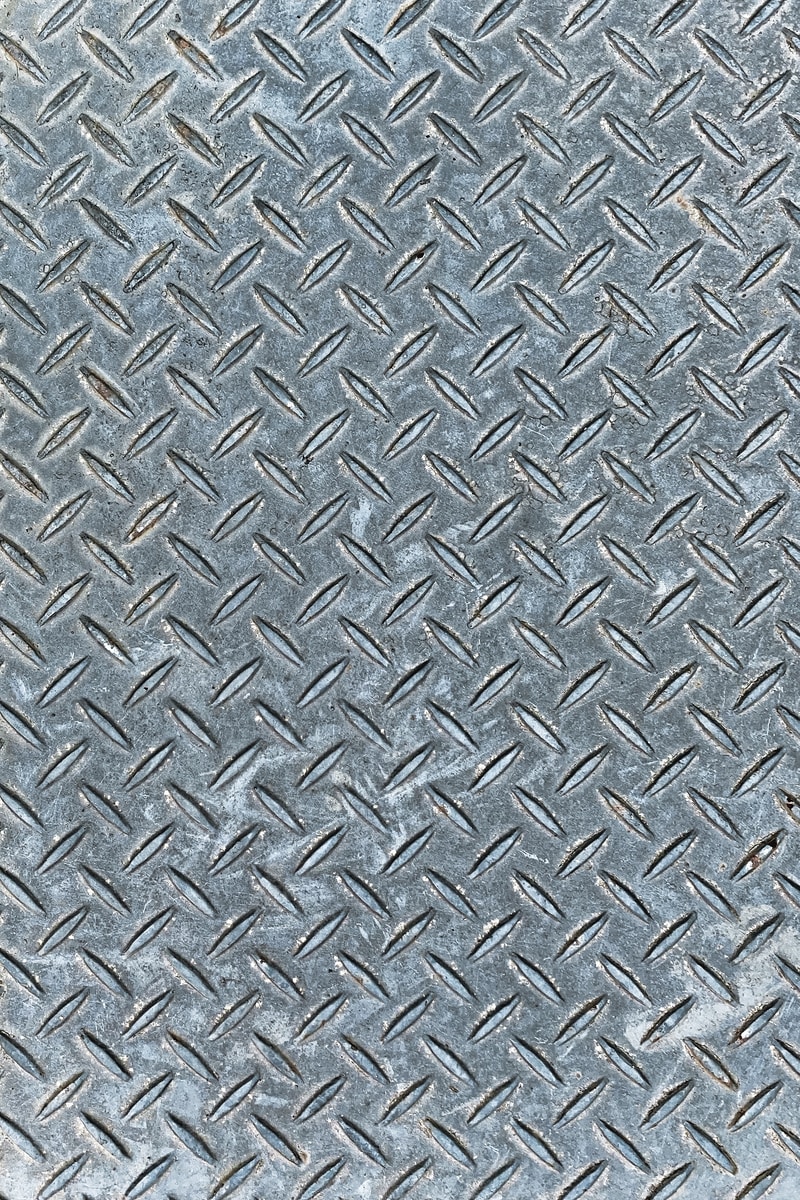
Metal Processing Equipment
Find innovative metal equipment and connect directly with world-leading technology suppliers
We carry dozens of metals around every day. The ubiquitous smartphone is built with no less than 20 metals, each with specific behaviors and purposes. Metals are a pervasive class of materials that have defined entire eras of human development. It is no exaggeration to say that metal processing equipment is the core of our metallic world. But, paradoxically, this manufacturing technology itself is mainly made of metal.
Top picks for processing metal
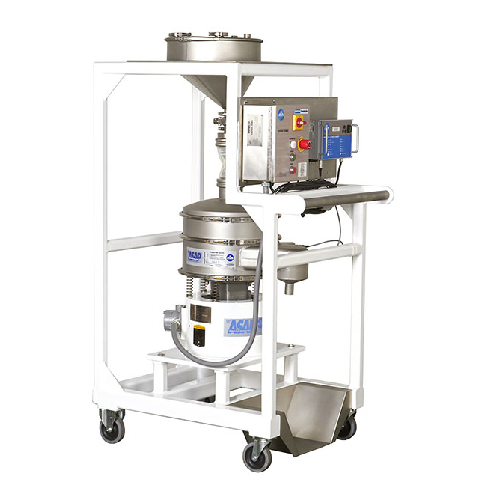
3d metal printer powder screening system
Enhance your 3D metal printing workflow by efficiently reclaiming and rebottling u...
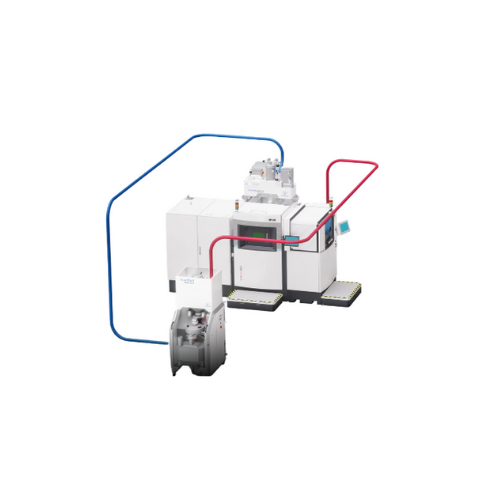
Closed powder handling loop for Eos metal Am printers
Effortlessly manage metal 3D printing powders with a solution that ...
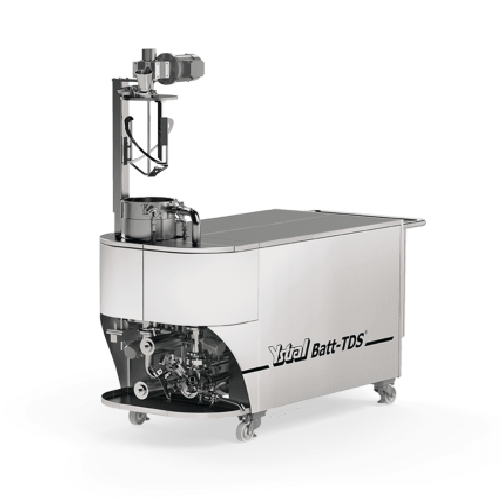
Inline disperser for lithium-ion electrode slurry mixing
Achieve highly efficient dispersion and homogeneity for battery ...
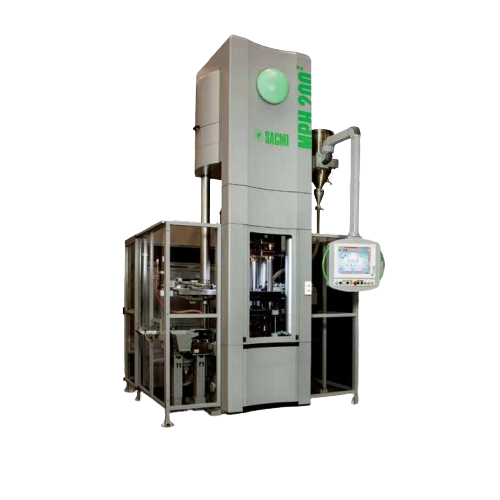
Presses and furnaces for metal powder components
Achieve precise forming and consistent quality in metal components produc...
Select your metal process
What are you making?
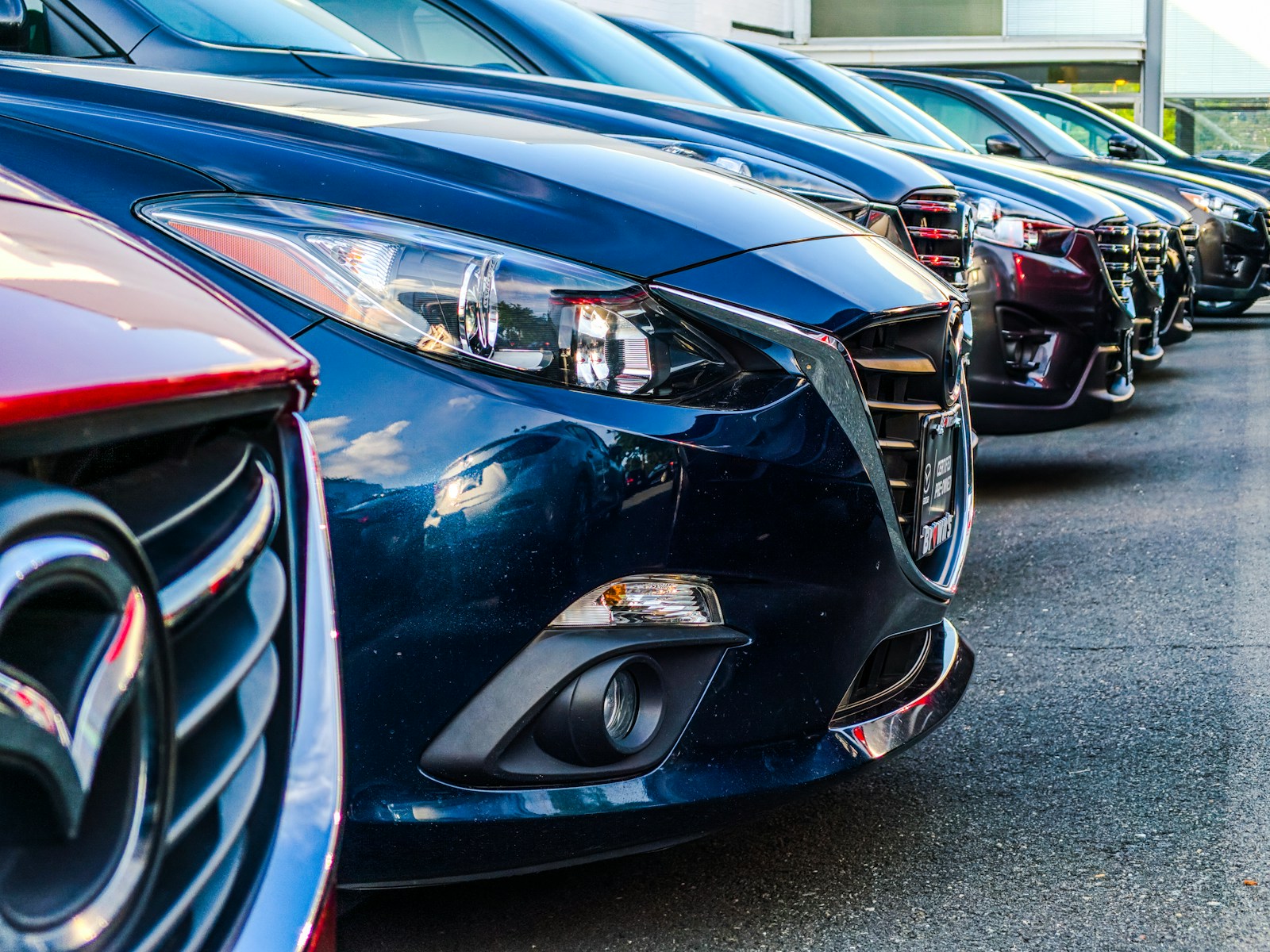
Automotive
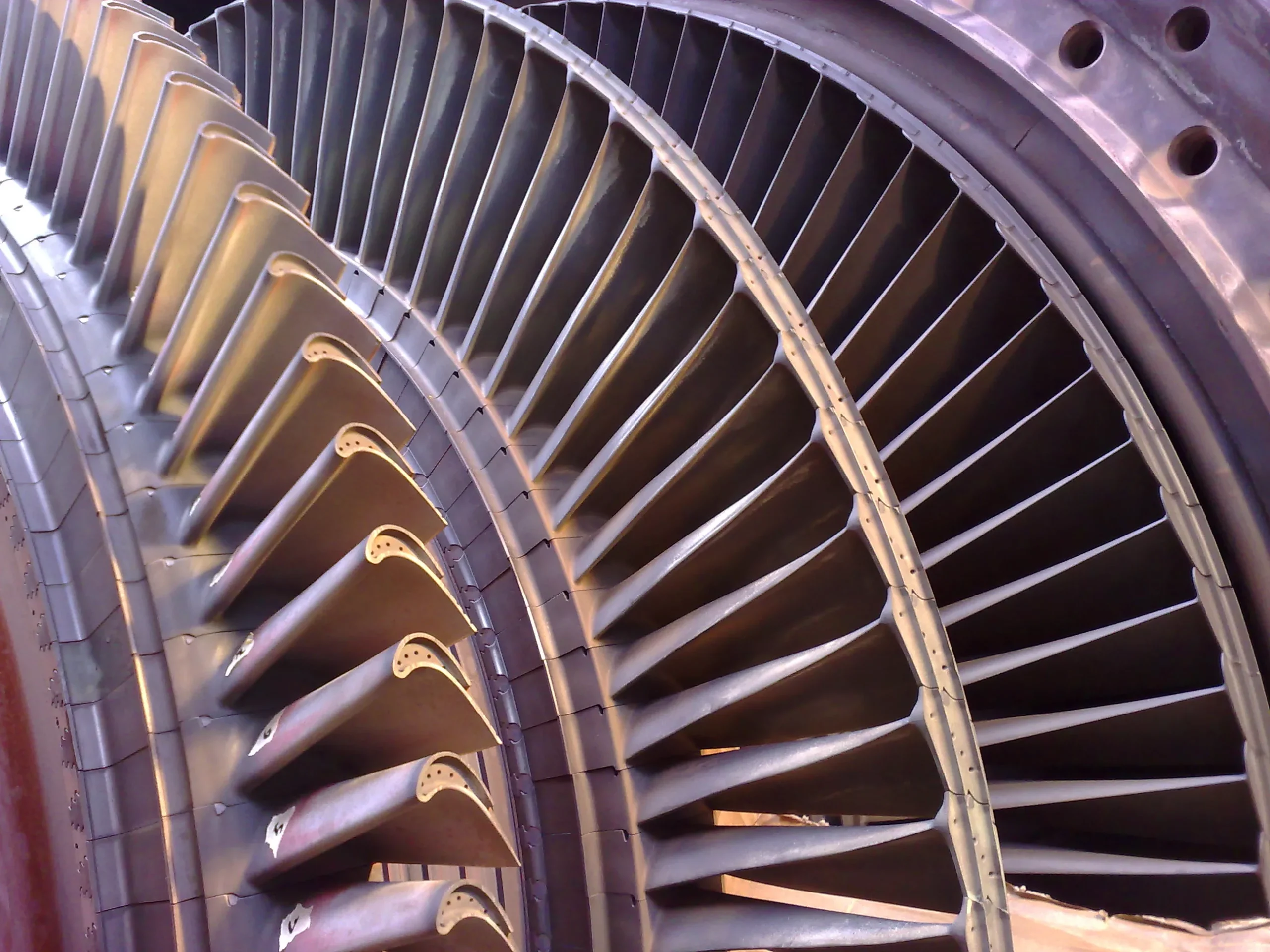
Turbine blades
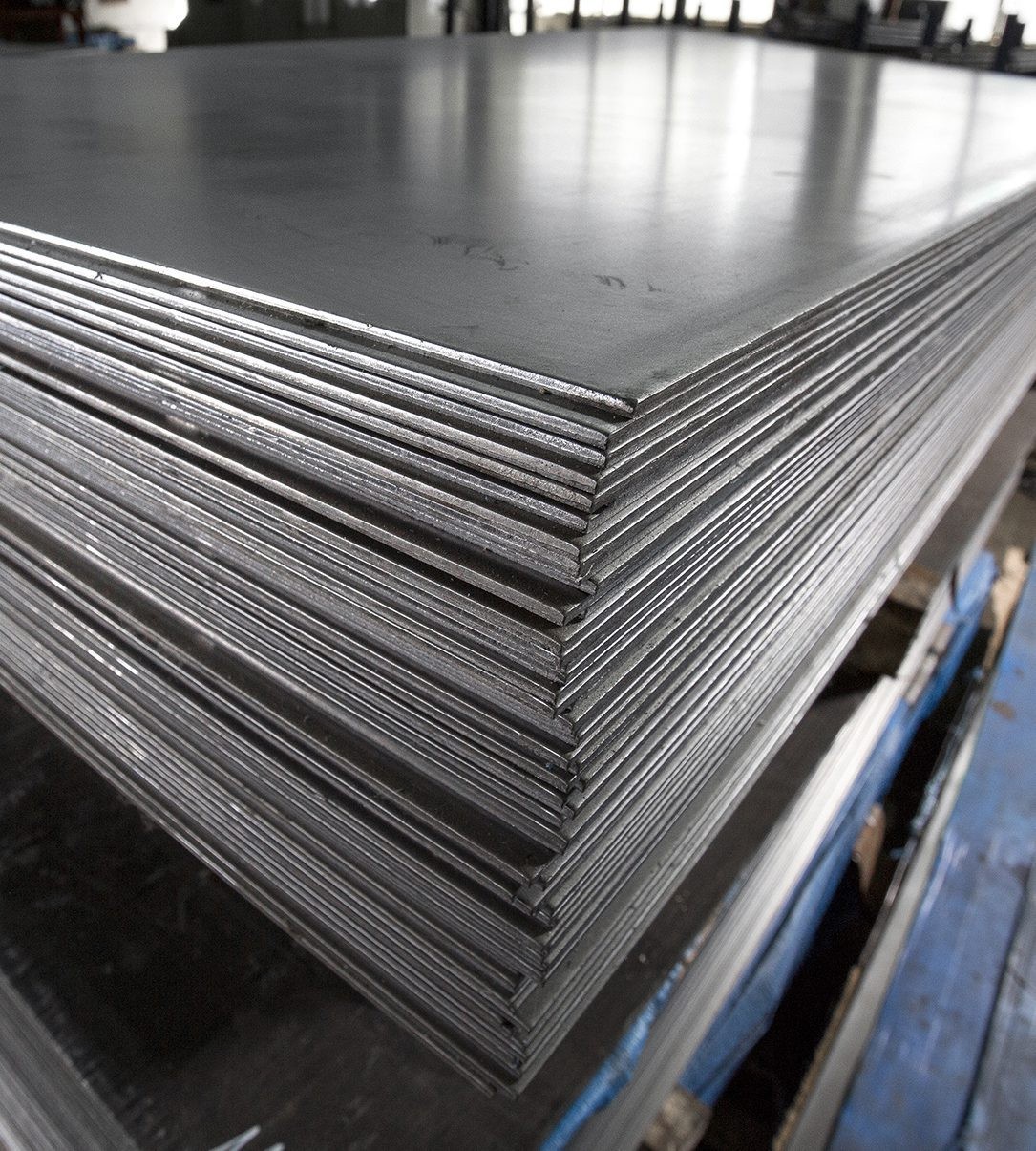
Steel sheets
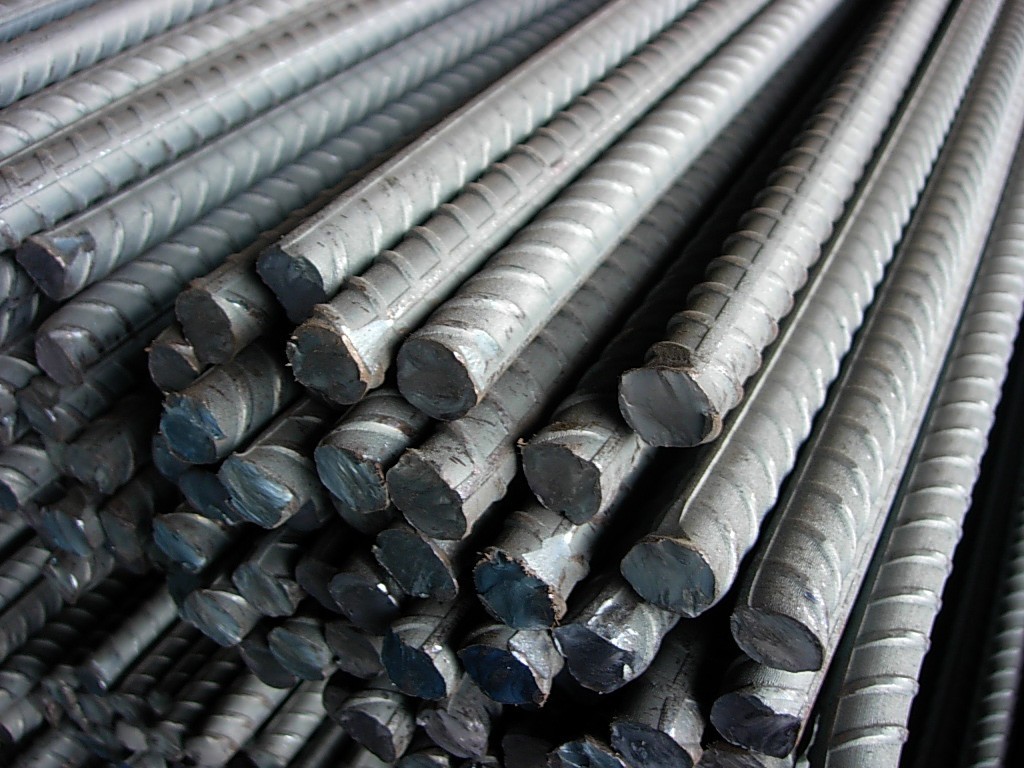
Steel rods
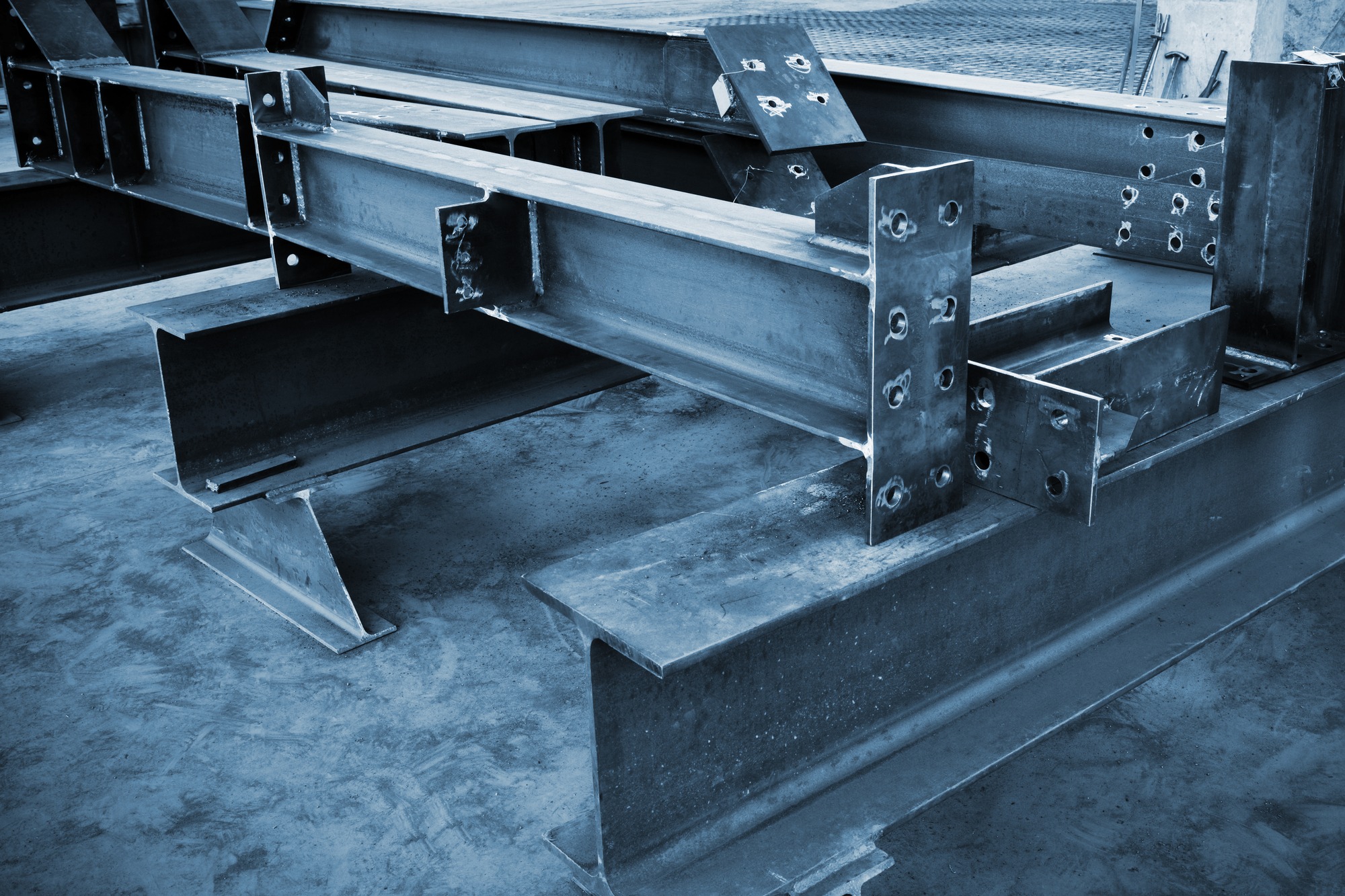
Steel beams
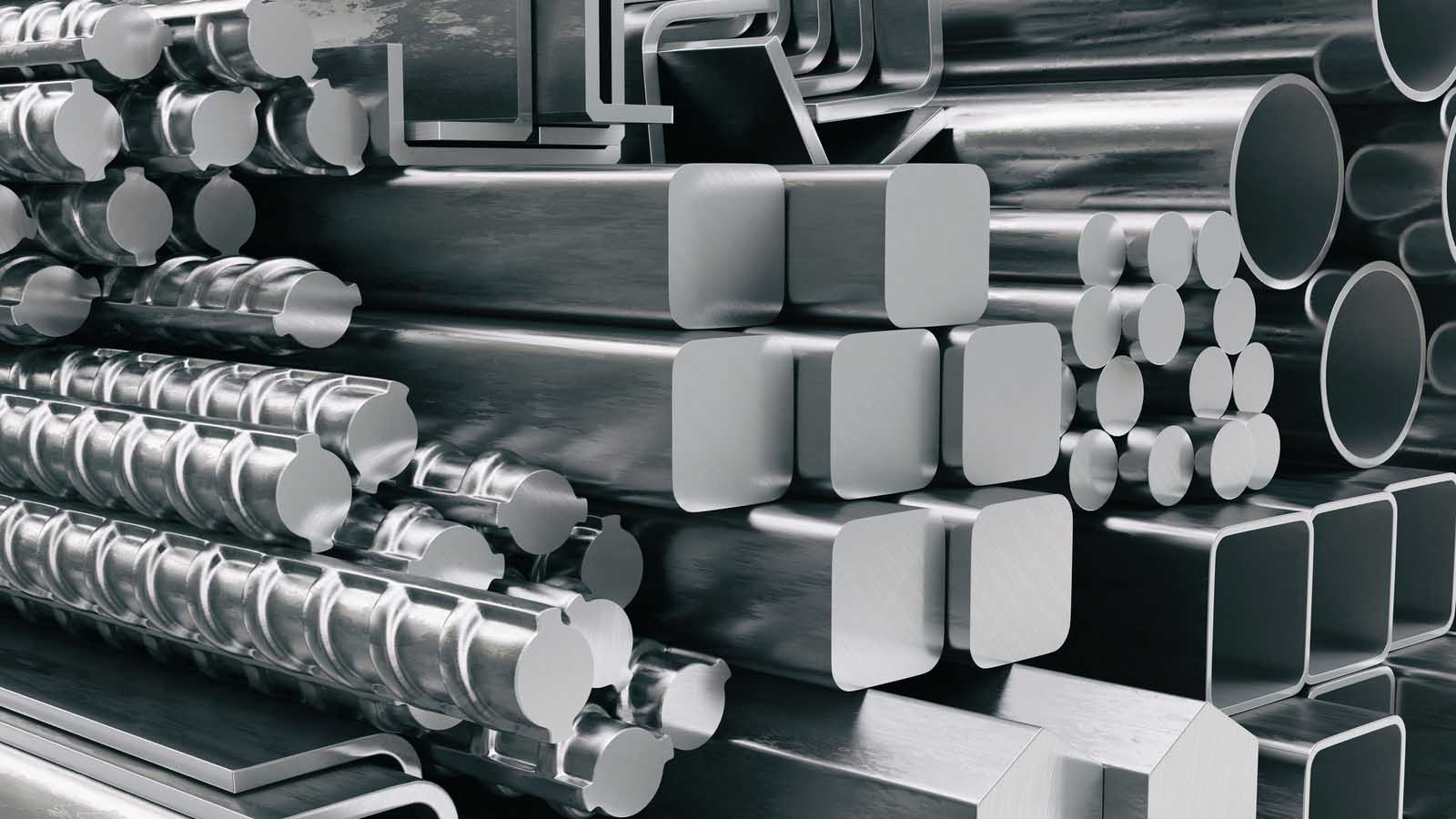
Steel
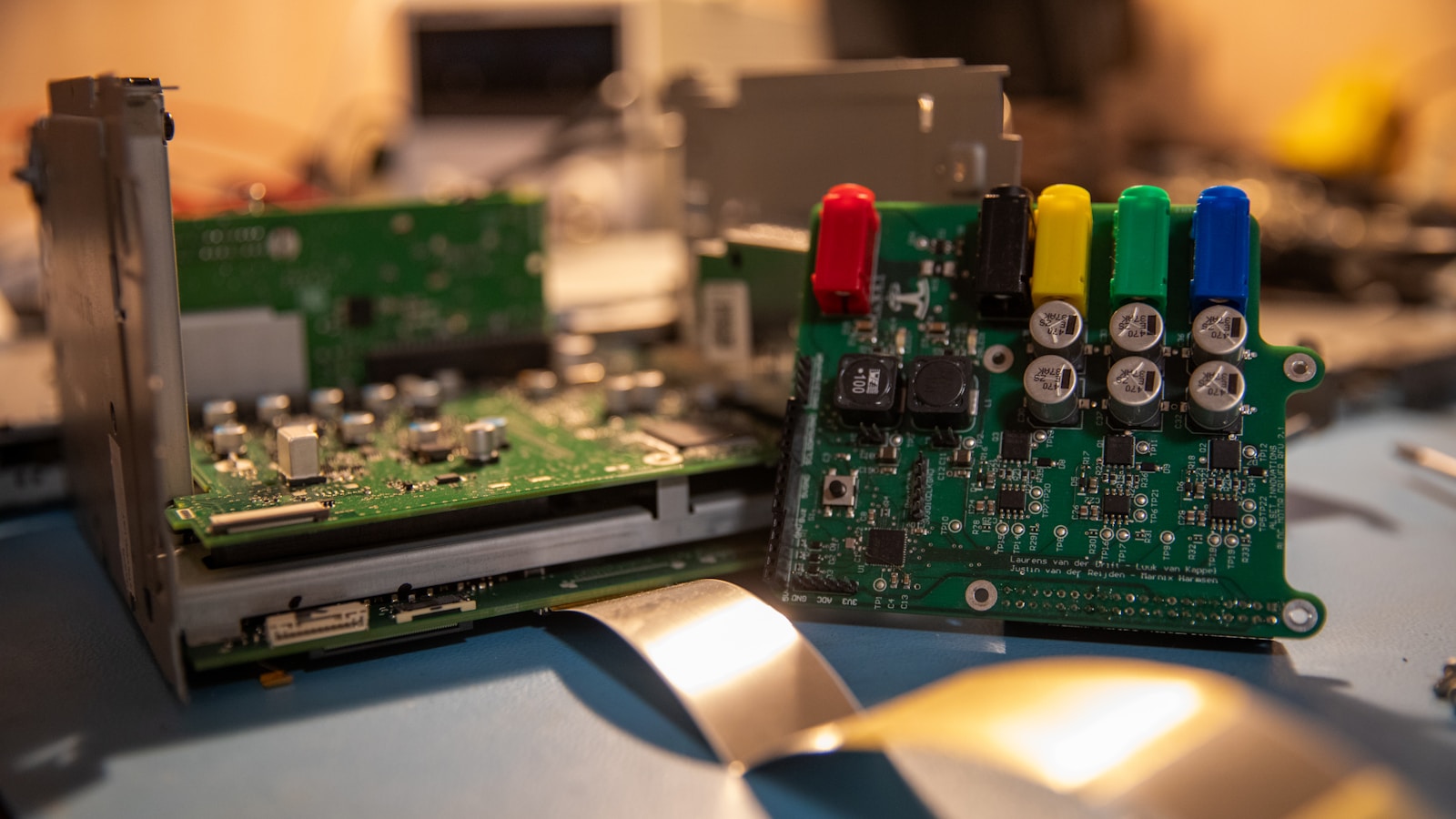
Printed circuit boards
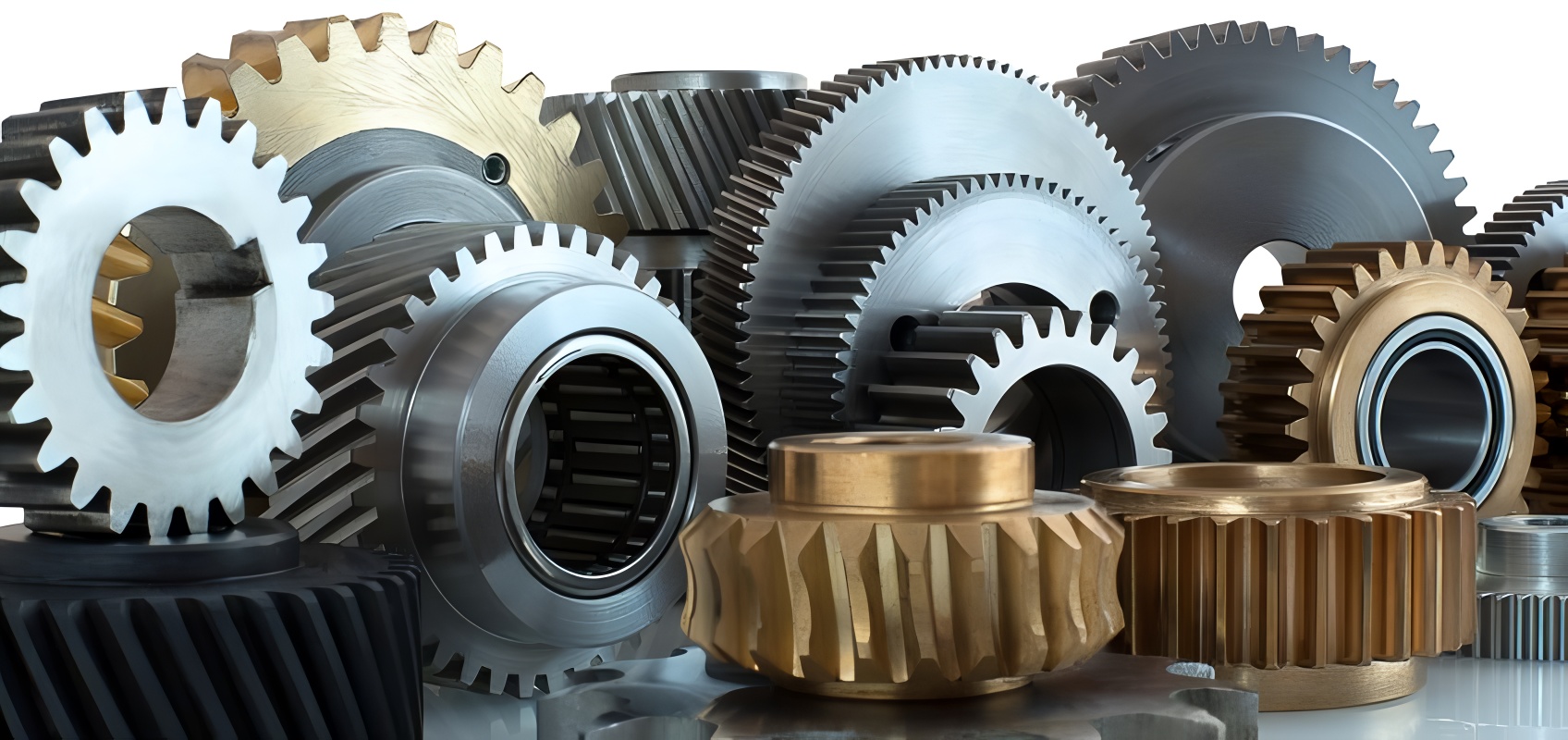
Precision gears
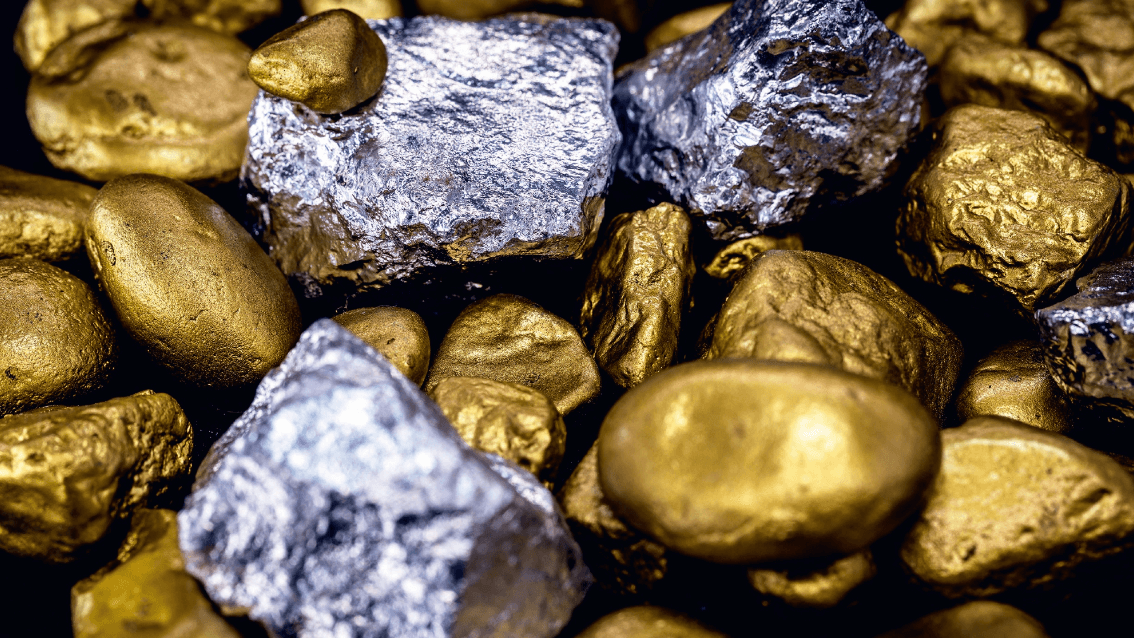
Precious metals
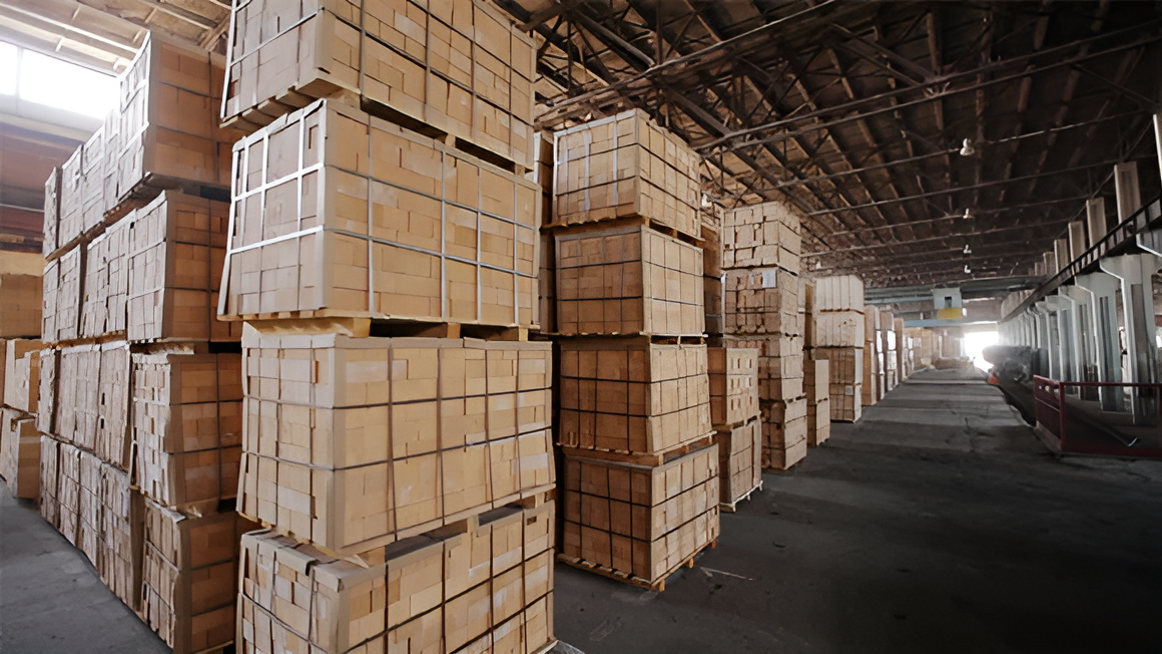
Refractory products
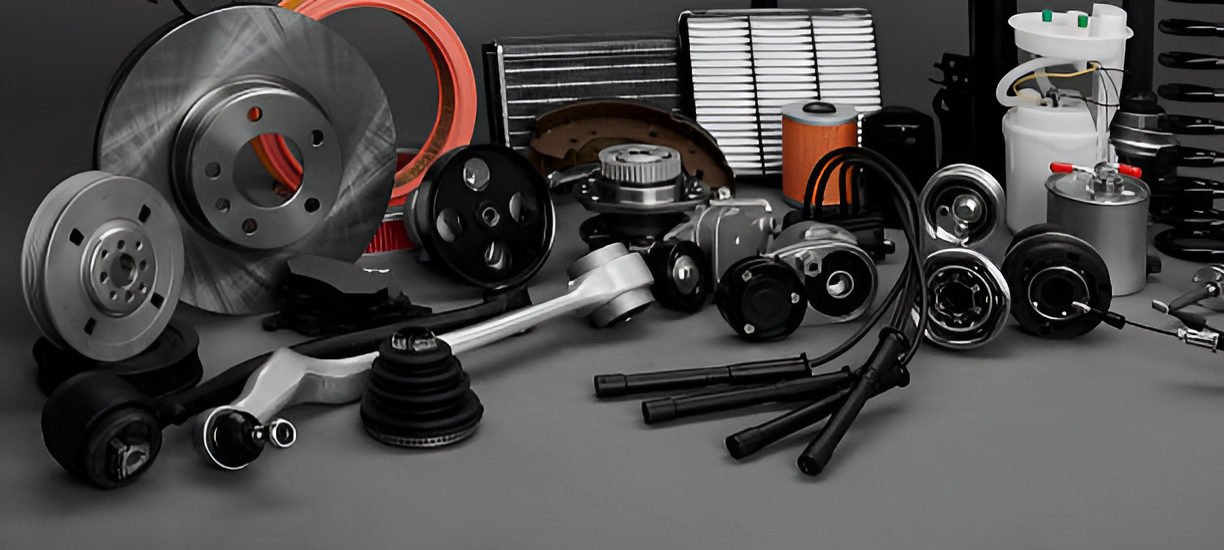
Machine parts
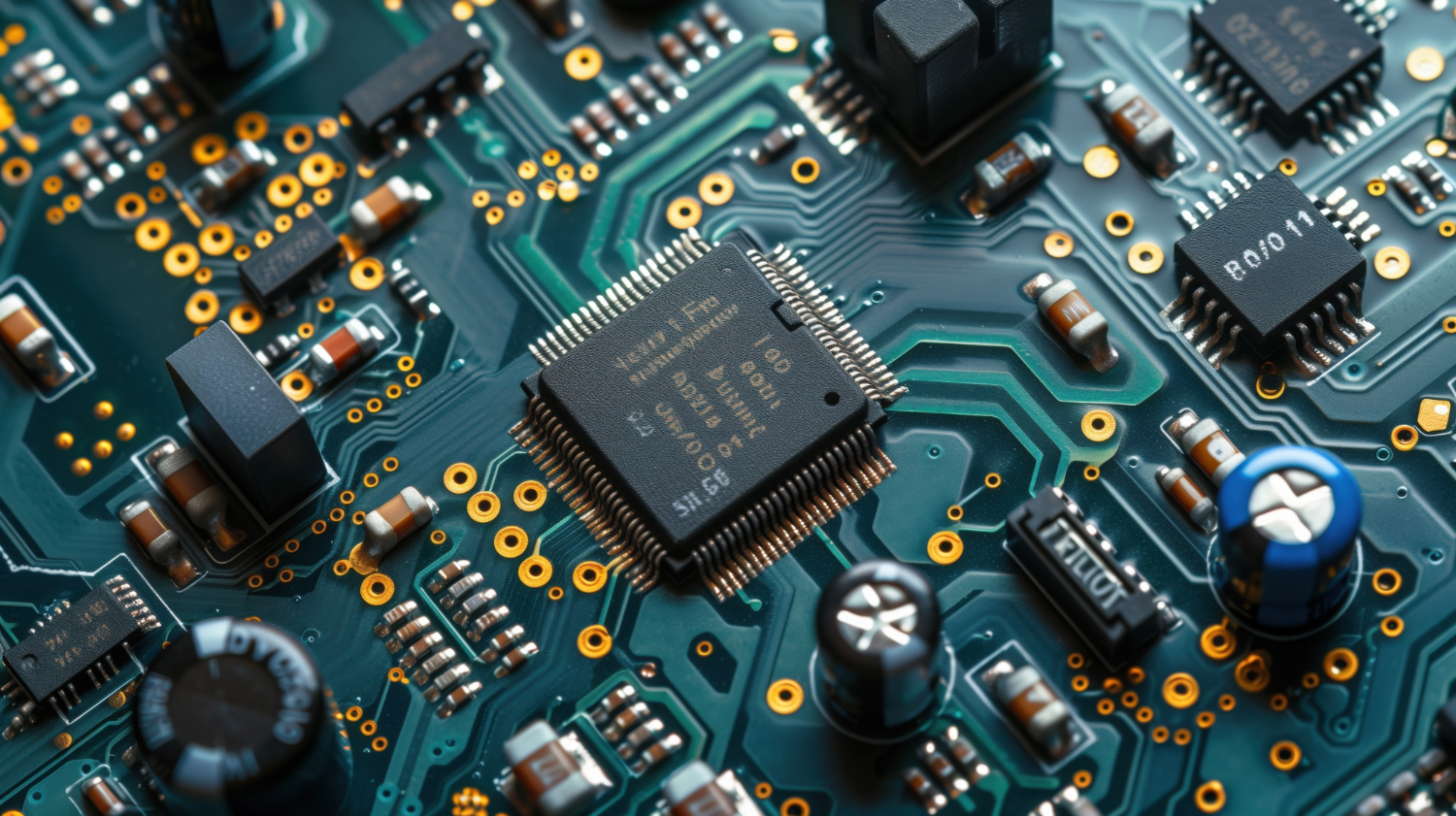
Microchips
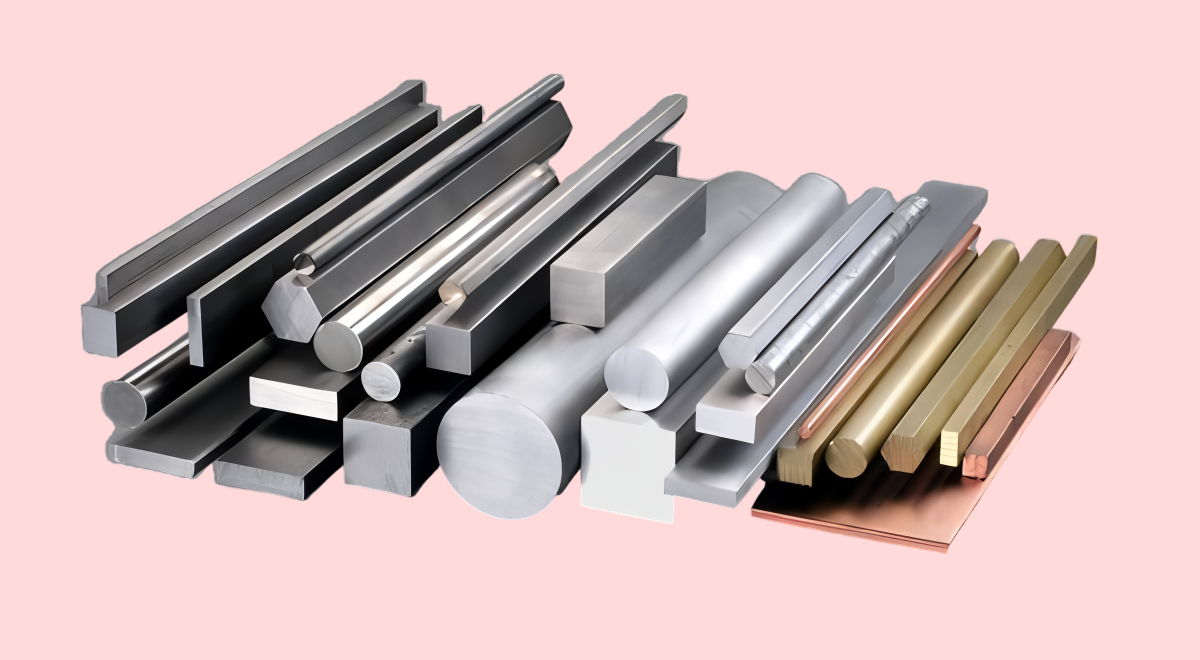
Metals
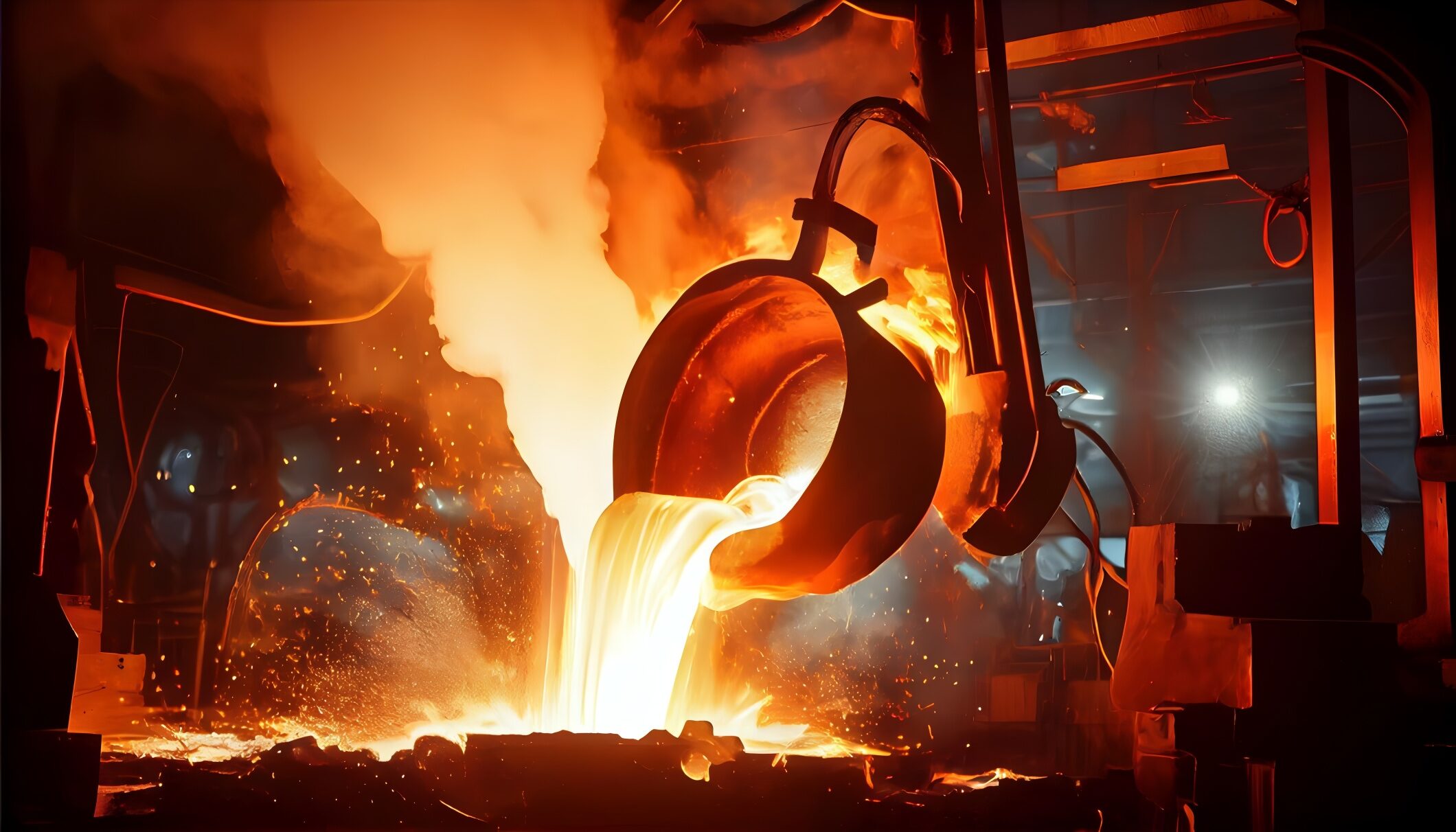
Metallurgy
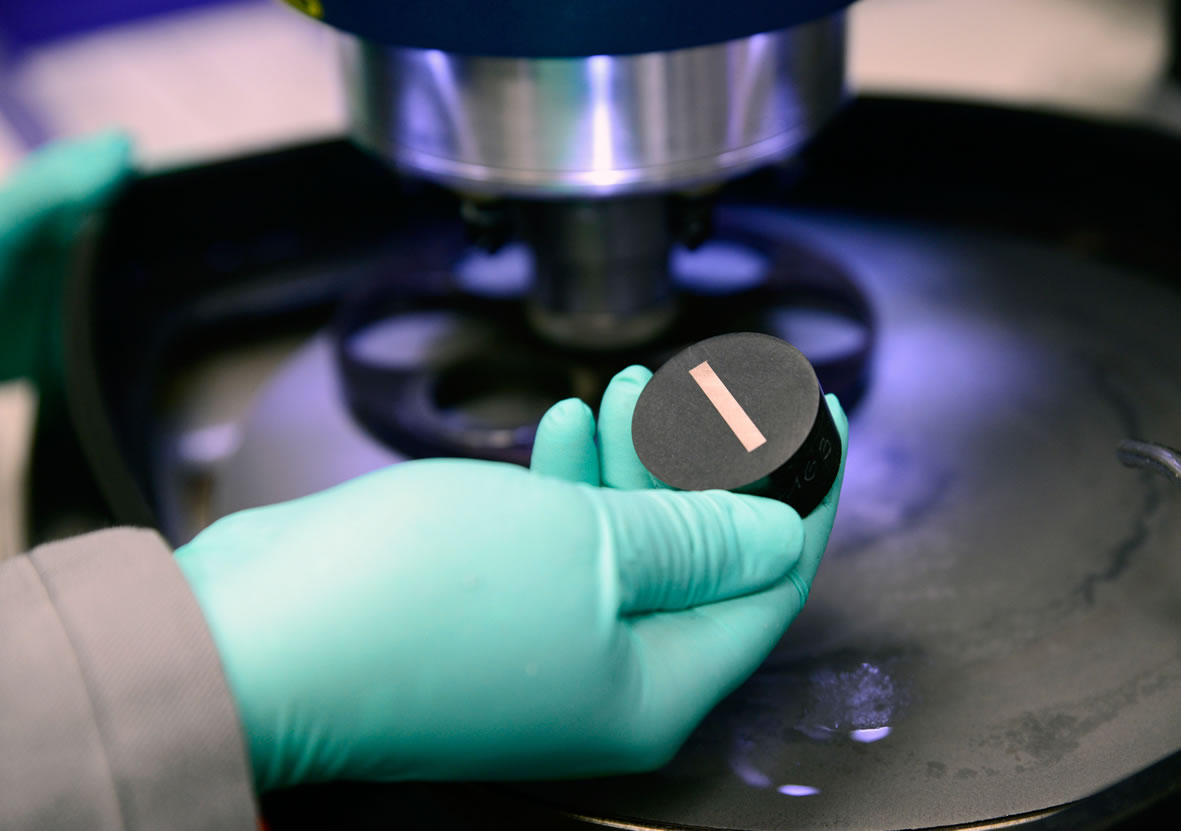
Metallography
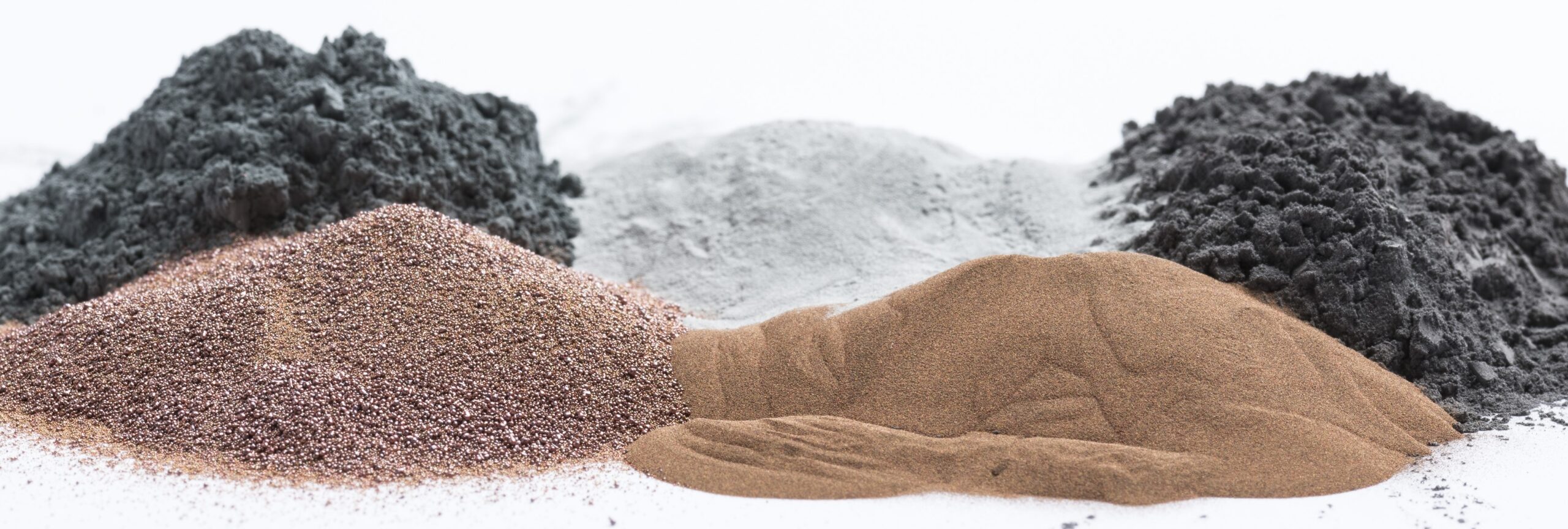
Metallic powders
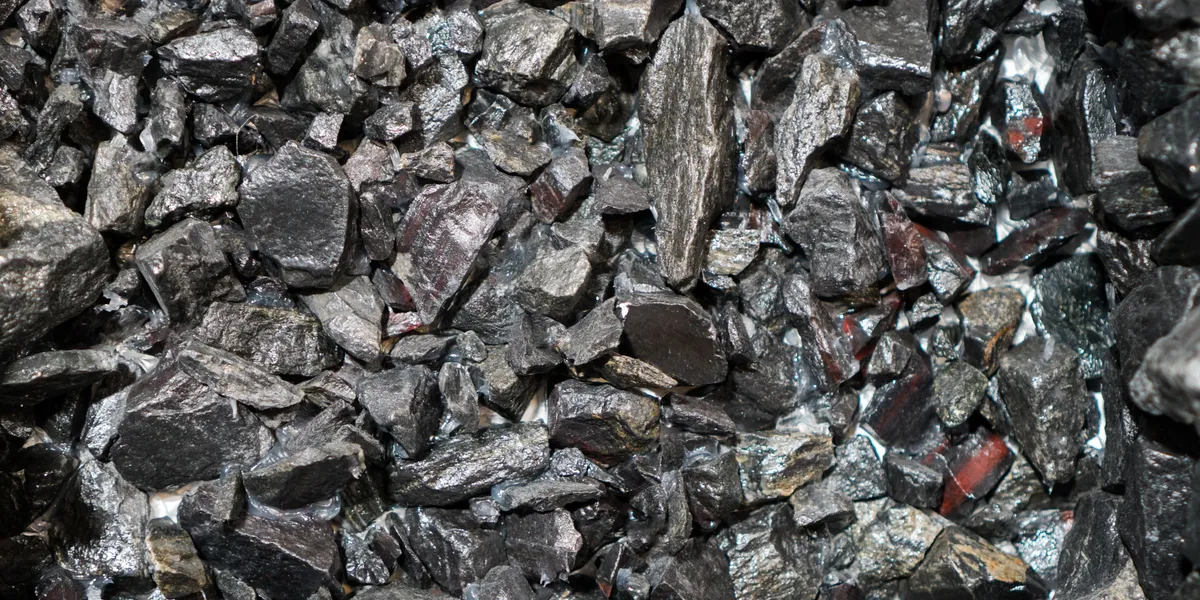
Iron ore concentrate

Metal recycling
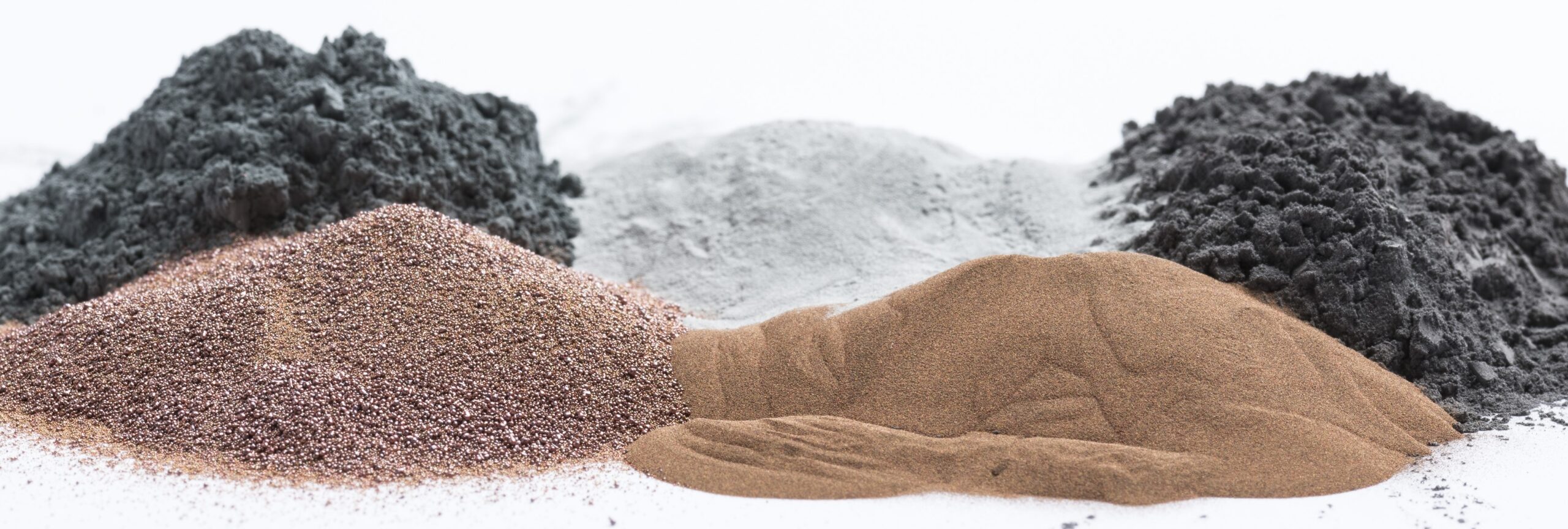
Metal powders
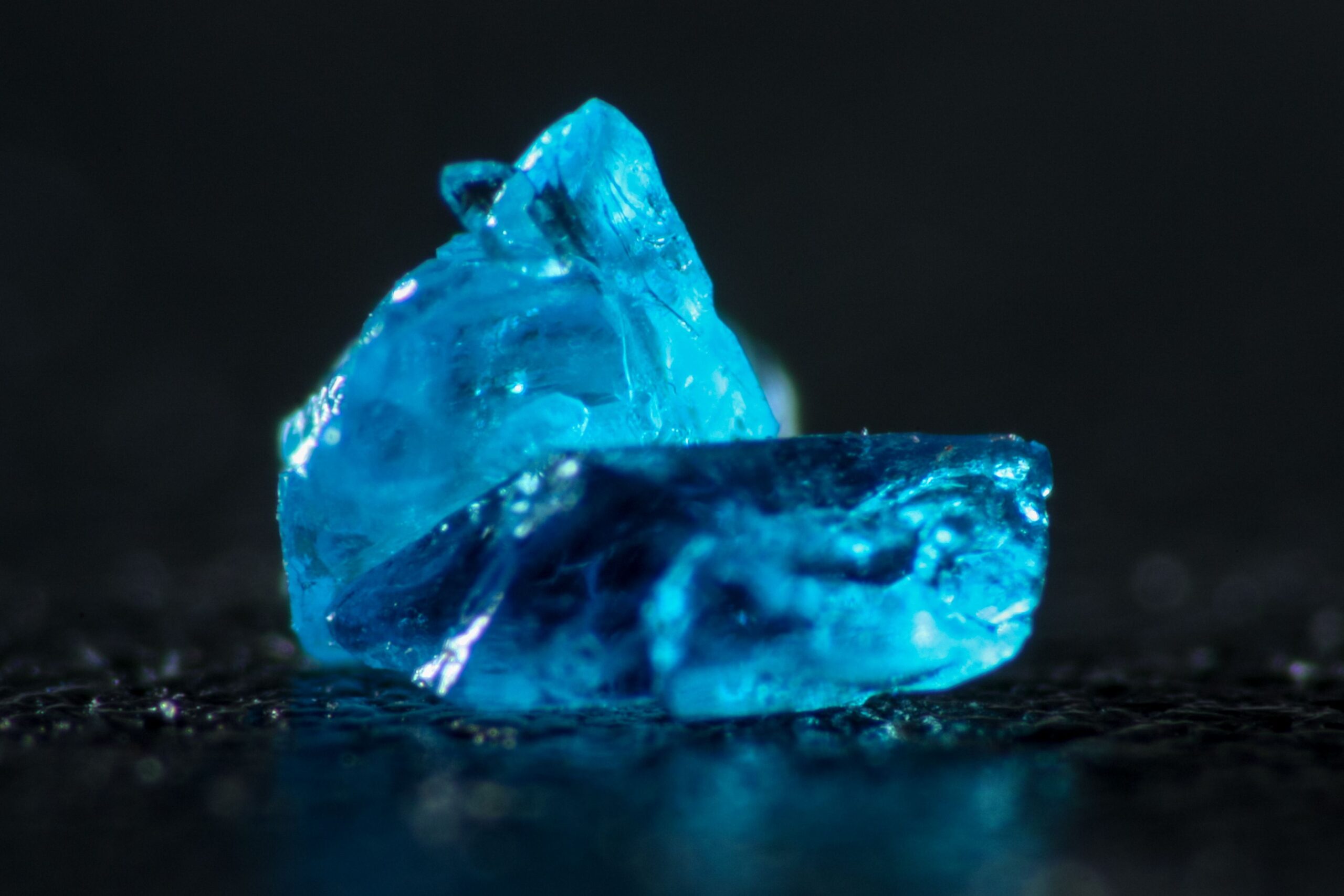
Metal oxides
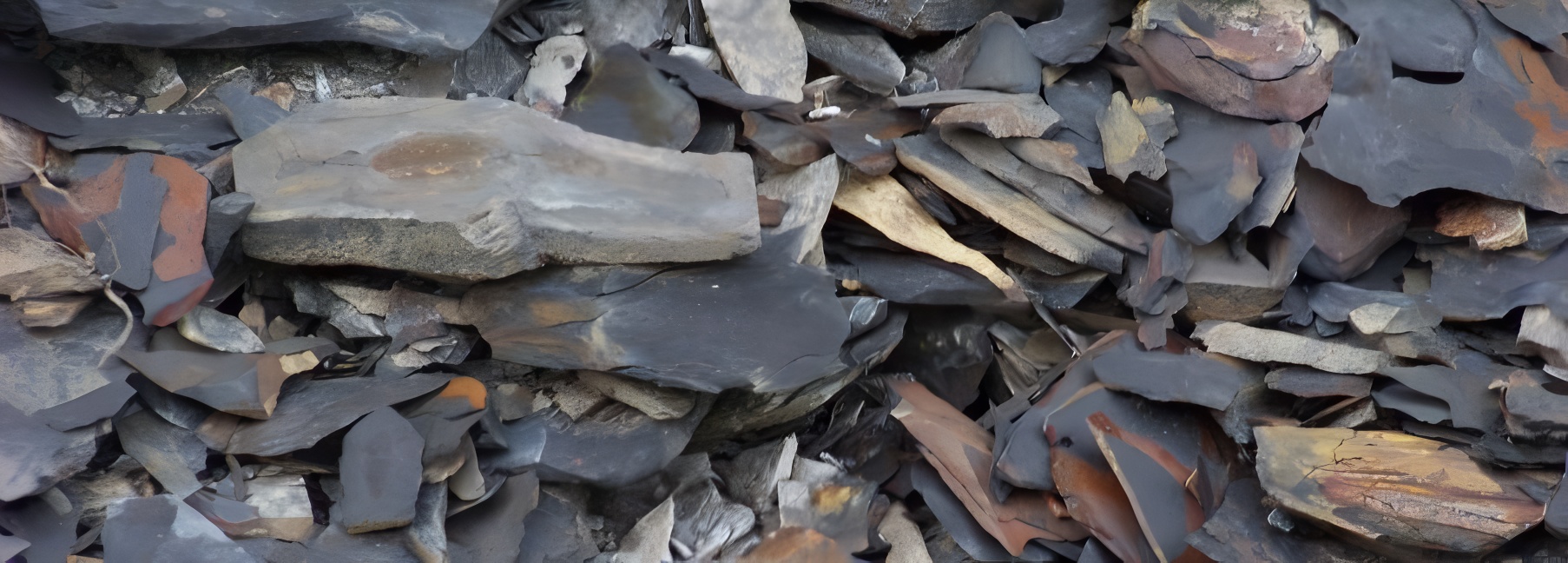
Metal ores
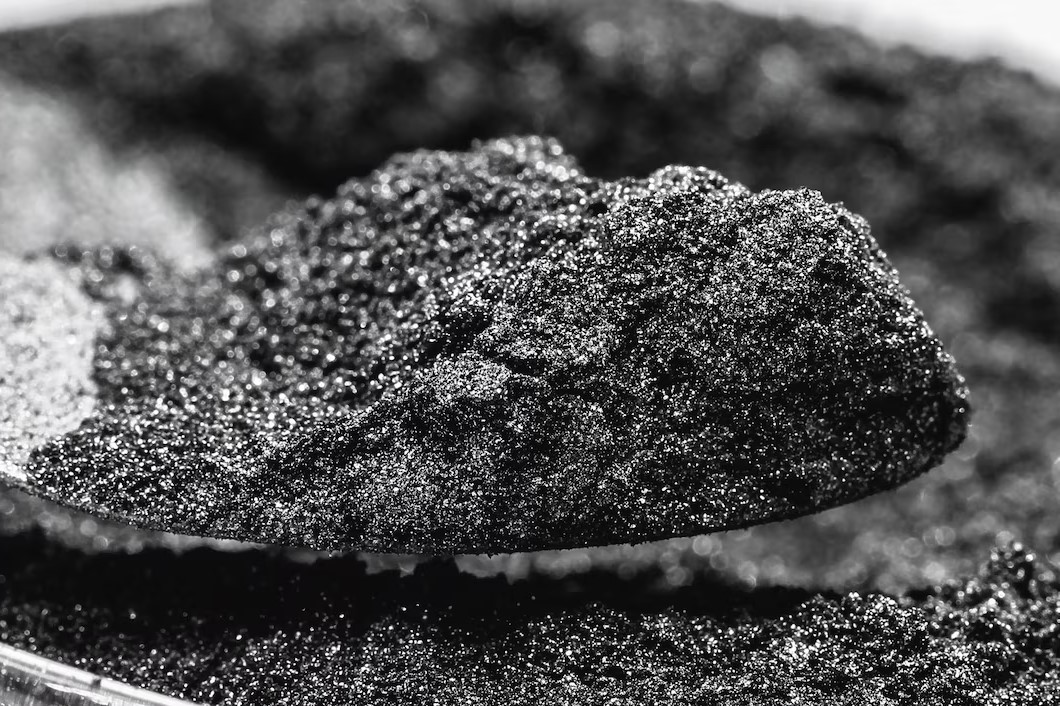
Metal alloy powders
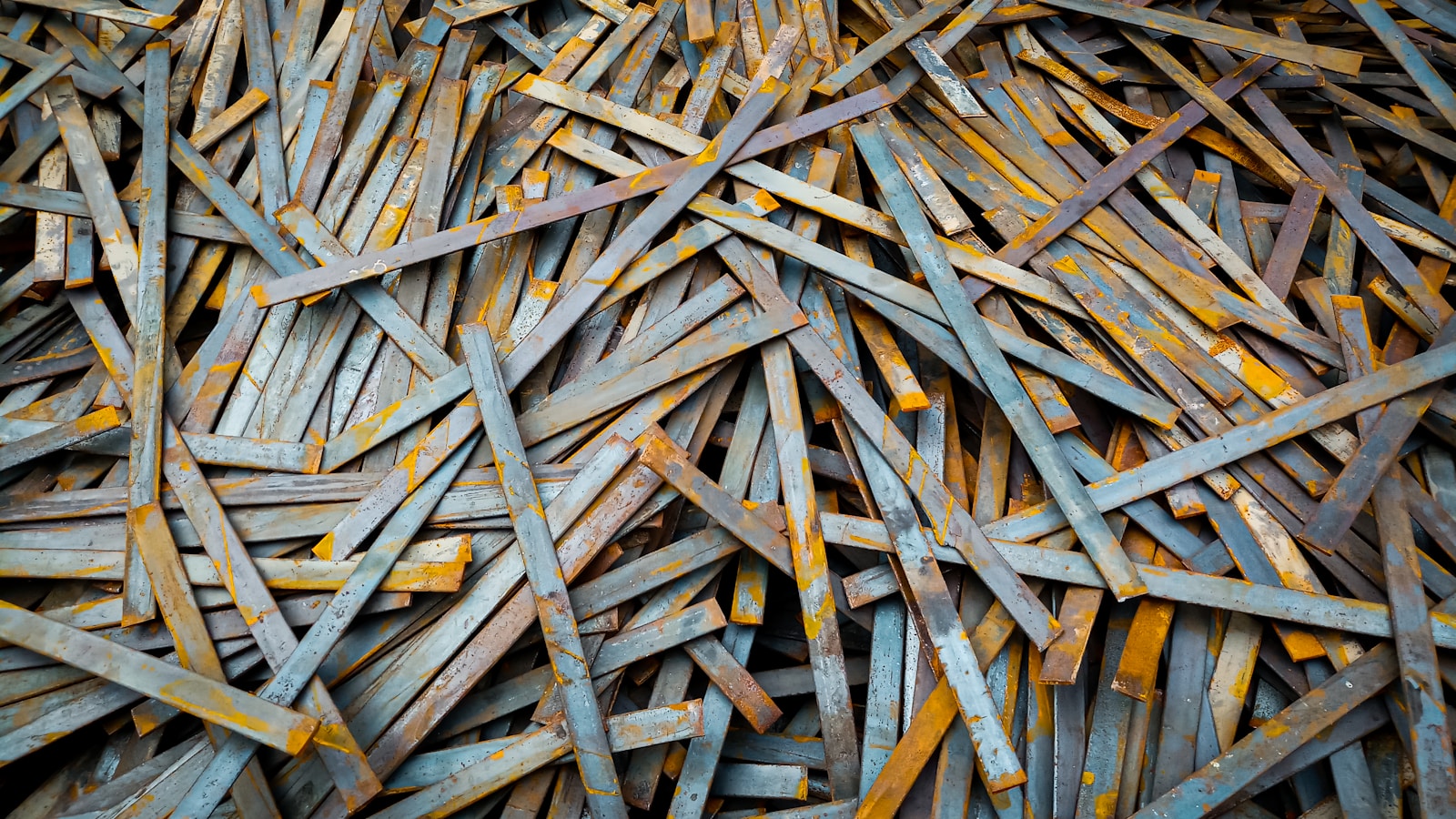
Iron
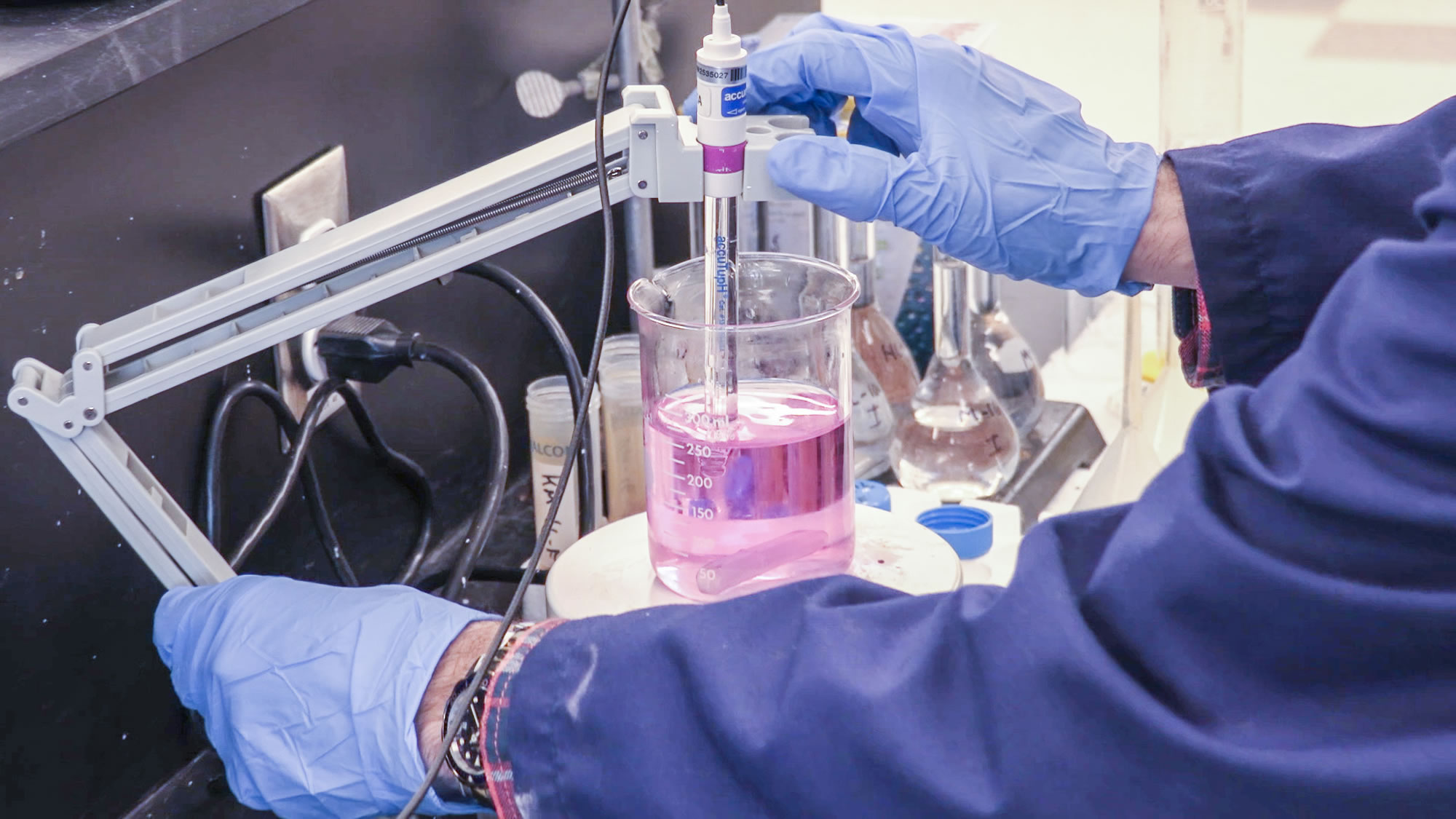
Hydrometallurgy
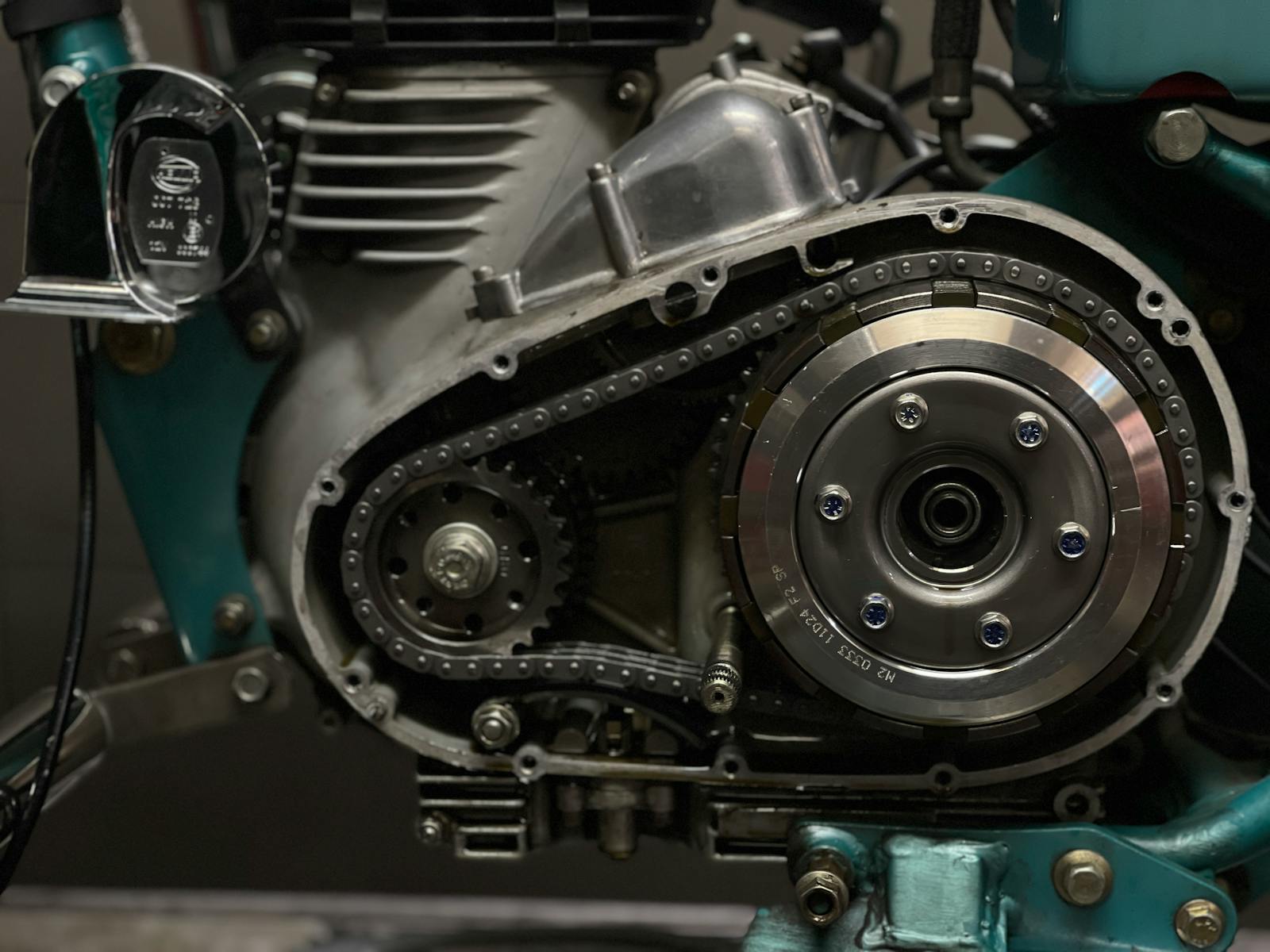
Engine components
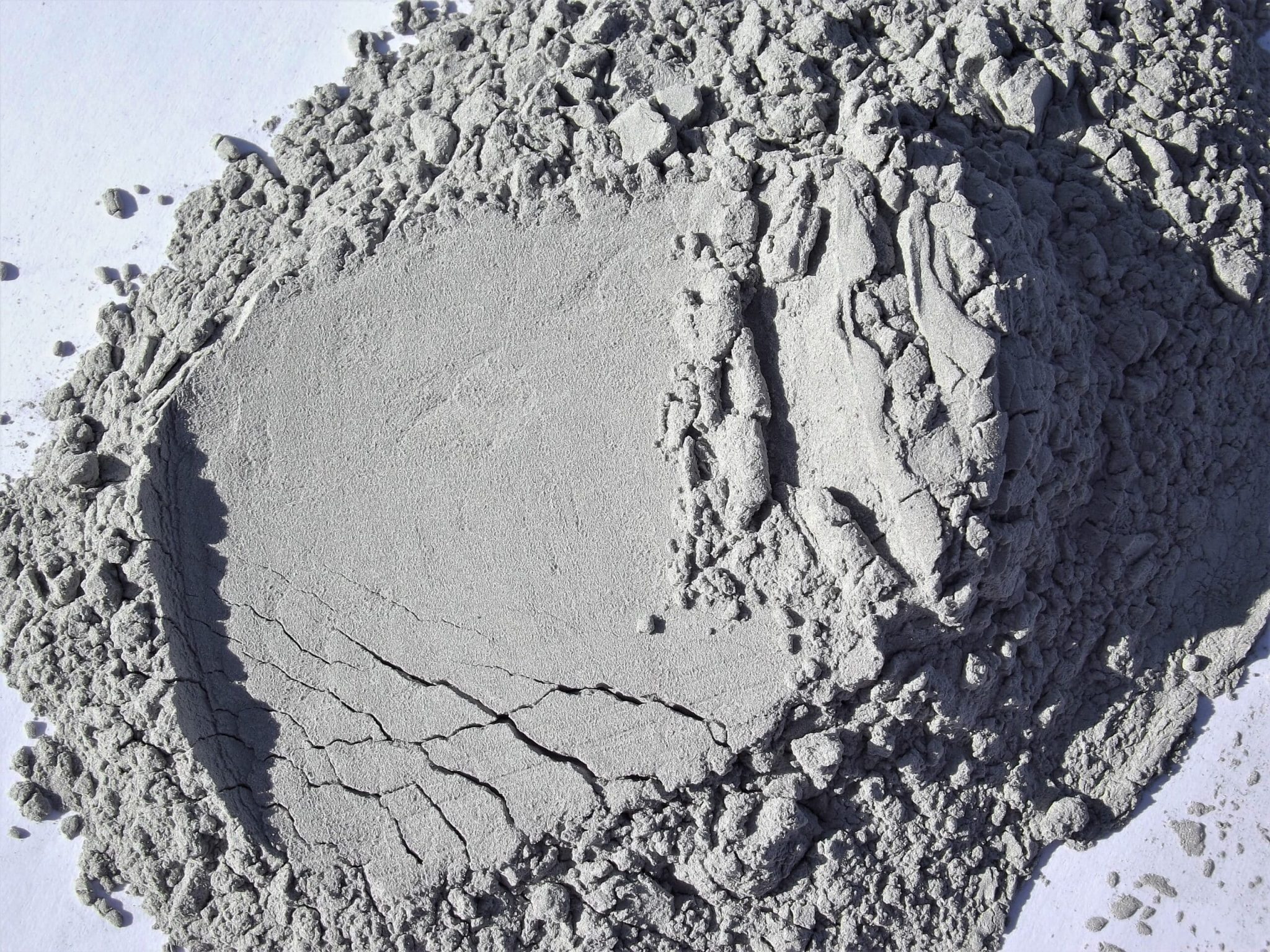
Aluminum powder
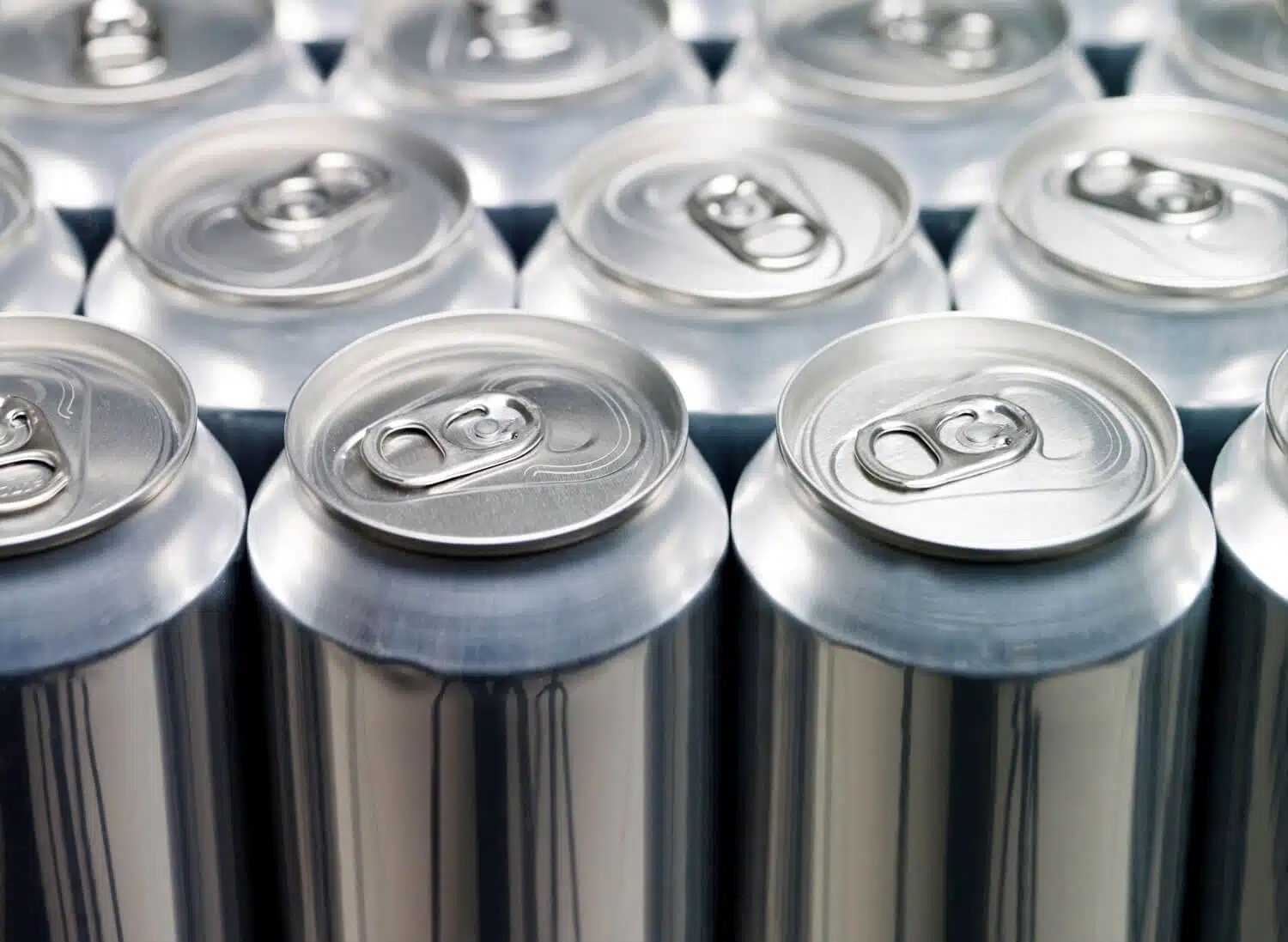
Aluminum beverage cans
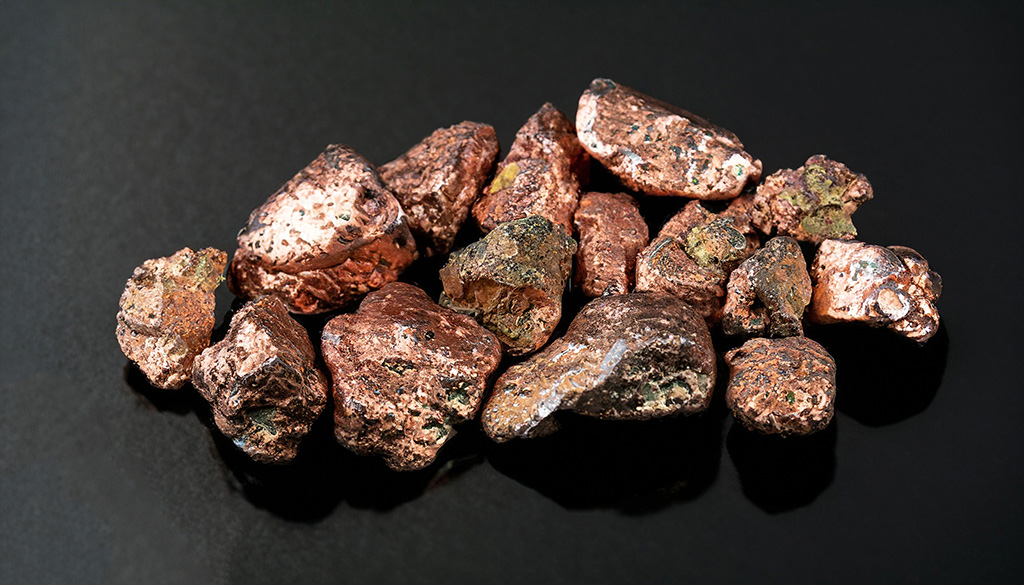
Copper concentrate
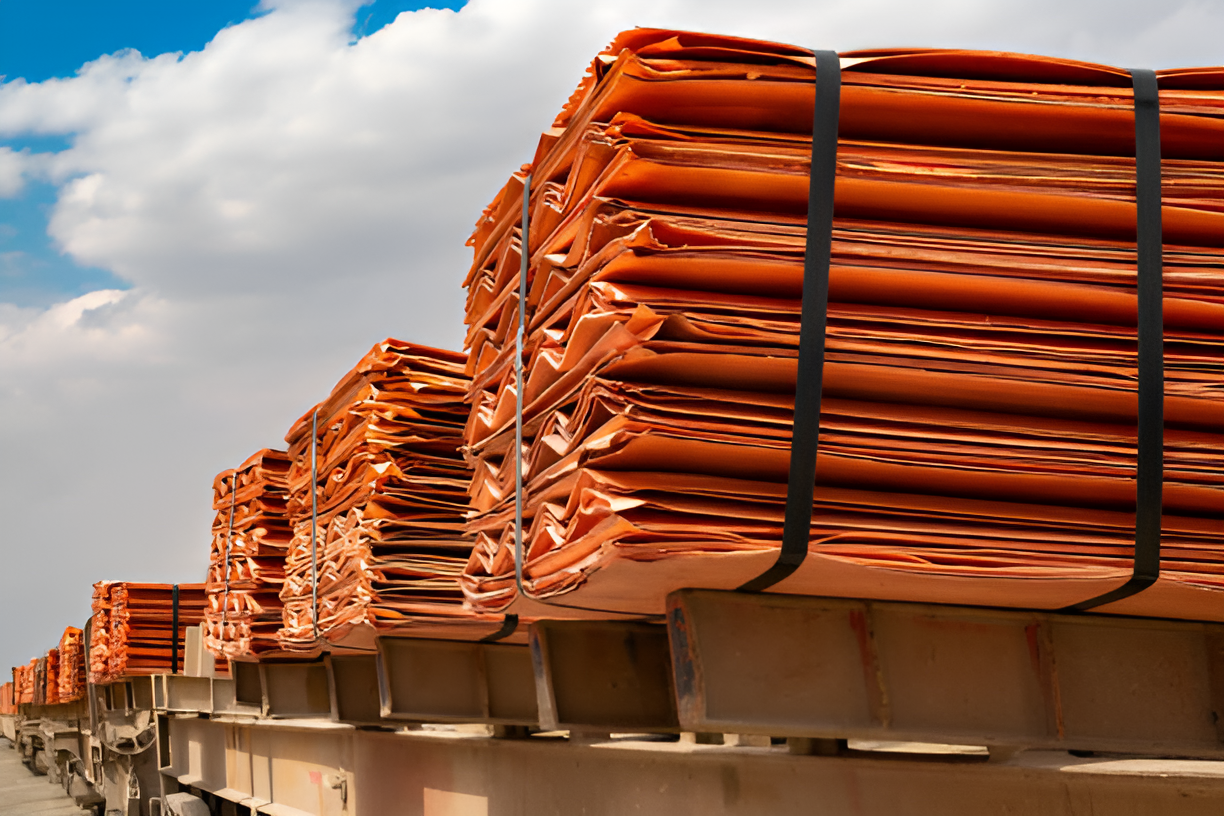
Copper cathodes
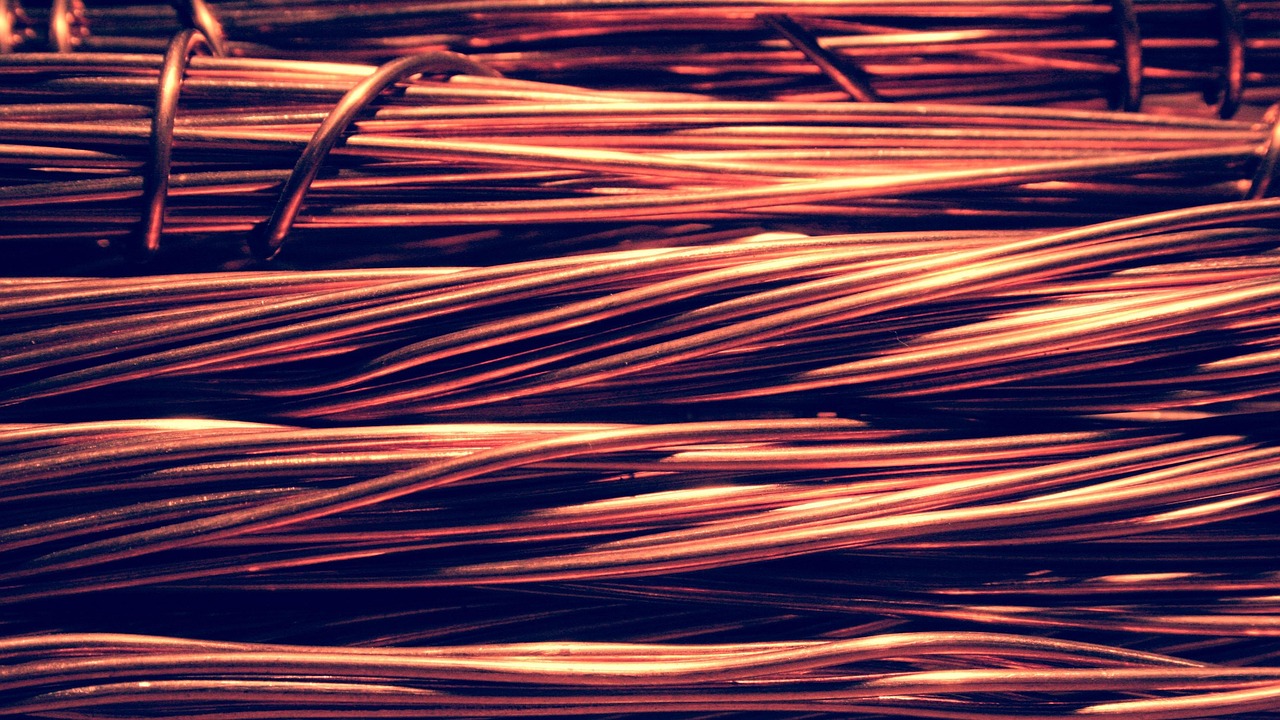
Copper
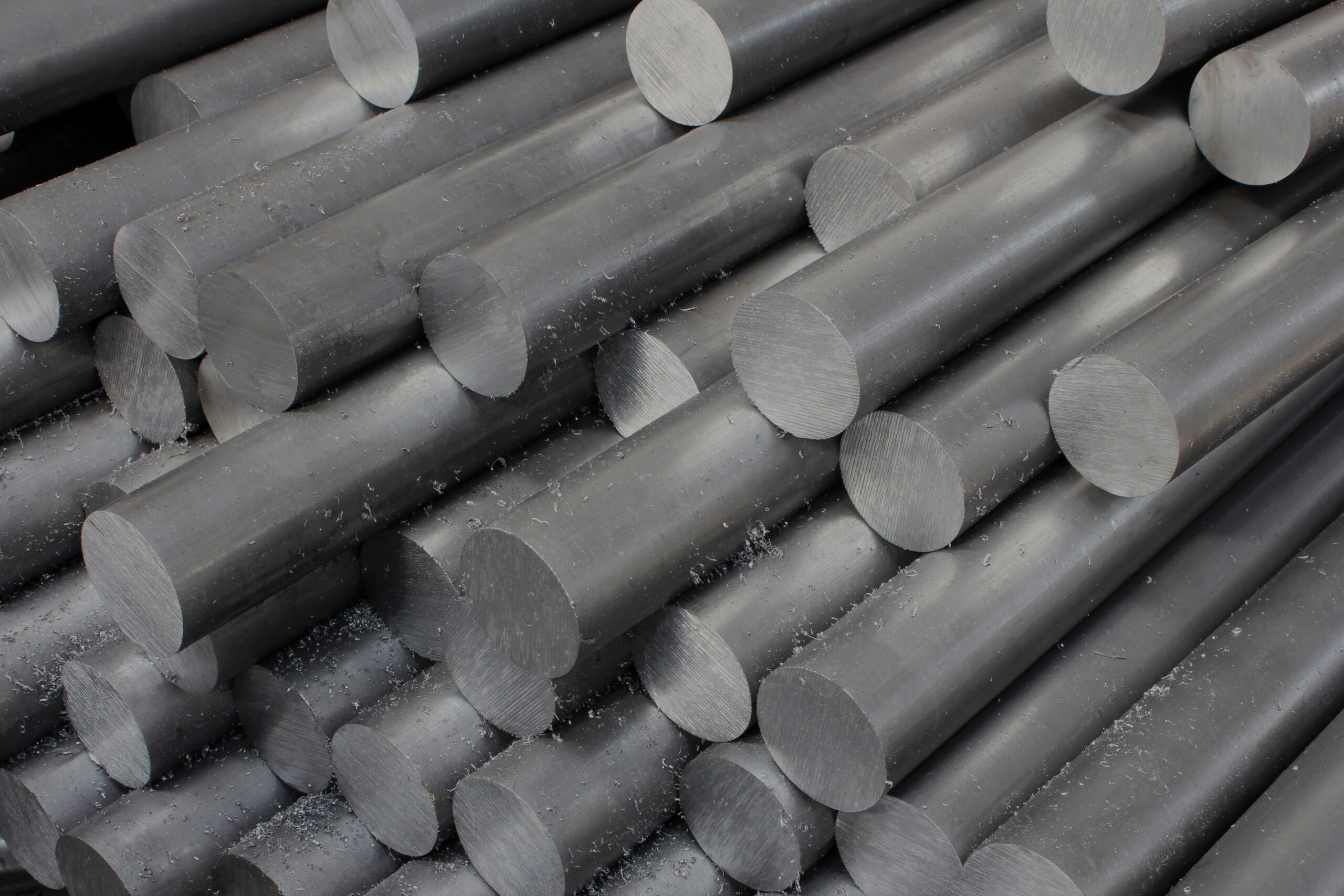
Alloys
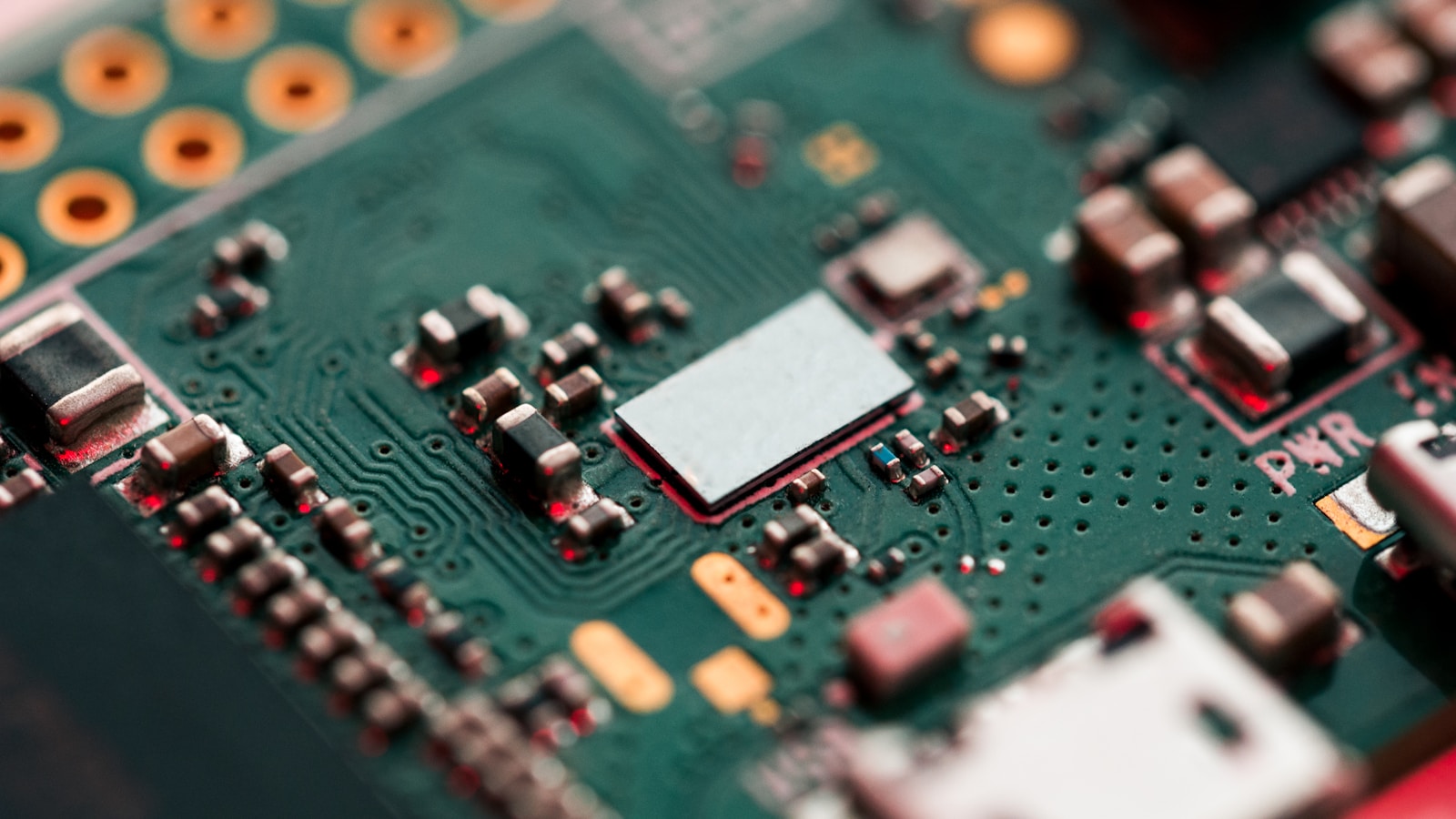
Circuit boards
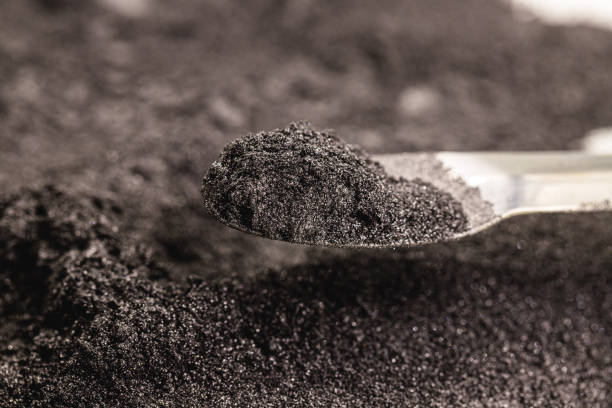
Powder Metallurgy
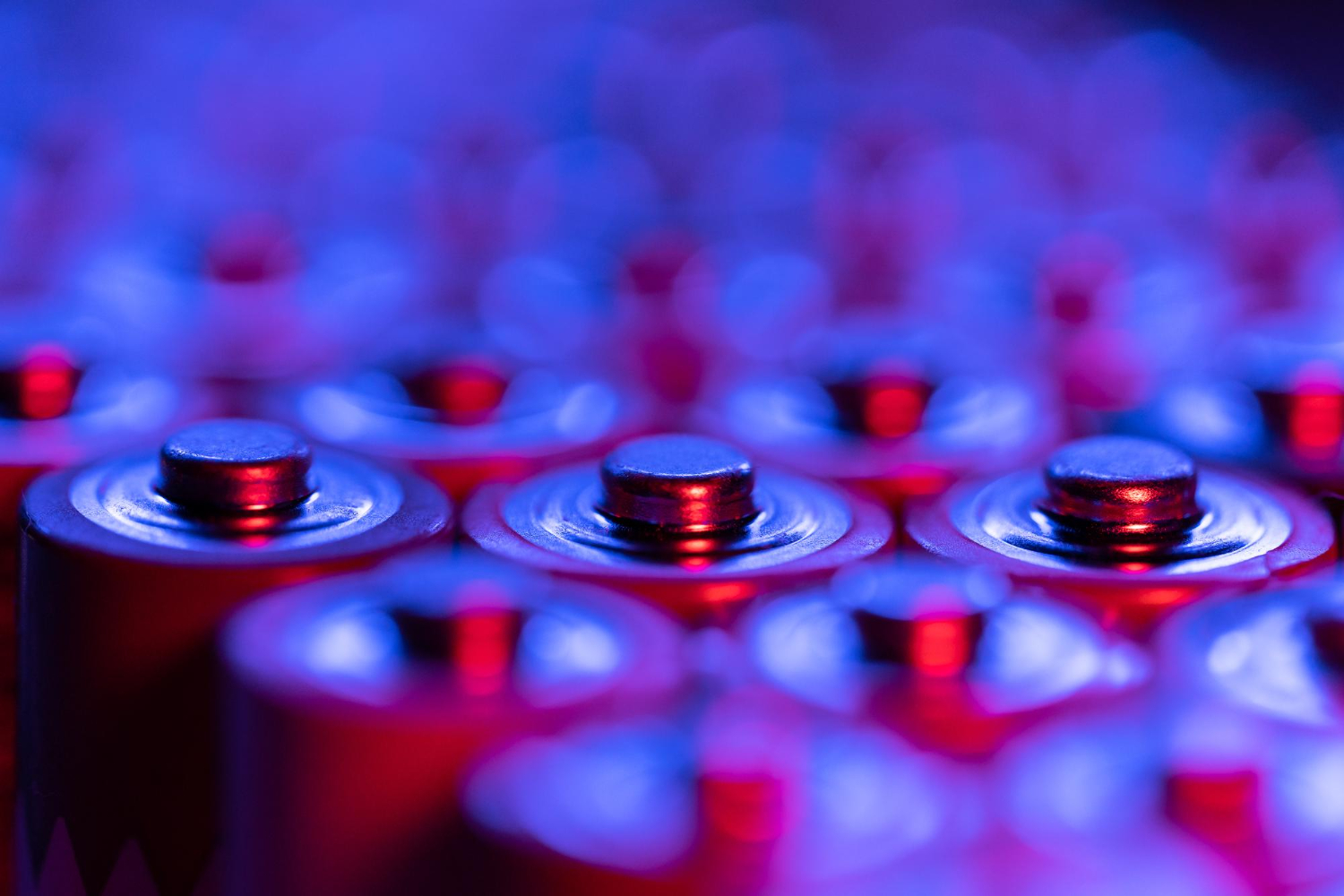
Lithium-ion batteries
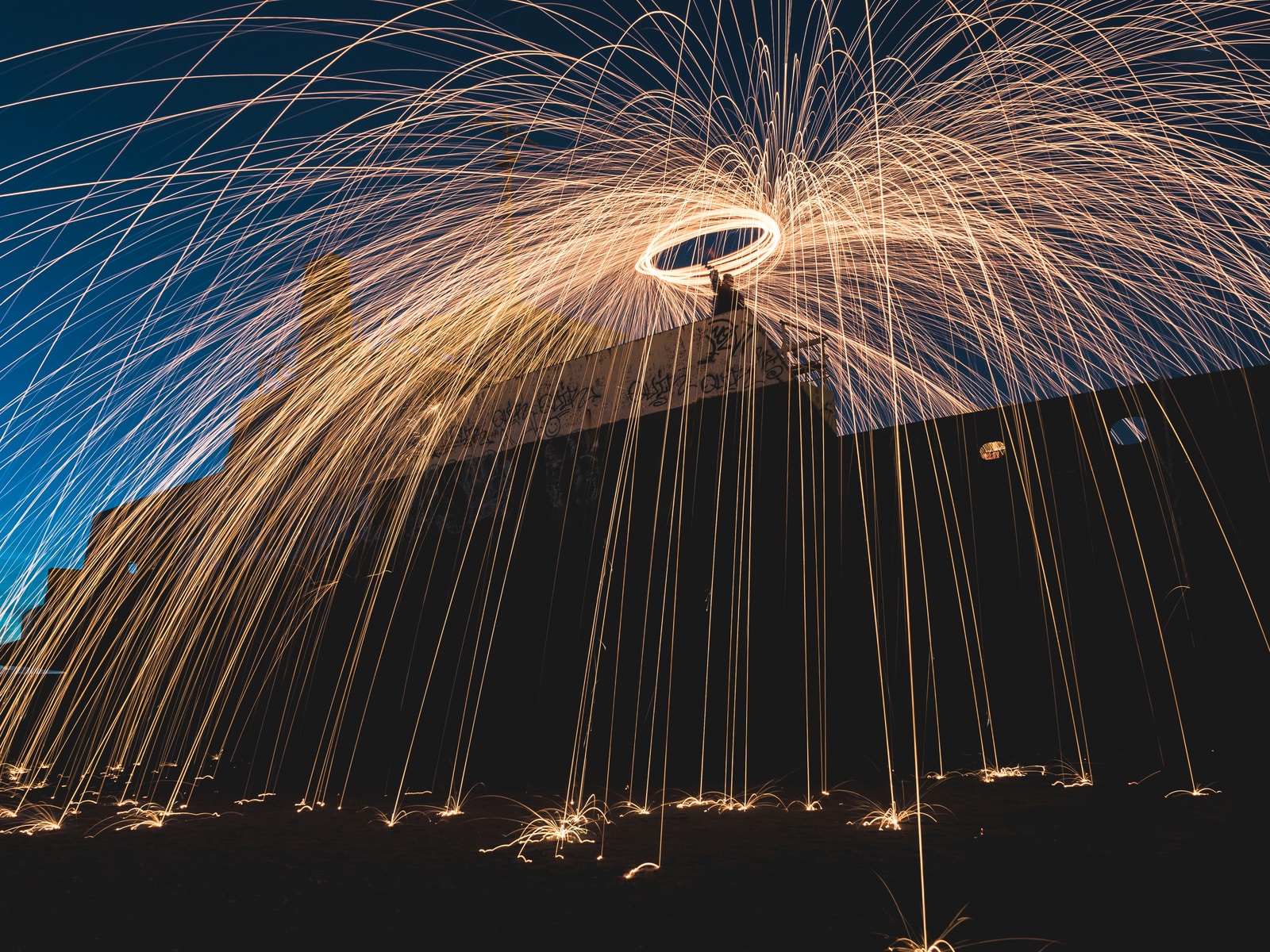
Metal powder
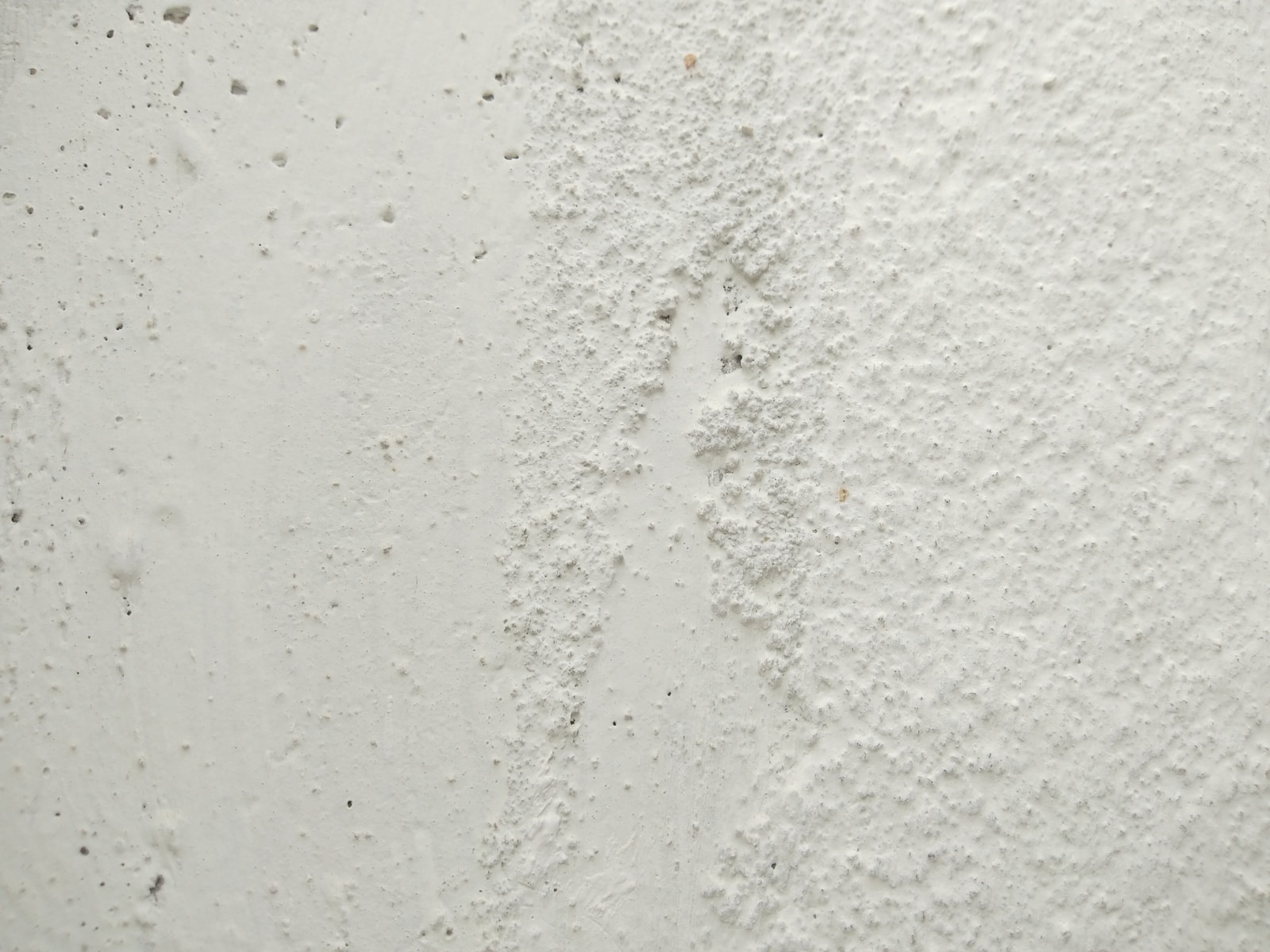
Aluminium oxide
Tell us about your production challenge
Reduce the metal ore with a reactive agent to separate it from impurities
Smelting is an ancient craft that has continued to develop with new metal manufacturing equipment. Treat the ore to high thermal pressure in a blast furnace until the heat exceeds the melting point of the metal.
Add a reducing agent such as coke to strip away the oxides in materials and separate the metals from rock and gangue. The coke reacts with oxide and splits it into carbon dioxide and metallic content.
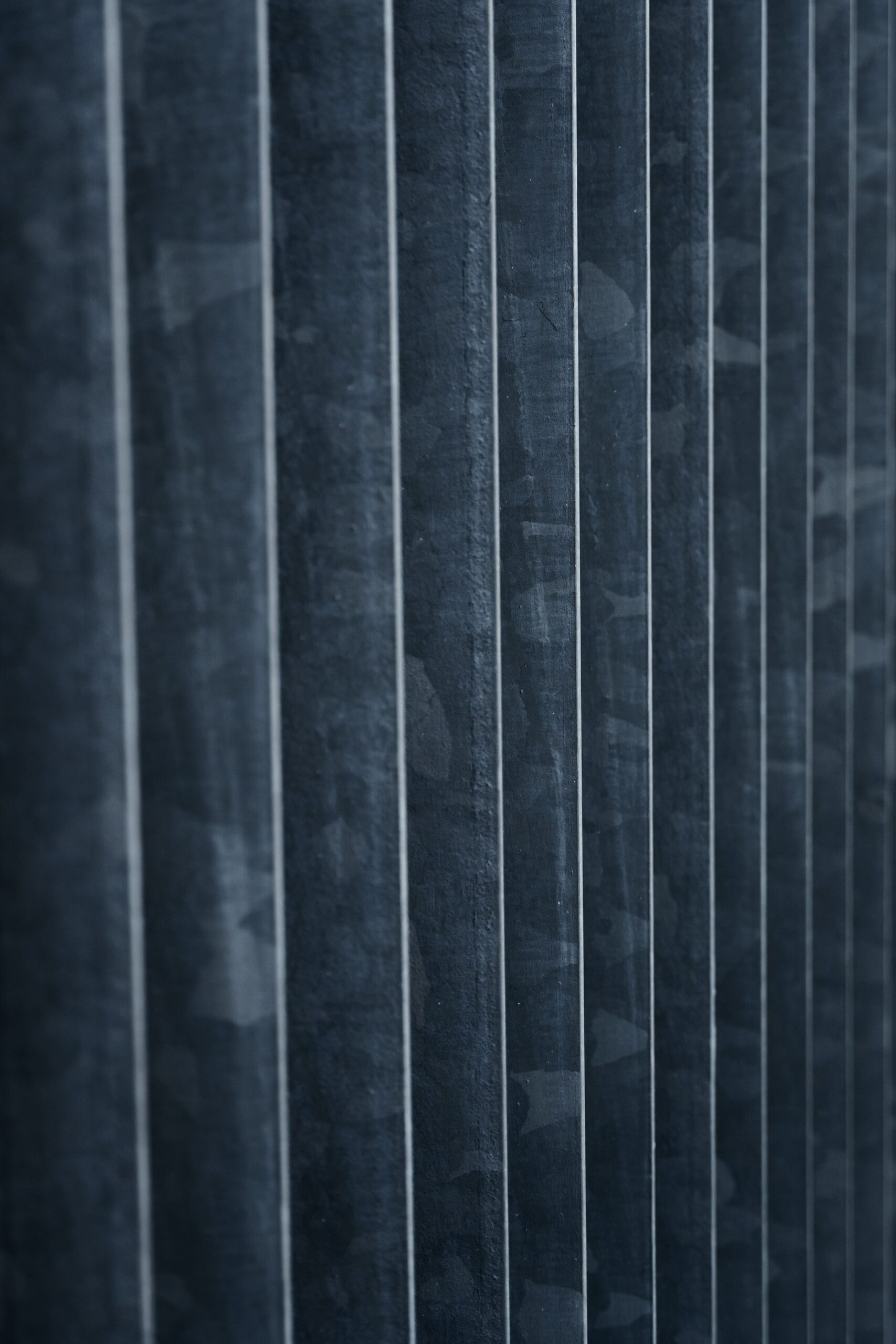
Cast the molten metal to form an ingot
The molten metal is channeled out of the furnace and deposited in molds. Allow the material to cool down and solidify into casts.
The two main types of mold casting are expendable casts and permanent casts. The former class needs to be broken to release the cast metal, while the latter type is fabricated out of ductile material and can be reused.
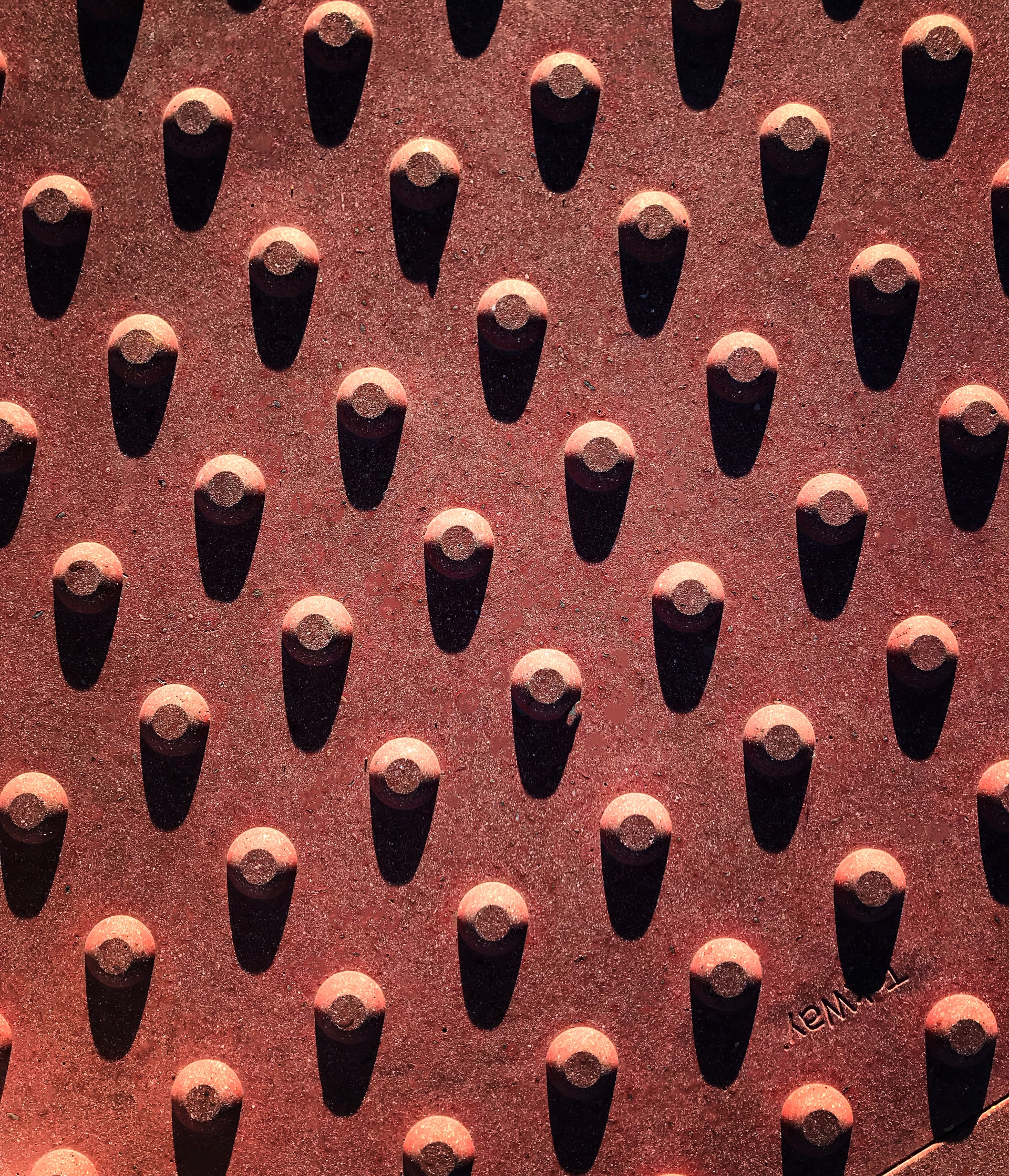
Finish metals for bulk manufacturing with the deformation process
Metal deformation prepares the material for the intended industrial application. One method for bulk deformation is rolling the metal to reduce it to a uniform thickness and smoothen the surface.
Extrusion and drawing are more suitable for alloys. The blend of metals is moved through a die opening by a ram. In the case of extrusion, no tensile forces are exerted, and the material is pushed out. On the contrary, drawing applies tensile force and pulls the metal out of the opening.
Manufacturing metal powder from the ore
An alternative way to finish metal for further production is to process it into powder. The atomization technique passes the molten metal through a narrow opening against a jet of air or liquid.
The pressure causes the liquid metal to split into droplets, quickly turning into solids as the temperature decreases.
Which metal technology do you need?
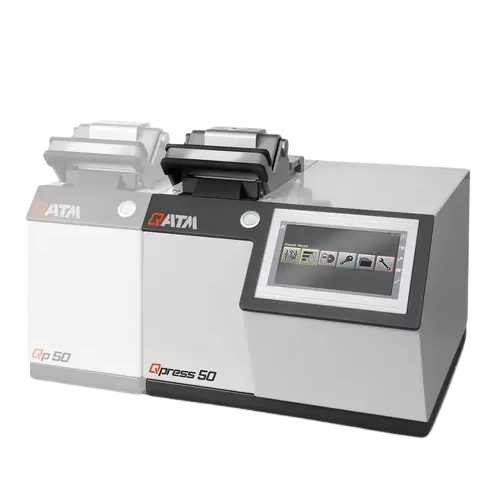
Hot mounting press for metallographic samples
Streamline your sample preparation with high-speed, modular hot mounting pre...

Grinding and polishing robot for metallographic samples
Optimize your metallographic workflow with a high-speed solution ...
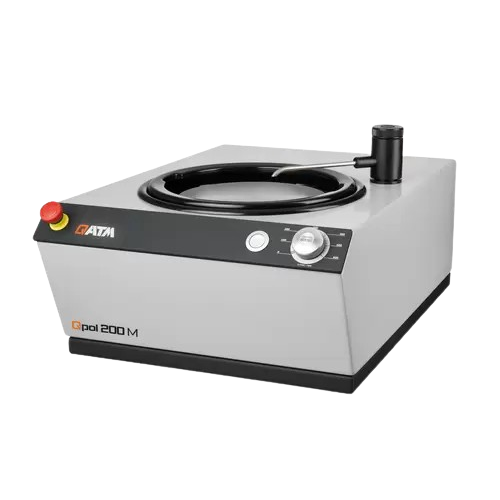
Manual grinder & polisher for metallographic samples
For precise metallographic sample preparation, ensure accurate analy...
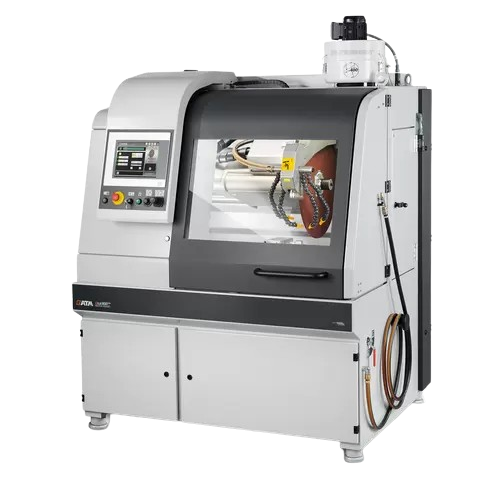
Metallographic cutting robot with 5 axes
Streamline complex metallurgical analysis with precise and versatile 5-axis cuttin...
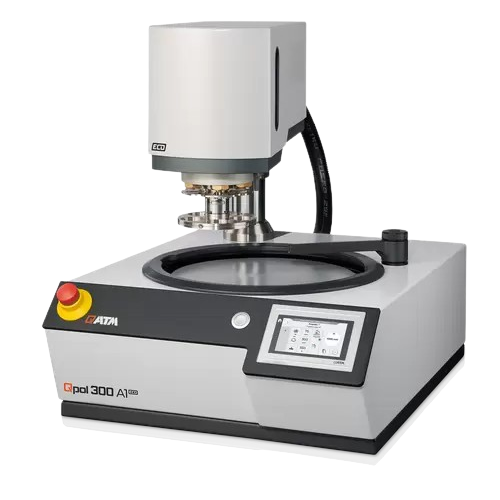
Automatic grinder and polisher for metallographic sample preparation
Easily transition from grinding to polishing with ...
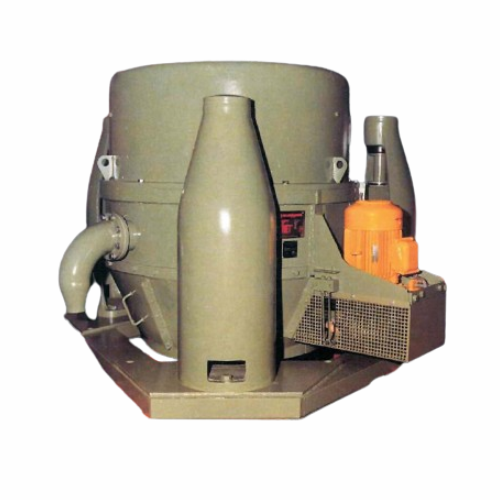
Separation of cutting fluids from metal chips
Enhance your production line efficiency by effectively separating cutting fl...
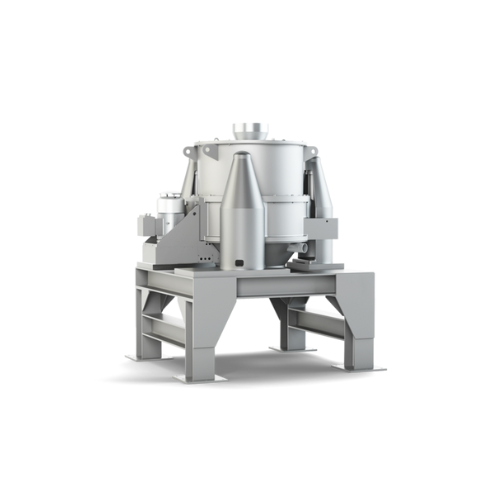
Continuous de-oiling centrifuge for metalworking industry
Efficiently de-oil and process diverse metalworking residues w...
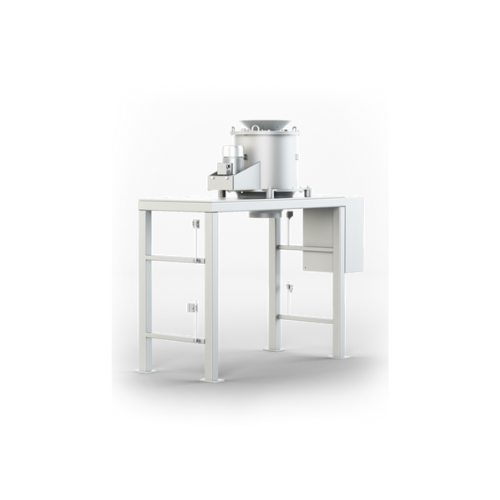
Continuous de-oiling system for metalworking chips
Optimize your metalworking process with a system that continually de-o...
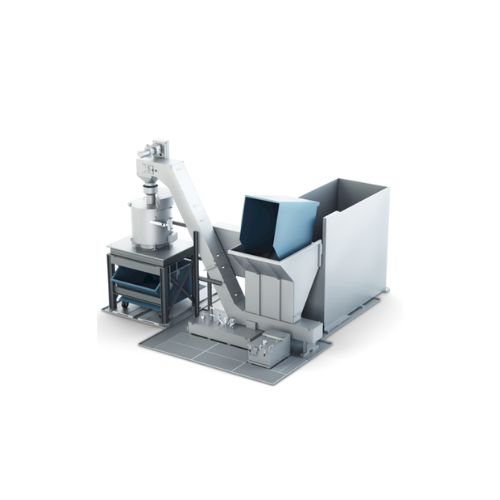
Automated de-oiling centrifuge system for metalworking chips
Enhance metal recovery and efficiency with a de-oiling cent...
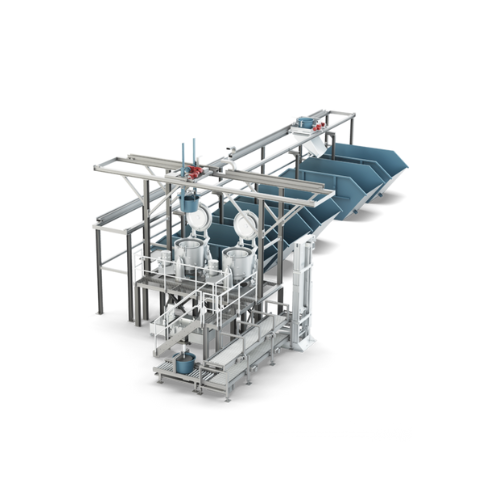
Modular system for metal chip de-oiling
Streamline your metal chip processing with a versatile centrifuge system that de-oi...
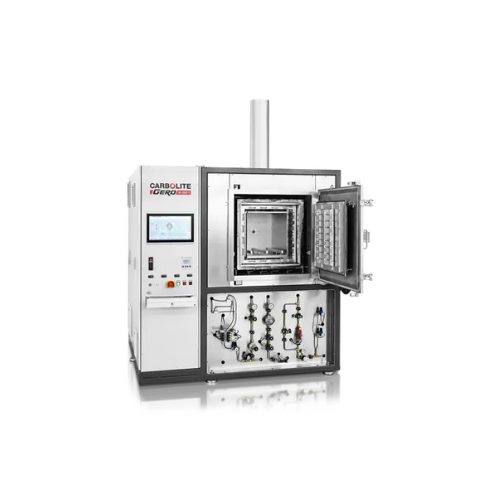
Vacuum chamber furnace with metal insulation
Achieve high-temperature processing with precision and purity using advanced ...
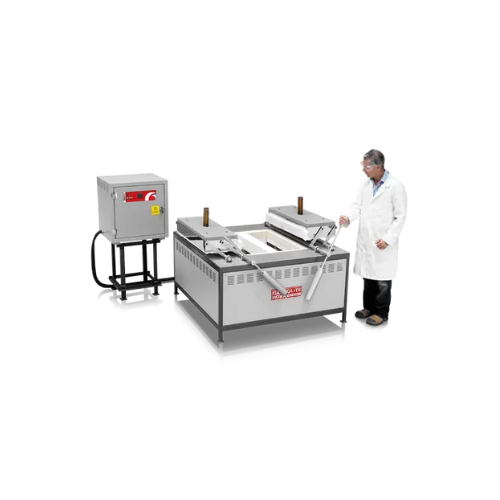
Smelting furnace for precious metals
Effortlessly achieve precise smelting and refining with advanced temperature control, ...
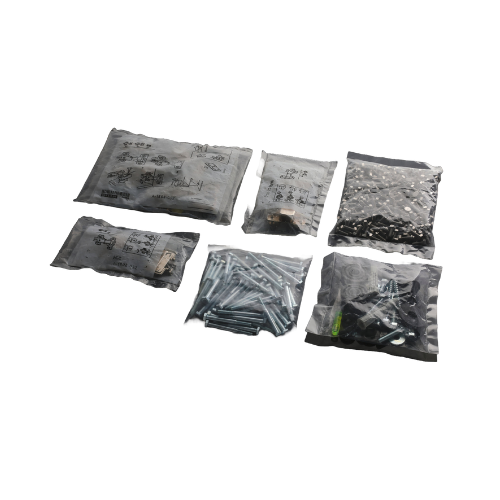
Small metal parts packaging line for Diy furniture kits
Ensure precision in assembling DIY furniture kits with this integ...
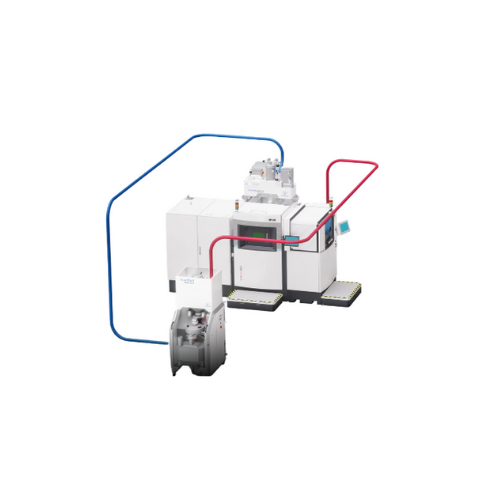
Closed powder handling loop for Eos metal Am printers
Effortlessly manage metal 3D printing powders with a solution that ...
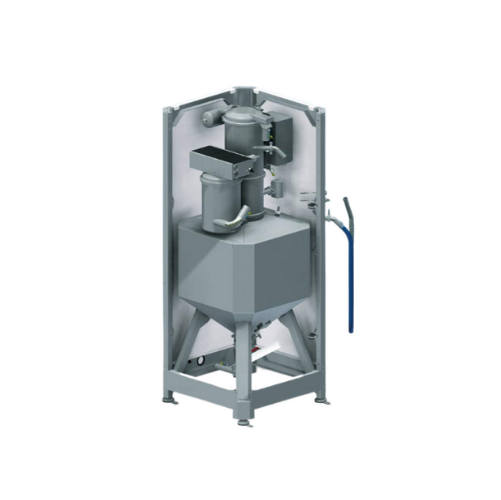
Metal powder buffer storage for additive manufacturing
Streamline your additive manufacturing workflow with our advanced ...
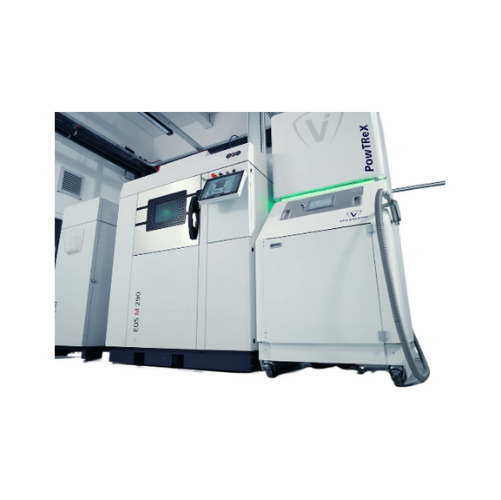
Metal powder recovery system after 3d printing
Effectively reclaim and purify metal powders after 3D printing to enhance c...
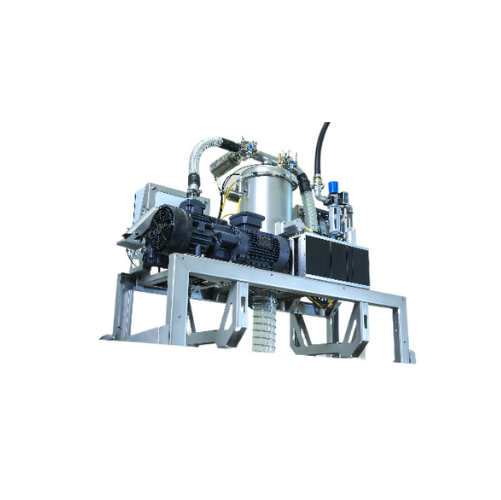
Automatic metal powder filling system for 3d printers
Ensure seamless operation of your 3D printing process with a system...
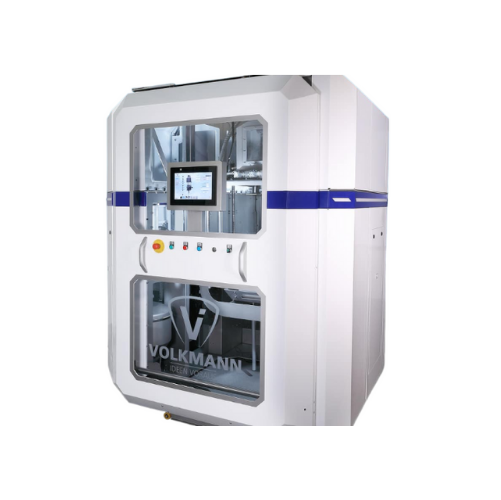
Automatic unpacking and depowdering station for metal 3d prints
Streamline your post-printing process with a solution th...
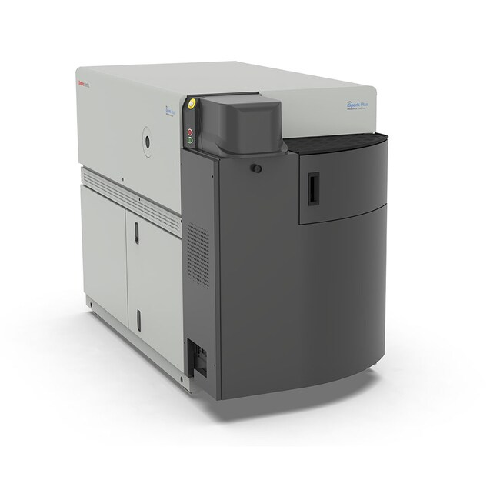
Optical emission spectroscopy for metal analysis
Achieve precise elemental analysis of solid metals to enhance quality con...
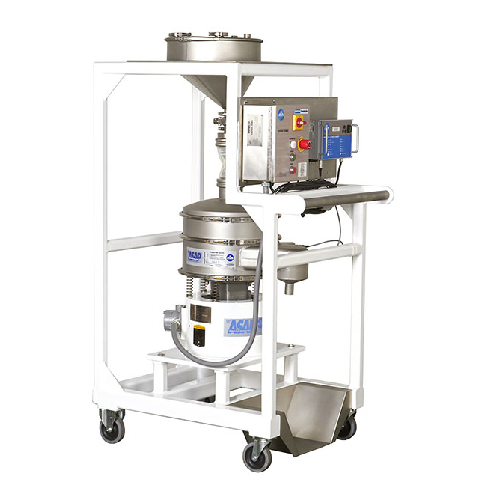
3d metal printer powder screening system
Enhance your 3D metal printing workflow by efficiently reclaiming and rebottling u...
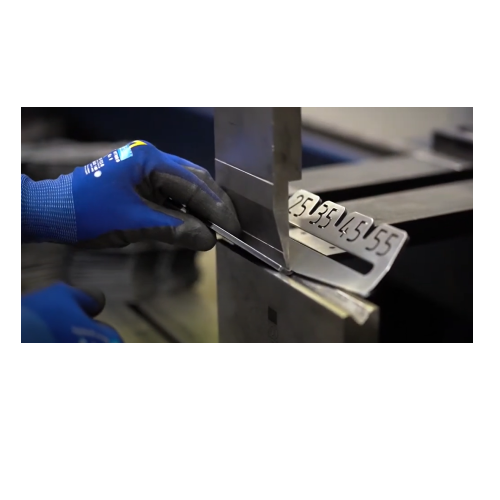
Precision metal bending and forming service
Elevate your production capabilities with precise metal forming solutions that...
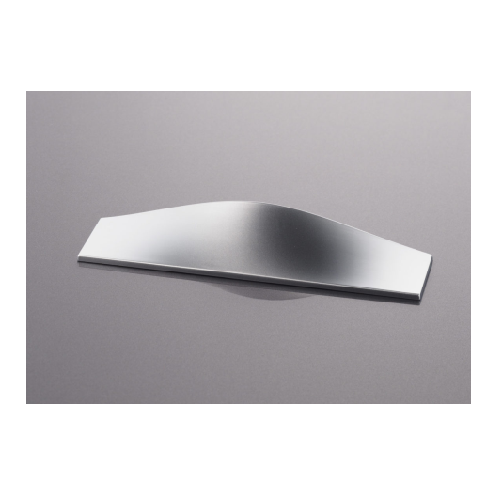
Quality assurance for metal surface treatment
Achieve unparalleled accuracy in metal surface treatments with advanced qual...
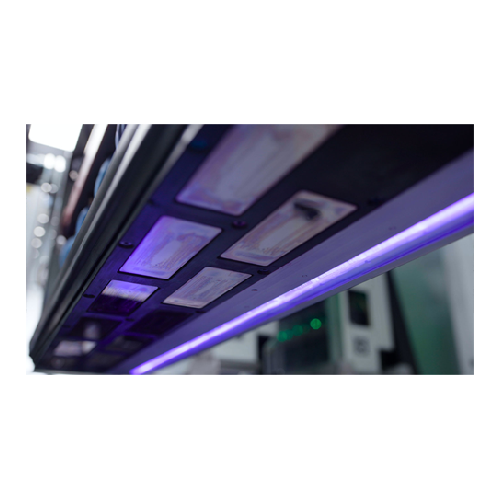
Digital inkjet decoration for metal packaging
Transform your metal packaging line with high-quality, efficient digital ink...
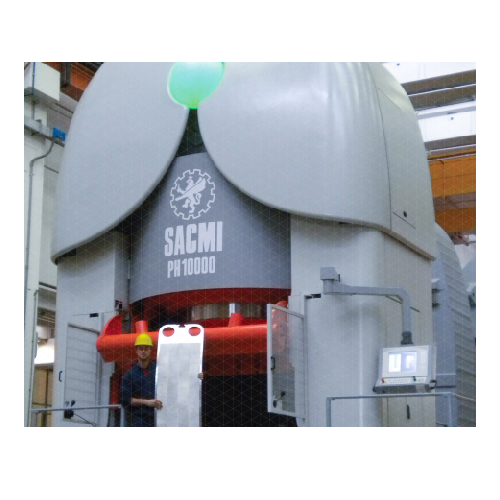
Metal sheet forming solution
Achieve unparalleled precision and efficiency in shaping metal components with advanced forming...
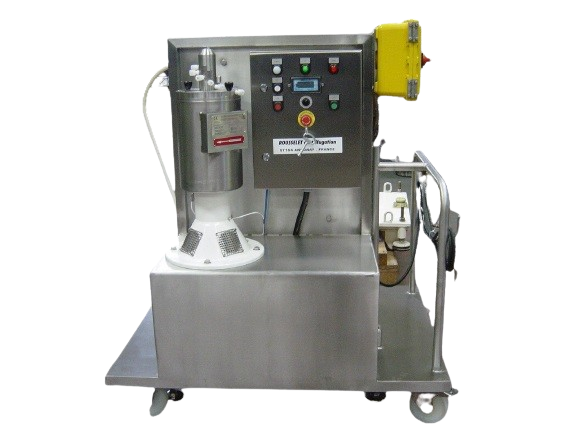
Continuous Multistage Centrifugal Extractor
When working with complex liquid-liquid separations, when handling pharmaceuti...
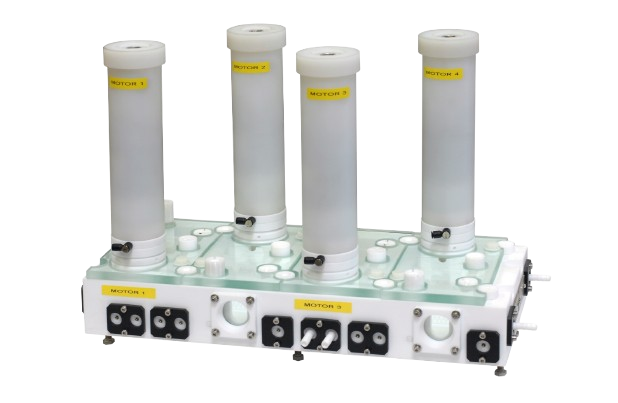
Mixer-Settler for Solvent Extraction and Purification
For solvent extraction processes requiring longer residence times, ...
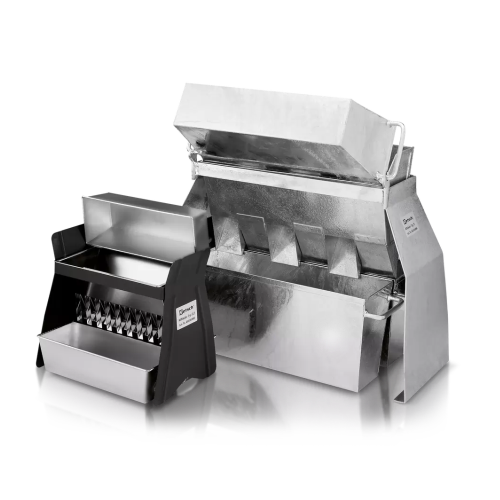
Sample divider for on-site reduction of bulk materials
Ensure consistent sample analysis with precise on-site material di...
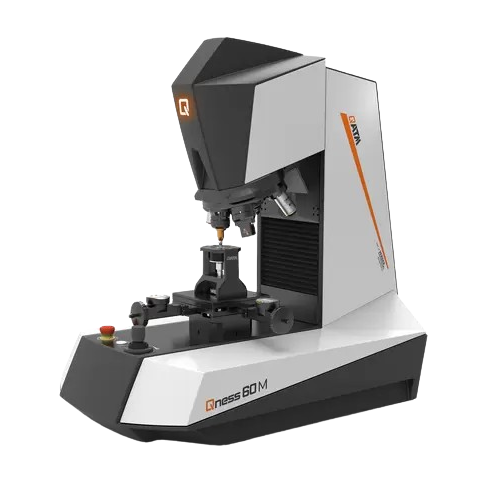
Micro hardness tester for vickers, knoop, and brinell
Ensure precise and efficient hardness testing with versatile soluti...
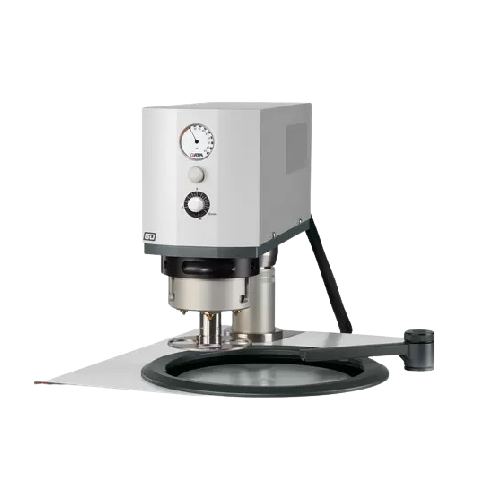
Automatic grinder/polisher for sample preparation
Streamline your sample preparation with a versatile grinder and polishe...

Laser diffraction particle size analyzer
Achieve precise particle size analysis with laser diffraction technology, ensuring...
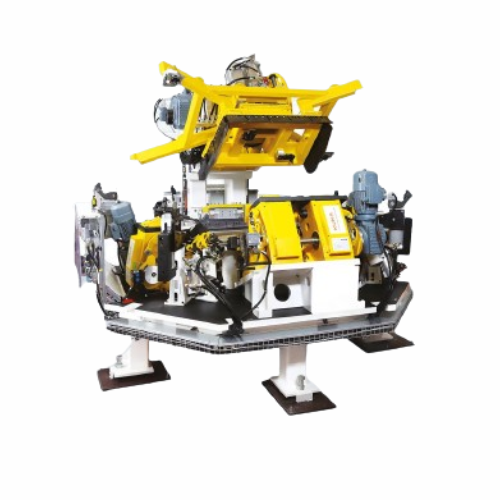
Automated hemming solutions for the automotive industry
Optimize your production line for flexible, high-volume hemming w...
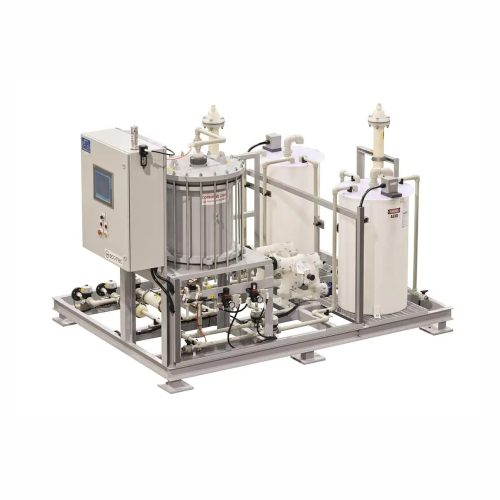
Continuous acid purification for aluminum anodizing
Eliminate costly impurities from your process acids and ensure consis...
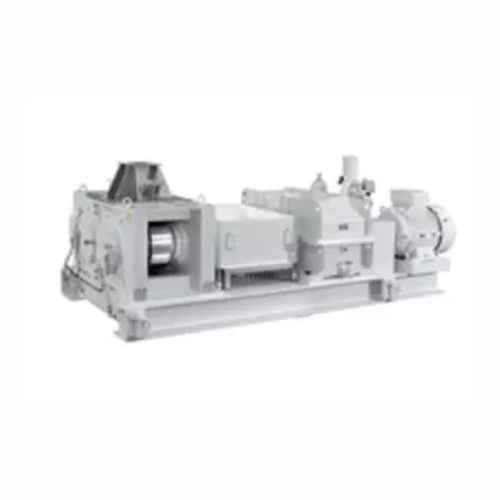
High-pressure roller mill for medium-fine crushing
Achieve precise granule distribution in medium-fine crushing applicati...
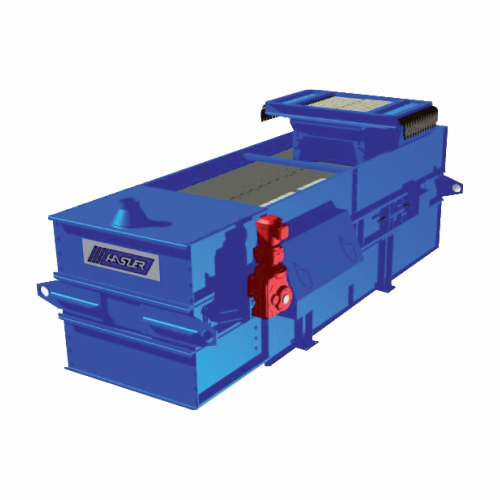
High-temperature extractor weigh belt feeder for clinker
Handle hot, abrasive products like clinker seamlessly with a rob...
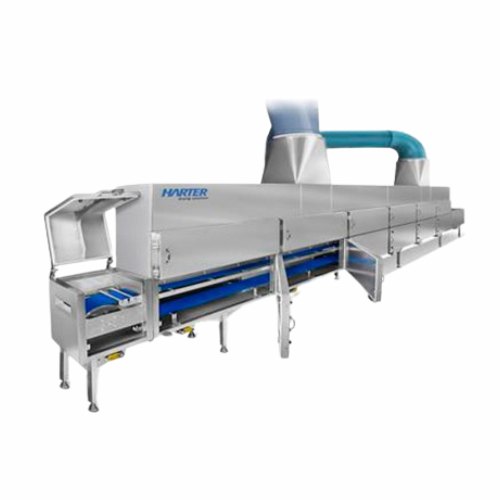
Continuous conveyor belt dryer for endless products
Optimize your continuous production line with a high-speed drying sol...
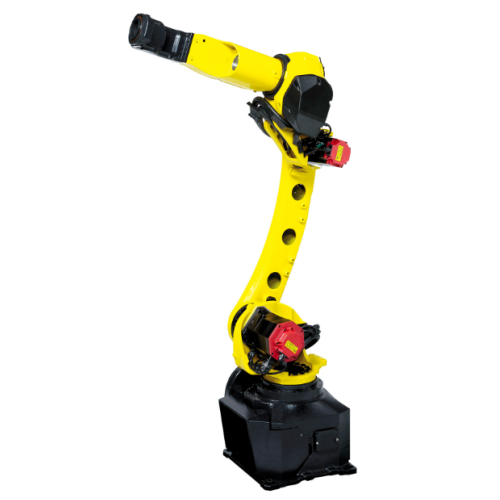
Industrial arc welding robot
Achieve precise and consistent welds in high-speed operations with this advanced arc welding ro...
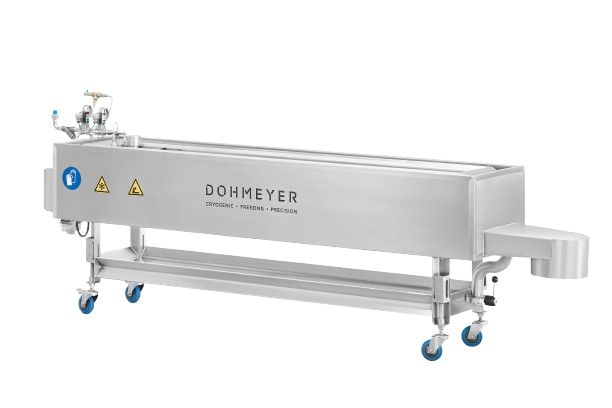
Cryogenic immersion bath for rapid freezing
Achieve rapid and intense cooling by immersing products in liquid nitrogen, id...
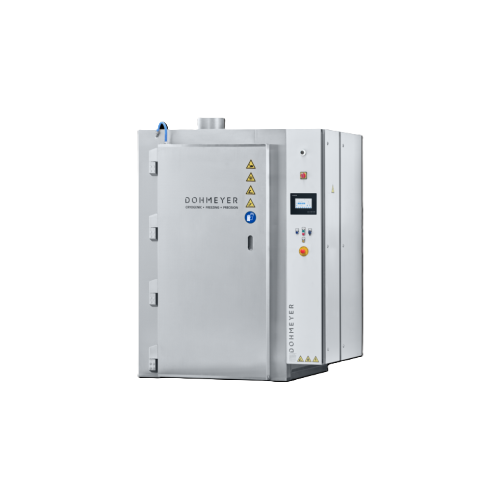
Cryogenic batch freezer for industrial processing
Achieve precise temperature control for sensitive materials with a cryo...
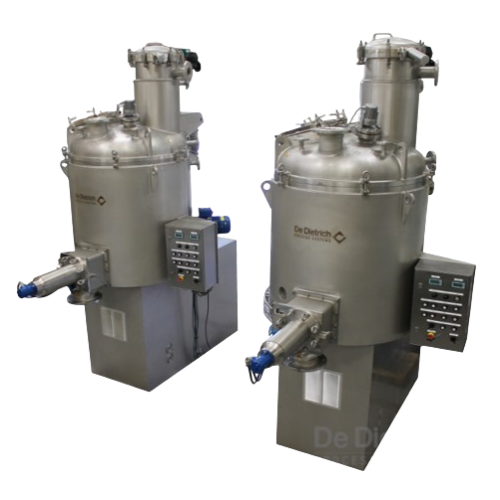
Industrial pan dryer for pharmaceuticals
For heat-sensitive powders and pastes requiring precise moisture levels, this pan ...
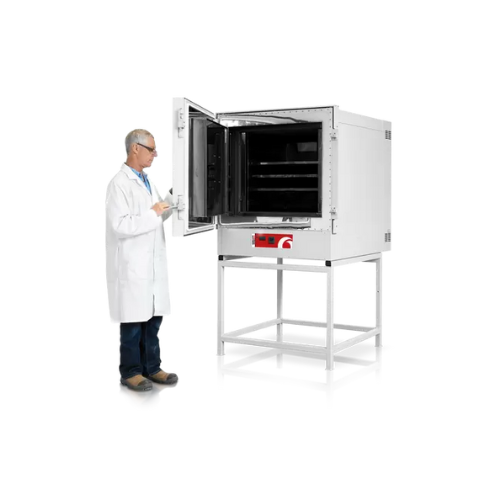
High temperature industrial oven for advanced heating processes
Achieve precise heat treatment for critical components, ...
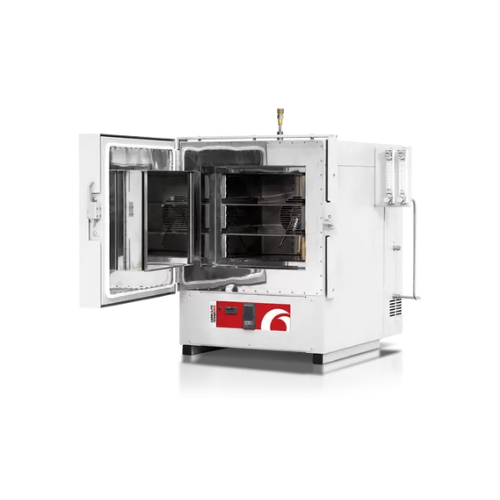
Controlled atmosphere oven for high-temperature applications
Achieve precise atmosphere control and uniform heating for ...
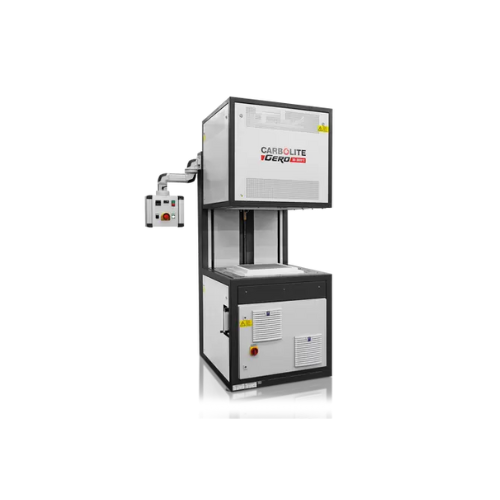
Top hat industrial furnace for high-temperature applications
Achieve precise high-temperature processing with this advan...
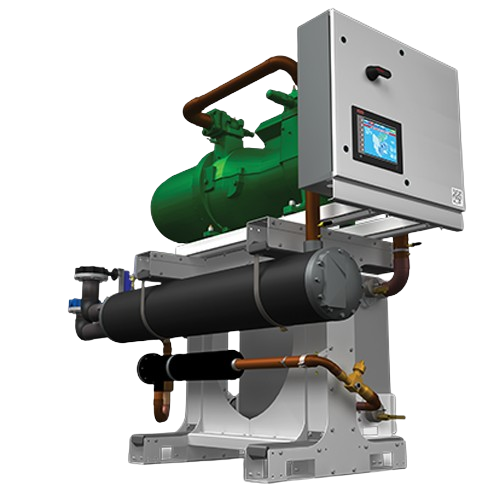
Central chiller for consistent process cooling
Optimize your production with modular central chillers offering scalable co...
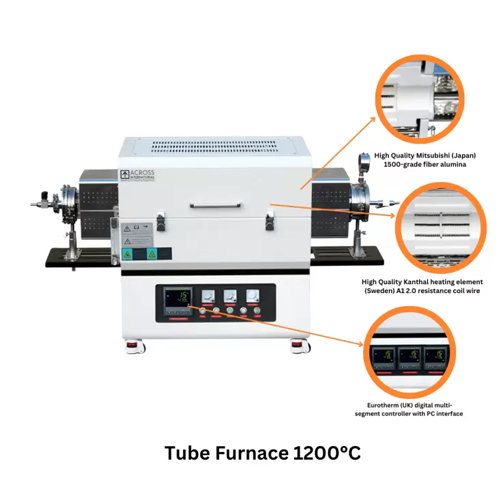
High-temperature top-open tube furnace for laboratory applications
Achieve precise thermal processing with this high-te...
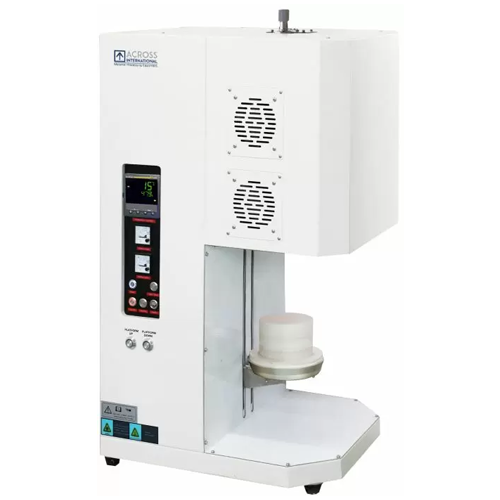
Table-top bottom loading furnace for high-temperature applications
For precise thermal processing and advanced experime...
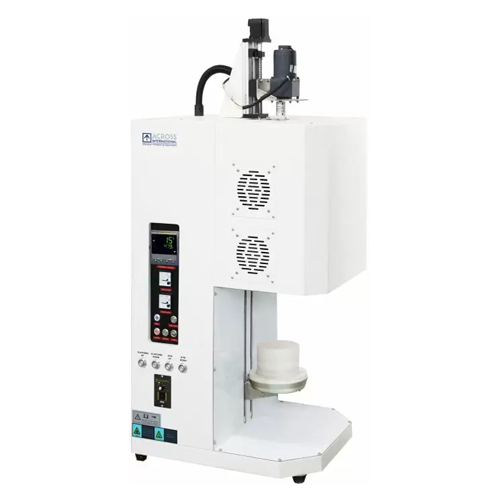
Table-top bottom loading furnace with stirring capability
Achieve precise thermal processing with controlled heating and...
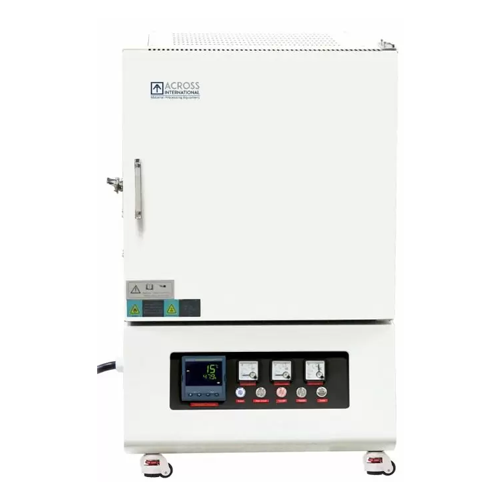
1200°c benchtop muffle furnace
Ensure precise thermal processing and testing with this high-capacity benchtop furnace, ideal...
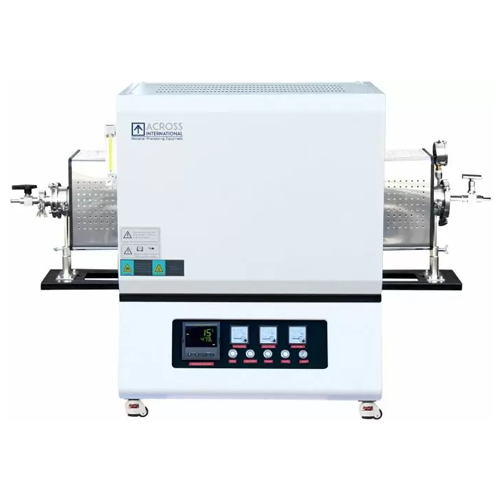
High-temperature tube furnace for laboratory applications
Achieve precise thermal treatment with this high-temperature t...
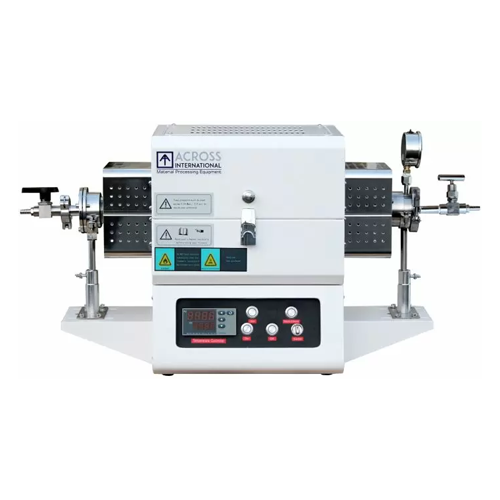
Controlled atmosphere top-open tube furnace
Achieve precise thermal processing and sintering with this versatile tube furn...
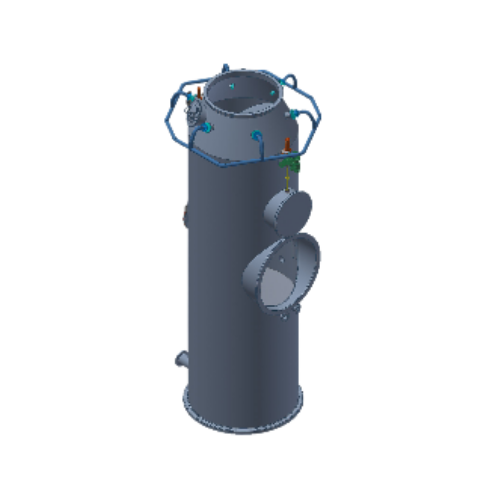
Linear flow scrubber for dust and particulate removal
Optimize your emission control with a high-efficiency solution that...
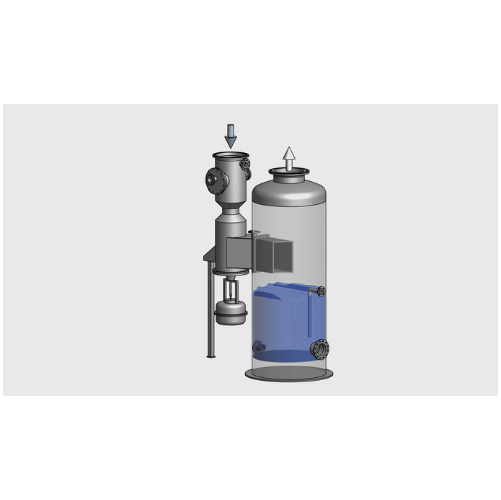
Radial flow scrubber for industrial gas cleaning
Optimize your gas cleaning process with a radial flow scrubber capable of...
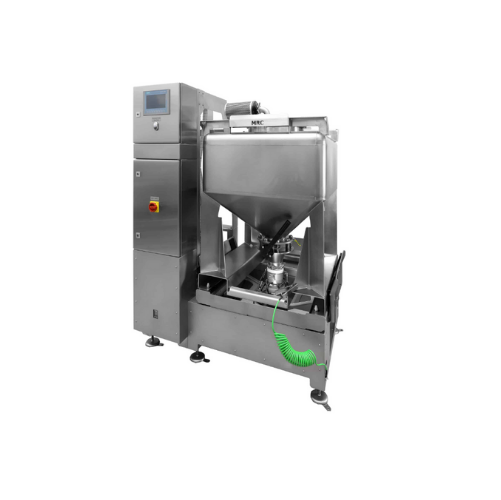
Docking station for intermediate bulk container (ibc)
Streamline your metal powder management by efficiently connecting a...
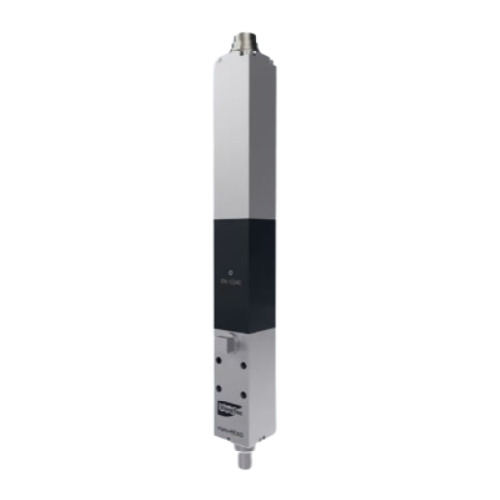
3d print head for high-viscosity fluids and pastes
Enhance your 3D printing capabilities by reliably handling high-viscos...

3d screening solution for recycling facilities
For facilities handling diverse recycling materials, a solution that effect...
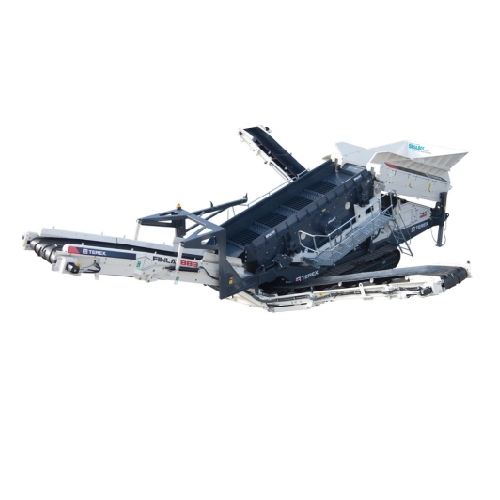
Mobile screening solution for sticky and wet materials
Effortlessly tackle challenging, sticky or wet materials with a mo...
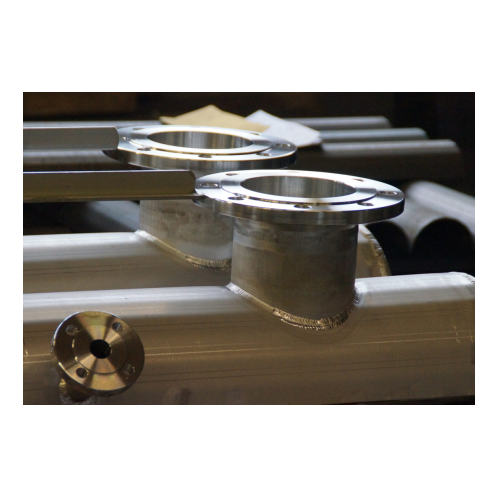
Expert welding assembly for industrial applications
Optimize complex fabrication tasks with precision-engineered welding ...
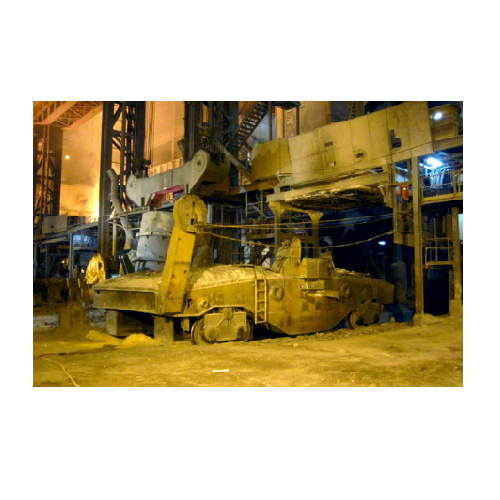
Ladle ferry weighing system for pig iron production
Ensure precise transport and weighing of liquid pig iron and steel bi...
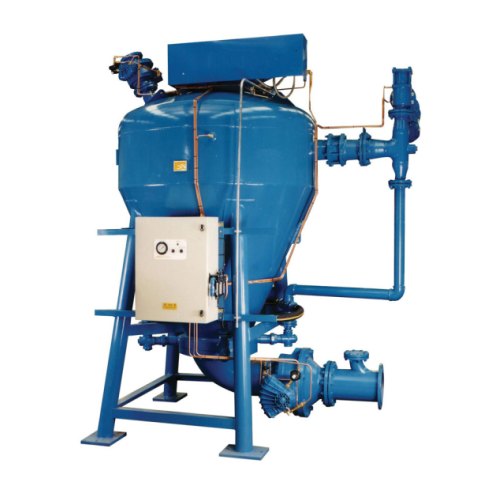
Dense phase conveying pumps for bulk material transfer
Optimize your material handling with pneumatic conveying solutions...
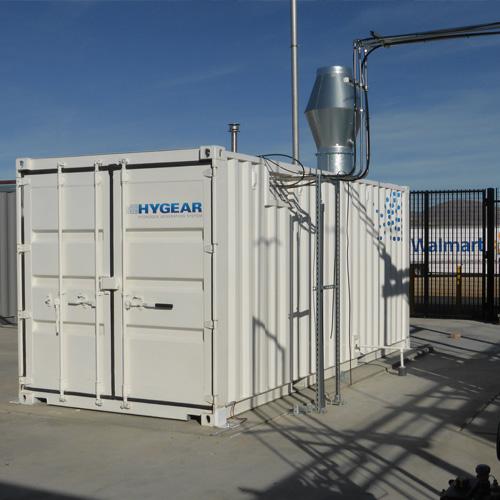
Plug and play natural gas to hydrogen generator
Hydrogen is an all-purpose element and can be simply defined as energy’s S...
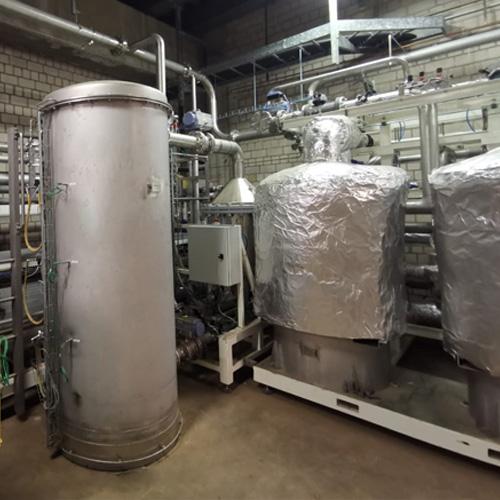
Gas recovery for the glass industry
A reliable and constant supply of industrial gases is essential in producing quality fl...
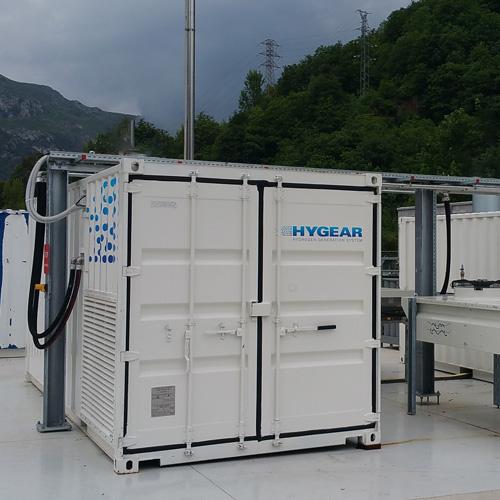
Plug & play water to hydrogen generator
One of the highest volume industrial gases, hydrogen serves a wide range of applica...
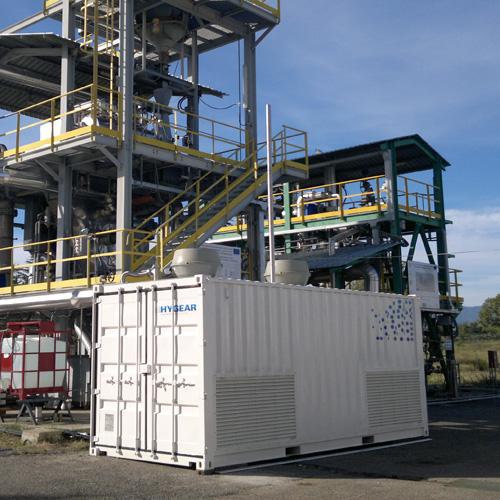
Containerized hydrogen upgrading system
Usually, all spent protective gas is vented from metal treatment processes, such as...
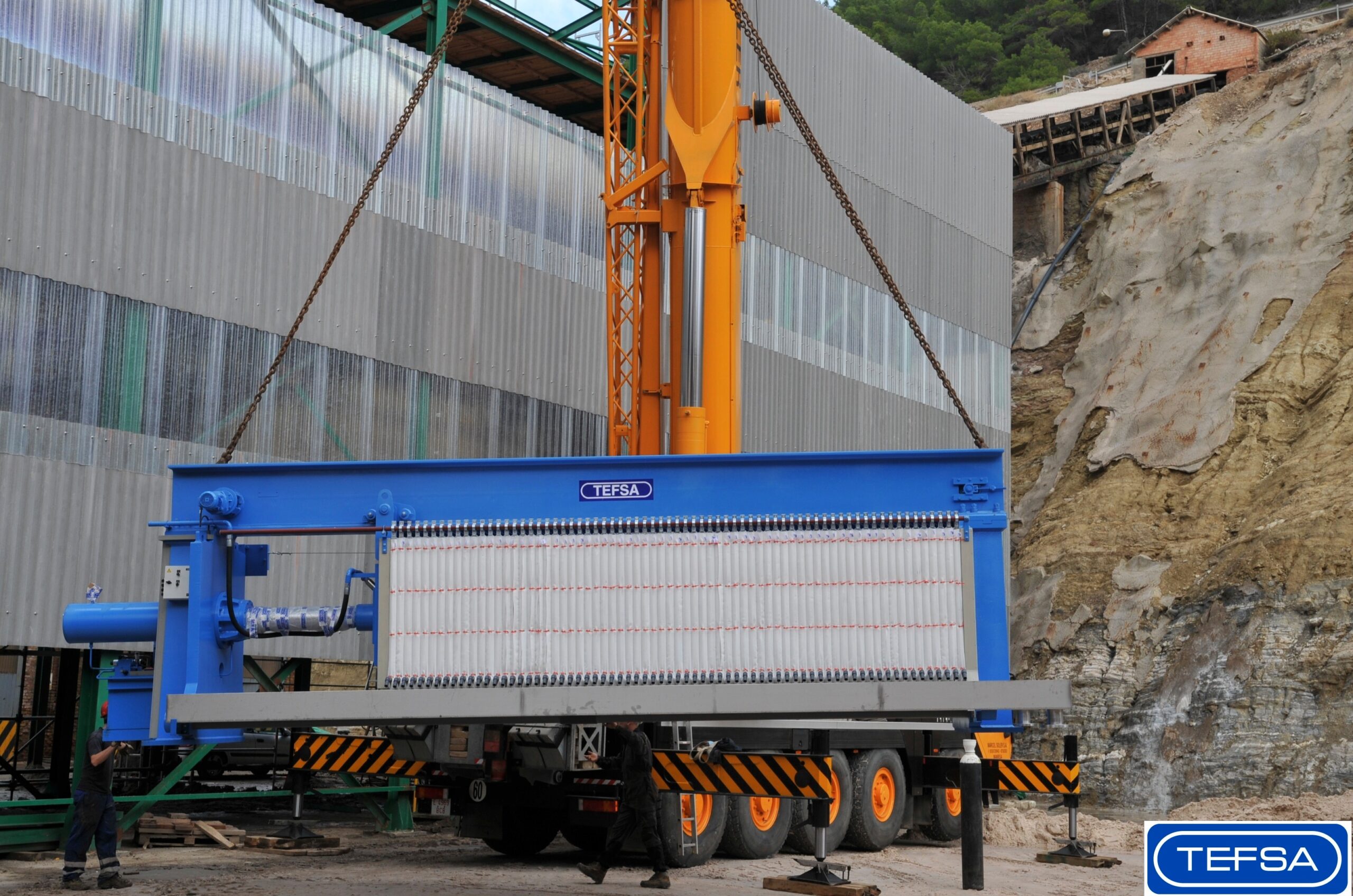
High yield filter press
When a saturated slurry or sludge must be dehydrated with high yield results mining and other heavy i...
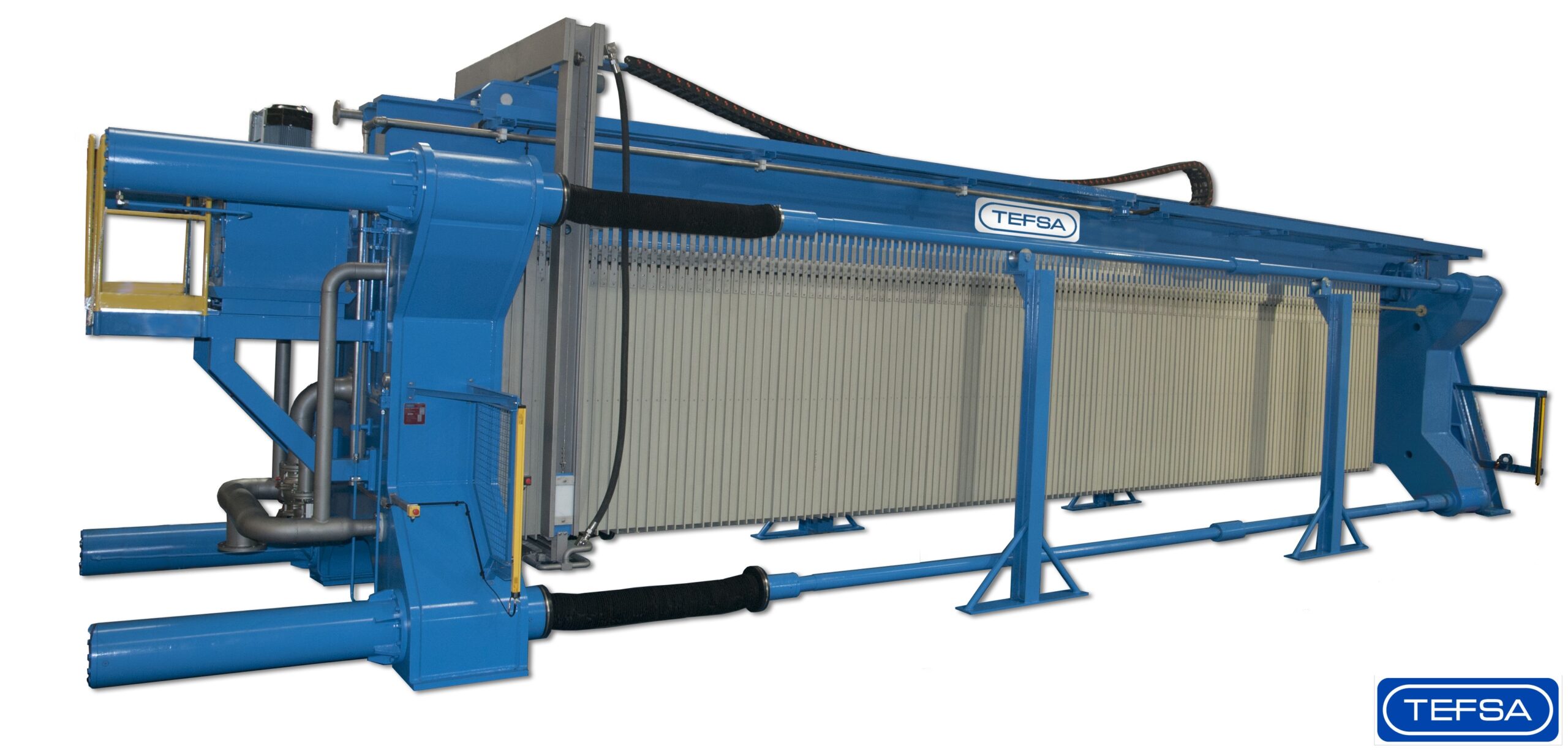
Overhead filter press
To name just a few of the myriad applications for overhead filter presses: industrial mineral industrie...
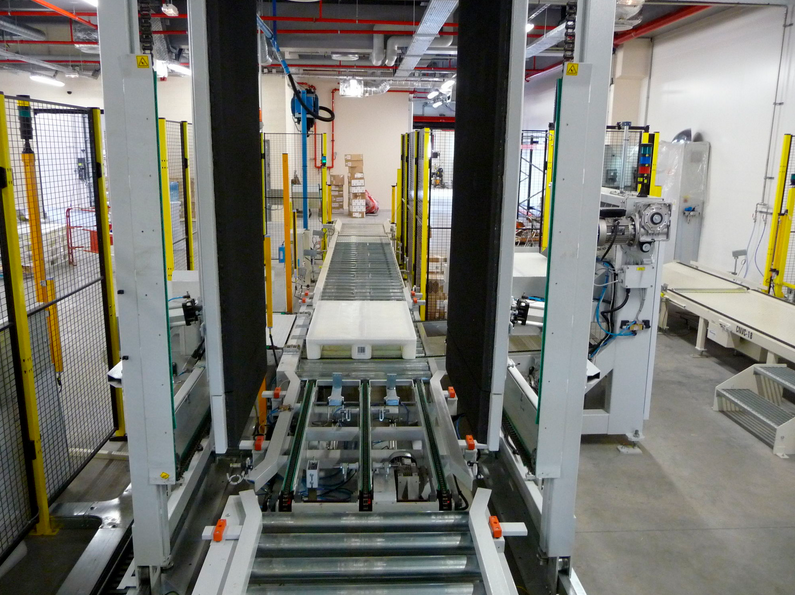
In-line pallet changer
When you need to transfer load from one pallet to another without tilting or turning, then selecting t...
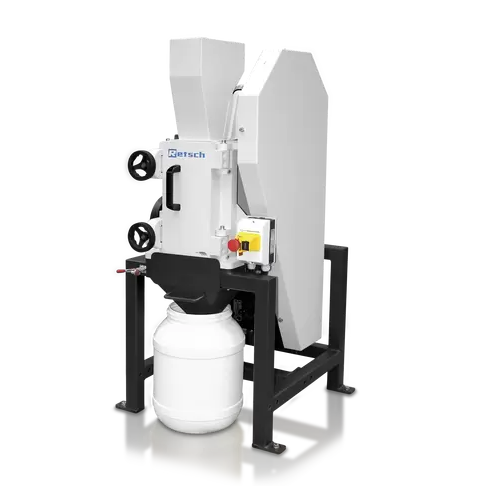
Jaw crusher for medium-hard to hard materials
Optimize your material processing with a powerful solution for efficiently r...
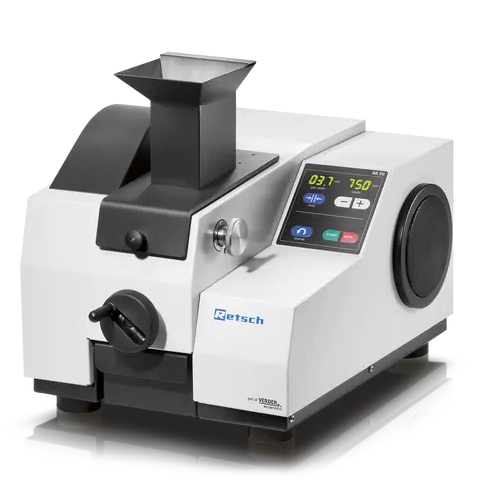
Laboratory jaw crusher for sample preparation
Achieve precise size reduction and sample preparation with this compact jaw ...
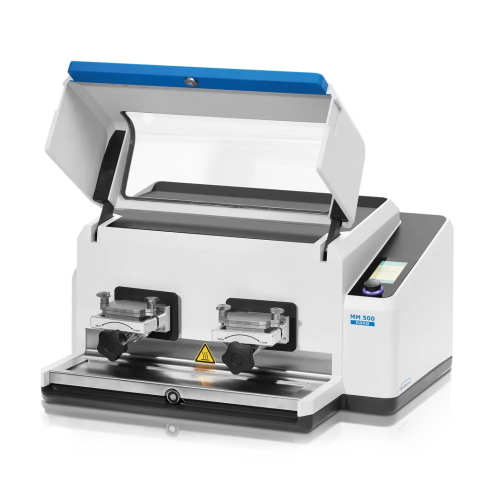
Ultrafine grinding solution for nanoparticles
Achieve ultrafine particle sizes with high-speed precision, ideal for labora...
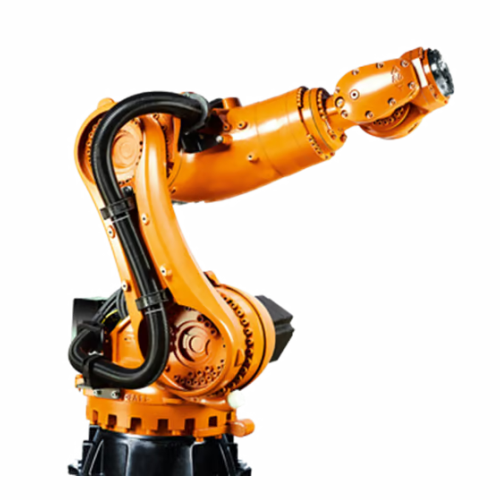
Spot welding robot for confined spaces
Optimize spot welding efficiency in tight manufacturing spaces with a compact robot ...
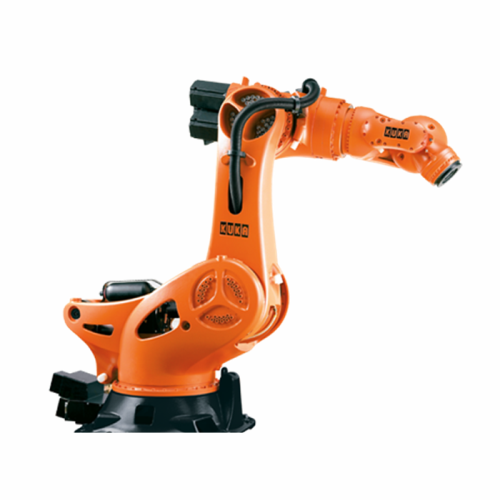
Heavy-duty robot for industrial applications
Effortlessly manage ultra-heavy components with precision and speed, enhancin...
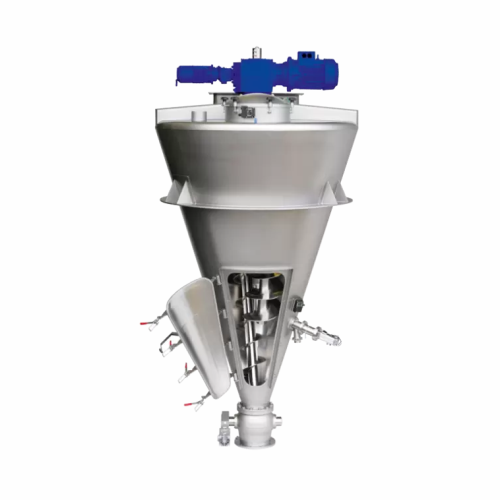
Batch mixer for segregative, free-flowing powders and pastes
Achieve precise and gentle batch mixing for delicate produc...
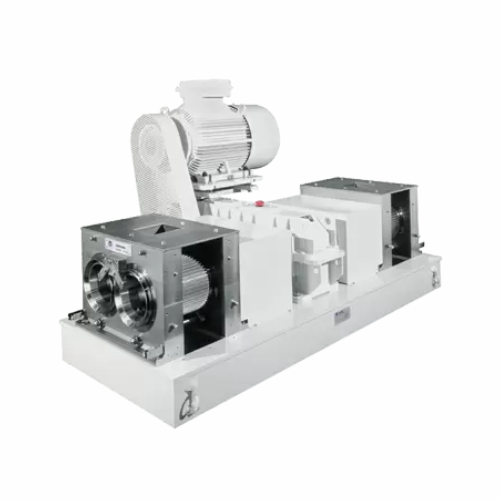
Compactors and granulators for powdery products
Transform loose powders into dense, free-flowing granules that enhance han...
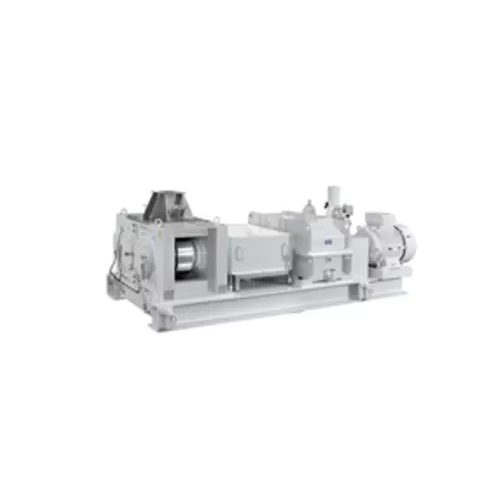
High pressure roller mill for medium-fine crushing
Achieve precision in particle size with high-pressure roller mills, id...
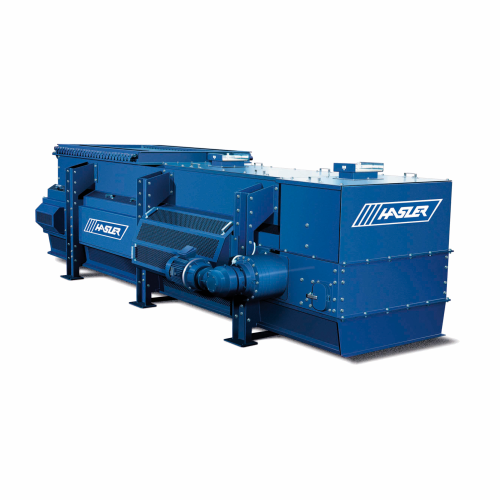
Apron extractor weigh feeder for large-scale material extraction
Achieve precise material dosing and metering under chal...
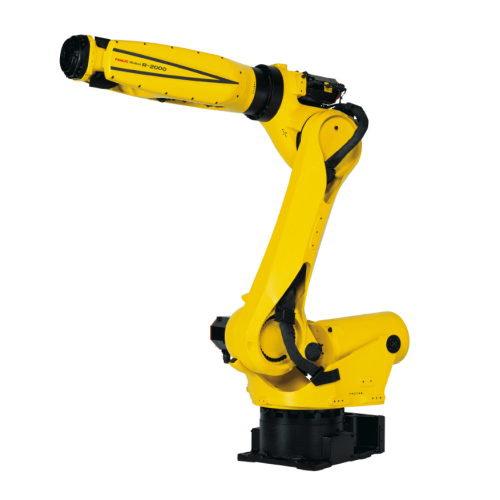
Large industrial robot for heavy-duty tasks
Boost efficiency in your production line with cutting-edge robotic arms design...
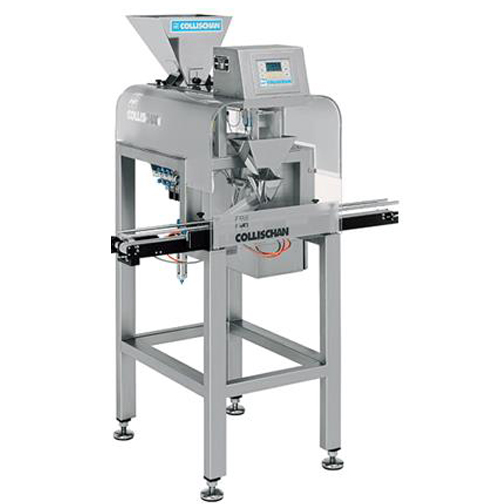
Weight filler for small batches in explosive areas
Efficiently handle and weigh small batch products with precision, even...
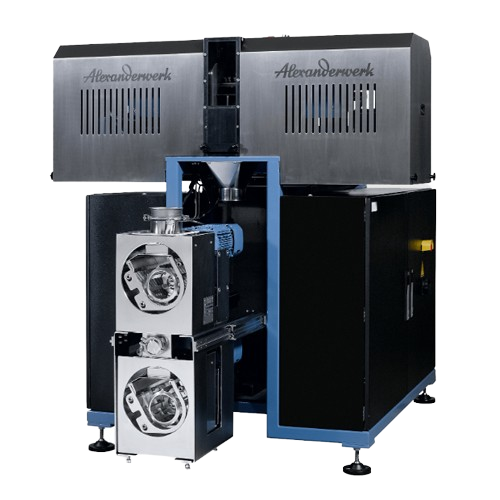
Industrial roller compaction for chemical applications
Enhance material flow and density with advanced roller compaction ...
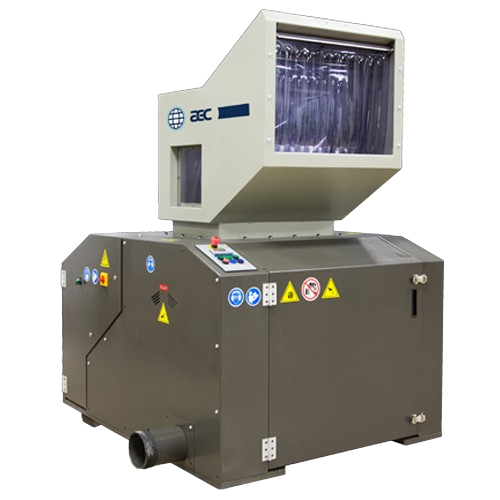
Beside-the-press granulators for injection molding
Optimize your plastic production by efficiently reclaiming resin with ...
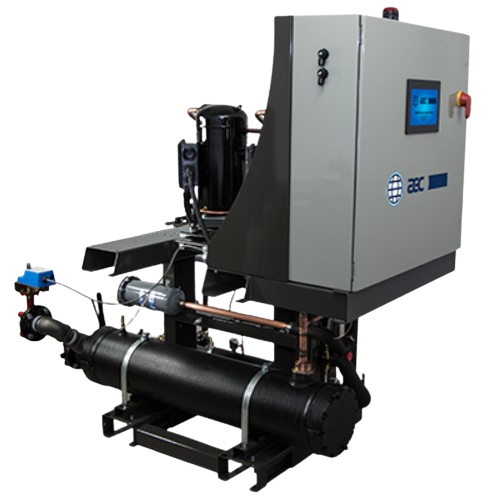
High efficiency central chiller for industrial cooling
Achieve remarkable energy savings with this modular chiller system...
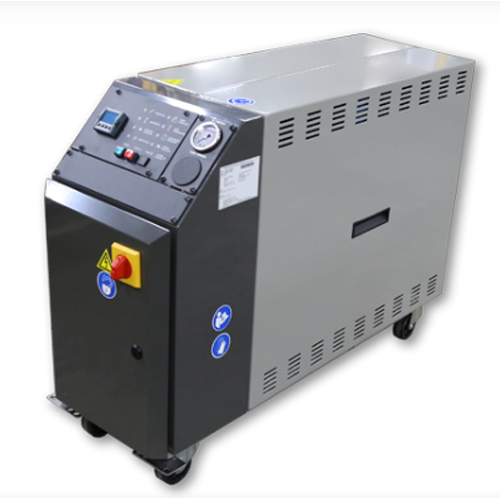
Positive/negative pressure temperature control unit for cooling circuits
Ensure precise temperature regulation and prev...
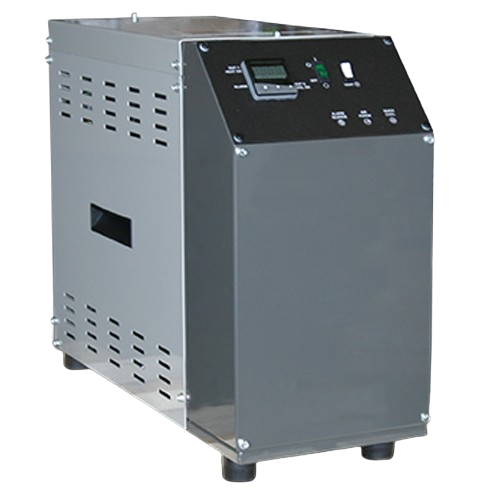
Compact water temperature control unit
Achieve precise temperature control in cramped production spaces, enabling consisten...
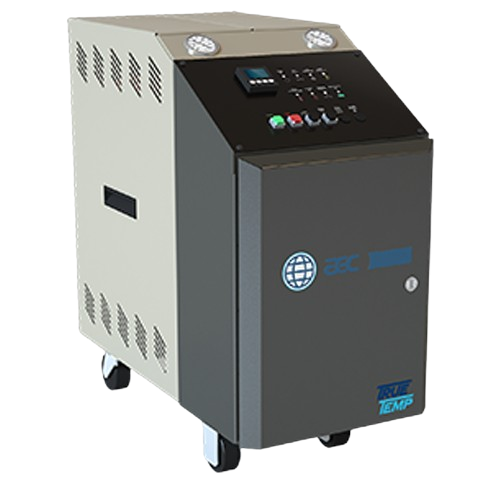
Water temperature control unit for production applications
Enhance your production efficiency by precisely managing wate...
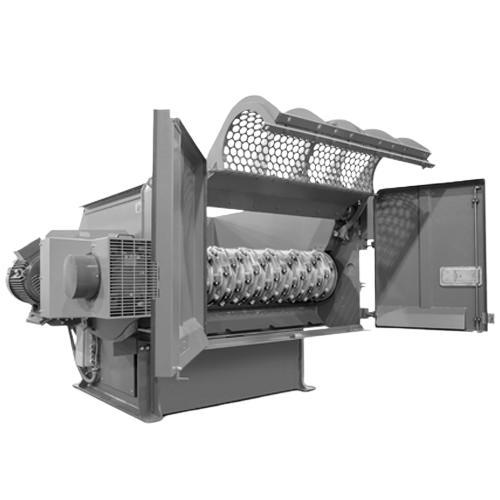
Industrial shredder for recycling and waste management
Efficiently transform challenging waste streams into valuable raw ...
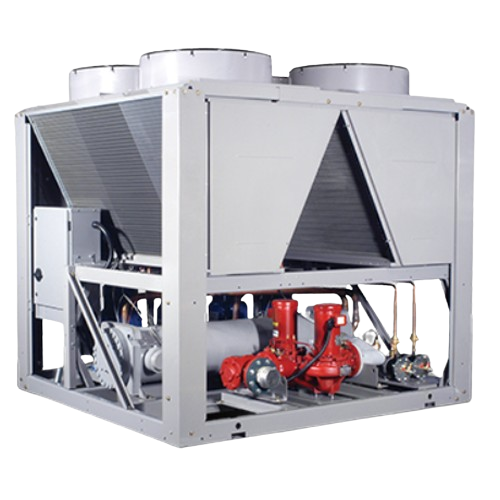
Outdoor central chiller for process cooling
For facilities needing reliable process cooling without sacrificing indoor spa...
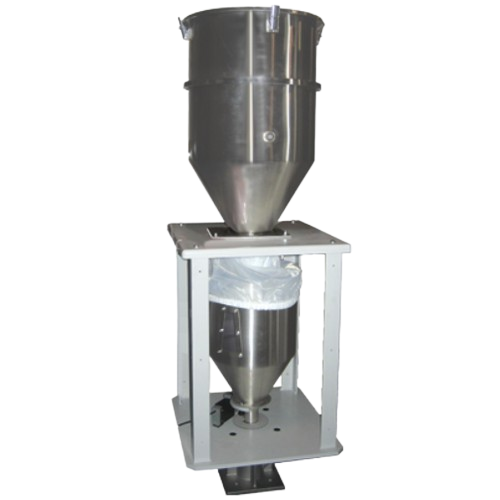
Extrusion control units for high precision manufacturing
Optimize your extrusion process with precision control over thro...
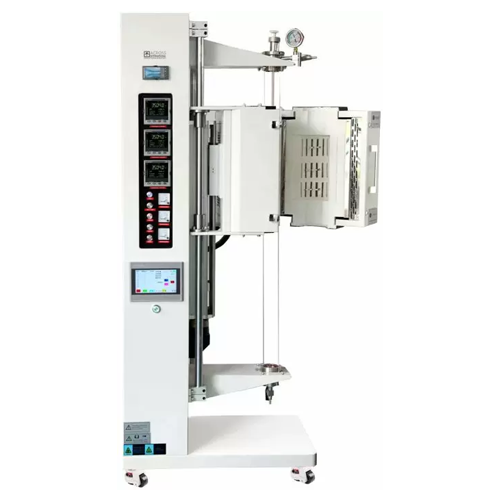
Bridgman crystal growth tube furnace
Achieve precise control over crystal growth processes with this advanced tube furnace,...
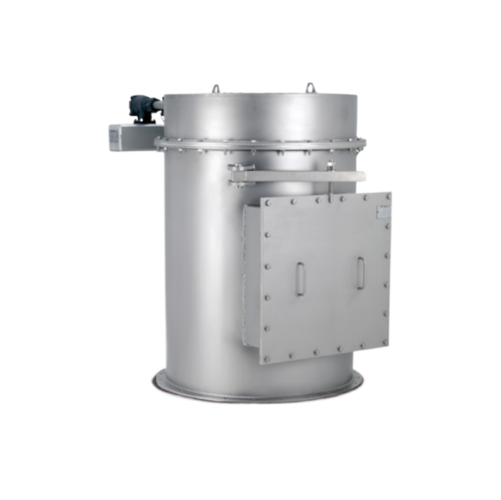
Industrial bin vent filter for fine dust particles
Enhance your production line with efficient fine dust filtration to en...
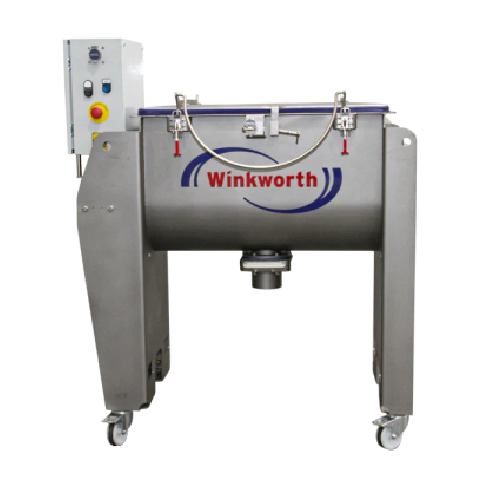
Horizontal shaft mixer for free-flowing materials
Achieve consistent mixing of diverse free-flowing materials with a reli...
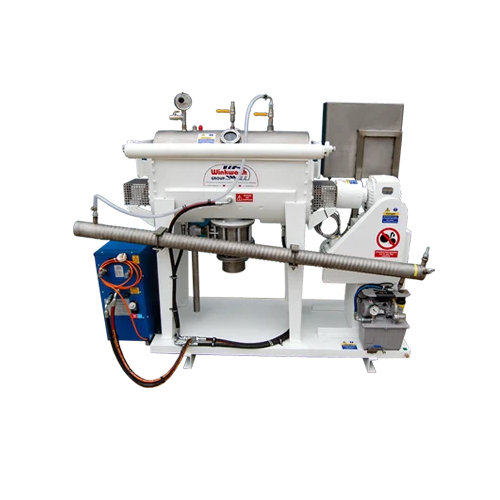
Industrial blenders for powder and granule mixing
Optimize your production line with advanced mixing solutions designed f...
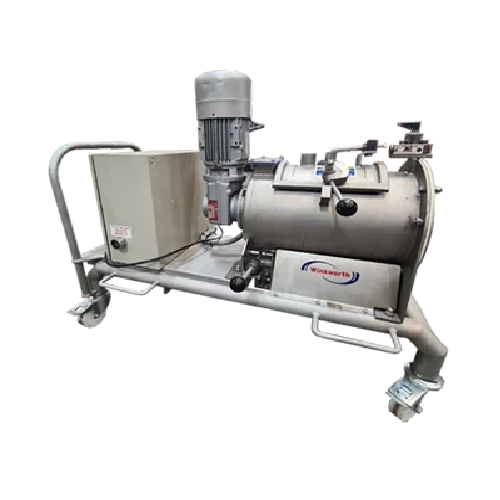
Industrial mixers for hire
Optimize your production line with versatile mixers designed for precision blending, heating, and...
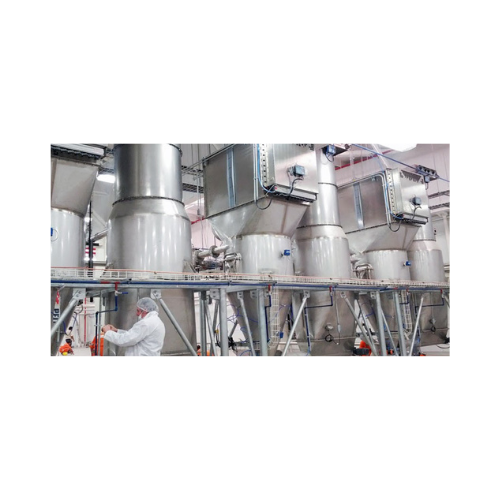
Industrial dust collection system for air filtration
Optimize air quality in your production line with this compact dust ...
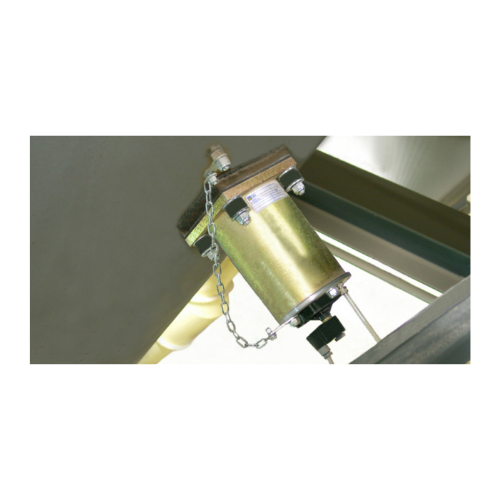
Single impact pneumatic hammers for flow aids
Combat material clogs and ensure smooth flow in your production line with pn...
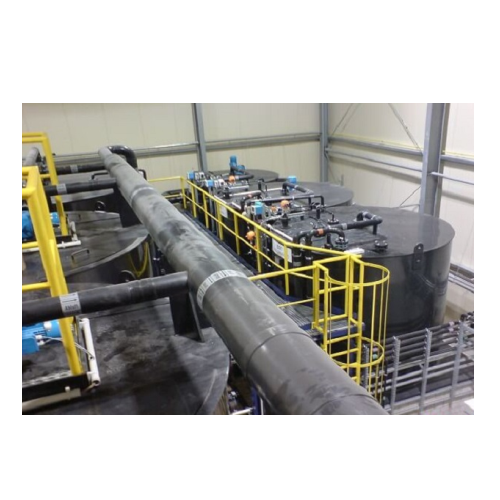
Industrial water recirculation treatment system
Optimize your resource management with an advanced water recycling and tre...
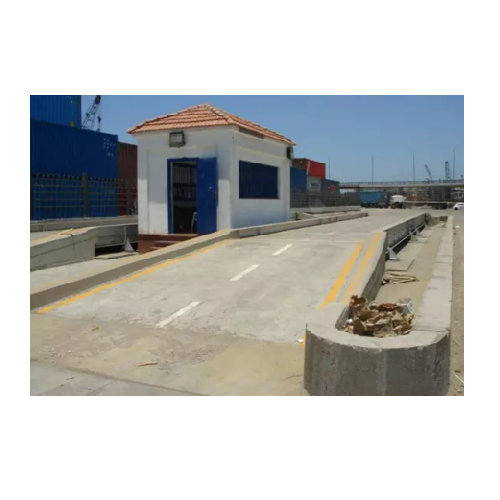
Industrial steel weighbridge for heavy load weighing
Optimize your material handling processes with precise weight measur...
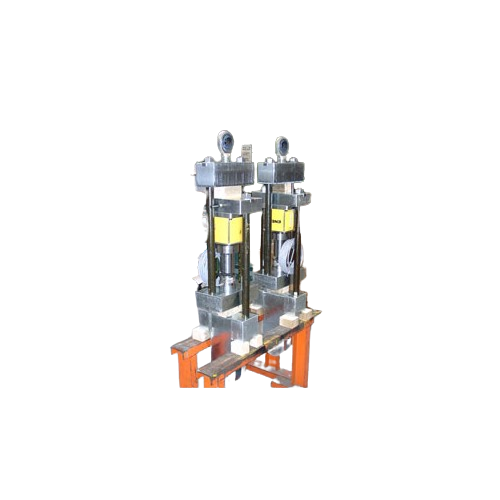
Mobile check weighing system for pig iron production
Ensure precise hopper scale adjustments in challenging environments ...
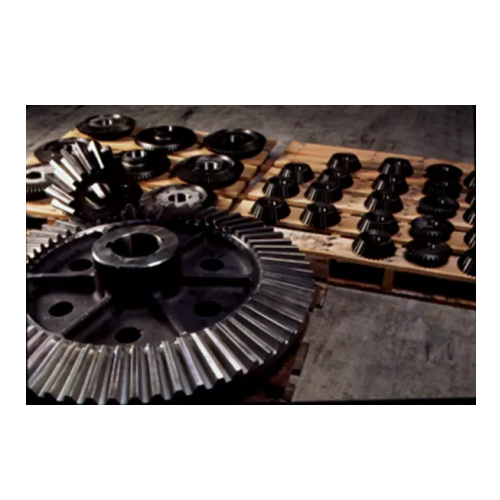
Industrial grinding mill replacement parts service
Optimize production efficiency with high-precision grinding solutions ...
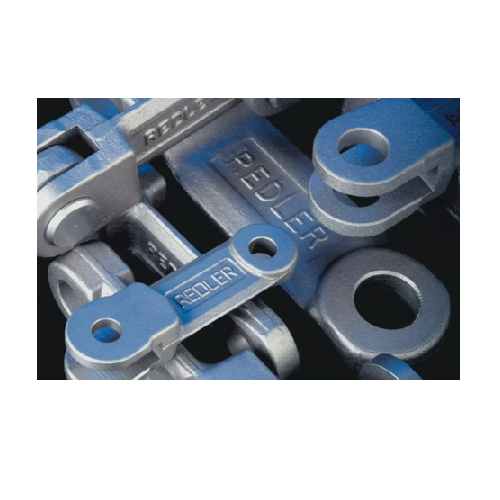
Drop forged chain for drag chain conveyors
Enhance your material flow efficiency with a robust drop forged chain designed ...
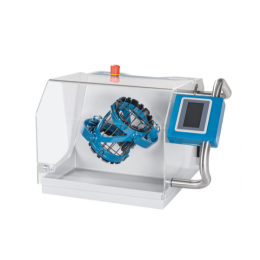
R&D shaker mixer for battery powders and chemicals
Material heterogeneity, agglomeration, and contamination are key param...
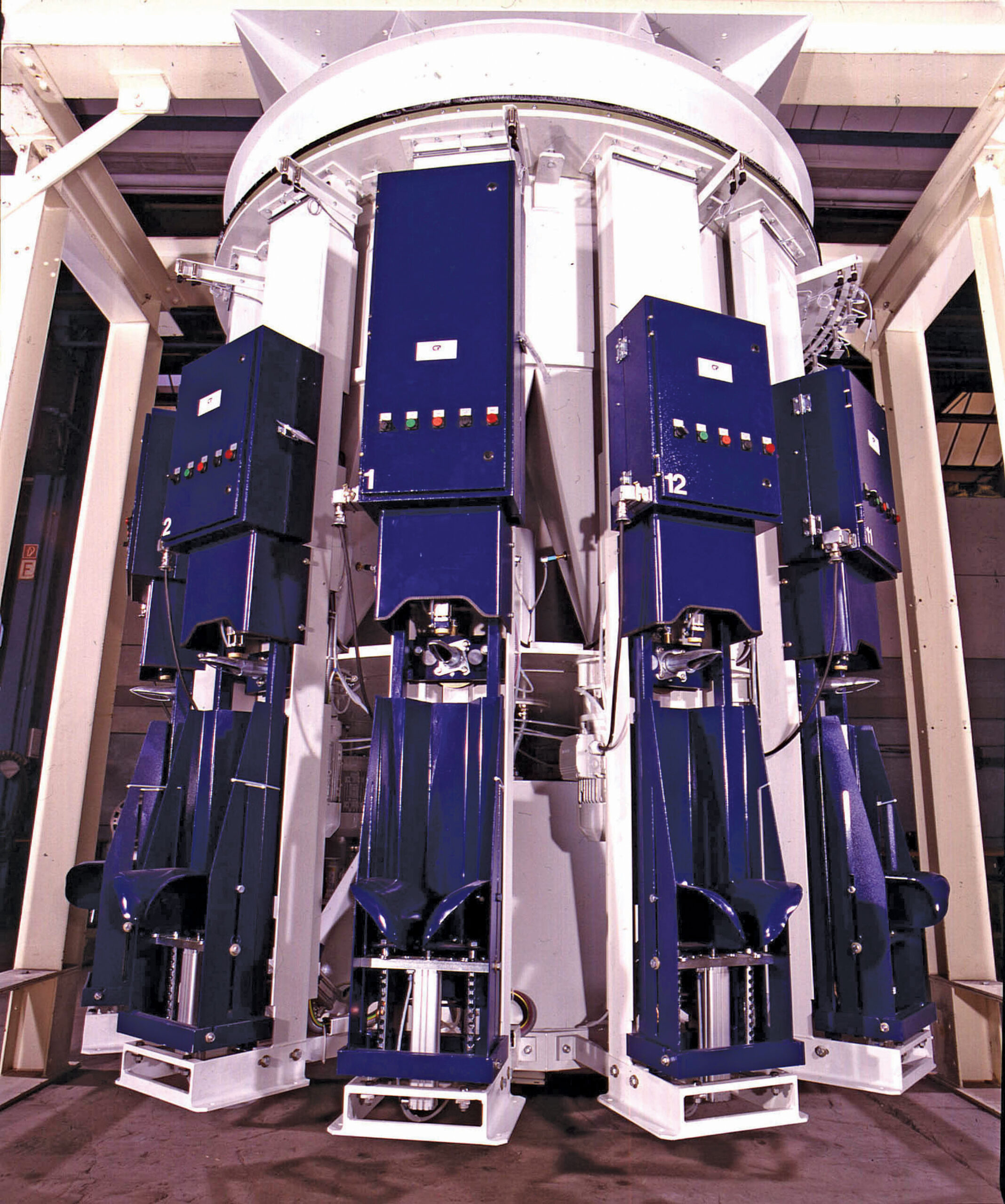
Rotary cement packer
The cement industry requires efficient and reliable packaging solutions for transport and distribution o...
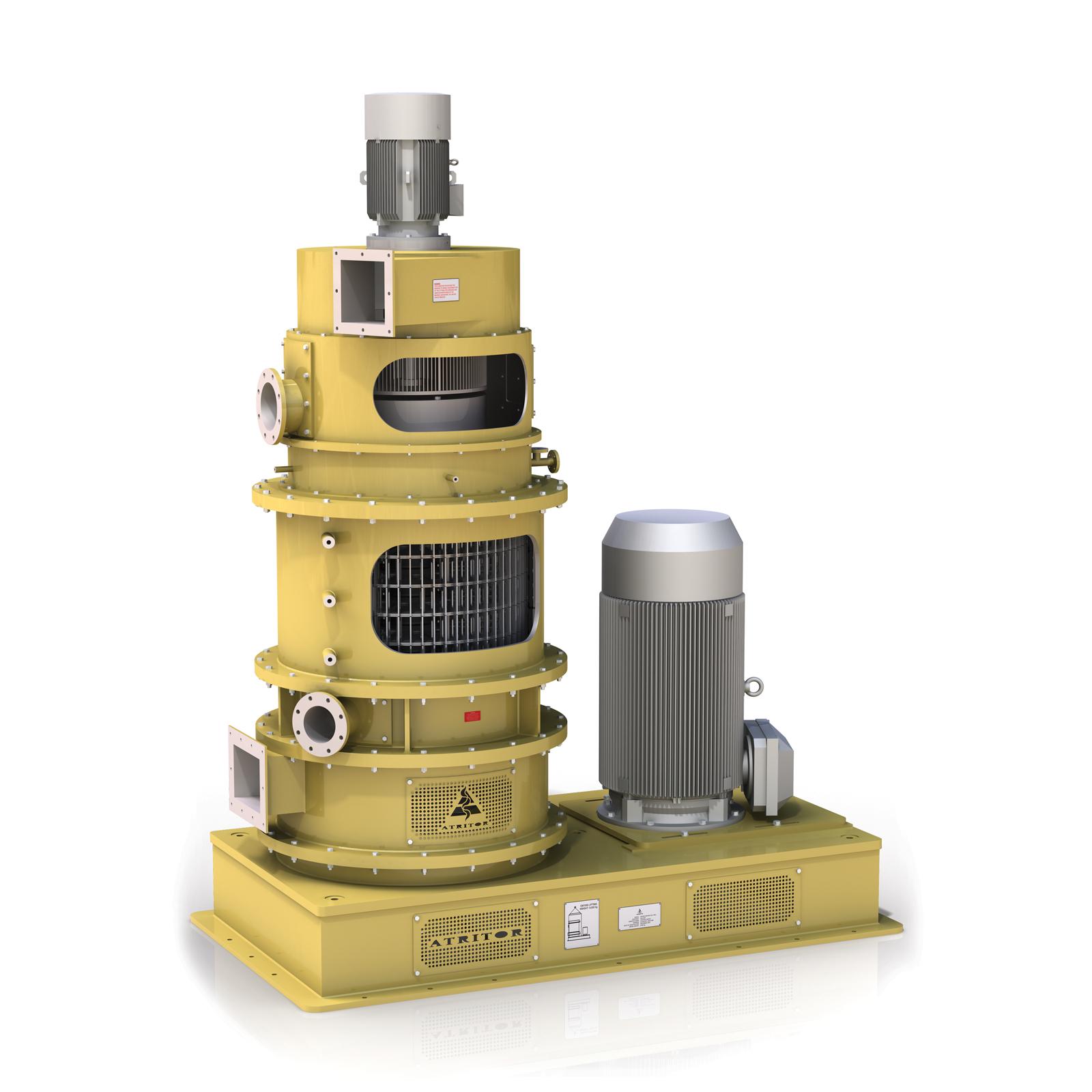
Milling and drying machine for fine powders
When you need to produce ultra-fine powders, the milling and drying process em...
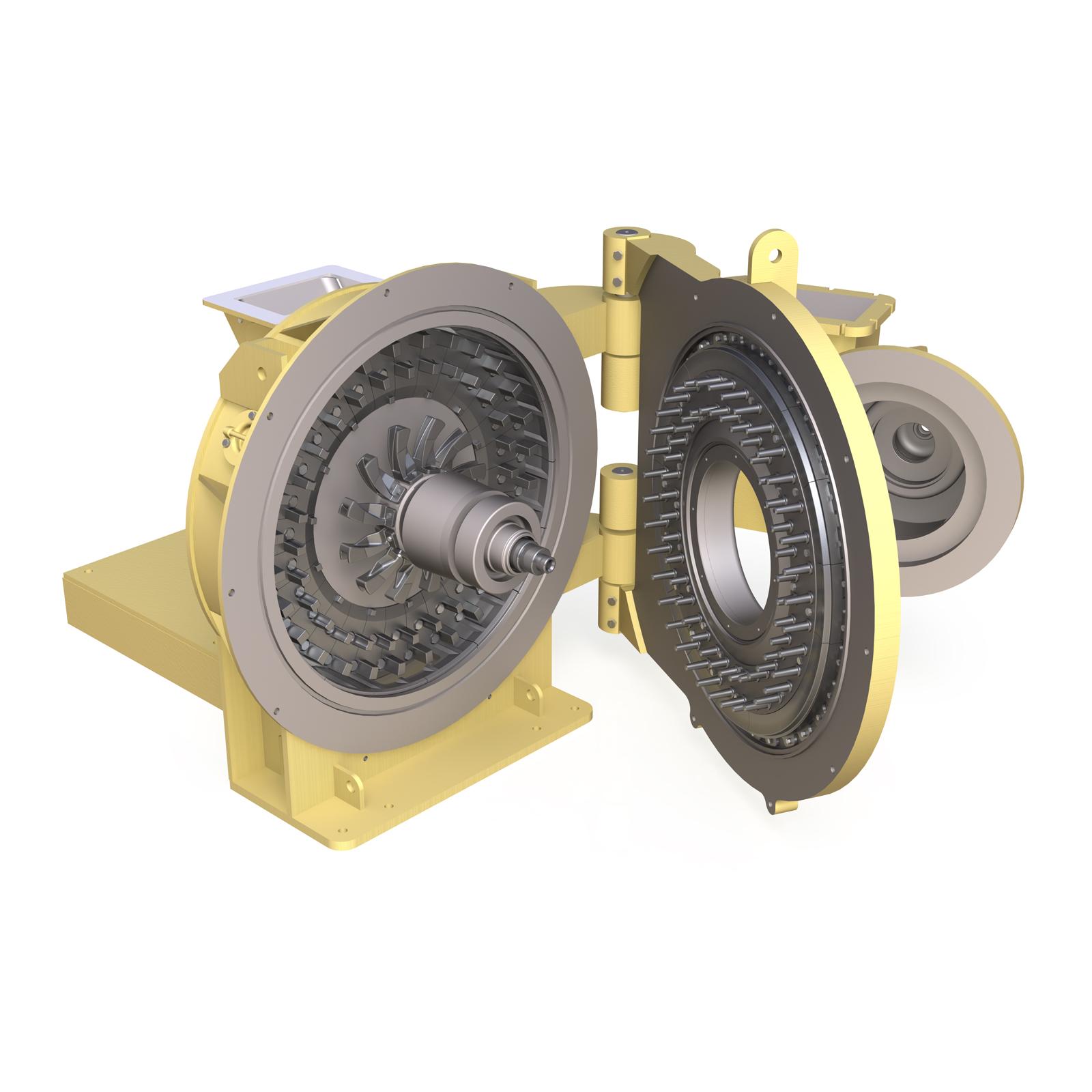
Flash drying grinder for powders
Drying and grinding can be an important feature when trying to process products such as raw...
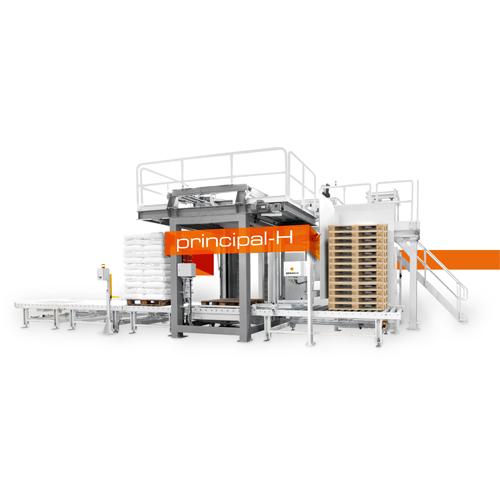
Automatic palletizer machine for bags and boxes
The effective placement and positioning of bags and boxes can be a challen...
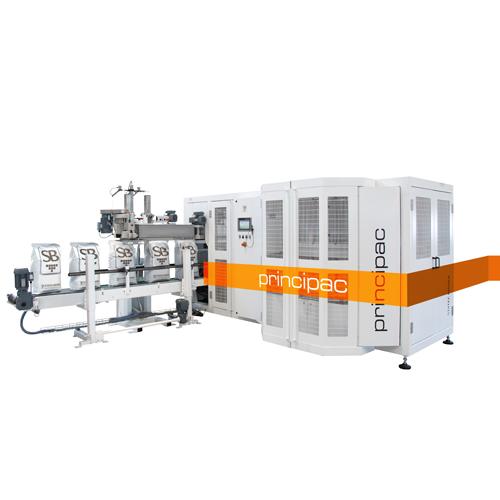
Open mouth bagging machine
If you are a manufacturer of fertilizers, bulk chemicals, sugar, seeds, or any grains it is likel...

Open mouth bag filling machine for powders
The packaging of powdery products such as flour can be challenging as it is cru...
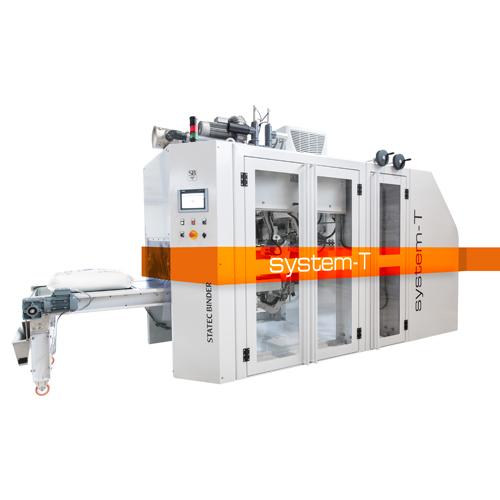
Form fill seal bagging machine
If you are in industries such as petrochemicals, fertilizers, animal feed, food, etc, you mus...
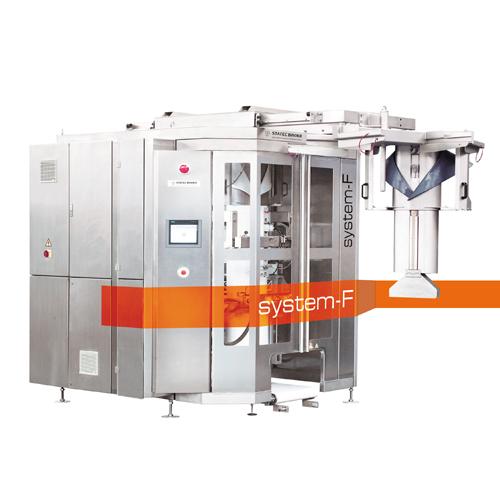
Vertical form fill seal machine
There is an increasing demand for a range of different package sizes of the same product. If...
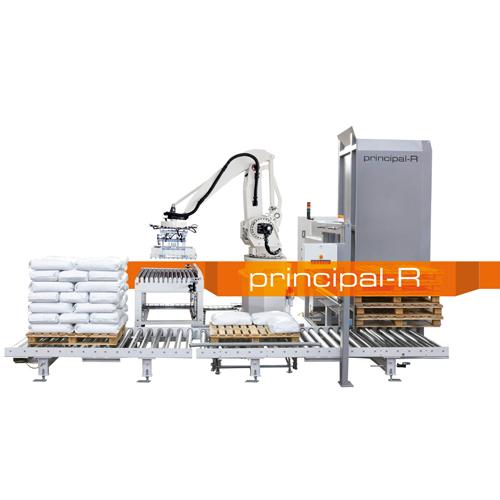
Robot palletizing system
If you are a relatively large-scale producer, packing and transporting large quantities of products ...
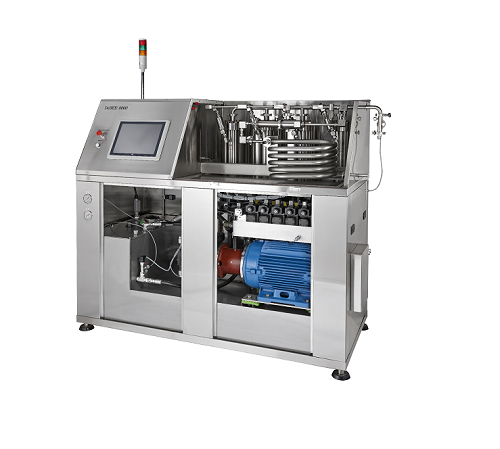
High pressure industrial homogenizer
For any industrial pharmaceutical process that relies on high pressure homogenization ...

Simple valve sack packer
Sometimes in the packing process, product leaks out of the top of a bag that has just been filled. A...
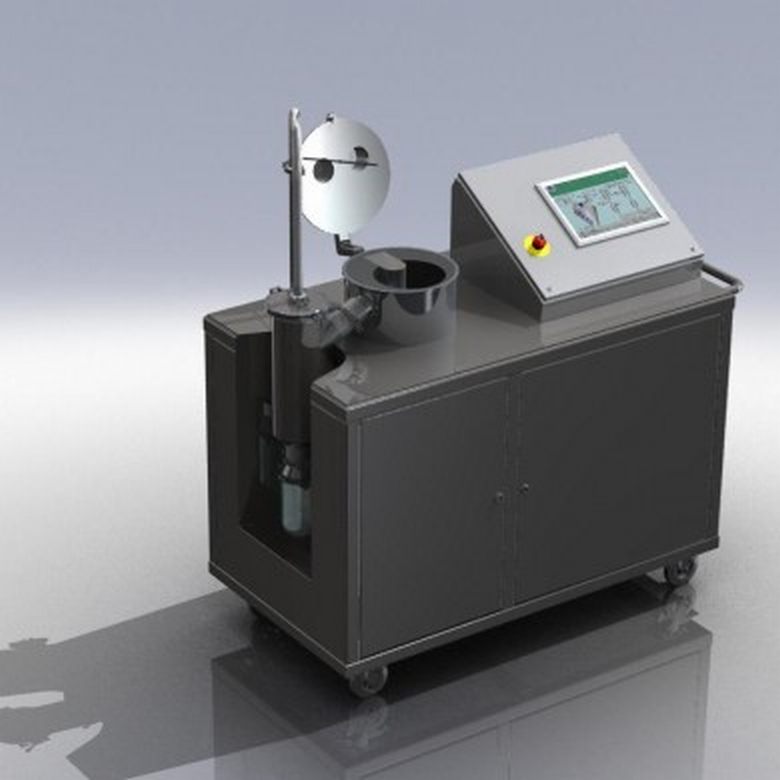
Laboratory scale active freeze dryer
The laboratory-scale active freeze-drying is used for dehydrating high-value products ...
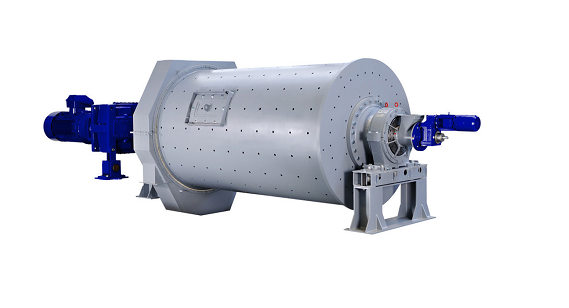
Horizontal rotary ball mill drum
A horizontal rotary ball mill drum can be used for grinding of dry hard materials, such as ...
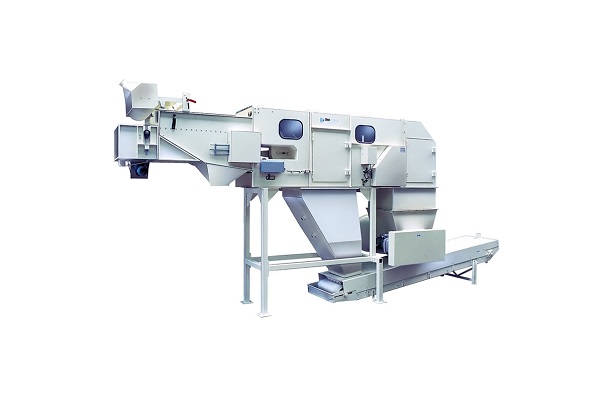
Automatic bag slitter
Unacceptably high dust levels can be generated whilst manual emptying and handling of bags, also produc...
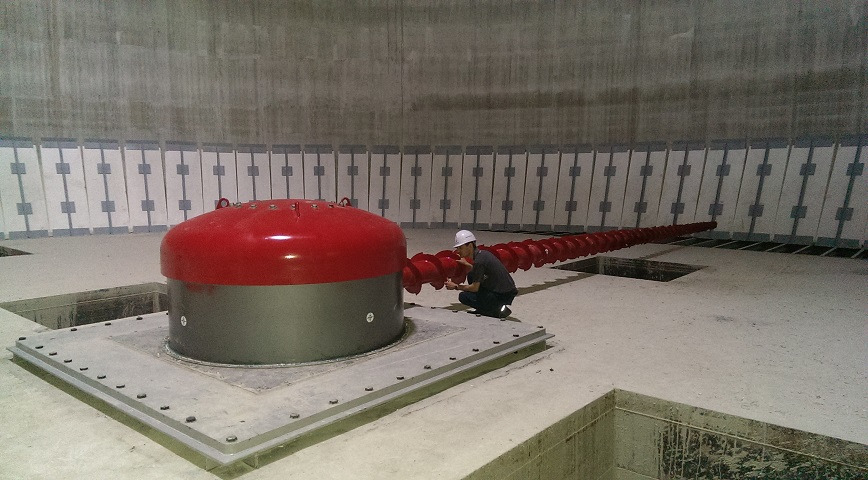
Silo extraction system
Materials without natural flowing properties are difficult to unload, even with the assistance of grav...
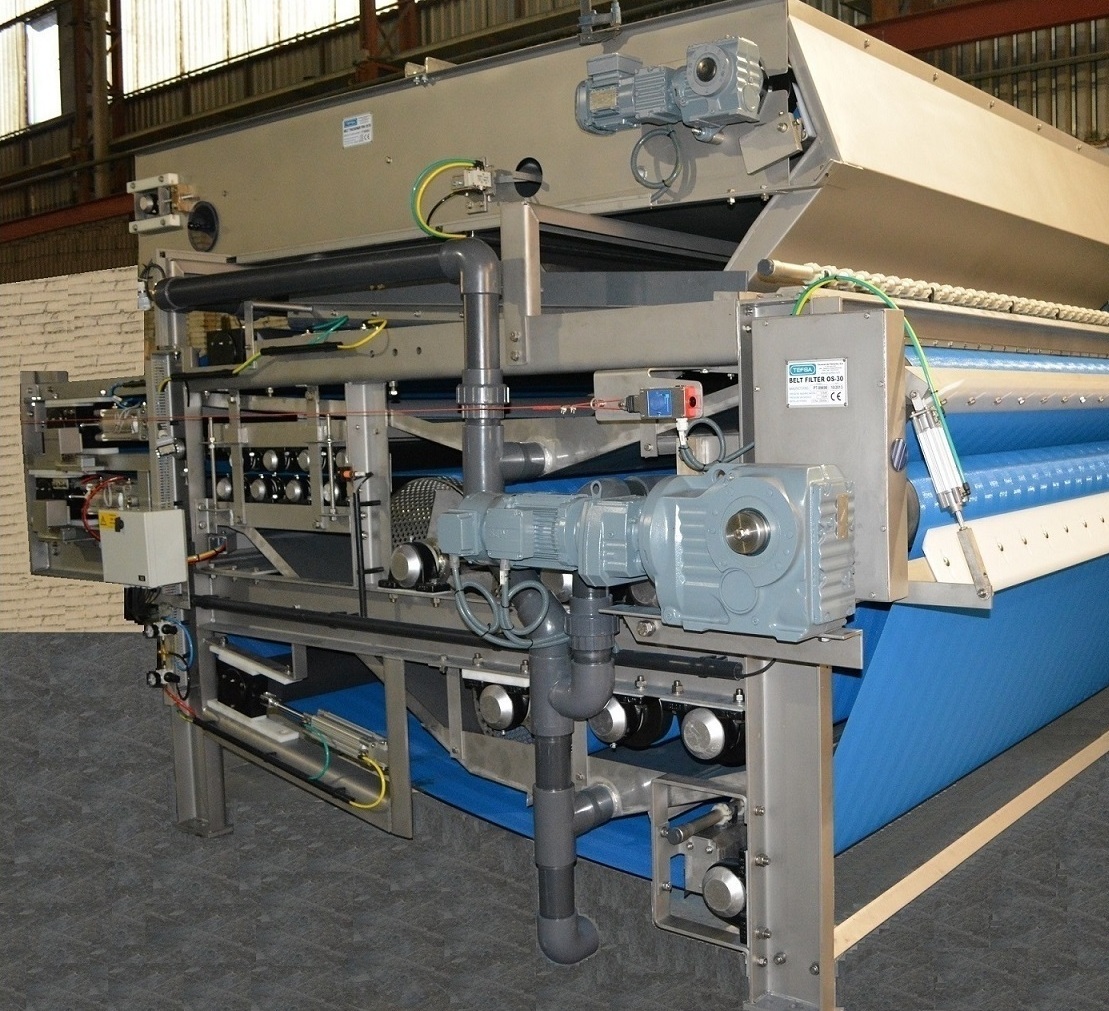
Belt filter press
When a saturated slurry or sludge must be dehydrated in a continuous process municipal waste water treatmen...
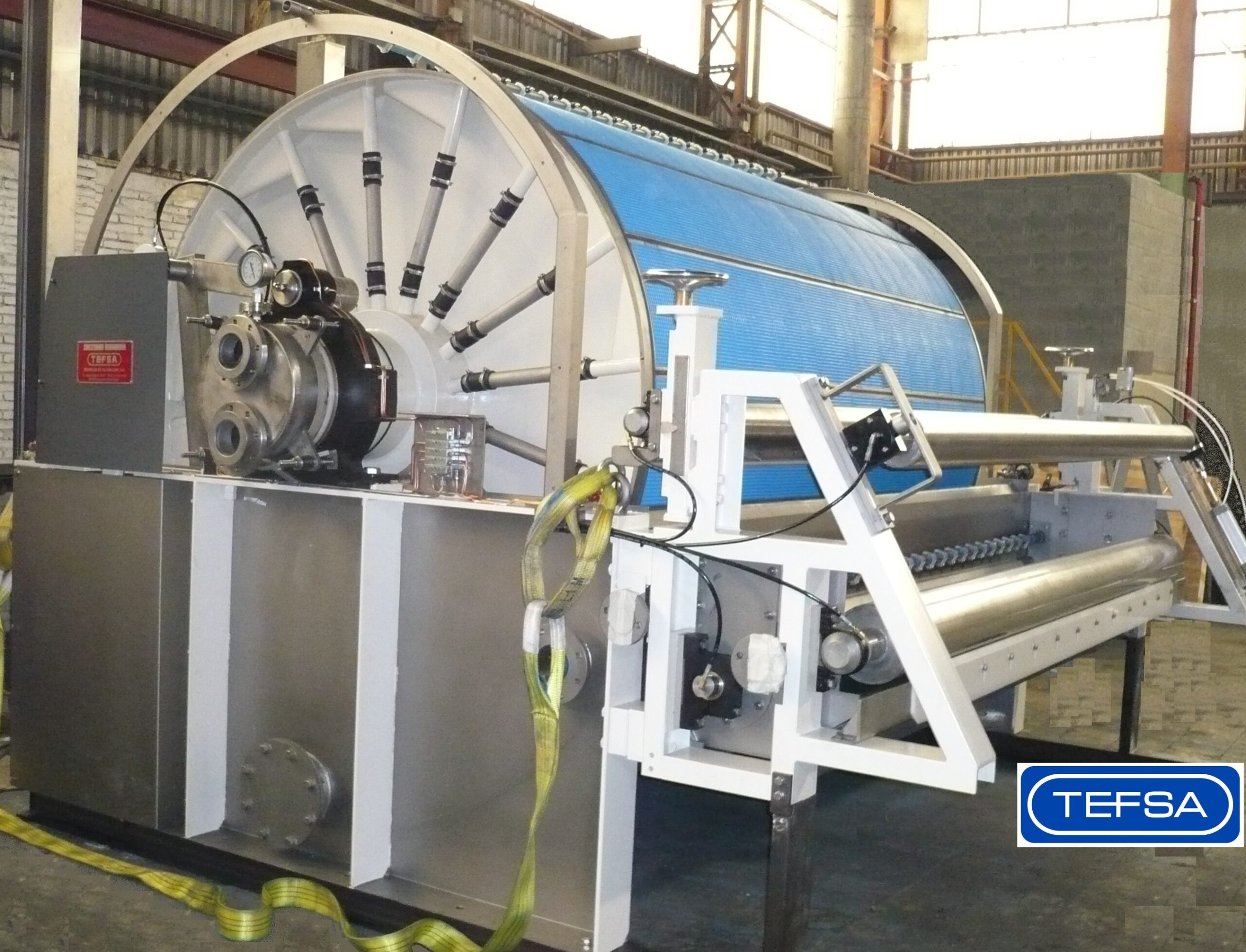
Vacuum drum filter
Manufacturer’s in all fields need peace of mind that their filtration process is efficient and relia...
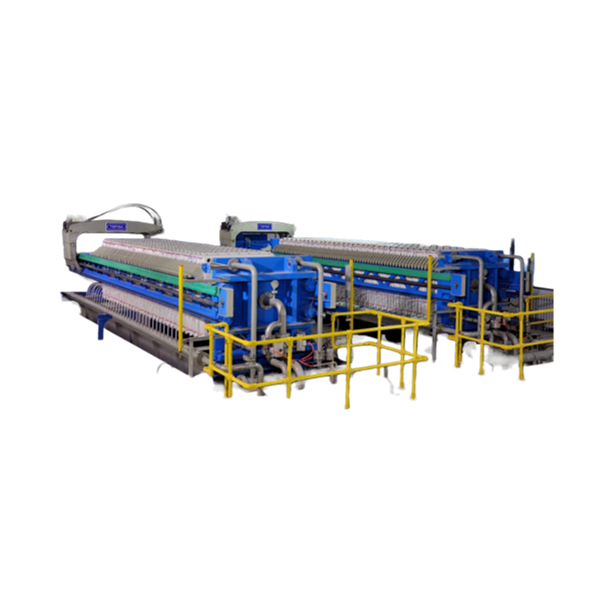
Side bar filter press
Production of dry cakes is required in a variety of industries and robust, low-cost side bar filtration...
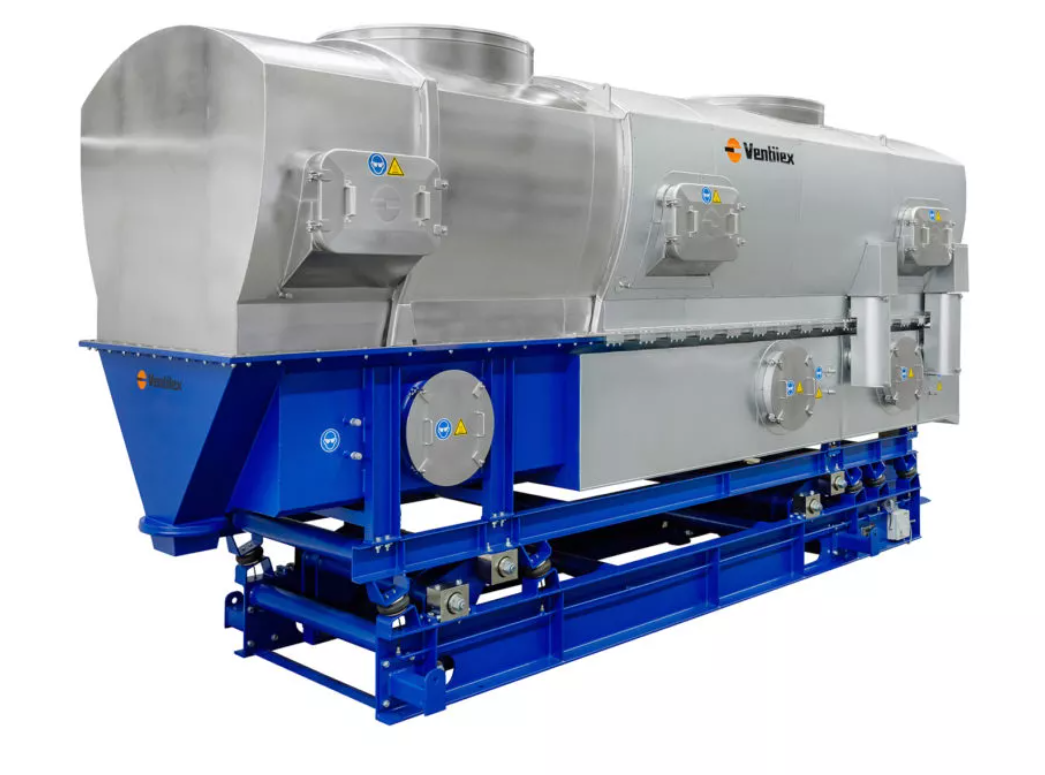
Continuous fluid bed dryer
In a Fluid Bed, a product or solid is made fluid by an upward moving flow of gas. The mechanical ...
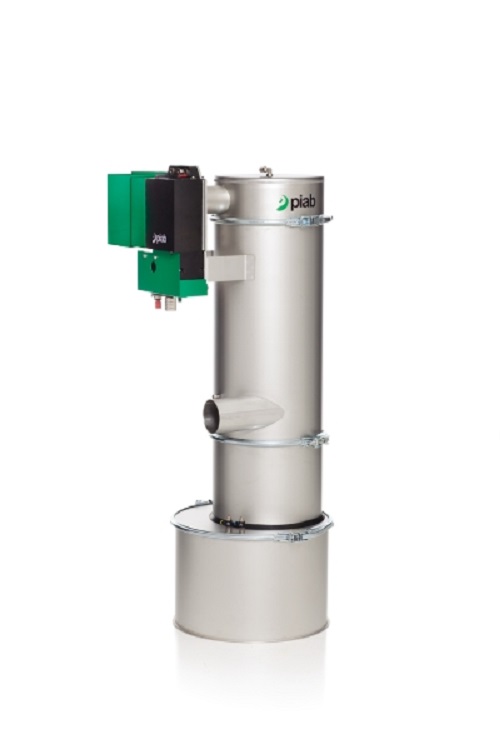
Industrial vacuum conveyor
Oftentime utilized as an alternative to mechanical conveyors when a requirement for dust free con...
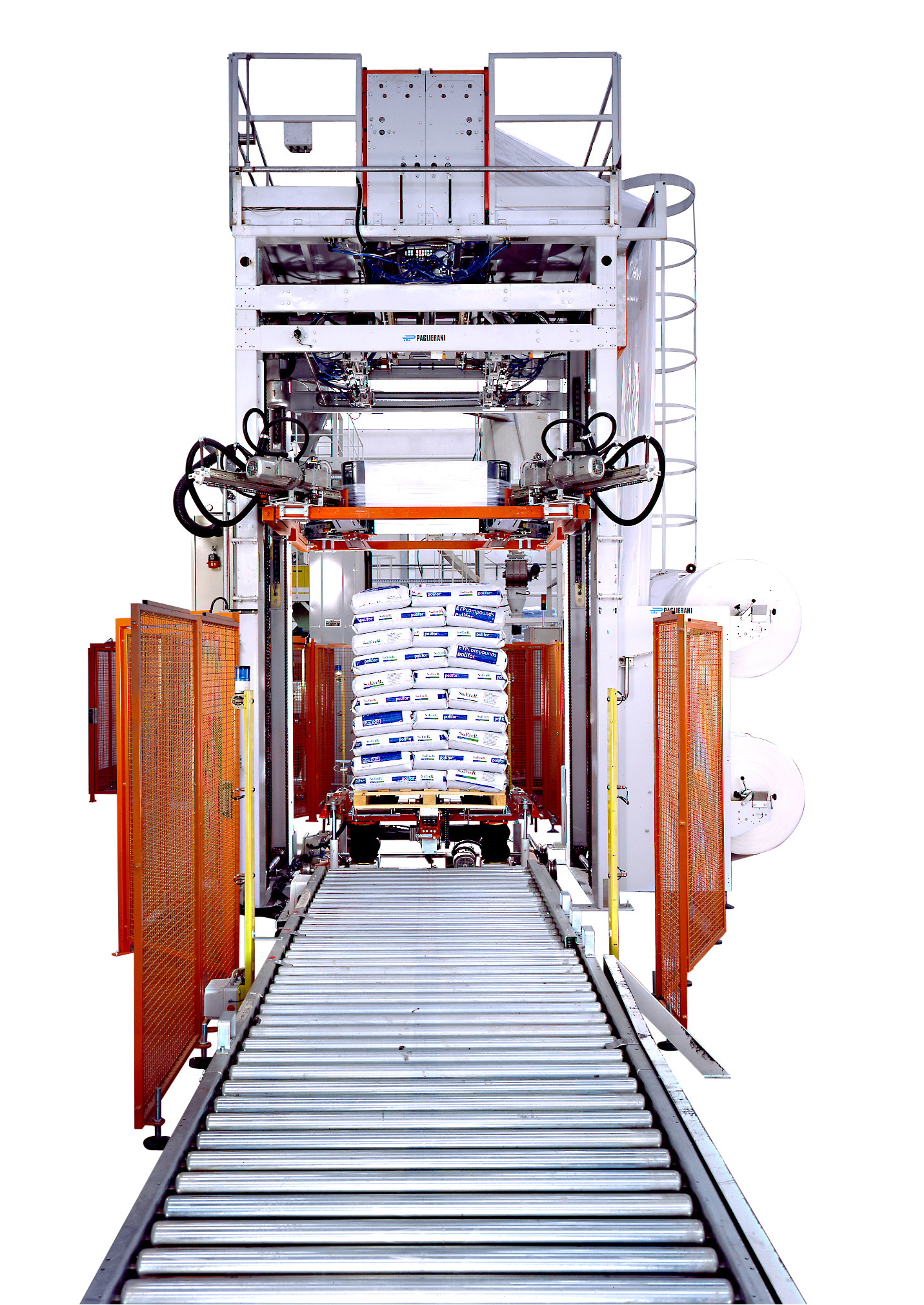
Stretch pallet hooder
Palletised loads need to be securely wrapped in order to protect them from shifting, crushing, ripped o...
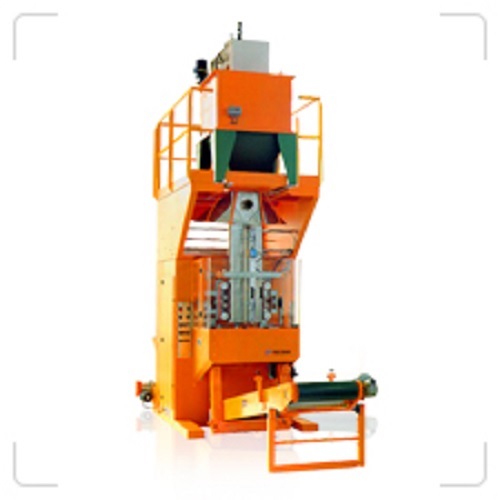
Vertical form, fill and seal machine for bags from 5 to 50 kg
To securely create, dose and pack larger quantities of mat...
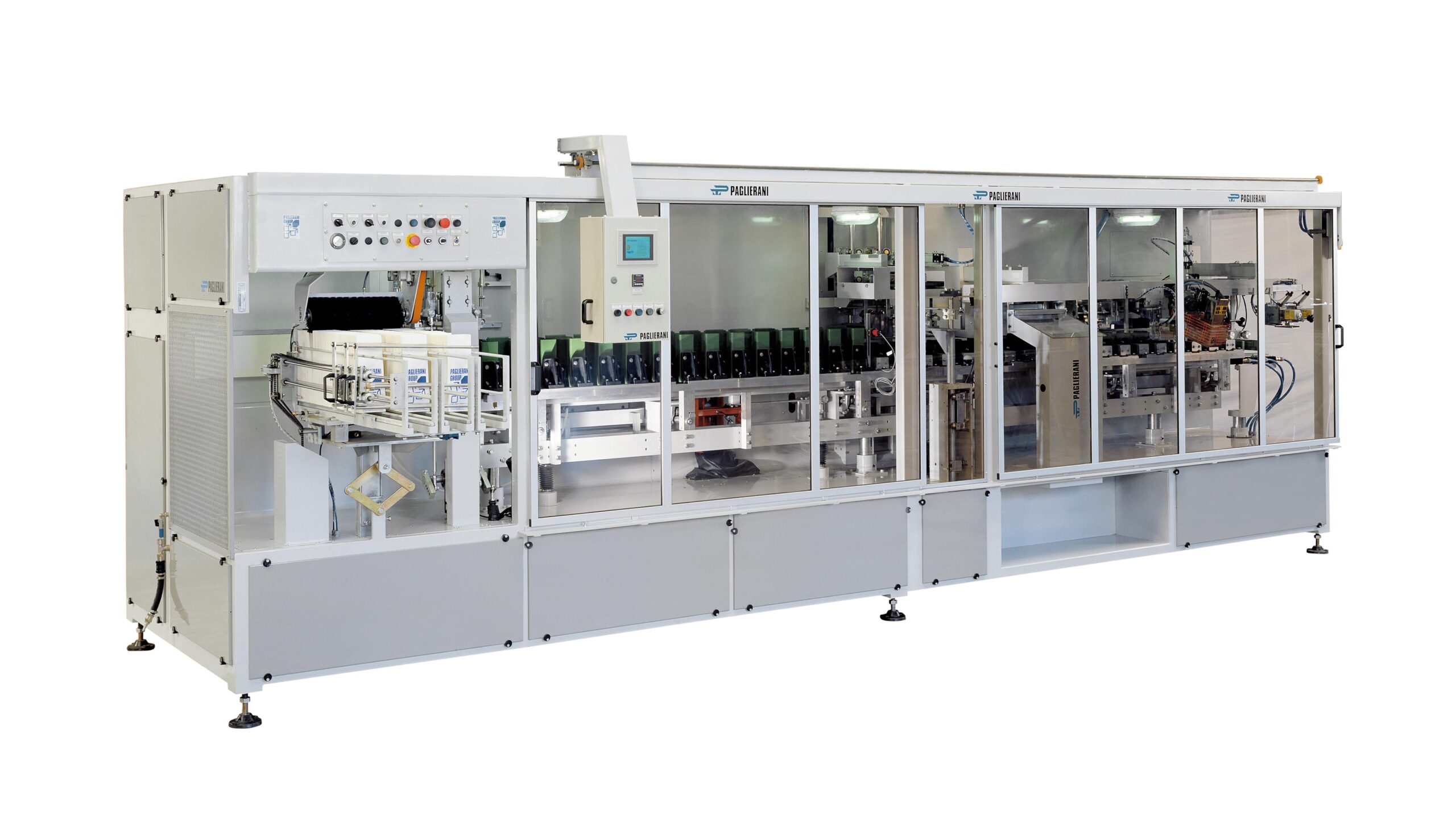
Packaging machine for preformed paper bags from 500 g to 5 kg.
Paper bag filling and closing for larger quantities of ma...
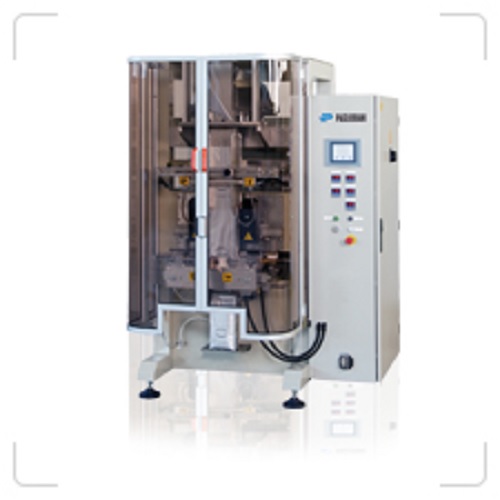
Packaging machine for sealed plastic bags from 250 g to 10 kg
Sealing small quantities of solids or liquids into plastic...
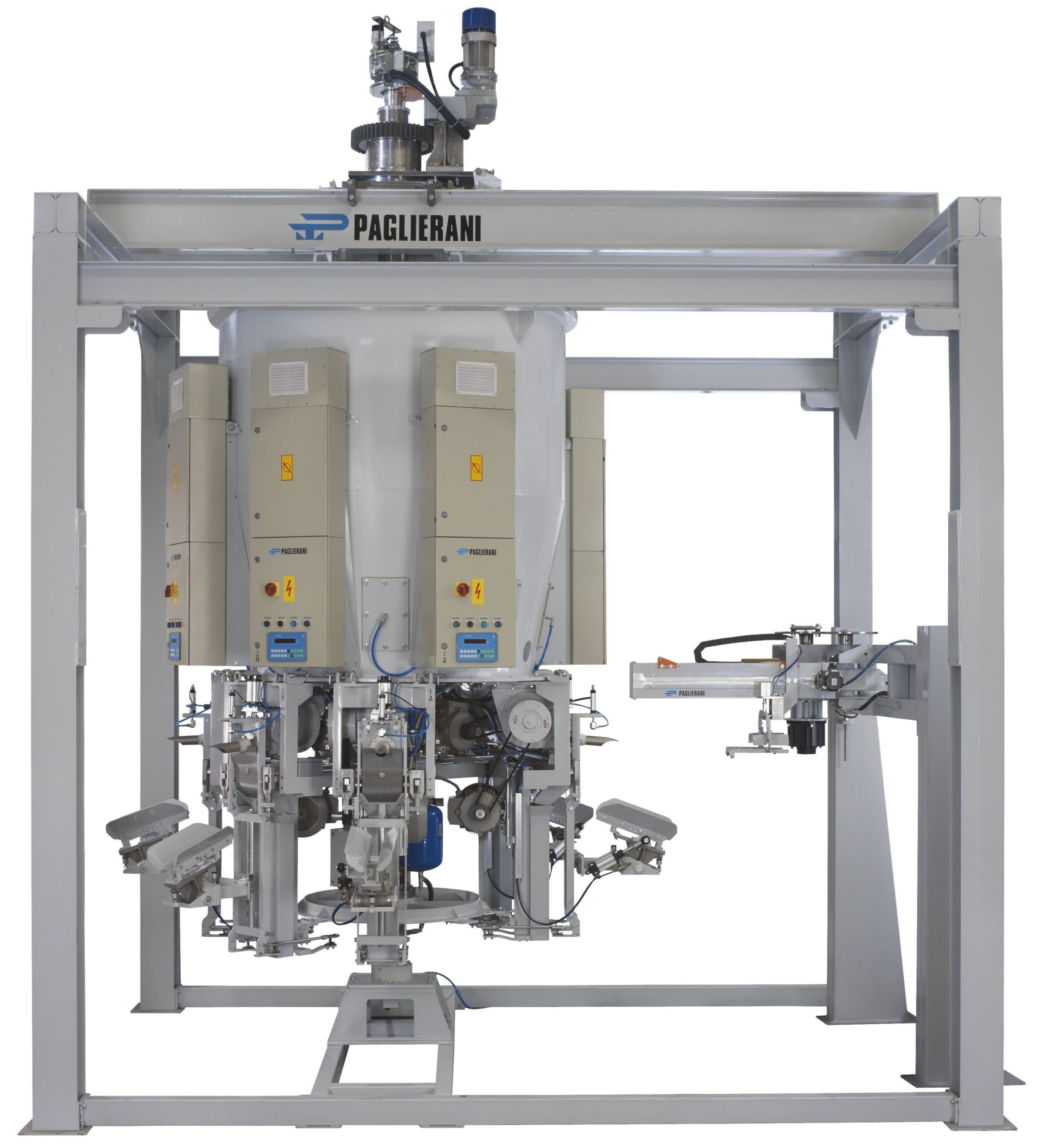
Rotary bag packers for valve bags
Quick filling of bags while avoiding leakage out of the top of a bag can be challenging o...
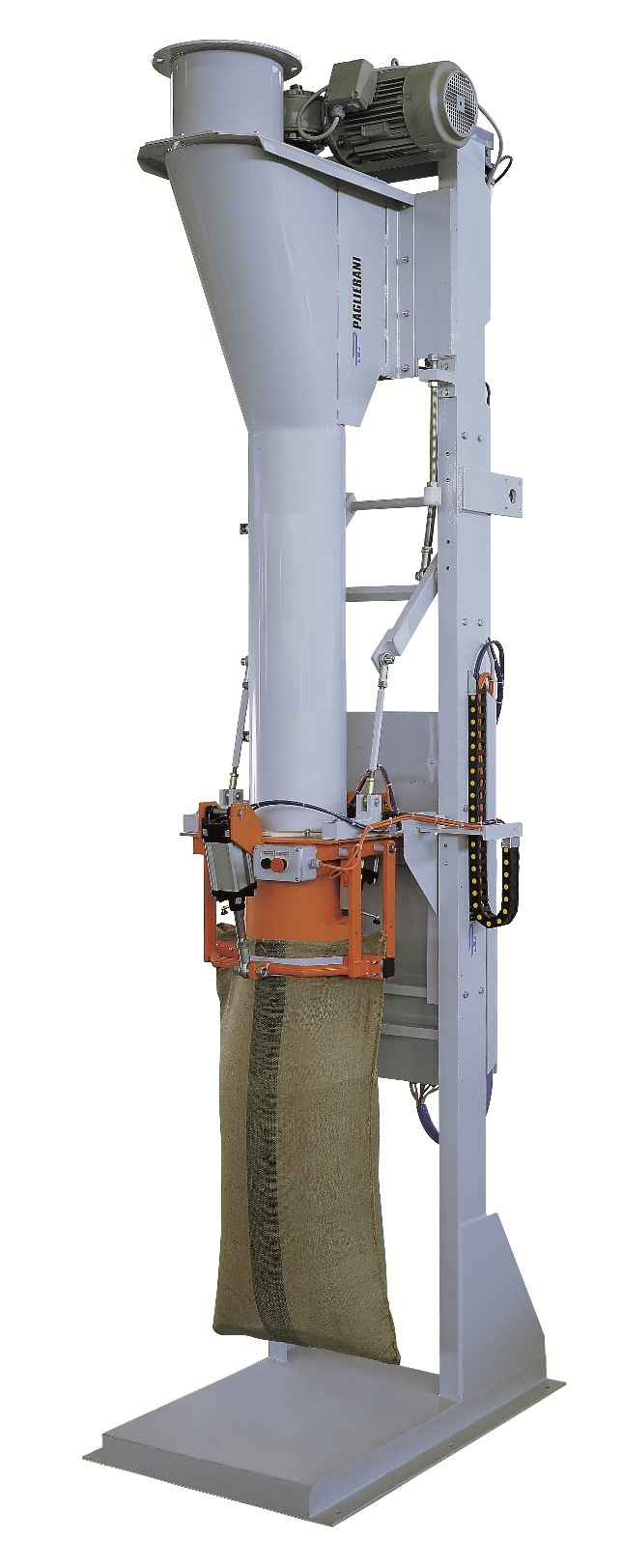
Bagger for open mouth bags
Where a stand-alone bagger is required for filling large, open mouth bags, a delivery method is n...
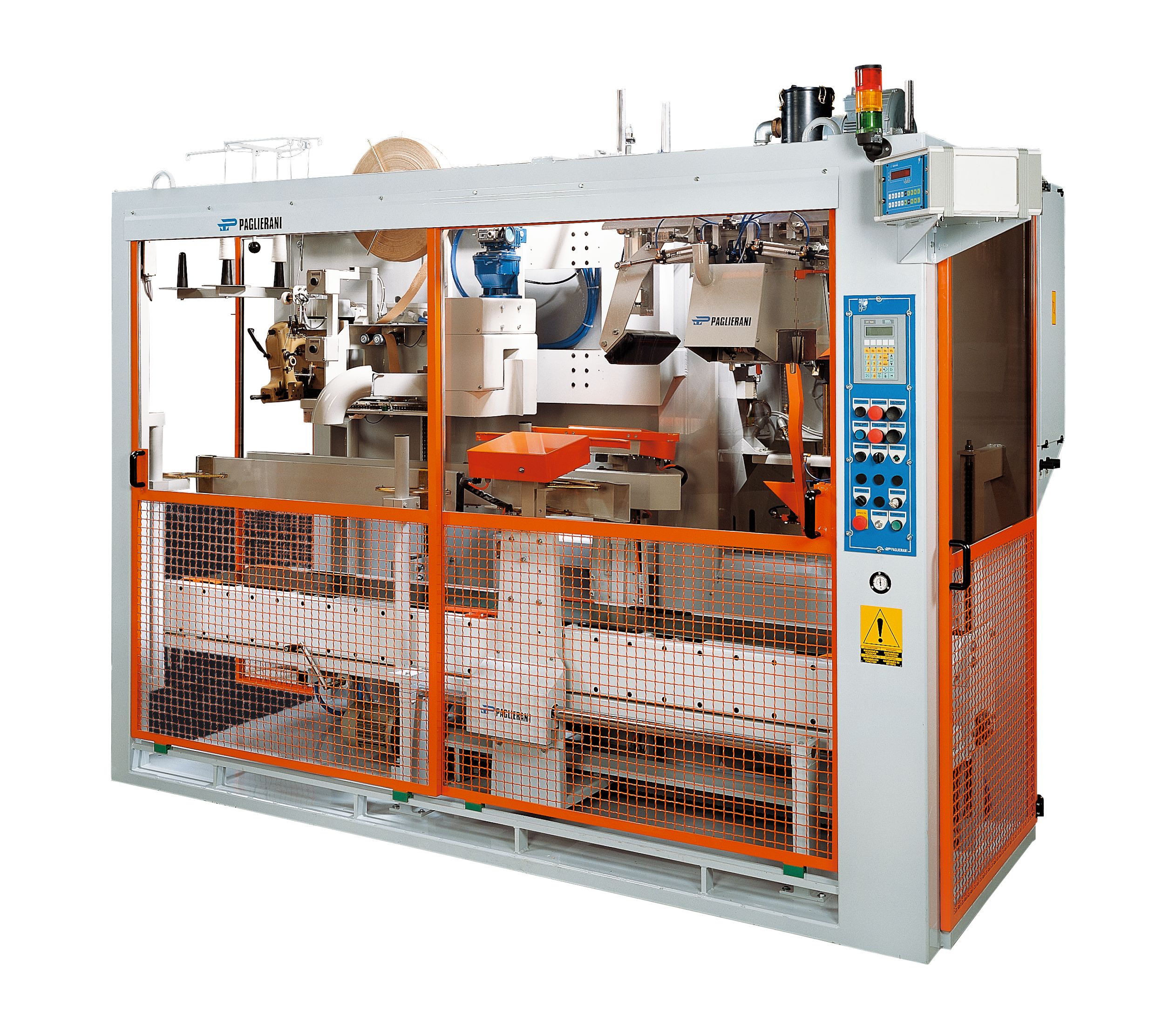
Automatic bagging machine for open mouth bags
Open mouth bags allow for a variety of different products to be packaged, wi...
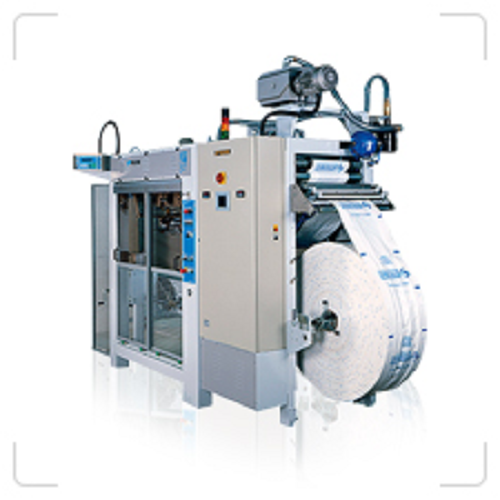
Horizontal form, fill and seal machine for bags up to 10kg
Bagging small quantities of solids or liquids, whether in pap...
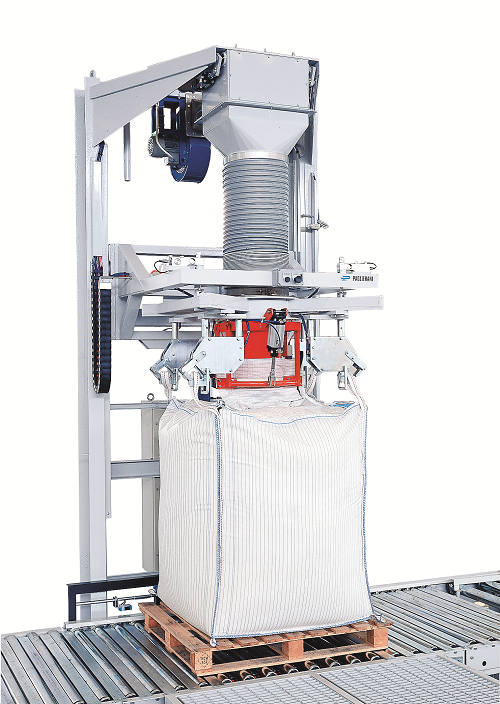
Big bag solutions
Management of big bags requires specialist handling and selection of cost-effective configurations for fill...
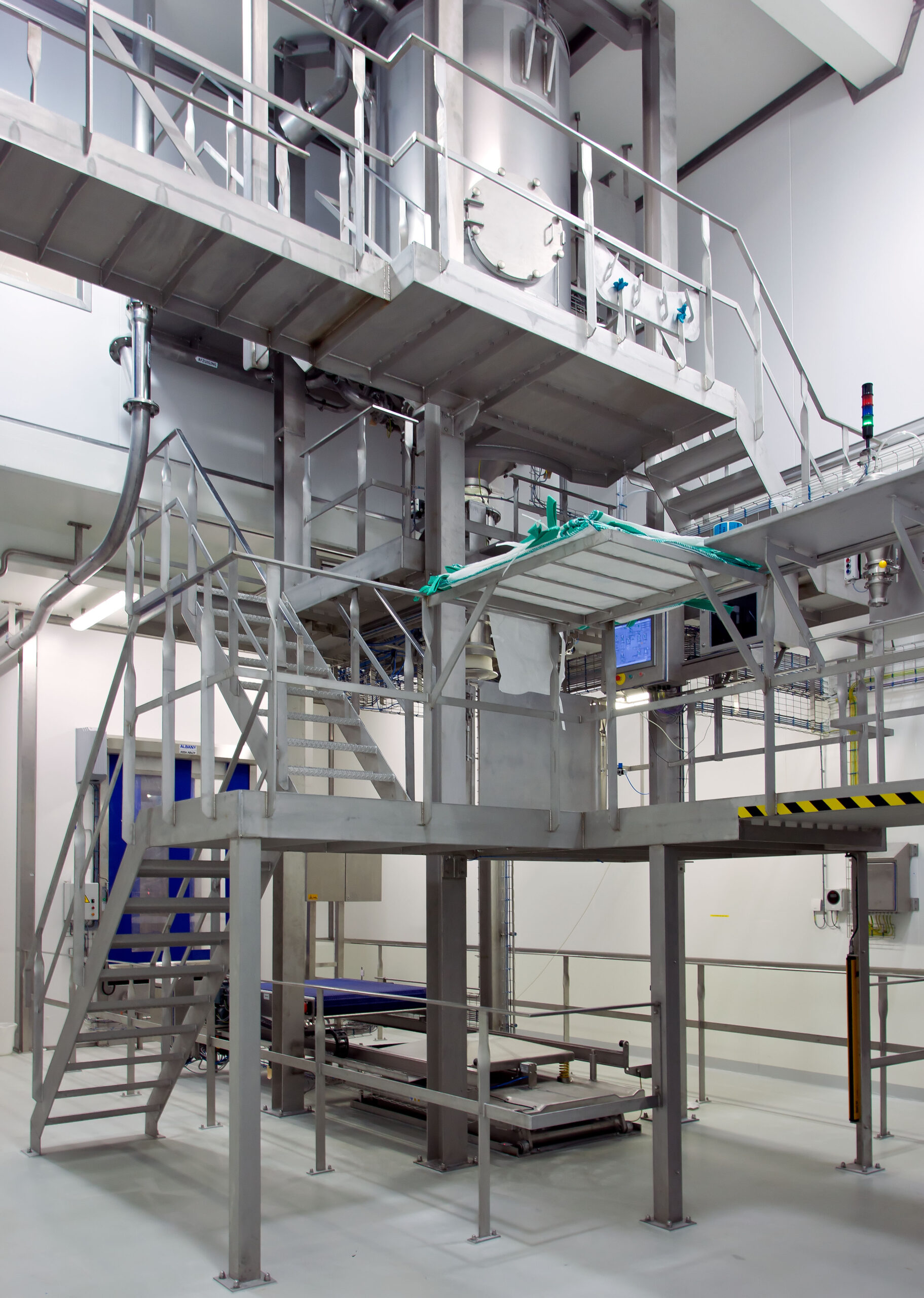
Hygienic FIBC handling line
There are many considerations when handling FIBC’s (Flexible Intermediate Bulk Containers)...
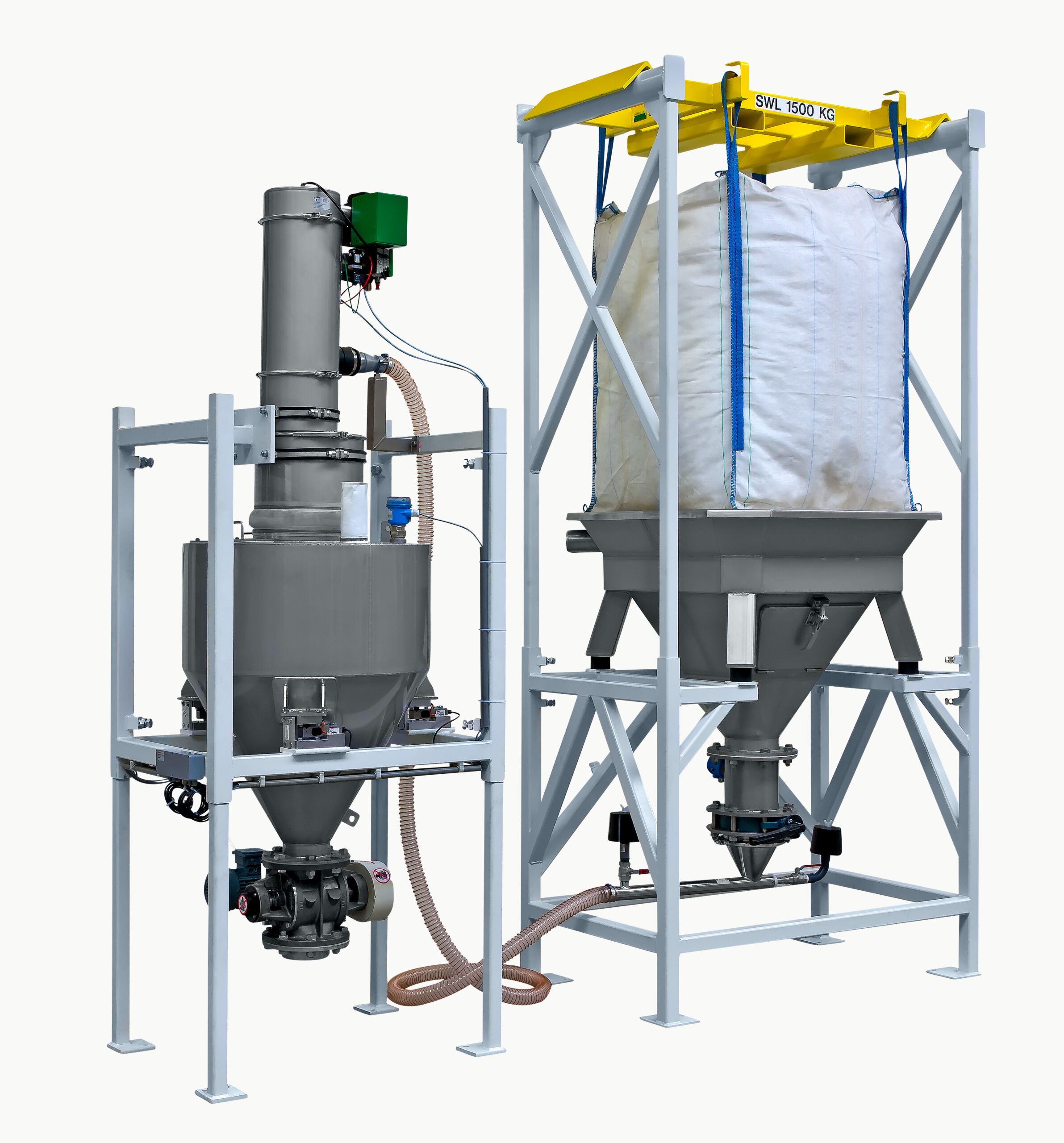
Big bag discharge system
Dust emissions, product loss and product contamination are the main risks when discharging products ...
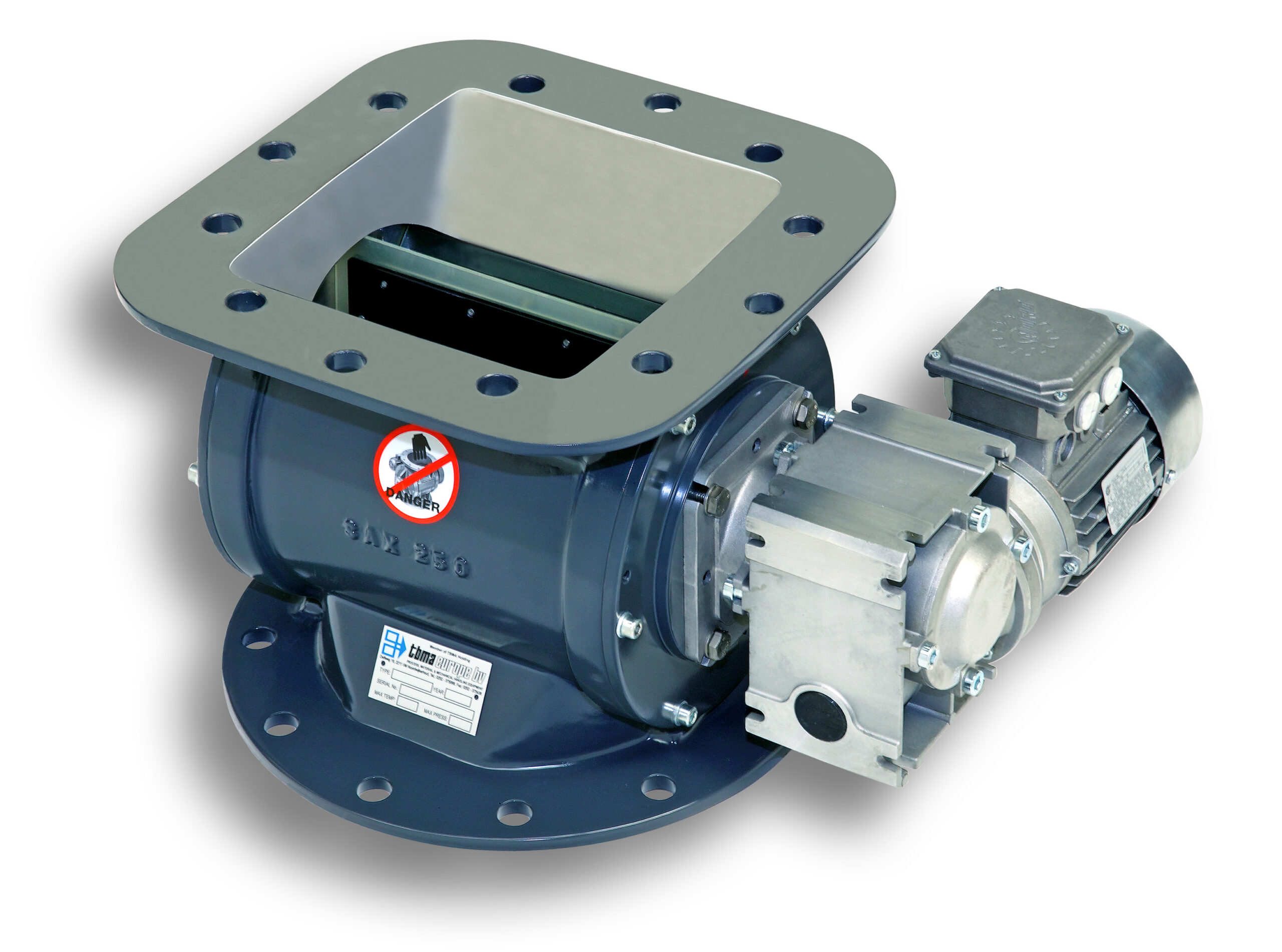
Light duty rotary dust valve
In some light industrial applications there is limited pressure differential for valve operation.
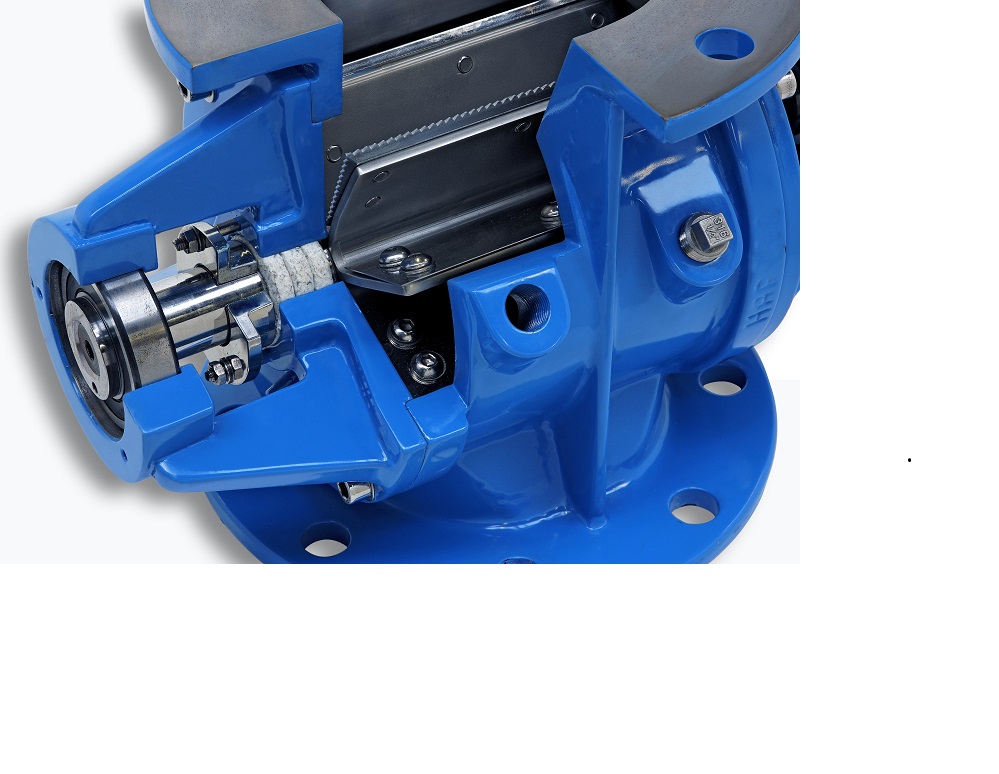
Heavy duty rotary valve
Handling powdered and granulated materials in pneumatic conveying systems requires consistent, safe v...
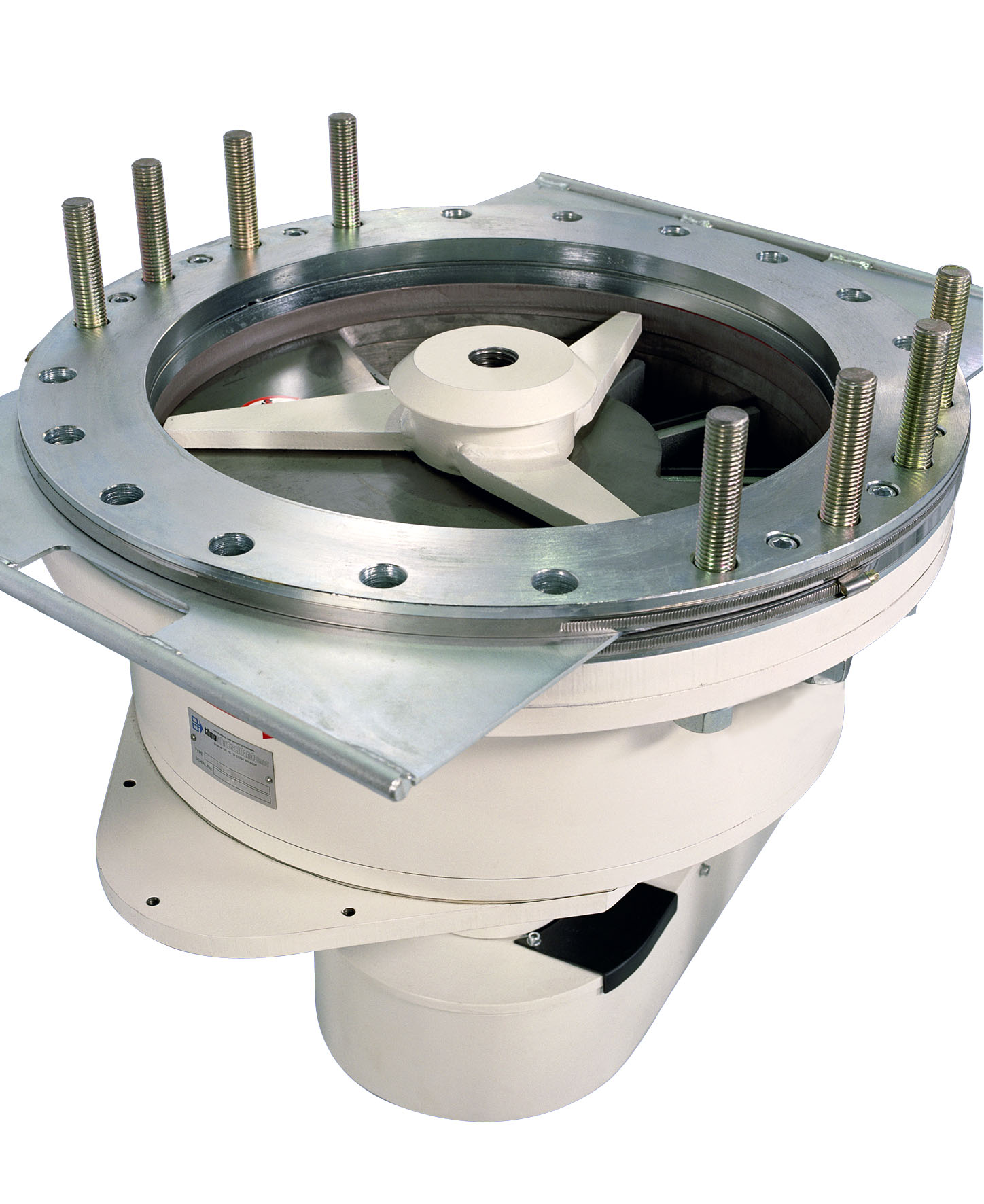
Special duty horizontal metering valve
Occasionally, there is no suitable standard valve available for a particular conveyi...
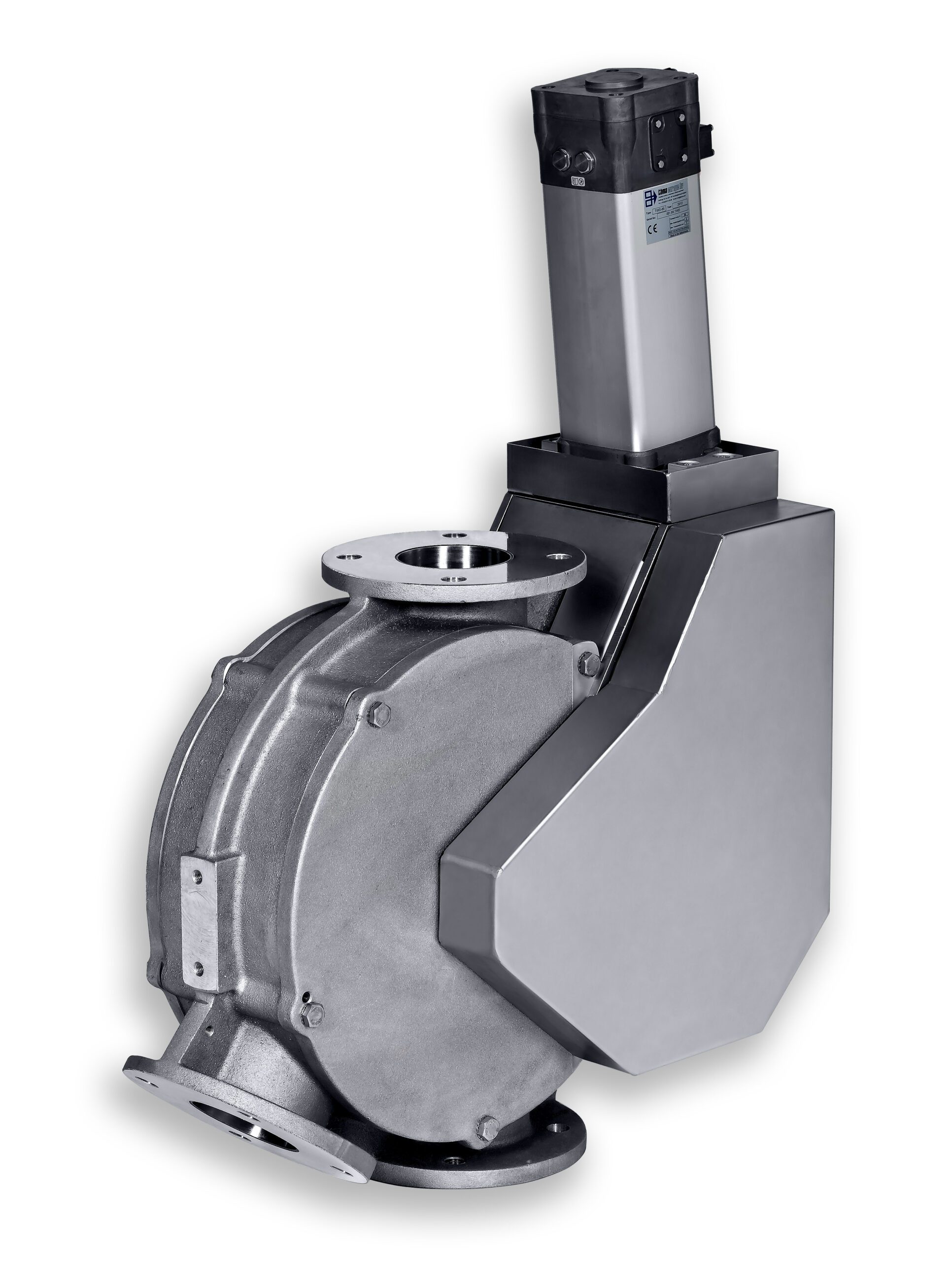
Dual channel plug diverter valve
Short switching times are often required when diverting or combining powder or granular sol...
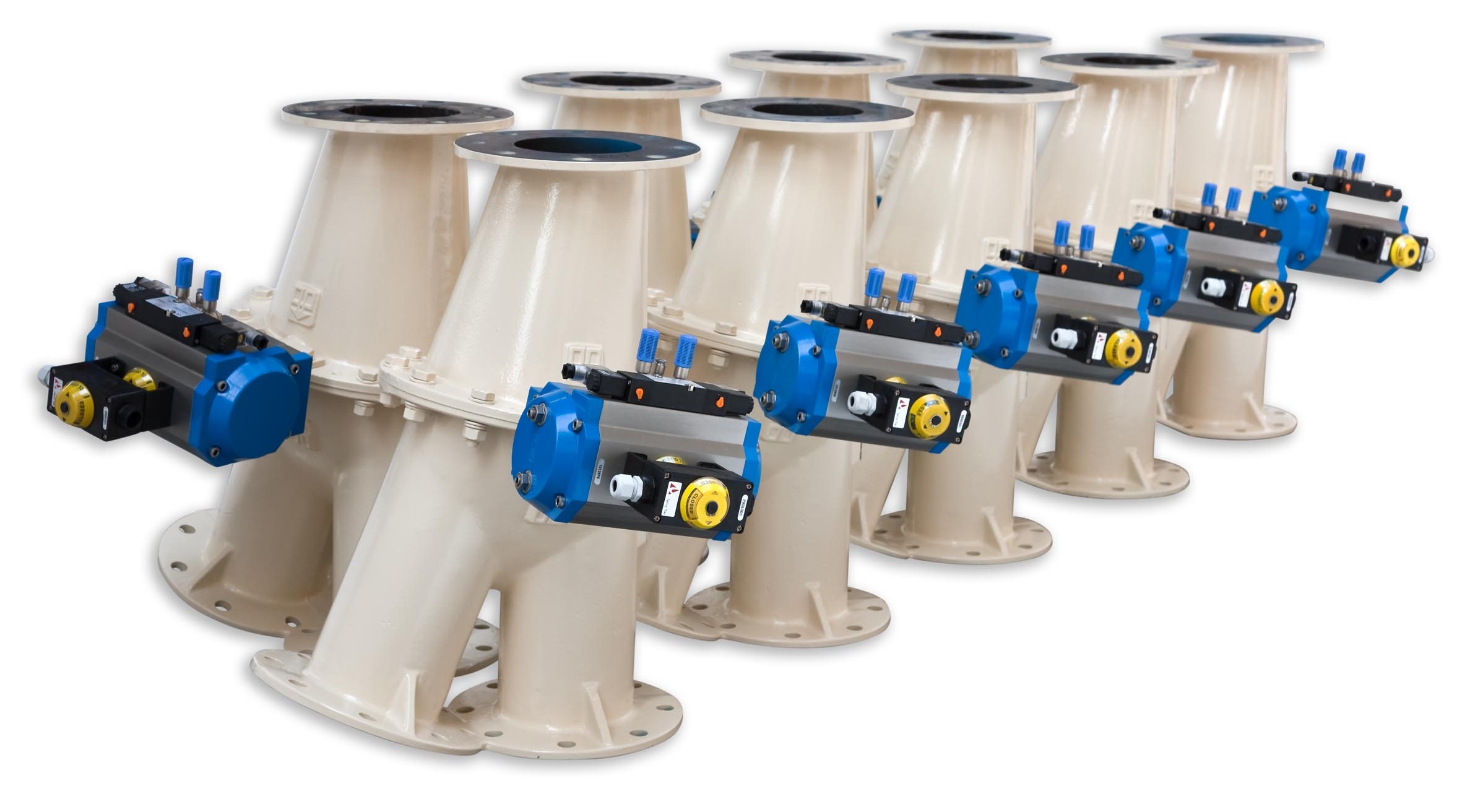
Two-way flap type diverter valve
Routing powder, pellets or granules from a product source to two receiving points must be d...
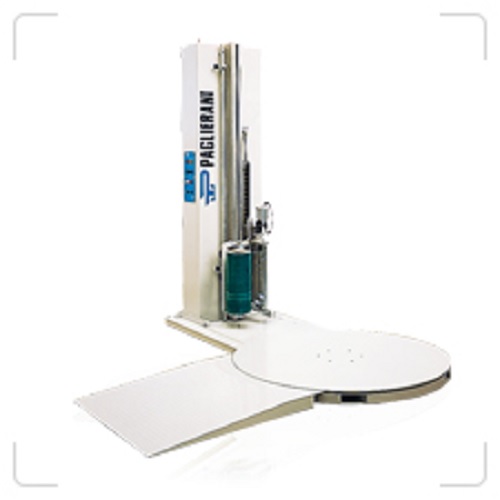
Semi-automatic stretch wrapping machine
At lower speeds, some level of automation is required to provide a cost-effective m...
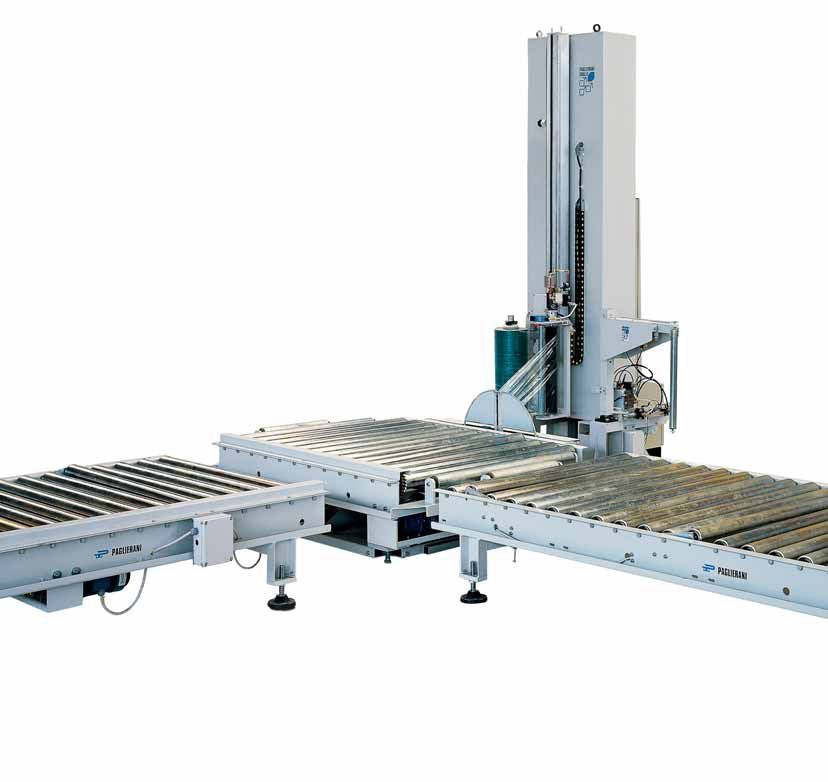
Automatic stretch wrapping machine for medium speed
For secure, automated stretch wrapping at medium speeds, the key is e...
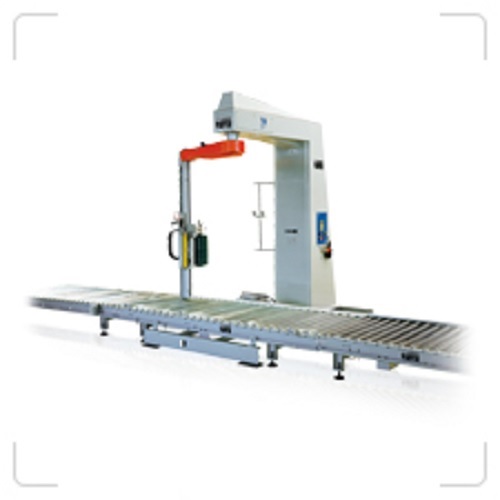
High speed stretch wrapping machine
Where high speed wrapping, without toppling, is required in tightly securing palletised...
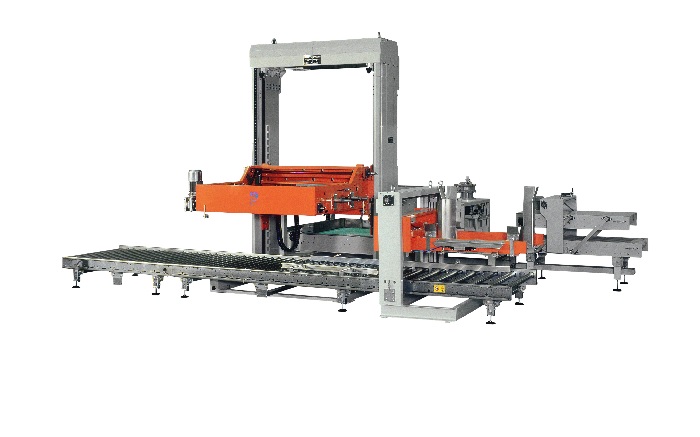
Traditional palletizer for bags
Packaging lines may require a single, flexible solution that can handle many different palle...
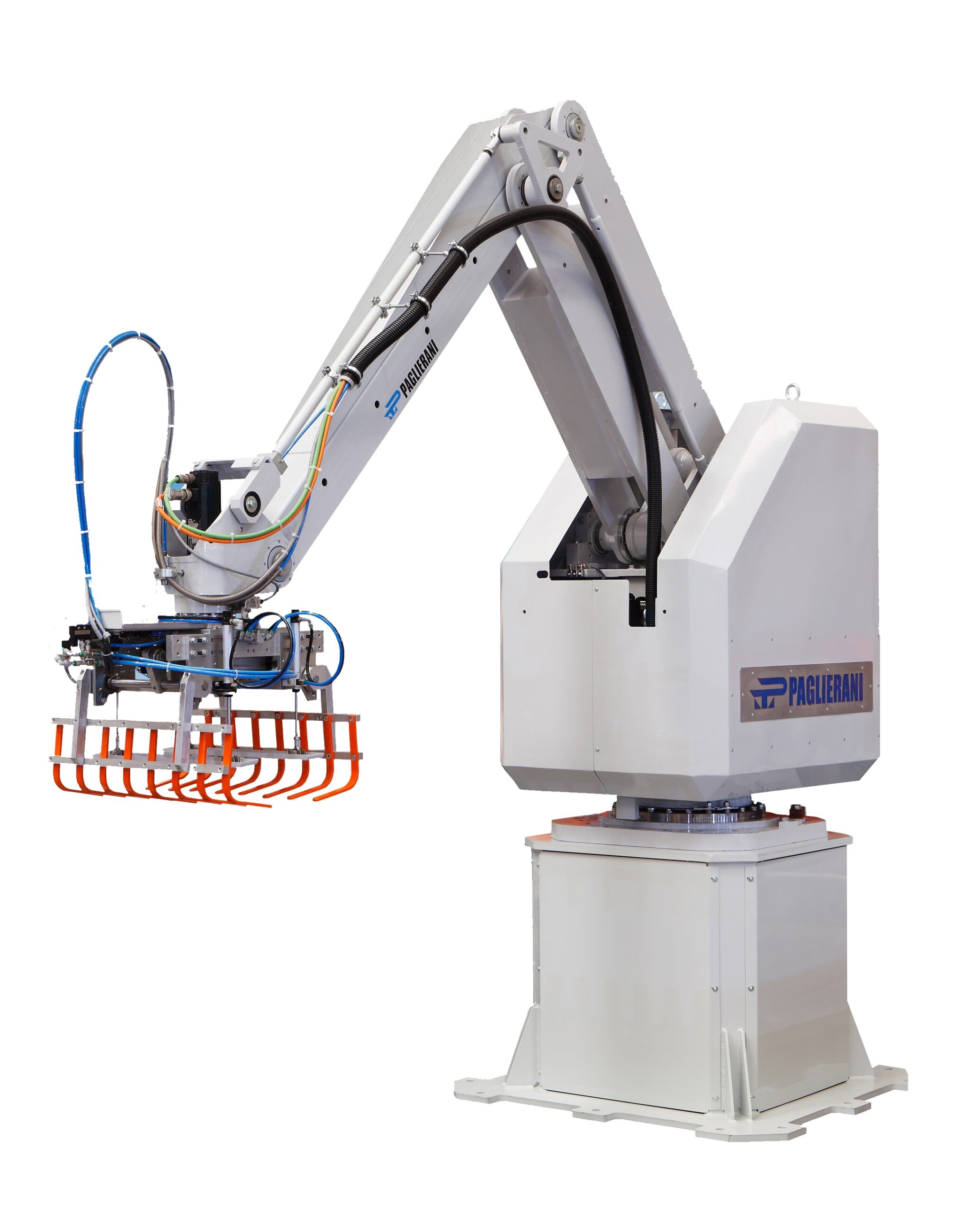
Palletizing robot arm
For high speed palletizing, palletizing high payloads, or just where greater flexibility is required, i...
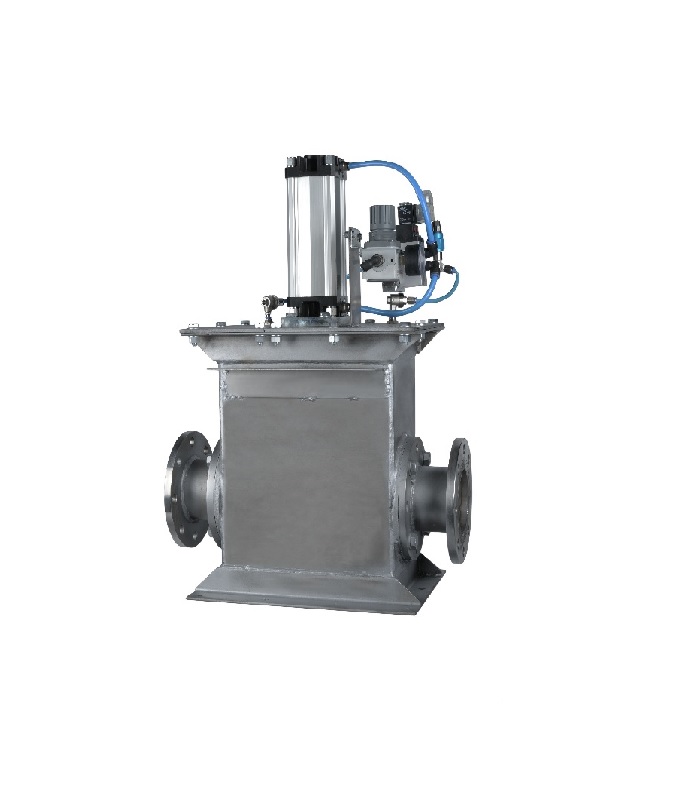
2-way diverter valves for pneumatic conveying
Products conveyed through pneumatic conveyor lines often need to be diverted...
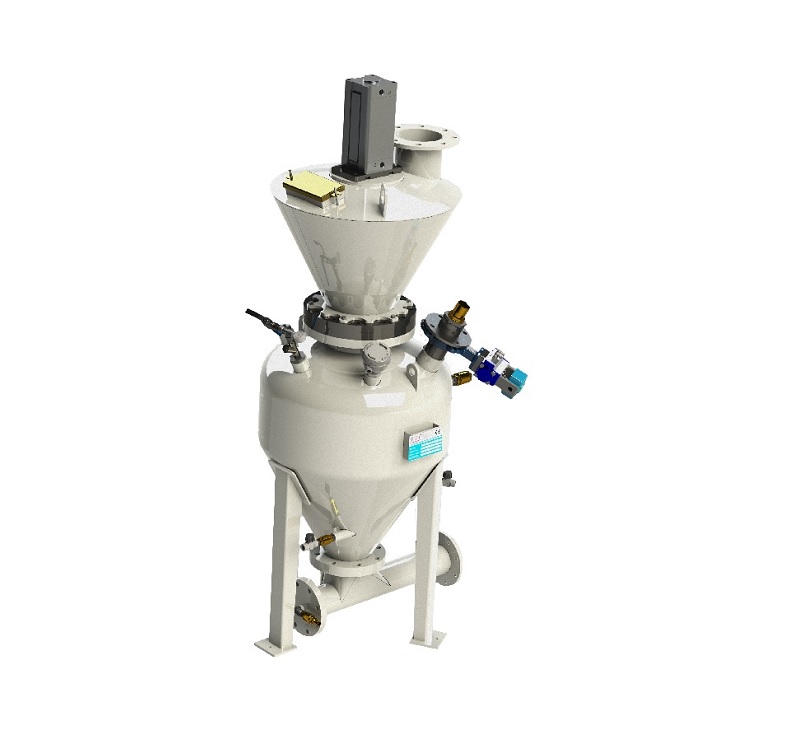
Dense phase conveyor for abrasive materials
Transporting abrasive materials using pneumatic conveyors can cause excessive ...
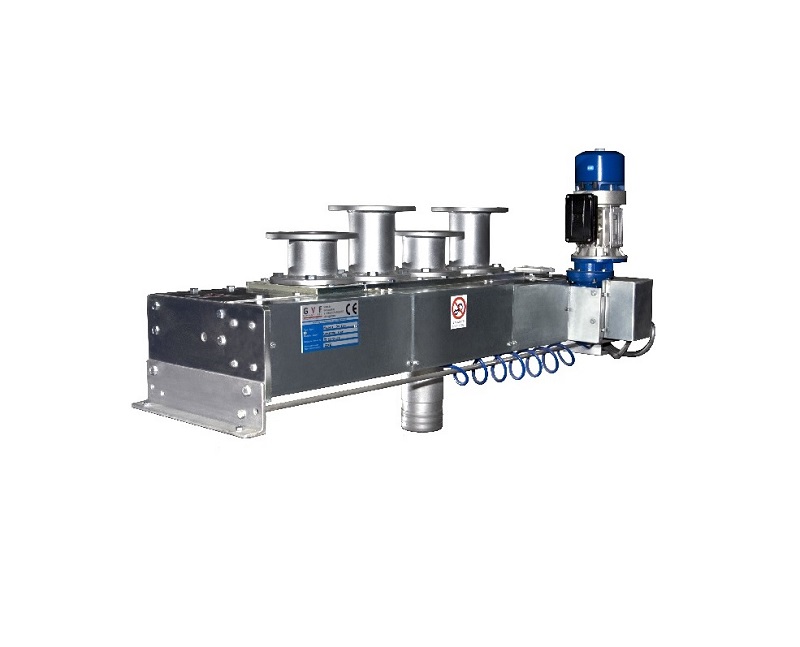
Multi-way diverter valve for pneumatic conveying
Products conveyed through pneumatic conveyor lines often need to be diver...
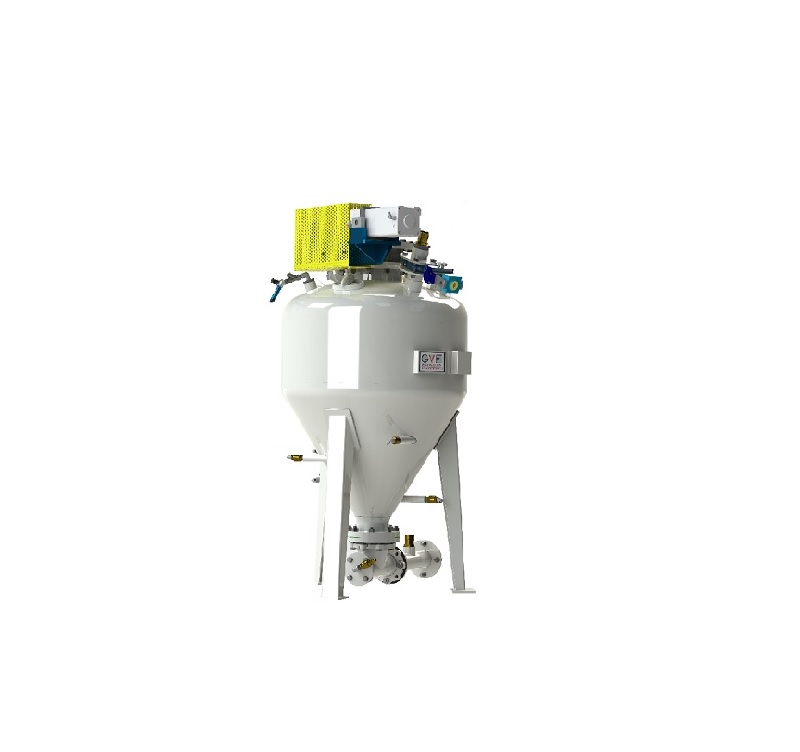
Dense phase conveyor for normal wearing materials
Dense phase pneumatic conveying is used for powders, granules, and grai...
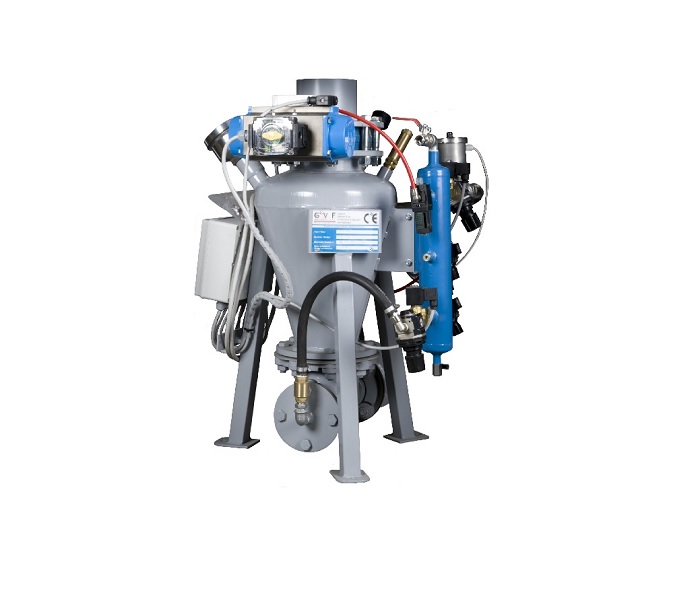
Dense phase conveyor for powders and granules
Some manufacturing and filling operations require a smaller pneumatic transp...
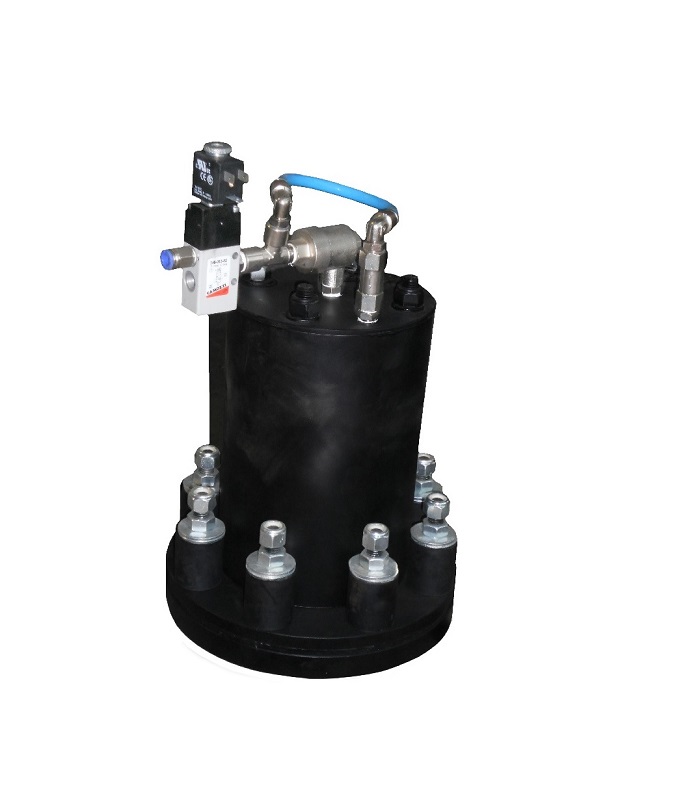
Airshocking hammer
Silos, hoppers, bins, and other containers can build up a layer of powdered product on the internal walls....
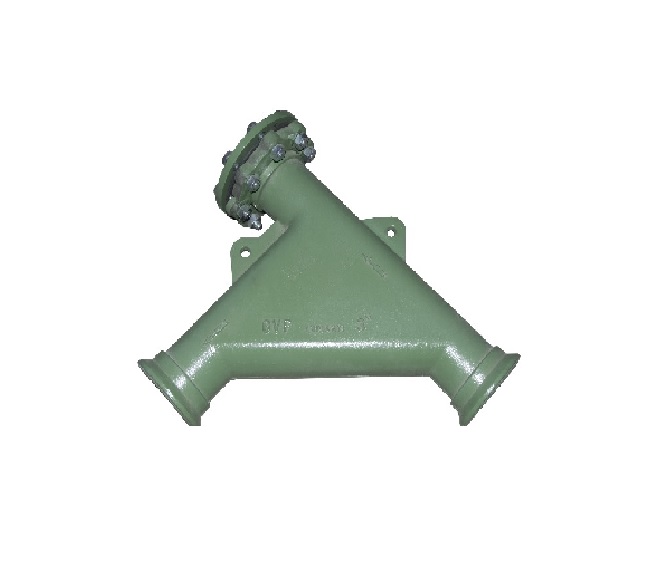
Wear resistant bends for pneumatic conveying
Bends in pneumatic conveyor lines cause load loss leading to lower flow rates...
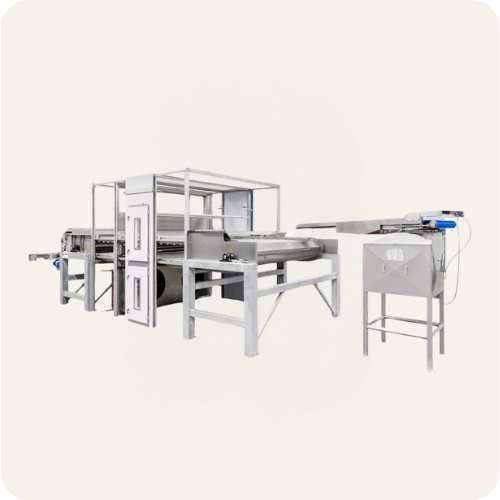
Hygienic belt dryer
A belt dryer typically applies the product through an infeed chamber onto a perforated horizontal belt, w...
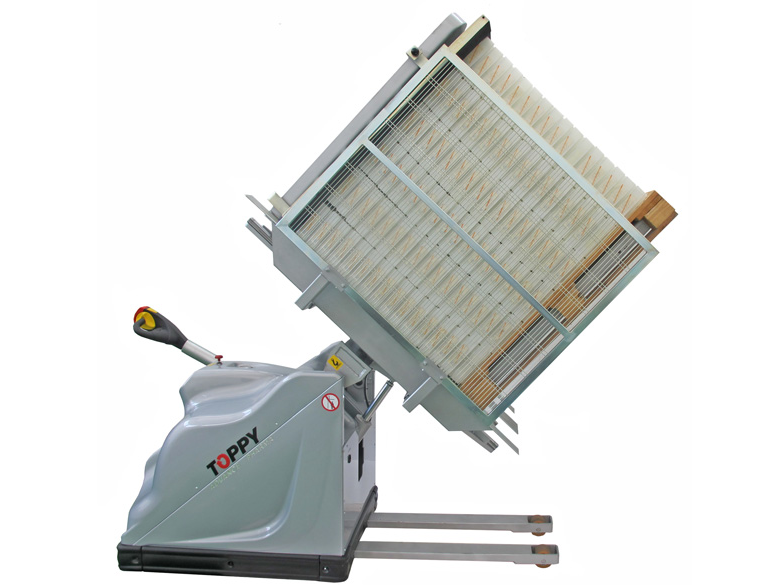
Mobile pallet turner
Turning your pallet may allow for more effective pallet changing than the conventional lifting and grabb...
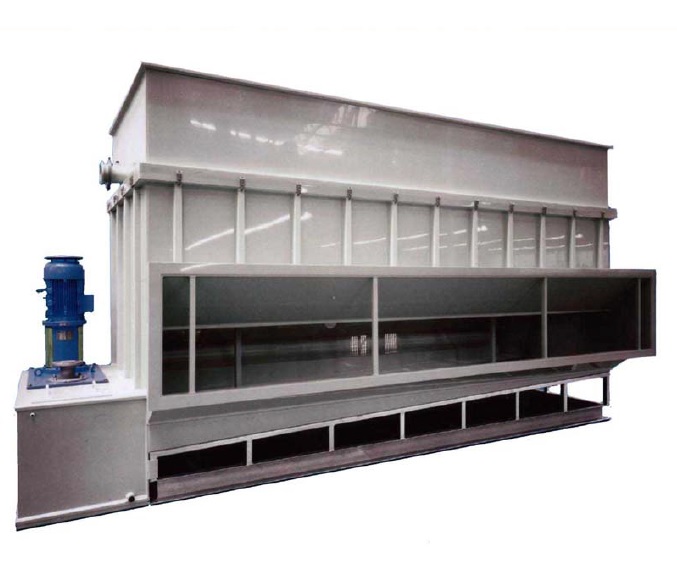
Air dehumidifier for bulk products
When your product or process is sensitive to humidity, using an air dehumidifier may res...
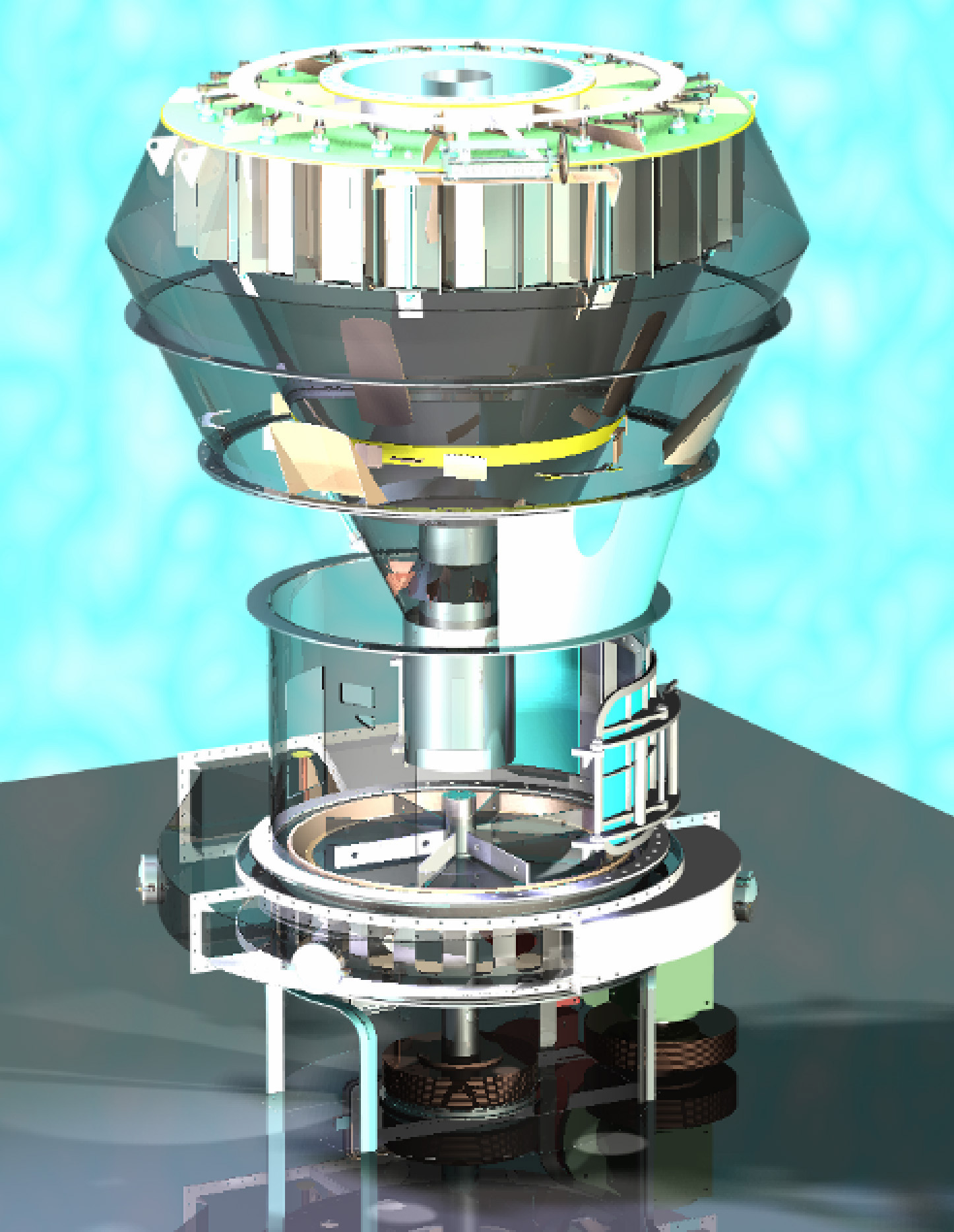
Horizontal impact calciner
Quality of synthetic gypsum and stucco products is highly influenced by the quality of the calcin...
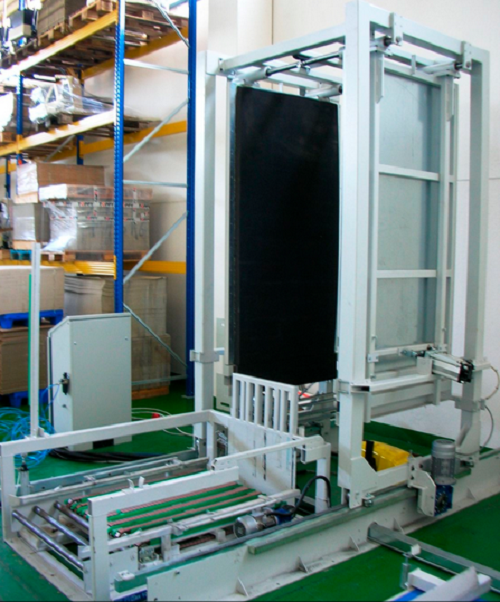
Non-tilting pallet changer
Stable vertical lifting of the load from the pallet to enable EPAL or industrial pallet exchange.
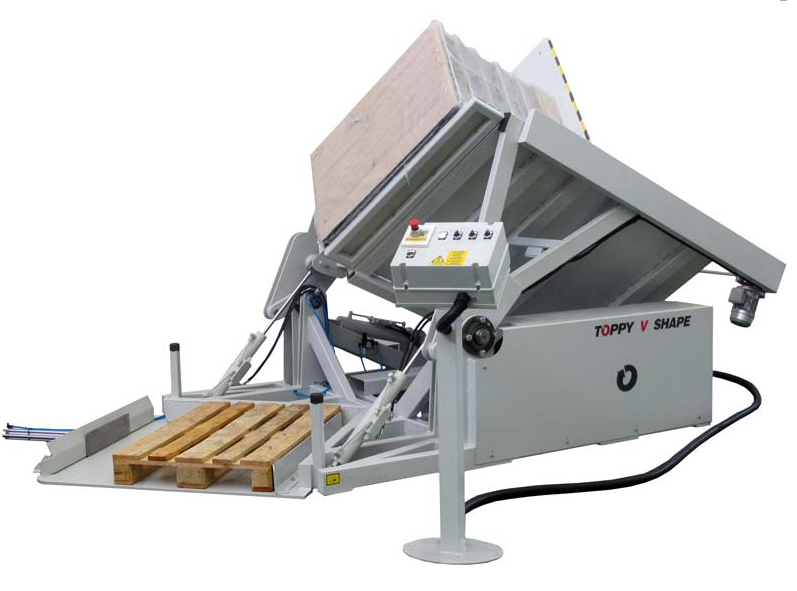
V-shaped pallet changer
If you are looking for a sturdy pallet changing solution, a stationary V-shaped pallet changer can be...
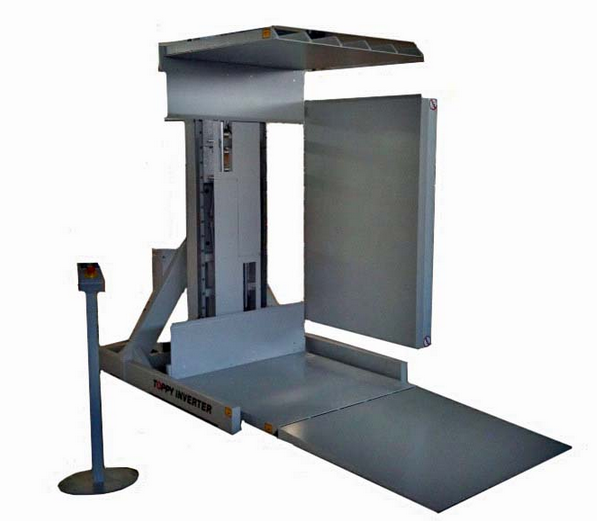
Pallet changer floor level
For transferring goods from wooden pallets to plastic pallets, or vice-versa, this Pallet changer...
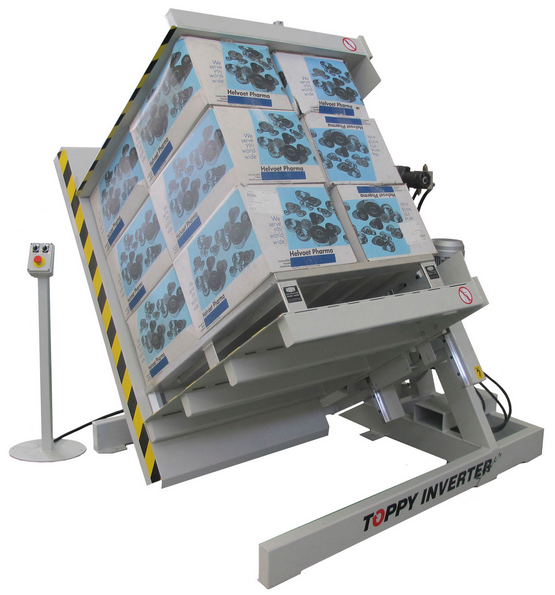
Pallet changer
For turning loads and exchanging them on pallets, here is a stationary pallet changer that will load and unload...
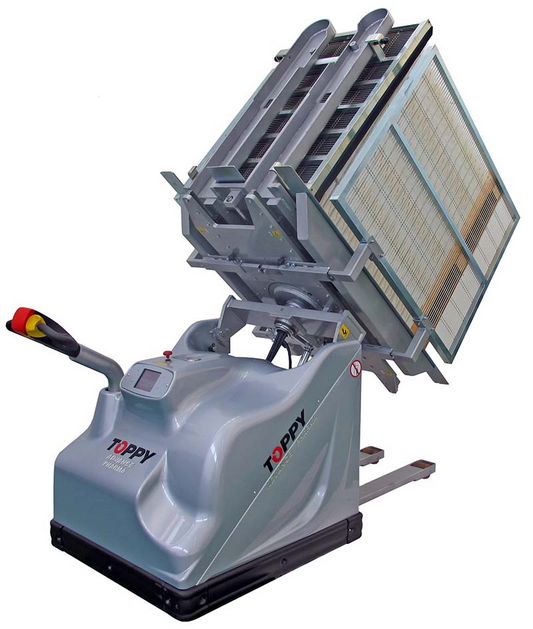
Mobile pallet changer without turning
If you are looking to change the pallet without turning the load, through a lateral p...
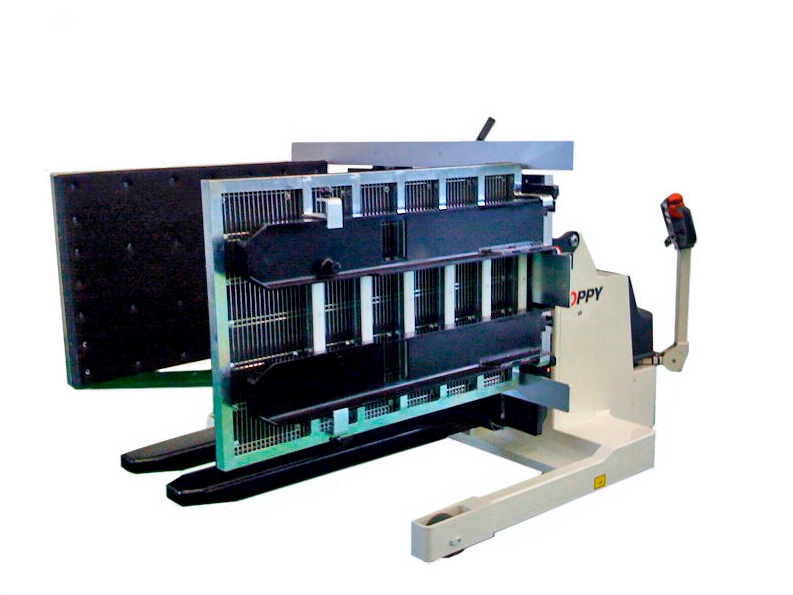
Versatile mobile pallet turner
Here is the versatile mobile pallet turner that completes the typical features of all mobile ...
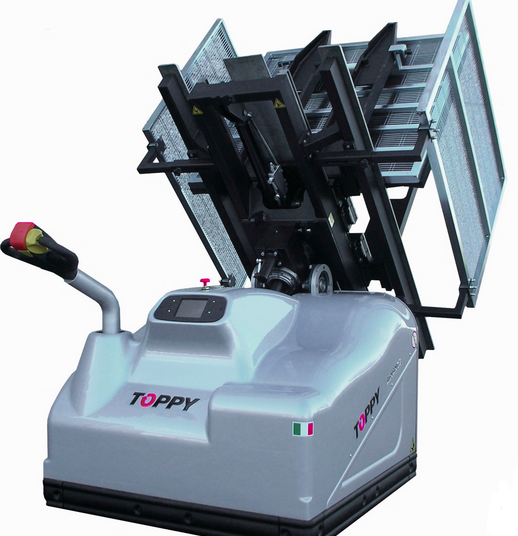
Mobile pallet turner for higher stacks
When you need to opt a pallet changer that is capable of lifting and turning loads a...

Circuit-air classifier
For high throughputs, with a fineness range of approx. d97 = 32 µm – 200 µm. Ideal for use in th...

Vertical agitated dry media mill
A vertical agitated media mill is used for grinding ultrafine particles, in an agitated (or...
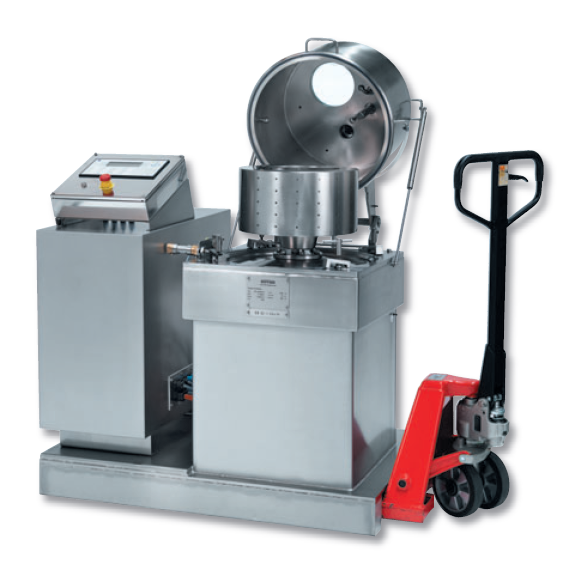
Mobile pilot plant centrifuge
The system is perfectly suited for pilot plants as well as small-quantity productions in the f...
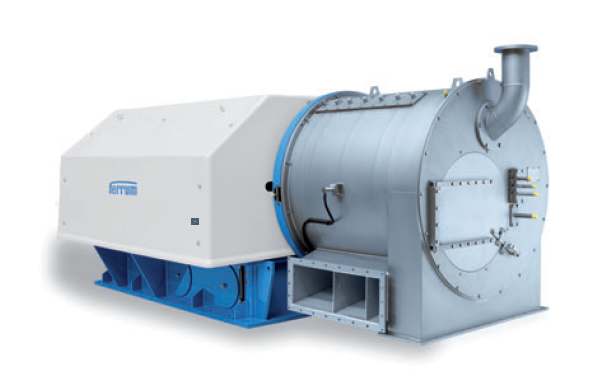
Pusher centrifuge
Pusher centrifuges are continuously operating filter centrifuges and can have several basket stages dependi...
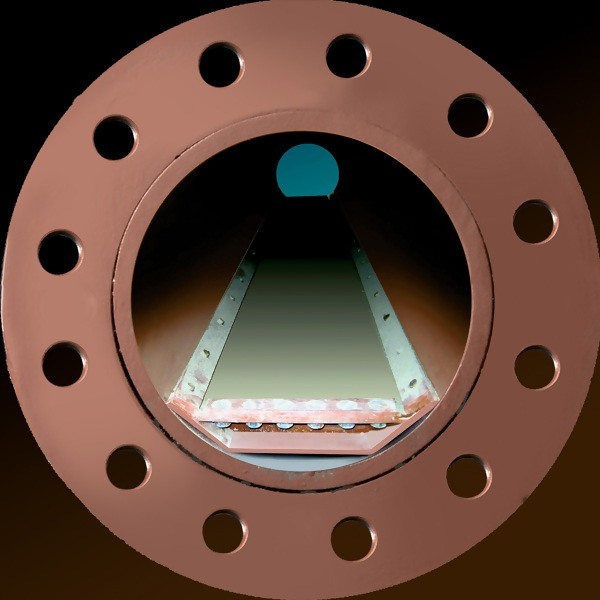
Long distance pneumatic conveyor
Pneumatic conveying of dry bulk materials is a desirable option for many industries because...
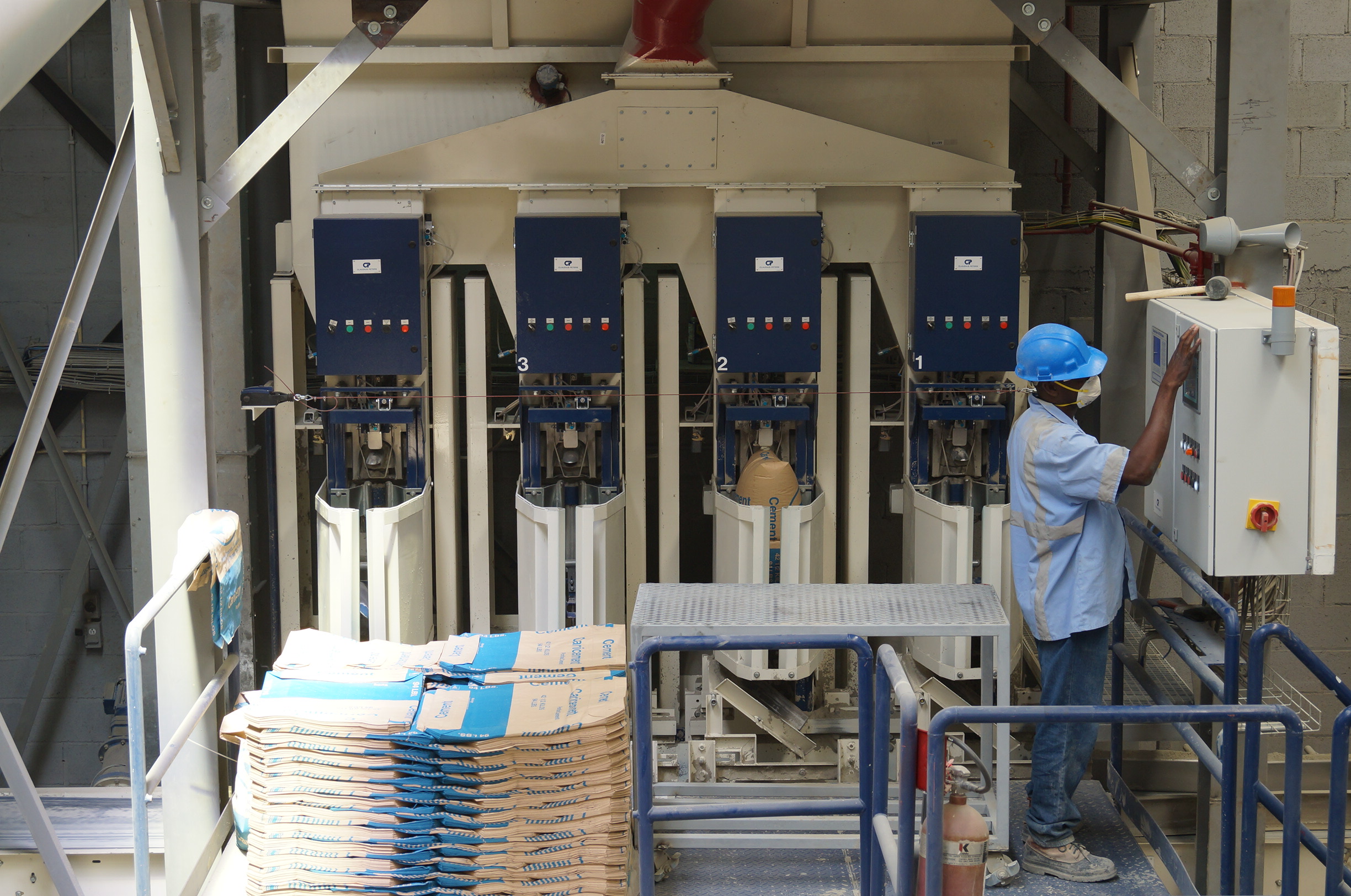
In-line cement packer
The cement industry requires efficient and reliable packaging solutions for the transportation and dist...
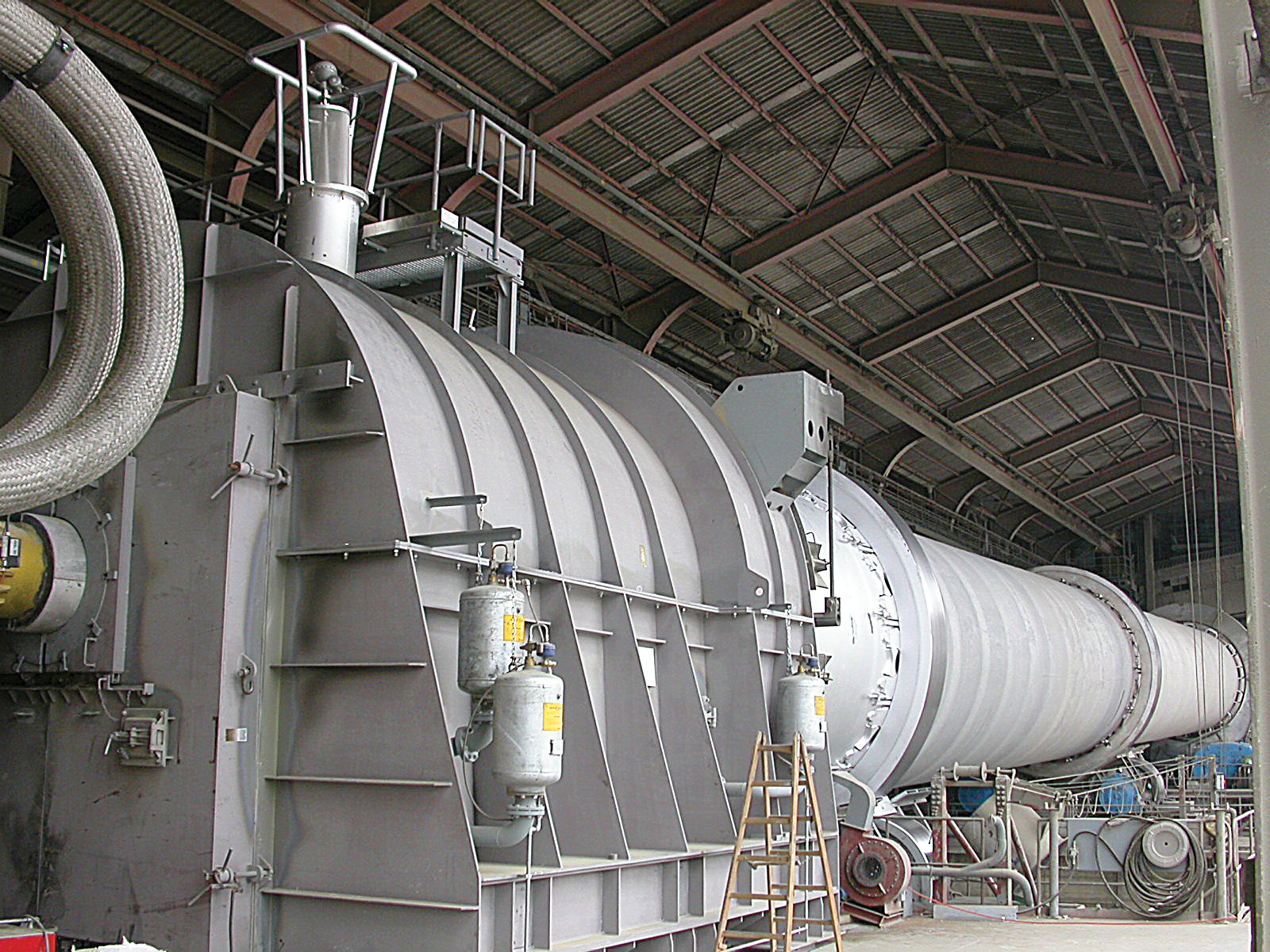
Clinker cooler
Competitive clinker production and cooling is essential to cement producers over the world. Now there is a next...
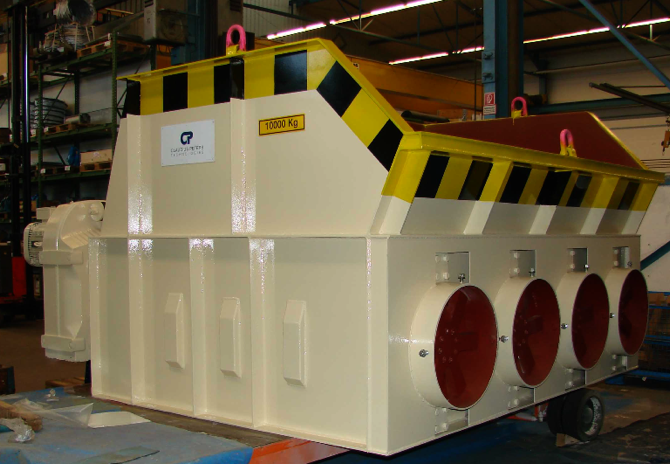
Reclaim crusher
Waste products and rejected materials are inevitably generated from any gypsum products manufacturing process....
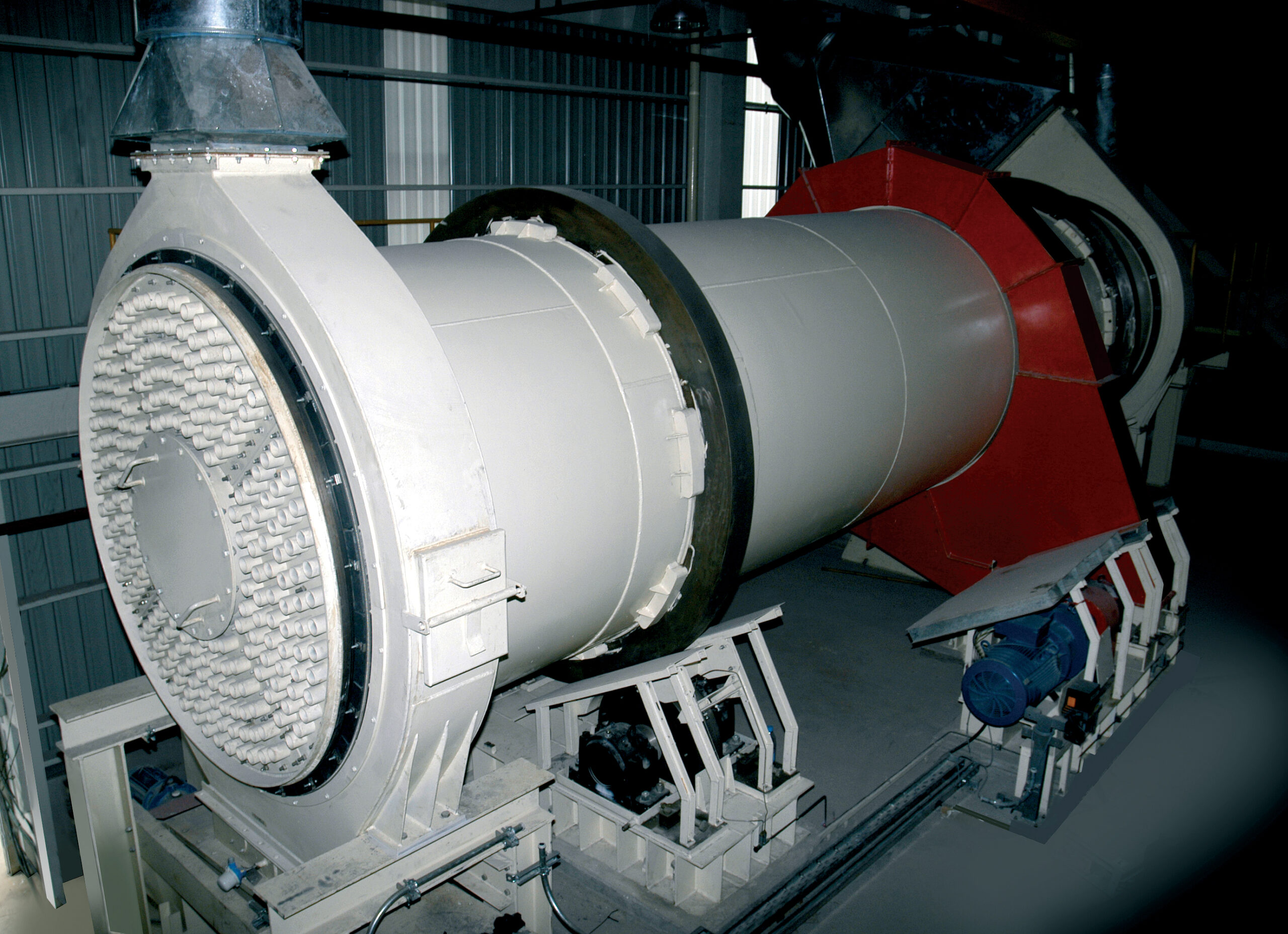
Rotary drum cooler for calcined gypsum products
After the calcining process gypsum products must be cooled from temperatur...
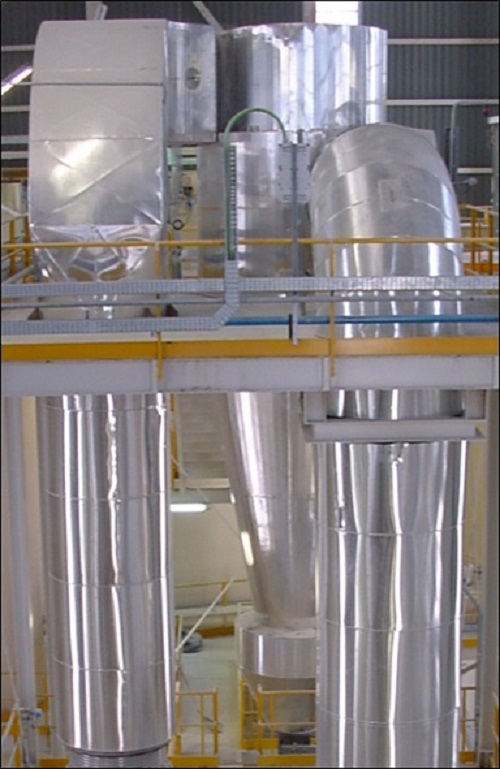
Flash calciner
Quality of gypsum plaster products is highly influenced by the quality of the calcining process employed in pro...
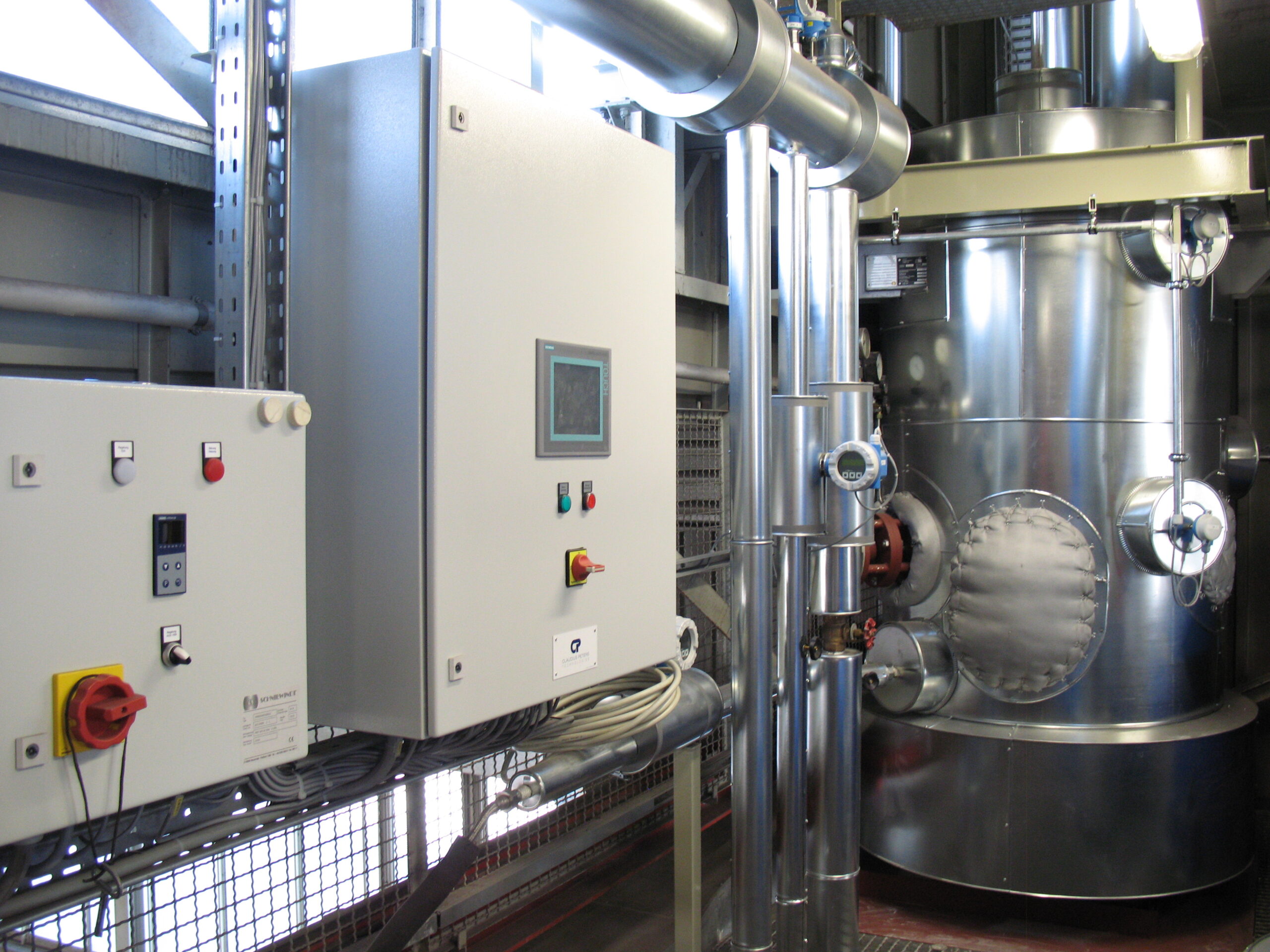
Gypsum homogenizer
The quality of gypsum and stucco products is highly influenced by the quality of the calcining process uti...
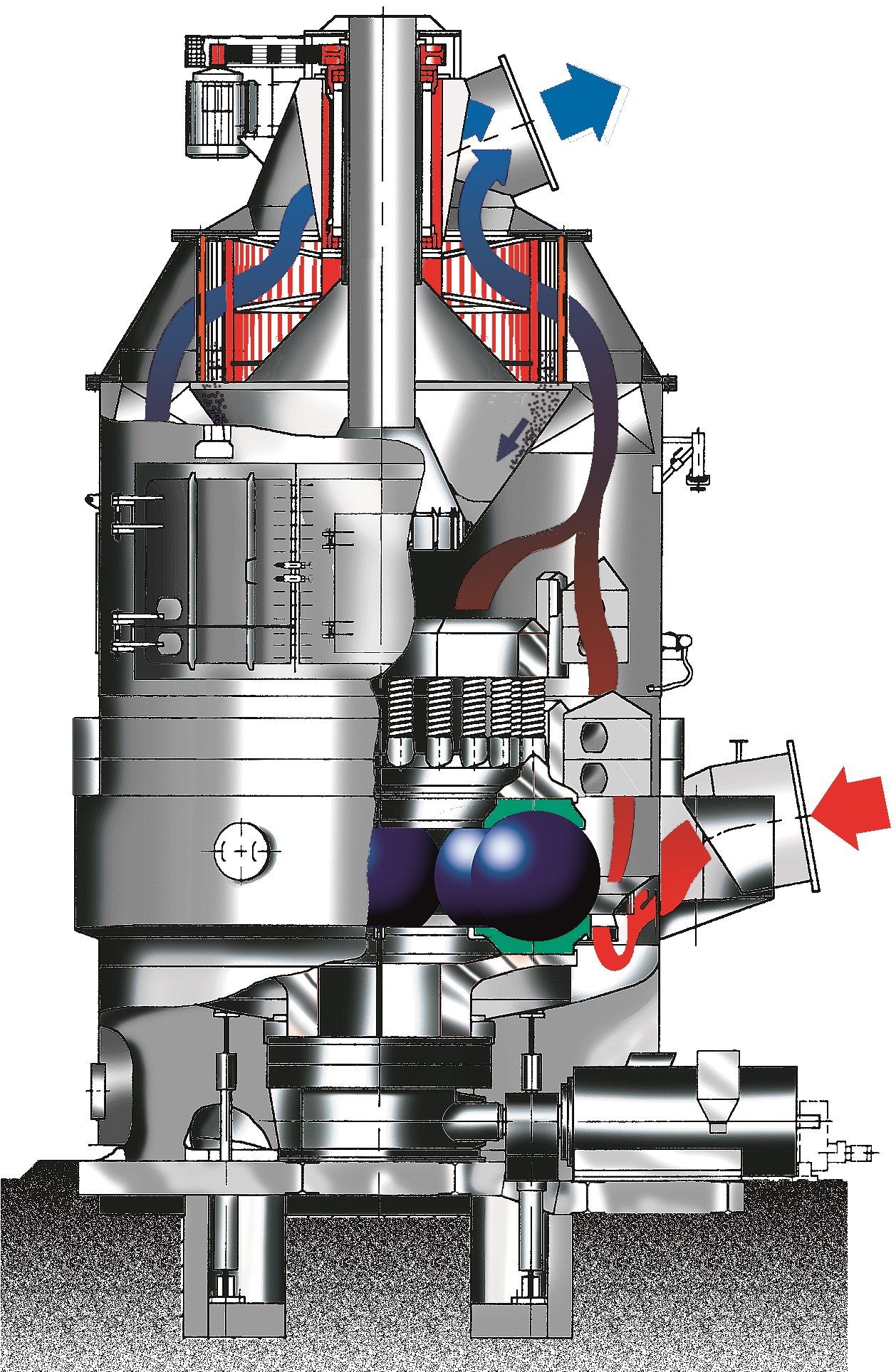
Mill for calcining gypsum
Quality of gypsum and stucco products are highly influenced by the quality of the calcining proces...
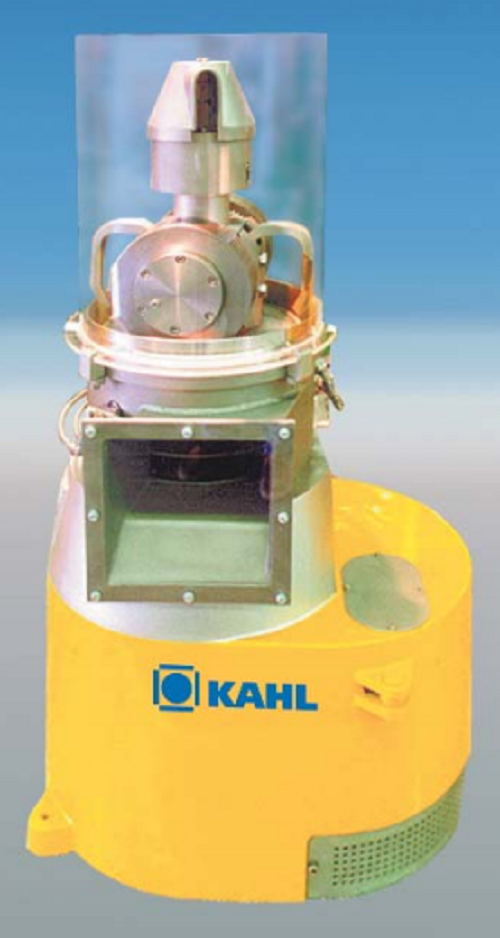
Small scale pelleting press
Many industries require reliable pelletizing equipment with smaller scale production capacities....