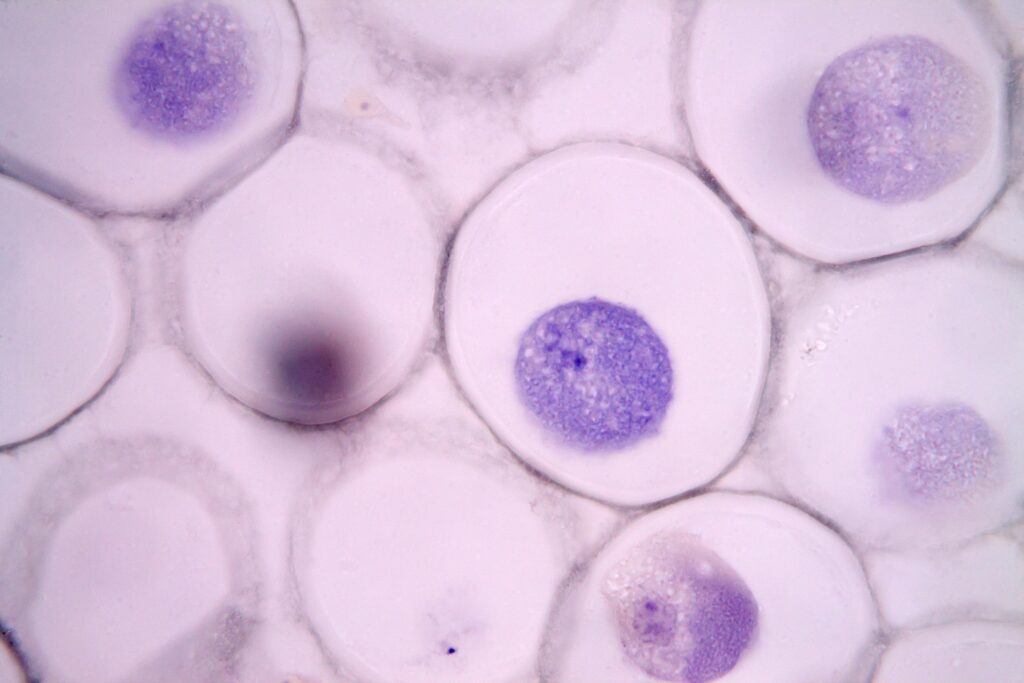
Biopharmaceutical Production Technology
Find innovative biopharmaceuticals equipment and connect directly with world-leading technology suppliers
Biopharmaceuticals are drugs in which the active substance is manufactured or extracted from biological origin materials. They are usually produced in bioreactors by plant cells, microbial cells, yeast cultures, or mammalian cells. Also known as biomanufacturing, they are used to either treat or diagnose and prevent a patient’s medical condition or disease. Biopharmaceuticals are typically complex macromolecules administered by injection or infusions, and examples include vaccines, serums, and insulin.
New solutions for making biopharmaceuticals
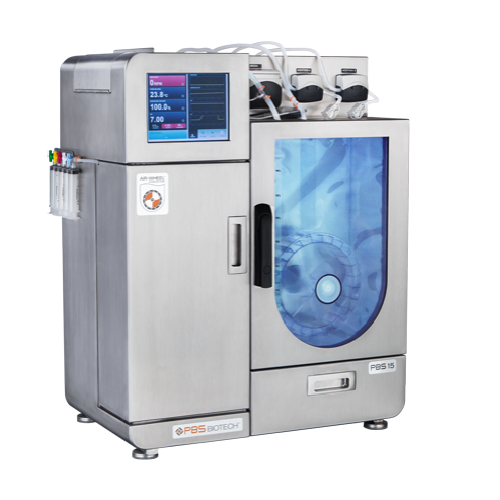
15l vertical-wheel bioreactor for cell therapy scale-up
Accelerate your cell therapy scale-up with a bioreactor that offe...

3d printer for high-precision microbioreactors
Achieve unprecedented precision in bioprocessing with a 3D printer capable ...
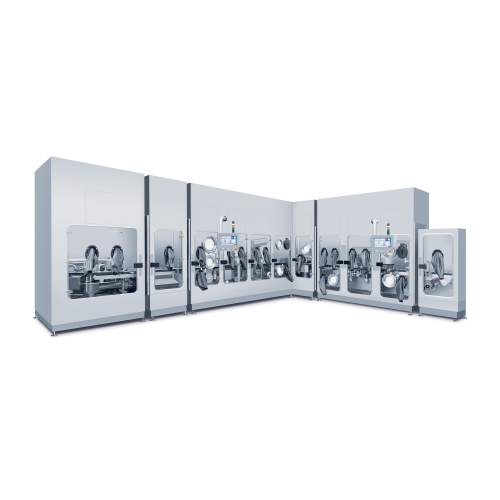
Aseptic filling and capping for vials and syringes
Ensure sterility and precision in vial and syringe filling with advanc...
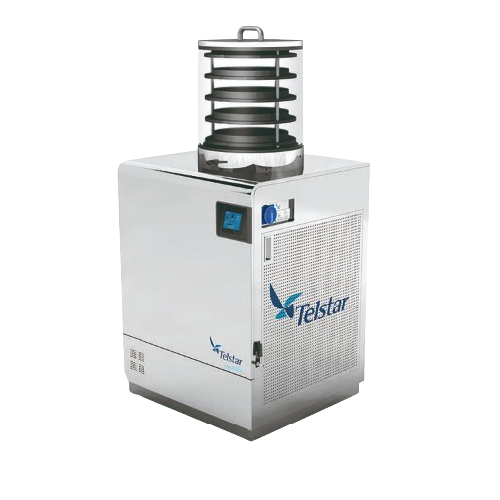
Basic research freeze dryer for biomedical applications
For laboratories seeking precise sample preservation, this bencht...
Select your biopharmaceuticals process
What are you making?
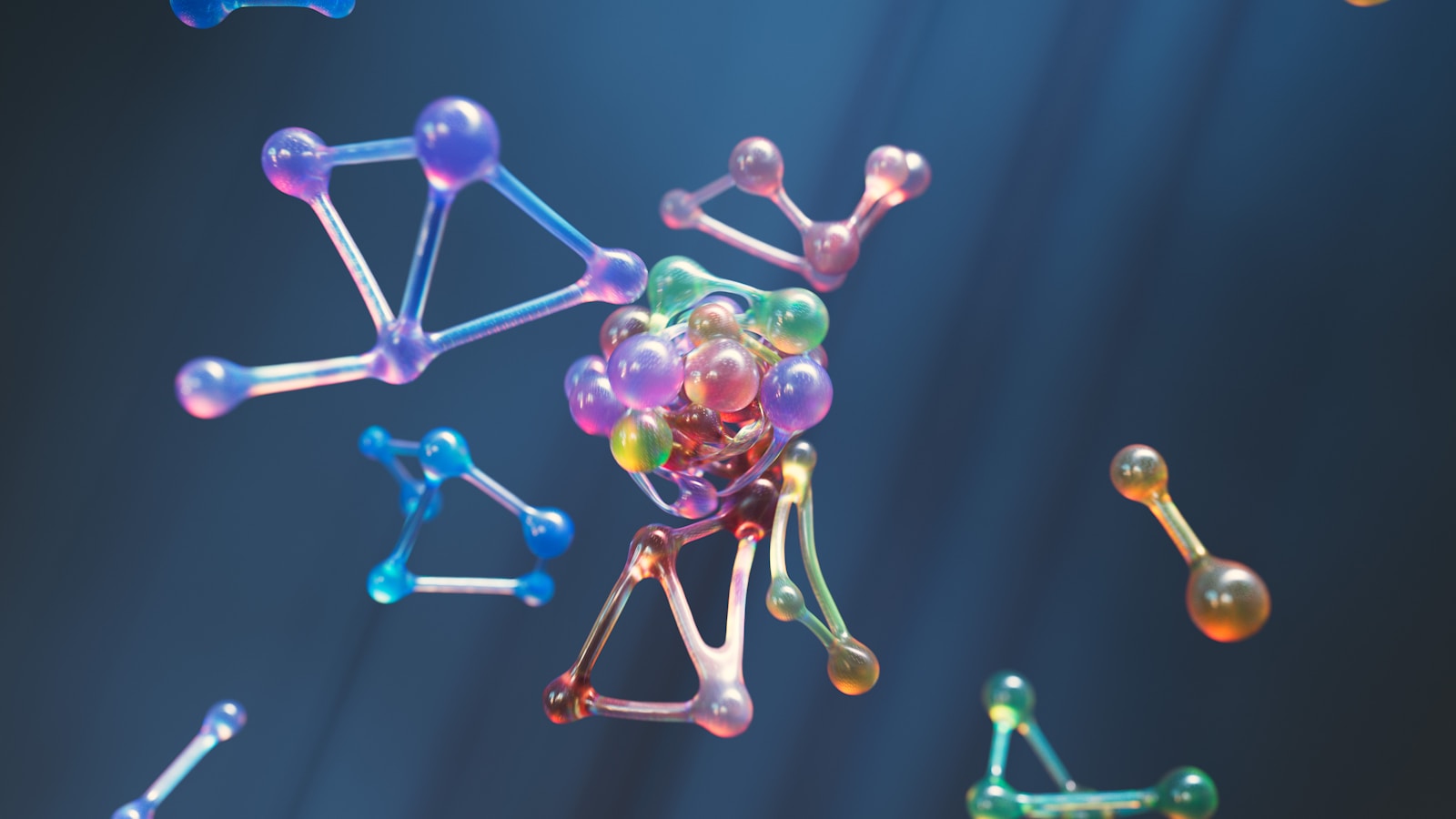
Biochemistry
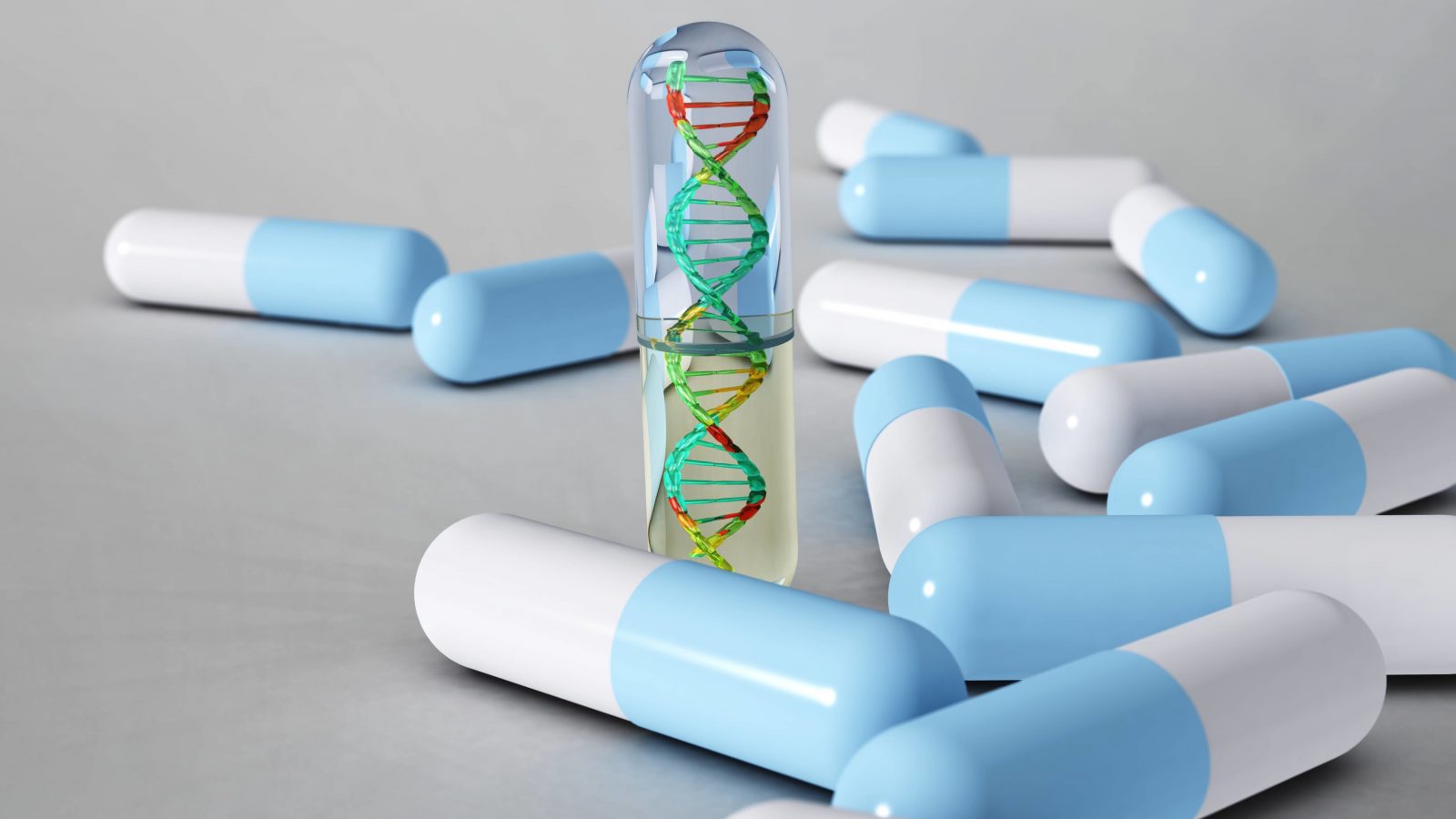
Biologic drug formulations
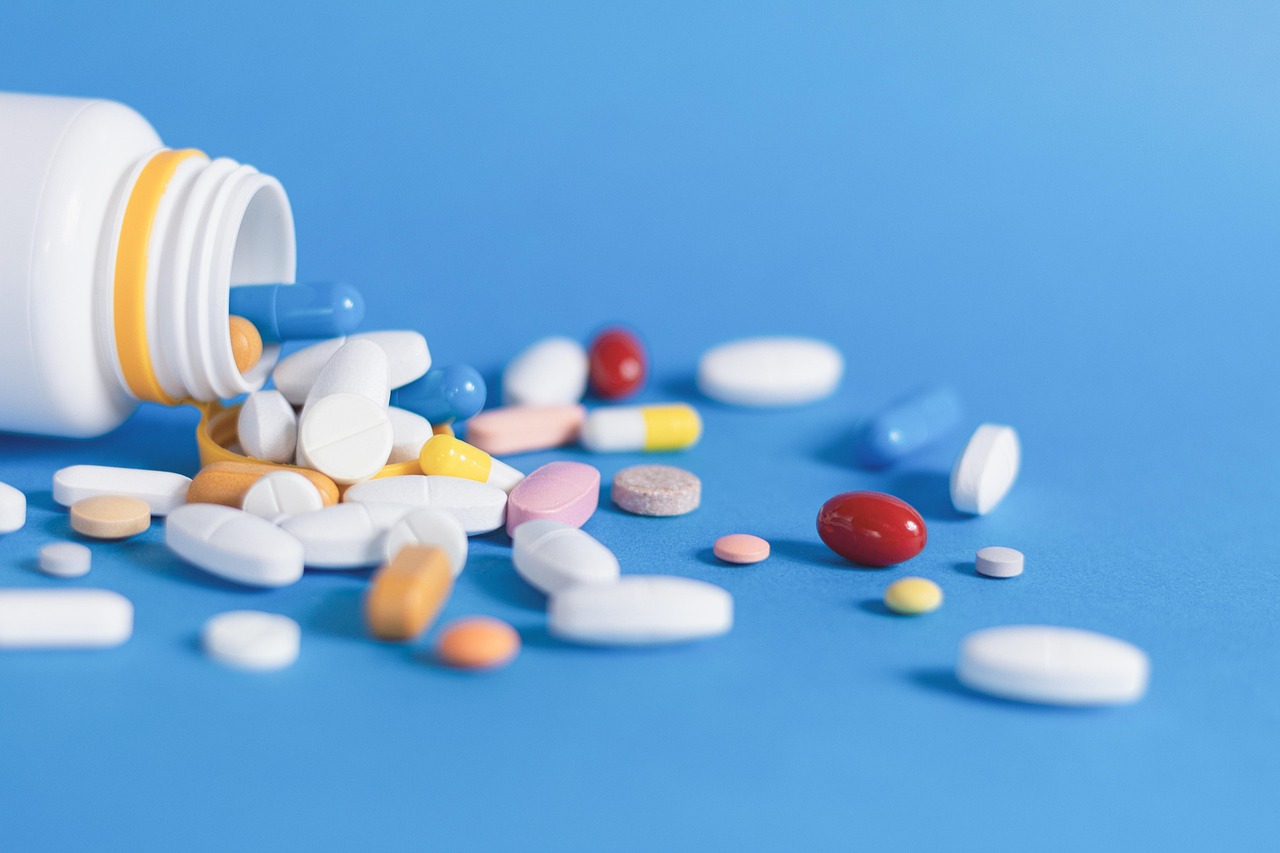
Bio-pharmaceuticals
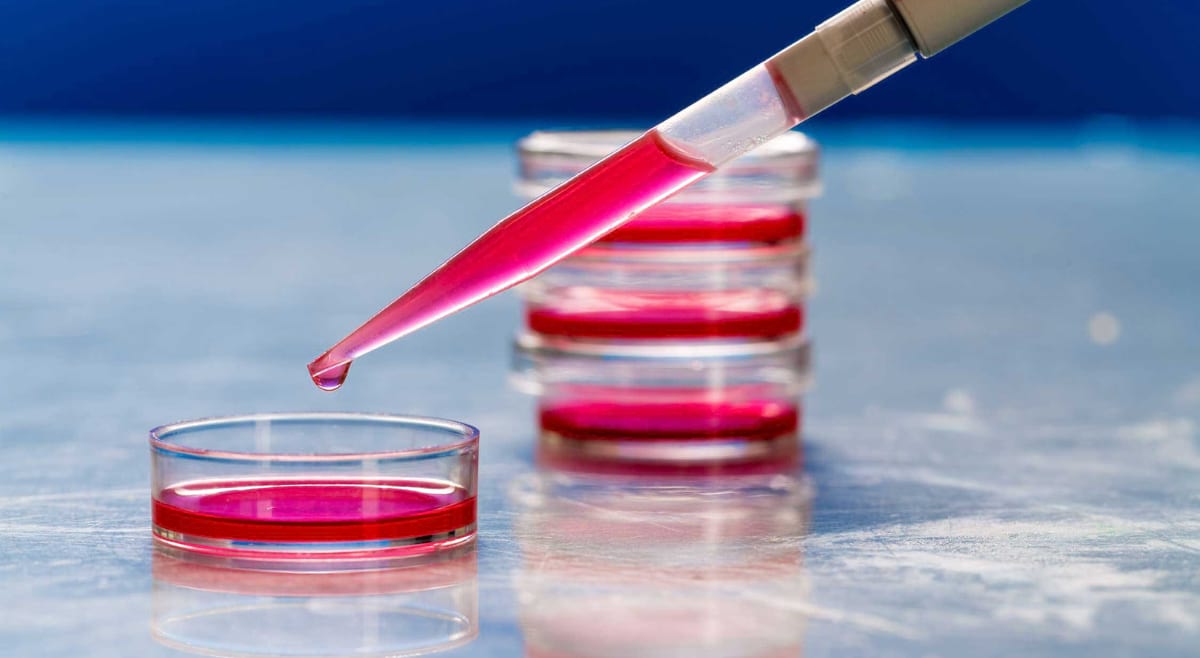
Cell culture media
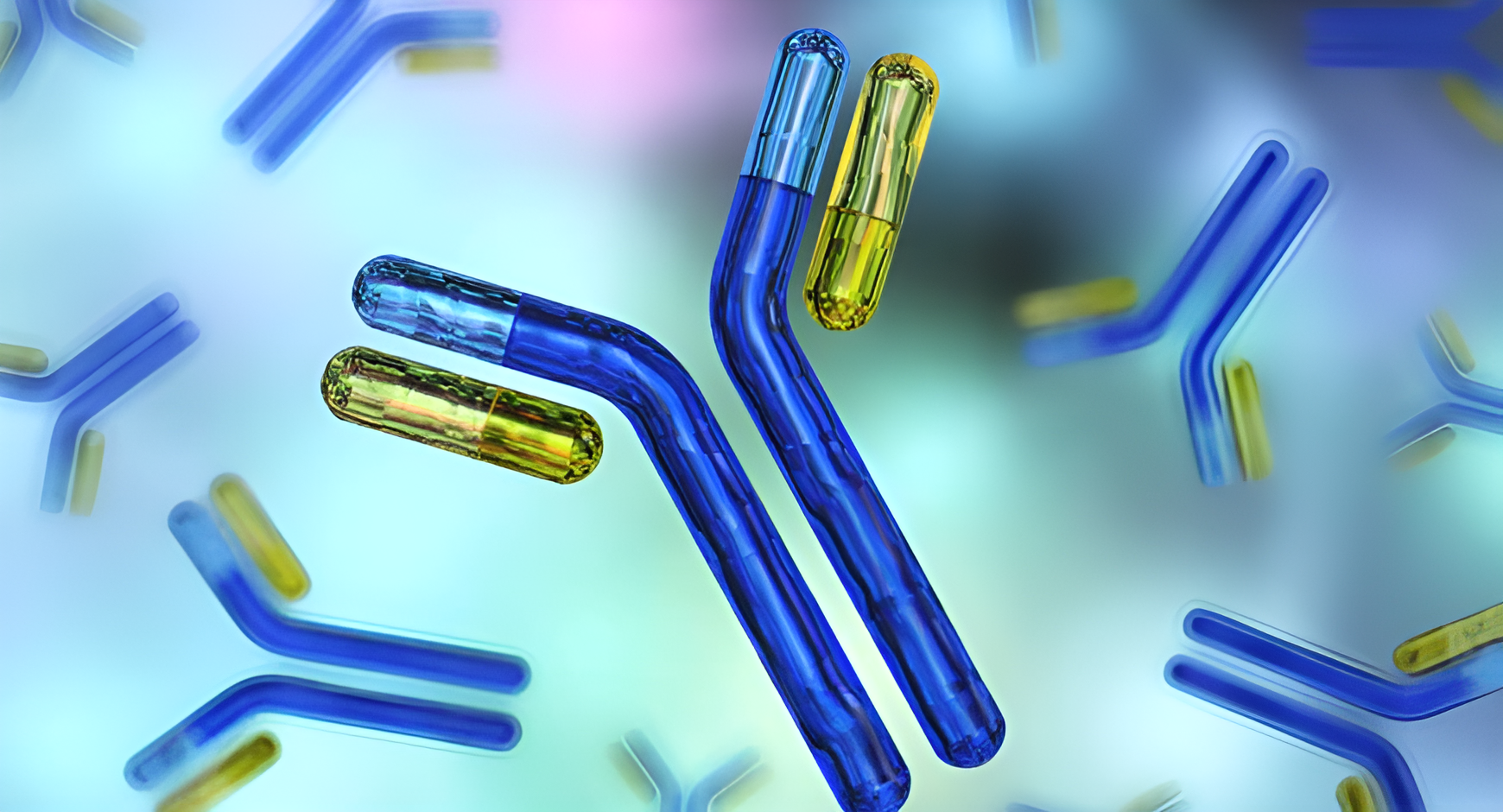
Biosimilars
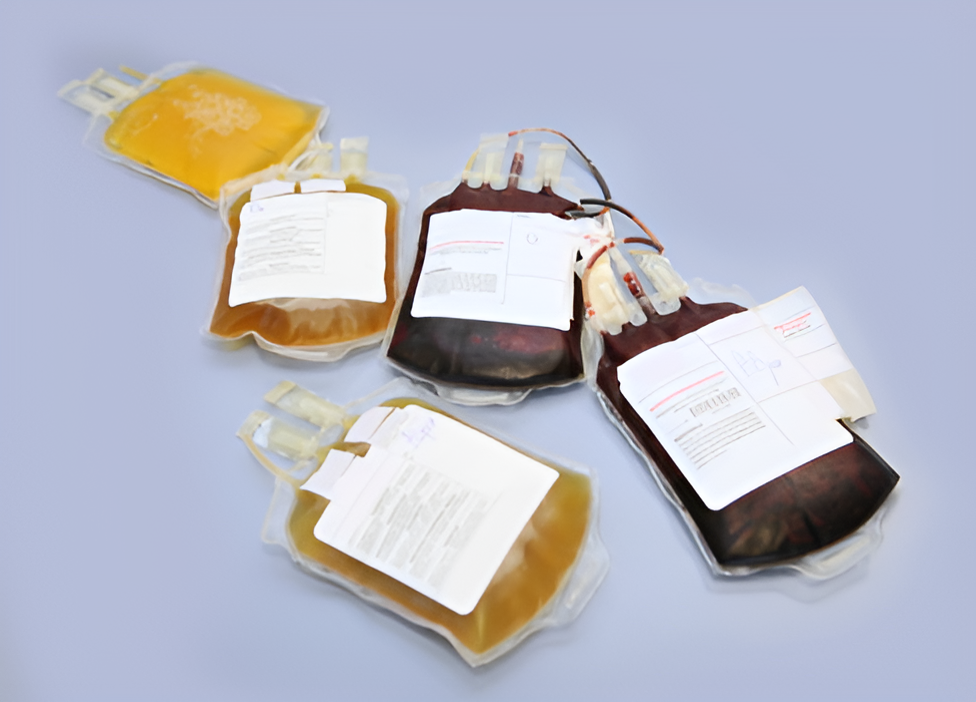
Blood plasma products
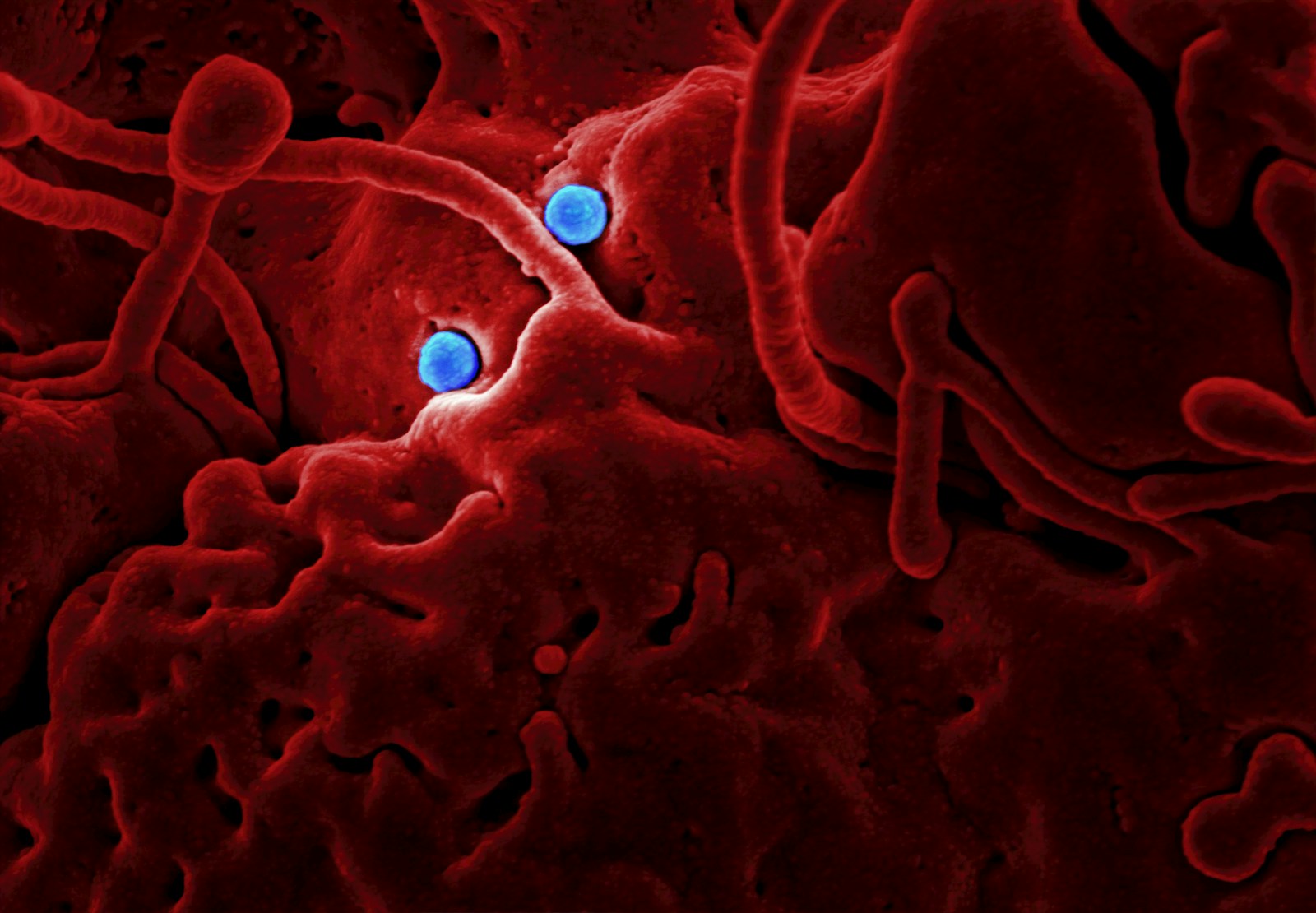
Therapeutic proteins

Stem cells
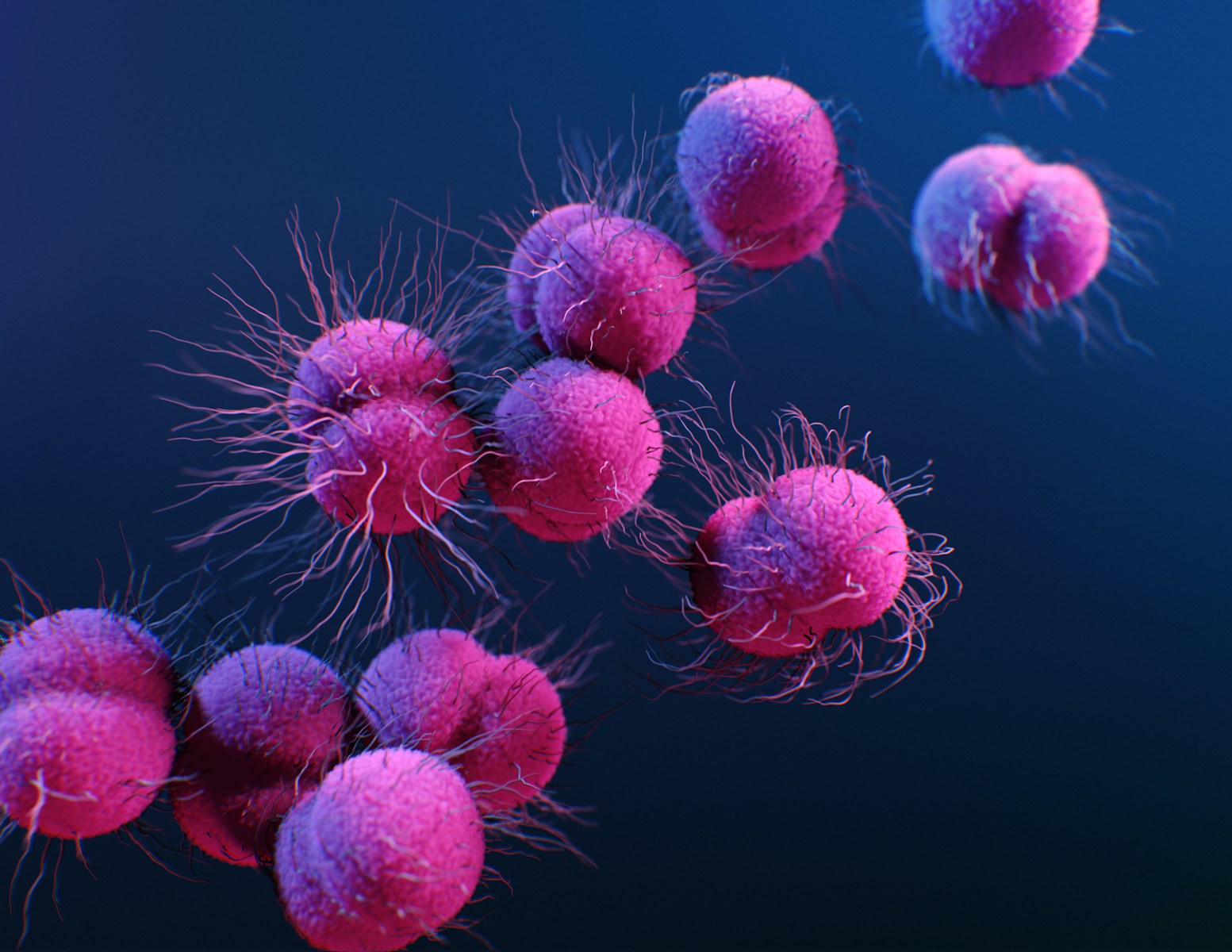
Stem cell therapies
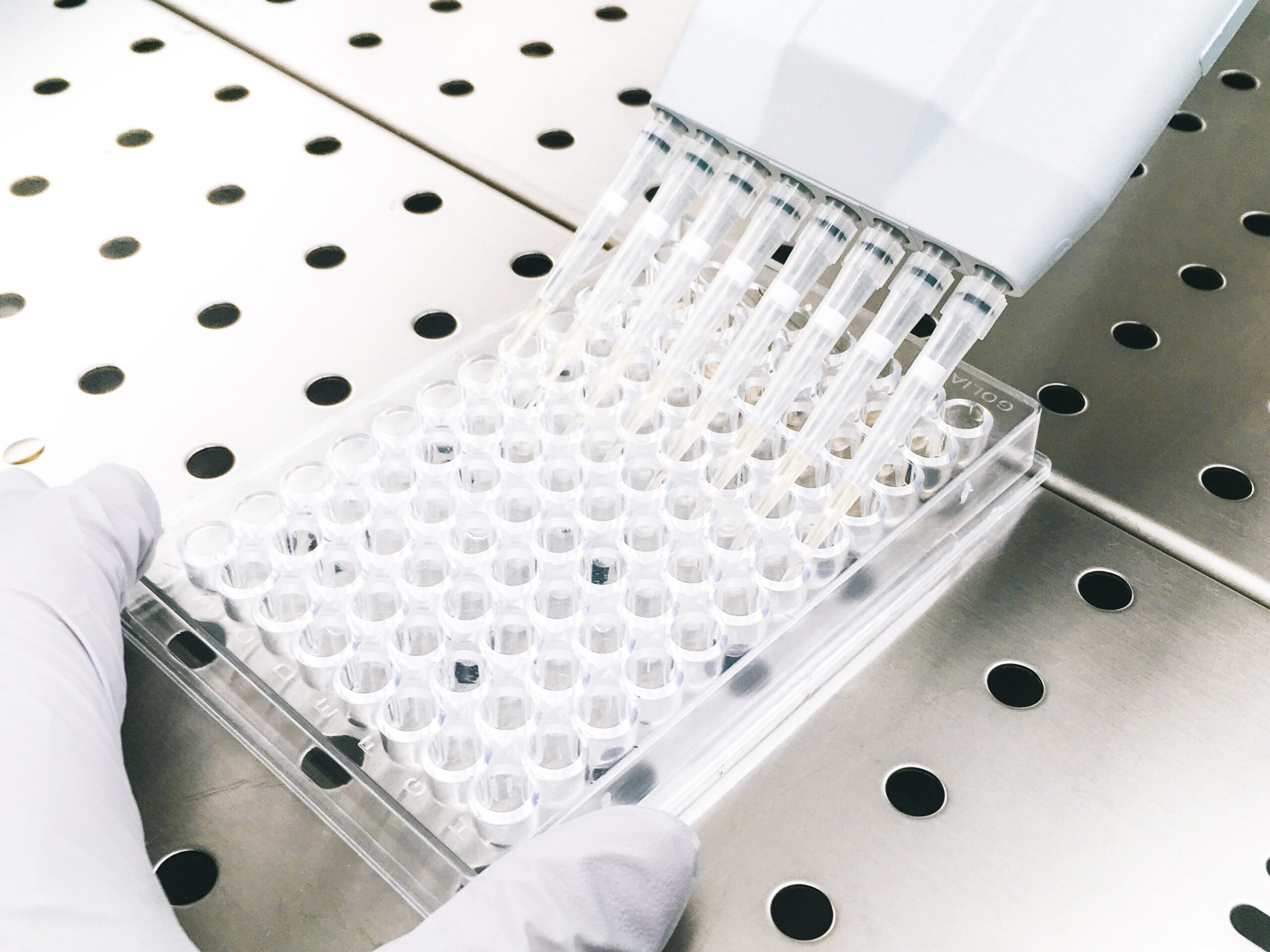
Recombinant proteins
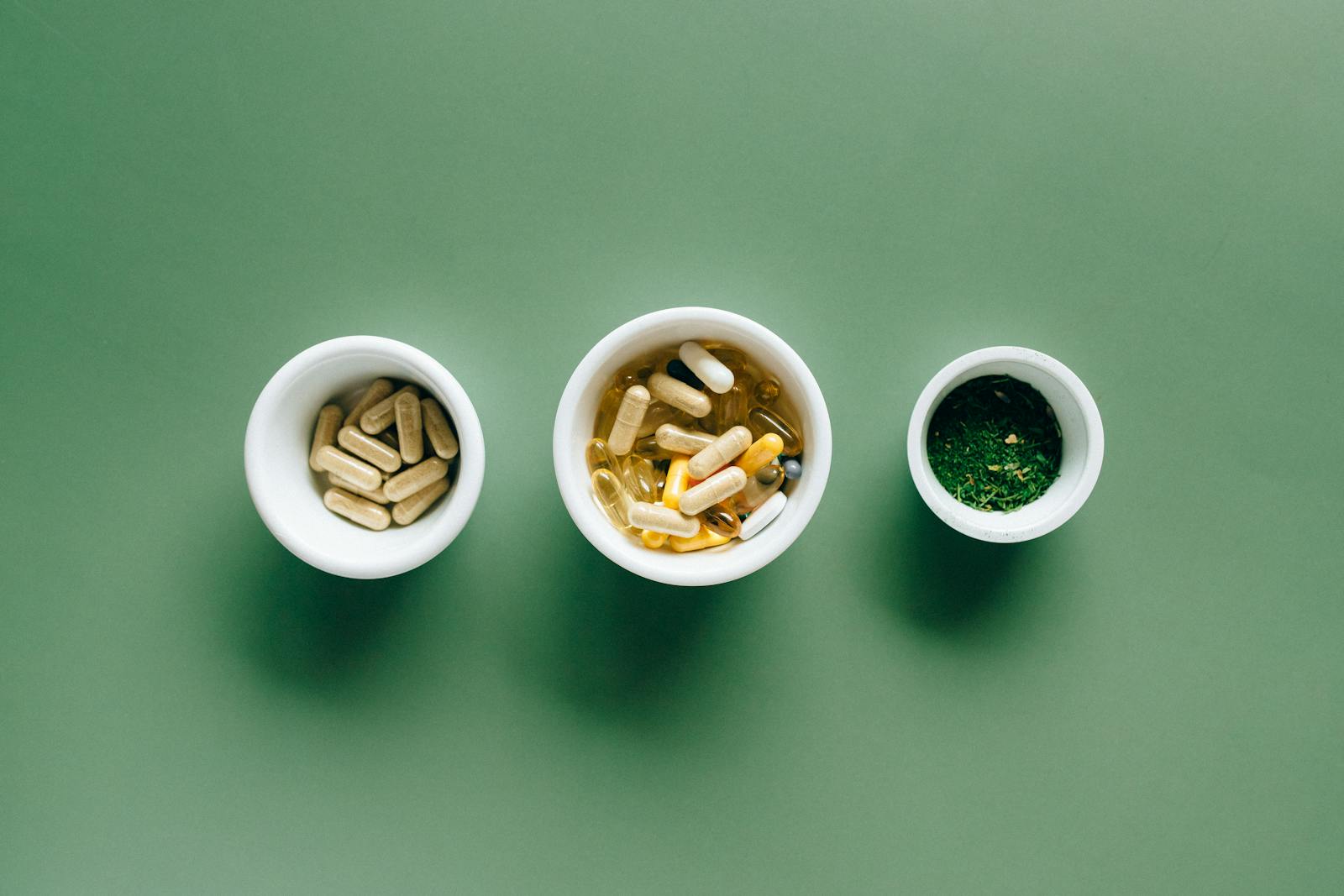
Protein-based drugs
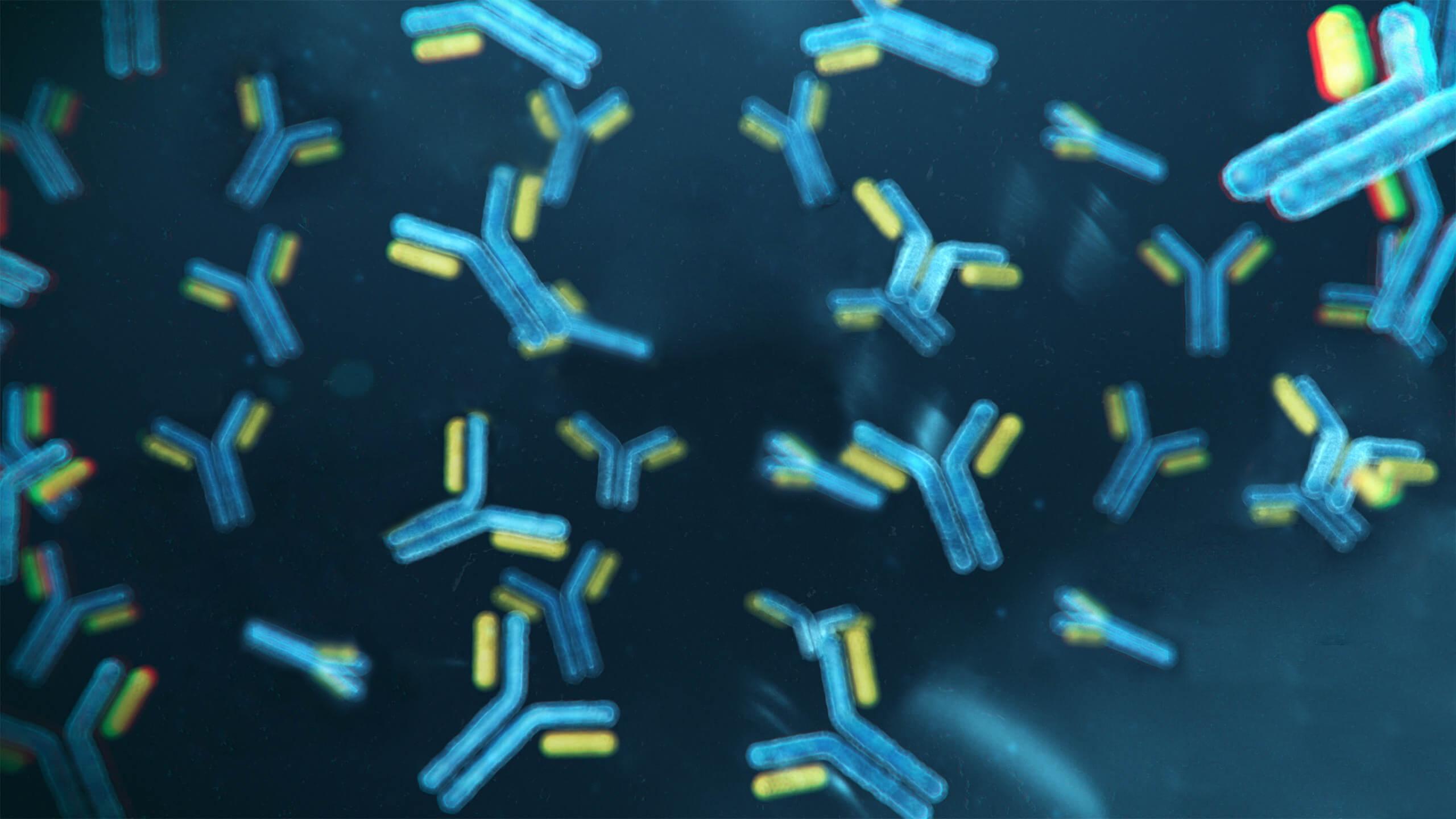
Protein therapeutics
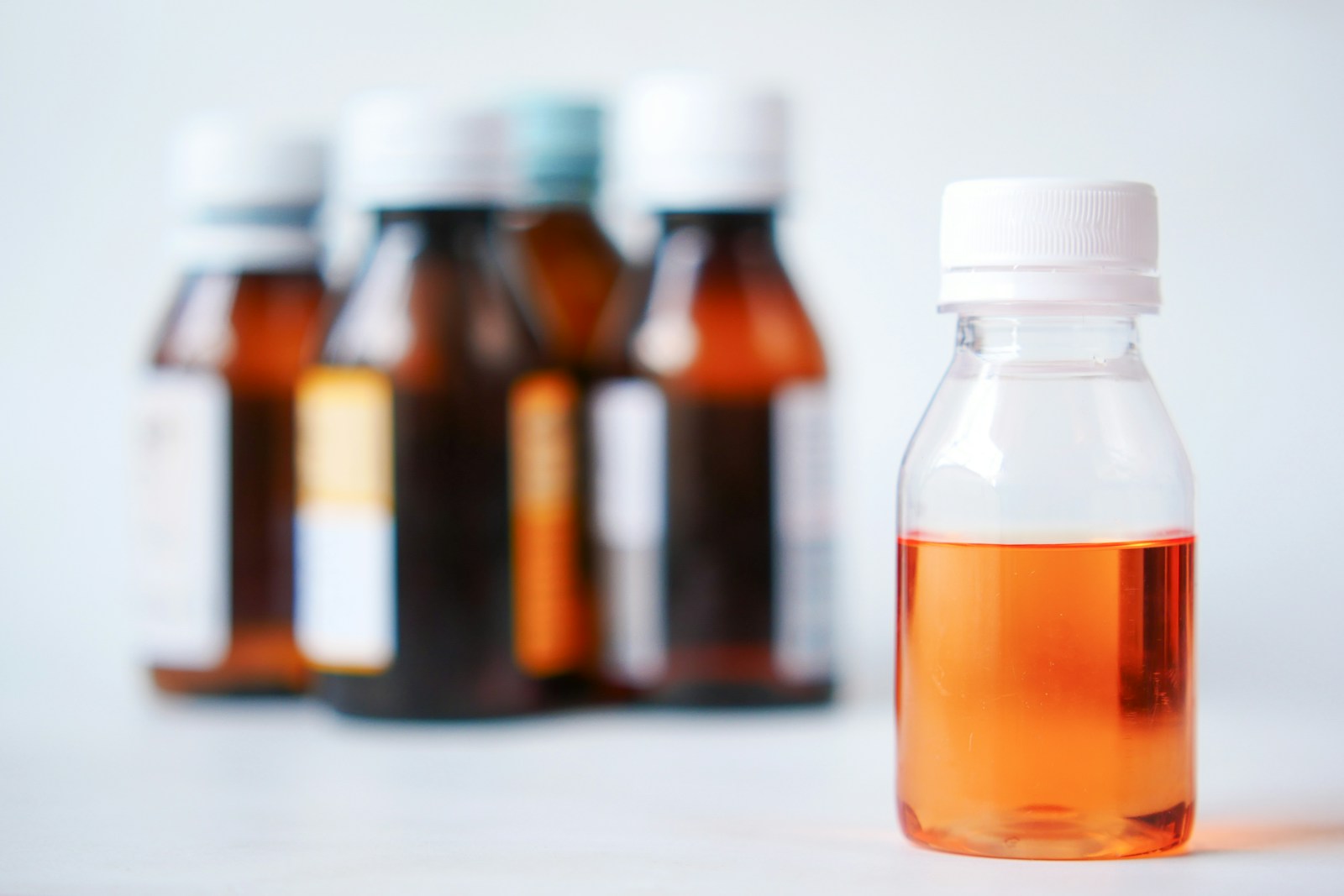
Rituximab
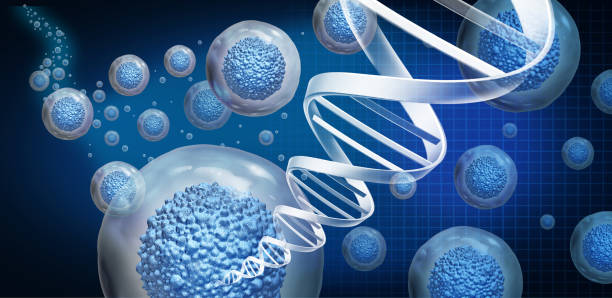
Regenerative medicine
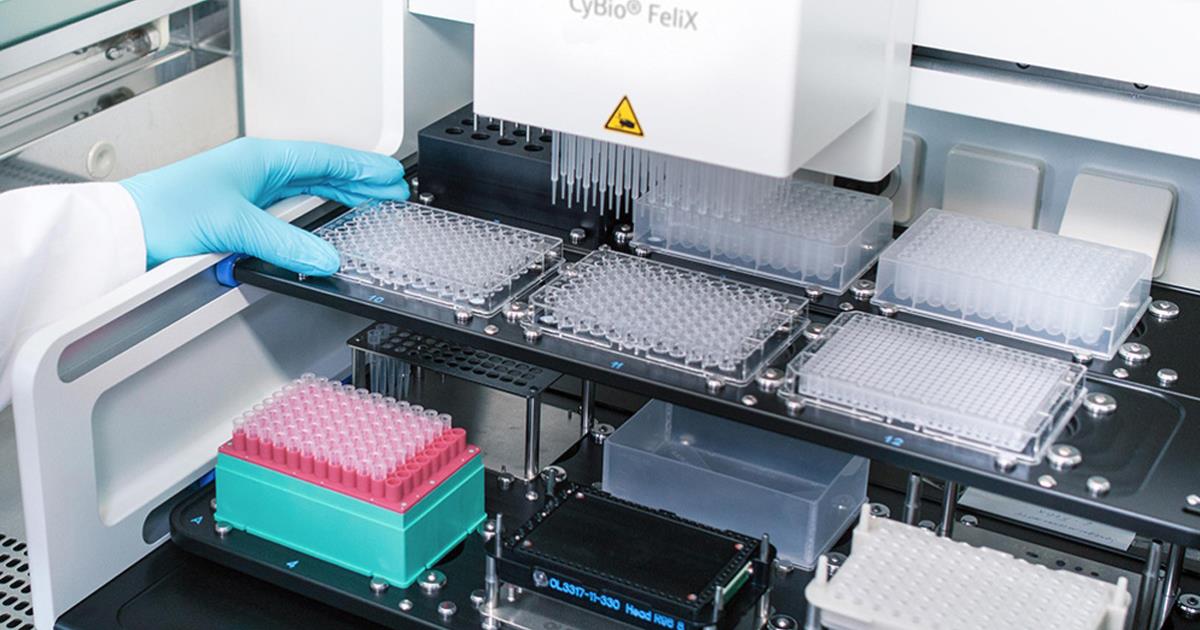
Plasmid dna
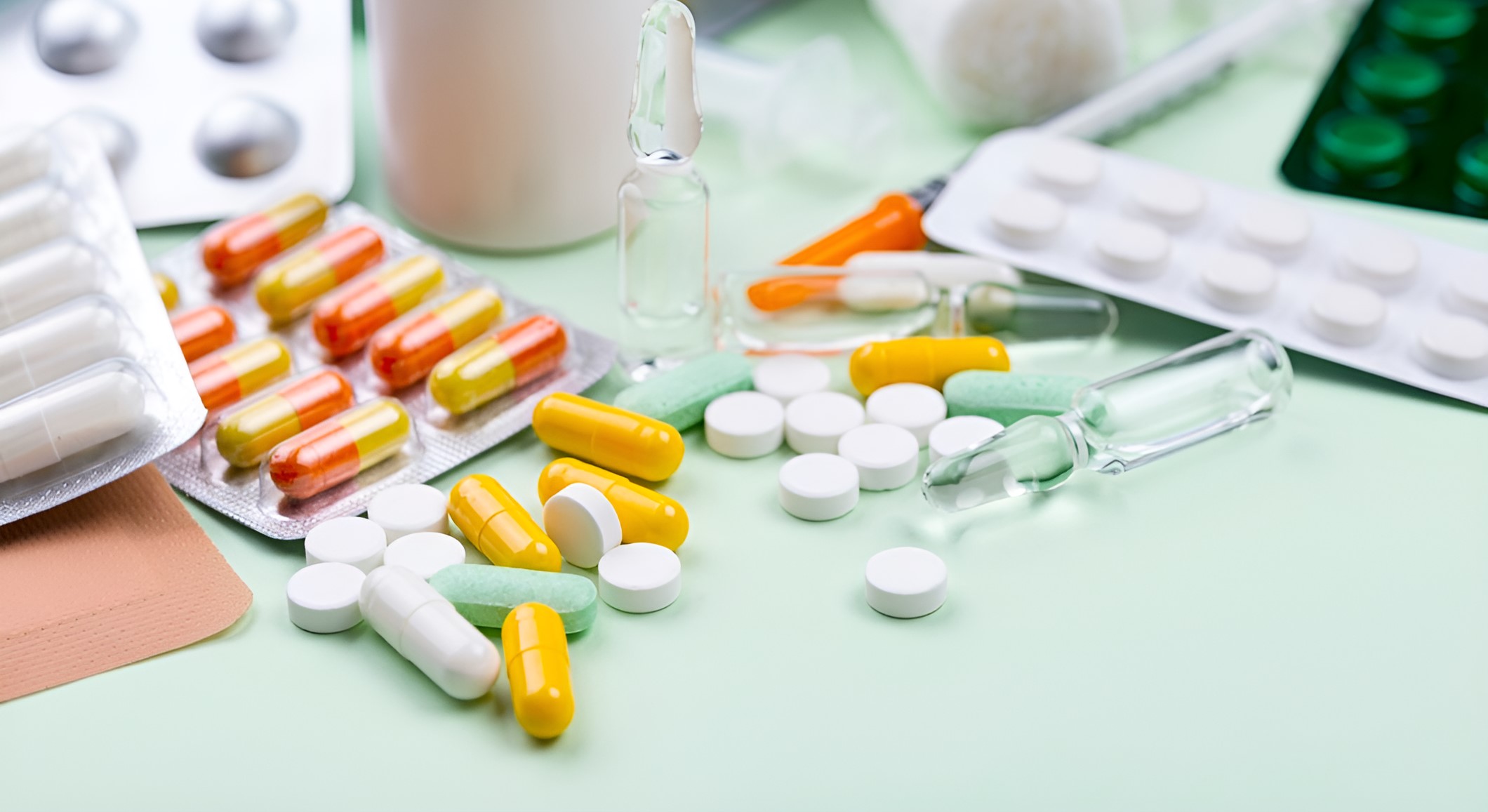
Personalized medicine
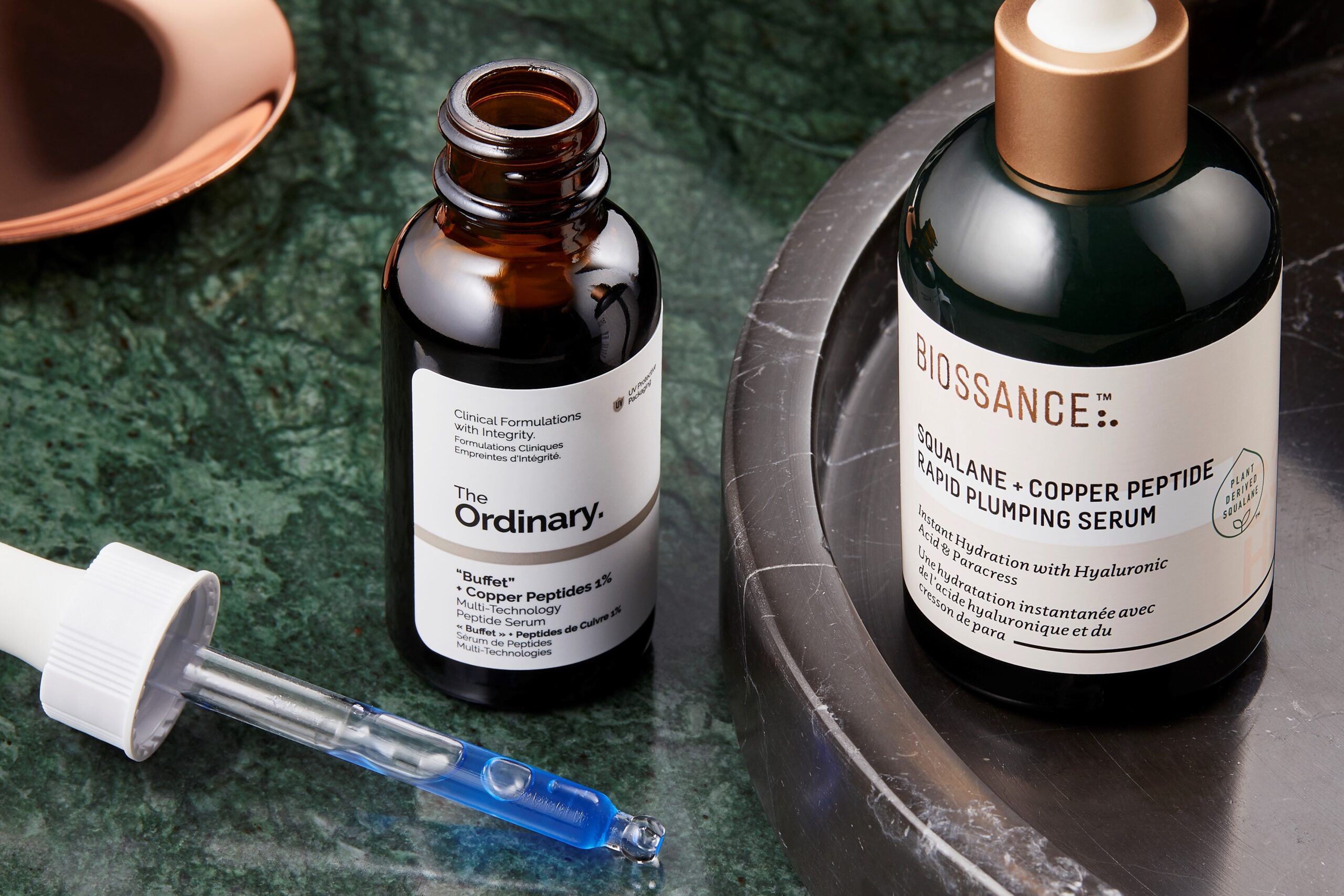
Peptides
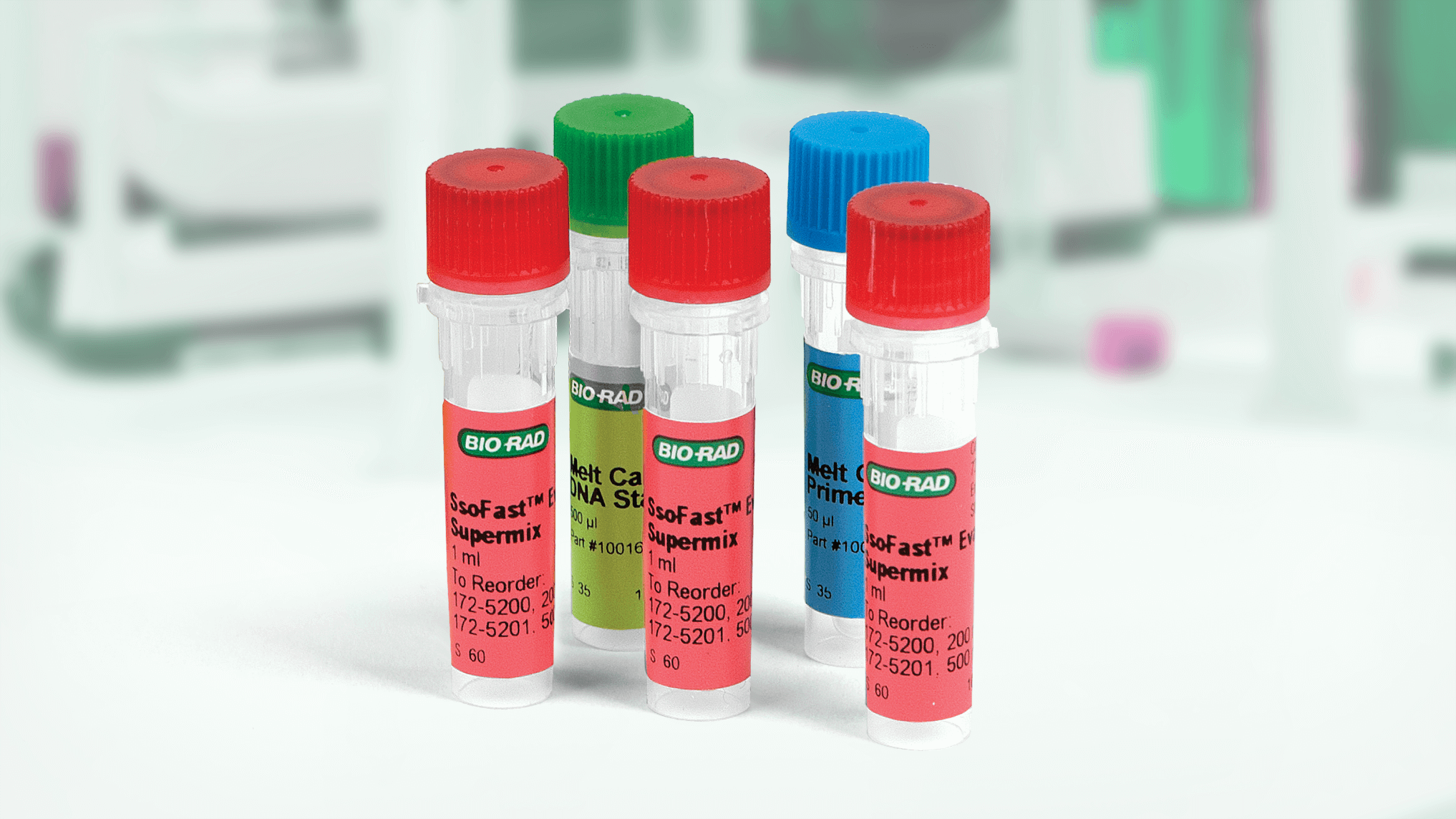
Pcr reagents
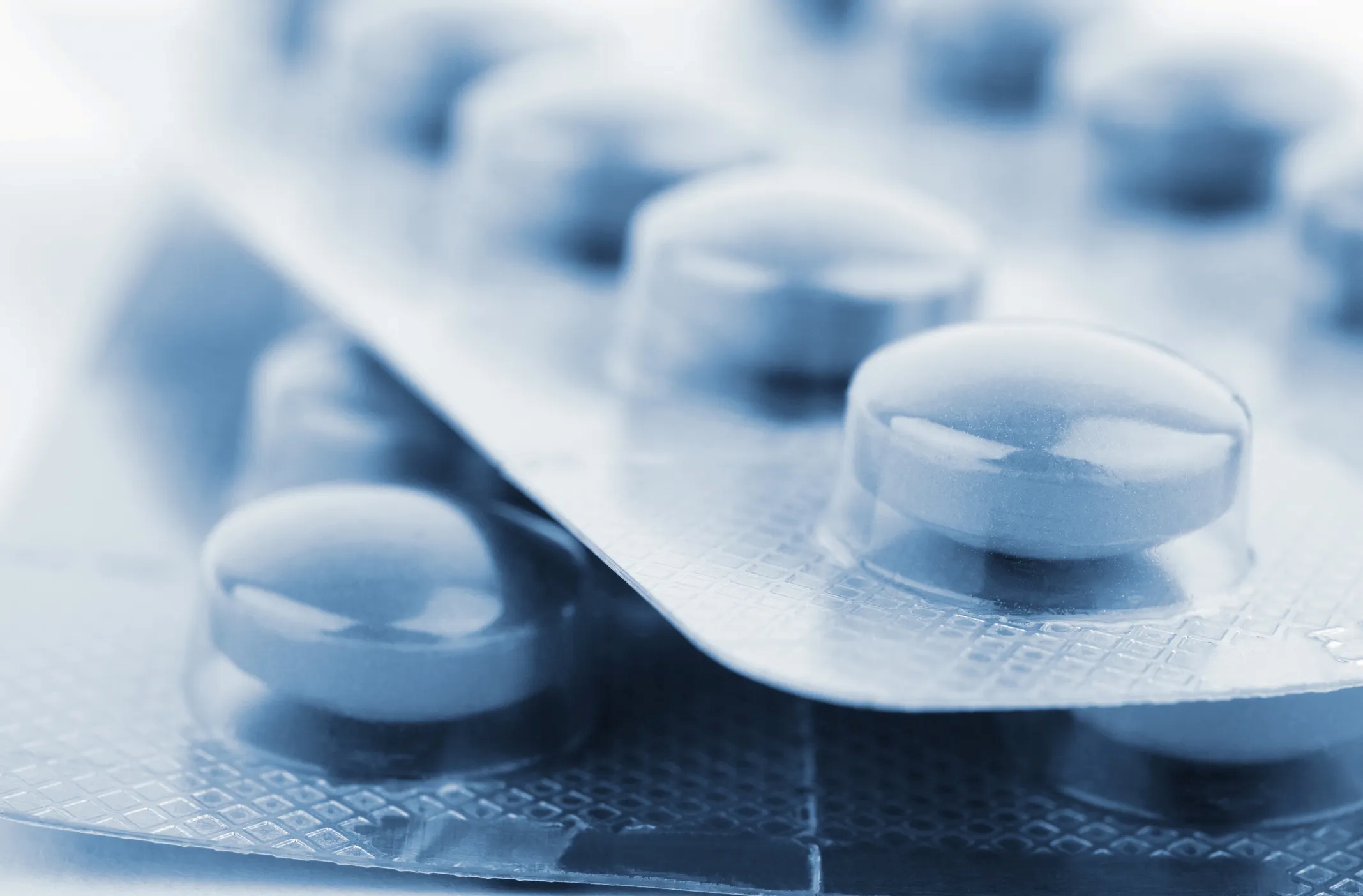
Oral vaccines
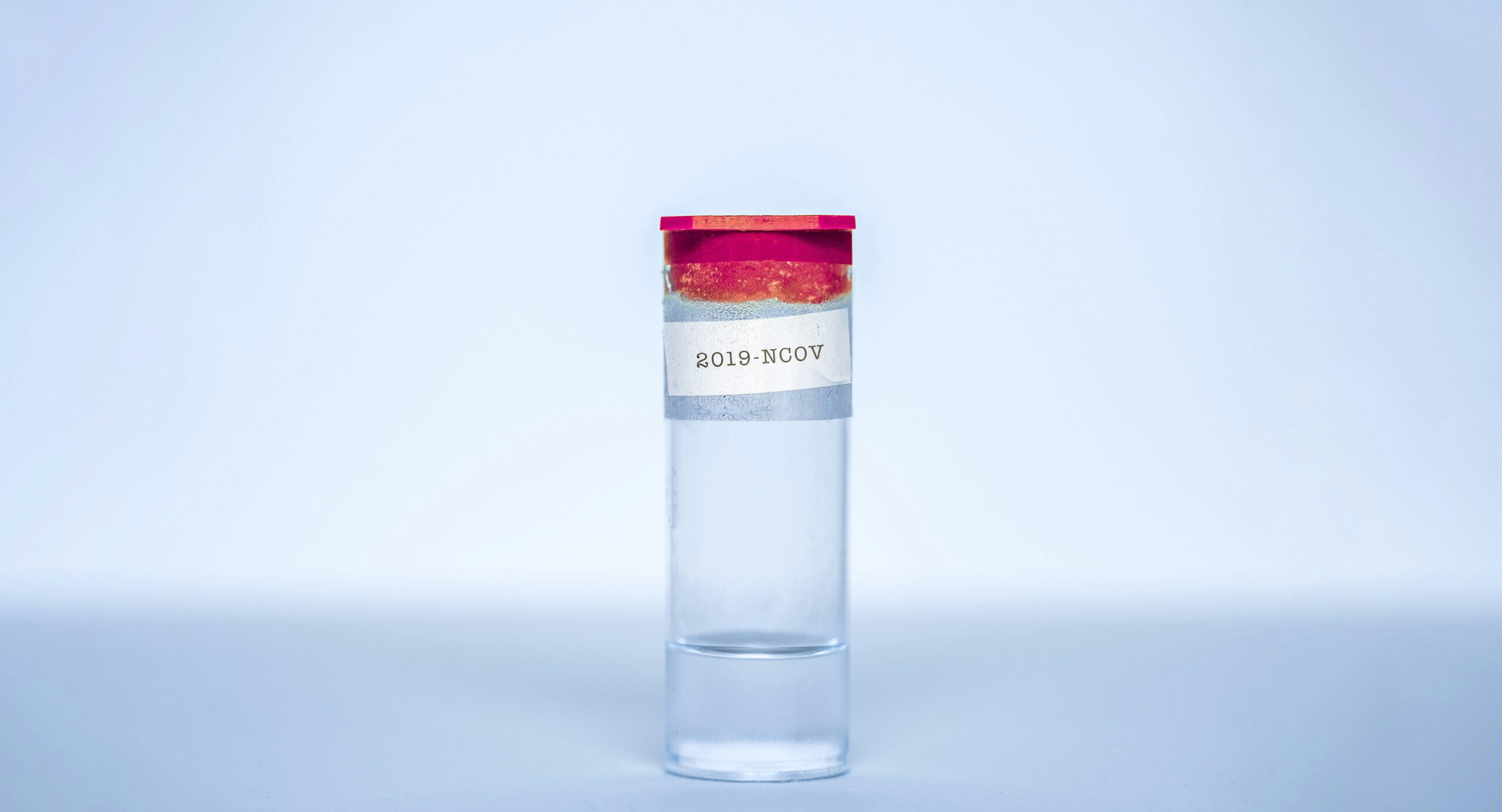
Lutetium-177
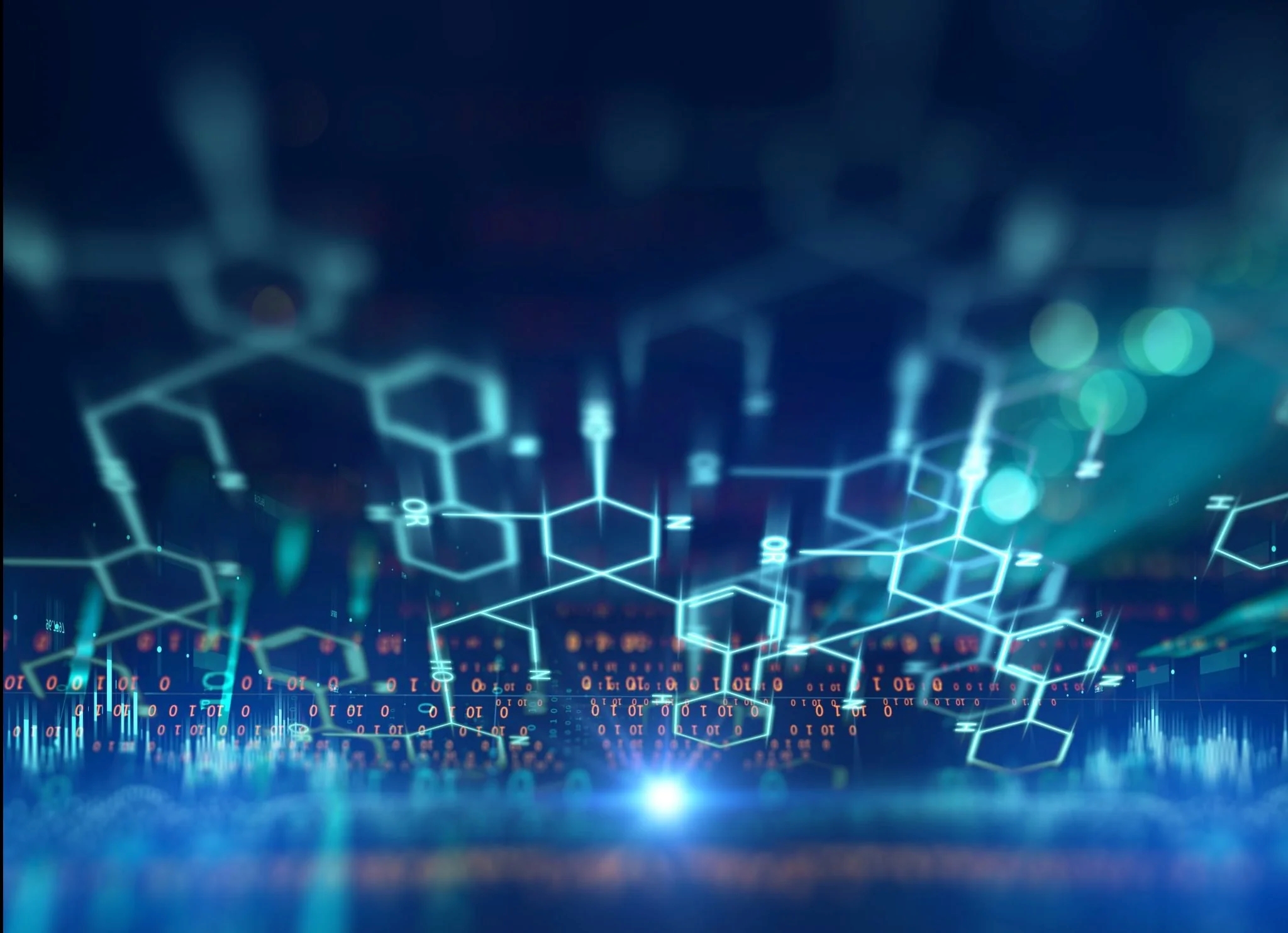
Next generation biologics
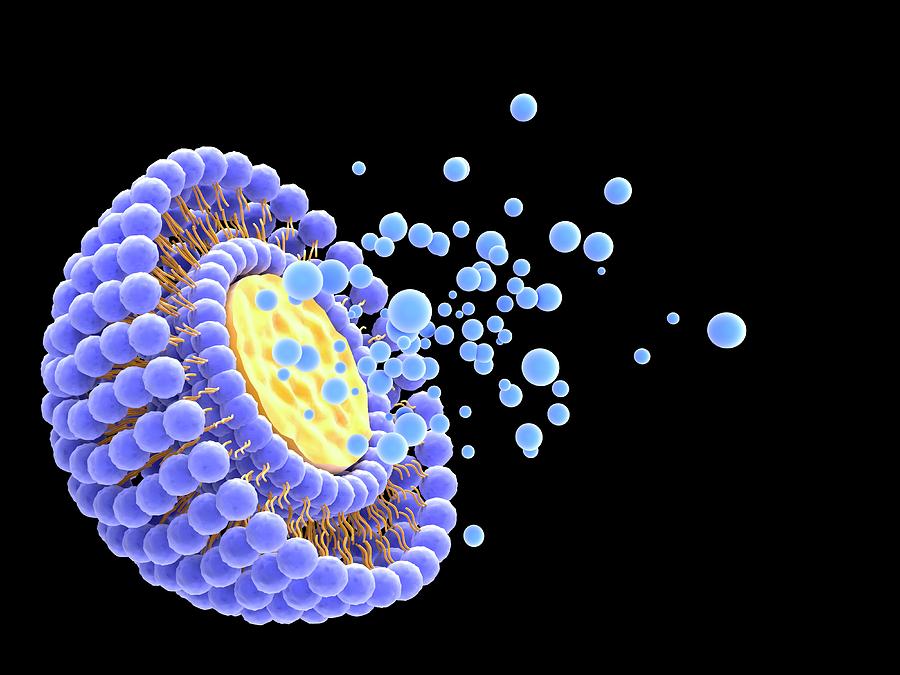
Nanosomes
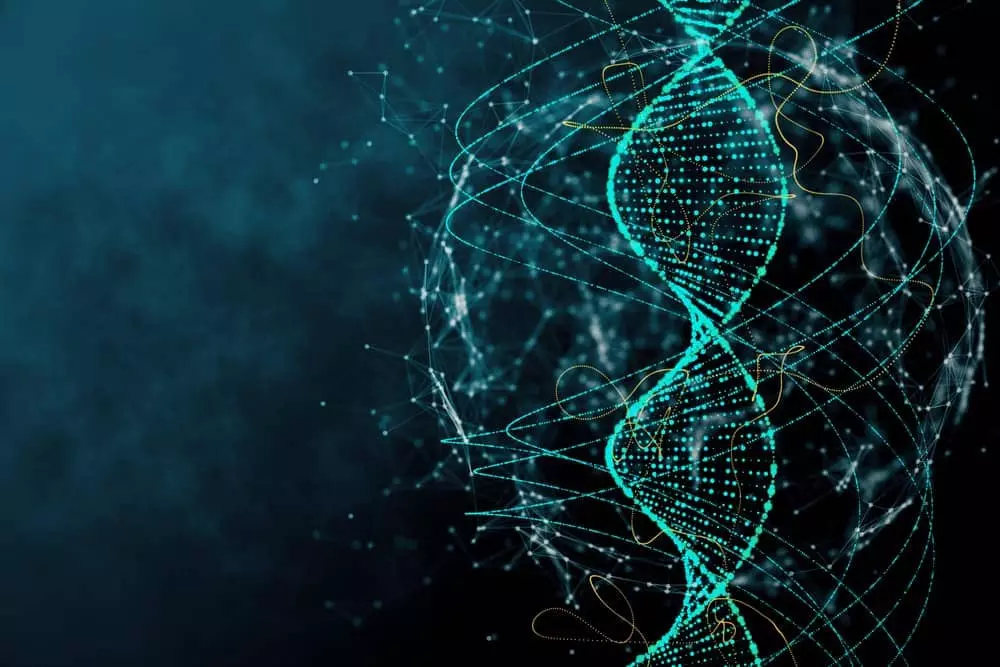
Life science
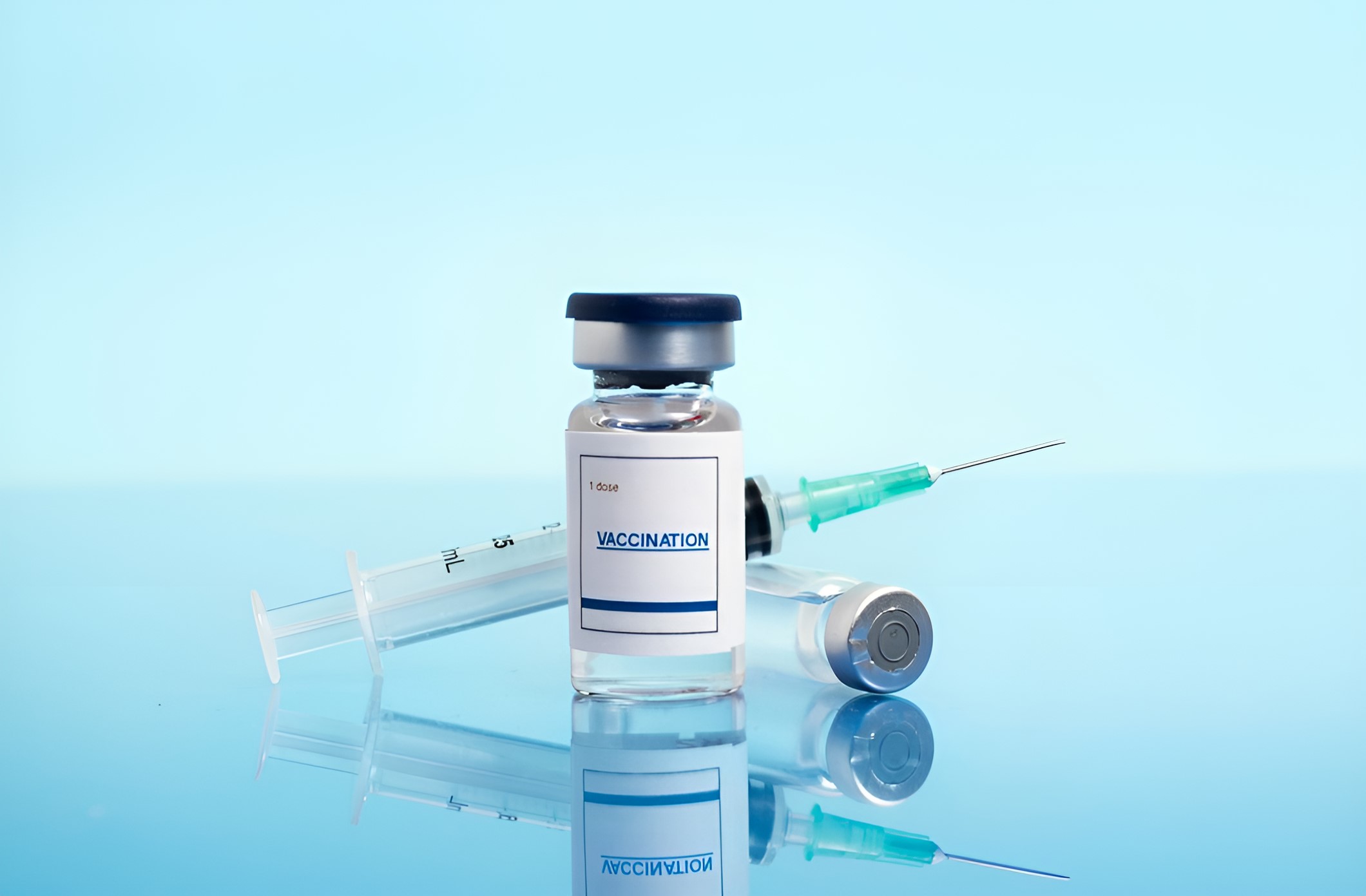
Mrna vaccines
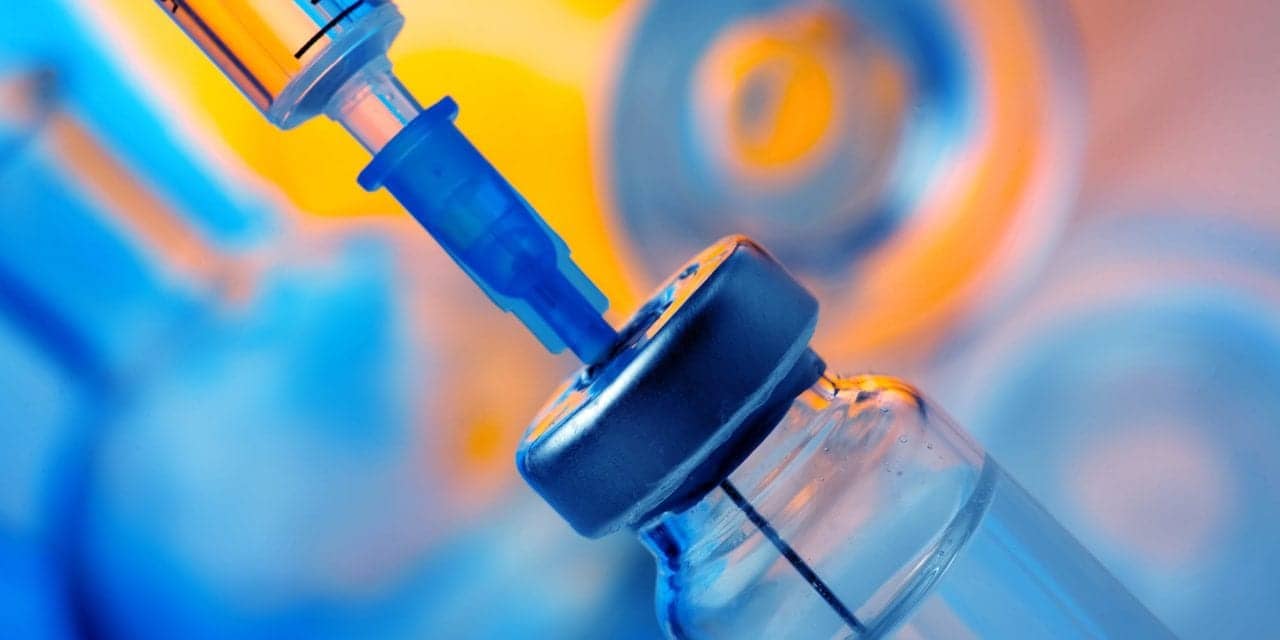
Monoclonal antibodies
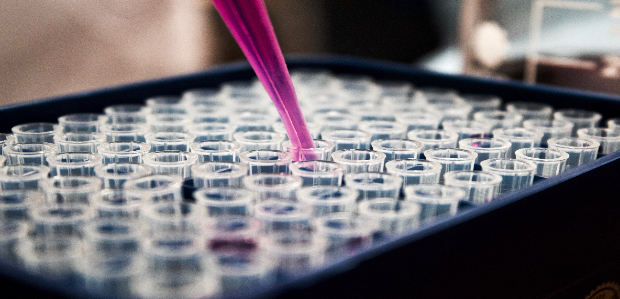
Molecular biology
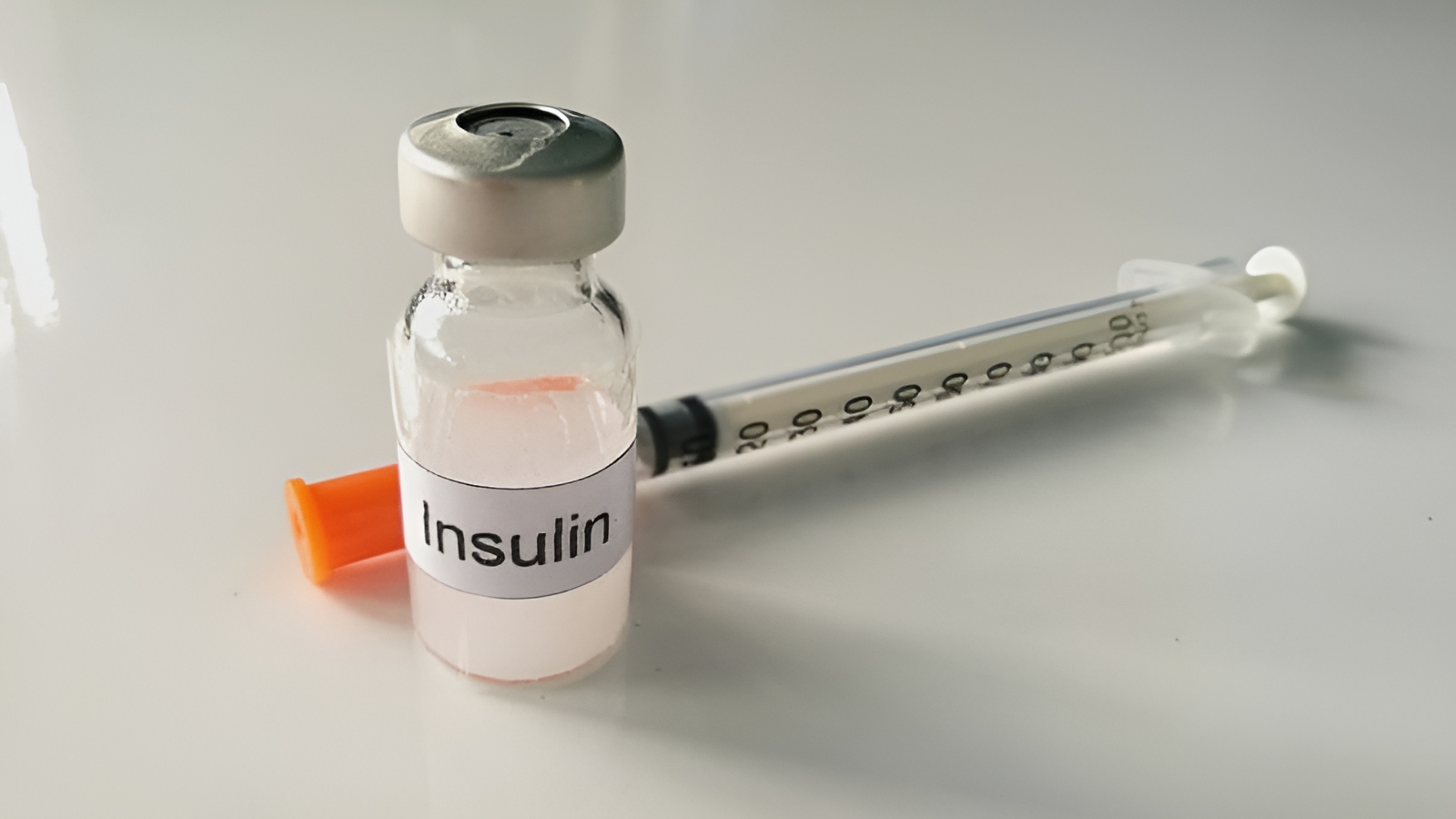
Insulin injections
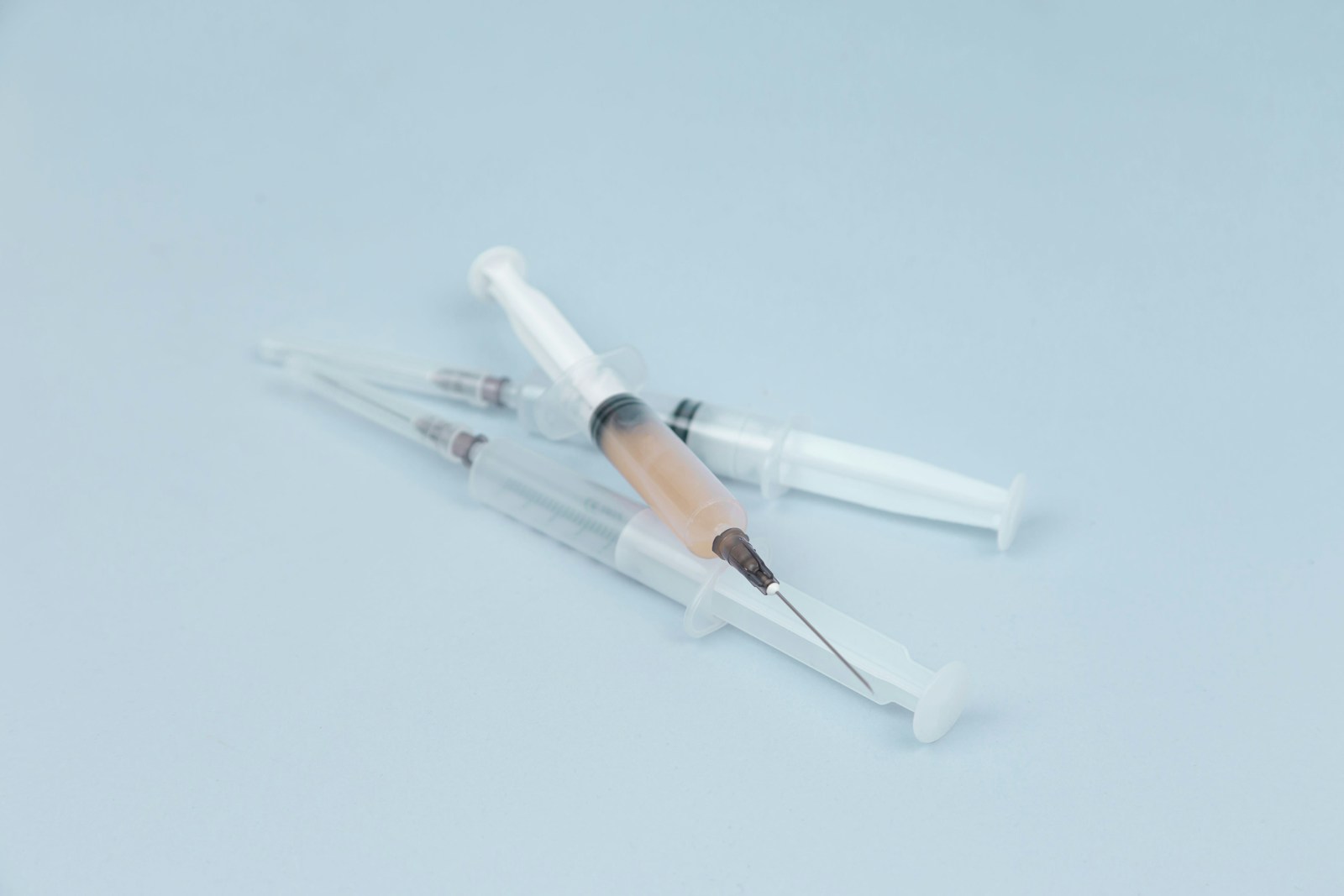
Injectable biologics
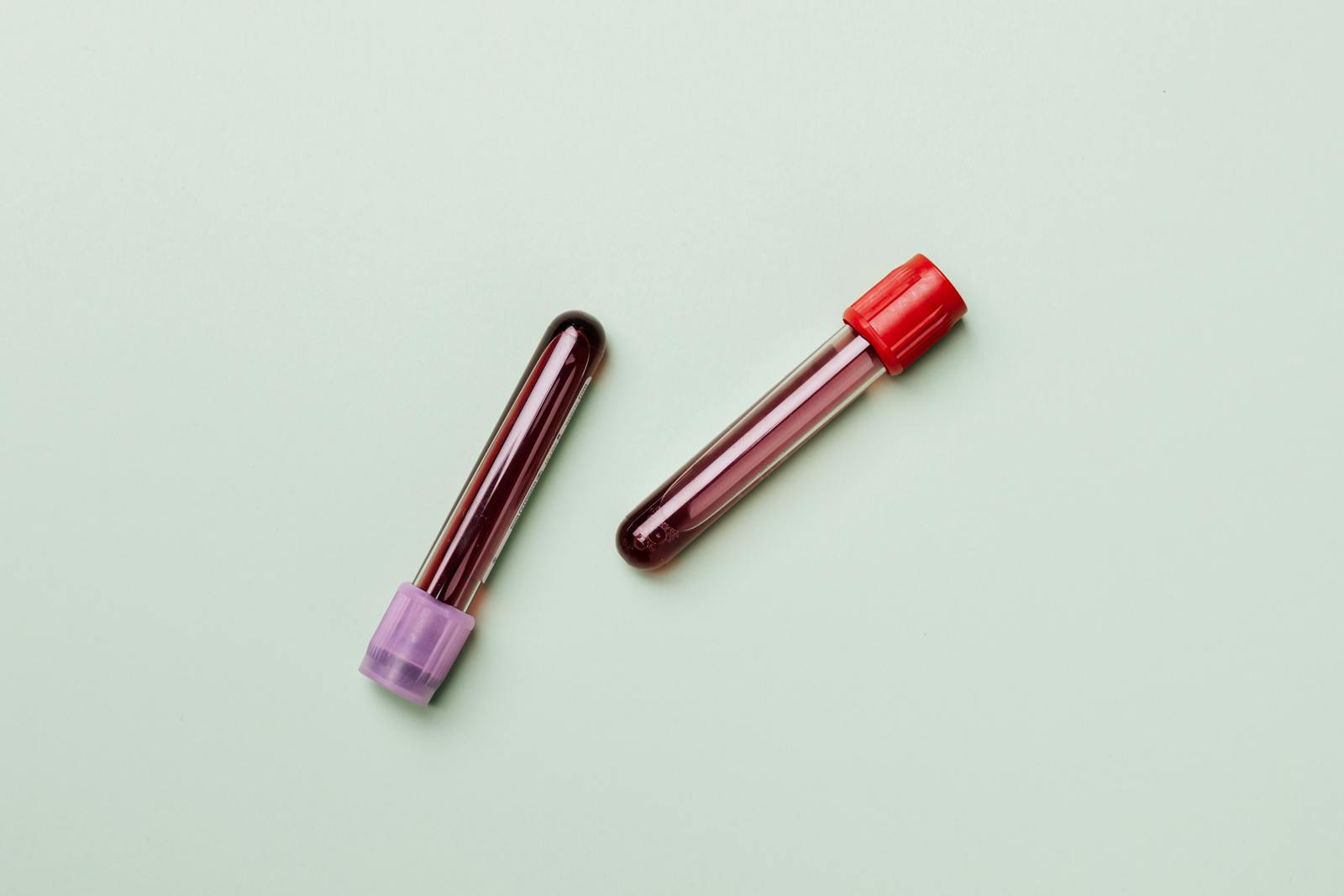
In-vitro diagnostics
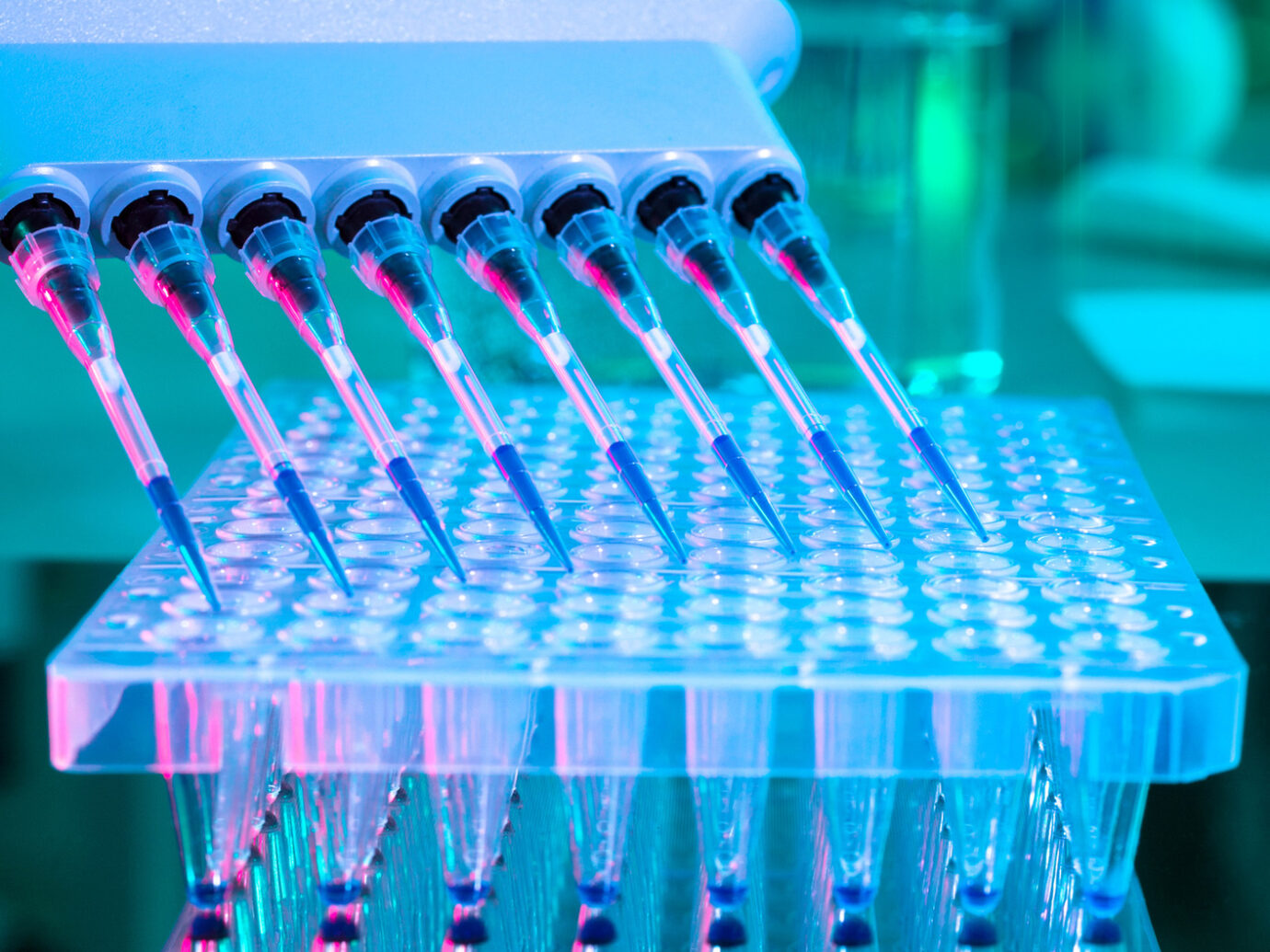
Immunochemistry
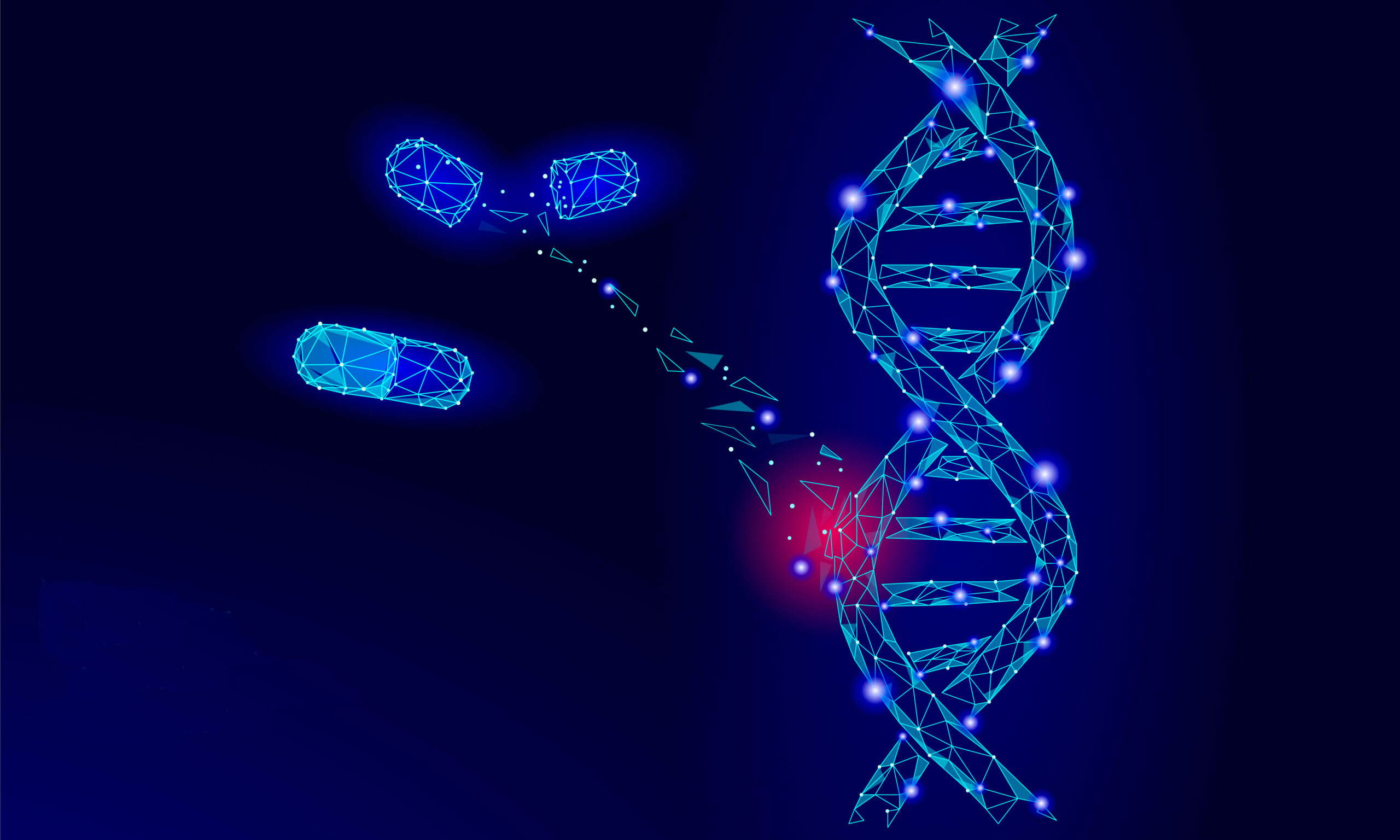
Gene therapy
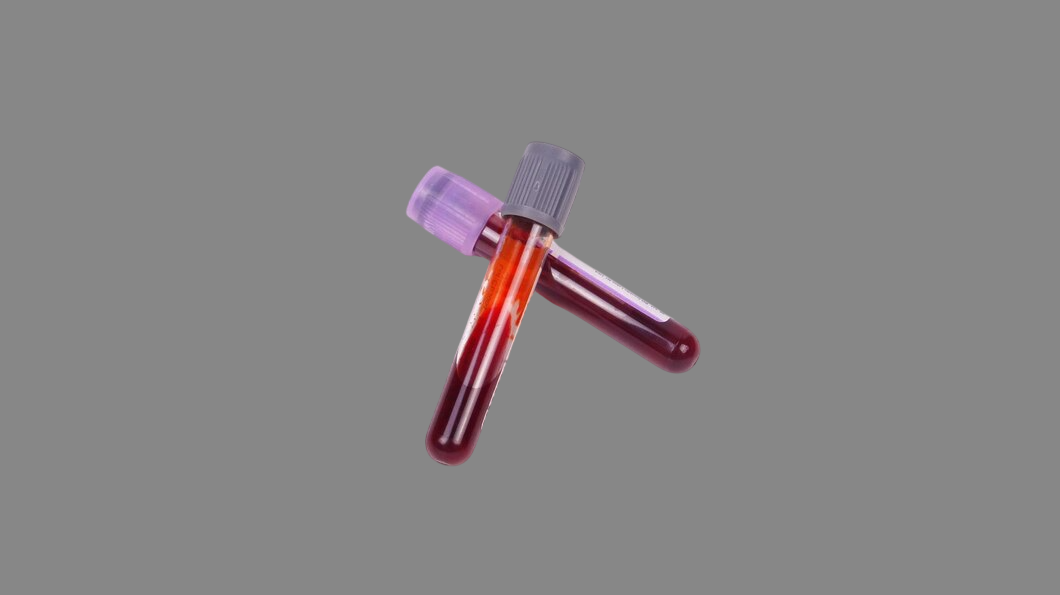
Freeze-dried plasma
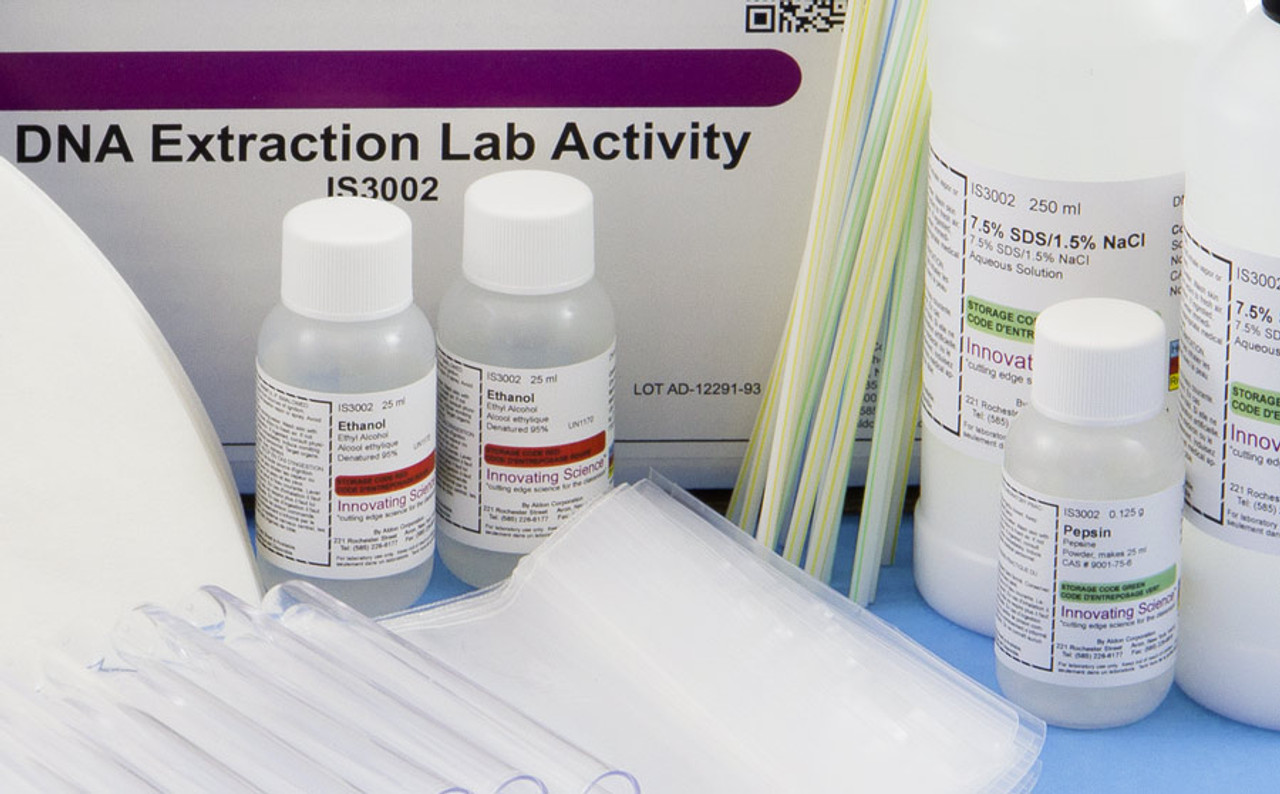
Dna extraction kits
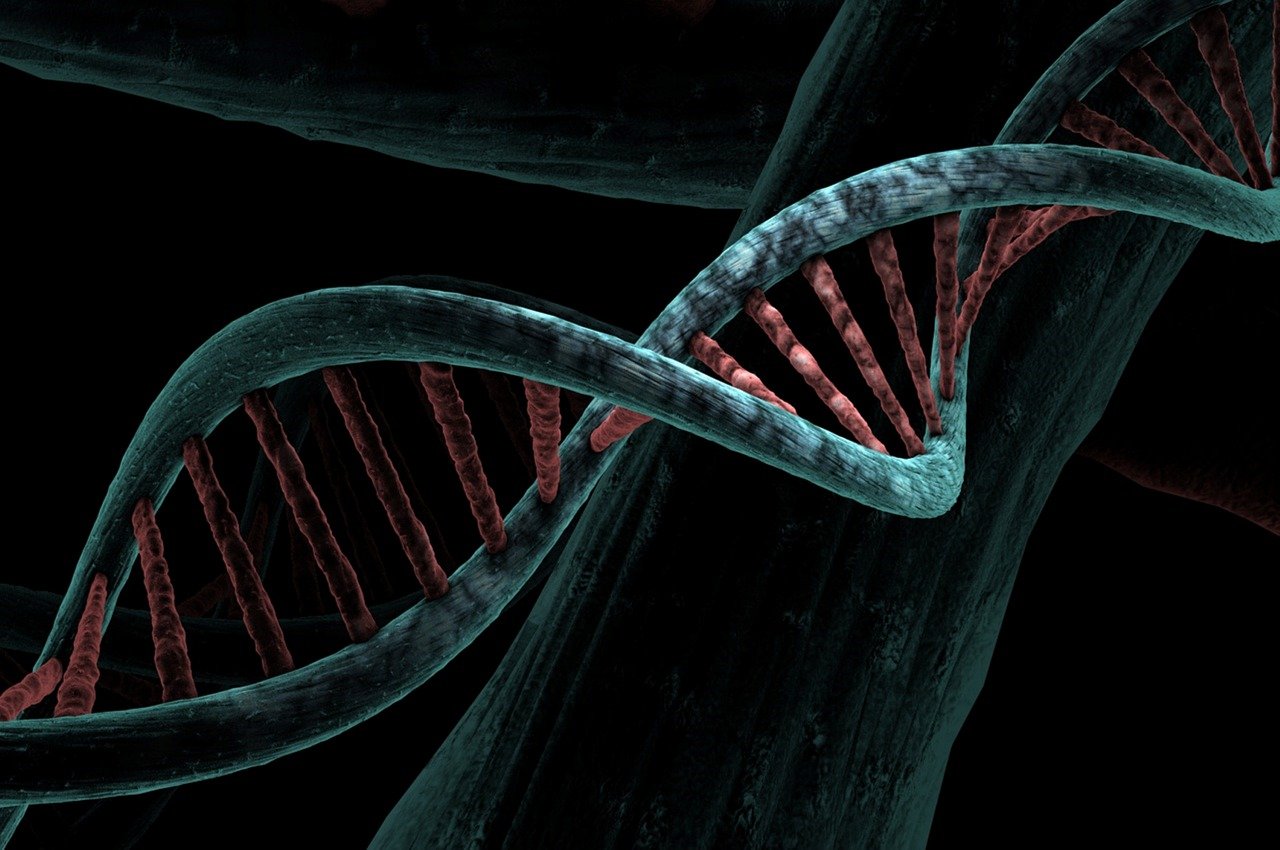
Dna
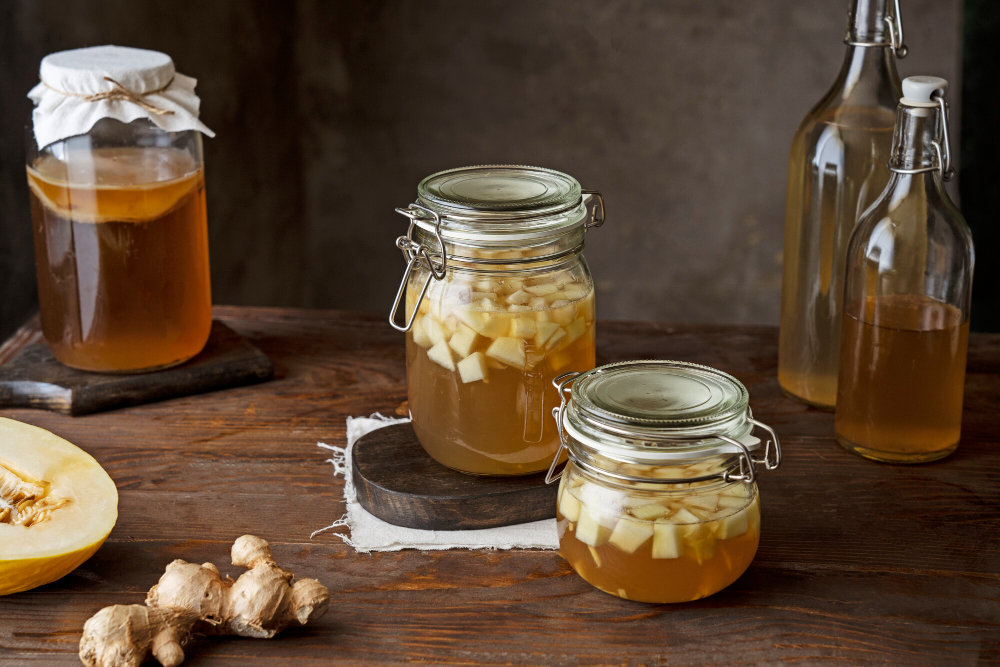
Fermentation broths
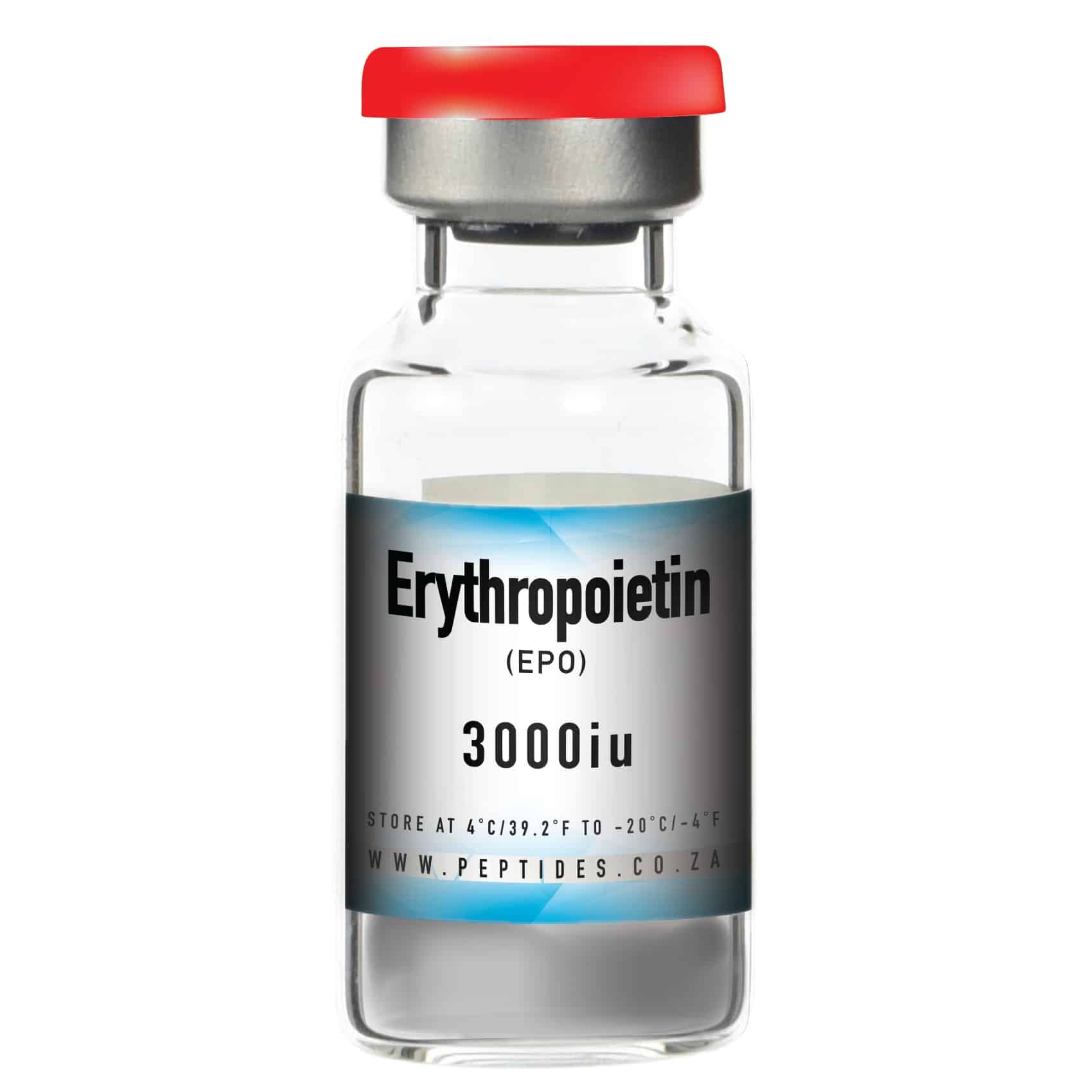
Erythropoietin
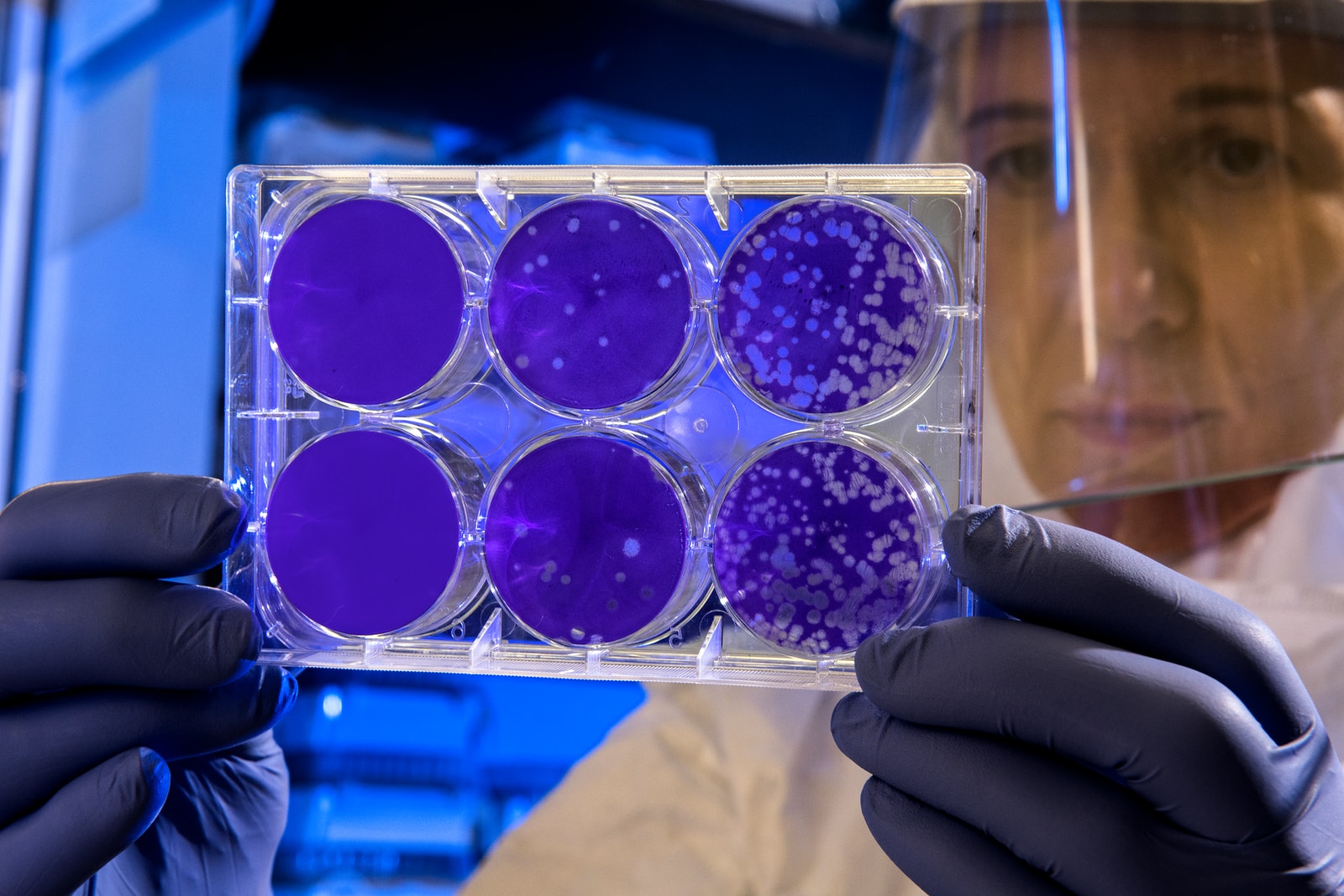
Biologics
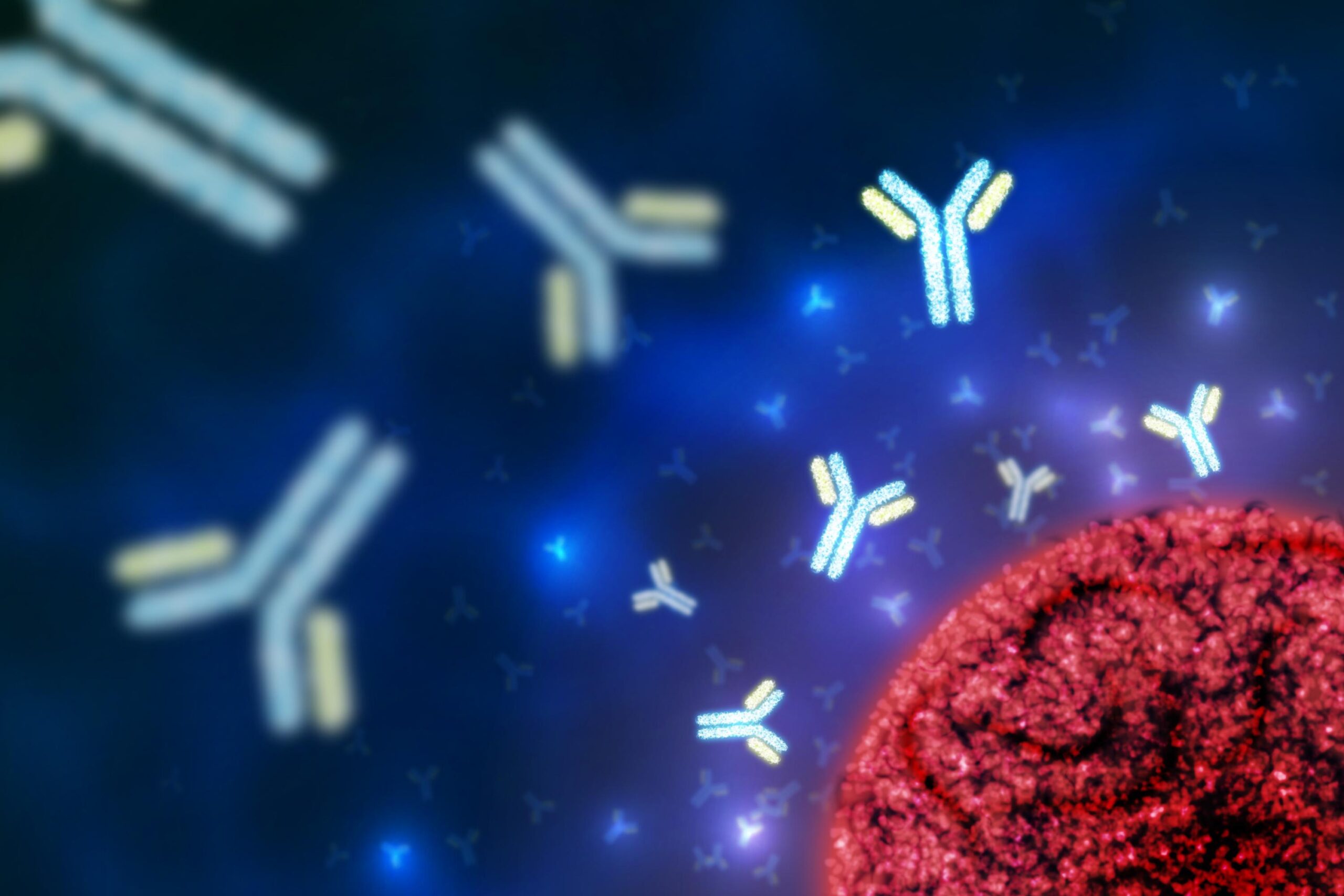
Antibodies
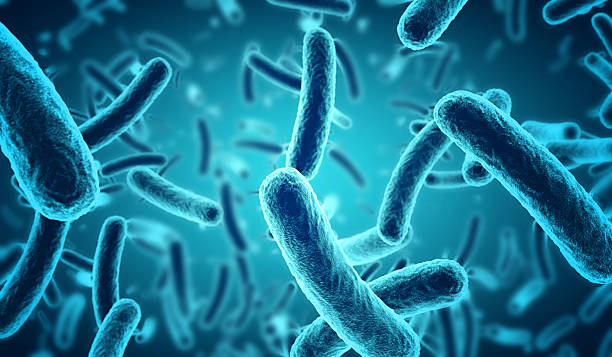
Bacteria
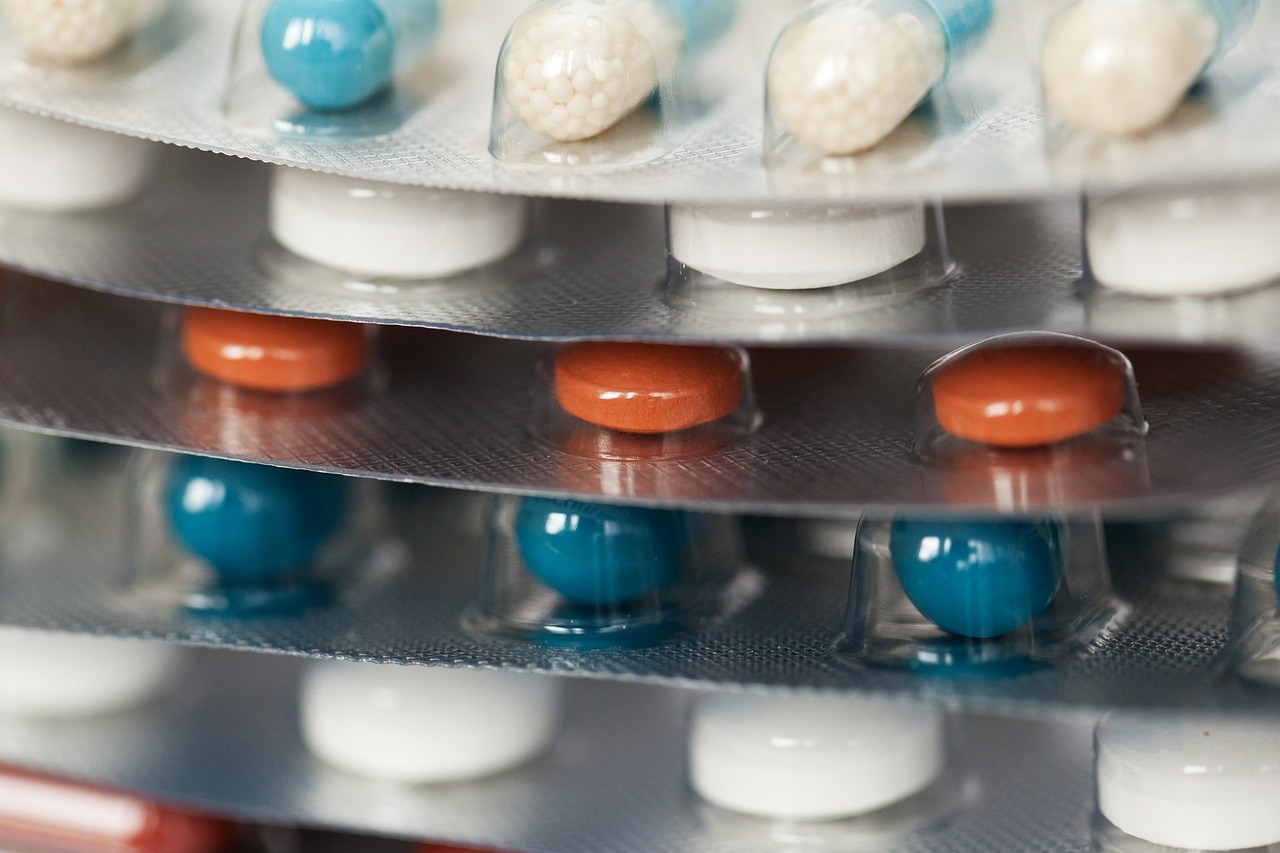
Antibiotics
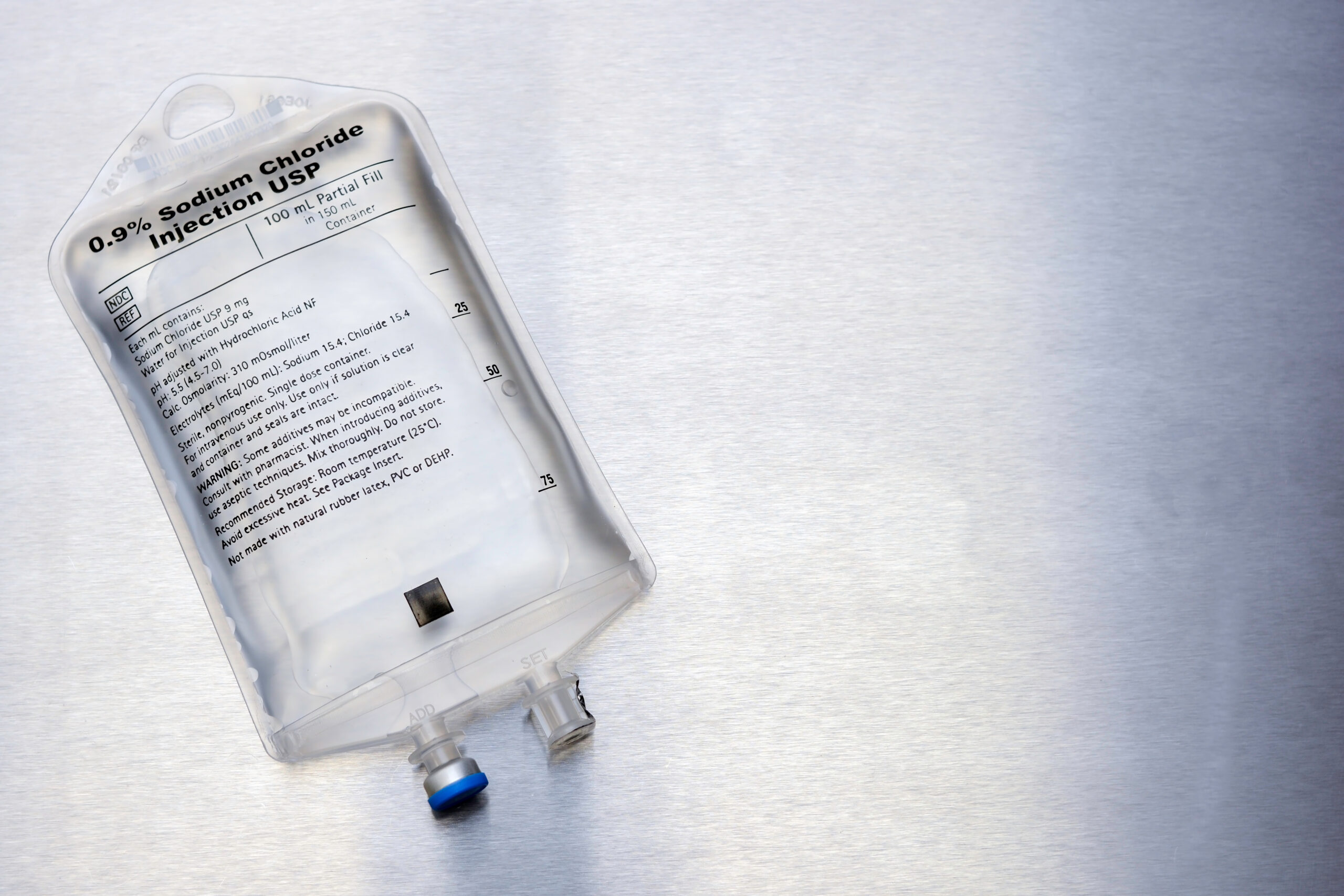
Single-use bags
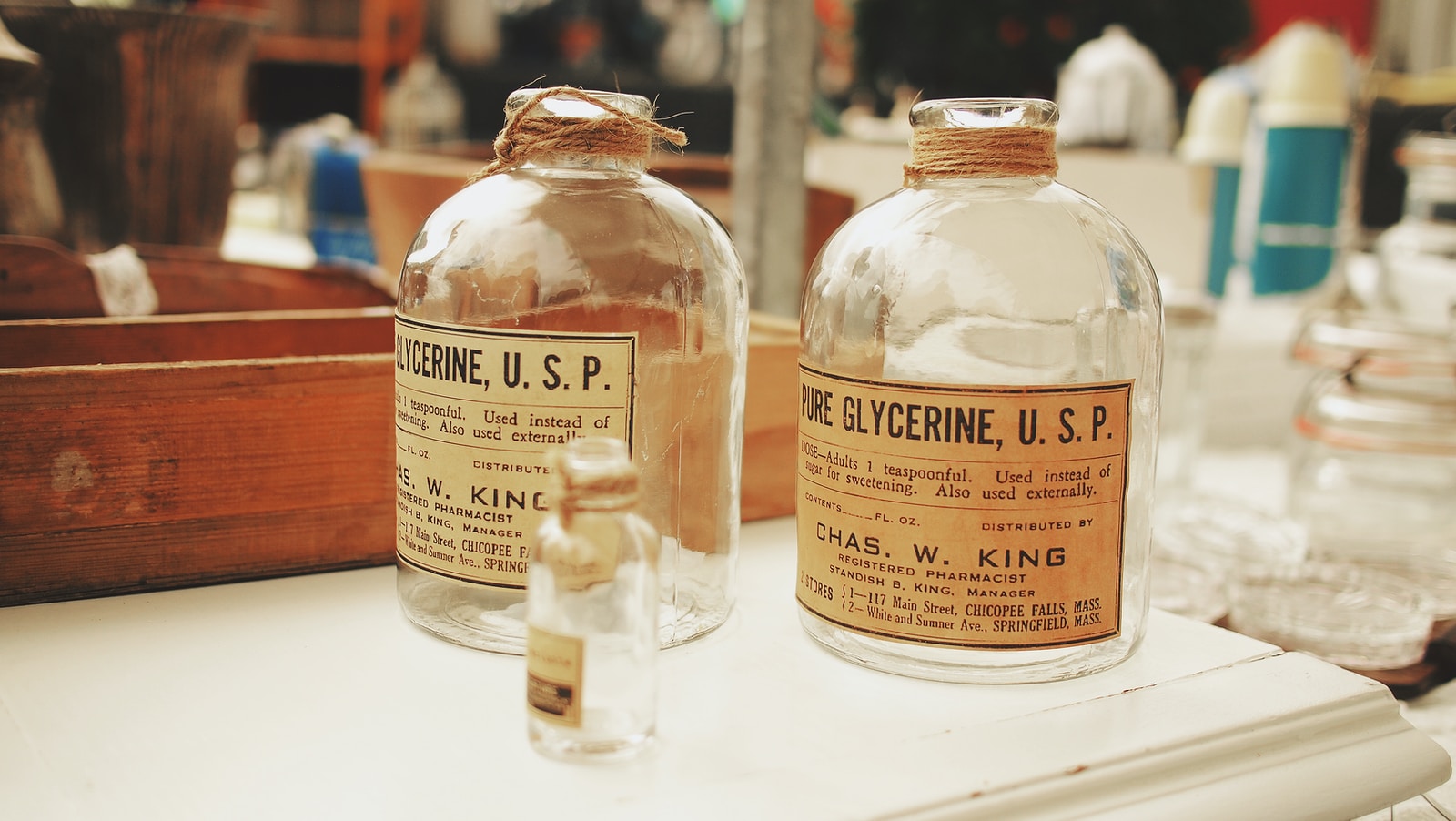
Glycerine
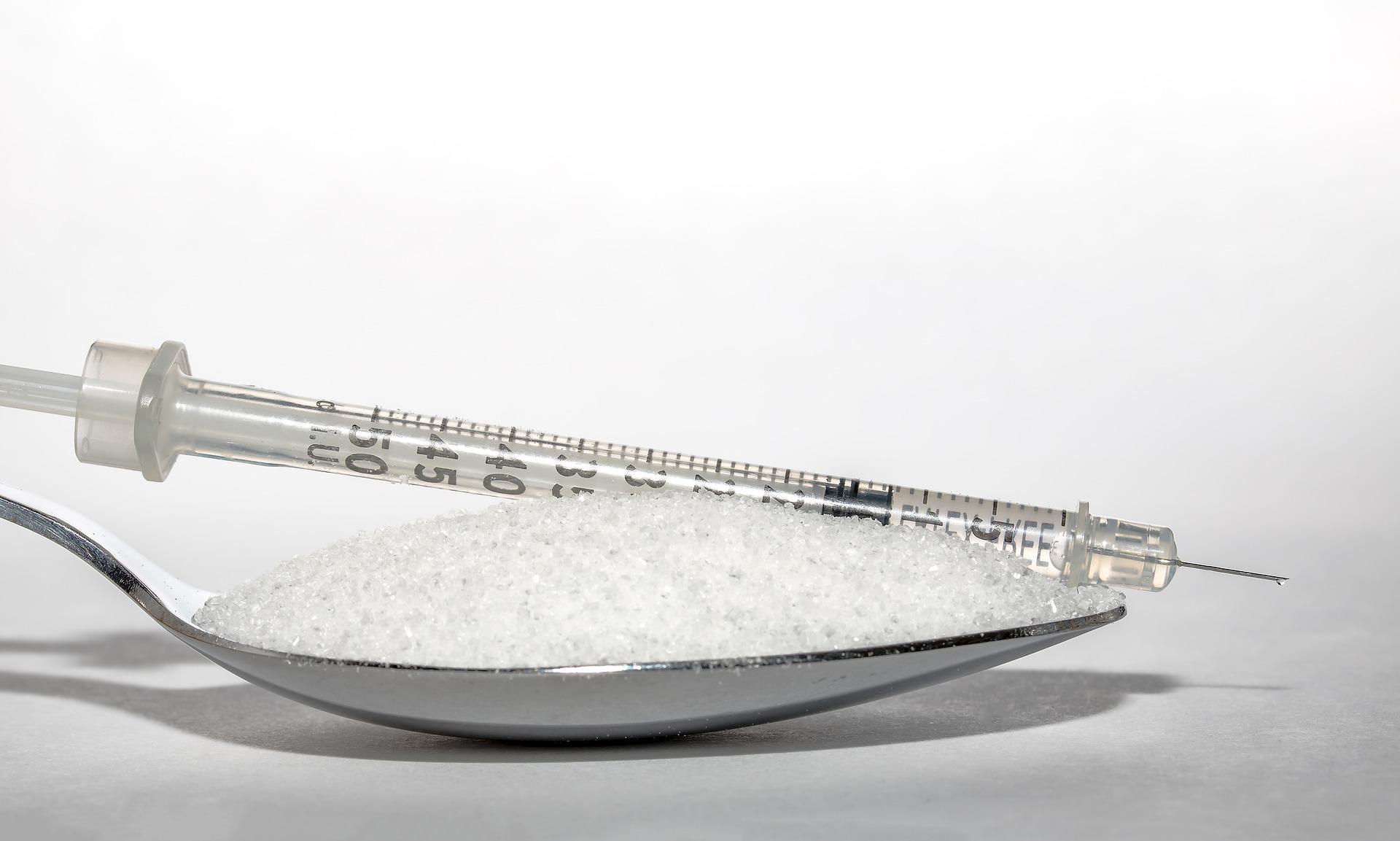
Insulin
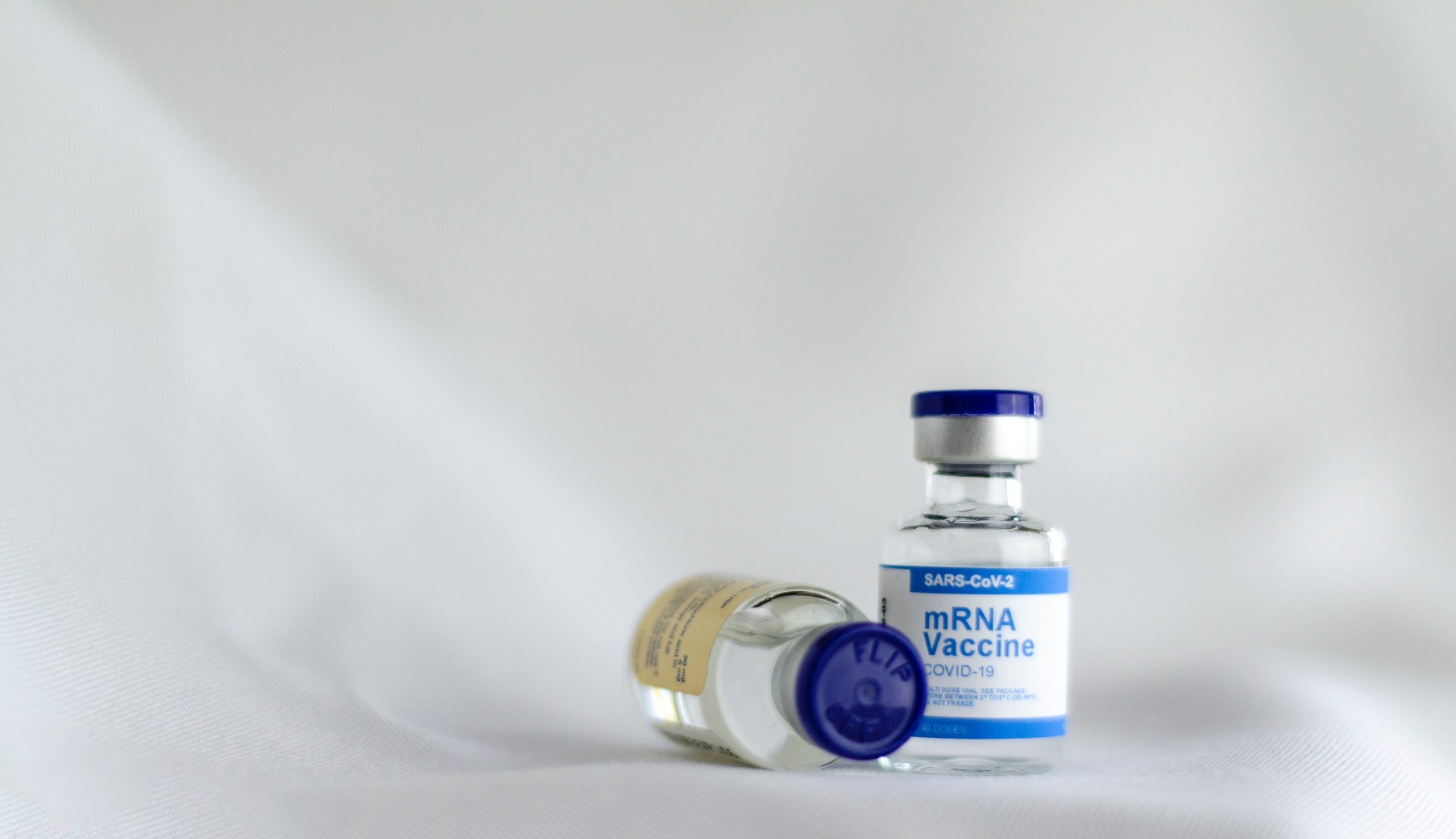
Vaccines
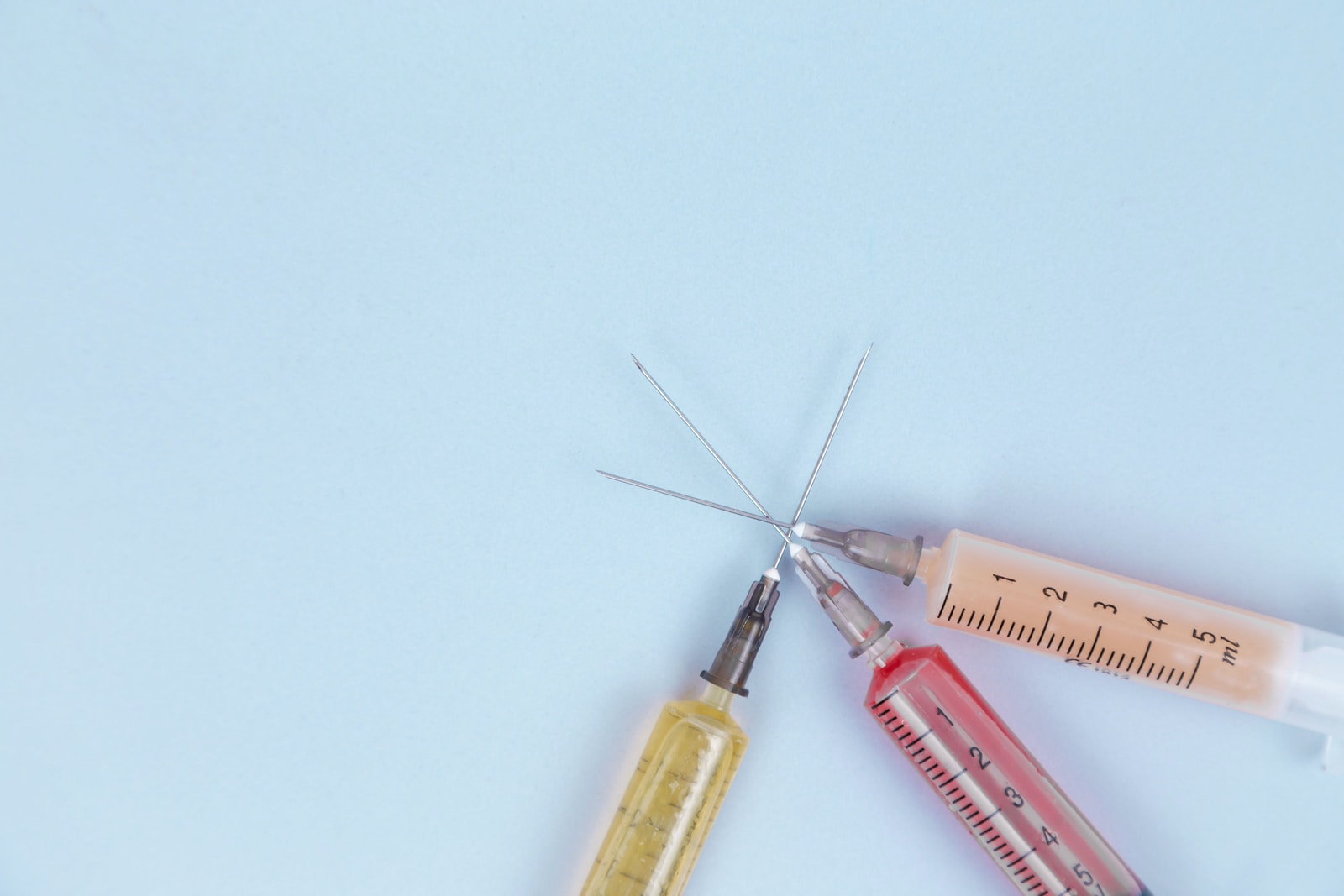
Parenterals
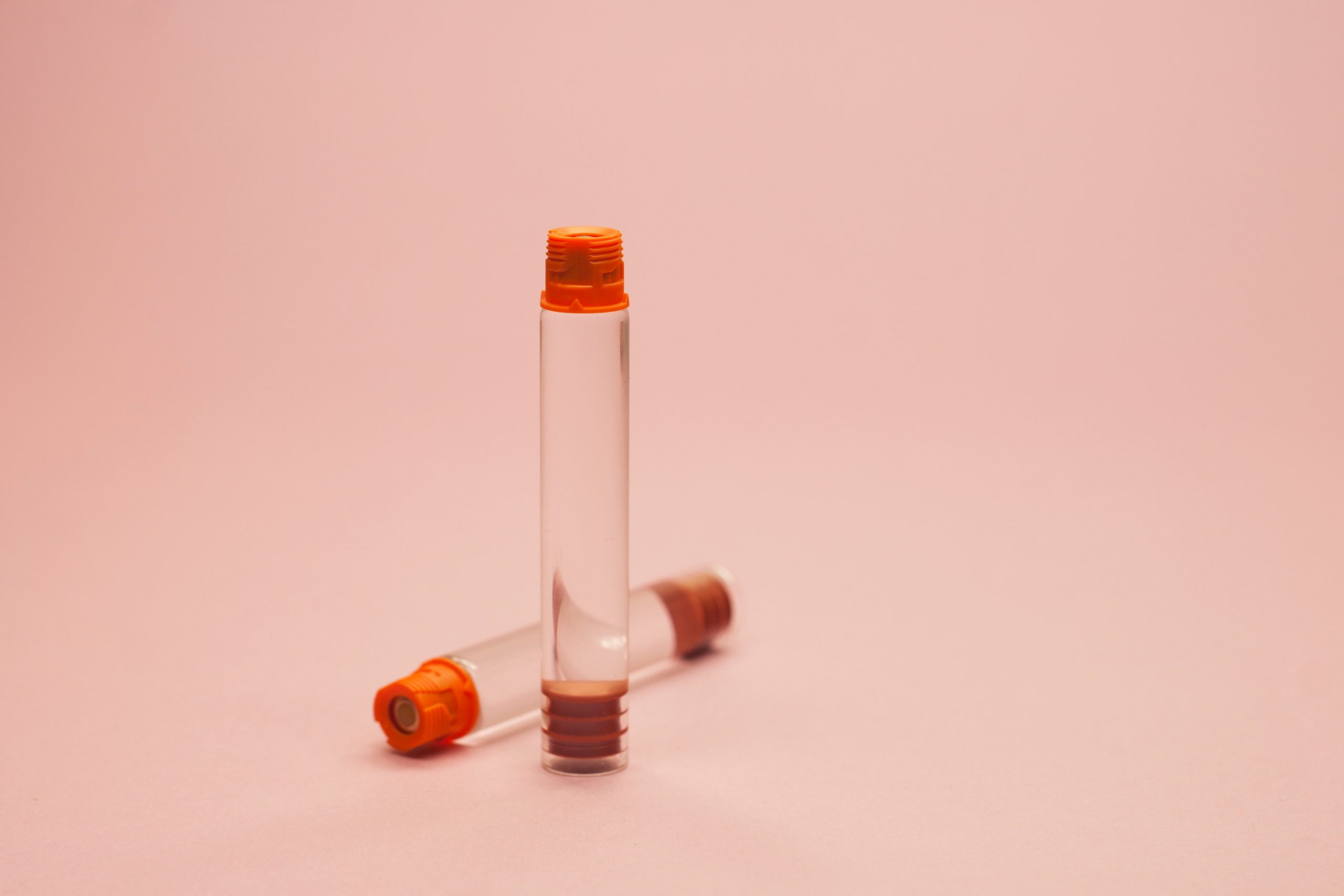
Pharmaceutical cartridges
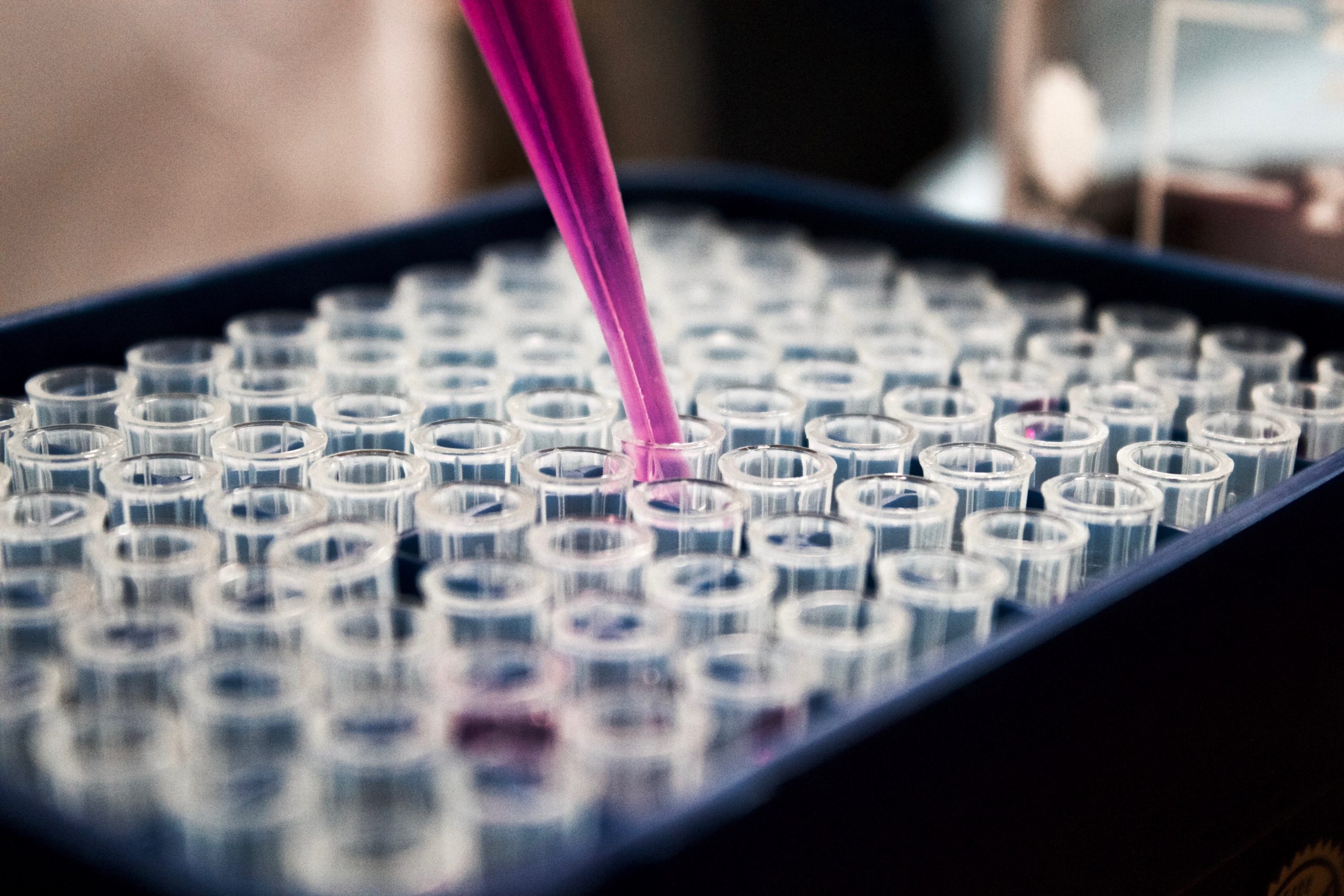
Vials
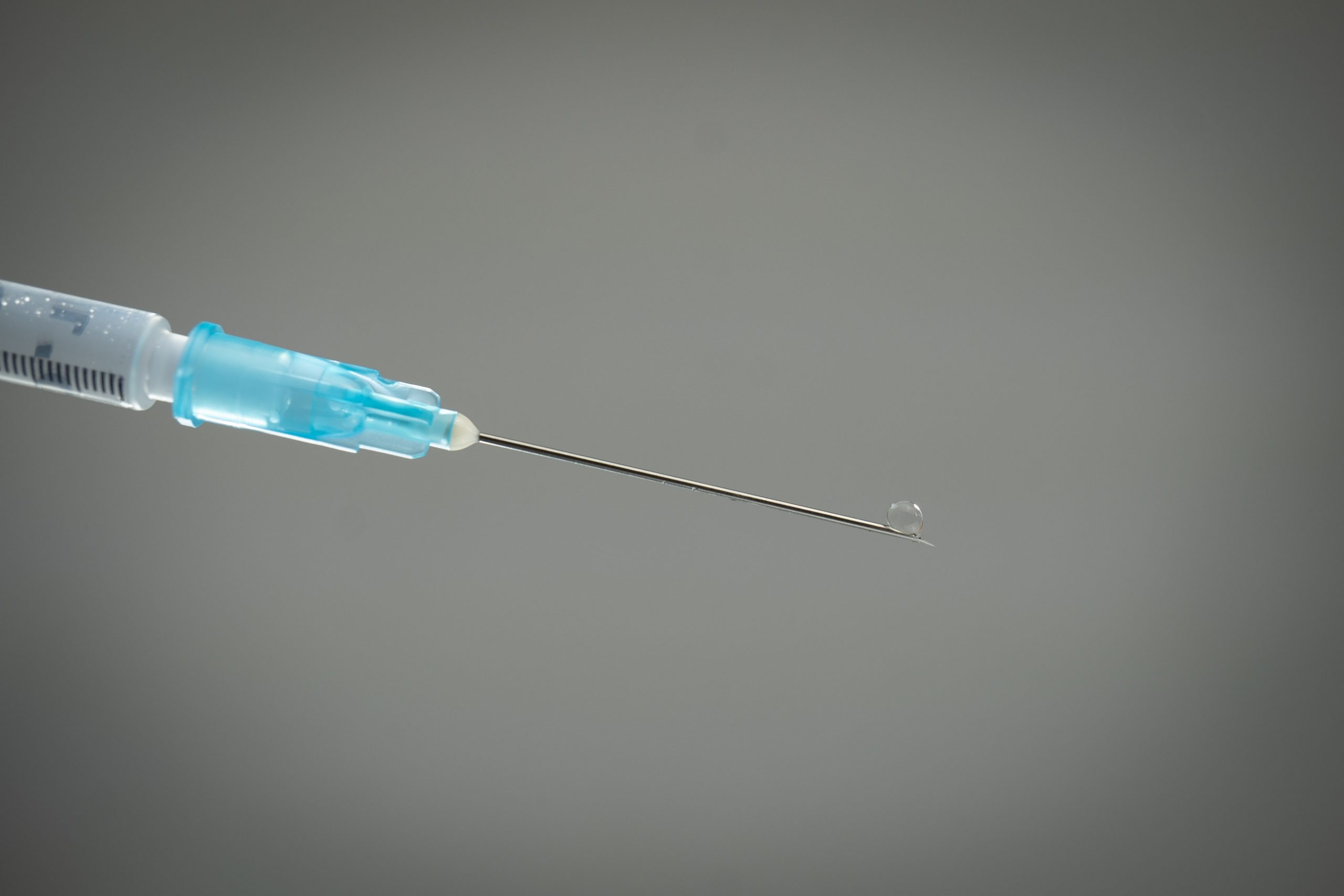
Water for injection
Tell us about your production challenge
Modify biopharmaceutical extracts to stimulate antibodies with vaccines
Recombinant DNA technology is used for medicines such as growth hormone or insulin, monoclonal antibodies, or fusion proteins. As part of their manufacturing process, vaccines are grown in tissue culture, and for gene therapy, viruses are artificially manipulated to include desirable parts of genetic material.
Different approaches or treatments for different types of biopharmaceuticals. Cell-based therapy involves modifying a patient’s own cells or donor cells to fight disease. Blood cells are tightly regulated by an interacting network of biological proteins such as hormones, cytokines, and growth factors. Vaccines contain antigenic components for a specific pathogen in order to activate a patient’s immune system so that it has a memory of the invading pathogen and offers protection when encountered. An example of this would be Covid vaccines. In contrast, monoclonal antibodies target antigens and destroy them, which is used for other purposes such as treatment for transplant rejection. Finally, biopharmaceutical extracts are also used for the production of different serums, hemoglobin, and collagen, which are not considered conventional drugs by the FDA.
Purify the extract during downstream preparation of biopharmaceuticals
Cell isolation, cultivation, cell banking, and culture expansion are called upstream processes. After the developed product is purified for the required density and ready to be harvested, production technology must meet the highest industry standard to ensure that medicines are safe and effective and move through the clinical development stage. Different types of bioreactor systems are used together with different systems for process control and monitoring. Using scalable equipment from R&D to industrial capacity and implementing the right monitoring strategies, for example, CMC regulations will reduce time to market significantly.
After harvest, the production process moves into a downstream process to meet purity and quality requirements. Downstream processing is usually divided into cell disruption, purification, and polishing. (Ultra-)centrifugation is carried out to separate biomass. If the desired product is intracellular, the cell biomass can be disrupted in order to release the product and allow extraction. If the product is extracellular, the medium can be further concentrated. Or, if necessary, de-watering is done by vacuum drying or reverse osmosis. Finally, a purified product is usually mixed with desired excipients before being packed and ready to enter the market.

Cultivate the media in a bioreactor
A bioreactor mixes the cell media together in a sterile, pressure-free environment. A main component of bioreactor systems is the agitator that facilitates the bundling of contents, facilitating the reactions between them.
One of the primary challenges of bioreactors is controlling the center of gravity. An integrated baffle arm minimizes the formation of internal vortex effects that cause this while keeping the temperature at a constant.
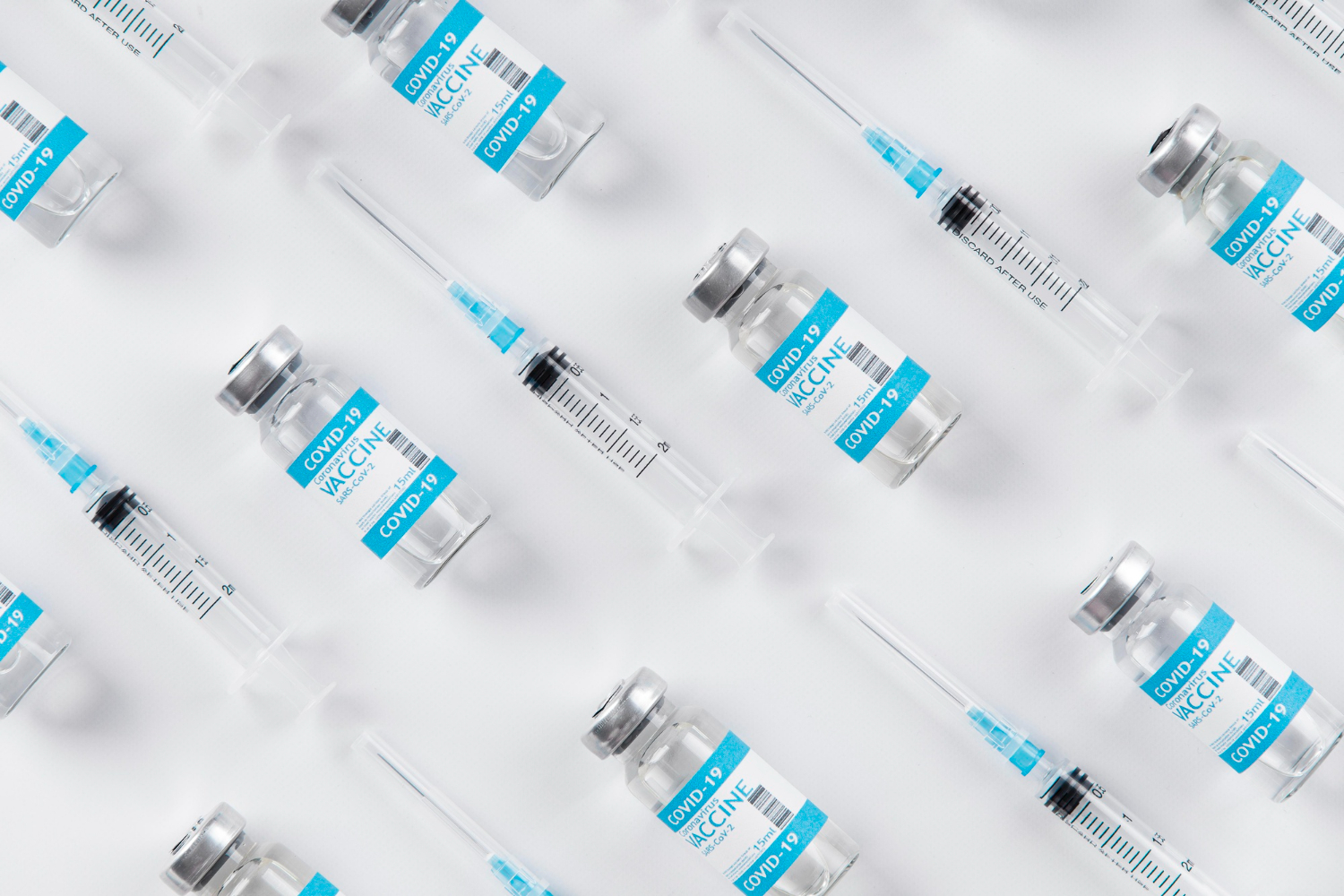
High performance liquid chromatography for biopharmaceutical manufacturing
High-performance liquid chromatography (HPLC) offers high-accuracy separation using columns. CIM monoliths are made of porous methacrylate polymers composed of interconnected channels that range in size from 1-6 μm. It is these channels that account for the media separation power and flow characteristics and ability to purify large biomolecules, such as large proteins, viruses, plasmid DNA, and immunoglobulins with their activity intact.
Safe processing and packing in biopharmaceutical manufacturing
The majority of biopharmaceuticals on the market are parenteral formulations and administered by direct injection usually distributed in single-dose vials or prefilled syringes. Product is provided either as a solution, or more commonly as a lyophilized cake, and strict requirements for product purity, activity, and shelf life dictate a very high standard for injectable drug packaging.
All injectables need to be evaluated for leachables that may have migrated over the product shelf life during formal stability testing. These analytics are crucial when it comes to biopharma manufacturing. Many biotech products are lyophilized in the vial before the stopper and seal are introduced. Lyophilization, therefore, presents its own packaging requirements on vial shape and rubber enclosures. Contact us to find out more about the biopharmaceutical technology that is right for your production needs.
Which biopharmaceuticals technology do you need?
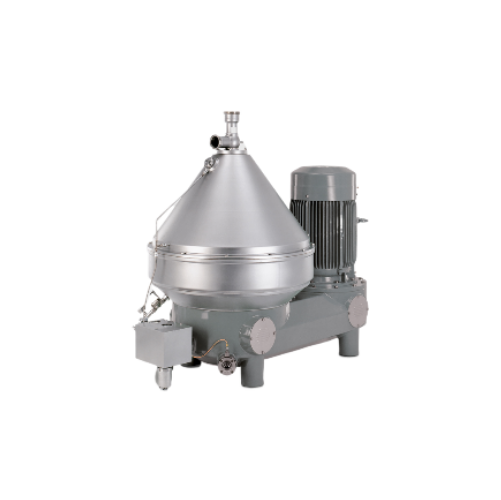
Clarifiers for biochemical separation
Achieve seamless liquid-solid separation with high-speed disk-type clarifiers, ensuri...
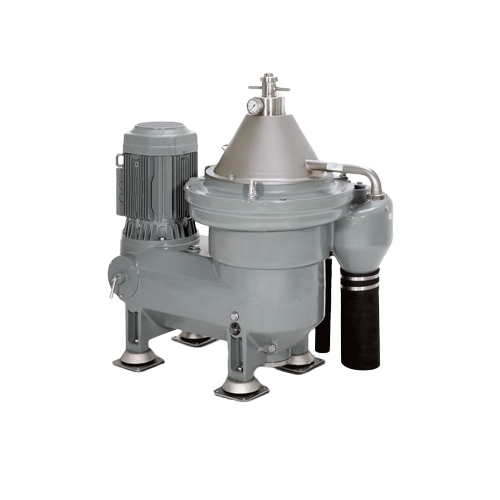
Aseptic separator for biopharma applications
Achieve high purity for your pharmaceutical liquids with a centrifuge that en...
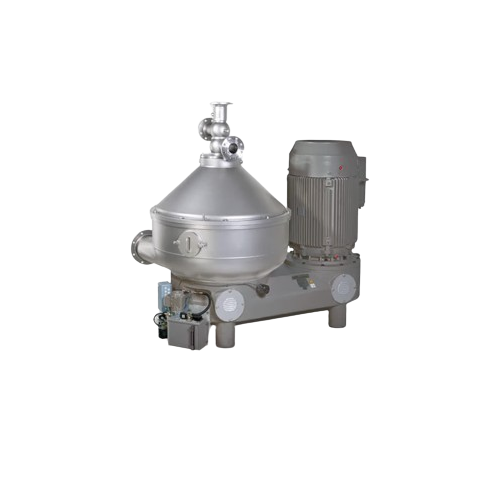
Biopharma separator for low to medium solid content
Ensure precise separation and high yield in biopharmaceutical product...
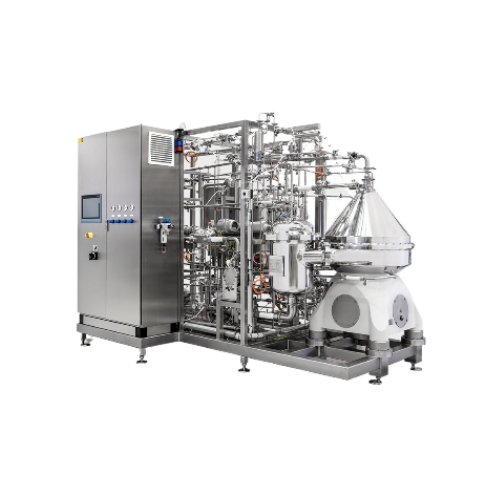
Aseptic separator for high solid content in biopharma
Ensure high yield and optimal purity in biopharmaceuticals with thi...
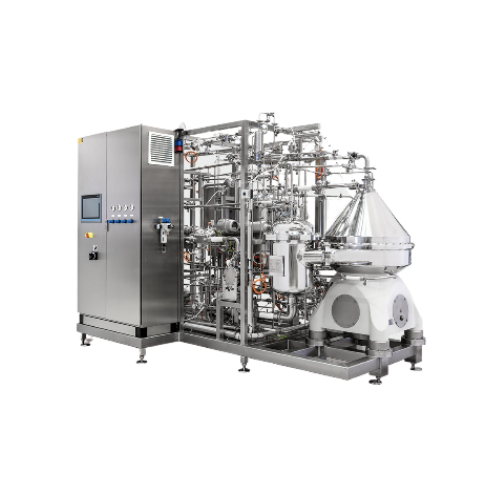
Pharma separator for aseptic biopharma processing
Achieve precise separation and concentration of sensitive biopharmaceut...
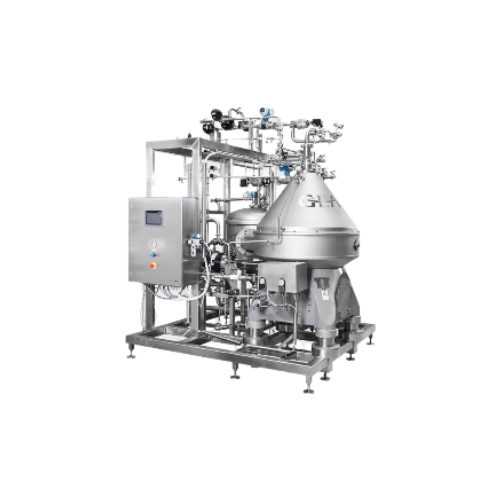
Pharma separator for biopharma processing
Streamline your production with this advanced separator, designed to efficiently...
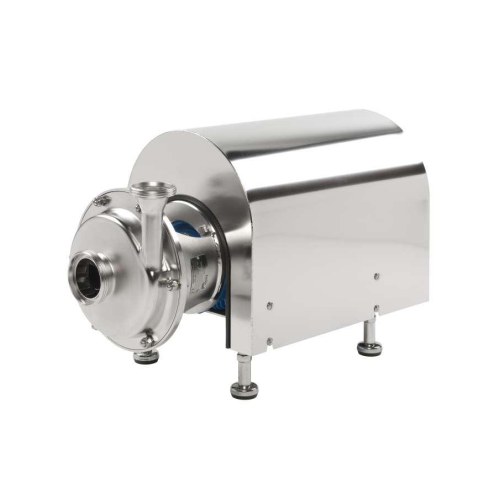
Centrifugal pumps for food & beverage and biopharmaceutical applications
Optimize your liquid transfer processes with p...
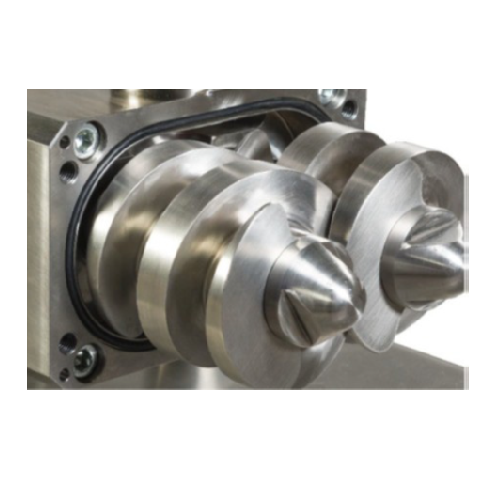
Aseptic sampling devices for biopharmaceutical applications
Secure aseptic sampling ensures your high-value biopharmaceu...
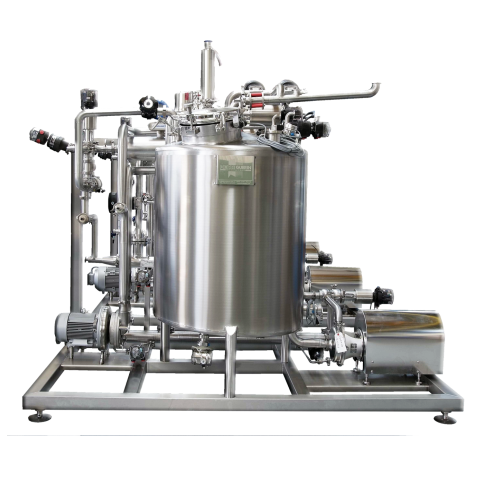
Single use cleaning in place units for biopharma
Eliminate cross-contamination risks in biopharmaceuticals with precision ...
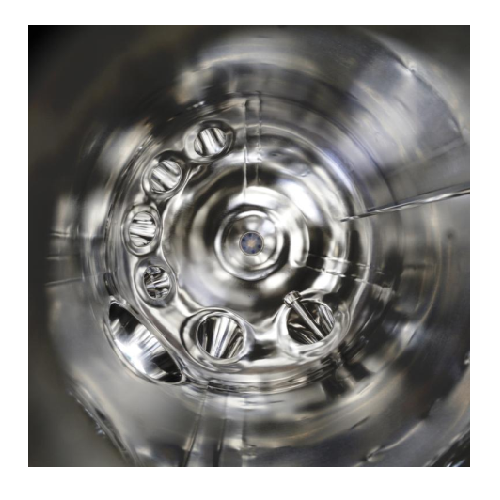
Stainless steel process vessels for biopharmaceutical applications
Ensure seamless mixing and sterilization with engine...
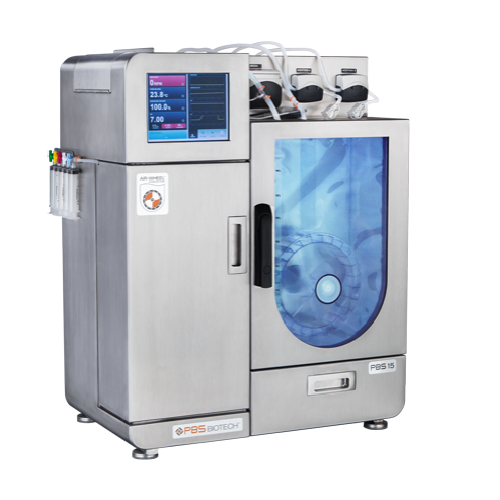
15l vertical-wheel bioreactor for cell therapy scale-up
Accelerate your cell therapy scale-up with a bioreactor that offe...
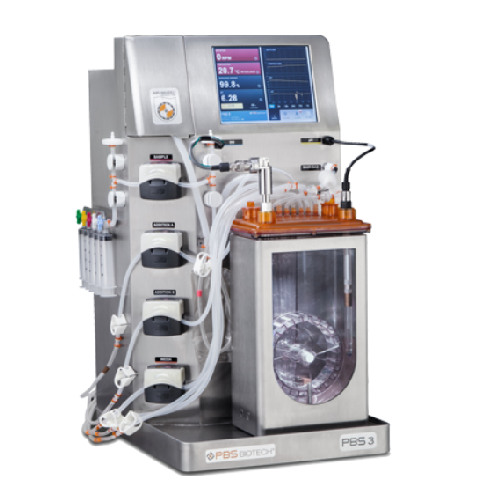
Vertical-wheel bioreactor for cell therapy applications
Elevate your cell culture process with a bioreactor designed for ...
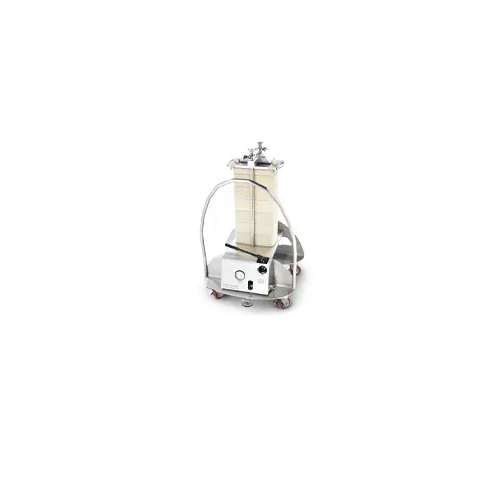
Virus filtration systems for biologics processing
Ensure efficient virus retention in biopharmaceutical production by int...
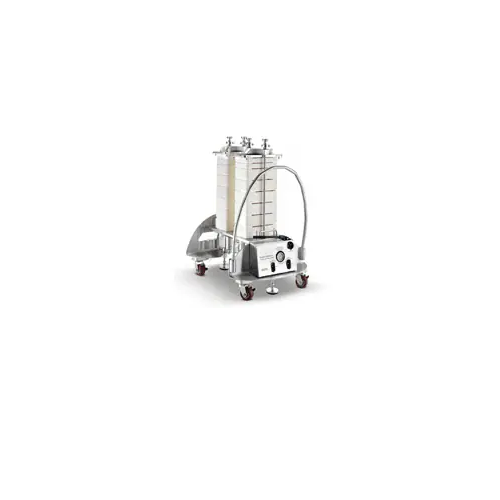
Virus filtration systems for biologics manufacturing
Enhance virus filtration efficiency in biologics with scalable, easy...
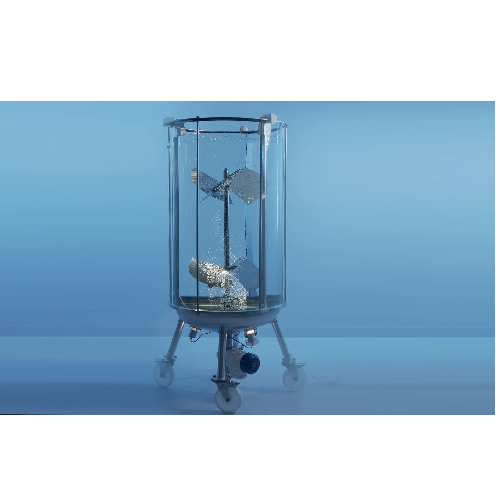
Bioreactor mixer for gentle mixing applications
When handling sensitive biomaterials, ensuring optimal mixing while mainta...
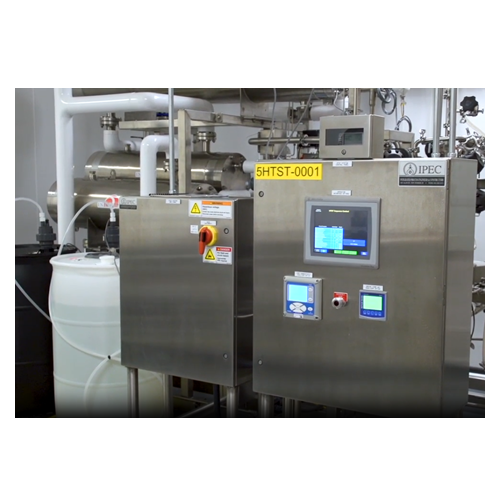
Bioprocessing liquid cell culture media
Streamline your bioprocessing with sterile liquid media solutions that ensure optim...
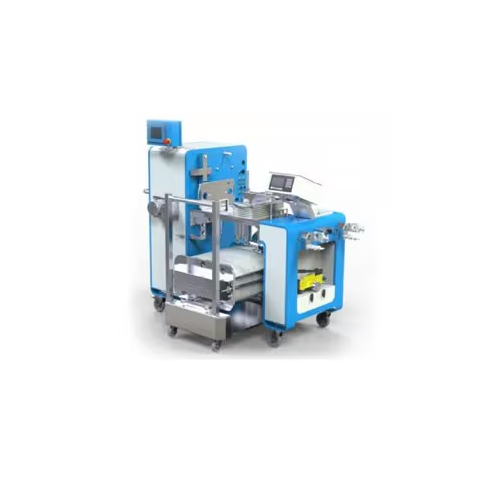
Virus filtration system for biologics manufacturing
Ensure safe and effective biopharmaceutical production by integrating...
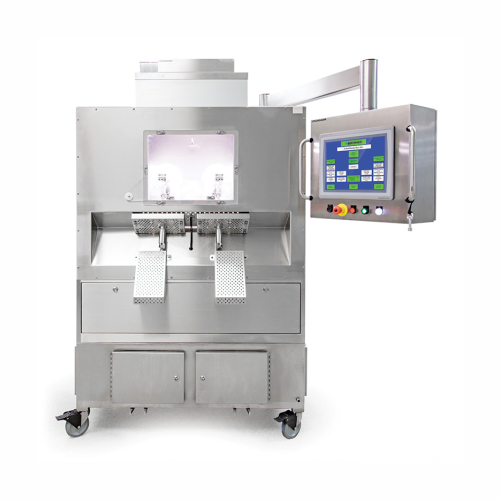
Aseptic filling system for biopharmaceutical products
This system ensures sterility in high-volume aseptic filling operat...
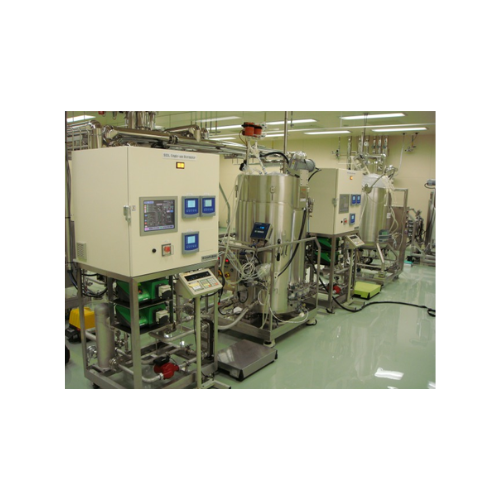
Single use bioreactor control system
Effortlessly customize your control strategy for single-use bioprocesses, ensuring sea...
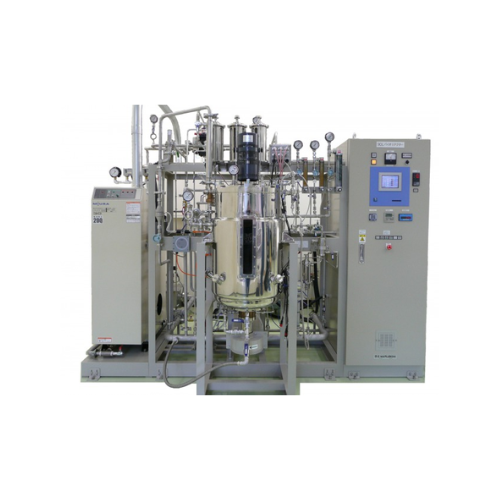
Sterilization in place fermentor for bioprocess applications
Optimize your fermentation processes with seamless integrat...
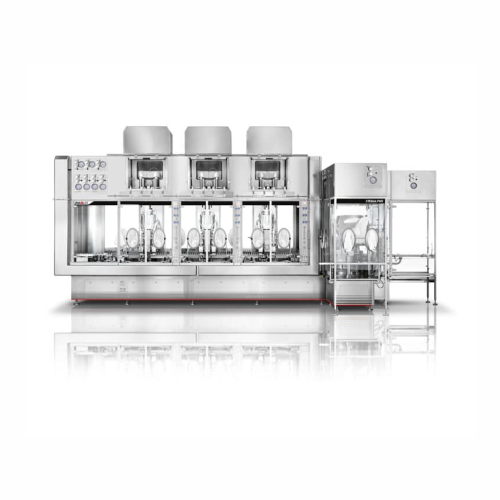
High speed powder dosing and stoppering for antibiotics
Address the threat of antibiotic-resistant bacteria with precisio...
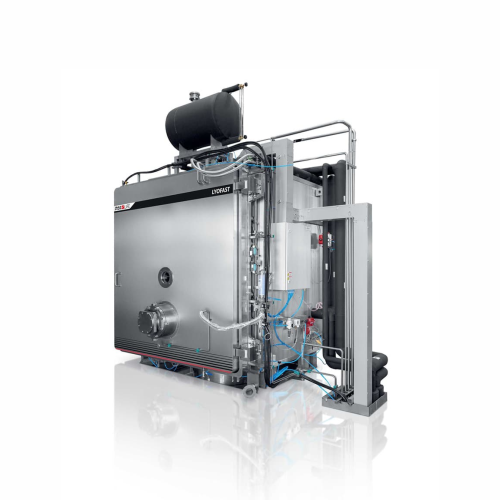
Industrial freeze dryer for biopharmaceuticals
Ensure the stability and longevity of your sensitive biopharmaceuticals thr...
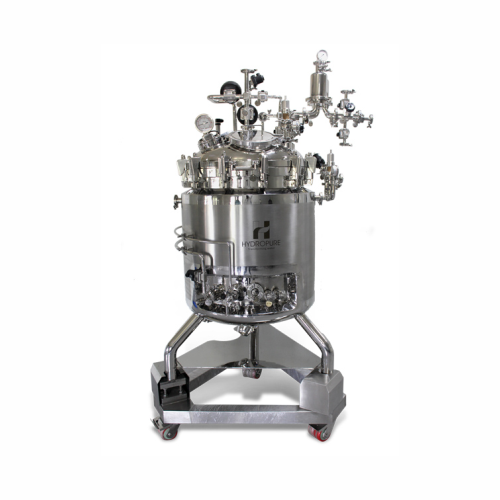
Pharma and biopharma manufacturing vessels
Optimize critical processes with customizable manufacturing vessels designed to...
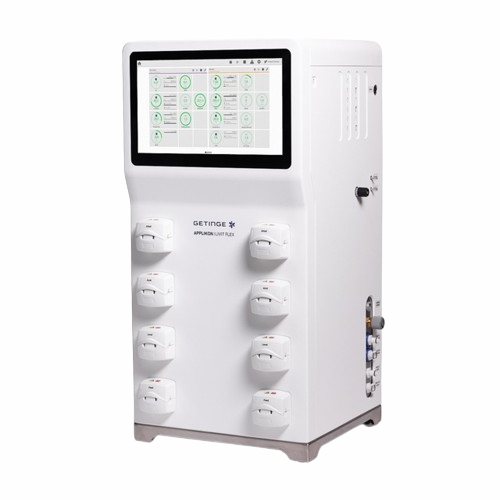
Controller for lab-scale bioreactors
Optimize your bioprocessing capabilities with a versatile controller that manages both...
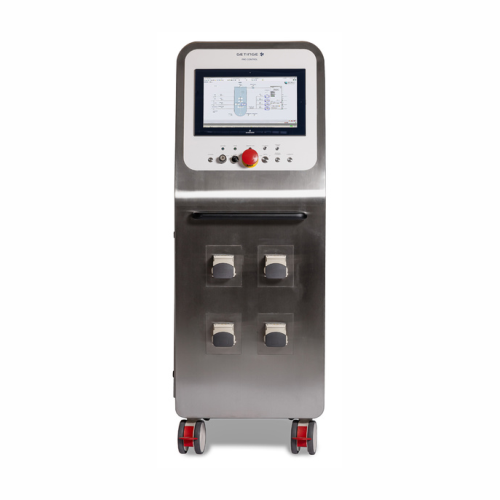
Controller for pilot and production scale bioreactors
Optimize your bioprocess with a robust, configurable controller des...
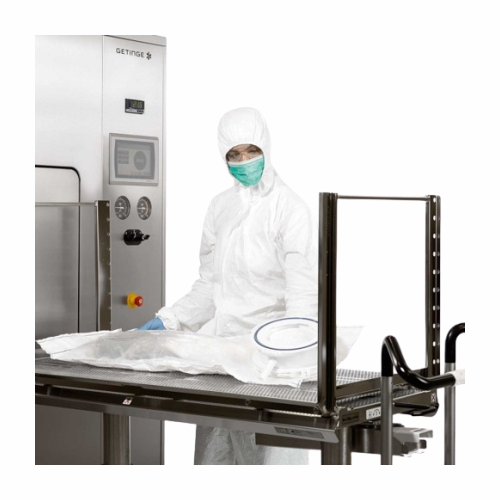
Sterilizer loading solutions for biopharma and research laboratories
Streamline your sterilization process with ergonom...
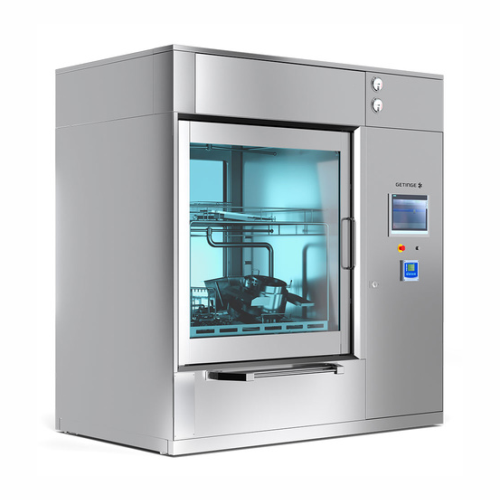
Cgmp washer/dryer for biopharmaceutical cleaning
Achieve optimal cleanliness with precise washing and drying for biopharma...
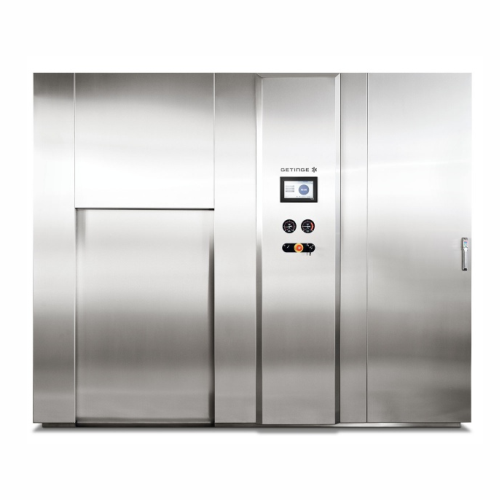
Steam sterilizer for biomedical lab research
Ensure the highest level of biosafety and scientific integrity with this stea...

Scalable bioprocess control system
Optimize your bioprocesses with a configurable control system that ensures seamless data...
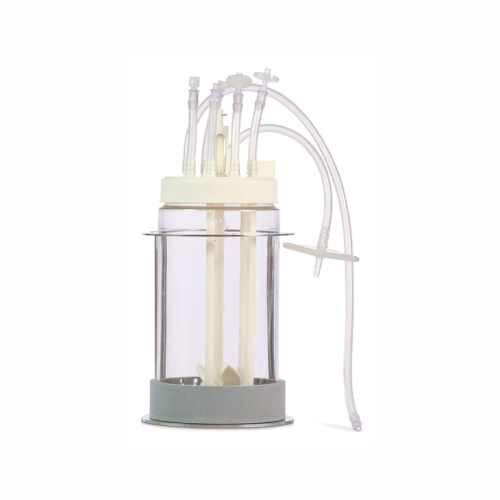
Single-use lab-scale bioreactor for upstream bioprocessing
Streamline your bioprocess development with a customizable, s...
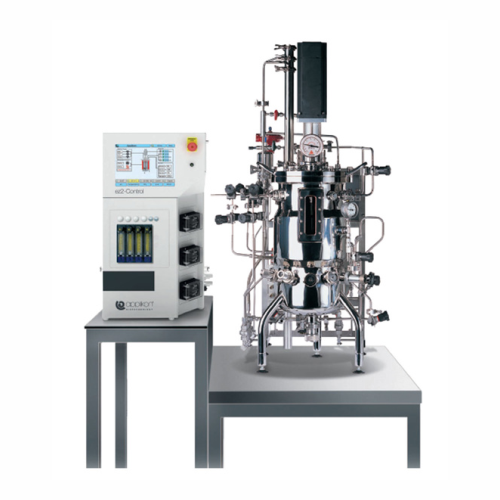
Bench top bioreactor for microbial and cell cultures
Optimize your bioprocessing workflow with this versatile bench top s...
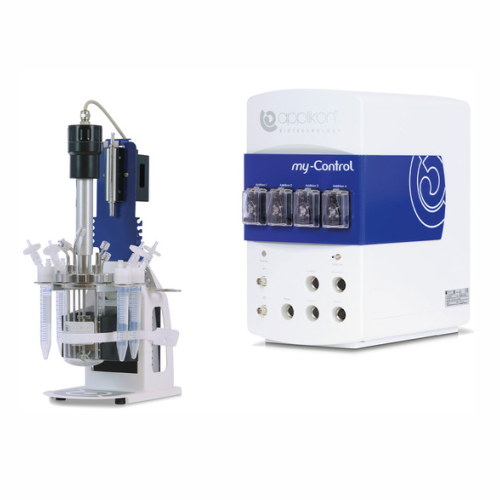
Turnkey bioreactor system for cell culture
Streamline your bioprocessing with a complete cultivation system; ideal for pro...
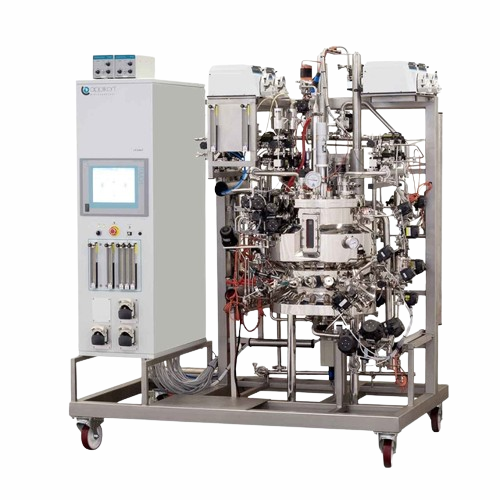
Stainless steel bioreactor for small-scale bioprocess production
Optimize your bioprocess development with a modular sta...
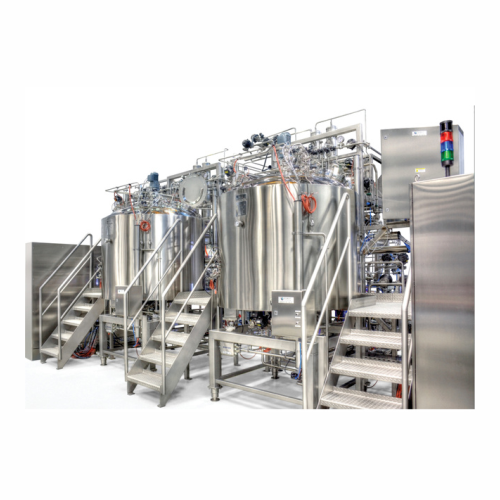
Stainless steel bioreactor for cgmp production
Achieve reliable and scalable production of life-saving medicines with a cu...
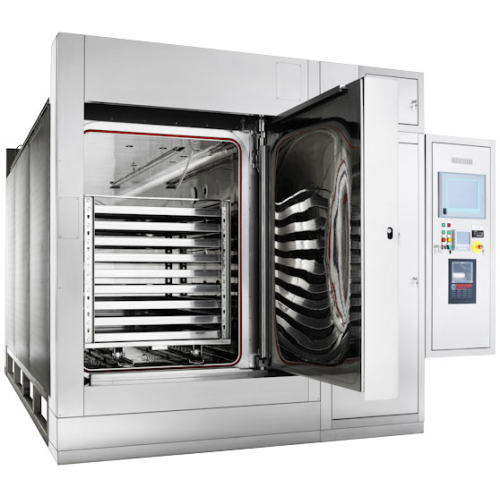
Saturated steam sterilizer for bio-pharma applications
Ensure sterility and compliance in your production line with versa...

Bio-decontamination unit for heat-sensitive loads
Ensure the integrity of heat-sensitive biopharmaceutical products by em...
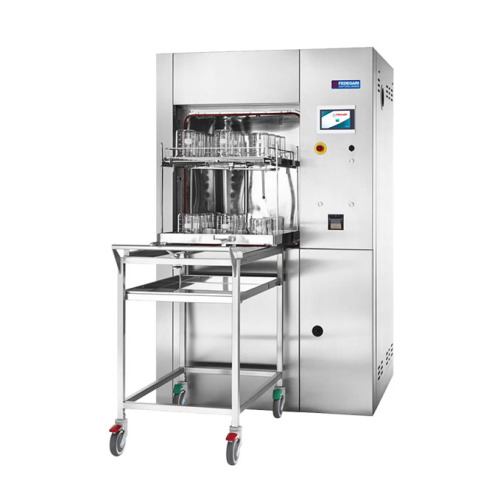
Lab glassware washer for food and bio-pharmaceutical applications
Ensure precision cleaning of complex lab glassware us...
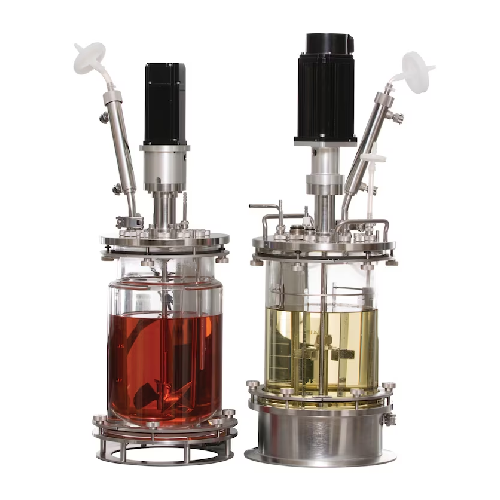
Bioreactor for mammalian and microbial cell cultivation
Optimize your bioprocesses with advanced temperature and heat tra...
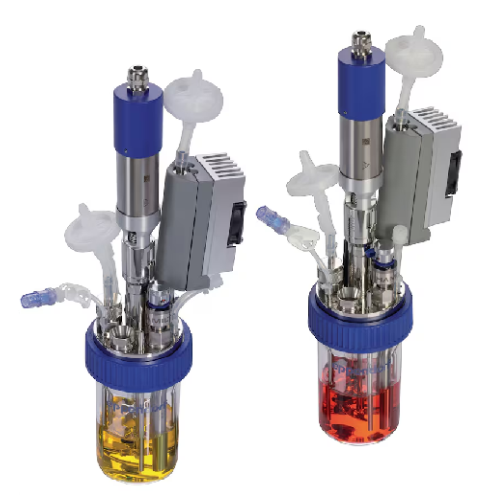
Mini bioreactor for cell culture and microbial process development
Achieve precise control and reproducibility in small...
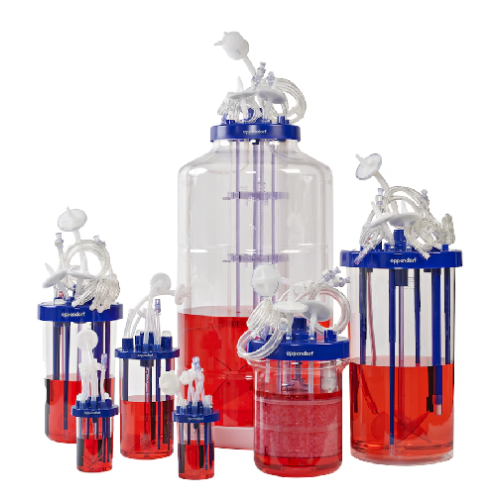
Single-use bioreactors for mammalian and insect cell cultivation
Optimize your bioprocesses with scalable, single-use bi...
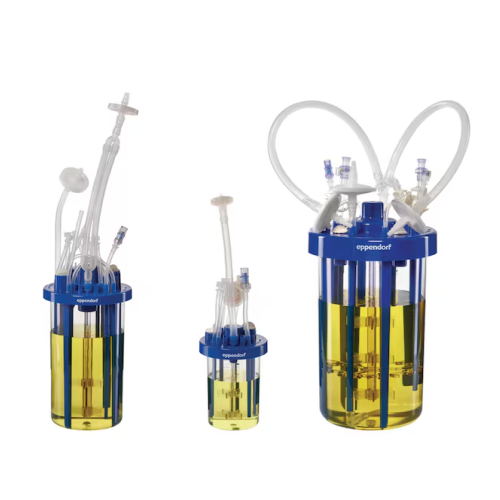
Single-use bioreactors for microbial fermentation
Optimize high-density fermentation with advanced single-use bioreactor ...
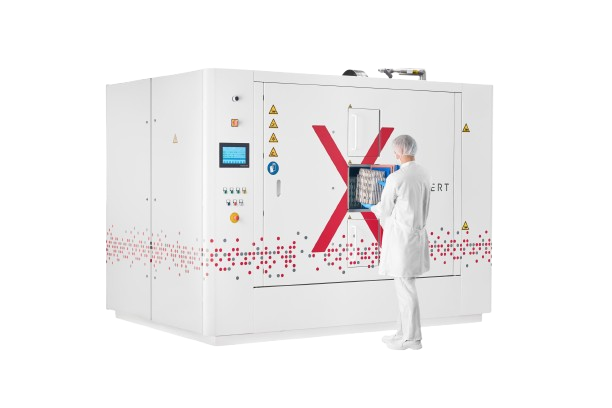
Controlled rate freezer for biological and medical research
Ensure the integrity of biological samples while minimizing ...
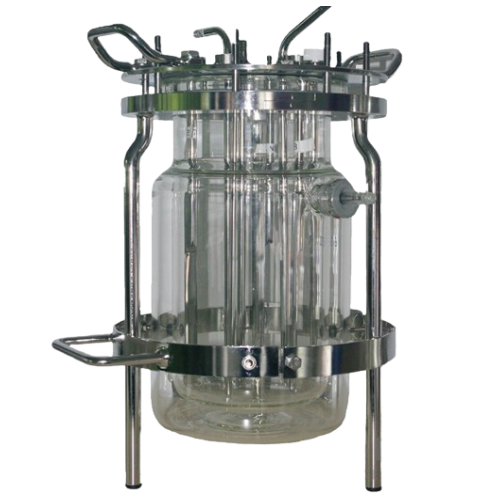
Bioreactor for cell culture yield optimization
Streamline complex cell culture processes with a bioreactor designed to enh...
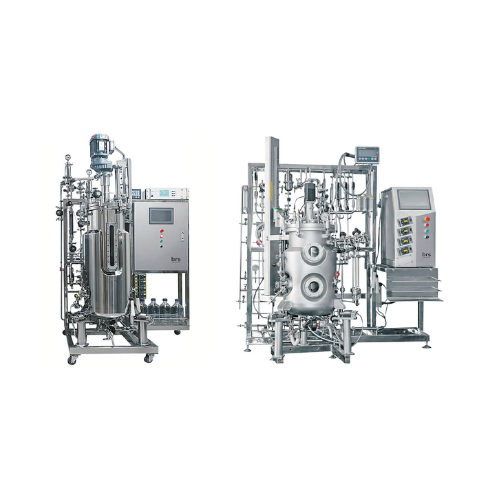
Industrial fermentors for large-scale bioprocessing
Enhance yield and consistency in fermentation processes with precise ...
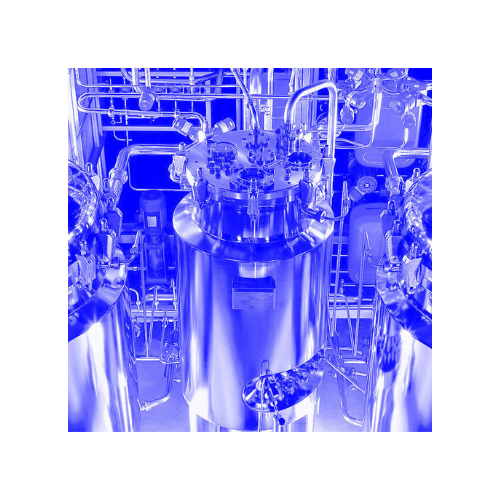
Media and buffer preparation solution for bioprocessing
Achieve seamless media and buffer preparation with precise dosing...
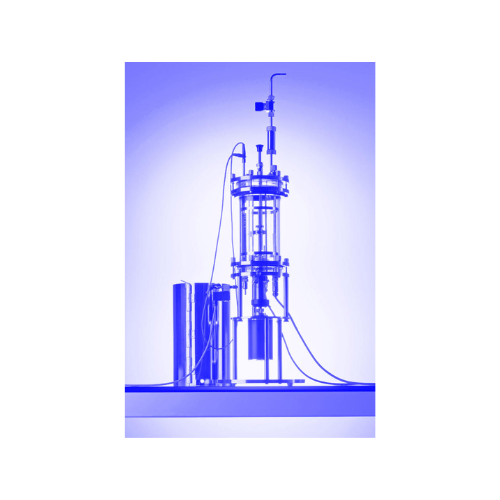
Lab-scale in-situ sterilizable bioreactor
Ensure precision in your laboratory and pilot projects with this bioreactor, des...
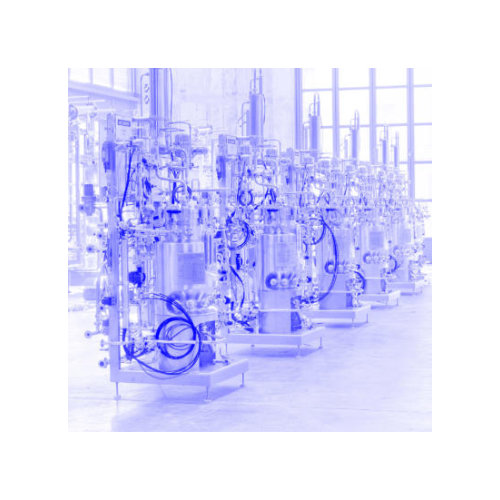
Modular bioreactor for low-volume production
Optimize your bioprocessing with a scalable solution designed for precise con...
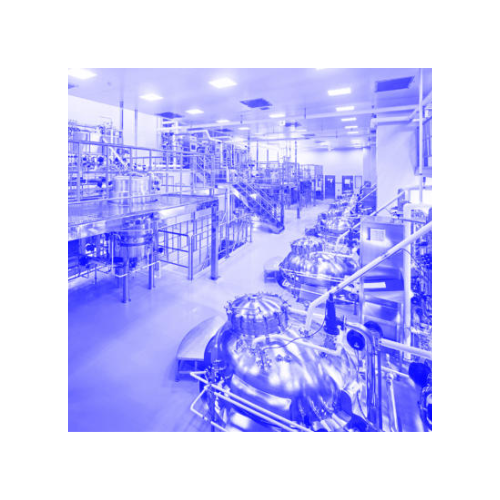
Bioreactors for cell culture processes
Efficiently cultivate sensitive cell lines with customizable bioreactors designed to...
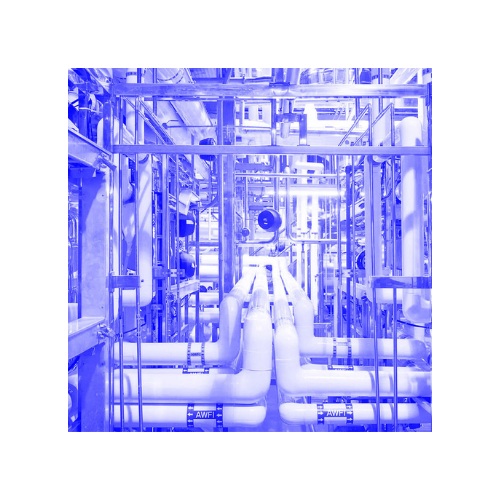
Cleaning in place systems for bioreactors
Ensure seamless sanitization with a mobile cleaning system designed to maintain ...
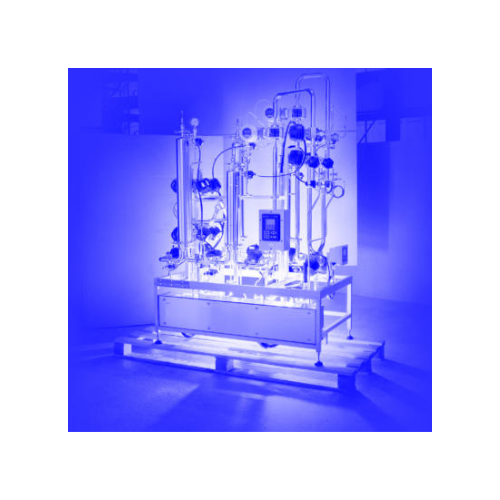
Filter stations for sterile filtration in biopharmaceuticals
Ensure sterility and precision in your biopharmaceutical pr...
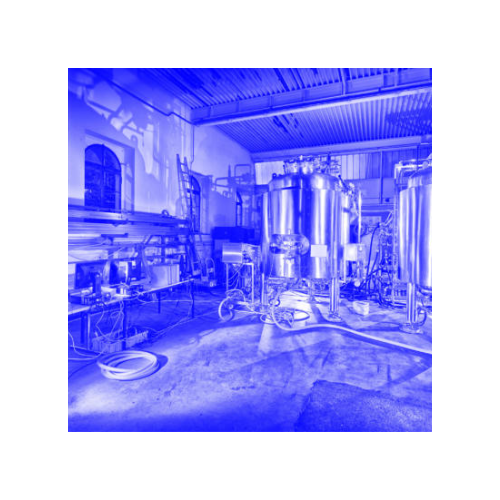
Formulation vessel for biopharmaceutical homogeneity
Achieve precise homogeneity in liquid formulations with vessels opti...
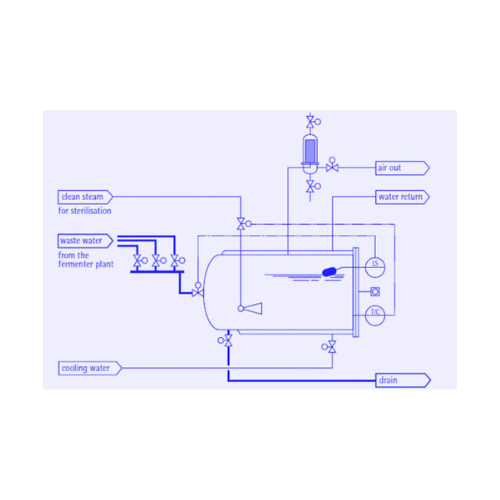
Biowaste decontamination system
Ensure safe handling of pathogenic and genetically modified organisms in wastewater with pre...
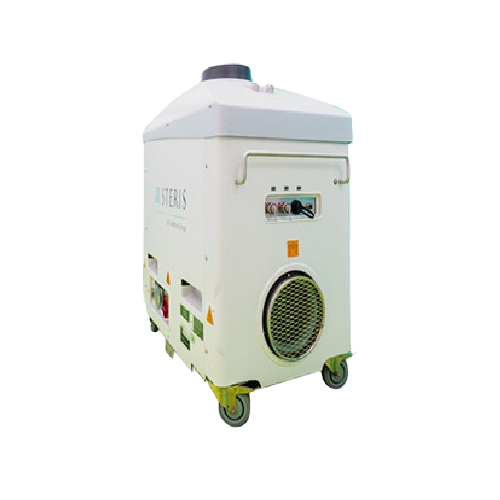
Hydrogen peroxide sterilizer for biosafety applications
Ensure optimal biosafety and contamination control with swift hyd...
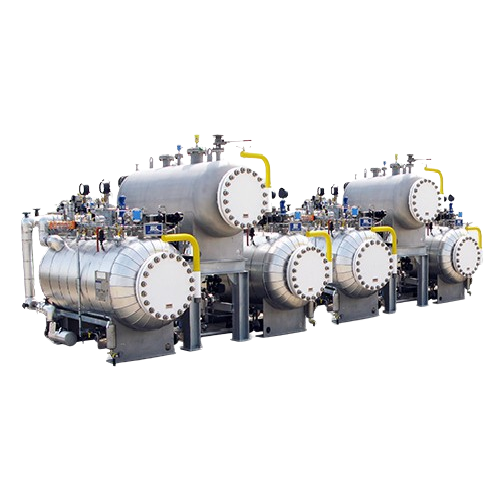
Wastewater inactivation system for biosafety
Ensure laboratory and pharmaceutical wastewater is safe for disposal with pre...
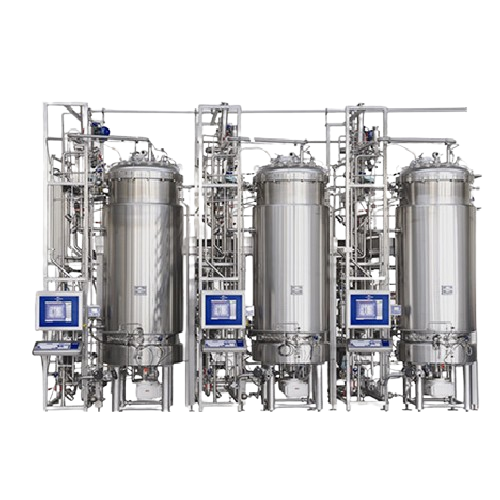
Biological fermentation tank for pharmaceutical production
Ensure consistent high-yield biological culture results with ...
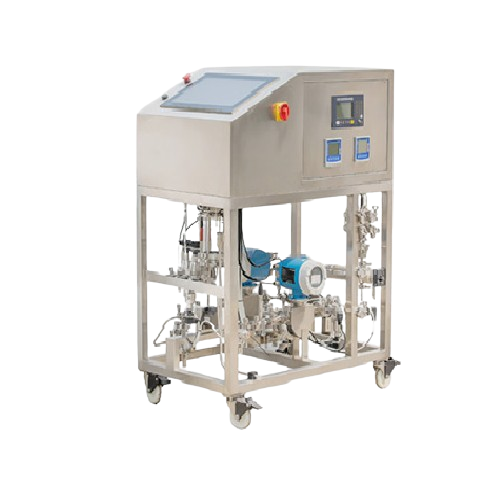
Customized chromatographic system for bioprocess purification
Streamline your bioprocess purification with advanced chro...
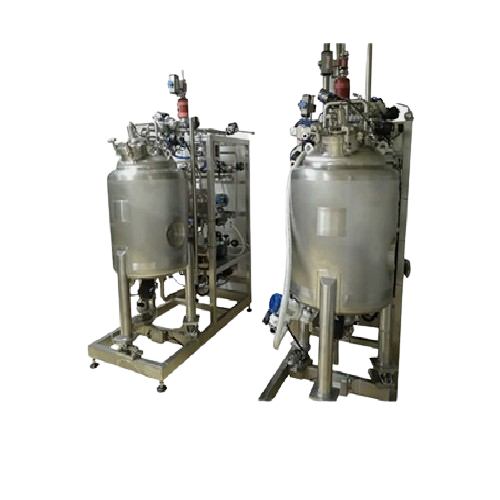
Ultrafiltration and depth filtration system for biopharmaceuticals
Achieve precise separation and purification of bioph...
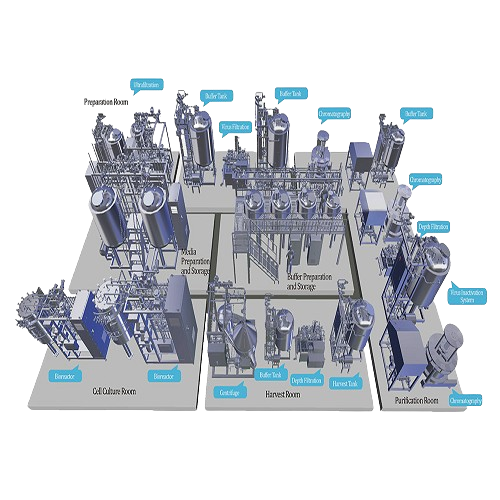
Bioprocess system for protein and antibody drugs
Streamline biopharmaceutical production with a system engineered to optim...
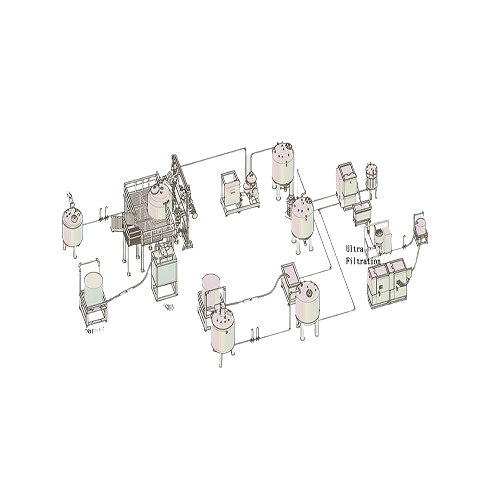
Hybrid bioprocess system for cell culture and purification
Streamline your bioprocessing operations with a versatile sol...
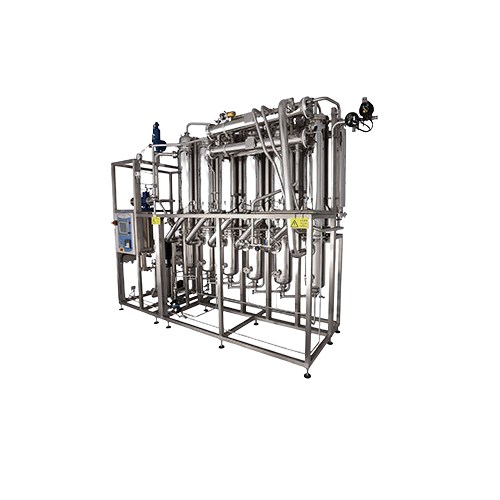
Multi-effect water distiller for pharmaceutical and biological applications
Achieve unmatched water purity for sterile...
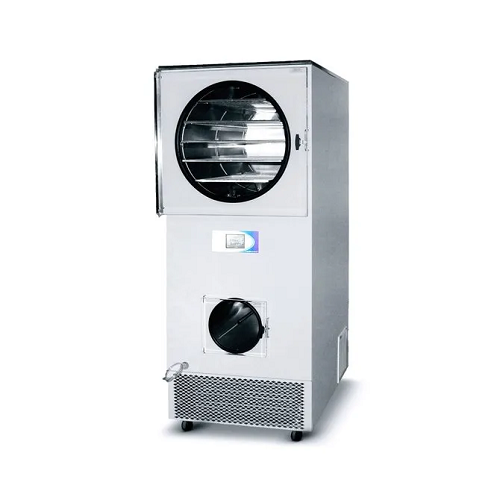
General purpose freeze dryer for archaeological and biological samples
Preserve and restore cultural and scientific tre...
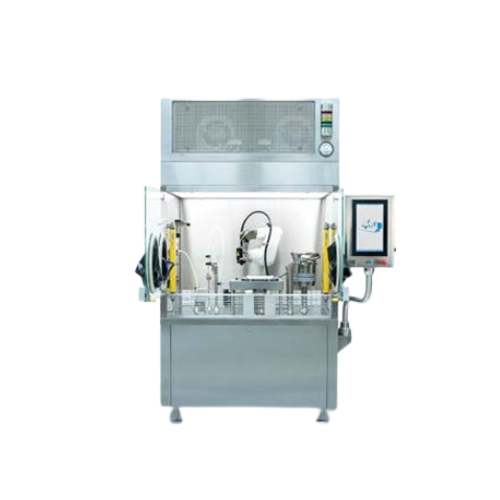
Aseptic filling line for biopharmaceuticals
Streamline your aseptic filling process with precision dosing and minimal spac...
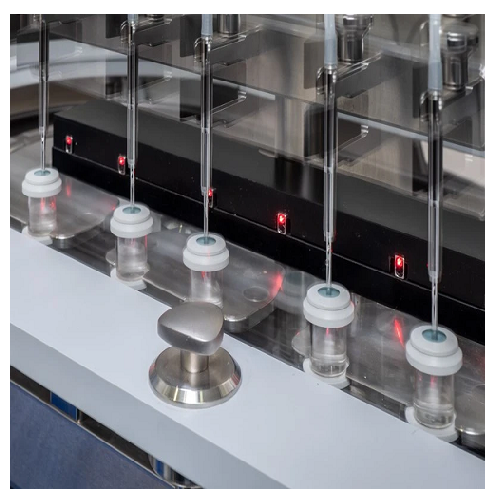
Aseptic filling line for biopharmaceutical products
Achieve precision and sterility in high-speed liquid filling operatio...
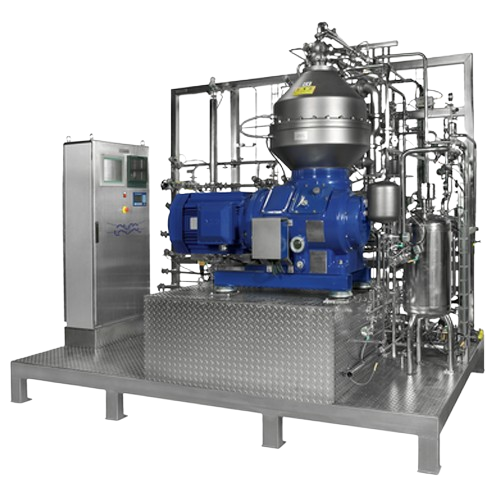
Biotech fermentation centrifuge for continuous solids discharge
Ensure high-density fermentation processes achieve optim...
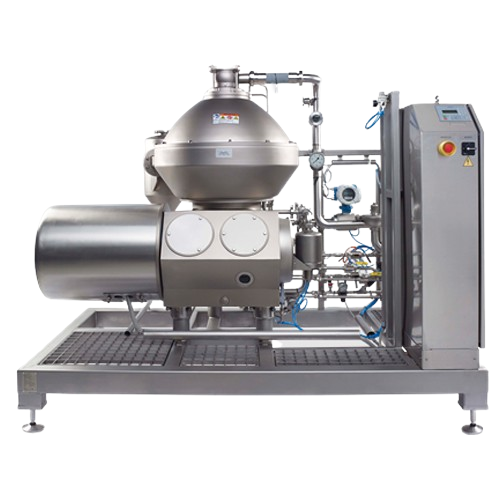
Biopharma cell centrifuge for gentle protein recovery
Ensure gentle cell harvesting and enhanced yield in bioprocessing w...
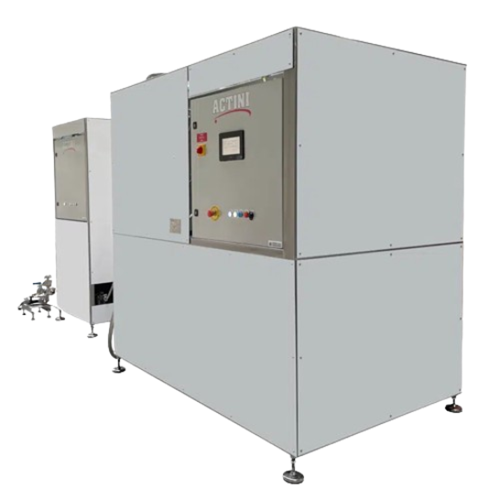
Effluent decontamination system for biological production
Ensure safe handling of high-containment effluents with an all...
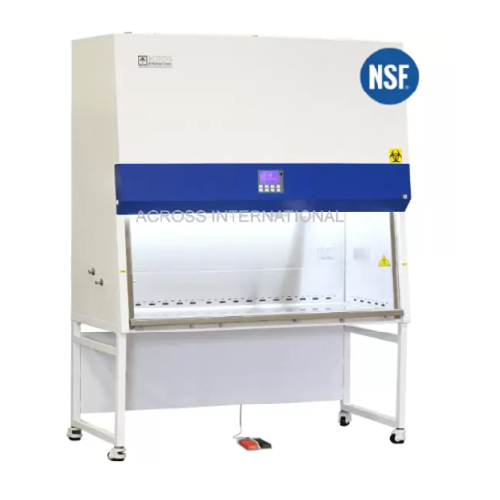
Nsf certified class Ii a2 biosafety cabinet
Ensure laboratory safety and specimen integrity with a biosafety cabinet desig...
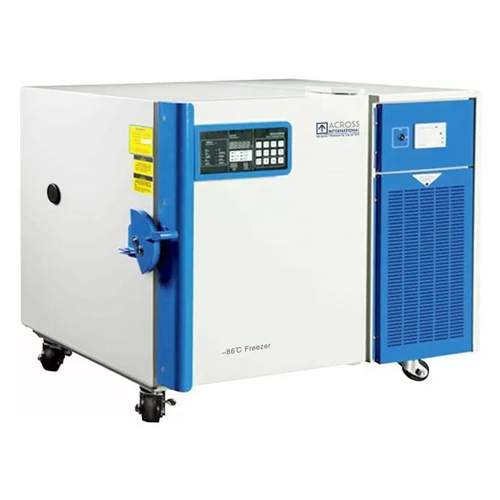
Ultra-low upright freezer -86°c for biological sample storage
Preserve vital biological samples with precise ultra-low t...
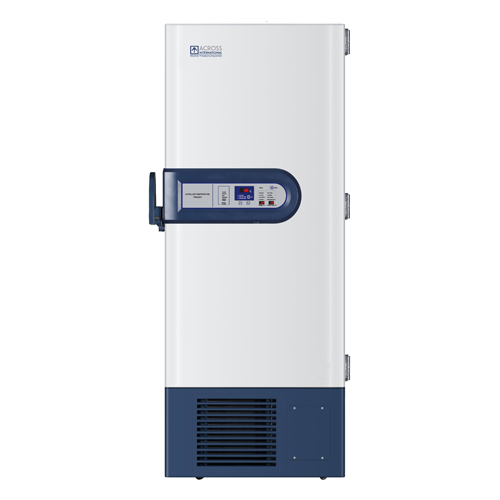
Ultra-low freezer for medical and biological storage
For critical preservation of sensitive samples, this ultra-low tempe...
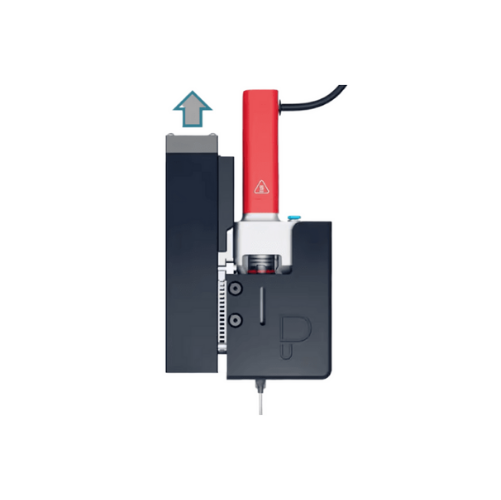
Temperature control system for bioprinting with gelatin
Ensure precise bioprinting outcomes by maintaining accurate tempe...
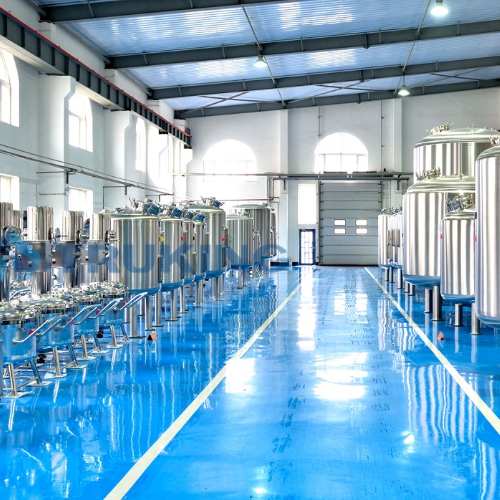
Stainless steel craft tanks for biopharmaceuticals
Ensure precise temperature control and customized capacity for your fo...
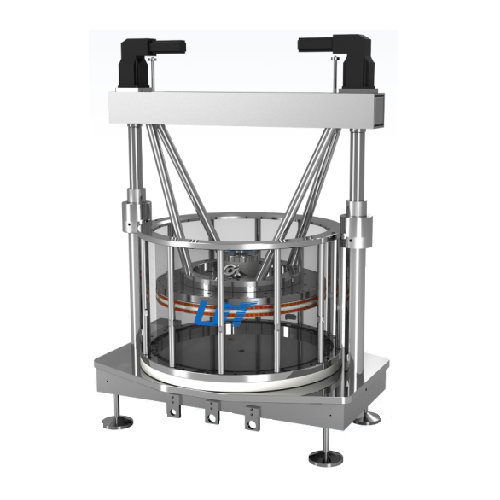
Automatic chromatography column for biopharmaceutical separation
Ensure high-purity monoclonal antibodies and herbal ext...
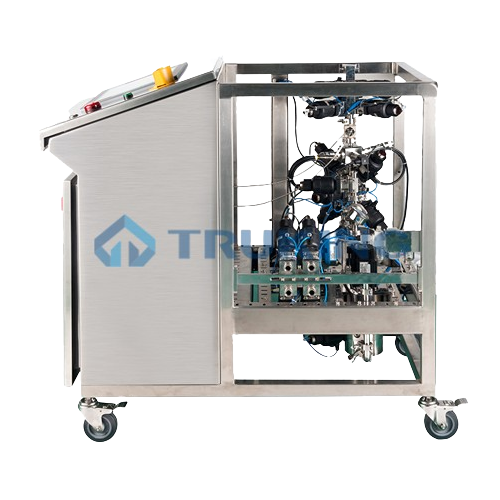
Chromatography systems for large-scale biopharmaceutical purification
Ensure precision purification of biopharmaceutica...
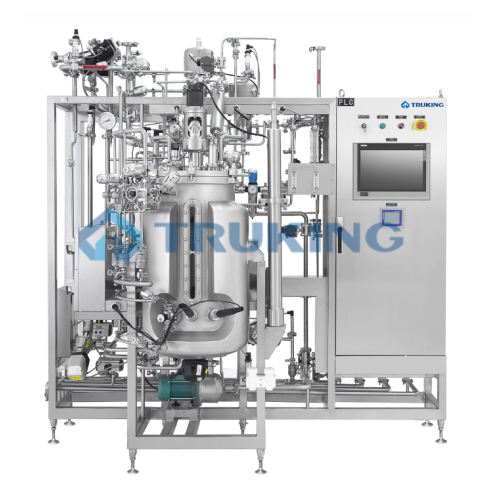
Bioreactor system for protein and enzyme reaction
Ensure precise control in biopharmaceutical production with a bioreacto...

Single use bioreactor for cell culture and fermentation
Optimize your cell culture processes with scalable, single-use bi...
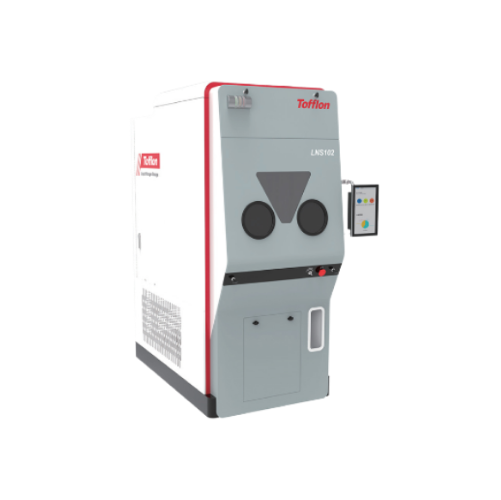
Automatic liquid nitrogen storage system for biological samples
Ensure the integrity of your biological samples with a m...
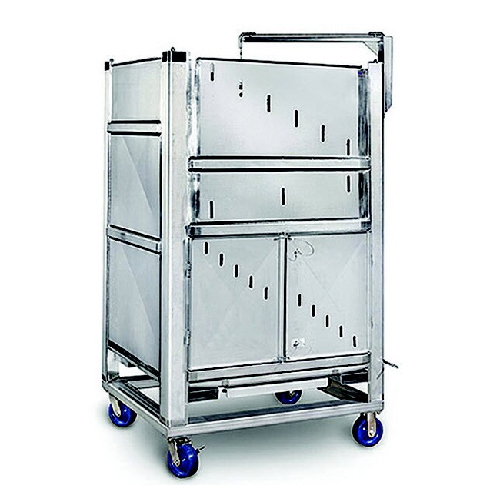
Stainless steel container for bioprocessing
Optimize the containment and handling of large-volume biopharmaceutical liquid...
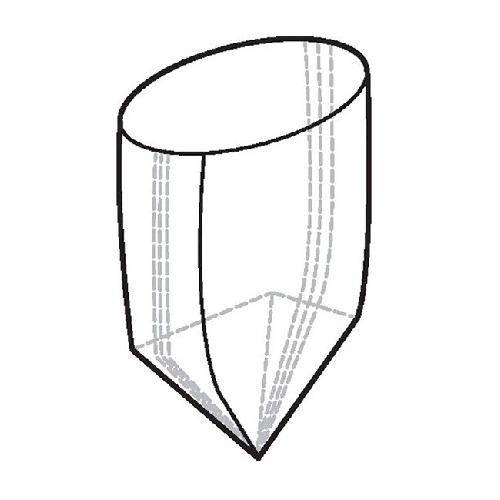
200l sterile tank liners for bioprocessing
Streamline your bioprocessing operations by eliminating tank cleaning steps and...
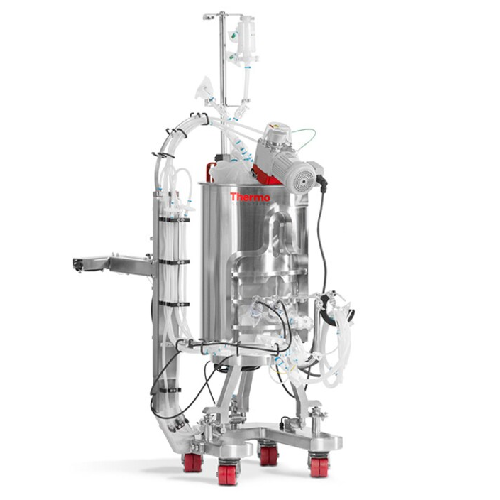
Single-use bioreactor for protein expression
Optimize your biopharmaceutical production with an advanced single-use biorea...
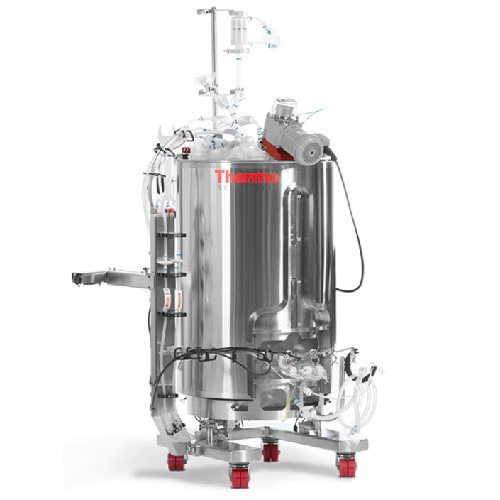
Single-use bioreactor for cell culture applications
Achieve optimal cell growth and product yield with a single-use biore...
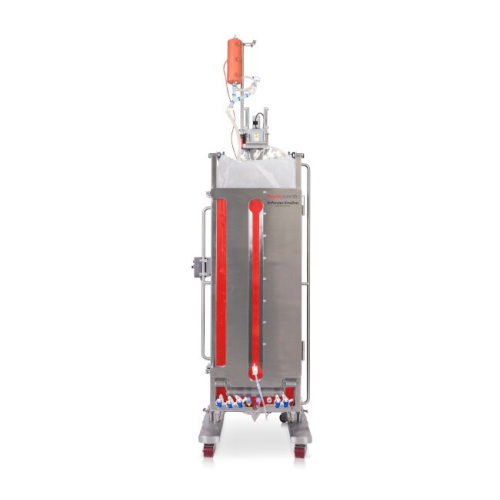
Single-use bioreactor for high volume cell cultures
For optimizing cell culture efficiency, this advanced bioreactor revo...
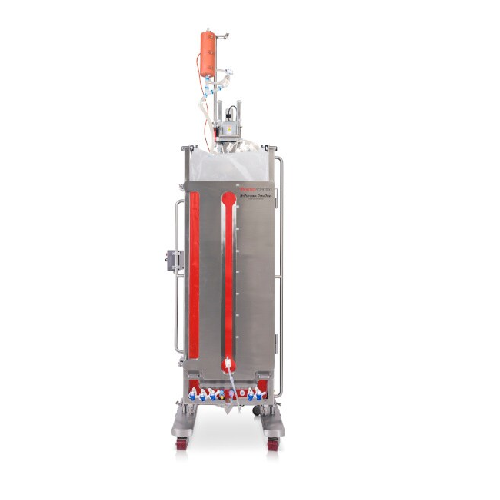
Single-use bioreactor for cell culture processes
Optimize your cell culture productivity with advanced mixing dynamics tha...
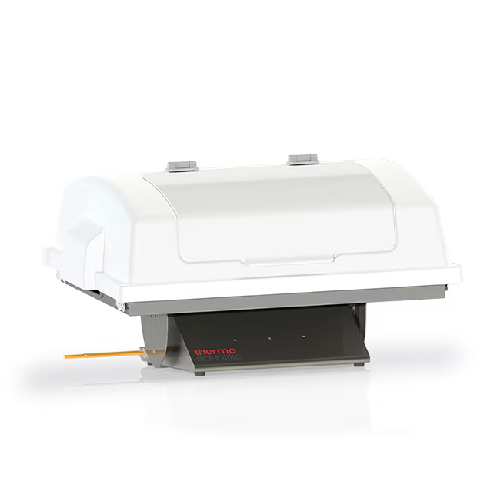
Rocker bioreactor for cell culture processes
Achieve precise control over cell culture conditions with this rocker bioreac...
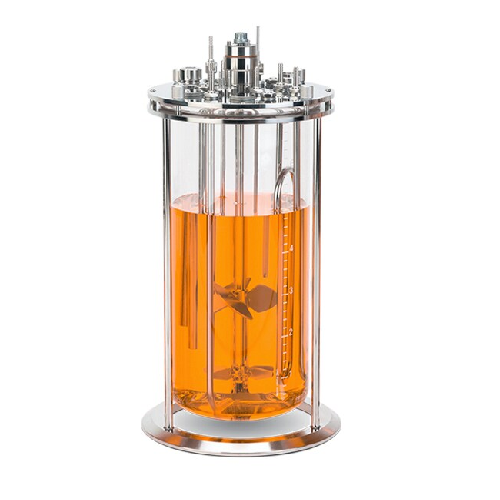
Glass bioreactor for mammalian cell culture
Optimize your bioprocessing with advanced mixing and cooling capabilities, des...
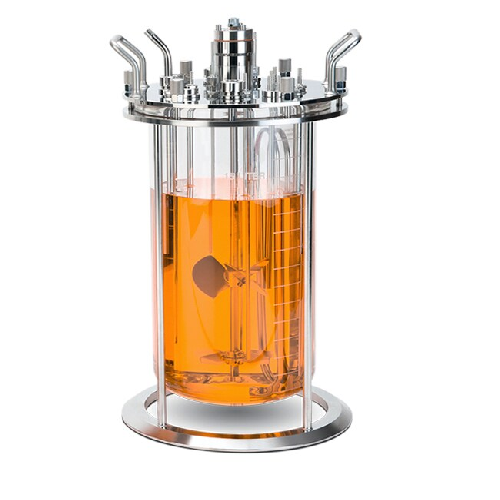
Glass bioreactor for cell culture processes
Optimize your cell culture and fermentation processes with a high-efficiency b...
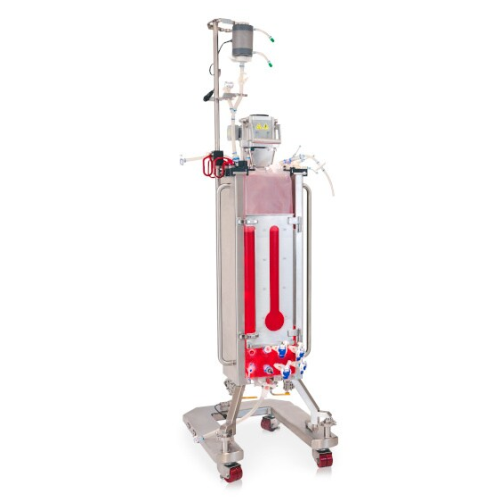
Single-use bioreactor for cell cultures
Enhance your cell culture efficiency and minimize contamination risks with a state-...
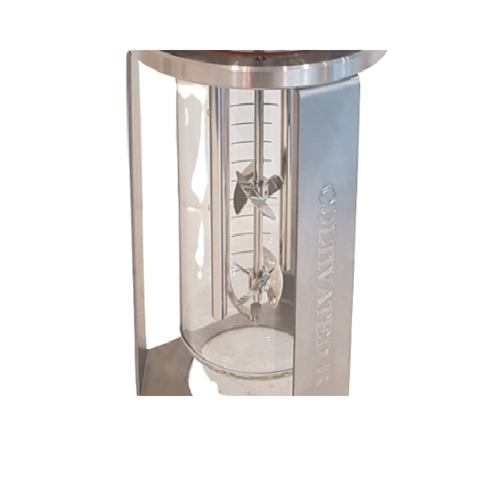
Benchtop bioreactor for research and development
Achieve precise control over fermentation and cultivation processes with ...
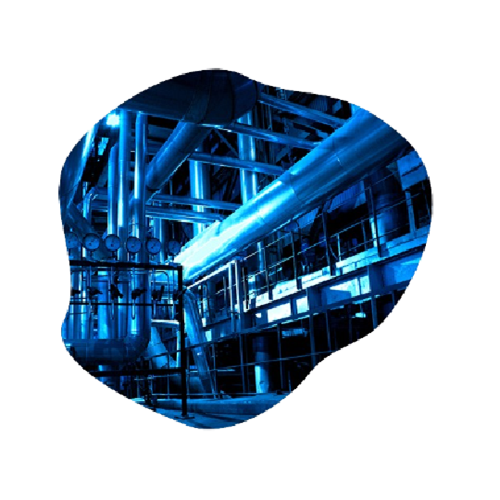
Industrial-scale bioreactors for large-scale biomanufacturing
When producing at large volumes, efficient and reliable bi...
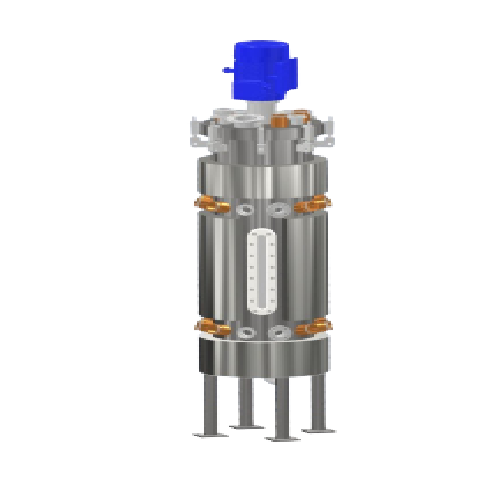
Pilot-scale bioreactors for bioprocess scale-up
Bridge the gap between experimentation and large-scale production with pil...
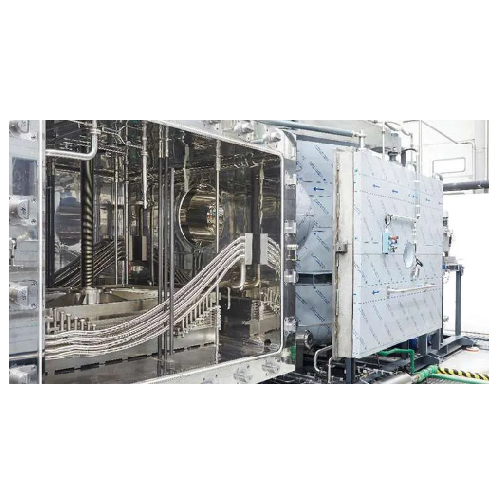
Cryogenic freeze dryer for biotherapy microbiotics
Achieve precise temperature control and efficient moisture removal in ...
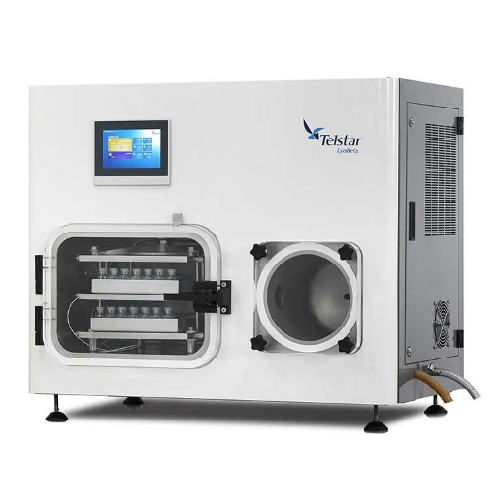
Freeze dryer for small batch scale-up in biotech and pharma
Optimize freeze-drying processes for small batches or high-v...
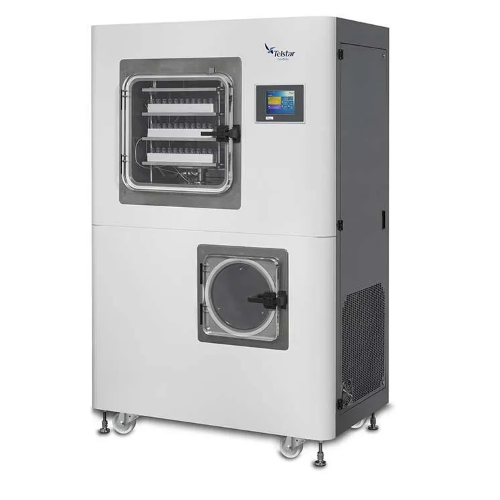
Research and scale-up freeze dryer for biological and pharmaceutical applications
Allows efficient scale-up of lyophi...
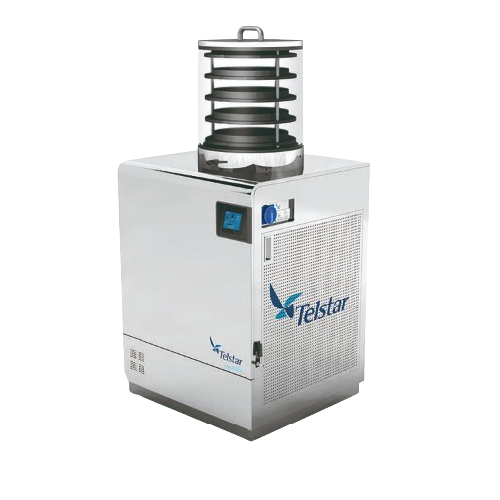
Basic research freeze dryer for biomedical applications
For laboratories seeking precise sample preservation, this bencht...
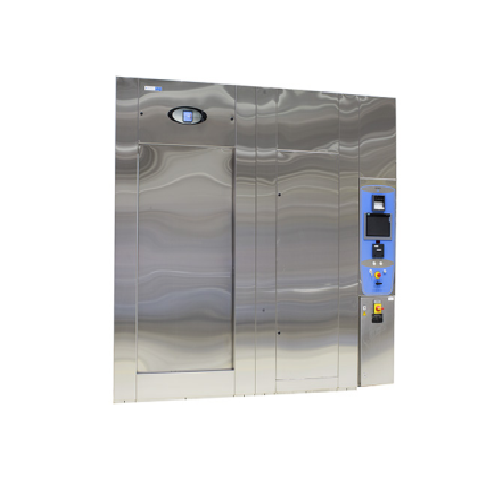
Sterilization system for biosafety applications
Ensure sterility and compliance in critical manufacturing processes with a...
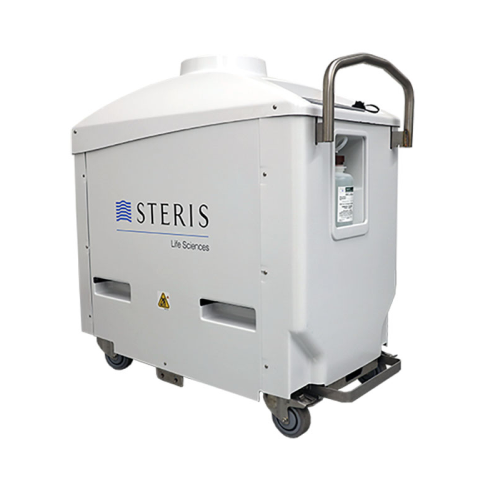
Mobile biodecontamination unit for cleanroom environments
Achieve rapid, high-capacity sterilization in cleanrooms effor...

3d printer for high-precision microbioreactors
Achieve unprecedented precision in bioprocessing with a 3D printer capable ...
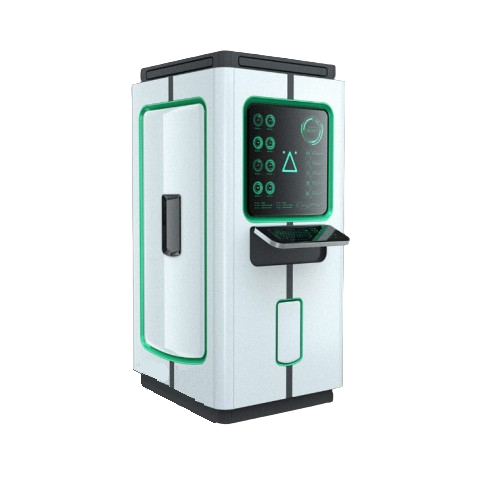
Desktop bioprocessor for continuous biomanufacturing
Shrink your biotech facility to a bench-top unit, achieving seamless...
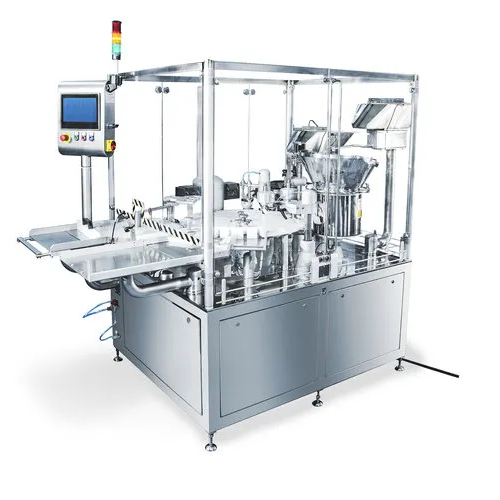
Micro-line vial filling solution for biopharmaceuticals
Ensure batch consistency and sterility in fill-finish operations ...
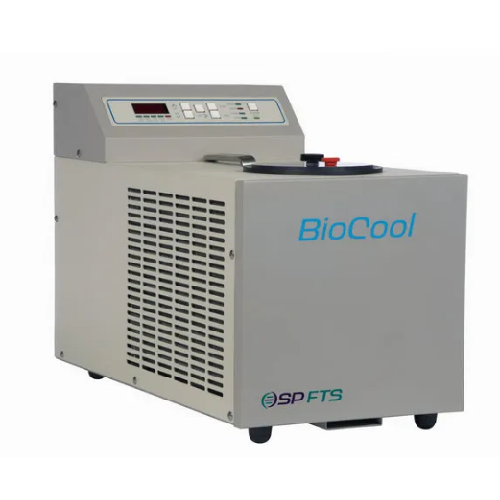
Controlled freezer for biological samples
Achieve precise and reliable freezing without hazardous refrigerants, ensuring t...
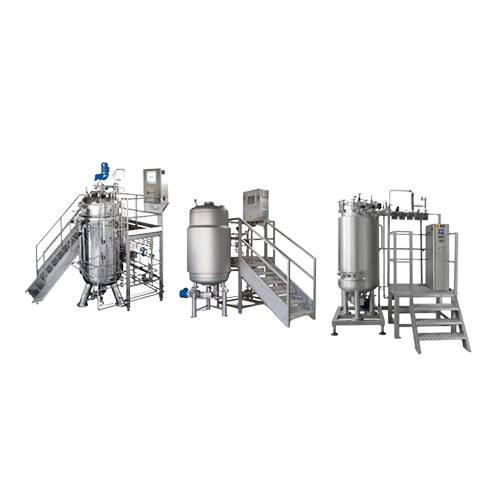
Reactors and tanks for bioreactors and fermenters
Enhance bioprocessing efficiency with robust solutions for mixing, aera...
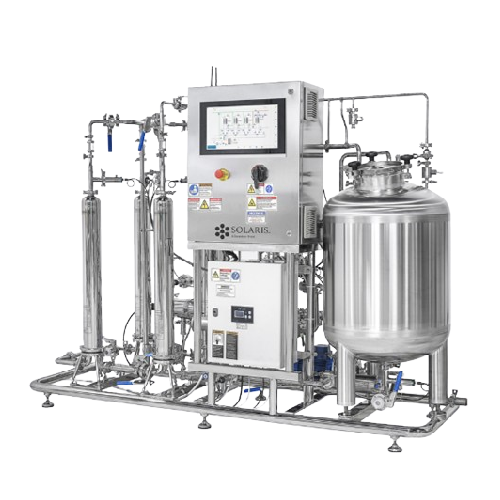
Full flow filtration system for bioprocess applications
Ensure sterile filtration of process liquids and aseptic chemical...
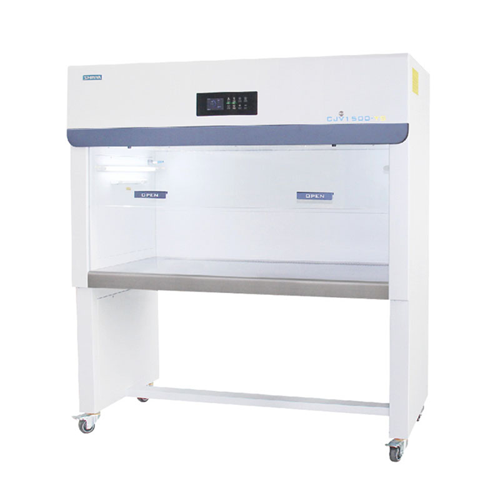
Intelligent clean bench for biosafety labs
Ensure sterile conditions with advanced airflow control and real-time monitorin...
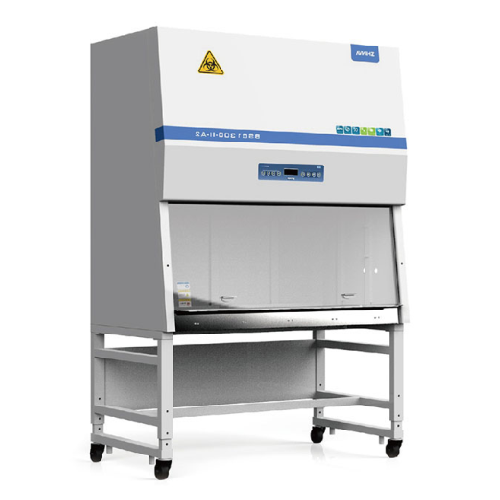
Class Ii biological safety cabinet for laboratory use
Ensure maximum protection for your laboratory personnel and samples...
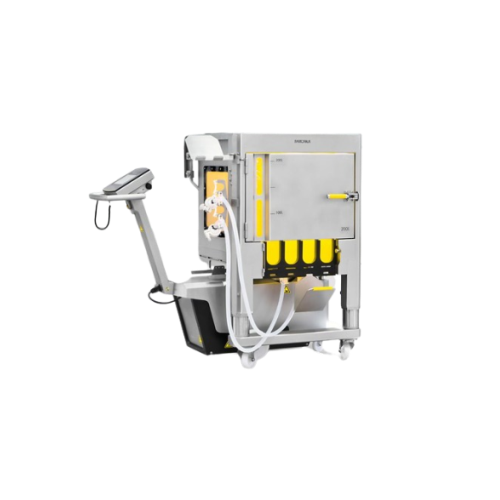
Single-use mixing system for biopharmaceutical production
Achieve precise blending and homogenization of shear-sensitive...
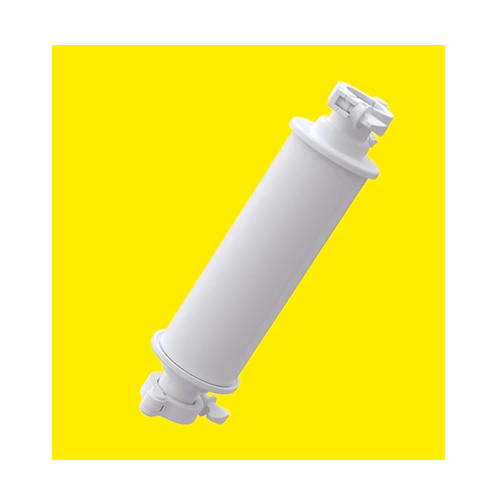
Single-use batch chromatography systems for biopharmaceuticals
Streamline your purification process with high productivi...
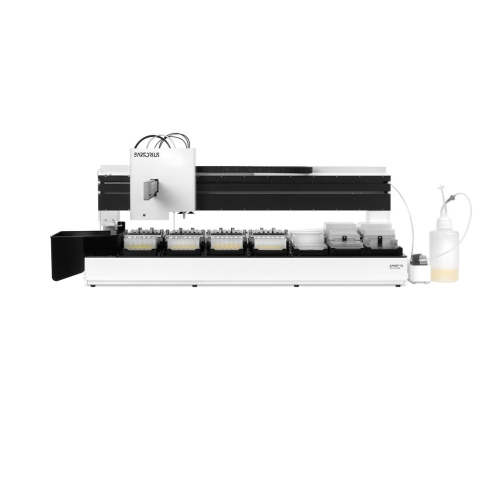
Multi-parallel bioreactors for cell line selection and process development
Enhance your biopharmaceutical production w...
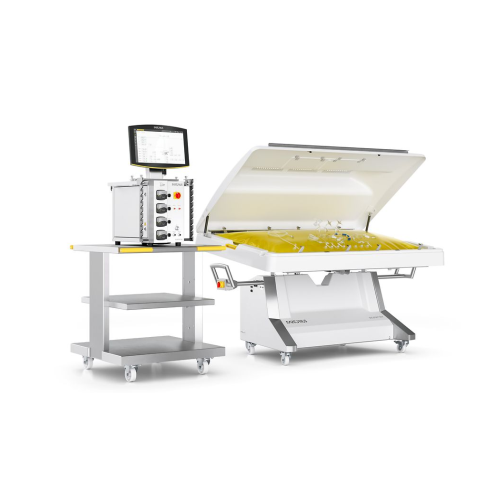
Cell culture bioreactor for mabs and vaccines
Optimize your biopharmaceutical production with advanced cell culture capabi...
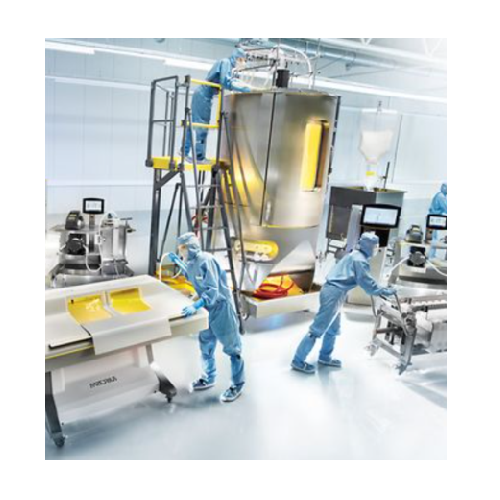
Single-use bioreactors for mammalian cell culture
Enhance agility and cut costs with scalable, single-use bioreactors ide...
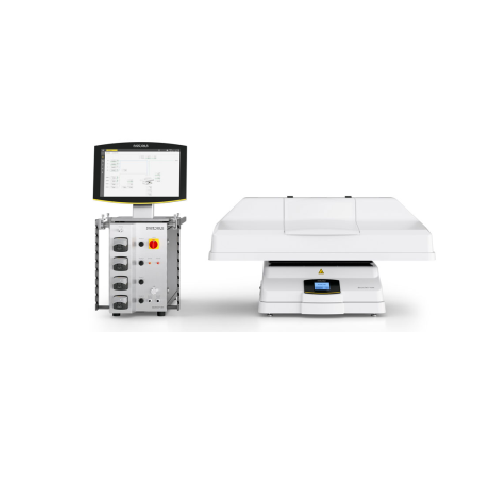
Wave-mixed bioreactor for shear-sensitive cell cultures
Optimize cell cultivation with a modular, wave-induced mixing sys...
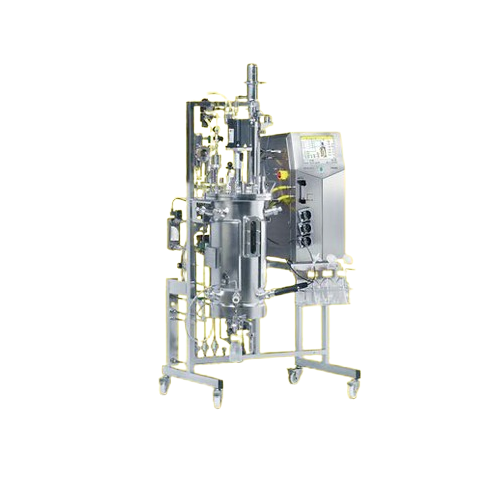
Stainless steel bioreactors
Enhance your bioproduction capabilities with robust solutions designed for efficient fermentatio...
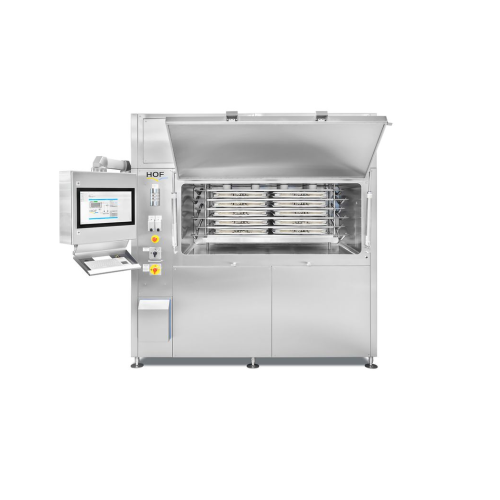
Frozen storage and shipping for biopharmaceuticals
Ensure the integrity of critical biopharmaceuticals with a robust solu...
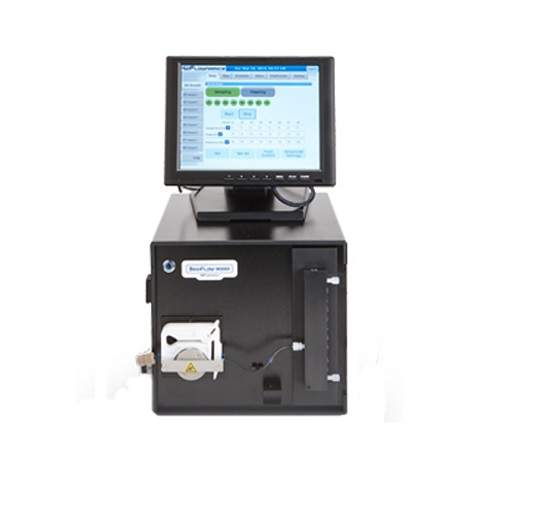
Online sampling system for larger scale bioprocesses
Accurate sampling is vital for improving a wide variety of industria...
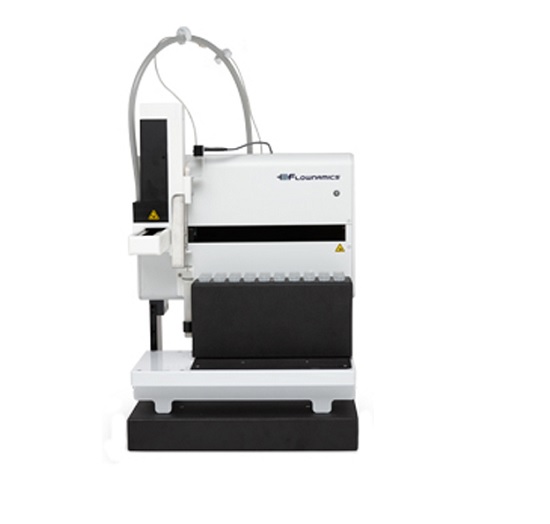
Online fraction collector for offline bioprocess analysis
Many bioprocesses require offline analysis of samples to monit...
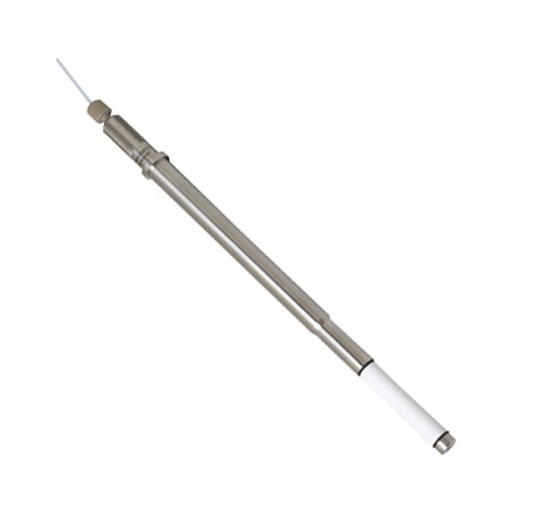
Sampling probe for bioreactor samples
In biopharmaceutical and chemical industries, sampling is vital to develop, maintain,...
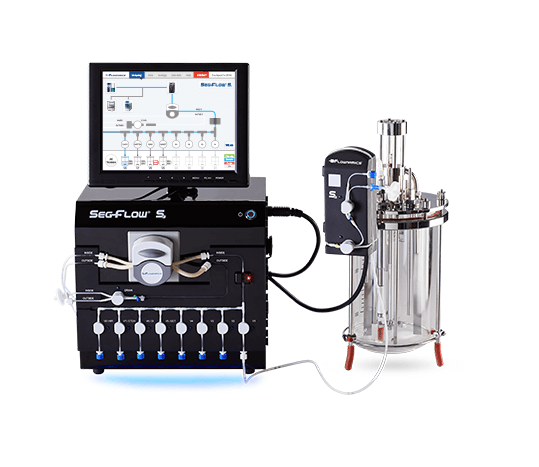
Fully Automated On-Line Sampling for Bioprocesses
Accurate sampling is a critical tool in the design and improvement of a...
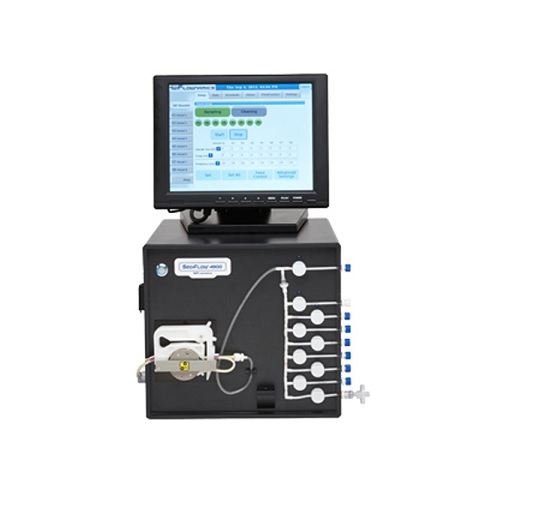
Automatic sampling system for bioprocess monitoring
An accurate, automated sampling of cultures is a key requirement in t...
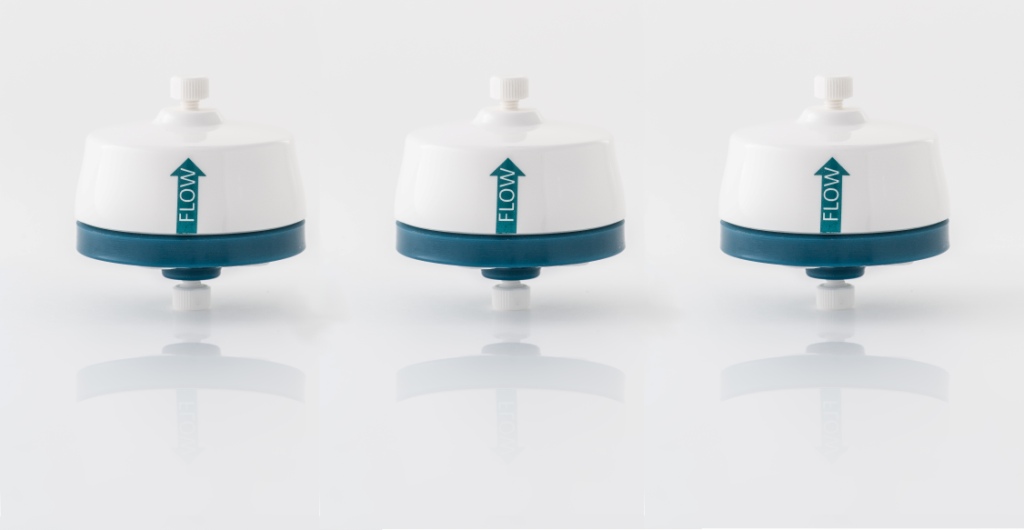
Purification screening kit for large biomolecules
To purify a specific large biomolecule, for example IgM or a virus or v...
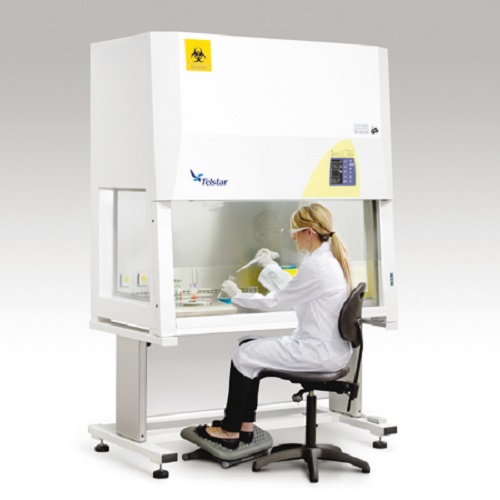
Microbiological safety cabinet class II
This handy device offers the most advanced features in product-operator protection ...
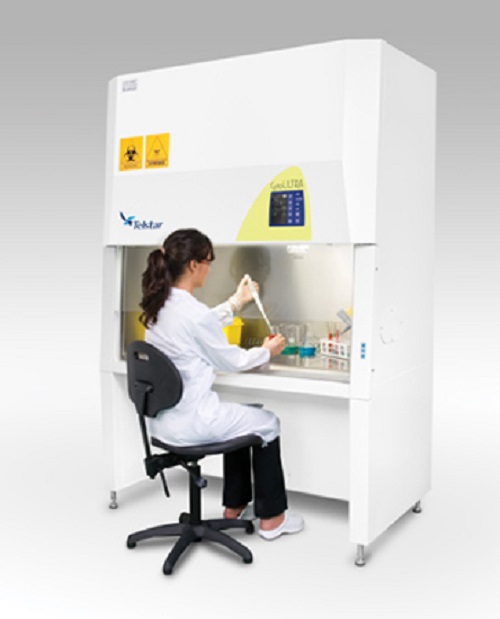
Biosafety cabinet class II for cytotoxic medicines
For the manipulation of hazardous substances utilized during the prepa...
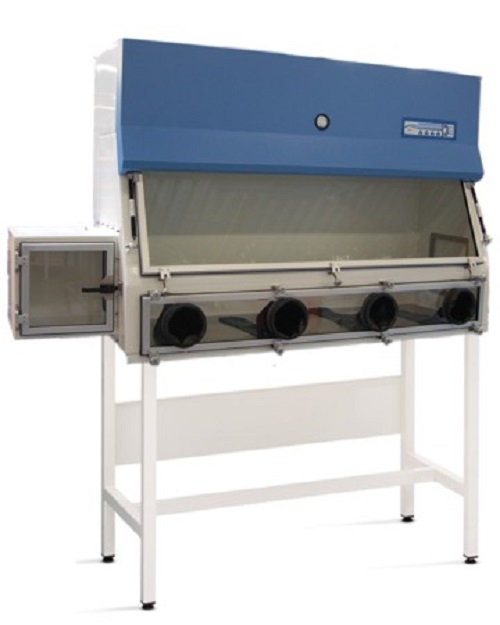
Biological safety cabinet class III
Specially designed for the handling of microbiological agents, when working with indige...
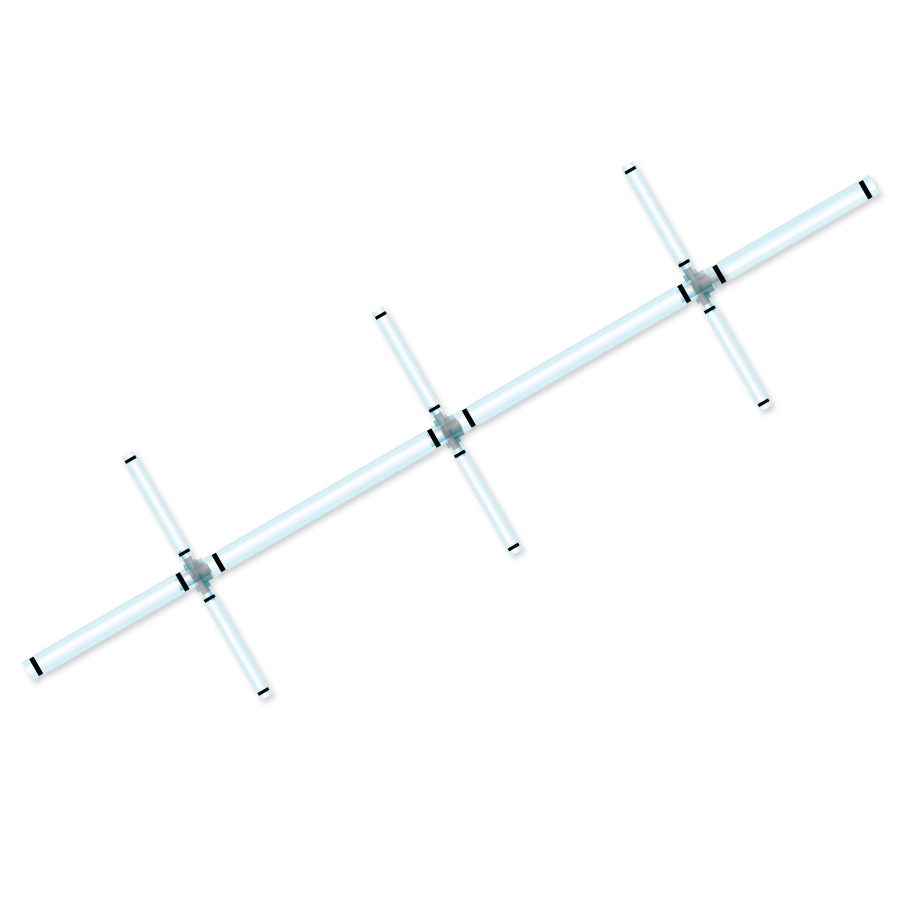
Disposable tubing for manifolds in bioprocesses
Manufacturers in the bioprocessing industries are increasingly turning to ...
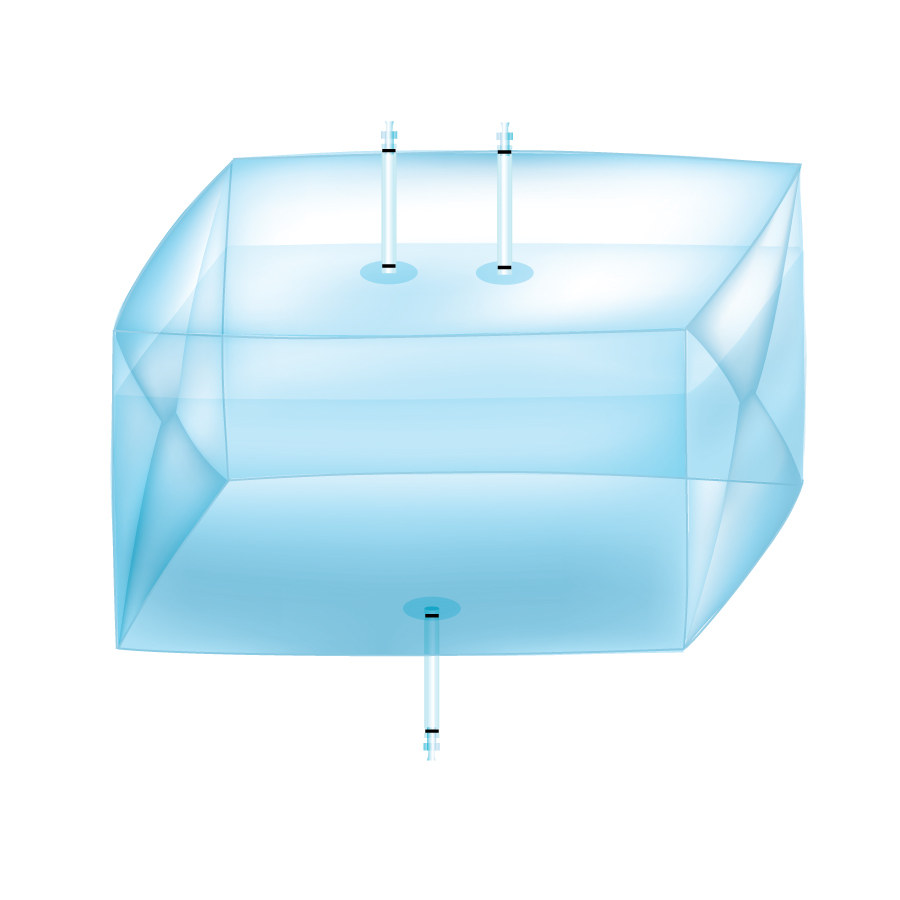
3D disposable bags for bioprocesses
Manufacturers in the bioprocessing industries are increasingly turning to single-use so...
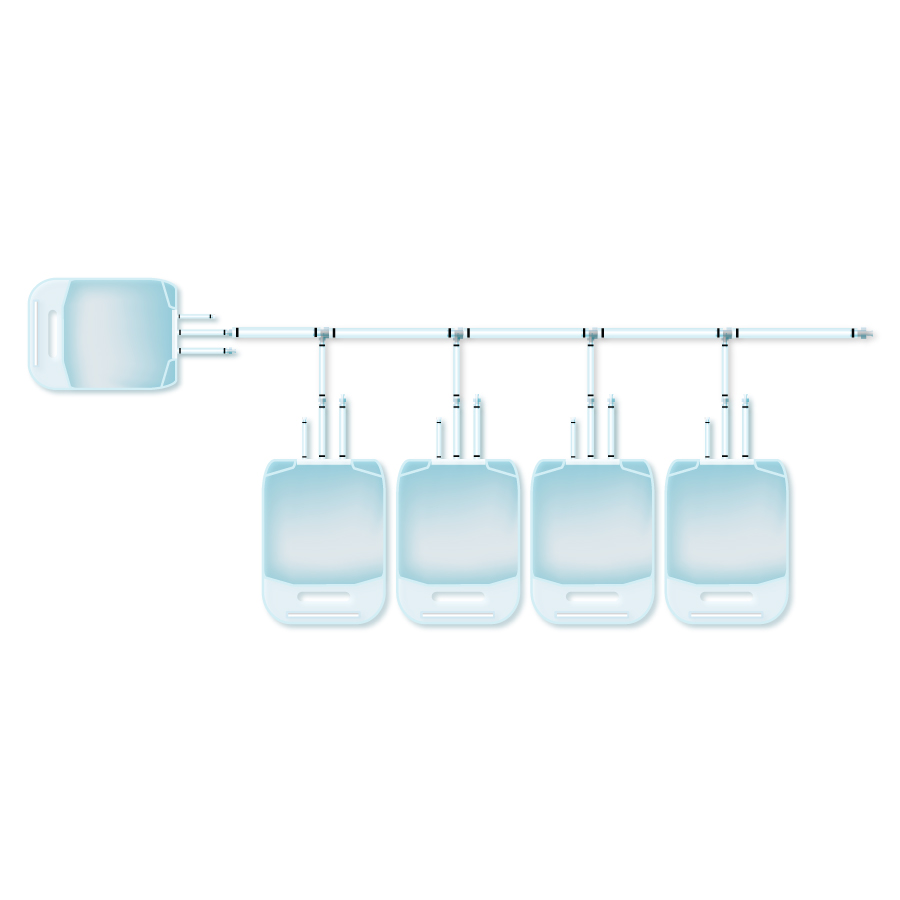
Disposable manifold bags for bioprocesses
Manufacturers in the bioprocessing industries are increasingly turning to dispos...
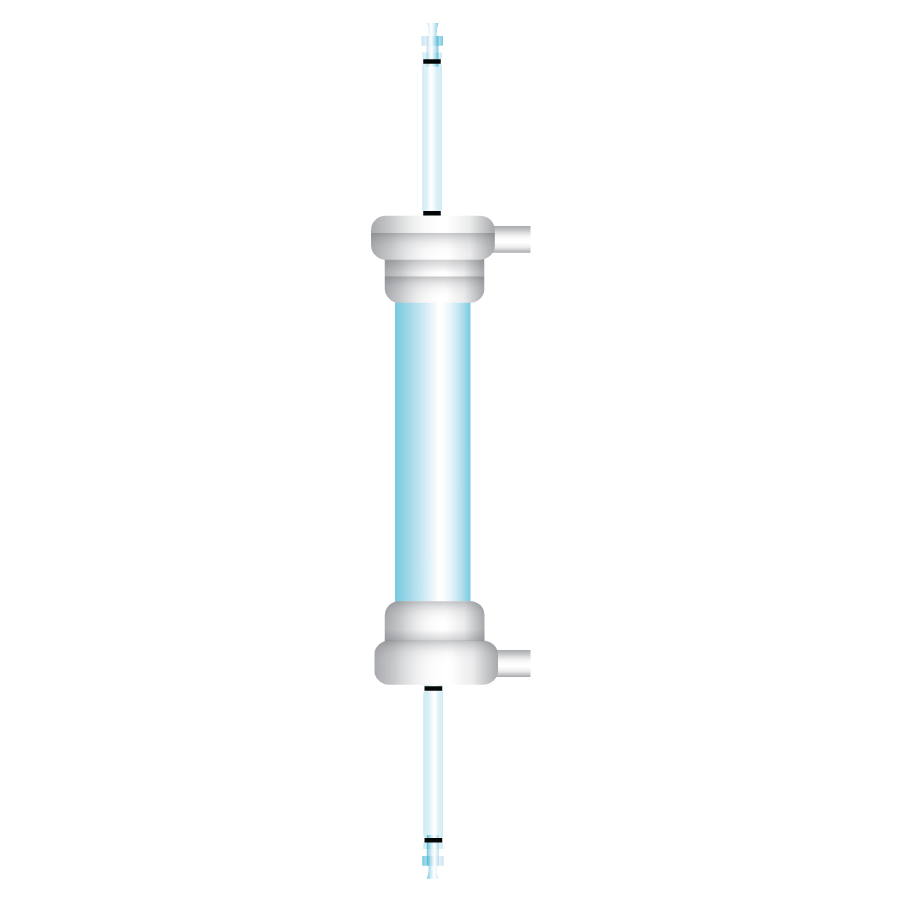
Normal flow filtration sets for bioprocesses
Bio-processors require reliable, high quality, easy to maintain, filtration e...
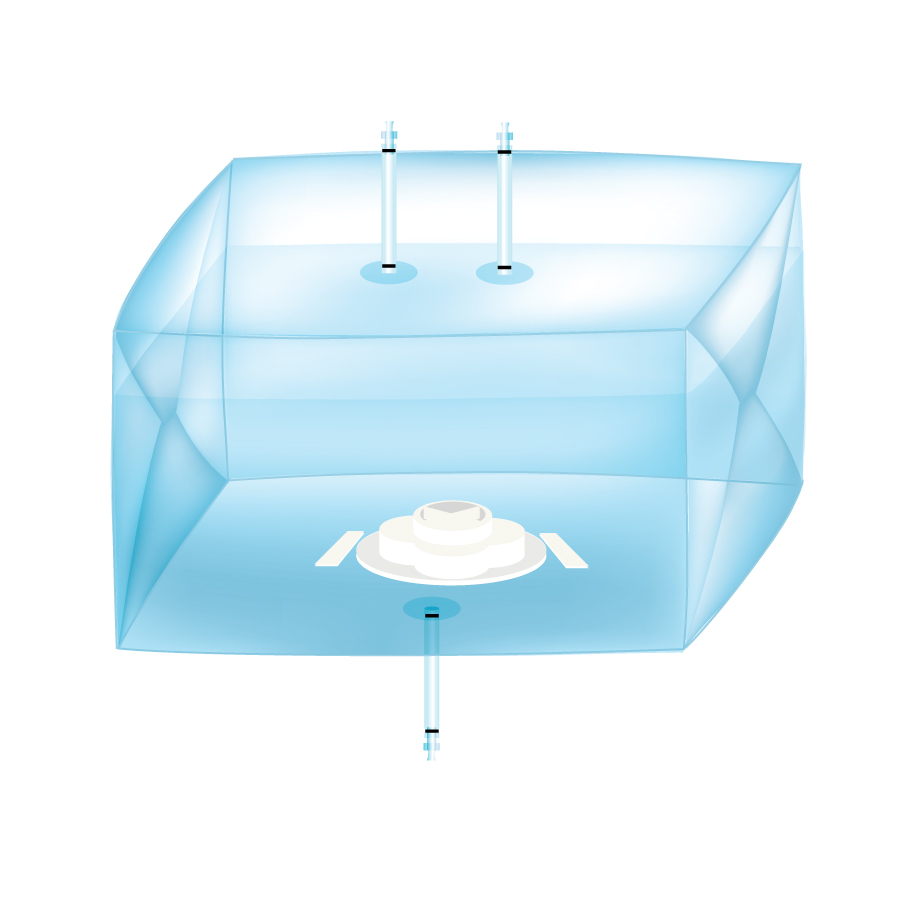
Disposable mixer bags for bioprocesses
Bioprocessors must use ingredients of known high quality and consistency. Inconsist...
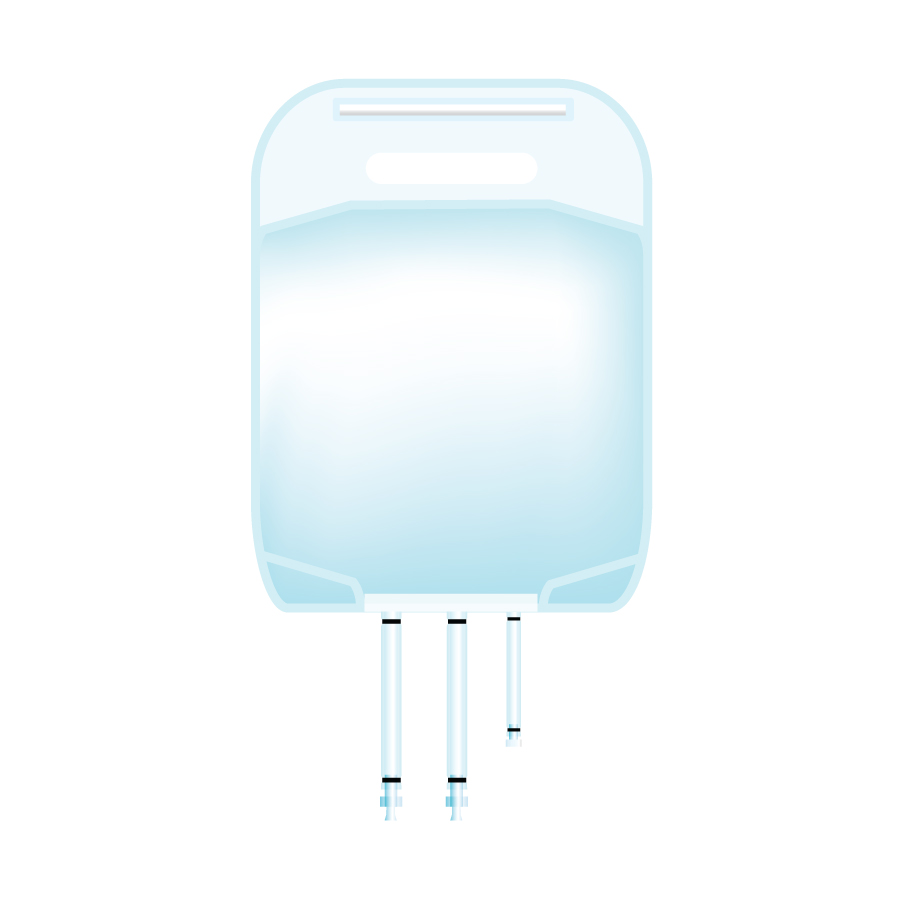
Disposable pillow bags for bioprocesses
Manufacturers in the bioprocessing industries are increasingly turning to single us...
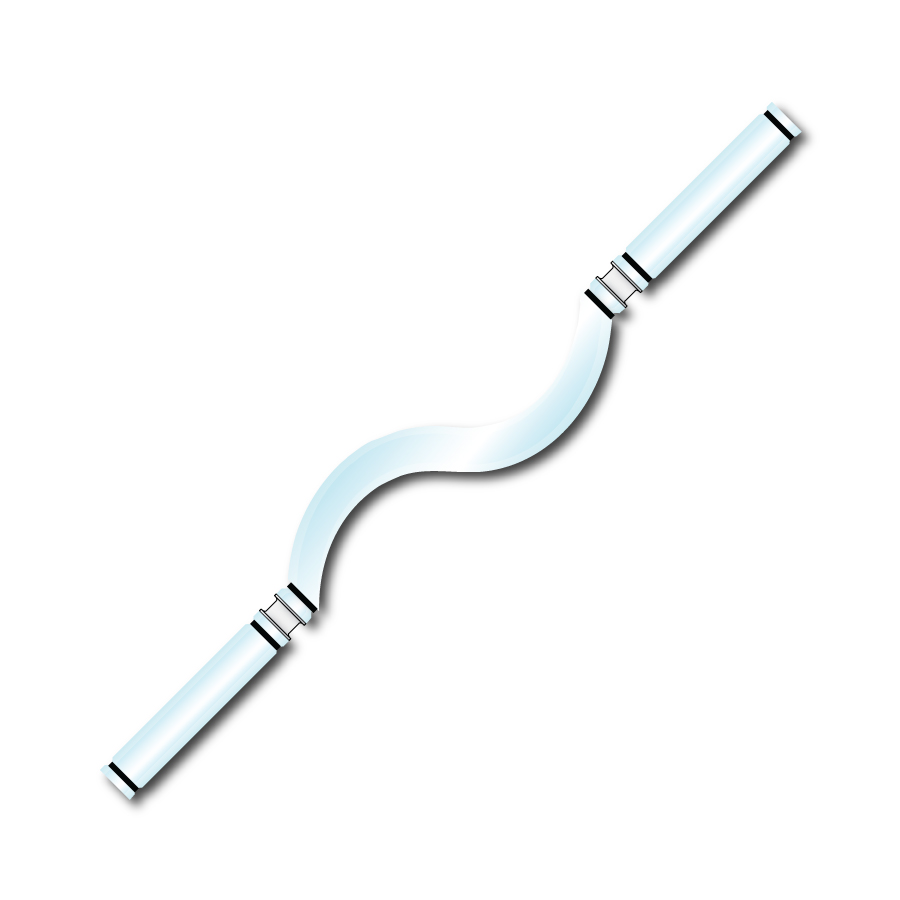
Biocompatible tubing for peristaltic pumps
Sensitive bioprocess applications requires equipment that will not interfere wi...
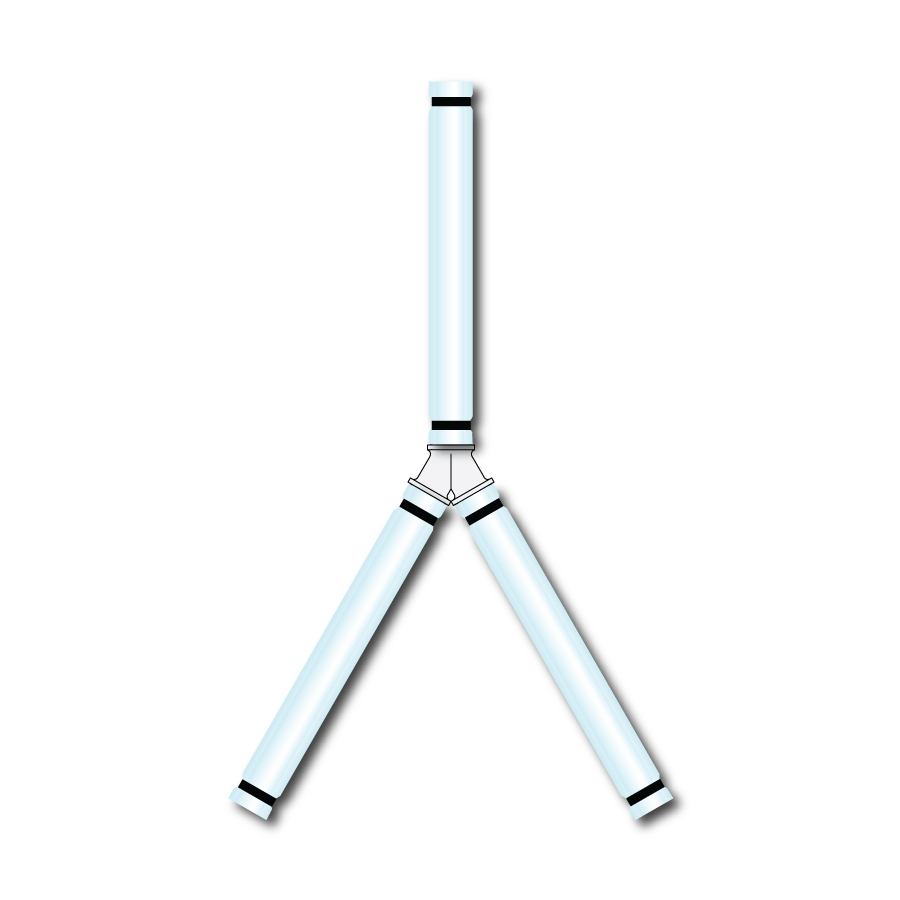
Y sets tubing for bioprocesses
Manufactueres in the bioprocessing industries are increasingly turning to single use solution...
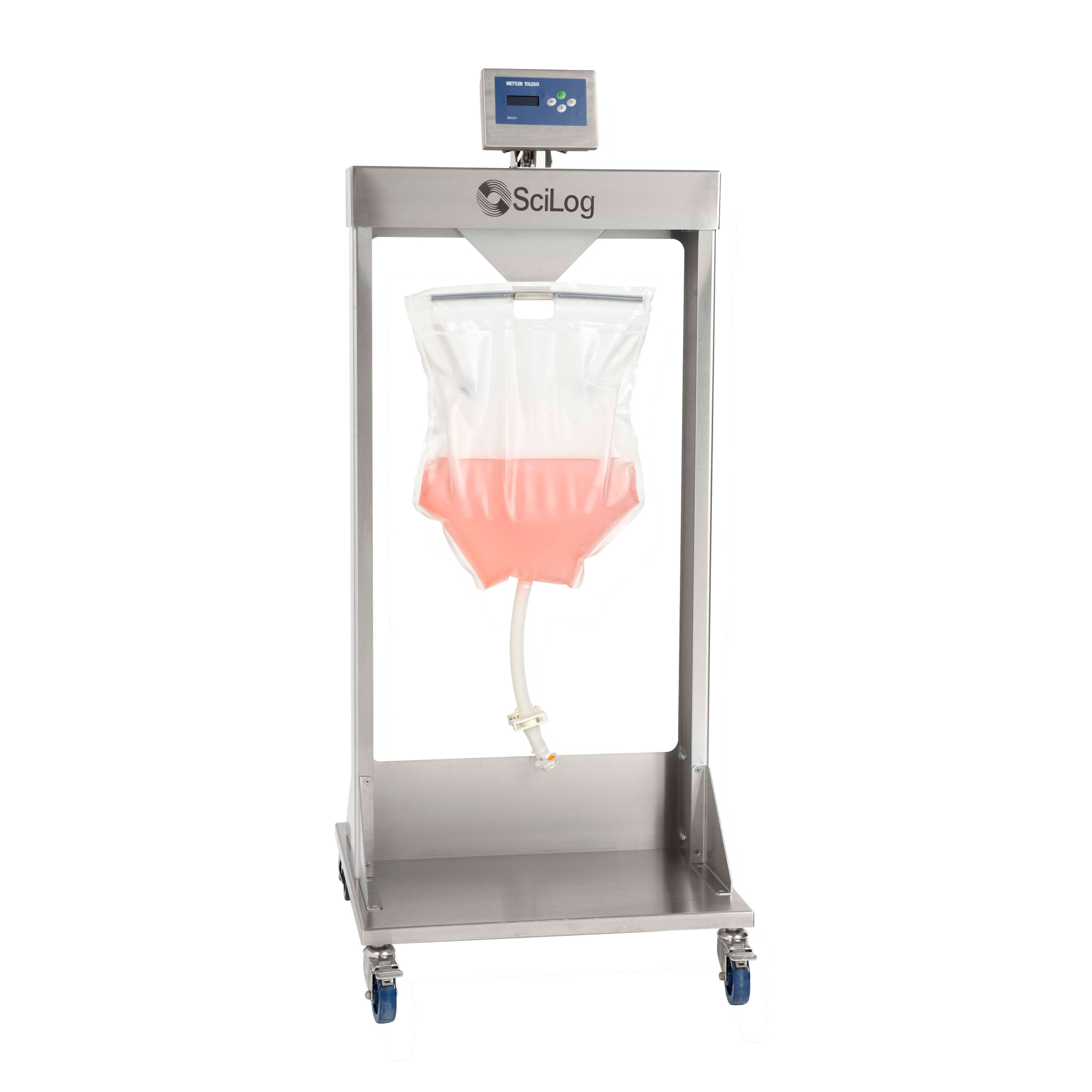
Bag holder and weighing platform for bioprocesses
Single use bags for biopharmaceutical process containment and liquid st...
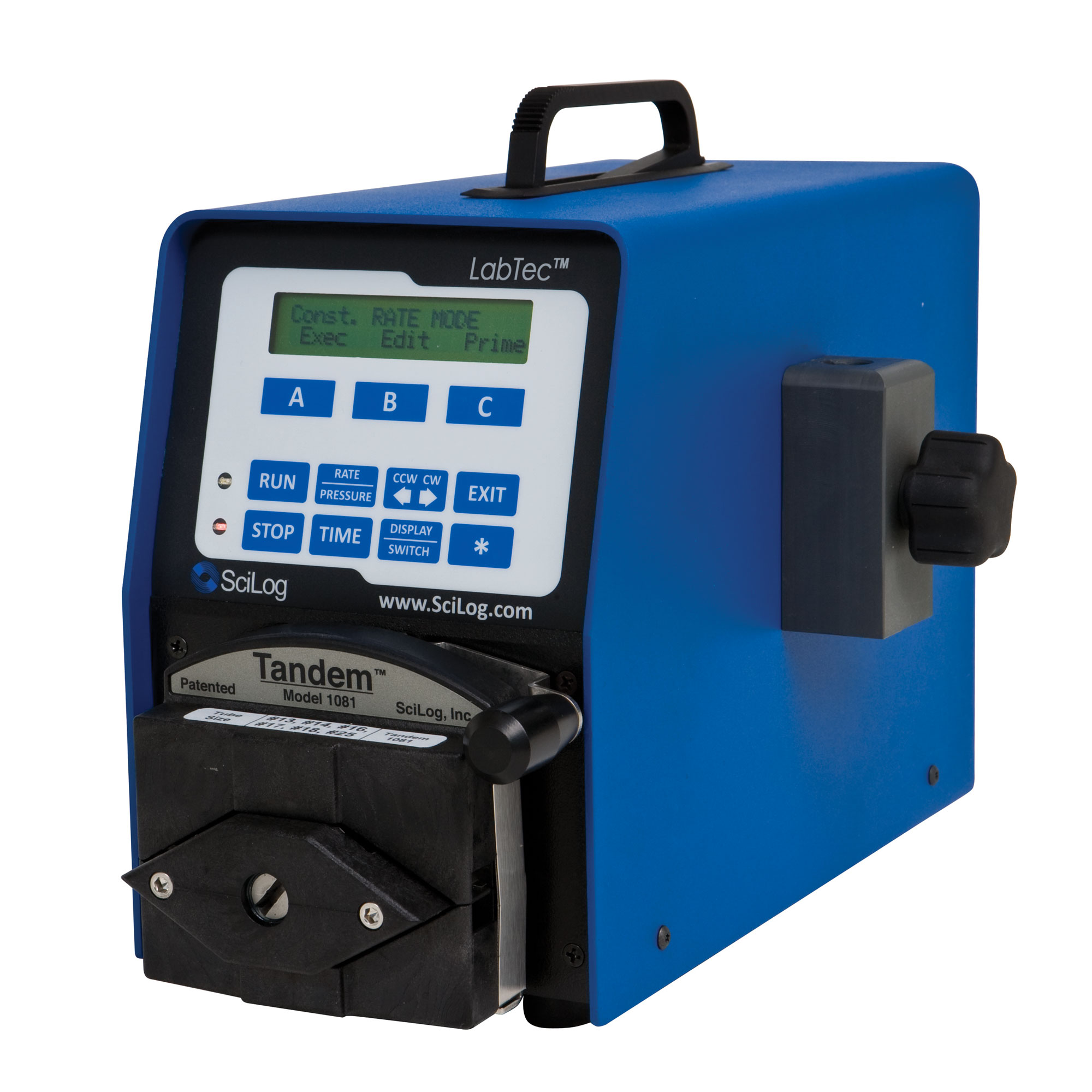
Automated dispensing system for bioprocesses
Biopharmaceutical manufacturers require precisely known liquid quantities for...
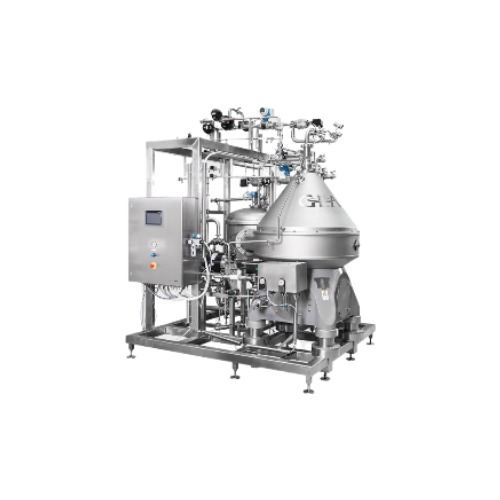
Pharmaceutical separator for high solid contents
Ensure optimal purity in biopharmaceutical processing with a separator de...

Laboratory nutsche filter dryer for solid-liquid separation
Optimize your lab processes with a versatile benchtop filter...
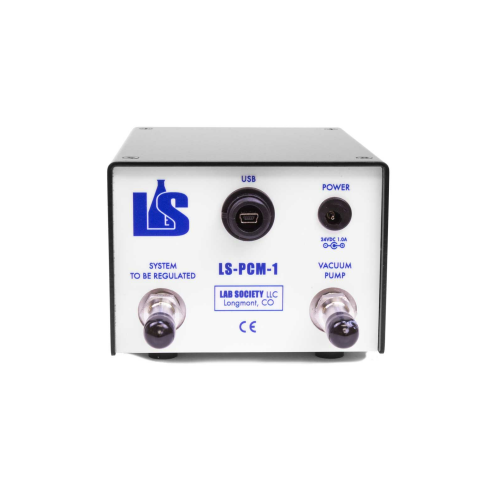
Pressure control monitor for laboratory vacuum systems
Effortlessly maintain precise vacuum pressure in your lab operatio...
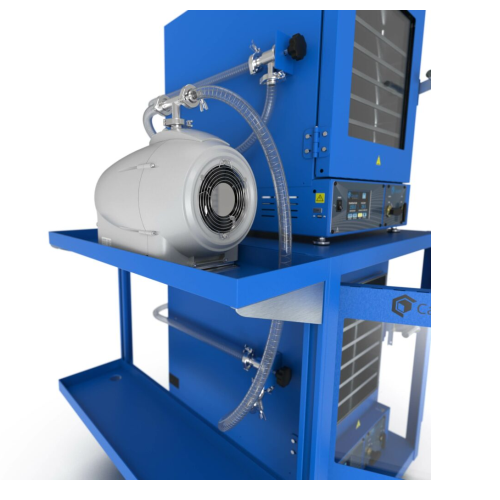
Dry scroll vacuum pumps for laboratories and manufacturing
Ensure a clean, oil-free environment with advanced dry scroll...
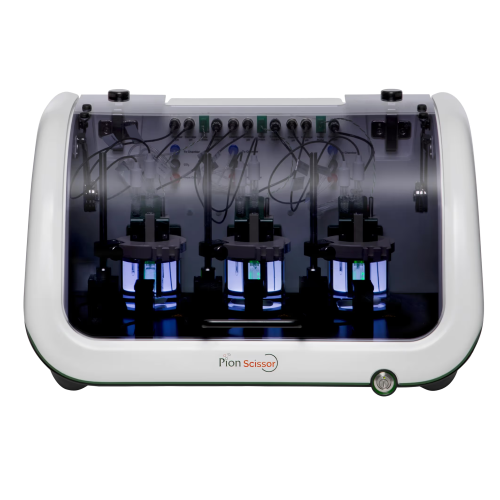
In vitro subcutaneous injection simulator
Optimize drug formulation screening and selection with an innovative solution th...
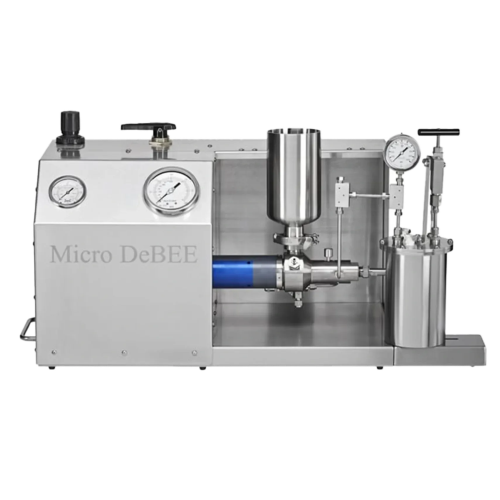
Laboratory homogenizer for nanoemulsions and dispersions
Elevate your laboratory capabilities with a bench-top homogenize...
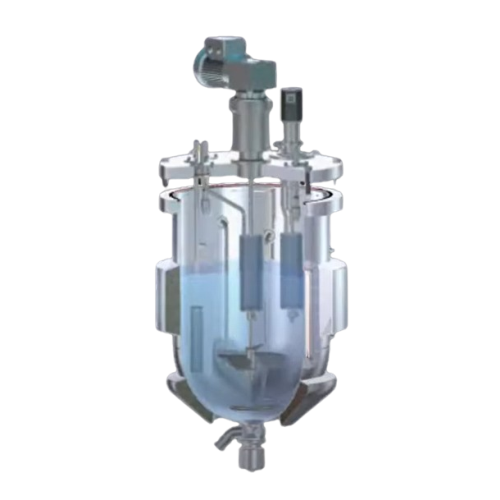
Industrial agitation and mixing solutions
Enhance your production line efficiency with engineered agitation and mixing sys...
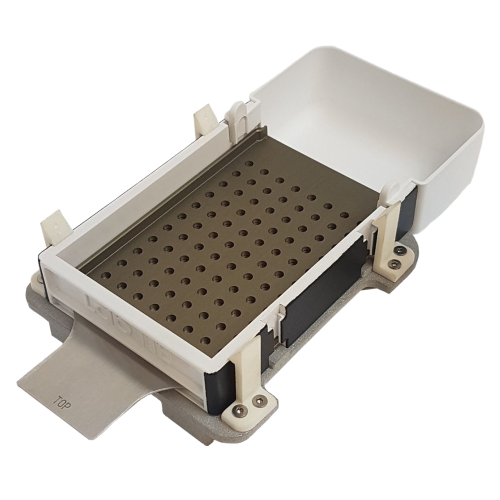
Lab powder dispenser for precision measurements
Effortlessly streamline your lab’s powder dispensing tasks with a ve...
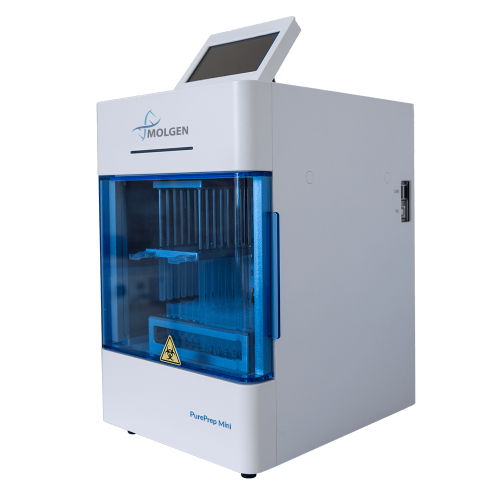
Compact automated nucleic acid extraction system
Quickly automate nucleic acid purification to reduce hands-on time and mi...
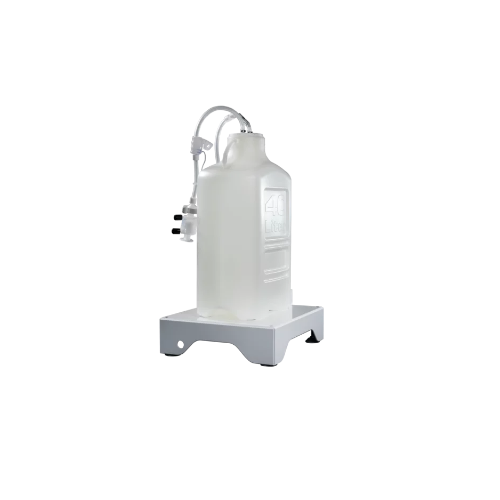
Single-use mixing solutions for downstream processes
Designed for safe and efficient one-time use, this mixing solution e...
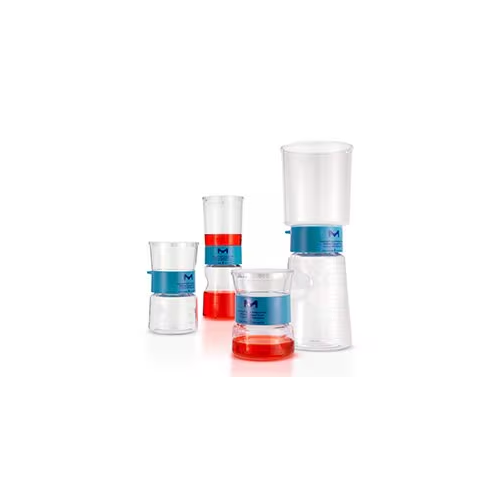
Sterile filtration for cell culture media
Ensure sterility in cell culture and bioprocessing with advanced filtration solu...
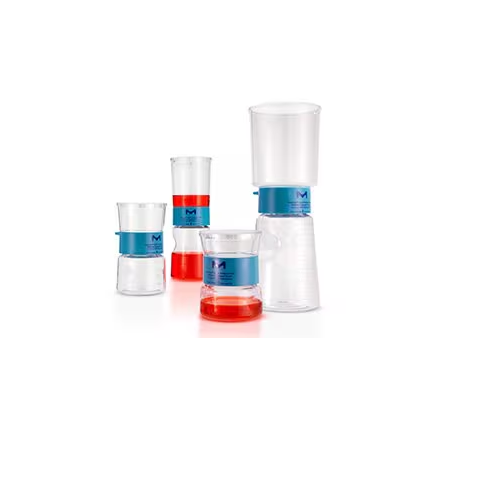
Vacuum filtration for sterile media and buffer preparation
Achieve reliable sterilization and filtration of cell culture...
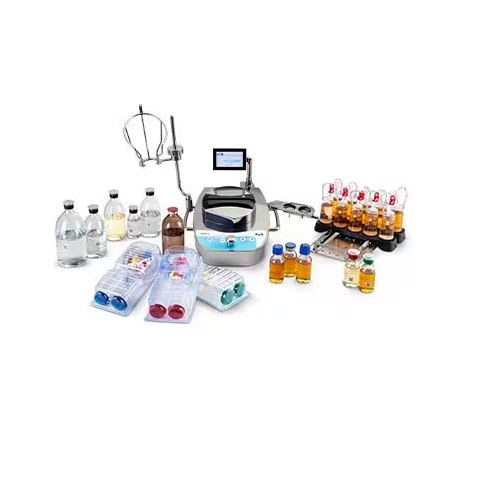
Sterility testing consumables, media & instruments
Ensure your products meet sterility standards with advanced testing to...
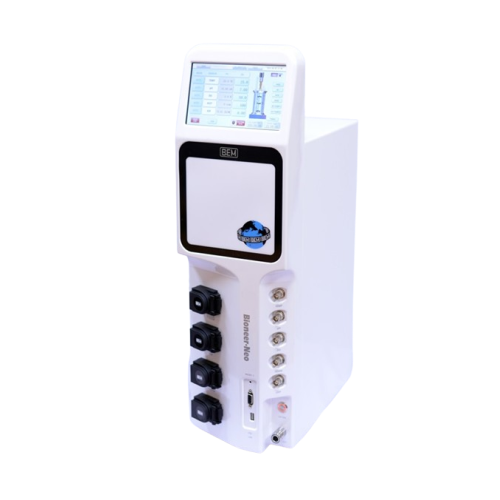
Compact fermentor for research and scale-up studies
Optimize your bioprocess development with a desktop fermentor that of...
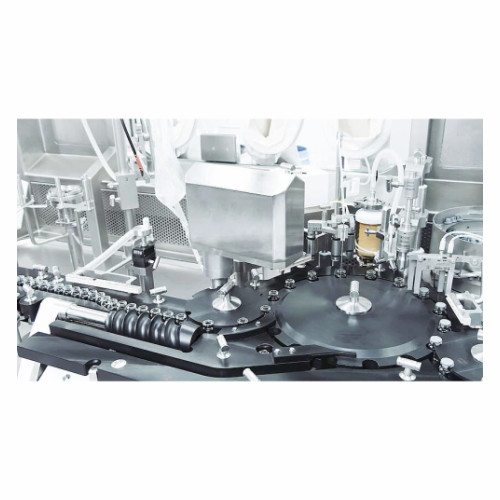
Aseptic filling solutions for Rtu vials, cartridges, and syringes
Optimize your aseptic filling processes with a system...
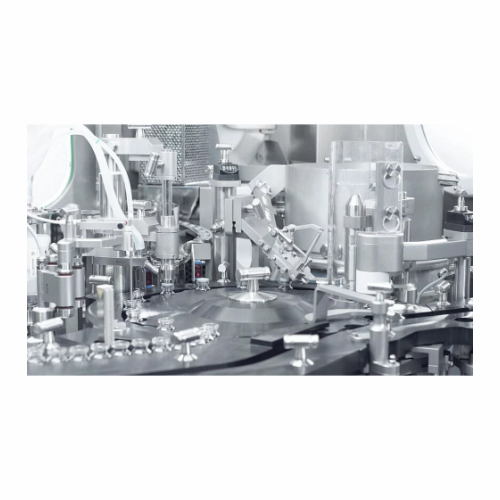
Vial filling for pharmaceuticals
Streamline your aseptic processing with vial filling machines that ensure sterile, precise,...
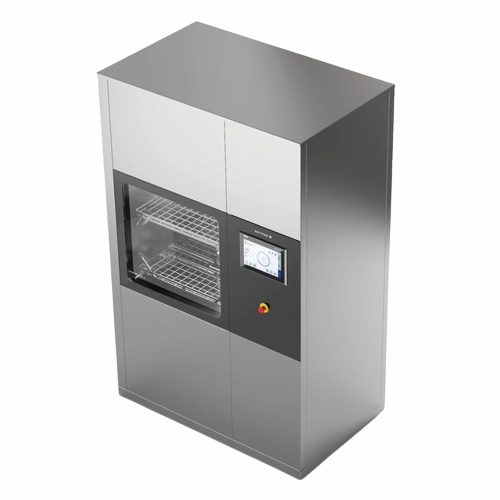
High-capacity cgmp washer/dryer for cleanrooms
Optimize your cleanroom operations with this compact washer/dryer, designed...
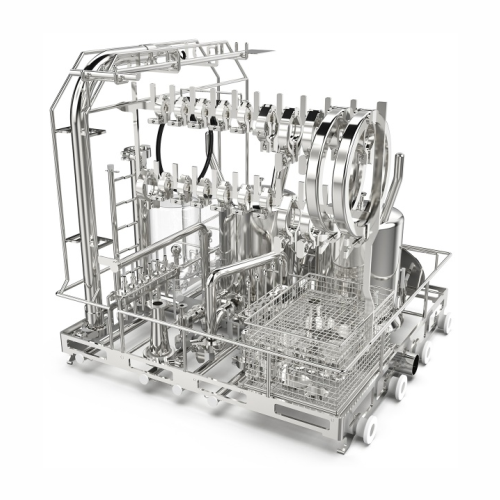
Loading solutions for Gmp washers
Ensure thorough cleaning and drying of biopharmaceutical components with modular loading ...
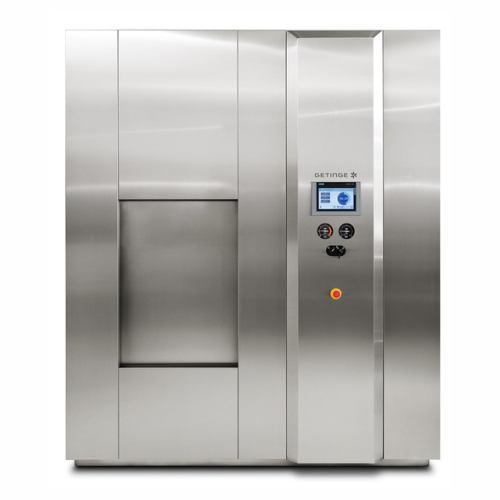
Steam sterilizer for pharmaceutical production
Ensure consistent, contamination-free sterilization of pharmaceutical compo...
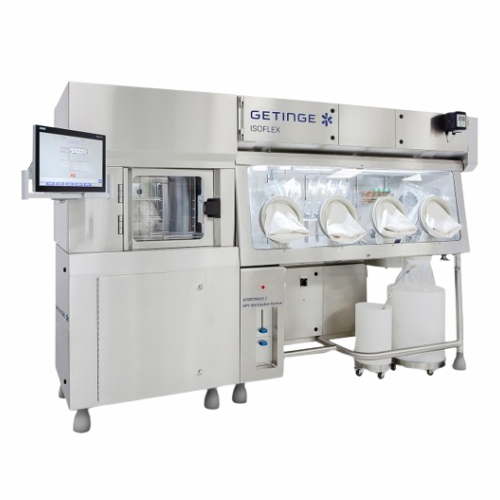
Modular Gmp isolator for aseptic processing
Ensure contamination-free production with this modular aseptic isolator, desig...
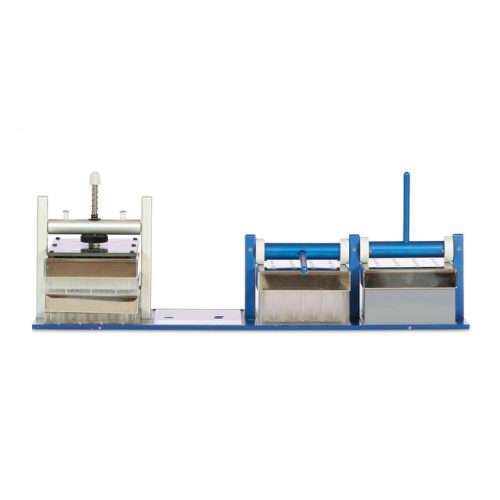
Cultivation system for microtiter plates
Accelerate your strain cultivation process with a micro-bioreactor system that ena...
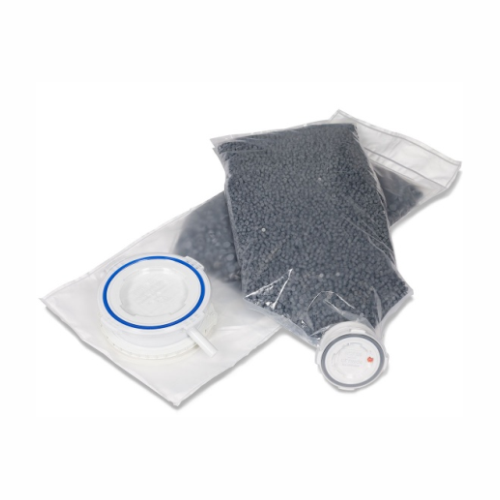
Sterile transfer bags for aseptic production
Ensure contamination-free and efficient component transfer in high-speed asep...

Mini-mill for fine comminution of small sample quantities
Achieve precise homogenization and fine comminution of small s...
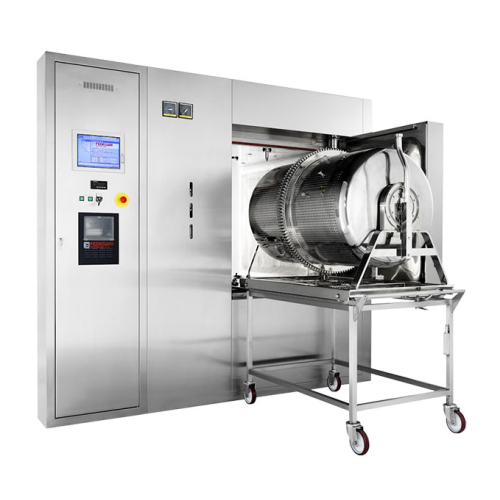
Elastomeric stopper sterilization system
Ensure sterilization and cleanliness of elastomeric vial stoppers with a system de...
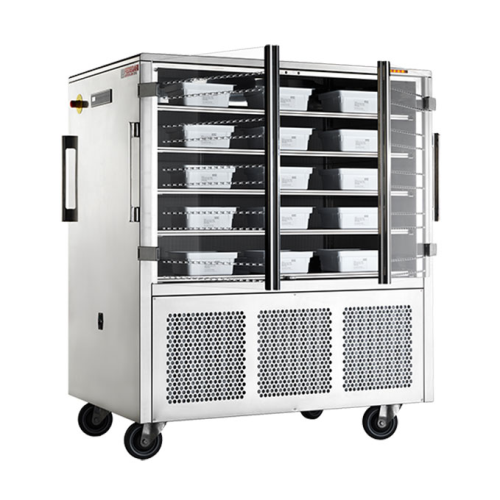
Iso 5 Hepa cart for aseptic material transfer
Ensure aseptic conditions during storage and transfer with this compact HEPA...
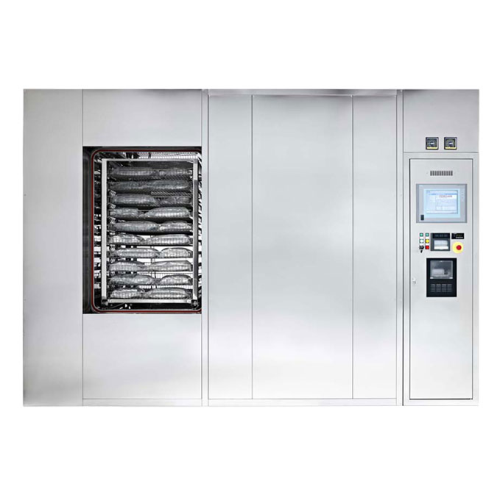
Steam air sterilizer for aqueous solutions
Overcome the pressure challenge in sterilizing aqueous solutions, effectively p...

Liquid dispensing isolator for sterile environments
Maintain product sterility by utilizing a liquid dispensing isolator ...
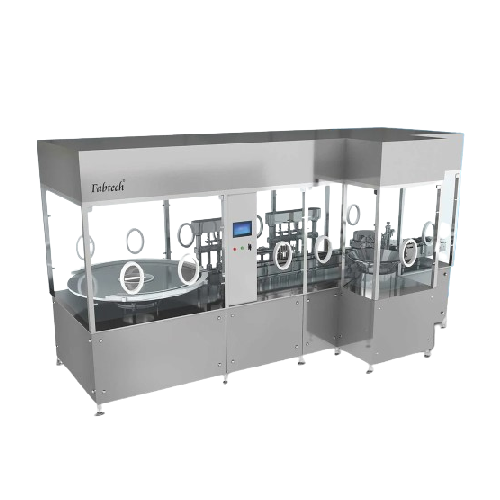
Pharmaceutical turnkey project consultants
Streamline your biopharma production with turnkey solutions that cover everythi...
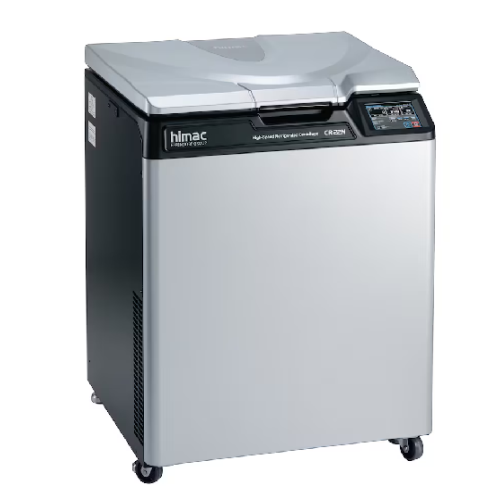
High-speed centrifuge for laboratory applications
Maximize efficiency in high-volume centrifugation tasks with this versa...
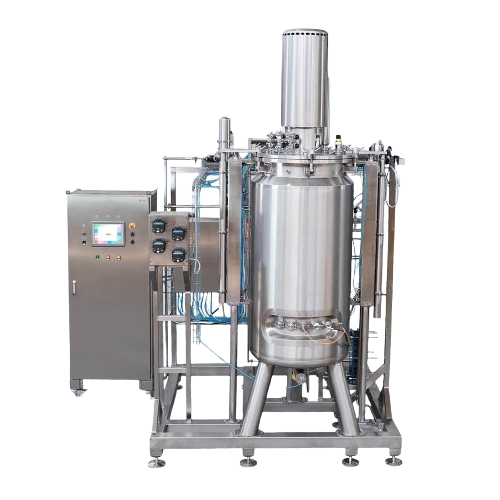
Fermenter for microbial fermentation processes
Optimize your fermentation and biopharmaceutical production with stainless ...
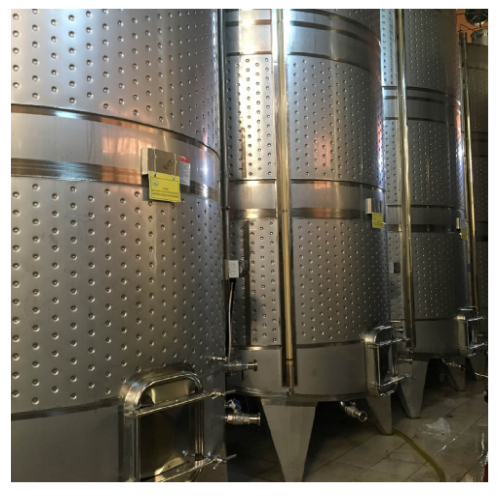
Stainless steel fermentation tanks
Optimize your fermentation efficiency with stainless steel tanks that provide precise te...
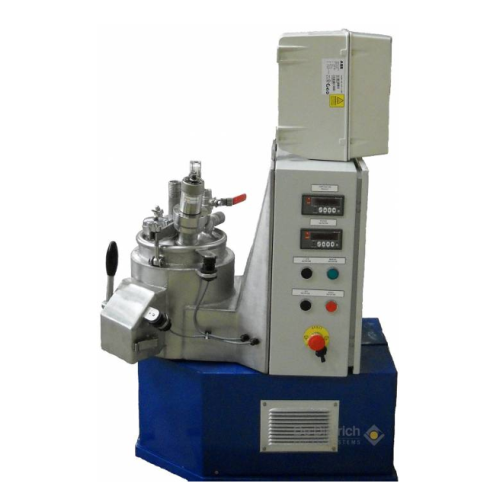
Powder blender for efficient mixing and discharge
Achieve precise mixing and efficient discharge with advanced powder ble...
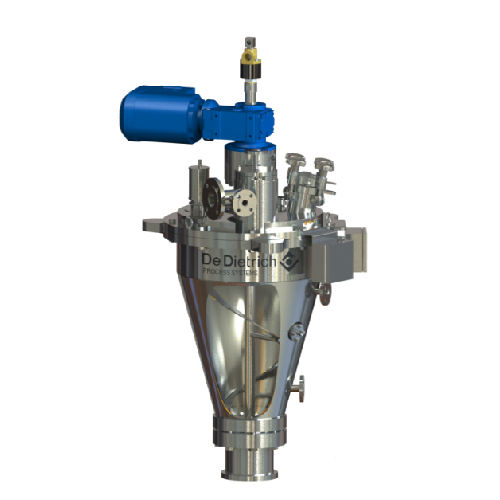
Vacuum drying for heat-sensitive products
Ensure moisture-sensitive formulations are dried efficiently without compromisin...
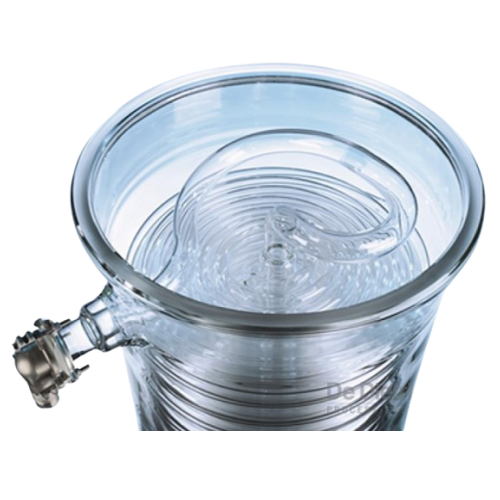
Heat exchanger for corrosive substance handling
Optimize your process of handling corrosive substances with a heat exchang...
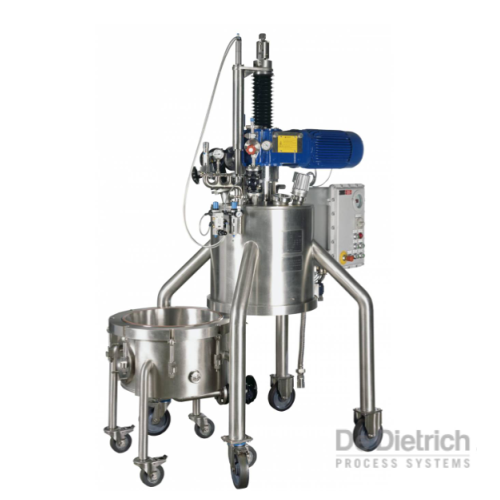
Pilot scale filter-dryer for pharmaceutical and chemical batches
Streamline small-batch production with a mobile filter-...
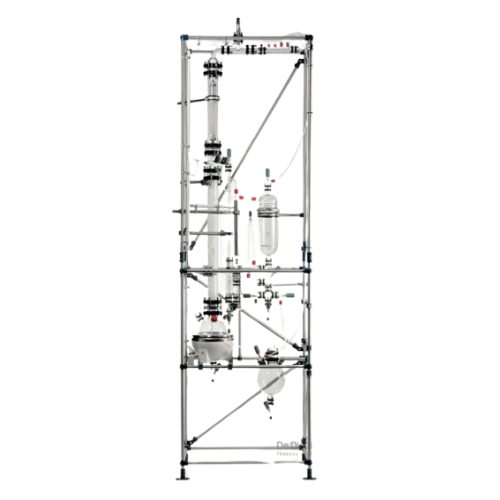
Solid/liquid extraction unit for process development
Optimize your extraction processes with flexible operation modes for...
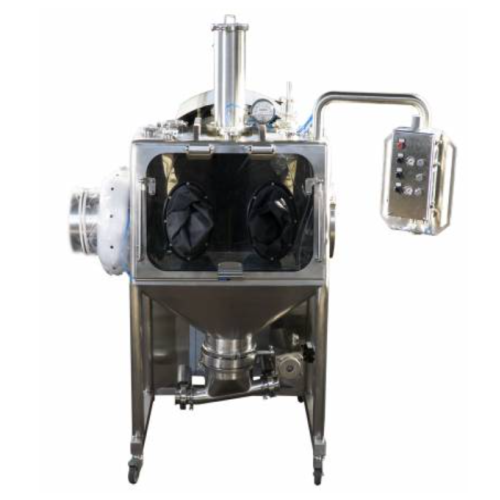
Powder handling drum dock station
Ensure safe and efficient powder transfers with high containment levels, minimizing opera...
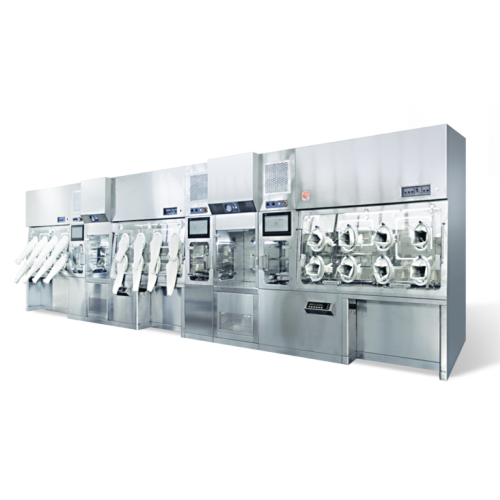
Cell and gene therapy modular isolator
Enhance your cell and gene therapy production with a modular isolator that integrate...
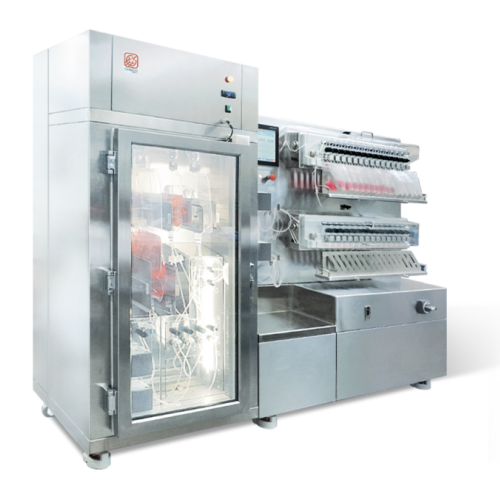
Semi-automatic filling system for cell and gene therapy
Optimize your cell and gene therapy processes with a modular fill...

Cell & gene therapy isolator with integrated incubation
Enhance your cell and gene therapy workflow with a modular isolat...
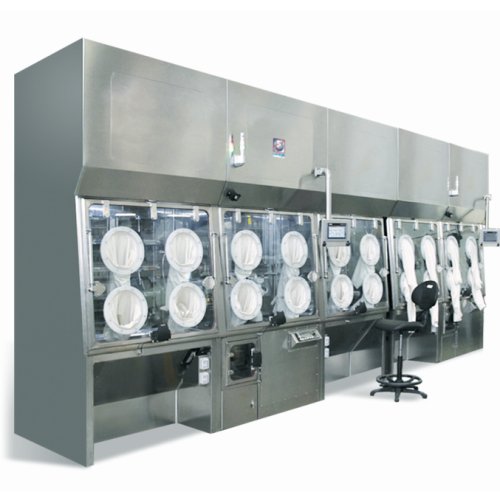
Isolator for aseptic cell culture processing
Ensure sterility and reduce cross-contamination risks in your cell culture pr...
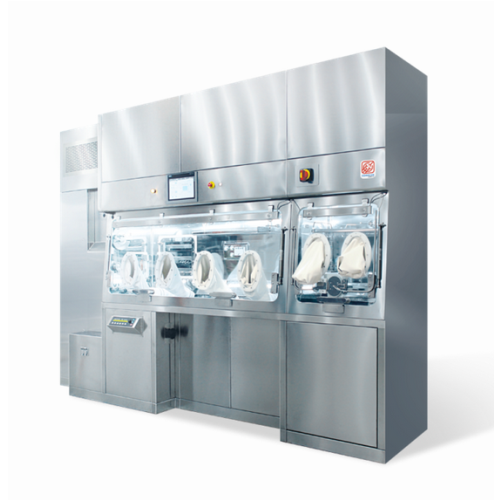
Cell culture isolator for regenerative medicine
Ensure aseptic conditions for cell and gene therapy by maintaining a conta...
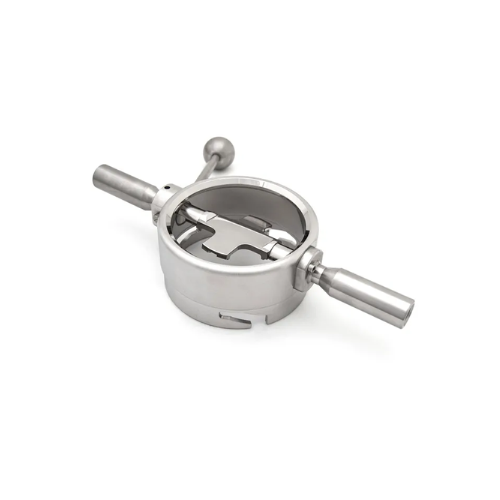
Autoclave passive opener for sterilisation of passive valves
When sterilising passive valves, ensuring maximum exposure ...
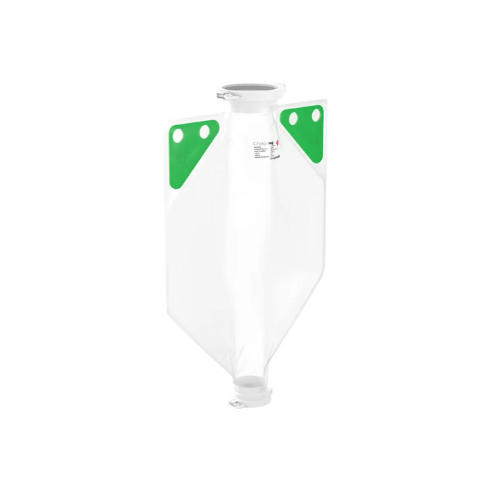
Single use powder handling bags for pharmaceutical ingredients
Achieve contamination-free powder transfers with ease, ma...
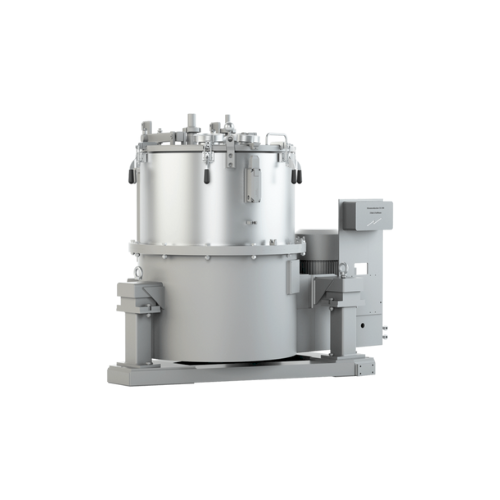
Industrial filter centrifuges for high solids content processing
Optimize processing of high-solid slurries with efficie...
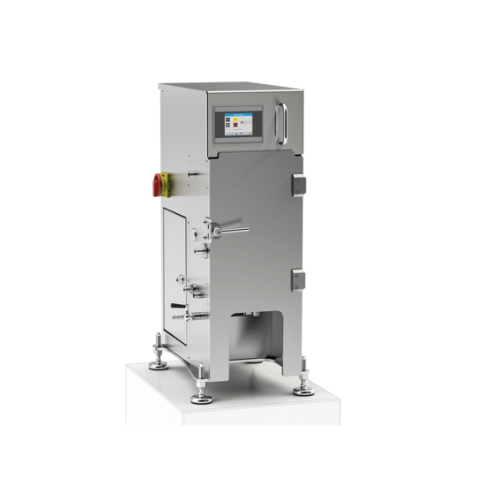
High-speed tubular centrifuges for solid-liquid separation
Efficiently separate microscopic solids from liquids in high-...
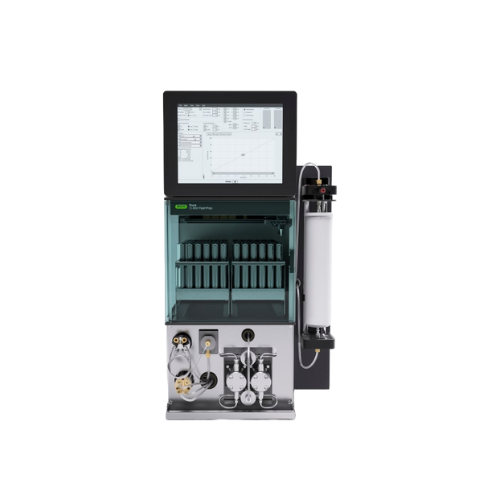
Compact flash and prep Hplc chromatography system
Streamline your purification processes with a versatile system that int...
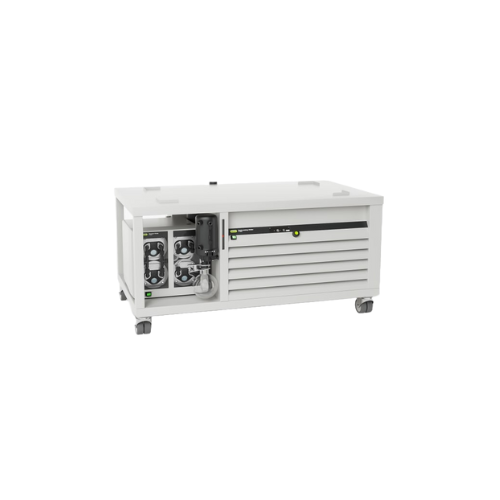
Industrial recirculating chiller for laboratory applications
For consistent distillation results, maintain accurate temp...
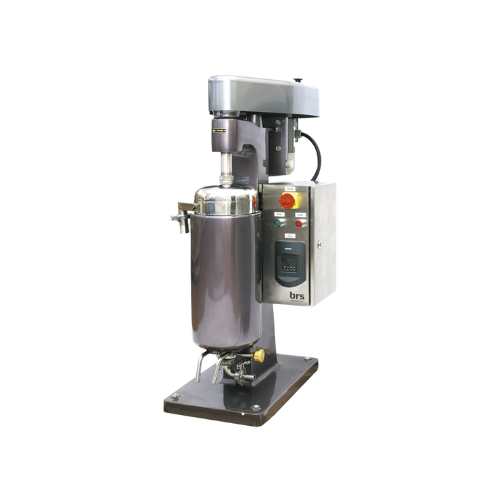
High-speed tubular centrifuges for liquid-solid separation
For efficient component separation in high-viscosity fluids, ...
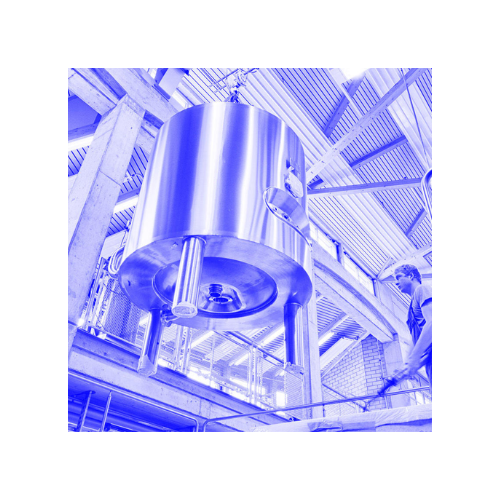
Sterile media and buffer storage tanks
Ensure uninterrupted bioproduction with our tanks designed for secure storage and pr...
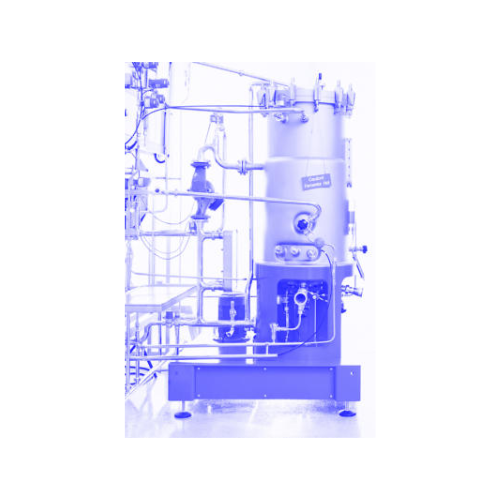
Autoclavable and in-situ sterilizable lab-scale fermentors
For researchers seeking precise control in bioprocessing, the...
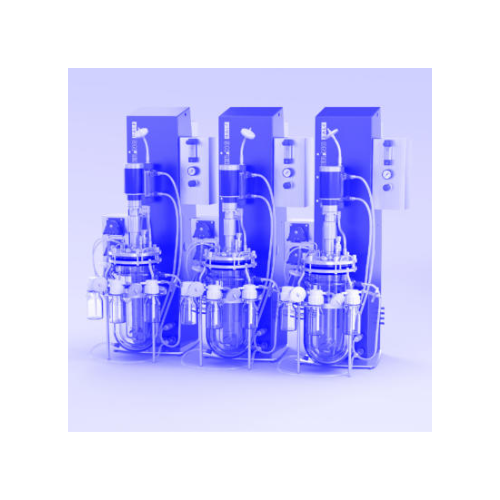
Lab-scale fermenters for research and development
Optimize your small-scale production with compact bioreactors designed ...
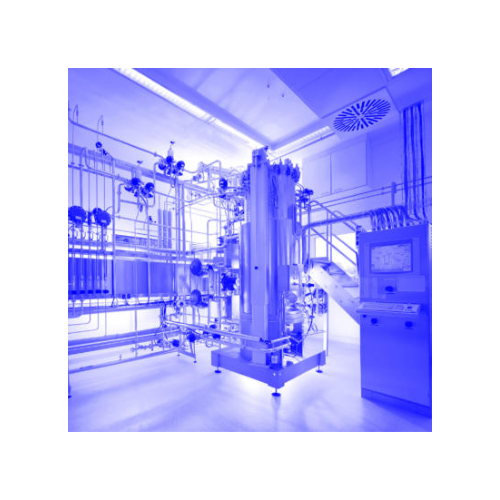
Lab-scale fermentors for microbial cultivation
Optimize microbial cultivation with lab-scale fermentors designed for preci...
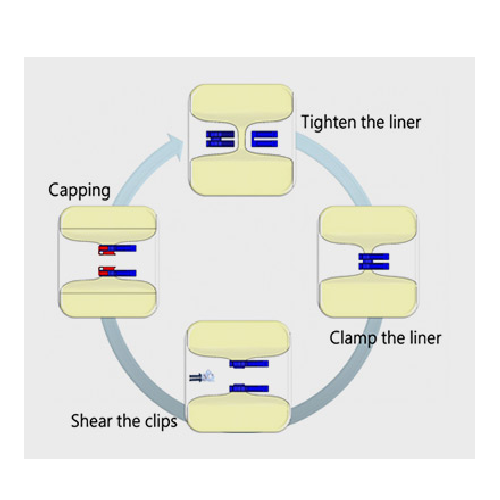
Closure system for aseptic containment
Achieve secure and verifiable seals for sterile pharmaceuticals with advanced closur...
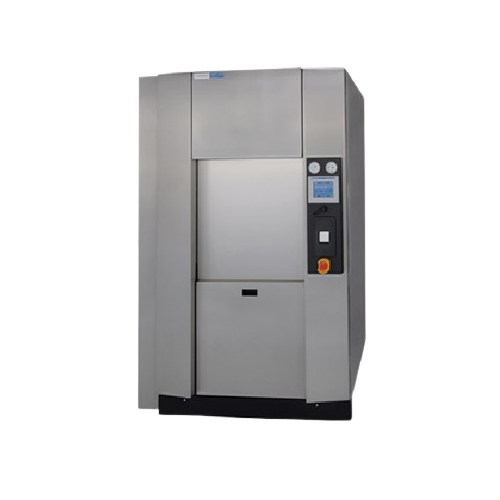
Sterilizer cabinet for laboratory use
Ensure optimal sterility and safety in your laboratory with a cabinet designed for pr...

Space spray decontamination system for clean rooms
Ensure complete sterilization of your cleanroom environments with a sy...
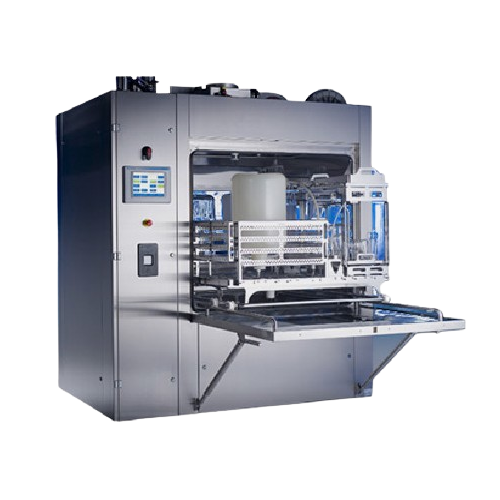
Gmp washer for pharmaceutical contamination control
Ensure verifiable cleaning and drying of critical components in bioph...
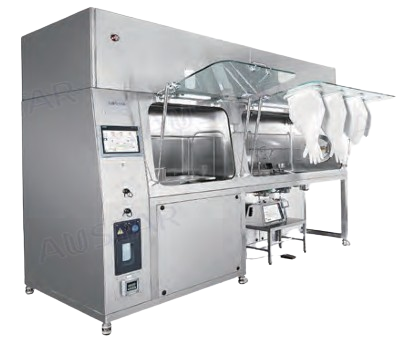
Sterilisable isolator workstation for aseptic containment
Ensure precise contamination control and sterile conditions du...
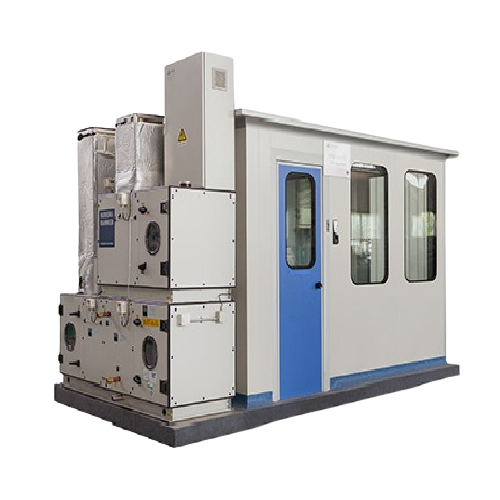
Customized Hvac system for pharmaceutical clean rooms
Achieve seamless sterilization and contamination control in clean r...
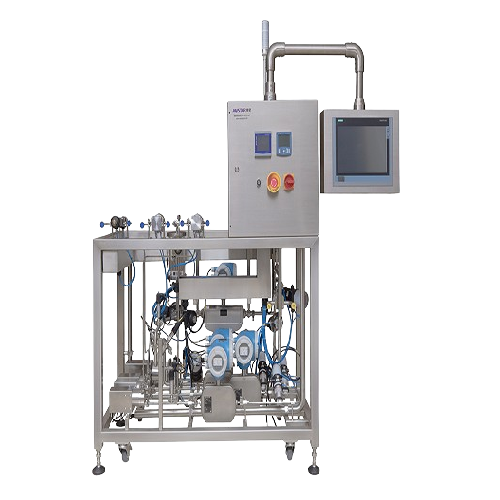
In-line conditioning system for buffer preparation
Optimize your buffer management with precise in-line conditioning, ens...
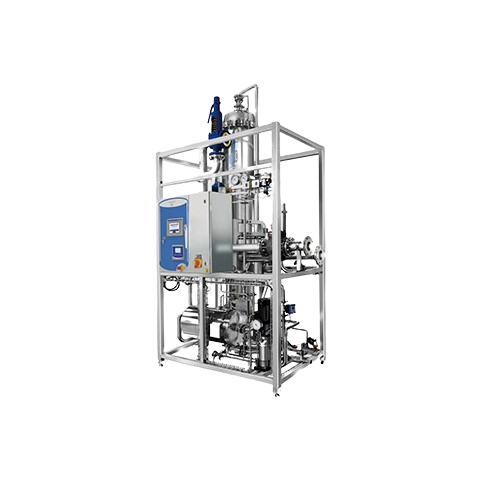
Pure steam generator for pharmaceutical sterilization
Achieve ultra-pure steam for critical sterilization tasks, ensuring...
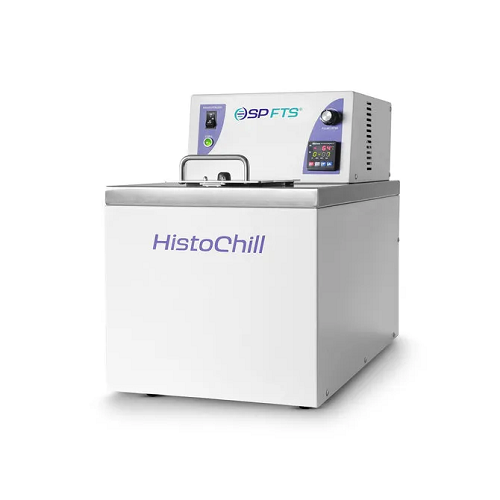
Temperature-controlled bath for tissue sample freezing
Achieve rapid and reliable tissue freezing for precise histologica...
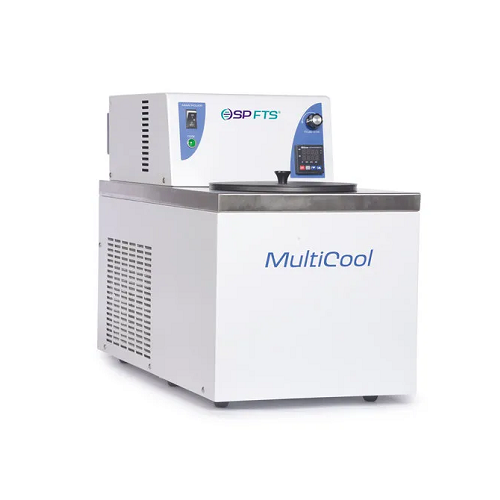
Low temperature bath for precise temperature control
Achieve precise sample freezing from -80°C to 100°C with this low te...
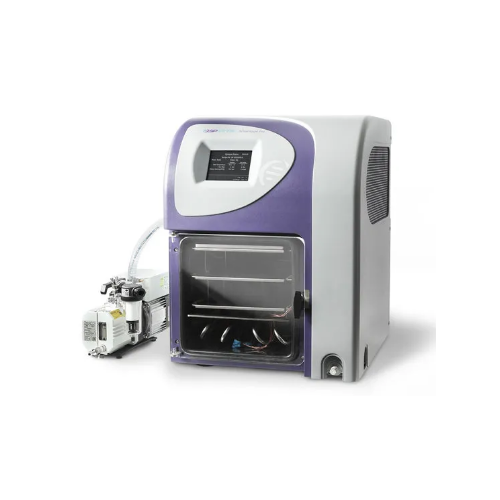
Benchtop freeze dryer for laboratory and small production use
Optimize your lab’s efficiency by adding precise, space-sa...
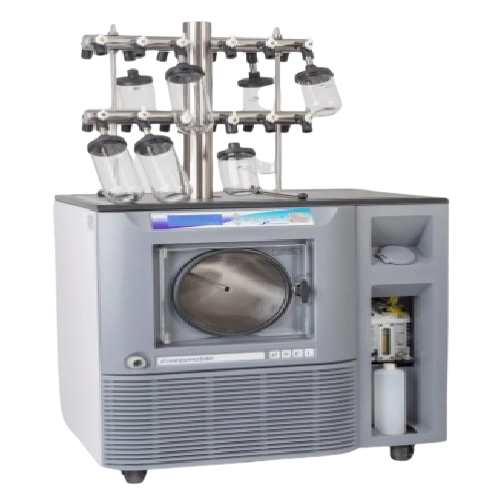
Laboratory freeze dryer for peptide production
Achieve precise moisture removal and stability with a versatile freeze-dryi...
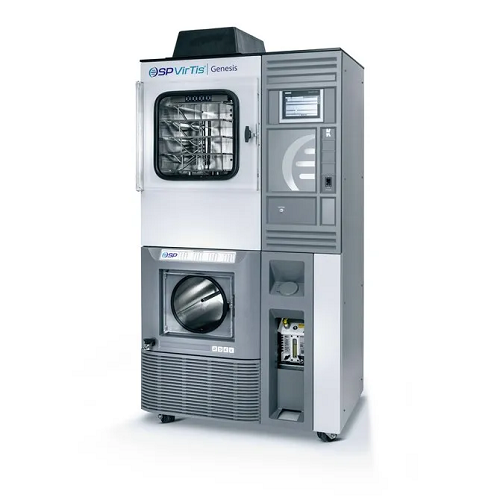
Pilot freeze dryer for research and small-scale production
Optimize moisture removal and sample preservation with this v...
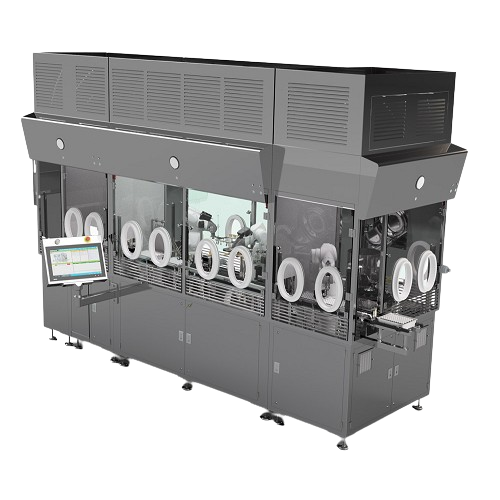
Aseptic small batch filling and closing system
Optimize your small-batch aseptic processing with this versatile system, de...
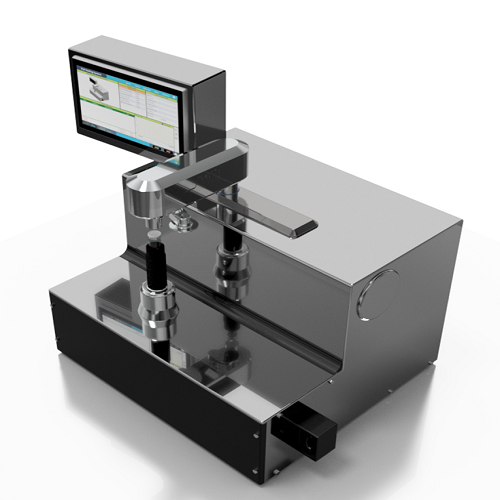
Bench-top vial sealing system for pharmaceutical use
Ensure precise sealing of pharmaceutical vials with a system designe...
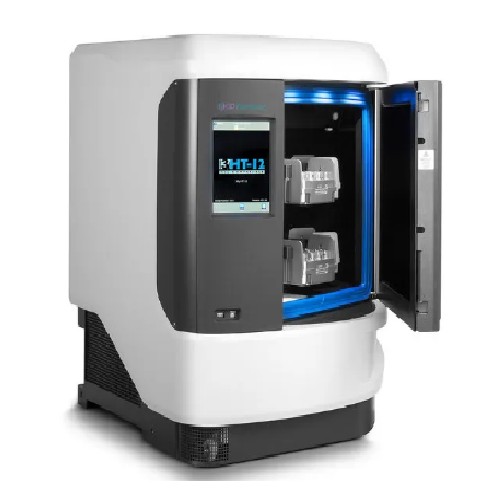
High-throughput vacuum evaporator for laboratory applications
Achieve precise solvent removal and efficient sample handl...
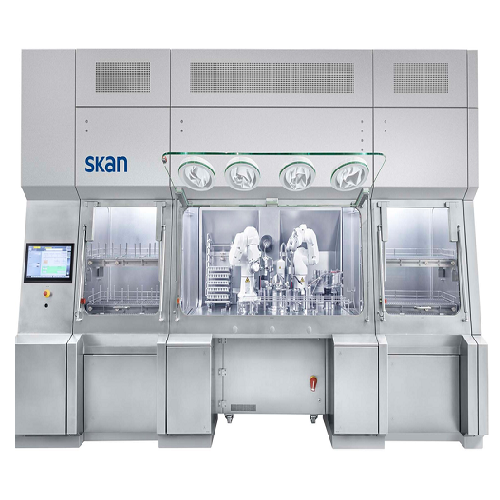
Aseptic vial filling system for gene therapy products
Elevate the sterility of your fill-and-finish process with a high-s...
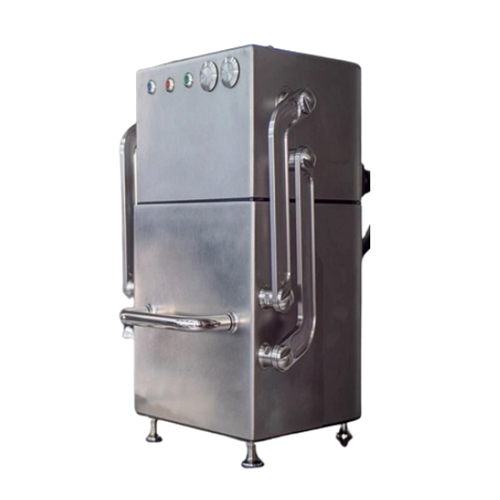
Aseptic filling isolator for small cgmp batches
Guarantee aseptic integrity for small-scale batches with this isolator, of...
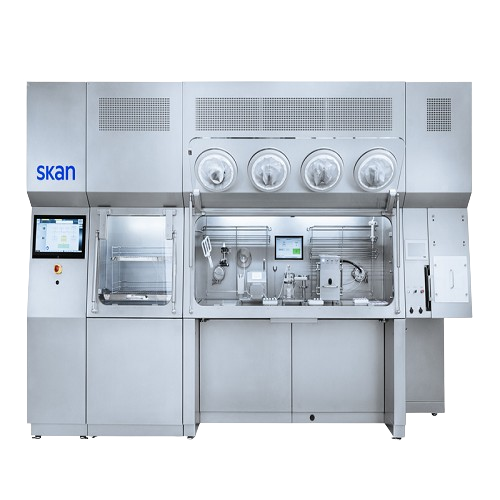
Aseptic filling solution for small cgmp batches
Ensure sterile and efficient filling of small-volume parenterals while mai...

Ultrafiltration module for high-viscosity products
Achieve enhanced separation efficiency with a versatile module designe...
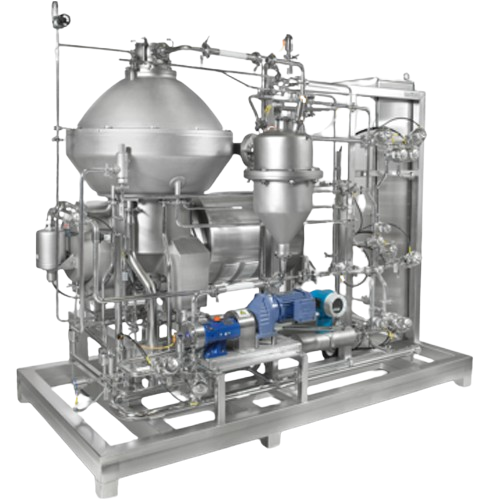
Microbial cell clarification solution
Achieve high-yield, foam-free microbial cell clarification with minimal shear stress ...
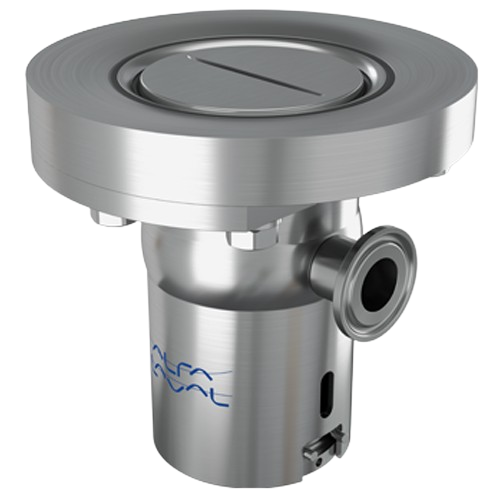
Cleaning nozzle for pharmaceutical tank cleaning
Ensure complete tank hygiene with innovative cleaning technology that tar...
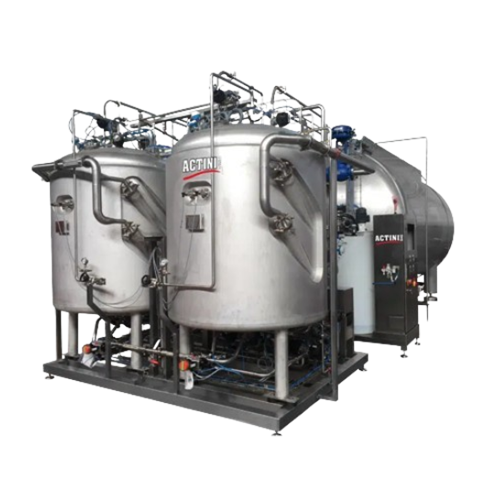
Batch decontamination system for effluents with particles and variable viscosity
Effectively manage complex effluent s...
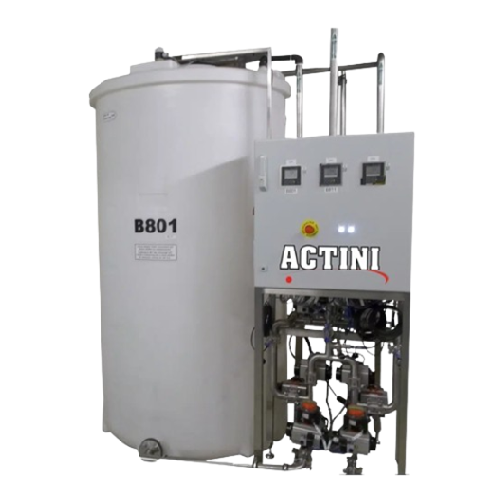
Industrial effluent ph neutralization system
Effectively balance effluent pH levels with a system designed to optimize che...

Industrial effluent decontamination solution
Ensure safe and compliant liquid effluent management with a modular decontami...
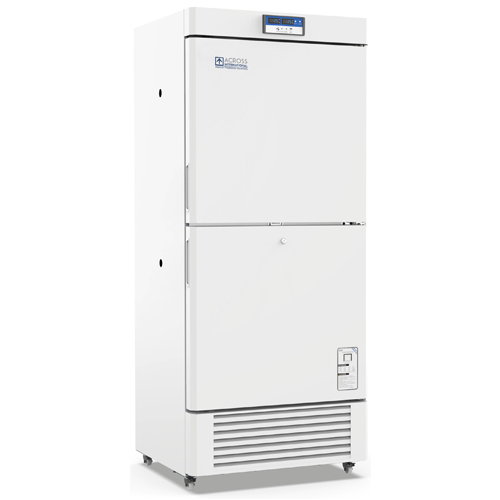
Laboratory -40°c upright freezer
Ensure optimal preservation of sensitive biological samples with a freezer engineered for u...
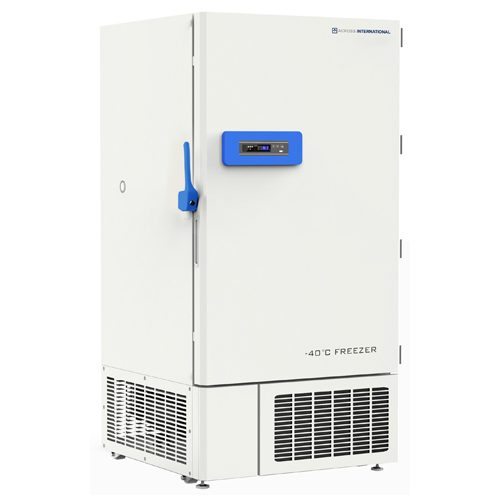
Medical freezer for -40°c storage
Ensure optimal preservation of critical samples with an ultra-low temperature solution de...
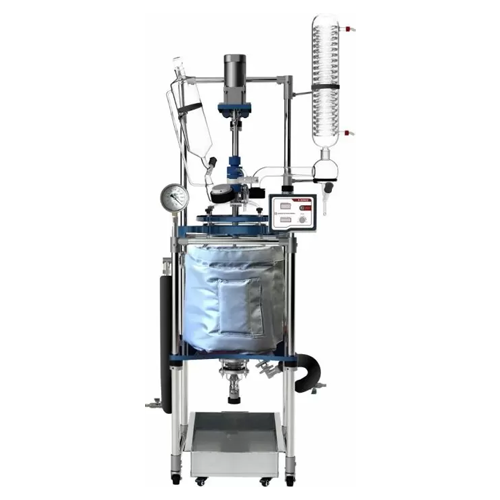
20l jacketed glass reactor system for laboratory synthesis
Achieve precise chemical synthesis and enhanced material reco...
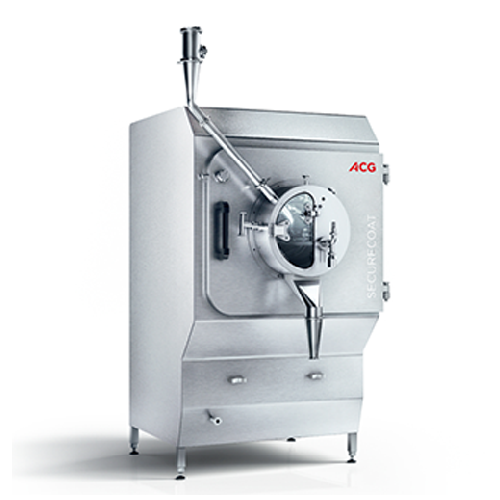
Containment tablet coater for high-potency pharmaceuticals
Ensure operator safety and maintain stringent OEB 4 complianc...
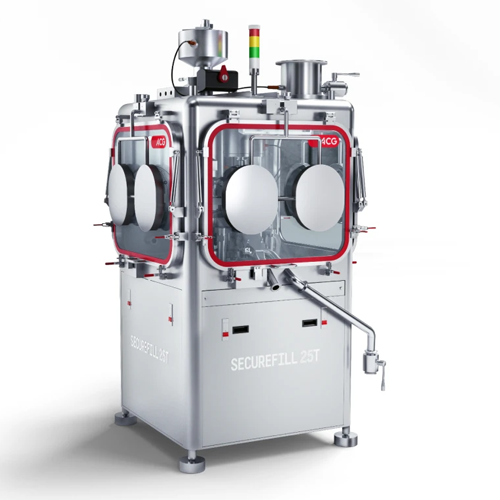
Containment capsule filler for highly potent drugs
Achieve complete operator safety while encapsulating potent pharmaceut...
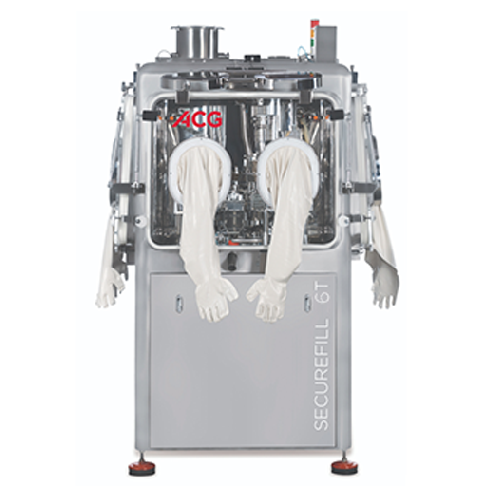
Containment capsule filling system for highly potent drugs
Ensure operator safety while filling capsules with high-poten...
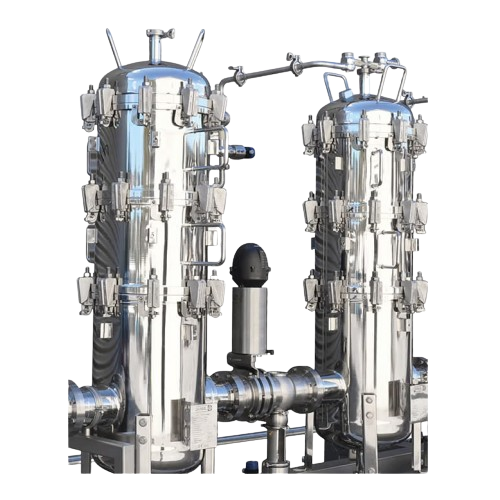
Aseptic spray dryer for pharmaceutical products
Optimize your sterile powder production with precise control over particle...

Laboratory freeze dryer for small batch processing
Ensure precise moisture control and stability in sensitive samples wit...
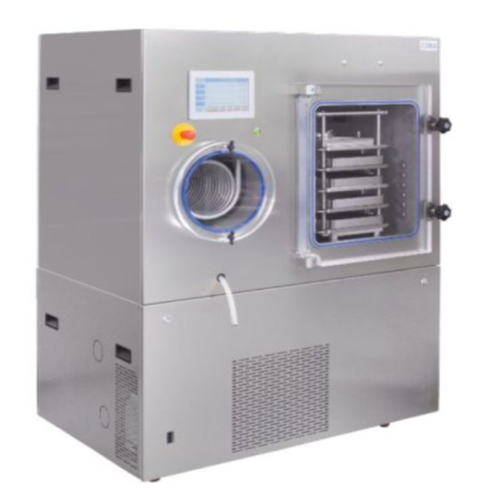
Pilot freeze dryers for research and development
Ensure precise dehydration of sensitive samples while maintaining structu...
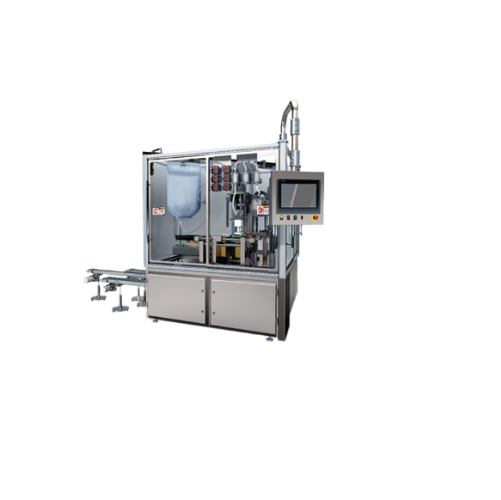
Blow/fill/seal packaging for laboratory and clinical trials
Streamline your small-scale pharmaceutical production with p...
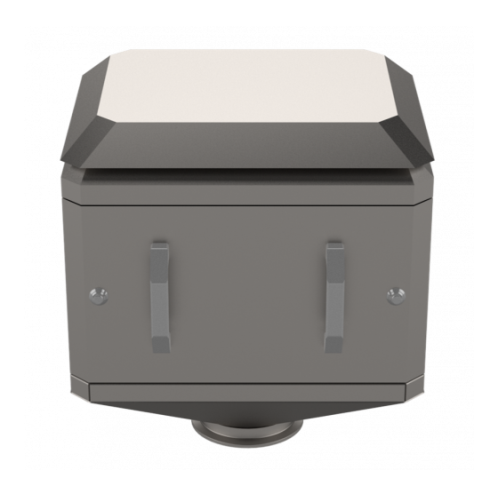
Laboratory dedusting systems
Designed for high-containment lab environments, this solution efficiently captures and manages ...
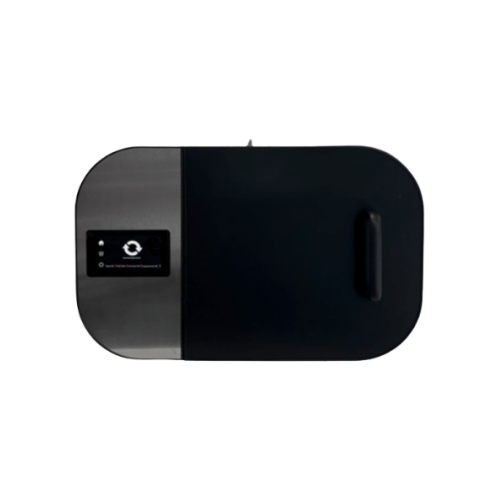
Automated cell manufacturing system for stem cells
Revolutionize cell culture with a fully automated system designed to s...
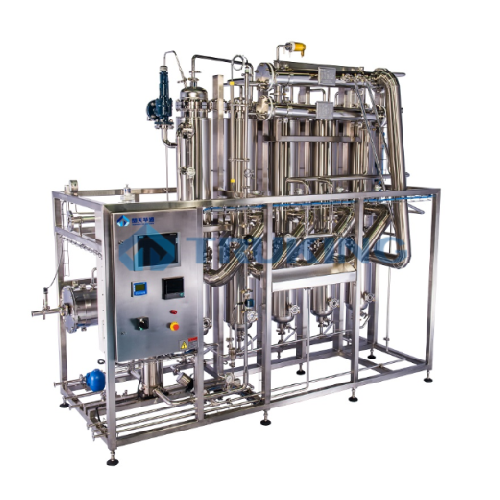
Multi-effect water distillator for pharmaceutical applications
Ensure your production line meets stringent regulatory st...
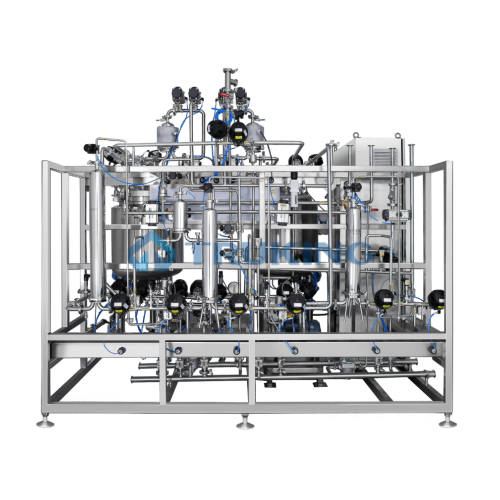
Pharmaceutical preparation system
Achieve seamless integration in pharmaceutical processes with a preparation system that o...

Hybrid laboratory extruders for reproducible scale-up applications
Easily switch between screw diameters to enhance fle...
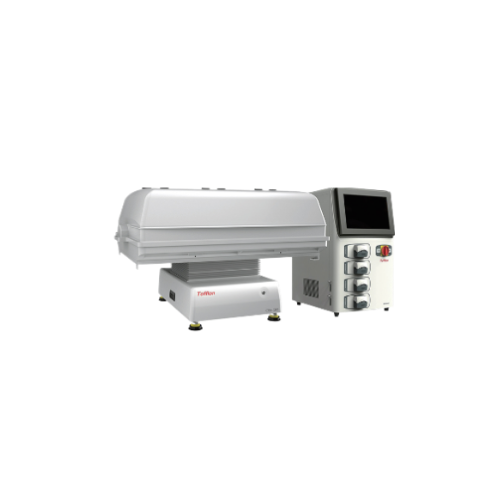
Cell expansion system for antibody drug production
Enhance your biopharmaceutical production with efficient cell expansio...
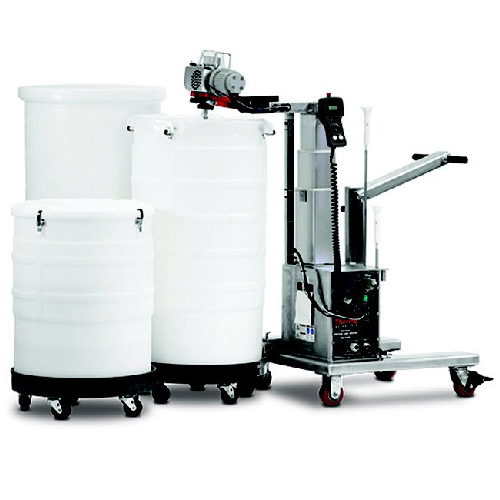
Single-use mixer for buffer sterile mixing
Enhance mixing efficiency with a versatile single-use mixer designed to handle ...
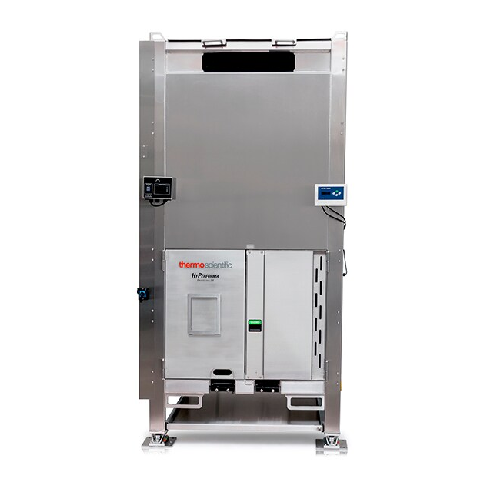
Large-volume sterile liquid storage solution
Efficiently store and transfer large volumes of sterile process liquids with ...
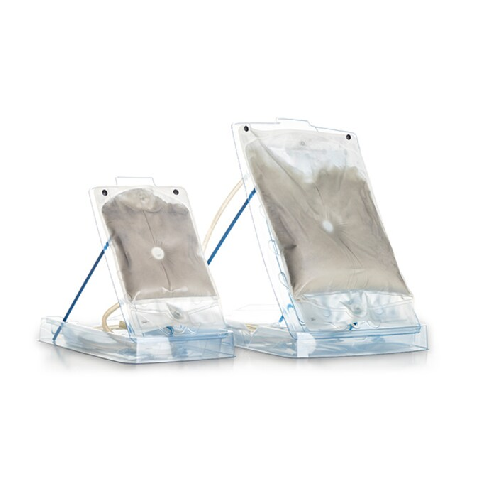
Microcarrier separation system for adherent cell cultures
Enhance your production efficiency with a scalable, single-use...
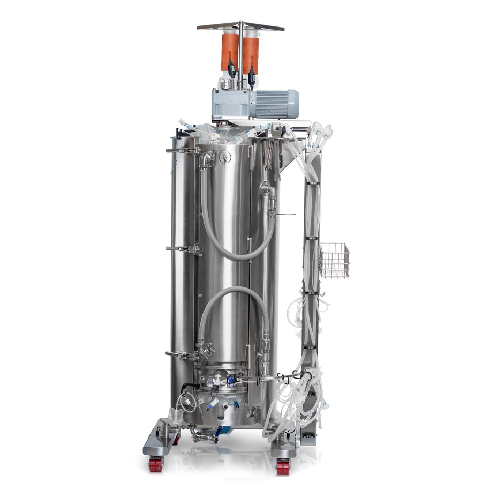
Single-use fermentor for microbial fermentation
Enhance your microbial fermentation processes with a system designed for p...
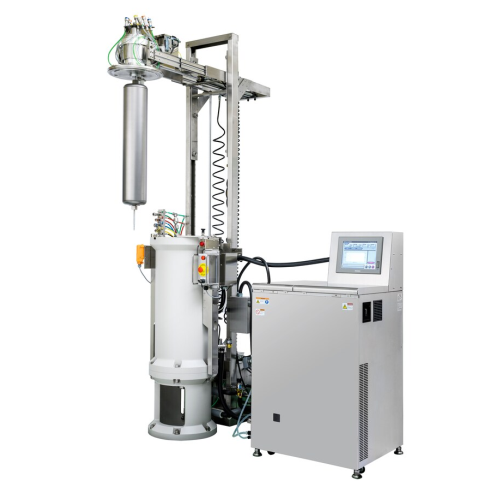
High-capacity centrifuge for vaccine purification
Optimize vaccine production with high-speed centrifuging that ensures p...
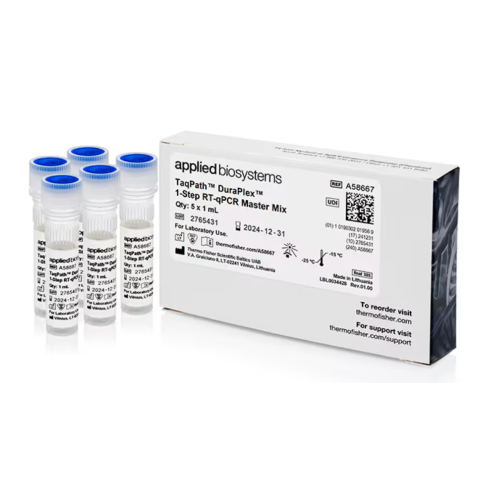
Multiplex Rt-qpcr master mix for diagnostic development
Efficiently multiplex up to six targets with high sensitivity, ev...
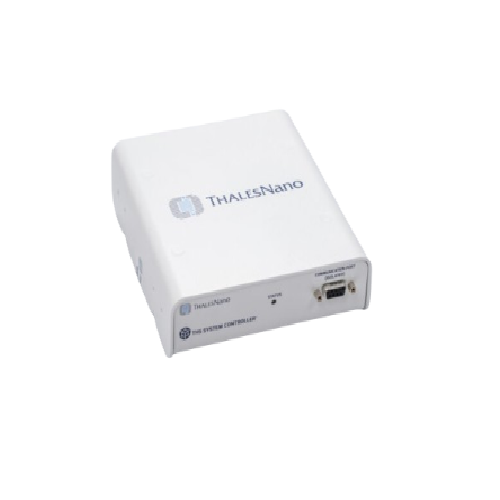
Remote control software for laboratory flow reactors
Streamline your laboratory experiments with a system that provides s...
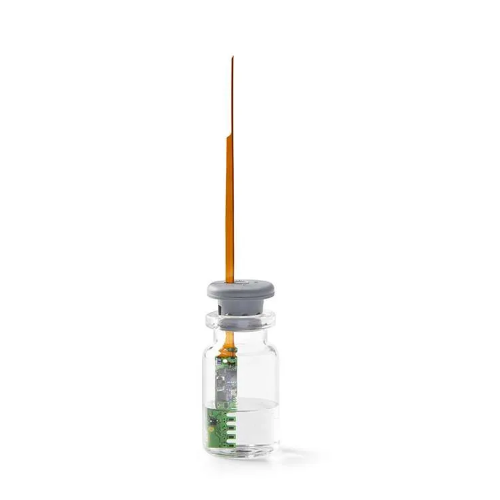
Sublimation front monitoring system for freeze drying
Ensure precise control over your freeze-drying process with real-ti...
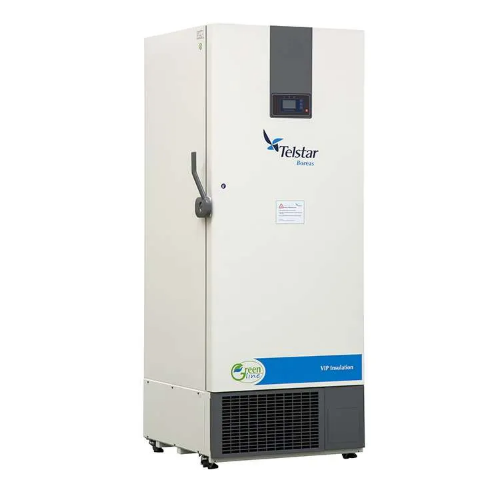
Upright ultra low temperature freezer for laboratory use
Ensure long-term preservation of biological integrity and high-v...
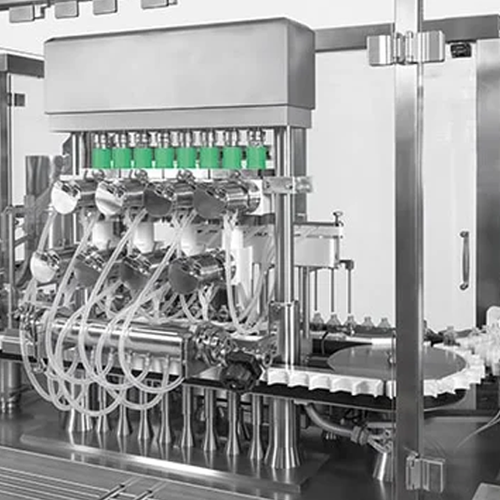
Bulk vial liquid filling system
Ensure reliable and efficient processing of critical biopharmaceutical and pharmaceutical li...
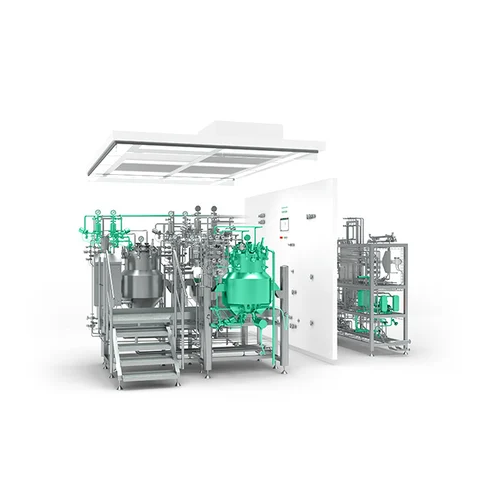
Modular pharmaceutical formulation systems
Achieve unparalleled flexibility and efficiency in liquid pharmaceutical formul...
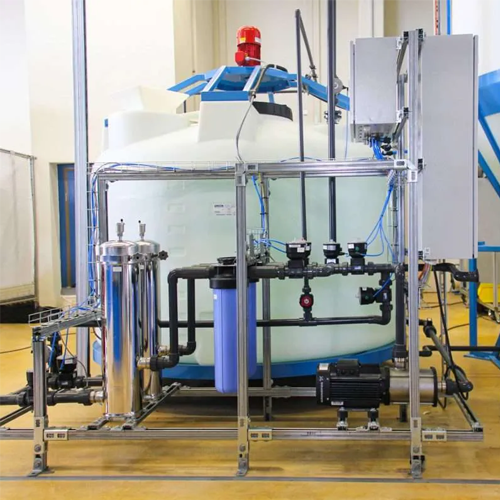
Microalgae cultivation infrastructure
The microalgae cultivation infrastructure streamlines your production with integrated...
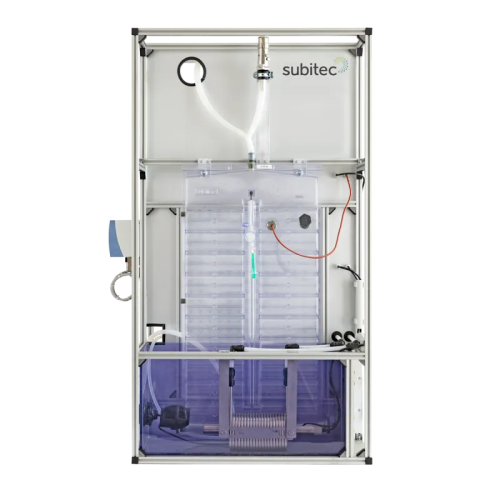
Lab-scale microalgae cultivation system
Achieve precise control of microalgae cultivation with optimized growth conditions ...
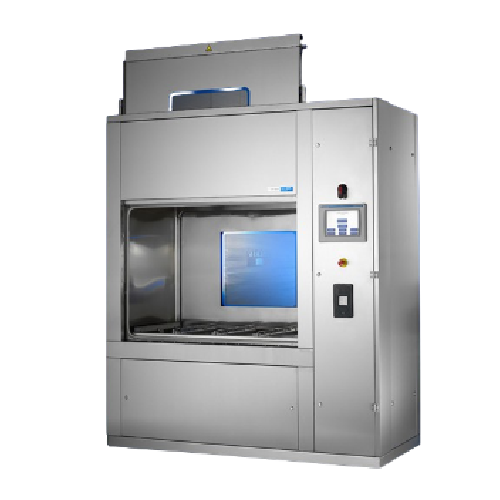
Pharmaceutical glassware and component washer
Optimize your cleaning processes with a high-capacity system that efficientl...
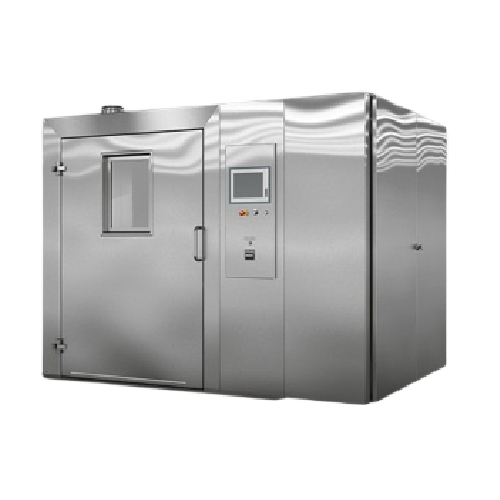
Pharmaceutical grade washer for large components
Ensure compliance and maximize productivity with a high-performance solut...
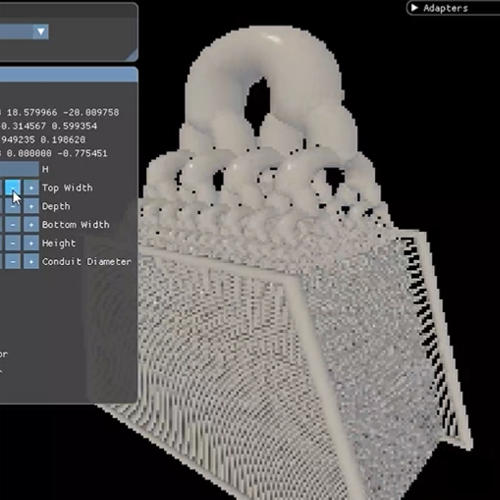
Microvascular system design suite
Tackle the challenges of visualizing and rendering large-scale microvascular systems with...
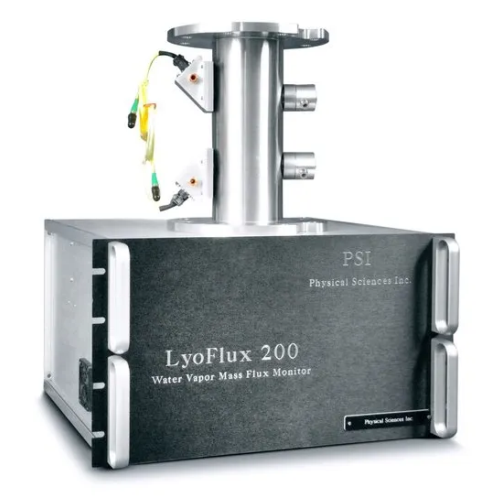
Lyophilization process optimization sensors
Achieve precise real-time monitoring of water vapor during freeze-drying, stre...
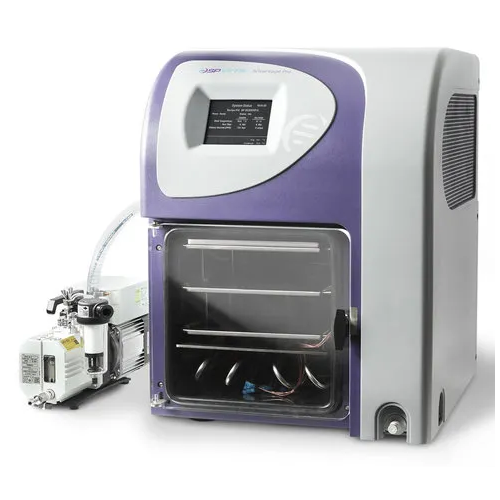
Benchtop freeze dryer for laboratory research
Streamline your lab’s freeze-drying processes with precision temperatu...
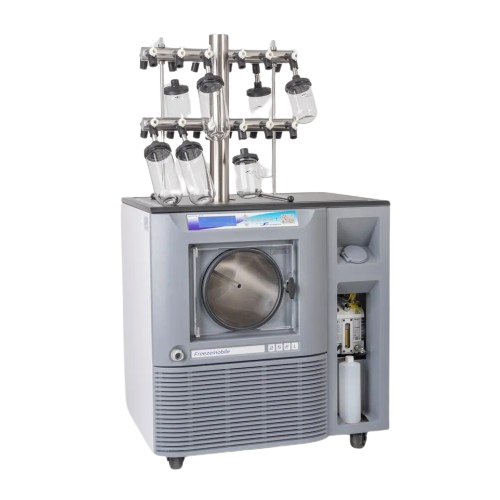
Laboratory freeze dryer
Achieve precise moisture control and enhanced product stability with this advanced freeze-drying solu...
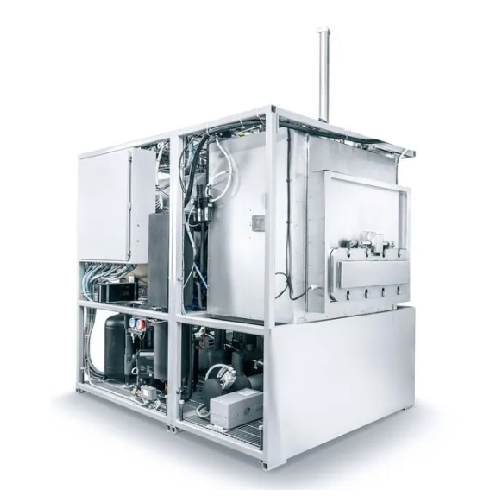
Pilot lyophilizers for therapeutic proteins and clinical trials
Optimize your freeze-drying process with advanced lyophi...
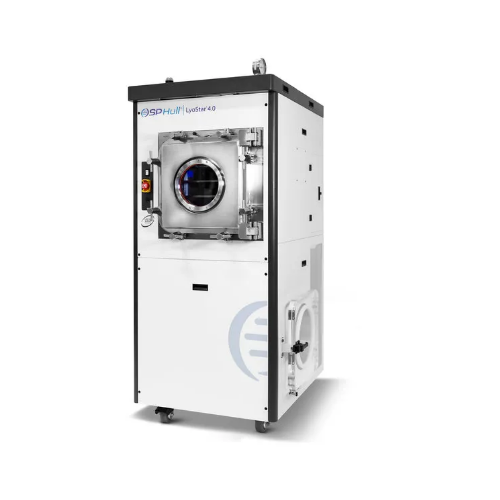
R&d and process development freeze dryer
Speed up your biologic development with precise lyophilization control, ensuring r...
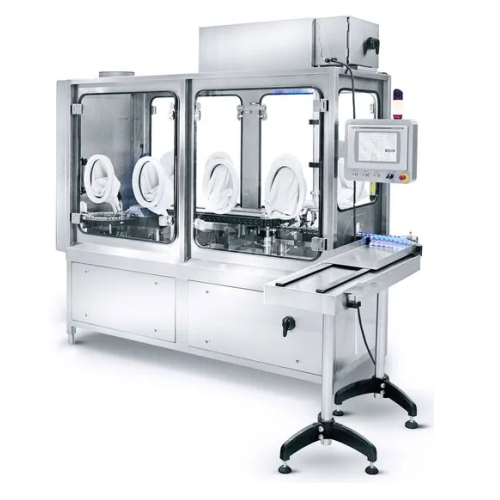
External vial washer for pharmaceutical industry
Ensure complete decontamination of vial exteriors with precision washing ...
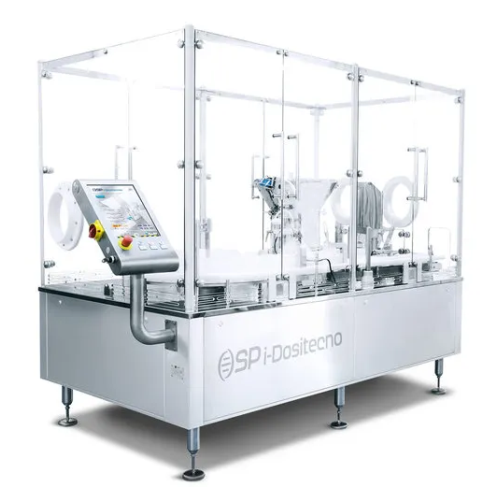
Vial capping system for aseptic processing
Ensure precise vial sealing under aseptic conditions while maintaining high thr...
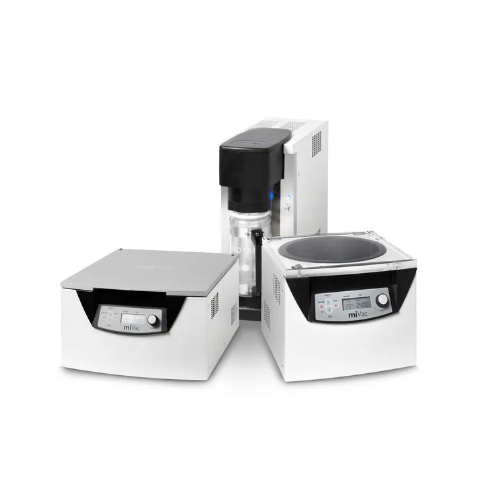
Centrifugal evaporator for solvent evaporation
Achieve precise solvent removal with a versatile system designed for effici...

Low temperature bath for sample freezing and temperature control
Achieve precise temperature control from -80°C to +100°...
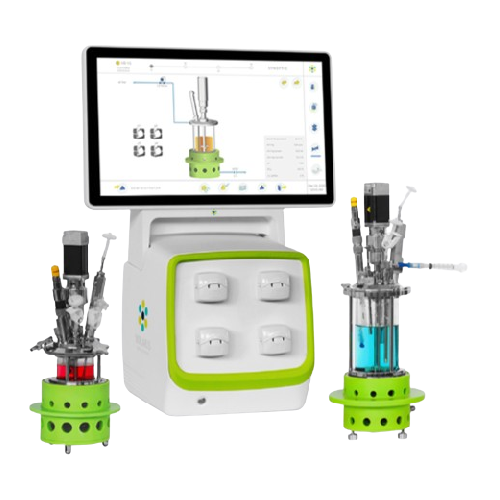
Benchtop electric mini fermenter for process development
Optimize your process development with a compact benchtop fermen...
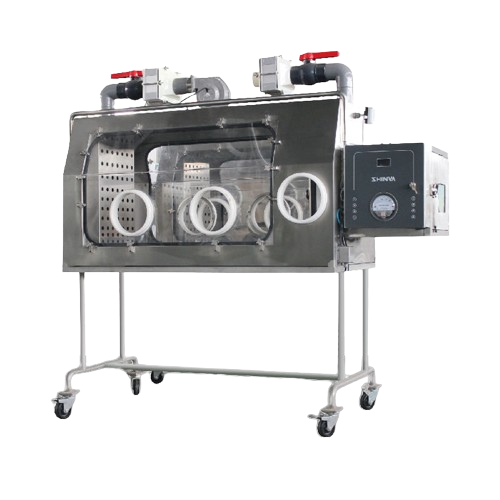
Soft pack isolator for rats and mice
Ensure a sterile and controlled environment for laboratory mice and rats with this sof...
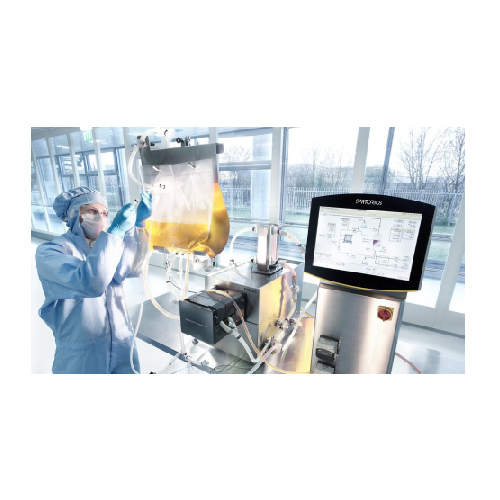
Tangential flow filtration system for cell harvesting
Optimize your biopharmaceutical production by integrating a versati...
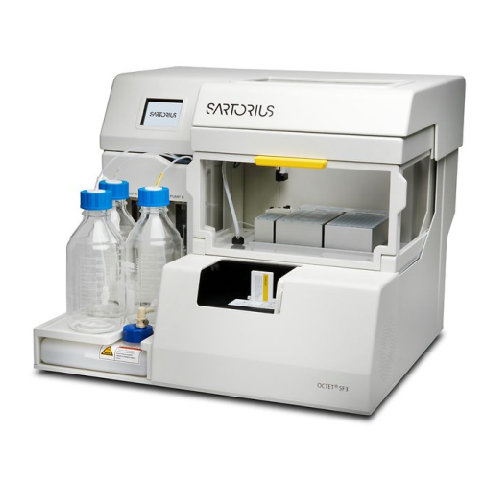
High-throughput surface plasmon resonance (spr) system
Rapidly achieve high-quality binding kinetics for drug discovery w...
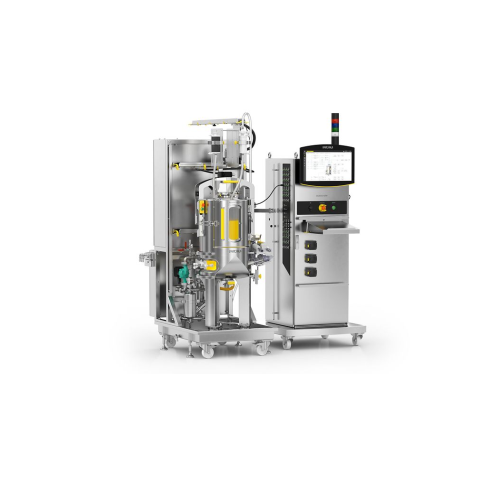
Single-use fermenter for microbial applications
Optimize biopharmaceutical production with a single-use fermenter engineer...
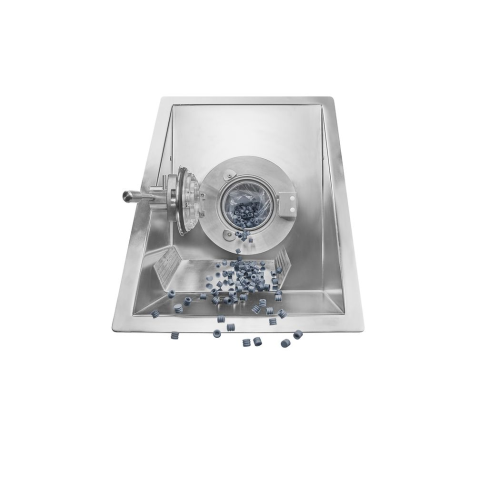
Single-use transfer and filling solutions in barrier isolated filling lines
Ensure sterile, high-volume liquid transfe...
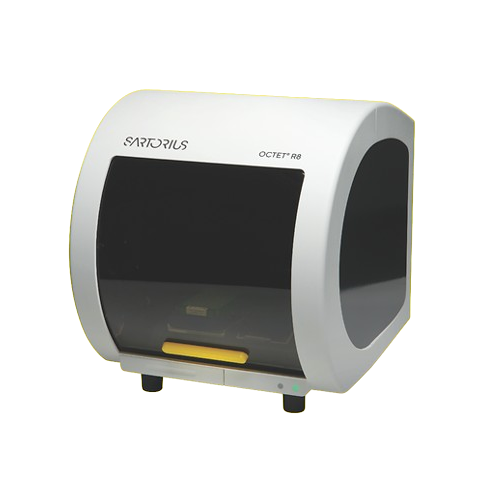
High throughput protein analysis system
Enhance your laboratory’s capability to perform high-throughput kinetic and q...
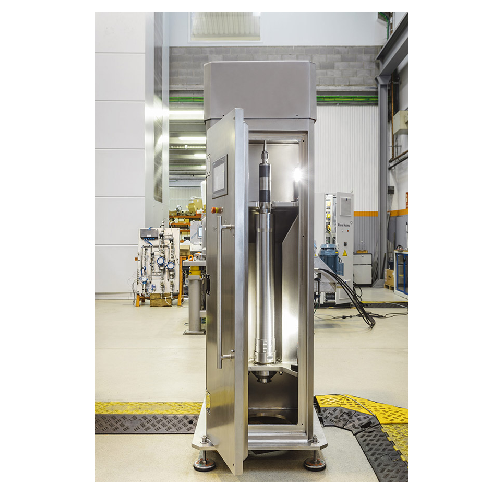
Supercentrifuge for solid-liquid separation and liquid phase separation
Optimize your separation processes with advance...
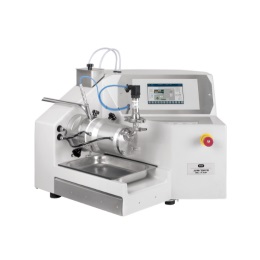
Flexible laboratory bead mill for vaccines
For precise, efficient, and reproducible cell disruption, optimization of proce...
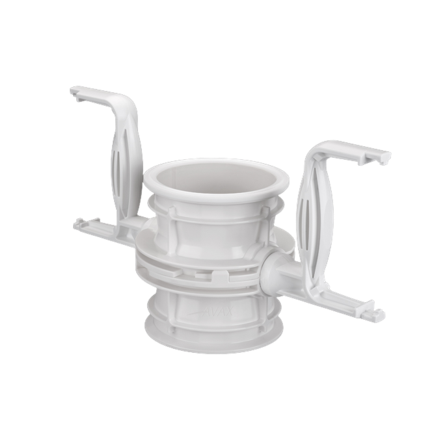
Single-use containment valves
From GMP and HSE perspective material transfer is critical for chemical and pharmaceutical for...
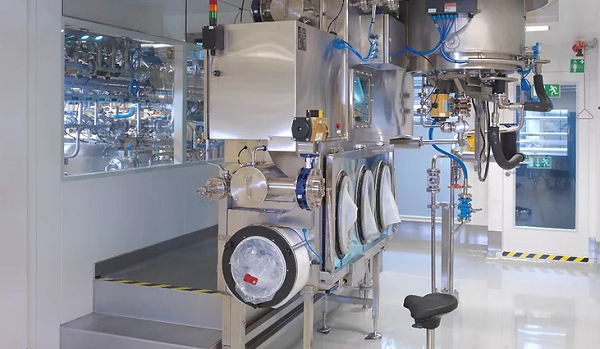
Filter dryer discharging isolator
Contained discharging is critical to the quality of filtration and drying processes. But ...
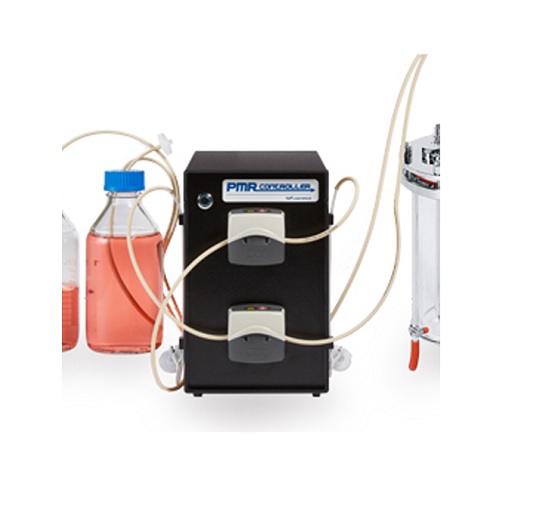
Perfusion process controller
Advanced biopharmaceutical and lab systems involving microcarrier and stem cell applications re...
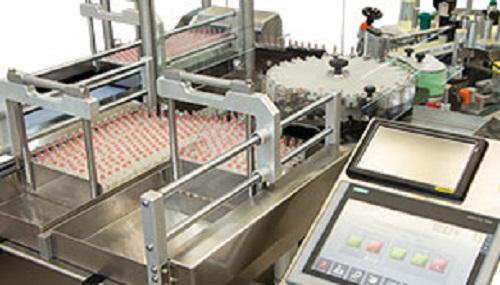
Pharmaceutical rotary labeling machine for vials
Small, cylindrical-shaped glass bottles or vials are mainly used for vacc...

Lab-scale Radial Flow Chromatography columns for virus clearance
The use of appropriate and compatible chromatography co...
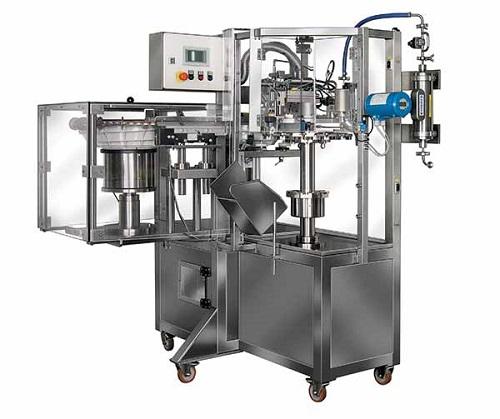
Low speed Filler for large-volume parenterals
Large-volume parenteral bottles are usually manufactured with a resin that c...
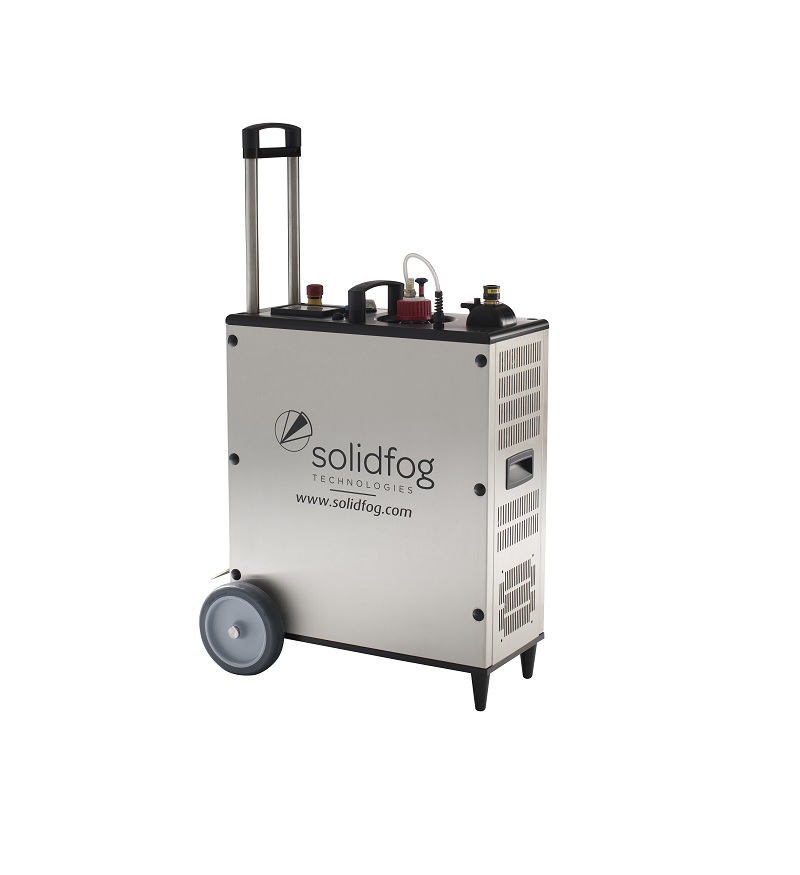
Compact H2O2 disinfection system
Dry fogging provides safe, effective microbiological cleaning of critical areas in biotech,...
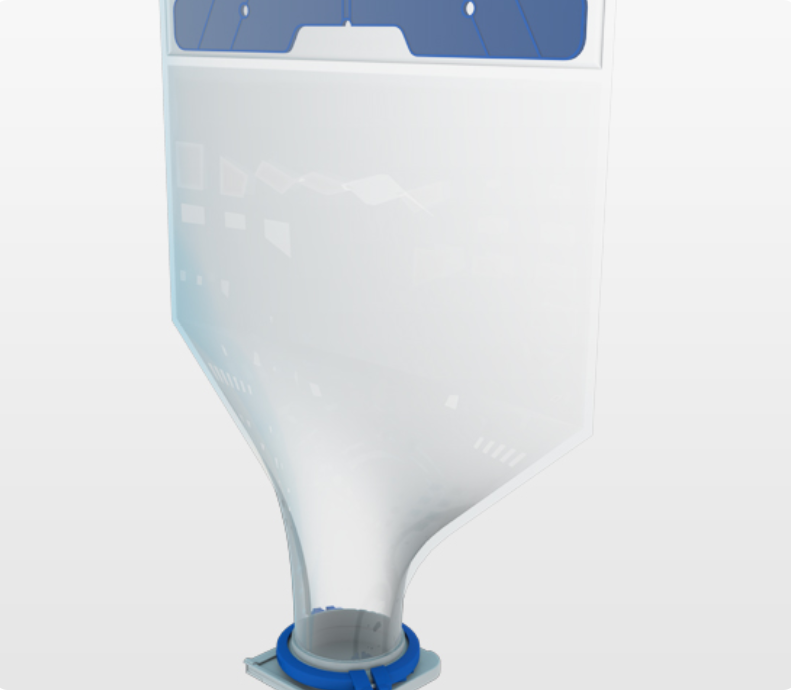
Single-use powder handling bag
Containers for handling pharmaceutical and biopharmaceutical powders may be disposable, to av...
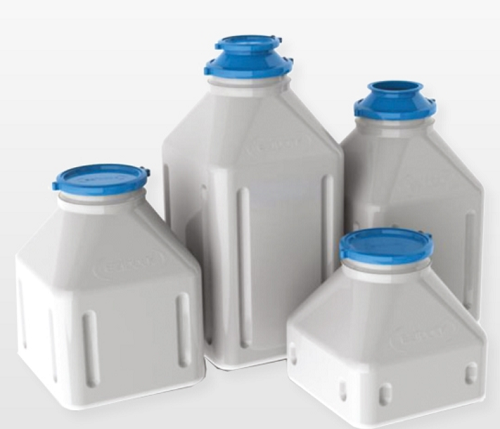
API powders storage bottle
Users who prefer rigid storage over single-use pharma charge bags, require lightweight solutions ...
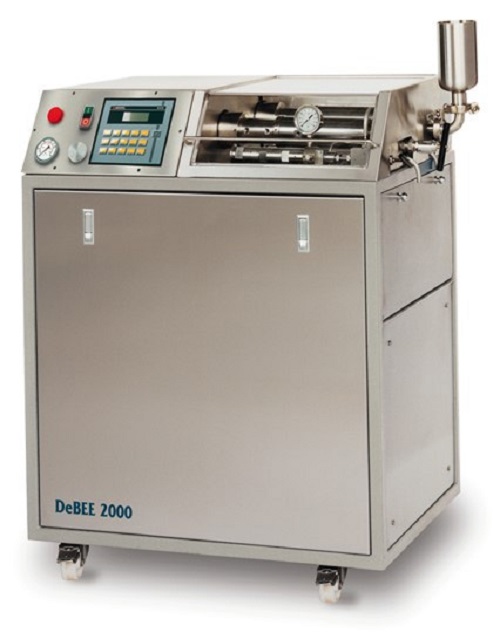
High pressure pilot homogenizer
Biotech and pharmaceutical development programs often require a mixing method that achieves ...
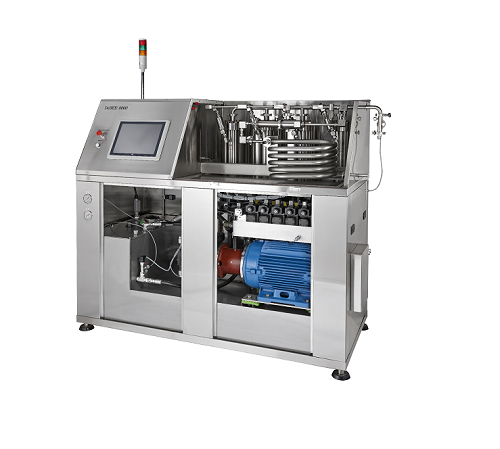
High pressure industrial homogenizer
For any industrial pharmaceutical process that relies on high pressure homogenization ...
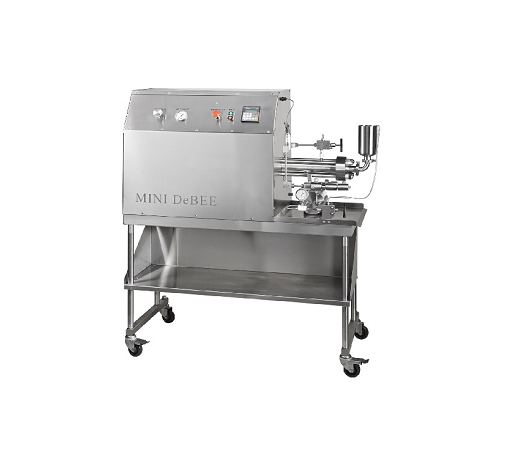
Pilot high pressure homogenizer
For maximum value, a high-pressure homogenizer that’s suitable for both laboratory and pilot...
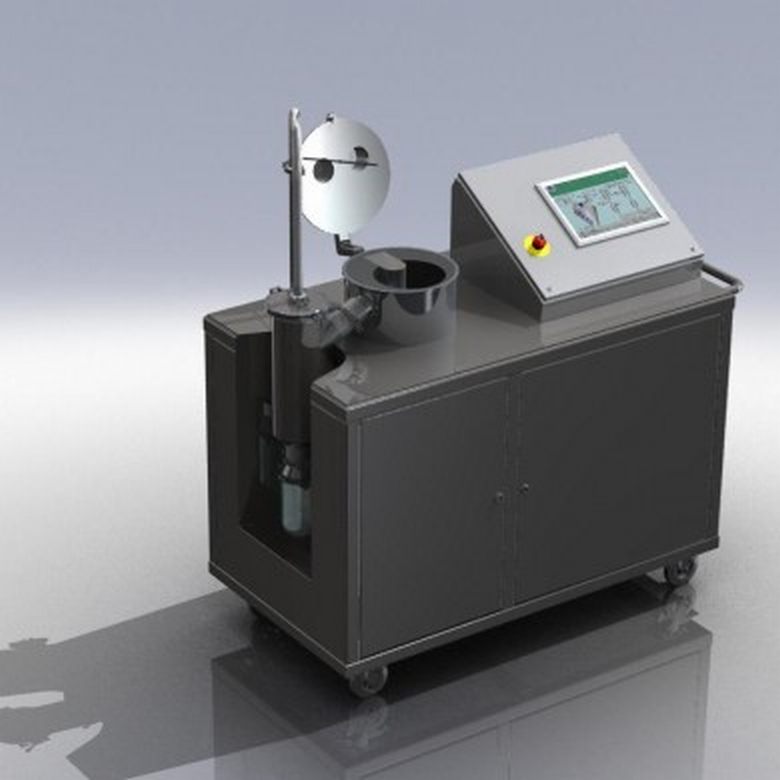
Laboratory scale active freeze dryer
The laboratory-scale active freeze-drying is used for dehydrating high-value products ...
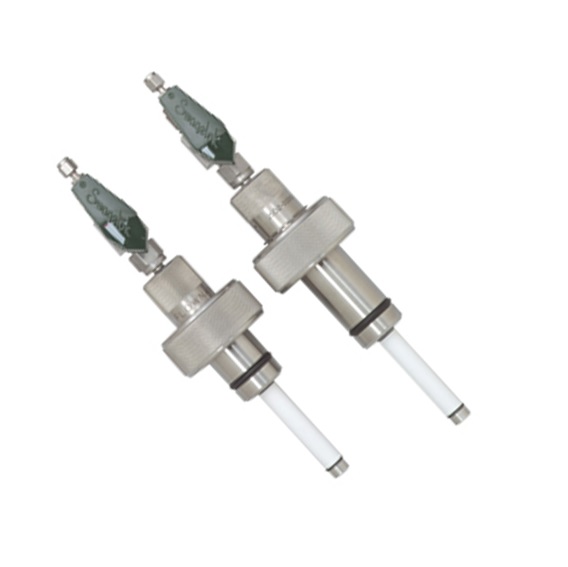
Sampling probe suitable for fermenter samples
Accurate, sterile sample collection is vital across a range of biopharmaceut...
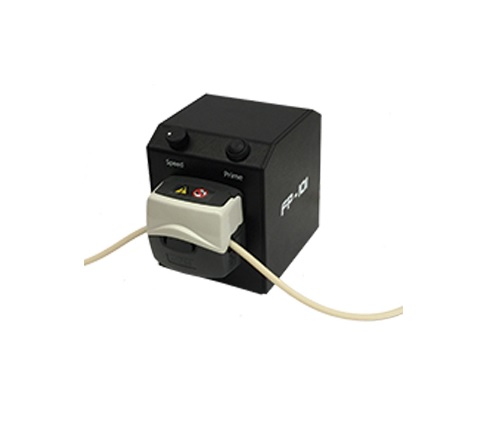
Accessory feed pump for various applications
In many biopharmaceutical or chemical development processes, lab work can be ...
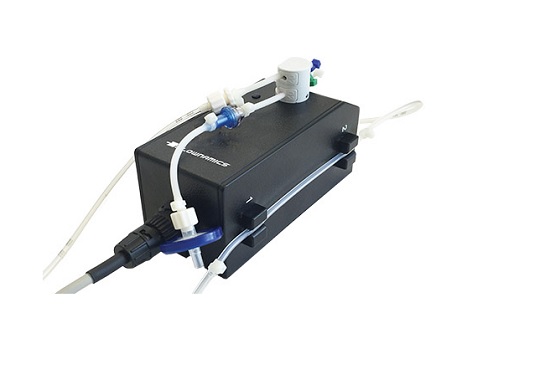
Fluid sensor technology for flow rate measurement
For many bioprocesses, precise measurement of media flow rates is vital...
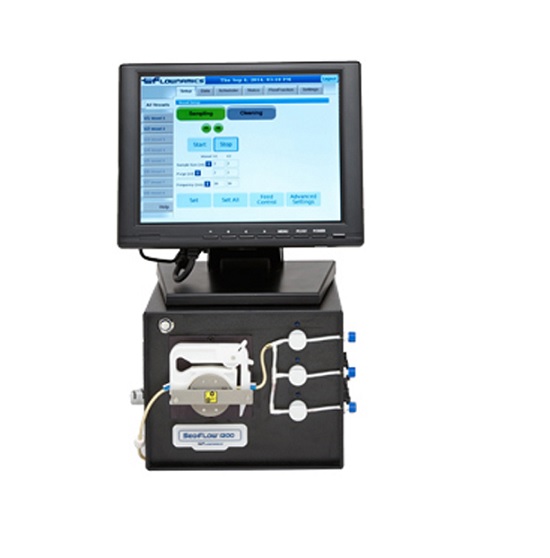
Entry-level automated online sampling system
An accurate and sterile sampling of cultures is vital throughout the biopharm...
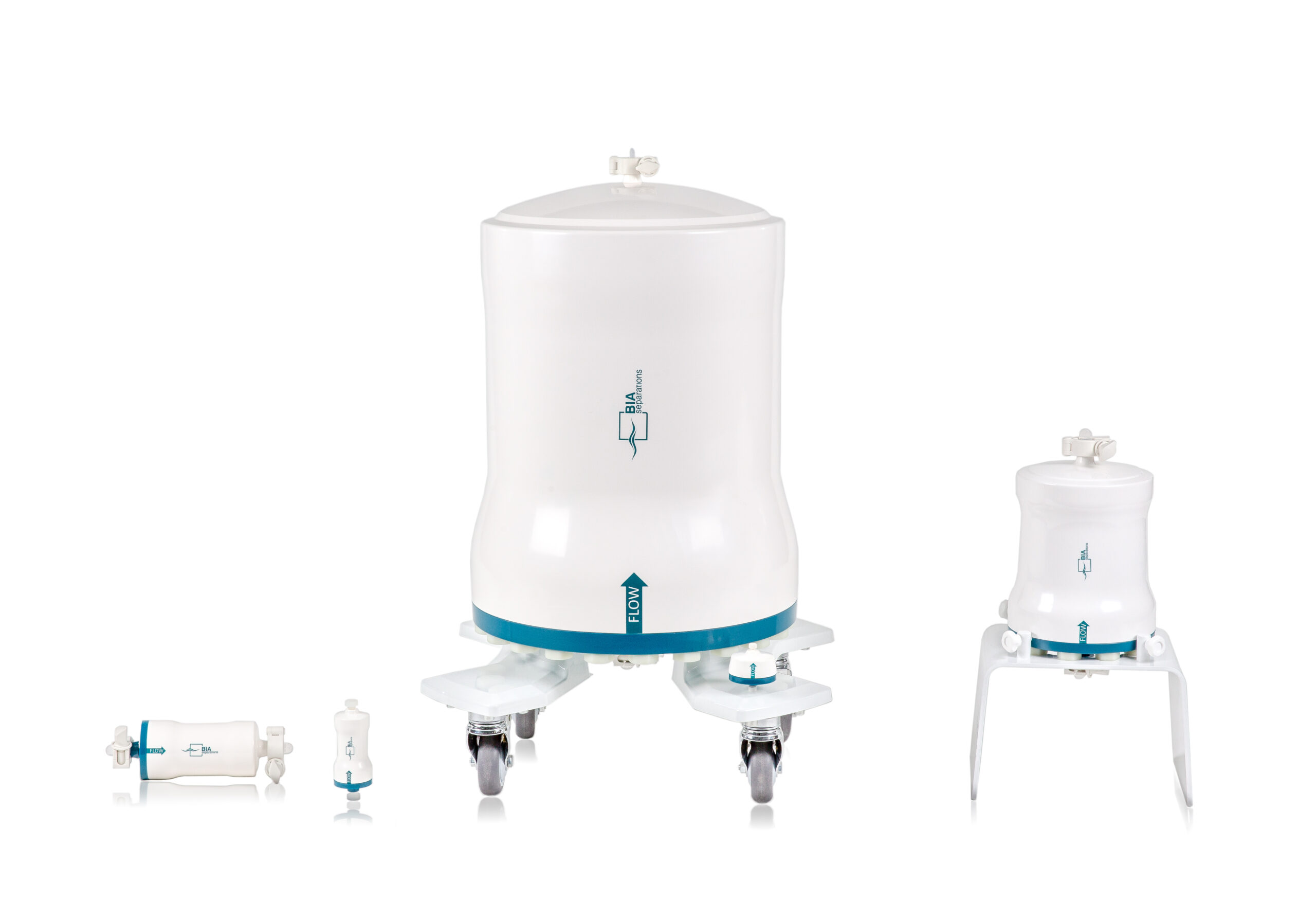
Disposable monolithic columns
Chromatographic monolithic columns for working with large proteins, viruses, VLPs and pDNA req...

Short bed monolithic columns for analytics
Samples taken at various process steps need to be analysed quickly and accurate...
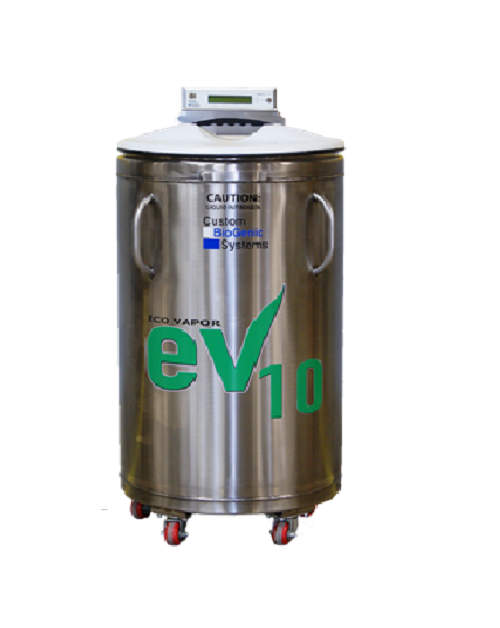
Liquid nitrogen vapor storage freezer
For biotech and pharmaceutical cryopreservation, liquid nitrogen vapor storage provid...
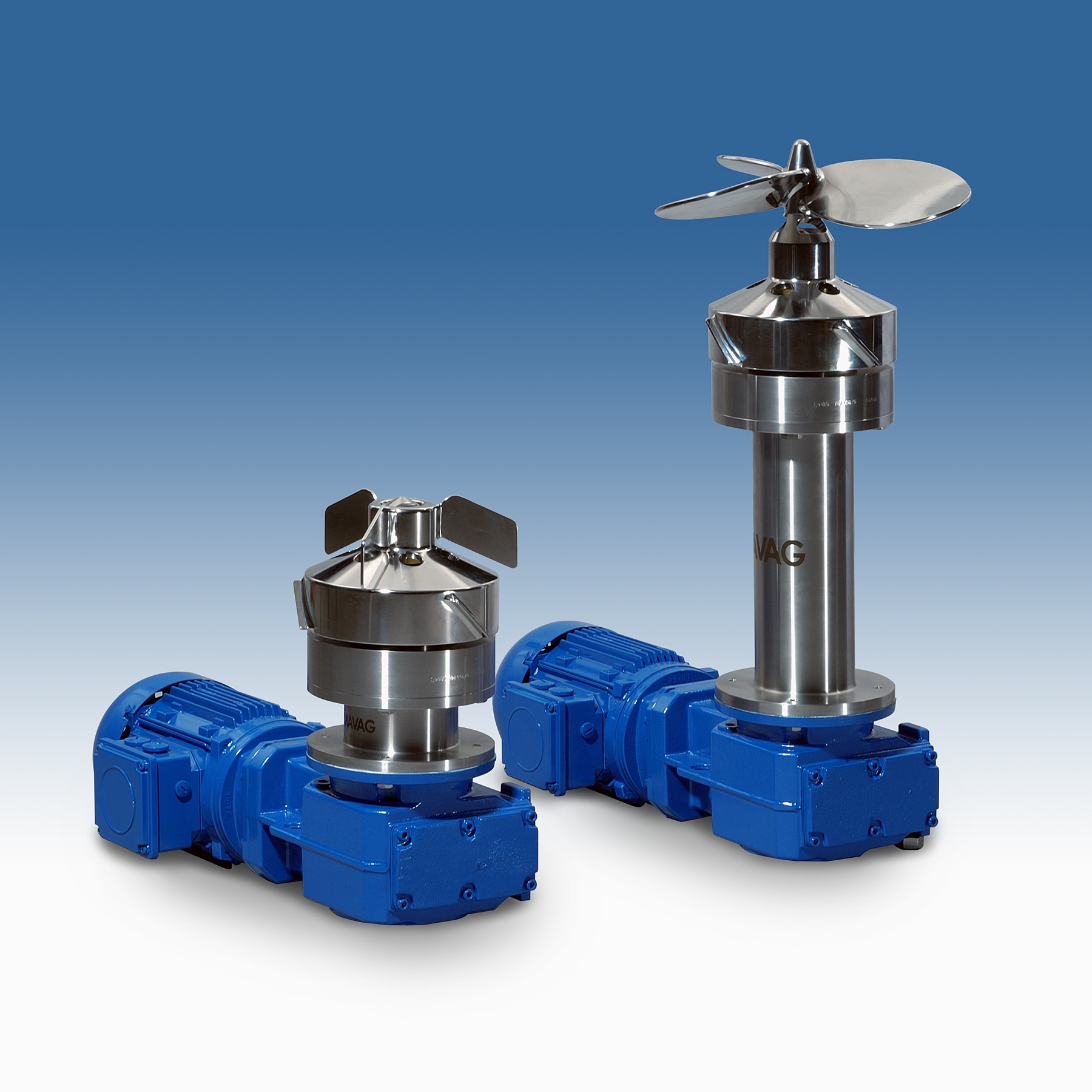
Magnetic agitator
Reliable mixing and agitation are essential to any quality production process that involves a fluid. This n...
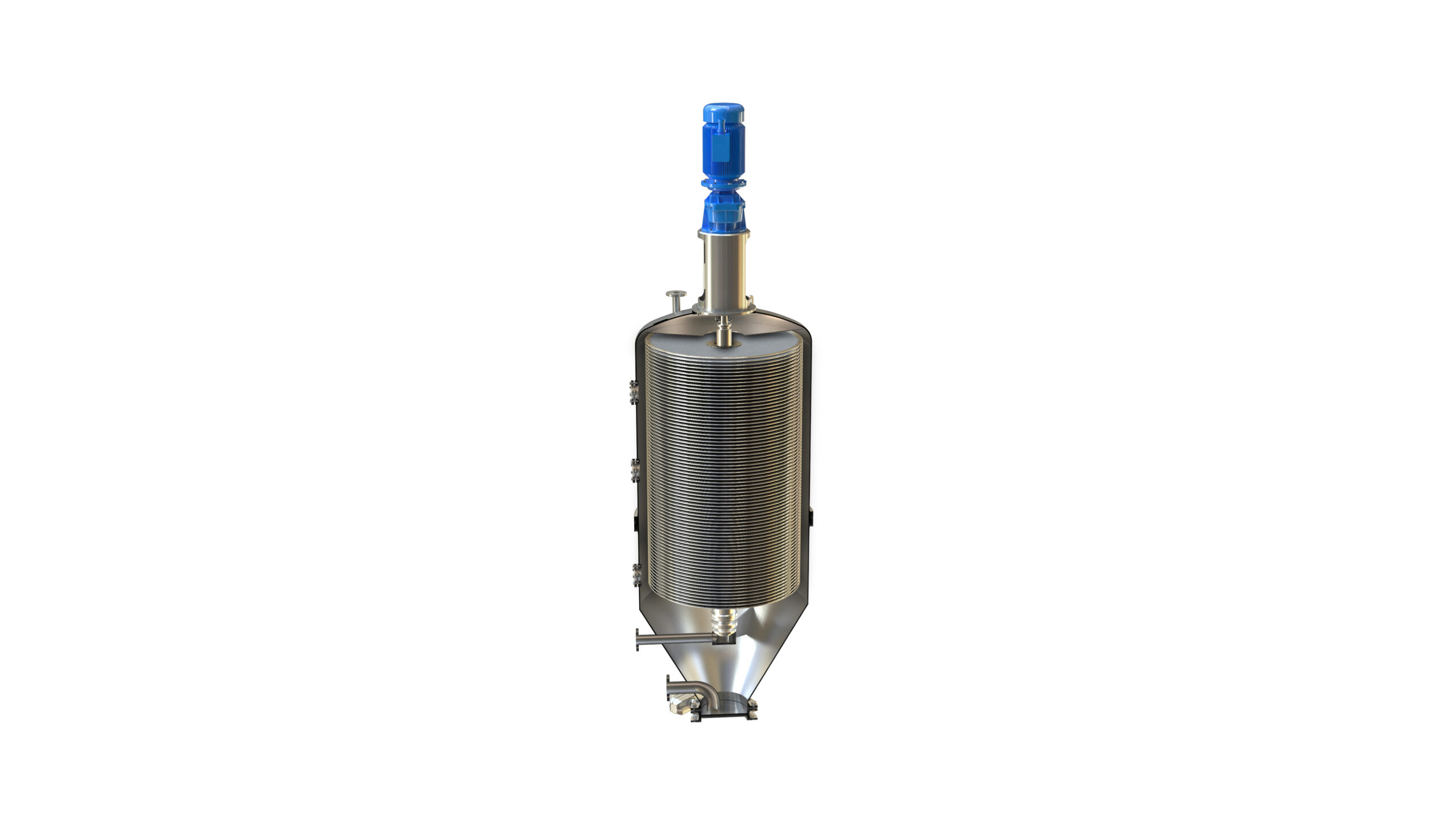
Centrifugal disc filter
The pharmaceutical and bioprocess industries need filtration processes of particularly high quality t...
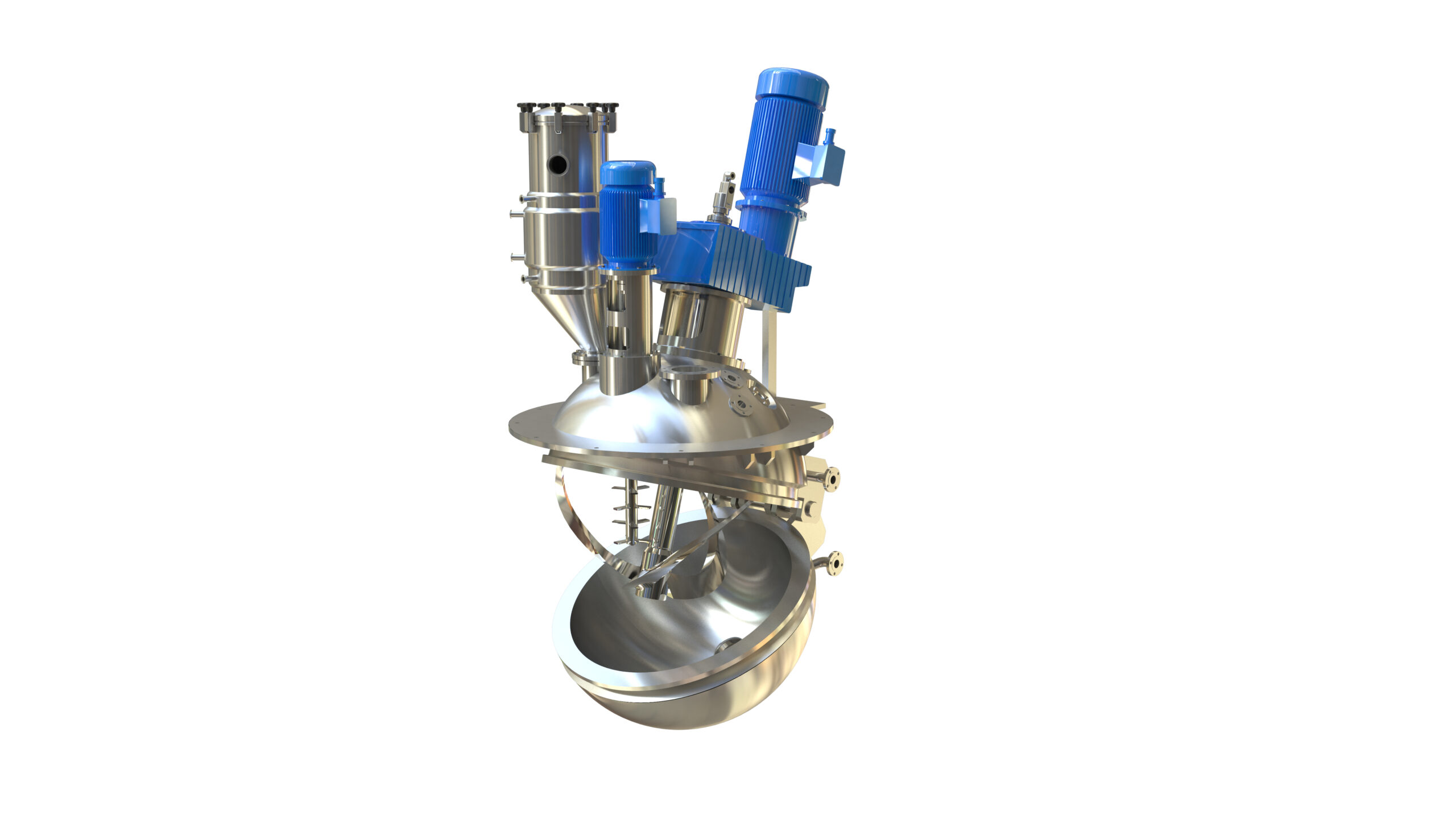
Spherical dryer
Drying vessels that are simple, reliable, and easy to maintain increases product quality and process efficienc...
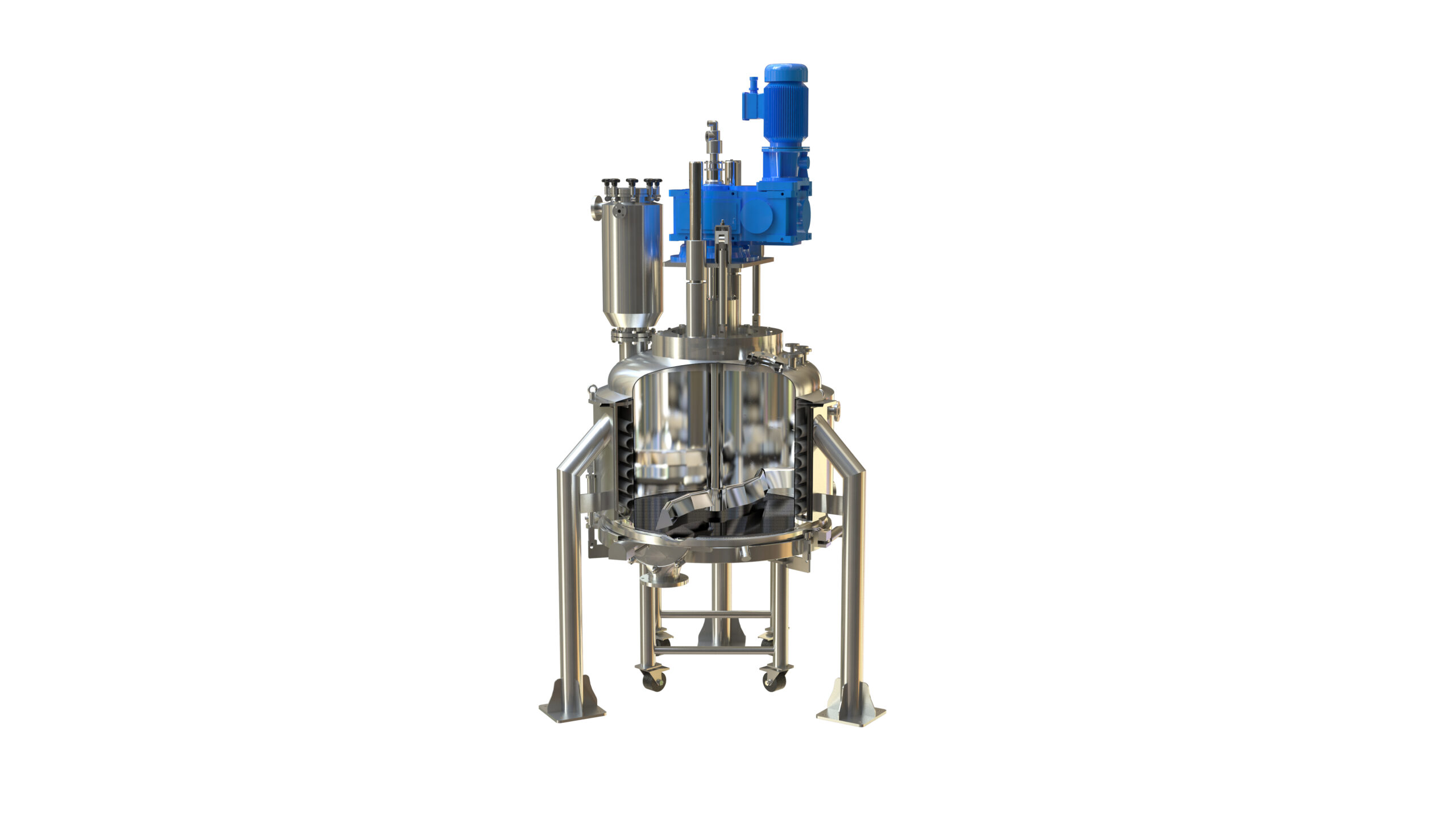
Filter dryer
The pharmaceutical and bioprocess industries need filtration processes of particularly high quality to ensure the...
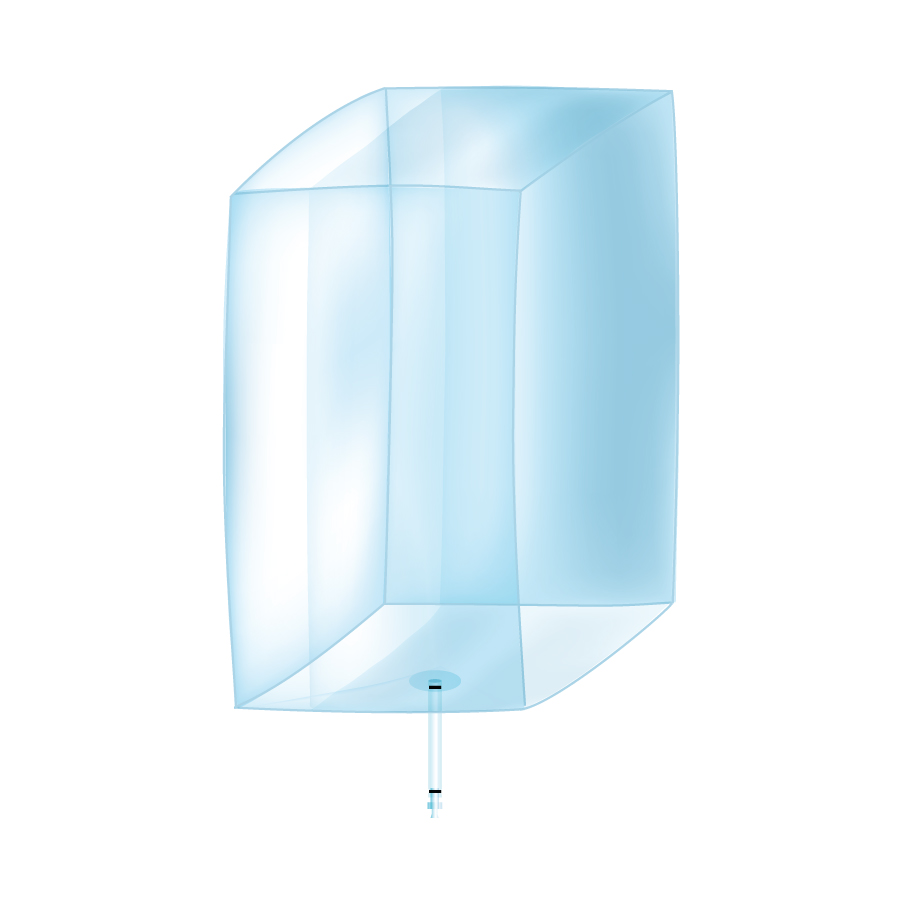
Disposable tank liners
Manufacturers in the bioprocessing industries are increasingly turning to single use solutions for the...
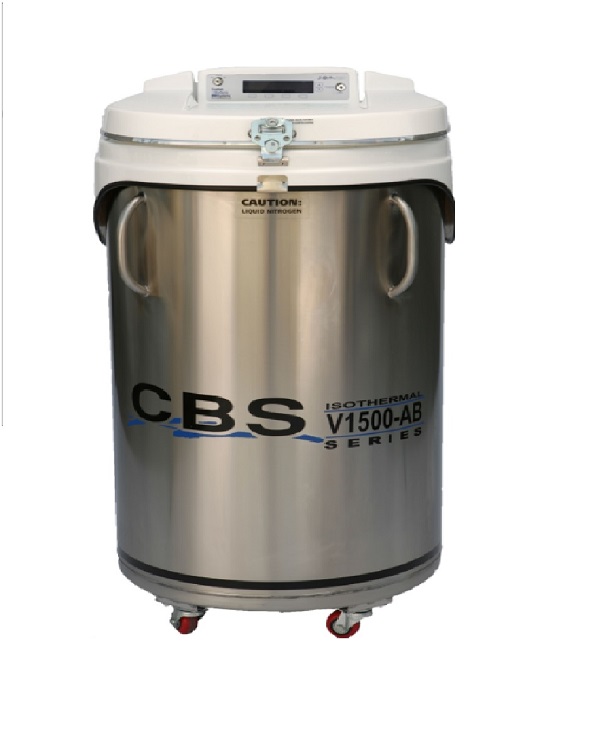
Liquid nitrogen freezer for safe and dry storage of your samples
Remove the risks of cross-contamination and liquid nitr...
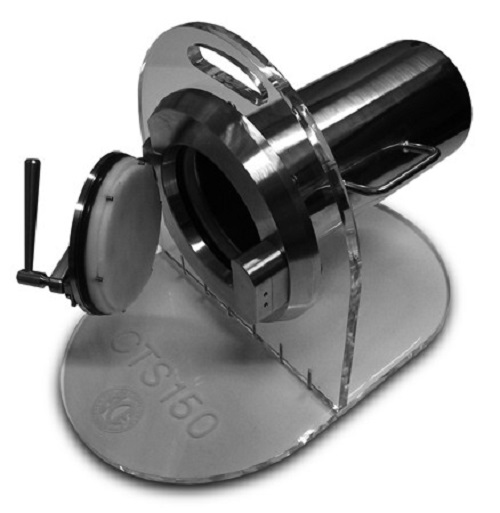
Transfer system for high-containment environments
A high-performance transfer port system that combines ultimate safety, ...
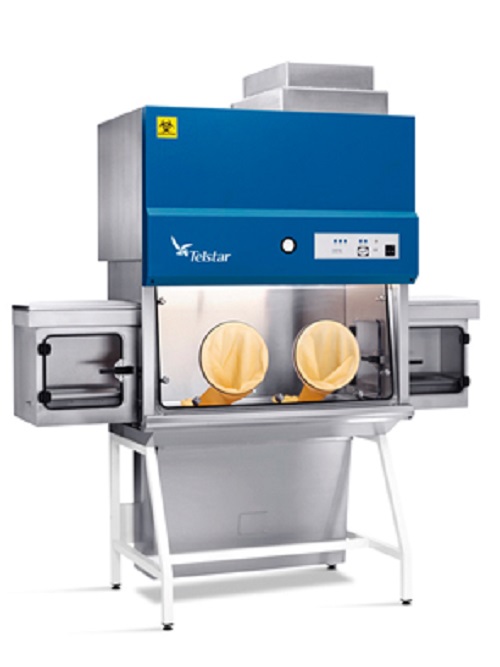
Negative pressure isolator
Used for products biologically hazardous, that also require minimized cross contamination.
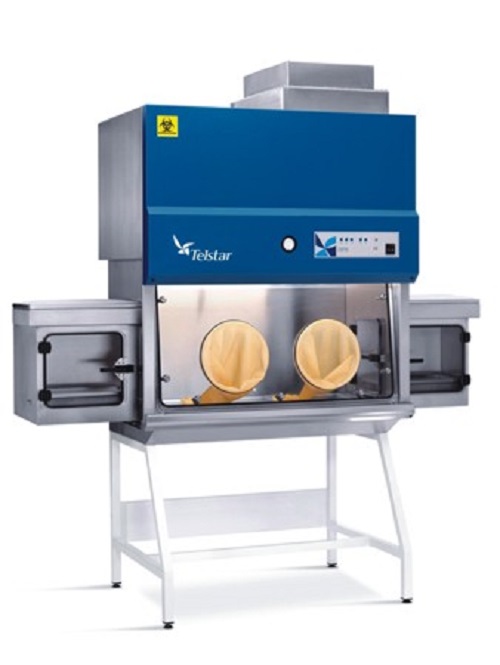
Positive pressure isolator
Ideal for products which have no biological risk but require high sterile conditions.
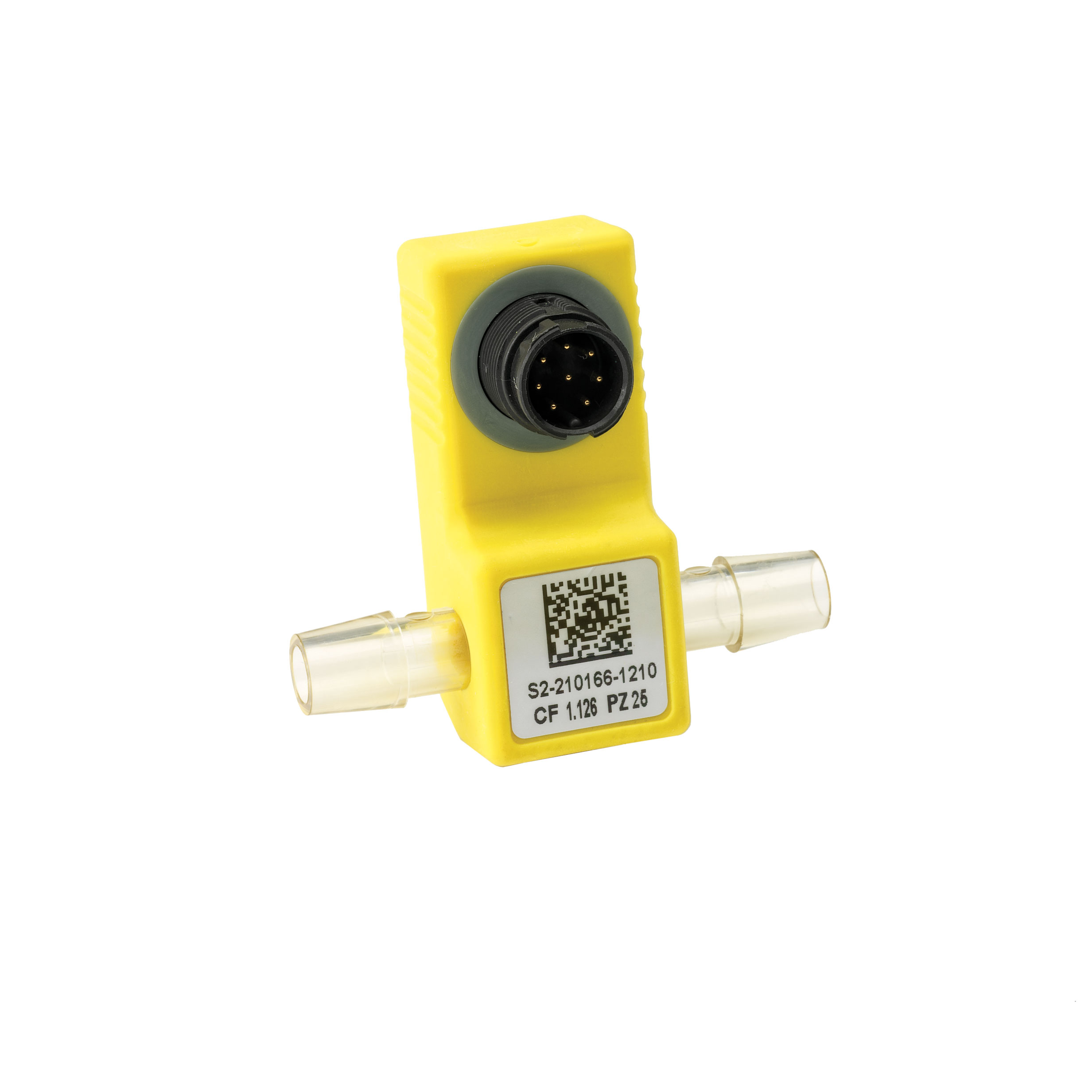
Single-use pressure sensor
Biopharmaceutical manufacturers are increasingly making use of Single-use pressure sensors to enh...
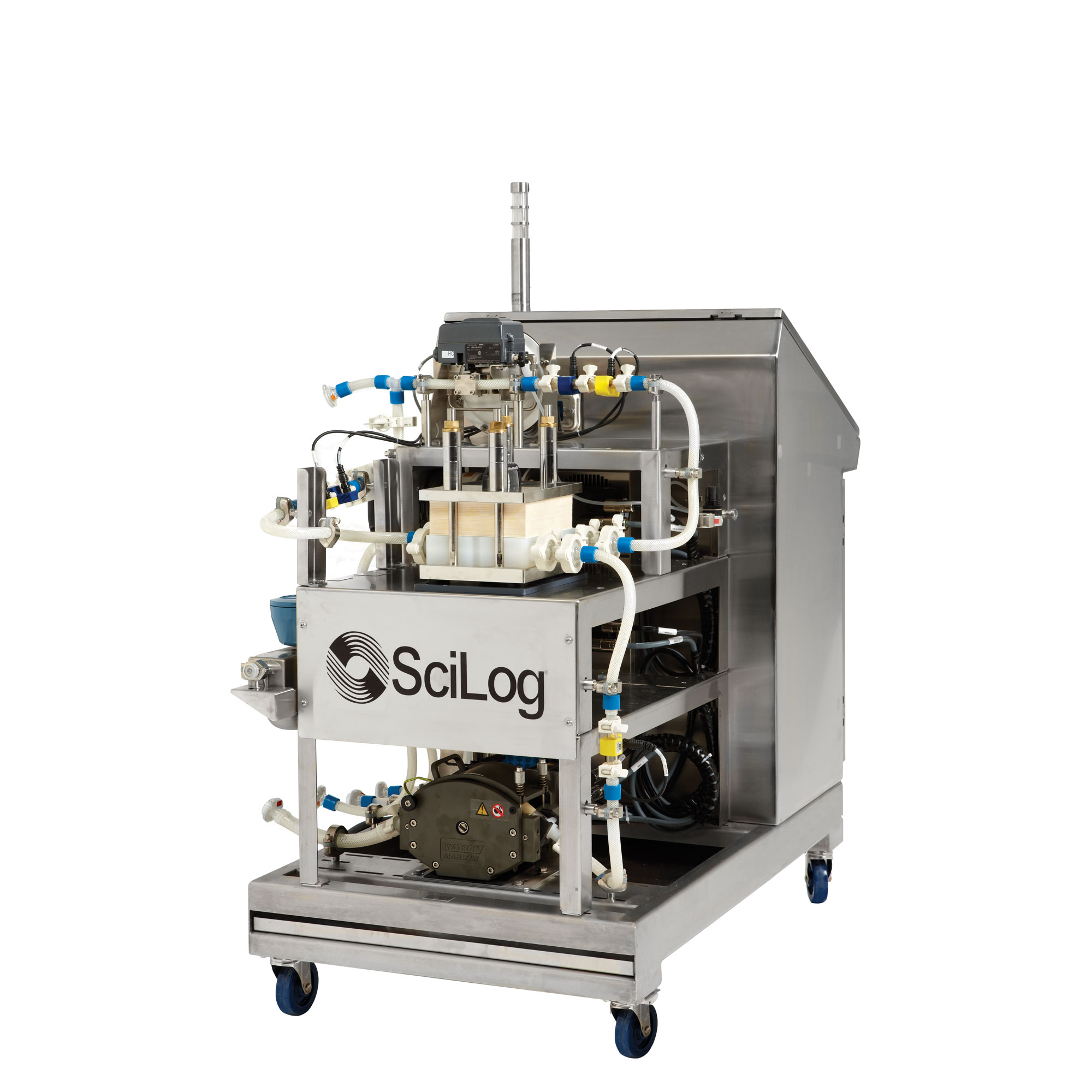
Automated single use tangential flow filtration system
Tangential Flow Filtration is an essential to the biopharmaceutica...
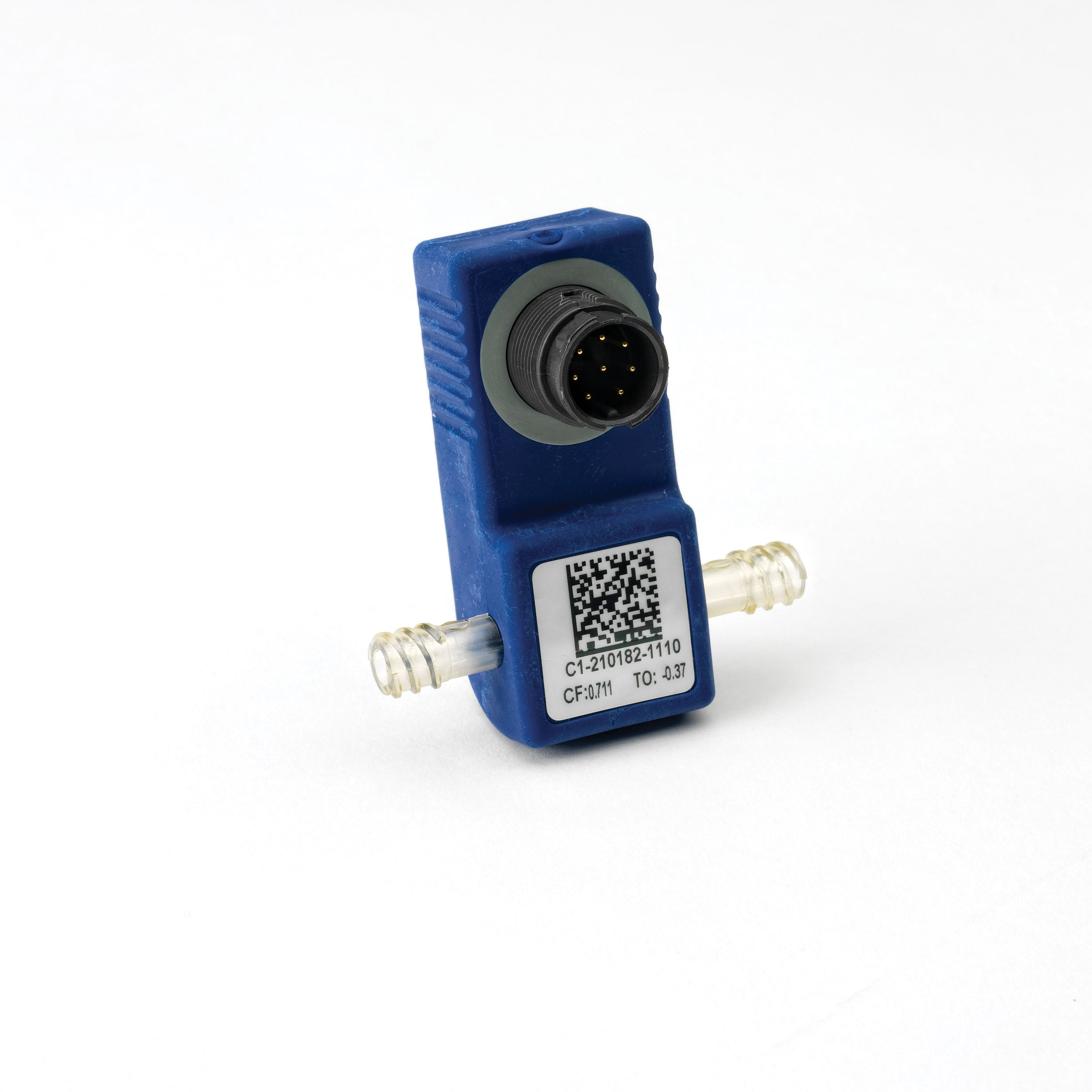
Single-use conductivity sensor
Biopharmaceutical manufacturers are increasingly making use of single-use conductivity sensor...

Single-use temperature sensor
Biopharmaceutical manufacturers are increasingly making use of single-use temperature sensors ...
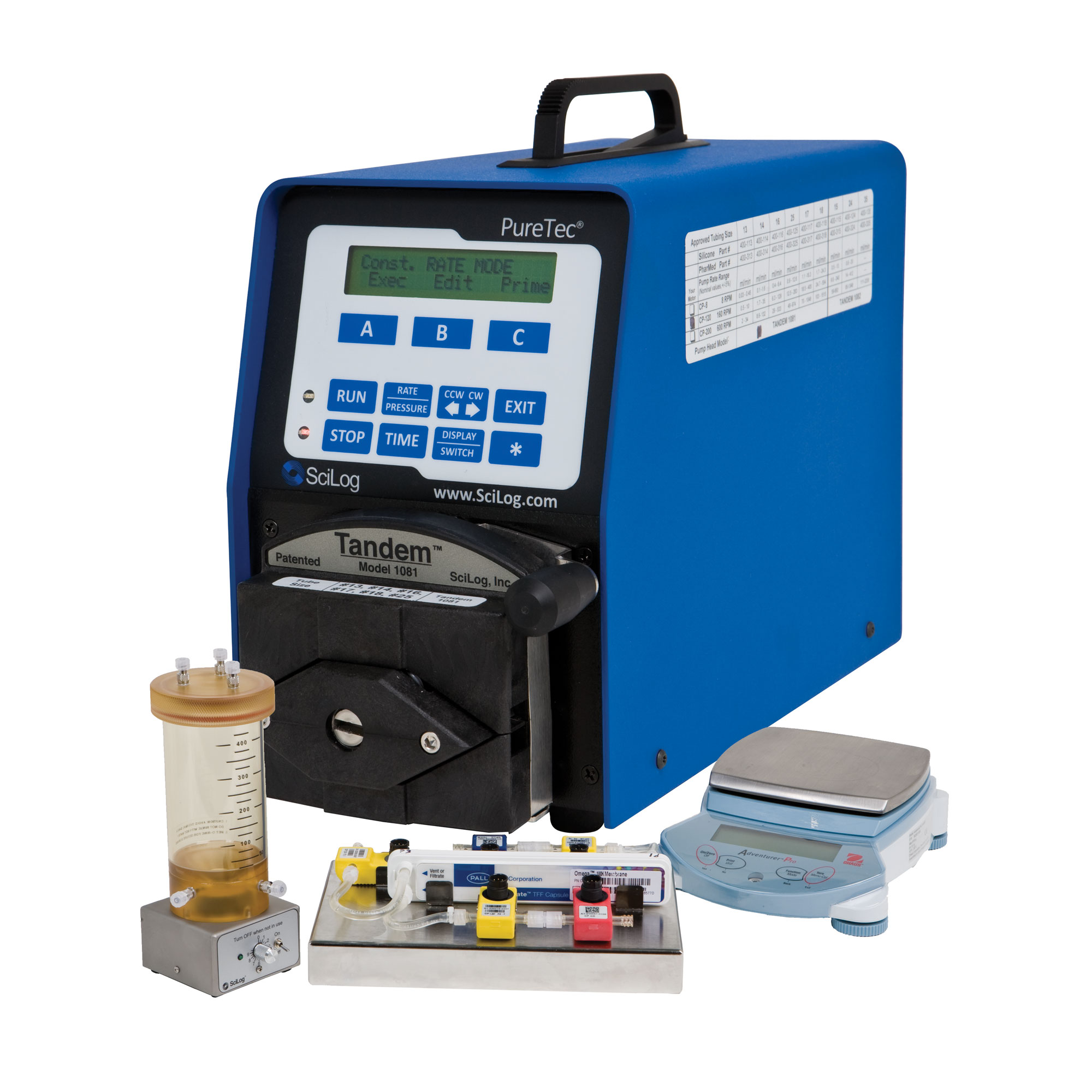
Lab scale tangential flow filtration system
Tangential Flow Filtration is an essential to the biopharmaceutical processing...
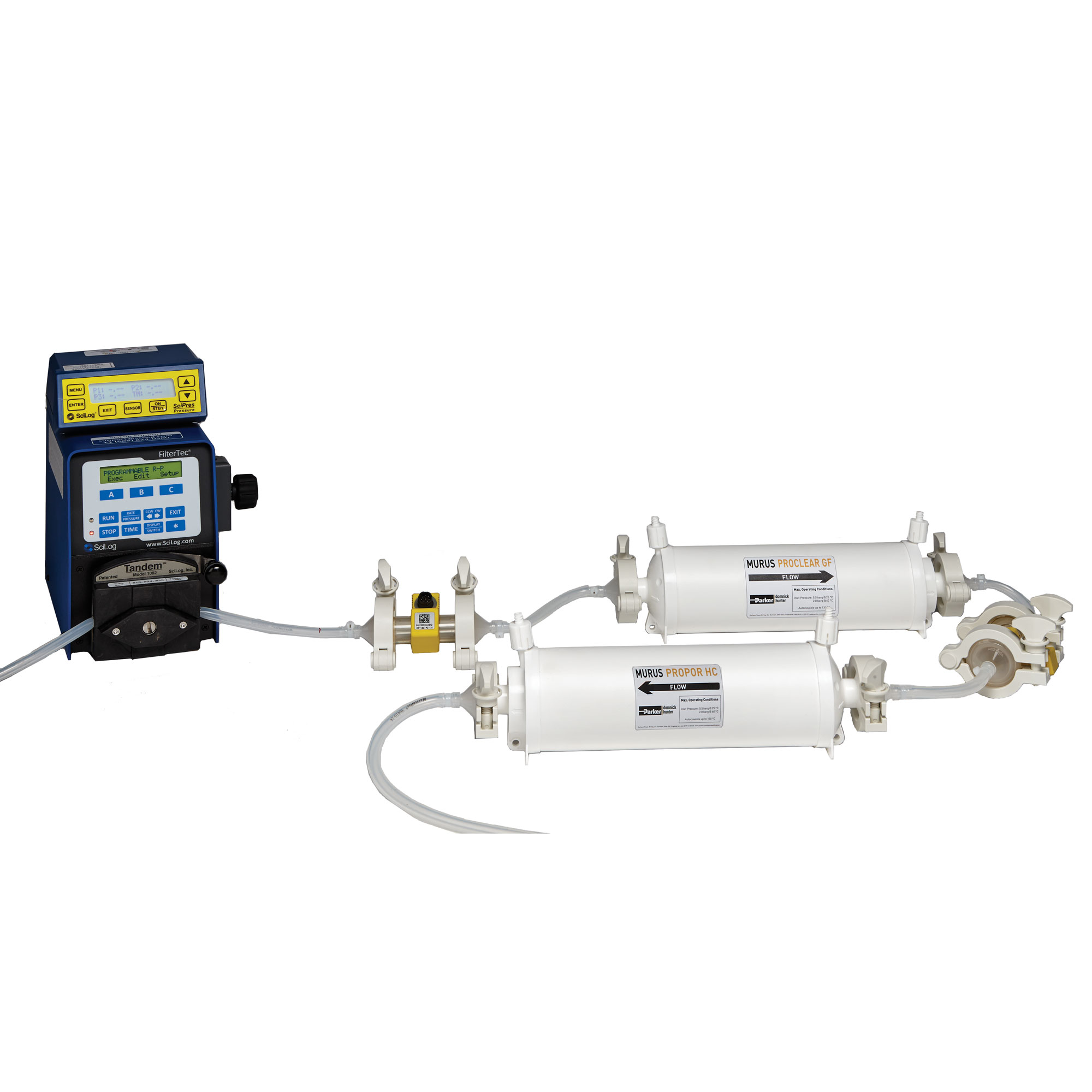
Automated cell culture clarification system
Efficient harvest from the bioreactor is essential to any successful cell cult...
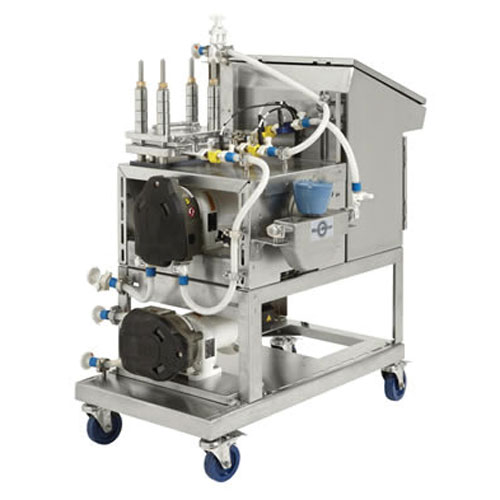
Semi-automated tangential flow filtration system
Tangential Flow Filtration is an essential to the biopharmaceutical proce...
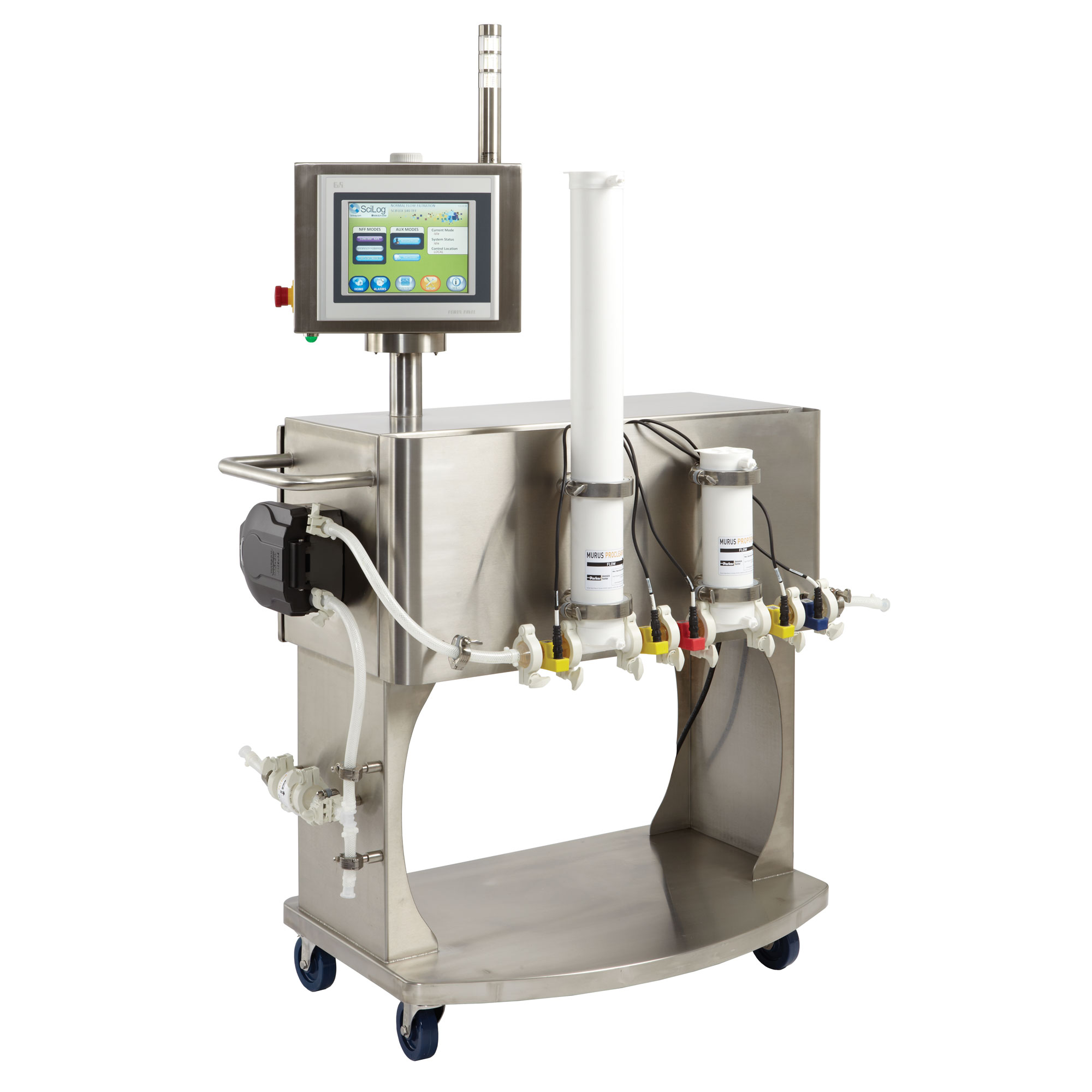
Semi-automated normal flow filtration system
Normal Flow Filtration is frequently used the biopharmaceutical processing in...
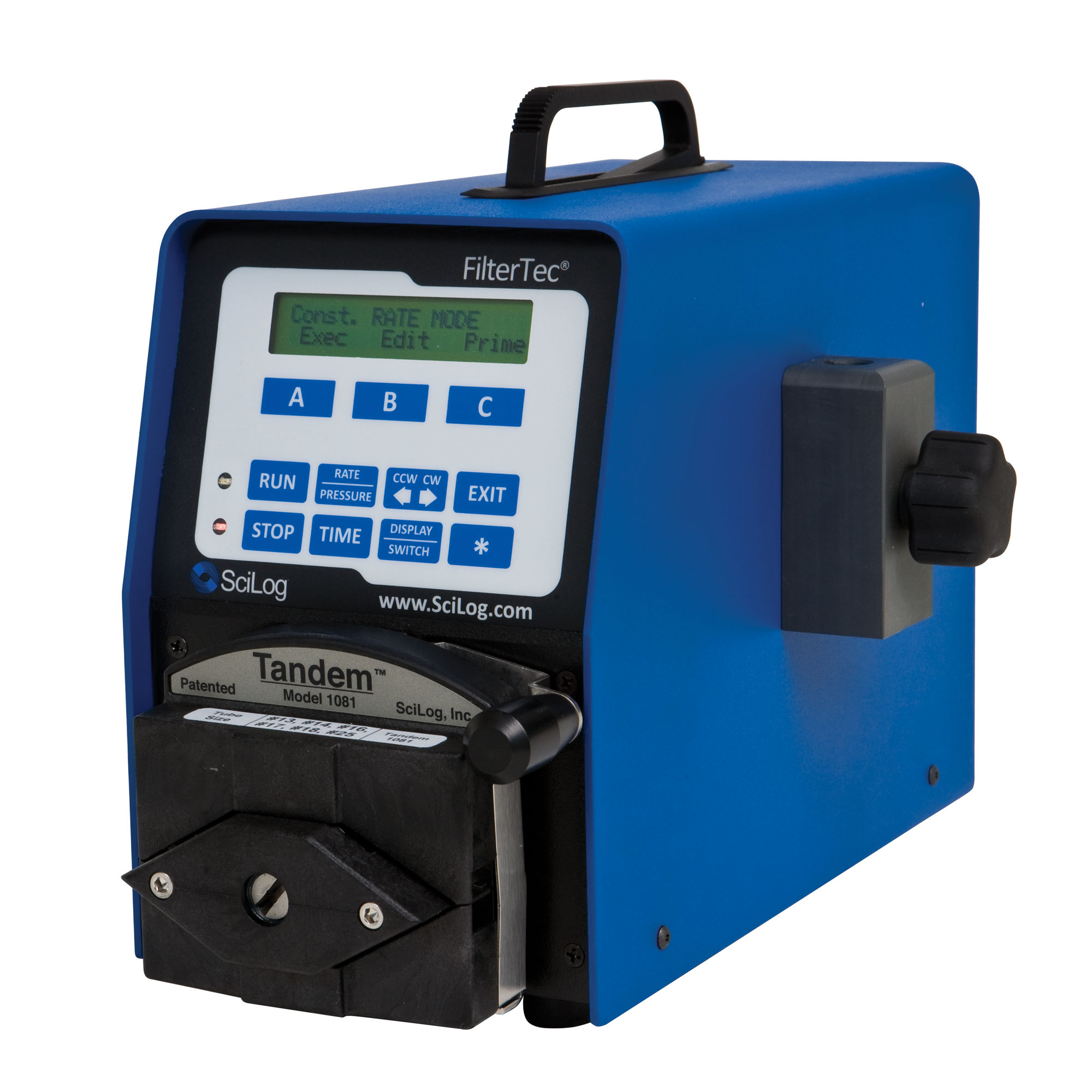
Lab scale normal flow filtration system
Normal Flow Filtration is frequently used the biopharmaceutical processing industry...
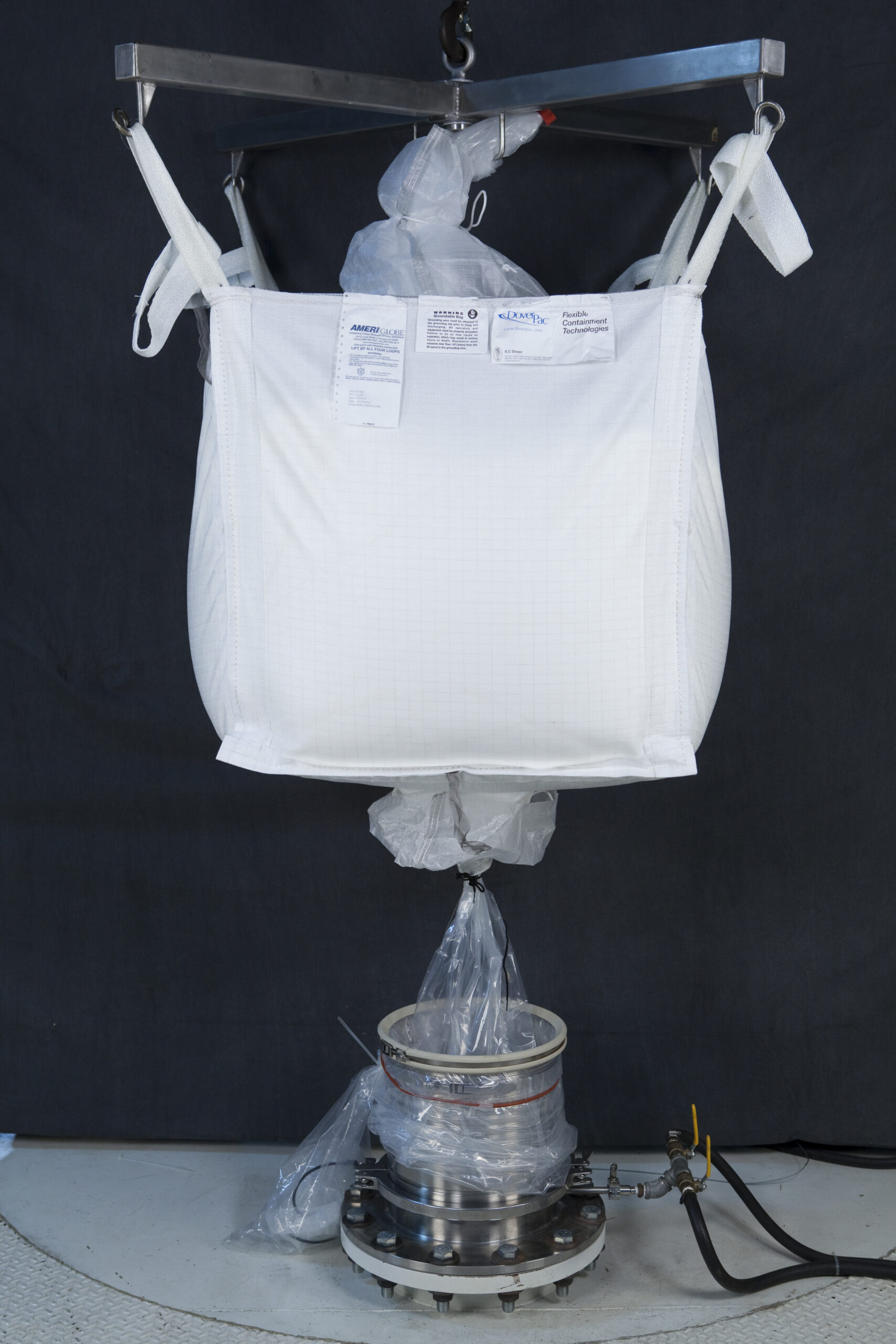
Flexible contained powder charging solution
Filling of transportation bags and discharging them into mix tanks or reactor ...
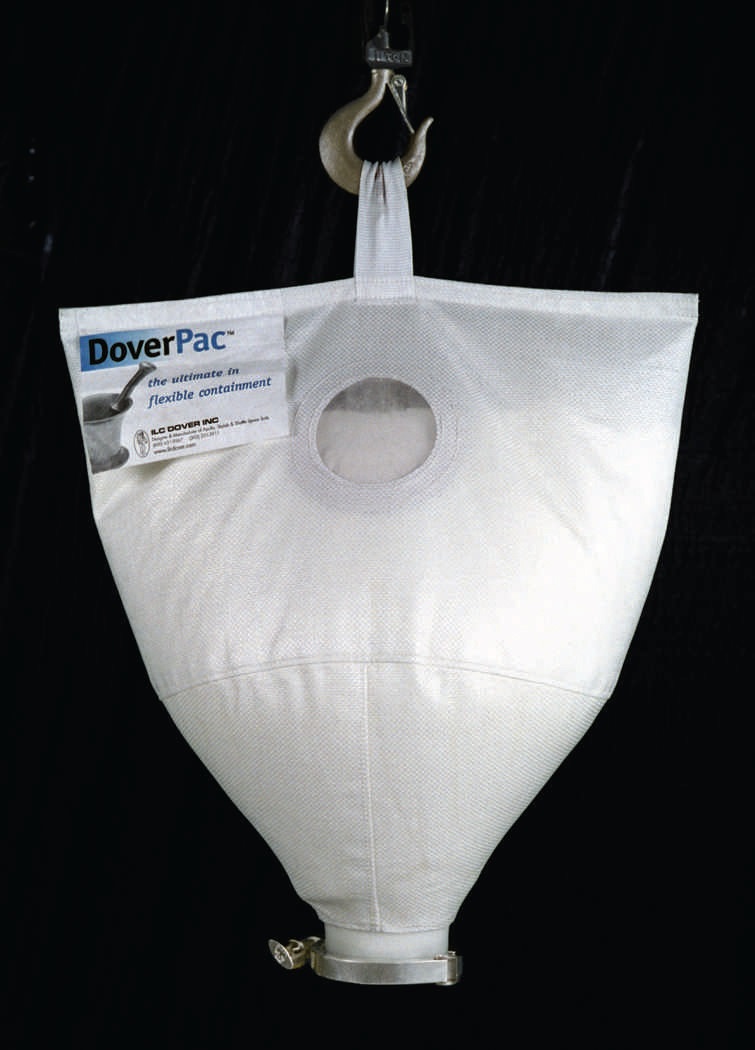
Flexible contained charging for split butterfly valves
Poly bottles with split butterfly valves are often used to transfe...
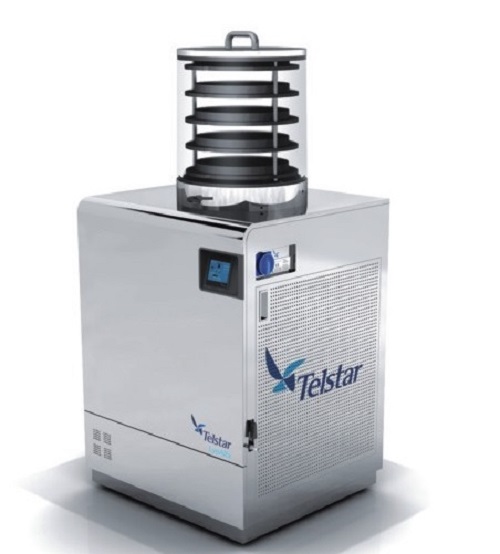
Compact laboratory freeze dryer
Particularly suitable for research centers requiring greater freeze drying capacity. Some of...
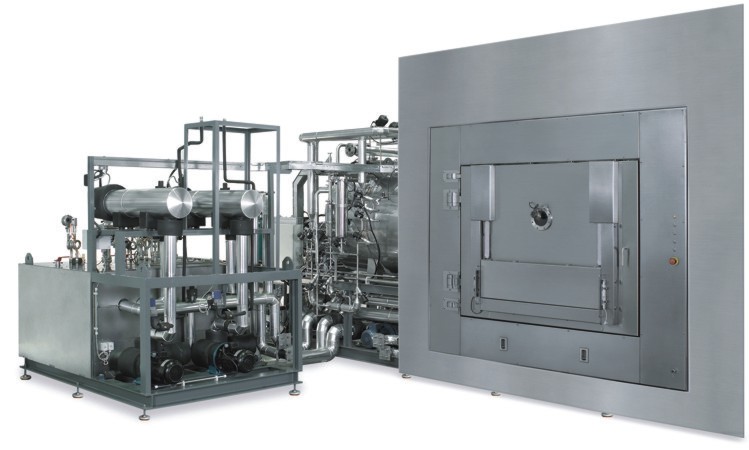
Custom engineered freeze dryer
For either bulk format or liquid in vials, ampoules or syringes, the Lyomega units are design...
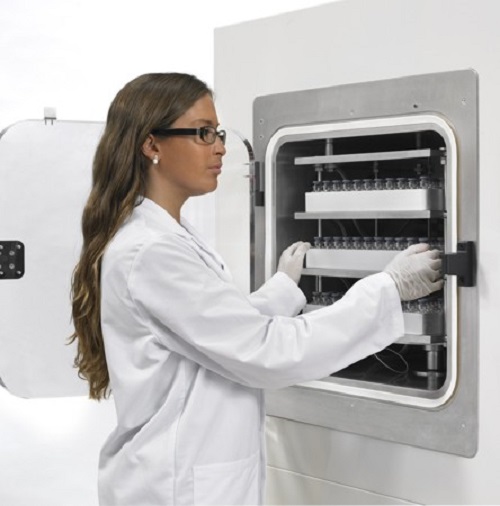
Pilot freeze dryer for scale up
Designed for biological, pharmaceutical and food products formulation and “scale up...
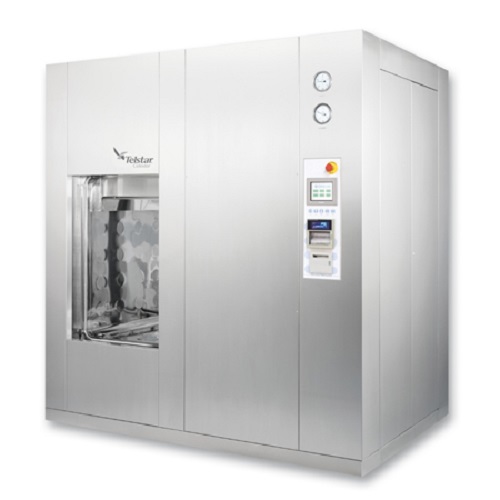
GMP autoclave
When sterilizing and dealing non-thermolabile products, you will want to get a hold of those resistant to the te...
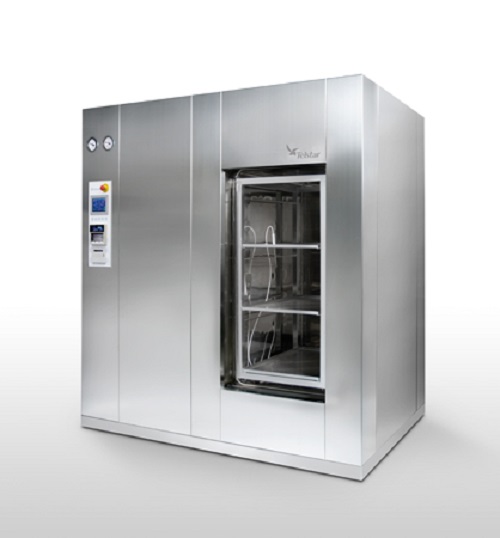
Saturated steam GMP laboratory autoclave
For processing a wide range of products: solid, porous and liquids in a laboratory...
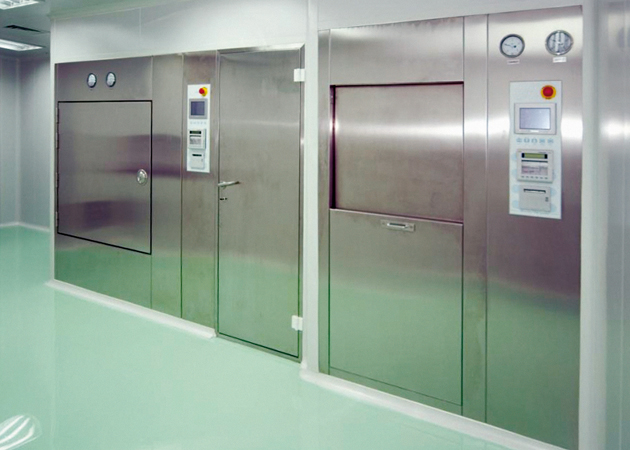
Dry heat depyrogenation oven
Specially designed for the drying and sterilization of glass containers, vials or ampoules, and...
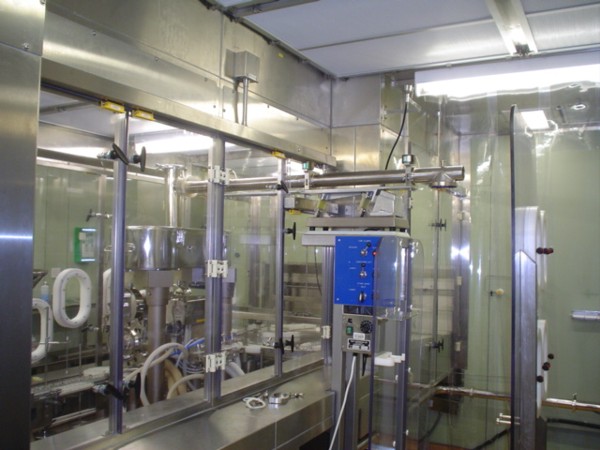
Restricted-access barrier systems
Create a physical barrier between the operator and the product. More flexible than an iso...
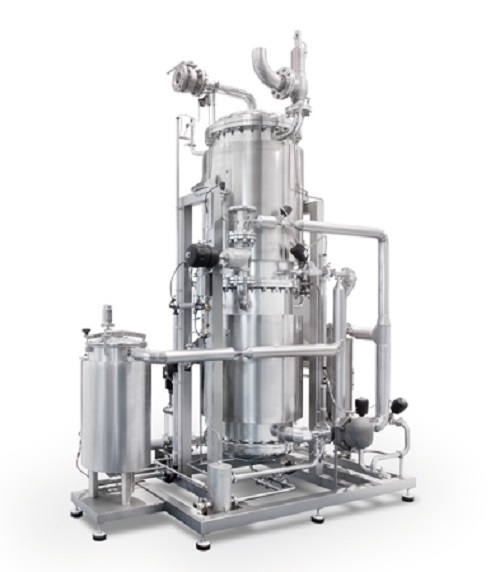
Pure steam generator
Pure steam is mainly used in the pharmaceutical industry and in biotechnology for sterilization, water f...
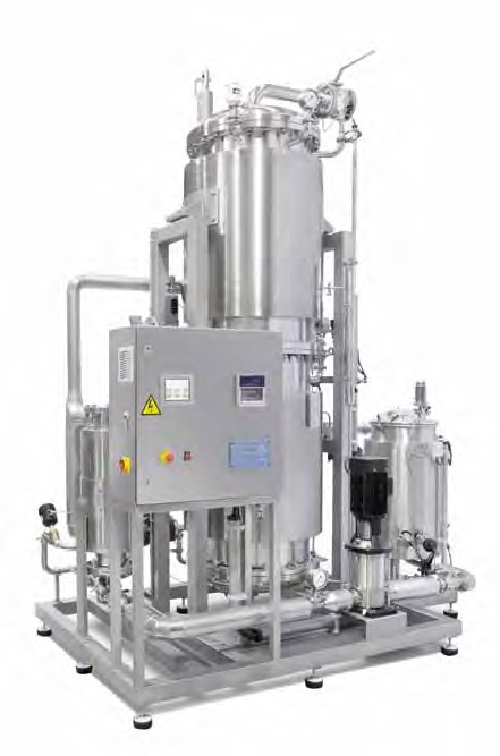
Electrical pure steam generator
Pure steam is defined as the steam which when condensed becomes WFI quality water in accorda...
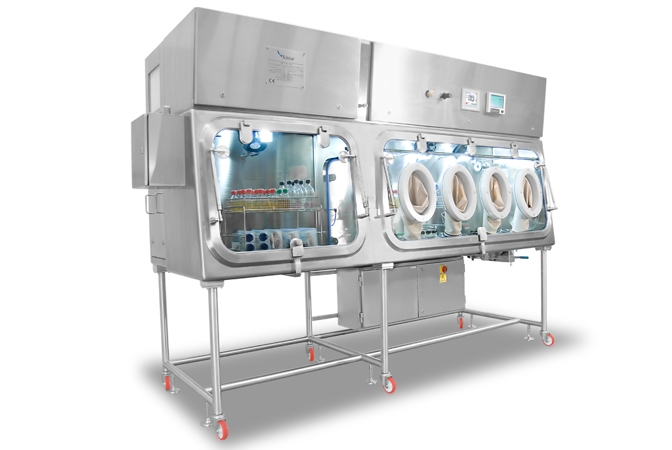
Sterility test isolators
Designed to avoid this risk and protect the product from both the process and externally generated f...
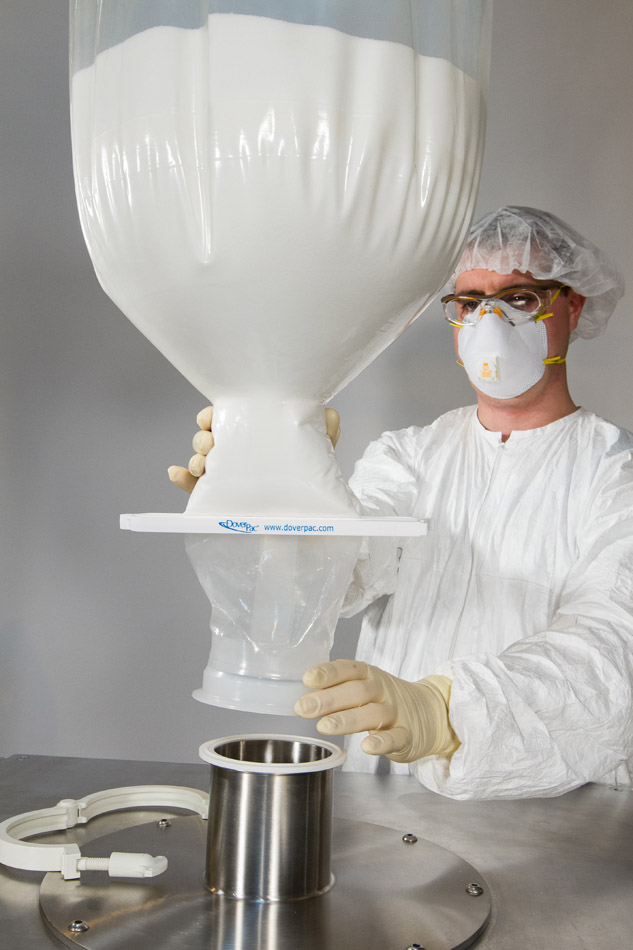
Flexible contained handling of powder transfer bags
Filling of transportation bags and discharging them into mix tanks or...
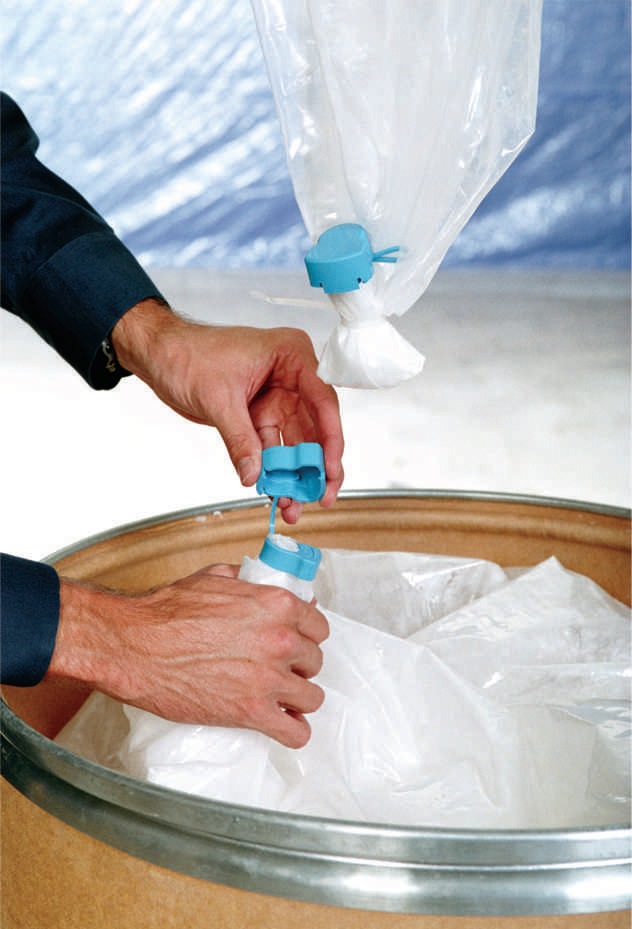
Crimping system
Flexible disposable containment systems in the form of specially designed plastic bags are an excellent choice...
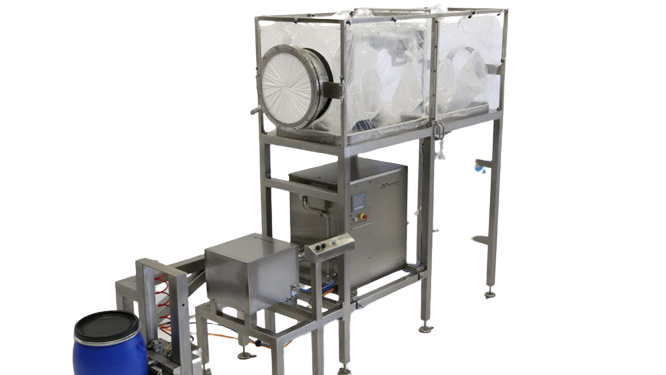
Flexible contained drum transfer system
Transferring powders from drums to process equipment such as reactors or mills can ...
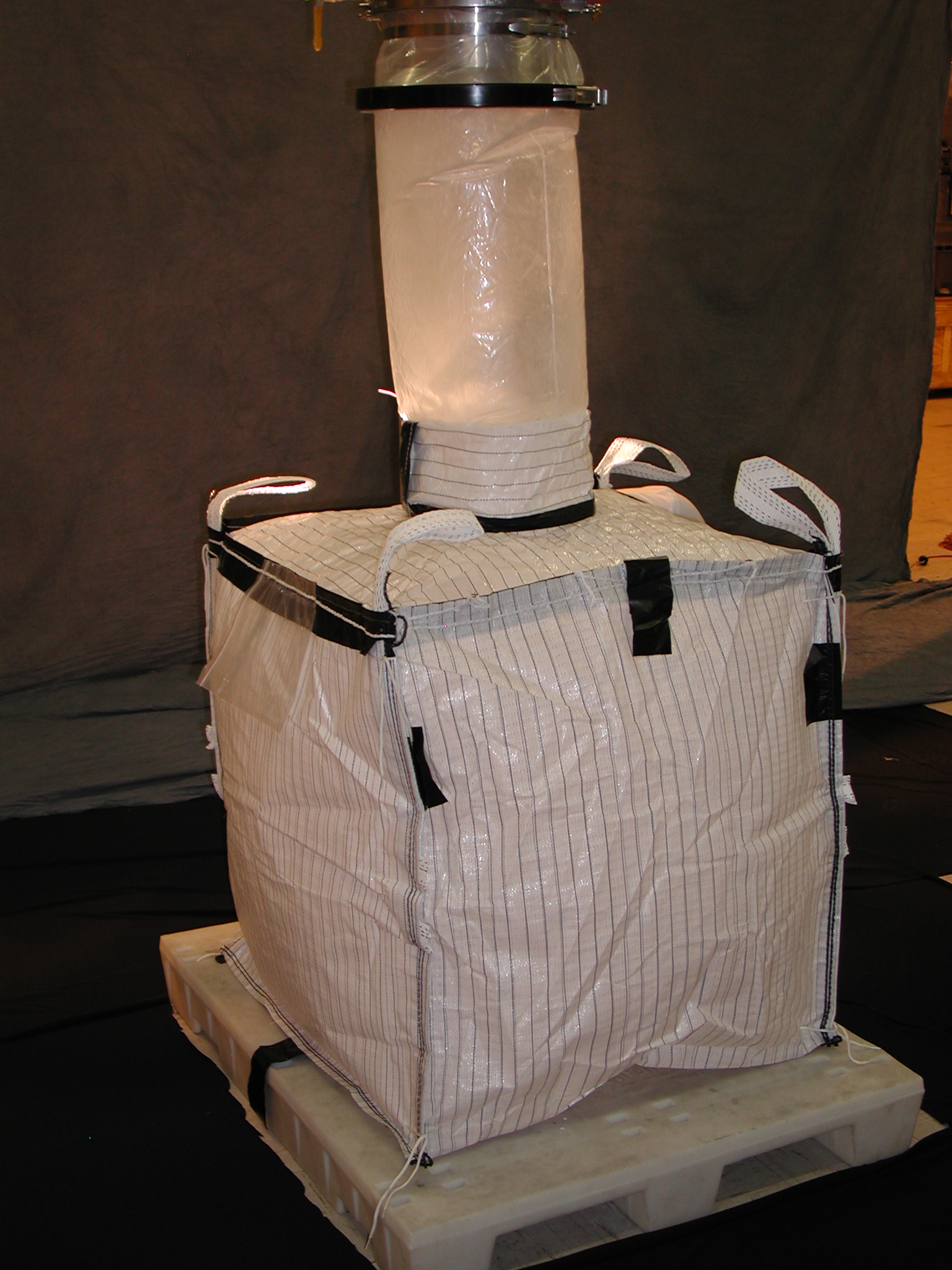
Flexible contained powder discharge into FIBC’s
Flexible intermediate bulk containers known as FIBC’s are commonly used in...
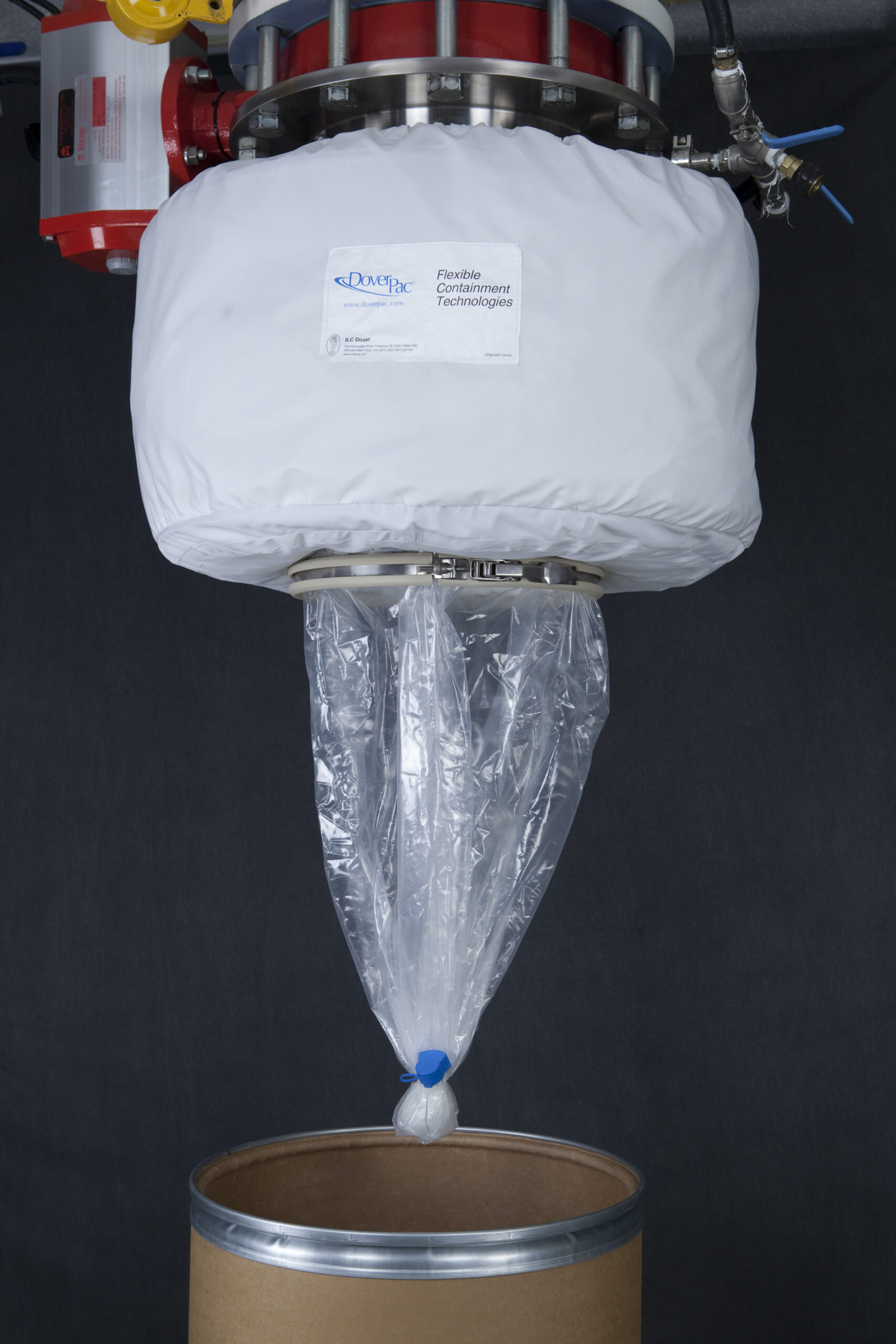
Flexible contained powder discharge into drums
Powdered products are handled every day in the pharmaceutical and bioproces...
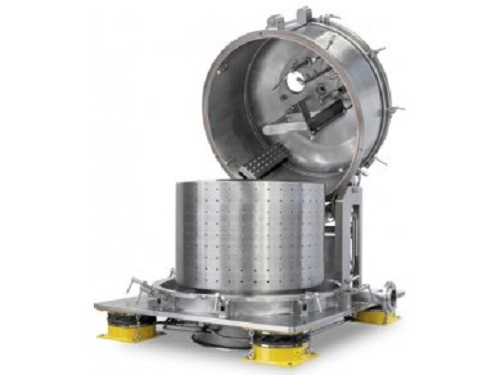
Vertical peeler centrifuge
A vertical peeler centrifuge is used to separate solids, usually to separate fine particles from ...
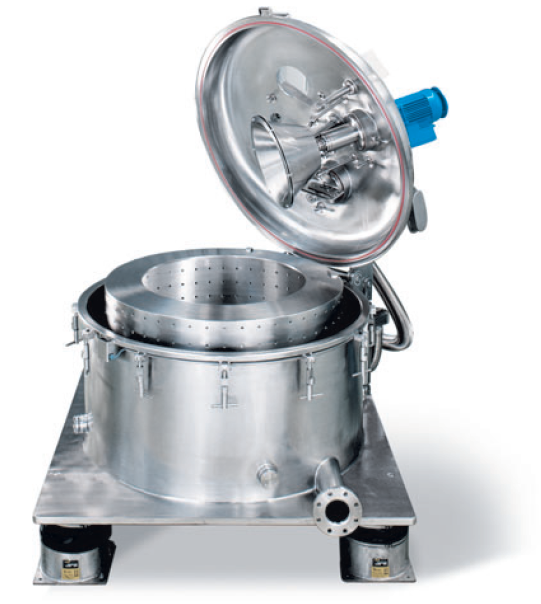
Vertical scraper centrifuges
Vertical Bottom discharge Centrifuges work discontinuously, discharging the solids to the botto...
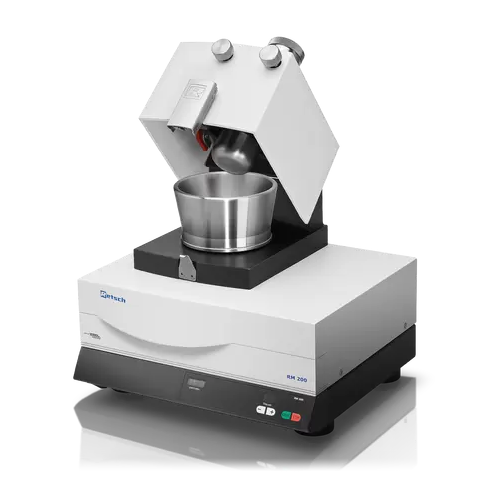
Mortar grinder for reproducible sample preparation
Achieve precise and consistent material preparation with this mortar g...
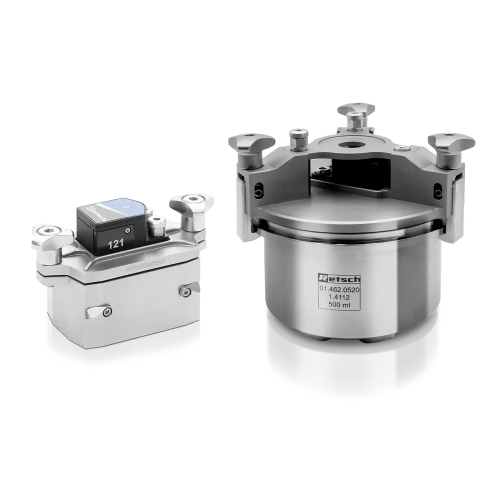
Pressure and temperature monitoring system for ball mills
Ensure optimal grinding conditions and enhance product quality...
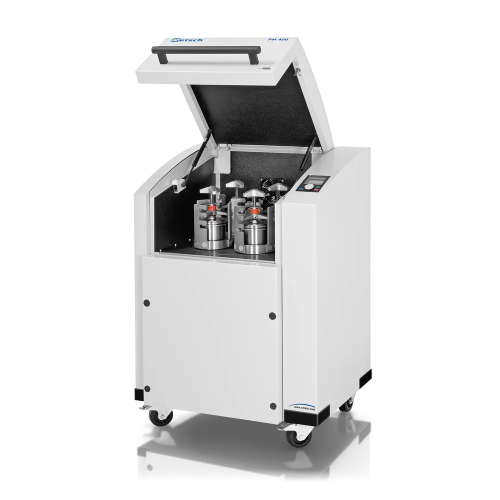
Planetary ball mill for high throughput grinding
For precise material engineering, achieve efficient size reduction, homog...
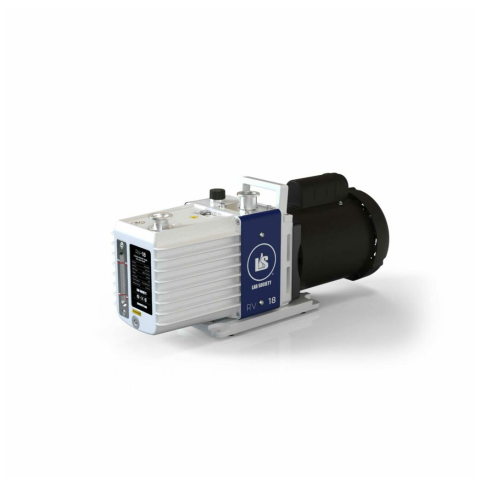
2-stage rotary vane vacuum pump for laboratory applications
Ensure reliable and efficient vacuum conditions for distilla...
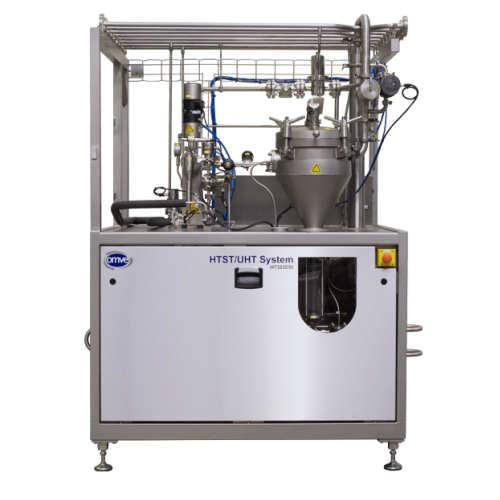
Laboratory in-line sterilization system
Ensure precise temperature control and rapid cooling for diverse liquid application...
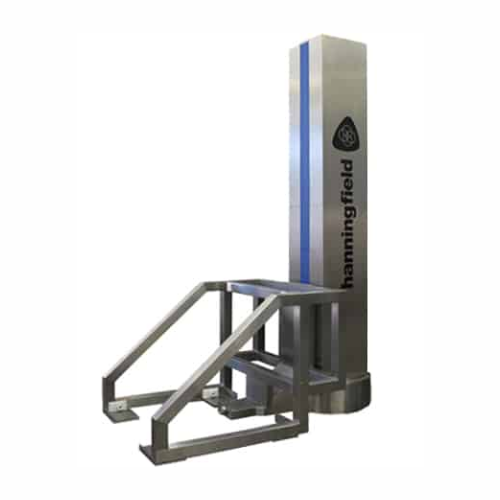
Industrial container and drum handling solution
Effortlessly maneuver and position heavy containers such as IBCs and drums...
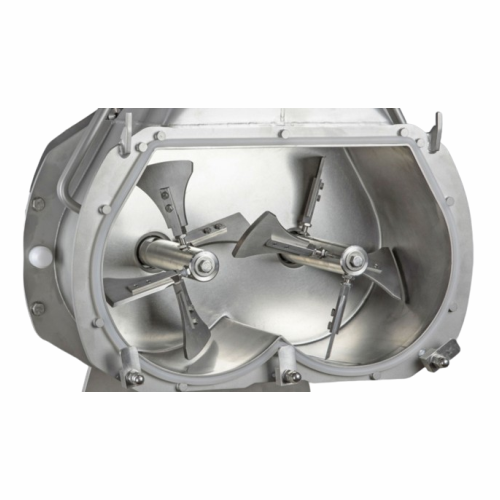
Laboratory mixer for r&d and small batch production
Achieve superior mixing precision for R&D and pilot production w...
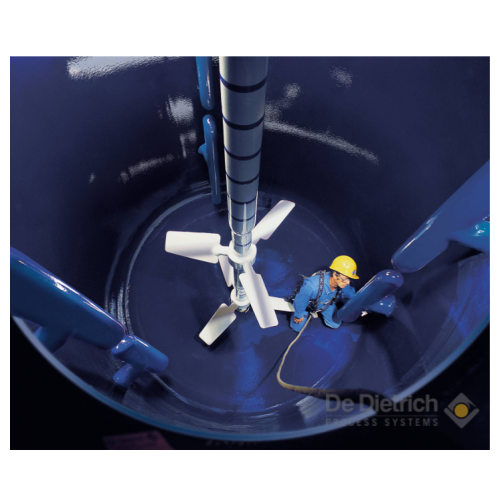
Glass-lined reactor for enhanced mixing performance
Optimize your chemical processes with a reactor that enhances mixing ...
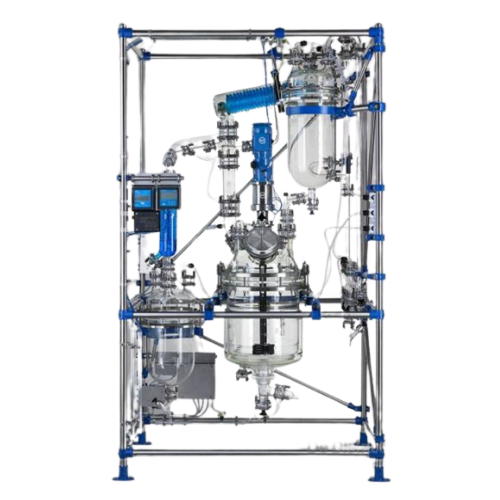
Industrial universal reactor for large-scale chemical synthesis
For chemical producers scaling past laboratory setups, t...

Corrosion-resistant shell and tube heat exchangers for pharmaceuticals
Ensure efficient thermal management in high-puri...
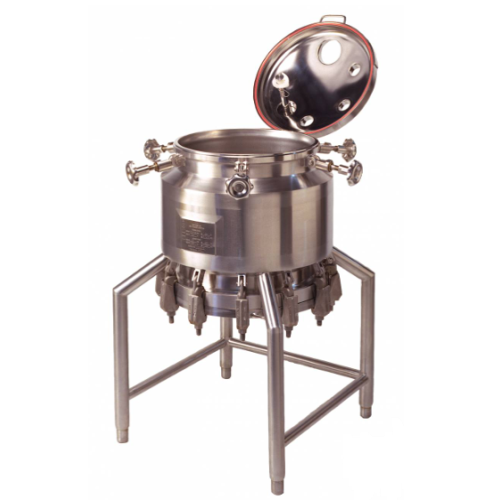
Static nutsche filters for liquid-solid separation
Achieve efficient separation of solids from liquids with precise contr...
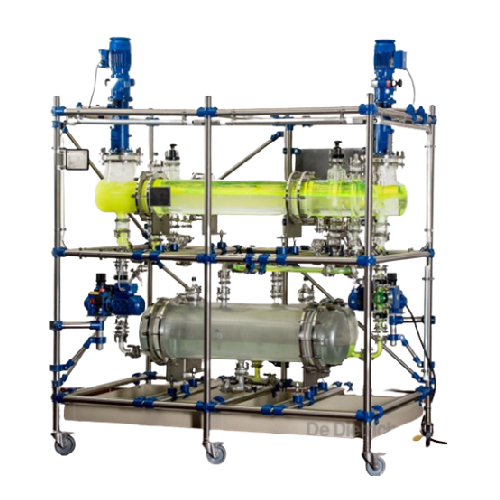
Liquid/liquid extraction mixer-settler plant
Optimize your extraction processes with a highly efficient mixer-settler syst...
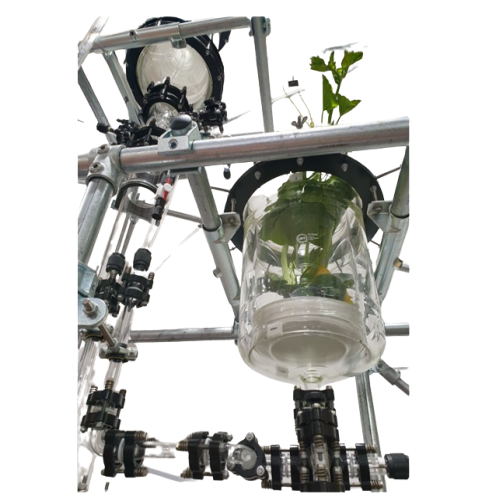
12l solid/liquid extractor for pilot plant solutions
Optimize your extraction processes with a versatile extractor that a...
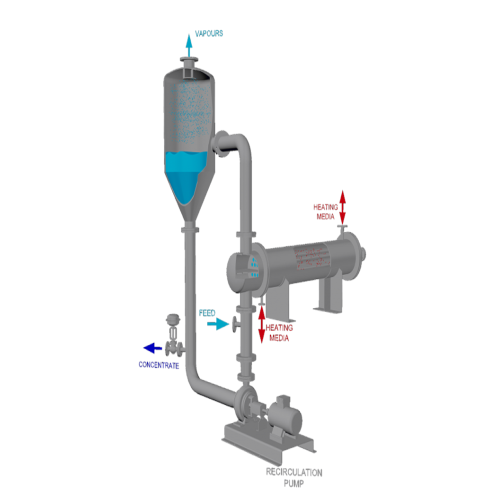
Force circulation evaporator for high viscous products
Optimize energy efficiency and manage challenging liquid compositi...
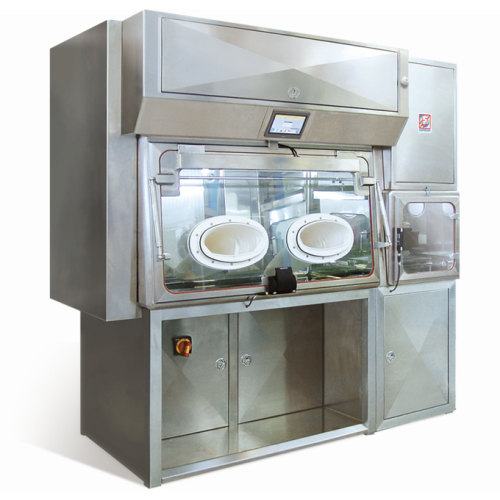
Sterile isolator for cellular labeling
Ensure sterility and protection in cellular labeling processes with an isolator that...
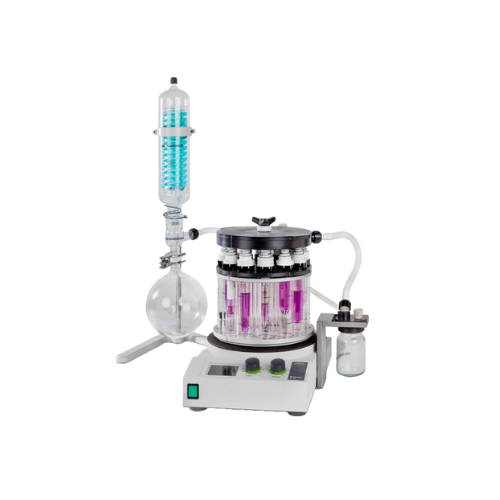
Parallel sample evaporator
Process multiple samples efficiently with precise control, ensuring quick evaporation and consist...
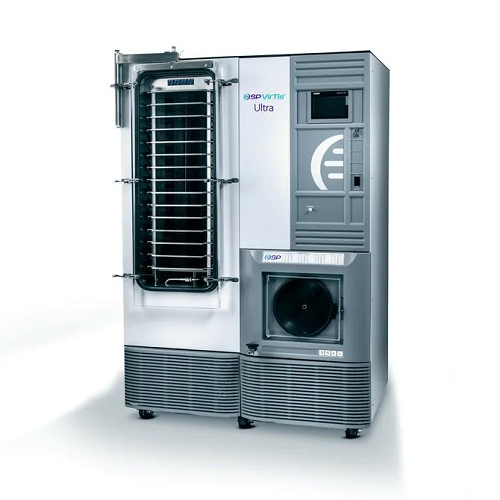
Pilot-production freeze dryers for diagnostic kits and tissue banking
Optimize your freeze-drying process with compact,...
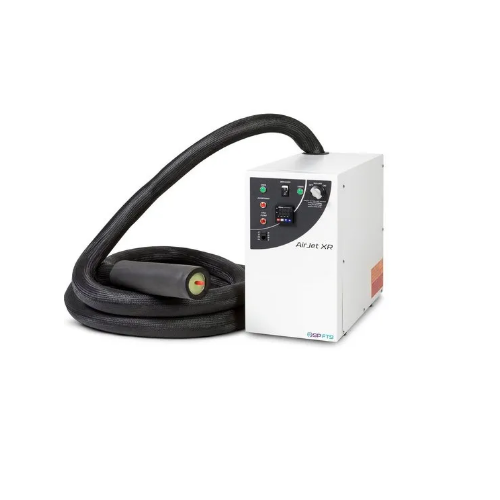
Precise low-temperature sample cooler for Nmr and Epr
Achieve unparalleled temperature stability and precision in your la...
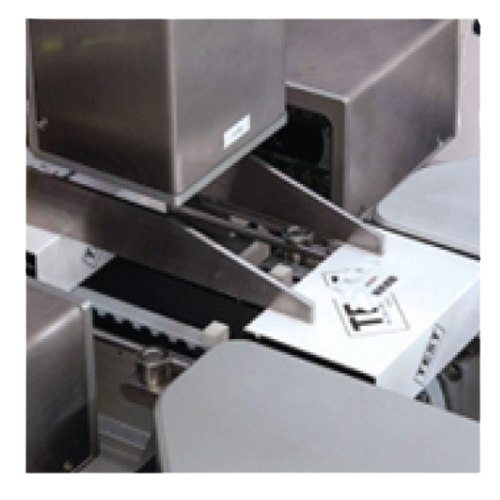
Serialization and inspection kit for packaging machines
Effortlessly enhance packaging integrity and compliance with high...
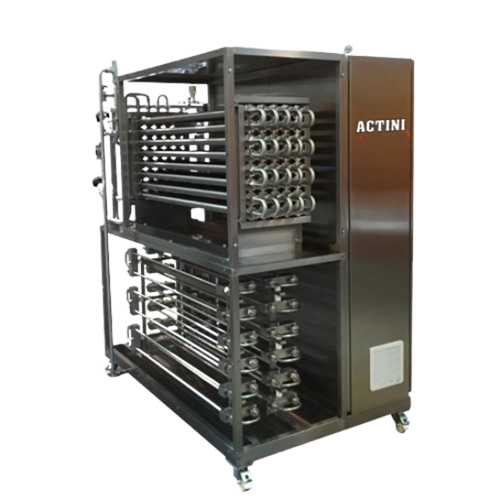
Sterilization pilot systems for small batch heat treatment
Optimize product safety and quality in small batch production...
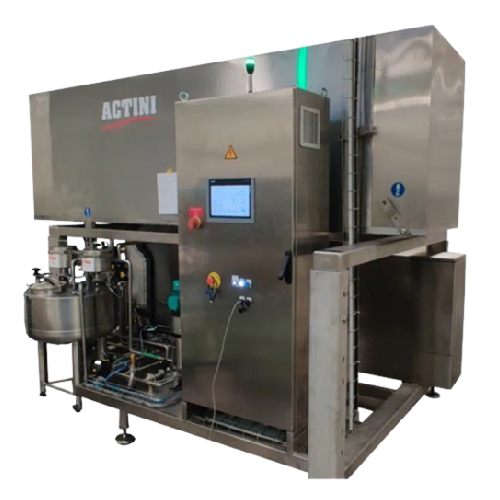
Sterilizer for finished liquid products
Ensure precise thermal control and asepsis in your liquid product sterilization pro...
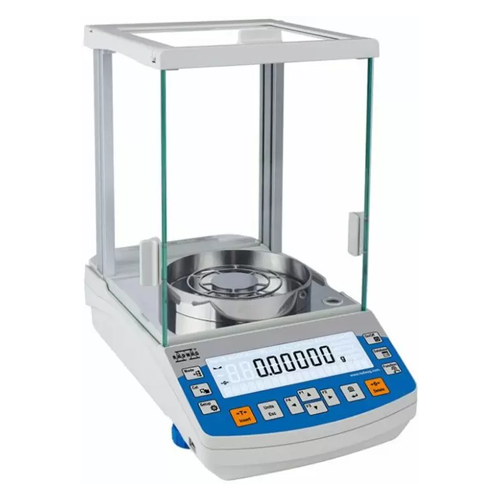
Analytical balance for precise laboratory measurements
Achieve unparalleled precision and reliability in your lab’s...
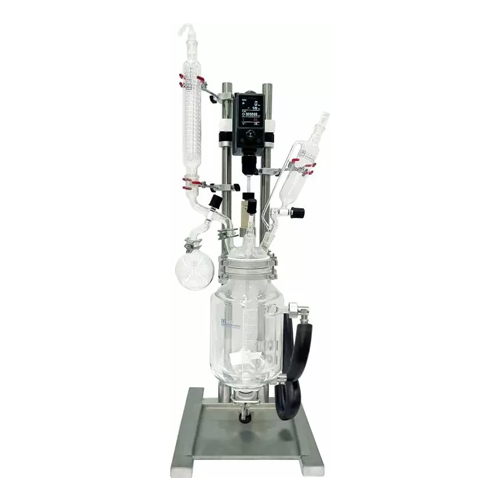
2l single jacketed glass reactor system
Enhance your laboratory’s efficiency with a versatile reactor system, ideal f...
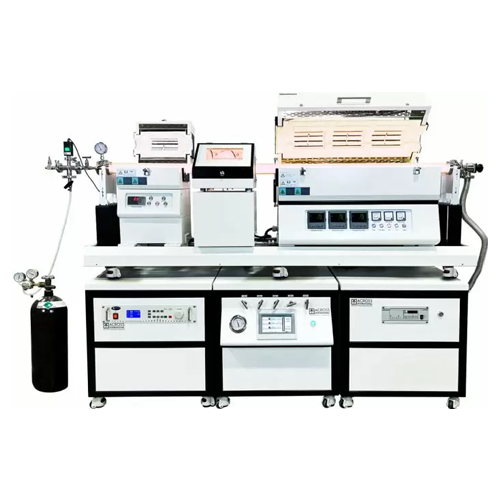
1200°c Pe/cvd furnace for high-temperature material synthesis
Enhance your material processing capabilities with precise...
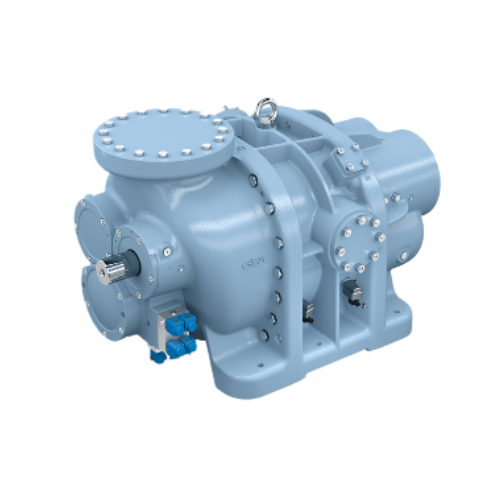
Low-temperature screw compressor for industrial refrigeration
Optimize your refrigeration system with this high-capacity...

Laboratory and pilot plant horizontal bead mill
Achieve precision milling with minimal product waste, ensuring consistent ...
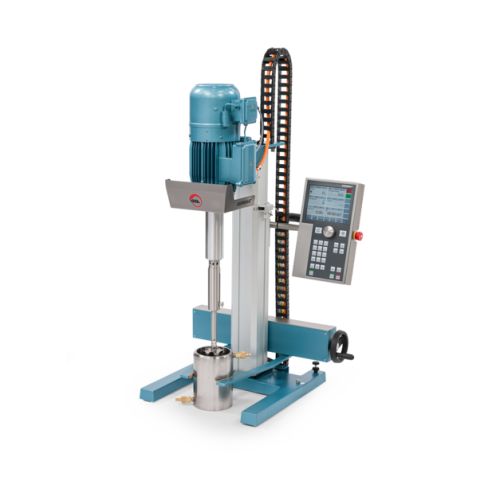
Rotary homogenizer for laboratory and pilot plant
For achieving optimal dispersion in complex formulations, this solution...
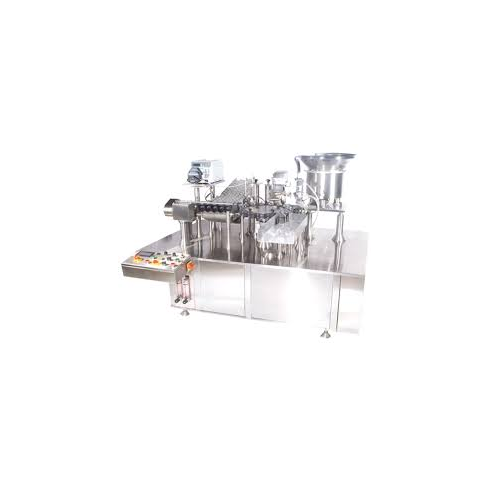
Combi r&d ampoule and vial filling equipment
Optimize your R&D operations with a versatile machine designed for preci...
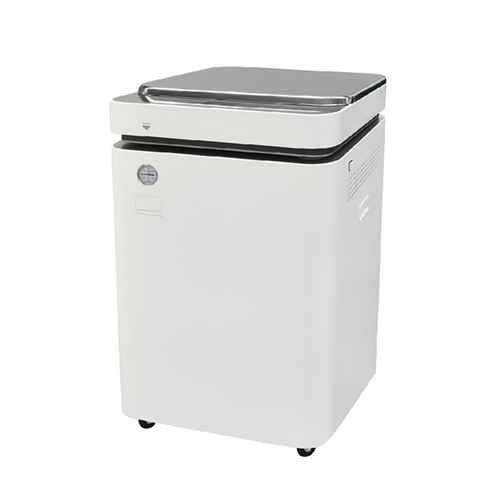
Laboratory series steam sterilizers
Ensure the sterility of your labware and culture media with reliable steam-based steril...
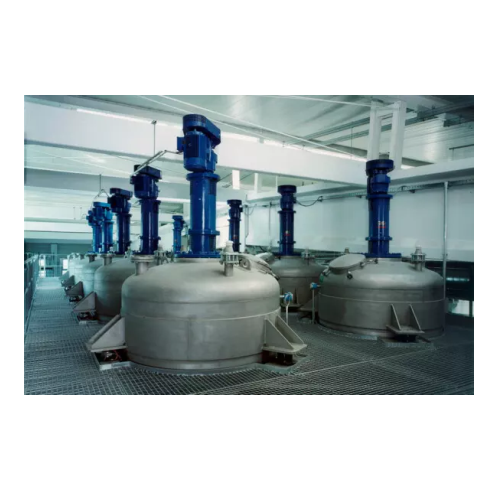
Bin weighing system kits for precise weight control
Ensure accurate material measurement in challenging environments with...
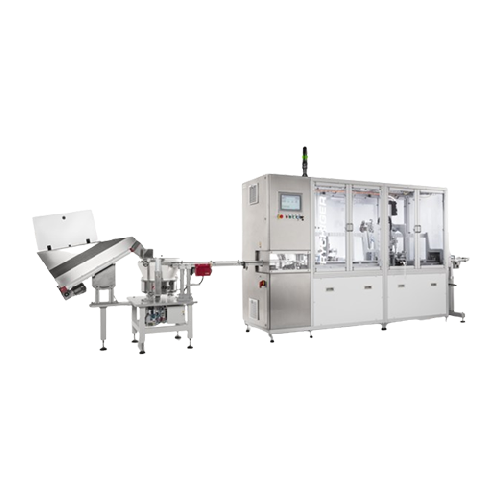
Filling and sealing multi-well cassettes for molecular diagnostics
Streamline your small to medium-scale diagnostic pro...
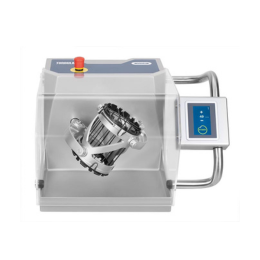
3D powder mixer for active pharmaceutical ingredients
Proper mixing and homogenization are essential to achieve a reliabl...
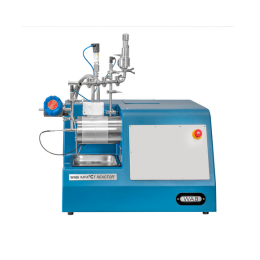
Agitator bead mill reactor for molecular synthesis by mechanochemistry in continuous flow
To achieve cleaner, safer,...
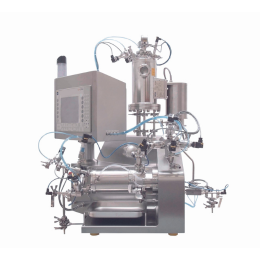
Agitator bead mill for API
To achieve precisely defined API properties and safe and reproducible production, rigorous implem...
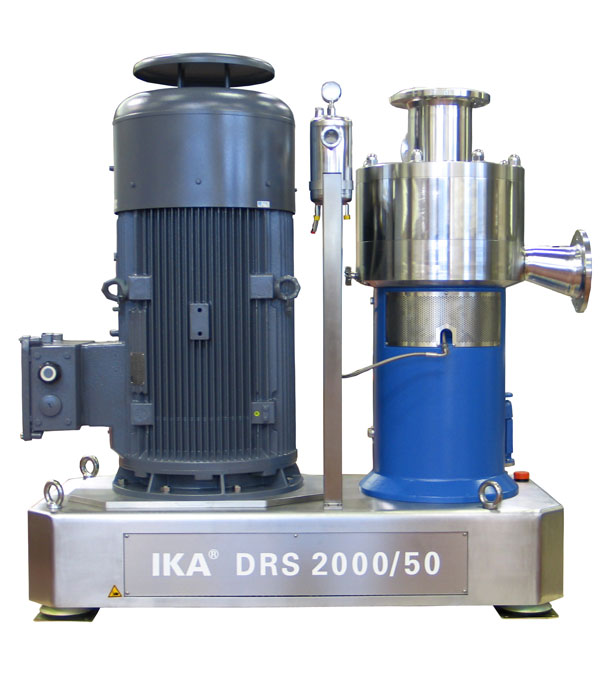
GMP dispersing machine for liquid formulations
Multi-staged rotor/stator mixers generate the high shear forces required to...
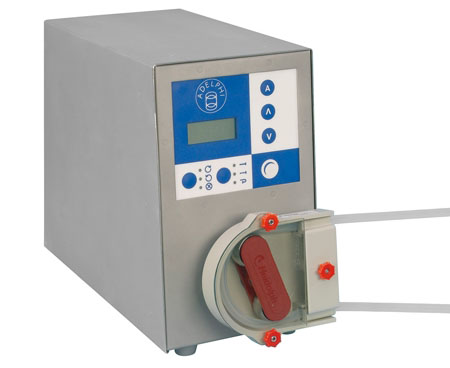
Benchtop peristaltic dispenser
When you fill vials and ampoules, high standards of hygiene are required to avoid the risk of...
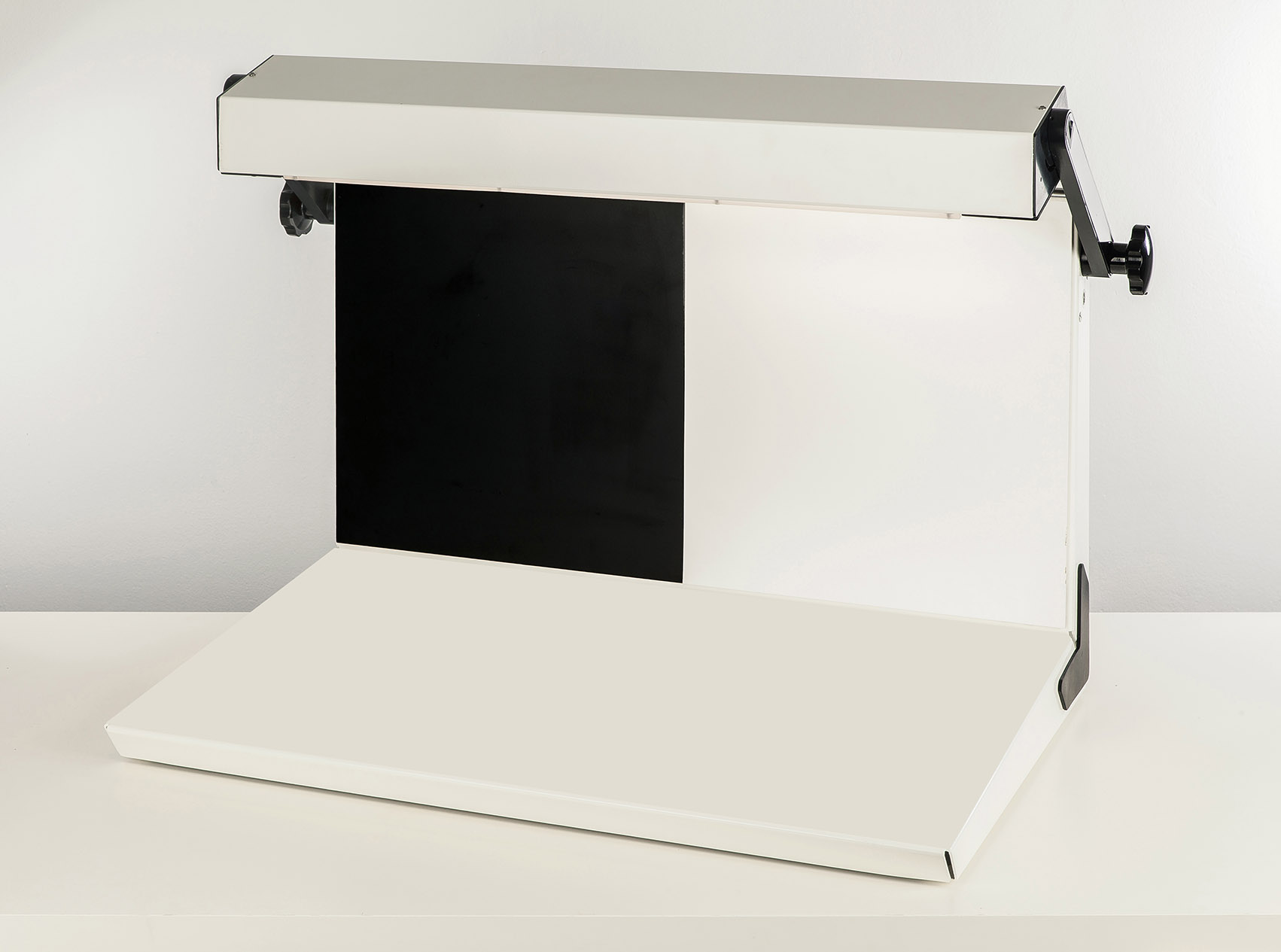
Laboratory liquid viewer for colored glass bottles
In the pharmaceutical industry, an inspection to detect any particulat...
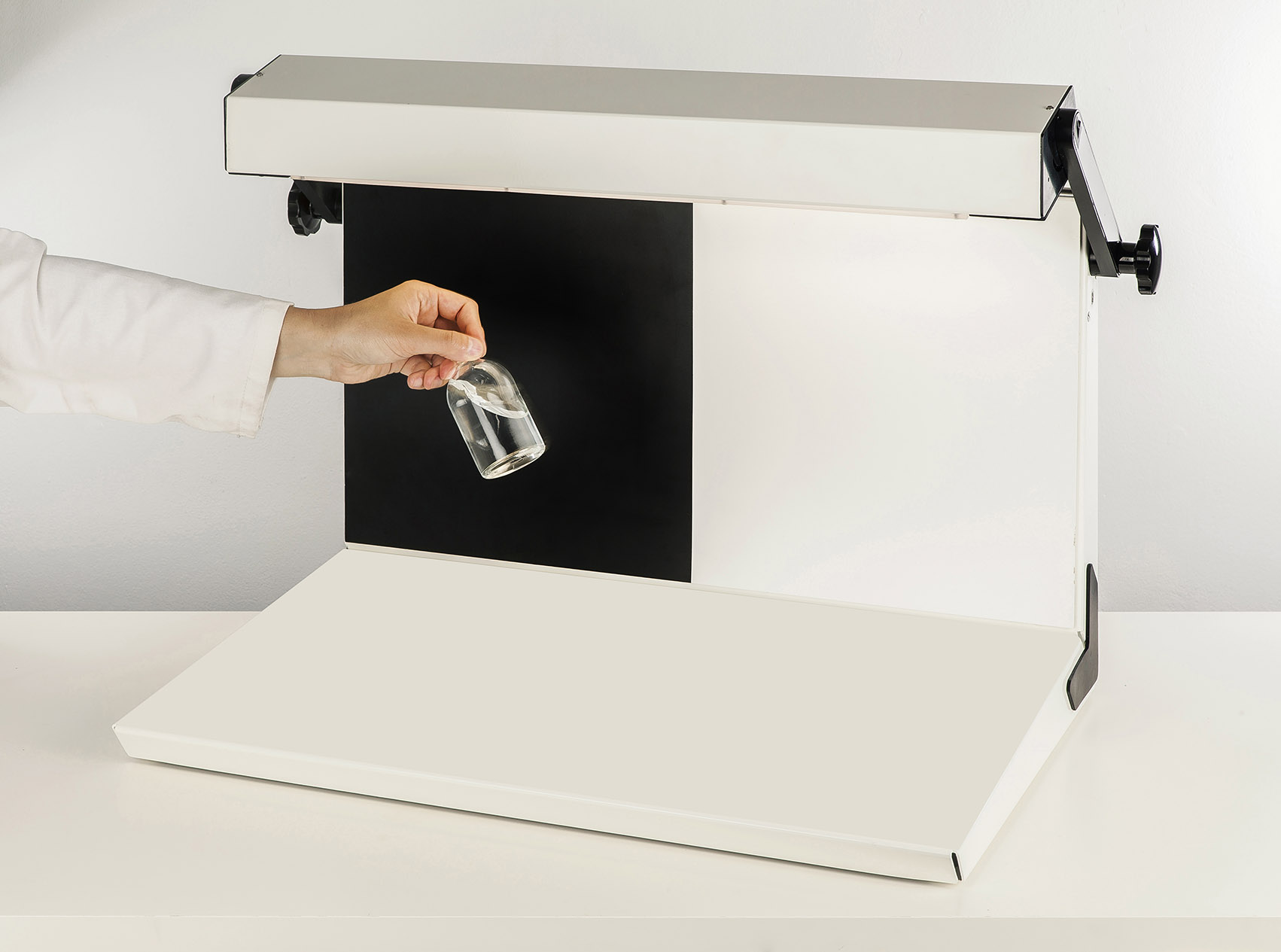
Laboratory liquid viewer for varying light conditions
In the pharmaceutical industry, you must inspect liquids in vials o...
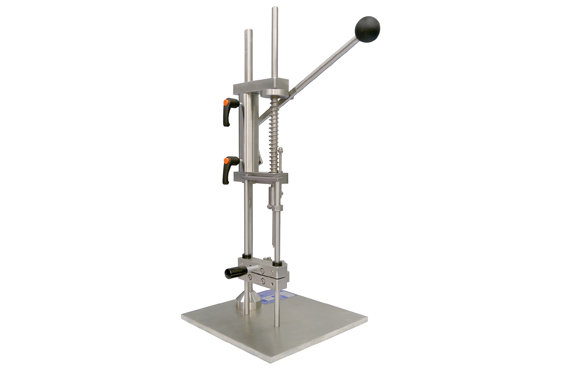
Manual stoppering equipment for pre-filled syringes
Air present in the empty space of pre-filled syringes may prevent you...
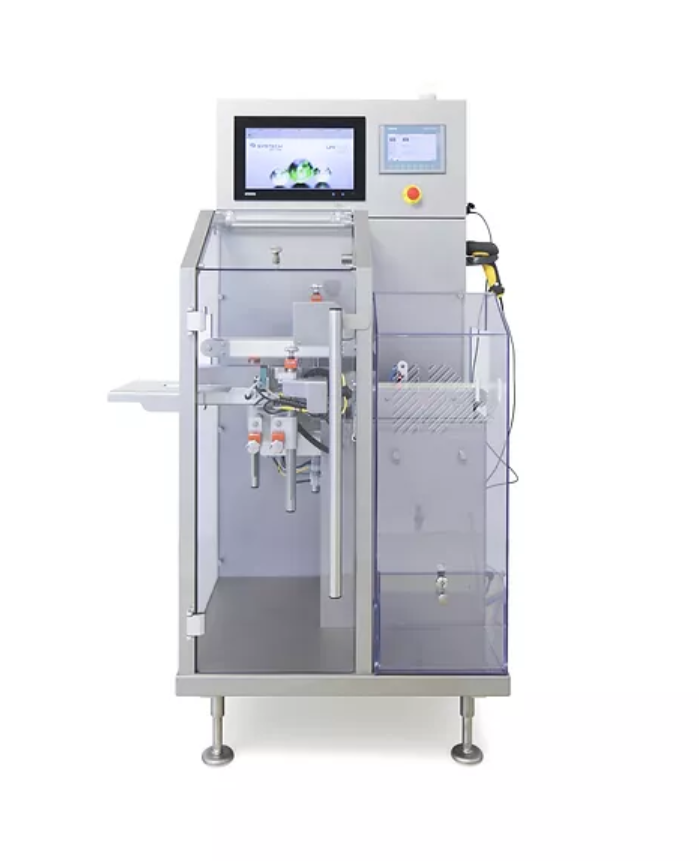
Individual item serialization equipment
Traceability is critical to quality assurance in the pharmaceutical sector. But ser...
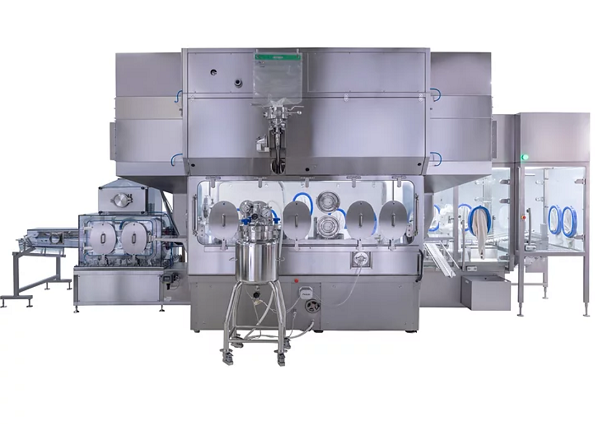
Aseptic filling machine for liquids and powders
Aseptic filling of containers such as vials, syringes, bottles, and cartri...
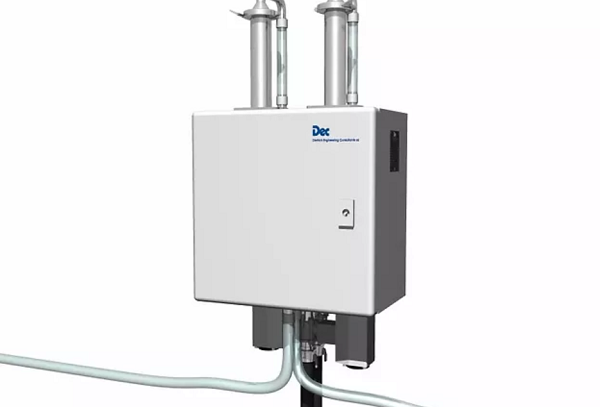
Powder dosing system
Dosing of powder products must be done in a continuously controlled manner to provide a precise amount o...

Semi-automatic forming and sealing blister machine
As a manufacturer of medical device, the packaging is a critical facto...
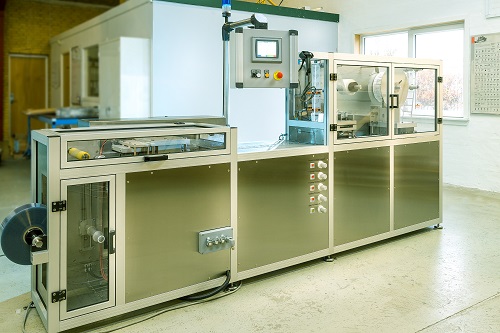
Automatic medical forming and sealing blister machine for packing capsules and tablets
Product safety is very importa...
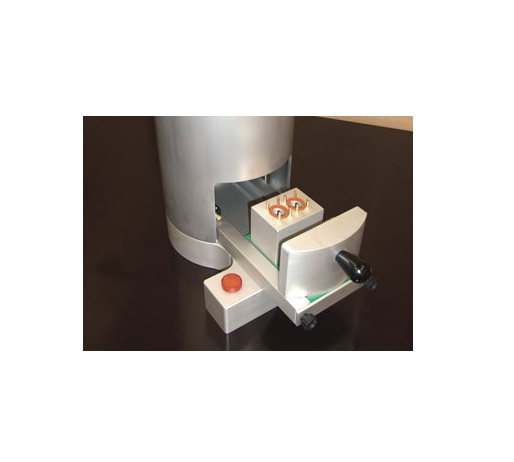
Clinical trial lab sealer for a laminar airflow bench
When running small production for clinical trials, stability studie...
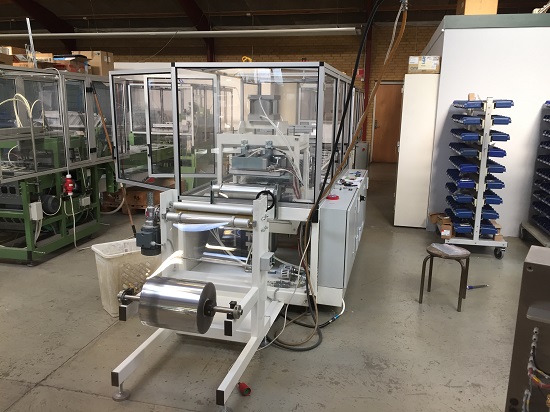
Automatic forming and sealing blister machine for packing syringes
Controlling contamination is on every manufacturer...
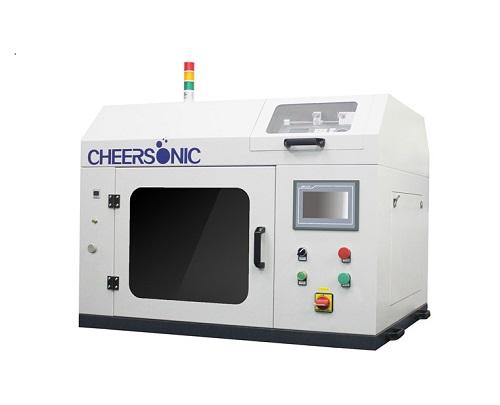
Ultrasonic spraying system for small scale coating and research processes
Ultrasonic spraying technology has the abili...
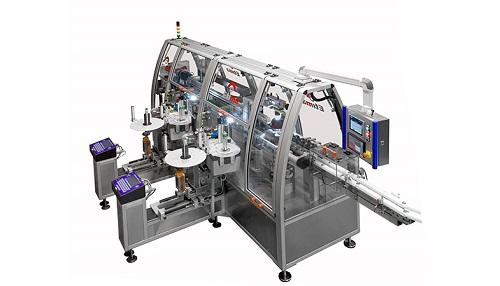
Labeling machine for BFS containers
The pharmaceutical sector is unquestionably one of the major industries that rely on th...
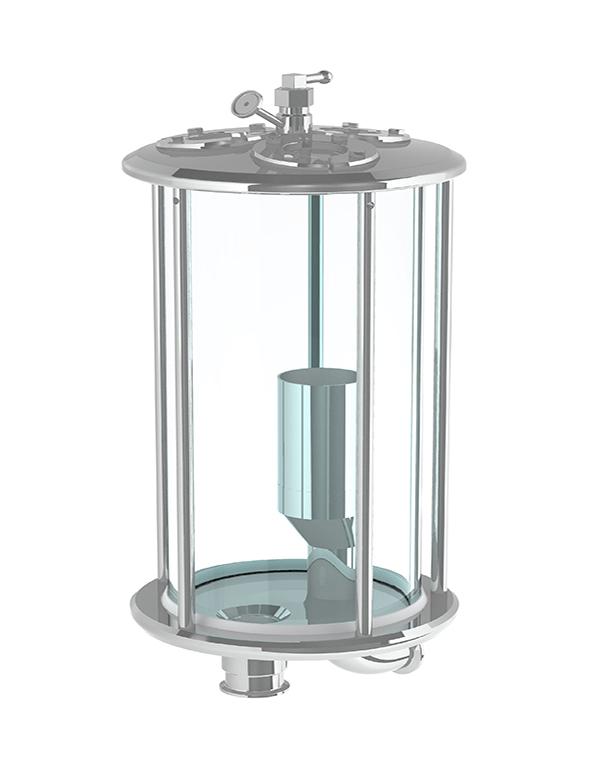
Automated bubble traps for chromatography
Radial flow chromatography processes require special attention and the right use...
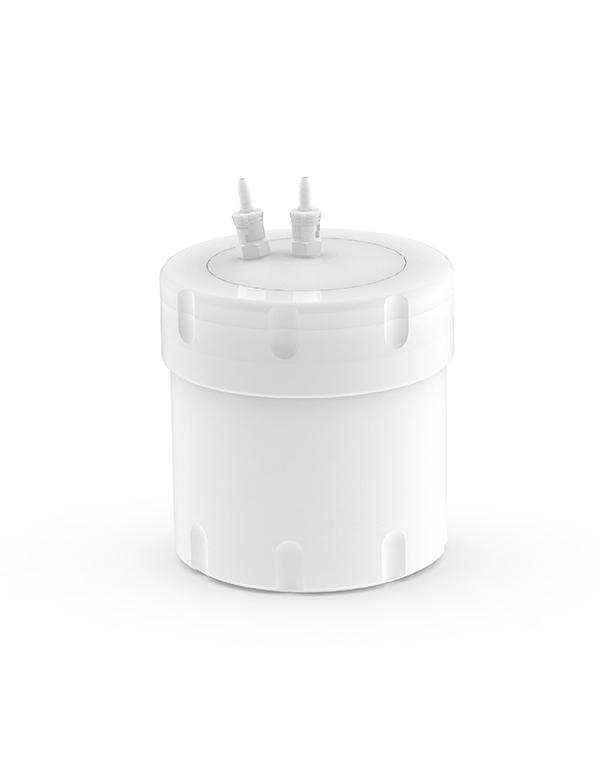
Pre-packed and pre-validated chromatography columns
In chromatography, you must always take into account the apparatus th...
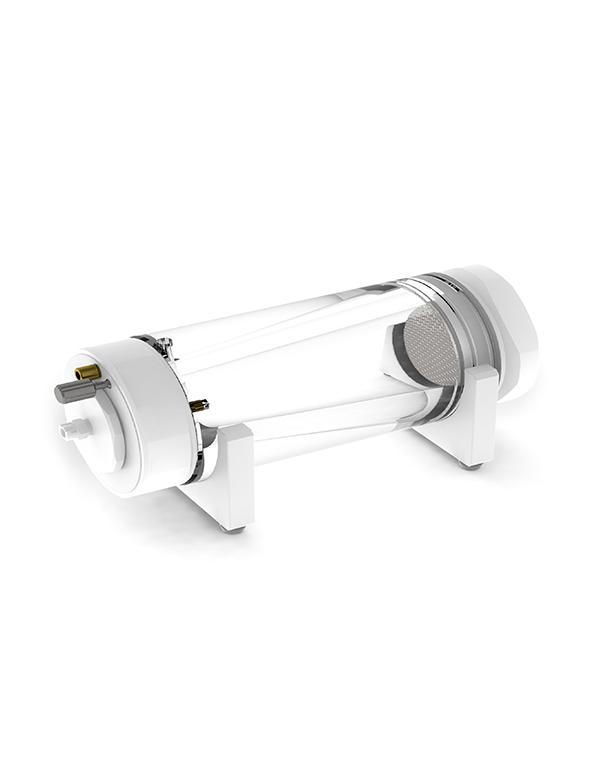
Lab-scale radial chromatography columns for virus validation
In the food industry, as an example, during lab-testing and...
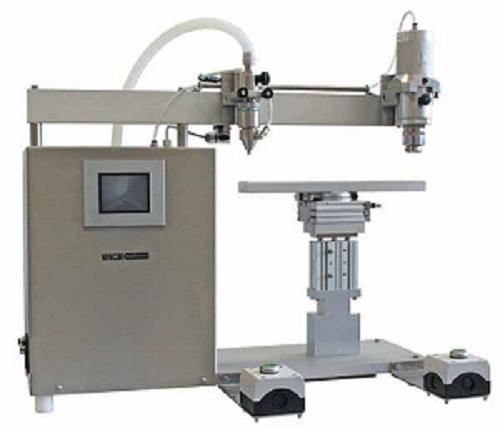
Entry-level filler for large-volume parenterals
Large volume parenterals are unit-dose containers that are larger than 100...

Ethylene oxide sterilizer
When medical devices like syringes, catheters, dialysis cartridges, plastic dressings and sutures ...
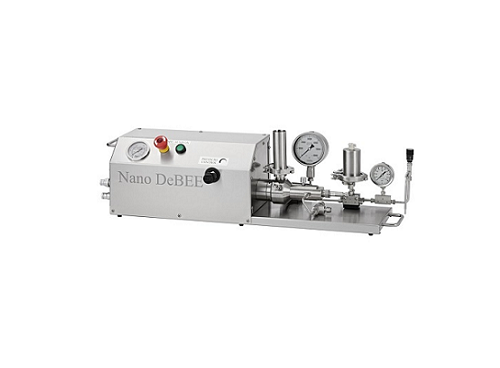
High pressure electric laboratory homogenizer
It’s vital that small units for experimentation can scale up with 100% accur...
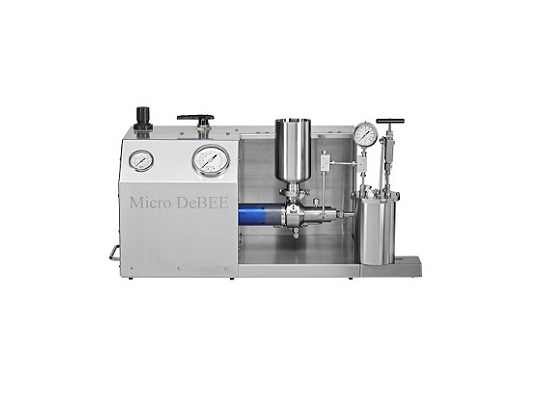
High pressure air powered laboratory homogenizer
Offering lab-scale to small pharmaceutical production scale output for in...
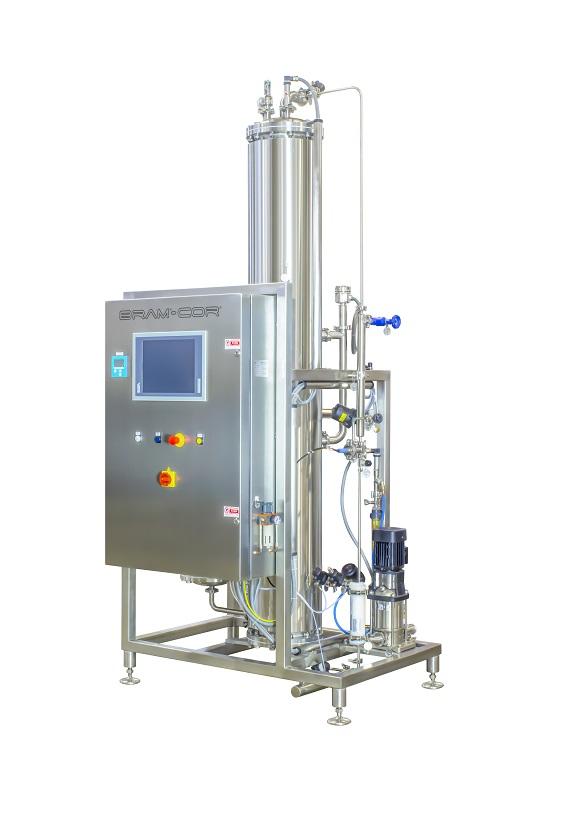
Pharmaceutical pure steam generator
Dry, saturated steam can be used to sterilise pharmaceutical manufacturing equipment, a...
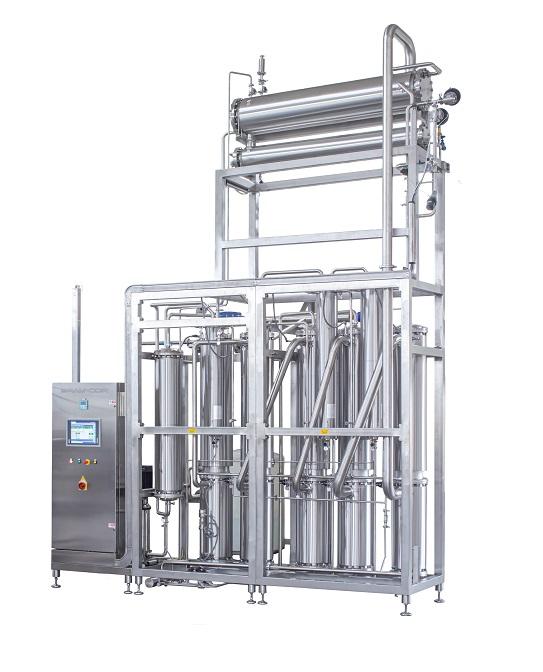
Water distillation system
Water used in pharmaceutical processes must meet high standards of regulatory bodies. These includ...
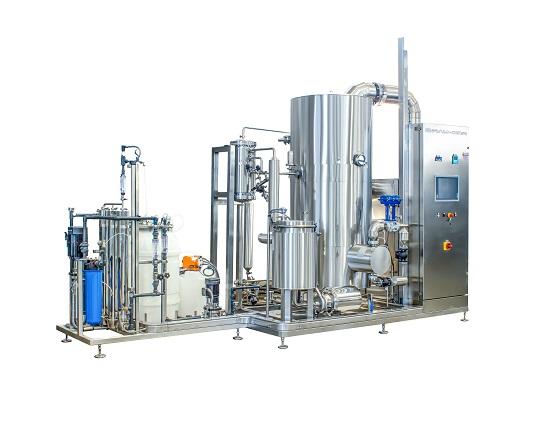
Vapor compression distiller
Water for injections must be of highest achievable quality to eliminate the possibility of conta...
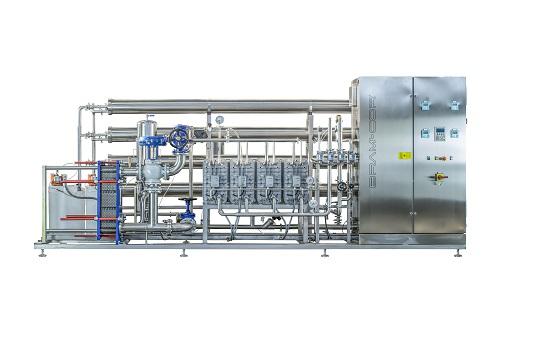
Reverse Osmosis water filtration system
Reverse osmosis uses a partially permeable membrane to remove undesirable molecules...
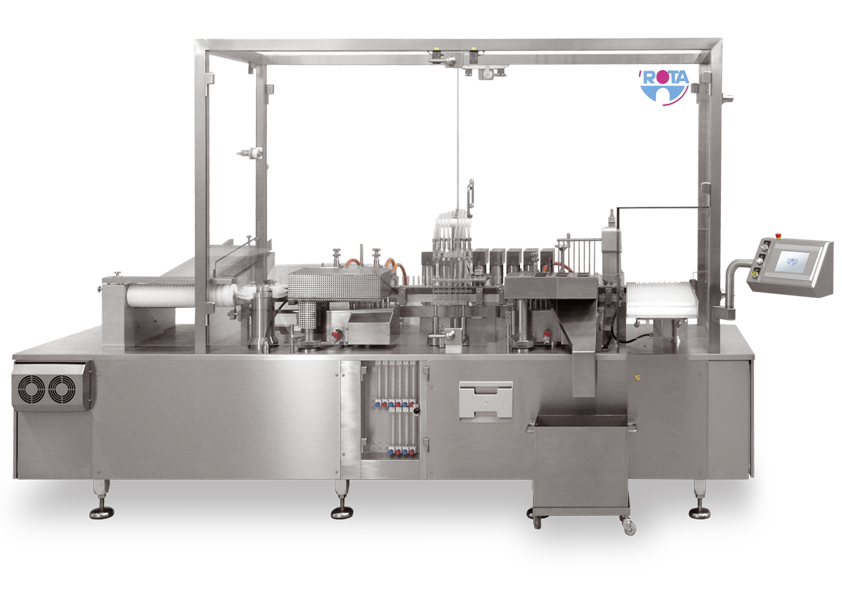
Ampoule filling machine
Filling ampoules or vials with parenteral fluids are an essential matter for which you need to consid...
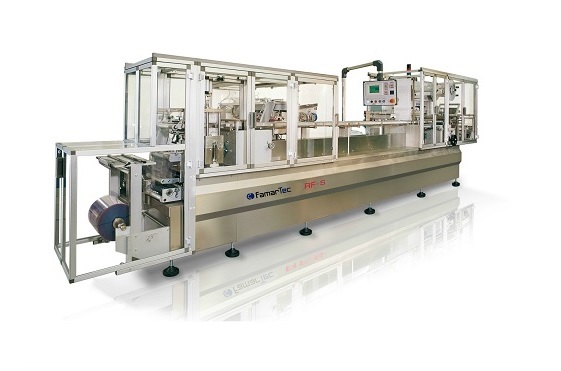
Packaging machine for syringes in trays
Pre-dosed syringes are rapidly becoming the method of choice for the delivery of in...
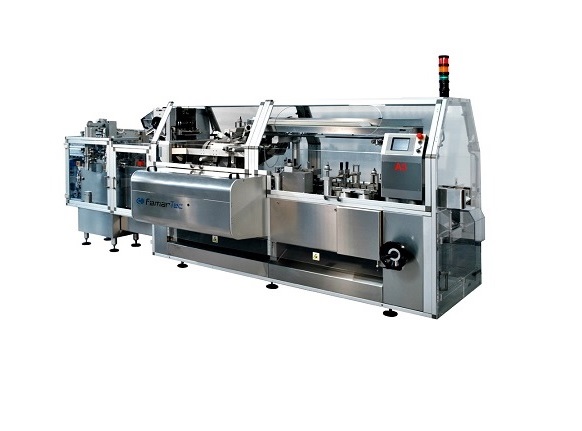
Continuous pack cartoner
High volume automatic cartoning is vital for large scale production of cosmetic or pharmaceutical pr...
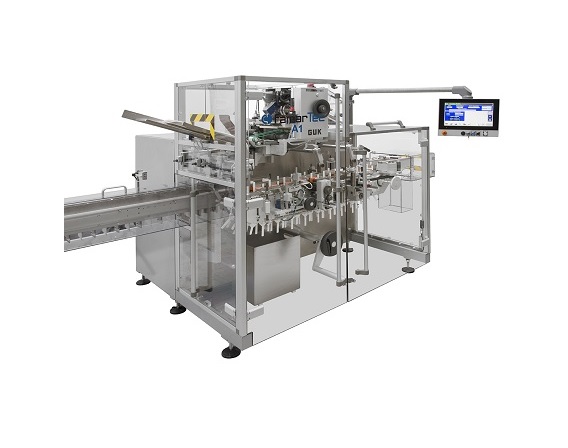
Horizontal cartoner for pharmaceutical applications
Automatic cartoning for cosmetic or pharmaceutical products is a requ...
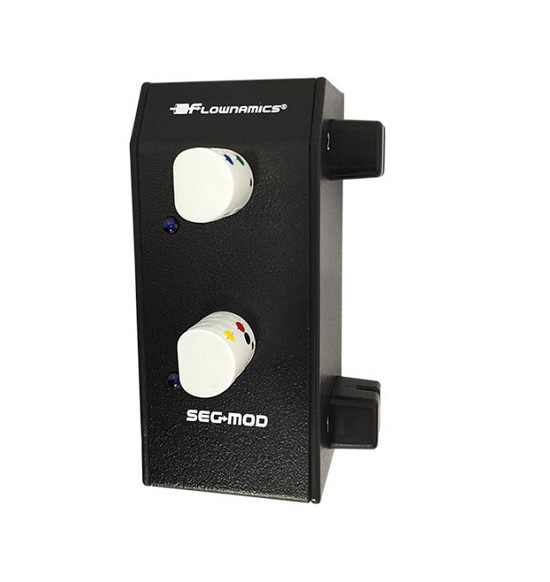
Fluid sample-taking module for high cell density cultures
Automatic sampling of reactor vessels requires careful fluid m...
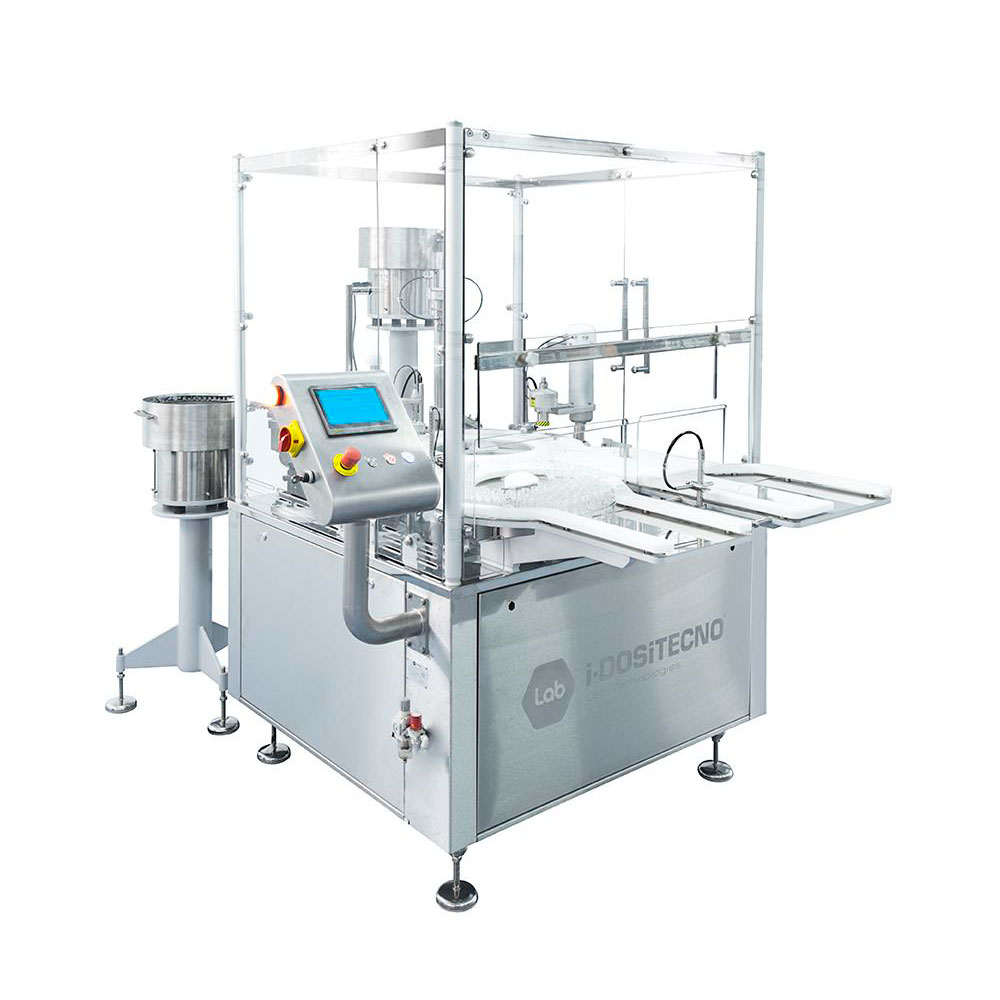
Start-up sterile filling line for injectables
For smaller-scale production of vials and syringes for the injectables marke...
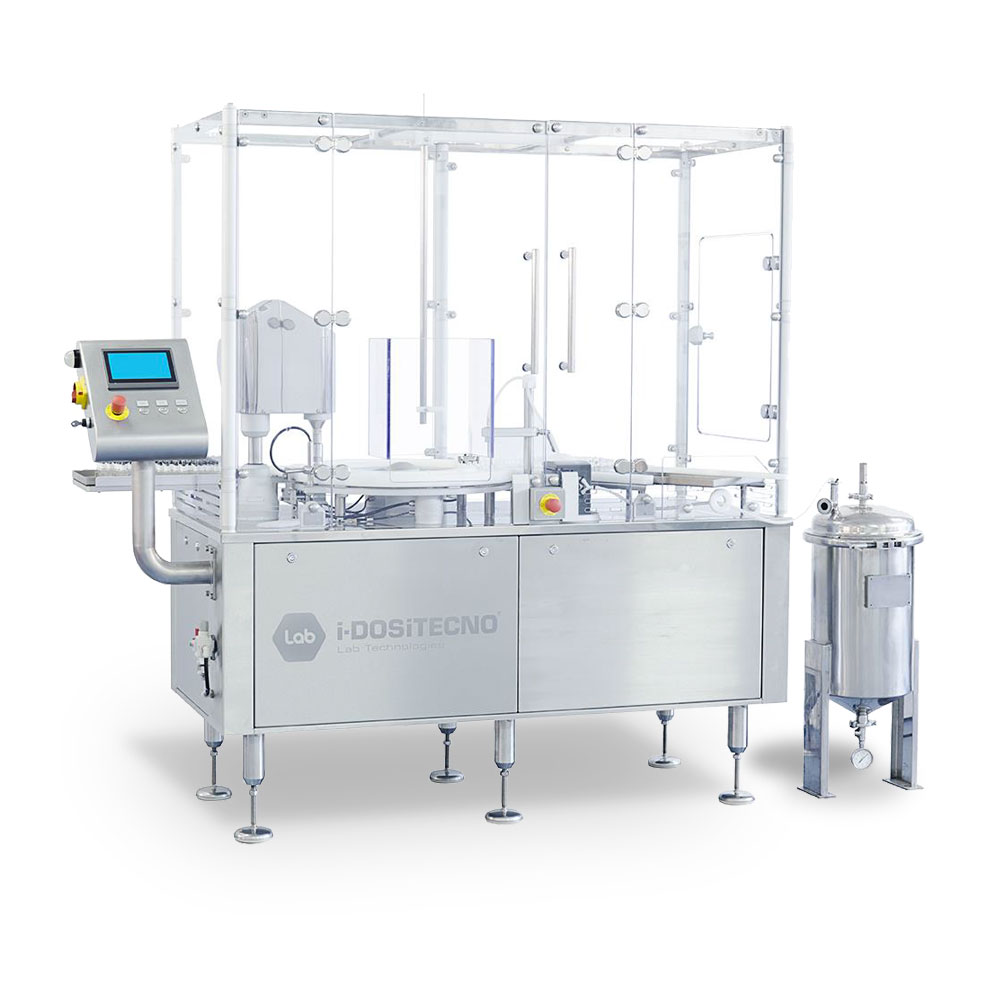
Table top sterile filling line for injectables
Where a compact solution is required for filling vials for the injectables ...
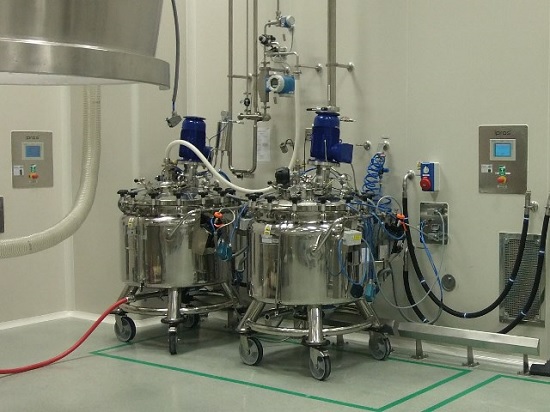
Vacuum mixer for suspensions
The production of high quality pharmaceuticals often requires mixing of suspensions and similar...
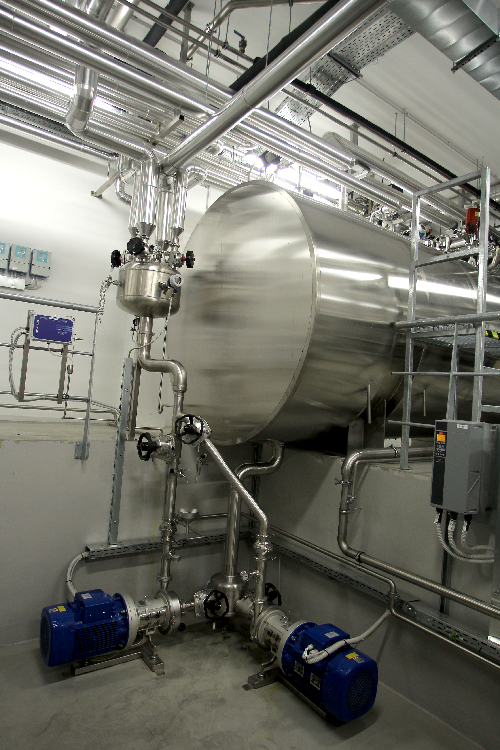
Purified water storage tank
Many pharmaceutical and cosmetic production lines require holding vessels for the storage of liq...
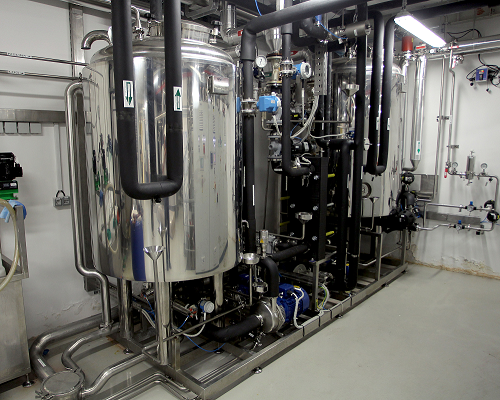
Cleaning and sterilization systems
An increasingly vital part of high quality pharmaceutical production is a dedicated Clea...
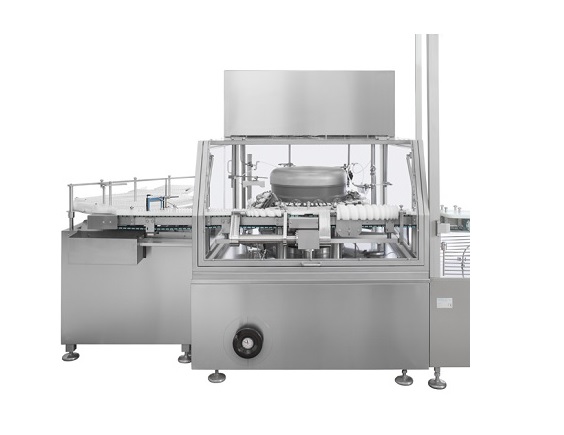
Rotary vial washing machine
When washing vial, ampoules, or cartridges for pharmaceutical production there is often a trade-...
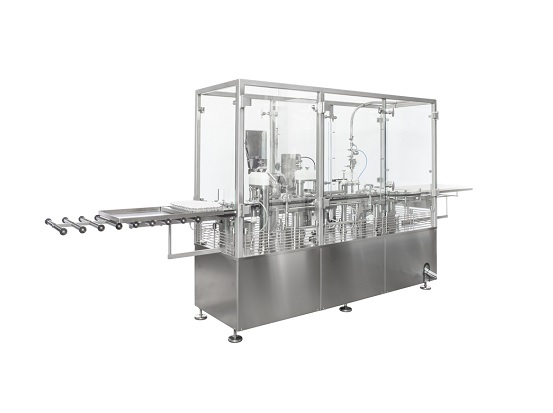
Industrial vial capping machine
The high capacity production of pharmaceuticals delivered in vials and cartridges requires a...
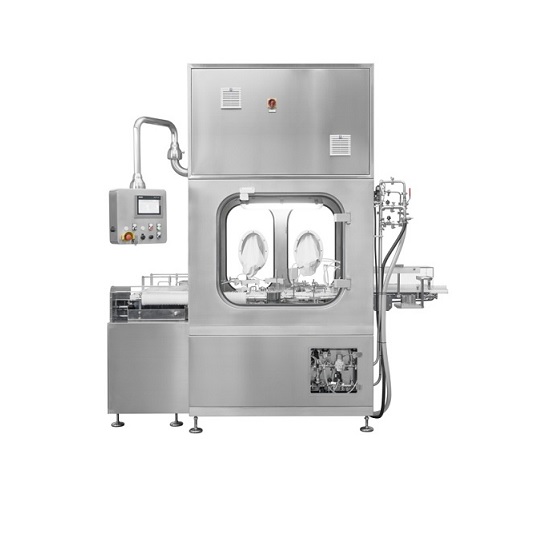
External vial washing machine
Exterior washing solutions for vials often suffer from high water consumption and low throughp...
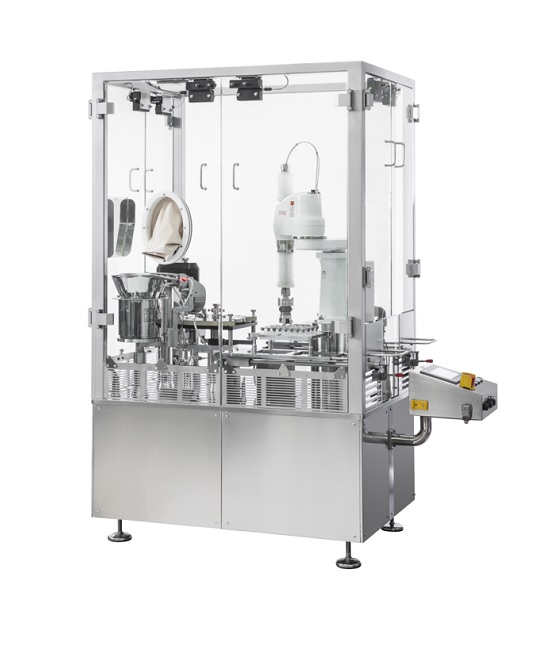
Aseptic vial cap sealing machine
Aseptic production methods are at the heart of the latest development in pharmaceuticals in...
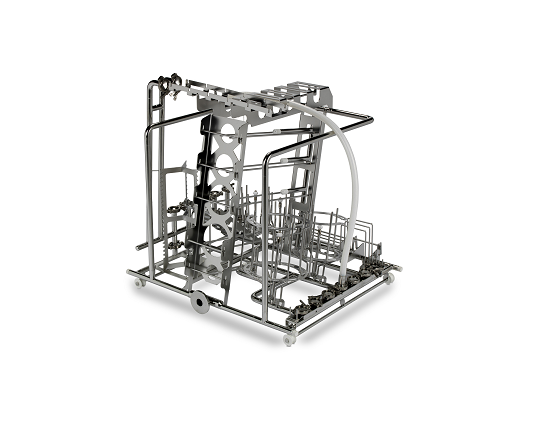
Loading basket for GMP washer
To ensure perfect cleaning of contact parts they must be placed in the GMP washer in such a wa...
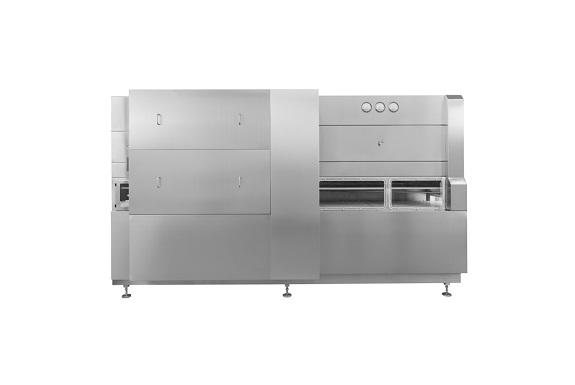
Vial sterilization tunnel
Sterilization of vials, ampoules and syringes before filling is a vital step in the production of ...
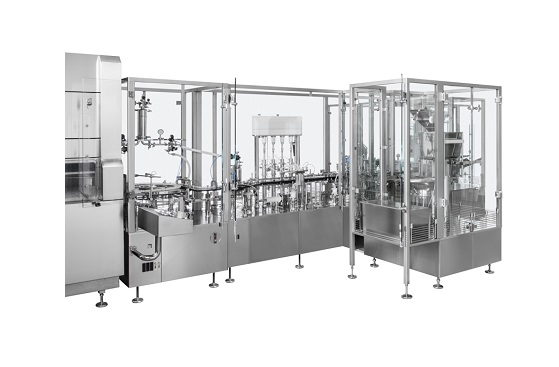
Vial filling machine
The volume filling of vials, cartridges and syringes is a vital part of the production of a wide range o...
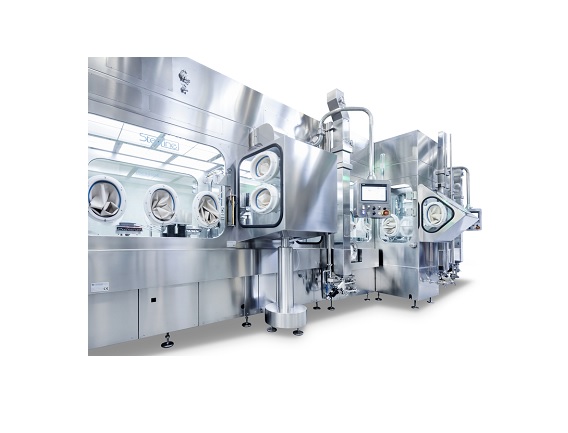
Aseptic automatic vial filling machine
Current and future developments in pharmaceuticals increasingly rely on aseptic prod...
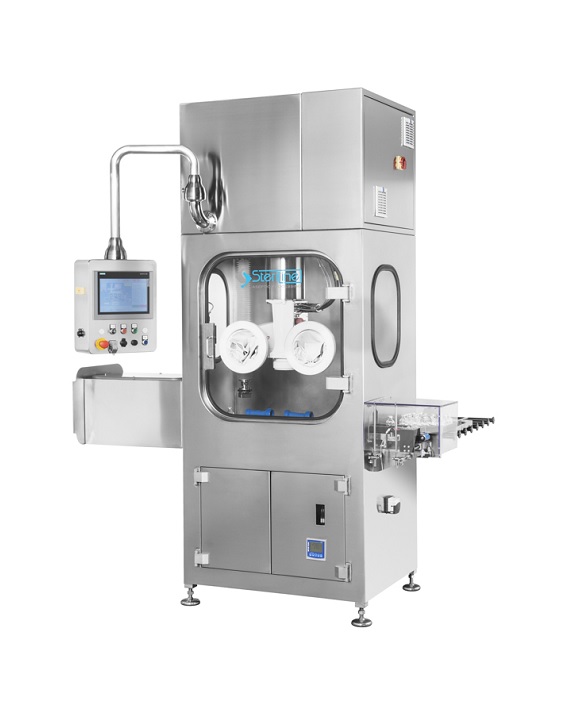
Aseptic automatic vial washing machine
The production of the latest high value pharmaceuticals often requires aseptic handl...
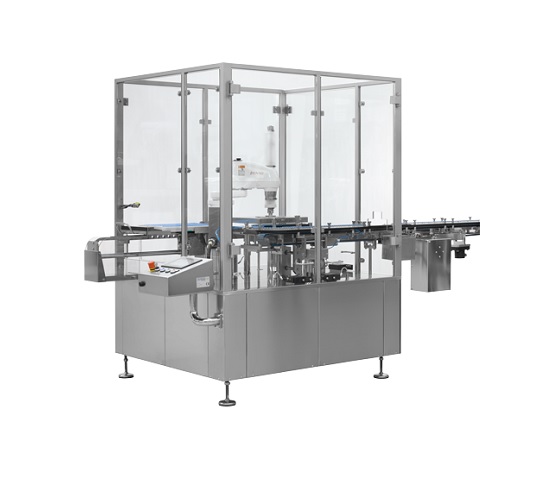
Automatic vial tray loader
In modern pharmaceutical production, end-line processes are often still manual or slow. This can ...
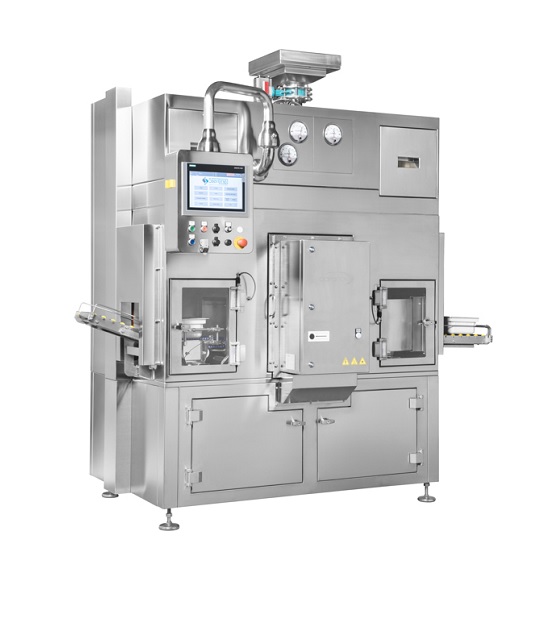
Syringe tub sterilizer
A common challenge is how to transfer nested syringe tubs to the aseptic filling area without compromi...
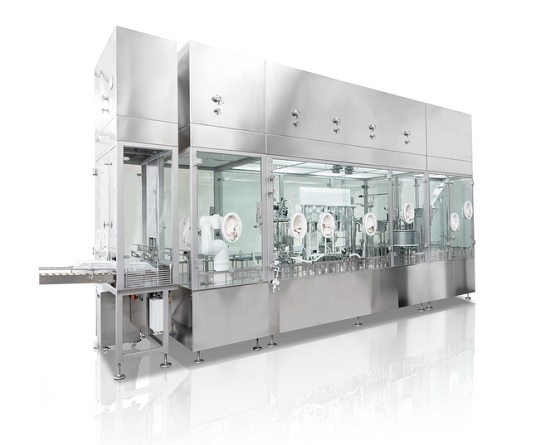
Nested syringe filling machine
Increasingly, pre-sterilized Ready To Use (RTU) nested vials, cartridges and syringes are the...
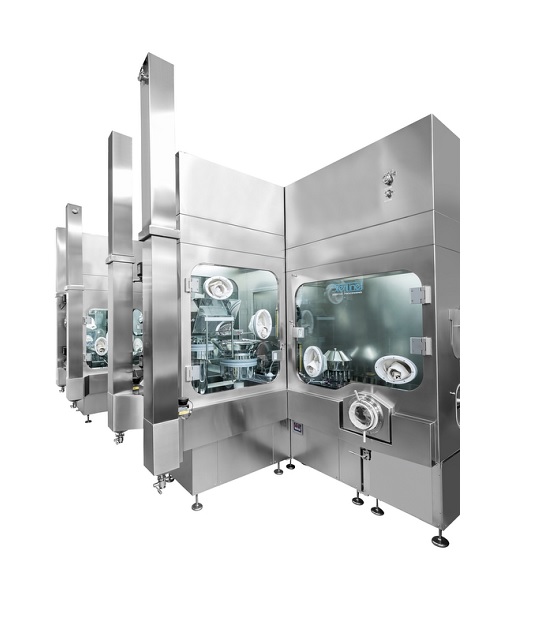
Closed restricted access barrier system
Pharmaceutical production techniques often require isolation of compounds and chemi...
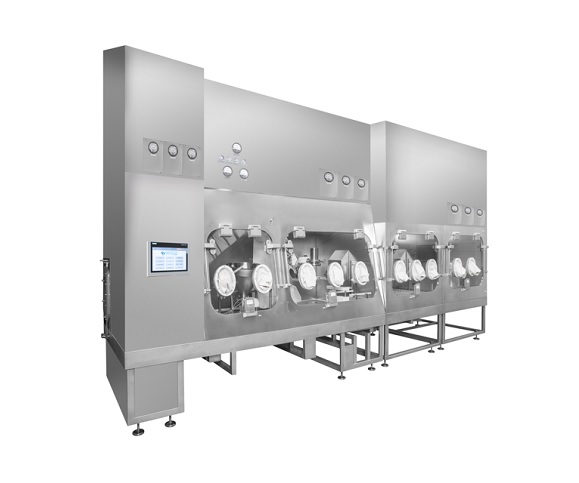
Compounding aseptic isolator
Bespoke aseptic isolators designed for production environments don’t meet the needs of small-sc...
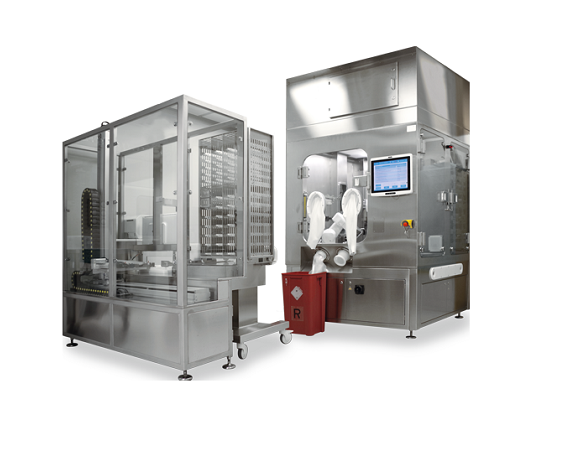
Sterile compounding system
Hospitals and compounding centres have traditionally used manual aseptic compounding processes. A...
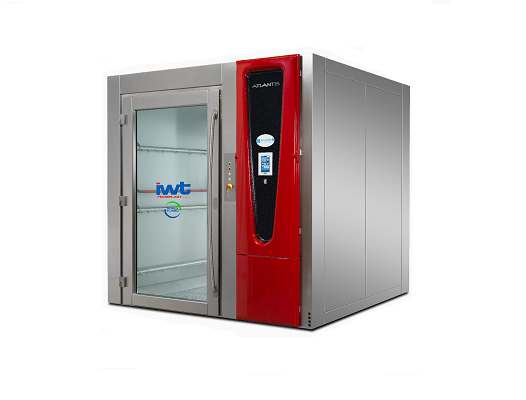
Bulk chamber washer
The production of cosmetics, nutraceuticals or unregulated pharmaceuticals often requires the cleaning an...
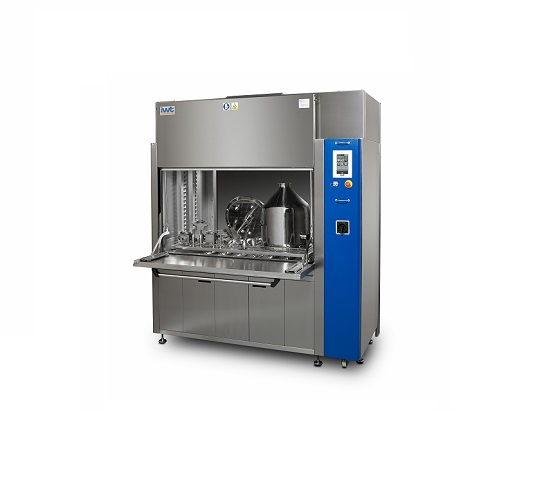
Entry-level chamber washer
When cleaning smaller products contacting filling or compressing components used in the productio...
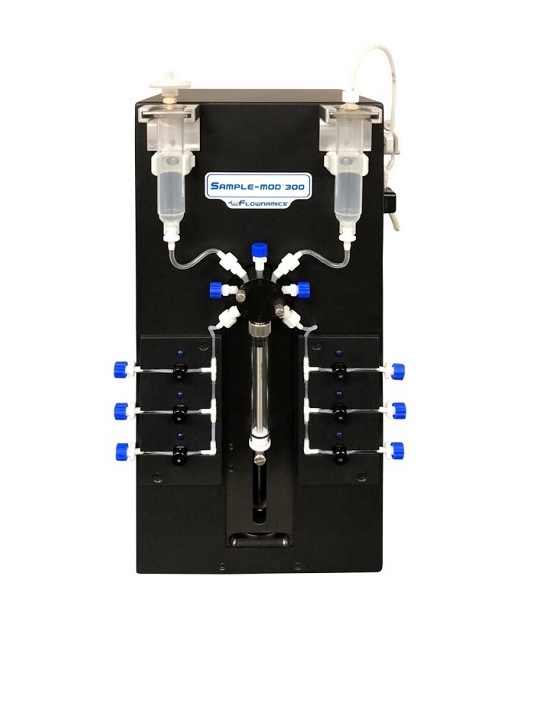
Distributor of samples to different devices
The ability to expand your automatic sampling solution provides increased flex...
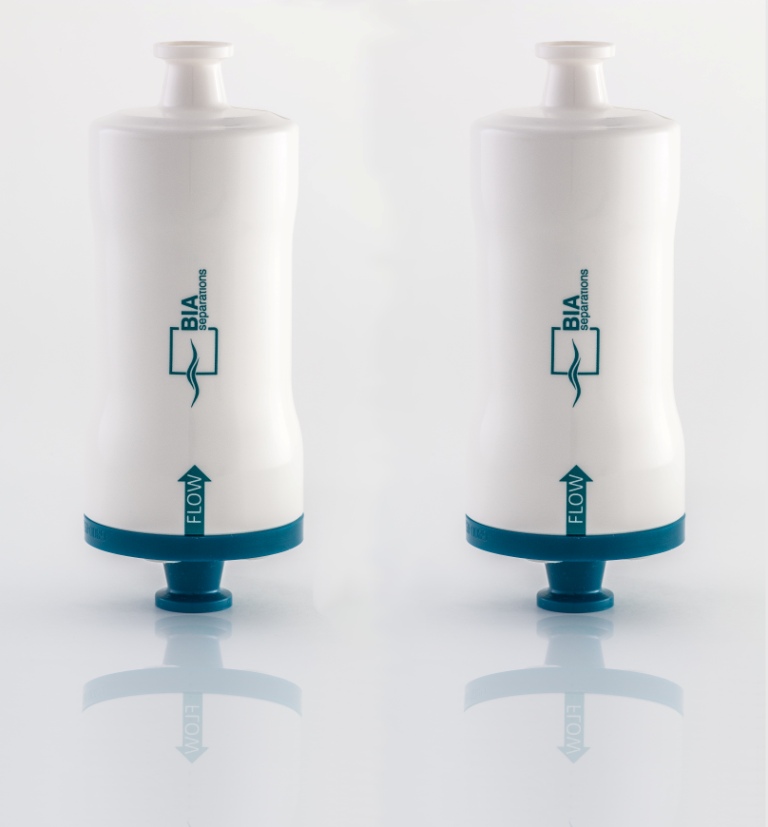
Plasmid process pack for your pDNA purification process
When developing a pDNA purification process for eventual transfer...
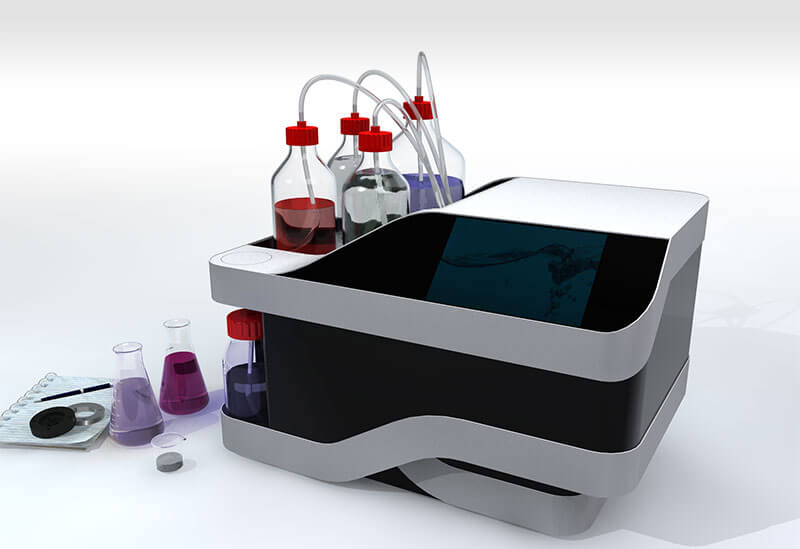
Microencapsulation system for your drug delivery system
Whether you want to improve the stability of nutrients, protect a...
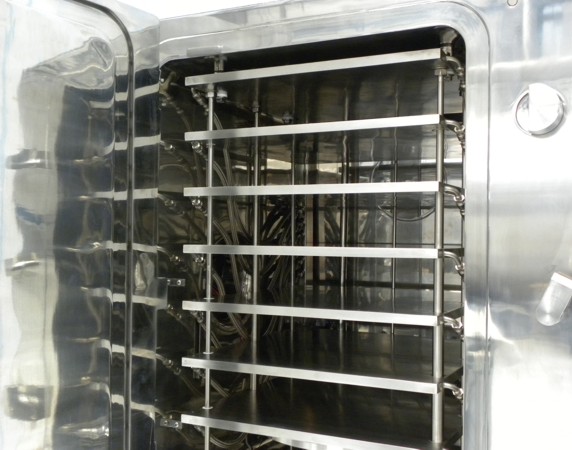
GMP laboratory freeze dryer
Freeze dryer designed for aseptic and small-scale production of high-value products.
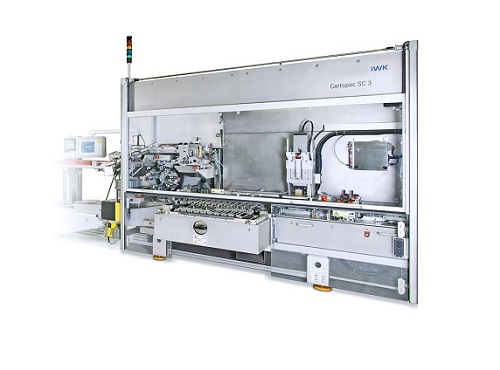
High-capacity horizontal cartoner for pharma and cosmetics appliances
Cartoners take carton blanks which are formed and...
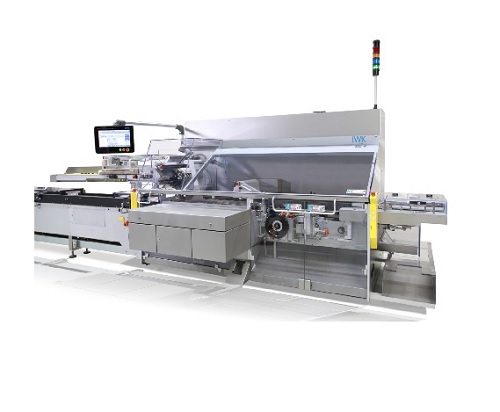
Automatic cartoner for applications in pharma and cosmetics
For high capacity production of cosmetics and pharmaceutical...
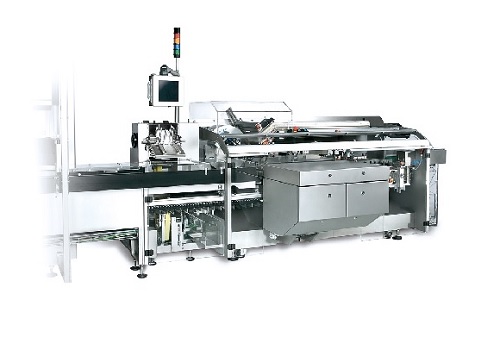
Pharmaceutical and cosmetic industry products cartoner
A large number of cosmetic and pharmaceutical products are packed ...

Horizontal cartoner for pharma and cosmetics
Most pharmaceutical and cosmetics products are packed in cardboard cartons fo...
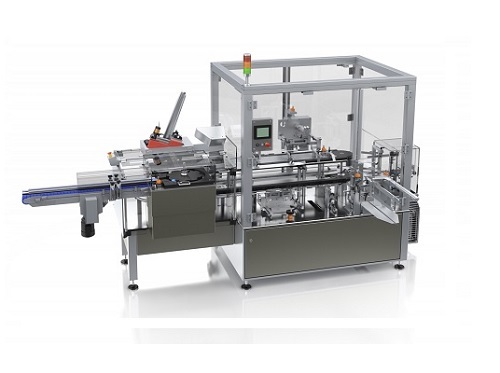
High capacity cartoner for pharmaceutical applications
Many pharmaceutical products are packed in protective and decorati...
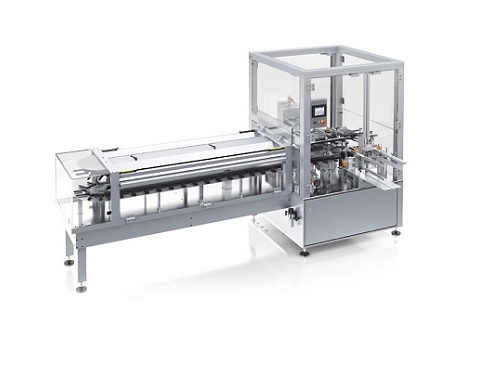
Vertical cartoner for pharmaceutical applications
Many pharmaceutical and cosmetic products are sold in protective and de...
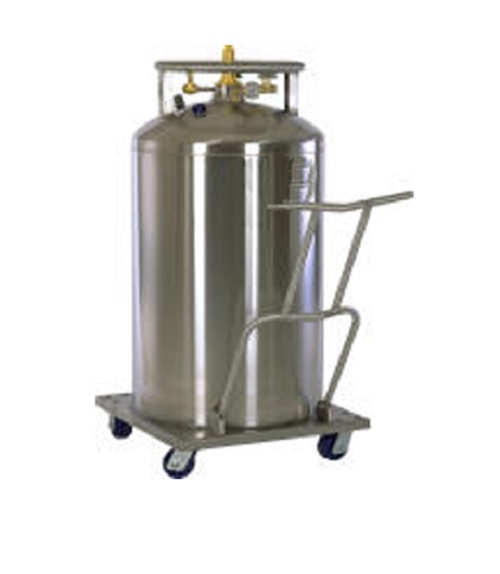
Cryogenic industrial gases transportation supply tank
For safe and convenient delivery of liquid nitrogen a robust and po...
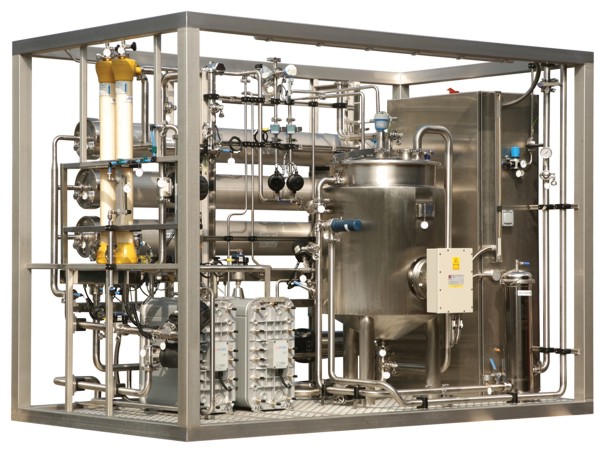
Purified water systems
Highly Purified water is used in the preparation of medicinal products where bacterial endotoxins need...

Half-suit tester
Designed to allow operators to perform sterility testing in an aseptic environment providing assurance of mat...
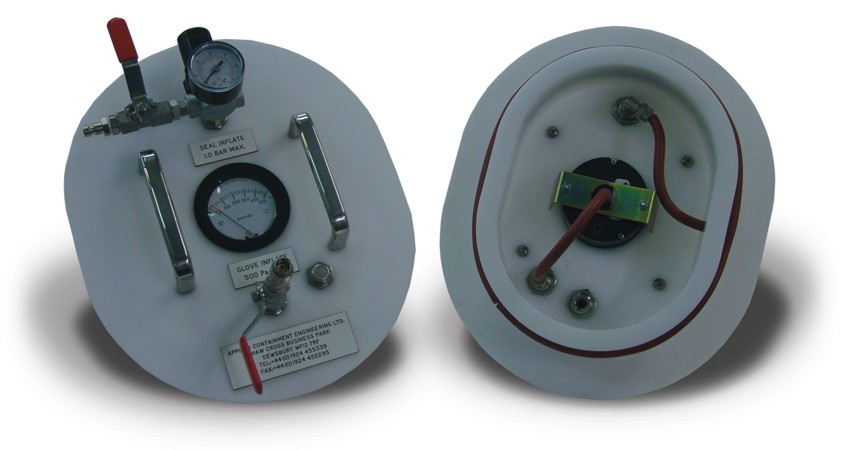
Glove tester
Testing device of the containment capability of gloves, which is as important as the other parts of the integrate...
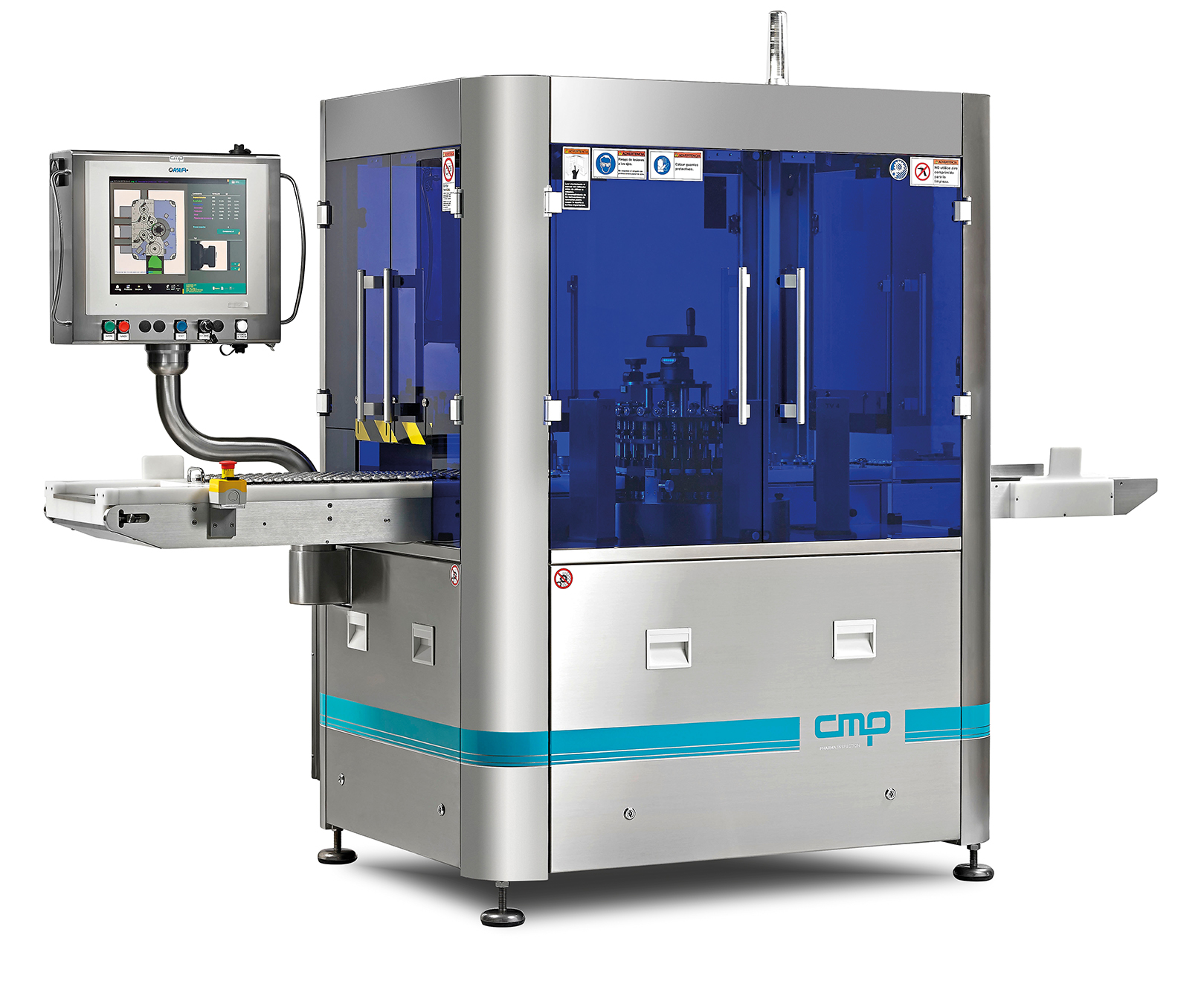
Flexible automatic inspection machine for ampoules, vials, cartridges
If you are looking to improve the efficiency of y...

Flexible automatic inspection machine for syringes
Manufacture of pre-filled syringes requires the highest quality inspec...
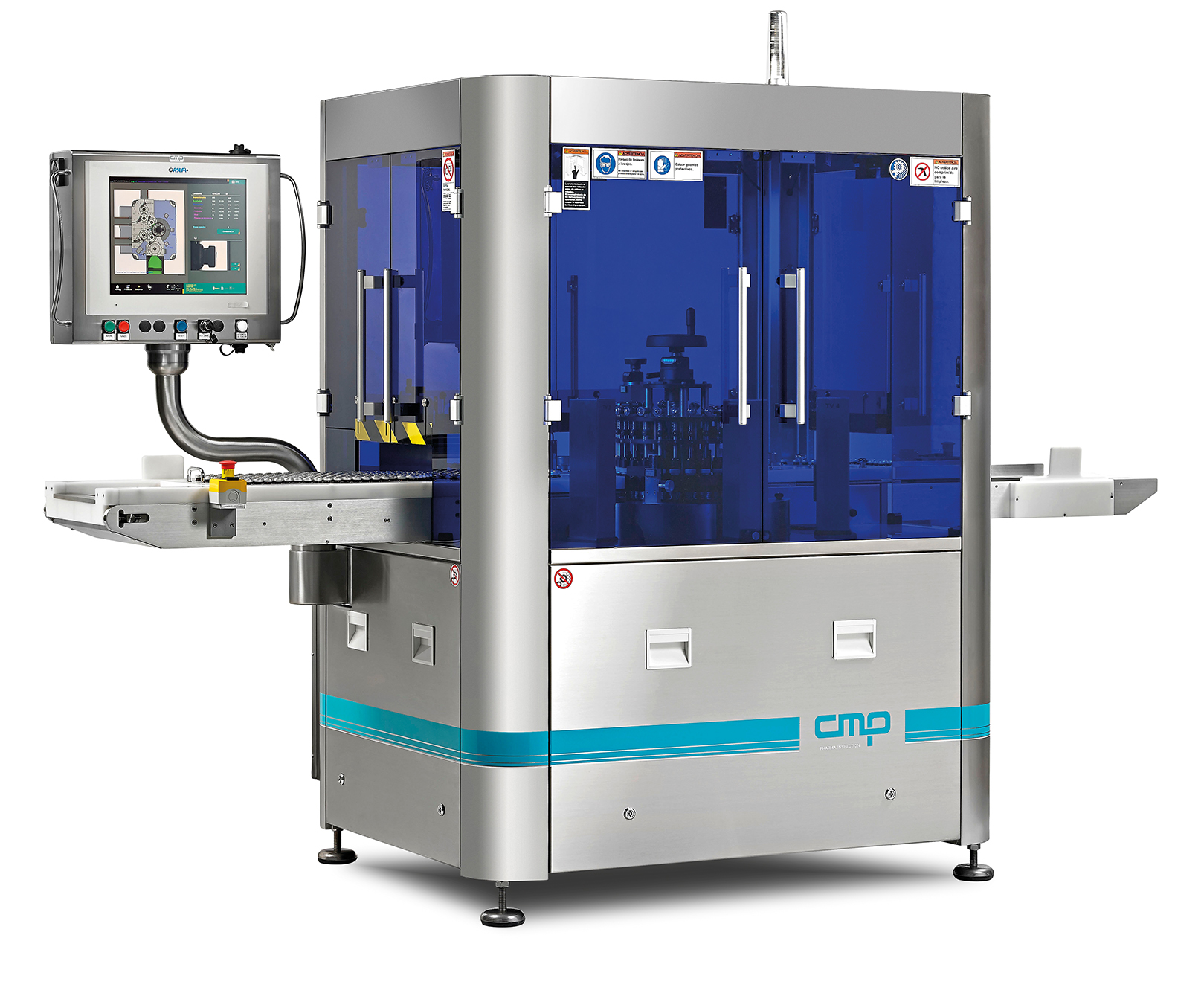
Small automatic inspector for ampoules, vials, or cartridges
Inspect small batch production of ampoules, vials, or cartr...
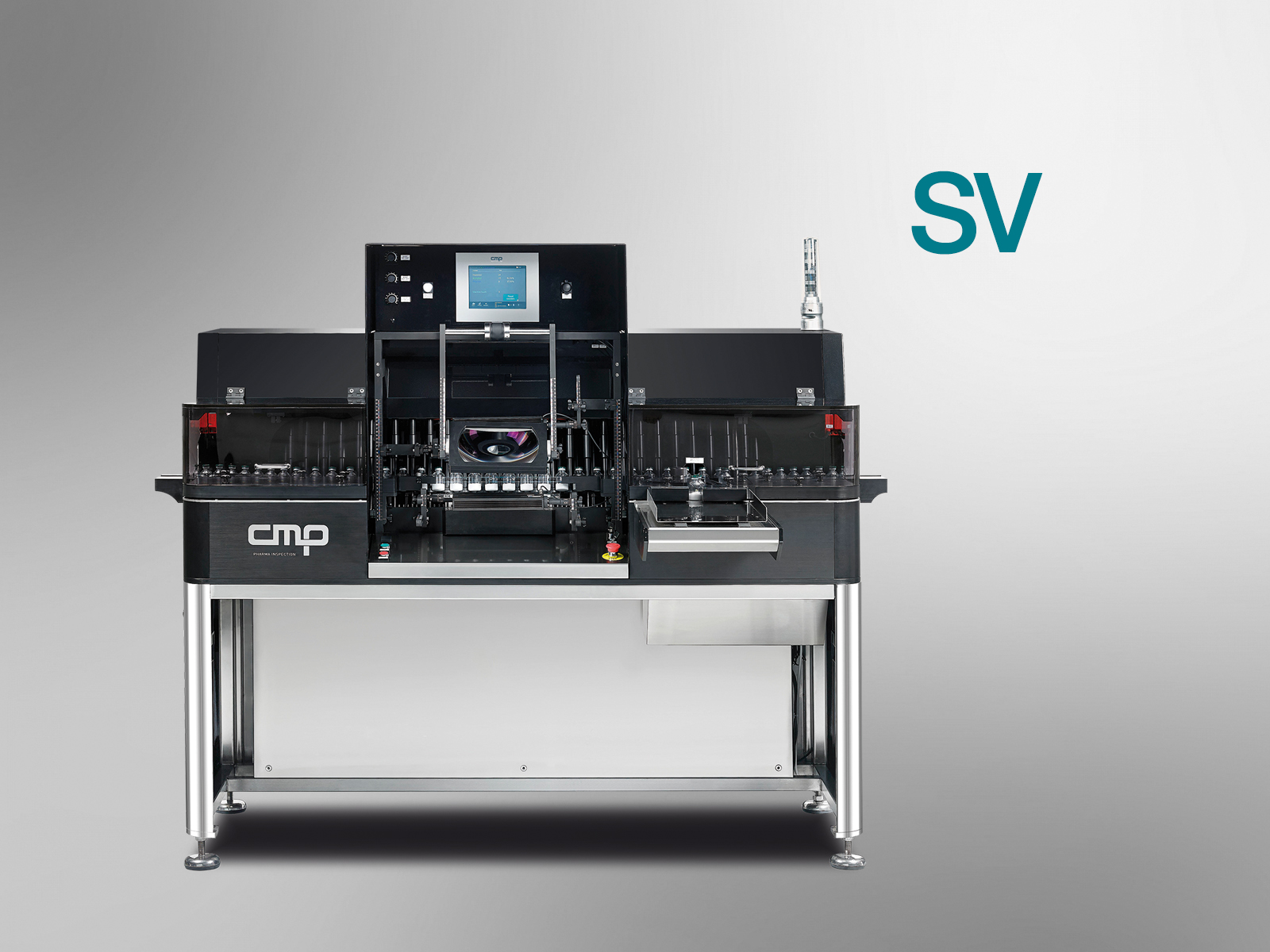
Semi-automatic inspection machine for ampoules, vials or cartridges
If you need to increase the efficiency of your manu...
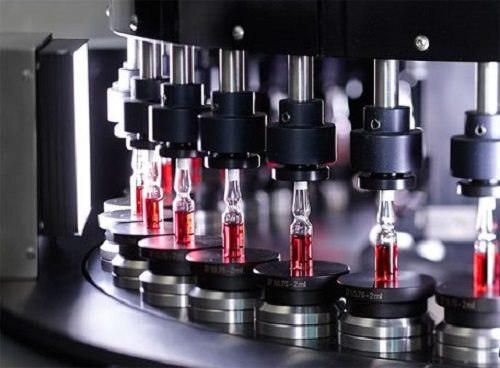
Visual and HVLD inspection for ampoules, vials and cartridges
Do you need to improve the efficiency and capability of yo...
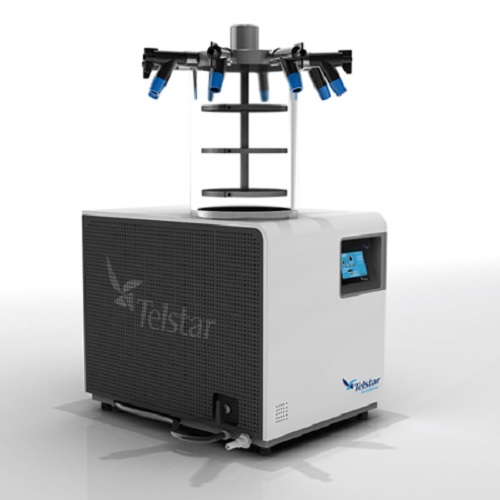
Multipurpose and R&D freeze dryer
A multipurpose unit in the research and development field. Some of the most common applic...
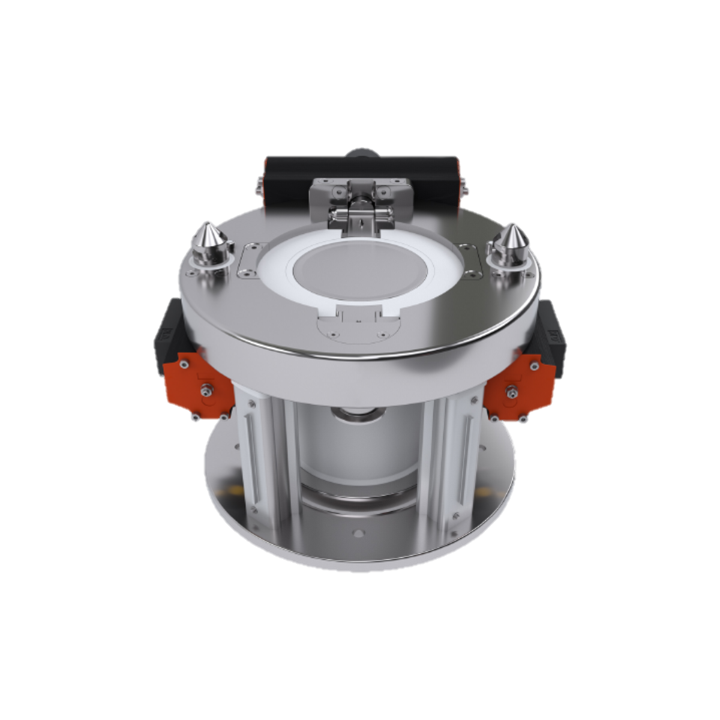
High containment split butterfly valve
Powder containment is the cornerstone of chemical and pharmaceutical manufacturing. ...
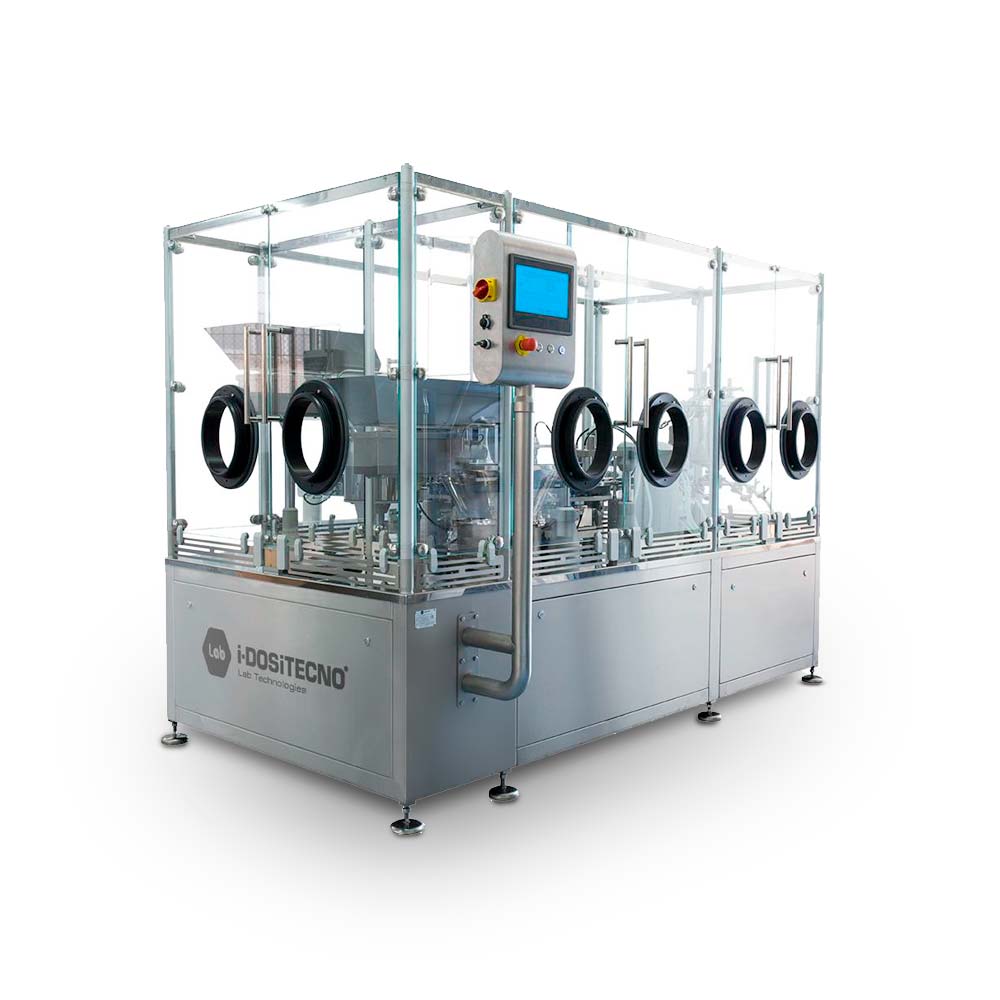
Sterile filling line for injectables
Sterile filling of liquids and powders for the pharmaceutical and cosmetic industries ...
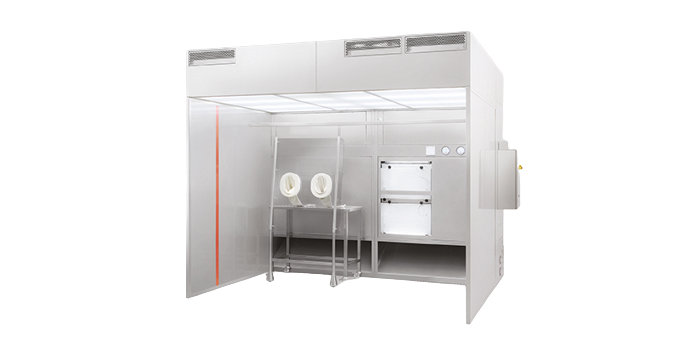
Downflow booth
Provides the highest levels of operator protection from potentially harmful airborne contaminants generated dur...
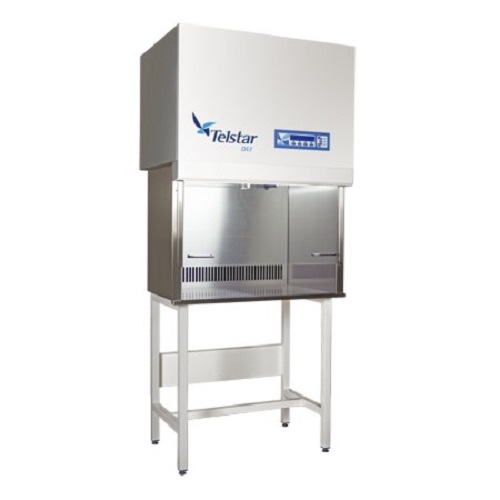
Vertical laminar flow cabinet
HEPA filtered vertical laminar airflow (down flow) creates an ISO 14644-1 (Class 5) work area ...
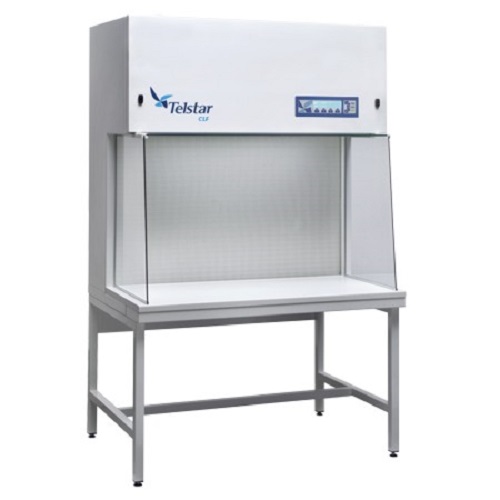
Horizontal laminar flow benches
HEPA filtered horizontal laminar airflow (crossflow) creates an ISO 14644-1 (Class 5) work a...
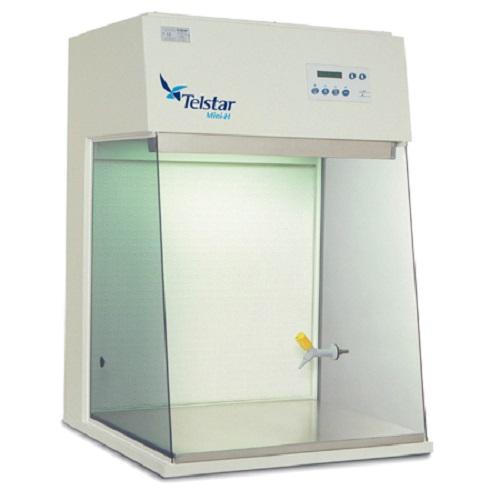
Compact horizontal laminar flow bench
HEPA filtered horizontal laminar airflow (cross-flow) creates an optimized free space...
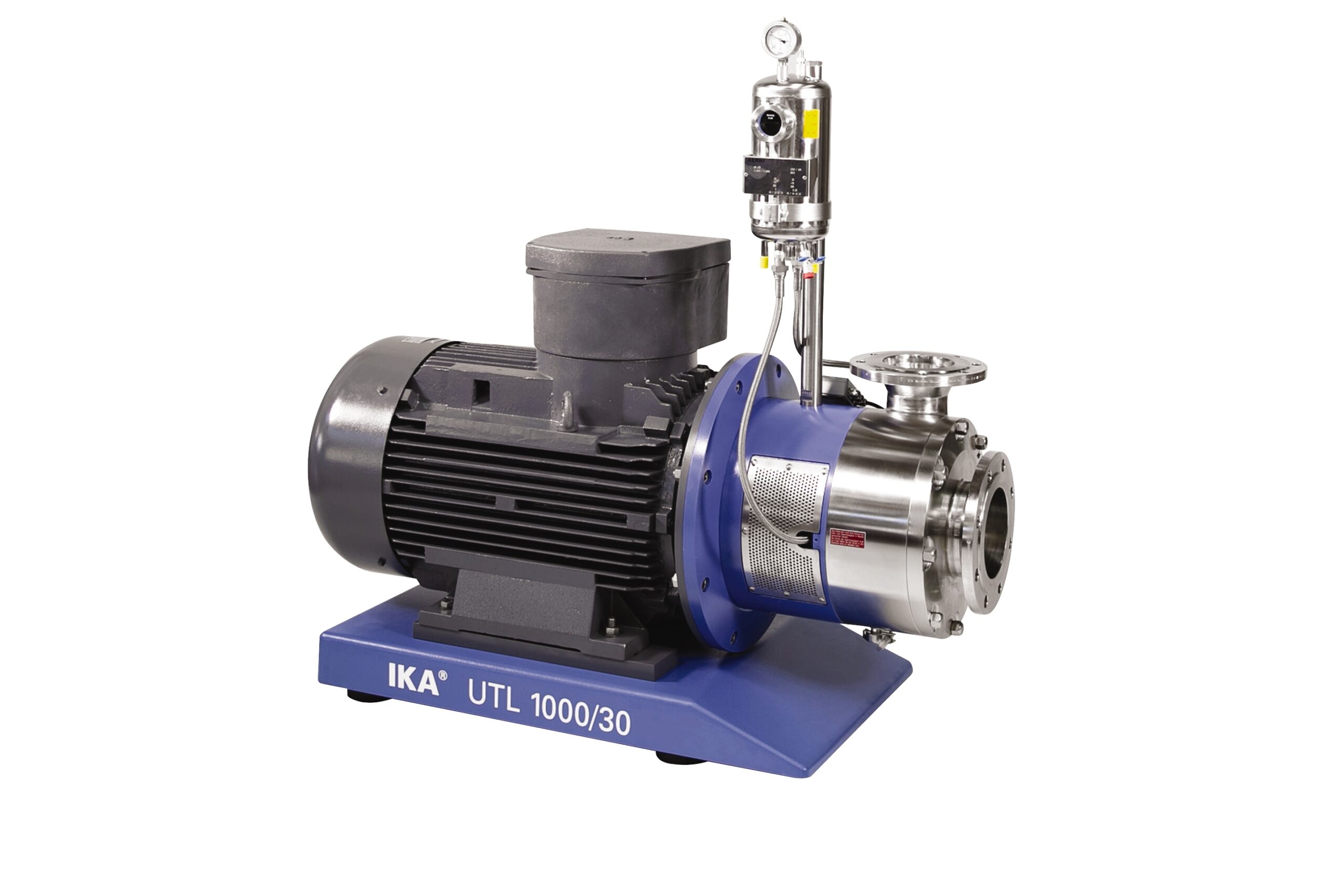
Economic dispersing machine for emulsions and suspensions
For products of medium viscosity and relatively consistent par...
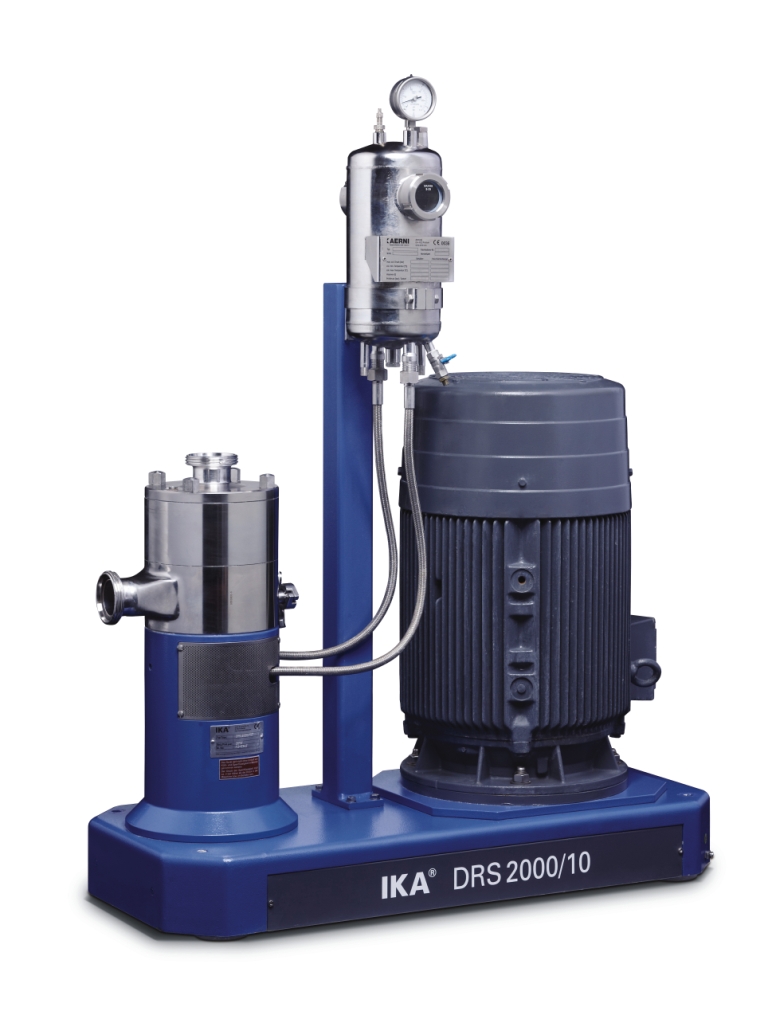
Ultra-fine dispersing machine for emulsions and suspensions
Producing the finest micro-emulsions and suspensions require...
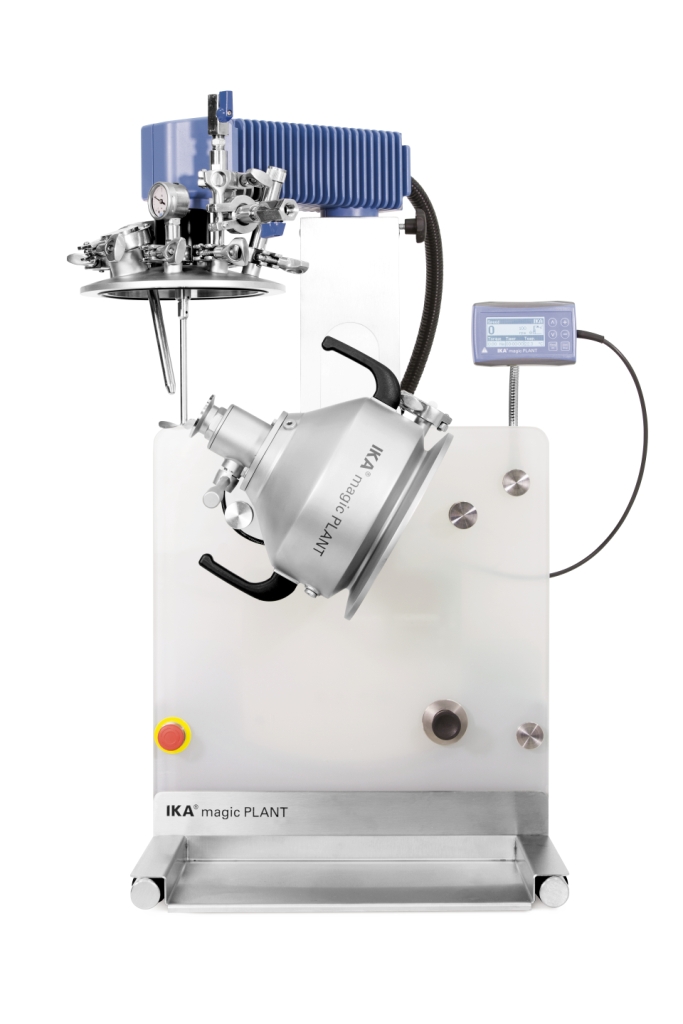
Laboratory dispersing machine for low-viscous masses
Laboratory mixers have not always been easy to work with. Getting a...
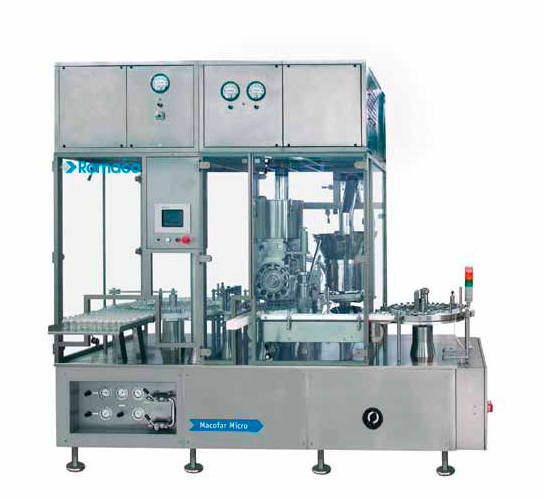
Microdosing machine for sterile powders
Fill sterile pharmaceutical powders into vials under aseptic conditions with a spee...
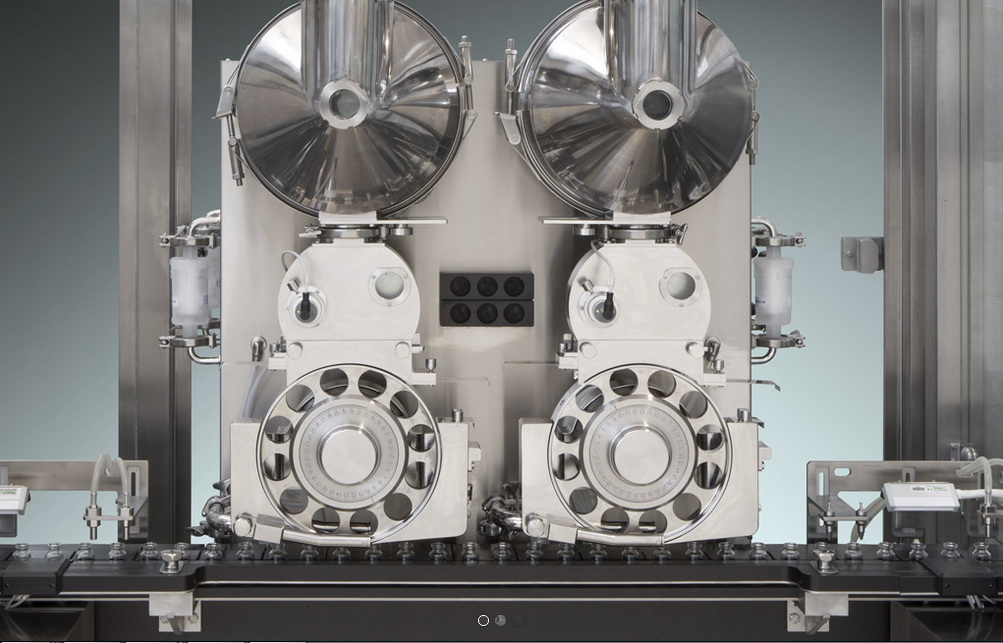
High-speed aseptic injectable vial filling machine
Fill up to 24,000 vials per hour with pharmaceutical powders or liquid...
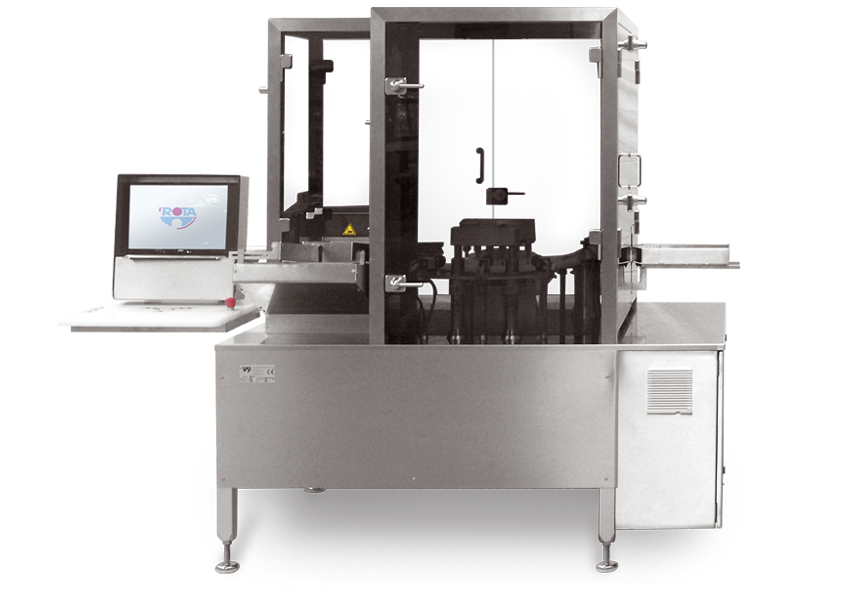
Pharmaceutical bottles inspection machine
For the visual inspection of small to medium batch-sizes of vials, ampoules or b...
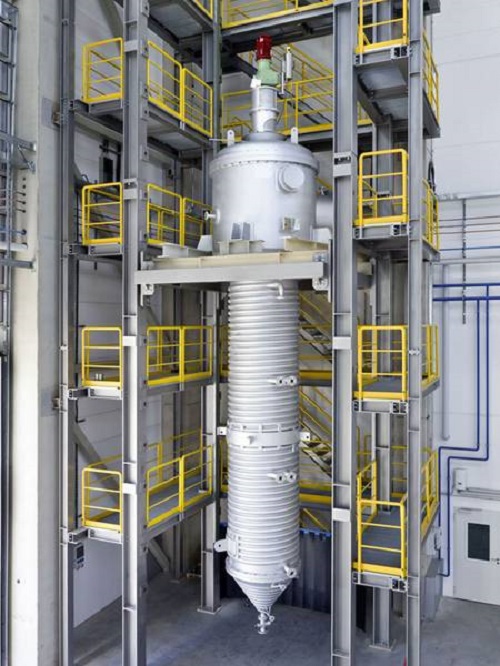
Wiped film evaporator
With wiped film distillation, a substantial decrease of boiling temperature is obtained by reducing the...
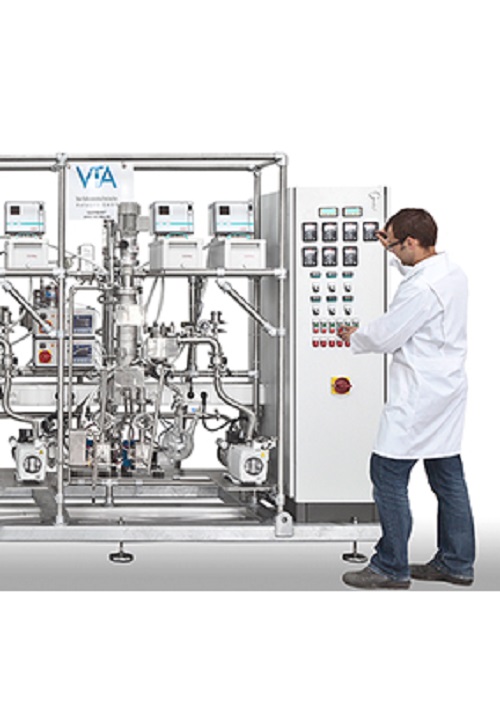
Pilot multi-stage distiller
If generating an scalable data and bring in results with small sample quantities of high-boiling...
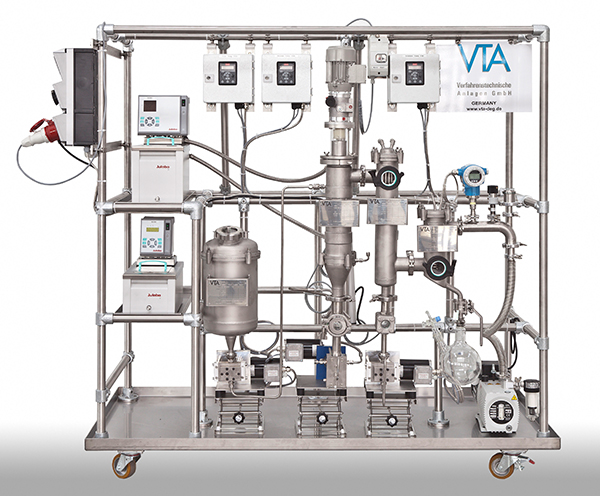
Pilot wiped film distiller
Generate scalable data and results during the pilot tests with wiped film distillation, distill ...
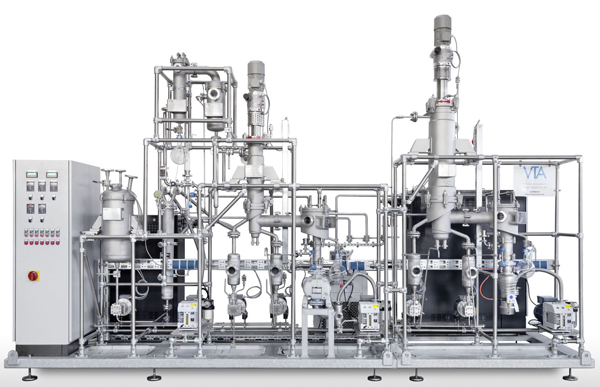
Pilot short path distiller
Generate scalable data and results during the pilot tests with short path distillation, distill o...
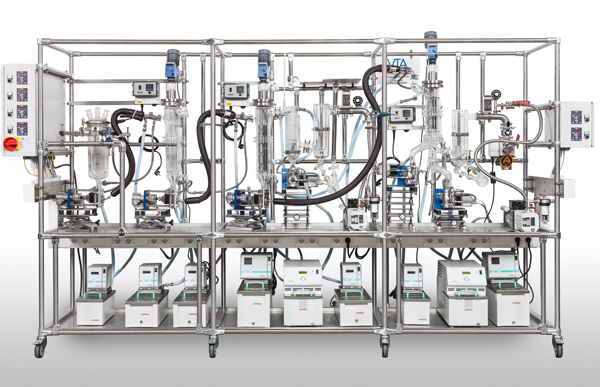
Laboratory multi-stage distiller
A laboratory multi-stage distillers that combines the wiped film and short path distillatio...
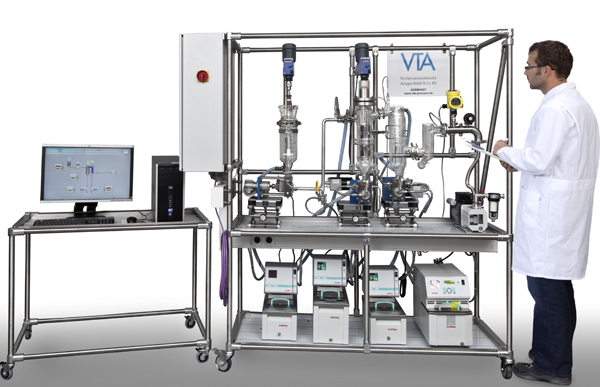
Laboratory wiped film distiller
Reach reliable conclusions testing the distillation of high-boiling or highly viscous materi...
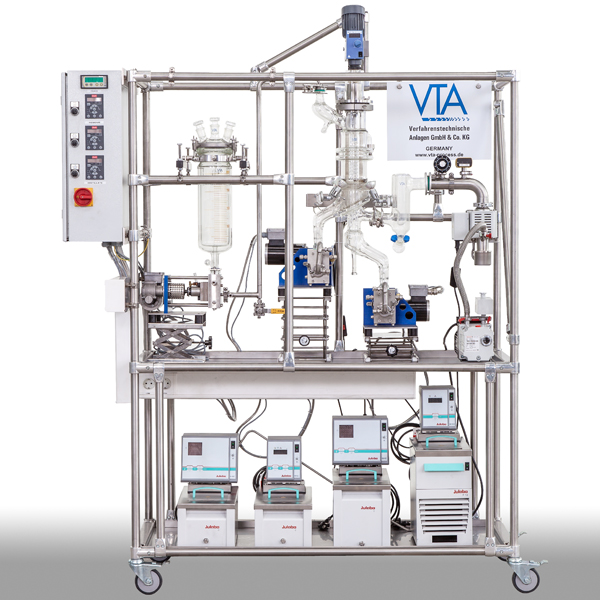
Laboratory short path distiller
Get to reliable conclusions for the separation of high-boiling and heat-sensitive products u...
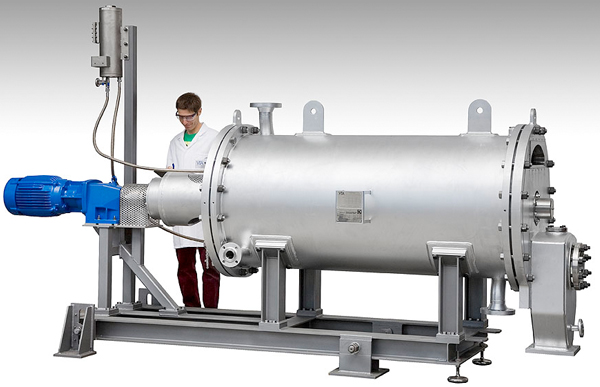
Horizontal thin film evaporators
Horizontal thin film evaporators can increase the residence time of the product and achieve...
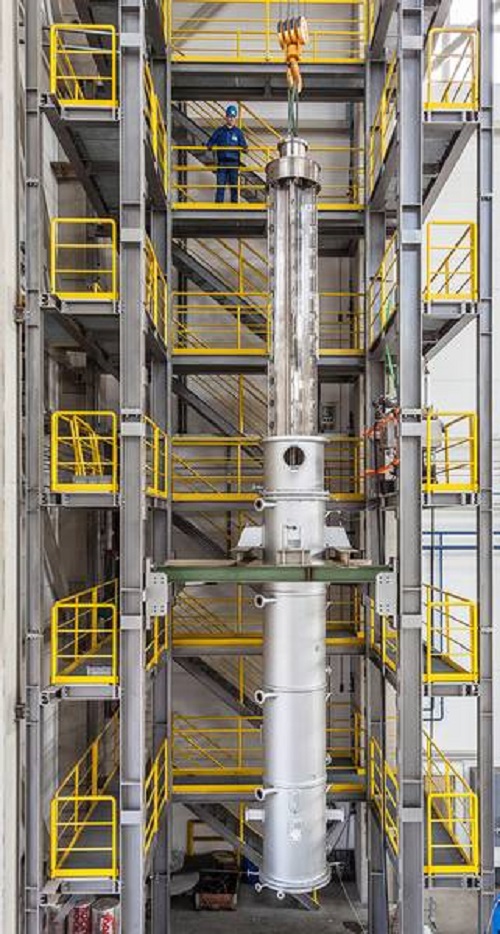
Thin film dryers
Dry dissolved or slurried crystallizing or amorphous products to a pourable powder.
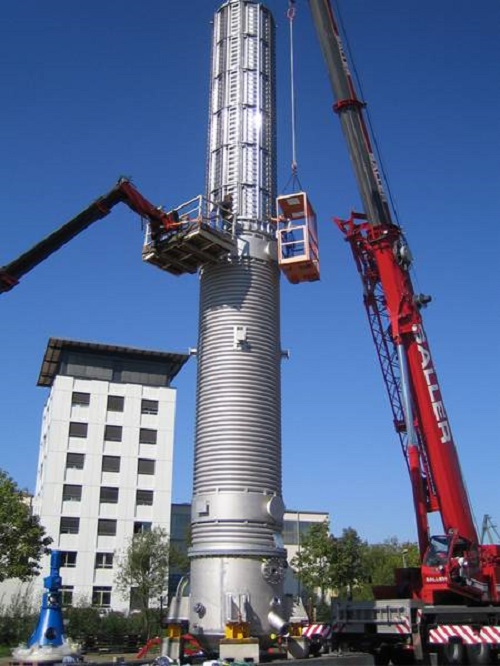
Short path evaporators
With short path distillation, a substantial decrease of boiling temperature is obtained by reducing th...
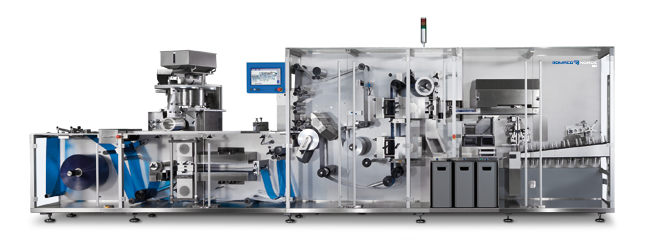
High-speed blister machine
If you are looking for a compact machine that produces blisters with an output of up to 700 blist...

Horizontal intermittent motion cartoner
User-friendly cartooning solution with an intermittent motion for a wide range of p...
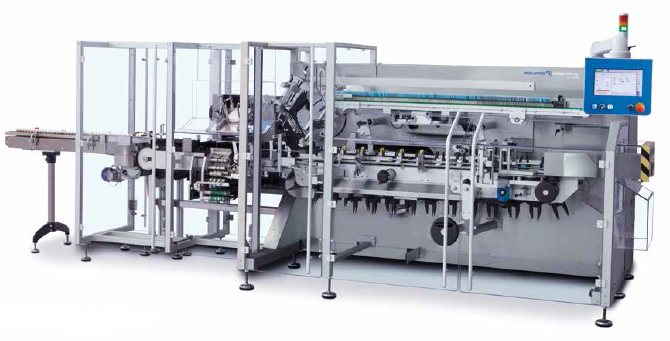
Horizontal continuous motion cartoner
An automatic cartoning machine designed for both high-speed operations and medium pac...
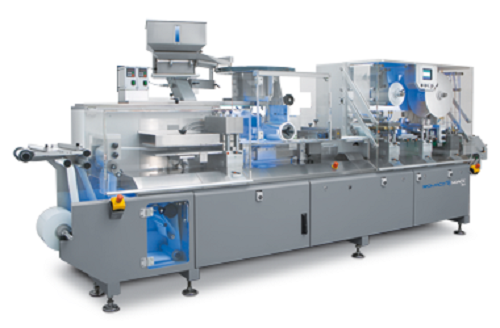
Compact blister machine
A compact blister machine ideal for packing tablets, capsules, ampoules and syringes and other applic...
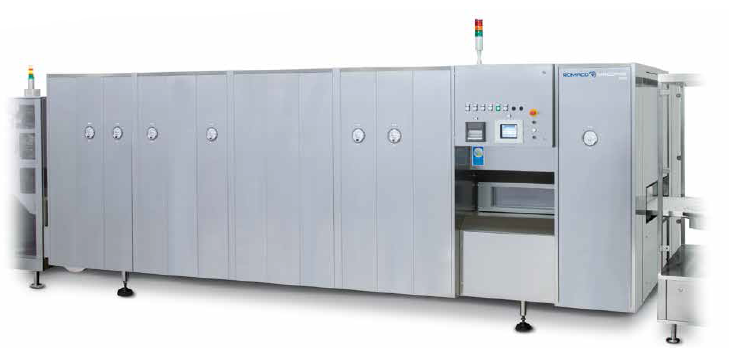
Depyrogenation tunnels for ampoules, vials and bottles
Sterilize and depyrogenize ampoules, vials, bottles and similar gl...
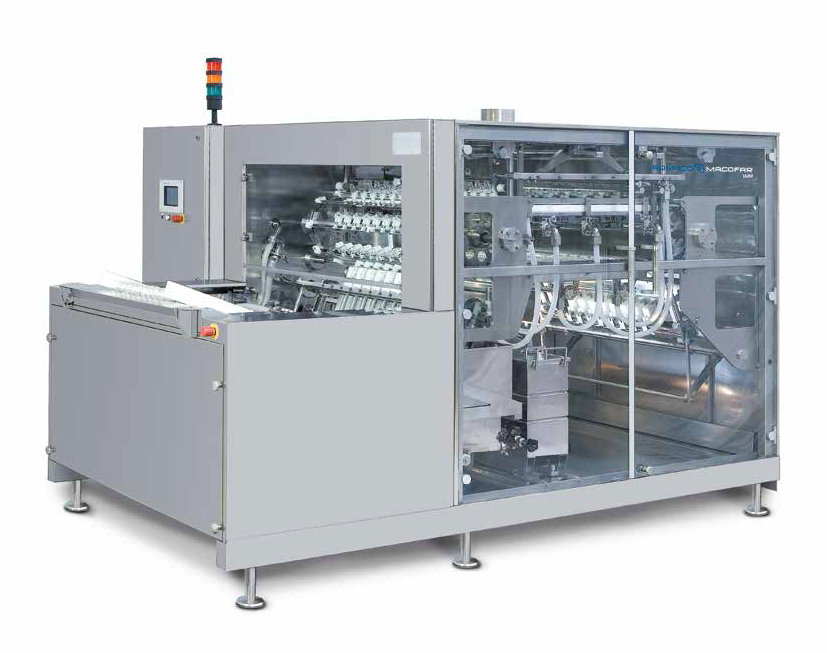
Automatic washing machine for ampoules
Automatic washing machine designed for cleaning ampoules and achieving a maximum out...
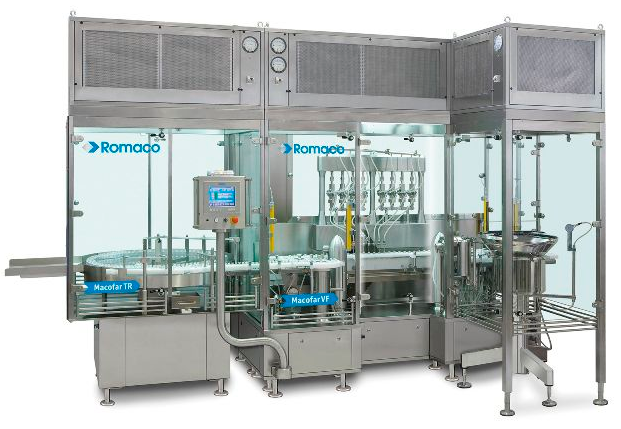
Aseptic liquid filler for vials
Compact modular aseptic filler of vials with parenteral medicines and freeze-dried products.
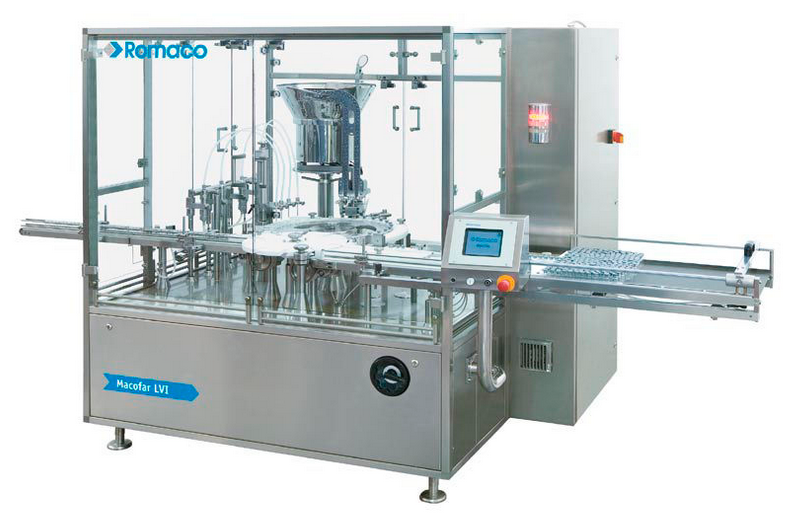
Monobloc small volume liquid filler
These intermittent motion monobloc machines are designed for filling various liquids in...
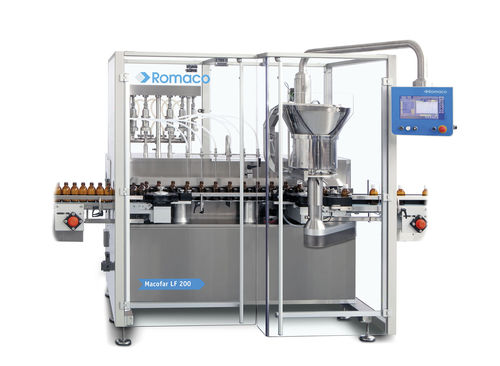
High-speed small volume liquid filler
Fill liquid pharmaceutical, nutraceutical and cosmetic products in ampoules and bottl...
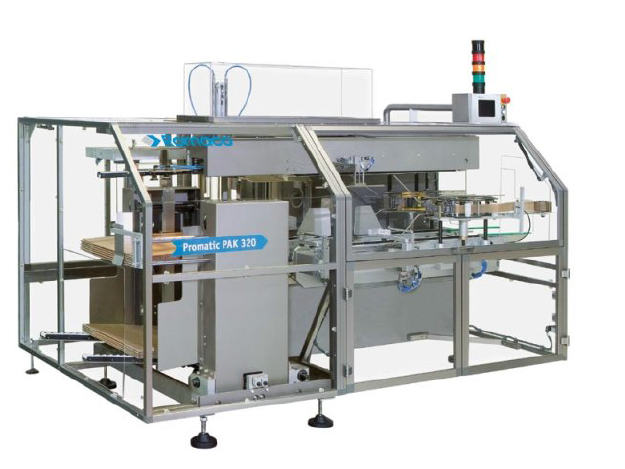
Case packer for cartons and bundles
Pack cartons and bundles into RSC (Regular Slotted Case) cases and perform functions li...
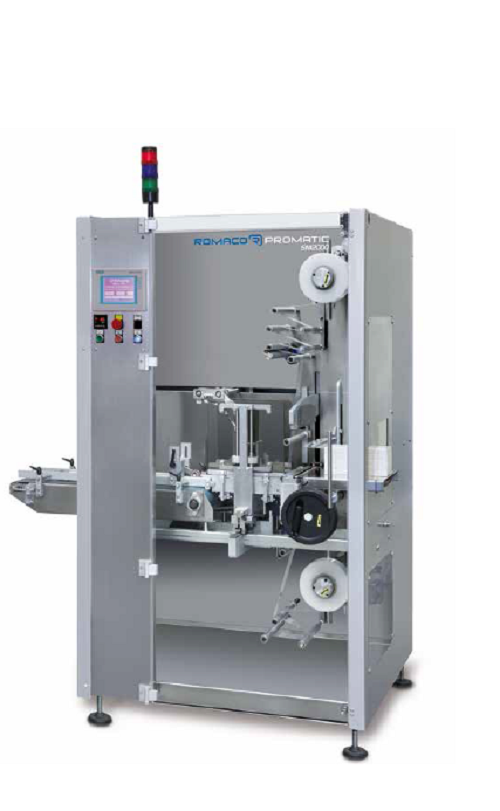
Stretch bander
A compact wrapping machine to seal your boxes with a max speed of 50 packs per minute.
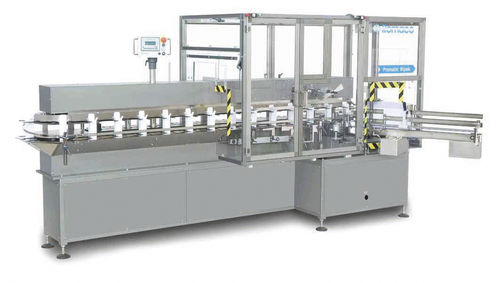
Vertical cartoner
A cartoning solution that can be operated in either continuous or intermittent mode depending on the carton...
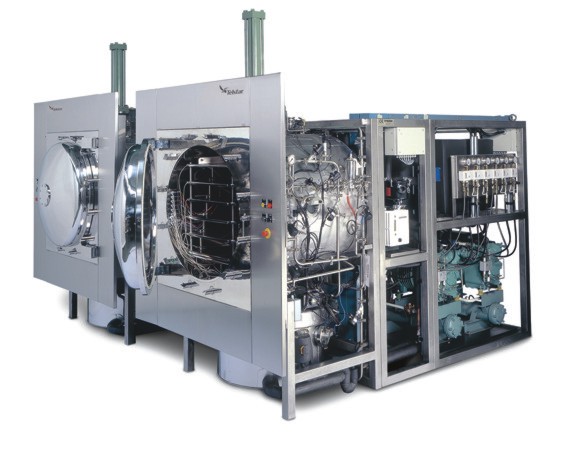
GMP freeze dryer
Designed to perform clinical trials, pilot, and small scale or large scale industrial drying processes, in ac...
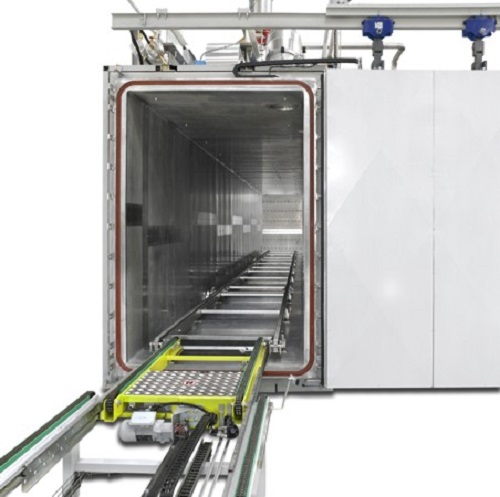
Ethylene oxide sterilization chamber
Designed for the terminal sterilization of temperature sensitive medical-health produc...
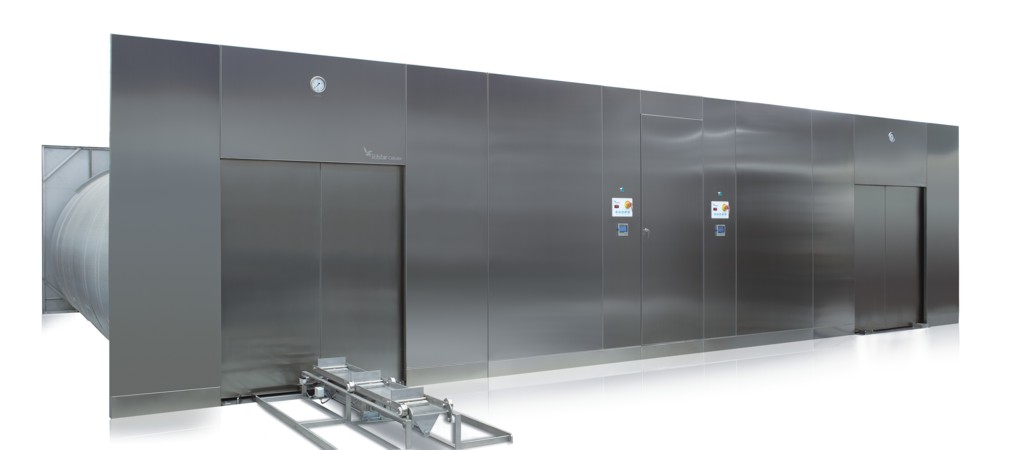
Superheated water shower autoclave
Specially designed for sterilizing large batches of parenteral solutions.
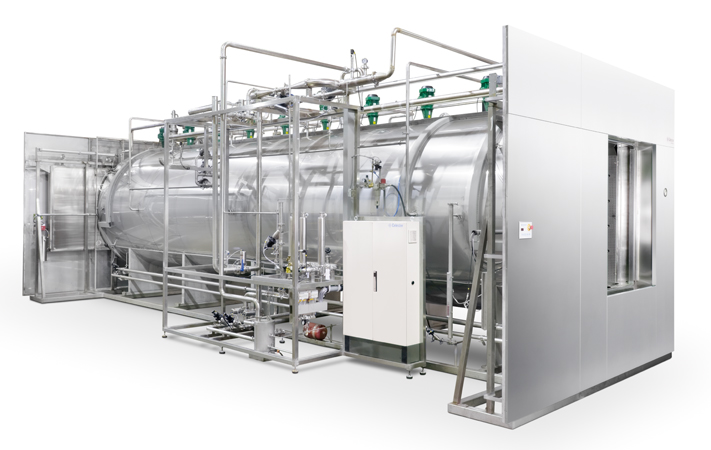
Steam and air mixture sterilization autoclave
Specially designed for sterilizing large batches of parenteral solutions.
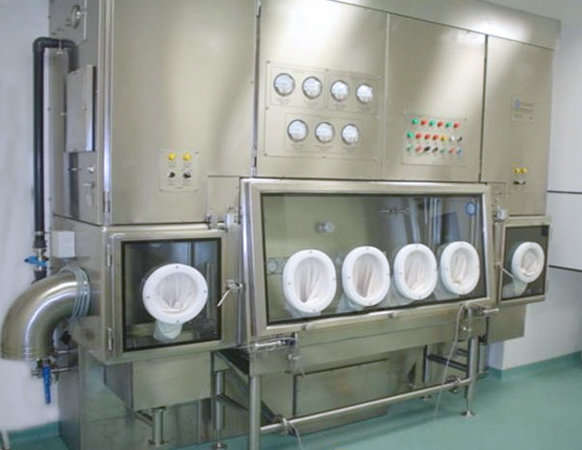
Aseptic barrier systems
Designed for sterile product and Potent API’s either with low or high OEL requirements.
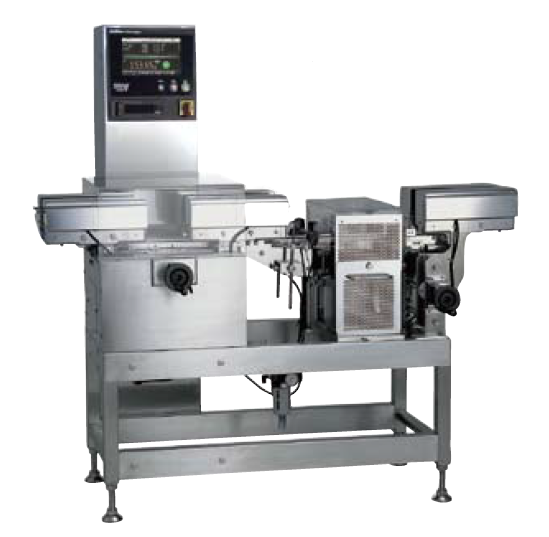
Small bottle checkweigher
Any small-diameter bottle, containing prescription medication or cosmetic applications, can be pro...
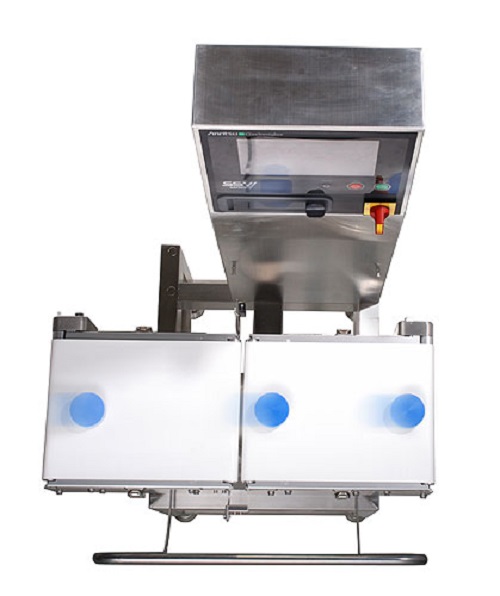
Versatile checkweigher
This Versatile checkweigher is equipped with a highly versatile strain gauge load cell. It is also sui...