Ultra-hygienic vacuum conveyor for pharmaceutical industry
Optimize powder transfer with ultra-hygienic vacuum conveying, ensuring dust-tight material handling that reduces manual intervention and enhances operational efficiency for high-speed processing environments.
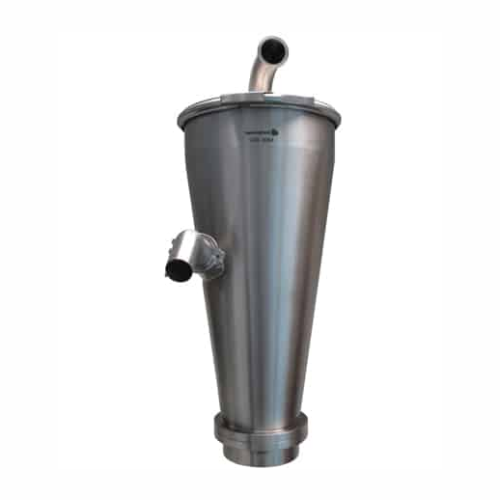
Transfers and Automates Powder Conveying Operations
The Uni-Vac V-Series V10 from Hanningfield is a versatile vacuum conveyor designed to enhance material handling processes in the pharmaceutical, food and beverage, and chemical industries. It features a rolled and seam-welded hopper body, customizable for specific application requirements, ensuring ultra-hygienic operations. Operating with a powerful electric pump, it eliminates the need for compressed air, optimizing energy use across continuous and high-speed operations. Ideal for handling a variety of products, including pharmaceutical tablets, protein powders, and cannabis-infused edibles, it supports efficient vacuum conveying, suck-and-dump, and direct loading processes. With a maximum throughput of 900 kgs/hr, it integrates seamlessly into pre-processing and processing operations, minimizing manual handling and enhancing operational efficiency. All contact parts are constructed from 316L stainless steel, ensuring product integrity, while its crevice-free design facilitates easy cleaning and supports GMP compliance.
Benefits
- Enhances material handling efficiency by automating bulk powder transfer.
- Decreases operational costs with energy-efficient electric pump operation.
- Ensures product purity with ultra-hygienic, GMP-compliant design.
- Offers flexible customization to fit specific application needs and constraints.
- Facilitates rapid cleaning and maintenance with crevice-free construction.
- Applications
- Nutraceuticals, Oral solid dosage (osd), Chemical, Food and beverage, Powders, Cannabis, Pharmaceutical
- End products
- Pharmaceutical tablets, Vitamin supplements, Chemical compounds, Oral solid dosage forms, Cannabis-infused edibles, Protein powder, Powdered drink mix
- Steps before
- Material Preparation, Grinding, Blending
- Steps after
- Packing, Sterilization, Tablet Pressing, Coating
- Input ingredients
- powder, material
- Output ingredients
- transferred materials, processed powders
- Market info
- Hanningfield Process Systems is known for manufacturing high-quality, customized process handling, and containment equipment for industries such as pharmaceutical, food, and chemical, specializing in milling, sieving, and powder handling solutions.
- Automation
- Electric pump (no compressed air required)
- Capacity
- 10 litres
- Material Transfer
- Dust-tight transfer
- Throughput
- 900 kgs/hr (2000 lbs/hr)
- Hopper Diameter
- 450mm (17.7")
- Hopper Height
- 1000mm (39.3")
- Standard Hose Diameter
- 1.5 inches
- Material Construction
- 316L and 304 stainless steel
- Automation level
- PLC / SCADA
- Batch vs. continuous operation
- Batch / Inline Continuous
- CIP/SIP
- CIP 121°C / SIP 135°C
- Cleaning method
- CIP / Manual
- Changeover time
- Fast changeover
- Energy efficiency
- Low energy consumption
- Height adaptability
- Customizable for low ceiling rooms
- Integrated steps
- Suck-and-dump, direct loading
- Material transfer method
- Gravity feed and vacuum transfer
- Working mechanism
- Electric pump driven
- Cleanability
- Crevice-free, GMP design
- Density/particle size
- 0.5–2.5 g/cm³ / 50–1000 µm
- Hopper Diameter
- 450 mm (17.7")
- Hopper Height
- 1000 mm (39.3")
- Hopper Capacity
- 10 litres
- Material
- 316L stainless steel for contact parts, 304 stainless steel for non-contact parts
- Discharge method
- Gravity feed or vacuum transfer
- Mounting options
- In-line mounting for feeding downstream process
- Hopper customization
- Customizable size and shape
- Assembly method
- Clamp assembly for easy cleaning