
Powder Manufacturing Equipment
Find innovative powder equipment and connect directly with world-leading technology suppliers
The building blocks of matter have driven the imagination of philosophers, scientists, and artists for millennia. But, for manufacturers, these elements have a more concrete existence as powders. Powder processing technology conditions these primary materials to create a vast range of products, from chemicals and foods to pharmaceuticals and ceramics.
Top picks in powder process equipment
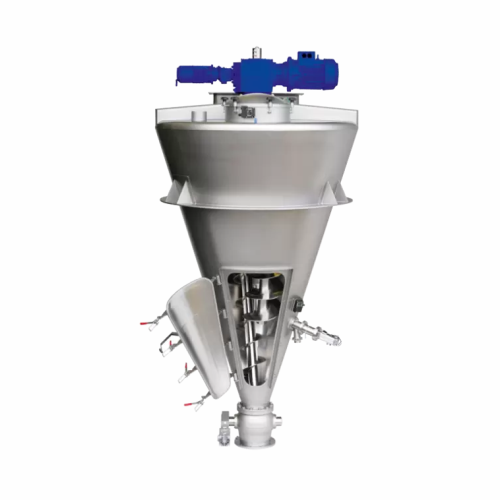
Batch mixer for segregative, free-flowing powders and pastes
Achieve precise and gentle batch mixing for delicate produc...
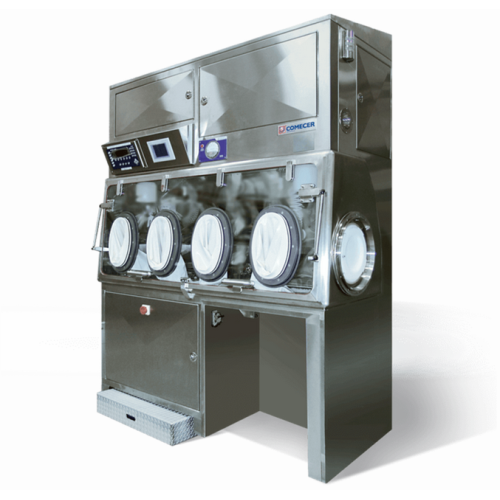
Atex compliant isolator for dispensing powder procedures
Ensure safe weighing and transfer of explosive and pharmaceutica...
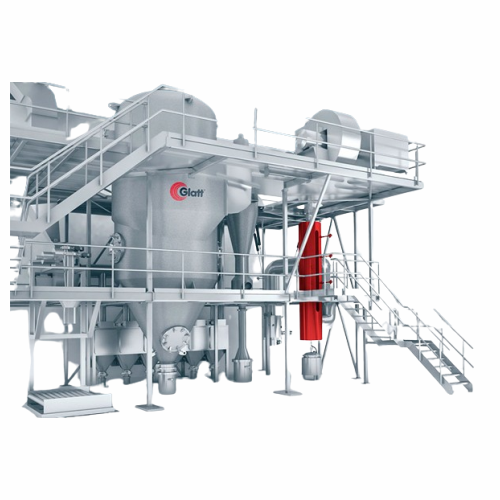
Powder synthesis reactors for nanometer and micrometer particles
Achieve precise particle control and enhance material p...
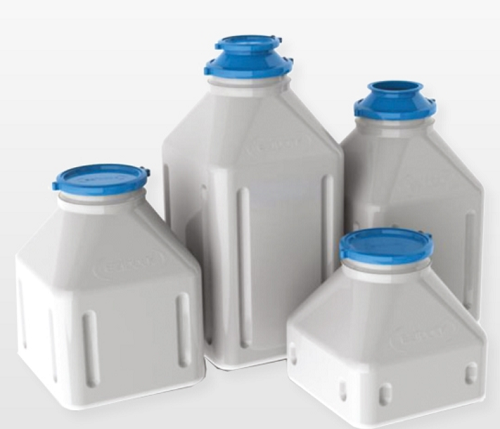
API powders storage bottle
Users who prefer rigid storage over single-use pharma charge bags, require lightweight solutions ...
Stories about powder
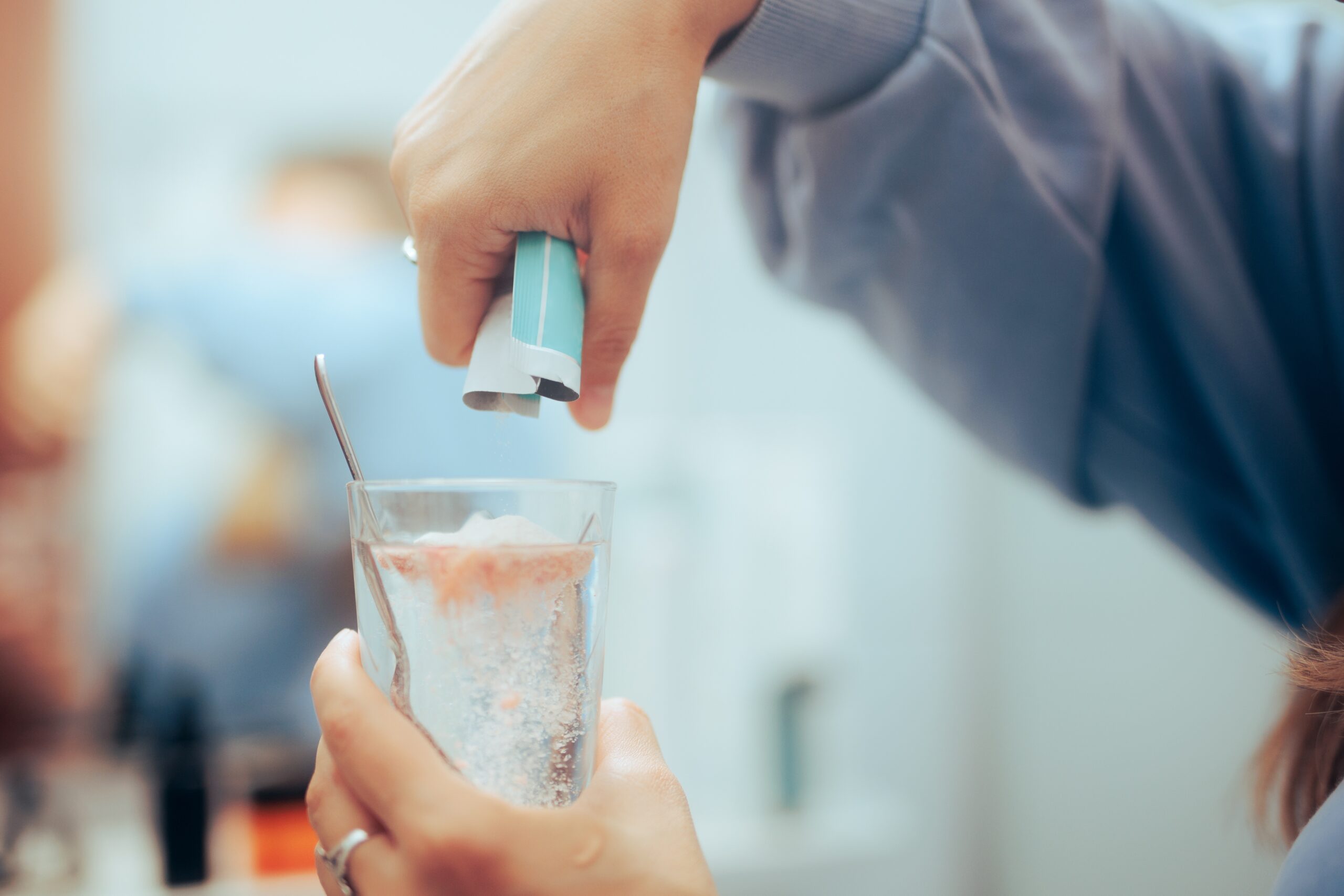
Keeping up with the trends: cartoning sustainable materials and utilizing AI all at once
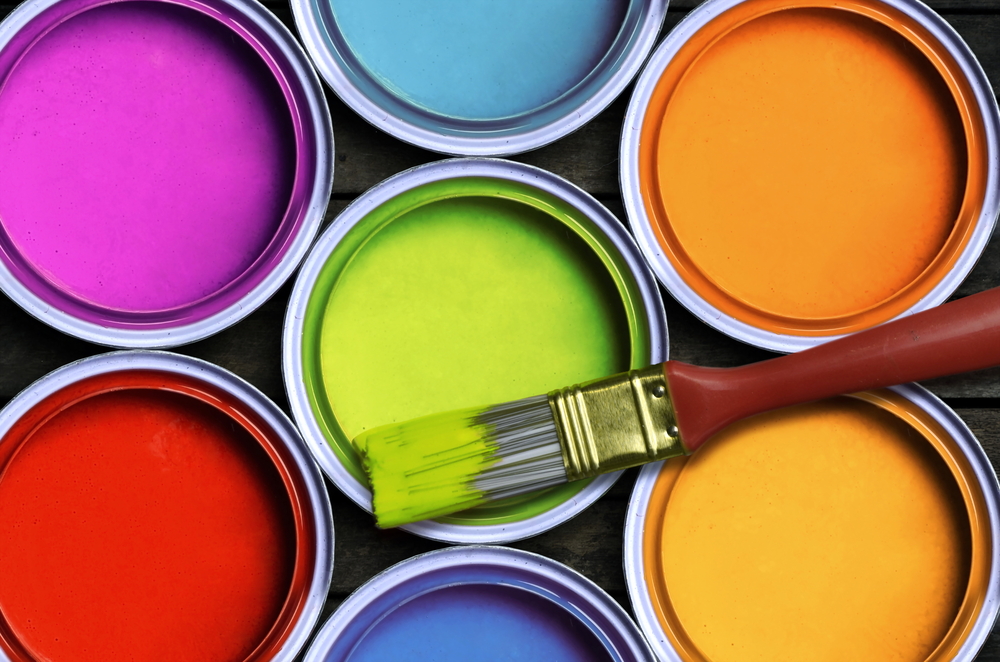
Powder and liquid, a delicate equilibrium in paint production
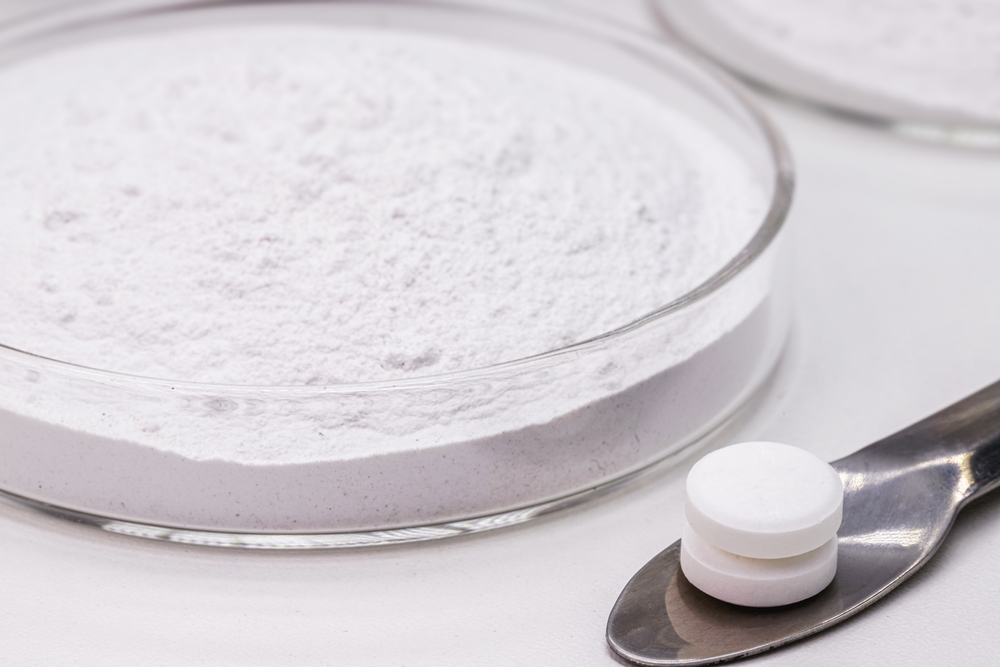
Wet milling: The revolution in the API production
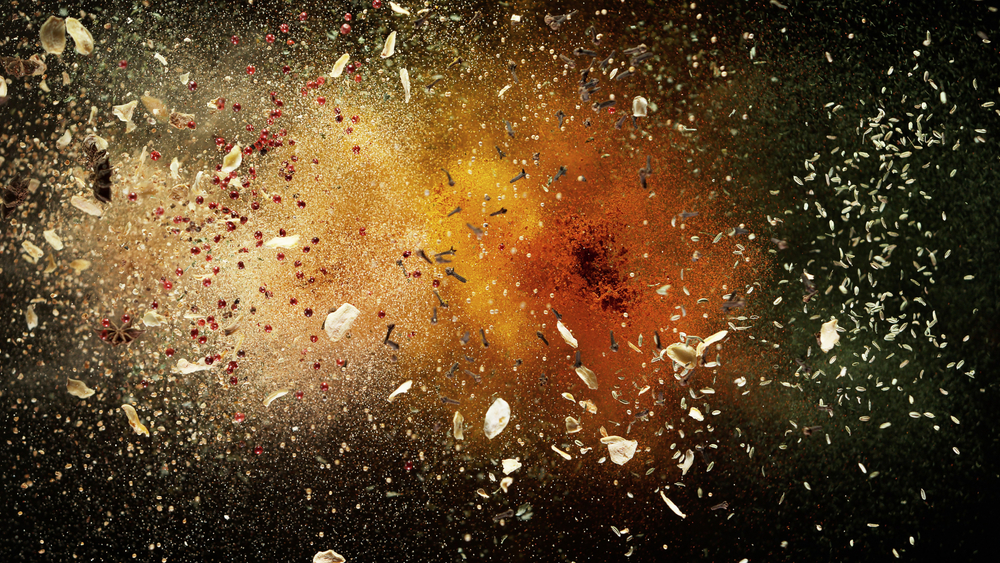
From flavorless to fabulous: unlocking the full potential of reaction flavors for tasty plant-based food
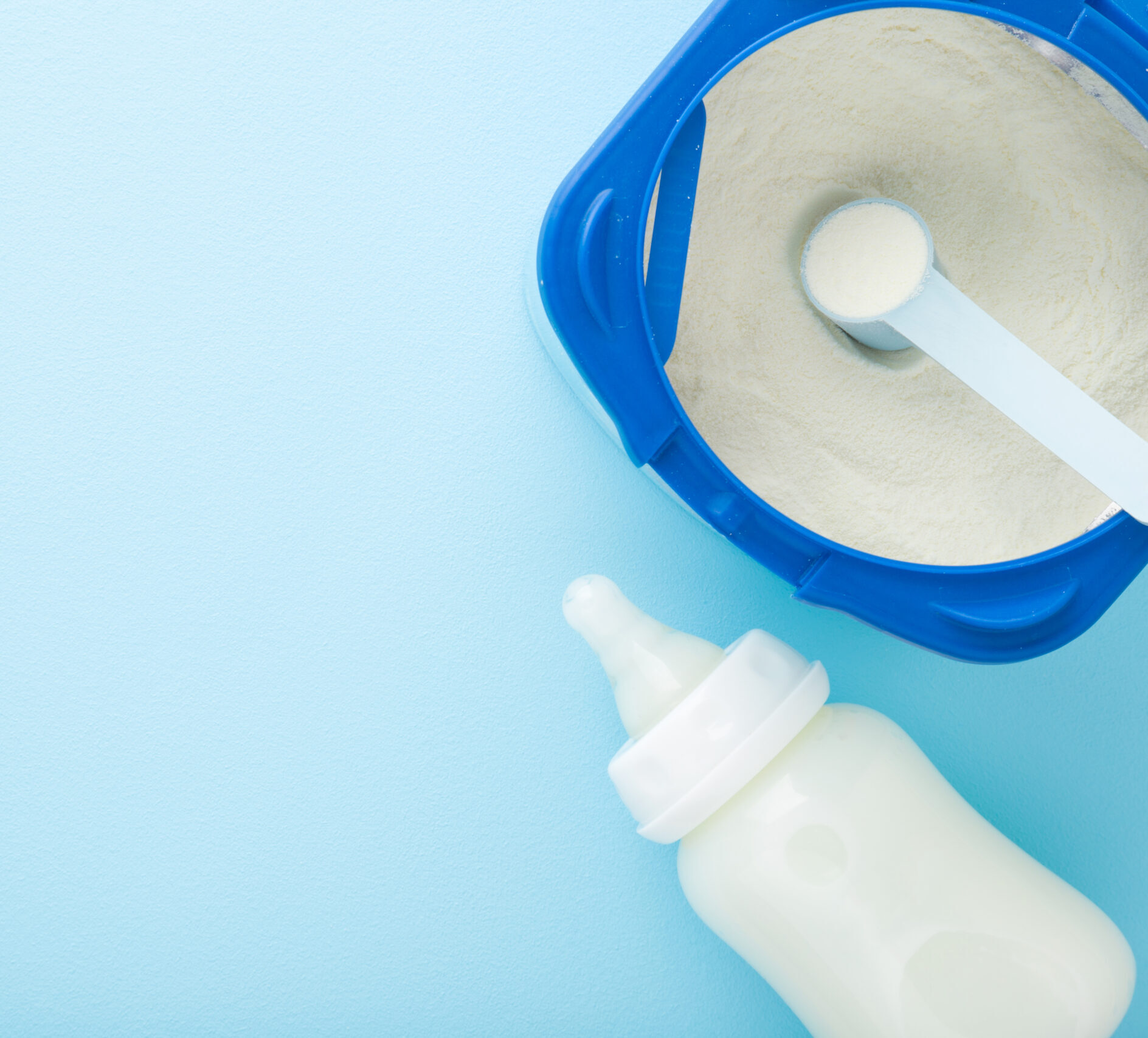
Preserve your milk powder during transportation. Big Bags: “Challenge accepted!”
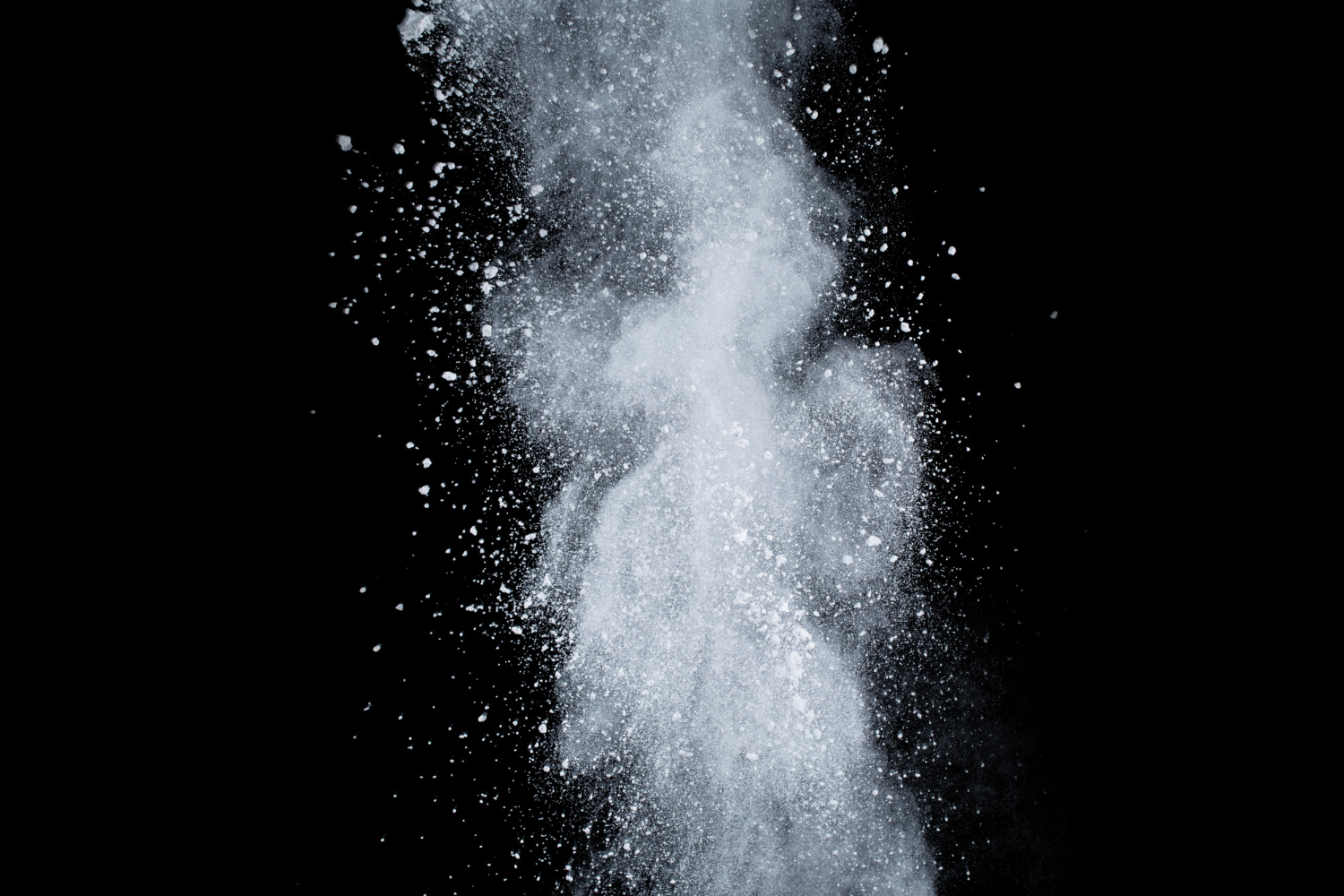
Closing the containment loop in HPAPI manufacturing
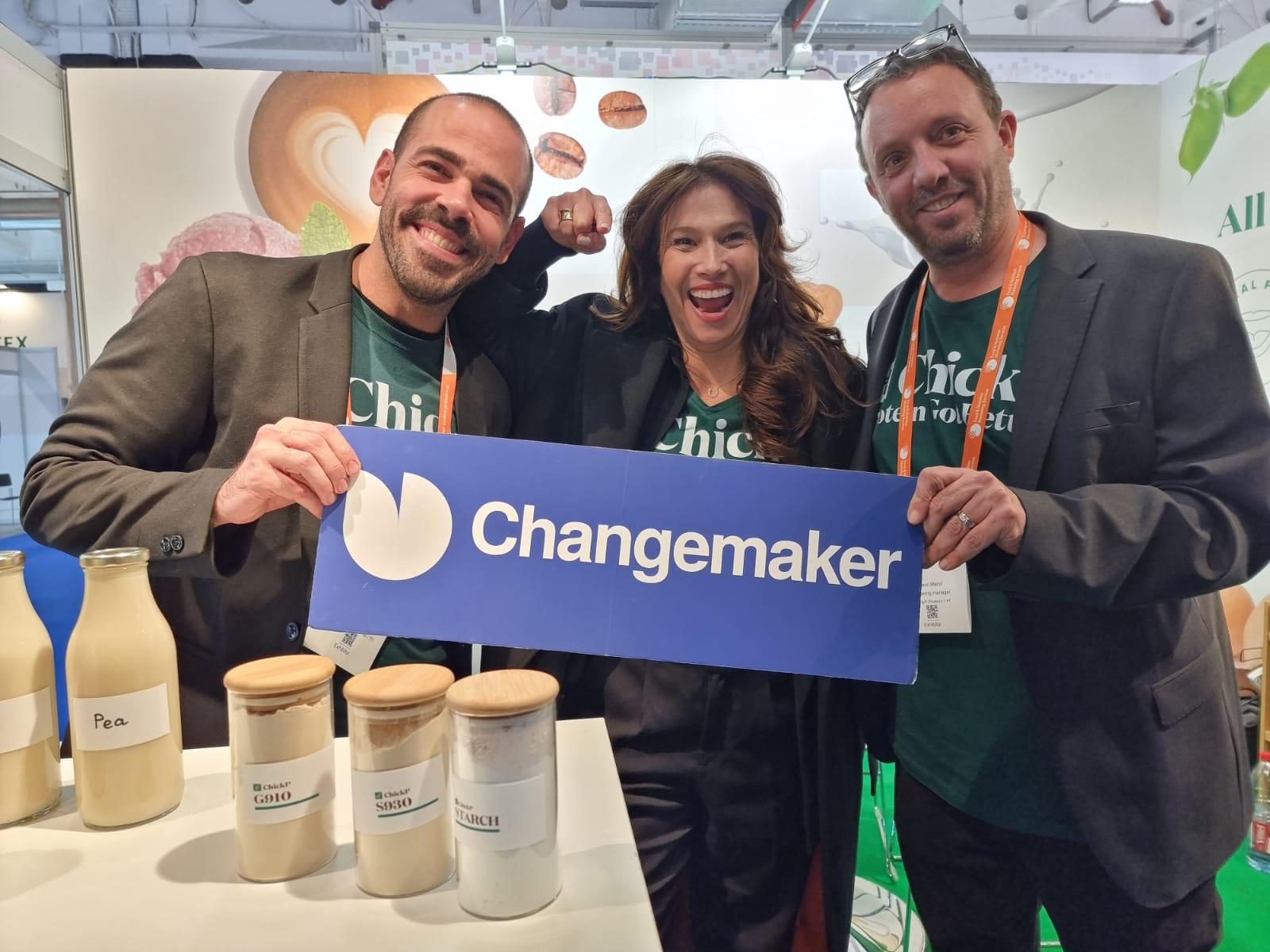
#Changemaker: Chickpea protein for your plant-based food product!
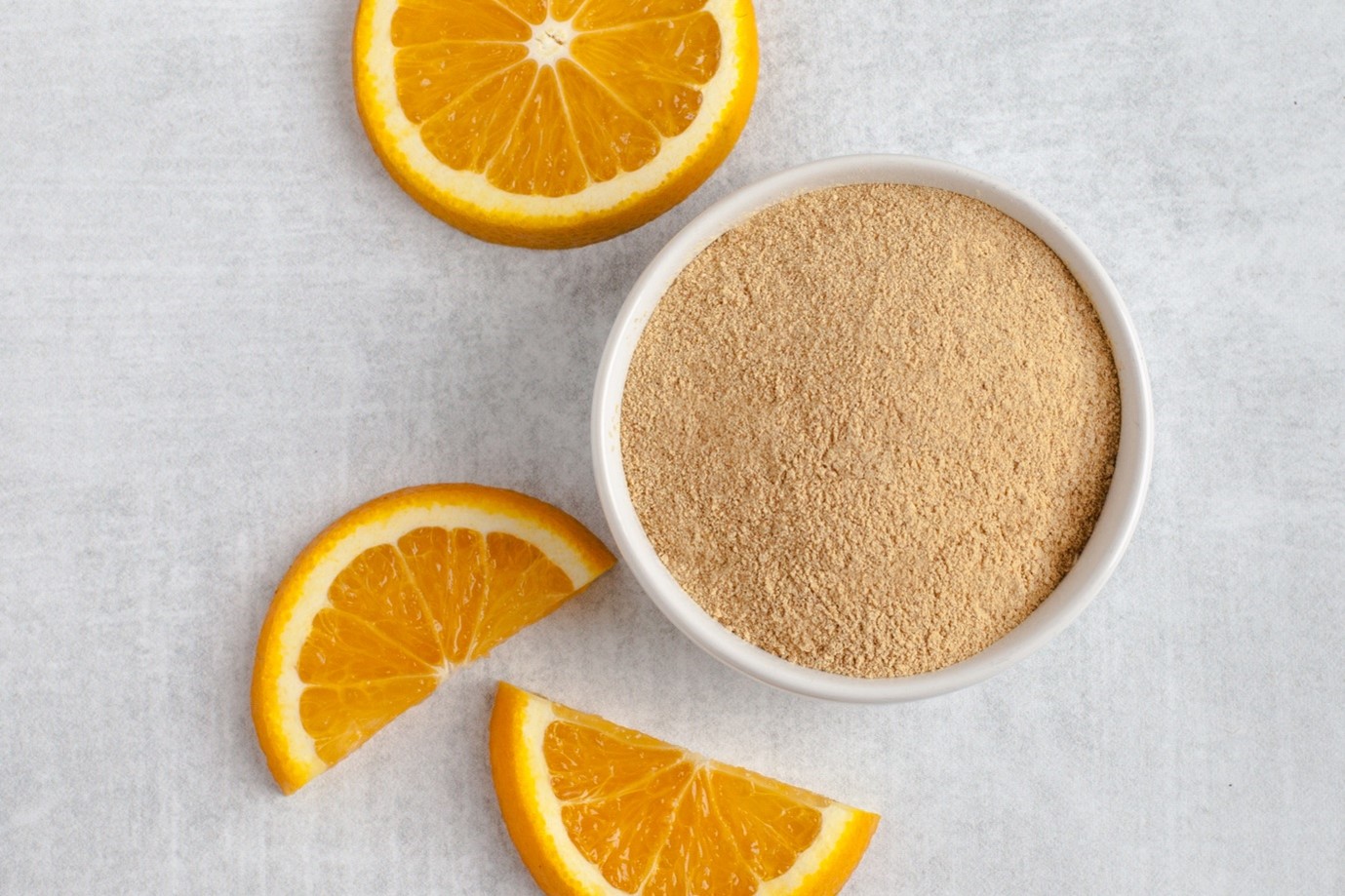
Clean up your label, drying fruit extracts without using carriers
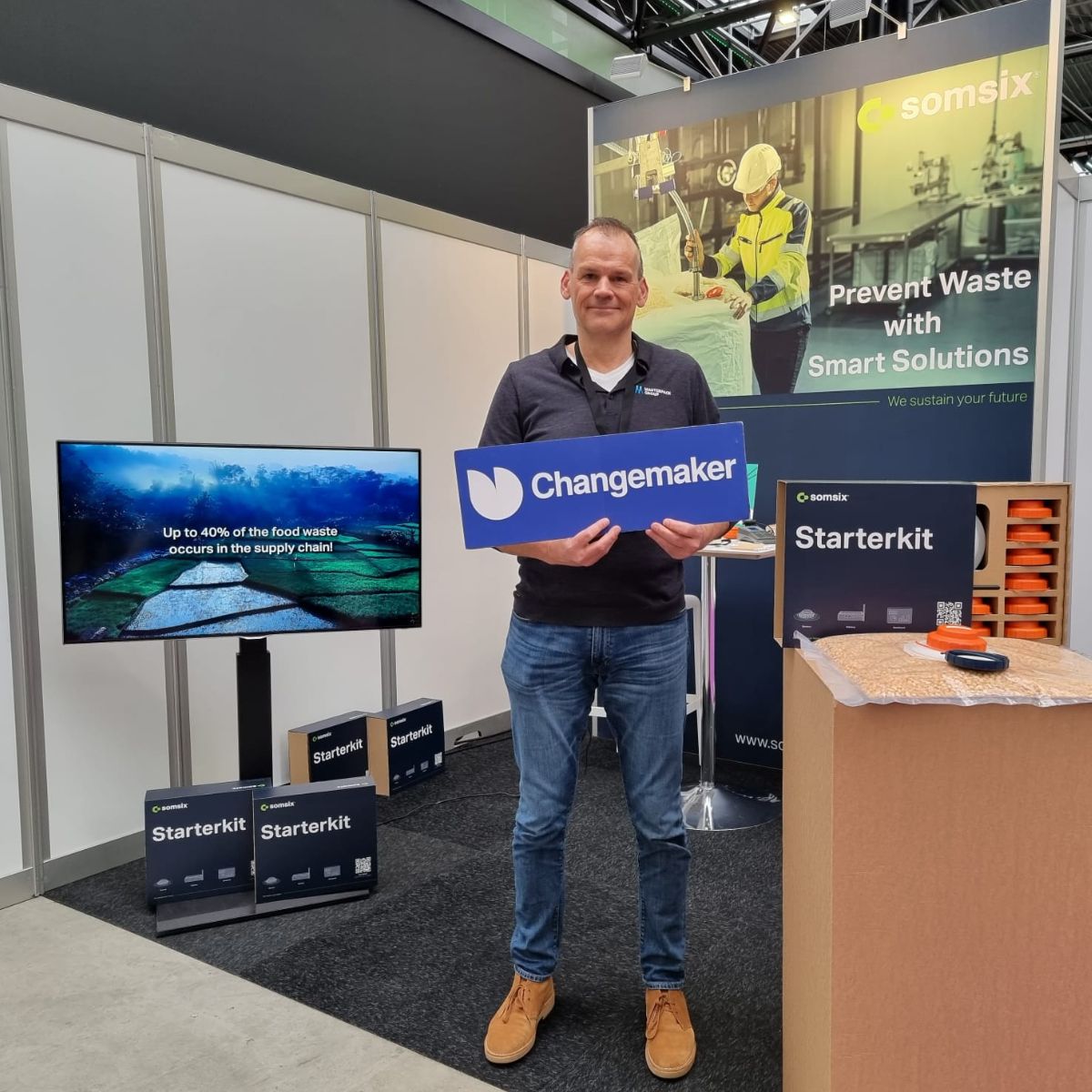
#Changemaker: FIBC with brains
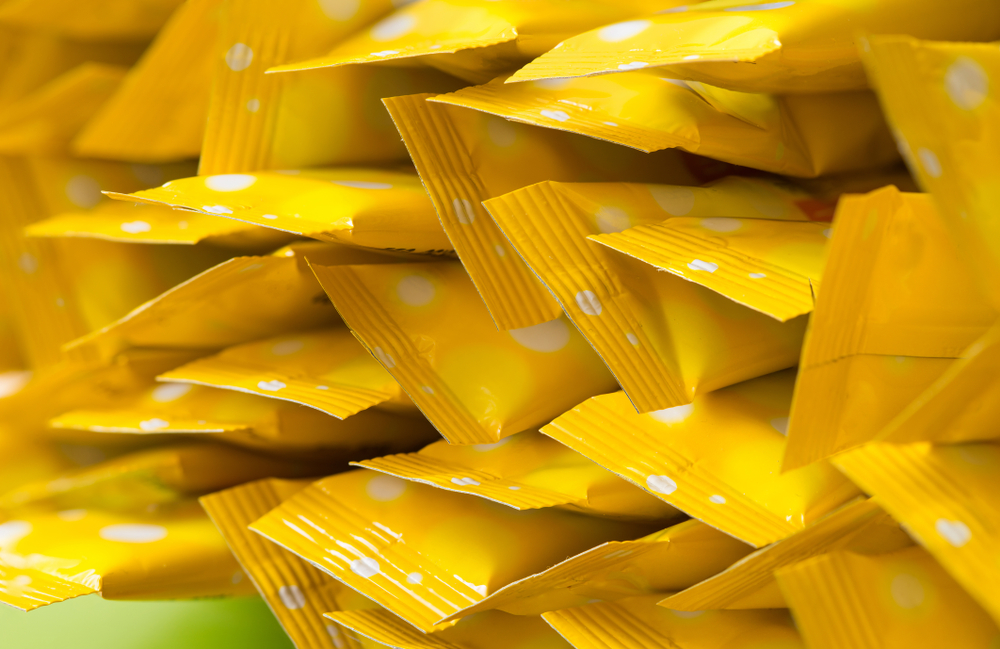
Unpacking the world of stick pack cartoning
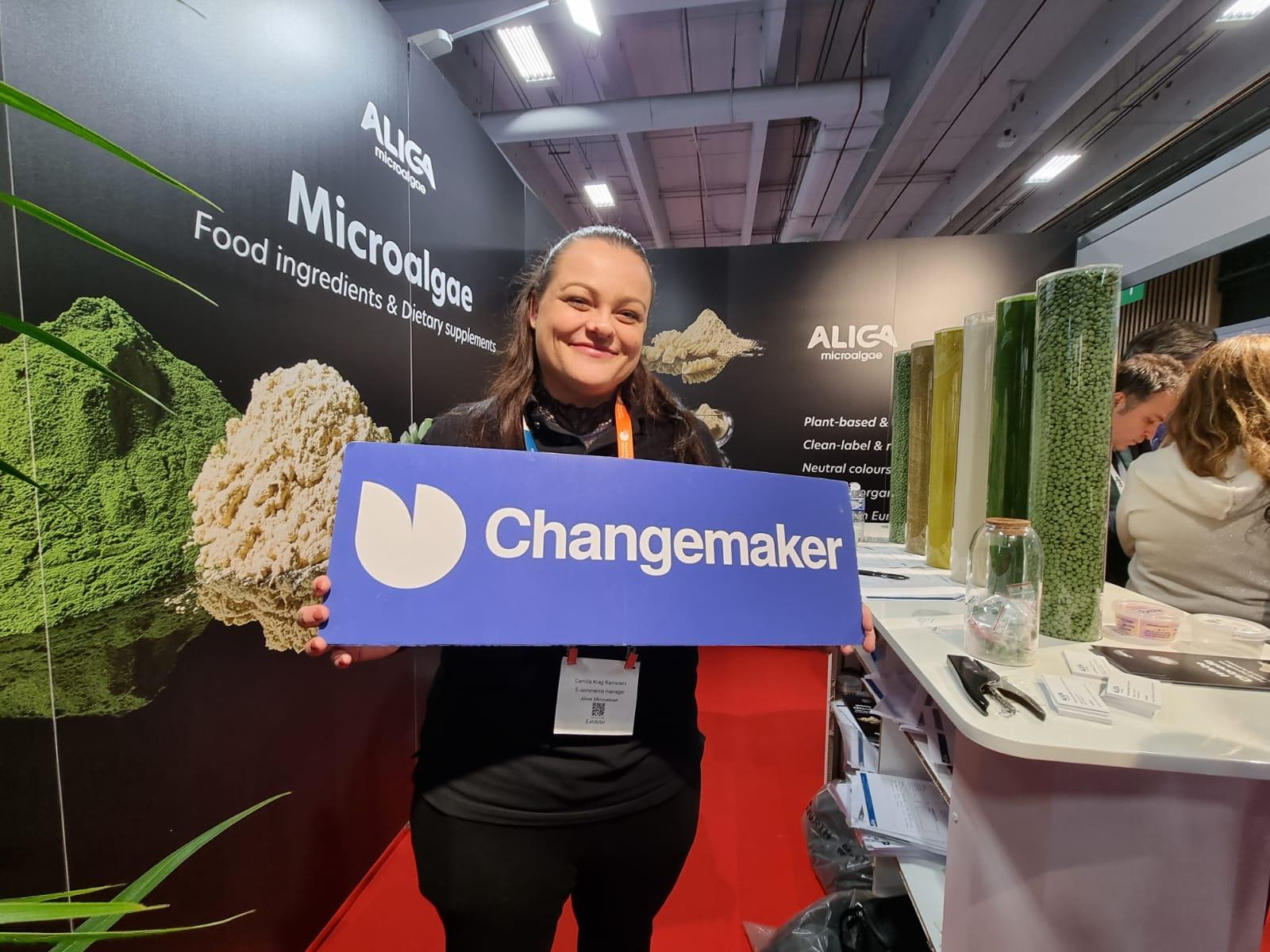
#Changemaker: white chlorella as your next protein source!
What are you making?
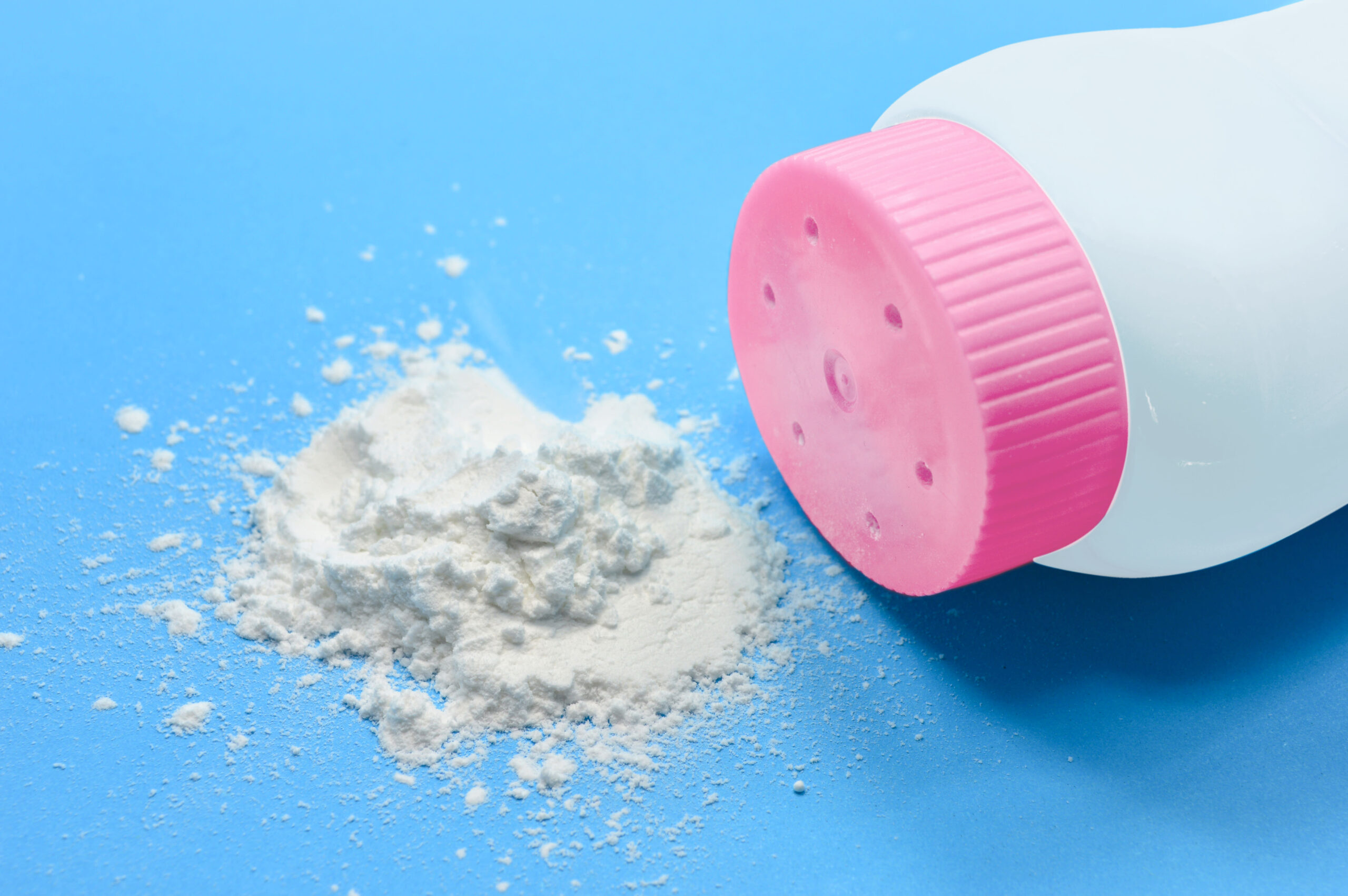
Talc powder
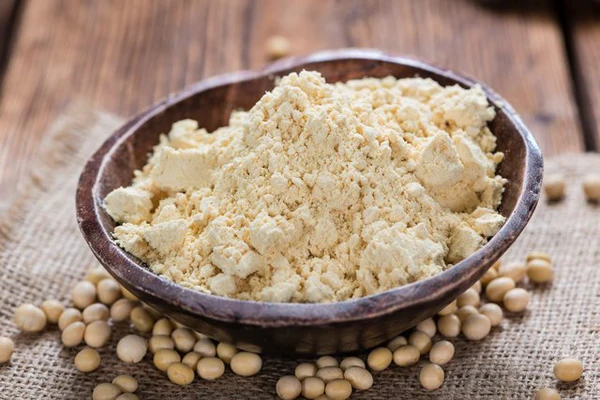
Soy flour
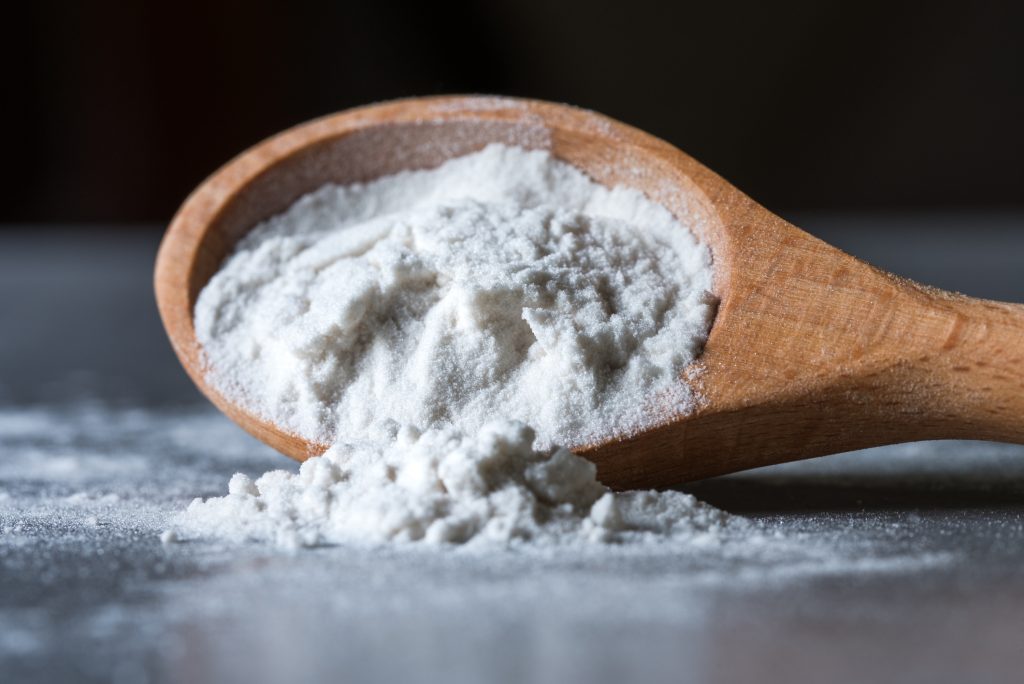
Solids
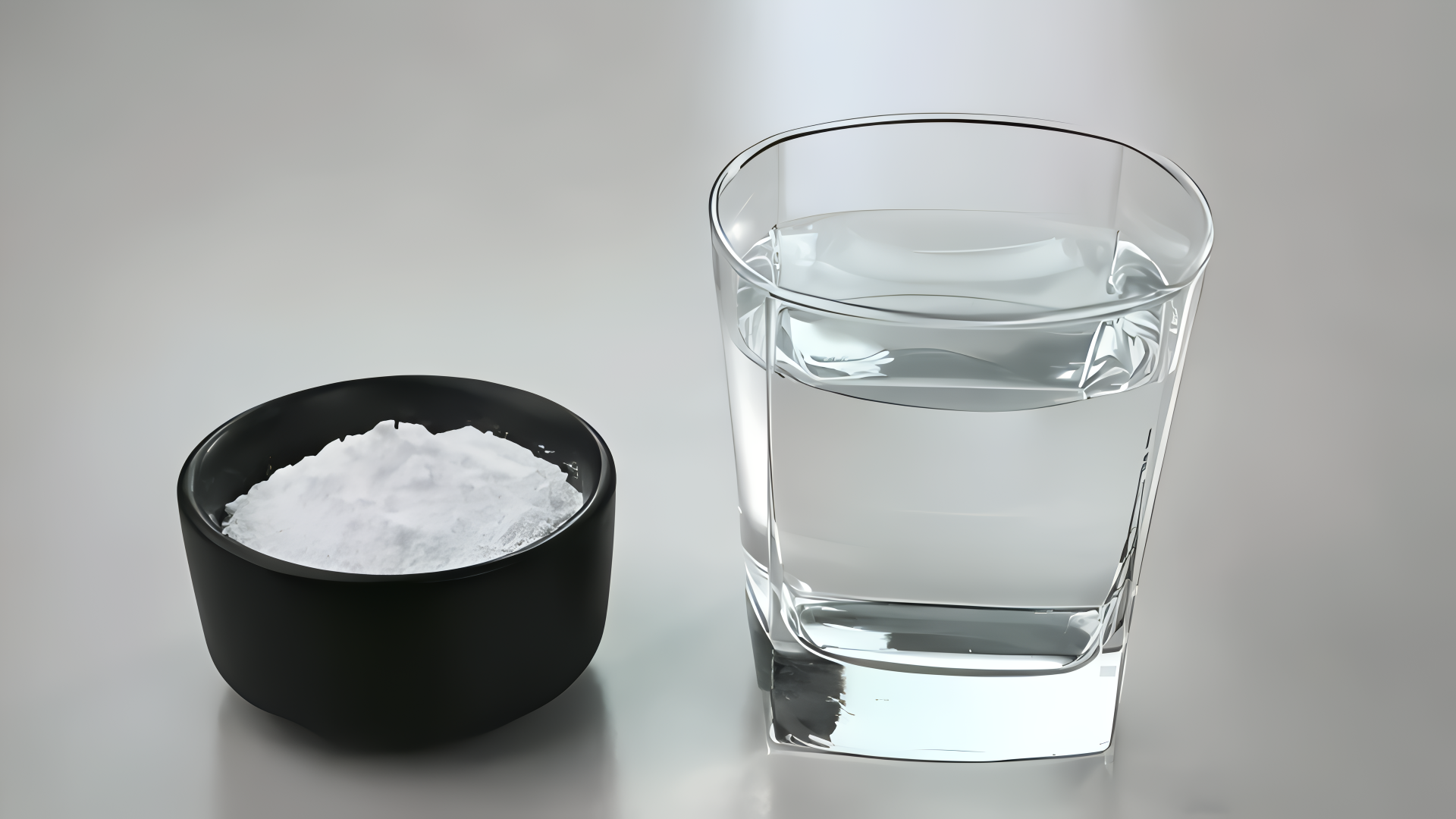
Powder dissolving
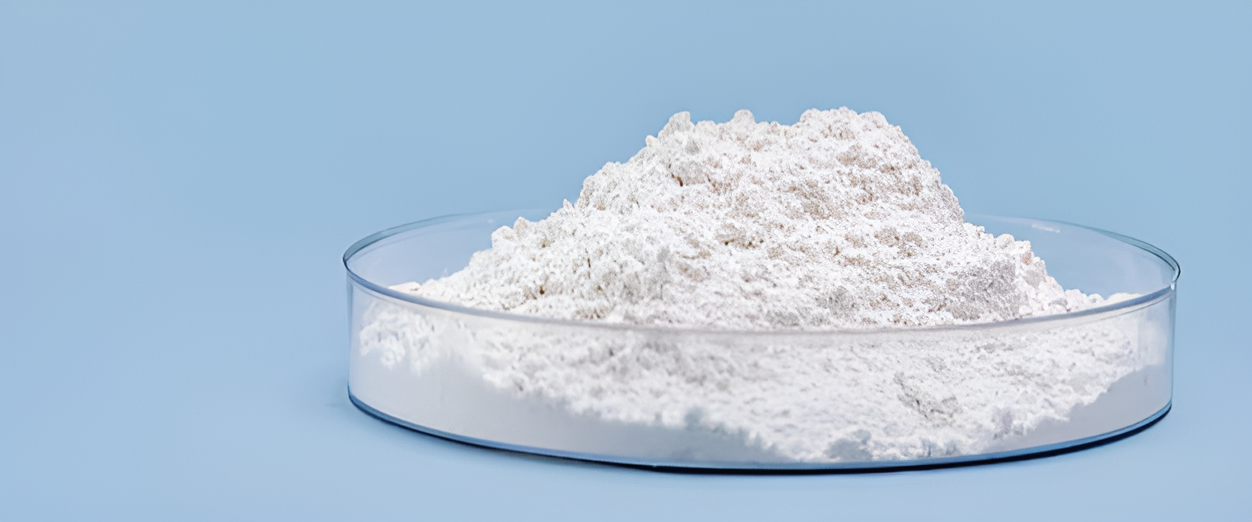
Polymer powders
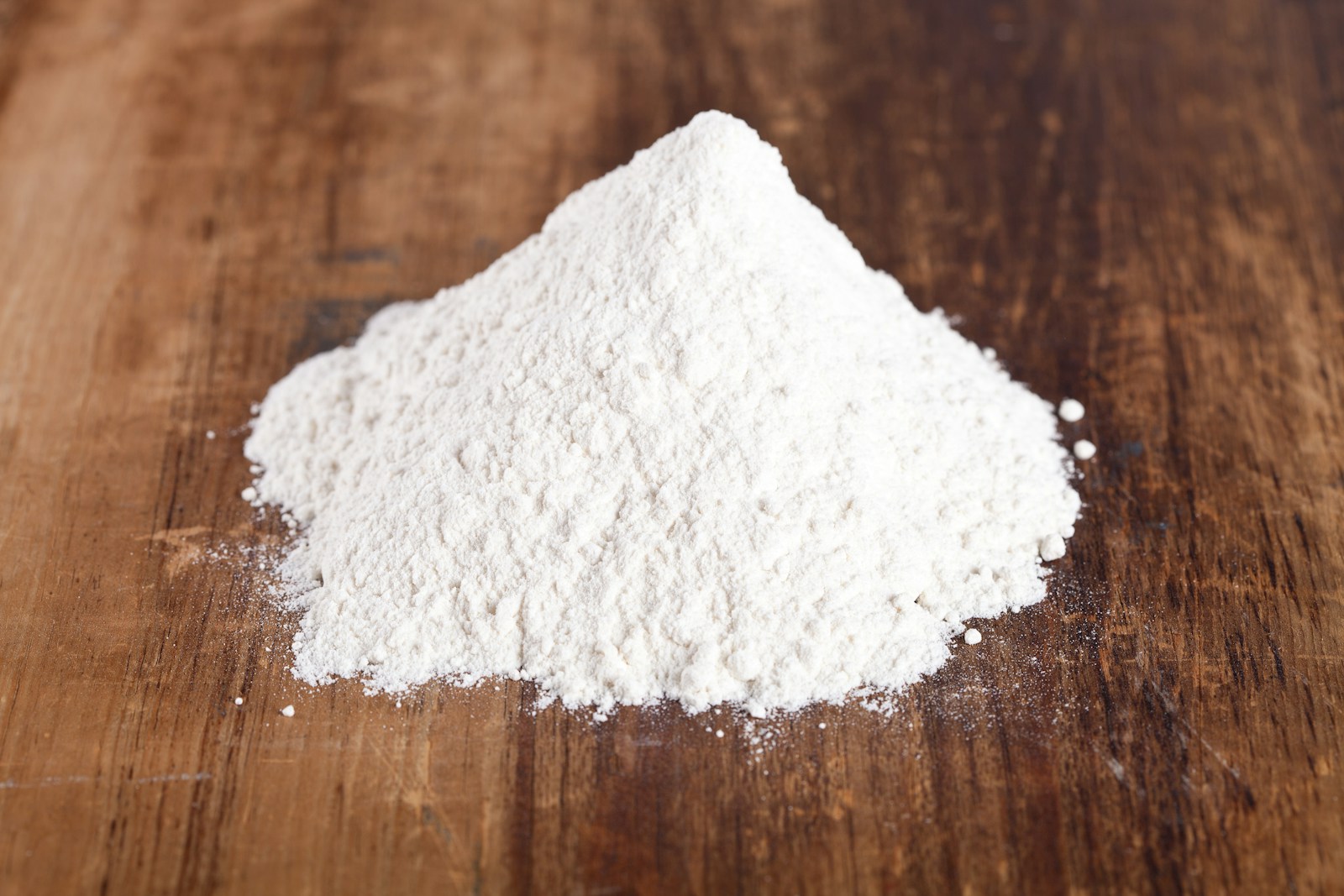
Polyethylene powder
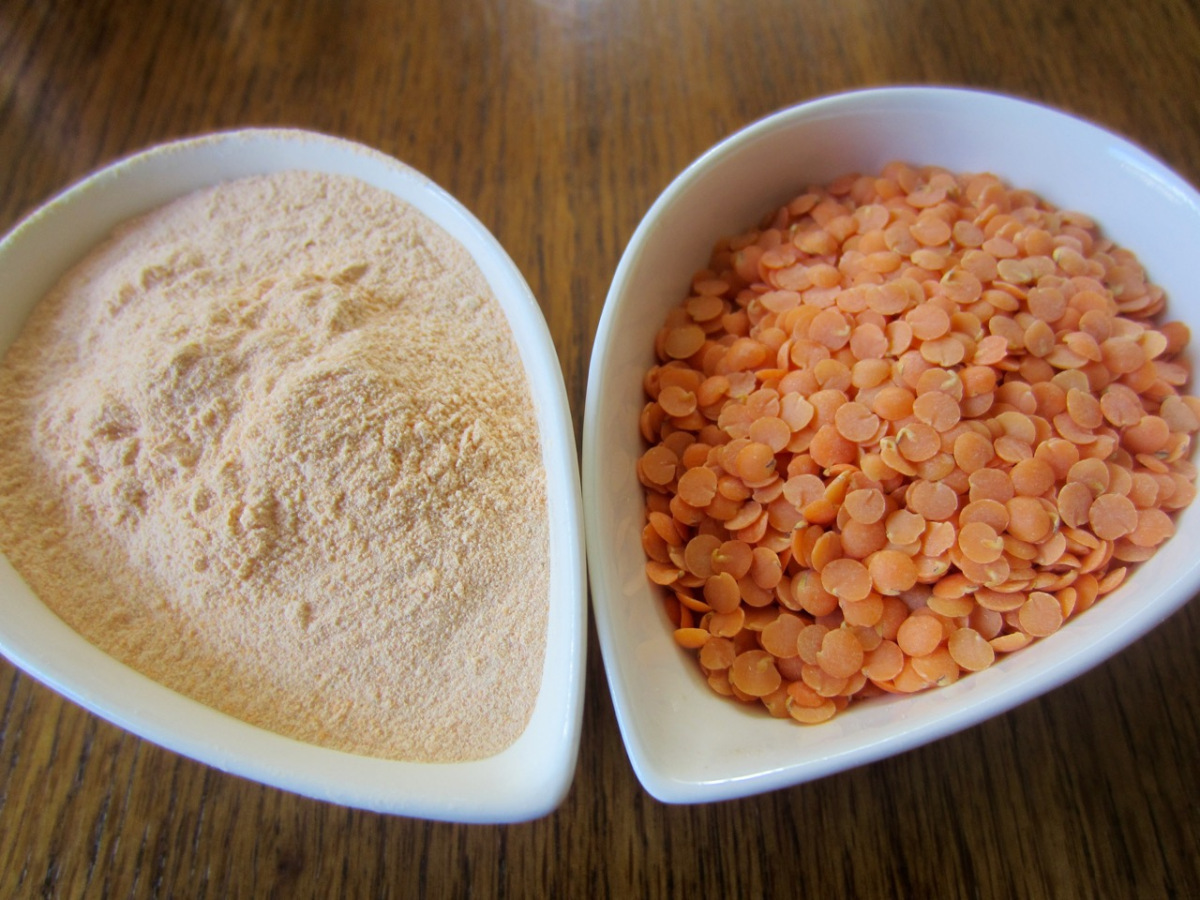
Lentil flour
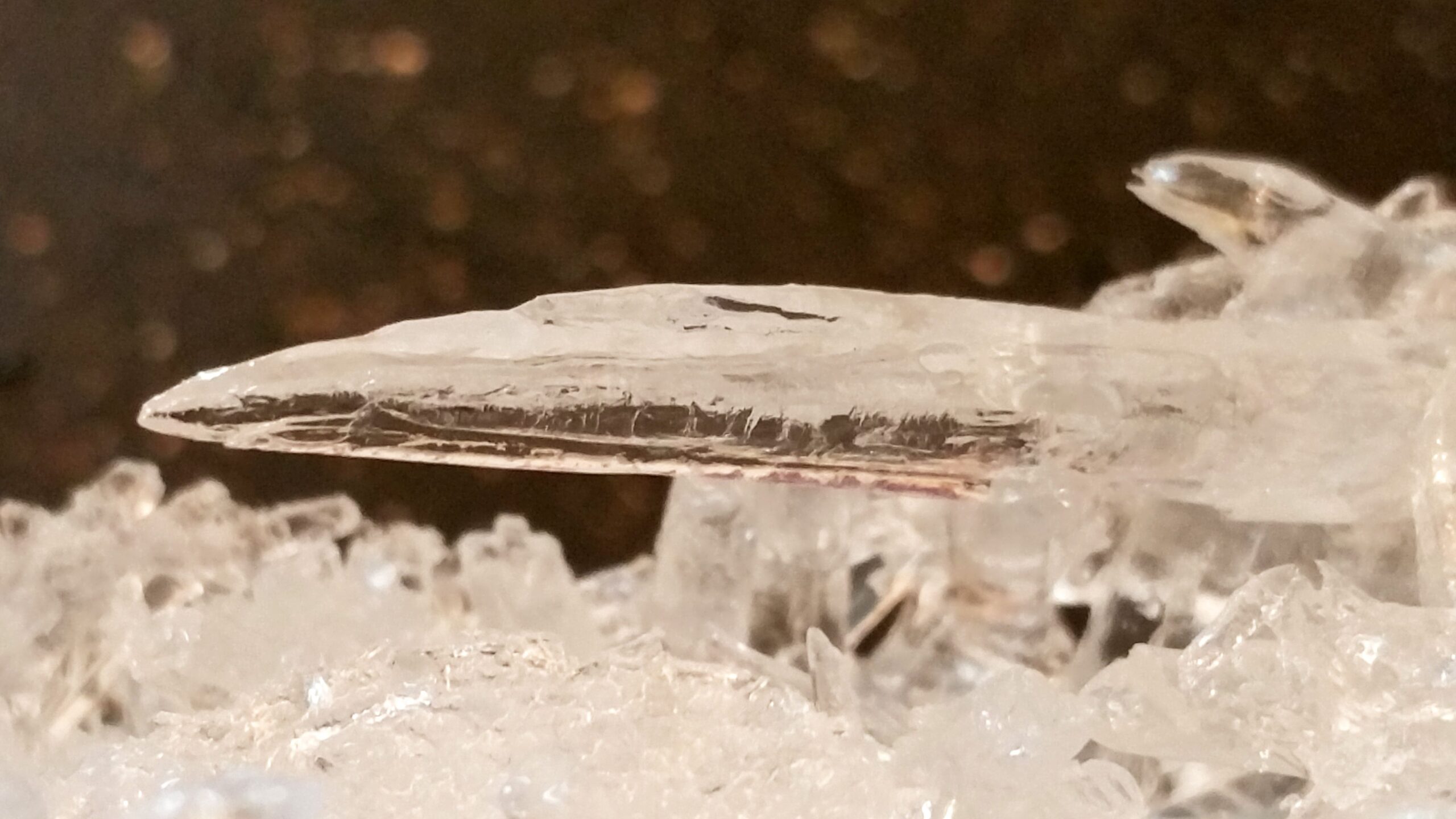
Hygroscopic products
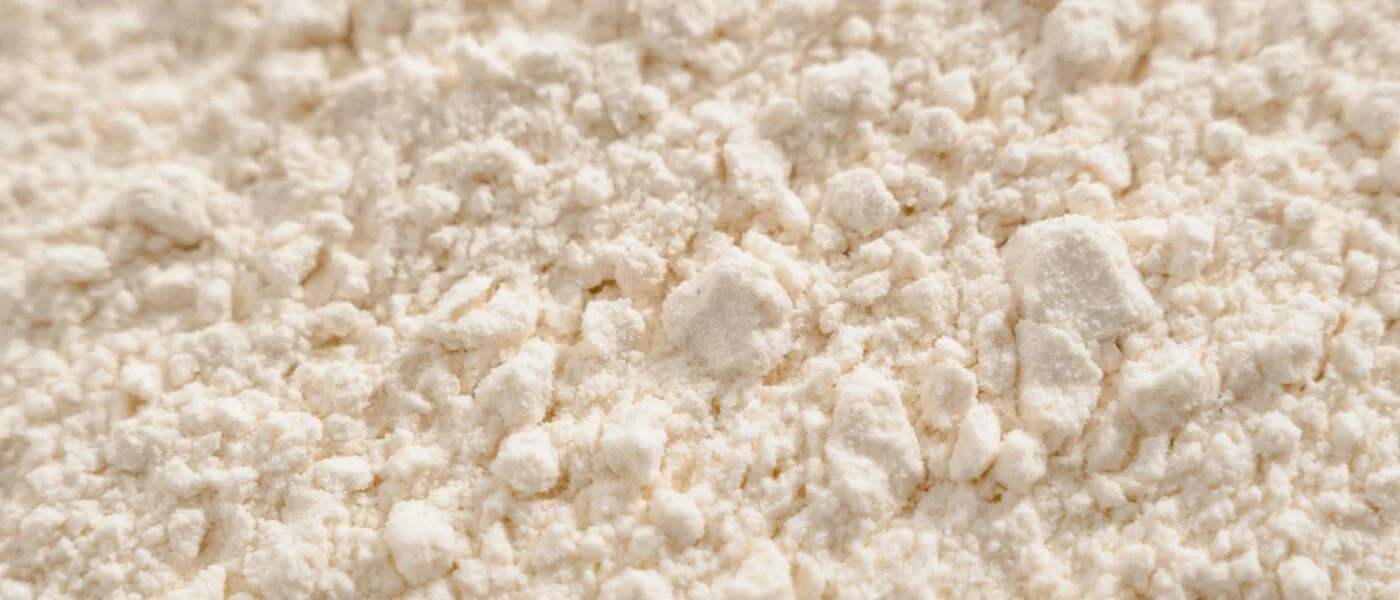
Free-flowing powders
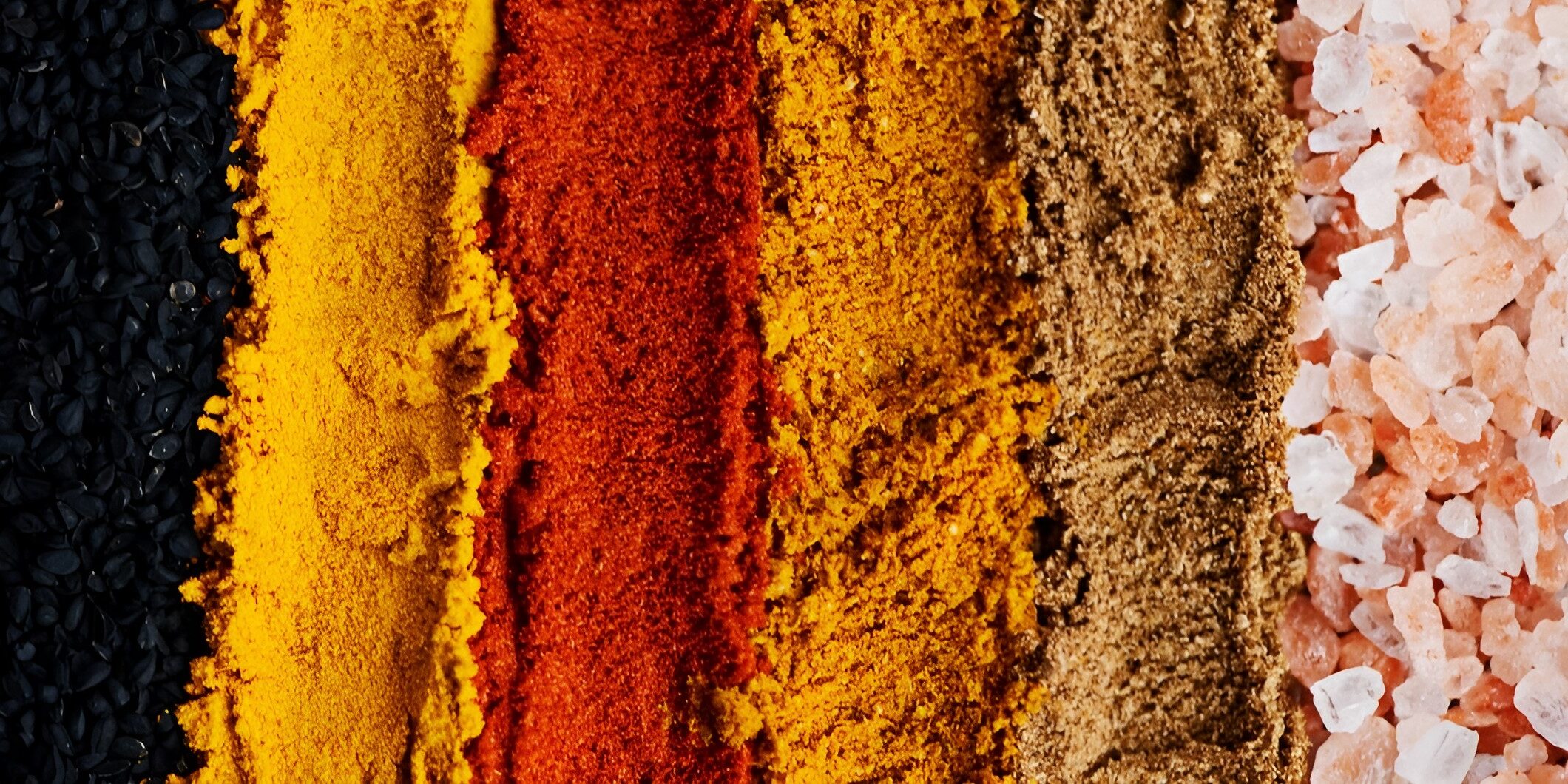
Food powders

Dry powders
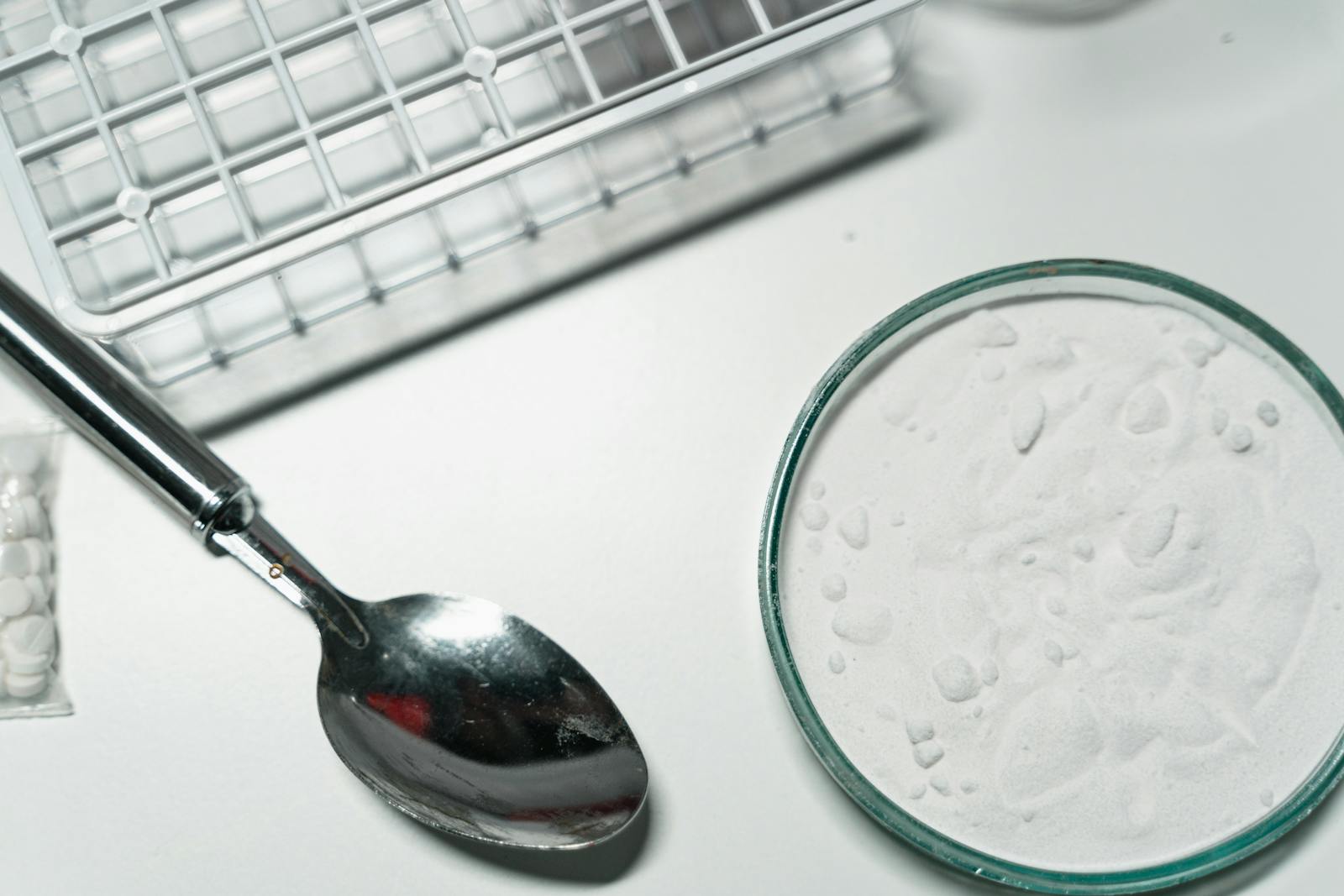
Chemical powders
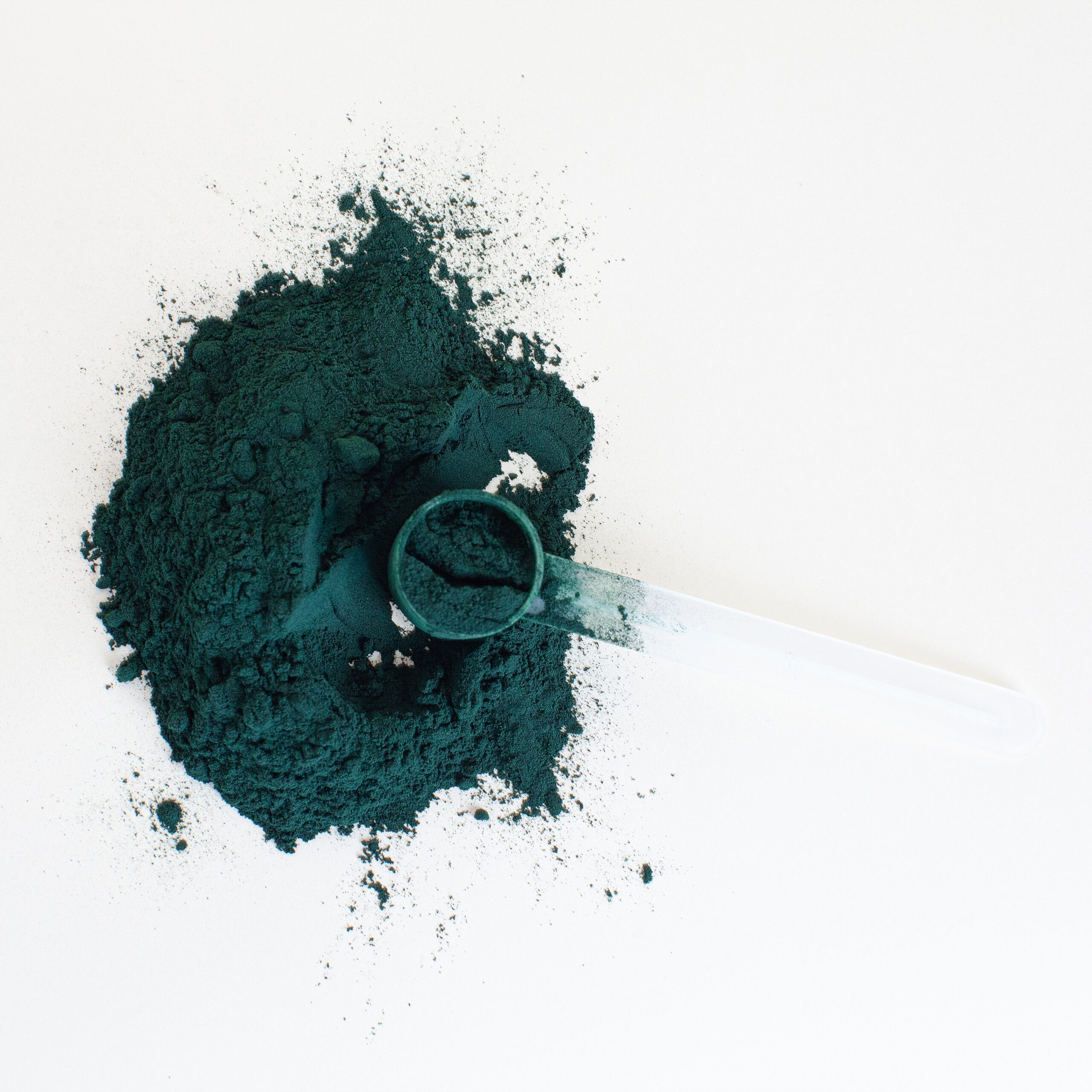
Spirulina powder
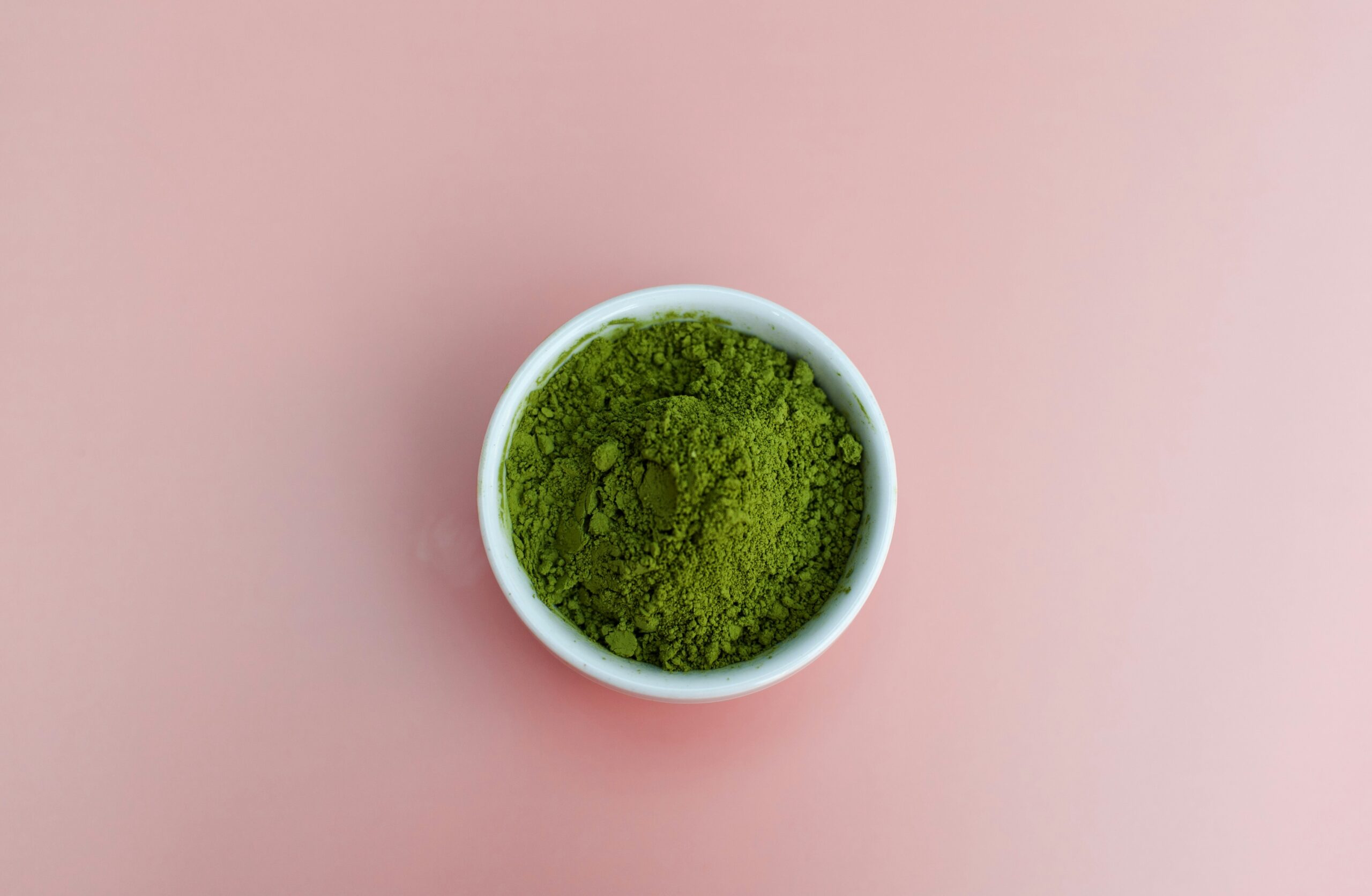
Chlorella powder
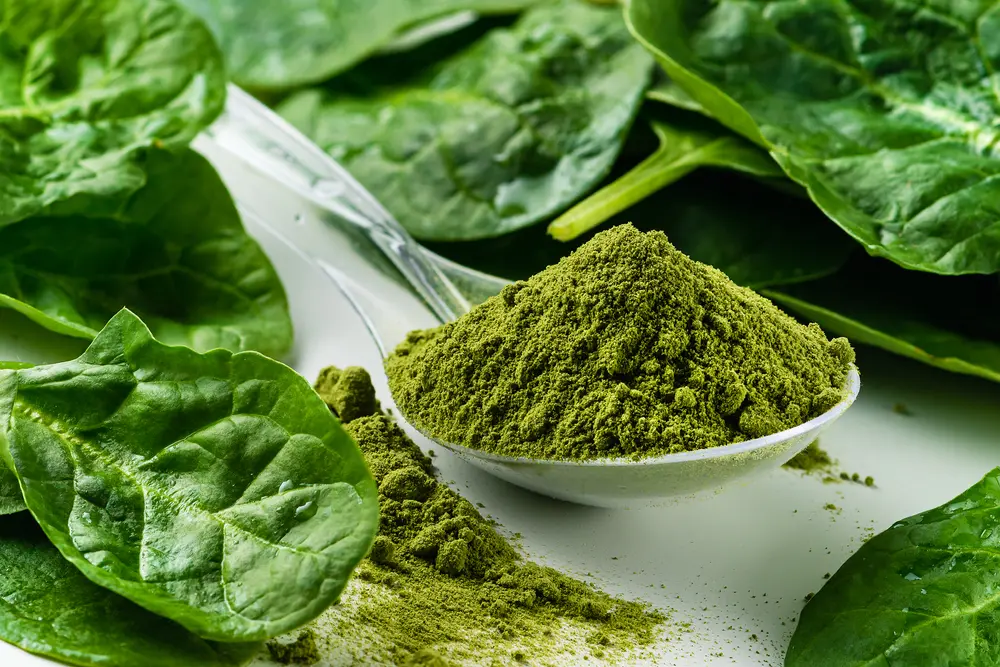
Vegetable powder
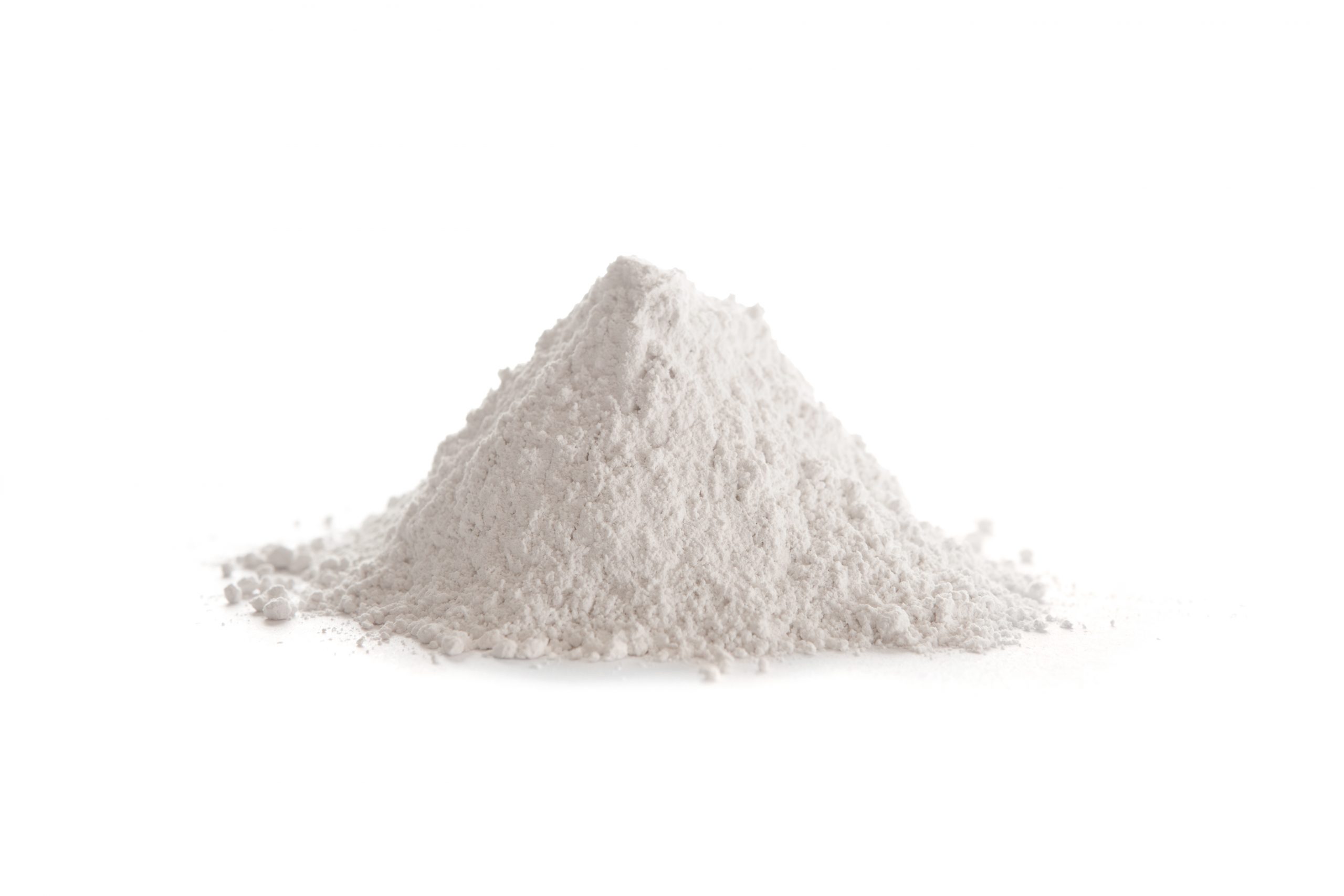
Gypsum
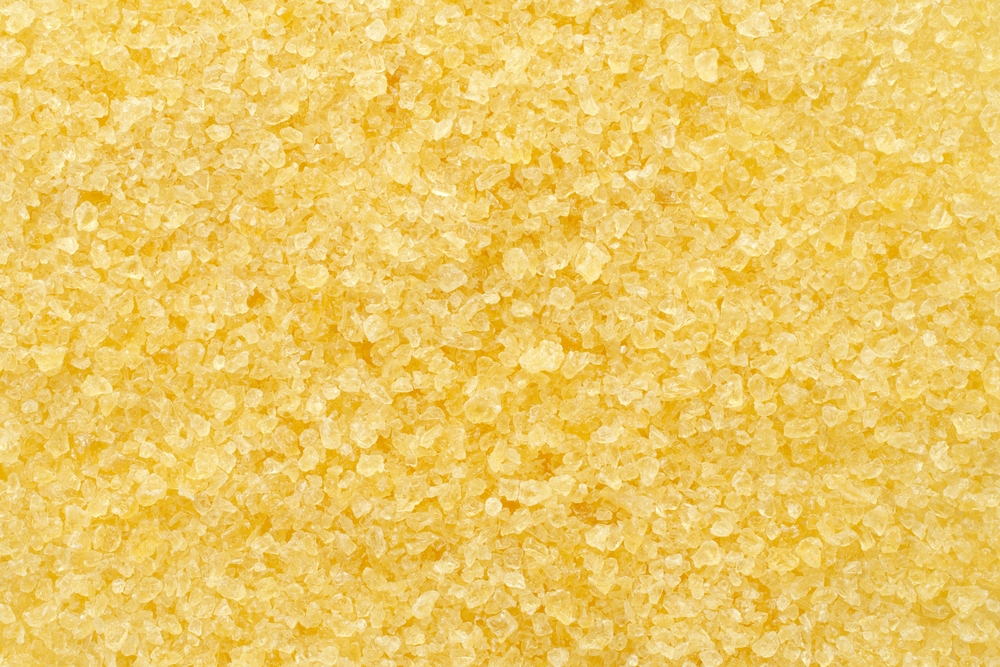
Gelatin powder
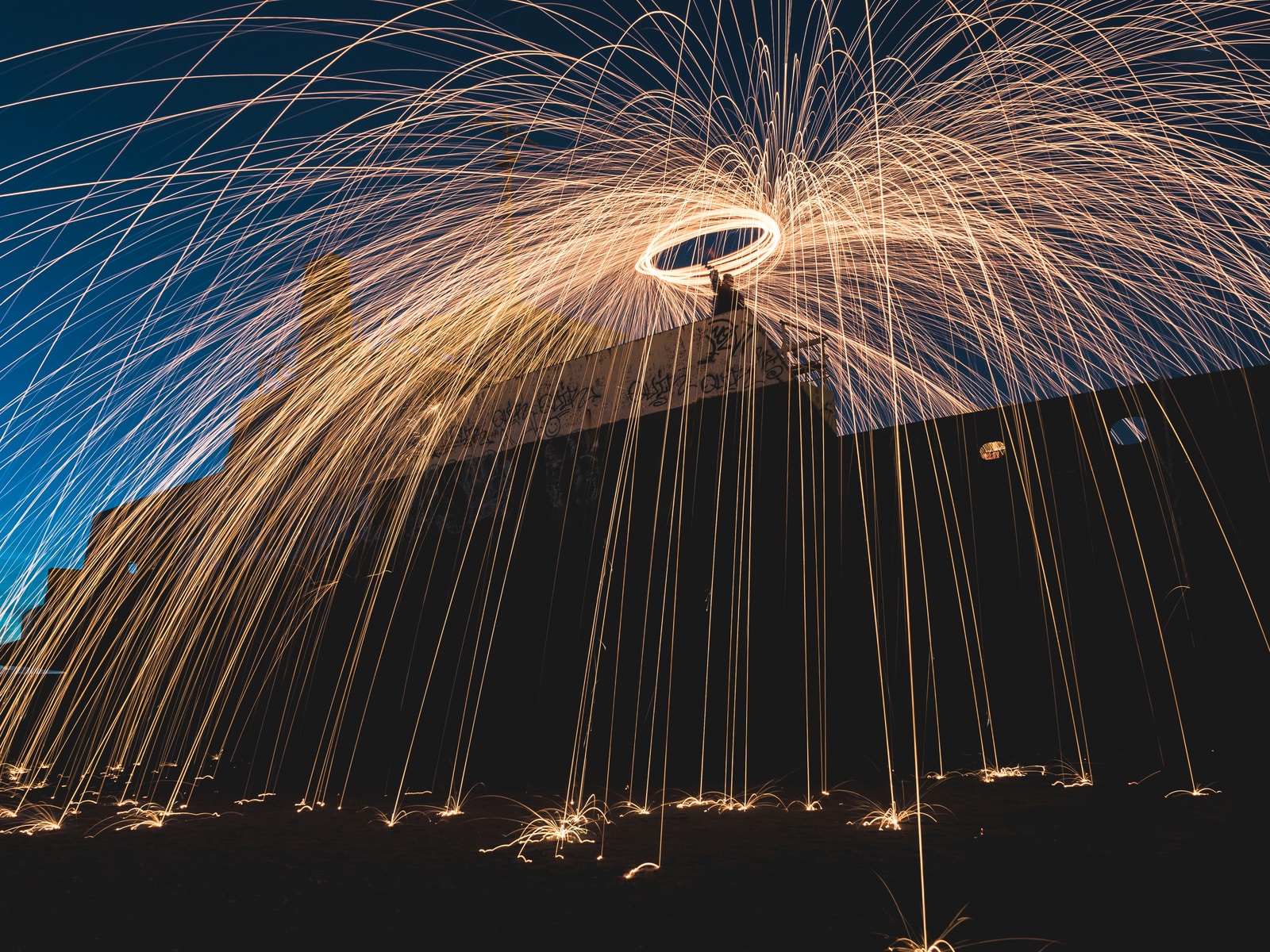
Metal powder
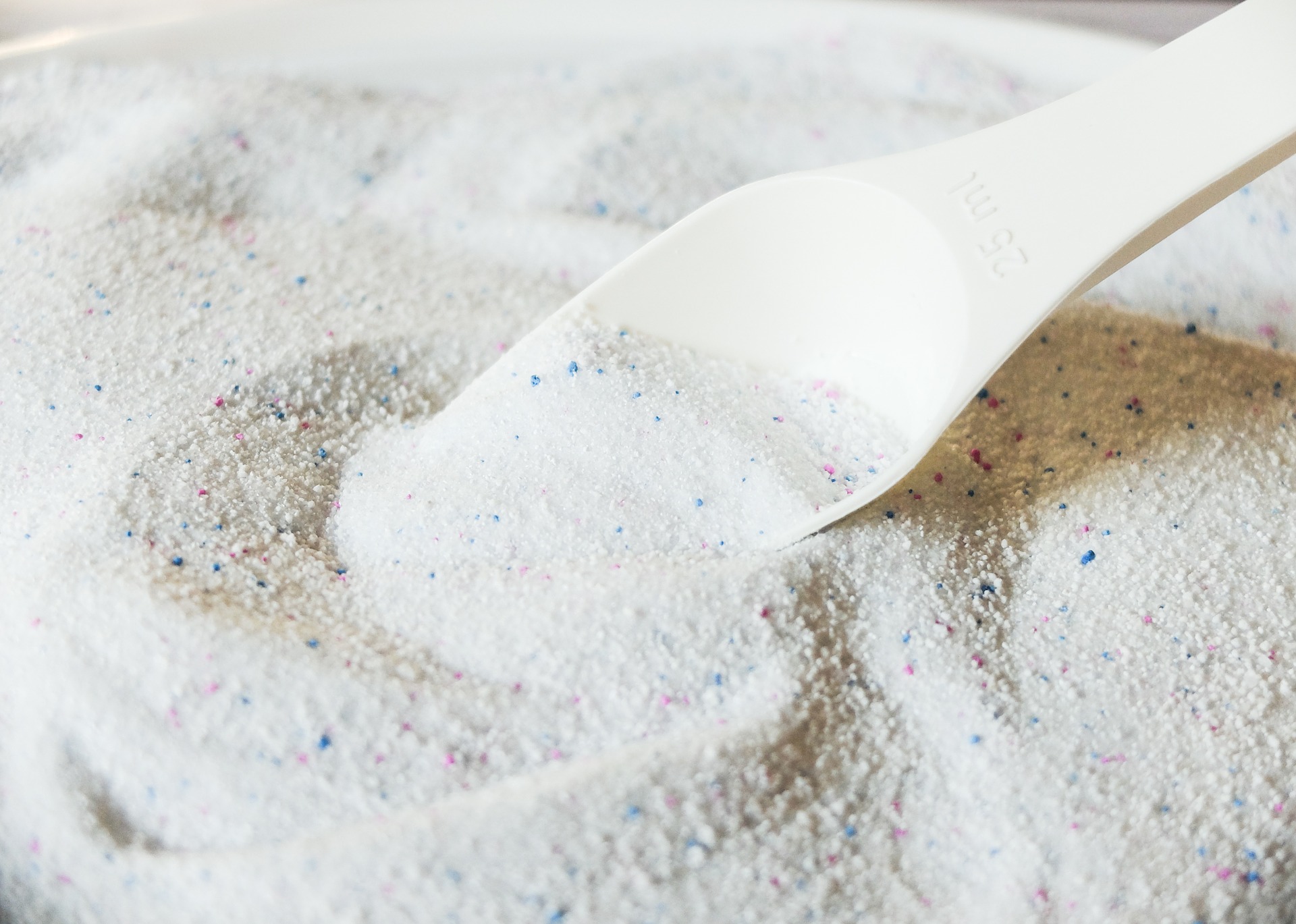
Powder detergent
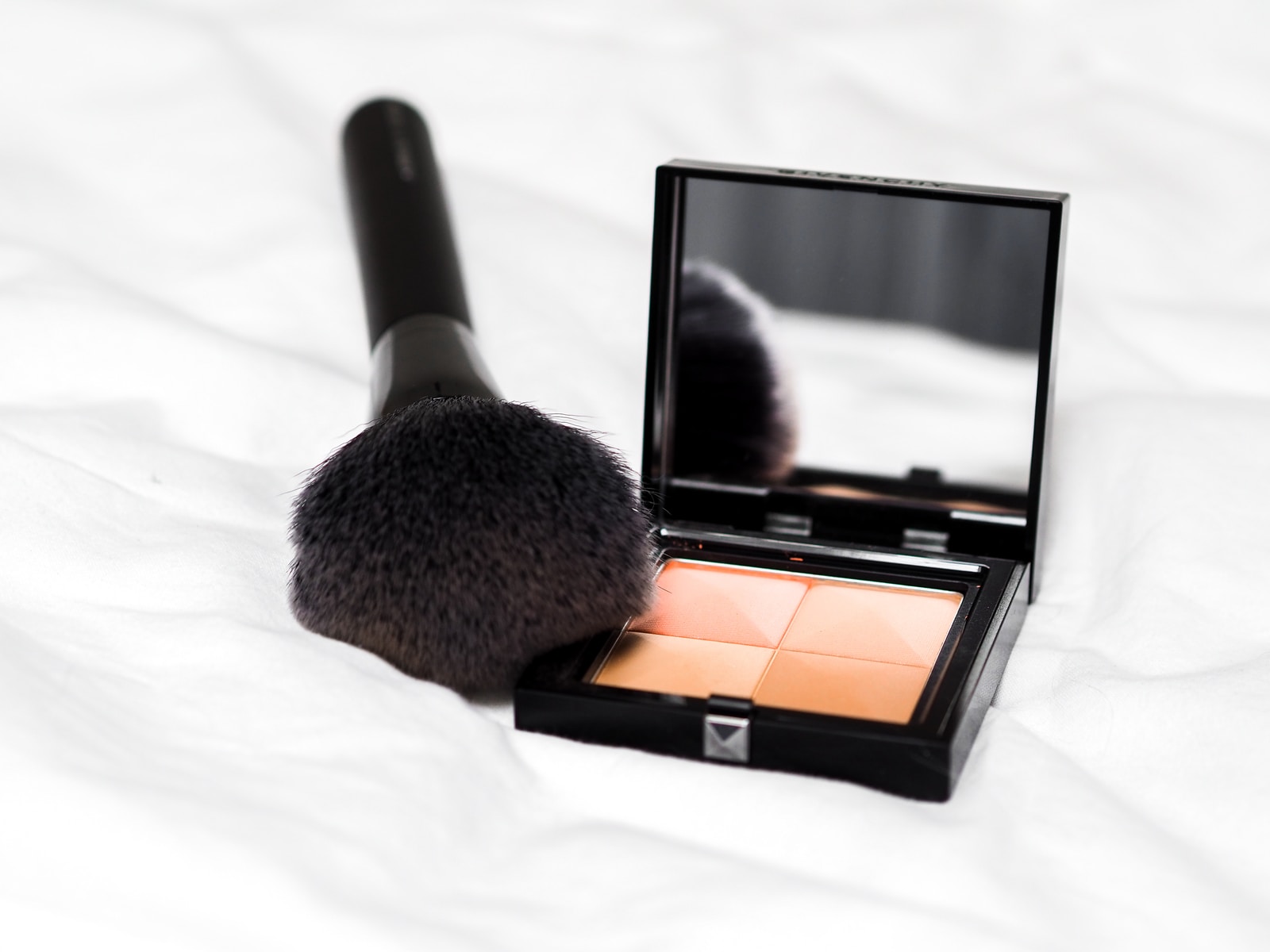
Face powder
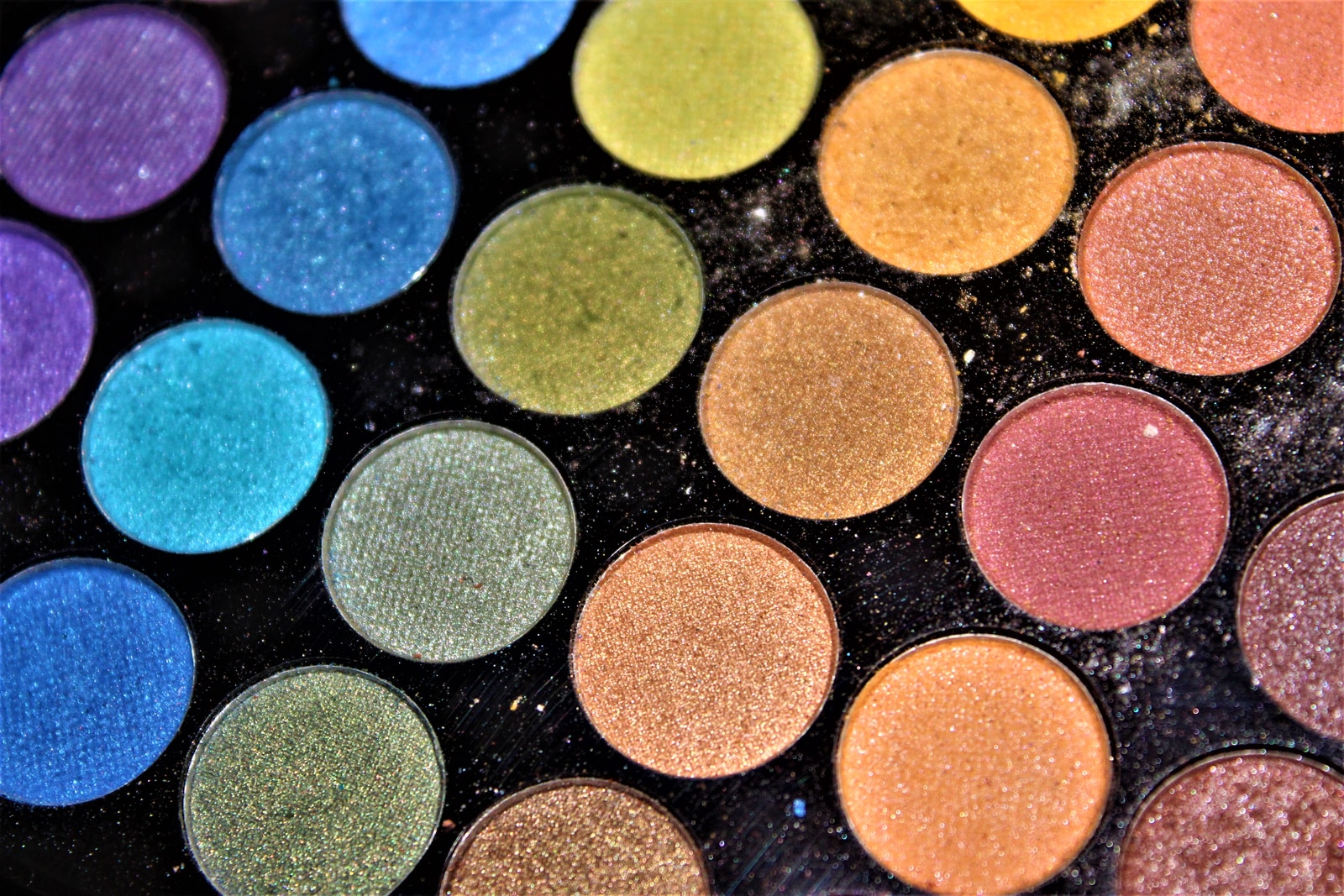
Eyeshadow
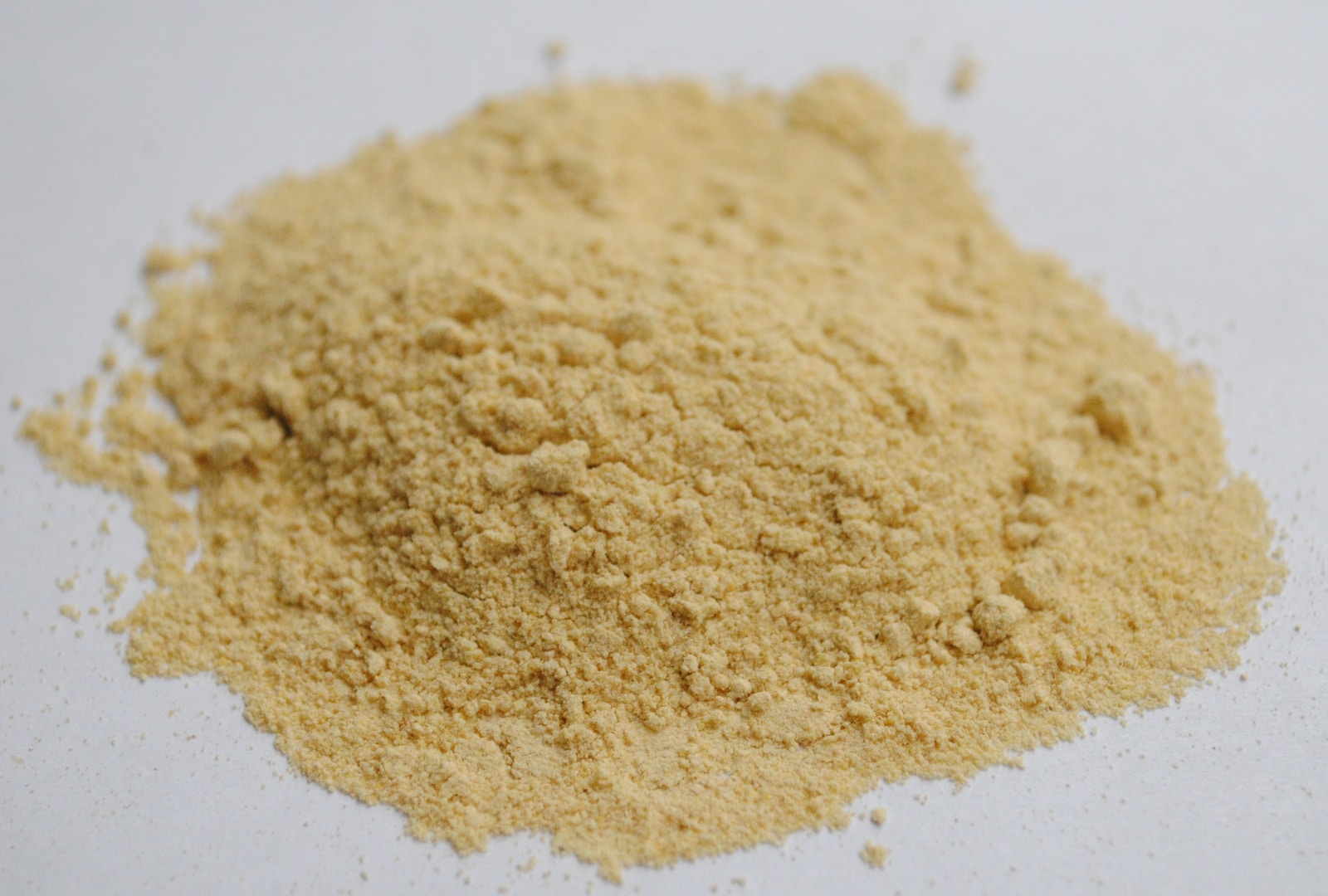
Protein powder
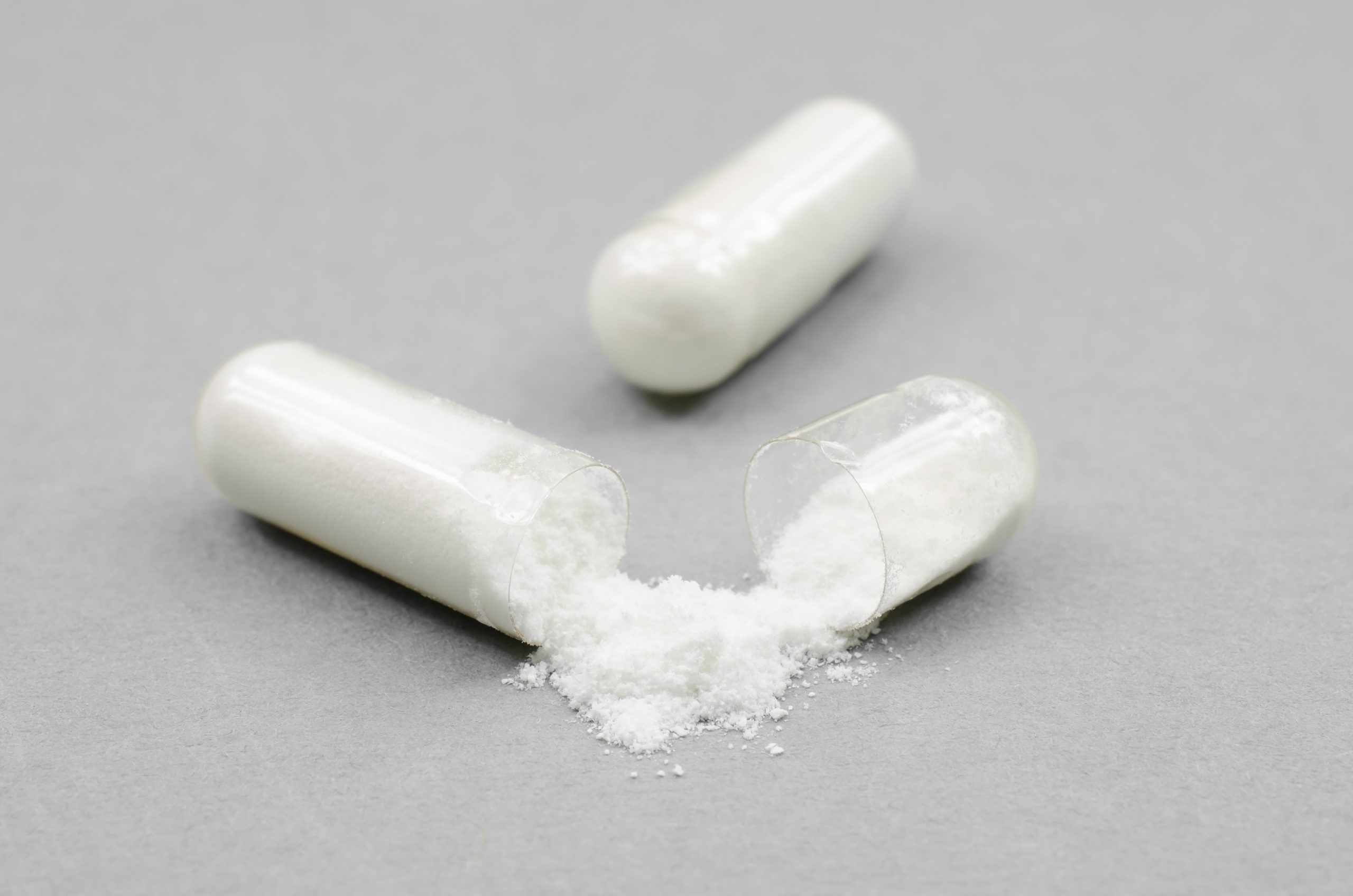
Active pharmaceutical ingredients (API)
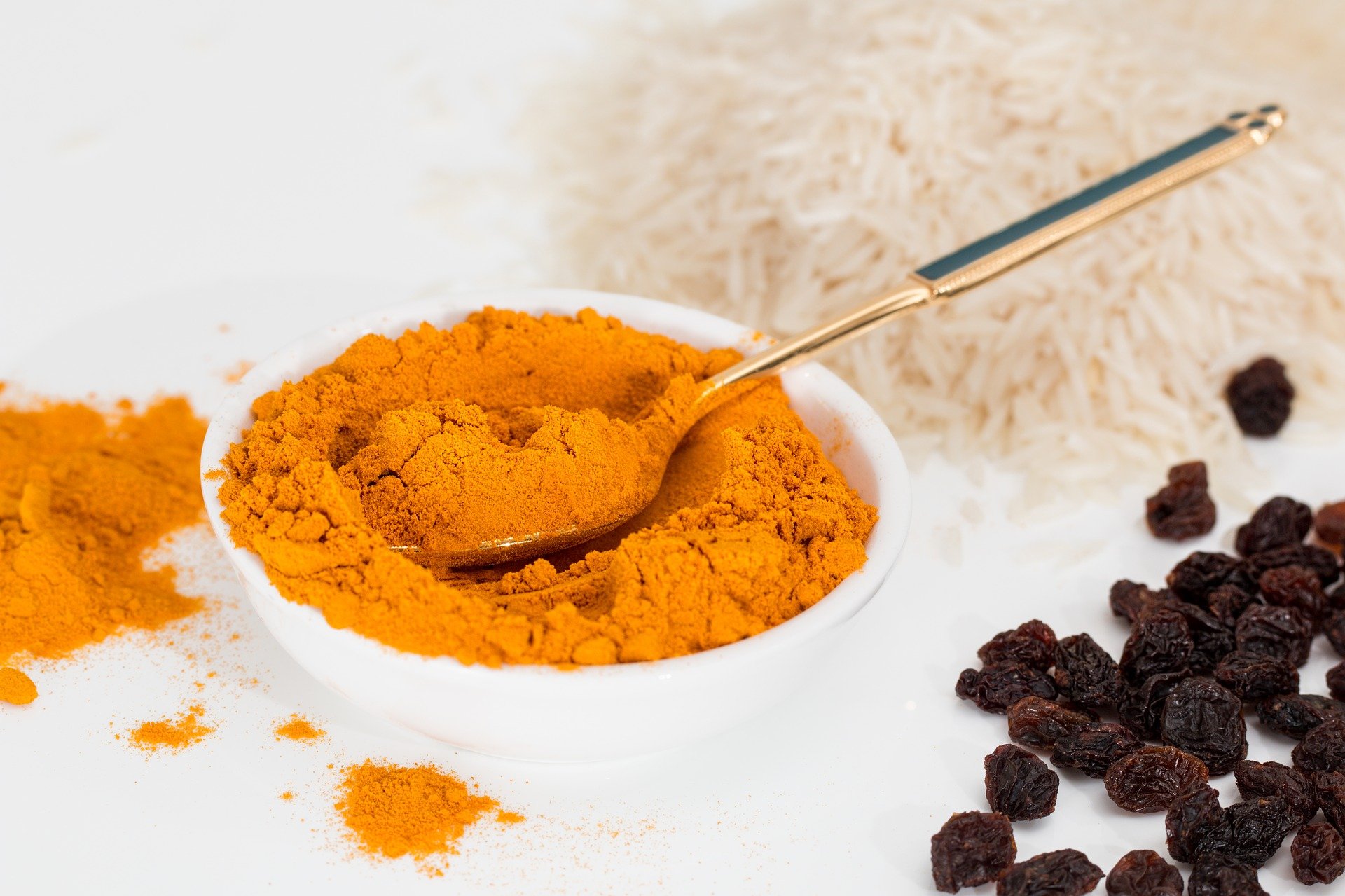
Curry powder
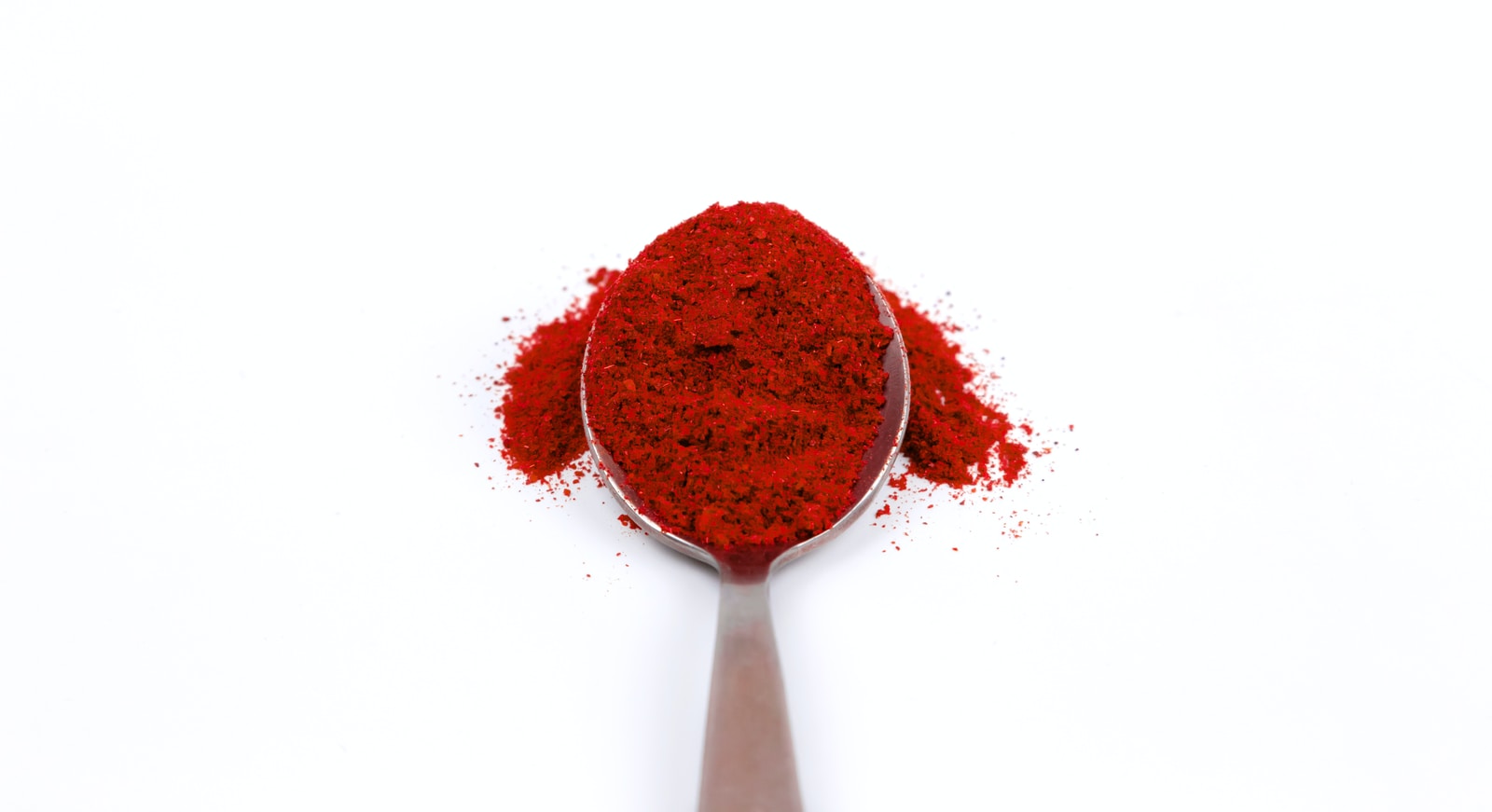
Chili powder
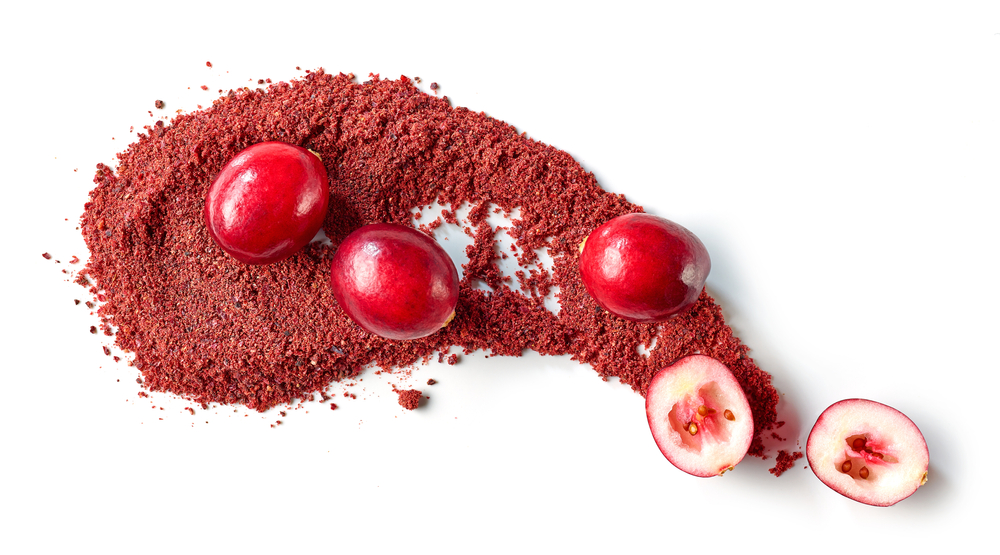
Fruit powder
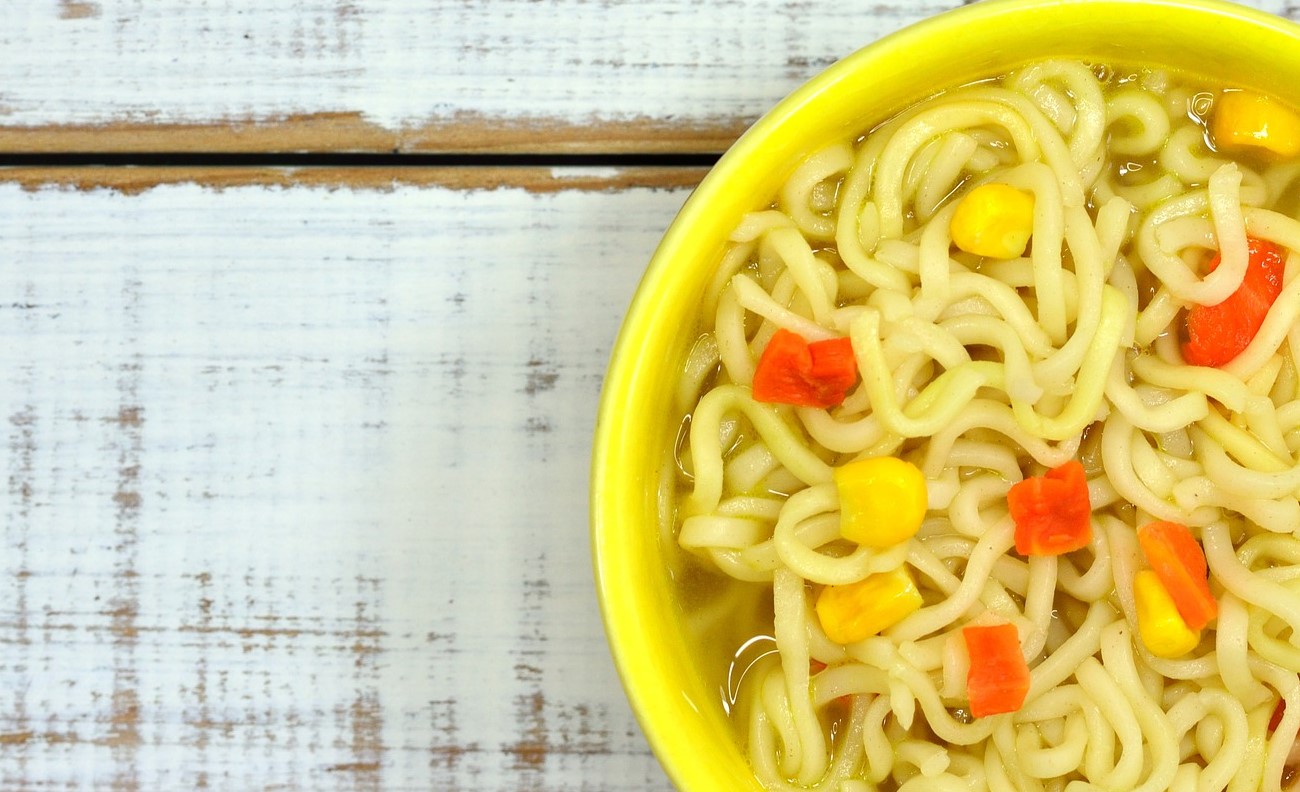
Instant soup
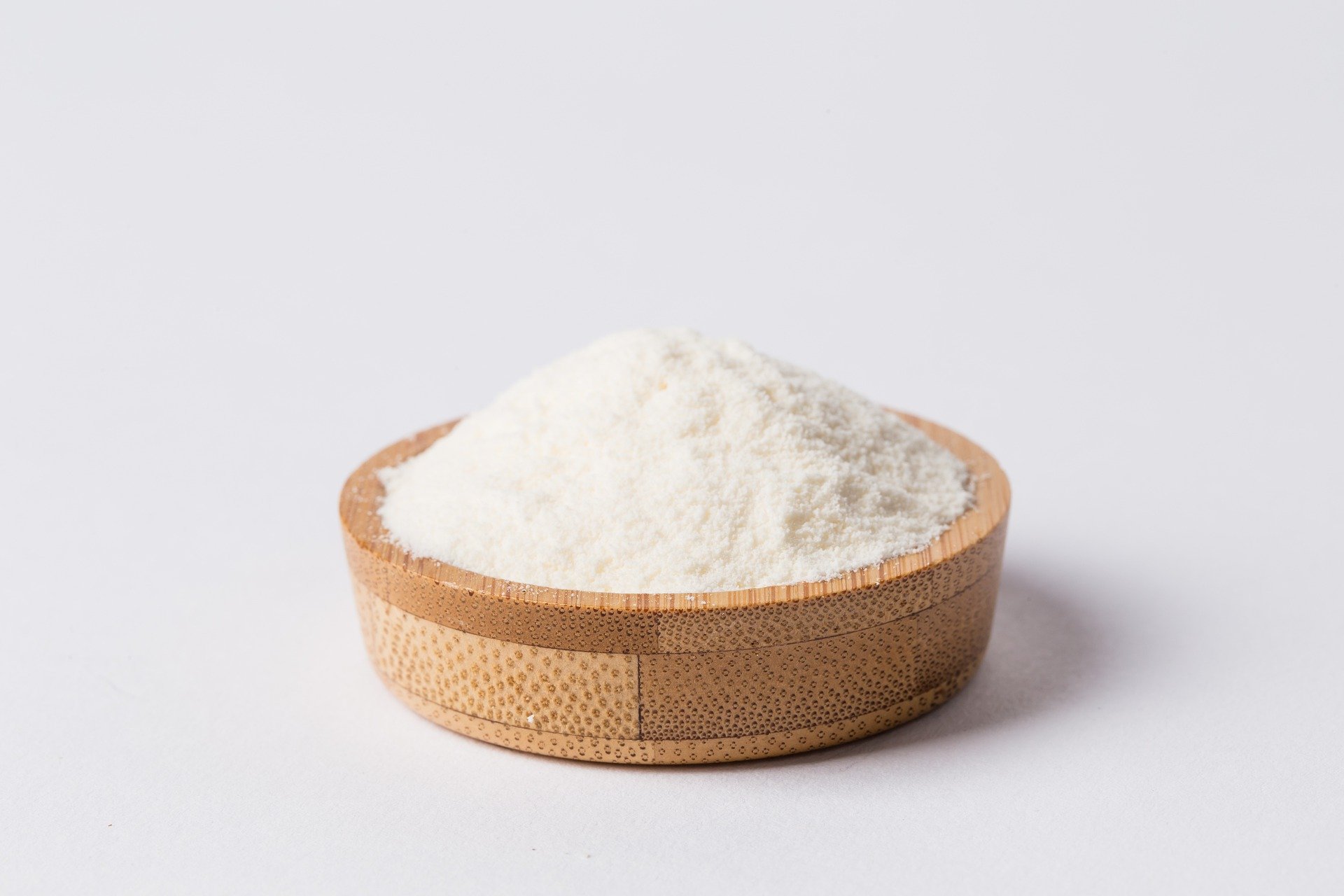
Milk powder
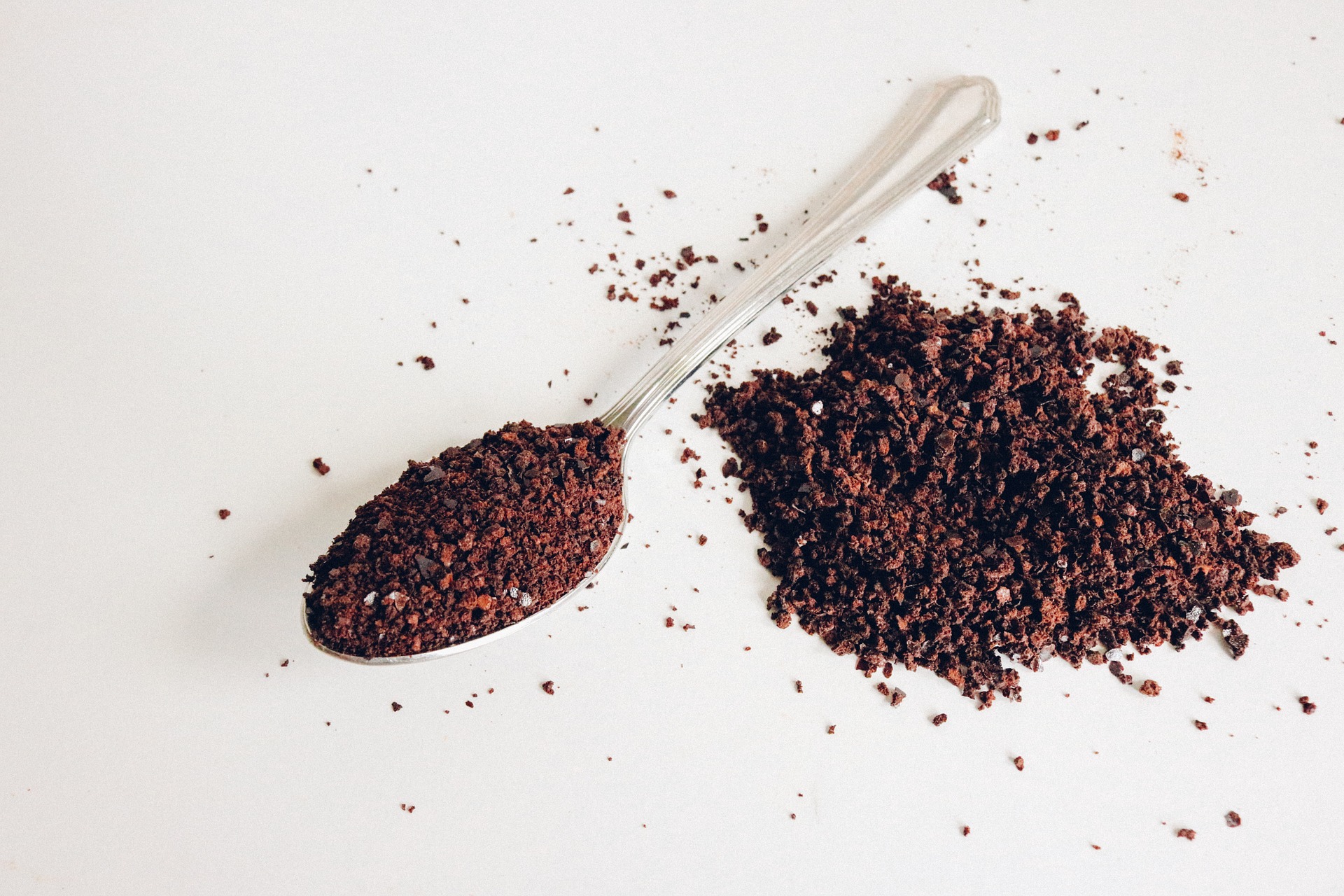
Instant coffee
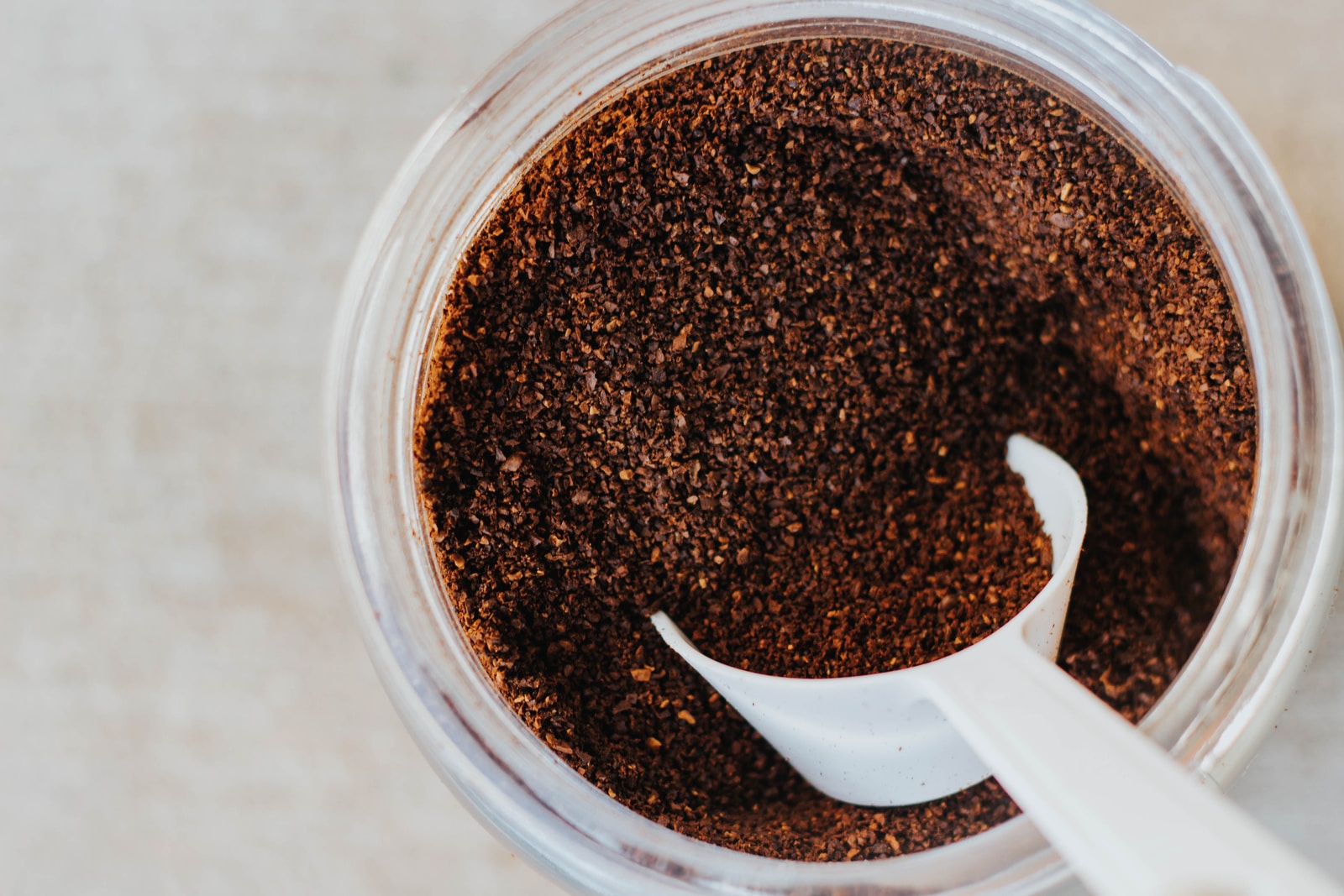
Ground coffee
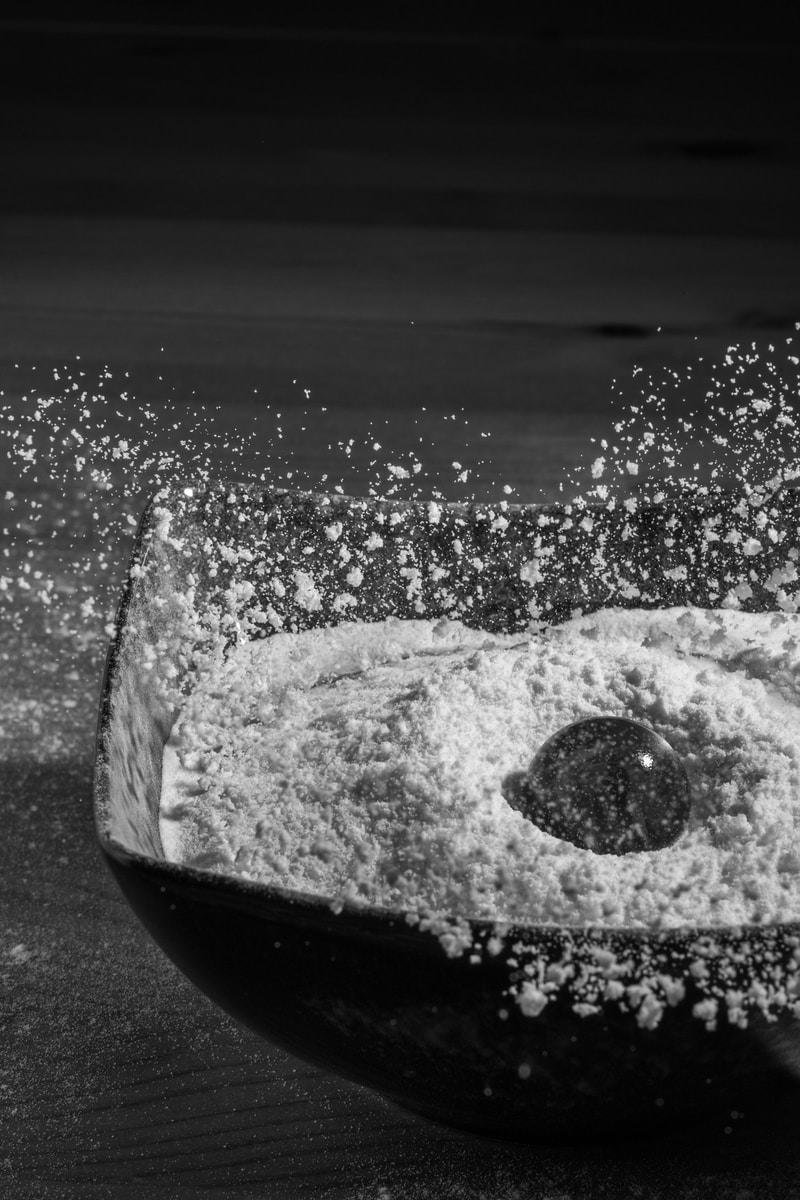
Flour
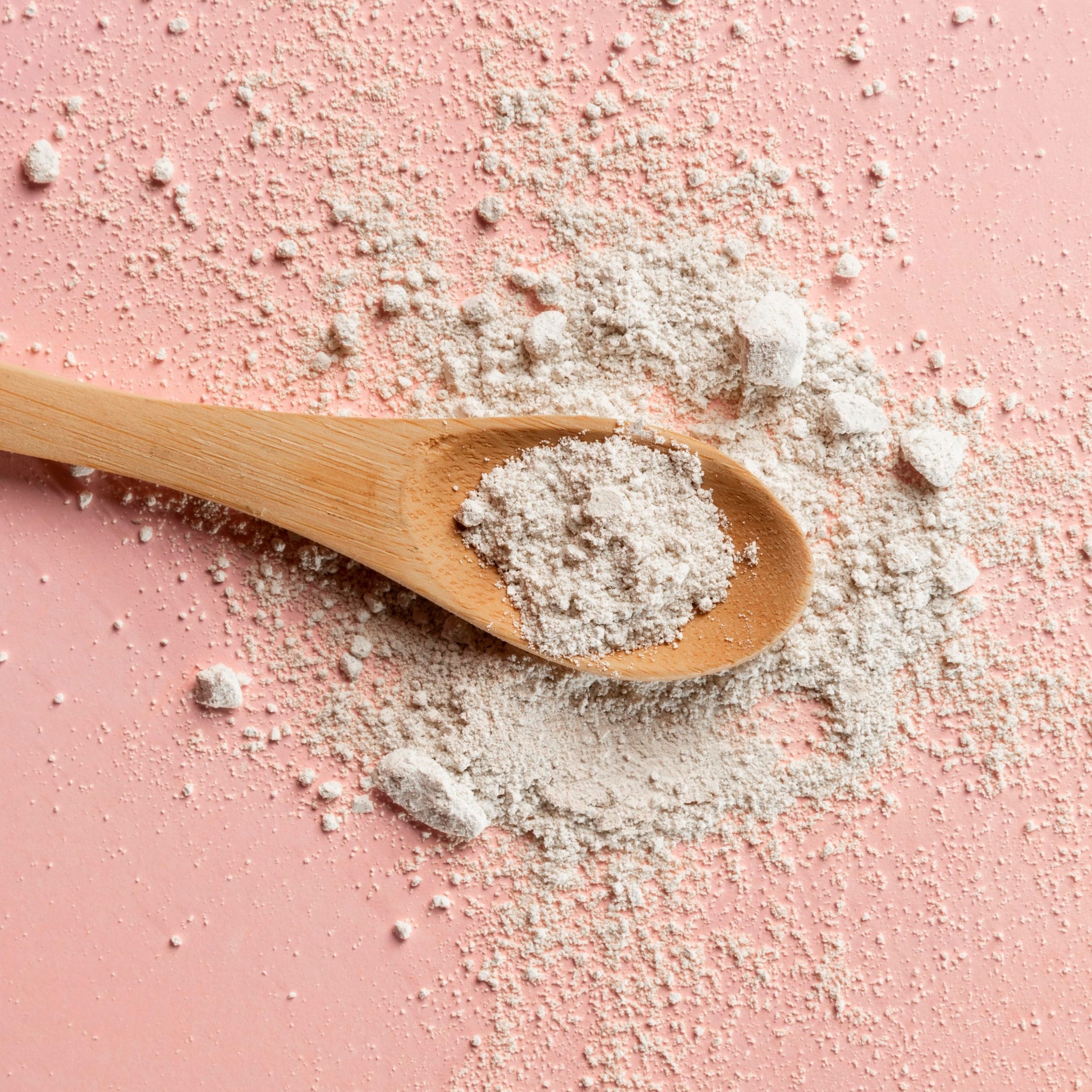
Baking powder
Tell us about your production challenge
Crush primary materials to free valuable grains from impurities
The first step to pulverizing a solid is through a crusher. The raw material is downsized to flakes, chips, or granules by crushing technology. Some bulk types, such as plastics or resins, are broken down into filaments.
Crushing breaks the grains away from gangue materials, particularly in the case of ore. Undesired compounds such as common silicate and carbonates are removed using separation technology like magnetic separators for metals and froth flotation for hydrophobics.
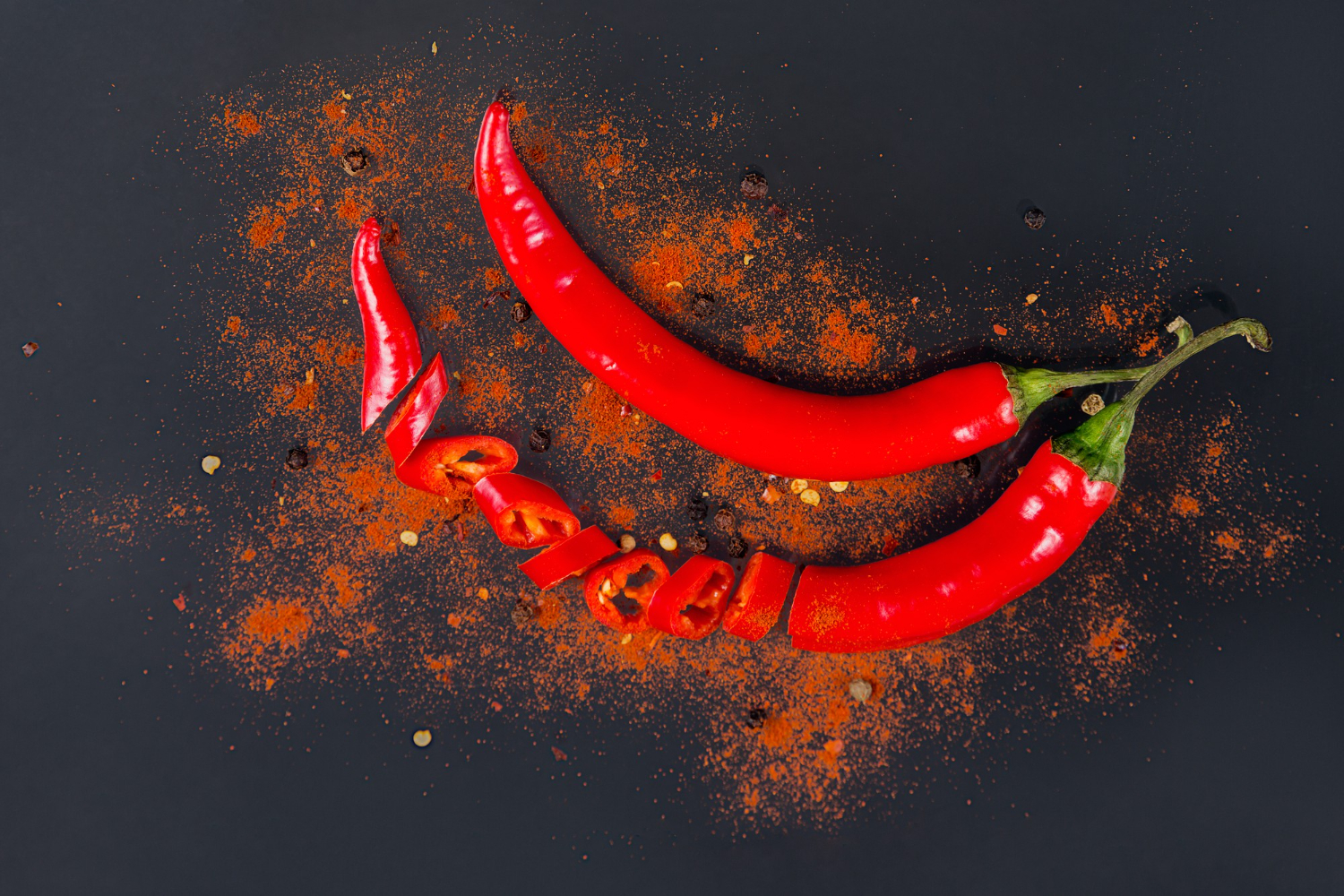
Use anti-clogging powder process equipment to ensure flowability
One of the main attributes of powders is flowability. Dry materials with a similar particle structure flow more easily than powders of different shapes. However, size is also an important variable in industrial powder handling.
Flowability decreases with the particle size as powders display greater cohesion and internal friction the smaller they become. To prevent ratholes or bridging and facilitate flow, advanced manufacturing equipment applies anti-clogging systems. These powder processing systems and techniques are designed to move fine to ultra-fine bulk in specialized powder applications from pharmaceuticals to food to cosmetics.
Avoid unwanted agglomeration by coating powders in anti-adherent components
Manufacturing technology often subjects powders to thermal stresses that could degrade their processability. High pressure friction and heat lead to surface diffusion, bonding particles together.
To prevent such undesired agglomeration, coat the powder particles in an anti-adherent substance like magnesium stearate. The water-insoluble compound is sprayed onto the material in a mixing drum to create a film around the particles.
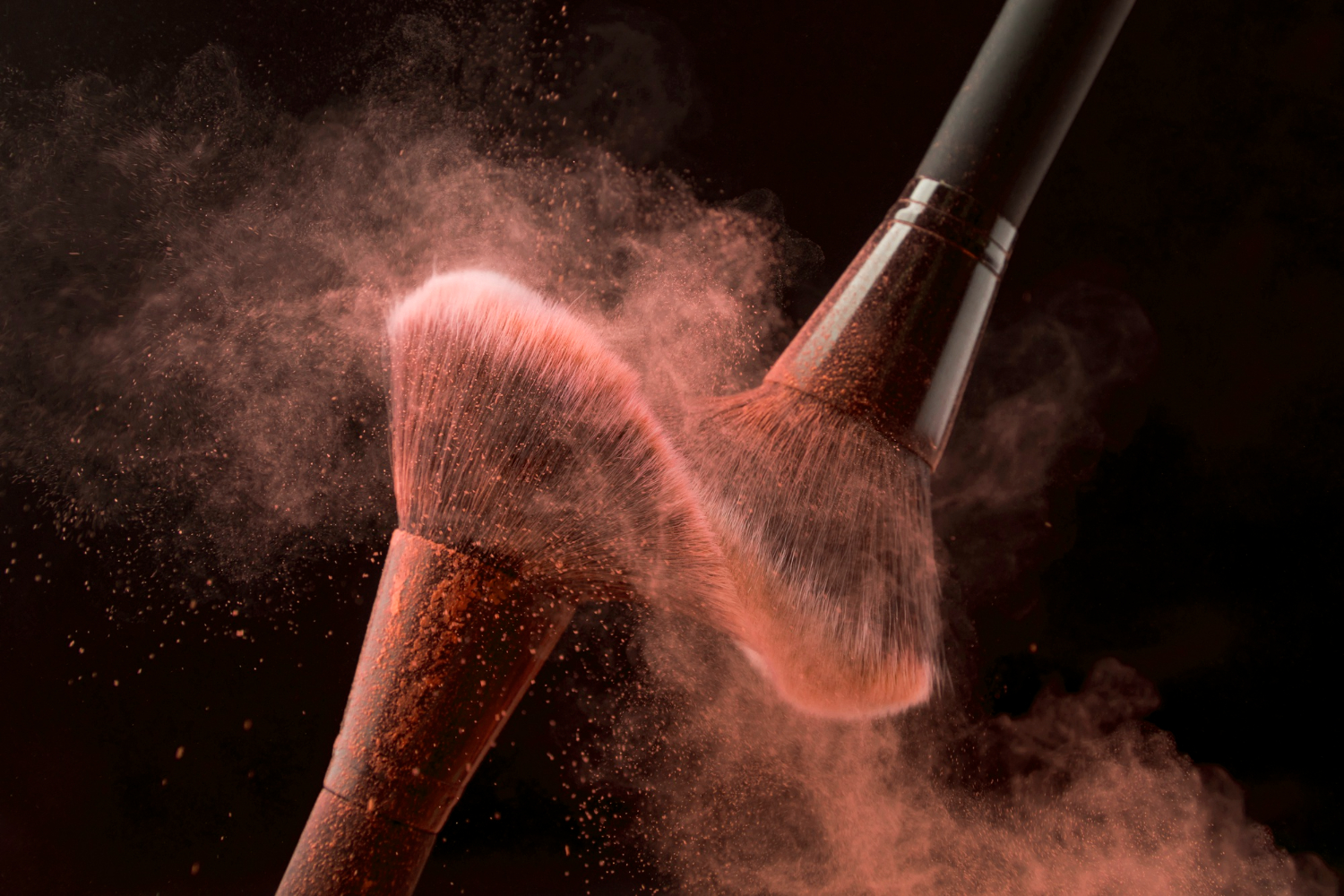
Heat mineral and metal fine powders to overcome resistance to compaction
Mineral and metal powders present unique challenges in terms of processing, particularly when they are comminuted to finer materials. Particles become harder as their surface area increases, making them more challenging to densify.
Ductile metals like aluminum and copper retain plastic deformation properties down to particle sizes of 50-100 nanometers. But beyond that, powders need to be subjected to high temperatures to be effectively compacted.
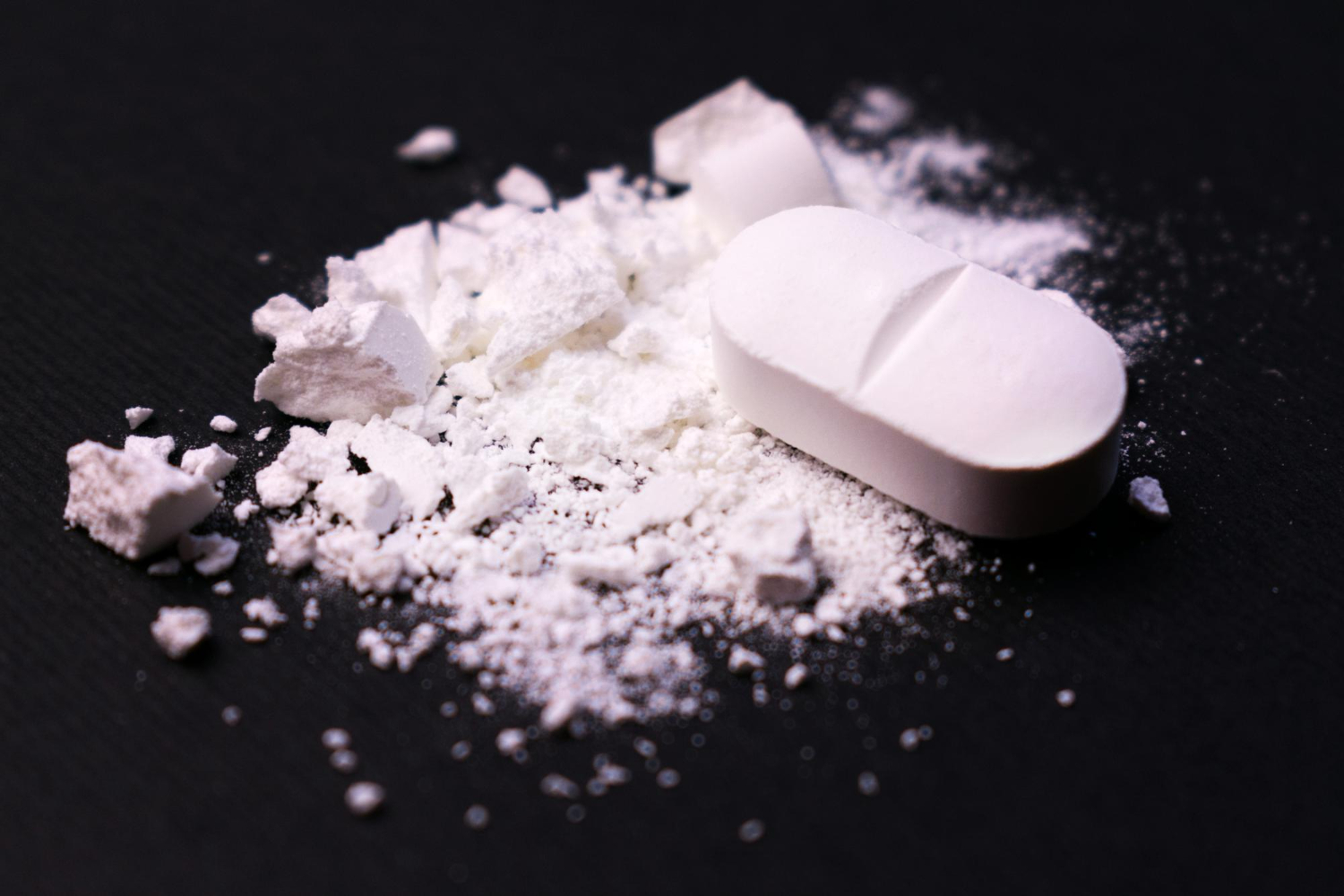
Reduce powders to their nanostructures to maximize their properties
Particles of nanometric scale bond together to form nanopowders. As the ratio between surface area and volume increases, the characteristics of the atoms become more pronounced.
For instance, nanocrystalline materials such as titanium alloys nickel exhibit enhanced hardness and plasticity. Advancements in powder processing technology allow engineering at the nanoparticle level, opening opportunities for new lightweight materials with solid structural stability.
Develop nanopowders either by bonding particles or downsizing granules
There are two ways to approach the production of nanopowders: large-to-small or small-to-large. When working with large materials like metals or minerals, the powders are generated by attrition. The techniques here are primarily mechanical, using dry milling equipment like jet mills or roll mills.
If you work with molecules such as sodium, the process goes from small to large by bonding molecules together to form the particle. This involves electromagnetic techniques like electrospinning and electrodepositing.
Which powder technology do you need?
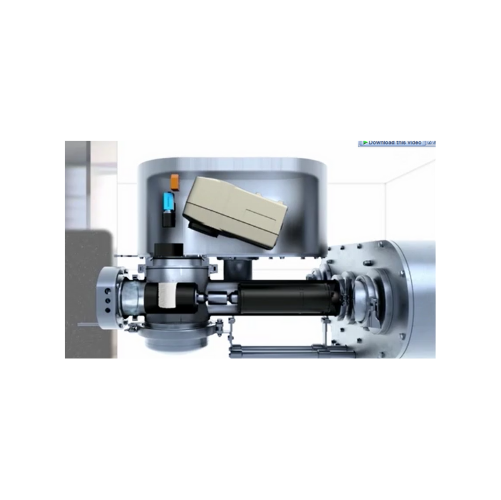
Inline powder analysis system
Ensure optimal powder quality with real-time measurement of moisture, density, and contaminant...
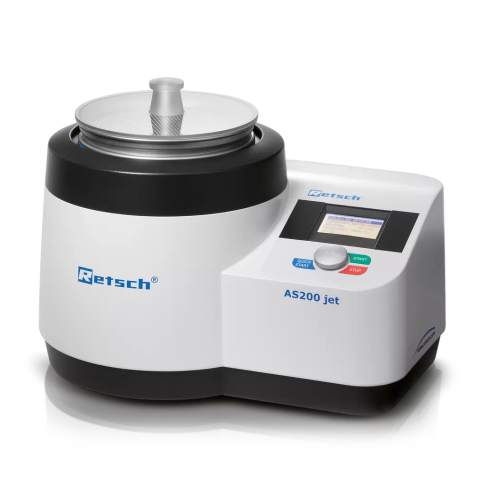
Air jet sieving system for powdered materials
Optimize particle distribution with precision air jet sieving, designed to e...
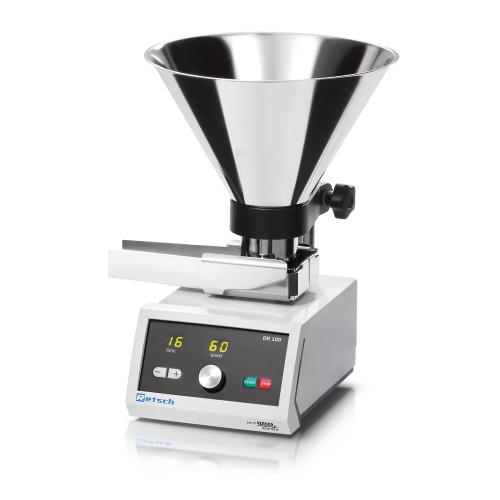
Vibratory feeder for bulk materials and fine powders
Ensure consistent material flow and precise feeding for optimized pr...
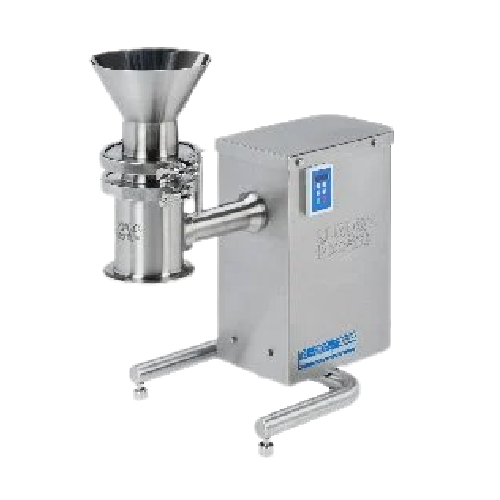
Industrial powder security screening and de-agglomeration
Ensure product purity by efficiently screening and de-agglomer...
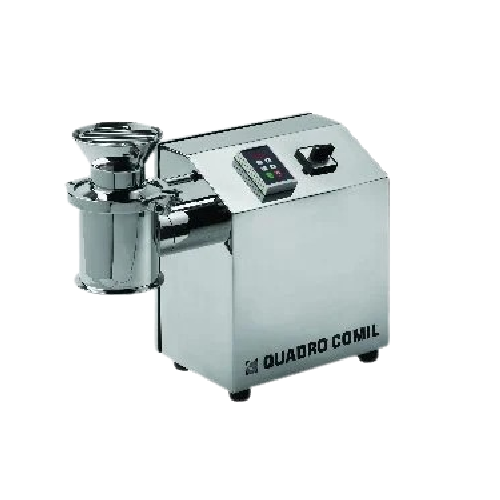
Conical mill for high-capacity powder milling
Optimize your powder milling process with efficient conical milling systems ...
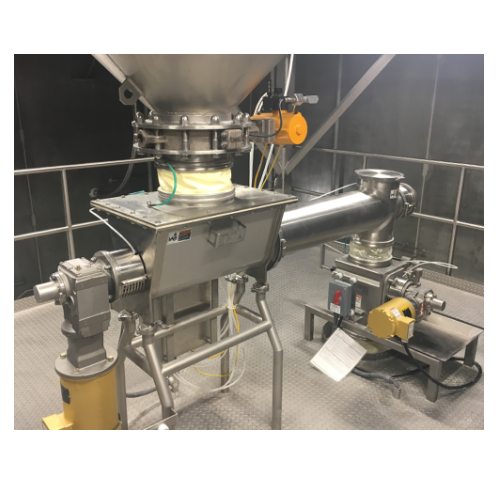
Mechanical conveyors for powder transport
Optimize your powder and granule handling with precise, customizable conveying s...
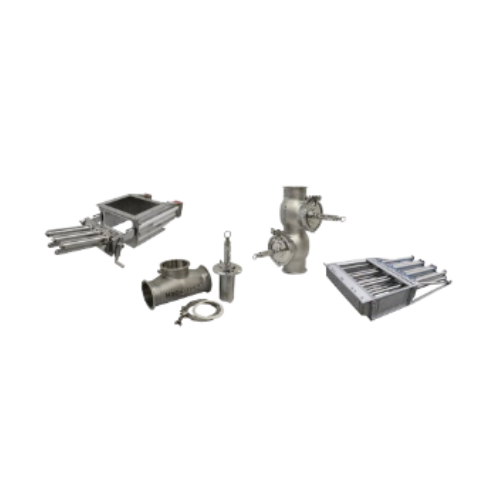
Magnetic separators for metal contaminant removal in powder processing
Ensure product purity and safety by effectively ...
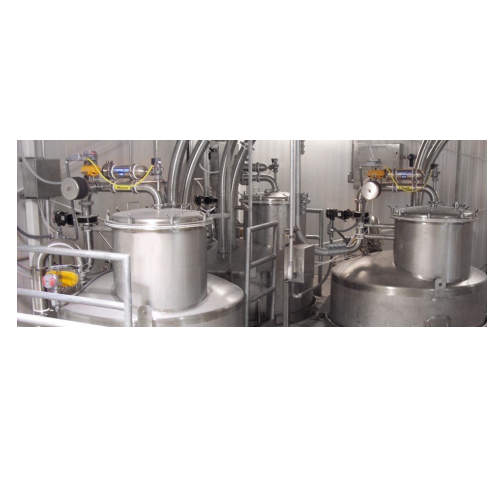
Air filtration system for dairy and food powder processing
Optimize powder processing with advanced air filtration, ensu...
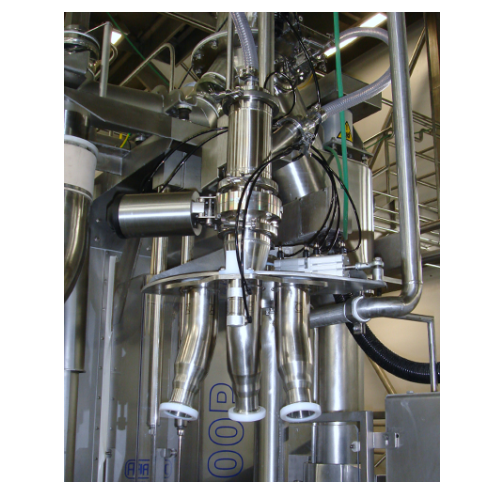
Powder sampler systems for food and dairy plants
Ensure precise quality control by implementing advanced sampling techniqu...
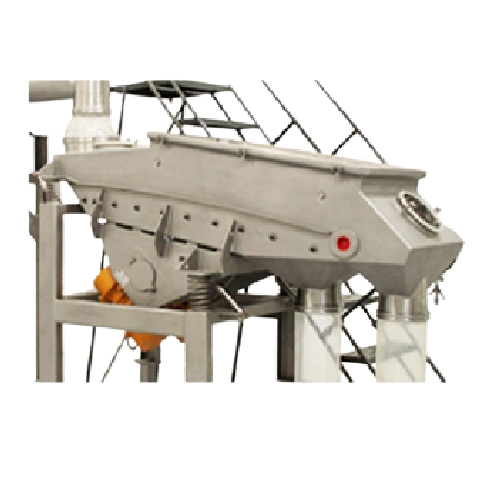
Powder sifters for industrial applications
Optimize powder consistency and enhance production flow with advanced sifting t...
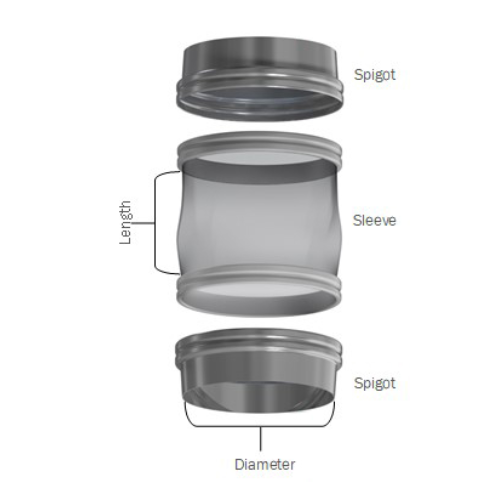
Flexible connector for bulk powder manufacturing
Eliminate leakage and enhance hygiene in your powder processing with a sn...
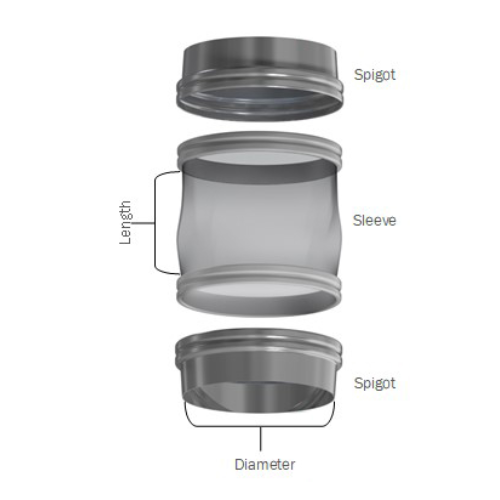
Flexible connector system for bulk powder processing
Eliminate leaks and enhance hygiene in your powder processing line w...
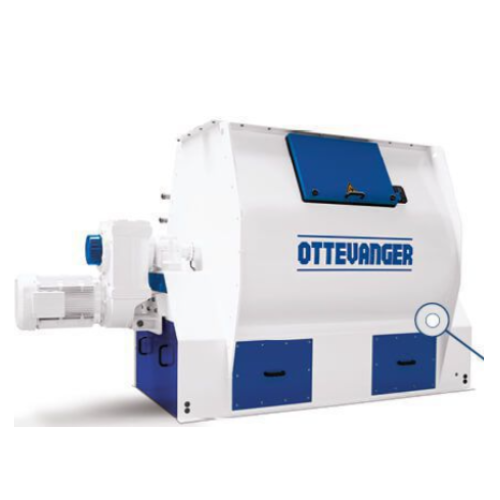
Single shaft paddle mixers for dry powders and granulates
Achieve uniform and precise mixing for your batch processing n...
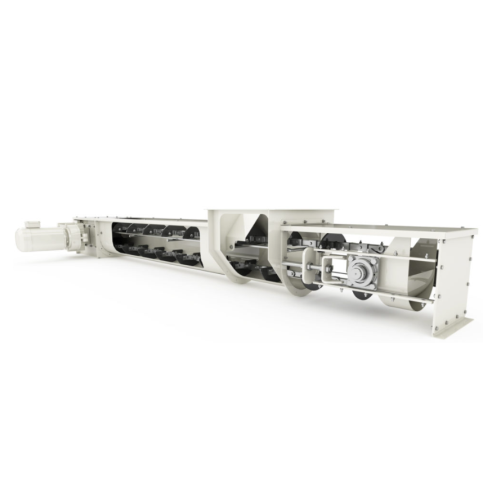
Efficient powder and granulate flight conveyors
Elevate your production efficiency with our cutting-edge flight conveyors,...
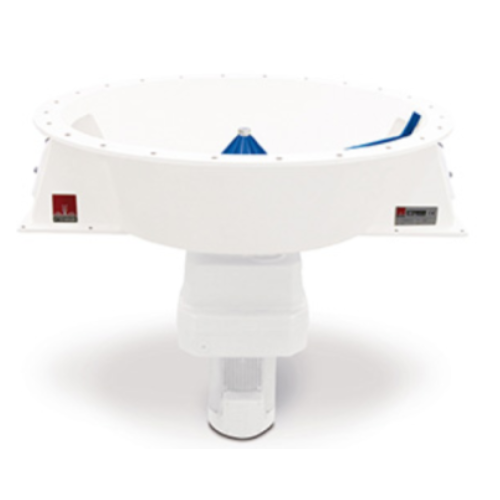
Rotary dischargers for powders and granules
Prevent production halts with this solution designed for efficient discharge o...
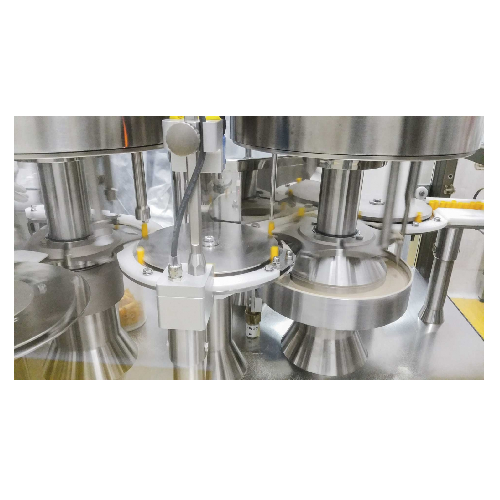
Continuous motion micro dosing system for nutraceutical powders
Streamline your powder processing with a high-speed, con...
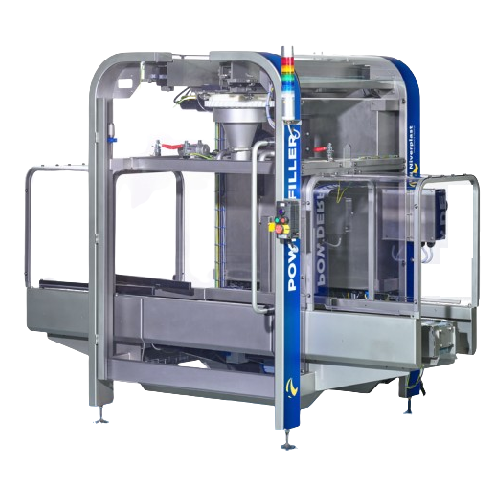
Accurate powder filling solution
When precision is paramount, this solution offers exceptional accuracy, filling powders up ...
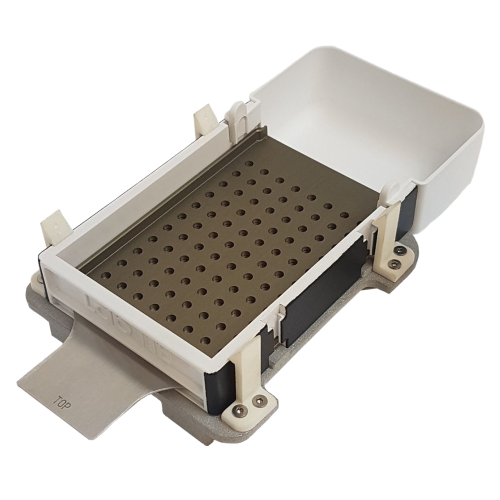
Lab powder dispenser for precision measurements
Effortlessly streamline your lab’s powder dispensing tasks with a ve...
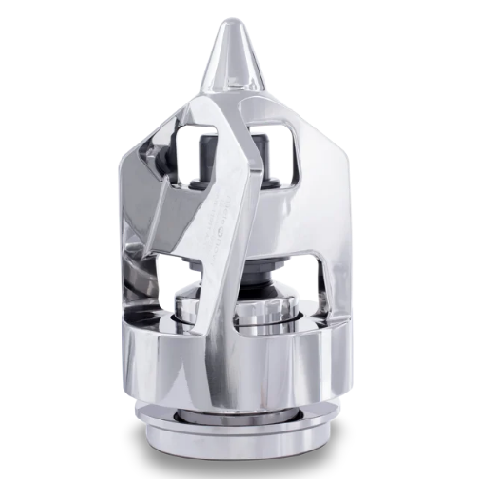
High power mixing solution for powder applications
Achieve rapid, uniform mixing of challenging powders and non-shear sen...
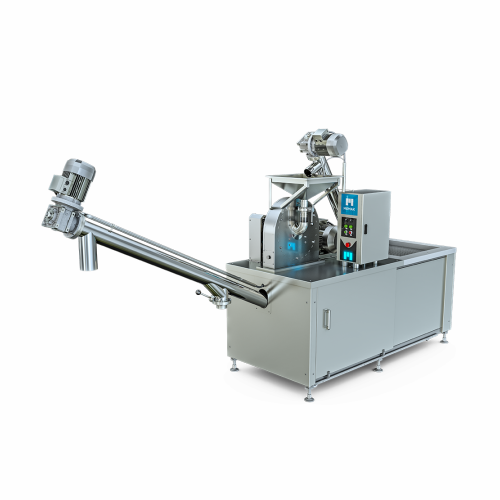
Industrial sugar powder mill
Achieve precise sugar granulation with a high-speed mill designed for continuous production, en...
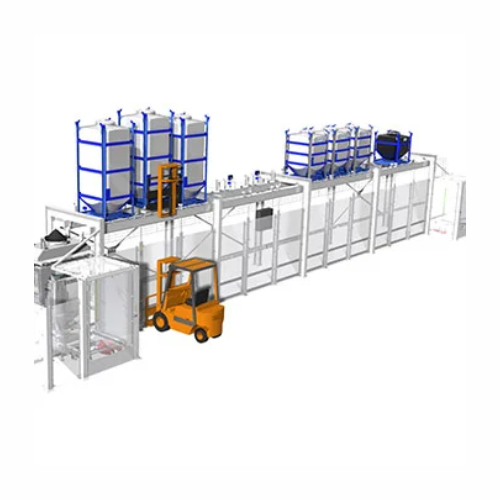
Flexible powder recipe formulation system
Streamline your batch production with efficient, dust-tight formulation and blen...
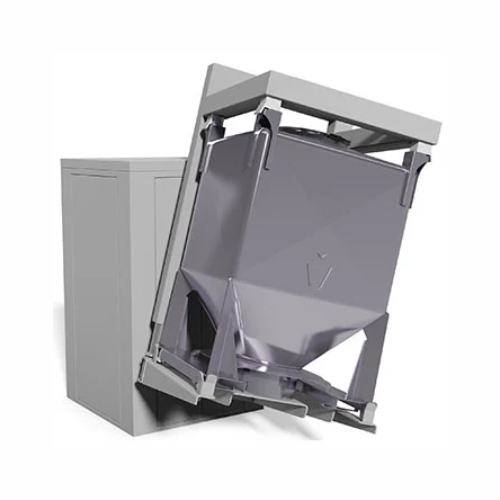
Ibc blender for industrial powder mixing
Streamline your powder mixing with rapid batch changeovers and reduced cleaning do...
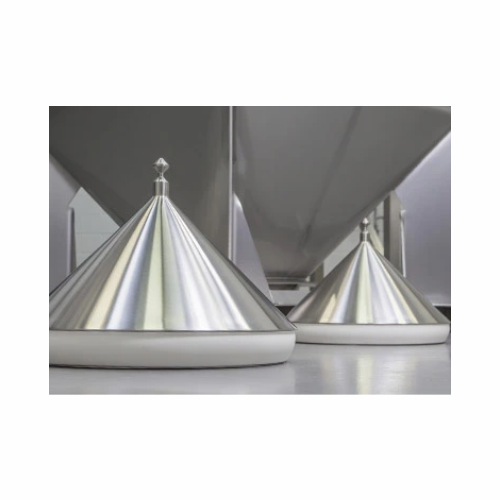
Valves for bulk powder flow control
Ensure efficient and controlled discharge of diverse powder forms while minimizing flow...
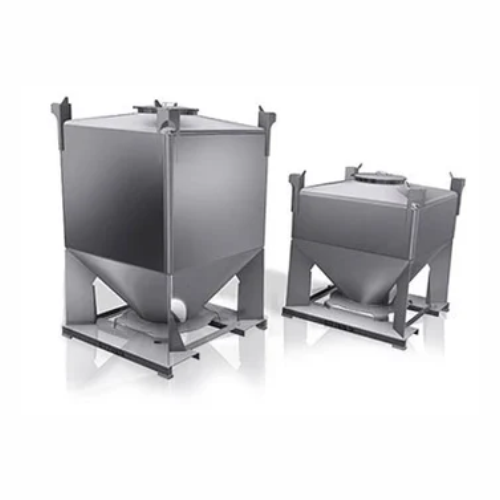
Powder handling system for industrial applications
Overcome powder flow issues and enhance production efficiency with adv...
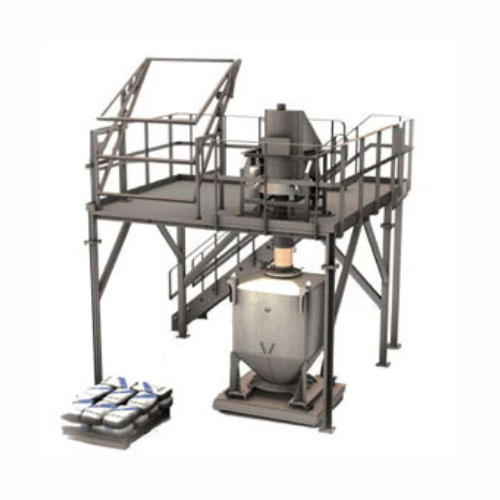
Small powder recipe formulation system
Streamline the formulation of diverse powder recipes with seamless integration into ...
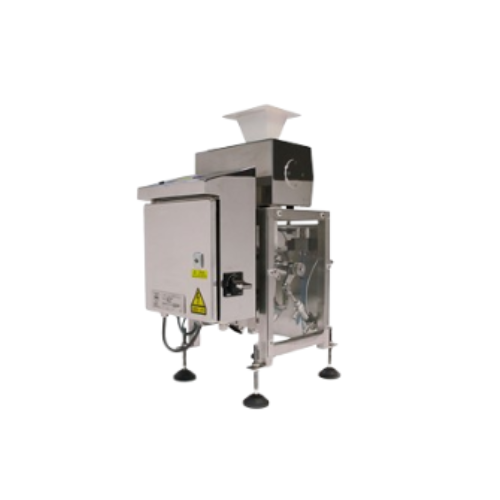
Pharmaceutical powder and granule metal detection system
Ensure the integrity of your pharmaceutical and nutraceutical pr...
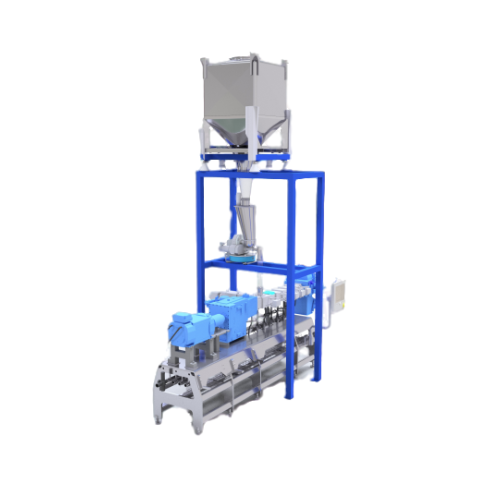
Powder handling systems for battery production
Optimize your battery production with a versatile powder handling system th...
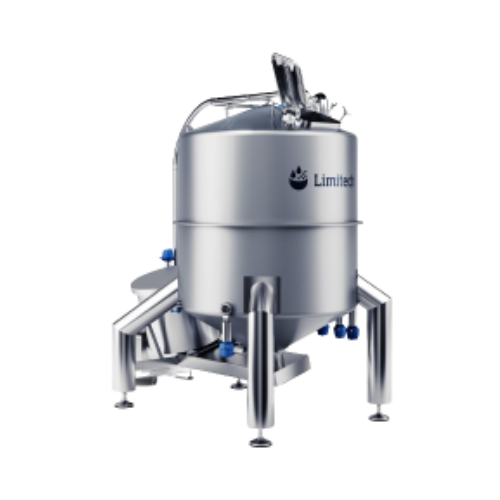
High shear mixer for viscous powder dissolution
Need consistent, homogeneous blending of high-viscosity liquids and powder...

Pre-mixer for dissolving powders fast
Quickly dissolve powders without lumps or “fisheyes,” ensuring a smooth a...
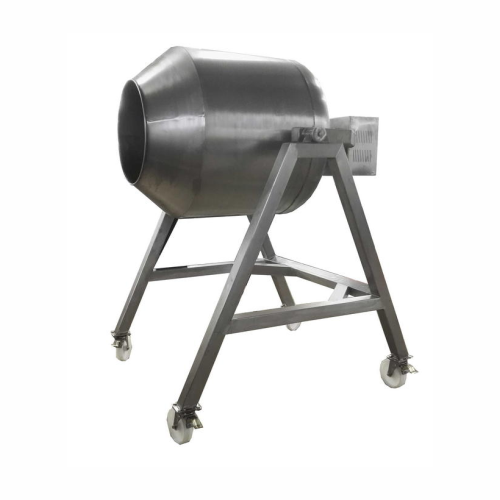
Industrial food mixer for vegetables and powder mixing
Enhance your production efficiency with a versatile mixer designed...
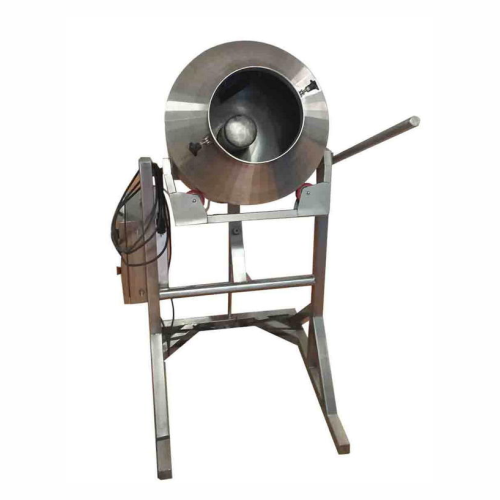
Industrial mixer for vegetable, powder, rice, noodle blending
Effortlessly achieve consistent blends with this 100-liter...
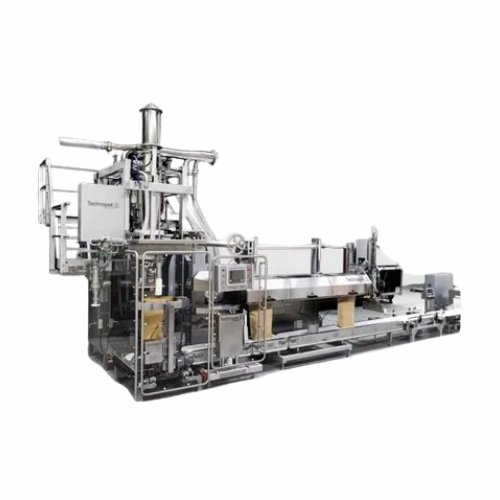
25kg automatic dry powder packaging system
Optimize your packaging line efficiency with precise, high-speed handling for 2...
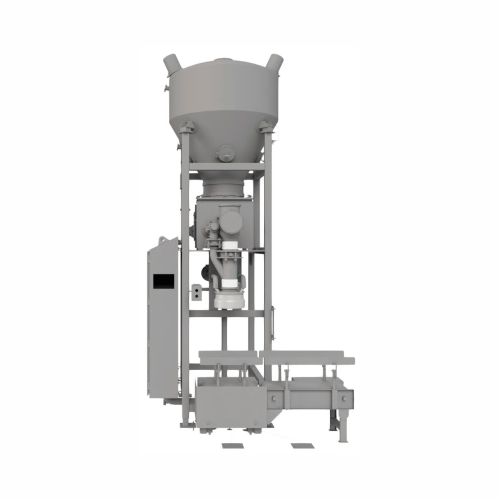
25kg powder packaging system for sanitary applications
Achieve high accuracy and hygiene in powder packaging with a syste...
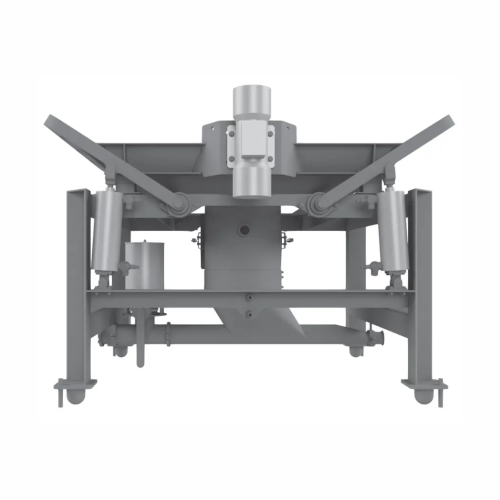
Sanitary bulk bag unloader for powdered products
Efficiently manage powder discharge with enhanced dust control and stream...
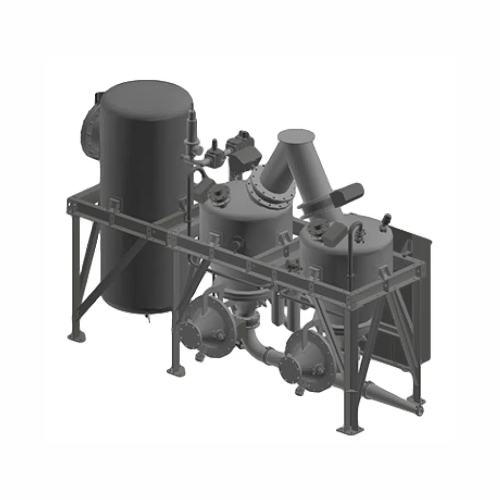
Dense phase pressure conveying system for fragile powders
Ensure gentle handling and long-distance transport of fragile ...
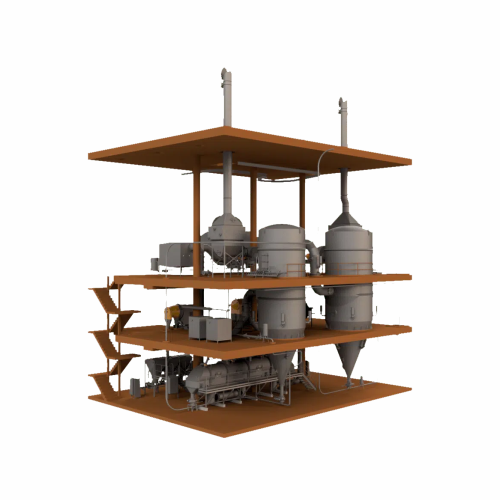
Lactose drying system for high-quality edible powder
Achieve precise and cost-effective lactose transformation into high-...
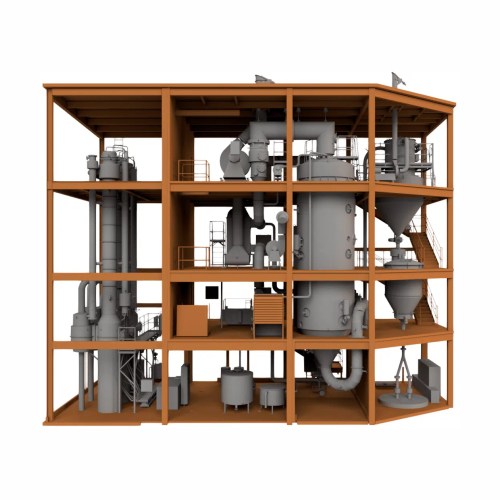
Compact drying solution for regular skim and Wpc powders
Streamline your drying process with a compact solution that effi...
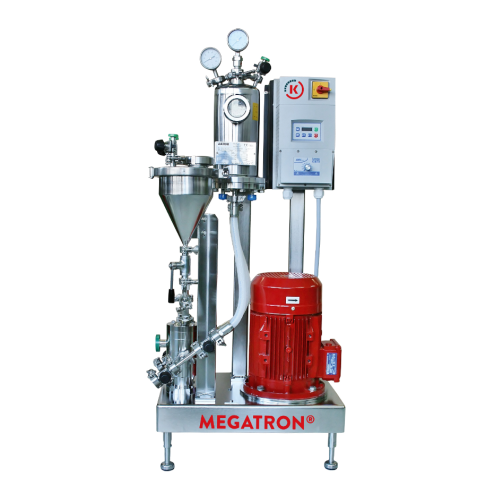
Powder induction system for high solid concentrations
Optimize your production line with this advanced system designed to...
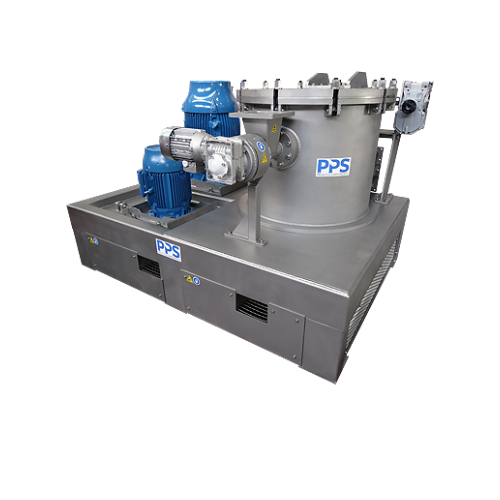
Air classifier mill for ultra-fine powder grinding
Optimize your milling operations with precision particle size control ...
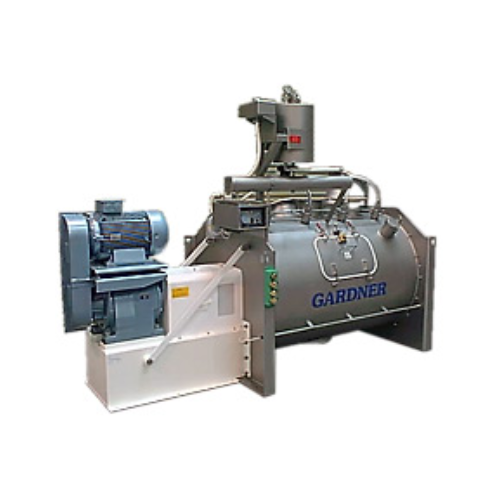
High shear plough mixer for powders, granules, and pastes
Achieve rapid and efficient blending with high shear mixers de...
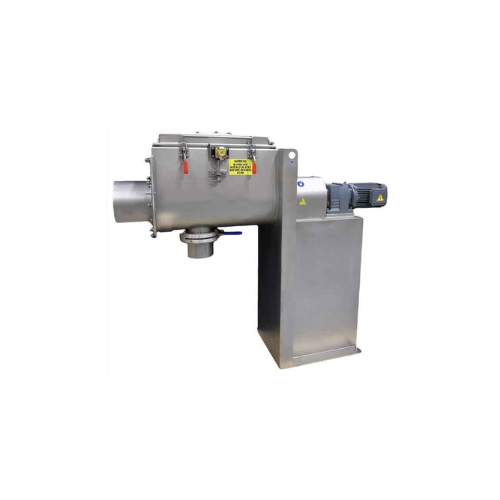
Homogenous blending solution for powders and granules
Achieve precise, homogenous blending of challenging materials like ...
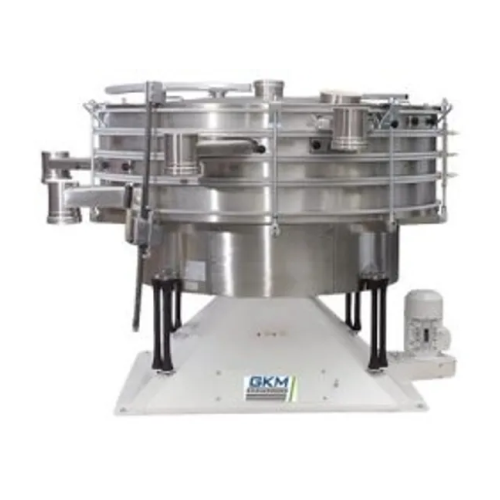
Tumbler screener for multi-deck screening in powders and granules
Achieve precise separation and de-dusting of powders ...
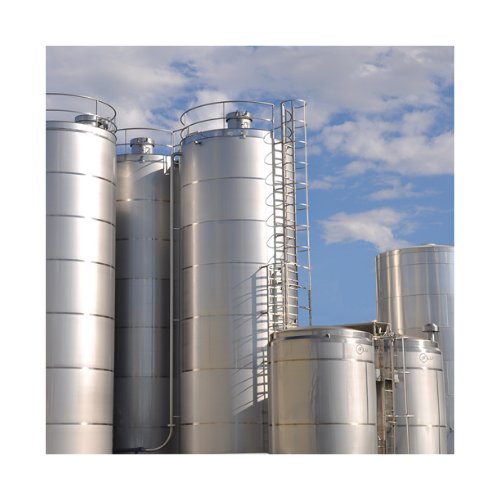
Industrial silos for powdered and granulated products
Optimize your storage and material flow for powdered and granulated...
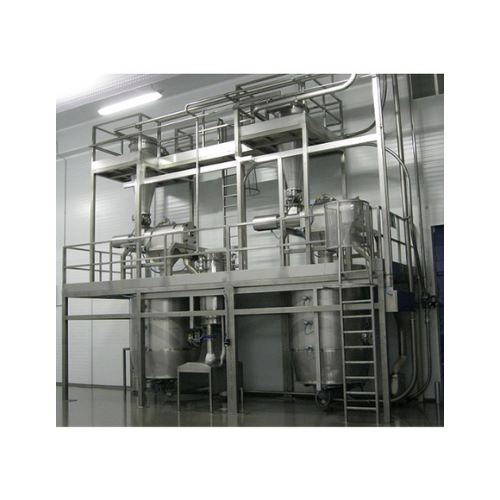
Buffer tanks for powdered or granulated solids storage
Enhance your production line with buffer tanks designed for precis...
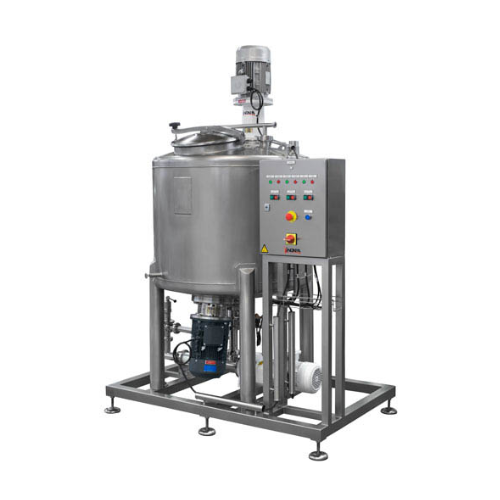
Hydrocolloid powder dispersion unit
Achieve seamless dispersion of hydrocolloid powders in liquids, eliminating common issu...
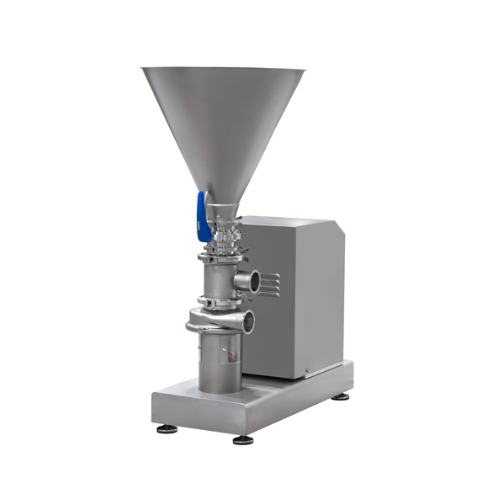
Powder liquid blender for food processing
Achieve seamless integration of solids into liquids with precision-engineered bl...
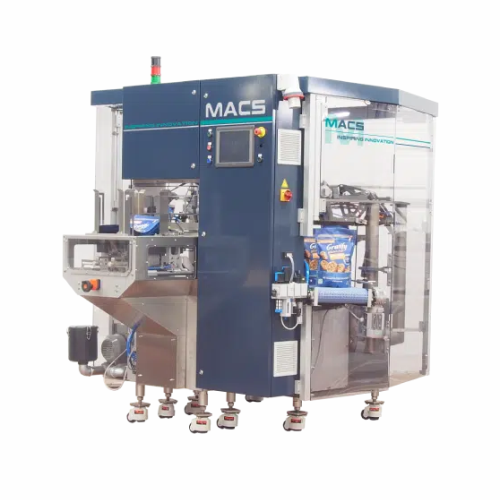
Rotary doypack for granules, liquids, and powders
Enhance your packaging line with a rotary doypack system designed to ef...
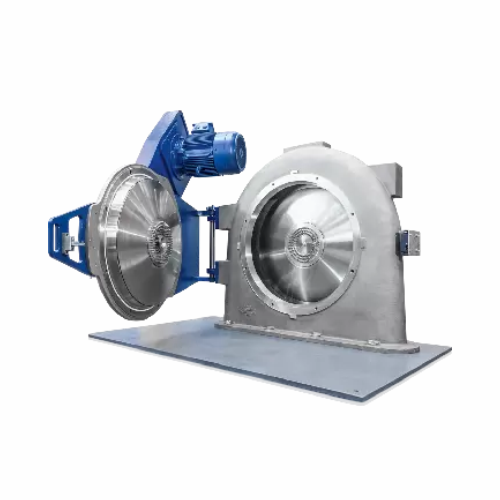
Industrial powder grinder
Achieve precise particle size reduction and classification with advanced equipment designed for co...
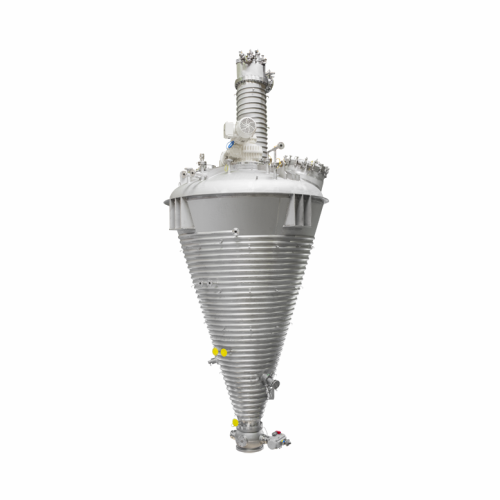
Vacuum dryers for powders and bulk solids
Achieve precise drying and mixing of sensitive materials with advanced vacuum te...
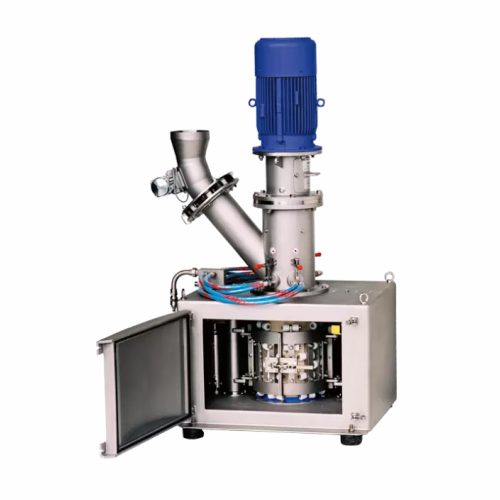
High impact mixer for powders and liquids
Achieve highly homogeneous mixtures with precision. This high impact mixer excel...
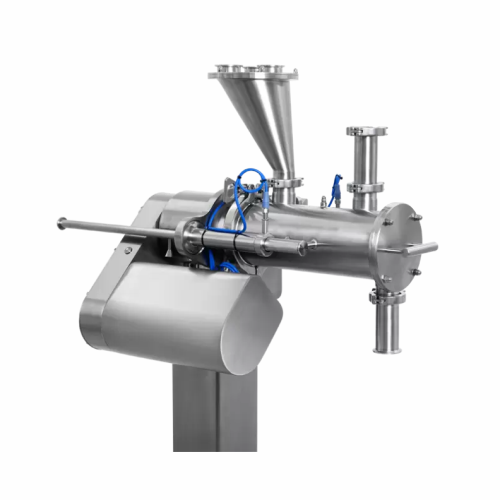
Continuous mixing for fine and cohesive powders
Achieve unparalleled mixing precision for cohesive powders while reducing ...
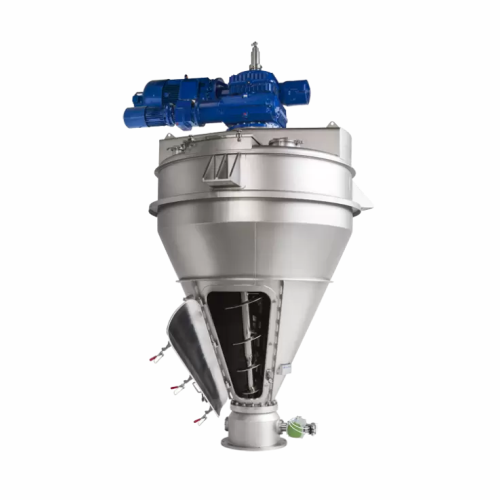
Mid-shear mixer for powders and bulk solids
Achieve ultra-short mixing cycles and superior homogeneity without the need fo...
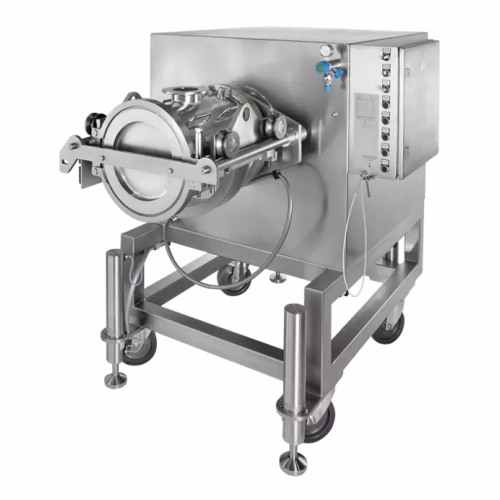
Super high shear mixer for nano to micron powders
Achieve high-precision mixing and surface treatment of nano to micron-s...
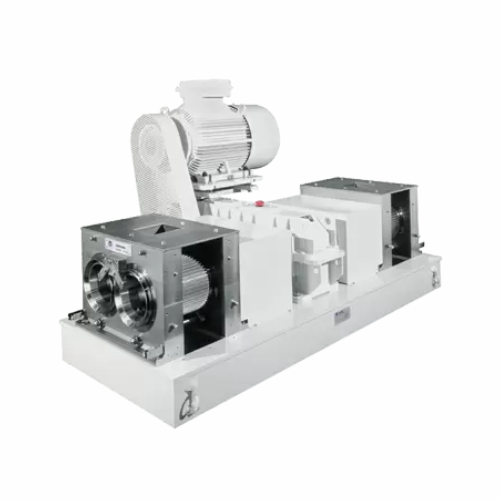
Compactors and granulators for powdery products
Transform loose powders into dense, free-flowing granules that enhance han...
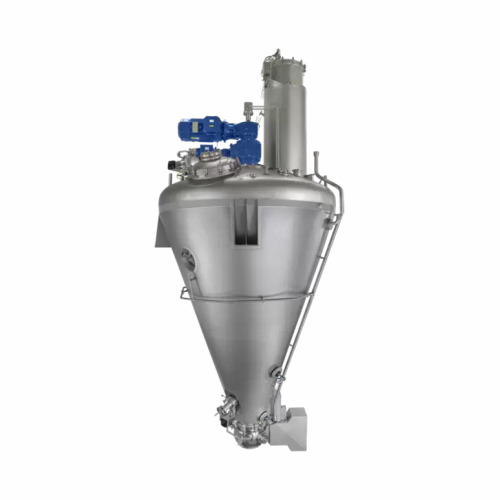
Vacuum dryer for powders and granules
Achieve precise moisture control for sensitive materials with a versatile vacuum dryi...
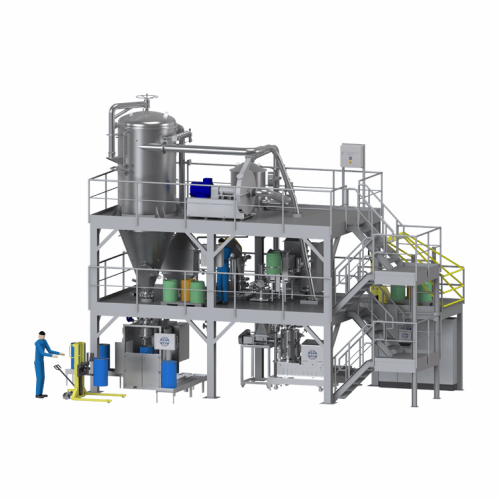
Drying systems for powders and bulk solids
Enhance your production line with precise control of moisture content in powder...
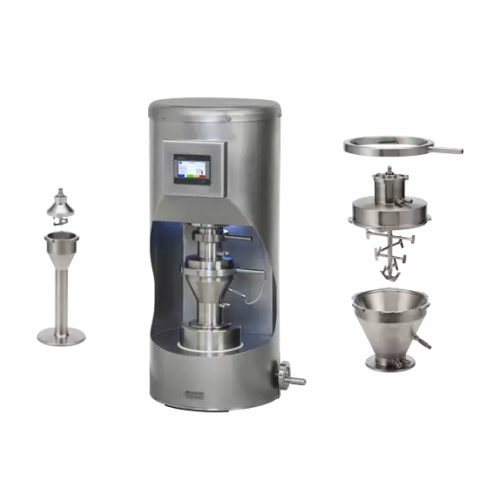
Lab mixer for powder formulations
Achieve precise particle mixing and coating with this stand-alone high-shear lab mixer, d...
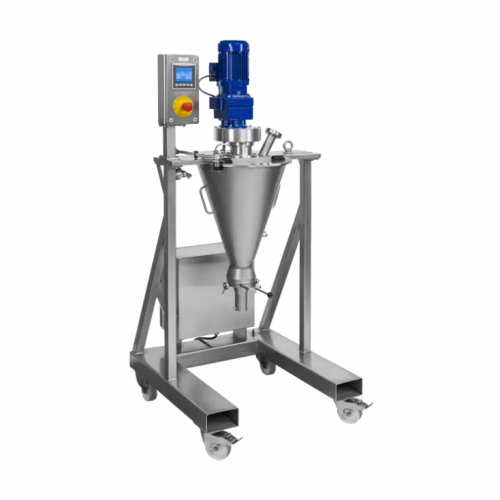
Lab mixer for high-accuracy powder and paste mixing
Achieve precise mixing of powders and pastes with a gentle convective...
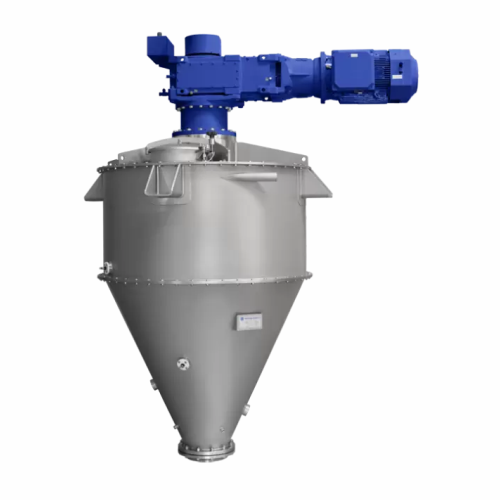
Conical paddle mixer for accurate powder blending
Achieve precise blending of fragile powders and liquids with a versatil...
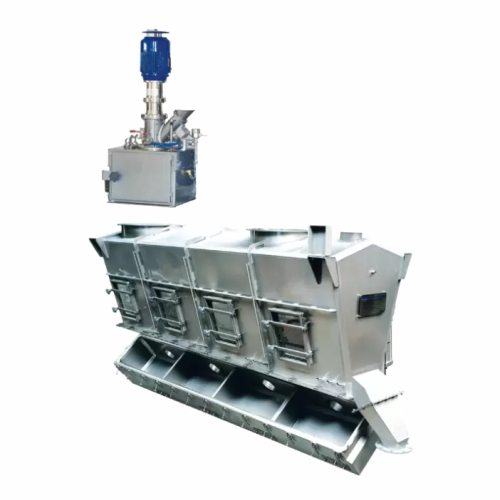
Continuous powder agglomeration system
Enhance product solubility and flowability while minimizing energy consumption with ...
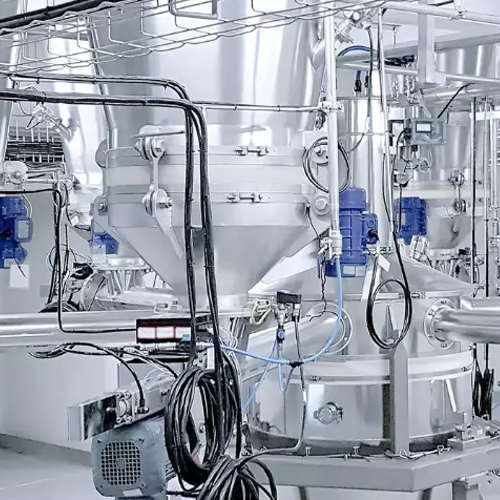
Conical screw mixer for powder blending
Achieve precise and homogeneous blending with the conical screw mixer, ensuring uni...
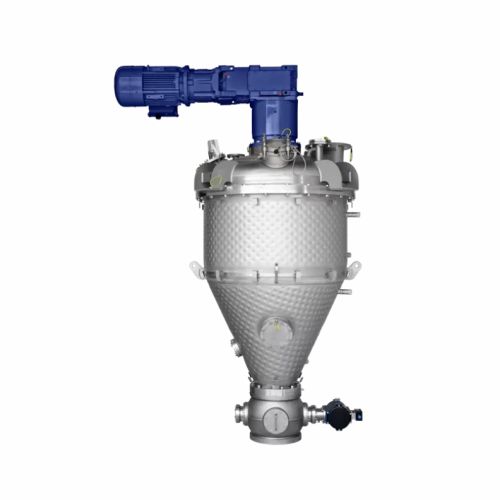
Conical paddle vacuum dryer for powders and granules
Achieve efficient drying of sensitive materials with this versatile ...
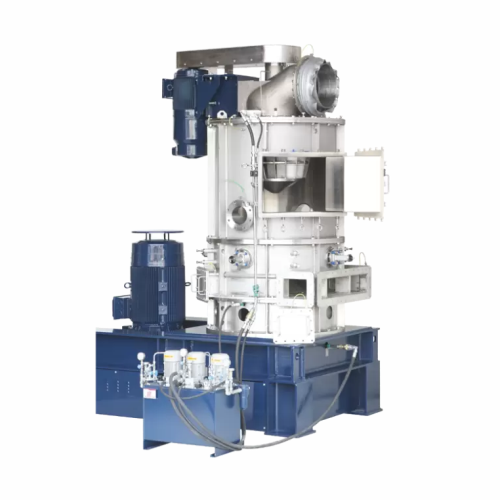
Ultra-fine powder flash drying system
Achieve rapid moisture removal and particle refinement with this integrated system, d...
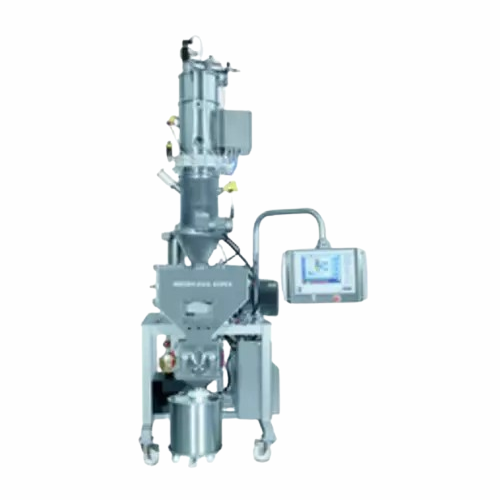
Compactor for powder processing
Designed for transforming powdered materials into uniform granules, this compactor enhances ...

Ultra-fine powder grinding with jet mills
Achieve unparalleled fineness and purity in powder production with cutting-edge ...
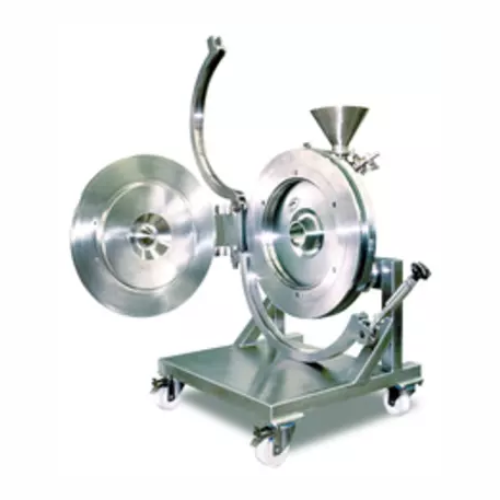
Spiral jet mill for superfine powder production
Achieve consistent ultra-fine powder with precise particle size control, c...
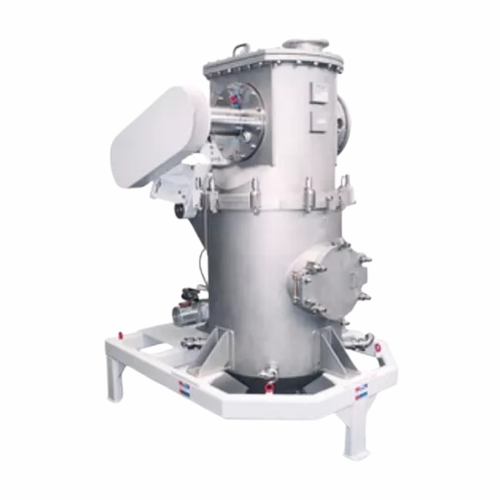
Fluidised bed opposed jet mill for ultrafine powder production
Achieve contamination-free ultrafine powder milling with ...
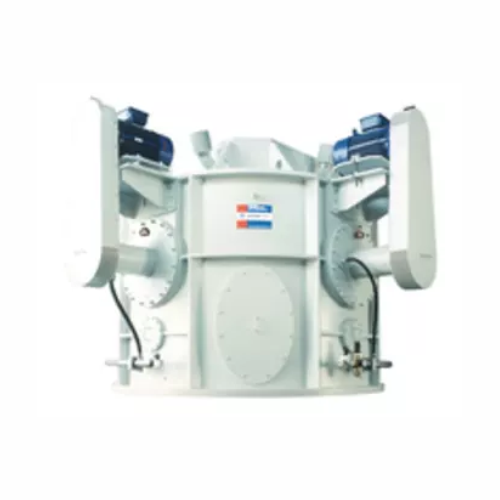
Ultrafine air classifier for powder separation
Achieve precise particle separation with technology designed to enhance you...
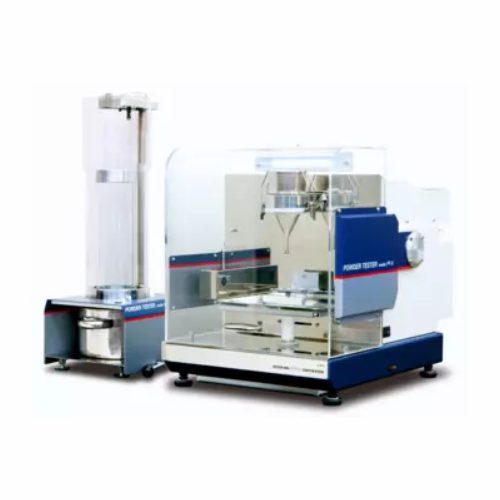
Powder flowability and compressibility analysis
Ensure accurate powder flowability and compressibility data with this adva...
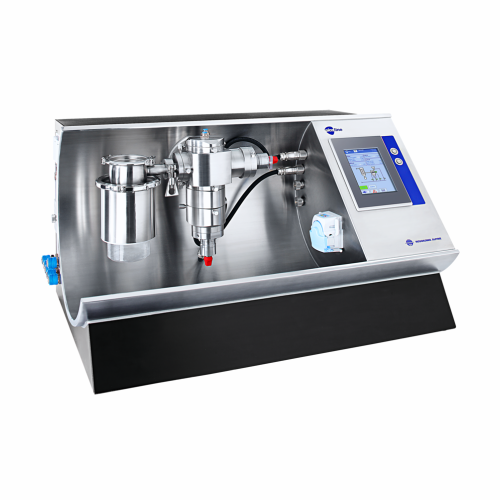
Laboratory system for powder and particle processing
When precision in powder processing is crucial, this versatile labor...
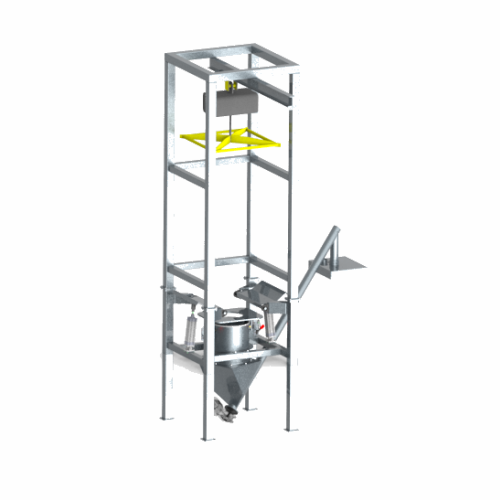
Powder dosing system for big-bags
Efficiently dose and fill various powdered materials directly from big-bags into your pro...
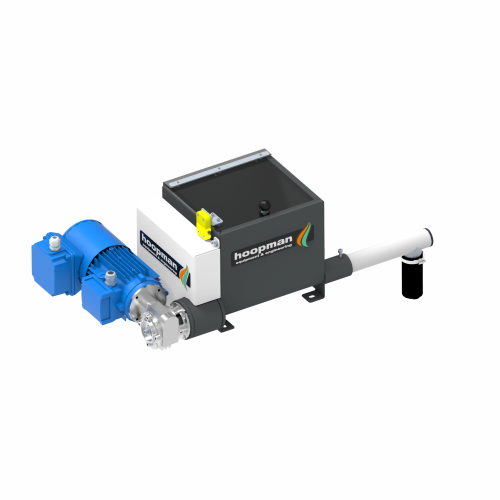
Powder feeder for consistent mixing in pan coating processes
Ensure precise dosing and mixing of pharmaceutical powders ...
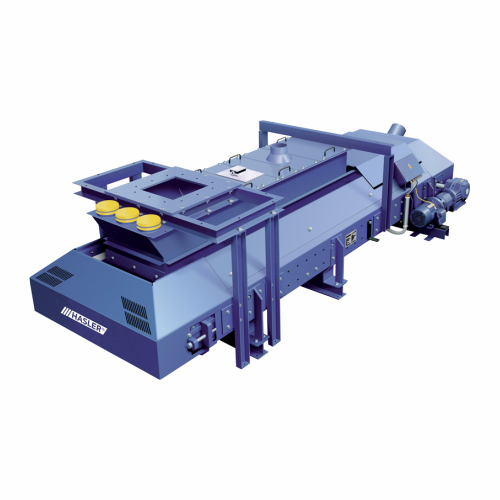
Powder belt feeder for accurate powder metering
Achieve precise powder metering with a specialized feeder that maintains d...
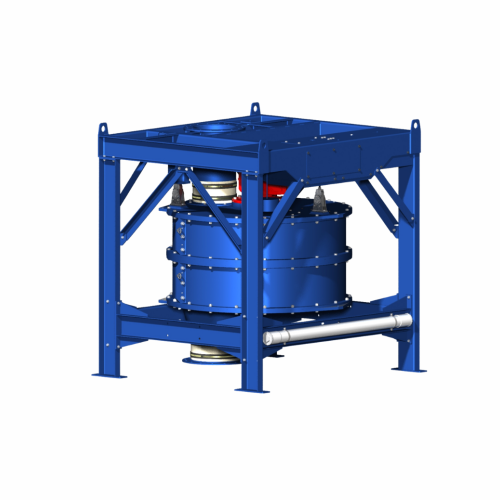
Double-stage rotary weigh feeder for precise powder dosing
Ensure consistent dosing and precise weighing of challenging ...
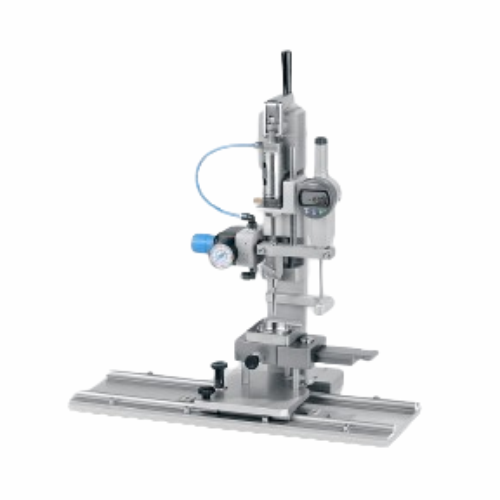
Powder dosing for lab and galenics
Ideal for precise dosing needs, this compact lab device streamlines powder filling proce...
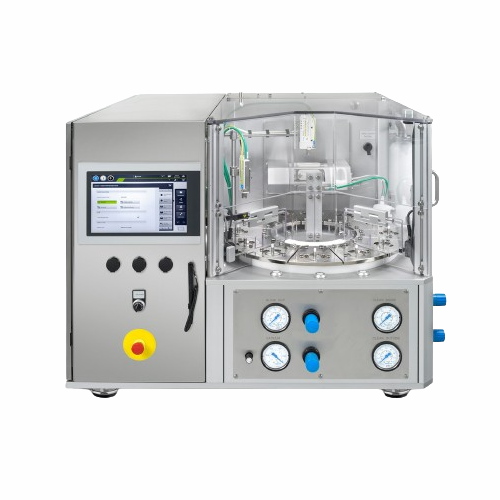
Semi-automatic powder dosing system
Achieve precise micro-dosing for pharmaceutical powders with a flexible system ideal fo...
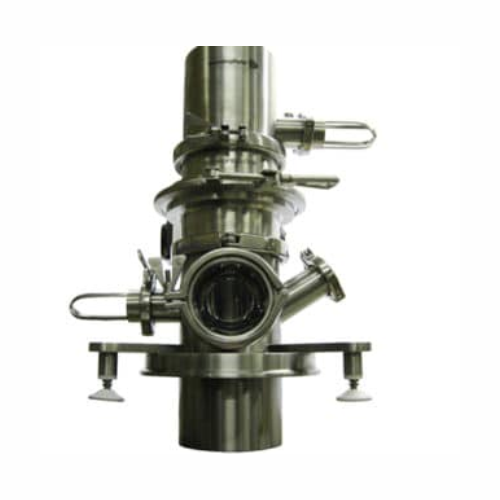
Powder flow control system for gravity transfer
Ensure precise dosing and prevent spillage during powder transfers in your...
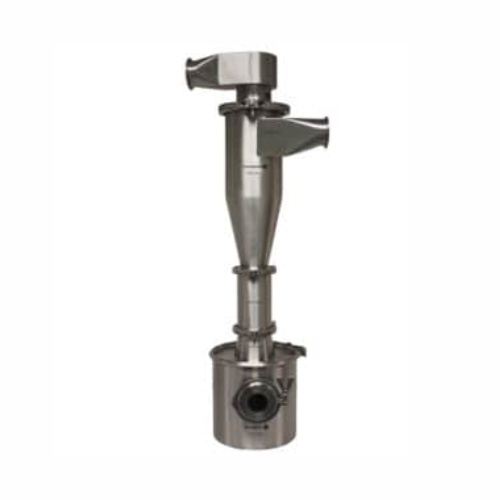
Waste powder recovery cyclone for pharmaceutical processes
Efficiently recover up to 99.9% of waste powder from oral sol...
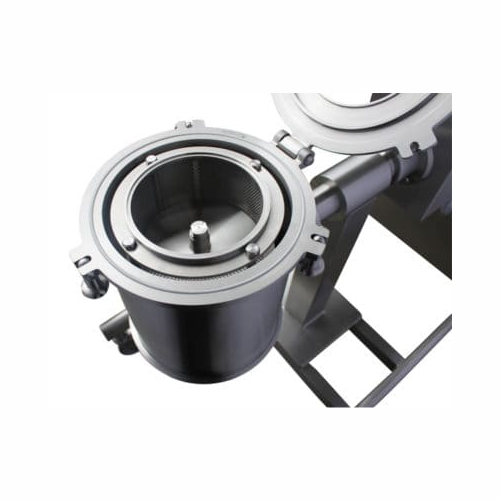
Centrifugal powder sifter for particle separation
Achieve consistent material quality with efficient powder sifting and d...
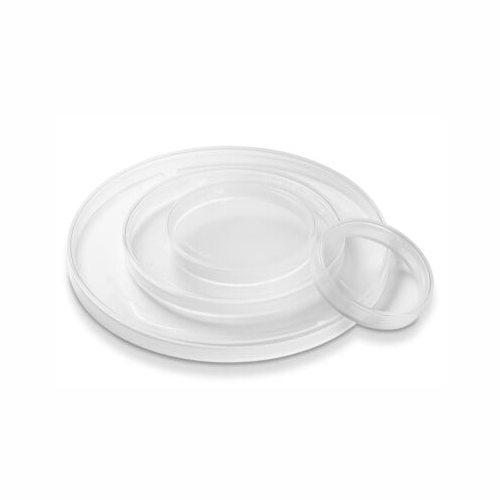
Silicone dust caps for dust-tight powder transfer
Achieve dust-tight containment and efficient powder transfer with flexi...
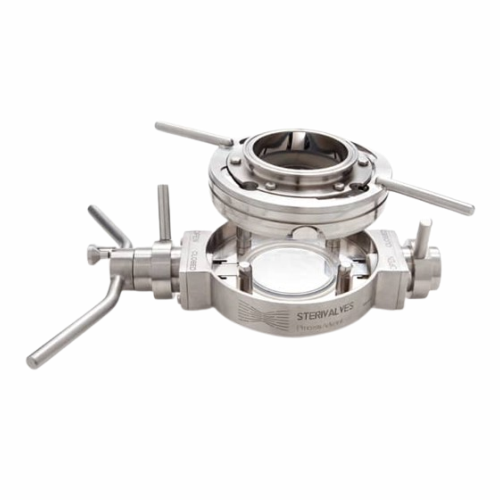
Split butterfly valve for sterile powder transfer
Ensure safe and sterile transfer of powders with unparalleled containme...
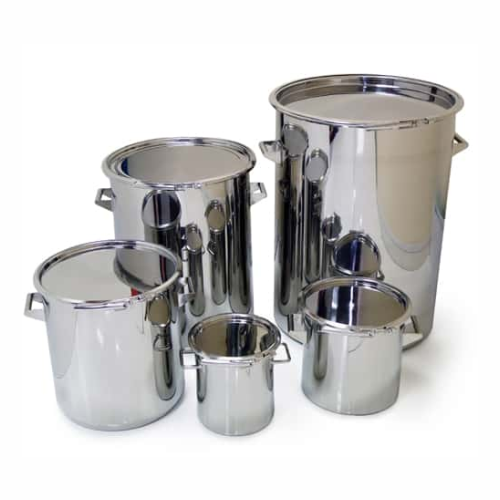
Stainless steel drums for powder storage
For high-value powder storage, these stainless steel drums offer reliable containm...
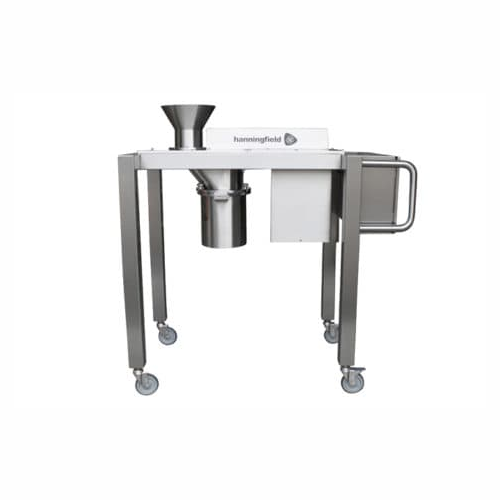
High capacity conical mill for powder processing
Optimize your milling process with a versatile solution that ensures prec...
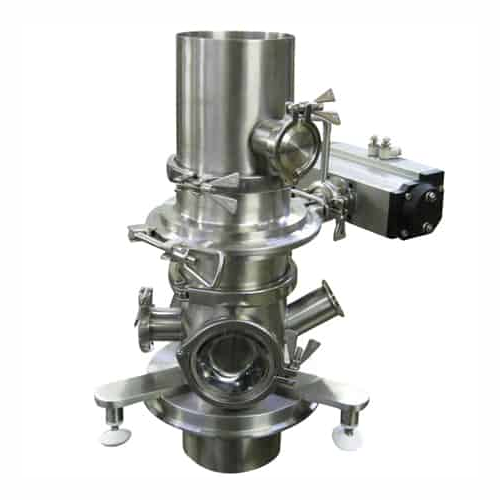
Powder flow control systems for precise gravity transfer
Achieve seamless powder flow control in your production line wit...
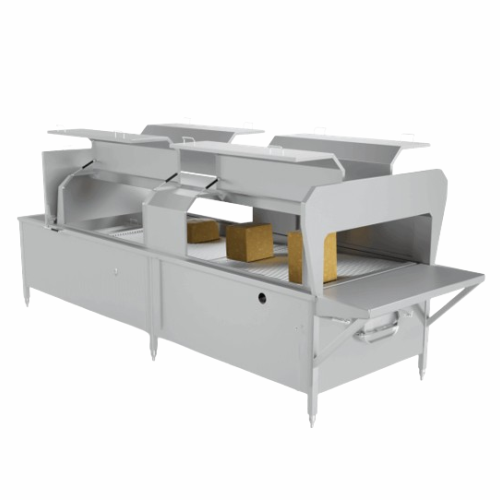
Industrial melting unit for chocolate and powders
Enhance your production efficiency by seamlessly melting and homogenizi...
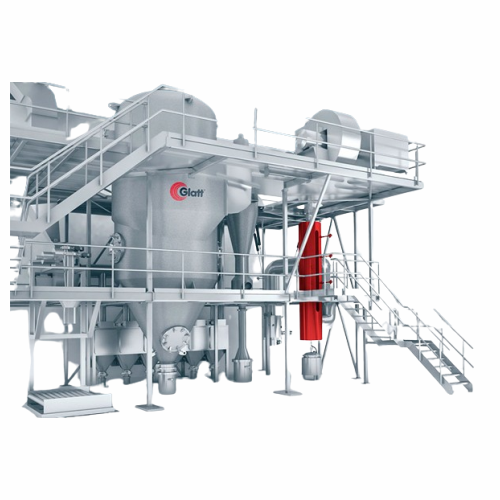
Powder synthesis reactors for nanometer and micrometer particles
Achieve precise particle control and enhance material p...
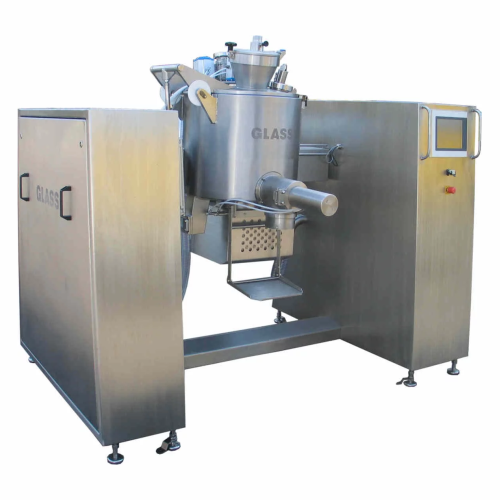
High-speed mixer for granulating and mixing powders
Achieve consistent granulation and mixing with precise temperature co...
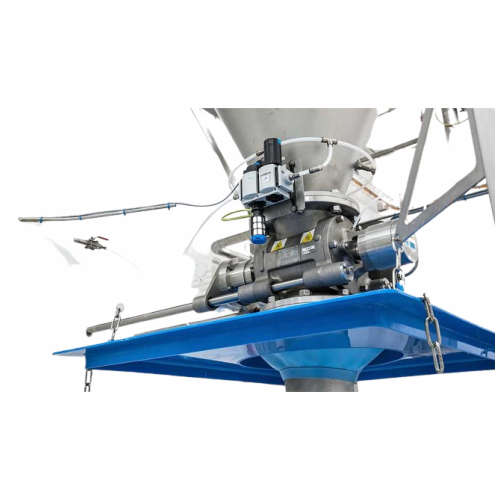
Heavy duty rotary valves for powder handling
Ensure precise material flow and safety in harsh processing environments with...
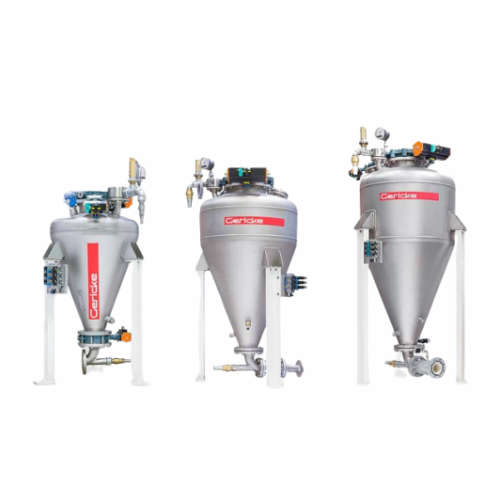
Dense phase pneumatic conveying system for powder transfer
Ensure gentle and efficient material transport with minimal m...
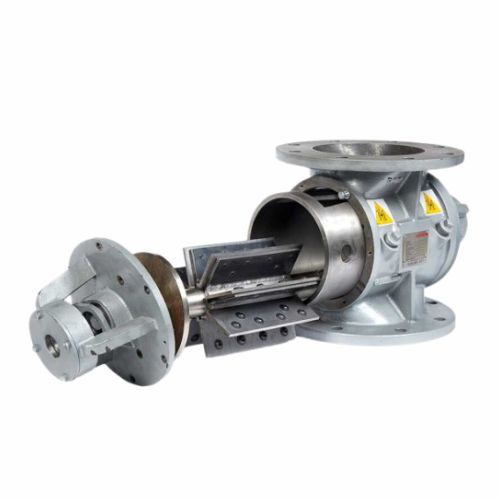
Pneumatic dilute phase conveying system for powders and bulk materials
Optimize your production line’s efficiency...
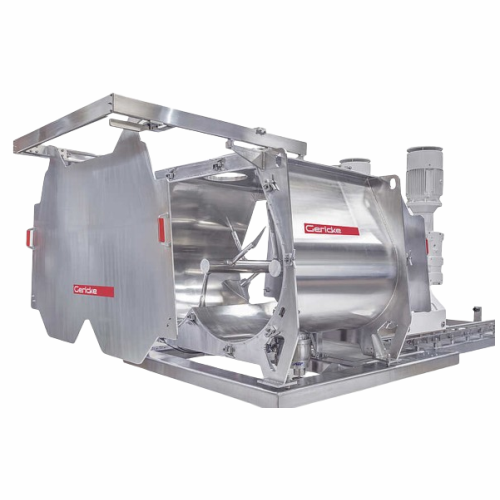
Double shaft powder batch mixer
Achieve high homogeneity and gentle handling with a double shaft mixer designed for efficien...
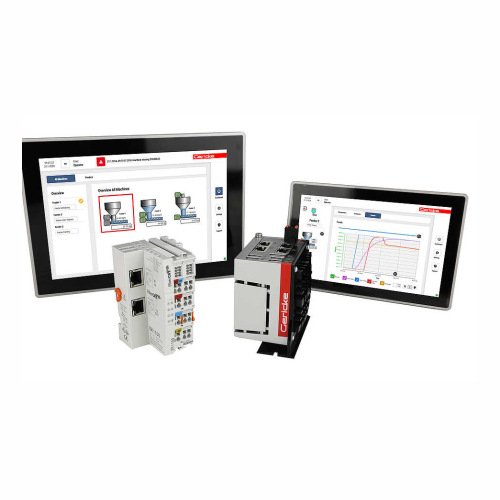
Universal controller for feeders in powder handling applications
Simplify and enhance your powder handling with precise ...
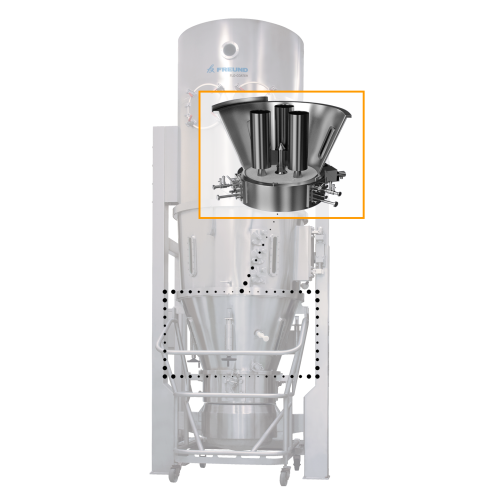
Wurster coating system for fine powders and pellets
Achieve precision coating for multiparticulate cores and mini-tablets...
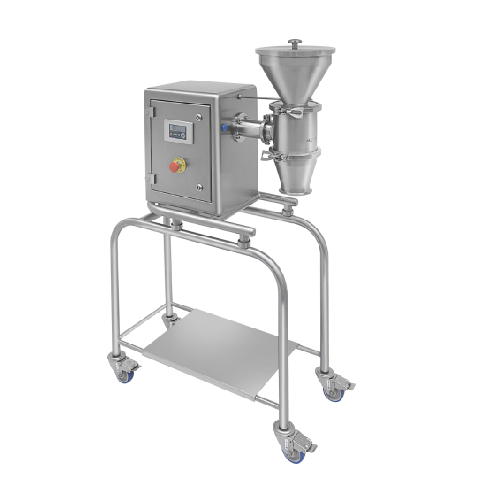
Laboratory conical screen mill for powder calibration
Achieve precise particle size control with this compact laboratory ...
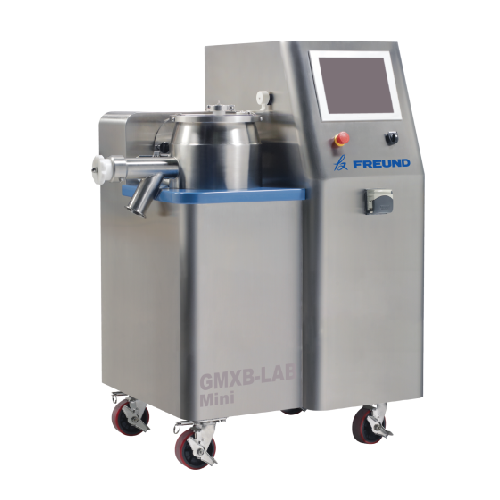
High shear granulator for wet granulation of powders
Achieve consistent granule density and size with a high shear granul...
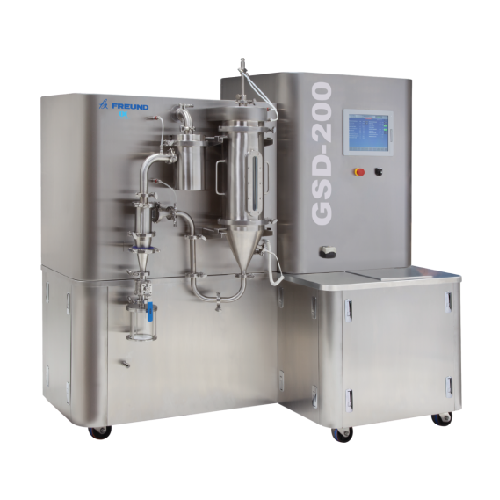
Laboratory spray dryer for sub-gram powder samples
Achieve precise control in developing fine chemical and pharmaceutical...
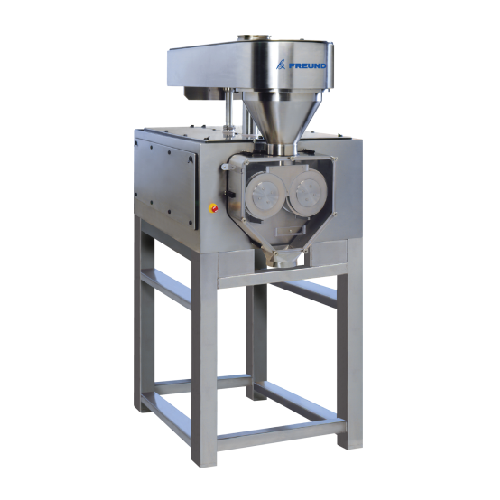
Dry granulation system for powder compaction
Achieve consistent sheet hardness and increased density in powdered materials...
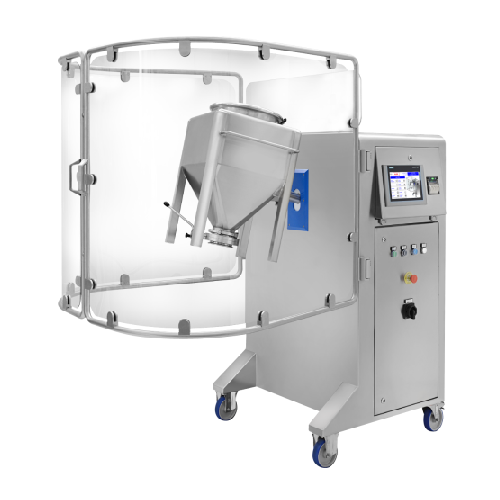
Pilot blender for small batch powder blending
Optimize your R&D processes with this versatile mobile blender, ideal f...
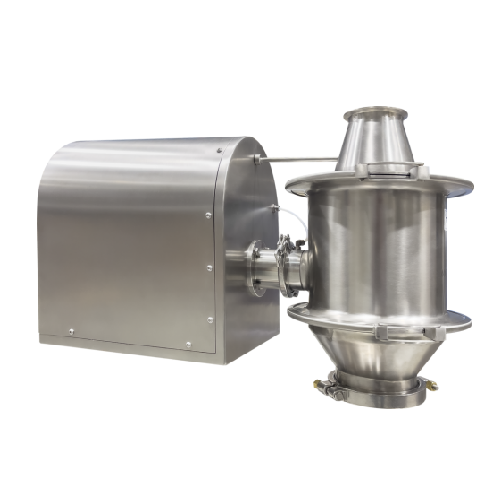
Conical screen mills for powder calibrating
Achieve precise particle size distribution for your powders and granules with ...
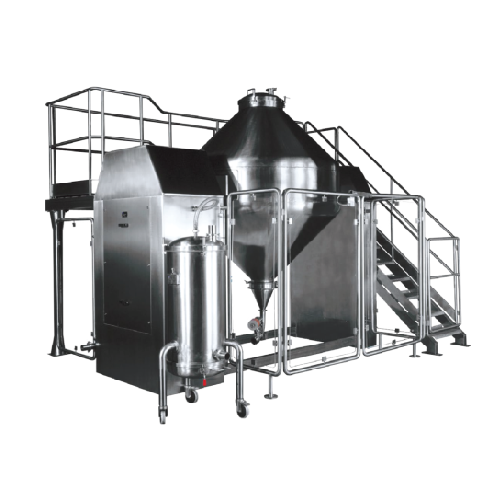
Pharmaceutical powders and granules dry blending
Achieve uniform blending of diverse powder and granule formulations with ...

Sterility test isolator for injectables and sterile powders
Ensure sterility and compliance for injectables and biopharm...
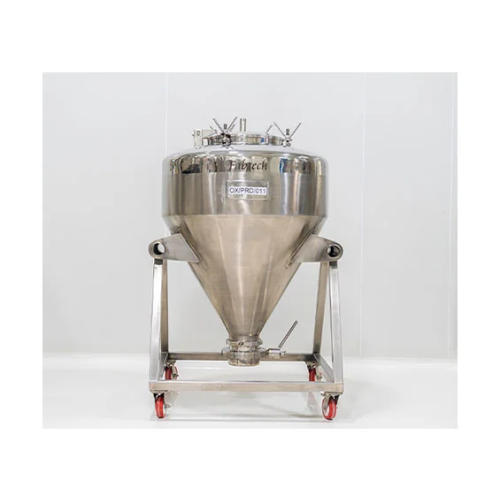
Vacuum transfer system for powders and granules
Effortlessly transfer and manage powders and granules with seamless integr...
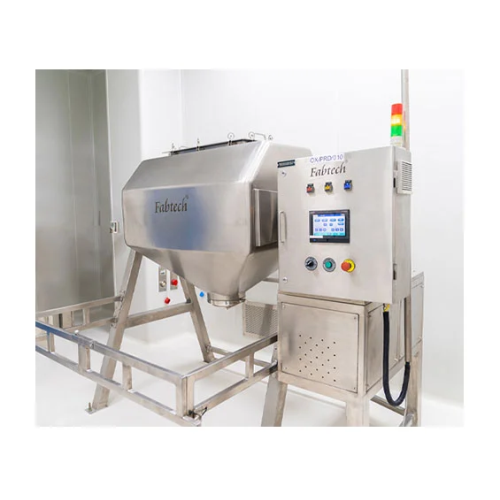
Pharmaceutical powder blender
Ensure uniform mixing of pharmaceutical powders and granules with advanced blenders designed f...
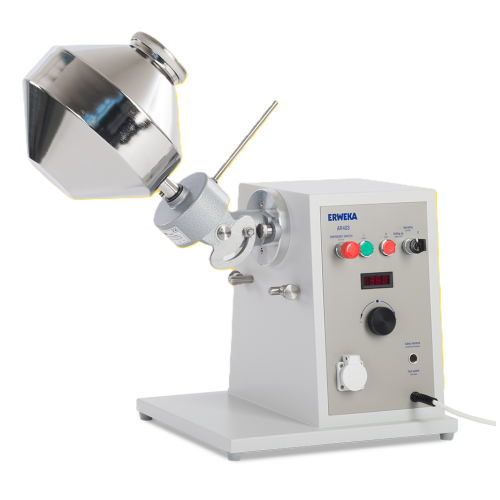
Double cone mixer for free flowing powders and granules
Achieve uniform blending of powders and granules with precision, ...
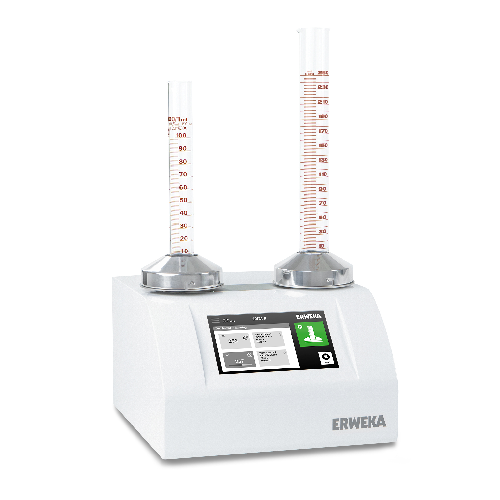
Tapped density tester for pharmaceutical and chemical powders
Ensure precise density measurements for pharmaceuticals an...
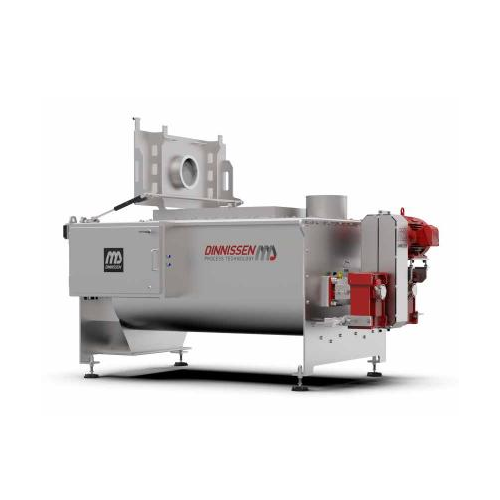
Continuous mixer for industrial powders and liquids
Achieve precise and efficient mixing of solids and liquids with minim...
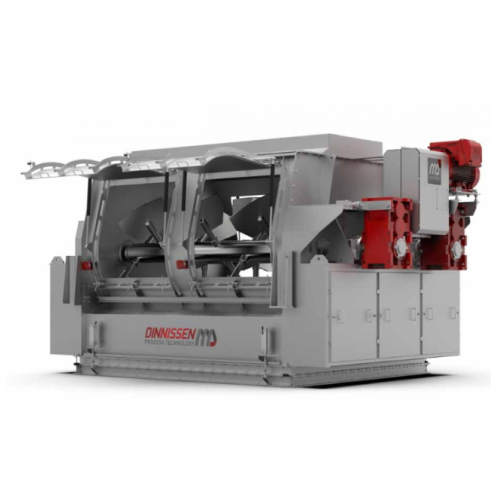
Batch mixer for powder and grain processing
Achieve ultra-fast, homogenous mixing in just 20 to 50 seconds with this versa...

Industrial pneumatic conveying system for powders and granulates
Achieve hygienic and dust-free transport of powders and...
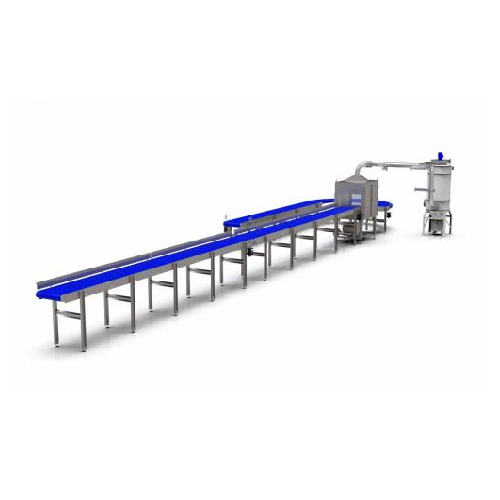
Mechanical horizontal conveyor for powders and granulates
Efficiently handle and transport your delicate powders and gra...
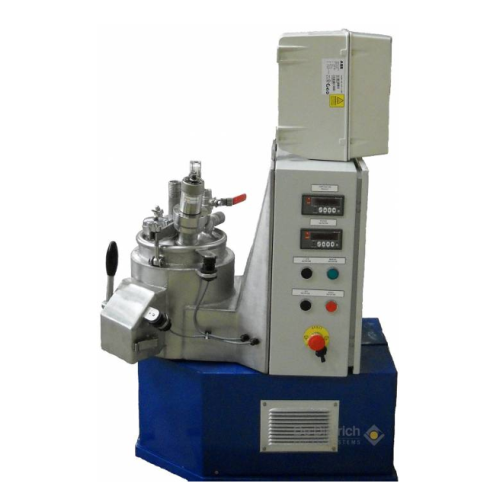
Powder blender for efficient mixing and discharge
Achieve precise mixing and efficient discharge with advanced powder ble...
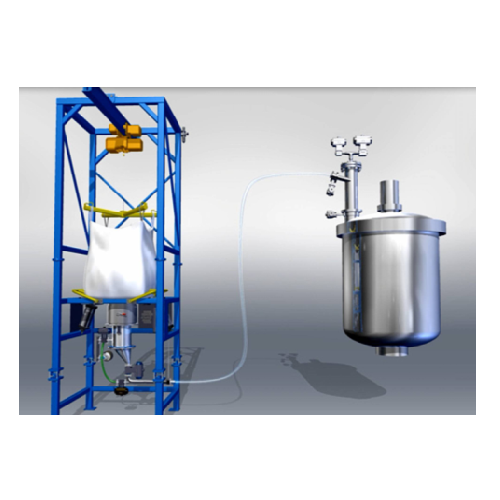
Big bag emptying station for powder handling
Ensure safe and efficient powder discharge with precision containment, adapta...
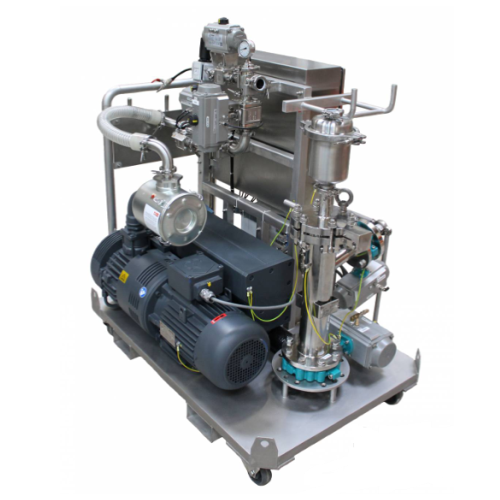
Mobile powder transfer system for pharmaceuticals and chemicals
Efficiently transfer and charge powders into various ves...
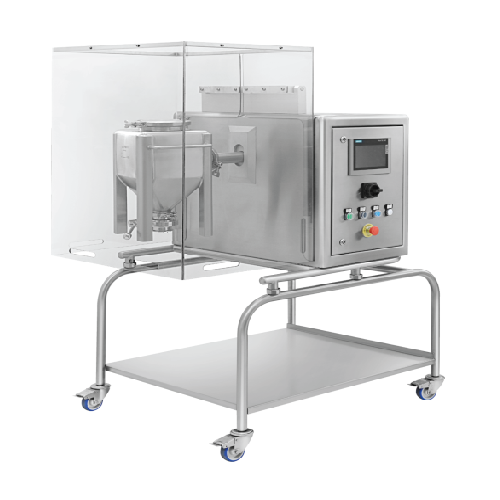
Benchtop laboratory powder blender
Perfect for R&D labs needing precise, small-batch powder blending and mixing, this ...
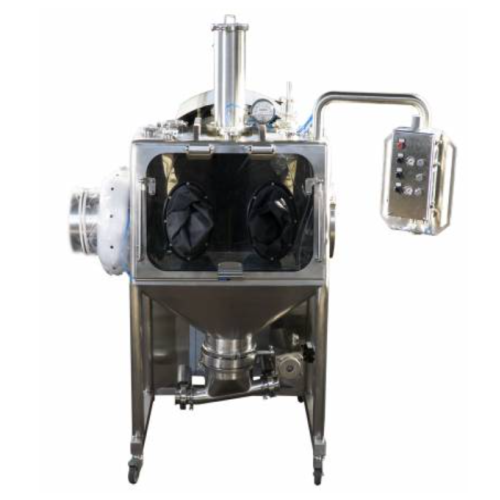
Powder handling drum dock station
Ensure safe and efficient powder transfers with high containment levels, minimizing opera...
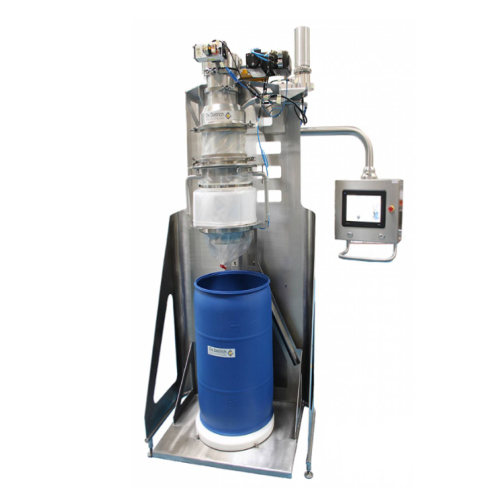
Powder conditioning station for high containment applications
Ensure safe and precise handling of hazardous powders with...
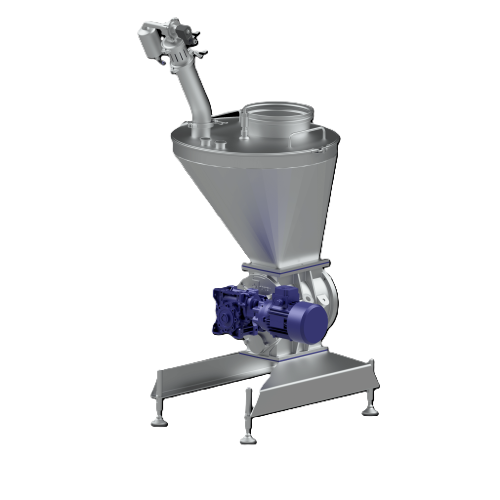
Dilute-phase conveying solution for powder handling
Efficiently transfer powders and granules with robust leak containmen...
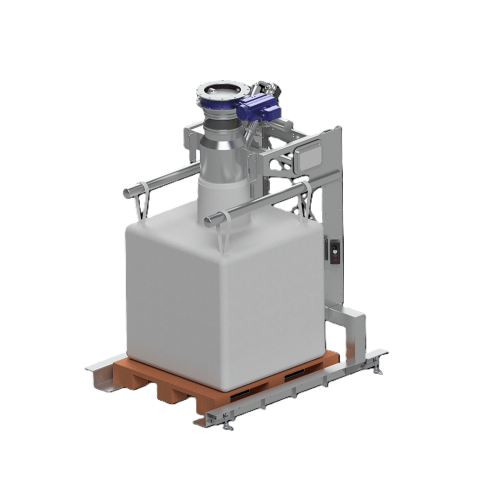
Bigbag filling system for powder and bulk materials
Ensure precise and dust-free bigbag filling with this versatile syste...
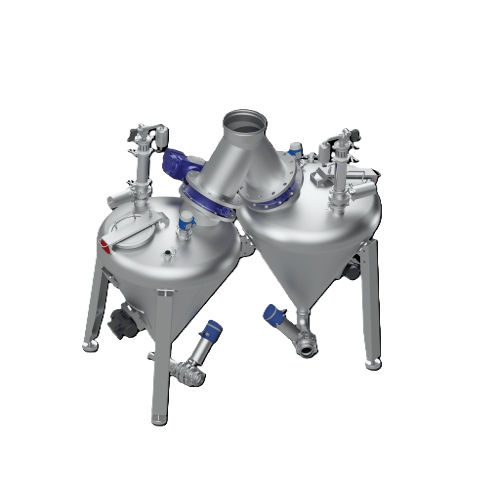
Dense-phase powder conveying system
Optimize your powder processing with a system designed to handle abrasive and fragile m...
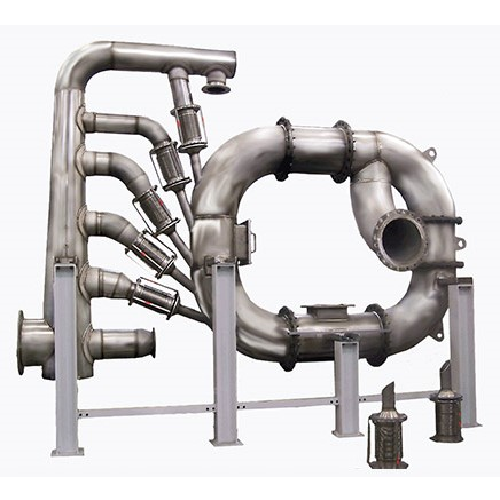
Milling flash dryer for fine powder processing
Achieve precise moisture control and prevent agglomeration in your processi...
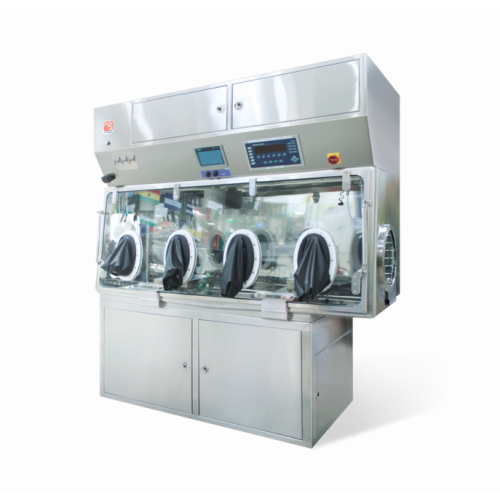
Production isolator for powder preparation and weighing
Ensure precise weighing and safe handling of pharmaceutical powde...
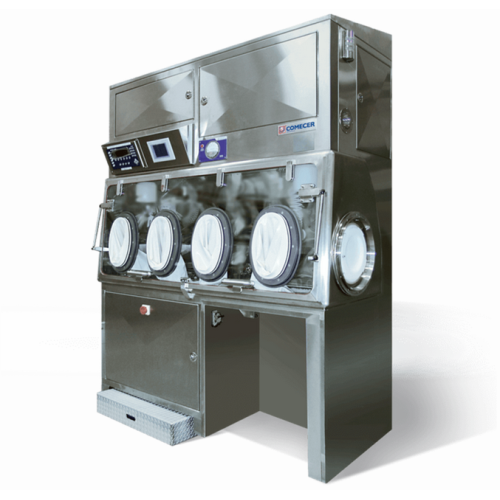
Atex compliant isolator for dispensing powder procedures
Ensure safe weighing and transfer of explosive and pharmaceutica...
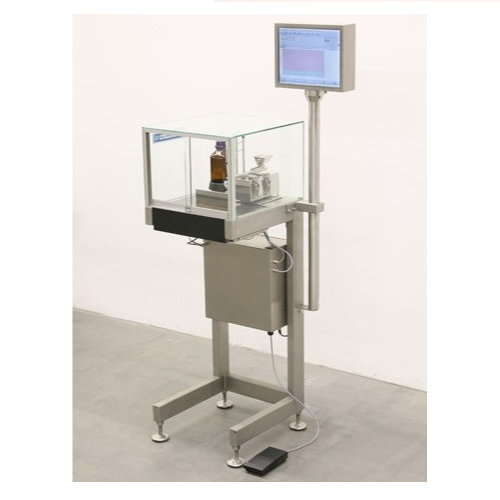
Microdosing system for granules and powder
Achieve precise dosing with minimal variance across all fills, ensuring consist...
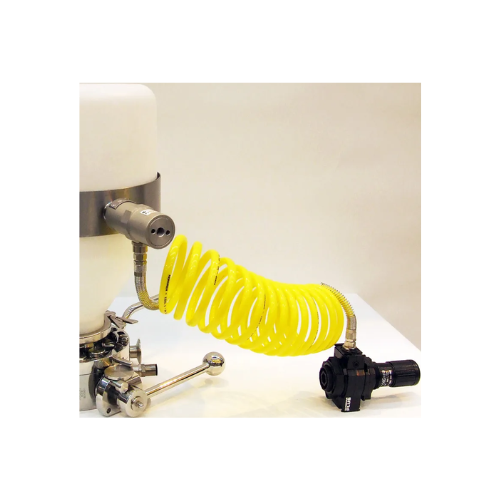
Vibratory collar for powder flow assistance
Struggling with sticky or poorly flowing powders during discharge? This vibrat...
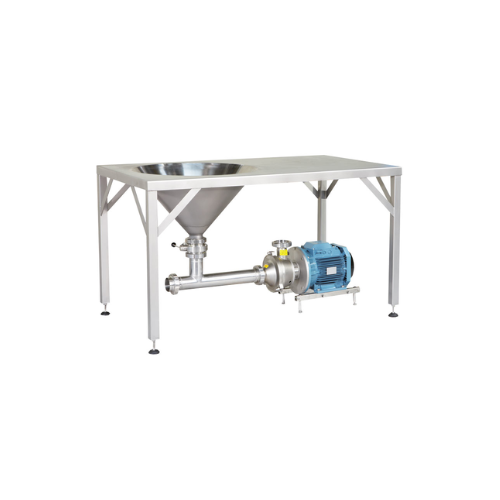
Powder addition system for oils and fats
Efficiently integrate powdered additives into your liquid processes with our hygie...
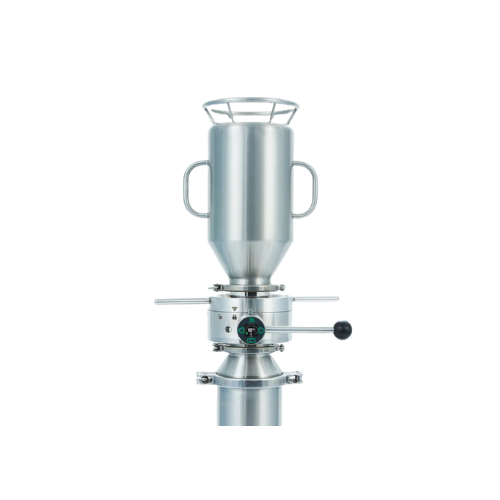
High containment powder transfer valve
Ensure high containment for potent powders in your production line, reducing contami...

High containment powder transfer valve for bulk material
Ensure operator safety and prevent cross-contamination with robu...
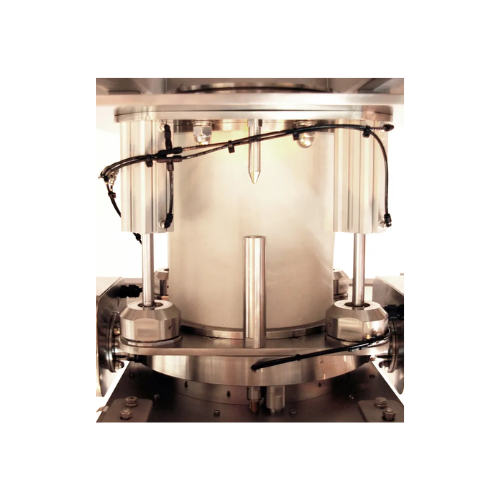
Automatic docking system for bulk powder handling
Optimize docking precision and ensure seamless alignment in bulk powder...
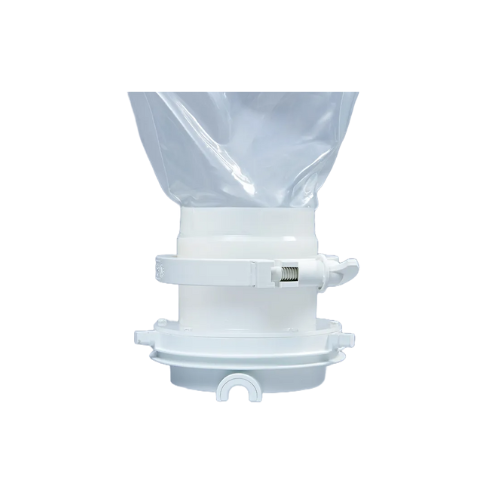
Single use valves for powder transfer
Efficiently transfer powder ingredients with a single-use containment solution, ensur...
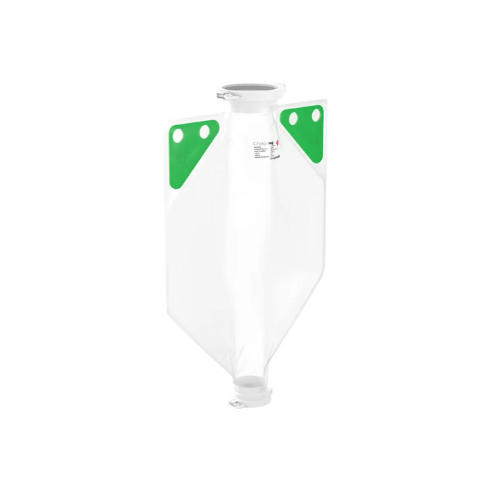
Single use powder handling bags for pharmaceutical ingredients
Achieve contamination-free powder transfers with ease, ma...
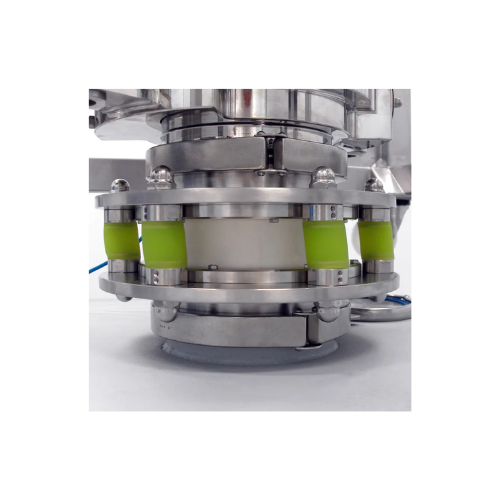
Bulk powder transfer safety device
Ensure stable and secure docking by minimizing equipment damage during powder transfer p...
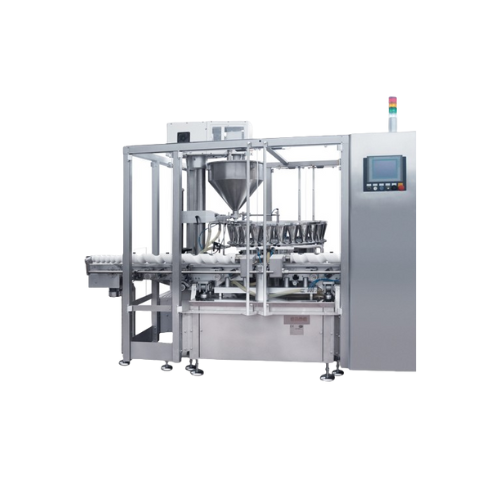
Continuous motion powder dosing system
Ensure precise dosing of pharmaceutical and nutritional powders with this continuous...
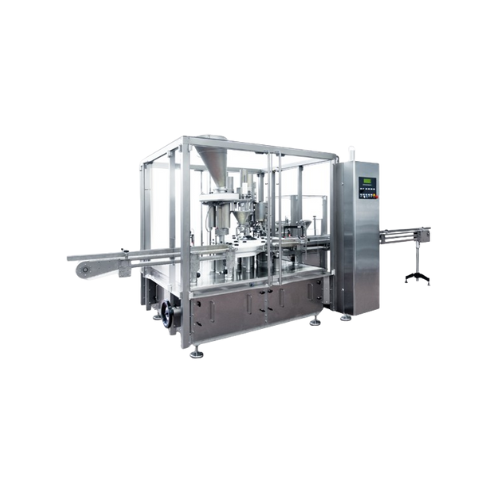
Intermittent motion powder dosing and capping system
Ensure precise powder dosing and secure capping in one seamless step...
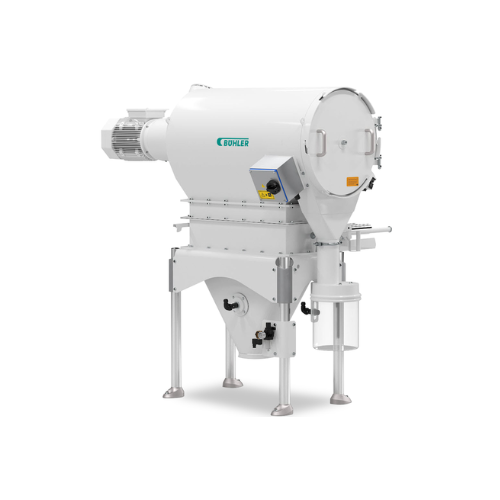
Industrial sieving solution for powders and granulates
Ensure top sanitation and food safety in your production line with...
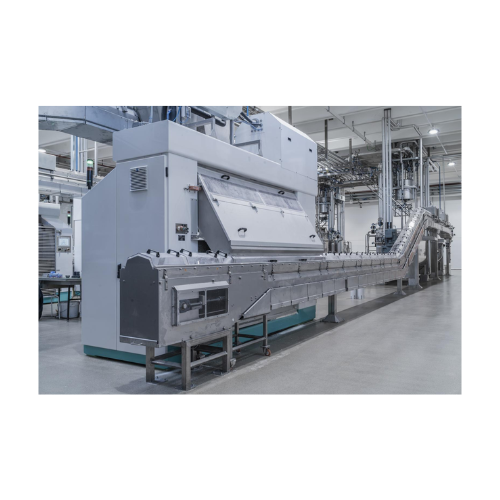
Systems for transporting cocoa powders and ingredients
Efficiently transport and dose your cocoa powders and semiliquid i...
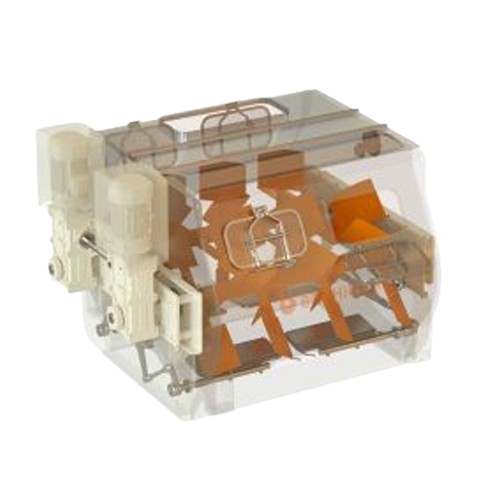
Double shaft paddle mixer for solids and powders
Achieve unparalleled mixing precision for fragile and diverse materials w...
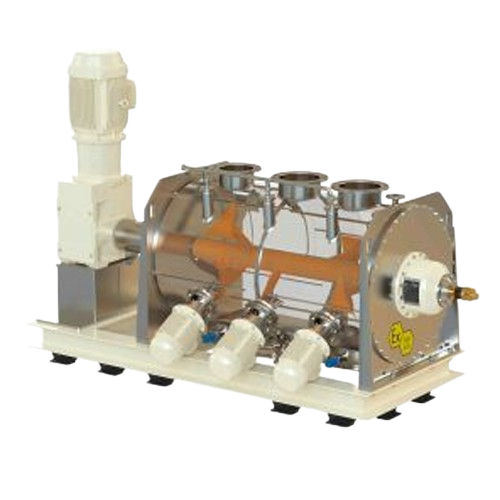
Horizontal ploughshare mixer for solids and powders
Achieve uniform blends of diverse solids and powders with precision a...
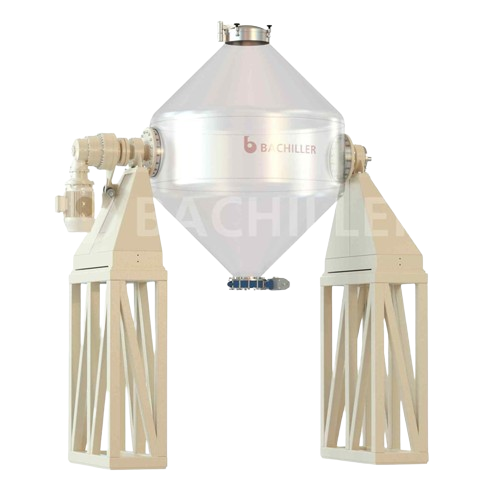
Double cone mixer for powders and solids
Ensure gentle mixing of fragile powders and solids with a low-speed, non-forced bl...
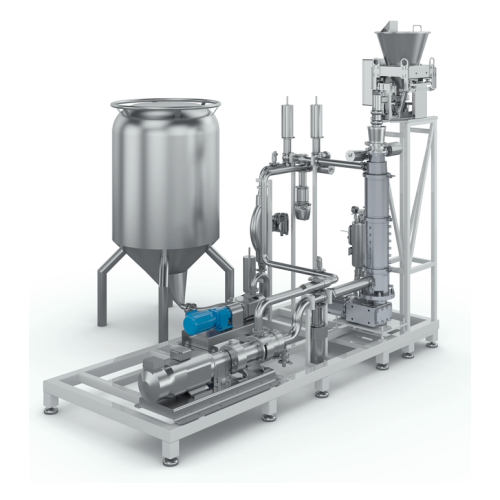
Advanced powder dosing system for continuous production
Achieve precise powder integration into your liquid processes, en...
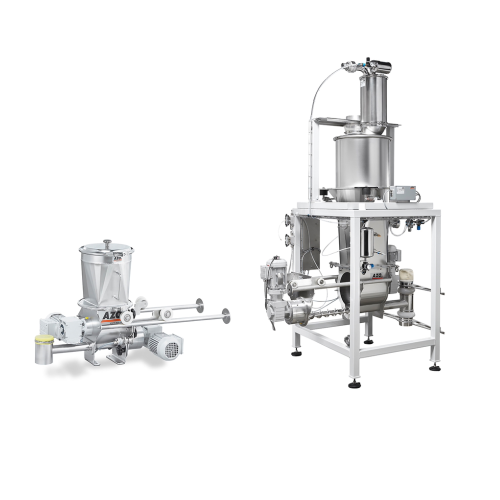
Accurate dosing for powder products
Ensure precise dosing and consistent flow of bulk powders in your production line to en...
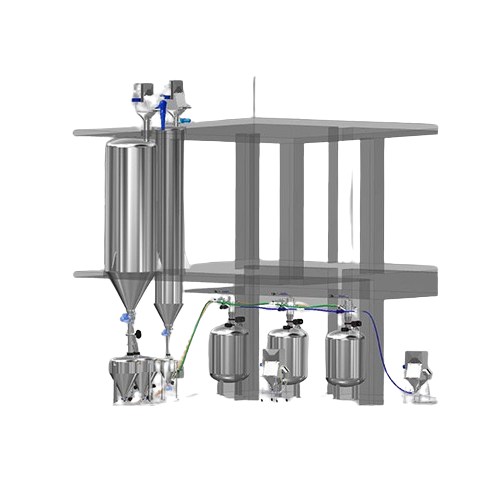
Automatic powder vacuum conveying system for infusion production
Enhance your production line with our vacuum conveying ...
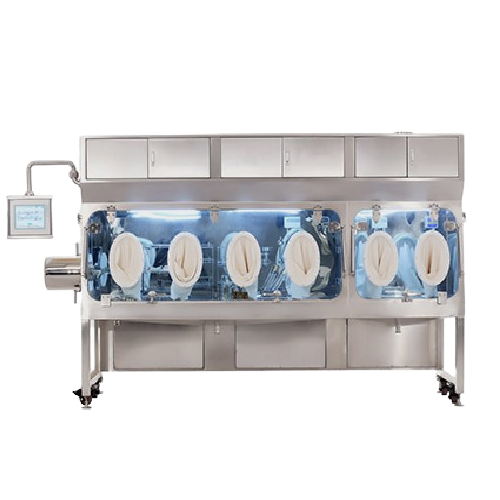
Fine chemical powder system
Optimize your powder processing with a solution tailored to handle complex feeding, conveying, a...

Sterile filling line for liquid and powder
Achieve seamless integration of filling, sterilization, and packaging with this...
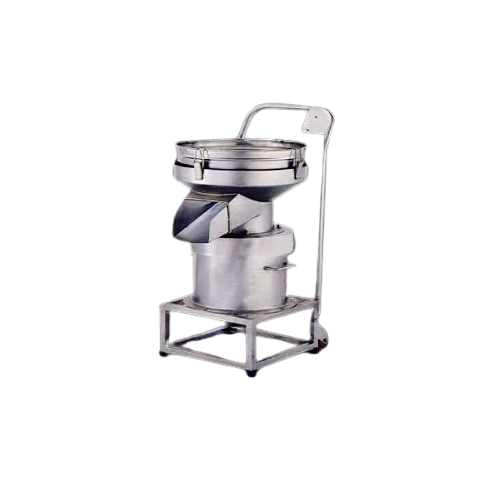
Powder ingredient vibro separator and filter
Effortlessly achieve uniform powder consistency and enhance flow efficiency b...
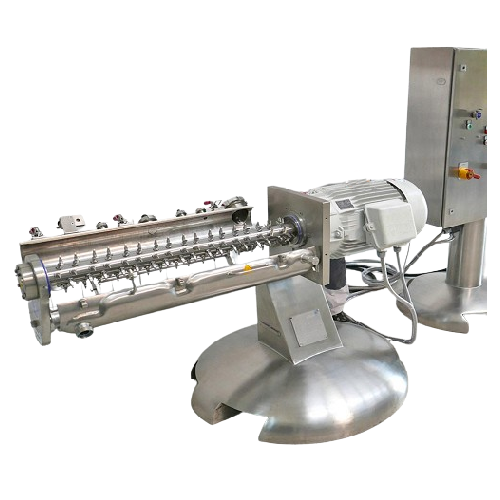
Continuous granulator for powdery goods
Achieve uniform particle size and structure with a continuous granulation process t...
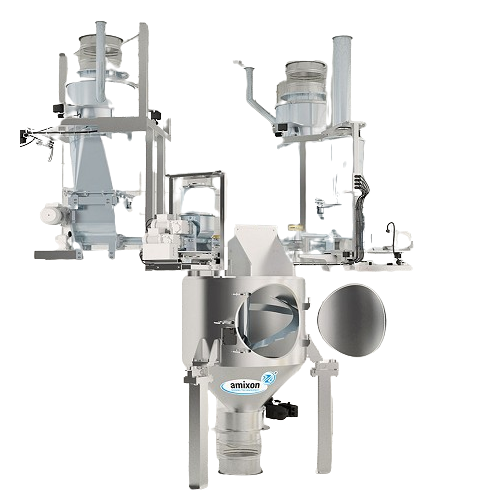
Continuous powder mixer for dry, moist and suspended goods
Achieve precise homogenization and deagglomeration with a con...
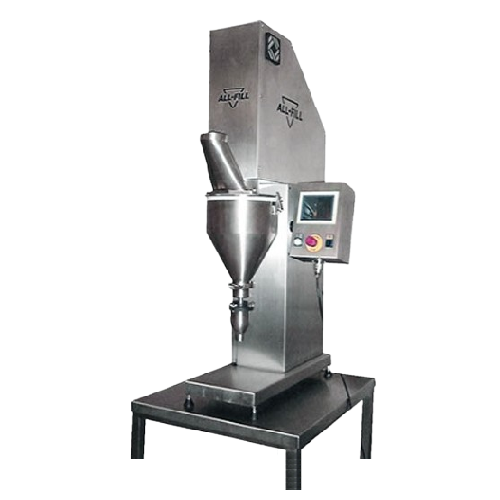
Miniature auger filler for precise powder filling
Achieve precision filling with a compact, bench-top auger solution desi...
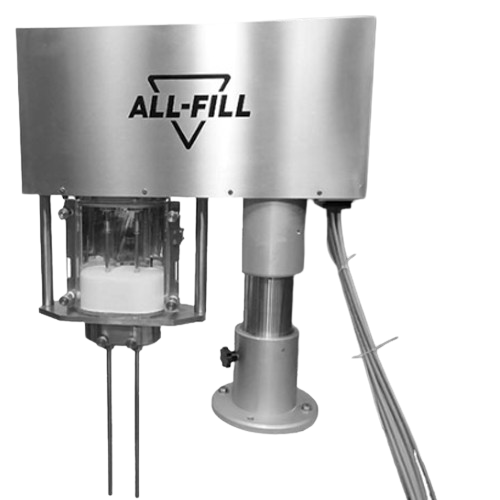
Multi-fill powder filling system
Achieve precise and consistent filling for your powdered and granulated products with a mod...
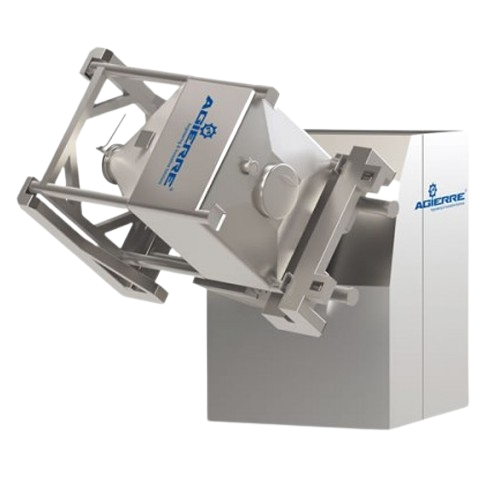
Bin blender for pharmaceutical powder mixing
Achieve uniform mixing and homogenization of dry powders directly in storage ...
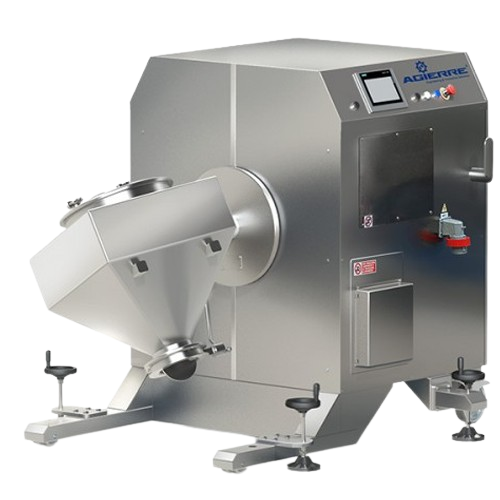
Mobile bin blender for mixing and homogenizing dry powders
Ensure thorough powder uniformity and eliminate cross-contami...
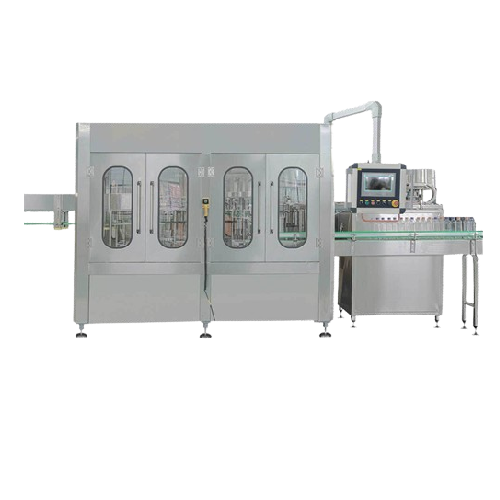
Drum blender for homogeneous powder mixing
Achieve precise powder homogenization directly in storage drums, minimizing han...
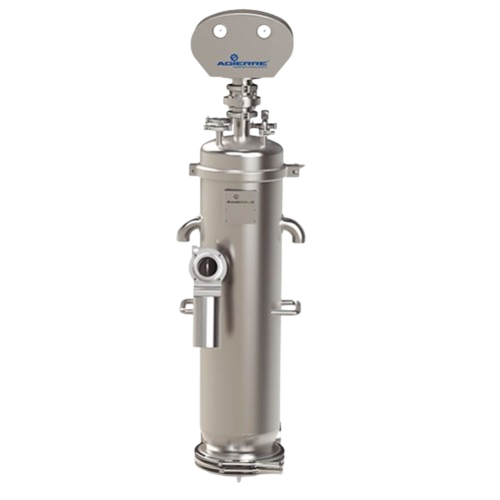
Vacuum conveyor for powder and granule transfer
Ensure efficient and contamination-free transfer of powders and granules w...
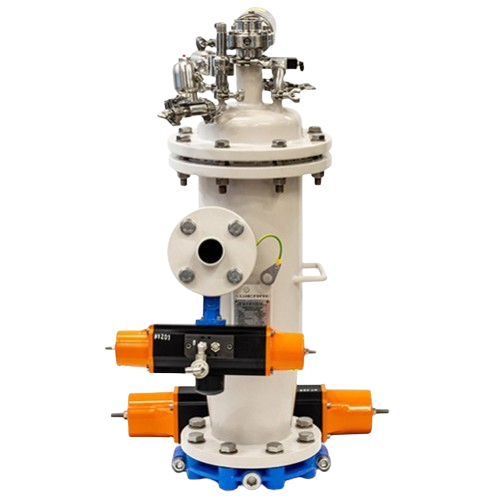
Conveyor for acidic and corrosive powders
Effectively handle corrosive and aggressive powders in chemical processes with t...
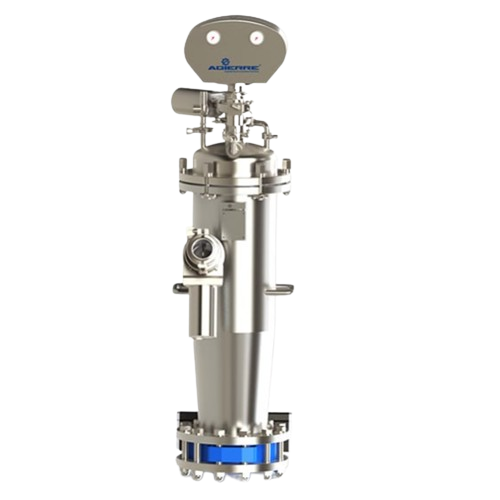
Ped-compliant vacuum conveyor for powder transfer
Achieve safe and efficient powder transfer in pressure environments wit...
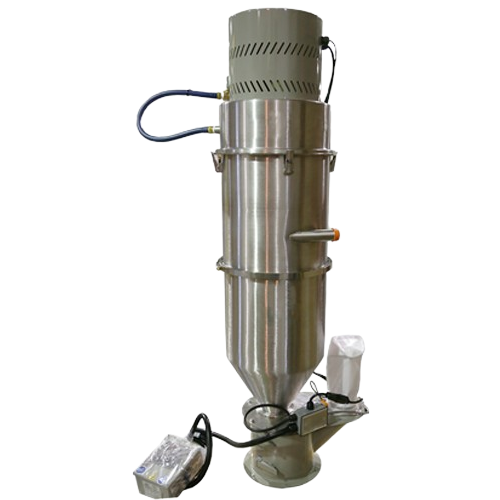
Powder hopper loaders for free-flowing materials
Efficiently transport free-flowing powders, including PVC and polyethylen...
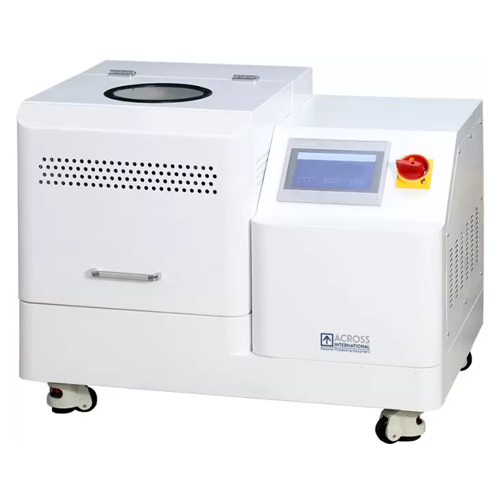
Planetary ball mill for powder material mixing and alloying
Achieve precise control in particle size reduction and homog...
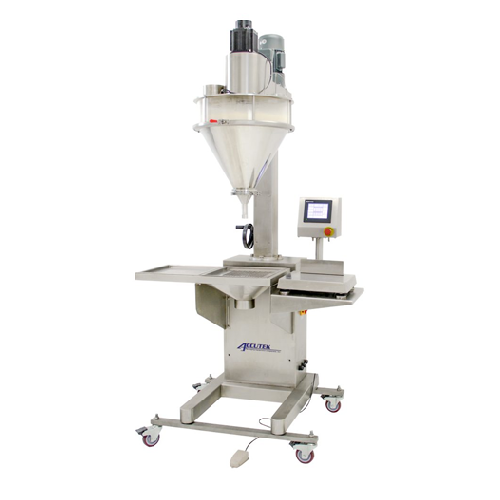
Powder filling machine for dry products
Achieve precision and consistency in filling dry powders and granules with a versat...
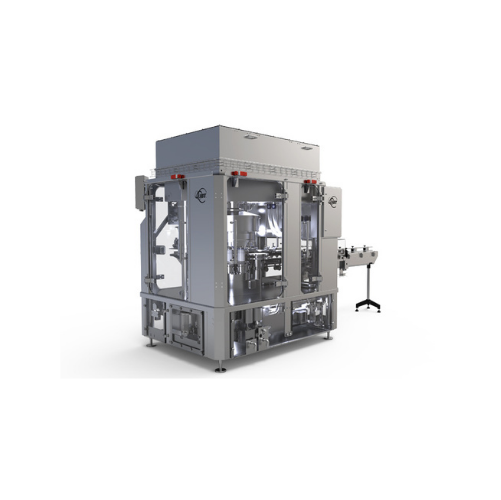
Powder can seamer for nutraceutical and beverage powders
Achieve precision and hygiene with this can seamer designed for ...
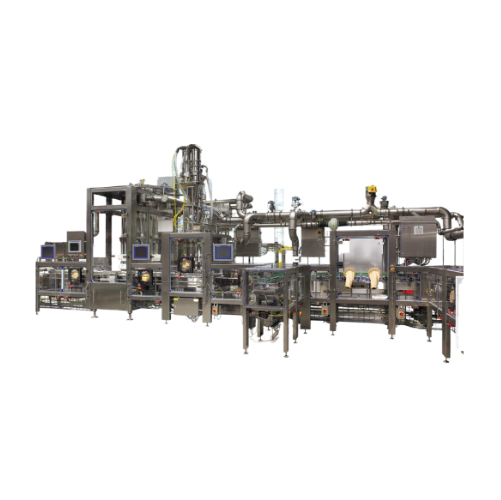
In-line gassing system for powder processing
Optimize shelf life and quality of your powdered products by effectively redu...
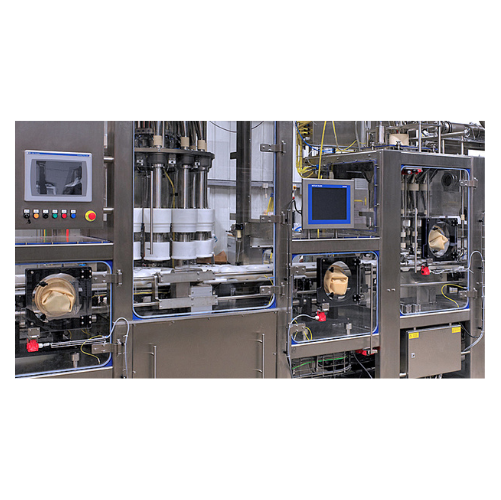
Vacuum powder filler for dairy and pharmaceutical products
Achieve precision and maintain product integrity with a versa...
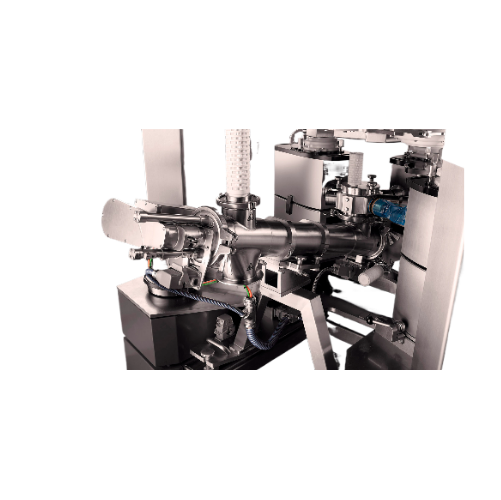
Continuous dosing and blending for pharmaceutical powders
Optimize your pharmaceutical production with precise dosing an...
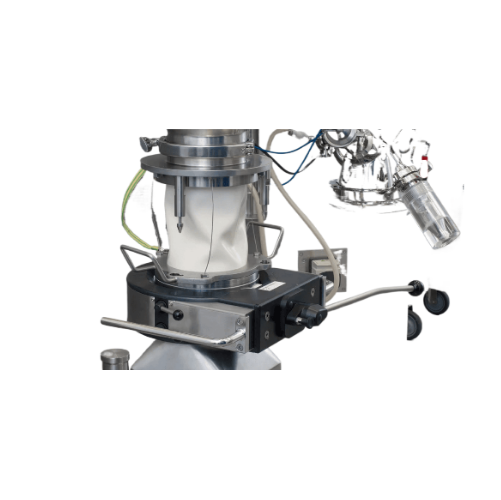
Containment valves for pharmaceutical powder transfer
Ensure safe transfer of highly potent pharmaceuticals with this mod...
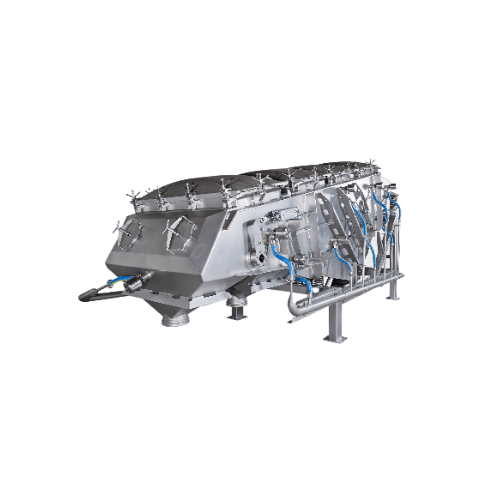
Industrial powder sifter with sanitary compliance
Optimize your powder processing with this versatile sifter, ensuring pr...
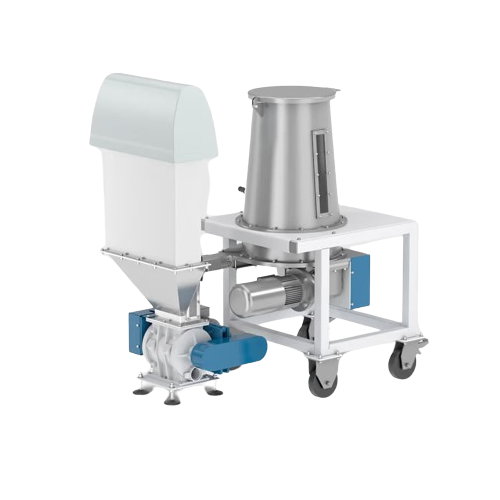
Micro-ingredients doser for precise powder additives
Maintain precision and hygiene in your production line with a specia...
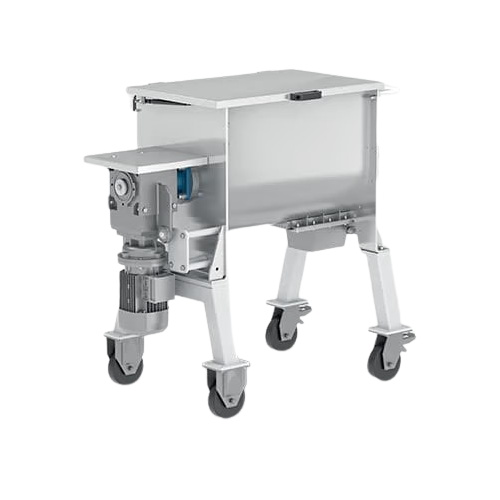
Powder and granulate premixer
Achieve consistent, homogenous blends of powders and granulates with our advanced premixing te...
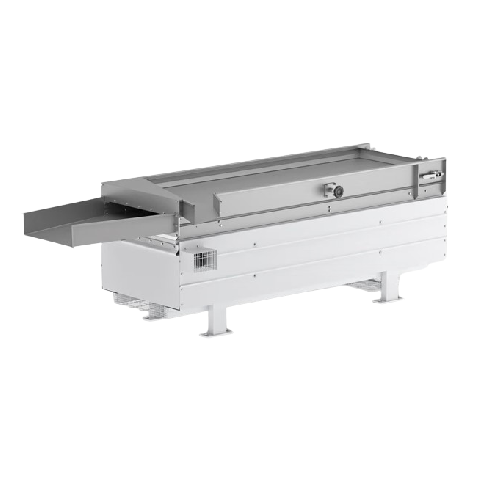
Industrial vibrating sieve for powder and lump separation
Ensure precise separation of powders and lumps with this oscil...
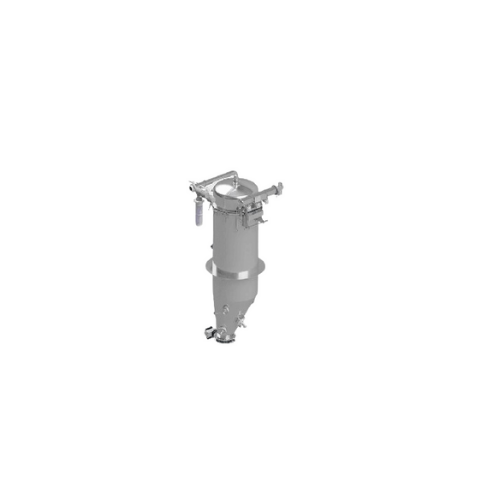
Dense phase vacuum conveying system for powder handling
Effortlessly transport delicate powders and fragile granules with...
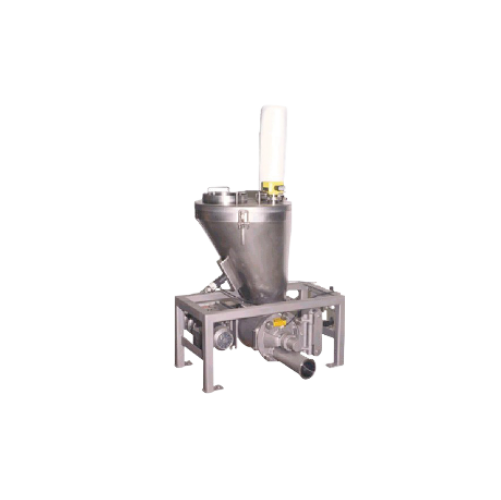
Lean phase pressure conveying for powder handling
Effortlessly transport and manage powdered materials with lean phase pr...
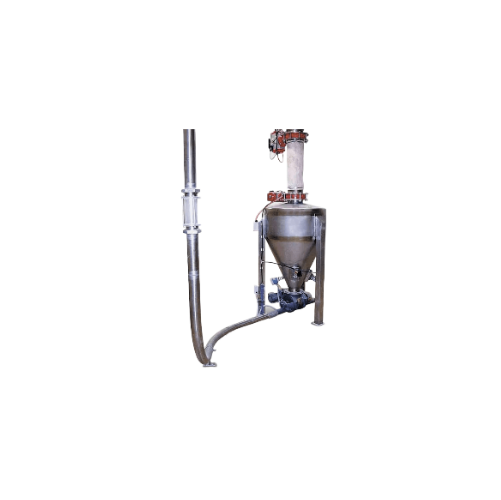
Lean phase vacuum conveying system for powder handling
Efficiently transport and separate powders and granules with preci...
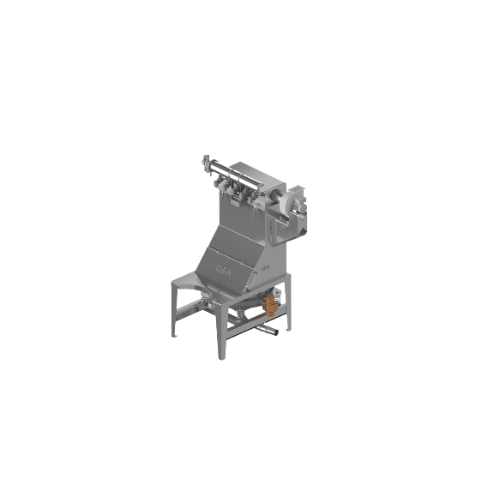
25kg bag tipping station for powder discharge
Efficiently discharge and sieve 25kg bags of powder while minimizing dust em...

Fibc emptying stations for powder processing
Streamline your bulk powder handling with single-operator FIBC emptying stati...
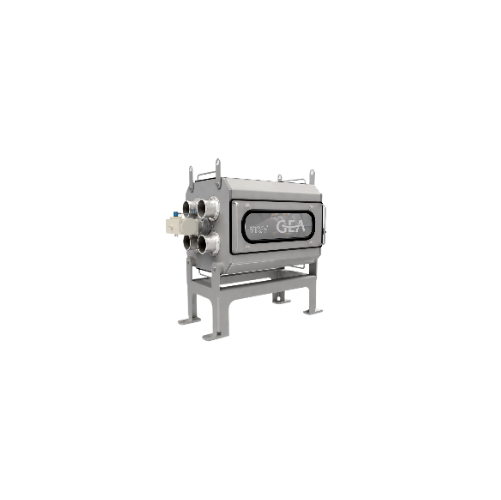
Rotary tube selector valve for powder conveying
Streamline your pneumatic transport system with a robust solution that div...
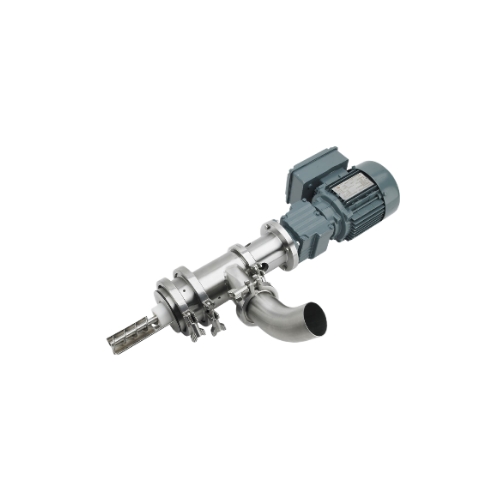
Auger powder sampler for industrial quality control
Ensure precise quality control by integrating an auger powder sampler...
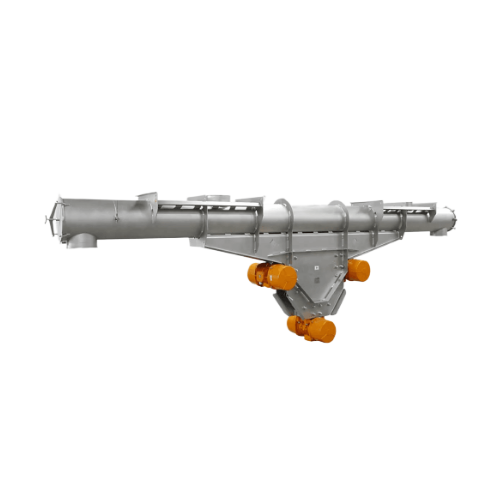
Vibrating conveyor for powder and granule handling
Effortlessly convey and process fragile products with precision, minim...
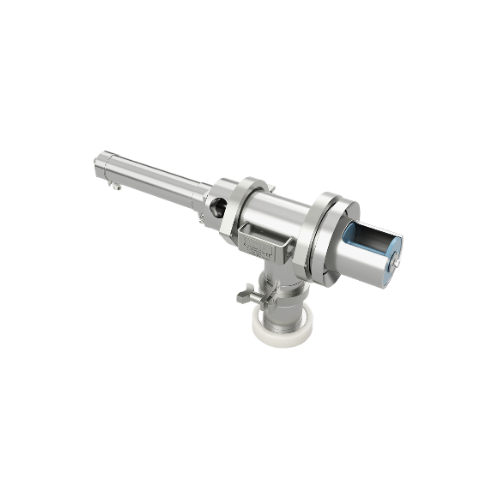
Powder sampling solution for dairy and food processors
Ensure precise quality control with a versatile sampling system de...
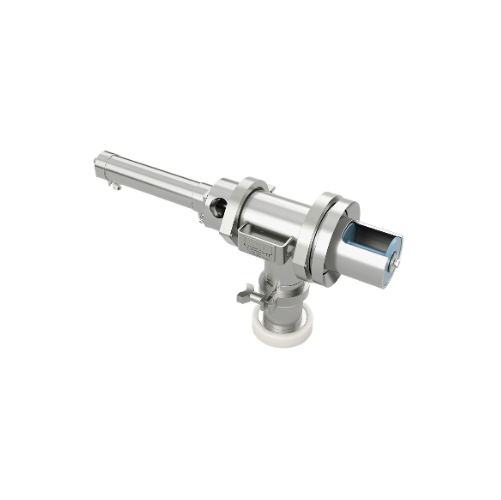
Powder spool sampler for dairy and food processors
Efficiently manage powder quality with a robust spool sampler designed...
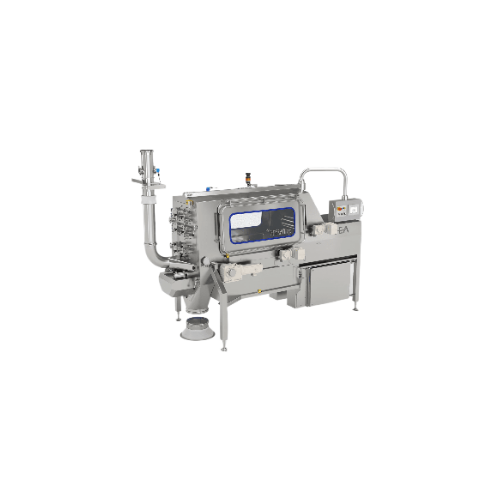
Automatic bag slitting and emptying for powders
Streamline your powder-processing operations by seamlessly integrating bag...
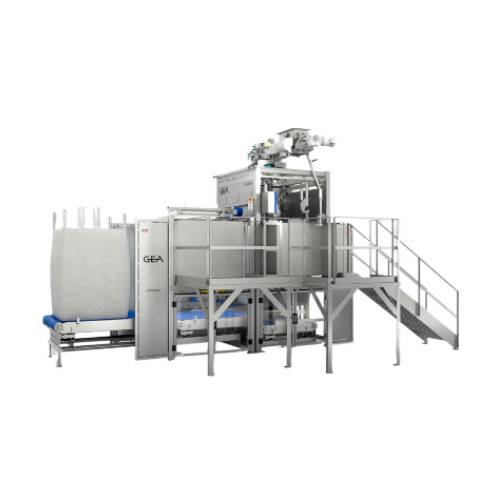
Bulk powder filler for food, dairy, and nutraceuticals
Optimize your bulk powder filling process with a system designed t...
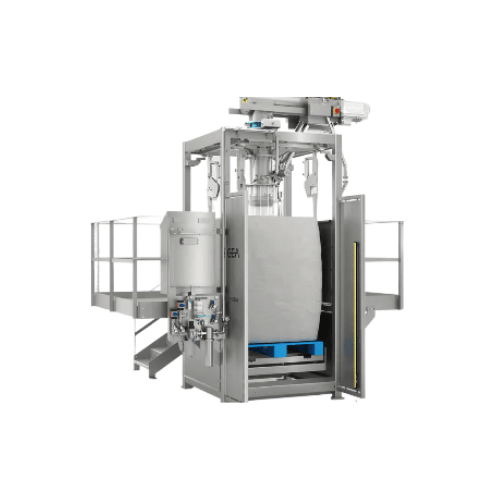
Low care bulk powder fillers
Optimize your production efficiency by accurately filling flexible bulk containers with dry pow...
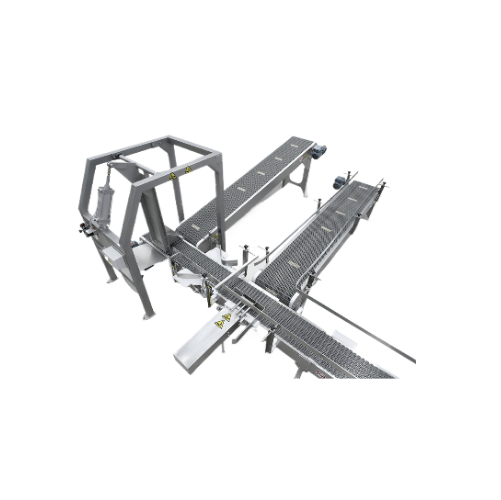
Bag, box, and drum container handling solutions for powder products
Optimize the flow and integrity of your powder pack...
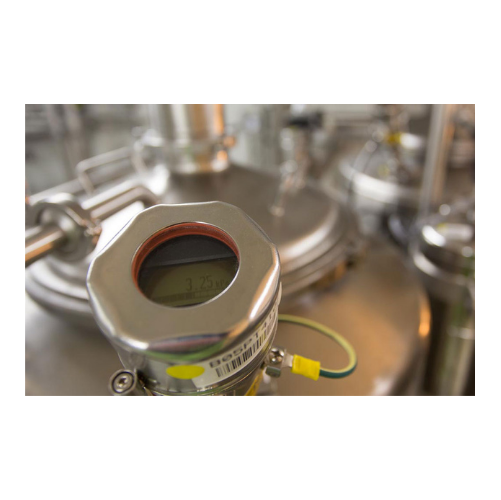
Powdered product shelf-life enhancement through inert gas packing
Extend the shelf life of sensitive powder products by...
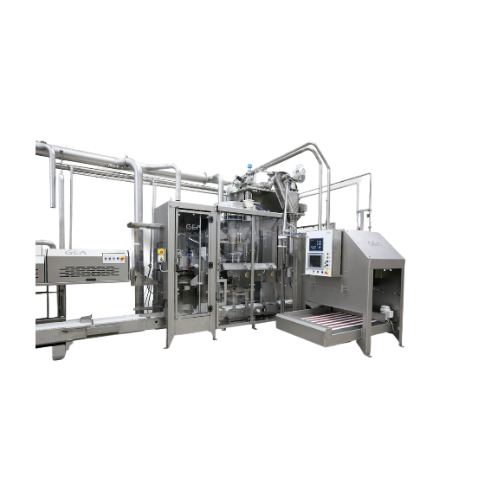
Inline automatic powder fillers for food and nutraceuticals
Ensure precise and efficient filling of sensitive powders in...

Continuous leveler and sealer for powder packing
Enhance efficiency in powder packaging with a system that ensures precise...
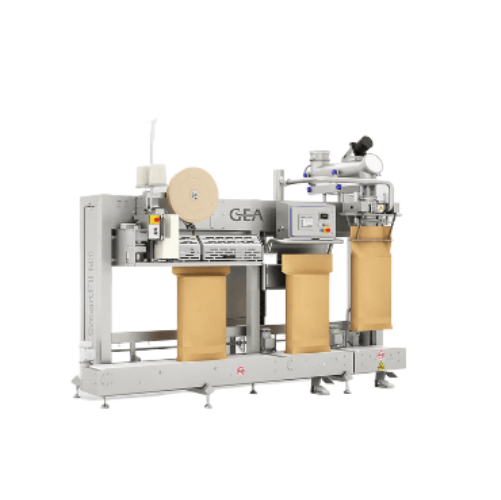
Semi-automatic powder filling system for food products
Achieve precise and flexible filling for food powders and granules...
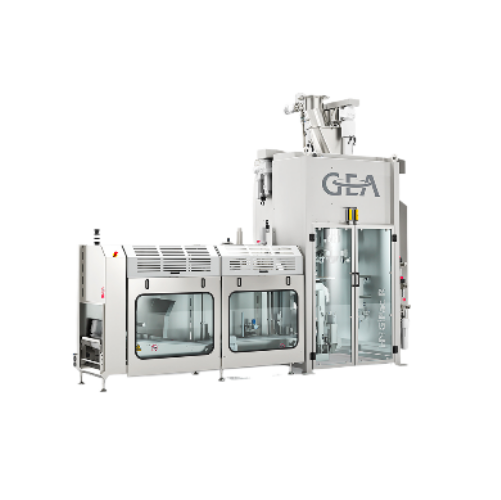
Hygienic powder filling system for low throughput
Ideal for compact production facilities, this filling system efficientl...
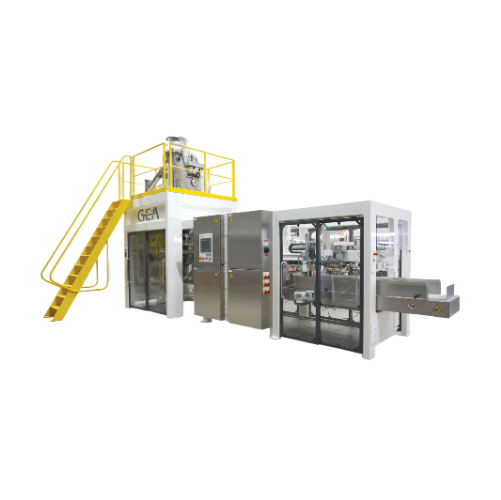
Automated powder bag filling system
Streamline your powder packaging operations with a fully integrated system that automat...
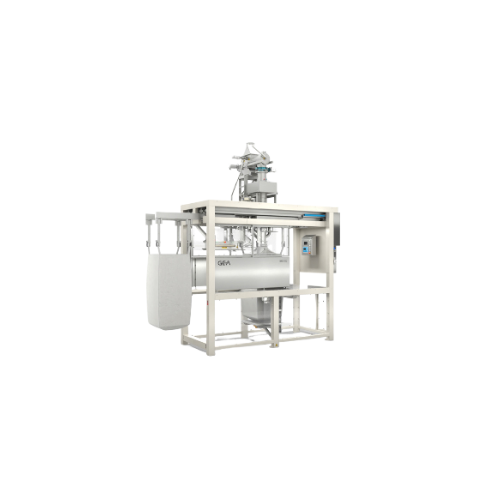
High care bulk powder fillers
Ensure hygienic packaging for your bulk powders with a system designed to enhance filling accu...

Lecithin adding system for dairy powders
Enhance your spray drying process by seamlessly integrating lecithin to improve so...
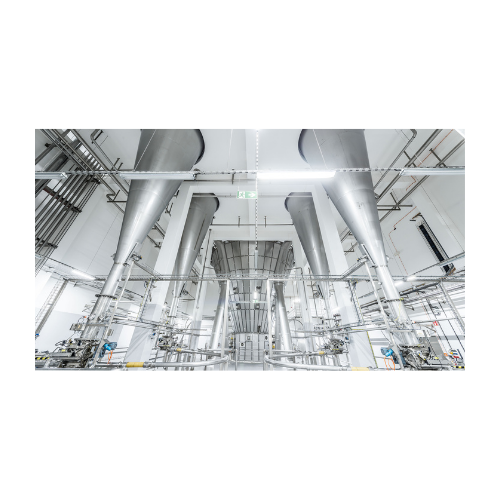
Spray dryer for nutritional and dairy powders
Achieve precise particle size and optimal drying of nutritional and dairy po...
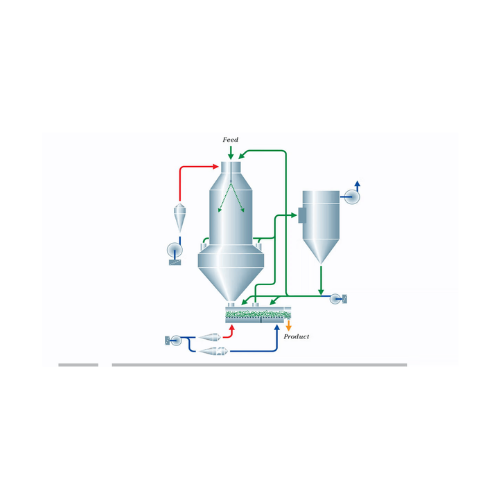
Spray drying solution for uniform powder production
Achieve seamless transformation of liquid feeds into uniform, free-fl...

Lab-scale spray dryer for small volume powder samples
When developing new formulations, achieving consistent powder quali...
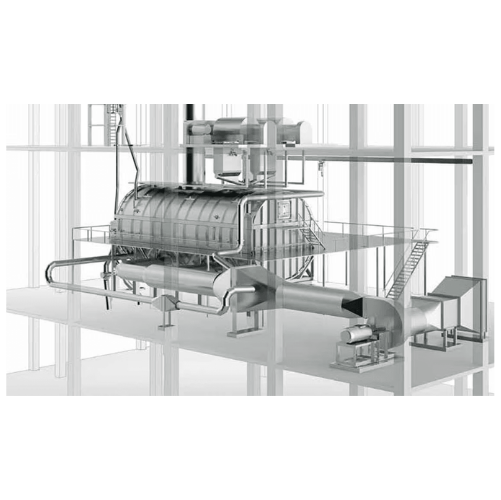
Fluid bed drying system for wet powder chemicals
Achieve efficient large-scale drying and cooling of wet powder chemicals ...
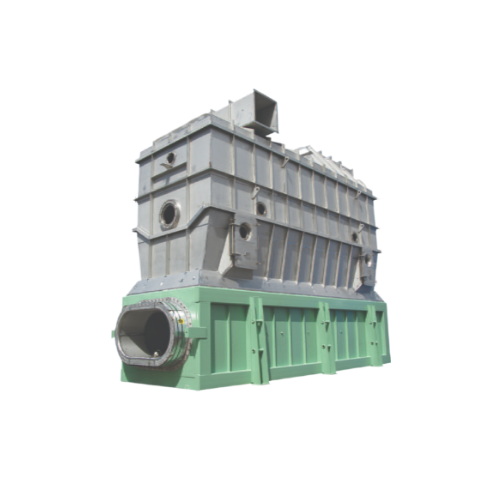
Static fluid bed dryer for powder and granular materials
Achieve optimal moisture control in powder and granular products...
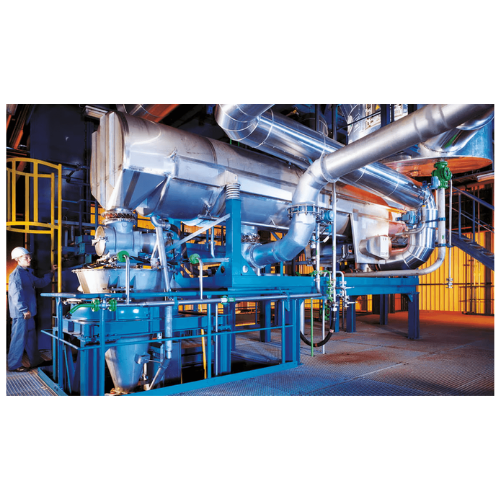
Vibrating fluid bed for final stage powder drying
Enhance powder processing precision with a vibrating fluid bed that ens...
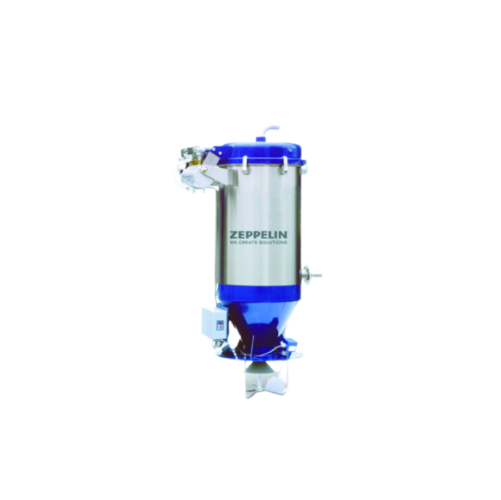
Vacuum hopper loader for automatic feeding of powders and pellets
Optimize your material handling with seamless automat...
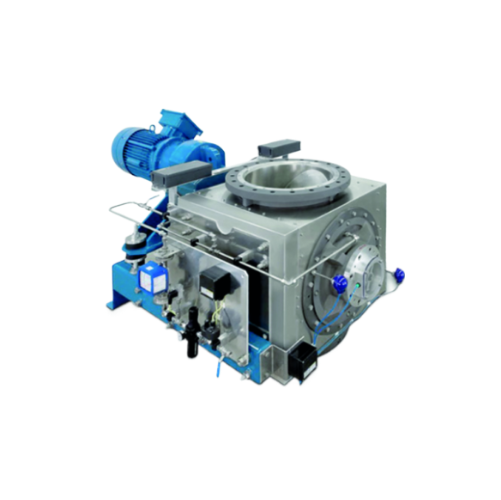
Industrial rotary feeder for powder and agglomerates
Achieve seamless integration in your production line with a robust s...
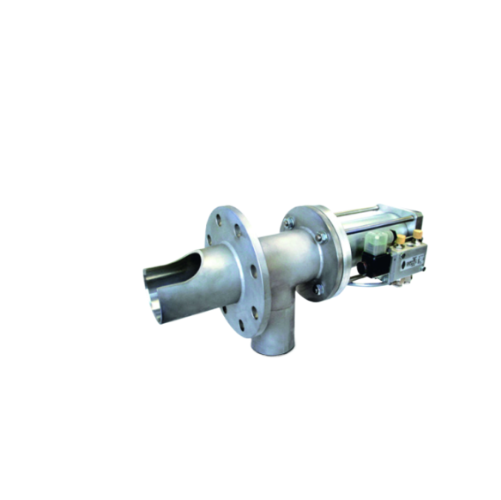
Sampler for powdered and granular bulk materials
Ensure precise sampling of powdered and granular materials under varied o...
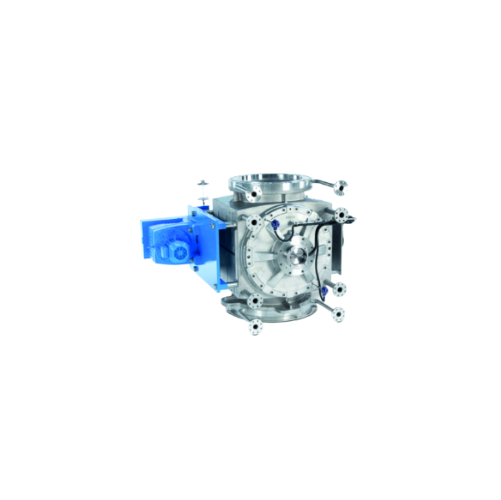
High-pressure rotary feeder for continuous powder handling
Optimize your production line with reliable powder handling, ...
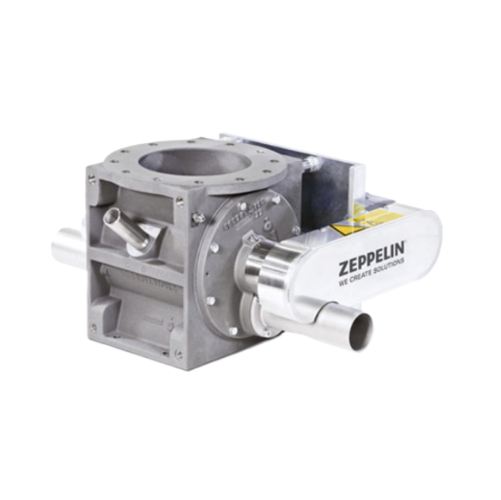
Rotary feeder for powdered bulk materials
Achieve precise control in feeding and discharging powdered materials with a rot...
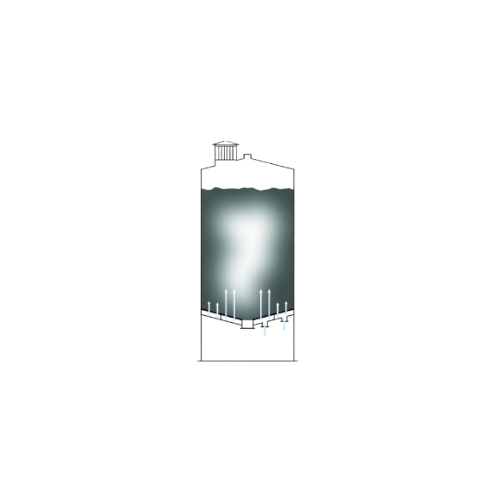
Fluidizing bed blending silo for powder mixing
Optimize your batch mixing process with a fluidizing bed blending silo, des...
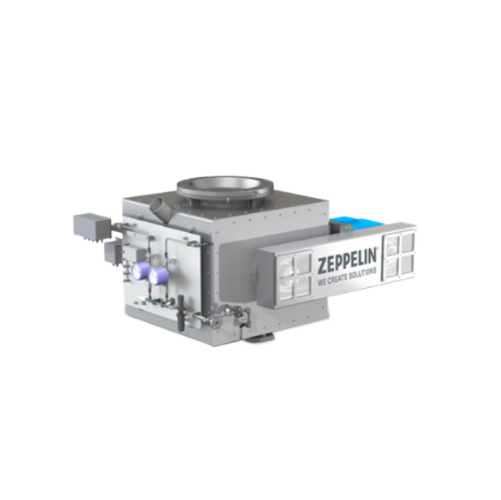
High-pressure rotary feeder for powder and agglomerates
Optimize your production line with a high-torque solution that ef...
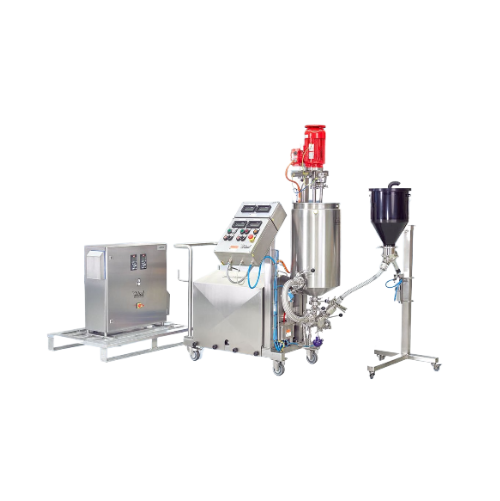
Laboratory disperser for powder induction and wetting
Optimize your pilot and laboratory processes with a high-speed disp...
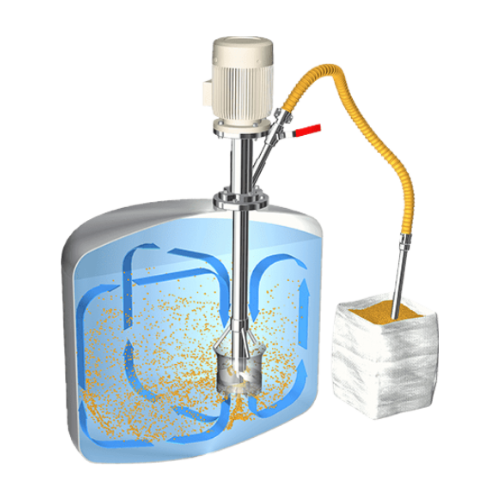
Low-dust powder induction mixer for liquids
Achieve dust-free induction and homogenization of powders in liquids with prec...
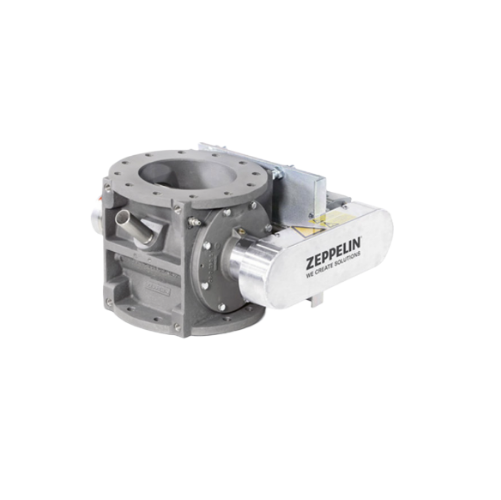
A-type rotary feeder for powder and pelleted bulk materials
Ensure precise feeding and discharging of powdered and pelle...
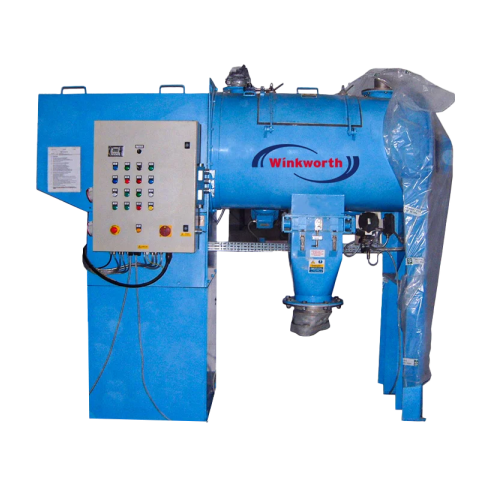
High-speed mixer for homogenous mixing of powders and pastes
Achieve rapid and precise mixing with high-speed dispersion...
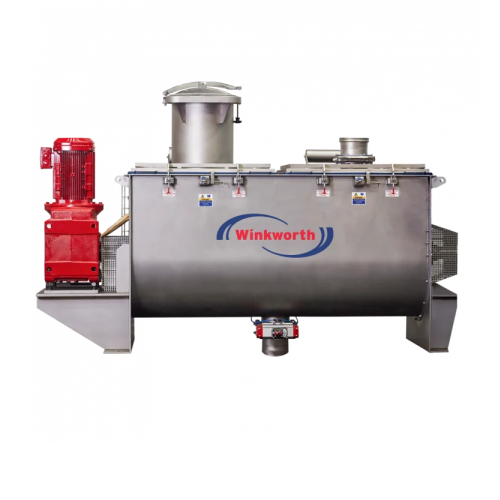
Efficient ribbon mixers for precise powder blending
Achieve consistent and uniform blending with this advanced U-Trough m...
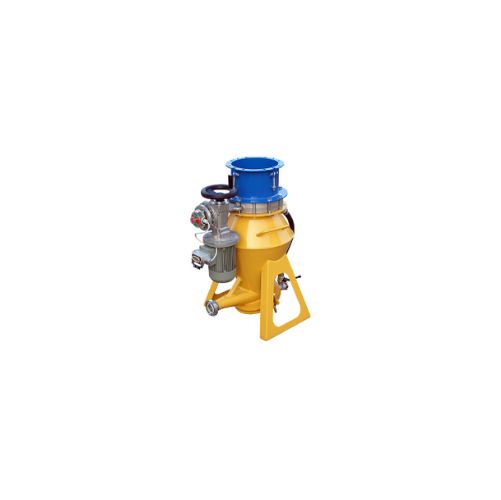
Butterfly valves for dry powder and granule flow interception
Ensure precise control over material flow in your processi...
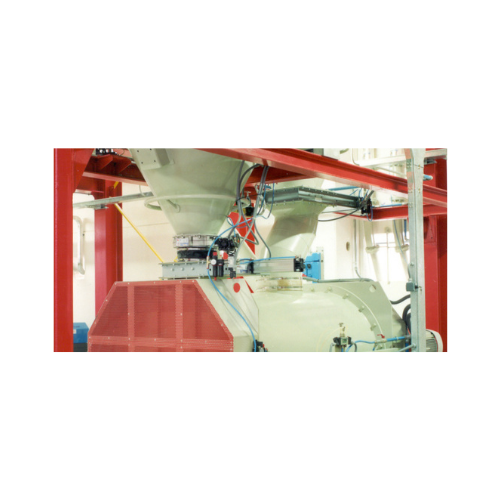
Butterfly valves for powders and granules
Ensure precise flow control and reliable sealing for gravity-fed or pneumatic sy...
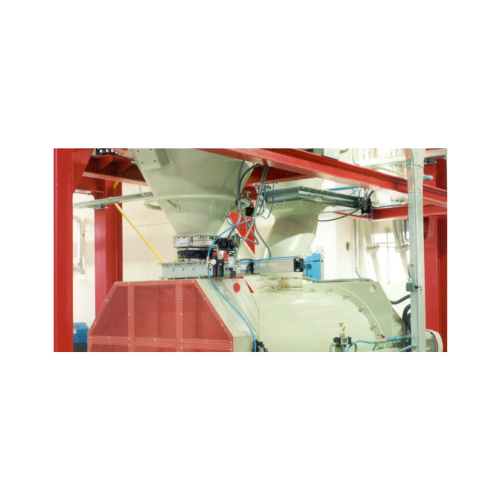
Butterfly valves for powder and granular material handling
Experience seamless material control with advanced butterfly ...
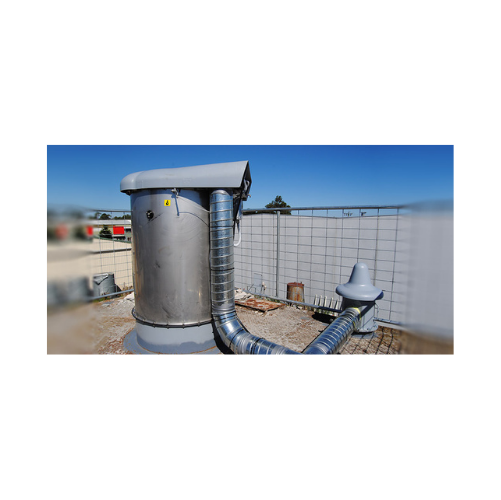
Low profile slide valve for controlling powder flow
Optimize your powder and granule flow management with precision-engin...
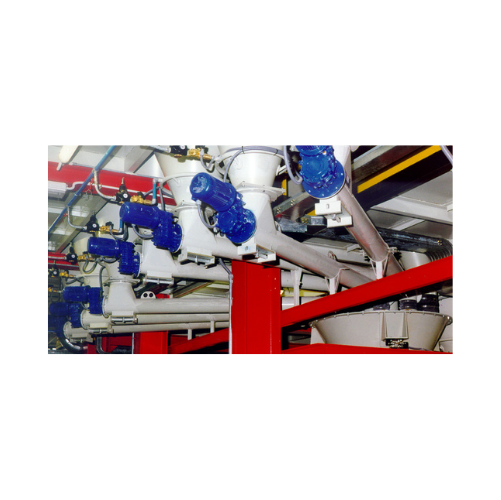
Tubular screw conveyor for powdery and granular materials
Optimize your material handling processes with a versatile sol...
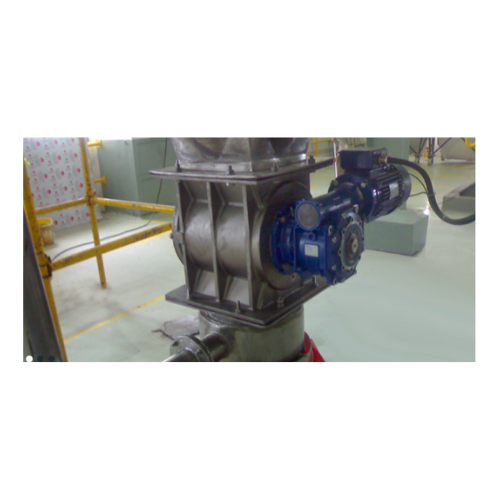
Drop-through rotary valve for powder and granular material feeding
Achieve precise control in discharging and feeding p...
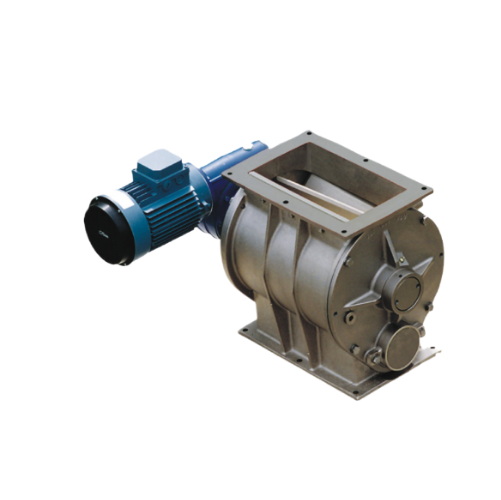
Drop-through rotary valve for precise powder and granule feeding
Ensure precise material handling with this drop-through...
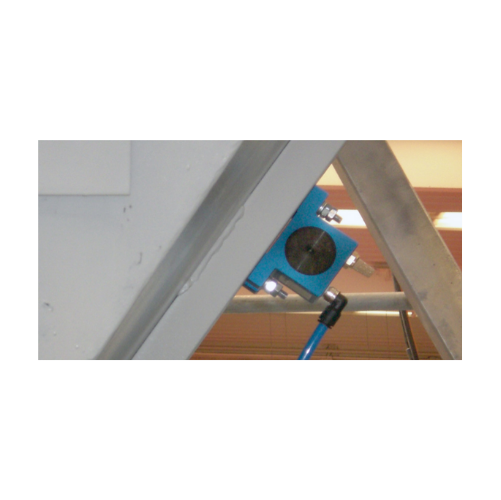
Rotary ball vibrators for fine powders and granular materials
Ideal for preventing material build-up and blockages, thes...
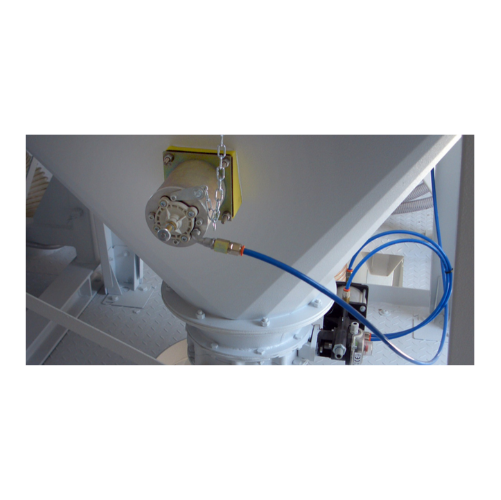
Combined hammer blaster for powder handling
Address powder flow issues with ease by preventing bridging and ratholing, ens...
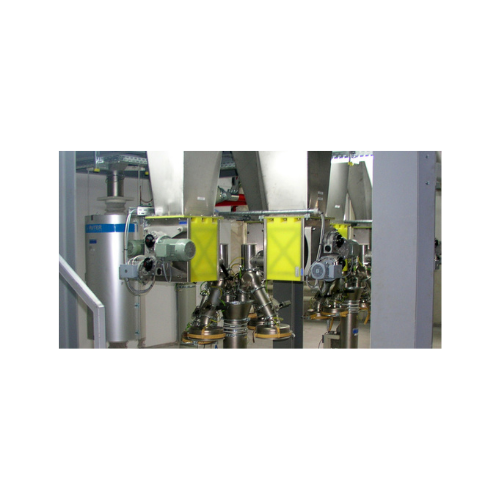
Micro-batch feeders for powder and granular material
Struggling with clog-prone powders? Gain precise control and consist...
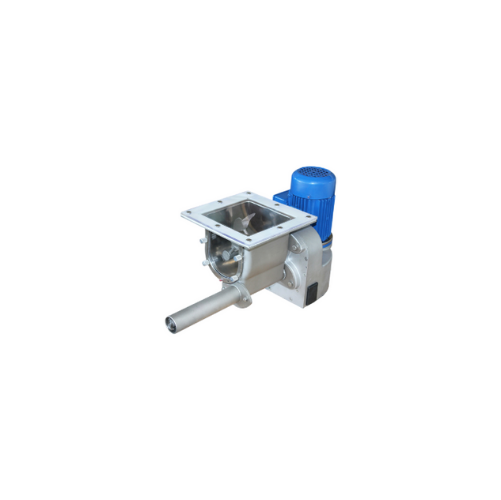
High efficiency micro-batch feeder for powdery or granular materials
Achieve precise volumetric feeding and metering of...
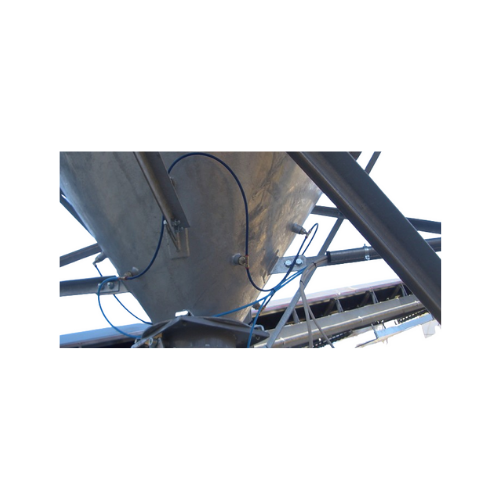
Aeration pads for powdery material flow in silos
Ensure consistent material flow in your silos and bins with a reliable ae...
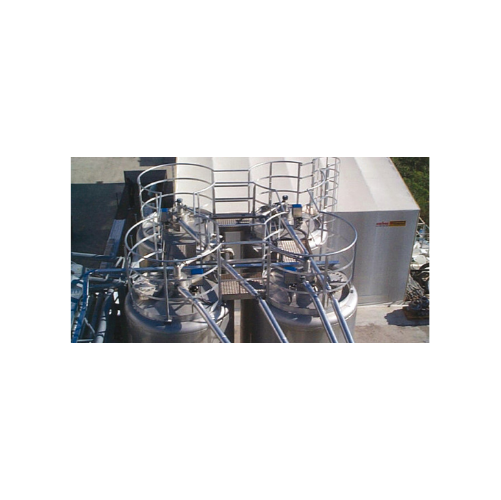
Continuous level measurement system for powdery or granular materials
Ensure precise inventory management and enhanced ...

Bin level indicators for powder and granular material
Ensure precise inventory management and prevent overflows in your p...
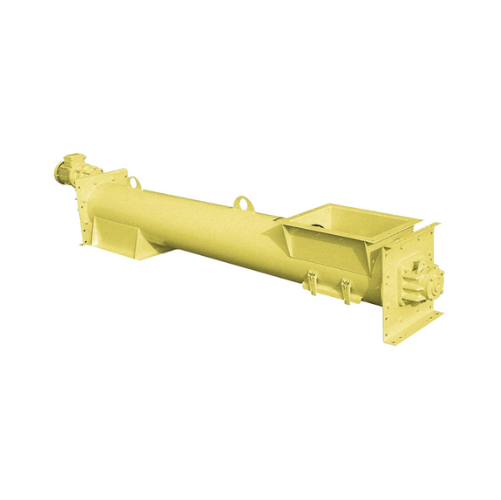
Tubular trough screw conveyors for gentle powder and granular material handling
Achieve precise powder and granular ma...
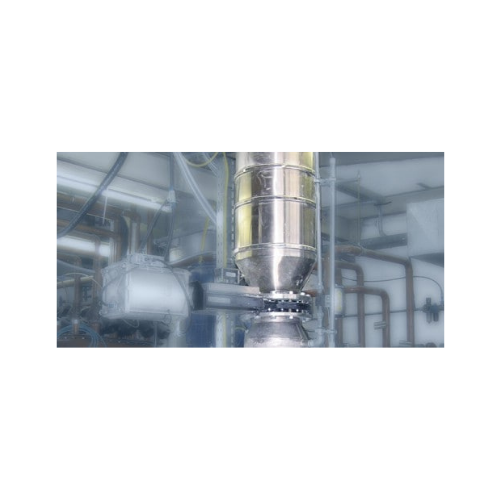
Powder locks for safe bulk material handling
Ensure containment and prevent contamination while processing sensitive bulk ...
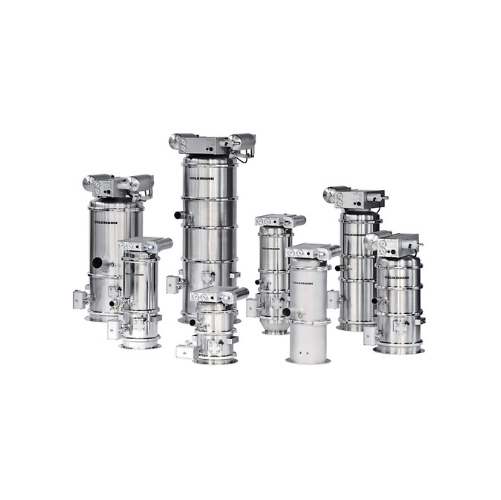
Powder handling vacuum conveyor system
Streamline your material transfer with a versatile vacuum conveyor system that ensur...
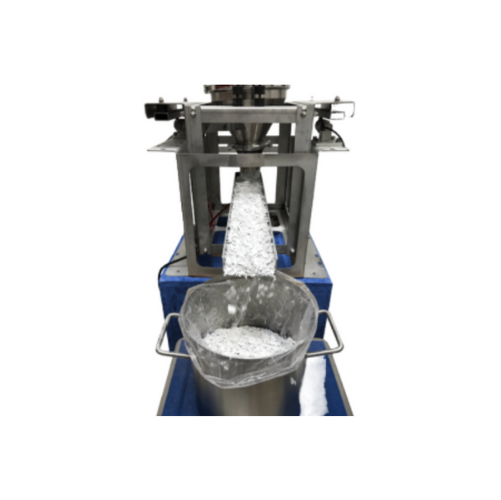
Vibratory feeder for dosing powders and bulks
Ensure precise feeding of powders and bulk materials with a system that inte...

Industrial vacuum pumps for efficient powder conveyance
Harness the power of efficient vacuum generation to streamline th...
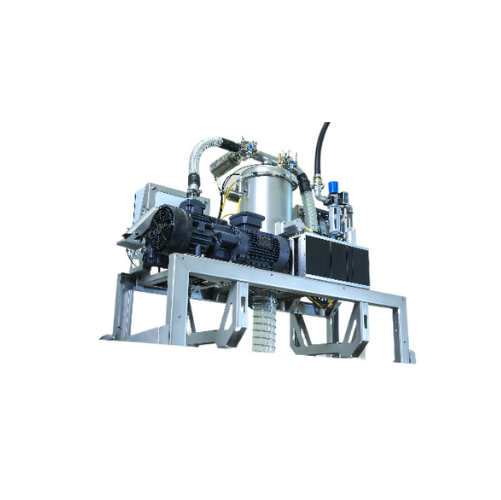
Automatic metal powder filling system for 3d printers
Ensure seamless operation of your 3D printing process with a system...
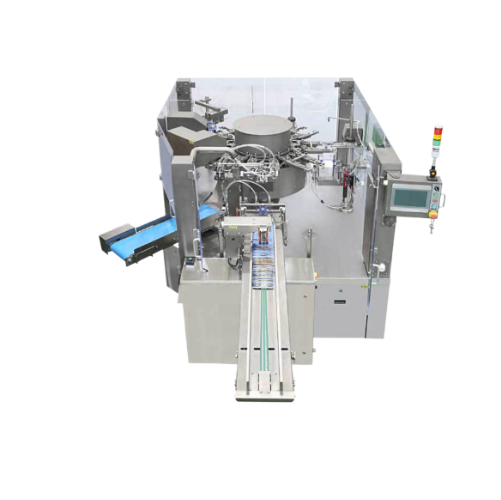
Rotary pouch packaging system for food and powder products
Streamline your packaging process with a rotary system that e...
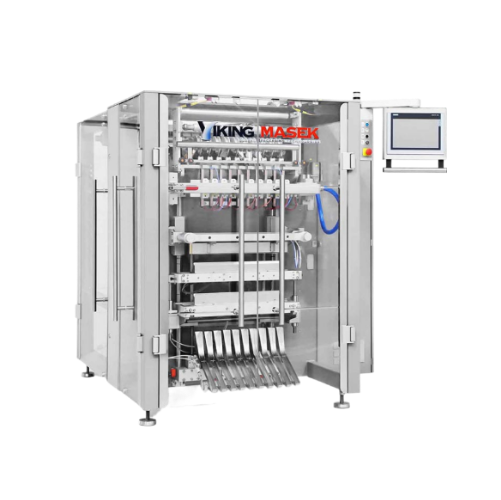
Stick pack packaging for powders and liquids
Streamline your packing process with high-speed, servo-driven stick pack mach...
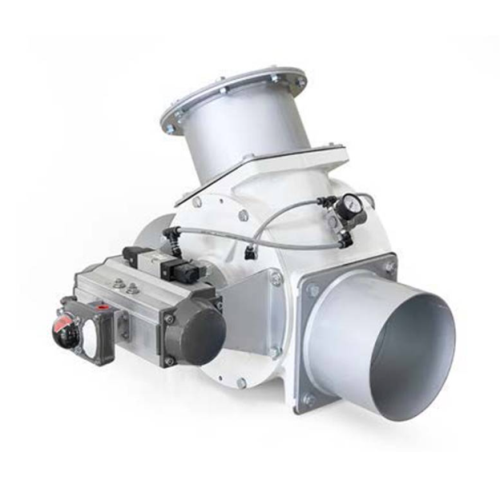
Pneumatic diverting valve for powder and granule transfer
Efficiently redirect bulk materials from one point to another ...
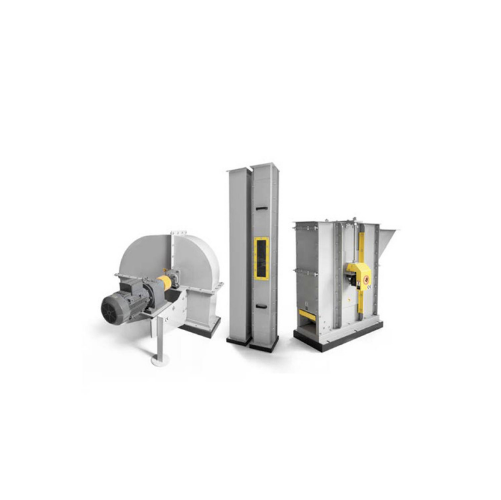
Bucket elevator for grain and powder products
Efficiently transport bulk materials like grain and powder vertically with p...
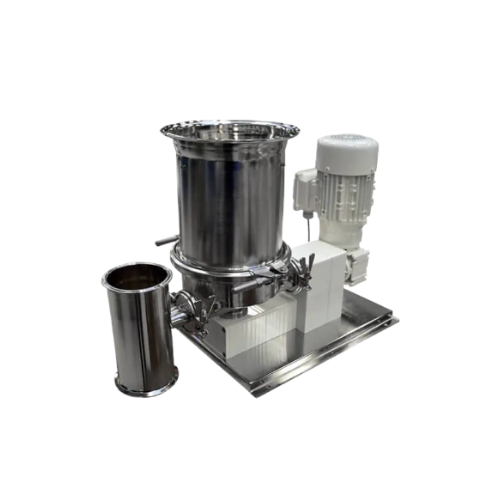
Flat-bottom twin-screw feeder for precise powder feeding
Achieve precise control in powder dispensing with this flat-bott...
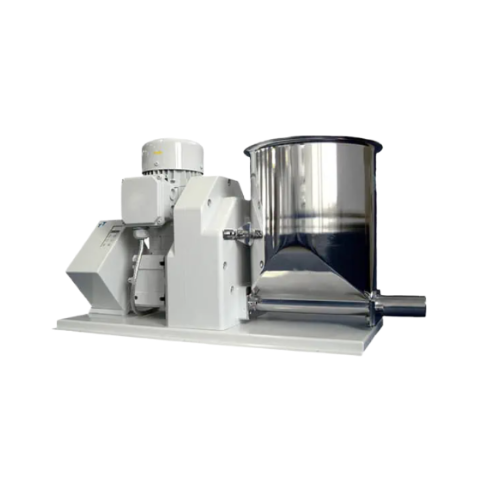
Volumetric twin screw feeder for powder and micro-granules
Optimize your production flow by ensuring consistent and prec...
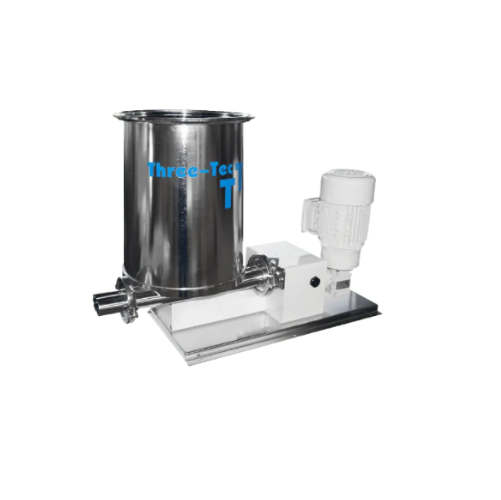
Volumetric twin-screw feeder for poorly flowing powders
For manufacturers dealing with powders that clump or cake, this f...
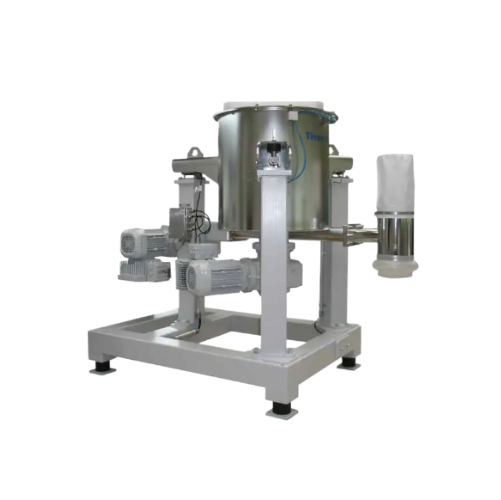
Twin screw feeder for poorly flowing powders
Optimize your process with precision feeding for powders that easily clump or...
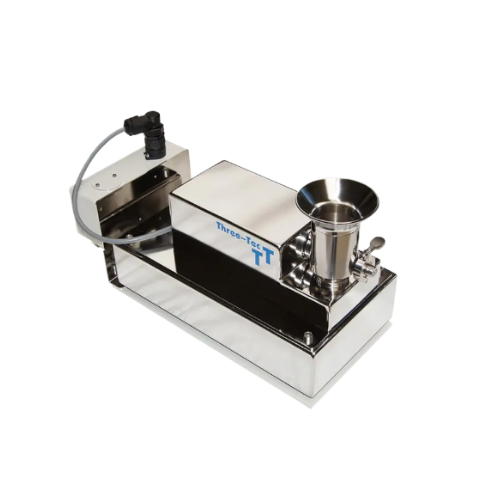
Small-scale twin-screw feeder for powder handling
Perfect for precision in lab environments, this small-scale feeder effi...
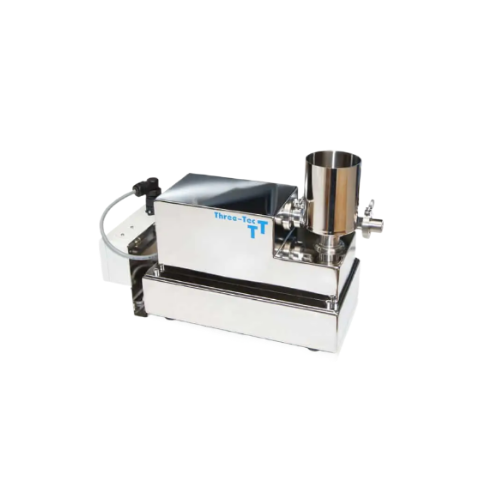
Precise volumetric or gravimetric powder feeder
For precise feeding of challenging powders prone to clumping and bridging,...
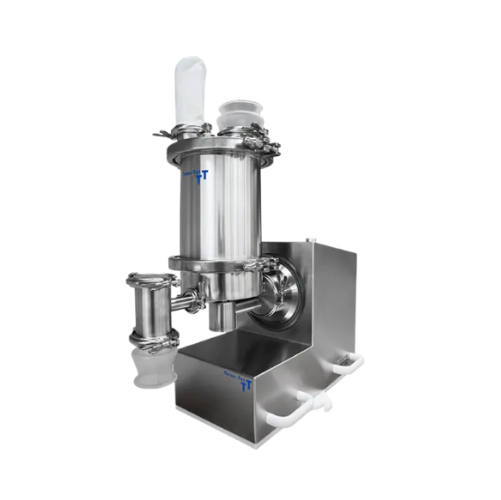
Gravimetric twin screw feeders for pharma powders
Optimize feeding for challenging materials with dust and water-resistan...
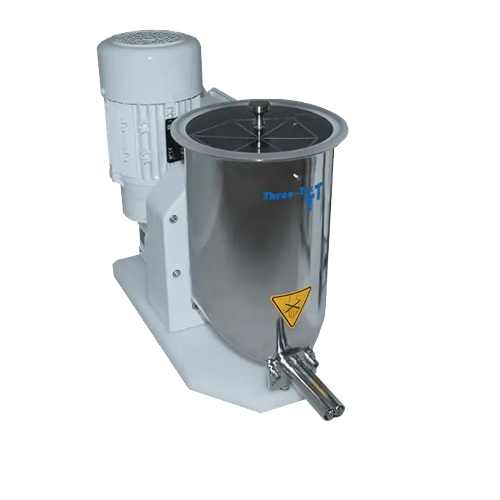
Twin-screw feeder for powders and micro-granules
Ideal for handling poorly flowing powders and granules, this advanced twi...
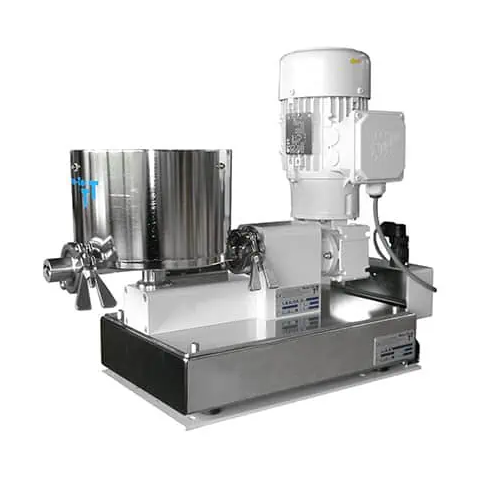
Volumetric flat-bottom twin-screw feeder for powders
When handling powders prone to clumping, a reliable feeder ensures u...

Volumetric auger filler for powder packaging
Streamline your powder packaging process with precise and efficient volumetri...
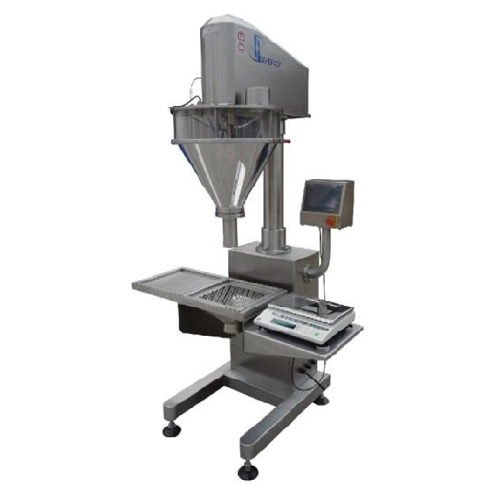
Volumetric auger filler for precise powder weighing
Optimize your production line with a high-speed volumetric auger fill...
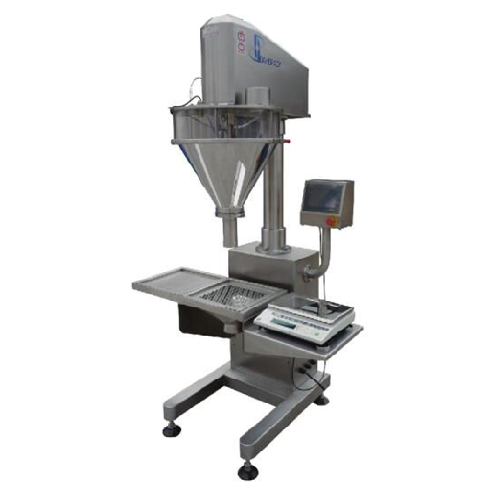
Volumetric auger for powder weighing and depositing
Ensure precise powder weighing and depositing for consistent product ...
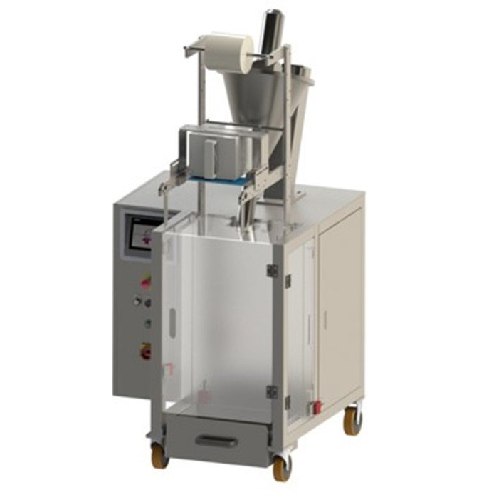
Sachet powder filling machine
Optimize your packaging line with this efficient solution for precise powder filling, ensuring...
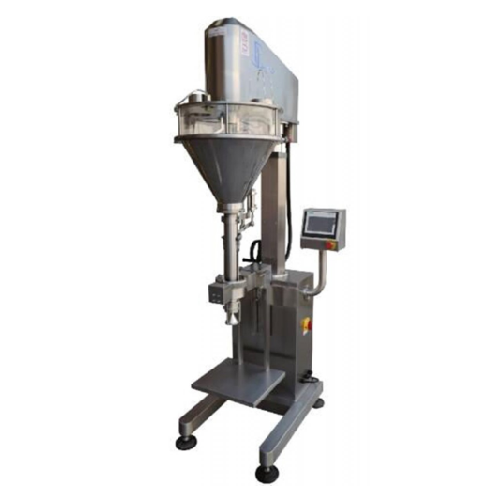
Gravimetric auger filler for powder weighing
Achieve precise powder filling with this gravimetric auger solution, ensuring...
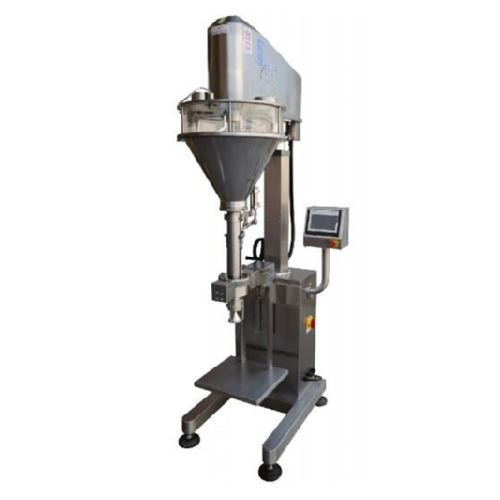
Powder auger filler for precise weighing and depositing
Ensure accurate and efficient powder filling with this innovative...
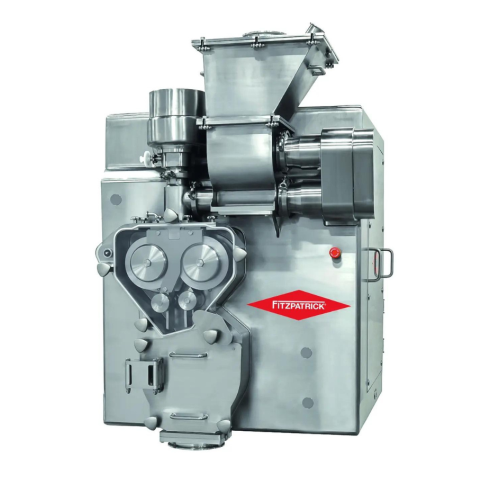
Dry granulation system for pharmaceutical powders
Streamline your powder processing with a dry granulation system that en...
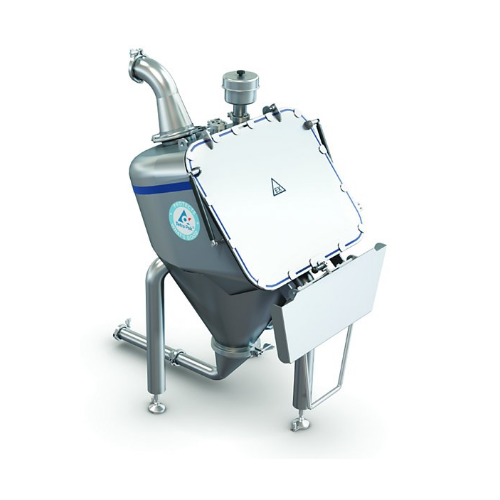
Bag tipping unit for Cip processes in powder handling
Ensure seamless powder handling and high hygiene standards in your ...
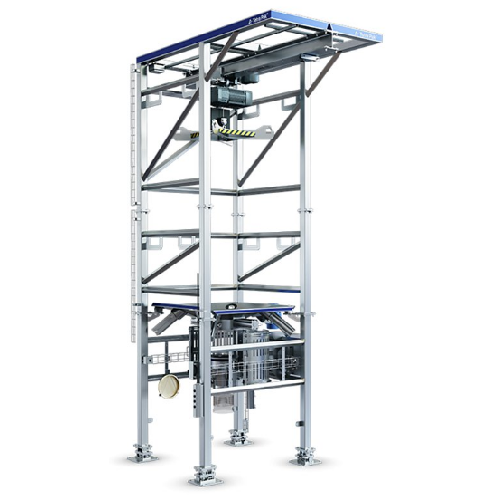
Big bag discharger for powder handling
Effortlessly discharge large bags of powdered ingredients with a modular, safe syste...
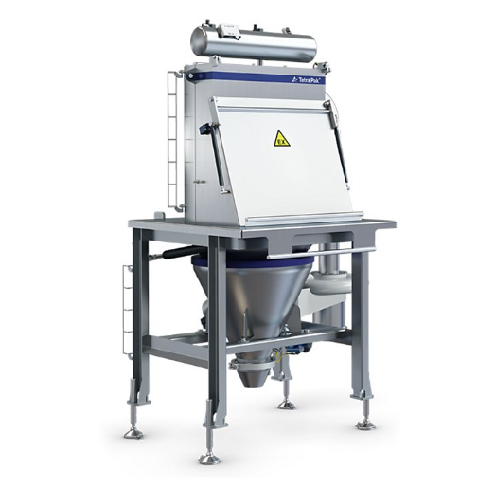
Manual bag tipping unit for powder handling
Ensure a contamination-free environment with a compact manual bag tipping unit...
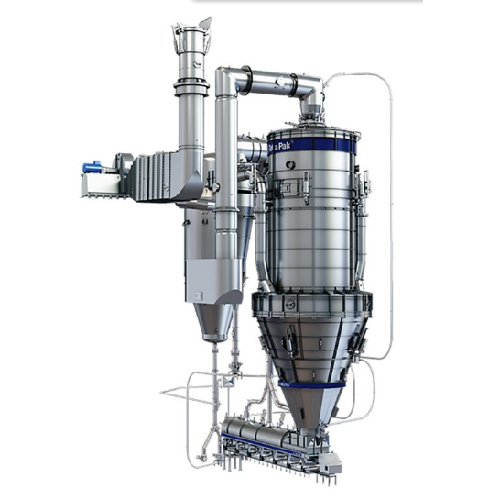
Spray dryer for heat-sensitive powders
Ensure high-quality drying of heat-sensitive powders, producing non-caking and non-h...
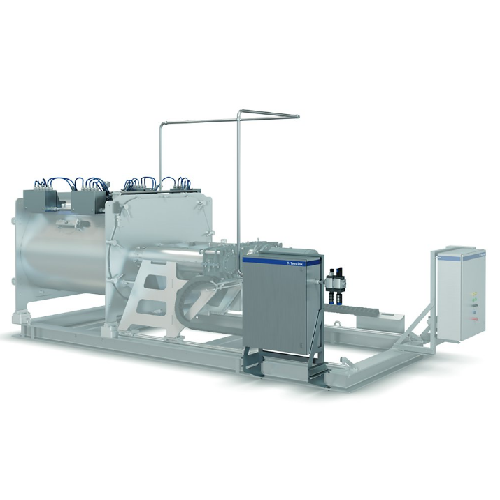
Air jet cleaning system for powder production
Eliminate water and chemical use while maximizing production efficiency with...
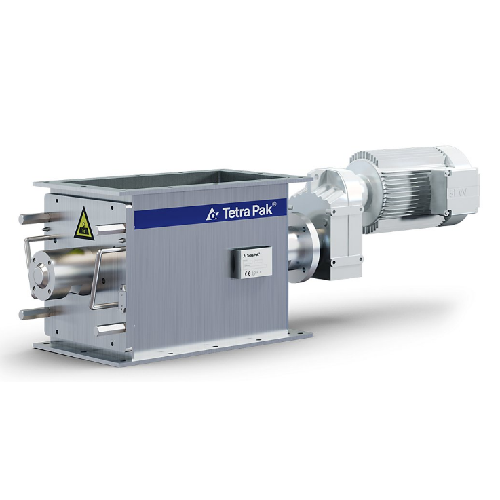
Lump breaker for dry powders and granulates
Optimize the consistency of your production line by efficiently breaking up lu...
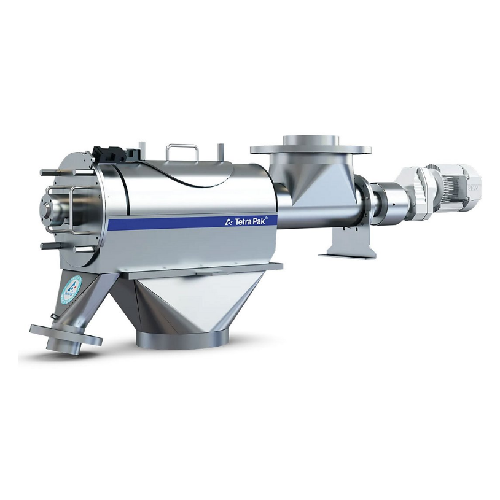
Centrifugal sifter for food and pharmaceutical powders
Ensure consistent particle size and remove contaminants in high-sp...
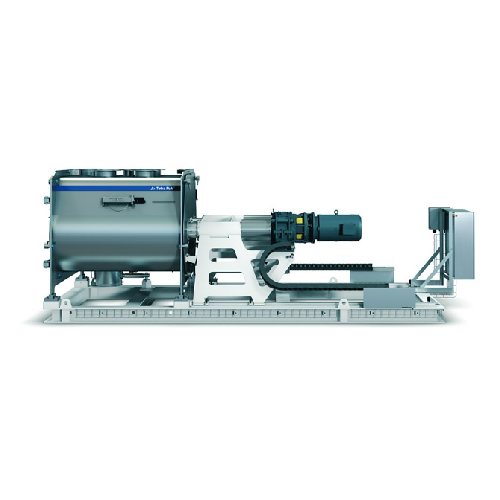
Industrial powder mixer for food production
Enhance your production line with a high-speed batch mixer designed for precis...
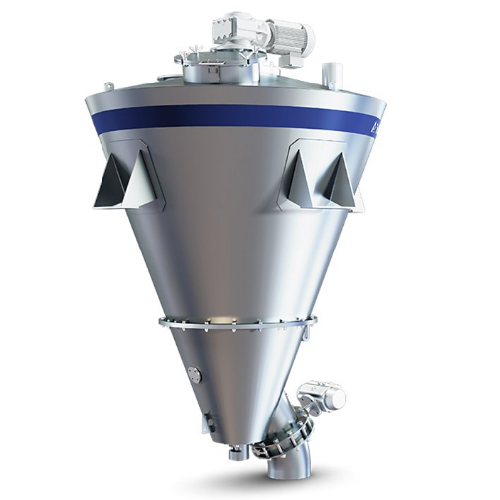
Conical homogenizer for powder and granulated products
Achieve seamless homogenization of diverse powders and granulated ...
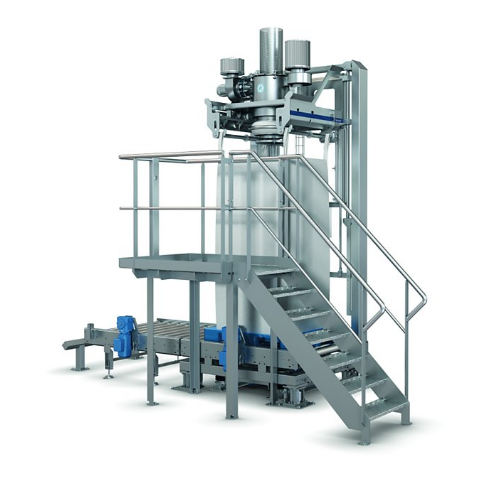
Big bag filler for granulated or powder components
Ensure precise and dust-free filling of large bags with a unit designe...
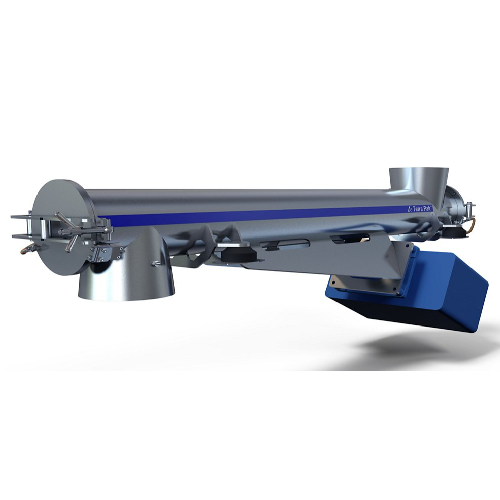
Vibrating conveyor for short-distance powder transport
Achieve precise and hygienic powder conveying and dosing with this...
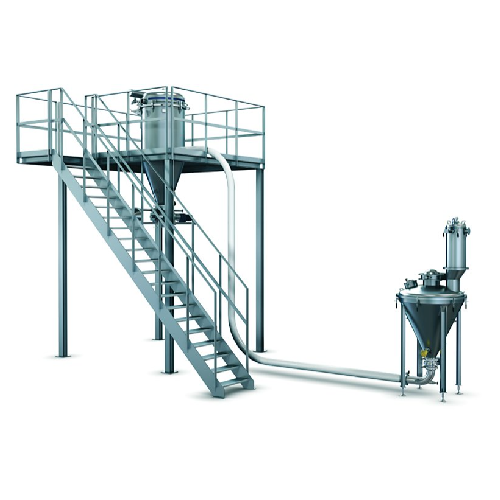
Pneumatic conveyor for fragile powders
Handle your delicate powders with care, ensuring minimal breakdown while achieving h...
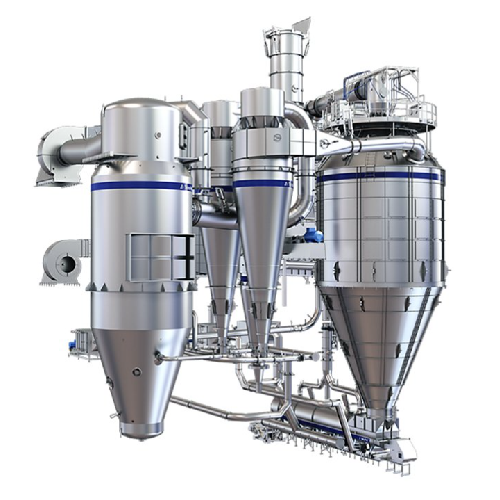
Spray dryer for nutritional powders
Ensure precise moisture control and enhance powder quality in nutritional products with...

Continuous spray dryer for permeate powder
Efficiently transform liquid whey and milk into high-quality, non-caking, and n...
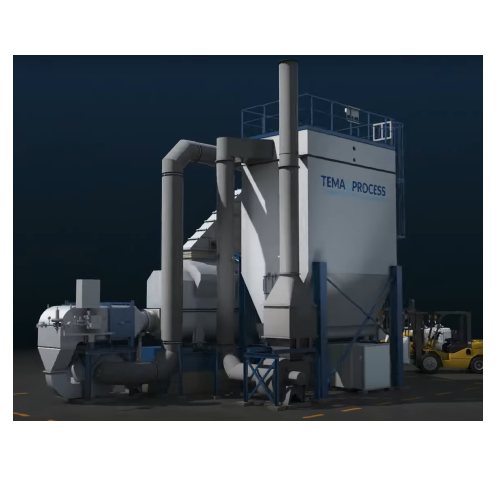
Continuous fluid bed dryer for powder and granules
Enhance your production line with precise moisture control and energy ...
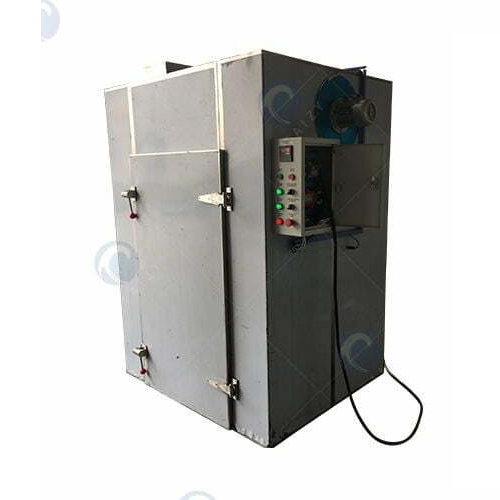
Ginger powder processing line
Optimize your spice production with comprehensive ginger powder processing, transforming fresh...
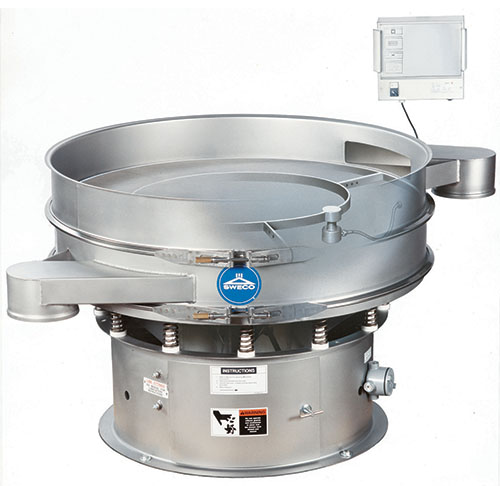
Ultrasonic round vibratory separator for fine powders
Efficiently prevent screen blinding during powder separation proces...
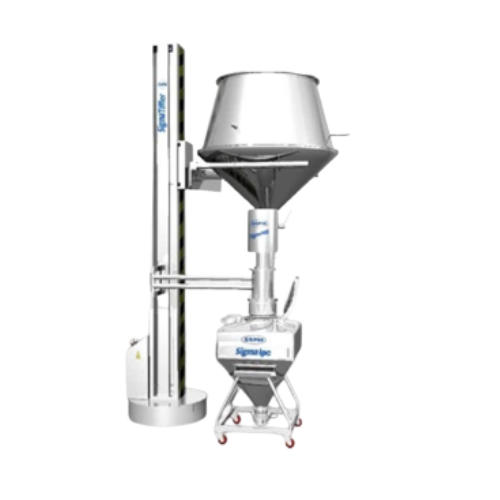
Material handling system for granules and powders
Optimize your production with seamless material handling specifically d...
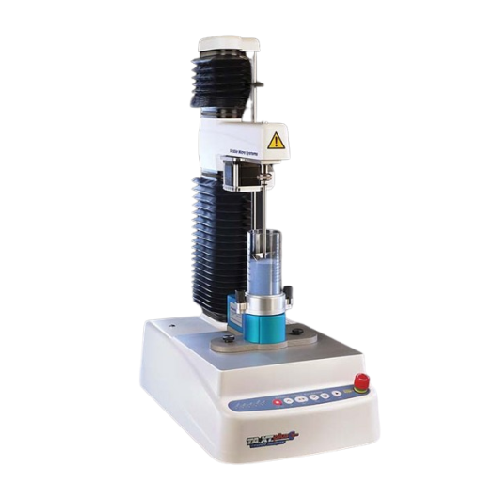
Powder flow measurement system
Achieve precise control over powder consistency and prevent process disruptions by assessing ...
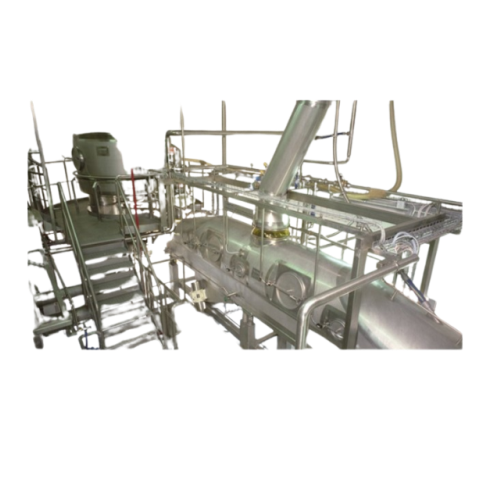
Spray bed dryer for agglomerated powder production
Efficiently transform liquid feedstock into consistent, dust-free powd...
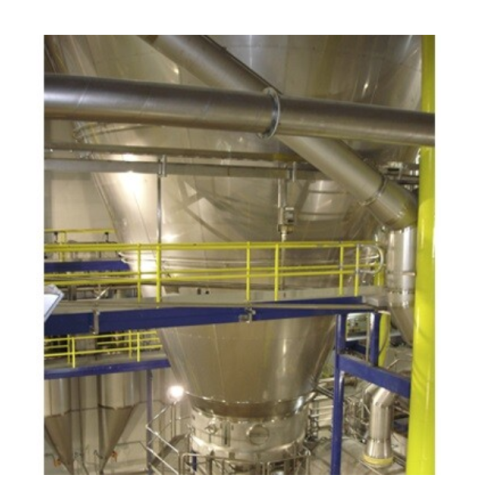
Spray dryers for producing free-flowing dustless powders
Achieve consistent product quality with customizable spray dryer...
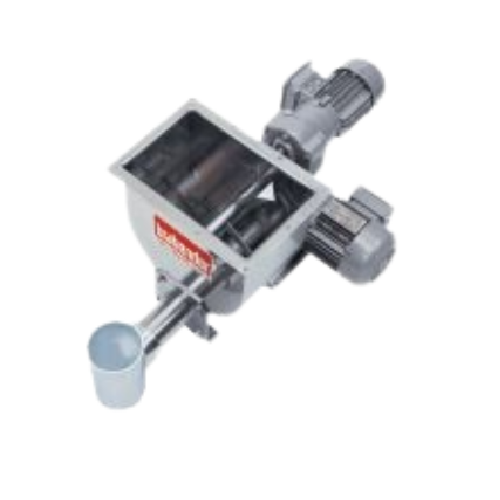
Single screw feeder with stirring agitator for powders and pellets
Ensure consistent mass flow and precise dosing with ...
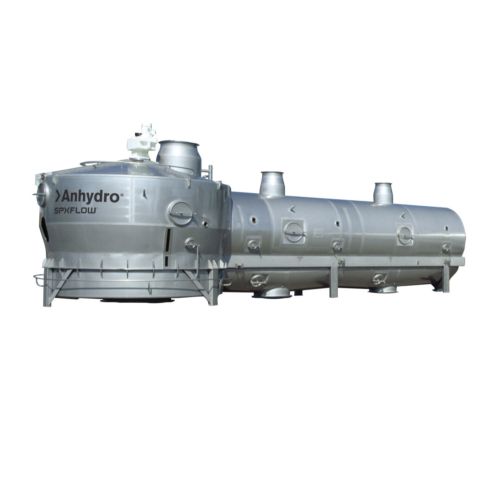
Industrial fluid bed dryers for powder processing
Enhance moisture control and uniformity in powder products with dynamic...
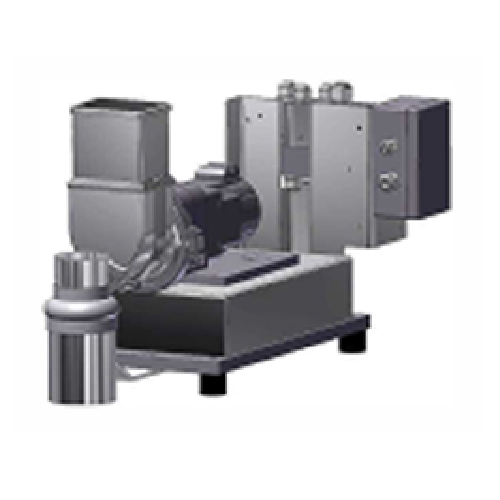
Laboratory loss-in-weight feeder for powders or pellets
Achieve precise dosing for lab-scale trials with this versatile f...
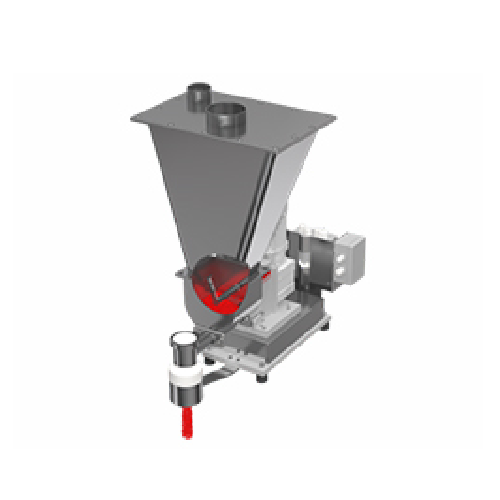
Double screw batch feeder for poorly flowing powders
Effectively manage challenging powders with precise batch dosing and...
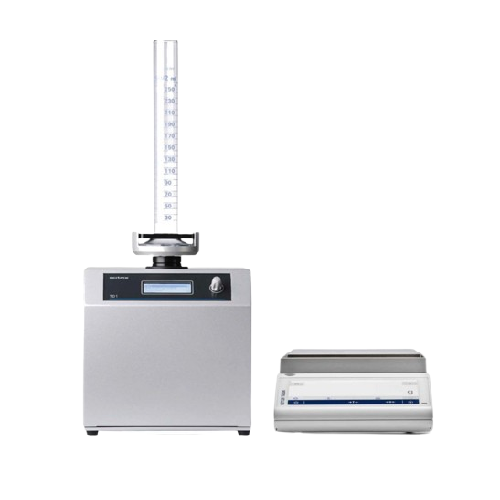
Tapped density tester for pharmaceutical powders
Ensure precise quality control in pharmaceuticals by accurately measuring...
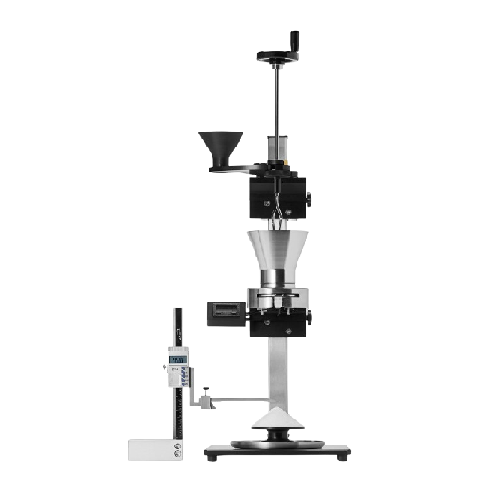
Powder flow tester for pharmaceutical powder flowability
Quickly assess powder flow characteristics to ensure consistent ...
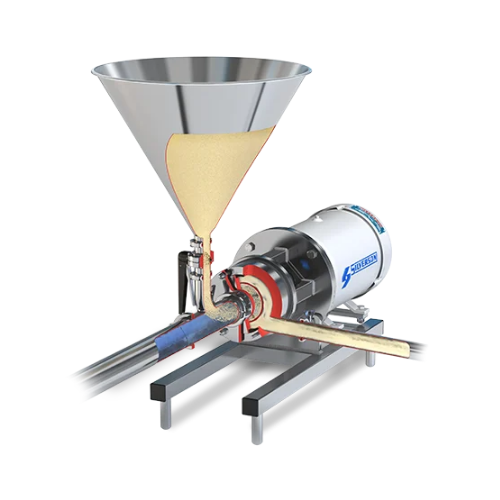
High shear powder mixing solution
Achieve agglomerate-free, homogeneous mixing of powders and liquids with high shear effic...

Laboratory scale powder/liquid mixer
Easily integrate powders into complex liquid formulations at a laboratory scale, ensur...

Pneumatic conveying system for dry bulk powders
Ensure seamless and contamination-free transfer of pharmaceutical powders ...
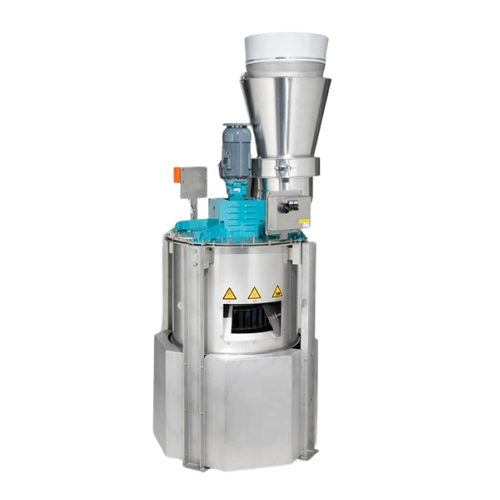
Mass flow rate feeder for bulk powders
Achieve precise control and consistent material flow in high-speed manufacturing env...
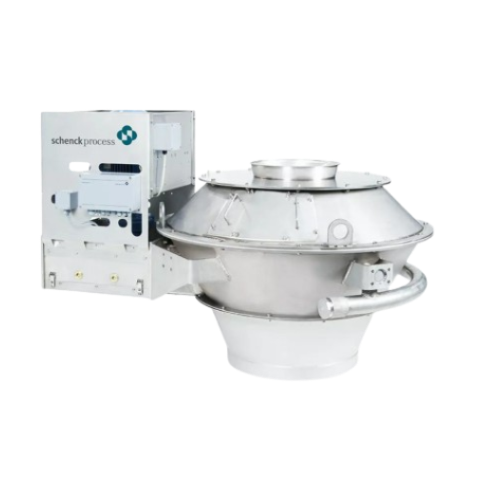
Coriolis mass flow meter for powdered materials
Achieve precise continuous feeding and control of bulk solids like cement ...
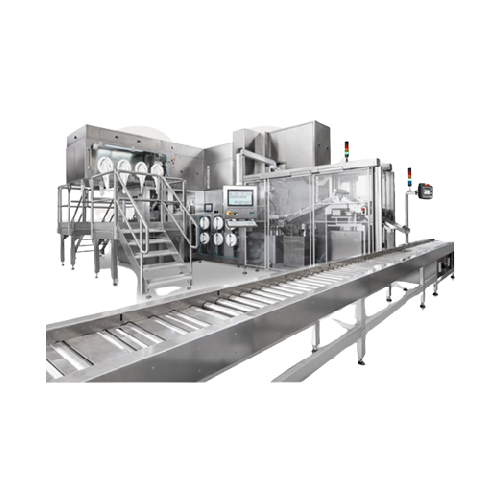
Filling solution for powders and liquids in diagnostics
Simplify precision filling of diverse products, from freeze-dried...
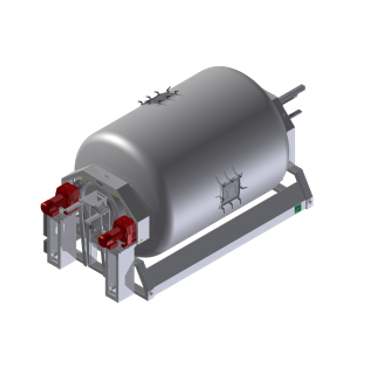
Gentle mixing solution for gelatin powder
The fragile nature of gelatin makes it a challenging material to blend homogeneo...
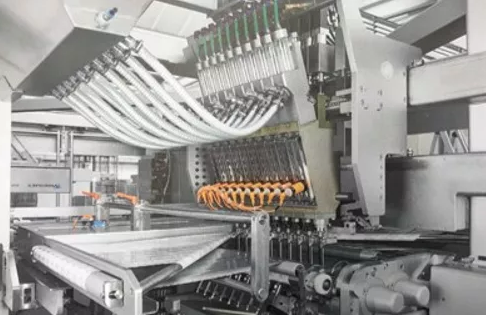
Accurate multiple dosing system for powders
Dosing multiple powders in a batch process is time inefficient, especially whe...
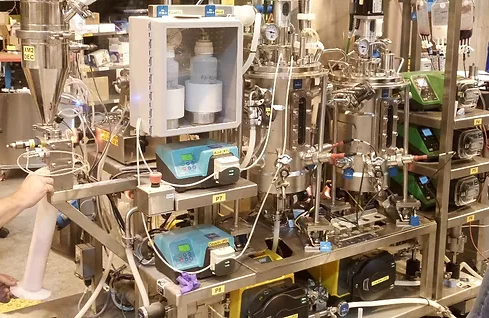
High-speed powder dosing system
Balancing speed and accuracy in powder dosing is crucial to fulfilling production viability....
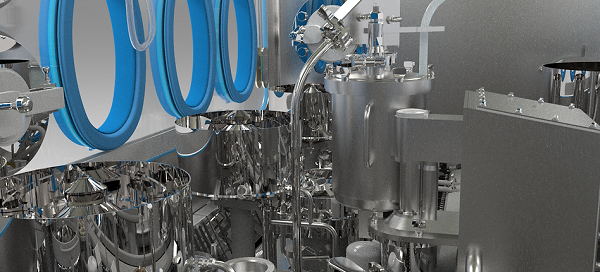
Powder micro-dosing system
Pharmaceutical powders in metered doses demand maximum filling precision. This is particularly ch...
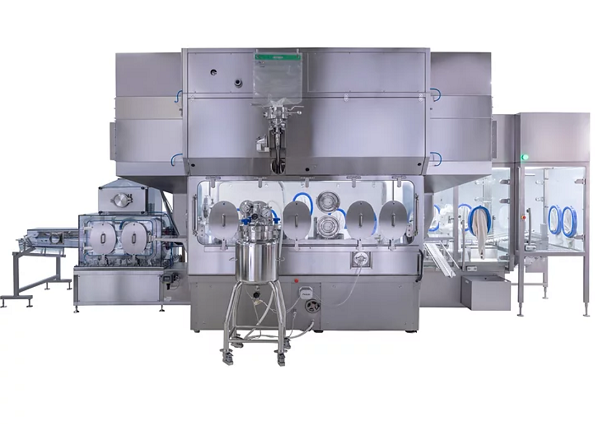
Aseptic filling machine for liquids and powders
Aseptic filling of containers such as vials, syringes, bottles, and cartri...
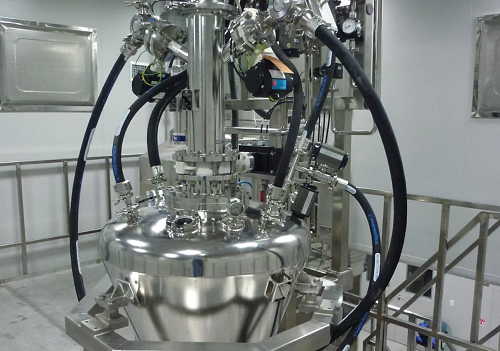
Pharmaceutical powder mixer
Large batches of powders with different characteristics are commonly mixed in pharmaceutical ind...
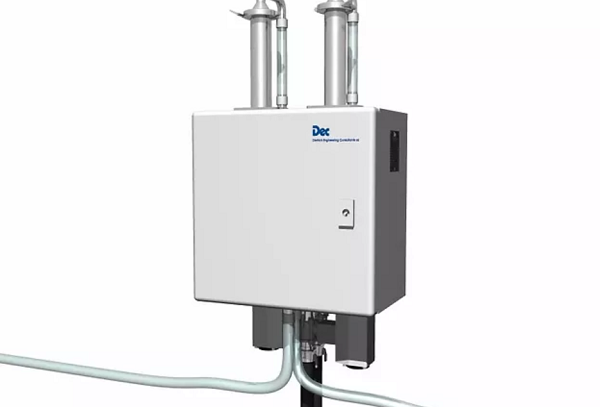
Powder dosing system
Dosing of powder products must be done in a continuously controlled manner to provide a precise amount o...
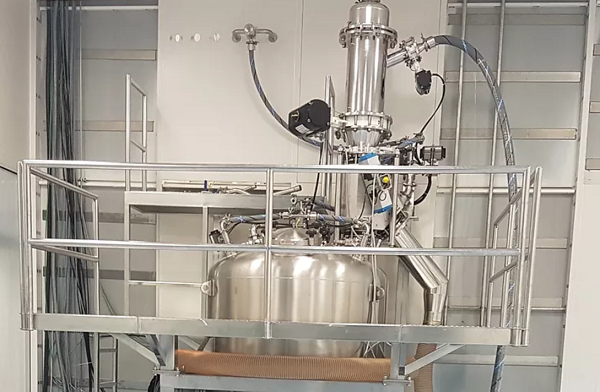
Powder transfer system
Loading powder from a container source to vessels, tanks, or mixers that are under pressure may be haz...
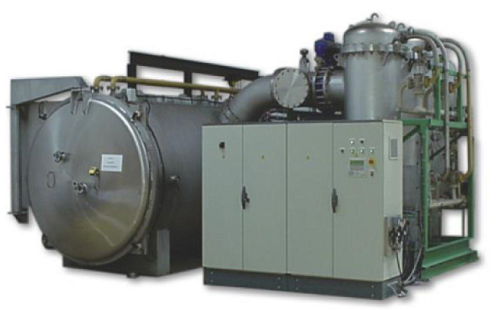
Freeze drying system for berries and fruit powders
Delicate fruits with high moisture levels, such as berries, risk losin...
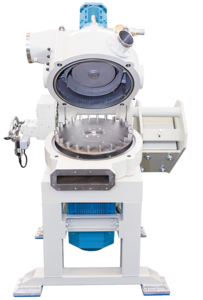
Classifier mill for powder coating
High-quality powder coatings are often required to manufacture equipment, appliances, an...
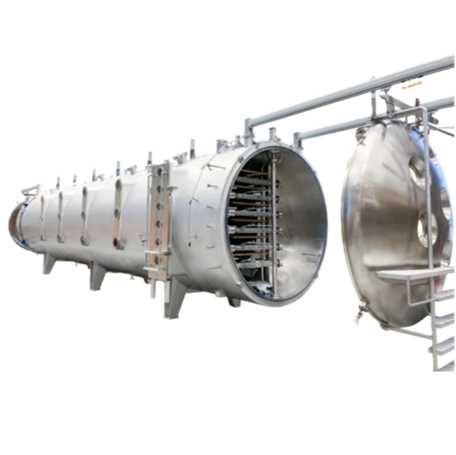
Vacuum belt dryer for instant drink powders
Extracting the essential acids and compounds from fruits and plants is a compl...
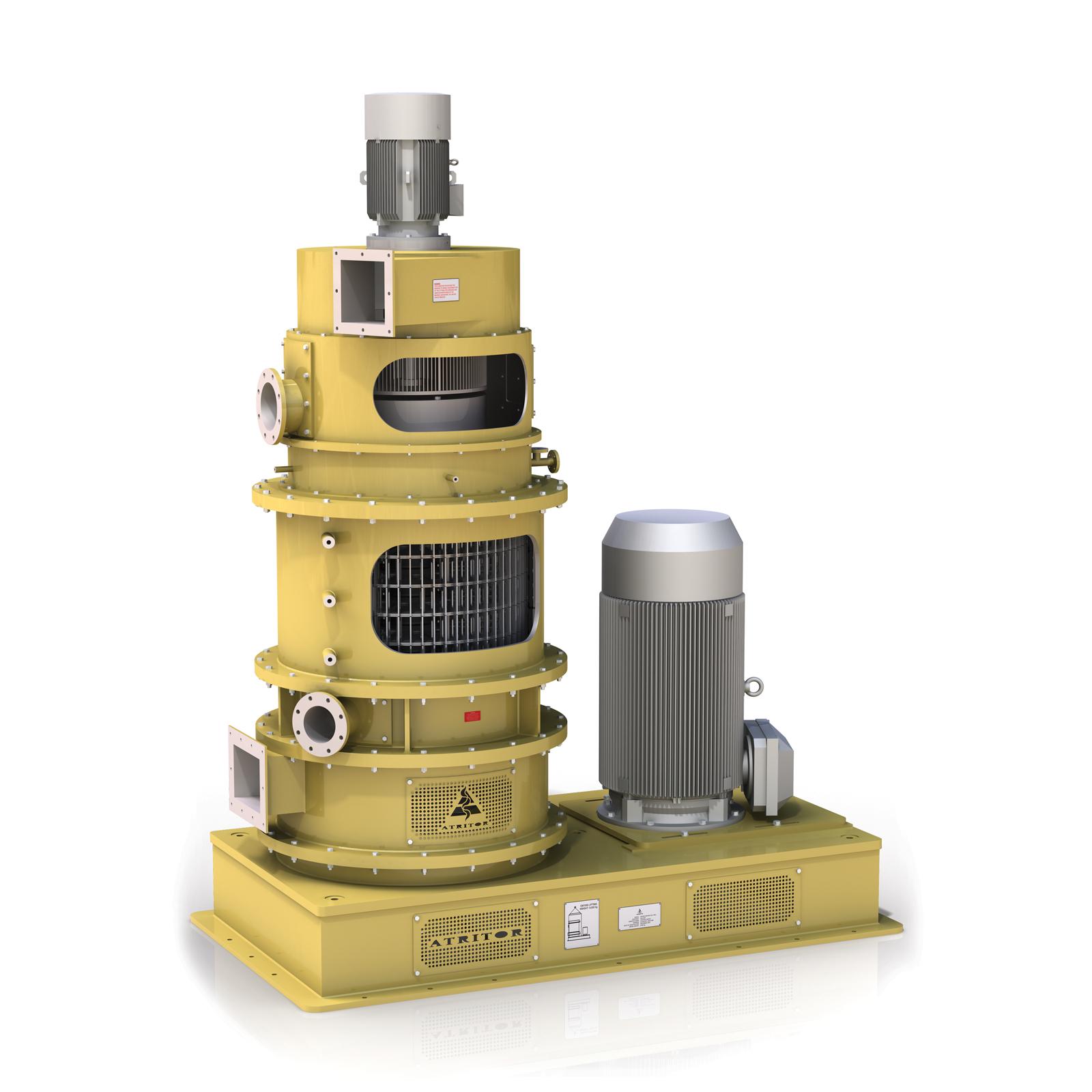
Milling and drying machine for fine powders
When you need to produce ultra-fine powders, the milling and drying process em...
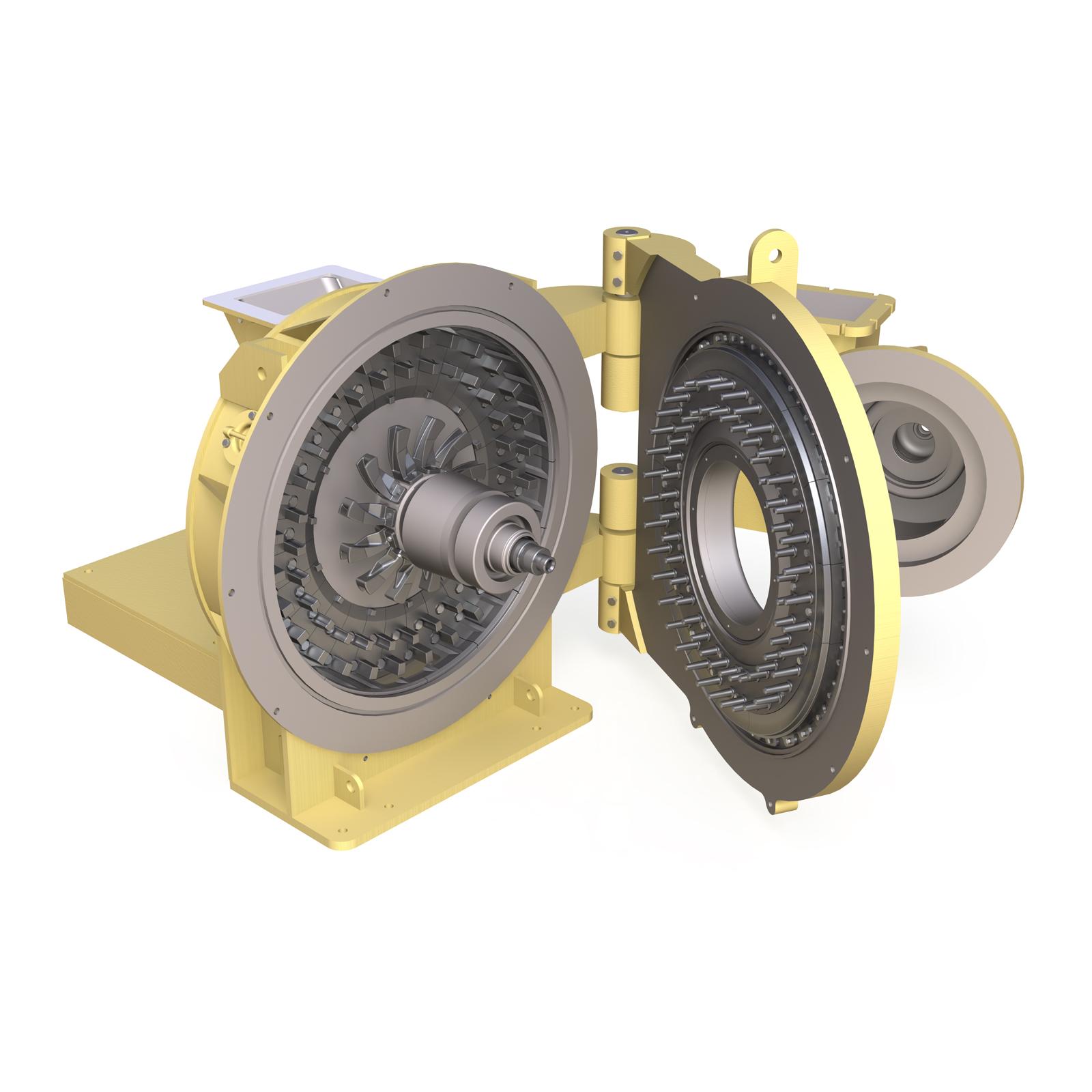
Flash drying grinder for powders
Drying and grinding can be an important feature when trying to process products such as raw...
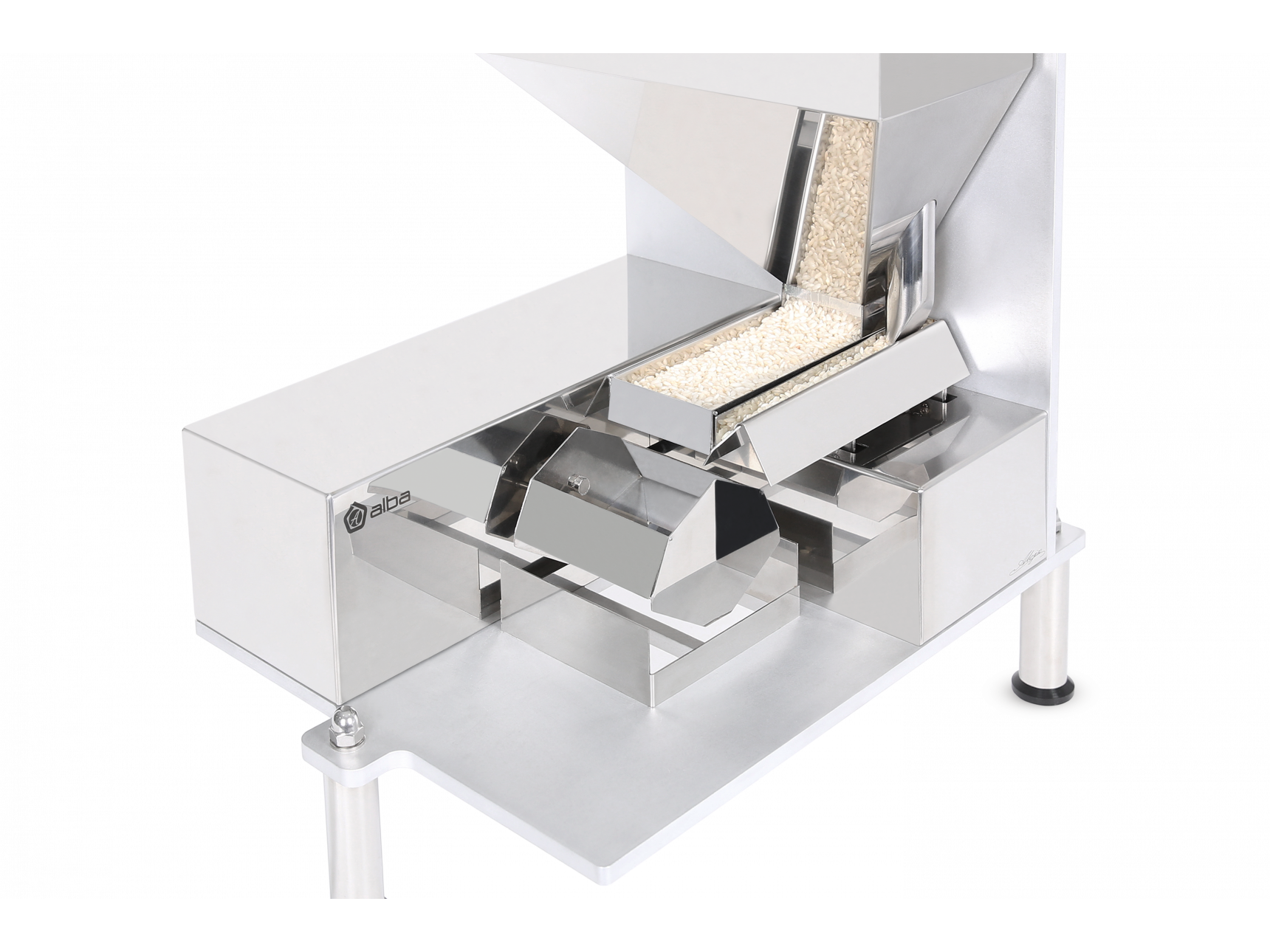
Fast gravimetric powder microdosing 50 - 200 g
Micro-dosing powders of high-value food or chemical products can be challen...
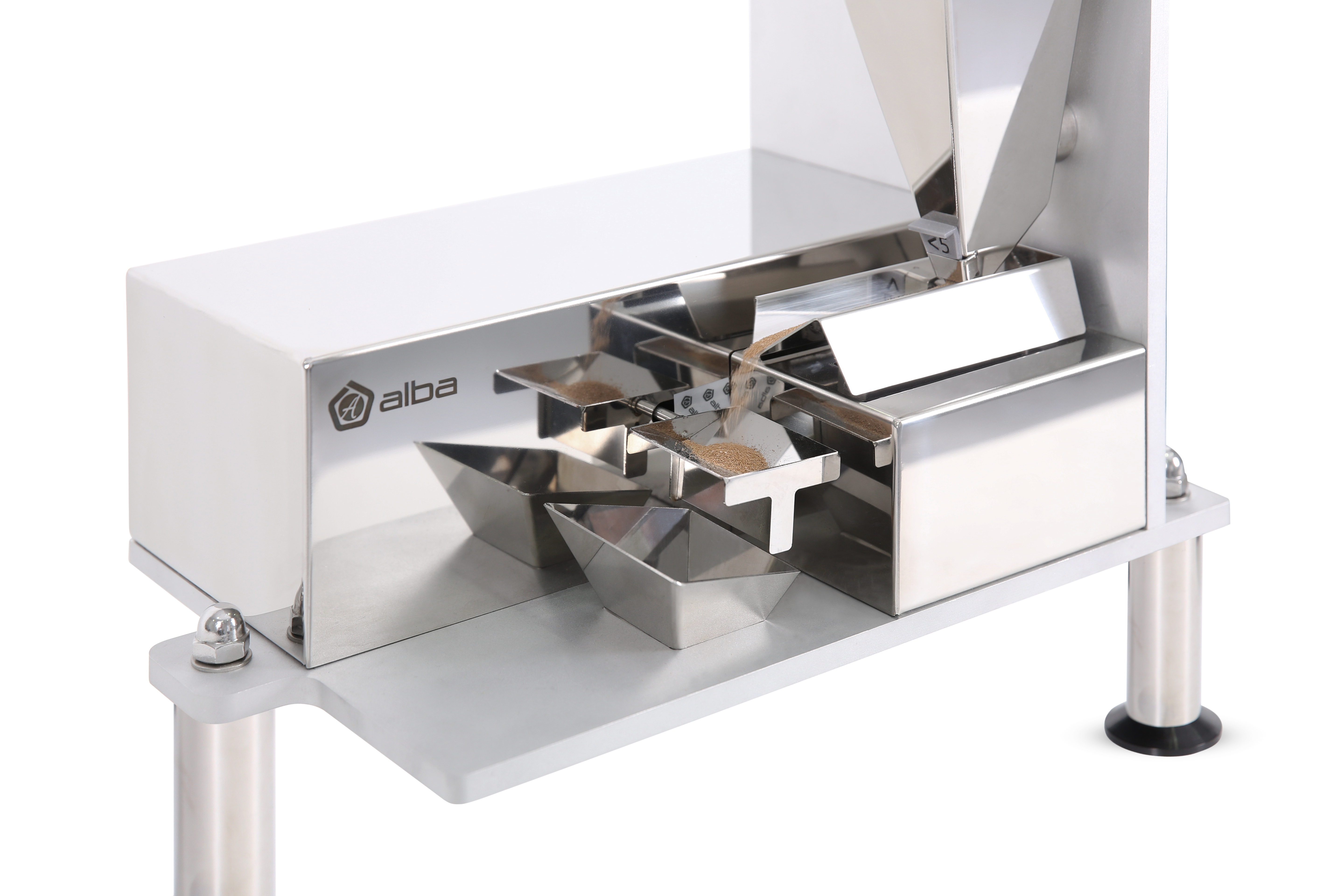
Gravimetric powder microdosing 2 - 100 g
Powders and granules are commonly dosed for the manufacturing of pharmaceuticals, ...
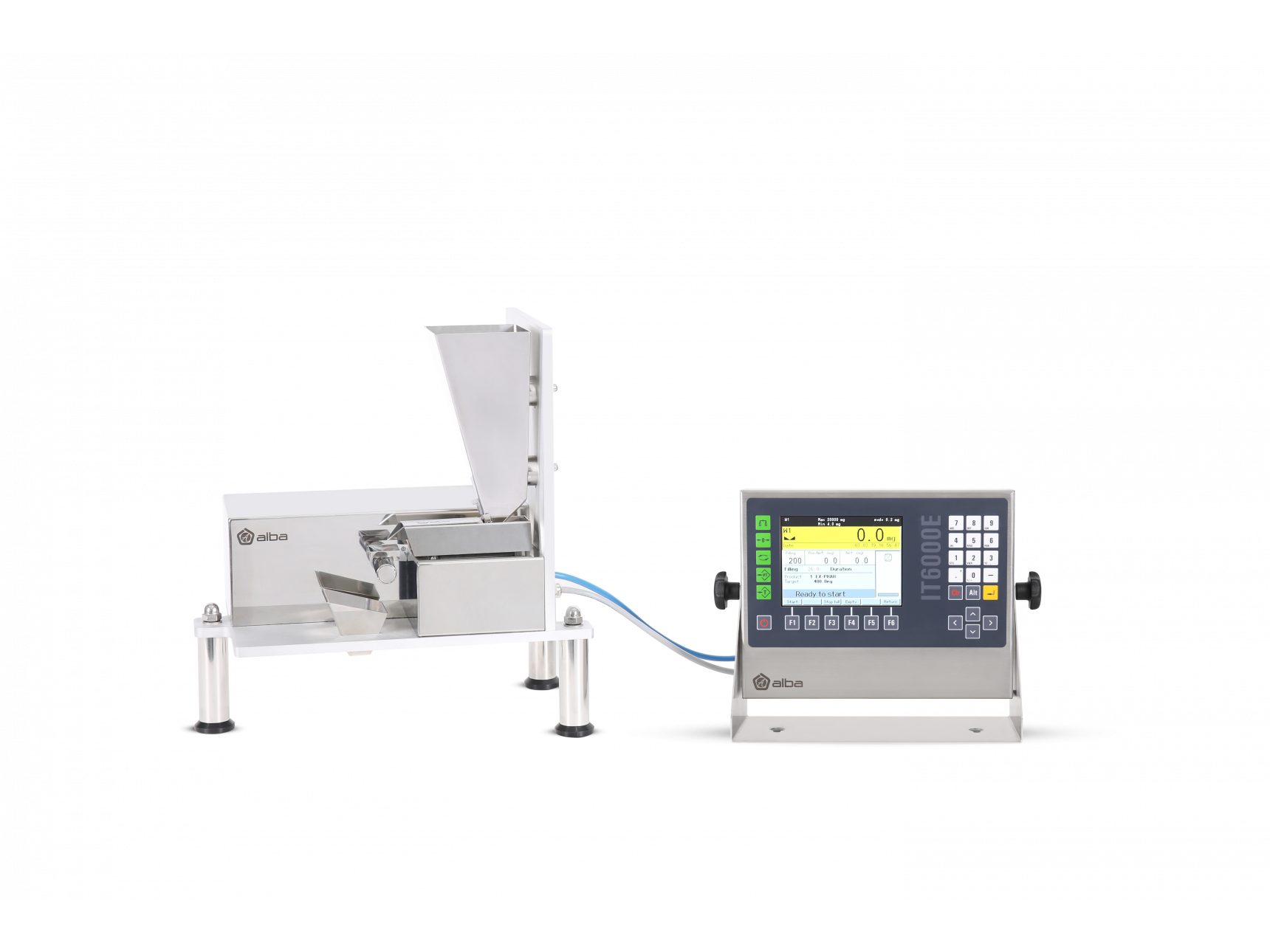
Gravimetric powder microdosing 0.400 - 2 g
If you need to process high value food, pharmaceuticals or chemicals, there is ...

Open mouth bag filling machine for powders
The packaging of powdery products such as flour can be challenging as it is cru...
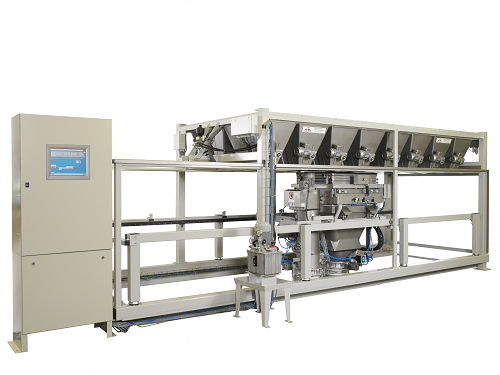
Micro powder dosing system
Micro dosing of powders and small components can be a major obstruction in the production process...
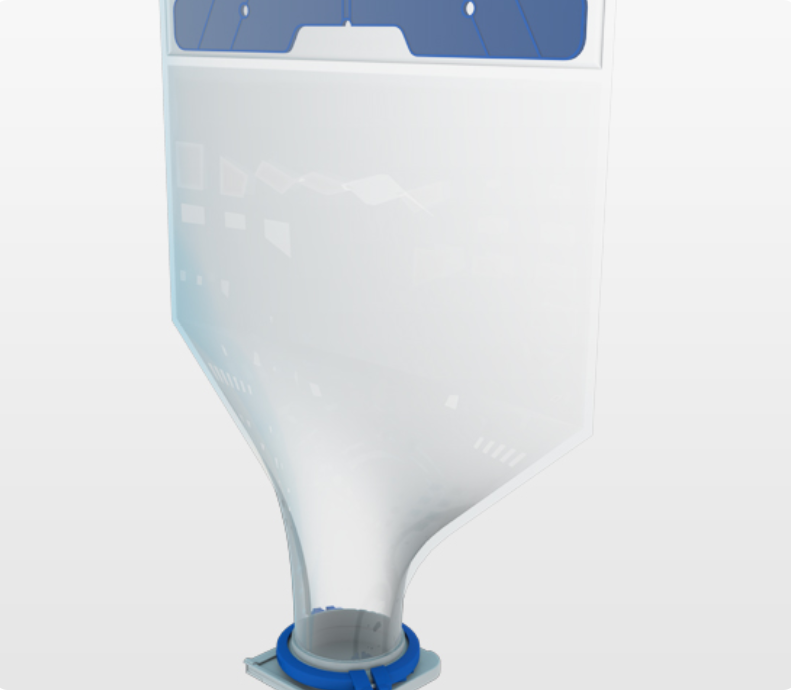
Single-use powder handling bag
Containers for handling pharmaceutical and biopharmaceutical powders may be disposable, to av...
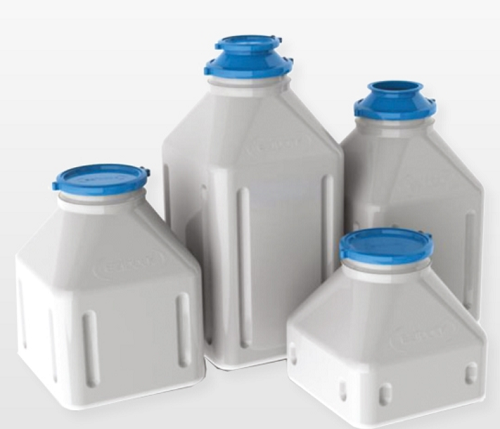
API powders storage bottle
Users who prefer rigid storage over single-use pharma charge bags, require lightweight solutions ...
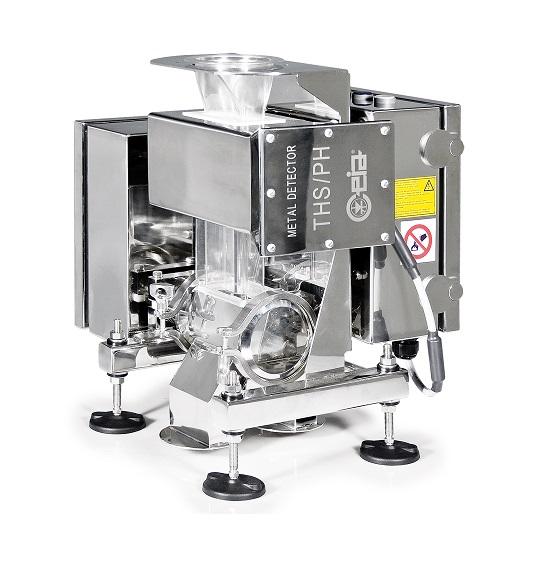
Metal detector for pharmaceutical powders
Powdered and granulated pharmaceuticals require careful screening against metal ...
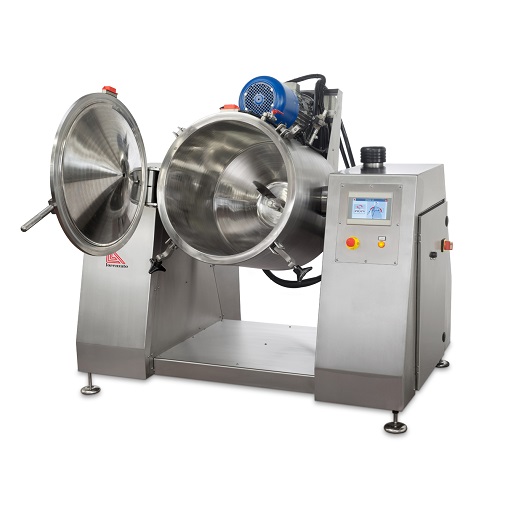
Blending tank for cosmetic powders
The production of high-quality cosmetics powders requires perfect mixing and dispersal o...

Manual cosmetic powder press
The design, manufacture and testing of new cosmetic powder products require a small-scale press...
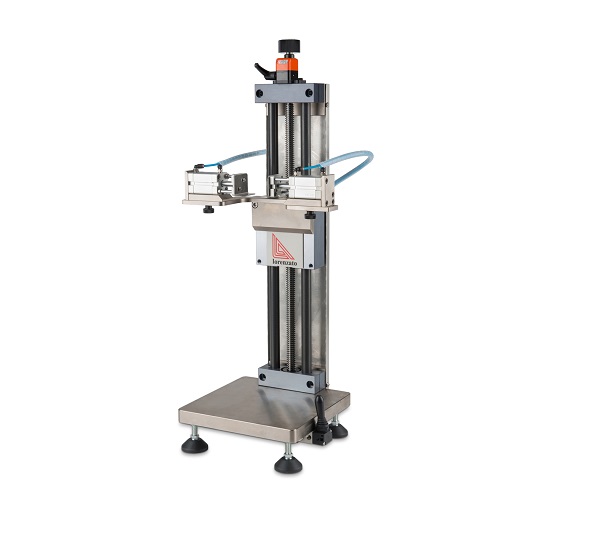
Drop tester for compacted powders
A key requirement for cosmetic compressed powder products is that they maintain their com...
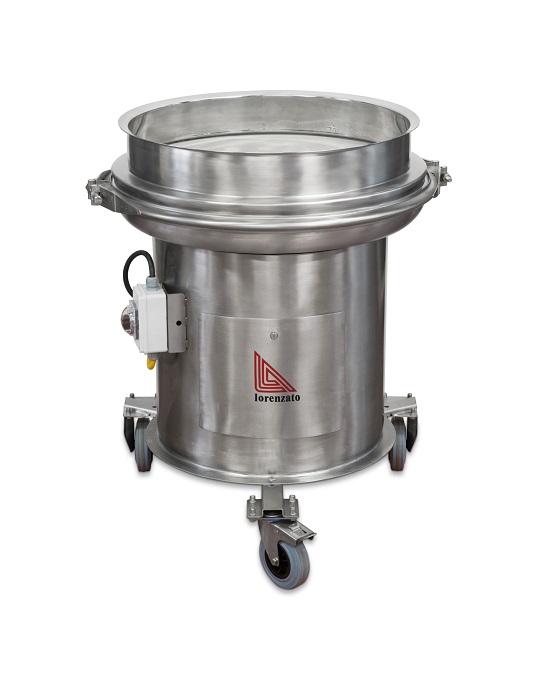
Vibrating screen for cosmetic powders
Dense or viscous compounds can be difficult to prepare for use in cosmetic products. ...
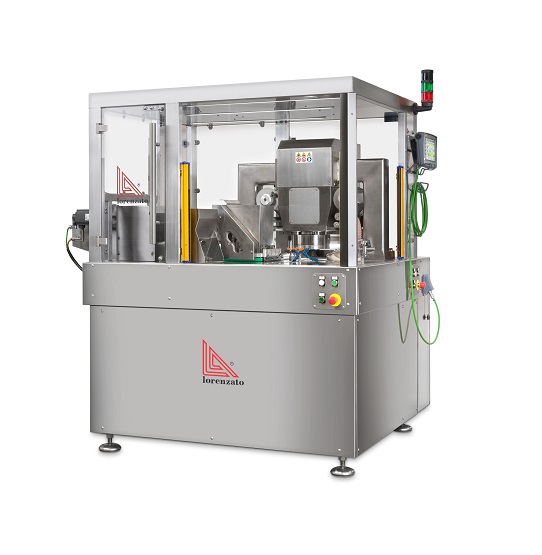
Cosmetic powder pressing machine
For the medium and large-scale production of compressed powder cosmetics, a fully-automatic...
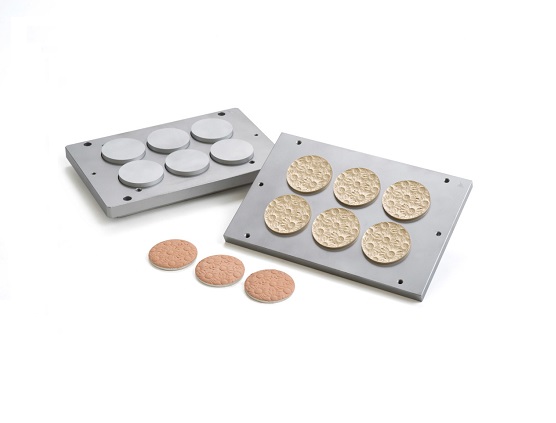
Powder pressing mould
Traditional powder pressing moulds are based on plain shapes or basic designs. In order to differentiat...
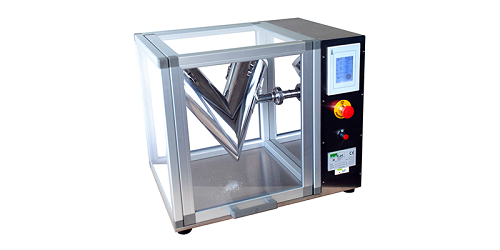
R&D V-type powder blender
Many pharmaceutical processes rely on the complete blending and homogenizing of different powdered...
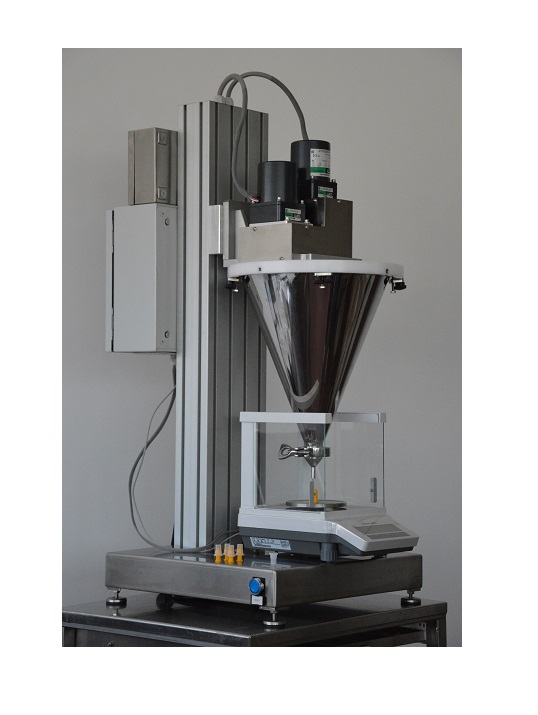
Semi-automatic powder dosing machine
Powders or granules are common dose types used in many pharmaceutical and nutraceutica...
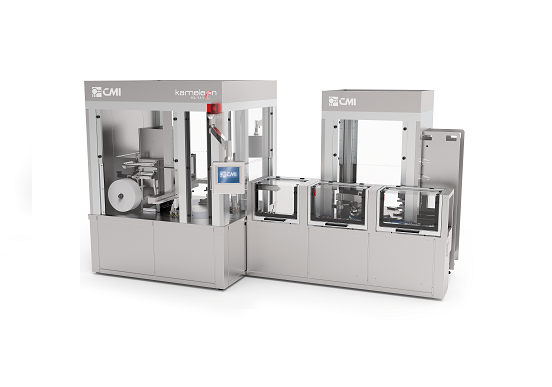
Compact powder pressing machine
Pressed powder products are extremely popular in cosmetics, but their production has challen...
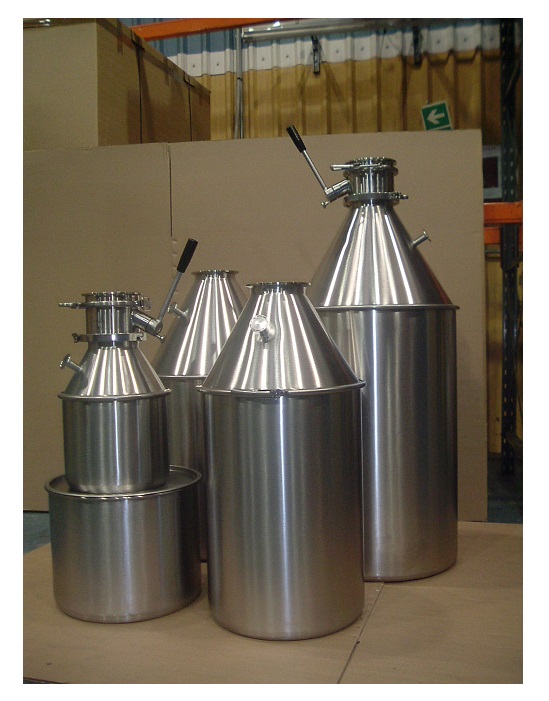
Powder transfer vessel
Intermediate bulk storage of pharmaceutical product requires specialist containers. For increased effi...
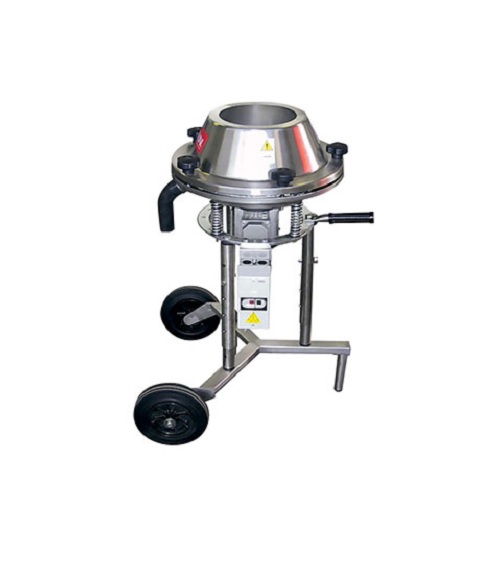
Screener and separator of dry powder
Many industries require the effective screening and separating of a range of dry powde...
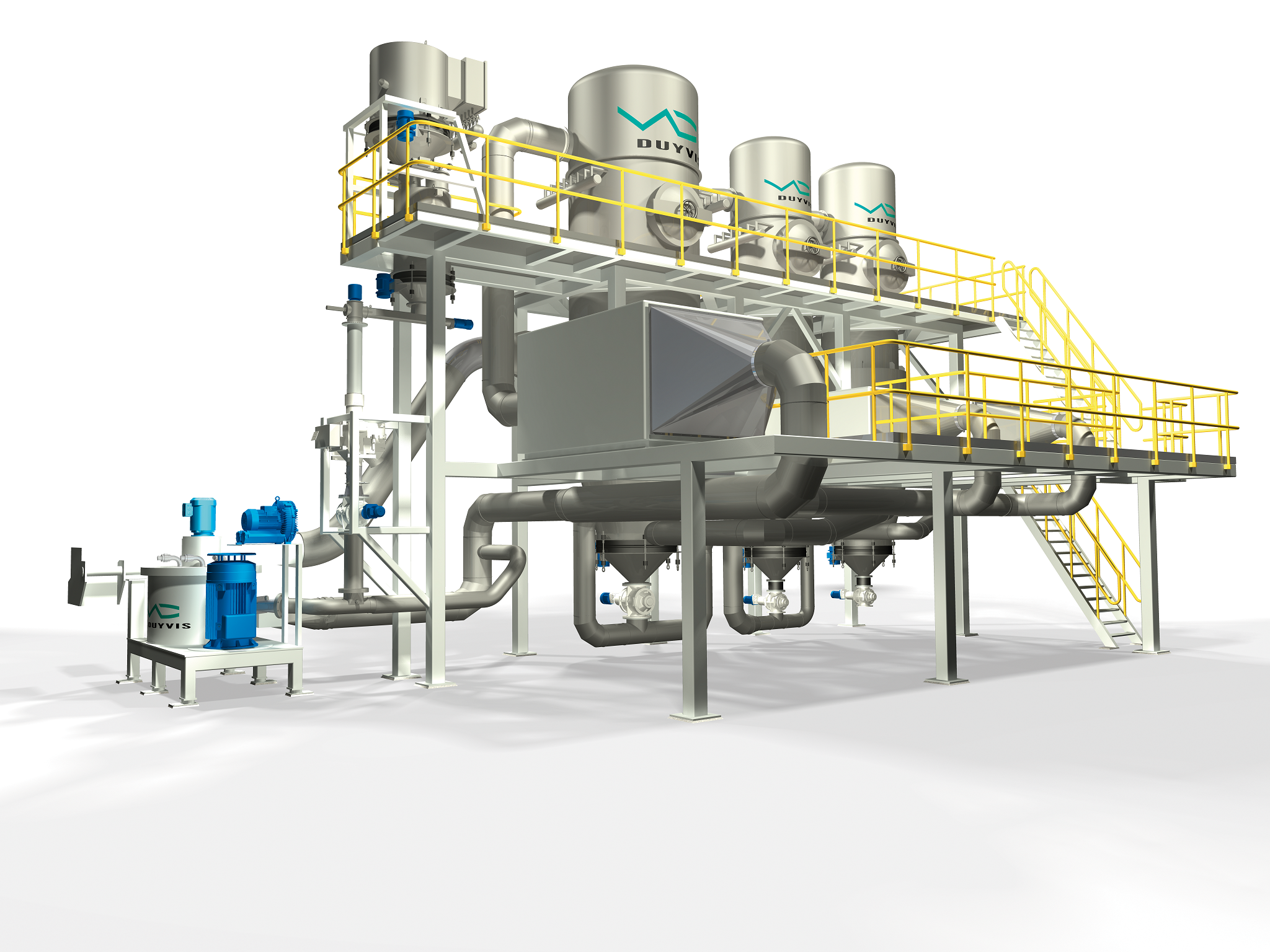
Cocoa powder processing line
Cocoa beans are first fermented, dried, roasted, and separated from their skins to obtain a coc...
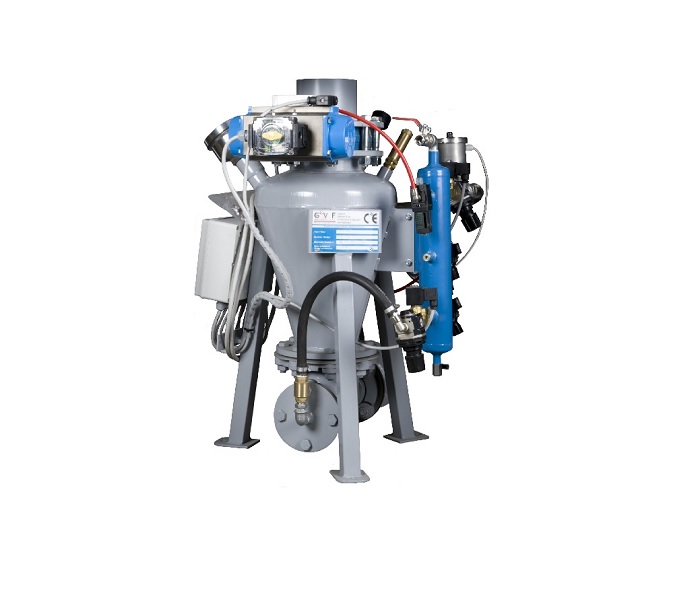
Dense phase conveyor for powders and granules
Some manufacturing and filling operations require a smaller pneumatic transp...
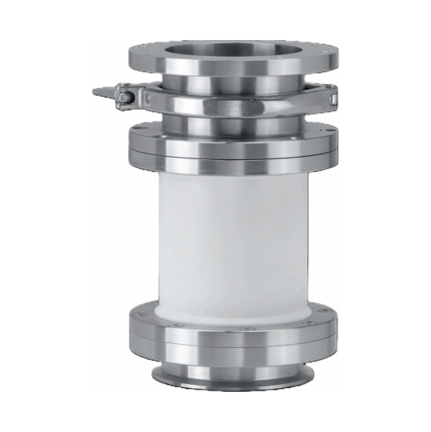
Bellows for pharmaceutical powders
Thermal and mechanical changes can lead to stresses in industrial piping systems. These ...
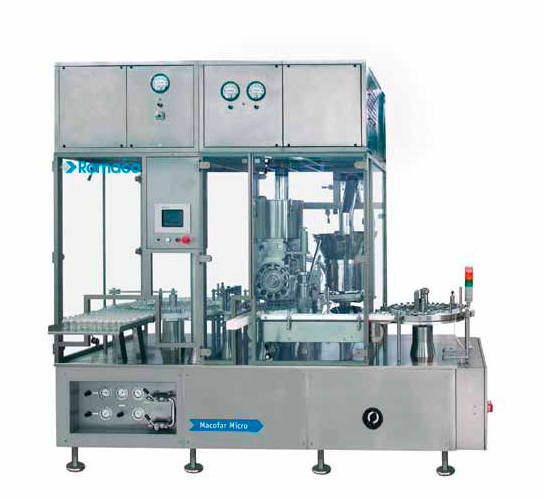
Microdosing machine for sterile powders
Fill sterile pharmaceutical powders into vials under aseptic conditions with a spee...
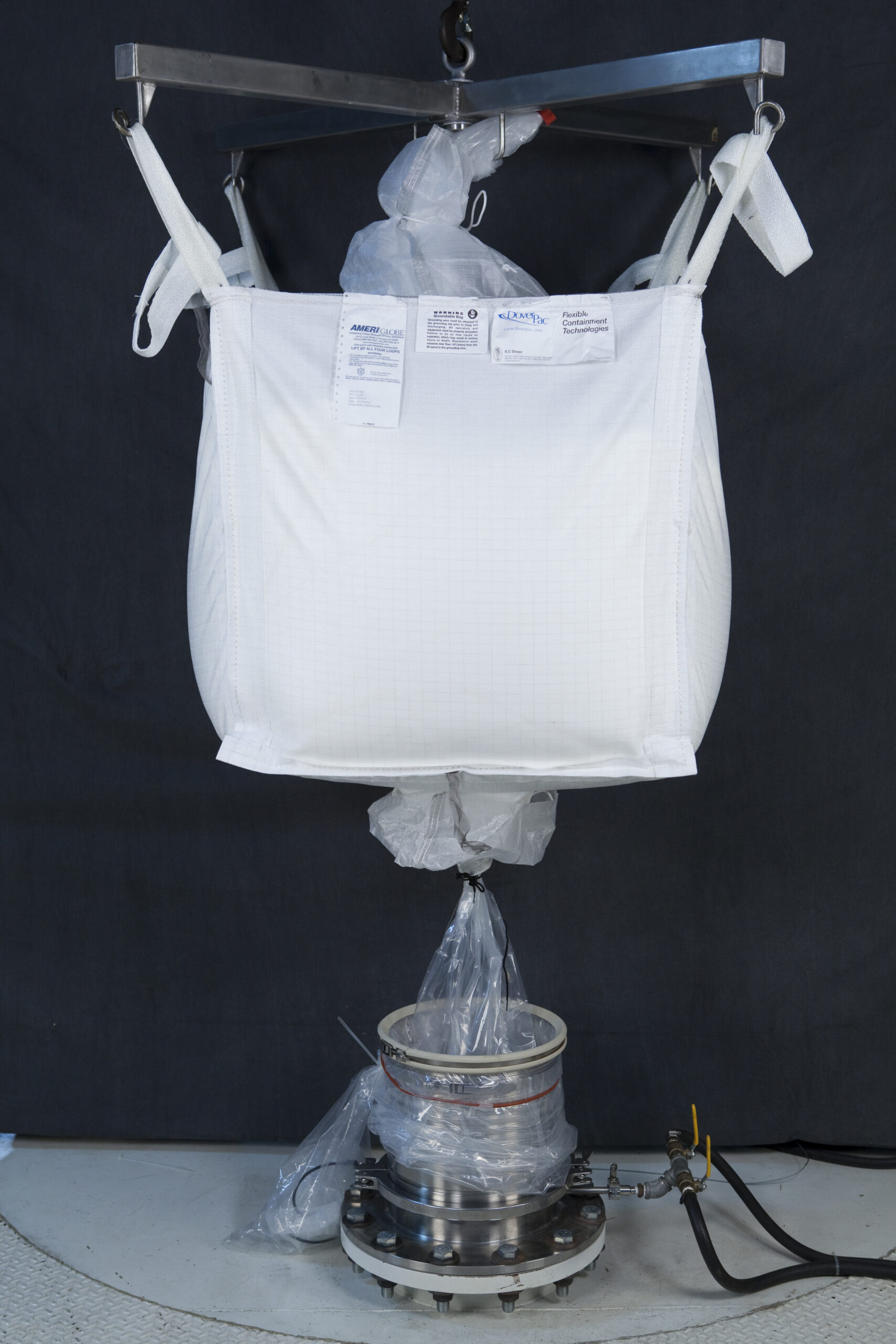
Flexible contained powder charging solution
Filling of transportation bags and discharging them into mix tanks or reactor ...
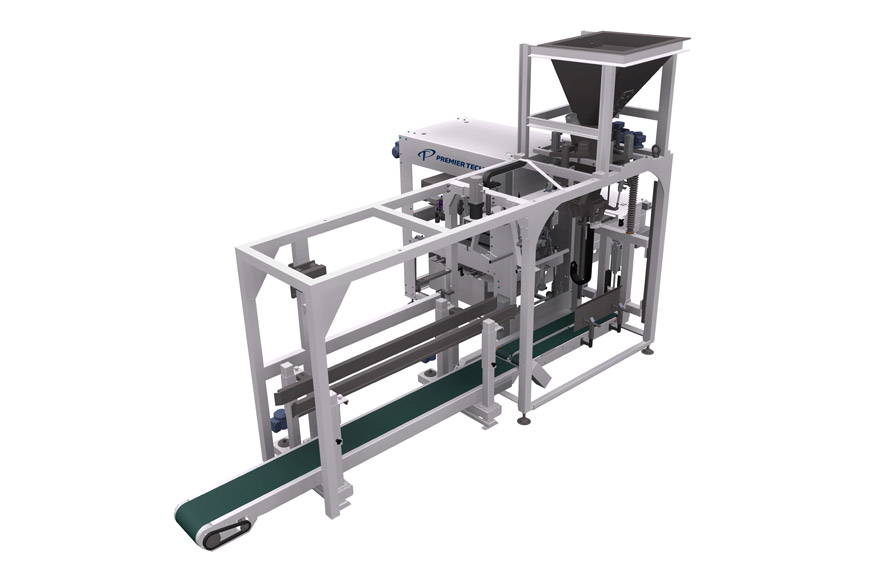
Open-mouth baggers for free flowing powders
For bagging free flowing materials into open mouth bags, this system is ideal....
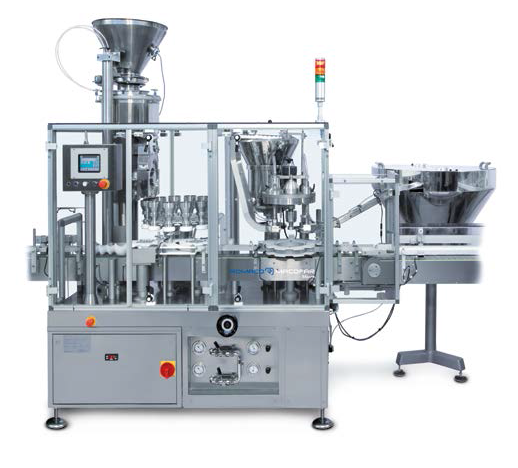
Dosing machine for nonfree-flowing powders
Fill poorly flowing powders, dry syrups and similar substances into various gla...
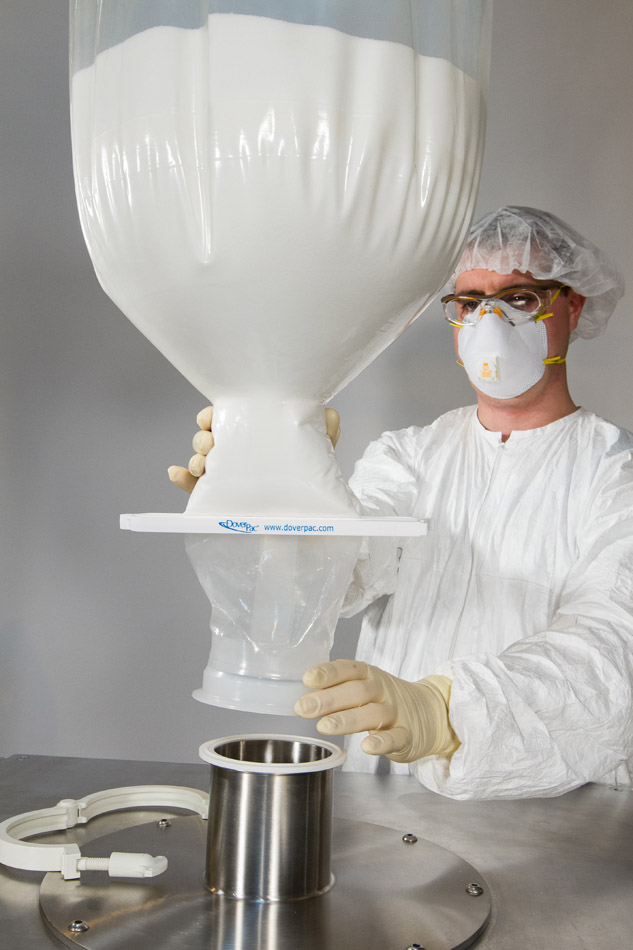
Flexible contained handling of powder transfer bags
Filling of transportation bags and discharging them into mix tanks or...
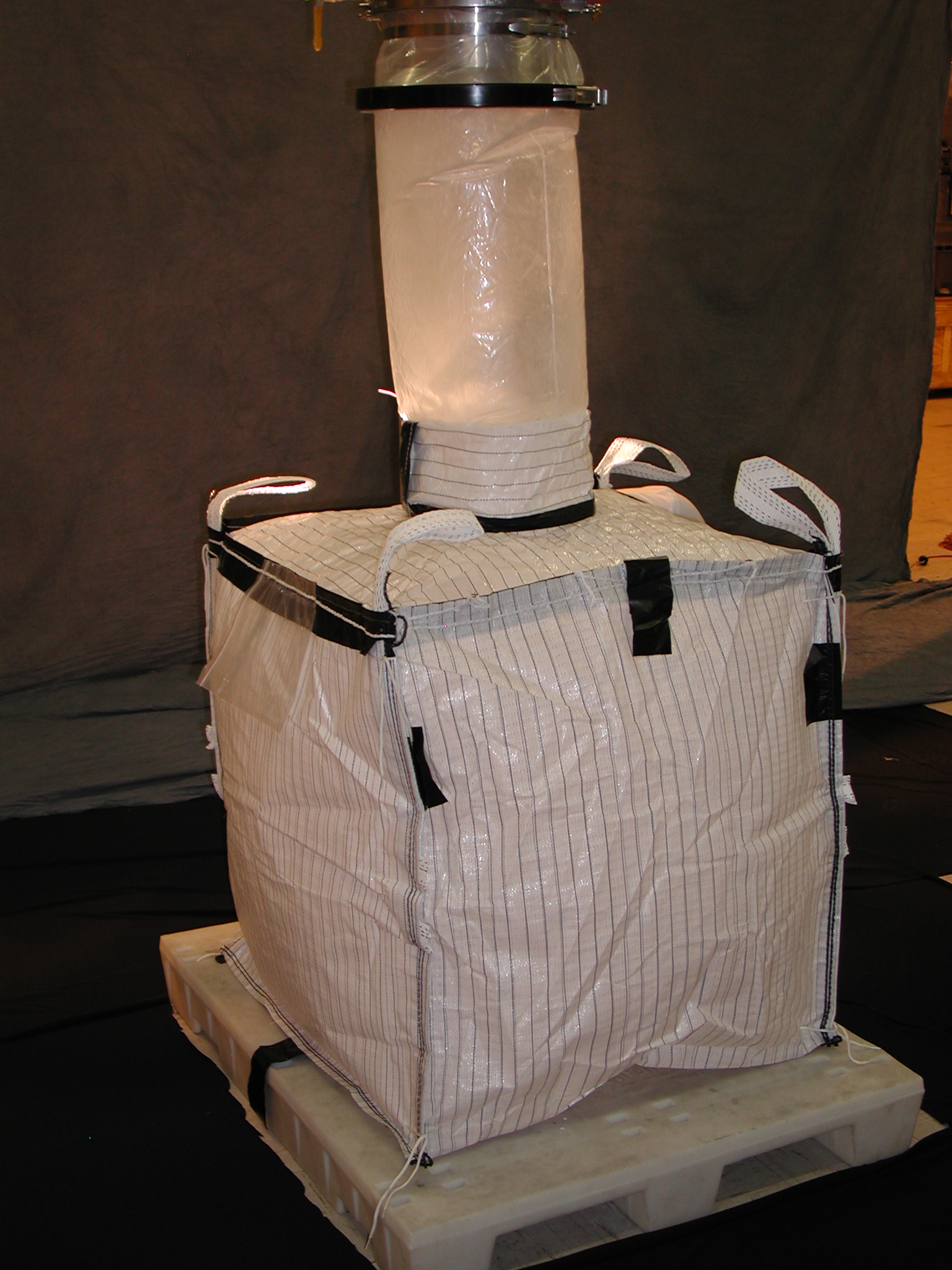
Flexible contained powder discharge into FIBC’s
Flexible intermediate bulk containers known as FIBC’s are commonly used in...
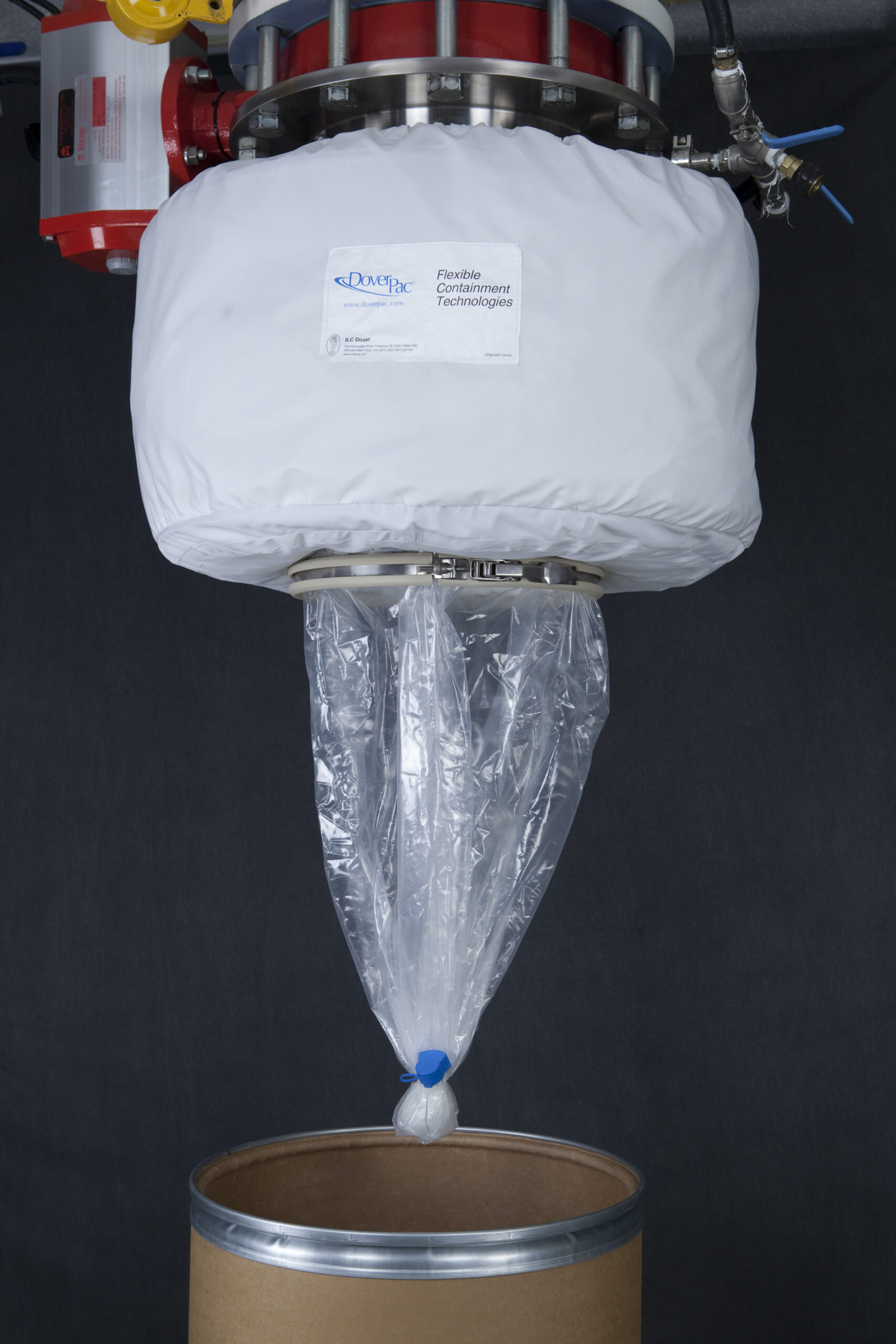
Flexible contained powder discharge into drums
Powdered products are handled every day in the pharmaceutical and bioproces...
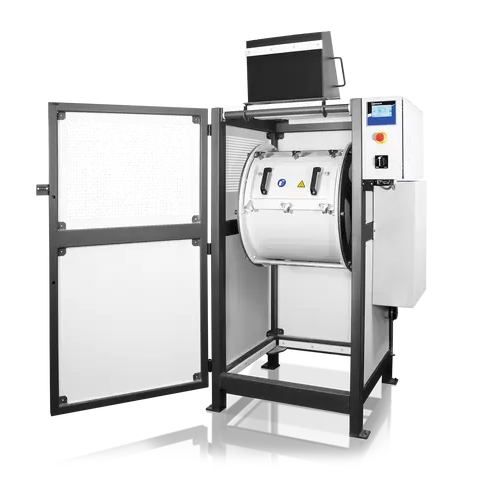
Drum mills for fine grinding of large volumes
Achieve consistent and precise pulverization of large sample volumes with dr...
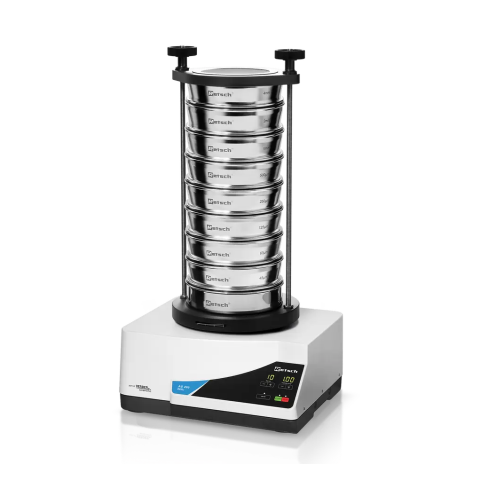
Vibratory sieve shaker
Enhance your quality control processes with this versatile sieve shaker, designed to efficiently separ...
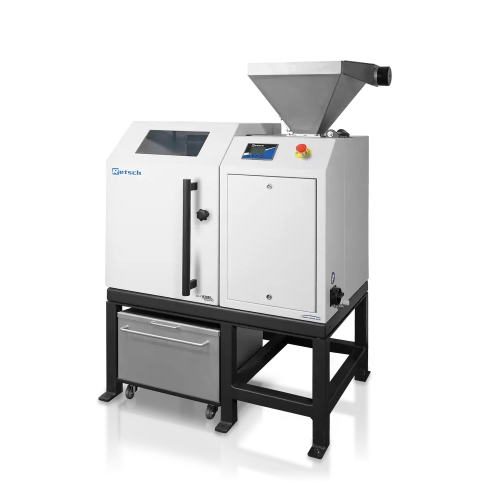
Rotating sample divider for large bulk materials
Achieve precise, dust-free division and volume reduction of bulk material...
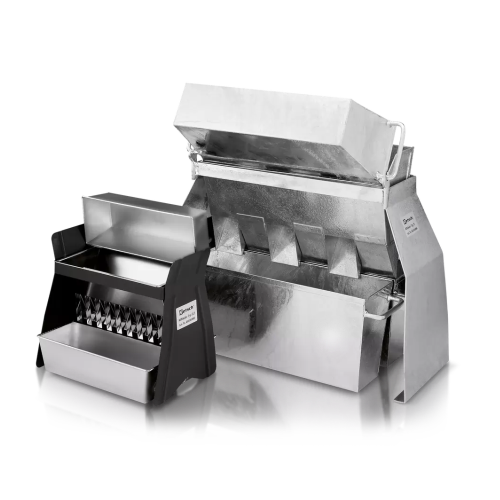
Sample divider for on-site reduction of bulk materials
Ensure consistent sample analysis with precise on-site material di...
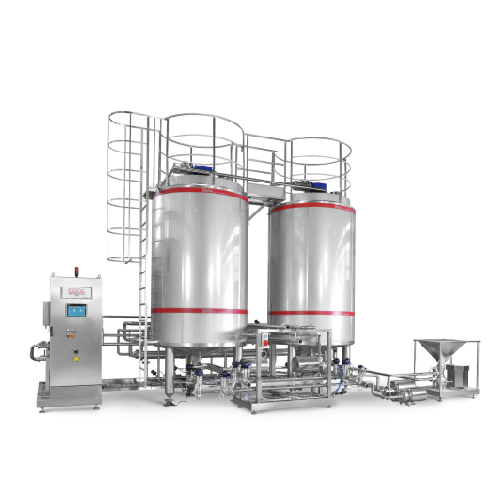
Blending and mixing unit for dairy and beverages
Achieve precise recipe control and high-quality results by seamlessly int...
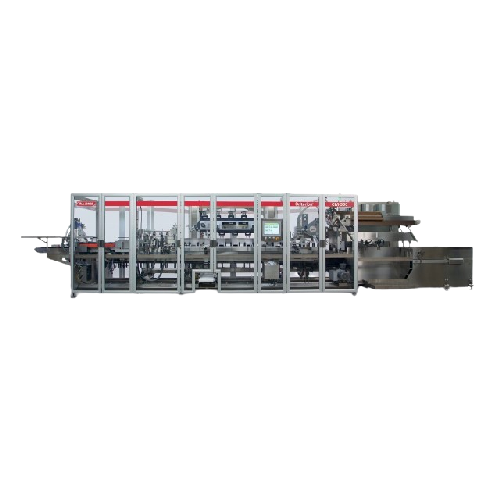
Medium-speed end load cartoner for food and beverage packaging
Streamline your packaging line with versatile cartoning c...
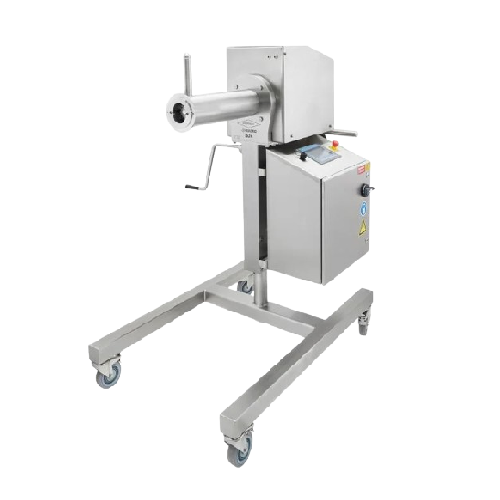
Production-scale milling and screening system
Achieve precise particle size distribution and high throughput rates with a ...
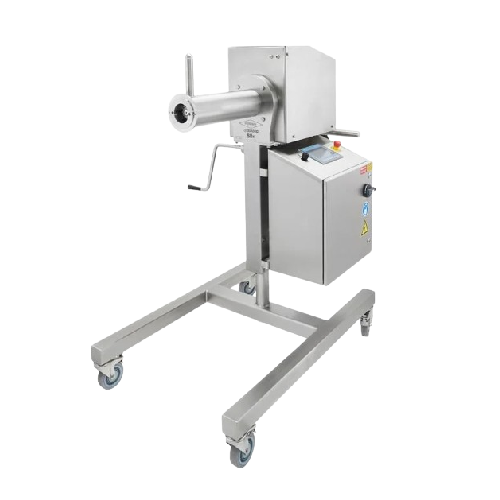
Mid-size milling platform for pilot-scale production
Achieve precise particle size control with this integrated milling s...
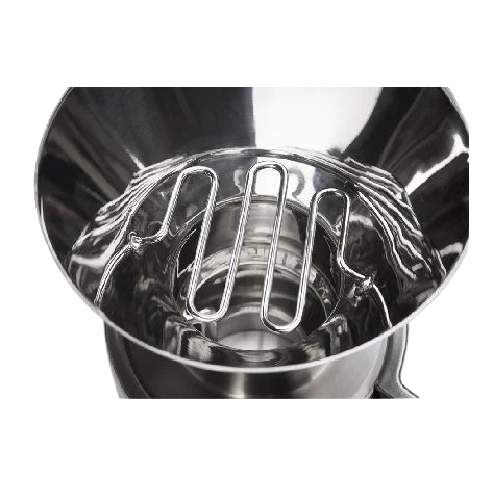
Deagglomeration and delumping system
Ensure product integrity and streamline operations by effectively breaking down agglom...
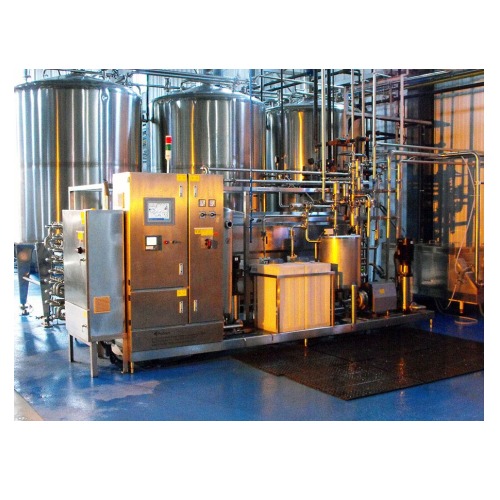
Soya milk production system
Efficiently transform soybeans into high-quality, non-beany soy milk with advanced processing te...
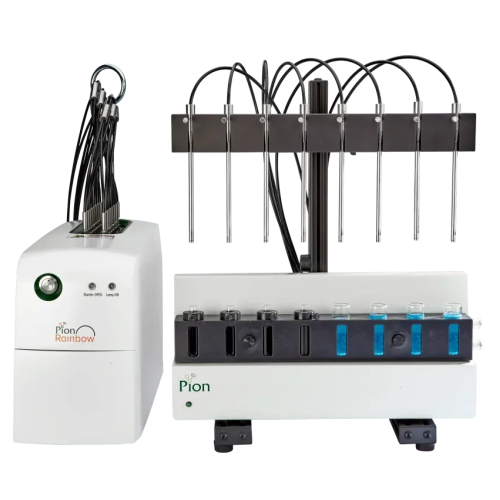
Uv monitoring system for small volume dissolution studies
Efficiently monitor small-volume dissolution processes in real...
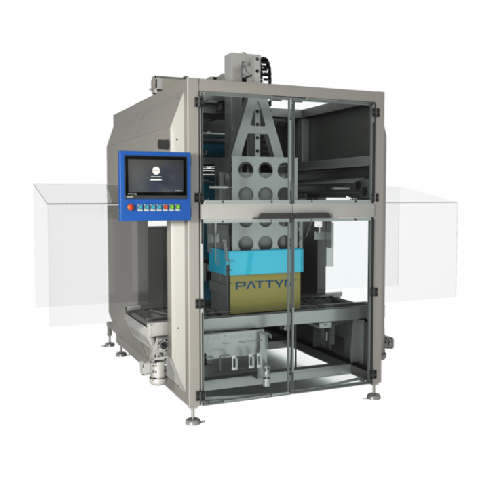
Automated bagmaker inserter for crystallizing products
Enhance your hygienic packaging efficiency by seamlessly integrati...
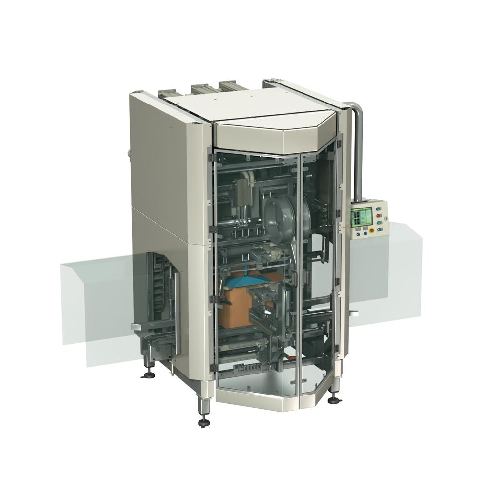
Industrial bag tie-wrapping solution
Ensure your bulk packaging is reliably sealed with a tamper-evident tie-wrap, allowing...
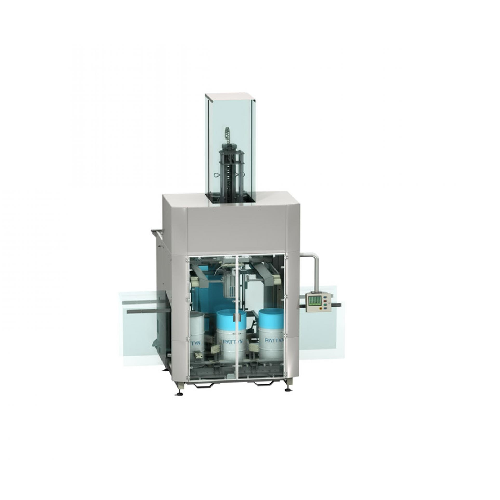
Bag inserter for drums
Effortlessly streamline your packaging process by automatically inserting custom-made bags into drums,...
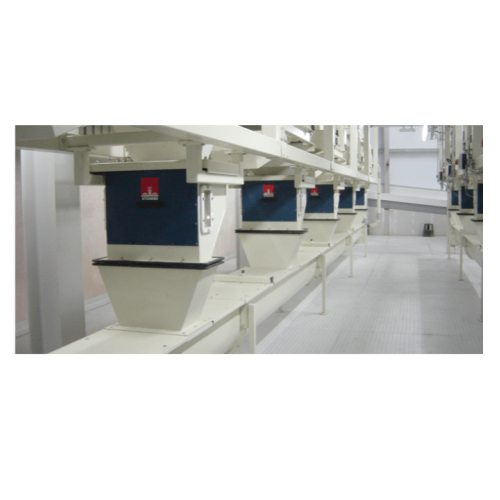
Inline and continuous weighers for accurate product flow management
Maintain precision and efficiency in your productio...

Bucket elevators for bulk material handling
Efficiently transport and discharge granular and powdered materials with preci...
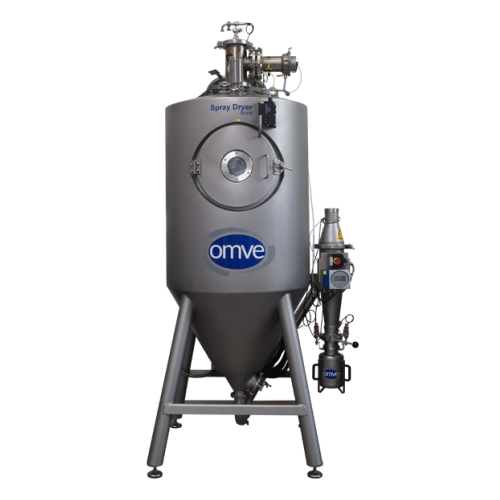
Pilot scale spray dryer for product development
Achieve precise moisture levels and product consistency in development env...
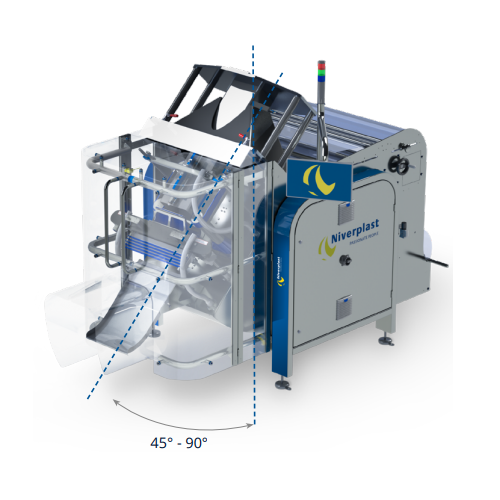
Vertical form fill seal packaging system
Enhance your packaging line with precision sealing and efficient throughput, ideal...
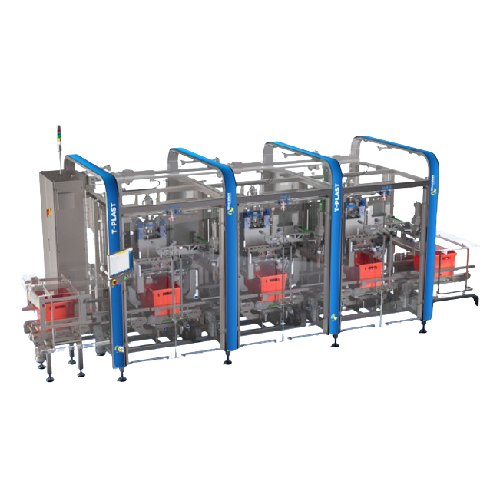
High-speed bag placing system for e-commerce fulfillment centers
Optimize your packaging line with a high-speed system t...
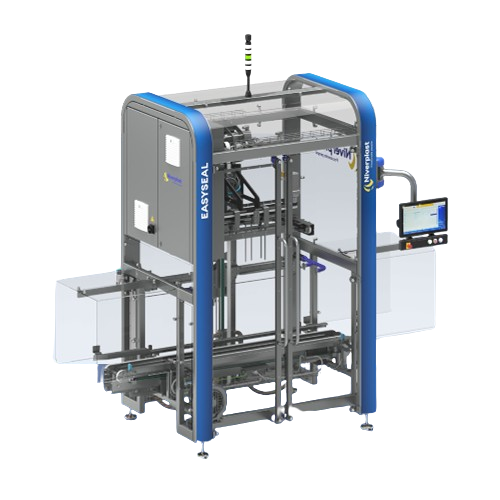
Automatic bag sealing system for packaging operations
Optimize your packaging efficiency with this high-speed sealing sys...
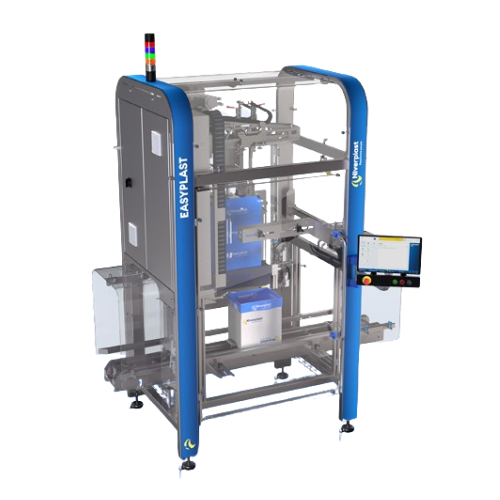
Manual bag placing solution for various materials
Increase your efficiency in manual bag placing with an ergonomic soluti...
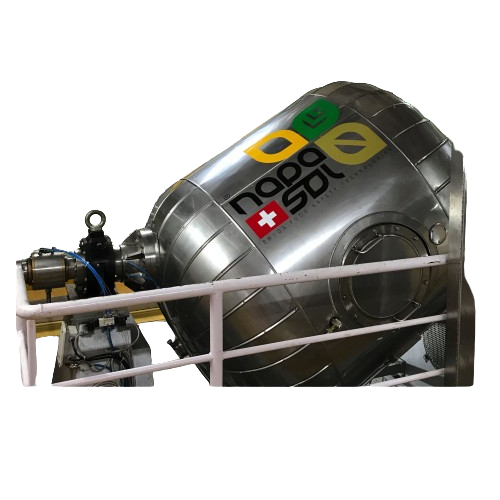
Roasting and pasteurization solution for nuts and seeds
Optimize your product line with seamless blending and pasteurizat...
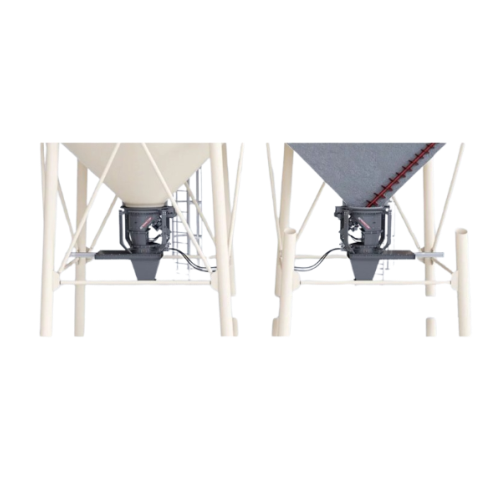
Unloader for conical bottom silos
Eliminate product flow challenges effortlessly with this hydraulic-driven unloader, ensur...

Laser diffraction particle size analyzer
Achieve precise particle size analysis with laser diffraction technology, ensuring...
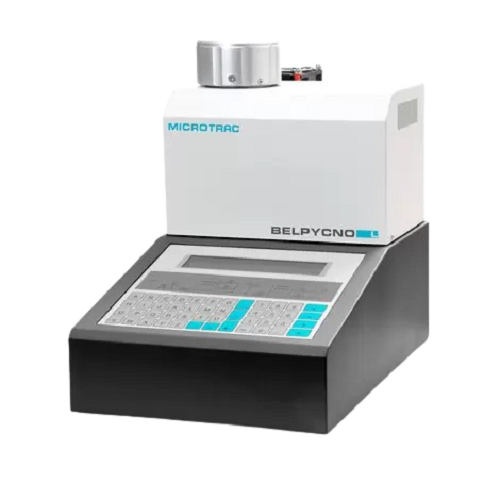
Gas pycnometer for precise density determination
Achieve accurate and reliable density measurements for a diverse range of...
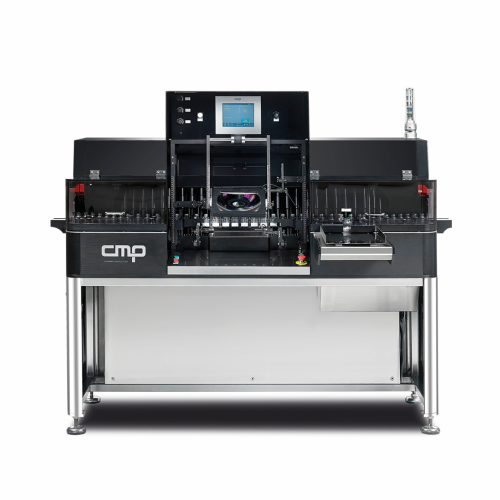
Inspection system for glass containers
Ensure precise inspection of liquid, freeze-dried, and powdered products in glass co...
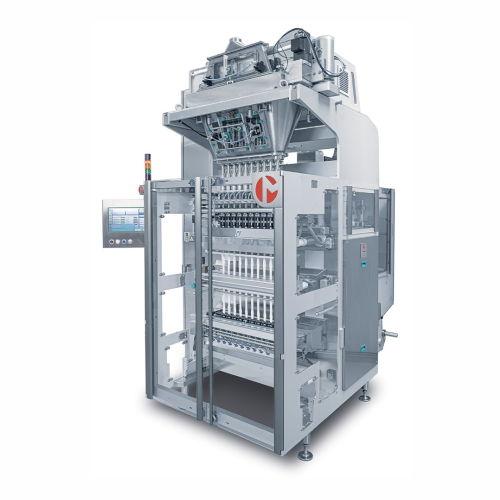
Stickpack filling and closing system
Optimize your stickpack production with precise dosing, uniform sealing, and seamless ...
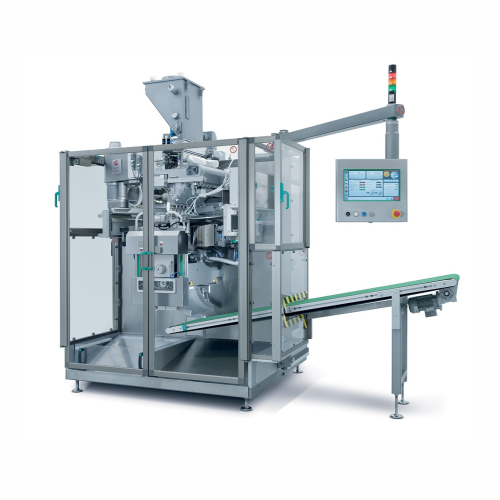
Sachet filling and closing system
Optimize your production line with a versatile solution designed to fill, seal, and count...
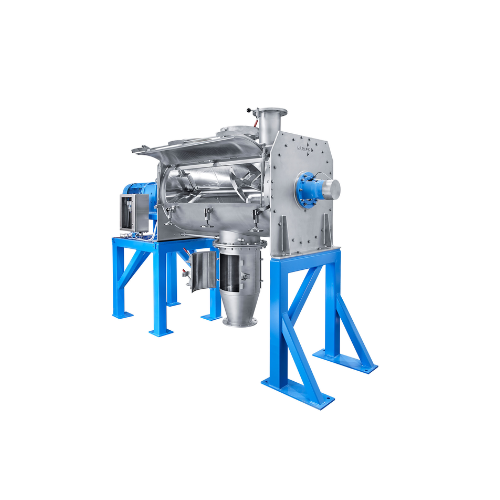
Ploughshare mixer for batch operation
Achieve superior mixing quality with a system designed for rapid batch operations. Ex...
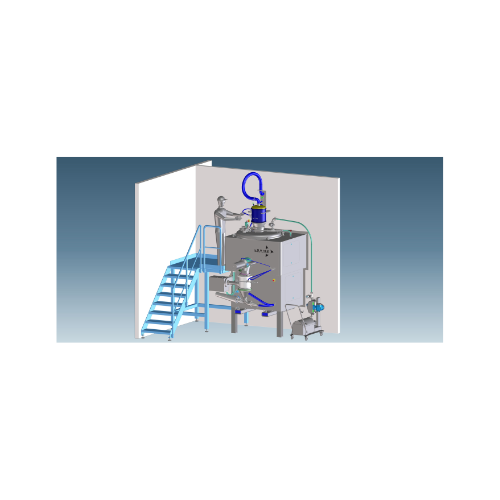
Mixing granulator for pharmaceutical and cosmetic industries
Achieve precise granulation and uniform mixing for high-qua...
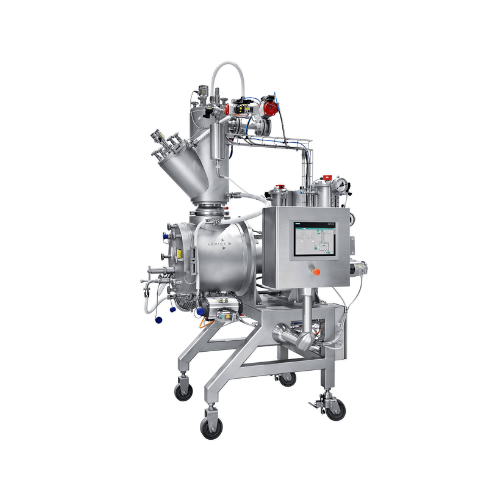
Vacuum paddle dryer for laboratory use
Achieve precise temperature and moisture control in your batches with this vacuum sh...

Automated headspace inspection for parenteral containers
Ensure the integrity and quality of pharmaceuticals by inspectin...

Commercial food drum mixer for sauerkraut and salads
Streamline your batch production with this versatile commercial food...

Bag break station for pneumatic conveying systems
Efficiently manage powder feeding and dust control in your production l...
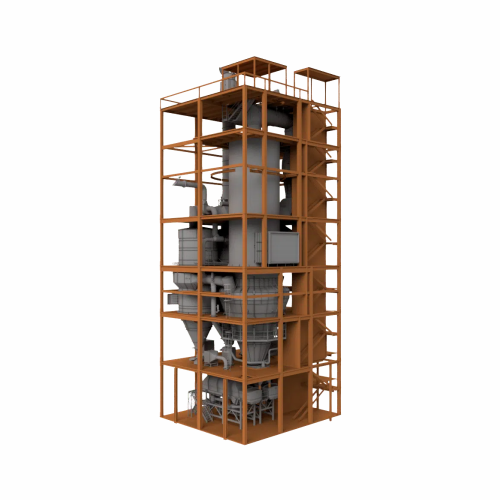
Milk drying system
Optimize your dairy production by efficiently transforming liquid inputs into high-quality, dry powders, e...
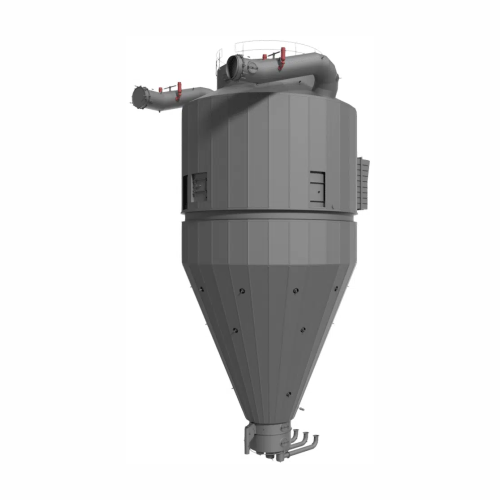
Wide body dryer for dairy and food products
Achieve precise moisture control and optimal powder agglomeration for dairy an...
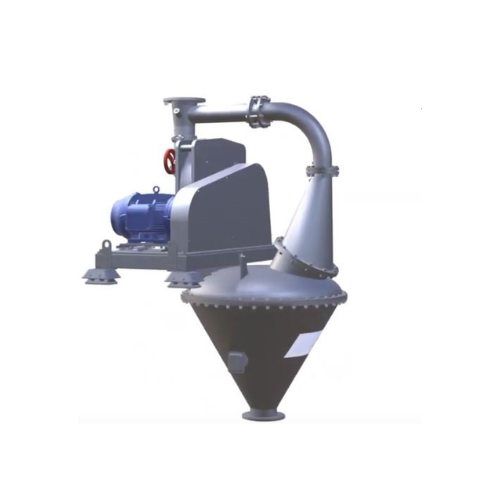
Universal mill for fine grinding in food and pharma industries
Achieve unparalleled particle size reduction with high-pe...
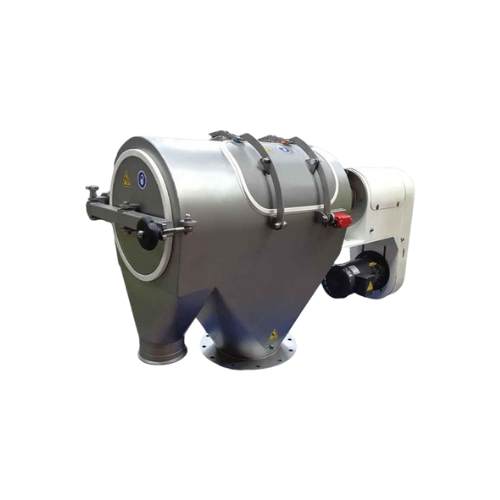
High-speed centrifugal sifter for food and pharma applications
Optimize your powder processing with a high-speed centrif...
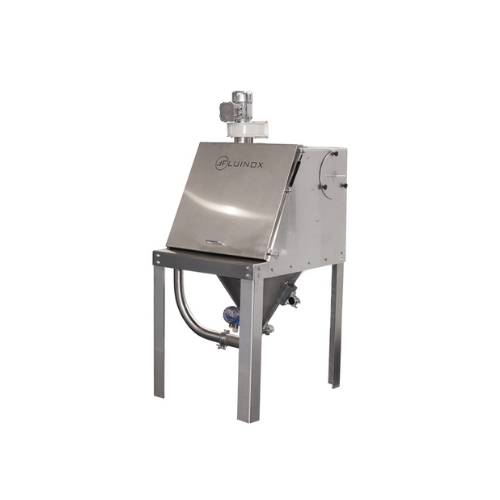
Bag dump station for handling solid foodstuffs
Efficiently manage manual dosing of solid foodstuffs and powders with this ...
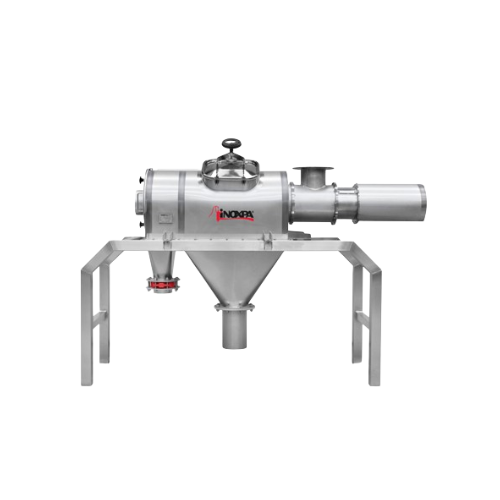
Industrial sieving solution for solid materials
Effortlessly separate impurities and adjust particle size for optimal prod...
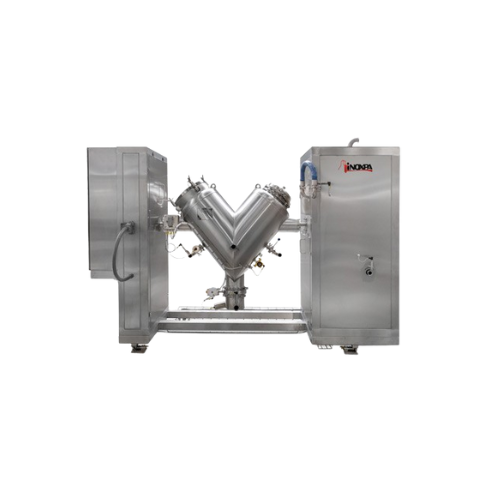
Industrial v-type solids blender for homogeneous mixture
Achieve precise blending of diverse powders and solids using the...
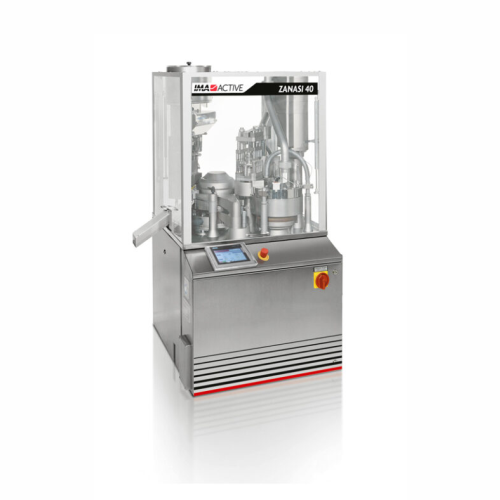
Automatic capsule filling machines
Efficiently fill capsules with precise doses of powders, liquids, and tablets to enhance...
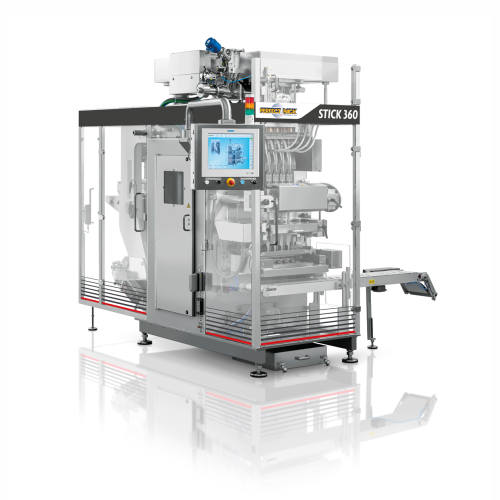
Vertical intermittent motion stick packaging
Experience seamless packing for diverse products, from powders to dense paste...
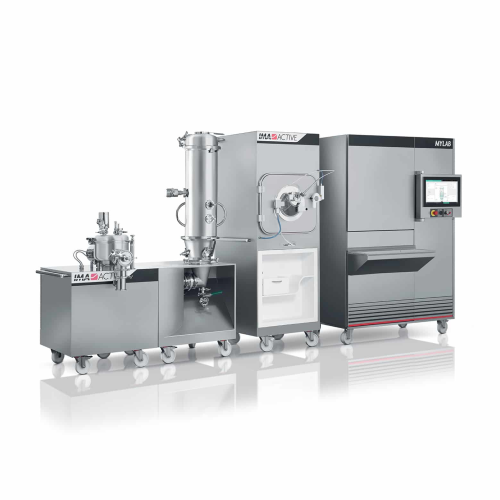
Fluid bed and coating system for small batch processing
Streamline your R&D process with a modular system that ensur...
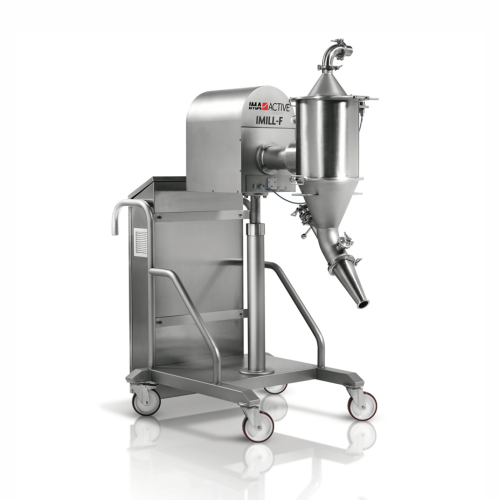
Cone mill for particle size reduction in pharmaceuticals
Achieve precise particle size control with this cone mill, desig...
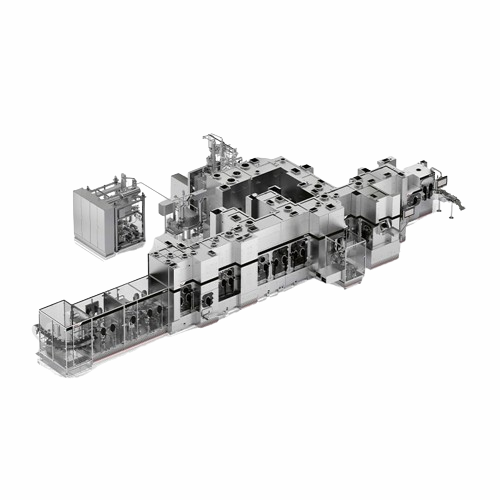
Isolation solutions for aseptic fill-finish lines
Achieve maximum product sterility with advanced isolation solutions, mi...
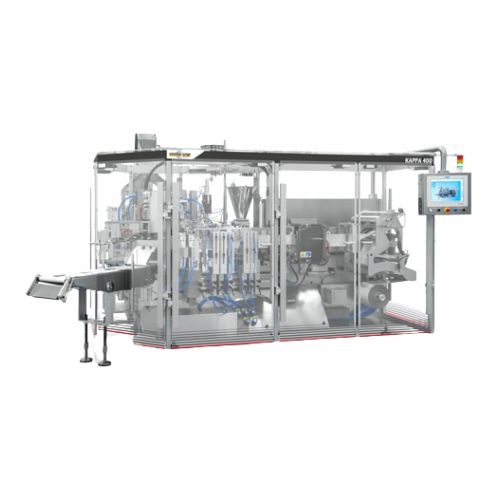
Horizontal intermittent motion sachet packaging solution
Optimize your packaging operations with a versatile sachet solut...
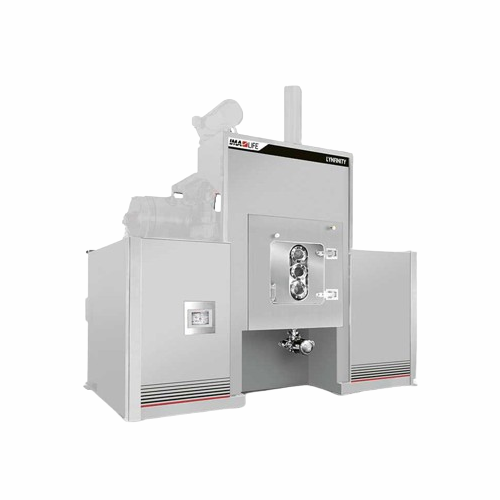
Continuous aseptic spray-freeze-drying system
Achieve higher sterility and improved product uniformity with a continuous a...
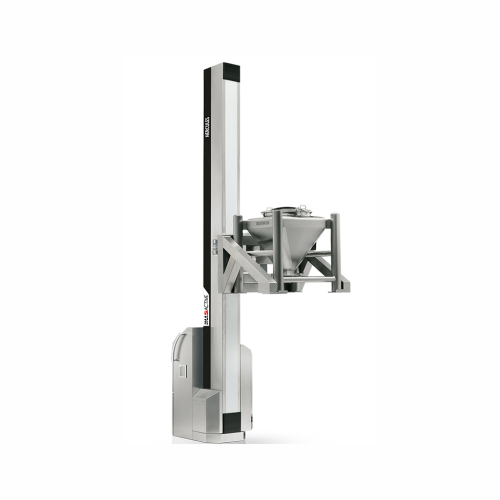
Lifting column for drums and containers
Streamline your production with lifting columns designed for precise handling, blen...

Rotary doypack packaging system for various materials
Enhance your packaging line with versatile doypack machines designe...
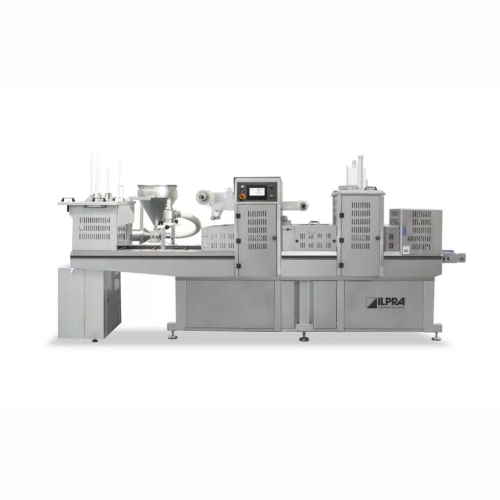
Tray sealing machine for buckets
Ensure efficient sealing and preservation with high-speed tray sealing for various food pro...
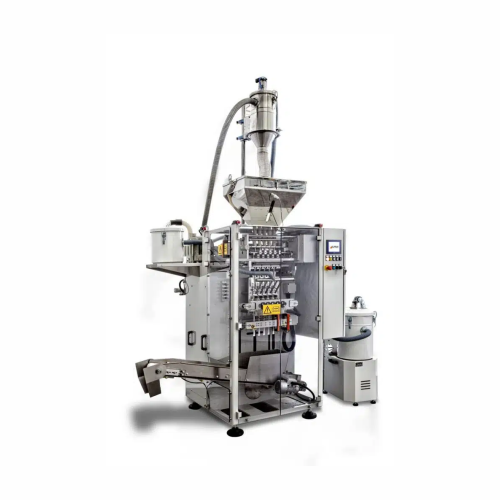
Vertical stick pack sachet packaging solution
Ideal for mid-scale operations, this vertical stick pack machine streamlines...
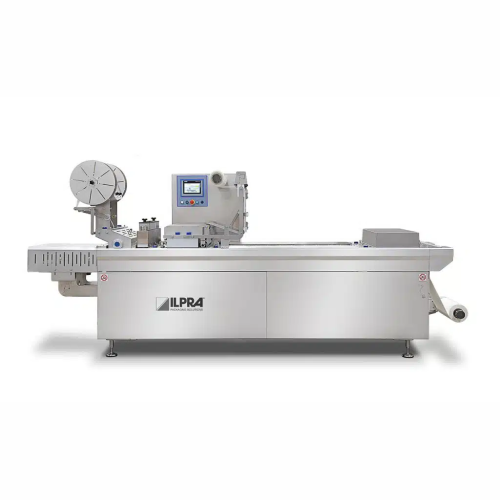
Thermoforming packaging solution for food and medical applications
Enhance your packaging line with a solution designed...
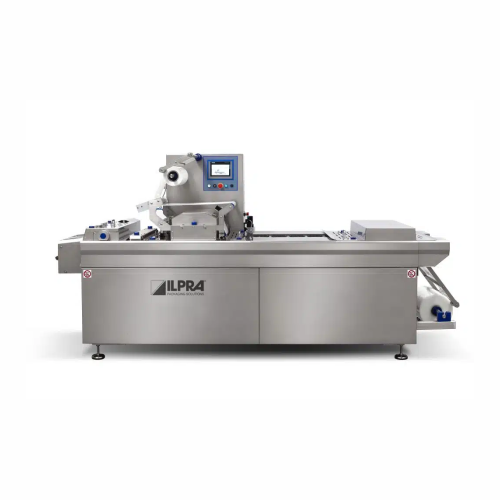
Compact thermoforming packaging system for food industry
Revolutionize your packaging line with a space-saving solution t...
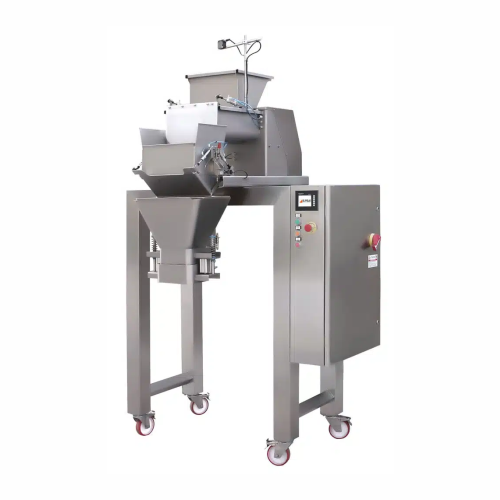
Linear and auger weighing systems for non-free-flowing products
Optimize your production line with precise weighing and ...
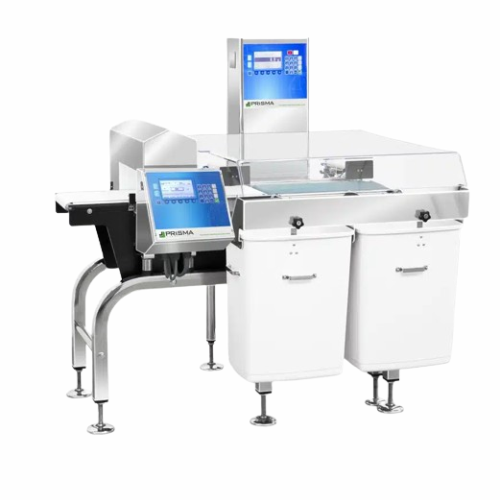
Metal detector for small to medium-sized products
Ensure product integrity and compliance by seamlessly integrating metal...
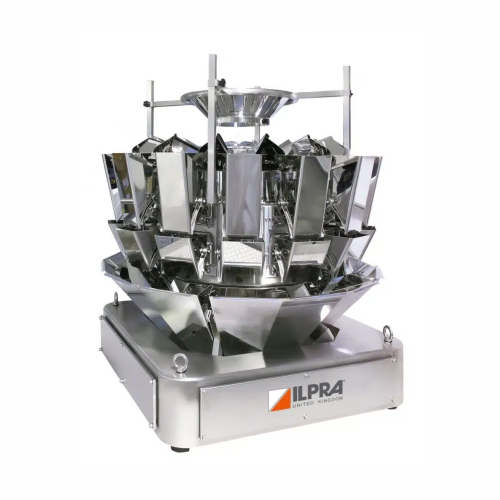
Multi head weigher for precise portioning
Ensure consistent product portions with our multi head weigher, ideal for high-s...
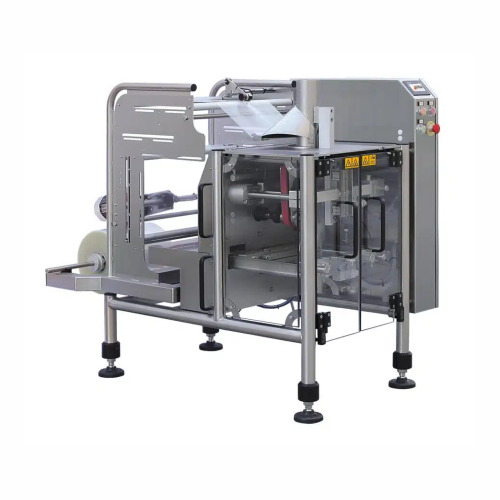
Vertical form fill seal for small to medium production runs
Ideal for scaling production, this compact packaging solutio...
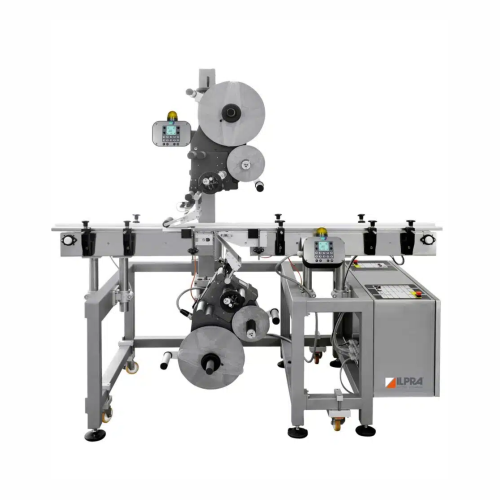
Automatic top & bottom labelling system
Enhance your packaging line efficiency by applying precise top and bottom labels to...
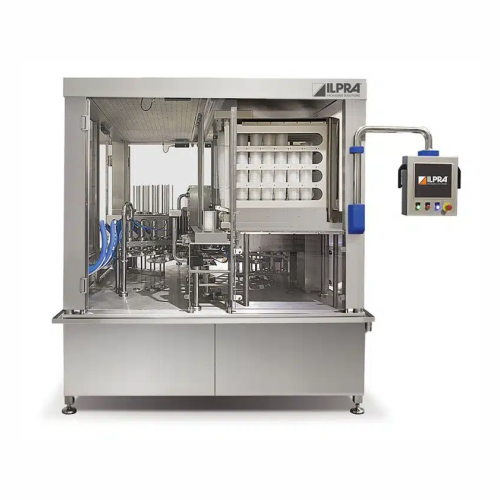
Rotary filler for optimized production processes
Streamline your fill and seal process with precise timing control and enh...
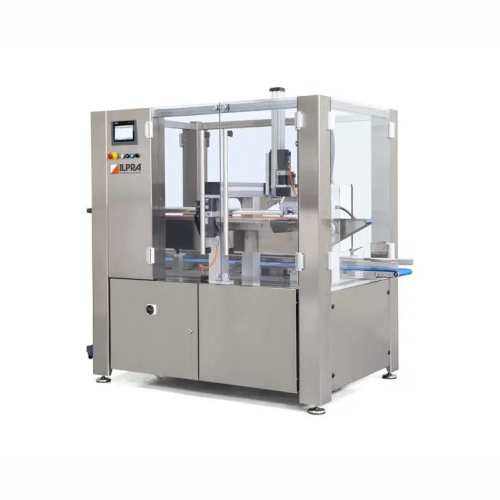
Industrial pick and place system for packaging
Streamline your packaging line with precise robotic pick and place operatio...
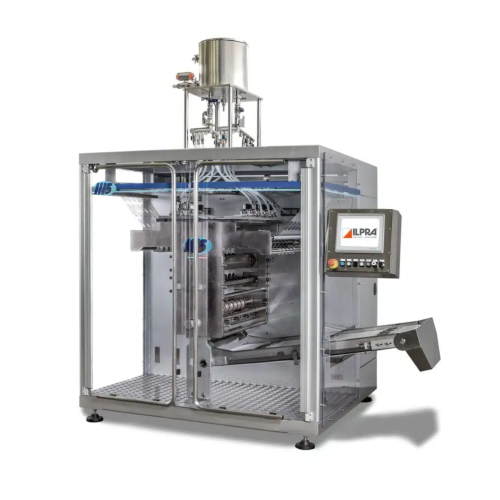
High-speed continuous rotating packaging solution
Transform your packaging efficiency with versatile operations, accommod...
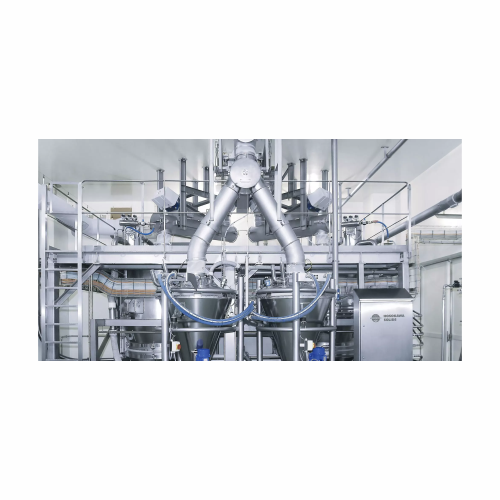
Pneumatic conveying system for bulk material handling
Efficiently transport bulk materials with precision through pneumat...
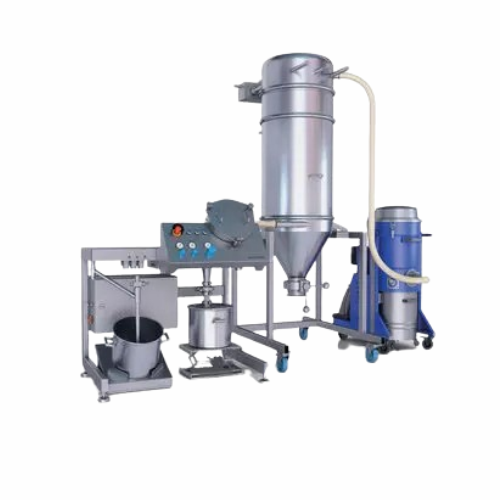
Spiral jet mill for ultrafine micronisation
Optimize your powder processing with precision-driven micronisation that ensur...
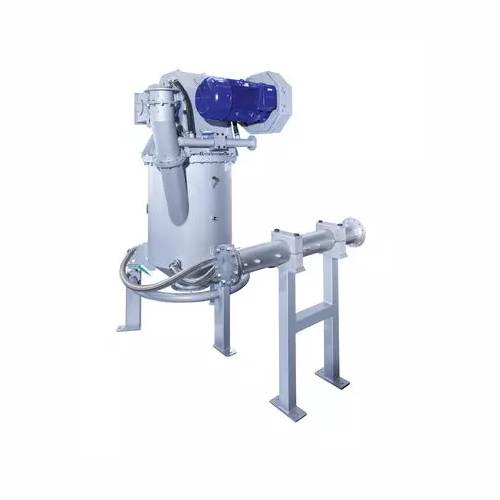
Fluidised bed opposed jet mill for fine particle processing
Achieve precise and consistent particle sizes with high-spee...
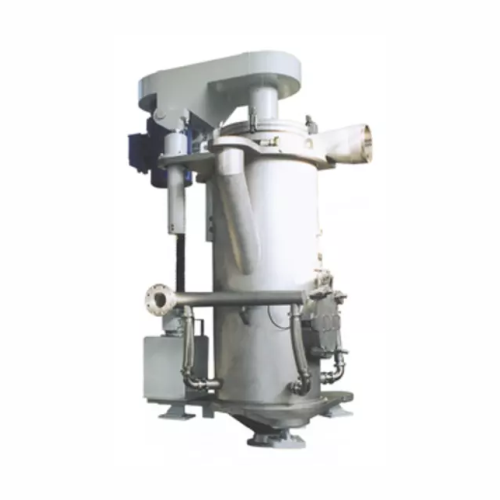
Jet mill for toner and pigment industries
Optimize particle size and distribution for high-demand applications with this h...
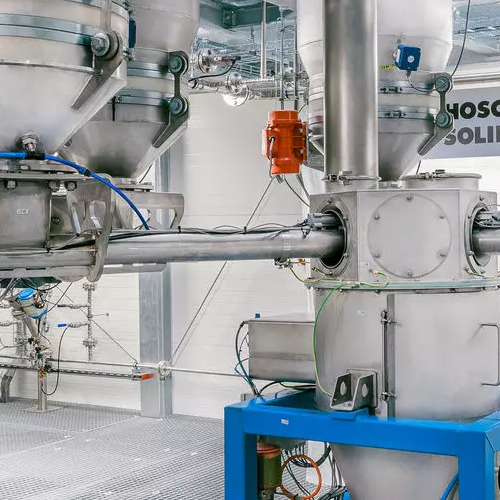
Mechanical conveying systems for bulk solids
Optimize your bulk material processes with advanced mechanical conveying syst...
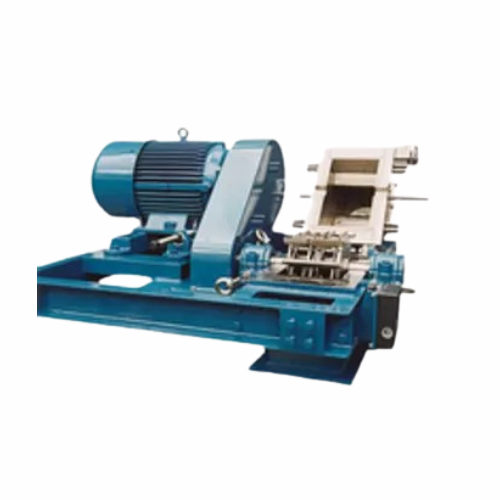
High-speed pulverizer for carbon black production
Achieve consistent particle size and optimal homogenization with high-s...
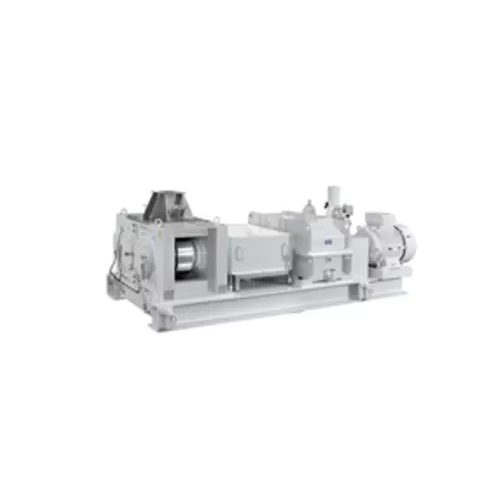
High pressure roller mill for medium-fine crushing
Achieve precision in particle size with high-pressure roller mills, id...
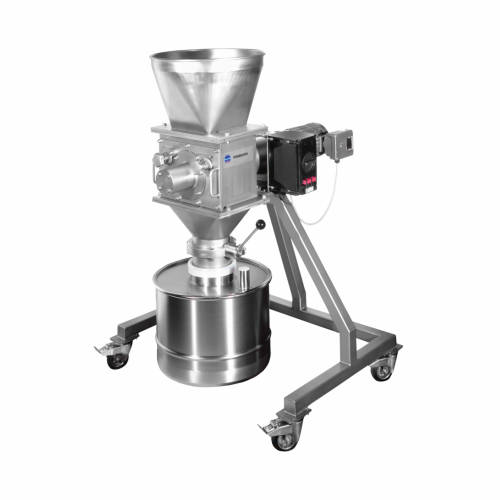
Flake crusher for hygroscopic substances and lumped salts
Efficiently turn fragile, aggregated materials into manageable...
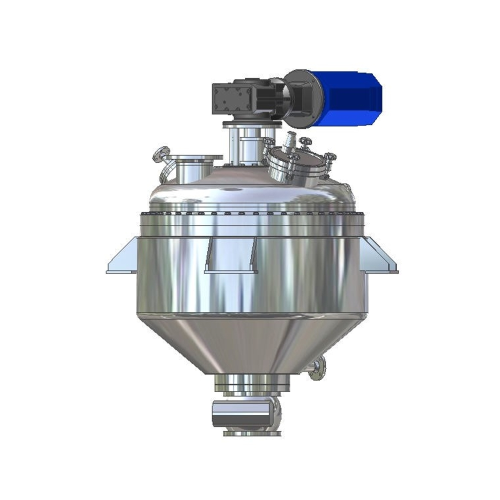
Vacuum drying solution for filter cake or viscous materials
When faced with the challenge of drying filter cake or trans...
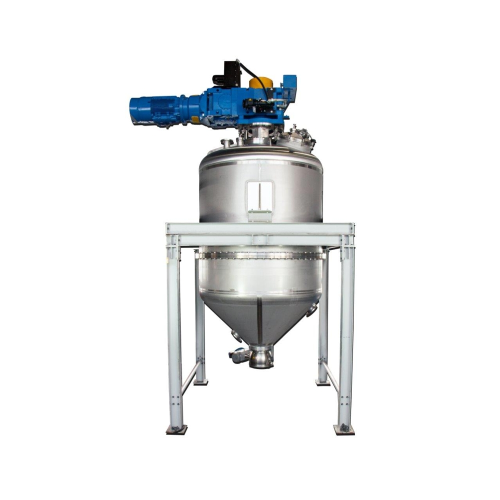
Cylindro conical mixer for batch mixing
Maximize mixing efficiency in compact spaces with this versatile solution, ideal fo...
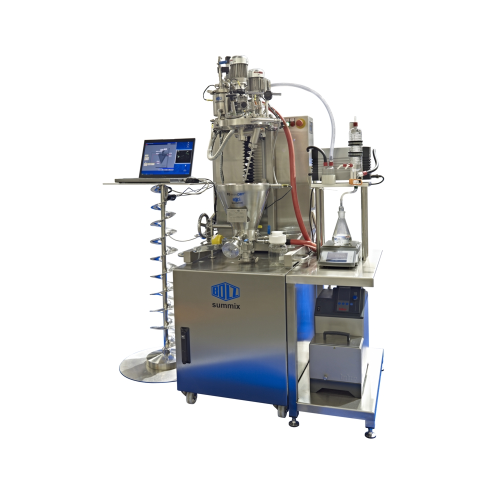
Laboratory system for drying and mixing processes
Enhance your R&D capabilities with precise drying and mixing contr...
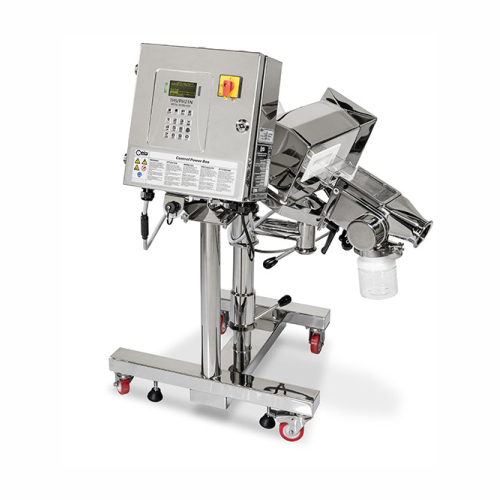
Pharmaceutical metal detectors
Ensure product purity by detecting and eliminating metal contaminants in pharmaceuticals, enh...
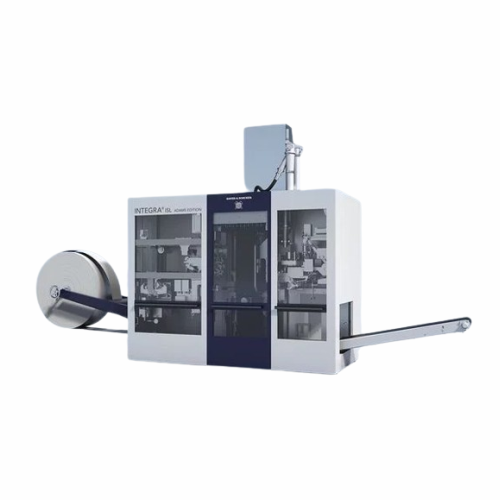
Integrated packaging system for cement and building materials
Streamline your packing operations with a fully enclosed s...
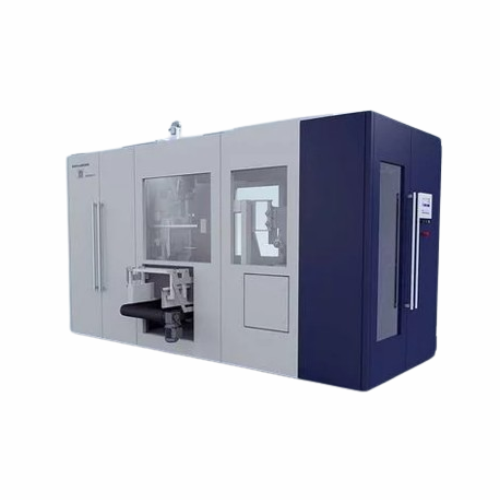
Integrated packaging system for valve and Ffs bags
Streamline your packaging operations with a versatile system designed ...
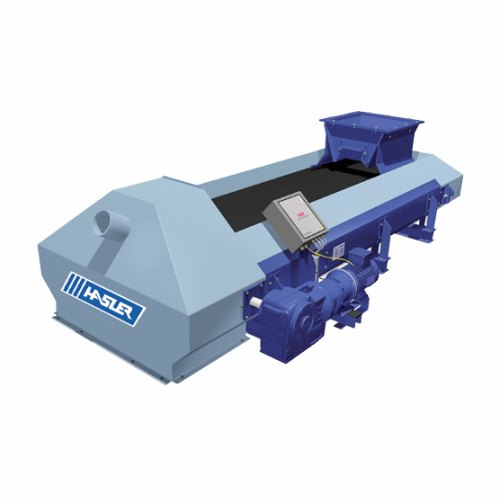
High-precision belt feeder for granular materials
Achieve precise material dosing and consistent flow in your continuous ...

Production system for multi-chamber portion packs
Efficiently produce multi-chamber portion packs with high precision for...
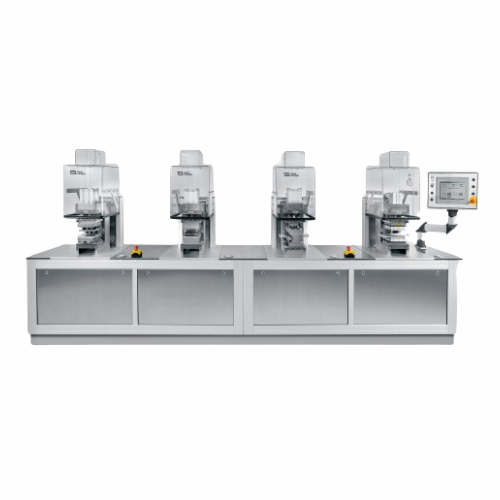
Lab machine for producing portion packs
Efficiently form, fill, seal, and punch portion packs in laboratory settings with c...
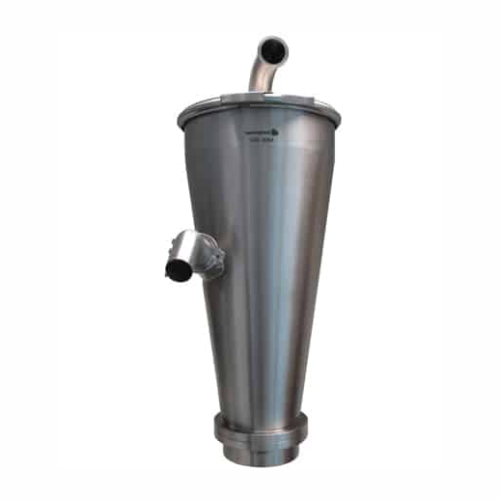
Ultra-hygienic vacuum conveyor for pharmaceutical industry
Optimize powder transfer with ultra-hygienic vacuum conveying...
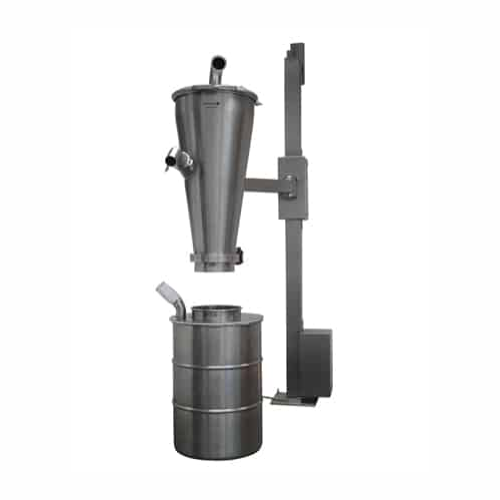
Vacuum conveyor for hygienic material transfer
For operations demanding swift, dust-free material handling, this solution ...
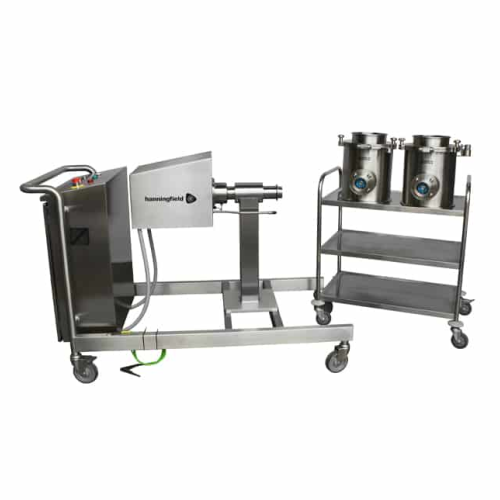
Particle sizing solution for milling and sifting
Streamline your milling and sifting processes with a flexible system desi...

Pre-breaker for initial material size reduction
Efficiently prepare your bulk materials for further processing by swiftly ...
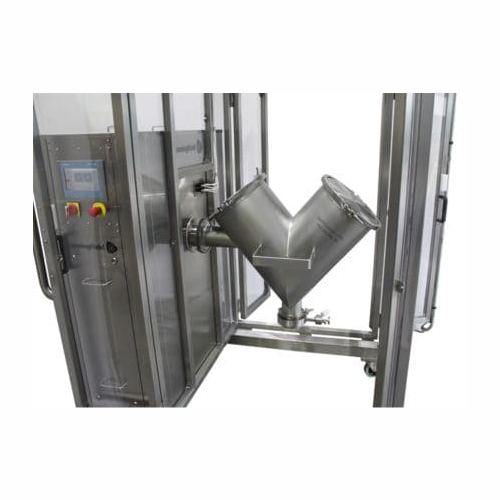
Laboratory and pilot scale blending module
Efficiently integrate multiple blending functions on a single drive for streaml...
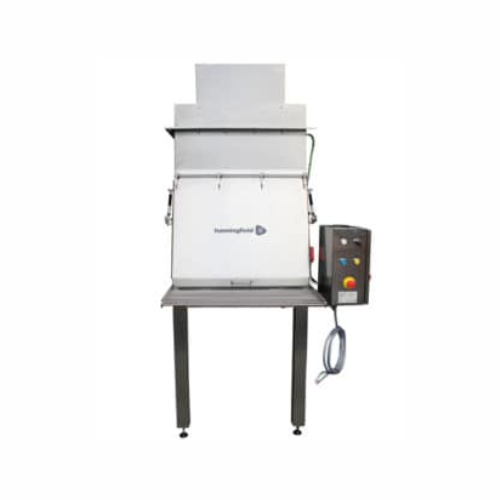
Dust control sack tip station for bag unloading
Ensure efficient powder unloading and minimize dust emissions in your prod...
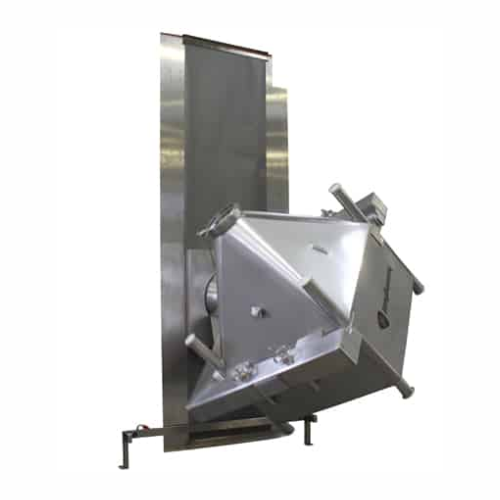
Industrial bin blenders for uniform batch production
Optimize your blending process by achieving uniform mixtures with in...
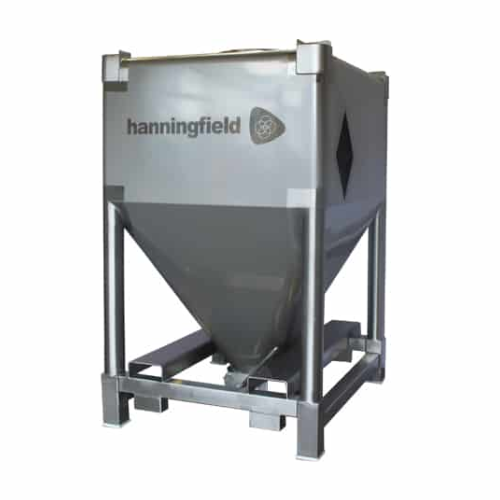
Stainless steel intermediate bulk containers for pharmaceutical use
Ensure safe, efficient transport and handling of po...
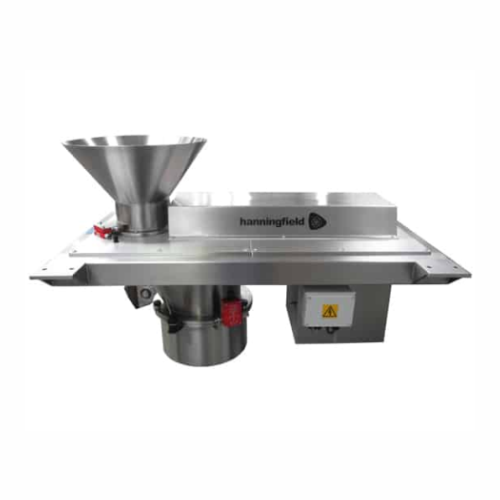
Conical mill for particle size reduction
Achieve precise particle size control and reduce thermal stress on materials with ...
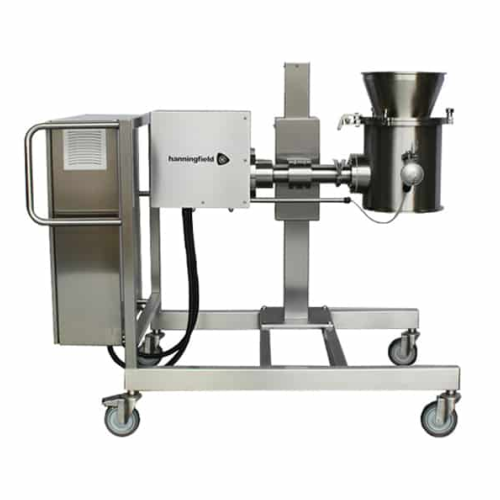
Conical mills for size reduction in pharmaceutical production
Achieve precise particle size control with an innovative m...
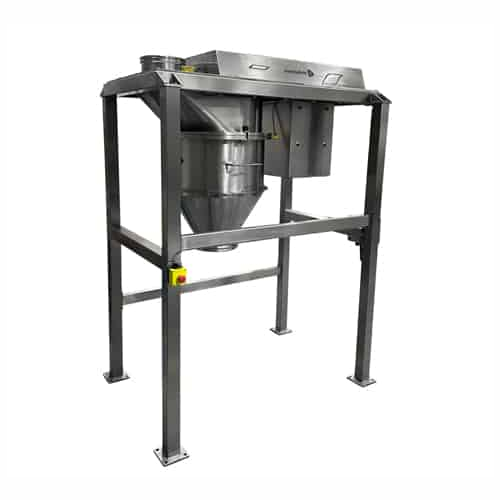
High capacity production milling for bulk materials
Optimize your production with our high-capacity milling solution, des...
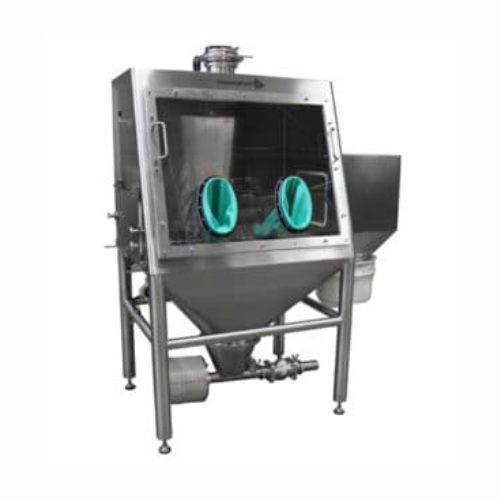
Dust-control sack tip station for industrial loading
Ensure seamless and safe unloading of powders with an integrated dus...
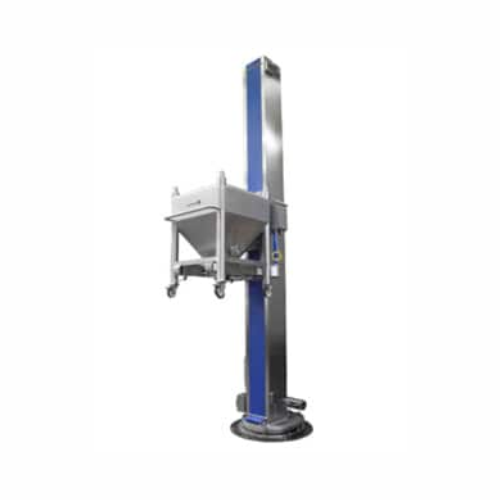
Industrial container lifting system
Optimize your production line with a versatile lifting solution designed to safely hand...

Ribbon blender for homogeneous blending of solids
Achieve perfectly consistent blends with a ribbon blender that ensures ...
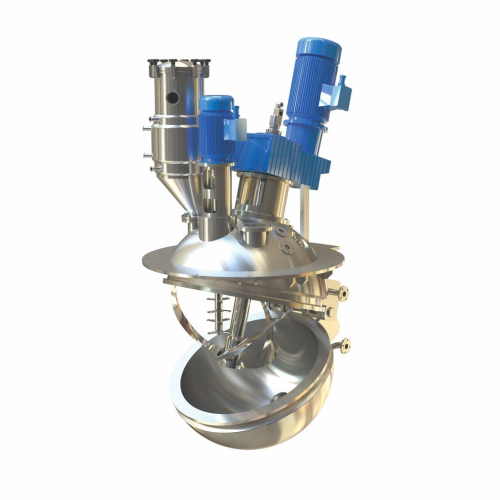
Spherical vacuum dryer for Apis and fine chemicals
Achieve precise moisture control and efficient drying for APIs and fin...
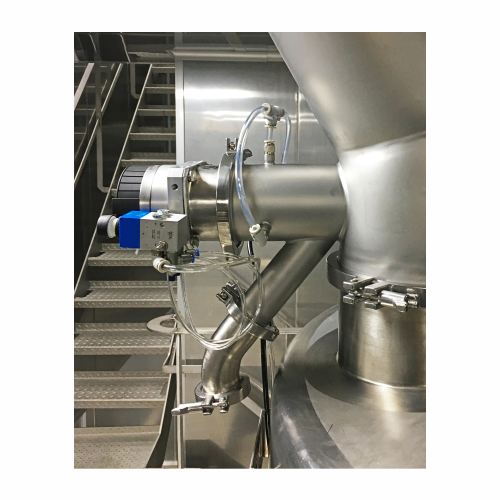
Sampling valve for secure sample extraction
Ensure product quality by safely extracting representative samples without hal...
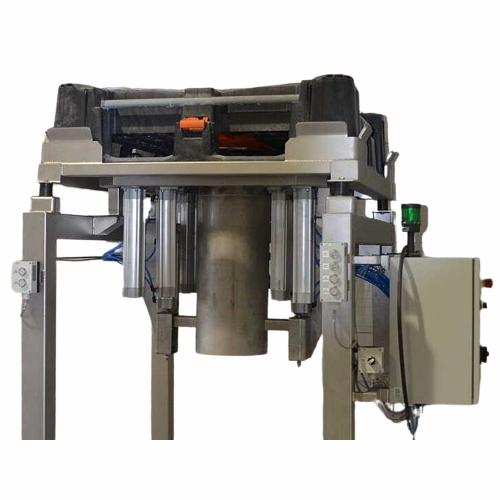
Big bag pallet unloader for bulk products
Efficient and reliable solution for unloading and transporting powders and bulk ...

Big bag unloader for industrial bulk materials
Efficiently handle bulk materials with this modular unloading system, desig...
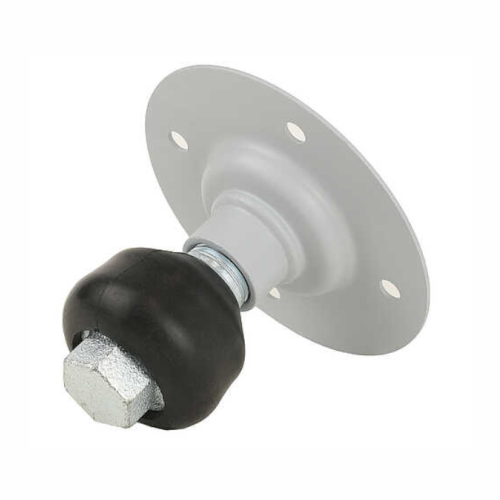
Bin aeration system for silo and hopper material flow
Optimize the flow of your stored powders and granules with an effic...
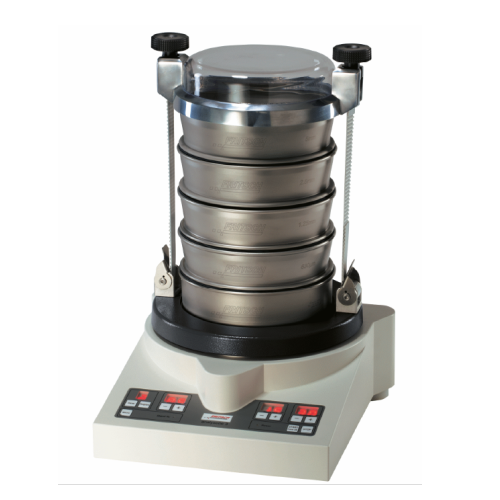
Vibratory sieve shaker for precise particle size distribution
Achieve precise particle size distribution with advanced v...
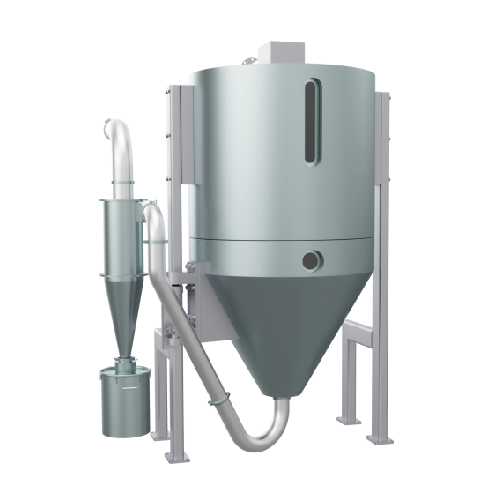
Commercial scale spray dryer for pharmaceutical materials
Optimize the drying of pharmaceutical and industrial materials...
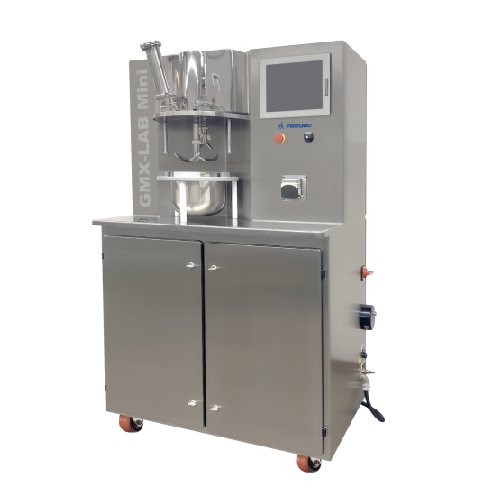
Mini High shear granulator for wet granulation
Optimize your powder granulation with precision and flexibility, ensuring c...
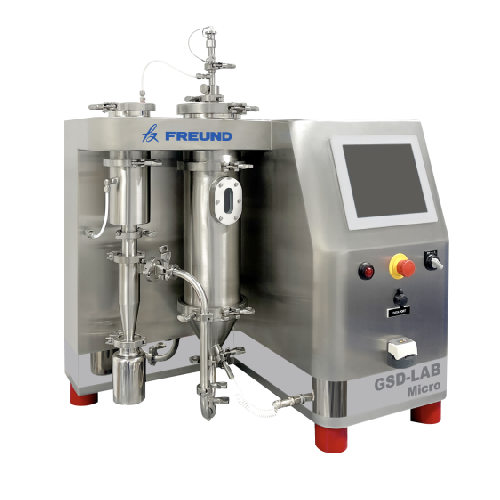
Benchtop spray dryer for drug discovery
Optimize your formulation development with a compact spray dryer that streamlines t...
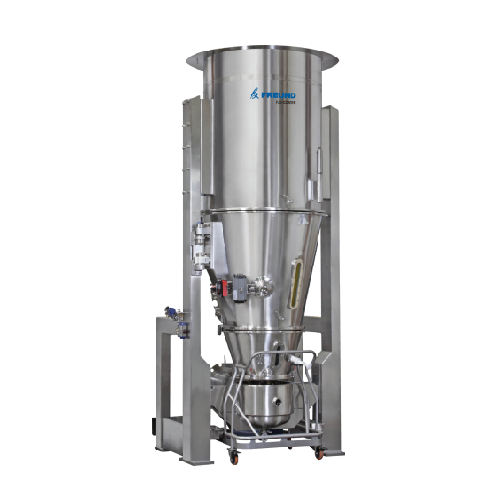
Fluid bed granulator for industrial granulation
Optimize your production efficiency with versatile fluid bed granulation, ...
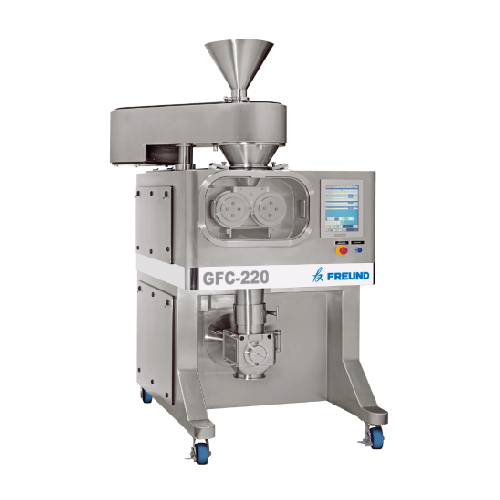
Roll compactor system for dry granulation
Achieve consistent tablet hardness and increased powder density with a versatile...
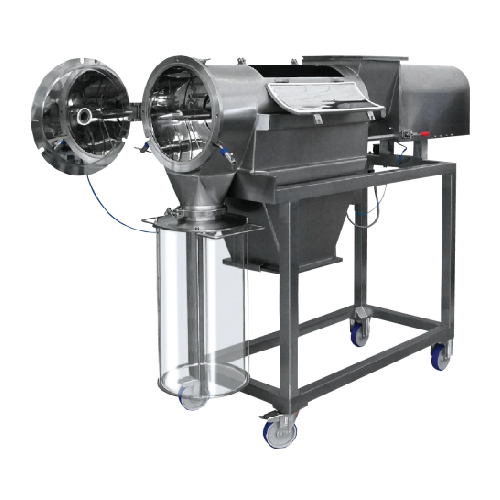
Centrifugal sifter for particle size classification
Achieve precise particle size control with high output efficiency, en...
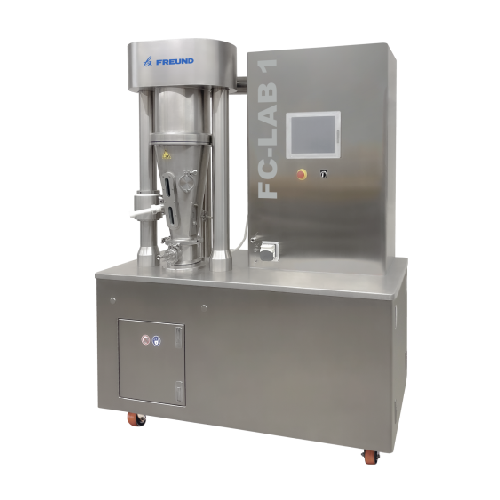
Laboratory scale fluid bed system for granulation and coating
For precise formulation and optimization, this fluid bed s...
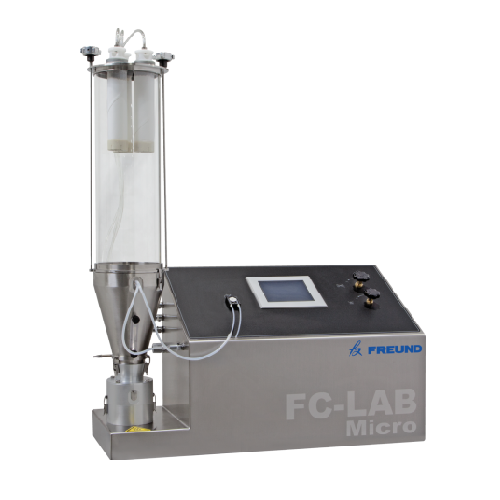
Development fluid bed system for feasibility studies
Explore precise granulation and coating capabilities for small batch...

Closed loop granulator for pharmaceutical production
Streamline your production with a fully automated closed-loop system...
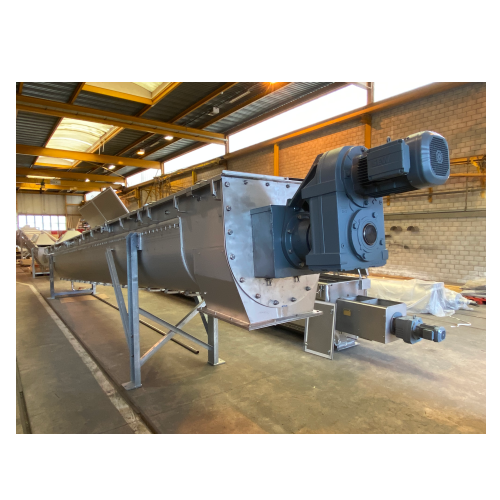
Screw heat exchanger for efficient thermal processing
Optimize your heating and cooling processes with this robust double...
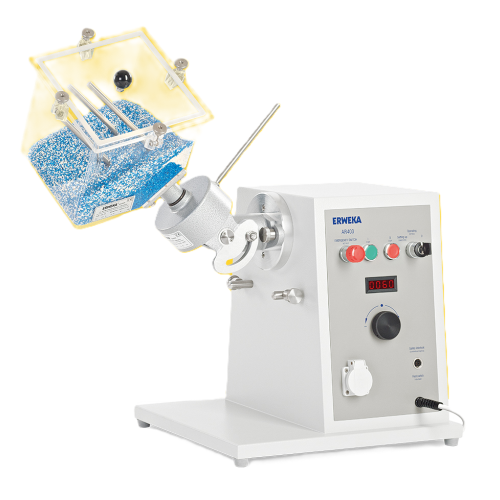
Tumbling cube mixer for homogeneous blending
Achieve uniform blending with precision using a cube mixer that enhances mixi...
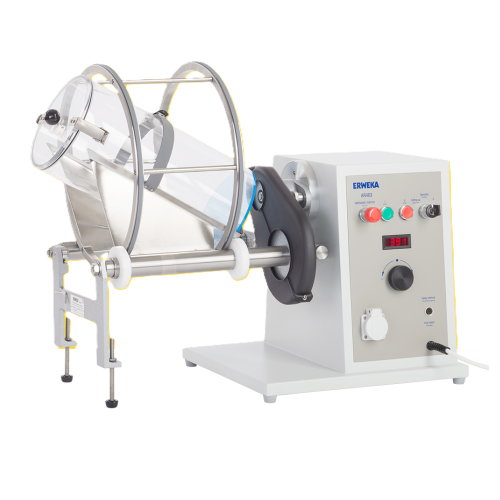
Drum hoop mixer for uniform three-dimensional mixing
Achieve consistent, homogenous mixing of powders and granules with a...
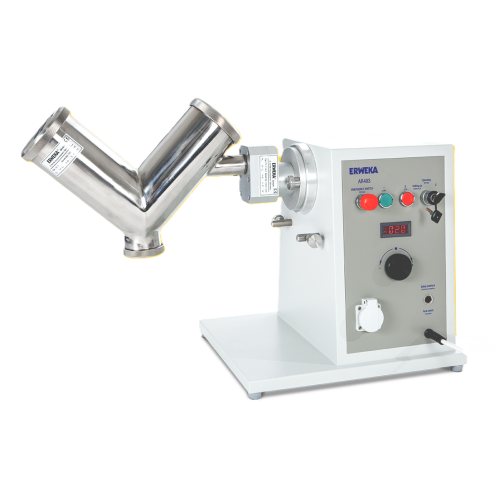
V-mixer for solid bulk material blending
Achieve precise and uniform mixing of sensitive powders with gentle treatment, ide...
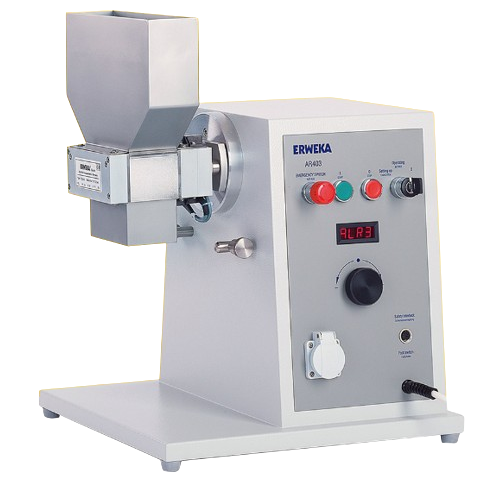
Double roll crusher for laboratory applications
Optimize material processing with a double roll crusher designed for preci...
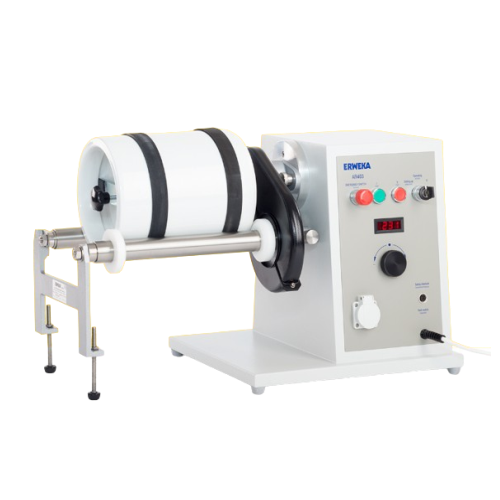
Lab-scale ball mill for crystalline material grinding
Effortlessly grind and mix crystalline materials into fine powders ...
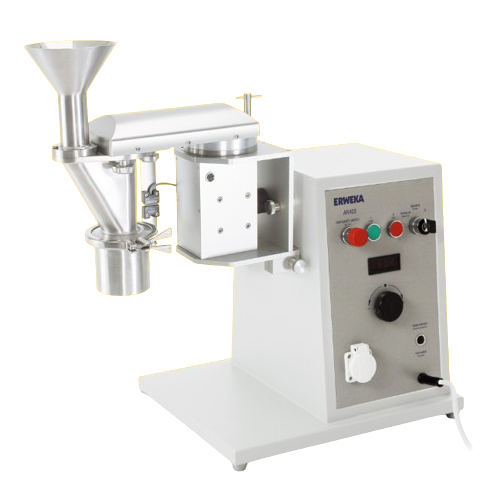
Conical mill for particle size reduction and homogenization
Achieve precise particle size reduction and homogenization w...
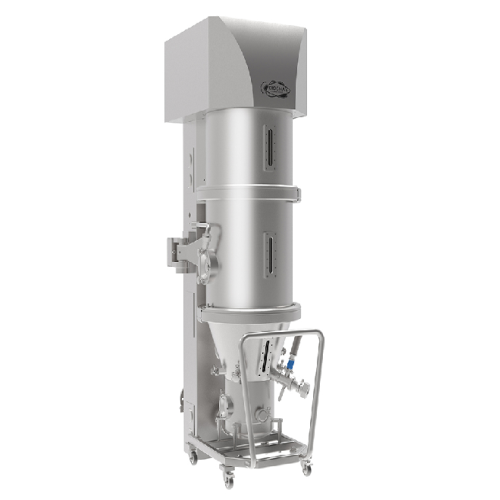
Fluid bed processor for granulating, drying, and coating in pilot scale
When scaling from laboratory to production, rel...
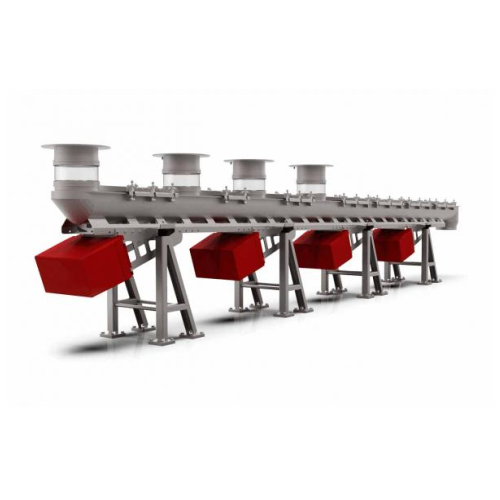
Vibration transport system for hygienic conveying of bulk goods
Optimize your production line with efficient and hygieni...
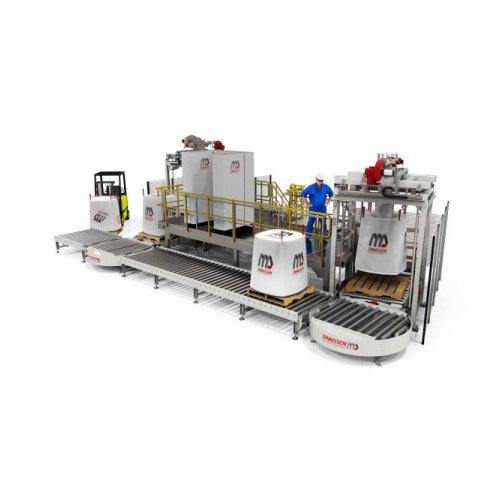
Product handling system for big bags and containers
Optimize your production line with a comprehensive system for transpo...
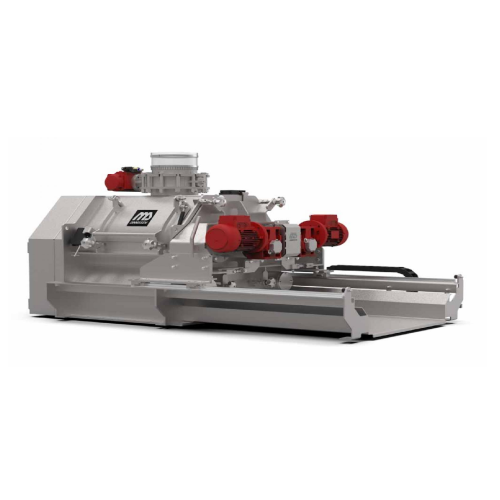
5-in-1 industrial mixer for food and chemical industries
Streamline your production with a multifunctional system that ef...
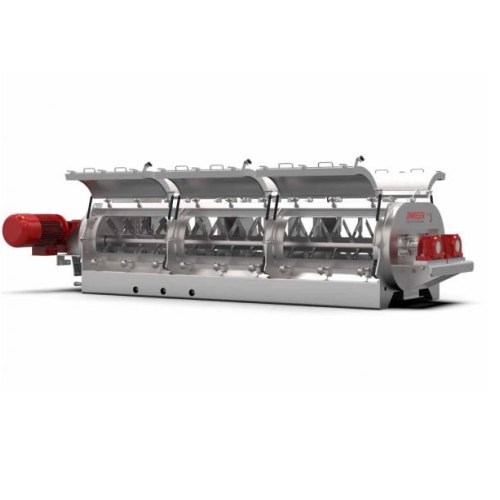
Industrial mixer for moisture conditioning
Ensure precise moisture levels and homogeneous mixtures for complex extrusion p...
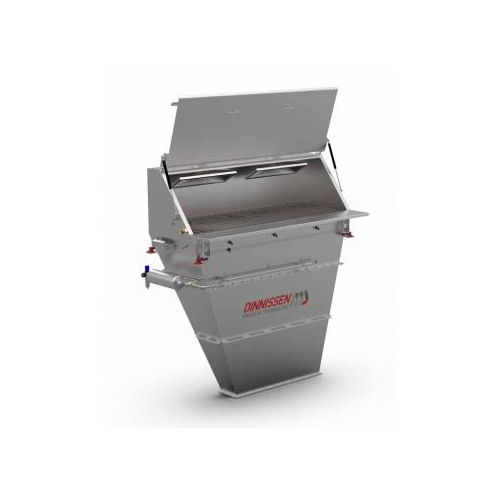
Bag emptying system for bulk material handling
Streamline your material processing operations with a versatile solution de...
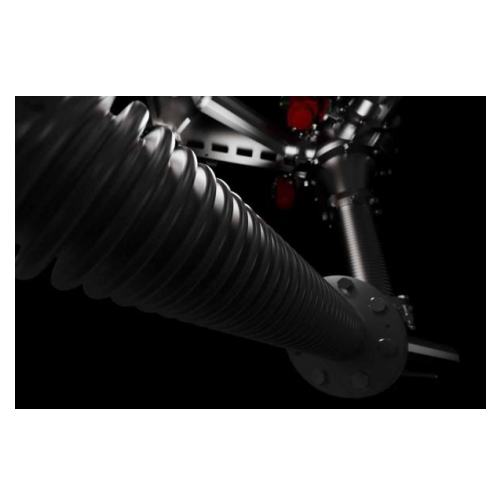
Lactose pneumatic conveying solution
Eliminate frequent production halts due to lactose buildup with our conveying solution...
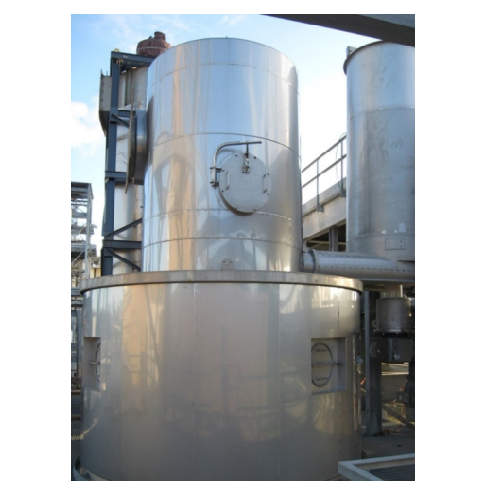
Industrial roto-flash dryer for chemical applications
Achieve uniform moisture and particle size in demanding drying proc...
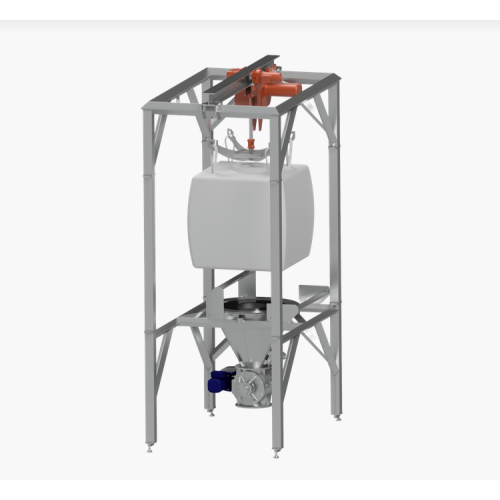
Bigbag discharge system for food, chemical, and pharmaceutical industries
Ensure precise and dust-free handling of bul...
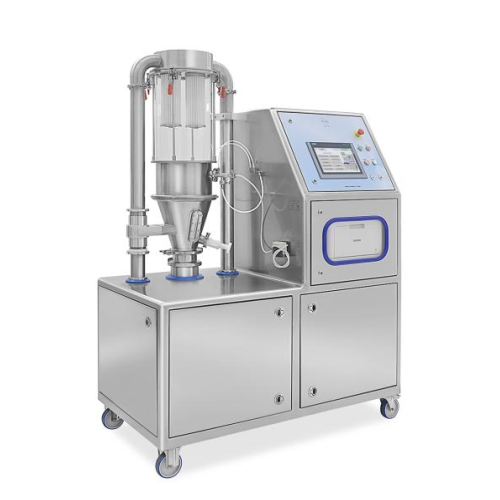
Laboratory fluid bed dryer for pharmaceutical granulation
Optimize your lab-scale drying and granulation processes with ...

Mini laboratory mixer for tabletops
Optimize your lab’s mixing precision with this compact tabletop bin mixer, design...
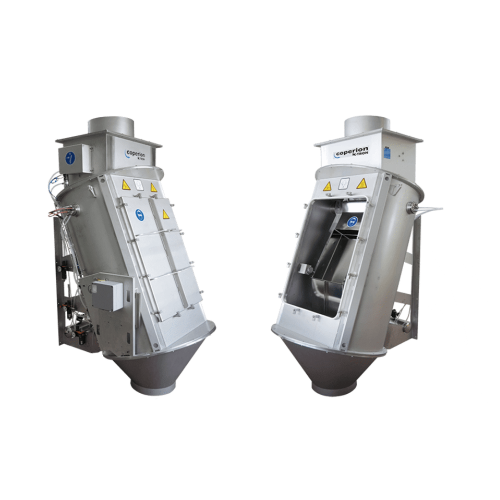
Industrial smart flow meter
Ensure precise metering and smooth handling of bulk materials with a device that eliminates movi...
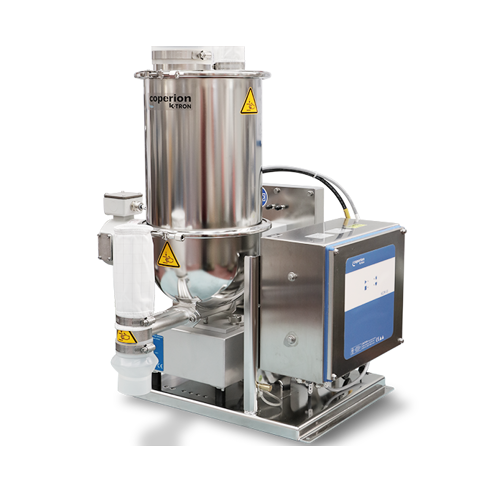
Twin screw feeders for difficult bulk materials
For manufacturers handling sticky or fine powders, twin screw feeders ensu...
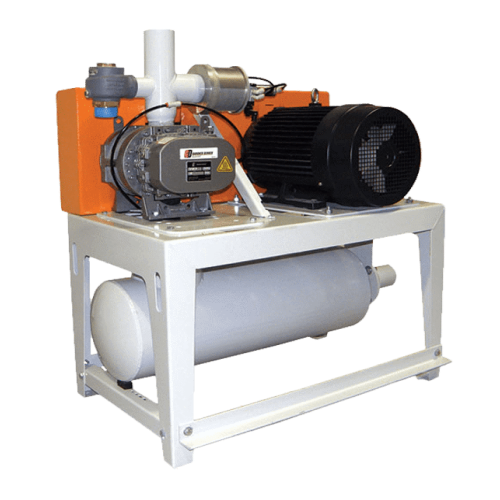
Industrial vacuum blower for continuous pressure conveying
Optimize your production line with reliable vacuum conveying,...
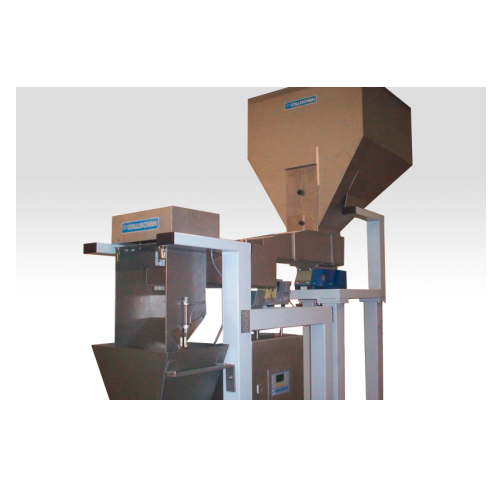
Weigh filler for bulk quantities 2-20kg
Optimizing your filling process with precision, this equipment handles bulk quantit...
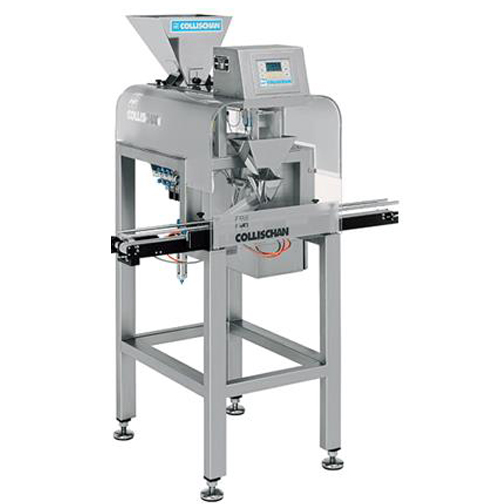
Weight filler for small batches in explosive areas
Efficiently handle and weigh small batch products with precision, even...
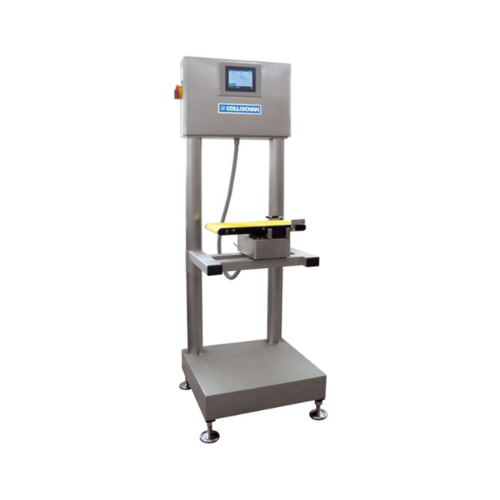
Basic checkweigher for weight control in low to medium performance
Ensure accurate weight control with a versatile chec...
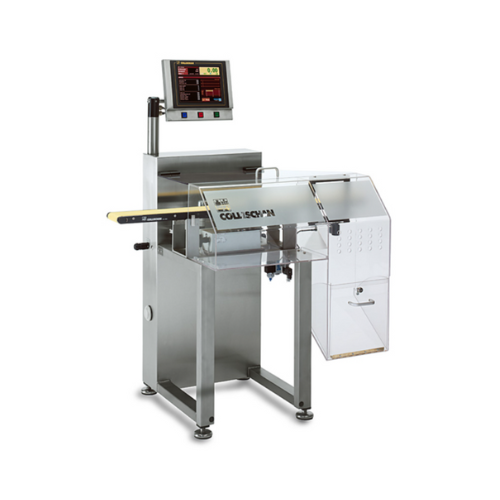
High-performance checkweigher for pharmaceutical tablet cartons
Achieve precision weighing at speeds up to 500 units per...
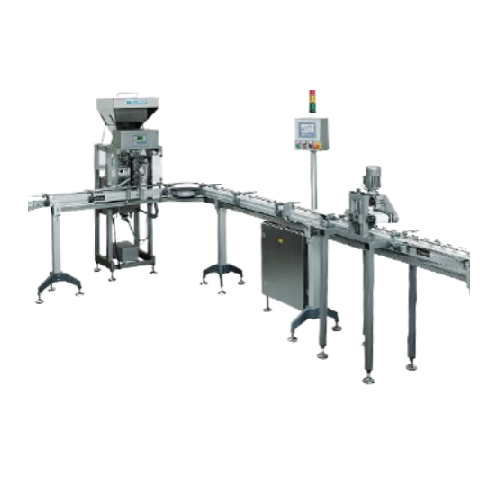
Precision weigh filler for food and pharma industries
Optimize precision in multi-component dosing with seamless integrat...
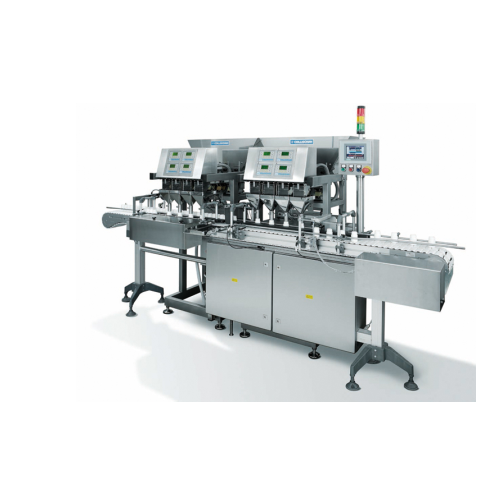
Complete packaging lines for various containers
Streamline your packaging process with versatile equipment capable of hand...
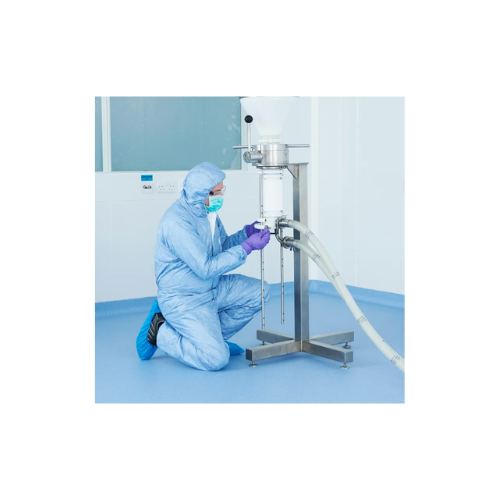
Bottle cleaning station for controlled environments
Ensure high-level decontamination of passive units and containers wit...
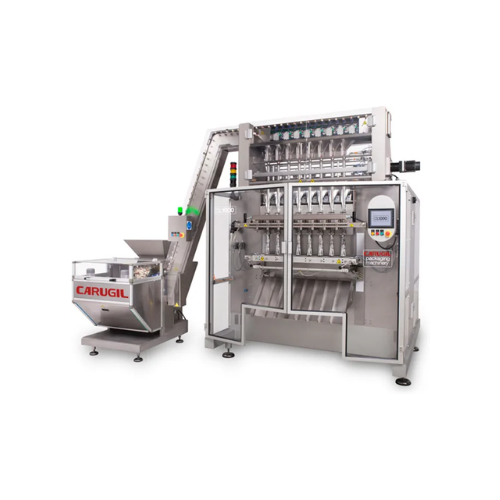
Stickpack wrapper for lollipops
Enhance your confectionery line’s efficiency by wrapping up to 480 lollipops per minut...
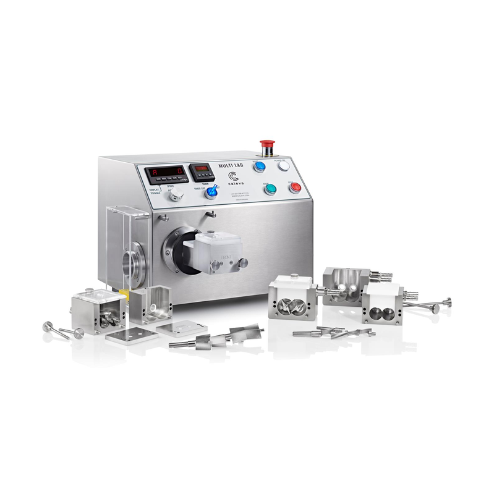
Small batch mixer granulator blender
Effortlessly manage small batch mixing, blending, and granulation with a compact solut...
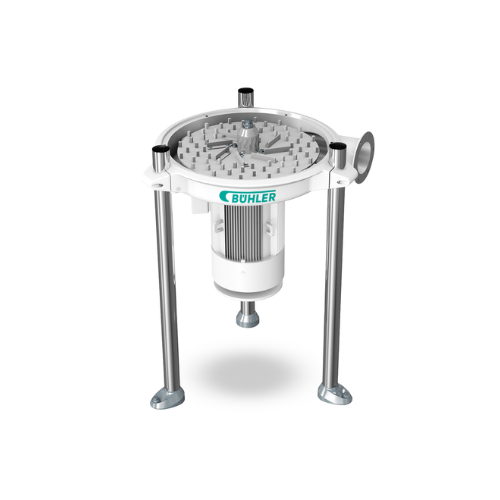
Impact machine for milling applications
Optimize your grain processing with this versatile impact machine, designed to refi...
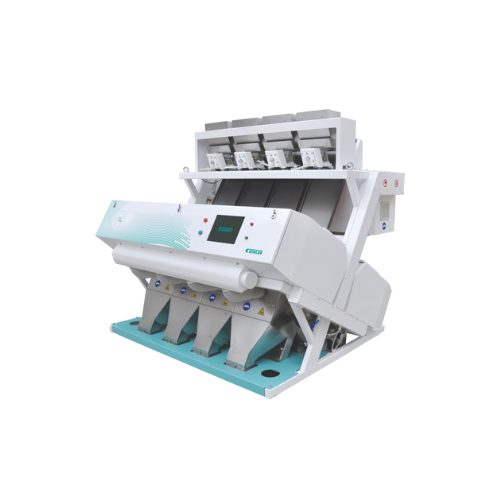
Optical sorter for grain and seed sorting
Ensure precise defect detection and efficient sorting of grains, pulses, and see...
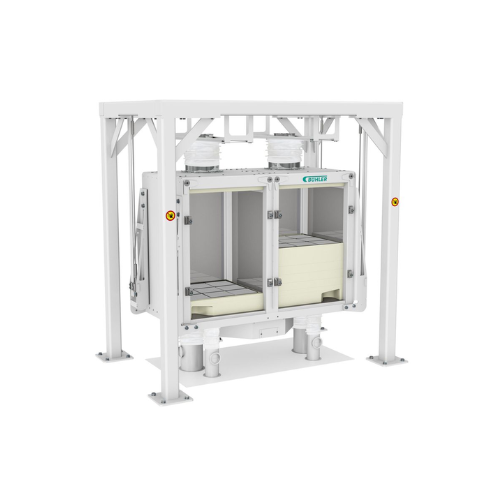
Small plansifter for grain milling
Optimize your grain milling with a compact plansifter designed for high-speed, precise s...
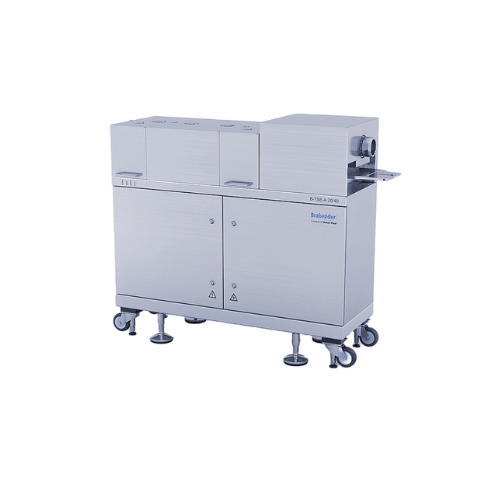
Lab-scale twin screw extruder
Optimize your material testing and production efficiency with our versatile twin screw extrude...
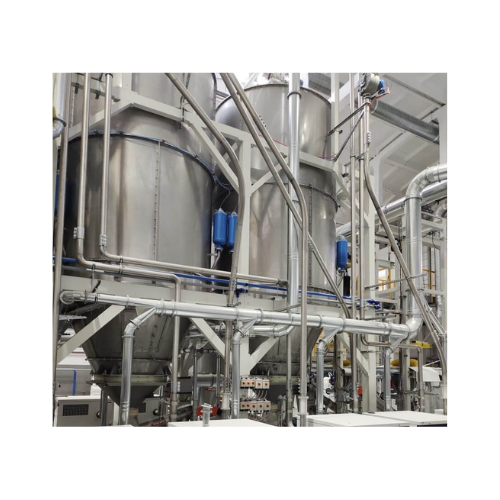
Raw material handling systems for plastic and pharmaceutical industries
Effortlessly manage and optimize the handling a...
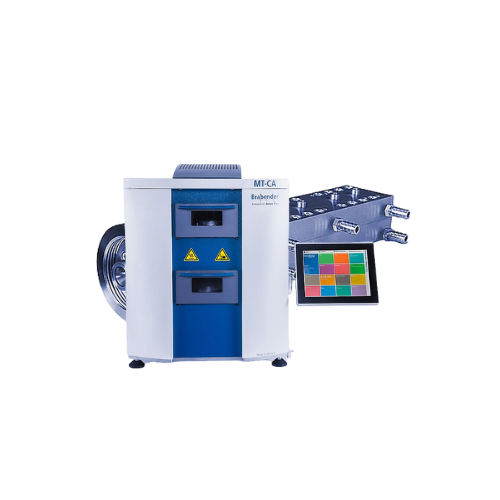
Moisture analyzer for flour and tobacco
Optimize your moisture measurement process with precision and speed, ensuring quali...
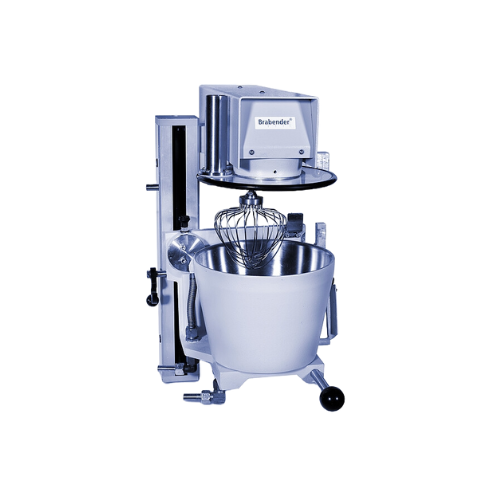
Planetary mixer for homogeneous material mixing
Achieve precise and consistent mixing of diverse materials from powders to...
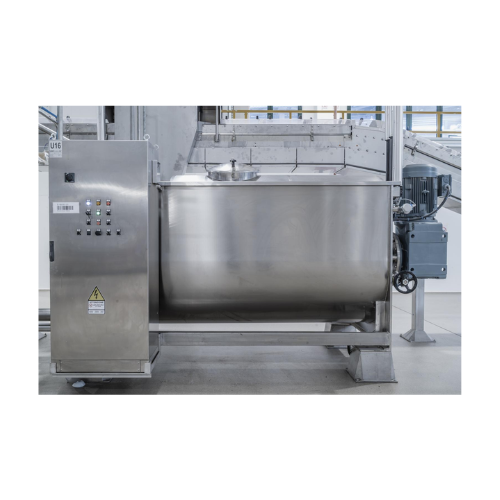
Horizontal mixer for creams
Achieve optimal and uniform mixing of creams, pasty products, and powders with advanced horizont...
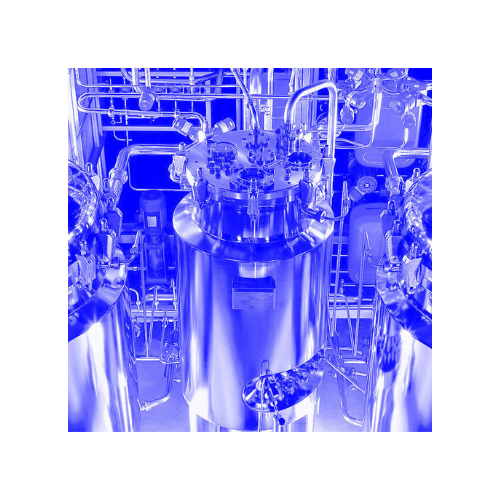
Media and buffer preparation solution for bioprocessing
Achieve seamless media and buffer preparation with precise dosing...
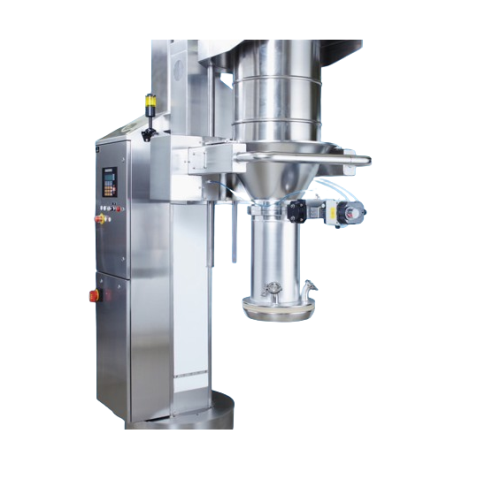
Lifting column for industrial packing drum handling
Efficiently handle heavy drums and containers with precision—streamli...
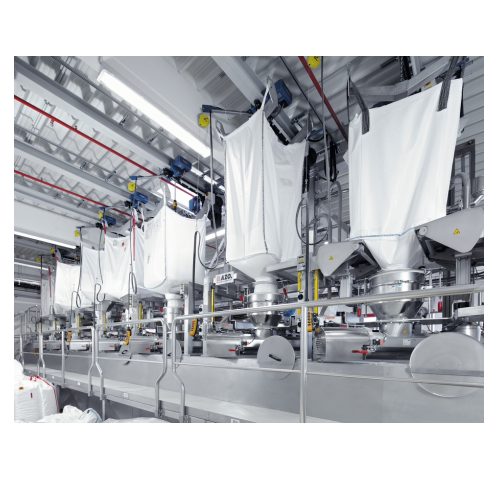
Big bag discharge station for bulk material handling
Ensure low-dust and efficient discharge of bulk materials with a sys...
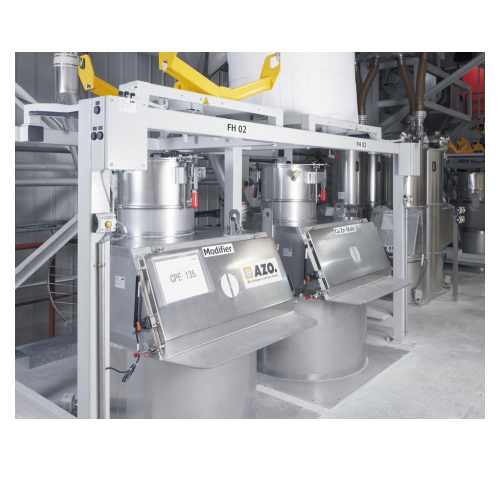
Integrated pickup station for bagged products and big bags
Streamline the handling and transition of bulk materials with...
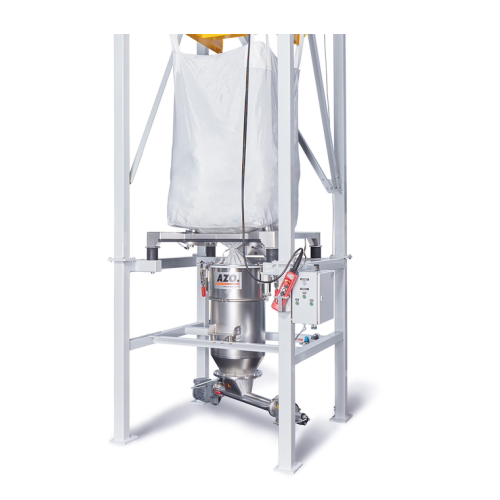
Modular big bag discharge station for bulk material handling
Streamline your bulk material handling with a customizable ...
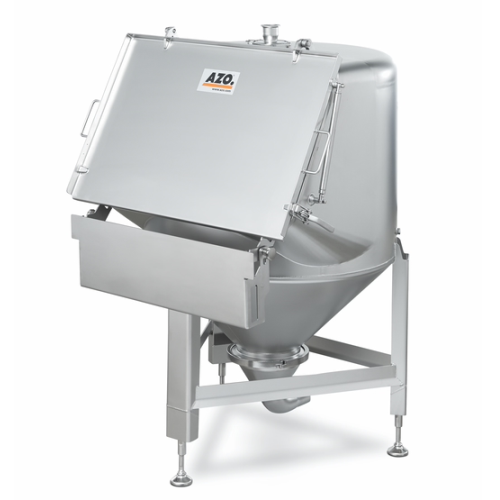
Precise weighing solutions for small batch production
Streamline handling of diverse ingredient blends with precise dosin...
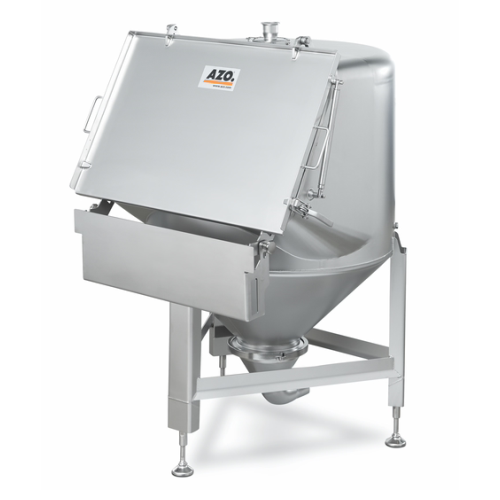
Hygienic feeding hopper for bulk solids
Ensure optimal hygiene in your powder and granular processing with a feeder that fa...
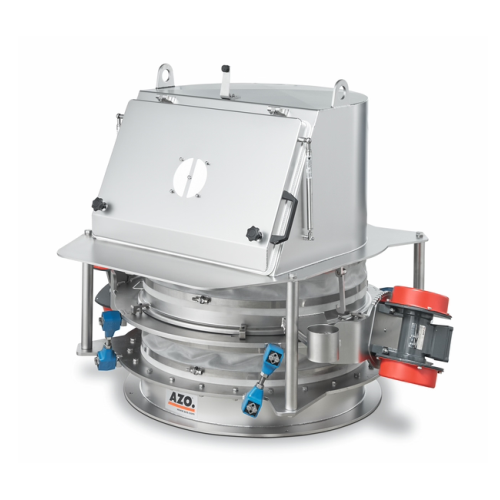
Bag feeding hopper for bulk solids
Optimize your material handling with a robust feeding hopper that seamlessly integrates ...
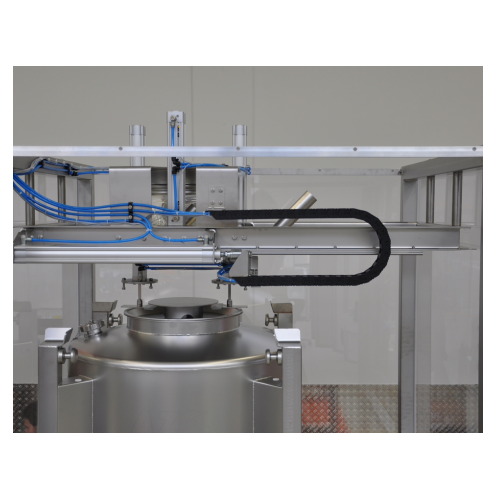
Dust-tight docking for dosing units to bulk solids containers
Ensure seamless, dust-free transfer and dosing of bulk sol...
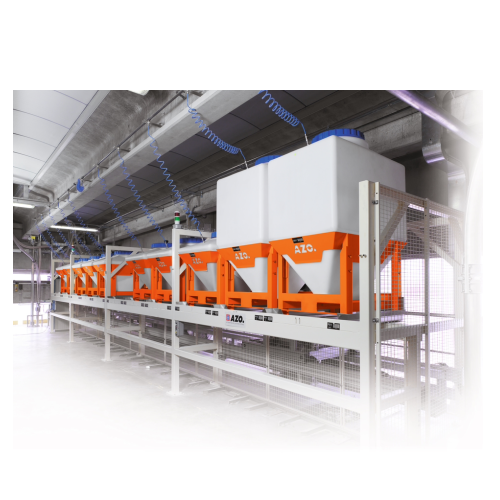
Cost-effective dosing container for minor ingredients automation
Optimize your production by streamlining ingredient han...
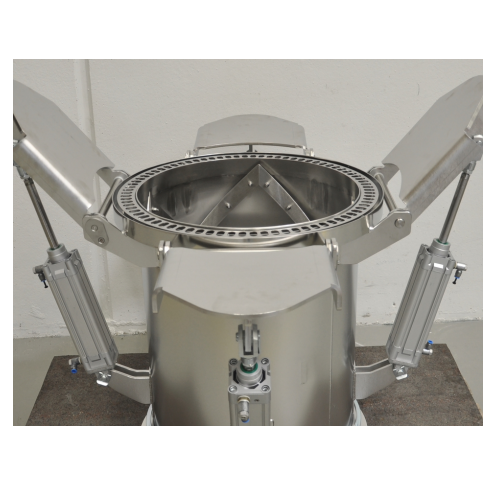
Dust-free big bag connection system for bulk solids
Eliminate dust and ensure reliable discharge with this vacuum docking...
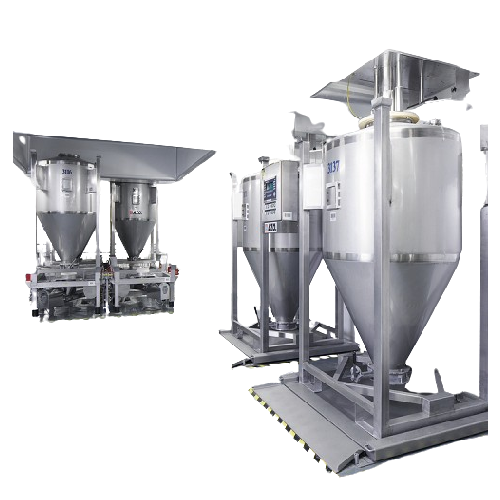
Automated bulk material handling system
Ensure precise batch tracking and efficient handling of challenging bulk materials ...
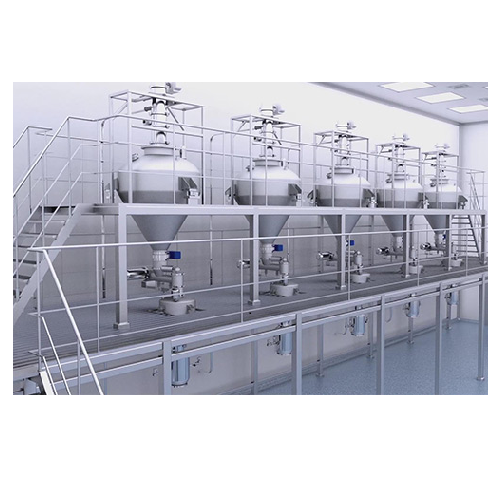
Integrated raw & auxiliary material pre-treatment system
Experience dust-free processing with an integrated system design...
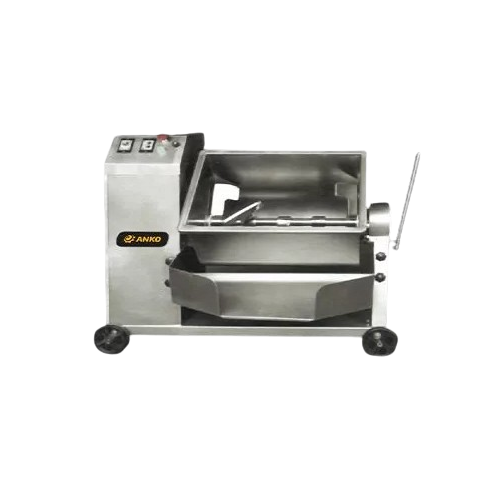
Automatic seasoning mixer for food production
Effortlessly blend diverse ingredients with precision in your production lin...
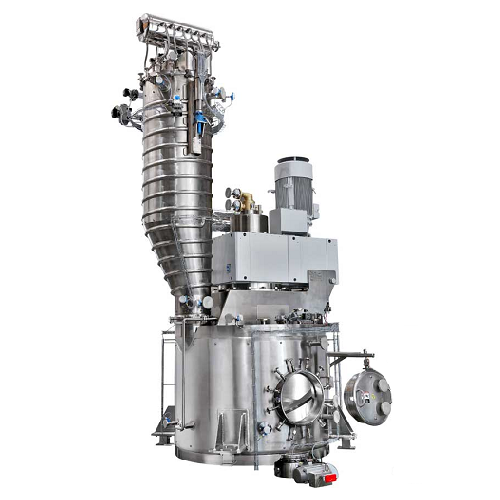
Vertical vacuum dryer and mixing reactor
Achieve precise control over drying and mixing processes with a versatile unit des...
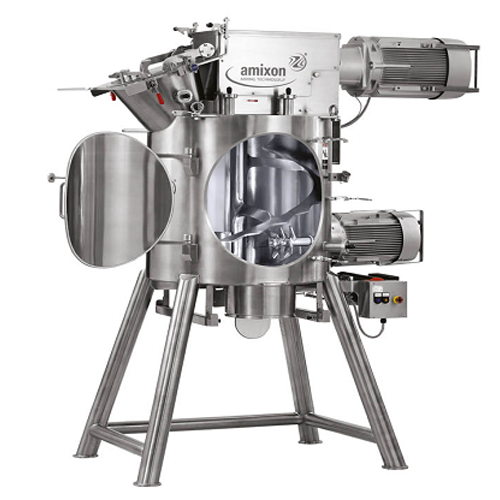
Vertical single-shaft mixer for dry, moist, and viscous materials
In industries requiring precise and thorough mixing o...
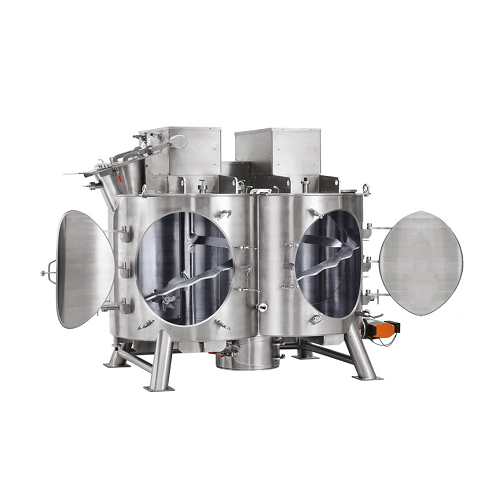
Vertical twin-shaft mixer for dry, moist, and viscous materials
Achieve consistent mixing and blending of diverse materi...
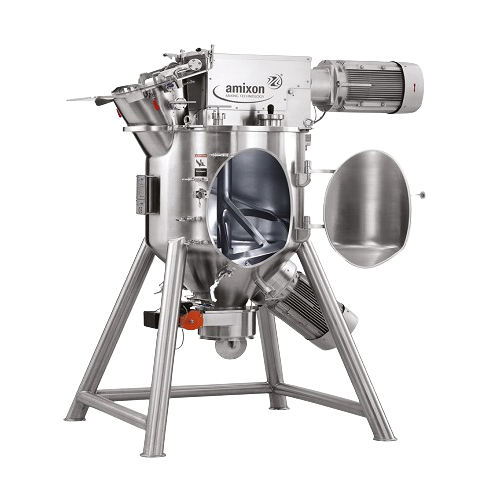
Conical mixer for dry, moist, and viscous materials
Achieve optimal mixing consistency and precision for diverse material...
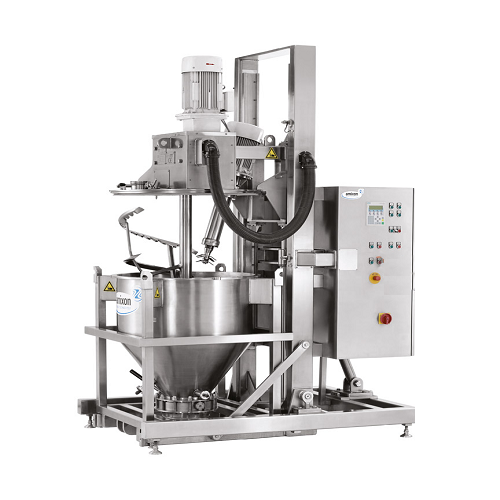
Container mixer for dry and moist materials
Achieve exceptional mixing quality with variable filling levels, ensuring cons...
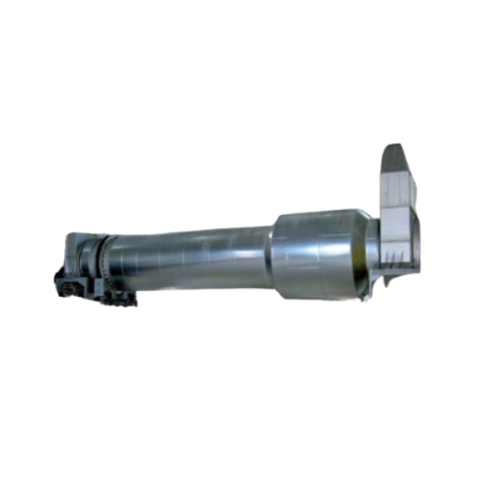
Indirect drying drums for solvent-based products
Optimize energy use and safety with our indirect drying drums, ideal for ...

Dryer for pigments and hydroxides
Achieve precision drying of complex suspensions and pastes into uniform powders, optimizi...
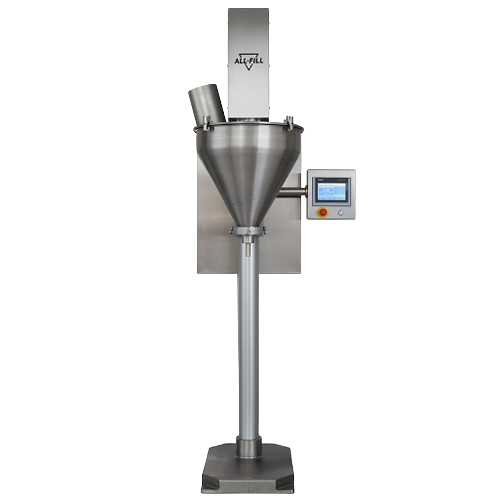
Volumetric filler for bags and rigid containers
Optimize precision filling of powders and granules with a versatile soluti...
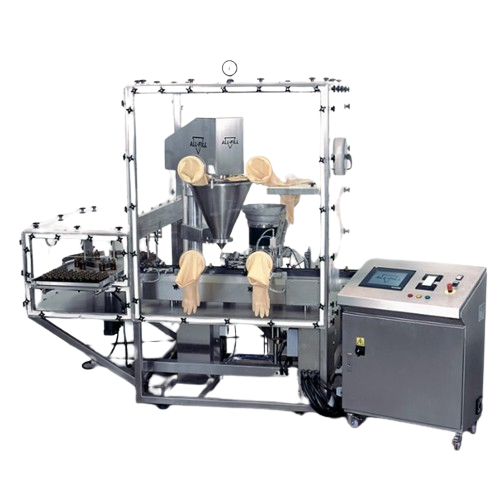
Special purpose auger filling systems for diverse industries
For manufacturers handling precise dosing, our advanced aug...
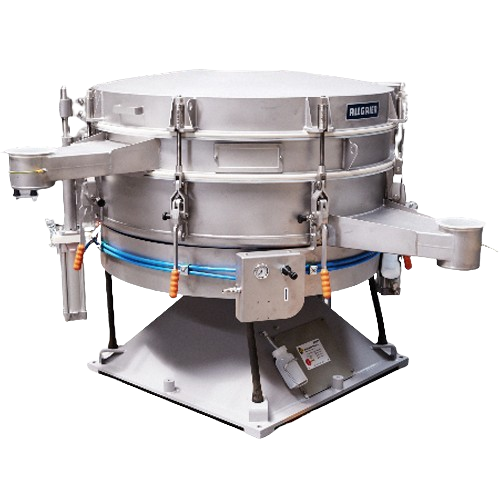
Tumbler screening for fine and ultra-fine sieving
For operations demanding precise particle separation, this solution off...
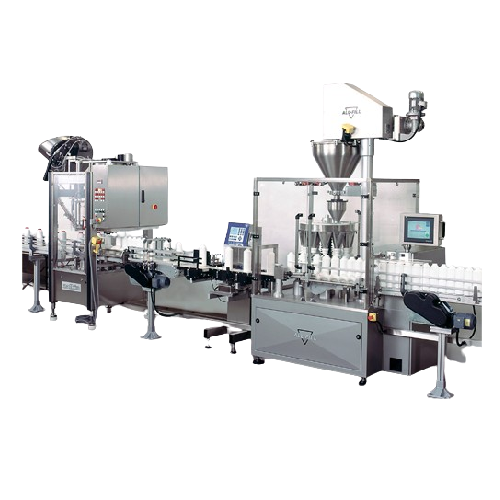
Turnkey filling lines for packaging solutions
Optimize your production line with our turnkey filling solutions, designed t...

In-line filling system for various container sizes
Streamline your production with versatile in-line filling solutions th...
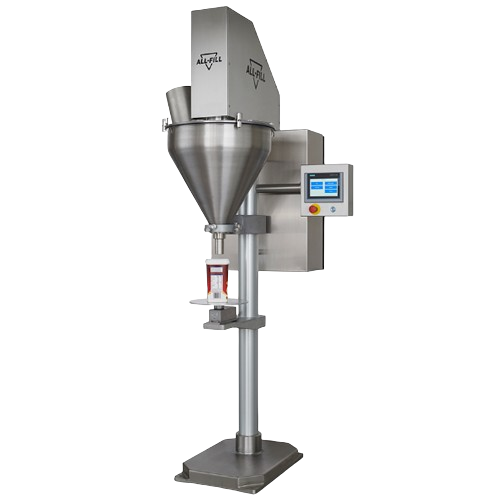
Gravimetric filling solution for inconsistent density products
Achieve precise weight accuracy in your filling processes...
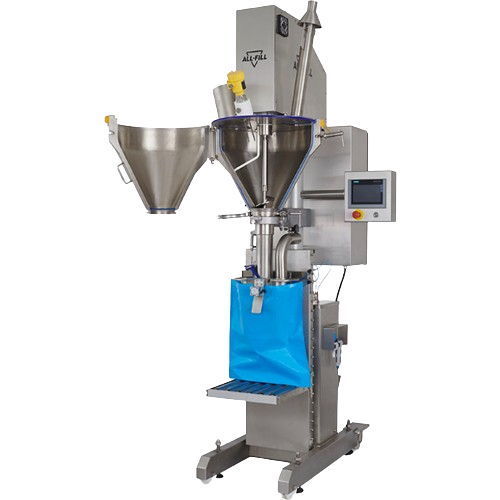
Industrial auger sack filler for large bags
Designed to efficiently fill large bags and sacks, this advanced filling machi...
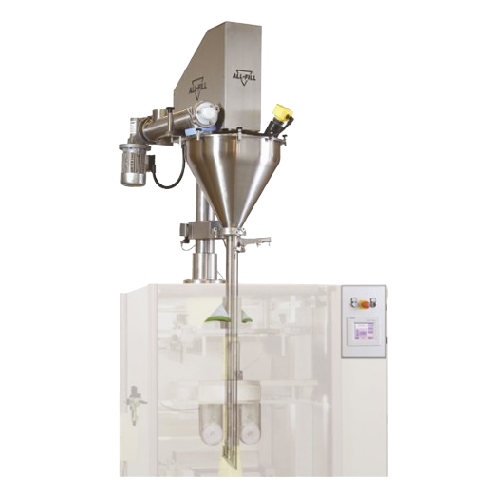
Vertical form fill seal filling system for auger applications
Effortlessly integrate precise powder and granule filling ...
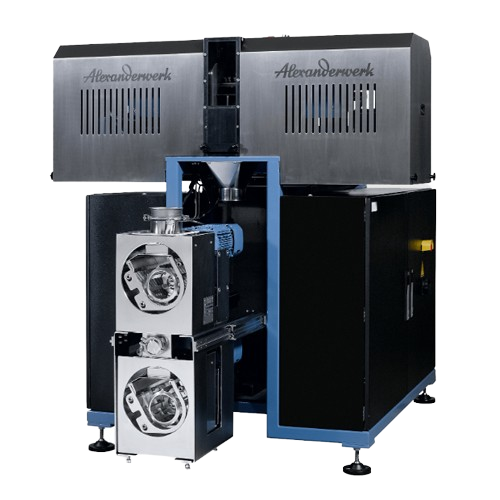
Industrial roller compaction for chemical applications
Enhance material flow and density with advanced roller compaction ...
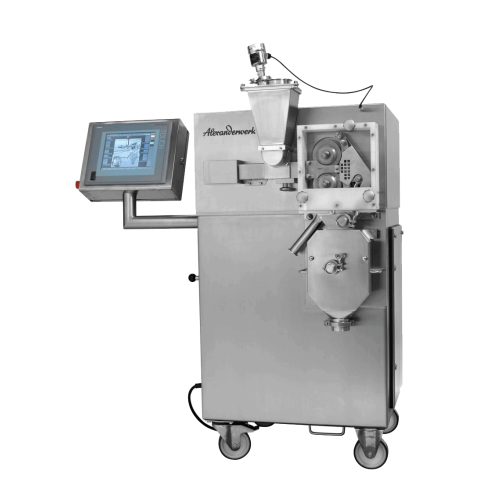
Pharmaceutical roller compactor
Achieve consistent granulate quality with optimized compacting processes, ideal for transfor...
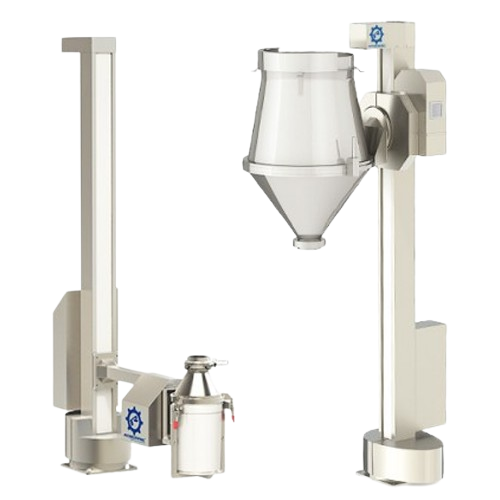
Lifting column for drums and bins
Optimize your powder handling operations with a versatile lifting solution designed for p...
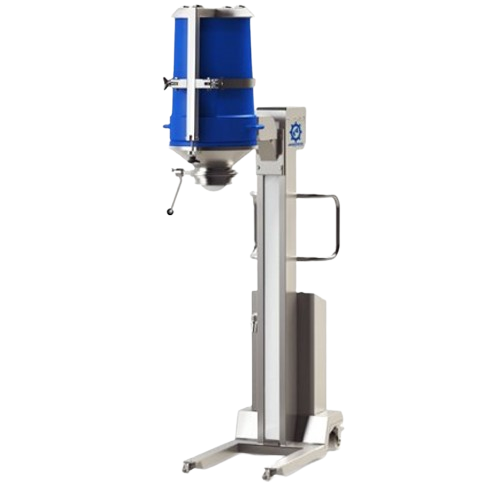
Mobile lifting column for drum handling
Streamline your powder and drum handling operations with this versatile mobile lift...
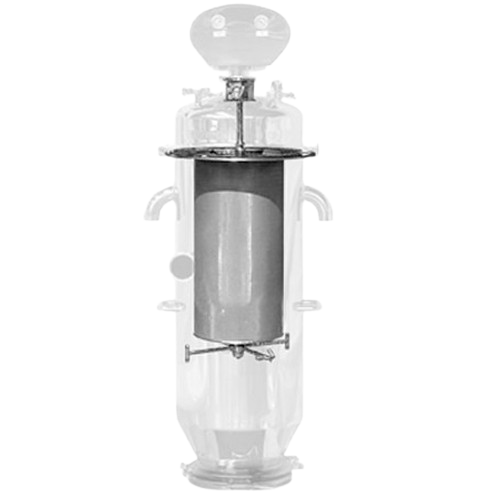
Vacuum transfer system with integrated cleaning
Ensure sterile powder handling and contamination-free production with vacu...
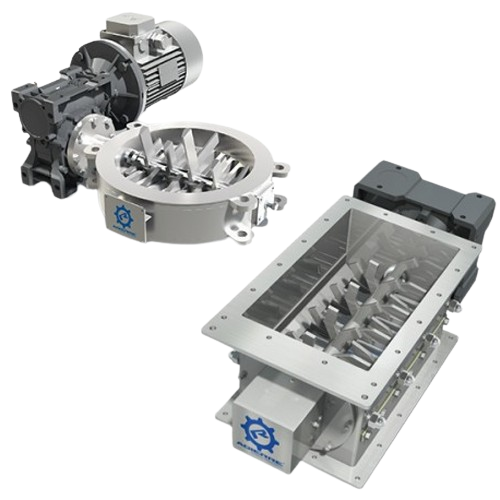
Hygroscopic material lump breaker
Ensure seamless processing by breaking down compacted or hygroscopic powders efficiently,...
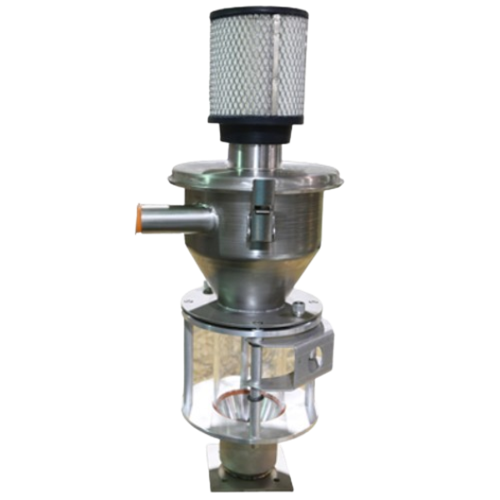
Compressed air loaders for material conveying
Efficiently convey diverse materials with minimal operator intervention, usi...
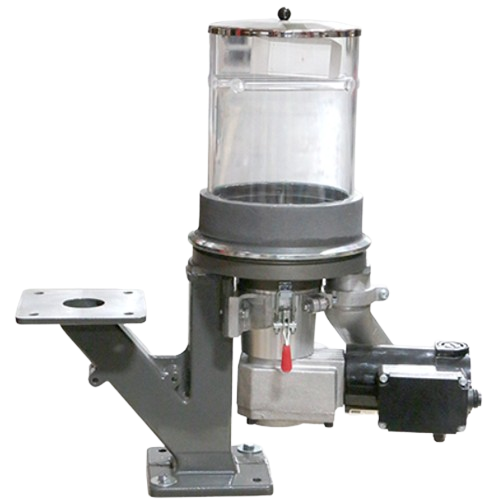
Digital doser system for plastics additive feeding
Achieve precise additive dosing for plastics, ensuring consistent qual...

High-precision analytical balance for laboratory use
Achieve precise measurements and ensure reliability in your laborato...
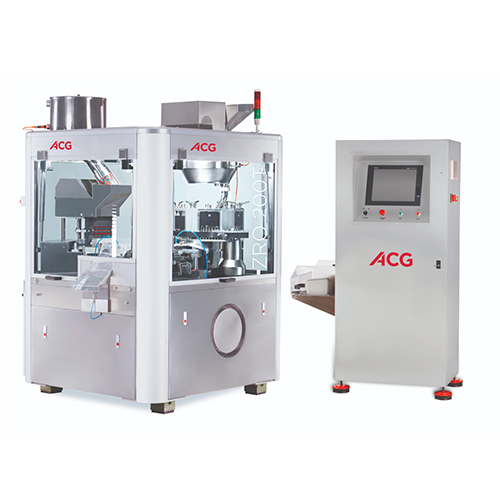
High-speed capsule filler for large batch production
Achieve higher yields and reduce powder waste with a capsule filling...
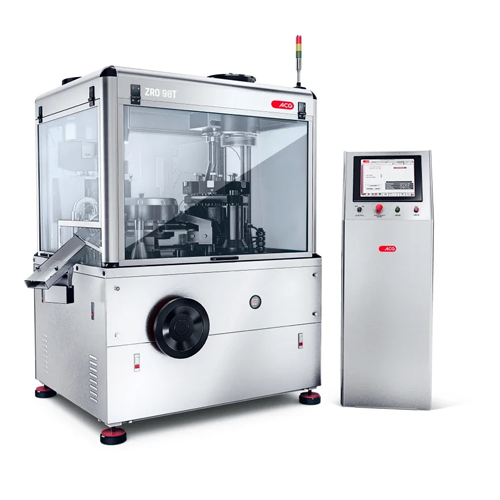
Capsule filler for high-speed, dust-free capsule production
Enhance your production efficiency with a solution designed ...
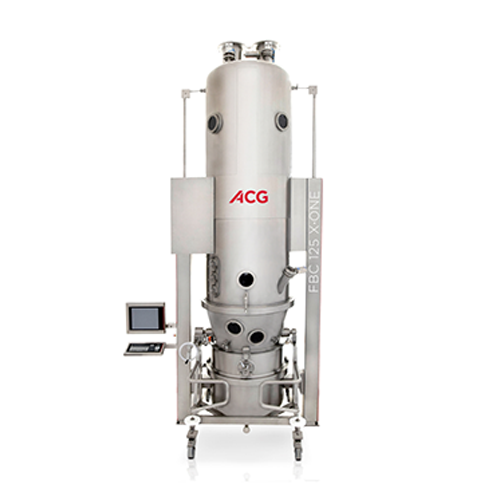
Fluid bed dryer with granulation and coating
Enhance your processing efficiency with a versatile system capable of combini...
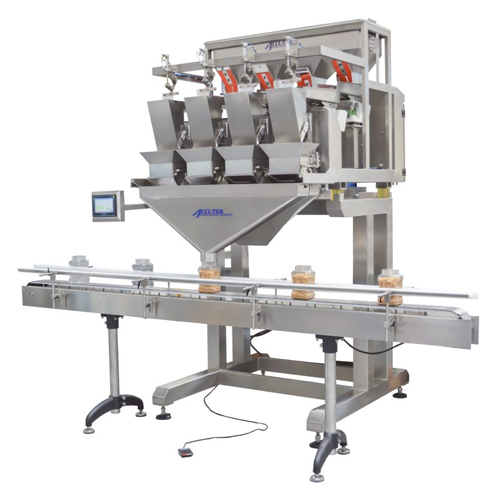
Automatic granular product weighing system
Effortlessly achieve precise fills for dry granular products and powders while ...

Desiccant inserter for pharmaceutical containers
Prevent product degradation by efficiently inserting desiccants into cont...
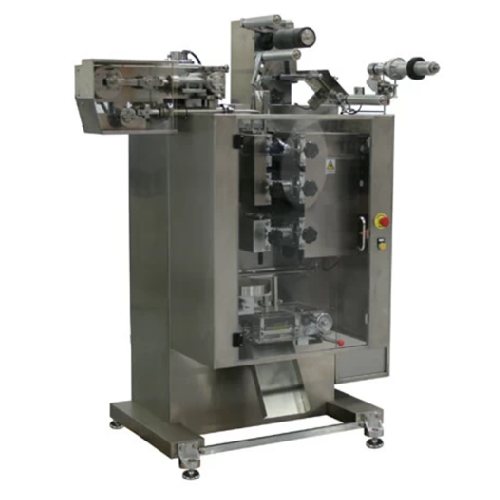
Form, fill, and seal system for single-use pouches
Achieve precise portion control and secure sealing with an integrated ...
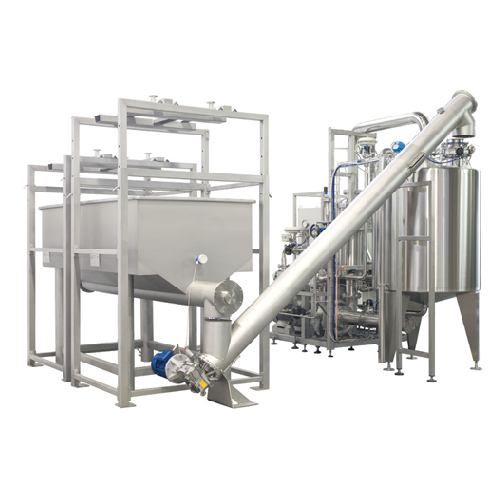
Granulated sugar storage and conveyance solutions
Optimize your sugar processing with versatile solutions for storage, pr...
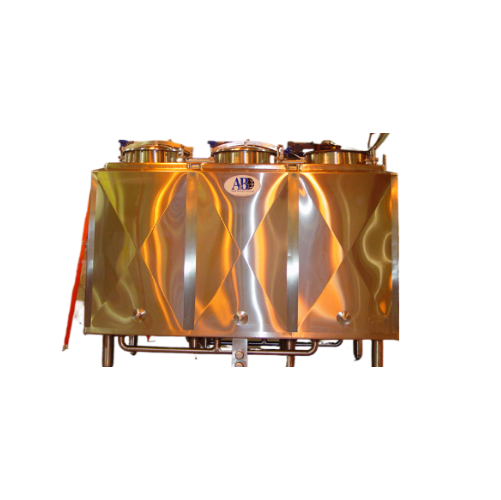
Flavor vats for ice cream and food production
Maximize your product line versatility with customizable flavor vats, design...
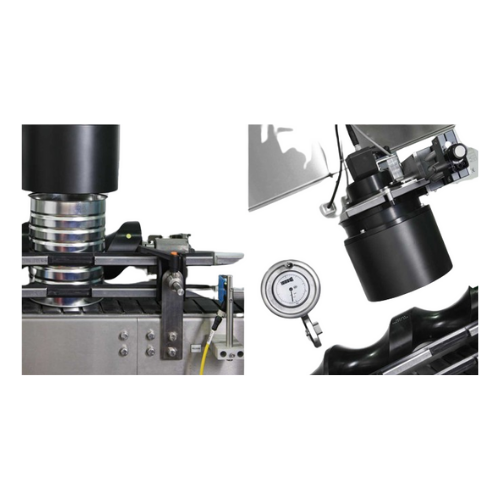
Container inspection and particulate detection system
Ensure product integrity and efficiency by accurately detecting and...
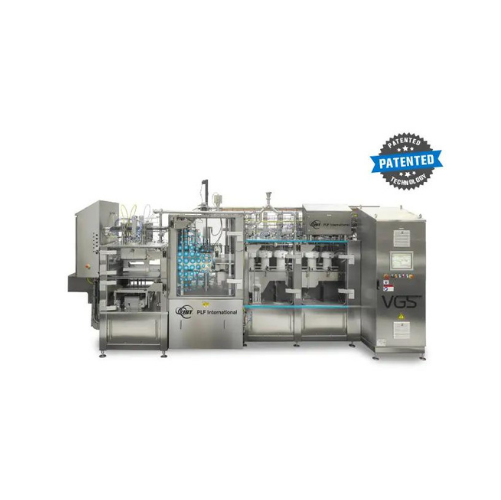
Vacuum gassing seamer for infant formula packaging
Ensure low residual oxygen levels in your powdered products with a spe...
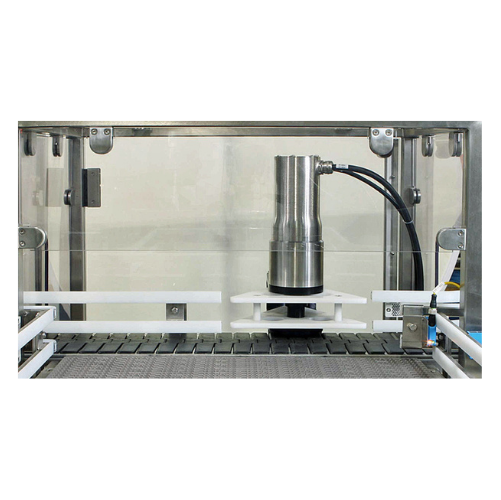
High-speed container reject system
Ensure product integrity by swiftly rejecting non-compliant containers at speeds up to 3...
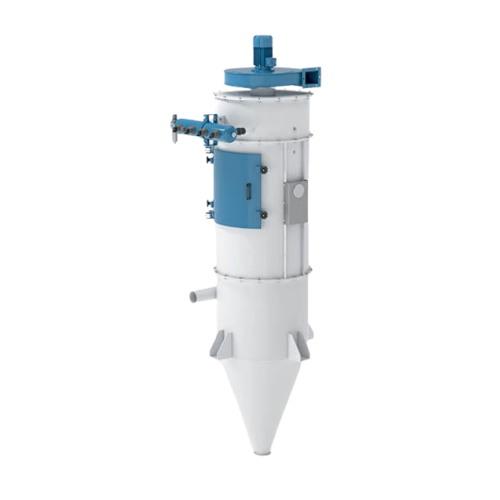
Cyclone filter for pneumatic conveying systems
Efficiently separate and filter airborne dust in pneumatic conveying lines,...
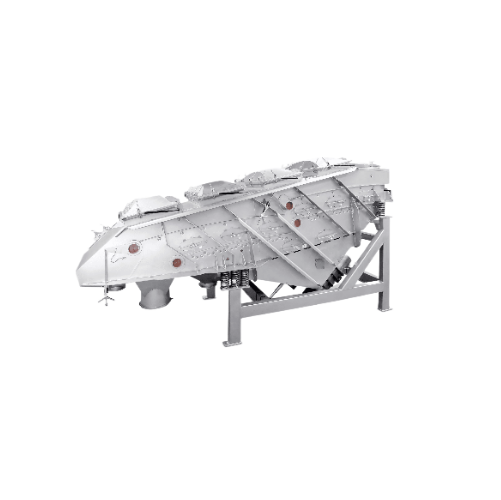
Vibrating sifter for chemical applications
Achieve precise particle separation with this vibrating sifter, ensuring optima...
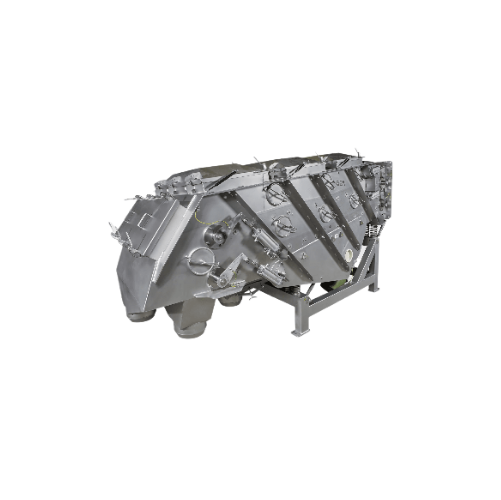
Sifter for pet food, fish feed, and animal feed
Achieve precise particle separation and enhance feed quality with this vib...
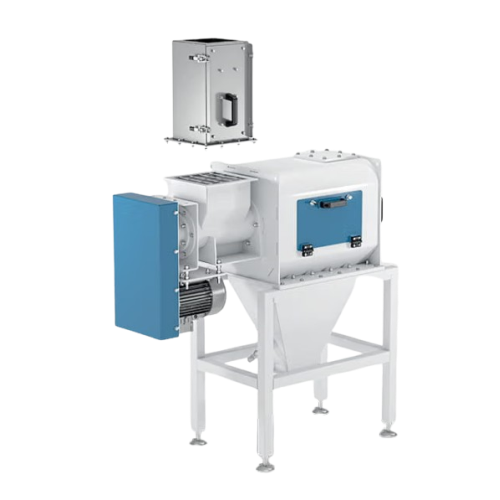
Rotary cleaner for raw material sieving
Ensure precise raw material quality with a rotary cleaner that efficiently sieves a...
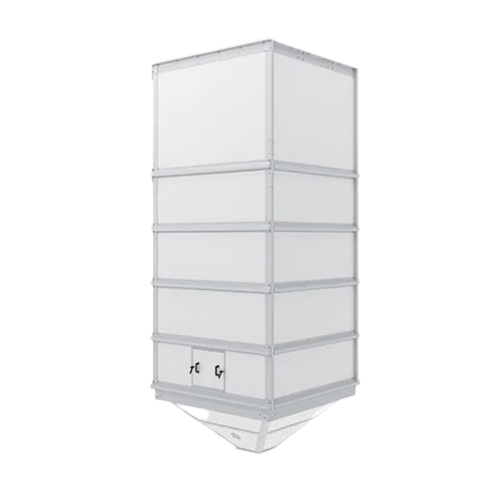
Finished product storage silos for industrial applications
Optimize your storage capabilities with silos that ensure saf...
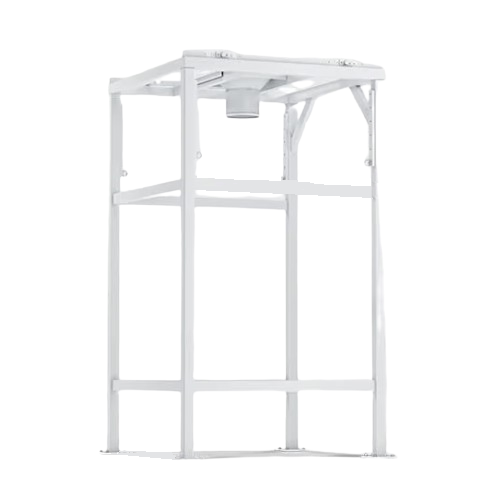
Big bag loading station for bulk product handling
Efficiently manage big bag handling with a system that combines hoistin...
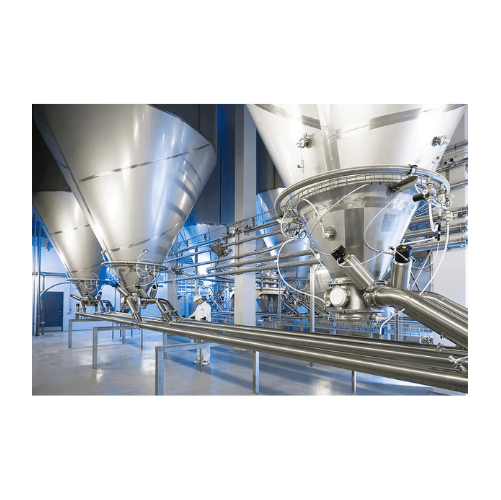
Bulk storage silos for food products
Ensure optimal powder storage and handling with versatile silos designed for efficient...
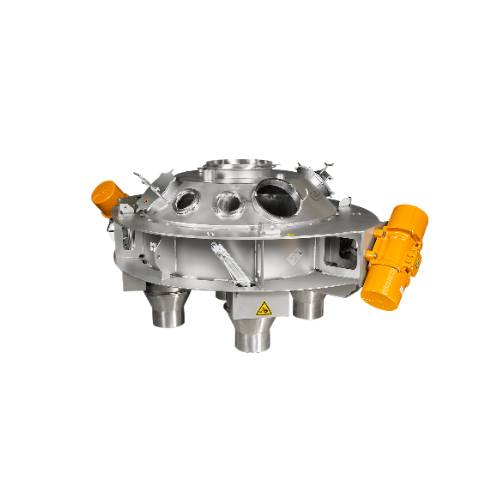
Circular distribution feeder for fragile product handling
Achieve precise dosing and reduced product damage with a versa...
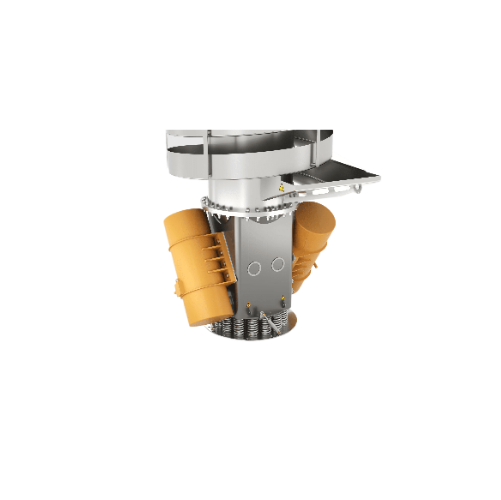
Vibratory spiral elevator for vertical transport
Achieve efficient vertical transport with precise temperature control, su...
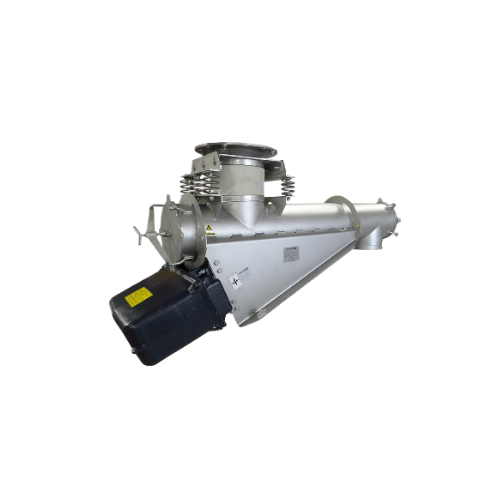
Vibrating feeder for food and pharmaceutical industries
Optimize your production line with precision dosing and gentle ma...
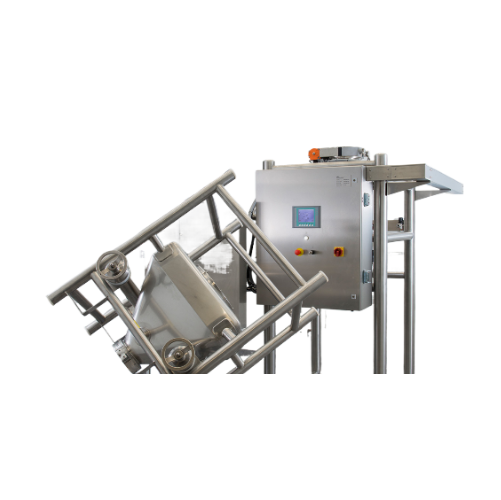
Intermediate bulk container (ibc) blending for pharmaceutical manufacturing
Streamline your pharmaceutical blending pr...
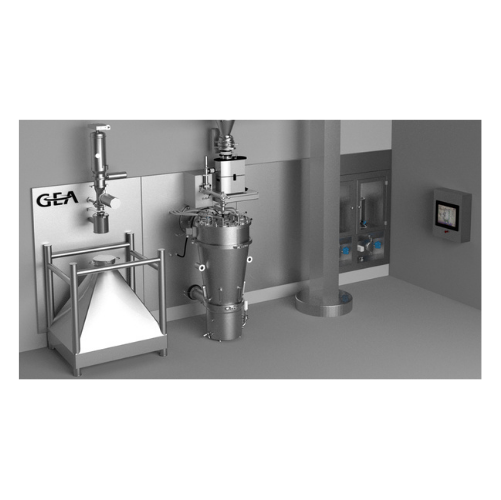
Continuous granulation and drying system for pharma production
Achieve precise control over granule quality with a conti...
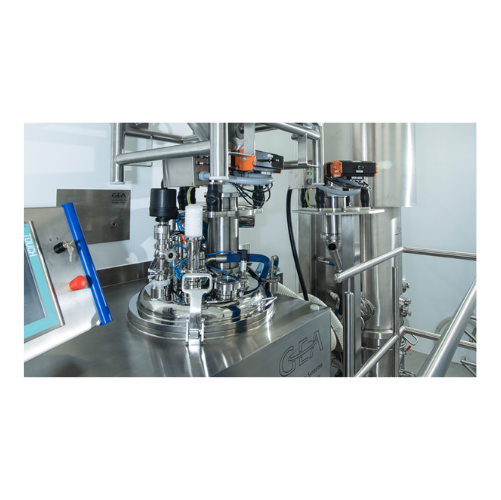
Pharmaceutical bottom-drive high shear granulator
Achieve optimal granule uniformity and precise control over moisture le...
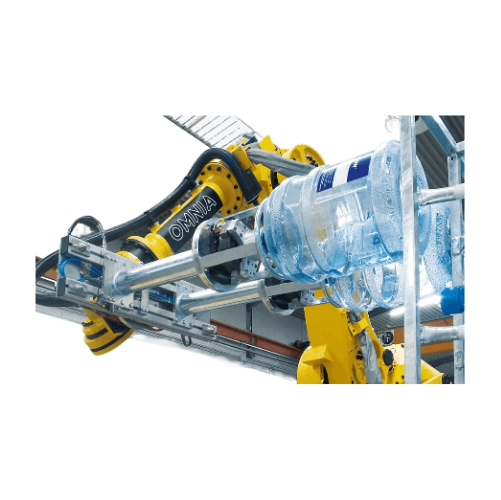
Robotic palletizer for food and beverage industries
Enhance your production line’s efficiency with a flexible robot...
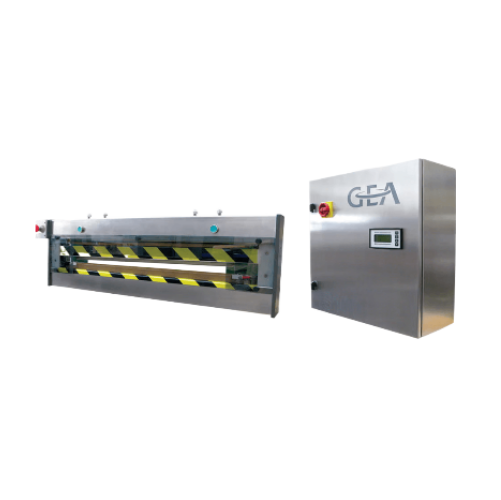
Plastic bag sealer for polyethylene bags
Achieve consistent hermetic sealing of polyethylene bags while preserving the inte...
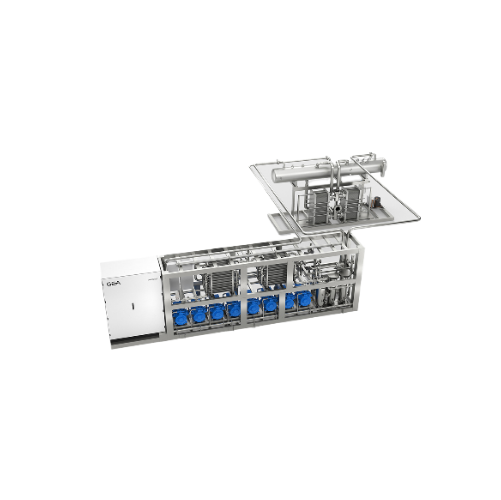
Heat pump solution for spray dryers
Enhance your spray drying efficiency and sustainability with an innovative heat pump sy...
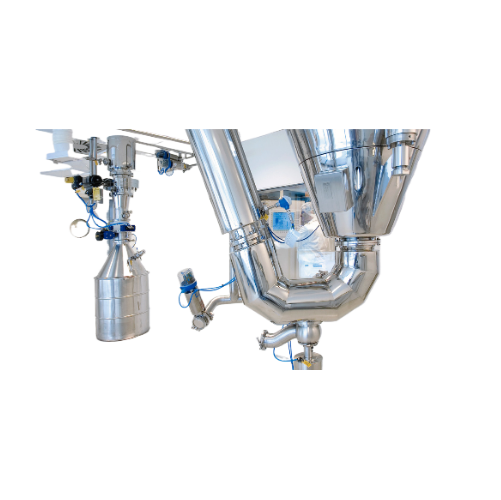
Pharmaceutical spray dryer
Unlock the potential of spray drying to enhance bioavailability, achieve controlled release, and ...
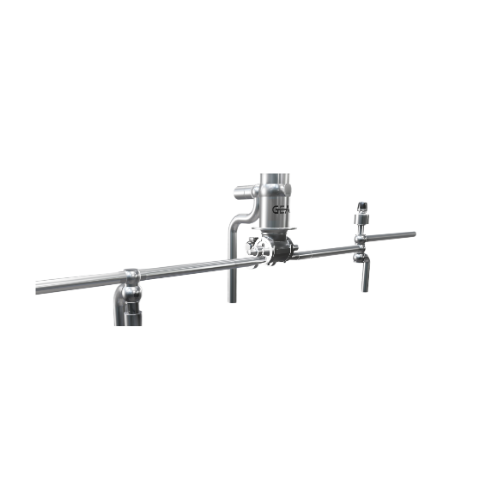
Automated fines return system for food and dairy spray dryers
Enhance your spray drying process by eliminating manual in...
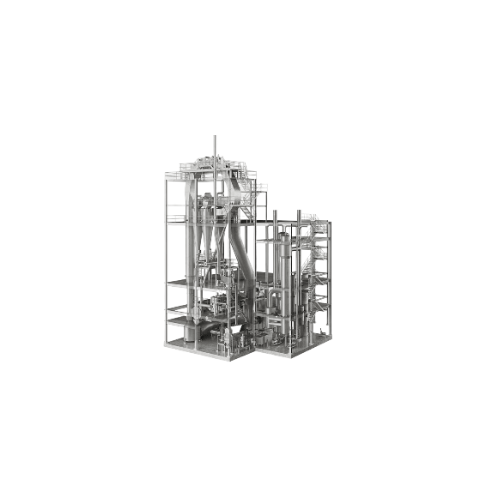
Feed-type ring dryer for industrial drying processes
Optimize your production with a versatile drying solution designed f...
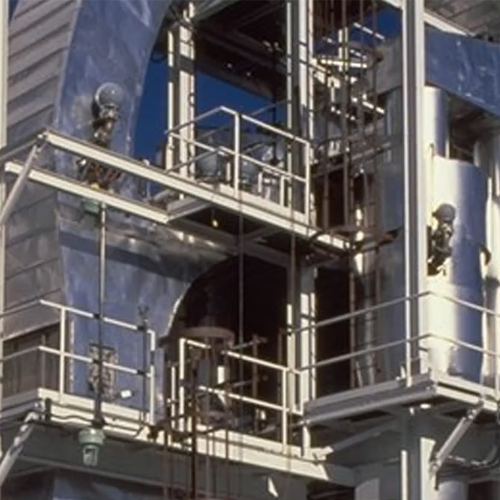
P-type ring dryer for thermally sensitive products
Optimize moisture control and prevent thermal degradation in your prod...
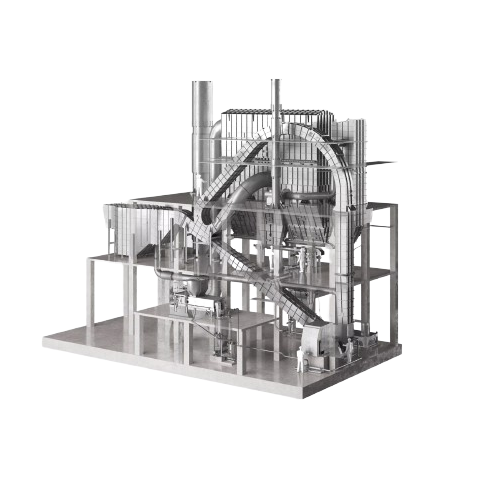
Industrial ring dryer for efficient particle processing
Control particle size and drying efficiency with precise recircul...
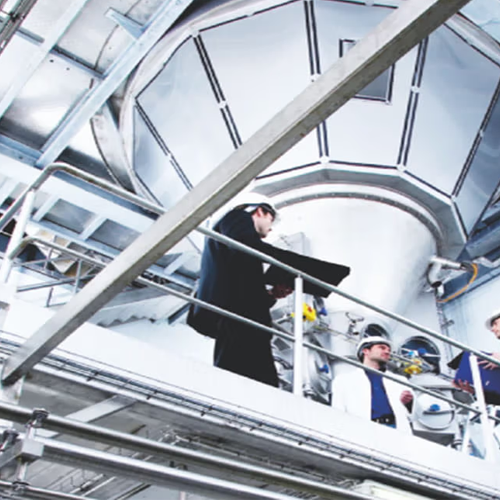
Conventional spray drying for chemical industry
Achieve optimal particle size uniformity in food powders with precision at...
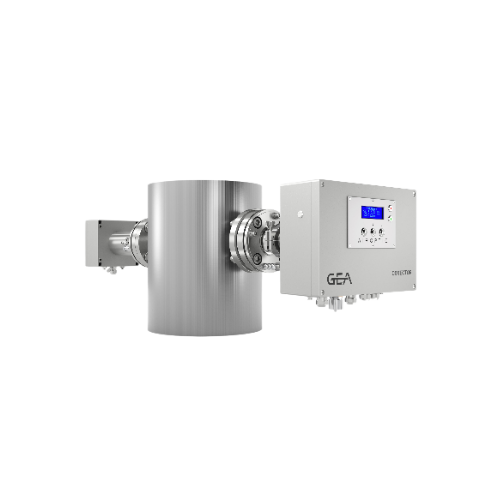
Co monitoring system for spray dryers
Ensure safety and prevent costly disruptions in your spray drying process by monitori...
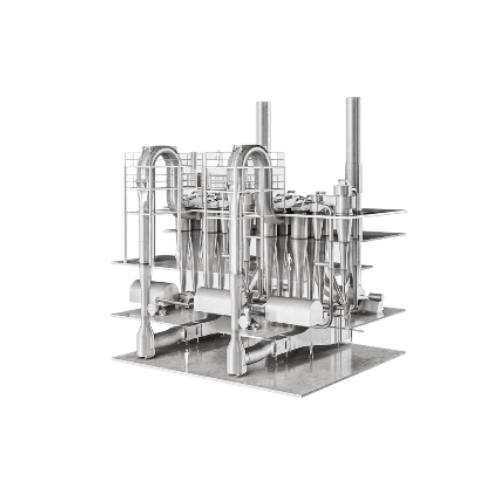
Flash dryer for industrial moisture removal
Optimize your production with rapid moisture removal, efficiently transforming...
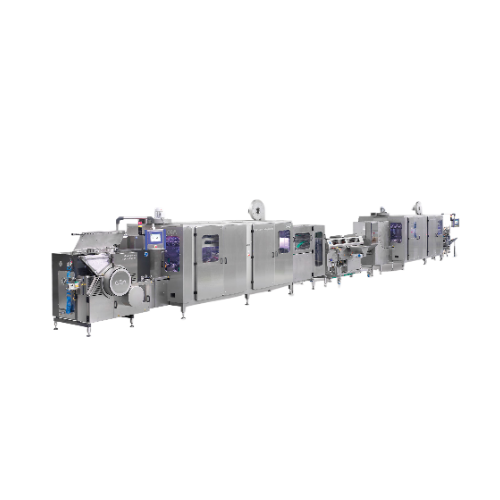
Coated lollipop production line
Transform your confectionery line with a solution that forms, cools, and coats 3D lollipops ...
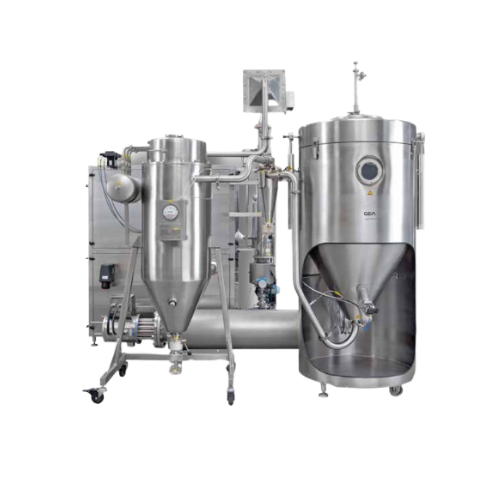
Spray dryer for food and dairy products
Achieve consistent drying for diverse powders and granulates with precision technol...
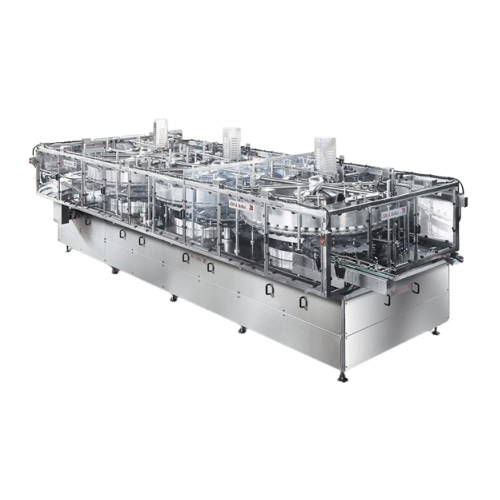
Fillers for solid products
Optimize your production line with versatile fillers that ensure precise handling and packaging o...
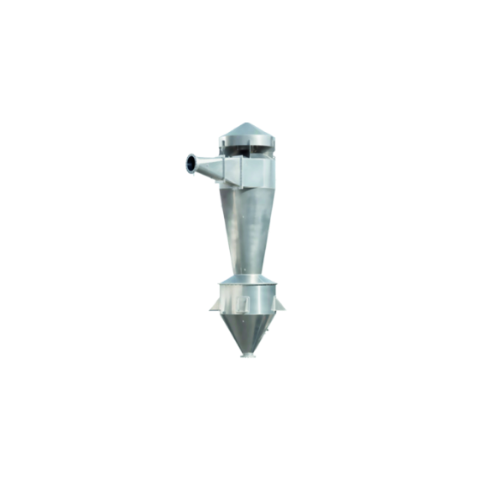
Cyclone separator for pneumatic conveyor systems
Enhance efficiency in pneumatic conveyor systems by effectively separatin...
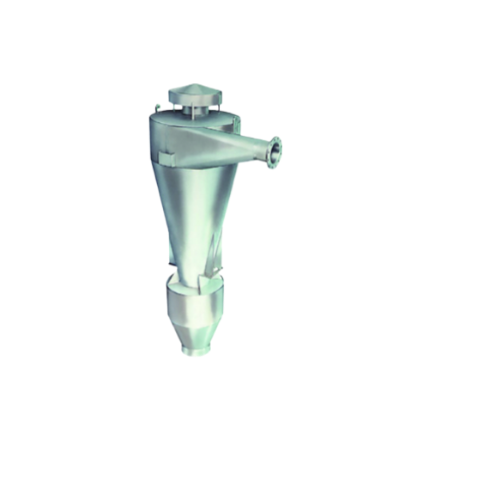
Cyclone separator for industrial dust separation
Optimize your dust separation process with this cyclone separator, design...
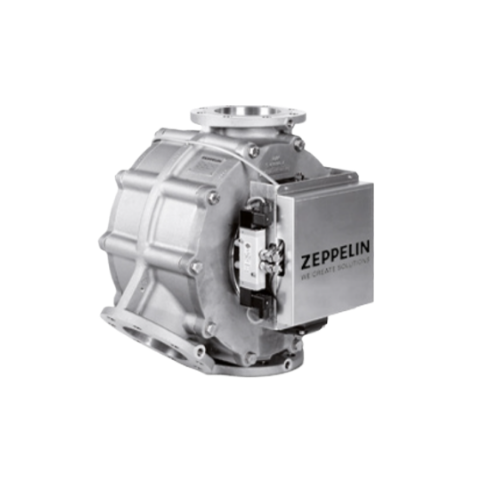
Pneumatic conveying diverter valve for abrasive bulk materials
Streamline the flow of abrasive materials in your pneumat...
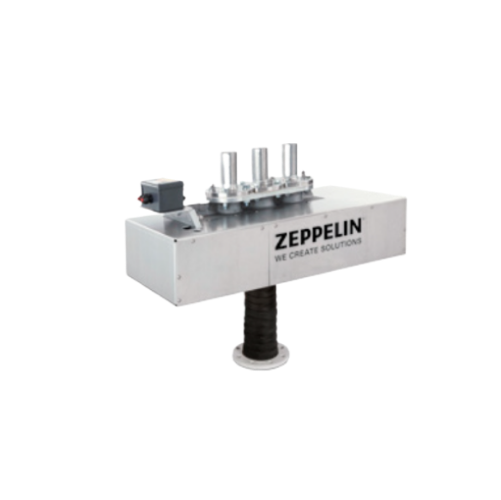
Industrial diverter valve for pneumatic conveying systems
Optimize your pneumatic conveying system with a versatile two-...
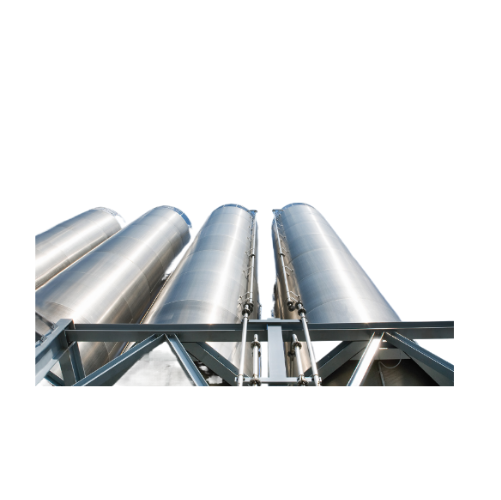
Short base skirt silo for bulk material storage
Optimize your bulk material handling with adaptable discharge and rapid lo...
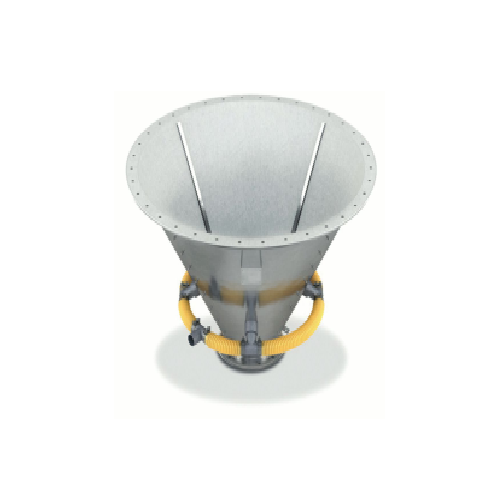
Automated material flow system for starch processing
Streamline the handling of powdered starches with precise dosing, mi...
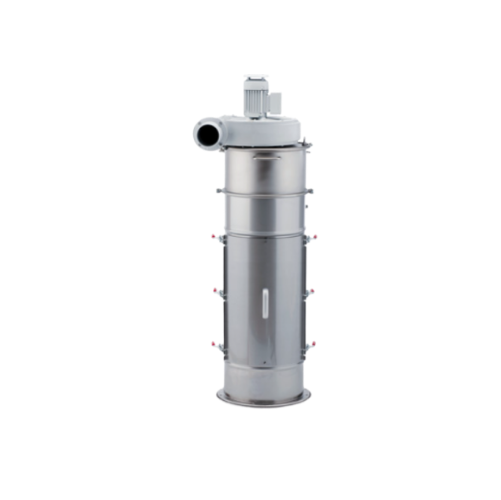
Industrial fine dust particle ventilation filter
Optimize your production line with a modular filtration system designed t...
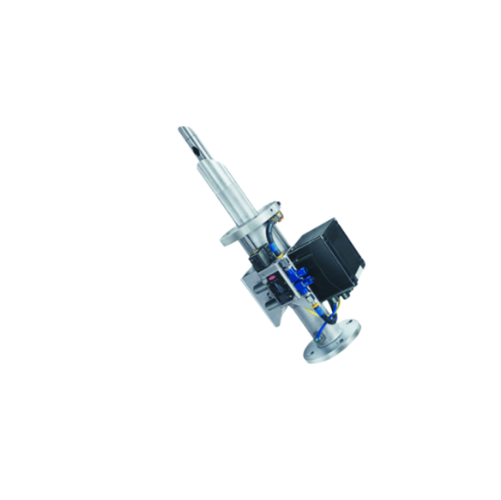
Sampler for free-flowing granular bulk materials
Efficient and precise sampling of granular bulk materials and coarse powd...
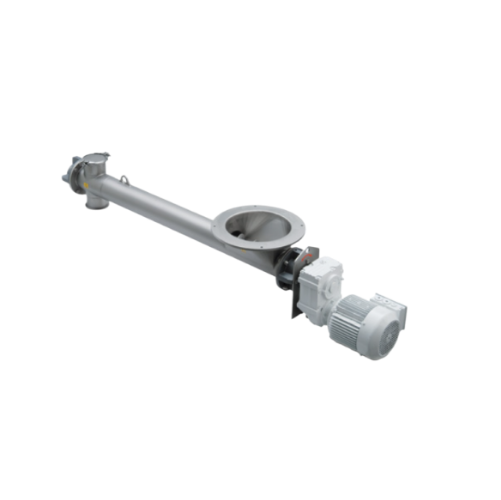
Dosing and conveying screw for dry bulk materials
Efficiently manage the precise dosing and conveying of dry, powder, and...
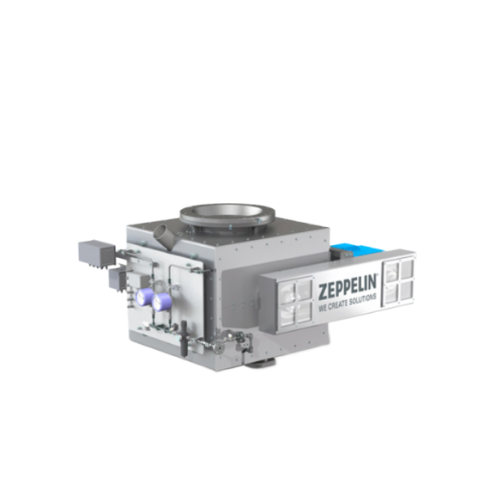
High-pressure rotary feeder for bulk material handling
Manage high-pressure bulk material distribution with precision, en...
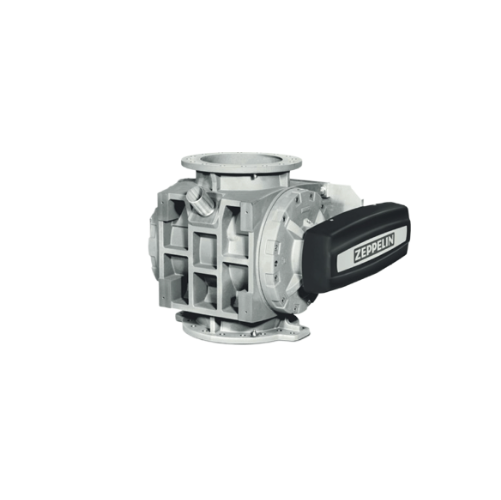
Rotary feeder for bulk material conveying
Enhance your material flow with precise metering and efficient conveying, ensuri...
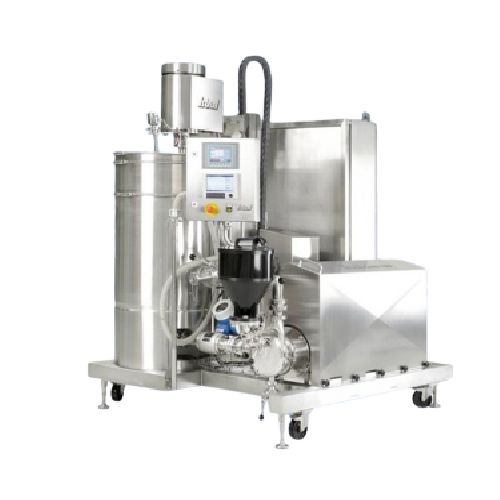
Inline disperser for food production
Quickly achieve stable, agglomerate-free dispersions and emulsions with minimal manual...
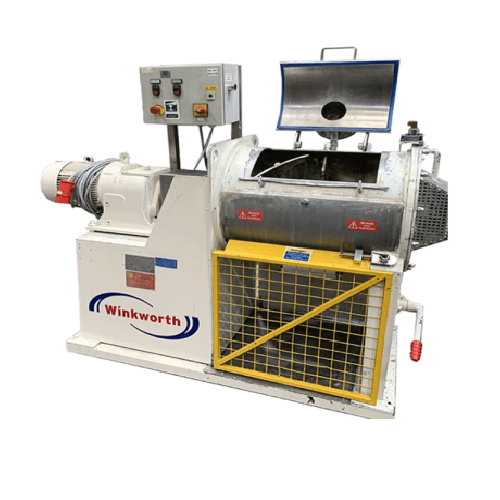
Industrial rapid turbulent mixer for homogeneous mixing
Achieve unparalleled homogeneity with rapid turbulent mixing, ess...
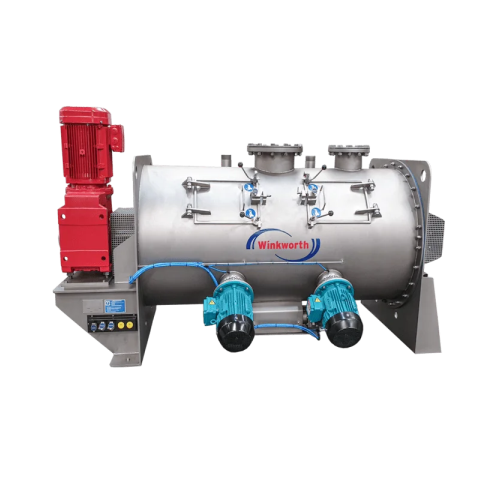
High-speed mixer for industrial mixing applications
Achieve rapid, consistent mixing and dispersion across diverse materi...
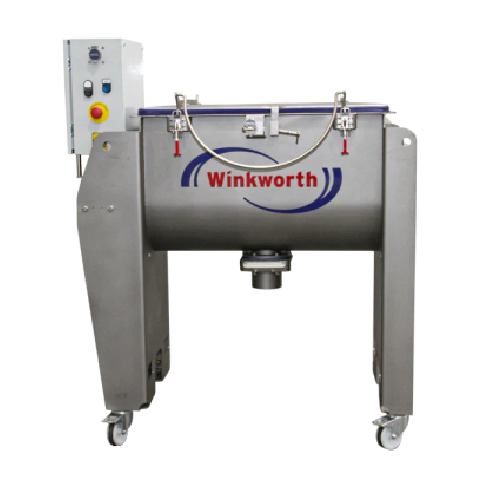
Horizontal shaft mixer for free-flowing materials
Achieve consistent mixing of diverse free-flowing materials with a reli...
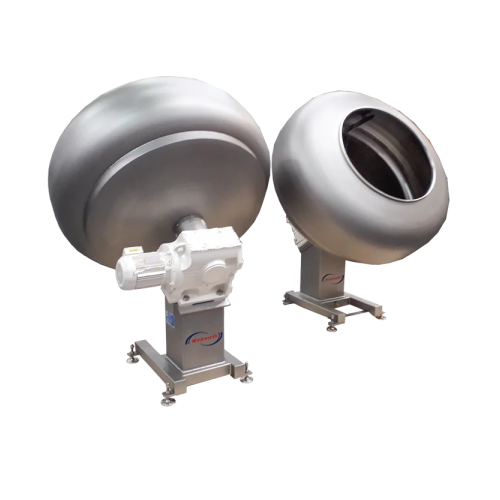
Industrial coating pans for sweets and confectionery
Ensure even and consistent coatings with high-capacity pans designed...
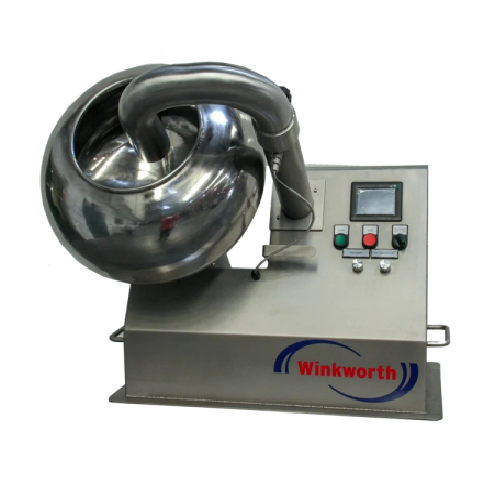
Industrial coating pan for food and pharmaceutical products
Optimize your production with precision mixing and coating, ...
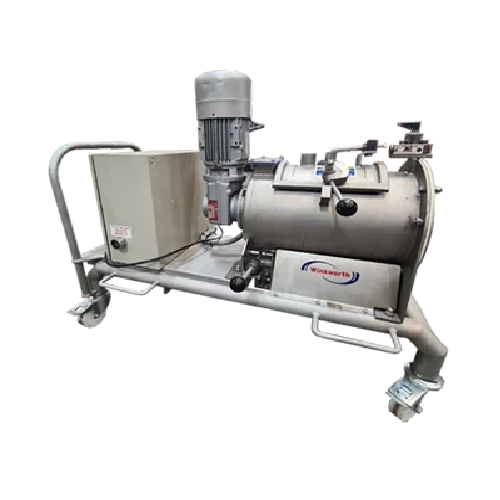
Industrial mixers for hire
Optimize your production line with versatile mixers designed for precision blending, heating, and...
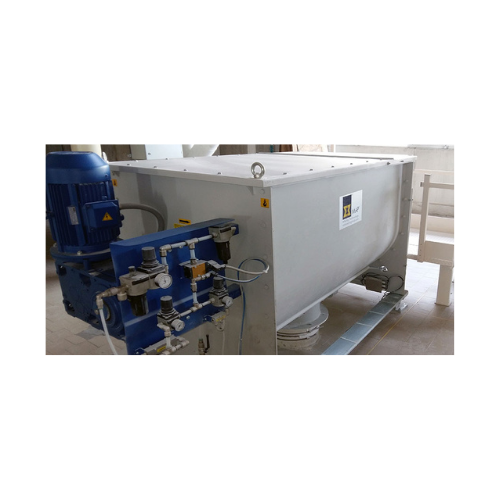
Single-shaft ribbon blender for homogeneous mixing
Achieve high-quality, precise blending of delicate and temperature-sen...
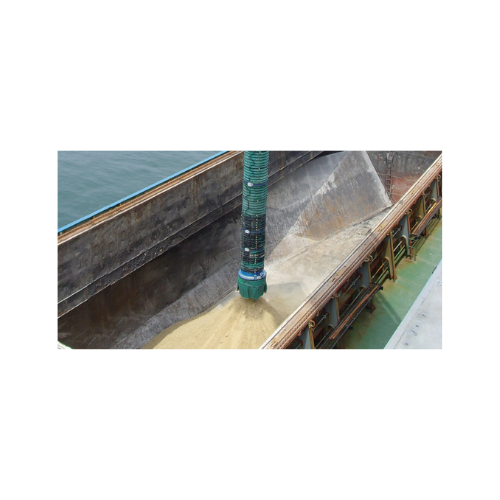
Telescopic loading bellows for bulk solids
Streamline your bulk material operations with high-capacity, dust-free loading ...
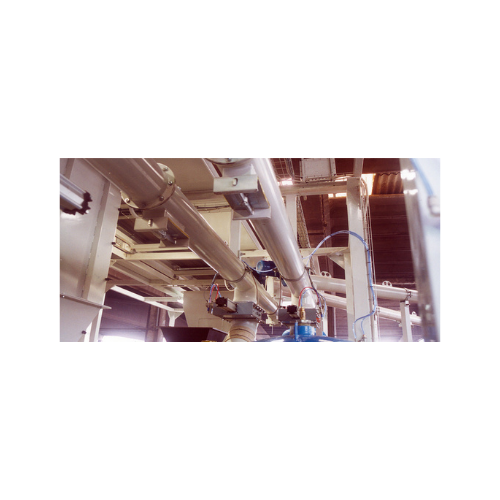
Bulk solids conveying systems
Efficiently move and manage bulk materials with precision and reliability, ensuring seamless i...
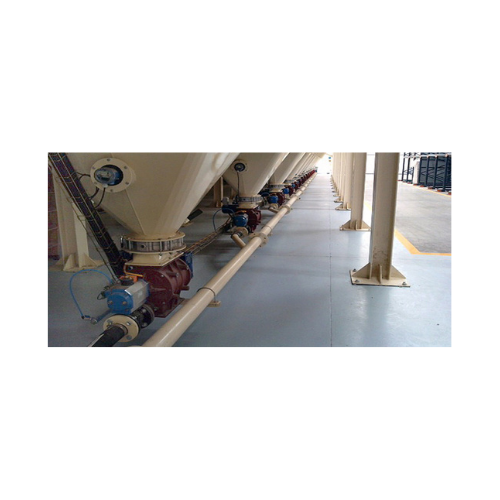
Pneumatic conveying system for bulk solids
Ensure efficient and dust-free transport of bulk materials with a pneumatic con...
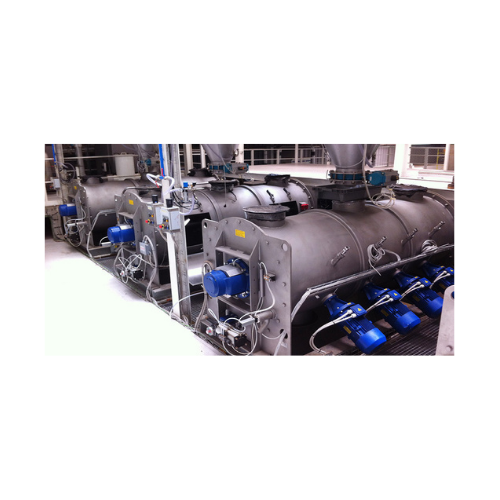
Batch-type single shaft mixer for industrial mixing
Achieve precise and uniform mixing with high-speed, single-shaft mixe...
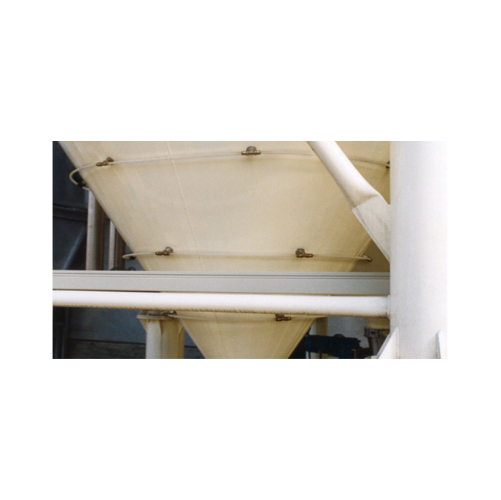
Aerator nozzles for material flow in silos and bins
Ensure optimal material flow from silos and bins with compact aerator...
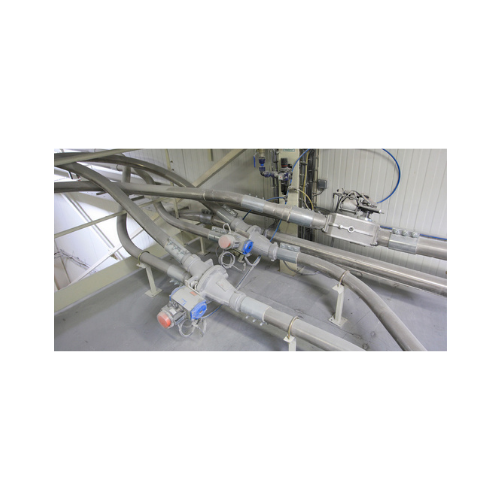
Flap diverter valves for pneumatic conveying
Streamline material flow in your pneumatic conveying system by effortlessly r...
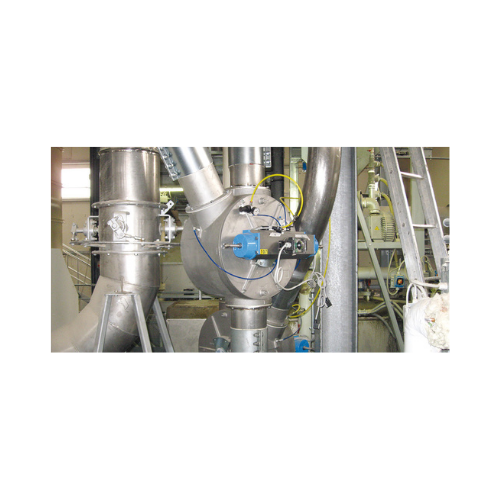
Drum-type diverter valves for pneumatic conveying
Optimize your pneumatic conveying system by effortlessly controlling th...
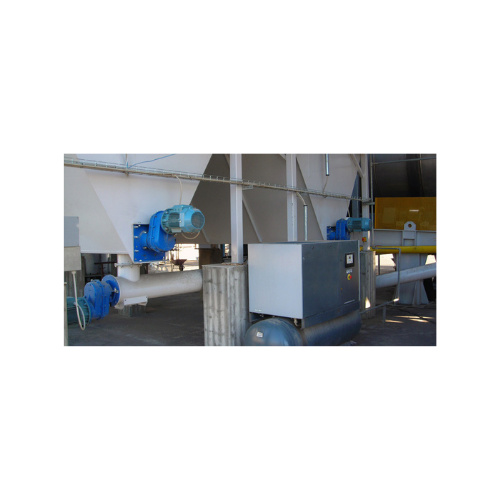
Filler dust feeder for asphalt plants
Ensure consistent asphalt mixture quality by efficiently feeding and conveying hot an...
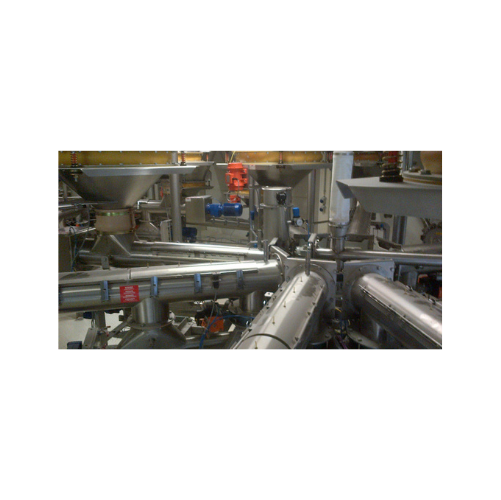
Stainless steel tubular screw conveyor for bulk solids handling
Ensure precise material handling with stainless steel tu...
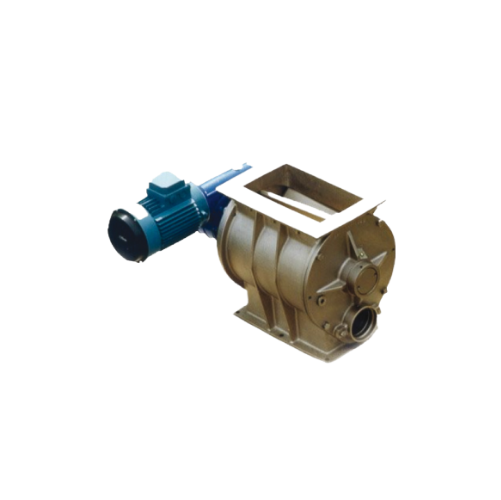
Blow-through rotary valves for pneumatic conveying
Optimize your pneumatic conveying systems with high-efficiency blow-th...
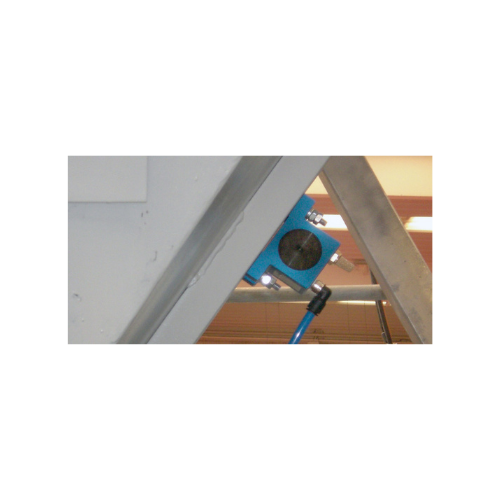
Rotary ball vibrators for aggregate reclaiming
Enhance efficiency in your production line with a solution that optimizes t...
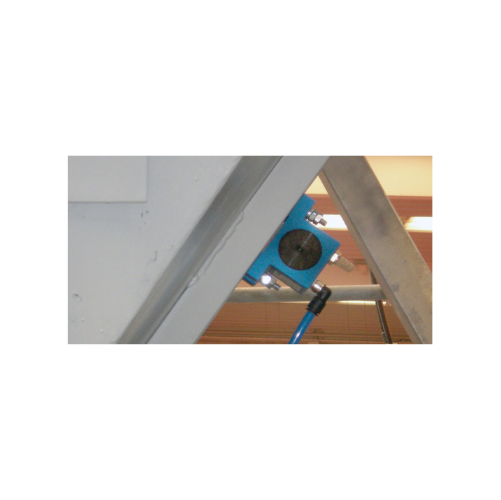
Rotary ball vibrators for bulk solids discharging
Ideal for enhancing material flow, this equipment efficiently handles f...
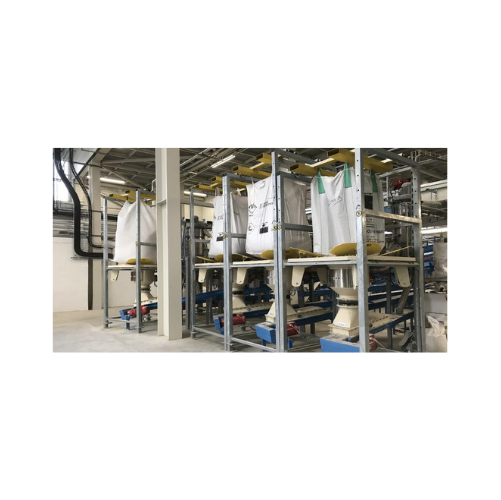
High flow rate Fibc discharger
Optimize your bulk material handling with a system designed for efficient and dust-free FIBC ...
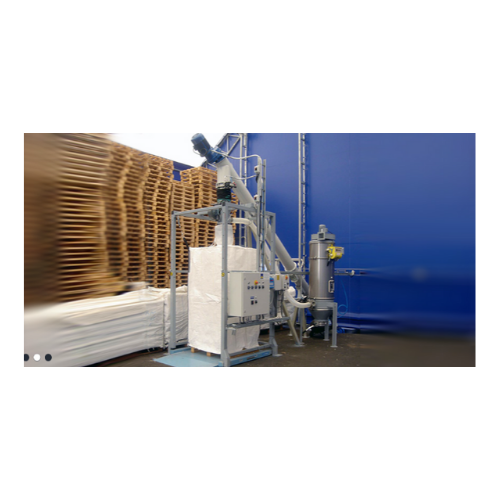
Dust-free bulk bag filling system
Achieve efficient, dust-free filling of bulk bags with our innovative system, ensuring se...
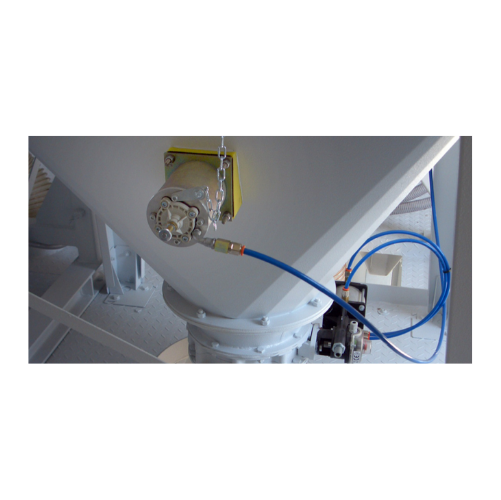
Hammer blaster for bridging and ratholing prevention
Eliminate material blockages with a dual-action system designed to p...
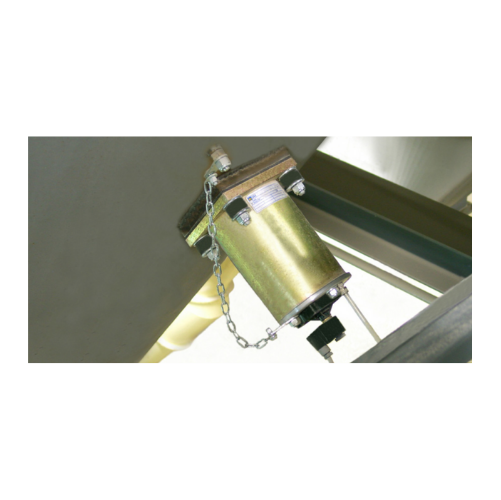
Pneumatic hammers for bulk solids discharging
Optimize your production efficiency and solve material flow challenges with ...

Pneumatic hammers for aiding material flow
Optimize material flow and eliminate blockages in your processing line with pne...
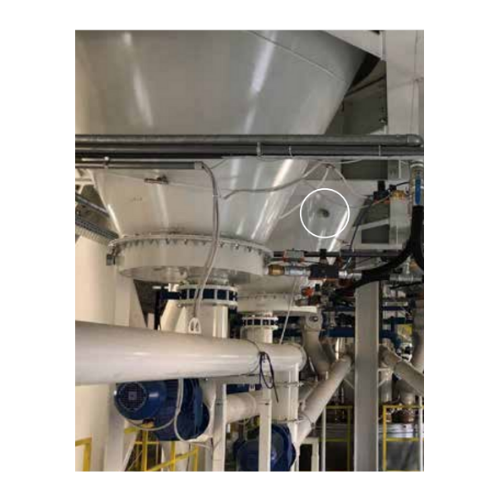
Continuous impact vibrators for bulk material removal
Combat material flow issues like bridging and rat-holing with our i...
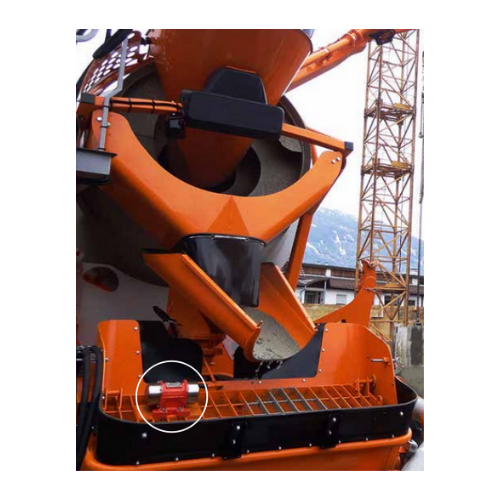
Continuous impact vibrator for aggregate reclaiming
Tackle material flow challenges head-on by preventing common issues l...
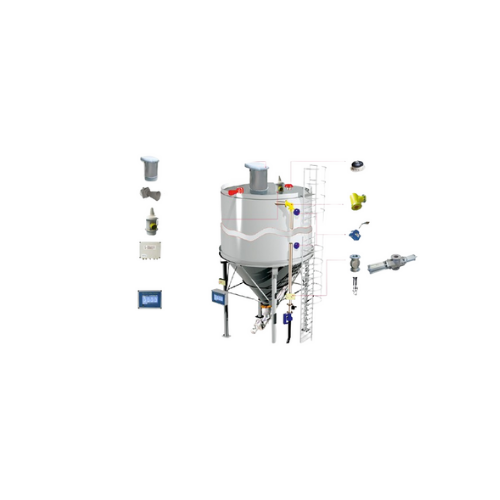
Silo overfill protection system
Prevent silo overfilling and excess pressurization with a system designed to safeguard silos...
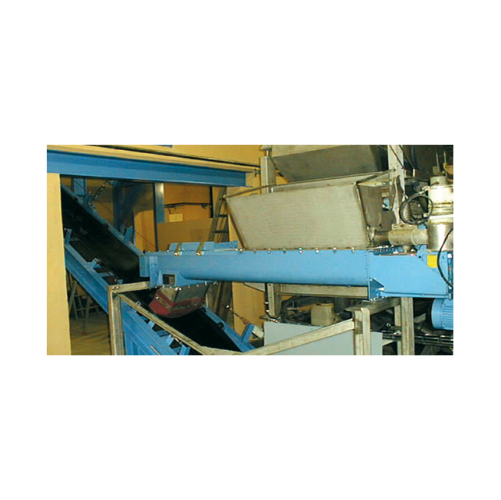
Continuous twin shaft paddle mixers for dust conditioning
Optimize your mixing process with twin shaft paddle mixers, en...
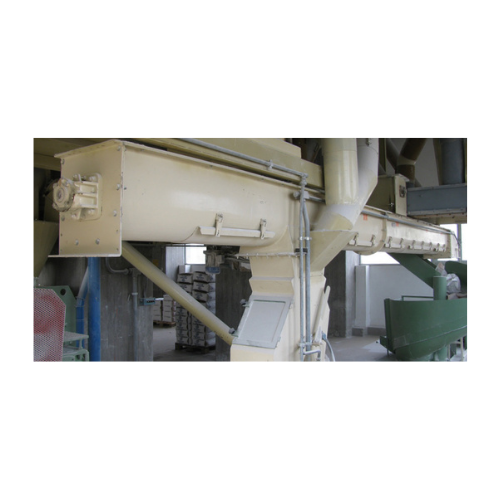
Trough screw conveyor for flour mills
Optimize your flour processing with efficient material handling, precisely designed f...
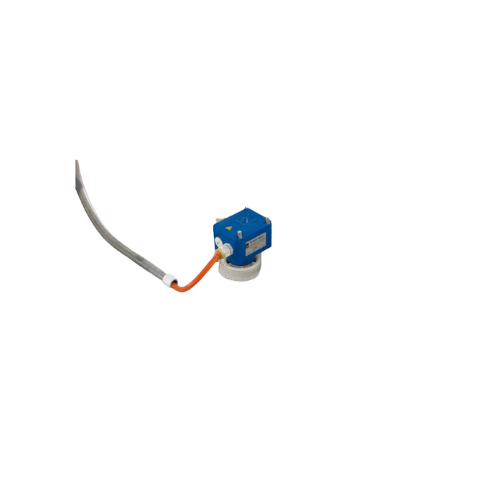
Bin level indicator for bulk solids
Ensure precise material level detection across your production processes, minimizing th...
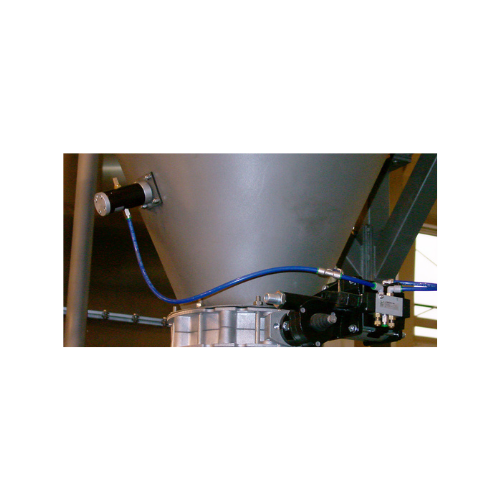
Cushioned pneumatic linear vibrators for bulk solids
Combat material bridging and rat-holing with silent vibratory techno...
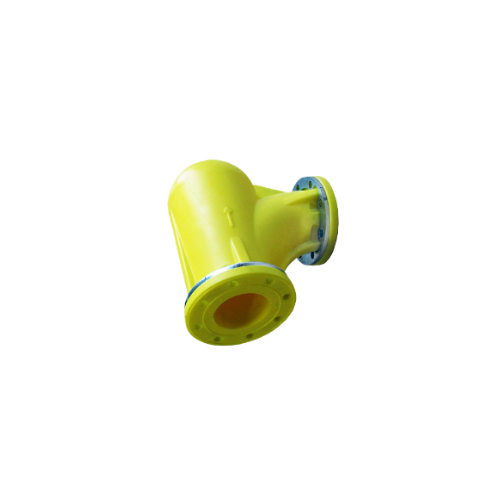
Anti-wear elbows for pneumatic conveying systems
Reduce wear and extend the lifespan of your pneumatic conveying systems w...
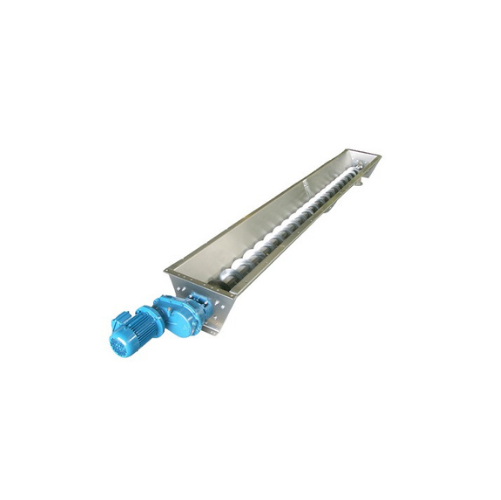
Stainless steel trough screw conveyor
Ideal for precise handling of powdery and granular materials, this solution ensures m...
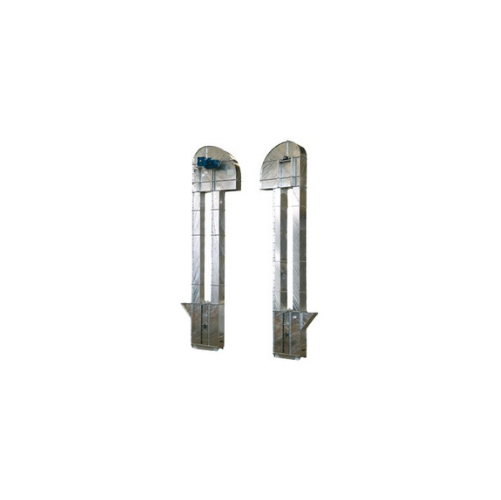
High capacity vertical conveying for flour
For consistent, high-speed handling of delicate and powdery materials, this eng...
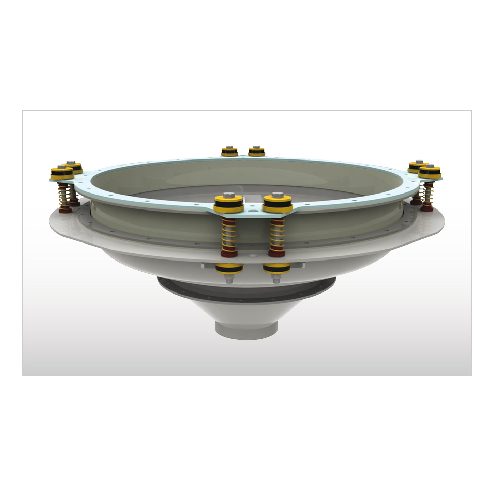
Industrial bin activator for smooth material flow
Enhance your material handling process with a solution that ensures con...
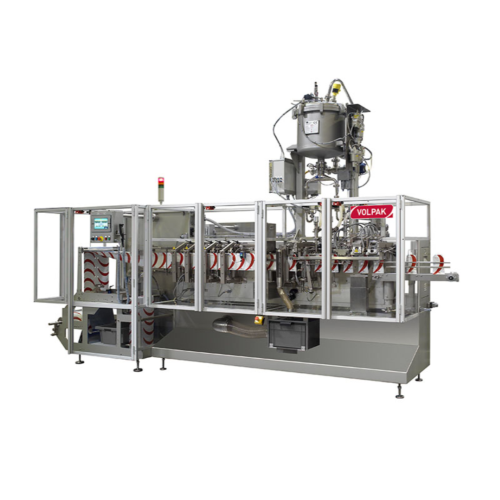
Stand-up pouch packaging for various products
For manufacturers seeking versatile packaging solutions, this machine delive...
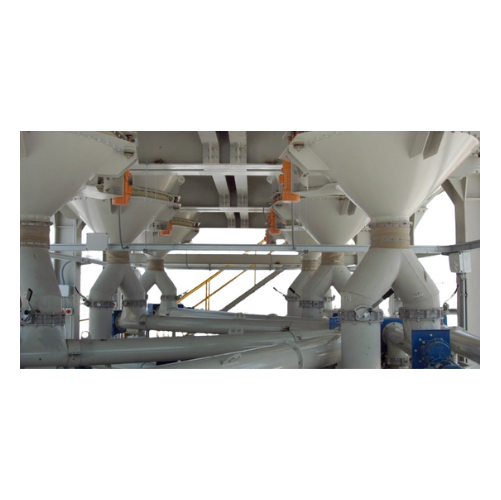
Bin activator for silo and hopper discharge
Ensure optimal material flow and prevent blockages in your storage systems wit...
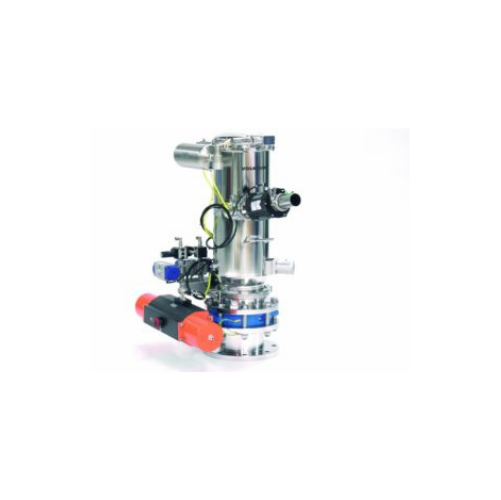
Vacuum conveyors for explosive and inert gas environments
Optimize the safe transfer of hybrid mixtures and fine powders...
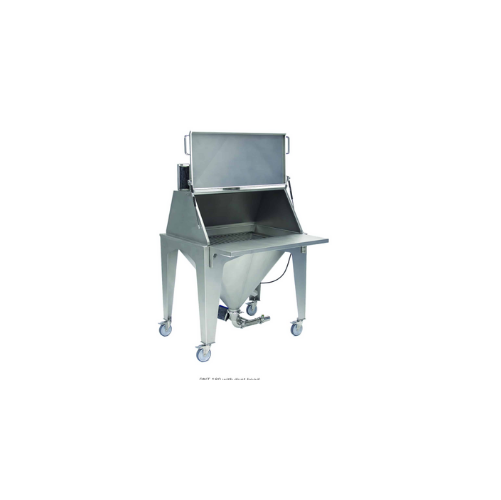
Bag rip-and-tip dump stations for bag emptying
Efficiently manage bag emptying operations with advanced dust containment a...
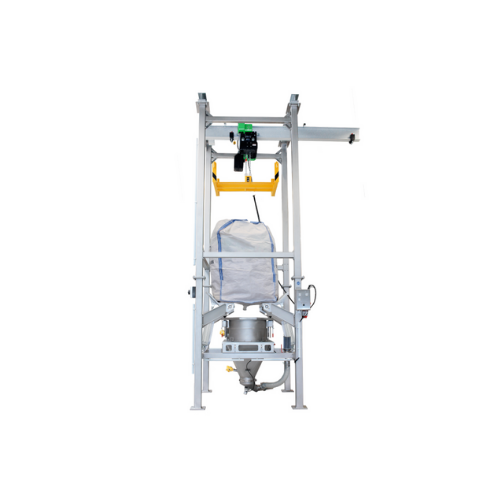
Big-bag unloading station for bulk materials
Facilitate seamless integration into your production line with efficient bulk...
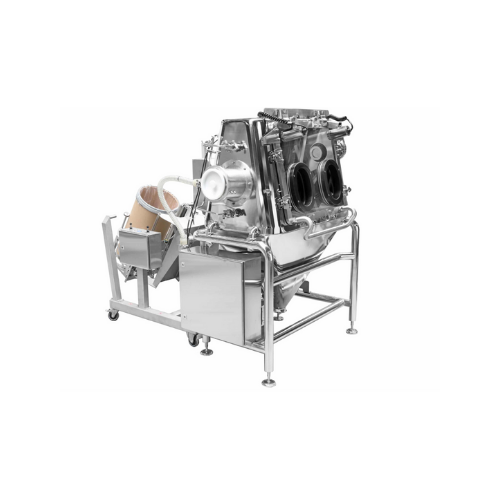
Containment system for product loading
Ensure safe handling of hazardous materials with this containment system, designed t...
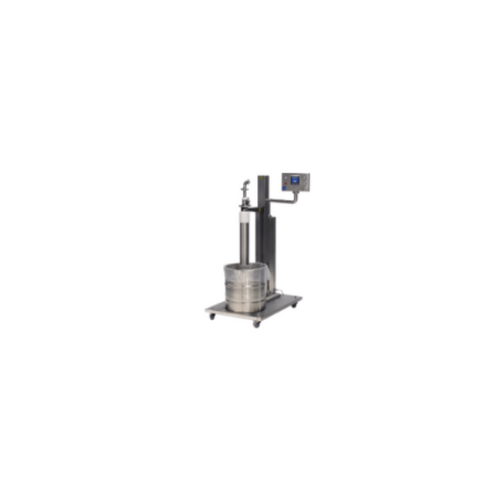
Drum discharge system for bulk material handling
Achieve precise, gentle transfer of sensitive pharmaceuticals and granula...
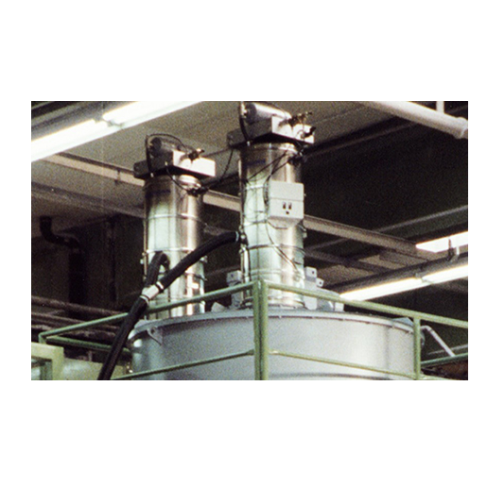
Continuous vacuum conveyors for material flow control
Ensure consistent material transfer and reduce downtime in your pro...
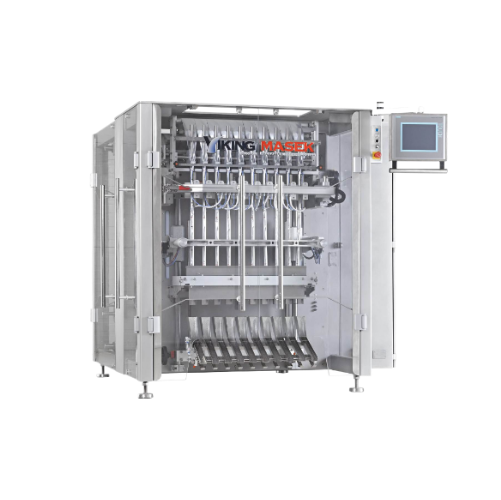
High-capacity stick pack packaging solution
Enhance your production efficiency by packaging diverse products like powders ...
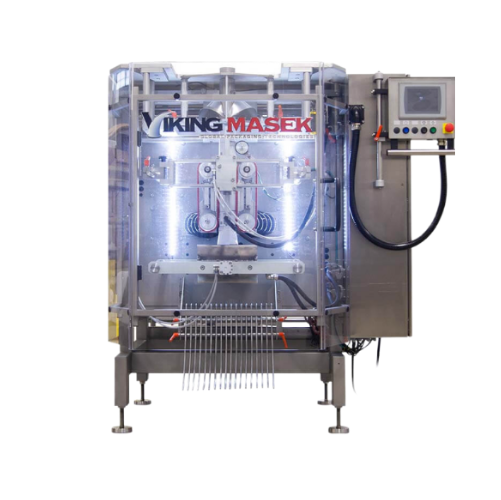
Vertical form fill seal for dusty and liquid products
Optimize your packaging line with a versatile solution designed to ...

Vertical form fill seal for large bag packaging
For operations requiring precise, large bag packaging, this equipment ensu...
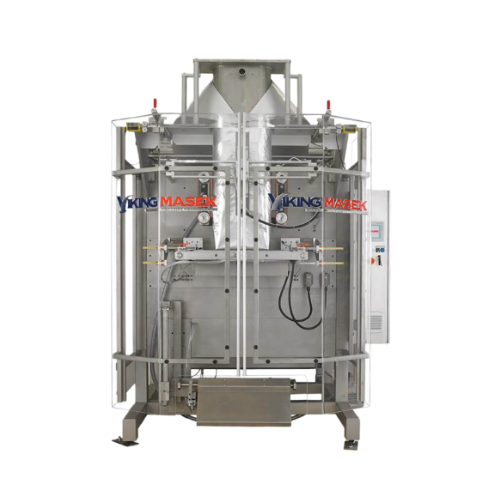
Vertical form fill seal for bulk bag packaging
Streamline your bulk bag packaging with efficiency and precision, ideal for...
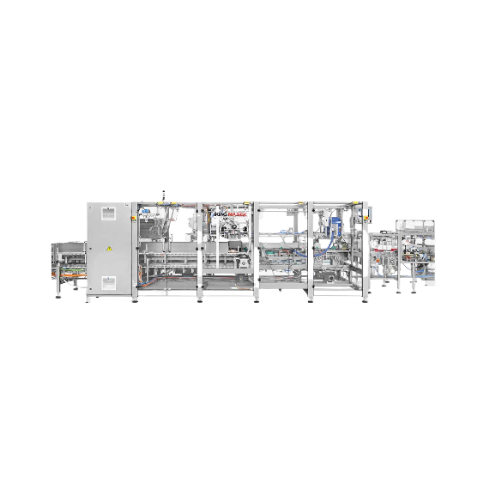
Endload automatic cartoning solution
Streamline your packaging line with this versatile cartoning solution, perfect for eff...
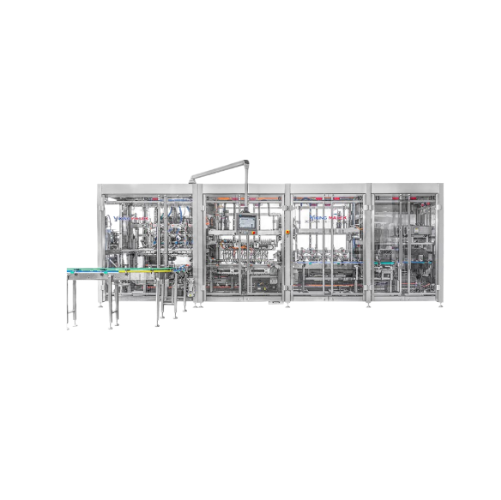
Topload cartoning system for efficient product packaging
Streamline your packaging line with this compact system that com...
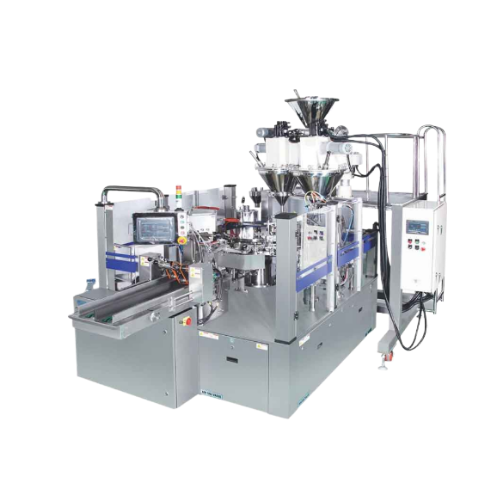
Automatic rotary filler and sealer for premade pouches
Enhance your production line efficiency with a dual-lane system th...
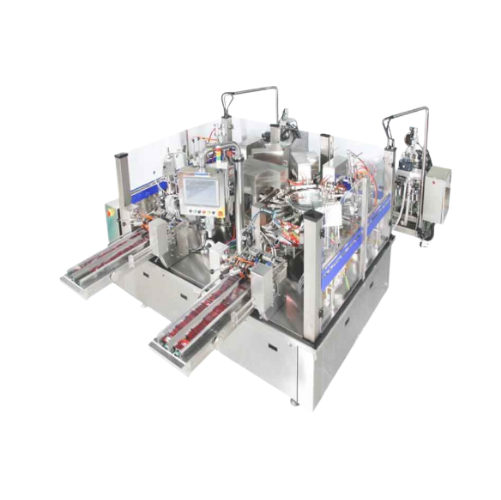
Automatic rotary premade pouch filler and sealer
Optimize your production line with high-speed pouch filling and sealing, ...
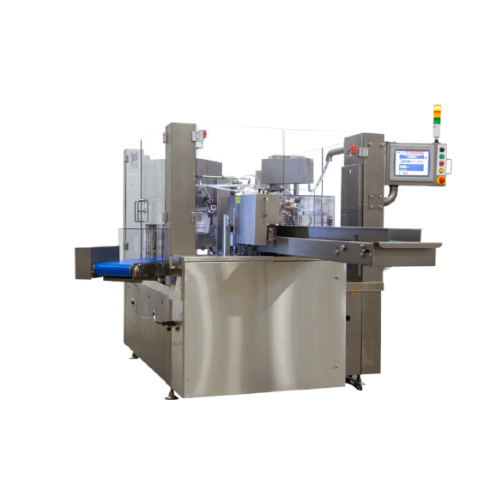
Automatic rotary premade pouch filler for various industries
Streamline your pouch packaging process with precision fill...
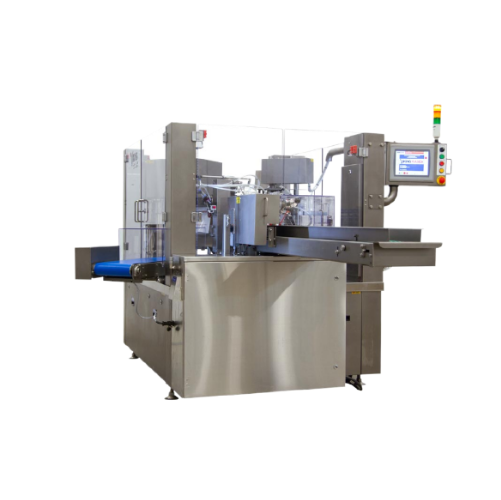
Automatic rotary premade pouch filler for food products
Enhance your packaging line with a high-speed solution designed t...
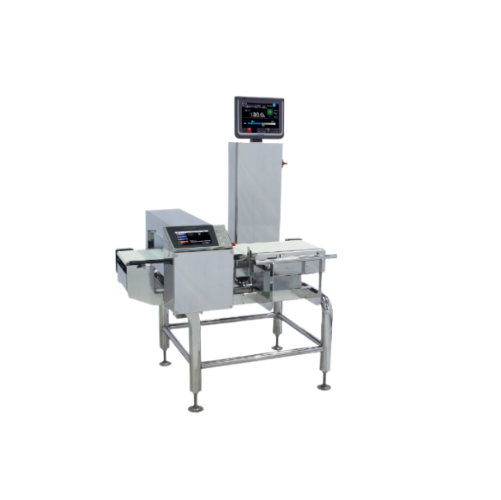
Product inspection systems for contamination control
Ensure product safety and compliance with precision inspection techn...
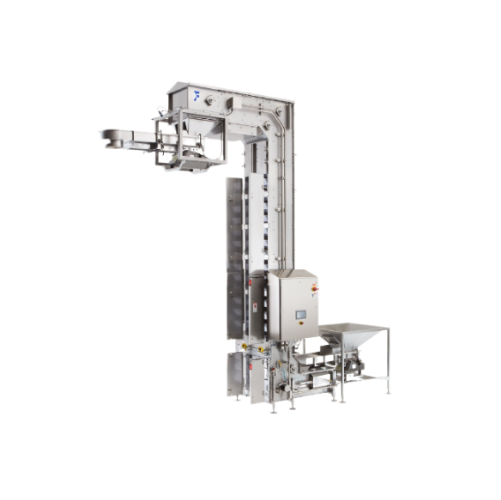
Automated infeed and outfeed systems for packaging lines
Streamline your production line by integrating reliable infeed a...
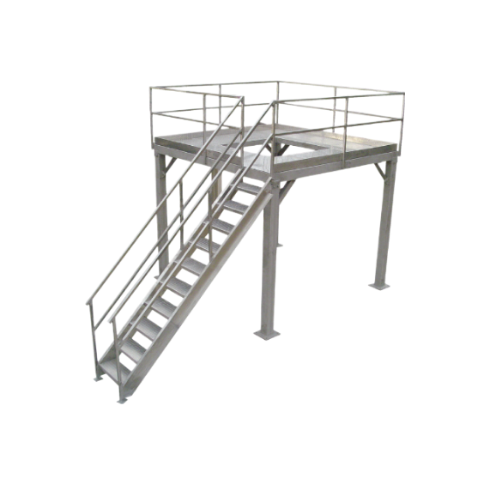
Support structures for packaging lines
Enhance safety and efficiency in your production line with robust support structures...
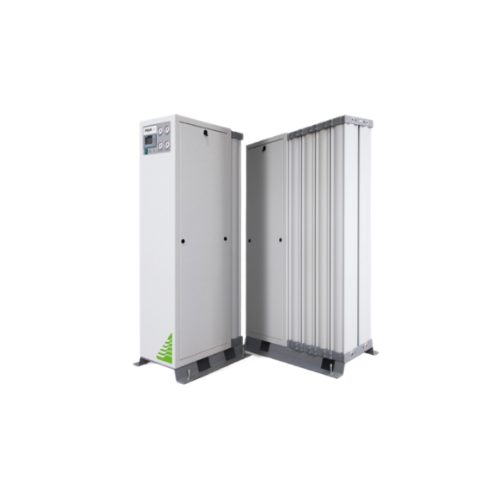
Modified atmosphere packaging solutions for perishables
Extend the freshness and shelf life of perishable goods with prec...
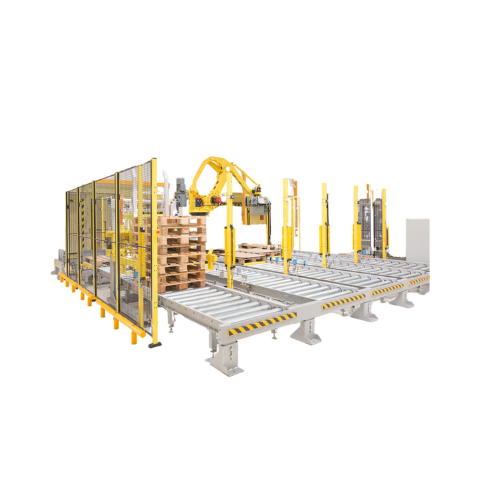
Robotic palletizing and depalletizing systems
Enhance your production efficiency by automating the repetitive and labor-in...
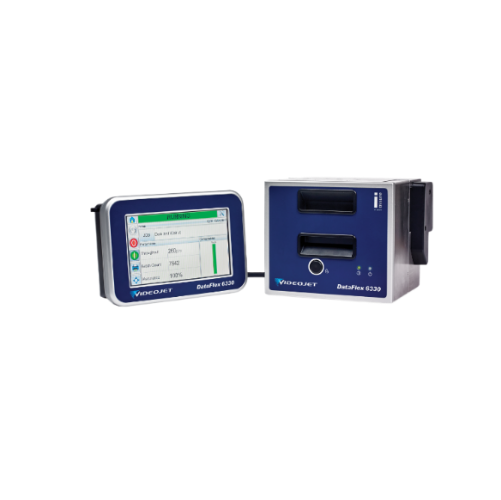
Industrial printers and labelers for packaging
Ensure precise package identification and traceability with robust printing...

Robotic packaging integration for automated systems
Enhance your production line efficiency with seamless robotics integr...
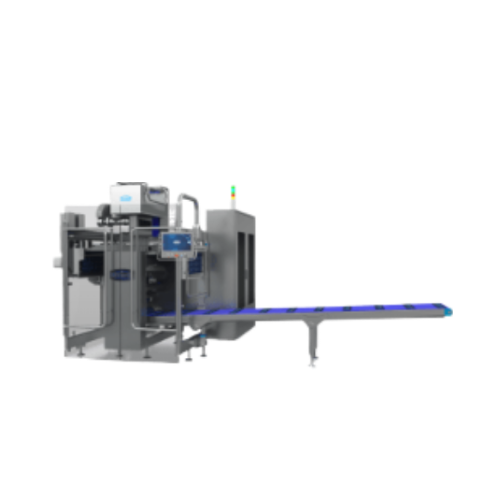
Sachet packaging for pharmaceuticals
Streamline your pharmaceutical packaging with high-precision sachet solutions, ensurin...
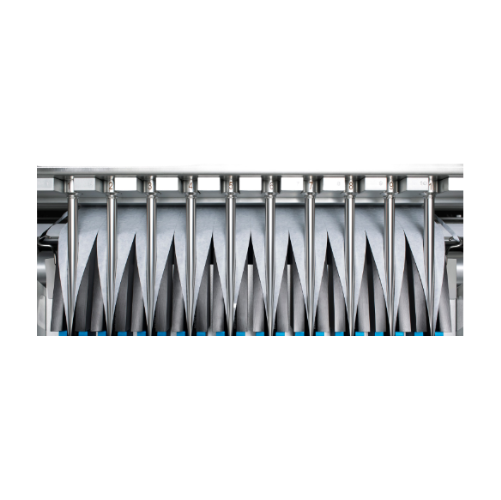
Stick pack packaging for pharmaceutical products
Enhance your production efficiency with compact stick pack solutions, off...
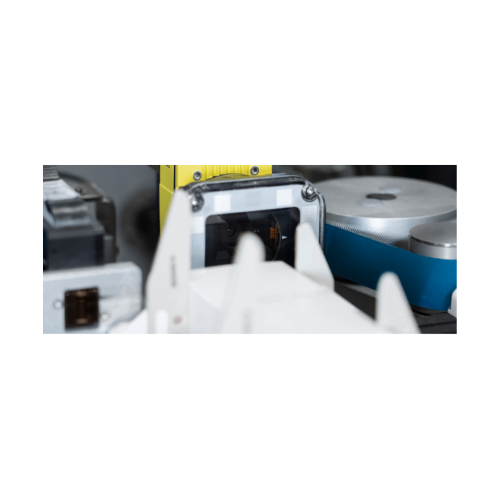
Sachet packaging lines for pharmaceuticals
Optimize your pharmaceutical production with high-speed sachet packaging lines ...
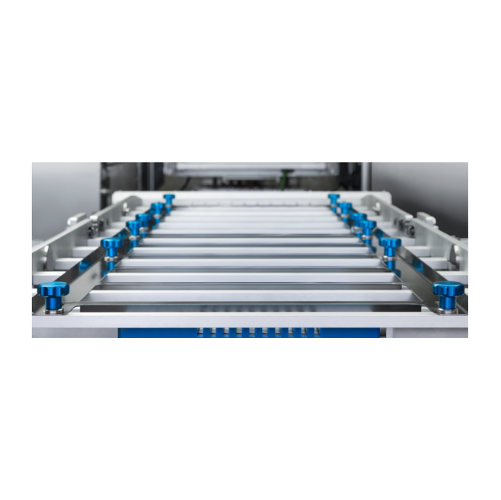
Stick pack packaging line for pharmaceuticals
Optimize your pharmaceutical production with stick pack packaging lines that...
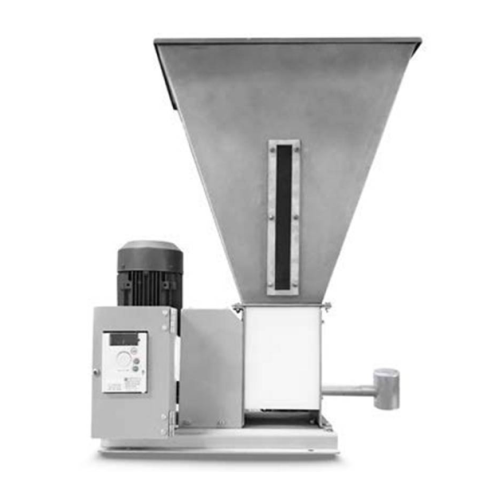
Vitamin adding system for ground products
Ensure precise vitamin dosing in continuous production lines, enhancing nutritio...

Industrial roller mill for high-stability milling
Optimize your milling process with a high-speed roller system designed ...
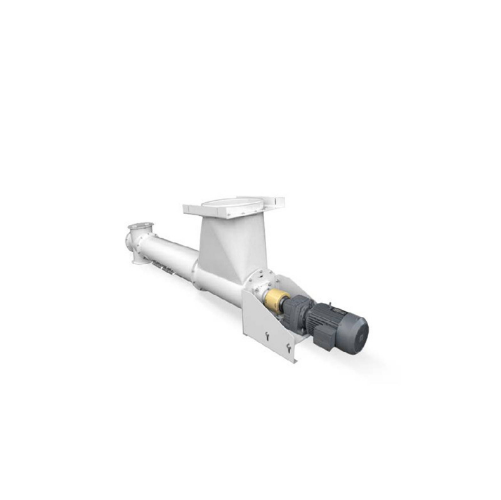
Tube screw conveyor for flour and fine-milled materials
Optimize your production line by efficiently transporting flour a...
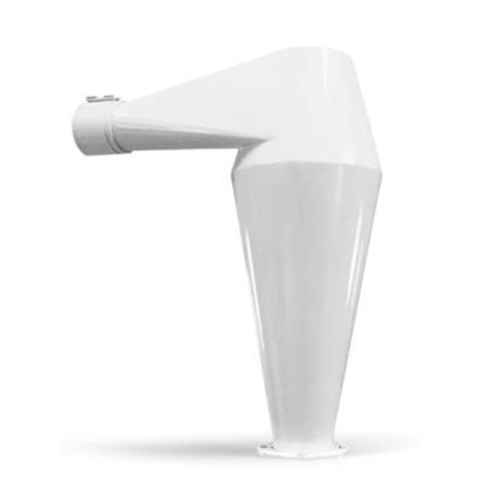
Pneumatic cyclone for effective product-air separation
Optimize particle separation with high-speed pneumatic cyclones, e...
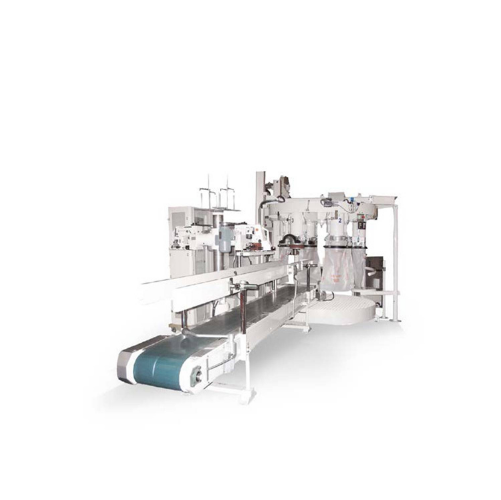
High capacity carousel packaging solution
For high-capacity milling operations, this packaging solution minimizes labor an...
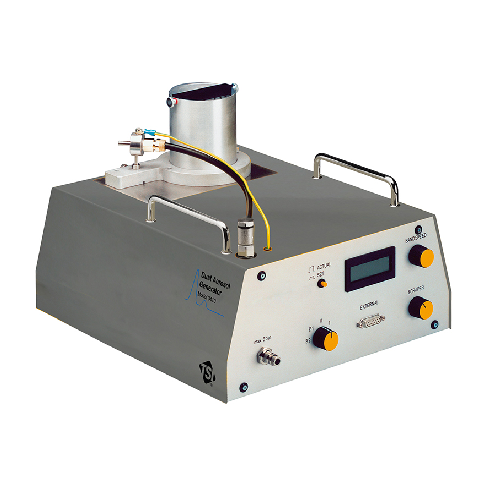
Dust aerosol generator for stable dosing and calibration
When precision is non-negotiable, this equipment disperses and d...
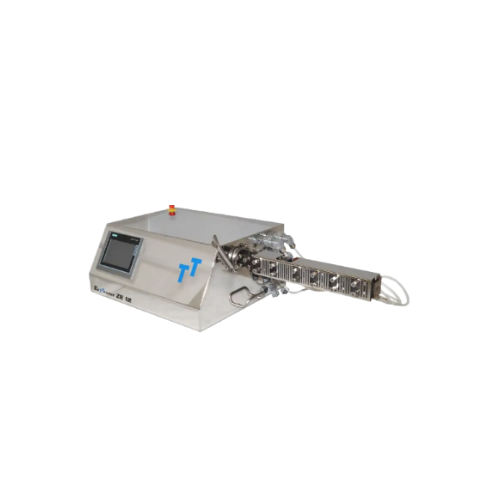
Table-top mini extruder for precision material processing
Achieve precise control over complex formulations with this fl...
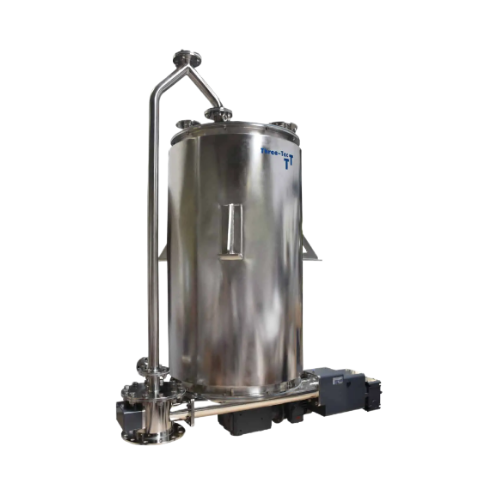
Twin screw feeder for bulk material handling
Optimize your bulk material processing with a solution designed for precise f...
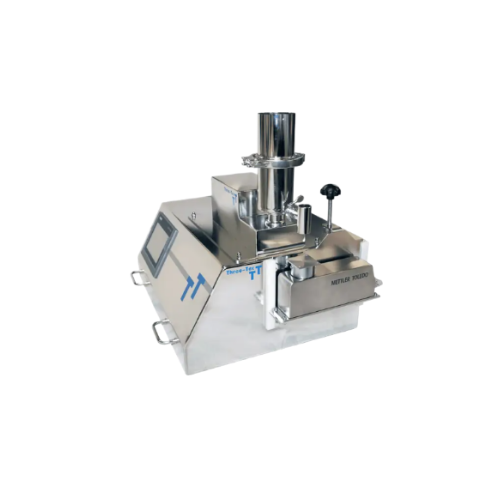
Table-top gravimetric feeding solution for precision batches
Achieve high-precision batch filling with integrated gravim...

Side feeding device for extruders
Enhance your extrusion process with a side feeding device that gently introduces powders,...
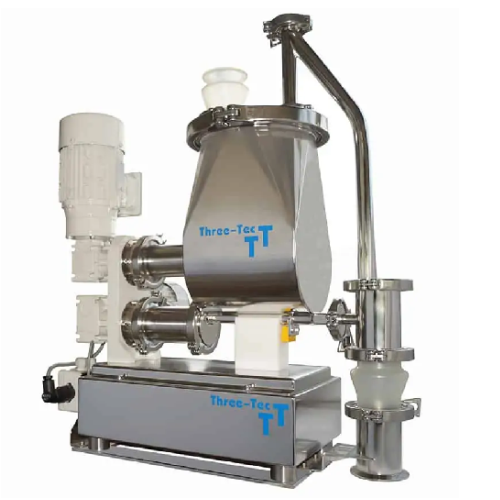
Quick change feeding devices for industrial applications
Experience seamless product transitions with quick-change feedin...
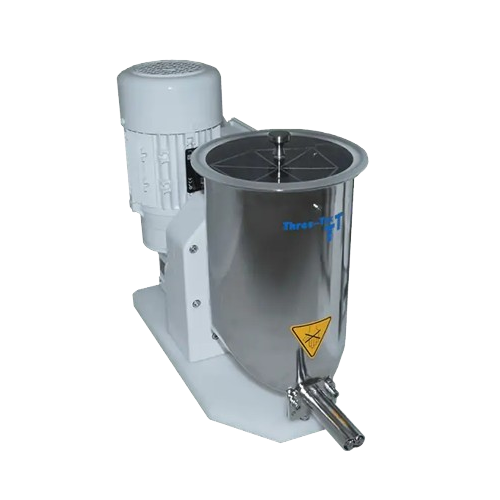
Twin screw feeder for dosing bulk solids
Ideal for precise bulk solids dosing, this twin screw feeder ensures consistent fl...
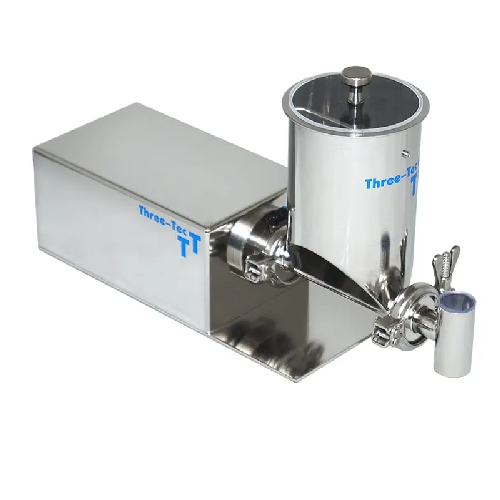
Volumetric single-screw feeder for fine dosing
Achieve precise and consistent dosing of fine powders and granules with a c...
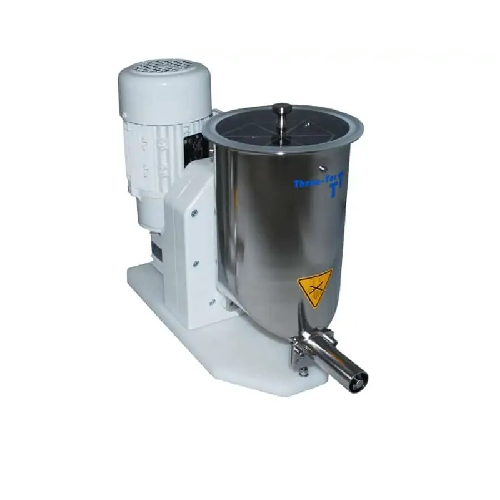
Volumetric single-screw feeders for free-flowing products
Achieve precise and continuous feeding of free-flowing powders...
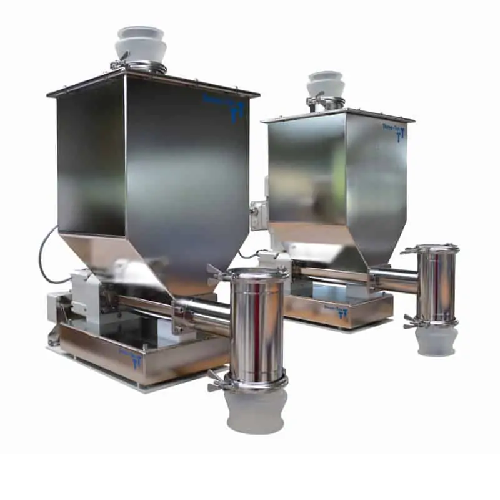
Gravimetric single-screw feeder for free-flowing products
Optimize your dosing precision for powders and granulates with...
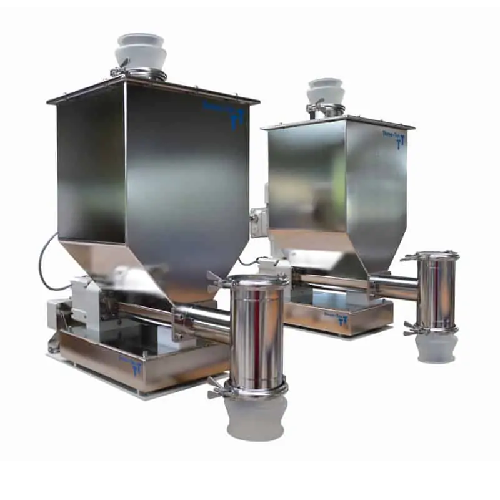
Volumetric single-screw feeder for free-flowing products
Optimize your production line with precise feeding and metering ...
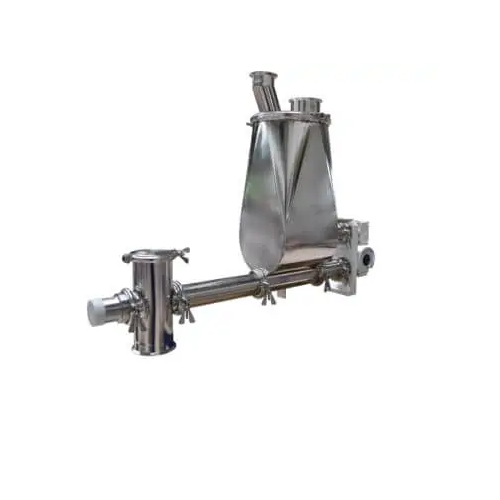
Quick change volumetric and gravimetric single-screw dosing device
Simplify your dosing process with a quick-change sin...
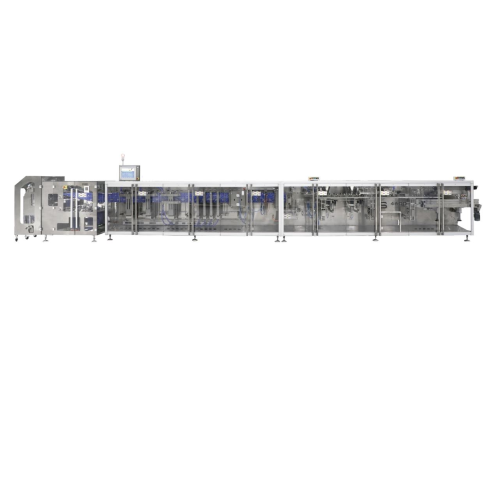
Horizontal form-fill-seal systems for pouch packaging
For production lines that demand efficient pouch creation, these hi...
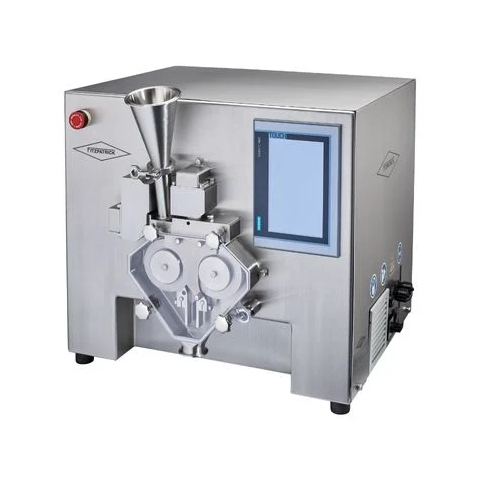
Lab scale roller compactor for dry granulation
Achieve seamless scale-up from lab development to full-scale production wit...
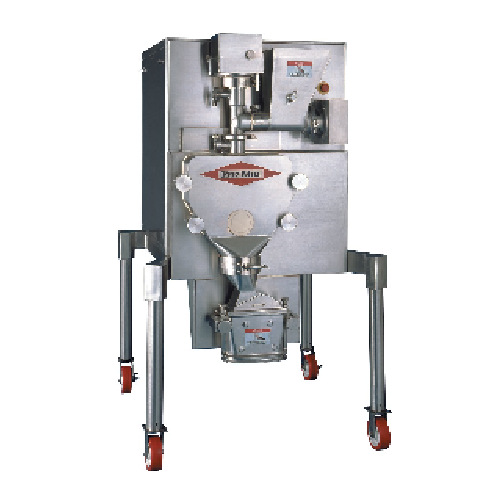
Pilot to full-scale roller compactor for dry granulation
Easily transition from pilot to full-scale production with this ...
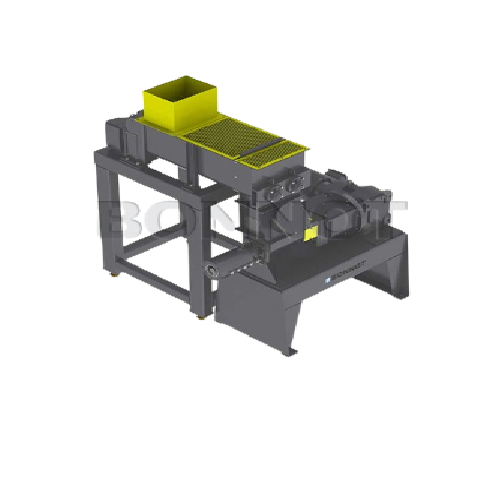
Twin shaft feeder for optimized material feeding
Achieve precise material flow and optimize downstream processing with adv...
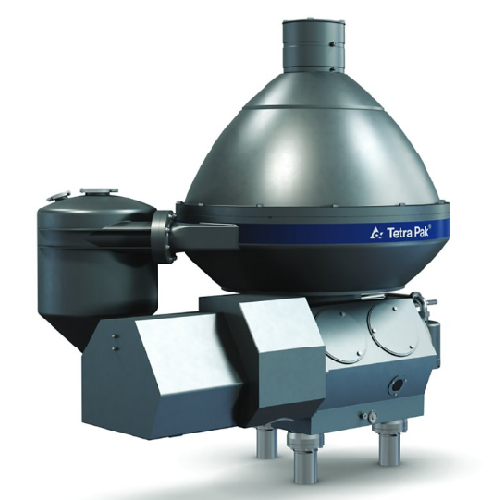
Spore and bacteria removal unit for dairy products
Ensure superior quality by precisely removing spores and bacteria from...
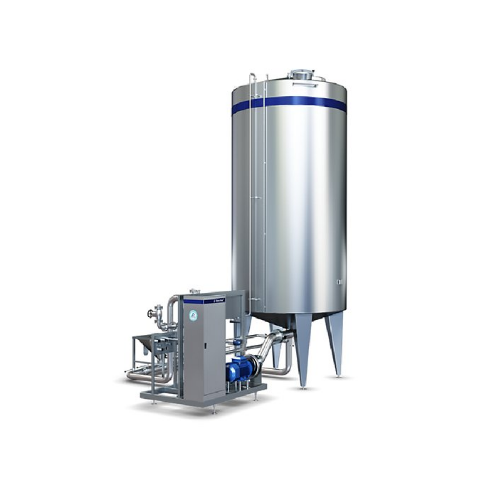
Batch dissolver for crystalline sugar and dextrose
Streamline your ingredient preparation with high-capacity batch dissol...
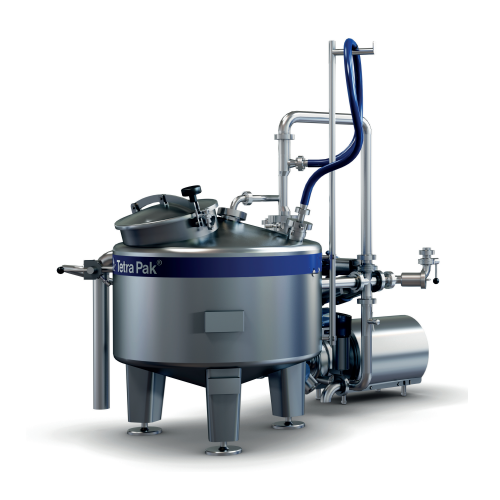
Ingredient dissolver for small batch processing
Optimize your mixing processes with a versatile dissolver designed for eff...
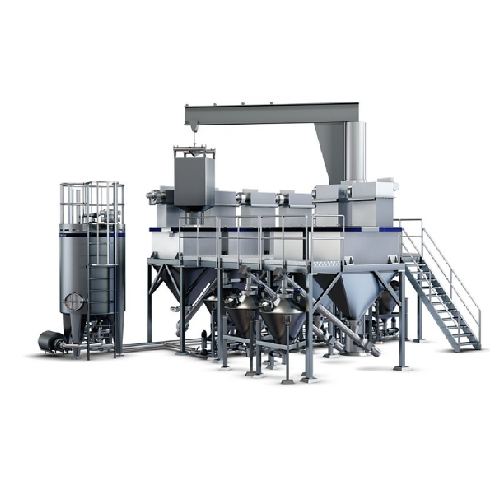
Autonomous ingredient dissolver for high-volume dry ingredient mixing
Efficiently mix multiple high volumes of dry ingr...
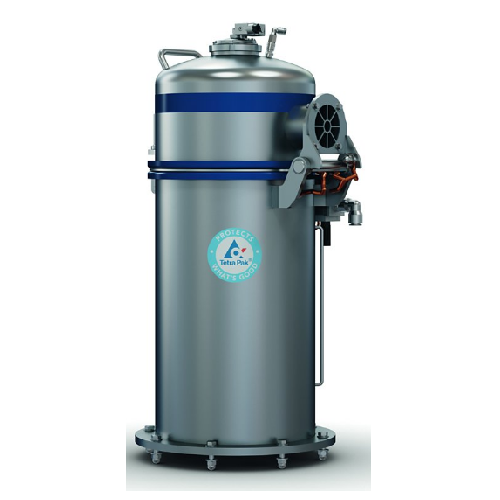
Dust filter for food processing
Ensure high-quality powder production with this self-cleaning dust filter, designed to minim...
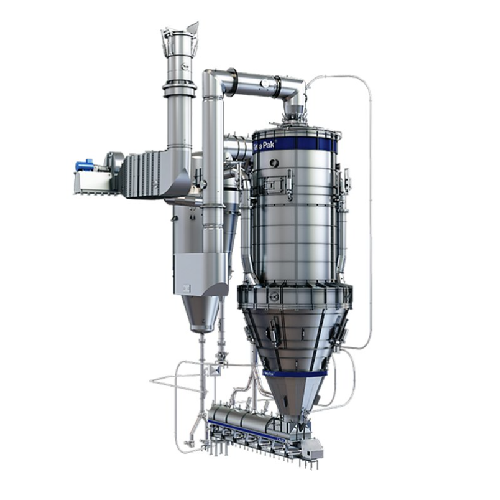
Spray dryer for heat-sensitive materials
Optimize your production line with a high-capacity spray dryer designed for precis...
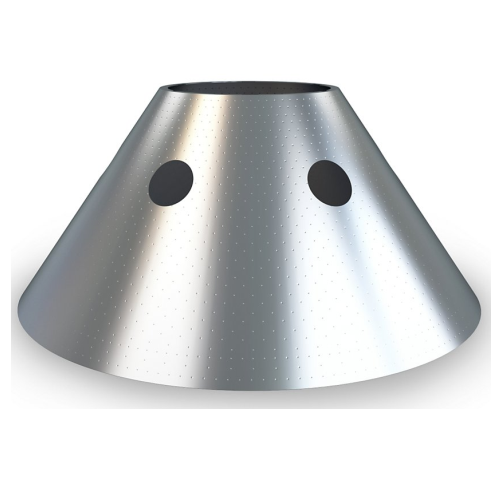
High capacity milk separator with polynode technology
Achieve unprecedented milk skimming efficiency and reduced environm...
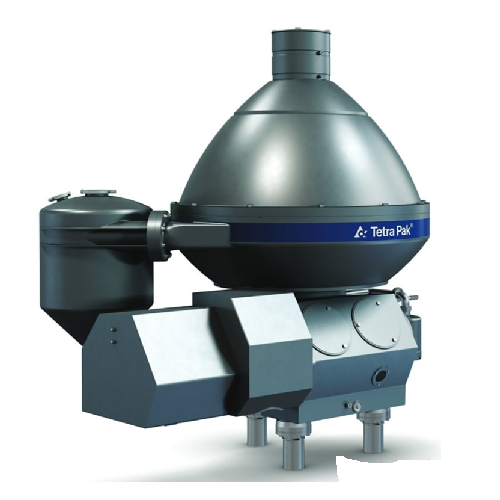
Spore removal unit for dairy processing
Optimize your dairy production by efficiently removing spores and bacteria, ensurin...
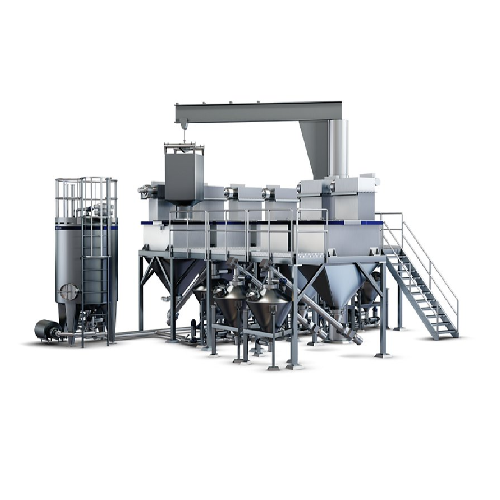
Autonomous ingredient dissolver for high volume dry ingredient mixing
Streamline your production by seamlessly mixing d...
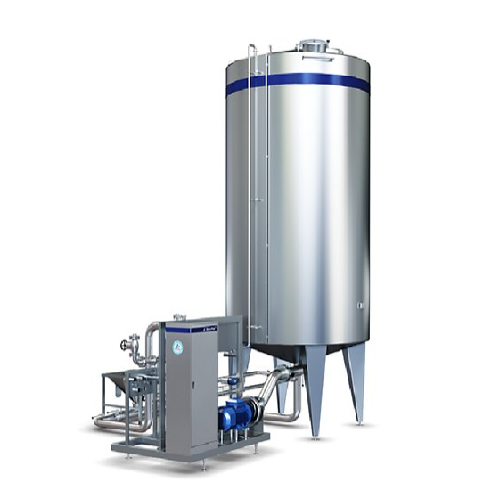
Batch dissolver for sugar or dextrose
Efficiently dissolve crystalline substances like sugar and dextrose with precision, e...
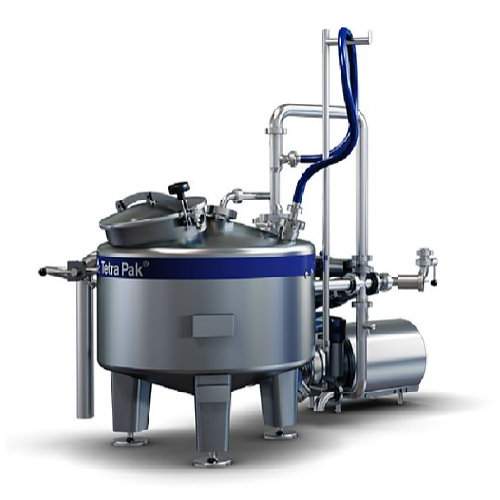
Ingredient dissolver for small batches
Efficiently dissolve water-soluble powders and concentrates up to 200 cP with precis...
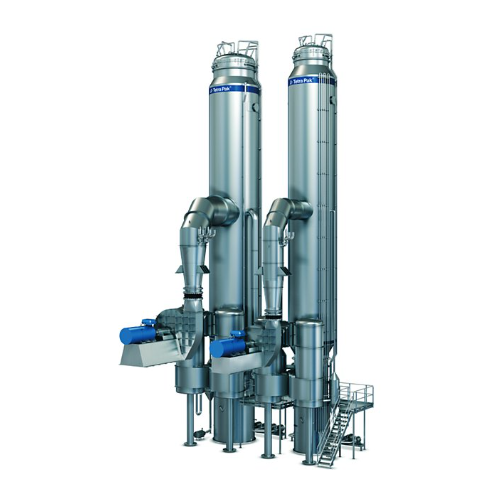
Low-energy evaporation system for dairy products
Enhance product quality and lower energy costs with a cutting-edge evapor...
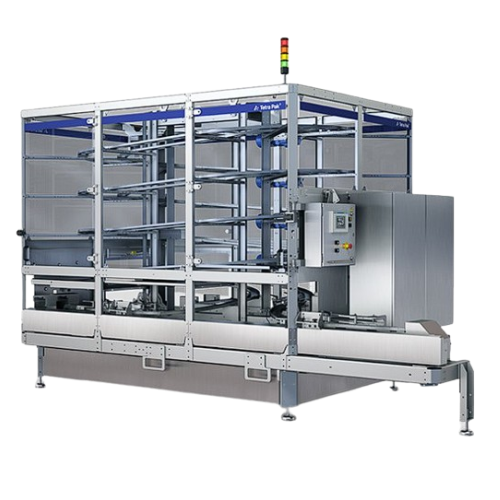
Vertical package accumulator for food and beverage production
Ensure seamless flow and precise order tracking of package...
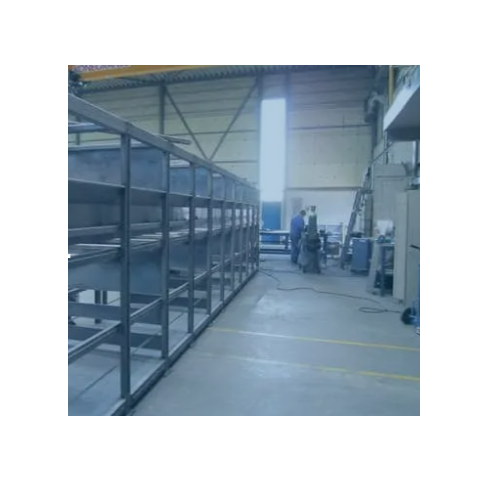
Continuous bulk fluid bed dryer
Achieve rapid and energy-efficient moisture removal across diverse materials with our advanc...
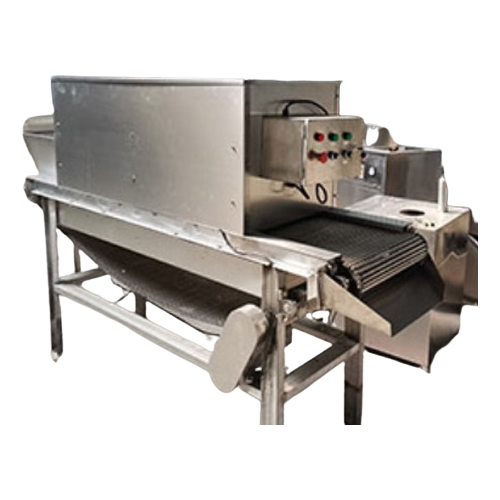
Garlic processing equipment for industrial applications
Streamline your garlic processing with equipment that automates p...
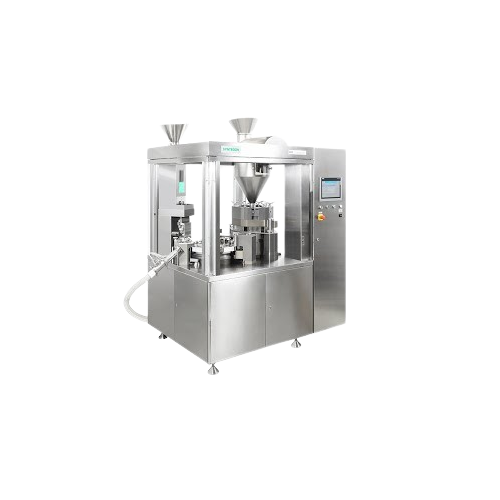
Capsule filling for nutrition and health products
Optimize your production line with advanced capsule filling capabilitie...
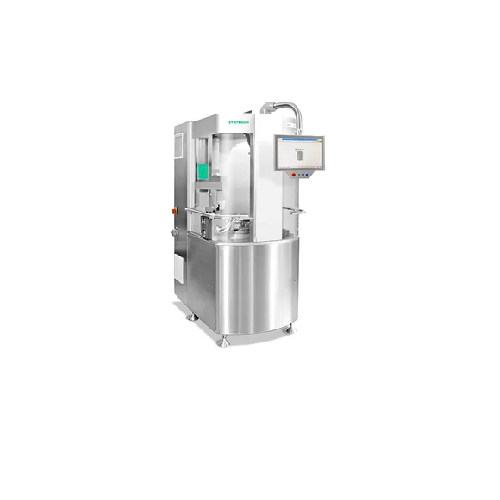
Capsule filling for pharmaceuticals and nutraceuticals
Enhance your capsule production capabilities with modular filling ...
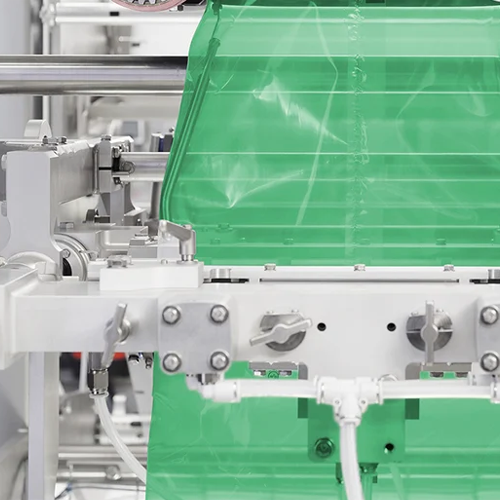
Vffs packaging solution for diverse bag styles and high hygiene standards
Enhance your packaging operations with high-...
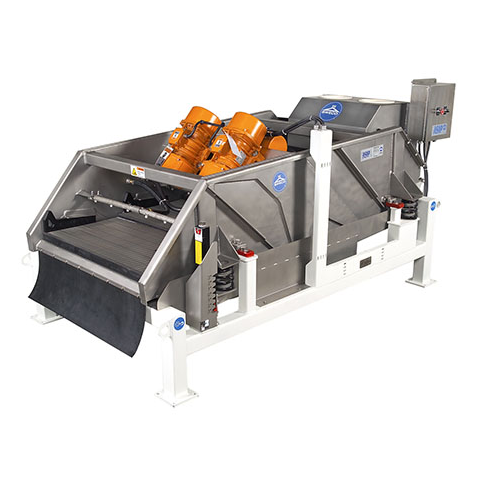
Multi-motion rectangular separator
Solve screen blinding effortlessly with an innovative system that combines elliptical an...
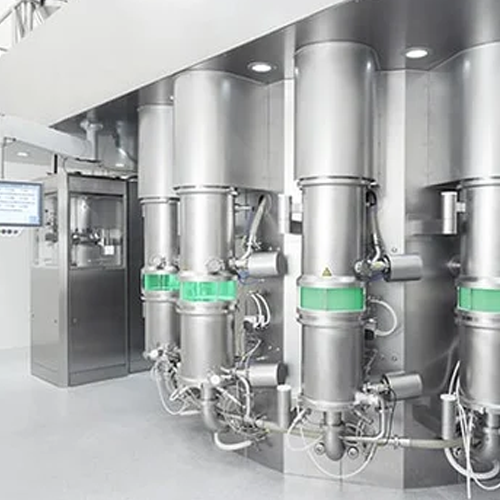
Pharma r&d equipment for solid dosage forms
Optimize your pharmaceutical production with cutting-edge equipment designed f...
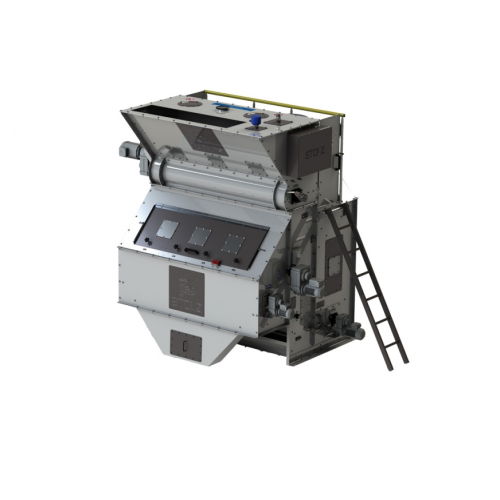
High-capacity pre-cleaner drum for grain silo storage
Optimize your pre-cleaning process with a high-capacity drum that e...
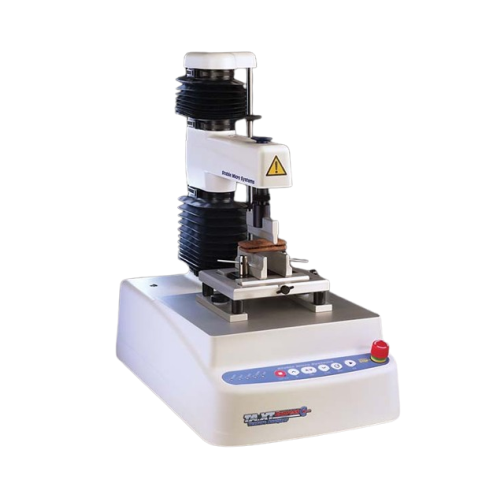
Entry-level texture analysis system for Qc applications
Perfect for quality control labs, this portable system streamline...
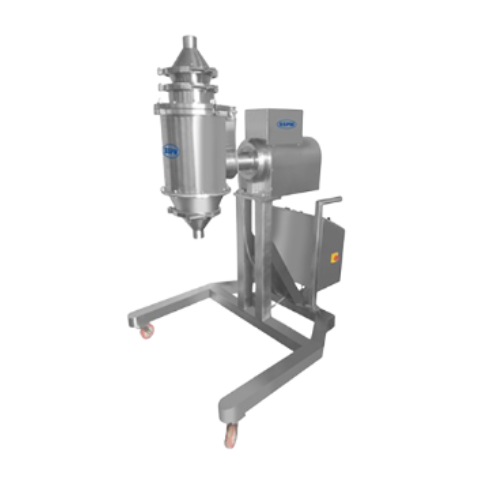
High-speed sifting for safety screening in pharmaceutical production
Achieve precise particle sizing with a high-speed ...
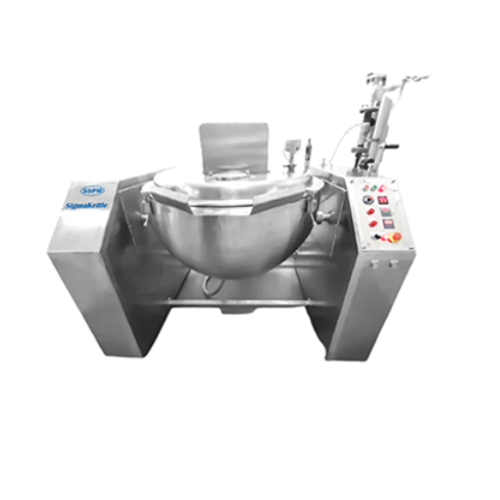
Steam/electrical kettle for wet granulation processes
Achieve precise moisture content and uniformity in your granulation...
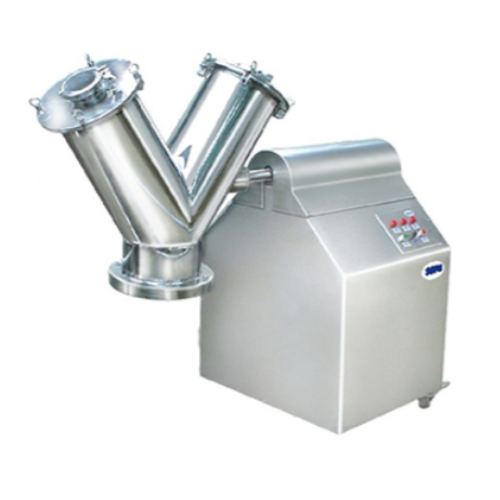
Industrial blender for uniform mixing
Optimize your process with precise mixing and consistent blending, ensuring uniformit...
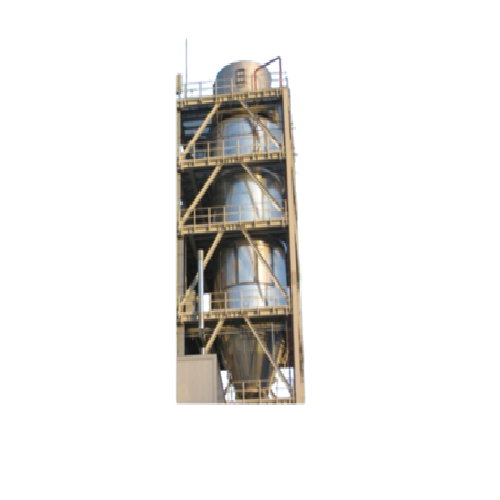
Tall form dryer for producing large non-agglomerated particles
Achieve precise particle size control and optimal moistur...
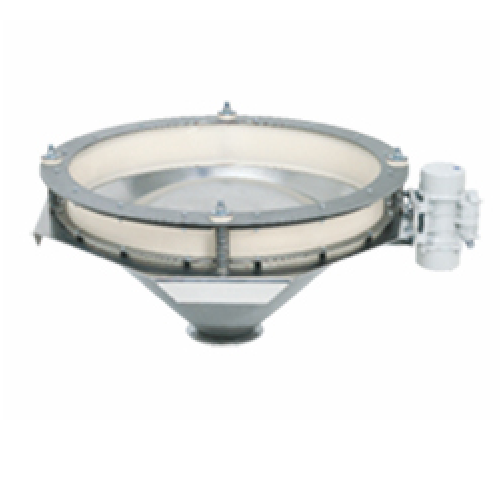
Bin activator for reliable bulk solids discharge
Ensure reliable flow and prevent compaction in your production line with ...
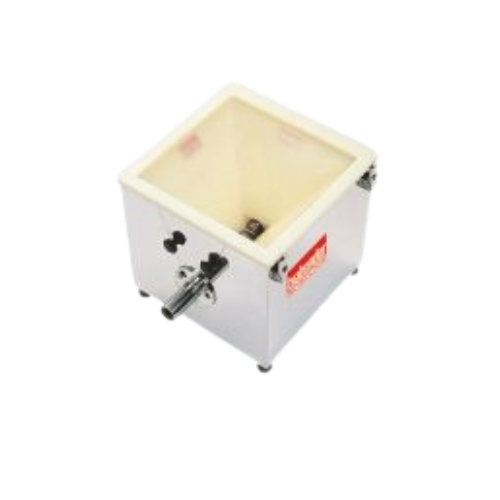
Volumetric feeder for flowable ingredients
Ensure consistent and precise dosing of diverse materials in your production li...
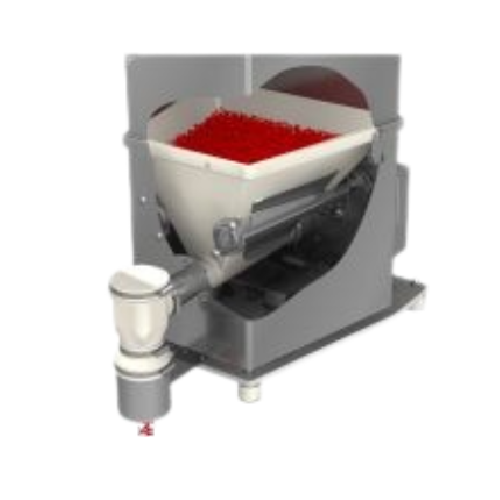
Volumetric feeder for consistent ingredient flow
Achieve precise and consistent ingredient dosing in your production line ...
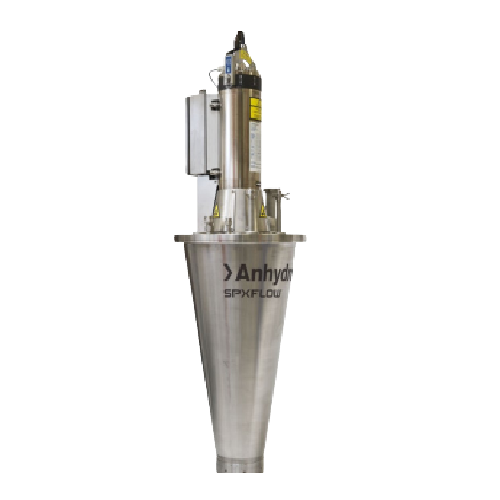
Centrifugal atomizer for precise spray drying
Achieve precise control over particle size and moisture content with centrif...
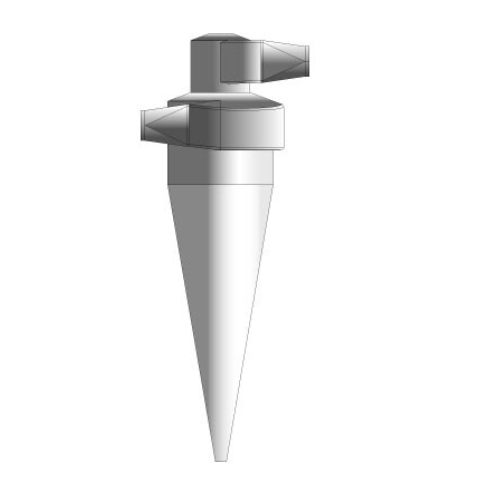
Industrial cyclone separators for air particulate removal
Optimize particulate removal in air streams with cyclone separ...
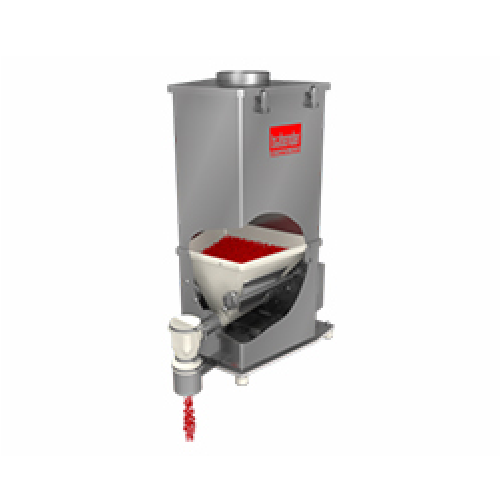
Loss-in-weight feeder for flowable ingredients
Achieve precise ingredient delivery with this feeder, designed to handle a ...
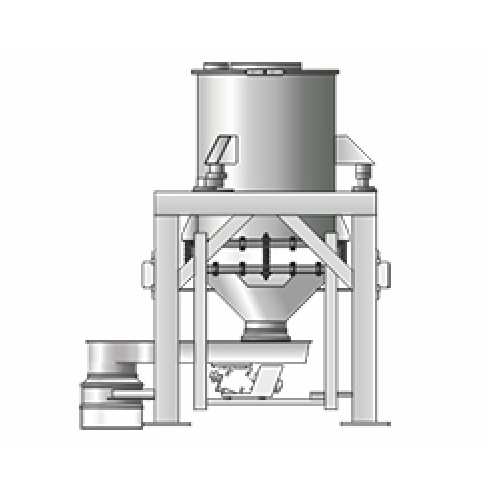
Loss-in-weight feeder for non-hygroscopic ingredients
Ensure precision in your dosing and weighing processes with this ad...
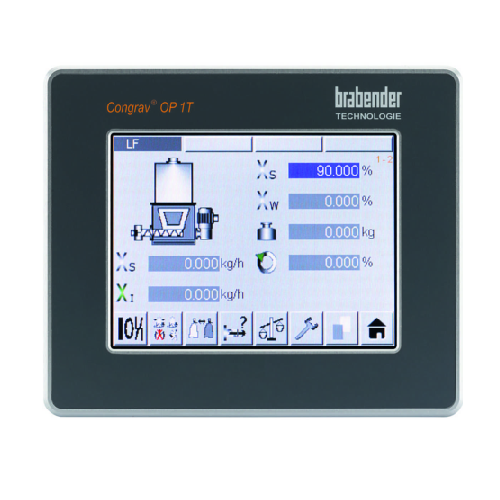
Single feeder operator interface for gravimetric feeders
Enhance precision in your dosing operations with an intuitive to...
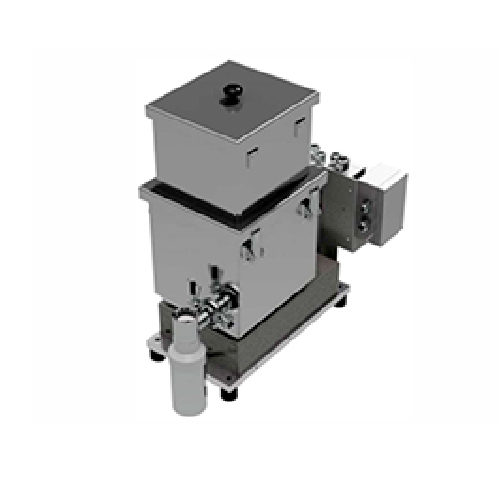
Loss-in-weight feeder for flowable particles
Ensure precise ingredient delivery with a feeder designed for high accuracy a...
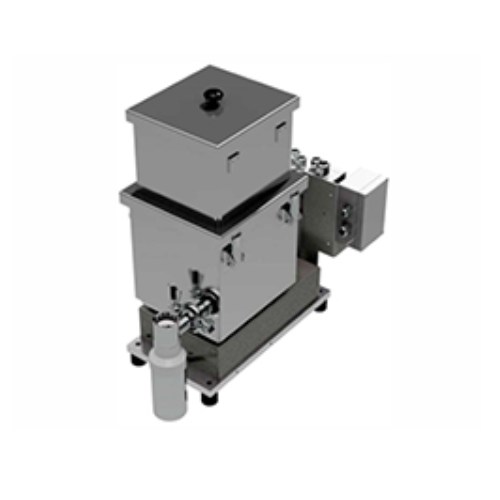
Batch feeder for bulk solids processing
Achieve precise batch dosing with this advanced feeder, designed to handle a variet...
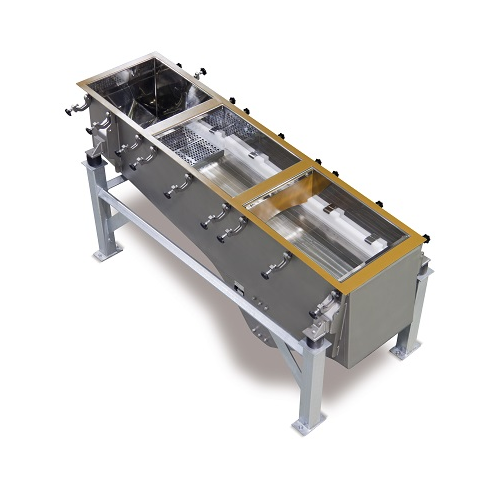
Pharmaceutical sieving equipment for high hygiene standards
Ensure the purity of pharmaceutical powders and granulates w...
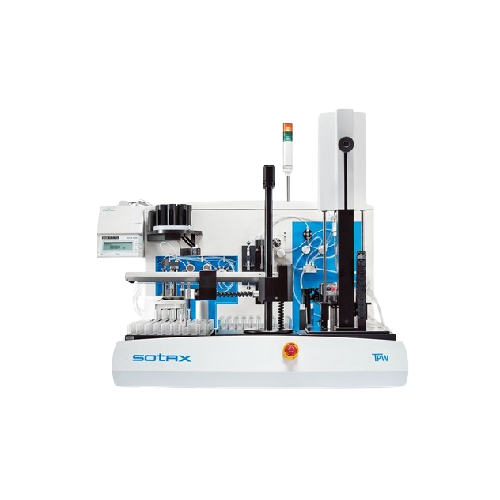
Automated sample preparation workstation for content uniformity testing
Streamline your laboratory workflows with autom...
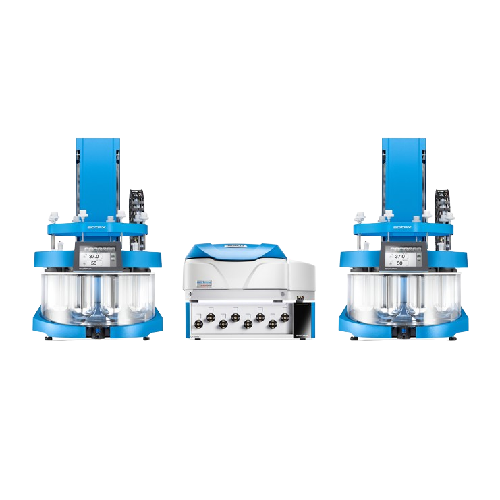
Real-time Uv-vis analysis for dissolution testing
Efficiently perform dual dissolution tests simultaneously, seamlessly i...
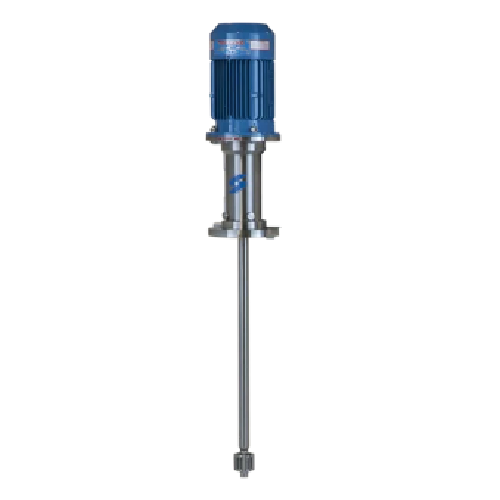
In-tank mixer for Ibc tote mixing
Overcome the challenge of incorporating buoyant or cohesive powders into liquid mixtures,...
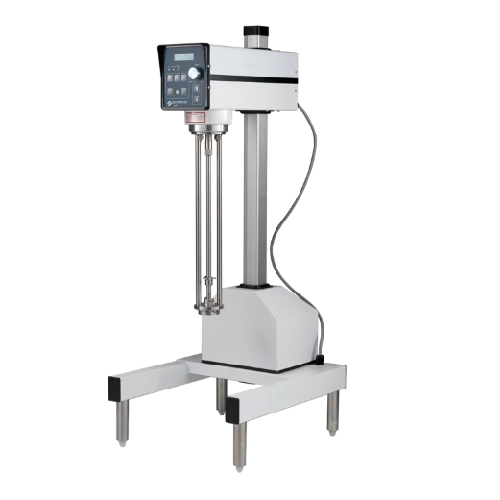
Pilot scale batch mixer for small scale production
Achieve precise control and consistency in small-scale production with...
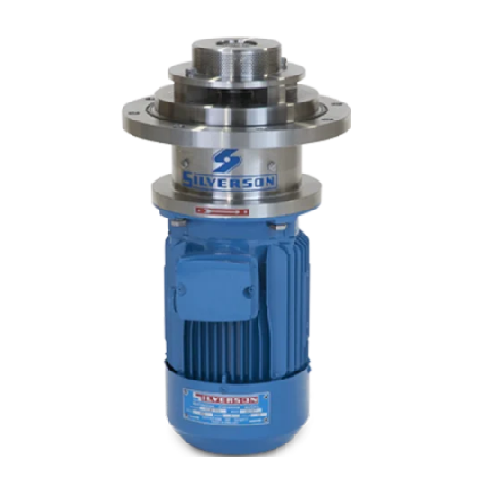
Bottom entry mixers for high viscosity products
Optimize your production line with mixers designed to handle both high and...

Efficient grinding and drying mill
Transform your production line with a versatile mill that simultaneously grinds, dries, ...
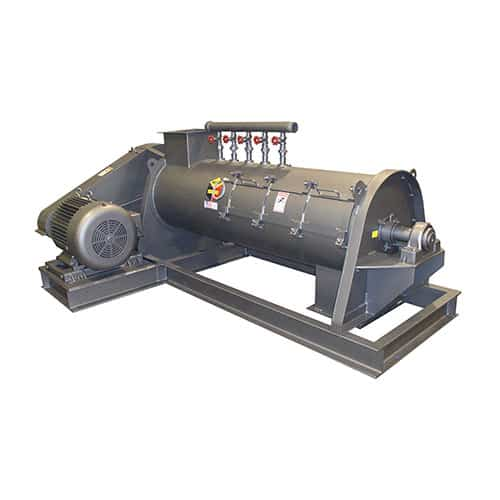
Industrial high-speed turbo blender
Achieve homogeneous blending with high-speed precision, ideal for creating fine product...
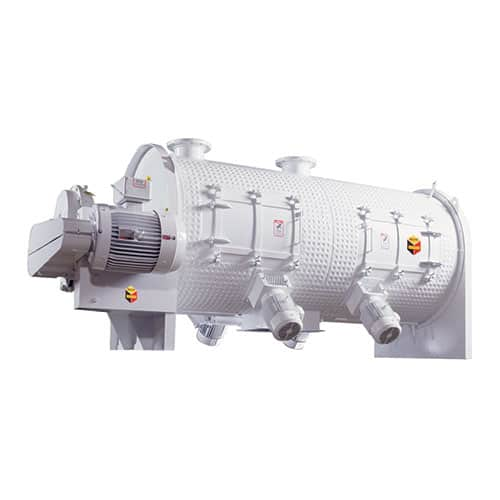
Industrial plow mixer for efficient solid and liquid mixing
Experience unparalleled mixing precision with high-speed plo...
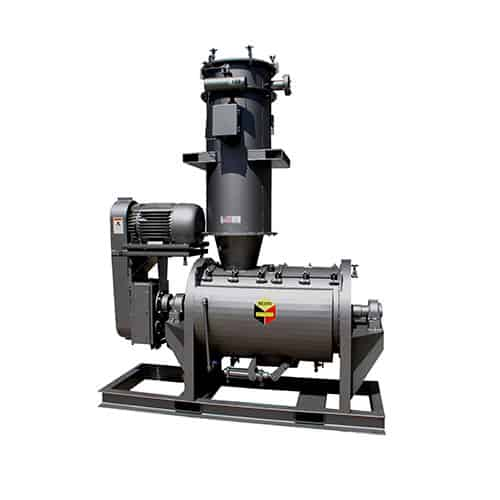
Industrial vacuum batch dryer for reducing moisture content
Achieve precise moisture control with a solution that handle...
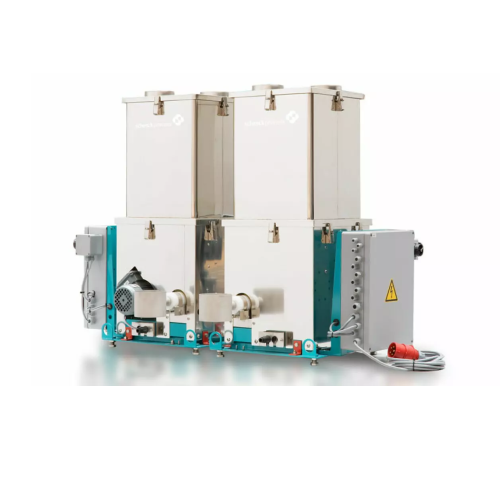
Loss-in-weight feeder for plastic compounding
Achieve precise material flow and improved production efficiency with an ada...
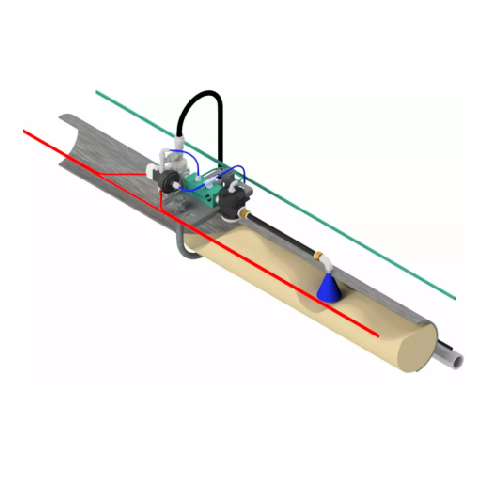
Injected density stabilizer for pneumatic conveying
Optimize your dense phase pneumatic conveying with a stabilizer desig...
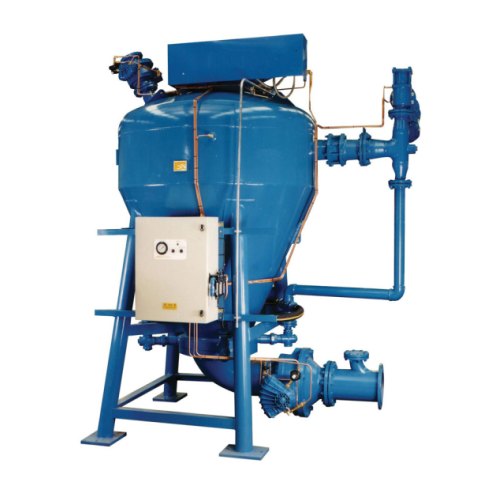
Dense phase conveying pumps for bulk material transfer
Optimize your material handling with pneumatic conveying solutions...
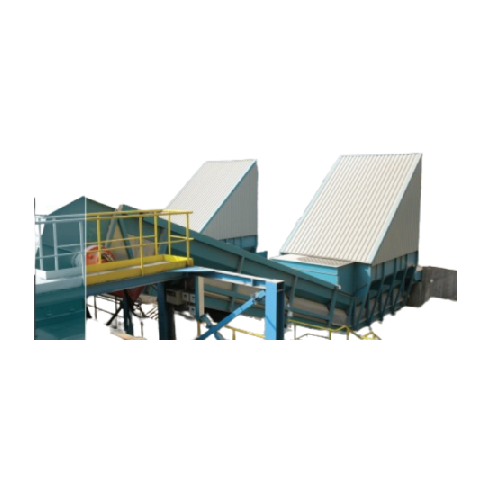
Bulk reception solution for industrial material handling
Optimize your operations with an above-ground bulk reception sys...
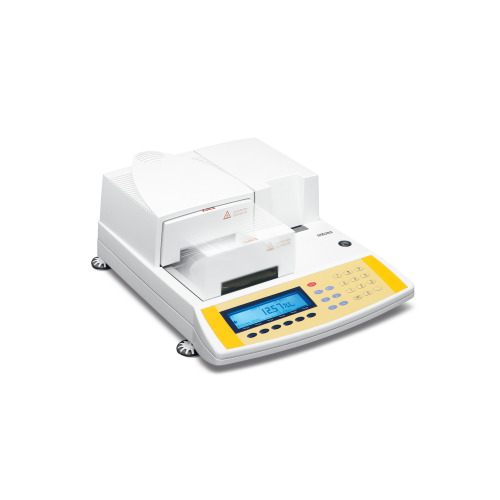
High-accuracy moisture analyzer for lab weighing
Achieve precise and reproducible moisture content determination for diver...
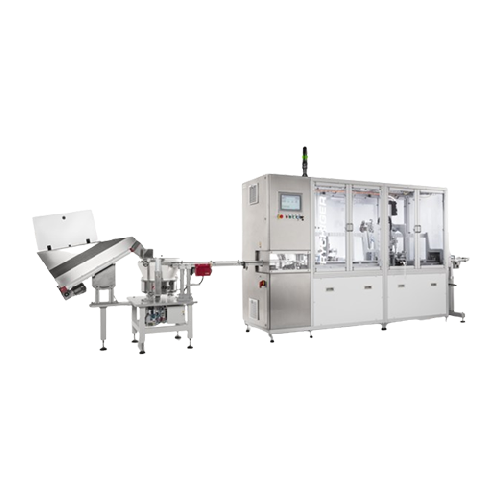
Filling and sealing multi-well cassettes for molecular diagnostics
Streamline your small to medium-scale diagnostic pro...
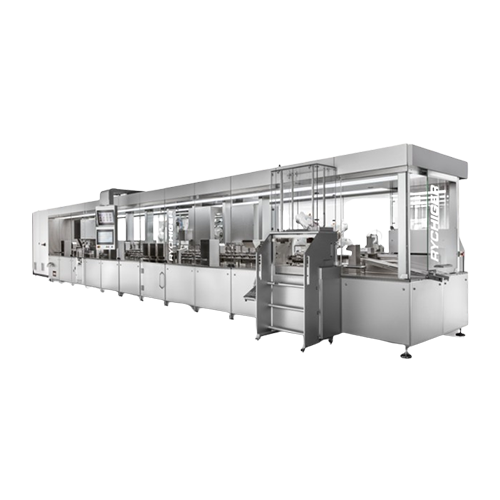
Production system for molecular diagnostics
Eliminate bottlenecks in molecular diagnostics production with a versatile sys...
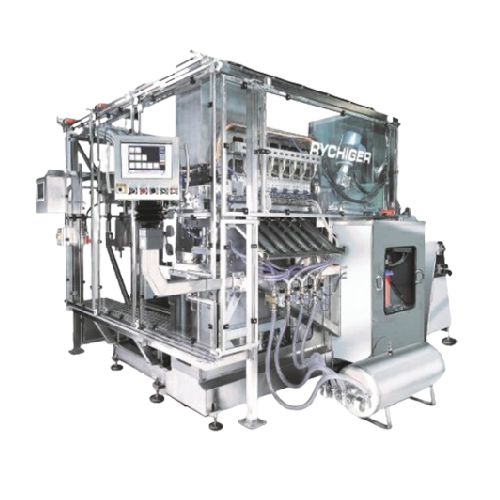
Convenience and pet food filling solution
Optimize your production line with high-speed, hygienic filling of diverse food ...
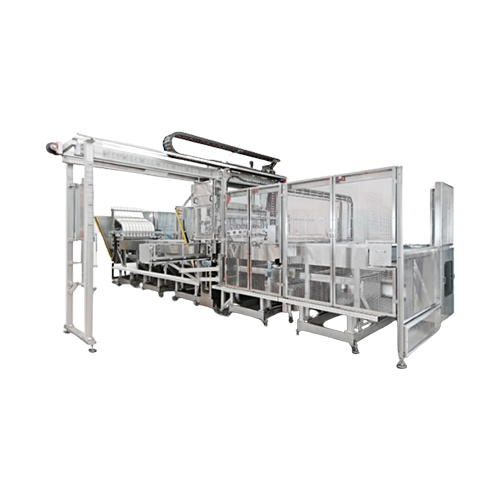
Precision filler for convenience and pet food
Achieve unparalleled precision and efficiency in filling solids, powders, li...

Particle size reduction air conveying system
Achieve precise particle size reduction and contamination-free processing for...
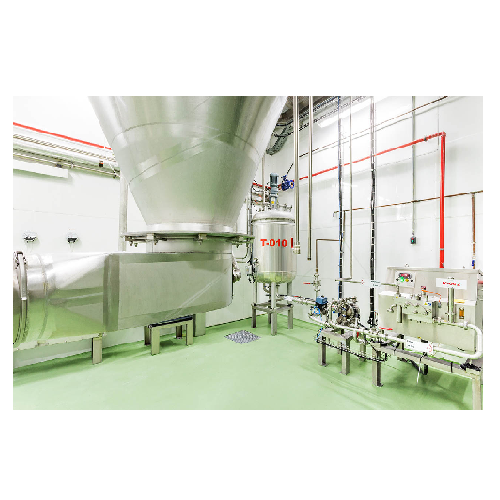
Continuous spray dryer for thermosensitive products
Ideal for processing thermosensitive slurries, this spray dryer ensur...
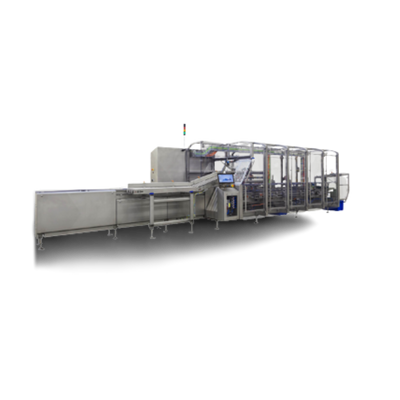
Intelligent Continuous Food Cartoner
Fully automated robotic packing solutions enable larger-scale food producers to pack a...
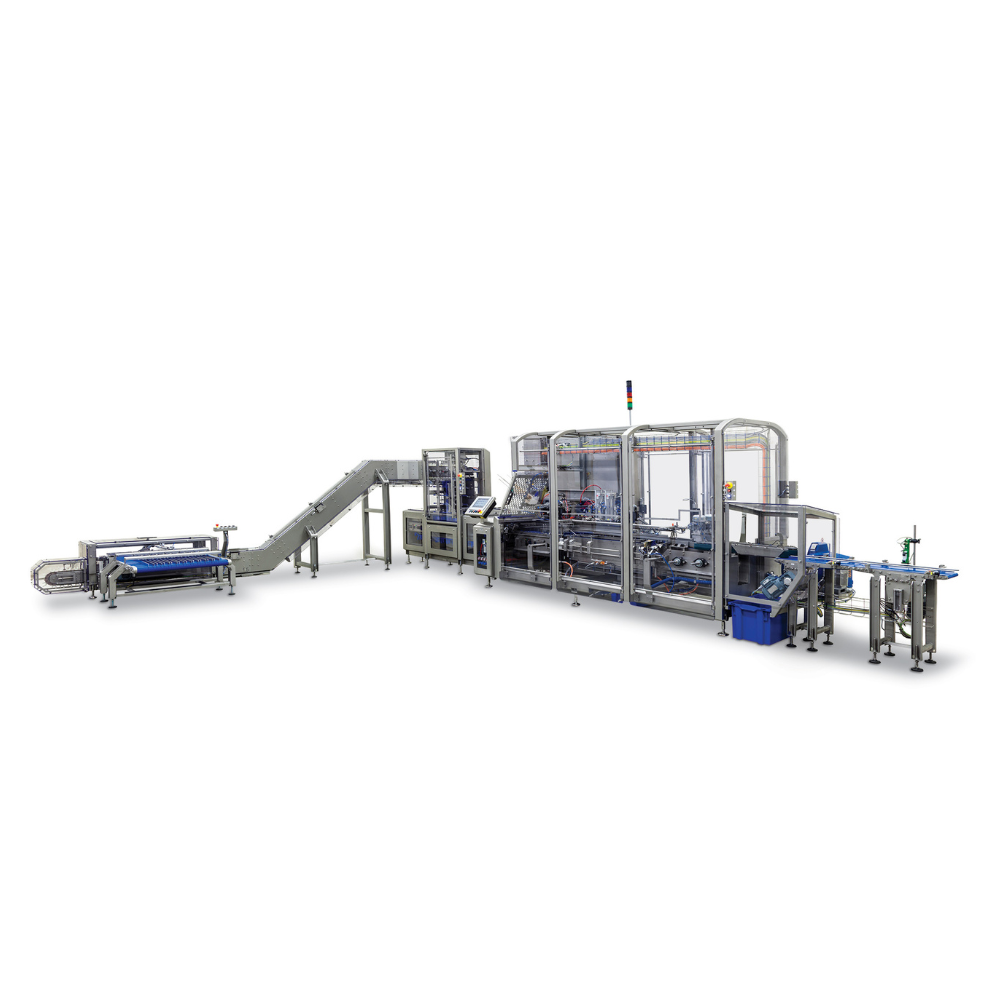
High-speed Cartoner For Single-Serve Products
Large-volume producers of single-serve packs, such as sugar sticks, instant ...
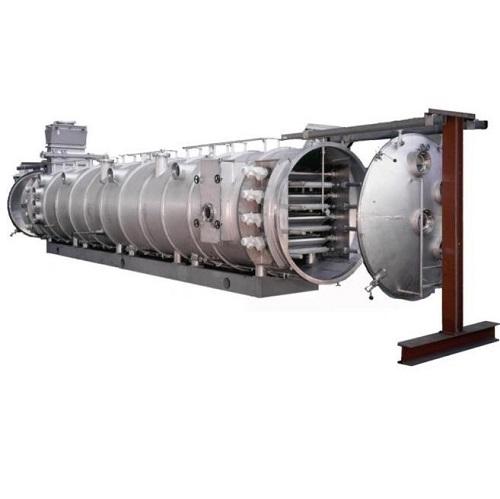
Vacuum belt dryer for fruit, vegetable and herbal extracts
Organic volatile compounds from fruits, vegetables and herbs ...
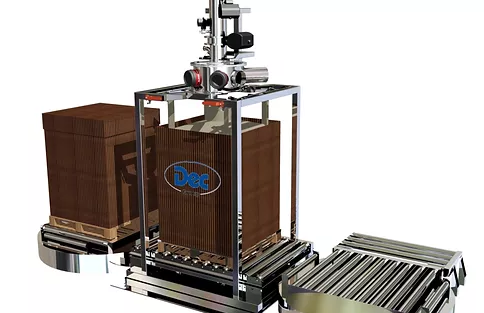
Big bag filling machine
Active pharmaceutical ingredients demand high handling standards to prevent cross-contamination. More...
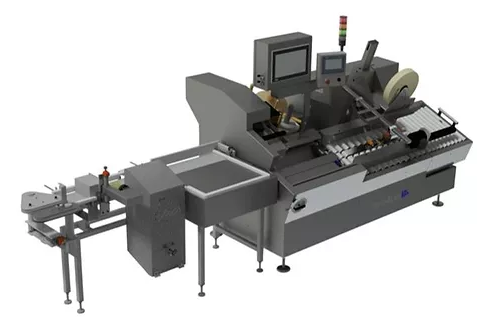
Serialization equipment for cases
Serialization is a multi-stage process that includes printing, inspection, and labeling. ...
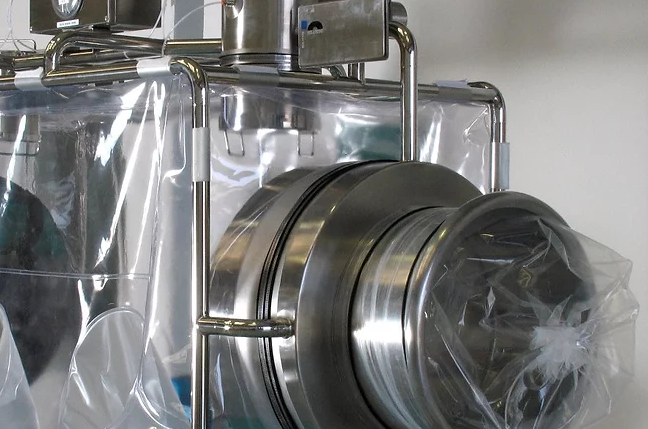
Disposable isolator
Pharmaceutical powders need to be contained in the strictest conditions. But handling powders and cleanin...
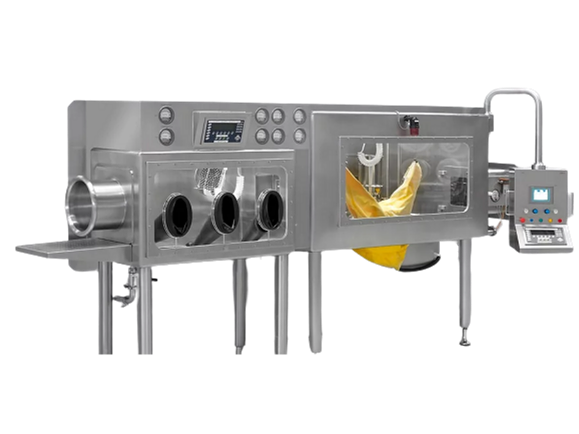
High containment micronizing isolator
Powder processing for chemical compounds demands product-specific micronizing solutio...
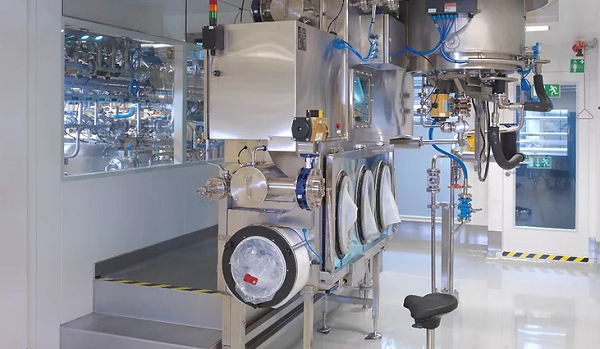
Filter dryer discharging isolator
Contained discharging is critical to the quality of filtration and drying processes. But ...
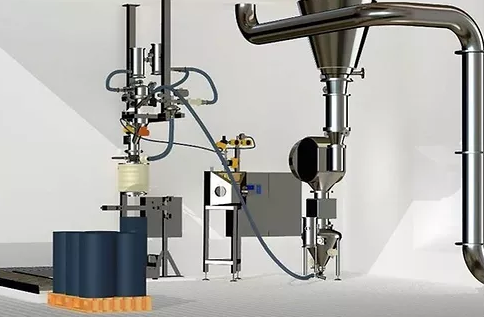
Contamination free filling system
Liners for powder handling across industries must prevent contamination of materials to c...
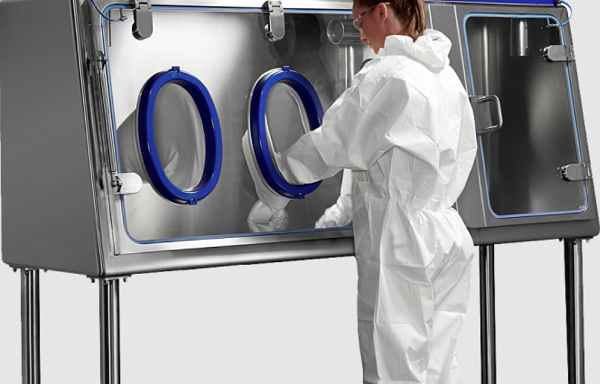
API containment isolator
Contamination is a major concern in powder handling, not least when processing pharmaceutical produc...
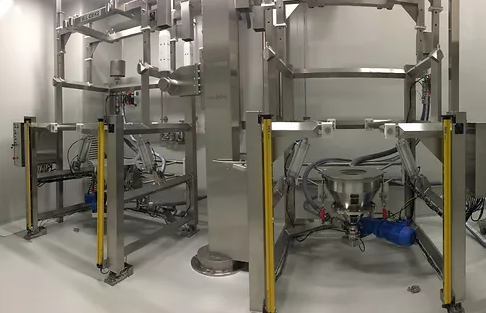
Big bag discharger
Big bags offer suitable material handling for powder products from pharma and food ingredients to bulk and...
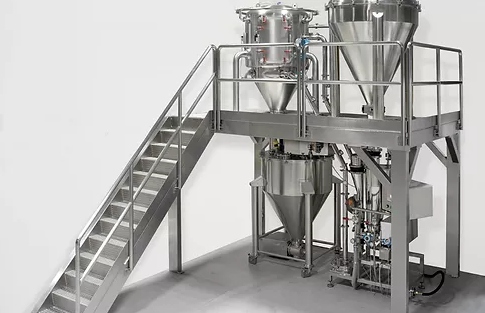
Production scale jet mill
Large volume manufacturers demand the most out of their production process, including powder milli...
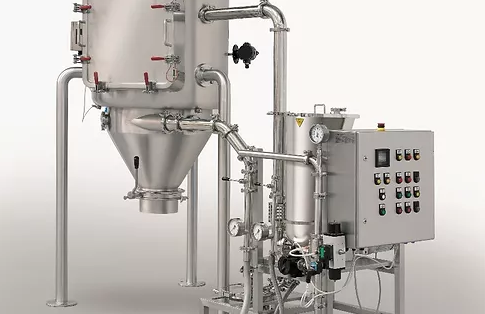
Jet mill micronizer
Small scale manufacturers that require effective micronization of powders for their process lines may nee...
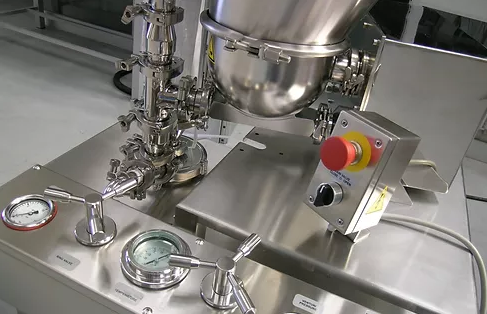
Pilot scale jet mill
In a pilot scale level or preliminary study, all the production process steps have to satisfy the small ...
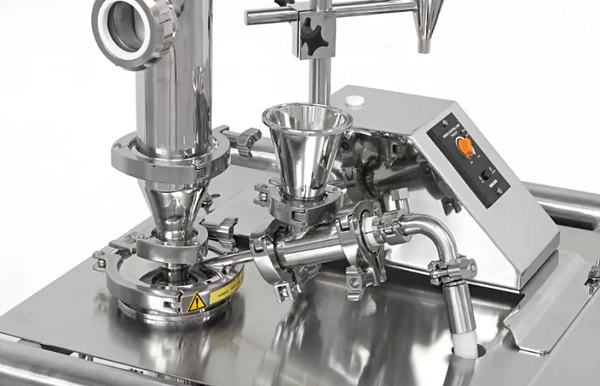
Laboratory jet mill
Manufacturing small quantities of high-value products requires efficient machines that can process these ...
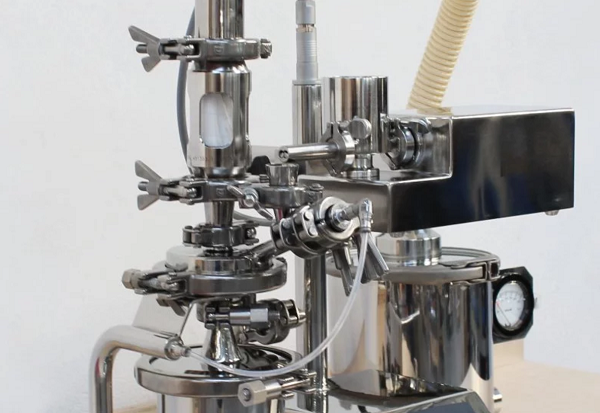
Jet mill for clinical trials
R&D laboratories may need to reduce the size of powder particles in small quantities for cl...
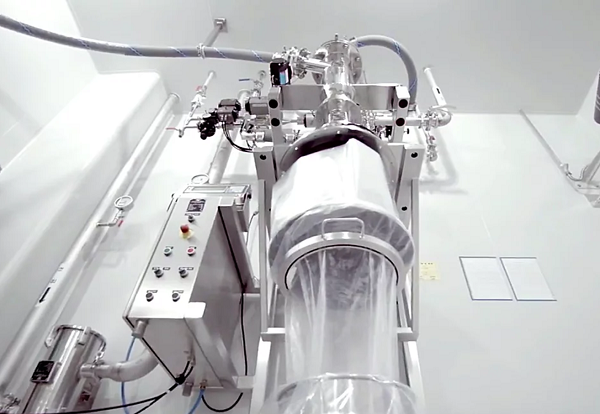
Drum filling system
Pharmaceutical and chemical products may be toxic or prone to contamination from environmental exposure. ...
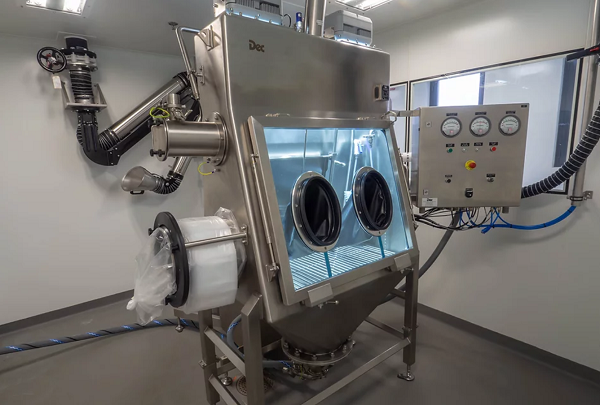
Drum emptying system
Handling products from the pharmaceutical and chemical industries requires careful attention and extreme...
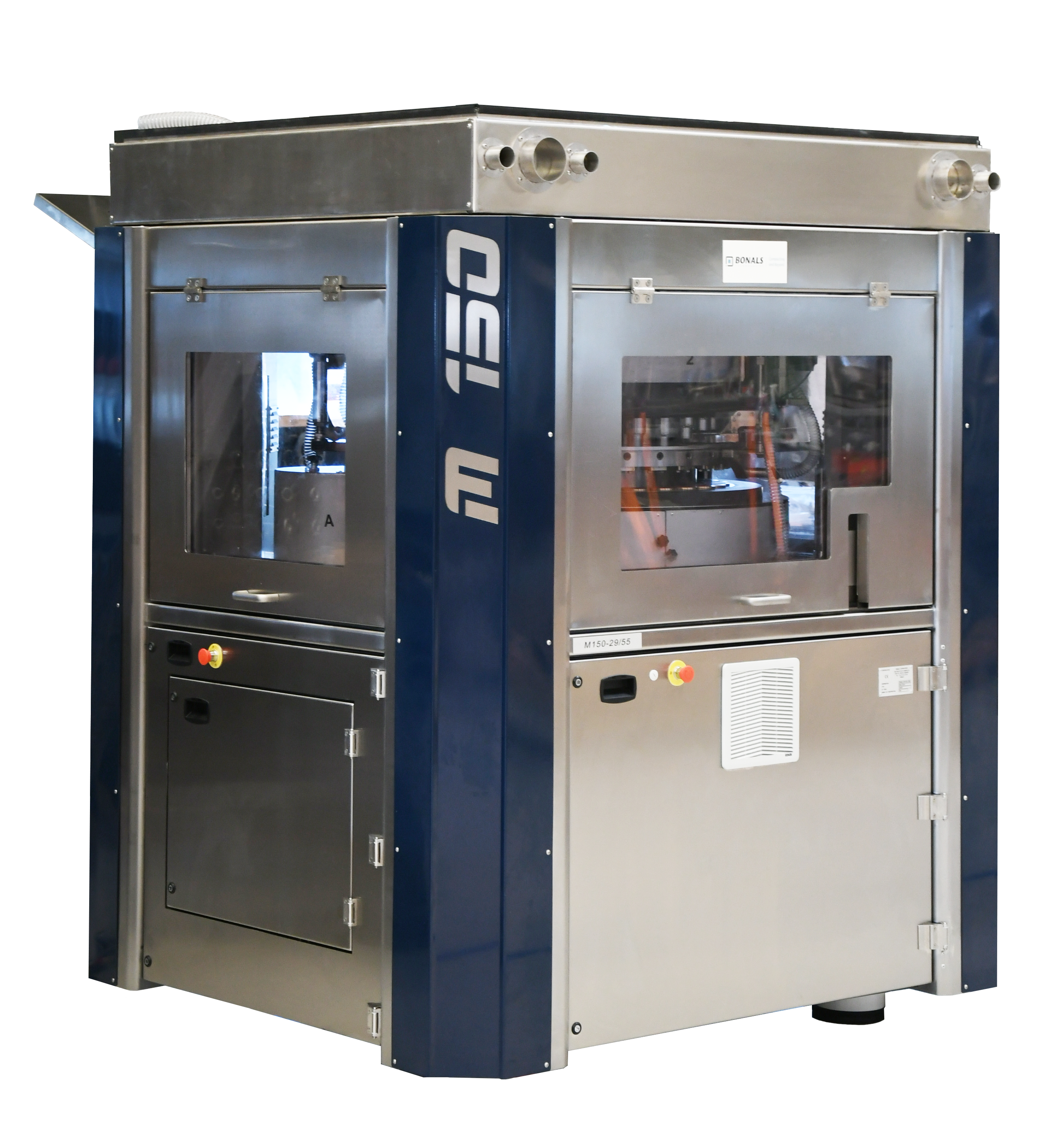
Fully automated dishwasher tablet press
The process of making dishwasher tablets that have more than one layer is very deli...
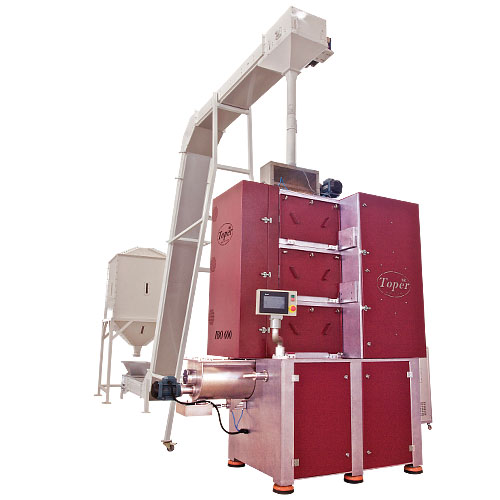
Roll mill for coffee beans
When you want flexibility to grin beans for filter coffee to Turkish coffee at particle sizes ran...
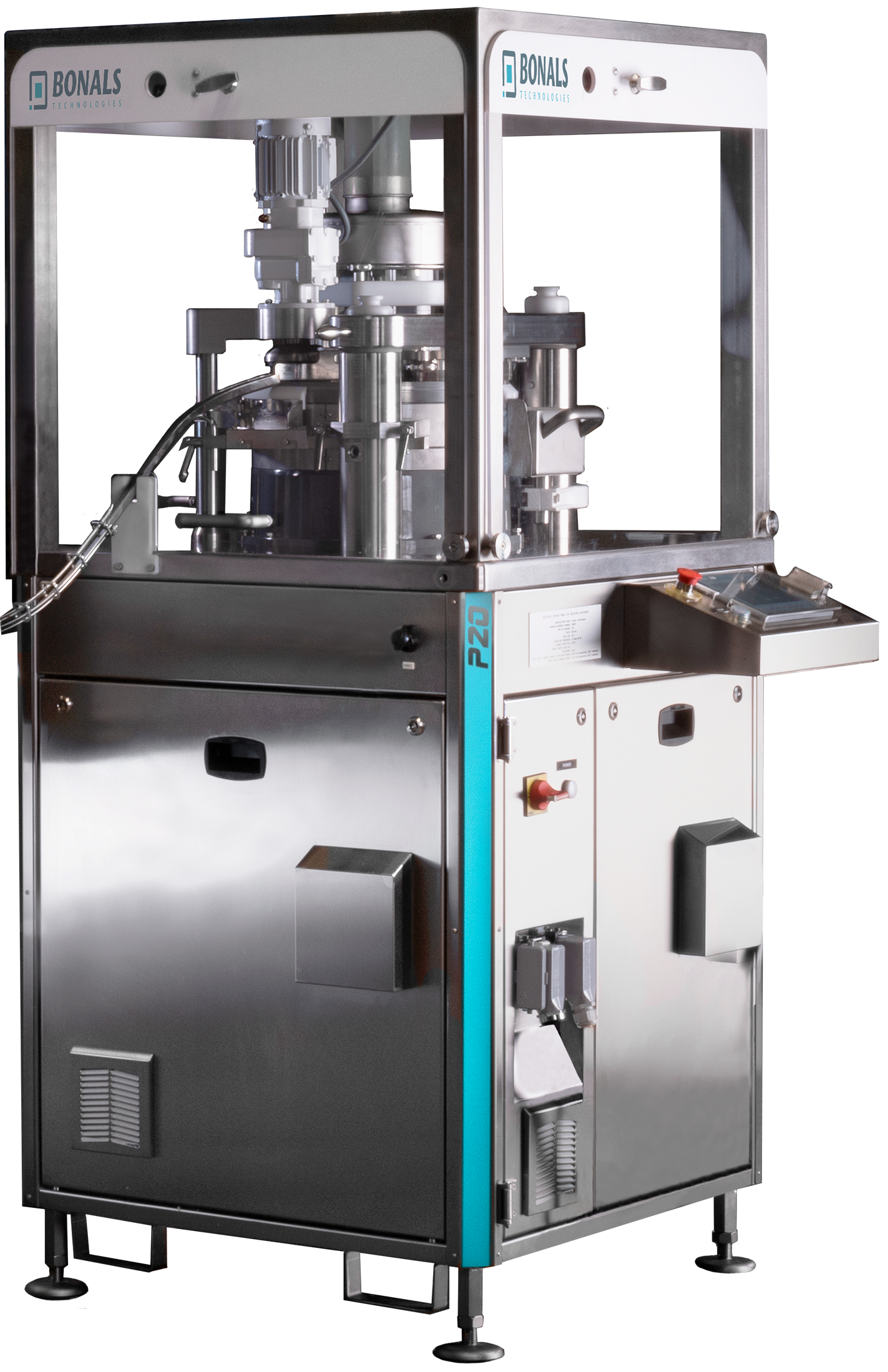
Bouillon cube press machine for medium-range batches
The pressing stage during the production of bouillon cubes or tablet...

Rotary Seed Pelleting Machine
When pelleting large batches of seeds like flower, vegetable, or agricultural types, it is imp...
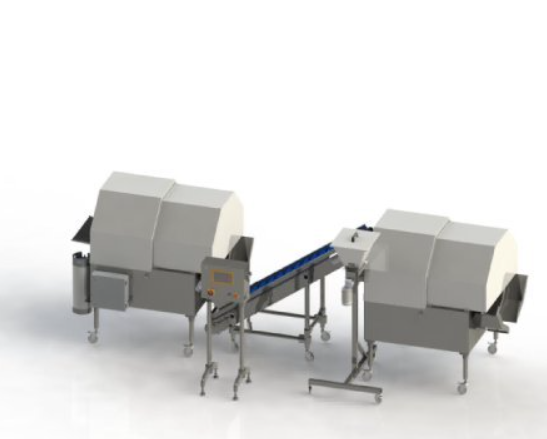
Flavouring system for healthy rice cakes and snacks
Being active on the market for healthy popped snacks asks for a flexi...
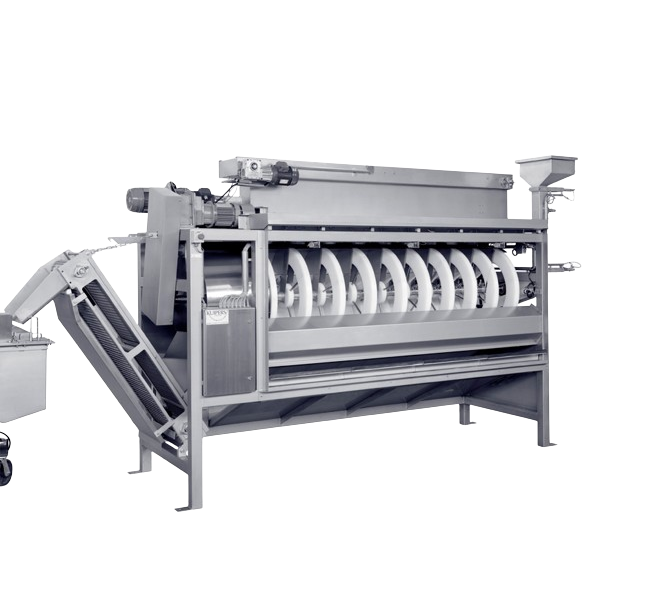
Continuous, automatic coating machine for peanuts
If you are in the peanut processing industry, bringing out delicious va...

Vertical ball mills for chocolate refining
Powders of extremely high fineness can easily be produced with ball mills and a...
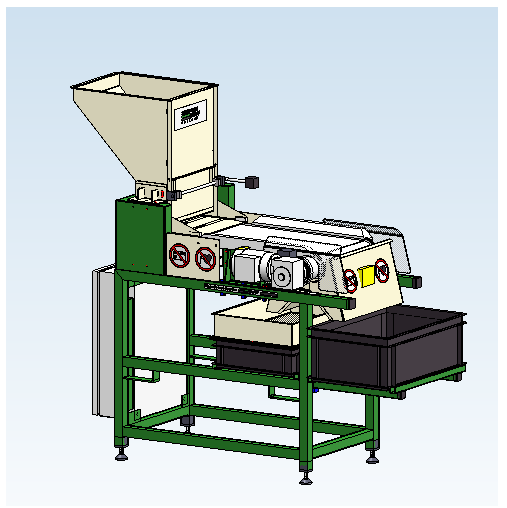
Magnetic Seed Separator Machine
It is challenging to separate seeds with cracks or holes from undamaged seeds. The way to do...
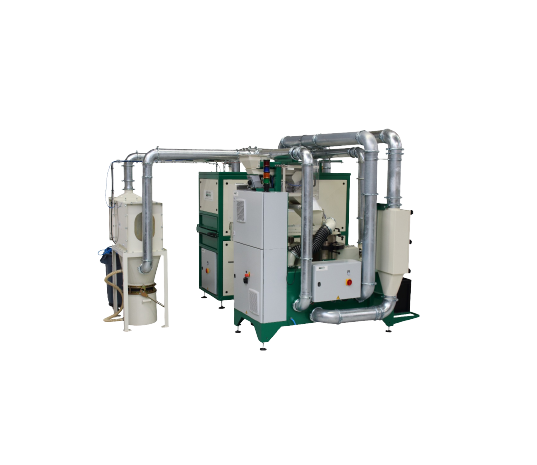
Seed Coating Machine With Integrated Dryer
Seed coating, also known as seed dressing, refers to the covering of seeds with...
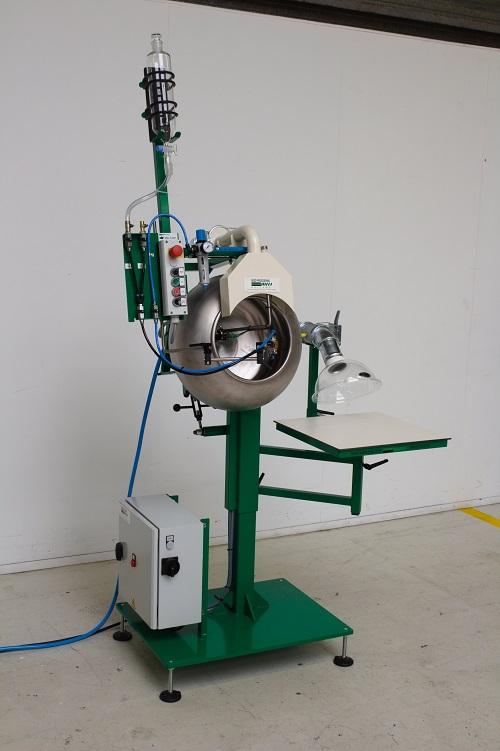
Seed Pelleting Machine
Seed pelleting or encrusting is the addition of materials like powders and liquids to seeds to increas...
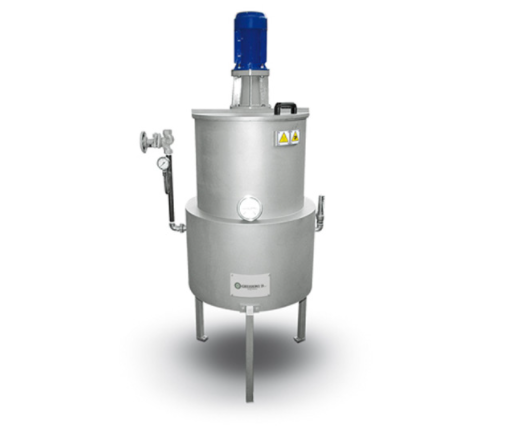
Emulsifier and mixer for gelling agent
When making jams and marmalades, gelling agents, such as pectin, are used to thicken...
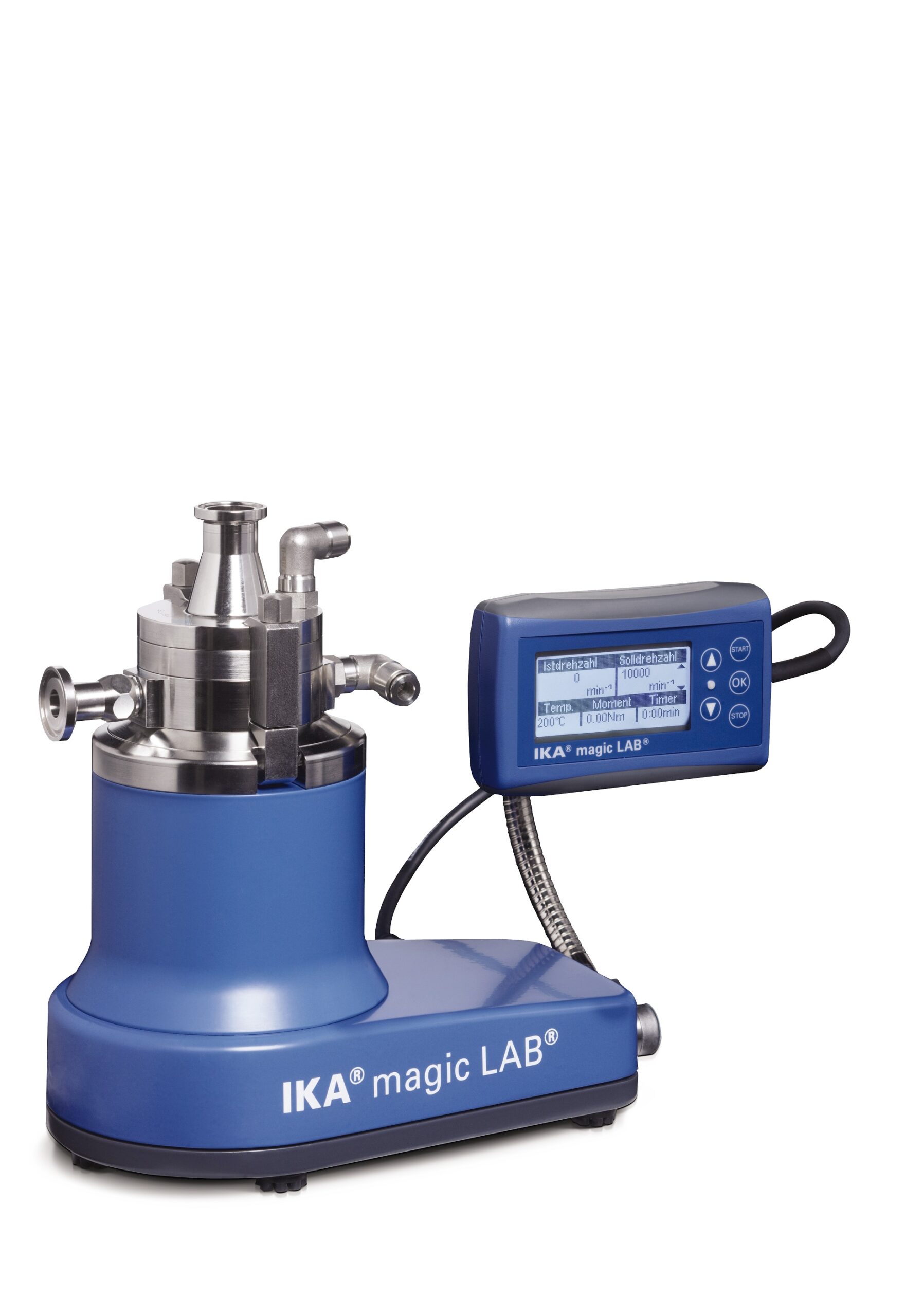
Small-scale laboratory dispersing machine
Developing and validating new processes requires reliable and highly versatile e...
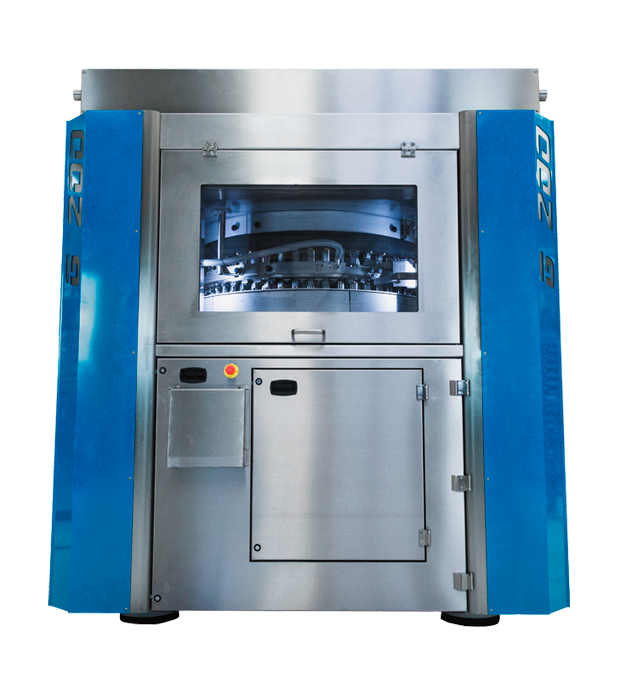
Three-layer dishwasher tablet press
Dishwasher detergent tablets come either in a single layer or multi-layer form. Multi-l...
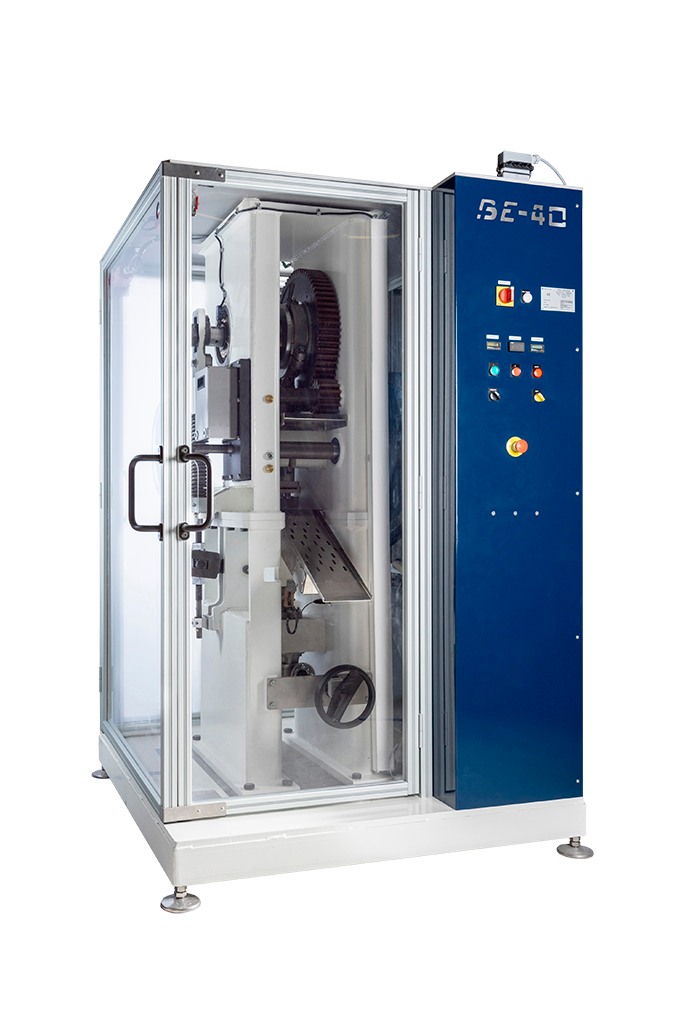
Eccentric press for refill tablets
Hundreds of different refill tablets, of various shapes or sizes, are on the market toda...
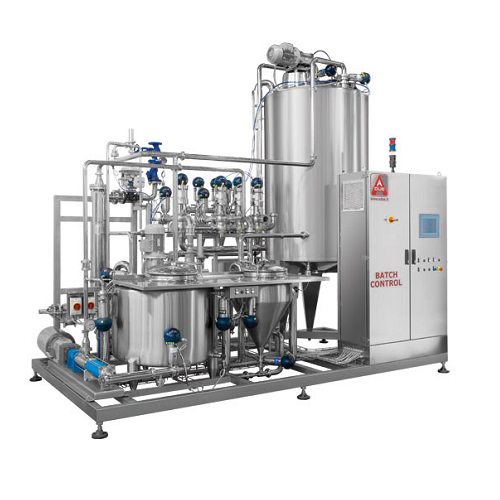
Mixing tanks for beverages
Juice production lines require multiple ingredients to be typically mixed with water. The incorpo...
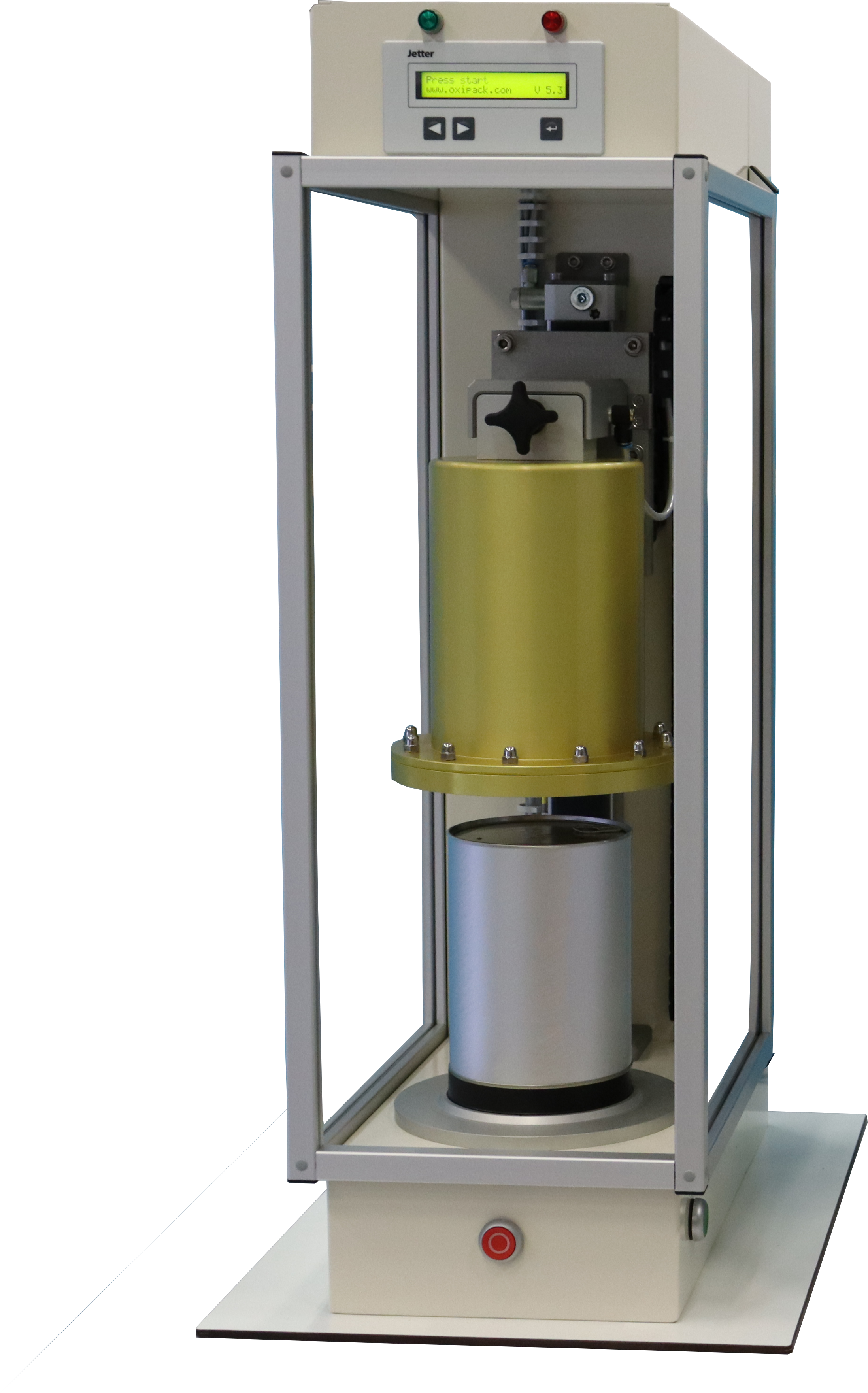
Can leak tester
Every canned pet food producer knows that their product should avoid the growth of microorganisms that could s...

Leak tester for pouches and MAP packaging
Nuts are packed with unsaturated fatty acids, which means they are prone to oxid...
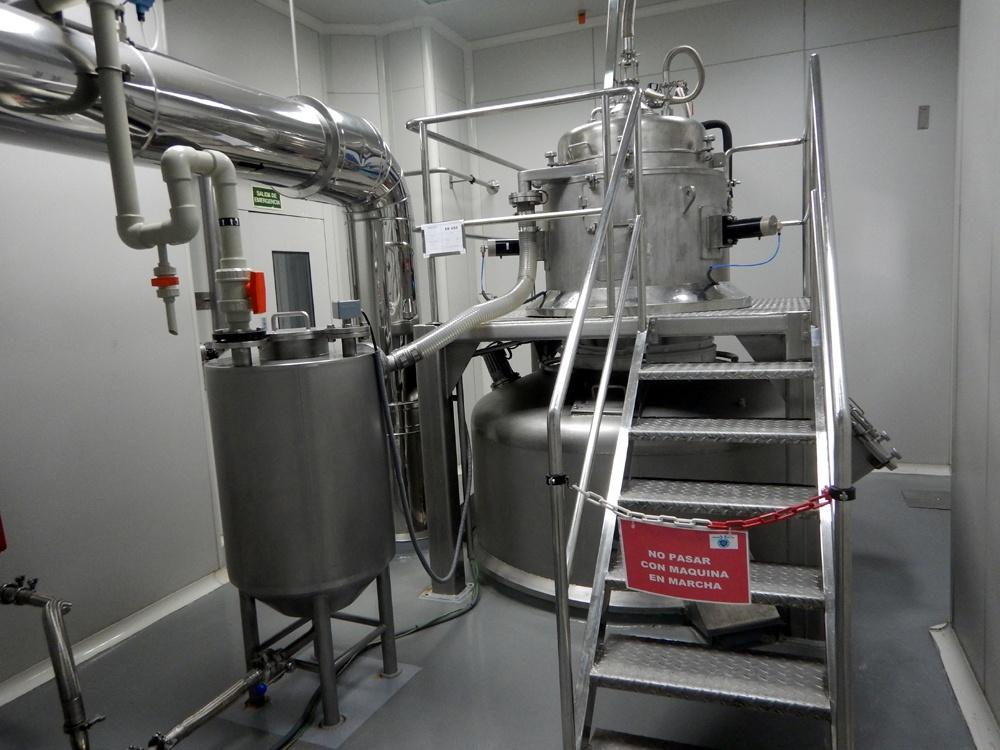
Continuous centrifuge for lithium hydroxide
Lithium hydroxide, a lithium compound used in making lithium batteries, is ind...
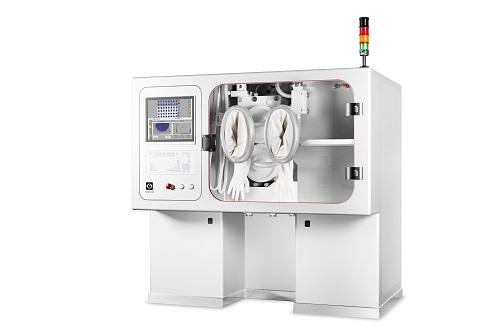
Contained Visual Inspection System
In the medicine industry, it is important to ensure there are no defects in tablets or c...
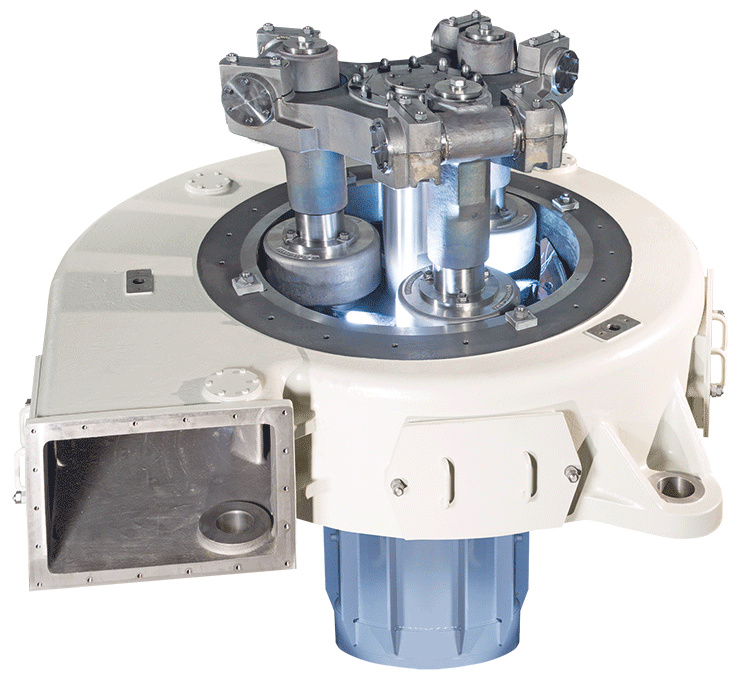
Grinding and drying of CaCO3
Widely used in the construction industry as filling materials, calcium carbonate is usually mad...
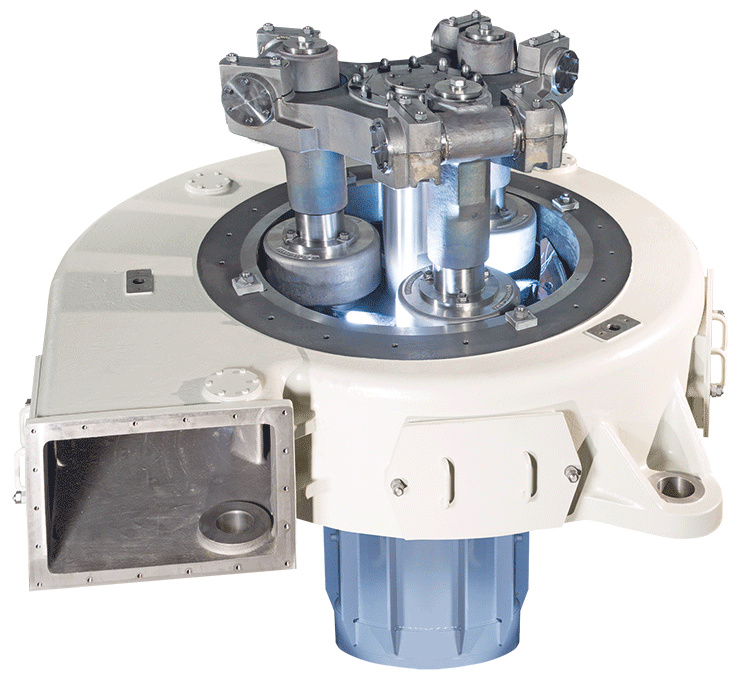
Grinding and drying of bentonite
After crushing and drying mined bentonite, this clay mineral is usually processed through a...
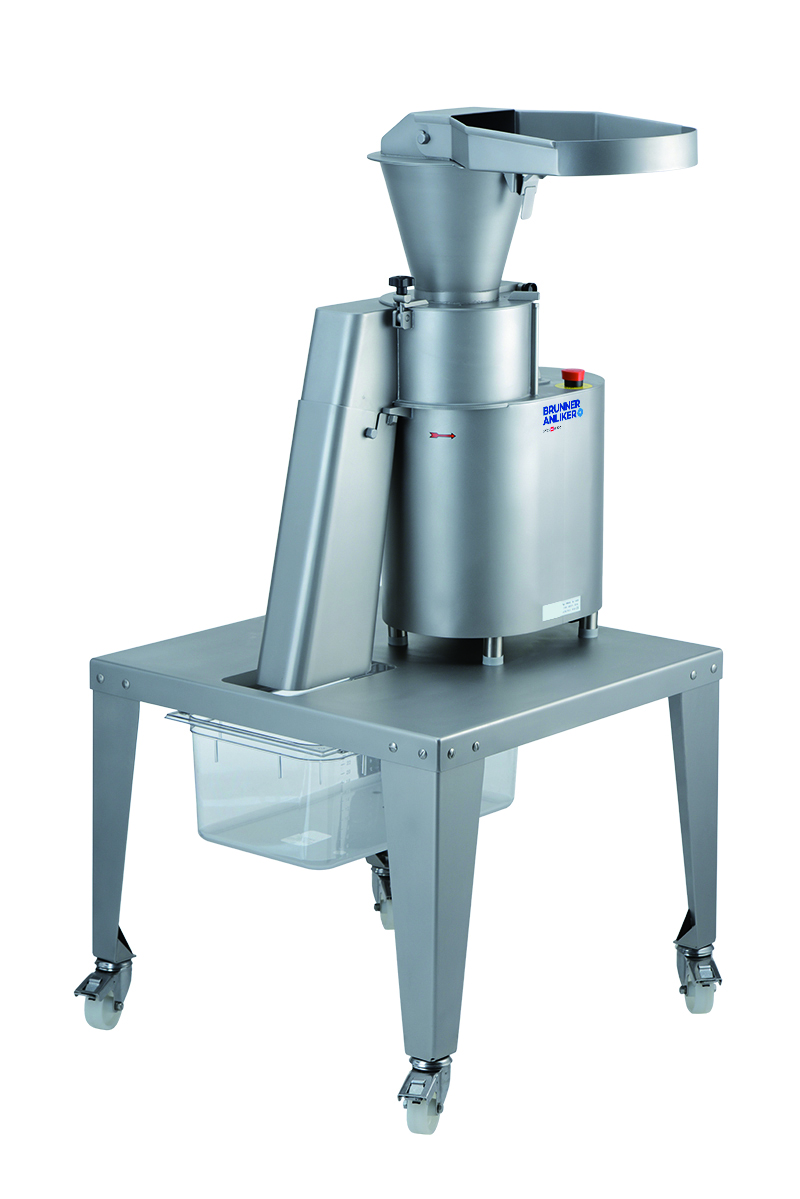
Nut and cheese grater
Smearing, clumping and crumbling are common problems when cheese and other soft textured foodstuffs are...
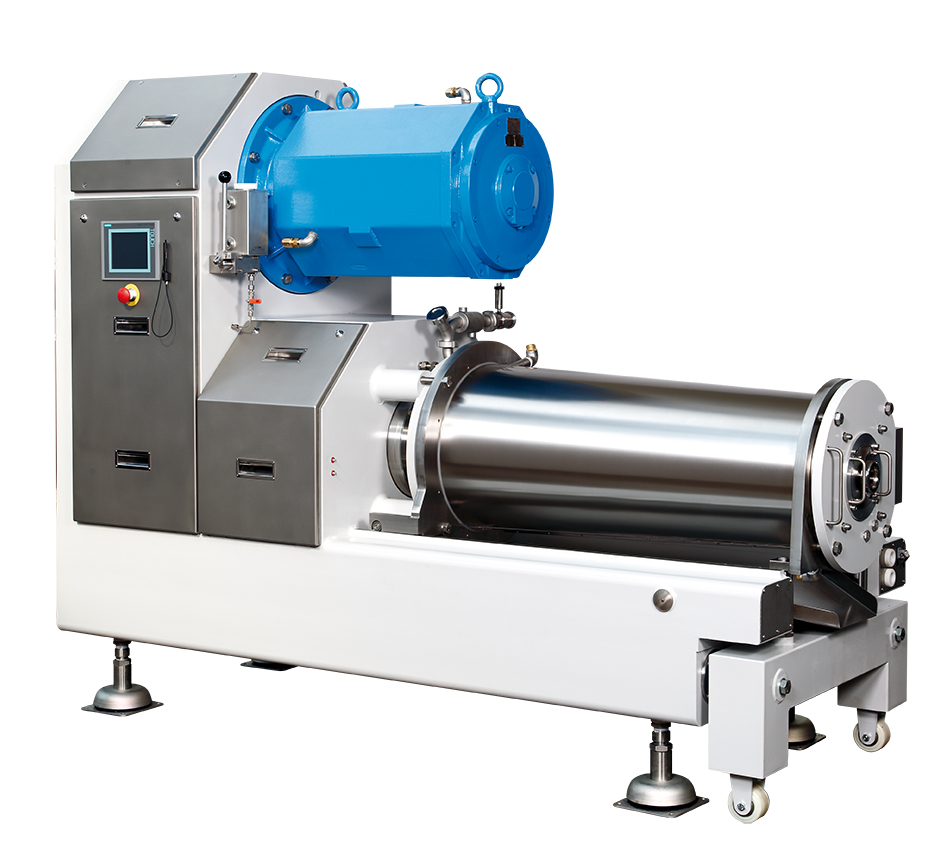
Horizontal ball mill for chocolate refining
Powders of extremely high fineness can be produced with ball mills and agitate...
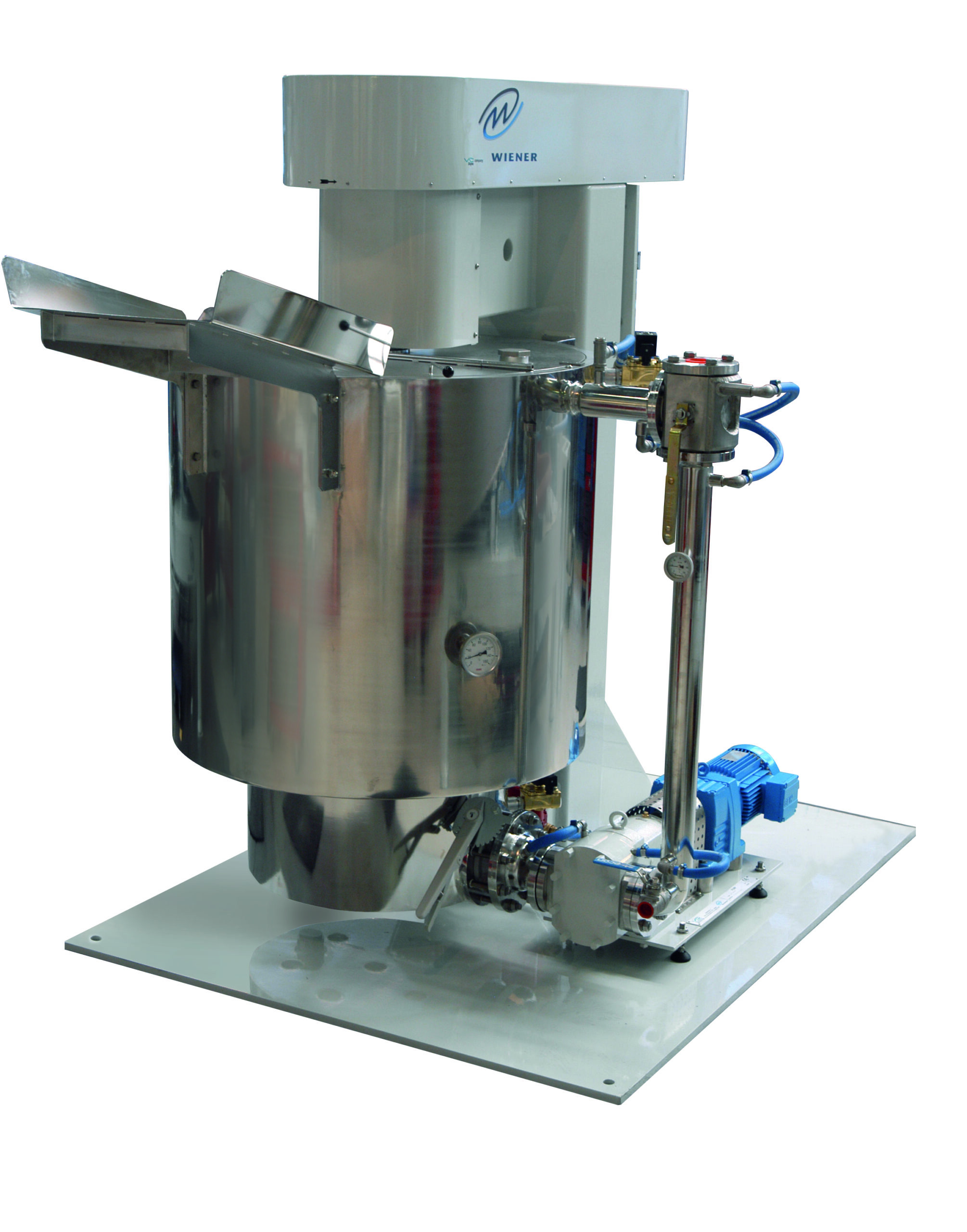
Mixer and refiner for chocolate compound
Mix cocoa liquor, cocoa powder, sugar, and lecithin in a small scale and refine sm...
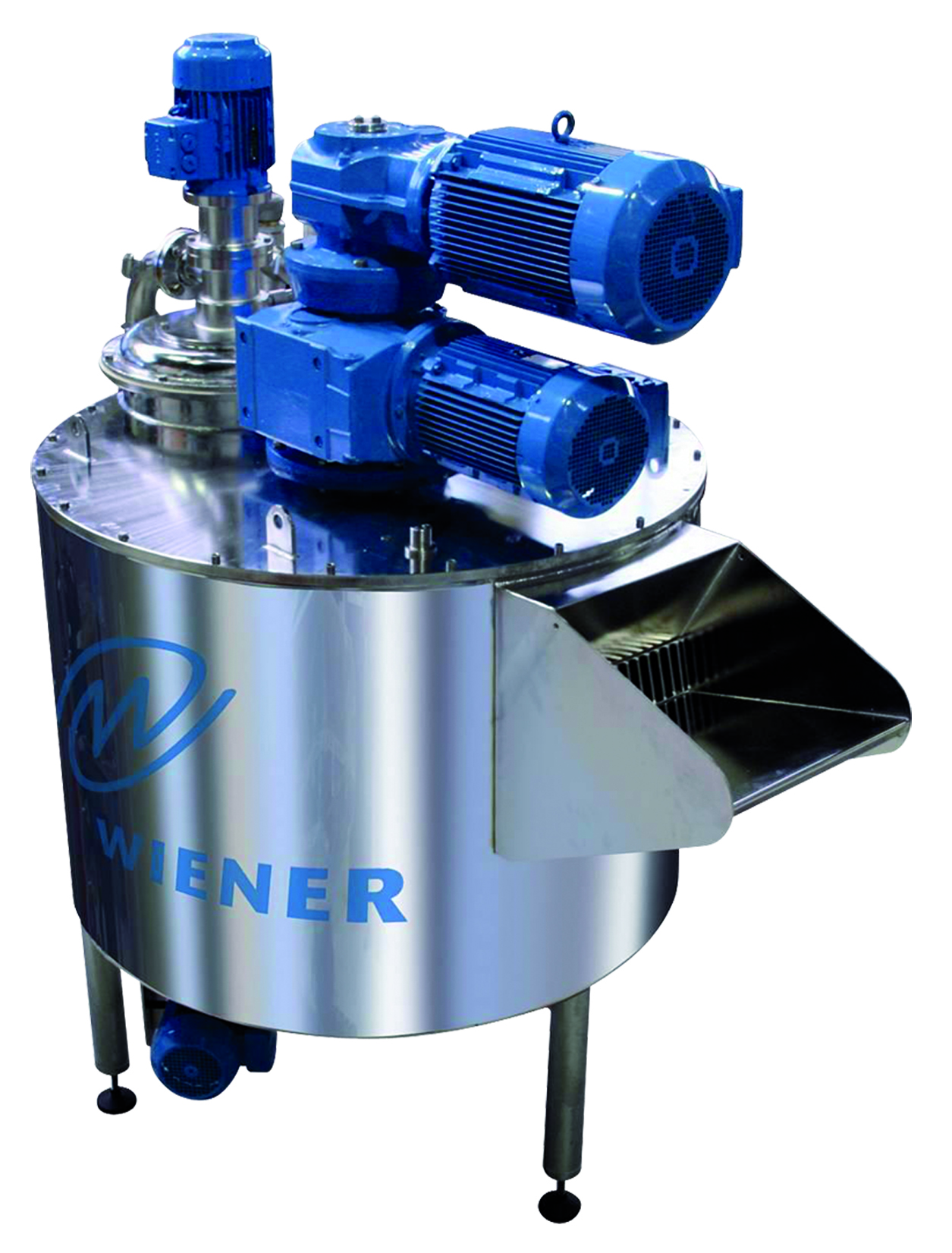
Batch chocolate machine with vertical ball mill
To mix and refine cocoa liquor, cocoa powder, sugar, and lecithin, several...
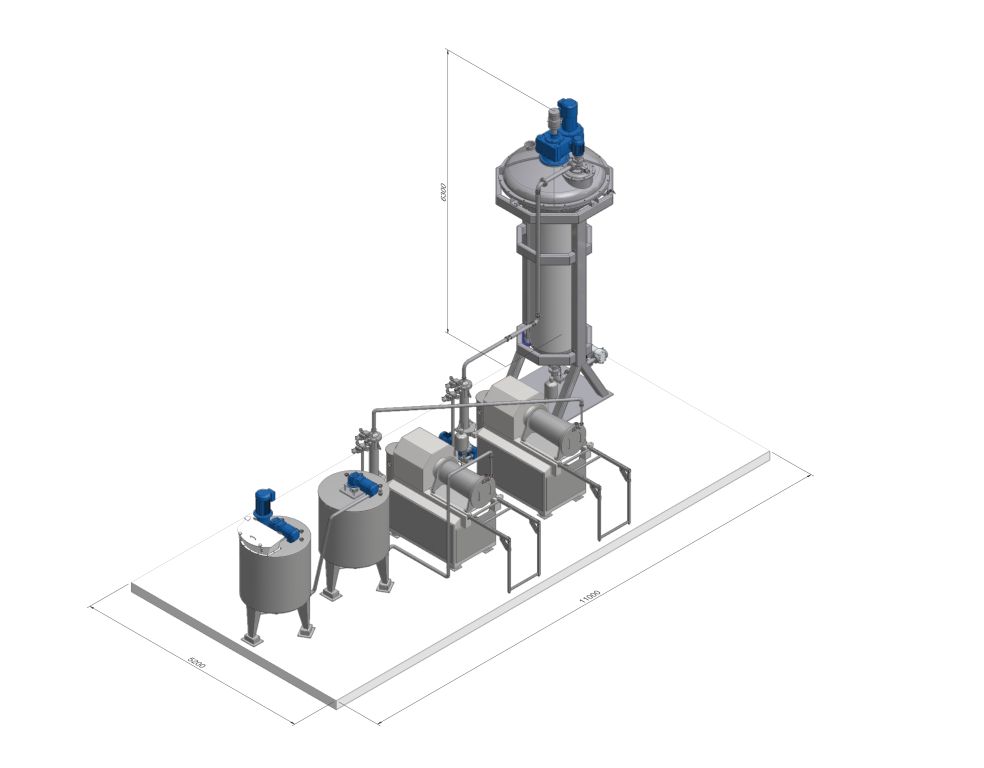
Continuous chocolate line with horizontal ball mills
For mixing and refining cocoa liquor, cocoa powder, sugar, and lecit...

Batch chocolate line with horizontal ball mill
To mix and refine cocoa liquor, cocoa powder, sugar, and lecithin, several ...
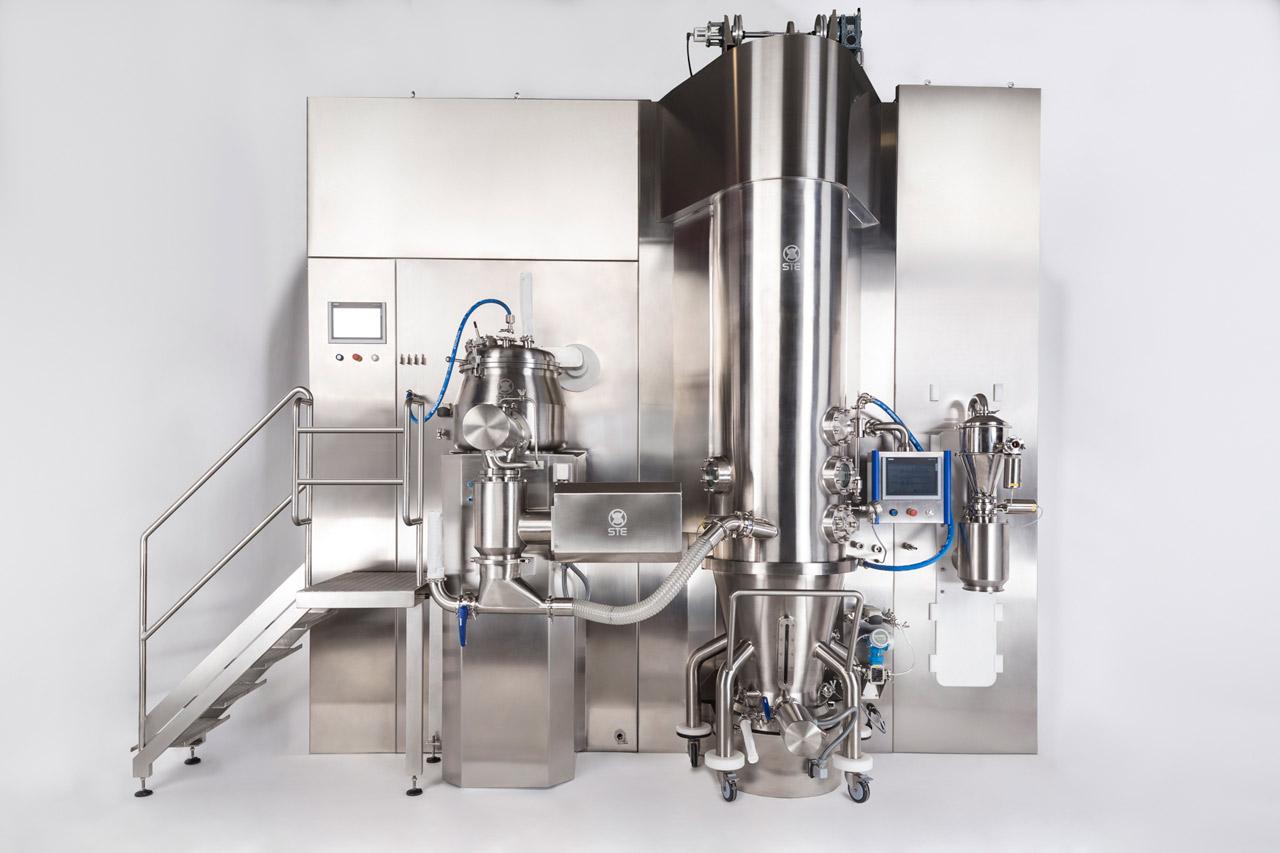
Granulation line for pharmaceutical solid dosage forms
Granulation is a common technique in production of pharmaceutical ...
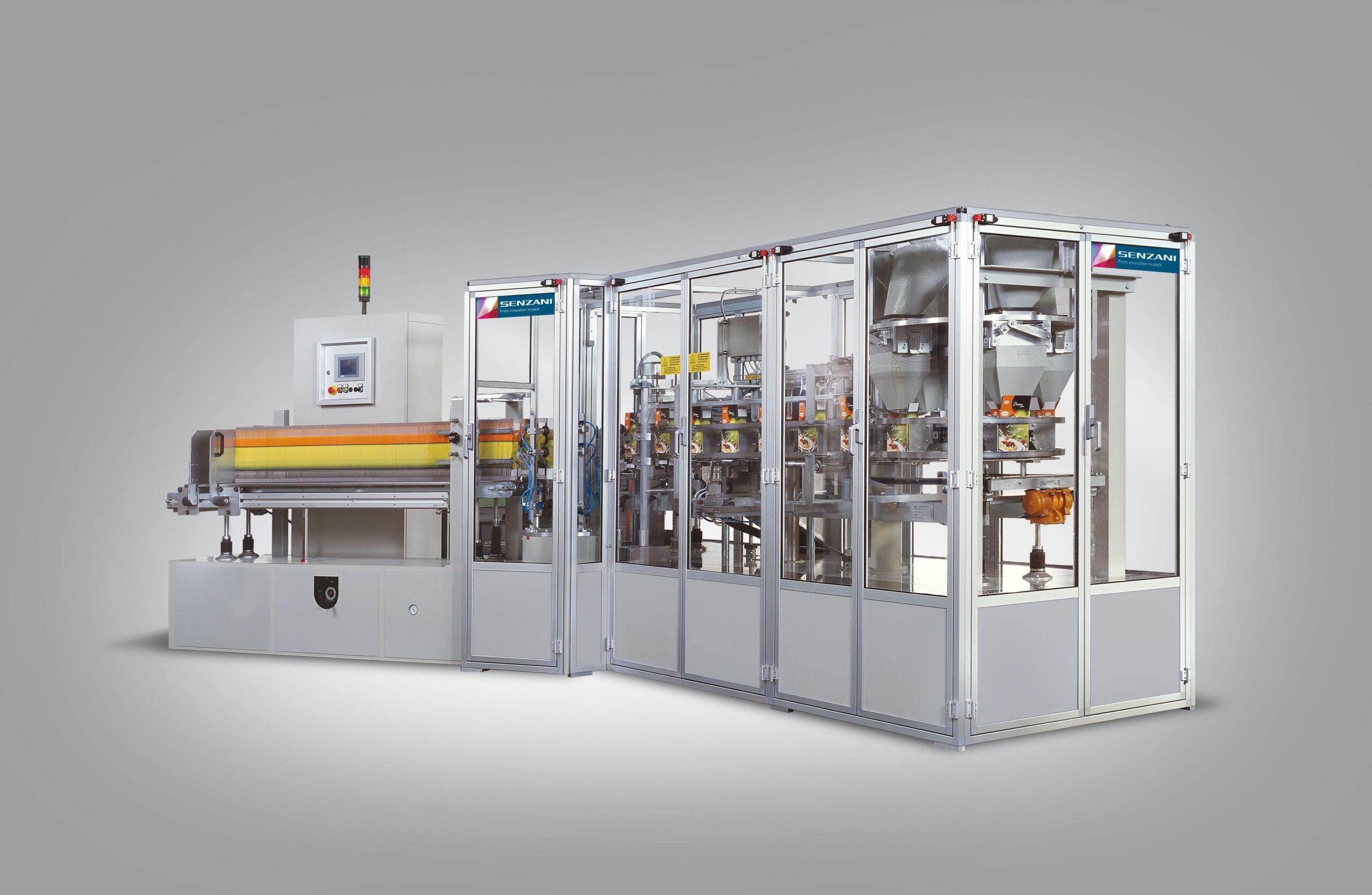
Vertical cartoning machine
In the food industry, a large number of bulk products like for example pasta, need to be packed i...
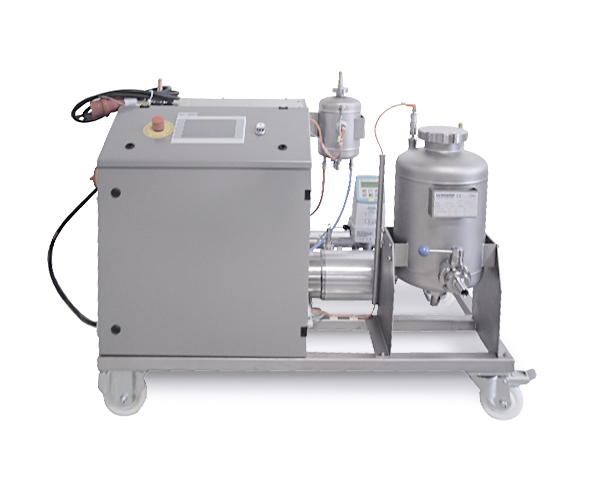
Aerator for high-viscosity media
Highly viscous ingredients in both the food and chemical processing industries require spec...
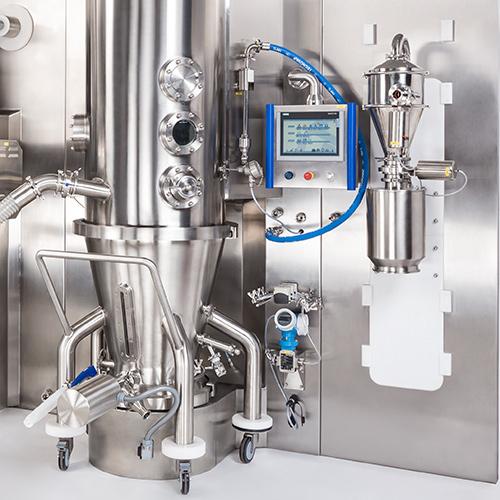
Fluid bed dryer for pharmaceutical solid dosage form
Fluid bed drying is a pharmaceutical process carried out to reduce t...

Industrial high shear mixer granulator for drug formation
It is rather difficult to successfully produce a pharmaceutica...
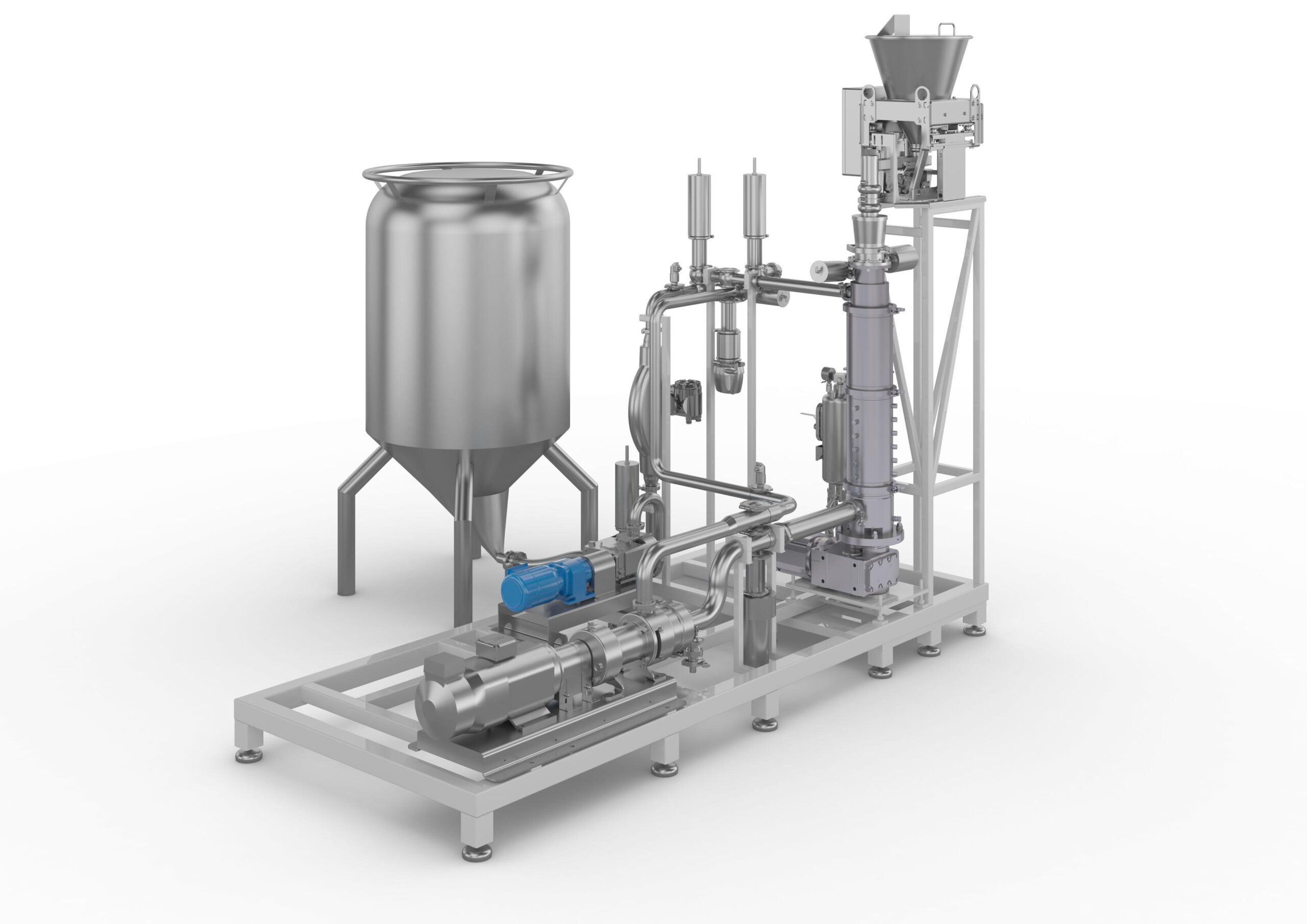
Continuous mixer for toothpaste production
When manufacturing toothpaste, dispersing and mixing powders into liquids to cr...
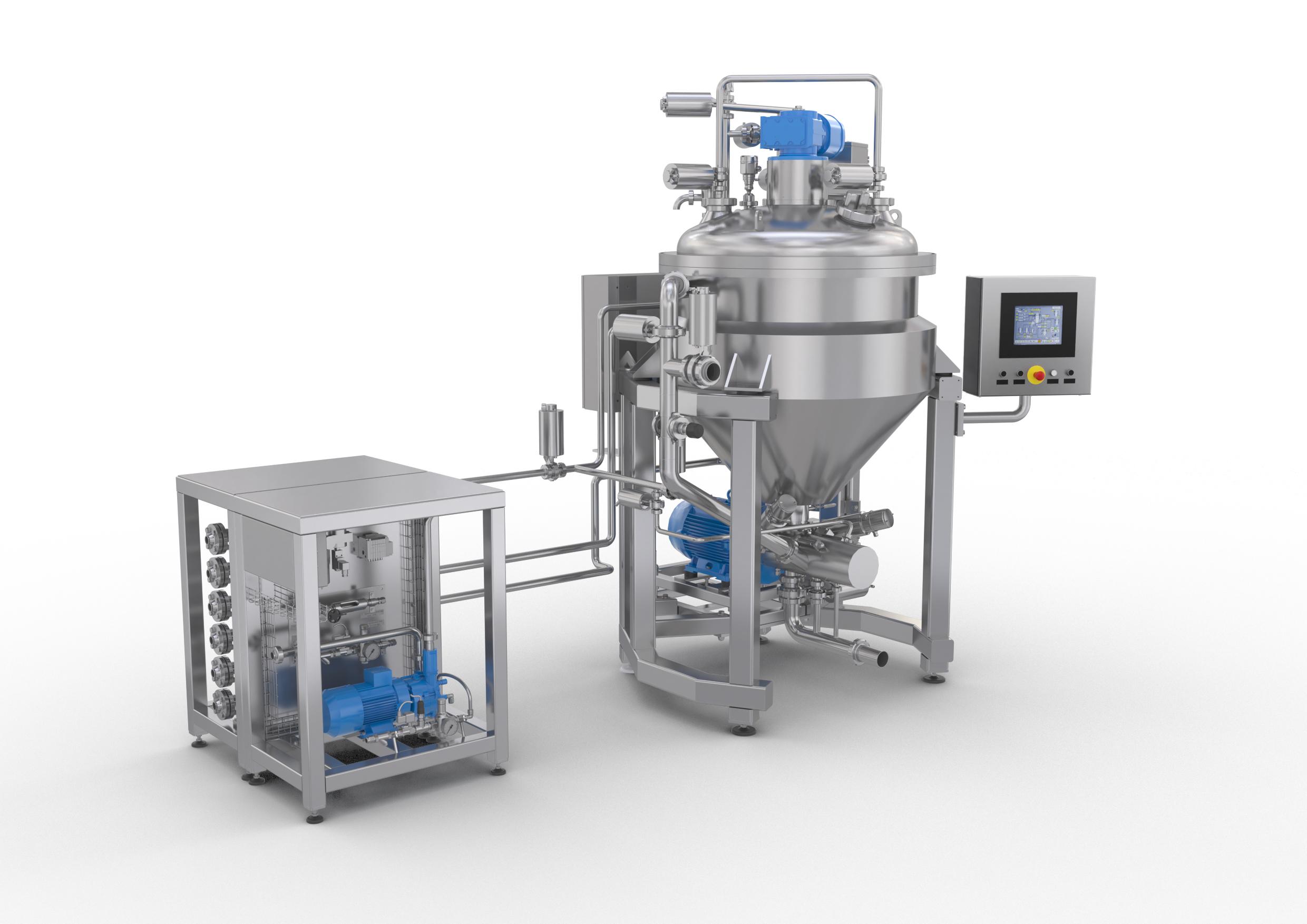
Batch vacuum mixer for emulsion-based products
The production of creams or ointments can be either be a water in oil (w/o)...
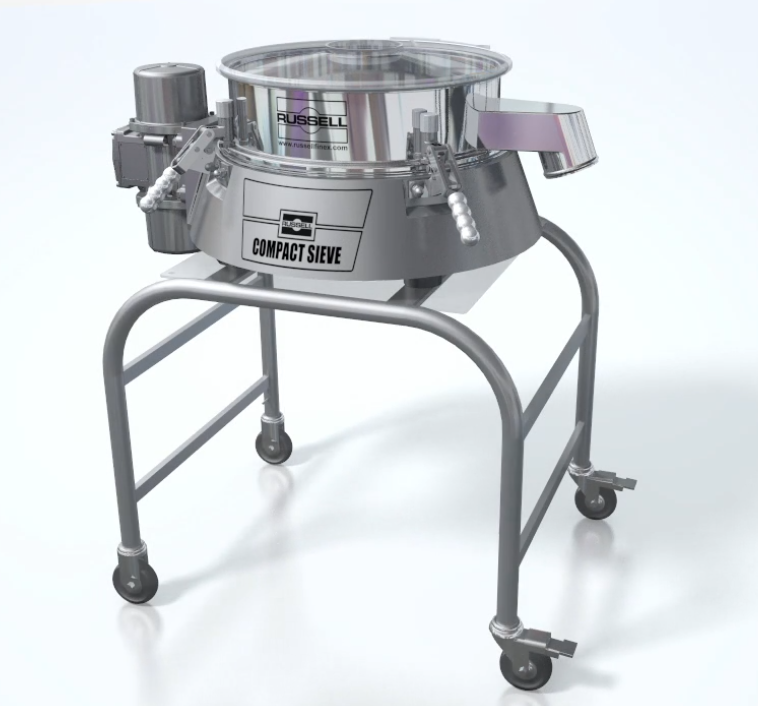
Vibrating screening machine for coffee
Coffee bean separation is one of the important steps during bulk coffee production. ...
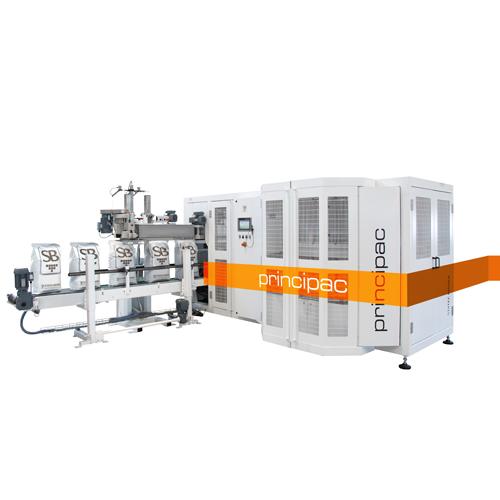
Open mouth bagging machine
If you are a manufacturer of fertilizers, bulk chemicals, sugar, seeds, or any grains it is likel...
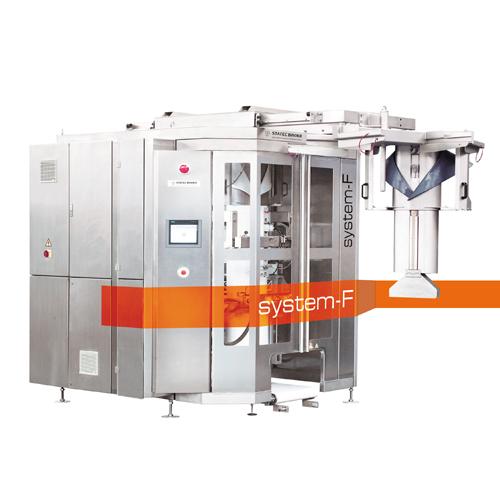
Vertical form fill seal machine
There is an increasing demand for a range of different package sizes of the same product. If...
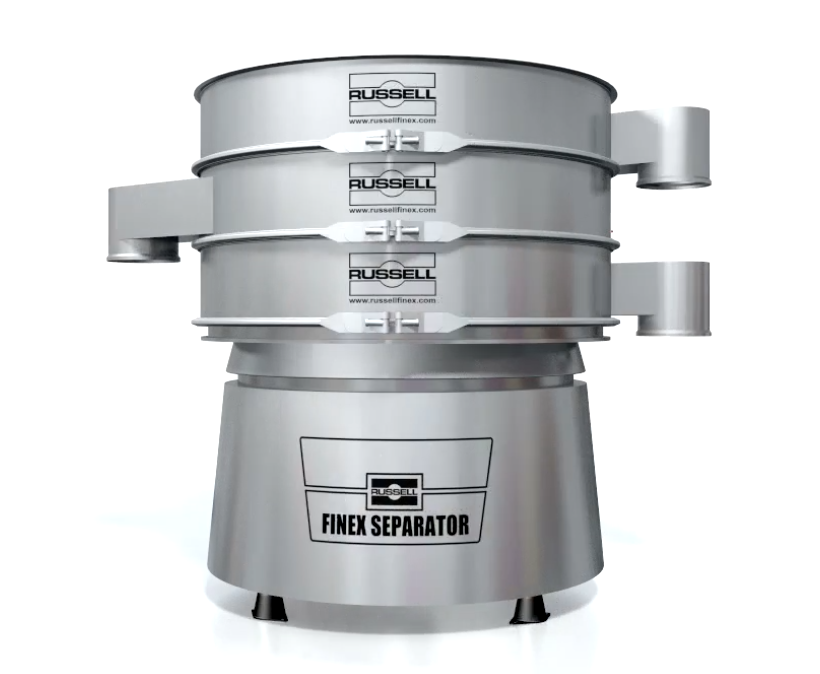
High capacity grading sieve
An industrial vibratory separator machine is multi-purpose, able to carry out a variety of diffe...
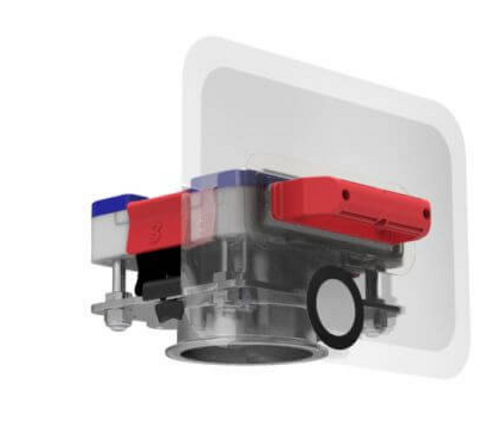
Single-use containment valve
Safe transfer of liquids and hazardous powders into systems can be a challenge in pharma, bioph...
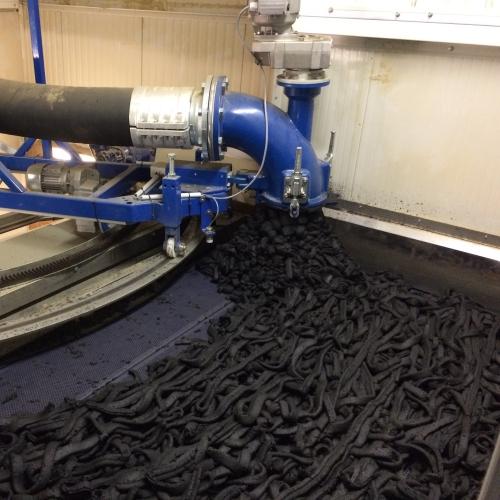
Belt dryer for sewage sludge
If your water treatment plant often facing difficulties with sewage sludge deposits, drying the...
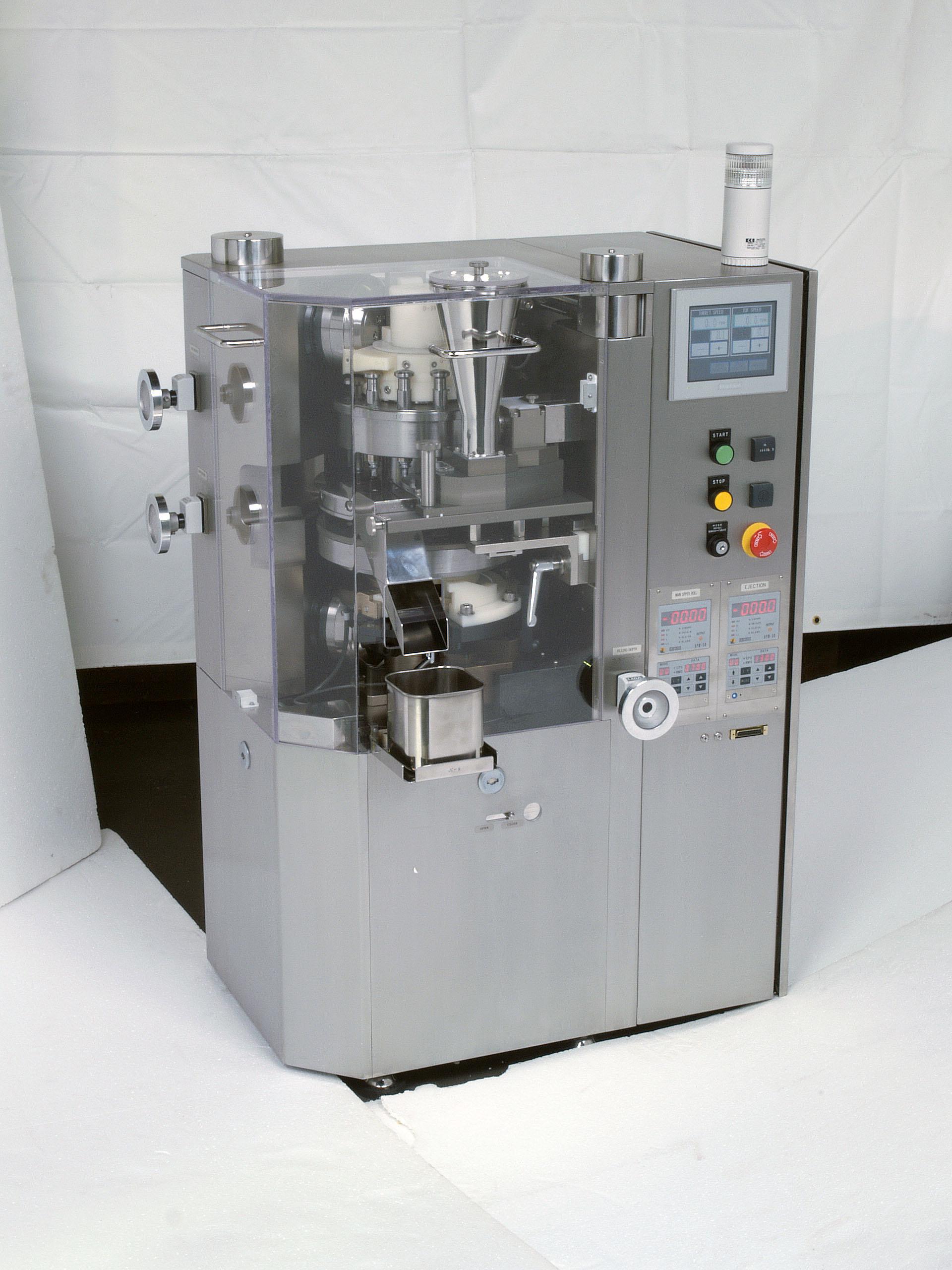
Laboratory Tablet Press
Pharmaceutical research and development projects may require small samples of high quality tablets fo...
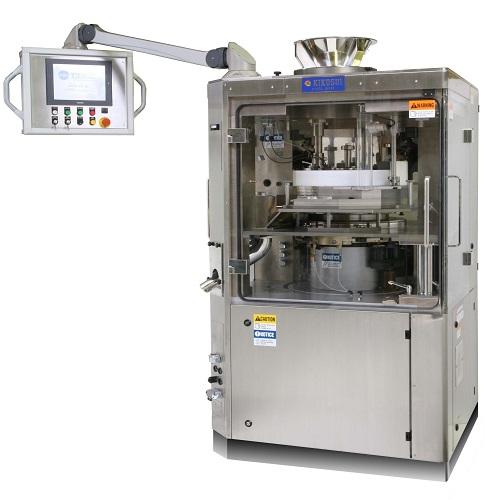
High Speed Tablet Press
High speed pharmaceutical tablet presses convert powder to tablets. The operations should be quick an...
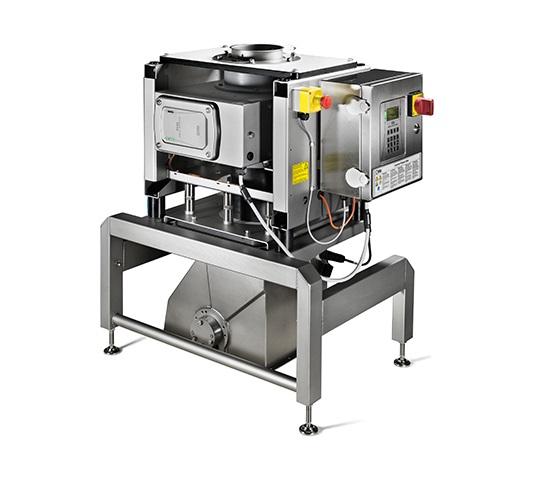
Metal detector for granulated products
Free-fall applications, such us flour, sugar, spices and other granulated or powdere...
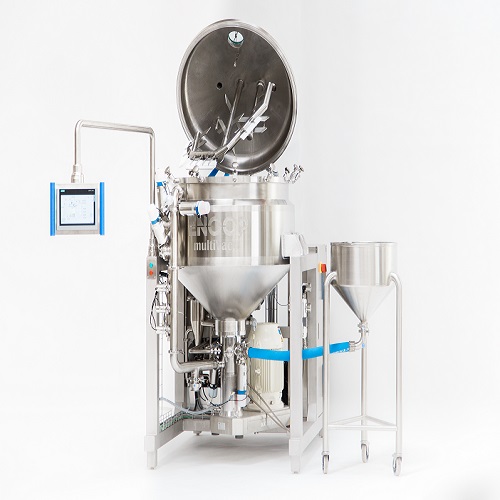
Vacuum based homogenizer
When producing liquid and viscous products such as mayonnaise, sauces, dressings and ketchup it’s vi...
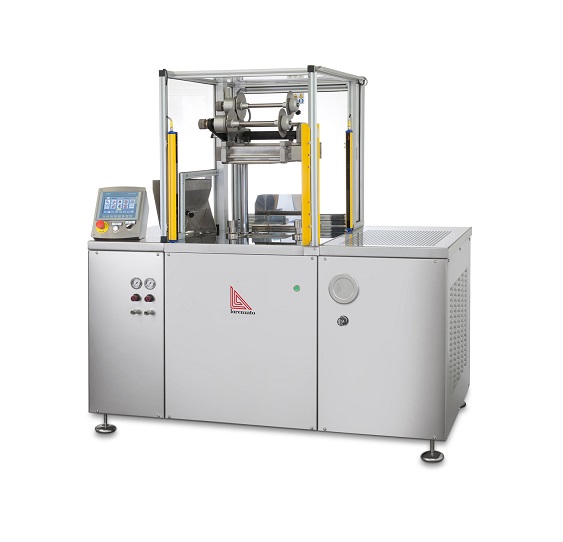
Makeup blusher compacting machine
When producing high-quality compressed powder cosmetics, control of the pressing process ...
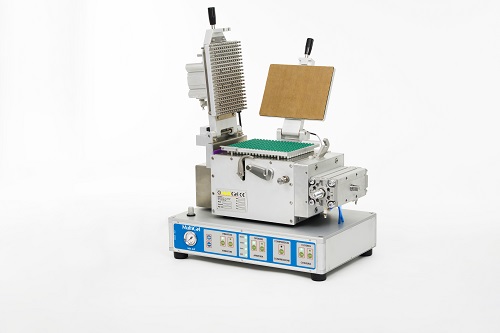
Semi-automatic capsule filler
Hard gelatin capsules are a popular format for delivering a wide variety of pharmaceutical dos...
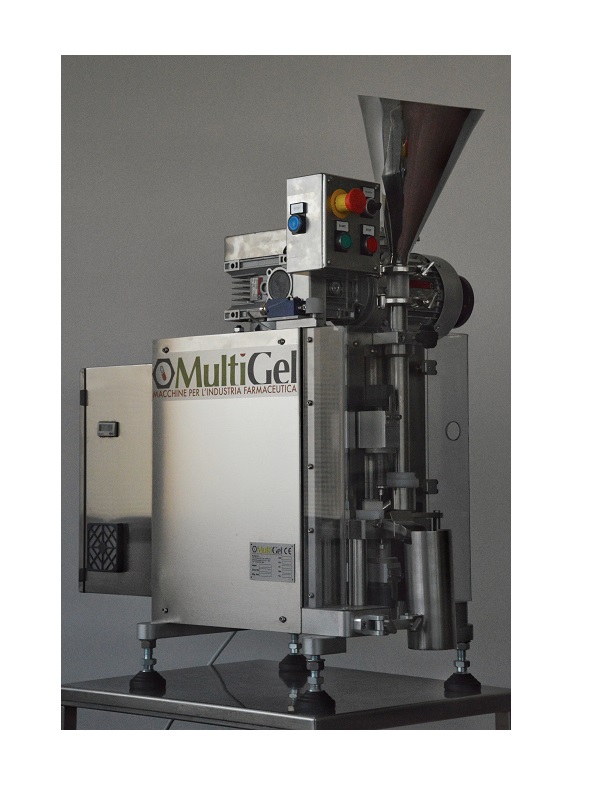
Benchtop tablet press
For lab work or small-scale production, a purpose-designed tablet press that meets your exact requireme...
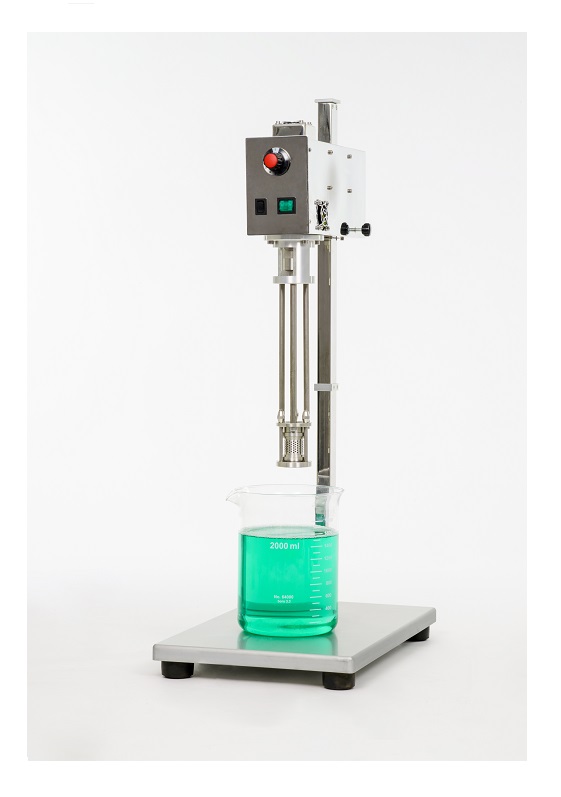
High shear lab mixer for creams
Lab-scale mixers are vital in the design or small-batch production of a range of pharmaceuti...
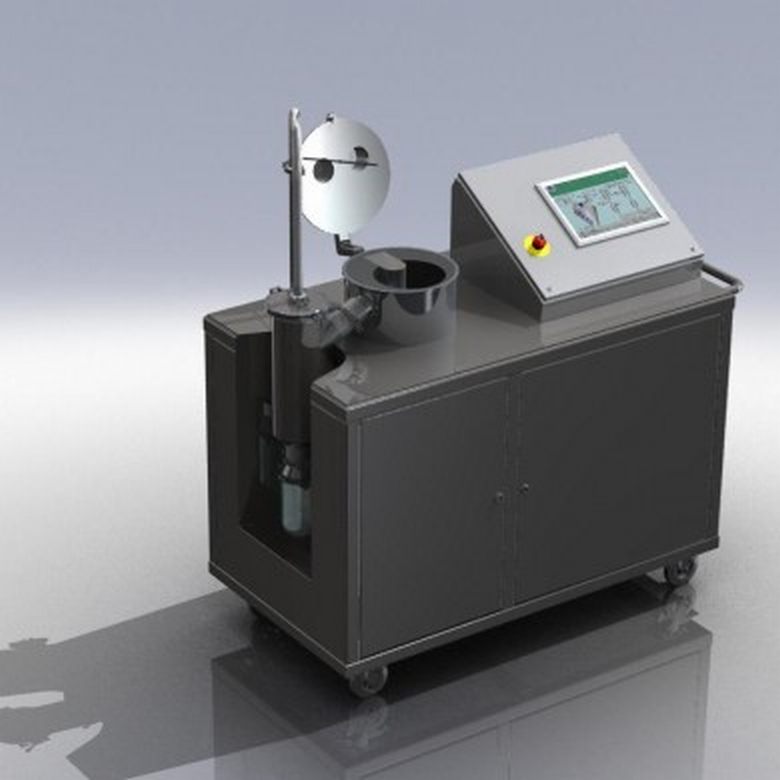
Laboratory scale active freeze dryer
The laboratory-scale active freeze-drying is used for dehydrating high-value products ...
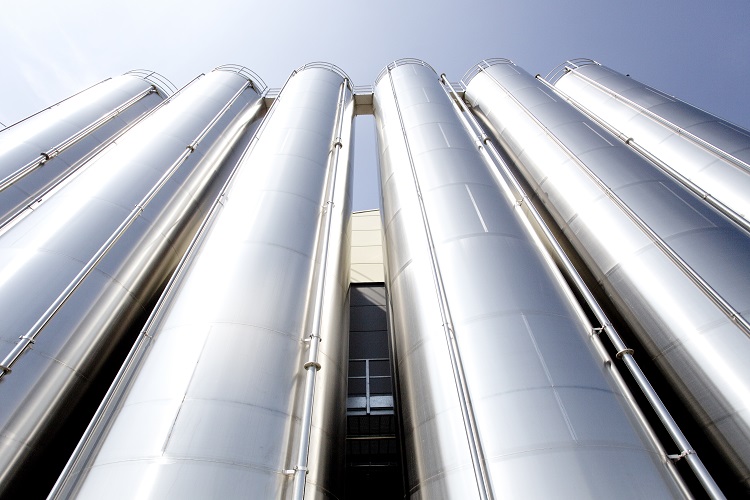
ATEX confirmed outdoor silo for flour
Bulk outdoor storage of flour, dry milk and other powder ingredients for the bakery i...
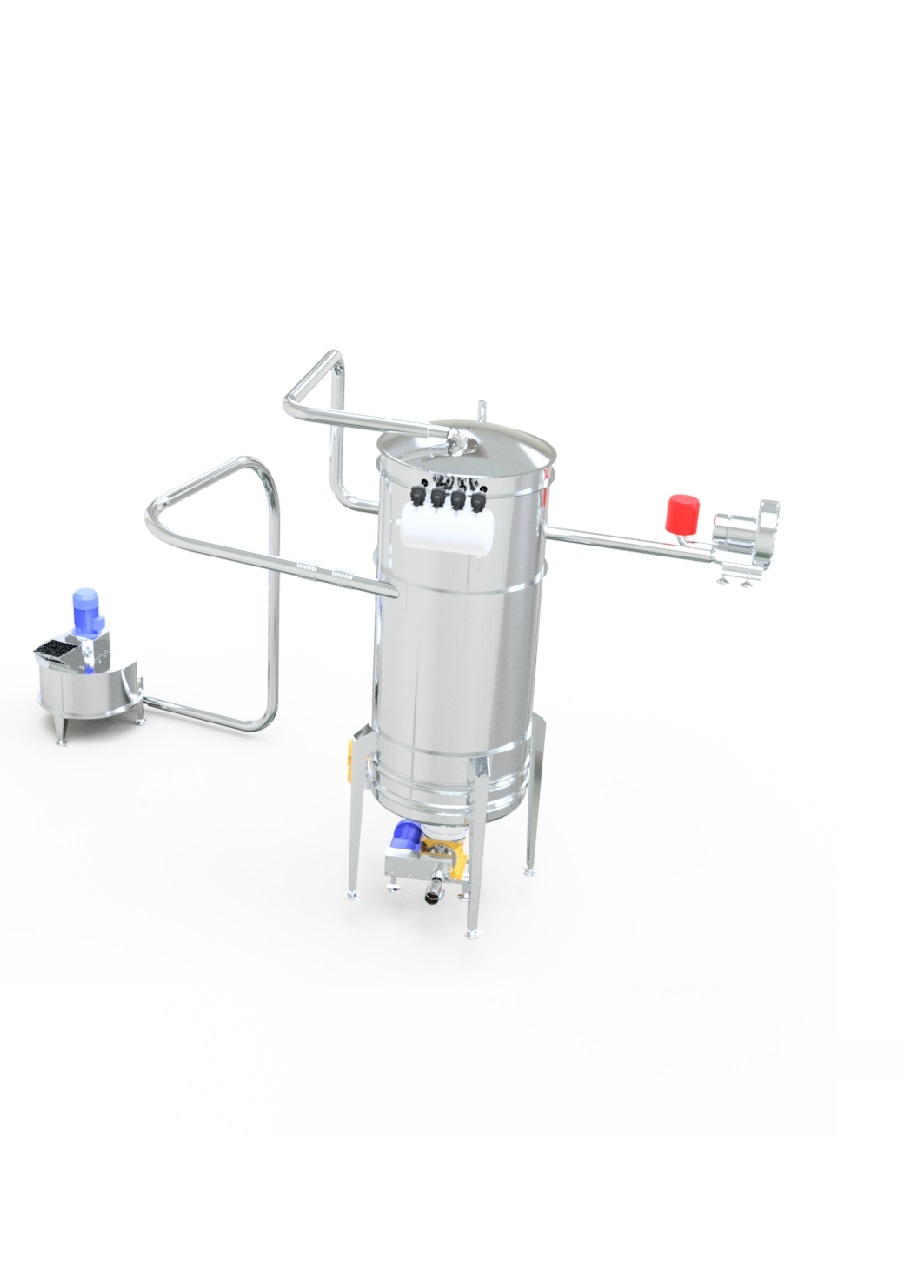
Automatic rework system for biscuit and bread scrap
Scraps are an inevitable byproduct of biscuit and bread production. W...
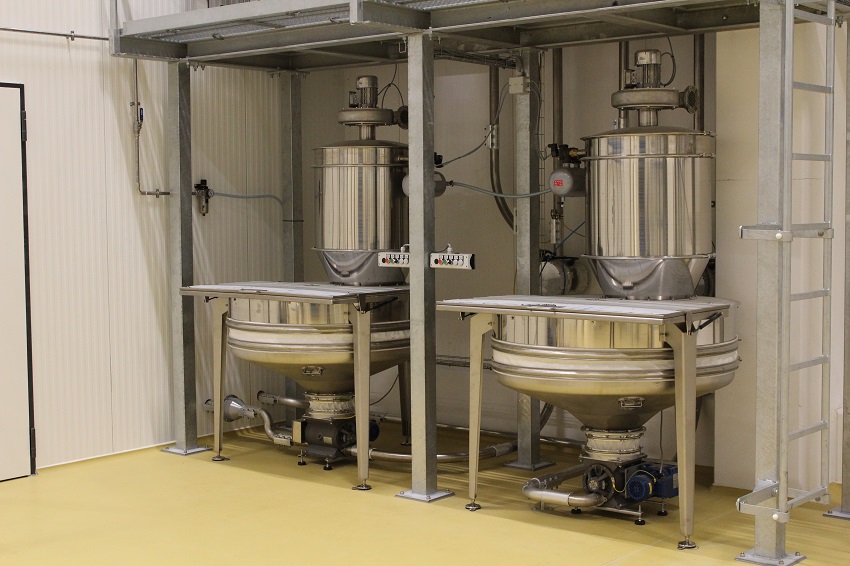
Manual bag discharger for bakery industry
Many minor and intermediate ingredients for bakery products are delivered in bag...
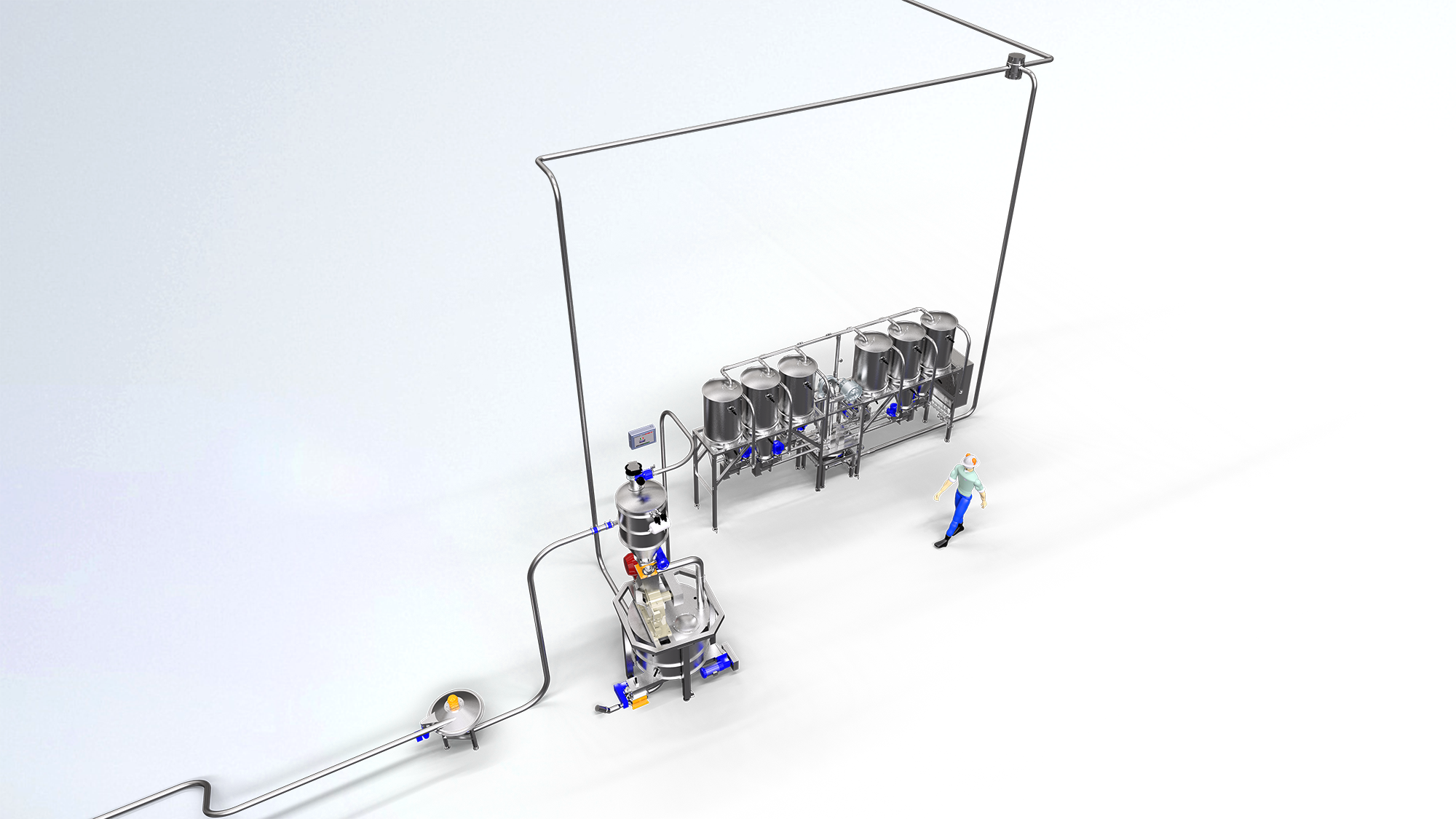
Microdosing system for bakery industry
Storage and dosing of powdered minor ingredients such as flavourings, colours and si...
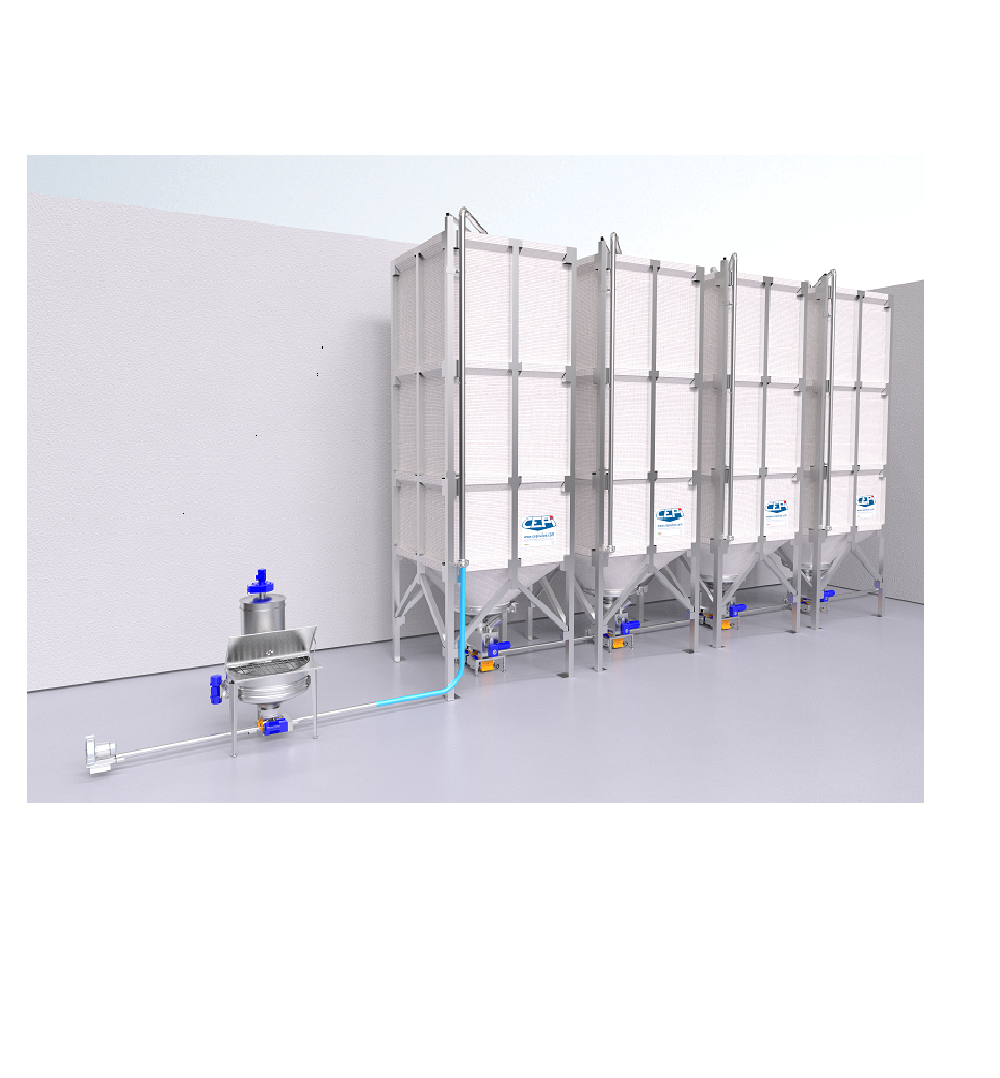
ATEX Indoor silo for sugar and flour
Storing granulated or powdered materials such as sugar and flour prior to processing r...
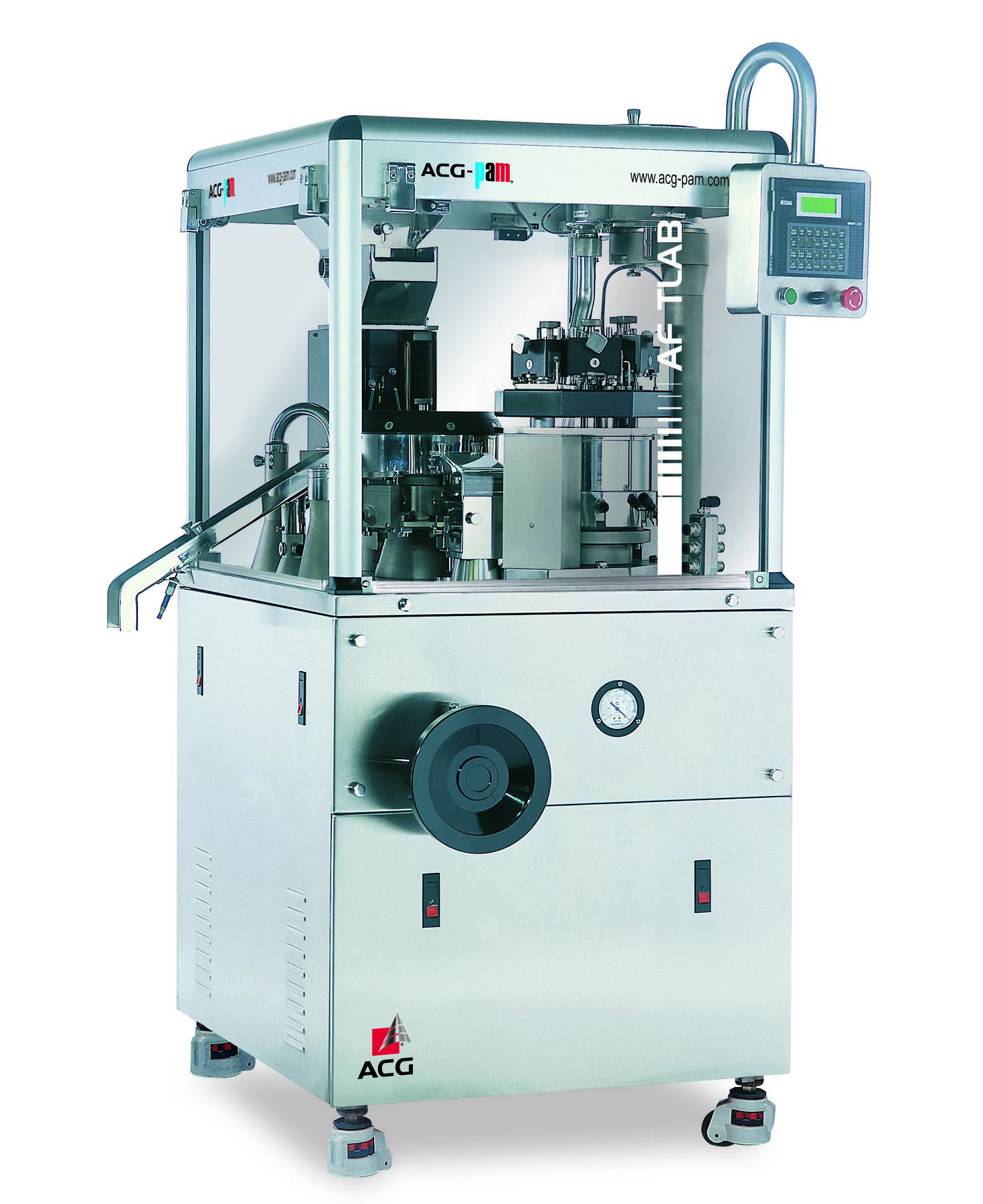
Automatic laboratory capsule filler
Innovators in the highly regulated and highly dynamic pharmaceutical market place need ...
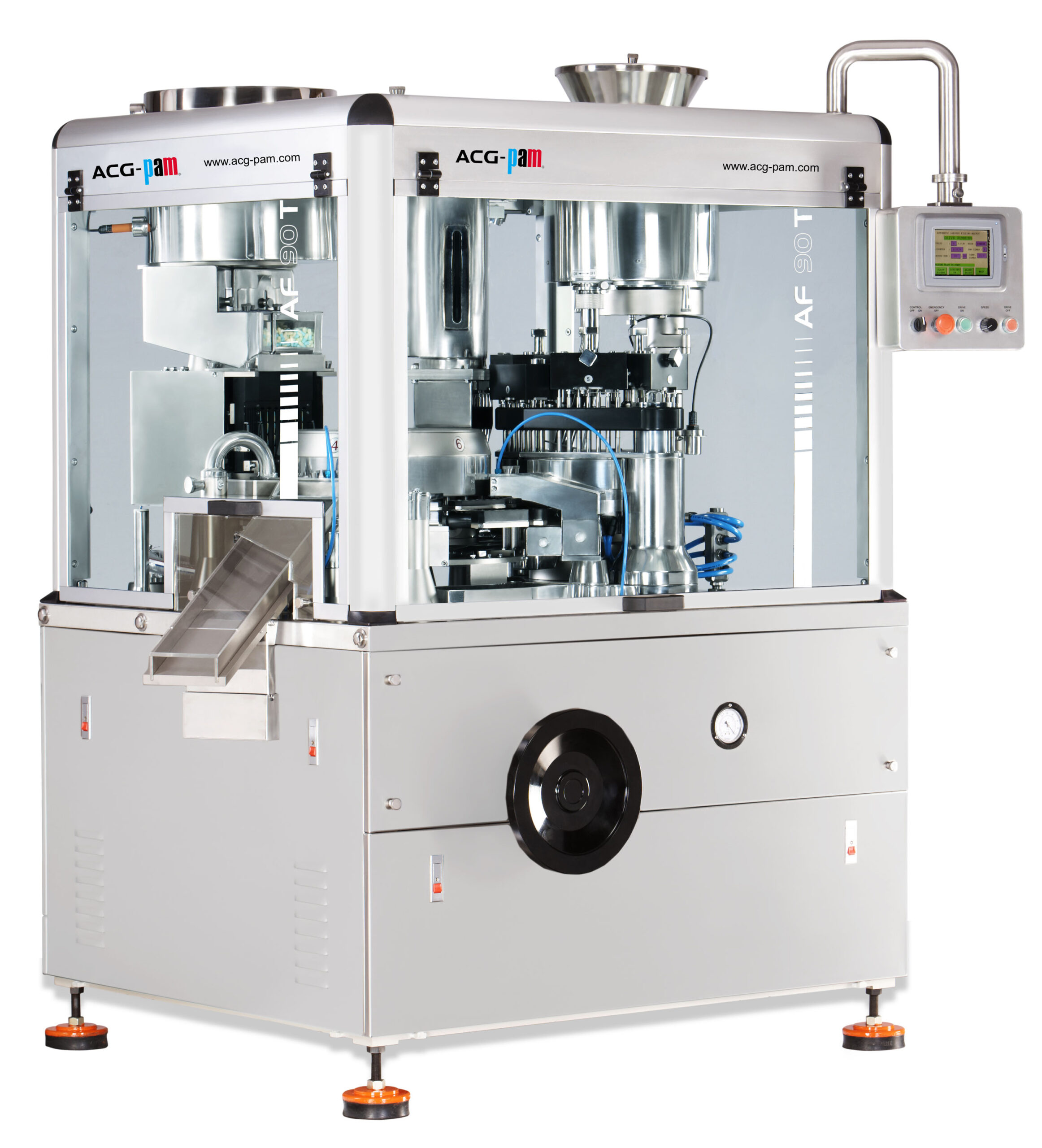
Automatic capsule filler
Capsule filling should be a worry-step in pharmaceutical and nutraceutical manufacturing. The right...

Cheese grater
Breaking down large blocks into grated, shredded, powdered or planed cheese requires multiple graded discs that ...
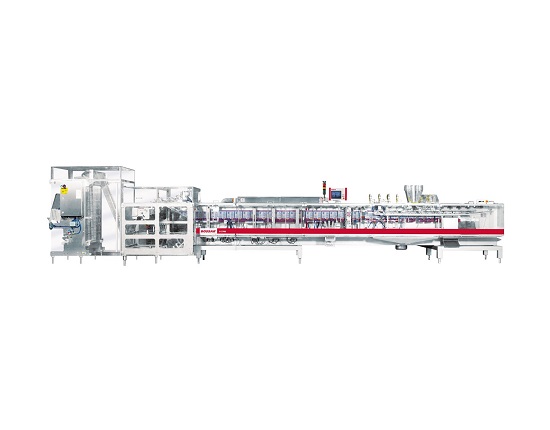
Dairy Packaging Machine
The use of sachets and pouches for powdered or shredded dairy products is an increasingly popular for...

High-Speed Pouch Packaging Machine
For large scale production of powders and liquids in a wide range of industry sectors, a...
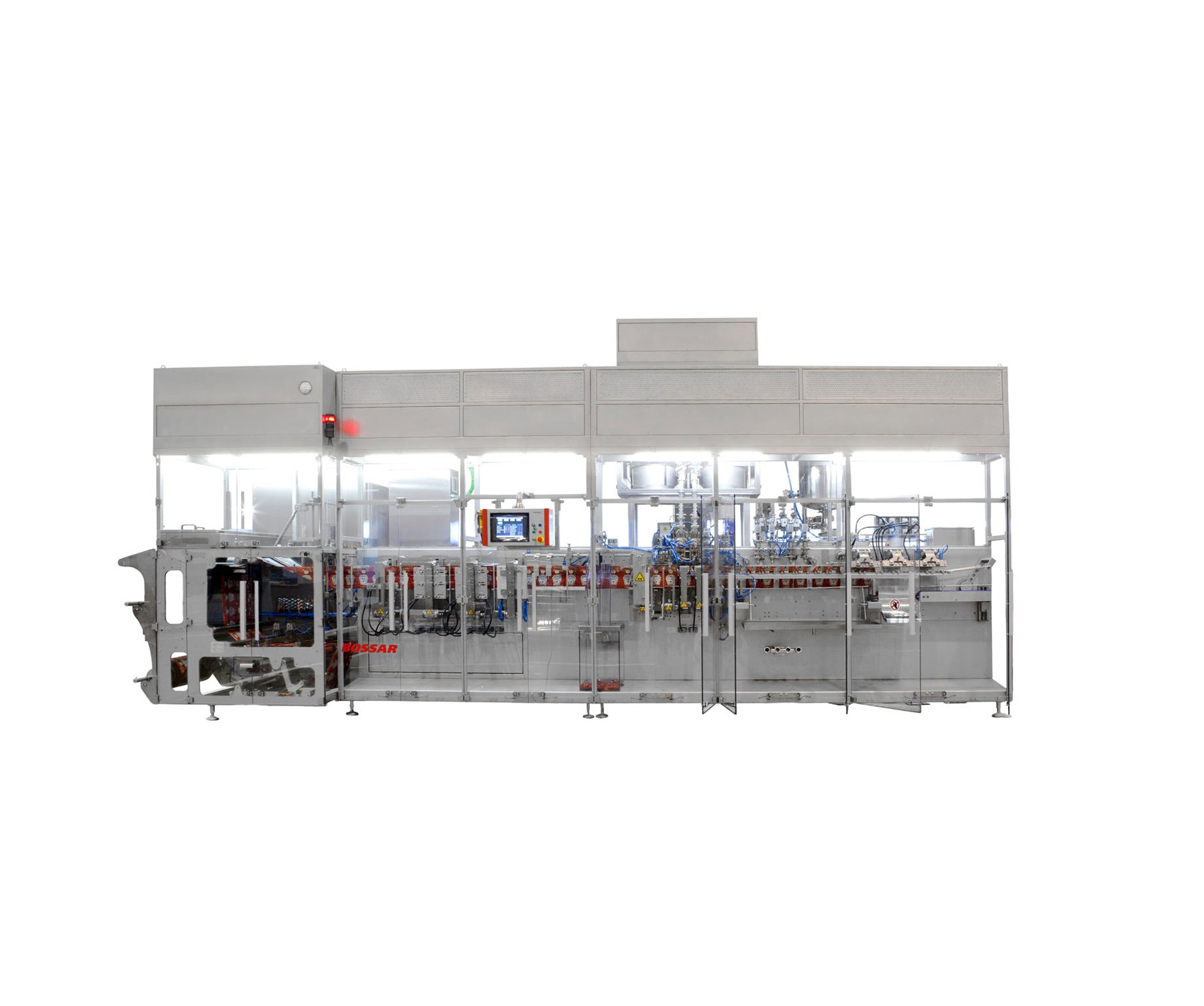
Modular HFFS Machine
A large range of sizes and types is available, with traditional horizontal form fill and seal machines b...
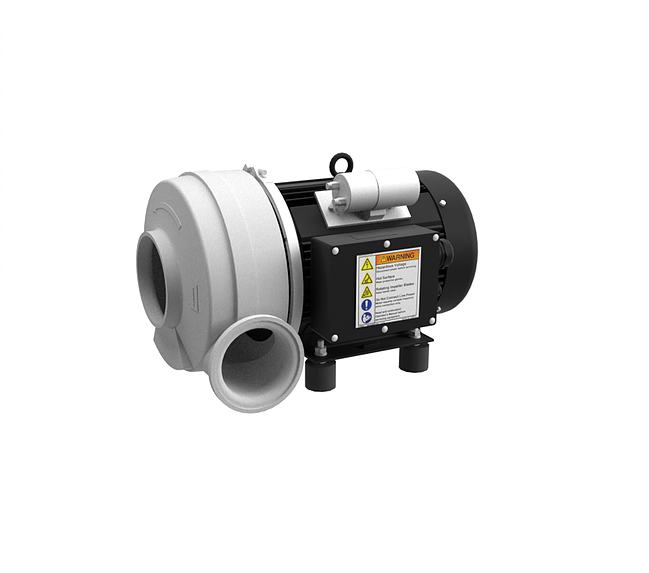
Blow off system for containers
Packaging powders into plastic or glass containers often leaves a residue that needs to be re...
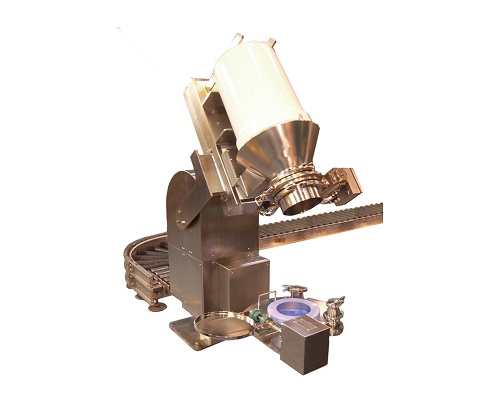
Drum tipper
Many pharmaceutical processes require drums of powders or liquids to be fed from one part of the process to the ne...
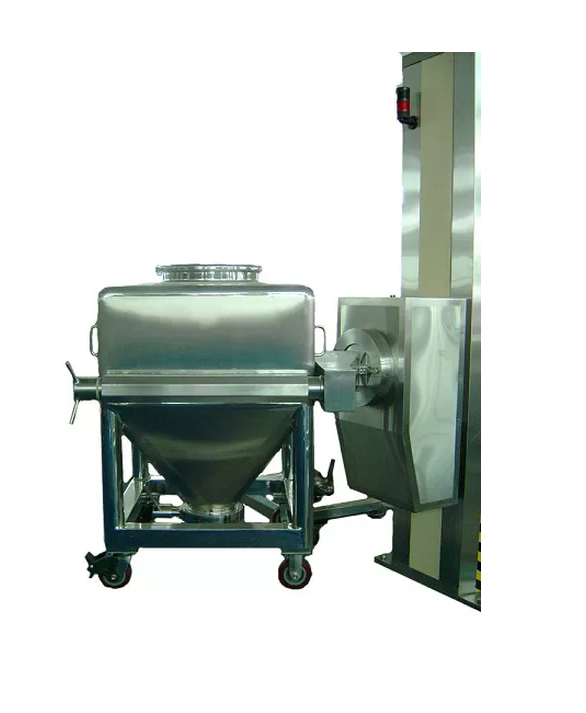
Bin blender
Many pharmaceutical processes require the blending of powders or other granular ingredients, the mixing of settled...
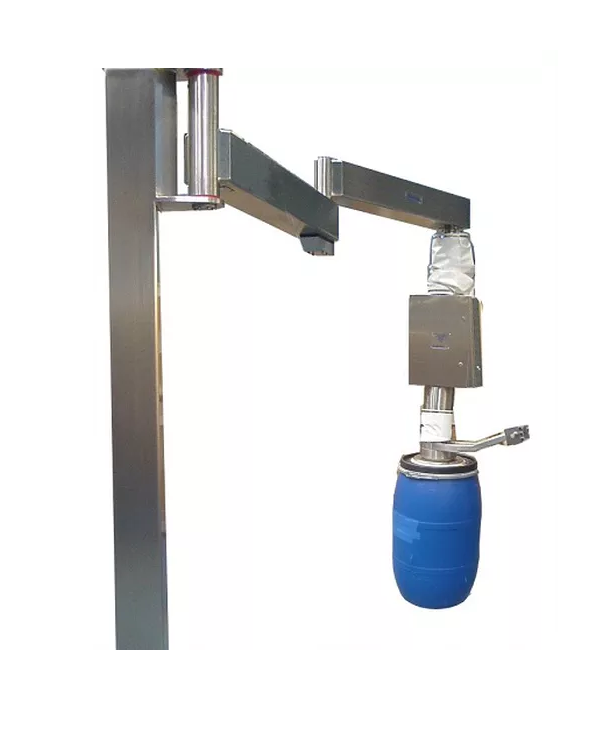
Container lifter
Container handling in the pharmaceutical industry brings its own set of unique challenges. Traditional barrel...
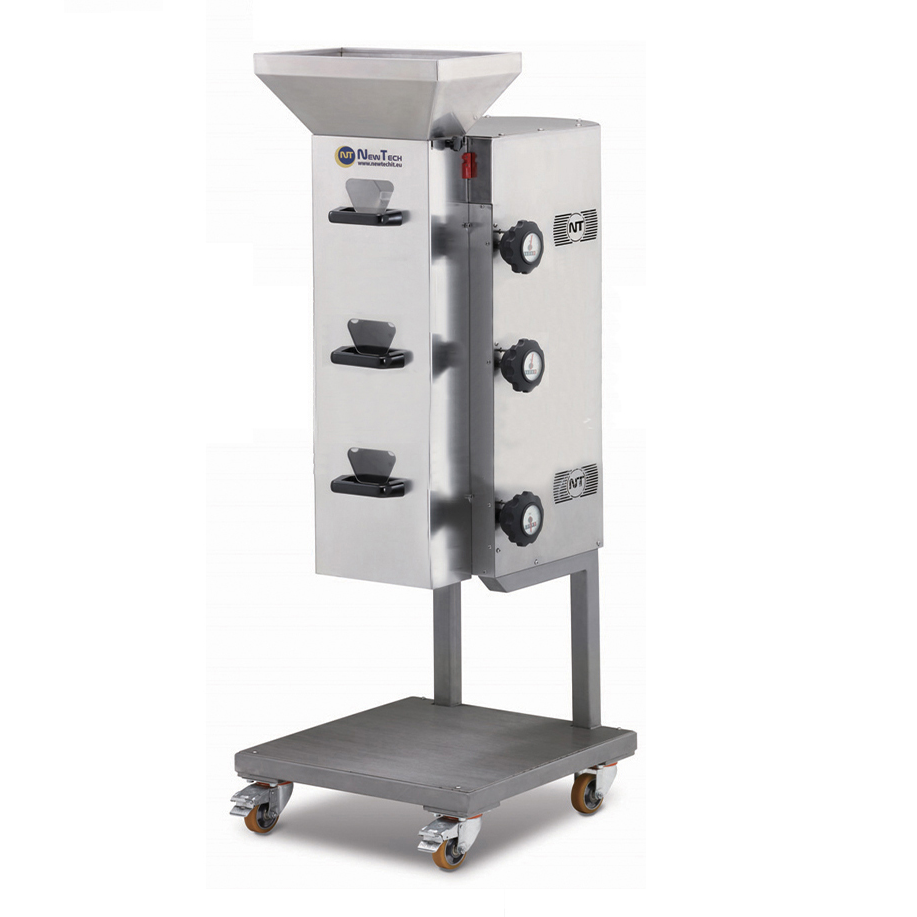
Small scale nut chopping machine
Many confectionery and bakery products use nuts as a key ingredient or decoration. The abil...
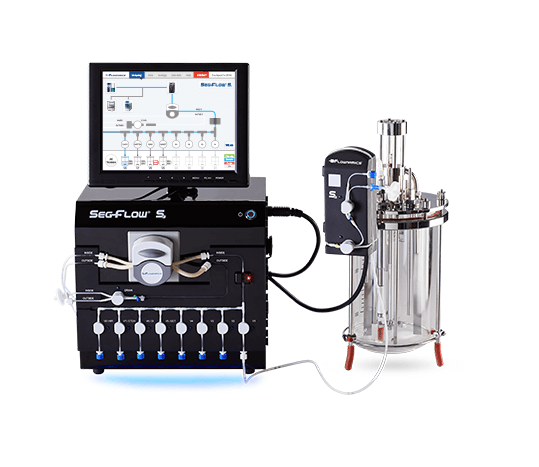
Fully Automated On-Line Sampling for Bioprocesses
Accurate sampling is a critical tool in the design and improvement of a...
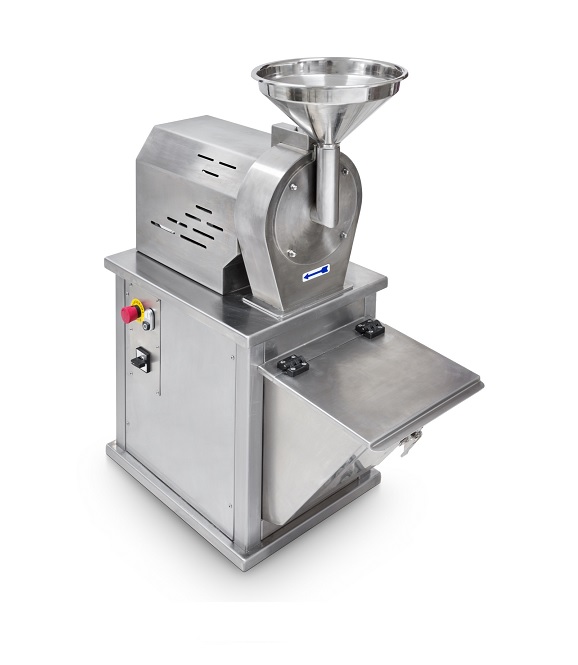
Small sugar mill for entry level production
Sugar powder is a key ingredient in a wide range of bakery, confectionery, and...
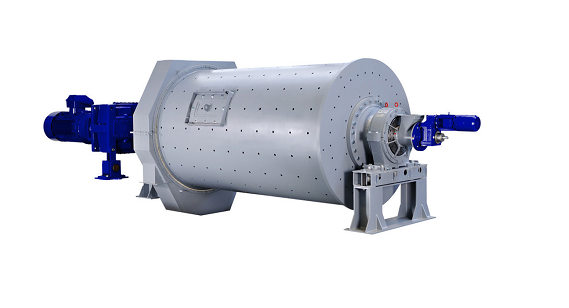
Horizontal rotary ball mill drum
A horizontal rotary ball mill drum can be used for grinding of dry hard materials, such as ...
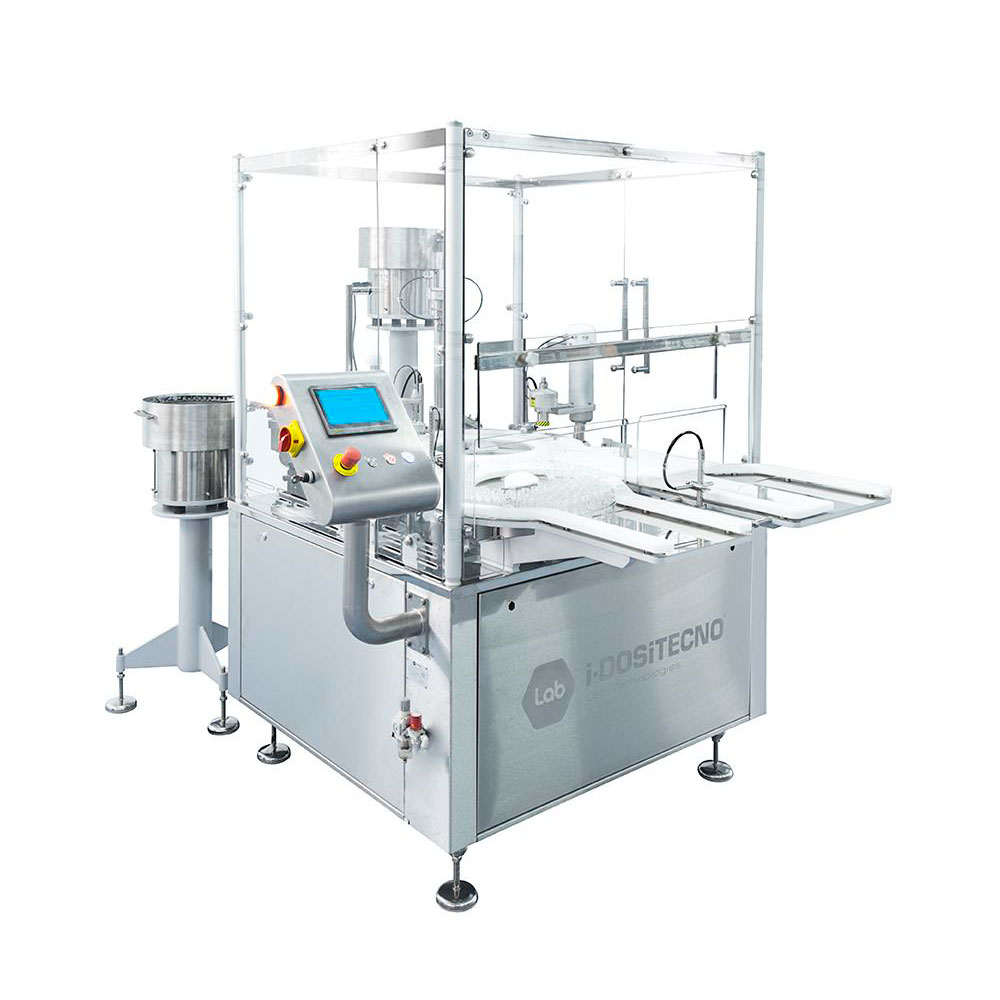
Start-up sterile filling line for injectables
For smaller-scale production of vials and syringes for the injectables marke...
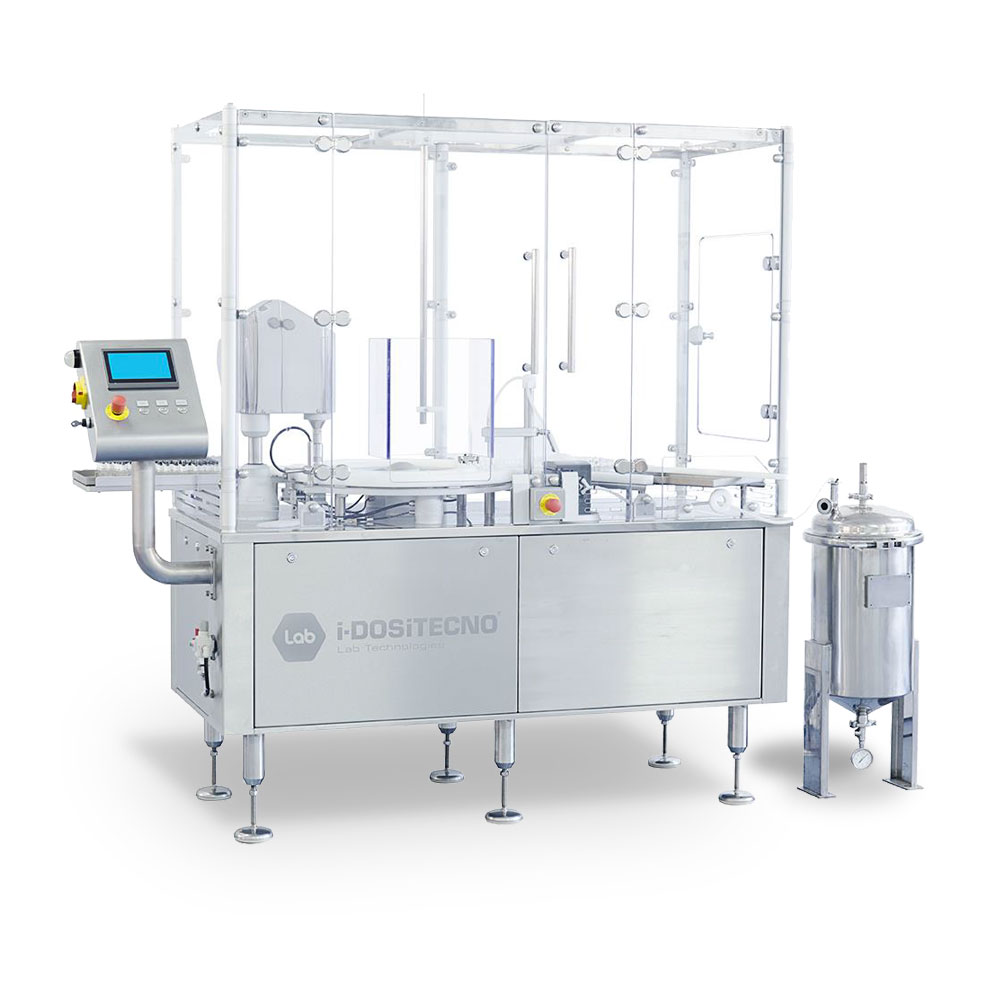
Table top sterile filling line for injectables
Where a compact solution is required for filling vials for the injectables ...
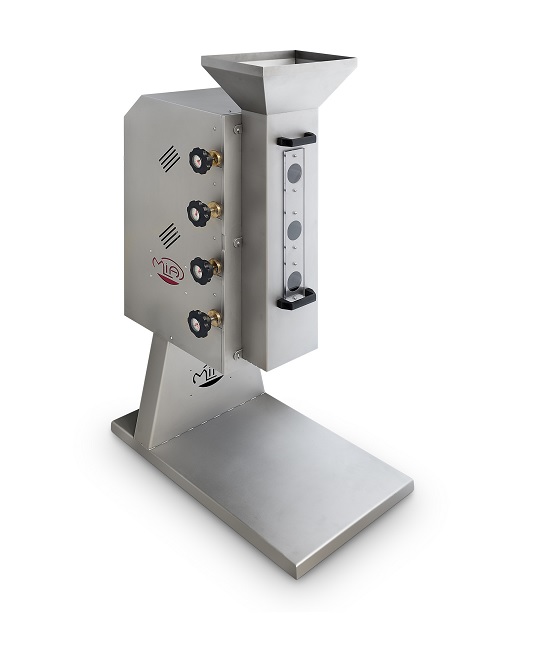
Small scale nut grinder
Many confectionery and bakery processes rely on the uniform grinding of raw ingredients such as nuts,...
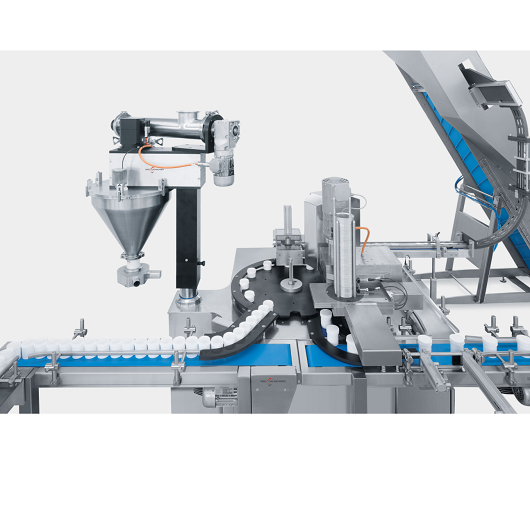
Can filling equipment
Having separate equipment for different process steps like filling and closing, can put a brake on grow...
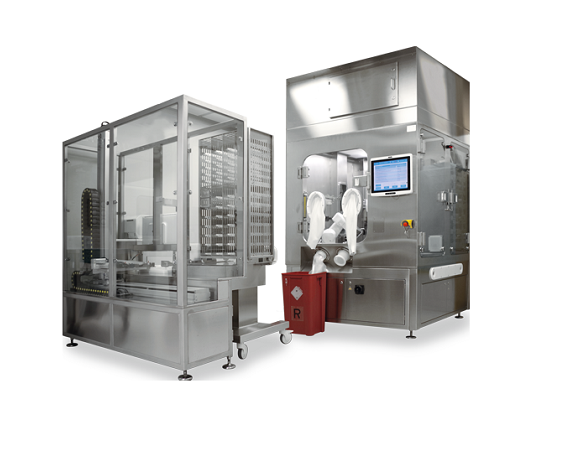
Sterile compounding system
Hospitals and compounding centres have traditionally used manual aseptic compounding processes. A...
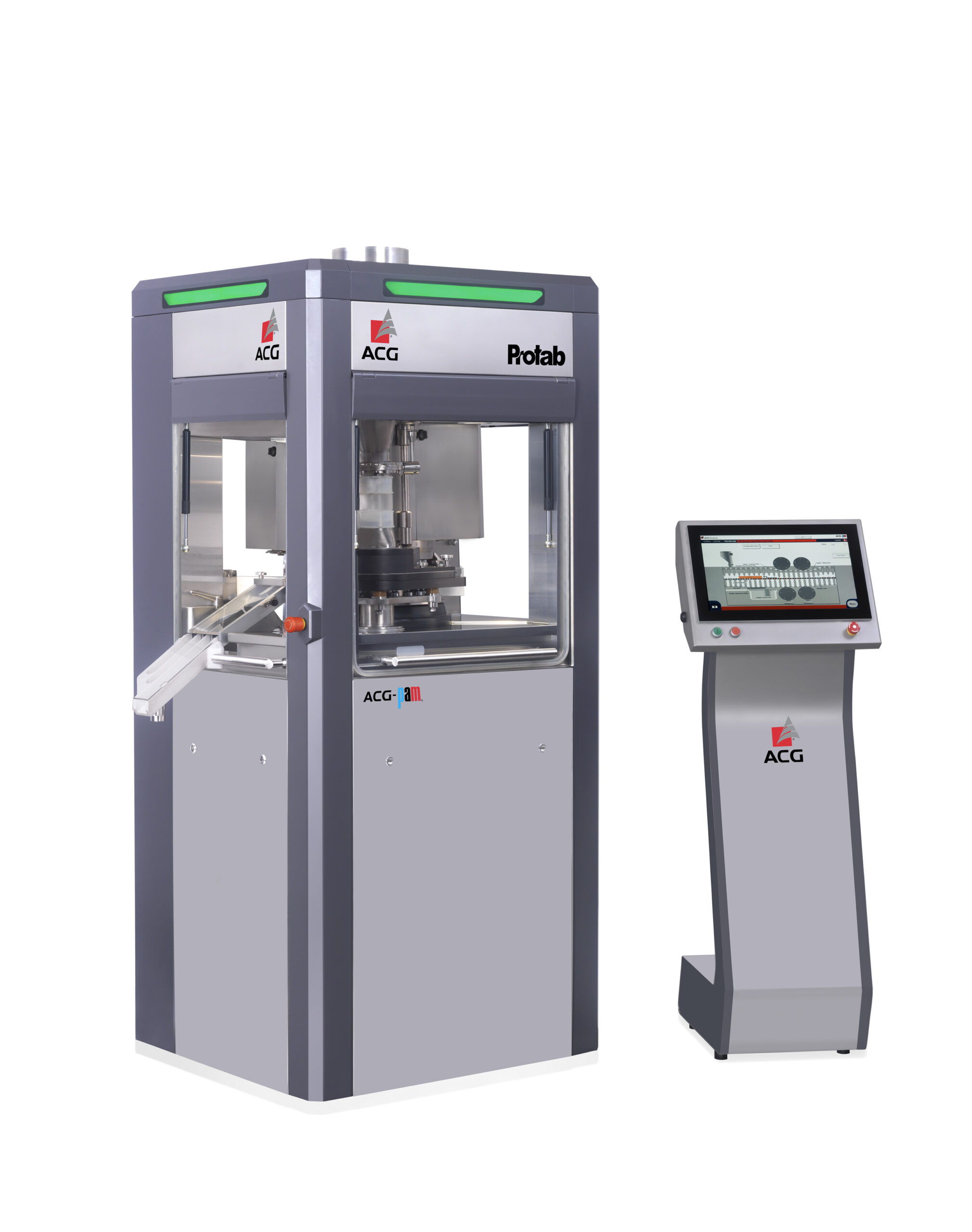
Single rotary tablet press
Creating batches of consistent high quality pharmaceutical grade tablets from your powdered ingre...
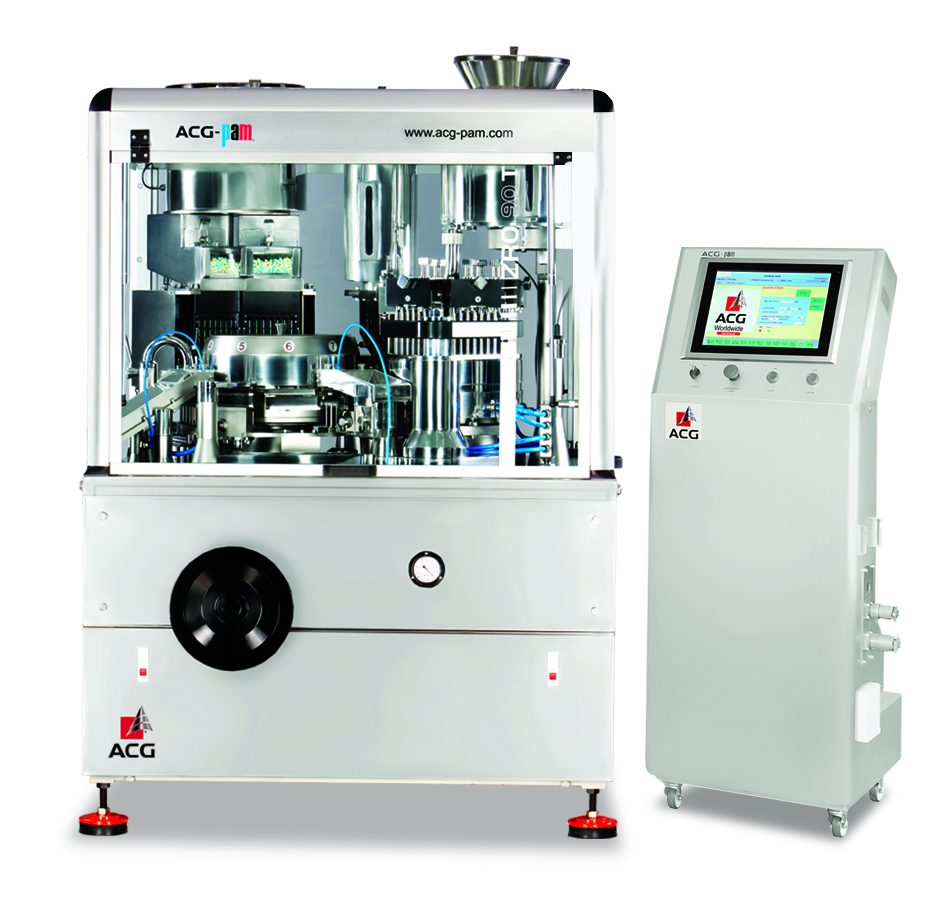
High-yield capsule filler
Pharmaceutical manufacturers require maximum yield from their encapsulation process for efficient ...
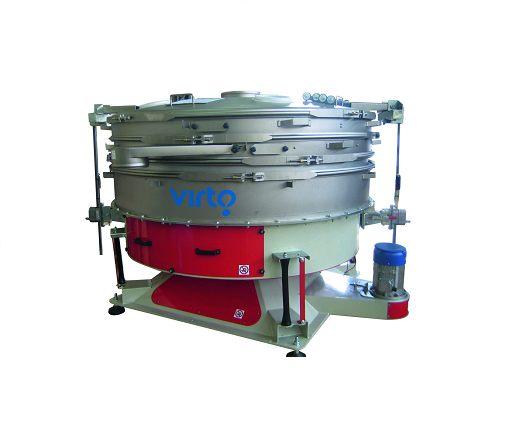
Tumbler sieve for classifying and dedusting granular materials
For the classification of delicate granular material, scr...

High volume particles separation sieve
For large scale production processes in the chemicals or food industries that requir...
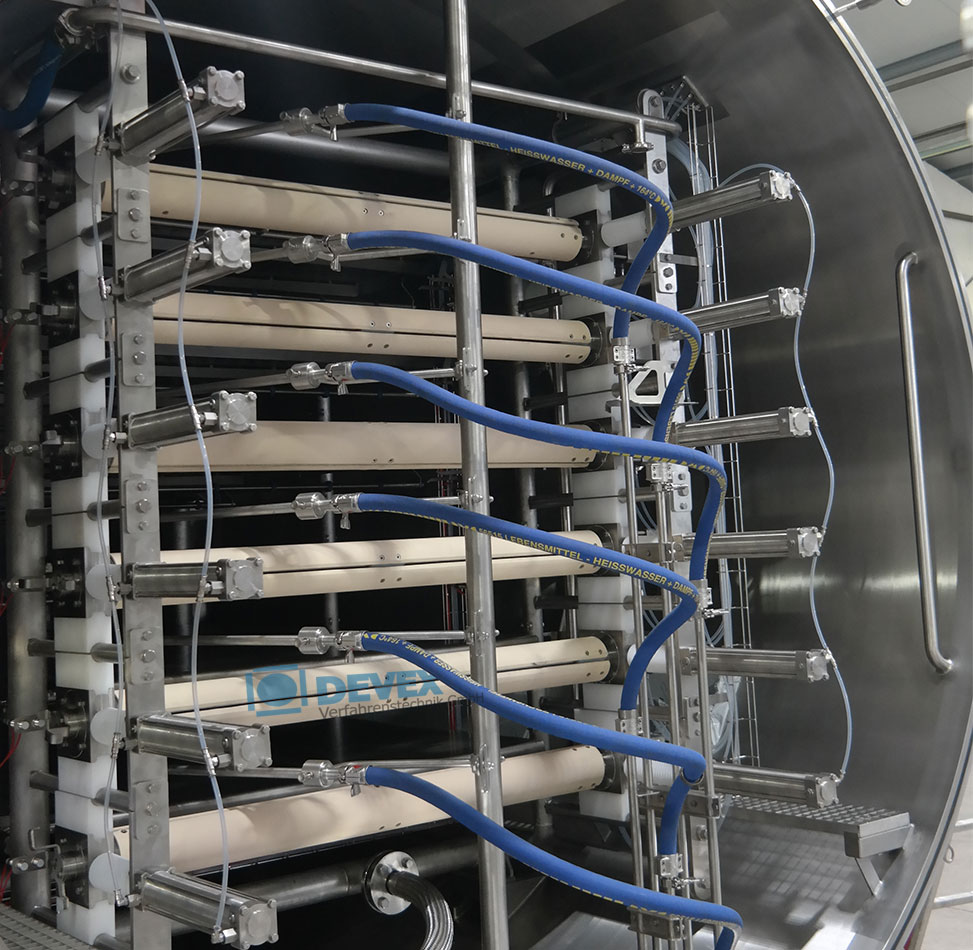
Continuous vacuum belt dryer
For gently drying liquid concentrates into granulates or powders, a vacuum drying solution is t...
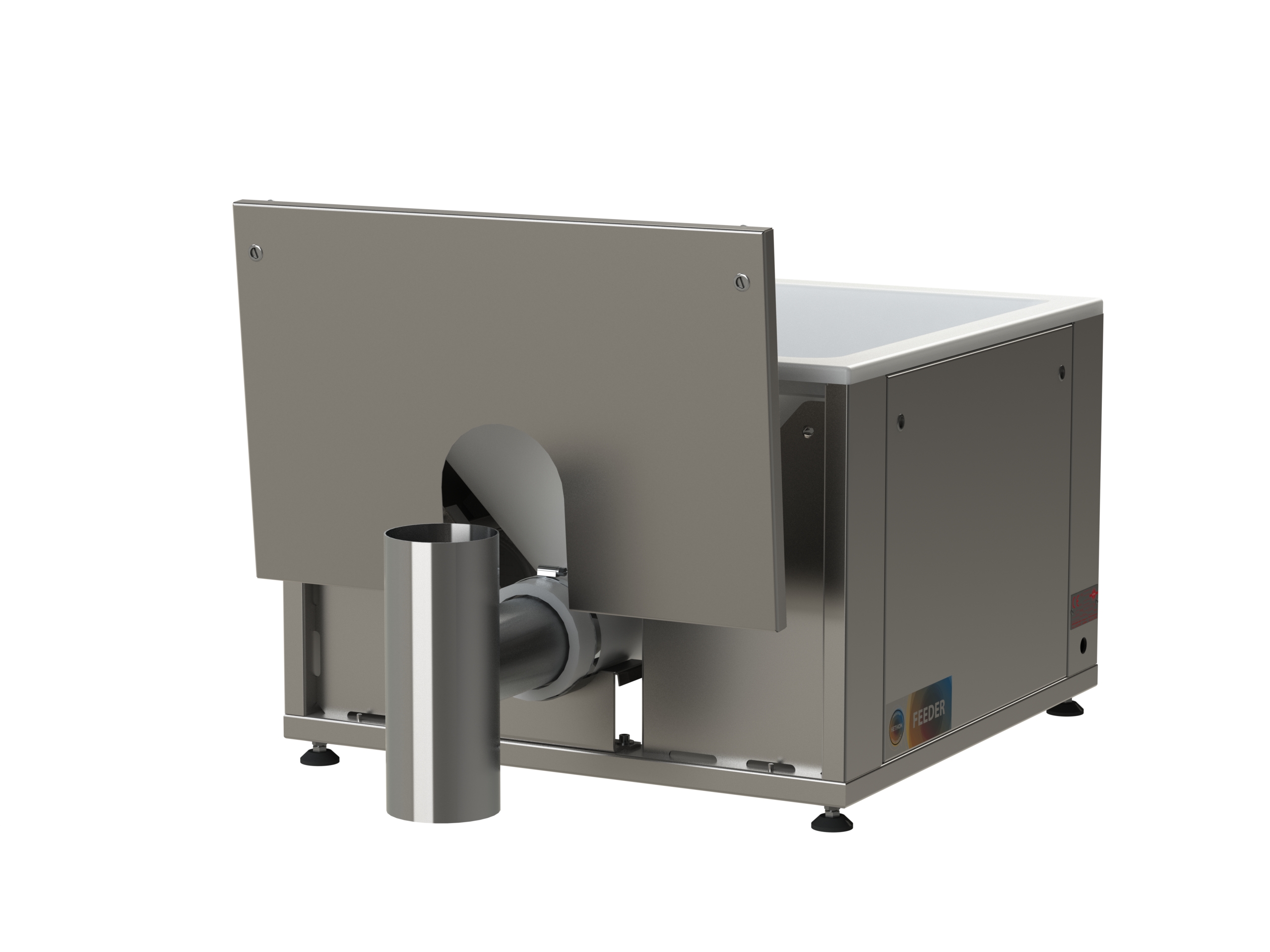
Feeder with flexible wall hopper
The varying properties of dry powder products mean that specialized feeders are required fo...
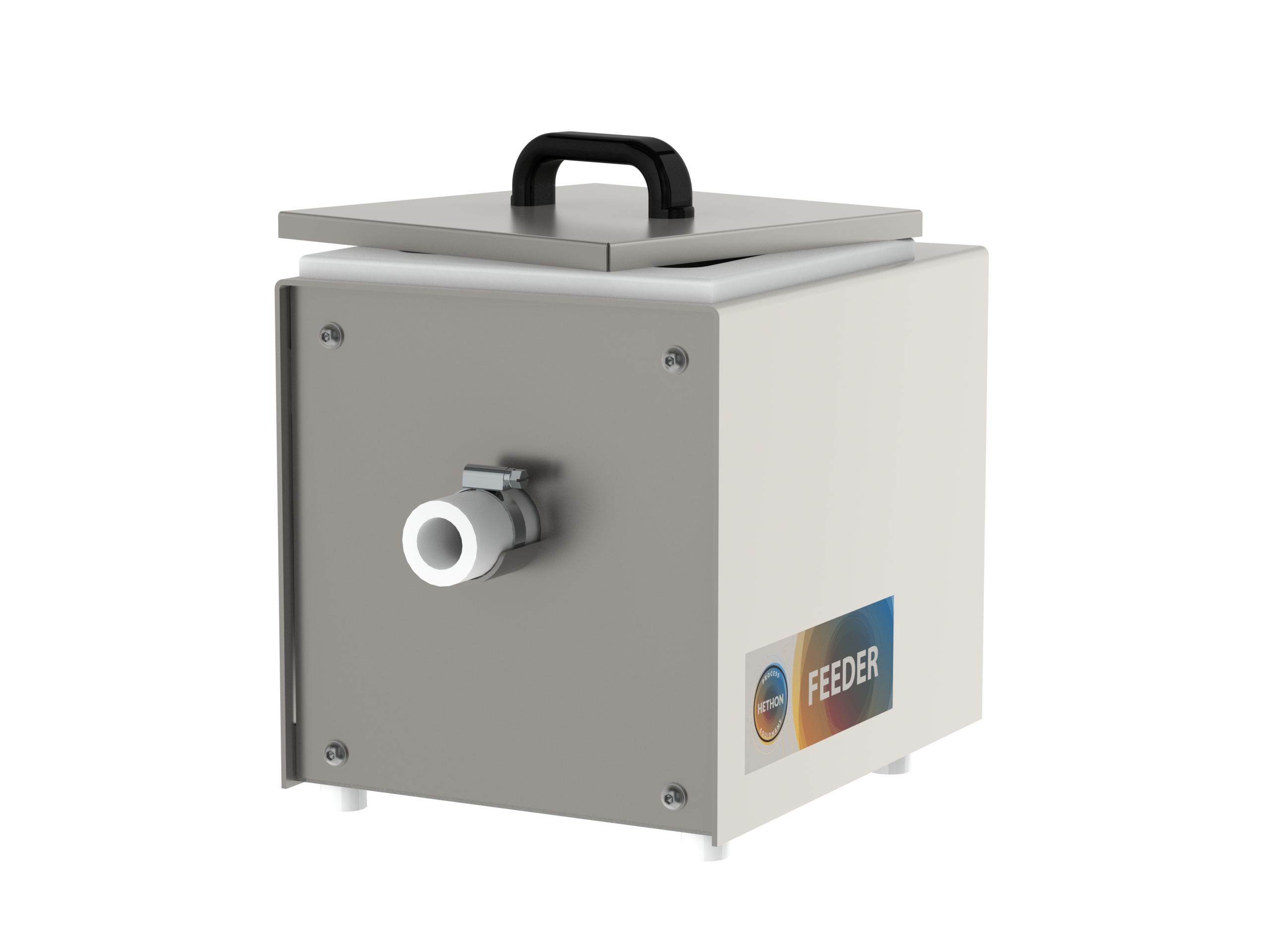
Small feeder with flexible wall hopper
In many laboratory applications and production processes, smaller quantities of powd...
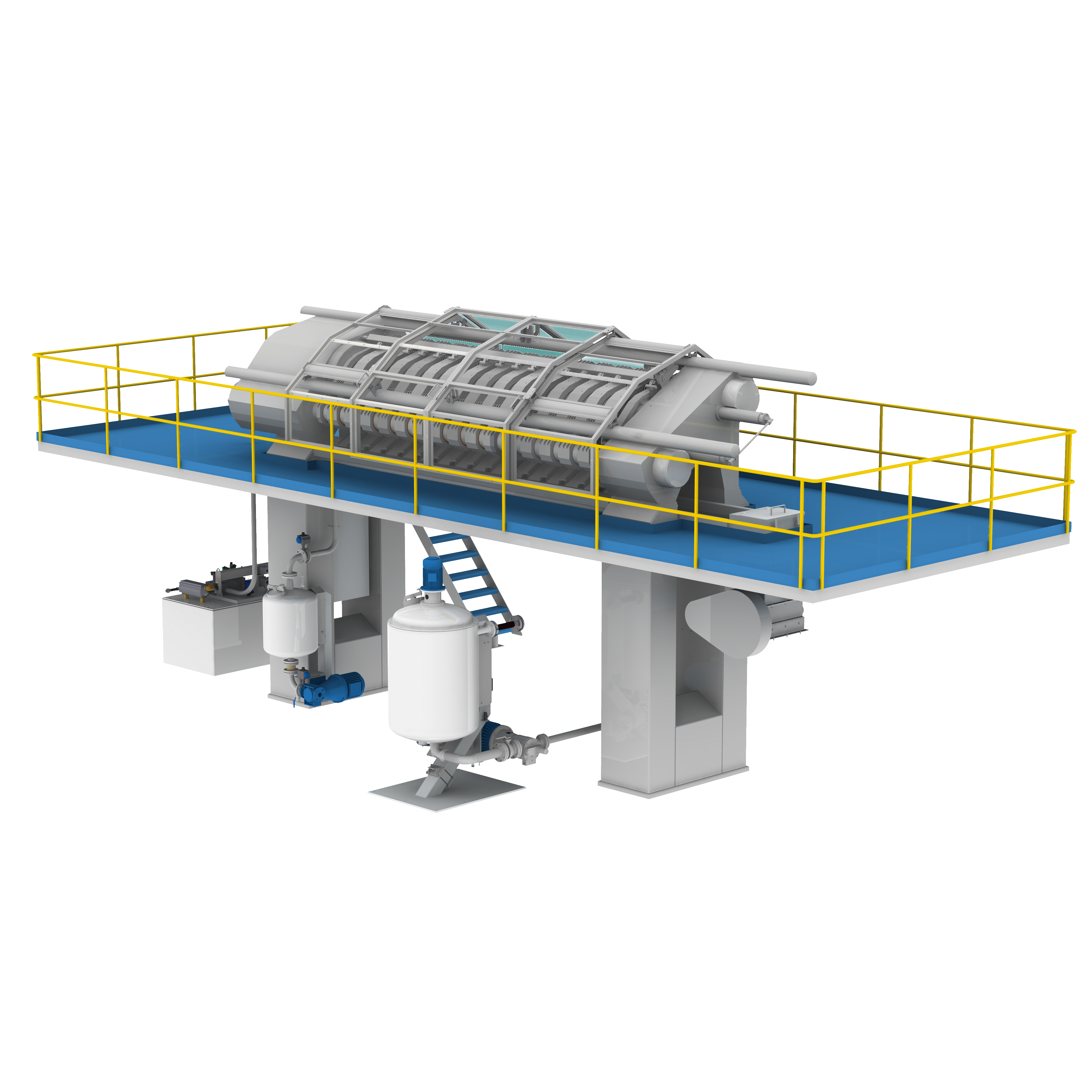
Cocoa press
After the cocoa beans have been fermented, dried, roasted, and separated from their skins, you obtain a cocoa mass...
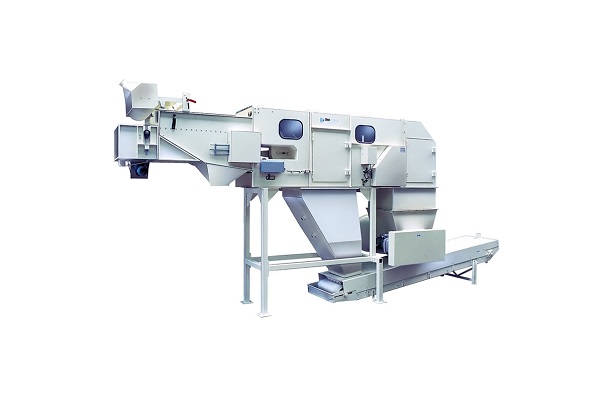
Automatic bag slitter
Unacceptably high dust levels can be generated whilst manual emptying and handling of bags, also produc...
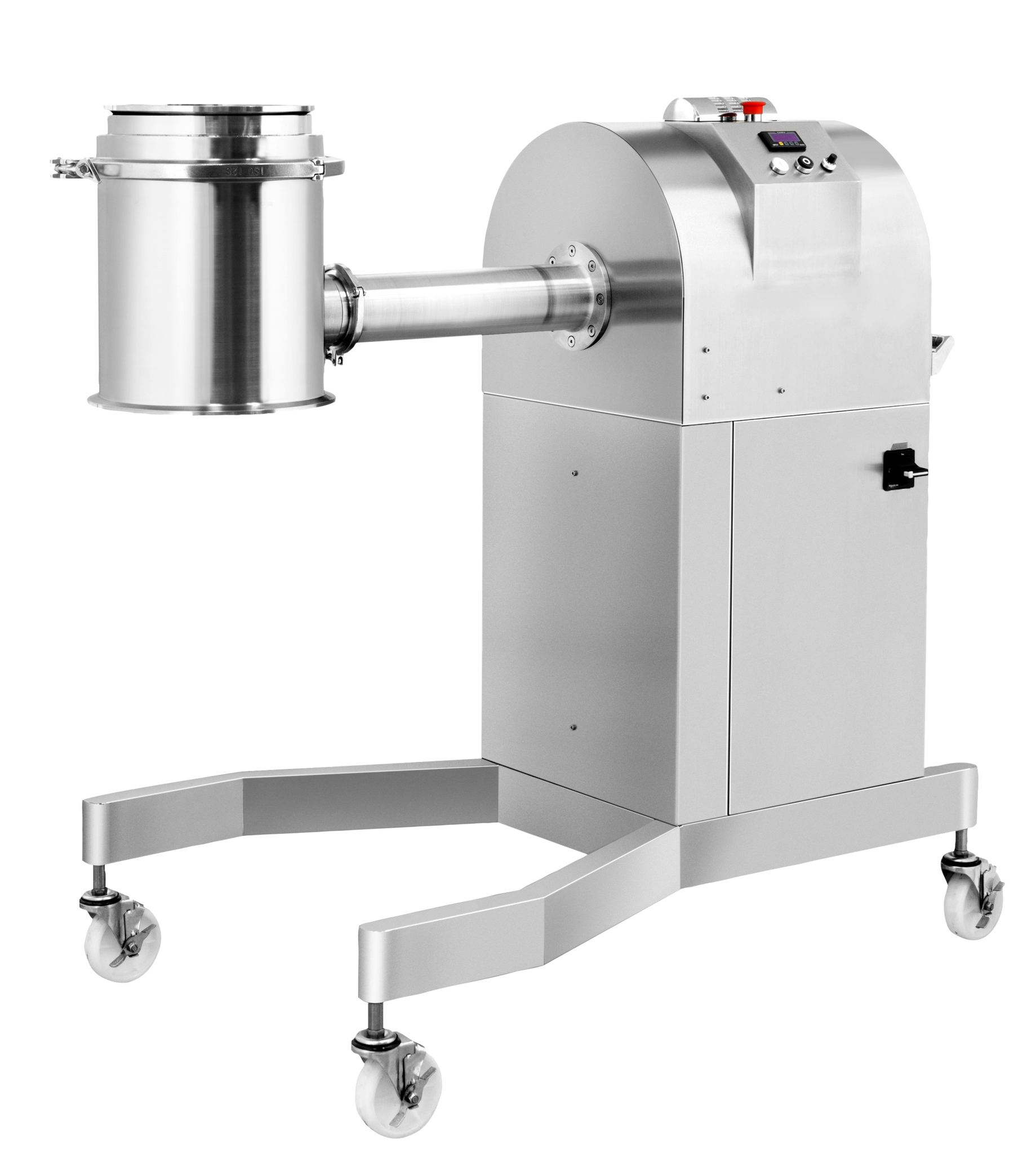
Conical mill for drug formulation
The efficient size reduction of granular powders is a key step in many pharmaceutical pro...
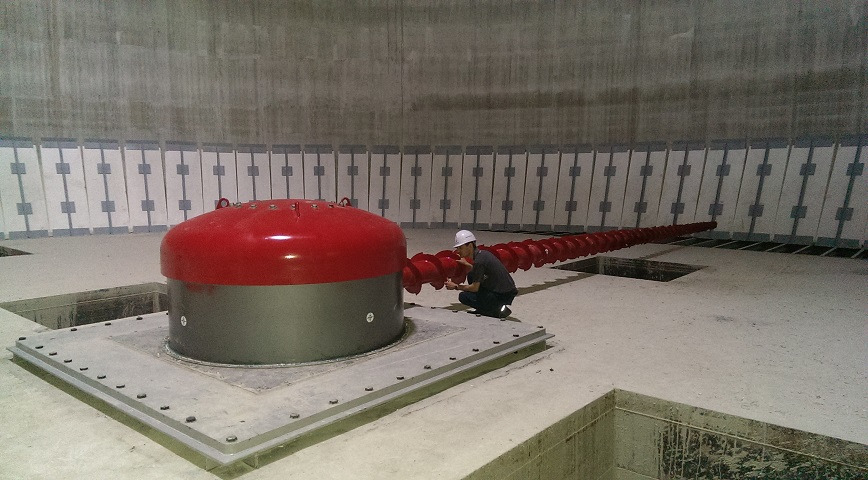
Silo extraction system
Materials without natural flowing properties are difficult to unload, even with the assistance of grav...
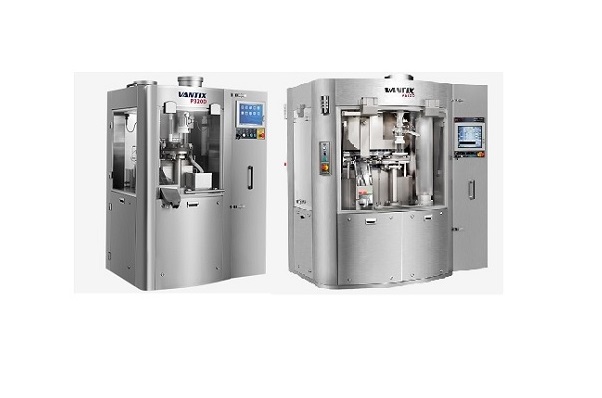
Single and double layer tablet press
High performance tablet presses that are capable of producing both single and double-l...
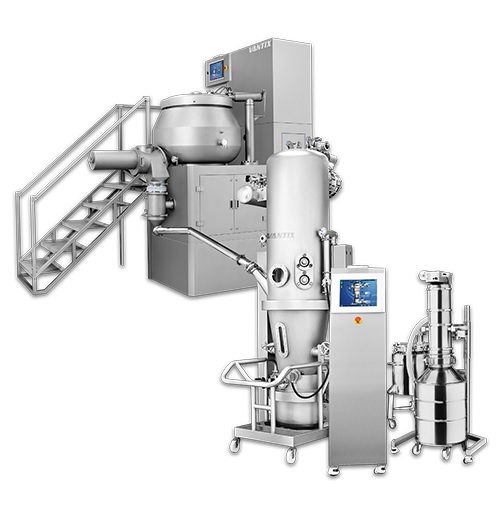
Granulation line of mixer and fluid bed dryer
A complete granulation line allows for the mixing and granulation of pharmac...
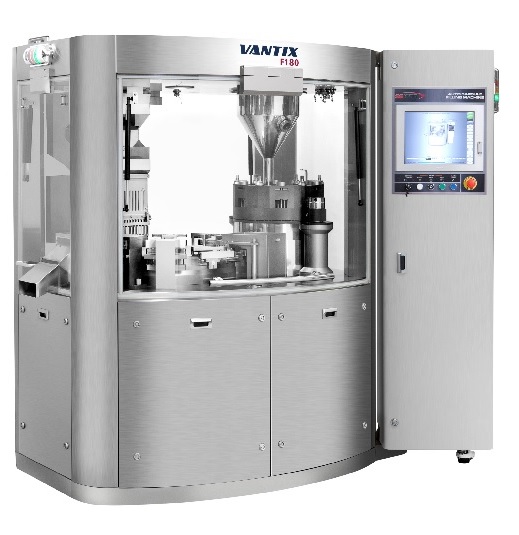
High capacity capsule filler
In the highest volume pharmaceutical production environments, capsule filling needs to be extre...
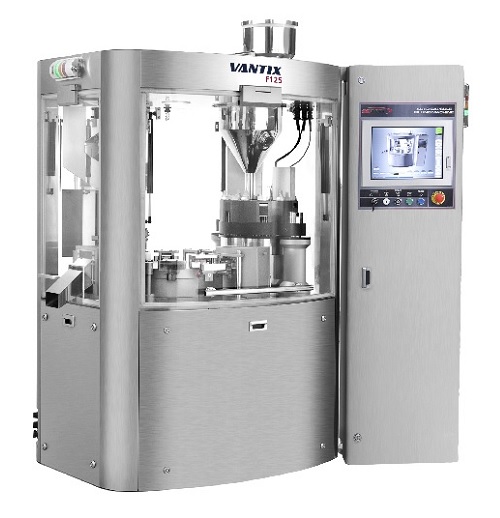
Scale up capsule filler
For higher production volumes of pharmaceutical capsules, speed, accuracy and reliability of producti...

Entry level capsule filler
For the production of pharmaceutical doses in capsule form complete accuracy of fill is paramount...
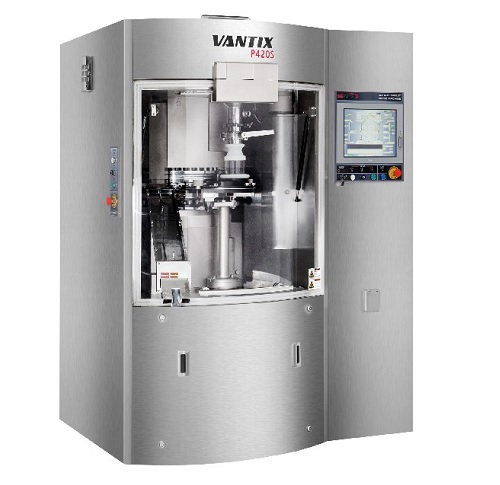
Single layer tablet press
High performance tablet presses for the modern production environment need to be fast, accurate an...
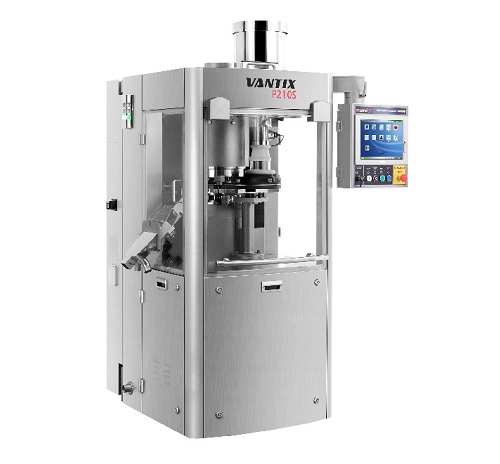
Rotary tablet press
For pharmaceutical tablet producers looking to reduce waste, costs and increase production volume, a hig...
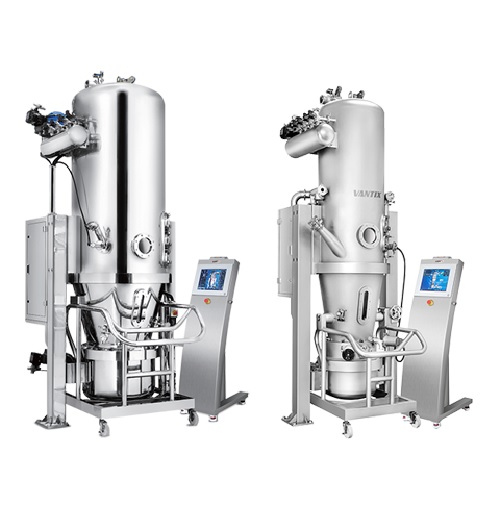
Fluid bed dryer for production scale
Fluidized bed drying (FBD) is a common process in the pharmaceutical industry for dryi...
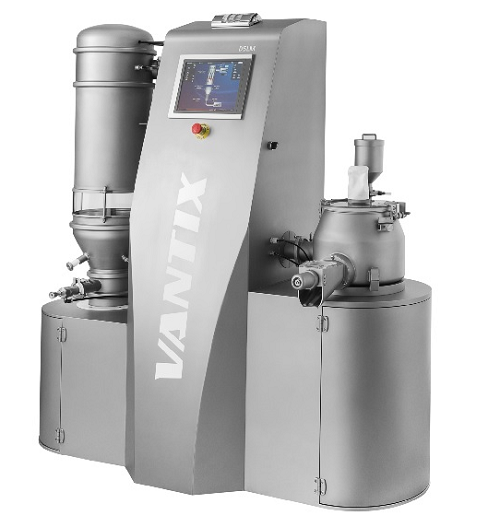
Fluid bed dryer and mixer for lab scale
Designed for pharmaceutical R&D, a lab-scale fluid bed dryer and mixer/granulat...
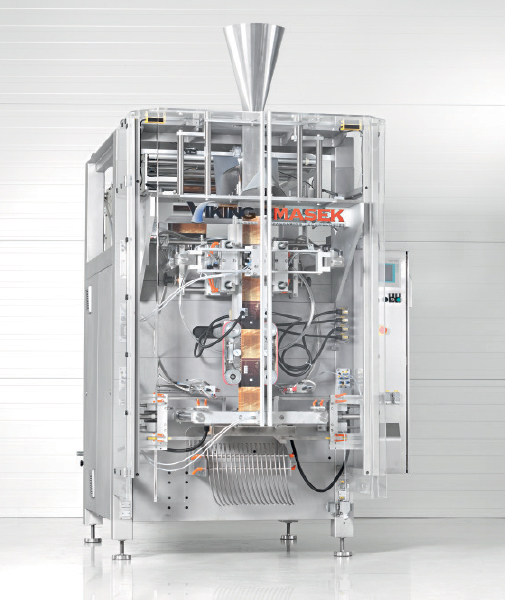
Bagger with servo driven jaw actuation
If you want to accommodate multiple bag designs and dimensions with fast speed and a...
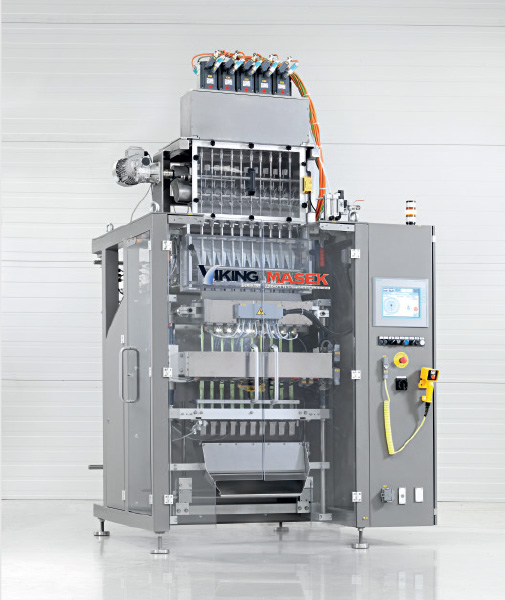
Stickpack Machine
If you are looking to pack your product into stick packs from 17 x 40 mm to 100 x 200 mm in size, you may b...
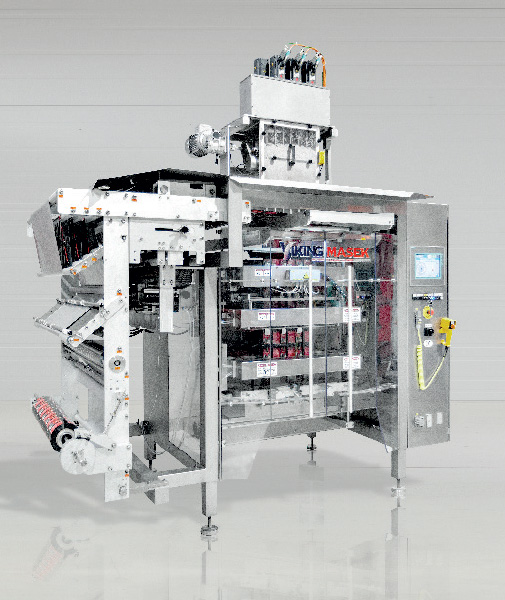
Sachet Machine
If you want to pack into eye-catching 4-side sealed sachets between 40×50 mm and 250×200 mm in size, ...
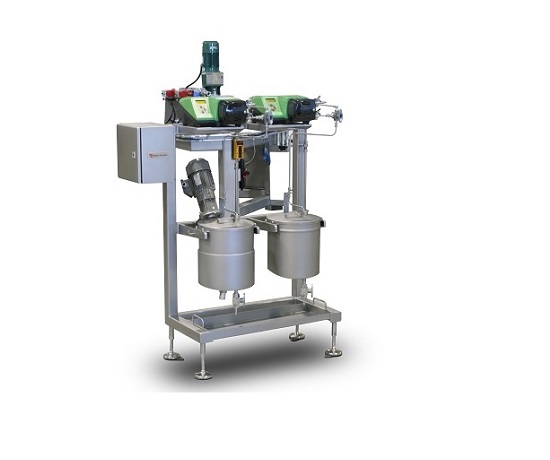
In-line colour or flavour addition for confectionery
The addition of colourings and flavourings increases value and quali...
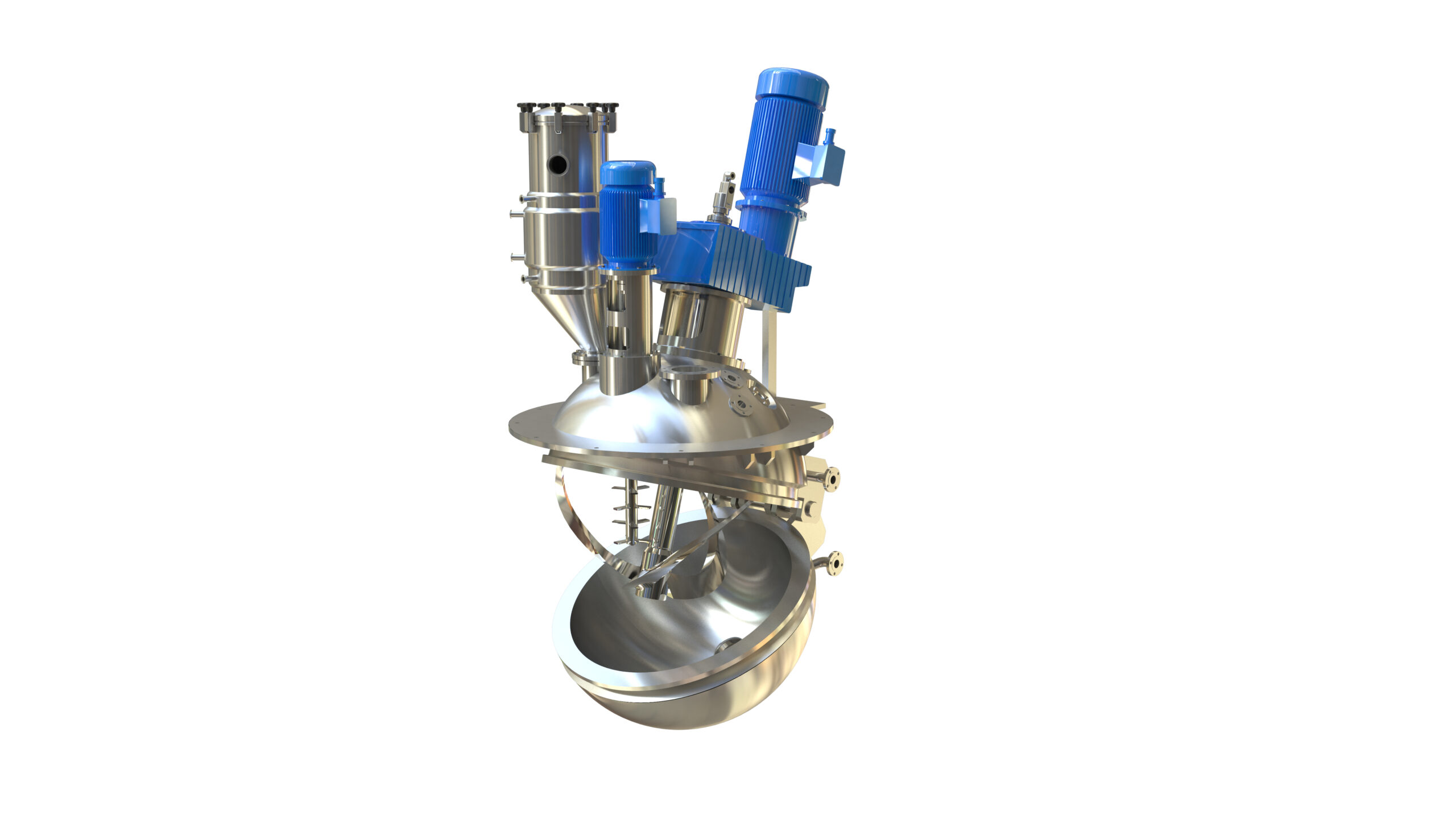
Spherical dryer
Drying vessels that are simple, reliable, and easy to maintain increases product quality and process efficienc...
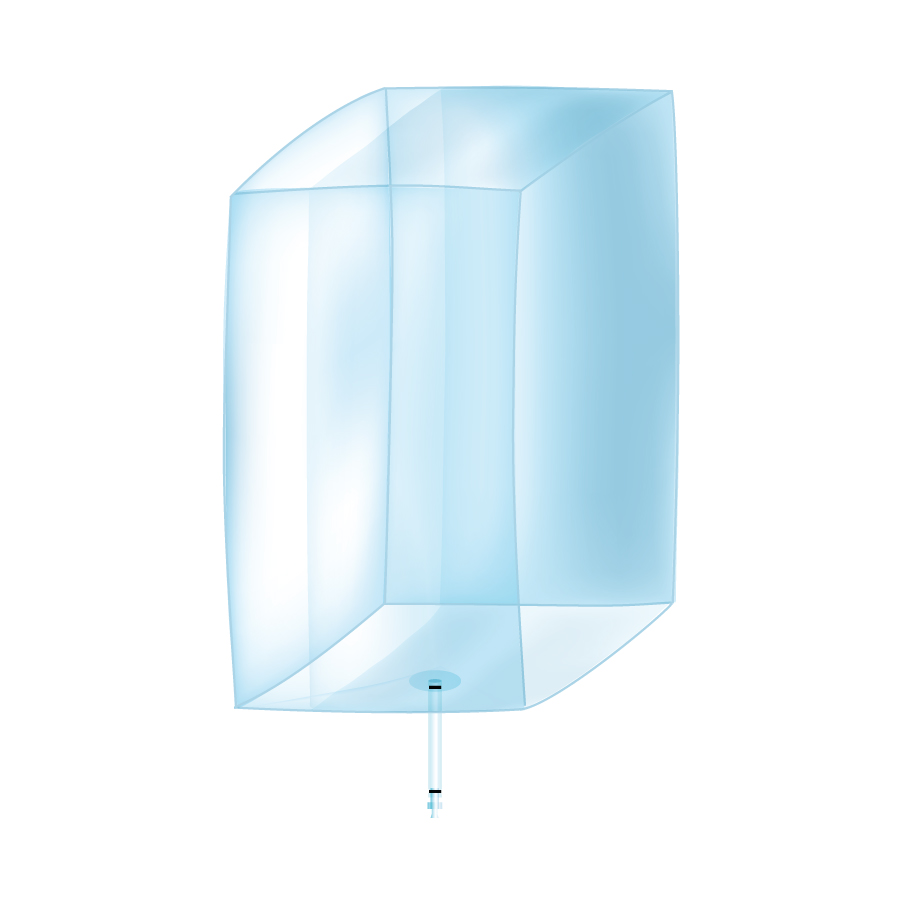
Disposable tank liners
Manufacturers in the bioprocessing industries are increasingly turning to single use solutions for the...
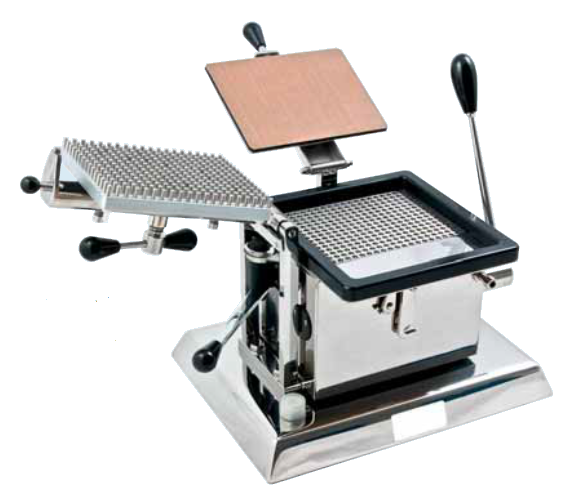
R&D semi-automatic capsule filler
Semi-automatic filling machine suitable to open, fill and close empty hard gelatin capsul...
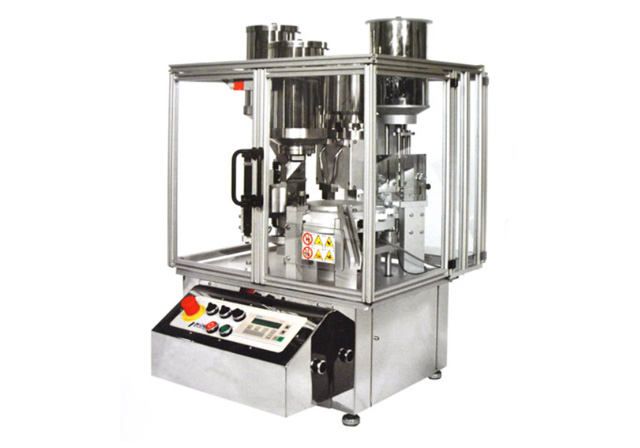
R&D automatic capsule filler
Automatic capsule filling machine for powders, pellets, tablets, mini-tablets, capsule in capsu...
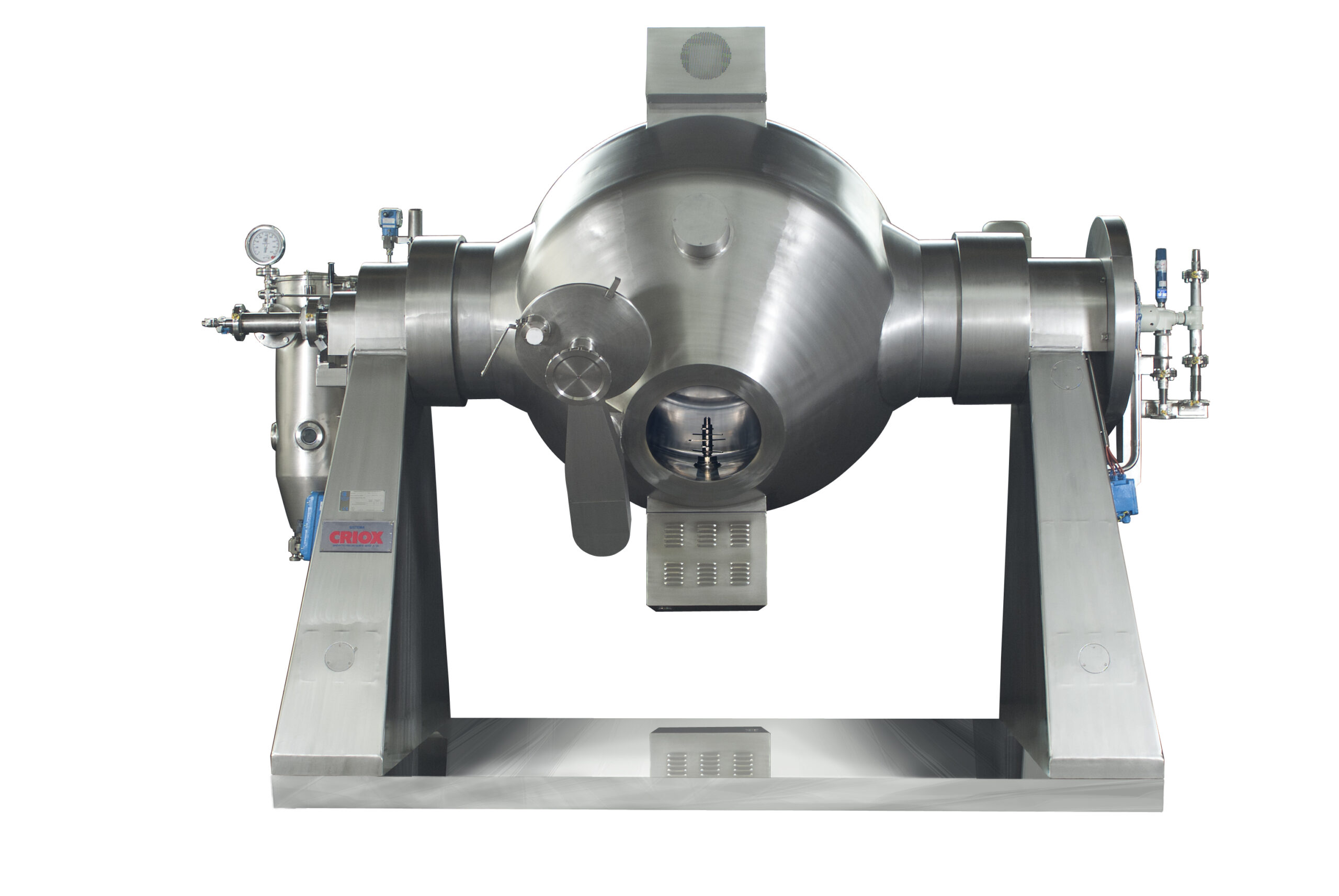
Rotary vacuum dryer
Powdered products tend to agglomerate during vacuum drying. This adds an additional step to the productio...
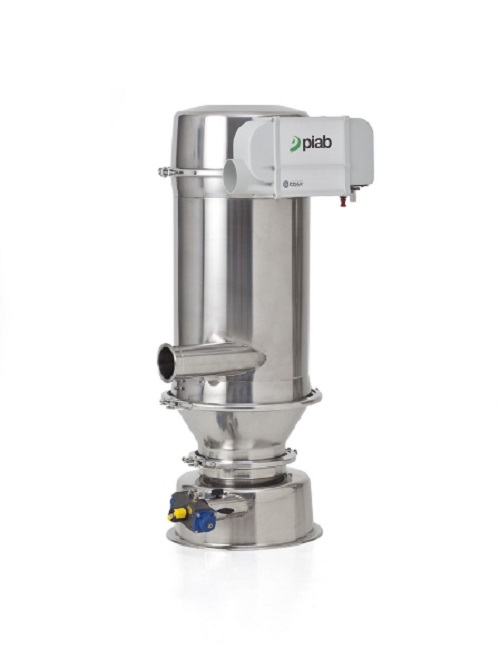
Premium vacuum conveyor
When you have a need to tailor make your conveyor and still have the high requirement on hygiene, e.g...
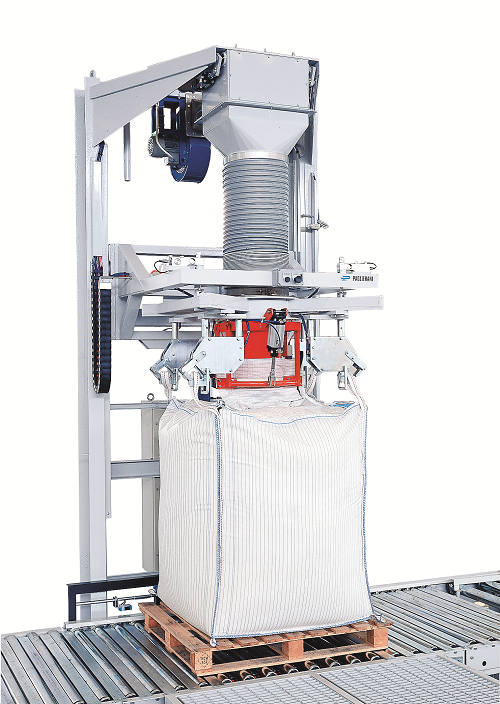
Big bag solutions
Management of big bags requires specialist handling and selection of cost-effective configurations for fill...
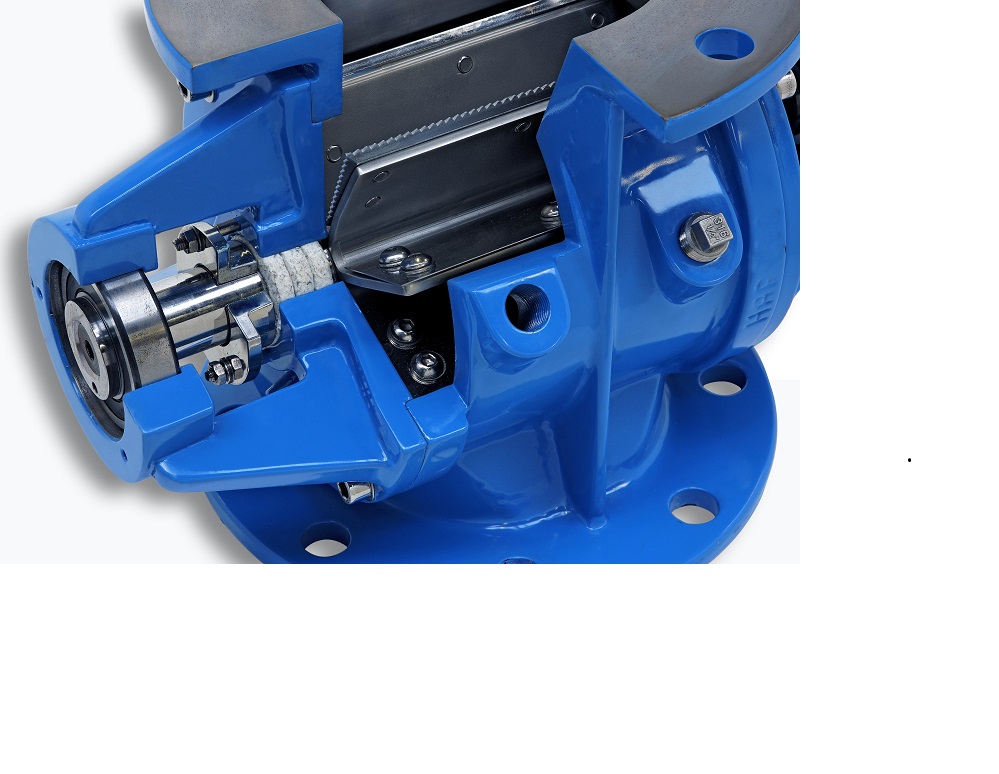
Heavy duty rotary valve
Handling powdered and granulated materials in pneumatic conveying systems requires consistent, safe v...
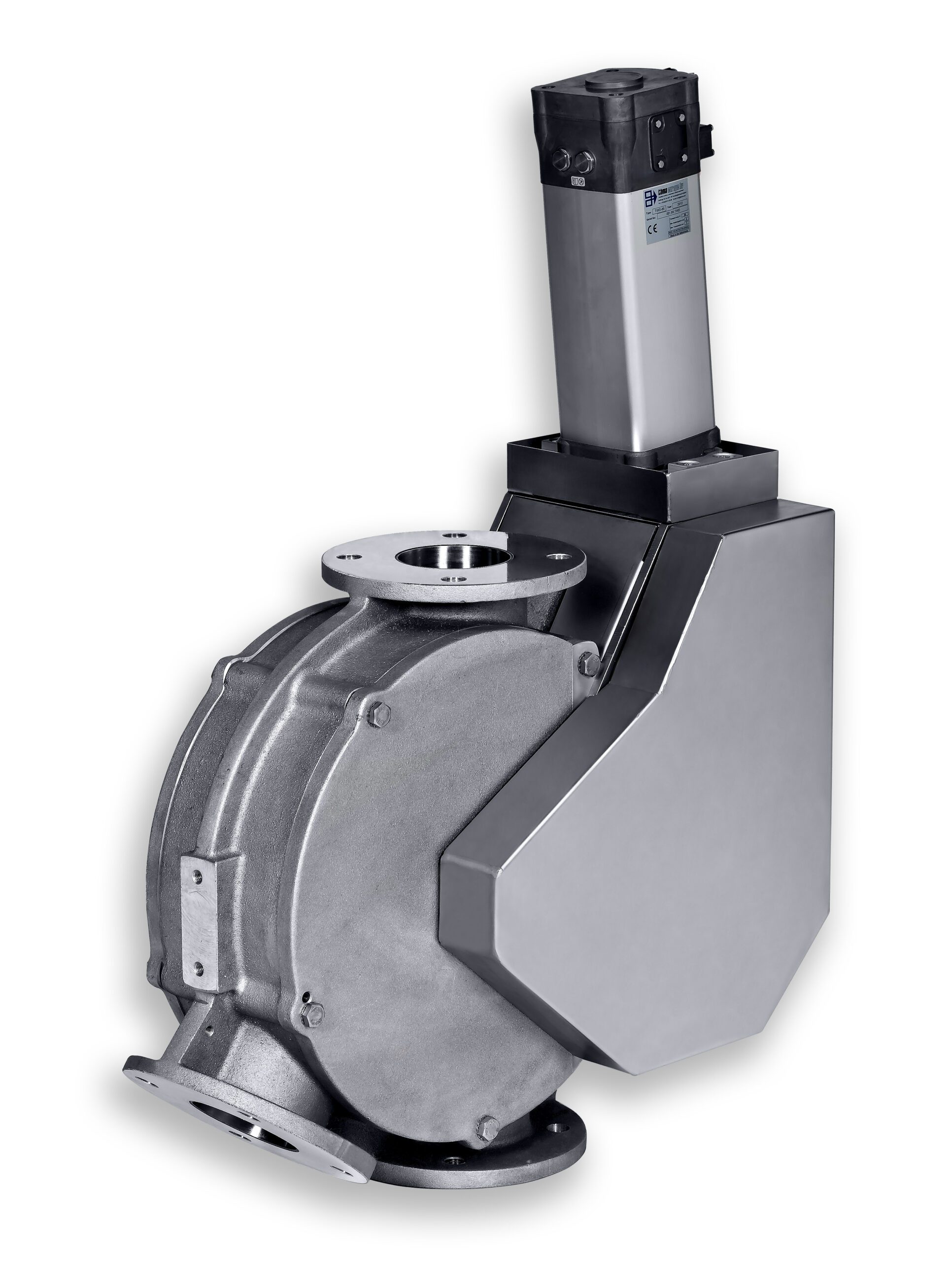
Dual channel plug diverter valve
Short switching times are often required when diverting or combining powder or granular sol...
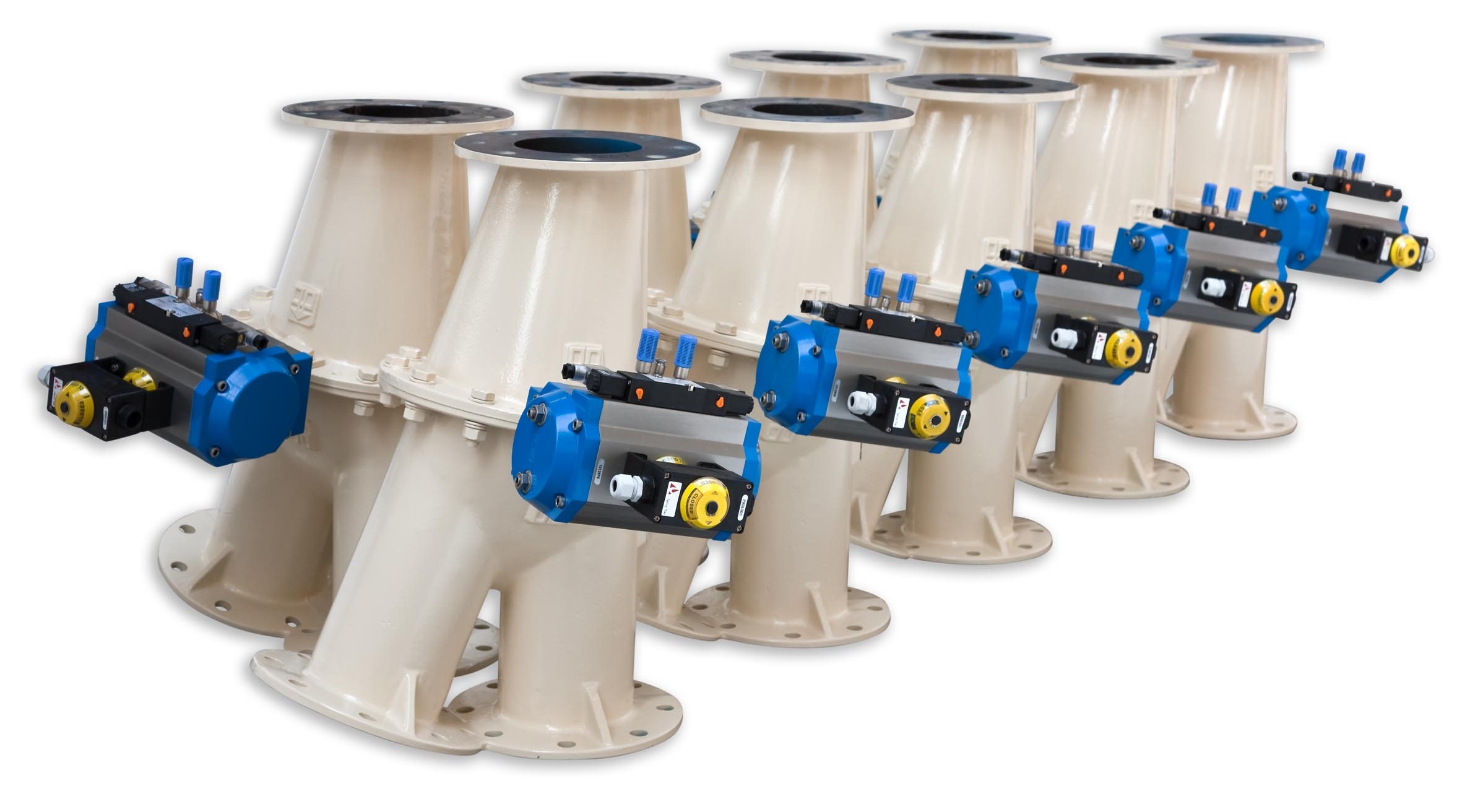
Two-way flap type diverter valve
Routing powder, pellets or granules from a product source to two receiving points must be d...
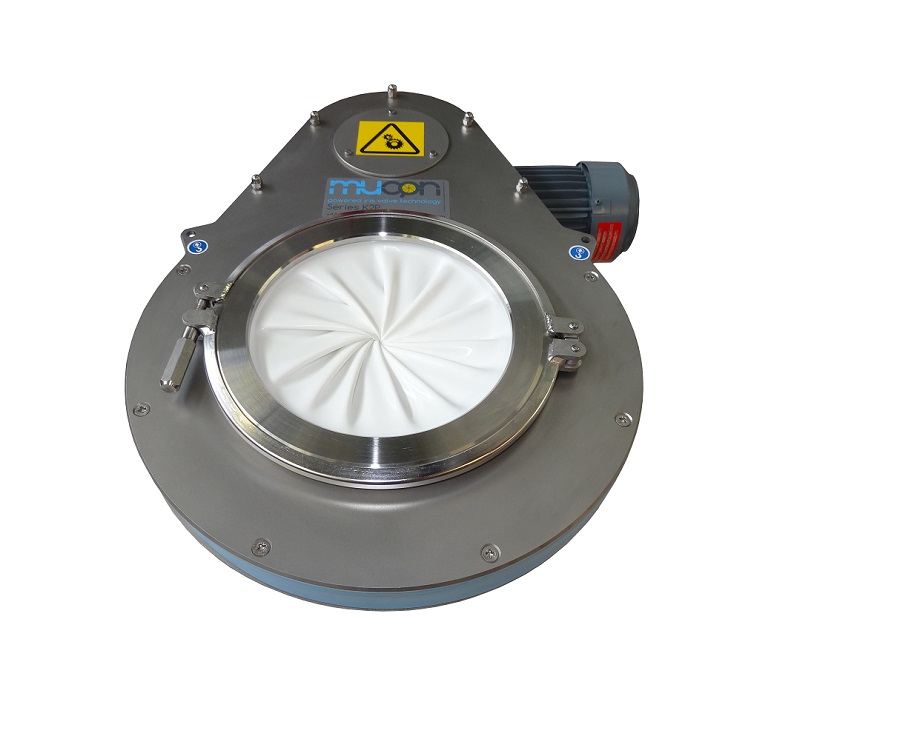
Hygienic automatic iris valve
In automated systems where controlled discharge of powders and bulk solids is required with a ...
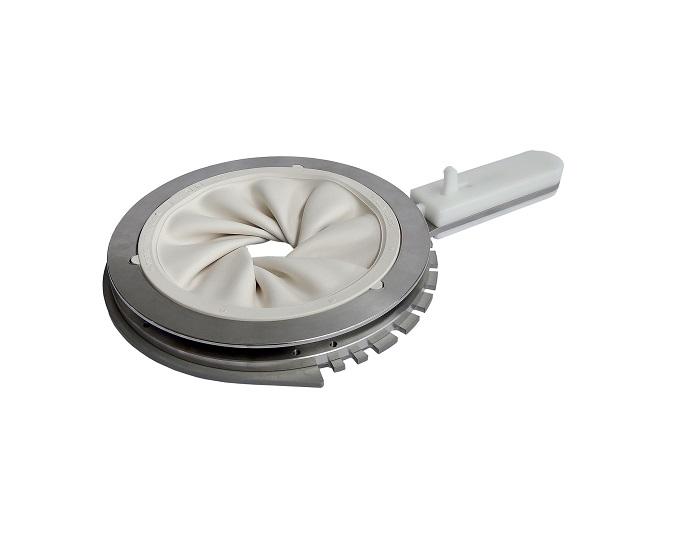
Hygienic hand-operated iris valve
Hand-operated valves are required for the walls of clean rooms for glanding around cables...
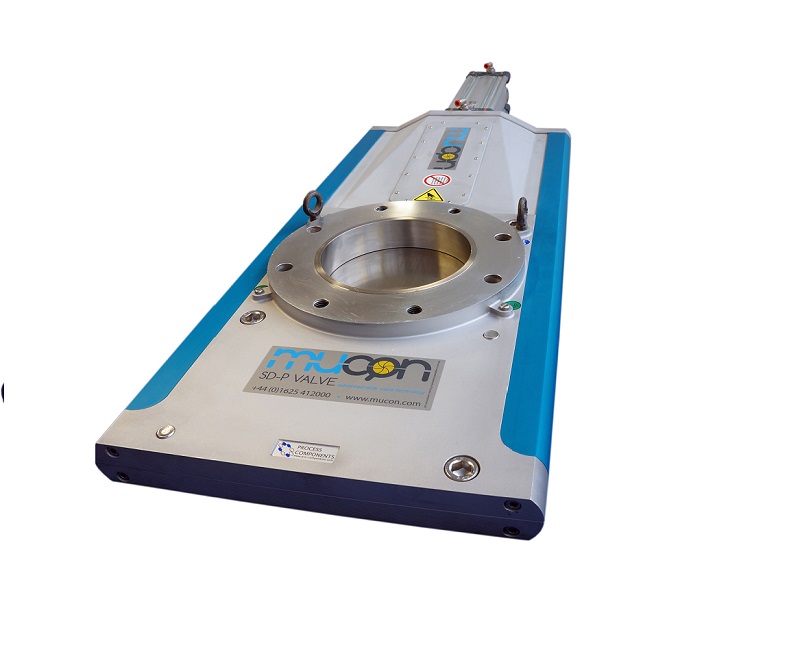
Slide gate valve
In the powder and bulk handling industries, in-line shut off valves are required to provide uninterrupted smo...
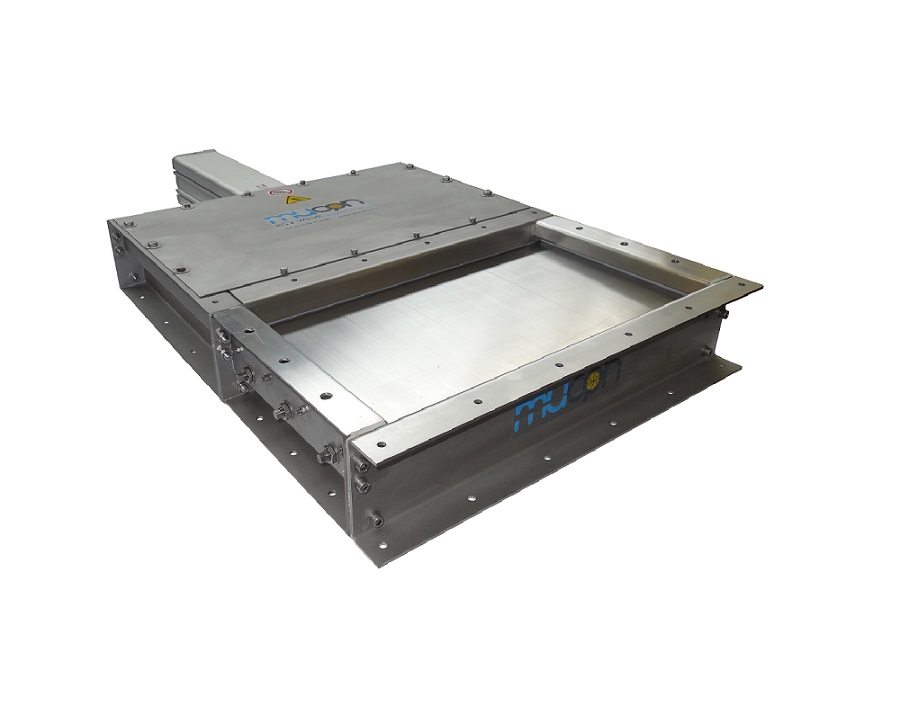
Roller gate valve
In large scale operations, modular and configurable valves are required to isolate and control dry powders,...
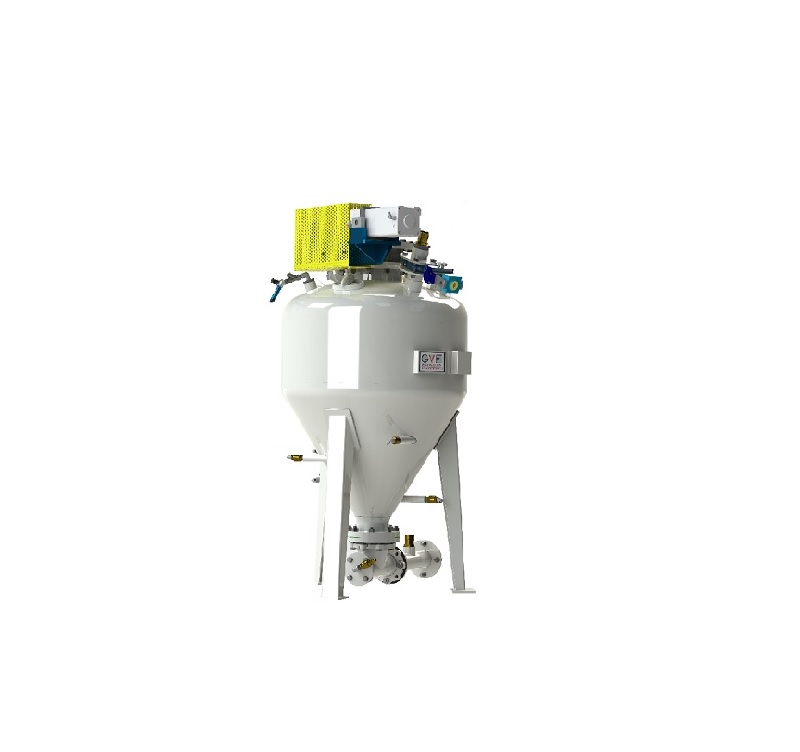
Dense phase conveyor for normal wearing materials
Dense phase pneumatic conveying is used for powders, granules, and grai...
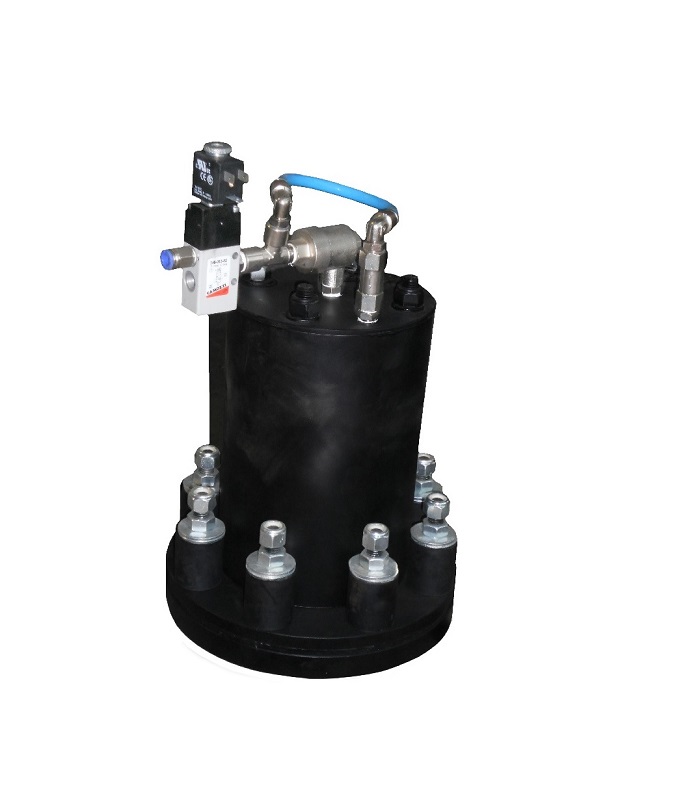
Airshocking hammer
Silos, hoppers, bins, and other containers can build up a layer of powdered product on the internal walls....
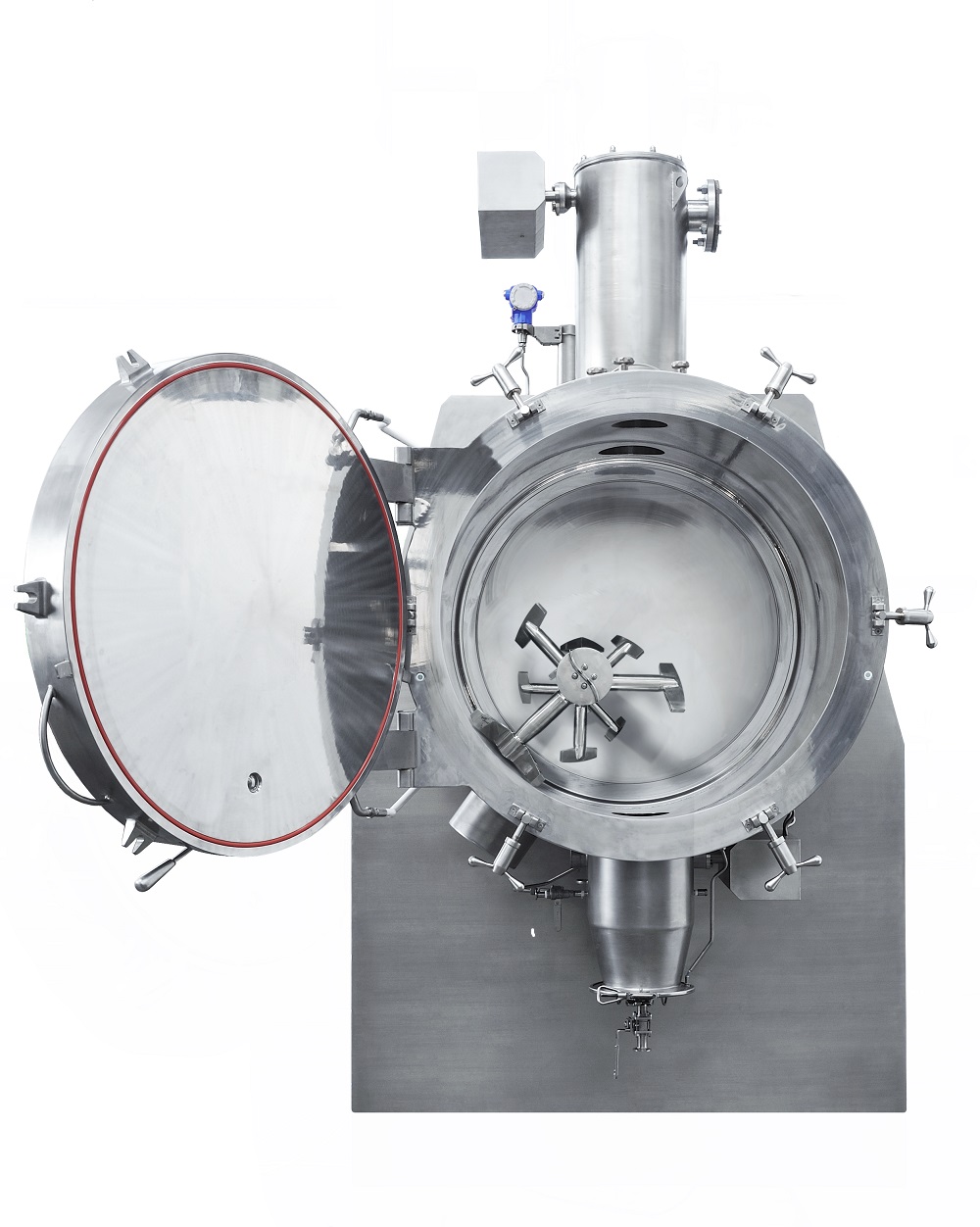
Horizontal vacuum dryer with eccentric agitator
Conventional dryers are inefficient and can lead to significant mechanical...
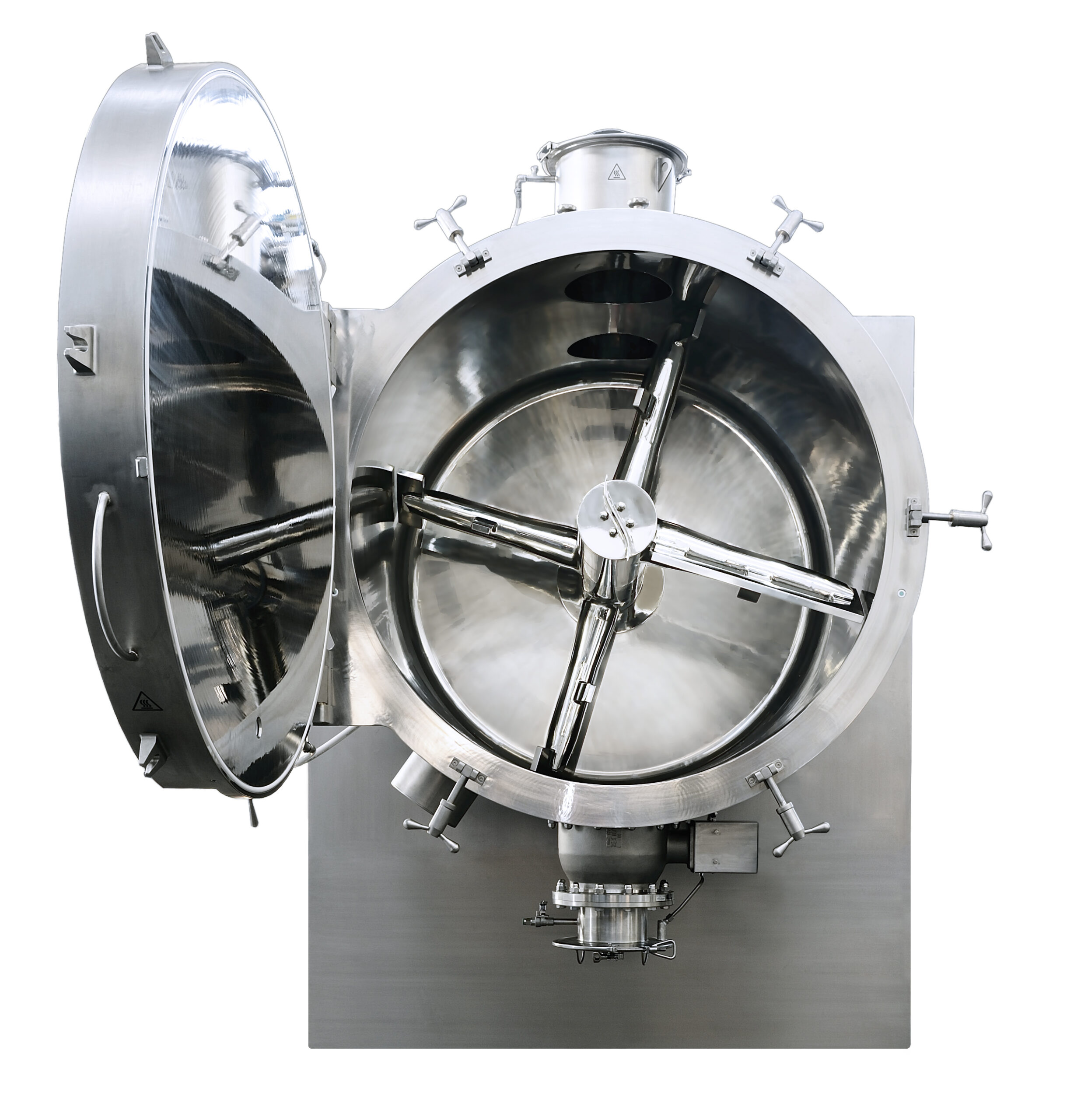
Horizontal paddle vacuum dryer
Agitated vacuum dryers can be difficult to clean which makes them unsuitable for multi-produc...
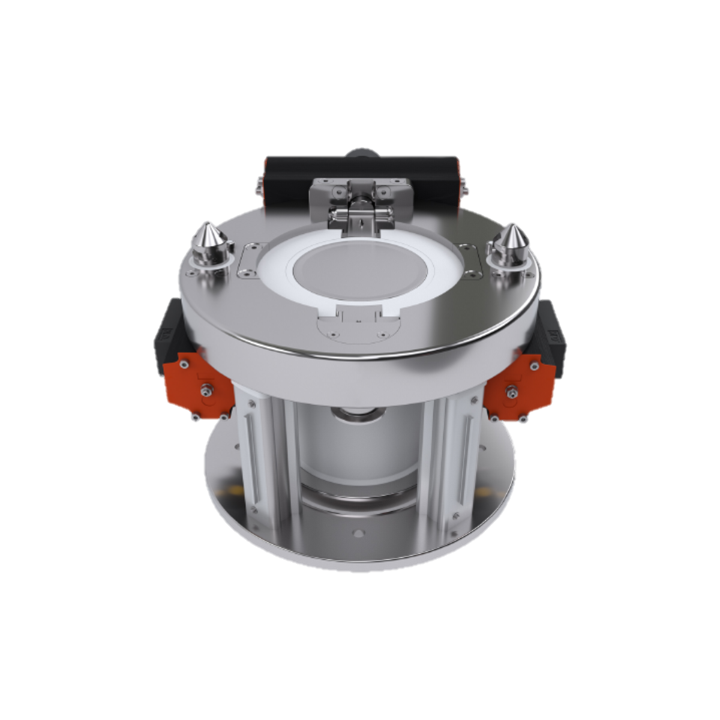
High containment split butterfly valve
Powder containment is the cornerstone of chemical and pharmaceutical manufacturing. ...
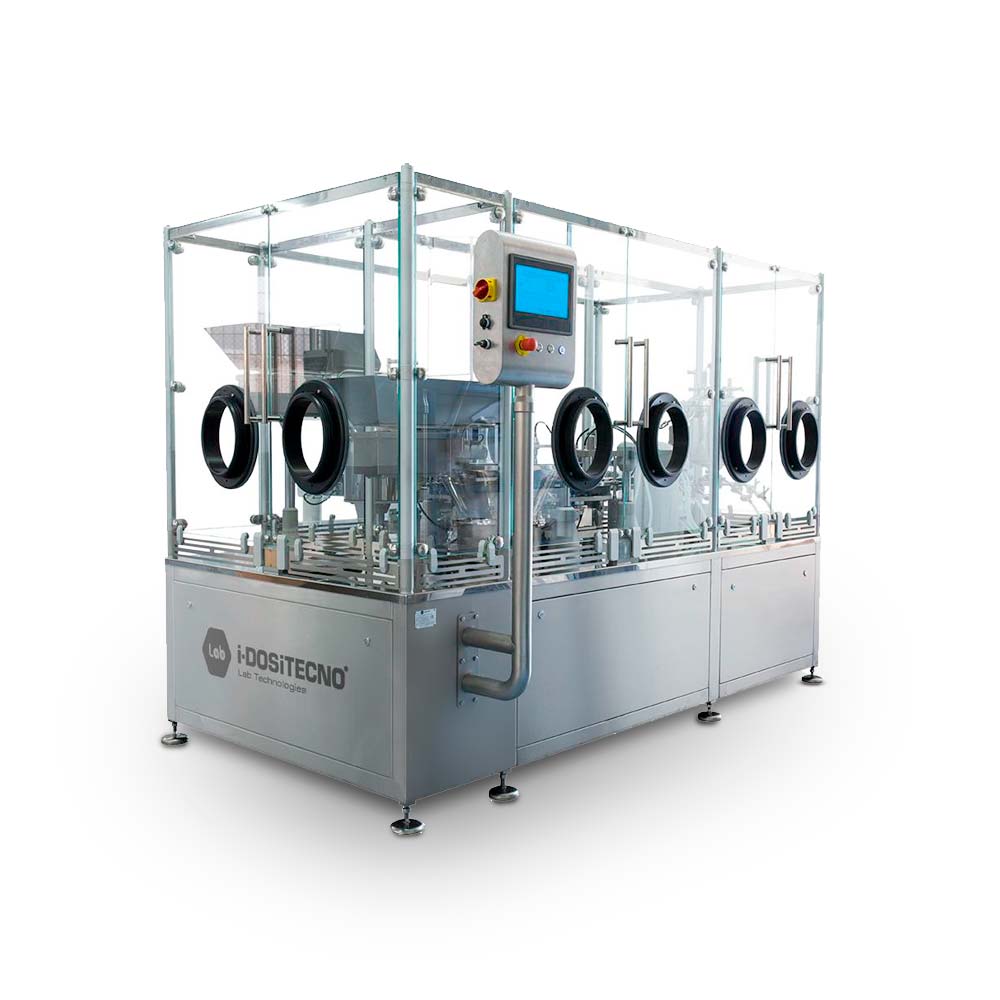
Sterile filling line for injectables
Sterile filling of liquids and powders for the pharmaceutical and cosmetic industries ...
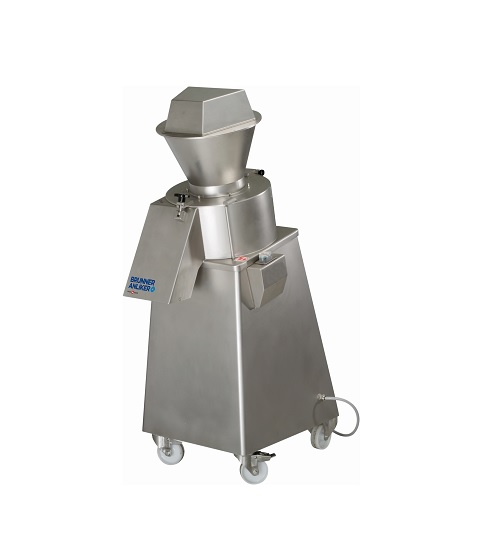
Industrial nut grater
Pressure from the grinding process can cause damage to food products as well as induce unwanted heating...
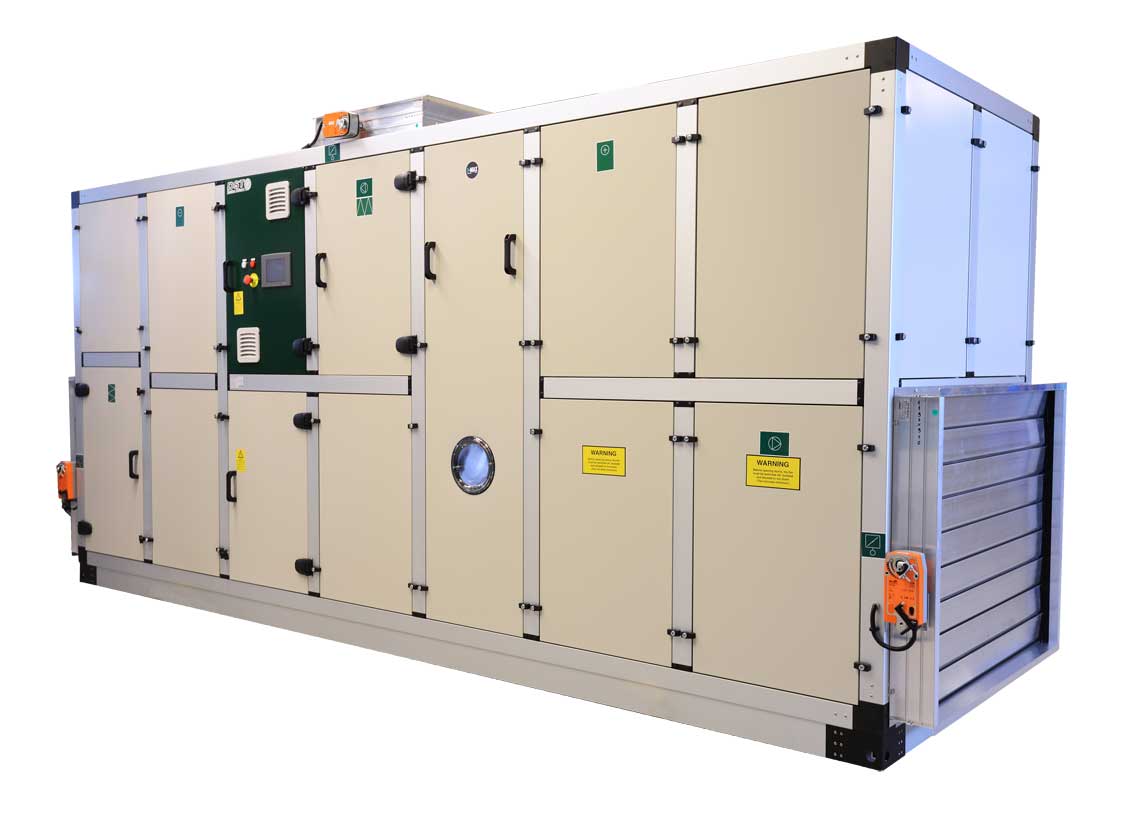
Customizable dehumidifier
Dehumidification needs can vary significantly from one project to another. Dehumidifiers with a fi...
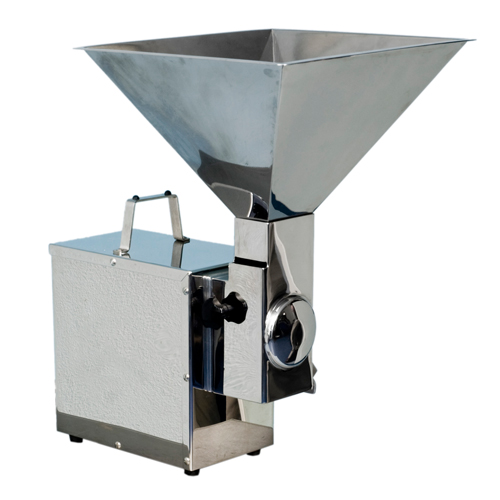
Nut dicer
Dicing nuts can generate a large volume of wasteful and messy powdered nut residue.
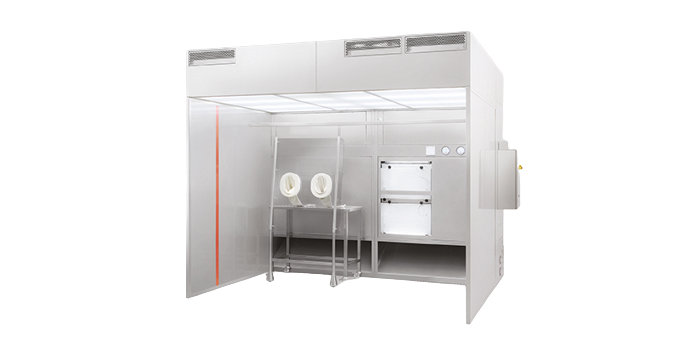
Downflow booth
Provides the highest levels of operator protection from potentially harmful airborne contaminants generated dur...
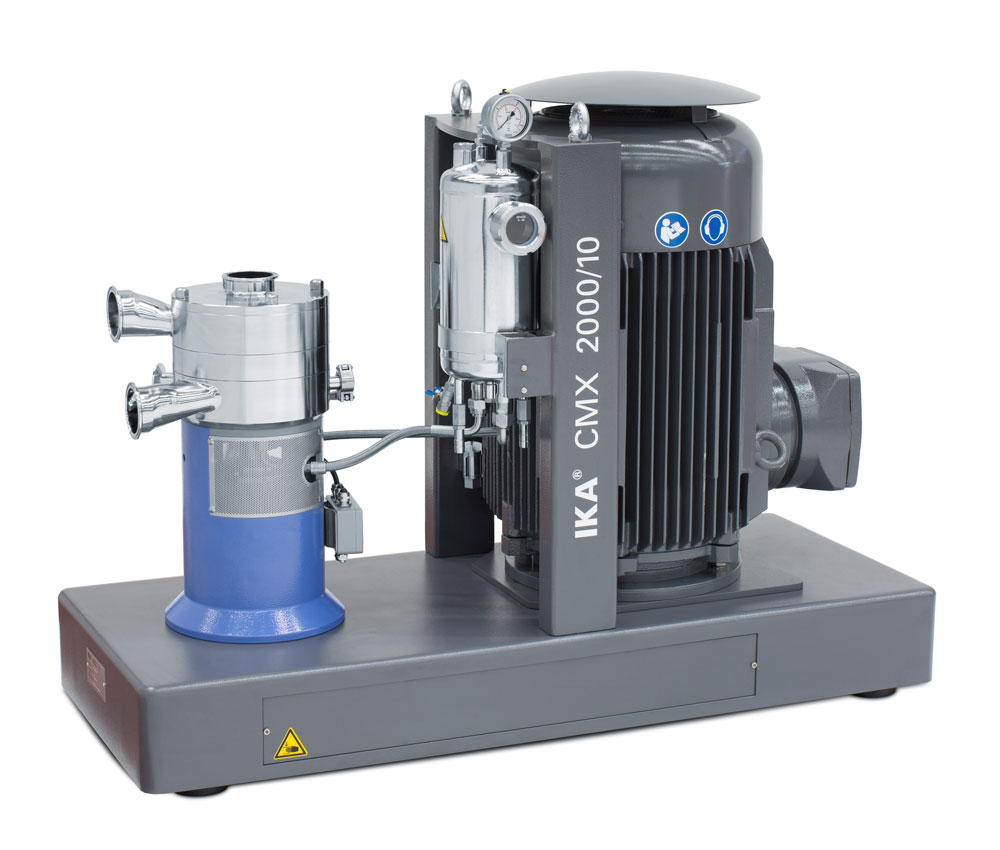
Inline batch mixer for solids and liquids
Several issues often arise when your process requires batch-wise mixing of powde...
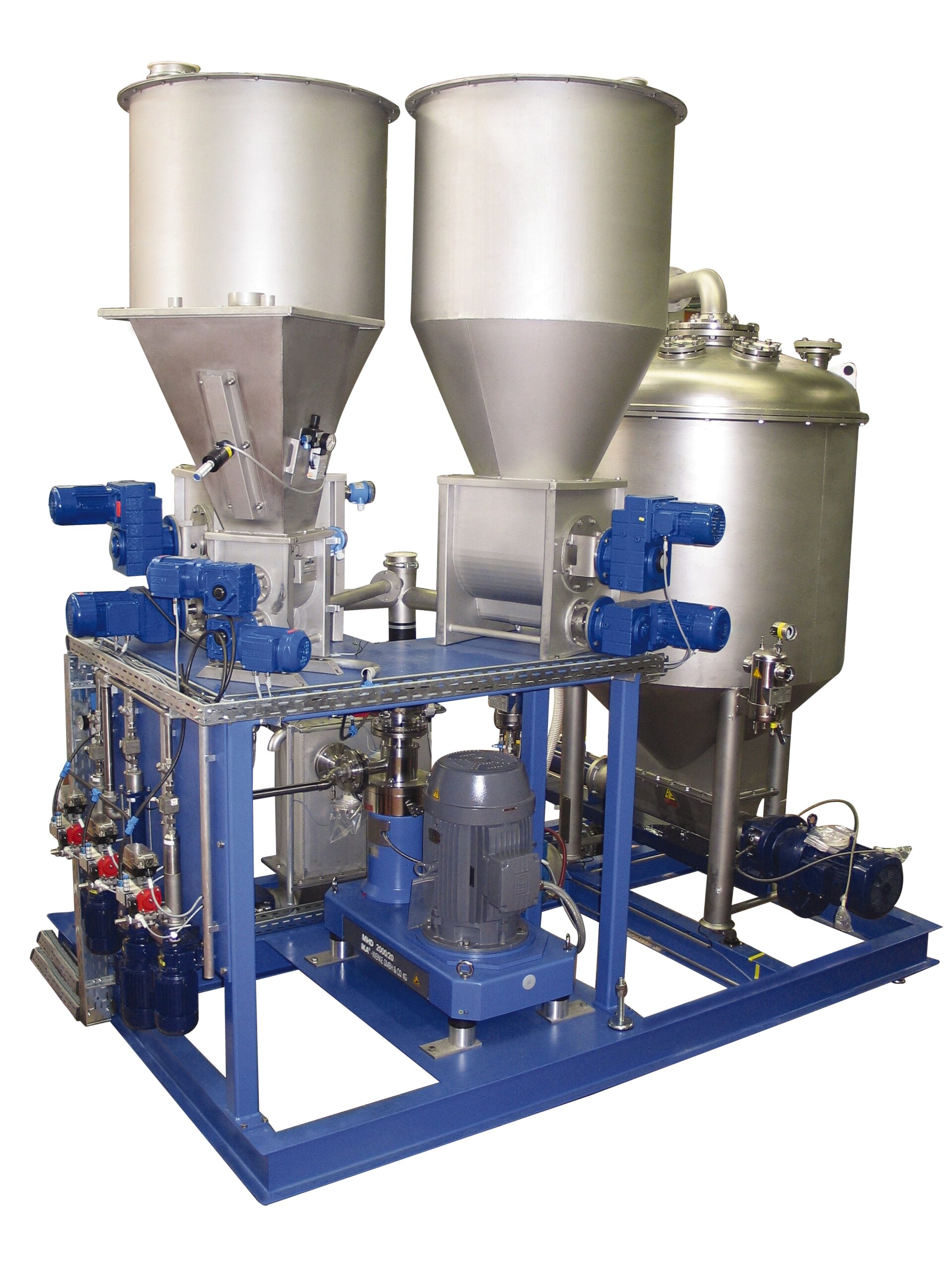
Dust-free continuous homogenizing system
Producers in a wide variety of industries benefit from equipment that can continuo...
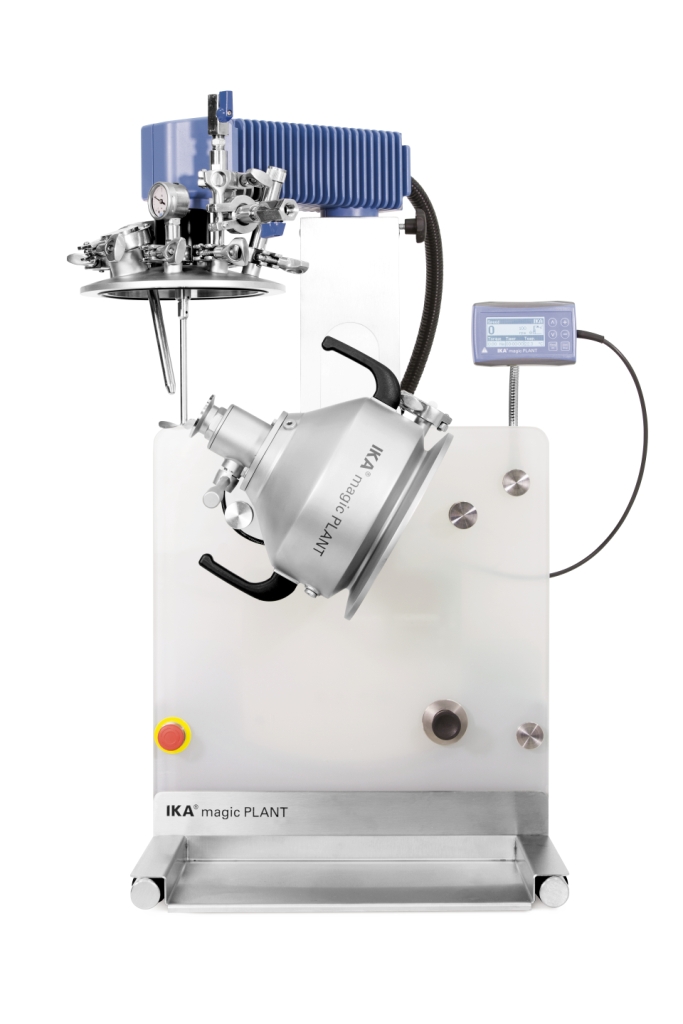
Laboratory dispersing machine for low-viscous masses
Laboratory mixers have not always been easy to work with. Getting a...
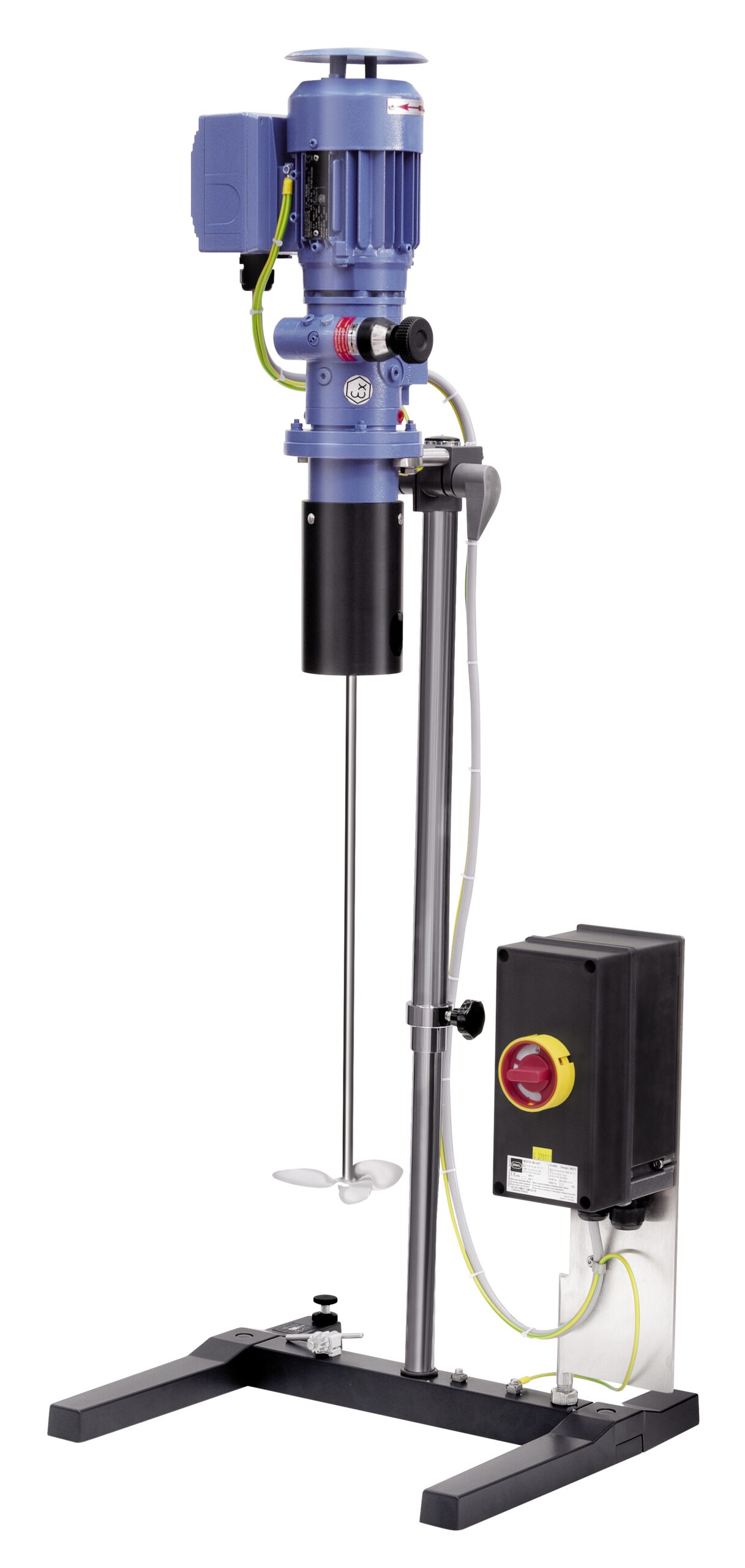
Agitator for medium viscosity media
Mixing fluids of medium viscosity for many production processes requires an agitator wi...
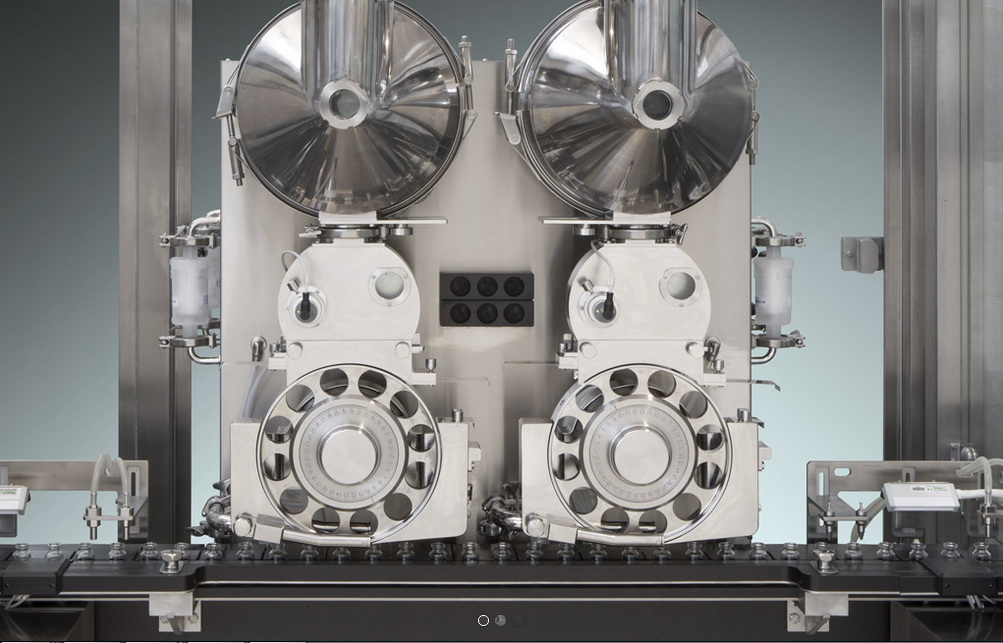
High-speed aseptic injectable vial filling machine
Fill up to 24,000 vials per hour with pharmaceutical powders or liquid...
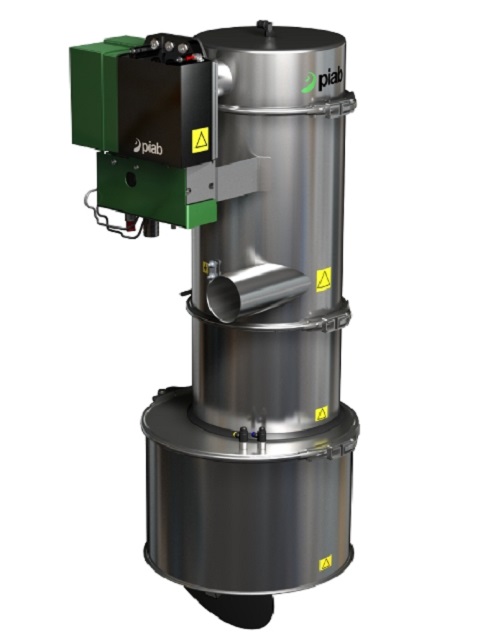
Food vacuum conveyor
Widely used in industries where a high rating in food quality is imperative.
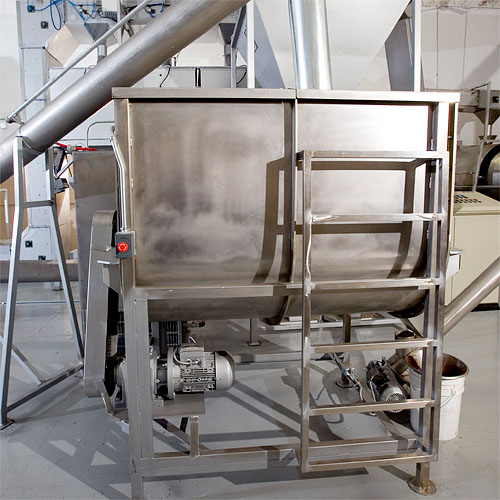
Basic mixer for granular foods
Straightforward blending solution for mixtures of beans, nuts, berries & powdered foods, ...
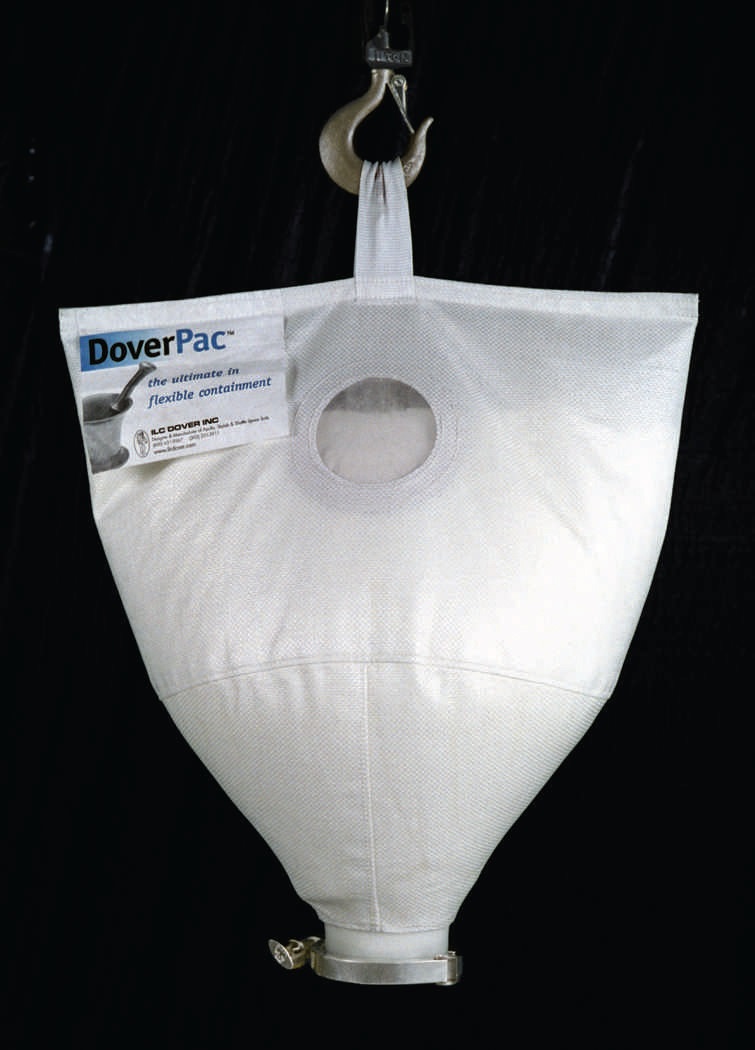
Flexible contained charging for split butterfly valves
Poly bottles with split butterfly valves are often used to transfe...
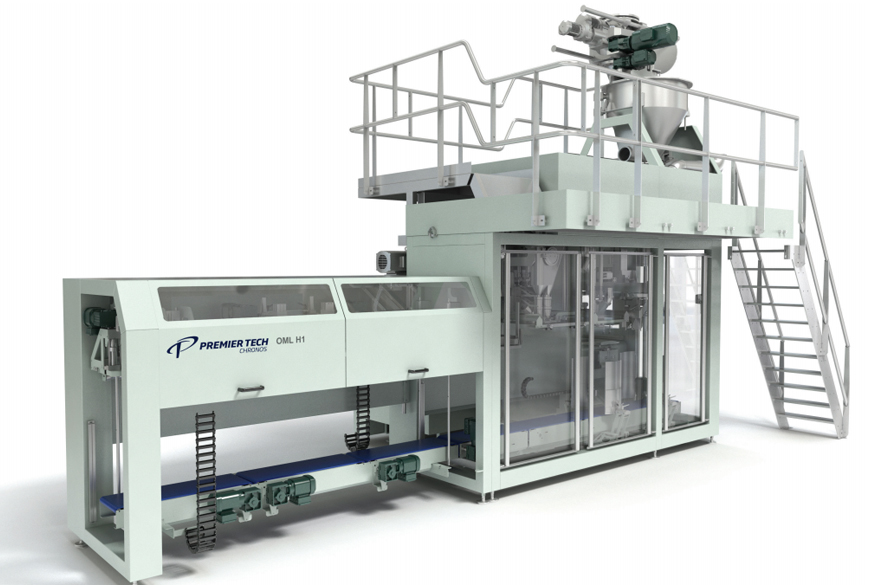
Hygienic open-mouth bottom-up baggers
Here are the open-mouth baggers that are specially designed for hygienic bagging of p...
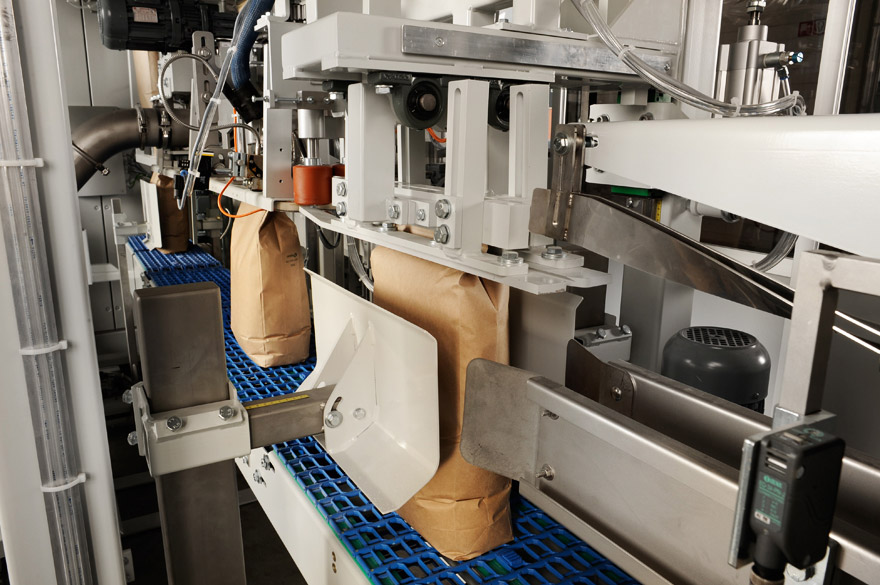
Open-mouth bottom-up baggers
Innovative bottom-up baggers for high-speed industrial packaging will help you create a dust-fr...
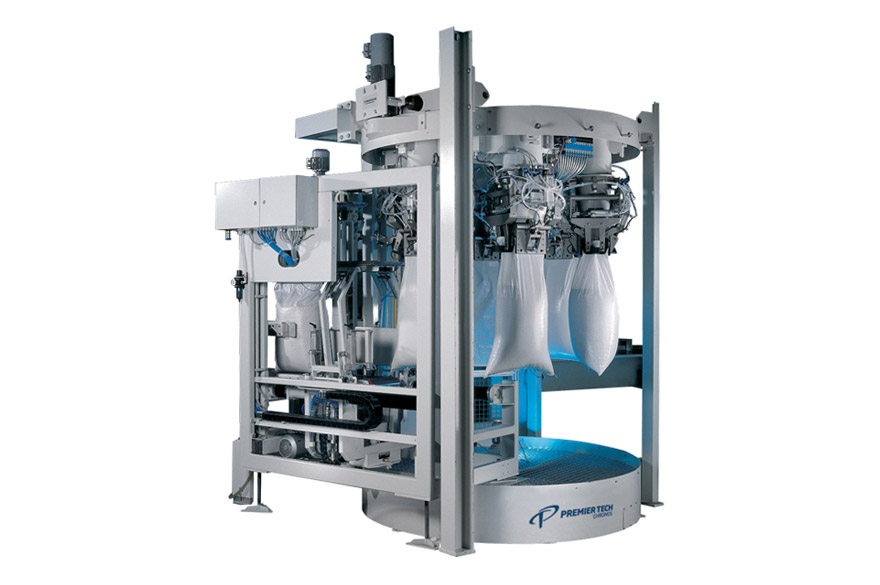
Open-mouth bagging carousel for flour
When you need a carousel for packing powdery bulk materials, the bagging carousel tha...
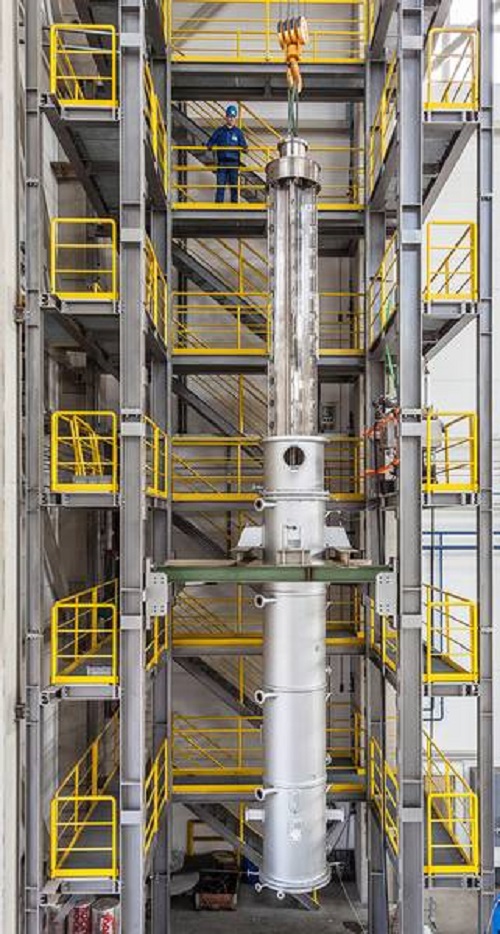
Thin film dryers
Dry dissolved or slurried crystallizing or amorphous products to a pourable powder.
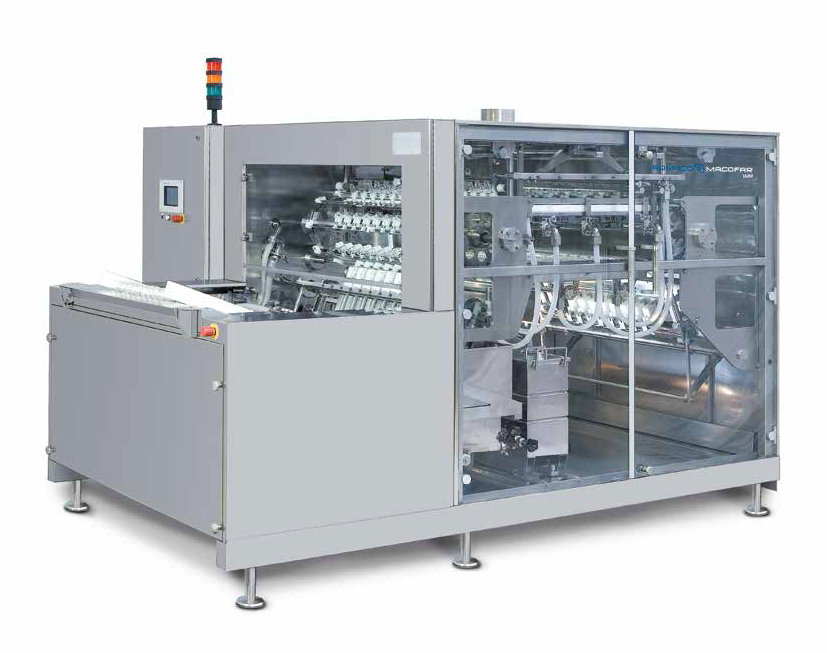
Automatic washing machine for ampoules
Automatic washing machine designed for cleaning ampoules and achieving a maximum out...
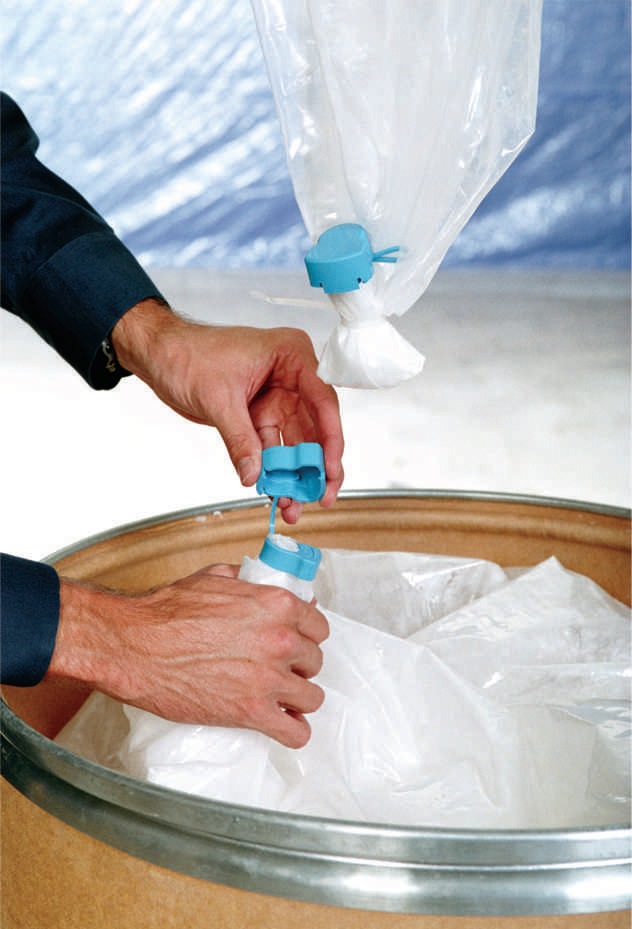
Crimping system
Flexible disposable containment systems in the form of specially designed plastic bags are an excellent choice...
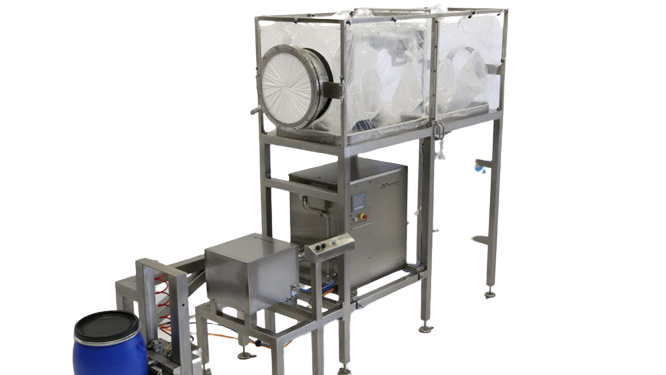
Flexible contained drum transfer system
Transferring powders from drums to process equipment such as reactors or mills can ...

Circuit-air classifier
For high throughputs, with a fineness range of approx. d97 = 32 µm – 200 µm. Ideal for use in th...
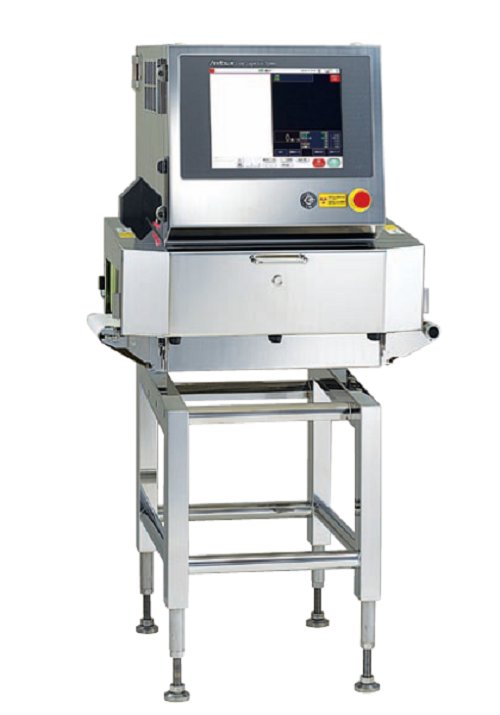
Versatile X-ray inspection system
Versatile X-ray inspection system for product weight, quantity and shape to detect the pr...
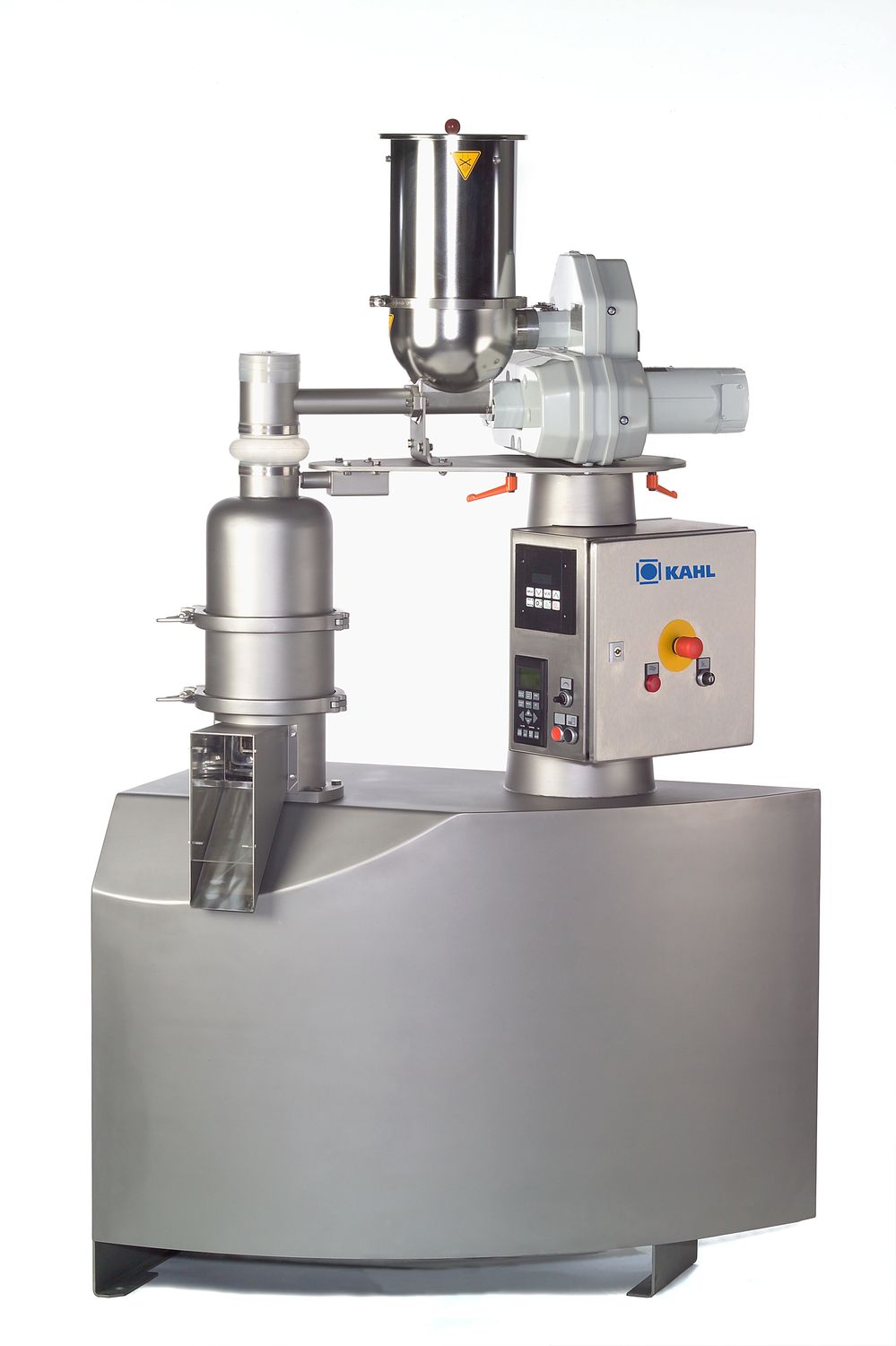
Hygienic pelleting press
The production of pelletized or granularized food products requires hygienic presses designed for hi...
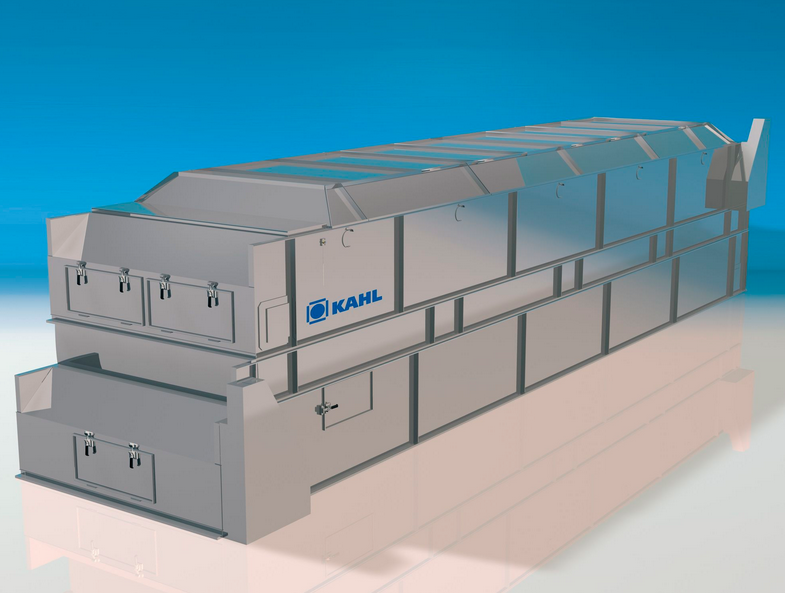
Belt dryer/cooler for pellets and granules
Many industries that process materials in pellet, powder, or crumble form need ...
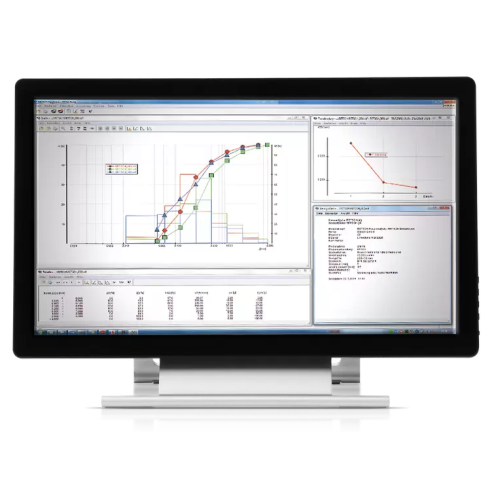
Sieve analysis software for automated evaluation
Streamline your sieving processes with automated data evaluation and prec...
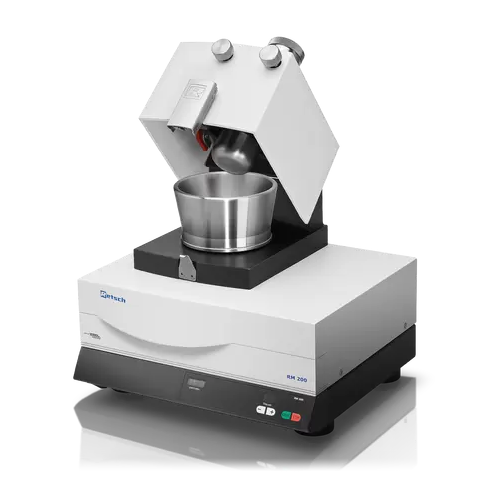
Mortar grinder for reproducible sample preparation
Achieve precise and consistent material preparation with this mortar g...
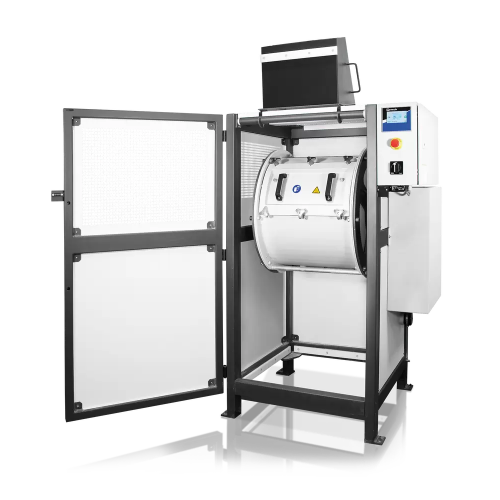
Laboratory drum mill for large sample volumes
Efficiently process large volumes of diverse materials into precise particle...
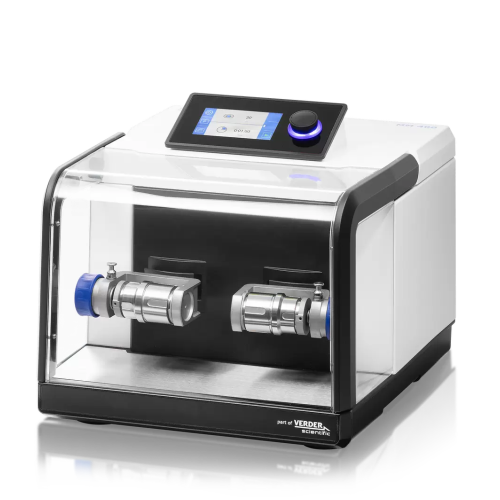
Laboratory mixer mill for small volume grinding
Designed for rapid homogenization and size reduction, this versatile mixer...
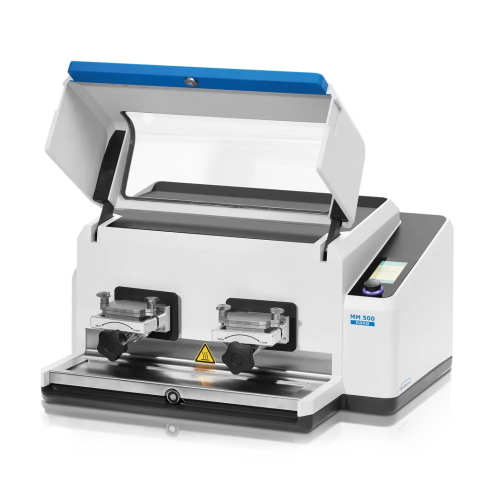
Ultrafine grinding solution for nanoparticles
Achieve ultrafine particle sizes with high-speed precision, ideal for labora...
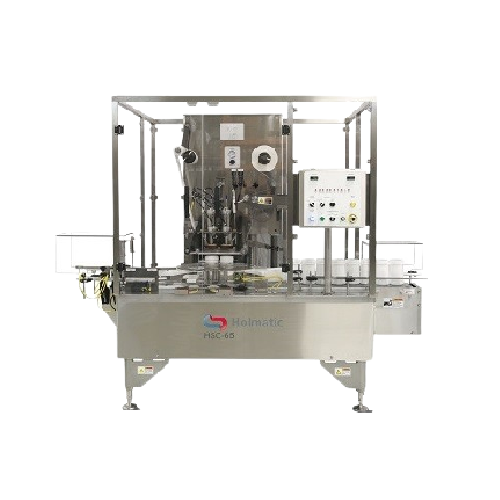
Rotary indexing sealer for cup filling
Streamline your production line with precise cup filling and sealing, ideal for a wi...
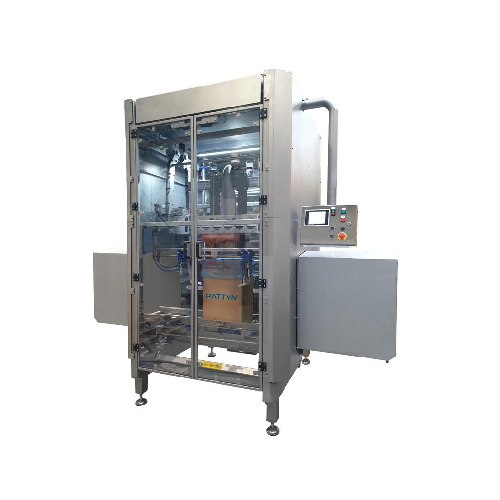
Hermetic bag sealer for extended shelf life
Achieve superior product protection and extended shelf life with precision her...

High-speed camera counting system for accurate product batching
Optimize your production line with a cutting-edge system...
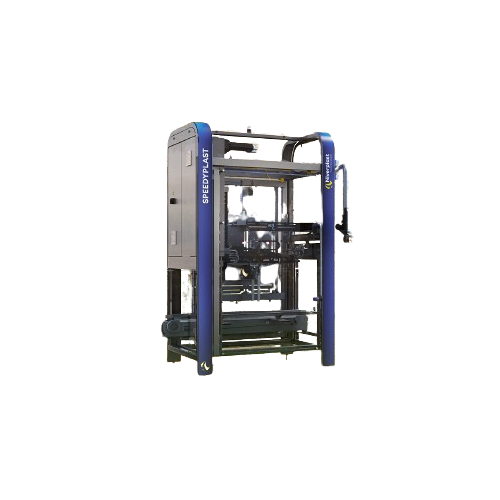
Automated system for placing bags in boxes and crates
Streamline your packaging process with high-speed bag placement tha...
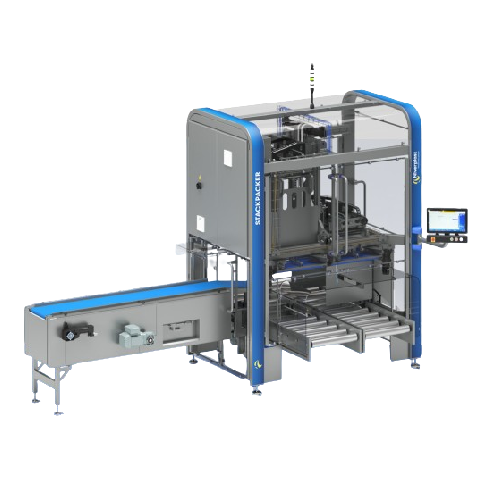
Touch-free layer packaging for bakery products
Optimize your packaging line with a touch-free solution that ensures hygien...
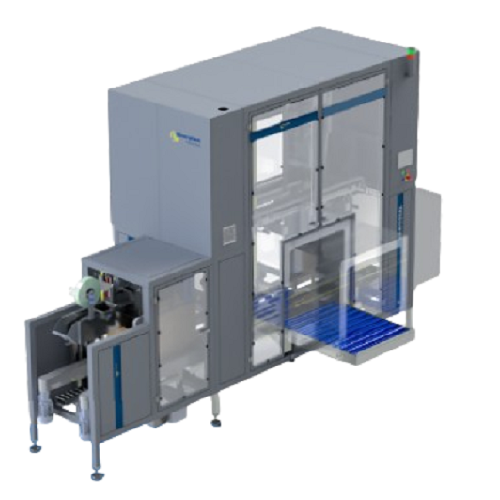
Automated bag sealing for packaging lines
Enhance your packaging efficiency by seamlessly integrating an automated bag sea...
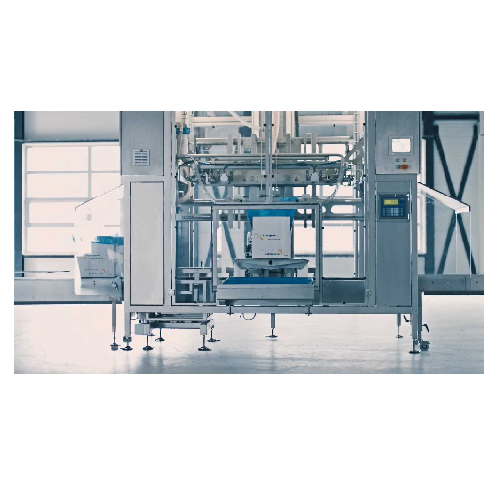
Automated bag folding for packaging
Streamline your packaging operations with a high-speed solution that seamlessly integra...
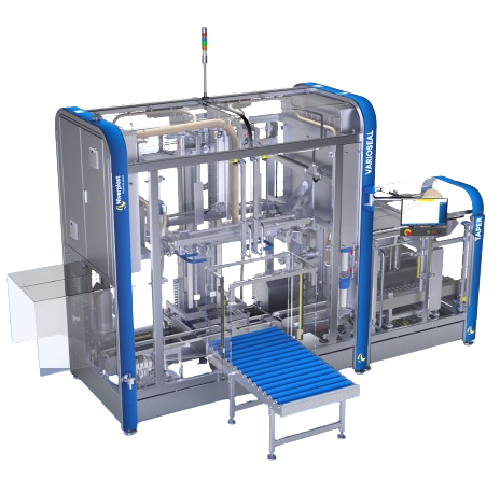
Automatic bag sealer for varied box sizes
Seamlessly integrate this high-speed bag sealing solution to enhance productivit...
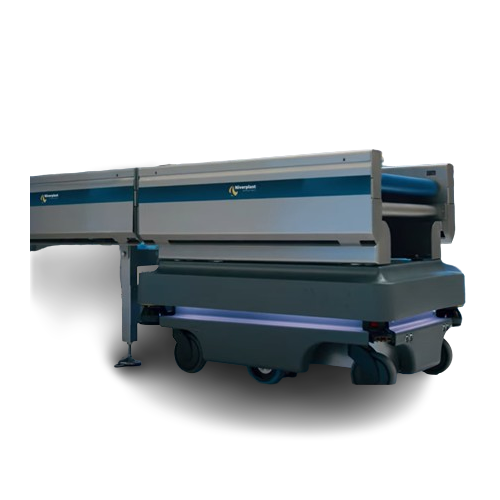
Self-driving transport system for industrial packaging
Streamline internal logistics with a self-navigating vehicle desig...

Compact palletizing solution for limited space
Optimize your space with versatile palletizing that adapts to diverse produ...
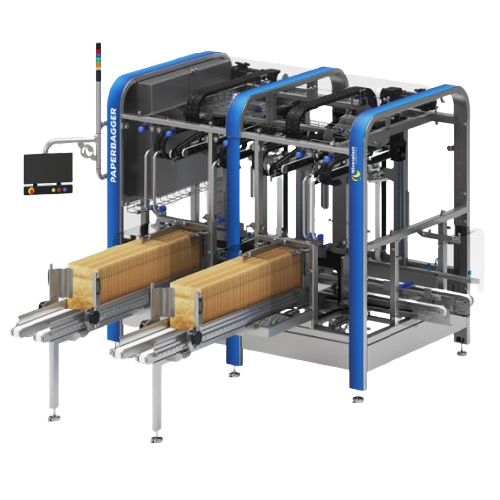
Automated paper bag placing system
Efficiently automate the placement of paper bags into totes or boxes with precision and ...
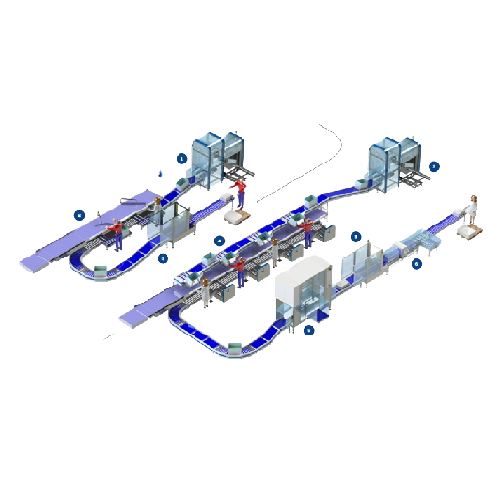
Camera quality control for industrial production
Ensure flawless product quality by integrating a precision optical inspec...

High-precision batch counting solution
Achieve precise product alignment and counting with advanced vibration and photocell...
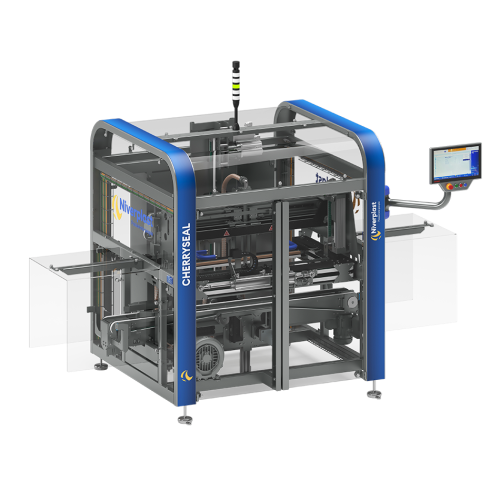
Compact sealing system for bags and boxes
Achieve seamless, high-speed packaging with a compact solution designed to handl...
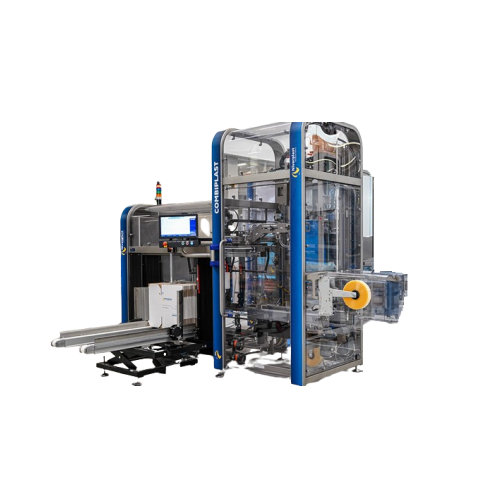
Case erecting and bag placing system
Streamline your packaging process with a compact system that integrates case erecting ...
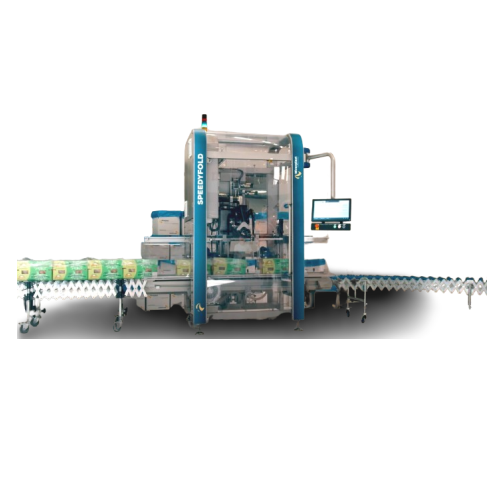
Bag folding solution for high-speed packaging
Effortlessly enhance your packaging line efficiency with this high-speed bag...
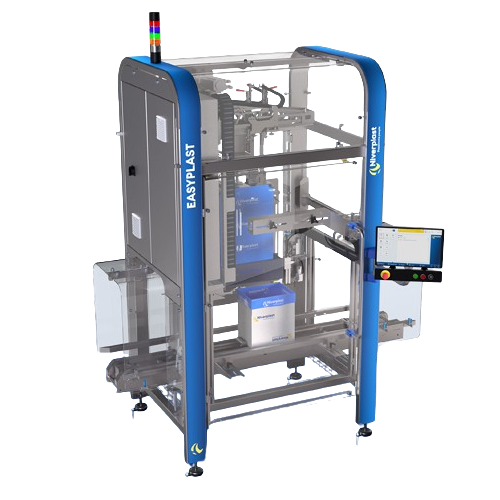
Automated bag placing solution for industrial packaging
Maximize efficiency with a versatile bag placing system designed ...
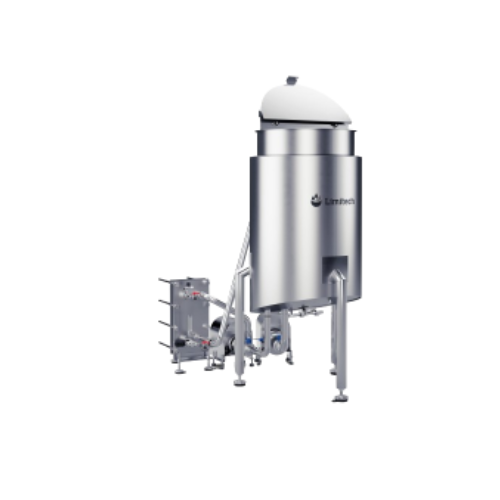
Oil cooling tank for fast product cooling
Accelerate your cooling process efficiently with an advanced oil cooling tank fe...
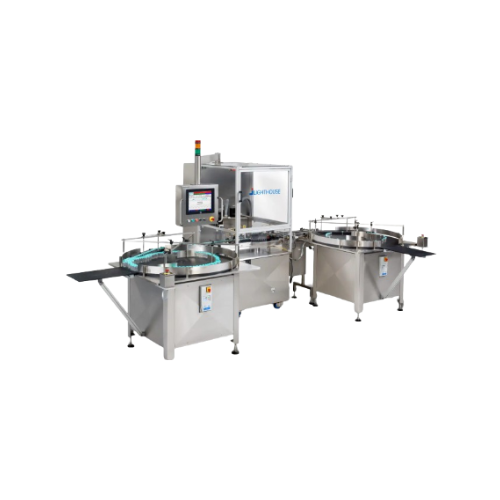
Automated headspace inspection system for parenteral containers
Ensure the integrity of pharmaceutical containers by pre...
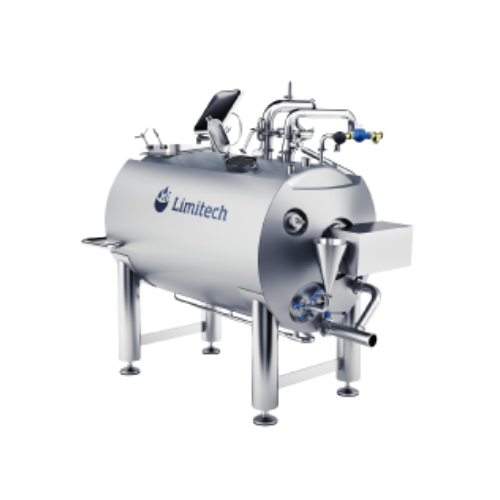
Emulsifying and blending system for liquid and semi-liquid food products
Efficiently emulsify and blend liquid and semi...
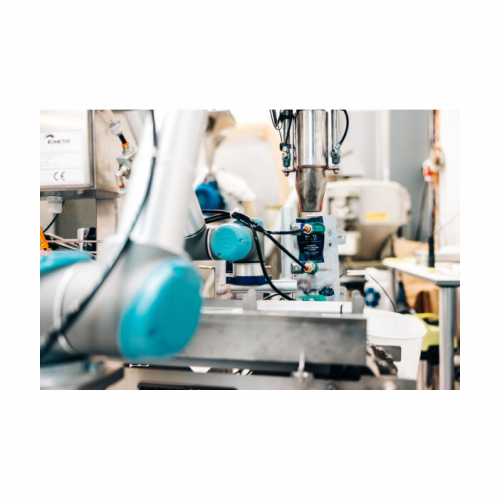
Dosing and tray handling lines for ready meals
Ensure precise dosing and seamless tray handling for a variety of ready mea...
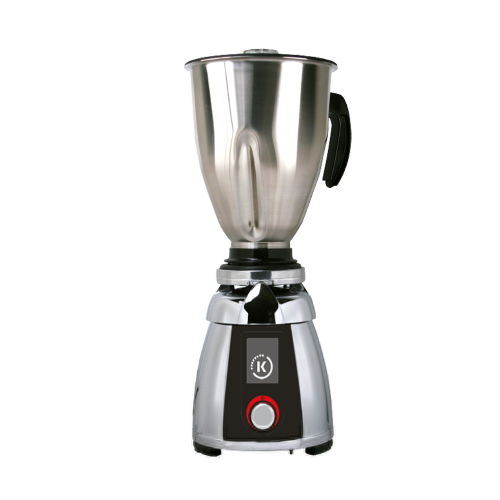
Laboratory mixer for homogenizing and mixing samples
Achieve precise sample preparation and efficient mixing with this ve...

Super high shear inline disperser for nanoparticle production
Achieve unmatched particle size reduction with cutting-edg...
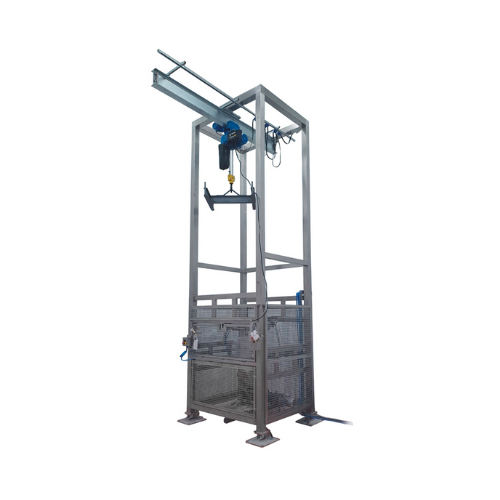
Big bag unloading station for solid materials
Streamline your production line by efficiently handling and dosing bulk soli...
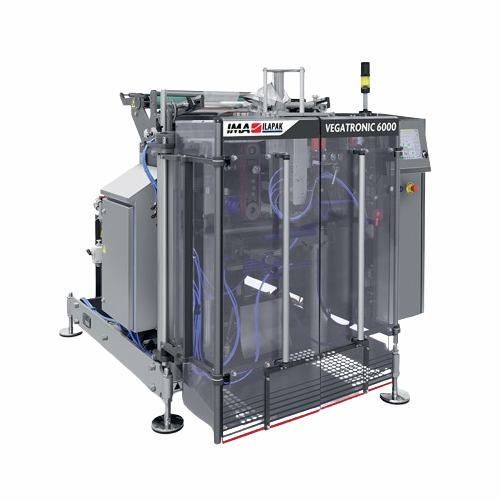
Continuous vertical form fill seal packaging solution
Experience unrivaled accessibility and efficiency in packaging fres...
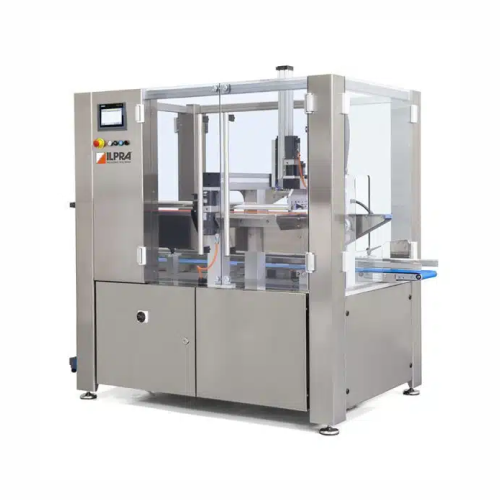
Automatic vertical casepacker for efficient packaging integration
Streamline your packaging process with a vertical cas...
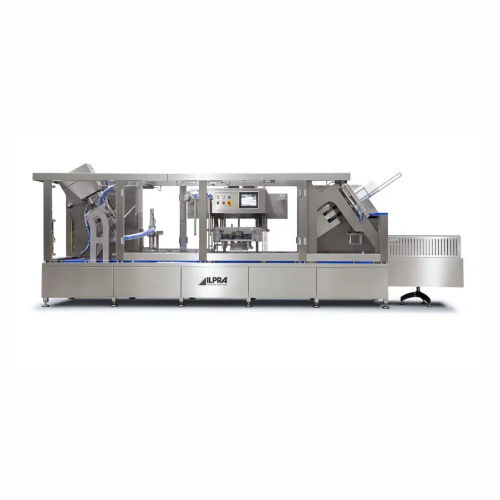
Tray sealer for food packaging buckets
Enhance your packaging efficiency with a highly adaptable tray sealer, designed for ...
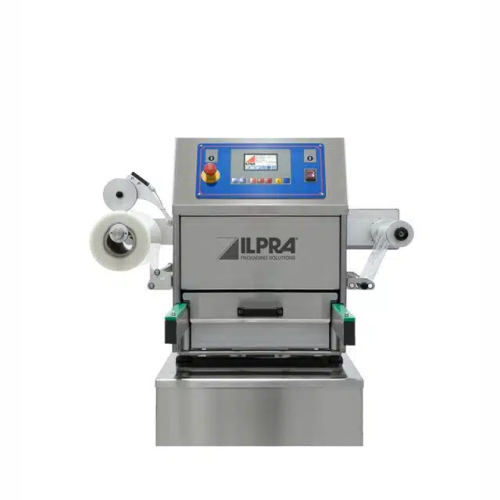
Tray sealer for packaged food products
Optimize your food packaging with precise sealing and advanced Modified Atmosphere P...
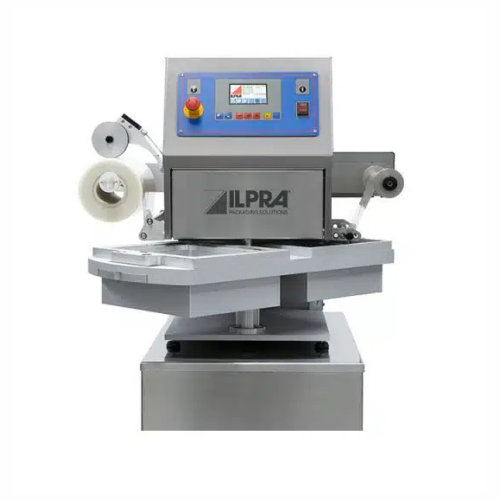
Traysealer for modified atmosphere packaging - food products
Optimize your packaging line with this semi-automatic trays...
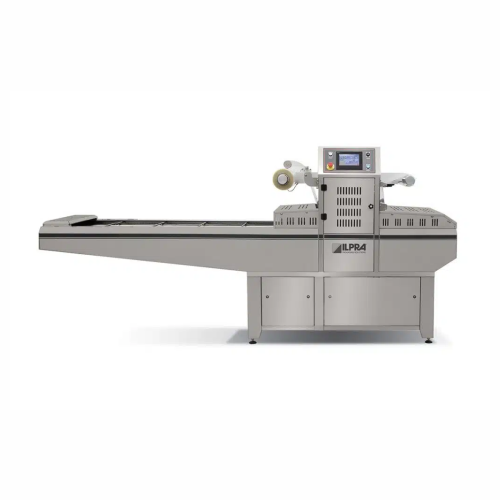
Traysealer for medium production
Streamline your packaging process with high-speed traysealing, ensuring freshness and exten...
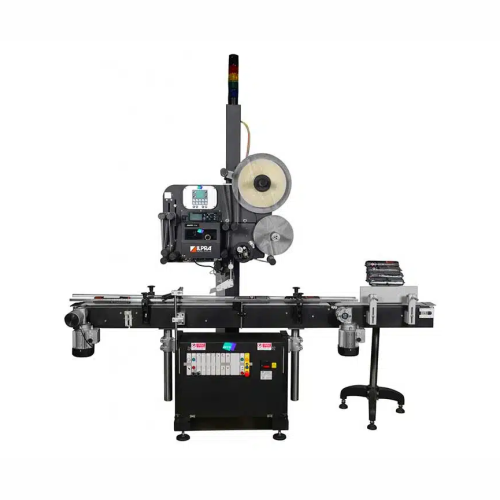
Automatic c-wrap labelling for packaged products
Enhance your production line with precise C-wrap labelling, seamlessly in...
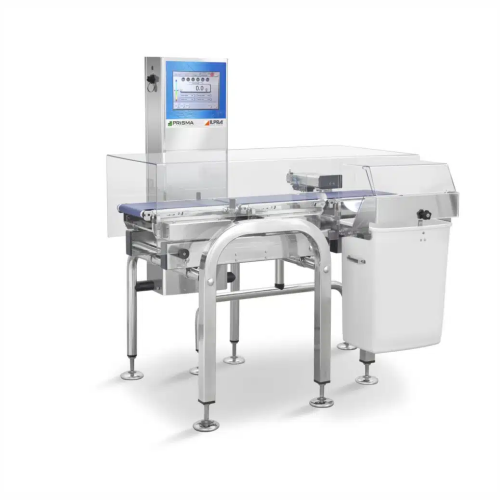
Industrial check-weigher for accurate product weight verification
Ensure precise weight compliance and reduce waste wit...
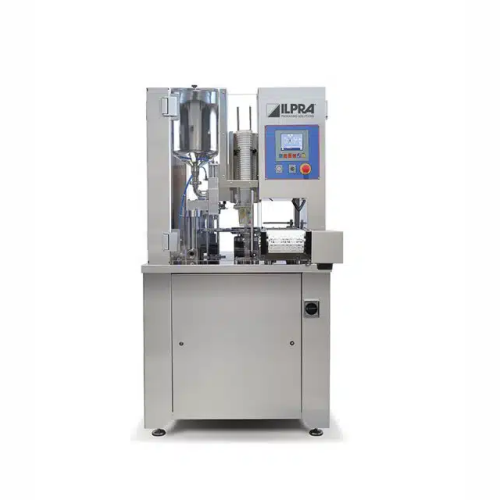
Rotary filler and sealer for dairy products
Optimize your filling and sealing needs with a compact solution designed for c...
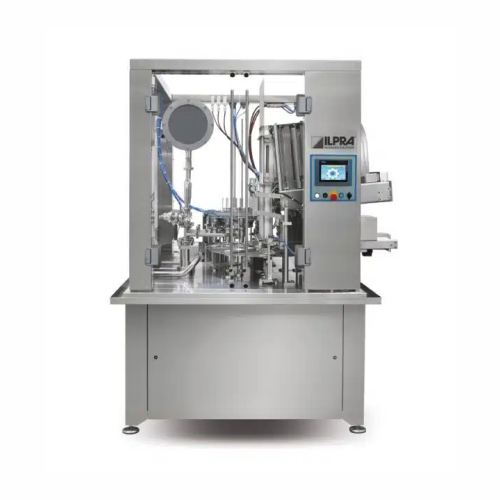
Automatic filling and sealing solution for medium to large production
Streamline your high-capacity filling and sealing...
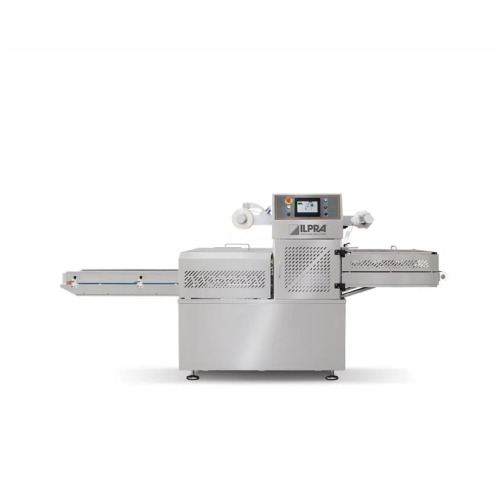
Entry-level in-line traysealer for ready-to-eat meals
Streamline your ready meal packaging with a compact traysealer that...
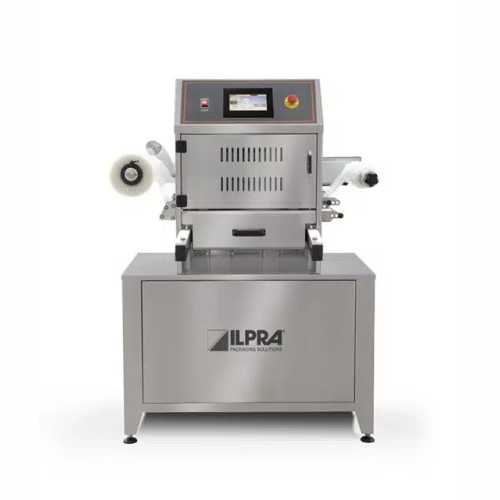
Semi-automatic tray sealer for skin packaging
Optimize your small-scale food packaging with a compact tray sealer designed...
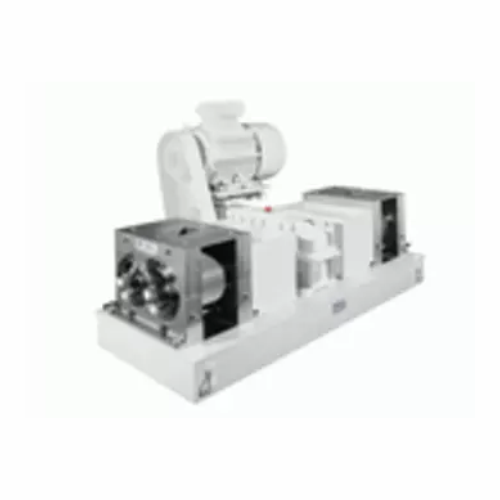
Gear pelletizer for stable cylindrical pellets
Achieve uniform pellet size and stability in your production line with a lo...
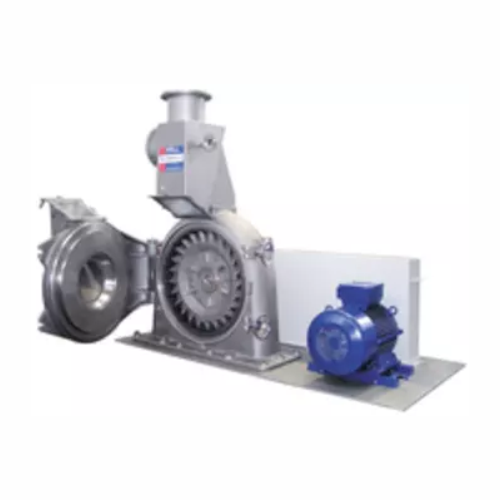
Versatile fine impact mill for soft materials
Achieve precision grinding with flexibility for a wide range of materials, e...
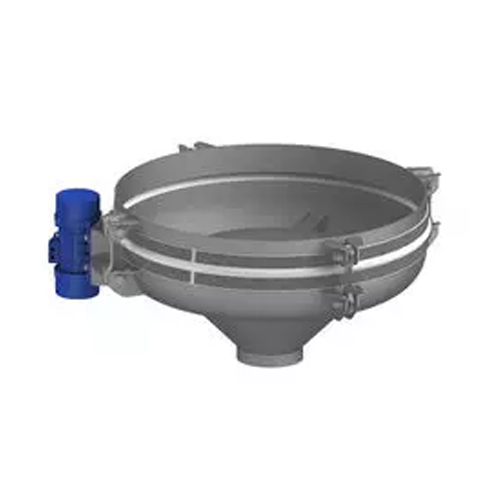
Discharge systems for difficult bulk materials
Achieve seamless bulk material discharge with our advanced systems that eff...
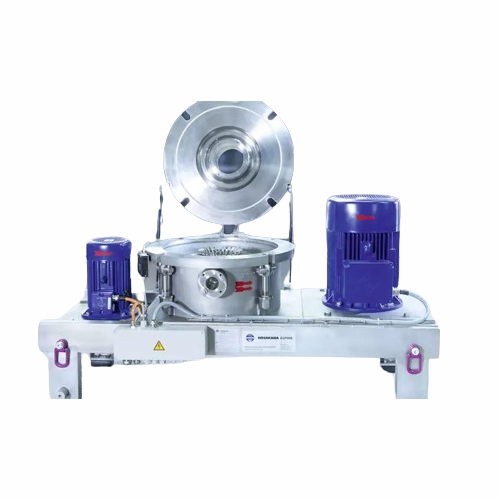
Classifier mill for ultrafine grinding
Achieve precise particle size distribution and contamination-free processing with th...
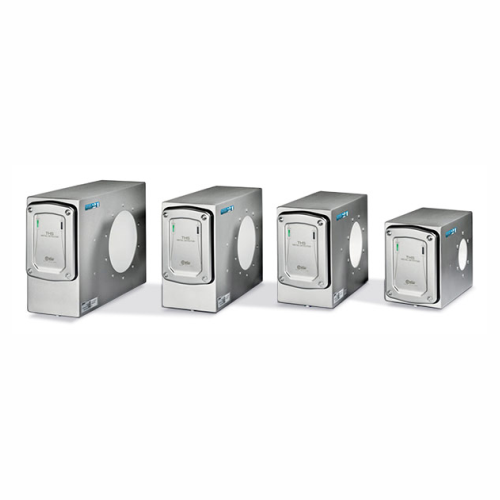
Industrial metal detector for gravity feed applications
Ensure the purity of your products by detecting and removing both...
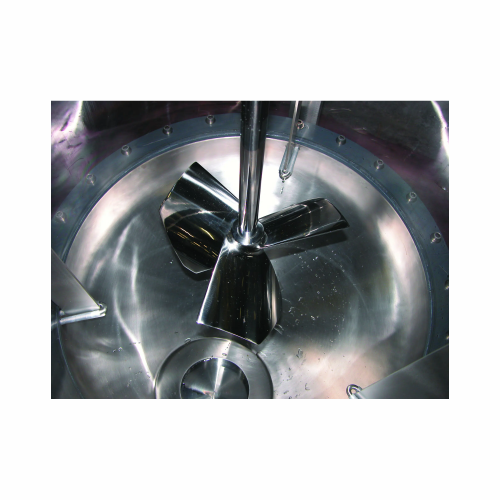
Sealless top-entry industrial mixer
Engineered for diverse industrial applications, this sealless top-entry mixer offers su...

Side entry mixer for industrial fluid mixing
Optimize your fluid mixing processes with high-speed side entry mixers, desig...
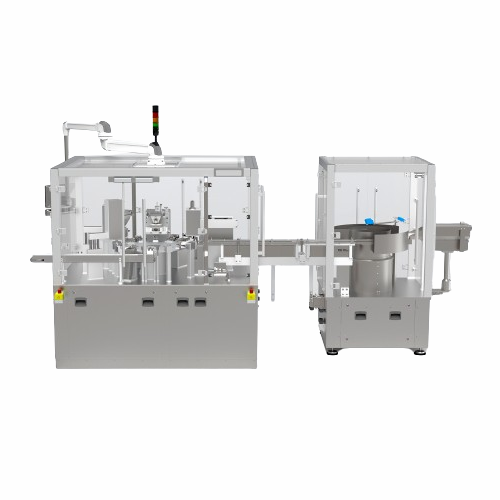
Rotary indexing table for dosing and assembly
Optimize production efficiency with a compact rotary indexing table that str...
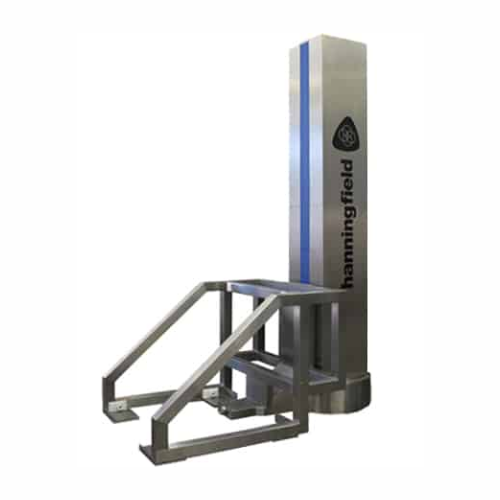
Industrial container and drum handling solution
Effortlessly maneuver and position heavy containers such as IBCs and drums...
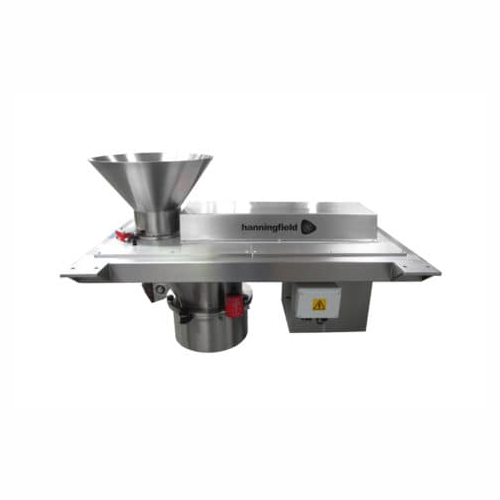
Over-driven conical mills for precise particle size reduction
Achieve consistent particle size reduction with minimal he...
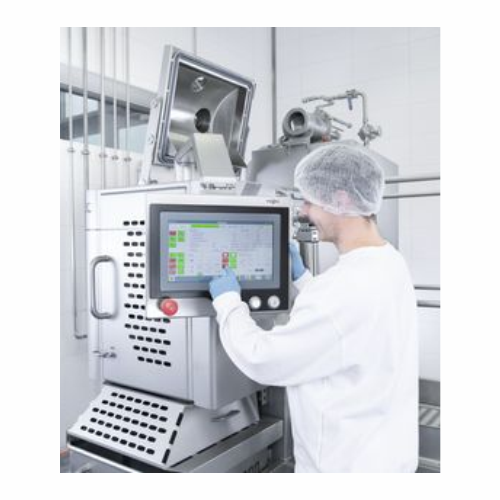
Flexible mixing system for meat and dairy products
This versatile mixing system delivers precise control over temperature...
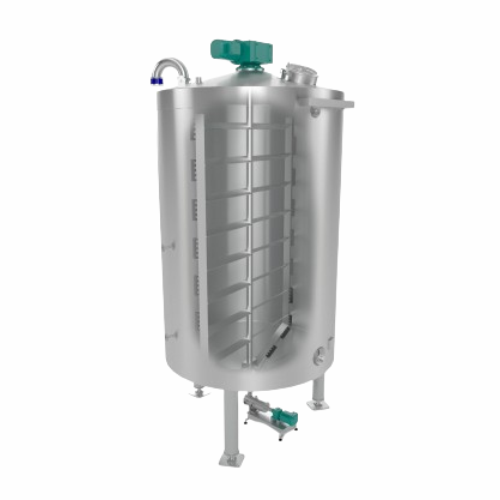
Stainless steel chocolate tank for storage and processing
Efficiently control temperature and consistency for chocolate ...
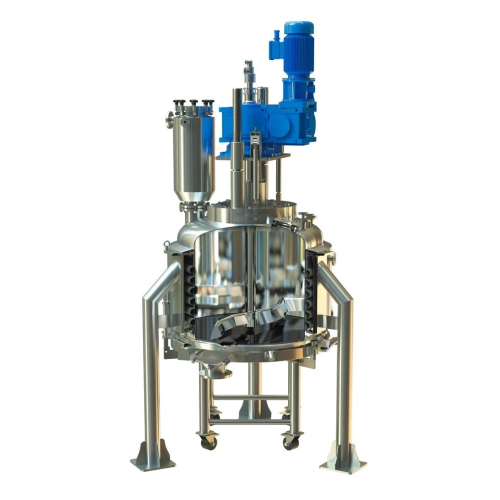
Nutsche filter dryer for pharmaceutical and chemical industries
Achieve precise filtration and efficient drying in one s...

Pilot Gmp spray dryer system for small-scale manufacturing
For precise control in spray drying, streamline your small-sc...
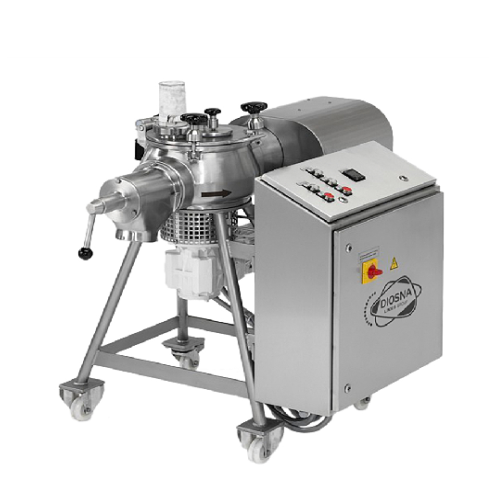
Versatile entry-level mixer granulator
Solve complex mixing and granulating challenges with this compact solution, offering...
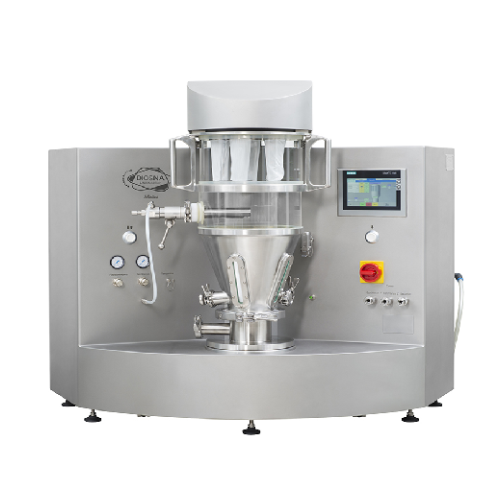
Laboratory coater and fluid bed processor
Optimize your research and development with a versatile benchtop unit that integ...
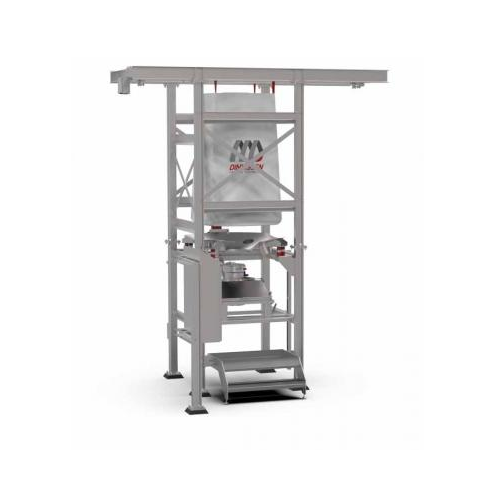
Modular big bag unloading station for various materials
For hassle-free handling of bulk materials, this modular solution...
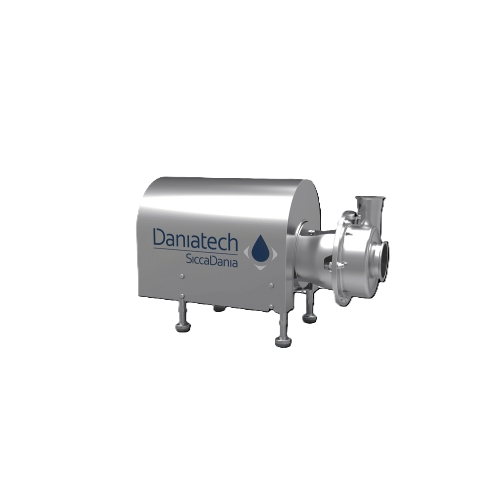
Inline high shear mixing unit for low to medium viscosity products
Achieve precise emulsification and size-reduction wi...
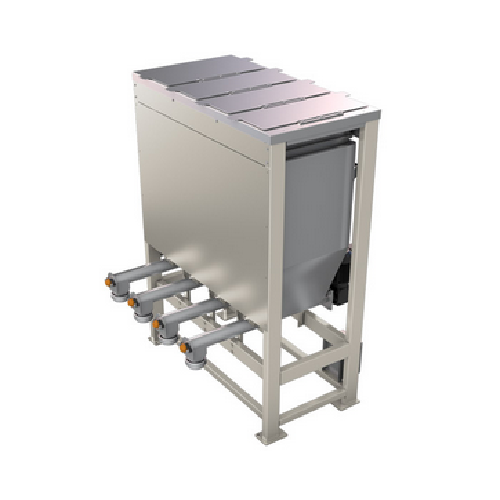
Loss-in-weight scale for micro ingredient batching
Enhance precision in your production line with advanced micro ingredie...

Laboratory twin screw extruder for small batch processing
Efficiently develop formulations and conduct precise research ...
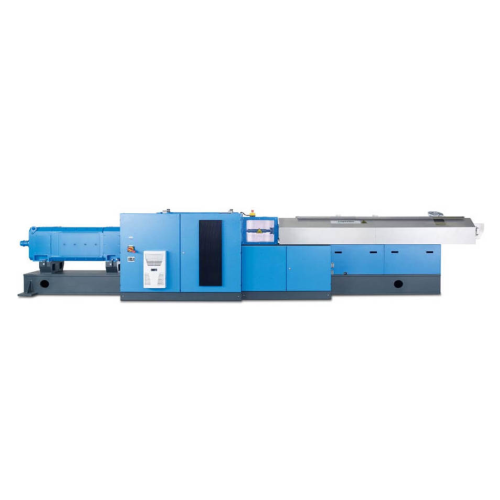
High throughput twin screw extruder for low bulk density products
When handling low bulk density materials, achieving m...
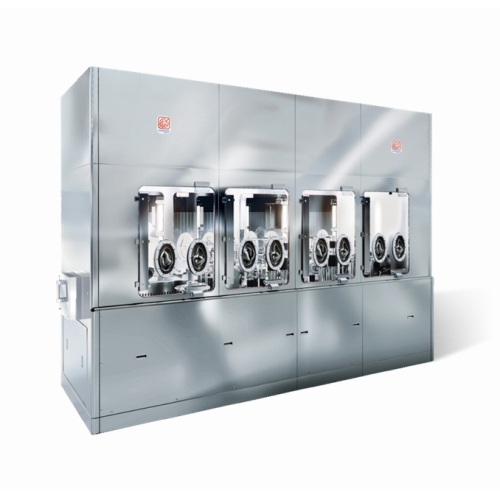
High quality sterile filling system
Experience unparalleled precision in aseptic filling with this advanced system, designe...
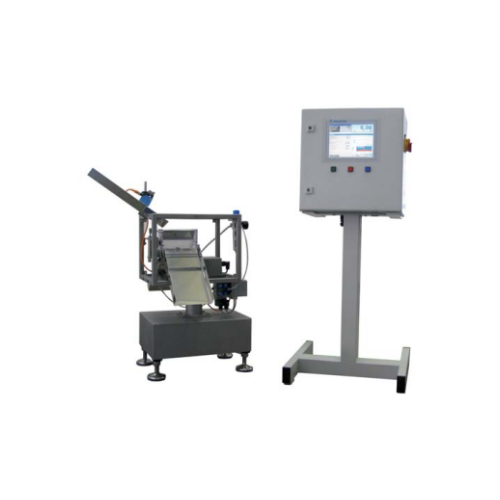
Static checkweigher for accurate measurement
For those needing unparalleled precision, this static checkweigher ensures ex...
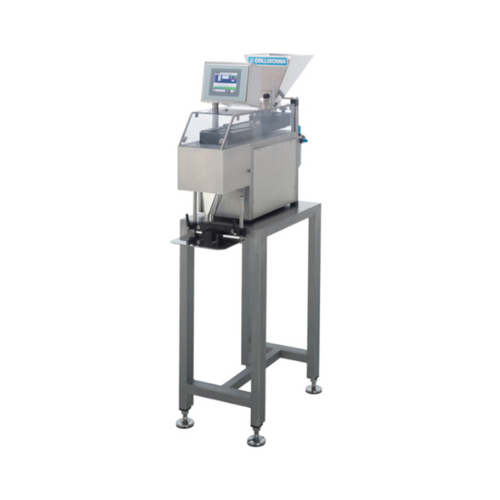
Counting system for tablets and capsules
Effortlessly count a variety of tablets, capsules, and dragées with precision, ens...
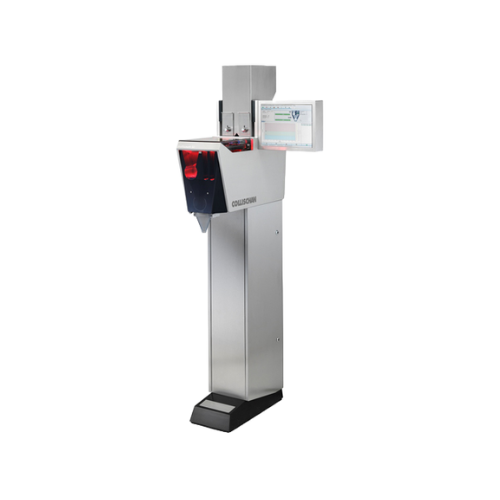
Tablet counting solution for pharmaceutical industry
Maximize dosing precision and reduce miscounts in high-speed pharmac...
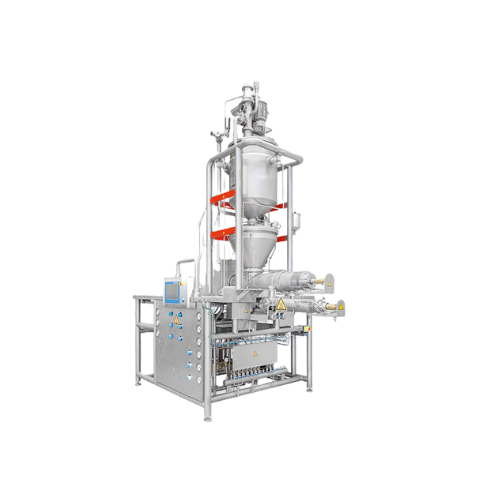
Hard candy production system
Enhance your candy production line with a comprehensive system that optimizes processes from co...
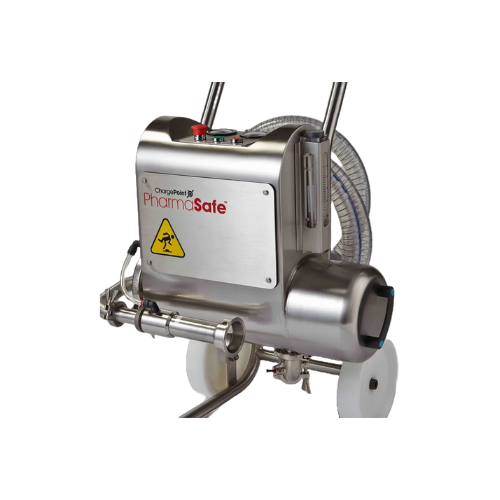
Dust particulate extraction system
Ensure safe containment and minimize airborne particulates in your production line with ...
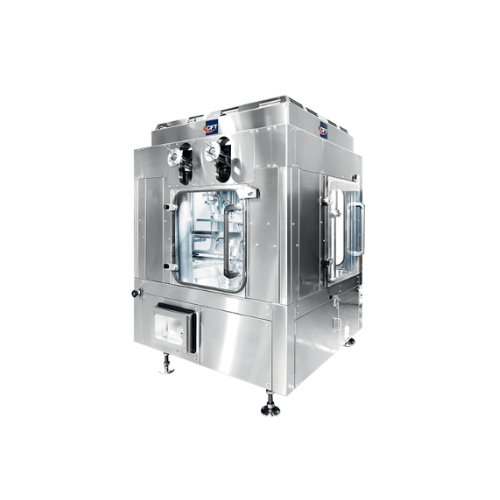
Industrial can seamers for food and beverage packaging
Streamline your canning process with precision seaming solutions d...
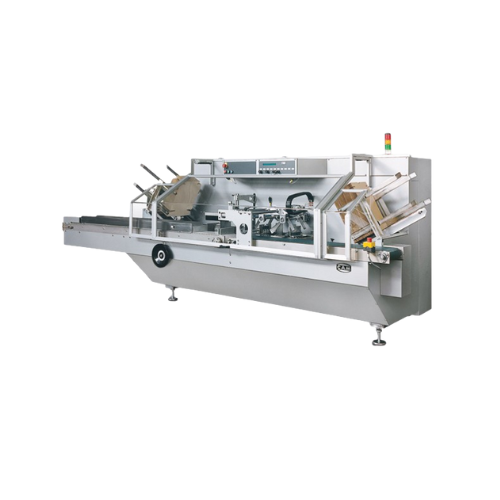
Tray and lid forming solution for food packaging
For manufacturers needing precision packaging, this machine seamlessly fo...
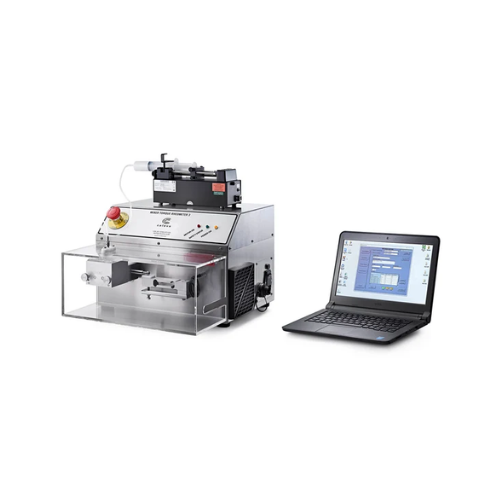
Analyze wet granulation properties for pharmaceutical formulation
Optimize your pharmaceutical and chemical formulation...
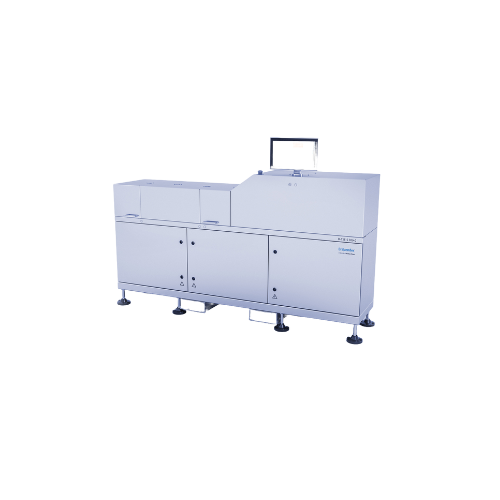
Lab- and pilot-scale twin screw extruders for small-scale production
Optimize extrusion techniques with lab and pilot-s...
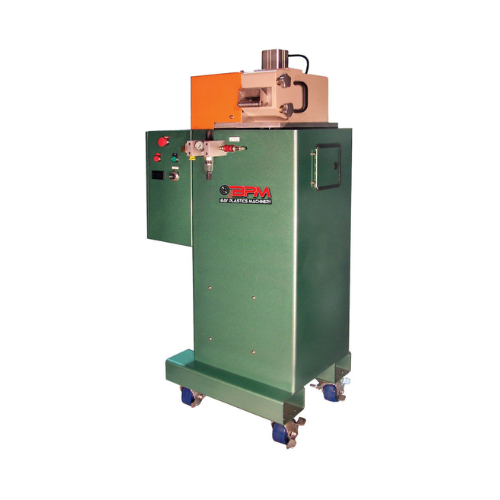
Strand pelletizer for small production lines
Achieve consistent and precise pellet sizes with our strand pelletizer, ideal...
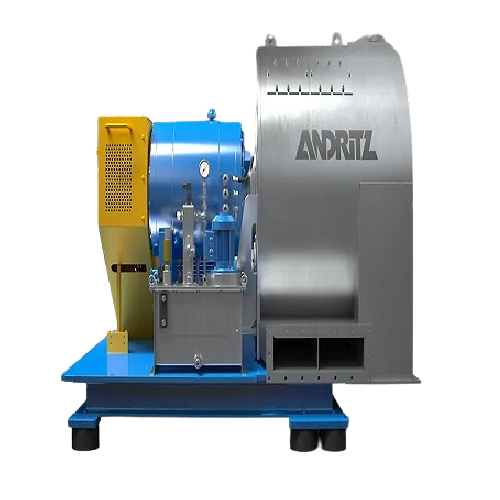
Screen scroll centrifuge for flexible dewatering
Ensure maximum uptime and consistent dewatering performance amidst variab...
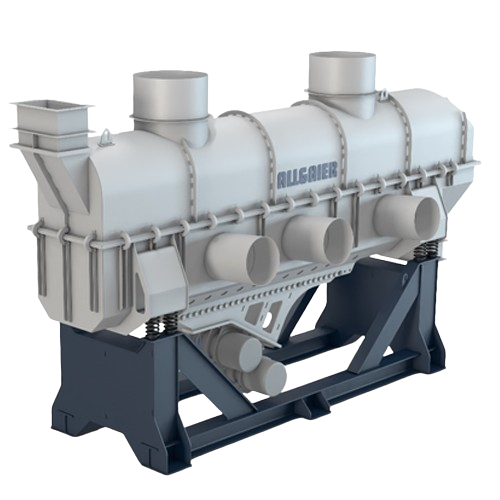
Fluidized bed dryer for industrial materials
Enhance product quality and energy efficiency with fluidized bed dryers, opti...
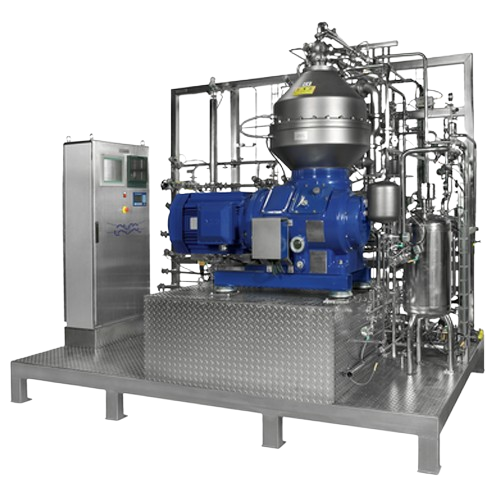
Biotech fermentation centrifuge for continuous solids discharge
Ensure high-density fermentation processes achieve optim...
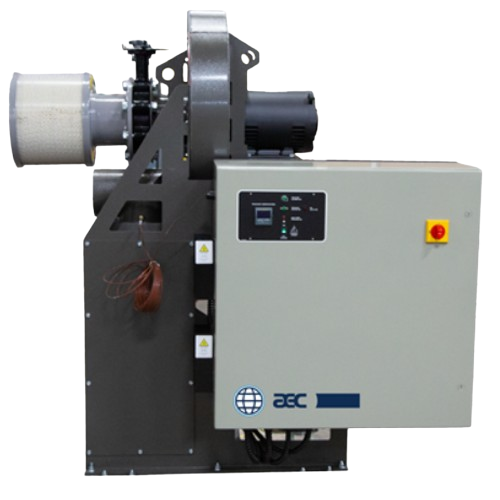
Hot air dryers for non-hygroscopic material
Ensure reliable material quality by effectively reducing moisture in non-hygro...
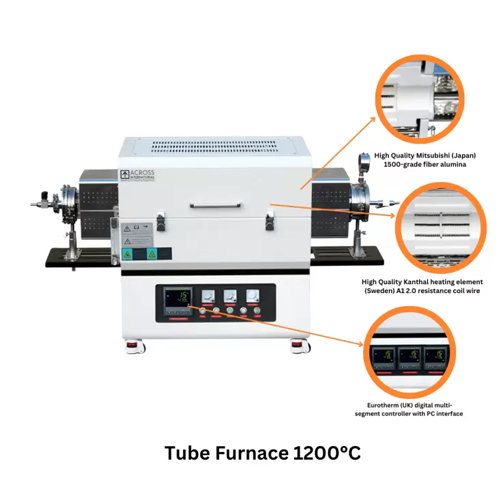
High-temperature top-open tube furnace for laboratory applications
Achieve precise thermal processing with this high-te...
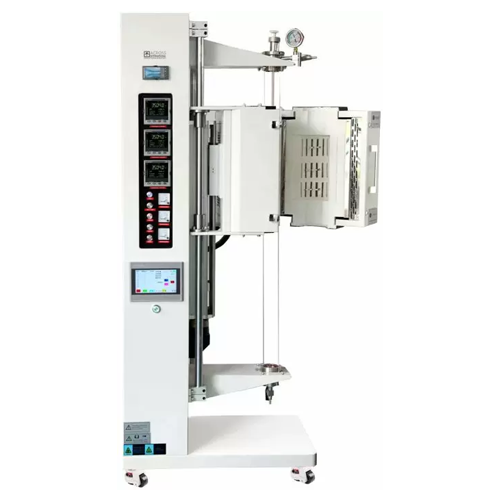
Bridgman crystal growth tube furnace
Achieve precise control over crystal growth processes with this advanced tube furnace,...
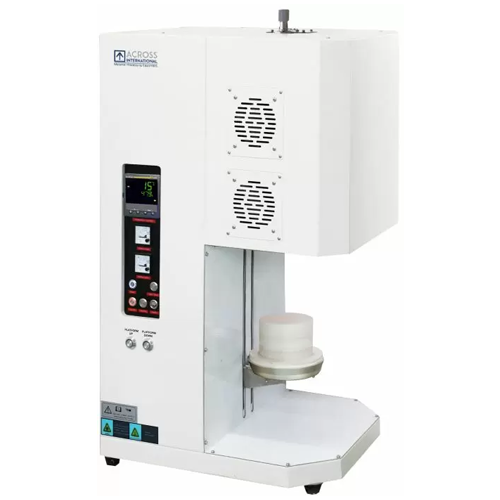
Table-top bottom loading furnace for high-temperature applications
For precise thermal processing and advanced experime...
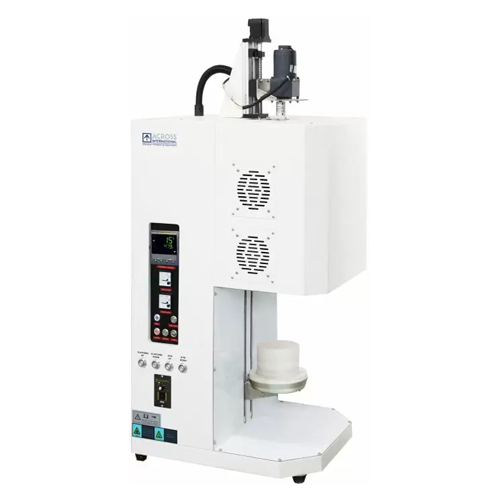
Table-top bottom loading furnace with stirring capability
Achieve precise thermal processing with controlled heating and...
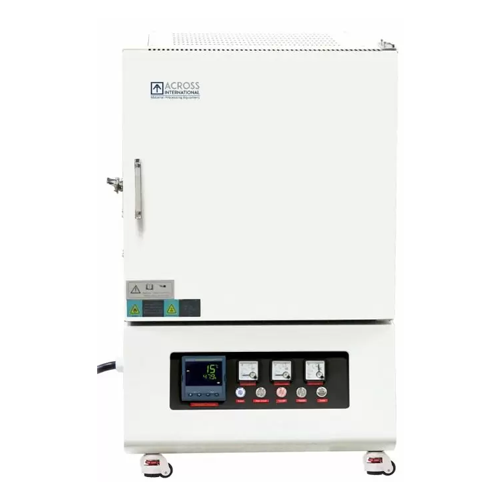
1200°c benchtop muffle furnace
Ensure precise thermal processing and testing with this high-capacity benchtop furnace, ideal...
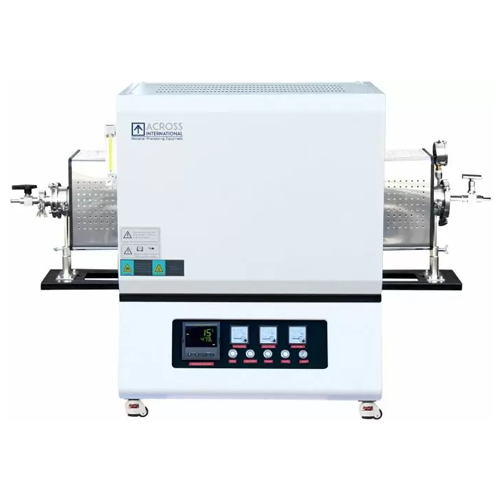
High-temperature tube furnace for laboratory applications
Achieve precise thermal treatment with this high-temperature t...
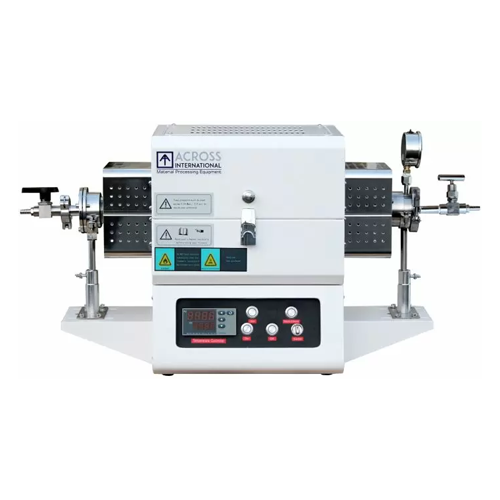
Controlled atmosphere top-open tube furnace
Achieve precise thermal processing and sintering with this versatile tube furn...
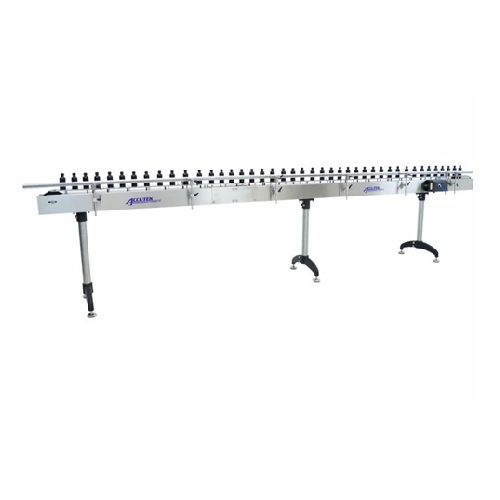
Customizable sanitary conveyor systems
Efficiently transport and handle diverse products with a sanitary conveyor system de...
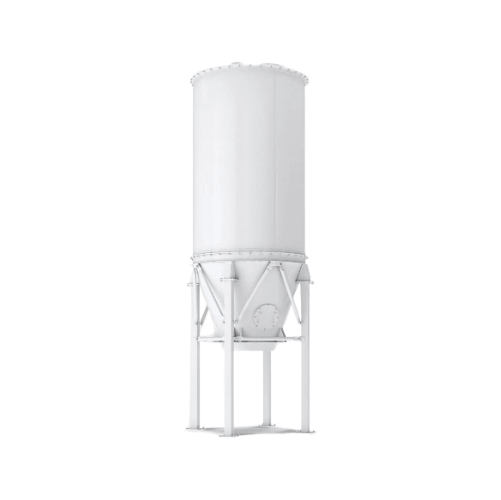
Storage silos for granular products
Enhance storage efficiency and flexibility with modular silos, ensuring precise monitor...
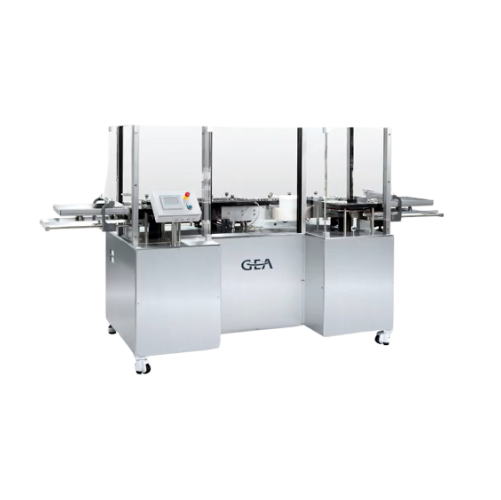
Automatic loading and unloading system for pharma freeze dryers
Enhance the efficiency and safety of your freeze-drying ...
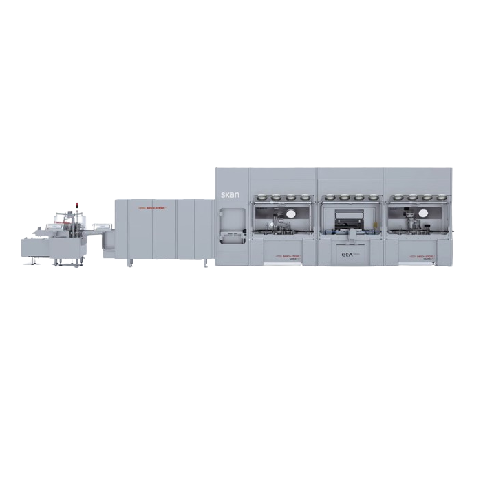
Freeze dryer for small-scale production
Optimize your production line with reliable lyophilization that ensures precise moi...
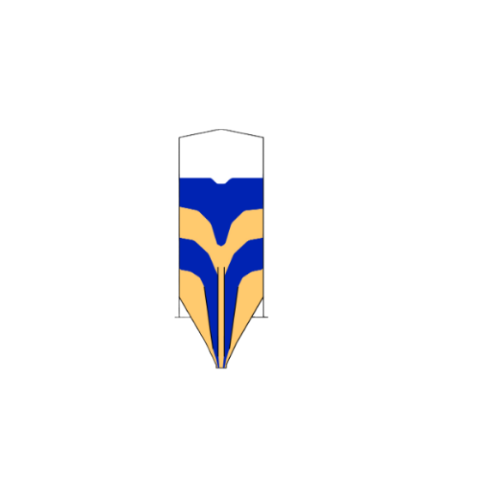
Blending silo for free-flowing and poorly flowing bulk materials
Achieve precise blending and mixing of diverse bulk mat...
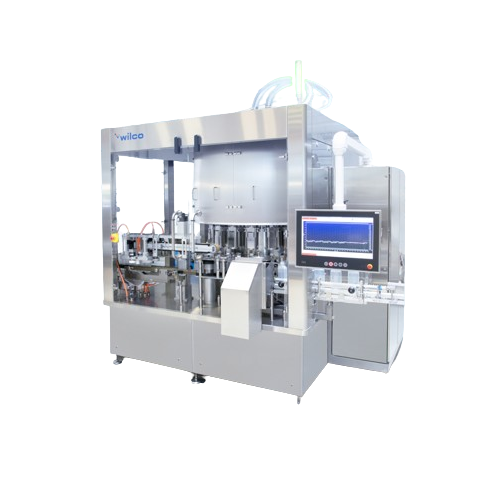
Automated Cci tester for pharmaceutical containers
Ensure the integrity of every pharmaceutical package swiftly with high...
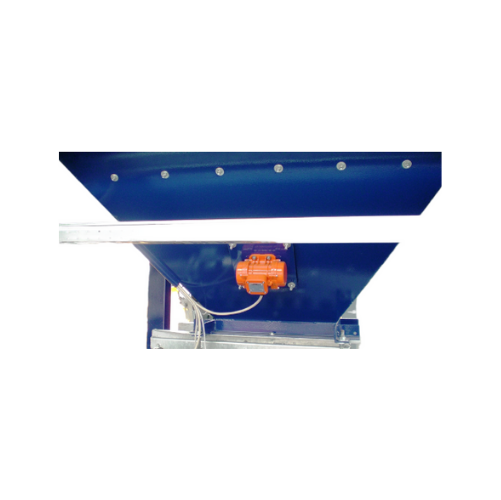
External electric motovibrators for bulk solids conveying
Enhance material flow efficiency and solve challenging dischar...

External electric motovibrators for hazardous materials
Ensure safety and efficiency in hazardous environments with relia...
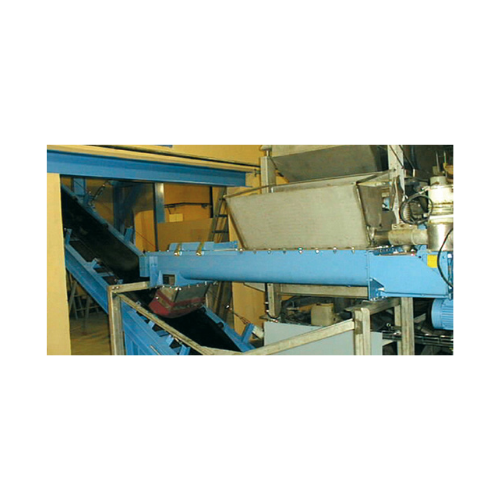
Continuous twin shaft paddle mixers for sludge conditioning
Optimize your sludge and waste treatment processes with a co...

Laboratory and pilot plant horizontal bead mill
Achieve precision milling with minimal product waste, ensuring consistent ...
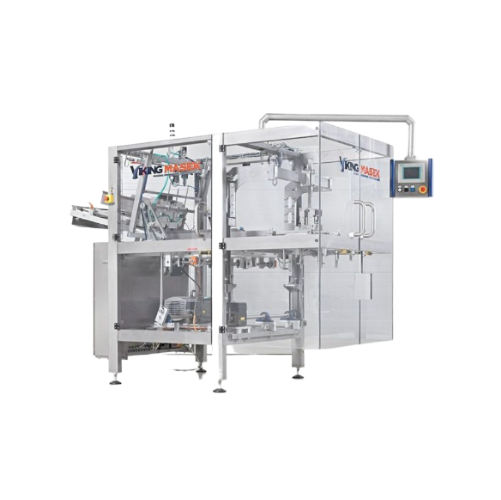
Top load cartoner for various carton shapes
Optimize your production line with a versatile cartoning solution, perfect for...
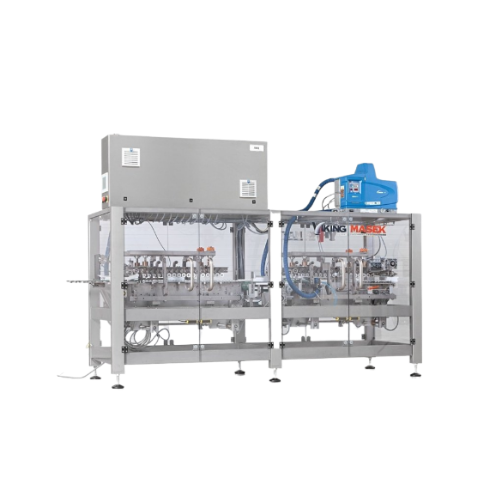
Topload cartoner for packaging cartons
Efficient flap closing for diverse carton sizes, ensuring gentle handling of sensiti...
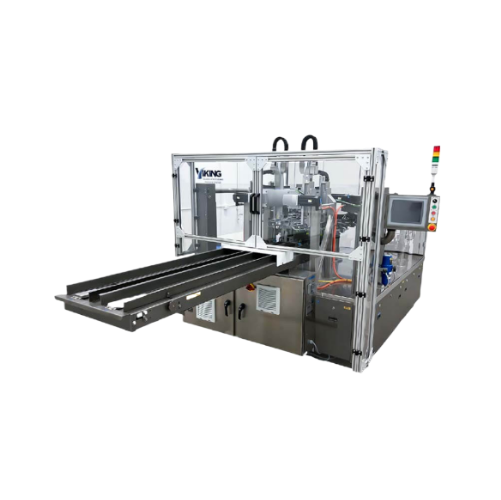
Rotary premade pouch filler and sealer
Maximize production efficiency by seamlessly filling and sealing diverse pouch sizes...
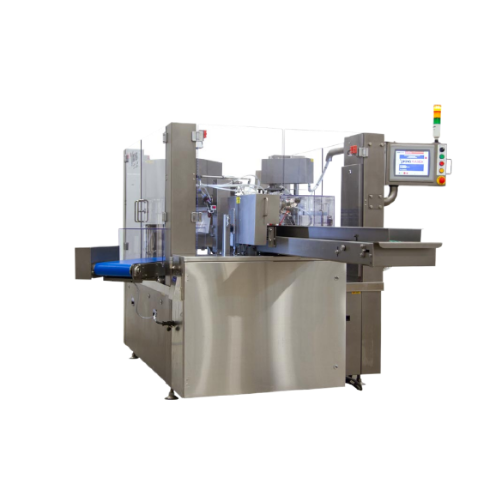
Premade pouch fill and seal solution
Effortlessly fill and seal various pouch sizes for streamlined packaging in diverse fo...
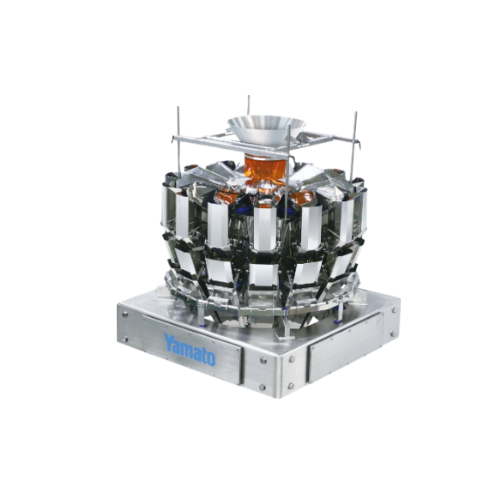
Industrial product fillers for precise packaging
Achieve consistent package weights and volumes with precision filling sol...
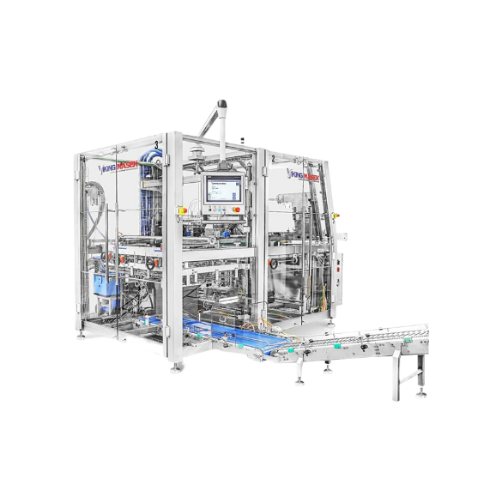
High-performance tray erector for packaging
Streamline your packaging process with a versatile tray erecting machine that ...
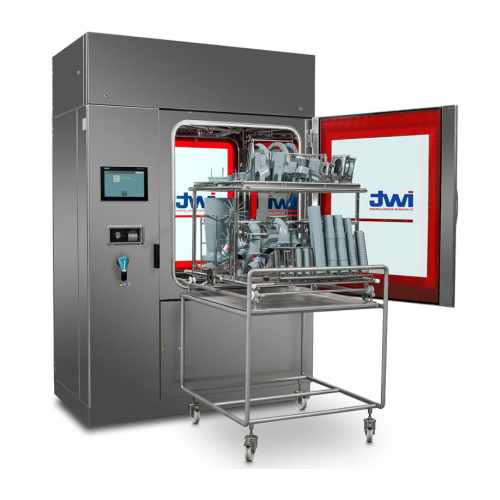
Gmp contact part washers for pharmaceutical industry
Ensure product integrity and hygiene with specialized washing system...
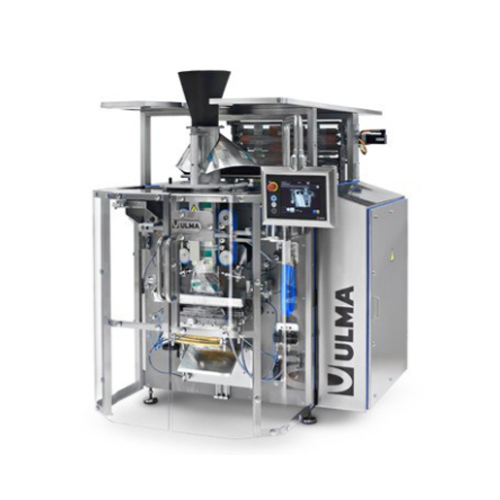
Vertical packaging system for medium-high speed applications
Optimize your packaging line with a system that delivers pr...
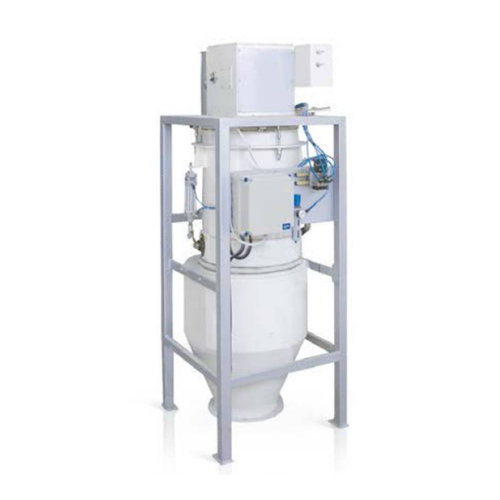
Industrial extraction scale for accurate material weighing
Ensure precise ingredient proportions in your milling operati...
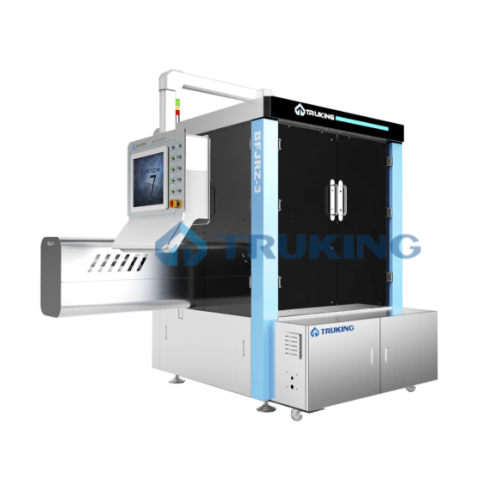
X-ray inspection for pharmaceutical vials
Ensure product purity by detecting contaminants in pharmaceutical vials with adv...
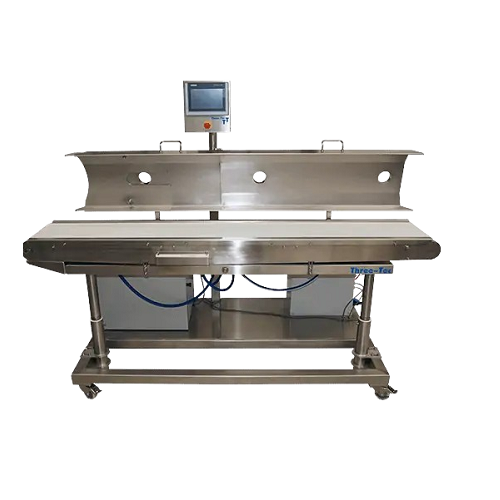
Cooling conveyor belt for extrudates and granules
Efficiently cool and convey extrudates and granules with precise temper...
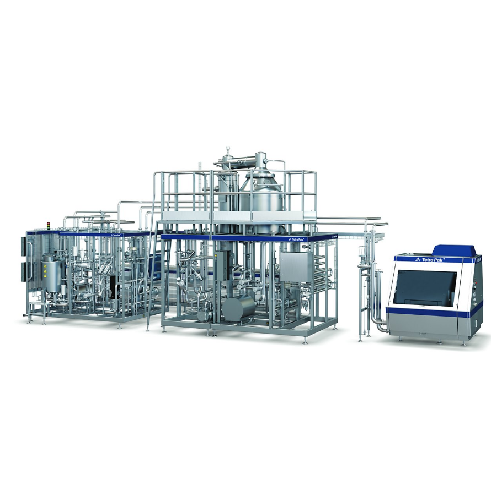
Direct Uht treatment for liquid foods
Optimize aseptic production with advanced UHT technology to preserve nutritional valu...
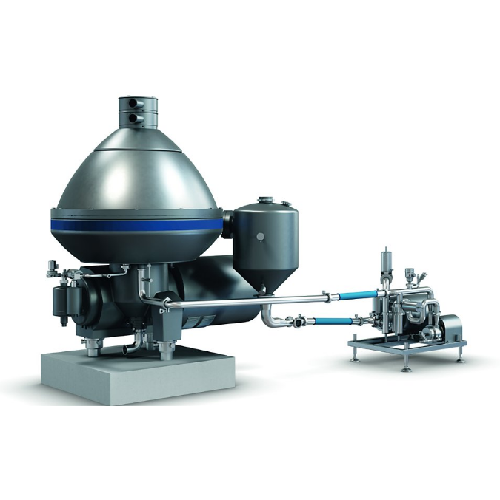
Efficient dairy product separator
Achieve precise fat separation and enhance product quality while reducing energy consumpt...

Automatic milk standardization unit
Achieve precise control over milk’s fat, protein, and solids content, reducing cr...
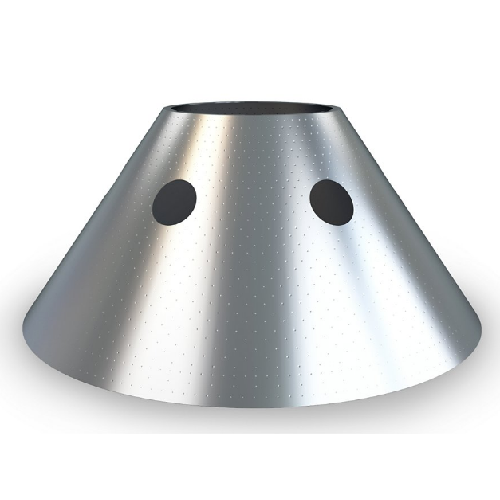
Polynode technology for enhanced dairy separation
Achieve higher separation efficiency and capacity with innovative disc ...
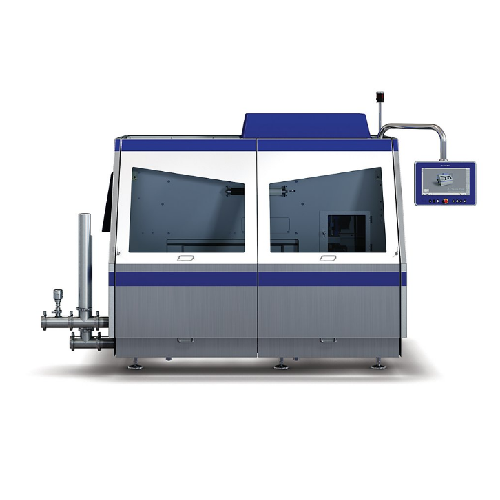
Homogenizer for high-capacity food processing
Achieve superior emulsification and suspension handling with this high-press...
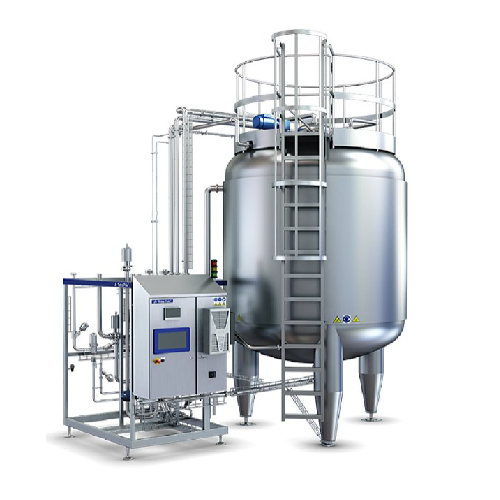
Aseptic tank with blending function for liquid food storage
Achieve seamless integration of aseptic buffering and in-lin...
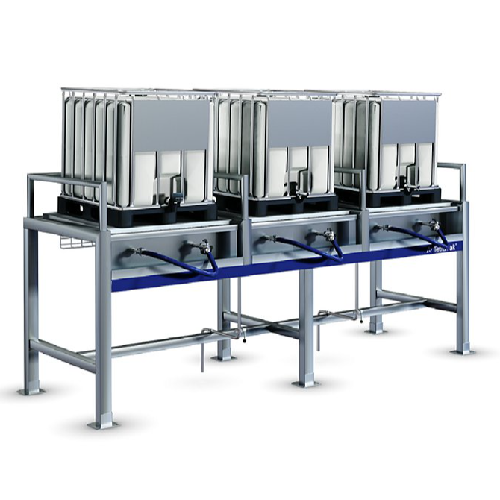
Ibc rack for storing and discharging intermediate bulk containers
Optimize liquid handling in your production line with...
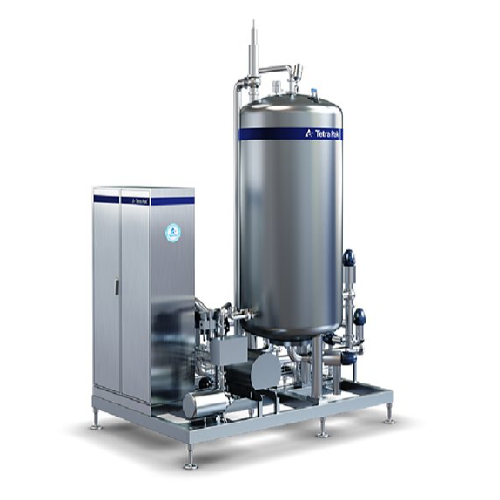
Continuous carbonator for beverage production
Optimize your beverage production with seamless continuous carbonation, ensu...
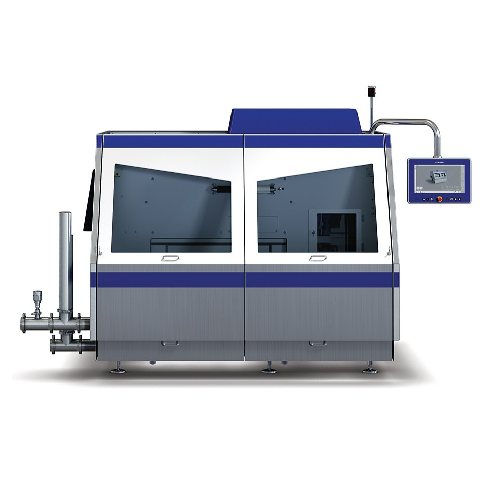
High-pressure homogenizer for dairy and beverage products
Achieve optimal product consistency and extend shelf life with...
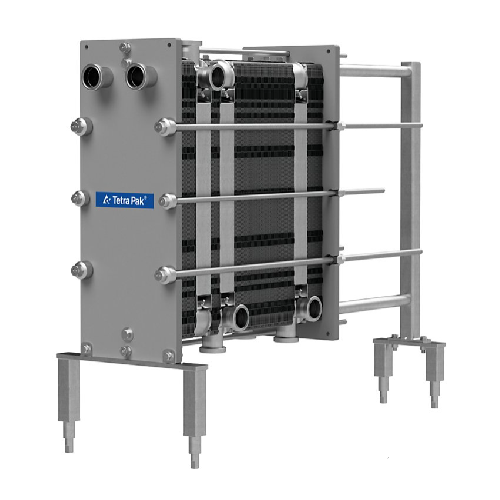
Industrial plate heat exchanger for food processing
Ensure consistent product quality with precise temperature control an...
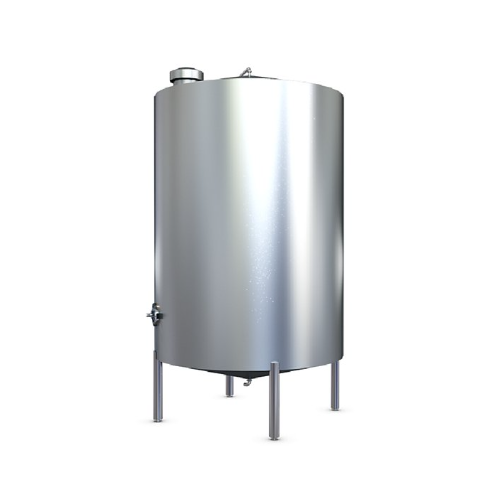
Storage tank for food liquid storage
Ensure seamless liquid product handling with precision-engineered storage tanks design...
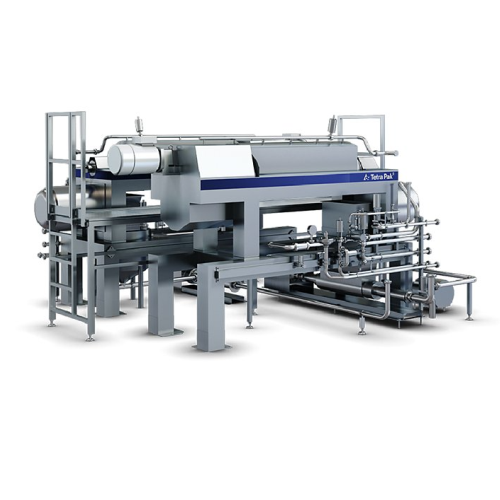
Plant-based beverage extraction system
Maximize yield and product quality in plant-based and dairy beverages with high-effi...
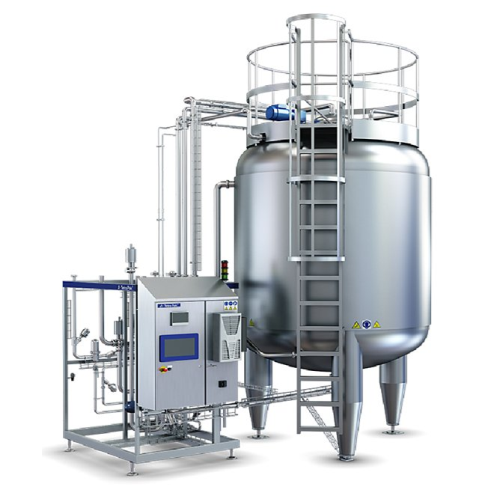
Aseptic tank for blending and buffering
Optimize your production line with a secure aseptic tank that ensures precise in-li...
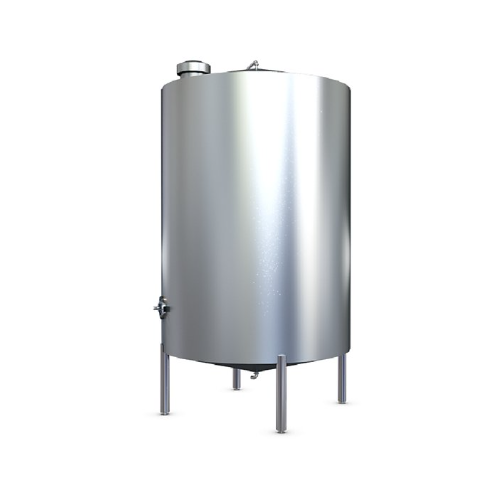
Liquid sugar storage tank
Ensure seamless liquid sugar management in your production line with advanced storage solutions de...
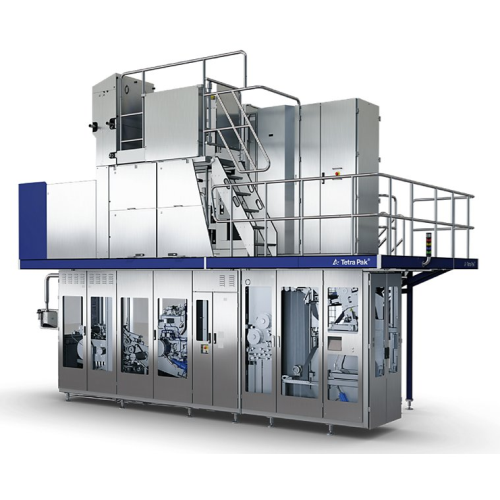
High-speed aseptic carton filling solution
Maximize production efficiency and meet growing demand with this high-output fi...
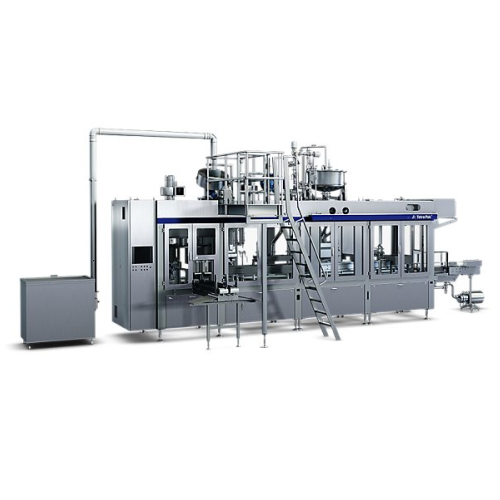
Filling system for gable top packages
Achieve precise, cost-effective filling with reduced energy consumption for chilled l...
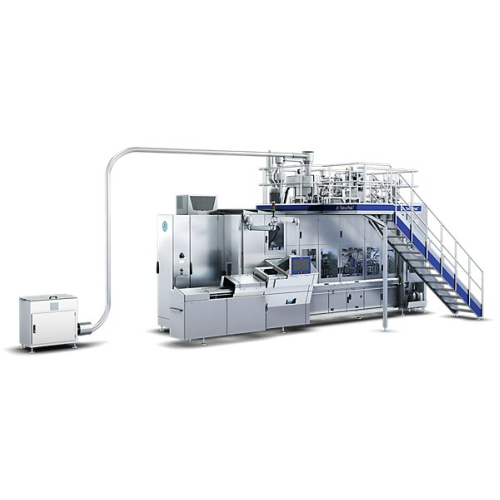
Filling machine for tetra rex® gable top cartons
Maximize efficiency and food safety in high-speed liquid filling with pre...
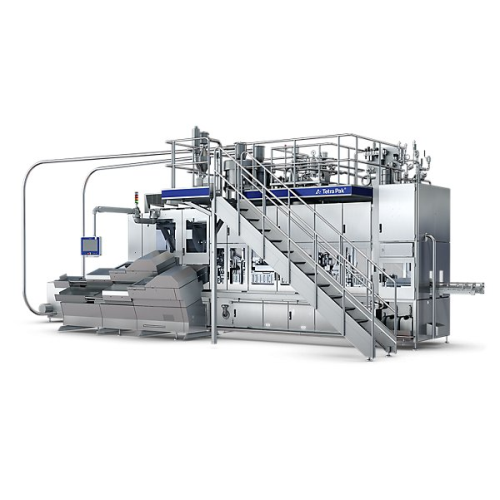
Filling system for gable top cartons chilled products
Achieve precise filling and reliable sealing for chilled beverages ...
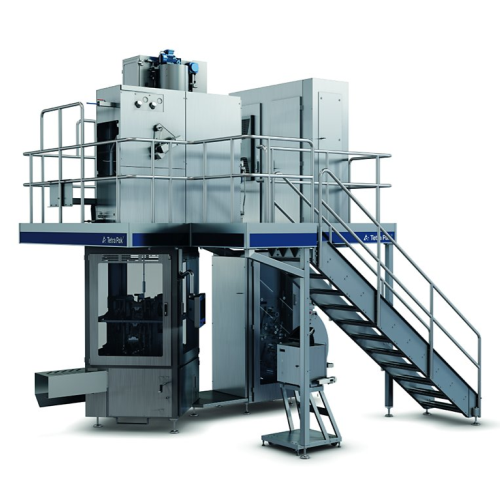
Aseptic filling solution for tetra classic packaging
Experience efficient aseptic packaging with high-speed operation, of...
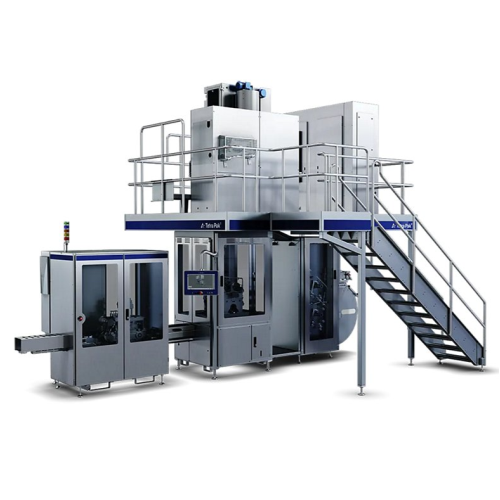
Filling system for tetra brik 100 slim packages
Optimize your chilled product packaging with a high-speed filling system d...
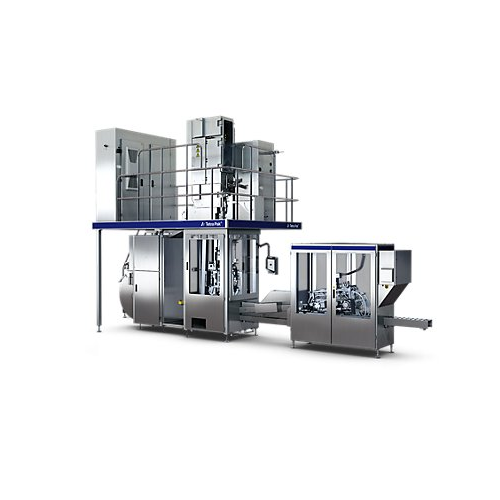
Filling system for tetra wedge aseptic packages
Optimize your production line with a reliable filling system designed to e...
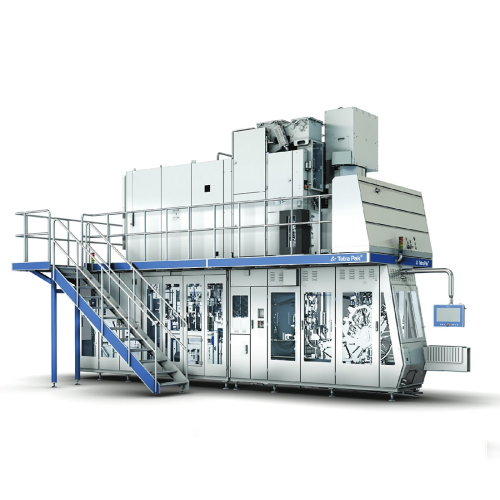
Versatile filling system for aseptic packaging
Achieve seamless integration in high-speed aseptic packaging with this flex...
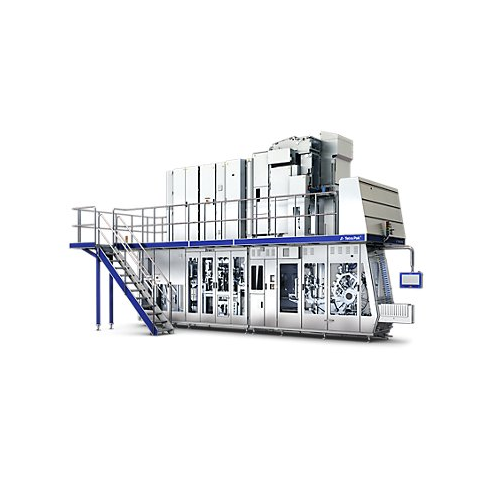
Filling solution for tetra brik® packages
Optimize your filling and packaging process with a system that seamlessly switch...
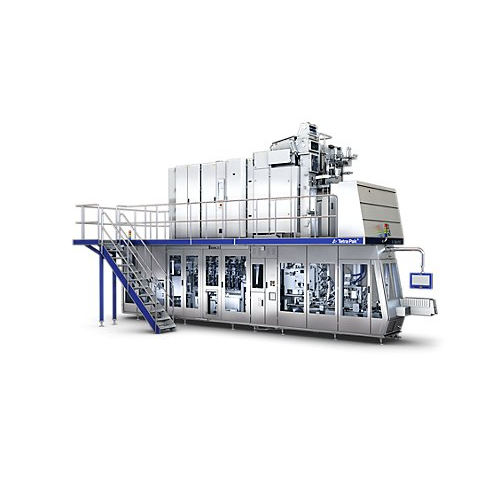
Aseptic filling solution for liquid food packaging
Optimize liquid food production with advanced aseptic filling, ensurin...
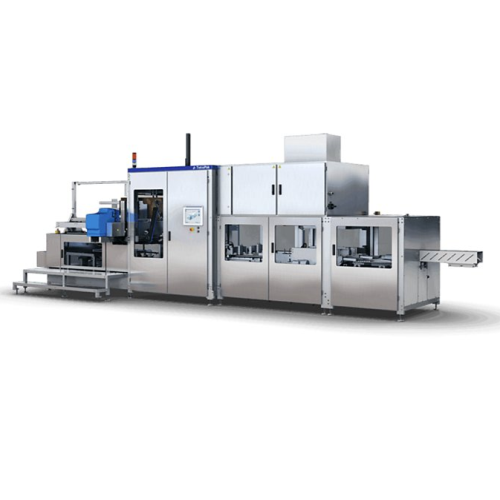
Cardboard packer for secondary packaging
Streamline your packaging process with a high-speed, automated cardboard packer th...
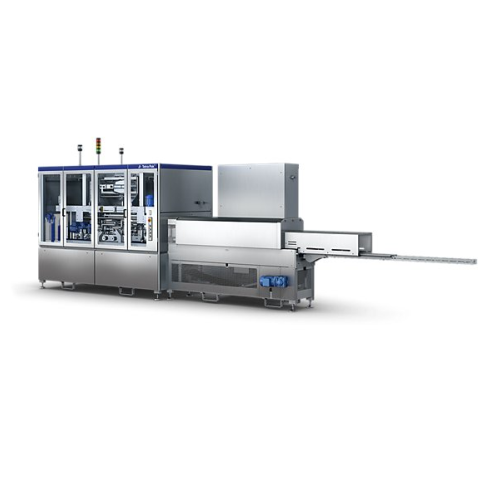
Shrink wrapping system for flex portion packages
Optimize your packaging line with a high-speed shrink wrapping system des...
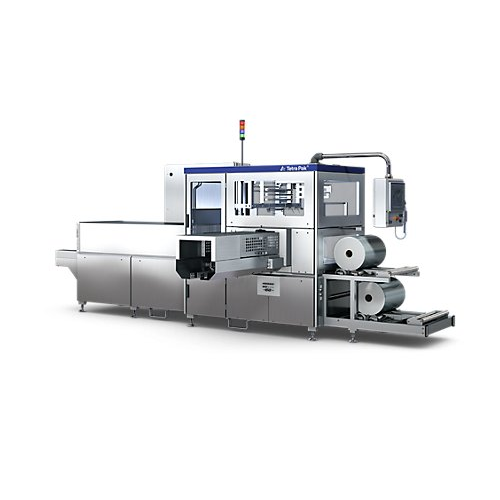
Industrial tray shrink wrapper
Optimize your packaging line with rapid, resource-efficient shrink wrapping, accommodating di...
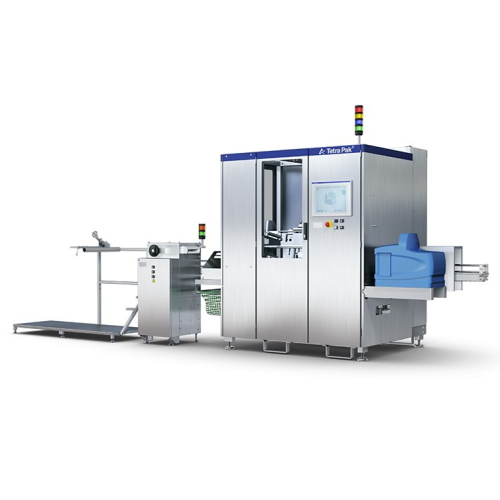
Straw applicator for tetra pak cartons
Ensure precise straw attachment and minimize production interruptions with a high-sp...
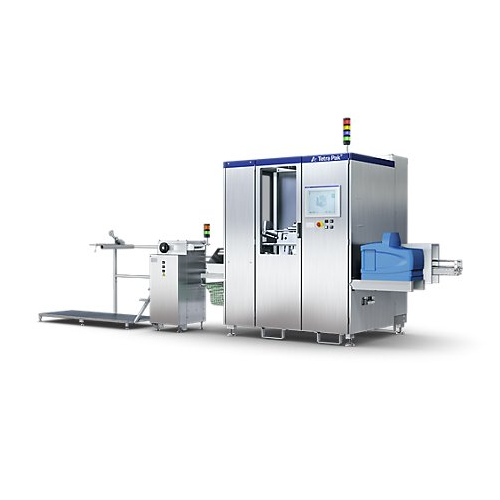
Straw applicator for tetra pak packages
Enhance your packaging efficiency with a high-speed solution that seamlessly attach...
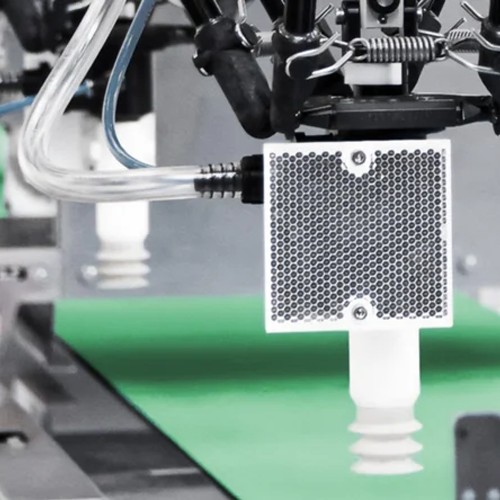
Robotic pick and place platform for food packaging
Enhance your packaging efficiency and product quality with a scalable ...
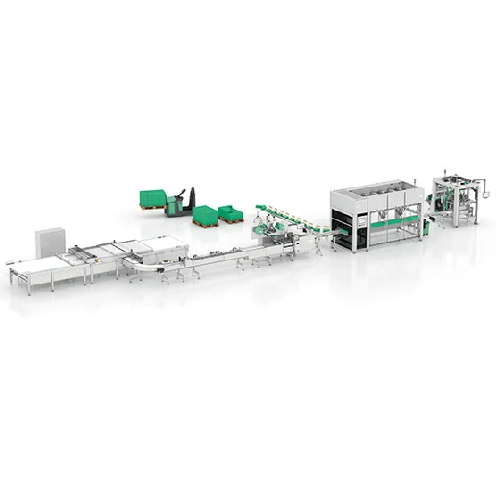
Automated visual inspection for pharmaceutical products
Ensure the integrity and safety of your parenteral products with ...
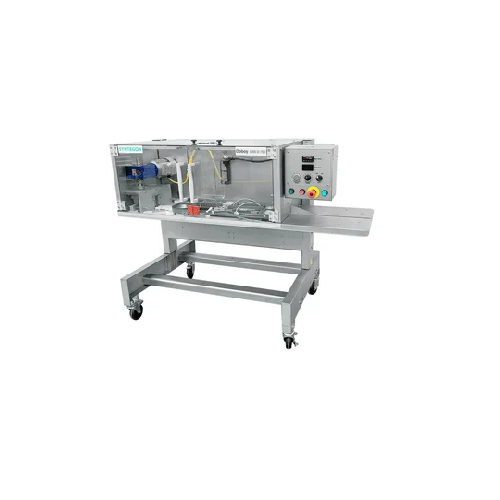
Industrial bag sealing solution for medical and food applications
Enhance your packaging line with reliable and versati...
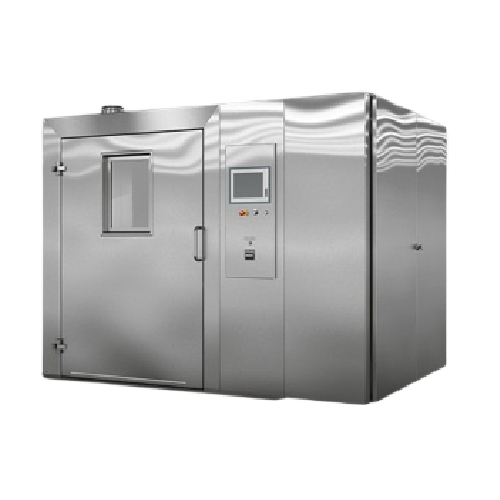
Pharmaceutical grade washer for large components
Ensure compliance and maximize productivity with a high-performance solut...
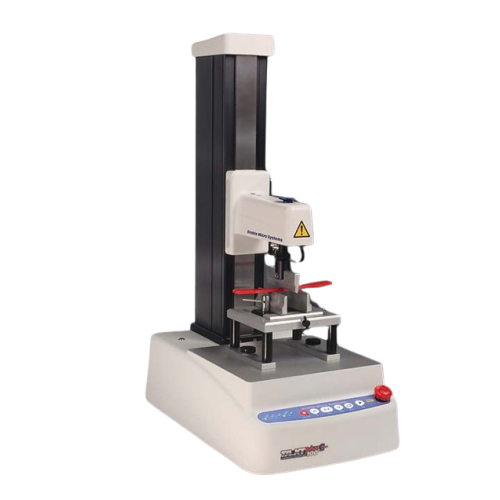
High-force texture analyser for precise measurement
Achieve unparalleled precision in texture analysis for high-force app...
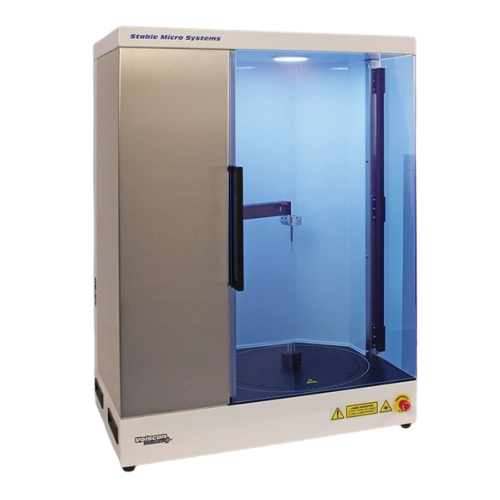
Laser-based volume measurement for bakery and solid products
For precision in product quality control, this laser-based ...
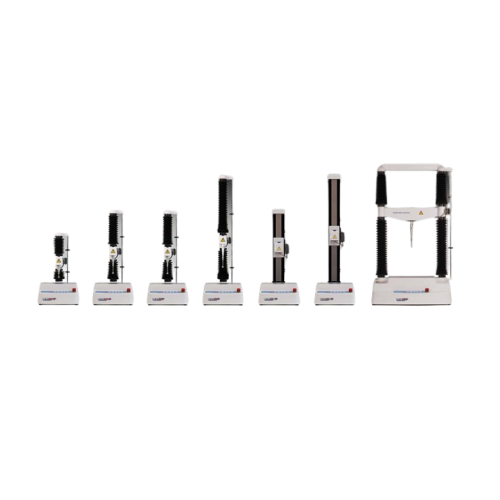
Portable texture analysis for low force applications
Easily perform precision texture measurements on low-force applicati...
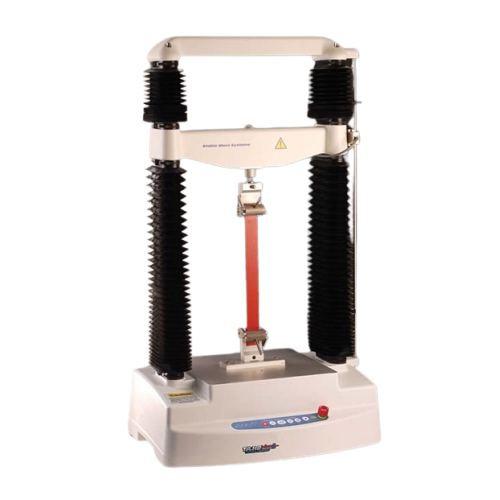
Texture analyzer for high force applications
Achieve precise texture measurement across a vast array of products with a so...
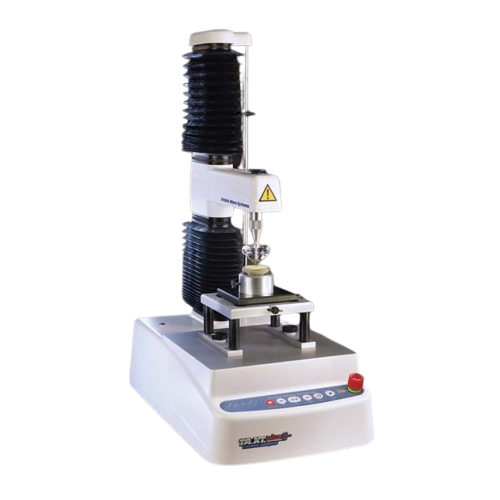
Texture analyser for food and cosmetics testing
Ensuring consistent product quality across diverse food and cosmetic appli...
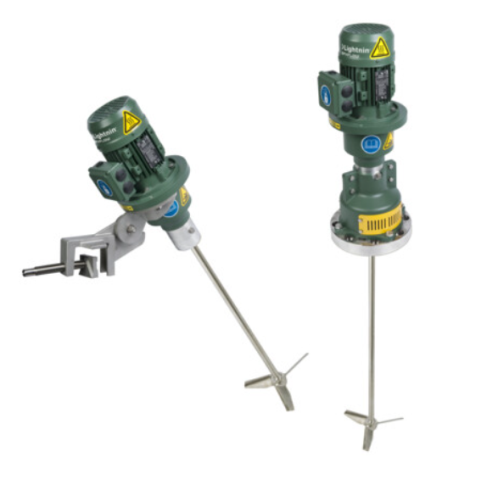
Portable and fixed mount mixing system
Optimize your mixing operations with a versatile system that adapts seamlessly betwe...
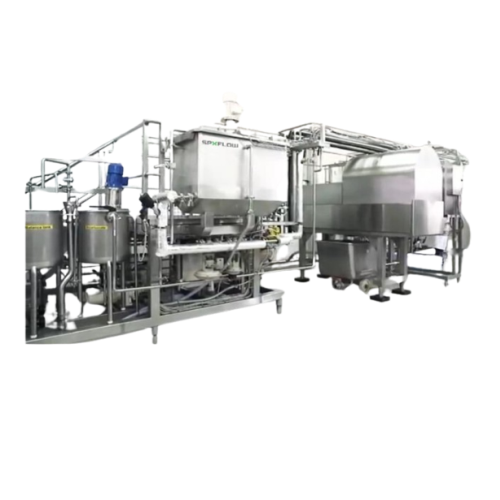
Soymilk processing plant
Enhance your plant-based production with our tailored soymilk processing plants, designed to efficie...
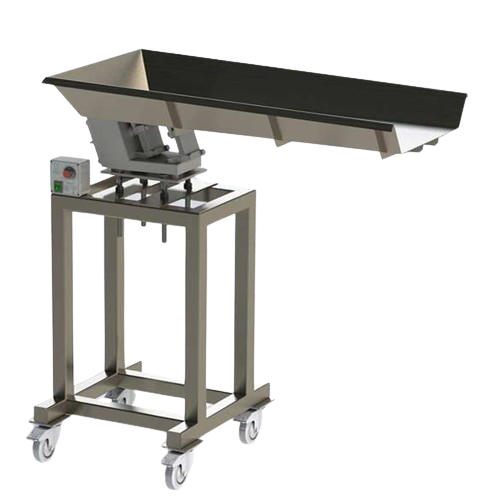
Electrostatic drum flavoring system for food processing
Enhance your snack production efficiency with a system designed t...
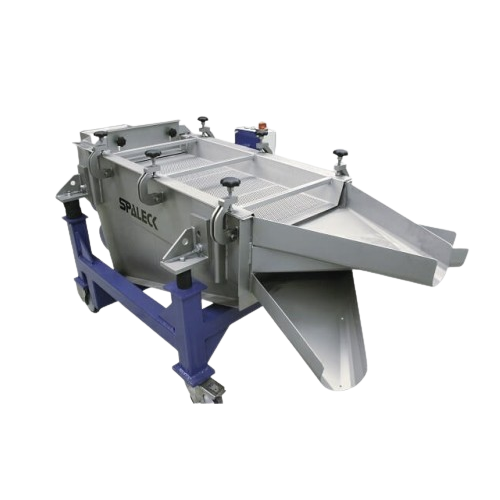
Granulate screening technology for precise particle size separation
Achieve exceptional sorting precision and maintain ...
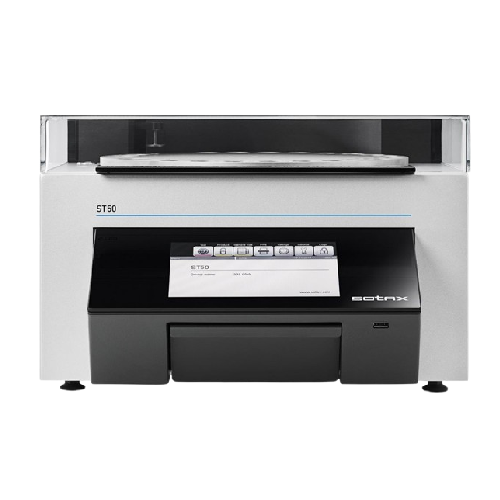
Semi-automatic tablet hardness tester
Optimize your tablet production with precise and reliable testing of hardness, dimens...
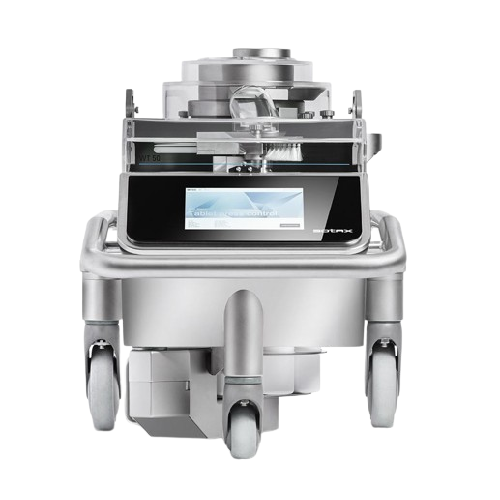
Automated weighing system for tablets
Ensure precision in pharmaceutical manufacturing by seamlessly integrating advanced w...
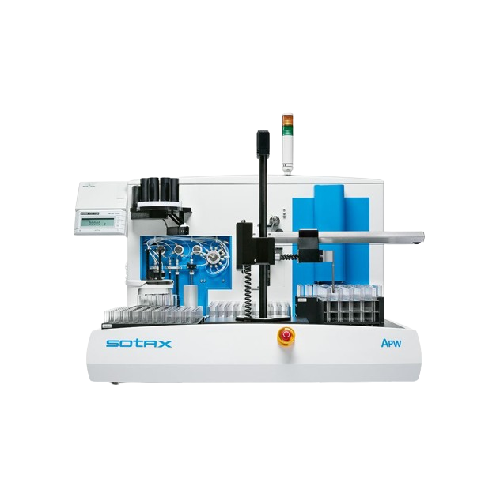
Automated sample preparation workstation for lab efficiency
Streamline laboratory operations by automating sample prepar...
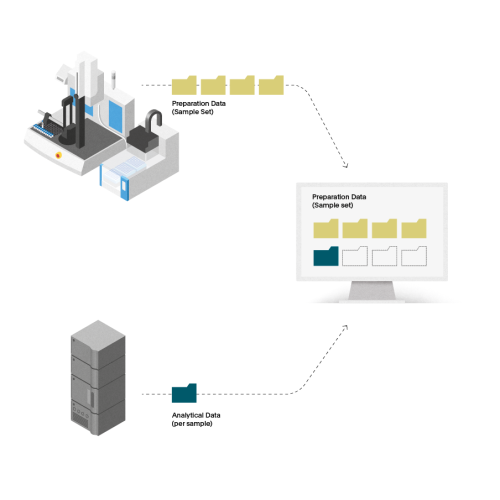
Automated sample preparation software for pharmaceutical testing
Streamline your laboratory’s sample preparation w...
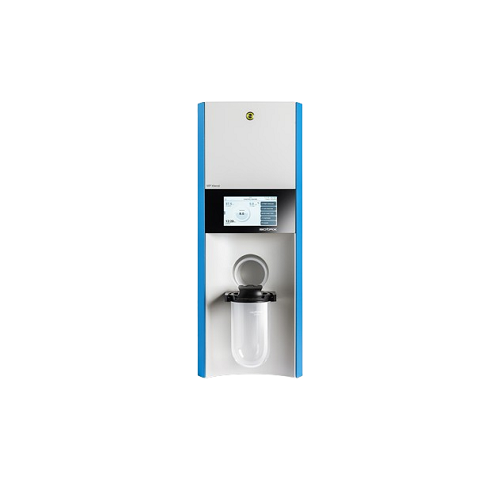
Dissolution medium preparation system
Streamline your laboratory workflows with a system that prepares and manages dissolut...
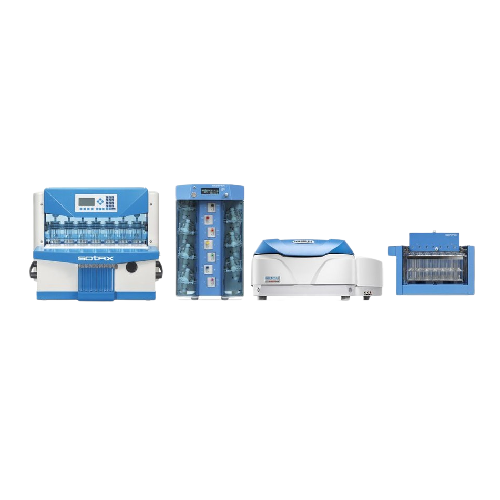
Automated flow-through cell dissolution testing system
Enhance precision in dissolution testing with real-time UV-Vis ana...
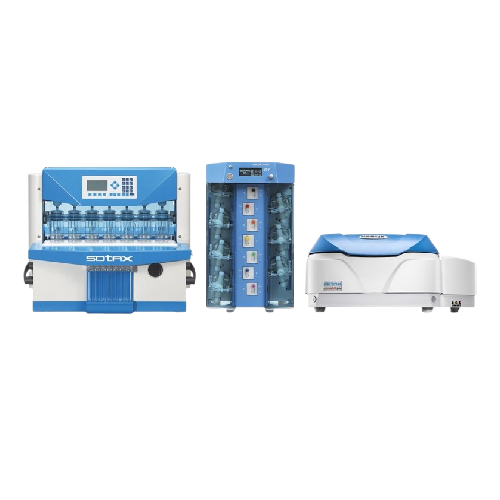
Flow-through cell dissolution testing with Uv analysis
Effortlessly monitor real-time dissolution with flow-through cell ...

Manual tablet disintegration tester
Ensure precise and reliable disintegration testing of pharmaceutical tablets, capsules,...
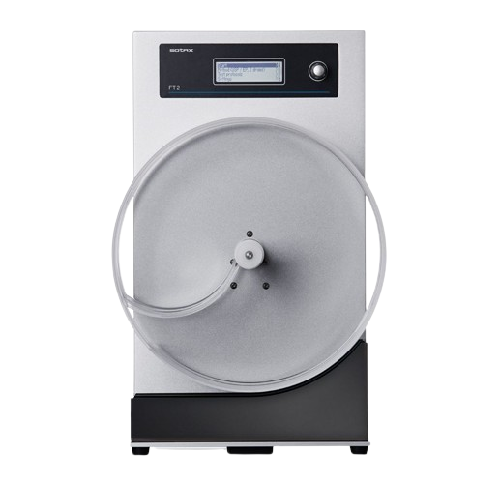
Tablet friability tester
Ensure your tablets meet rigorous quality standards by accurately measuring friability and abrasion,...
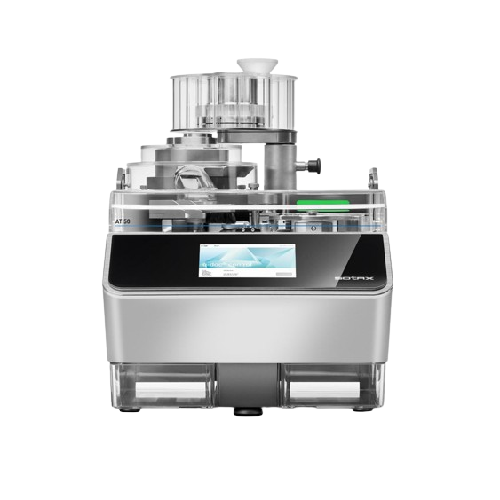
Multi-parameter tablet hardness tester for laboratories
Optimize your tablet production line with a versatile tester that...
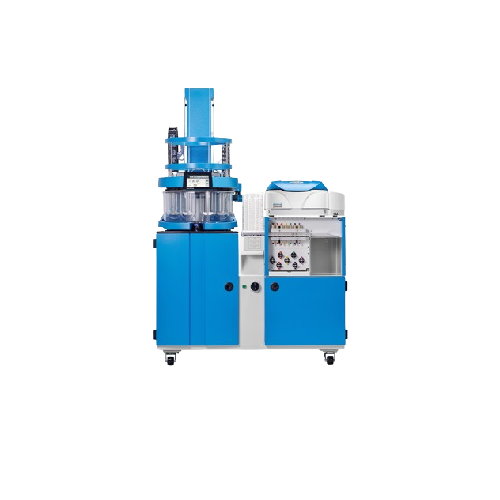
Advanced dissolution tester for pharmaceutical laboratories
Achieve consistent and reproducible dissolution results with...
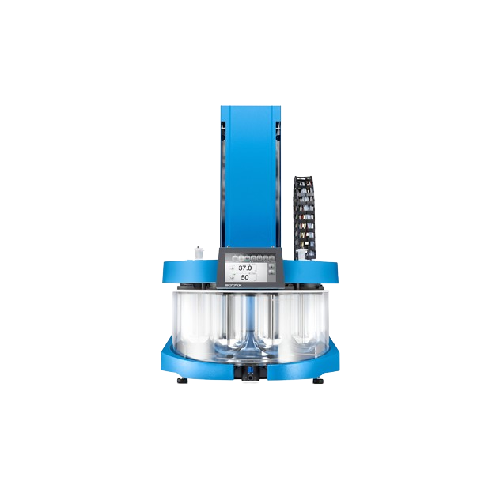
Manual dissolution tester for pharmaceutical applications
Achieve precise and repeatable sampling in pharmaceutical test...
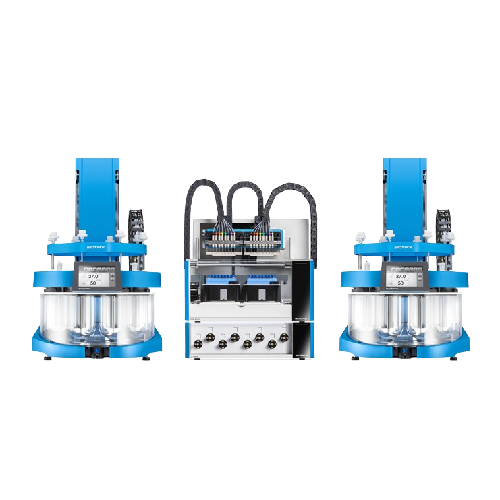
Automated dissolution sample collection system
Double your testing efficiency with parallel dissolution sampling, ensuring...

Automated dissolution testing with direct Hplc injection
Streamline your lab operations with precise and efficient direct...
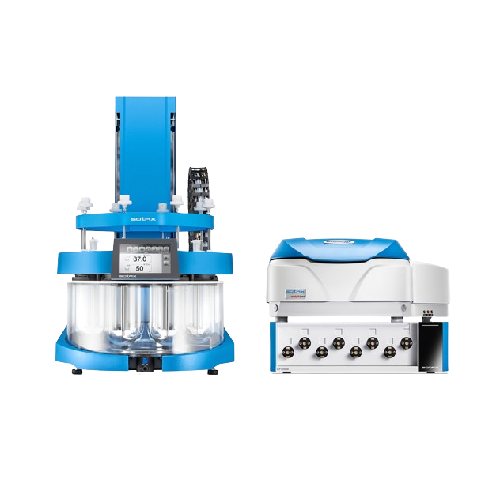
Integrated Uv-vis spectrophotometer for dissolution testing
Streamline your dissolution testing with real-time UV-Vis an...
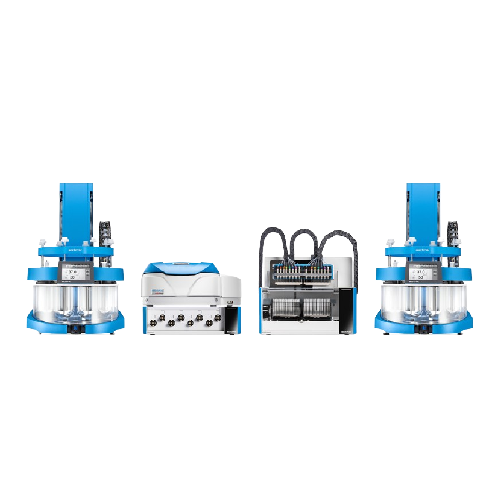
Automated dissolution testing system for 16 vessels
Maximize your laboratory throughput by conducting parallel dissolutio...

Dissolution testing software for automated analysis
Streamline your laboratory testing with seamless data capture and in-...
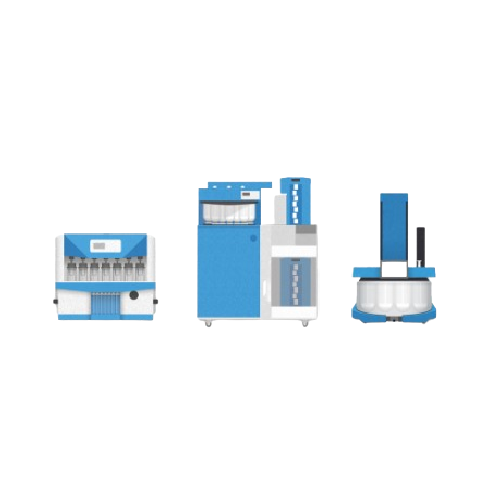
Dissolution testing software for pharmaceutical industry
Optimize dissolution testing with advanced software that manages...

Automated sample preparation software
Enhance your laboratory’s efficiency with a software solution that automates sa...
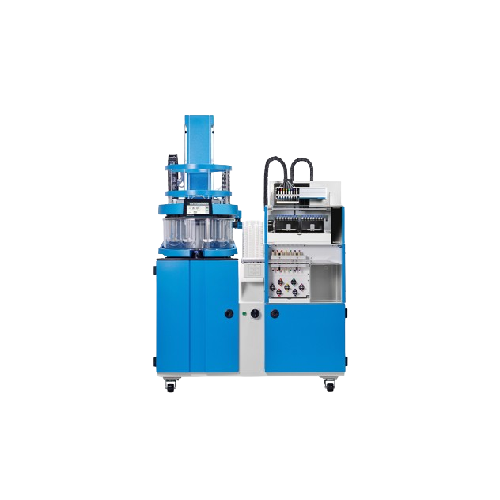
Self-cleaning dissolution tester for automated series testing
Achieve unparalleled precision in dissolution testing with...
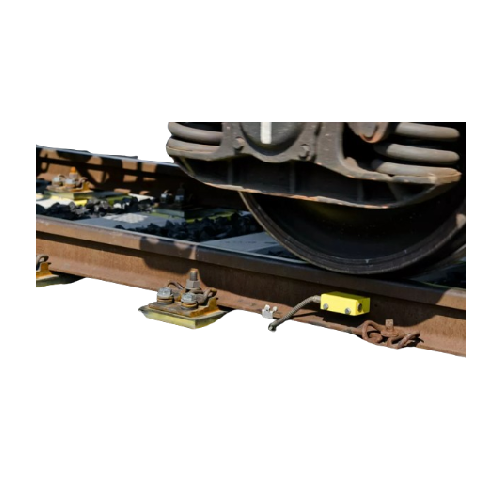
Dynamic weighing for solids and liquids
Ensure precision in rail transport with innovative dynamic scales that provide lega...
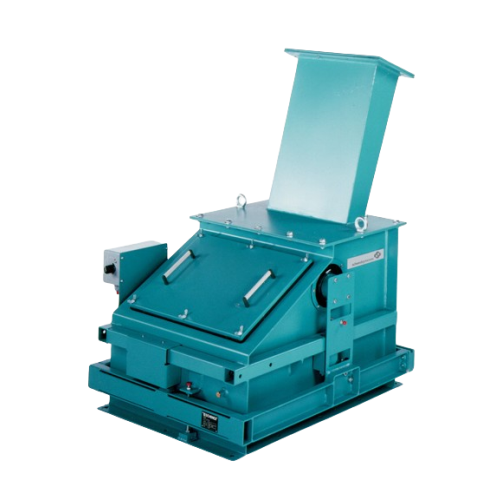
Solids flow meter for bulk solid streams
Ensure precise bulk material measurement with a system designed for accuracy and r...
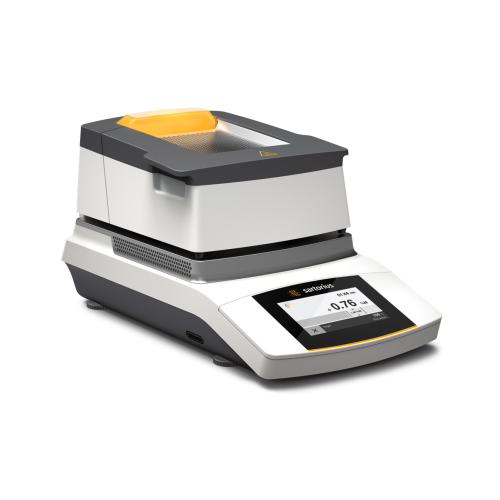
Basic moisture analyzer for laboratory weighing
Optimize moisture analysis tasks with precision and efficiency. Designed f...
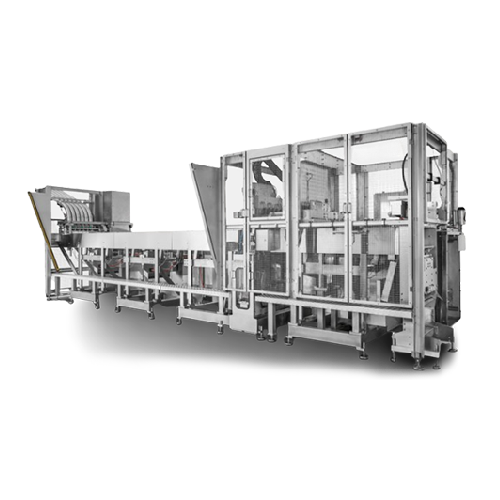
Filling system for solids, pastes, and liquids
Eliminate contamination risks while achieving high-speed, precise filling o...
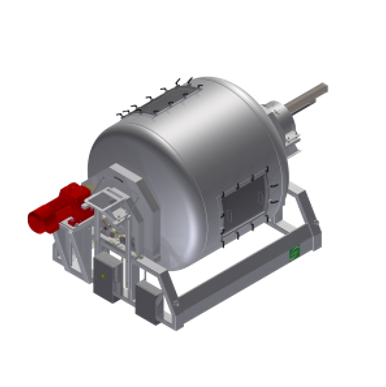
Gentle mixer for tea blending
The blending process is critical to the flavor quality of tea. But the physical impact of the ...
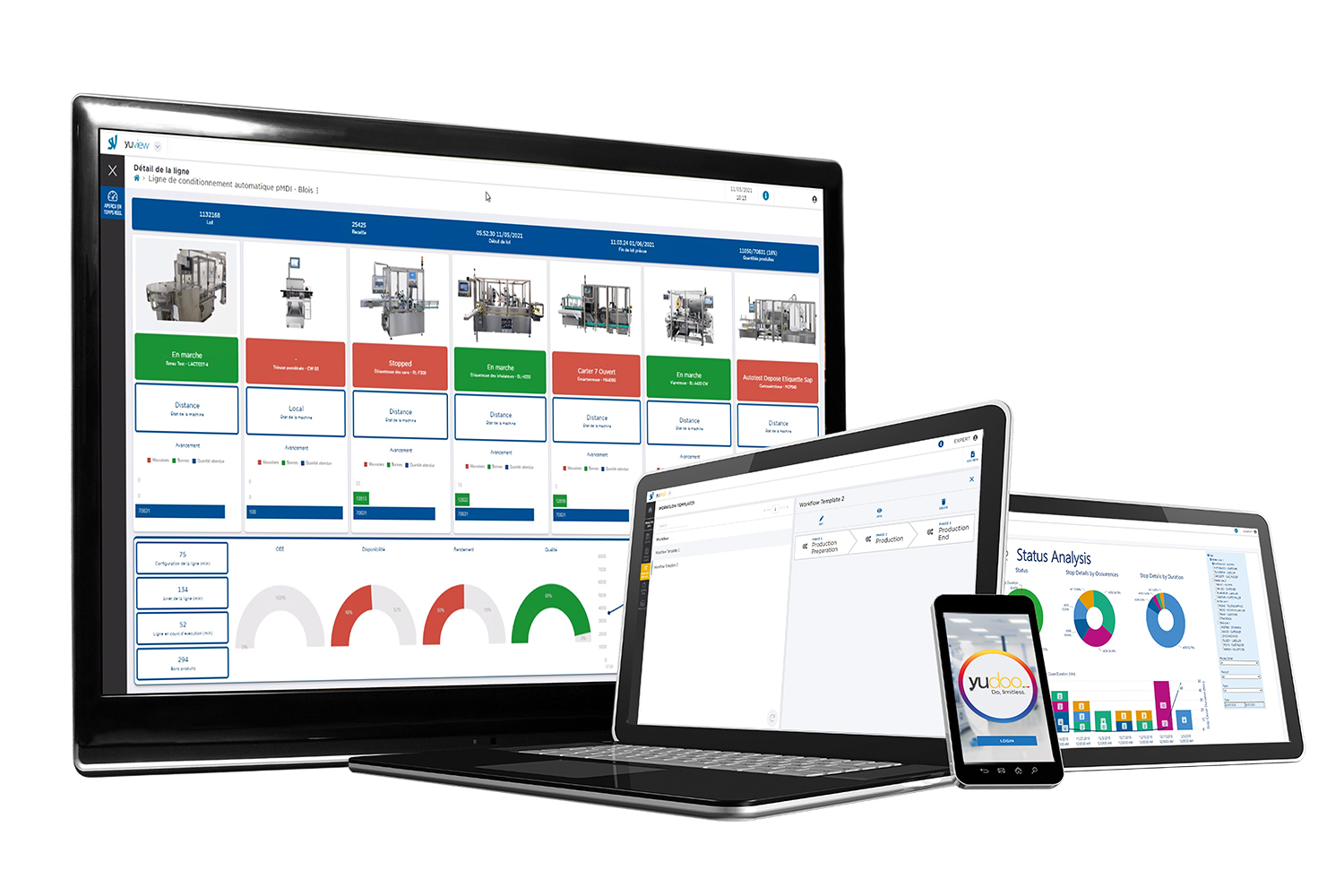
Pharmaceutical data management software
A typical pharmaceutical production handles numerous work flow activities like mana...
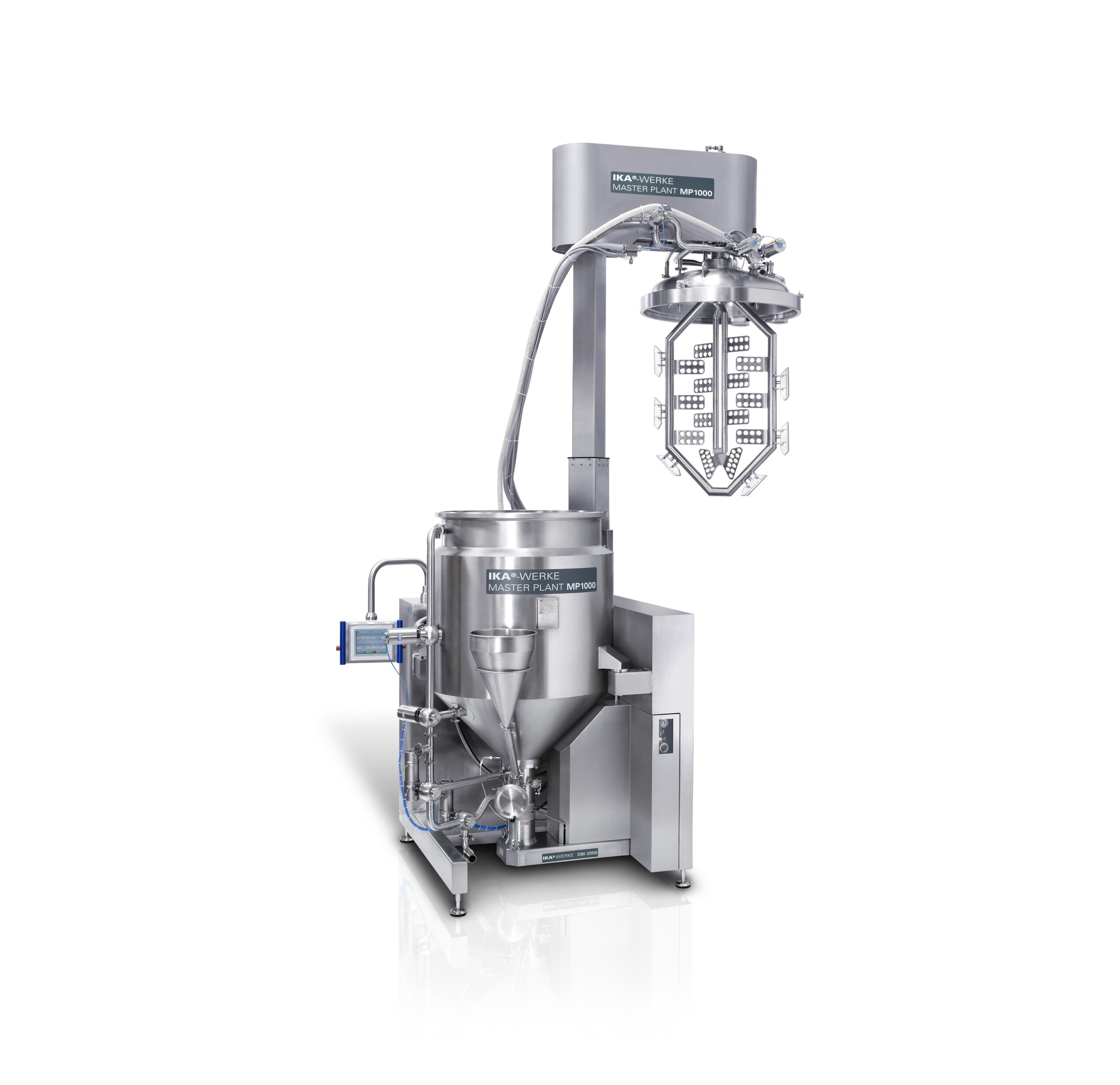
GMP homogenizing system
Manufacturers need production mixing equipment that is capable, flexible, and easy to maintain. Accur...
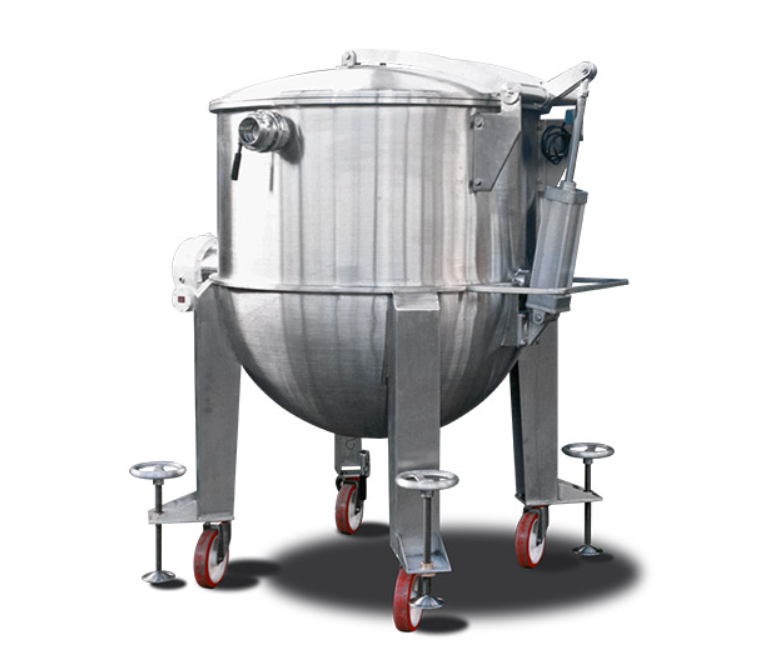
Batch cooker for fruit puree
The fruit pulp is used in many different bakery products, especially as a filling. Since fruit ...
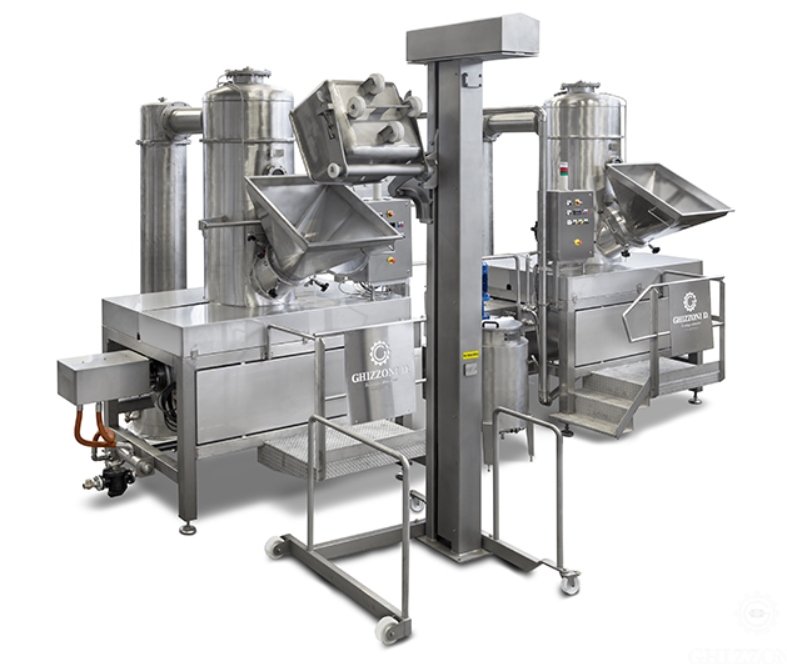
Concentrator for fruit puree preparation
Fruit puree is often an ingredient of various fruit-flavored yogurts, which someti...
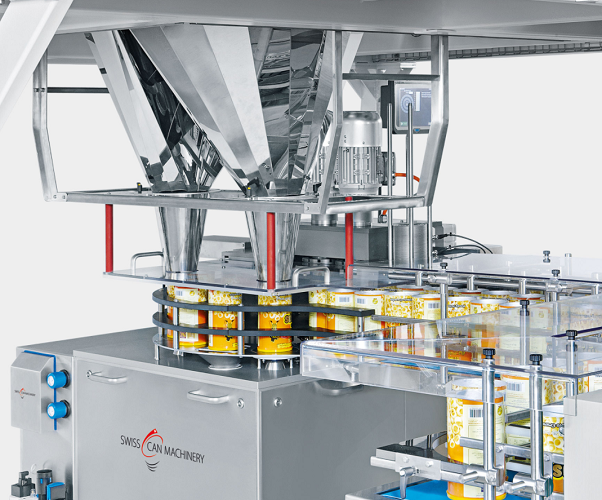
Filling and weight checking machine for food cans
Making sure the right quantity of product is in the packaging can be a ...
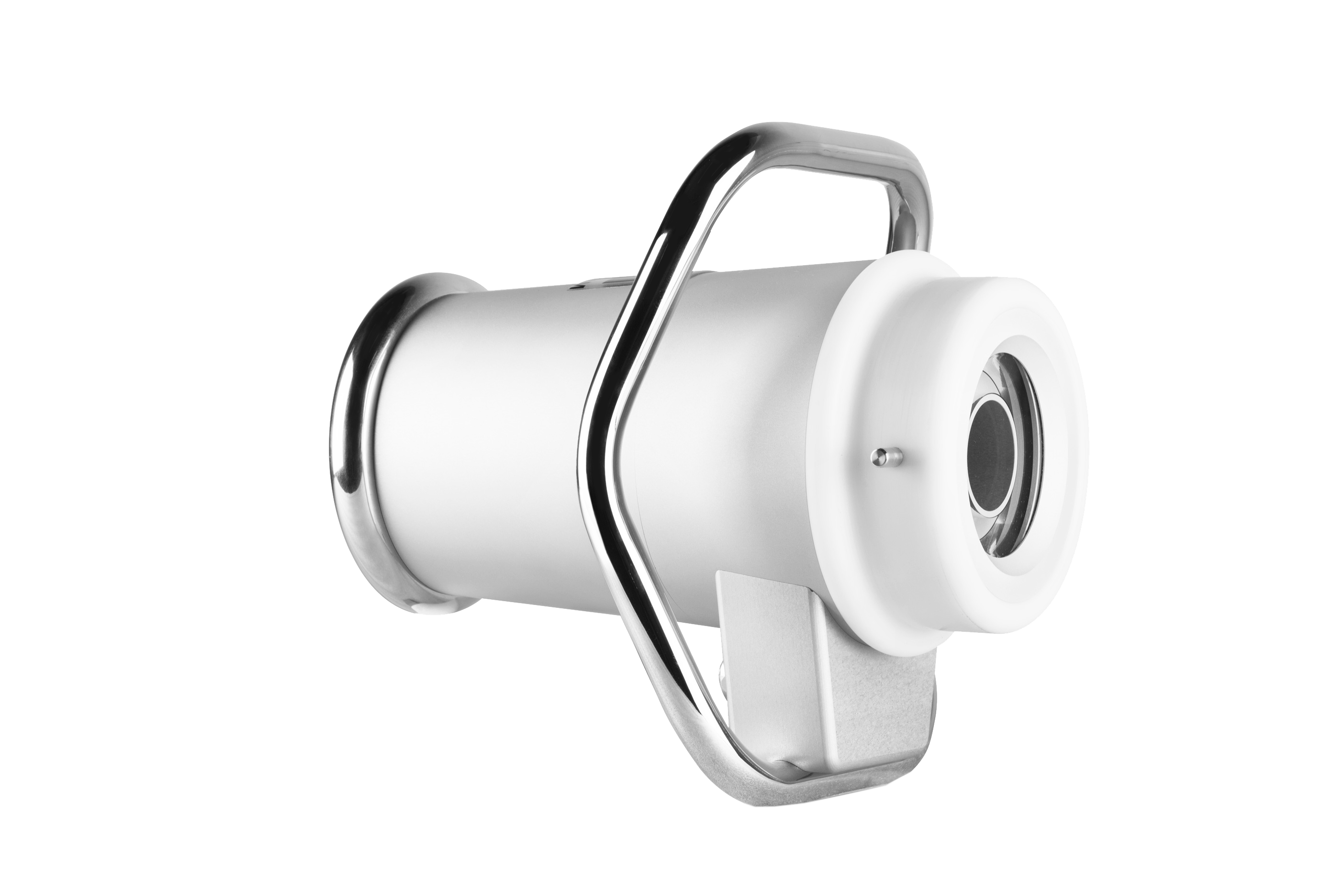
Particle analysation monitor
Products like granules, tablets and capsules require inspection at numerous steps in the produc...
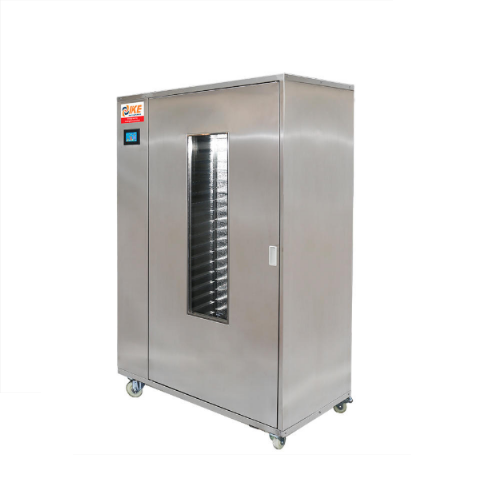
Industrial drying cabinet
The production of high-quality biltong and similar dried meat products can pose problems with main...
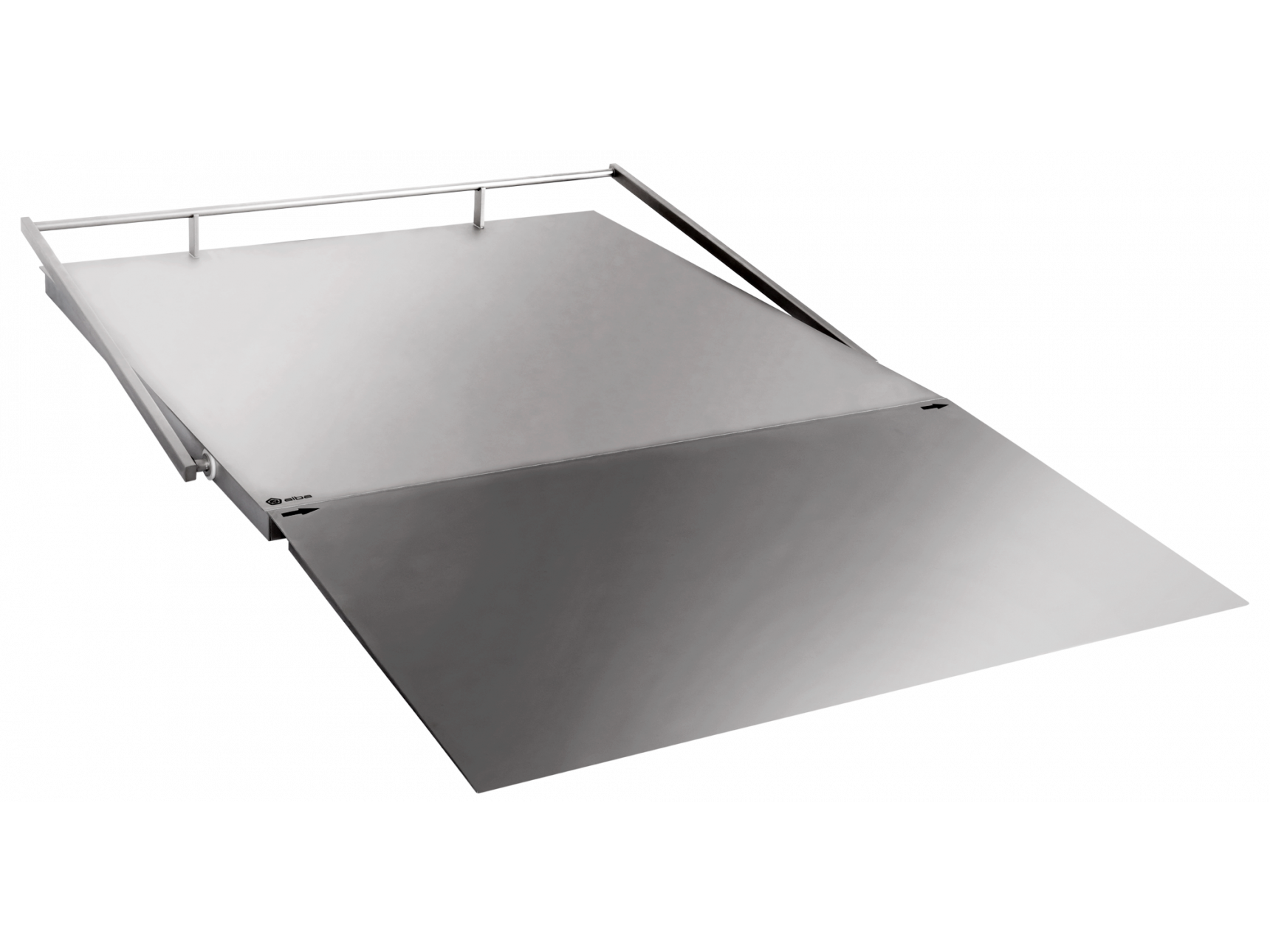
Hygienic floor scale
The food and pharmaceutical industries require maintaining high levels of sanitations as well as logisti...
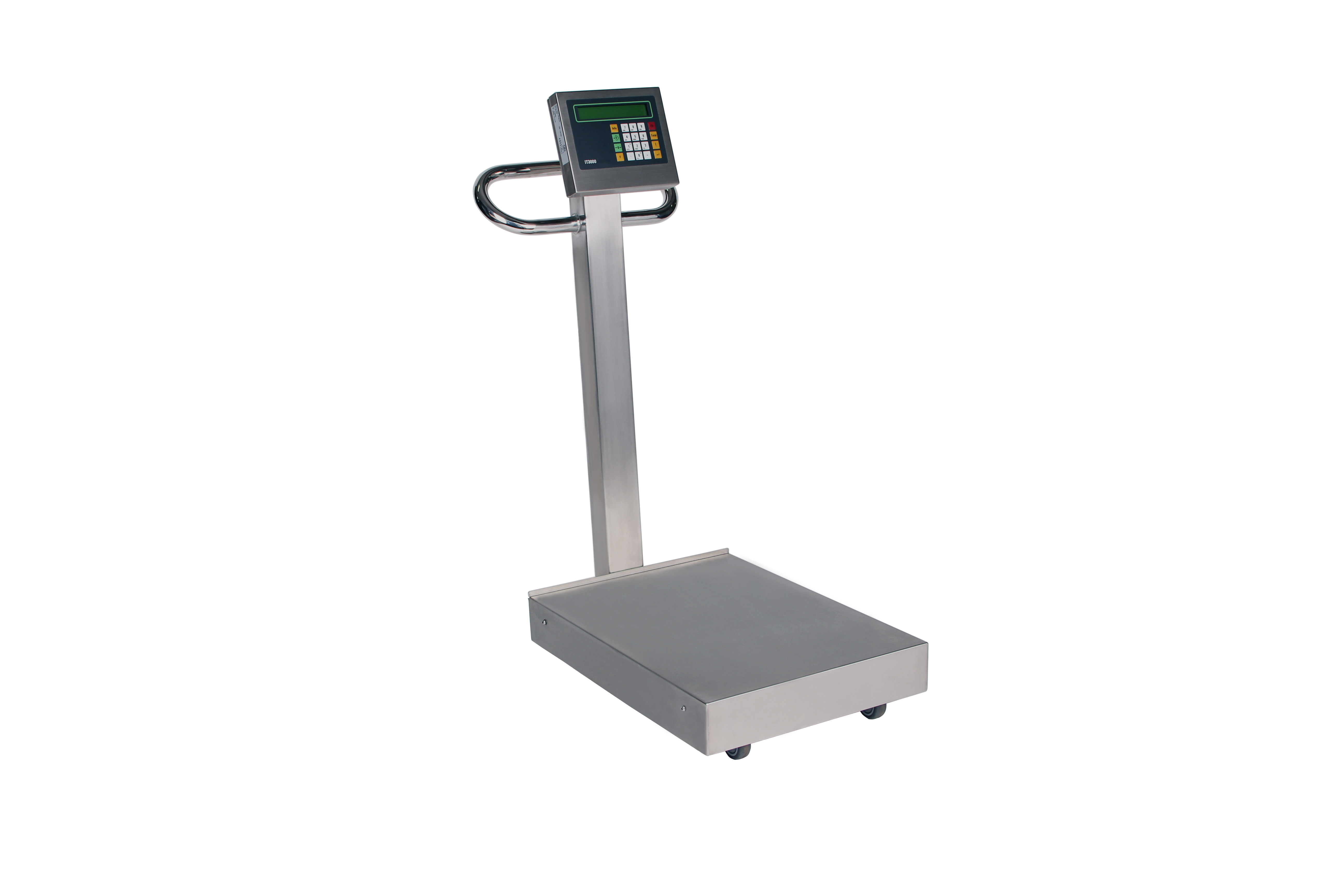
Hygienic mobile scale
Having a reliable and accurate weighing and measuring solution is absolutely essential, especially in t...
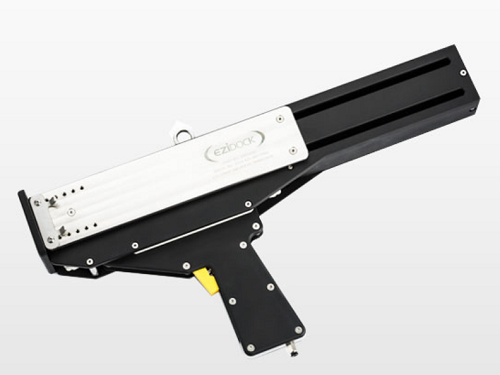
High containment closing system
Pharma and biopharma laboratories need fast effective solutions for tightly sealing bags for...
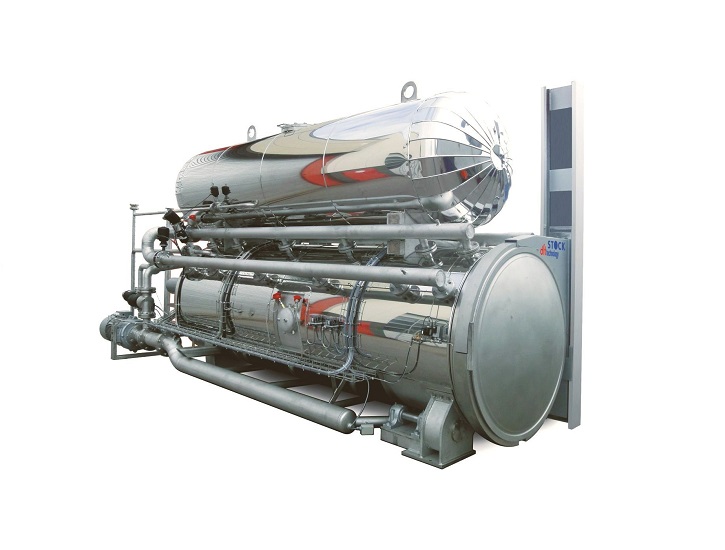
Flexible pasteurizer for packaged food
Autoclaves for sterilising and cooking food products are a mainstay of many producti...
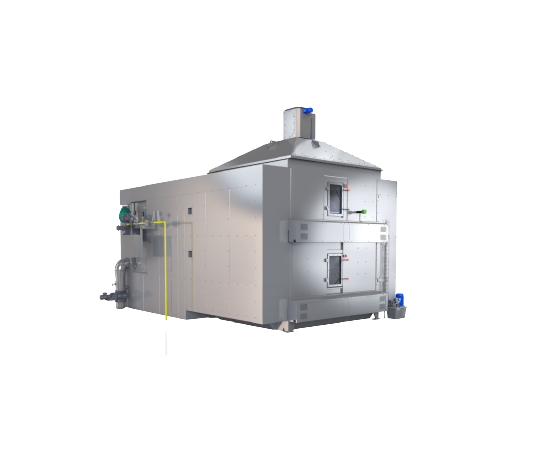
Continuous dryer machine
Traditional drying methods in the pet food, aquafeed, and extruded food industry can be the most ene...
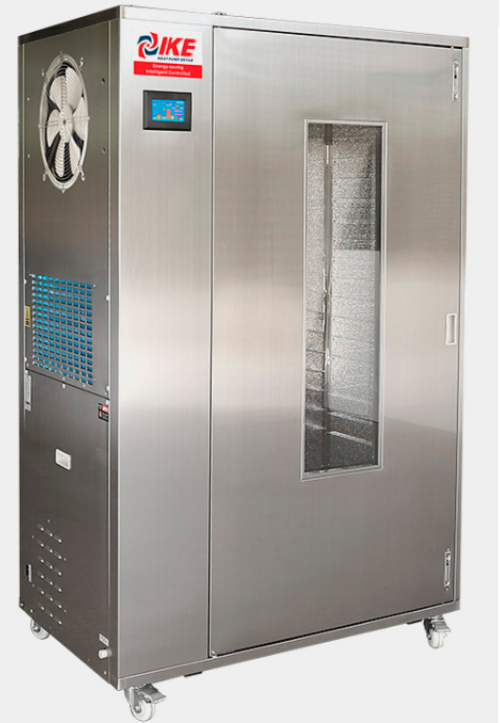
Industrial dehydration machine
Dried fruits are popular both as food in themselves and as ingredients. Traditional drying te...
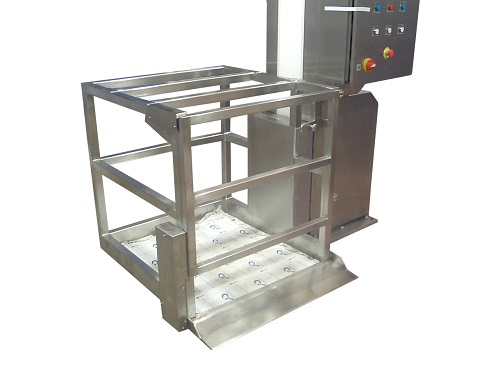
Pharmaceutical container lifter
Moving larger or heavier containers from height is out of the scope for standard handling eq...
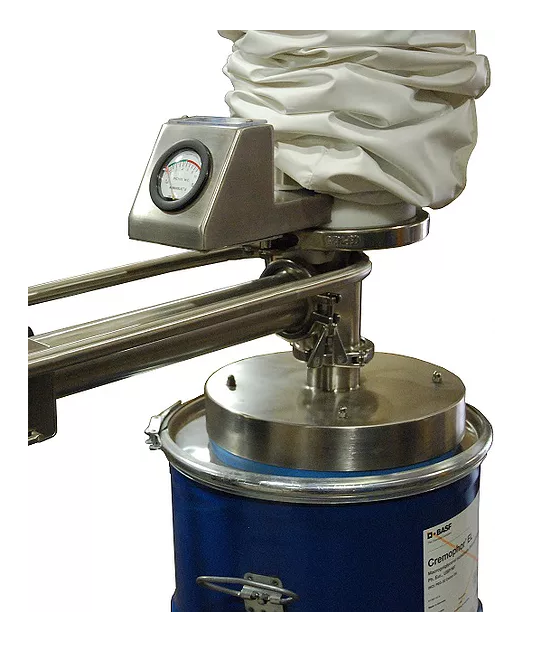
Vacuum sack lifter
In the production of pharmaceuticals and other high-hygiene environments, manual handling of inputs or int...
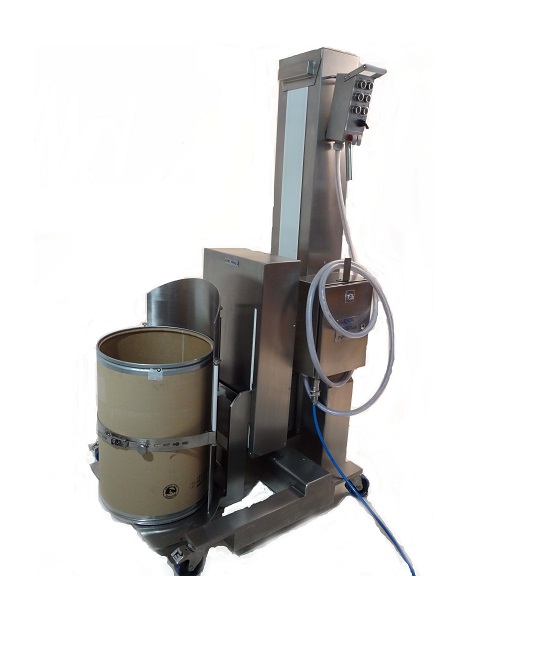
Mobile drum lifter
The production of pharmaceuticals and other hygienic products often requires the handling of large and bul...
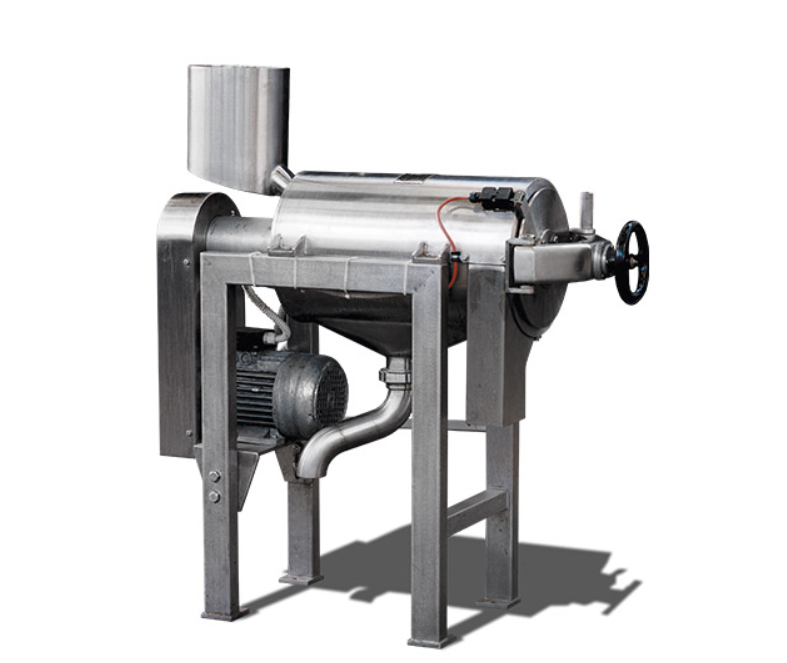
Fruit pulping machine
When making fruit pulp, a pulping machine helps you remove seeds, stems, and skins from your fruit. How...
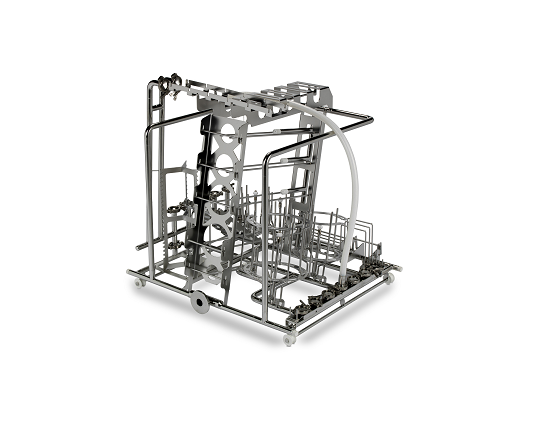
Loading basket for GMP washer
To ensure perfect cleaning of contact parts they must be placed in the GMP washer in such a wa...
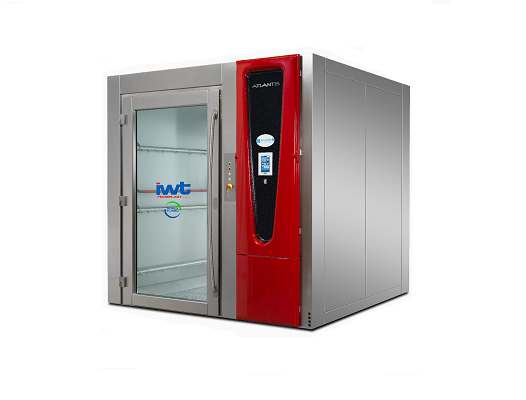
Bulk chamber washer
The production of cosmetics, nutraceuticals or unregulated pharmaceuticals often requires the cleaning an...
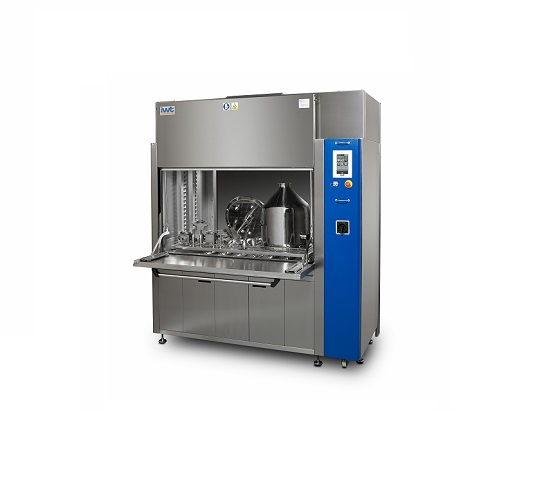
Entry-level chamber washer
When cleaning smaller products contacting filling or compressing components used in the productio...
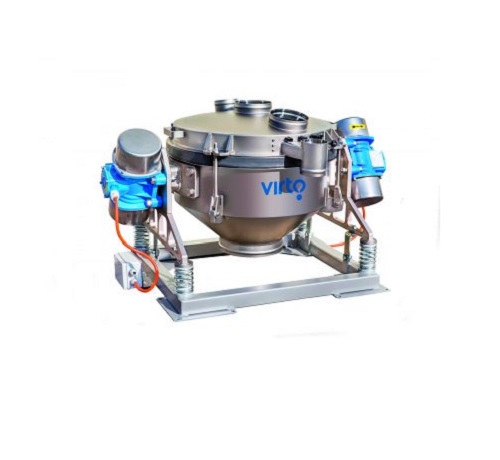
Multifrequency sieve for separation of difficult particles
Separating particles in difficult-to-process materials for pr...
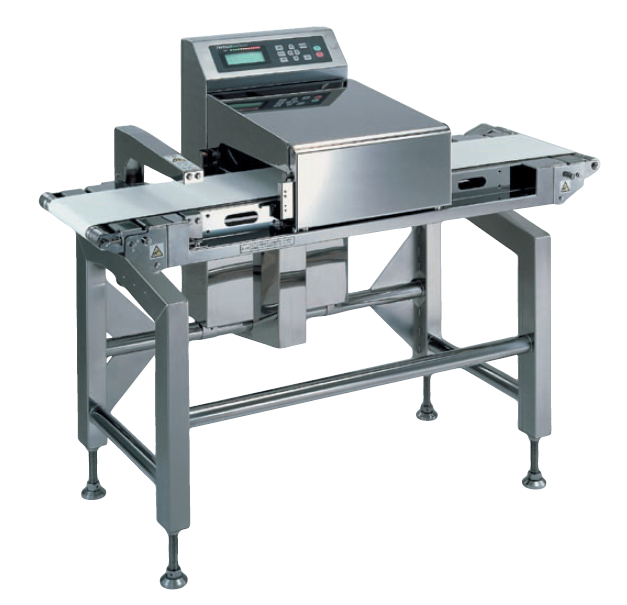
Metal detection system for aluminum packages
The magneto reflection system is ideal for detection of metals in aluminium f...
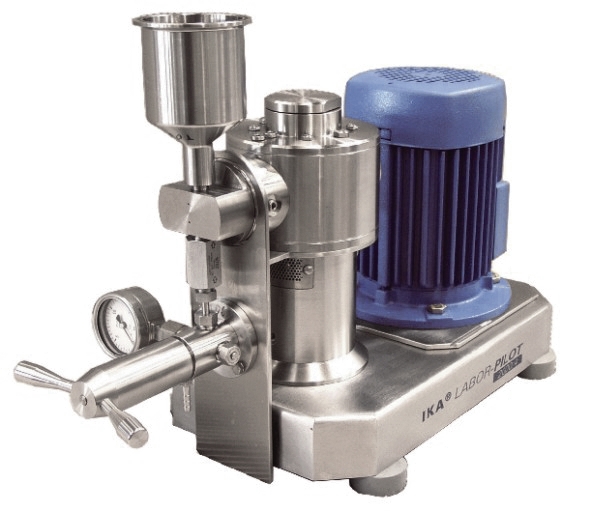
High-pressure homogenizer
When processes call for homogenized emulsions with extremely fine particle sizes the traditional t...
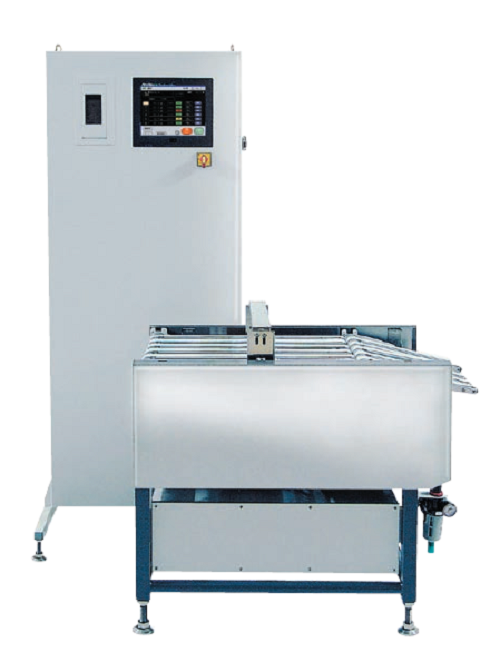
Checkweigher for sachets and sticks
The checkweighers for multiple lanes have a 1.5 times faster response speed and 2 times...
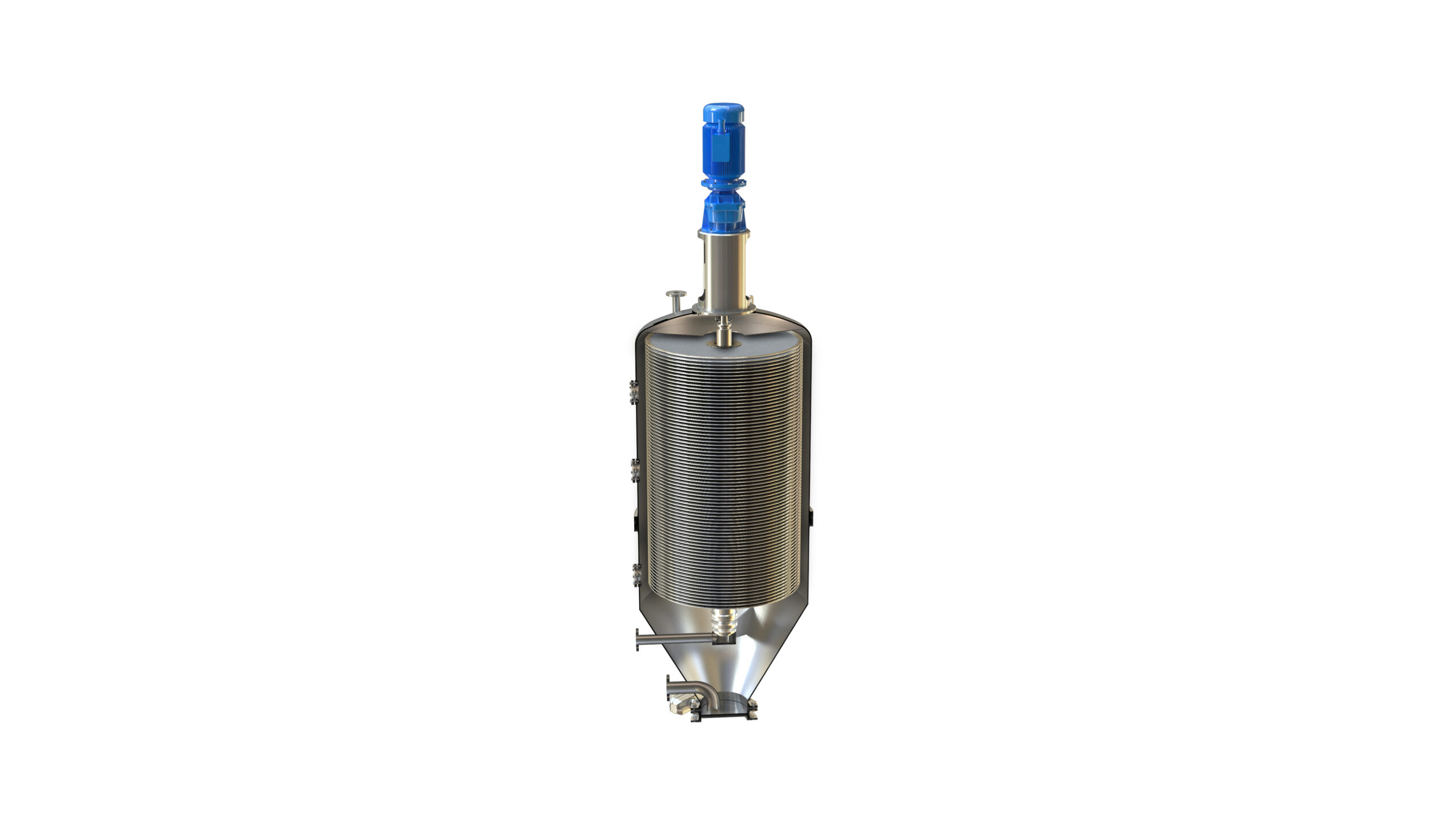
Centrifugal disc filter
The pharmaceutical and bioprocess industries need filtration processes of particularly high quality t...

Half-suit tester
Designed to allow operators to perform sterility testing in an aseptic environment providing assurance of mat...
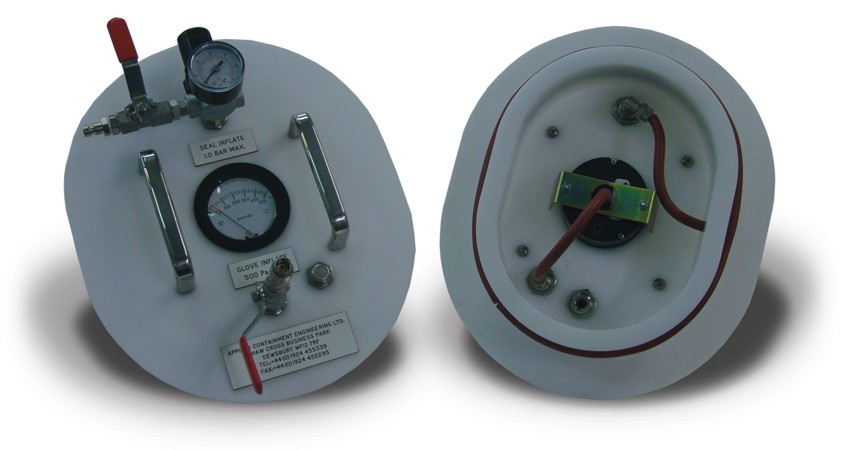
Glove tester
Testing device of the containment capability of gloves, which is as important as the other parts of the integrate...
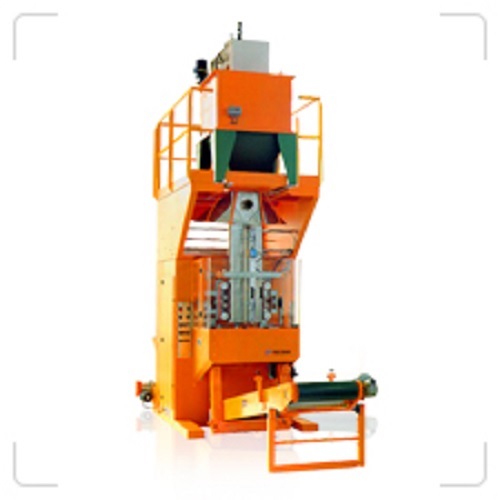
Vertical form, fill and seal machine for bags from 5 to 50 kg
To securely create, dose and pack larger quantities of mat...
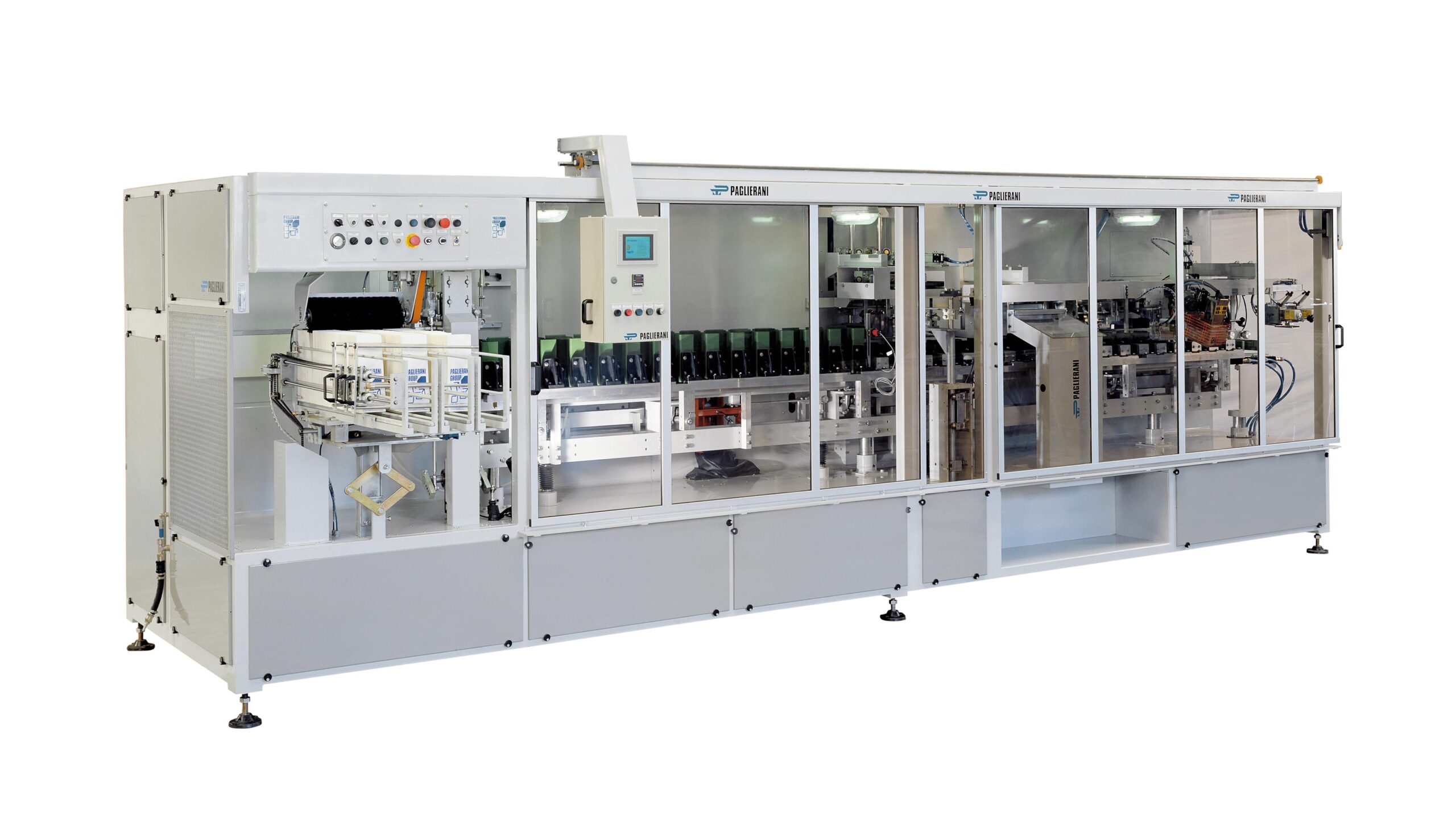
Packaging machine for preformed paper bags from 500 g to 5 kg.
Paper bag filling and closing for larger quantities of ma...
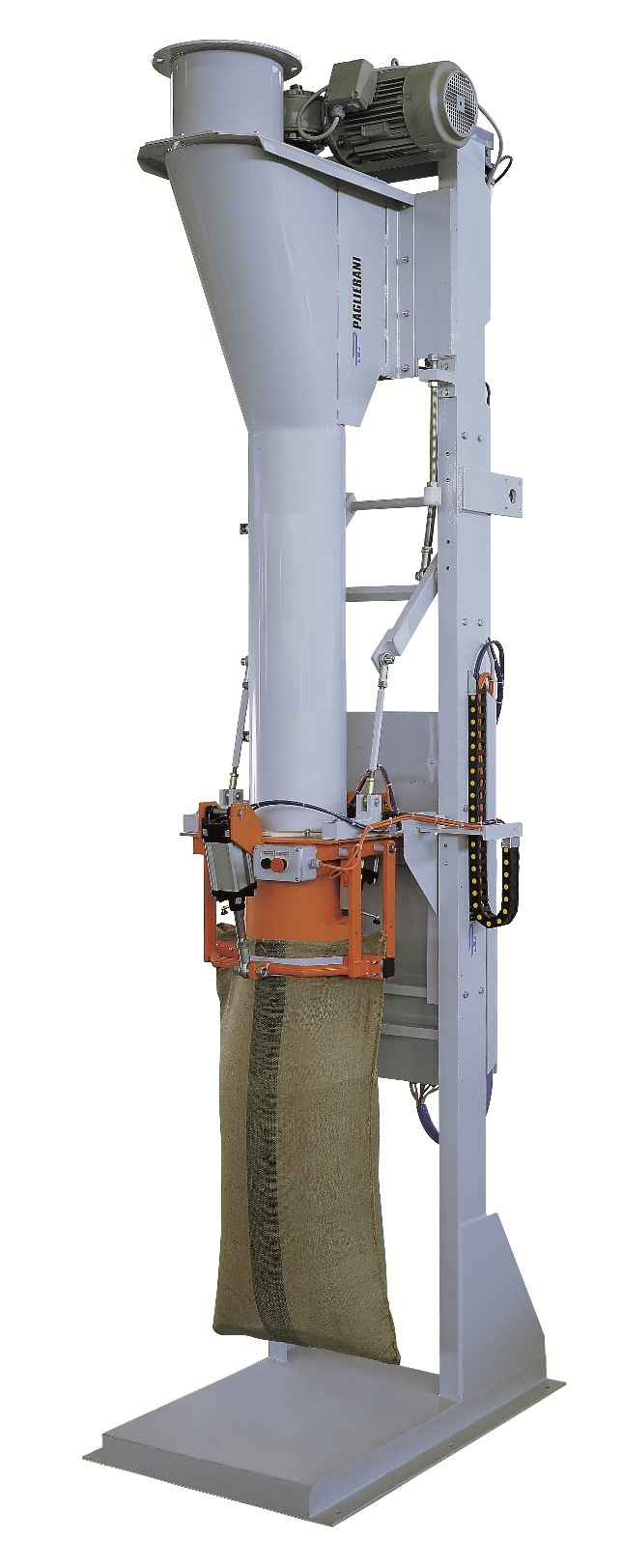
Bagger for open mouth bags
Where a stand-alone bagger is required for filling large, open mouth bags, a delivery method is n...
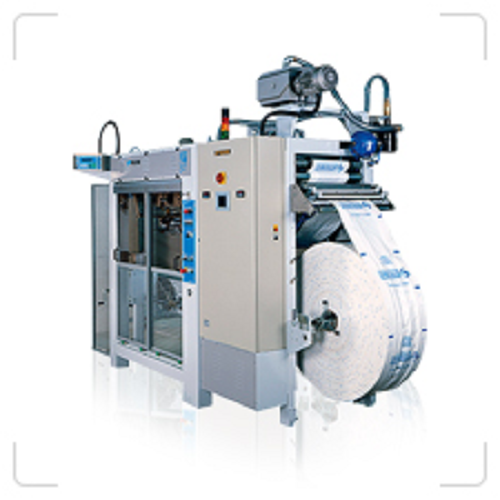
Horizontal form, fill and seal machine for bags up to 10kg
Bagging small quantities of solids or liquids, whether in pap...
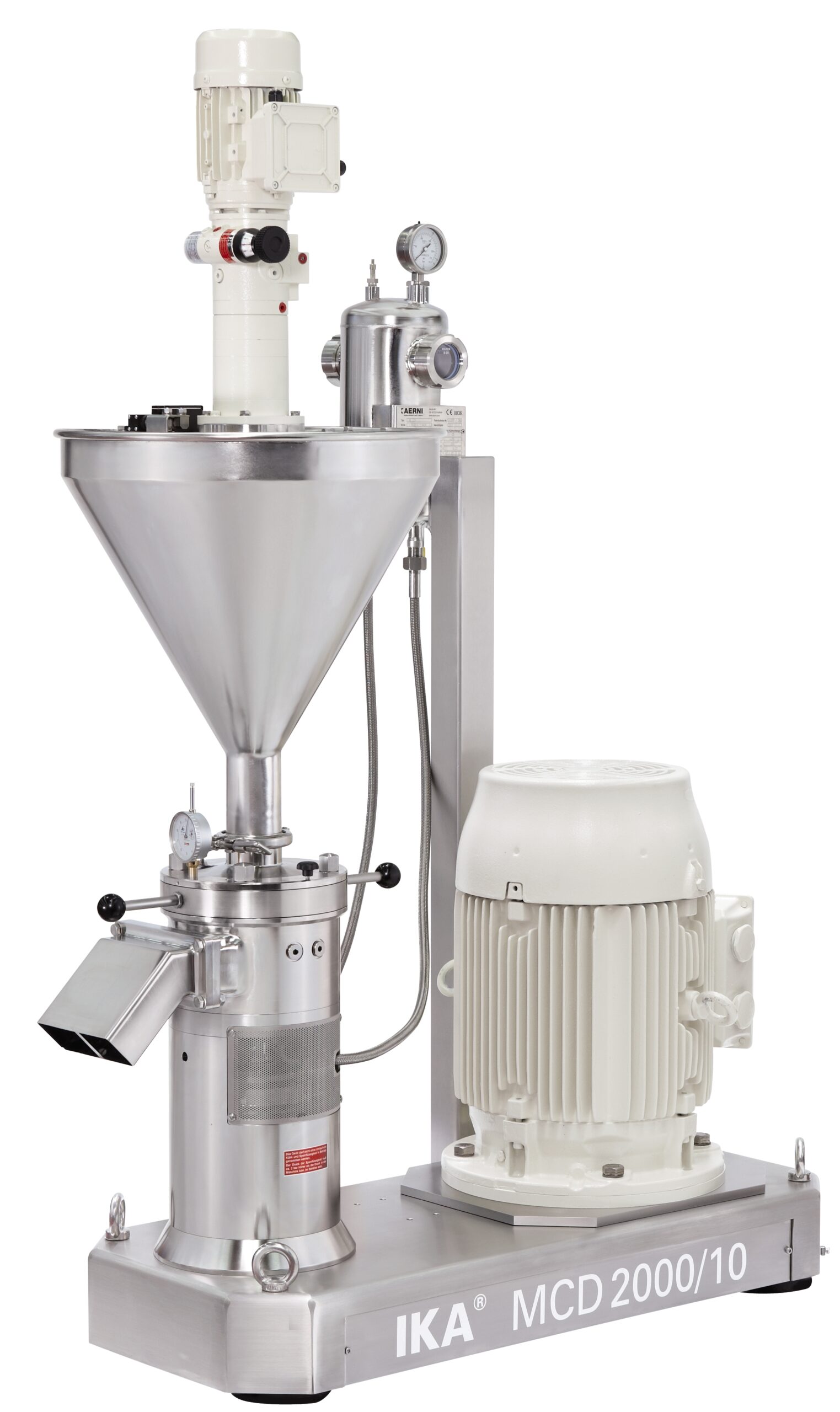
Corundum disk mill
Wet milling and grinding of viscous liquids or pastes containing solid particles such as peanut butter,mus...
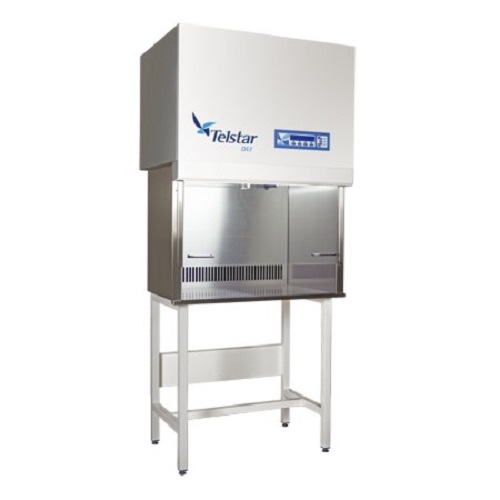
Vertical laminar flow cabinet
HEPA filtered vertical laminar airflow (down flow) creates an ISO 14644-1 (Class 5) work area ...
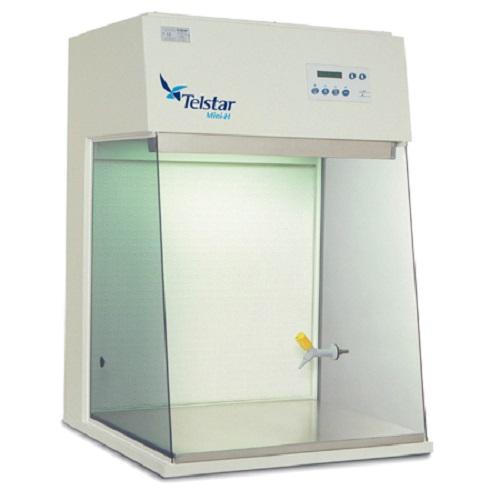
Compact horizontal laminar flow bench
HEPA filtered horizontal laminar airflow (cross-flow) creates an optimized free space...
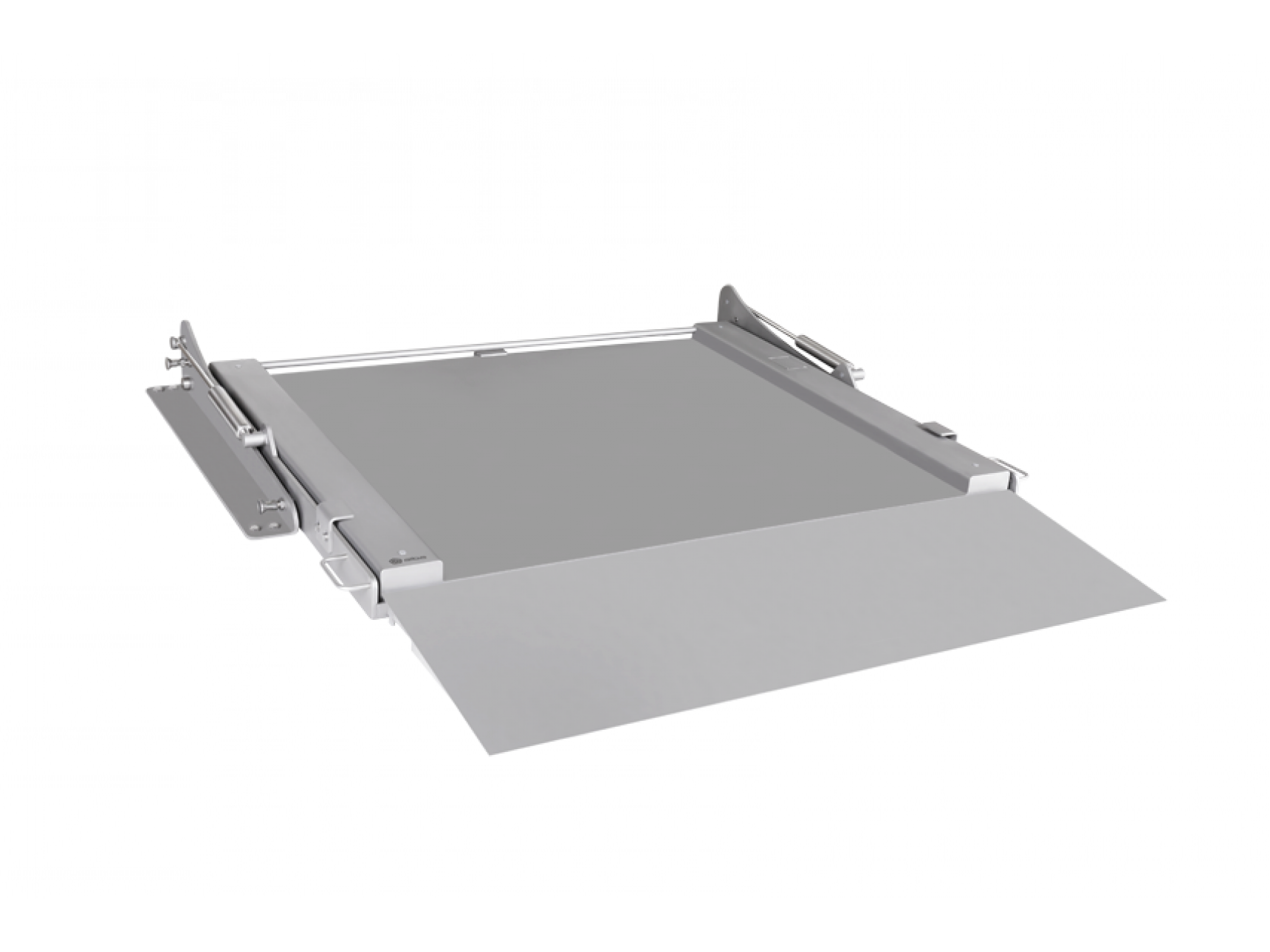
Hygienic floor scale with lifting device
The food and pharmaceutical industries require maintaining high levels of sanitati...
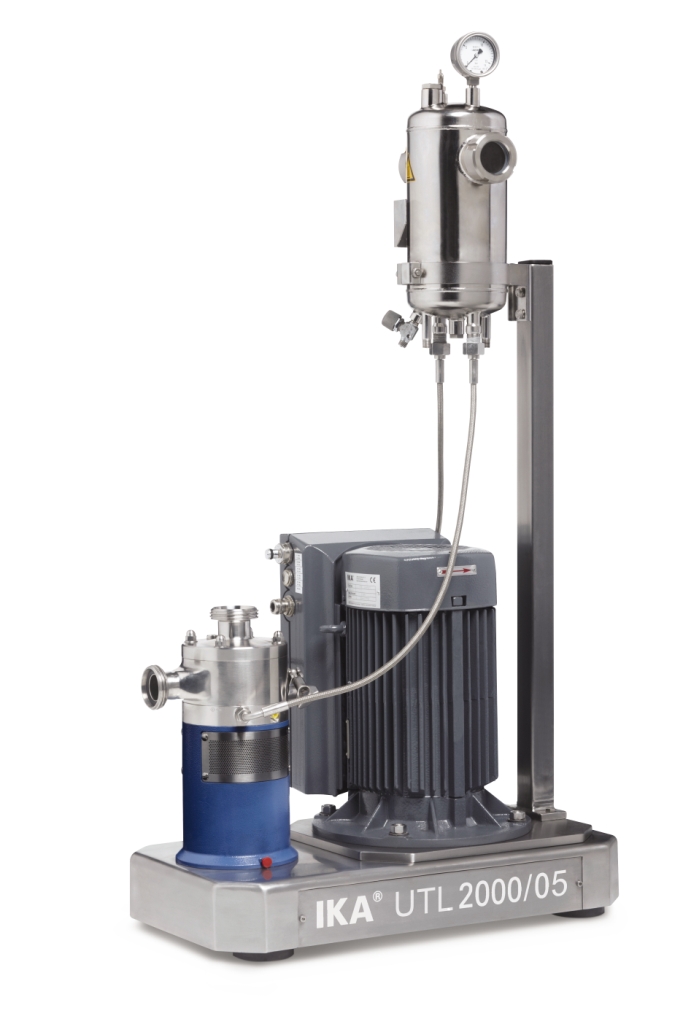
Dispersing machine for emulsions and suspensions
Equipment operating under the rotor/stator principal is often employed wh...
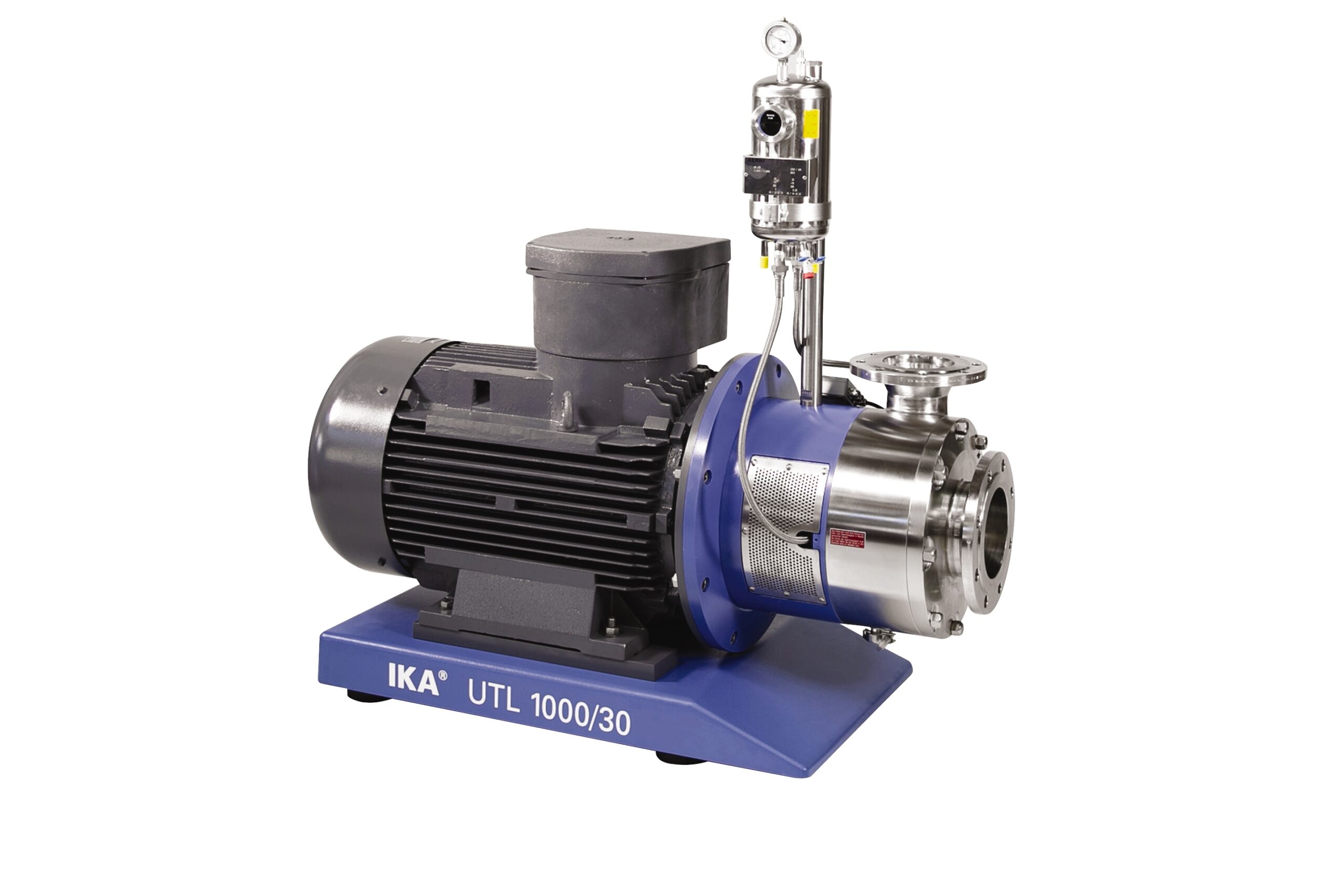
Economic dispersing machine for emulsions and suspensions
For products of medium viscosity and relatively consistent par...
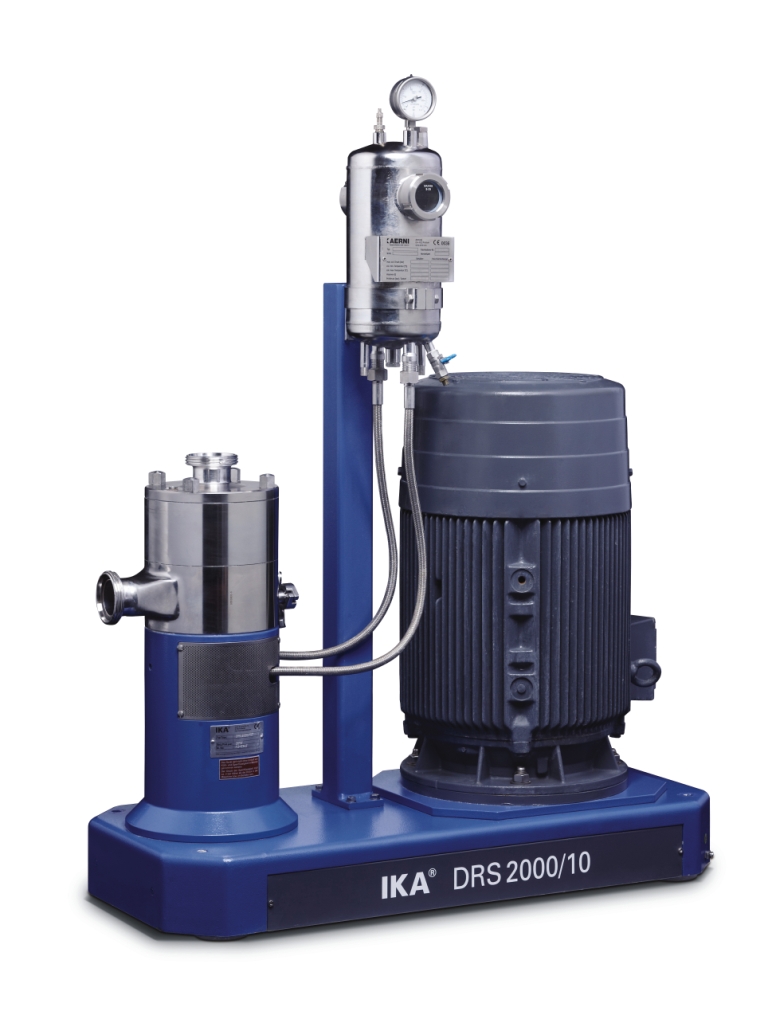
Ultra-fine dispersing machine for emulsions and suspensions
Producing the finest micro-emulsions and suspensions require...
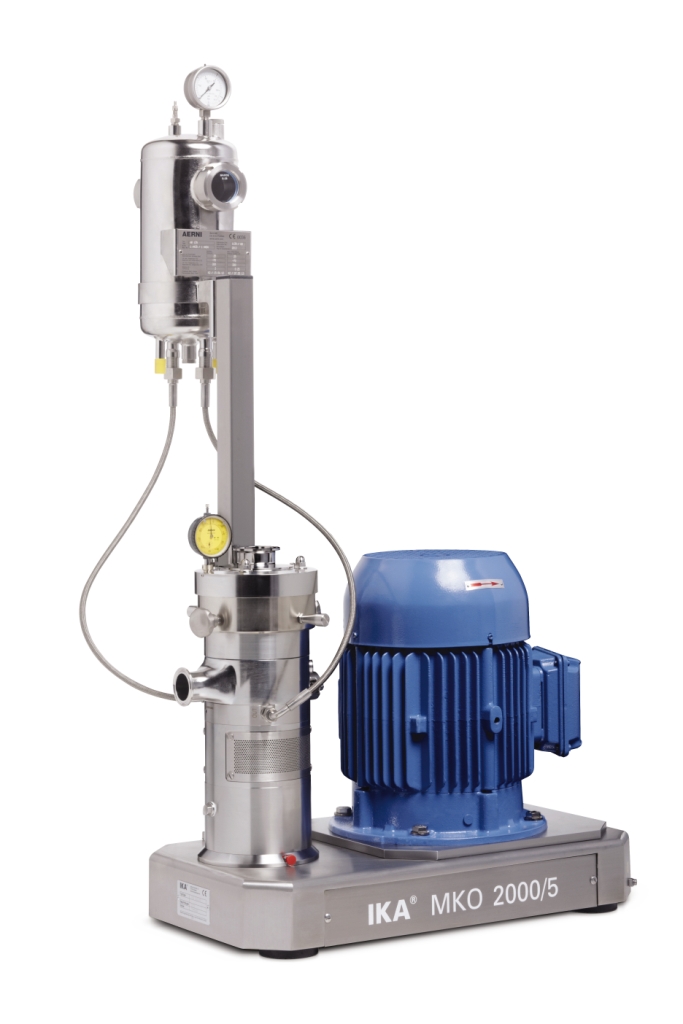
Cone mill machine
When your raw materials include agglomorated suspensions of grainy or crystalline solids and your process n...
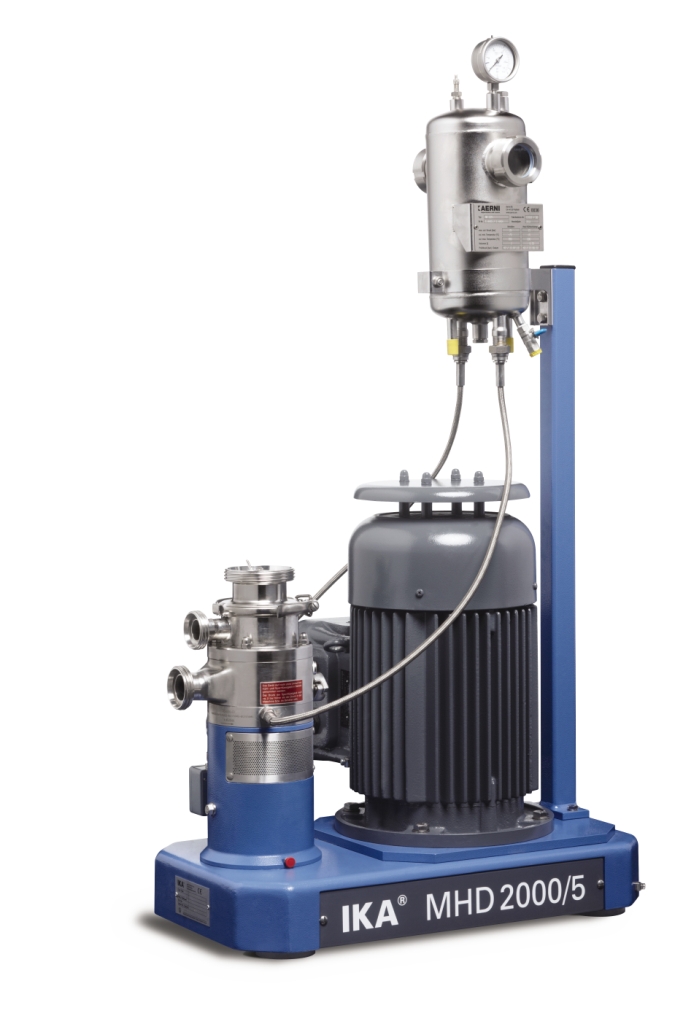
Continuous homogenizing system
Certain mixing tasks present unique challenges and manufacturers need equipment that is speci...
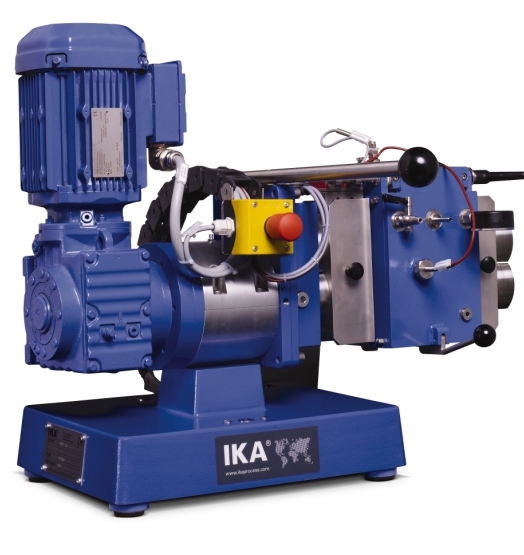
Horizontal kneader
For high viscosity products, better results and reduced process times can be achieved with kneading type r...
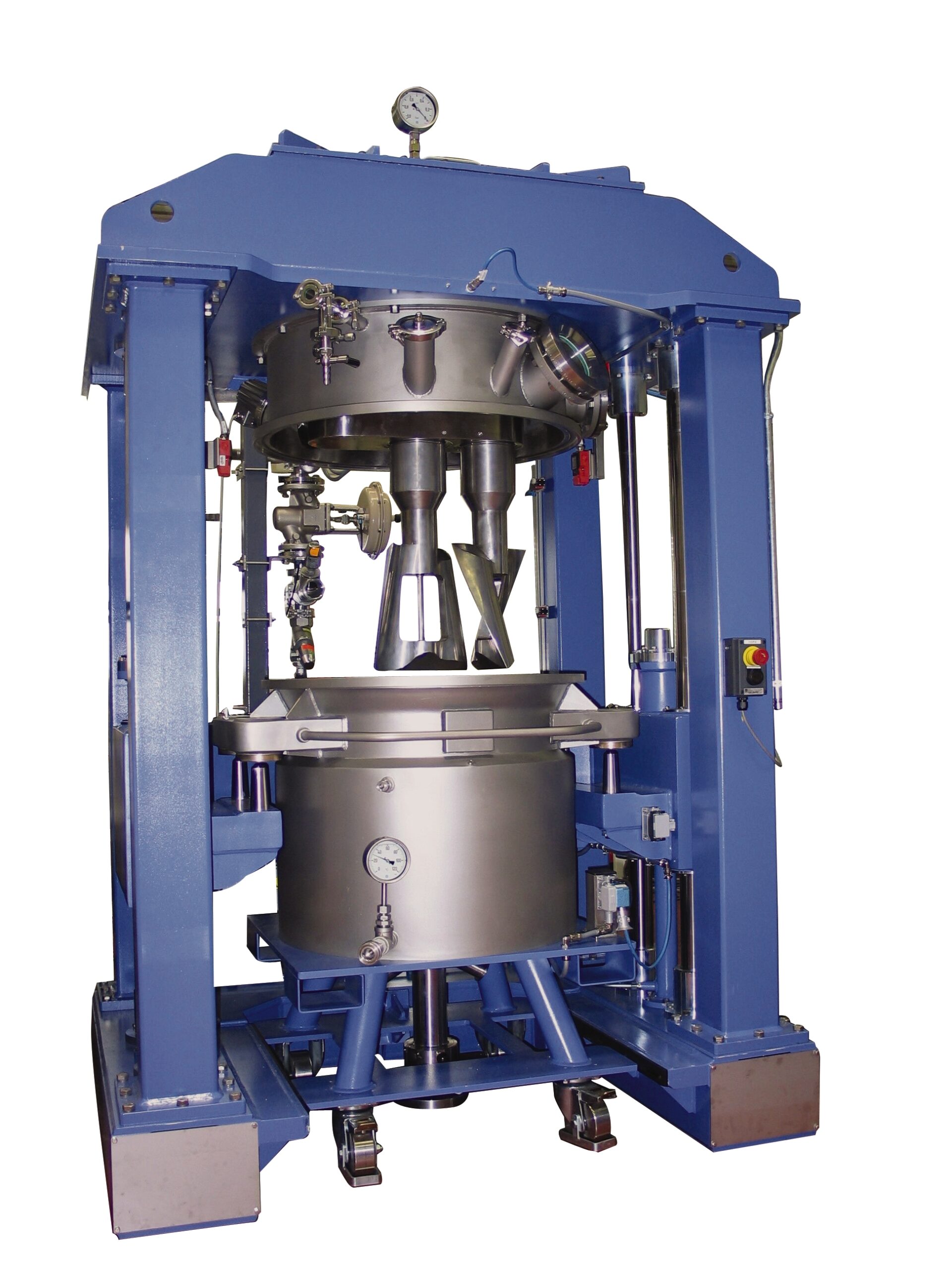
Vertical kneader
Production of highly viscous products with high solid content often benefits from kneading processes rather t...
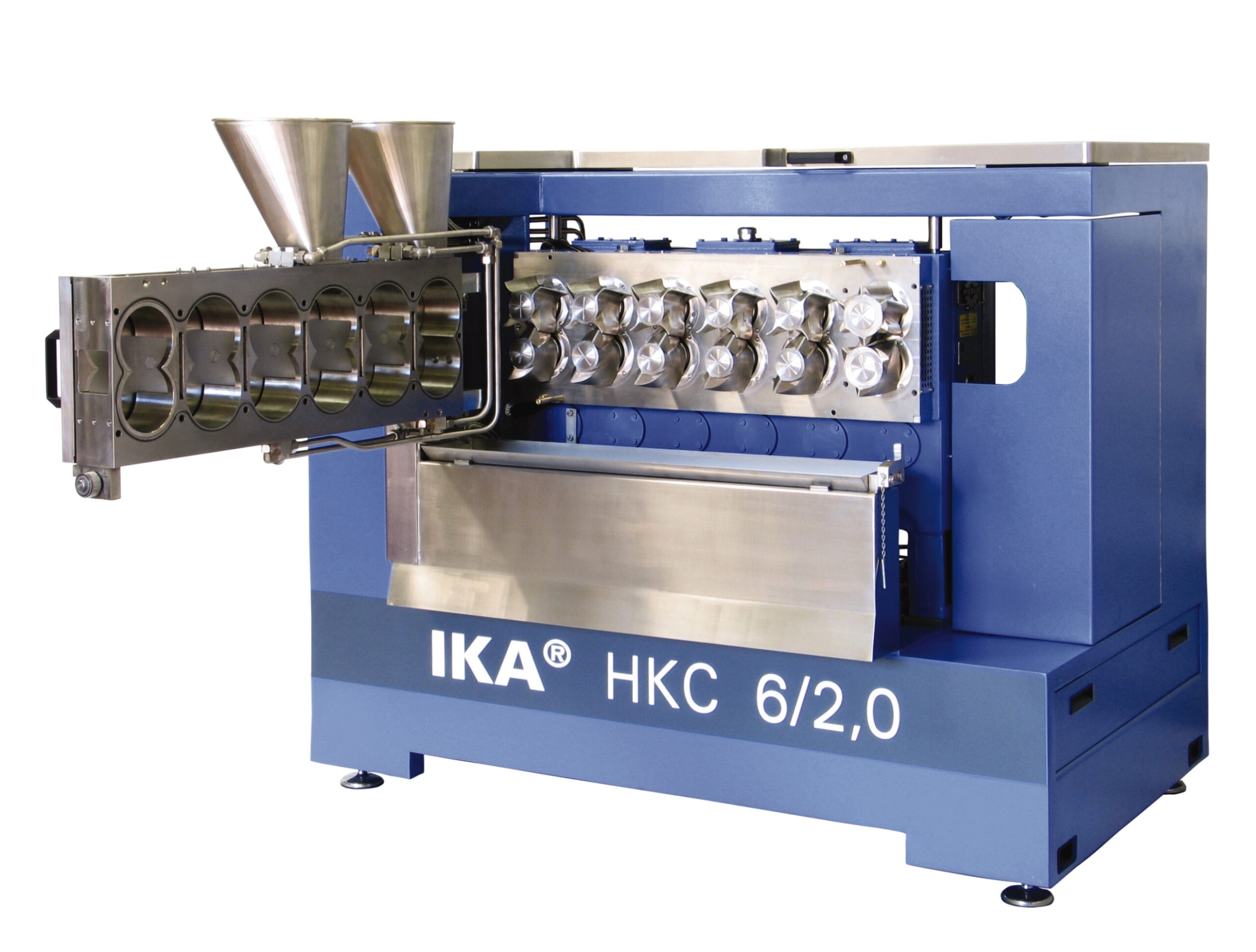
Continuous kneader
Effective mixing of highly viscous products with extremely high solids content can be difficult and the re...
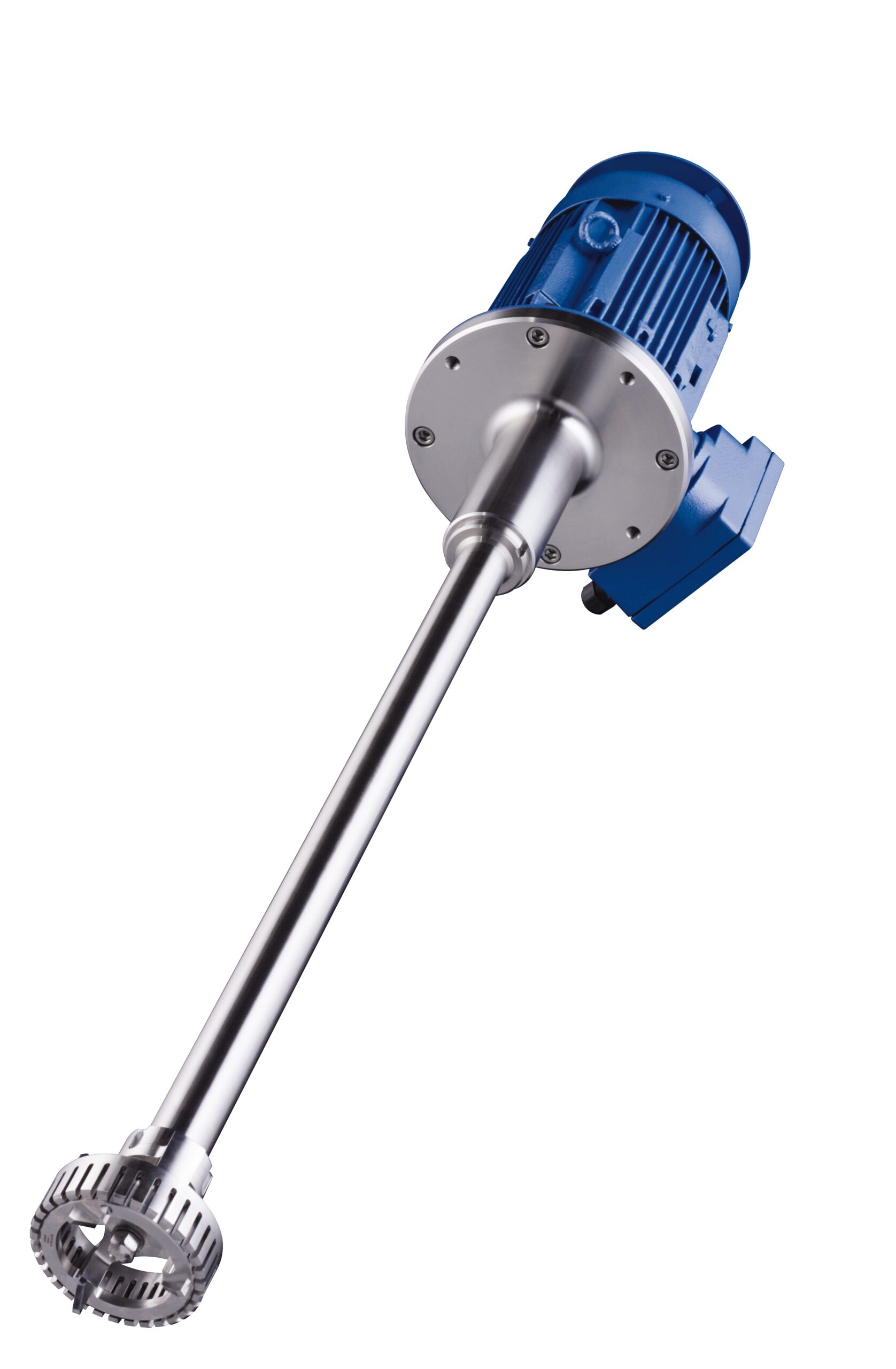
Batch dispersing machine
Equipment operating under the rotor/stator principal is often employed when more traditional methods...
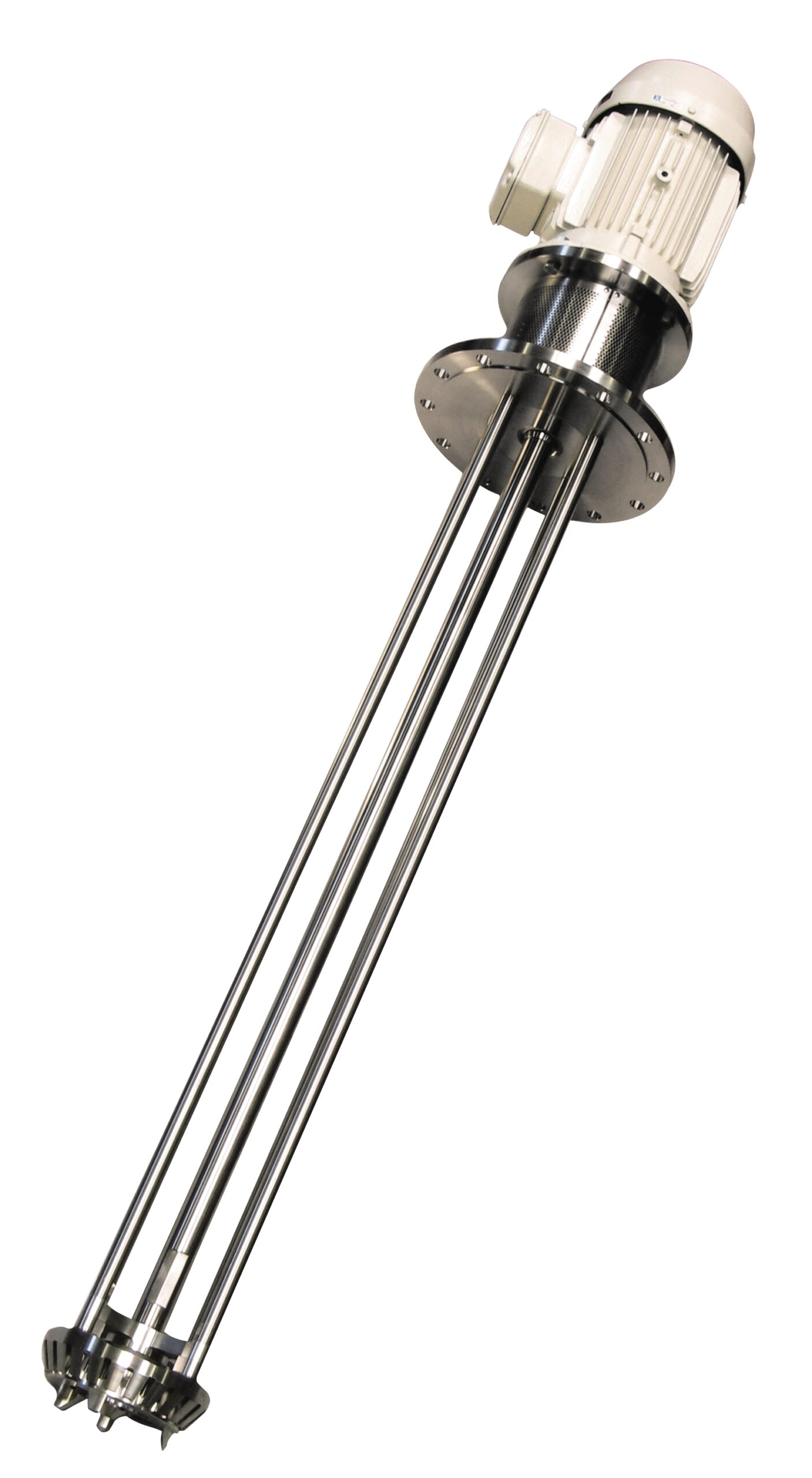
Batch dispersing machine for abrasive products
For mixing and dispersing tasks that cannot be completed by conventional st...
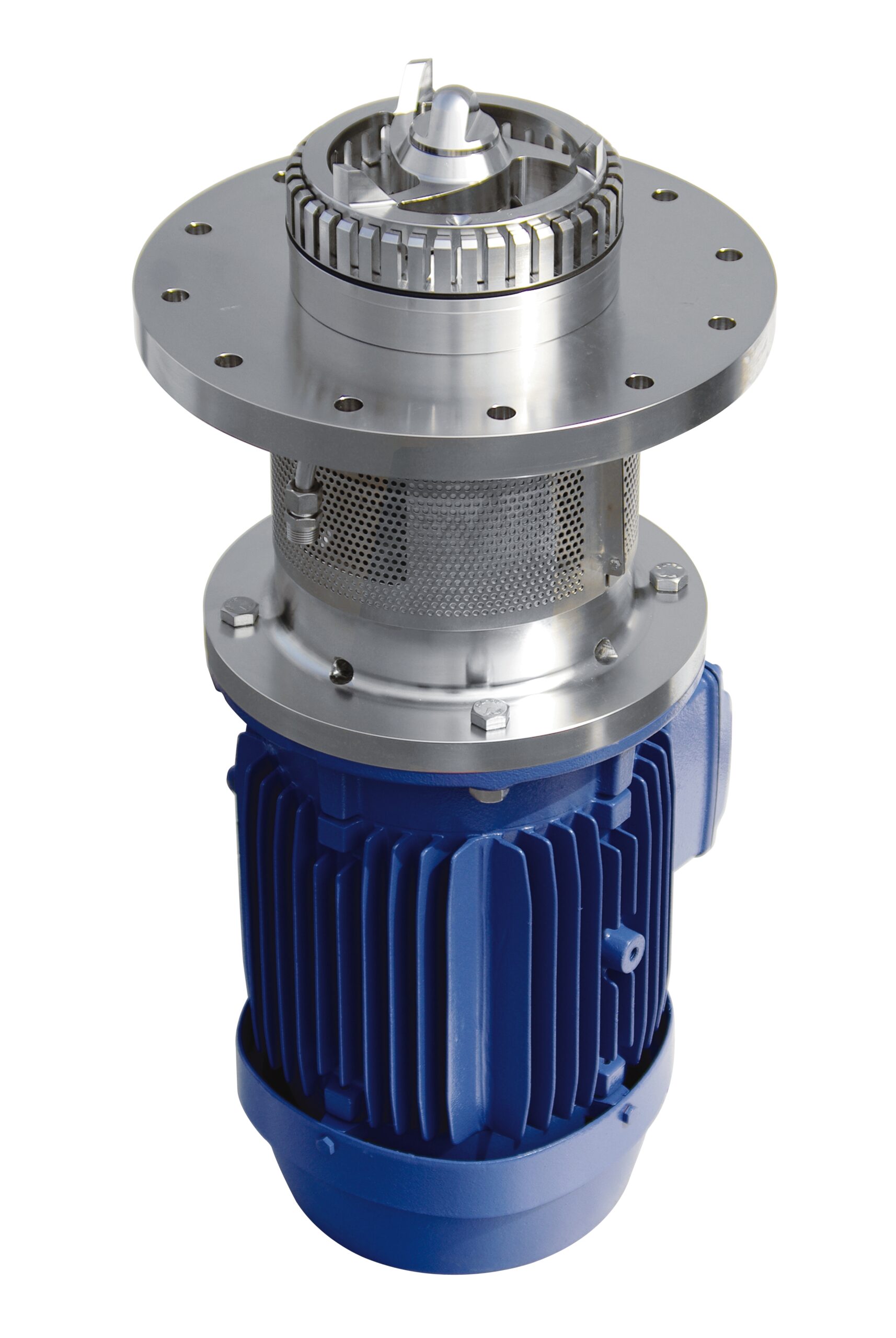
Batch dispersing machine for bottom entry into vessels
When your process requires high performance mixing or dispersion b...
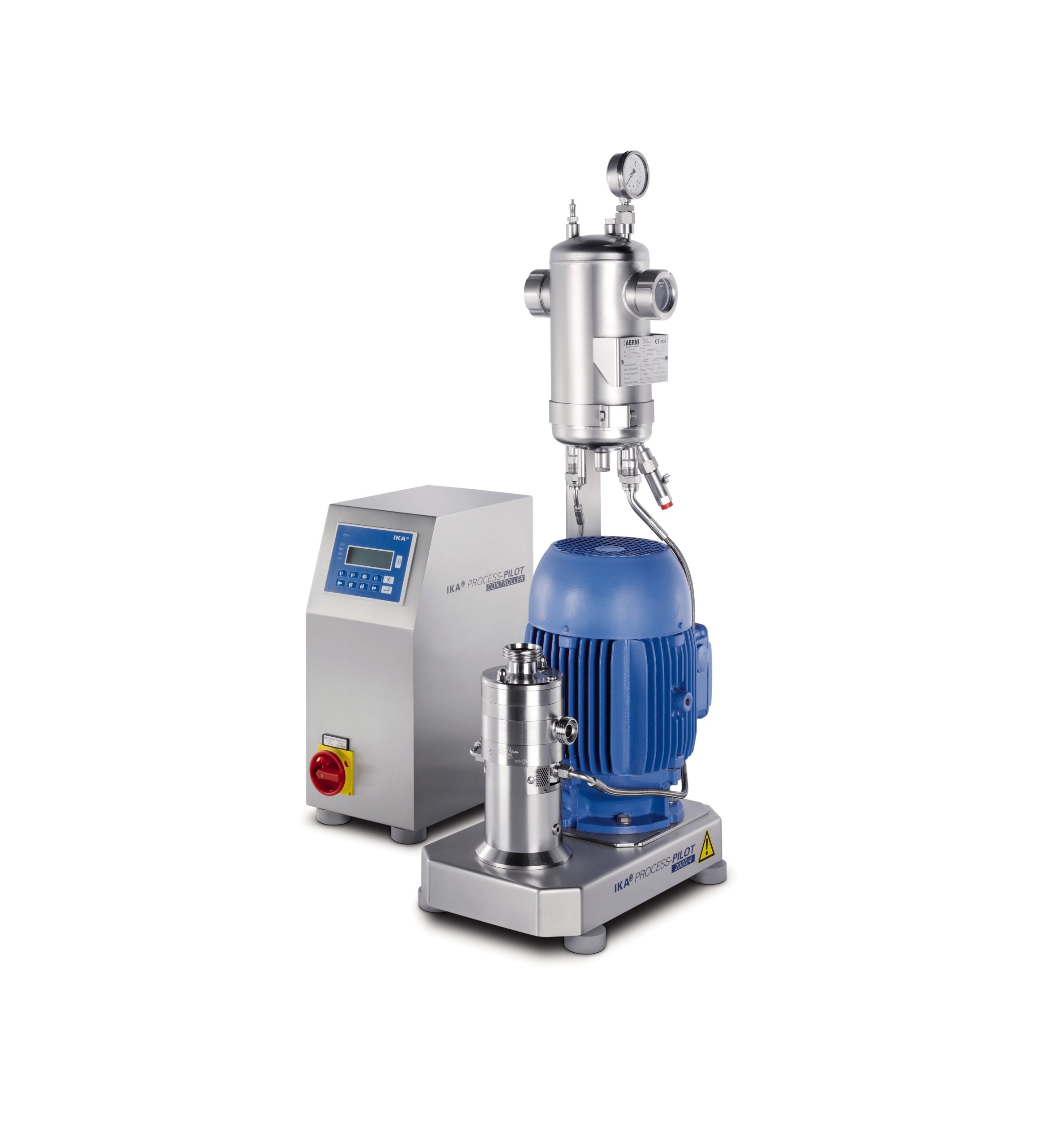
Dilution system for two or more liquids in one pass
Onsite dilution of liquid process ingredients has historically been a...
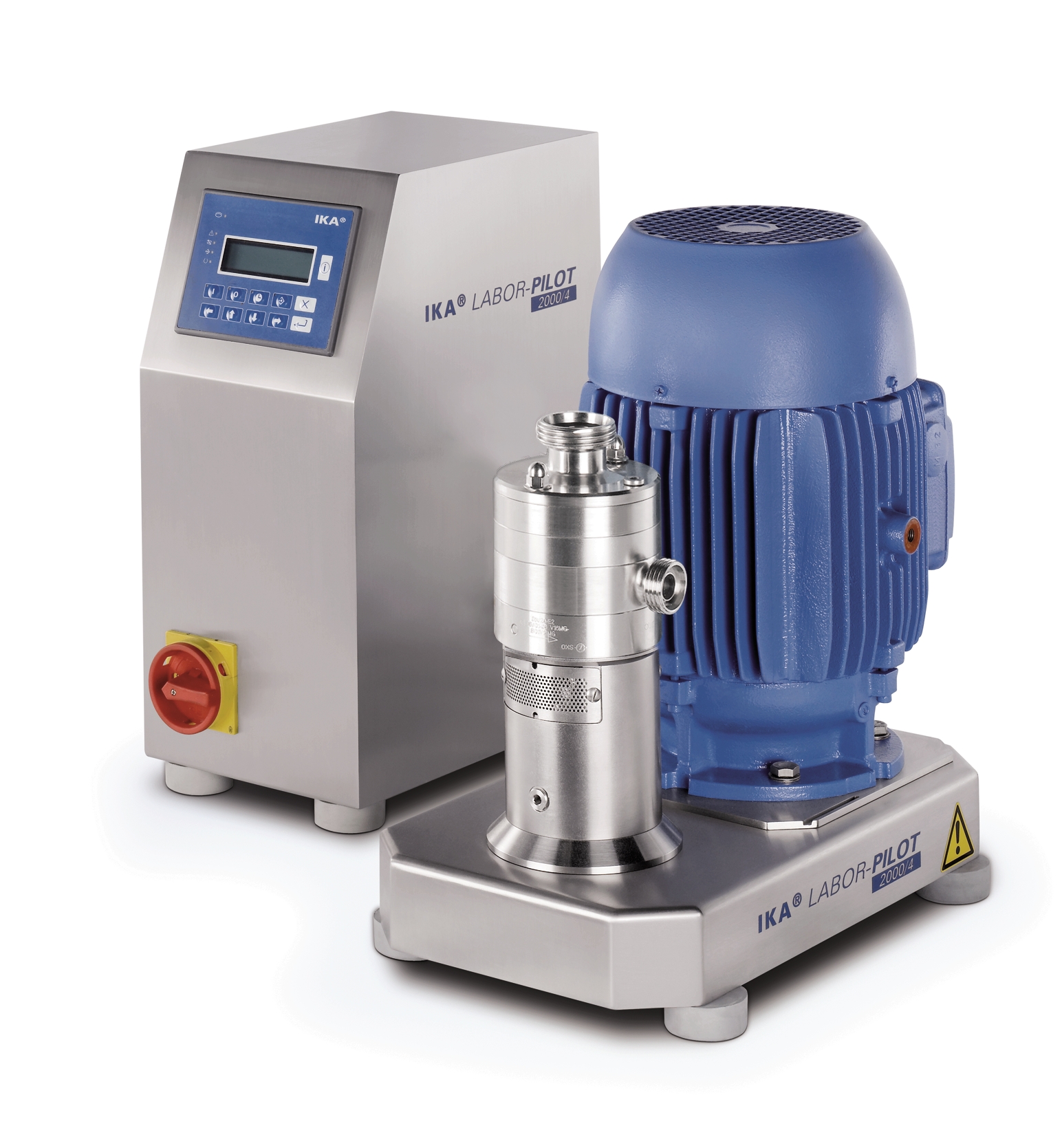
Pilot dispersing machine for testing and scale-up
Innovators in process development need laboratory equipment that helps ...
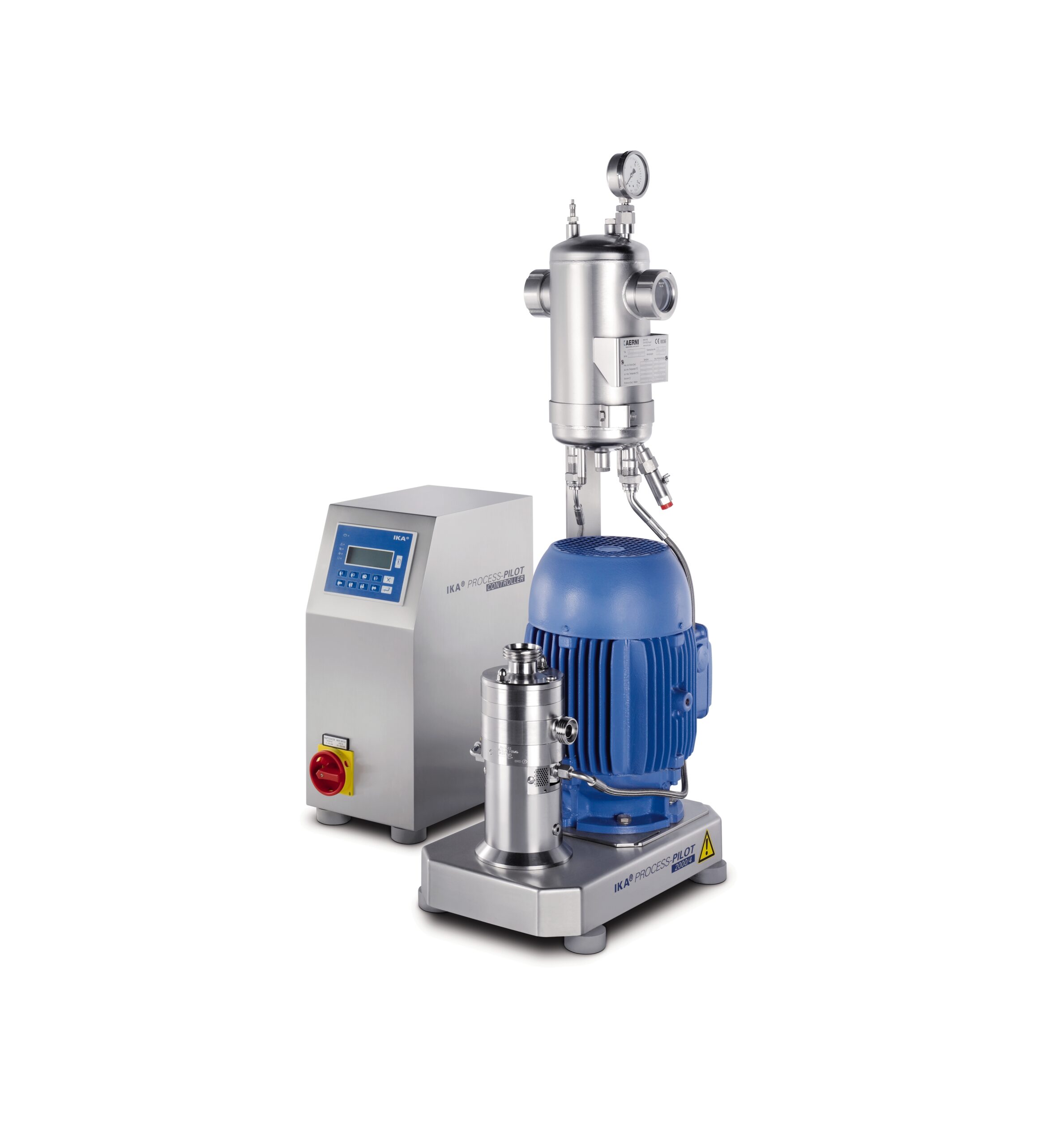
In-line laboratory dispersing machine
Innovators in a wide variety of industries need laboratory equipment on which process...
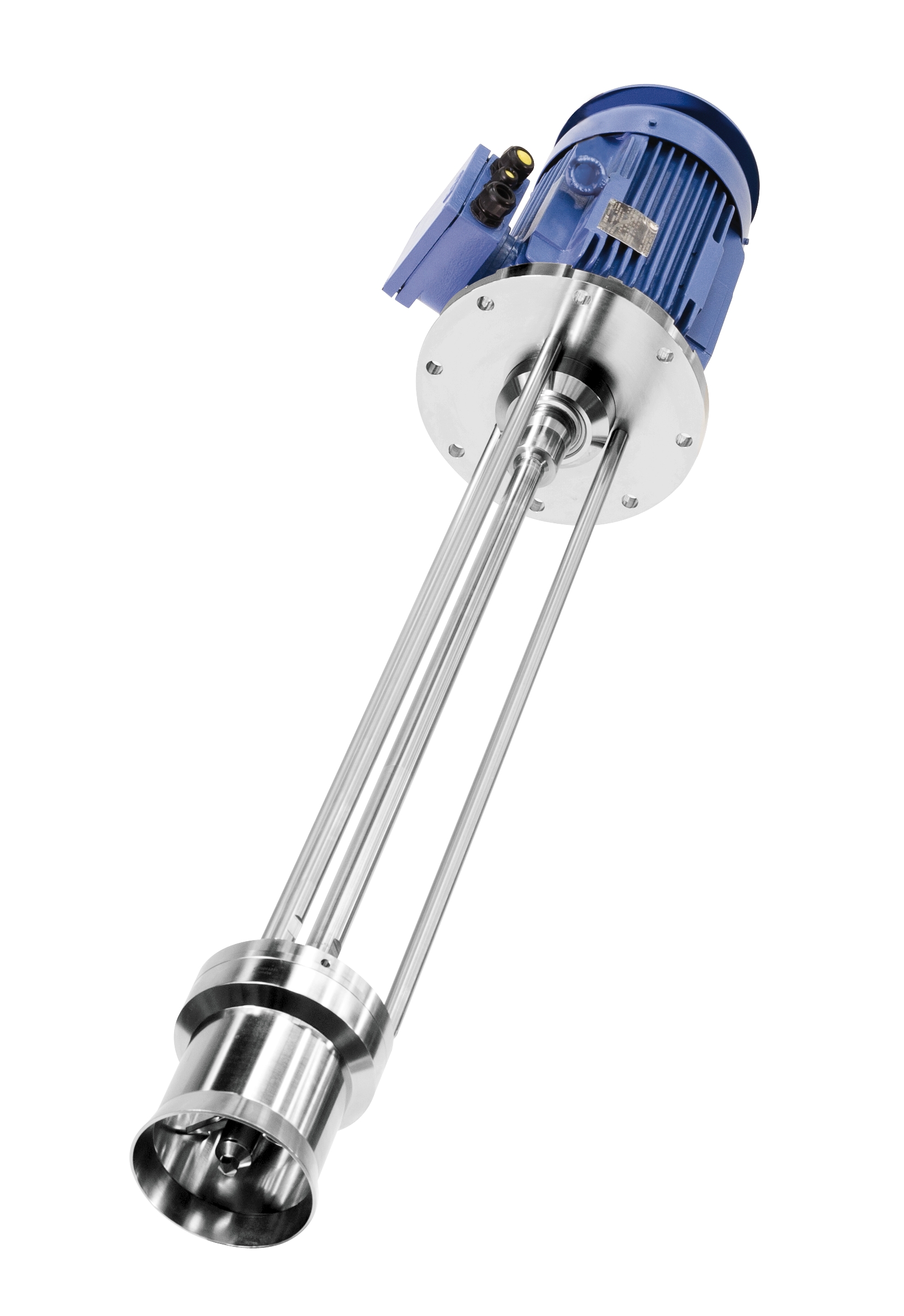
Jet flow agitator for high-viscosity media
Processes including homogenization, dispersing, suspension, emulsification and ...
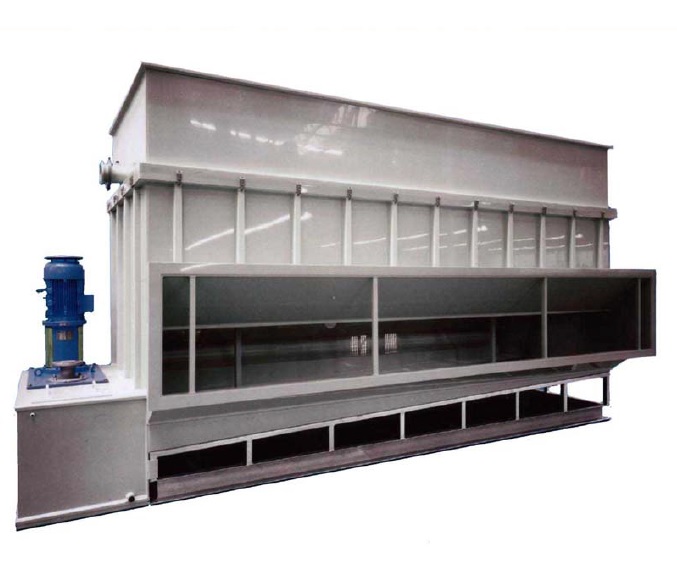
Air dehumidifier for bulk products
When your product or process is sensitive to humidity, using an air dehumidifier may res...

Manual bagger with gross weigher
This is a manual bagging set with an electronic gross weighing system to meet international...
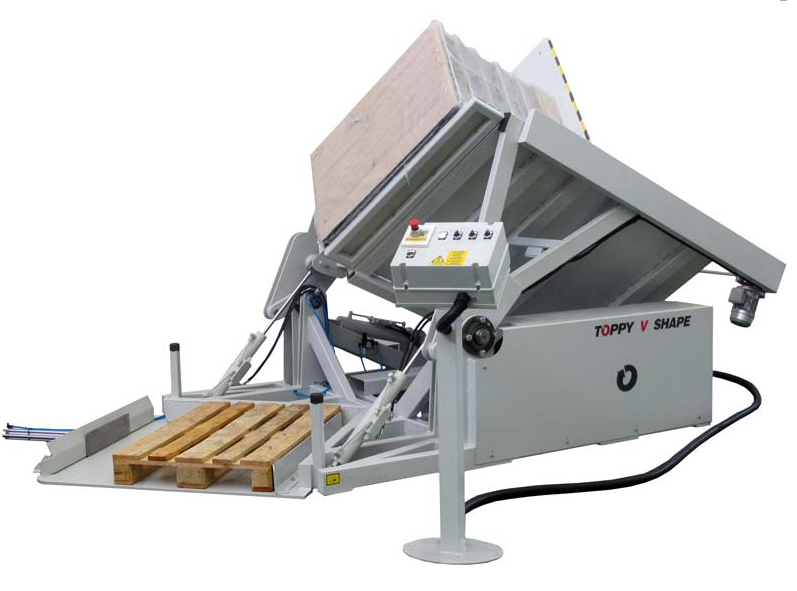
V-shaped pallet changer
If you are looking for a sturdy pallet changing solution, a stationary V-shaped pallet changer can be...
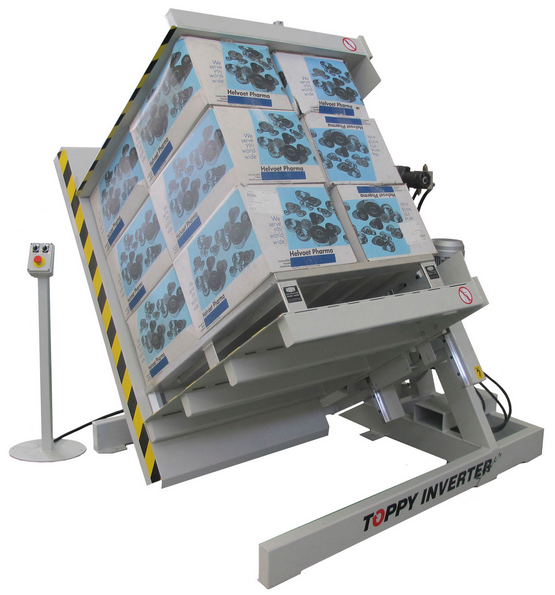
Pallet changer
For turning loads and exchanging them on pallets, here is a stationary pallet changer that will load and unload...
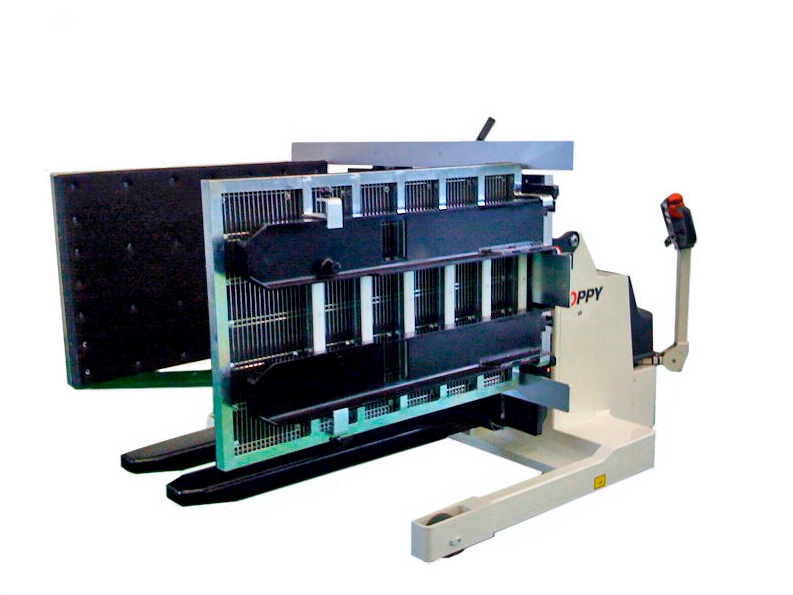
Versatile mobile pallet turner
Here is the versatile mobile pallet turner that completes the typical features of all mobile ...
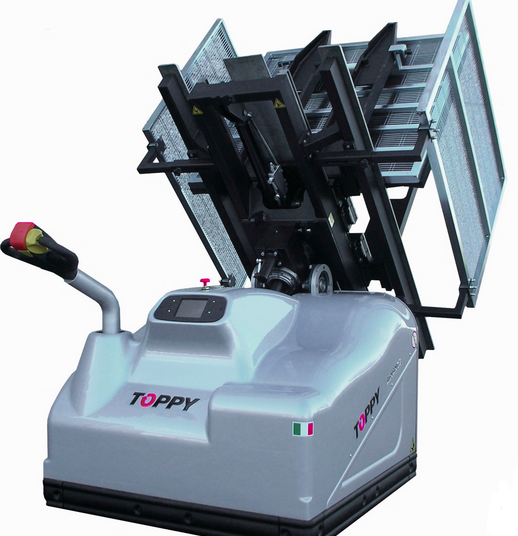
Mobile pallet turner for higher stacks
When you need to opt a pallet changer that is capable of lifting and turning loads a...
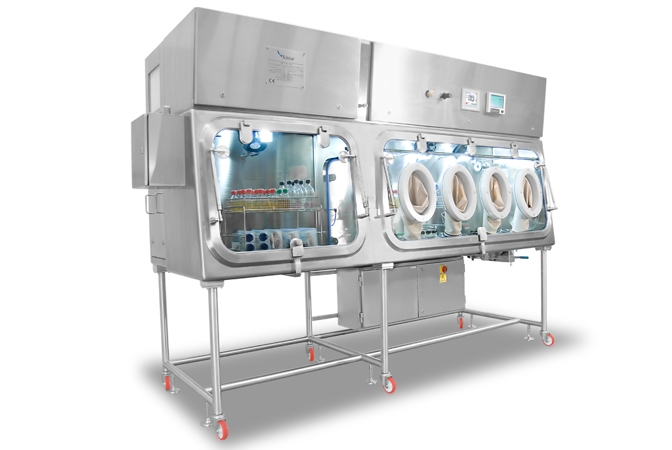
Sterility test isolators
Designed to avoid this risk and protect the product from both the process and externally generated f...
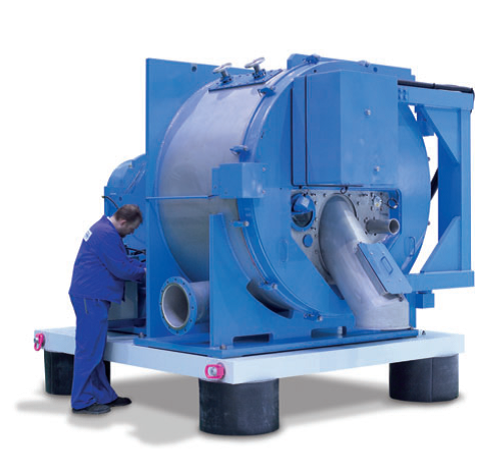
Horizontal chemical scraper centrifuge
For slurries difficult to discharge, a scraper can improve process reliability, effi...
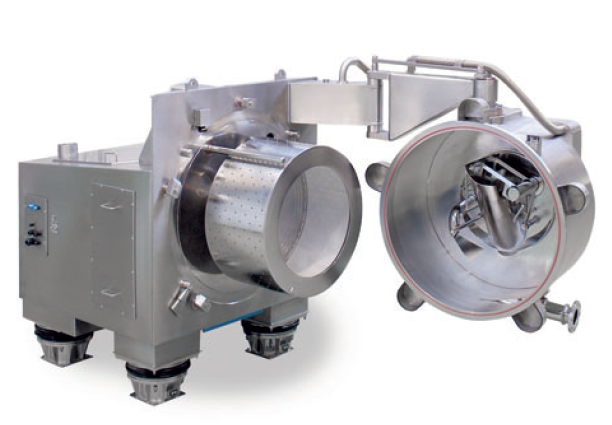
Horizontal pharmaceutical scraper centrifuge
For slurries difficult to discharge, a scraper can improve process reliabilit...
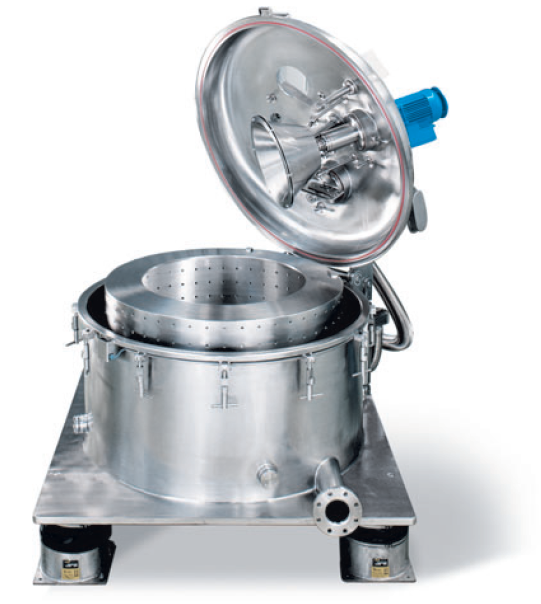
Vertical scraper centrifuges
Vertical Bottom discharge Centrifuges work discontinuously, discharging the solids to the botto...
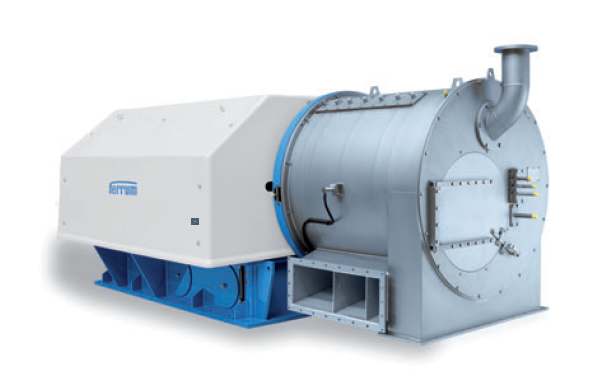
Pusher centrifuge
Pusher centrifuges are continuously operating filter centrifuges and can have several basket stages dependi...
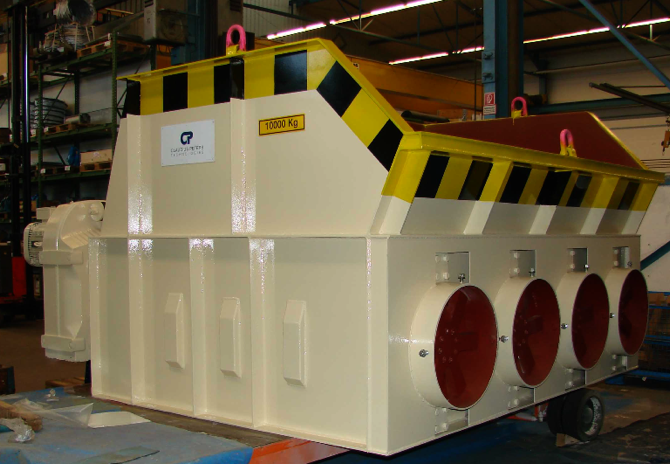
Reclaim crusher
Waste products and rejected materials are inevitably generated from any gypsum products manufacturing process....
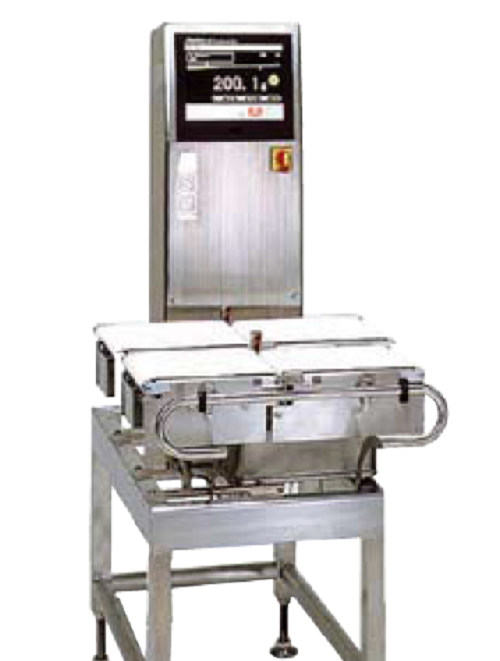
Checkweigher for stand-up pouches
When working with several lines of stand-up pouches, you can benefit from controlling the...