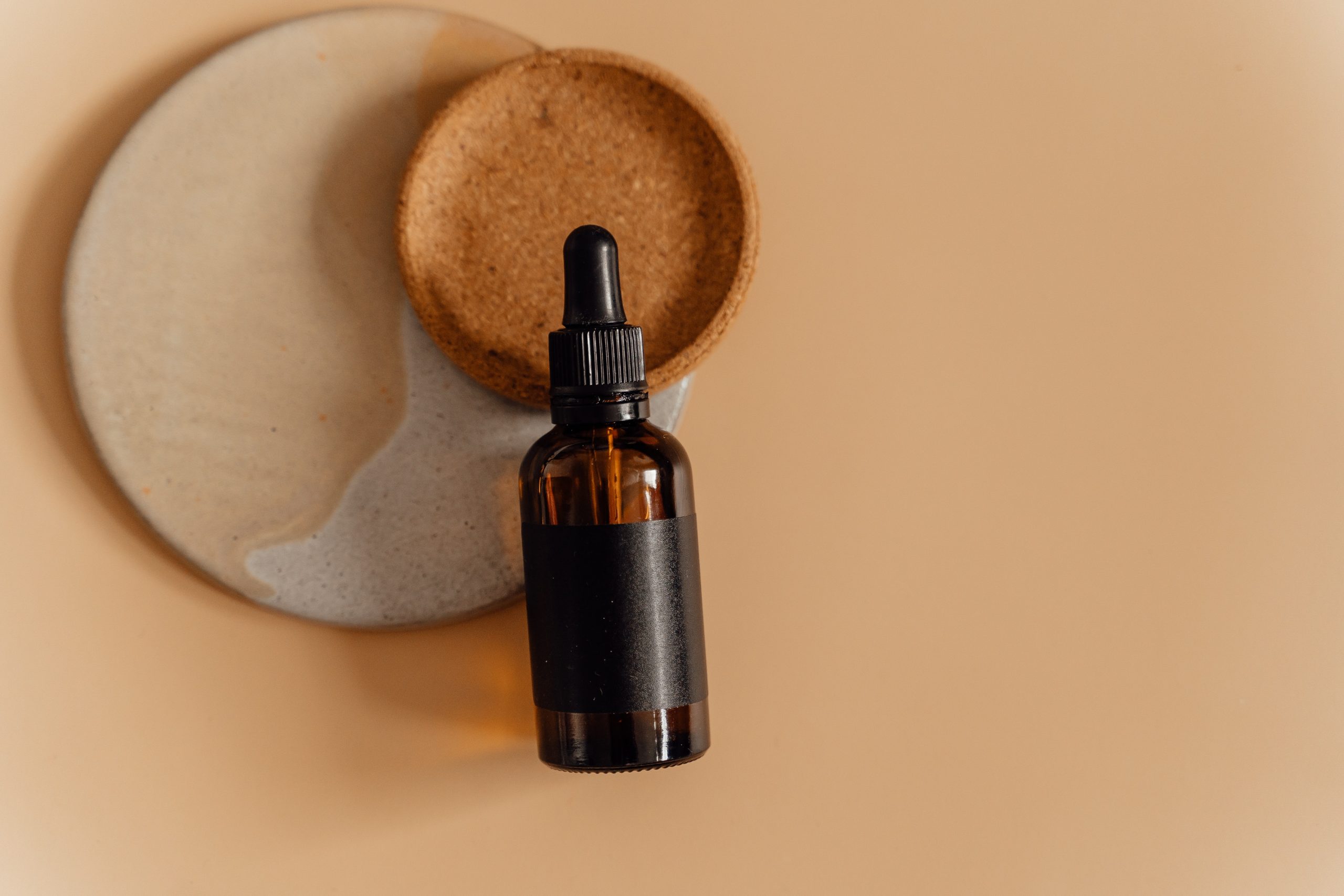
Hyaluronic acid
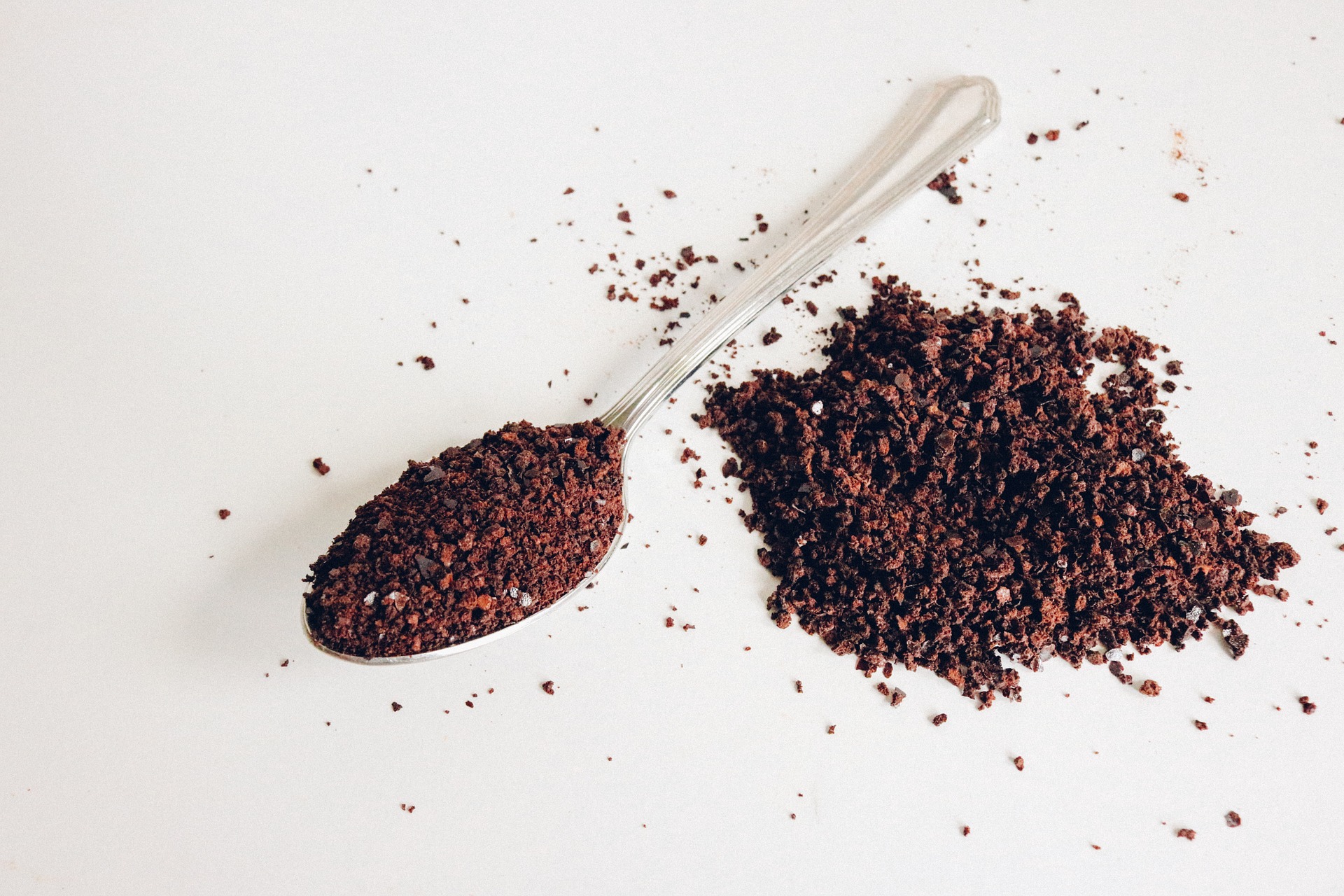
Instant coffee
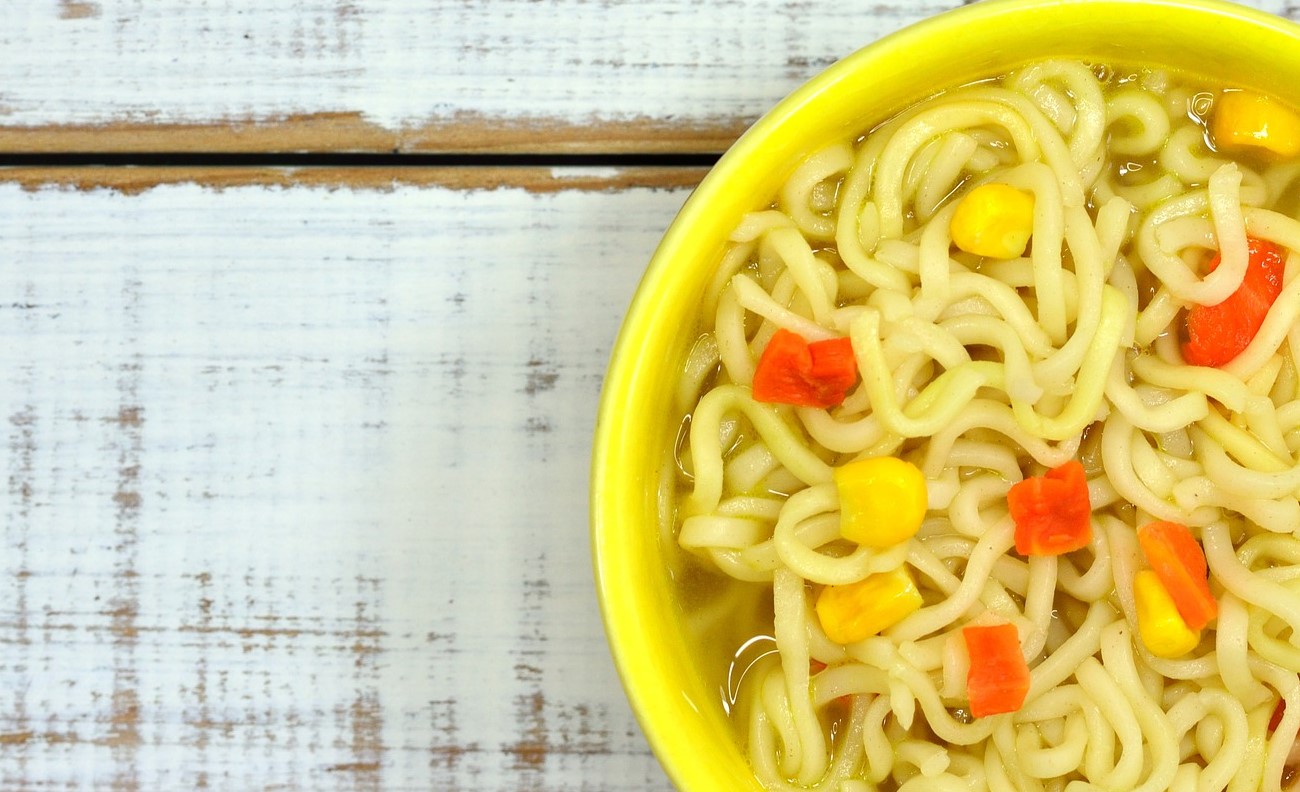
Instant soup
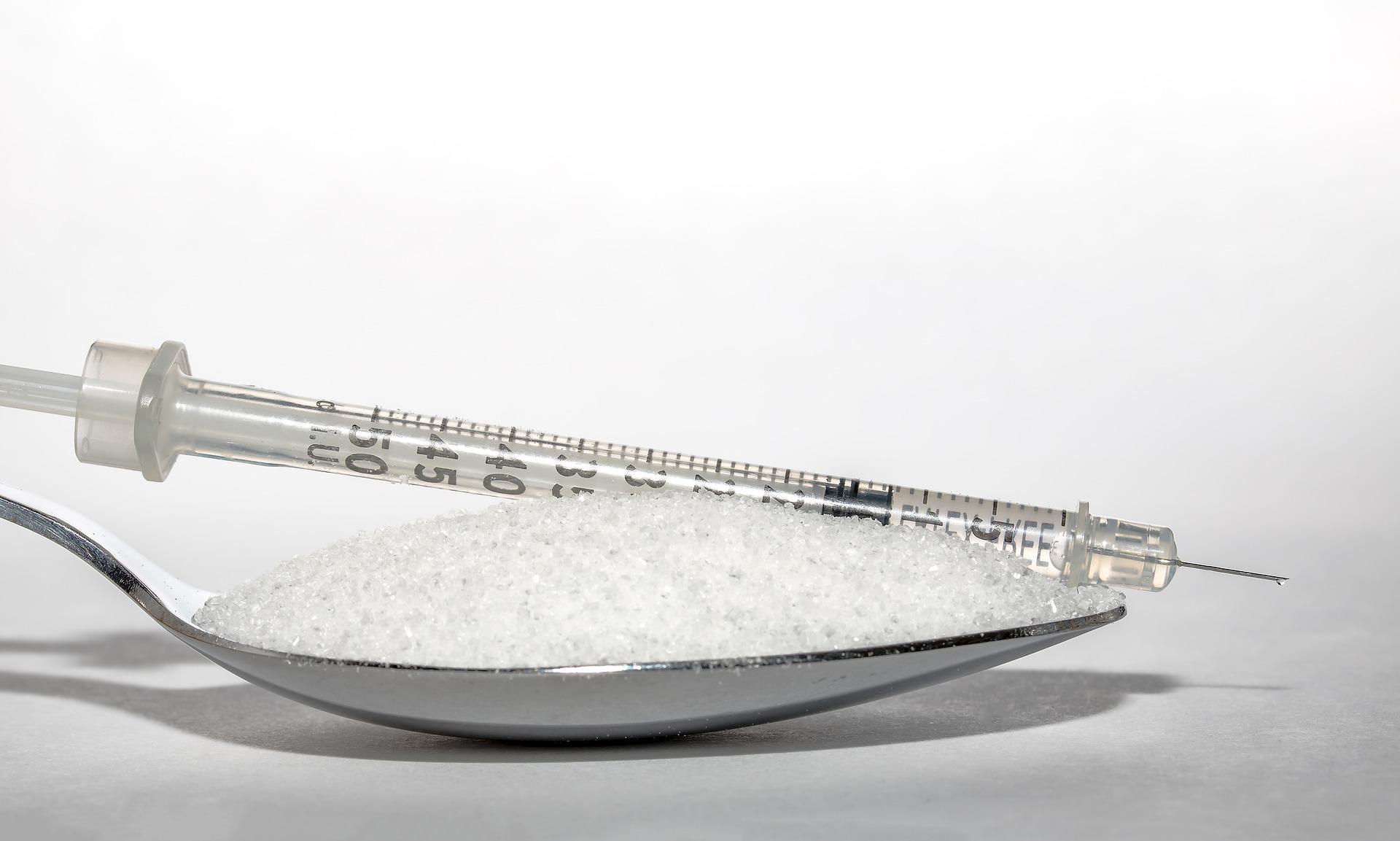
Insulin
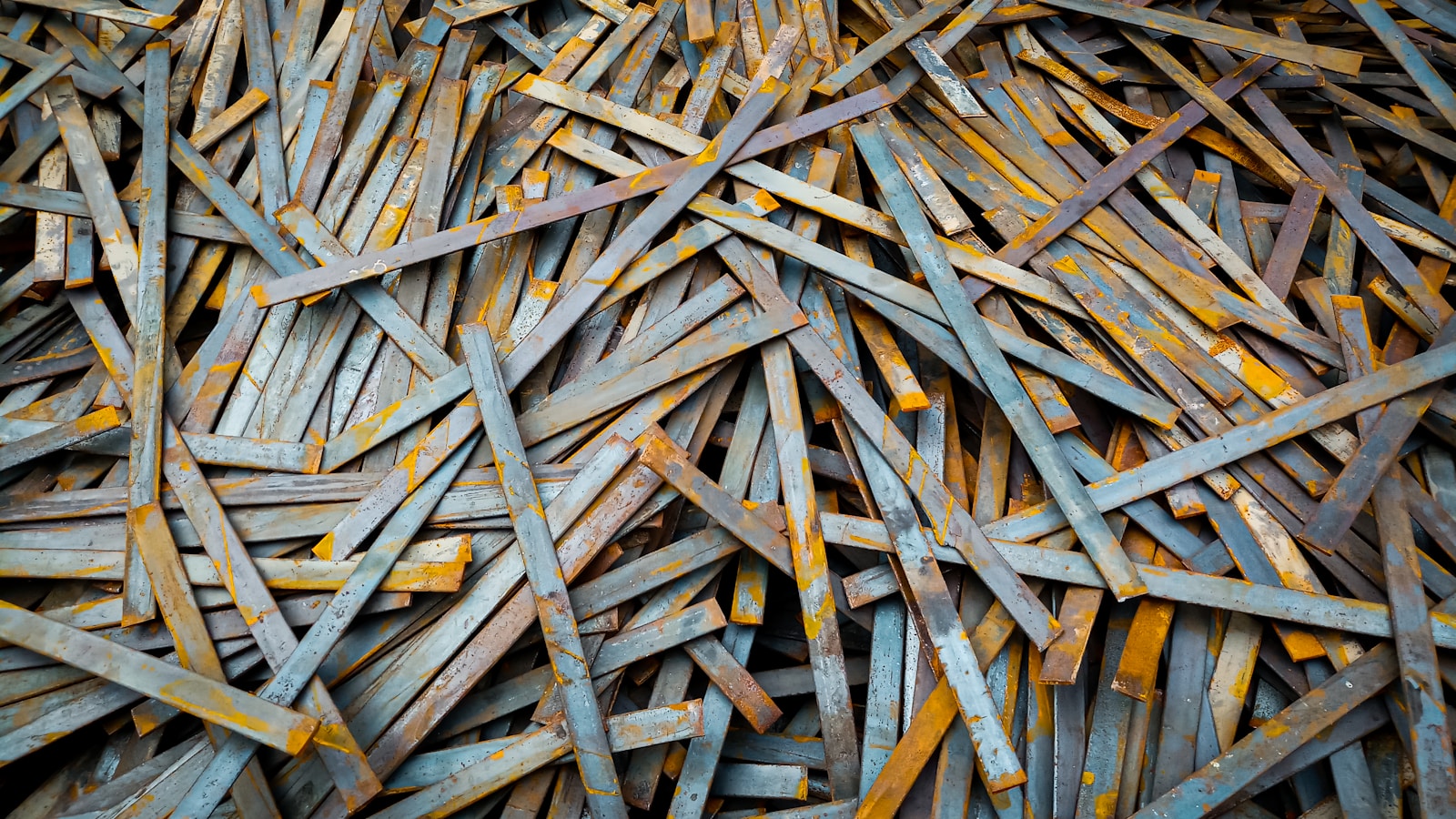
Iron
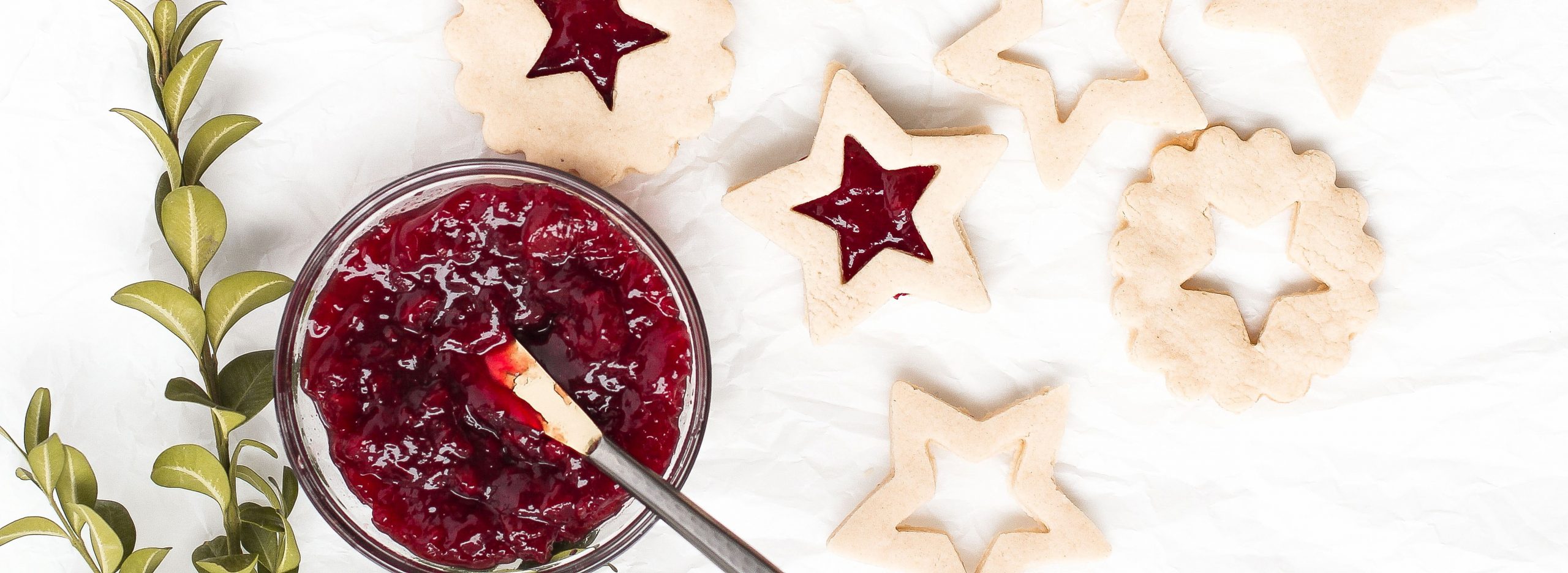
Jam
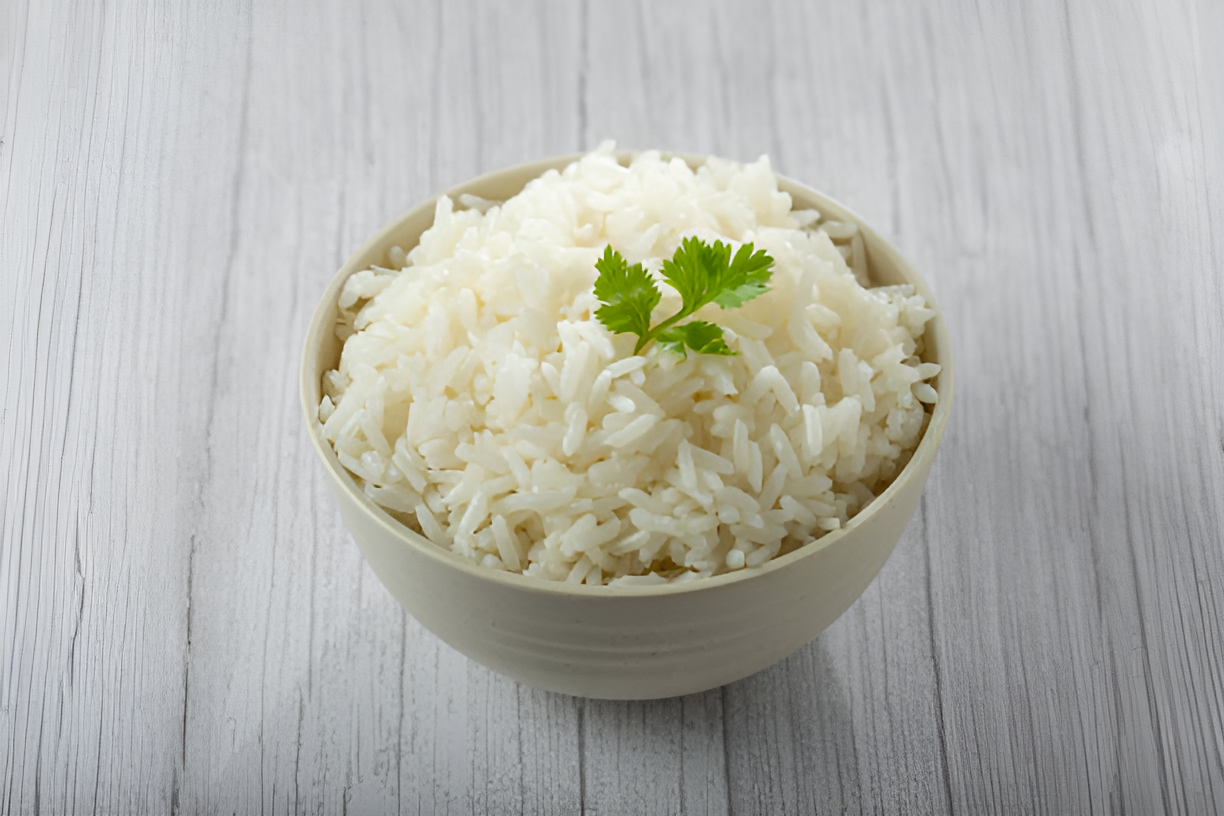
Jasmine rice
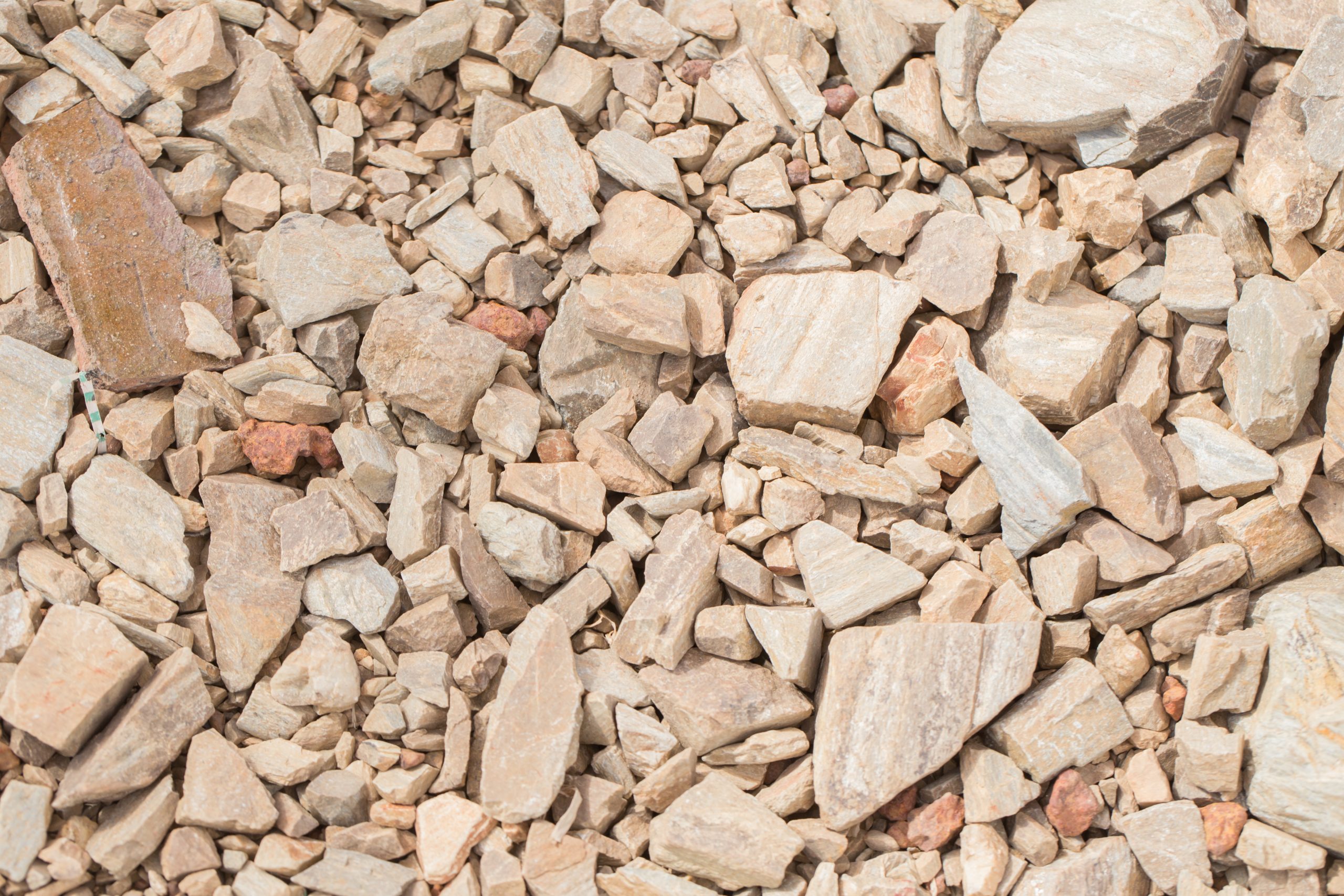
Kaolin
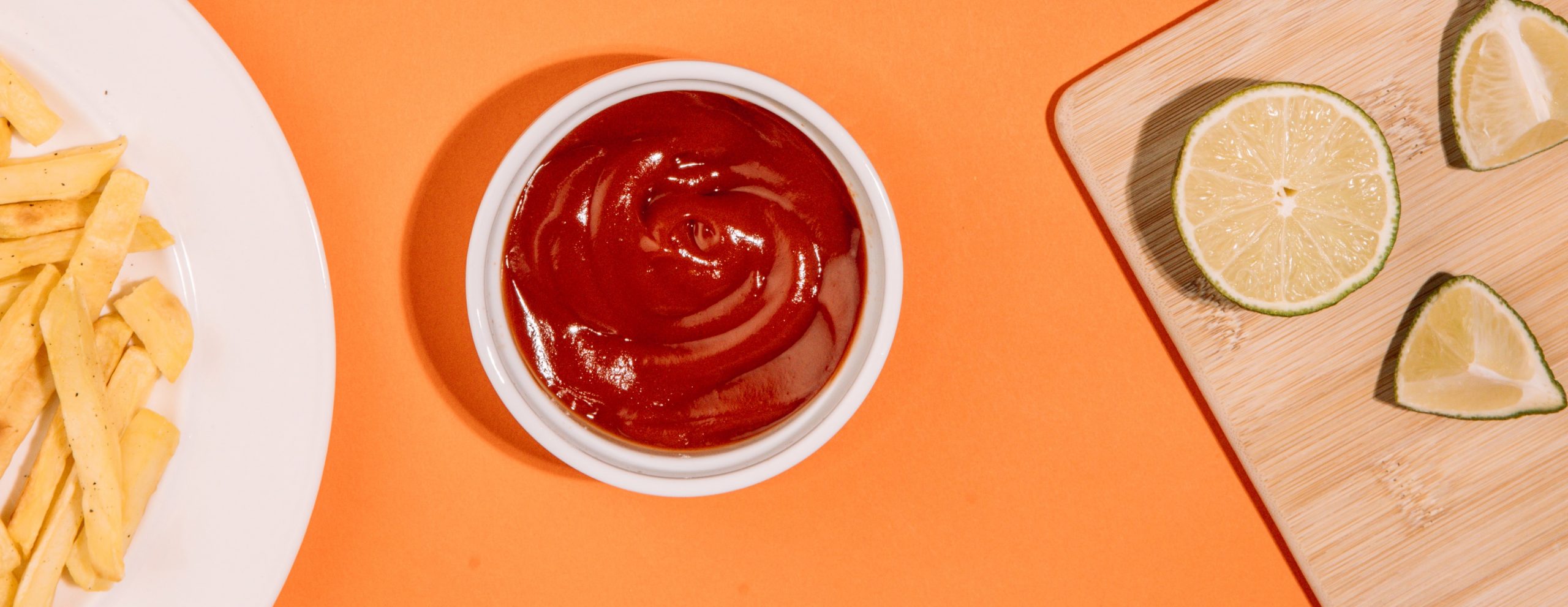
Ketchup
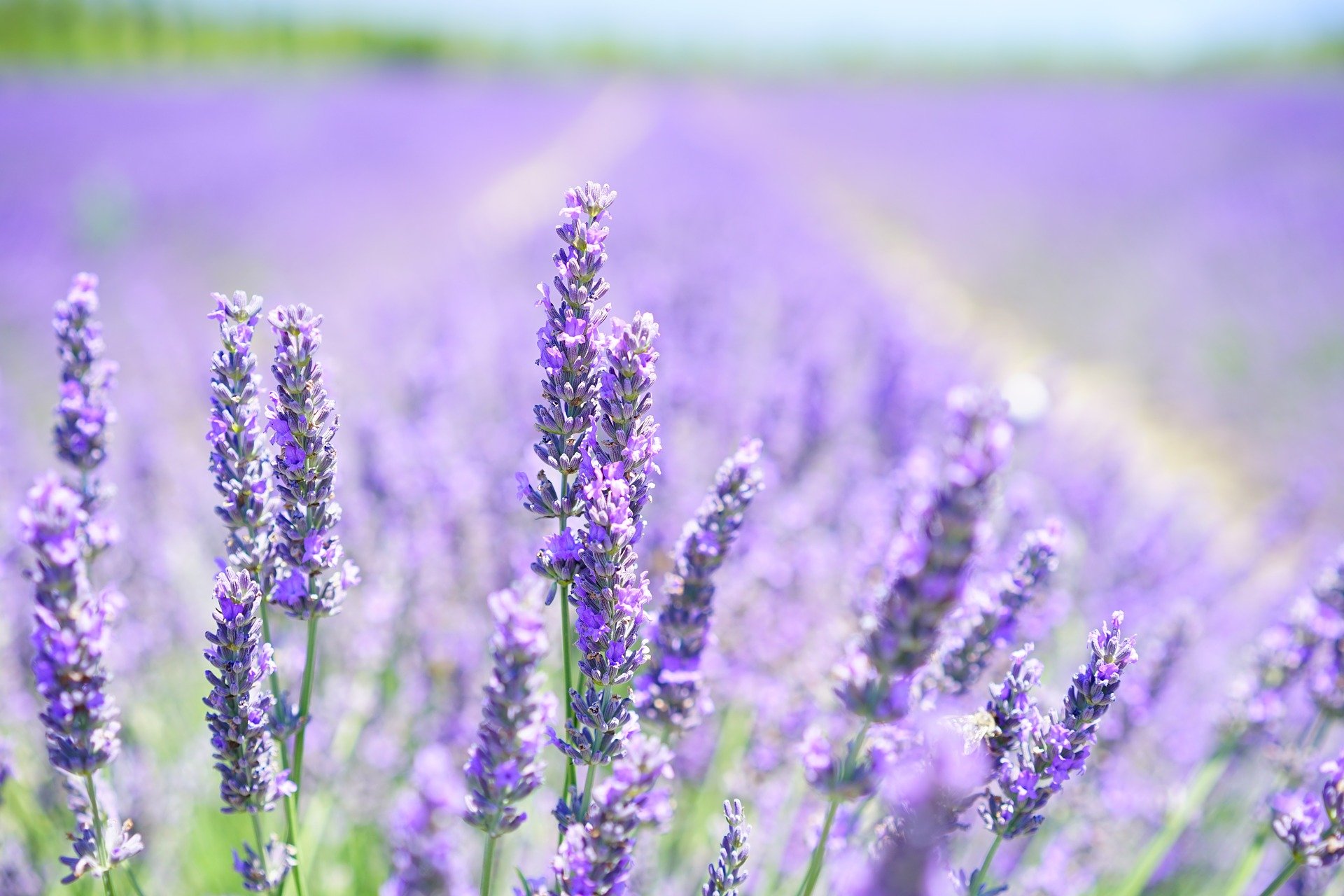
Lavender oil
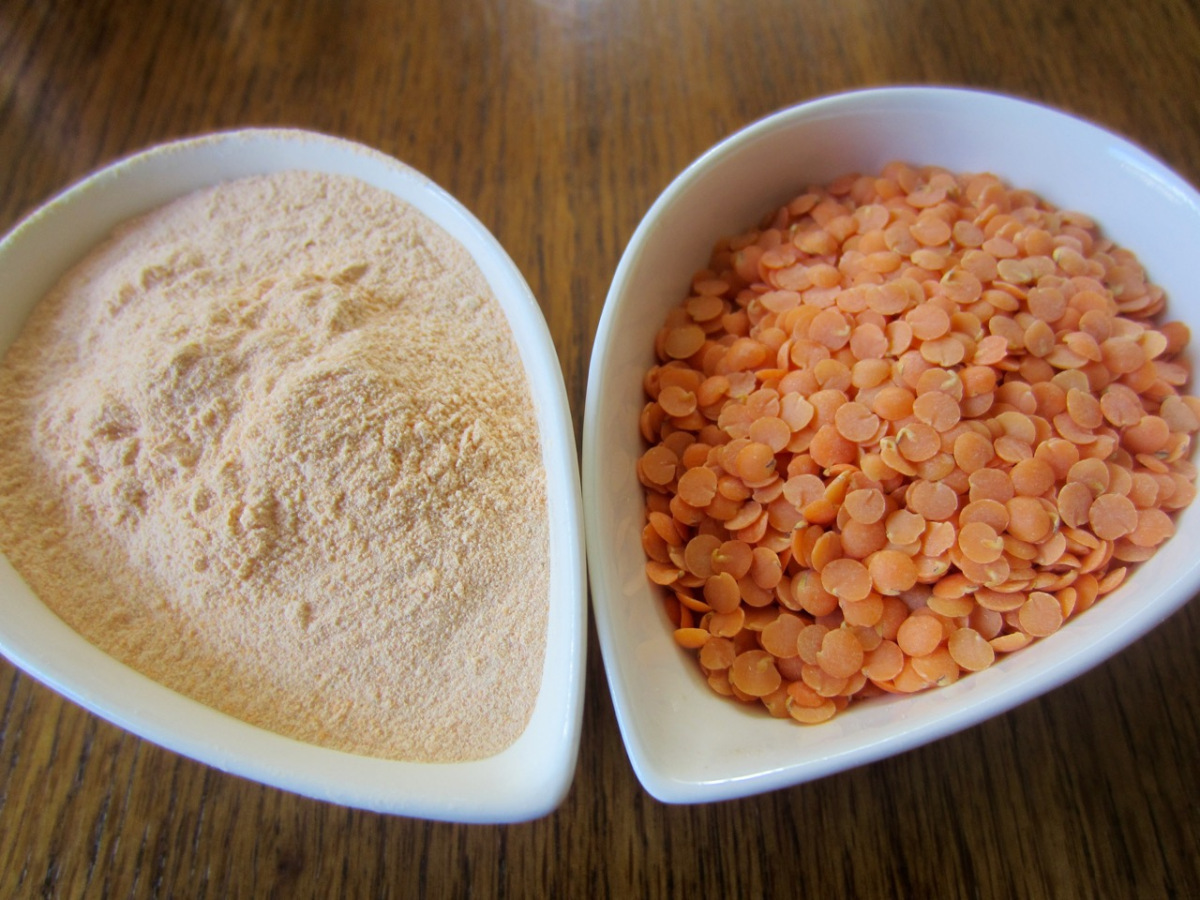
Lentil flour
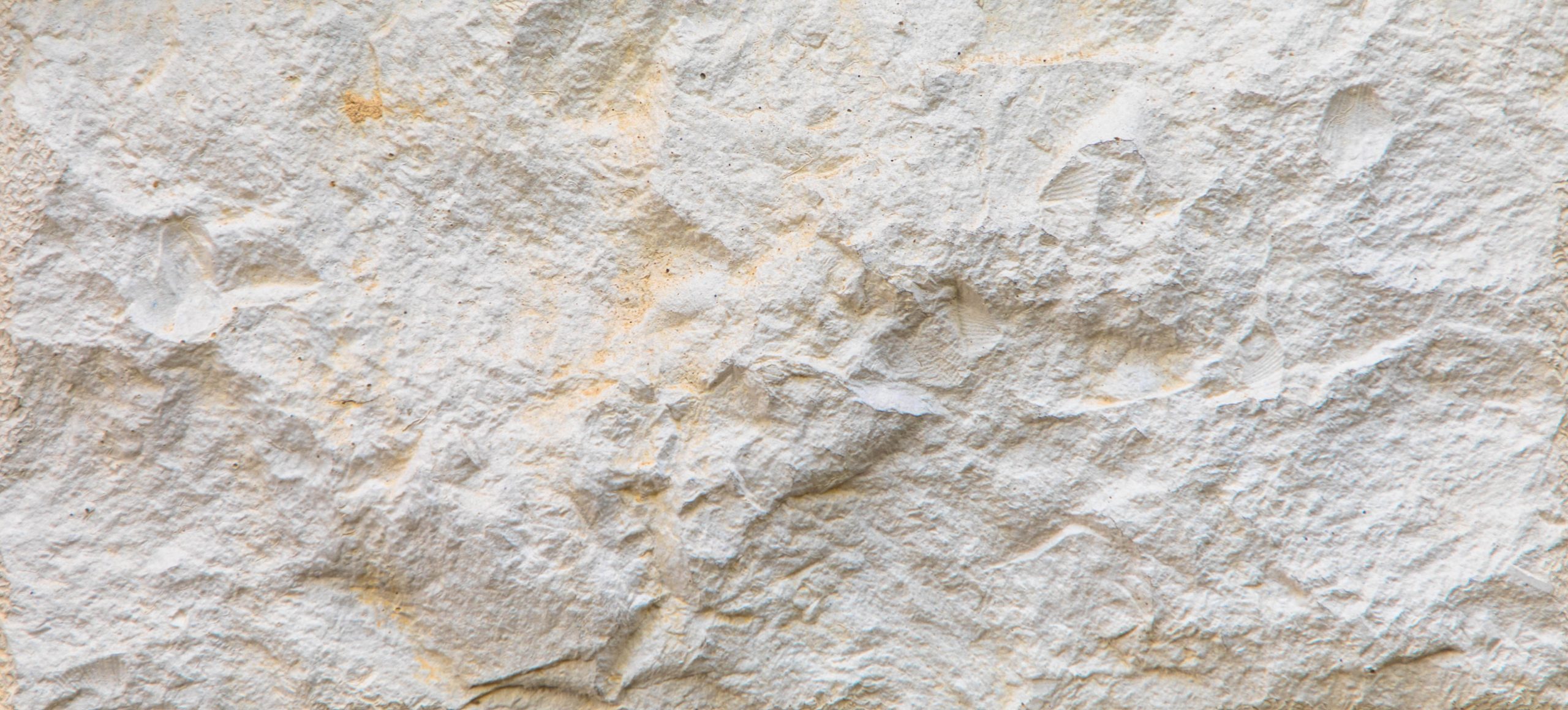
Limestone
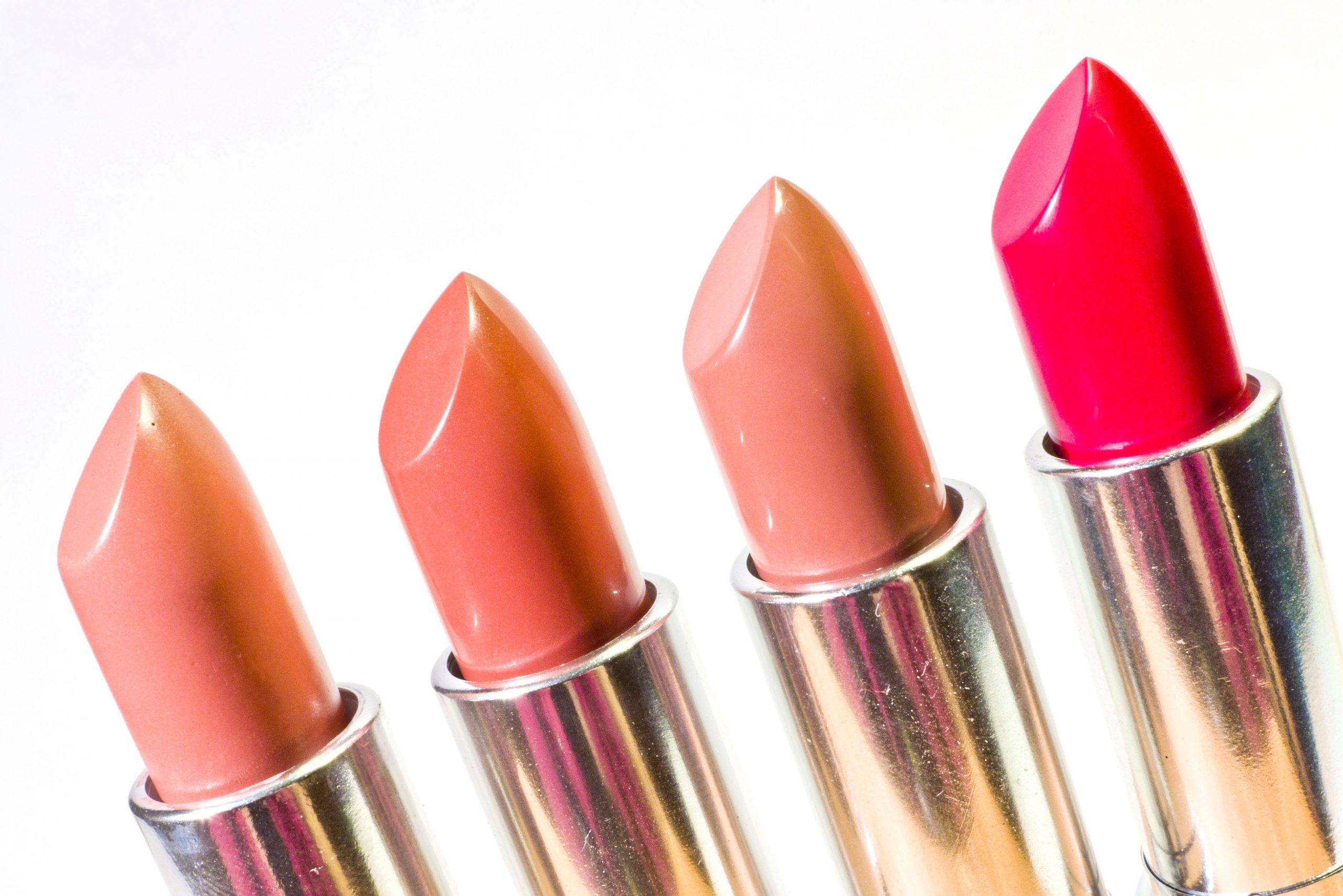
Lipstick
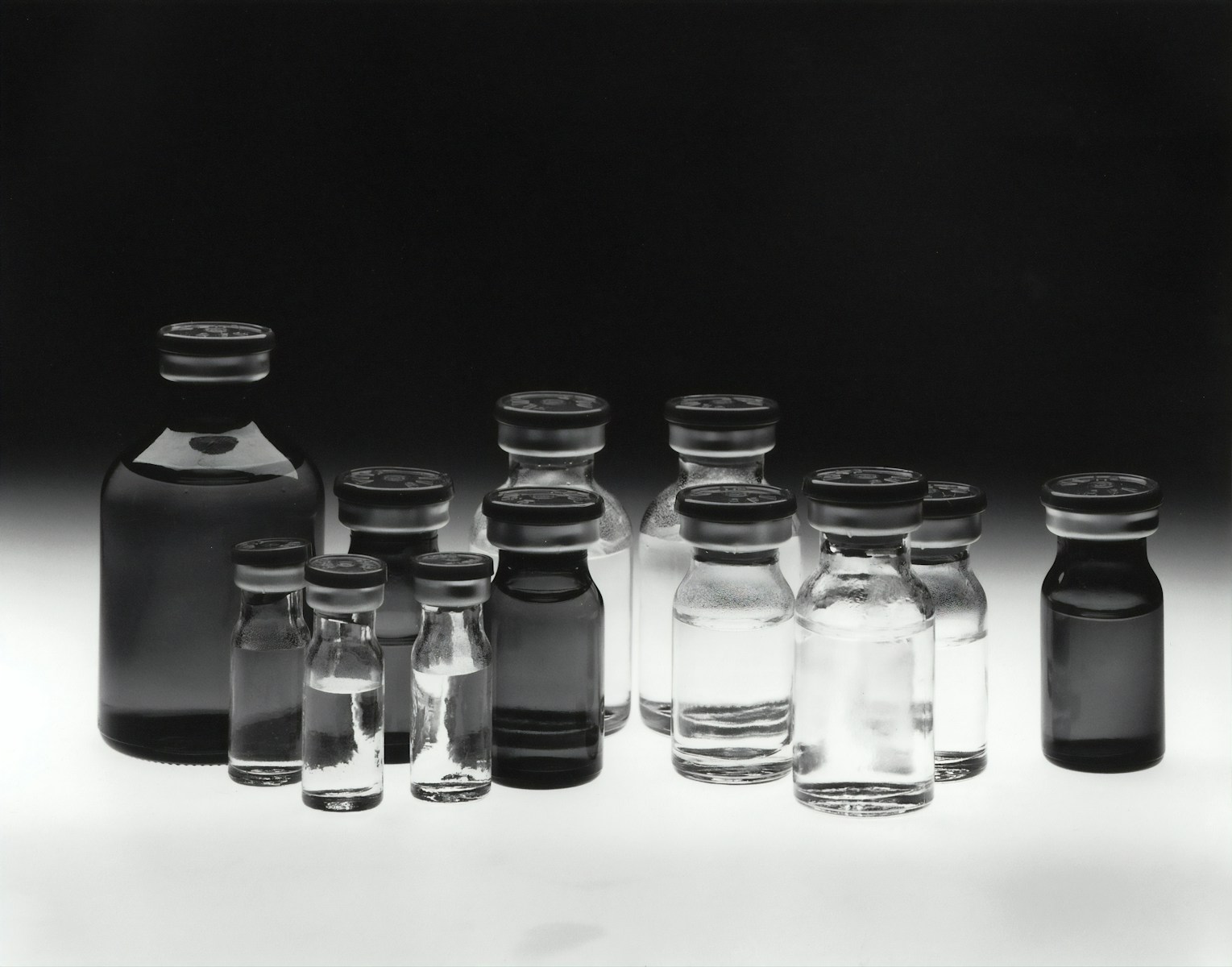
Liquid Formulations
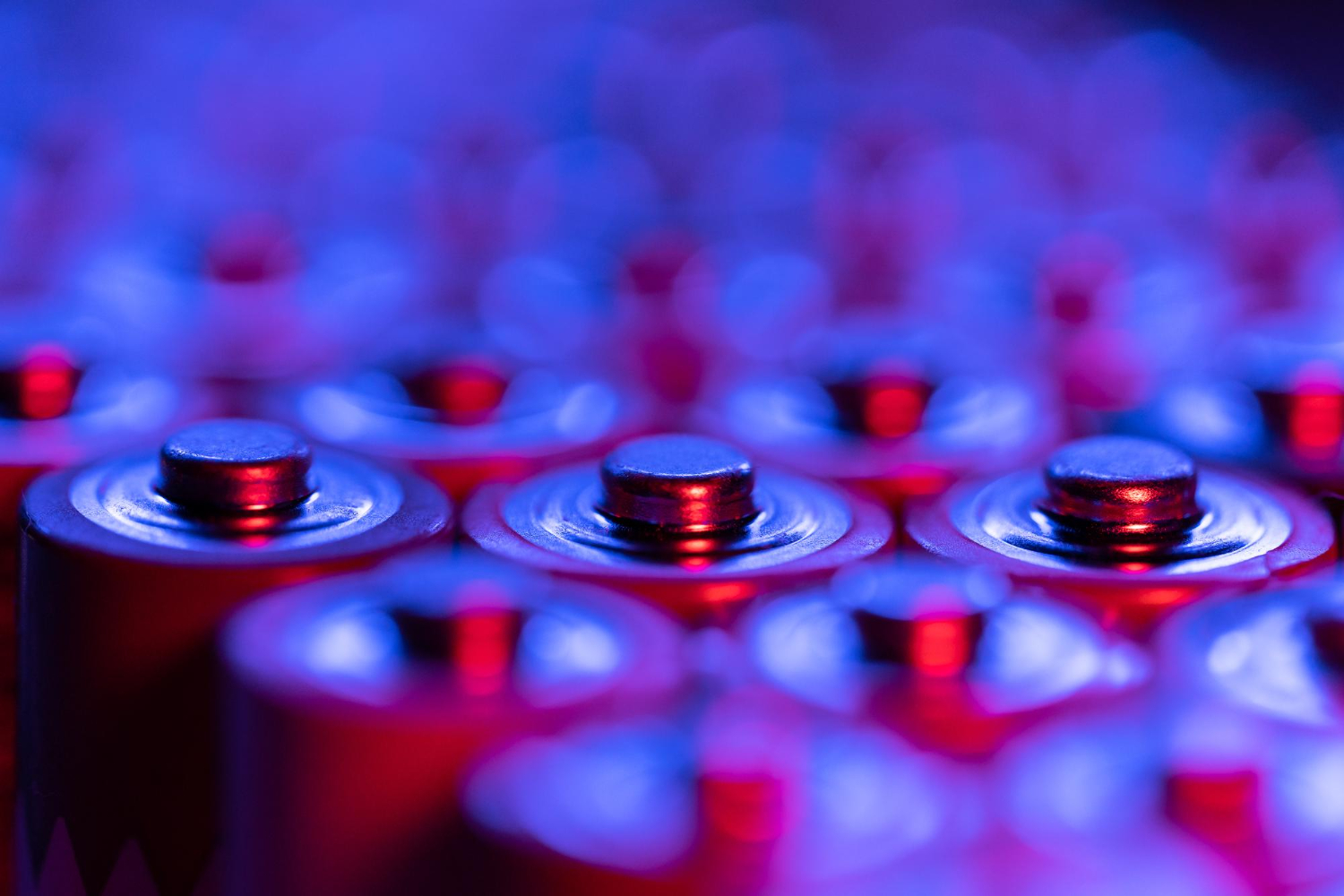
Lithium-ion batteries
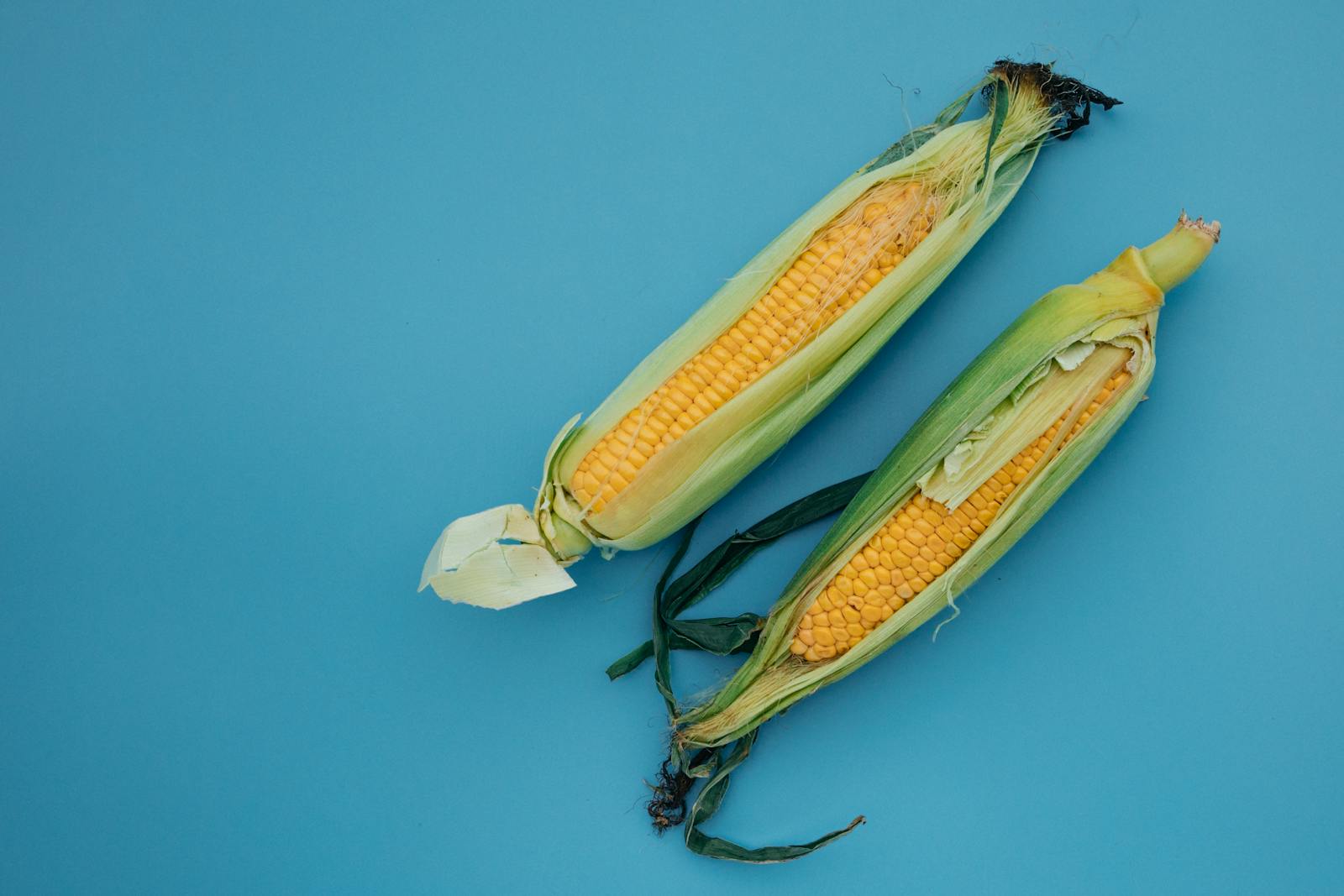
Maize
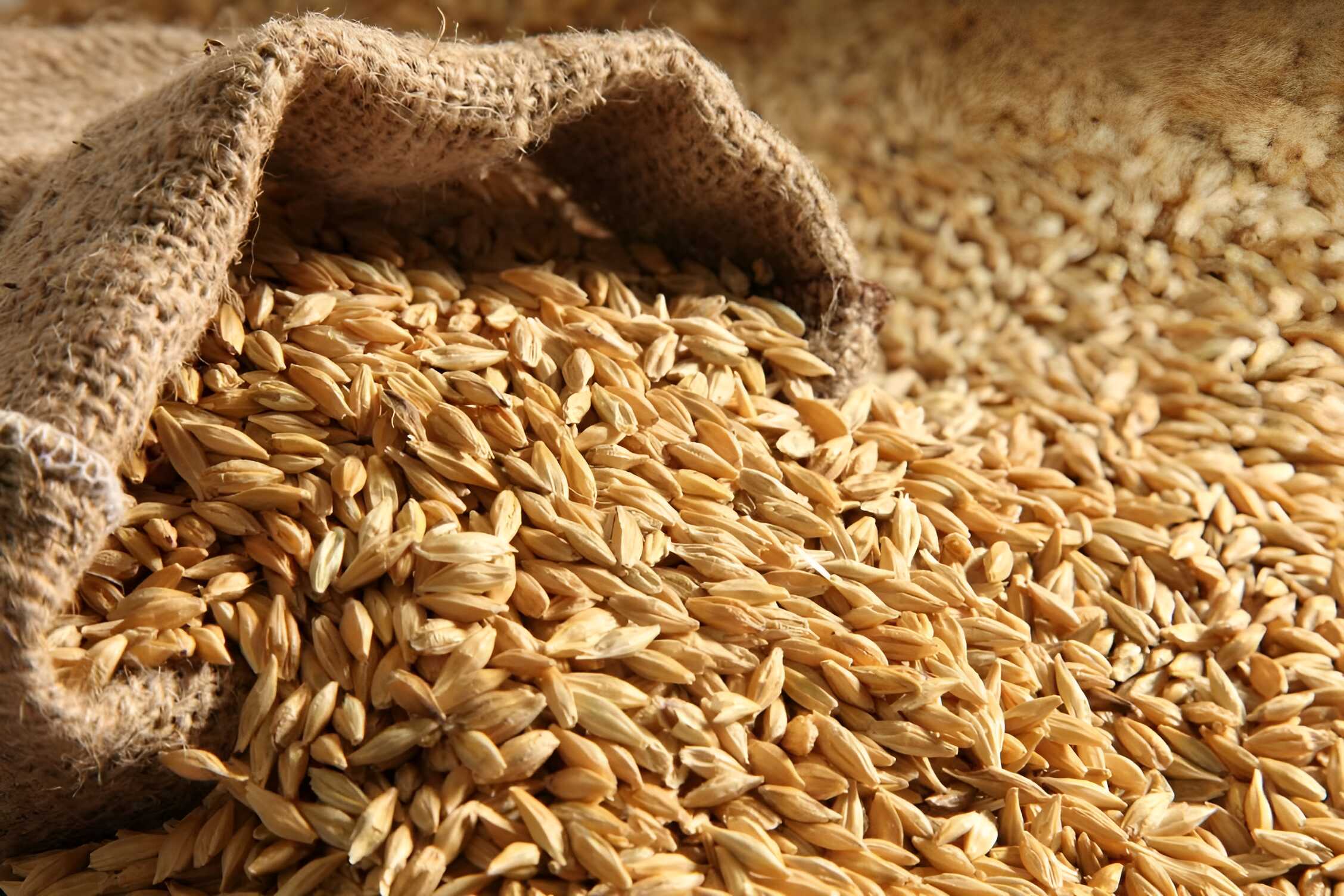
Malt
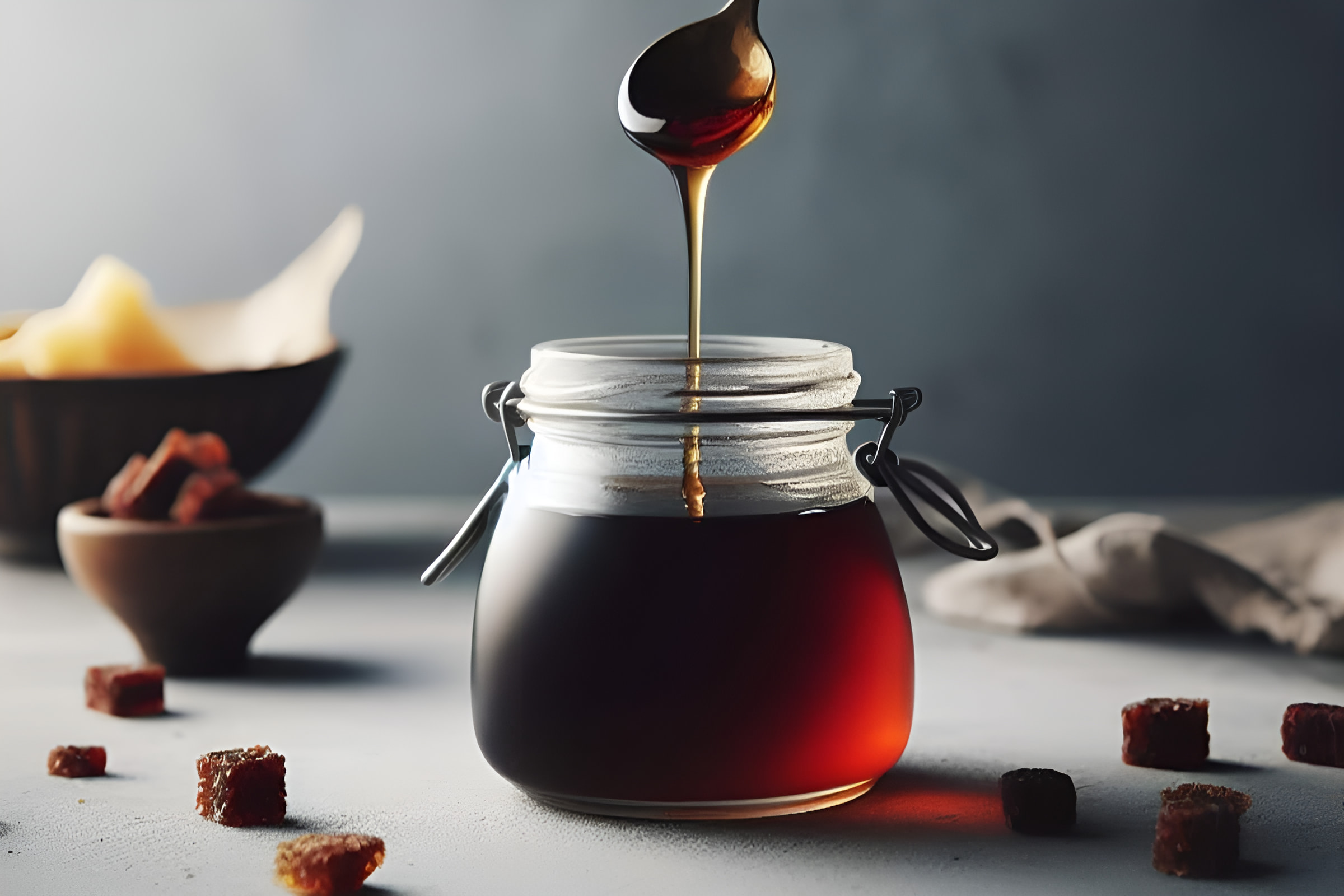
Malt extract
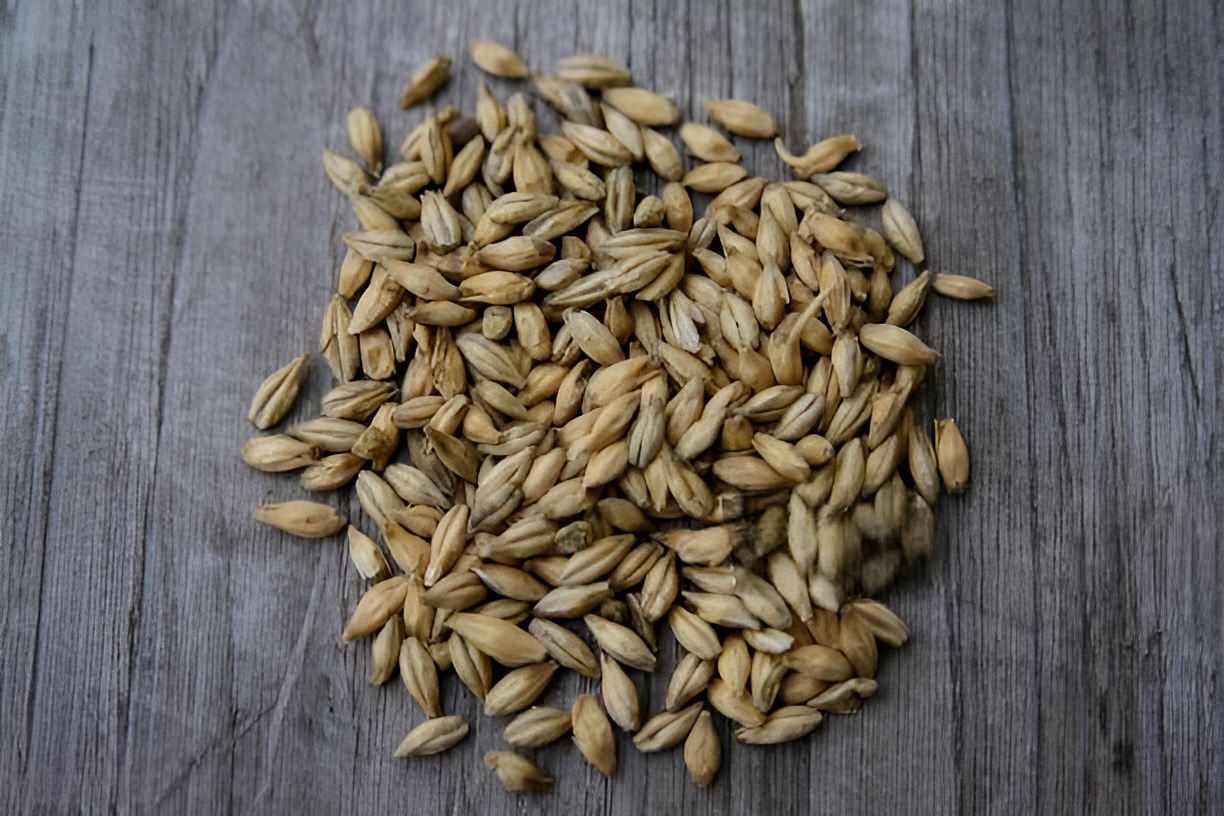
Malted barley
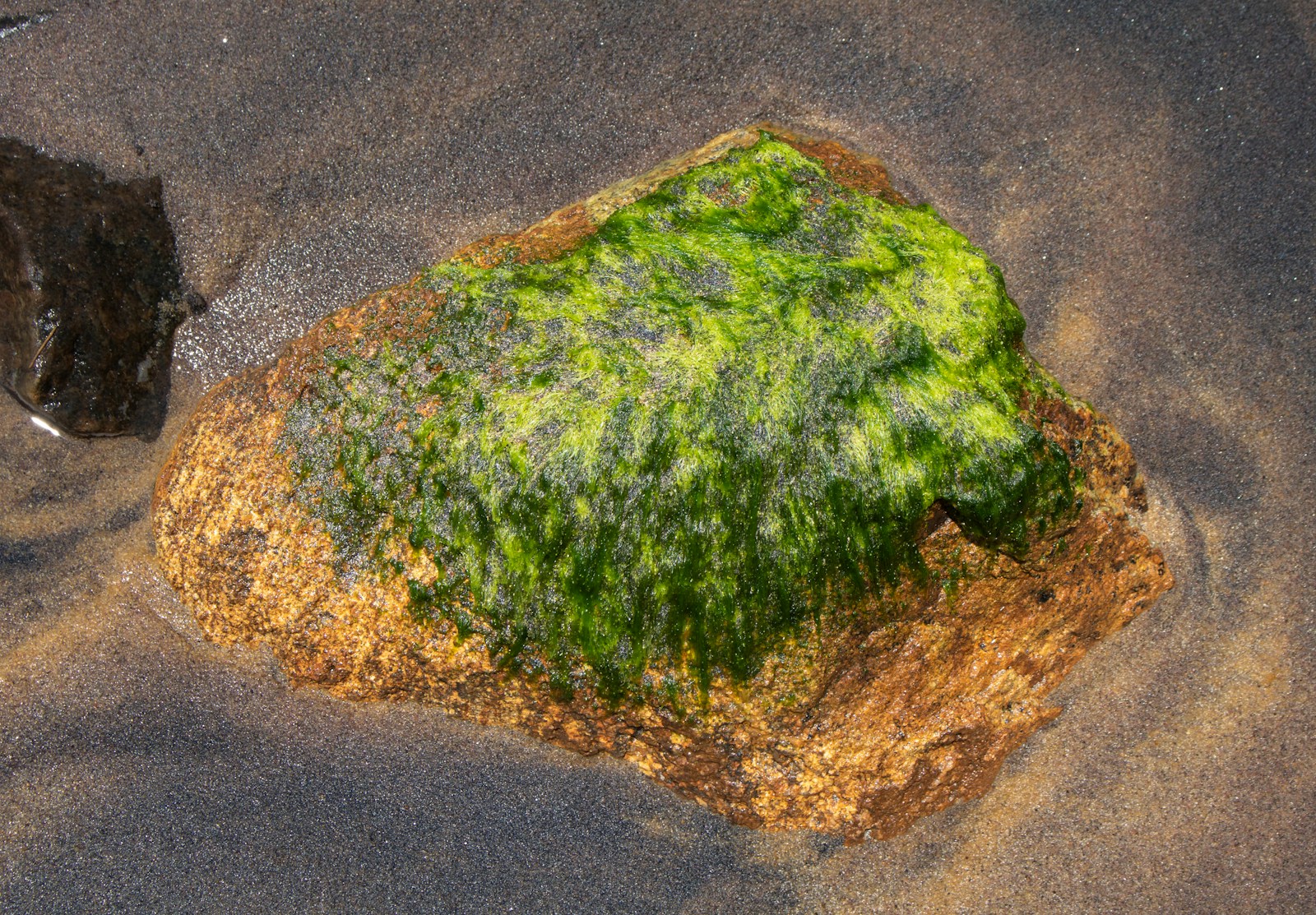
Marine algae
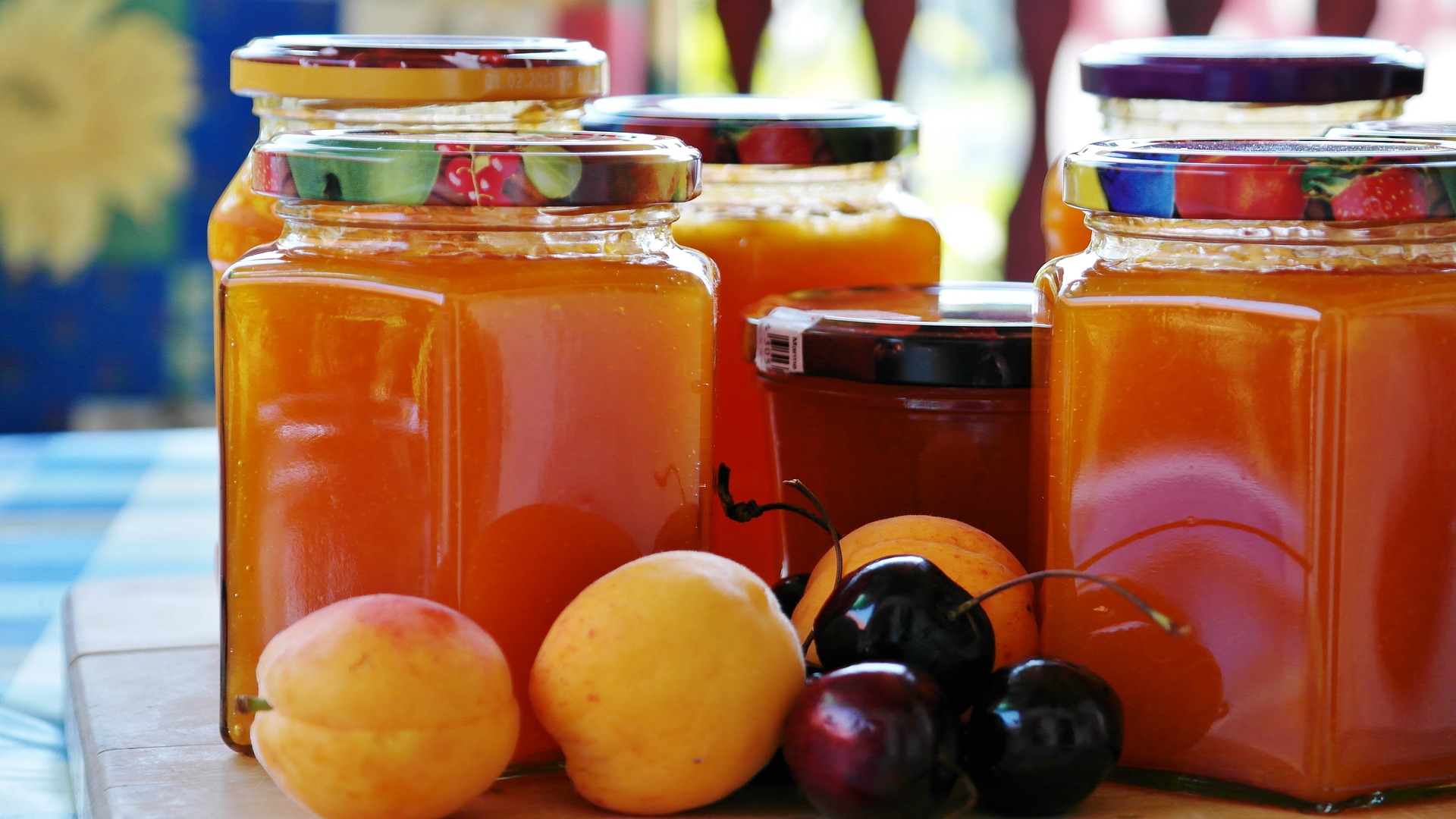
Marmalade
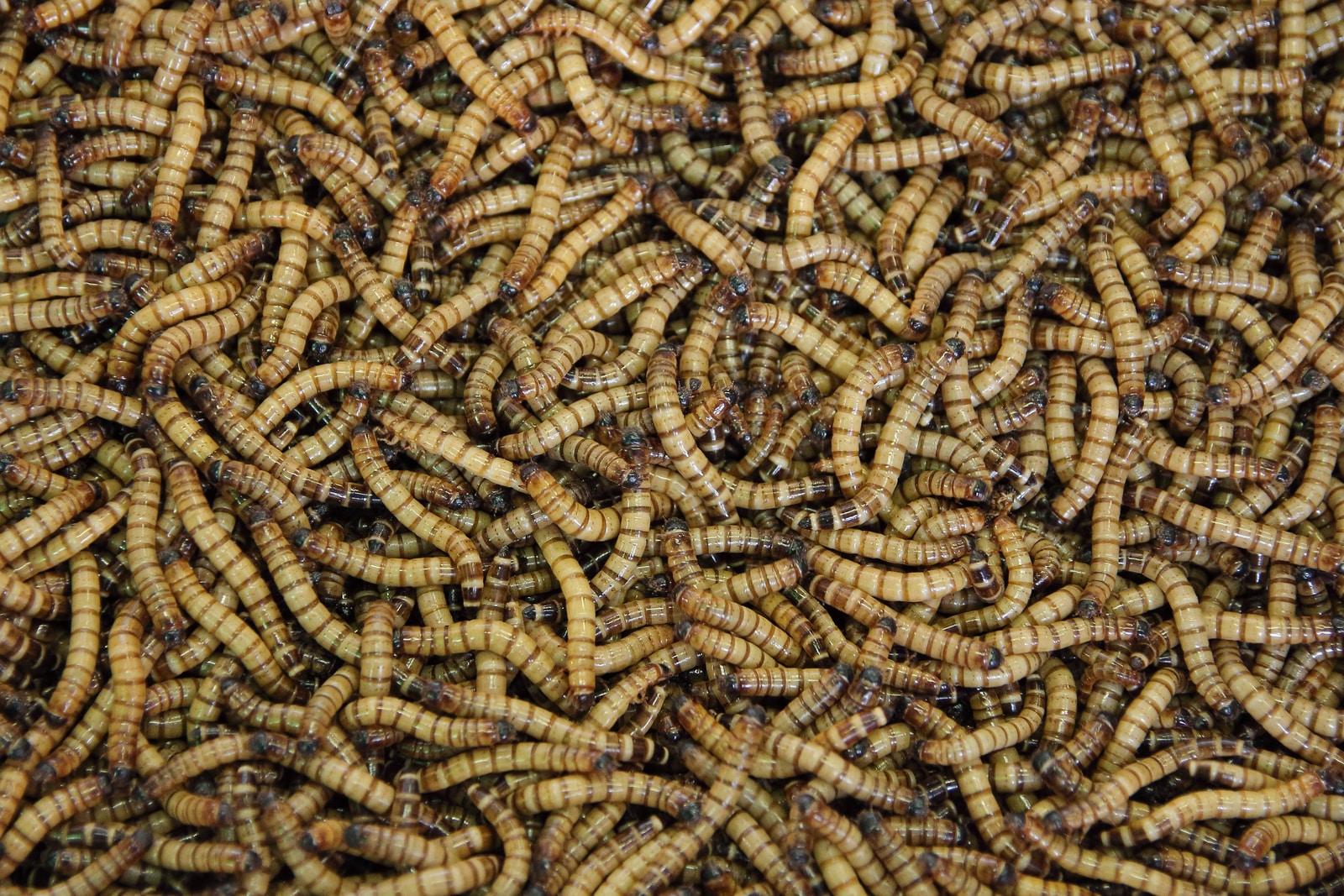
Mealworm protein
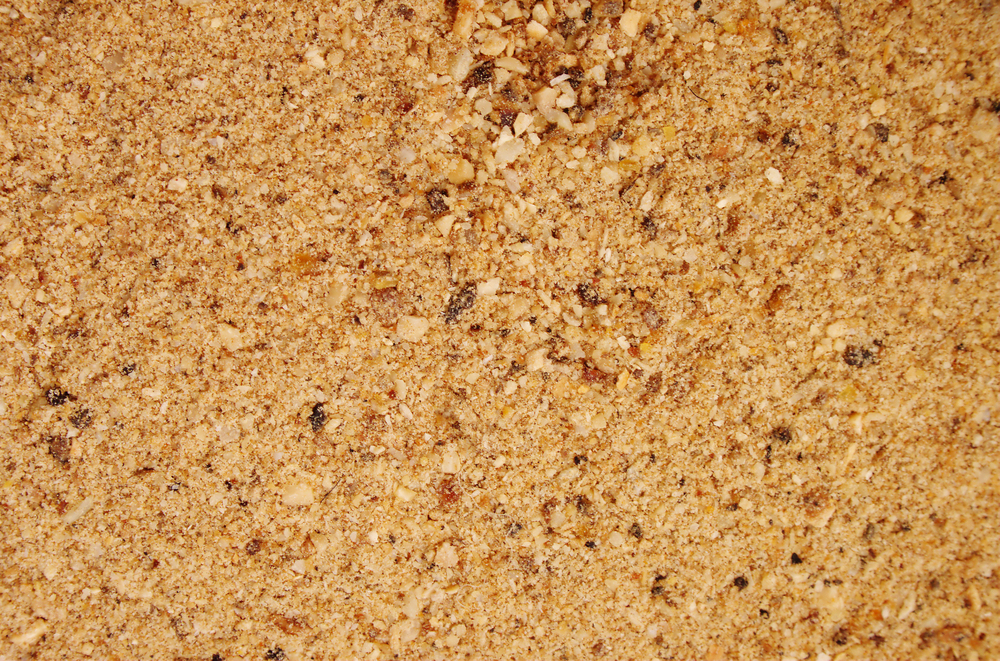
Meat and bone meal
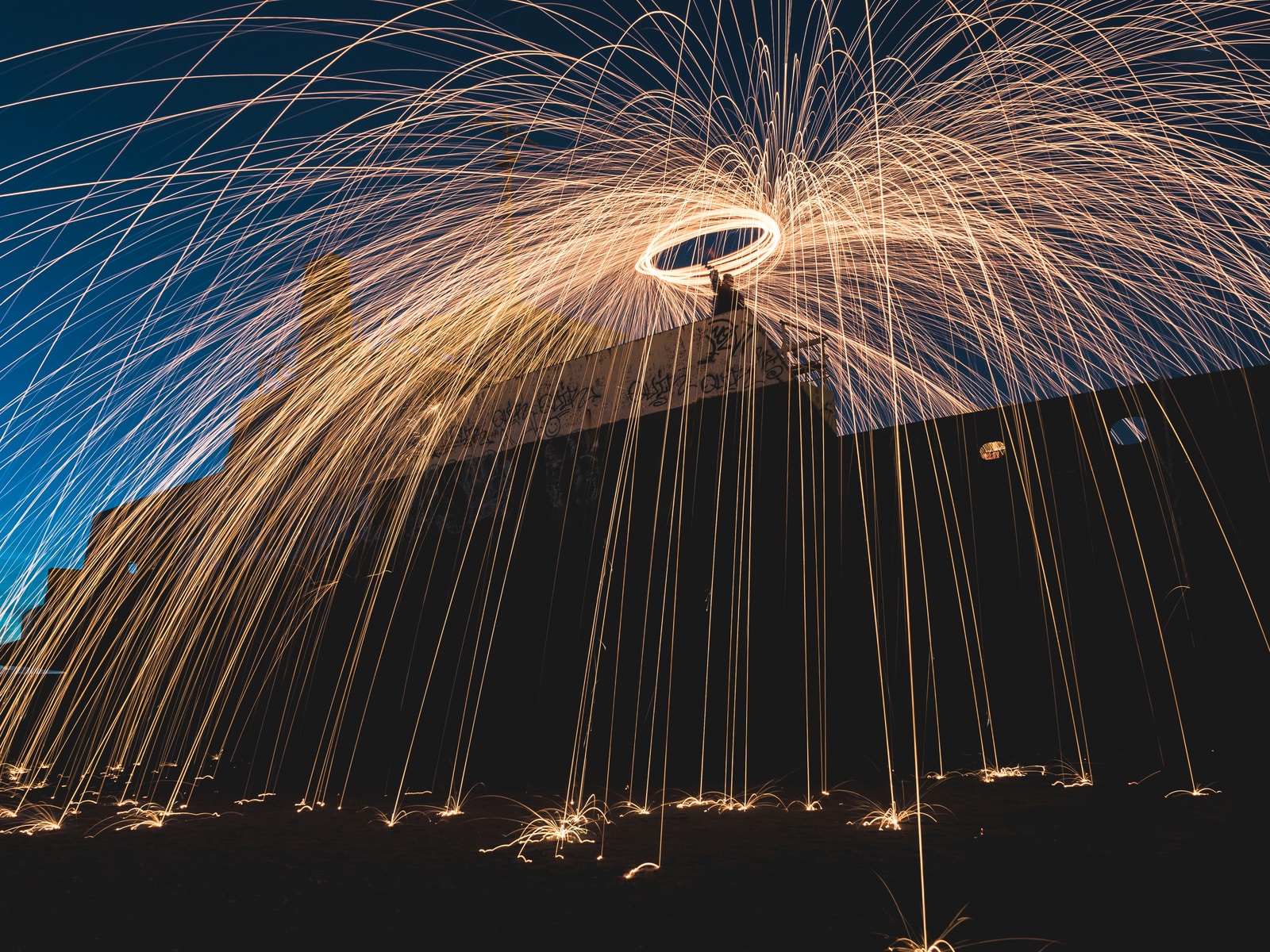
Metal powder
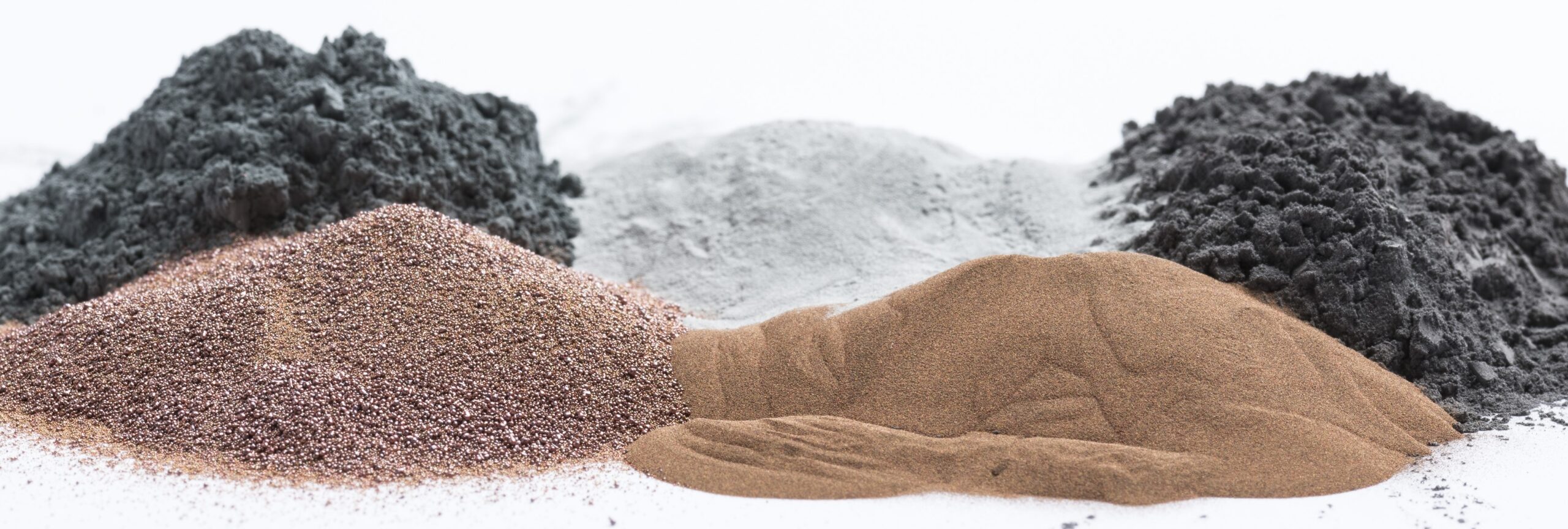
Metal powders
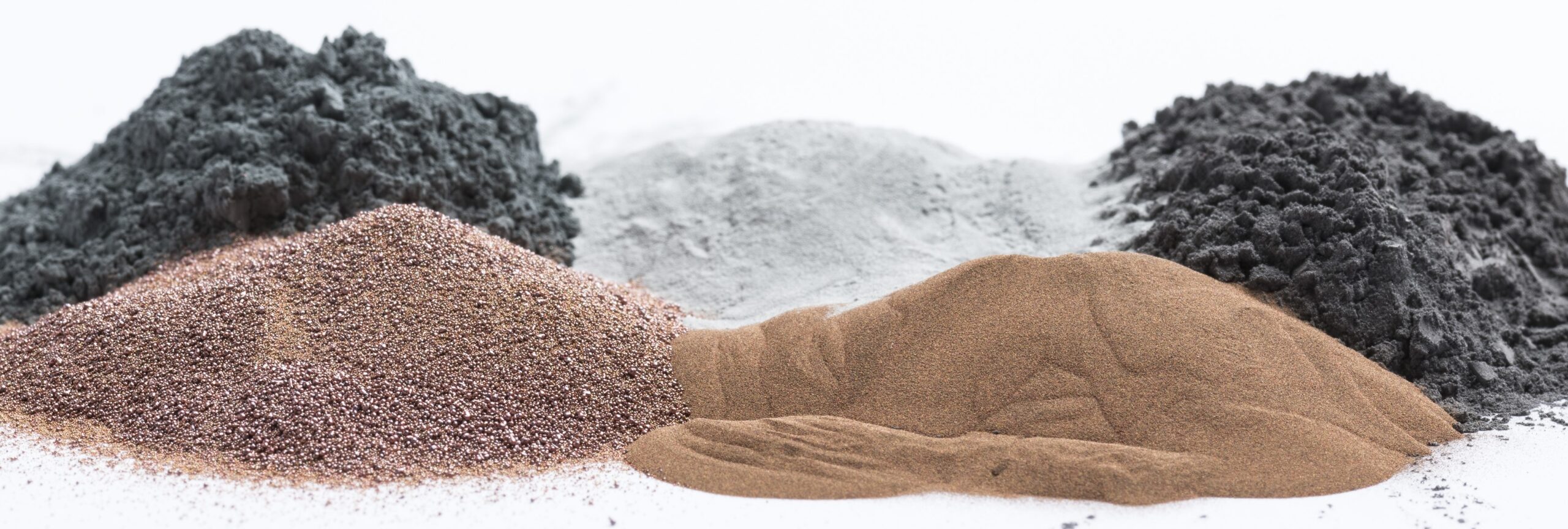
Metallic powders
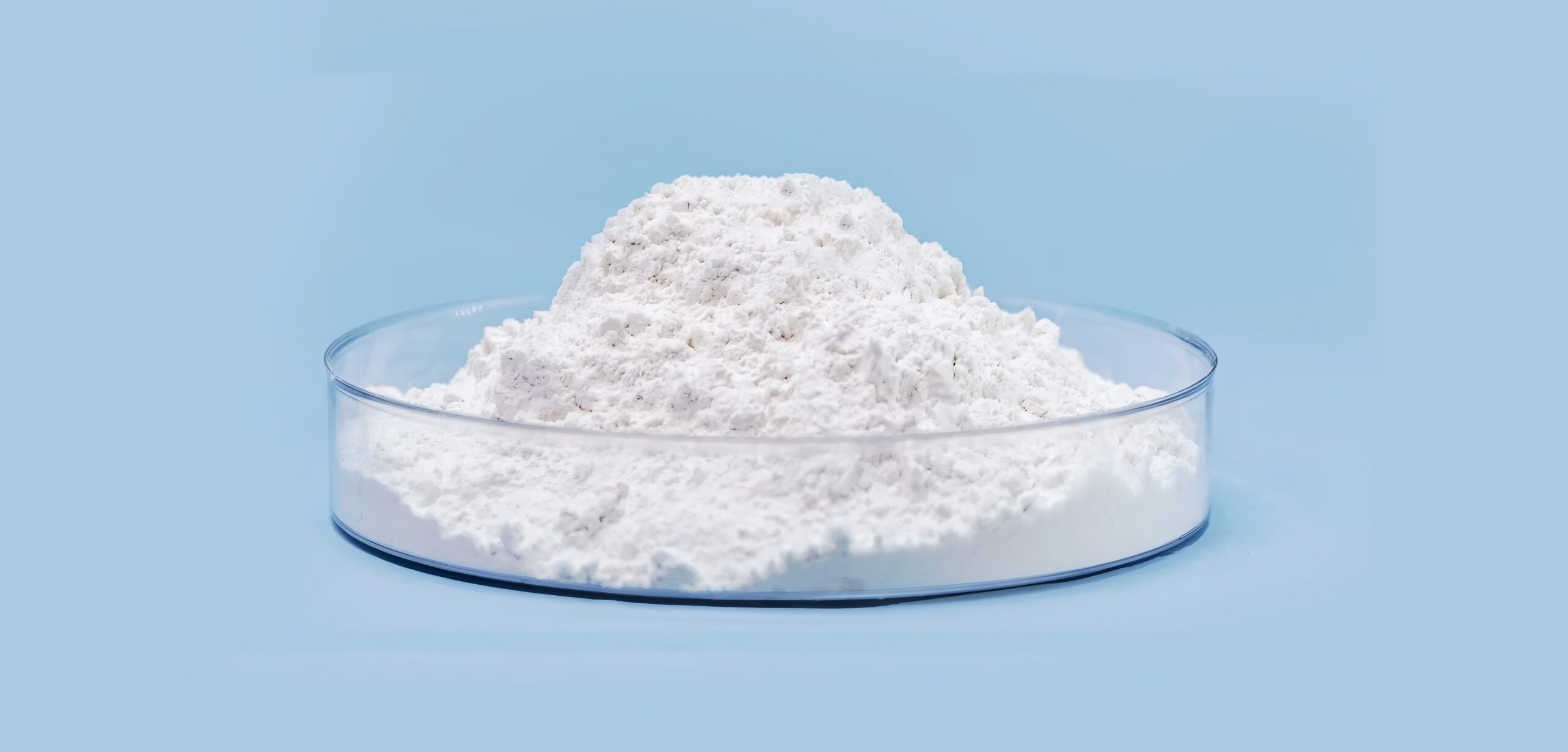
Microcrystalline cellulose
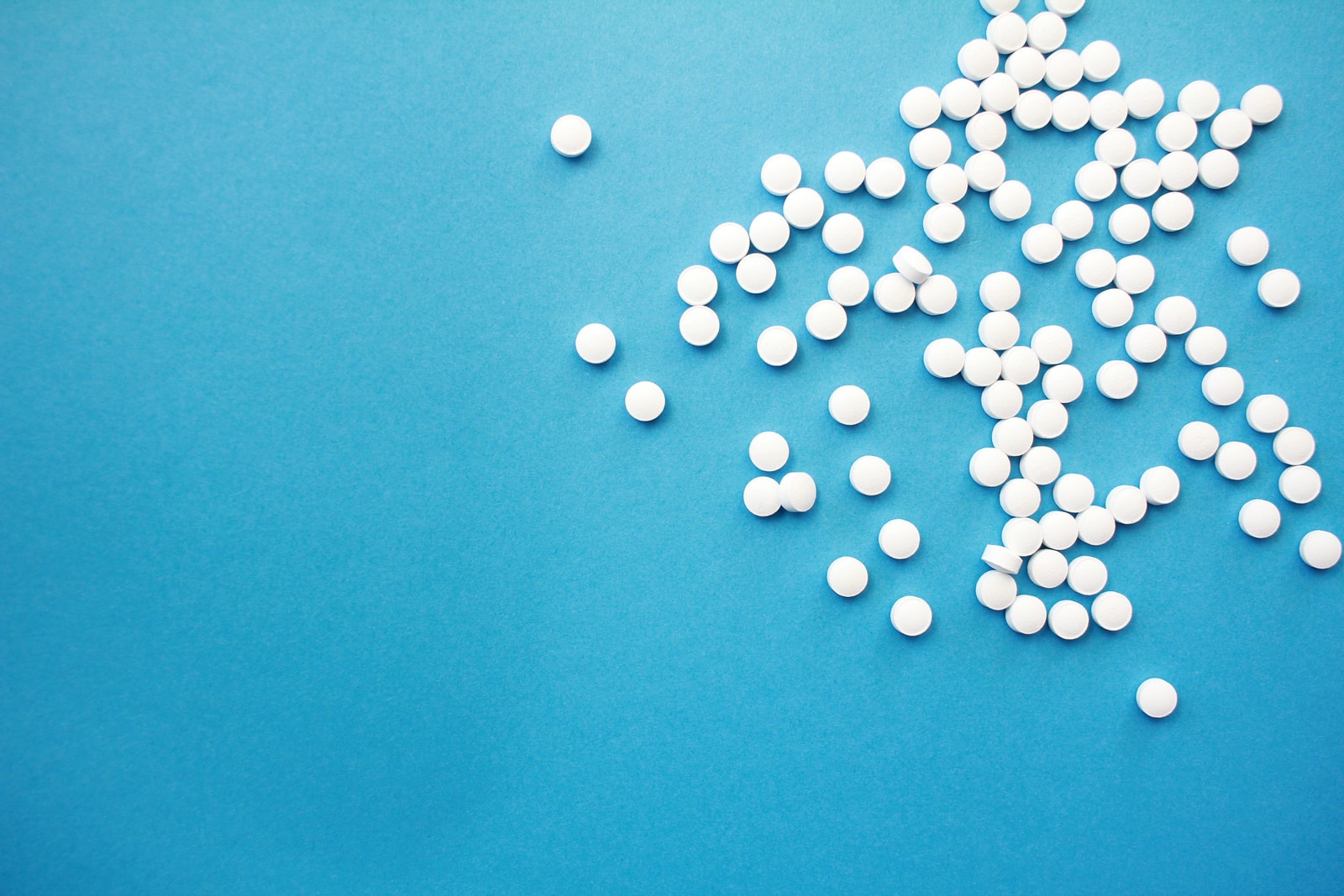
Microtablets

Mineral fillers
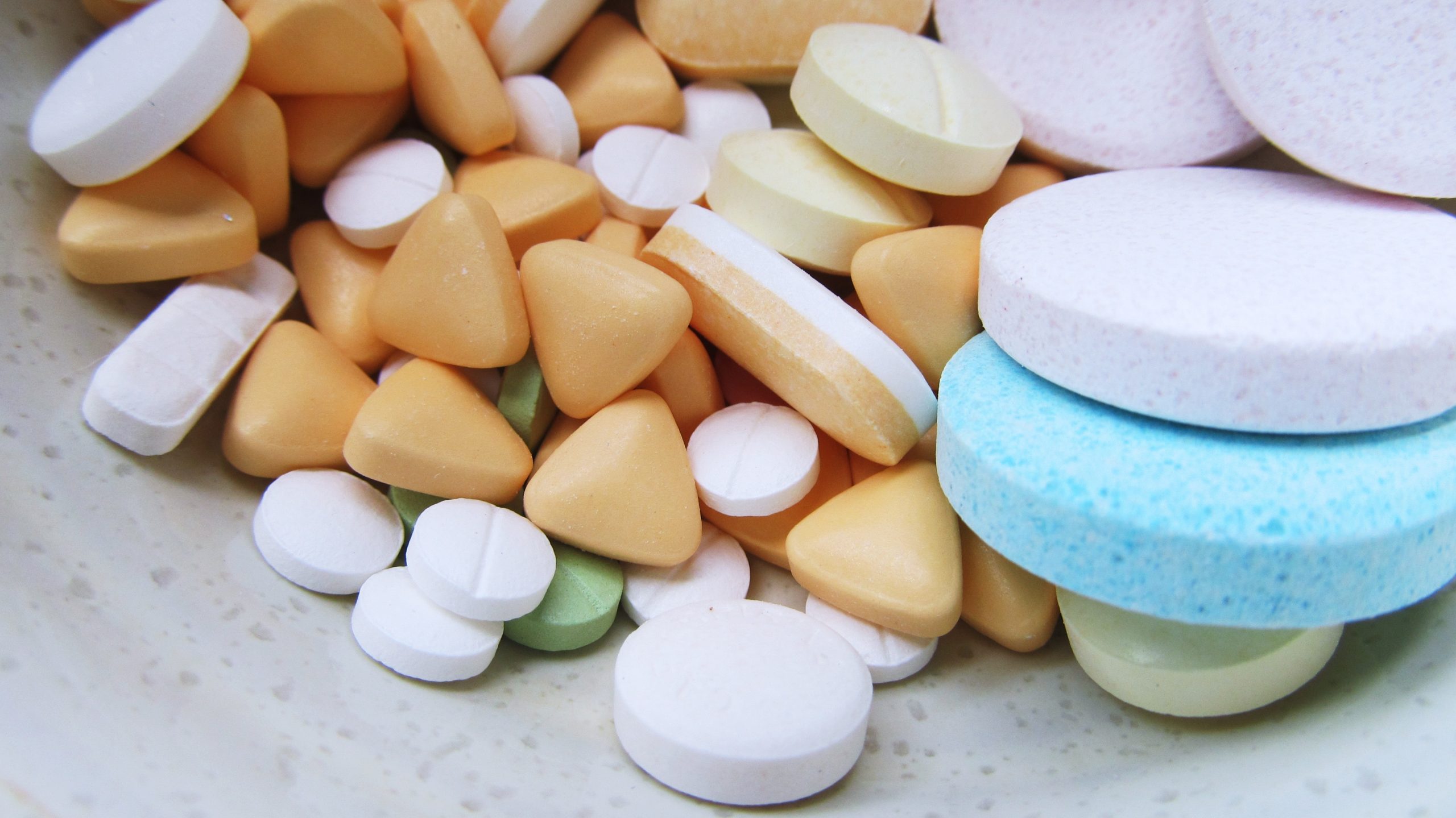
Multi-layer tablets
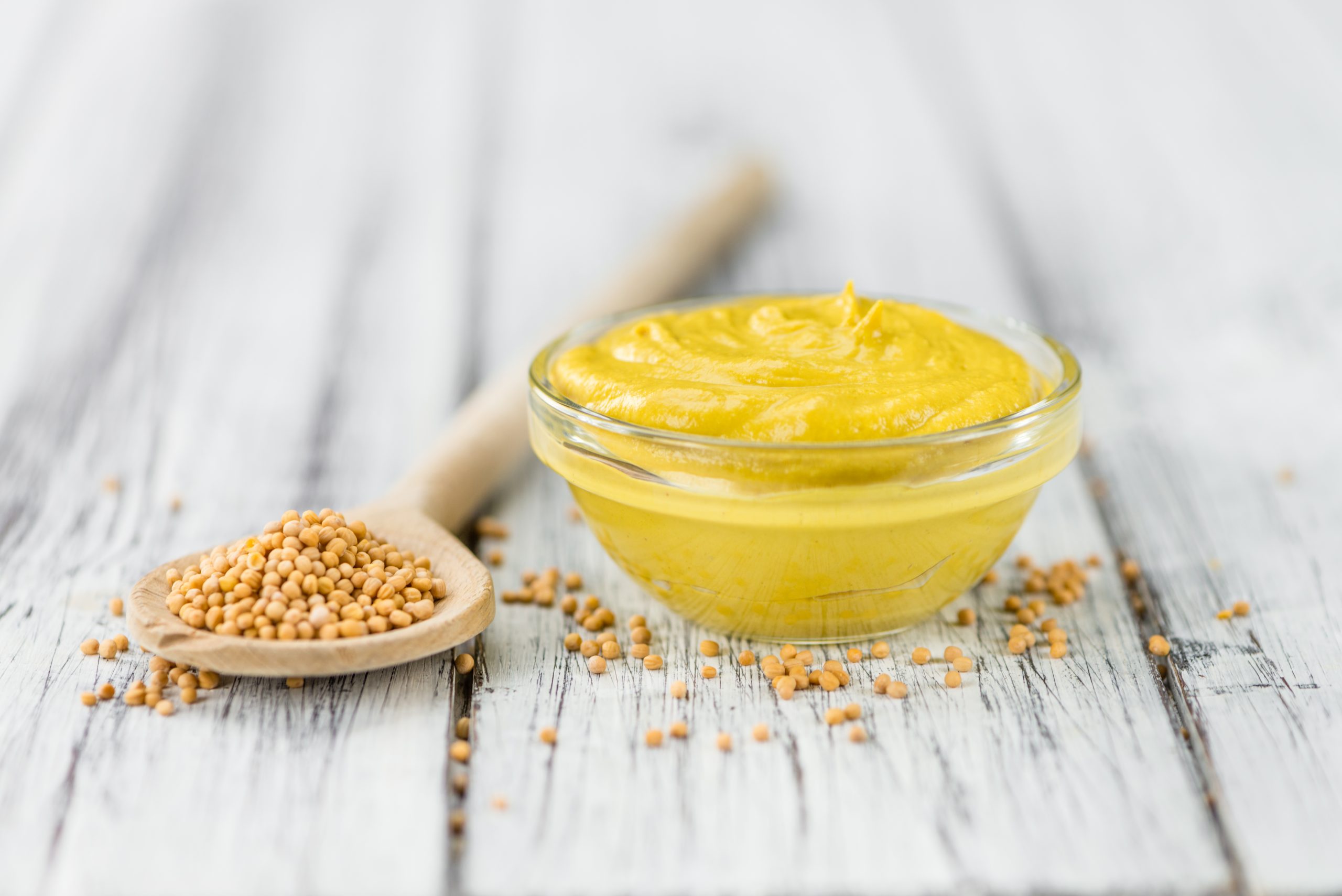
Mustard
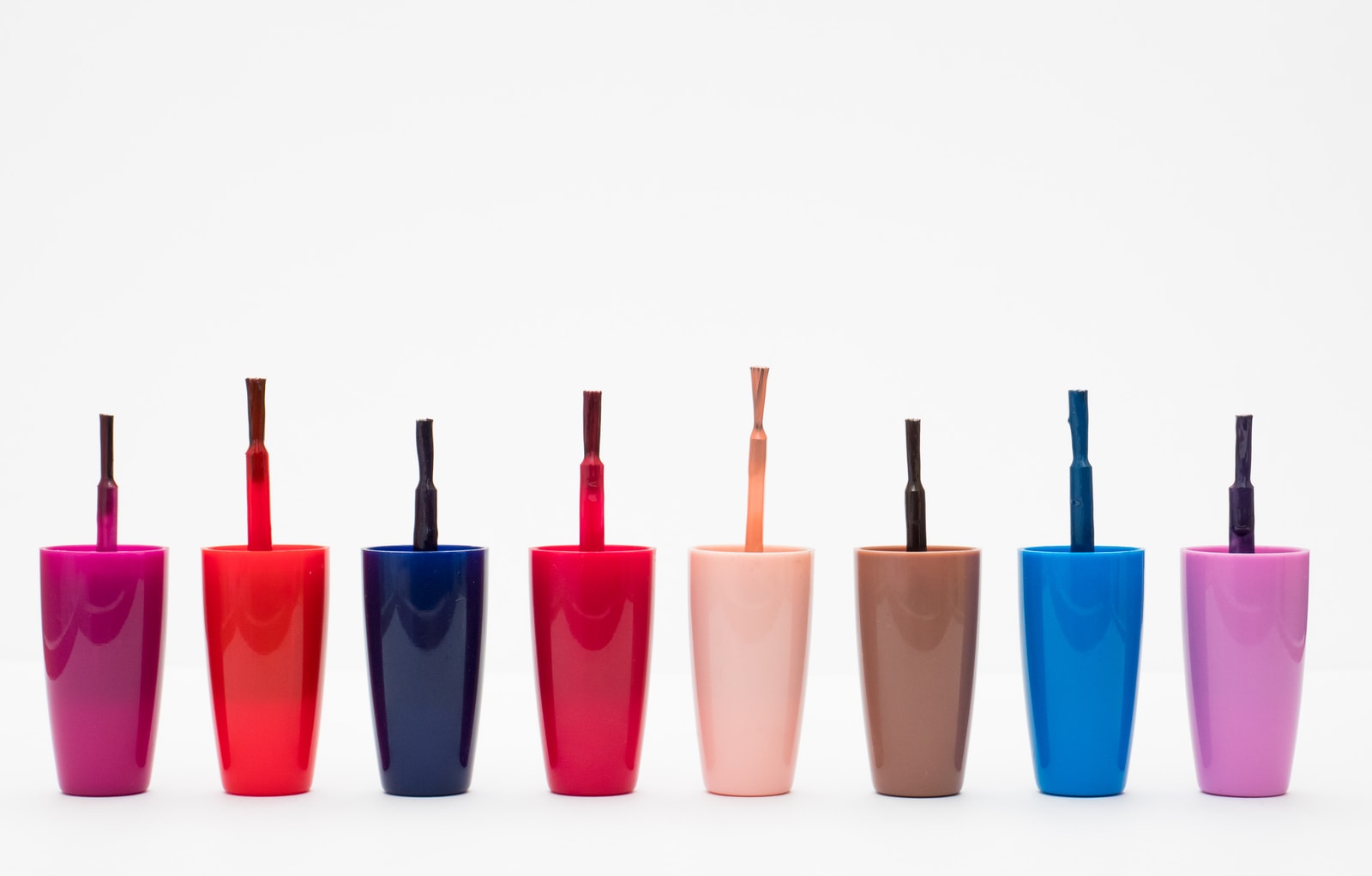
Nail polish
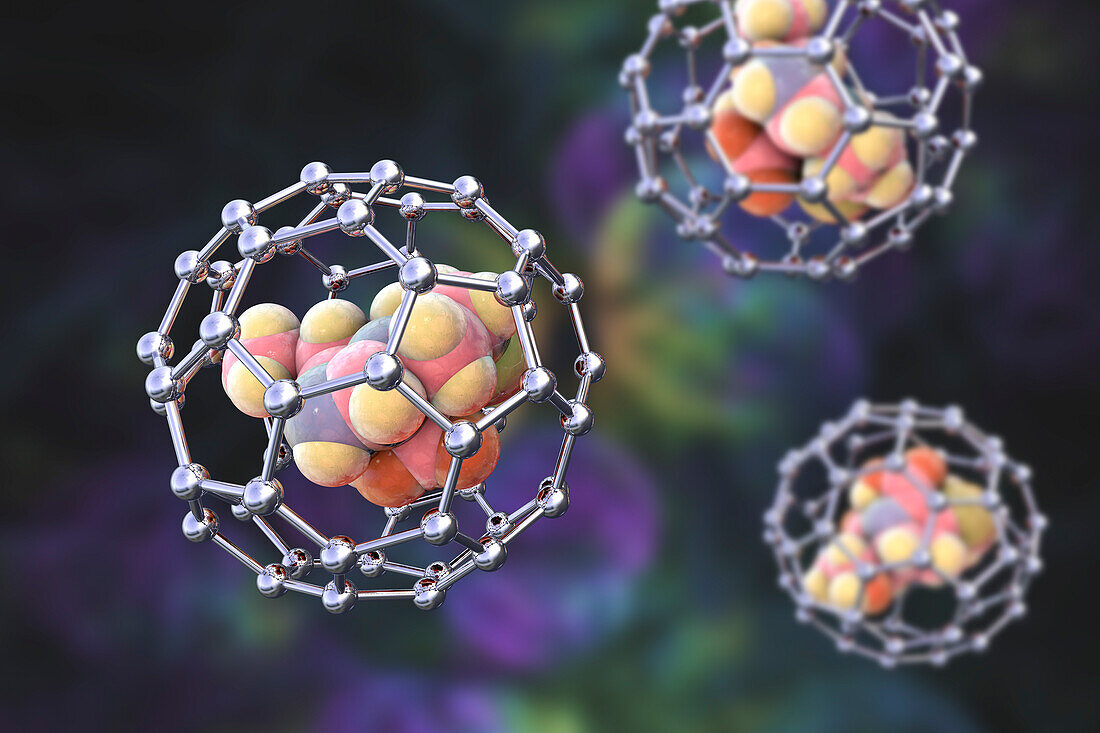
Nanoparticles
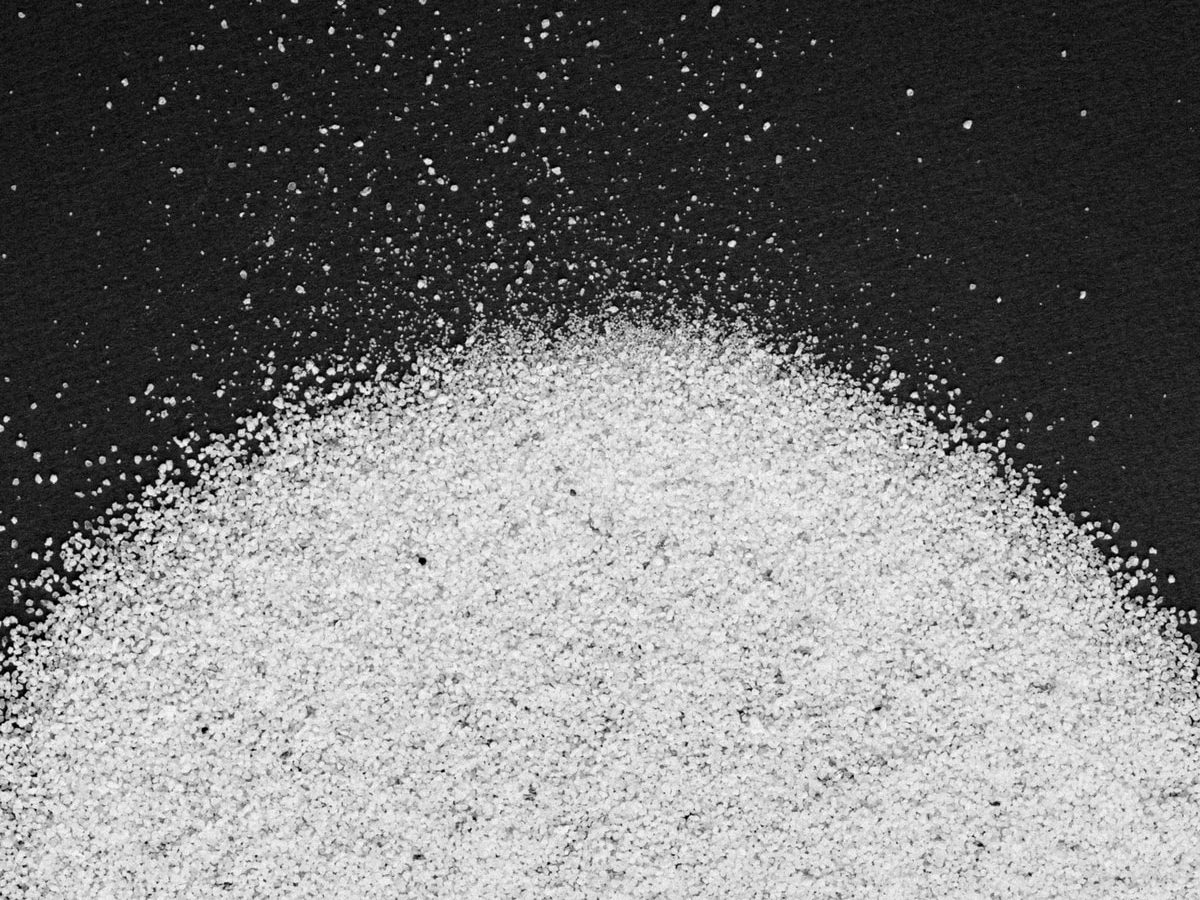
Nitrogen fertilizer
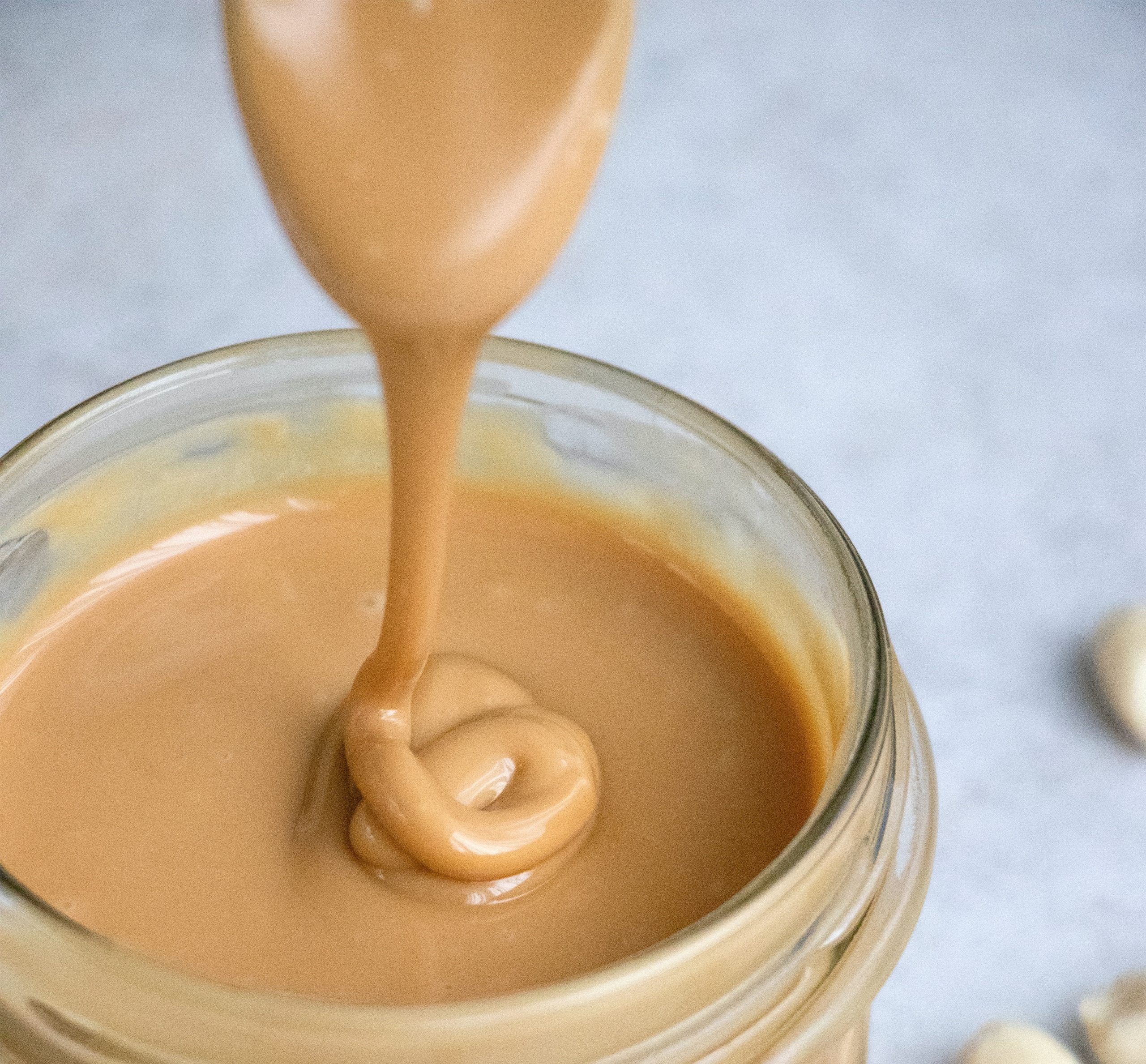
Nut butter
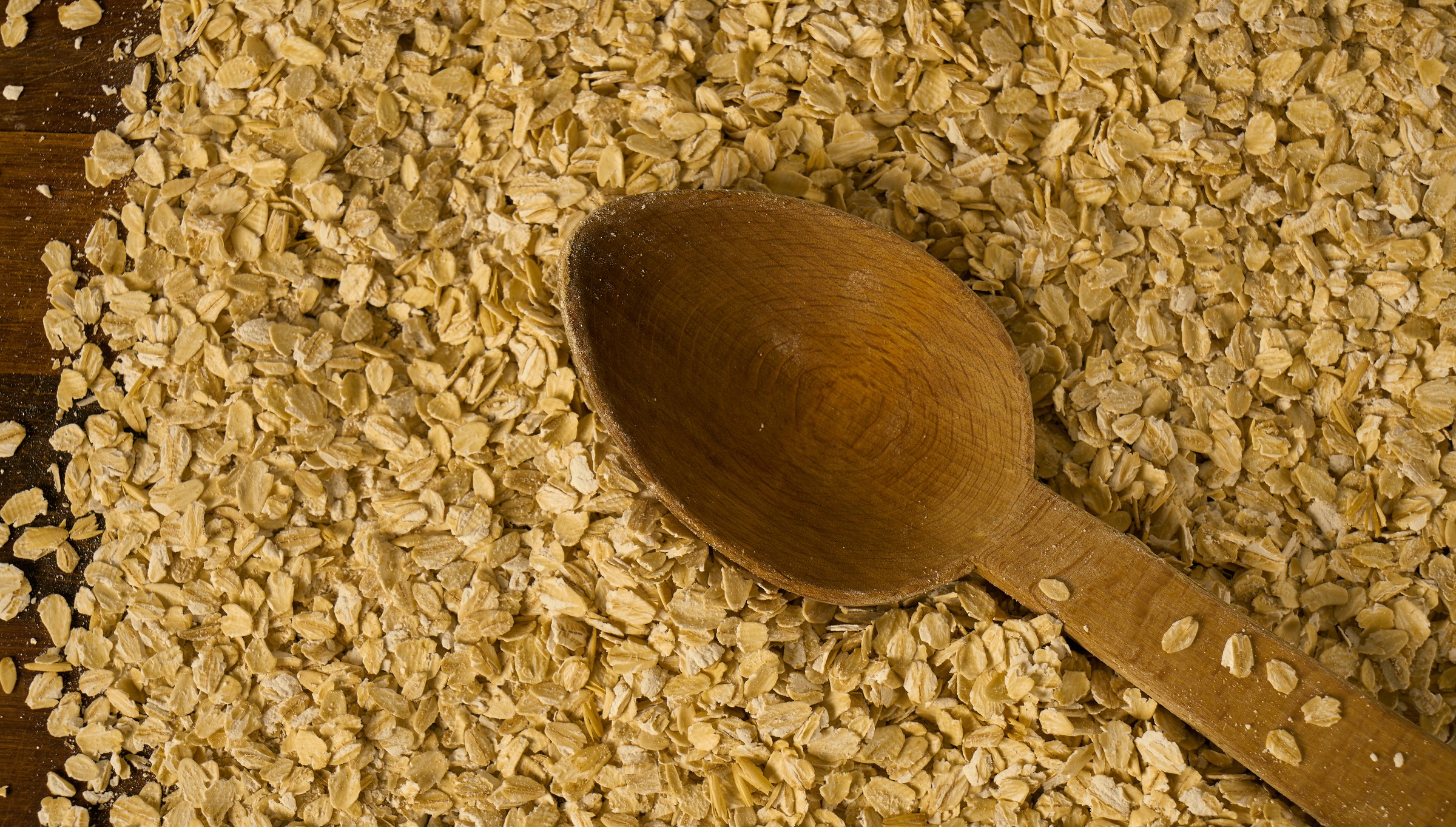
Oat bran
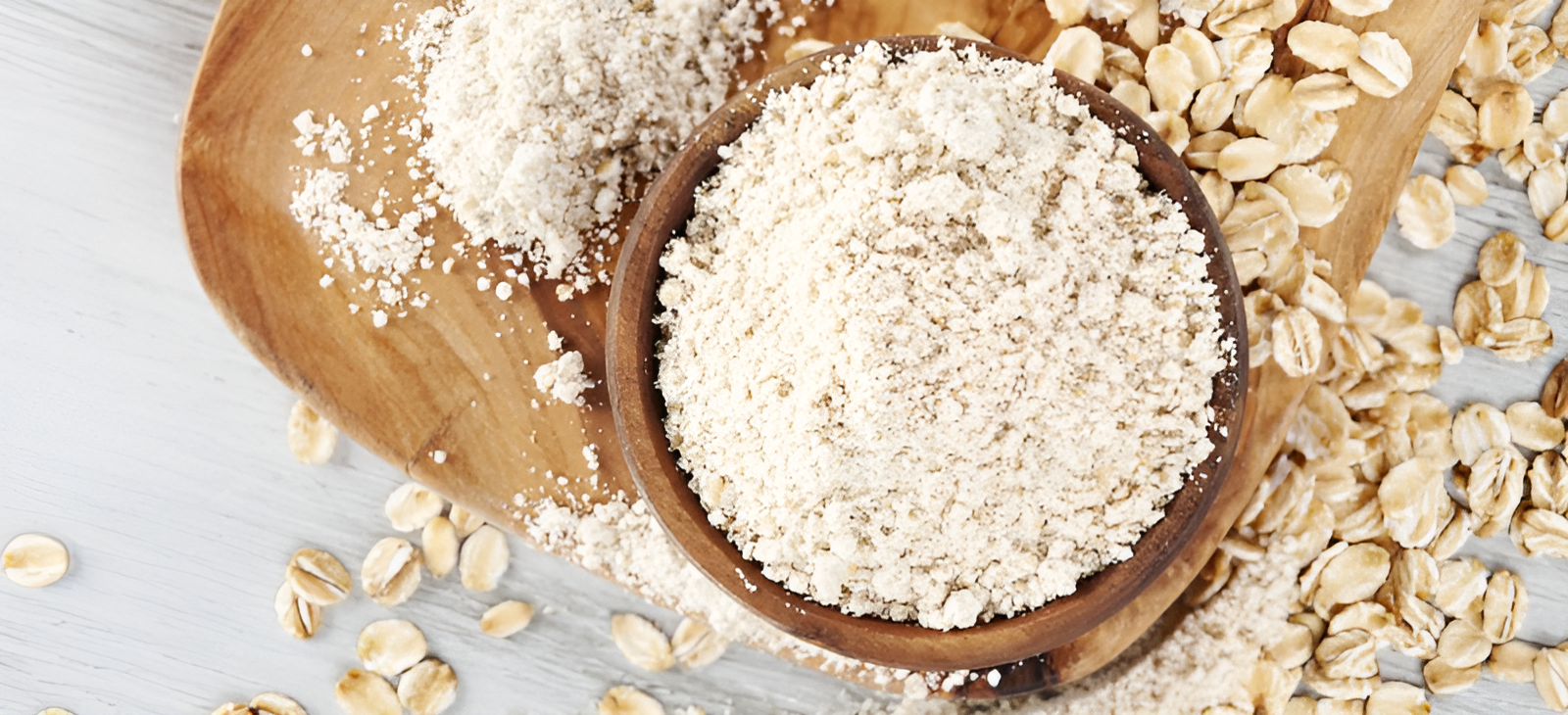
Oat flour
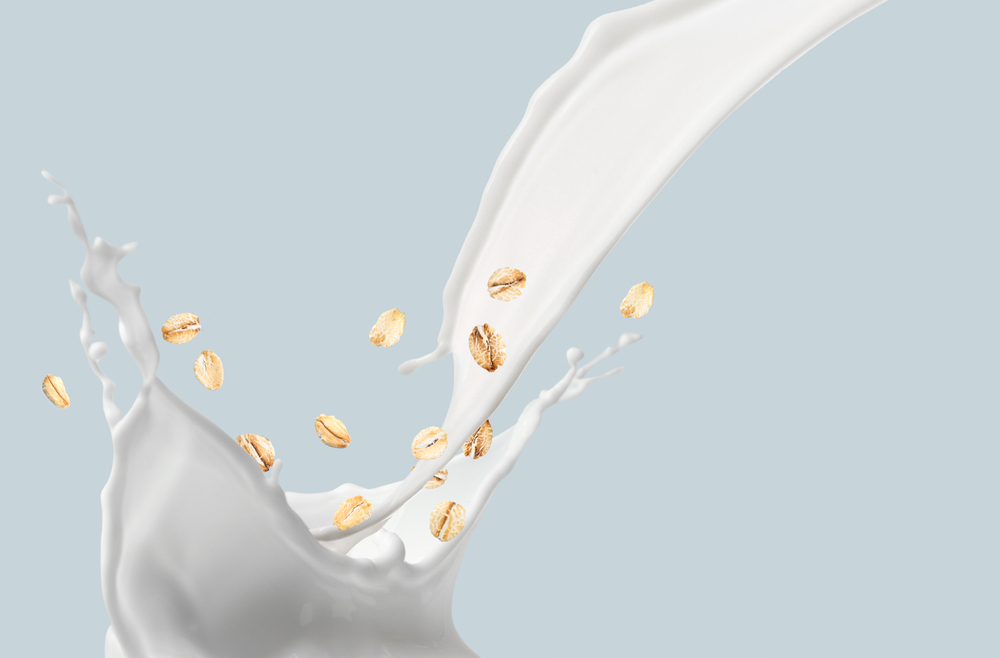
Oat milk
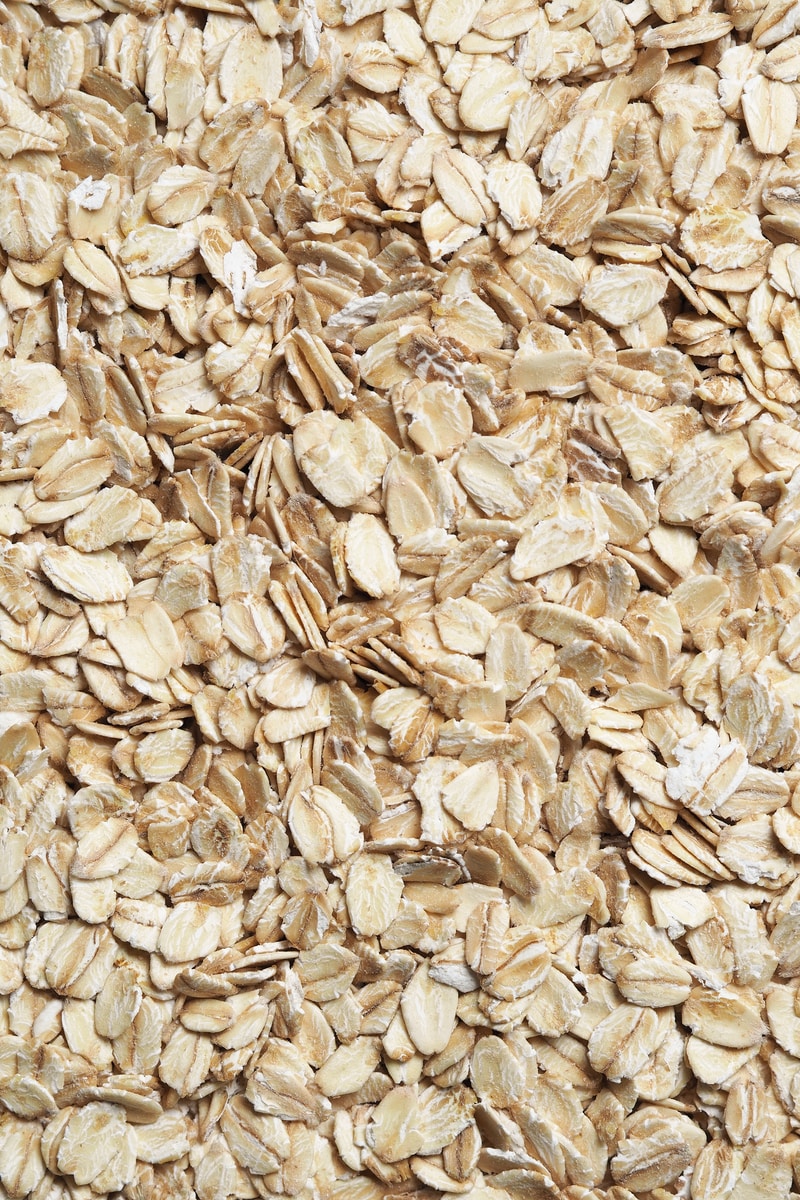
Oatmeal
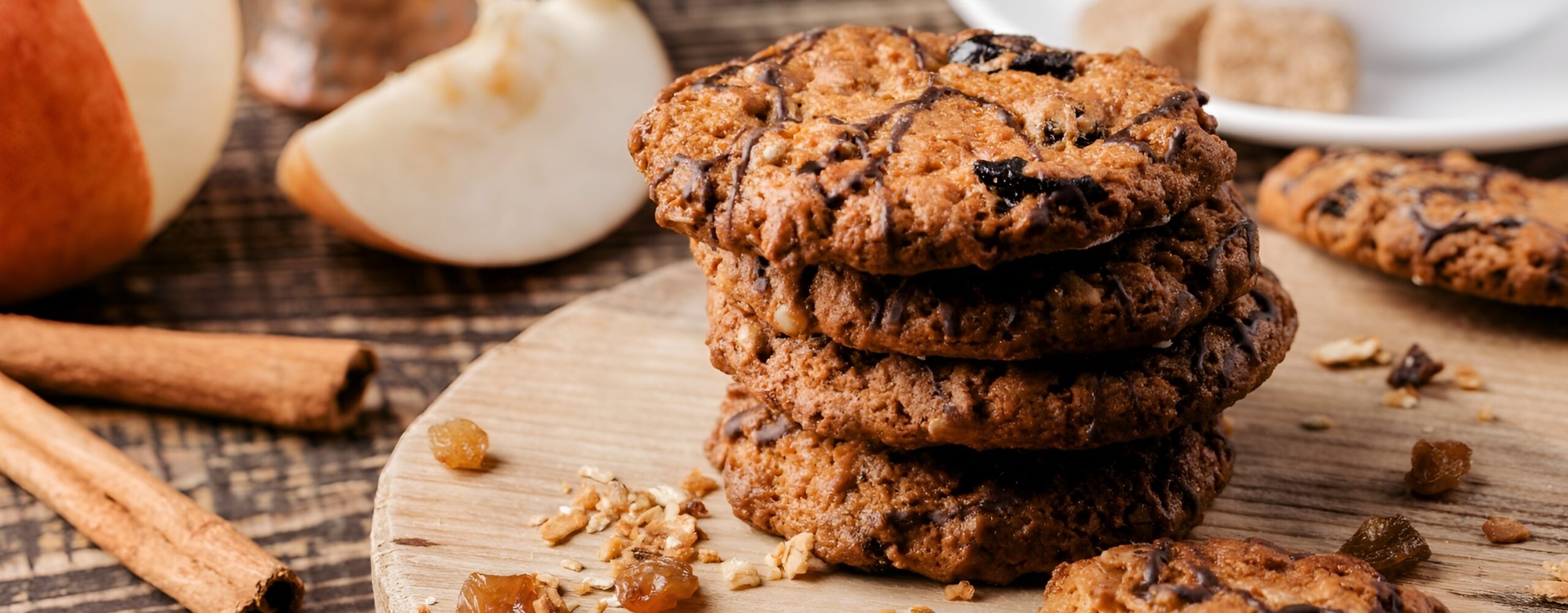
Oatmeal cookies
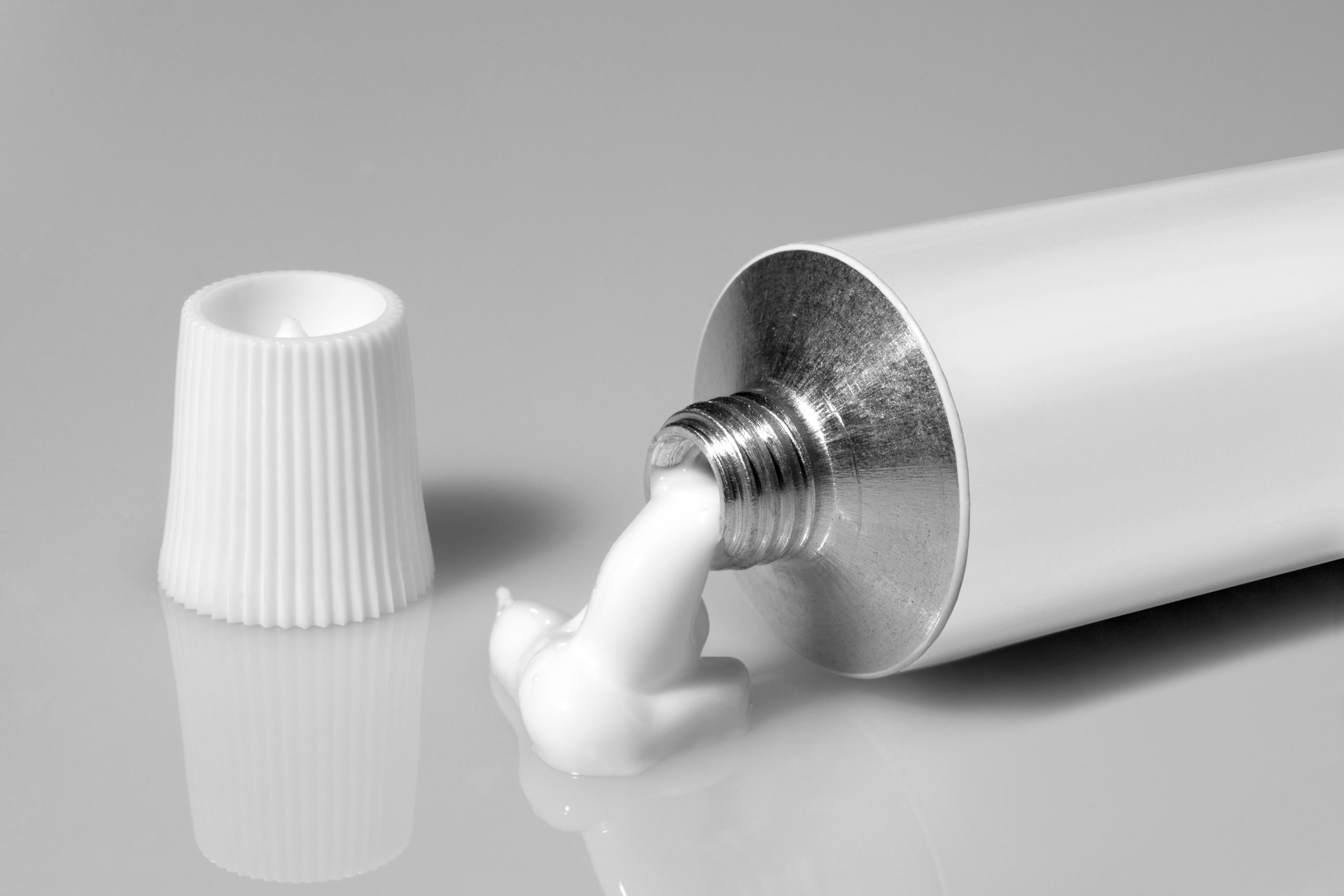
Ointment
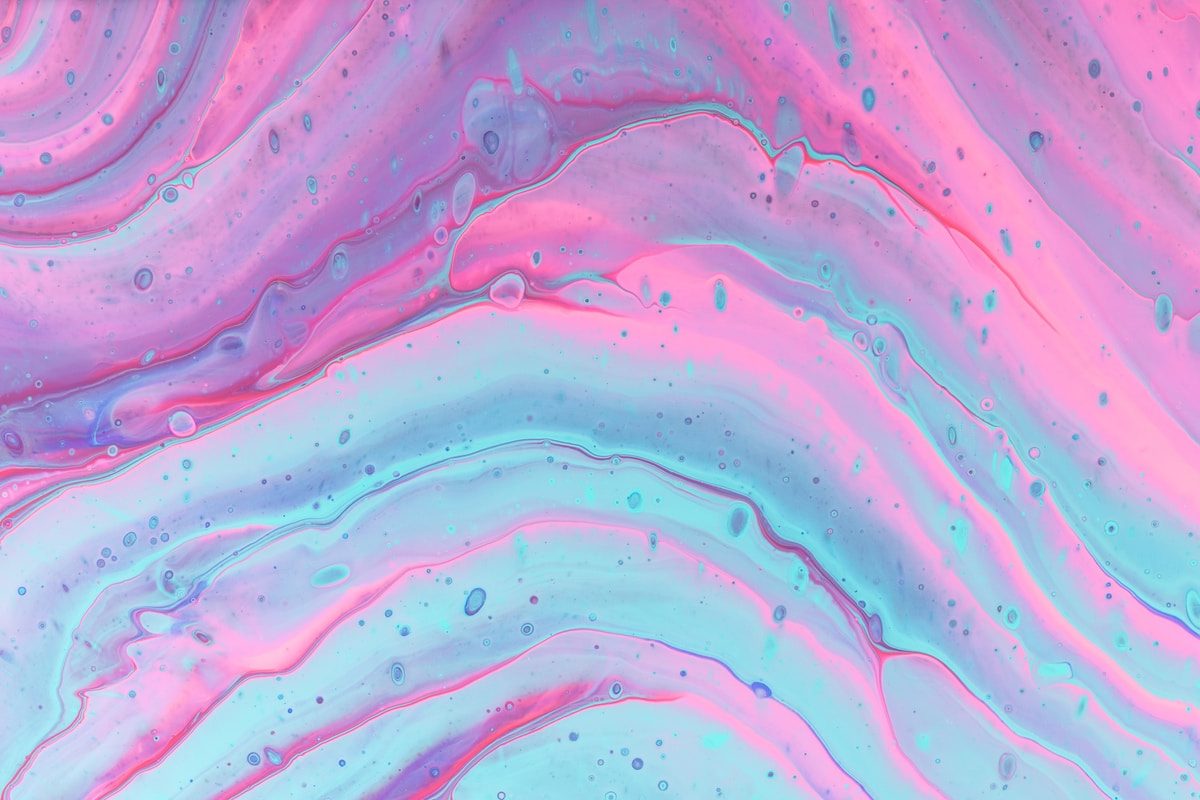
Paint
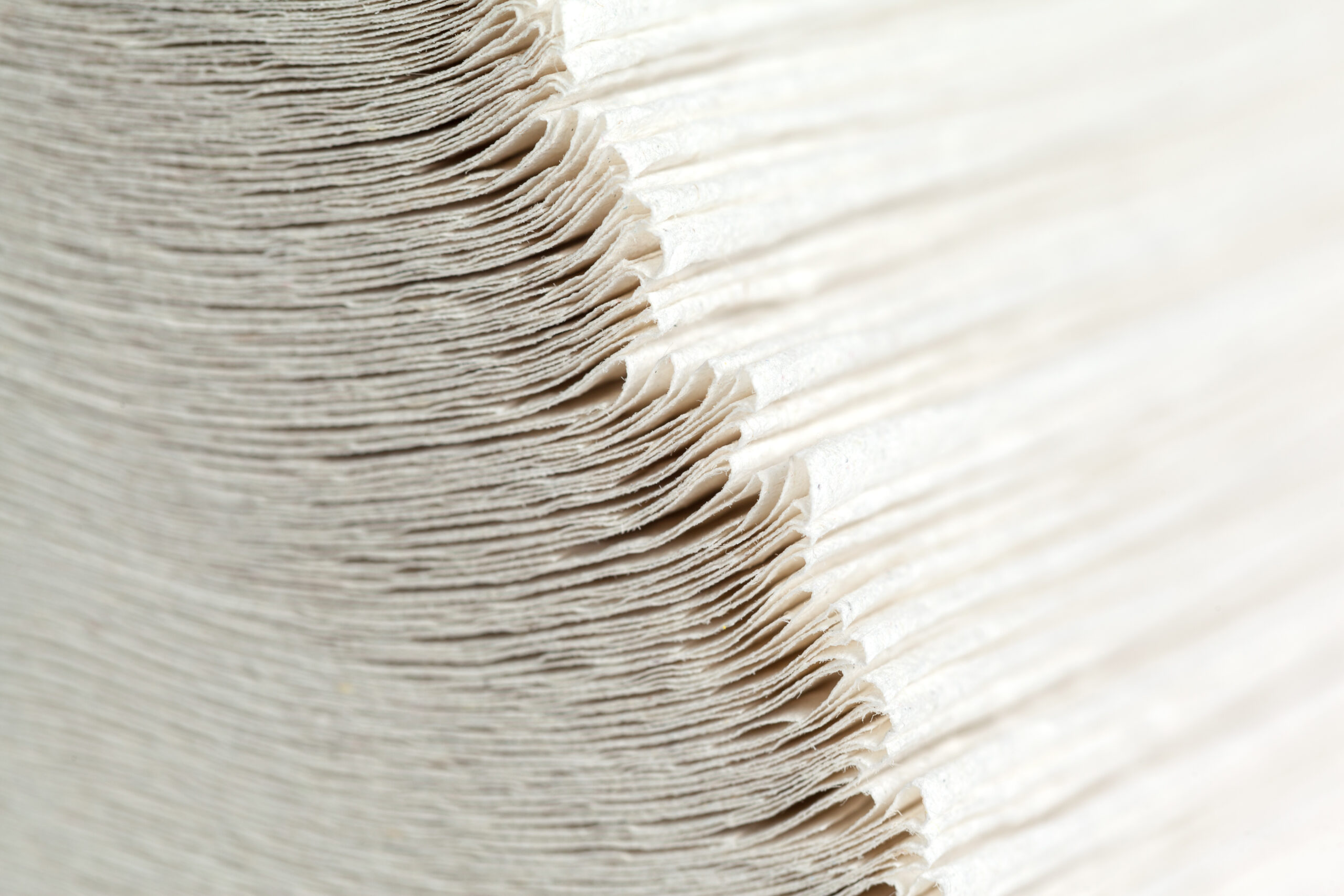
Paper pulp
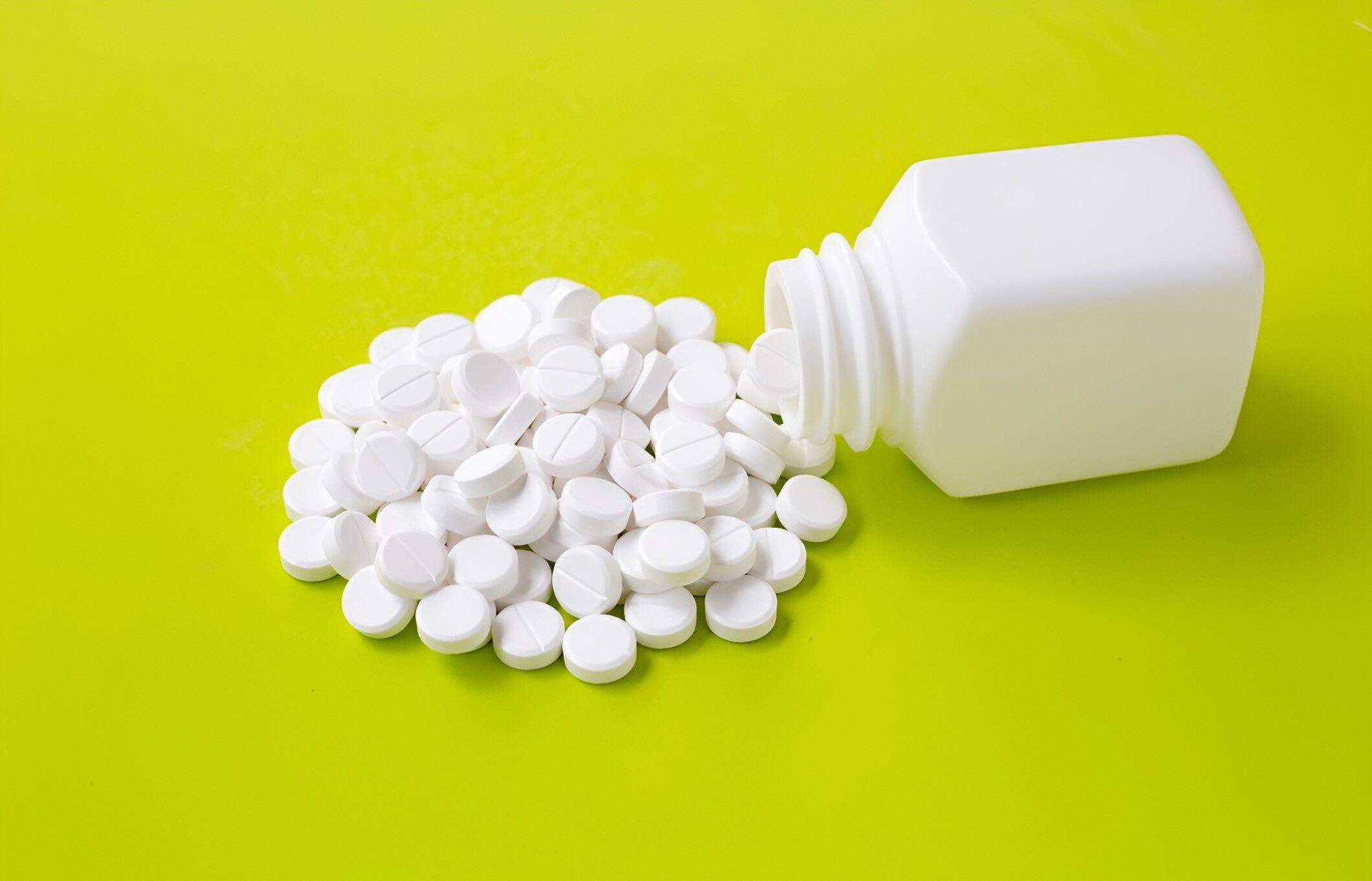
Paracetamol

Pea protein isolate
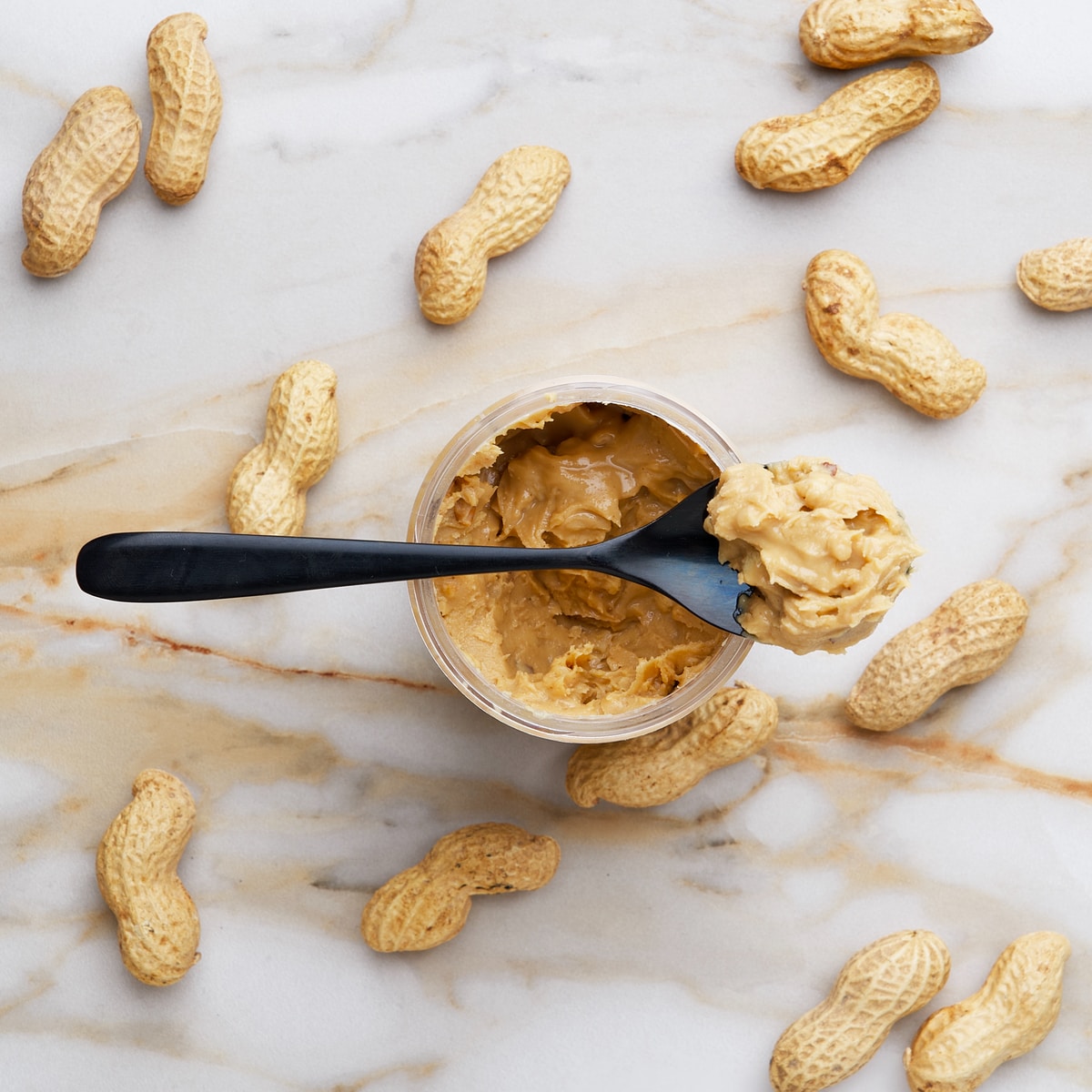
Peanut butter
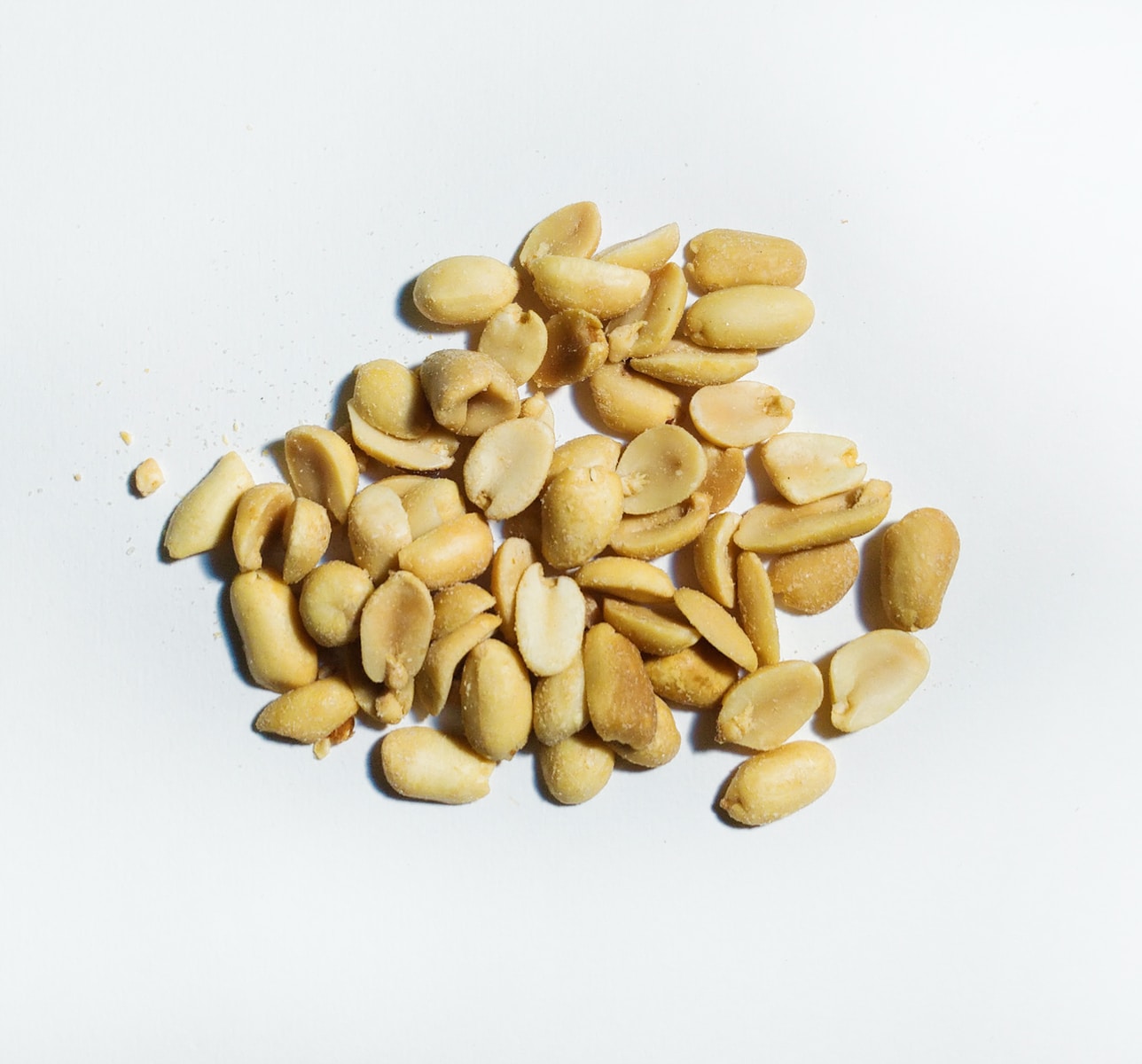
Peanuts
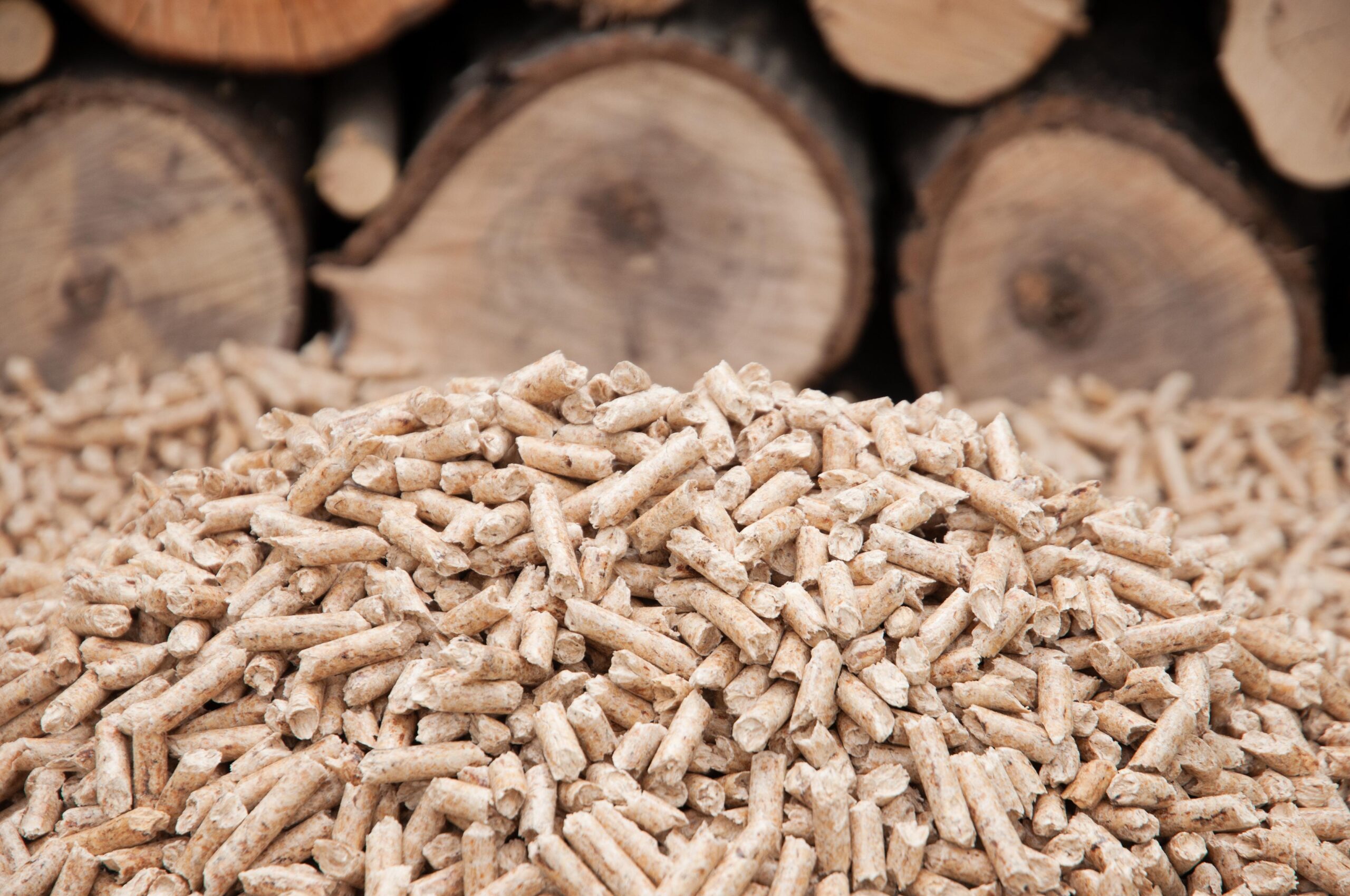
Pellet fuel
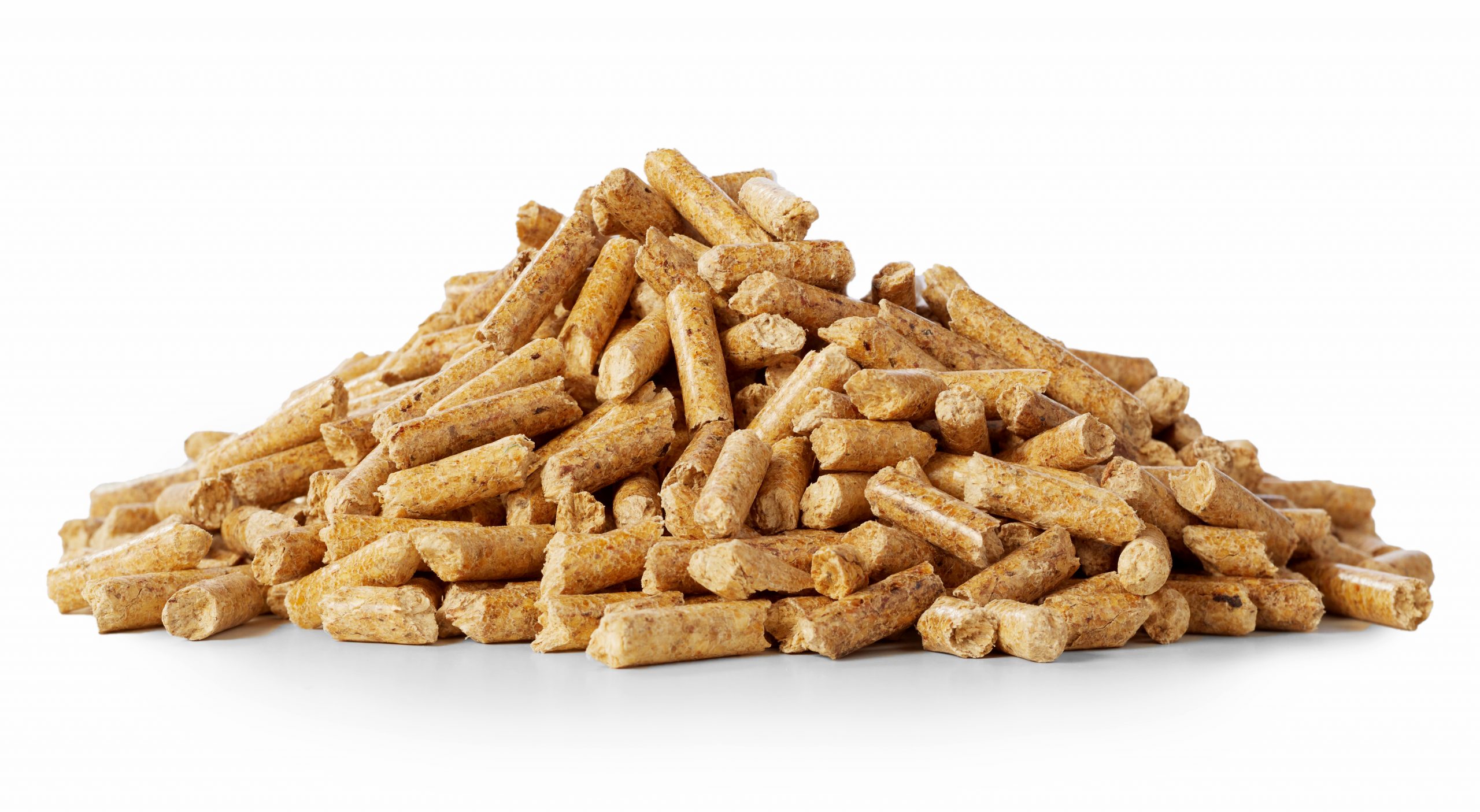
Pelleted feed
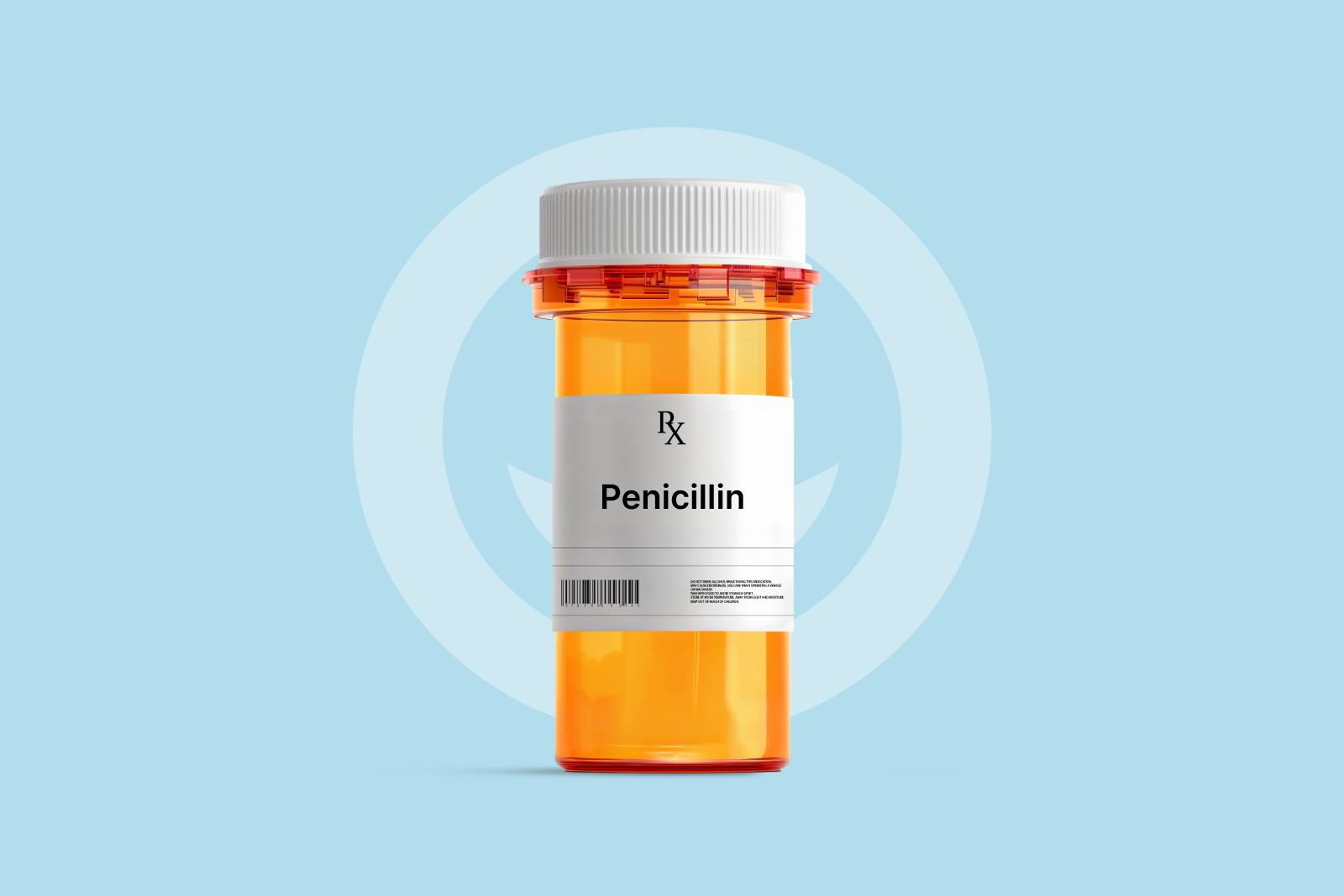
Penicillin
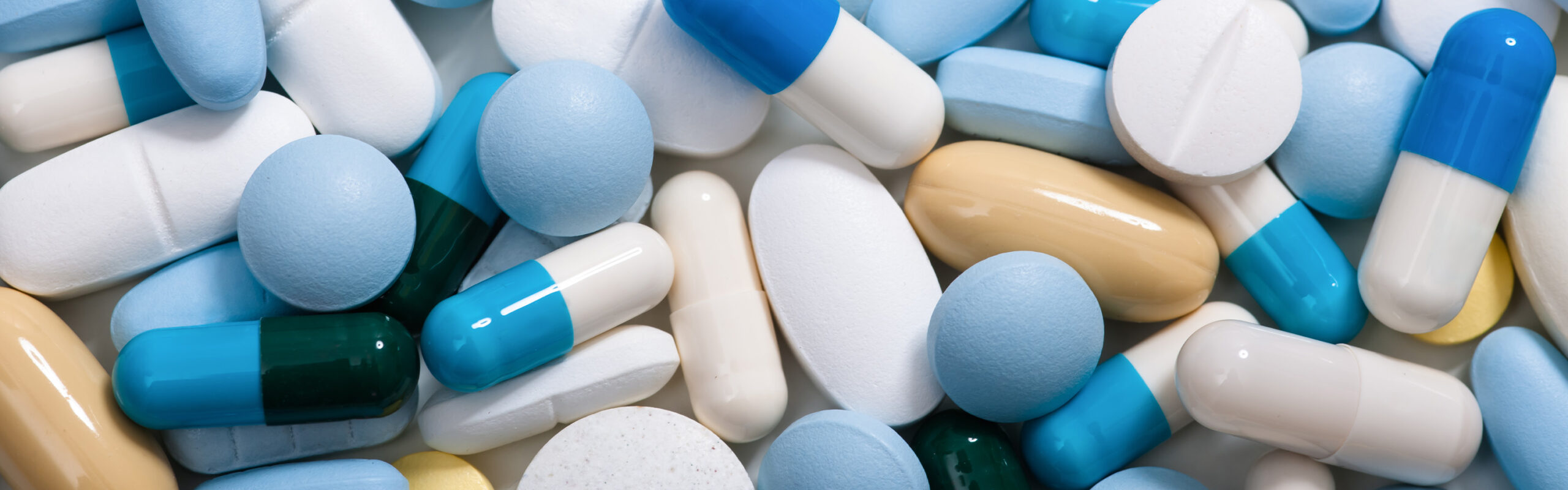
Pharmaceutical excipients
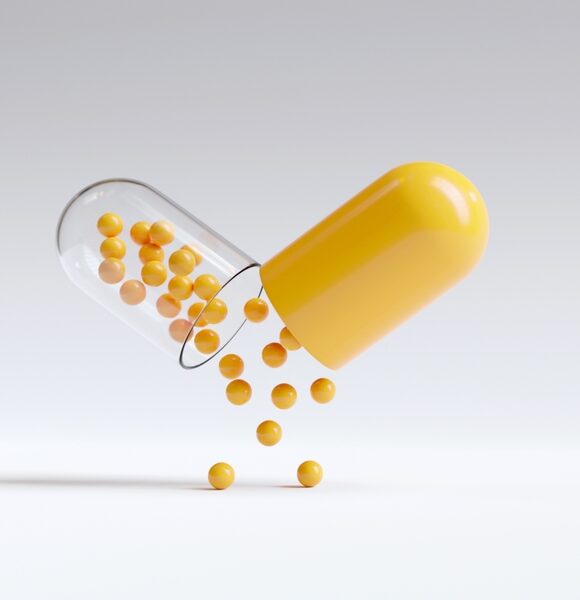
Pharmaceutical granules
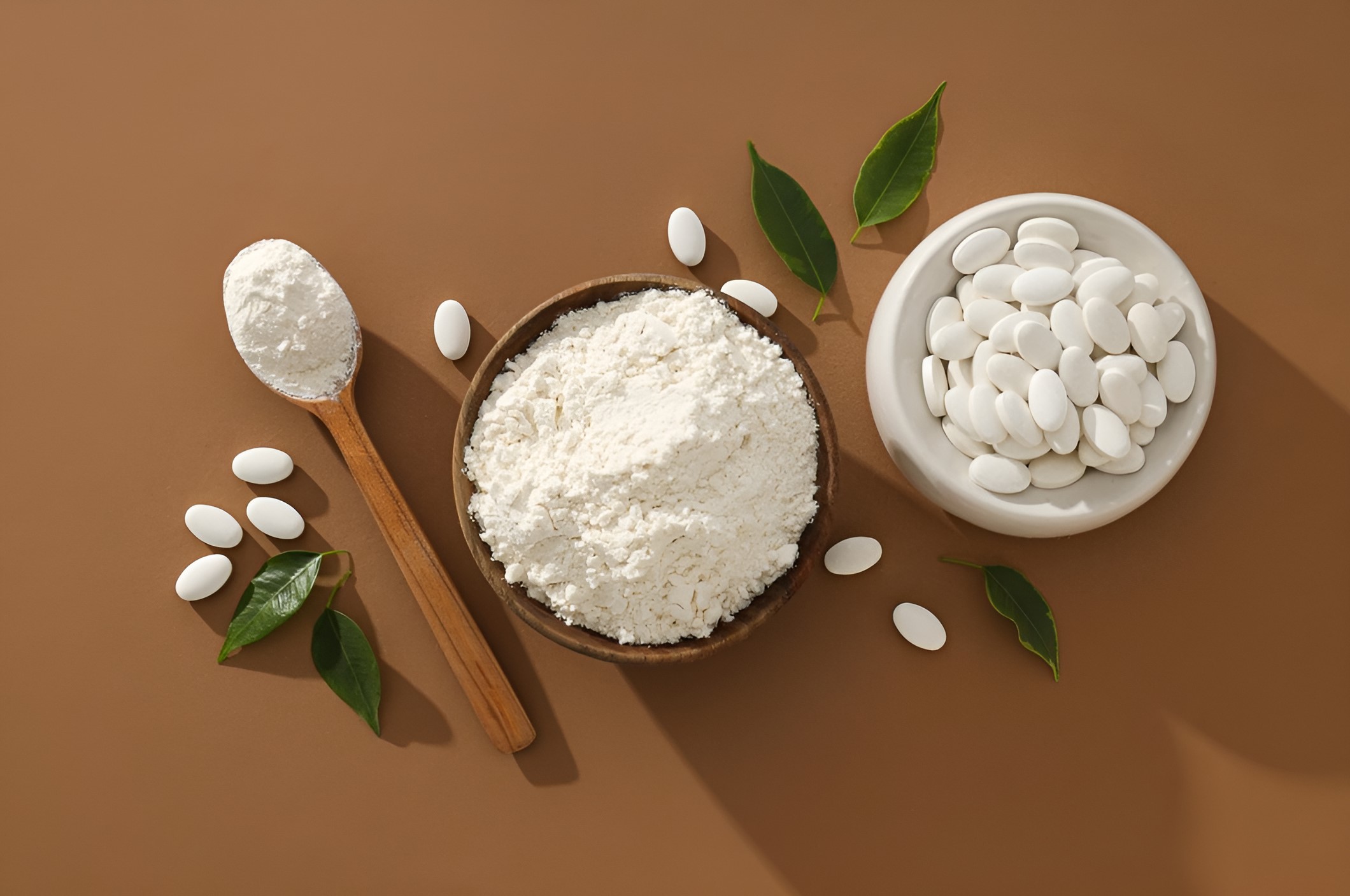
Pharmaceutical powders
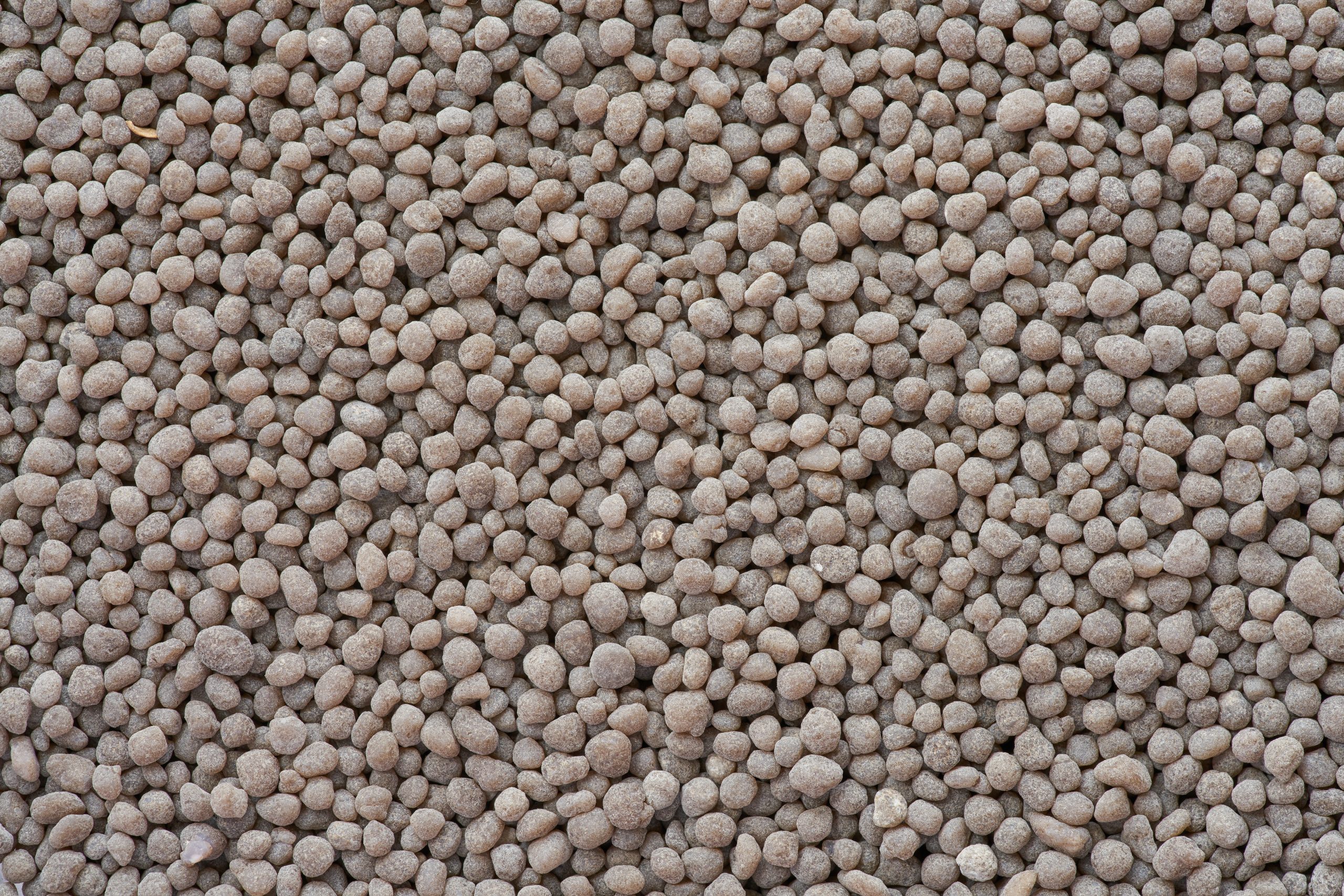
Phosphorus fertilizer
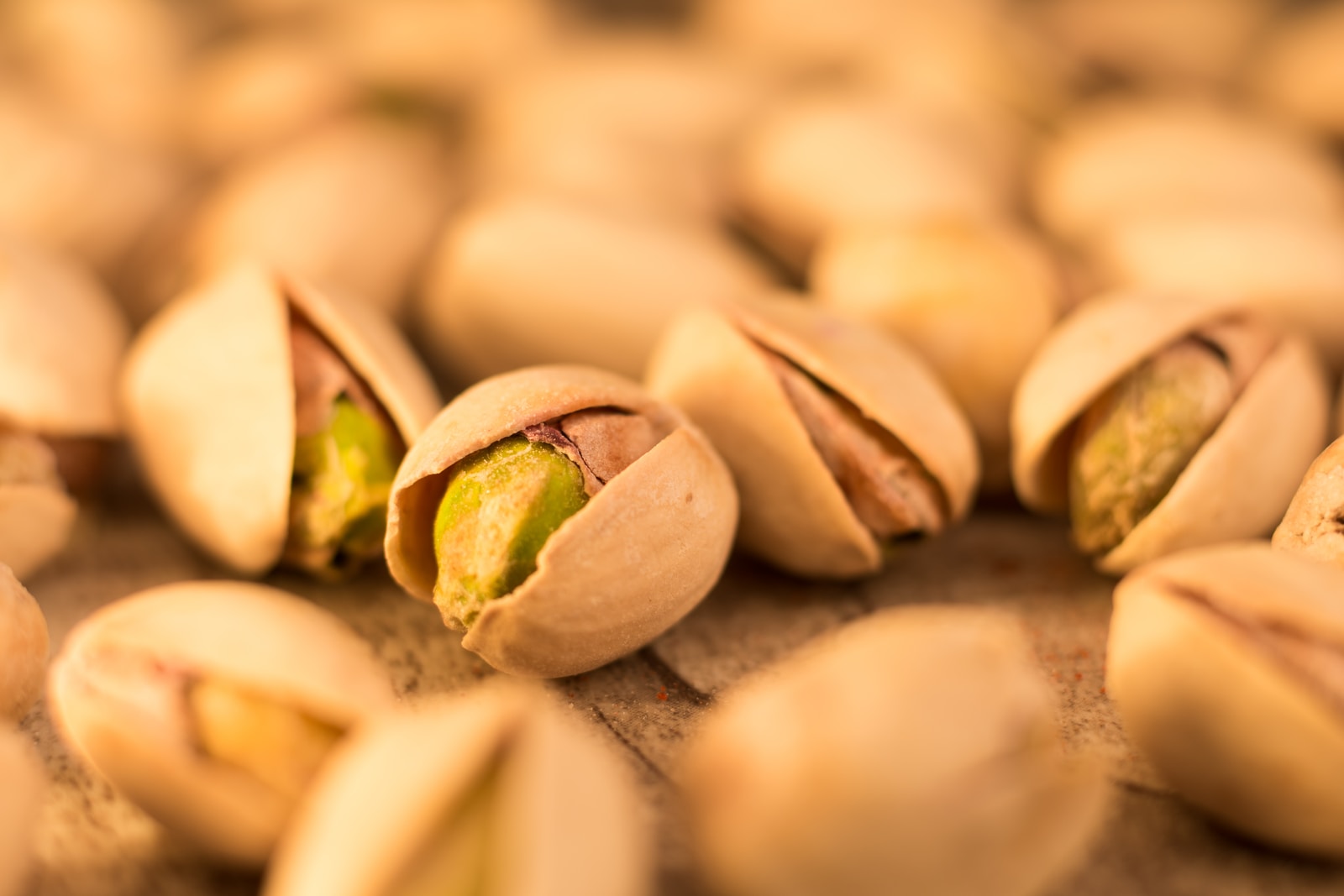
Pistachios
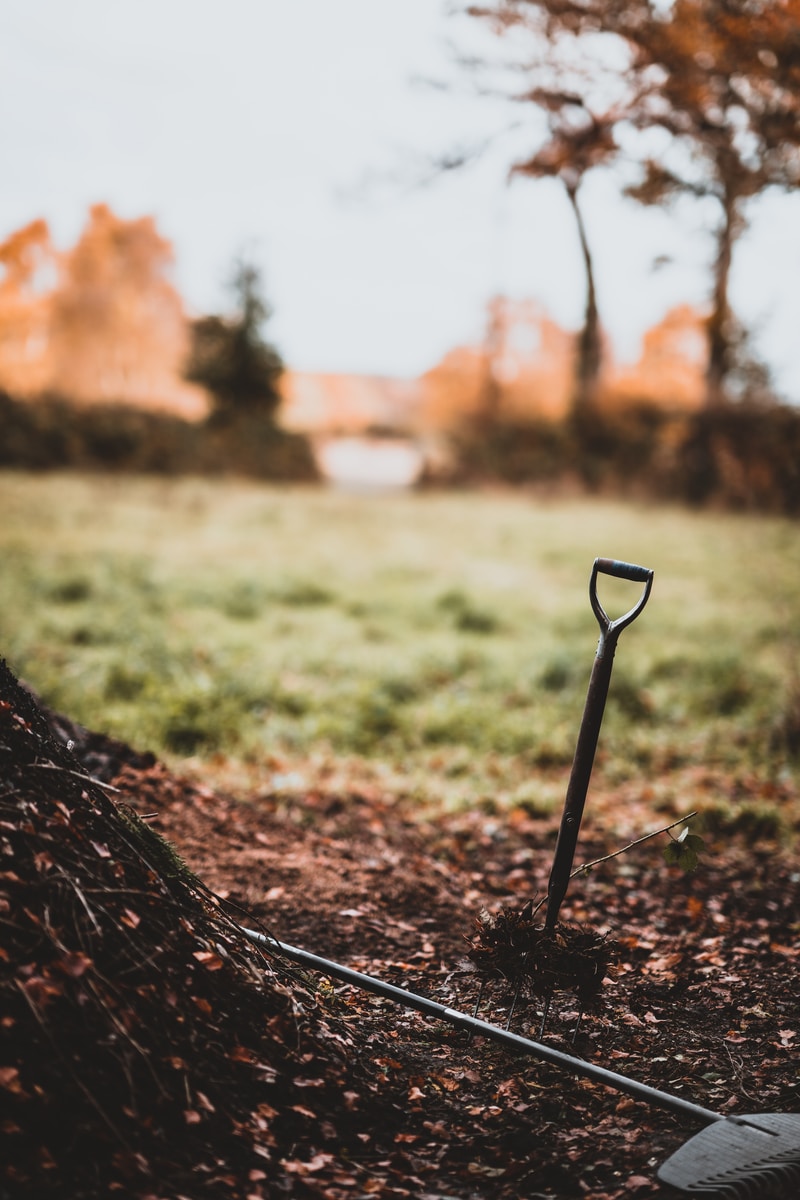
Plant waste
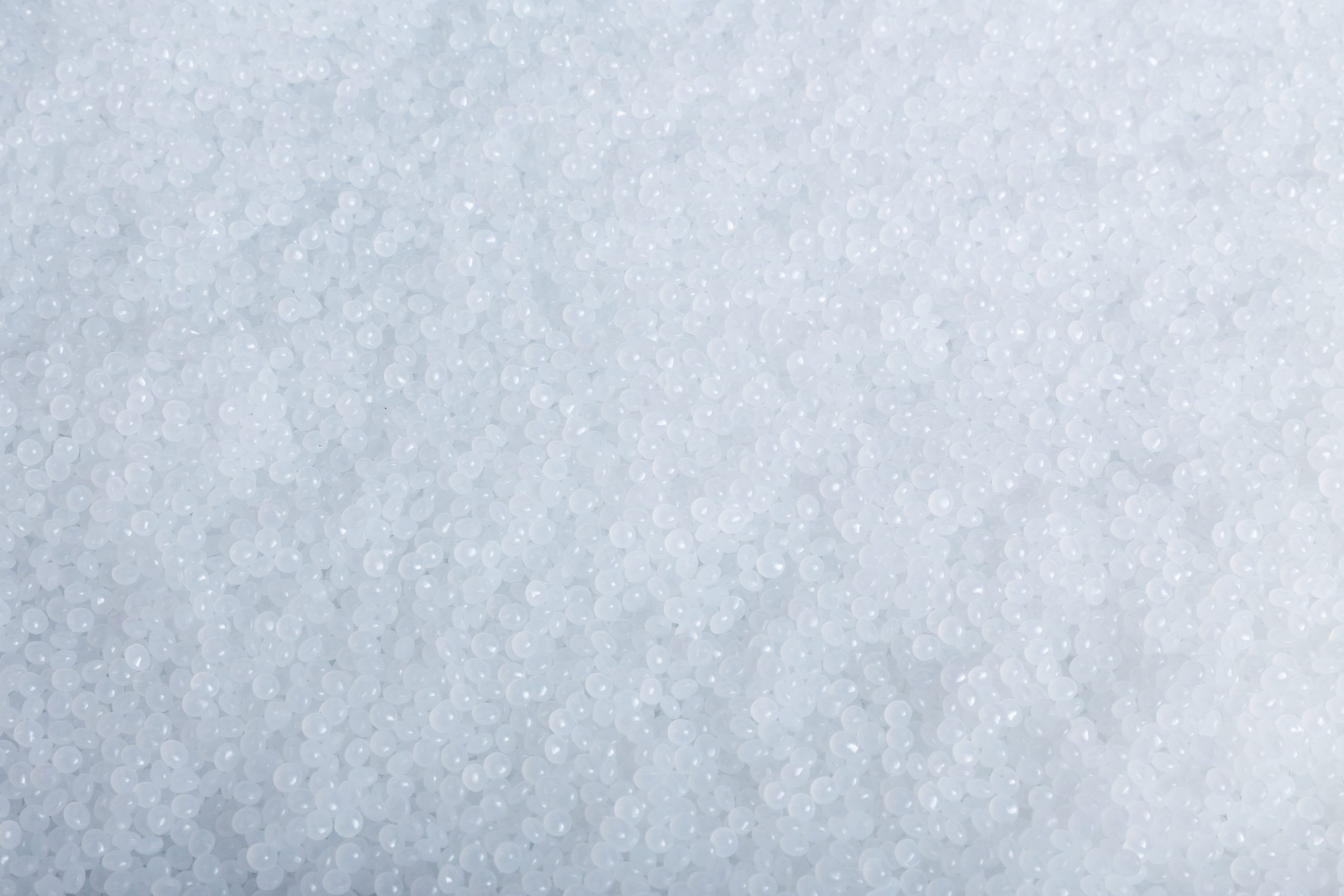
Polymers
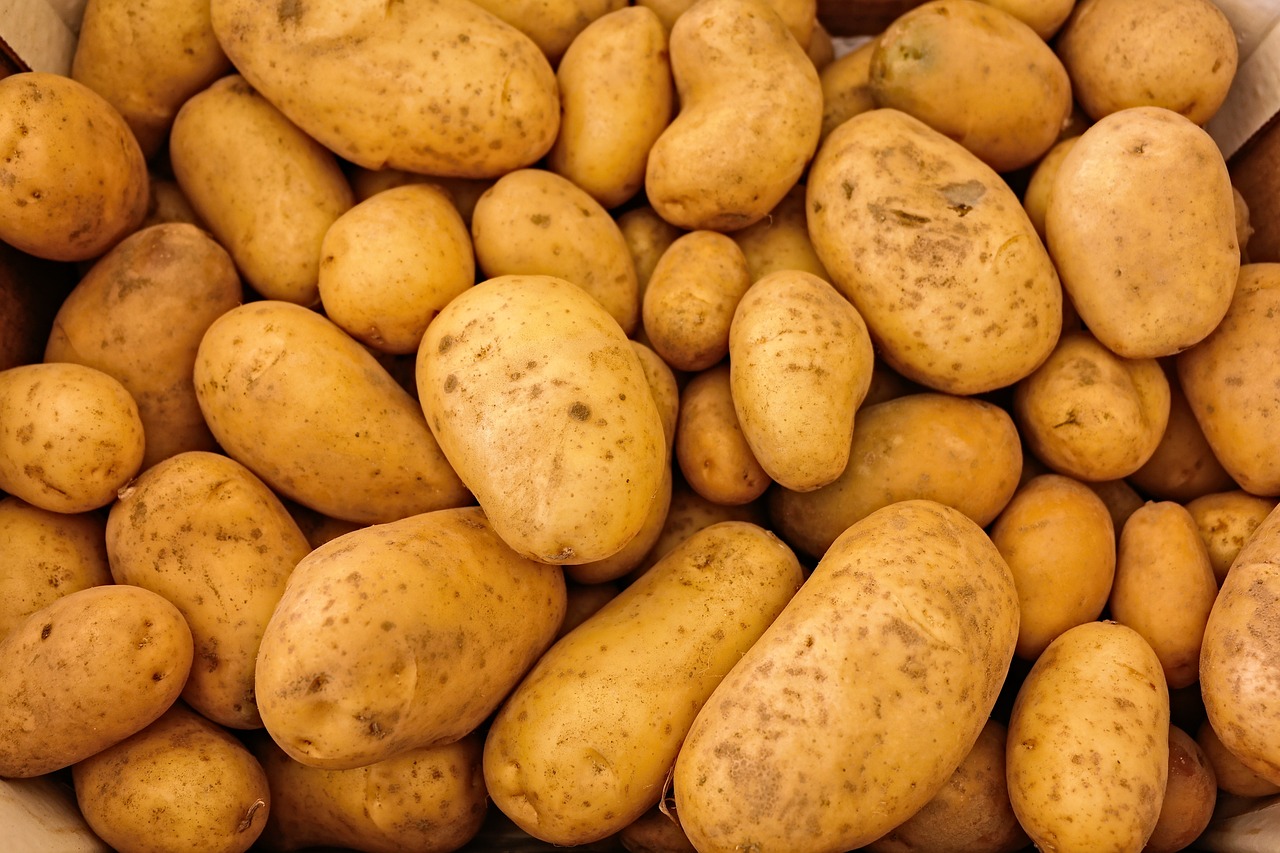
Potatoes
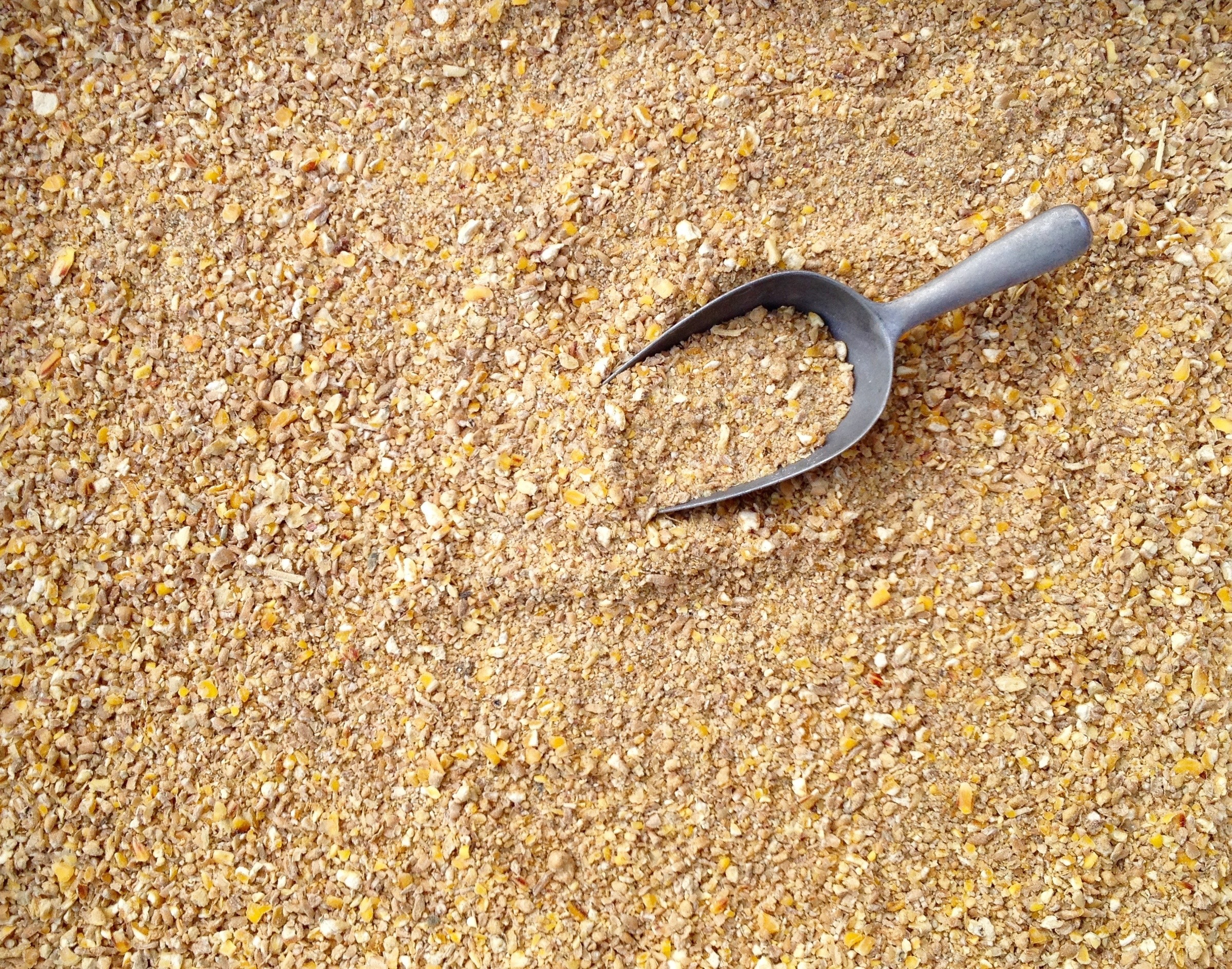
Poultry feed
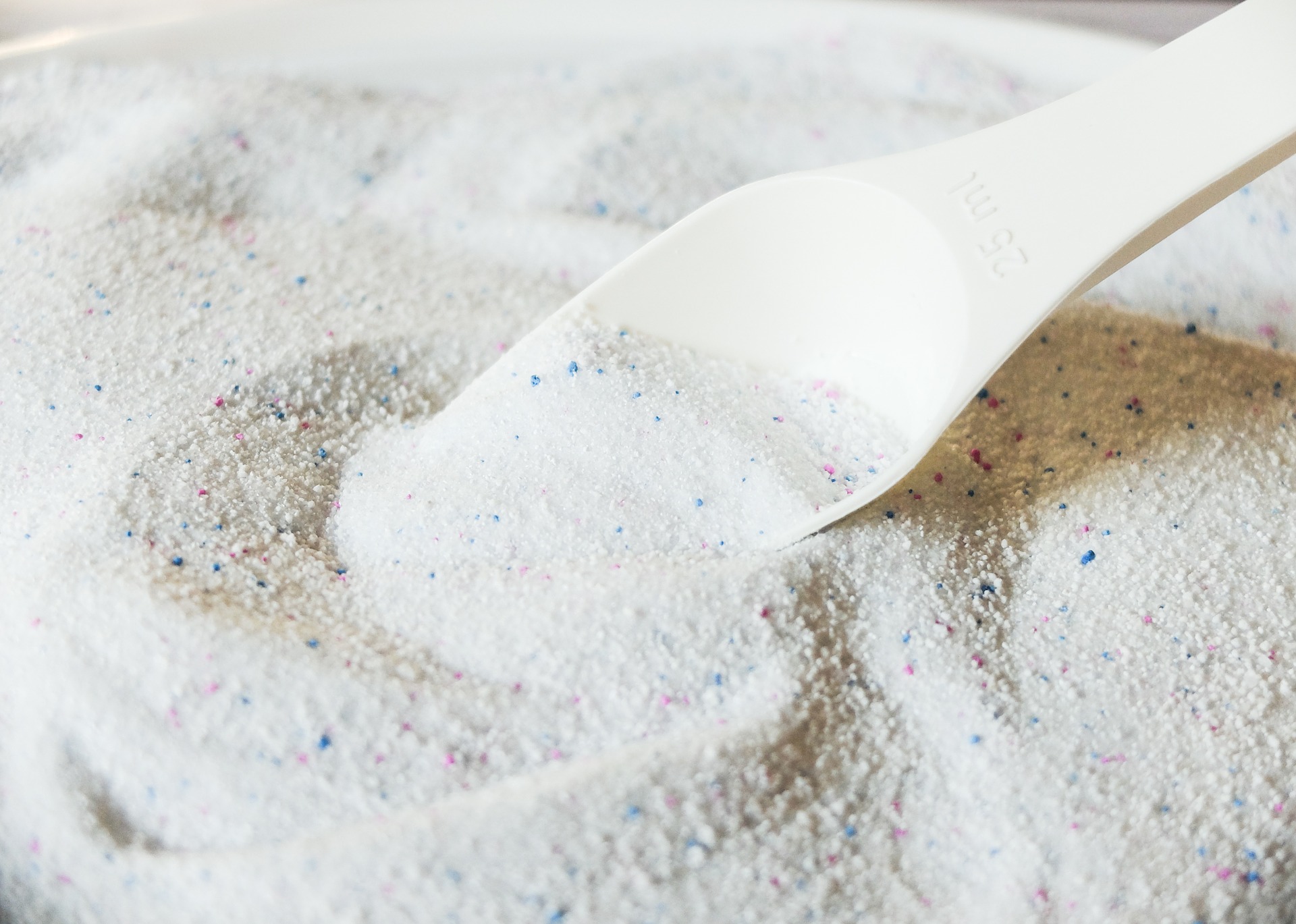
Powder detergent
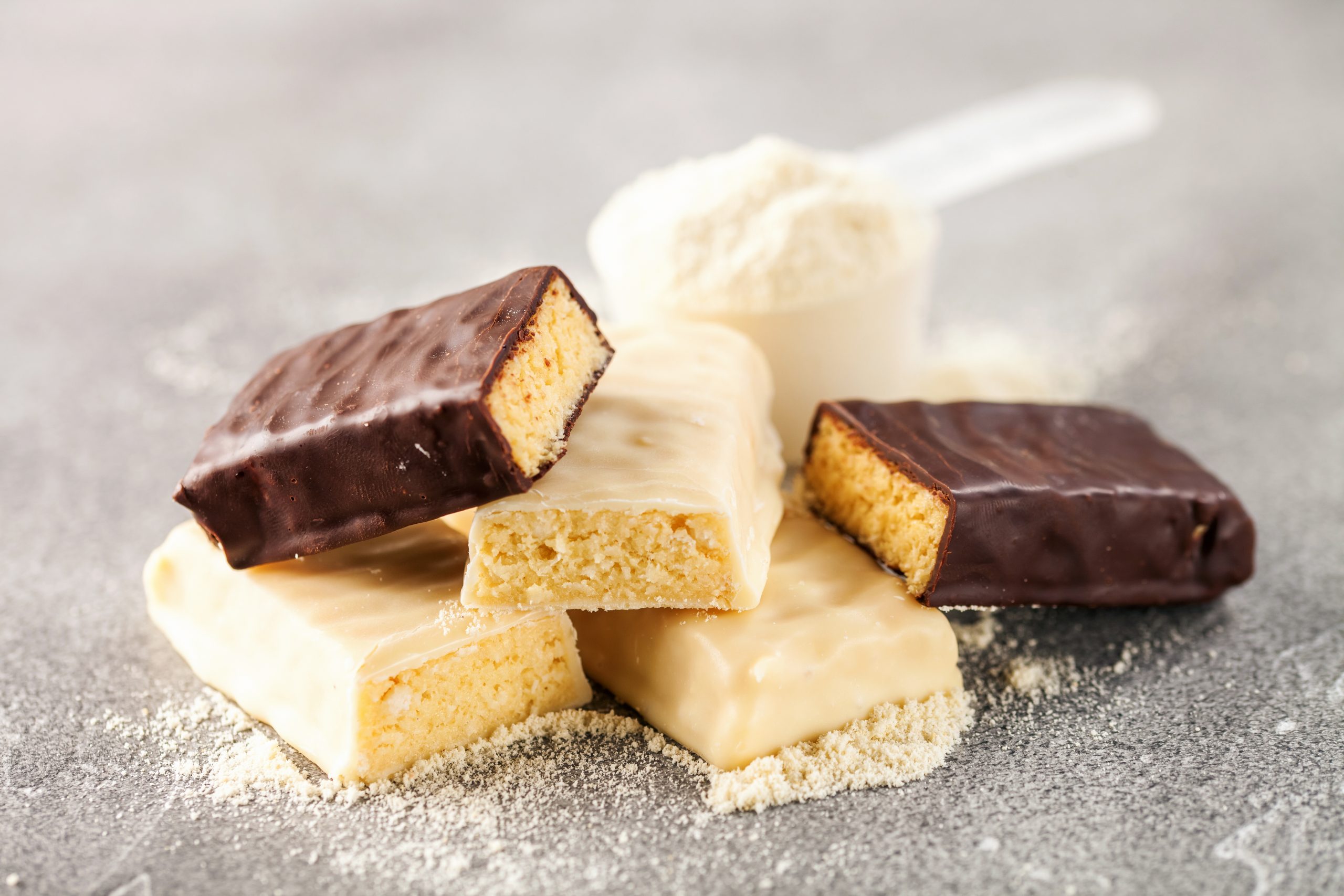
Protein bars
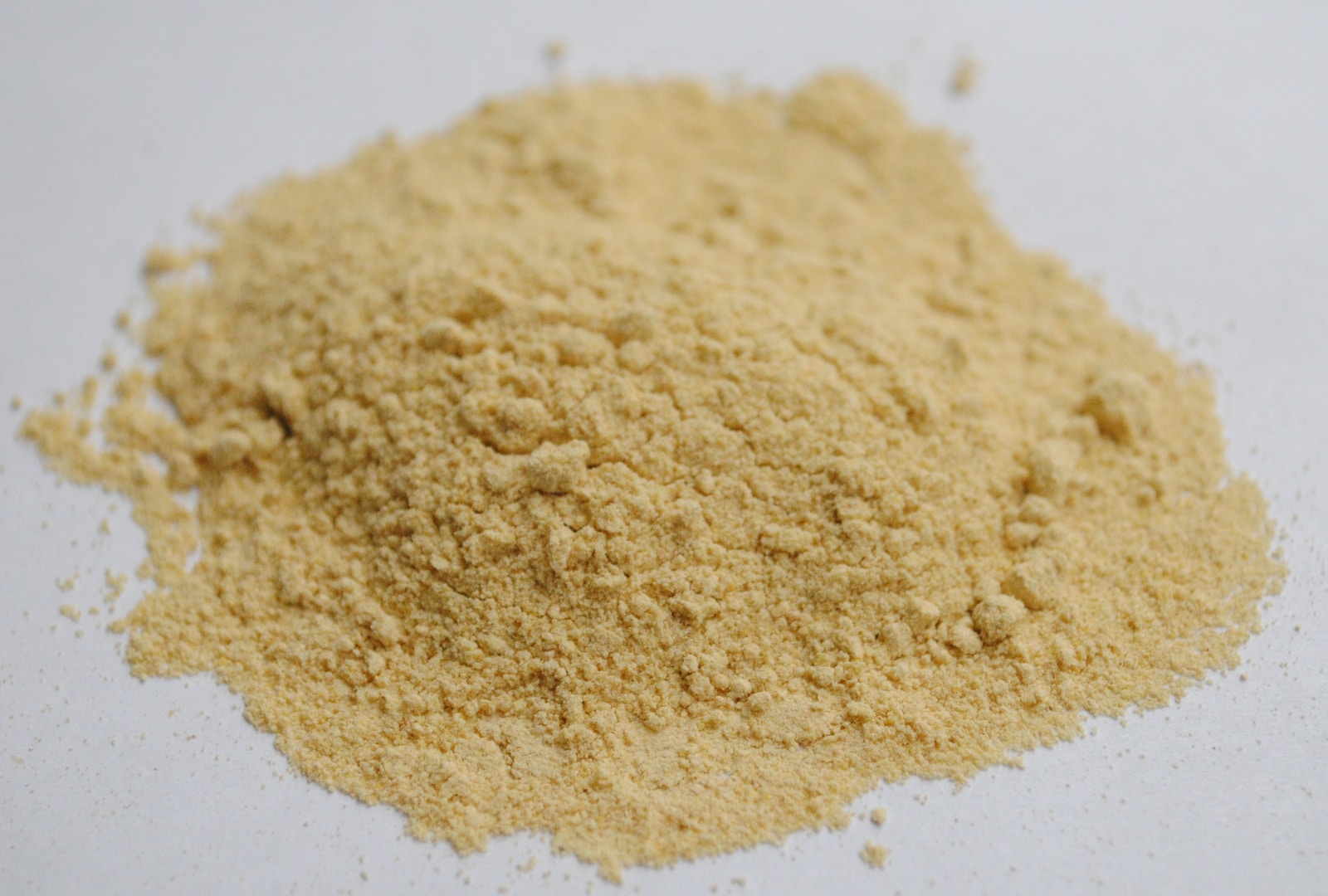
Protein powder
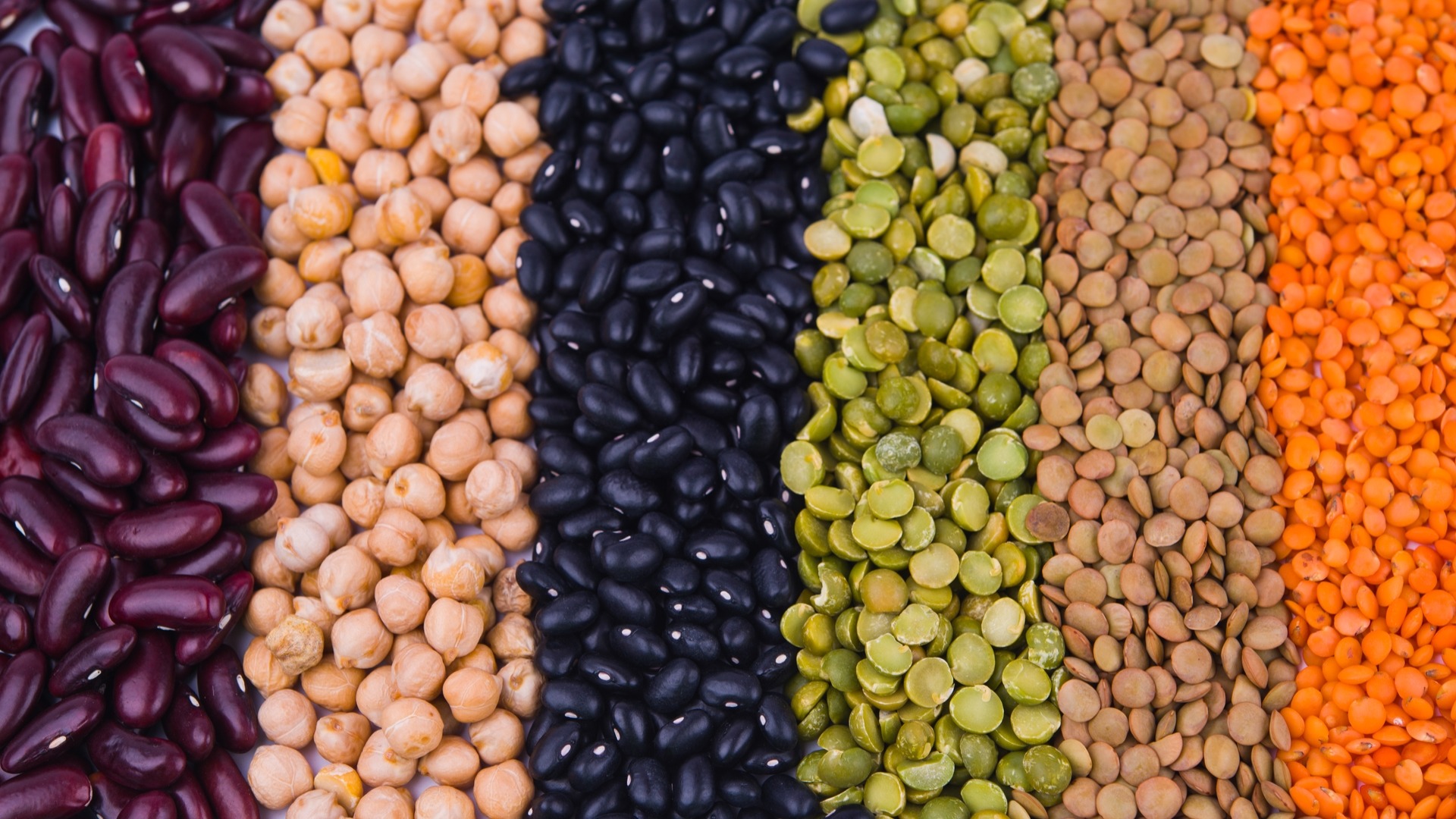
Pulses
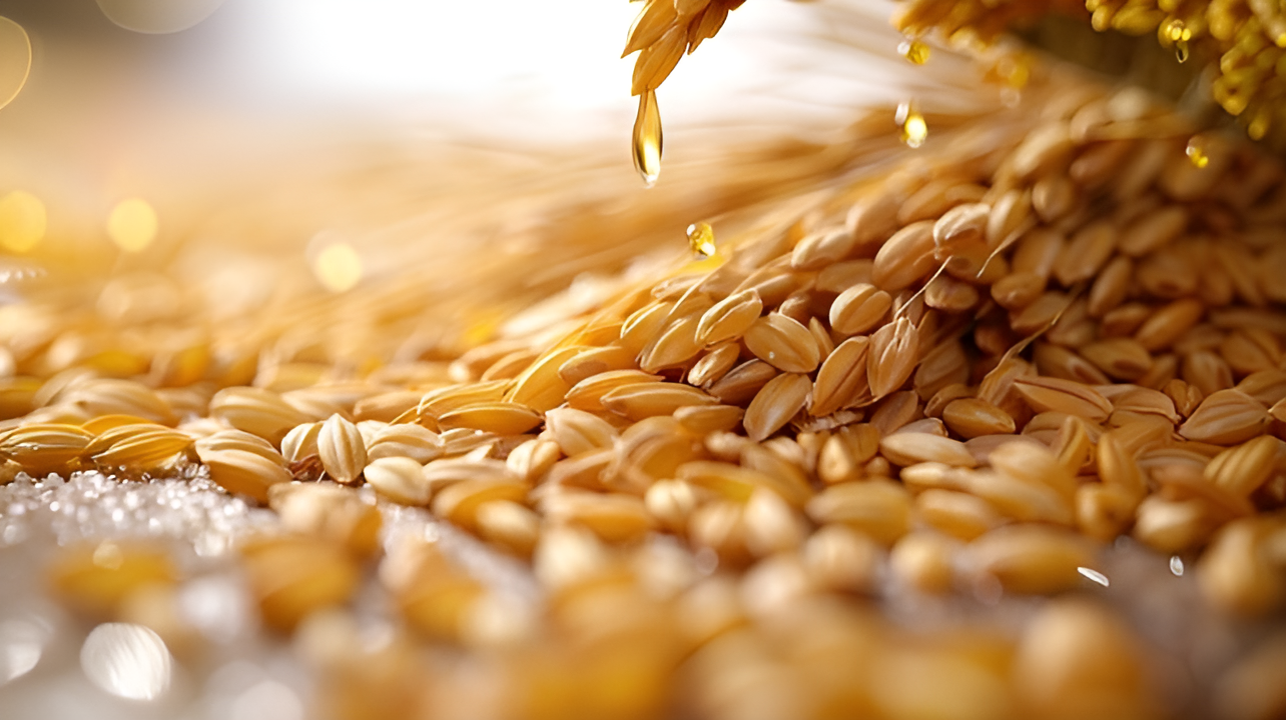
Rice bran
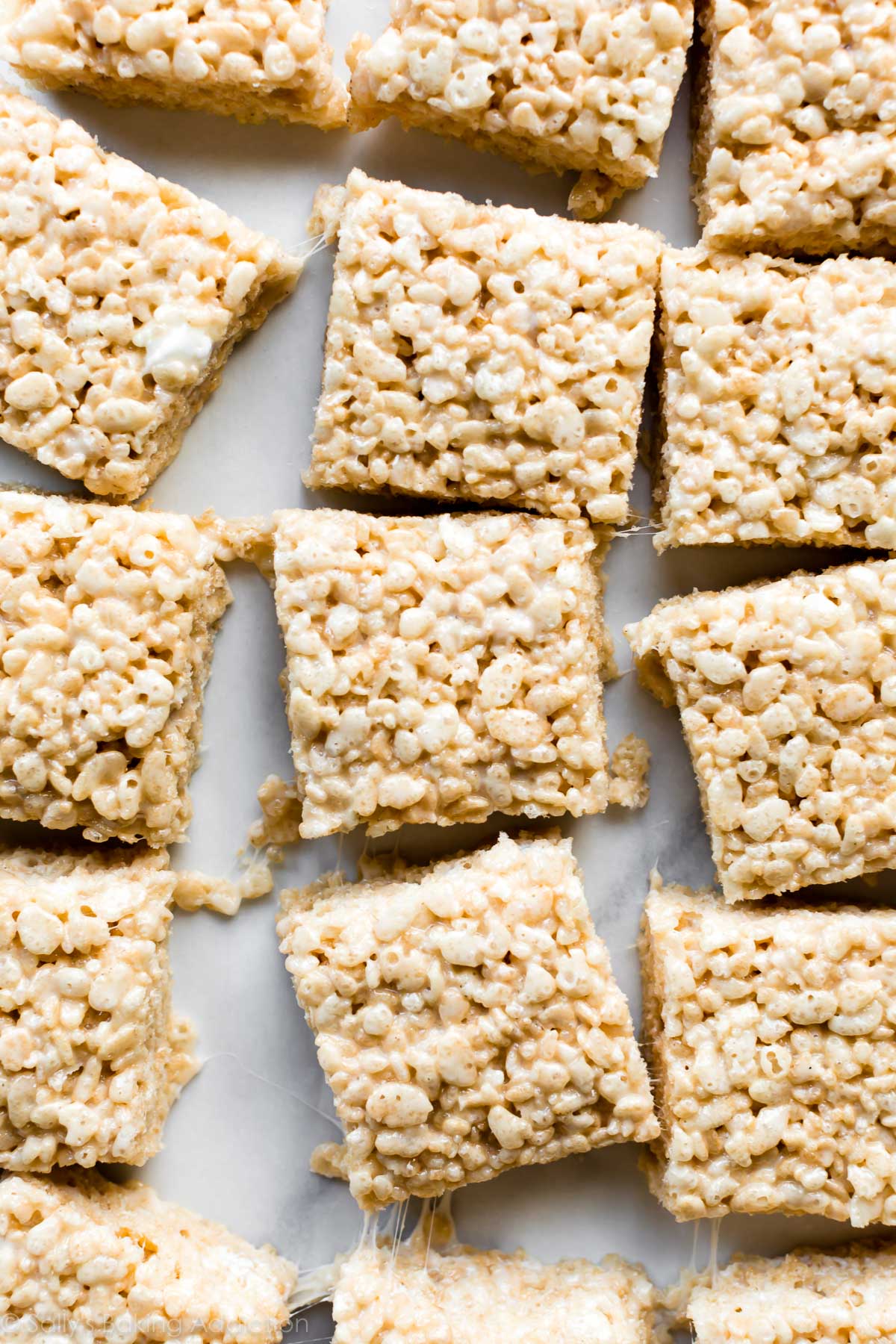
Rice Crispies
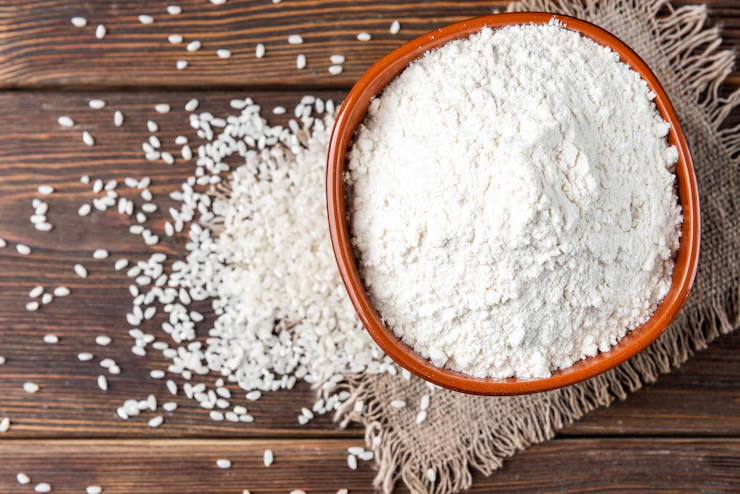
Rice flour
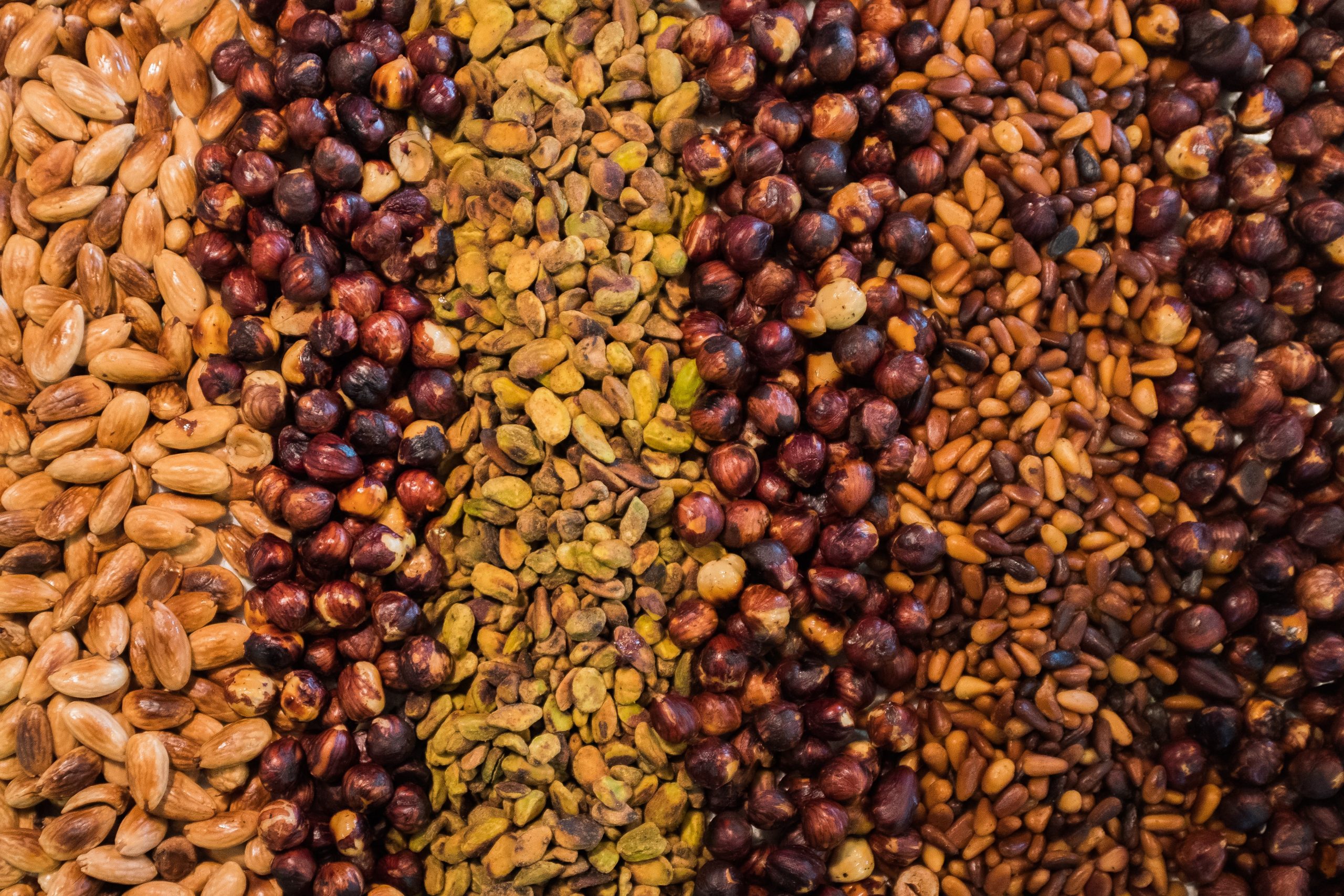
Roasted nuts
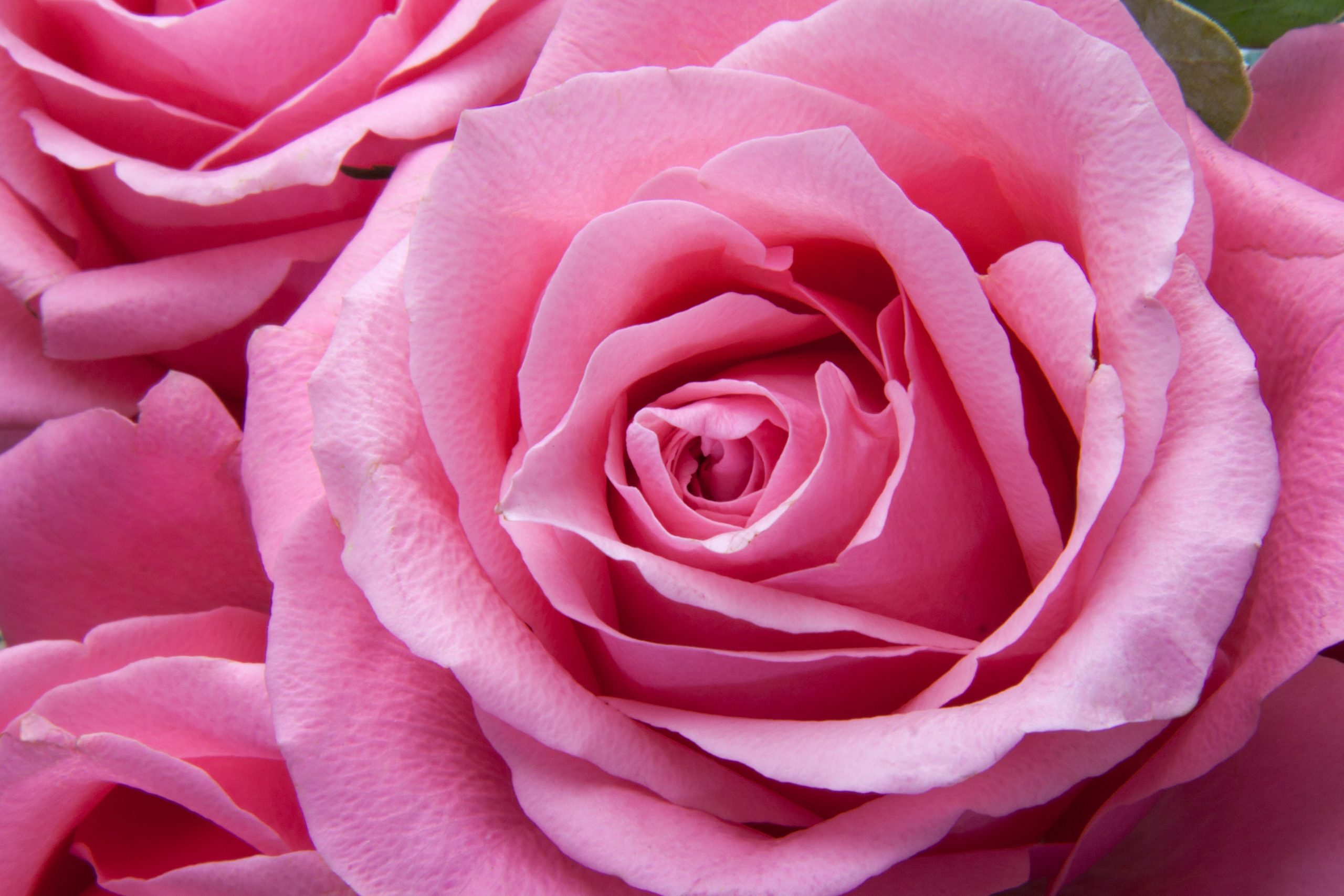
Rose oil

Rye
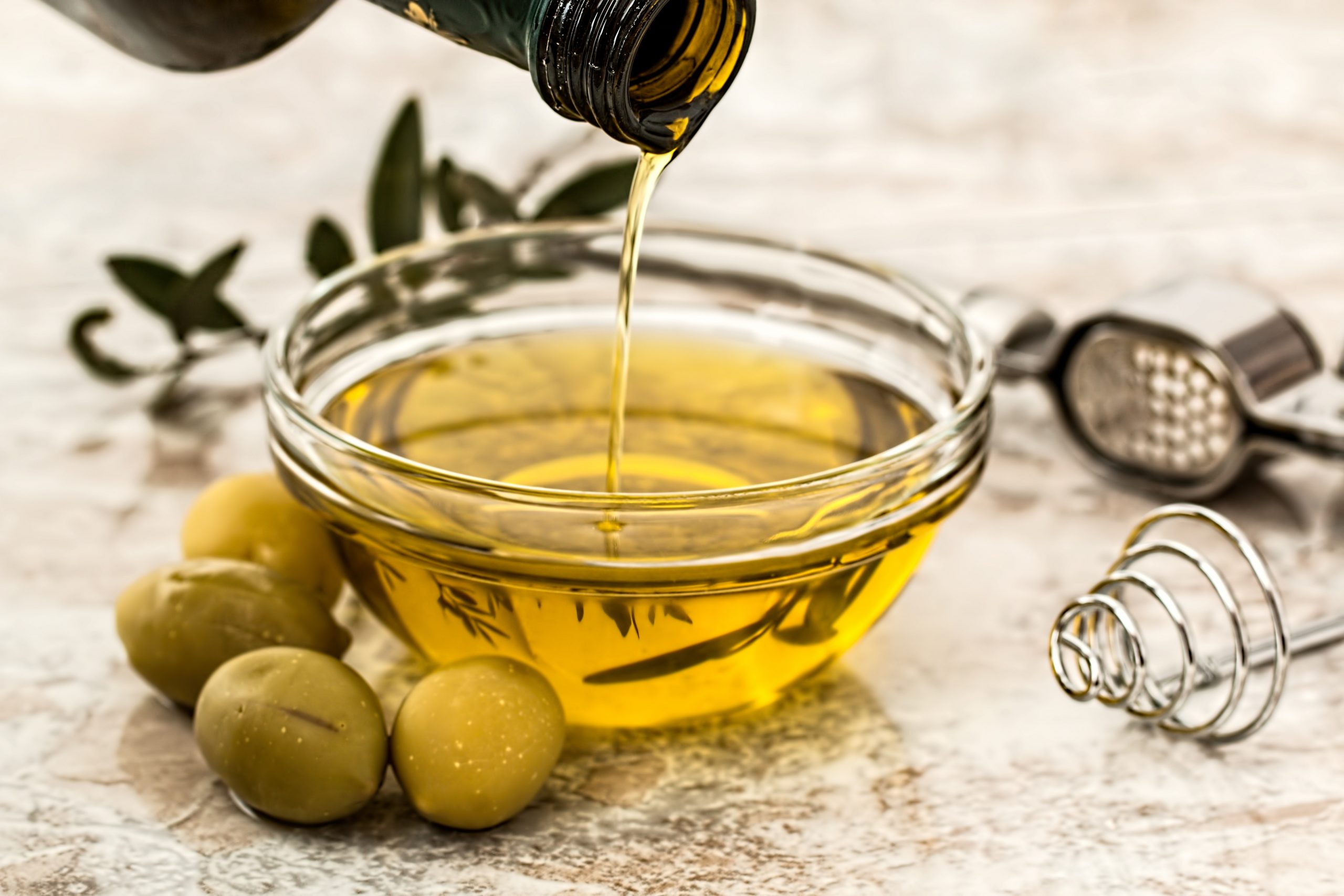
Salad dressing
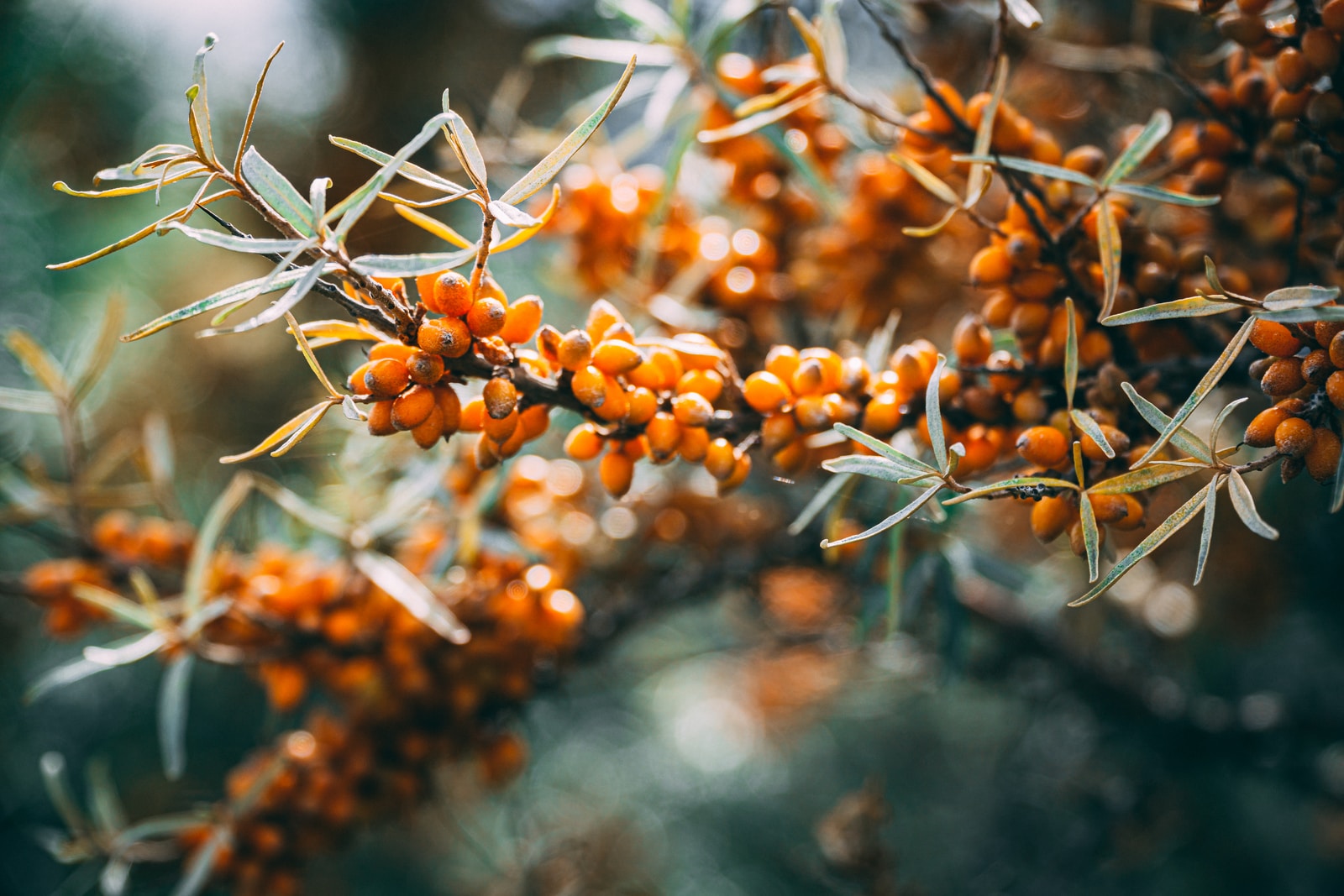
Sea buckthorn oil
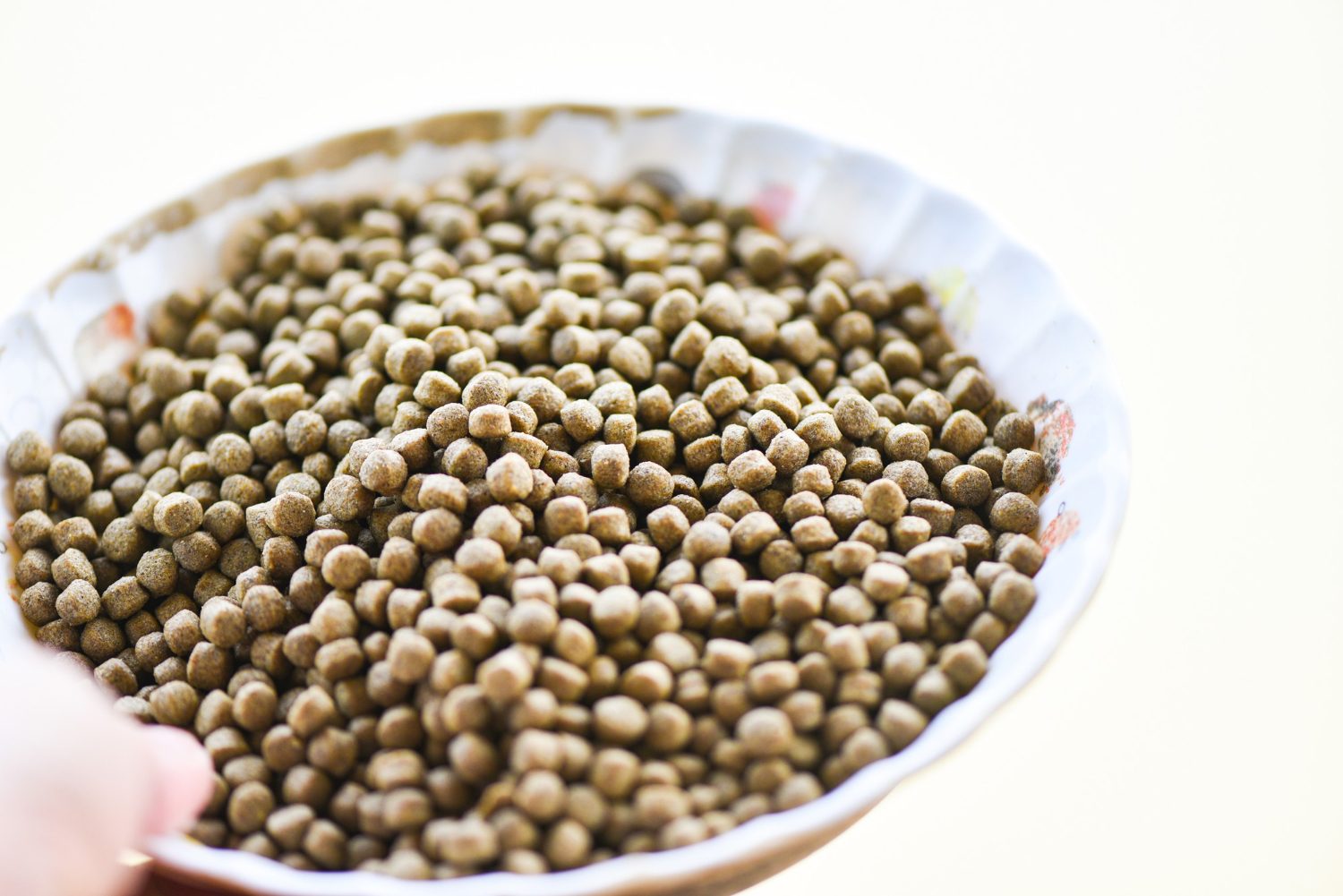
Slow sinking pellets
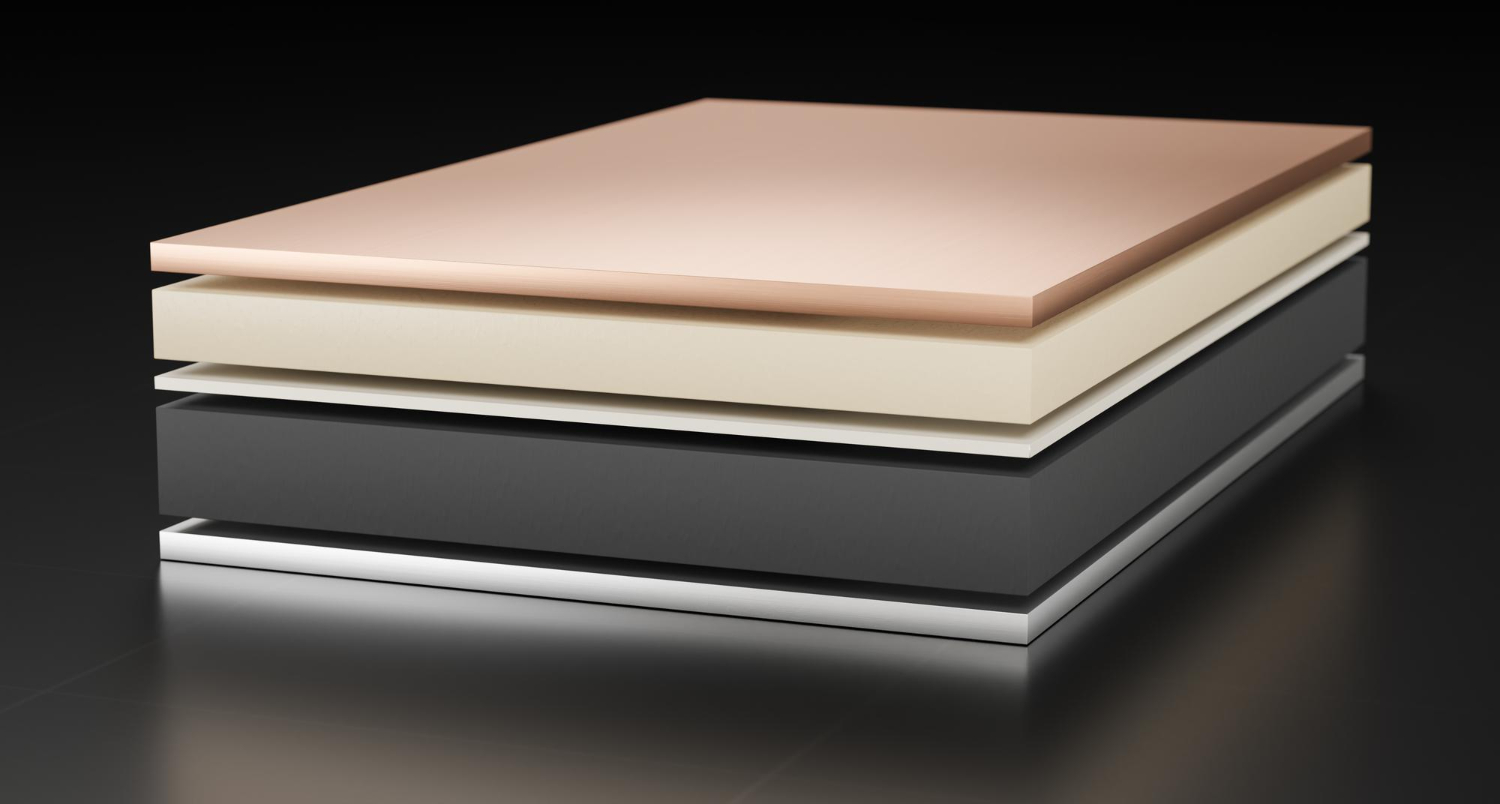
Solid-state batteries
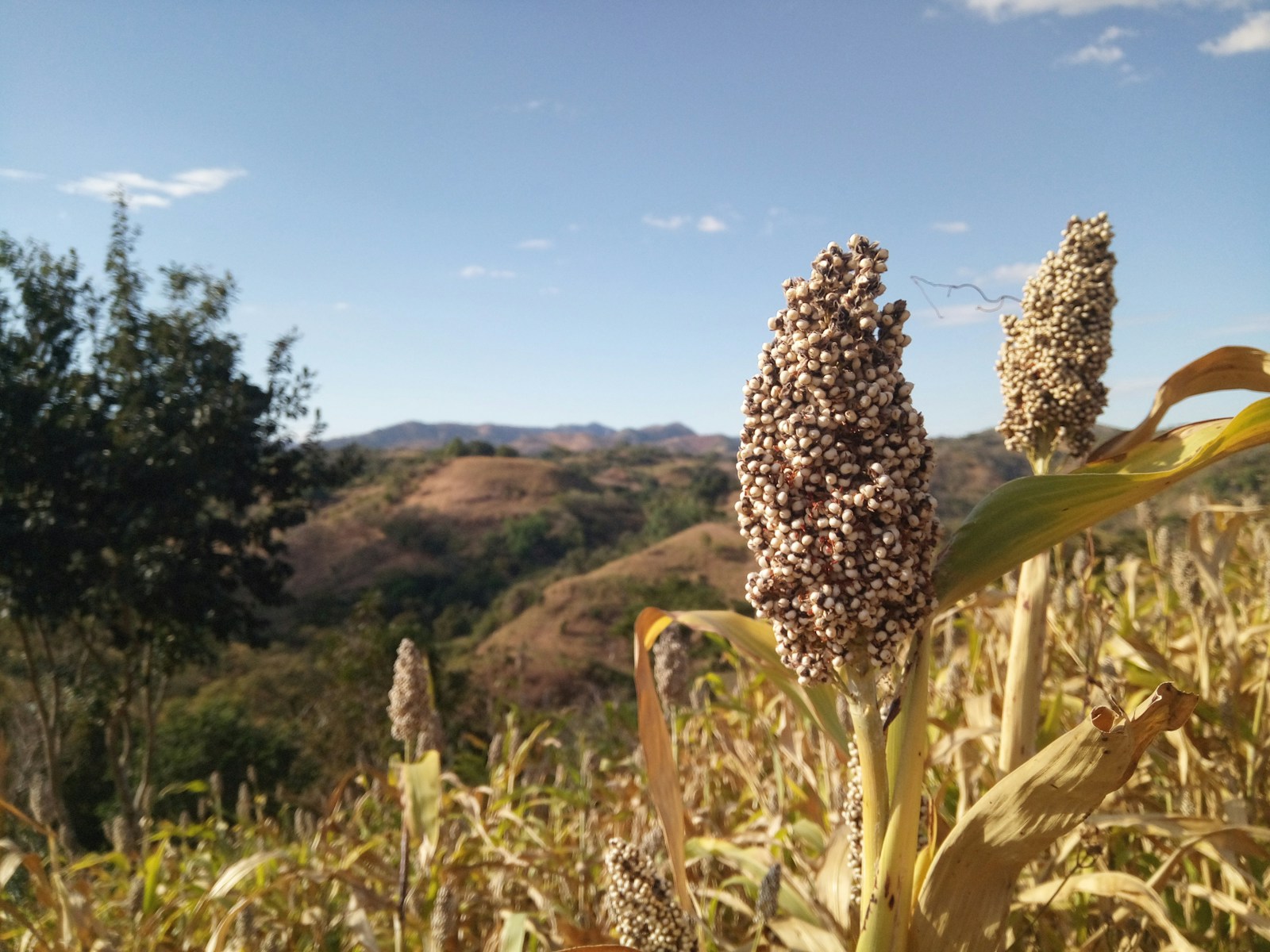
Sorghum
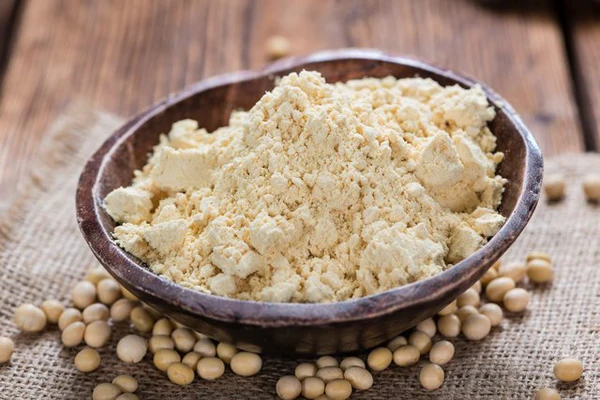
Soy flour
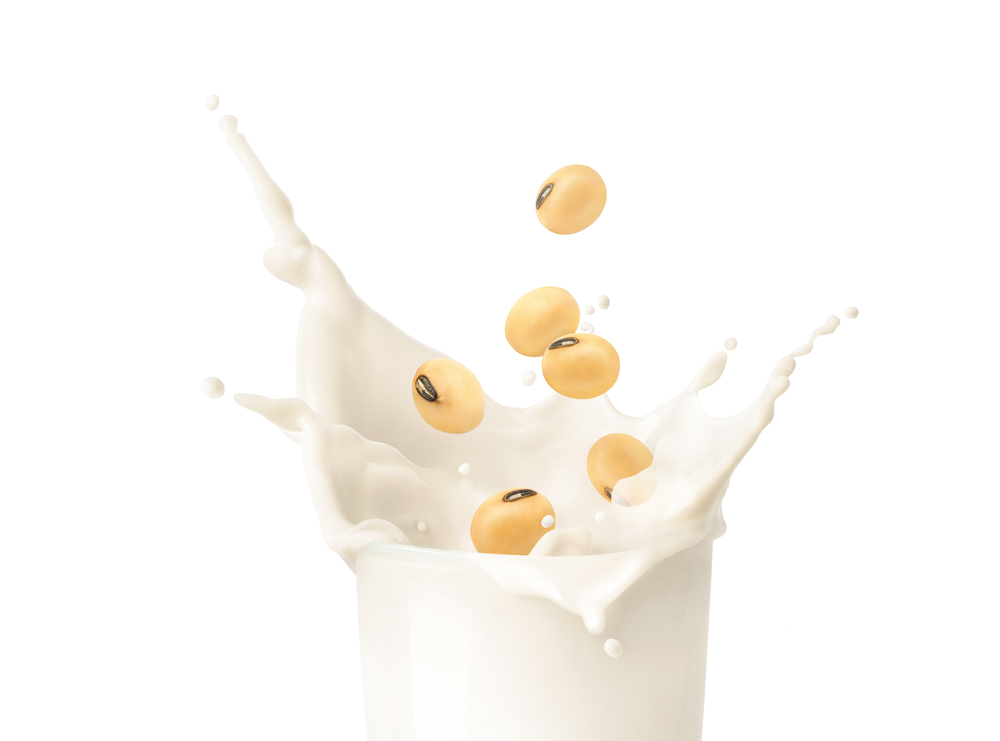
Soy milk
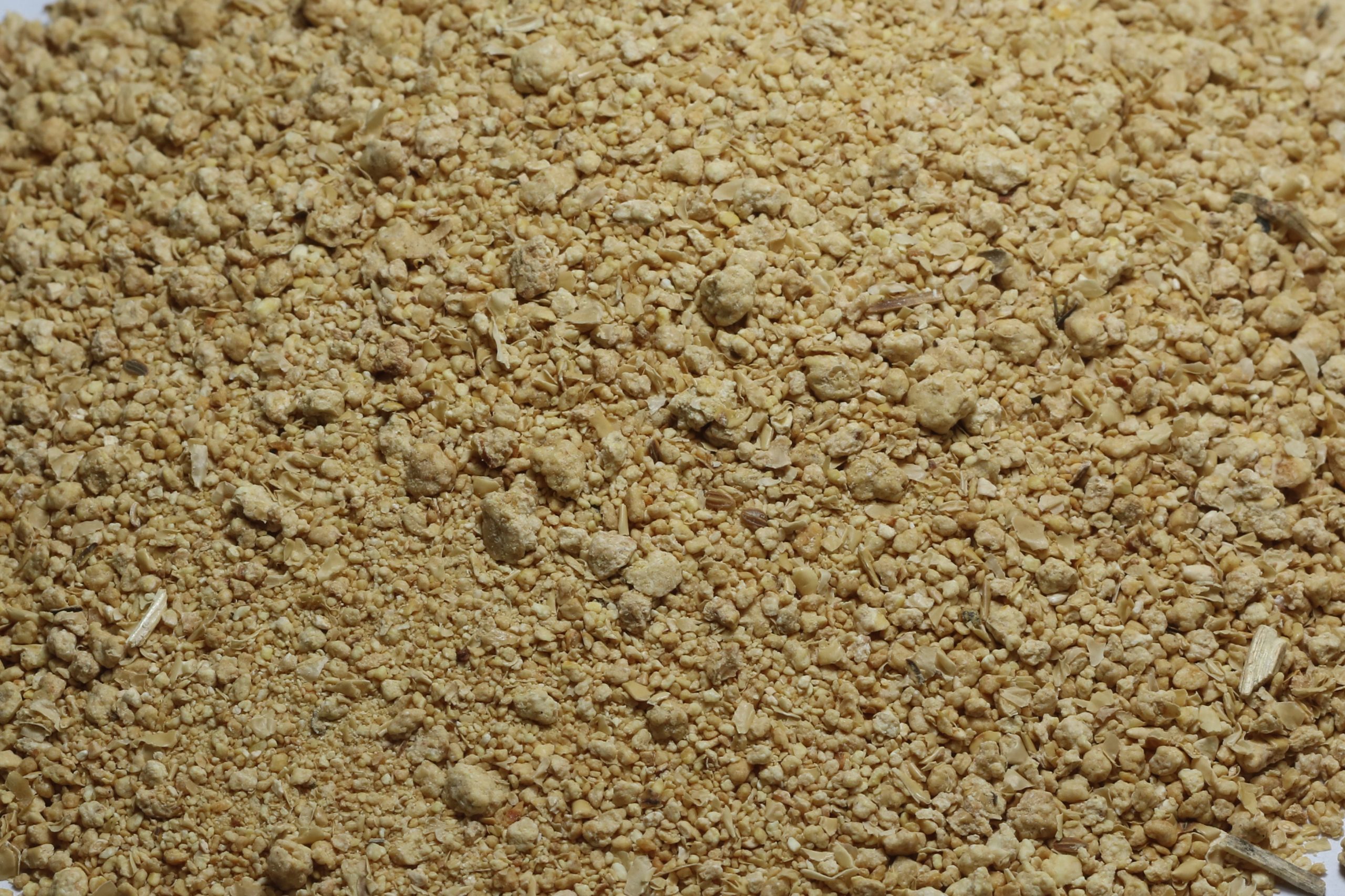
Soybean meal

Soybeans
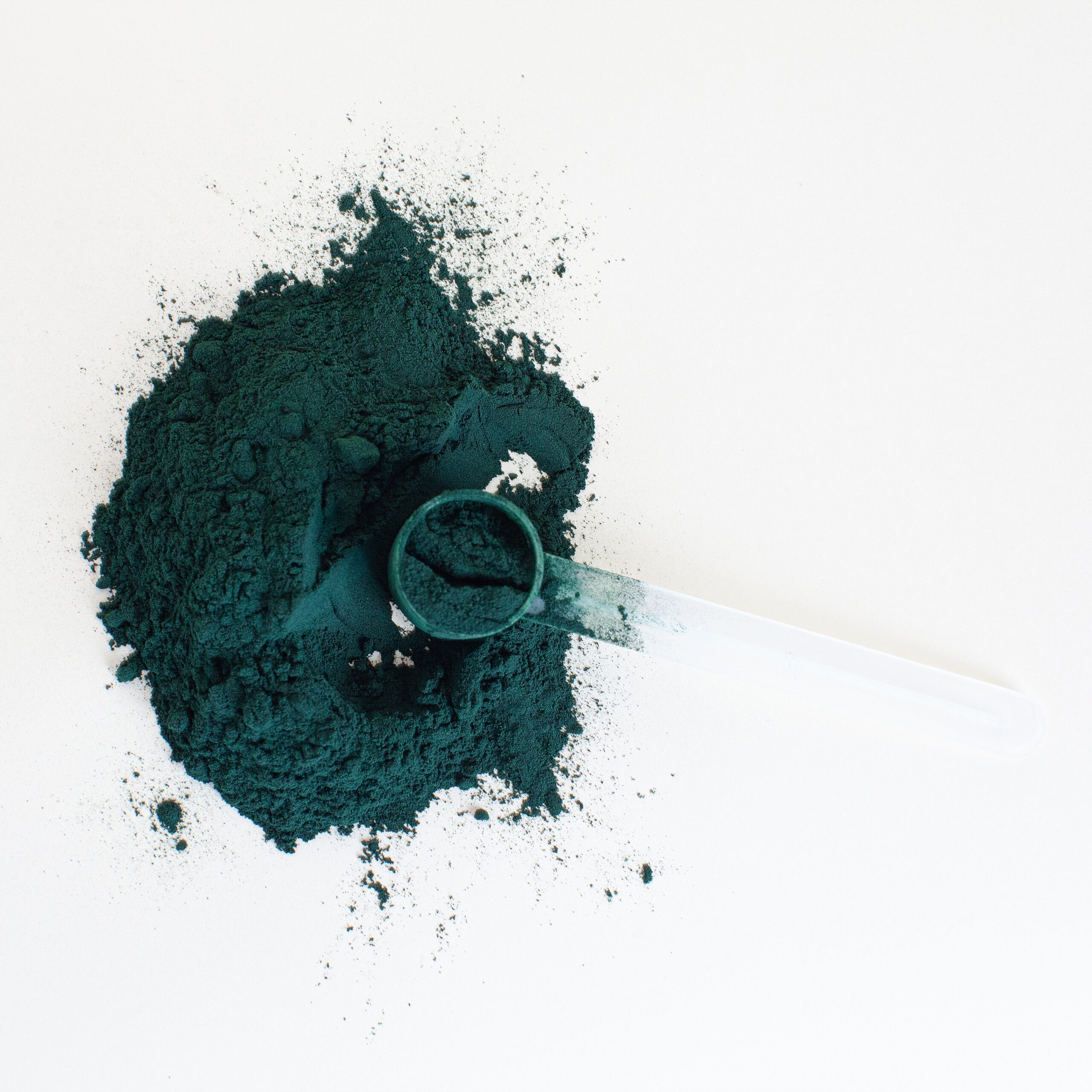
Spirulina powder
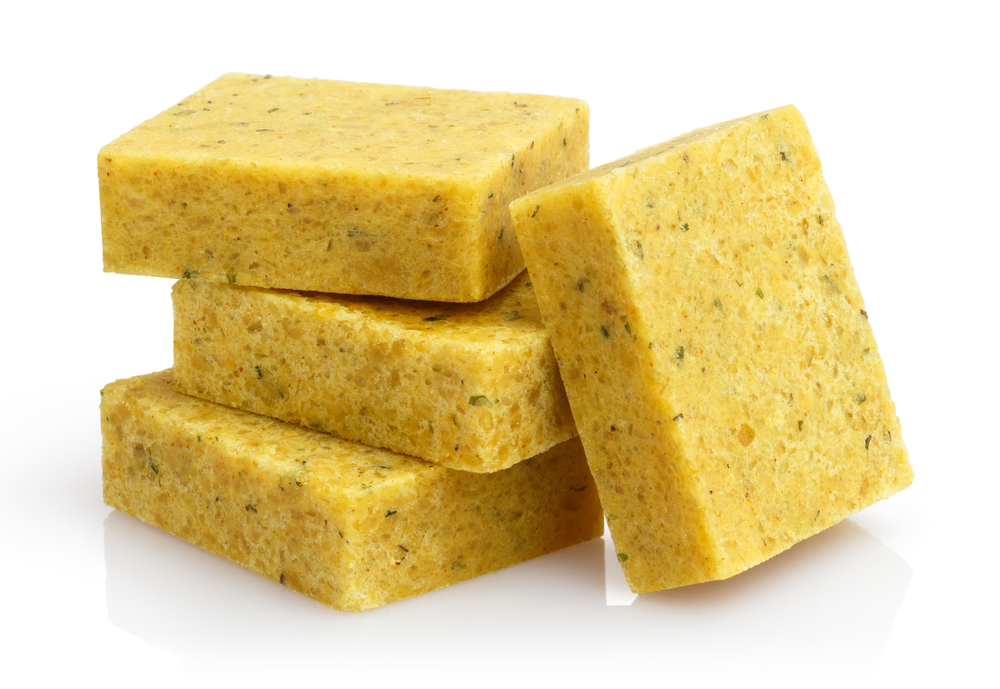
Stock cubes
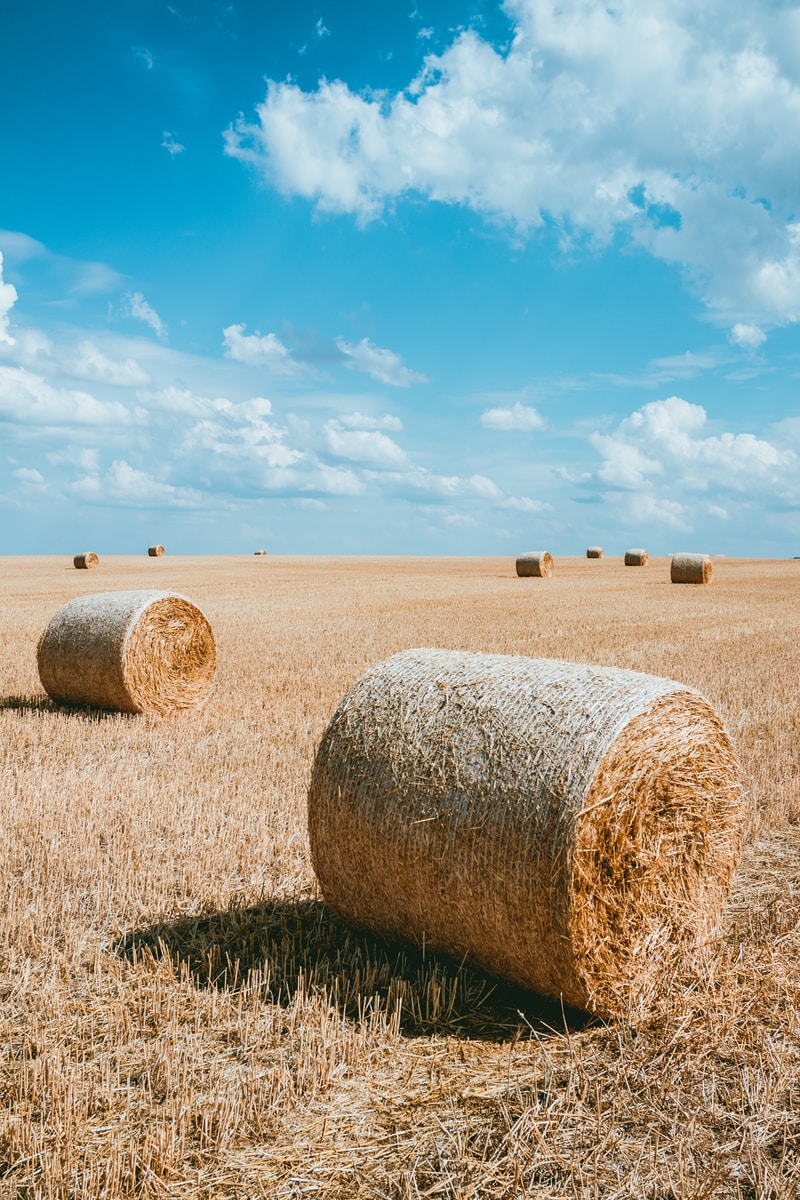
Straw
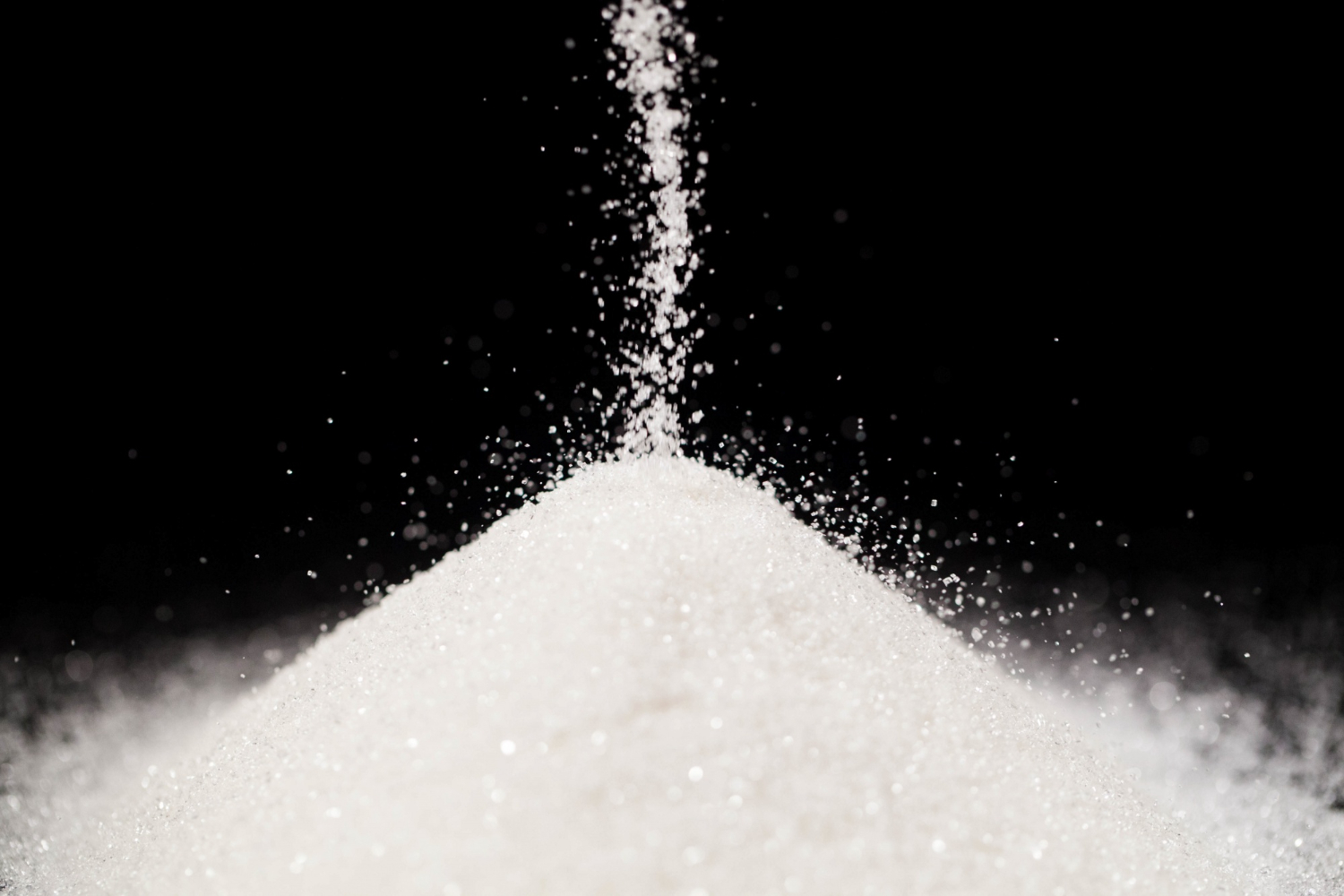
Sugar
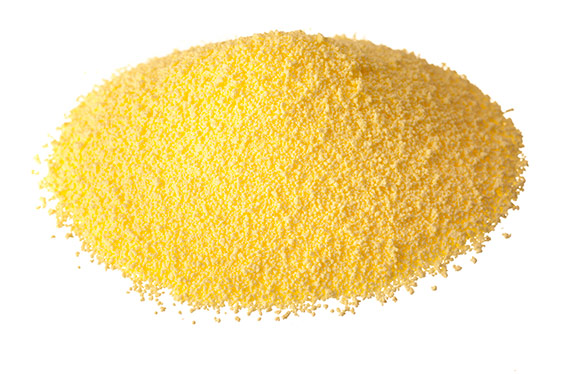
Sulphur
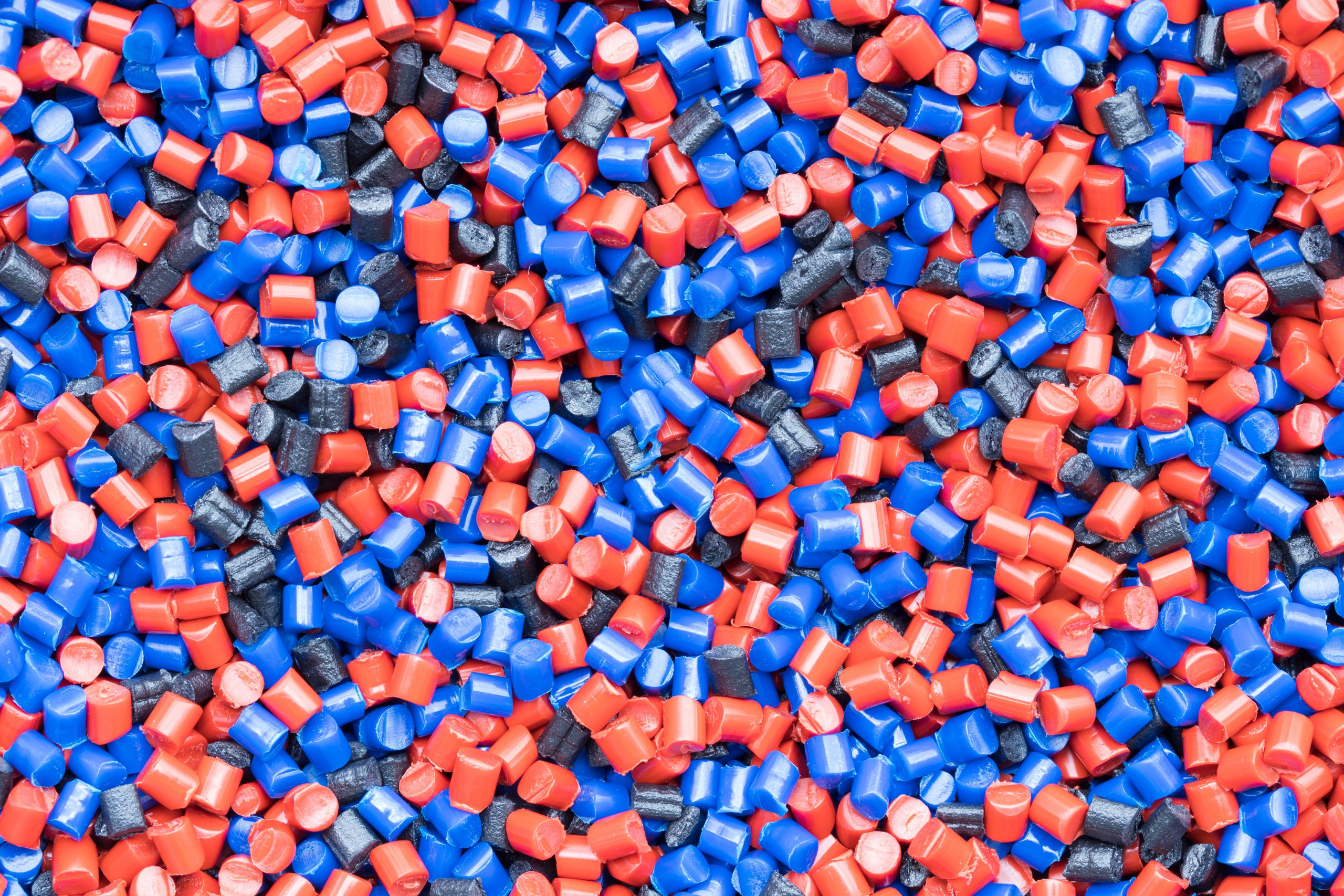
Synthetic resin
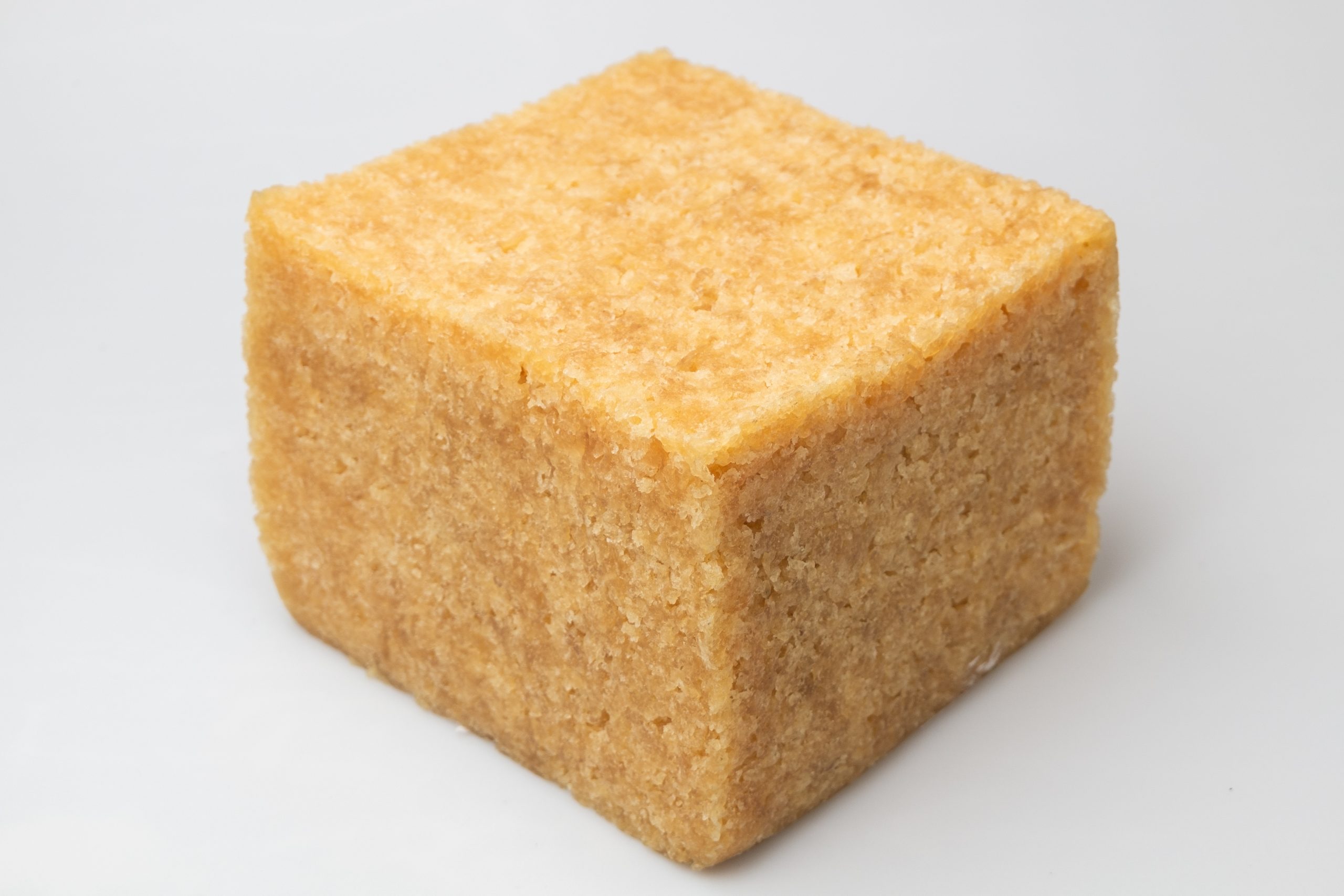
Synthetic rubber
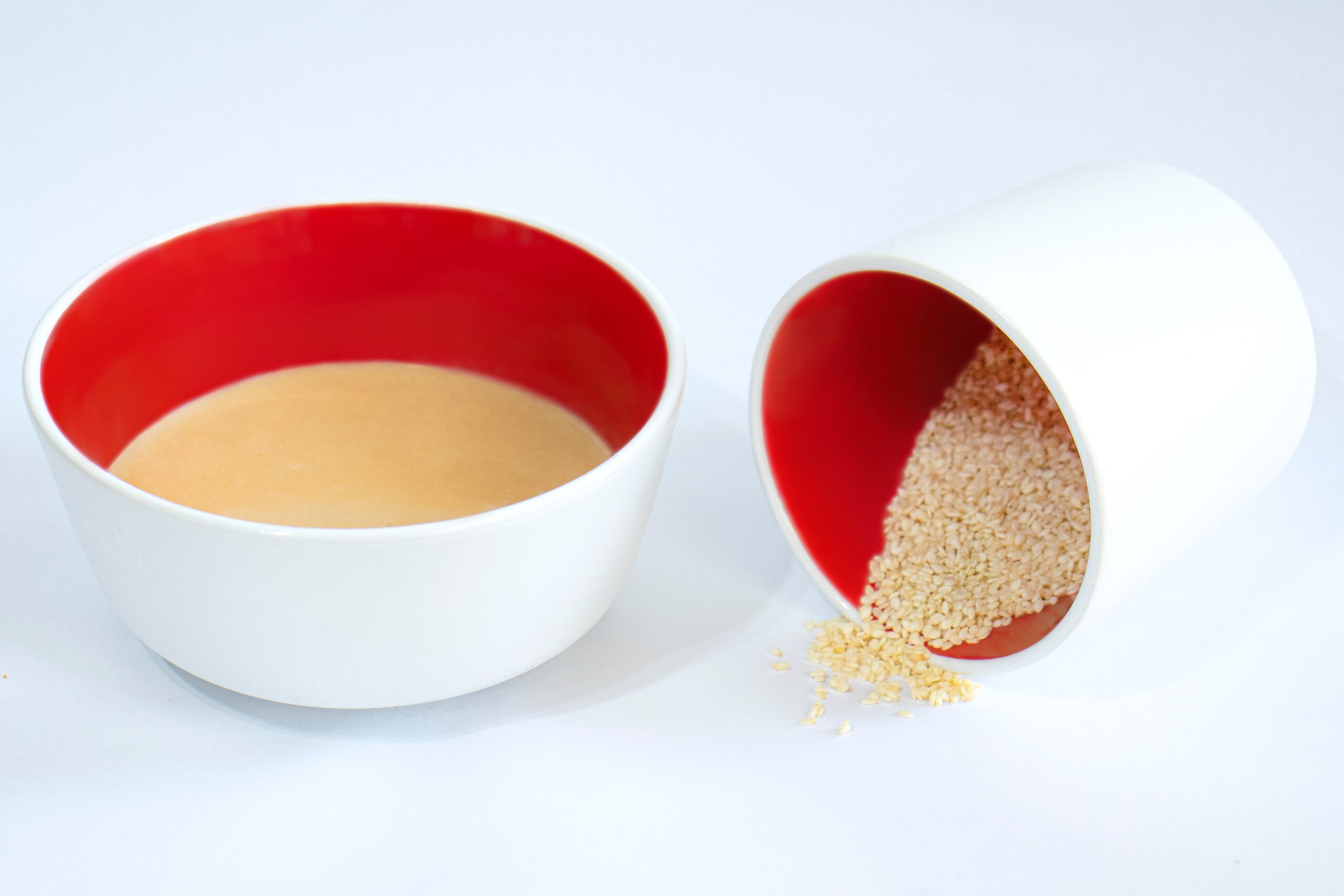
Tahini
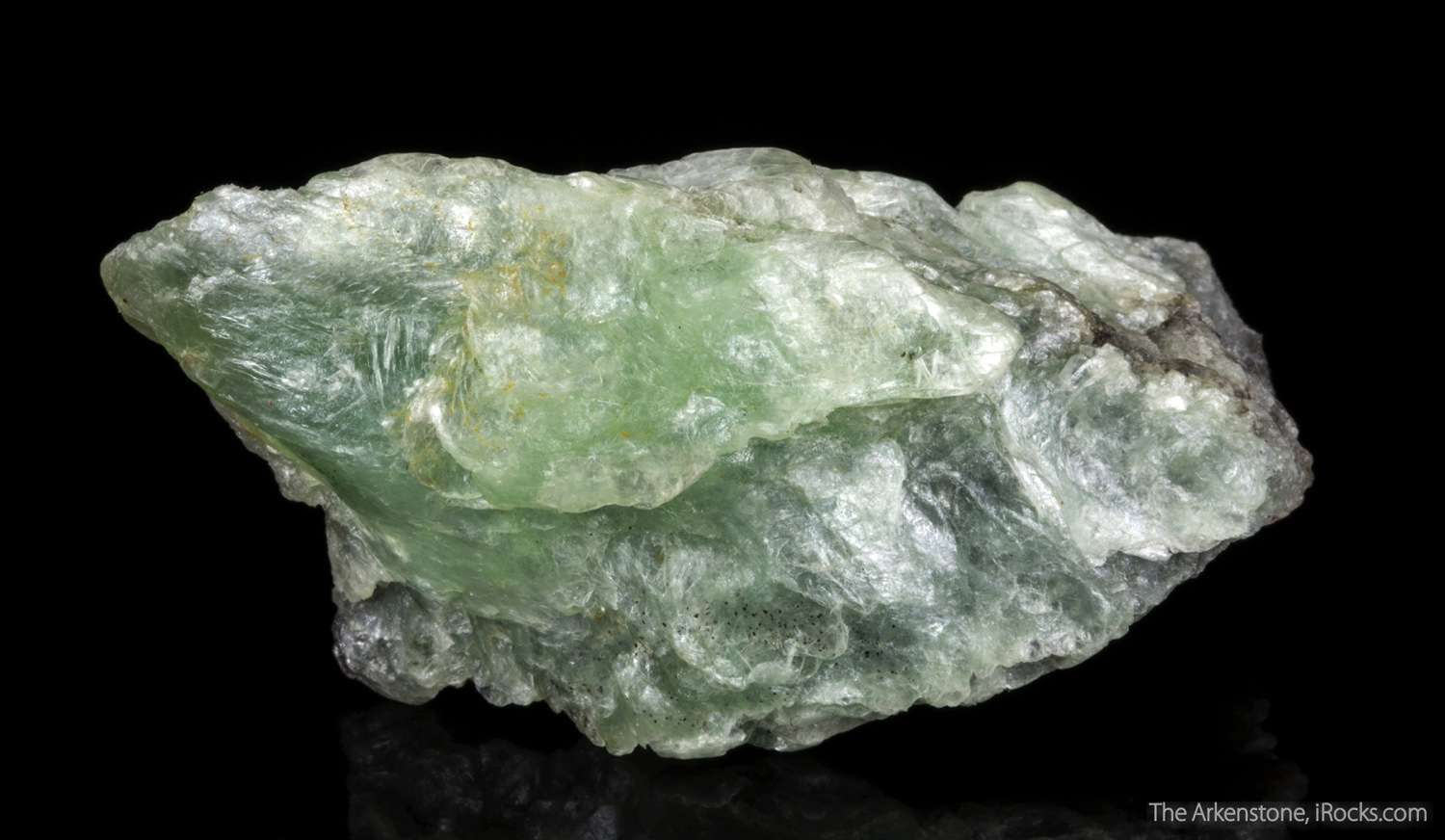
Talc
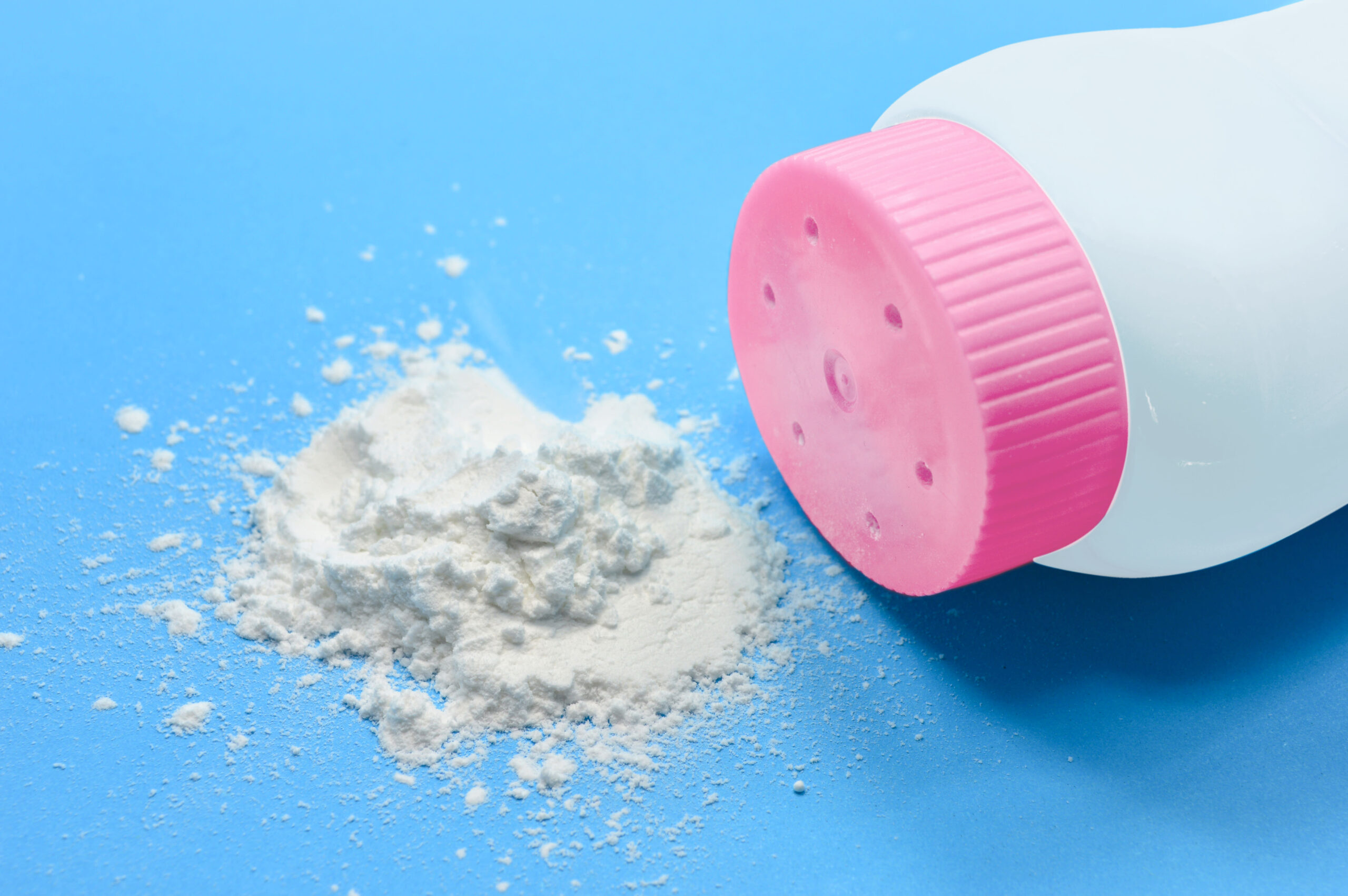
Talc powder
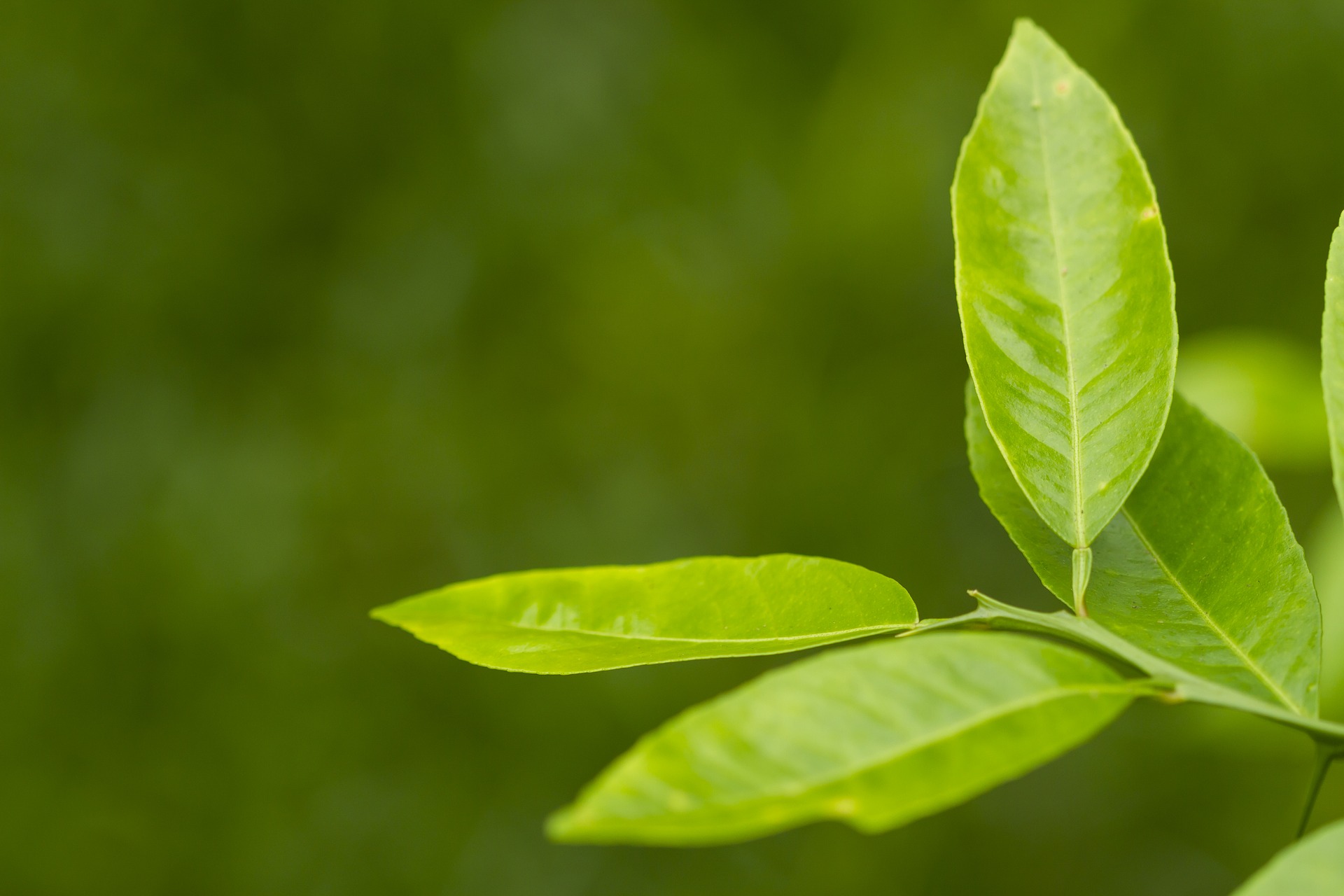
Tea tree oil
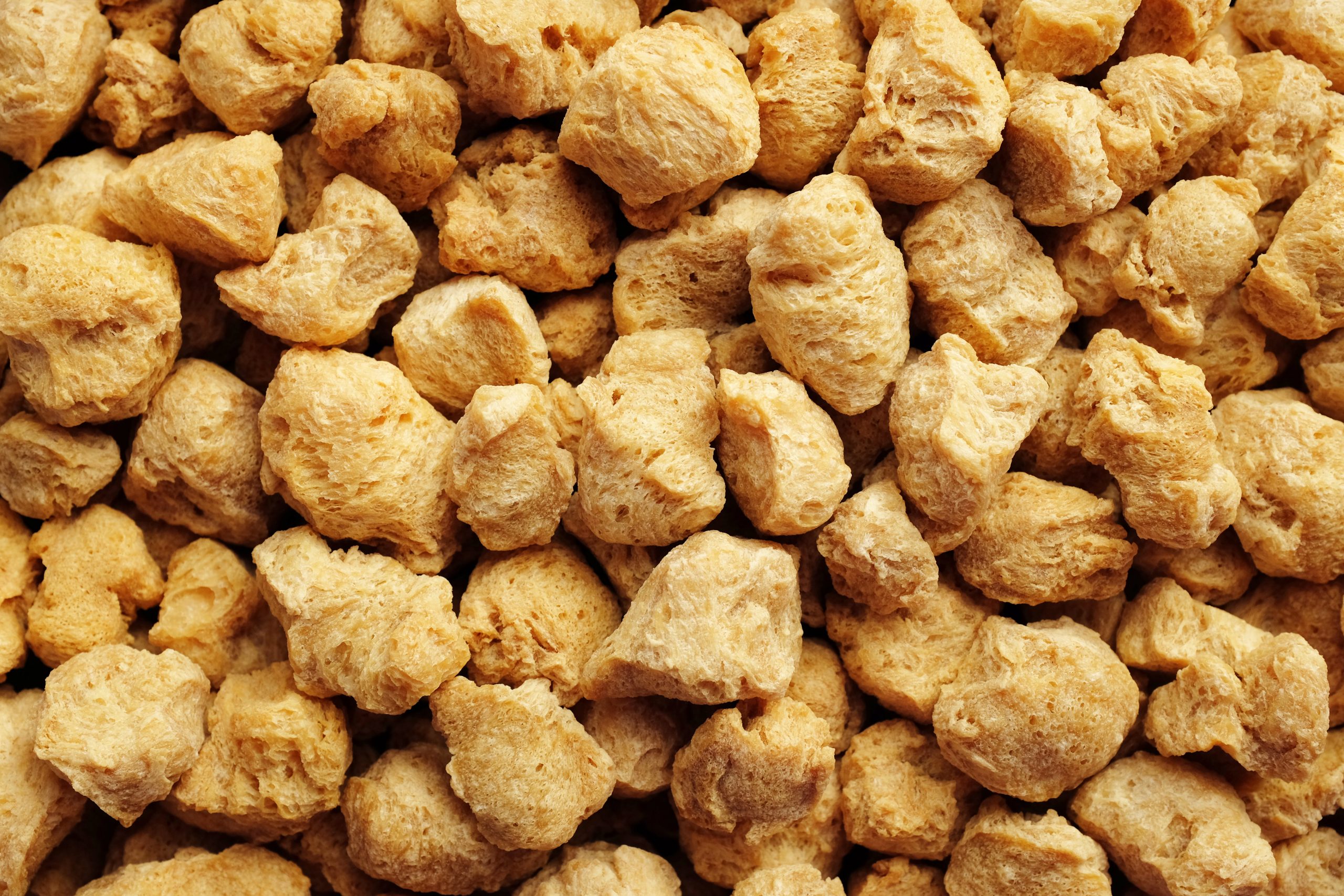
Textured Vegetable Protein
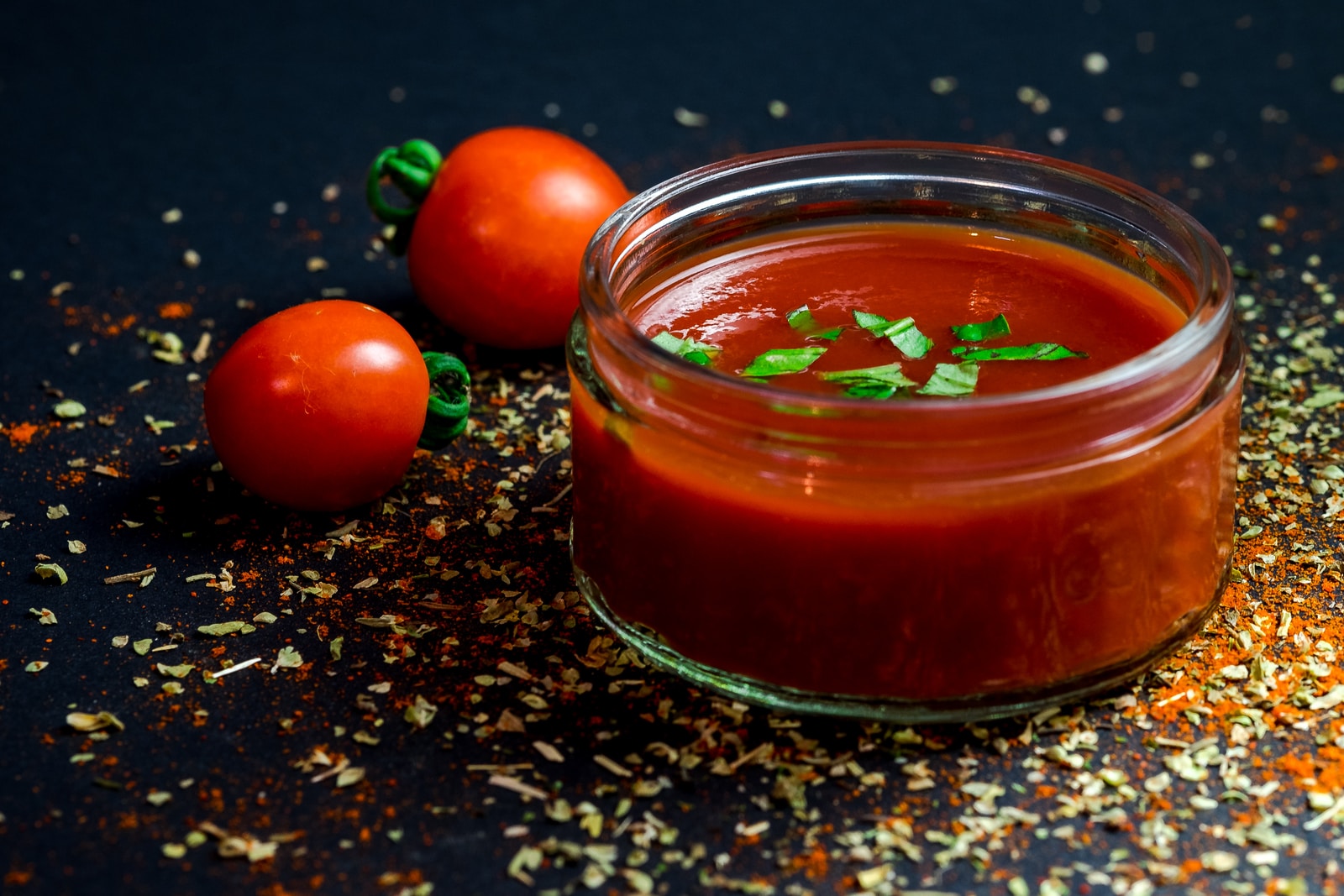
Tomato sauce
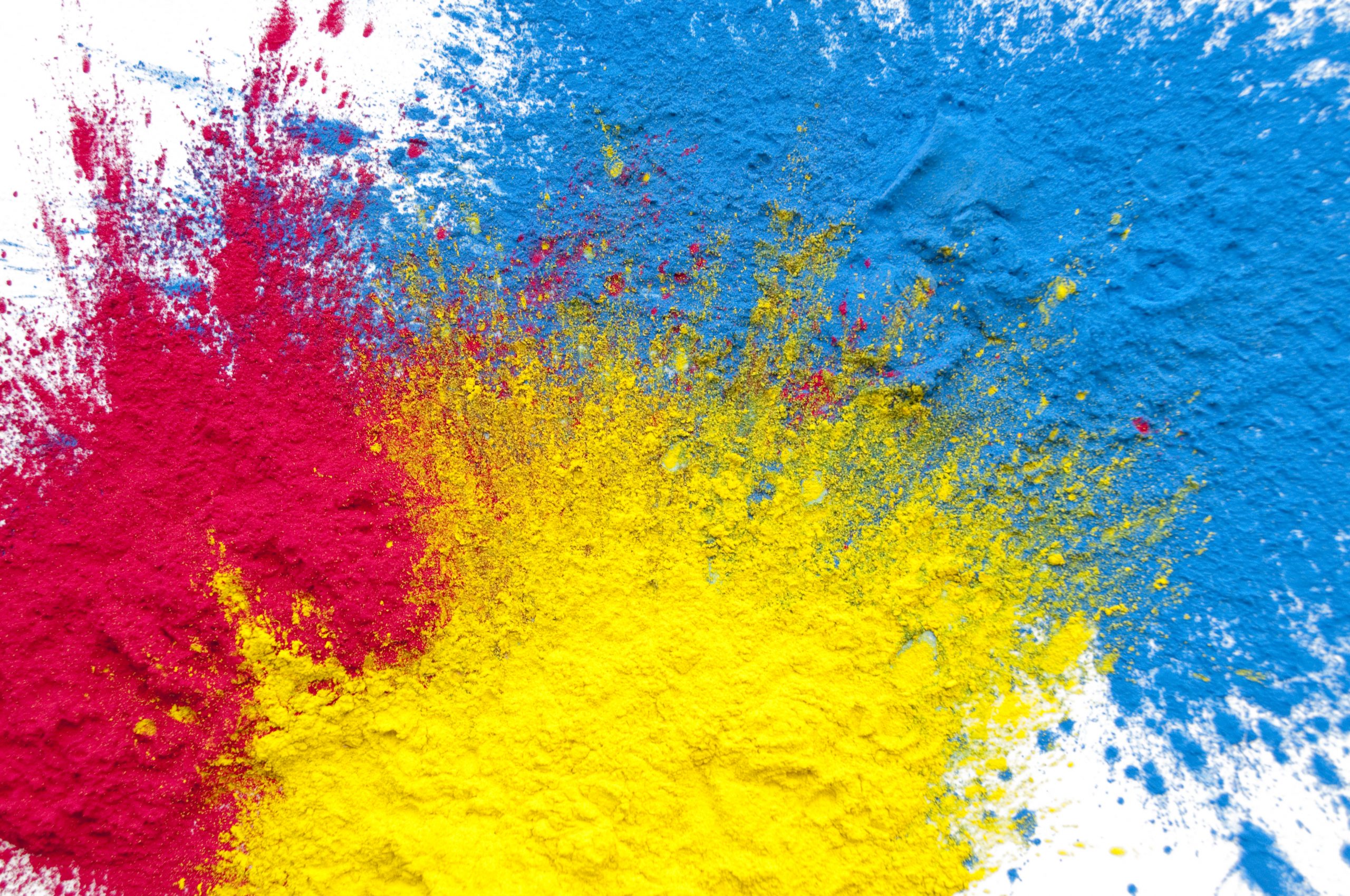
Toner
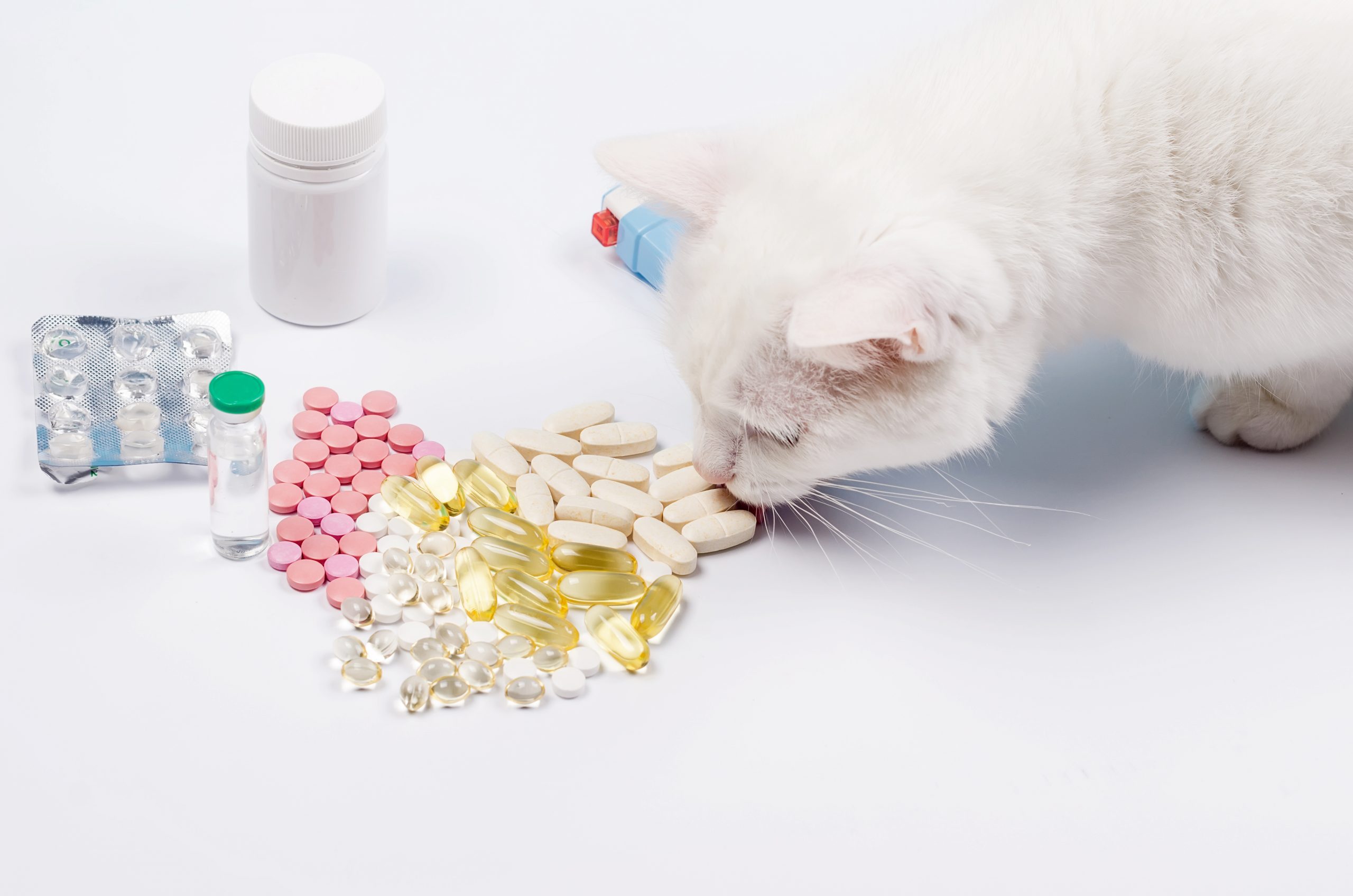
Veterinary tablets
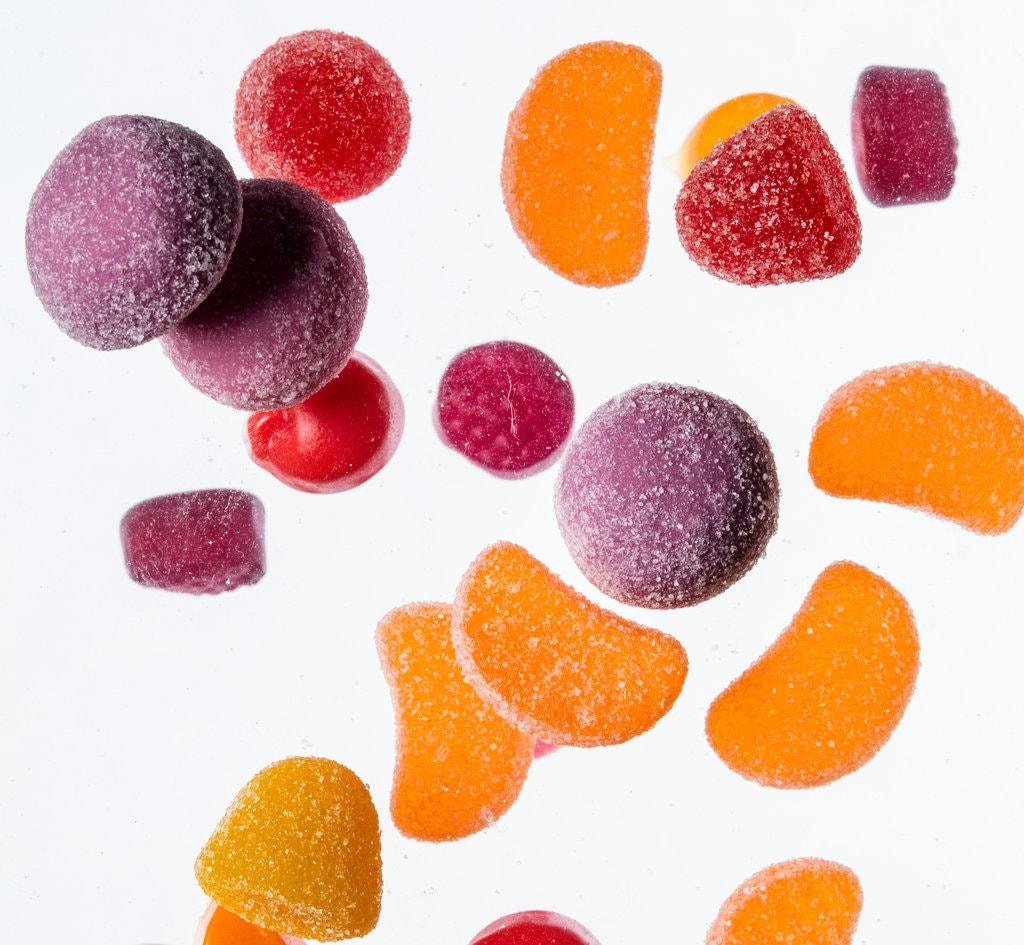
Vitamin gummies
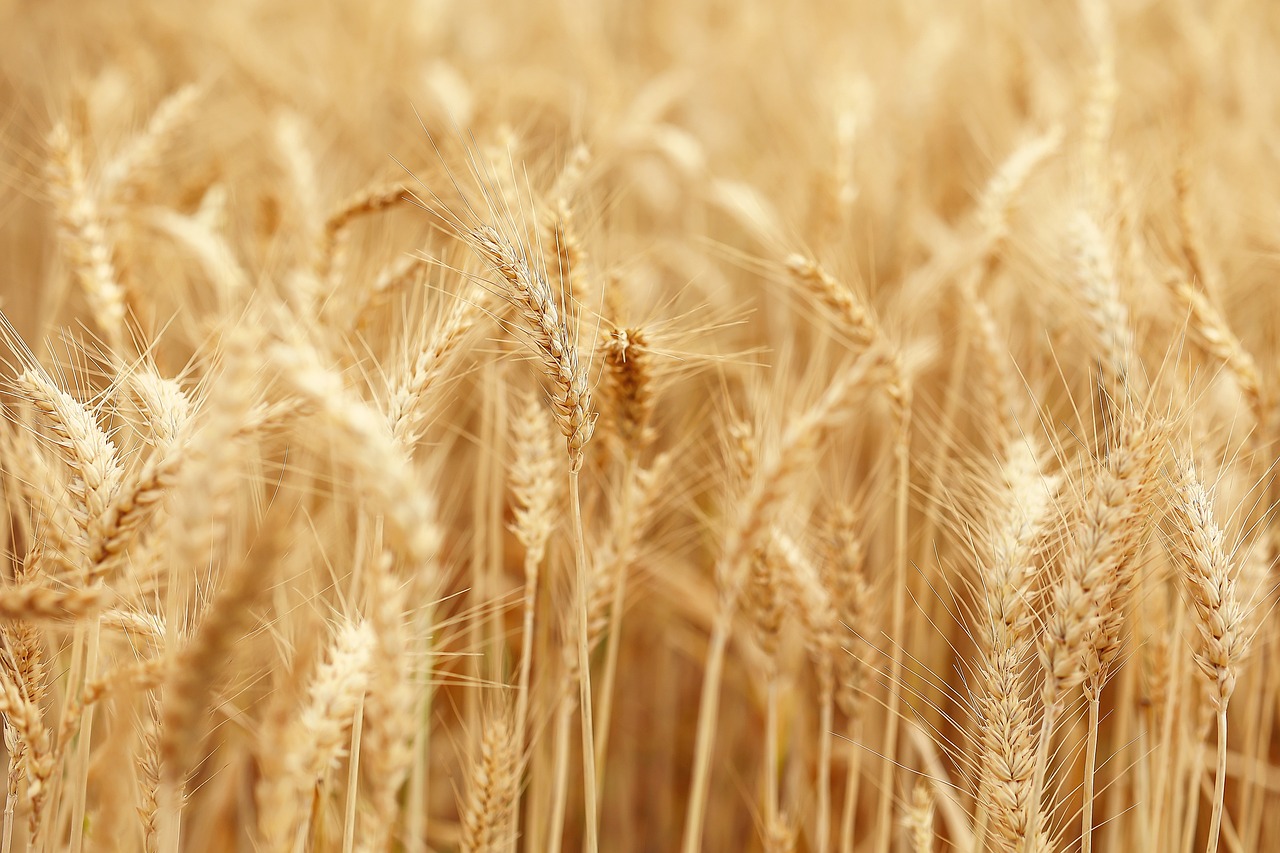
Wheat
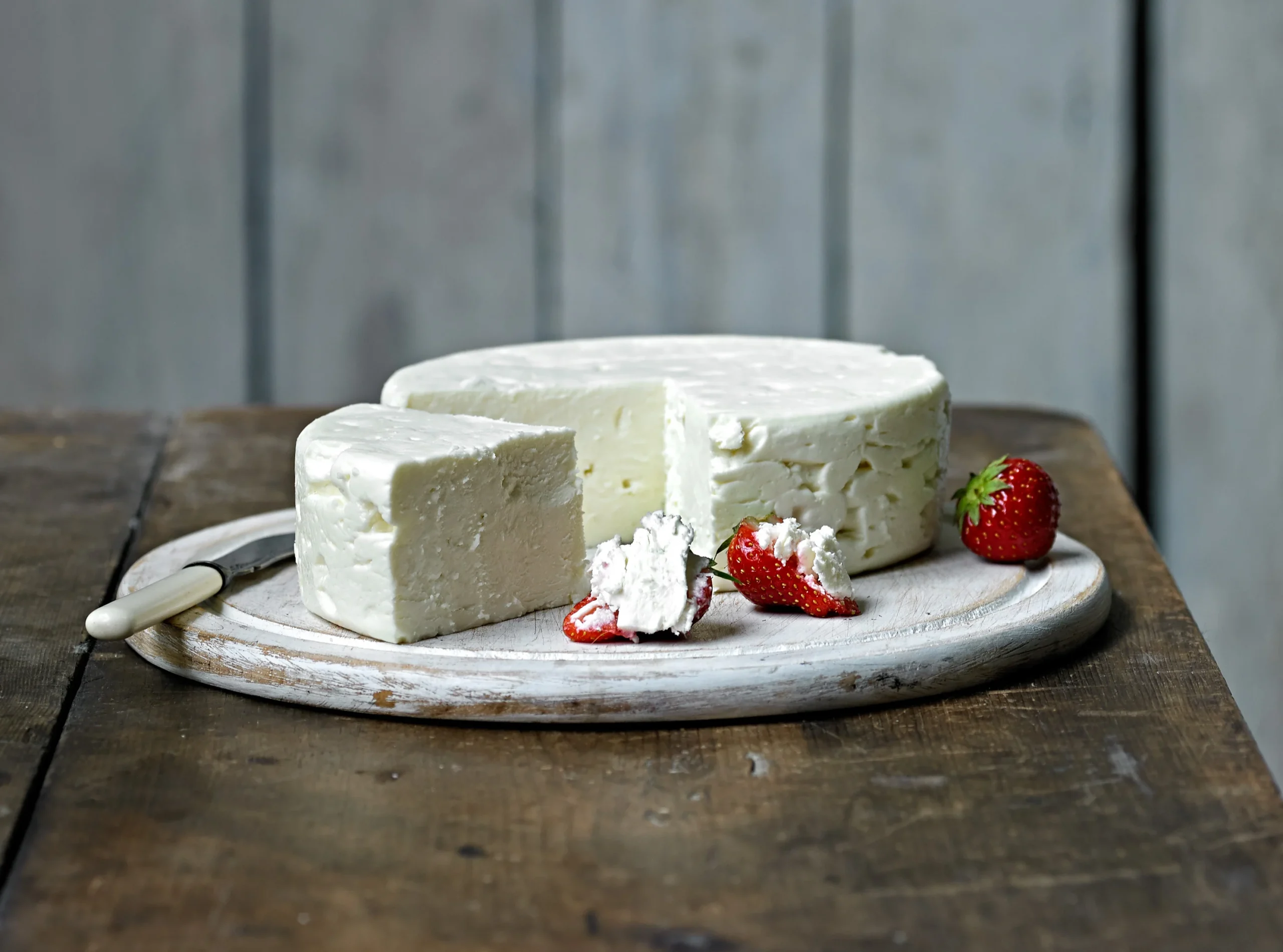
White cheese
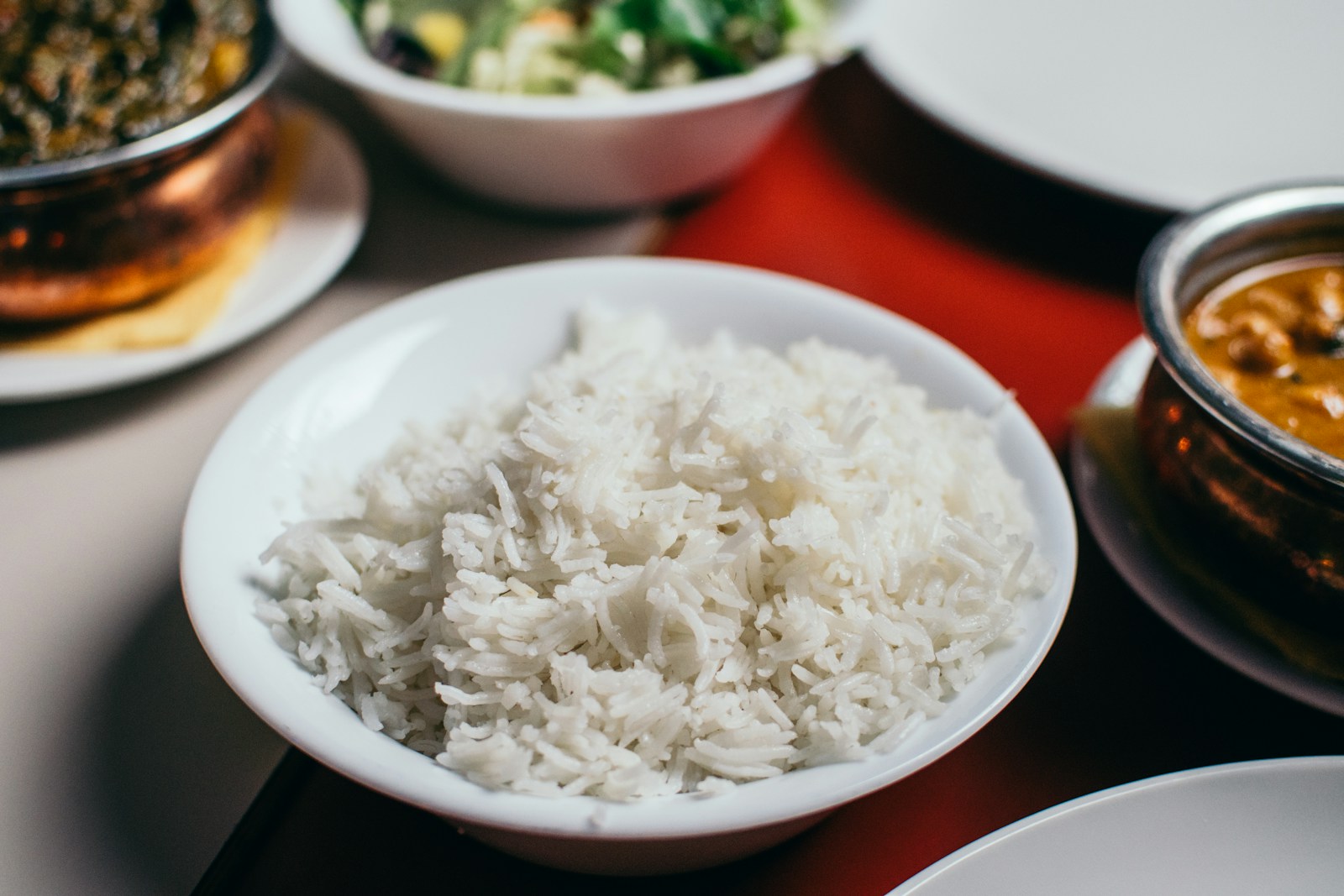
White rice
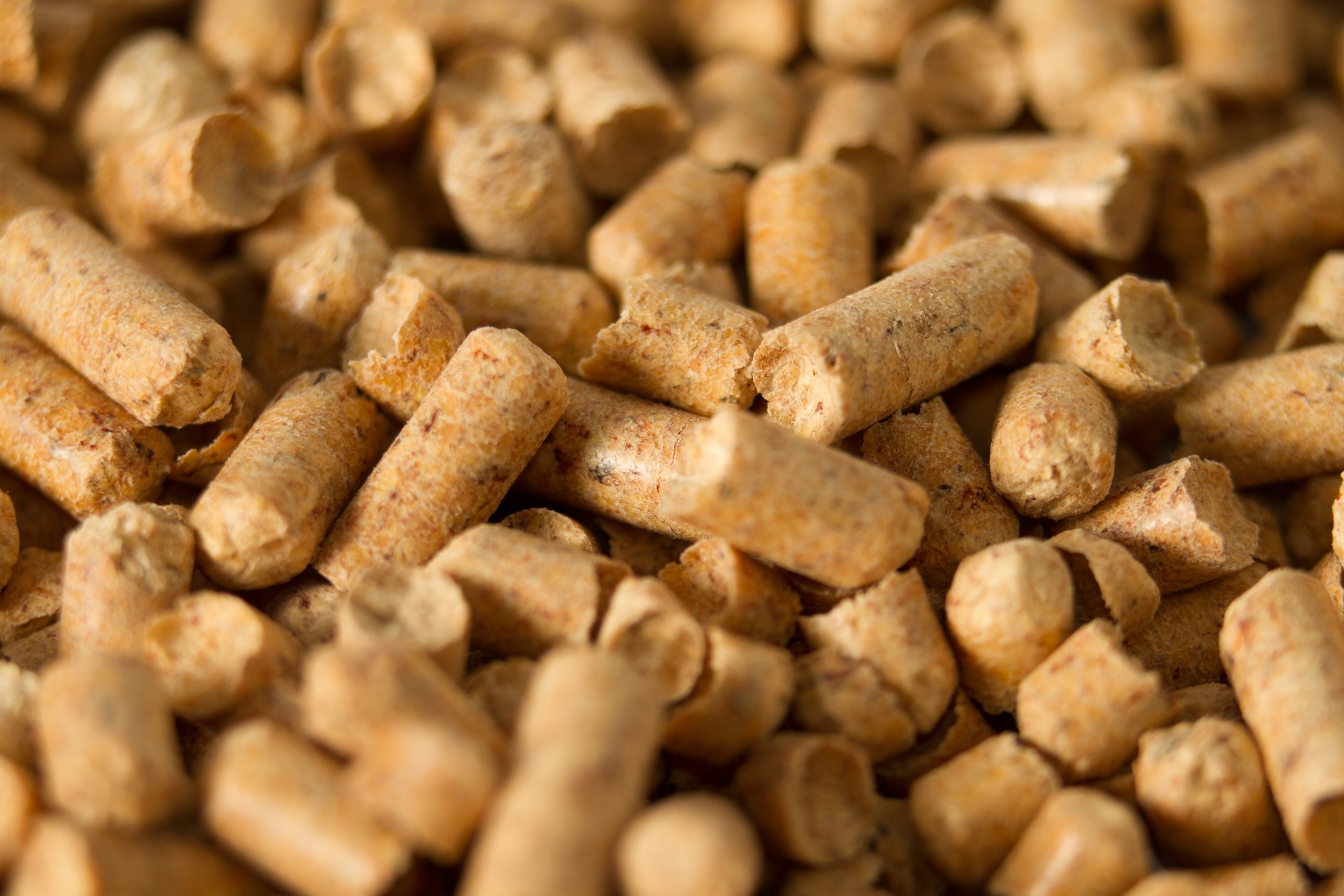
Wood pellets
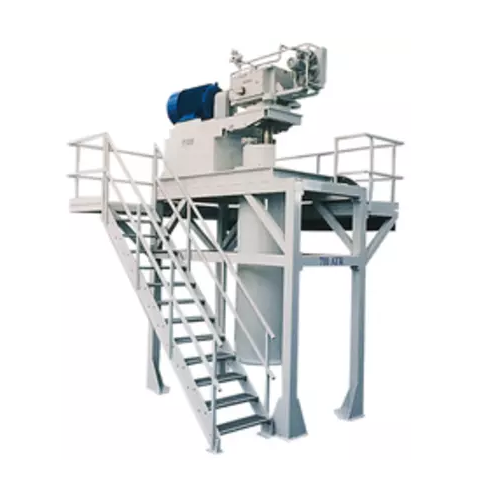
Agitated media mills
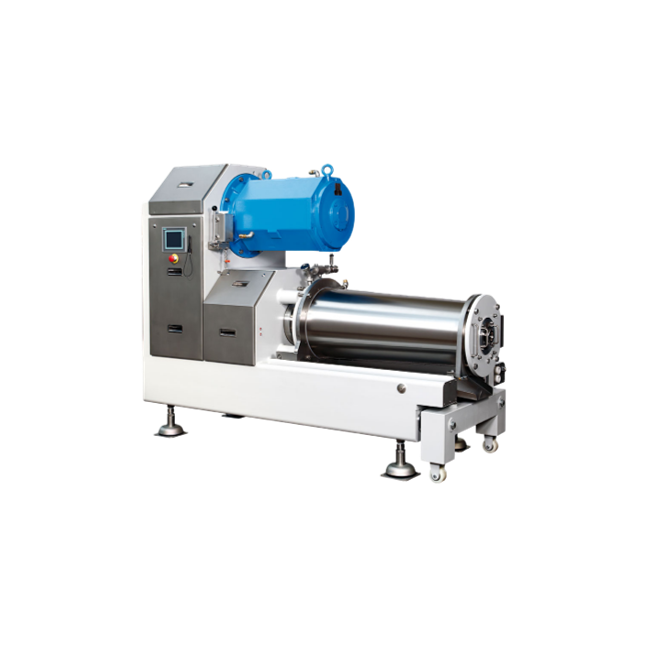
Ball mills
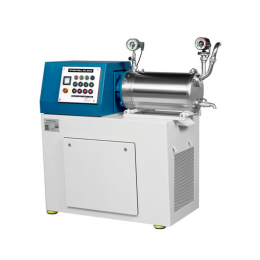
Bead mills
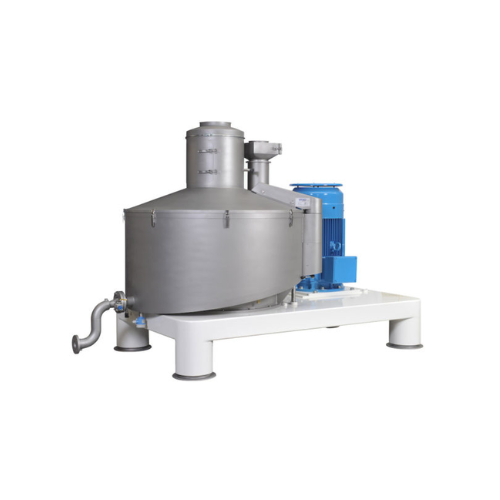
Beater blade mills
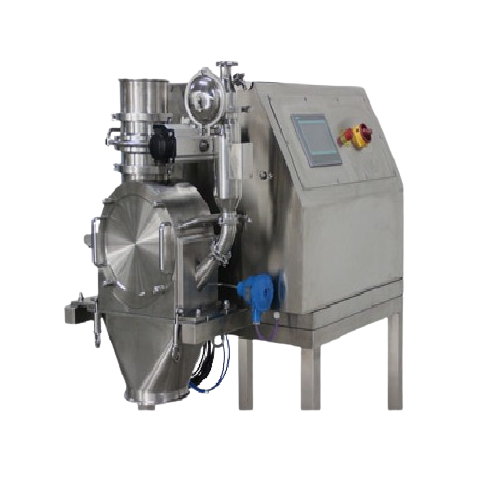
Centrifugal sieving mills
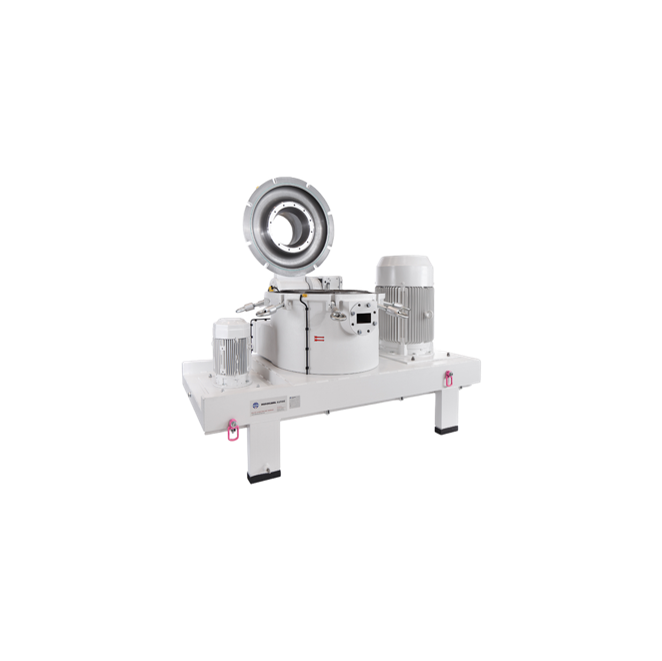
Classifier mills
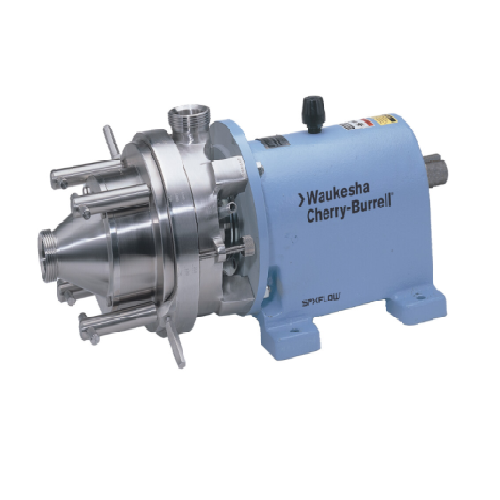
Colloid mills
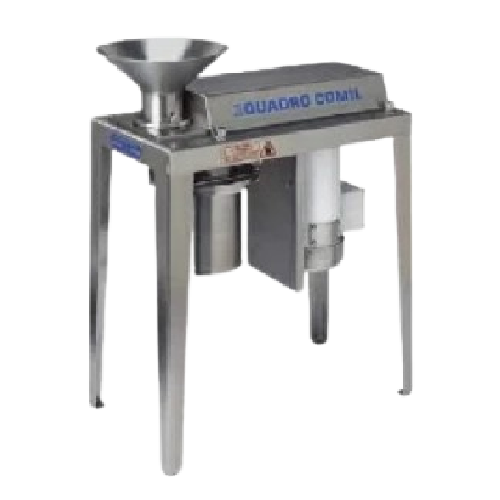
Conical mills
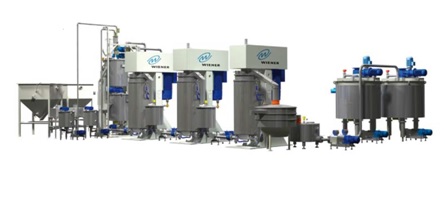
Continuous milling solutions
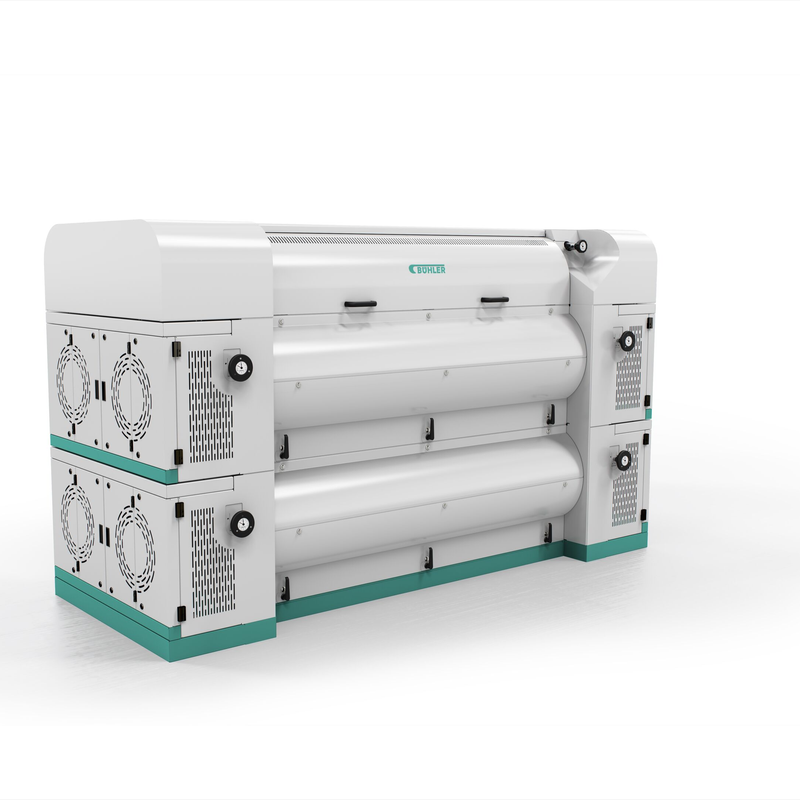
Cracking mills
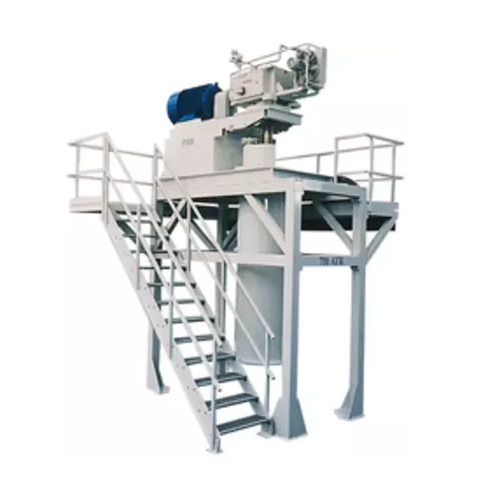
Cutting mills
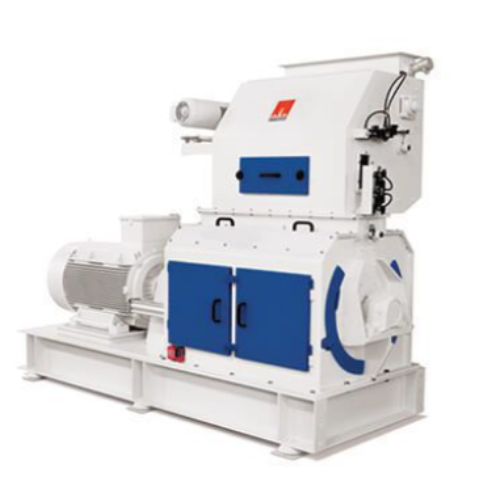
Disc mills
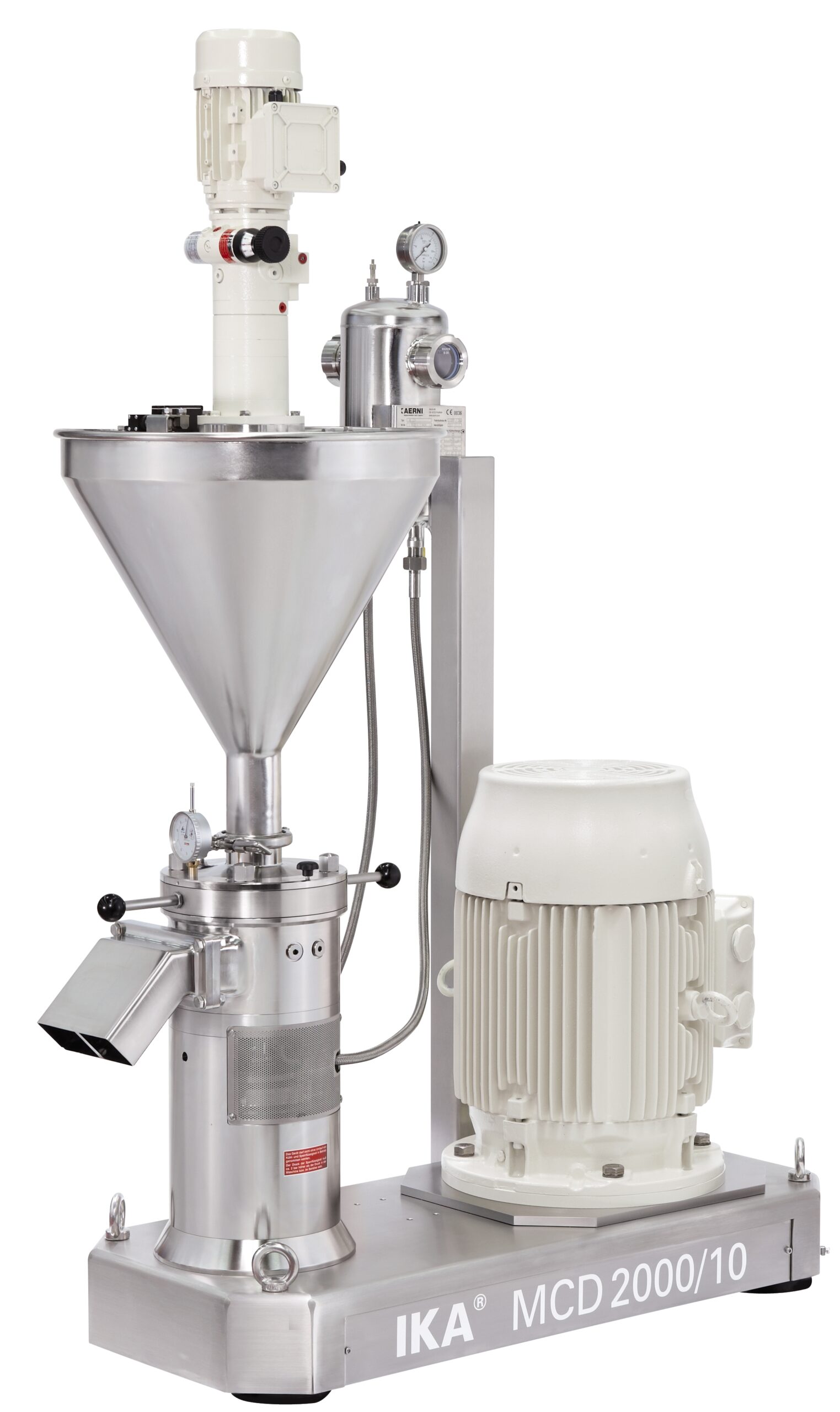
Disk mills
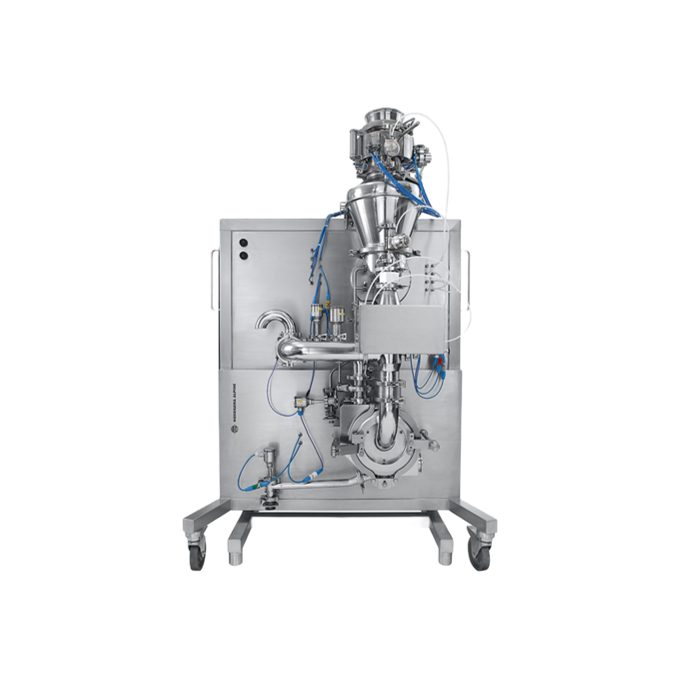
Fine impact mills
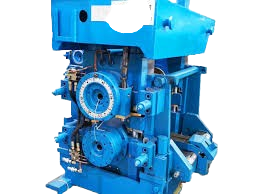
Finishing mills
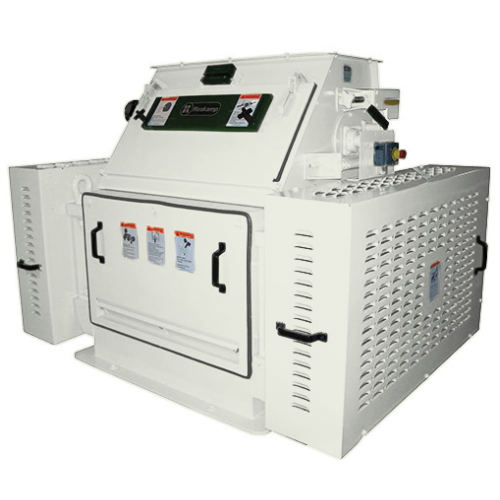
Flaking mills
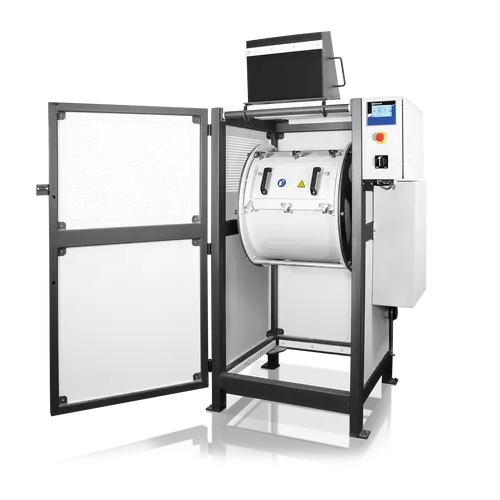
Grinding mills
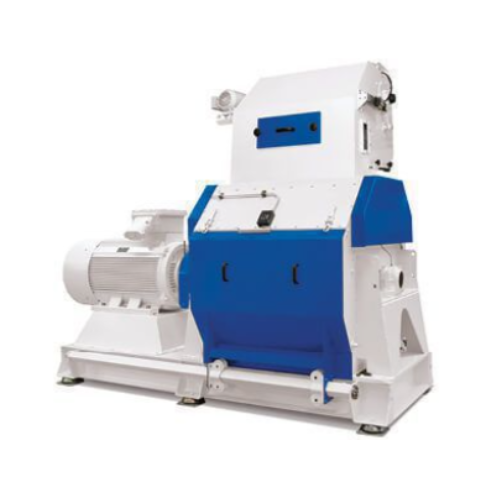
Hammer mills
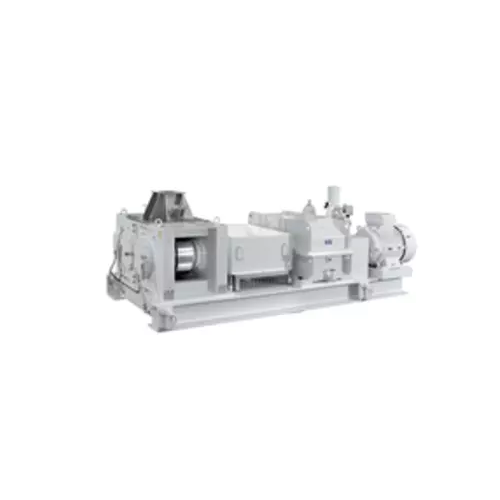
High pressure roller mills
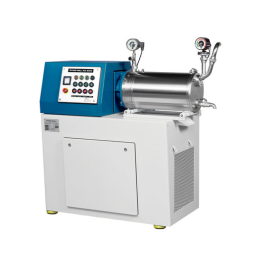
Horizontal bead mills
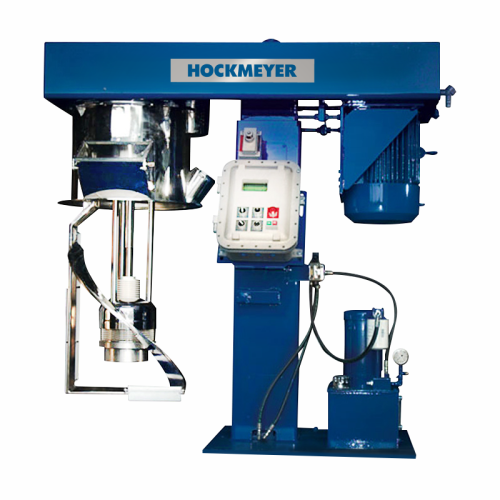
Immersion mills
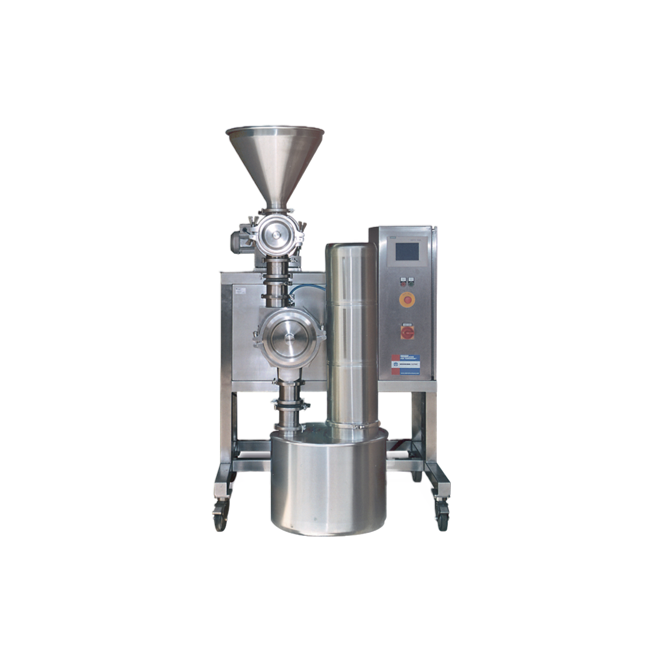
Industrial hammer mills
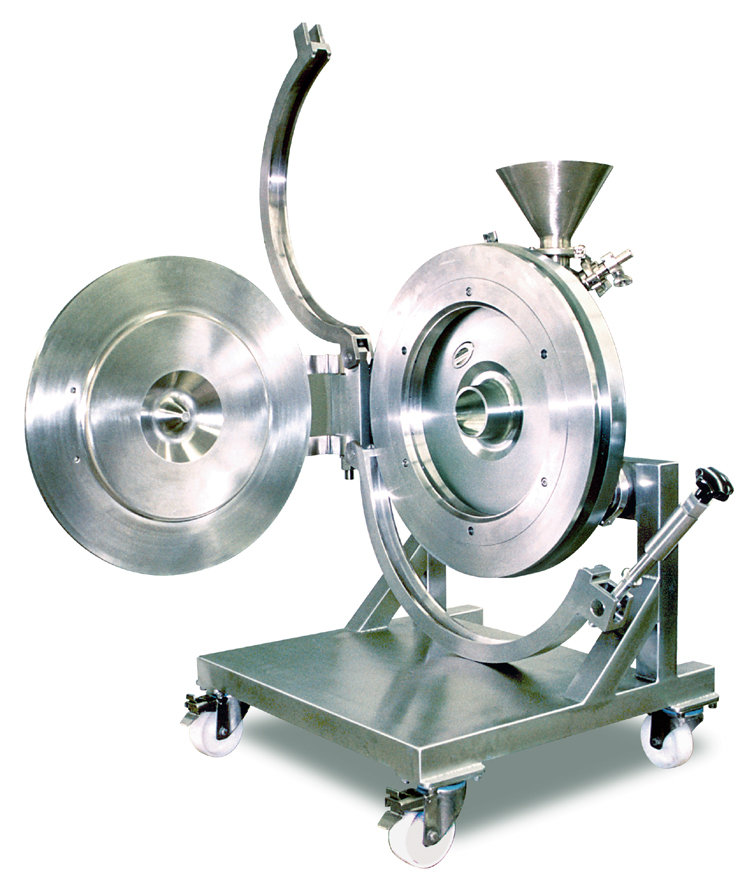
Industrial jet mills
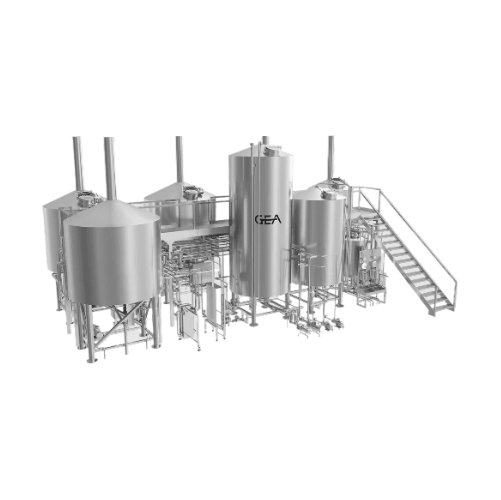
Jet mills

Laboratory mills
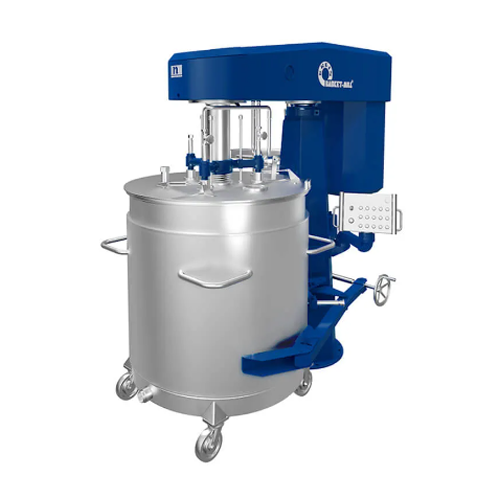
Milling beads
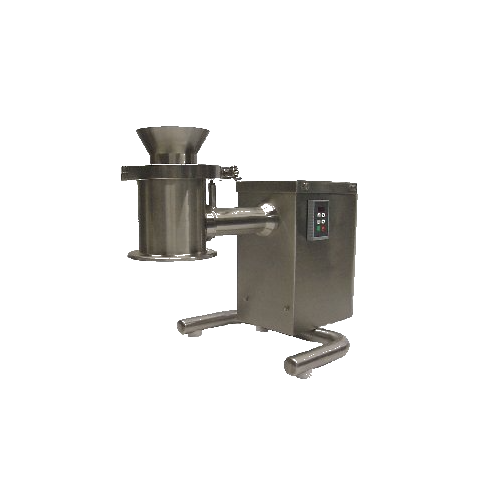
Milling equipment
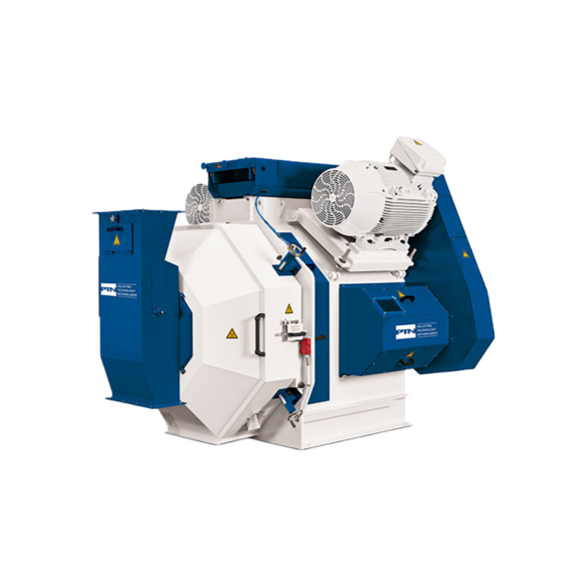
Pellet Mills
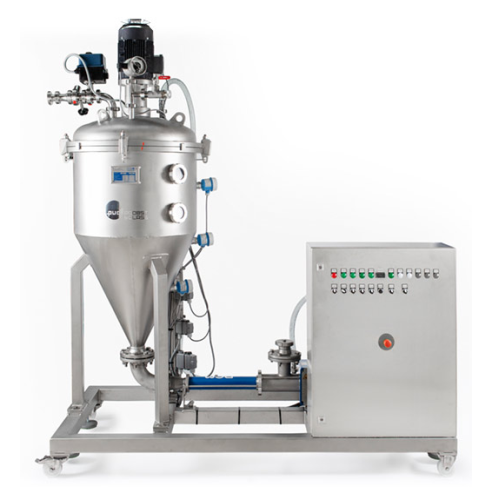
Perforated disc mills
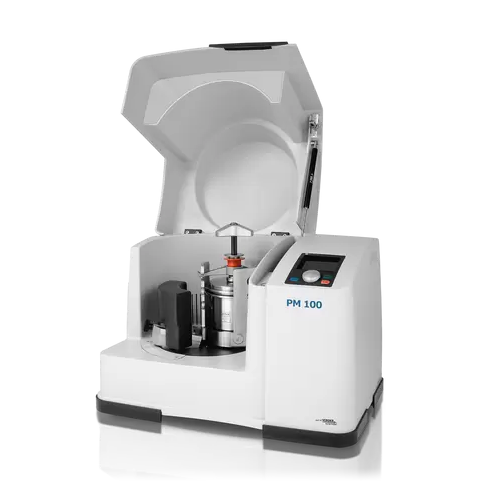
Planetary mills
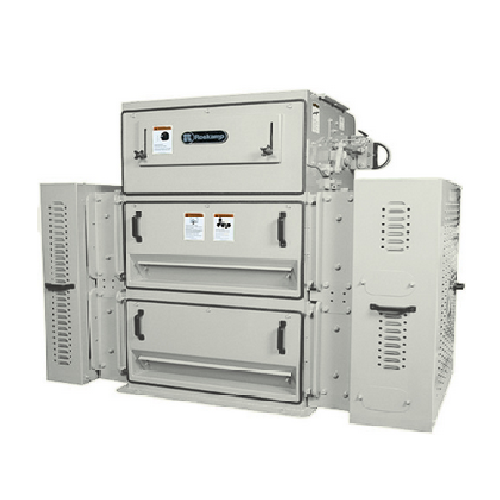
Roller mills
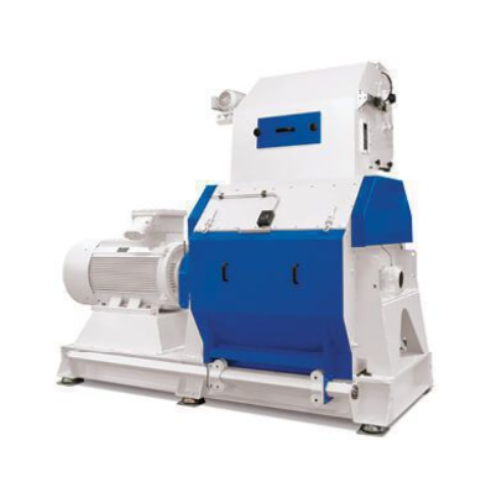
Rotor mills
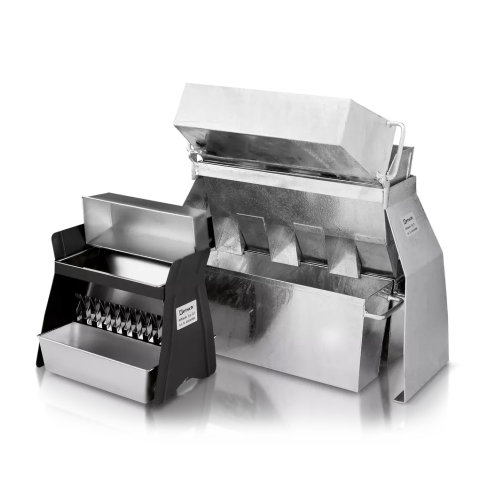
Size Reduction technologies
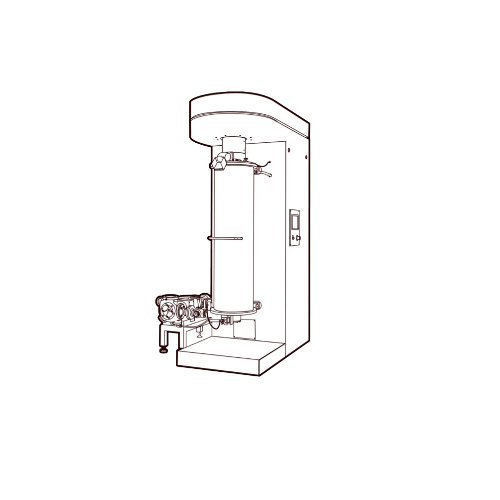
Spindle mills
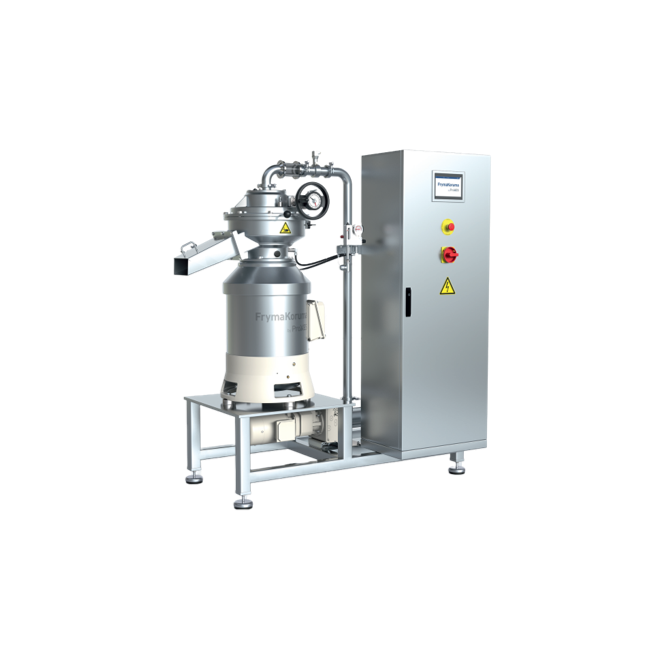
Stone Mills
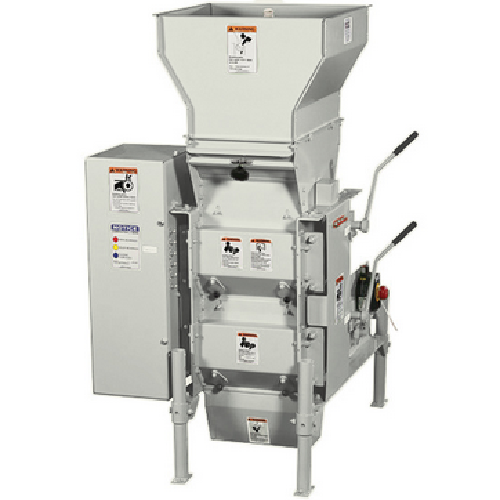
Table roller mills

Vacuum basket mills
Which milling technology do you need?
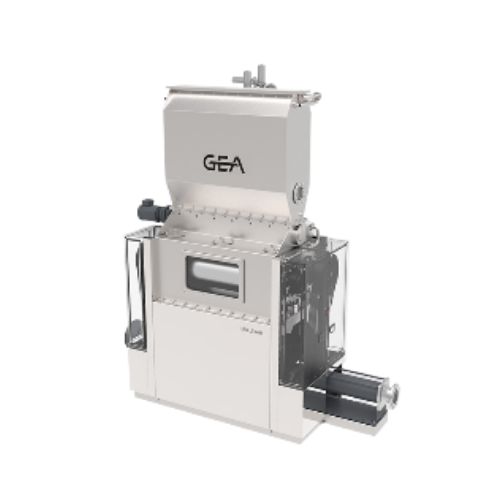
Milling system for breweries
Enhance your brewing process with a system that conserves grain husks while optimizing endosper...
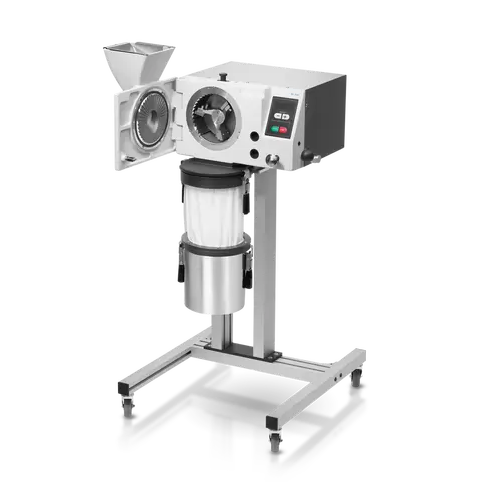
Cross beater mill for fine and coarse size reduction
Achieve precise size reduction of medium-hard and brittle materials ...
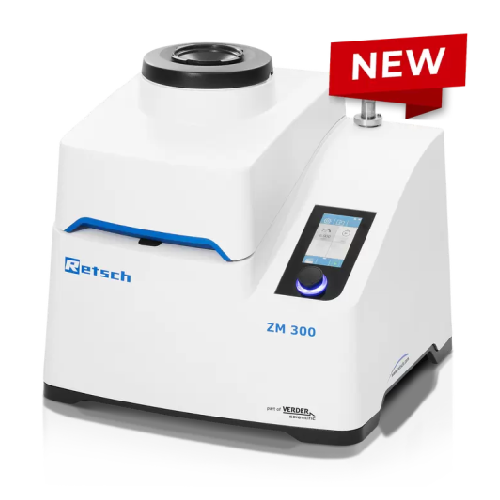
Ultra centrifugal mill for size reduction of soft and medium-hard materials
Achieve precise particle size reduction an...
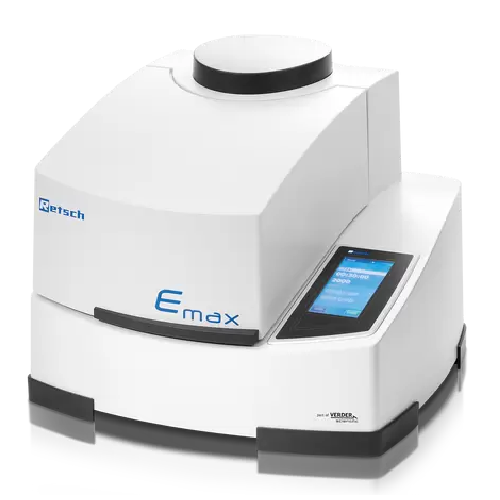
High energy ball mill for ultrafine grinding
Achieve nanoscale precision and unmatched particle uniformity with high-energ...
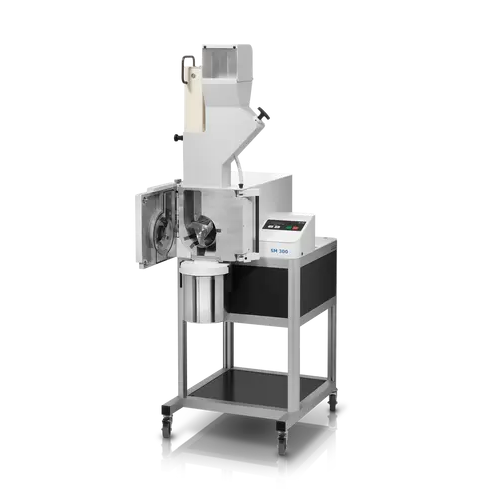
High-torque cutting mill for tough and fibrous materials
Tackle the toughest materials and ensure consistent particle siz...
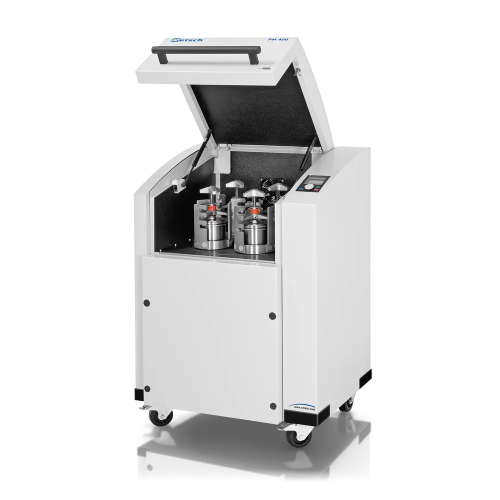
Planetary ball mill for high throughput grinding
For precise material engineering, achieve efficient size reduction, homog...
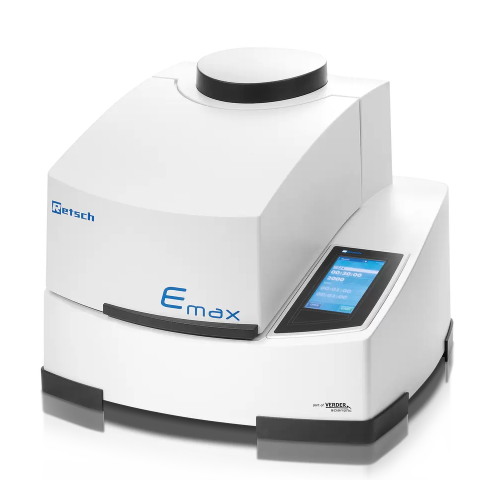
High energy untra fine ball mill
Achieve ultra-fine particle sizes rapidly with this high energy milling solution, designed ...
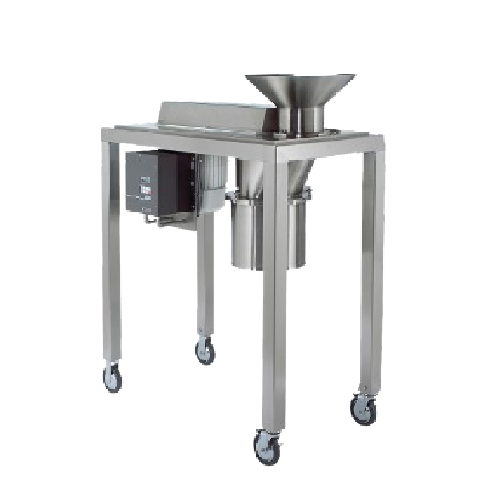
High efficiency milling solution for pharma and food industries
Achieve precise particle size control and enhance produc...
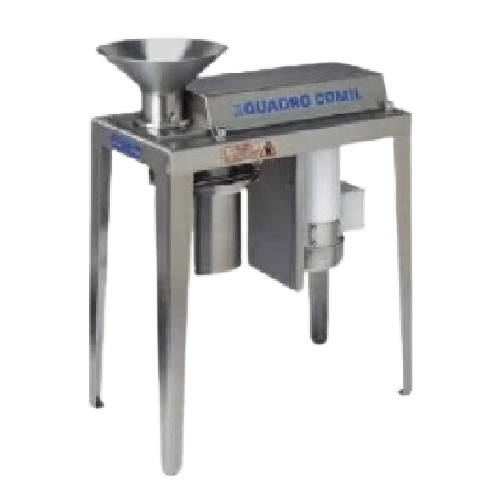
Conical milling for high-efficiency particle sizing
Maximize efficiency in your production line with conical milling tech...
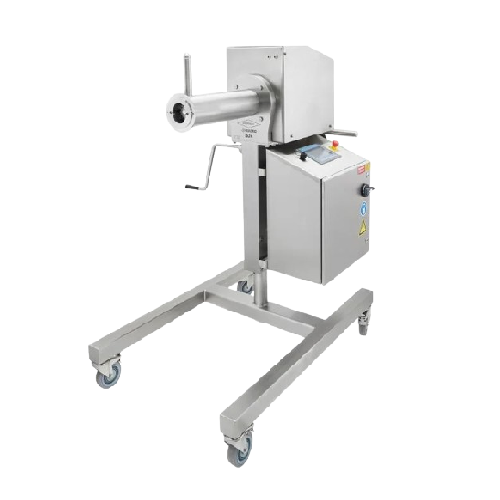
Production-scale milling and screening system
Achieve precise particle size distribution and high throughput rates with a ...
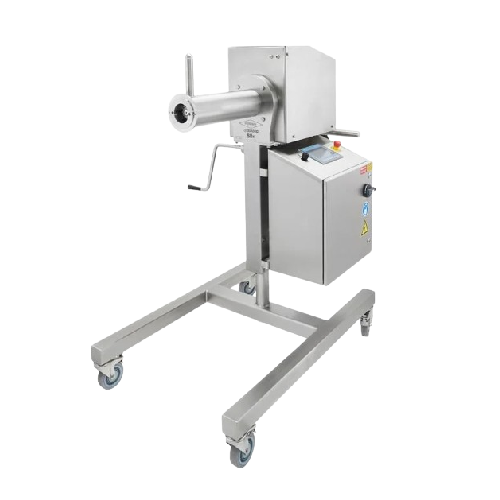
Mid-size milling platform for pilot-scale production
Achieve precise particle size control with this integrated milling s...
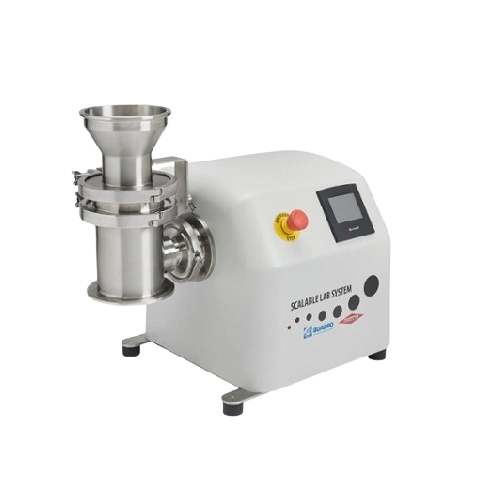
Lab-scale milling and processing platform
Effortlessly transition from lab-scale research to full production with a versat...
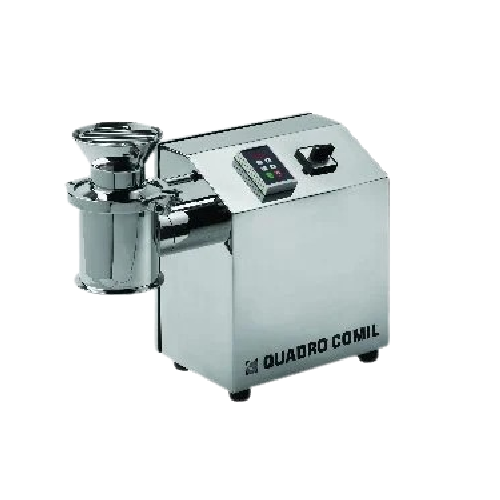
Conical mill for high-capacity powder milling
Optimize your powder milling process with efficient conical milling systems ...

Atex compliant milling equipment for explosive atmospheres
Ensure operator safety and process integrity with milling equ...
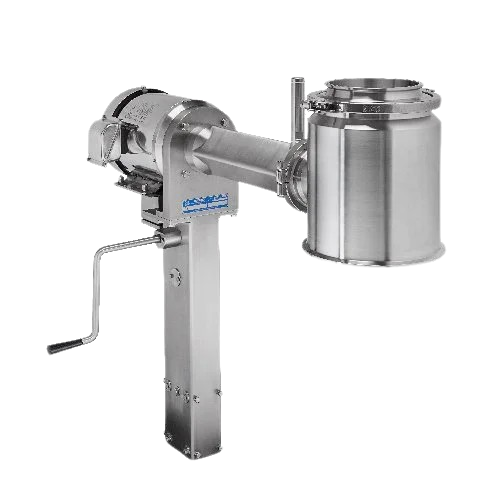
Cone mill for size reduction
Achieve precise particle size reduction and deagglomeration with minimal heat generation, ensur...
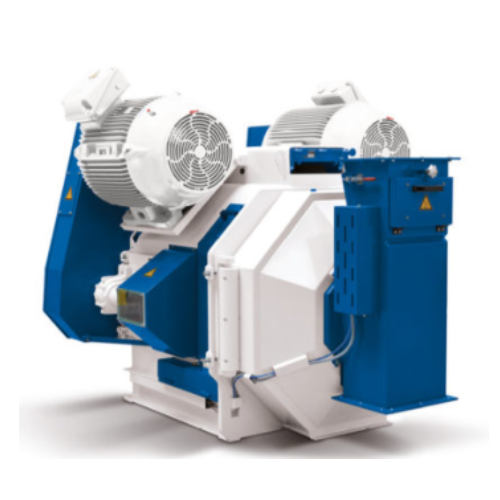
Pellet mill for high efficiency animal feed production
Achieve stable, vibration-free pellet production with enhanced ene...
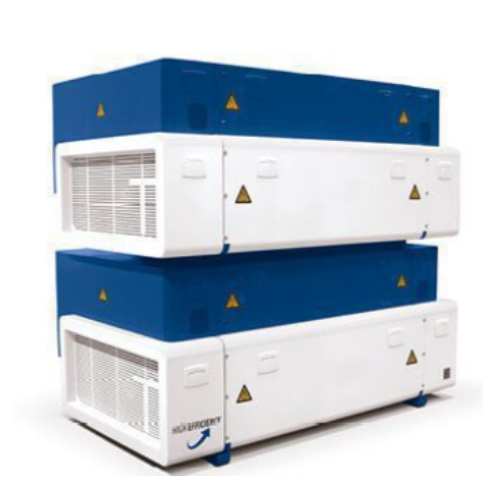
High efficiency roller mill for grain and oilseeds
Optimize your crushing and grinding processes with a versatile roller ...
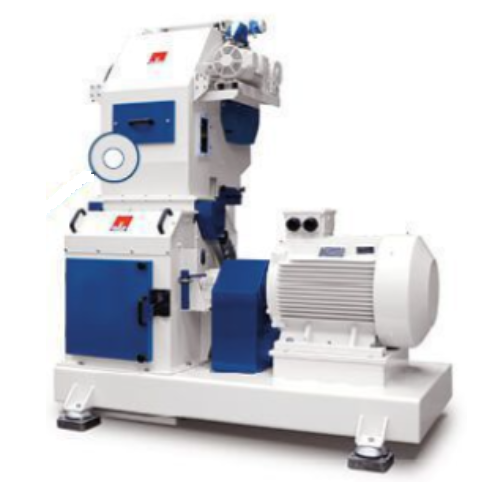
Industrial hammer mill for granulate grinding
Optimize the grinding process in feed production with a high-efficiency solu...

Hammer mill for efficient particle size reduction in feed mills
Optimize your feed milling operations with this hammer m...
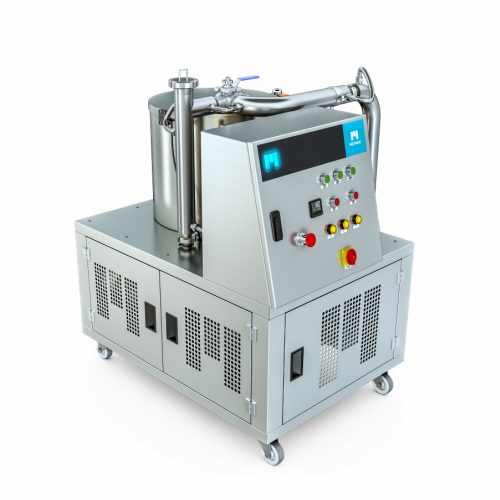
Laboratory type ball mill for chocolate and bakery applications
Optimize your R&D processes with precise grinding a...
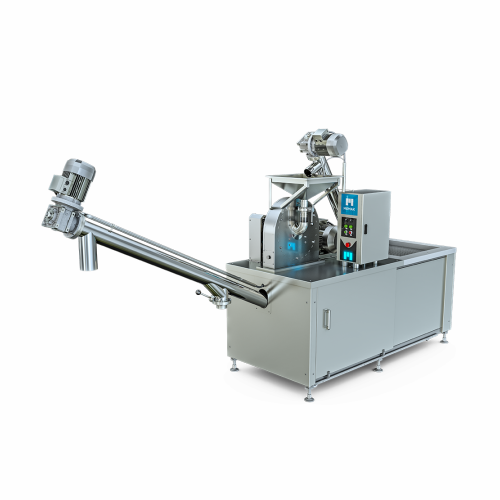
Industrial sugar powder mill
Achieve precise sugar granulation with a high-speed mill designed for continuous production, en...
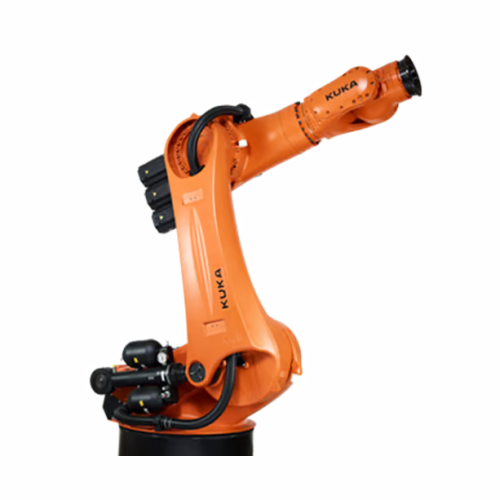
Heavy-duty industrial robot for precision milling
Designed for seamless integration in heavy-duty tasks, this robotic sol...
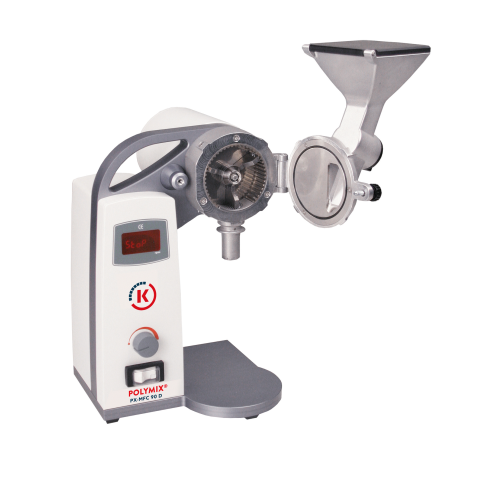
Laboratory mill for dry sample preparation
Achieve precise particle size reduction for pharmaceuticals and fine chemicals ...
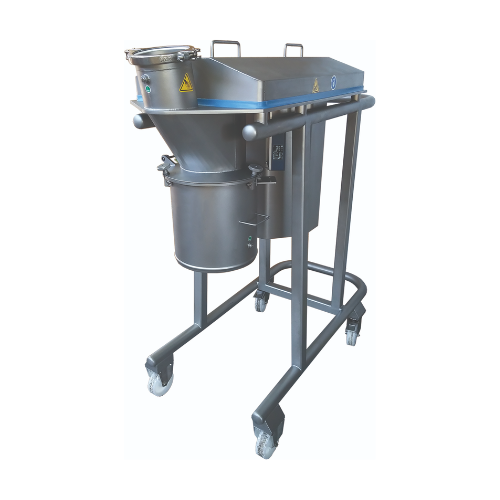
Versatile cone mill for uniform size reduction
Achieve precise particle size consistency and gentle deagglomeration across...
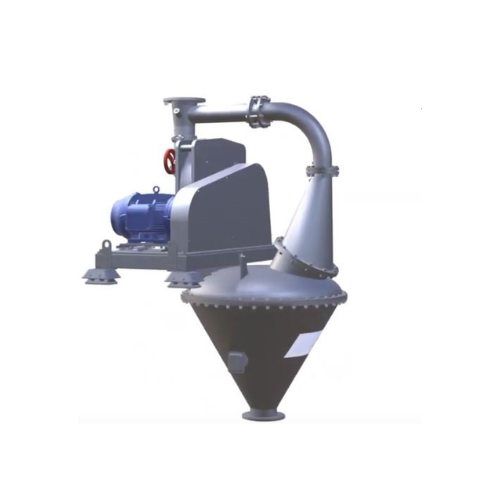
Universal mill for fine grinding in food and pharma industries
Achieve unparalleled particle size reduction with high-pe...
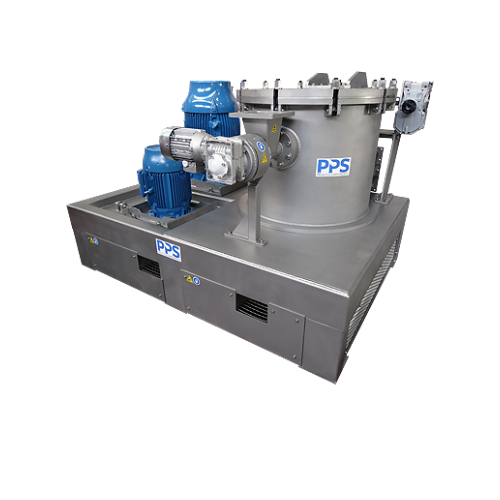
Air classifier mill for ultra-fine powder grinding
Optimize your milling operations with precision particle size control ...
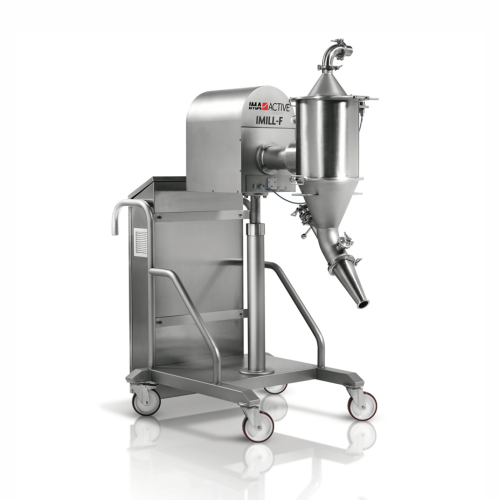
Cone mill for particle size reduction in pharmaceuticals
Achieve precise particle size control with this cone mill, desig...
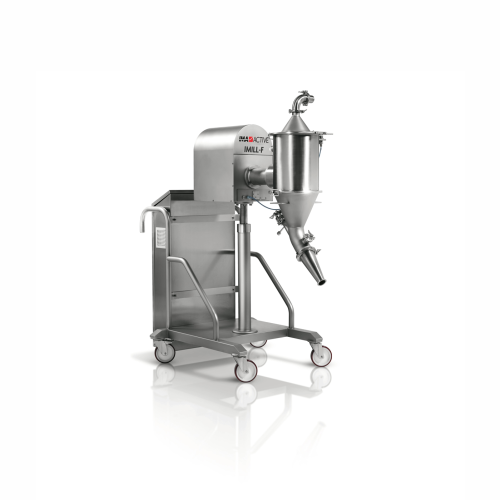
Cone mill for particle size reduction
For precise particle size reduction, the cone mill offers flexible screening options ...

Table roller mills for mineral raw material comminution
Achieve precise mineral raw material comminution and energy-effic...
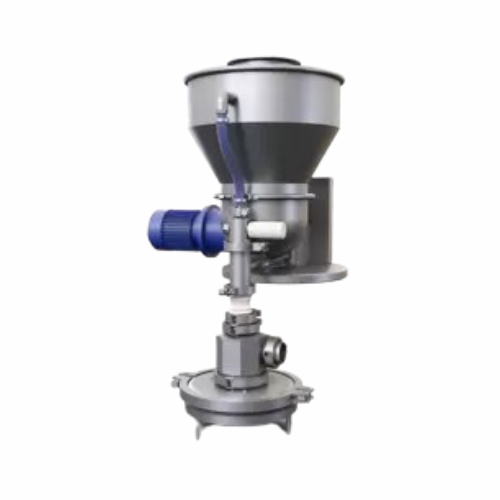
Ultra-fine grinding jet mill for coarse and fibrous materials
Effortlessly achieve ultra-fine particle sizes in coarse a...
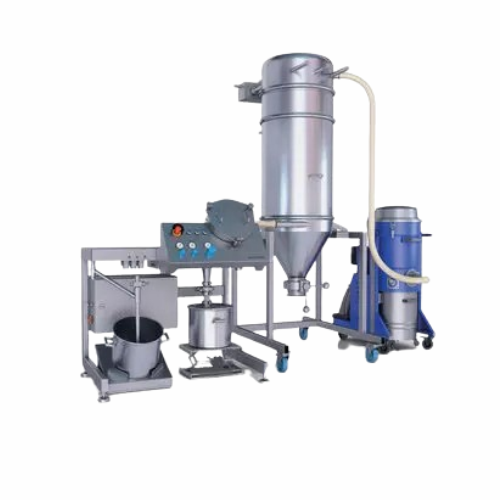
Spiral jet mill for ultrafine micronisation
Optimize your powder processing with precision-driven micronisation that ensur...
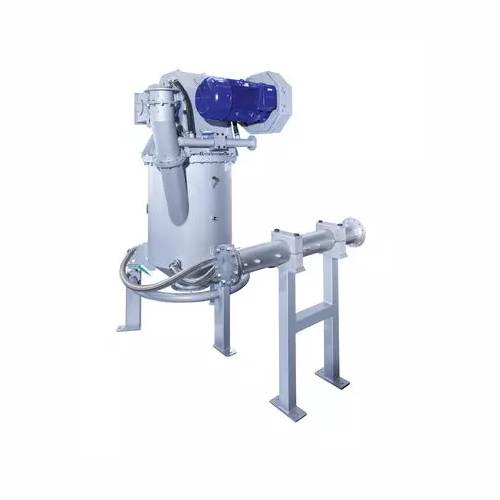
Fluidised bed opposed jet mill for fine particle processing
Achieve precise and consistent particle sizes with high-spee...
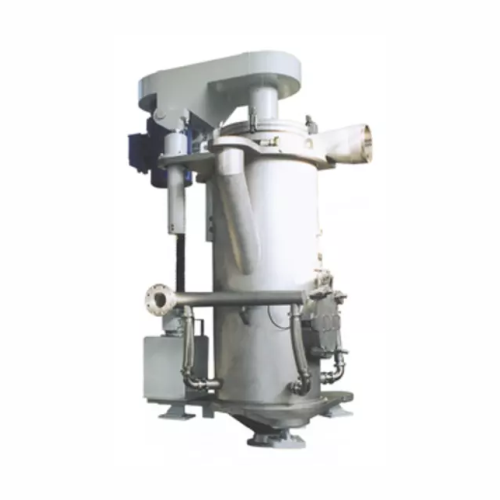
Jet mill for toner and pigment industries
Optimize particle size and distribution for high-demand applications with this h...

High-speed hammer mill for continuous operation
Achieve precise particle size reduction with high-speed hammer milling, id...
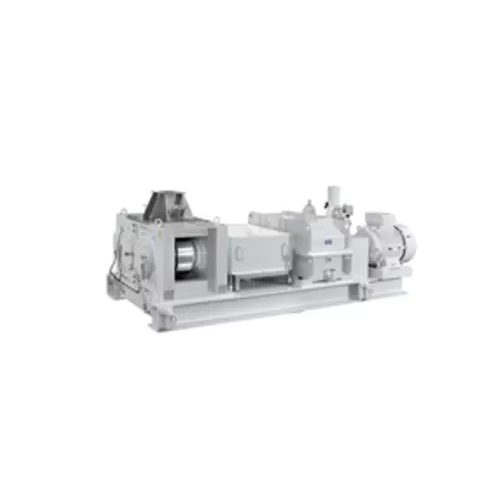
High pressure roller mill for medium-fine crushing
Achieve precision in particle size with high-pressure roller mills, id...
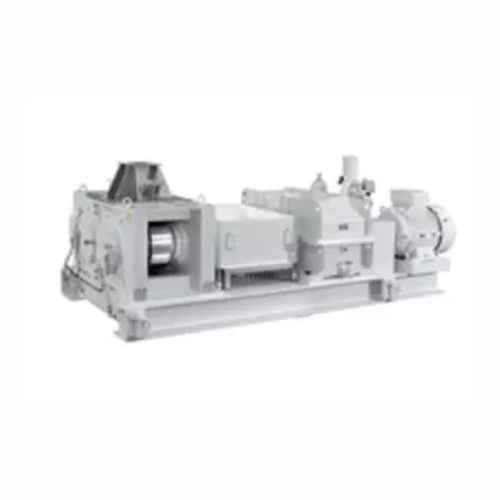
High-pressure roller mill for medium-fine crushing
Achieve precise granule distribution in medium-fine crushing applicati...
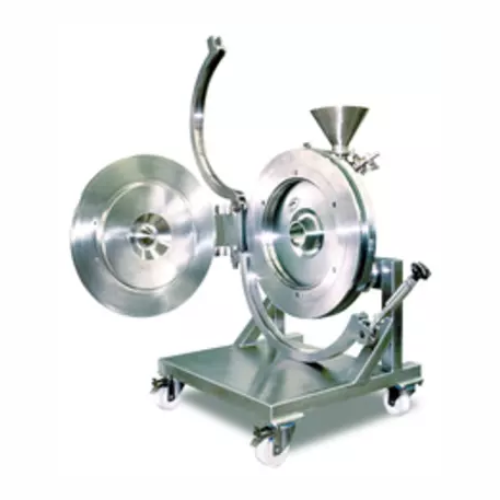
Spiral jet mill for superfine powder production
Achieve consistent ultra-fine powder with precise particle size control, c...
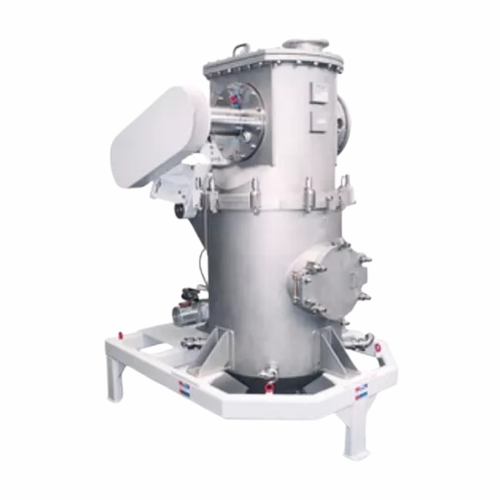
Fluidised bed opposed jet mill for ultrafine powder production
Achieve contamination-free ultrafine powder milling with ...
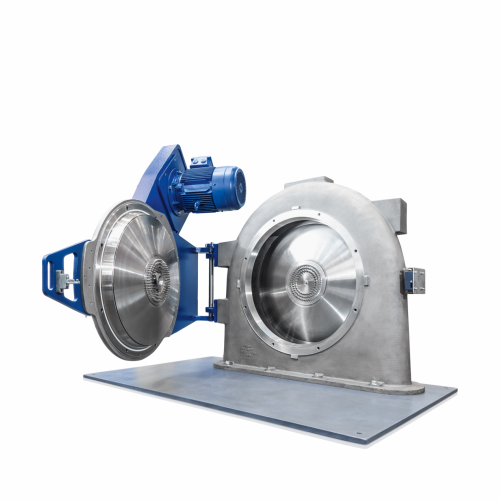
Pin mill for fine grinding of sticky materials
Achieve ultra-fine grinding of challenging materials with high speed and pr...
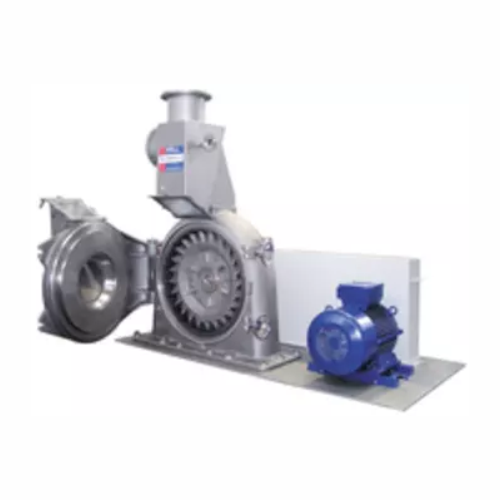
Versatile fine impact mill for soft materials
Achieve precision grinding with flexibility for a wide range of materials, e...
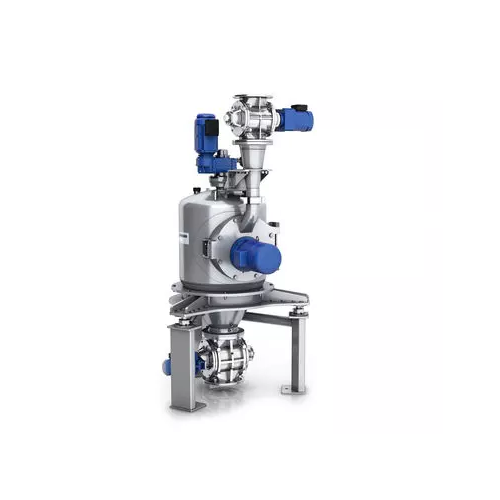
Fine impact mills for particle size reduction
Achieve precise particle size reduction with fine impact mills, essential fo...

Dry grinding mill for superfine products
Achieve high fineness in your comminution processes with this advanced dry grindin...
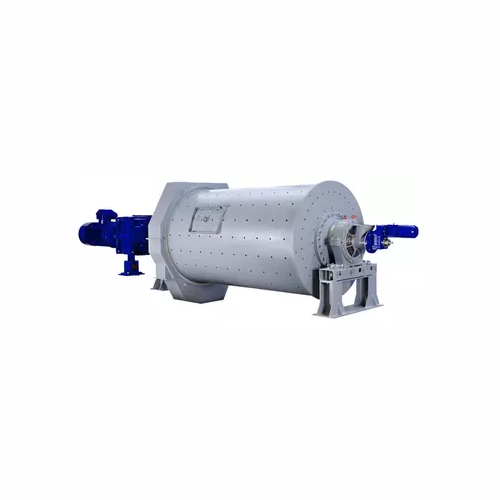
Ball mill for dry comminution of hard materials
Achieve ultrafine particle sizes and precise material breakdown with this ...
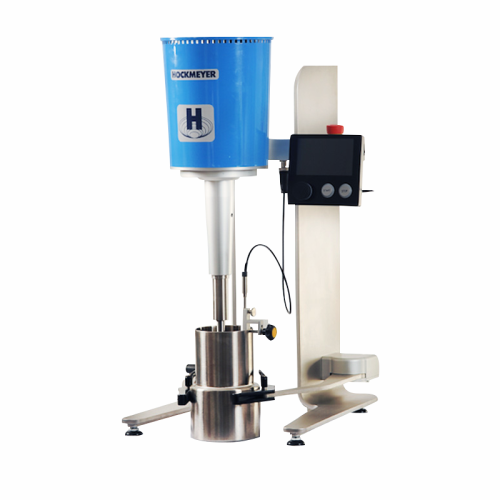
Lab and pilot scale immersion mill
Maximize process efficiency with a compact immersion mill designed for precise milling, ...
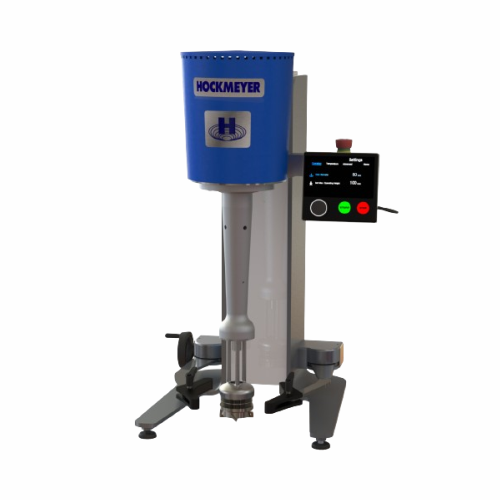
Lab-scale disperser and immersion mill
Achieve precise dispersing and milling with rapid changeover capabilities, ideal for...
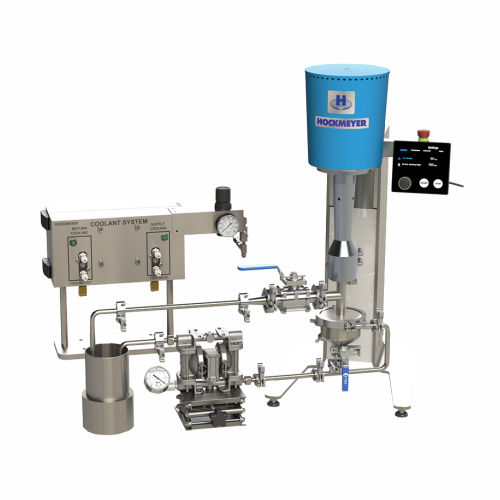
Laboratory vacuum milling for fine particle size reduction
Streamline your lab and pilot processes with high-speed vacuu...
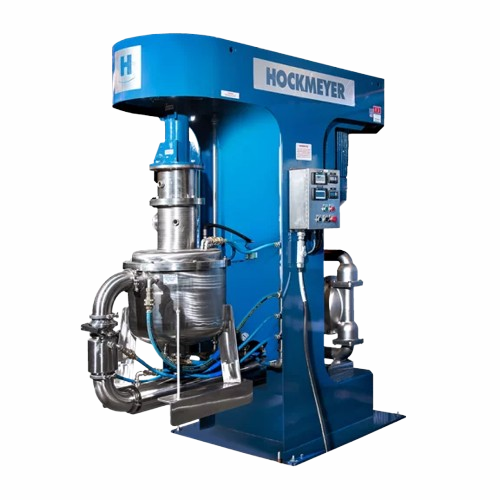
Vacuum recirculation mill for particle size reduction
Achieve precise particle size reduction and eliminate air entrapmen...
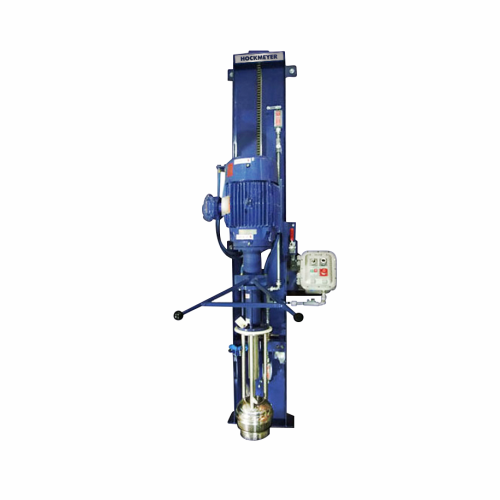
Immersion mill for pail and drum-sized batches
Streamline your production with a versatile solution that efficiently handl...
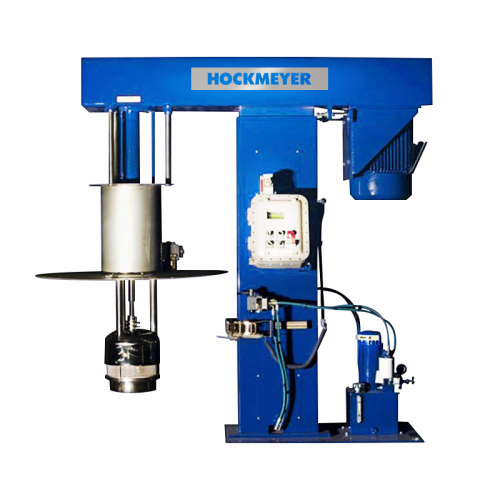
Immersion mill for particle reduction
Achieve streamlined particle size reduction and enhanced mixture homogeneity with imm...
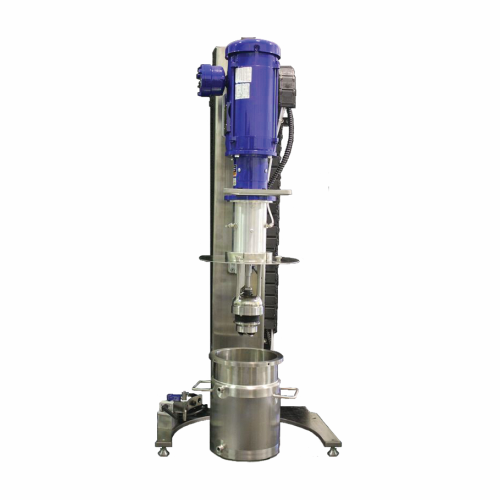
Immersion mill for lab to production scaling
Achieve consistent quality from lab to production with precision milling, mix...

Nanoparticle production immersion mill
Achieve precise nanoparticle production with immersive milling that enhances materia...
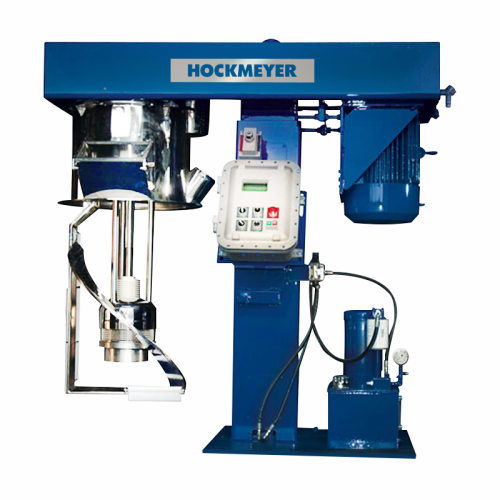
Immersion mill with sweep blade for high-viscosity products
Optimize your production line with this immersion mill desig...
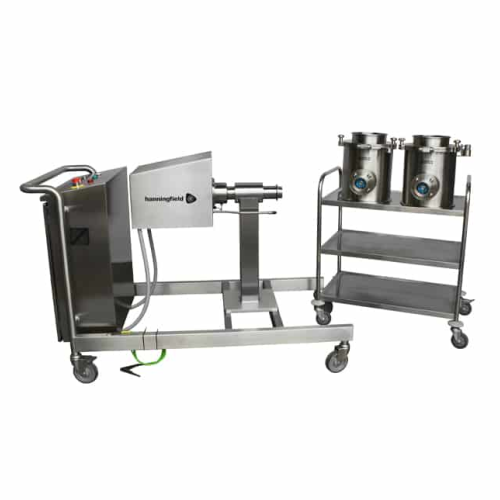
Particle sizing solution for milling and sifting
Streamline your milling and sifting processes with a flexible system desi...
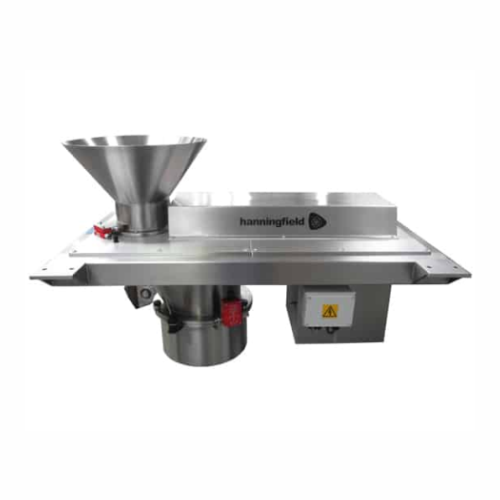
Conical mill for particle size reduction
Achieve precise particle size control and reduce thermal stress on materials with ...
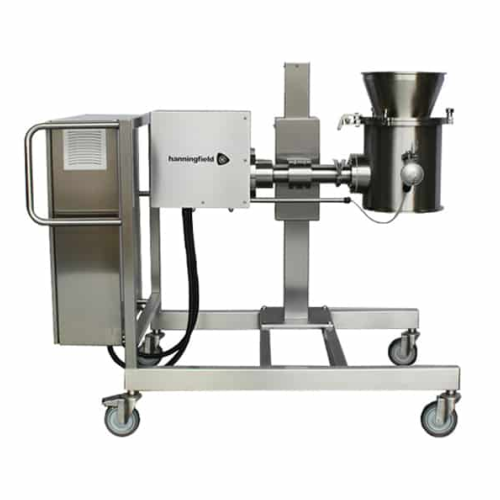
Conical mills for size reduction in pharmaceutical production
Achieve precise particle size control with an innovative m...
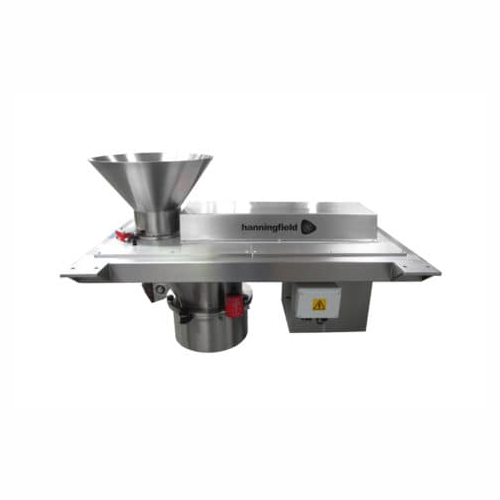
Over-driven conical mills for precise particle size reduction
Achieve consistent particle size reduction with minimal he...
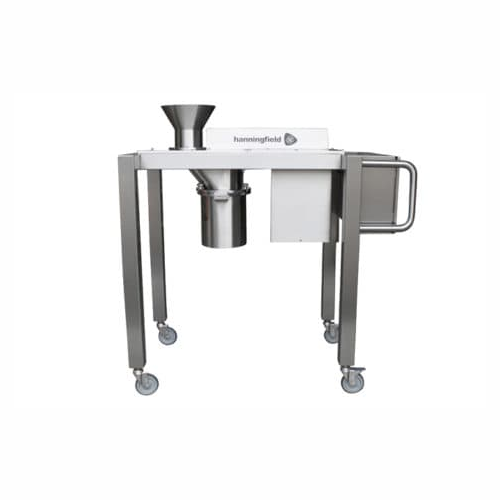
High capacity conical mill for powder processing
Optimize your milling process with a versatile solution that ensures prec...
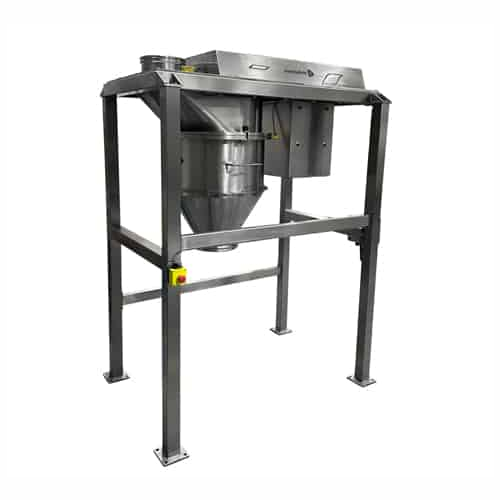
High capacity production milling for bulk materials
Optimize your production with our high-capacity milling solution, des...
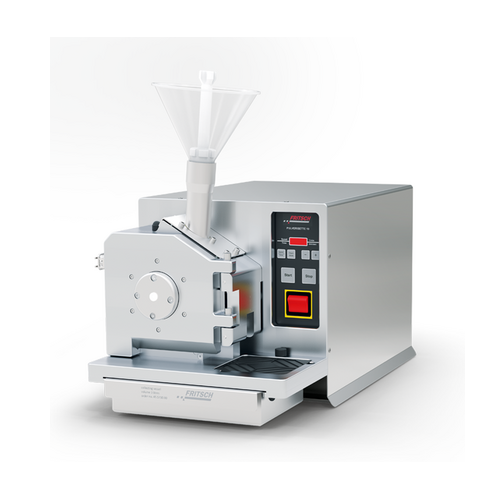
High-speed cutting mill for versatile material comminution
Efficiently transform diverse materials like plastics, textil...
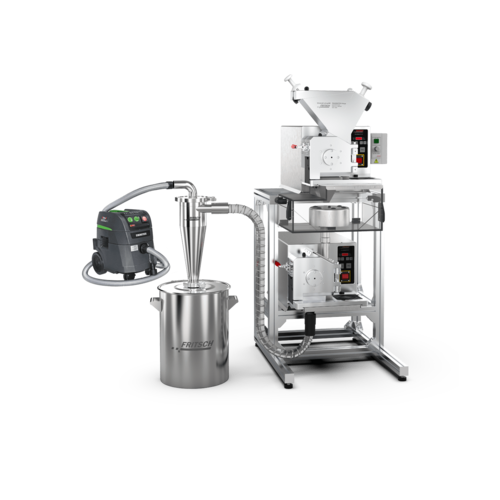
Cutting mill combination for heterogeneous material reduction
Achieve precise size reduction and material separation in ...
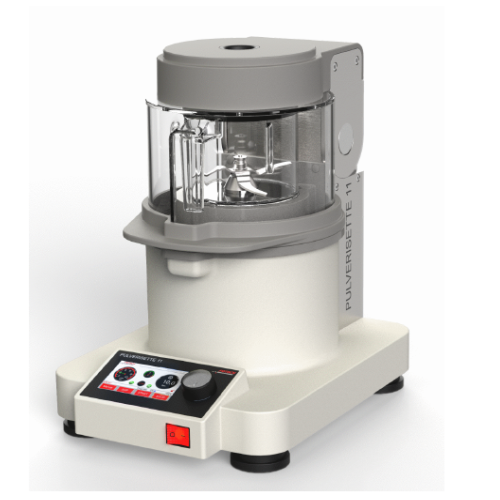
Laboratory knife mill for fast comminution
Achieve rapid and precise sample preparation with this versatile knife mill, de...
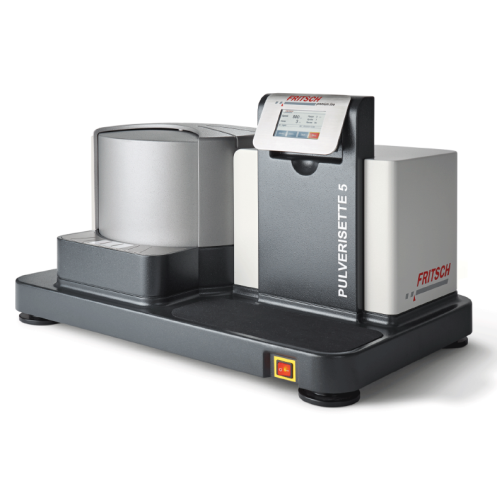
Planetary mill for nano grinding
Achieve precise nano-scale particle production and uniformity for demanding research enviro...
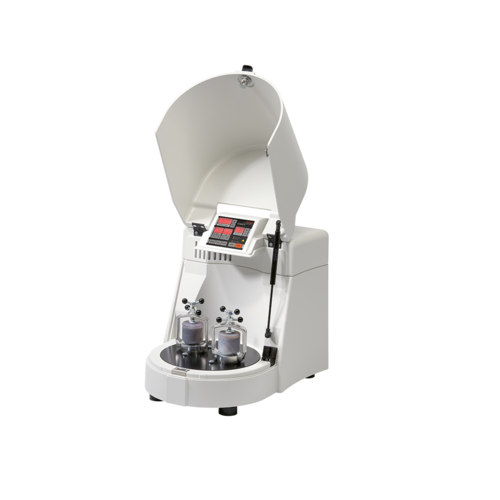
Planetary micro mill for fine comminution
Achieve unparalleled precision in micron-level materials processing with this co...
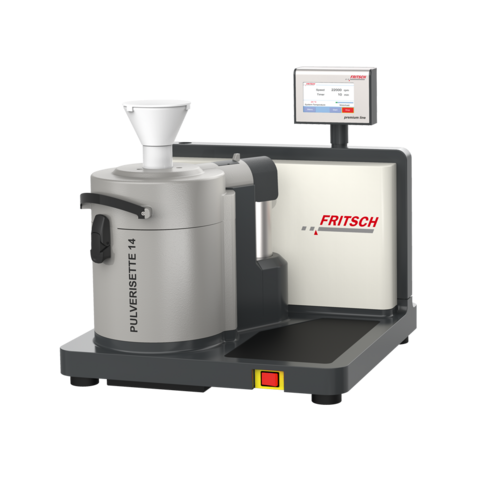
Variable speed rotor mill for sample preparation
Achieve rapid and precise grinding of various materials with a versatile ...
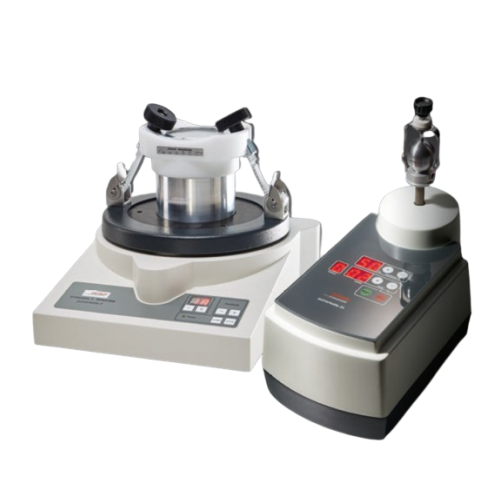
Vibratory micro mill for fine comminution
Achieve precise particle size reduction and homogeneity for medium-hard to britt...
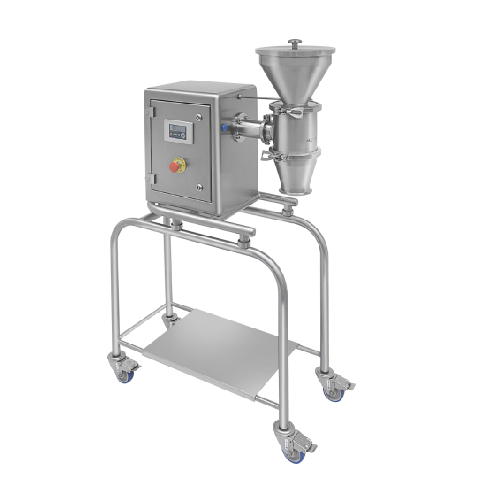
Laboratory conical screen mill for powder calibration
Achieve precise particle size control with this compact laboratory ...
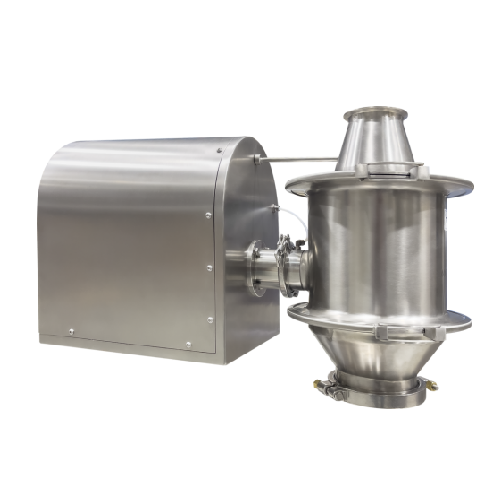
Conical screen mills for powder calibrating
Achieve precise particle size distribution for your powders and granules with ...
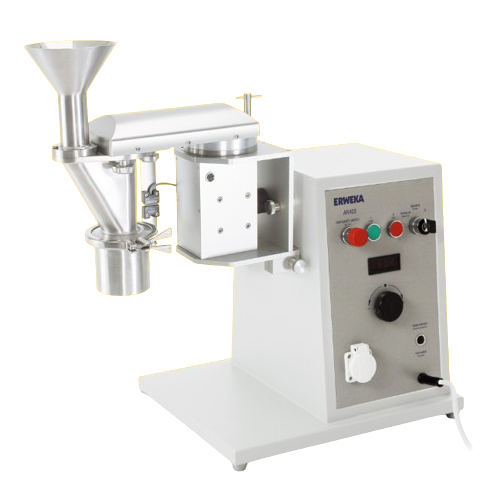
Conical mill for particle size reduction and homogenization
Achieve precise particle size reduction and homogenization w...
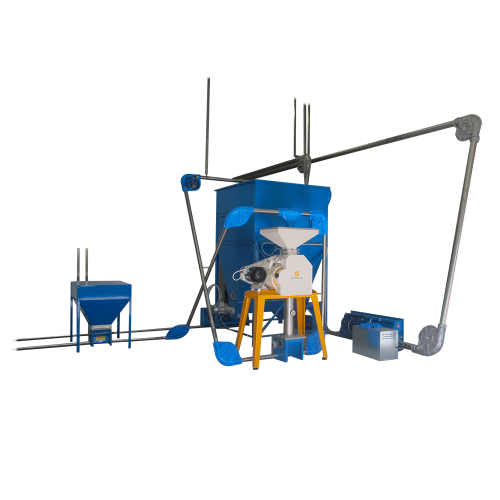
Malt transport and milling system for breweries
Streamline your brewing process with advanced malt transport and milling s...
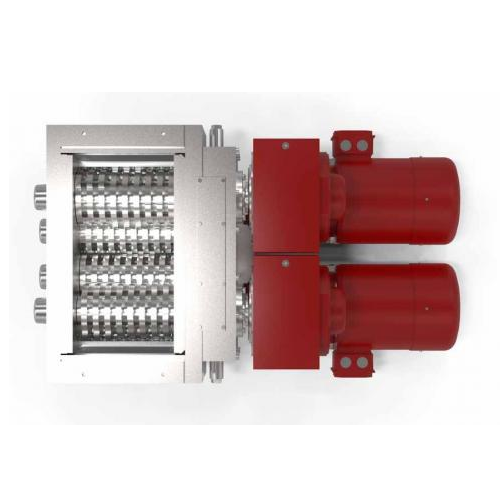
Industrial roller mill for grain size reduction
Achieve precise grain size reduction with minimal heat generation and opti...
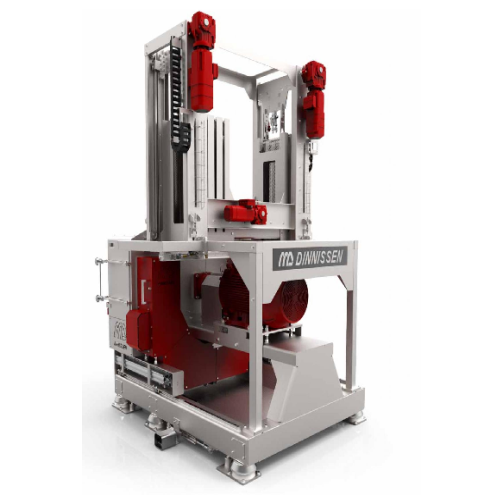
Hammer mill with automatic screen exchange
Optimize your milling operations with a high-speed solution that ensures seamle...
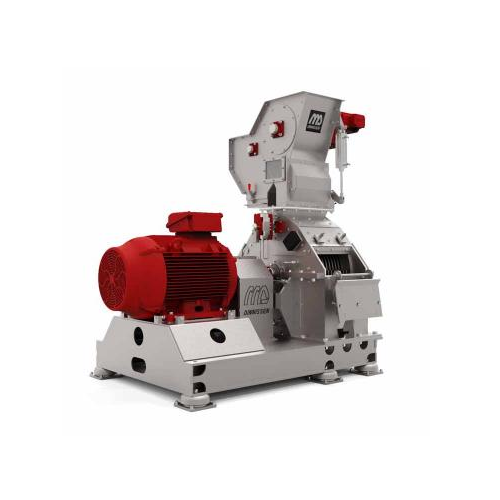
Industrial hammer mill for grinding and sifting
Ensure precise particle size reduction and consistent product quality with...
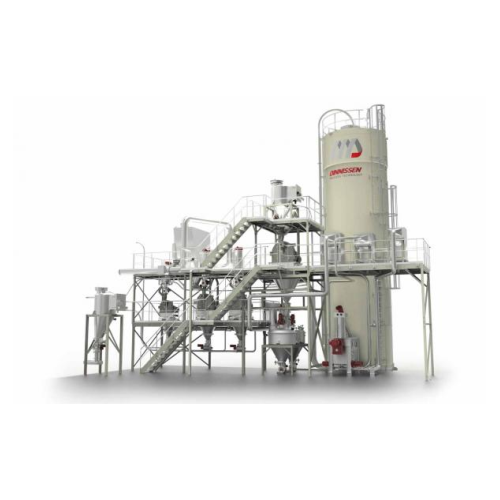
Centrifugal mill for fine grinding in industrial processes
Achieve exceptional fineness without overheating your materia...
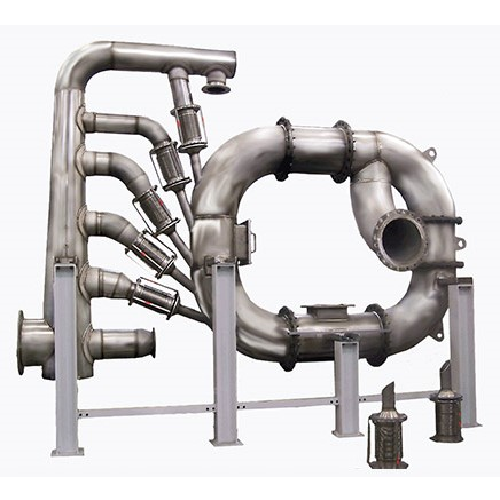
Milling flash dryer for fine powder processing
Achieve precise moisture control and prevent agglomeration in your processi...
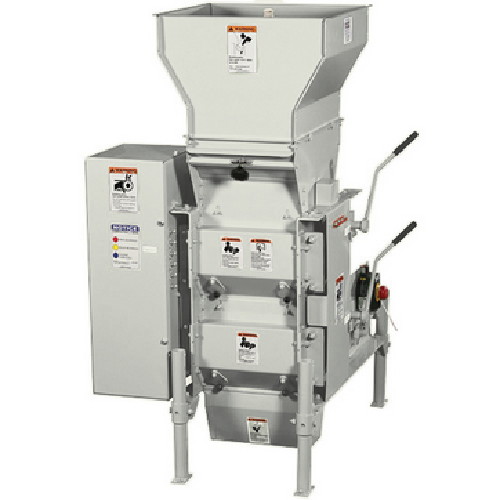
Efficient barley malt crushing with roller mills
Achieve precise particle size control in your processing line with a robu...
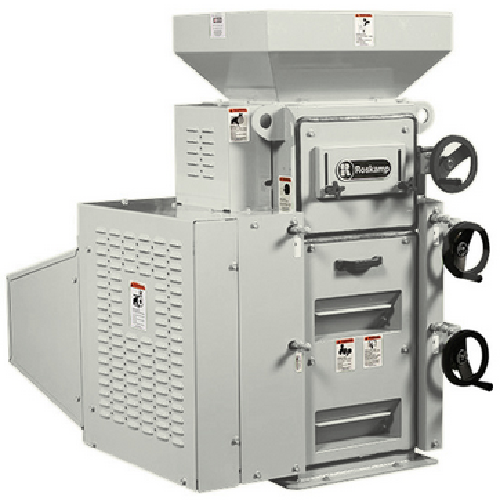
Industrial roller mill for barley malt crushing
Ensure precise barley malt crushing with minimized maintenance for enhance...
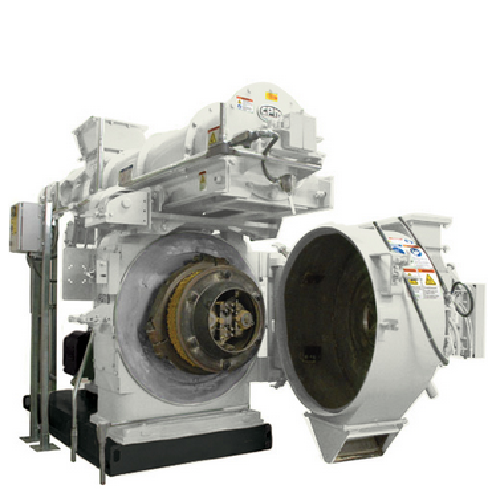
Small-scale pellet mill for animal feed production
Achieve precise pellet formulation for diverse feedstocks with an effi...

Pellet mills for feed, plastics, and industrial products
Optimize pelleting output across diverse materials with precisio...
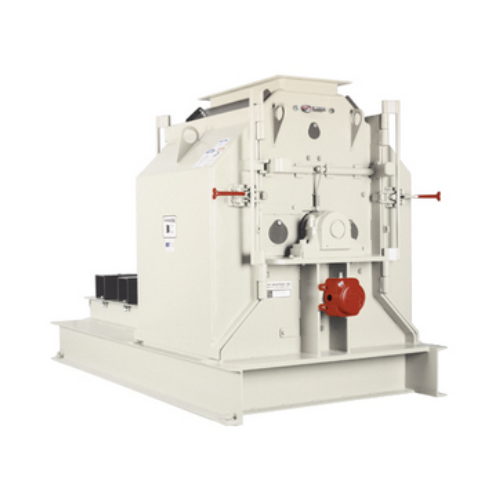
Hammermills for grinding tough products
Optimize particle size reduction with precision-designed hammermills that efficient...
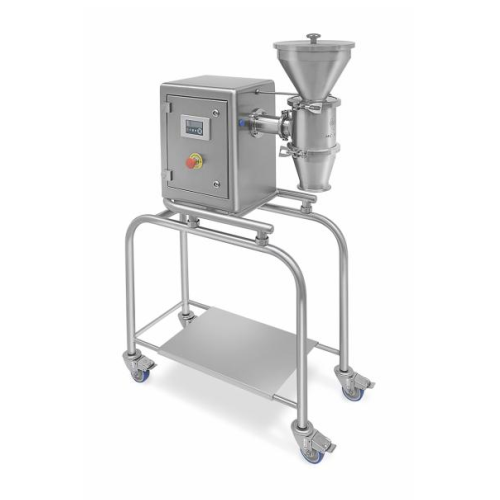
Laboratory cone mill for even grinding
Achieve consistent particle size for laboratory powders with precision calibration a...
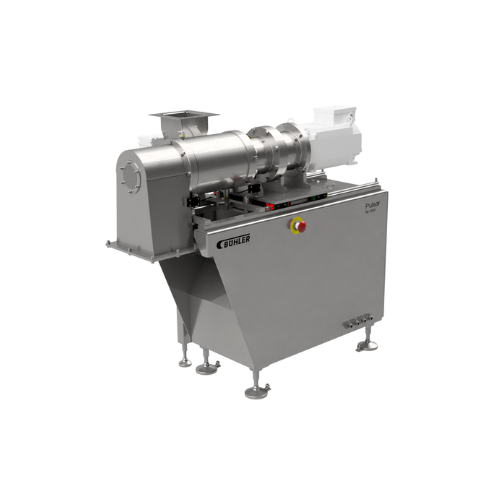
Universal mill for grinding nuts and seeds
Optimize your nut paste production with a high-speed, versatile milling solutio...
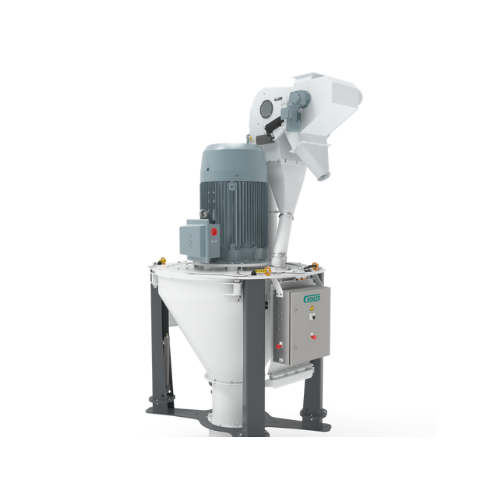
Vertical hammer mill for feed and grain processing
Optimize your milling operations and improve energy efficiency with th...
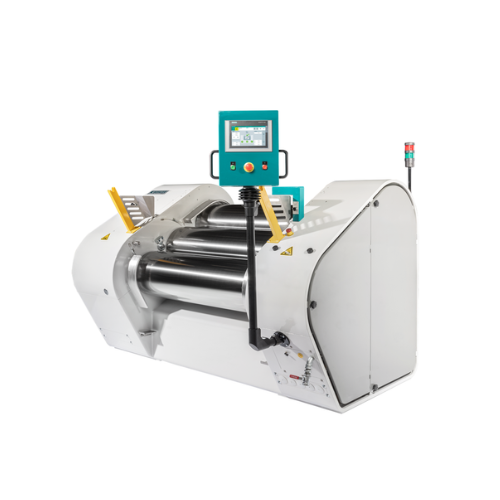
Industrial three-roll mill for high-quality grinding
Achieve unparalleled precision in grinding and dispersing with our a...
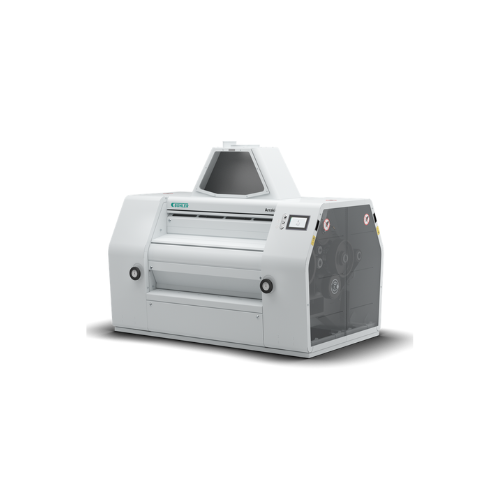
Four-roller and eight-roller mill for wheat and grain grinding
Optimize your grinding operations with this versatile rol...
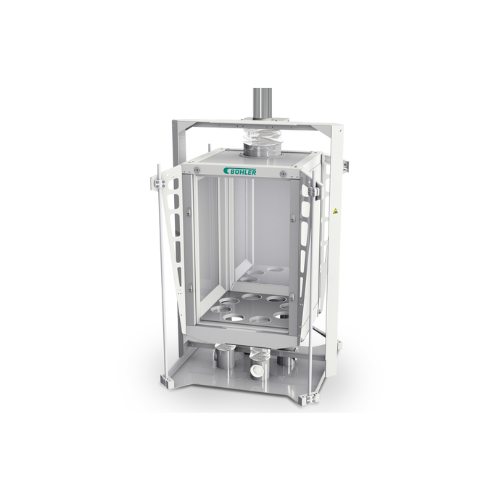
Grain sifter for milling applications
Optimize your grain processing by efficiently sifting and sorting a variety of produc...
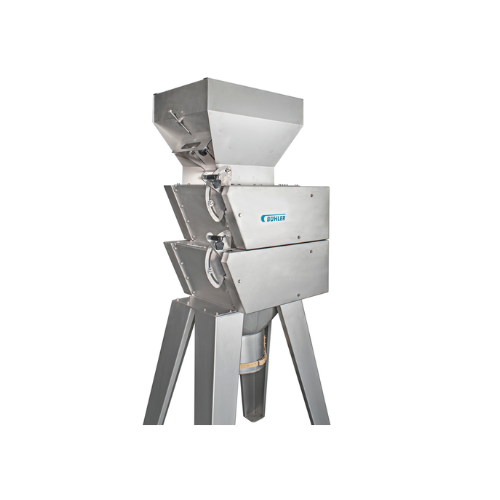
Grist mill for craft and small breweries
For breweries seeking precision grinding, this compact grist mill excels in millin...
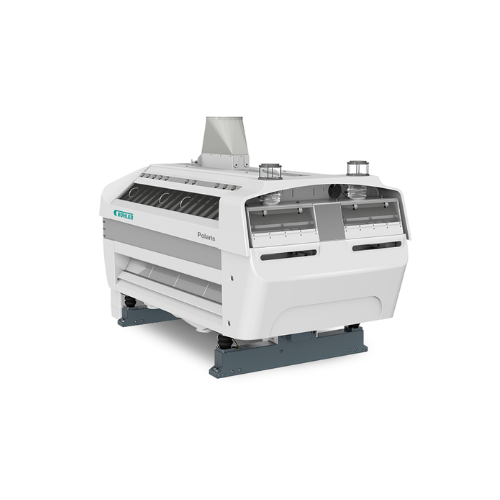
Grain purifier for wheat and corn milling
Optimize grain processing with a high-throughput purifier designed to enhance pu...
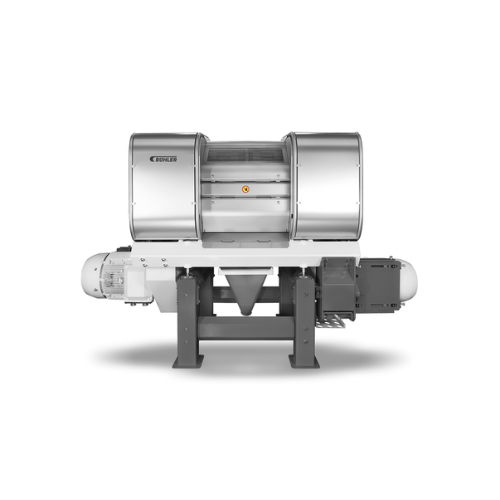
Flaking mill for grain and cereal production
Achieve consistent flake thickness and high throughput with advanced roller t...
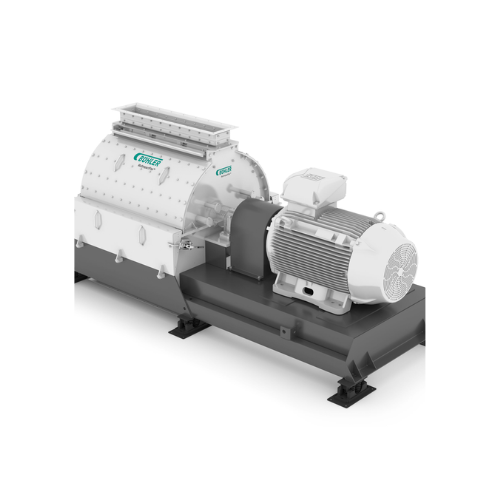
Hammer mill for fine grinding in food and feed industries
Achieve exceptionally fine particle-size distribution with a h...
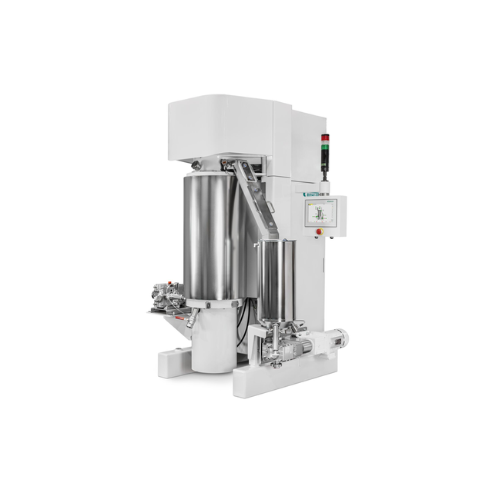
Ball mill for chocolate, cocoa, and nut products
Optimize your grinding processes and achieve perfect product consistency ...
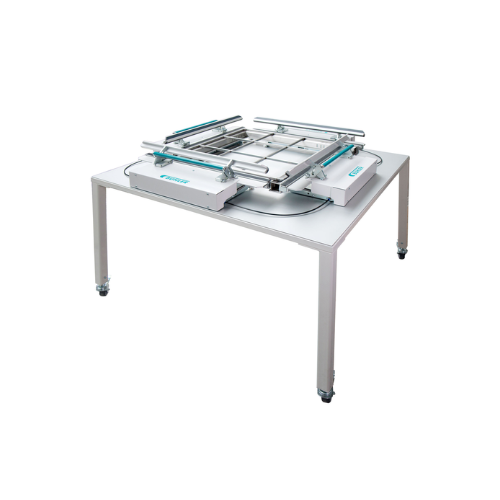
Sieve tensioning device for milling applications
Achieve precise and consistent tensioning across various sieve frames wit...
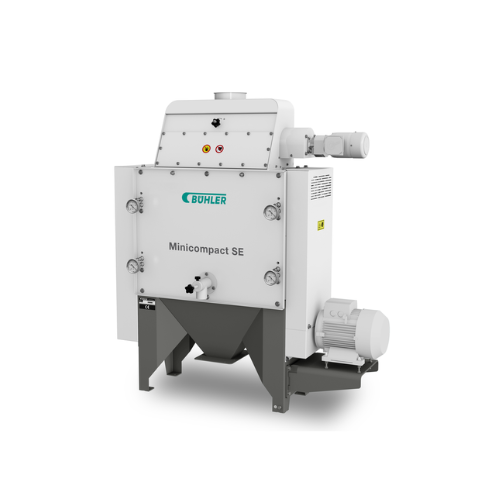
Grist mill for craft breweries and distilleries
Optimize your brewing and distilling efficiency with a compact, high-speed...
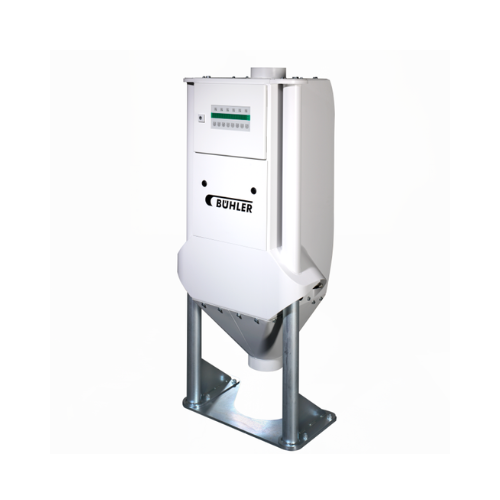
Moisture control system for grain milling
Optimize moisture levels precisely within your grain milling process, ensuring c...
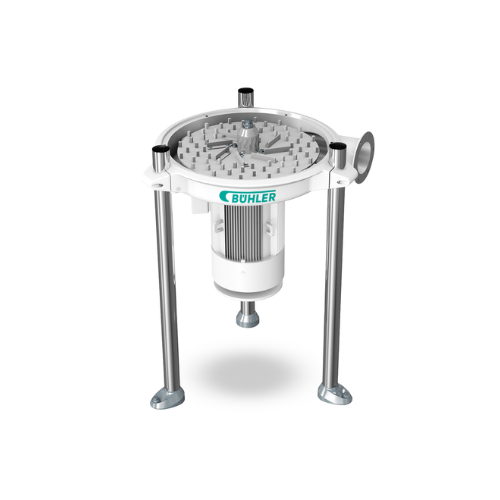
Impact machine for milling applications
Optimize your grain processing with this versatile impact machine, designed to refi...
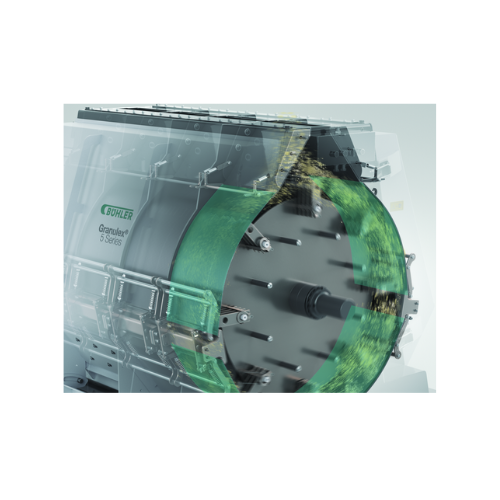
Horizontal hammer mill for grain processing
Optimize your grinding processes with our horizontal hammer mill, designed to ...
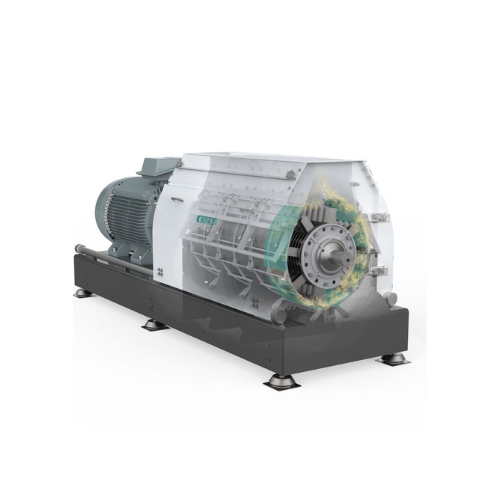
Industrial hammer mill for size reduction in food and feed processing
Achieve precise grinding and milling for diverse ...
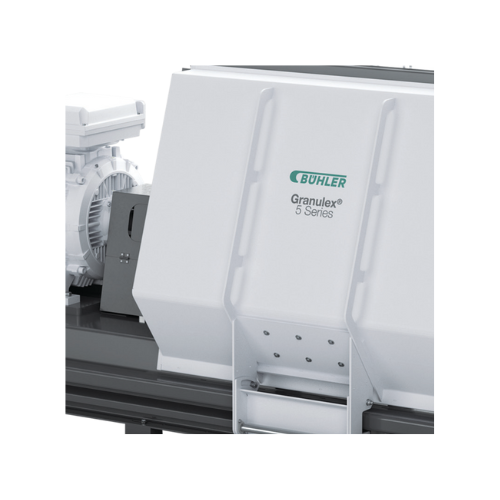
High-throughput hammer mill for animal feed production
Ideal for high-throughput operations, this hammer mill ensures pre...
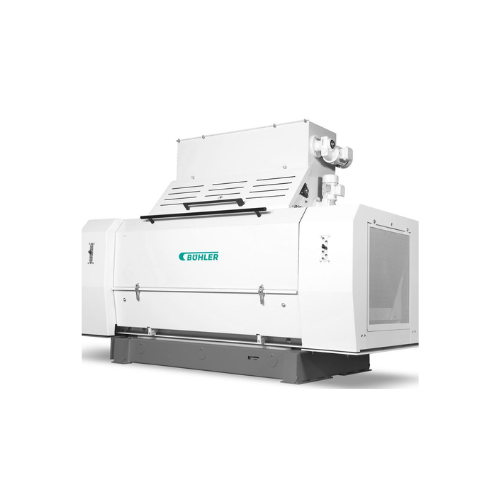
Oilseed flaking and milling system
Optimize your oilseed processing with a flaking system that enhances extraction efficien...
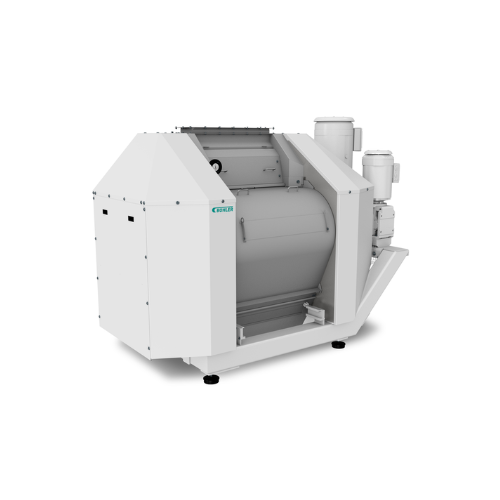
Industrial grain flaking mill
For efficient grain processing, achieve uniform flake quality with advanced temperature-contro...
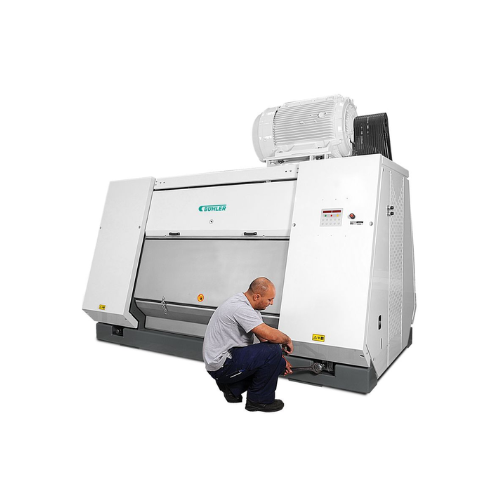
Flaking mill for oilseeds
Achieve consistent, high-throughput flake production with precise thickness control, ideal for enh...

Four-roller and eight-roller mill for grains
Optimize your grain processing with precise roller configurations, ensuring c...
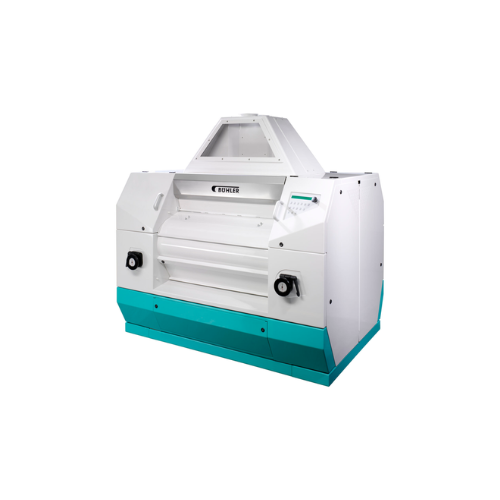
Roller mill for wheat and grain milling
Achieve consistent and high-quality grain milling with this robust, operator-friend...
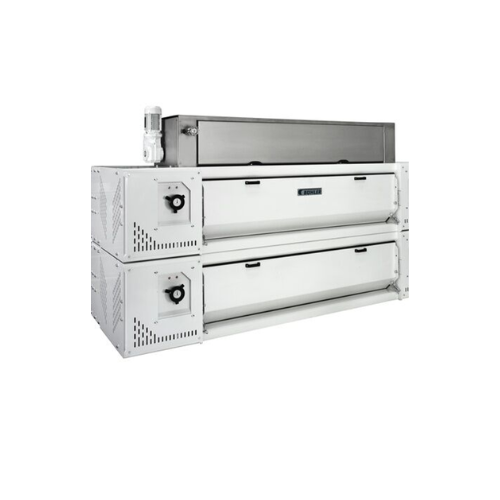
High-performance cracking mill for oilseeds
Optimize your oilseed processing with a versatile mill designed to enhance eff...
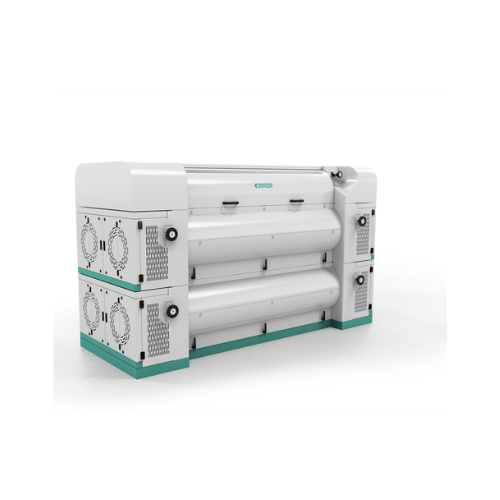
Cracking mill for oilseeds and feed
Enhance your production efficiency with a cracking mill that optimizes throughput and m...
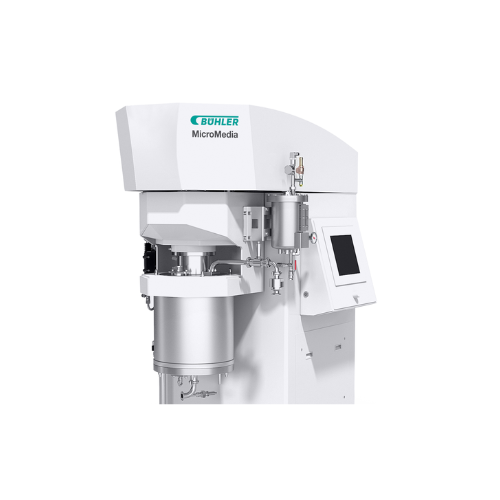
High-performance bead mill for wet grinding and dispersing
Optimize your production line with a bead mill designed for e...
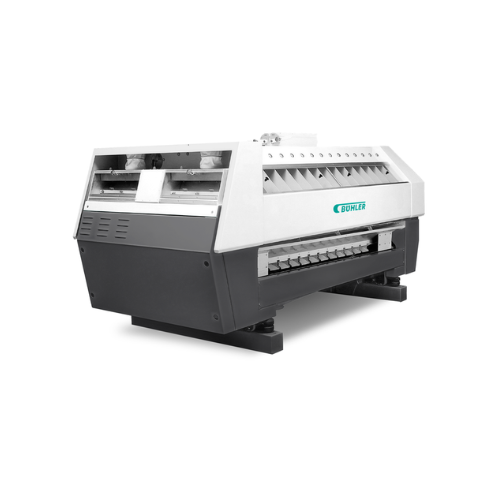
Purifier for semolina and middlings in grain mills
Upgrade your milling efficiency with a high-speed purifier that ensure...
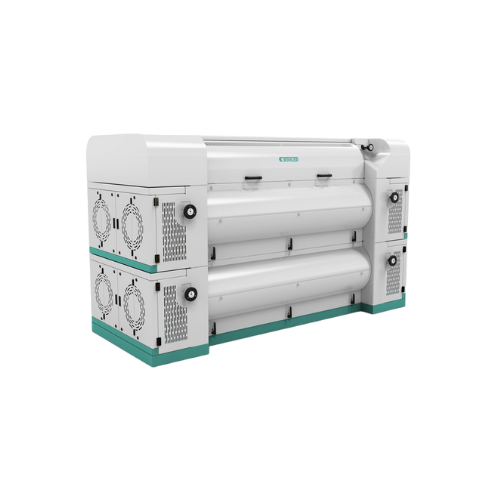
Cracking mill for oilseeds and feed processing
Maximize your production efficiency with advanced cracking and milling solu...

Hammer mill for size reduction in food and feed processing
Efficiently tackle size reduction challenges with a versatile...
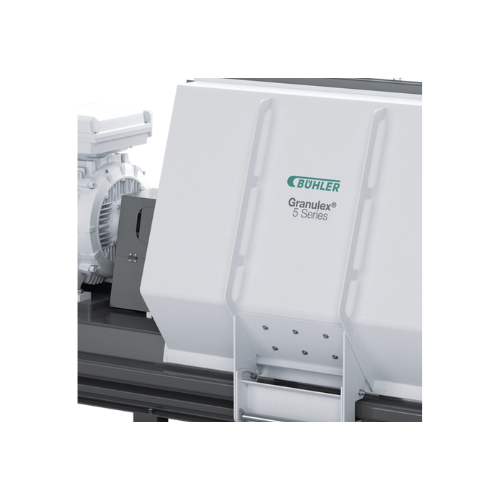
Hammer mill for animal feed grinding
Achieve precise granulation with high throughput and energy efficiency, while reducing...
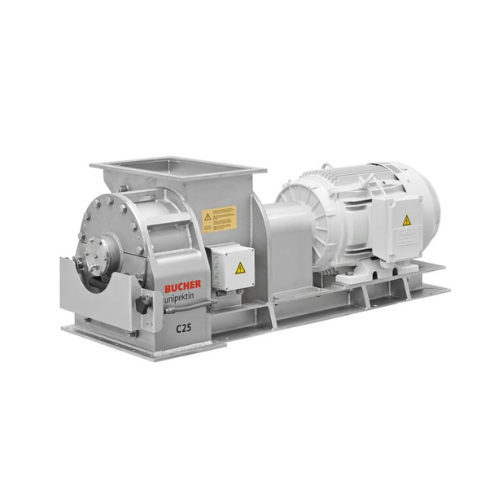
Grinding mill for apple and pear mash
Optimize your fruit and vegetable processing with a high-speed, energy-efficient grin...

Grinding mill for apples and pears
Optimize juice yield with tailored grinding for a variety of fruits and vegetables, ensu...
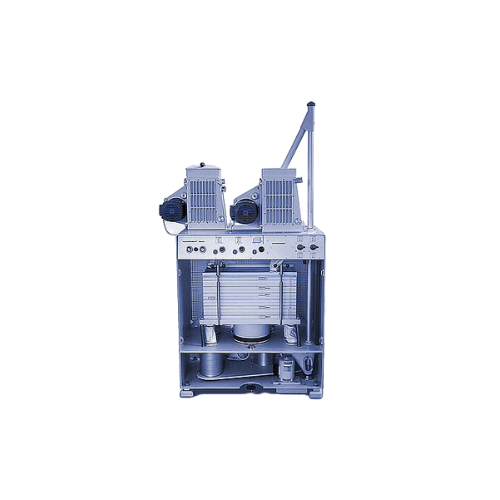
Laboratory grain milling system
Achieve precise grain milling and sample preparation with high-speed capability and gentle t...
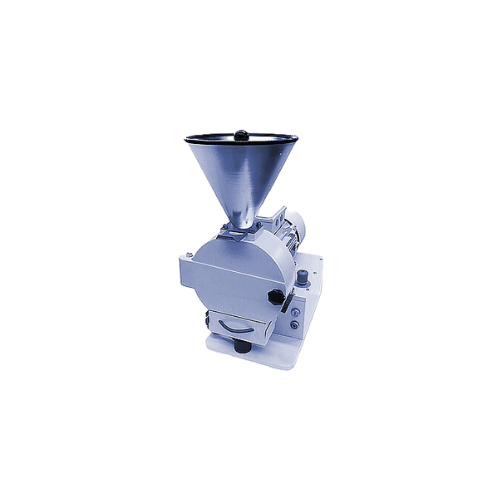
Rotary mill for tough and fibrous materials
Achieve precise material reduction with our Rotary Mill, ideal for transformin...
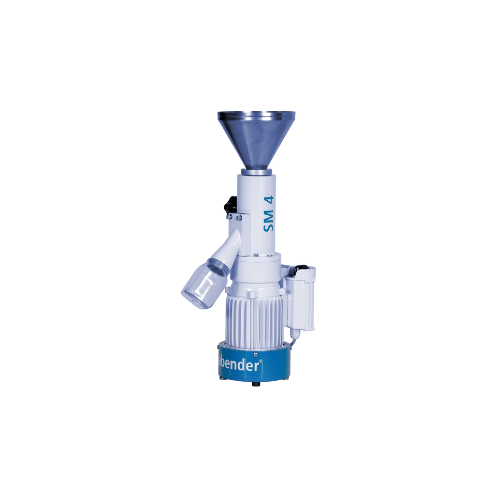
Industrial sample preparation mill
Ensure precise moisture, protein, and fat content analysis with this reliable milling so...
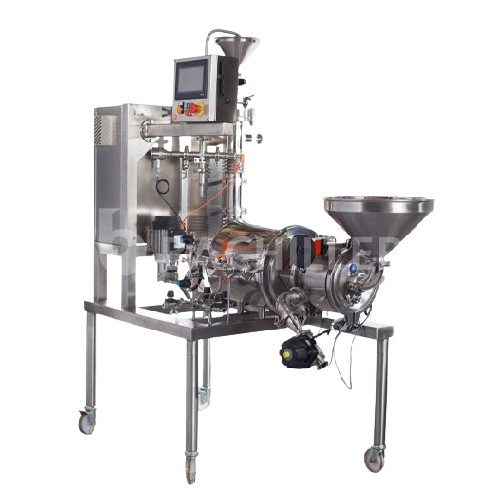
Colloidal mill for fine grinding and homogenisation
Optimize your liquid and semi-solid processing by achieving precise p...
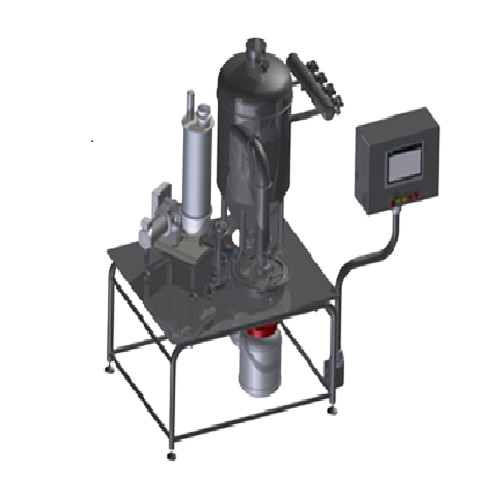
Jet mill for micronizing pharmaceutical powders
Achieve precise particle size reduction with a jet mill that leverages hig...
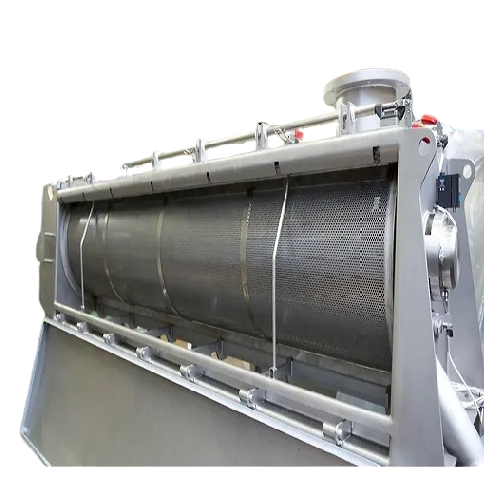
Mill sifter for precise bulk density and particle size distribution
Achieve precise particle size and uniform bulk dens...
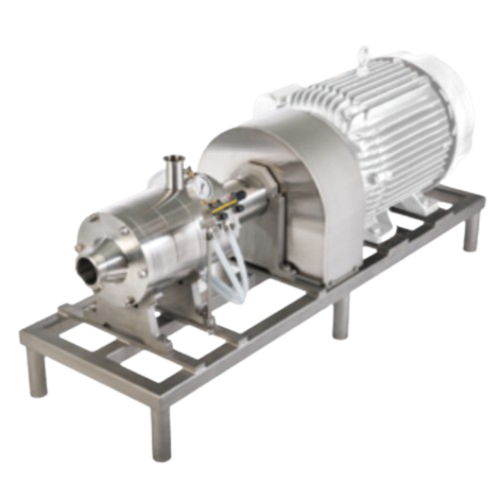
Inline wet mill for mayonnaise emulsions
Eliminate the challenges of achieving stable, uniform emulsions in your sauces and...
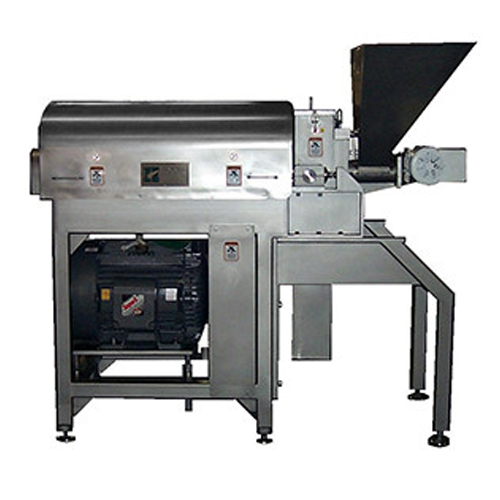
Stoneless corn masa mill for snack food processing
Achieve consistent grinding precision while eliminating the hassle of ...
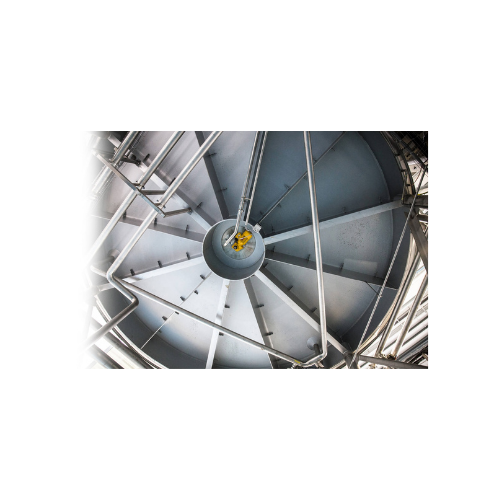
Grist milling unit for breweries and distilleries
Optimize your milling process with a versatile unit capable of handling...
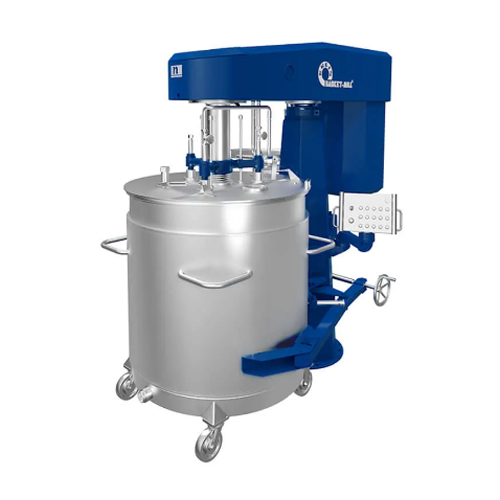
High-performance mill for paint and varnish industry
Achieve superior fine dispersing and grinding efficiency for liquid ...
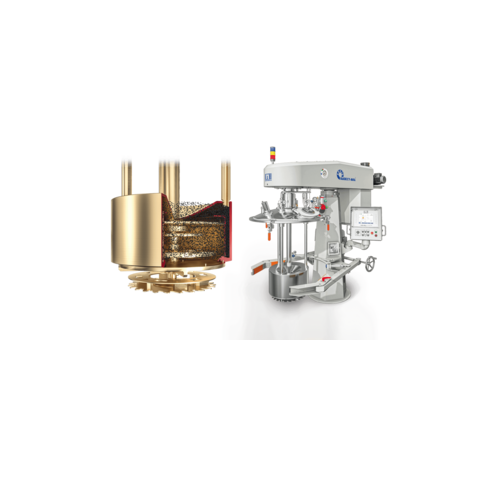
Milling beads for wet grinding in paint industry
Enhance product uniformity and grinding efficiency with specialized milli...
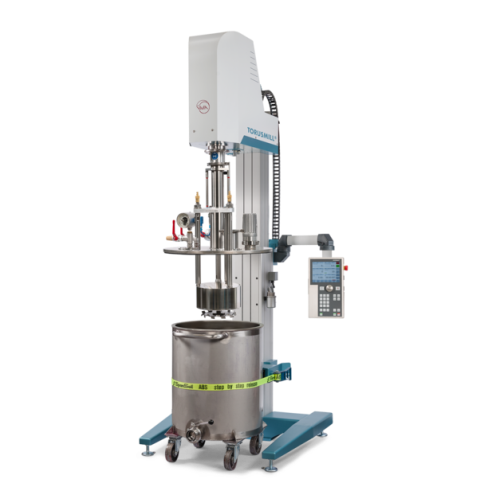
Vacuum basket mill for high-viscosity product processing
Achieve exceptional fine milling results while preventing air in...
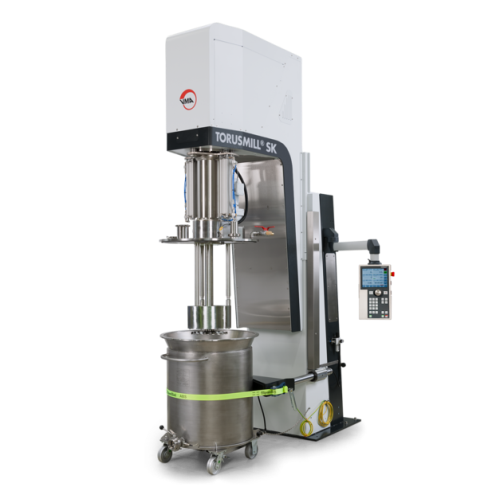
Vacuum basket mill for high viscosity products
Achieve efficient fine grinding of high-viscosity products while minimizing...
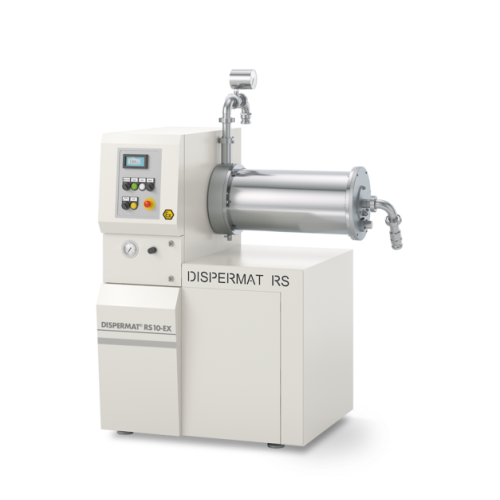
Explosion-proof bead mill for industrial grinding applications
For manufacturers seeking precise particle size control, ...
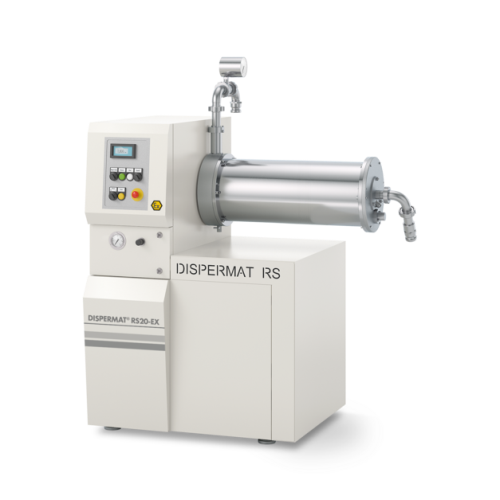
Explosion-proof horizontal bead mill for paint production
Ensure ultra-fine particle size and consistent quality with an...
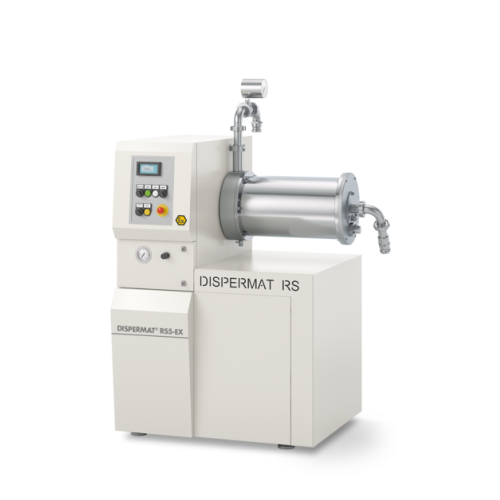
Explosion-proof horizontal bead mill
For manufacturers seeking precise particle sizing, this explosion-proof bead mill ensu...
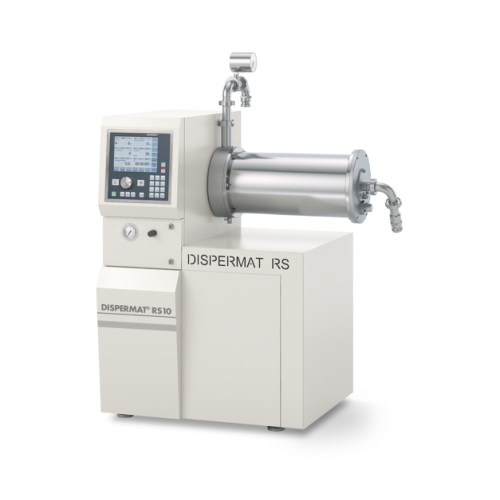
Horizontal bead mill for industrial production
Ensure ultra-fine particle size reduction in high-demand processes with thi...
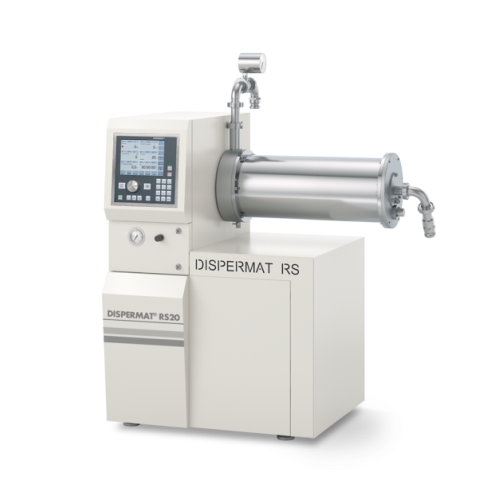
Horizontal bead mill for fine grinding in continuous process
Achieve ultrafine particle dispersion and consistent mixing...
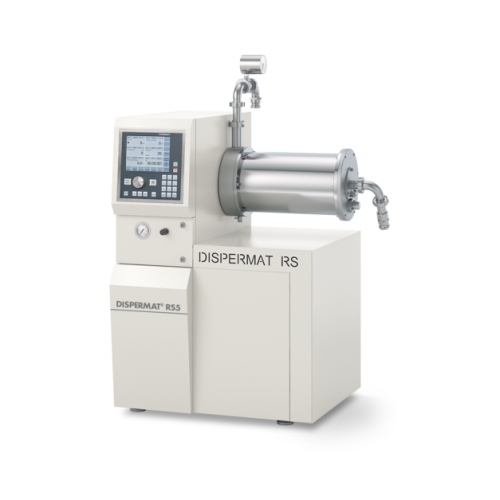
Horizontal bead mill for ultrafine particle grinding
Achieve precision in ultrafine grinding with a system that allows fo...
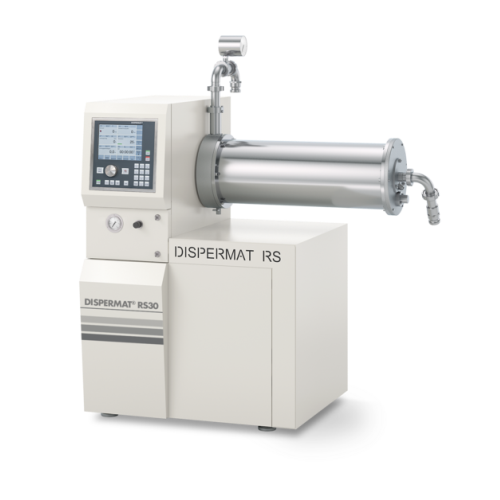
Horizontal bead mill for industrial nano grinding
Achieve precision in nano-scale grinding with this advanced bead mill, ...
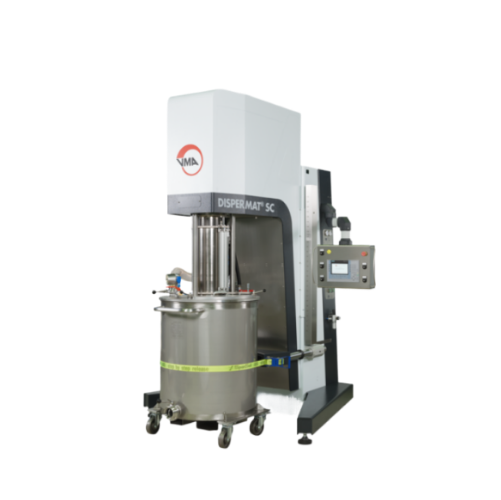
Modular basket mill for industrial dispersion
Effortlessly enhance your production efficiency with this versatile solution...

Industrial basket mill for medium viscosity products
Achieve precise particle size reduction and rapid pigment dispersion...
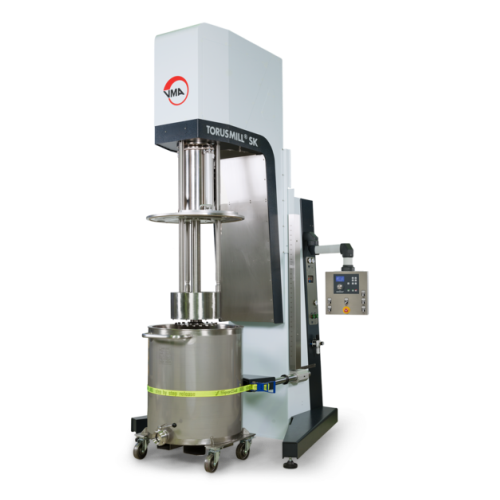
High-efficiency immersion mill for medium viscosity products
Achieve precise particle size reduction and superior disper...

High-efficient industrial immersion mill
Achieve rapid, efficient dispersion and fine grinding in demanding production envi...
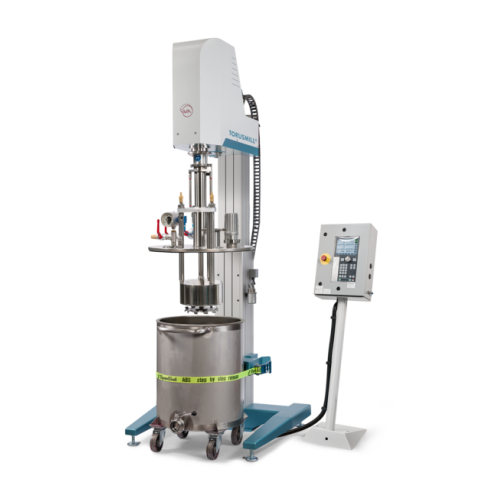
Vacuum basket mill for highly viscous products
Achieve precision in fine milling under vacuum to prevent air inclusions in...
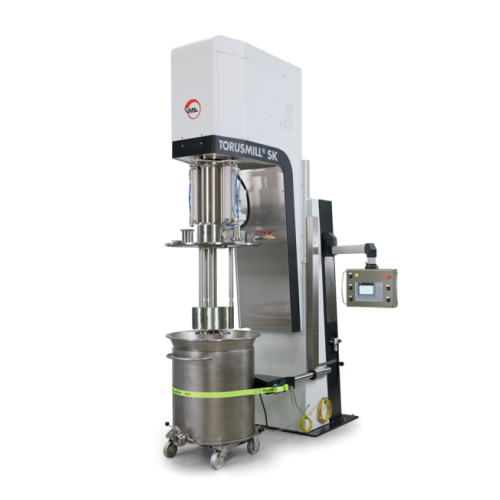
Vacuum basket mill for high-viscosity product milling
Achieve refined particle size and smooth texture in your high-visco...
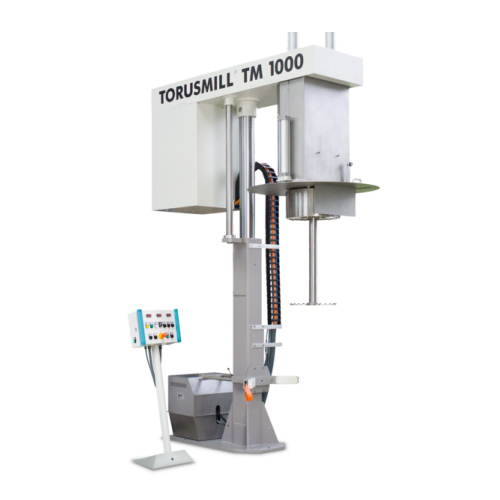
Basket mill with integrated dissolver for high viscosity products
Optimize your production efficiency by combining disp...
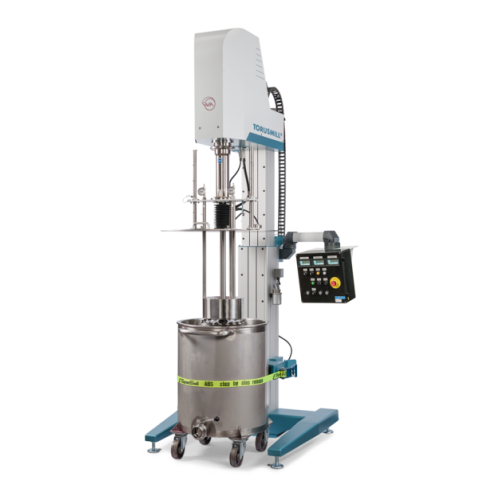
Explosion-proof basket mill for fine grinding
Achieve efficient and safe fine grinding with this innovative explosion-proo...
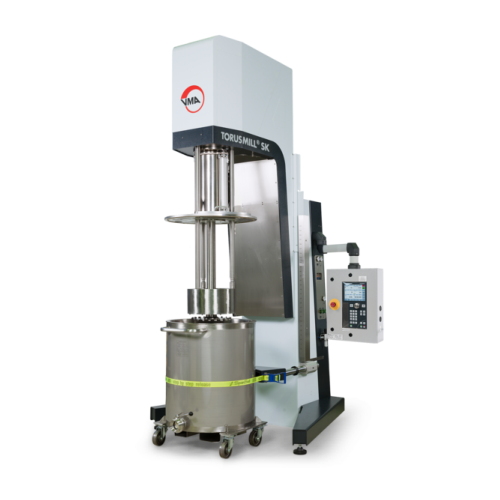
Explosion-proof immersion mill for paints and varnishes
Optimize high-performance coatings production with an explosion-p...
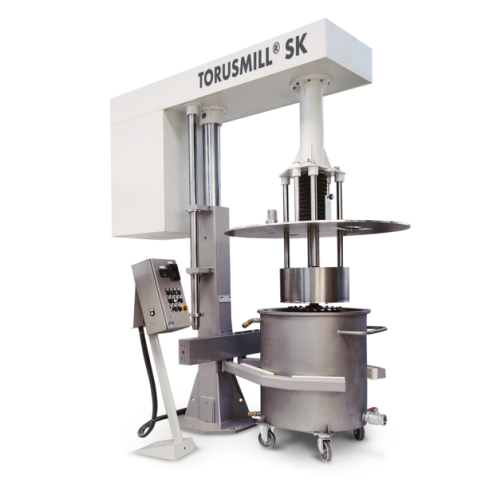
Explosion-proof basket mill for large scale production
Enhance your production line with an explosion-proof basket mill t...
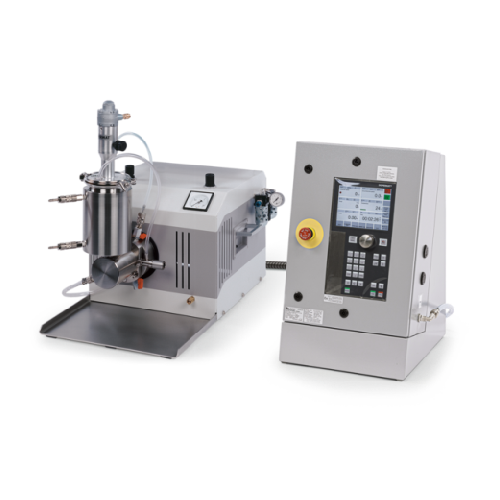
Explosion-proof horizontal bead mill for fine grinding
Ensure precise, explosion-proof grinding in hazardous environments...
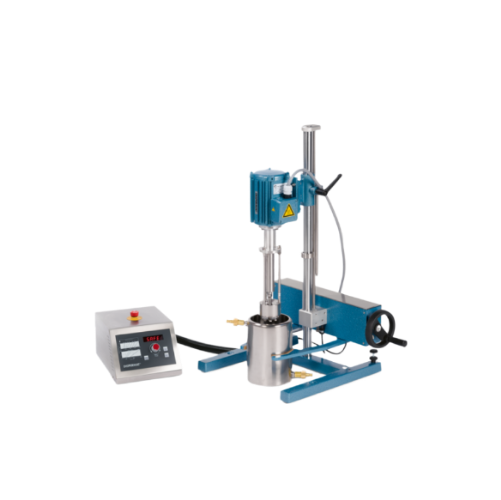
Laboratory bead mill for sample dispersion
Ensure precise particle size reduction with versatility and ease, enabling effi...

Laboratory and pilot plant horizontal bead mill
Achieve precision milling with minimal product waste, ensuring consistent ...
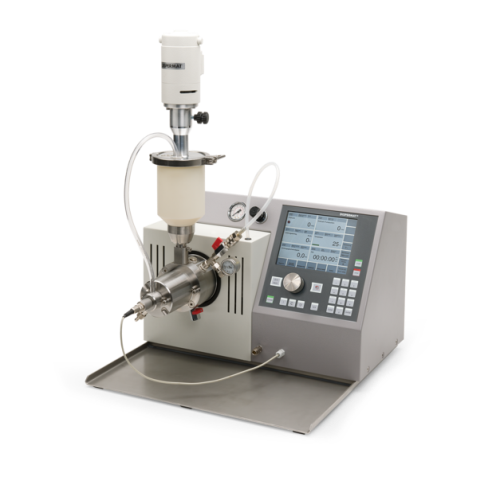
Nano bead mill for laboratory wet grinding
Achieve ultra-fine particle dispersion and consistent milling results with this...
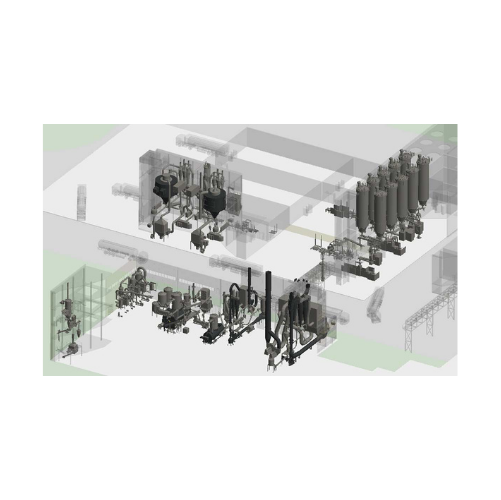
Corn wet milling plant drying systems
Optimize corn processing efficiency with integrated drying and dewatering systems des...
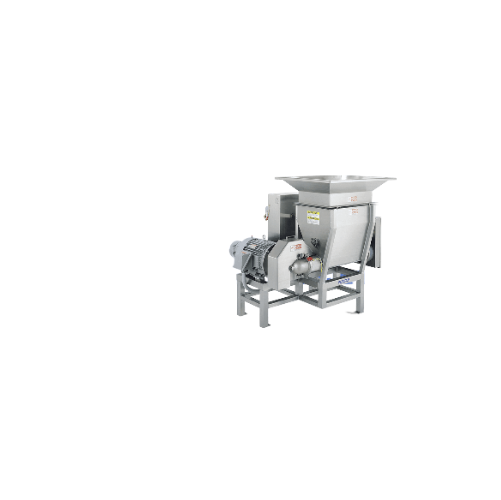
Industrial milling systems for food processing
Streamline your food production line with robust milling and cutting soluti...
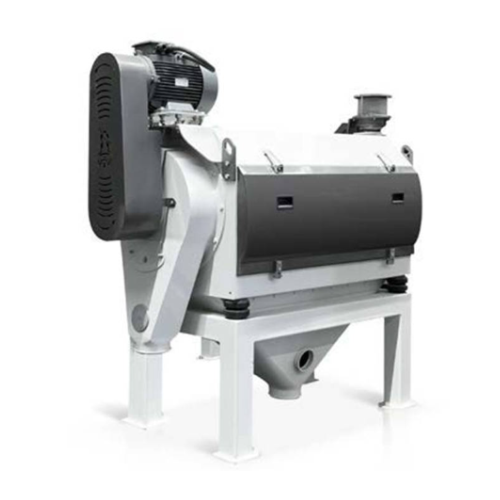
Vibro bran finisher for milling operations
Optimize your grain processing with an advanced vibratory system designed to en...

Industrial roller mill for high-stability milling
Optimize your milling process with a high-speed roller system designed ...
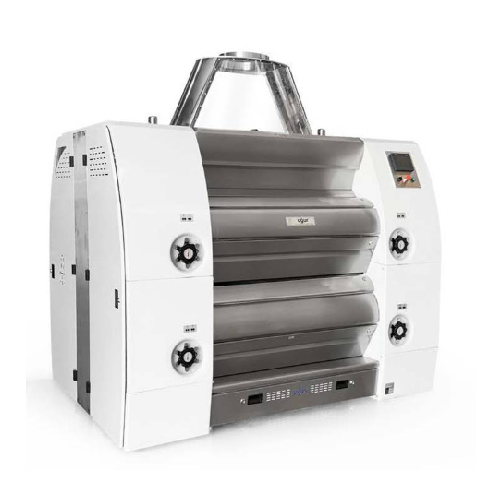
Double deck roller mill for grain milling
Achieve superior milling results with increased efficiency and hygiene in proces...
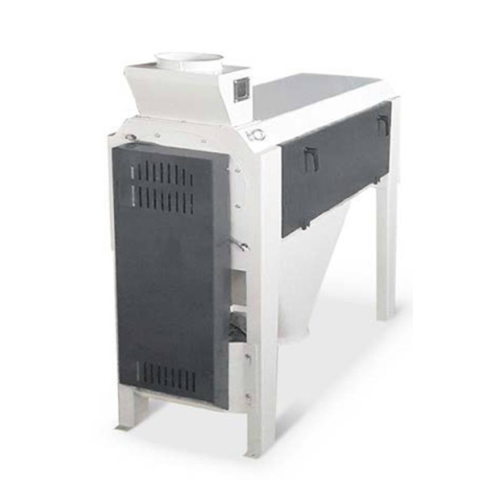
Turbo sifter for milling processes
Optimize your milling efficiency with a high-speed turbo sifter designed to precisely se...
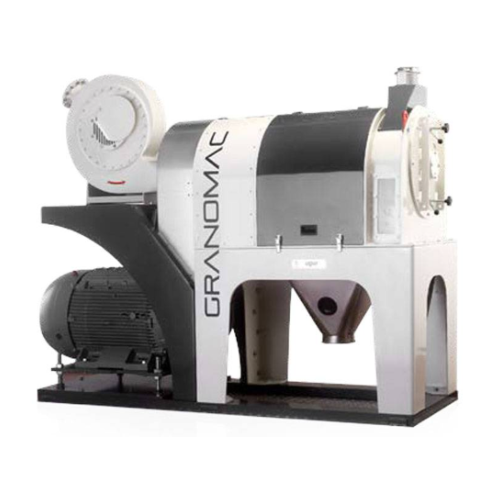
Maize flour and semolina milling solution
Efficiently transform corn into diverse food products by combining precision cle...
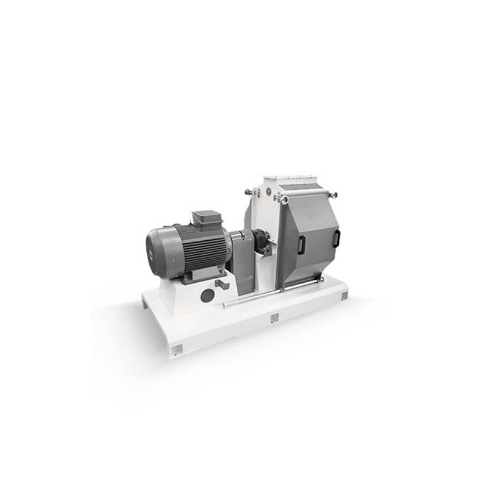
Hammer mill for grinding dry or low-moisture grains
Efficiently transform dry grains into high-quality feed and flour wit...
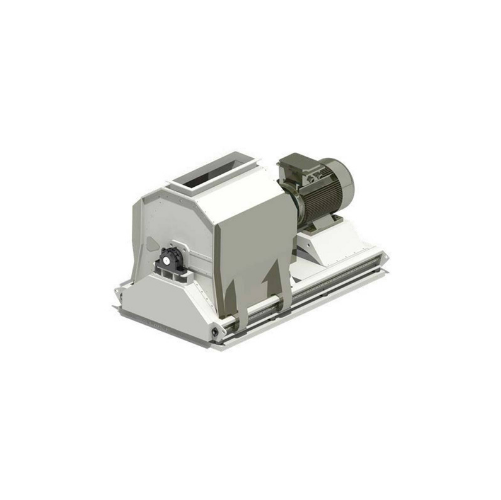
Industrial hammer mill for food industry grinding
Efficiently reduce raw material size with high-speed precision grinding...
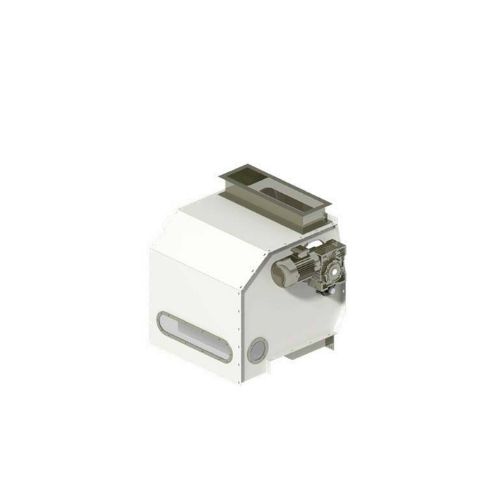
Hammer mill feeder for controlled grain processing
Optimize your feed production line with precise material control, redu...
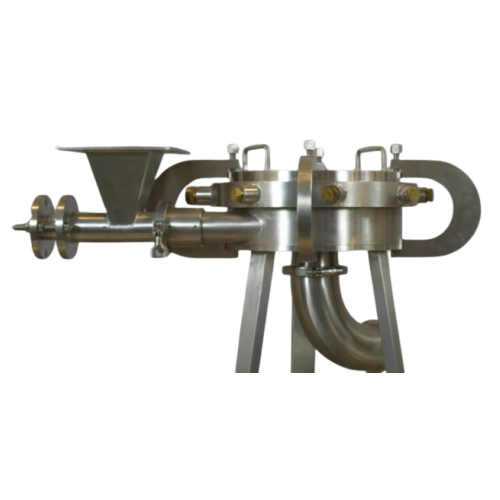
Jet milling system for super fine particle size reduction
Achieve ultra-fine particle sizes with precision milling techn...
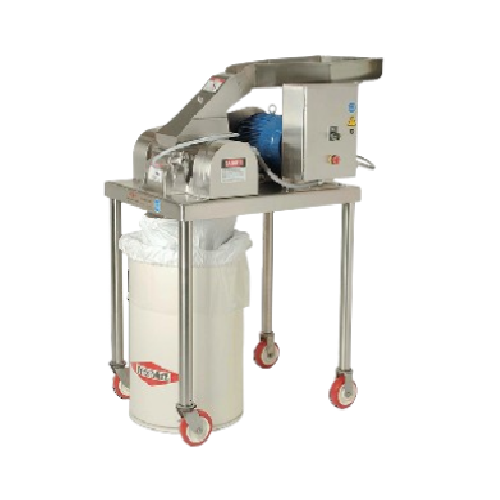
Atex approved hammer mills for high-capacity particle size reduction
Ensure precise and reliable particle size reductio...
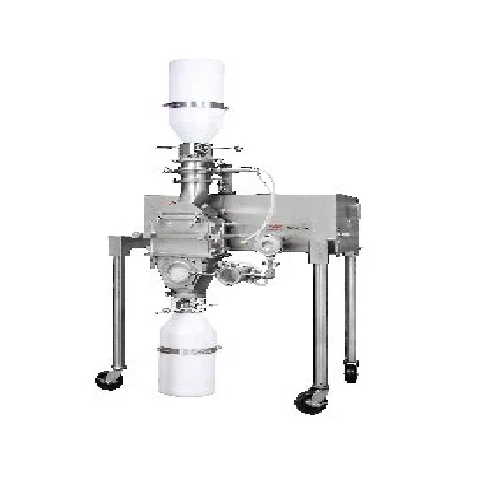
High accuracy hammer milling for precise particle size reduction
Achieve precise particle size control to enhance produc...
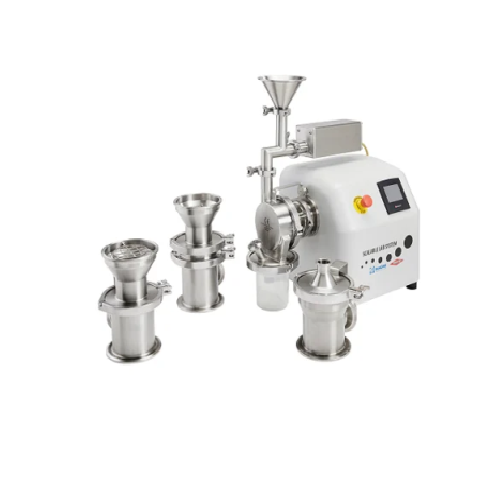
Lab scale hammer mills for fine particle size reduction
Optimize your R&D scaling efforts with versatile lab equipme...
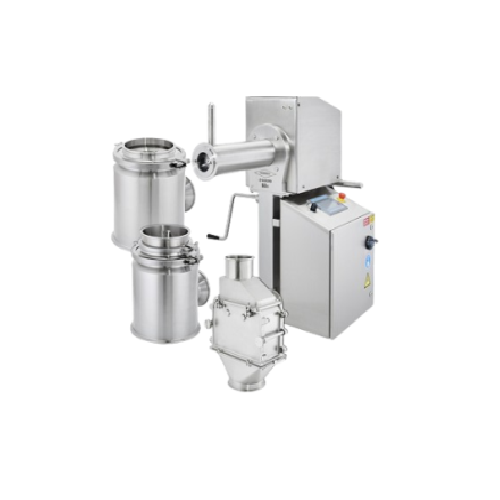
Pilot-scale milling and screening platform
Achieve precise powder consistency and integrity with flexible milling and scre...
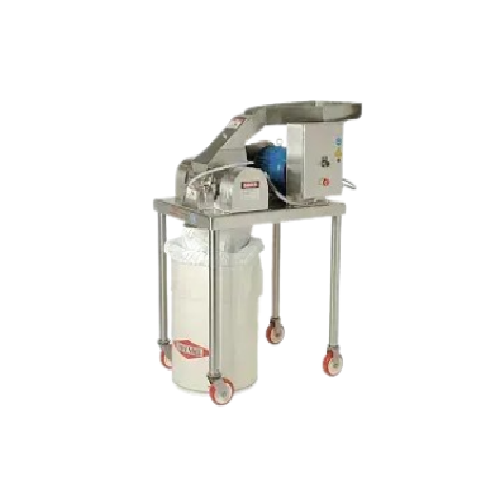
Industrial powder milling solution
Achieve precise particle size control and improve material flowability with this advance...
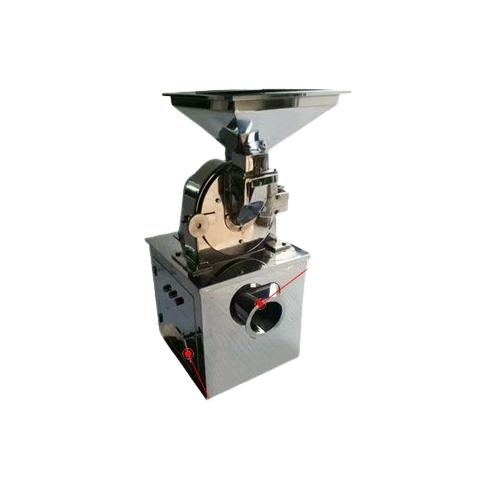
Chili powder milling machine
Transform raw spices into finely milled powders effortlessly with this high-speed grinding solu...
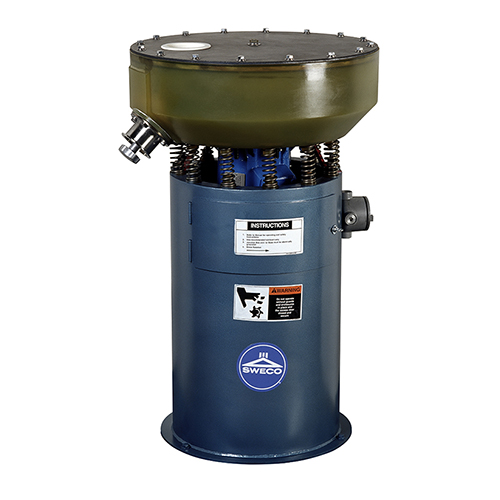
Sub-micron particle size reduction grinding mill
Achieve precise particle size reduction effortlessly with advanced vibrat...
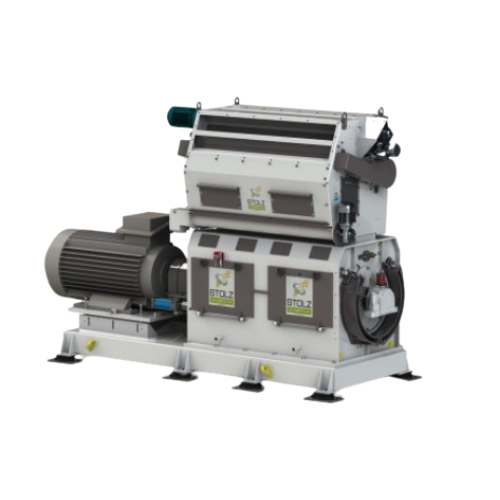
Industrial hammermill for fine grinding applications
Elevate your milling efficiency with hammermills designed for precis...
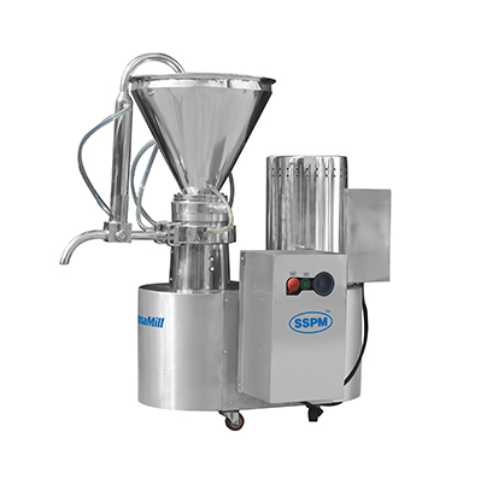
Colloid mill for particle size reduction and emulsification
Achieve precise particle size reduction and stable emulsions...
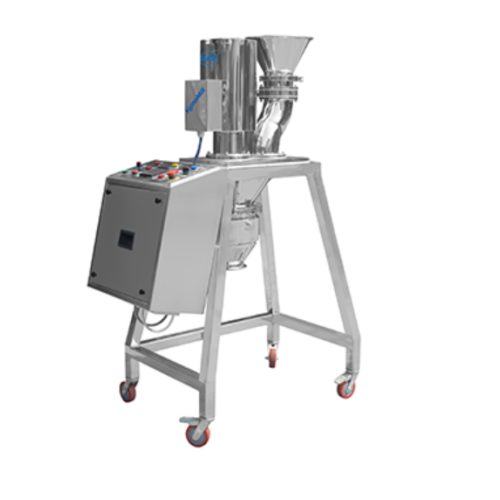
Wet granulation co mill for pharmaceutical formulations
Optimize your manufacturing process with precise particle size re...
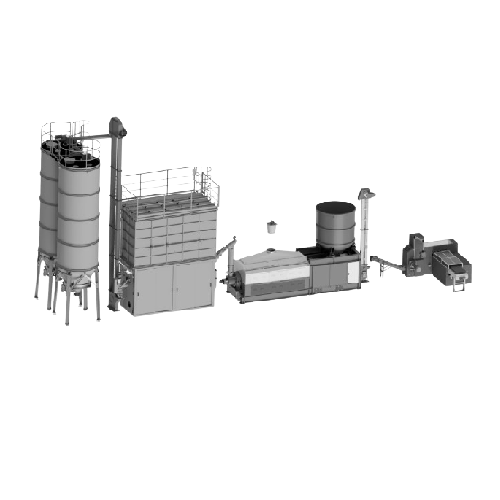
Lead oxide mill for battery production
Optimize your lead-acid battery production with chainless technology, ensuring consi...
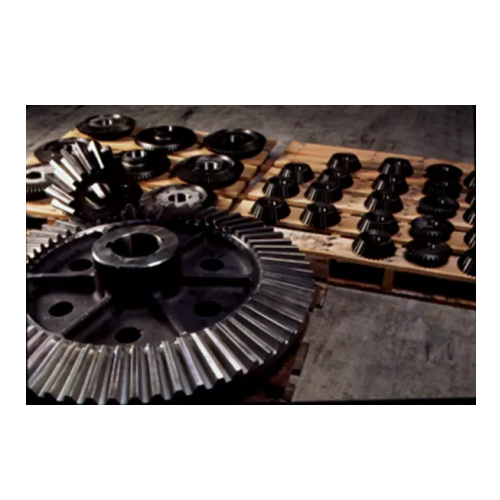
Industrial grinding mill replacement parts service
Optimize production efficiency with high-precision grinding solutions ...
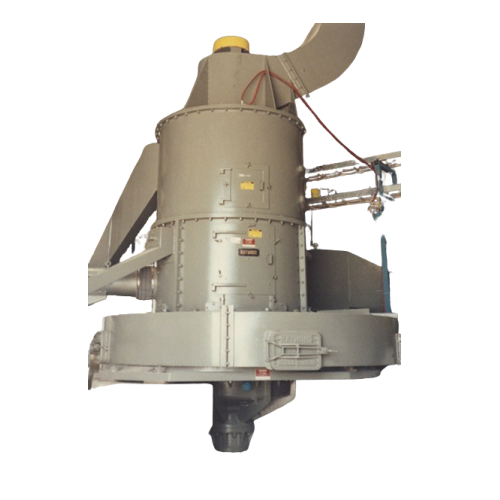
Vertical ring-roll mill for pulverizing minerals
Achieve precise particle size control and efficient material processing w...
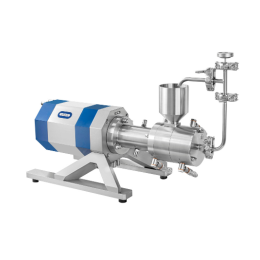
Agitator bead mill for flow chemistry
During the early stages of synthesis, generating only limited product quantities can ...
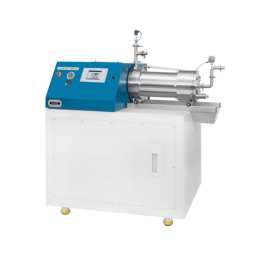
Bead mill for crop protection
To optimize qualities like particle size, distribution, solubility, and miscibility of active ...
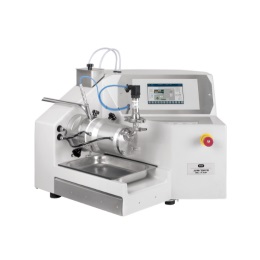
Flexible laboratory bead mill for vaccines
For precise, efficient, and reproducible cell disruption, optimization of proce...
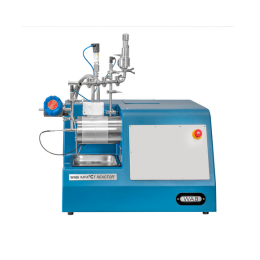
Agitator bead mill reactor for molecular synthesis by mechanochemistry in continuous flow
To achieve cleaner, safer,...
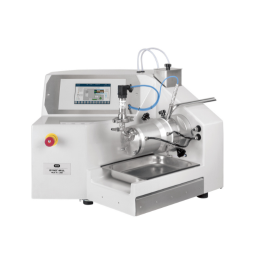
Flexible R&D wet agitator mill for cosmetics
Using nanoparticles in cosmetics requires precise control over material break...
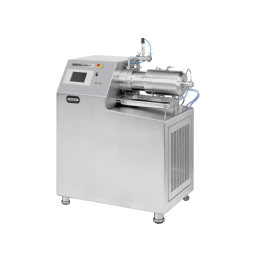
Ultra fine bead mill for nanosuspensions
Ensuring the quality, efficiency, and reproducibility of nanosuspensions throughou...
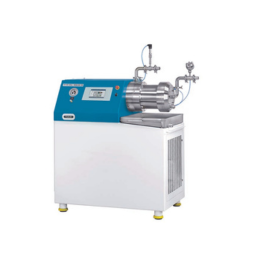
Self-cleaning bead mill for highly viscous materials
To prevent blockages, clogging, and cross-contamination coming from ...
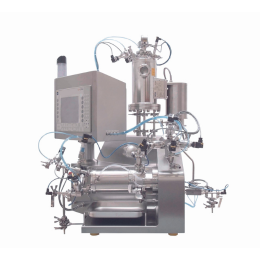
Agitator bead mill for API
To achieve precisely defined API properties and safe and reproducible production, rigorous implem...

Horizontal disc bead mill for liquid chemicals
Processing toxic chemicals requires high compliance with safety standards a...
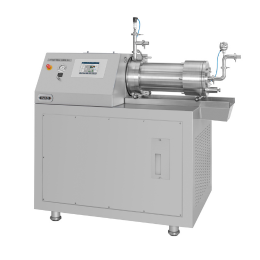
Agitator bead mill for functional foods and flavors
Fine-grinding solid flavors to improve taste properties and integrati...
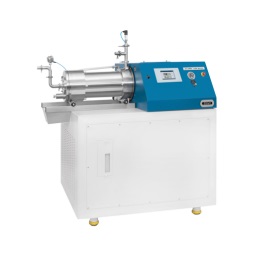
Ultrafine bead mill for battery materials
To facilitate the attainment of ultrafine particles and enhance electrode proper...
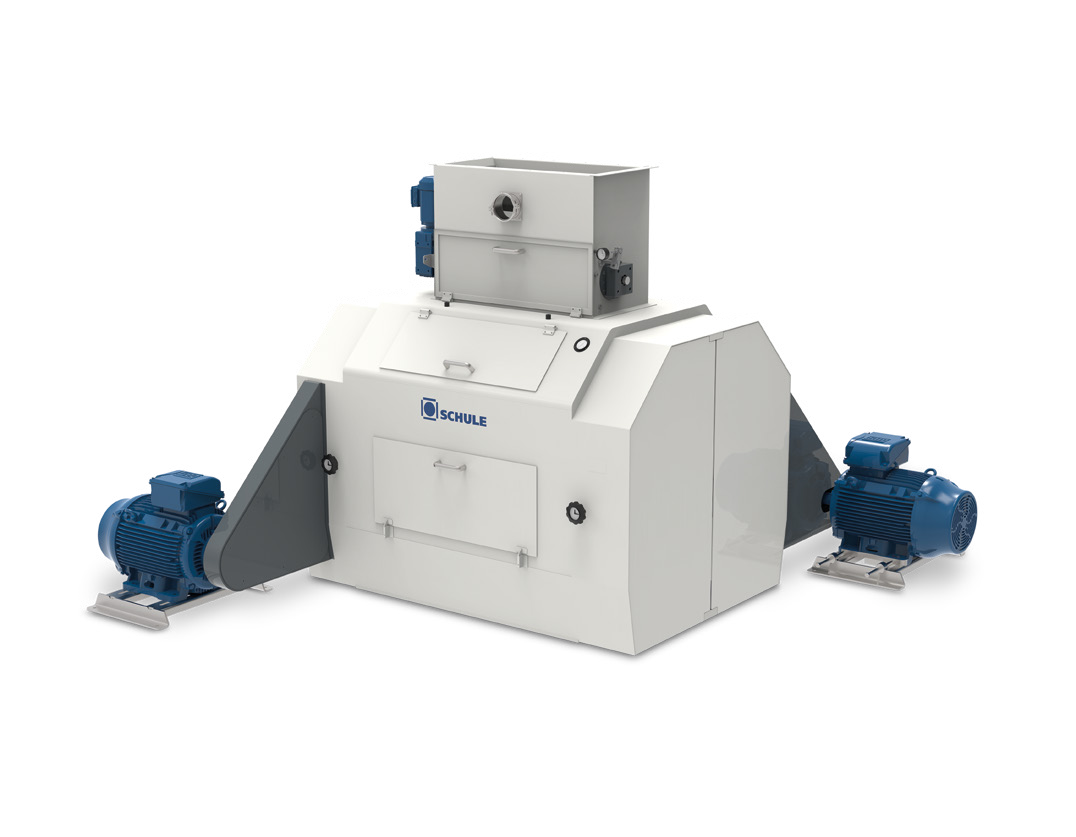
Flaking roller mill for oats
Consistent flake size is one of the main contributors to processed oat quality. But producing a...
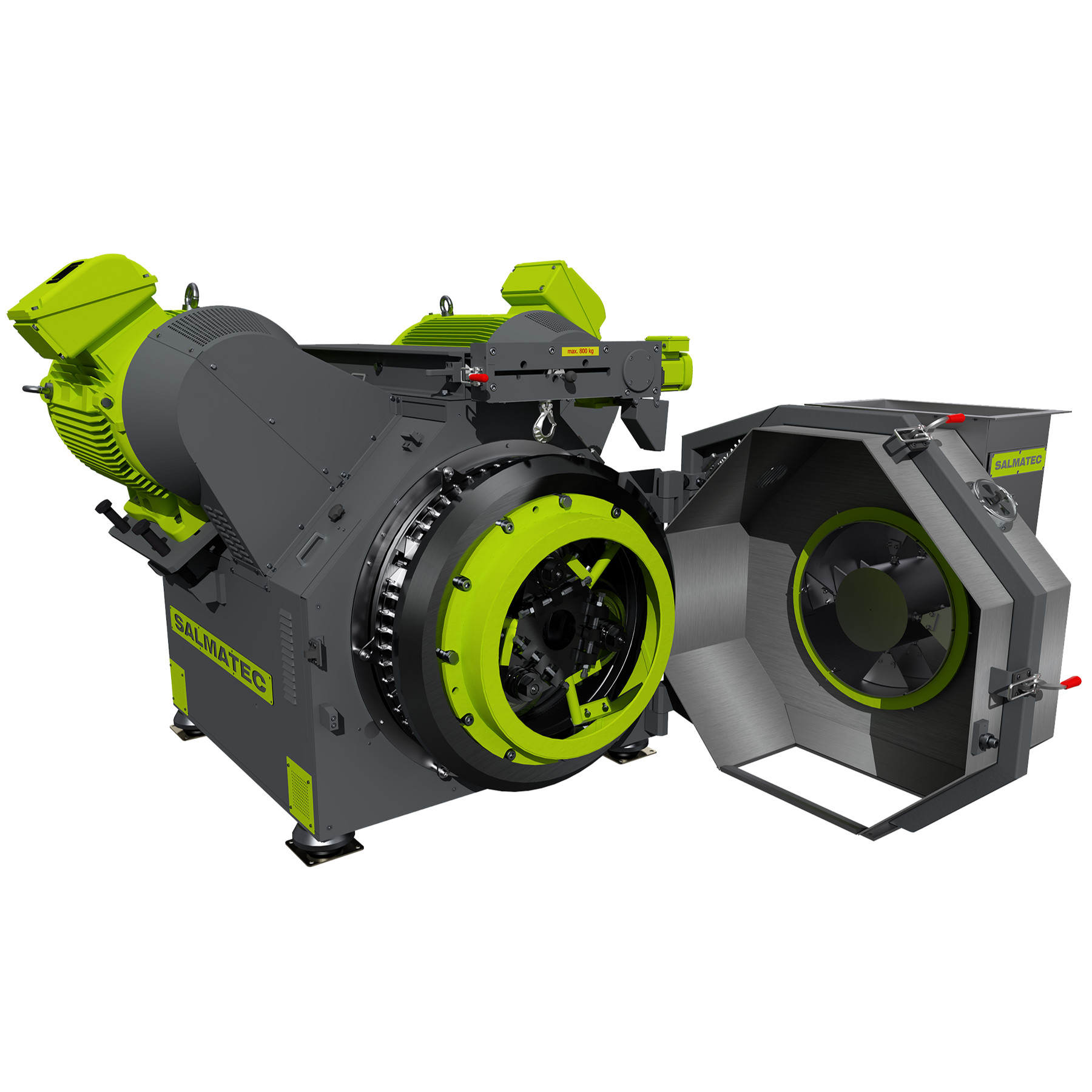
Industrial pellet mill
At the industrial level, the application areas of pellets range widely in fields such as feeds, biomas...
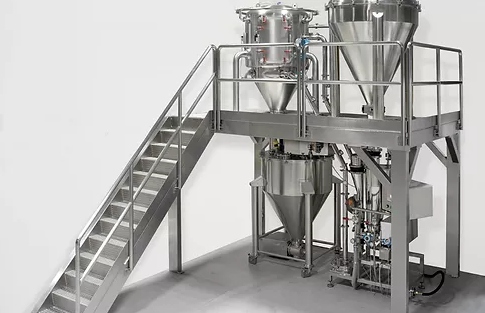
Production scale jet mill
Large volume manufacturers demand the most out of their production process, including powder milli...
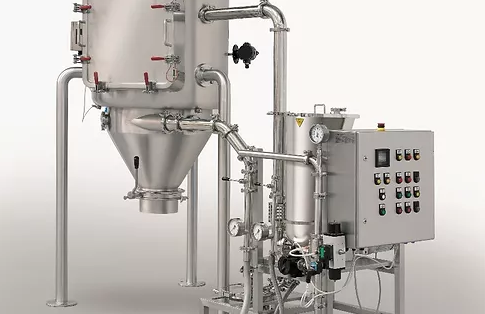
Jet mill micronizer
Small scale manufacturers that require effective micronization of powders for their process lines may nee...
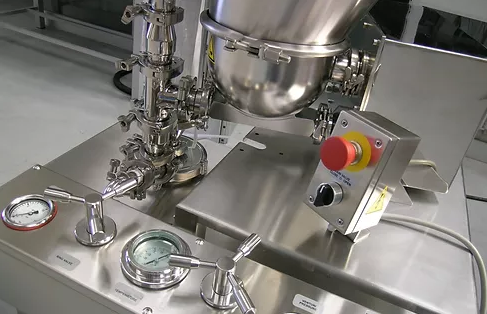
Pilot scale jet mill
In a pilot scale level or preliminary study, all the production process steps have to satisfy the small ...
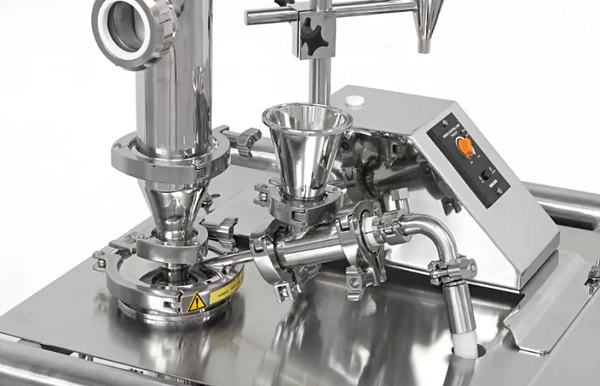
Laboratory jet mill
Manufacturing small quantities of high-value products requires efficient machines that can process these ...
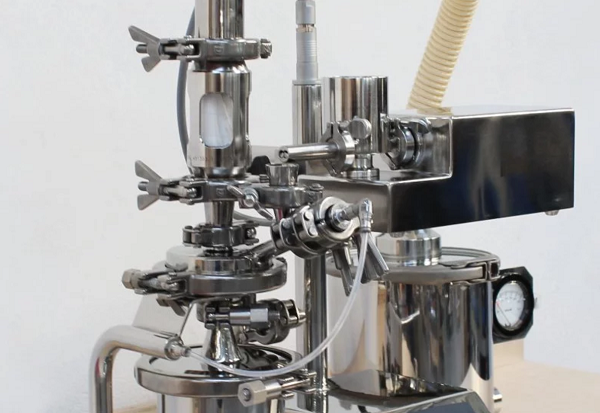
Jet mill for clinical trials
R&D laboratories may need to reduce the size of powder particles in small quantities for cl...
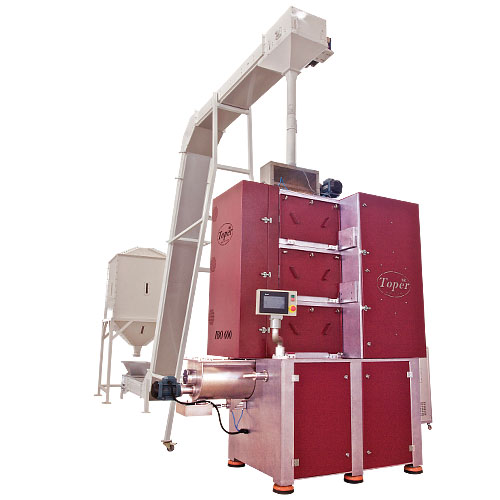
Roll mill for coffee beans
When you want flexibility to grin beans for filter coffee to Turkish coffee at particle sizes ran...

Vertical ball mills for chocolate refining
Powders of extremely high fineness can easily be produced with ball mills and a...
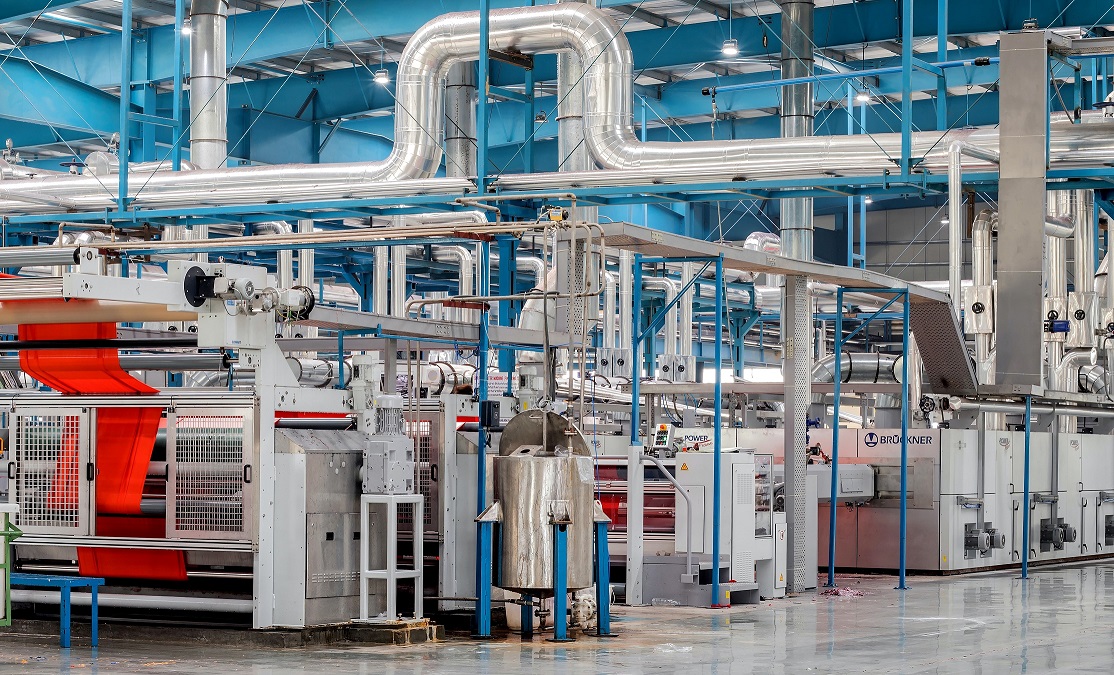
Industrial fine milling equipment for nuts
In a bakery environment fruit jams are often used for the decoration or filling...
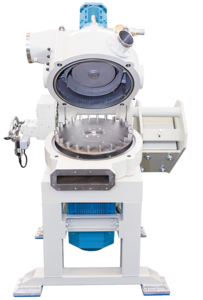
Classifier mill for recovered carbon black
Recovered Carbon Black (rCB) can be recycled back to the tire production chain ...
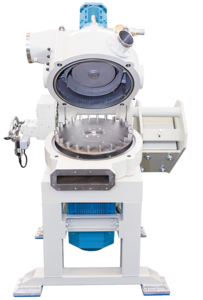
Classifier mill for powder coating
High-quality powder coatings are often required to manufacture equipment, appliances, an...
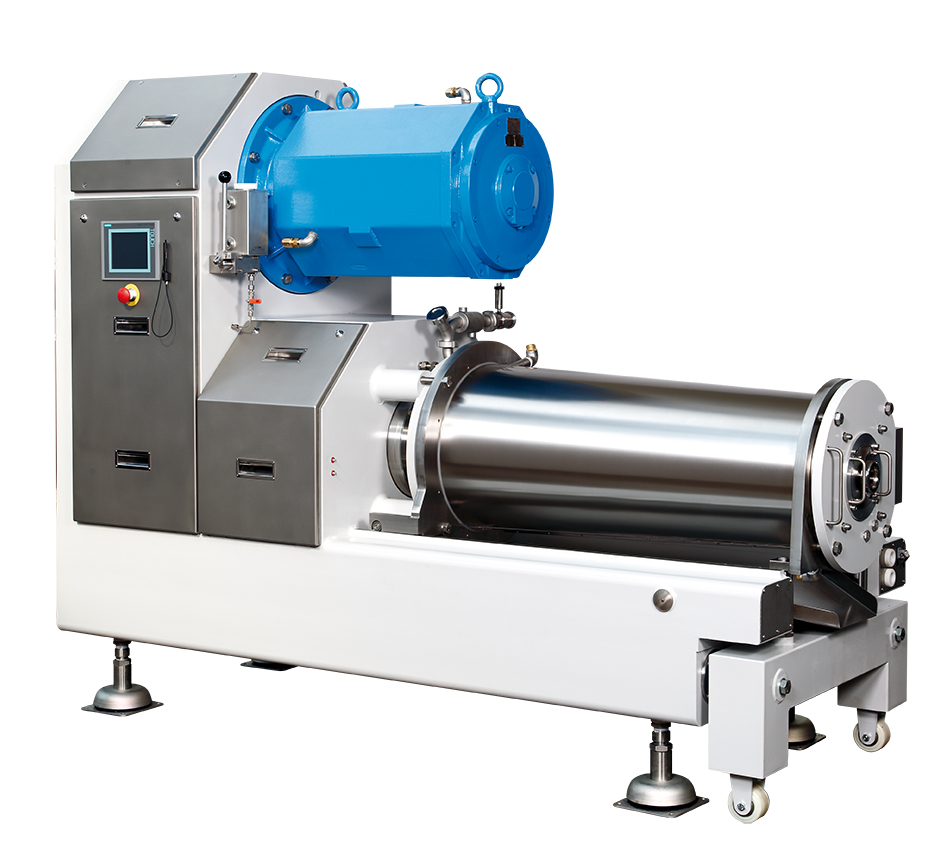
Horizontal ball mill for chocolate refining
Powders of extremely high fineness can be produced with ball mills and agitate...
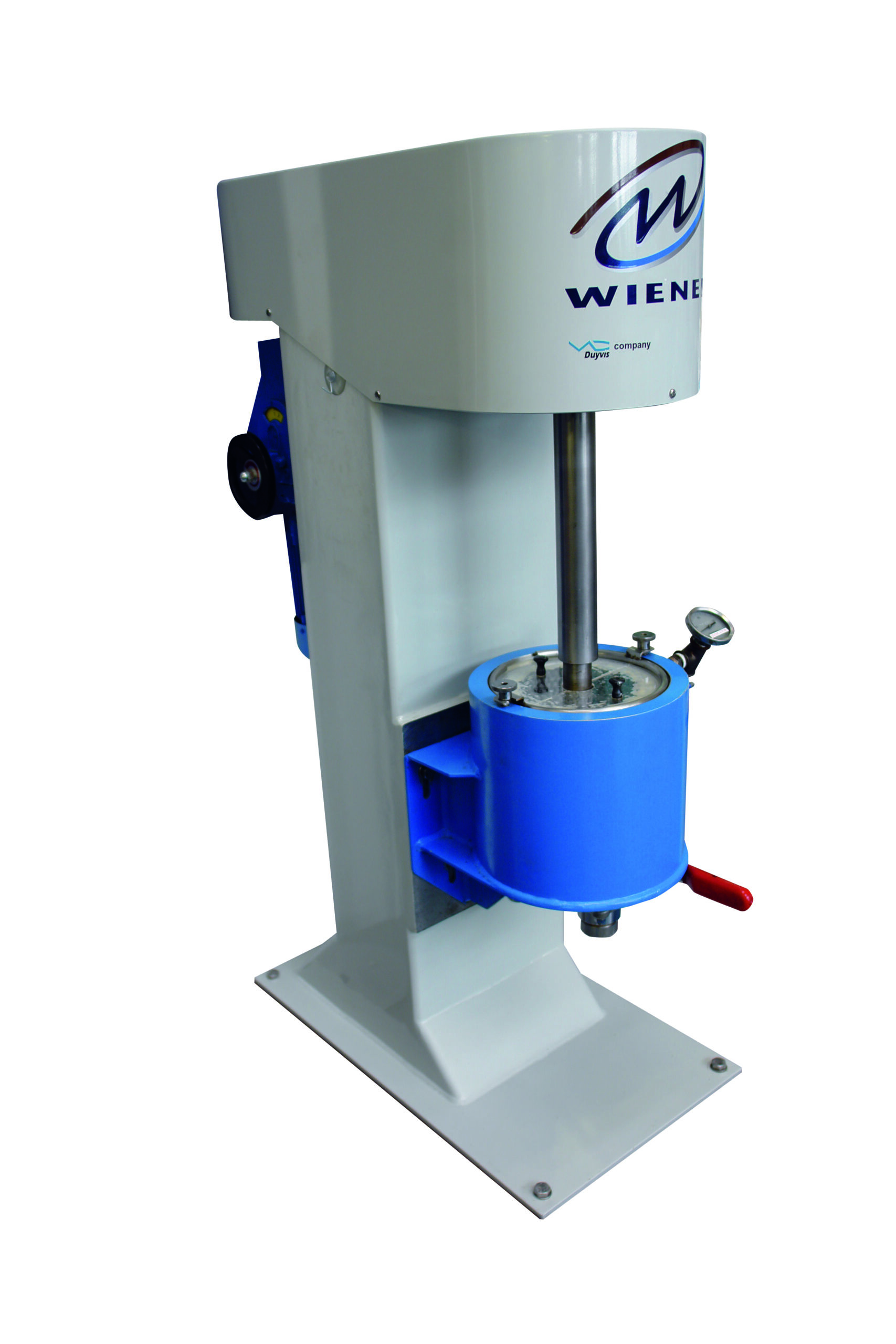
Chocolate laboratory ball mill
The ball mills are a type of grinder, with a cylindrical shape, used in the process of grindi...
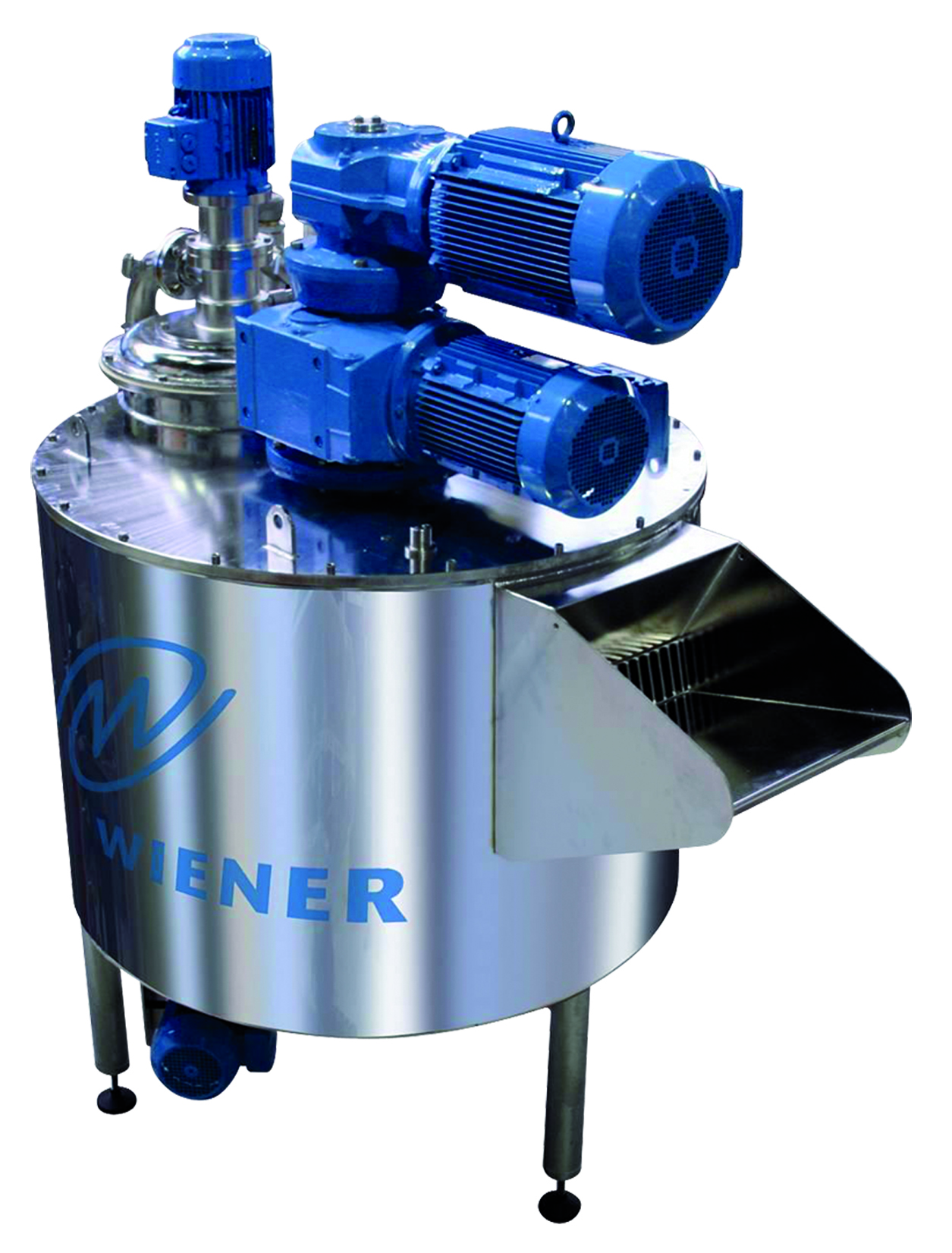
Batch chocolate machine with vertical ball mill
To mix and refine cocoa liquor, cocoa powder, sugar, and lecithin, several...
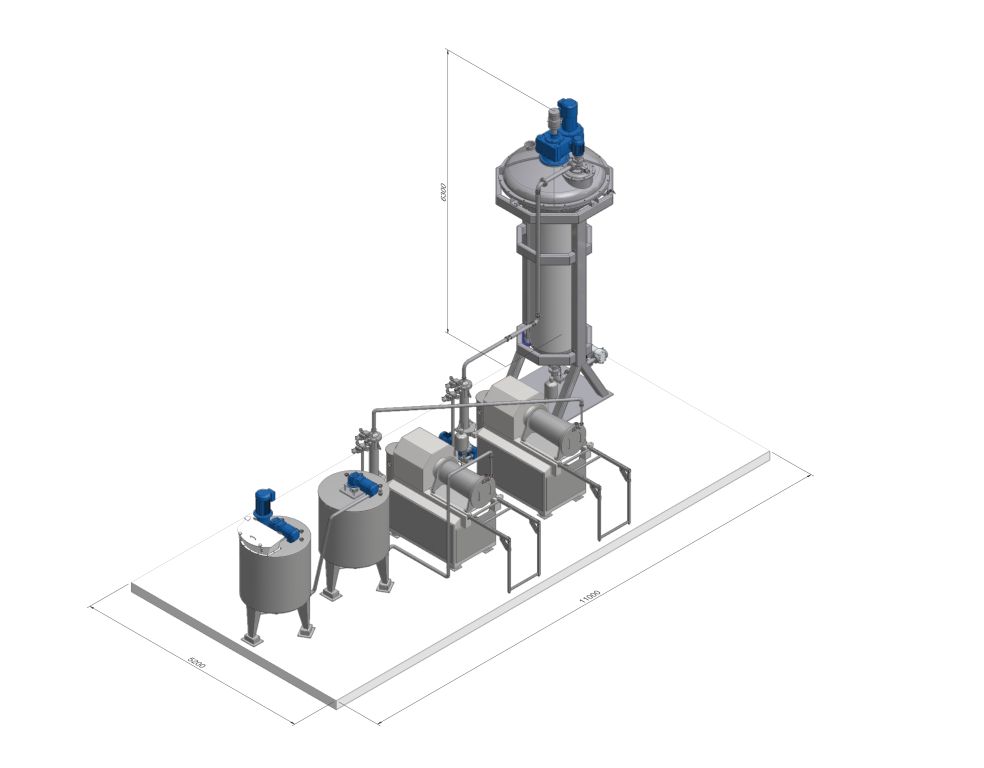
Continuous chocolate line with horizontal ball mills
For mixing and refining cocoa liquor, cocoa powder, sugar, and lecit...

Batch chocolate line with horizontal ball mill
To mix and refine cocoa liquor, cocoa powder, sugar, and lecithin, several ...
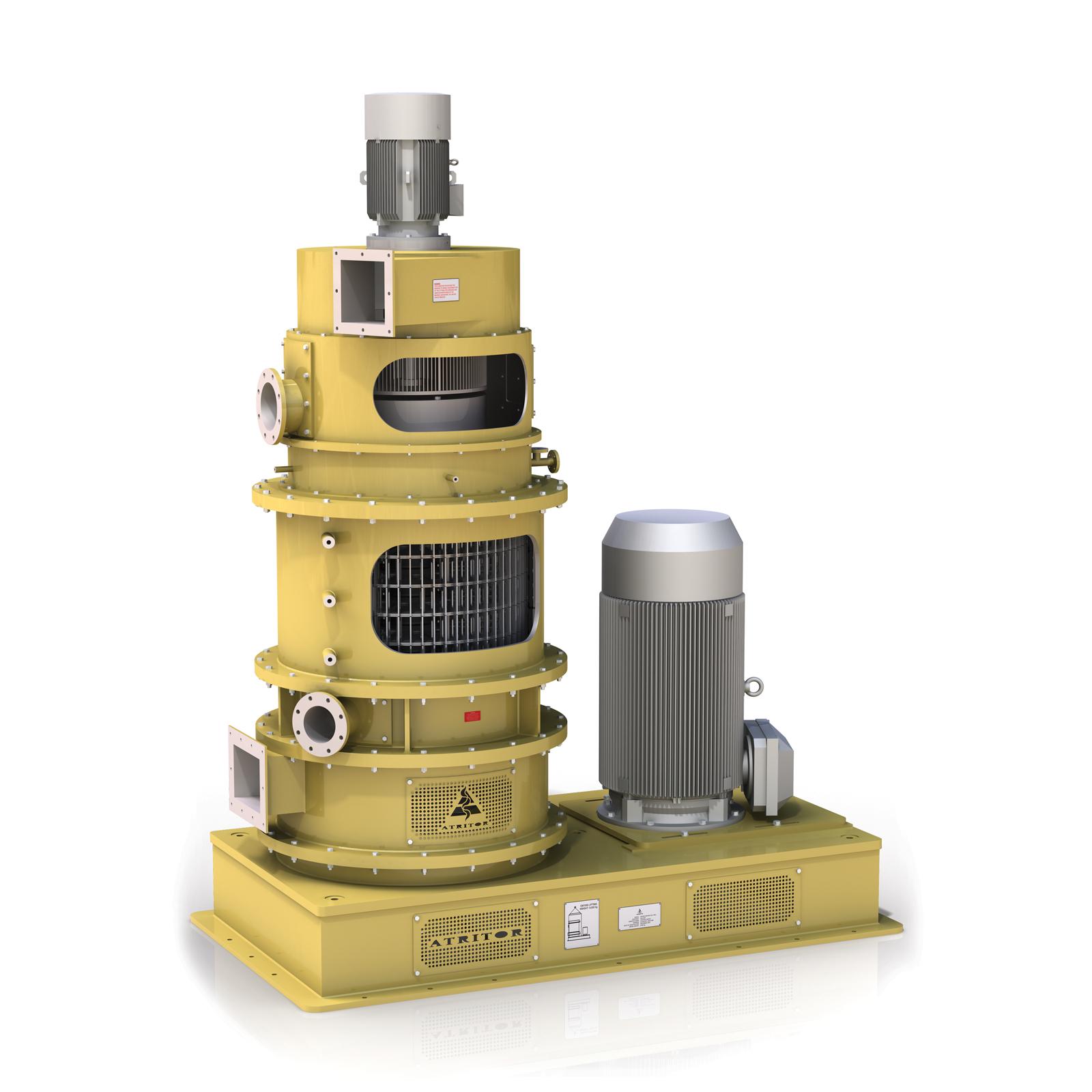
Milling and drying machine for fine powders
When you need to produce ultra-fine powders, the milling and drying process em...
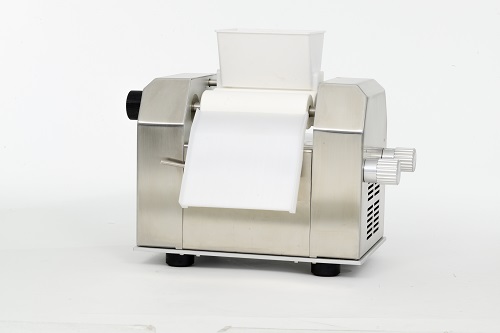
Benchtop mill for ointments
Pharmaceutical and cosmetic creams, ointments, gels and pastes can deliver a wide range of activ...
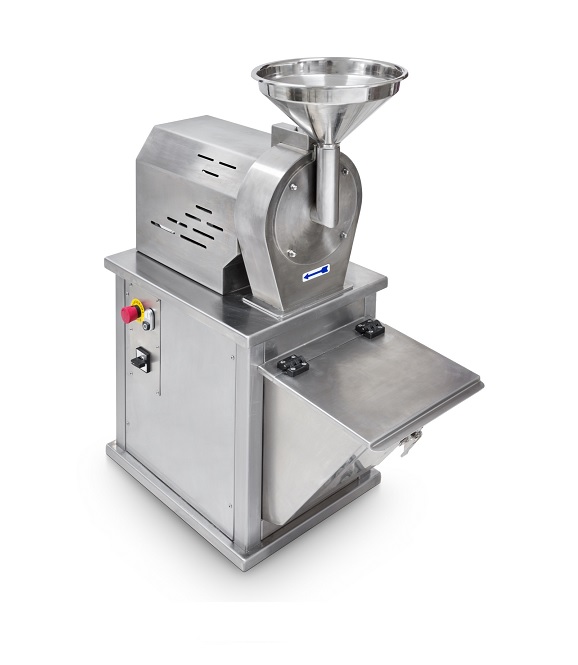
Small sugar mill for entry level production
Sugar powder is a key ingredient in a wide range of bakery, confectionery, and...
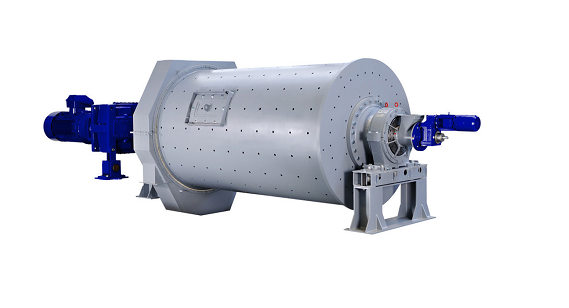
Horizontal rotary ball mill drum
A horizontal rotary ball mill drum can be used for grinding of dry hard materials, such as ...
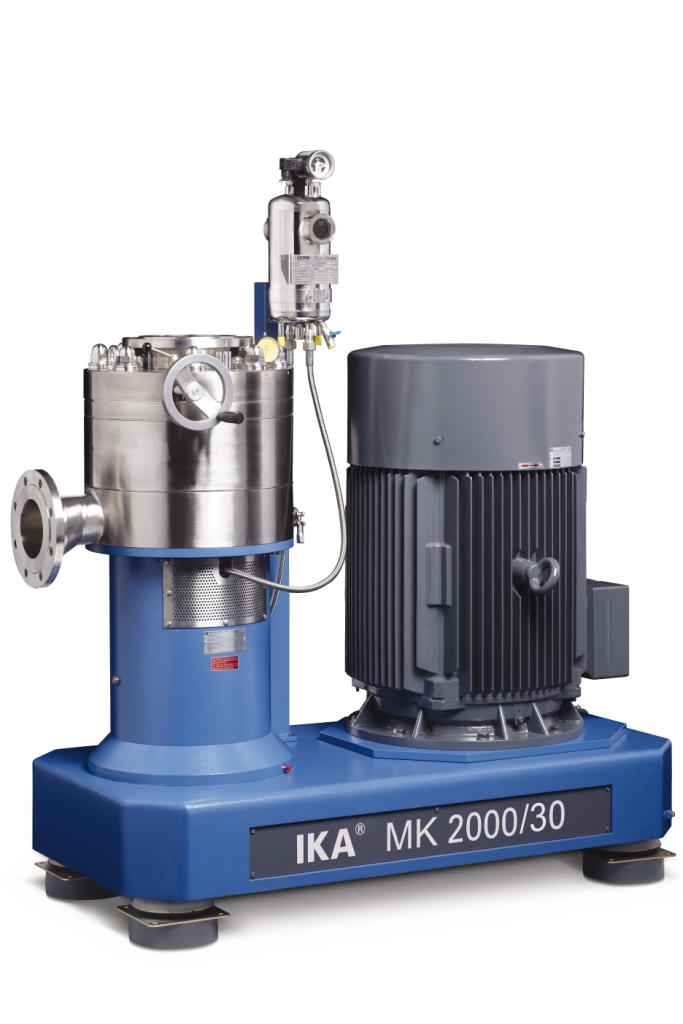
Colloid mill
For creating extremely fine emulsions and high quality dispersions a high pressure homogenizer is often chosen. ...
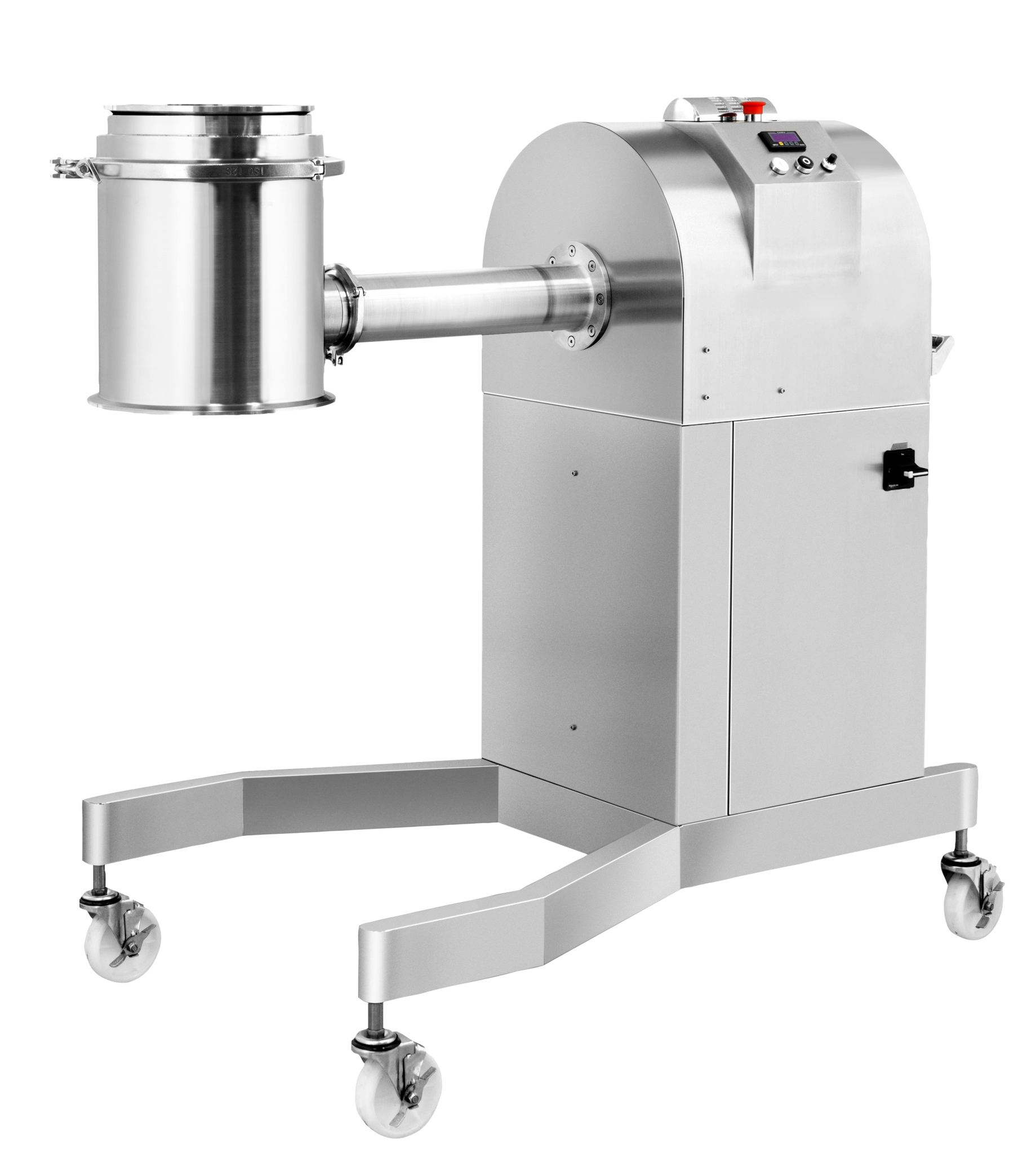
Conical mill for drug formulation
The efficient size reduction of granular powders is a key step in many pharmaceutical pro...
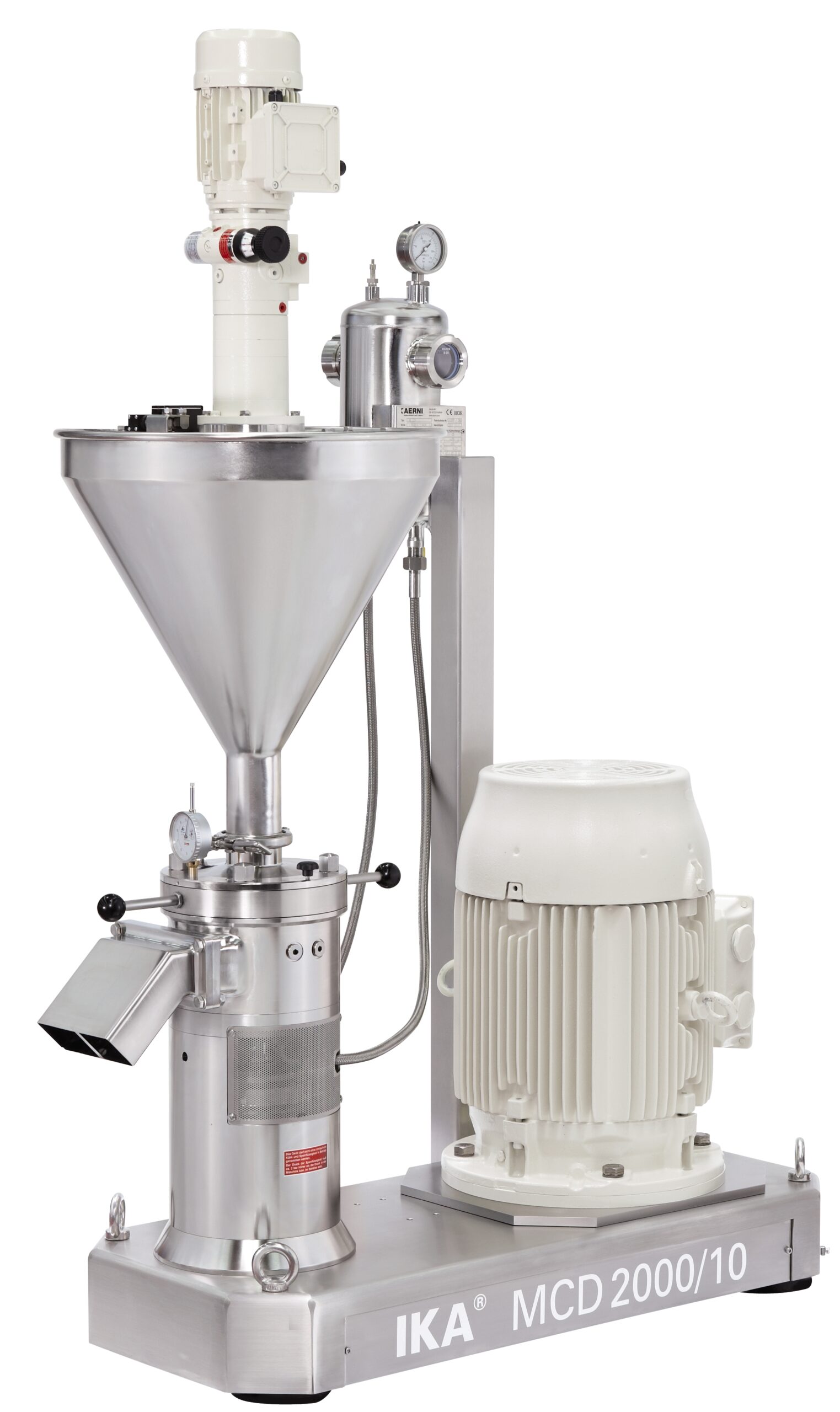
Corundum disk mill
Wet milling and grinding of viscous liquids or pastes containing solid particles such as peanut butter,mus...
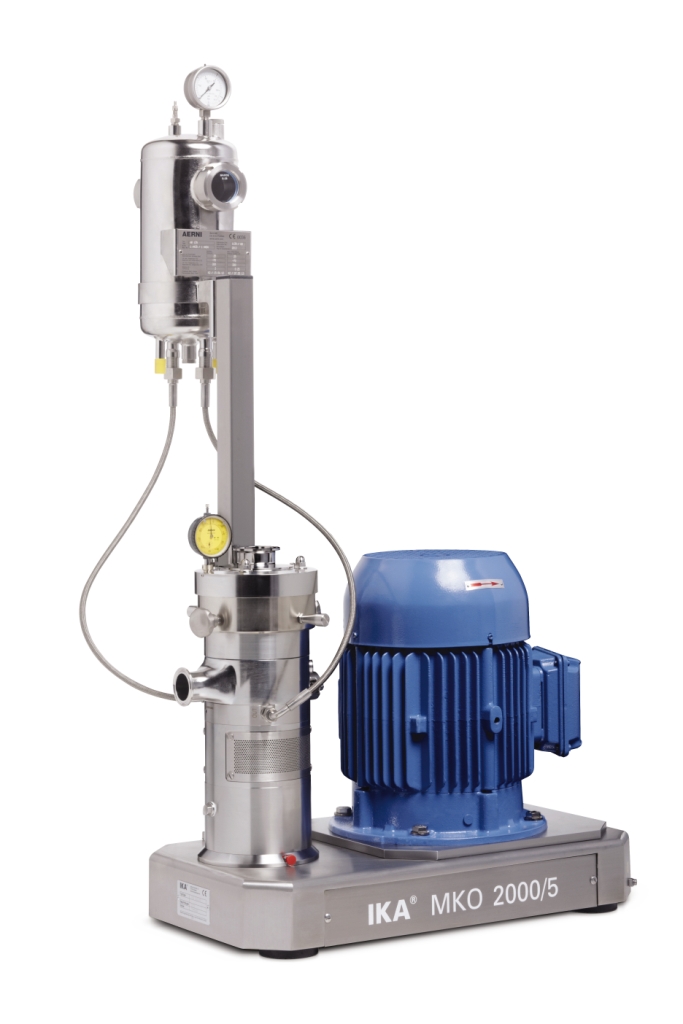
Cone mill machine
When your raw materials include agglomorated suspensions of grainy or crystalline solids and your process n...
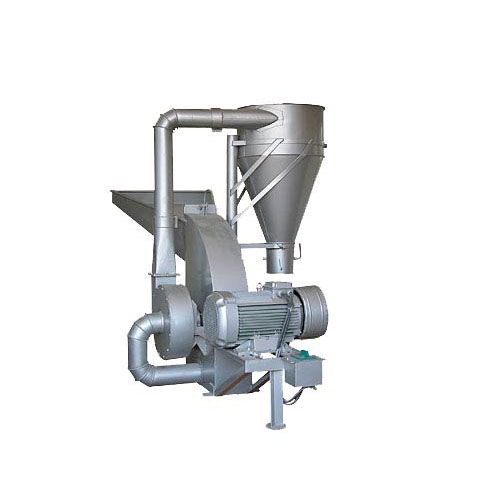
Hammer mill for coffee beans
Being able to obtain an on-point grinding is easily achievable with these hammer mills, from co...
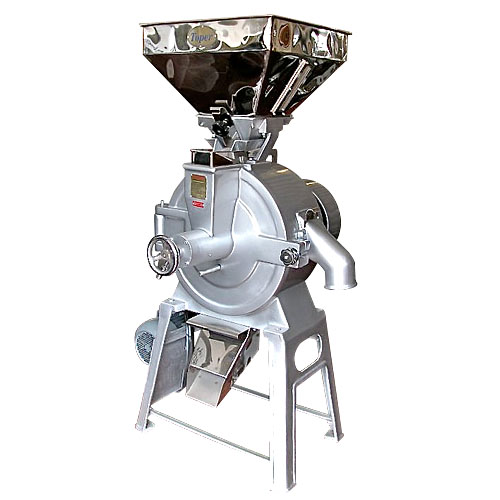
Stone mill for coffee beans
Traditional milling of coffee beans or seeds, with a stationary bedstone and a turning runner st...

Vertical agitated dry media mill
A vertical agitated media mill is used for grinding ultrafine particles, in an agitated (or...
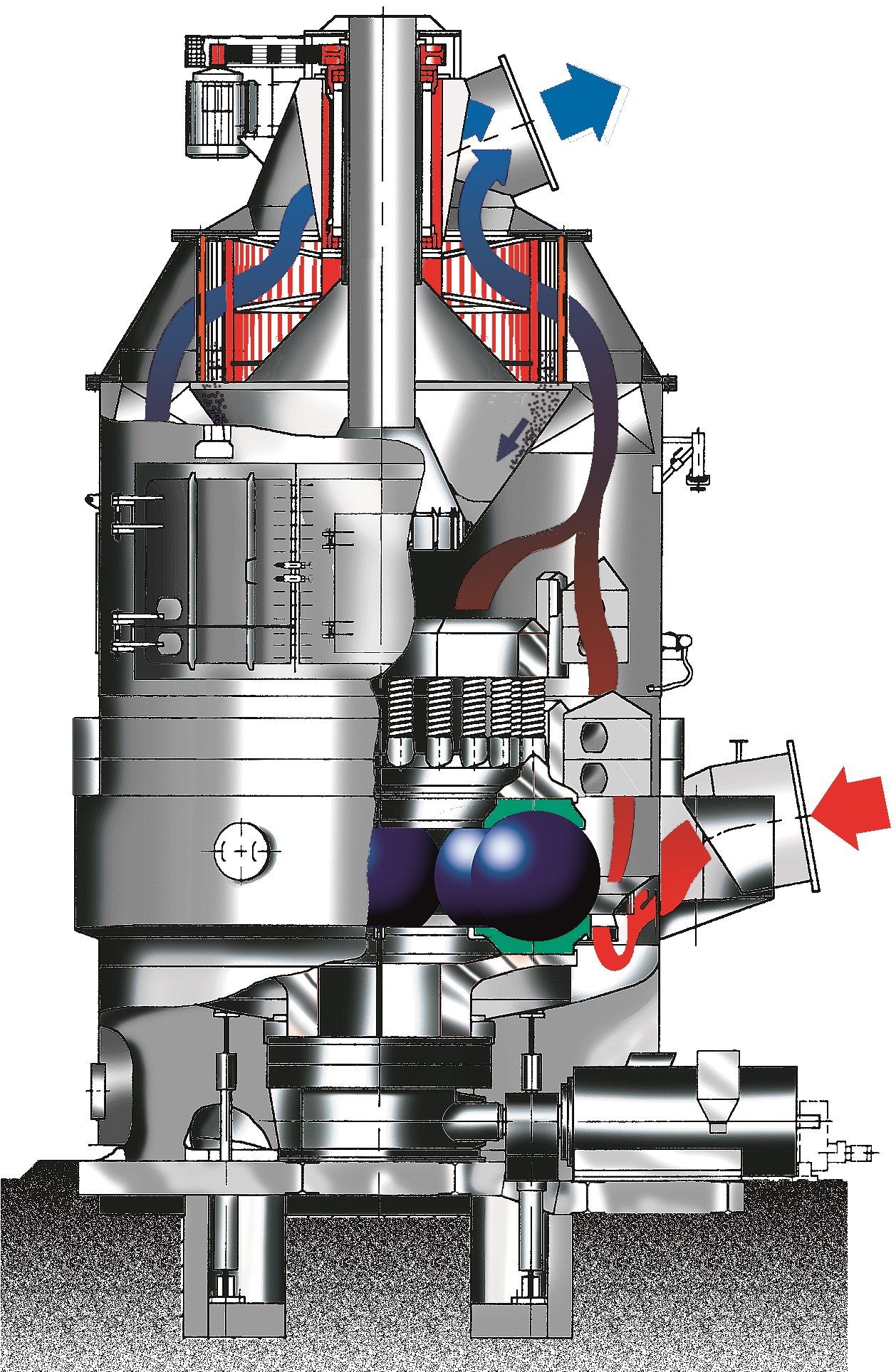
Mill for calcining gypsum
Quality of gypsum and stucco products are highly influenced by the quality of the calcining proces...
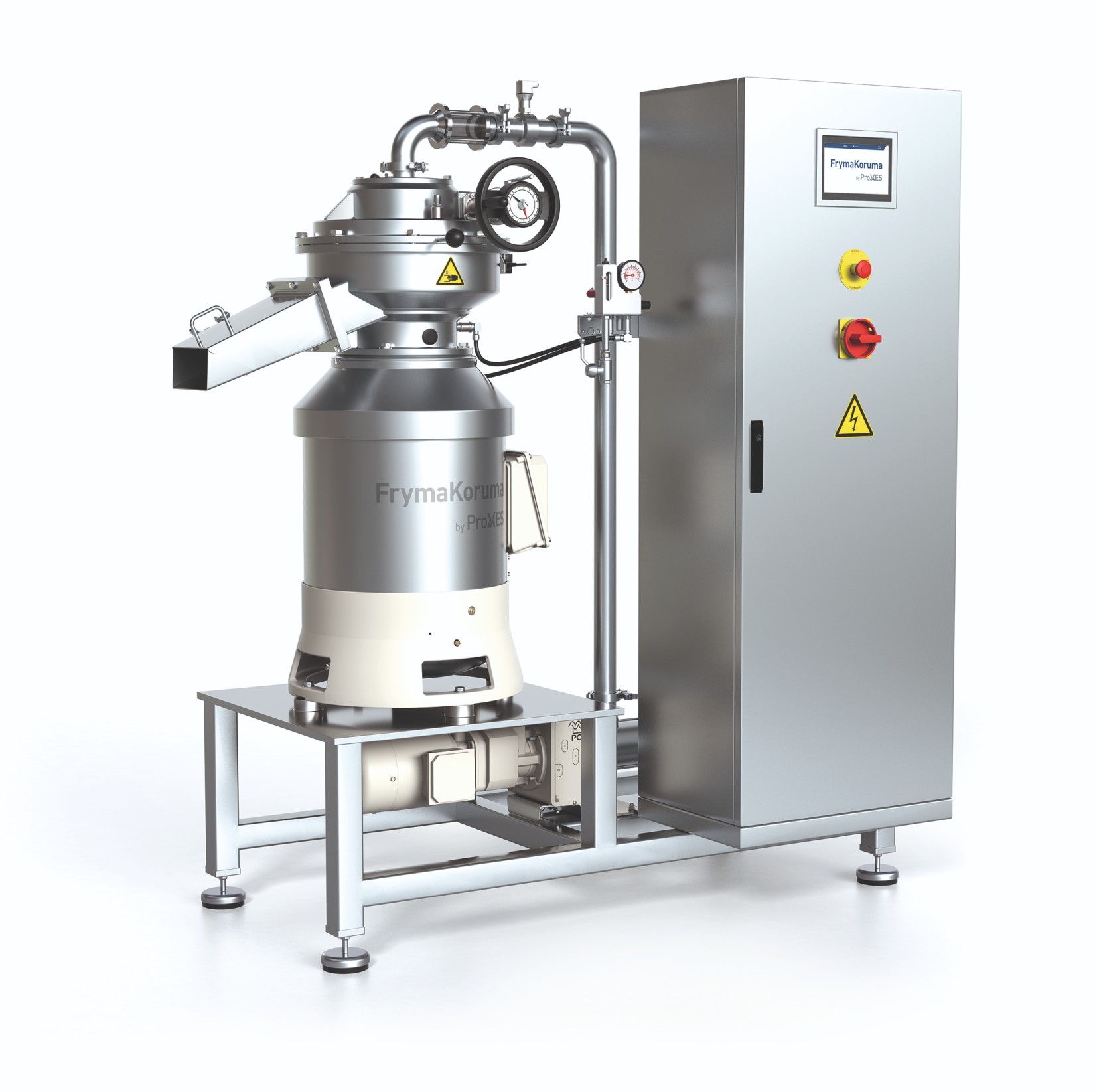
Versatile stone mill machine
In the food industry, when it comes to milling a wide range of products such as seeds and nuts ...
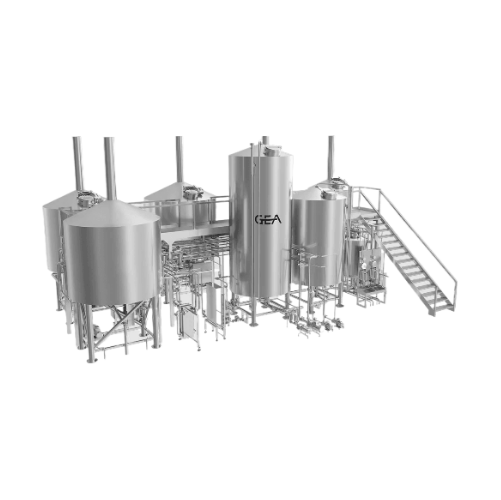
Craft brewhouse for medium to large breweries
Achieve unparalleled brewing flexibility and efficiency with a brewhouse tha...
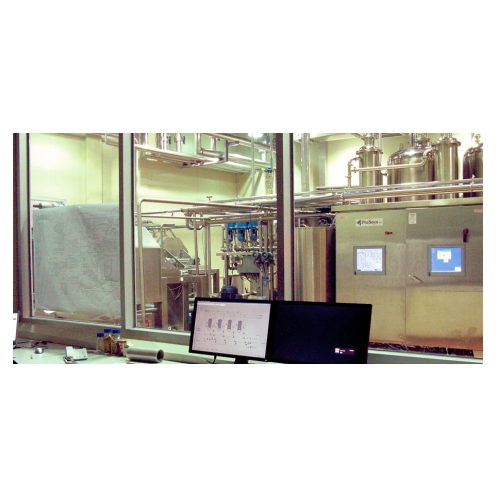
Oat milk processing plant
Transform whole oats into creamy, nutritious oat milk with precision, leveraging advanced continuo...

Nuts flour production system
Enhance your nut processing efficiency by transforming whole nuts into fine, consistent flour w...
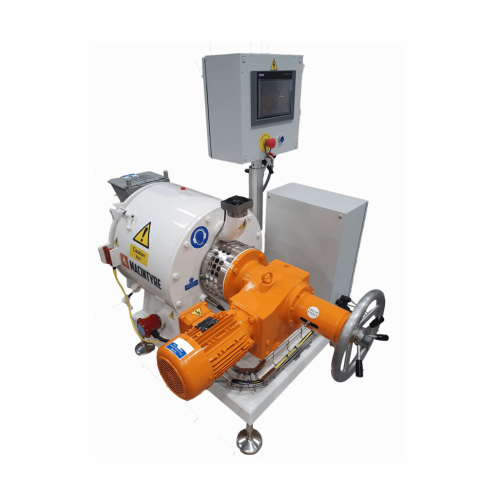
Laboratory refiner/conche for chocolate processing
For chocolate producers seeking precise control over texture and flavo...
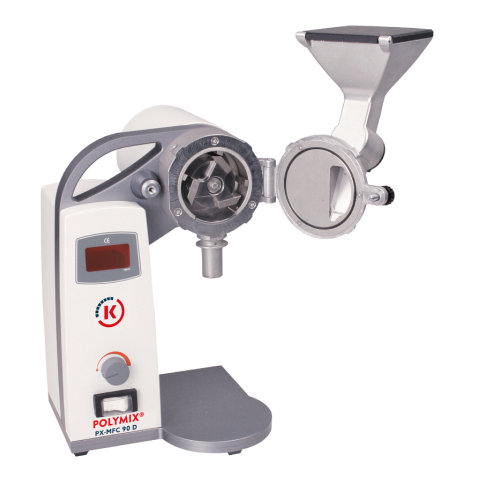
Dry sample preparation mil
Optimize your grinding processes with precision particle size reduction for various materials, en...
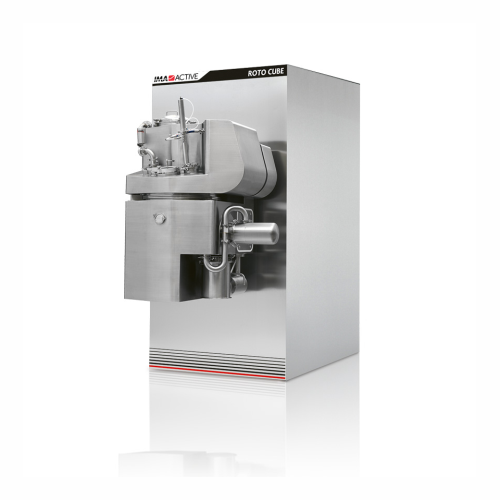
Single-pot granulation processor for pharmaceutical applications
For manufacturers needing precise granulation and dryin...
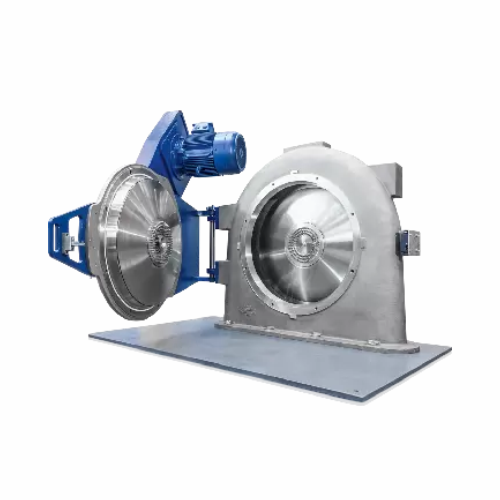
Industrial powder grinder
Achieve precise particle size reduction and classification with advanced equipment designed for co...
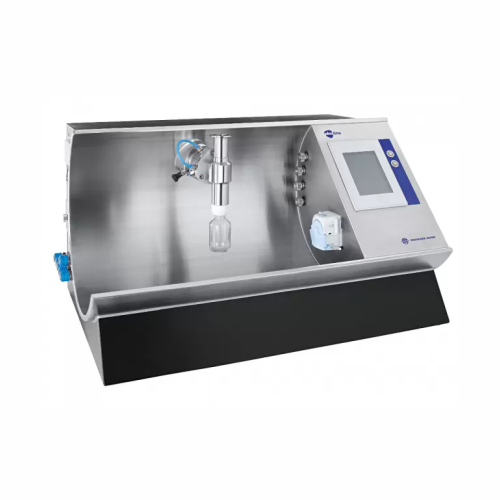
Lab-scale powder processing system
Achieve precise control in ultra-small batch processing with a versatile modular system,...
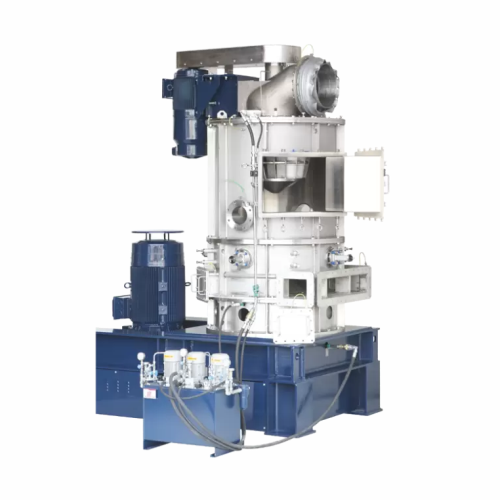
Ultra-fine powder flash drying system
Achieve rapid moisture removal and particle refinement with this integrated system, d...
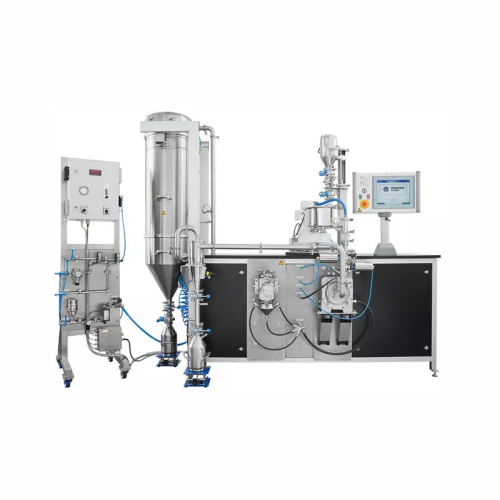
Multiprocessing system for flexible research and production
Optimize your process development with a versatile system th...

Sugar grinding and recrystallization system
Optimize your sugar production with a system that integrates grinding and recr...
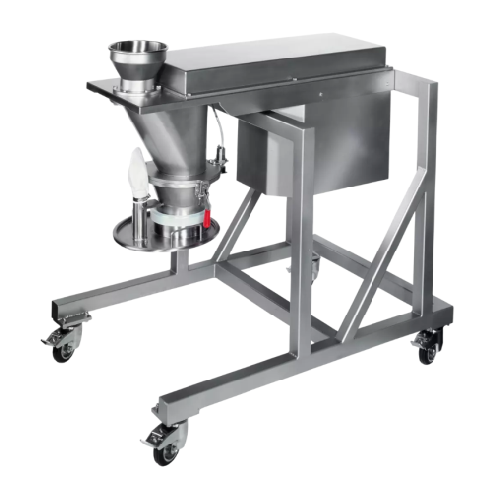
Flake crushers for gentle crushing of brittle materials
For processes needing precise granule control, our equipment ensu...
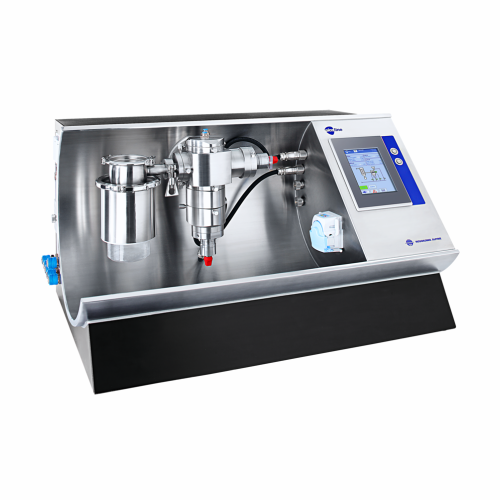
Laboratory system for powder and particle processing
When precision in powder processing is crucial, this versatile labor...

Pre-breaker for initial material size reduction
Efficiently prepare your bulk materials for further processing by swiftly ...
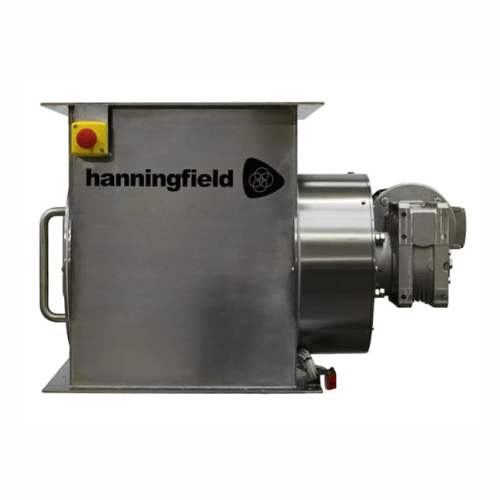
Industrial lump breaker for compact material deagglomeration
Efficiently deagglomerate compacted materials to enhance fl...
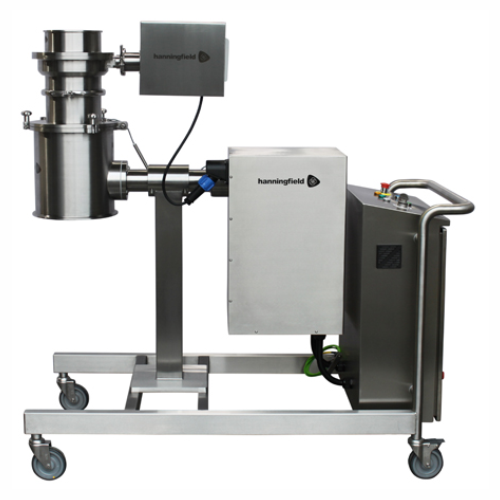
Pharmaceutical size reduction shredder
Achieve fast, efficient material size reduction with this shredder, enabling seamles...
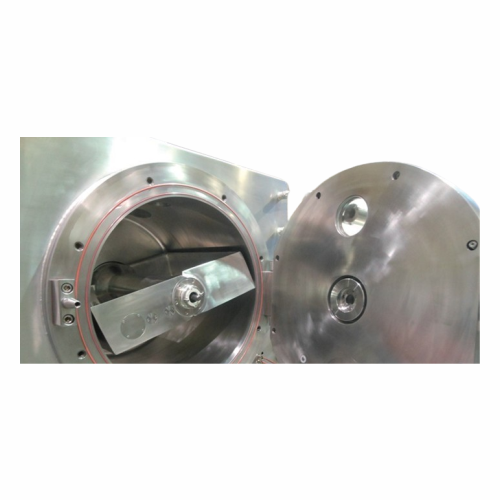
Rotary vacuum paddle dryer for pharmaceutical ingredients
Ensure precise moisture control and efficient drying for sensi...
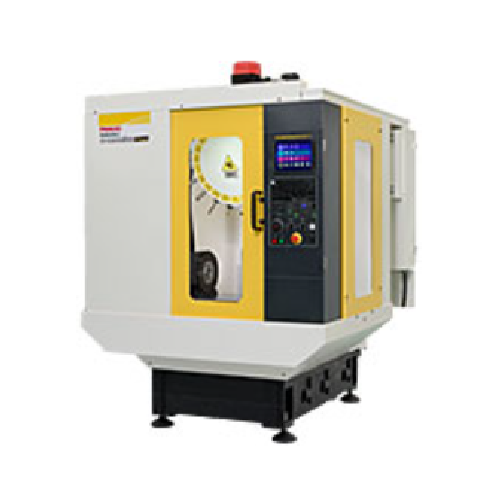
Compact machining center for high-precision manufacturing
Achieve unparalleled precision and speed in metal machining wi...
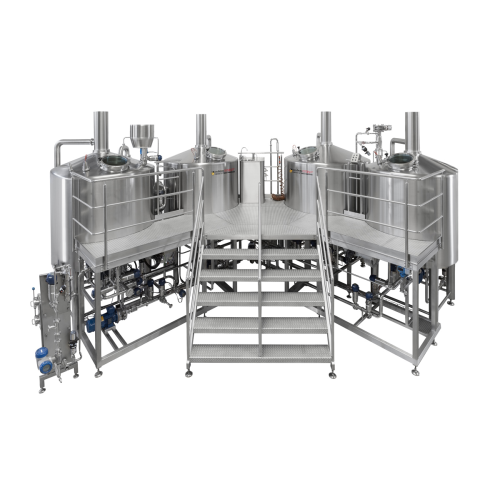
Flex-bräu beer brewing system
Achieve high-efficiency beer production with integrated milling, filtration, and energy-saving...
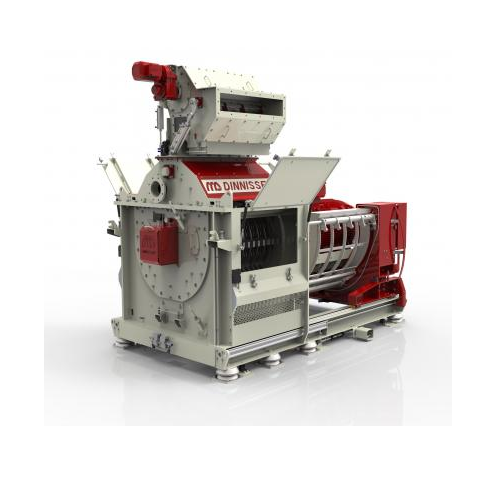
Fast screen exchange grinding solution for medium-hard products
Maximize your milling efficiency with a solution that al...
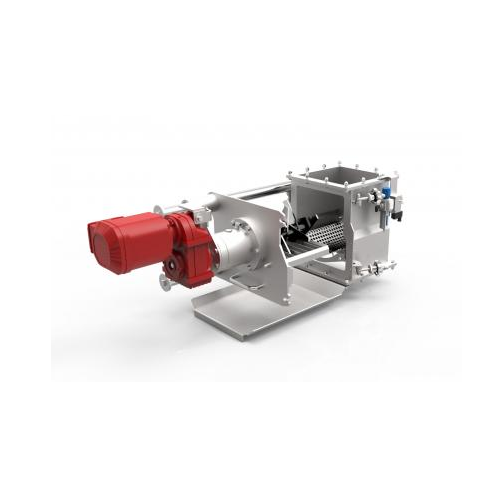
Industrial breaker for reducing large lumps and agglomerates
Efficiently break down challenging materials with a robust ...
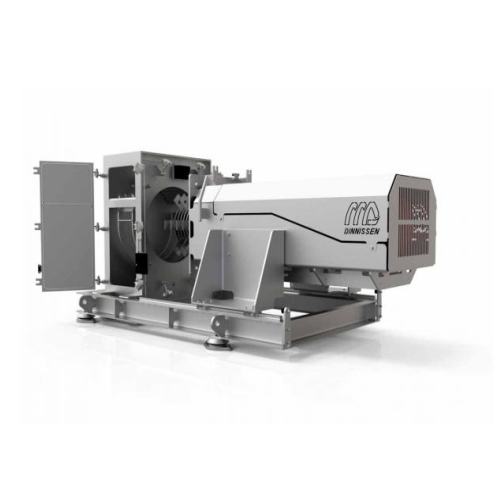
Hygienic industrial grinder for food and pharma applications
Achieve optimal hygiene and efficiency in your grinding pro...
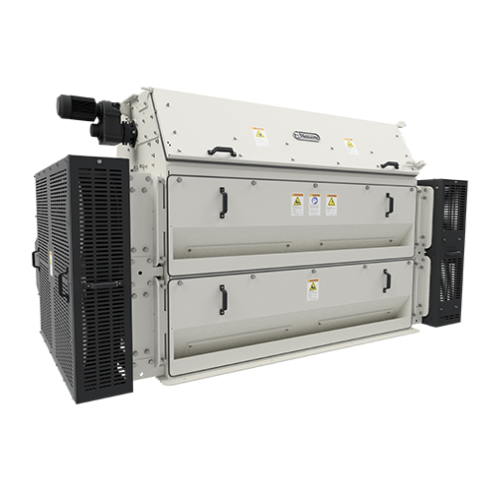
Oilseed cracking solution
Maximize throughput with precision cracking, ensuring optimal downstream processing for oilseed pr...
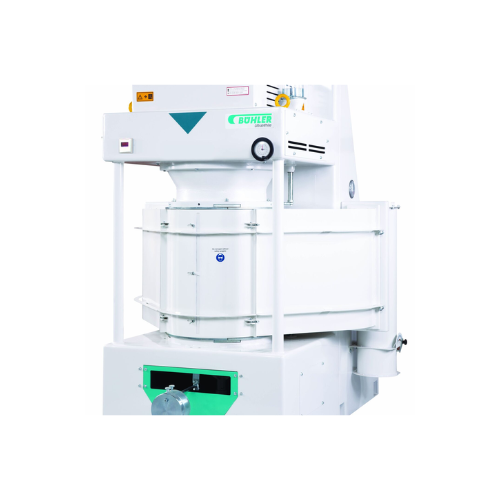
High-capacity rice whitener
Achieve uniform whiteness and optimal rice quality effortlessly with advanced vertical whitening...
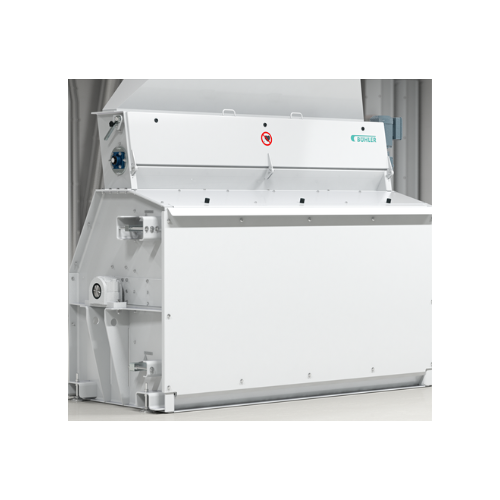
Sunflower seed dehulling system
Experience efficient dehulling for high-yield sunflower seed processing, enhancing kernel qu...
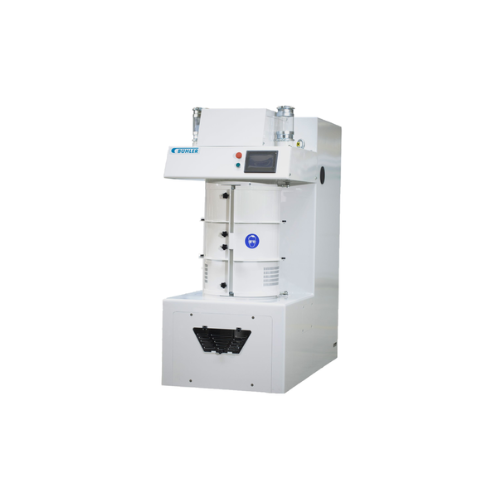
Automatic rice whitening solution
Need consistent rice whiteness and bran removal without manual intervention? This high-sp...
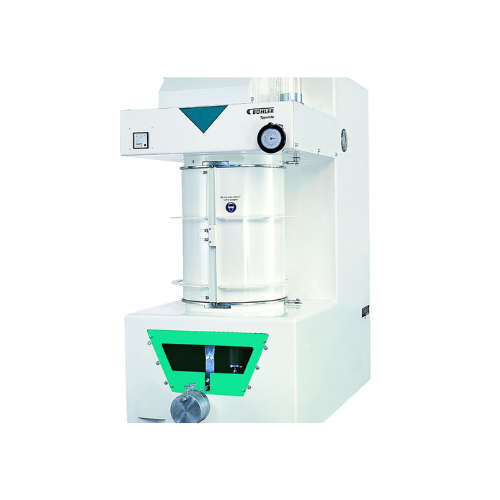
Vertical rice whitener
Optimize rice and grain outputs with high-yield vertical whitening technology, designed to preserve pr...
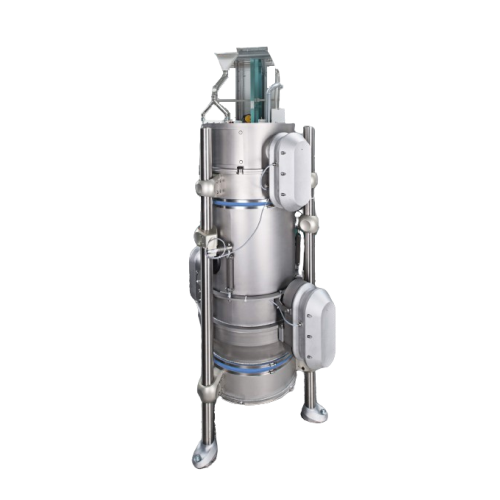
Advanced superheated steam drying solution
Harness the power of consistent drying technology to achieve optimal moisture c...

Vertical pearler for durum wheat and pulses
Optimize your grain and pulse processing with this high-efficiency pearling te...
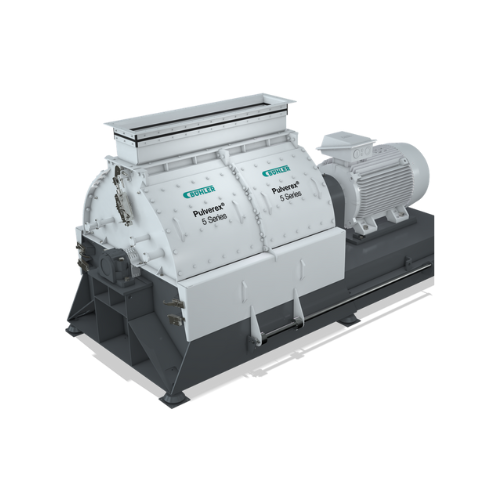
Pulverizer for fine grinding applications
Achieve optimal particle size distribution and enhance throughput with this adva...
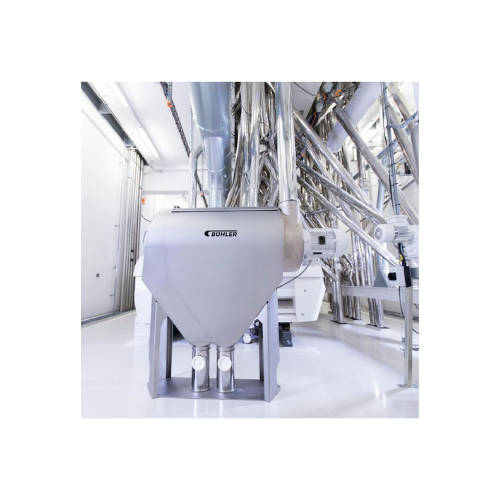
Bran finisher for wheat and rye
Enhance your milling efficiency by separating finer flour from bran with ease. This compact ...
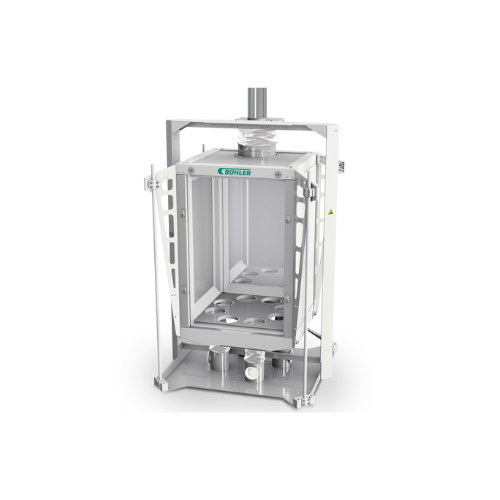
Grain product plansifter
Optimize your grain processing with a magnetic drive plansifter that efficiently sifts and sorts a d...
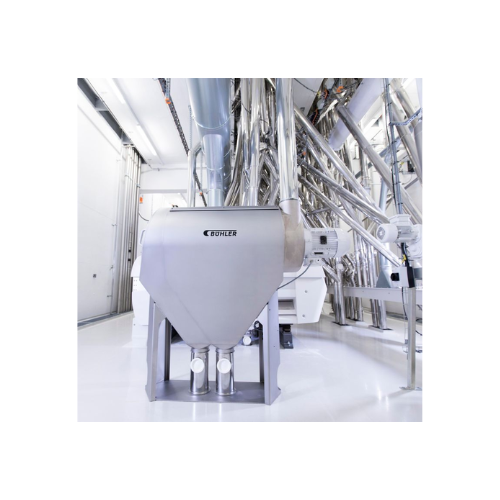
Bran finisher for efficient flour and bran separation
Optimize your grain processing efficiency with a solution designed ...
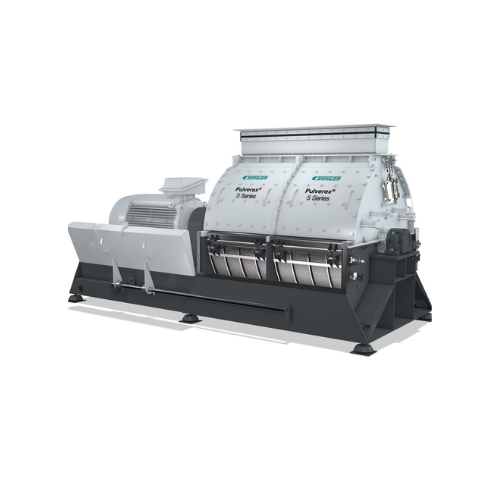
Industrial fine grinding pulverizer
Achieve consistent fine granulation at high capacity with reduced energy consumption, u...
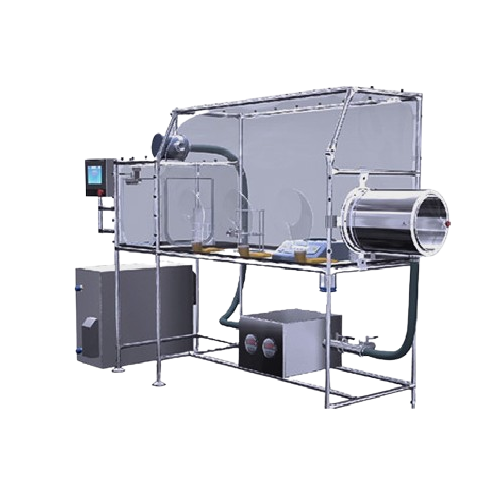
Flexible isolator for aseptic containment
Ensure sterility and safety with a flexible isolator designed for efficient cont...
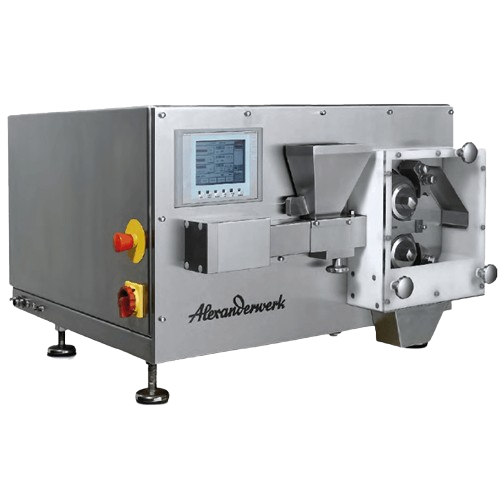
Dry granulation technology
Achieve precise control over particle size and density with our compacting and granulation soluti...
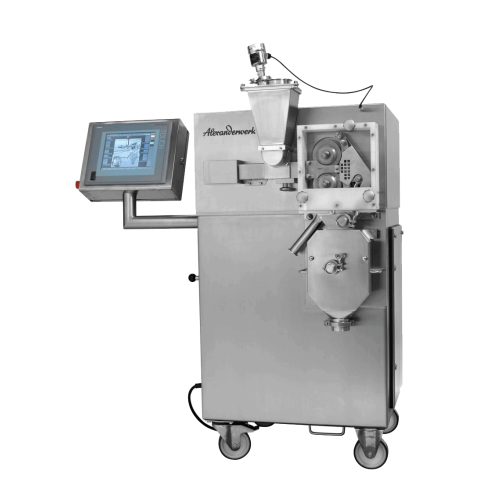
Pharmaceutical roller compactor
Achieve consistent granulate quality with optimized compacting processes, ideal for transfor...
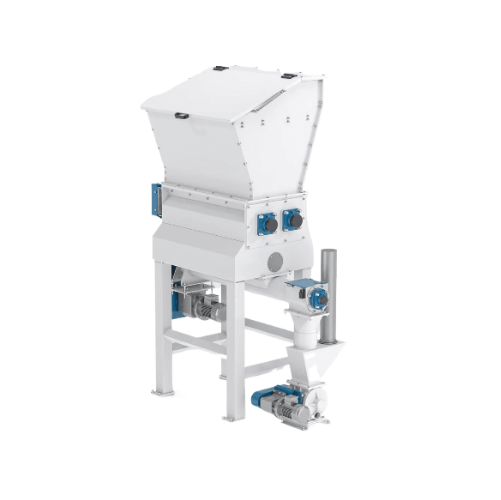
Scrap grinding system for reprocessing dry pasta
Efficiently reprocess dry pasta into reusable flour and dough, minimizing...
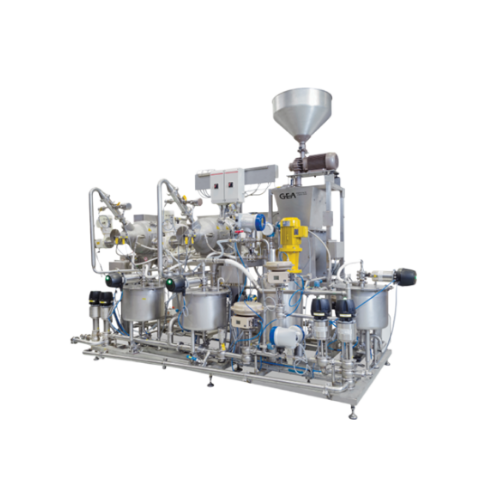
Wet grinding system for coffee flavor preservation
Achieve unparalleled coffee flavor and aroma by integrating a low-temp...

Laboratory disperser for high-viscosity products
Optimize your laboratory processes with precise mixing and dispersing of ...
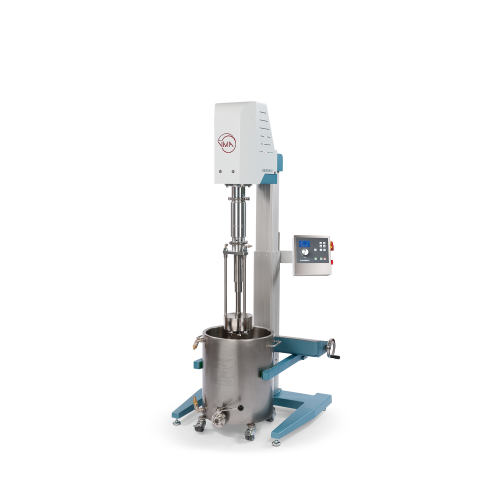
Entry-level vacuum dispersion system for laboratory applications
Achieve precise dispersion and milling with this versat...
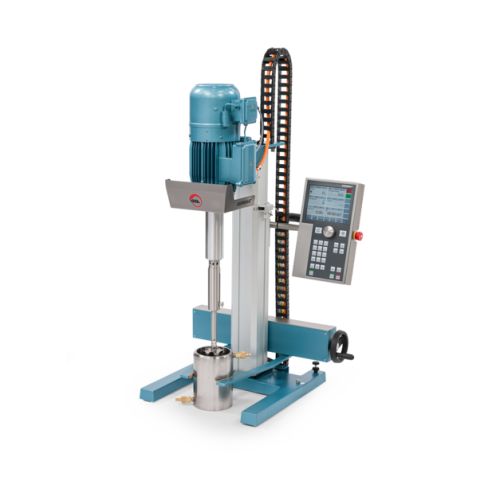
Rotary homogenizer for laboratory and pilot plant
For achieving optimal dispersion in complex formulations, this solution...
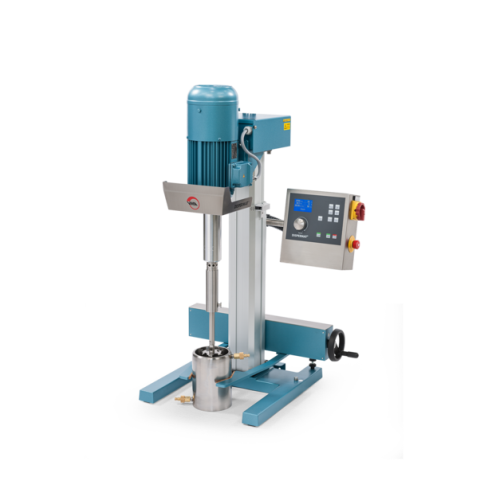
Dissolver for mixing and processing in lab and pilot plant
Optimize your material dispersion and homogenization processe...
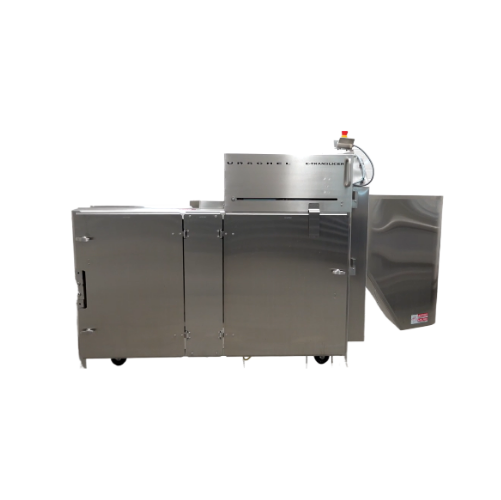
Slicer for food processing applications
Efficiently achieve precise cuts and textures for a variety of food products, enhan...
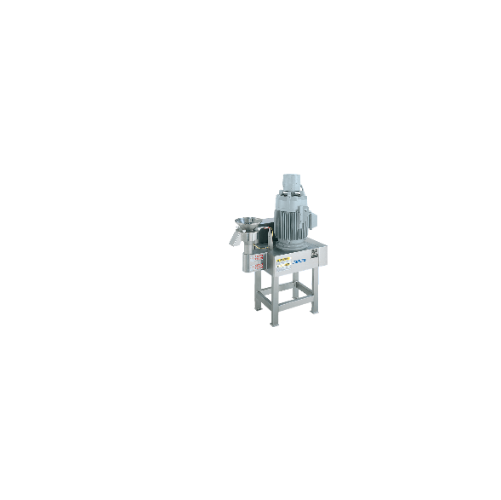
Industrial mixer for high moisture content products
Optimize the texture and consistency of high-moisture foods with prec...
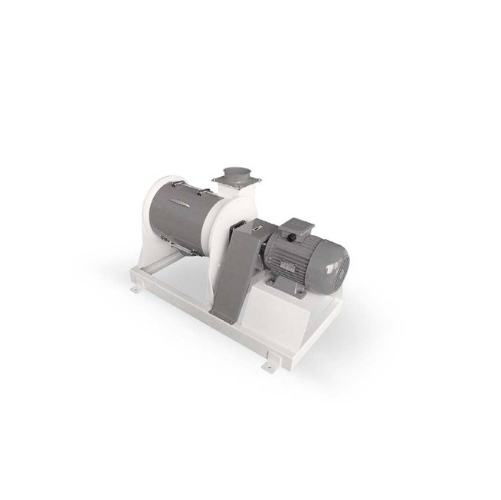
Industrial drum detacher for semolina and bran separation
Achieve precise separation of semolina and bran with minimal e...
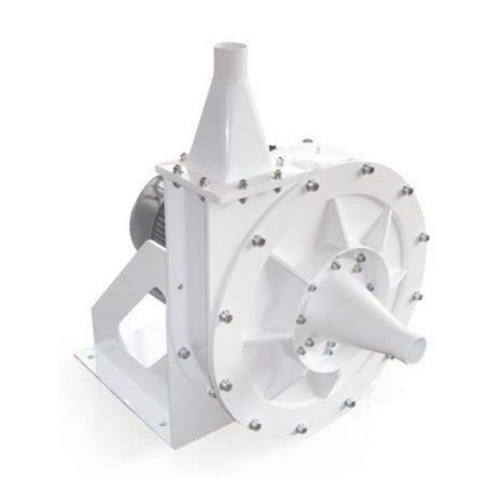
Flour insect control system
Eliminate pest contamination and preserve flour quality with high-speed larva destruction, ensur...
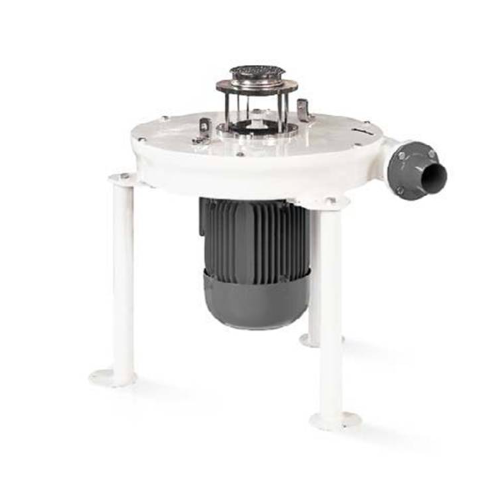
Industrial impact detacher for semolina processing
Optimize your grain processing line with a solution designed to enhanc...
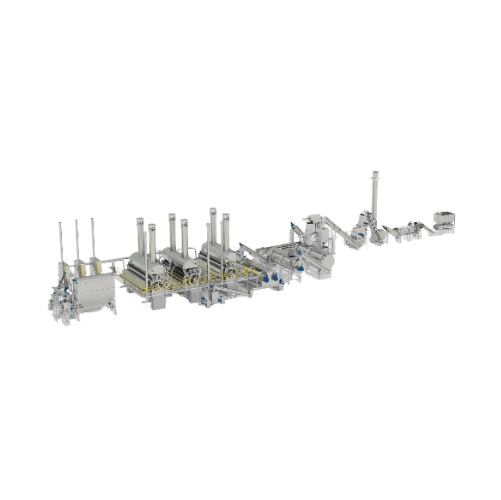
Turnkey potato flake processing line
Effortlessly transform raw potatoes into high-quality flakes with this integrated line...
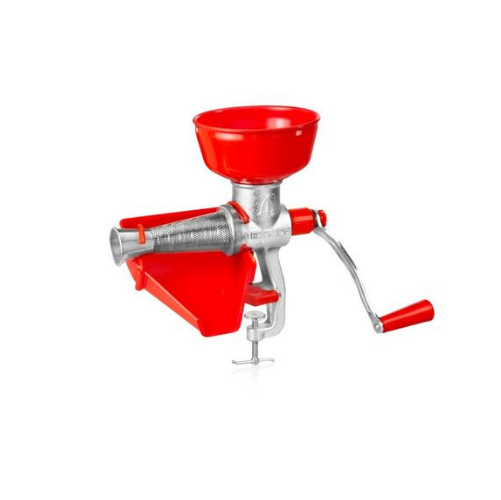
Tomato squeezer for efficient food processing
Efficiently transform raw tomatoes and other fruits into smooth sauces and p...

Micronization for pharmaceuticals
Achieve ultra-fine particle size reduction for complex materials, essential when precisio...
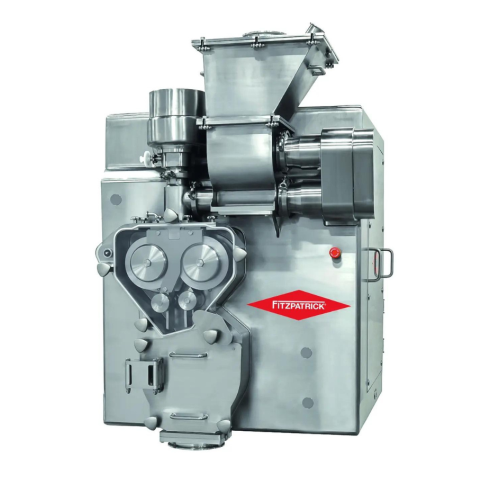
Dry granulation system for pharmaceutical powders
Streamline your powder processing with a dry granulation system that en...
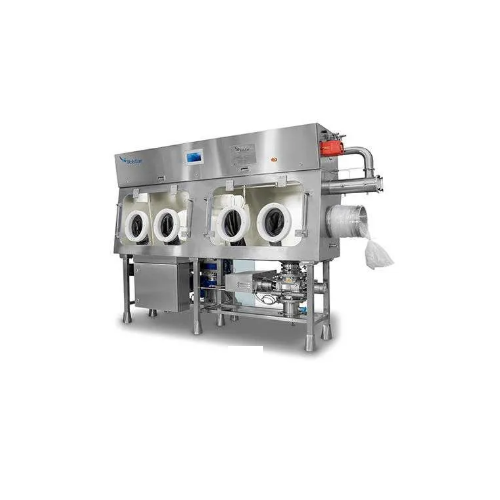
Sterile lyophilised filler
Achieve precise weighing and contamination-free lyophilisation with our cutting-edge sterile fill...

Spice and pharmaceutical powder grinder
Efficiently transform raw materials into fine powders, ensuring optimal consistency...
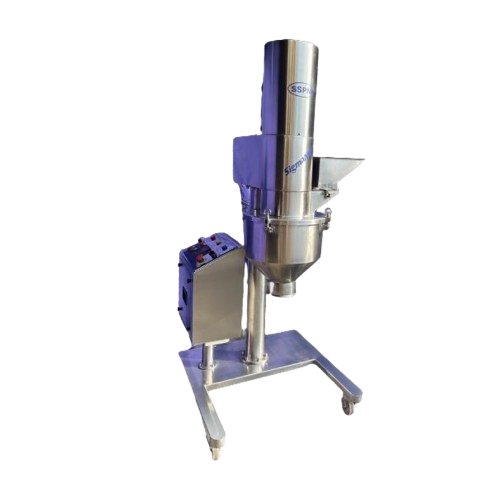
Wet granulation system for pharmaceutical tablets
Optimize your tablet production with precise particle size reduction an...
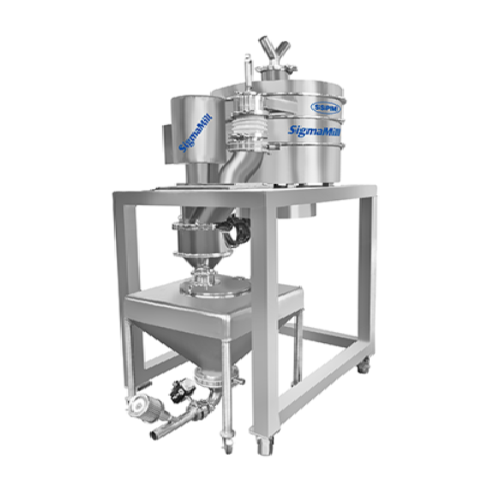
Wet granulation for pharmaceutical products
Achieve seamless integration of sifting and milling with precise powder handli...
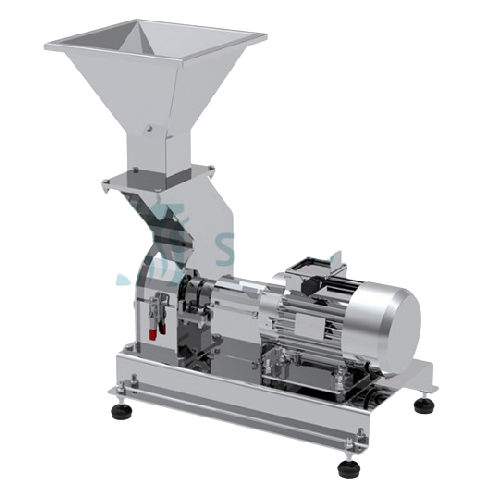
Semi-automatic seaweed grinder for efficient algae processing
Optimize seaweed processing with this stainless steel grin...
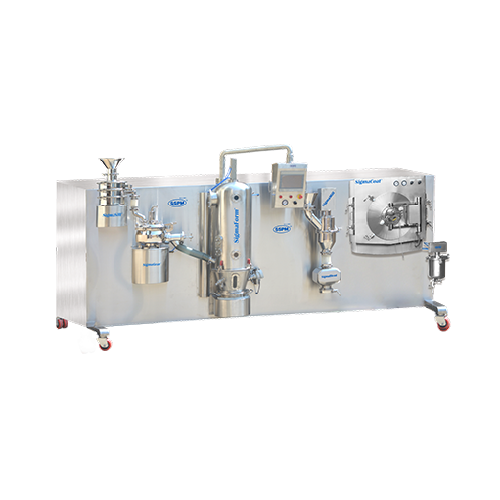
Compact wet granulation r&d system
Ensure precise formulation of pharmaceutical powders with a scalable, lab-friendly syste...
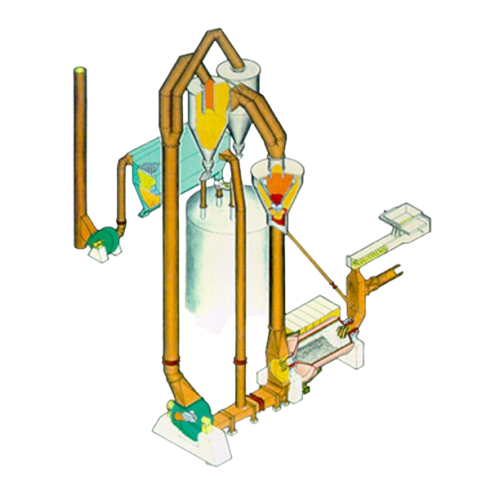
Industrial grinding solution for hard and abrasive materials
Efficiently grind and mill a spectrum of materials from coa...

Particle size reduction air conveying system
Achieve precise particle size reduction and contamination-free processing for...

Energy efficient grinder for plant-based milk
Buying pre-processed materials, such as flour, and handling and dispersing t...
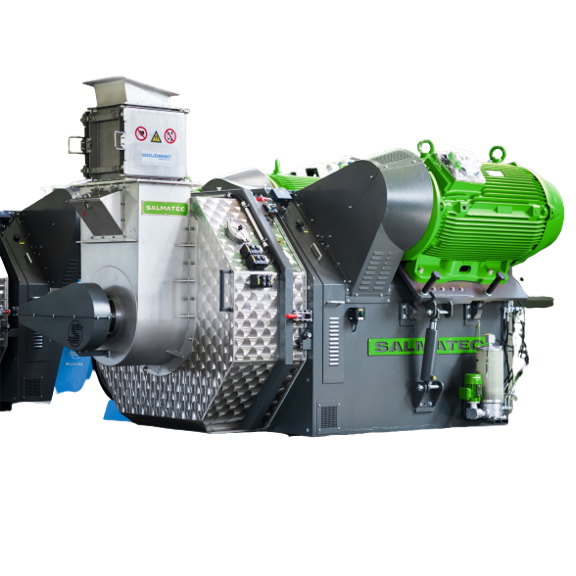
Complete pellet line
Large industries are shifting towards more environment-friendly technology, such as recycling wastes and...
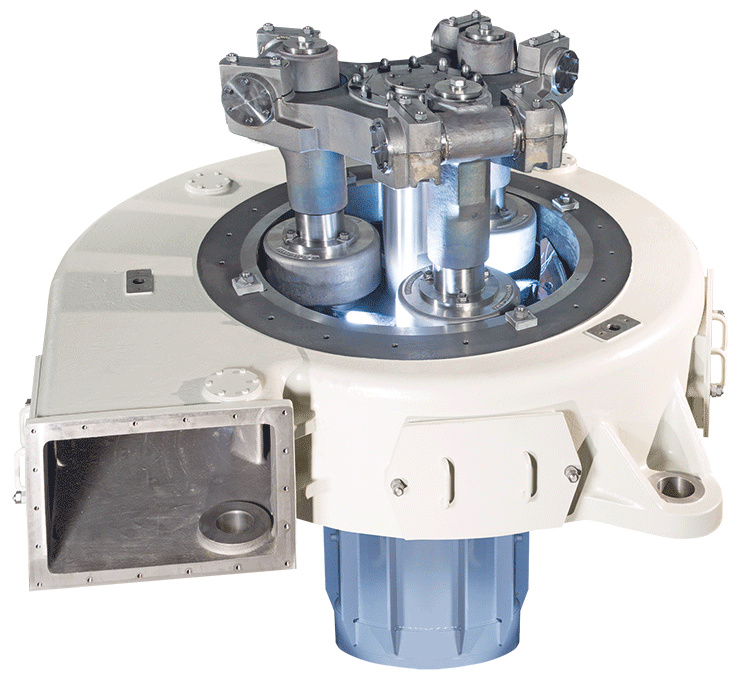
Grinding and drying of CaCO3
Widely used in the construction industry as filling materials, calcium carbonate is usually mad...
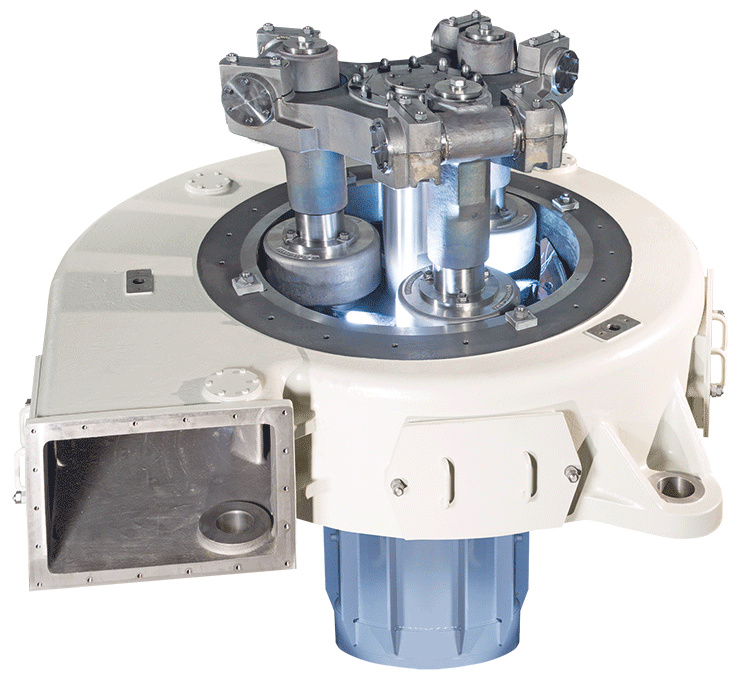
Grinding and drying of bentonite
After crushing and drying mined bentonite, this clay mineral is usually processed through a...
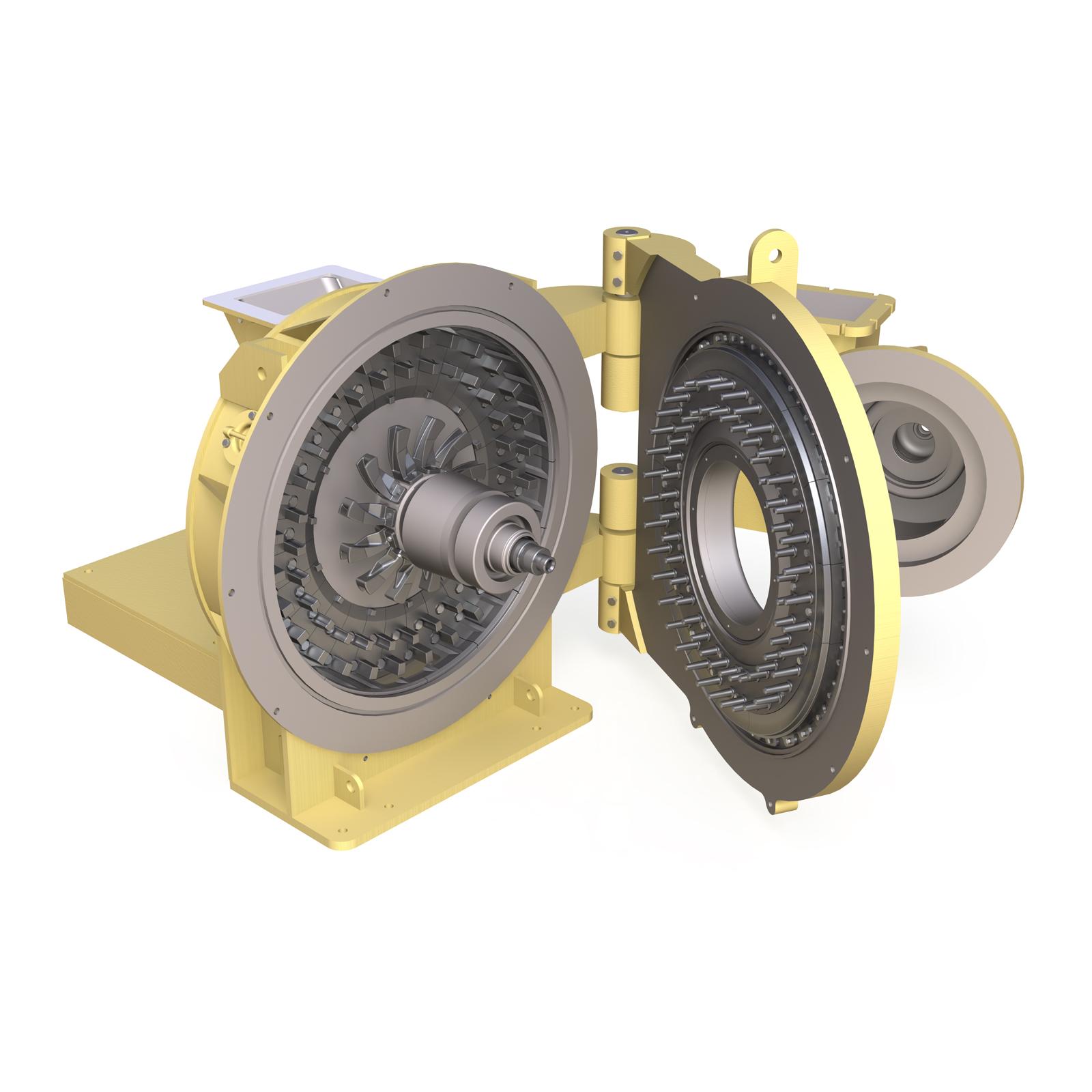
Flash drying grinder for powders
Drying and grinding can be an important feature when trying to process products such as raw...
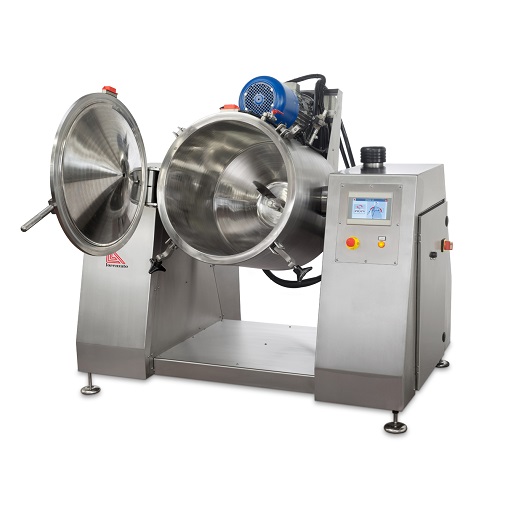
Blending tank for cosmetic powders
The production of high-quality cosmetics powders requires perfect mixing and dispersal o...
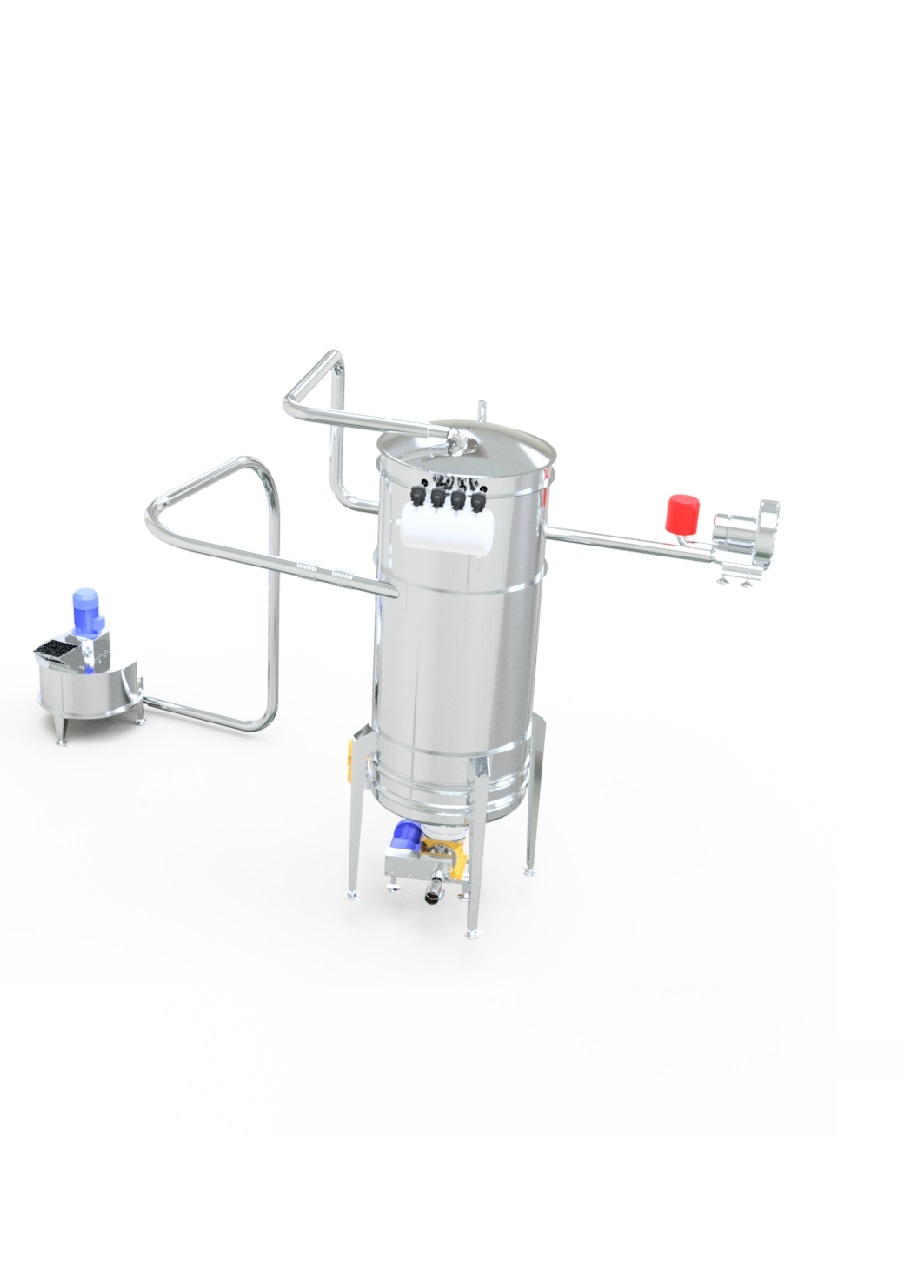
Automatic rework system for biscuit and bread scrap
Scraps are an inevitable byproduct of biscuit and bread production. W...
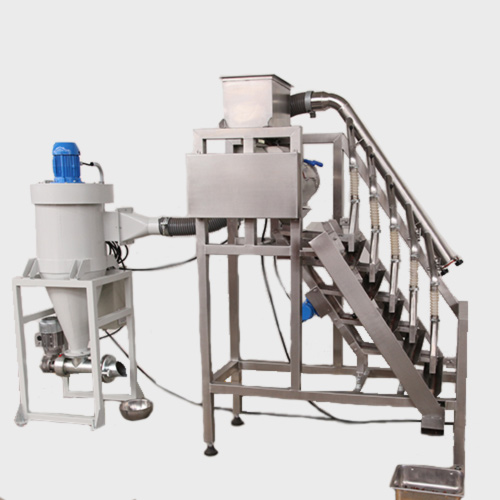
Five deck cocoa bean winnower
Skin and shell removal from cocoa beans is necessary to produce great tasting chocolate. Compl...
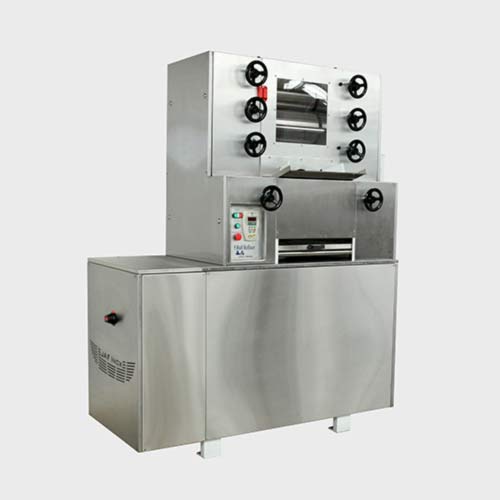
Chocolate refiner with chiller
Milled beans need further reduction in particle size before they can be sent to a conche for ...
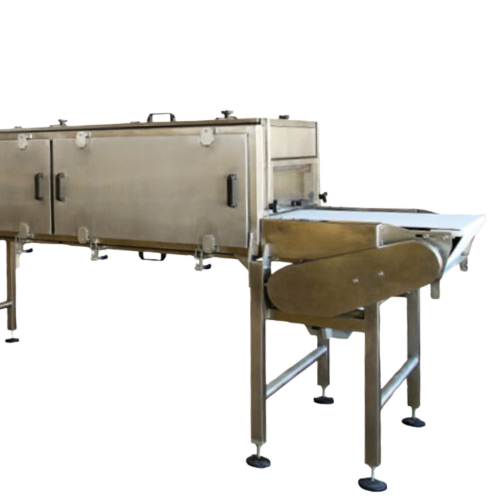
Chocolate bean to bar line 10kg
Developing new products, producing specialty chocolates, laboratory testing, and in-shop pro...
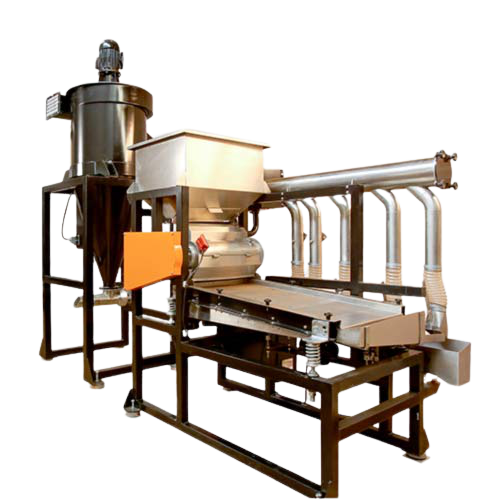
Chocolate bean to bar line 200kg
Installing a chocolate production line that works efficiently and smoothly can be a dauntin...
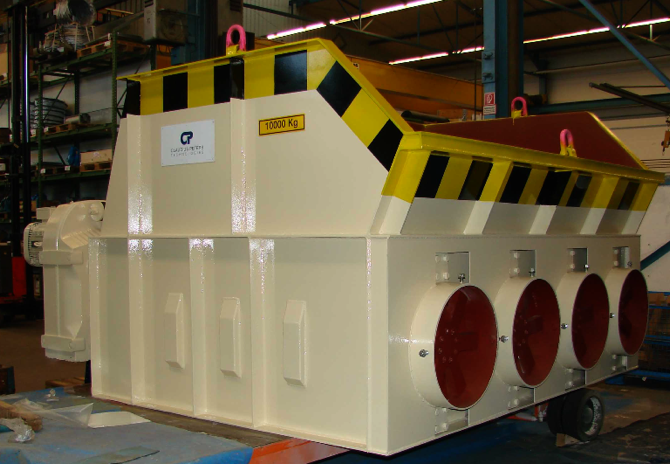
Reclaim crusher
Waste products and rejected materials are inevitably generated from any gypsum products manufacturing process....
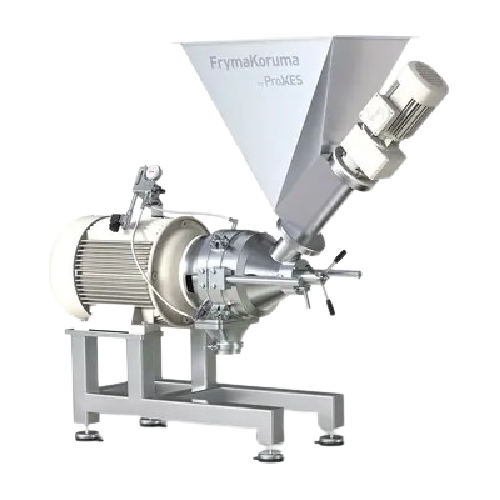
High shear emulsifier for food and pharmaceutical products
Optimize your production line with precise emulsification, ho...
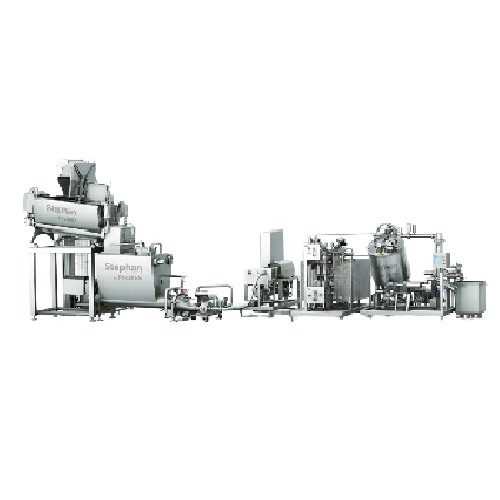
Cheese blending and heating line for processed cheese
Optimize your processed cheese production with a solution that seam...
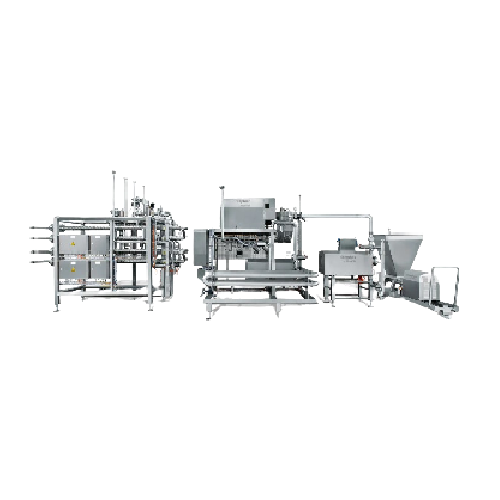
Continuous cheese line
Achieve precise temperature control and seamless product transitions with this equipment, ideal for en...
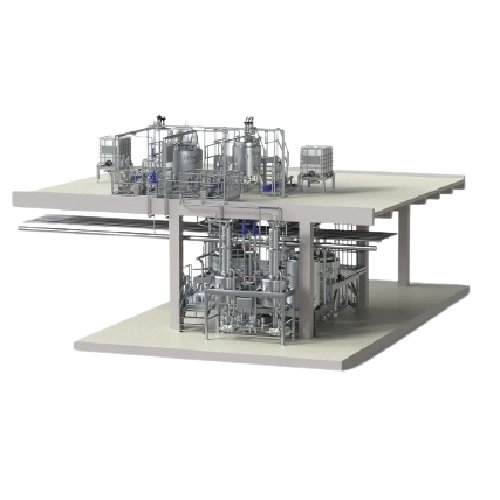
Continuous mustard line
Streamline mustard production with high-capacity continuous processing that reduces air pockets and e...

Continuous tahina production line
Streamline your tahina production with precise grinding and controlled cooling, ensuring ...
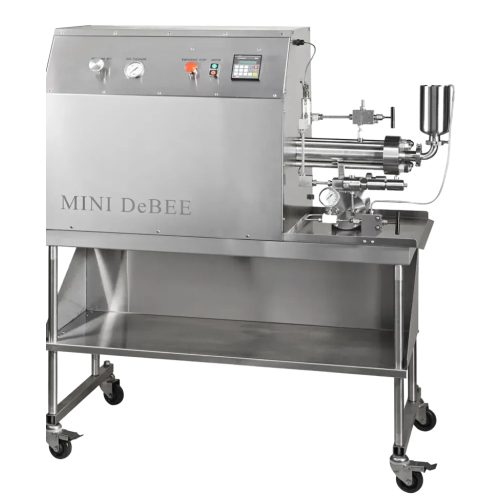
High-pressure homogenizer for small-scale production
Enhance your liquid formulations with precise particle size reductio...
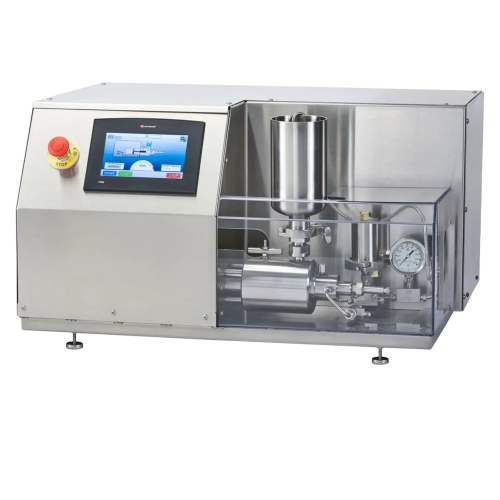
Benchtop homogenizer for r&d labs
Optimize your lab processes with precision particle size reduction and efficient emulsifi...
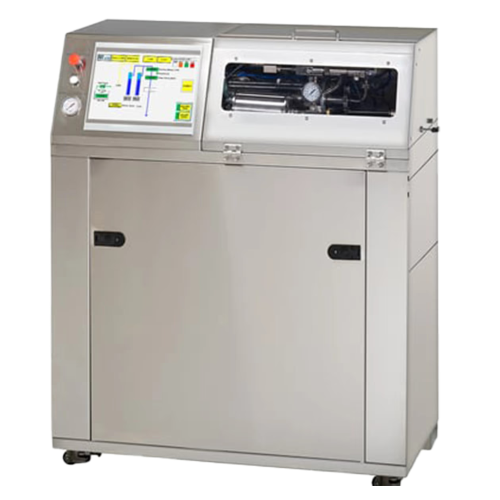
High pressure homogenizer for cell disruption and nanoemulsions
Achieve precise particle size reduction and enhanced bio...
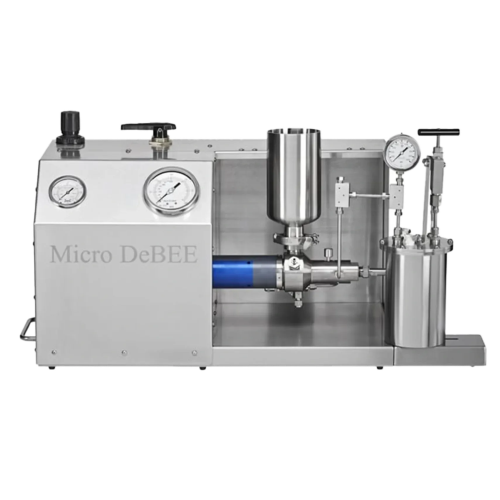
Laboratory homogenizer for nanoemulsions and dispersions
Elevate your laboratory capabilities with a bench-top homogenize...
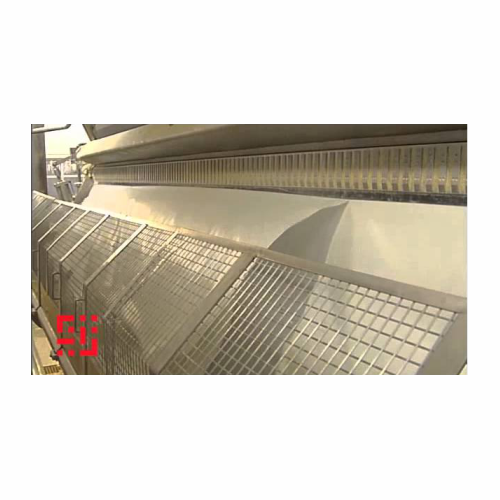
Industrial potato flake production line
Maximize yield and quality in potato processing by integrating advanced pre-cleanin...
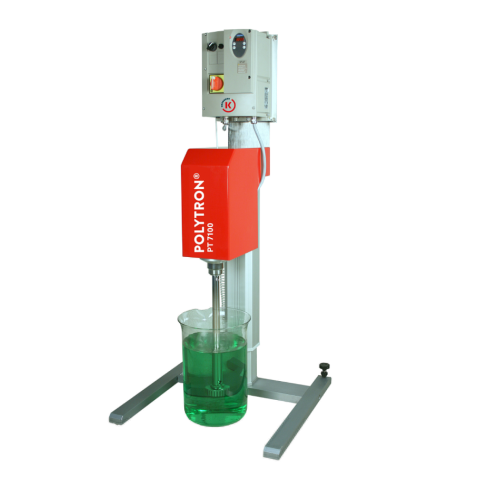
Stand dispersing unit for pilot plant applications
Achieve precise particle size reduction and efficient mixing with this...
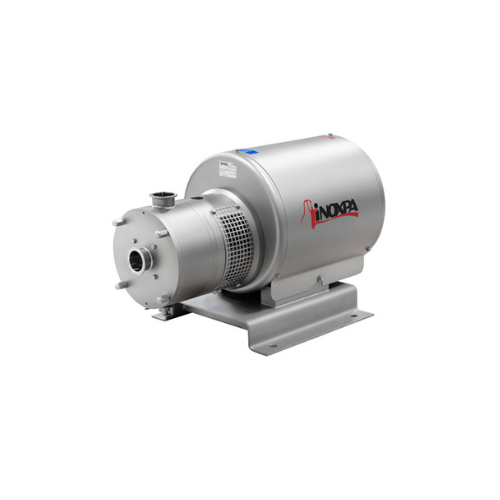
In-line high shear mixing solution
Achieve precise emulsification and particle size reduction with high shear capabilities,...
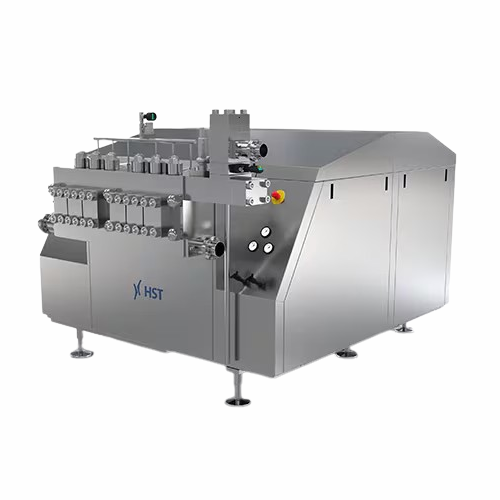
High-pressure homogenizers for liquid products
Achieve consistent emulsions and stable dispersions with high-pressure homo...
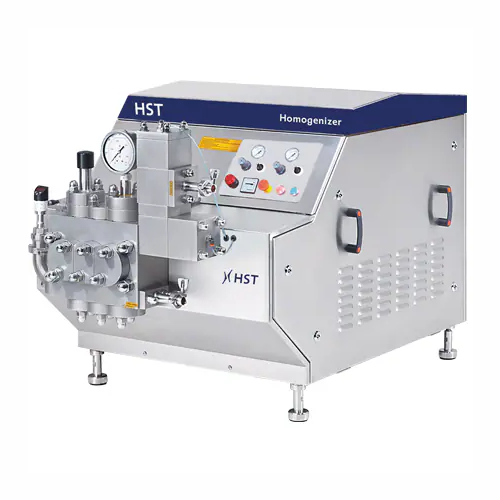
Industrial homogenizer for food and pharmaceutical applications
Ensure product consistency and stability with high-press...
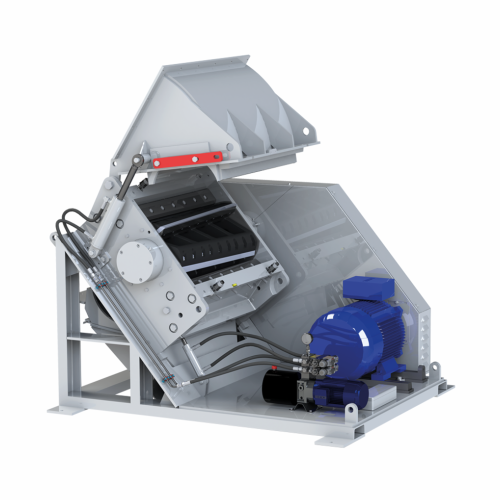
Low-dust granulator for plastic parts recycling
Achieve efficient comminution with minimized dust generation, ideal for pr...
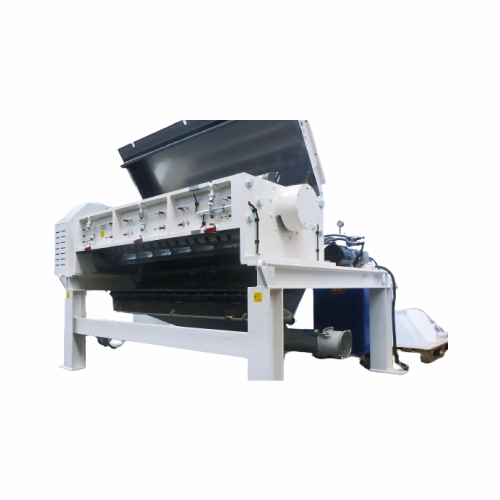
Industrial granulators for plastic recycling
Streamline your recycling operations with a solution that not only reduces en...
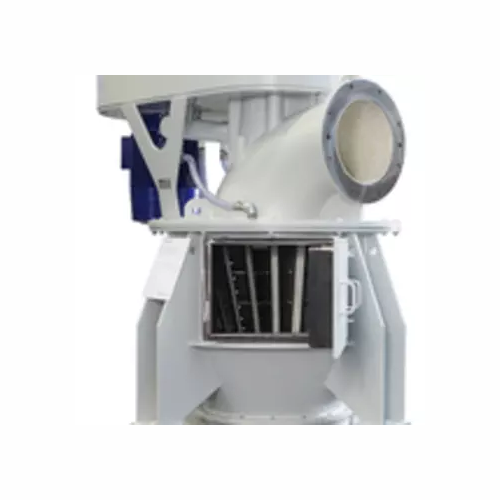
Ultrafine classifier for precise particle separation
Gain precise control over particle size with this ultrafine classifi...
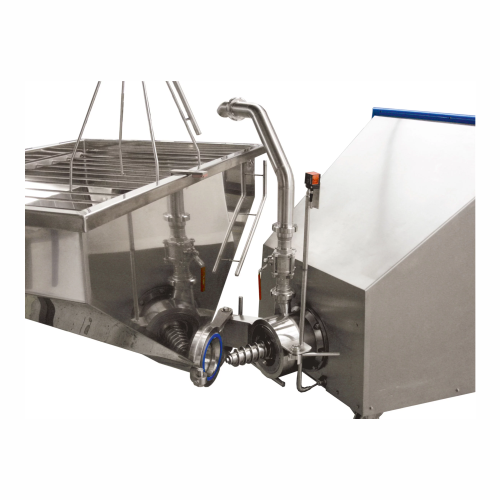
Precision emulsification equipment for food industry
Achieve precise comminution and emulsification for diverse food text...
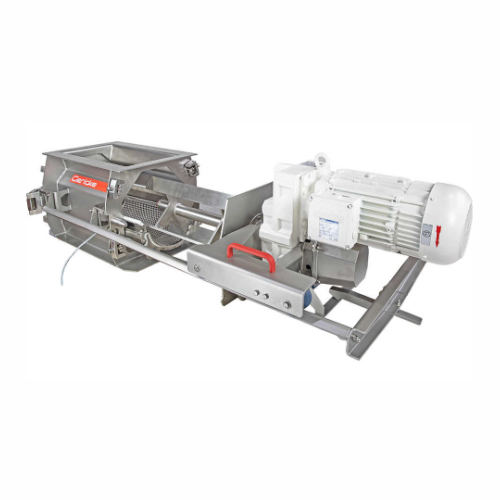
Deagglomerator for consistent particle size reduction
Struggling with inconsistent particle sizes or unwanted lumps in yo...
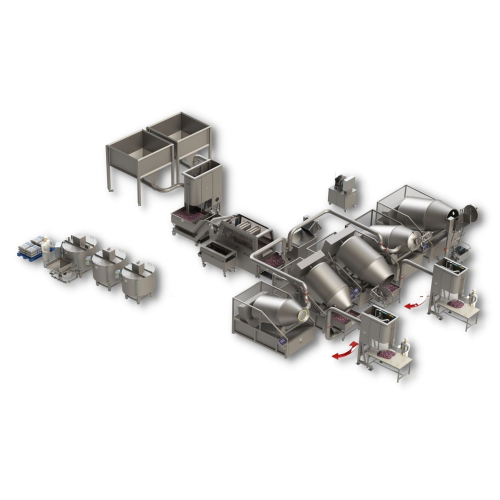
Fully automated meat processing line
Optimize your meat production with a seamlessly integrated line that boosts productivi...
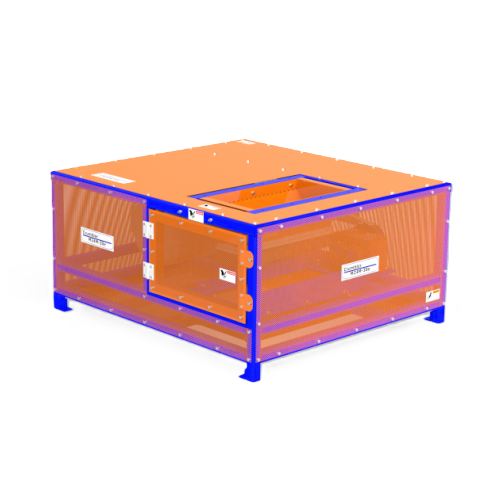
Rotary shear for wood chips and biomass processing
Efficiently transform diverse biomass materials into uniform particles...
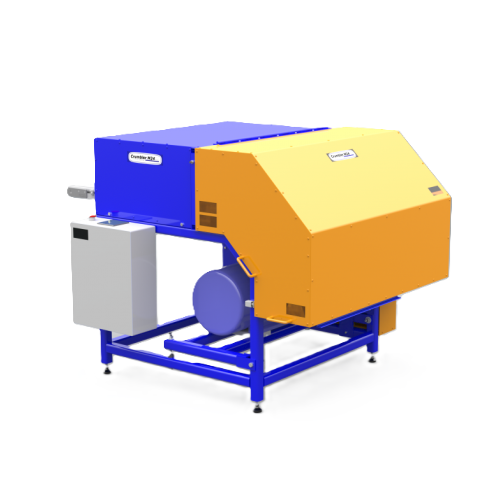
Pilot-scale commercial rotary shear for biomass processing
Optimize your biomass processing with efficient particle size...
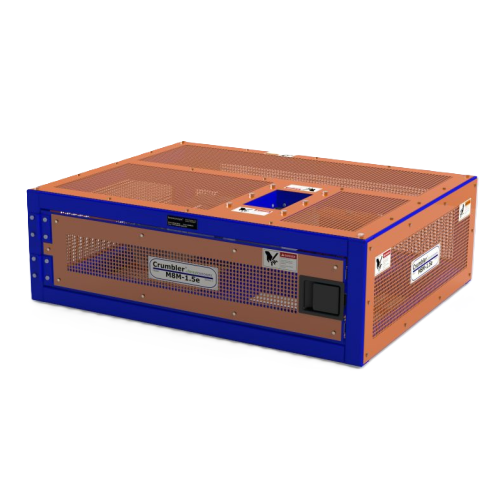
Micro-scale rotary shear for particle size reduction
Optimize your research with precise particle reduction, ideal for tr...
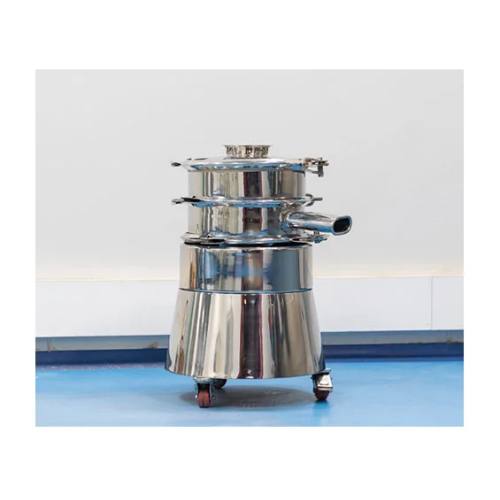
Particle sizer for precise sifting
Optimize your production line with high-speed particle sizing, ensuring precise control ...
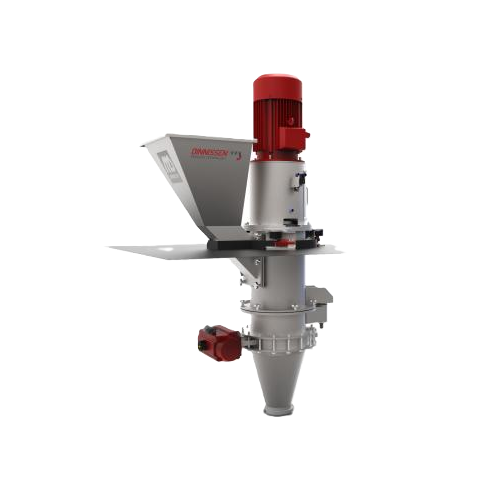
Industrial shredder for diverse material reduction
Achieve precise and efficient material resizing for diverse applicatio...
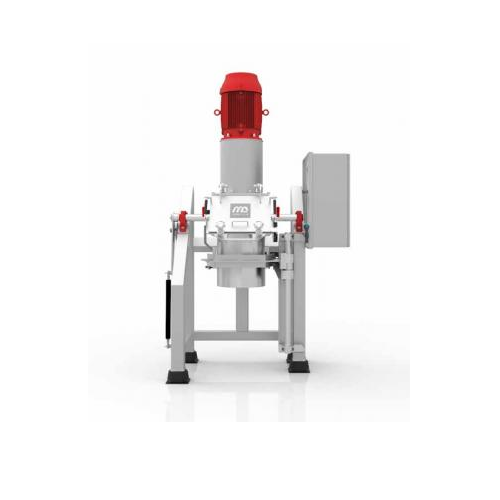
Industrial pulper for fresh produce
Achieve ultra-fine purees and pastes with this high-speed industrial pulper, designed t...
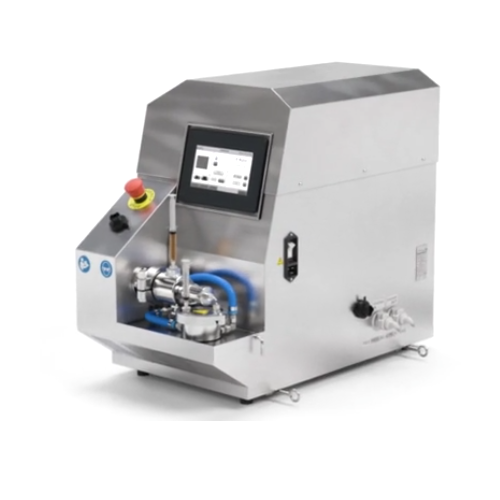
High-shear processors for uniform nanoparticles
Optimize particle size reduction and achieve uniformity in nanoparticle fo...
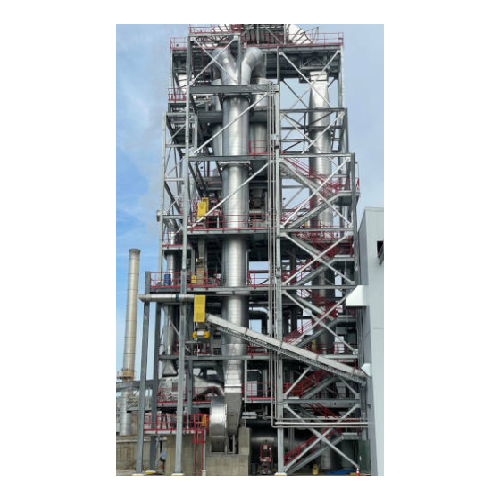
Industrial ring dryers for high-capacity drying applications
Maximize drying efficiency for diverse materials with ring ...
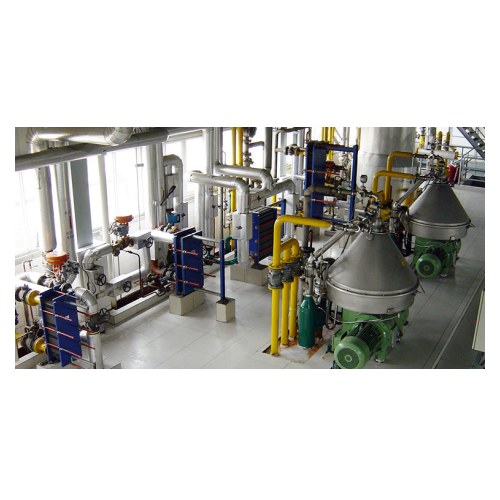
Oil and fat refining system
Ensure high-quality oil and fat production by efficiently removing contaminants such as phosphat...
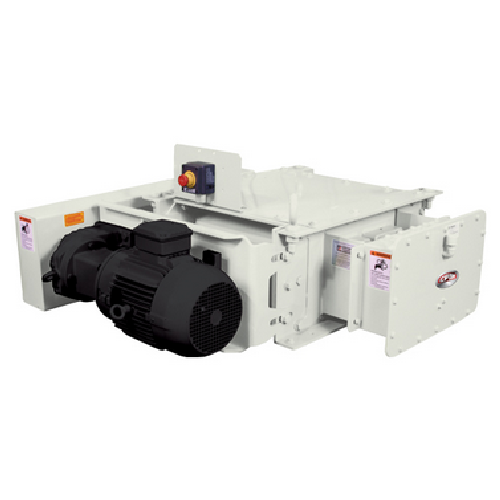
Industrial lump breaker for particle size reduction
Optimize your production line with an advanced solution for efficient...
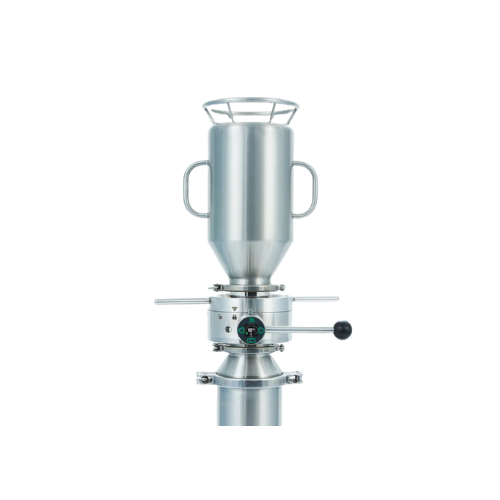
High containment powder transfer valve
Ensure high containment for potent powders in your production line, reducing contami...

High containment powder transfer valve for bulk material
Ensure operator safety and prevent cross-contamination with robu...
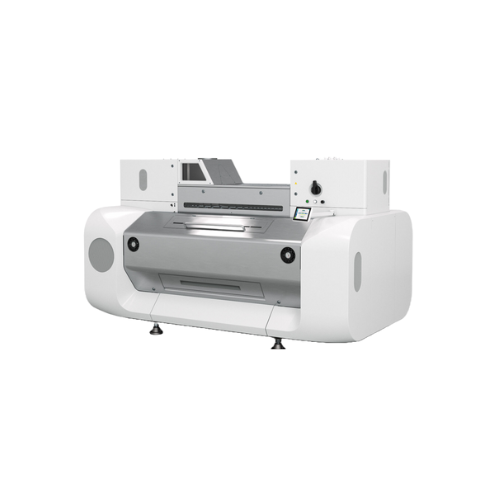
Integrated grinding system for wheat and grain
Optimize your grinding process with a system that delivers consistent parti...
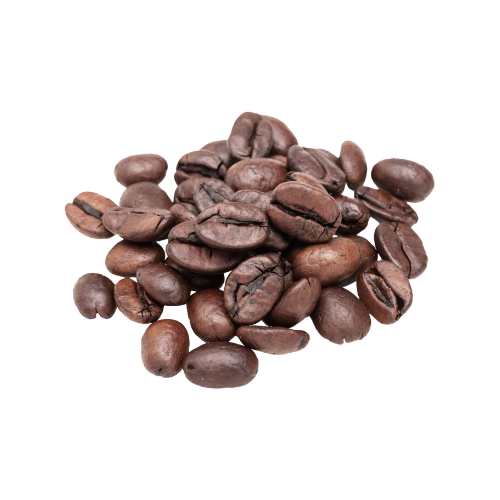
Coffee processing system for integrated coffee production
Enhance your coffee production with a versatile system that in...
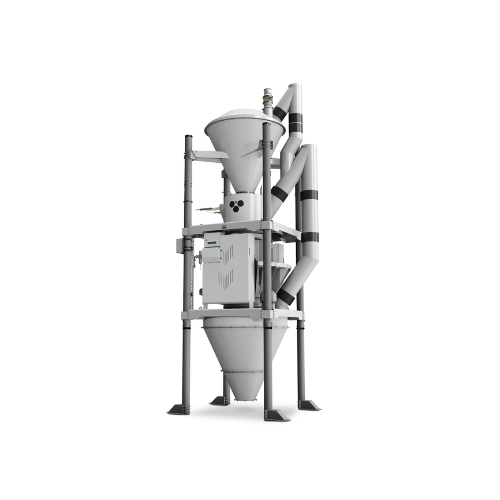
Fully automatic batch scale for powdery and granular products
Achieve precise and repeatable dosing for powdery and gran...
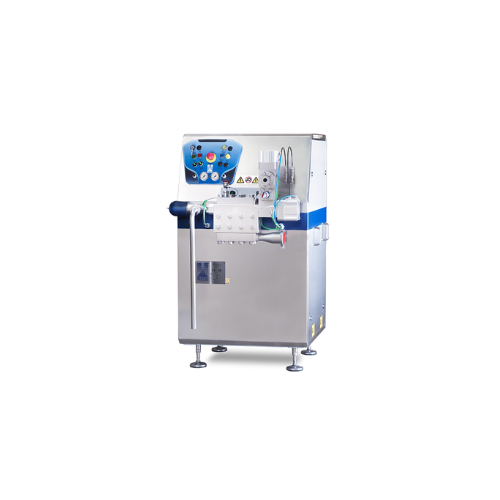
Industrial homogenizer for high pressure applications
Achieve consistent product texture and stability for your emulsions...
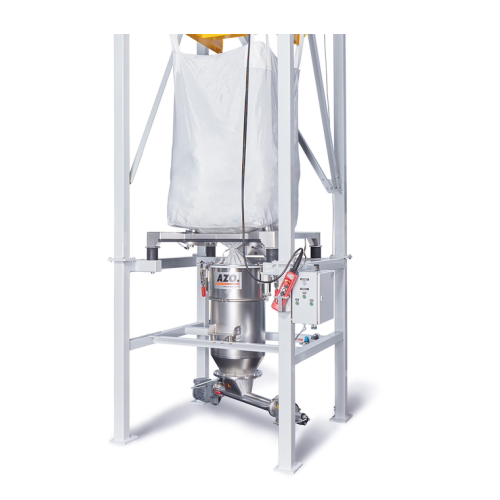
Modular big bag discharge station for bulk material handling
Streamline your bulk material handling with a customizable ...
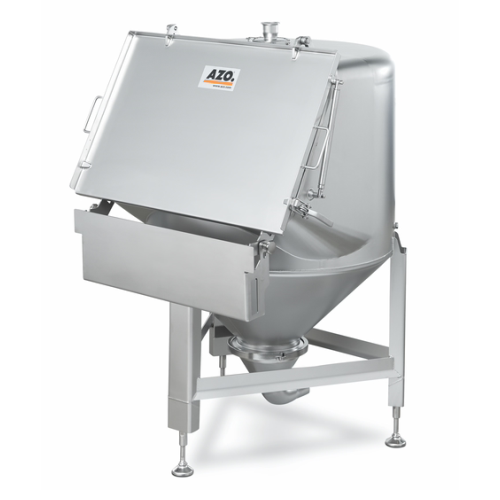
Hygienic feeding hopper for bulk solids
Ensure optimal hygiene in your powder and granular processing with a feeder that fa...
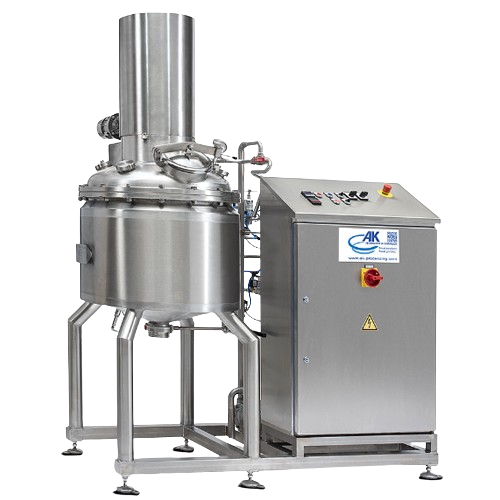
Hydro grind reactor for meat, vegetable, and vegan product processing
Achieve precision grinding and emulsification of ...

Inline continuous mixer for dairy and beverage processing
Achieve precise emulsification and particle size reduction for...

High shear emulsifier for hygienic applications
Achieve precise emulsification and consistent mixture quality with enhance...
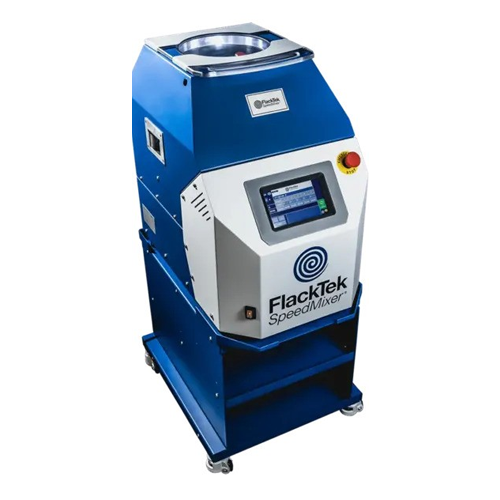
Dual asymmetric centrifugal mixer for epoxy and slurry mixing
Achieve precise mixing and consistency in your formulation...
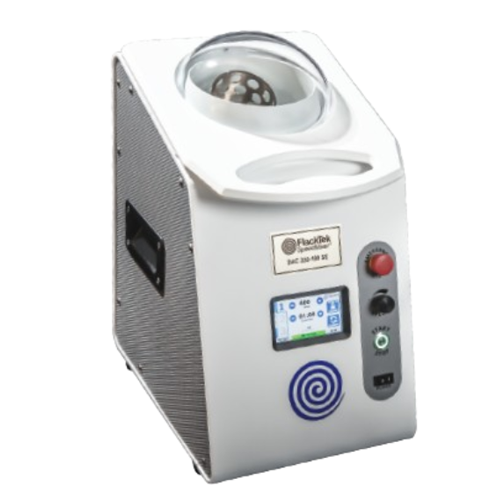
Dual asymmetric centrifugal processing system for epoxies and slurries
Streamline complex formulations with a system th...
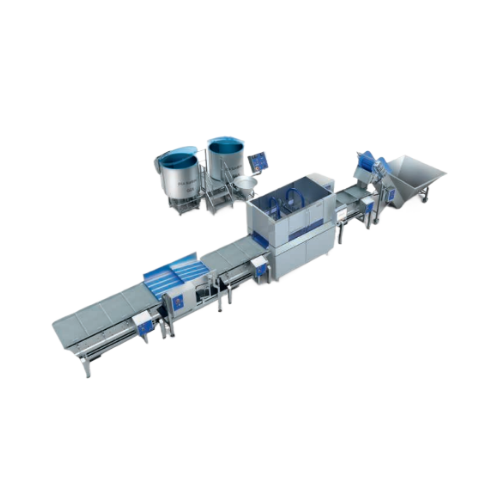
Marination injecting solution for fresh poultry
Enhance product consistency and maximize yield in your production line wit...
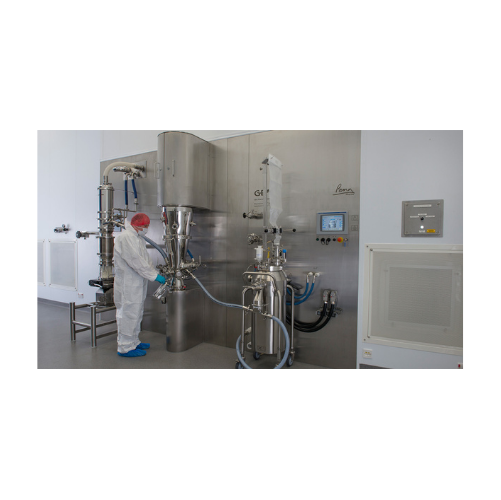
Pharmaceutical r&d granulation system
Optimize your pharmaceutical research with a versatile small-scale granulation system...
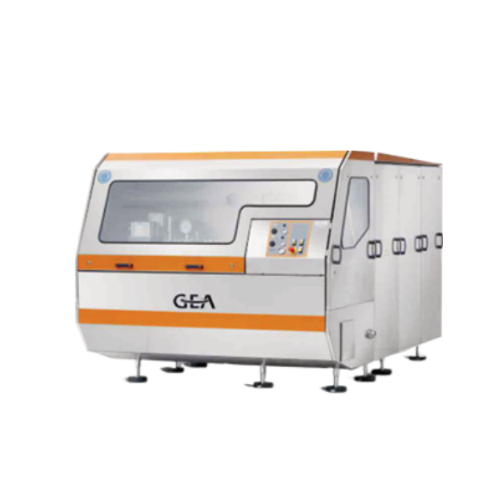
Industrial homogenizer for dairy, beverage, and pharmaceutical applications
Enhance your production efficiency with a ...
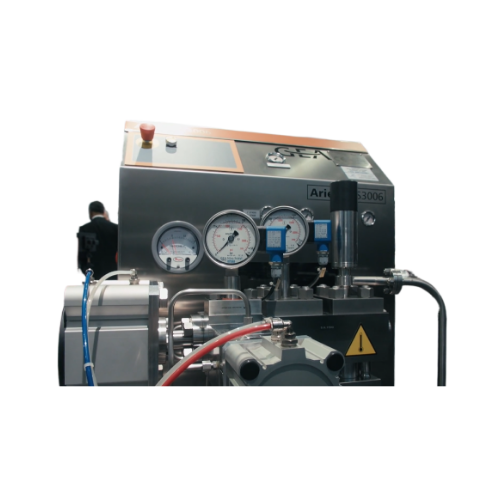
Pharmaceutical homogenization skid system
Achieve precise particle size reduction and efficient cell rupture with an auton...
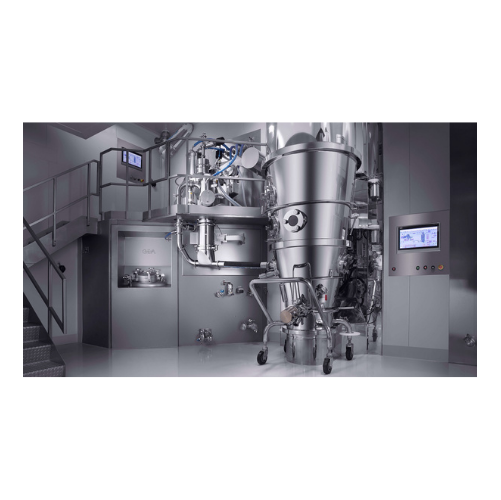
Integrated granulation and drying system for pharmaceuticals
Achieve seamless granulation and drying with our fully inte...
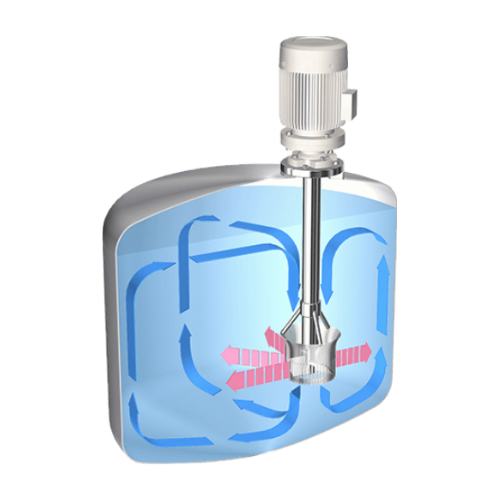
High-performance dispersing and mixing solutions
Enhance your mixing and dispersing processes with advanced fluid stream t...
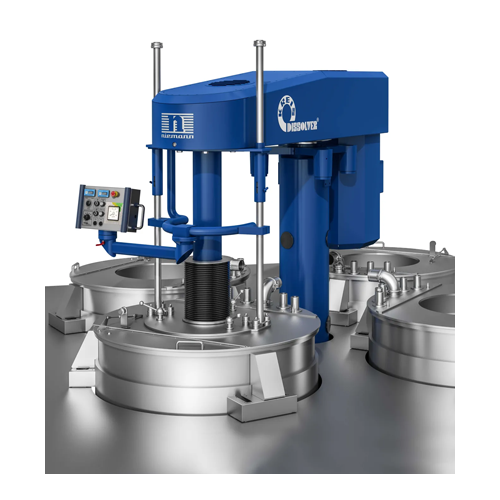
Dissolver for high-viscosity products through floor installation
Optimize production of ultra-high viscosity products wi...
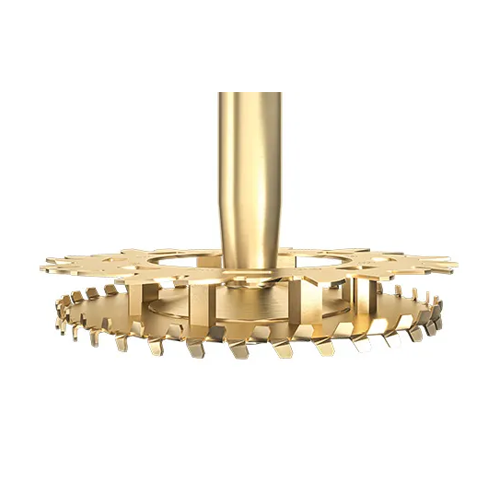
Mixer for high viscosity products
Enhance your production line with a versatile solution designed for precise mixing and di...
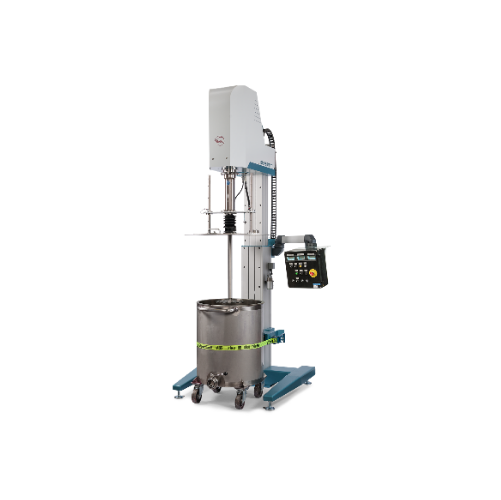
High-performance dissolver for large-scale production
Optimize your production line with precision-controlled dispersion ...
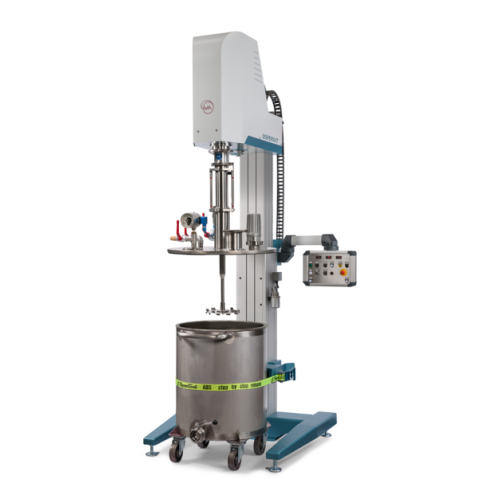
Vacuum dispersion system for high-viscosity products
Eliminate air inclusions during production with a modular vacuum sys...
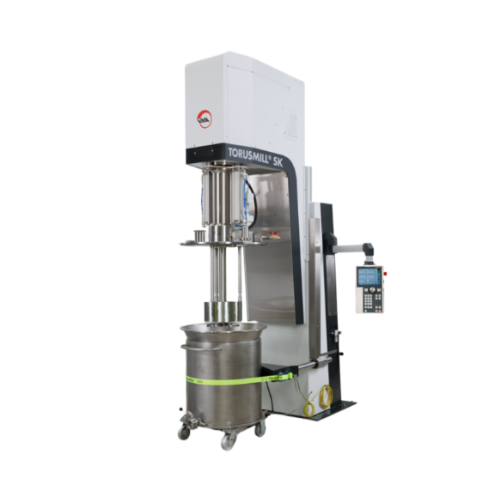
Vacuum dissolver for high viscosity products
Optimize your production with a vacuum dissolver designed to efficiently prev...
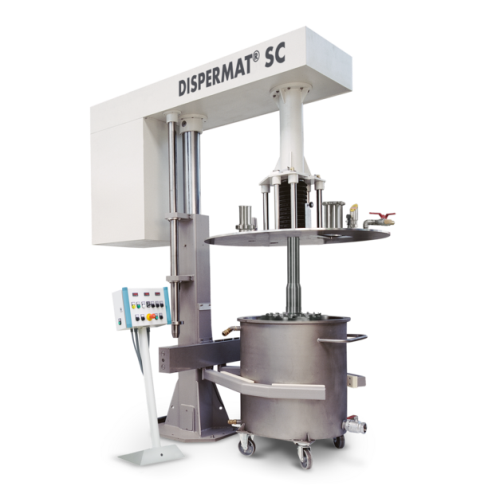
Vacuum disperser for high-viscosity products
Optimize high-viscosity product dispersion and prevent air inclusions with a ...
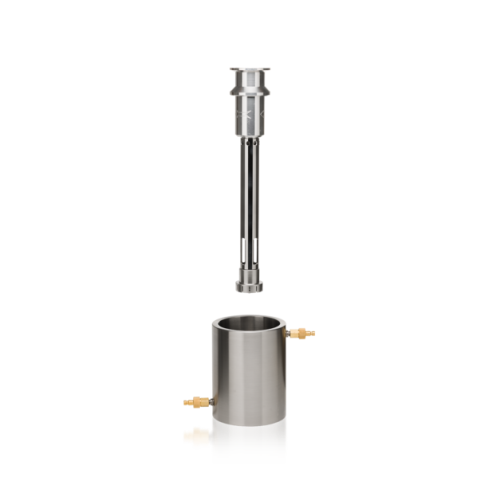
Vacuum dissolver for large batch production
Optimize your mixing processes with a versatile vacuum dissolver designed for ...
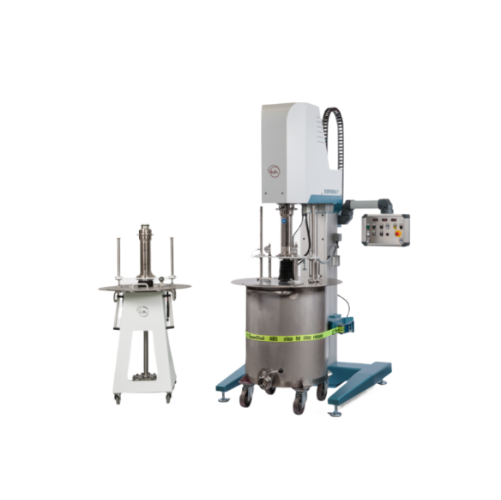
High-capacity dissolvers for industrial mixing
Enhance your production line with precision mixing, achieving consistent di...
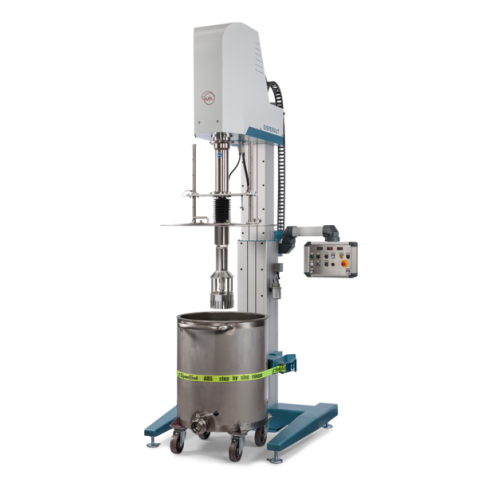
High shear batch process homogenizer for production
Achieve efficient emulsifying, homogenizing, and dispersing with prec...
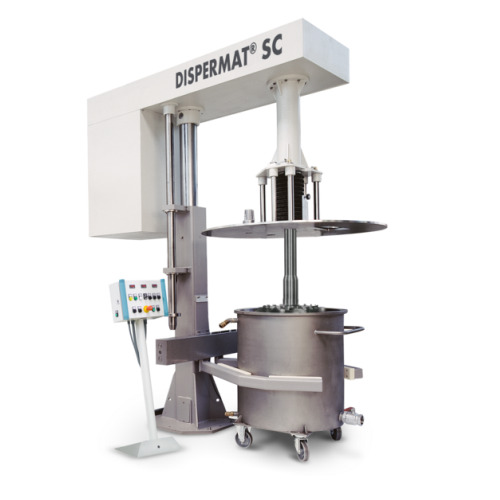
High-performance production dissolver for large batches
Achieve precise and repeatable dispersion for complex formulation...
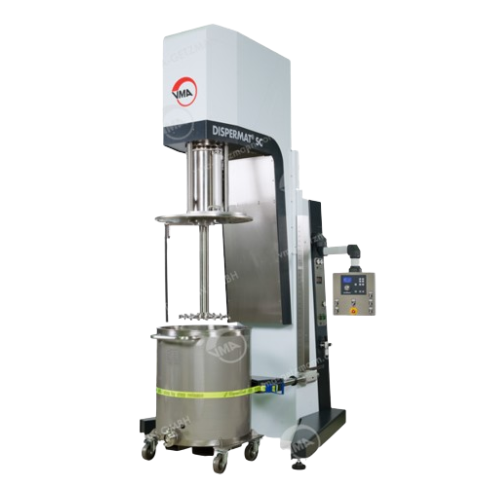
Production dissolver with scraper for high-viscosity products
Efficiently tackle high-viscosity material processing with...
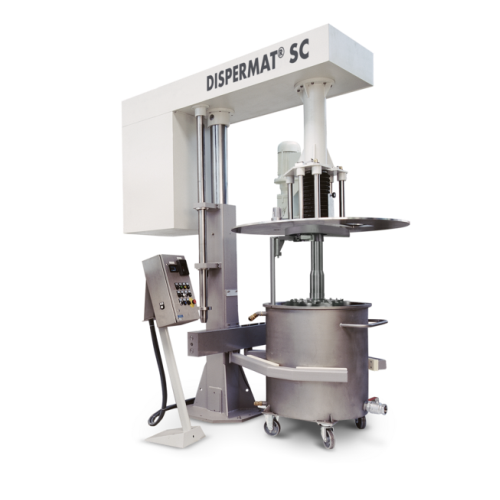
Explosion-proof dissolver for high viscosity products
Optimize your high-viscosity material processing with an explosion-...
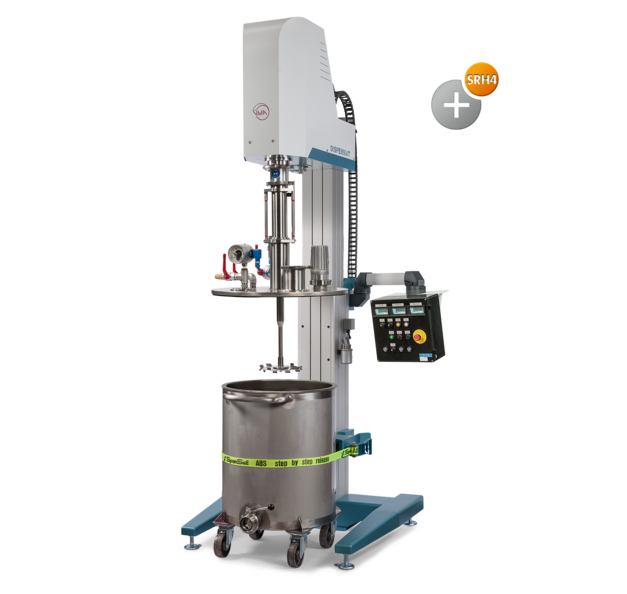
ATEX vacuum dissolver for high viscosity products
Ensure safe and efficient dispersion of high-viscosity materials under...
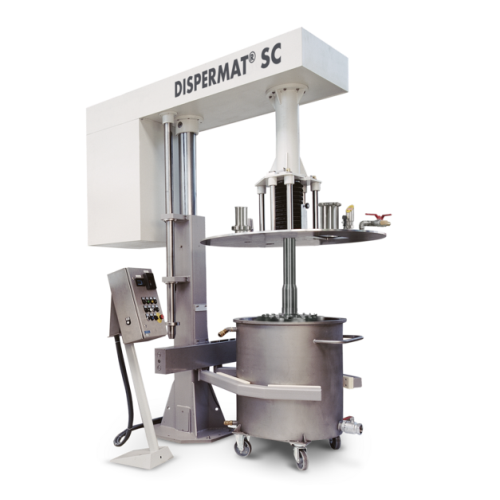
Explosion-proof vacuum dissolver for high viscosity products
Achieve precise dispersion of high-viscosity products under...
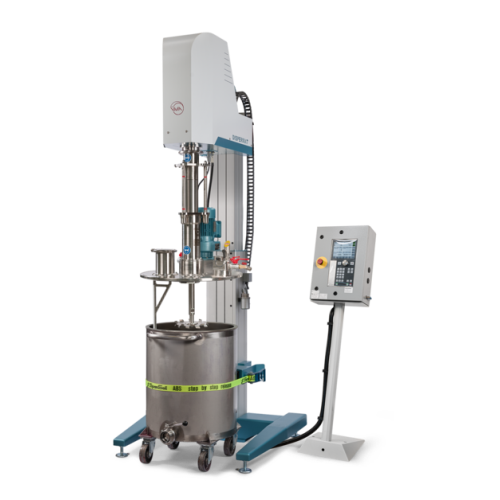
Explosion-proof vacuum dissolver for high viscosity applications
For operations requiring precise control in high-viscos...
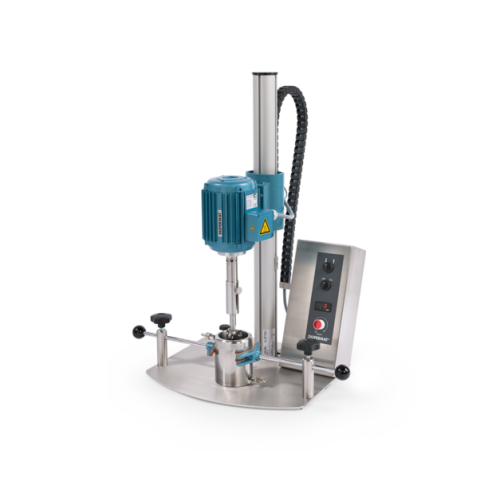
Laboratory stirrers for high viscosity materials
Efficiently mix and stir high-viscosity materials with ease, enabling pre...
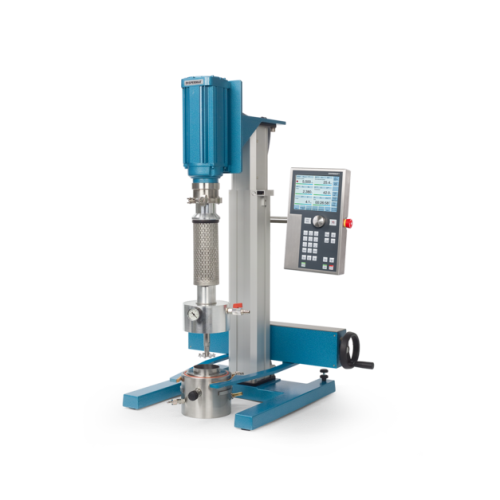
Vacuum dispersion system for laboratory applications
Achieve precise mixing and homogenization under vacuum conditions, e...
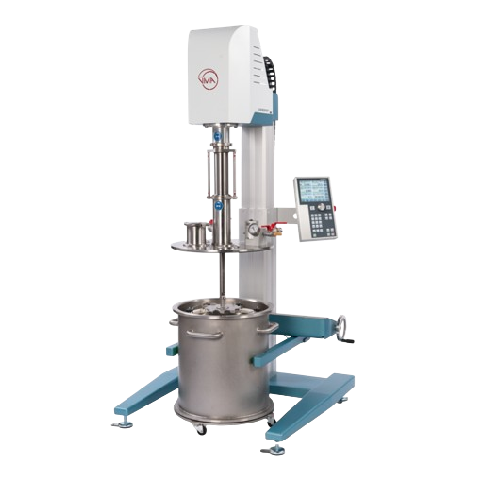
Vacuum dispersion system for single-walled containers
Optimize your production line with an adaptable vacuum dispersion s...
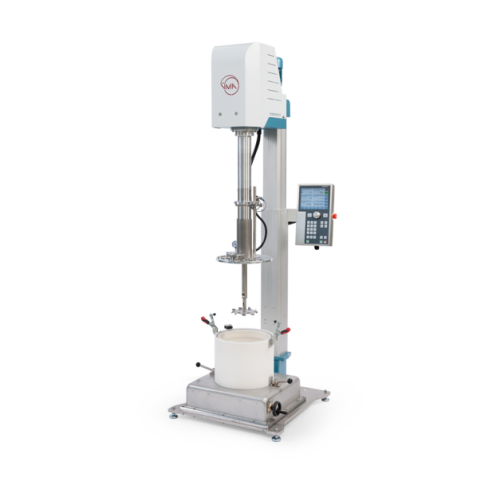
Laboratory vacuum dissolver
Experience precision vacuum processing for your high-viscosity formulations, ensuring optimal di...
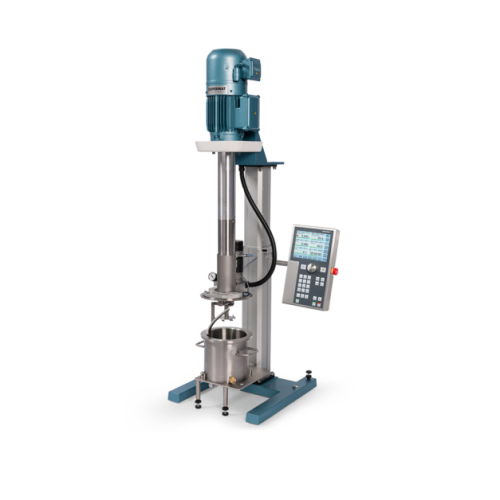
Vacuum dissolver for laboratory and pilot plant operations
Perfect for developing intricate formulations, this vacuum di...
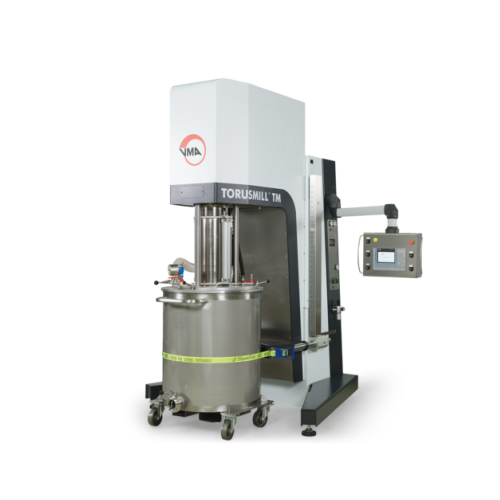
Dissolver for high-volume industrial dispersion
Achieve precise and efficient mixing with this dissolver, designed for sea...
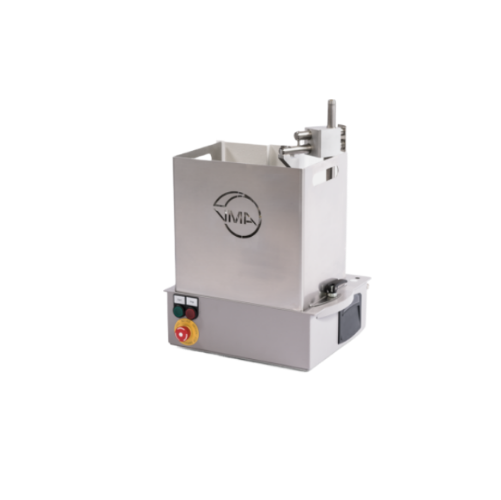
Industrial dissolver for high-viscosity materials
Efficiently disperse and mix high-viscosity materials with precision, e...
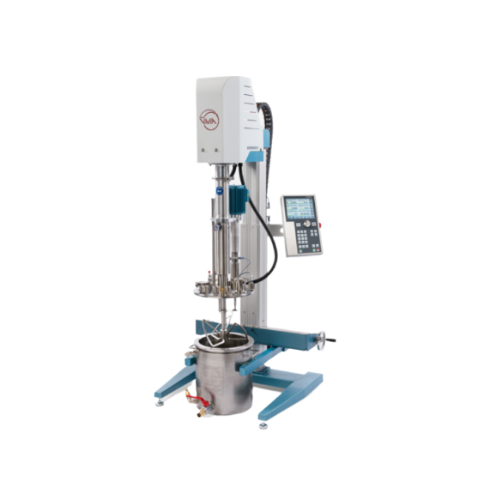
Vacuum dissolver for highly viscous products
Efficiently mix and disperse high-viscosity substances under vacuum to ensure...
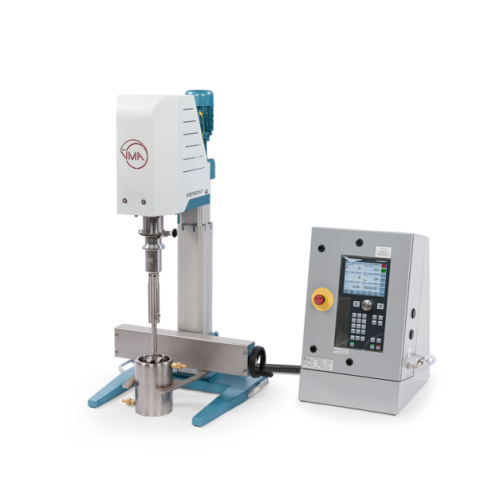
Explosion-proof dissolver for hazardous area mixing
When operating in hazardous environments, maintaining consistent and ...
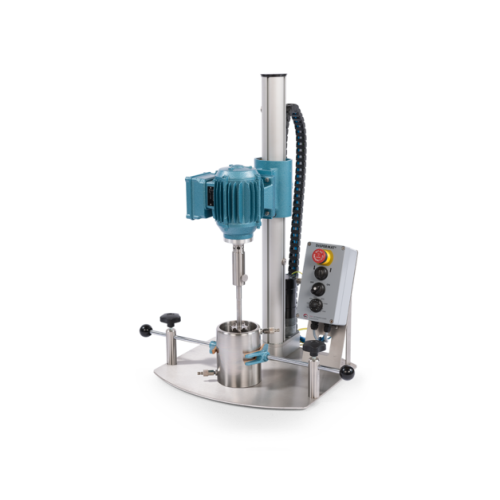
Explosion-proof dissolvers for laboratory use
Ideal for safely dispersing and mixing chemical substances in potentially ex...
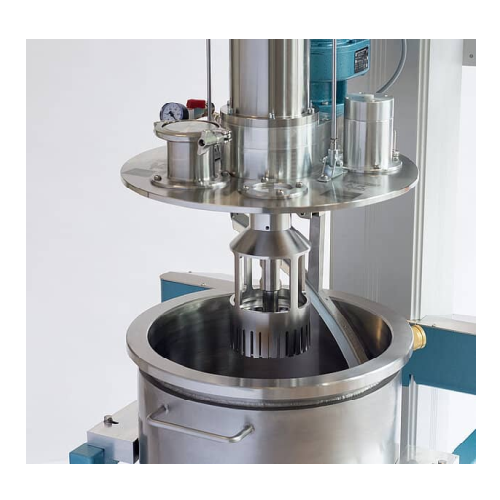
Efficient high-volume dissolver with scraper
For high-viscosity formulations, this advanced dissolver with integrated scra...
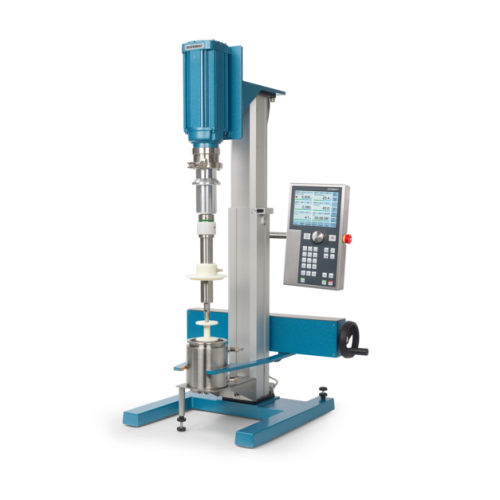
Laboratory disperser for small batch processing
Achieve precise dispersion and homogenization of high-viscosity mixtures w...
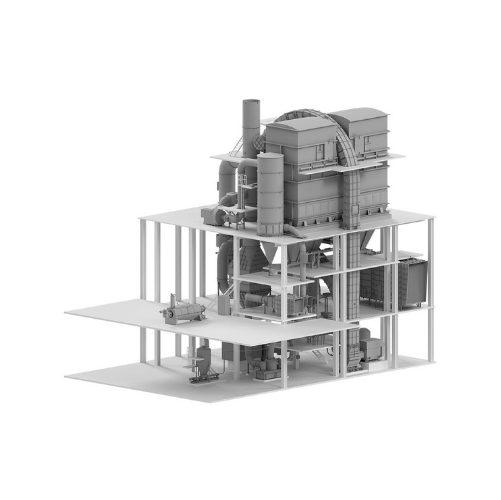
Flash dryer for corn starch
Reduce energy consumption and maintain product quality with efficient drying solutions designed ...
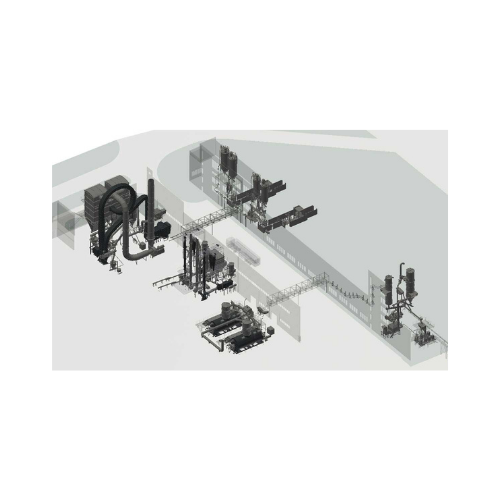
Wheat processing systems for industrial applications
Maximize efficiency in wheat processing with a system designed for p...
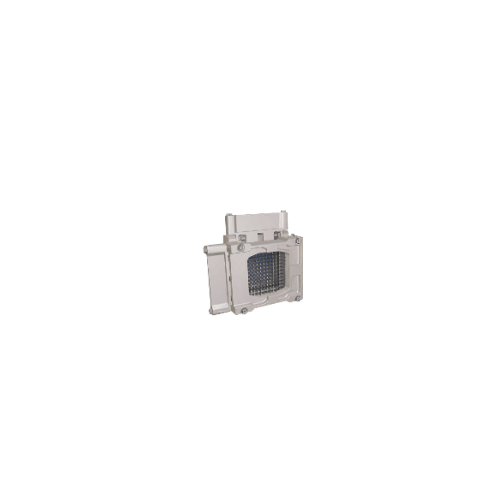
Segment cutter for potatoes and carrots
Achieve precise cuts on vegetables like carrots and potatoes with minimal featherin...
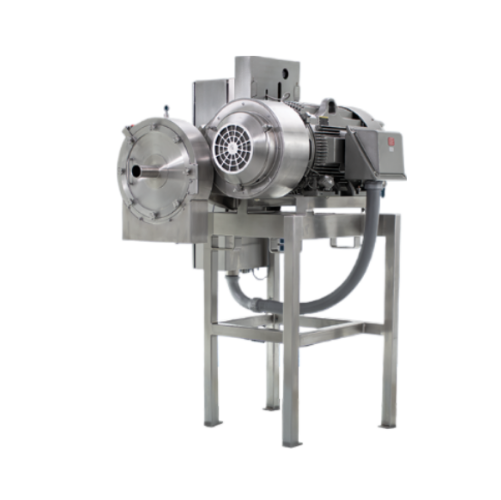
Industrial particle size reduction processor
Optimize your production line with high-capacity, continuous particle size re...

Slicer for elongated products
Effortlessly slice and prepare a wide range of elongated and firm products, transforming your ...
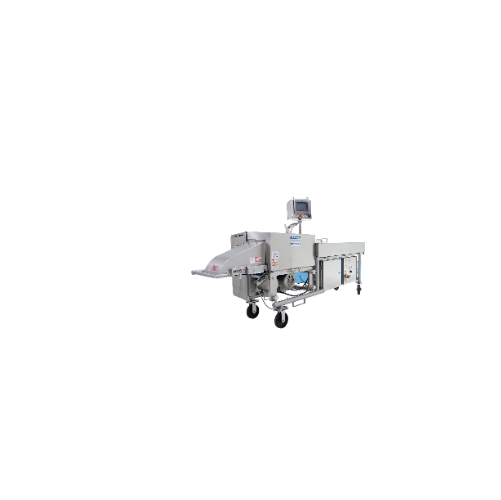
Industrial dicing solution for food products
Enhance processing efficiency with high-speed dicing and slicing solutions, e...
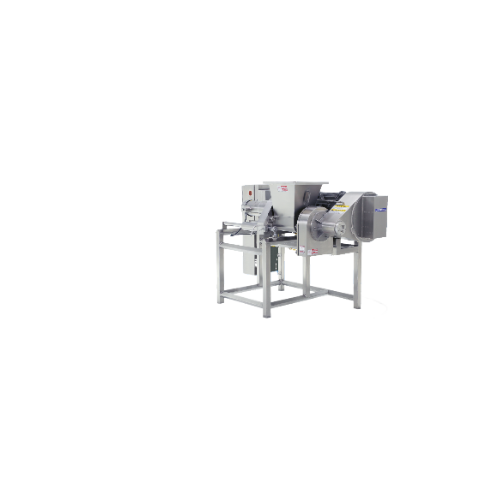
Industrial vegetable protein processor
Achieve precise size reduction and consistent texture in food processing with this h...
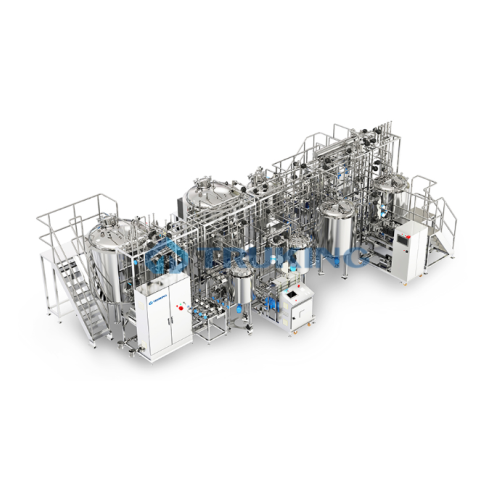
Complex preparation system for industrial microsphere production
Achieve precise particle size and uniform drug encapsul...
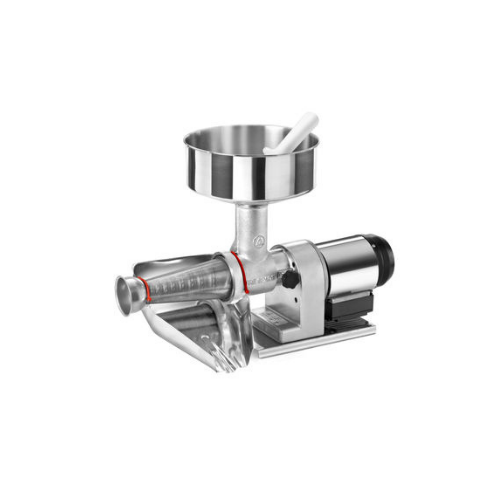
Electric tomato squeezer for large-scale production
Optimize your tomato processing with this high-capacity electric sque...
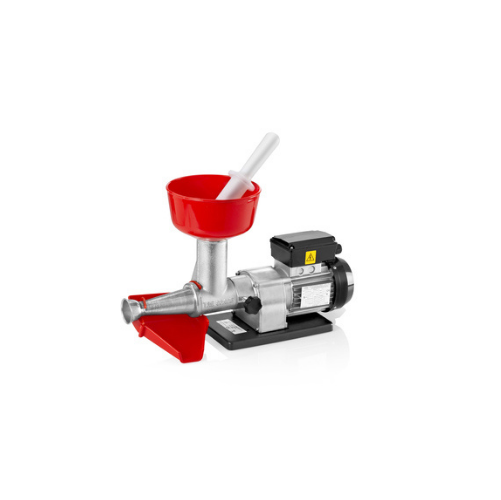
Electric tomato squeezer for family and small community use
Ideal for crafting homemade sauces and preserves, this elect...
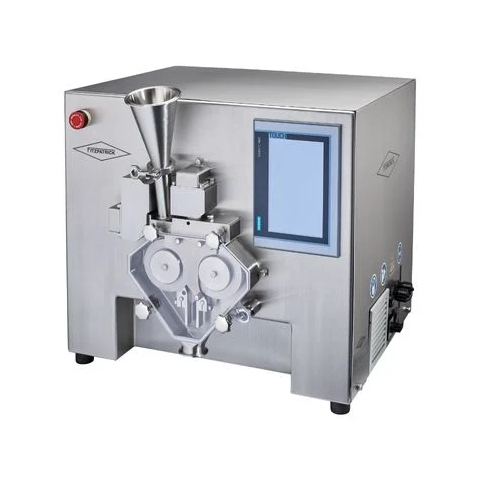
Lab scale roller compactor for dry granulation
Achieve seamless scale-up from lab development to full-scale production wit...
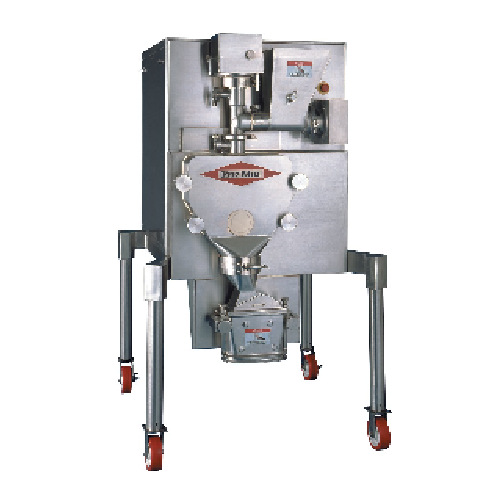
Pilot to full-scale roller compactor for dry granulation
Easily transition from pilot to full-scale production with this ...
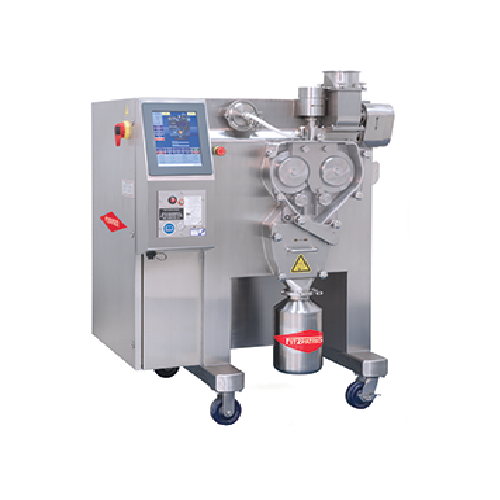
Roller compaction for dry granulation in pharmaceuticals
Ensure consistent granule size and density in your product line ...
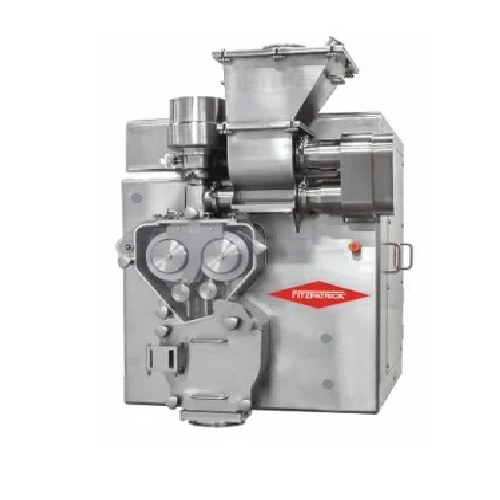
Roller compactors for dry granulation
Optimize your powder processing with advanced roller compaction, ensuring consistent ...
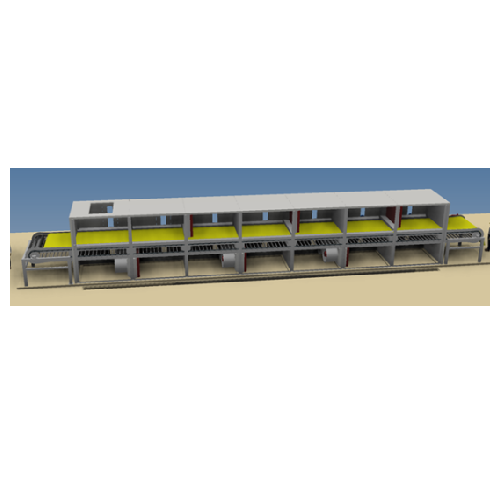
Belt dryers for gelatin processing
Efficiently transform liquid gelatin into high-quality solids with precise moisture cont...
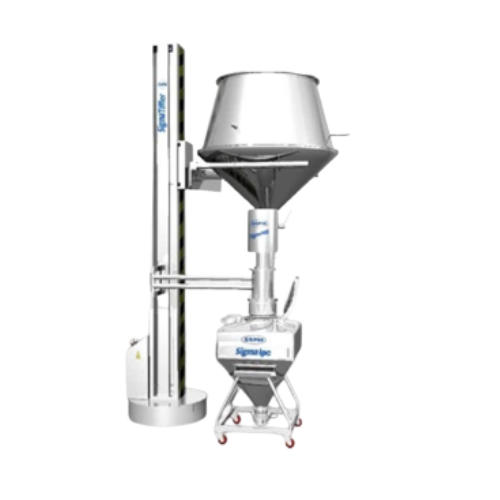
Material handling system for granules and powders
Optimize your production with seamless material handling specifically d...
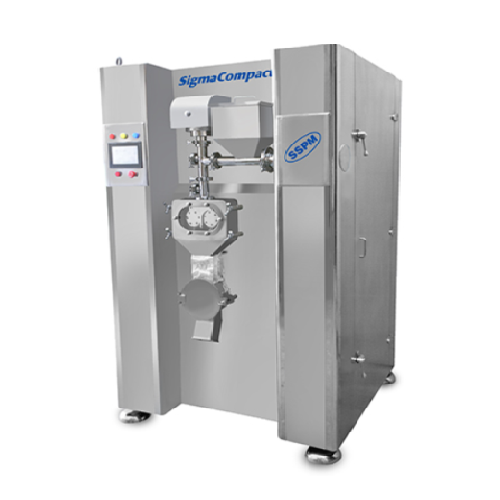
Dry granulation roll compactor
Optimize your tablet and capsule formulation by efficiently compacting and granulating powder...
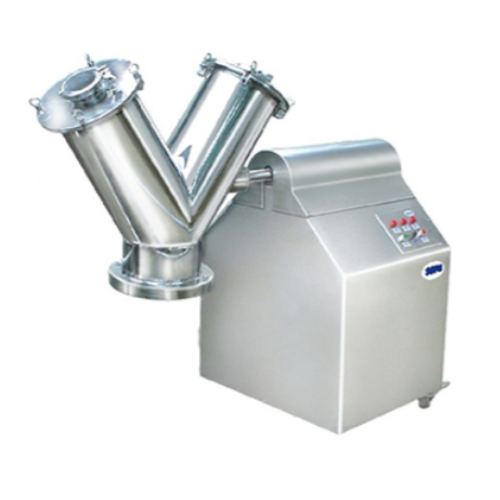
Industrial blender for uniform mixing
Optimize your process with precise mixing and consistent blending, ensuring uniformit...
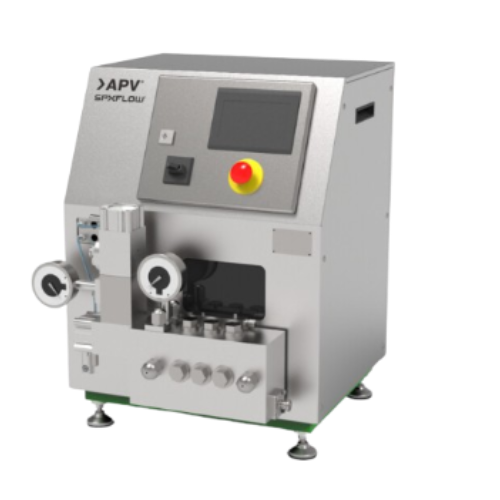
Pilot plant homogenizer for immiscible liquids
Streamline your R&D with precise homogenization, allowing you to test ...

High pressure homogenizer for food and beverage processing
Optimize your production line with a versatile high-pressure ...
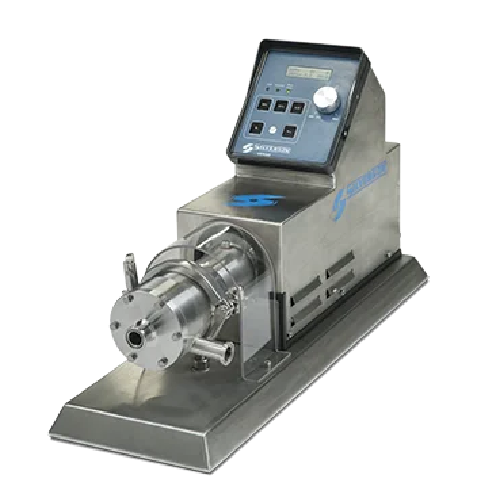
Laboratory in-line mixer for precise mixing and reproducibility
Achieve precise laboratory-scale mixing with rapid proce...

Laboratory scale powder/liquid mixer
Easily integrate powders into complex liquid formulations at a laboratory scale, ensur...
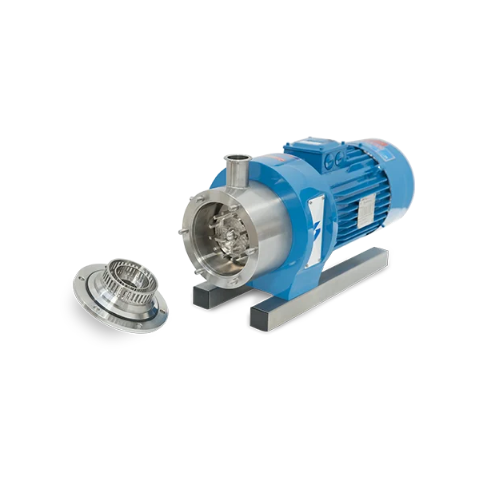
Homogenizers for creams and ointments
Achieve superior consistency and particle size reduction in skincare creams, sauces, ...
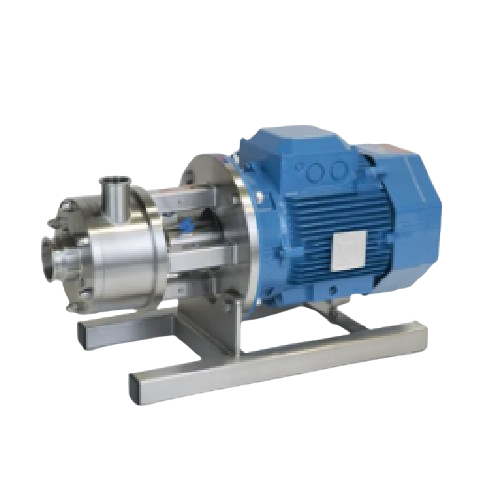
High shear mixer for efficient particle size reduction
Achieve rapid and precise blending and particle reduction in your ...
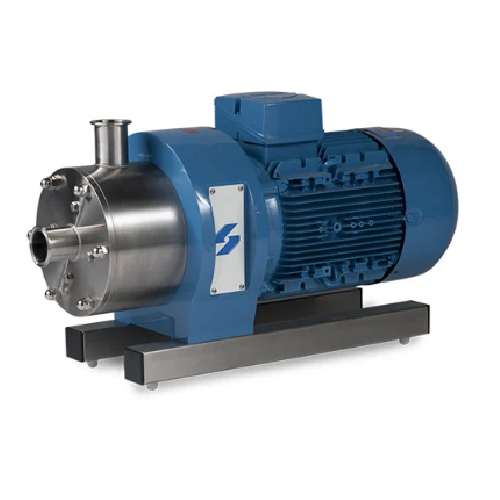
High shear inline mixer for continuous processing
Effortlessly streamline your mixing process with this solution capable ...
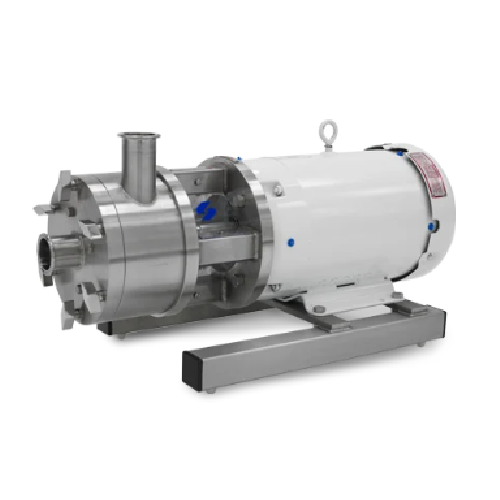
In-line ultra sanitary mixer for pharmaceutical and food applications
Enhance your liquid formulations with precision m...
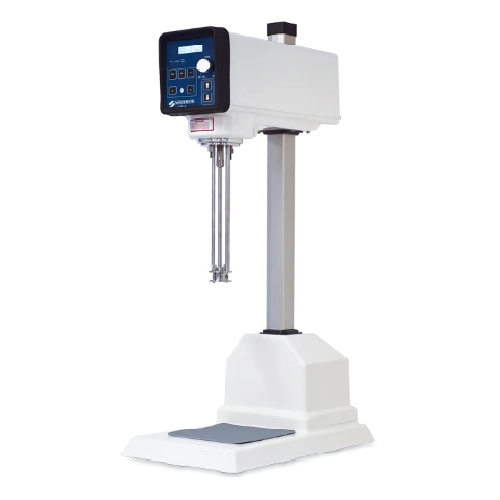
High shear lab mixer for laboratory work and r&d
Achieve unparalleled precision and consistency in laboratory and pilot-sc...
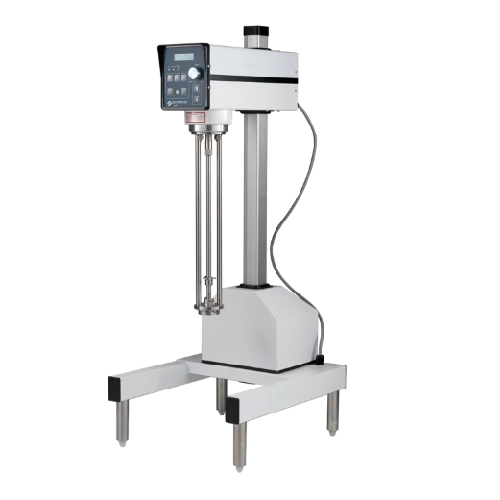
Pilot scale batch mixer for small scale production
Achieve precise control and consistency in small-scale production with...
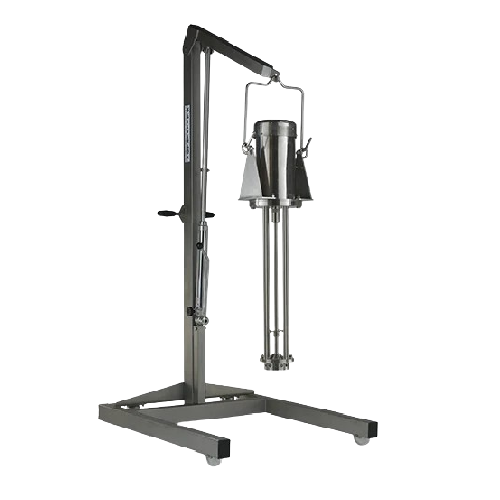
High shear batch mixer for industrial mixing
Optimize your production cycle with this high shear batch mixer, designed to ...
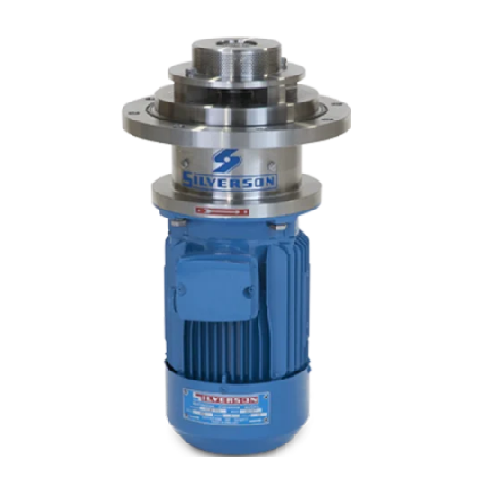
Bottom entry mixers for high viscosity products
Optimize your production line with mixers designed to handle both high and...
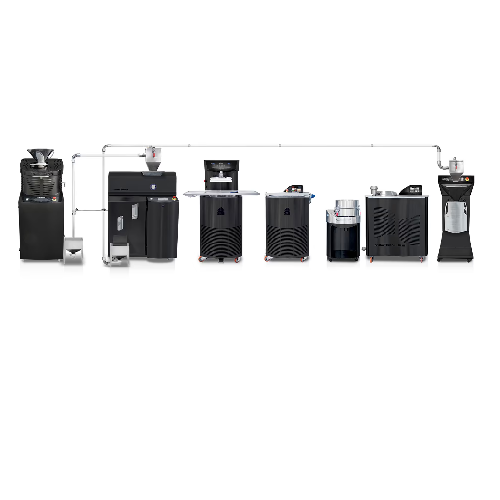
Bean to bar chocolate production equipment
Transform cocoa beans into exquisite single-origin chocolate with complete cont...
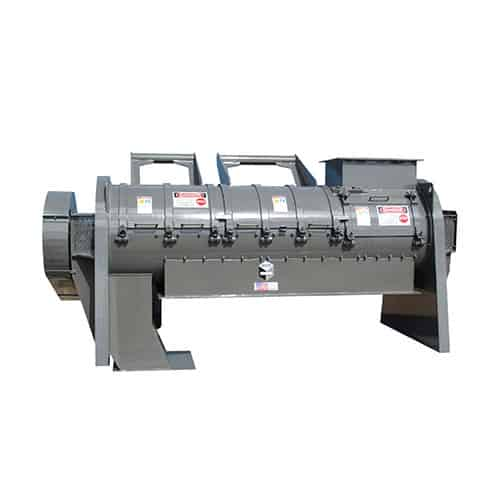
Turbo separator for Ddg agglomeration
Efficiently eliminate clumping and improve flow in your distillation process, ensurin...
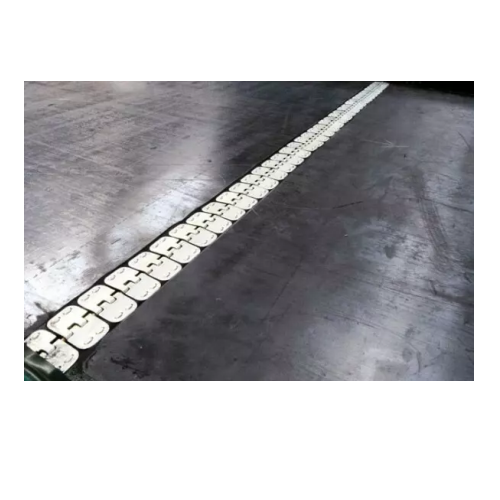
Optimal maintenance solution for industrial weighfeeders
Streamline your processing operations with a solution that minim...
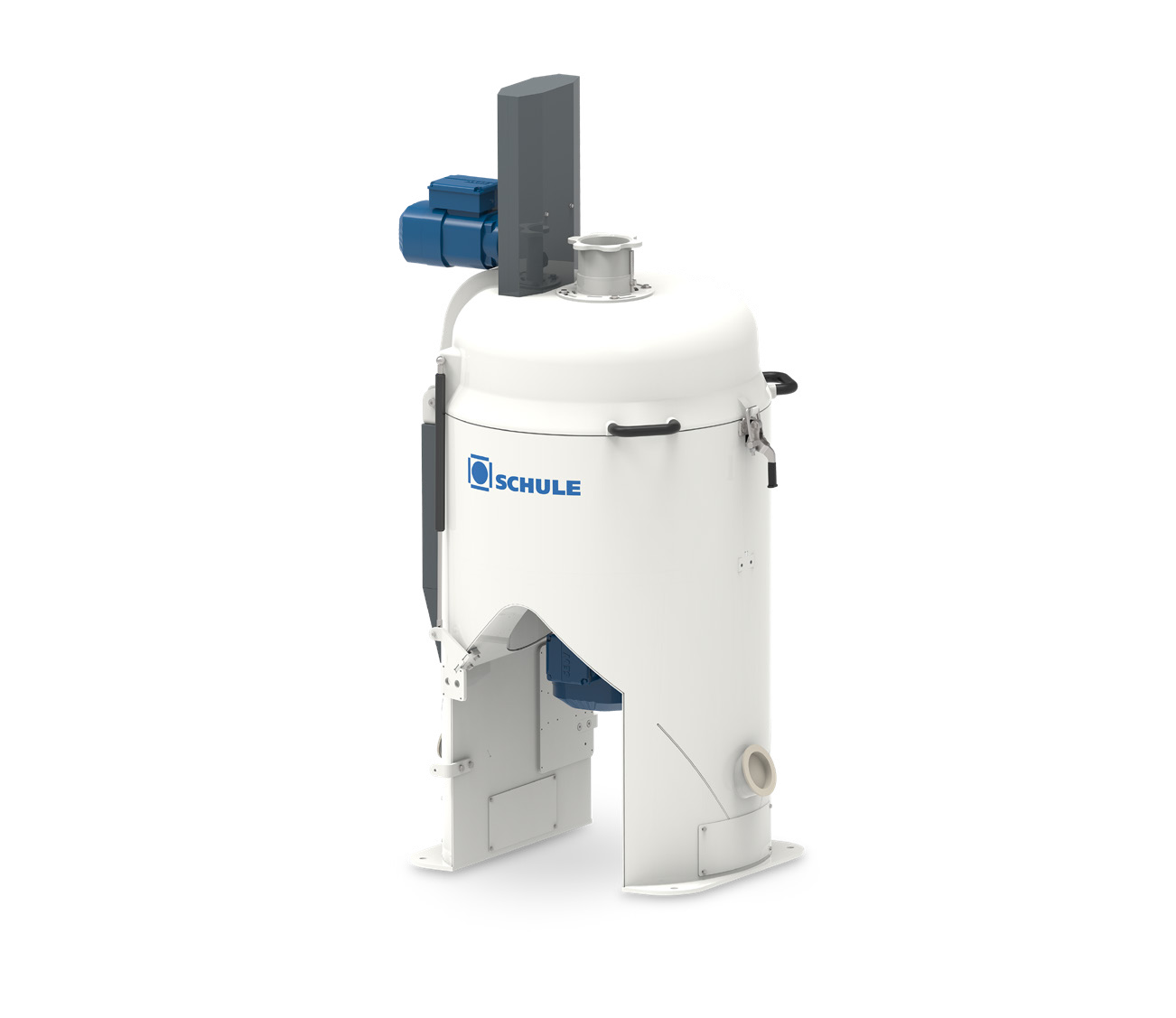
Impact huller for oats
Hulling technology risks breaking oat grains if the system is not adjustable to fragile materials. Agg...
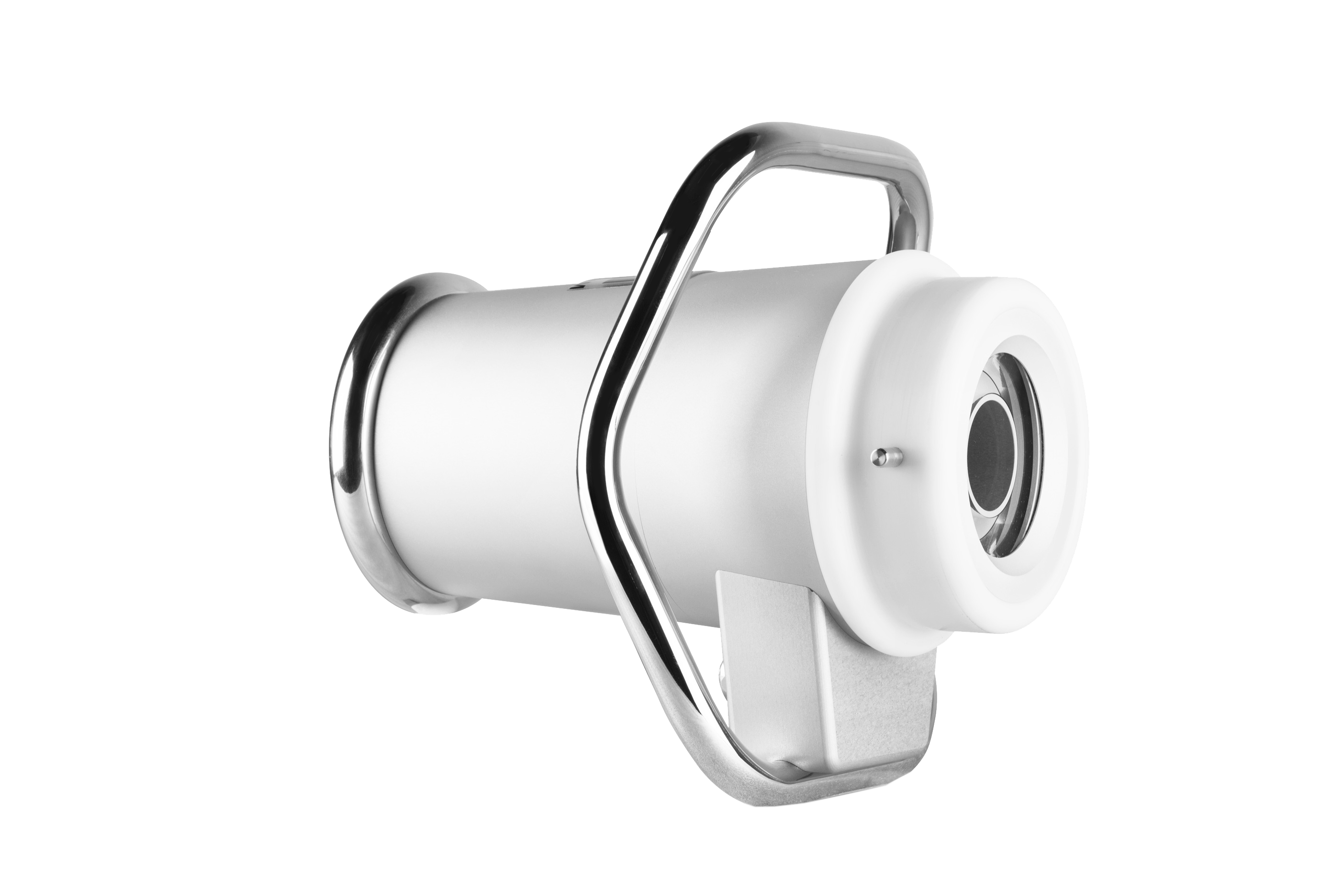
Particle analysation monitor
Products like granules, tablets and capsules require inspection at numerous steps in the produc...
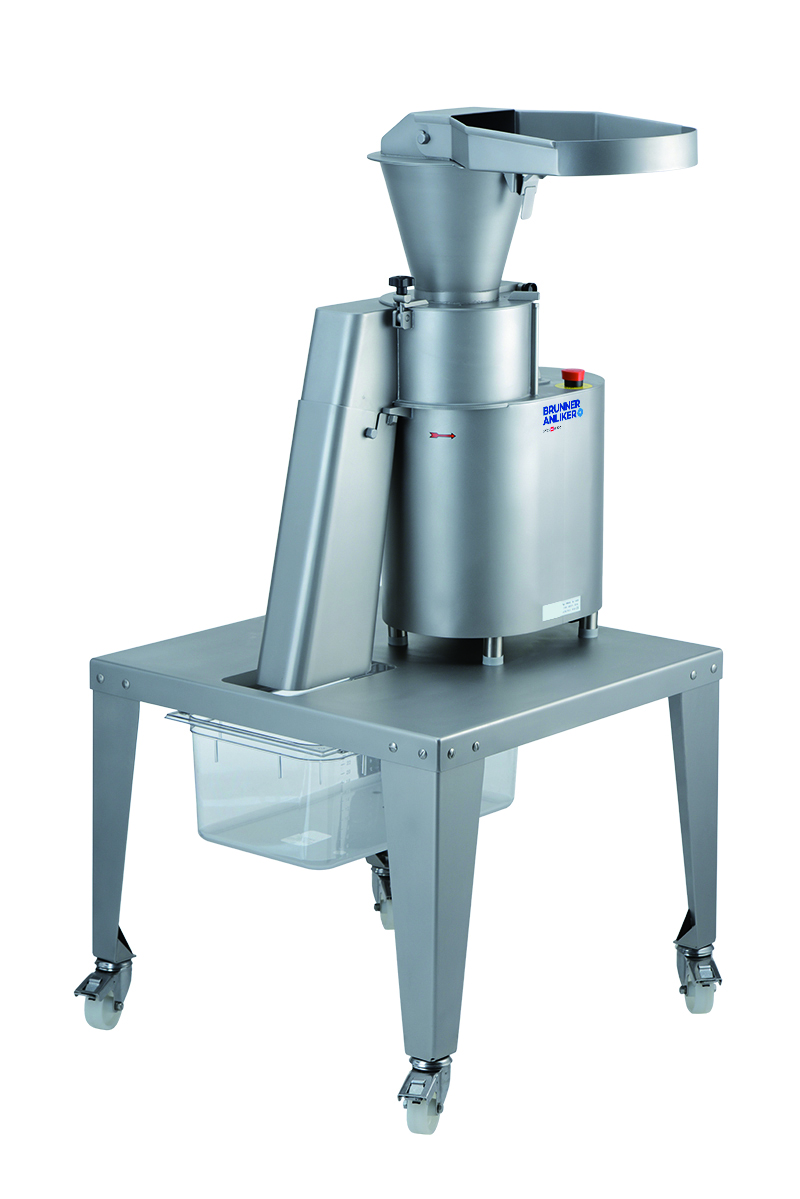
Nut and cheese grater
Smearing, clumping and crumbling are common problems when cheese and other soft textured foodstuffs are...
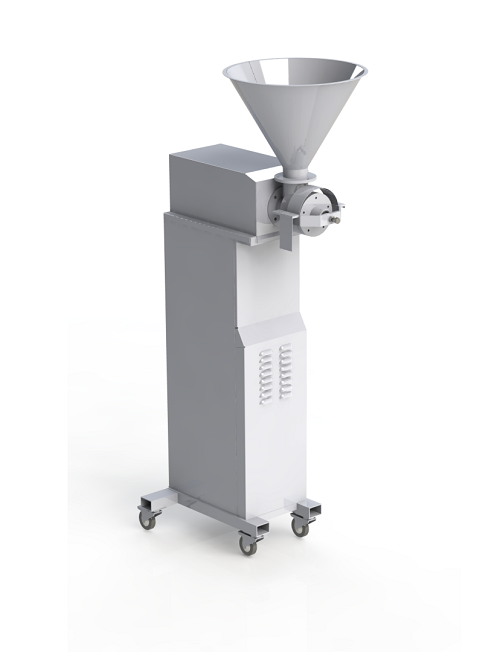
Small capacity cocoa grinder
The first step of producing almost any kind of chocolate starts with grinding cocoa beans to ge...
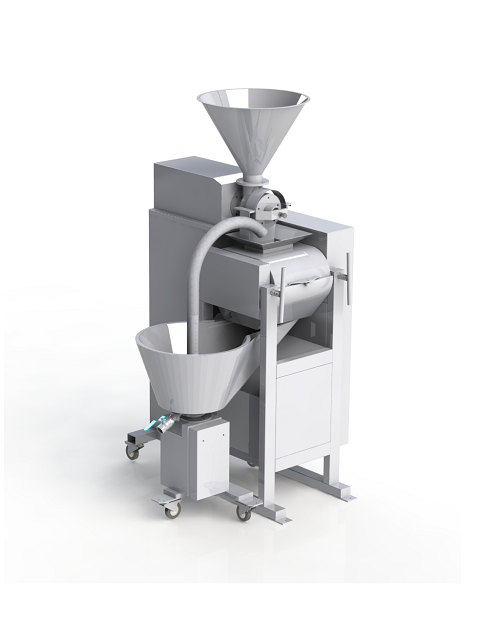
Entry level bean to bar line
One of the challenges when setting up a small-scale cocoa processing factory is making all of t...
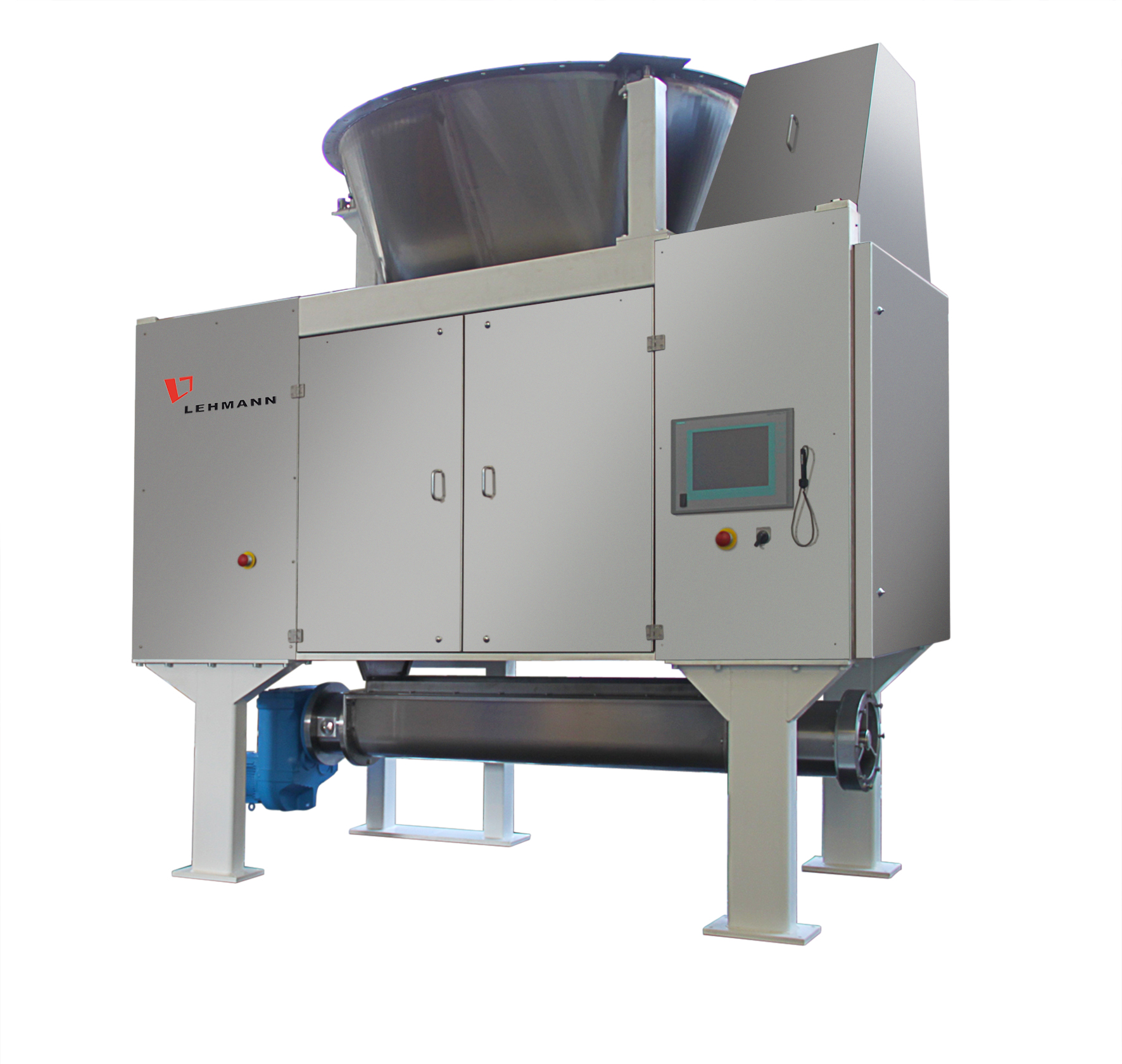
Two Roll chocolate pre-refiner
A pre-refiner is commonly utilized to refine and calibrate the sugar crystals in the chocolat...
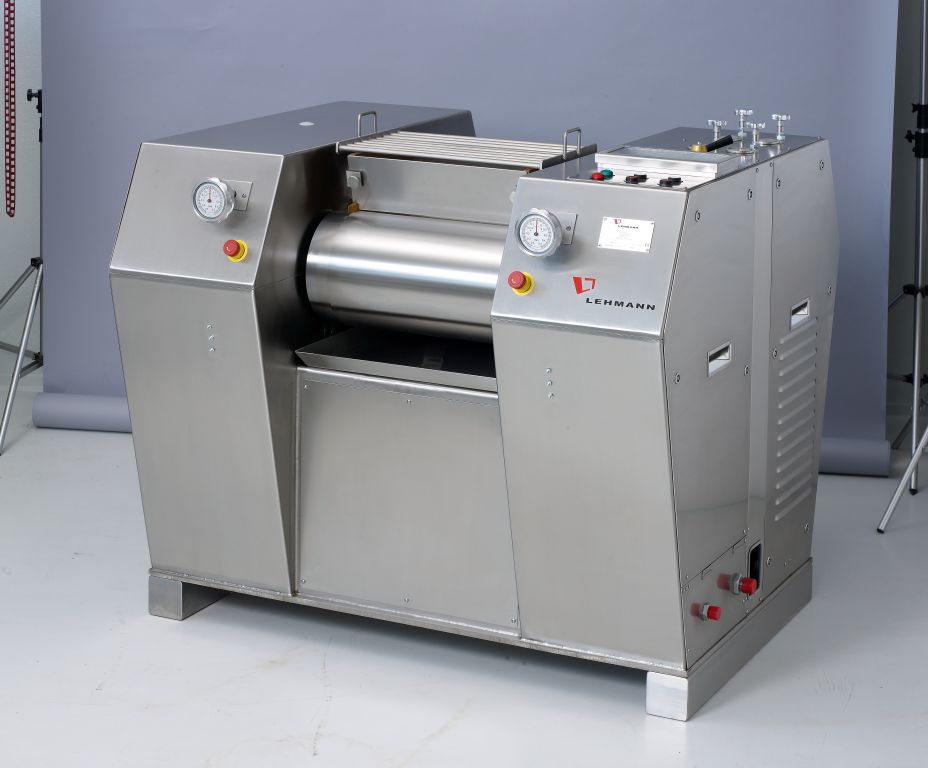
Three-Roll chocolate refiner
For mixing, rubbing and fine grinding in the production of chocolate mass, filling materials an...
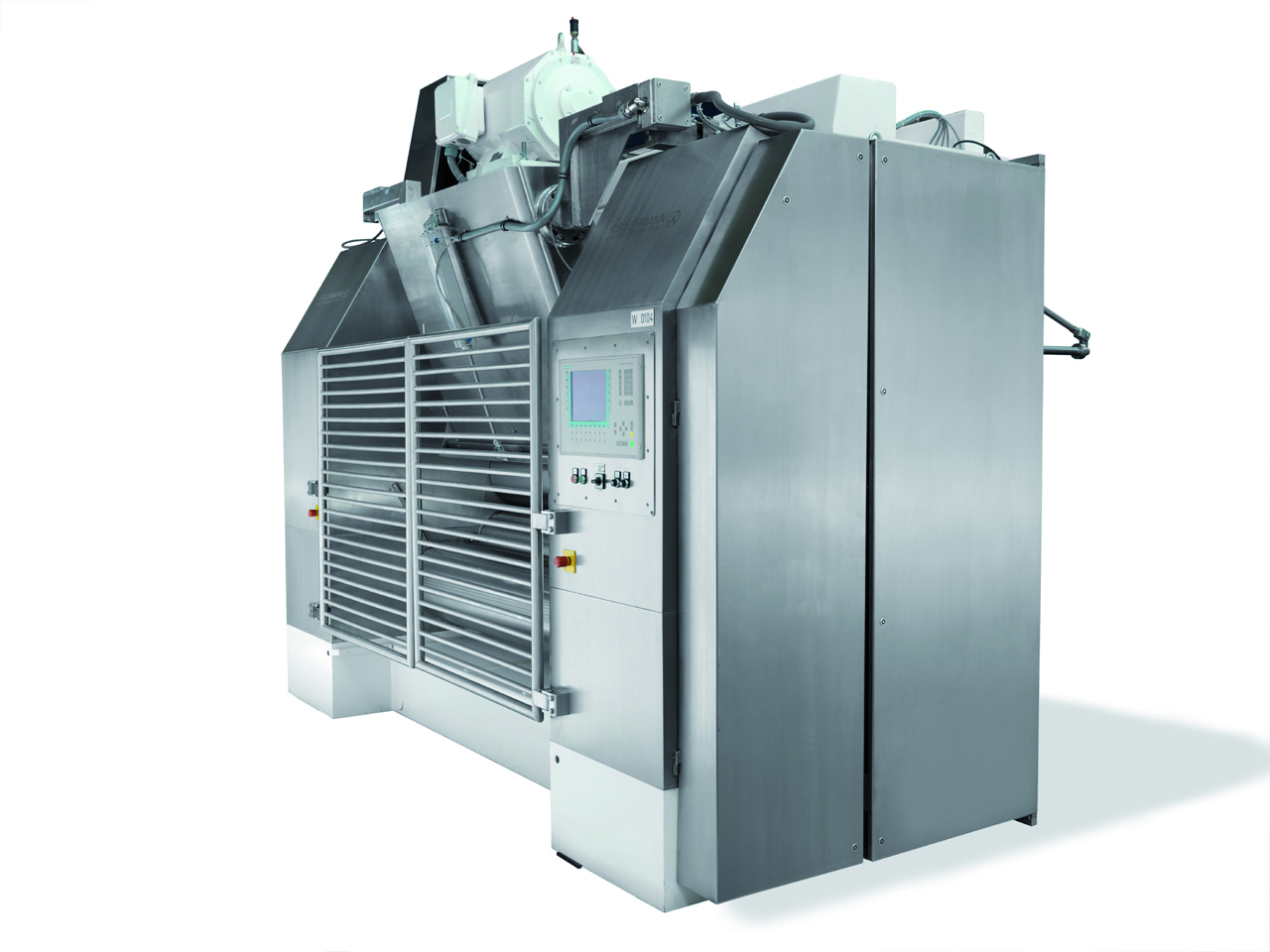
Five Roll chocolate refiner
When you want to produce high quality traditional chocolate, a 5 Roll Refiner gives you complete...
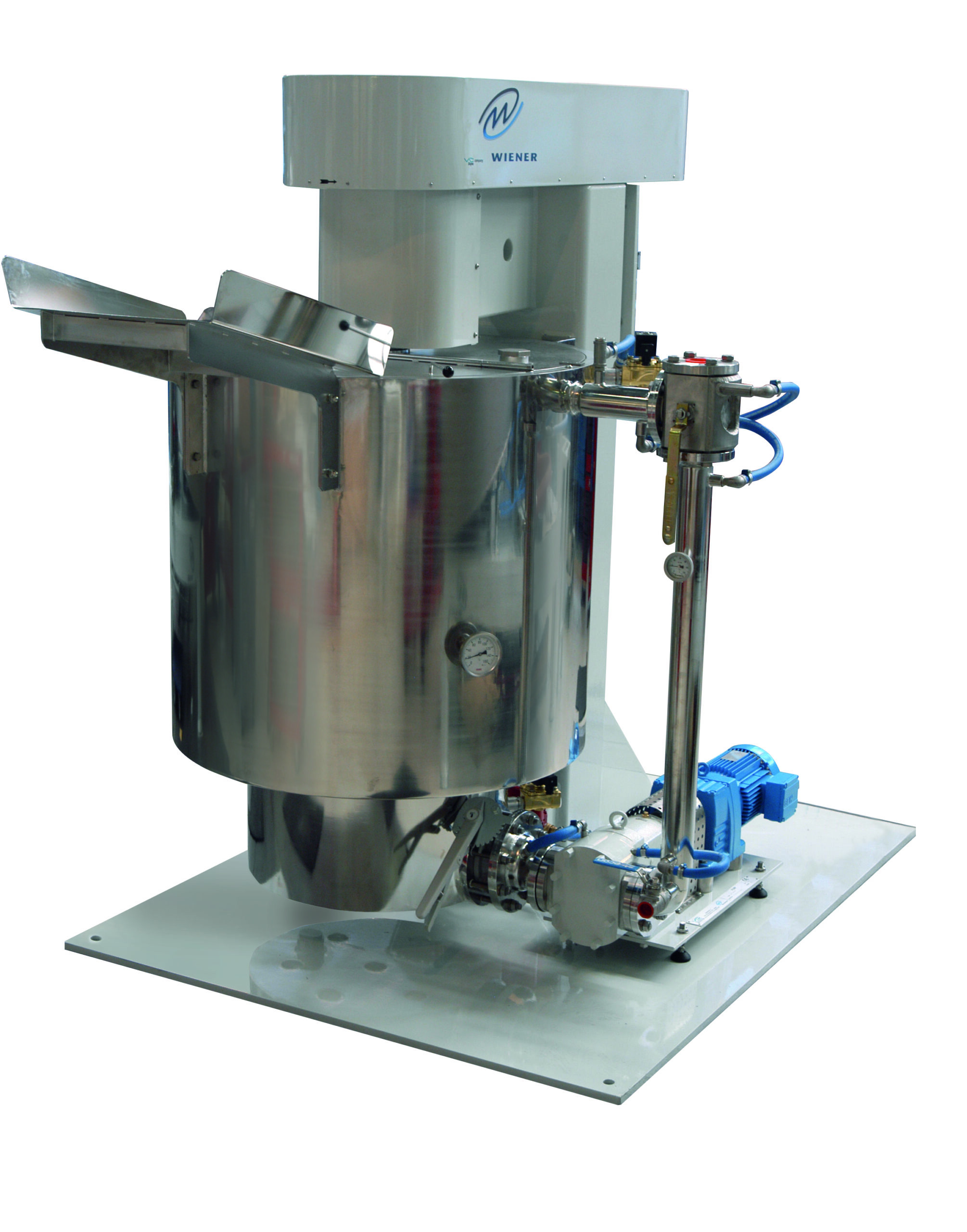
Mixer and refiner for chocolate compound
Mix cocoa liquor, cocoa powder, sugar, and lecithin in a small scale and refine sm...
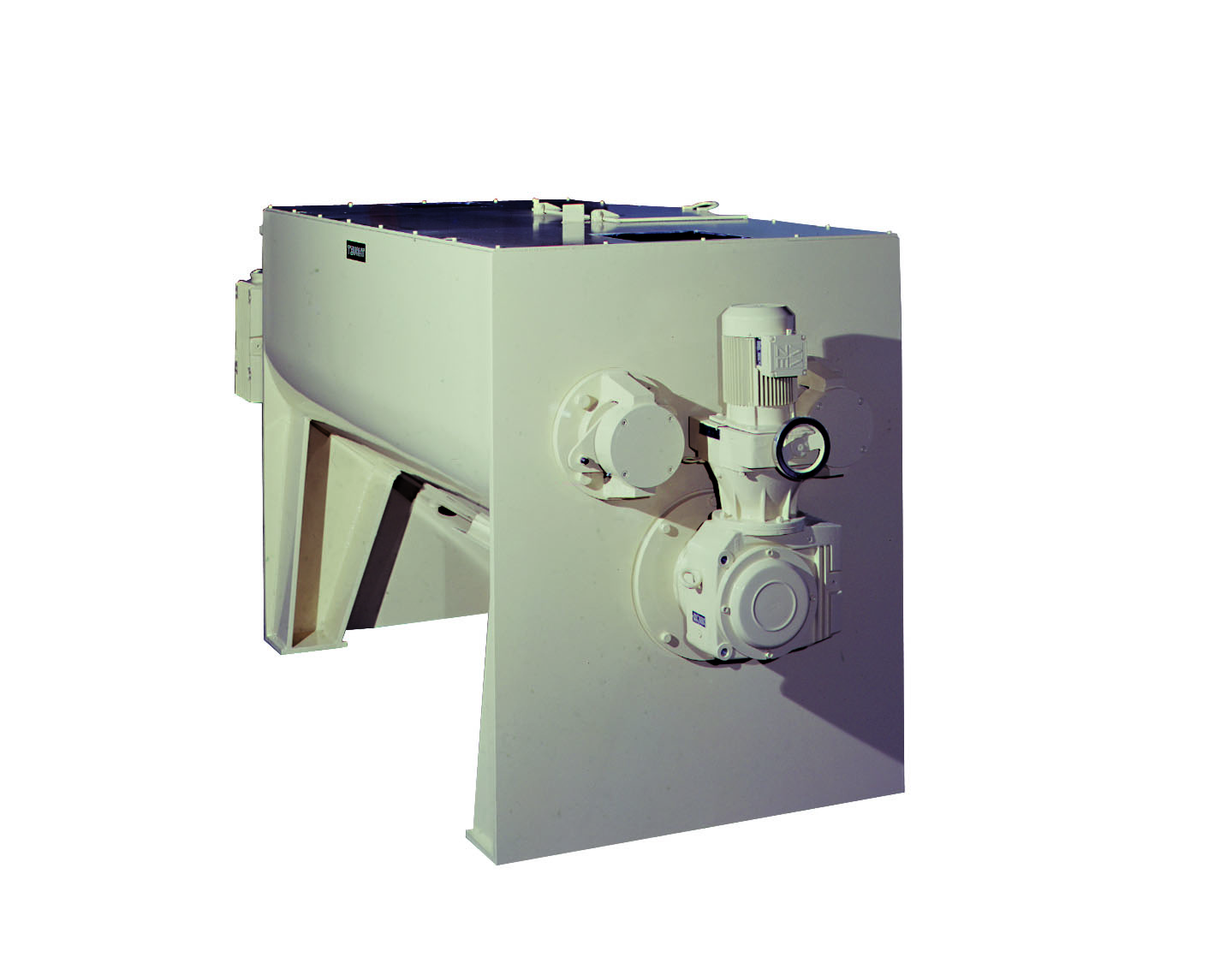
Mixer and kneader for sugar based recipes
For the production of chocolate paste based on refined or icing sugar, the decis...
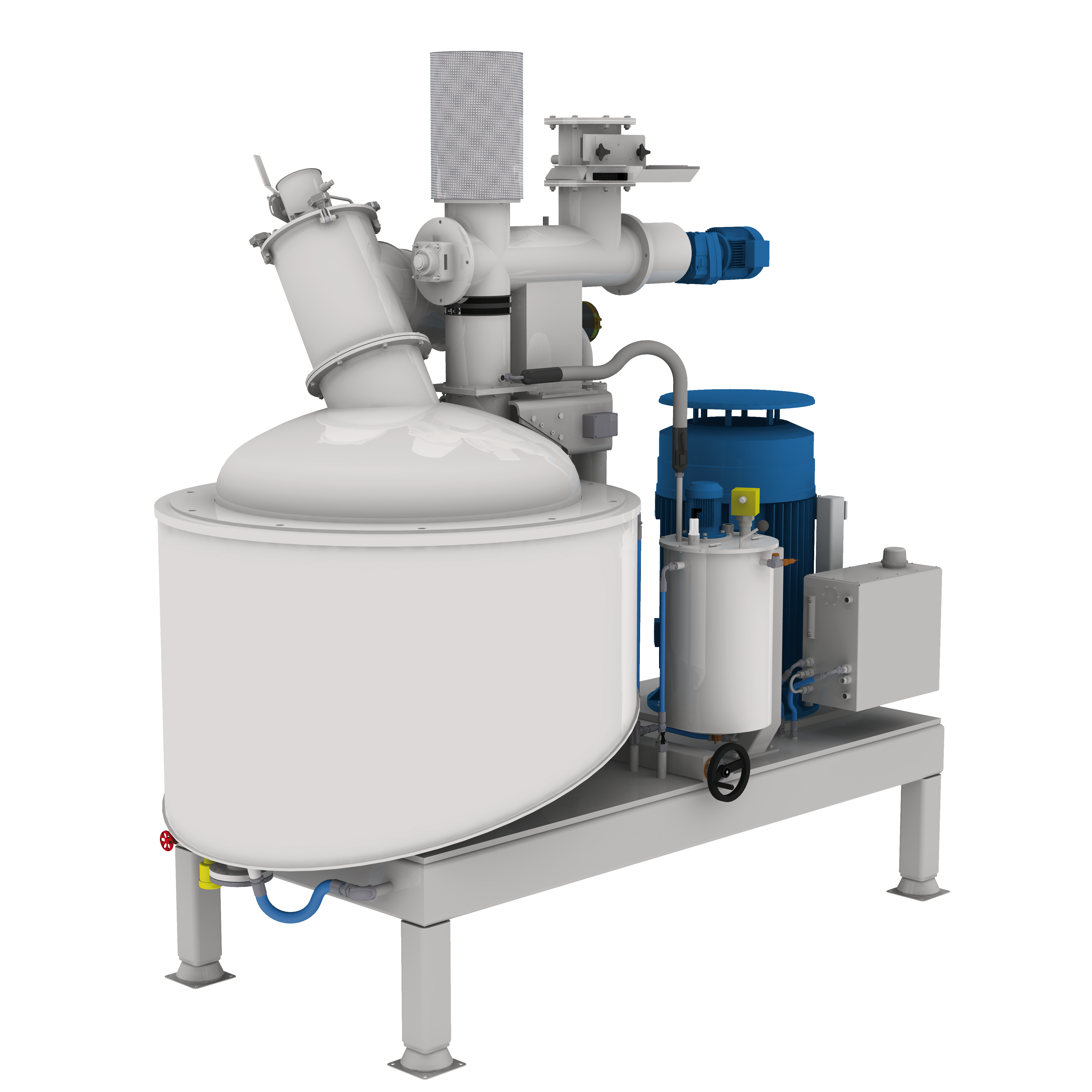
Cocoa liquor grinding line
After roasting and cracking chocolate beans (without husks), the following process is the grindin...
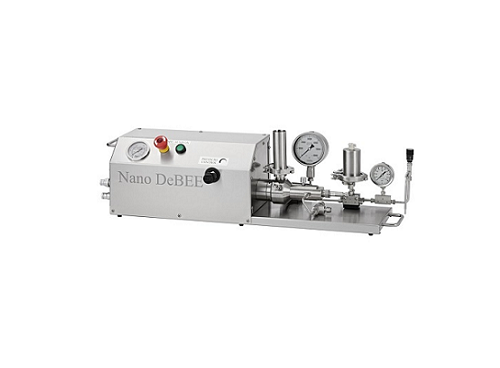
High pressure electric laboratory homogenizer
It’s vital that small units for experimentation can scale up with 100% accur...
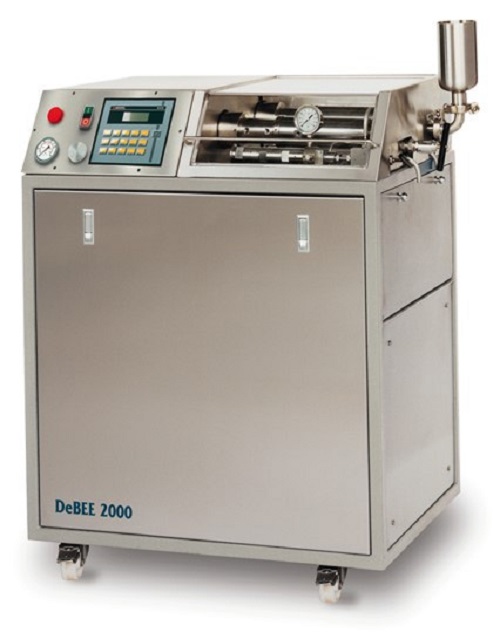
High pressure pilot homogenizer
Biotech and pharmaceutical development programs often require a mixing method that achieves ...
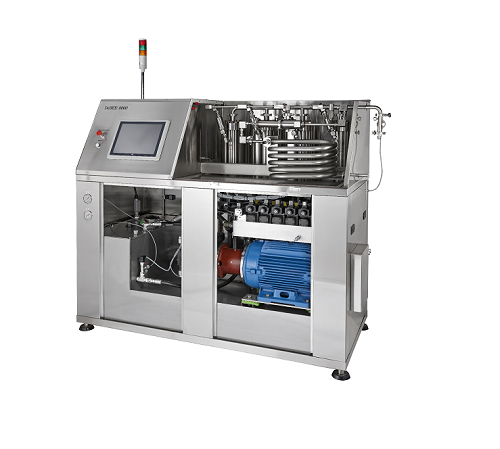
High pressure industrial homogenizer
For any industrial pharmaceutical process that relies on high pressure homogenization ...
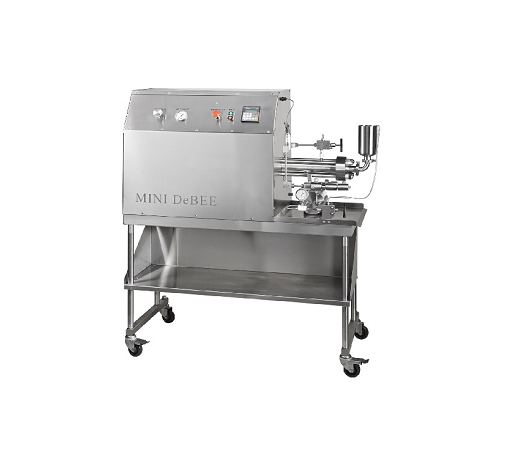
Pilot high pressure homogenizer
For maximum value, a high-pressure homogenizer that’s suitable for both laboratory and pilot...
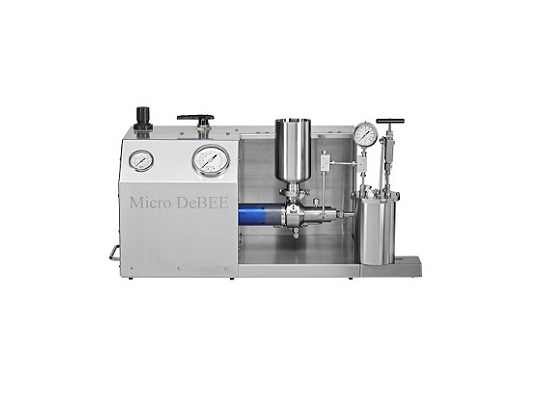
High pressure air powered laboratory homogenizer
Offering lab-scale to small pharmaceutical production scale output for in...

Cheese grater
Breaking down large blocks into grated, shredded, powdered or planed cheese requires multiple graded discs that ...
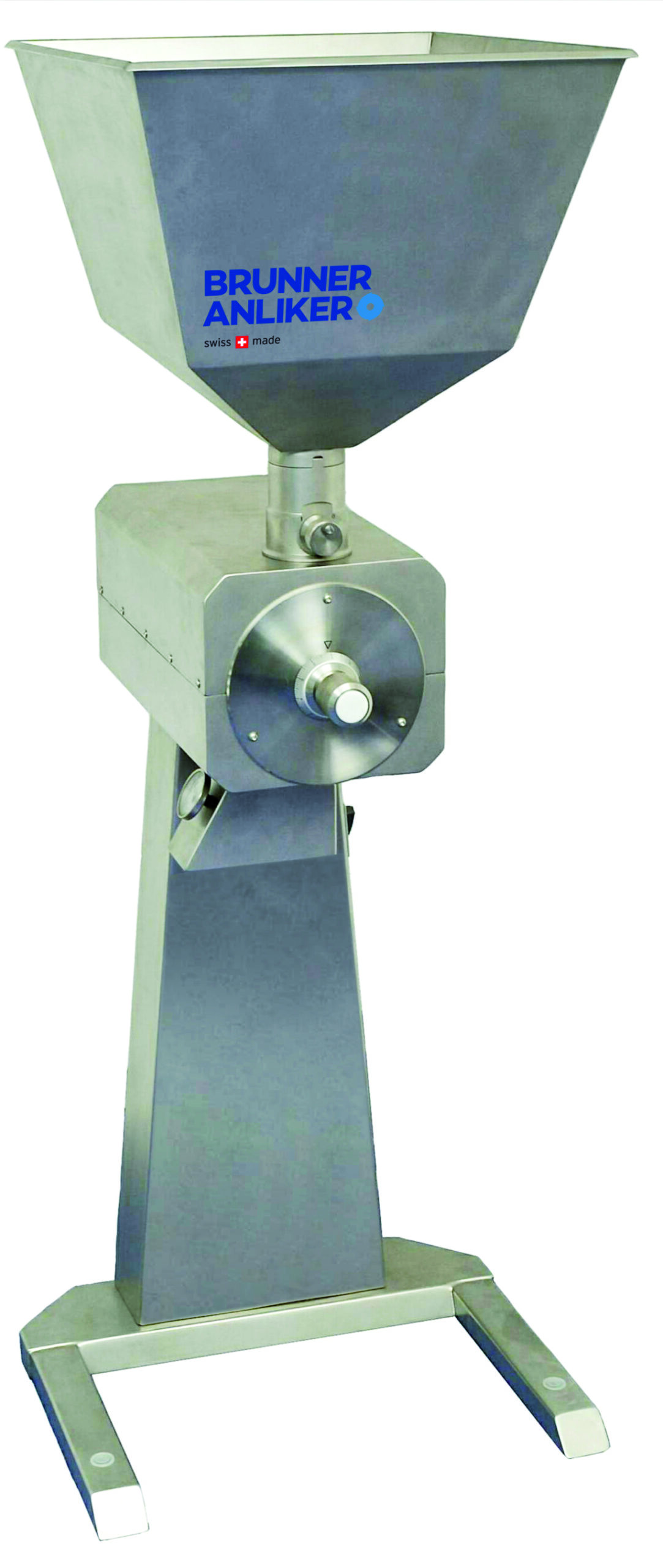
Grinder for spices and coffee
Gentle grinding of coffee down to all grades from coarse to fine requires high precision proce...
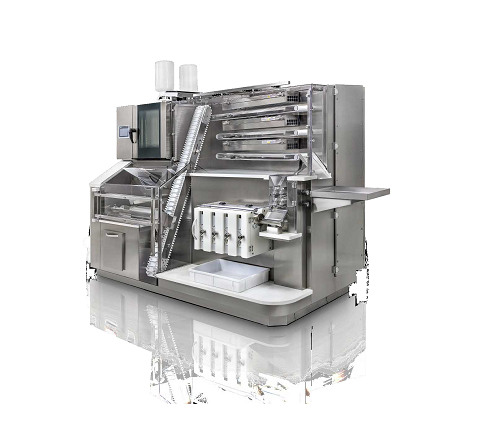
Small scale cocoa beans processing machine
For the highest quality chocolate production, complete control of the entire pr...
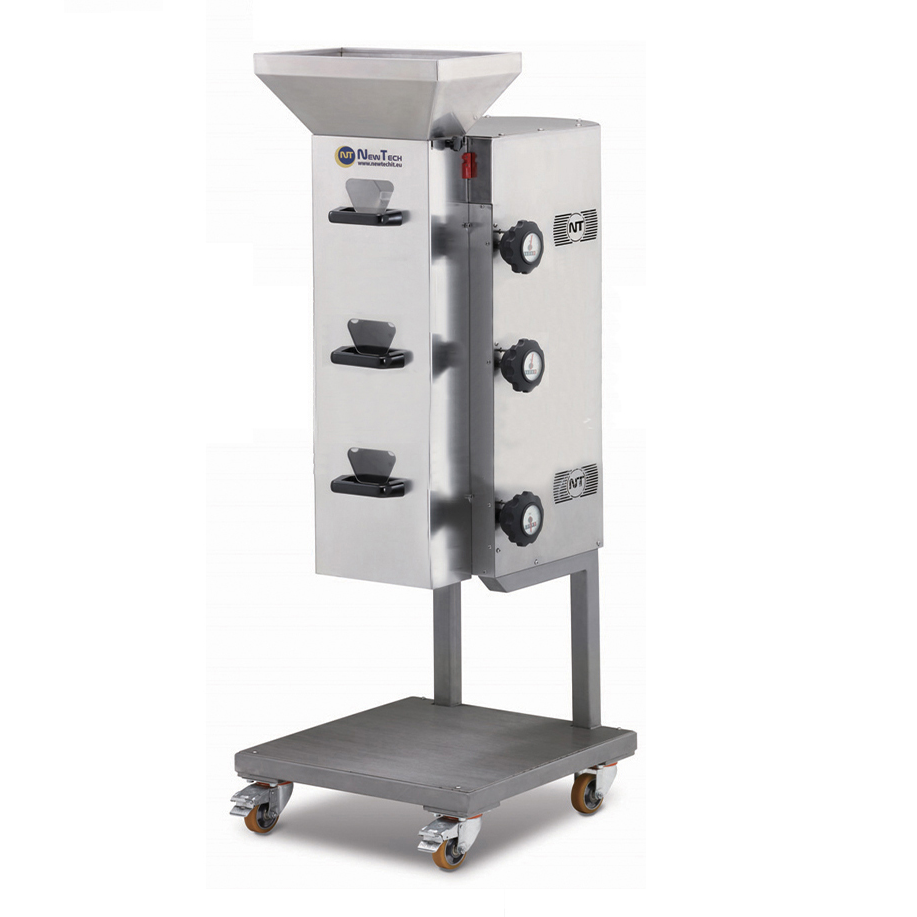
Small scale nut chopping machine
Many confectionery and bakery products use nuts as a key ingredient or decoration. The abil...
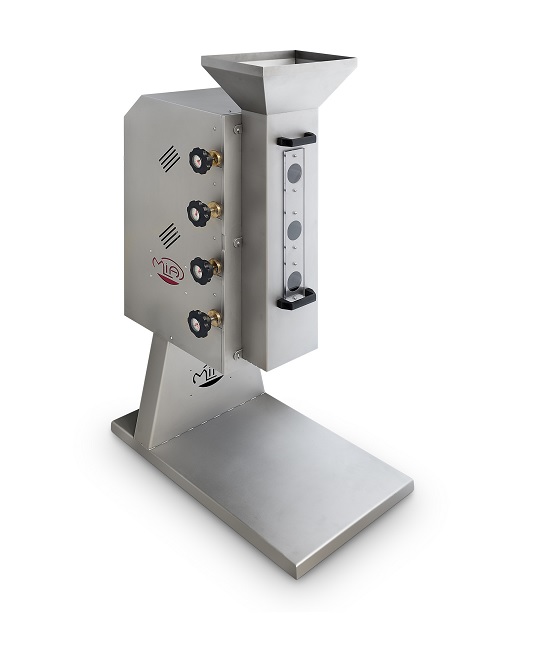
Small scale nut grinder
Many confectionery and bakery processes rely on the uniform grinding of raw ingredients such as nuts,...
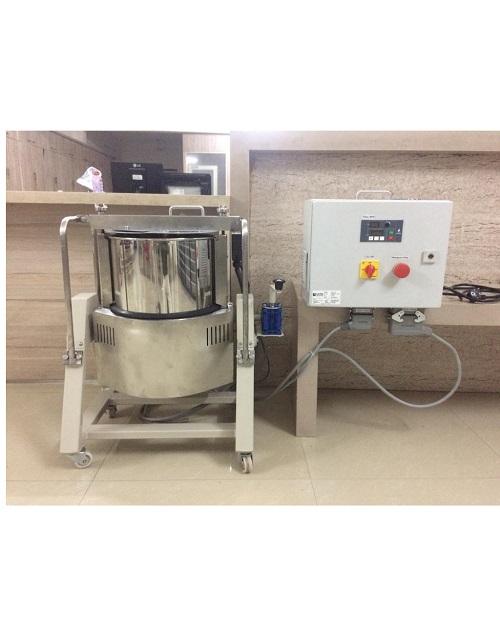
Small capacity chocolate melangeur
In order to produce the finest of chocolate products, you need the cocoa nibs to be grin...
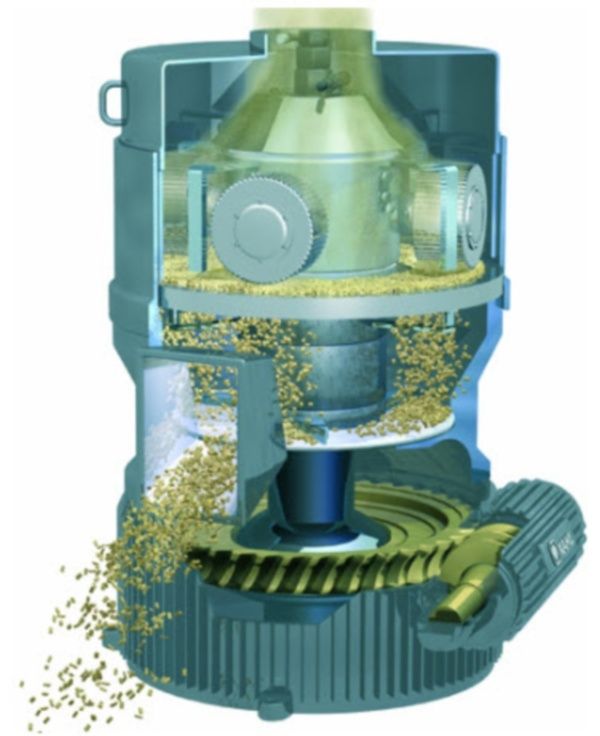
Pelleting press for biomass
Utilization of biomass for energy and other applications requires consistent and reliable compac...
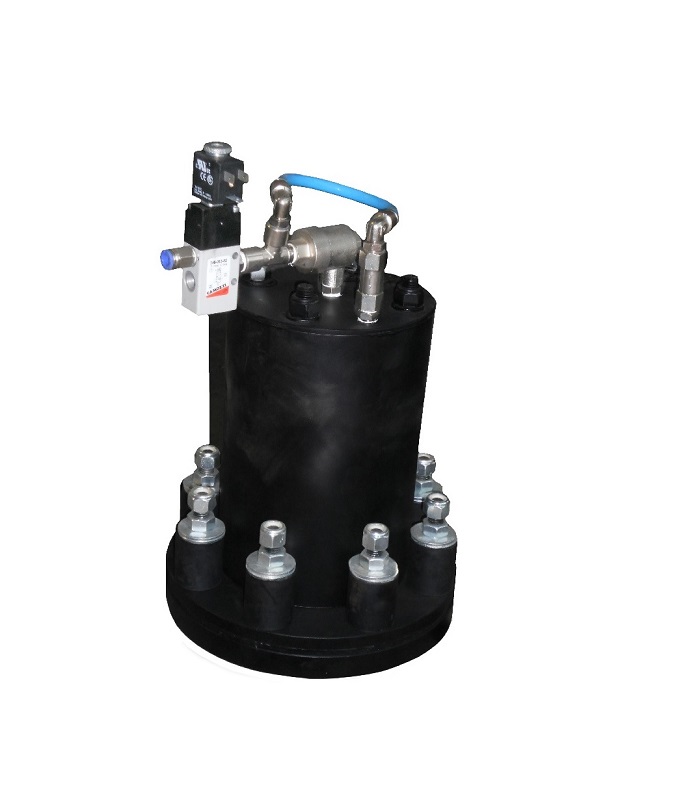
Airshocking hammer
Silos, hoppers, bins, and other containers can build up a layer of powdered product on the internal walls....
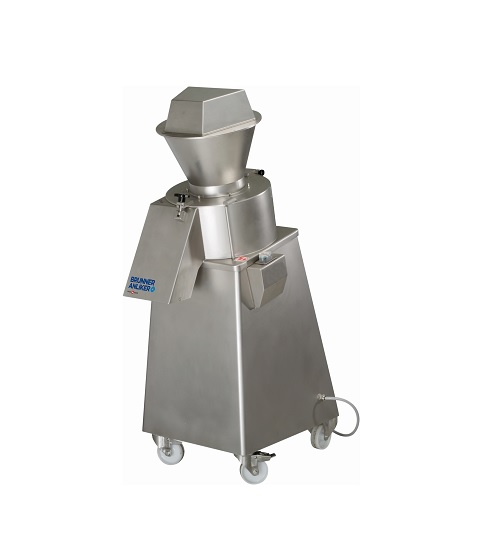
Industrial nut grater
Pressure from the grinding process can cause damage to food products as well as induce unwanted heating...
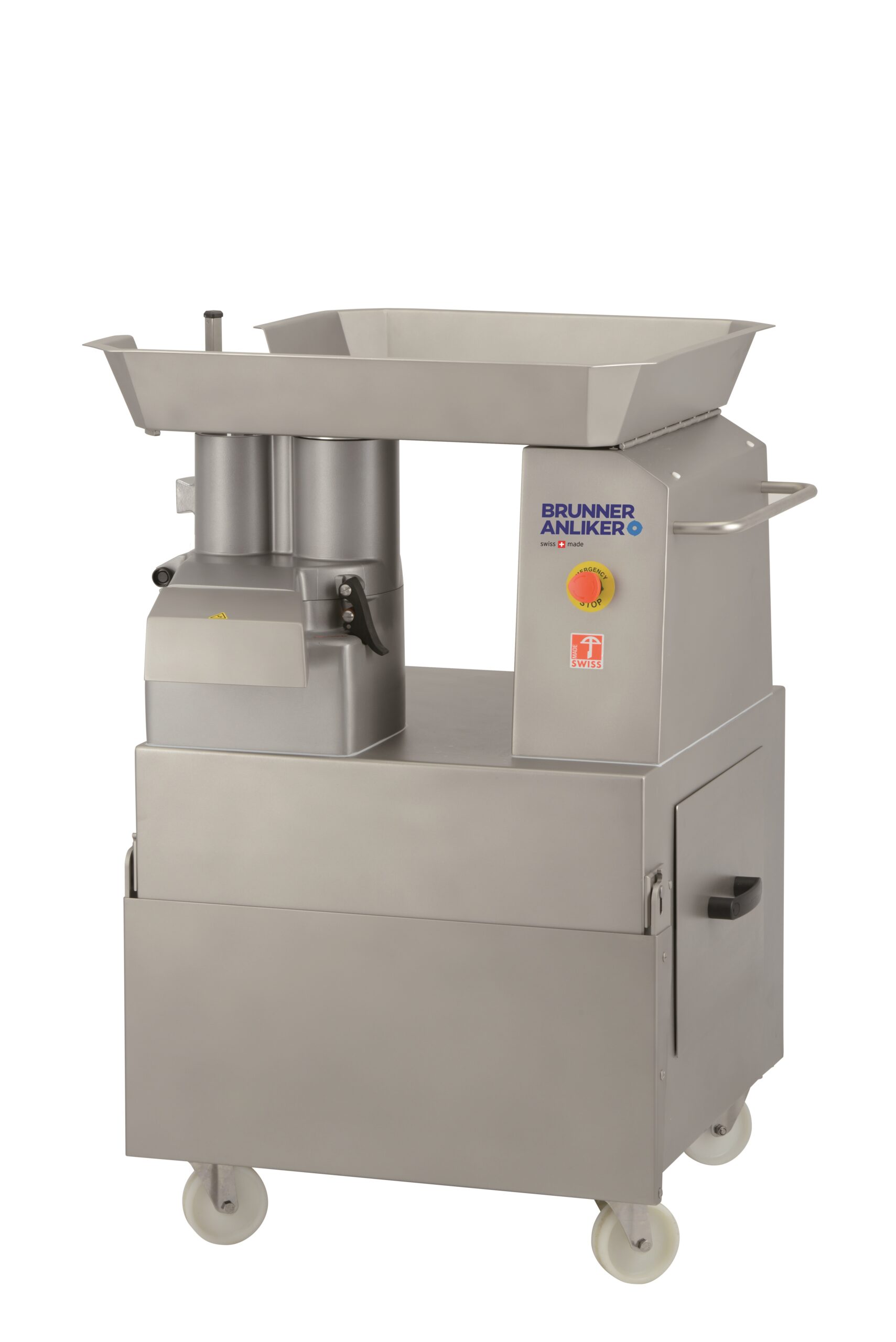
Industrial vegetable cutter
Retaining freshness in cut vegetables, as well as retaining vitamins and nutrients, is a top pri...
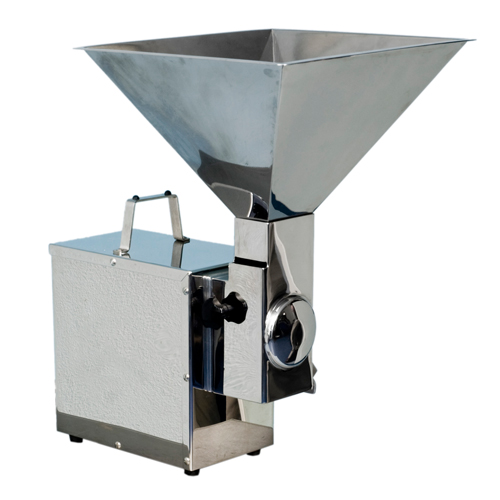
Nut dicer
Dicing nuts can generate a large volume of wasteful and messy powdered nut residue.
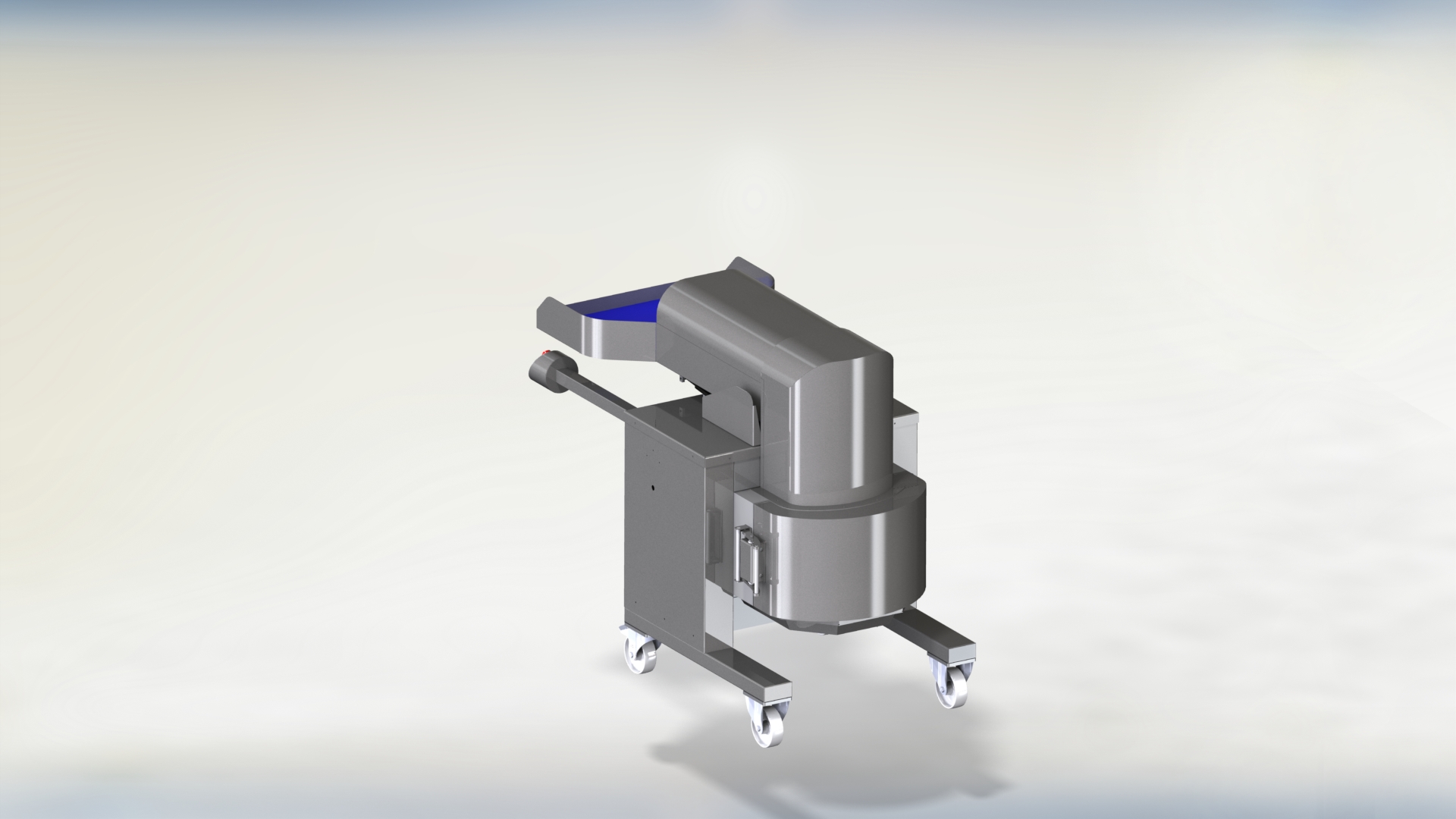
Declumping machine for dried fruit or frozen vegetables
Breaking up dried fruit neatly, without damage, requires gentle a...
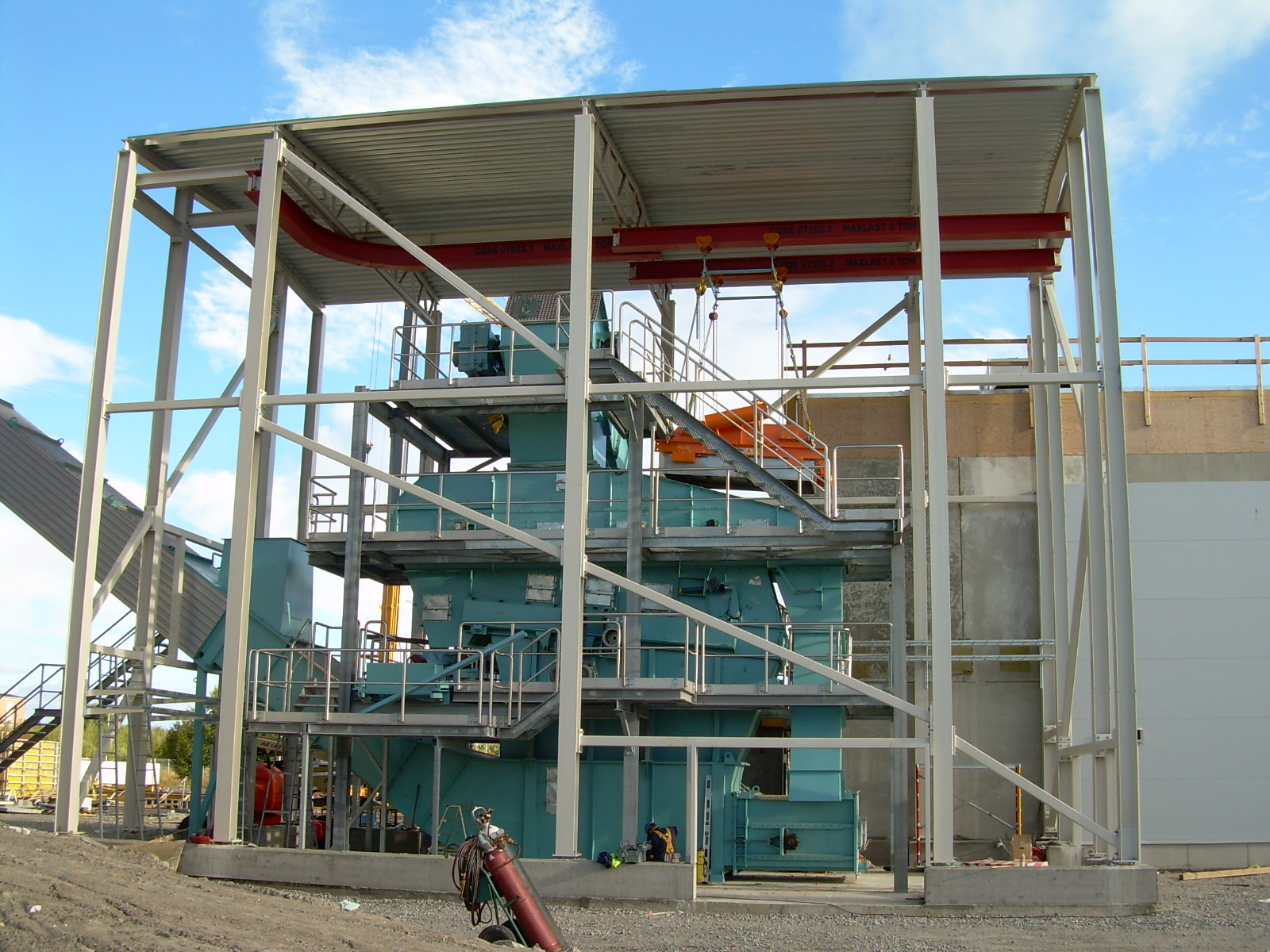
Solid biomass screening and crushing equipment
Biomass fuels come in many forms and often include impurities that can dama...
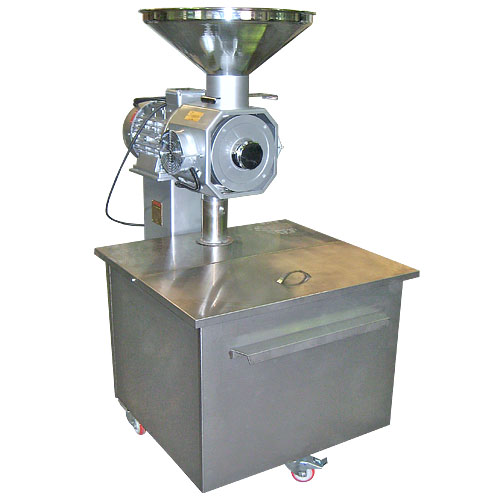
Industrial coffee bean grinder
If you are looking to grind up to 50 kg of fine coffee per our or up to 440kg of medium fine ...
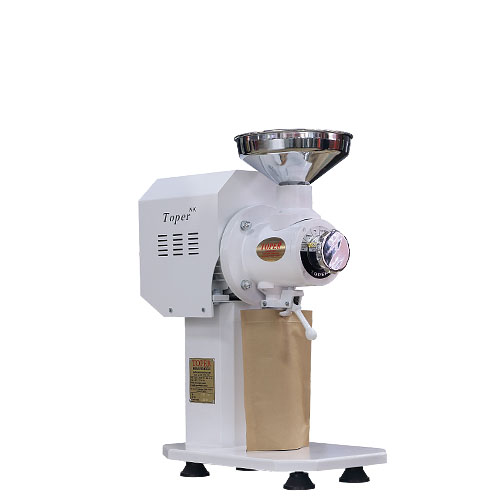
Shop coffee bean grinder
Do you want to grind your beans on-site at your coffee shop, but are you limited for space? Bench-to...
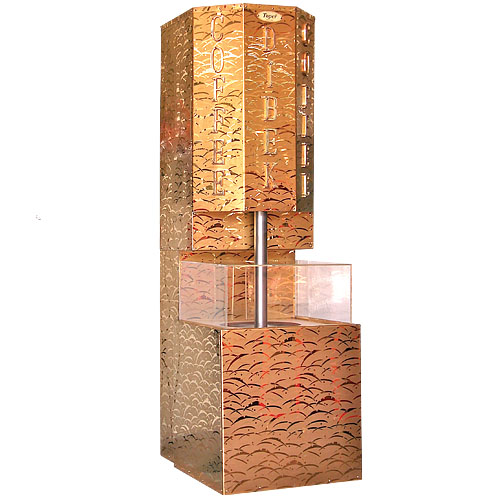
Mortar for coffee pounding
With a pounding capacity of 50 kg/h – 110 lbs/h this mortar for coffee pounding will guaran...