
Powder Drying Equipment
Discover techniques and equipment used in industrial powder drying. From spray drying to drum drying and more. Learn which method is best.
Drying is a core step before and after milling materials into powders. But the powder drying equipment and method depend on the substance category. For example, cabinet dryers and centrifuges are efficient solutions for biomass slurries or minerals, but they are not suited to thermo-sensitive materials. Delicate substances like fruit powders or pharmaceutical powders demand gentle systems like fluid bed dryers or vacuum drying. Industrial drying machines are designed to remove moisture from your powder product. But the drying process must cater to variations in the state of matter and molecular structure of the input material. Industrial dryer technology exploits the modes of heat transfer (convection, conduction, radiation, evaporative cooling) to control the moisture content.
Spray Drying Is A Popular Choice For Powder Drying
When it comes to drying powders, there are various types of methods and equipment available. But possibly one of the more popular methods is spray drying. Spray drying involves the atomization of a liquid feed into a fine mist or spray. Which is then exposed to hot air inside a spray dryer. The hot air causes the liquid droplets to evaporate quickly. Thus leaving behind a dry powder. The resulting powder is typically fine and free-flowing, making it easier to handle, store, and transport. Spray dryers are a key piece of equipment in this process. They consist of a large chamber, usually cylindrical in shape. Along with a drying tower and a spray nozzle at the top. Usually, the liquid feed is pumped into the nozzle. Which atomizes it into fine droplets that are sprayed into the drying tower. Hot air is then blown into the tower, and the droplets quickly dry as they fall through the hot air stream. Spray drying is typically used for large-scale production and continuous operation of powders. This is because it can handle high volumes. However, it can also be used in a batch mode, where smaller volumes of powder are processed at once.
Other Popular Powder Drying Methods
In addition to spray drying, other methods of drying, such as evaporation and granulation are commonly used in industrial settings. Here are some of the most popular methods for drying powders:
Drum Drying: In this method, a thin layer of slurry is spread onto the surface of a rotating drum. The hot drum surface causes the water in the product to evaporate. Thus, leaving behind a dried powder.
Freeze Drying: Also known as lyophilization. This method of freeze-drying involves freezing the raw materials and then subjecting them to a vacuum environment. As a result, the frozen water in the product sublimates. Which means it goes directly from a solid to a gas without passing through the liquid phase. This leaves behind a dry powder with a high degree of porosity.
Tray Drying: In this method, the liquid feedstock is spread onto a flat tray, which is then placed in a drying chamber. Hot air is circulated through the chamber, evaporating the water in the feedstock and leaving behind a dry powder. The tray is then removed from the chamber, and the powder is scraped off and collected.
Fluid Bed Drying: In the fluid bed drying process, the raw material is sprayed onto a bed of hot, fluidized particles. Typically sand or ceramic beads. Then, the hot particles circulate around the materials. Therefore, drying it quickly and evenly. The dried powder is then separated from the fluidized particles and collected.
Vacuum Drying: Vacuum drying involves placing the liquid feedstock in a vacuum chamber and subjecting it to reduced pressure. Reduced pressure causes the water in the raw materials to boil off at a lower temperature than it would under normal atmospheric pressure. This allows the feedstock to be dried quickly and at a lower temperature, which can be beneficial for heat-sensitive materials.
How To Choose Which Drying Method Is Best?
The choice of drying method will depend on several factors, such as the type of feedstock, the desired characteristics of the final powder, the scale of production, and the available equipment. For example, freeze-drying is commonly used for sensitive materials such as pharmaceuticals, while tray-drying may be preferred for smaller-scale operations or for feedstocks that are not suitable for spray drying.
In some cases, multiple drying methods may be used in a single production process to achieve the desired outcome. For example, a powder may be spray dried initially to remove most of the moisture, and then further dried using a different method to achieve a specific particle size or moisture content. An example of this would be drying milk powders or fruit powders.
Therefore, while spray drying is a popular and effective powder drying technique, it is not always the most common or appropriate method for every application. The choice of drying method will depend on a variety of factors, and it is important to consider all options when selecting the most appropriate technique for a particular application.
Which powder drying technology do you need?
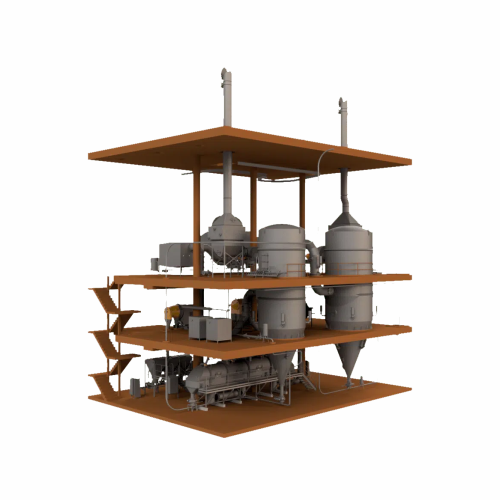
Lactose drying system for high-quality edible powder
Achieve precise and cost-effective lactose transformation into high-...
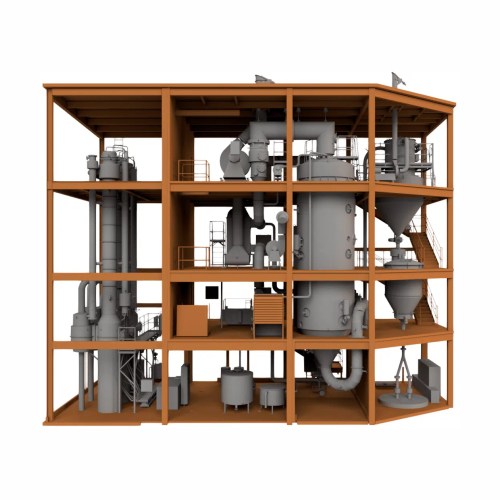
Compact drying solution for regular skim and Wpc powders
Streamline your drying process with a compact solution that effi...
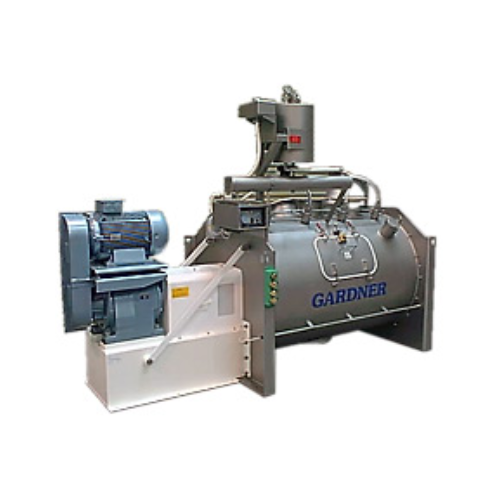
High shear plough mixer for powders, granules, and pastes
Achieve rapid and efficient blending with high shear mixers de...
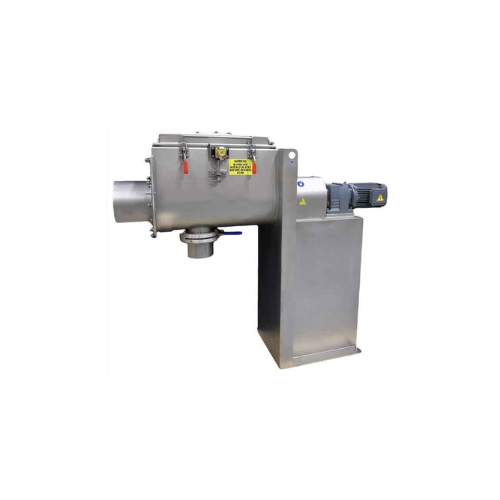
Homogenous blending solution for powders and granules
Achieve precise, homogenous blending of challenging materials like ...
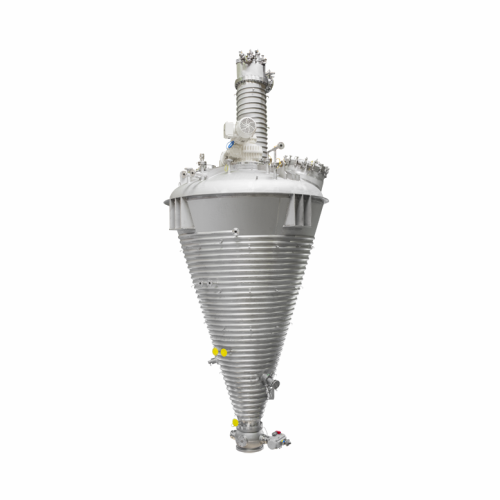
Vacuum dryers for powders and bulk solids
Achieve precise drying and mixing of sensitive materials with advanced vacuum te...
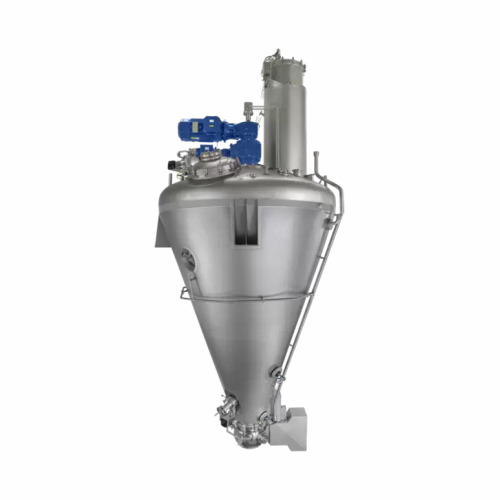
Vacuum dryer for powders and granules
Achieve precise moisture control for sensitive materials with a versatile vacuum dryi...
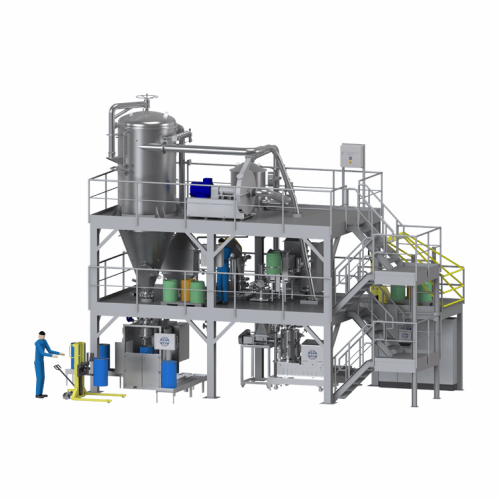
Drying systems for powders and bulk solids
Enhance your production line with precise control of moisture content in powder...
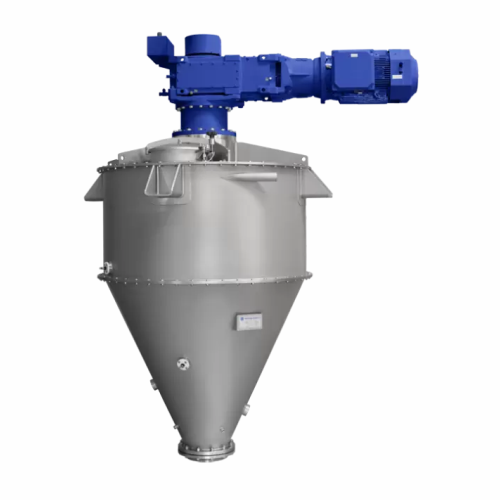
Conical paddle mixer for accurate powder blending
Achieve precise blending of fragile powders and liquids with a versatil...
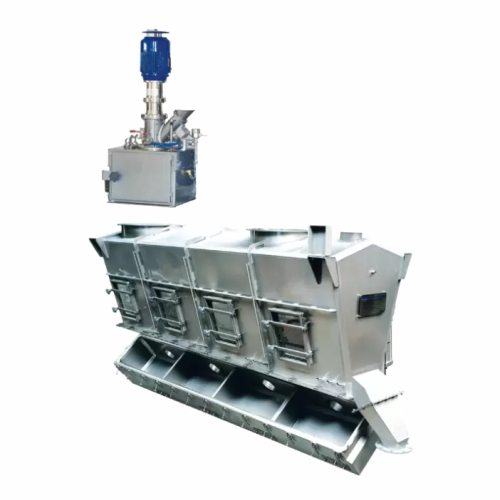
Continuous powder agglomeration system
Enhance product solubility and flowability while minimizing energy consumption with ...
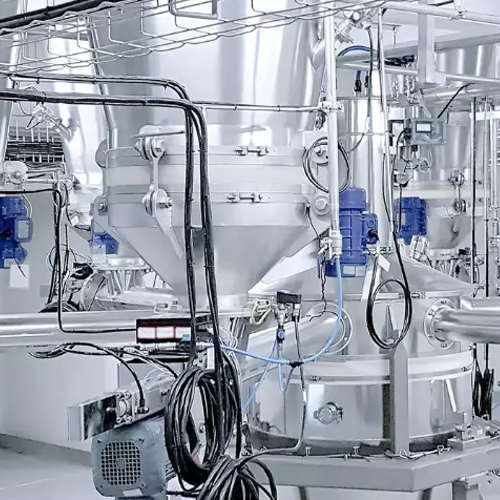
Conical screw mixer for powder blending
Achieve precise and homogeneous blending with the conical screw mixer, ensuring uni...
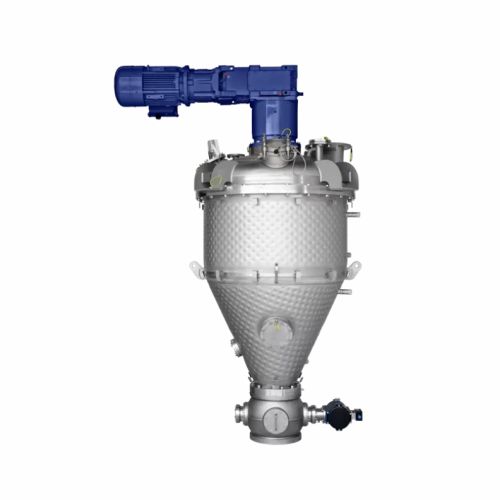
Conical paddle vacuum dryer for powders and granules
Achieve efficient drying of sensitive materials with this versatile ...
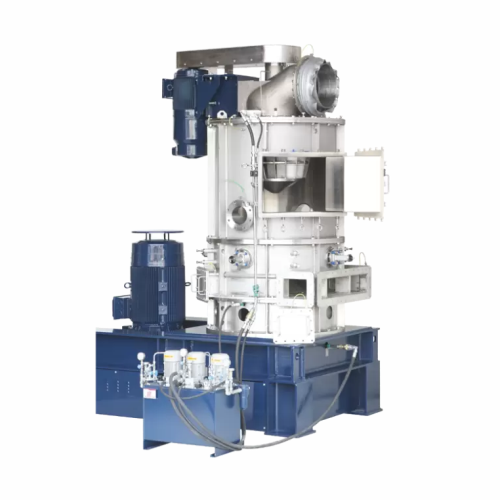
Ultra-fine powder flash drying system
Achieve rapid moisture removal and particle refinement with this integrated system, d...
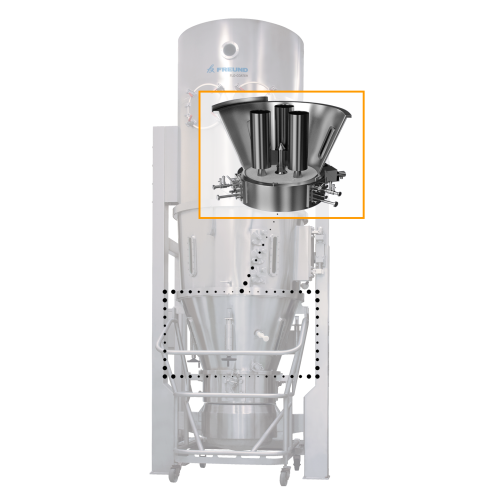
Wurster coating system for fine powders and pellets
Achieve precision coating for multiparticulate cores and mini-tablets...
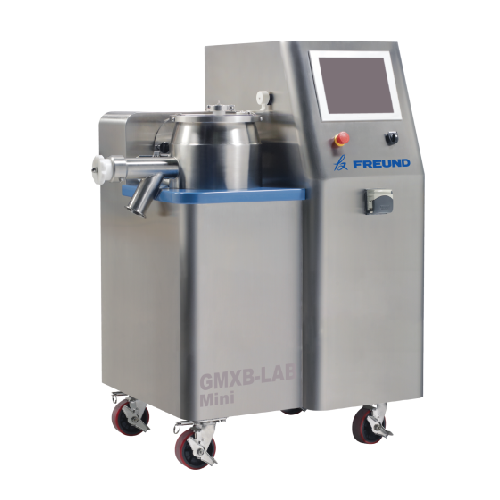
High shear granulator for wet granulation of powders
Achieve consistent granule density and size with a high shear granul...
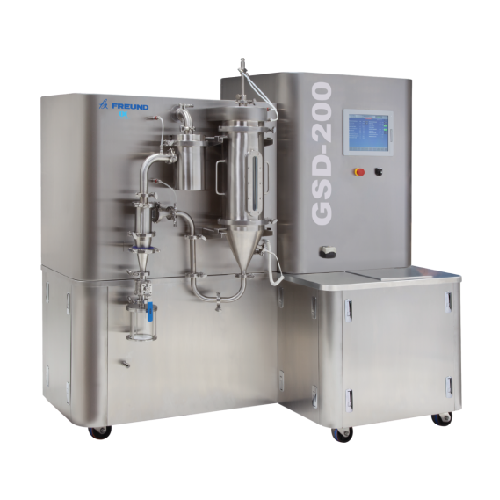
Laboratory spray dryer for sub-gram powder samples
Achieve precise control in developing fine chemical and pharmaceutical...
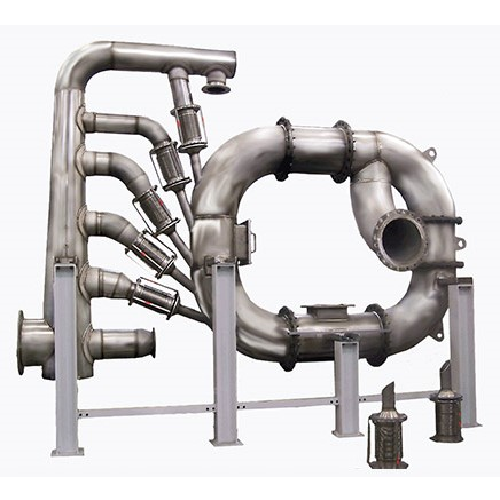
Milling flash dryer for fine powder processing
Achieve precise moisture control and prevent agglomeration in your processi...
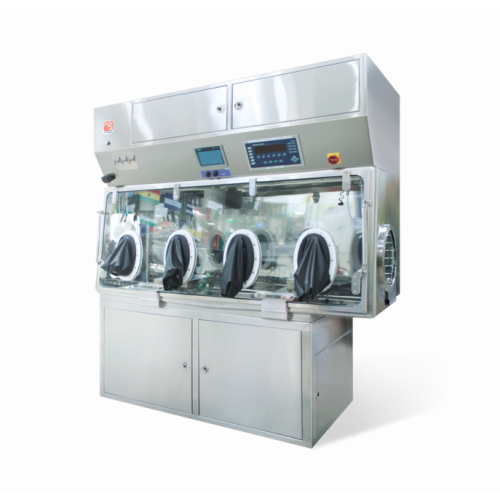
Production isolator for powder preparation and weighing
Ensure precise weighing and safe handling of pharmaceutical powde...
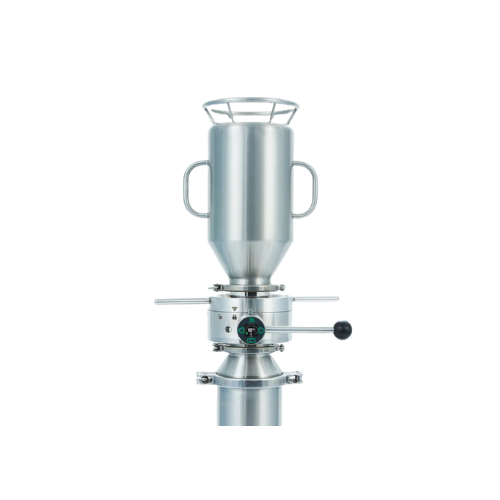
High containment powder transfer valve
Ensure high containment for potent powders in your production line, reducing contami...
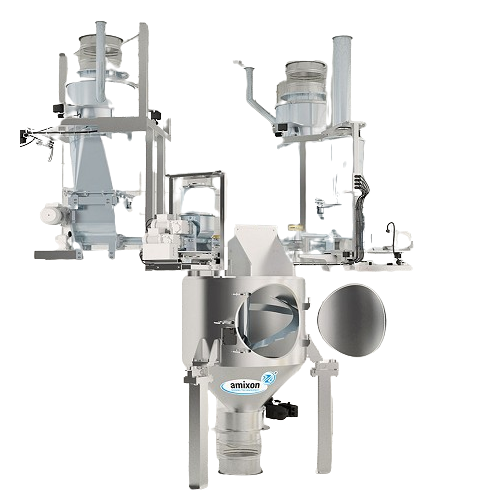
Continuous powder mixer for dry, moist and suspended goods
Achieve precise homogenization and deagglomeration with a con...
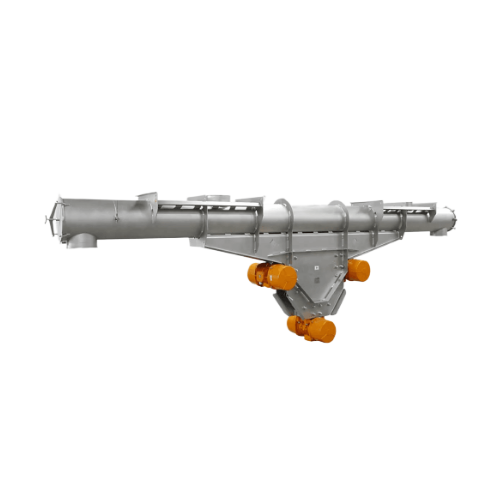
Vibrating conveyor for powder and granule handling
Effortlessly convey and process fragile products with precision, minim...

Lecithin adding system for dairy powders
Enhance your spray drying process by seamlessly integrating lecithin to improve so...
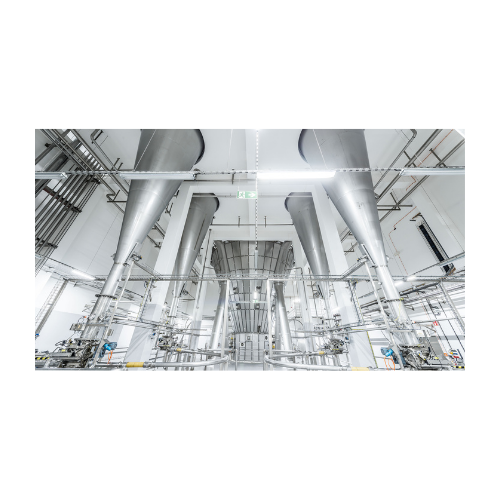
Spray dryer for nutritional and dairy powders
Achieve precise particle size and optimal drying of nutritional and dairy po...
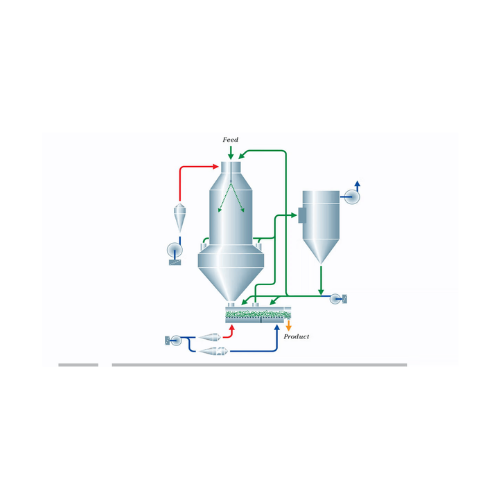
Spray drying solution for uniform powder production
Achieve seamless transformation of liquid feeds into uniform, free-fl...

Lab-scale spray dryer for small volume powder samples
When developing new formulations, achieving consistent powder quali...
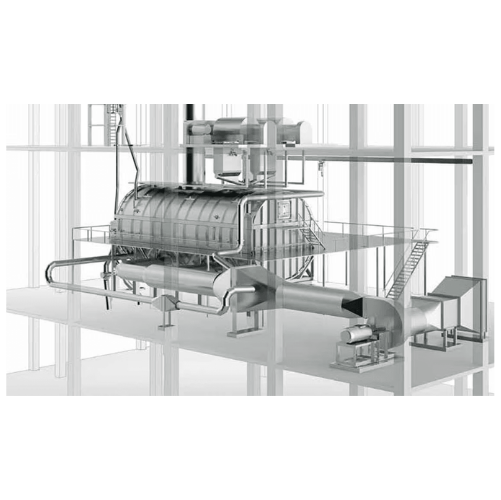
Fluid bed drying system for wet powder chemicals
Achieve efficient large-scale drying and cooling of wet powder chemicals ...
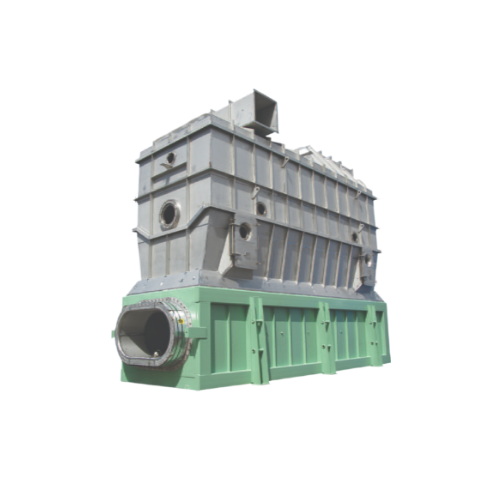
Static fluid bed dryer for powder and granular materials
Achieve optimal moisture control in powder and granular products...
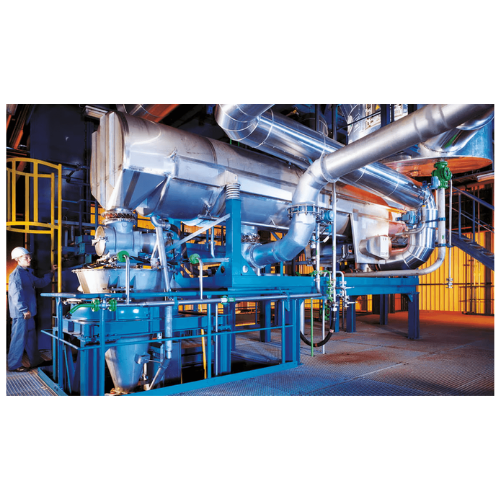
Vibrating fluid bed for final stage powder drying
Enhance powder processing precision with a vibrating fluid bed that ens...
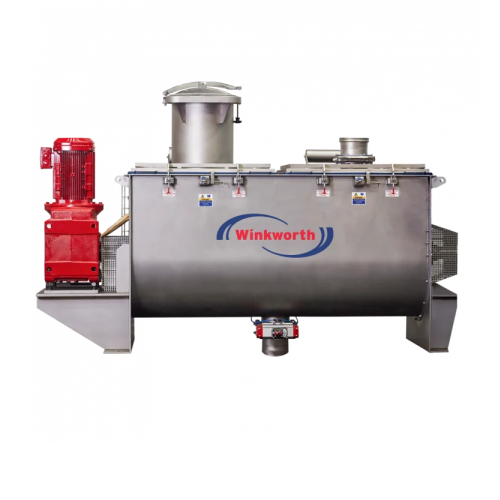
Efficient ribbon mixers for precise powder blending
Achieve consistent and uniform blending with this advanced U-Trough m...
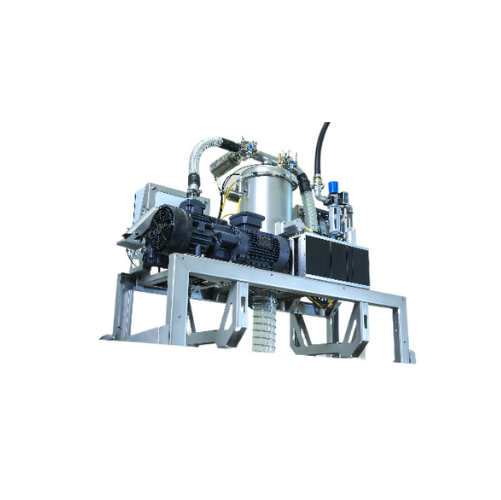
Automatic metal powder filling system for 3d printers
Ensure seamless operation of your 3D printing process with a system...
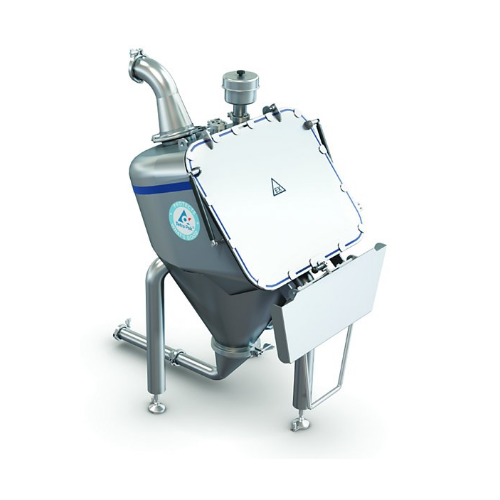
Bag tipping unit for Cip processes in powder handling
Ensure seamless powder handling and high hygiene standards in your ...
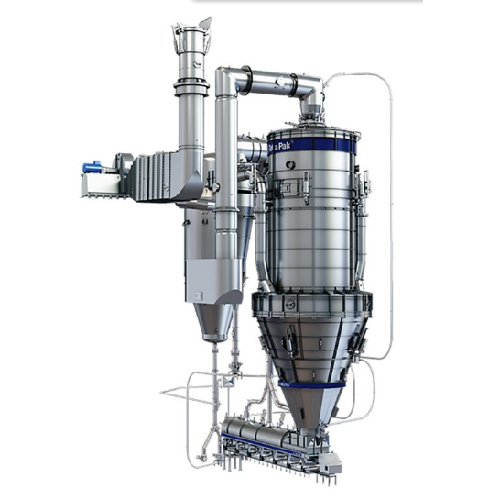
Spray dryer for heat-sensitive powders
Ensure high-quality drying of heat-sensitive powders, producing non-caking and non-h...
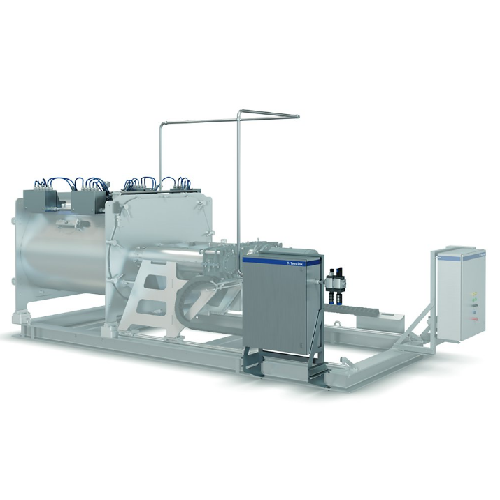
Air jet cleaning system for powder production
Eliminate water and chemical use while maximizing production efficiency with...
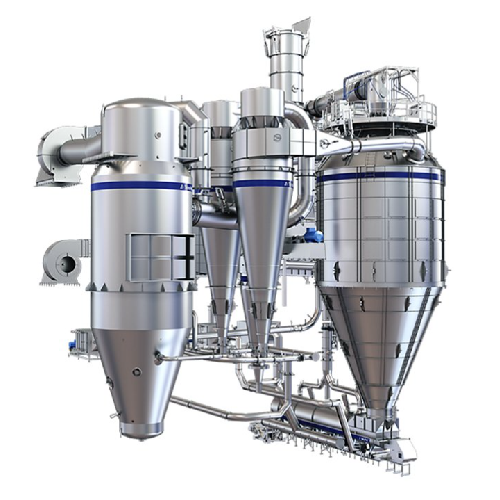
Spray dryer for nutritional powders
Ensure precise moisture control and enhance powder quality in nutritional products with...

Continuous spray dryer for permeate powder
Efficiently transform liquid whey and milk into high-quality, non-caking, and n...
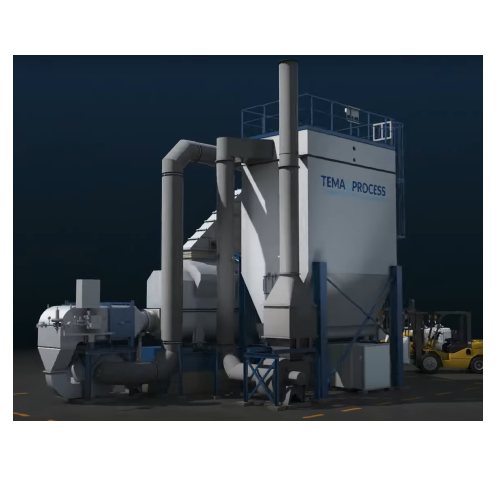
Continuous fluid bed dryer for powder and granules
Enhance your production line with precise moisture control and energy ...
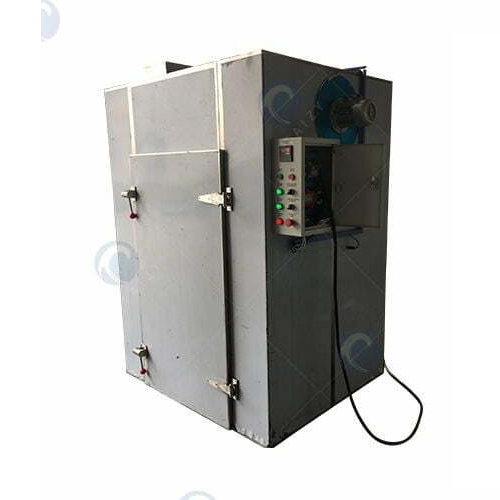
Ginger powder processing line
Optimize your spice production with comprehensive ginger powder processing, transforming fresh...
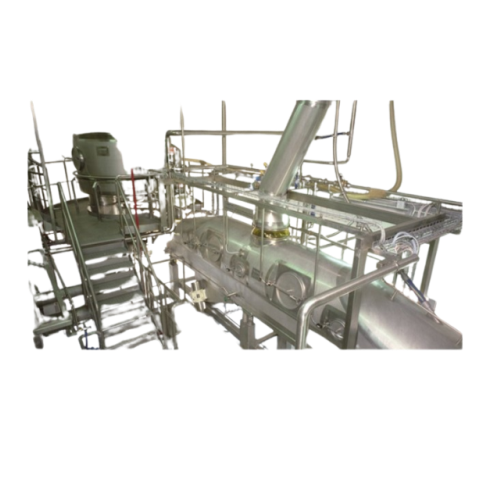
Spray bed dryer for agglomerated powder production
Efficiently transform liquid feedstock into consistent, dust-free powd...
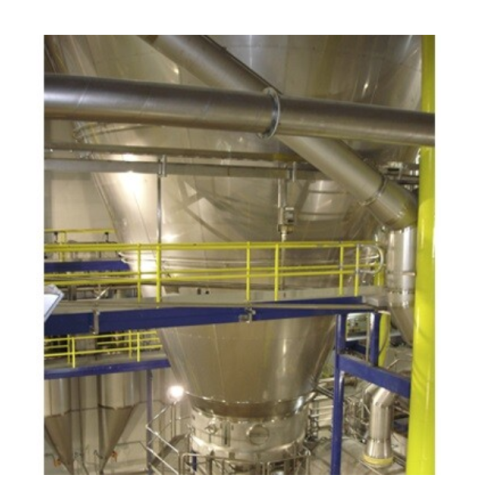
Spray dryers for producing free-flowing dustless powders
Achieve consistent product quality with customizable spray dryer...
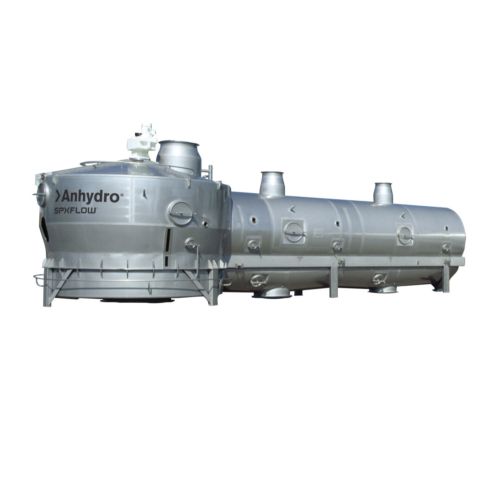
Industrial fluid bed dryers for powder processing
Enhance moisture control and uniformity in powder products with dynamic...
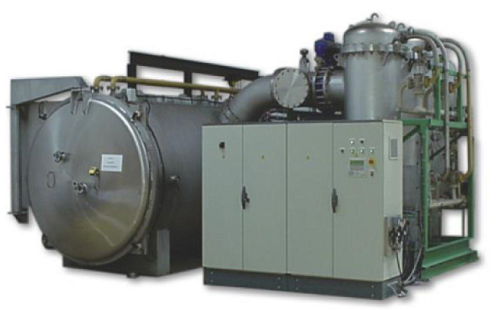
Freeze drying system for berries and fruit powders
Delicate fruits with high moisture levels, such as berries, risk losin...
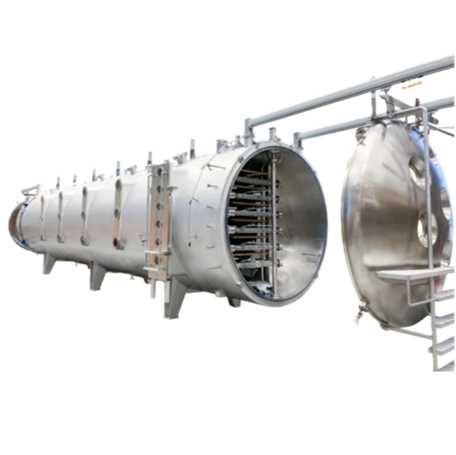
Vacuum belt dryer for instant drink powders
Extracting the essential acids and compounds from fruits and plants is a compl...
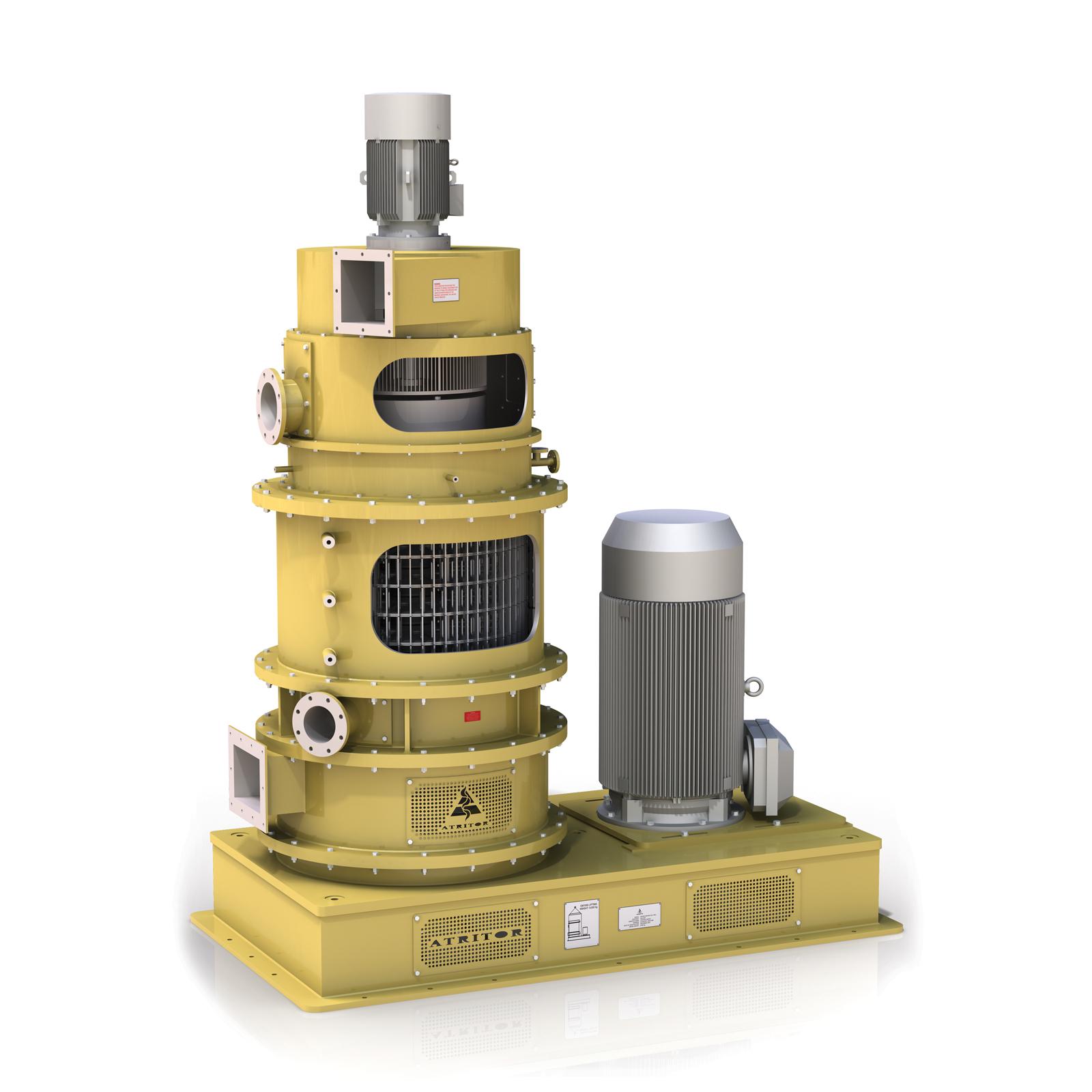
Milling and drying machine for fine powders
When you need to produce ultra-fine powders, the milling and drying process em...
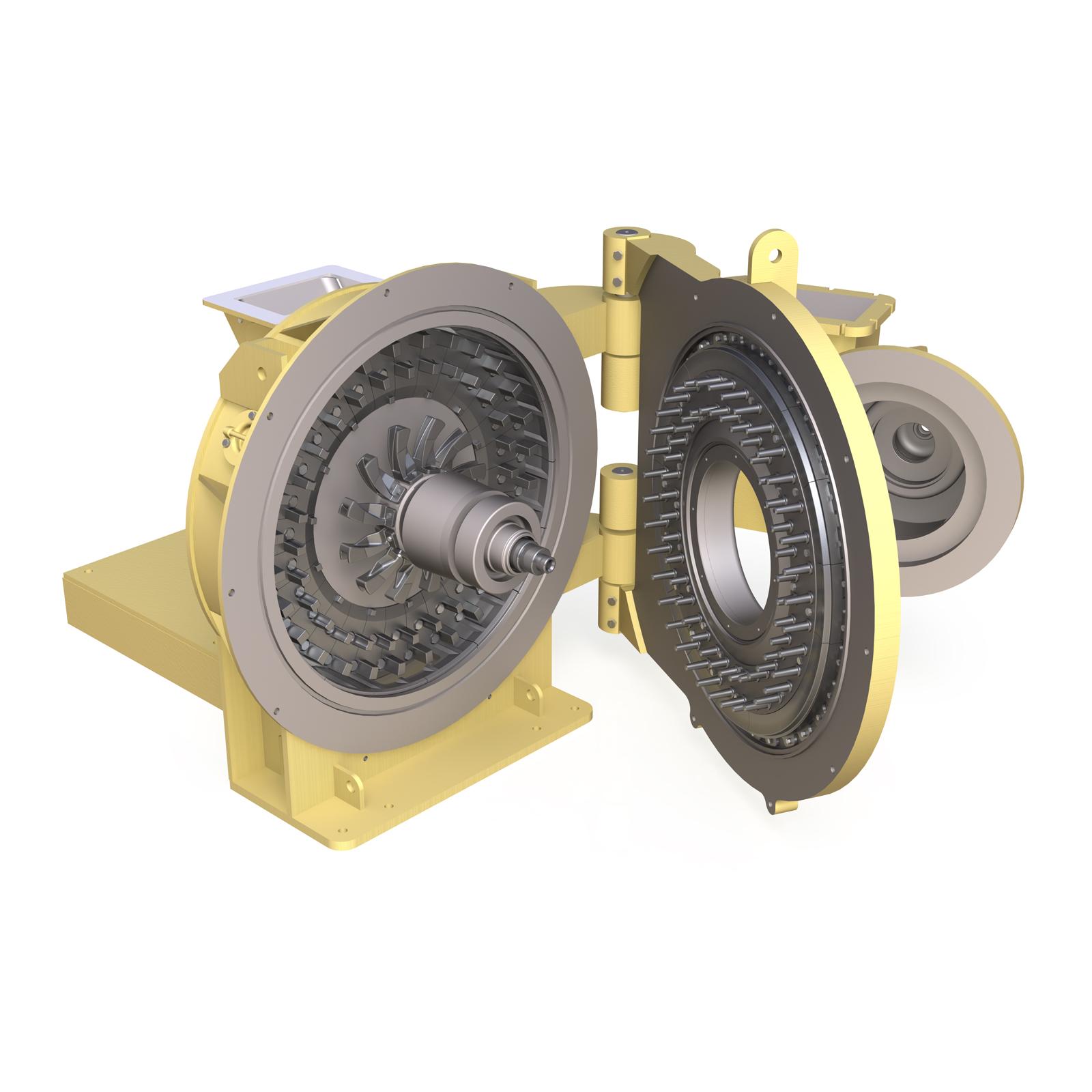
Flash drying grinder for powders
Drying and grinding can be an important feature when trying to process products such as raw...
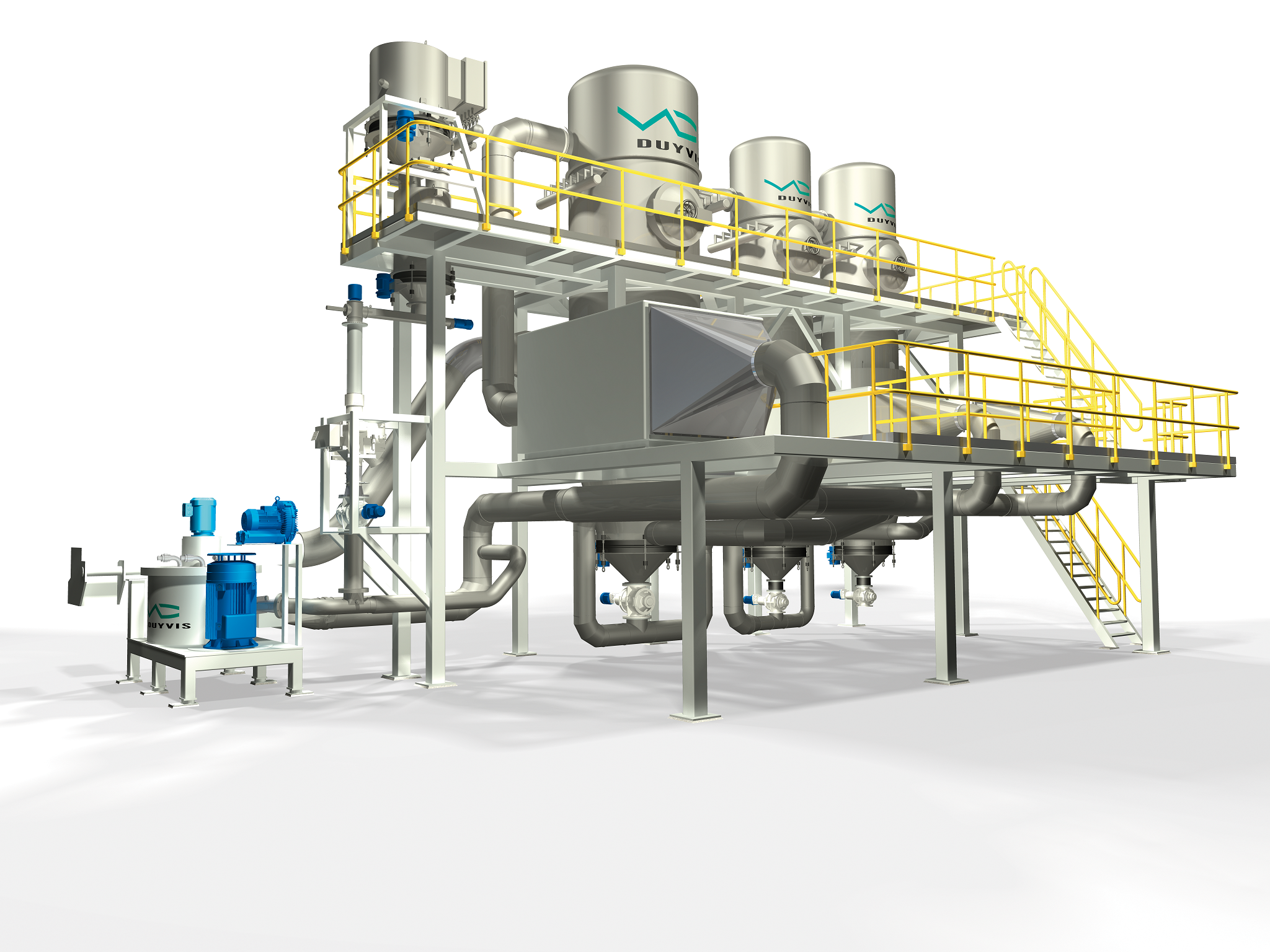
Cocoa powder processing line
Cocoa beans are first fermented, dried, roasted, and separated from their skins to obtain a coc...
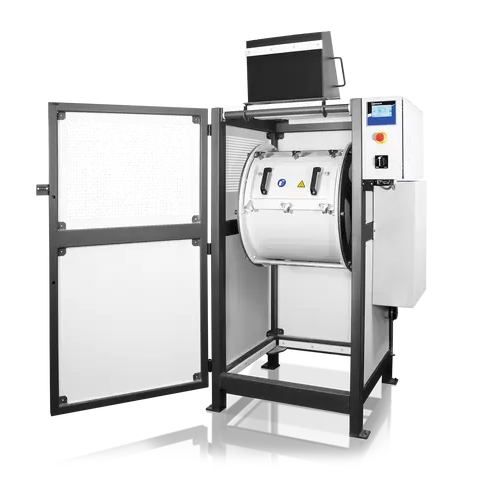
Drum mills for fine grinding of large volumes
Achieve consistent and precise pulverization of large sample volumes with dr...
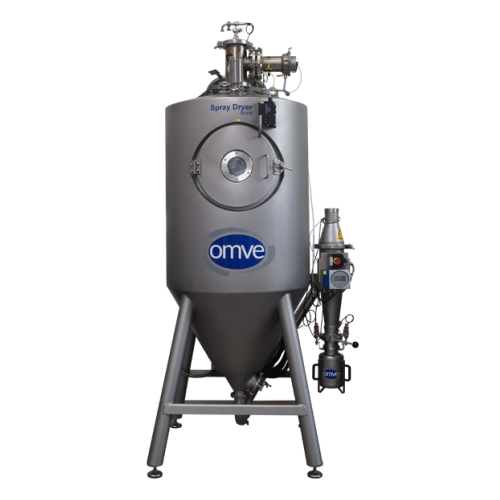
Pilot scale spray dryer for product development
Achieve precise moisture levels and product consistency in development env...
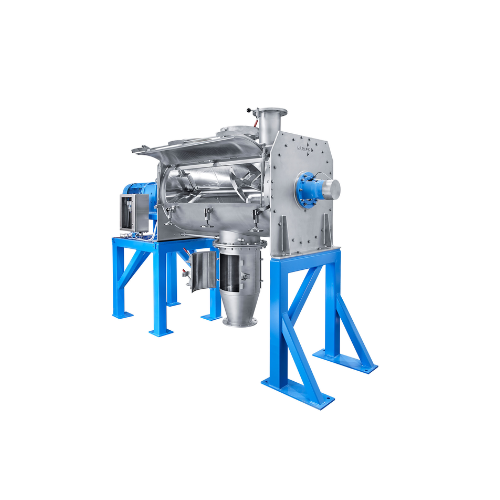
Ploughshare mixer for batch operation
Achieve superior mixing quality with a system designed for rapid batch operations. Ex...
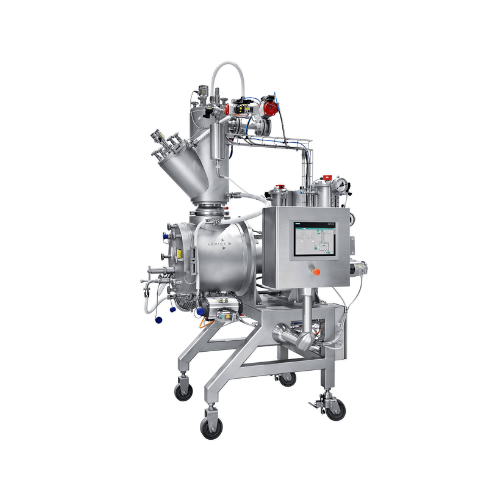
Vacuum paddle dryer for laboratory use
Achieve precise temperature and moisture control in your batches with this vacuum sh...
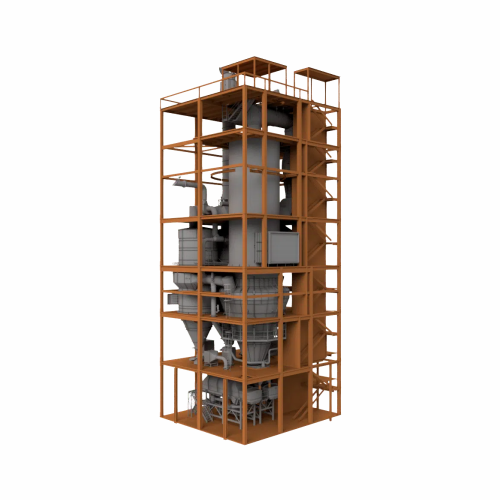
Milk drying system
Optimize your dairy production by efficiently transforming liquid inputs into high-quality, dry powders, e...
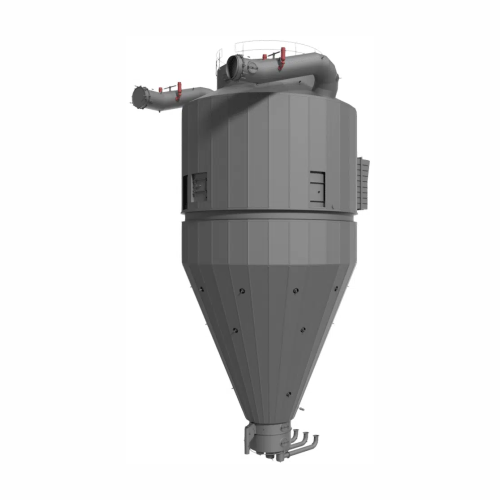
Wide body dryer for dairy and food products
Achieve precise moisture control and optimal powder agglomeration for dairy an...
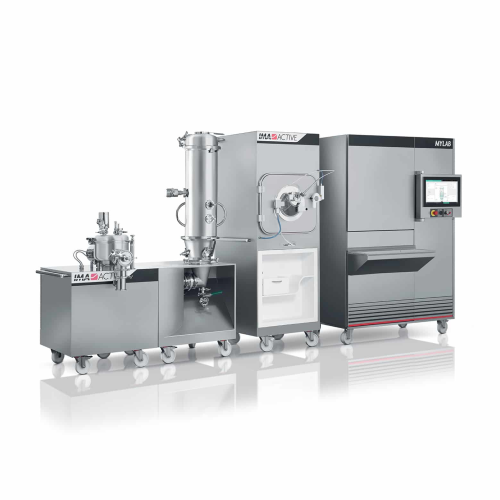
Fluid bed and coating system for small batch processing
Streamline your R&D process with a modular system that ensur...
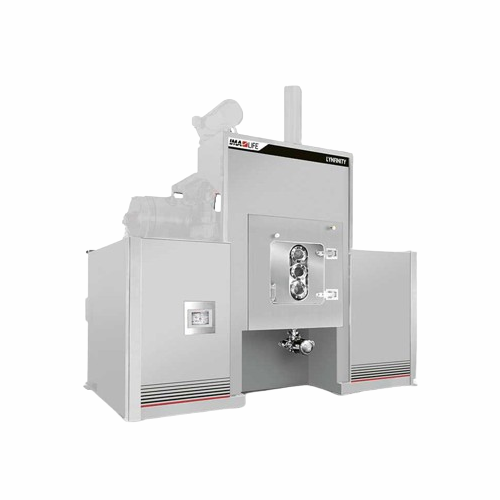
Continuous aseptic spray-freeze-drying system
Achieve higher sterility and improved product uniformity with a continuous a...
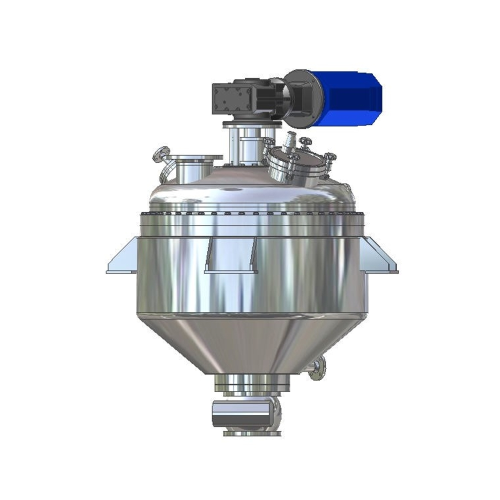
Vacuum drying solution for filter cake or viscous materials
When faced with the challenge of drying filter cake or trans...
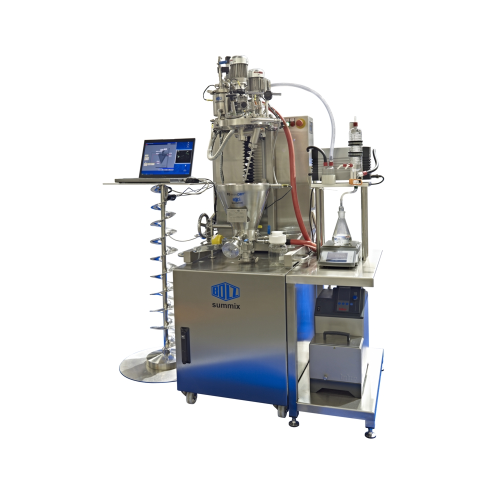
Laboratory system for drying and mixing processes
Enhance your R&D capabilities with precise drying and mixing contr...
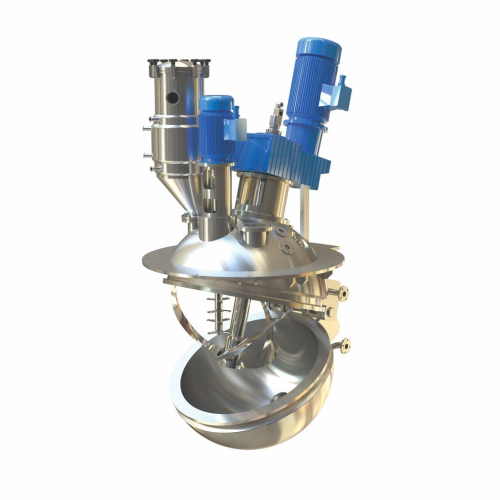
Spherical vacuum dryer for Apis and fine chemicals
Achieve precise moisture control and efficient drying for APIs and fin...
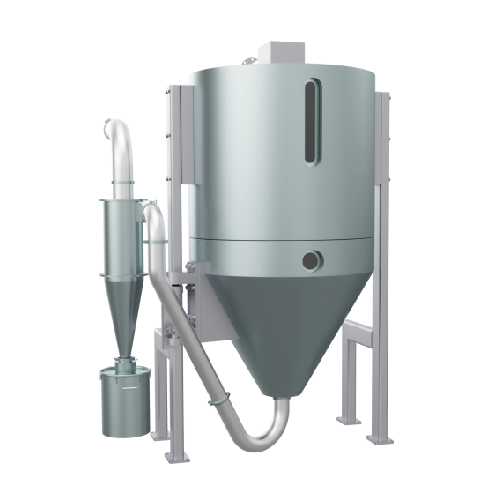
Commercial scale spray dryer for pharmaceutical materials
Optimize the drying of pharmaceutical and industrial materials...
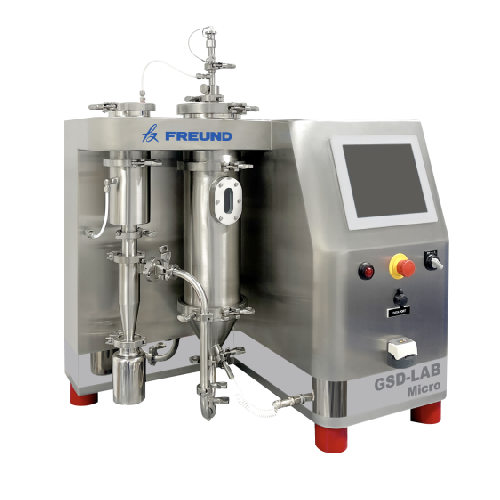
Benchtop spray dryer for drug discovery
Optimize your formulation development with a compact spray dryer that streamlines t...
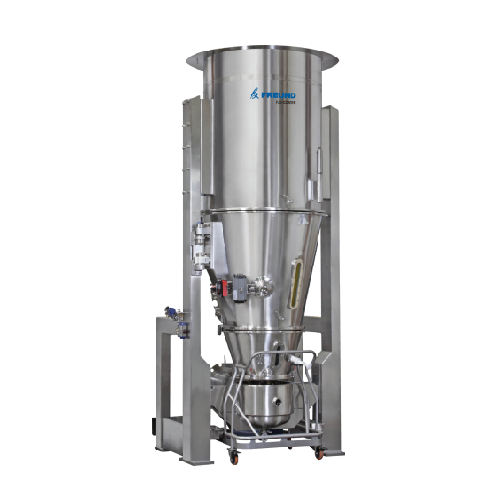
Fluid bed granulator for industrial granulation
Optimize your production efficiency with versatile fluid bed granulation, ...
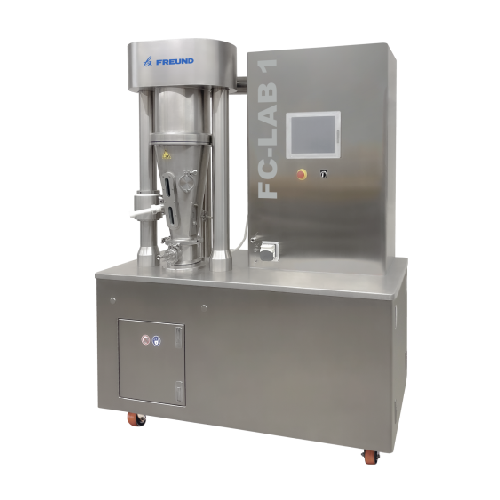
Laboratory scale fluid bed system for granulation and coating
For precise formulation and optimization, this fluid bed s...
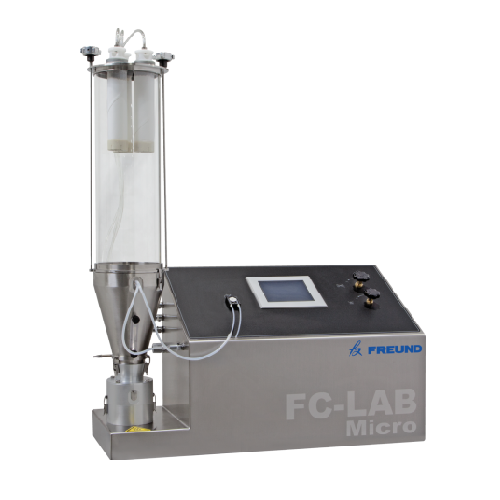
Development fluid bed system for feasibility studies
Explore precise granulation and coating capabilities for small batch...

Closed loop granulator for pharmaceutical production
Streamline your production with a fully automated closed-loop system...
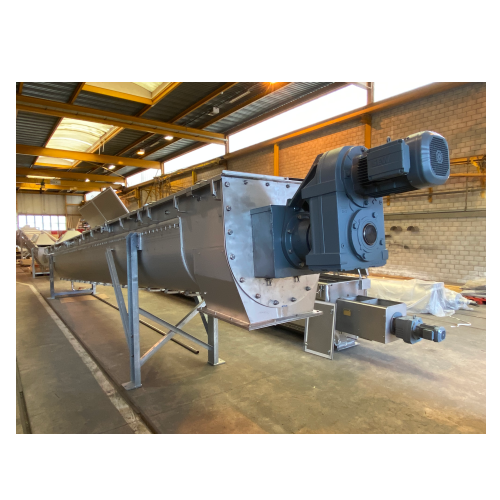
Screw heat exchanger for efficient thermal processing
Optimize your heating and cooling processes with this robust double...
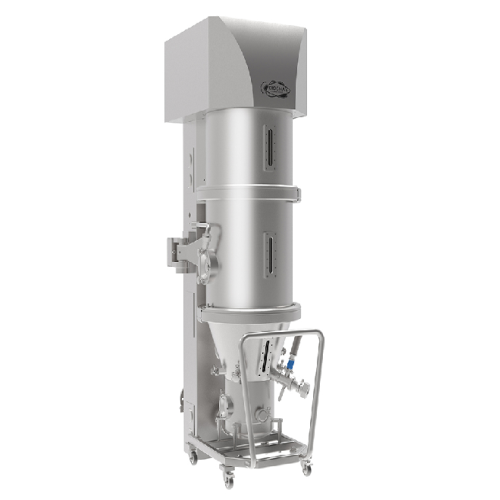
Fluid bed processor for granulating, drying, and coating in pilot scale
When scaling from laboratory to production, rel...
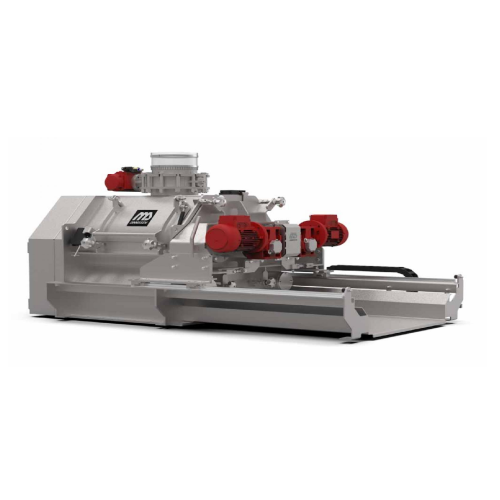
5-in-1 industrial mixer for food and chemical industries
Streamline your production with a multifunctional system that ef...
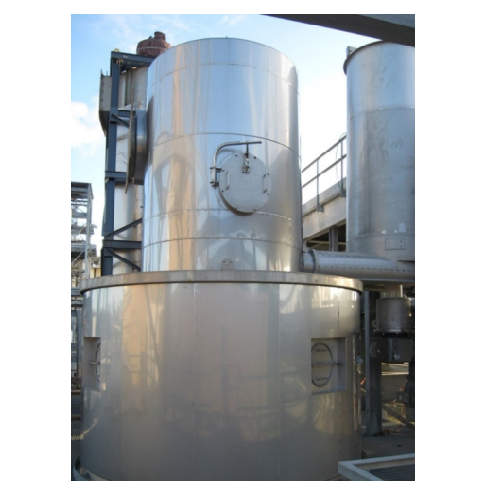
Industrial roto-flash dryer for chemical applications
Achieve uniform moisture and particle size in demanding drying proc...
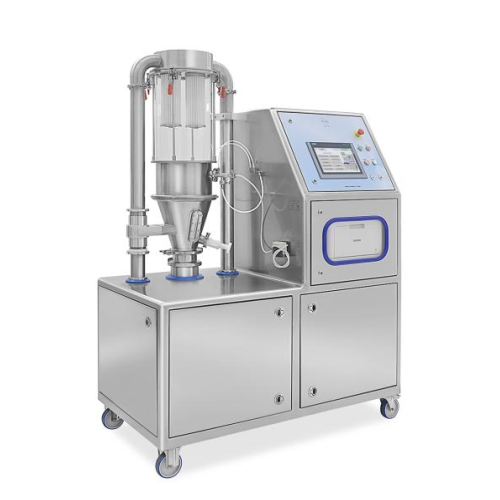
Laboratory fluid bed dryer for pharmaceutical granulation
Optimize your lab-scale drying and granulation processes with ...
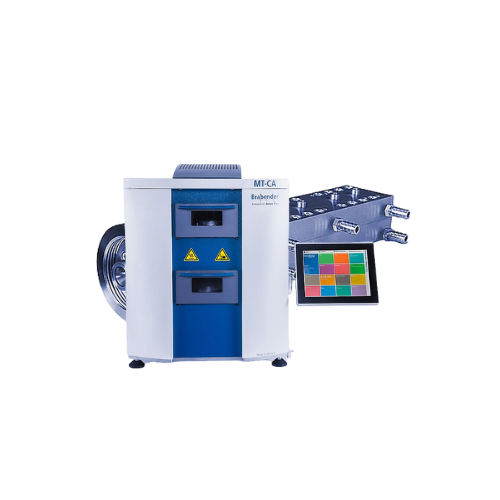
Moisture analyzer for flour and tobacco
Optimize your moisture measurement process with precision and speed, ensuring quali...
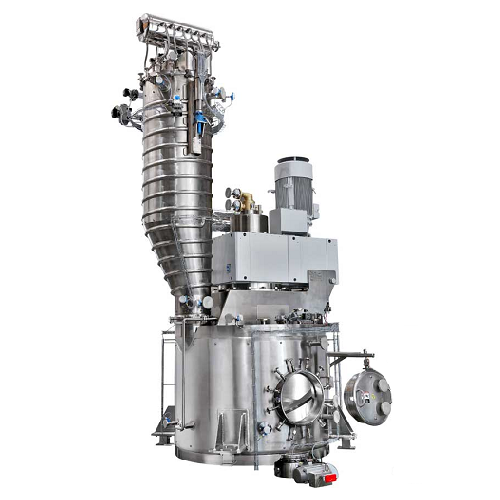
Vertical vacuum dryer and mixing reactor
Achieve precise control over drying and mixing processes with a versatile unit des...
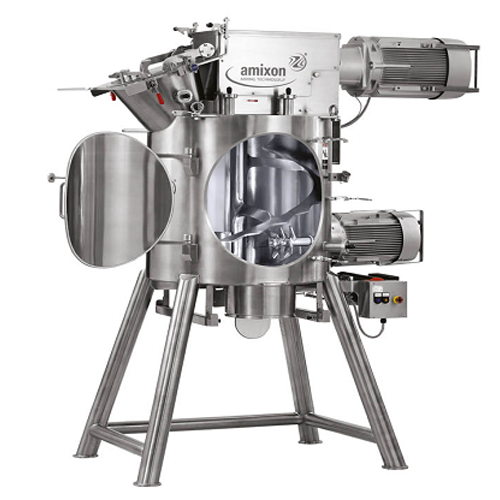
Vertical single-shaft mixer for dry, moist, and viscous materials
In industries requiring precise and thorough mixing o...
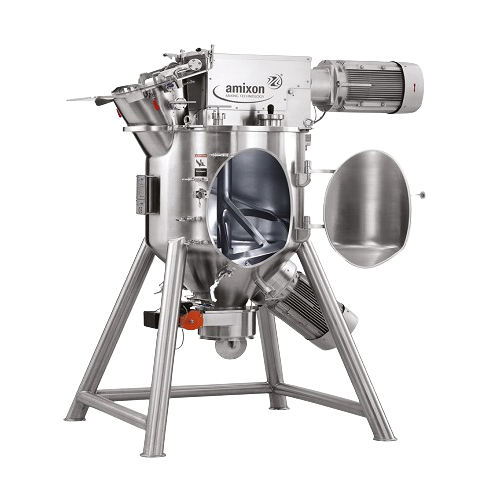
Conical mixer for dry, moist, and viscous materials
Achieve optimal mixing consistency and precision for diverse material...
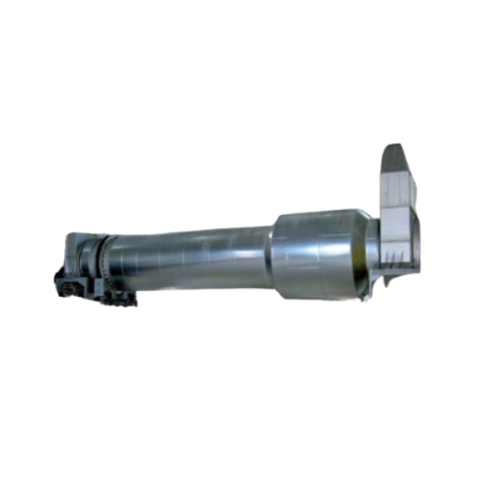
Indirect drying drums for solvent-based products
Optimize energy use and safety with our indirect drying drums, ideal for ...

Dryer for pigments and hydroxides
Achieve precision drying of complex suspensions and pastes into uniform powders, optimizi...
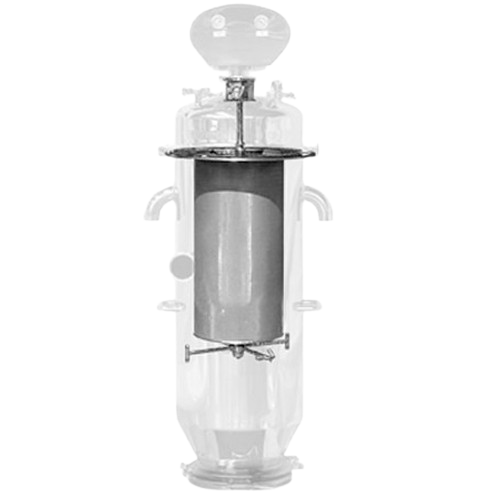
Vacuum transfer system with integrated cleaning
Ensure sterile powder handling and contamination-free production with vacu...
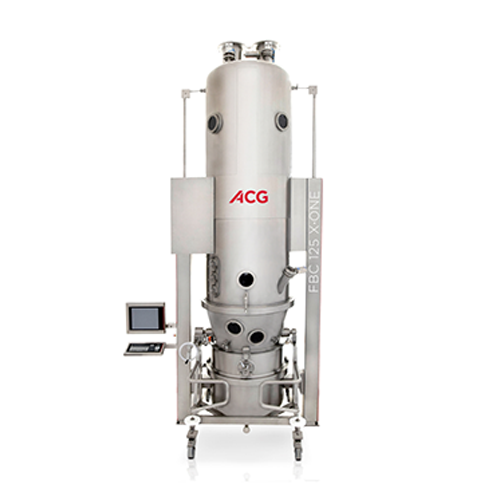
Fluid bed dryer with granulation and coating
Enhance your processing efficiency with a versatile system capable of combini...
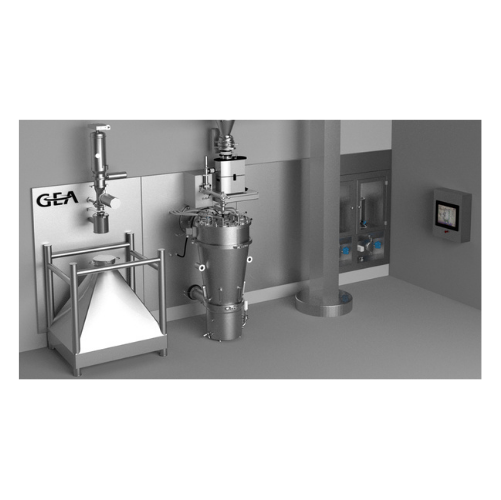
Continuous granulation and drying system for pharma production
Achieve precise control over granule quality with a conti...
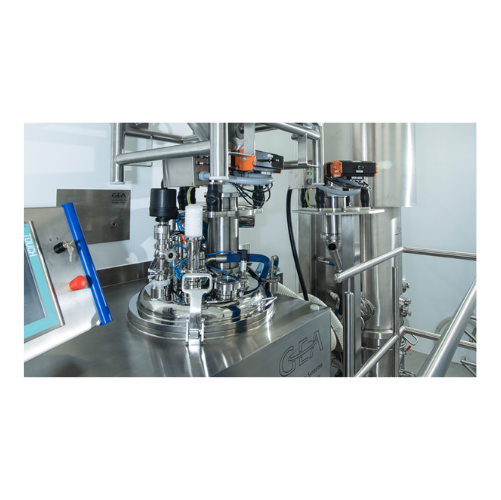
Pharmaceutical bottom-drive high shear granulator
Achieve optimal granule uniformity and precise control over moisture le...
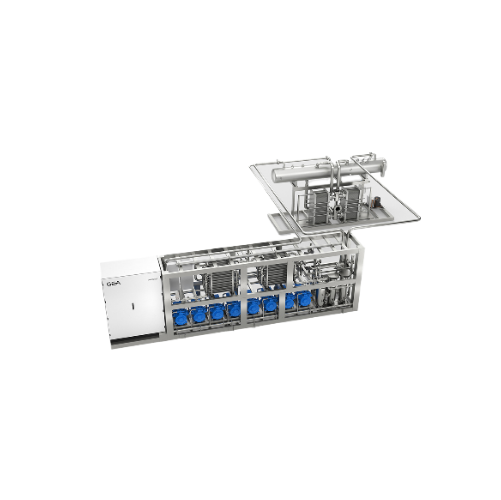
Heat pump solution for spray dryers
Enhance your spray drying efficiency and sustainability with an innovative heat pump sy...
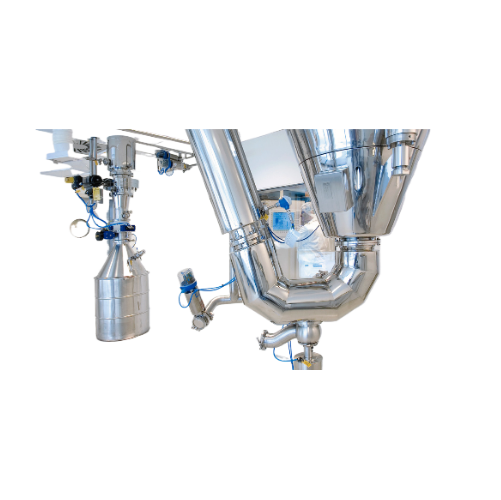
Pharmaceutical spray dryer
Unlock the potential of spray drying to enhance bioavailability, achieve controlled release, and ...
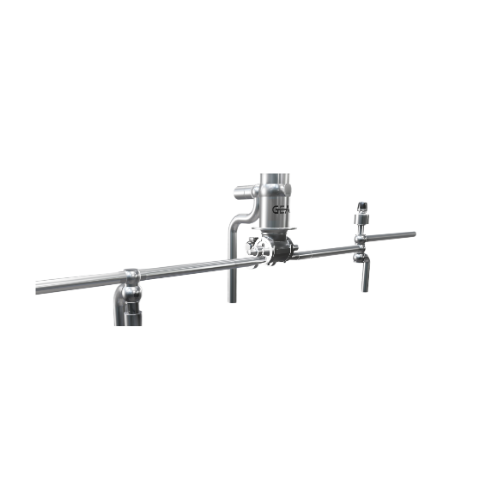
Automated fines return system for food and dairy spray dryers
Enhance your spray drying process by eliminating manual in...
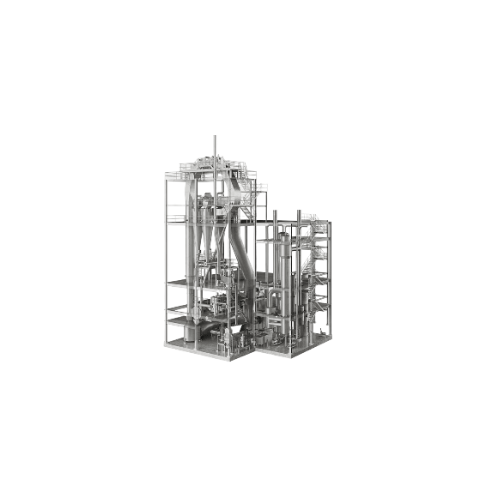
Feed-type ring dryer for industrial drying processes
Optimize your production with a versatile drying solution designed f...
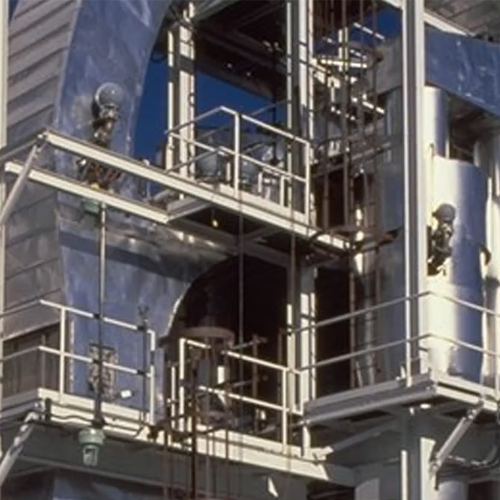
P-type ring dryer for thermally sensitive products
Optimize moisture control and prevent thermal degradation in your prod...
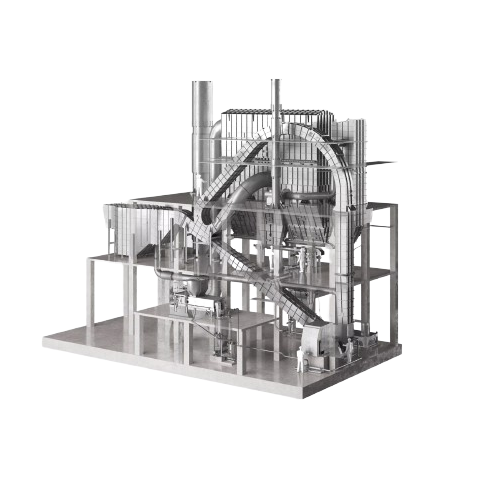
Industrial ring dryer for efficient particle processing
Control particle size and drying efficiency with precise recircul...
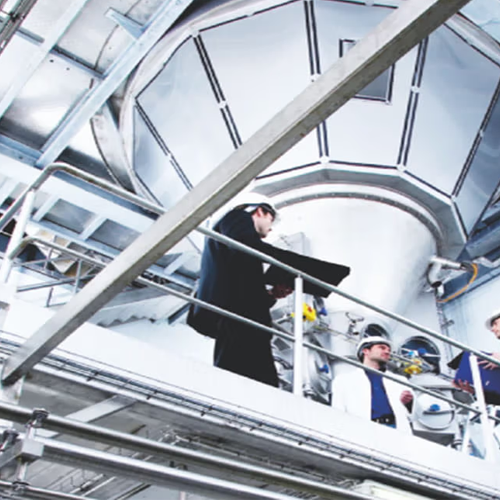
Conventional spray drying for chemical industry
Achieve optimal particle size uniformity in food powders with precision at...
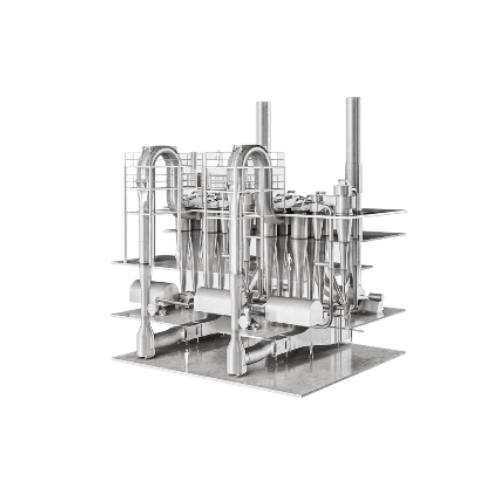
Flash dryer for industrial moisture removal
Optimize your production with rapid moisture removal, efficiently transforming...
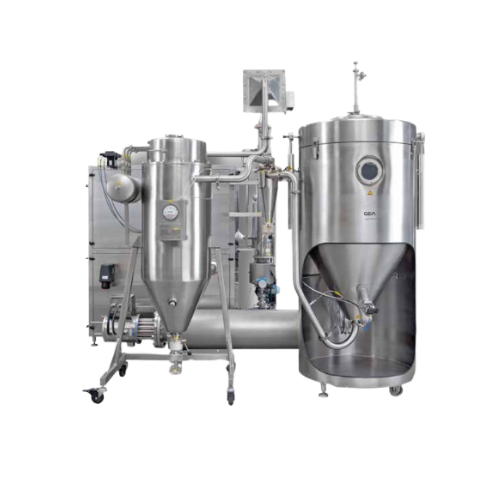
Spray dryer for food and dairy products
Achieve consistent drying for diverse powders and granulates with precision technol...
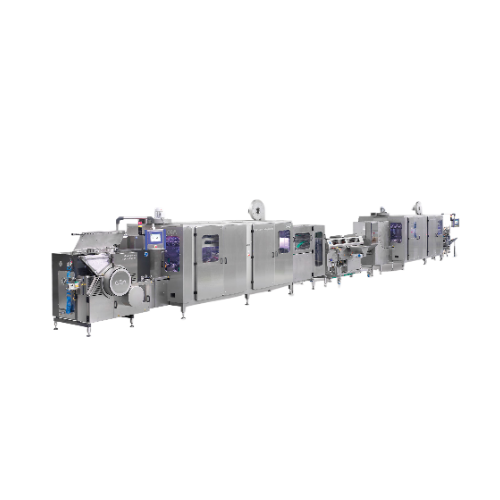
Coated lollipop production line
Transform your confectionery line with a solution that forms, cools, and coats 3D lollipops ...
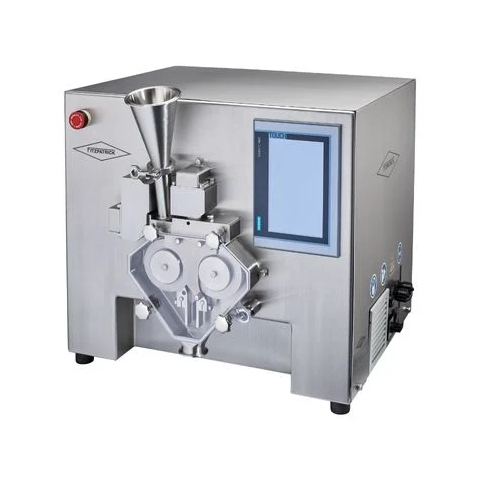
Lab scale roller compactor for dry granulation
Achieve seamless scale-up from lab development to full-scale production wit...
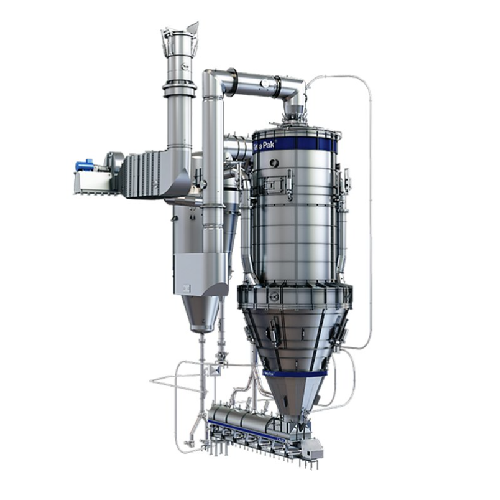
Spray dryer for heat-sensitive materials
Optimize your production line with a high-capacity spray dryer designed for precis...
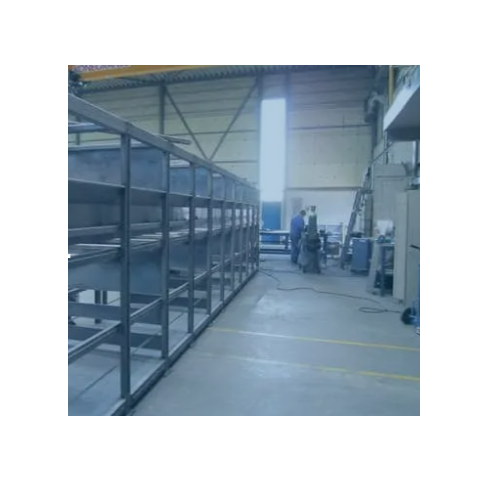
Continuous bulk fluid bed dryer
Achieve rapid and energy-efficient moisture removal across diverse materials with our advanc...
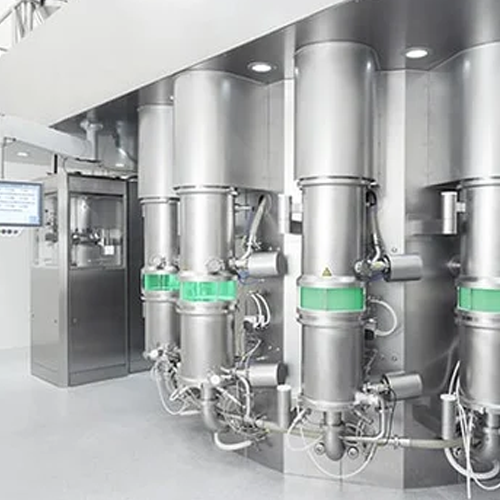
Pharma r&d equipment for solid dosage forms
Optimize your pharmaceutical production with cutting-edge equipment designed f...
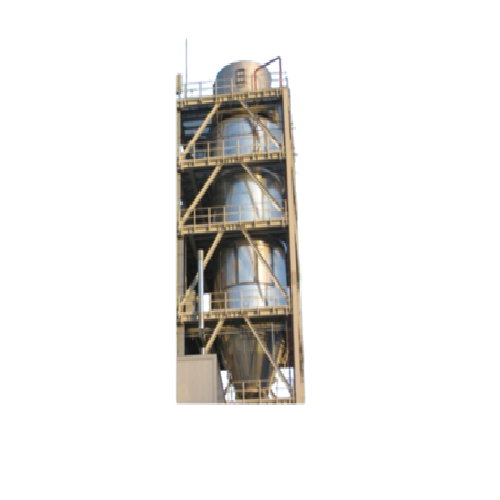
Tall form dryer for producing large non-agglomerated particles
Achieve precise particle size control and optimal moistur...
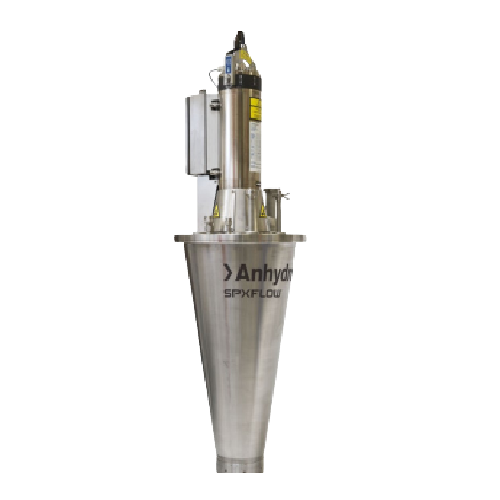
Centrifugal atomizer for precise spray drying
Achieve precise control over particle size and moisture content with centrif...

Efficient grinding and drying mill
Transform your production line with a versatile mill that simultaneously grinds, dries, ...
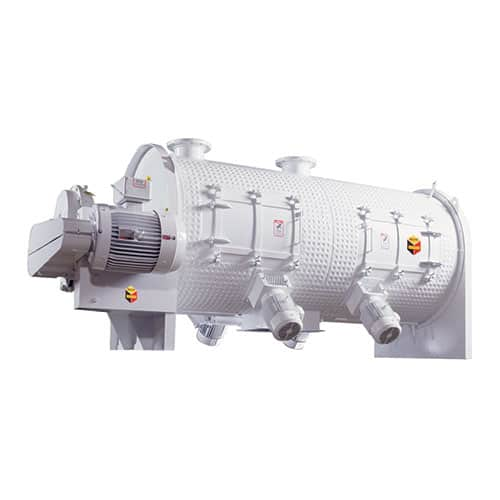
Industrial plow mixer for efficient solid and liquid mixing
Experience unparalleled mixing precision with high-speed plo...
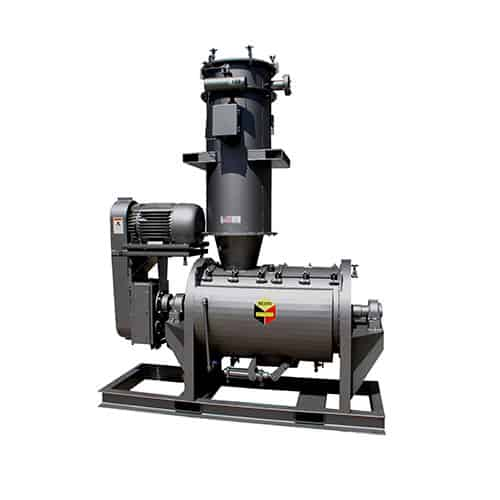
Industrial vacuum batch dryer for reducing moisture content
Achieve precise moisture control with a solution that handle...
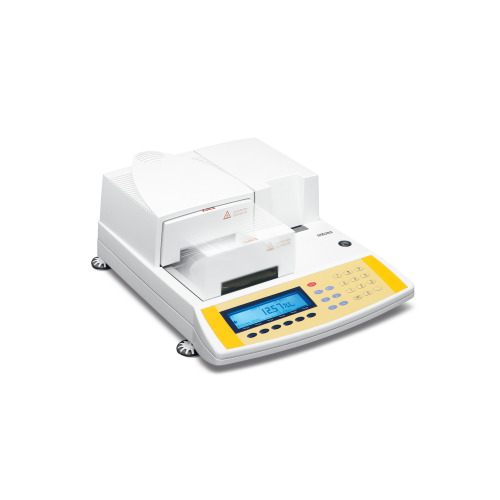
High-accuracy moisture analyzer for lab weighing
Achieve precise and reproducible moisture content determination for diver...
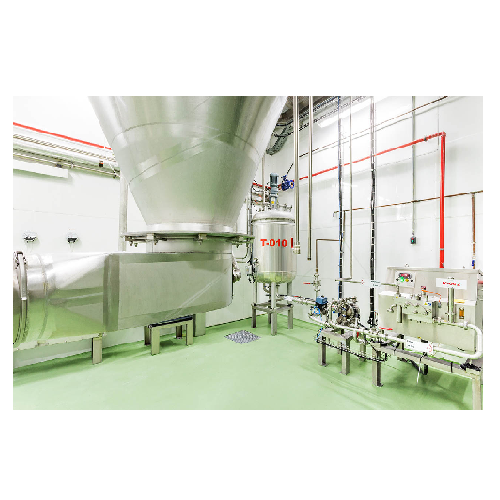
Continuous spray dryer for thermosensitive products
Ideal for processing thermosensitive slurries, this spray dryer ensur...
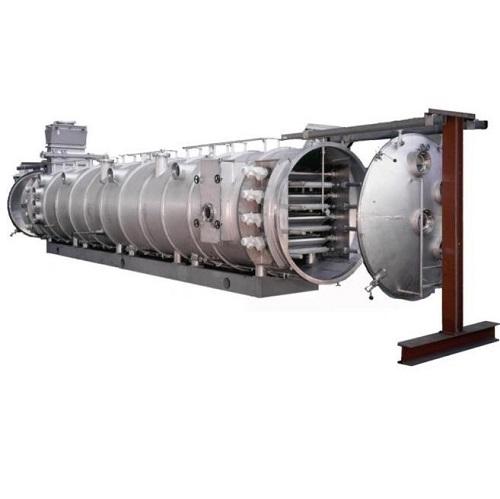
Vacuum belt dryer for fruit, vegetable and herbal extracts
Organic volatile compounds from fruits, vegetables and herbs ...
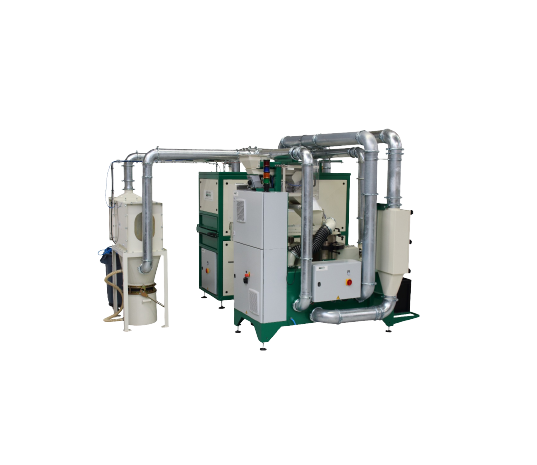
Seed Coating Machine With Integrated Dryer
Seed coating, also known as seed dressing, refers to the covering of seeds with...
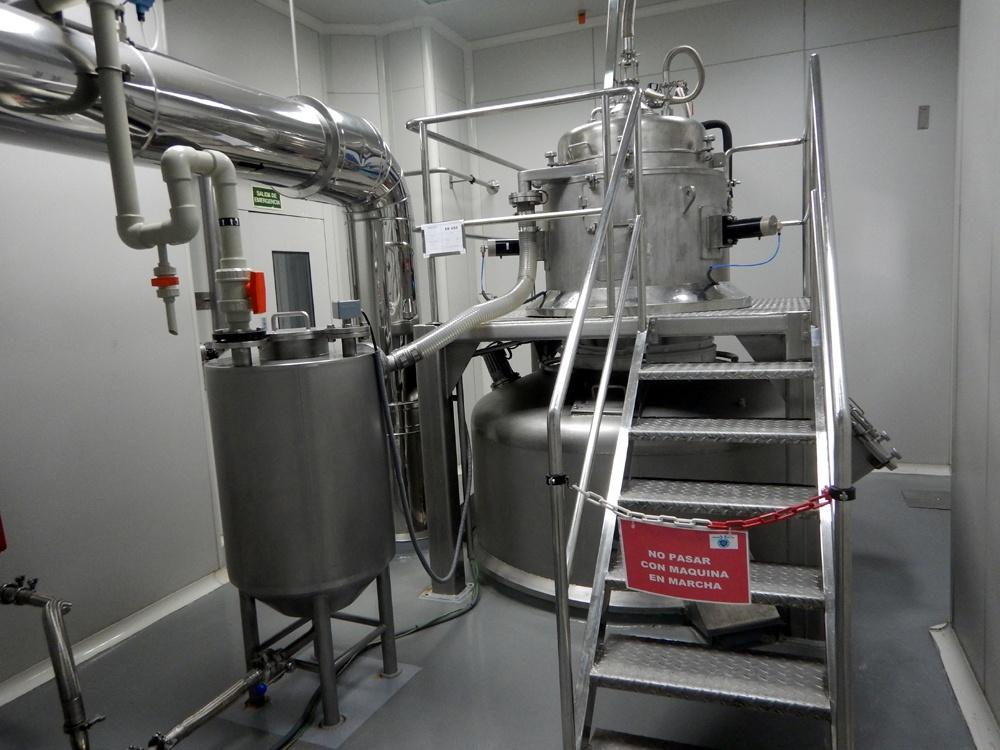
Continuous centrifuge for lithium hydroxide
Lithium hydroxide, a lithium compound used in making lithium batteries, is ind...
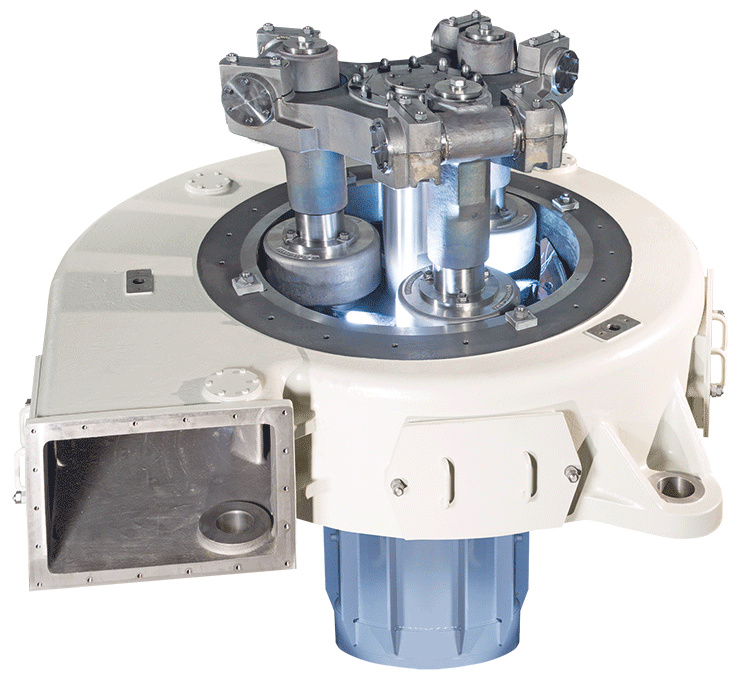
Grinding and drying of bentonite
After crushing and drying mined bentonite, this clay mineral is usually processed through a...
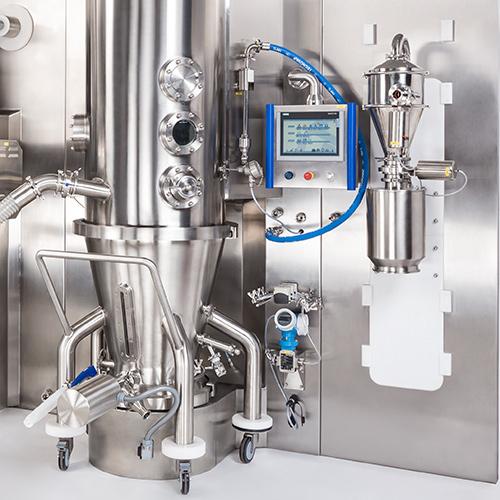
Fluid bed dryer for pharmaceutical solid dosage form
Fluid bed drying is a pharmaceutical process carried out to reduce t...

Industrial high shear mixer granulator for drug formation
It is rather difficult to successfully produce a pharmaceutica...
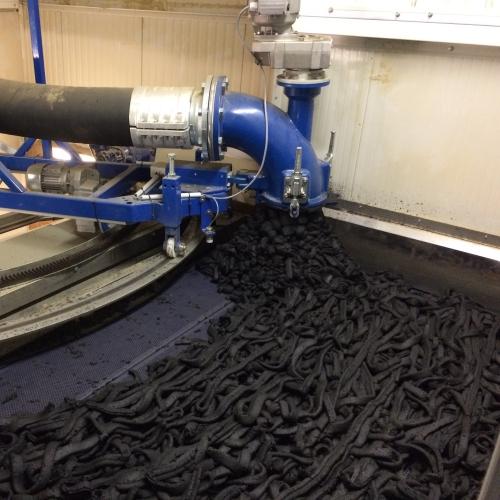
Belt dryer for sewage sludge
If your water treatment plant often facing difficulties with sewage sludge deposits, drying the...
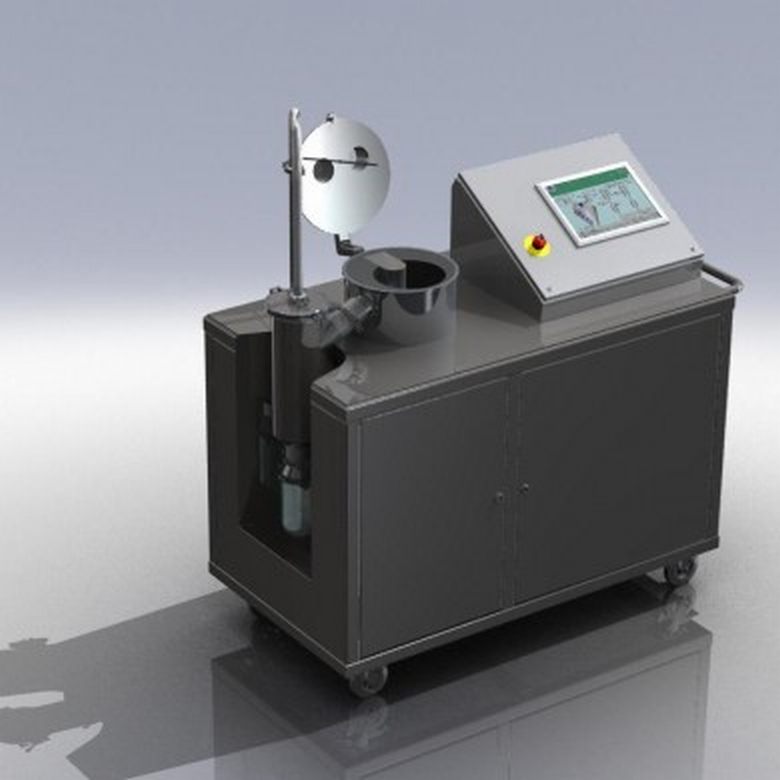
Laboratory scale active freeze dryer
The laboratory-scale active freeze-drying is used for dehydrating high-value products ...
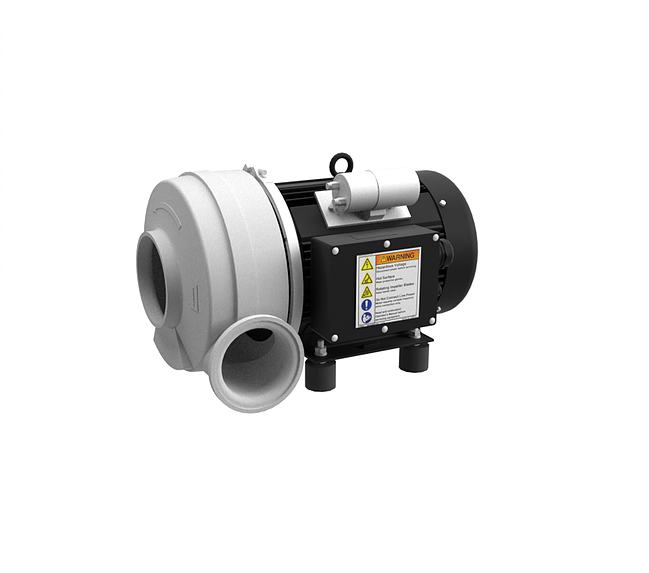
Blow off system for containers
Packaging powders into plastic or glass containers often leaves a residue that needs to be re...
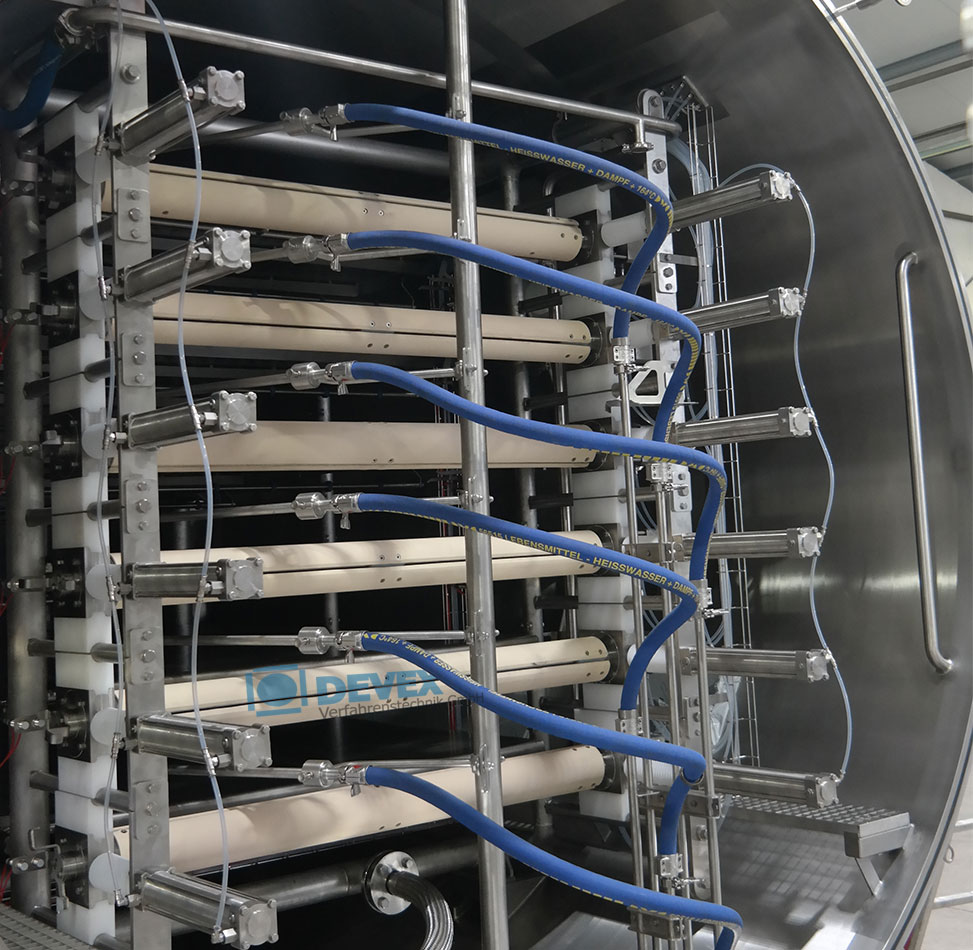
Continuous vacuum belt dryer
For gently drying liquid concentrates into granulates or powders, a vacuum drying solution is t...
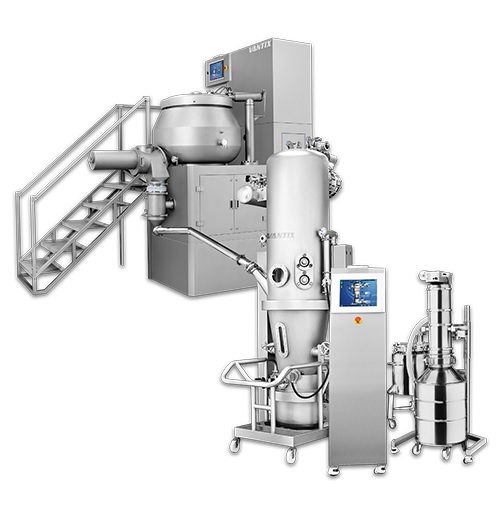
Granulation line of mixer and fluid bed dryer
A complete granulation line allows for the mixing and granulation of pharmac...
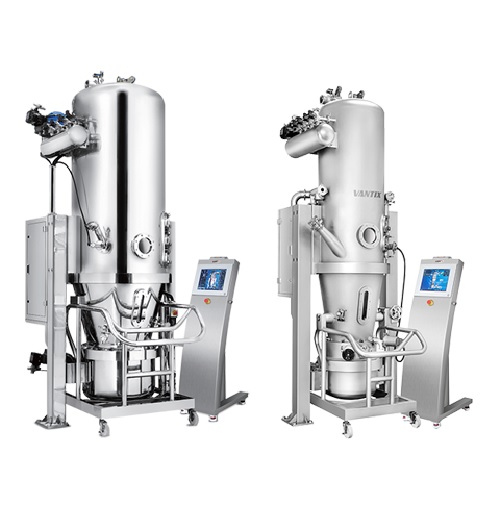
Fluid bed dryer for production scale
Fluidized bed drying (FBD) is a common process in the pharmaceutical industry for dryi...
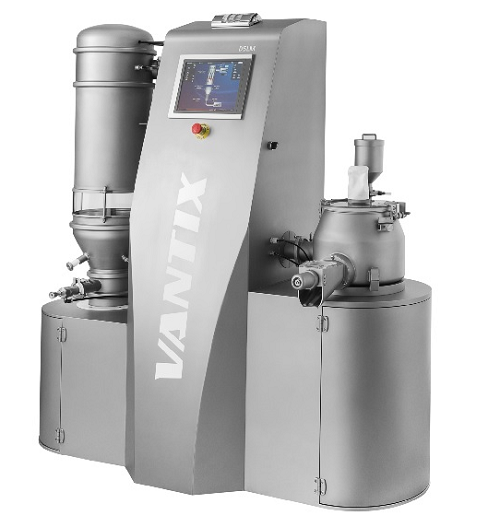
Fluid bed dryer and mixer for lab scale
Designed for pharmaceutical R&D, a lab-scale fluid bed dryer and mixer/granulat...
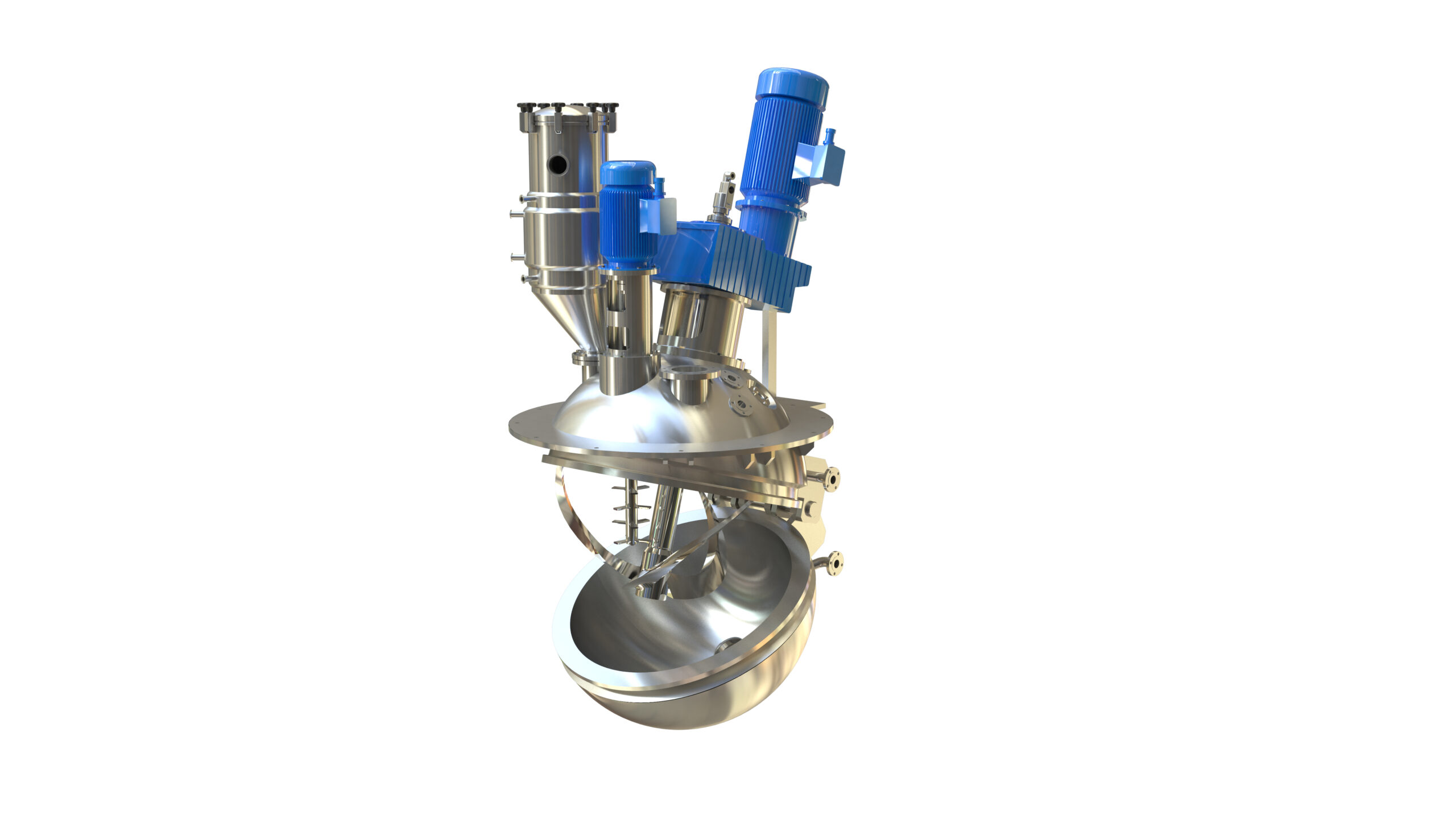
Spherical dryer
Drying vessels that are simple, reliable, and easy to maintain increases product quality and process efficienc...
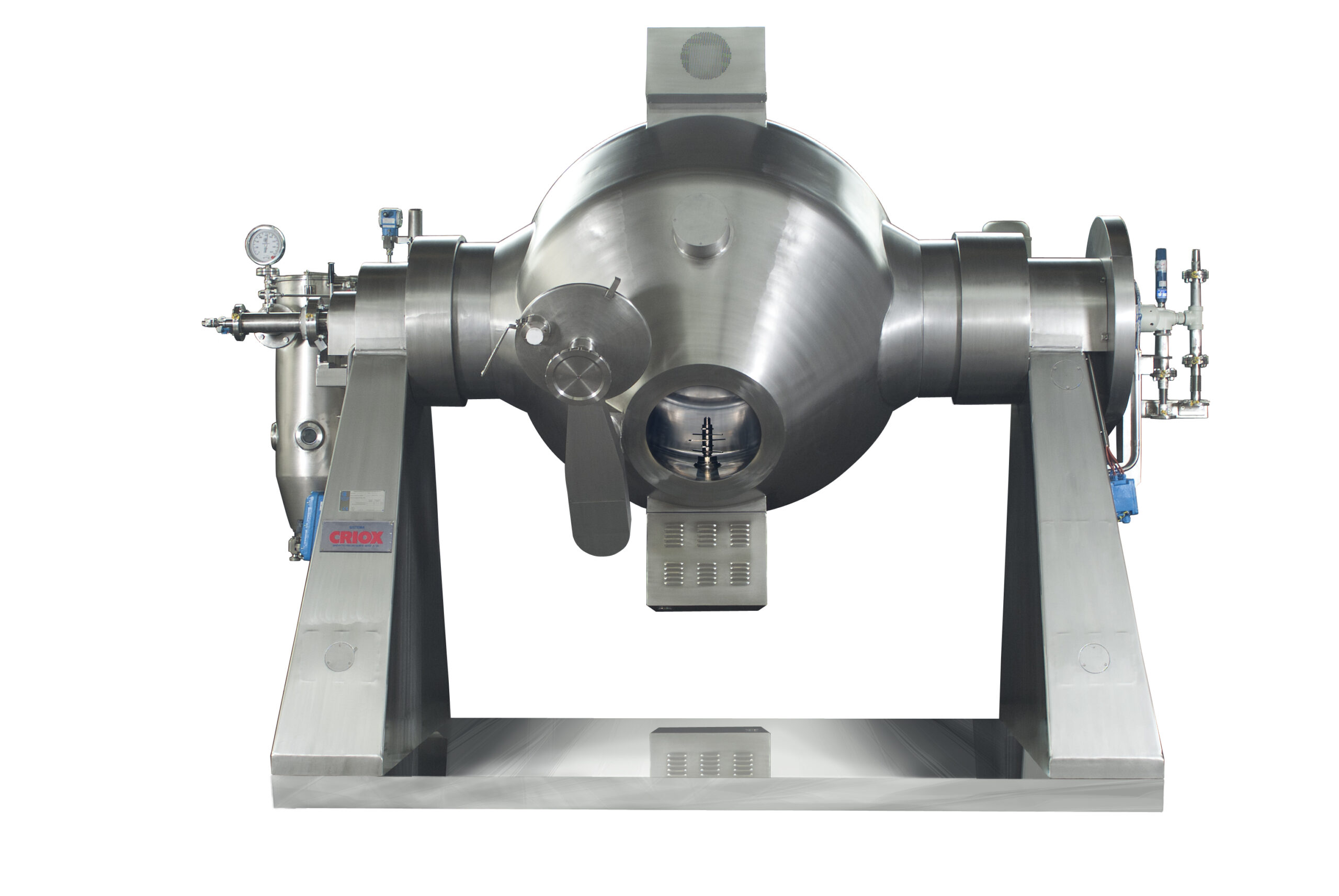
Rotary vacuum dryer
Powdered products tend to agglomerate during vacuum drying. This adds an additional step to the productio...
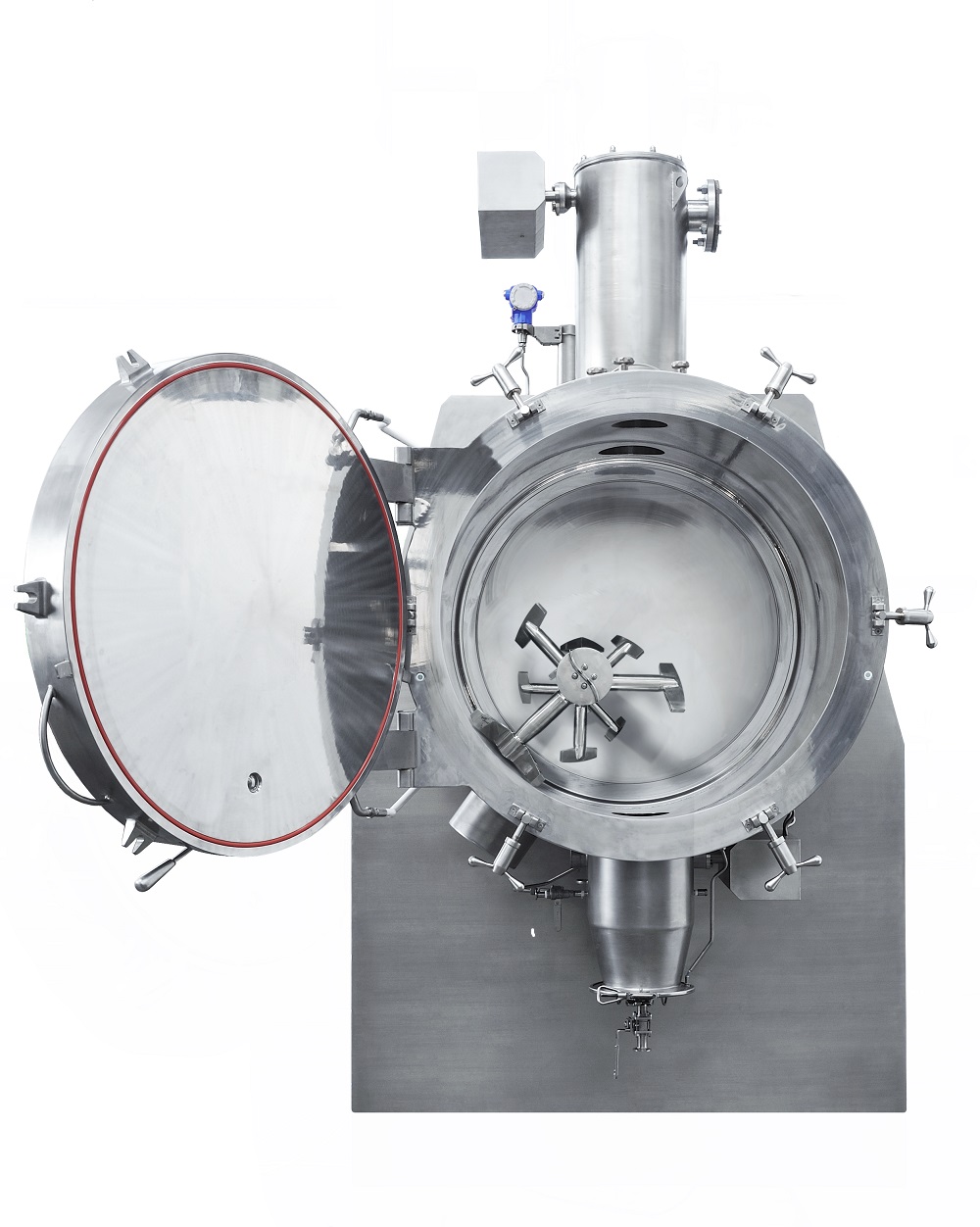
Horizontal vacuum dryer with eccentric agitator
Conventional dryers are inefficient and can lead to significant mechanical...
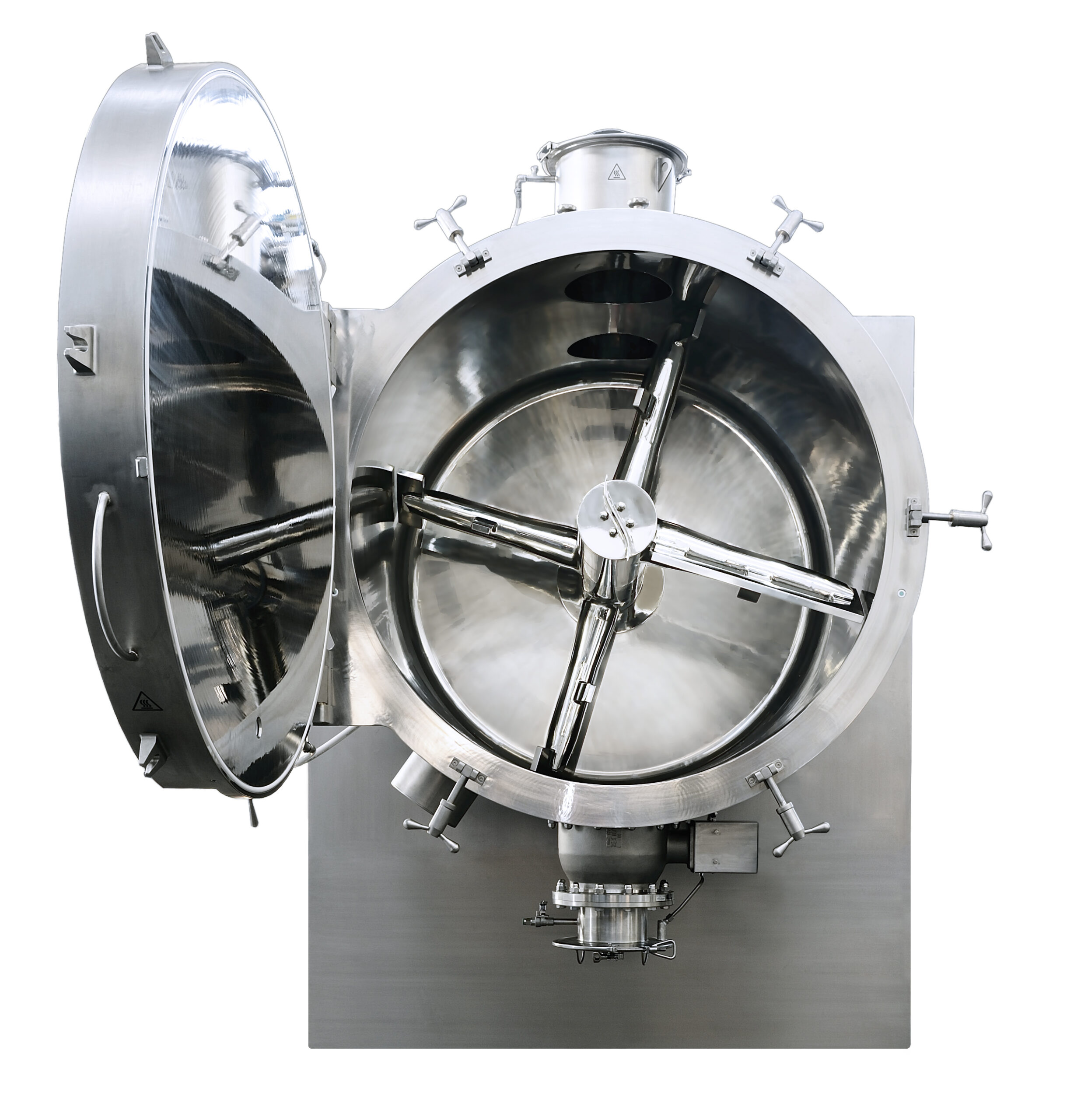
Horizontal paddle vacuum dryer
Agitated vacuum dryers can be difficult to clean which makes them unsuitable for multi-produc...
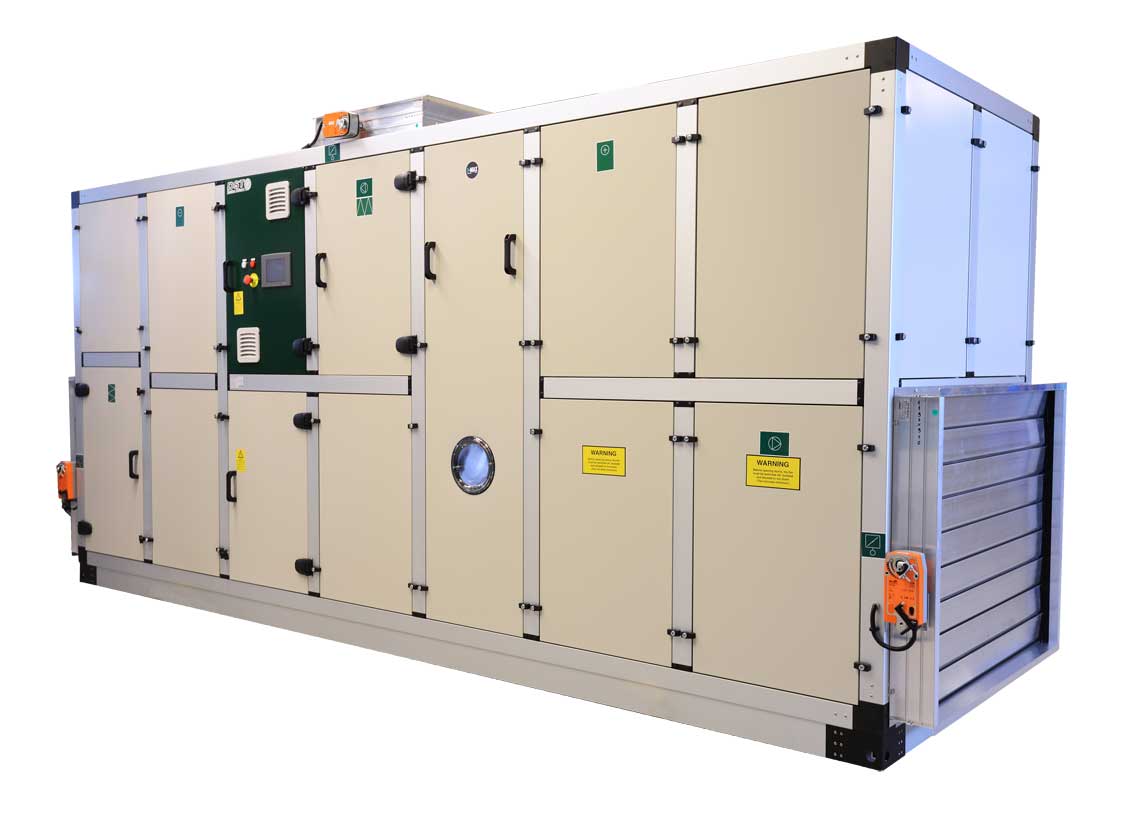
Customizable dehumidifier
Dehumidification needs can vary significantly from one project to another. Dehumidifiers with a fi...
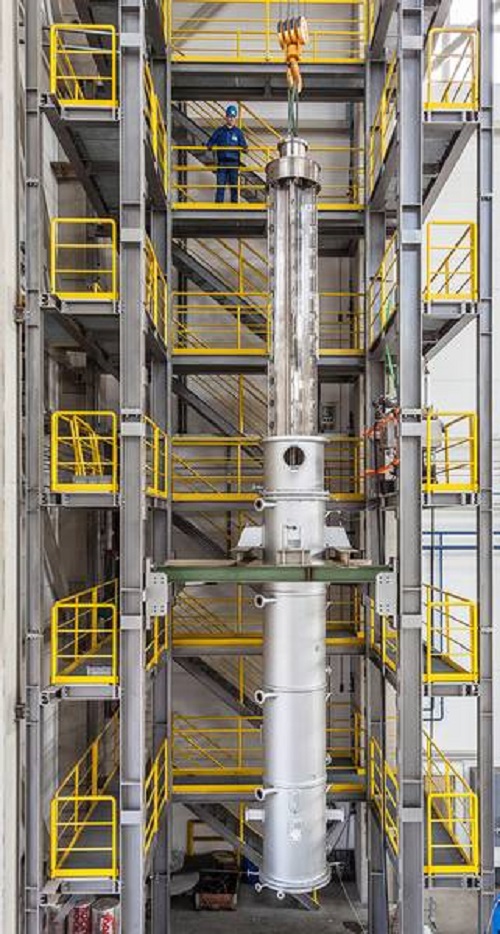
Thin film dryers
Dry dissolved or slurried crystallizing or amorphous products to a pourable powder.
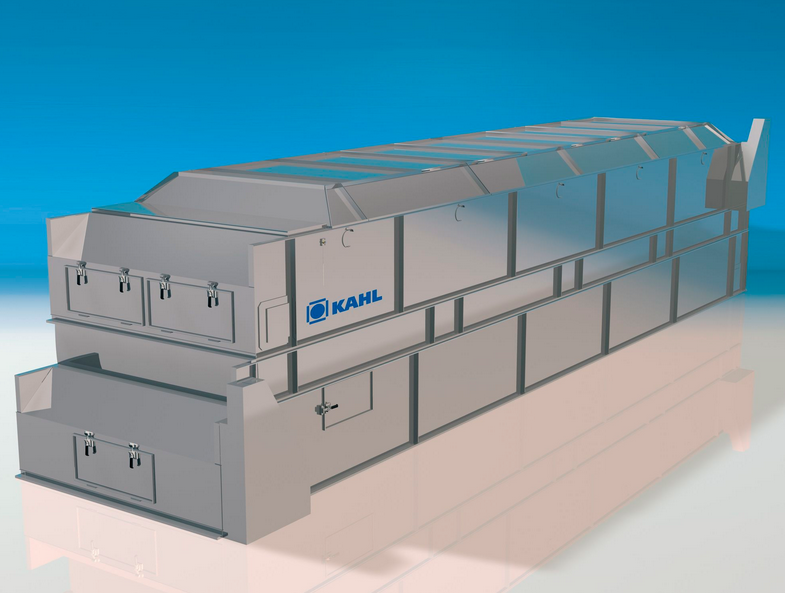
Belt dryer/cooler for pellets and granules
Many industries that process materials in pellet, powder, or crumble form need ...
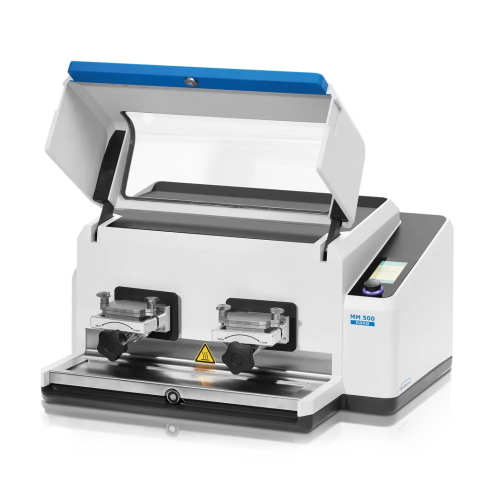
Ultrafine grinding solution for nanoparticles
Achieve ultrafine particle sizes with high-speed precision, ideal for labora...
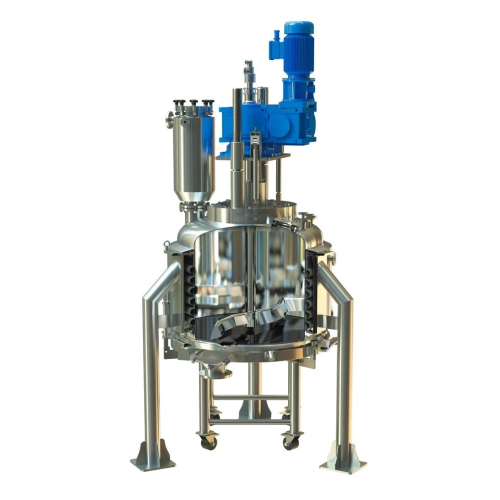
Nutsche filter dryer for pharmaceutical and chemical industries
Achieve precise filtration and efficient drying in one s...

Pilot Gmp spray dryer system for small-scale manufacturing
For precise control in spray drying, streamline your small-sc...
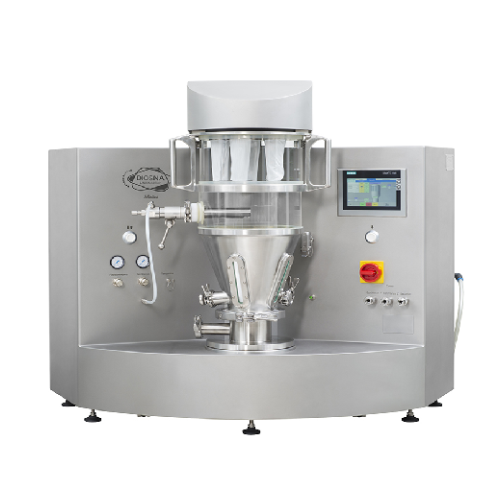
Laboratory coater and fluid bed processor
Optimize your research and development with a versatile benchtop unit that integ...
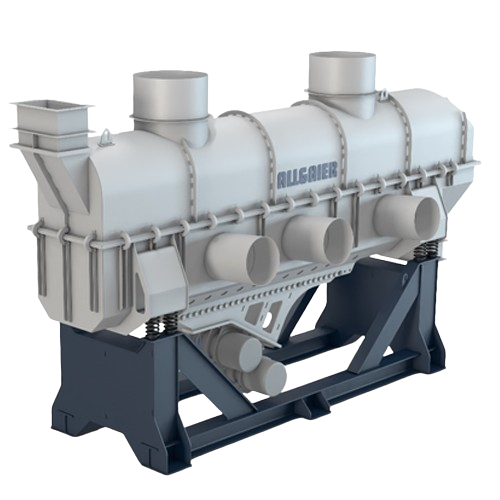
Fluidized bed dryer for industrial materials
Enhance product quality and energy efficiency with fluidized bed dryers, opti...
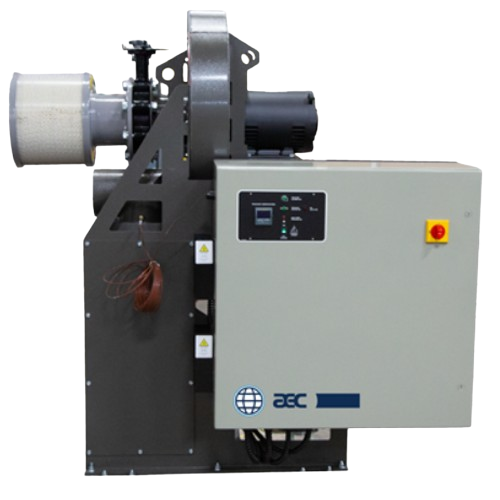
Hot air dryers for non-hygroscopic material
Ensure reliable material quality by effectively reducing moisture in non-hygro...
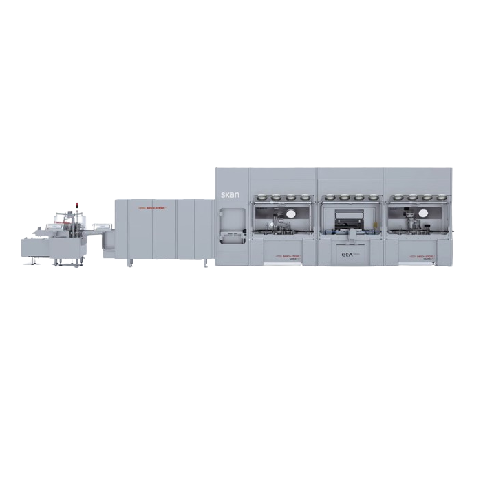
Freeze dryer for small-scale production
Optimize your production line with reliable lyophilization that ensures precise moi...
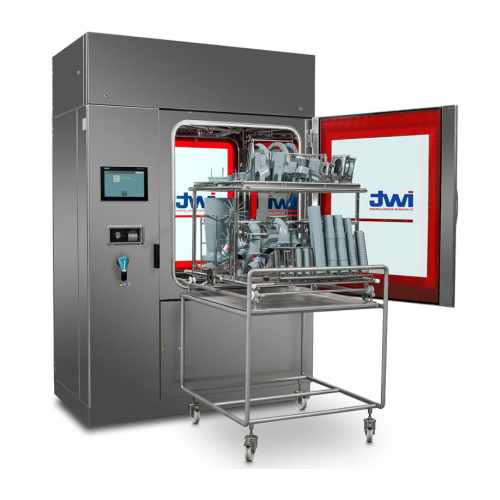
Gmp contact part washers for pharmaceutical industry
Ensure product integrity and hygiene with specialized washing system...
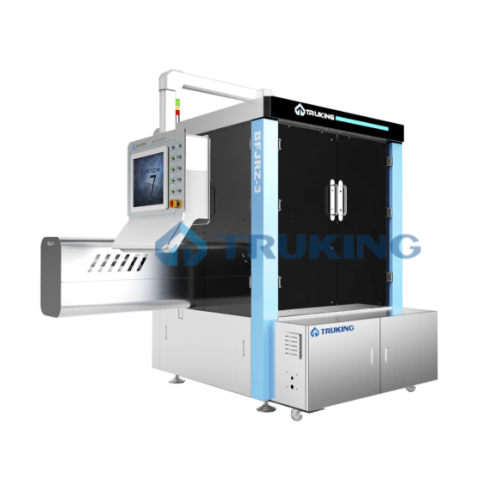
X-ray inspection for pharmaceutical vials
Ensure product purity by detecting contaminants in pharmaceutical vials with adv...
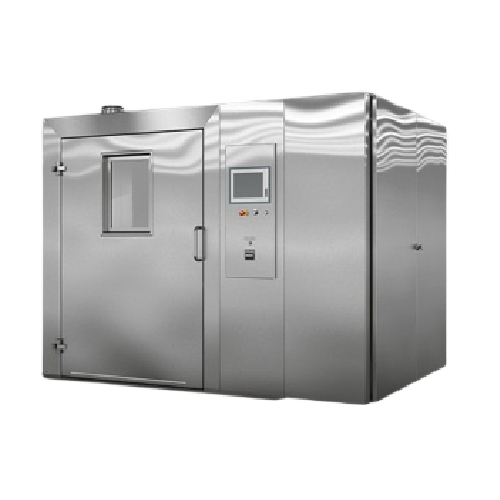
Pharmaceutical grade washer for large components
Ensure compliance and maximize productivity with a high-performance solut...
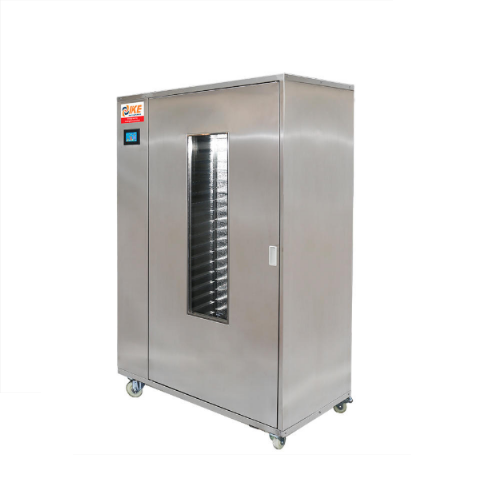
Industrial drying cabinet
The production of high-quality biltong and similar dried meat products can pose problems with main...
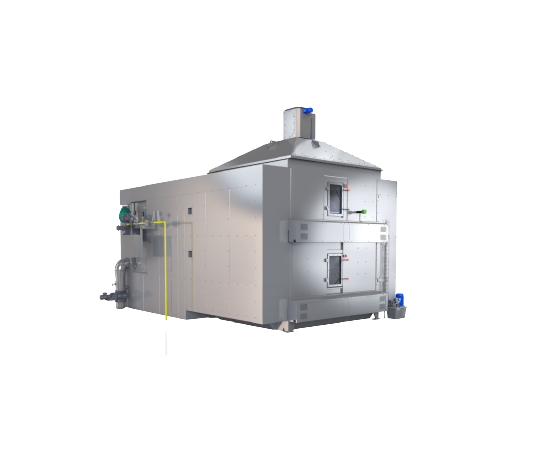
Continuous dryer machine
Traditional drying methods in the pet food, aquafeed, and extruded food industry can be the most ene...
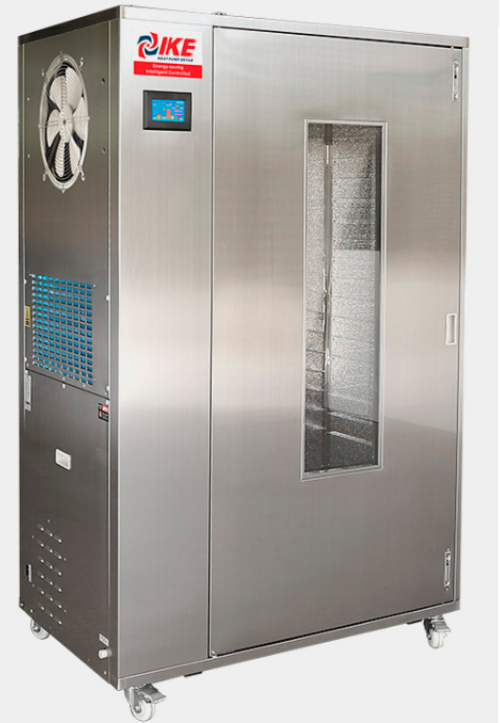
Industrial dehydration machine
Dried fruits are popular both as food in themselves and as ingredients. Traditional drying te...
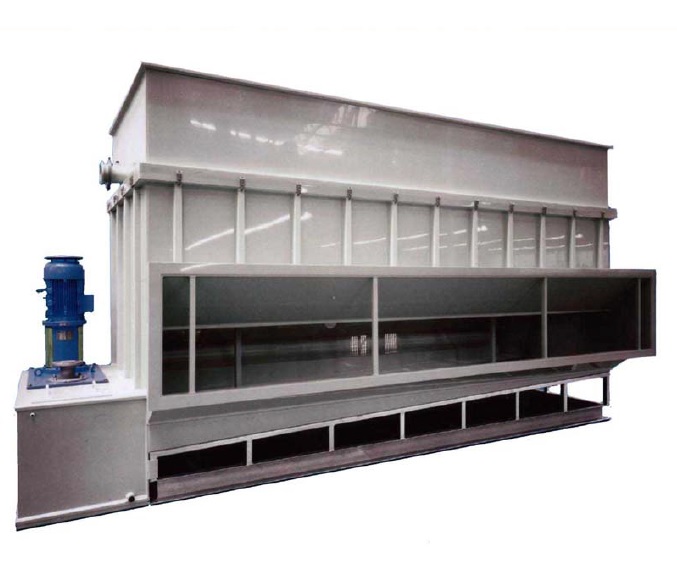
Air dehumidifier for bulk products
When your product or process is sensitive to humidity, using an air dehumidifier may res...
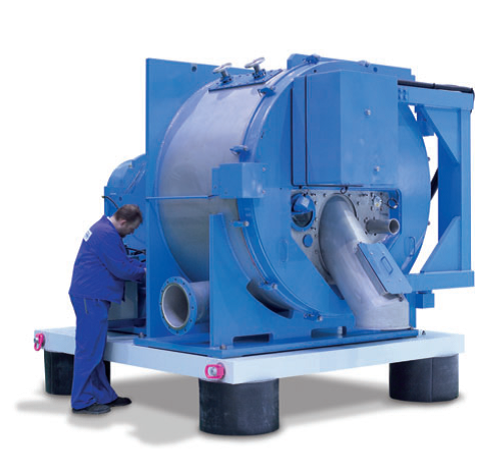
Horizontal chemical scraper centrifuge
For slurries difficult to discharge, a scraper can improve process reliability, effi...
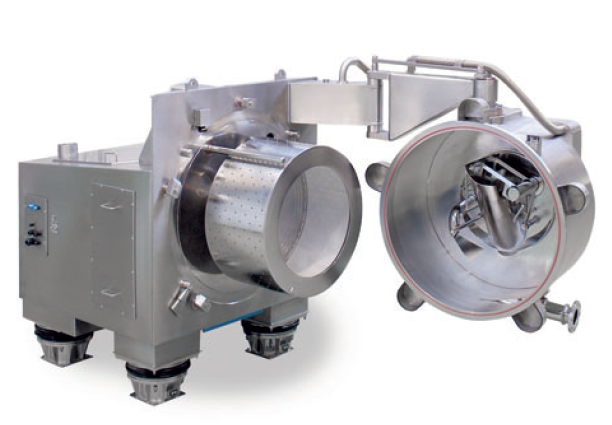
Horizontal pharmaceutical scraper centrifuge
For slurries difficult to discharge, a scraper can improve process reliabilit...
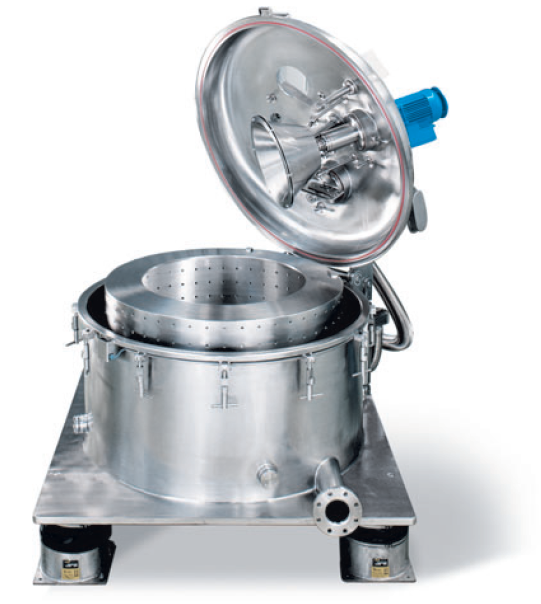
Vertical scraper centrifuges
Vertical Bottom discharge Centrifuges work discontinuously, discharging the solids to the botto...
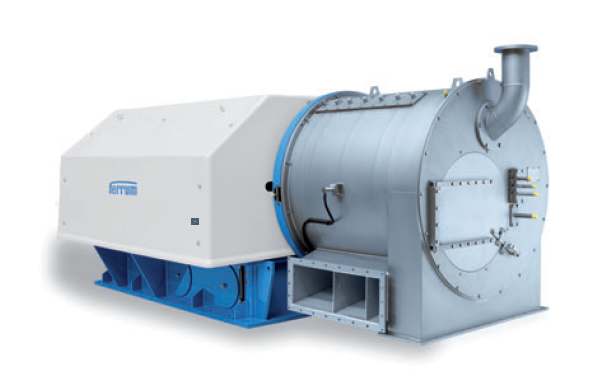
Pusher centrifuge
Pusher centrifuges are continuously operating filter centrifuges and can have several basket stages dependi...