Flash drying grinder for powders
Drying and grinding can be an important feature when trying to process products such as raw and refined minerals, organic and inorganic chemicals, food ingredients and waste streams. It is crucial to maintain particle size and consistent quality of the finished product during such processes. You will need an efficient and abrasion resistant attrition solution to pulverise and dry your product into your required particle size.
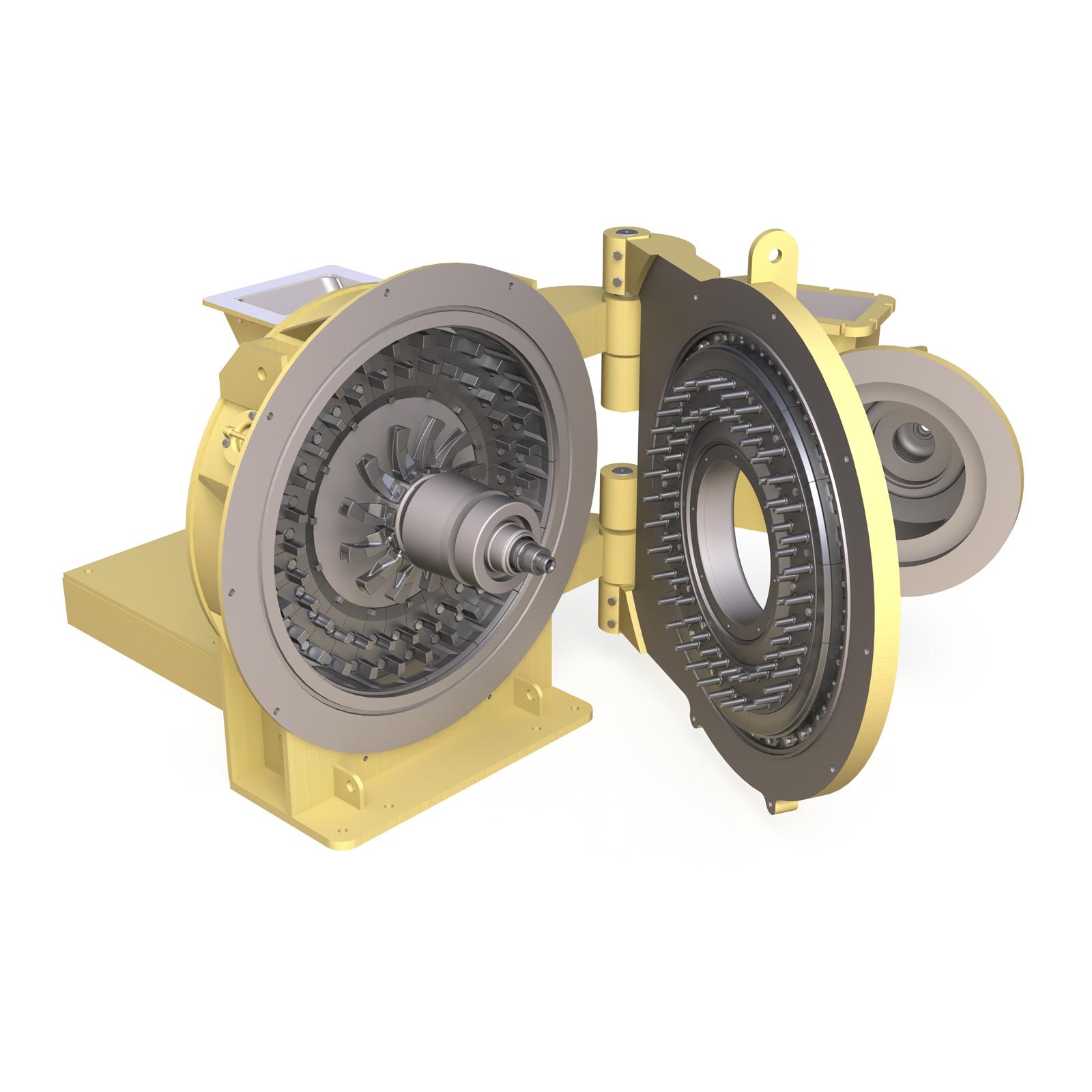
A simplified process while drying and grinding ensuring high product quality
Atritor’s Dryer-Pulveriser is able to grind and dry the product simultaneously. It is an air-swept mill that uses an air stream to efficiently process the product and controls the final particle size. It is able to process feedstocks of up to 50+mm and production capacities from 100kg/h up to 30t/h with evaporation rates up to 6,000 kilograms per hour.
The mill acts as an efficient dryer when the process air is heated using a hot air generator or waste heat from another process. It can reach an inlet temperature of up to 550ºC. Heat energy from the process can be recovered from the heated air stream. After flash drying, the product is kept cool due to evaporative cooling. The output temperature of the product is maintained accordingly to control the moisture content of the product.
The Flash drying grinder for powders is configured with a combination of variable speed rotor, hammer arrangement and fixed pins. Turbulence inside the grinding area creates attrition to reduce the particle size, which can be controlled for simple deagglomeration of the product. An internal classifier configuration can also be used to further control particle size.
The ‘A’-series is constructed with internals that are resistant to abrasion for applications that can cause high amounts of wearing to the equipment. Where the desired amount of evaporation required far exceeds the grinding duty, the ‘B’-series machine of a lighter weight, fully fabricated configuration permitting higher airflows can be used for non-wearing product or duties, as well as for for applications in which stainless steel contact parts may be necessary.
Benefits
- Simultaneously used as a dedicated grinder or dryer
- Simple to maintain with interchangeable wear parts that are easy to access
- Variable internal configurations allow customised designs
- Production scale pilot plant for proving trials