Flexible contained charging for split butterfly valves
Poly bottles with split butterfly valves are often used to transfer powders from bulk containment equipment to the point of use while avoiding cross contamination. However, rigid bottles present several challenges which hinder production and reduce process efficiency. Experienced biopharmaceutical manufacturers know that equipment designed for general industry use often falls short and rigid containment and transfer solutions for the biotech industry are often awkward and inefficient. Producers that embrace flexible solutions designed specifically for the challenges of our industry will find an advantage over competitors.
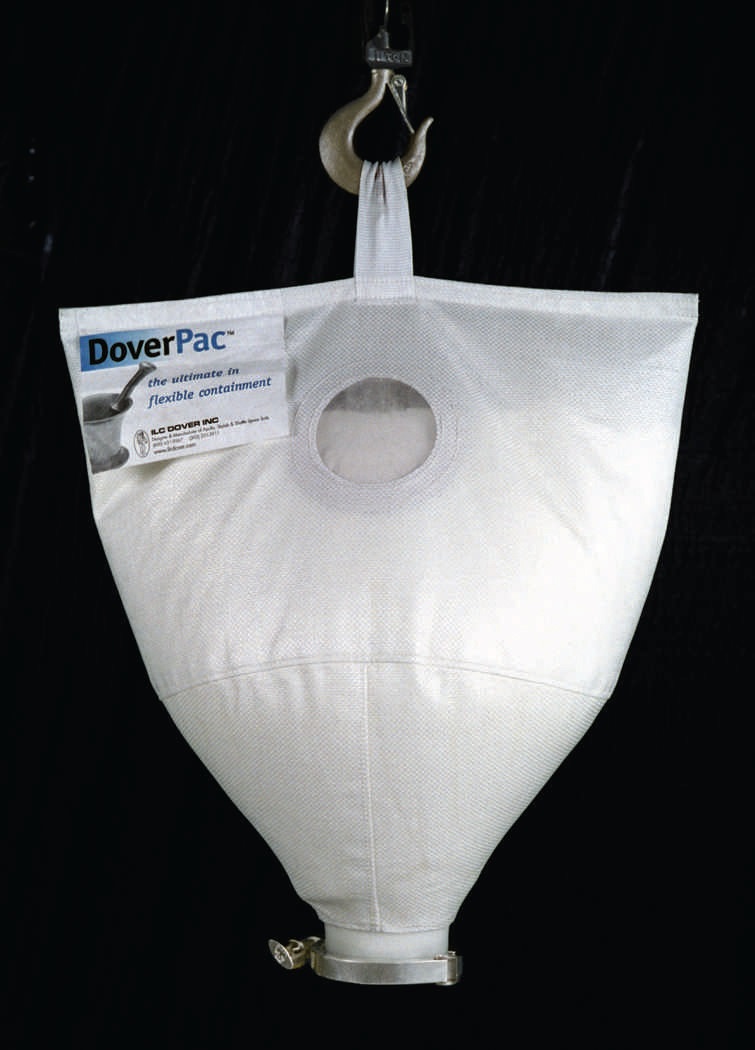
A powder transfer solution for split butterfly valve operations with excellent product recovery and no required cleaning
ILC Dover is an industry leader in contained material handling solutions for high-tech manufacturers and end users including NASA. The company’s Standard Doverpac SF system is a powder transfer solution for split butterfly valve operations that replaces the polybottles traditionally used in these applications. The system consists of a rugged plastic bag with a split butterfly valve type adapter on the bag’s sole opening. After interfacing with your equipment via the split butterfly valve, the bag is filled and removed and its side of the valve adapter closed. Its contents are then carried to the next point of use and emptied from the bag via the split butterfly valve interface. The bag is one time use and disposed of after emptying—avoiding the need for cleaning and cleaning validation. New bags are stored in a tightly folded package—reducing the storage space required when compared to poly-bottles. The plastic bags are specifically designed for optimum powder flow and product recovery rates better than 99.5% can be achieved. A removable and reusable physical restraint consisting of a durable fabric sling with integrated lifting features is available for use to contain and protect the plastic bag during transfer operations. Use of the physical restraint allows exposure to pressure differentials up to .499 bar with a 2x safety factor.
Benefits
- Available in 5 to 100 Liter capacities
- Used for both charging and offloading applications
- Uses ArmorFlex film which is static dissipative and accepted by both the EU and FDA
- Excellent product recovery rate—95.5%
- No cleaning and minimal storage space is required