Hard candy production system
Enhance your candy production line with a comprehensive system that optimizes processes from cooking to tempering, ensuring quality consistency and reduced flavor loss in hard and sugar-free candies.
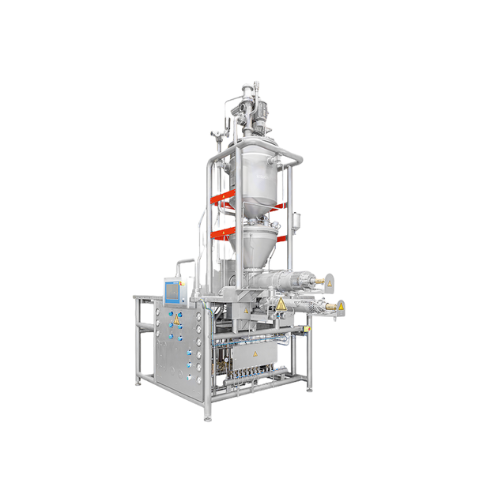
Processes and Vacuumizes Hard Candy Mass
The SUCROMASTER® from CHOCOTECH is a specialized hard candy cooking and vacuum system designed to enhance operational efficiency for confectionery manufacturers. It employs a high vacuum system to minimize flavor loss and reduce inversion by processing the candy mass at low temperatures. The system offers a versatile cooking solution capable of producing a range of candies, from sugar-free butterscotch to aerated and medicated candy, through its comprehensive suite of integrated processes: weighing, dissolving, cooking, vacuumizing, tempering, and optional aerating.
With a processing capacity of up to 4000 kg/h, the SUCROMASTER® can handle high-speed continuous operations, accommodating up to four different candy ropes with distinct colors and flavors. It seamlessly integrates into existing production lines with its PLC-controlled automation, which allows for minimal manual intervention and enhanced productivity.
Additionally, this system supports a vast array of applications, including the production of boiled sweets, lollipops, and milk chocolate-flavored candies. Its construction provides robust performance in demanding environments, and customization options are available to adapt to specific production requirements. Maintenance is streamlined with a design that facilitates easy access and cleaning, ensuring sustained hygienic operations.
Benefits
- Enhances product quality by minimizing flavor loss and inversion with low-temperature processing.
- Maximizes production efficiency, processing up to 4000 kg/h with multi-rope capabilities.
- Reduces labor costs through automated and PLC-controlled operations.
- Versatile production capabilities accommodate a wide range of candy types, from sugar-free to medicated.
- Streamlines maintenance with easily accessible components and design optimized for hygienic operations.
- Applications
- Sugar-free candy, Milk candy, Aerated candy, Liquid filled candy, Sweets, Hard candy, Laminated candy, Powder filled candy, Medicated candy
- End products
- Liquid-filled fruit candy, Aerated chocolate, Medicated throat lozenges, Laminated fruit-flavored candy, Sugar-free butterscotch, Milk chocolate-flavored candy, Lollipops, Powder-filled mint candy, Boiled sweets
- Steps before
- Weighing, Dissolving, Cooking
- Steps after
- Vacuuming, Cooling, Tempering, Forming, Packing
- Input ingredients
- sugar masses, sugar free masses, liquid for filling, powder for filling, milk for hard candy, medicinal ingredients
- Output ingredients
- hard candy, liquid filled hard candy, powder filled hard candy, milk hard candy, aerated hard candy, laminated hard candy, medicated hard candy
- Market info
- CHOCOTECH is known for providing innovative solutions in the confectionery industry, specializing in machinery for processing and manufacturing chocolate, candies, and other sweets, with a reputation for precision engineering and tailored, high-quality equipment solutions.
- Capacity
- 500 kg/h to 4000 kg/h
- Automation
- PLC-controlled
- Temperature Management
- Variable Temperatures in Zones
- Vacuum System
- High vacuum for low inversion
- Processing Capability
- Up to four different ropes, each with individual colors and flavor
- Bringing Multiple Masses Into Sync
- Individual color and flavor ropes
- Integrated Production Steps
- Cooking, Vacuumizing, Screw Extraction, Dynamic Mixing, Tempering
- Aeration Capability
- Optional Aeration
- Temperature Control
- Uniform cooling and folding at various zones
- Vacuum System Efficiency
- High vacuum with low inversion
- Flexible Throughput
- 500 kg/h to 4000 kg/h
- Product-forming Versatility
- Sugar/Sugar-free, Filled, Milk, Aerated, Laminated, Medicated Candy
- Batch vs. Continuous Operation
- Inline Continuous
- Flavor and Color Variability
- Up to four different ropes
- Corrosive resistance (e.g. acids)
- Yes
- Density/particle size
- 0.5–2.5 g/cm³ / 50–1000 µm
- Compact footprint
- Yes, designed for optimized space usage
- Machine footprint
- Customizable based on production line configuration
- Discharge method
- Dynamic mixing with screw extraction of mass
- Control panel type
- Available as per client requirements
- Cooling zones
- Multiple temperature-controlled zones
- Control panel type
- Touchscreen HMI
- Integration possibilities
- PLC / SCADA systems
- Customization for candy types
- Sugar, sugar-free, liquid filled, powder filled
- Rope color and flavor options
- Up to four different colors and flavors
- Optional aeration
- Yes
- Tempering belt length
- Varies based on throughput