Industrial universal reactor for large-scale chemical synthesis
For chemical producers scaling past laboratory setups, this versatile reactor safely handles large-batch reactions under a broad range of temperatures and pressures, ensuring precise control and efficient processing of complex formulas.
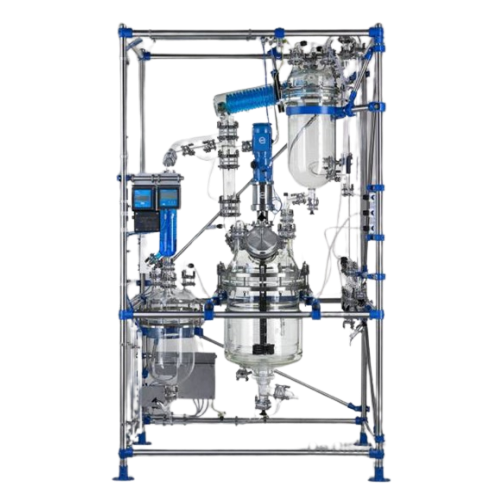
Synthesizes, Distills, and Mixes Large-Scale Chemical Reactions
The QVF Universal-Reactor from De Dietrich Process Systems is your go-to solution for scaling up chemical reactions that exceed lab-scale capabilities. Designed for the pharmaceutical, fine chemicals, and specialty chemicals sectors, it allows for precise control in synthesizing active pharmaceutical ingredients, monoclonal antibodies, specialty polymers, and more. By employing a versatile, inert gas-compatible design, this reactor excels in handling liquid and gas processes under vacuum and EX-rated conditions. It facilitates seamless integration into existing lines with its robust, digitally controlled stirrer and OptiMix® baffle system, offering extraordinary mixing performance without splashing. Featuring a borosilicate glass construction and PTFE components, it ensures optimal chemical resistance and longevity. The reactor is equipped with CIP-nozzles, ensuring easy and reliable cleaning between batches, thus minimizing downtime. Compliance with European EX regulations guarantees safe operation in volatile environments. Whether for pilot studies or full-scale production, you can request custom configurations to best meet your specific operational needs.
Benefits
- Enhances scalability for production beyond lab capabilities, supporting larger batch sizes.
- Ensures safety in volatile environments with EX-rated design and materials.
- Reduces downtime with efficient cleaning via CIP system.
- Optimizes reaction control with precise temperature and mixing adjustments.
- Maintains chemical integrity with corrosion-resistant borosilicate glass and PTFE construction.
- Applications
- Specialty chemicals, Agricultural chemicals, Fine chemicals, Bio-pharmaceuticals, Precious metal, Pharmaceuticals
- End products
- Active pharmaceutical ingredients (apis), Agrochemicals, Monoclonal antibodies, Specialty polymers, High-purity gold, Catalyst complexes, Platinum group metal compounds
- Steps before
- Mixing, Reactant Addition, Vacuum Application, Inert Gas Preparation, Jacketed Vessel Tempering
- Steps after
- Distillation, Temperature Control, Vacuum Distillation, Product Transfer, Cleaning via CIP-Nozzles
- Input ingredients
- reactants, inert gas, light boiling components, thermo liquids
- Output ingredients
- light boiling components, distillate receiver, solvents, temperature sensitive products
- Market info
- De Dietrich is renowned for manufacturing high-quality engineered-to-order (ETO) equipment, specializing in chemical process systems, glass-lined reactors, and filtration technologies, with a strong reputation for innovation, reliability, and safety in the chemical and pharmaceutical industries.
- Temperature Range
- -50°C to 200°C
- Operating Pressure
- up to +0.5 barg
- Material
- Borosilicate Glass 3.3
- Stirrer Drive
- Electric motor with adjustable gearbox
- Cleaning Method
- CIP via CIP-nozzles
- Distillation Capability
- Light boiling components
- Automation
- Manual adjustment
- Working Mechanism
- Batch synthesis with inert gas
- Temperature Range
- -20°C to +150°C
- Pressure Control
- Inert gas overpressure up to +0.5barg
- Vacuum Operation
- Yes, with vacuum and overpressure operation
- Cleaning Method
- CIP with self-draining construction
- Mixing Performance
- OptiMix® baffle system
- Distillation Capability
- Light boiling component distillation
- Automation Level
- EX-rated instrumentation for automated operation
- Heating/Cooling Integration
- Jacketed vessel with a thermo liquid
- Density/particle size
- 0.5–2.5 g/cm³ / 50–1000 µm
- Machine Footprint
- Compact
- Reactor Shape
- Jacketed Vessel
- Reactor Size
- Customizable
- Discharge Method
- Distillation/Withdrawal
- Feed Method
- Handhole and Vacuum Feed
- Construction Material
- Borosilicate Glass 3.3
- Stirrer Drive
- Robust Electric Motor
- Temperature Control
- Thermo Liquids
- Pressure Control
- Max +0.5barg
- Seal Type
- Single Mechanical Seal
- Cleanability
- CIP Nozzles
- Baffle System
- OptiMix® Baffles
- OptiMix Baffles
- Triple-walled reactor
- Vacuum connection
- Including pressure release valve and bursting disc
- CIP-Nozzle
- Made of PTFE or stainless steel