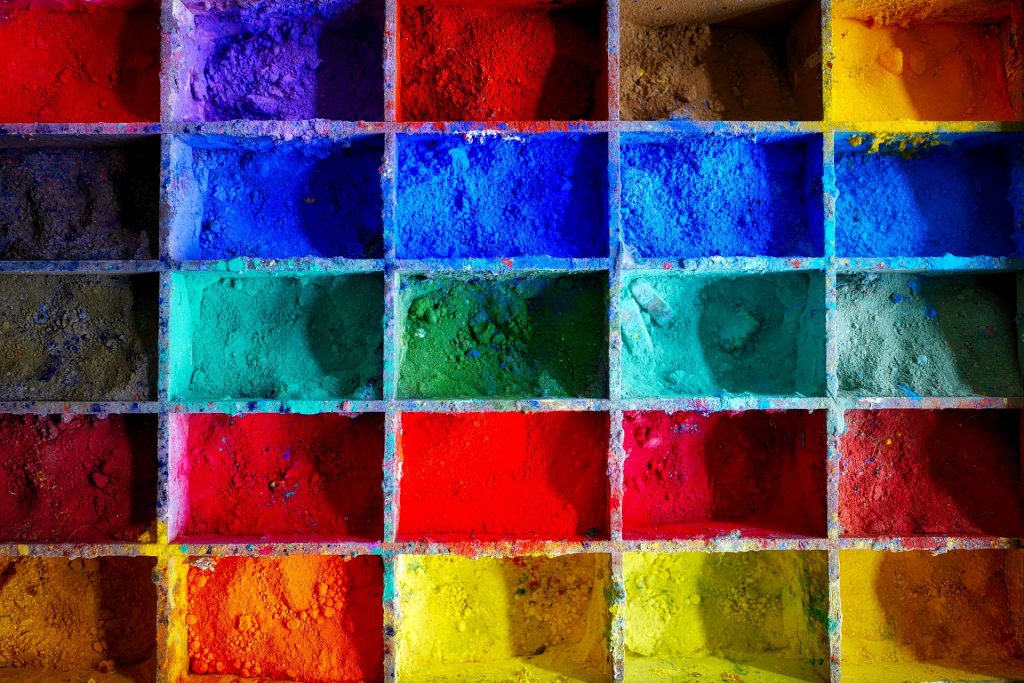
Pigment Manufacturing
Find innovative pigment equipment and connect directly with world-leading technology suppliers
Pigments are colorants that are not soluble in the host material and scatter light and are therefore opaque. Pigments can be organic or man-made and derive from animals, plants, rocks or minerals and metal oxides, like for example titanium oxide.
Top picks for pigment processing

Dryer for pigments and hydroxides
Achieve precision drying of complex suspensions and pastes into uniform powders, optimizi...
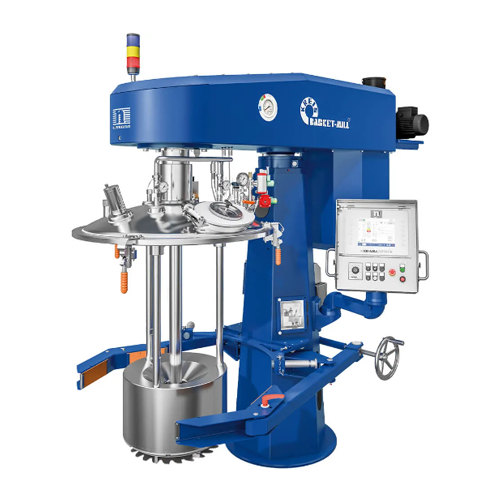
Basket mill for paint and varnish production
Achieve optimal particle size and product consistency with this advanced bask...
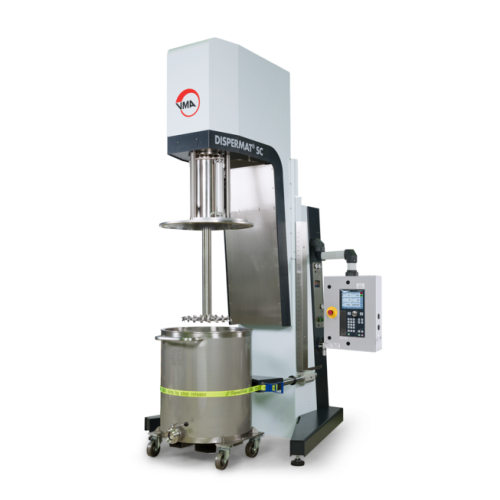
Explosion-proof production disperser for paint manufacturing
Ensure safe and efficient dispersion in volatile environmen...
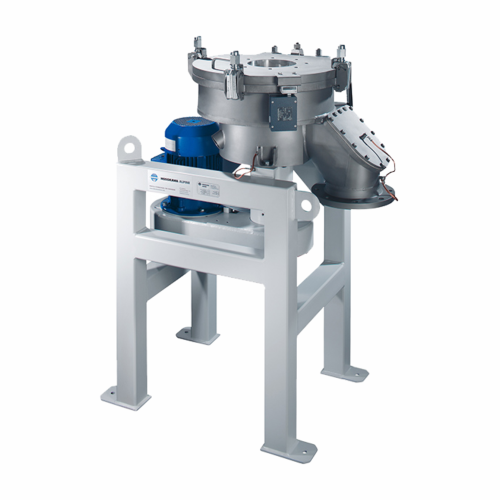
Ultrafine classifier for toner and pigments
Achieve unparalleled precision in classifying fine powders essential for high-...
Stories about pigment
Select your pigment process
Tell us about your production challenge
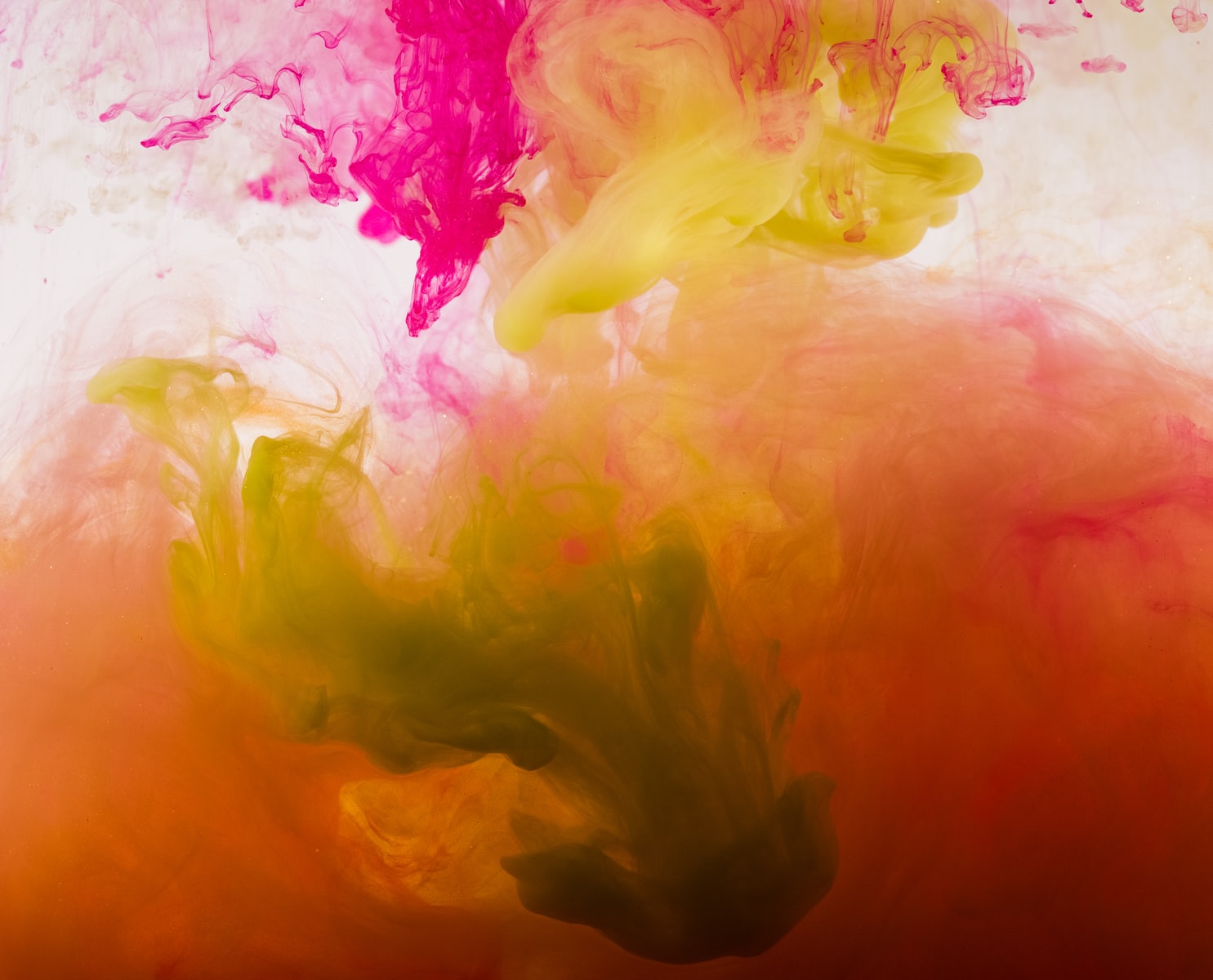
Generally, pigments and paints are not bound chemically to the covered surface, water-soluble dies react with fibers in a mordant bath. Apart from colored, decorative paints, white and black pigments have high importance. White titanium dioxide plays an important role in the painting industry, due to its stability, high covering effect, and UV-light absorbing property. Approximately 4.6 million tons of TiO2 pigment are produced annually worldwide, and its use continues to rise. On the other end of paints, carbon black is essential as a toner of the laser printer and filler in tires and other plastics, also due to its stability and UV-light absorbing capability.
Pigment manufacturing process
Natural sources of paint lost their importance. Lead oxide pigment dispersed in oil was widely used as primer paint, due to its excellent anticorrosive feature. Since heavy metal lead is poisonous, this red paint is nowadays forbidden. Indigo was extracted from plants cultivated in Asia, nowadays the blue die for denim cloth coloration is synthesized almost exclusively by the chemical industry. The coloring materials were solved in organic solvents, benzene, toluene, xilols, turpentine, and nitro thinner. All these solvents pollute the environment, and some of them are carcinogens. Nowadays water-based products are common; however most part of paints are not water-soluble. In order to avoid segregation, stable dispersion should be formed where the pigments do not sediment.
In order to eliminate solvents, powder coating is used for painting and decorating vehicles and other metal surfaces. Pigments are mixed with polymers, then extruded and milled. Classifier mills are preferable for a narrow particle size distribution
High sheer mixing for powder paints
Powder coatings are a solvent-free painting form where pigment is mixed with a polymer, a carrier material that melts in the painting oven so that the pigments adhere to metal objects. Pigments are micronized to have a smooth surface and become miscible with polymer beads. High shear mixing is necessary to break the force of cohesive powders and form polymer-pigment particles avoiding sedimentation in further processing. The video below shows a high-shear mixer for this purpose with a conical shape that provides a vertical upward movement along the wall.
How dispersion improves paint quality
In emulsion paint, the binding agent is dispersed in water. Dispersion as such an important process that has a big influence on the quality of the final product. Dispersing machines process immiscible materials in a high shear chamber, where sharp edge tools of high-speed rotor reduce the size of the paint particles and disperse them into the oily or water base matrix. A rotor can have paddles as well, to serve as a recirculation pump. The video below shows how at the top of the rotor a vacuum occurs, sucking in the ingredients, liquids, and powders.
Which pigment technology do you need?
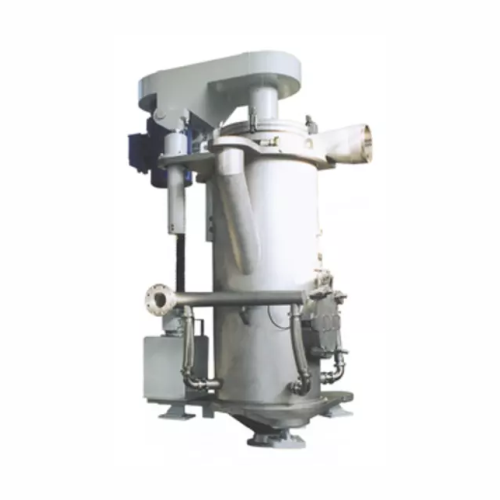
Jet mill for toner and pigment industries
Optimize particle size and distribution for high-demand applications with this h...
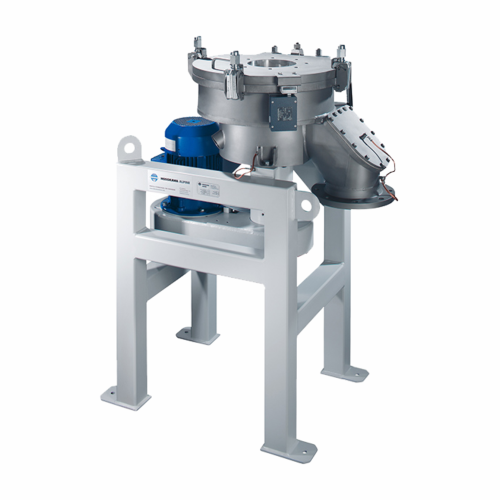
Ultrafine classifier for toner and pigments
Achieve unparalleled precision in classifying fine powders essential for high-...

Dryer for pigments and hydroxides
Achieve precision drying of complex suspensions and pastes into uniform powders, optimizi...
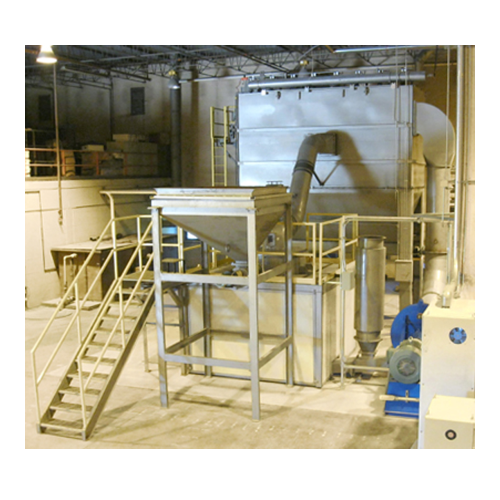
Ultrafine powder mill for coatings and pigments
Optimize your ultra-fine powder production with this precise grinding and ...
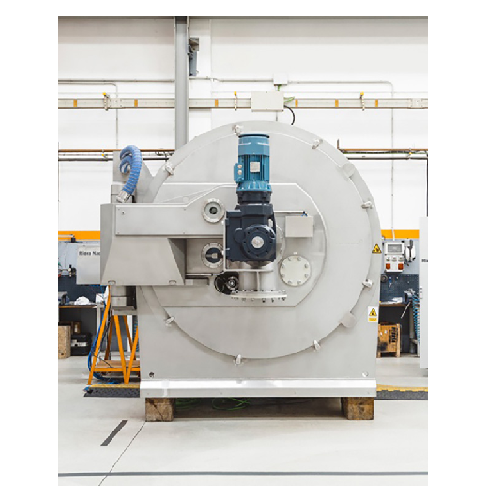
Horizontal batch centrifuge for chemical industry
Optimize your solid-liquid separation with a centrifuge designed for pr...
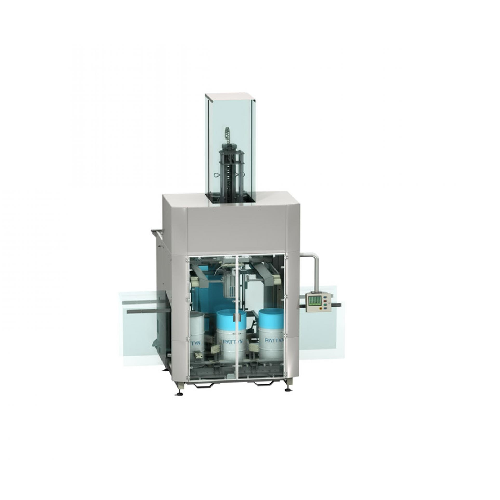
Bag inserter for drums
Effortlessly streamline your packaging process by automatically inserting custom-made bags into drums,...
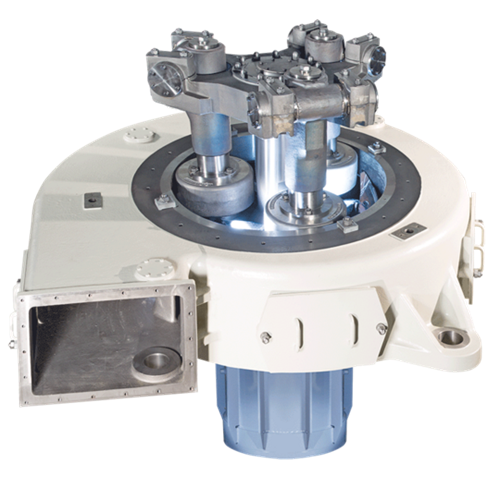
Pendulum mill for fine grinding and drying
Achieve efficient and precise grinding for soft to medium-hard materials while ...

Bag break station for pneumatic conveying systems
Efficiently manage powder feeding and dust control in your production l...
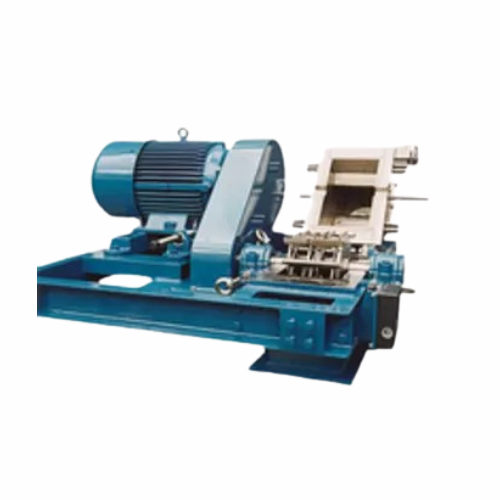
High-speed pulverizer for carbon black production
Achieve consistent particle size and optimal homogenization with high-s...
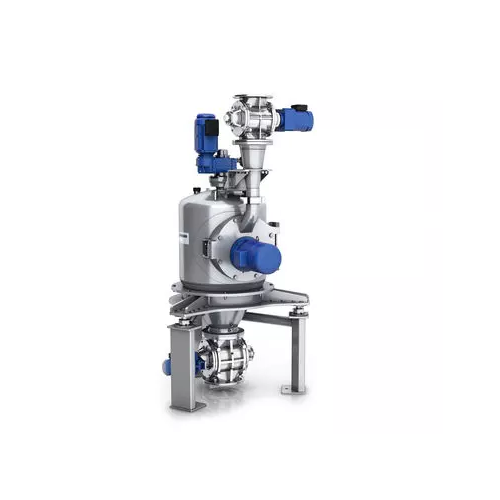
Fine impact mills for particle size reduction
Achieve precise particle size reduction with fine impact mills, essential fo...
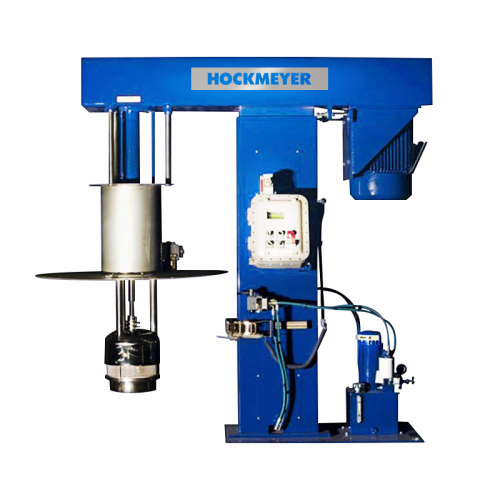
Immersion mill for particle reduction
Achieve streamlined particle size reduction and enhanced mixture homogeneity with imm...
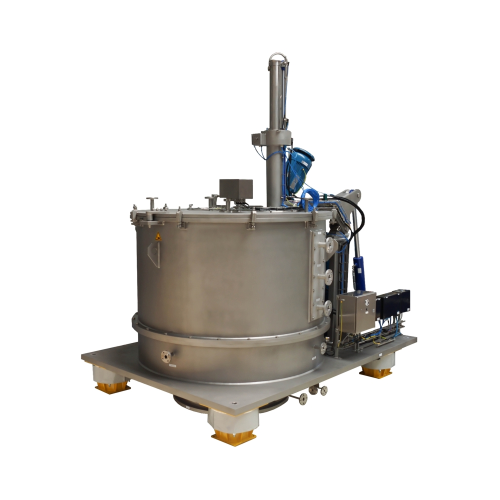
Vertical peeler centrifuge for chemical industry
Maximize throughput in continuous chemical processes with a versatile ver...
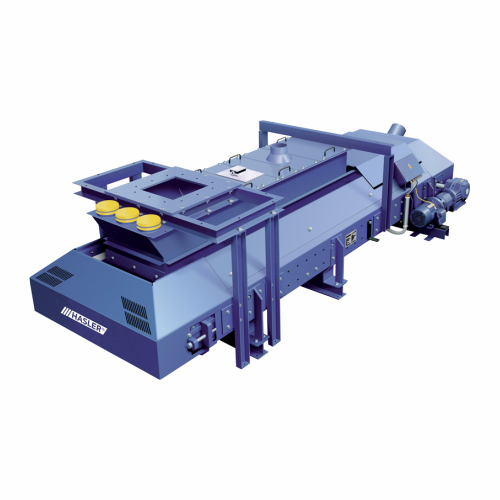
Powder belt feeder for accurate powder metering
Achieve precise powder metering with a specialized feeder that maintains d...
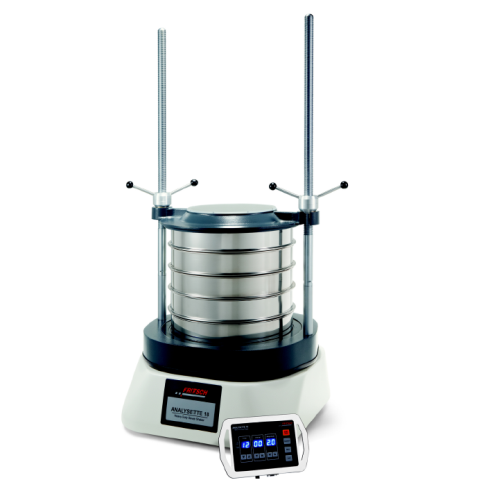
Heavy duty analytical sieve shaker for coarse-grained materials
Need precise particle size distribution for large minera...
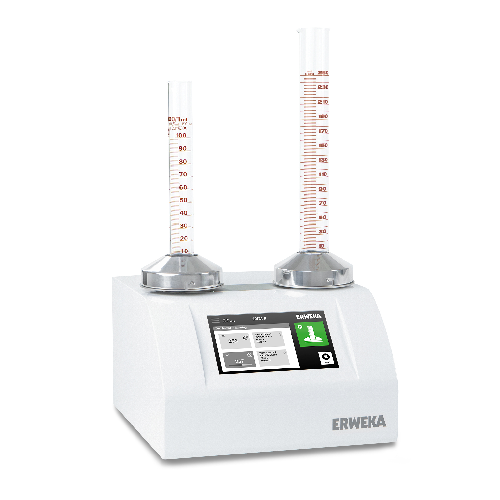
Tapped density tester for pharmaceutical and chemical powders
Ensure precise density measurements for pharmaceuticals an...
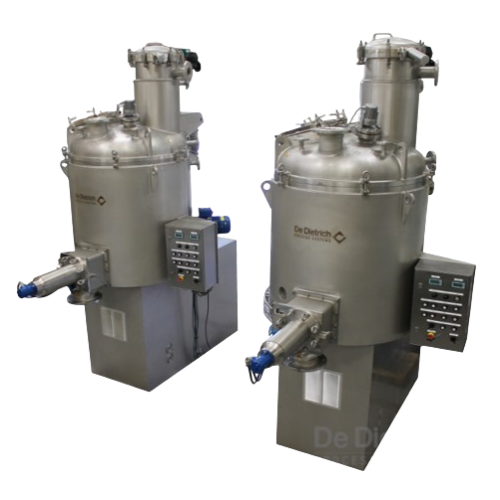
Industrial pan dryer for pharmaceuticals
For heat-sensitive powders and pastes requiring precise moisture levels, this pan ...

Twin-screw extruder for breakfast cereal
Optimize your production with a robust twin-screw extruder that accommodates high ...
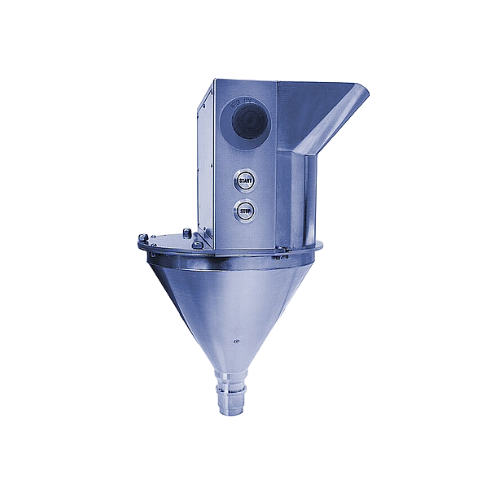
Vertical forced feeder for extruders
Enhance your extrusion process with a vertical forced feeder designed for precise dosi...
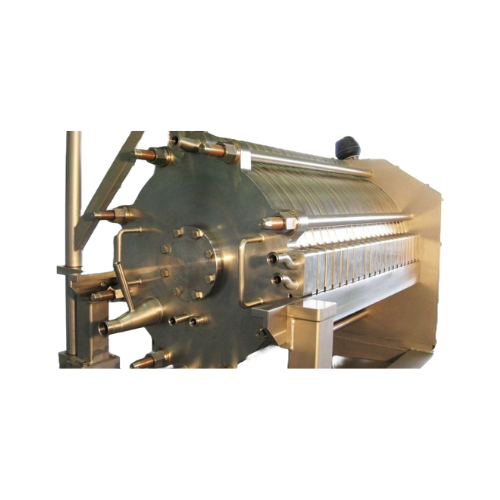
Crossflow filtration for microfine to nanoscale suspensions
Optimize your production line with advanced crossflow filtra...
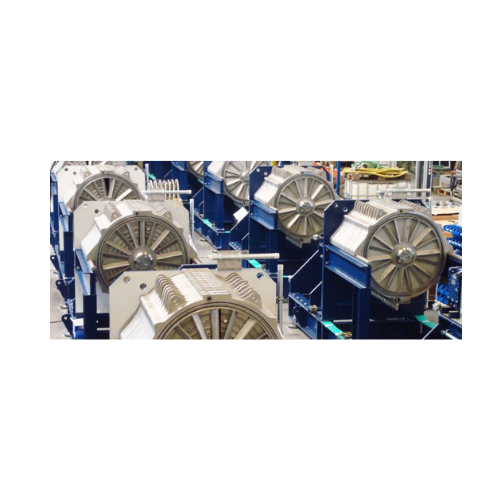
Crossflow filtration with sieve filter for difficult suspensions
Achieve precise separation and recovery in challenging ...
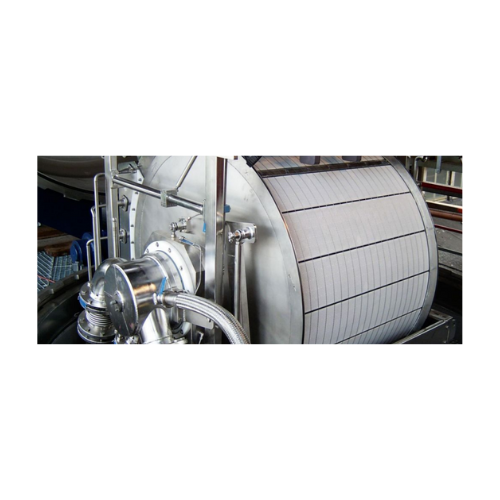
Pressure drum filter for fine-grained products
Achieve exceptional precision in fine particles processing with this pressu...
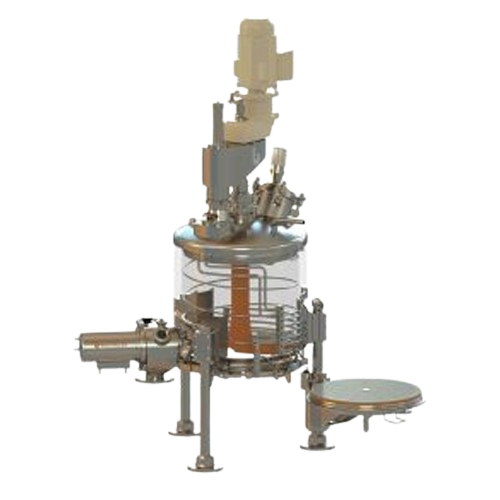
Agitated nutsche filter for solid-liquid separation
Ensure high-purity solid-liquid separation with minimized contaminati...
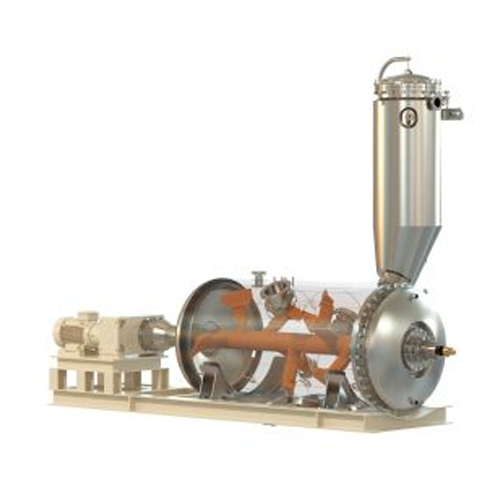
Horizontal vacuum paddle dryer for thermosensitive products
For high-viscosity products like active pharmaceuticals or p...
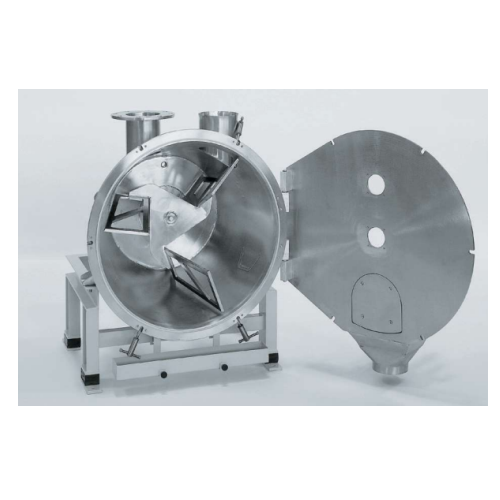
Feeding, dosing, weighing and mixing system for granulate
Achieve precise granulate mixing and rapid color changes with ...
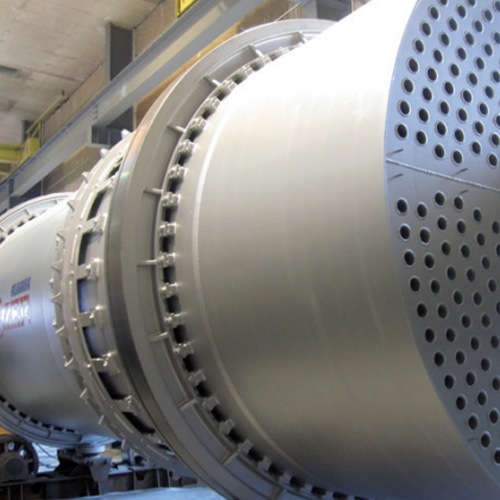
Indirect cooling drums for process heat recovery
Optimize your production by effectively cooling hot solids while recaptur...
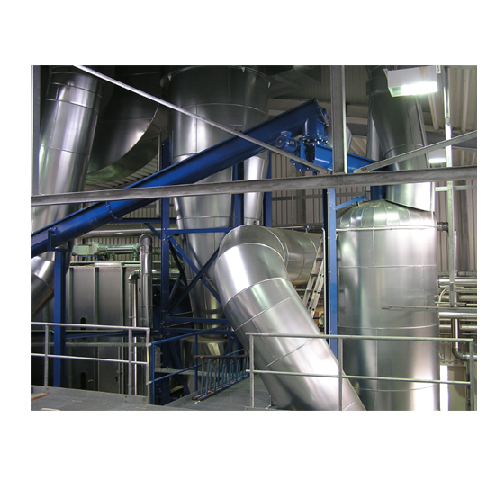
Flash dryer for high-moisture bulk materials
Tackle high-moisture challenges head-on with rapid drying solutions that effi...
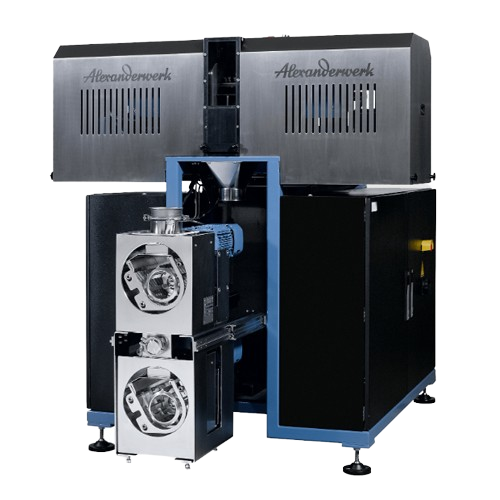
Industrial roller compaction for chemical applications
Enhance material flow and density with advanced roller compaction ...
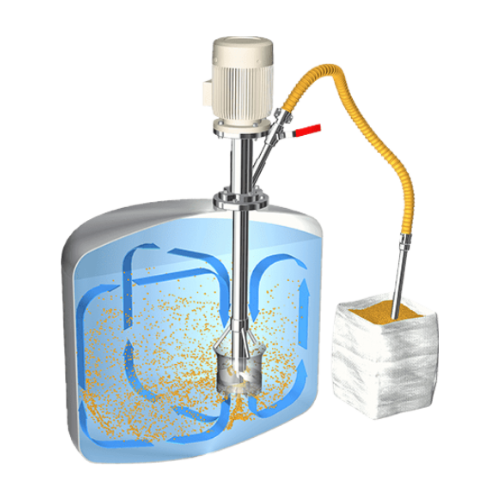
Low-dust powder induction mixer for liquids
Achieve dust-free induction and homogenization of powders in liquids with prec...
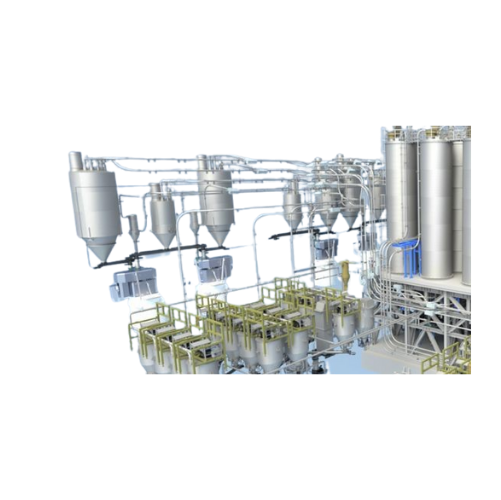
Dispersion paint production systems
Achieve 100% color accuracy and flexible production with our advanced system, ensuring ...
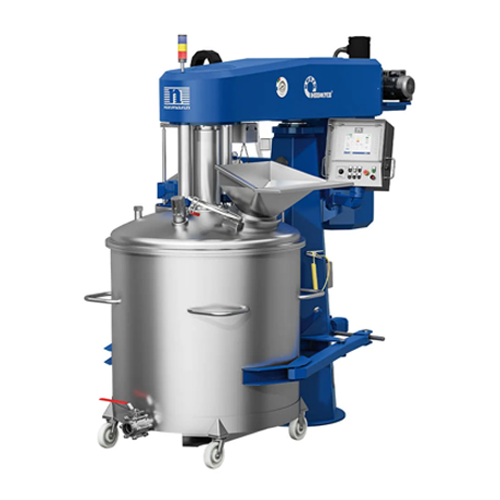
Vacuum dissolver for high-viscosity products
Elevate your production with precision mixing and deaeration, ideal for tackl...
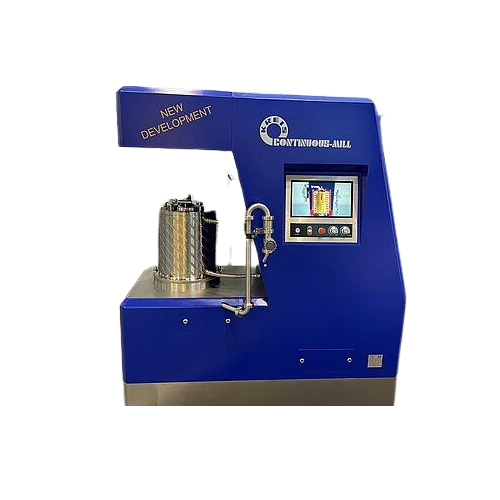
Continuous mill for nano range fine grinding
Achieve ultra-fine particle size in continuous processes, ensuring consistent...

Industrial basket mill for medium viscosity products
Achieve precise particle size reduction and rapid pigment dispersion...
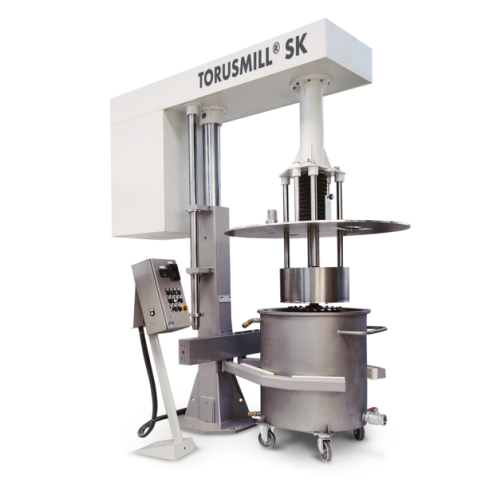
Explosion-proof basket mill for large scale production
Enhance your production line with an explosion-proof basket mill t...
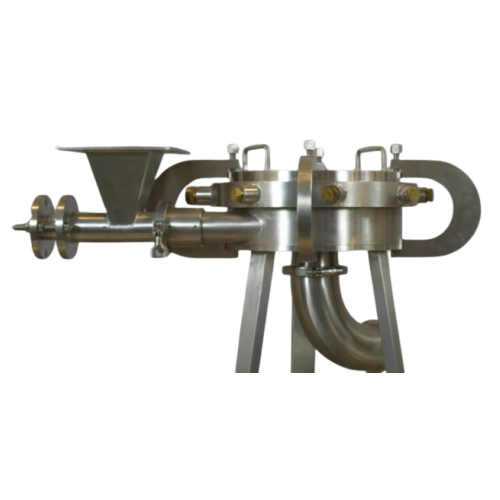
Jet milling system for super fine particle size reduction
Achieve ultra-fine particle sizes with precision milling techn...

Efficient grinding and drying mill
Transform your production line with a versatile mill that simultaneously grinds, dries, ...
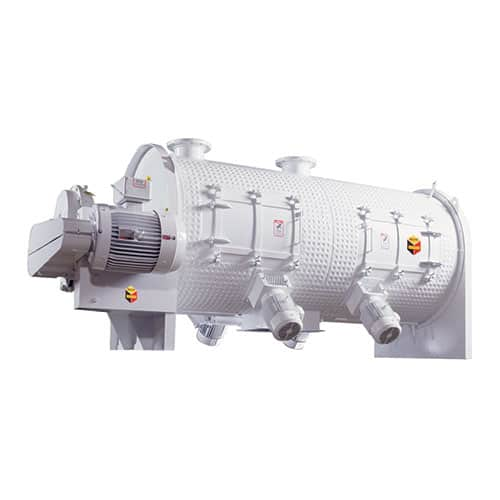
Industrial plow mixer for efficient solid and liquid mixing
Experience unparalleled mixing precision with high-speed plo...

Particle size reduction air conveying system
Achieve precise particle size reduction and contamination-free processing for...

Horizontal disc bead mill for liquid chemicals
Processing toxic chemicals requires high compliance with safety standards a...
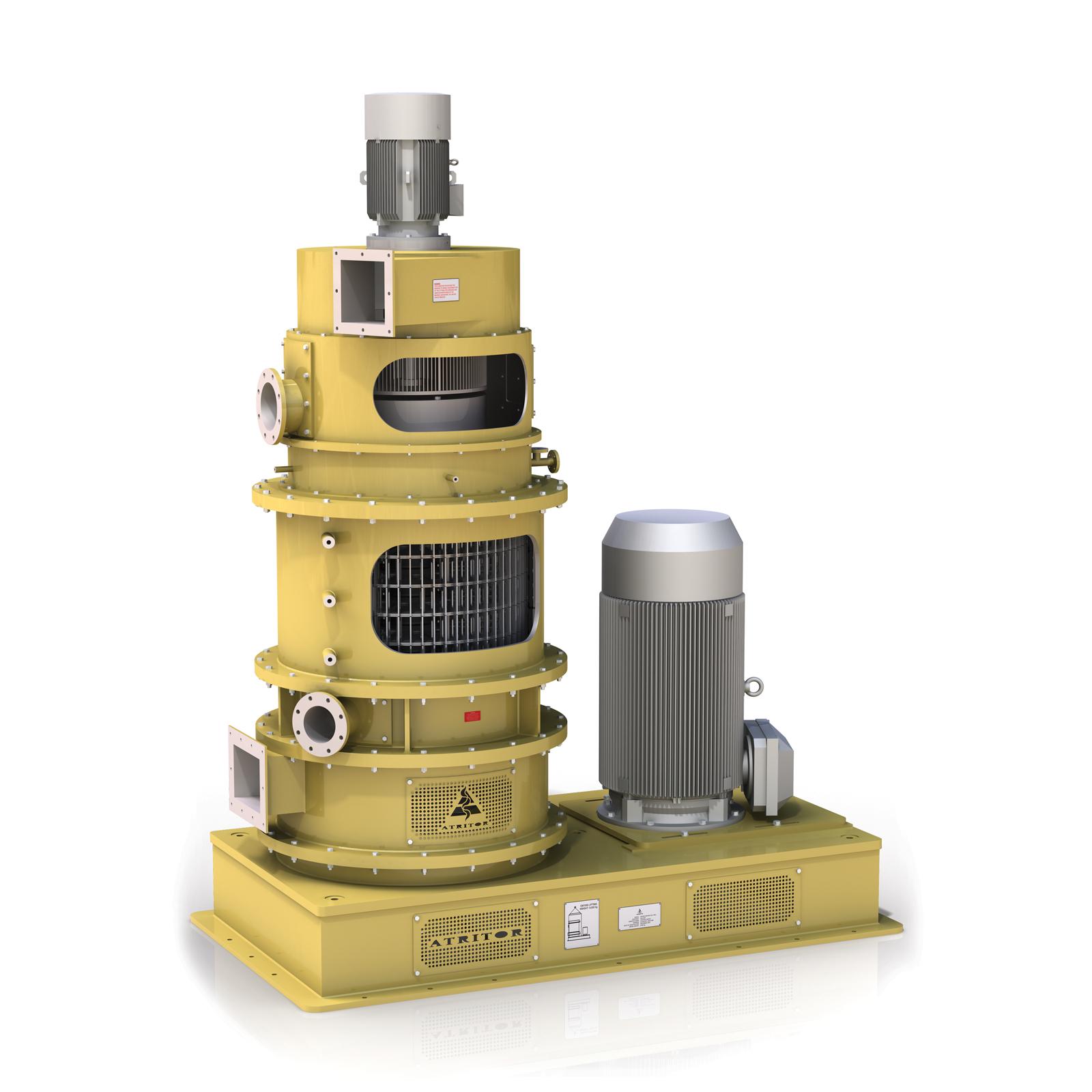
Milling and drying machine for fine powders
When you need to produce ultra-fine powders, the milling and drying process em...
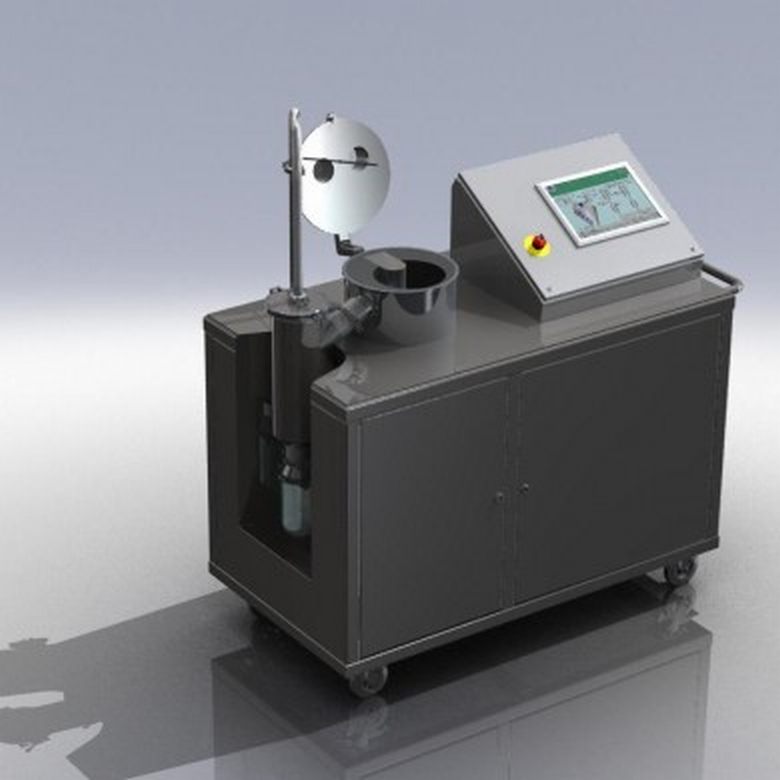
Laboratory scale active freeze dryer
The laboratory-scale active freeze-drying is used for dehydrating high-value products ...
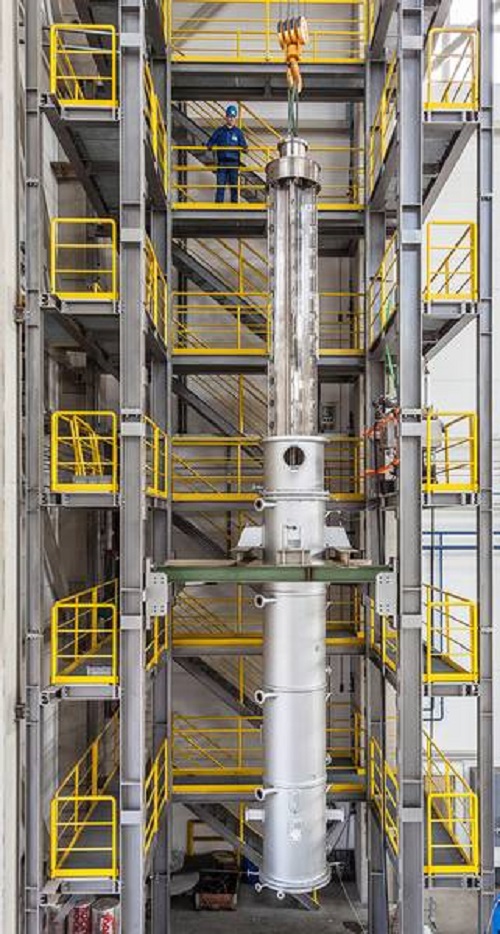
Thin film dryers
Dry dissolved or slurried crystallizing or amorphous products to a pourable powder.
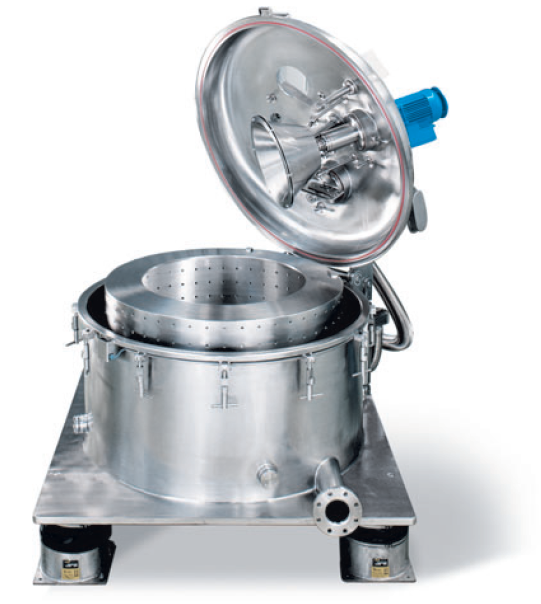
Vertical scraper centrifuges
Vertical Bottom discharge Centrifuges work discontinuously, discharging the solids to the botto...
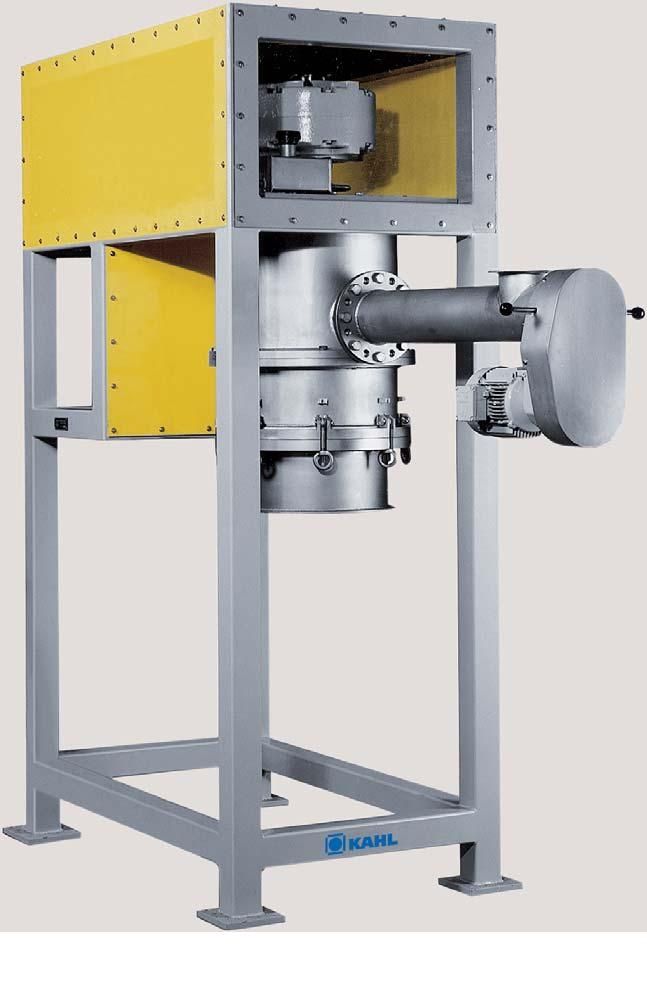
Pelleting press with overhead drive
Production of certain pelletized products requires working with output products of a pa...
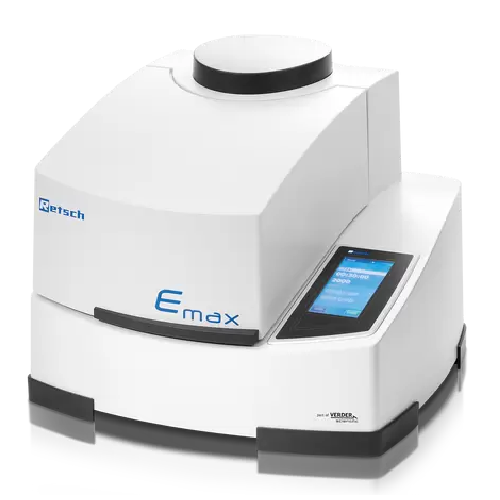
High energy ball mill for ultrafine grinding
Achieve nanoscale precision and unmatched particle uniformity with high-energ...
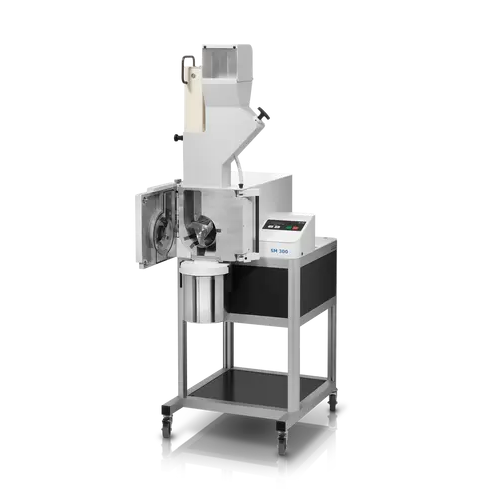
High-torque cutting mill for tough and fibrous materials
Tackle the toughest materials and ensure consistent particle siz...
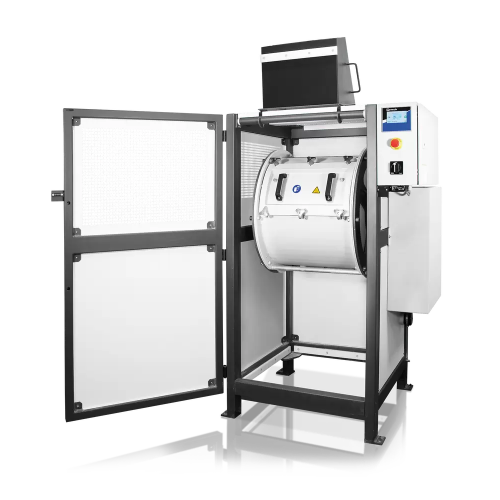
Laboratory drum mill for large sample volumes
Efficiently process large volumes of diverse materials into precise particle...
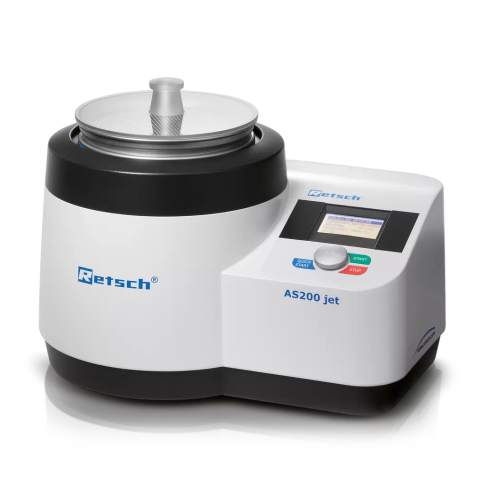
Air jet sieving system for powdered materials
Optimize particle distribution with precision air jet sieving, designed to e...
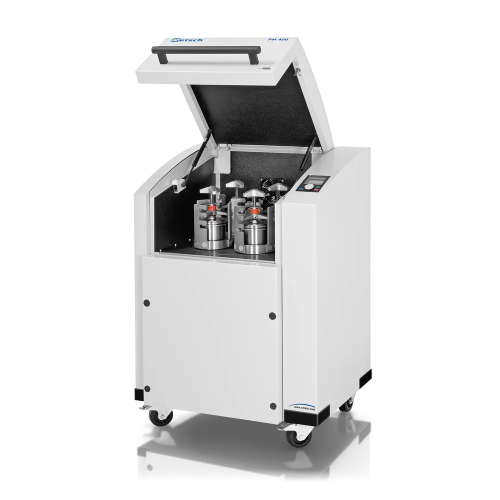
Planetary ball mill for high throughput grinding
For precise material engineering, achieve efficient size reduction, homog...
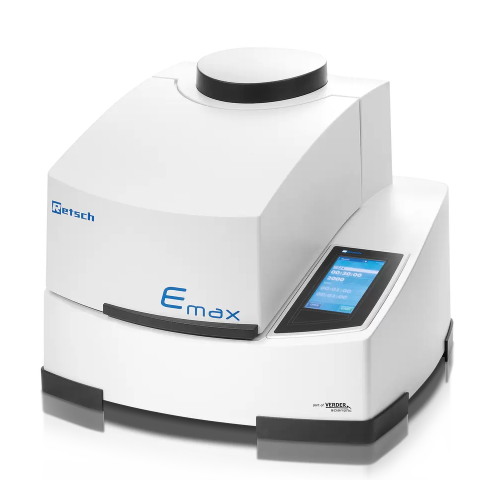
High energy untra fine ball mill
Achieve ultra-fine particle sizes rapidly with this high energy milling solution, designed ...
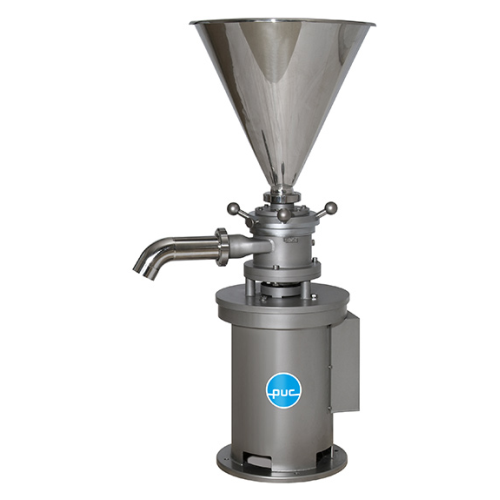
Vertical colloid mill for emulsifying and homogenizing
Optimize your production line with precise particle size reduction...
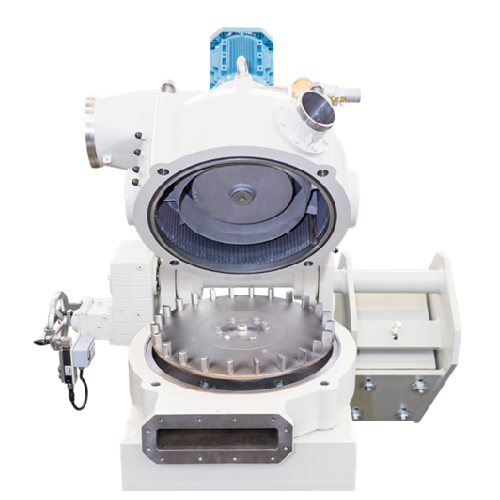
Impact classifier mill for fine grinding of brittle materials
Achieve precise particle size distribution with advanced g...
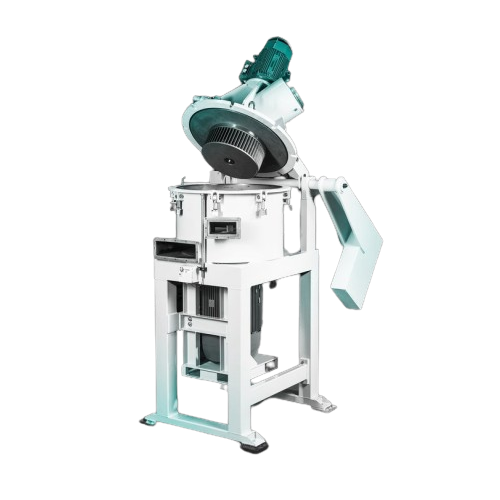
Energy-efficient impact classifier for superfine grinding
Achieve precise superfine grinding with energy efficiency, per...
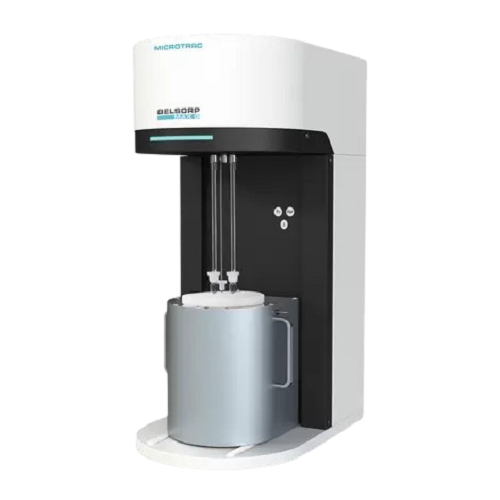
Specific surface area & pore size analyzer for materials
Achieve unparalleled precision in material characterization by m...
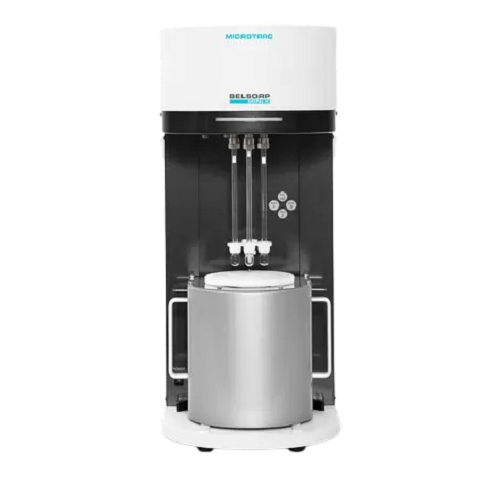
Pore size distribution analyzer
Optimize your material analysis with a system that delivers precise pore size distribution a...

Laser diffraction particle size analyzer
Achieve precise particle size analysis with laser diffraction technology, ensuring...
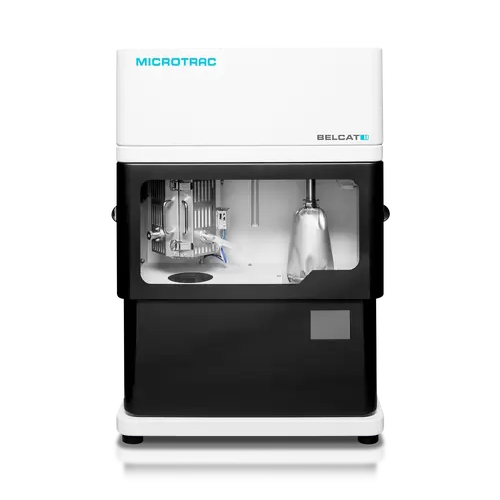
Catalyst characterization analyzer
Achieve precise catalyst characterization and optimization with advanced techniques like...
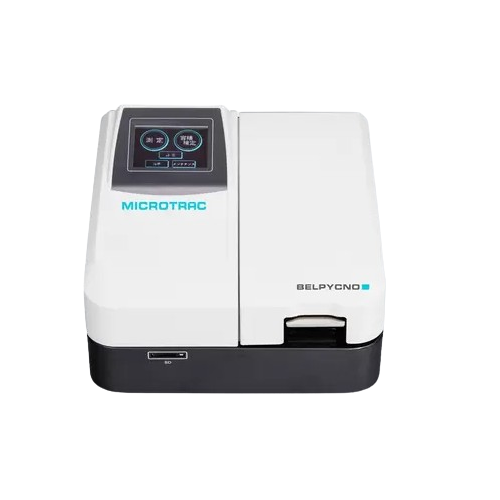
Gas pycnometer for true density measurement of solids and powders
Achieve highly precise density measurements of solid ...
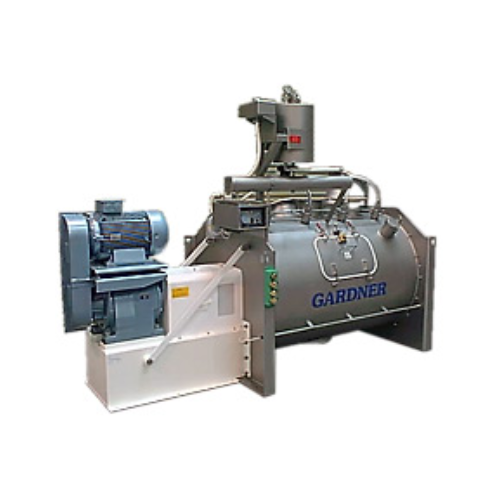
High shear plough mixer for powders, granules, and pastes
Achieve rapid and efficient blending with high shear mixers de...
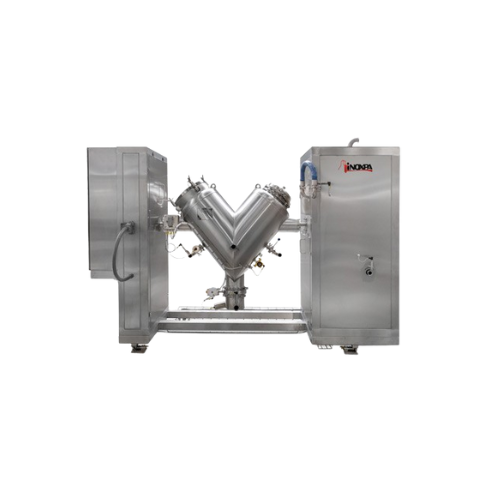
Industrial v-type solids blender for homogeneous mixture
Achieve precise blending of diverse powders and solids using the...
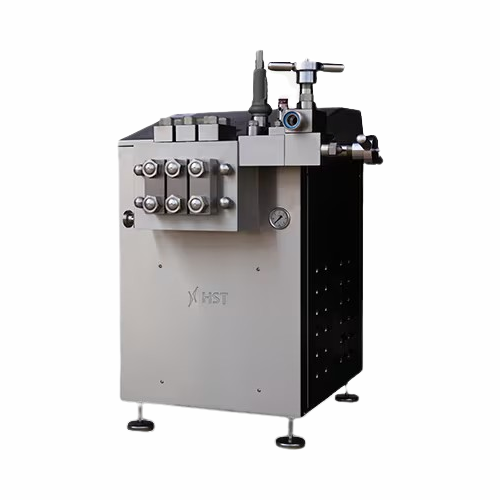
Homogenizer for high-pressure homogenization
Optimize your production with high-pressure homogenization, essential for ach...
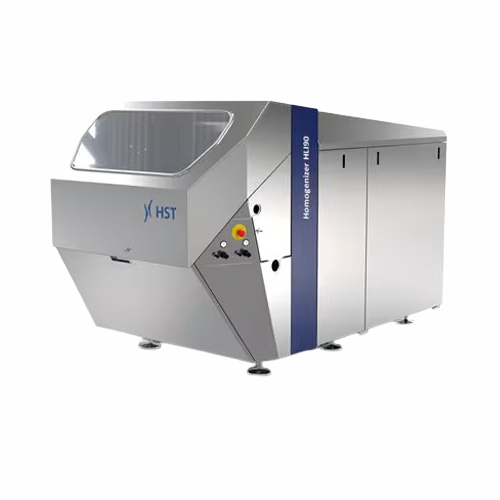
High-pressure homogenizer for food and pharmaceuticals
Achieve unparalleled consistency and stability in emulsions and di...
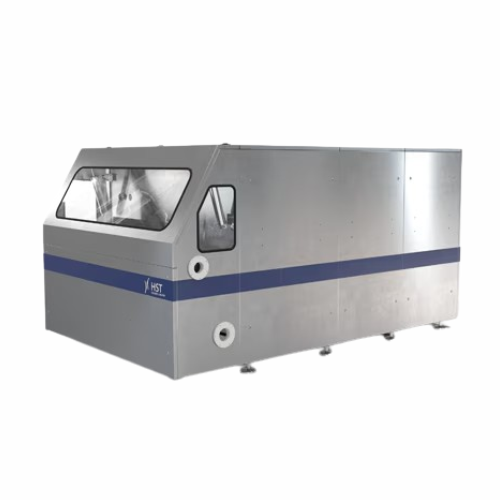
Homogenizers for high-pressure applications
Achieve unparalleled product consistency and stability with precision-engineer...
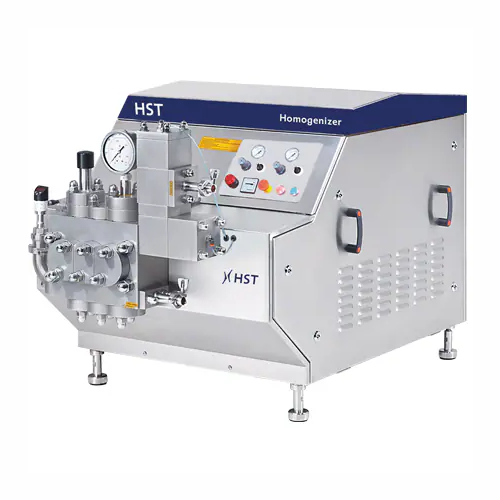
Industrial homogenizer for food and pharmaceutical applications
Ensure product consistency and stability with high-press...
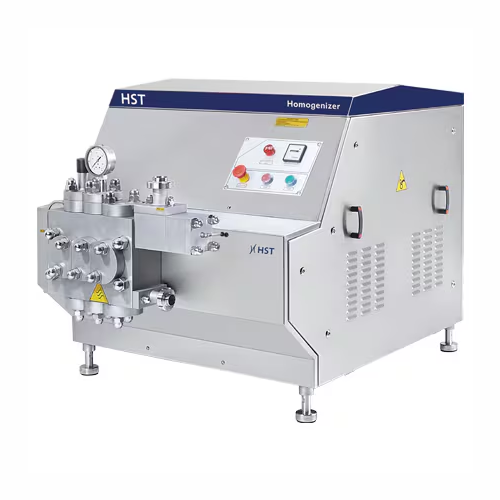
High-pressure homogenizers for dairy and food products
Achieve consistent texture and stability in your liquid products w...
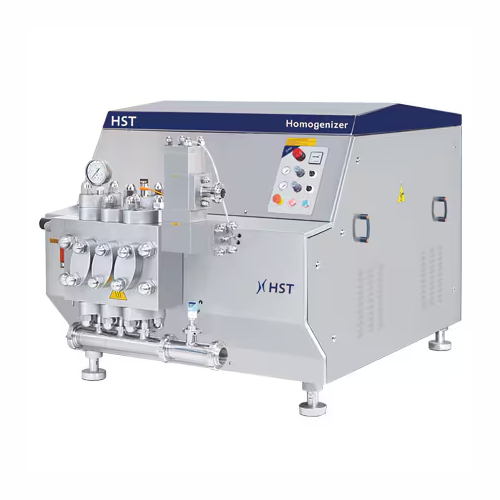
High-pressure homogenizers for dairy and beverage industries
Achieve precise emulsion stability and consistent particle ...
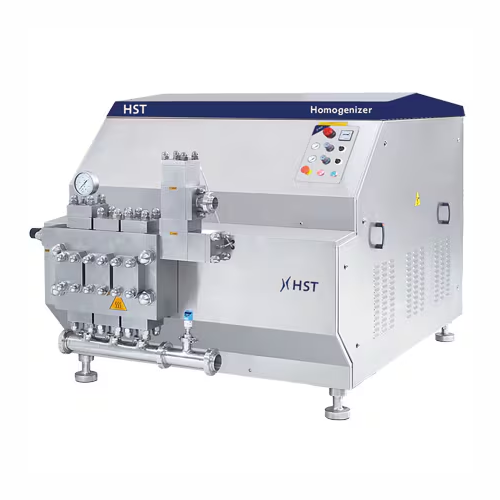
High-pressure homogenizers for dairy and juice processing
Ensure superior texture and stability in your liquid formulati...
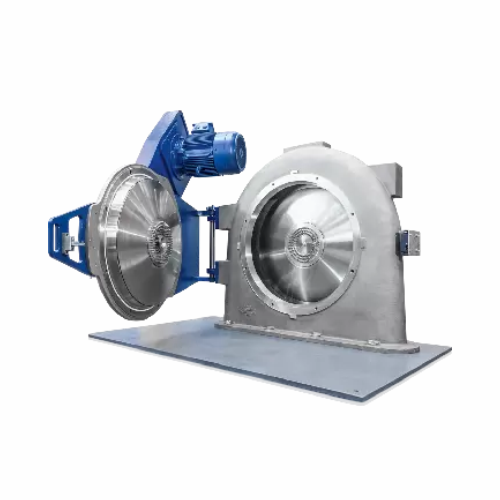
Industrial powder grinder
Achieve precise particle size reduction and classification with advanced equipment designed for co...
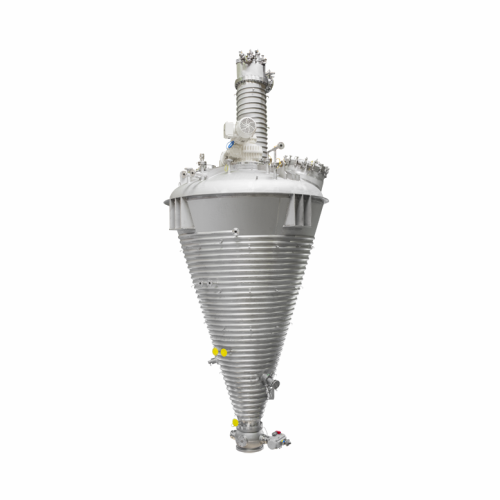
Vacuum dryers for powders and bulk solids
Achieve precise drying and mixing of sensitive materials with advanced vacuum te...
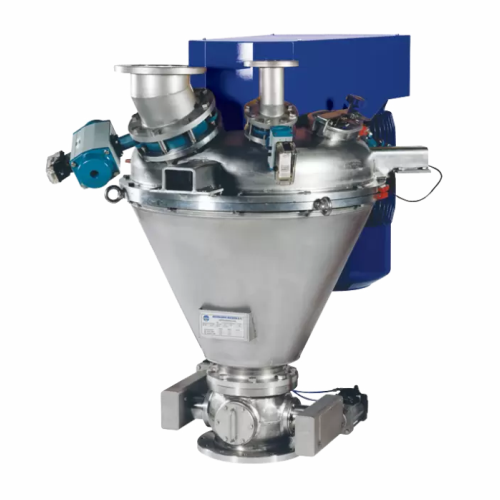
High shear impact mixer for agglomeration and dispersion
Achieve precise homogeneity and efficient agglomeration with a h...
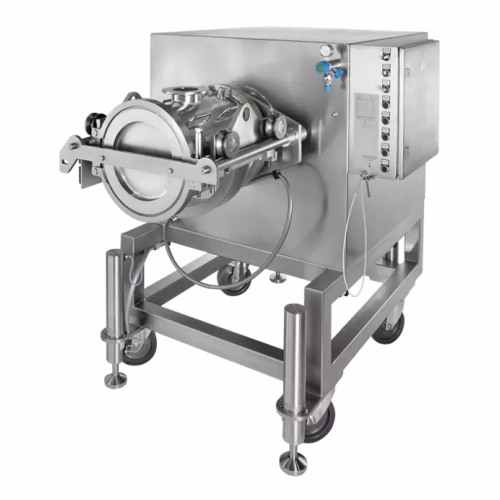
Super high shear mixer for nano to micron powders
Achieve high-precision mixing and surface treatment of nano to micron-s...
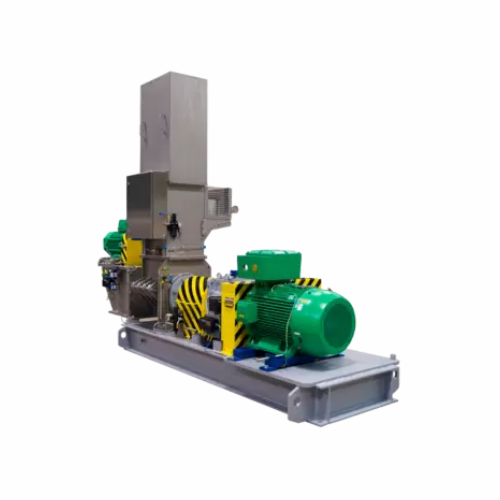
Choppers and disintegrators for industrial size reduction
Enhance your production efficiency by mastering size reduction...
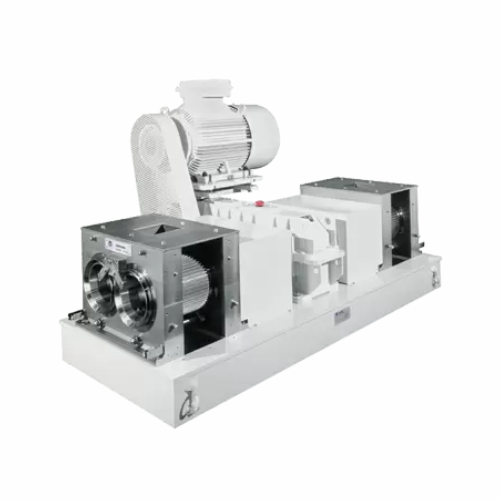
Compactors and granulators for powdery products
Transform loose powders into dense, free-flowing granules that enhance han...
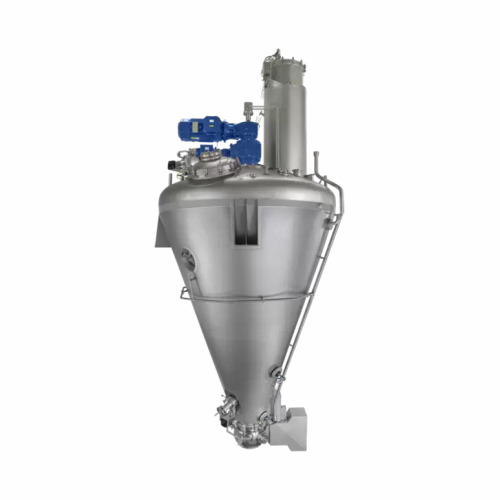
Vacuum dryer for powders and granules
Achieve precise moisture control for sensitive materials with a versatile vacuum dryi...
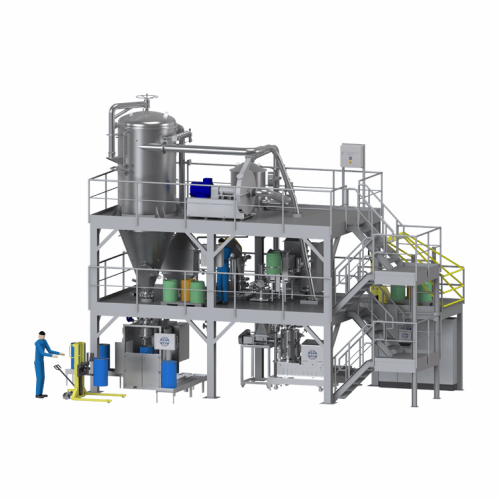
Drying systems for powders and bulk solids
Enhance your production line with precise control of moisture content in powder...
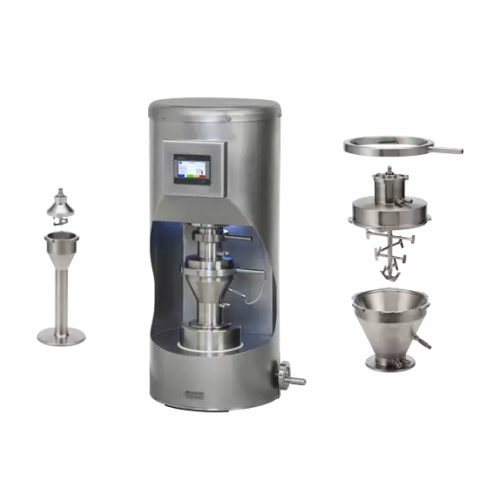
Lab mixer for powder formulations
Achieve precise particle mixing and coating with this stand-alone high-shear lab mixer, d...
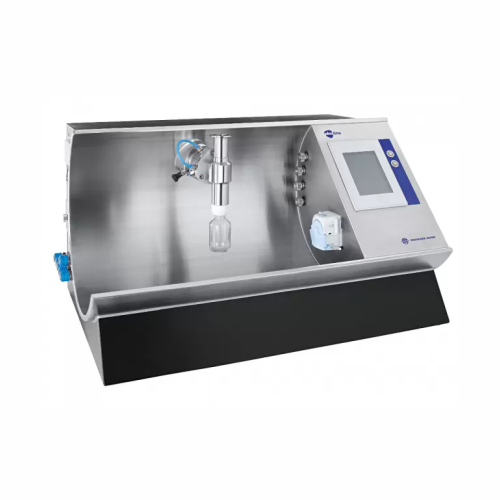
Lab-scale powder processing system
Achieve precise control in ultra-small batch processing with a versatile modular system,...
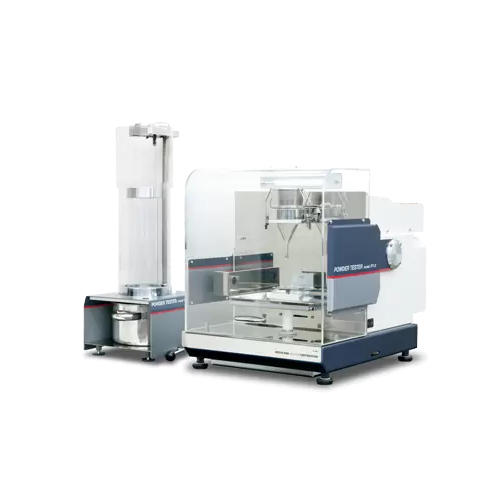
Powder characteristic evaluation
Ensure precise powder analysis and testing in your laboratory to optimize production qualit...
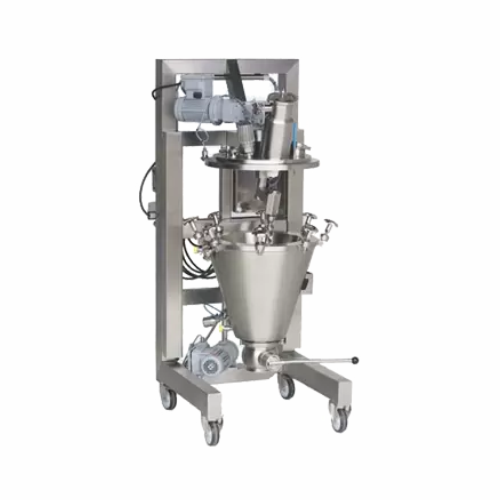
Laboratory vacuum dryer for heat-sensitive materials
Optimize moisture control in heat-sensitive materials with precise a...
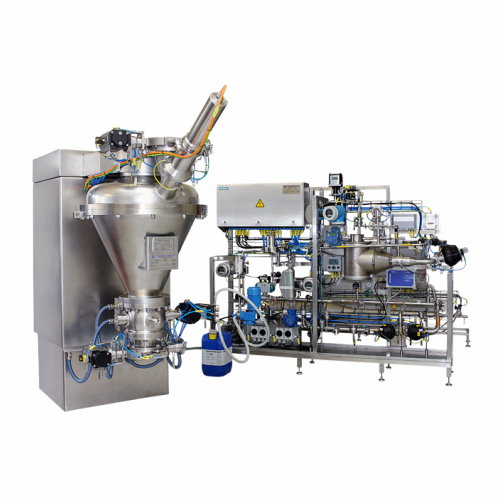
Cip/sip cleaning for solids processing systems
Ensure seamless transitions and maintain hygienic production environments w...
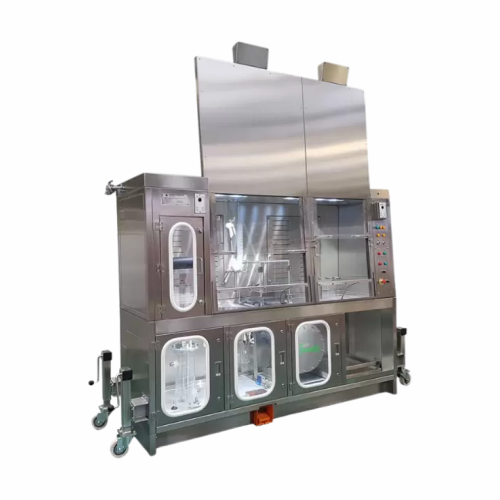
Containment solutions for hazardous material processing
Ensure safe and efficient processing of hazardous materials with ...
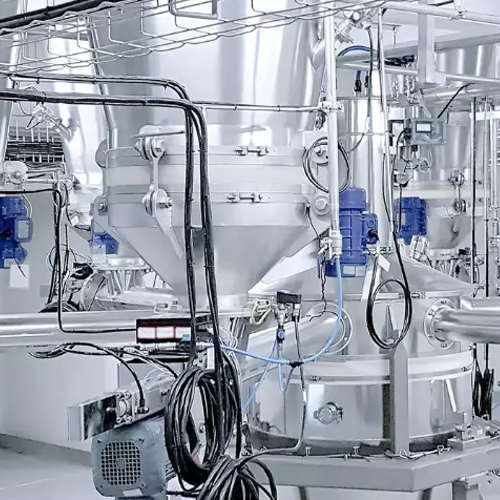
Conical screw mixer for powder blending
Achieve precise and homogeneous blending with the conical screw mixer, ensuring uni...
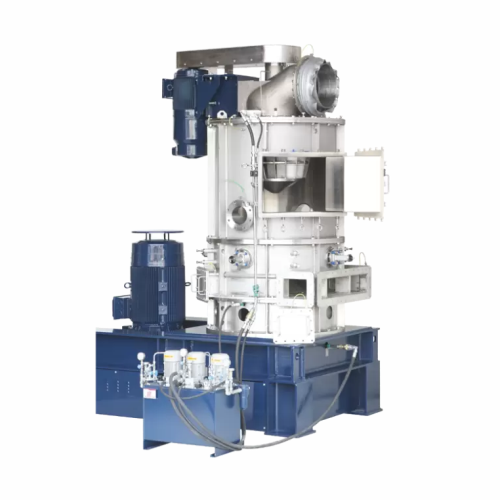
Ultra-fine powder flash drying system
Achieve rapid moisture removal and particle refinement with this integrated system, d...
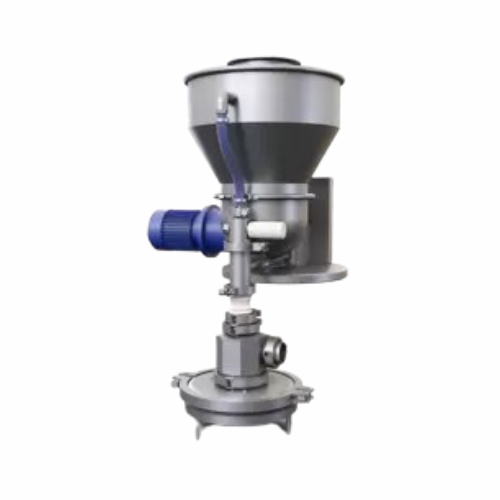
Ultra-fine grinding jet mill for coarse and fibrous materials
Effortlessly achieve ultra-fine particle sizes in coarse a...

Ultra-fine powder grinding with jet mills
Achieve unparalleled fineness and purity in powder production with cutting-edge ...
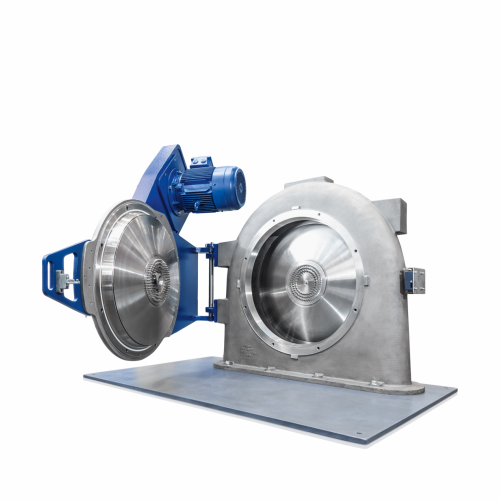
Pin mill for fine grinding of sticky materials
Achieve ultra-fine grinding of challenging materials with high speed and pr...
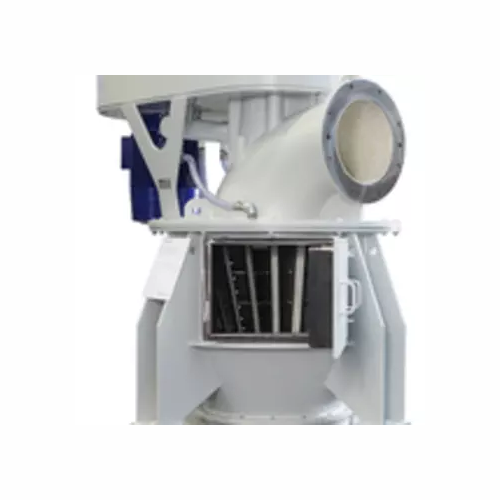
Ultrafine classifier for precise particle separation
Gain precise control over particle size with this ultrafine classifi...
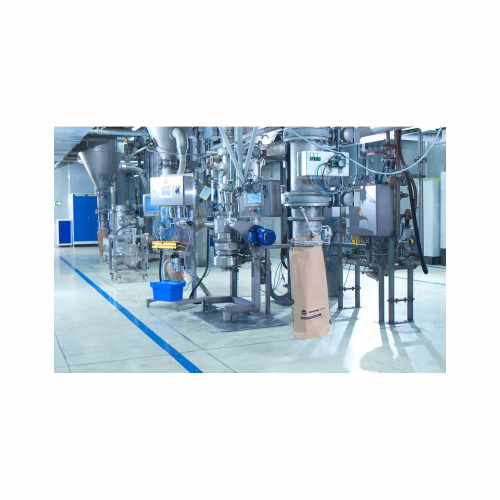
Air classifier for classifying industrial minerals
Achieve precise particle separation with advanced air classifiers, par...
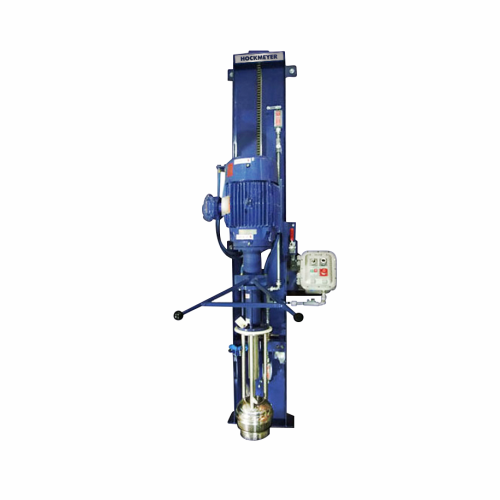
Immersion mill for pail and drum-sized batches
Streamline your production with a versatile solution that efficiently handl...
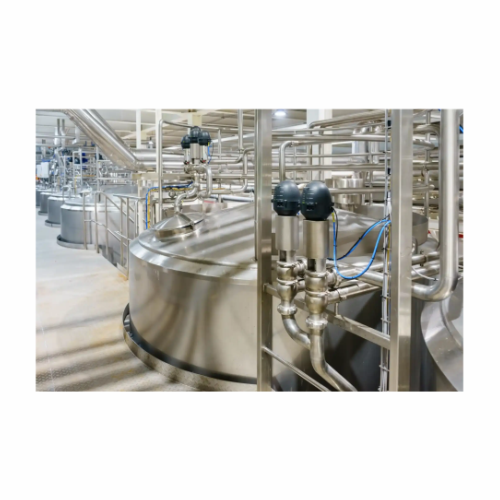
Filtration system for Cip cleaning in food production
Optimize your cleaning processes with a state-of-the-art filtration...
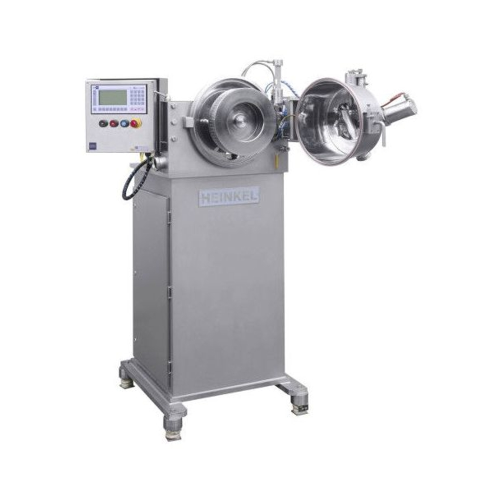
Horizontal pilot plant centrifuge for chemical processing
Enhance your R&D and pilot-scale processes with a centrif...
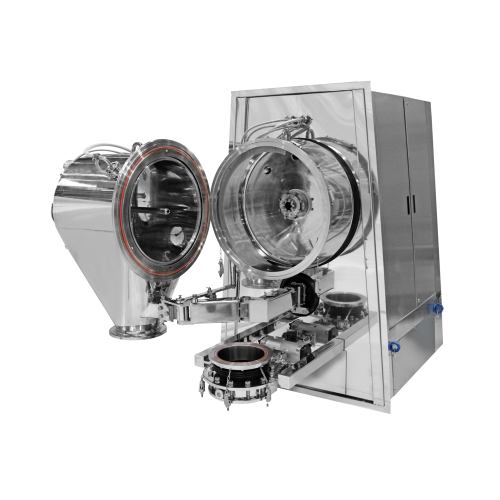
Inverting filter centrifuge for difficult-to-filter products
Designed for challenging filtration tasks, this centrifuge ...
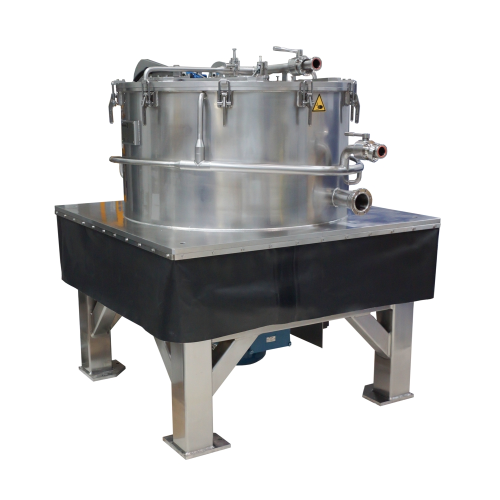
Top discharge centrifuge for pharmaceutical production
Optimize your product yield and quality with precise filtration an...
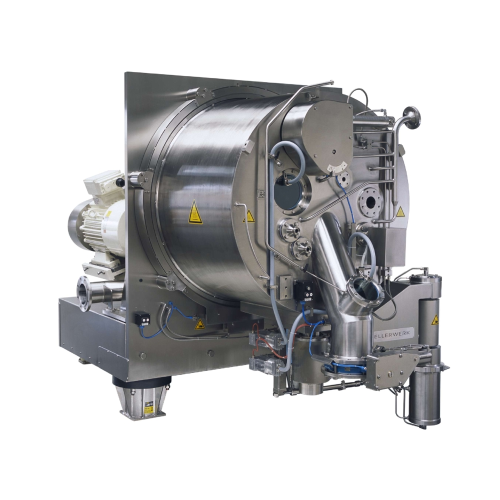
Pharmaceutical horizontal peeler centrifuge
Optimize product consistency and purity with precise separation and filtration...
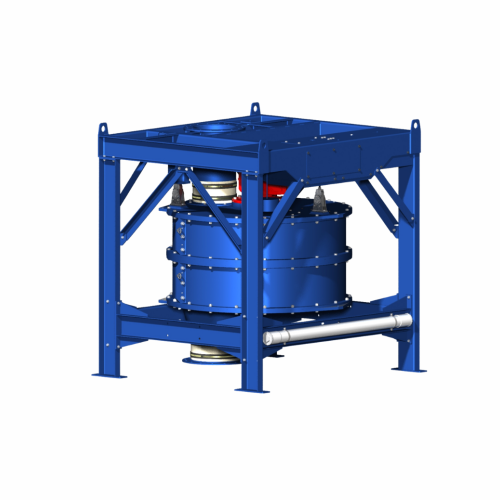
Double-stage rotary weigh feeder for precise powder dosing
Ensure consistent dosing and precise weighing of challenging ...
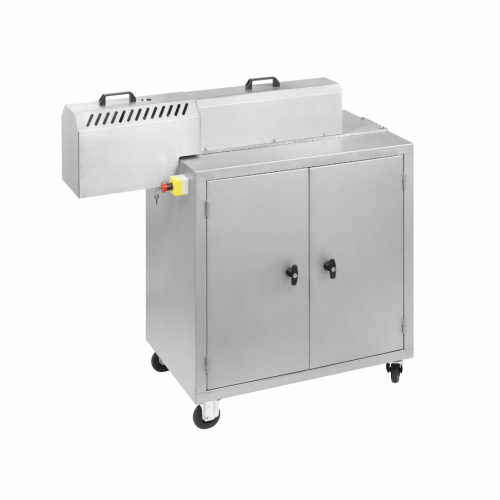
High-viscosity continuous industrial kneader for small volumes
Achieve consistent high-viscosity material processing wit...
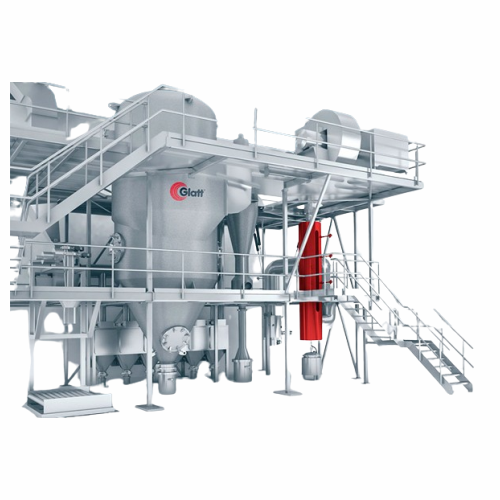
Powder synthesis reactors for nanometer and micrometer particles
Achieve precise particle control and enhance material p...
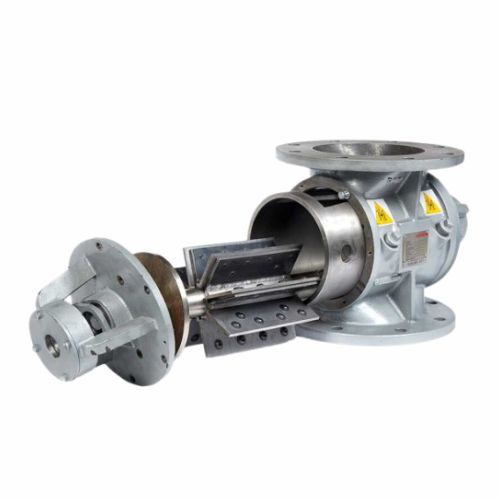
Pneumatic dilute phase conveying system for powders and bulk materials
Optimize your production line’s efficiency...
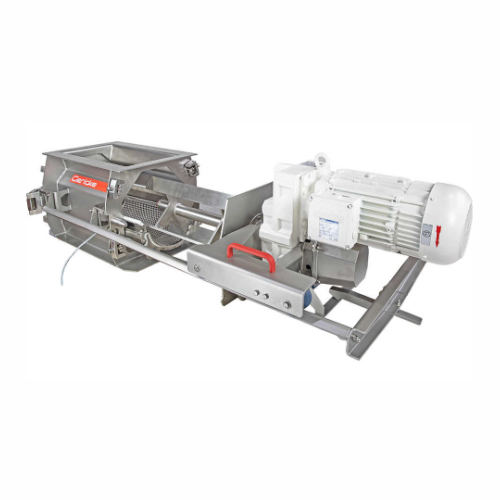
Deagglomerator for consistent particle size reduction
Struggling with inconsistent particle sizes or unwanted lumps in yo...
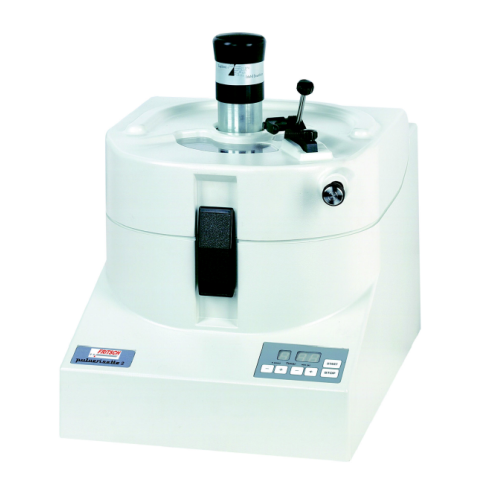
Laboratory mortar grinder for wet and dry grinding
Ensure precise blending of fine powders, pastes, and creams with contr...
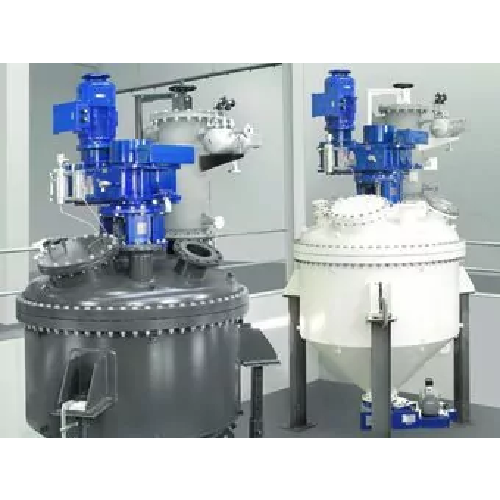
Vertical pharma vacuum blender for bulk solids
Optimize your mixing of fine chemicals and pharmaceutical powders with high...
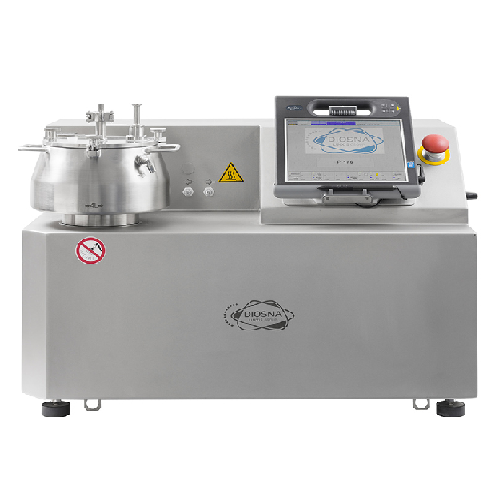
Compact laboratory mixer for high-shear granulation
Streamline your R&D processes with advanced mixing and granulati...
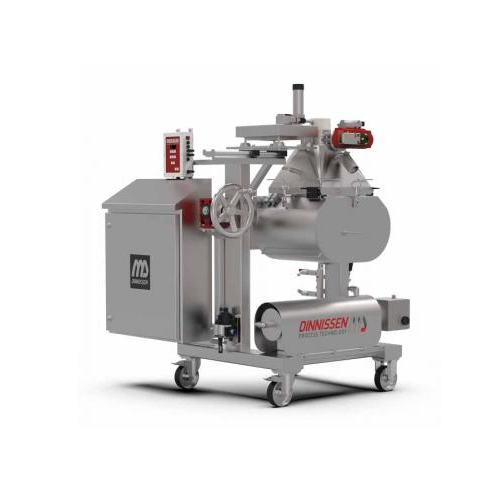
R&d mixer for small batch experimentation
Perfect your mixing techniques swiftly with precision-controlled small batch exp...
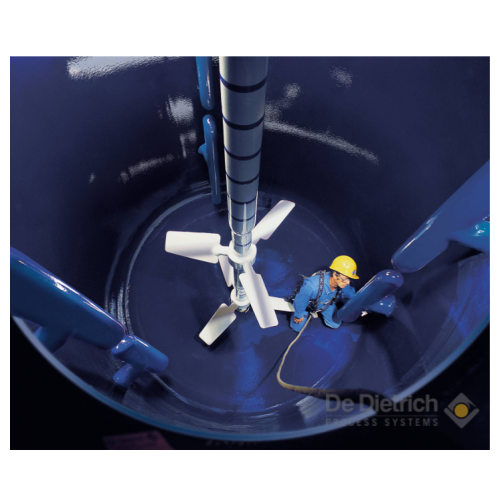
Glass-lined reactor for enhanced mixing performance
Optimize your chemical processes with a reactor that enhances mixing ...
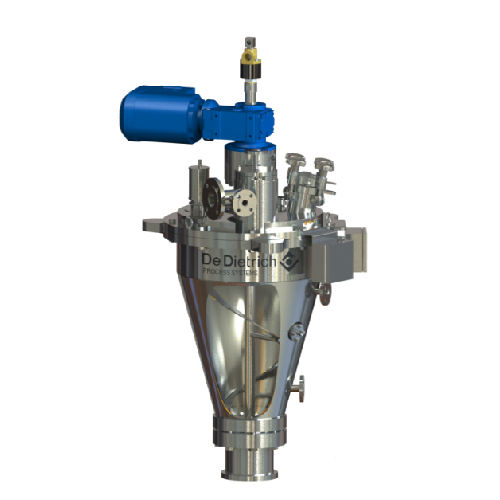
Vacuum drying for heat-sensitive products
Ensure moisture-sensitive formulations are dried efficiently without compromisin...

Corrosion-resistant shell and tube heat exchangers for pharmaceuticals
Ensure efficient thermal management in high-puri...
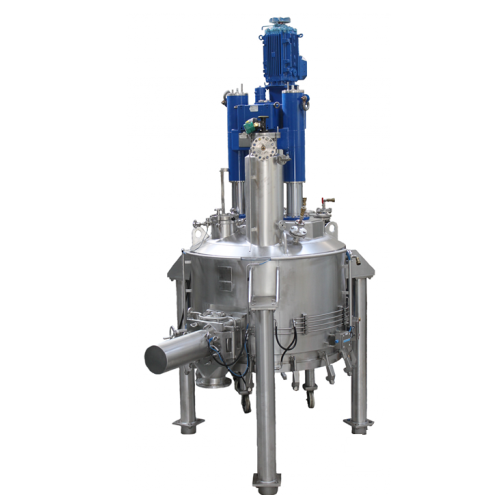
Agitated nutsche filter and filter-dryer for pharmaceuticals
Ensure precise filtration, washing, and drying of sensitive...
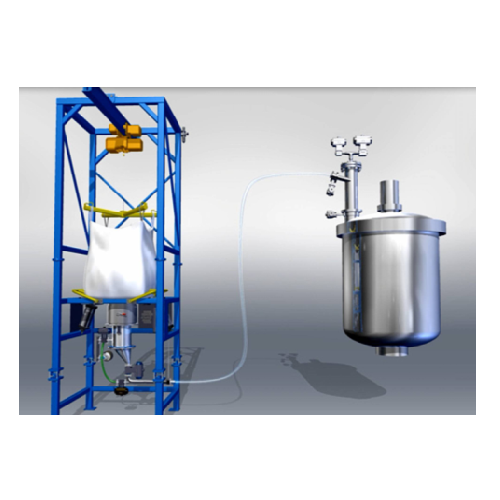
Big bag emptying station for powder handling
Ensure safe and efficient powder discharge with precision containment, adapta...

Condensation and separation unit for solvent handling
Enhance solvent management and VOC recovery with this compact conde...
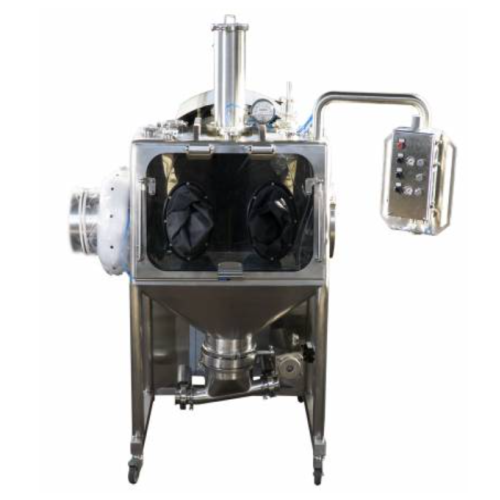
Powder handling drum dock station
Ensure safe and efficient powder transfers with high containment levels, minimizing opera...
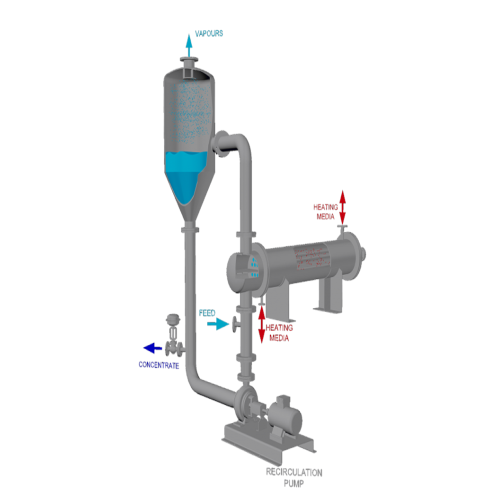
Force circulation evaporator for high viscous products
Optimize energy efficiency and manage challenging liquid compositi...
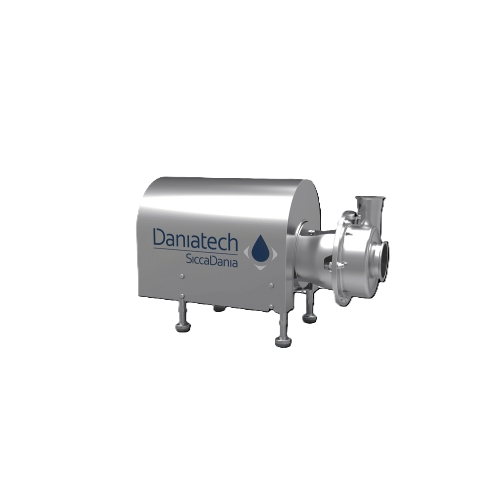
Inline high shear mixing unit for low to medium viscosity products
Achieve precise emulsification and size-reduction wi...
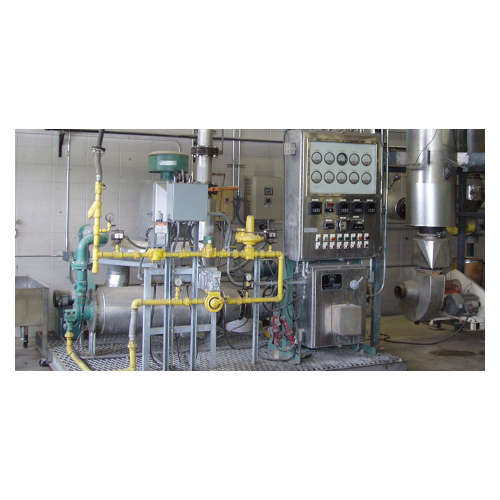
Vertical flash dryer for industrial drying applications
Optimize your production line with an energy-efficient vertical f...
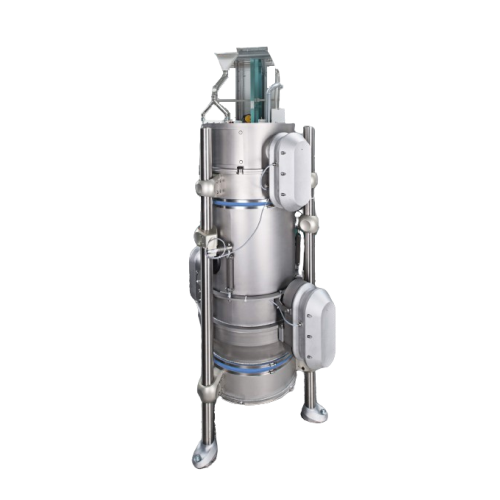
Advanced superheated steam drying solution
Harness the power of consistent drying technology to achieve optimal moisture c...

Four-roller and eight-roller mill for grains
Optimize your grain processing with precise roller configurations, ensuring c...
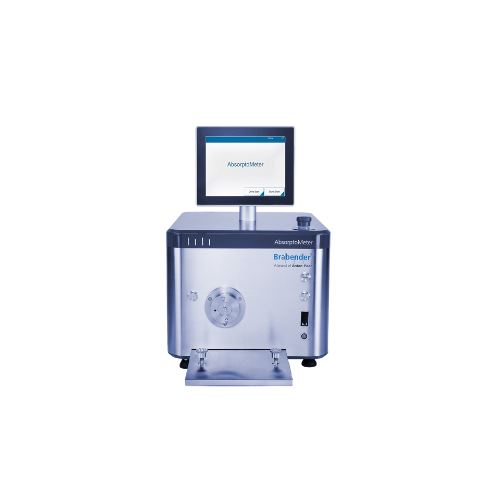
Oil absorption testing instrument for carbon black and silica
Accurately measure oil absorption in powders to enhance fo...
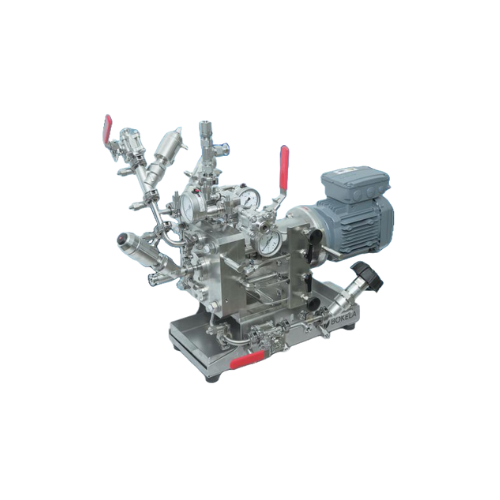
Laboratory crossflow filtration test system
Efficiently test and determine optimal filtration parameters with this portabl...
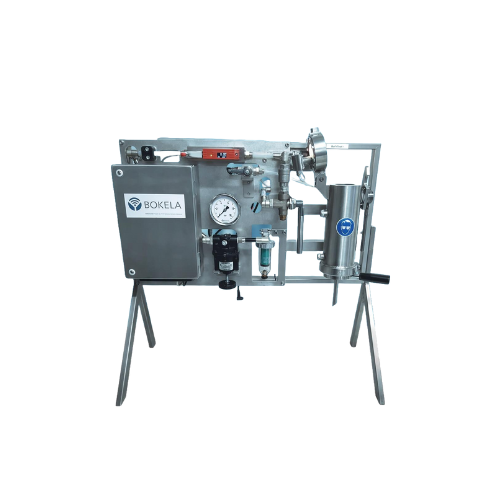
Compact filtration device for laboratory and field use
Achieve precise filtration with minimal sample sizes for rapid ana...
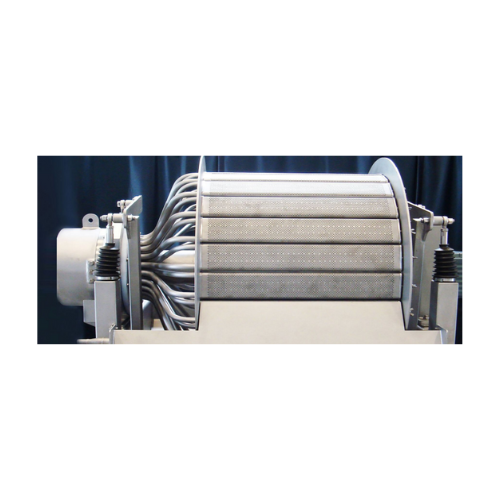
Industrial drum vacuum filter for filtration and washing
Efficiently manage filtration, washing, and dewatering tasks wit...
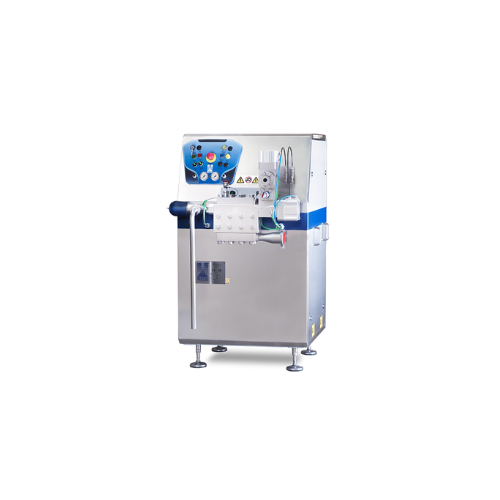
Industrial homogenizer for high pressure applications
Achieve consistent product texture and stability for your emulsions...
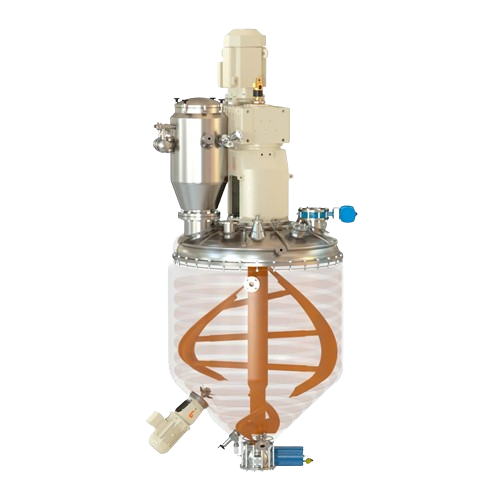
Vertical ribbon vacuum dryer for thermosensitive products
Achieve optimal drying of thermo-sensitive materials like powd...
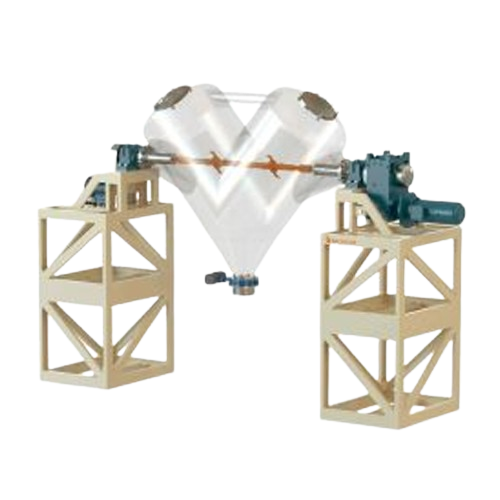
V shape mixer for solids and powders
Ideal for preserving the delicate structures of fragile materials, this mixer ensures ...
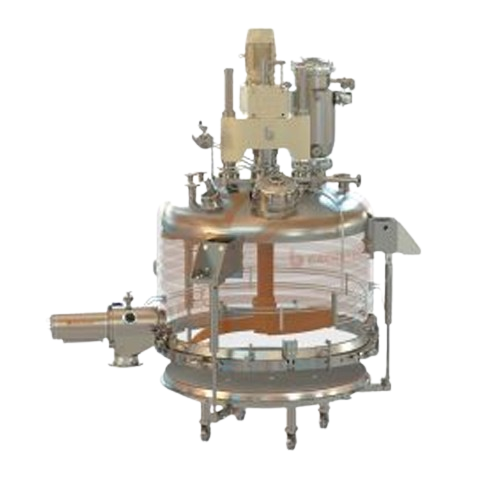
Agitated nutsche filter dryer for solid-liquid separation
Achieve high-purity solid-liquid separation with optimized thr...
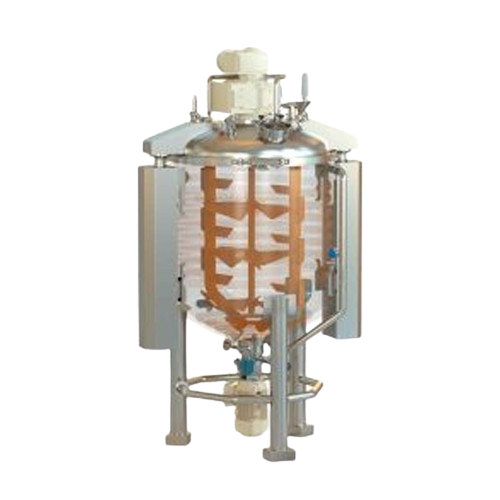
Industrial mixer for liquid and viscous products
Achieve precise mixing and homogenization of high-viscosity liquids and s...
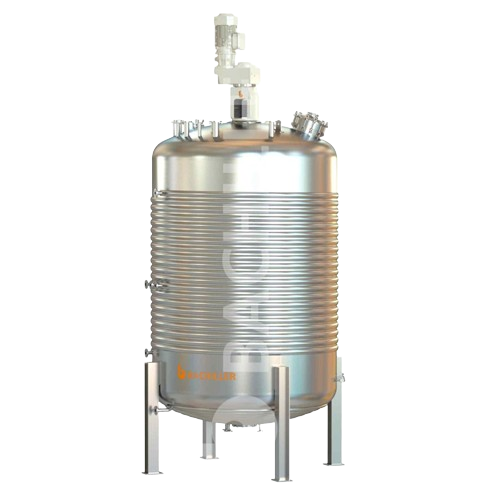
Stirred reactors with heating and cooling system
Optimize your production line with versatile stirred reactors, designed t...
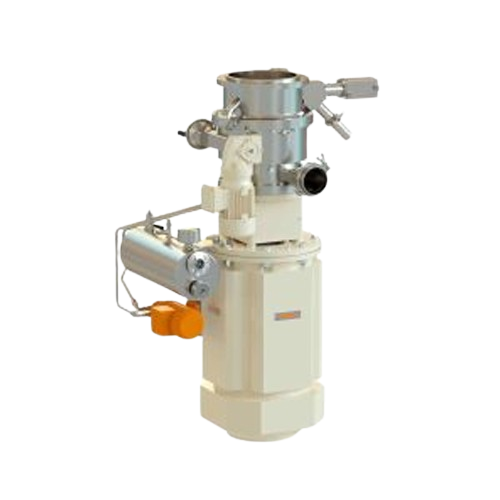
Homogenizer for high viscosity emulsion and dispersion
Achieve unparalleled dispersion and emulsification with a system d...
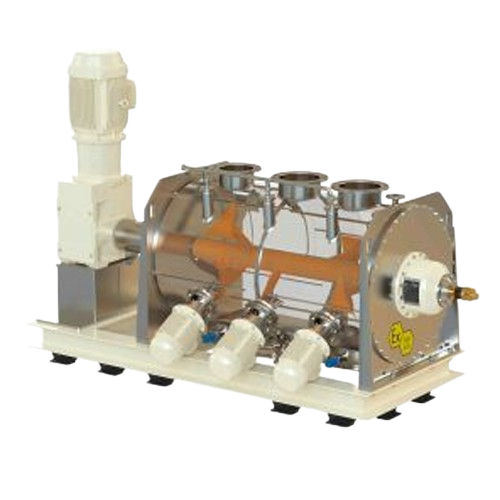
Horizontal ploughshare mixer for solids and powders
Achieve uniform blends of diverse solids and powders with precision a...
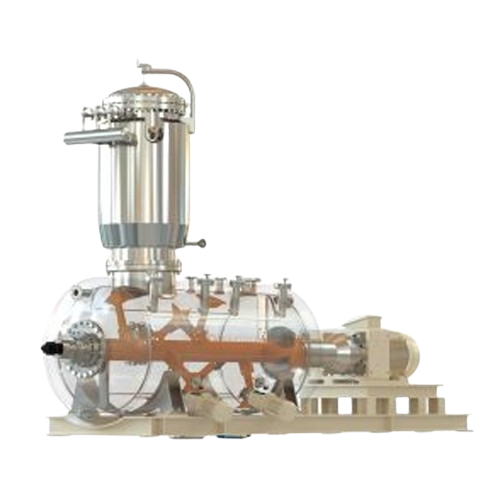
Horizontal vacuum paddle dryer for thermosensitive products
Achieve precise drying and mixing of high-viscosity, thermos...
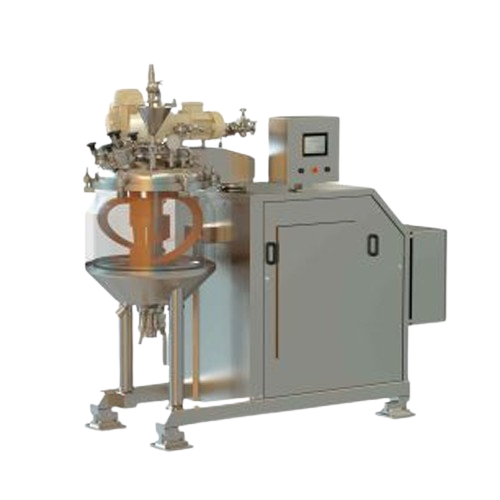
Vacuum mixer for liquids and semi-solids
Achieve precise mixing and homogenization of liquid and semi-solid formulations wi...
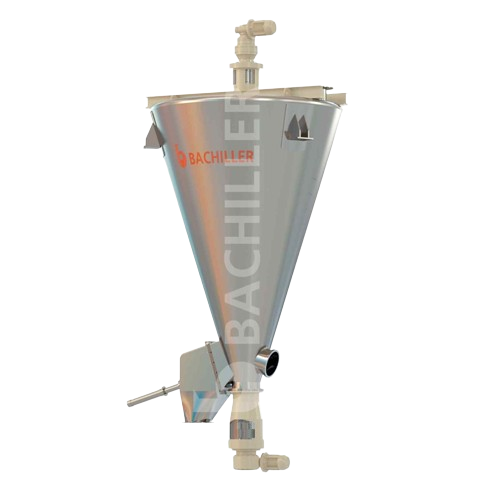
Conical screw mixer for solids and powders
Achieve precise homogenization of your solid and powder mixtures with minimal e...
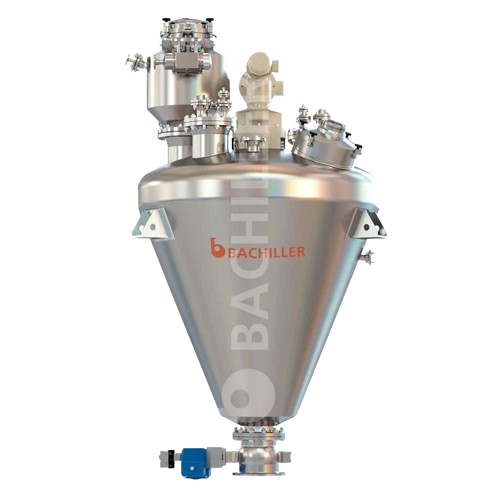
Vertical conical screw vacuum dryer
Achieve precise moisture control with ultra-vacuum batch drying, ideal for thermo-sensi...
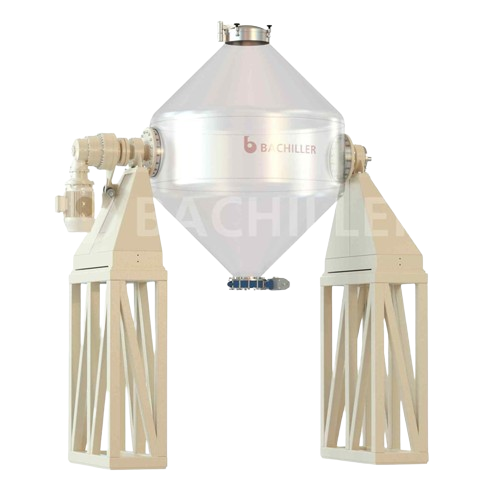
Double cone mixer for powders and solids
Ensure gentle mixing of fragile powders and solids with a low-speed, non-forced bl...
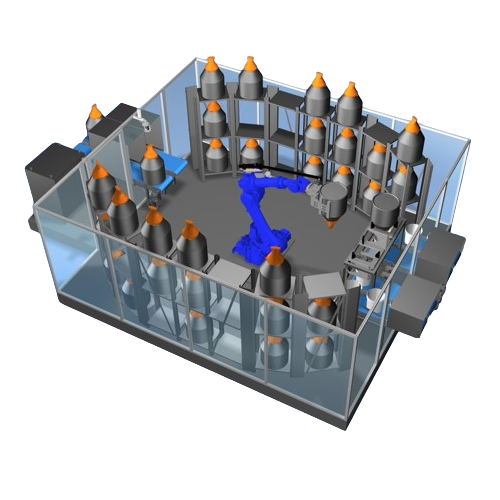
Robotic dosing system for accurate micro quantities
Achieve precise and reproducible micro dosing of challenging raw mate...
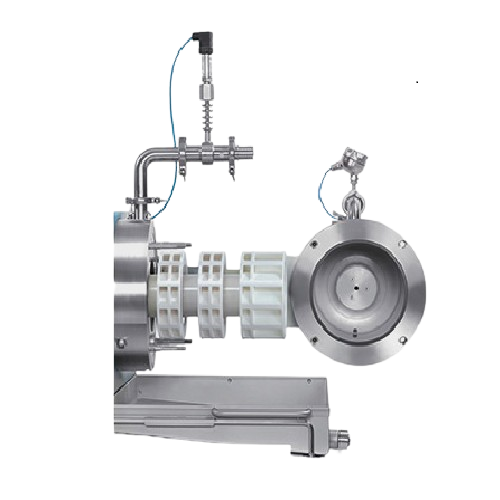
Bead mill for nano-preparation grinding
Achieve precise nano-processing and efficient wet grinding for pharmaceuticals and ...

Industrial filter press for dewatering and filtration
Optimize your dewatering and filtration needs with a highly adaptab...
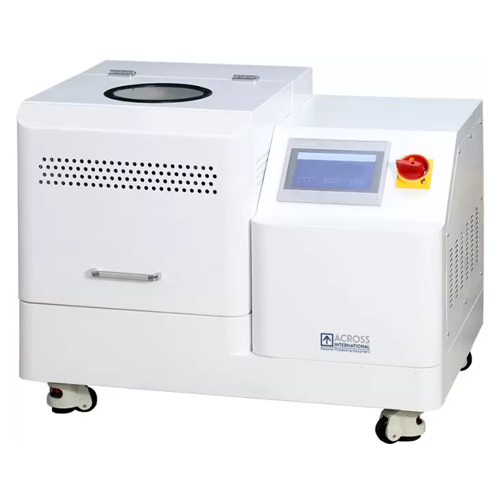
Planetary ball mill for powder material mixing and alloying
Achieve precise control in particle size reduction and homog...
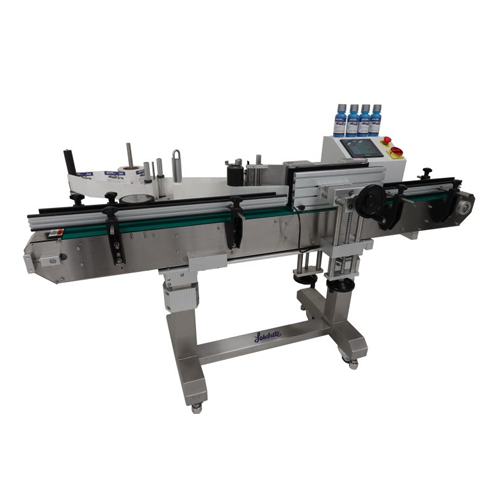
Automatic labeler for low profile containers
Optimize container labeling with precision and efficiency, addressing the cha...
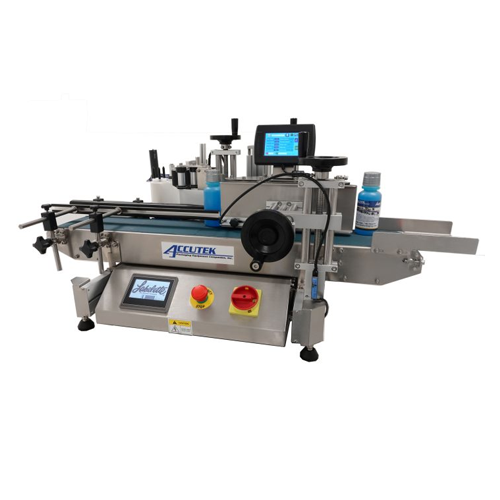
Tabletop labeler with integrated thermal printer for round containers
Efficiently label and print variable data on roun...
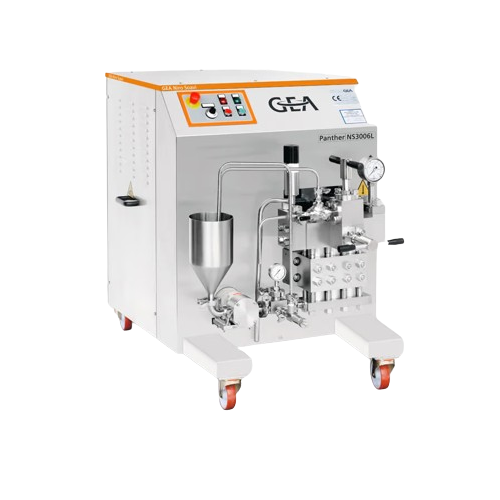
Pilot plant homogenizer for continuous operation
Achieve consistent fluid textures and prolonged shelf life with high-pres...
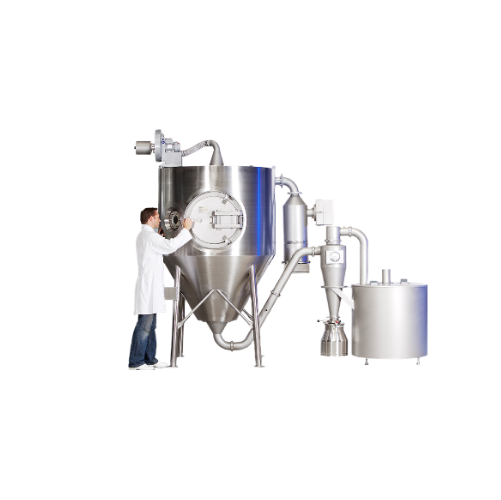
R&d spray drying solution for small batch production
Efficiently convert liquid solutions into precise, uniform powders f...
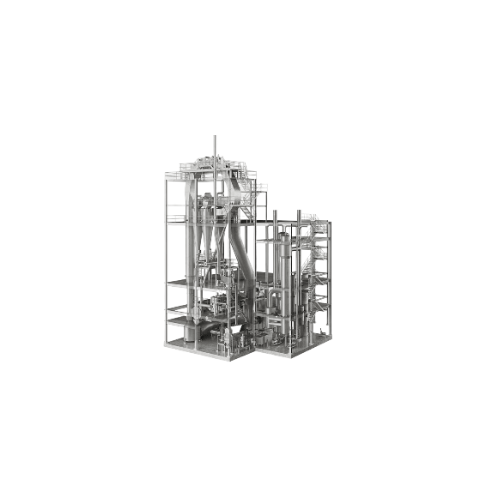
Feed-type ring dryer for industrial drying processes
Optimize your production with a versatile drying solution designed f...
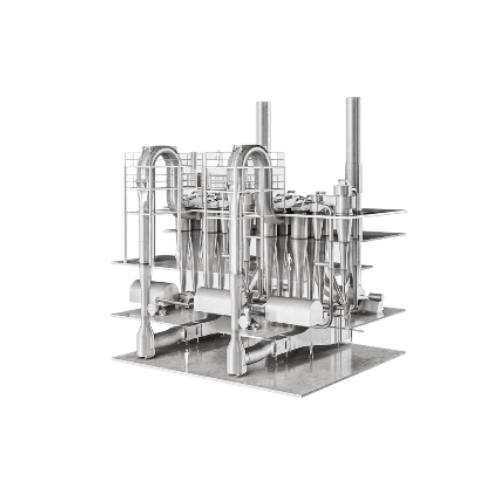
Flash dryer for industrial moisture removal
Optimize your production with rapid moisture removal, efficiently transforming...
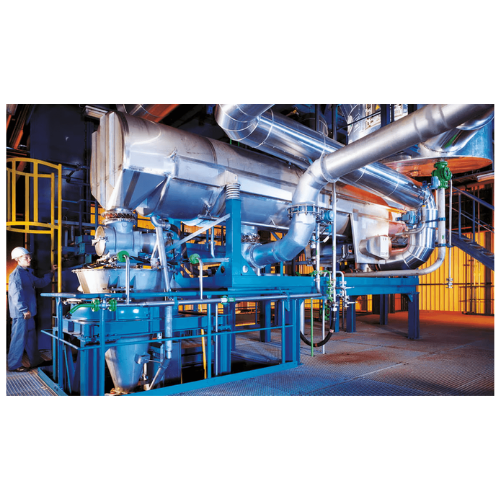
Vibrating fluid bed for final stage powder drying
Enhance powder processing precision with a vibrating fluid bed that ens...
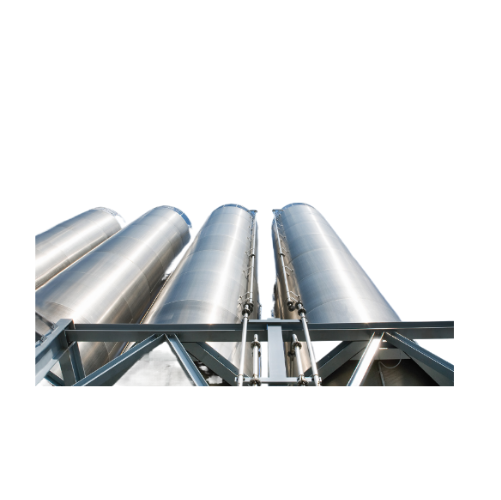
Short base skirt silo for bulk material storage
Optimize your bulk material handling with adaptable discharge and rapid lo...
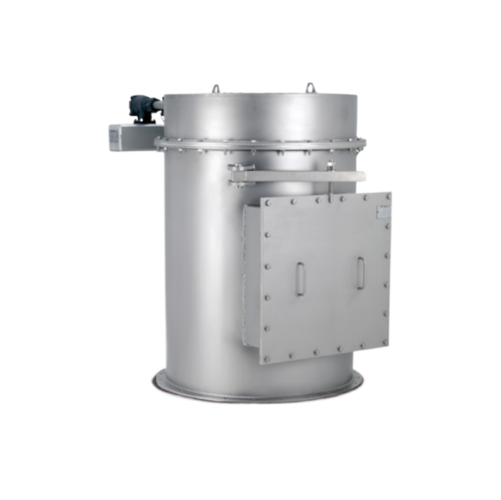
Industrial bin vent filter for fine dust particles
Enhance your production line with efficient fine dust filtration to en...
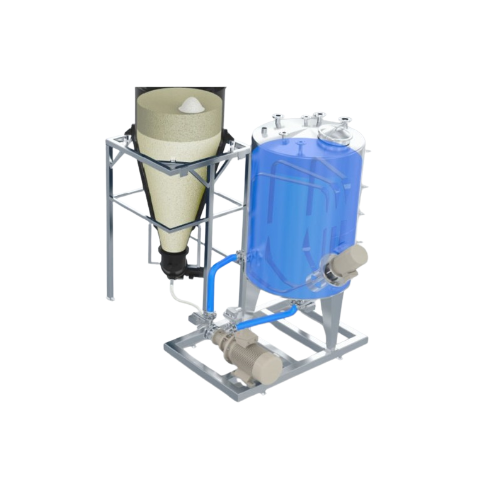
Powder wetting and dispersion system
Revolutionize your production with a system that seamlessly inducts, wets, and dispers...
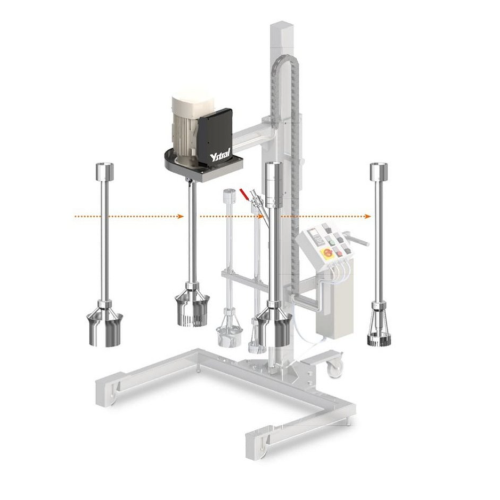
Multipurpose mixing equipment for chemical and pharmaceutical production
Achieve unparalleled flexibility with modular,...
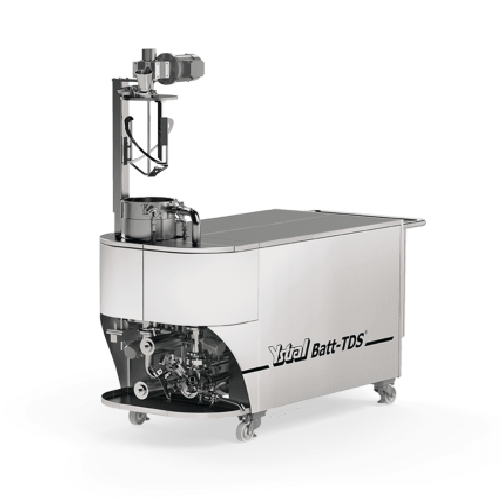
Inline disperser for lithium-ion electrode slurry mixing
Achieve highly efficient dispersion and homogeneity for battery ...
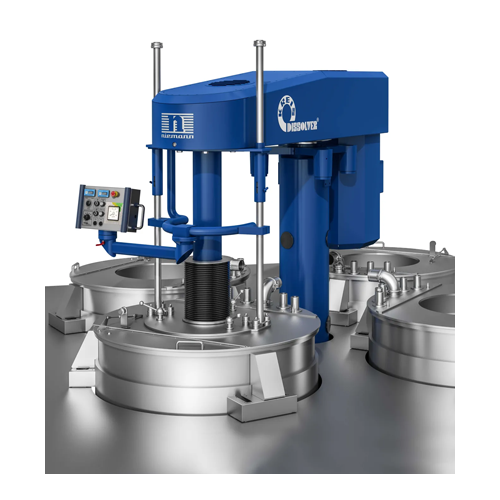
Dissolver for high-viscosity products through floor installation
Optimize production of ultra-high viscosity products wi...

Laboratory disperser for high-viscosity products
Optimize your laboratory processes with precise mixing and dispersing of ...
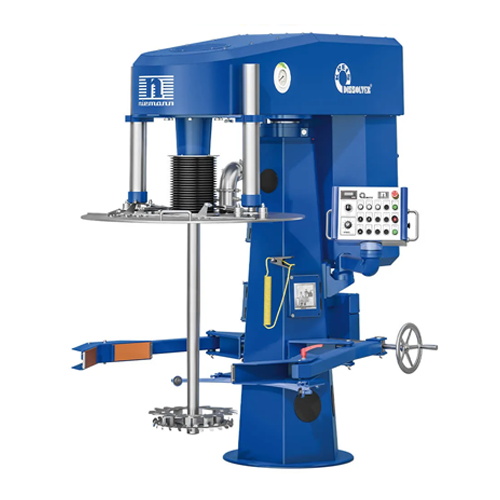
Dispersing system for high-viscous products
Achieve precise mixing and dispersing of high-viscous products with advanced f...
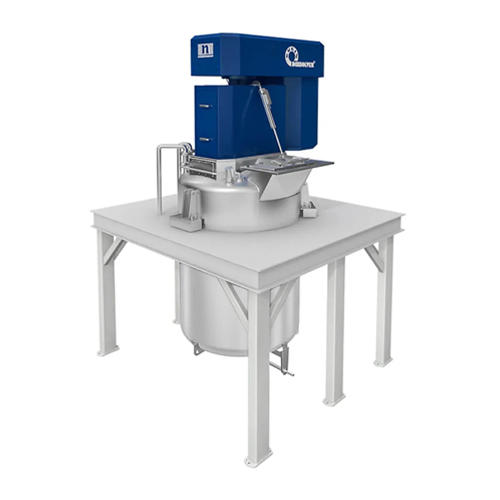
Top-mounted disperser for high-viscosity products
Achieve rapid, uniform dispersion of ultra-high viscosity materials wit...
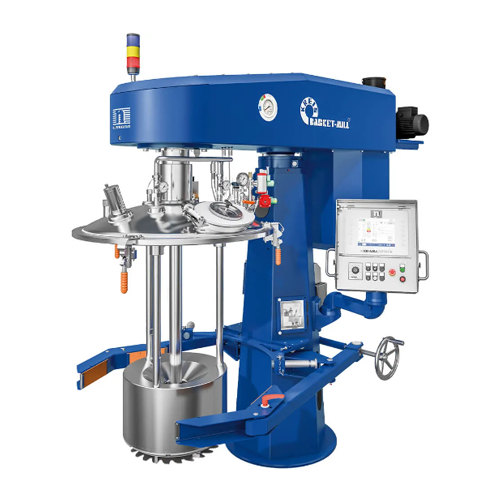
Basket mill for paint and varnish production
Achieve optimal particle size and product consistency with this advanced bask...
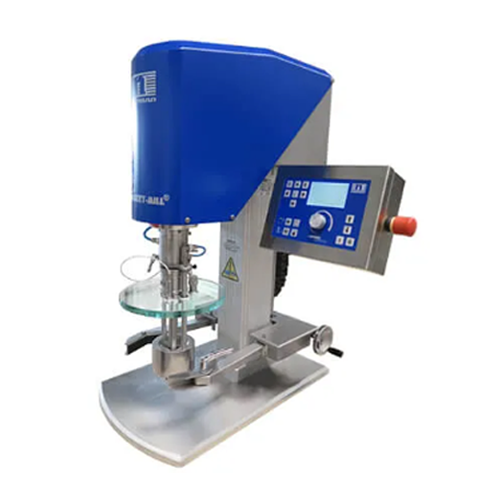
Laboratory basket mill for fine grinding in industrial applications
Optimize your laboratory’s efficiency with hi...
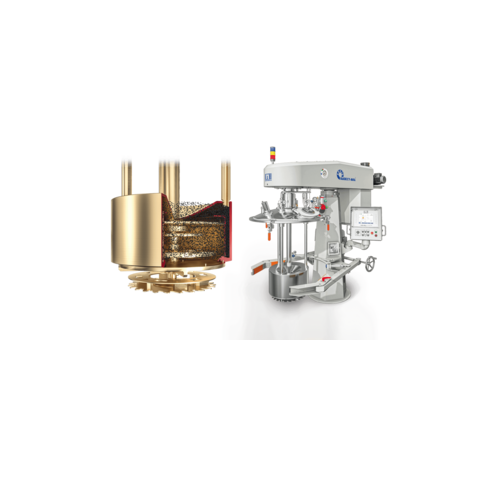
Milling beads for wet grinding in paint industry
Enhance product uniformity and grinding efficiency with specialized milli...
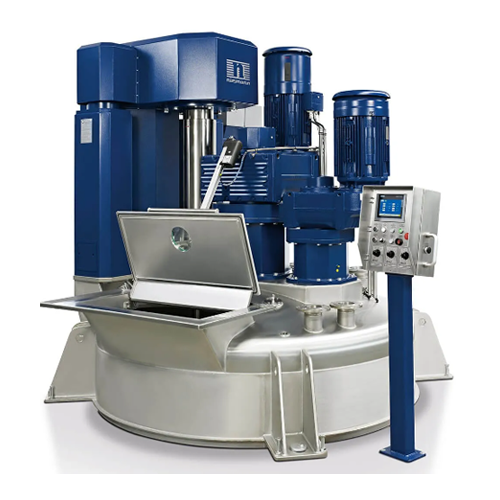
Triple shaft mixer for high-viscosity products
Achieve precision mixing and dispersing of high-viscosity products with a p...
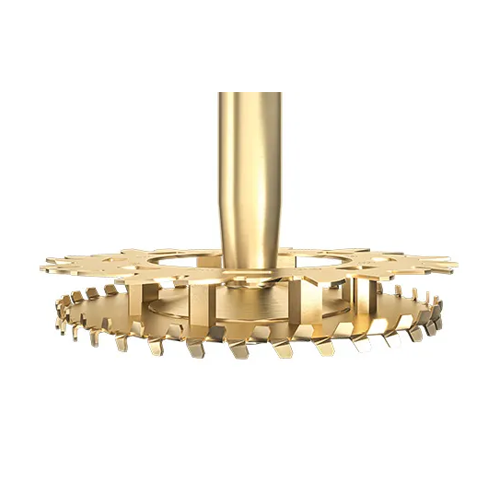
Mixer for high viscosity products
Enhance your production line with a versatile solution designed for precise mixing and di...
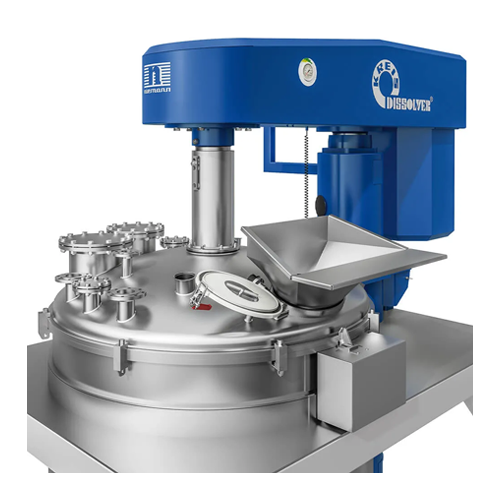
Advanced dissolver for high-viscosity products
Handle ultra-high viscosity mixing challenges effortlessly with this advanc...
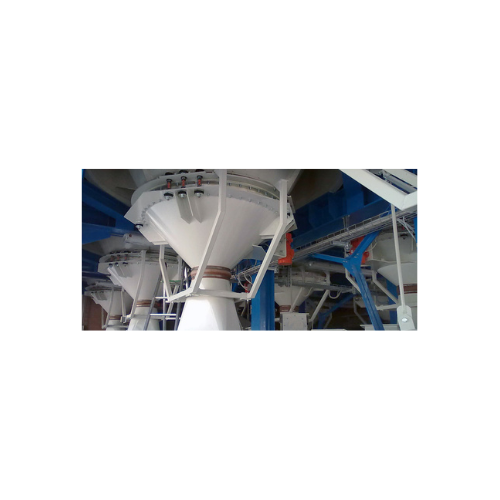
Bulk solids discharging and loading solution
Optimize your bulk material handling with equipment that ensures efficient an...
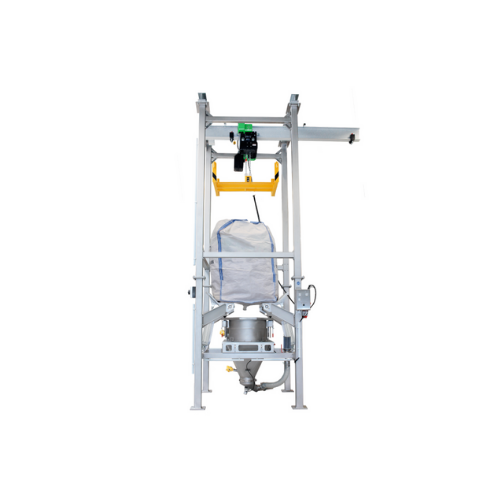
Big-bag unloading station for bulk materials
Facilitate seamless integration into your production line with efficient bulk...
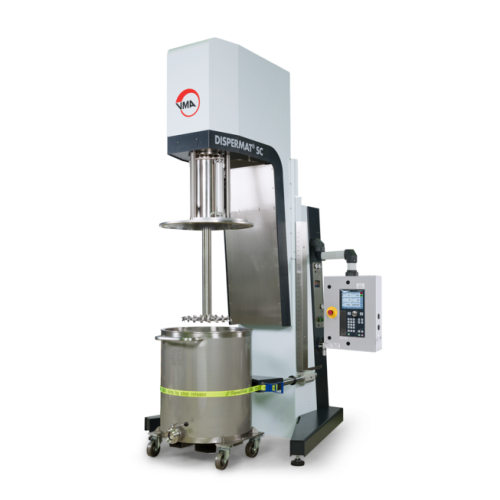
Explosion-proof production disperser for paint manufacturing
Ensure safe and efficient dispersion in volatile environmen...
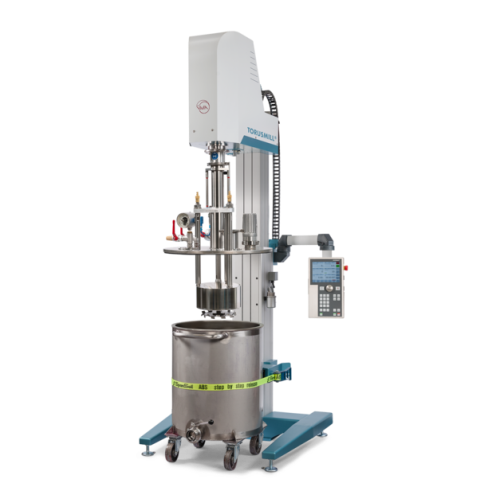
Vacuum basket mill for high-viscosity product processing
Achieve exceptional fine milling results while preventing air in...
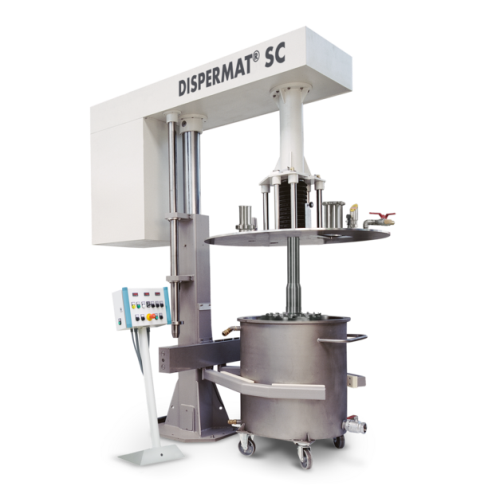
Vacuum disperser for high-viscosity products
Optimize high-viscosity product dispersion and prevent air inclusions with a ...

Vacuum dissolving system for high-viscosity products
Achieve flawless dispersion of high-viscosity substances under vacuu...
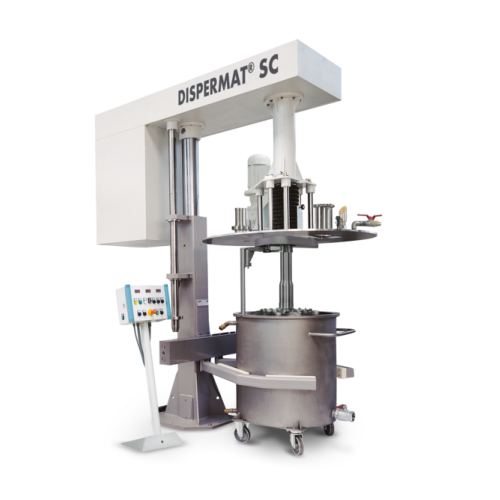
Production dissolver for high-viscosity products
Achieve optimal dispersion and grinding of high-viscosity substances with...
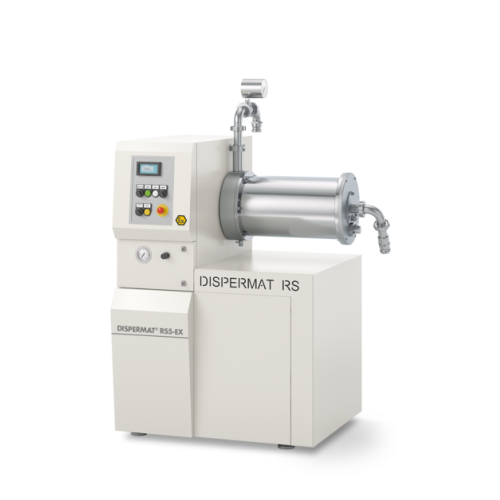
Explosion-proof horizontal bead mill
For manufacturers seeking precise particle sizing, this explosion-proof bead mill ensu...
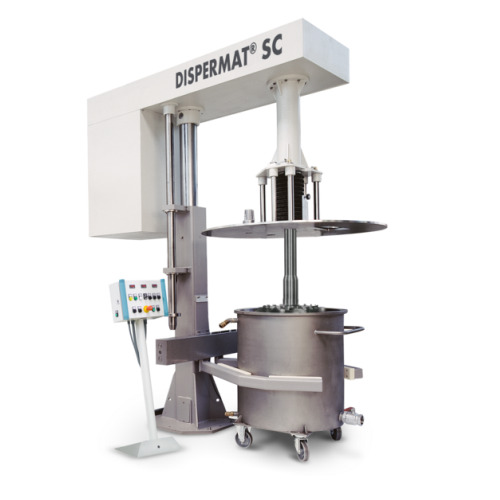
High-performance production dissolver for large batches
Achieve precise and repeatable dispersion for complex formulation...
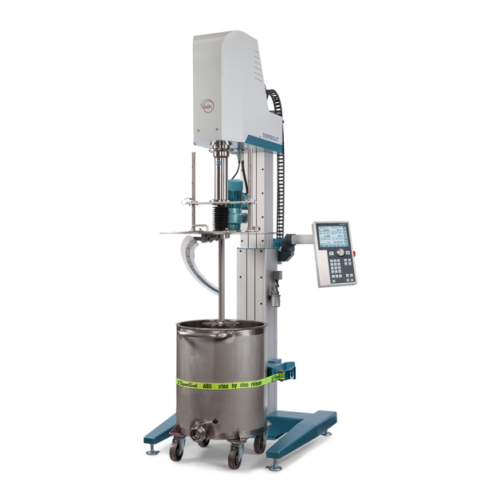
Dissolving system for high-viscosity products
Optimize the dispersion of high-viscosity liquids and pastes with this versa...
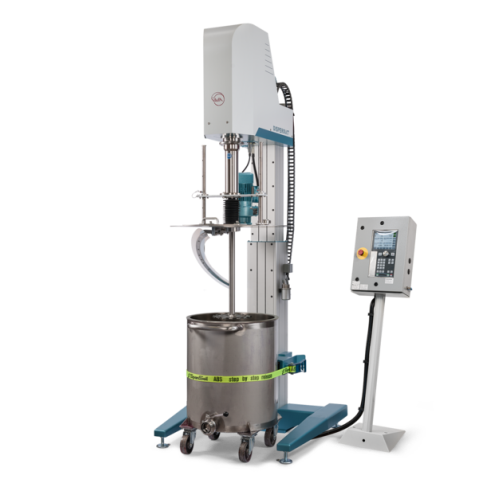
Explosion-proof dissolver with scraper for high viscosity substances
Ensure flawless dispersion with enhanced safety, d...

Explosion-proof dissolver for high-viscosity products
Optimized for safely processing high-viscosity products, this explo...
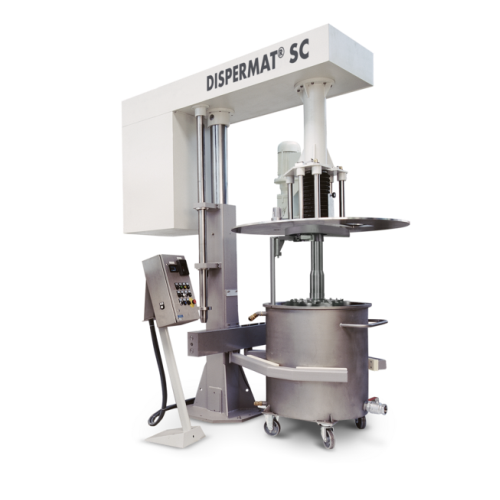
Explosion-proof dissolver for high viscosity products
Optimize your high-viscosity material processing with an explosion-...
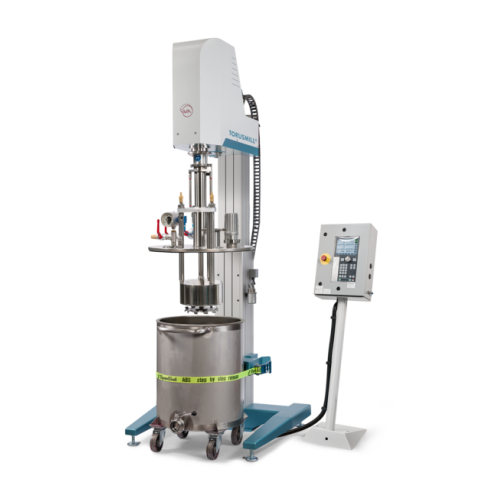
Vacuum basket mill for highly viscous products
Achieve precision in fine milling under vacuum to prevent air inclusions in...
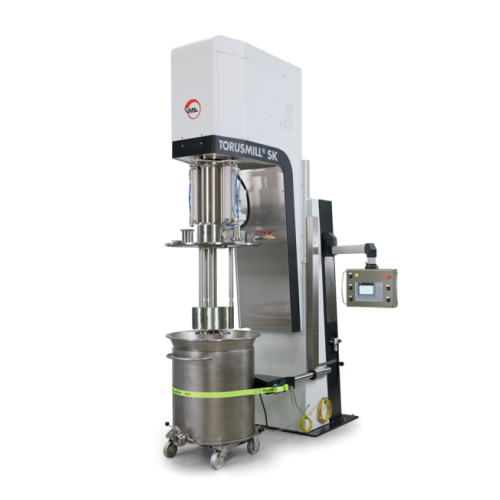
Vacuum basket mill for high-viscosity product milling
Achieve refined particle size and smooth texture in your high-visco...
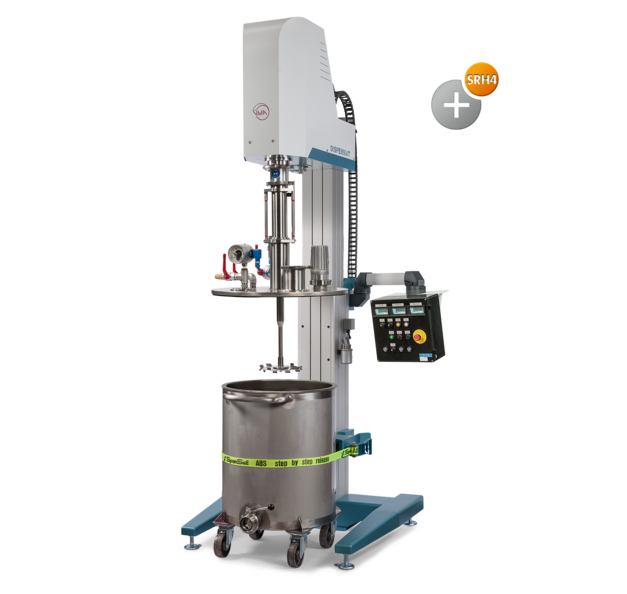
ATEX vacuum dissolver for high viscosity products
Ensure safe and efficient dispersion of high-viscosity materials under...
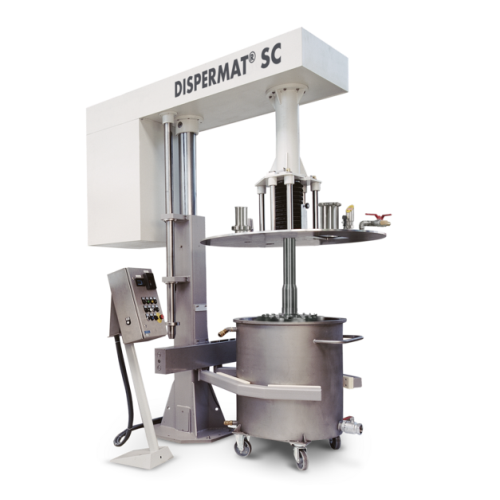
Explosion-proof vacuum dissolver for high viscosity products
Achieve precise dispersion of high-viscosity products under...
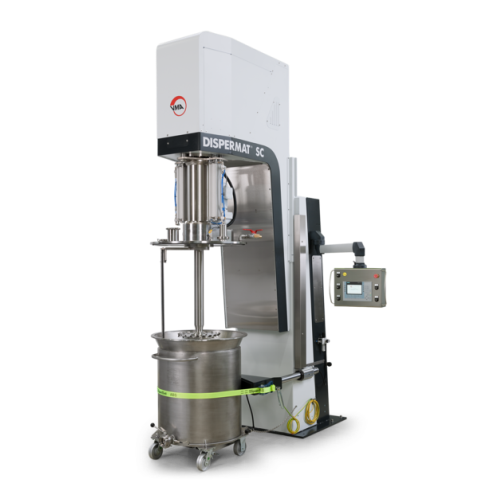
Explosion-proof vacuum disperser for high-viscosity substances
Achieve precise dispersion and eliminate air inclusions w...
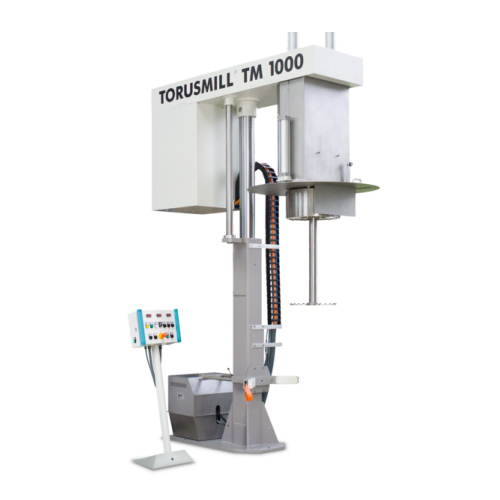
Basket mill with integrated dissolver for high viscosity products
Optimize your production efficiency by combining disp...
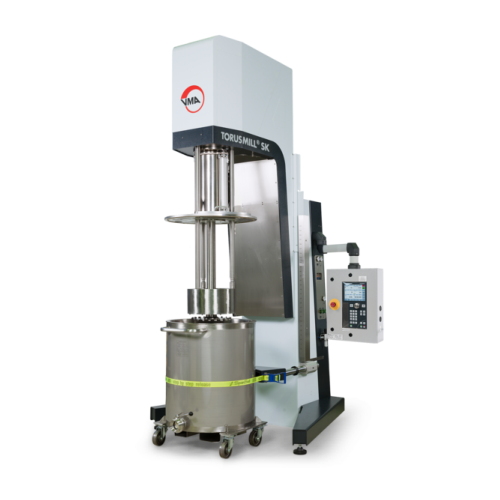
Explosion-proof immersion mill for paints and varnishes
Optimize high-performance coatings production with an explosion-p...
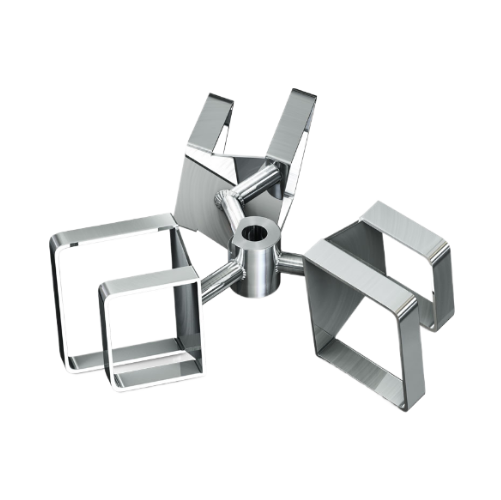
Agglomerate dispersion solution for high viscosity materials
Optimize your production efficiency by integrating a dual-f...
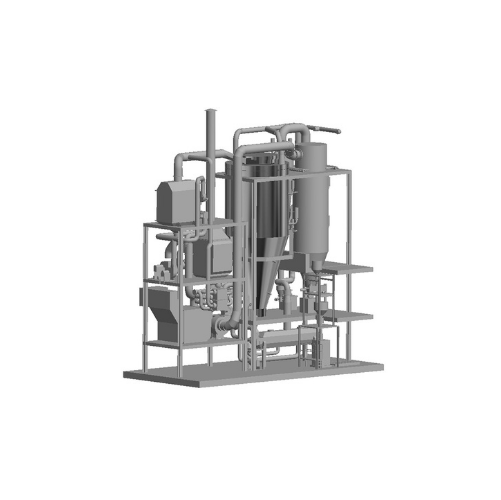
Spray drying system for heat sensitive products
For heat-sensitive products requiring precision drying, this spray drying ...
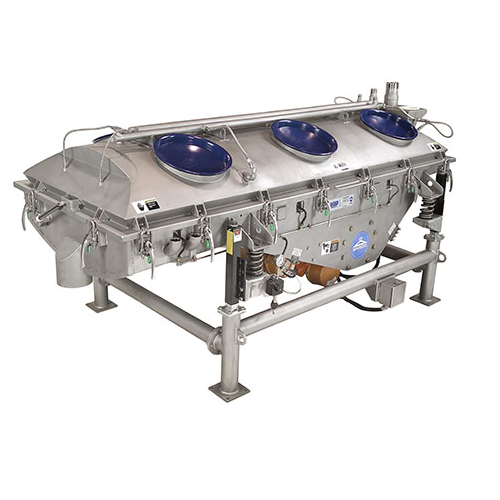
Dual-motion rectangular separator for pulp and paper industry
Optimize your production line with a versatile separation ...
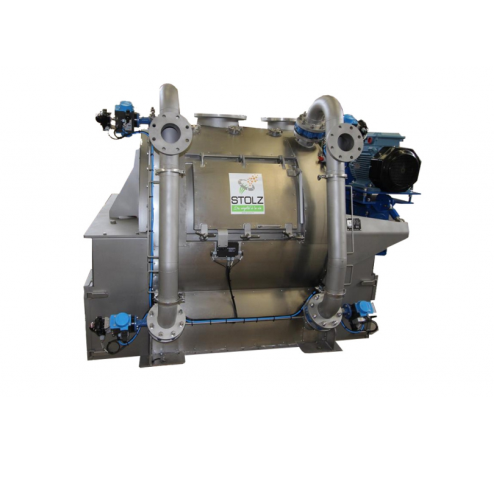
Vacuum coater for petfood and livestock feed
Enhance nutritional value and product quality with precision liquid incorpora...
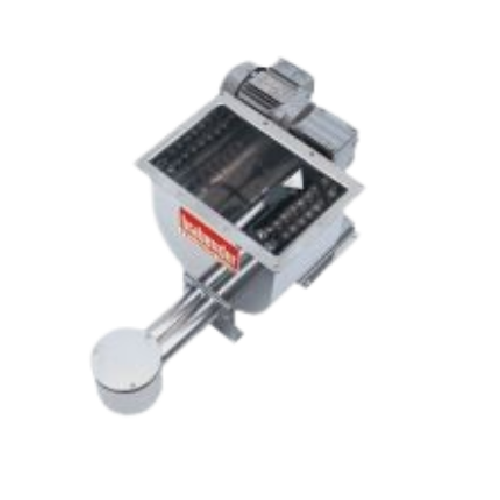
Twin screw feeder with stirring agitator for poor flowing powders
Optimize your processing line with a highly adaptable...
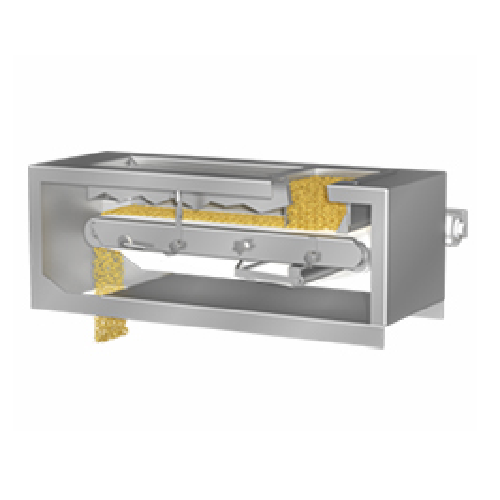
Weigh-belt feeder for industrial processes
Efficiently manage material flow and precision with a dependable weigh-belt fee...
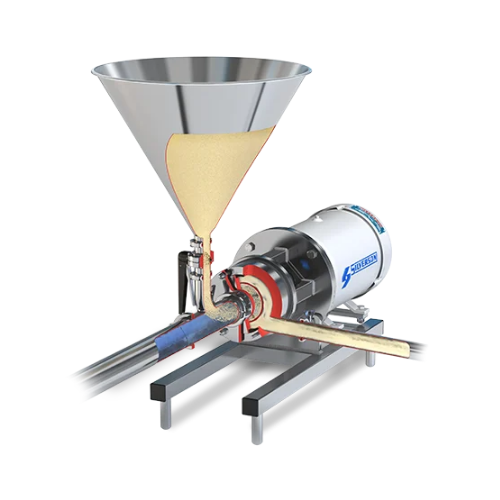
High shear powder mixing solution
Achieve agglomerate-free, homogeneous mixing of powders and liquids with high shear effic...
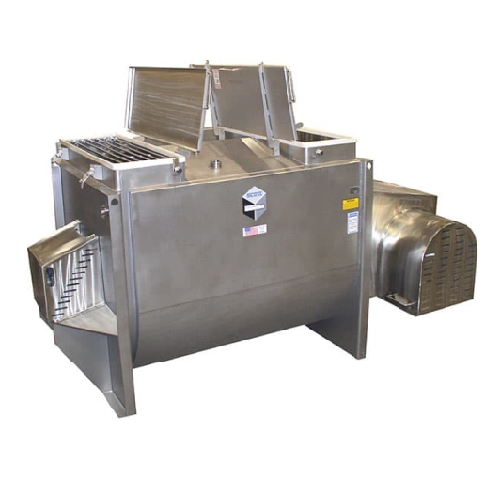
Industrial batch mixers for pet food
Achieve homogenous mixing of complex multi-ingredient formulations with precision and ...
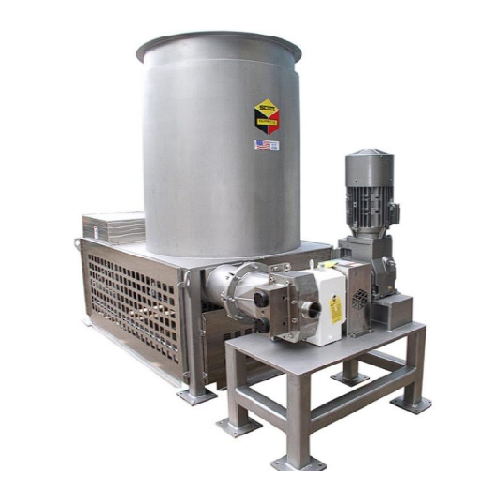
Feeding system for filter cake and wet pet food
Achieve seamless material handling and agitation for solid shortening and ...
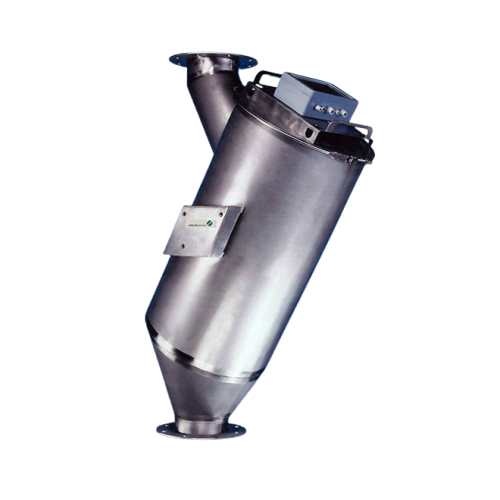
Solid flow meter for granular and powdered bulk materials
Ensure accurate mass flow measurement and seamless integration...
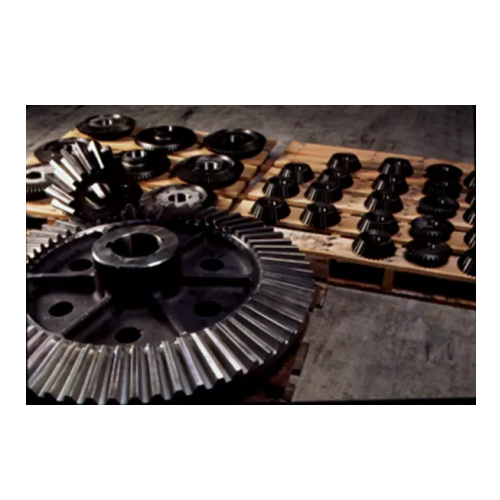
Industrial grinding mill replacement parts service
Optimize production efficiency with high-precision grinding solutions ...
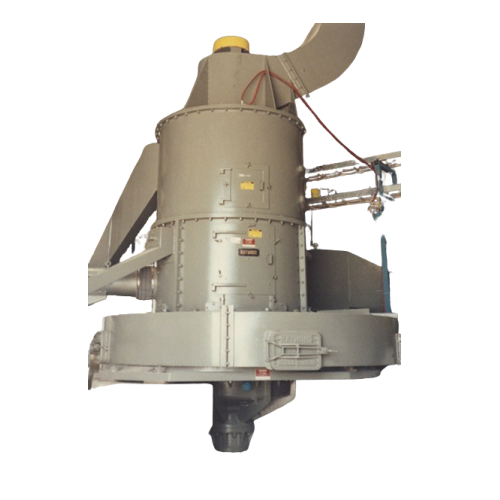
Vertical ring-roll mill for pulverizing minerals
Achieve precise particle size control and efficient material processing w...
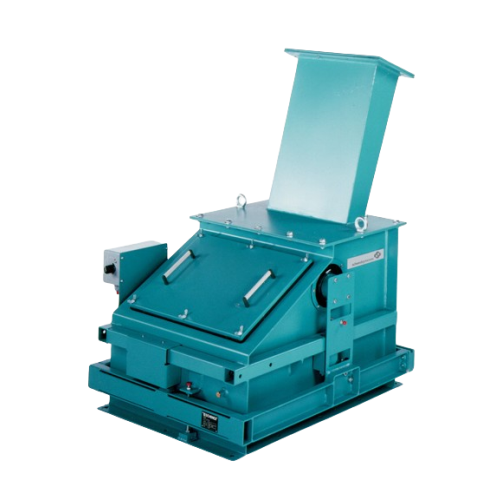
Solids flow meter for bulk solid streams
Ensure precise bulk material measurement with a system designed for accuracy and r...
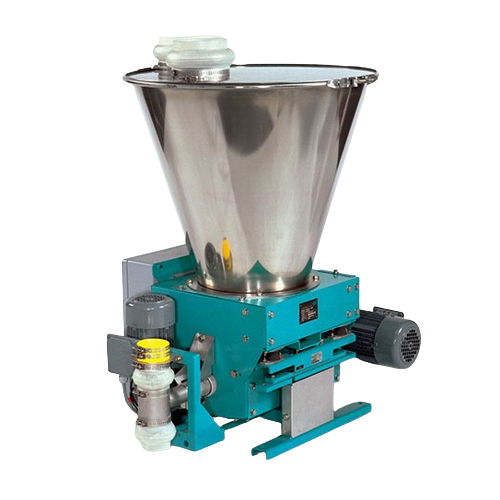
Loss-in-weight feeder for bulk solids
Ensure precise and reliable dosing of bulk solids with a compact feeder that eliminat...
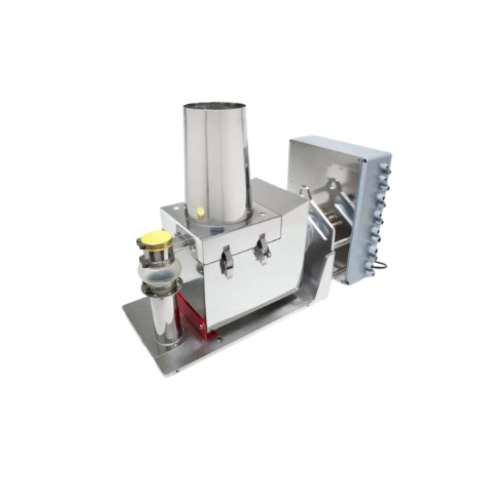
Loss-in-weight feeder for small volume bulk solids
Achieve precision feeding for small volume bulk solids with this advan...
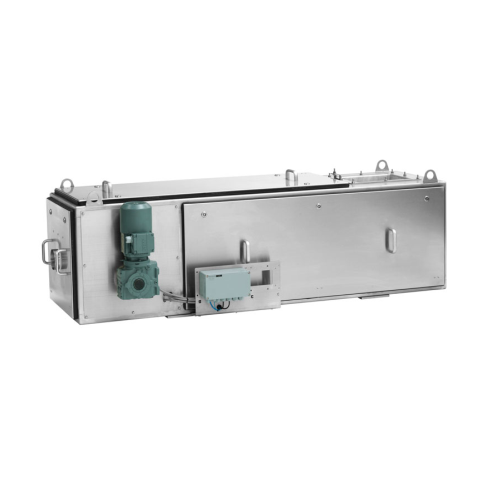
Continuous and batch feeding system for bulk materials
Achieve precise bulk material feeding with seamless integration in...
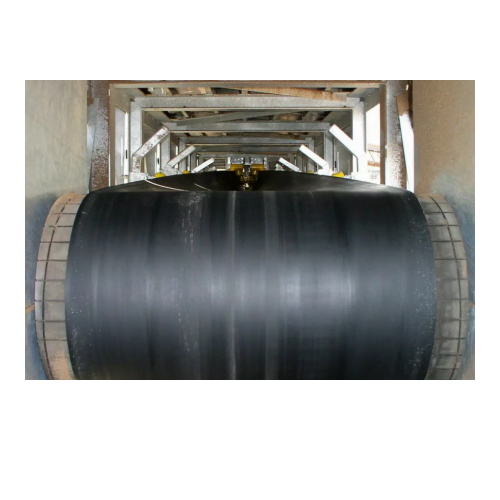
U-belt conveyor for bulk material transport
Optimize your high-speed bulk material transport with this space-saving convey...
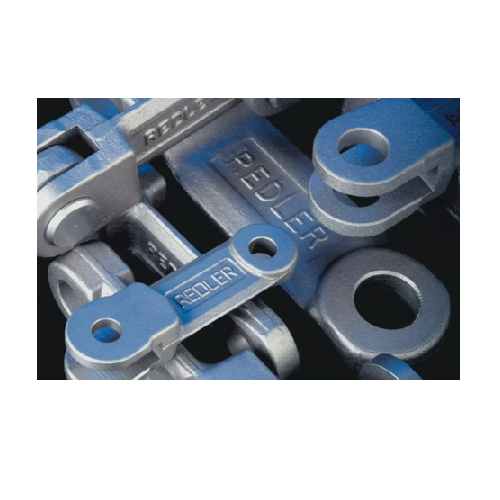
Drop forged chain for drag chain conveyors
Enhance your material flow efficiency with a robust drop forged chain designed ...
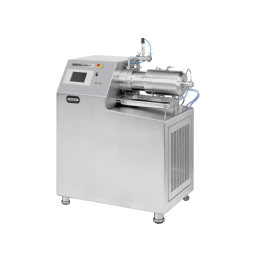
Ultra fine bead mill for nanosuspensions
Ensuring the quality, efficiency, and reproducibility of nanosuspensions throughou...
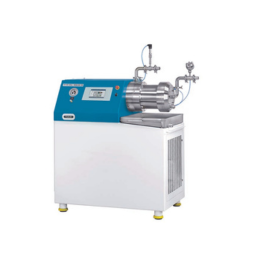
Self-cleaning bead mill for highly viscous materials
To prevent blockages, clogging, and cross-contamination coming from ...
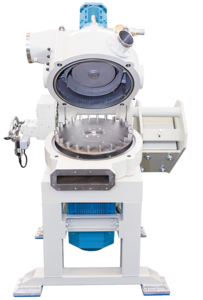
Classifier mill for recovered carbon black
Recovered Carbon Black (rCB) can be recycled back to the tire production chain ...
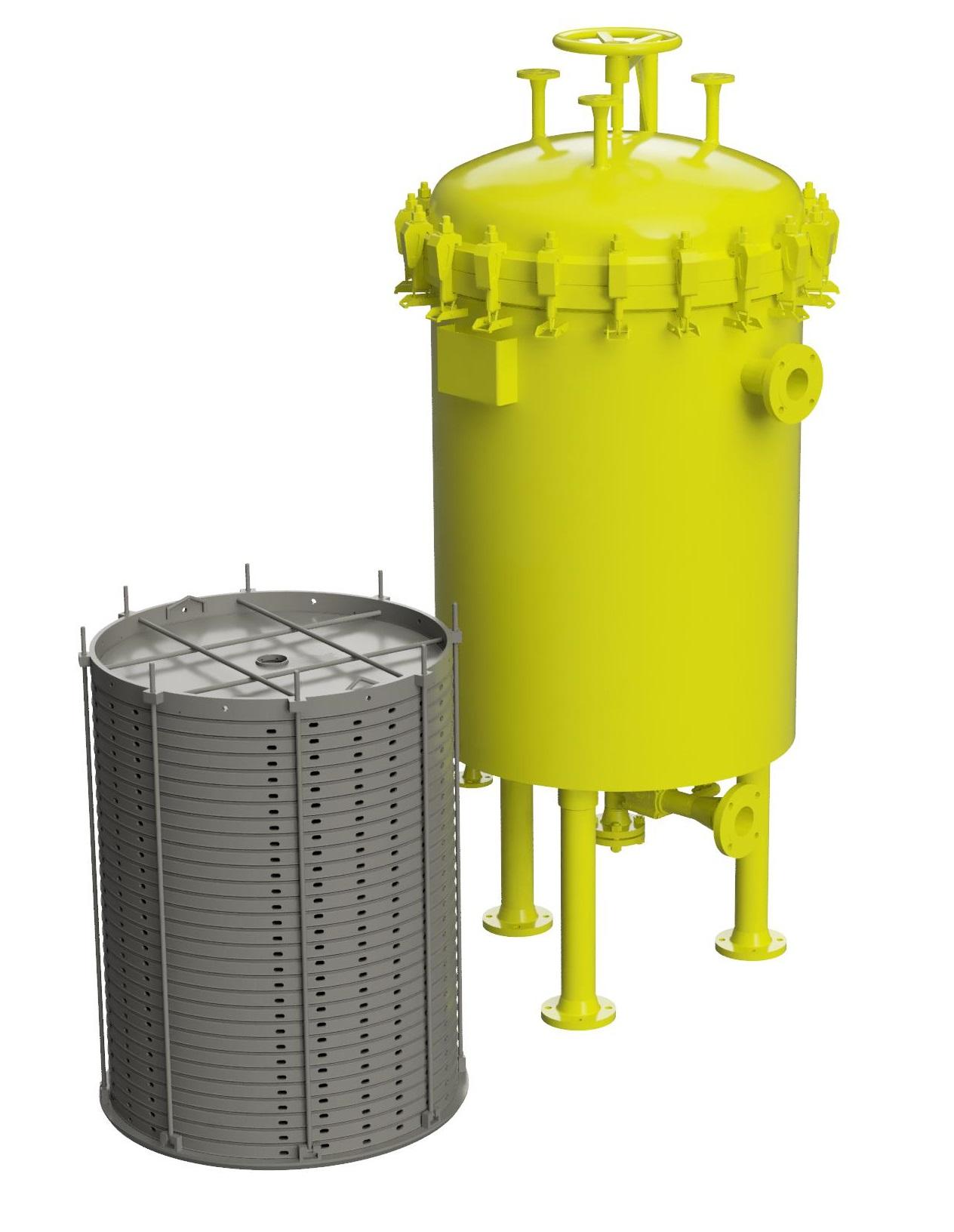
Industrial liquid filtration system
Systems for the filtration of liquids with suspended solid contents can be challenging ...
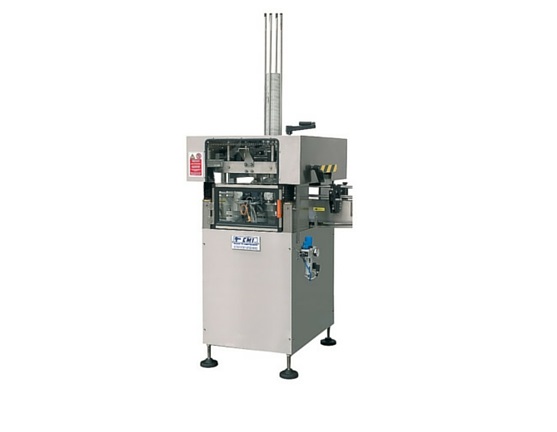
Automatic can sealer
If you need to cap paint, glues, and solvents containers and are currently manually placing the lids, yo...
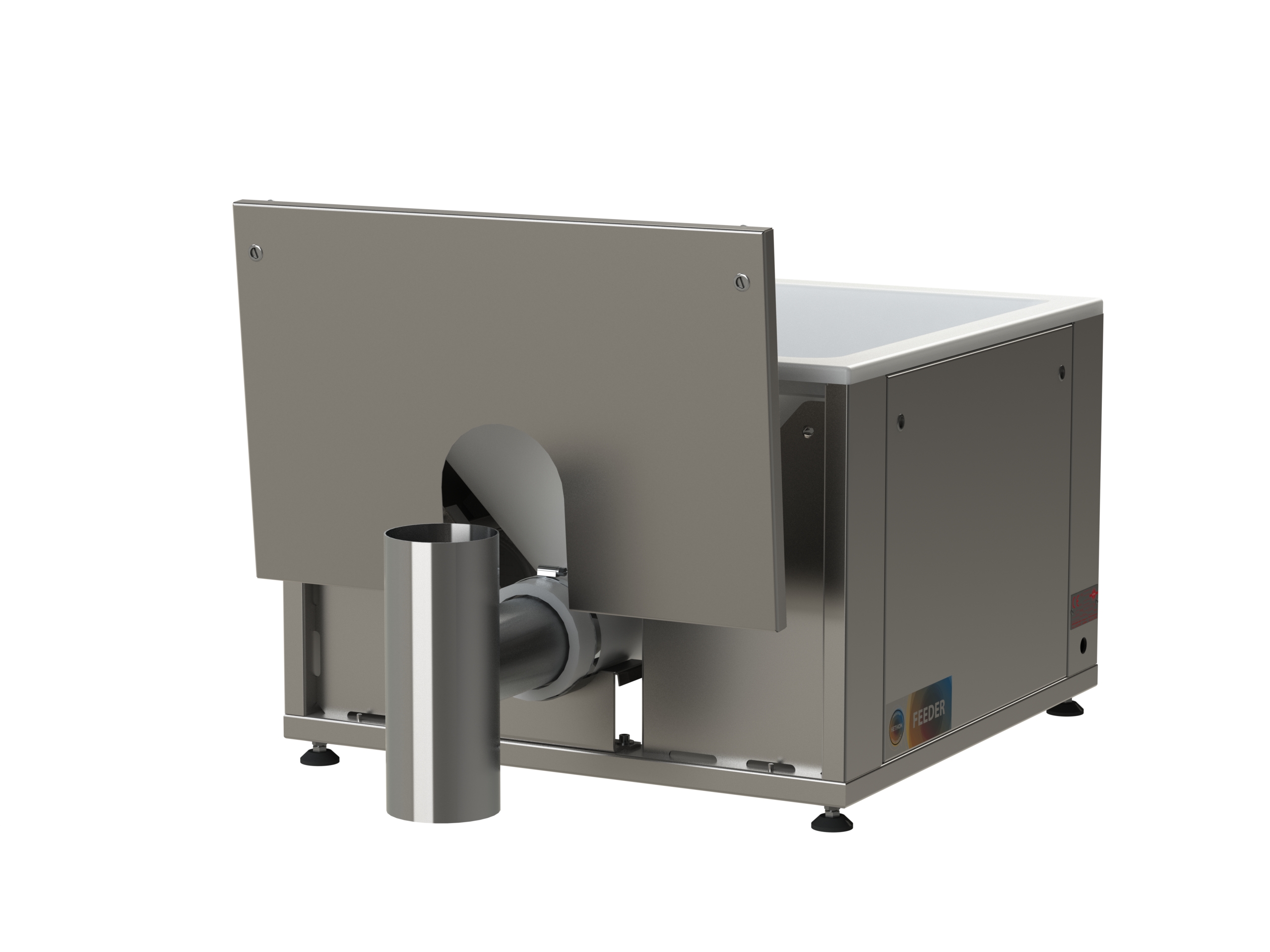
Feeder with flexible wall hopper
The varying properties of dry powder products mean that specialized feeders are required fo...
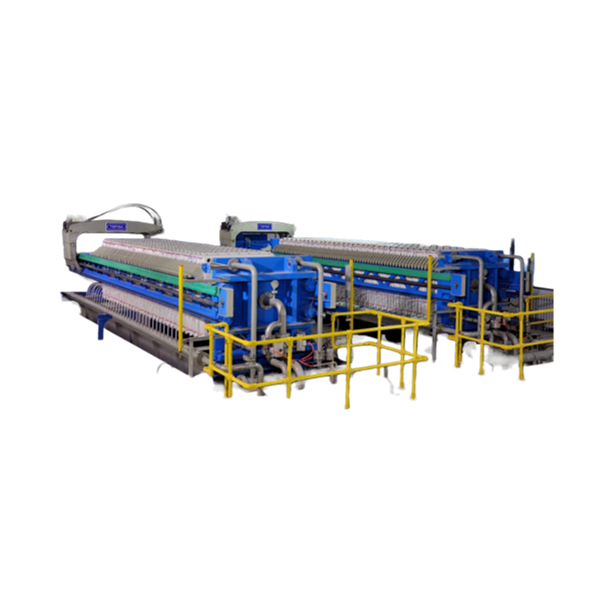
Side bar filter press
Production of dry cakes is required in a variety of industries and robust, low-cost side bar filtration...
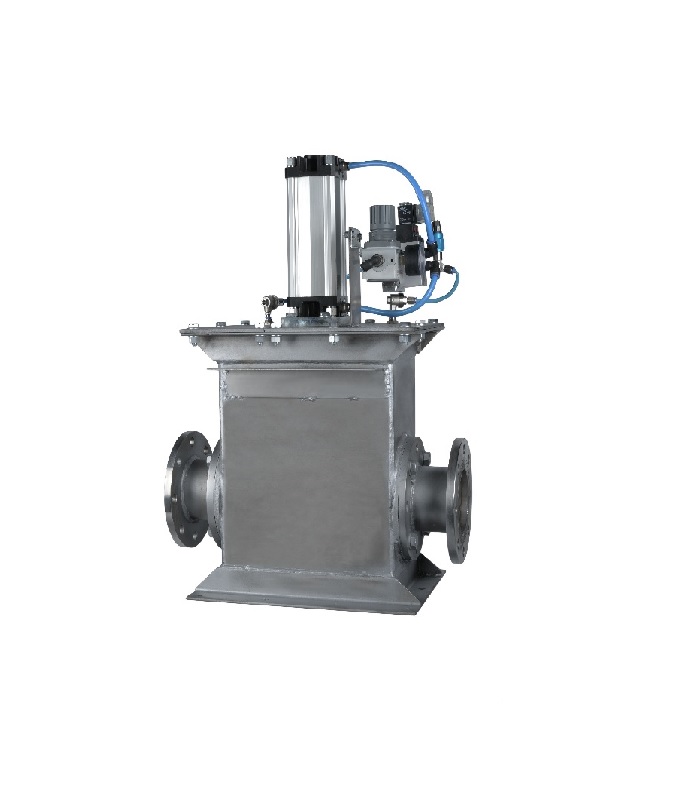
2-way diverter valves for pneumatic conveying
Products conveyed through pneumatic conveyor lines often need to be diverted...
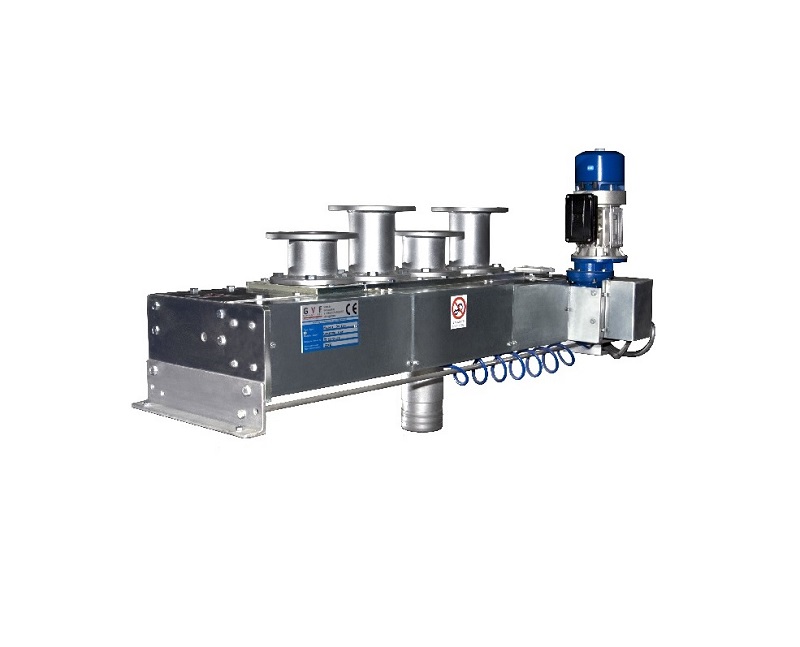
Multi-way diverter valve for pneumatic conveying
Products conveyed through pneumatic conveyor lines often need to be diver...
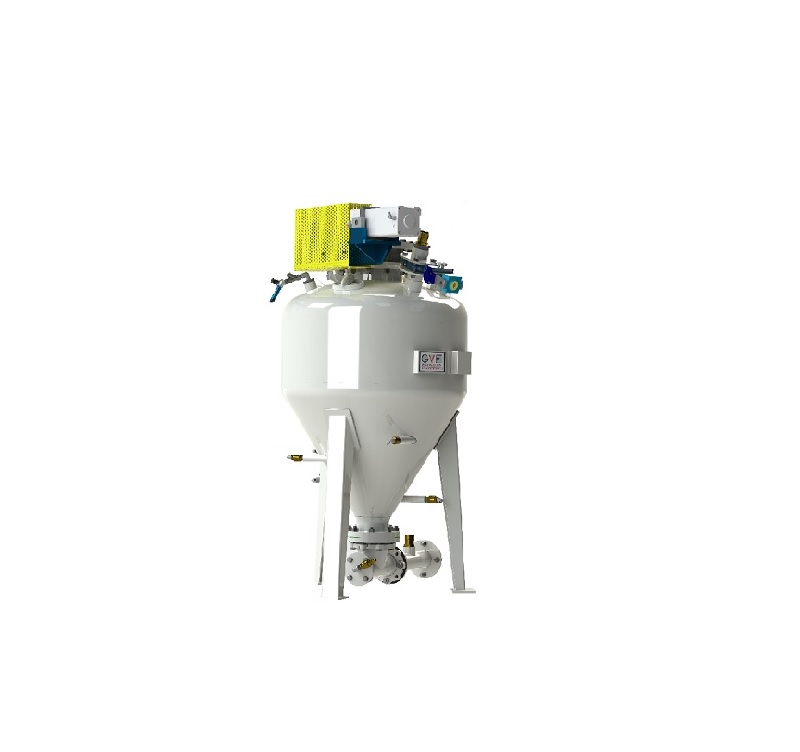
Dense phase conveyor for normal wearing materials
Dense phase pneumatic conveying is used for powders, granules, and grai...
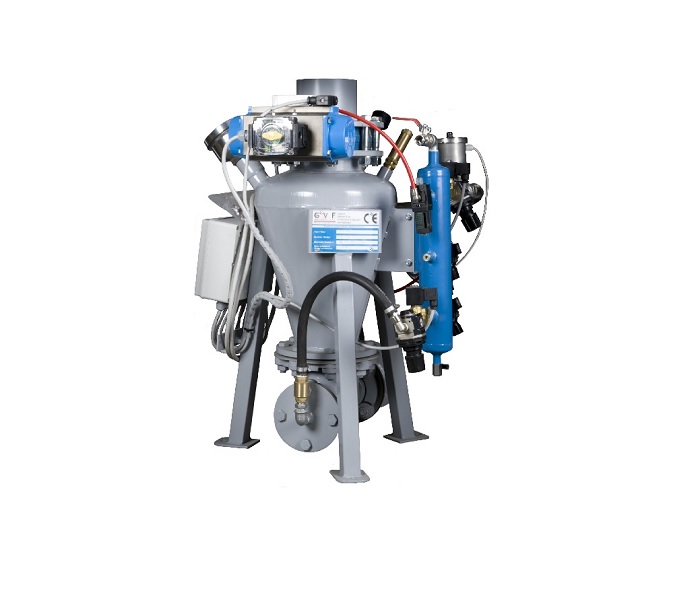
Dense phase conveyor for powders and granules
Some manufacturing and filling operations require a smaller pneumatic transp...
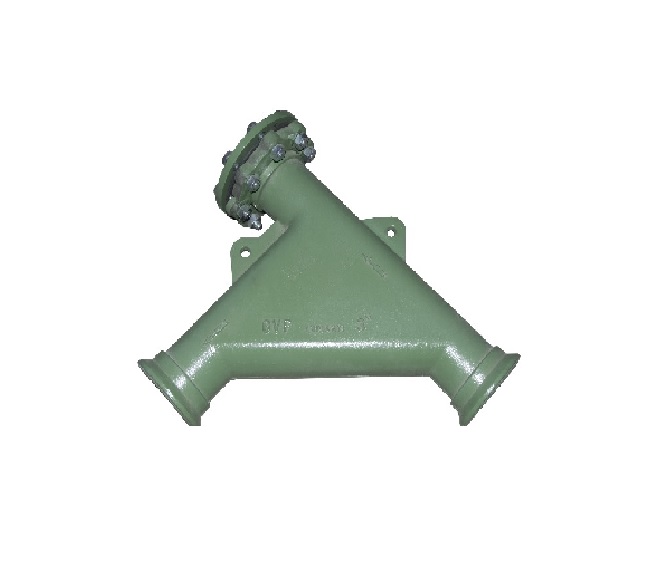
Wear resistant bends for pneumatic conveying
Bends in pneumatic conveyor lines cause load loss leading to lower flow rates...
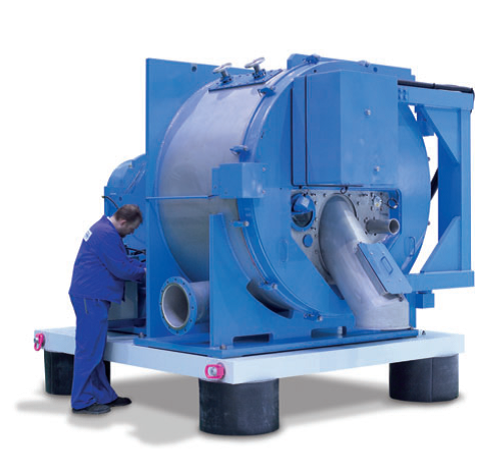
Horizontal chemical scraper centrifuge
For slurries difficult to discharge, a scraper can improve process reliability, effi...
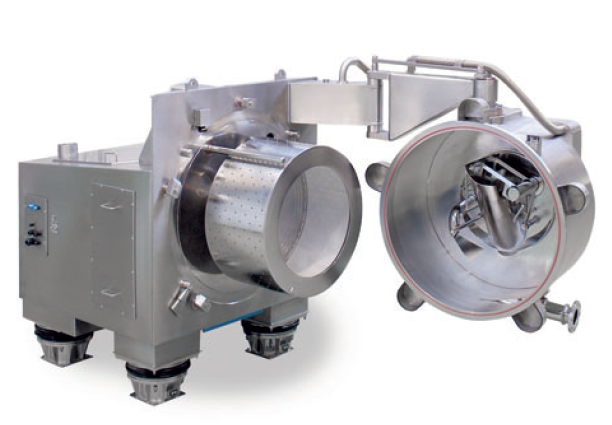
Horizontal pharmaceutical scraper centrifuge
For slurries difficult to discharge, a scraper can improve process reliabilit...
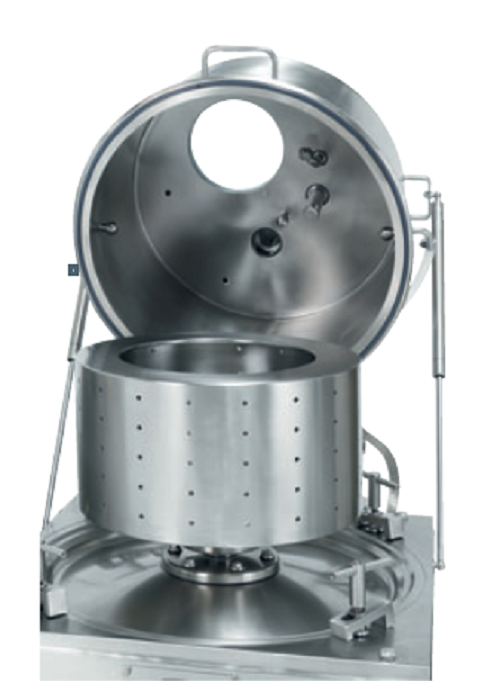
Isolator centrifuge
For transferring highly active pharmaceutical ingredients (HAPI) without contamination from the isolator ...
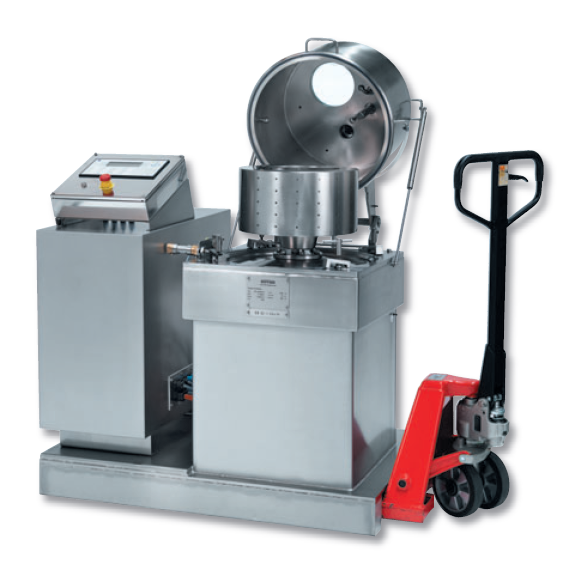
Mobile pilot plant centrifuge
The system is perfectly suited for pilot plants as well as small-quantity productions in the f...
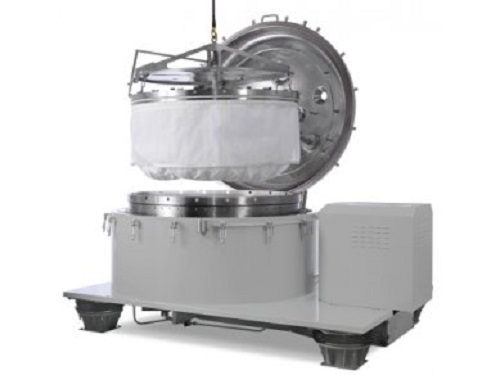
Vertical top discharge centrifuge
Discharge solids vertically upward through manual action, optionally using a filter bag o...
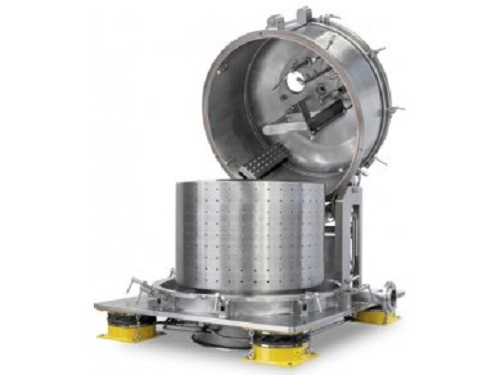
Vertical peeler centrifuge
A vertical peeler centrifuge is used to separate solids, usually to separate fine particles from ...
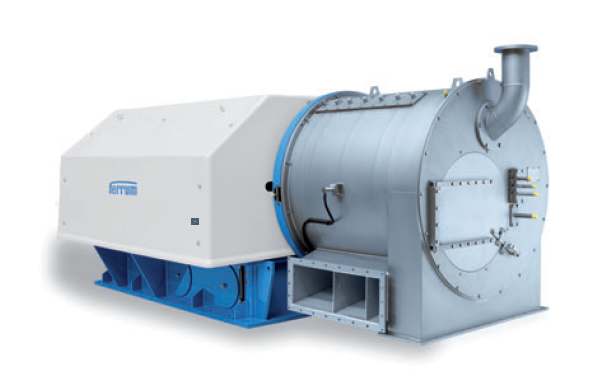
Pusher centrifuge
Pusher centrifuges are continuously operating filter centrifuges and can have several basket stages dependi...