Vacuum chamber furnace with metal insulation
Achieve high-temperature processing with precision and purity using advanced vacuum technology, ideal for enhancing sintering, debinding, and thermal processing of metal and ceramic components.
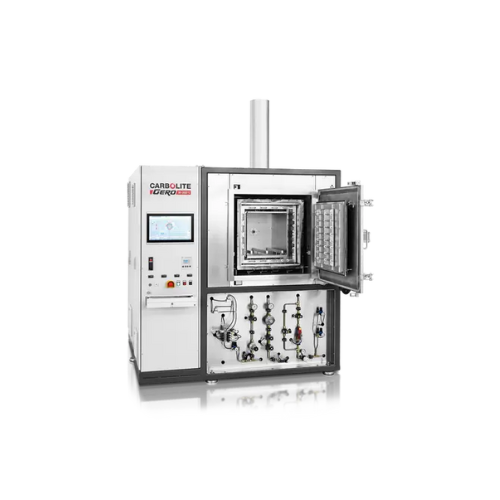
Controls High-Temperature Sintering and Debinding Processes
The HTK series from Carbolite Gero offers vacuum chamber furnaces with metal insulation, specifically designed for high-temperature applications up to 2200°C. This range is distinguished by its use of tungsten or molybdenum, ensuring a pure atmosphere and precise control over debinding and sintering processes. These furnaces are essential for producing high-performance ceramic components, metalized electrical contacts, and tungsten carbide cutting tools. Available in sizes ranging from 8 to 120 liters, they support both laboratory research and pilot manufacturing. The furnaces are PLC-controlled for seamless integration into automated production lines and offer high vacuum capabilities, ideal for aerospace, automotive, and electronics industries. They also feature energy-efficient thermal insulation and a choice of atmospheric gases, enhancing operational versatility and efficiency.
Benefits
- Achieves exceptional material purity by using tungsten or molybdenum insulation, ideal for sensitive manufacturing processes.
- Maximizes production flexibility with customizable sizes and modular automation controls.
- Enhances energy efficiency with multi-layer radiation shields, reducing operational costs.
- Supports advanced thermal processes with adjustable high vacuum and partial pressure capabilities.
- Improves safety and product quality using hydrogen-compatible design in demanding applications.
- Applications
- Metal injection moulding, Synthesis, Pyrolysis, Tempering, Annealing, Sintering, Thermal debinding, Metallization
- End products
- High-performance ceramic components, Advanced ceramics, Silicon carbide fibers, Metalized electrical contacts, Functionalized carbon materials, Heat-treated stainless steel components, Tungsten carbide cutting tools, Metal alloys, Electronic component coatings, Metal powder parts
- Steps before
- Preparation of components, Loading materials, Pre-heating, Gas selection and setup
- Steps after
- Unloading, Cooling, Inspection, Quality control, Packaging
- Input ingredients
- Molybdenum, Tungsten, Argon, Nitrogen, Hydrogen, Forming gas, Carbon free atmosphere, Metal injection moulding components, Pyrolysis materials, Debinding materials
- Output ingredients
- Sintered parts, Annealed materials, Tempered components, Consistent MIM part density, Debound materials
- Market info
- Carbolite Gero is renowned for designing and manufacturing high-temperature laboratory and industrial furnaces and ovens, offering expertise in heat treatment solutions, with a reputation for quality, reliability, and precise thermal processing across various industries.
- Maximum Temperature
- 1600 °C / 2200 °C
- Usable Volume
- 8 L / 25 L / 80 L / 120 L
- Number of Heated Zones
- 1 / 4
- Material Heating Elements
- Tungsten / Molybdenum
- Gas Types
- Nitrogen, Argon, Hydrogen, Mixtures
- Vacuum Level
- High Vacuum Upgrade Available
- Cooling System
- Water-Cooled
- Control Panel
- 12” / 19” Touch Panel
- Automation Level
- Manual / Full Automation
- Pressure Control
- 10–1000 mbar
- Debinding Option
- Torch / Condensate Trap
- Heating Cassette Material
- Tungsten / Molybdenum
- Operating Temperature Range
- 1600 °C / 2200 °C
- Automation Level
- Manual / Automatic
- Batch vs. Continuous Operation
- Batch
- Cleaning Method
- Manual / CIP
- Vacuum Level
- High Vacuum
- Gas Flow Control
- Yes
- Debinding Options
- Torch / Condensate Trap
- Abrasion resistance
- High
- Corrosive resistance (e.g. acids)
- High
- Cleanability
- High
- Density/particle size
- 0.5–2.5 g/cm³ / 50–1000 µm
- Heating element material
- Tungsten / Molybdenum
- Applicable gases
- Nitrogen, Argon, Hydrogen
- ISO Certifications
- ISO 9001
- Usable Volume
- 8 L, 25 L, 80 L, 120 L
- Dimensions (H x W x D) for HTK 8
- 160 x 180 x 180 mm
- Dimensions (H x W x D) for HTK 25
- 240 x 240 x 400 mm
- Dimensions (H x W x D) for HTK 80
- 380 x 410 x 500 mm
- Dimensions (H x W x D) for HTK 120
- 380 x 400 x 770 mm
- Number of Plates for HTK 8
- 3
- Number of Plates for HTK 25
- 3
- Number of Plates for HTK 80
- 4
- Number of Plates for HTK 120
- 6
- Plate Dimensions HTK 8
- 225 cm²
- Plate Dimensions HTK 25
- 860 cm²
- Plate Dimensions HTK 80
- 930 cm²
- Plate Dimensions HTK 120
- 930 cm²
- Max Temperature HTK W
- 2200 °C
- Max Temperature HTK MO
- 1600 °C
- Material of Construction
- Molybdenum or Tungsten
- Construction Type
- Vacuum Vessel
- Discharge Method
- Front Door
- Control panel type
- 12" or 19" touch panel
- Automation level
- Manual / PLC / SCADA
- Hydrogen partial pressure operation
- Optional available
- Heating elements
- Tungsten (HTK W) or Molybdenum (HTK MO)
- High vacuum upgrade
- Available upon request
- Number of programs
- 12 / 20
- Configuration program
- Simple / More complicated, hydrogen processes
- Remote access
- Yes / With Siemens software
- Remote maintenance
- No / Optional
- Online changes
- No / Yes
- MFC and Rotameter
- Yes / No
- Heated gas outlet
- Yes
- Sliding TC
- Yes
- Turbopump
- Yes