Double-stage rotary weigh feeder for precise powder dosing
Ensure consistent dosing and precise weighing of challenging fine-grained or powdered materials in continuous industrial processes, enhancing control and efficiency in variable conditions like humidity and material behavior changes.
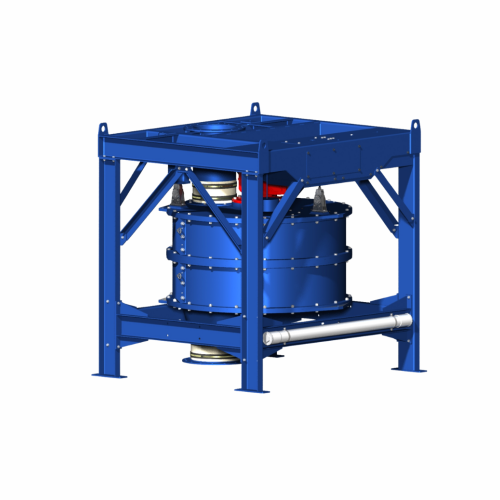
Accurately Doses and Weighs Fine-Grained Materials
The TWIN ROTAWEIGH from HASLER Group is a double-stage rotary weigh feeder designed for precise dosing and weighing of fine-grained and powdered materials. It incorporates a dual-chamber horizontal cellular impeller system, allowing for continuous industrial weighing and dosing, even when material properties vary due to humidity, temperature, or composition changes. This feeder excels in a range of applications, from cement and chemical industries to food processing, enabling reliable delivery of products such as Portland cement, calcium ammonium nitrate, and powdered sugar. With flow rates from 2 to 800 m³/h, it offers high-precision measurement with a ±0.5% accuracy. The TWIN ROTAWEIGH can be seamlessly integrated into existing production lines, utilizing an SCM control module for streamlined operation. It boasts a compact footprint with its vertically aligned input and output, and it is available in multiple configurations to fit diverse operational needs. Additionally, this equipment features high-temperature resistance and full sealing to ensure durability and performance in demanding industrial environments. Maintenance is straightforward, allowing on-site servicing to minimize downtime.
Benefits
- Ensures precise and consistent material flow, minimizing waste and optimizing production efficiency.
- Adapts to variable material behaviors, maintaining accuracy even with changes in humidity and temperature.
- Compact design optimizes space in existing production lines.
- Durable construction withstands high temperatures and harsh industrial conditions, reducing maintenance frequency.
- Quick, on-site maintenance reduces operational downtime.
- Applications
- Polymers, Amino acids, Dyes, Cosmetic pigments, Chemical powders, Hydrometallurgy, Food additives, Water treatment, Fertilisers, Metals recycling, Specialty acids, Technical ceramics, Mining, Resins, Minerals, Pigments, Flue gas desulphurization, Cement
- End products
- Phosphate fertilizers, Powdered sugar, Copper cathodes, Potable water, Gypsum slurry, Polyethylene pellets, Calcium ammonium nitrate, Epoxy resin, Portland cement, Iron oxide pigments, Stevia extract, Lysine, Azo dyes, Titanium dioxide, Processed kaolin, Citric acid, Zinc concentrate, Advanced ceramic components, Recycled aluminium
- Steps before
- Grinding, Drying, Purification, Mixing
- Steps after
- Packing, Storage, Distribution, Blending
- Input ingredients
- fine-grained products, powdered products, cement, kiln feed, ball mill feed, cosmetic pigments, powders, flour, powdered sugar, food additives, chemical powders, pigments, dyes
- Output ingredients
- weighed fine-grained products, weighed powdered products
- Market info
- HASLER Group is known for manufacturing and supplying industrial engineered-to-order (ETO) equipment, specializing in mixing, filtration, and sealing solutions for various industries, with a reputation for quality and innovation in handling challenging process applications.
- Precision
- ±0.5%
- Flow Rate Range
- 2 to 800 m³/h
- Temperature Resistance
- Up to 130°C
- Particle Size
- < 1 mm
- Material Moisture Content
- < 1 %
- System Design
- Two-stage horizontal cellular impeller
- Automation
- SCM control module
- Torque Limiter
- Built into the motor
- Sealing
- Completely sealed
- Mounting Options
- Frame or suspended beneath the silo
- Configuration Options
- Variety of sizes and configurations
- Rotation Control
- Included
- Footprint
- Reduced
- Working Mechanism
- Double-stage horizontal cellular impellers
- Integrated Steps
- Continuous dosing and weighing
- Batch vs. Continuous Operation
- Continuous
- Footprint
- Reduced, materials enter and exit on the same vertical axis
- Material Behavior Control
- Dual-chamber design
- Material Fusion Control
- Dual-chamber design allows controlled fusion
- Sealing
- Completely sealed
- Installation Flexibility
- Frame mounted or suspended beneath silo
- Maintenance
- On-site maintenance, low OPEX
- Robustness
- Mechanical and electrical strength, 24/7 operation
- Torque Limiter
- Built into the motor
- Temperature Resistance
- Up to 130°C in continuous operation
- Flow Rates
- 2 to 150 m³/h
- Precision
- ±0.5%
- Density/particle size
- 0.5–2.5 g/cm³ / 50–1000 µm
- Discharge method
- Aligned inlet and outlet
- Flow rate capacity
- 2 to 800 m³/h
- High-temperature version
- Up to 130°C
- Control panel type
- SCM control module
- Integration possibilities
- Direct connection to sensors
- Modularity
- Various sizes and configurations
- Installation flexibility
- Frame-mounted or suspended beneath the silo
- Footprint
- Reduced due to aligned inlet and outlet