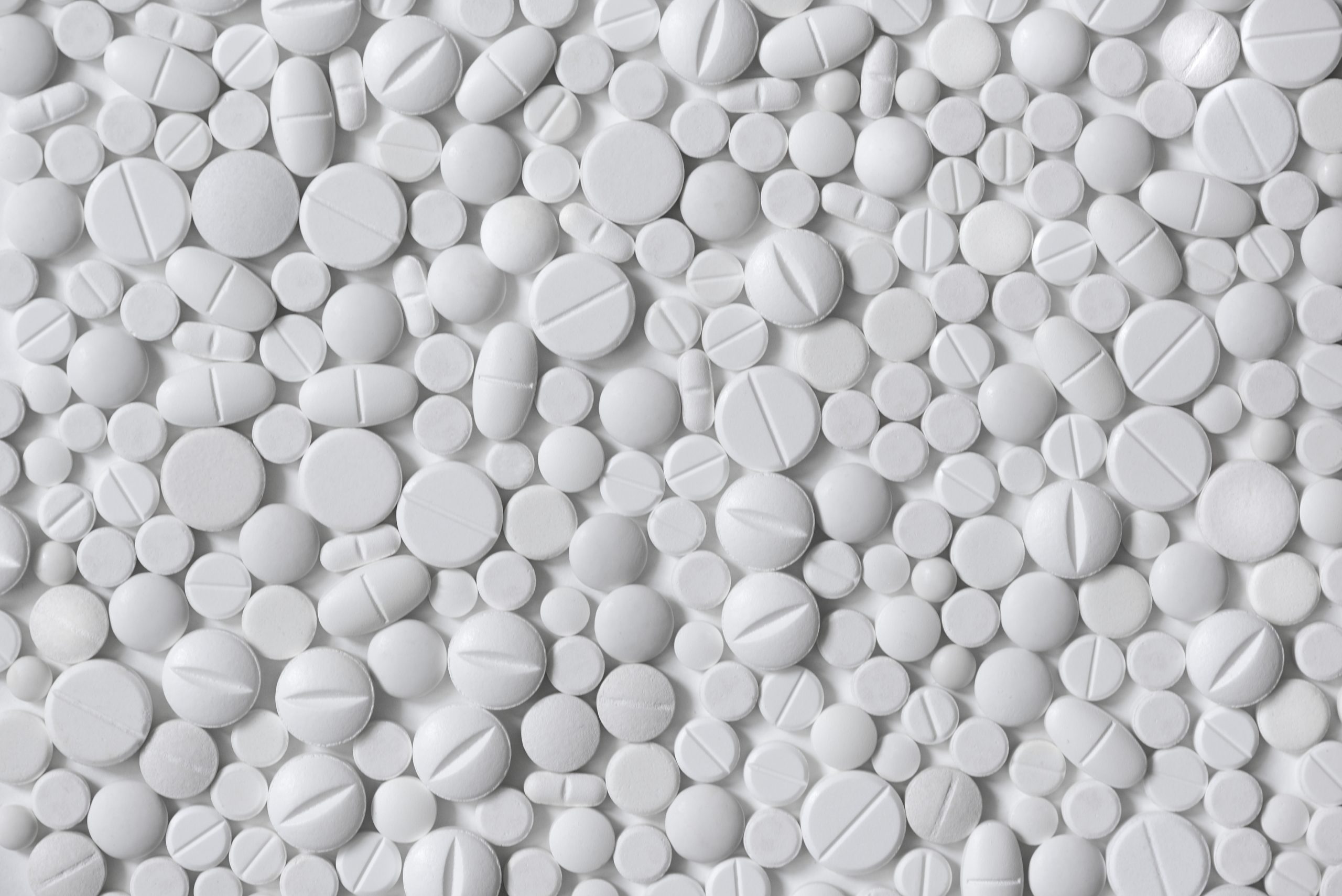
Tablet Making Equipment
Find innovative tablets equipment and connect directly with world-leading technology suppliers
Among all dosage forms in use today, tablets constitute the most common one. They are pharmaceutical solid dosage forms containing active ingredients and excipients such as diluents, binders, glidants, and lubricants. Using tablet making equipment, these solid dosage forms are made by compression of granules or powder blends and then shaped by molding.
Top picks for tablet manufacturing equipment
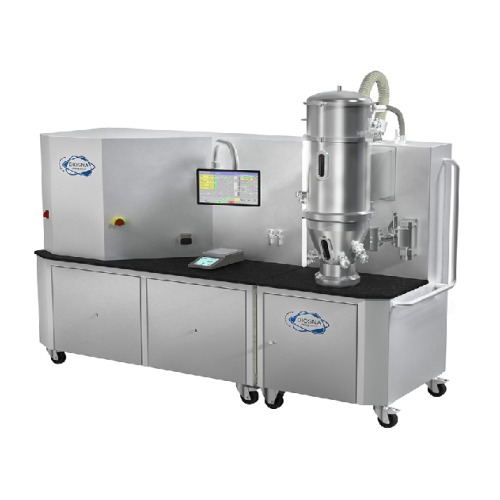
Laboratory fluid-bed dryer and tablet coater
Experience seamless transition from laboratory to production scale with a ver...
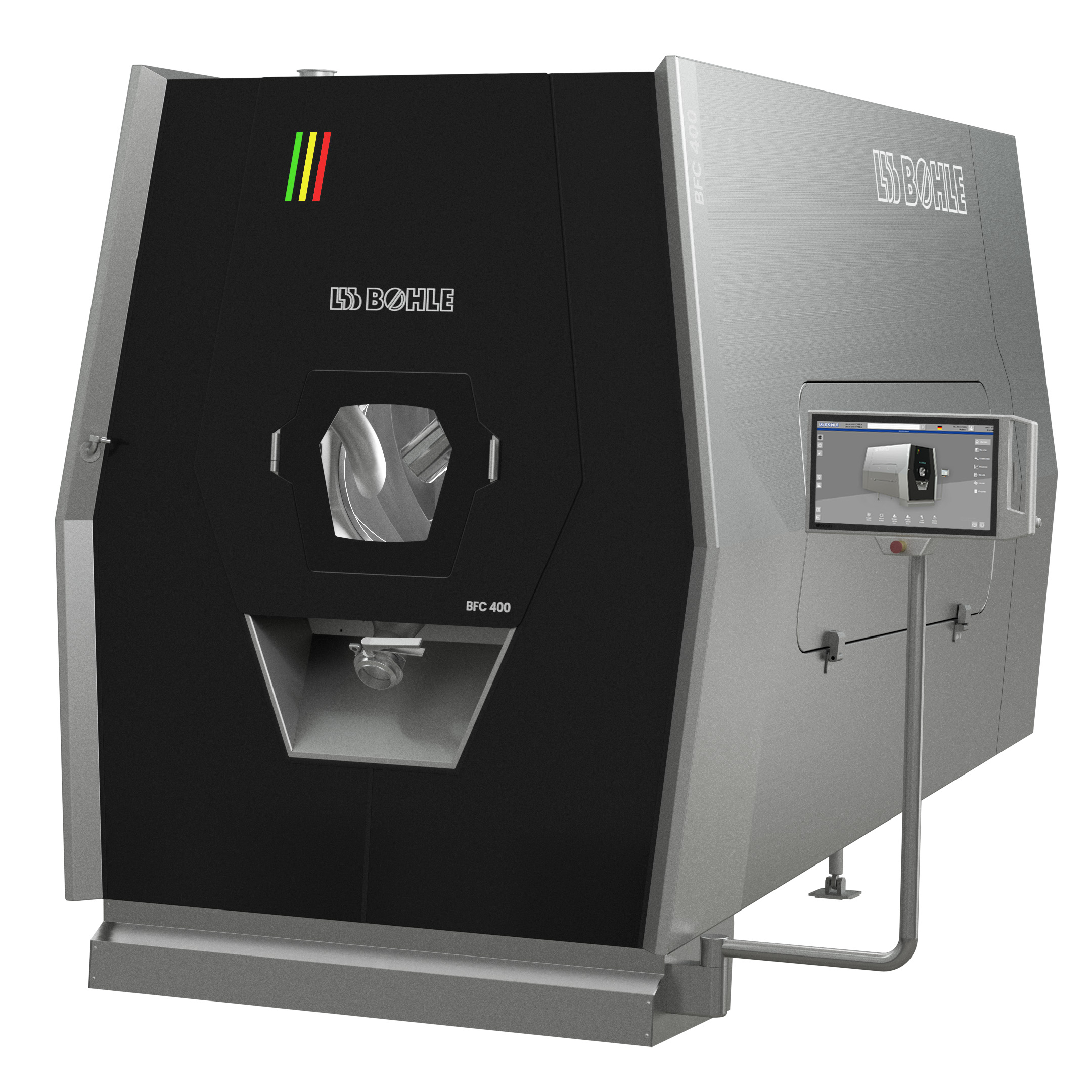
Energy-efficient film coating machine for pharmaceutical tablets
Tablet coating involves applying a thin layer of coatin...
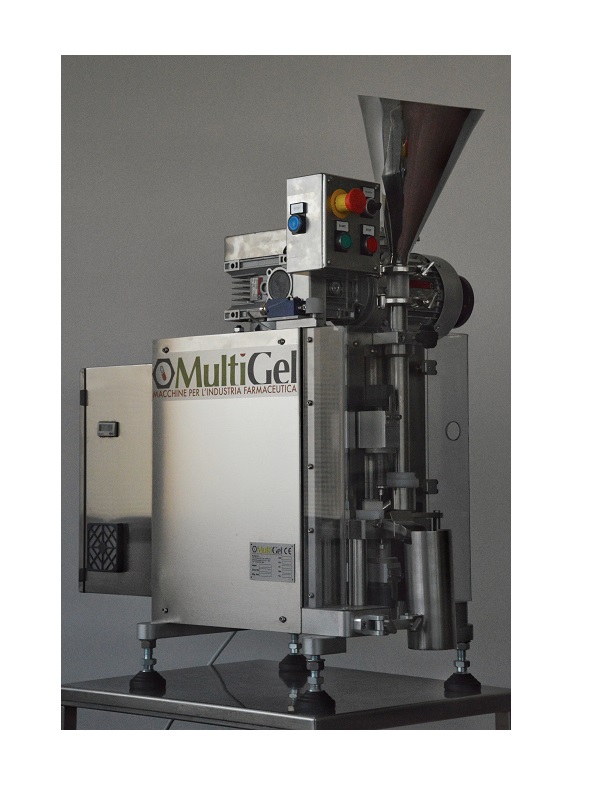
Benchtop tablet press
For lab work or small-scale production, a purpose-designed tablet press that meets your exact requireme...
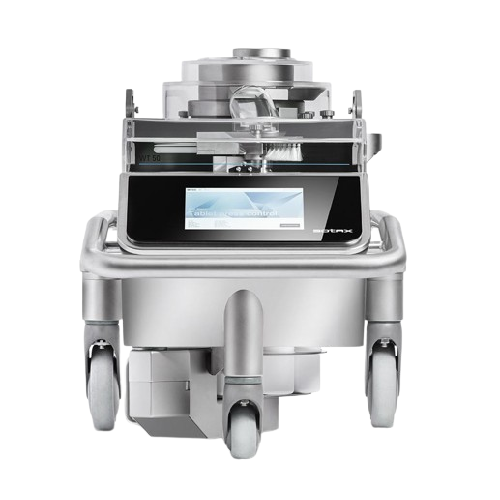
Automated weighing system for tablets
Ensure precision in pharmaceutical manufacturing by seamlessly integrating advanced w...
Stories about tablets
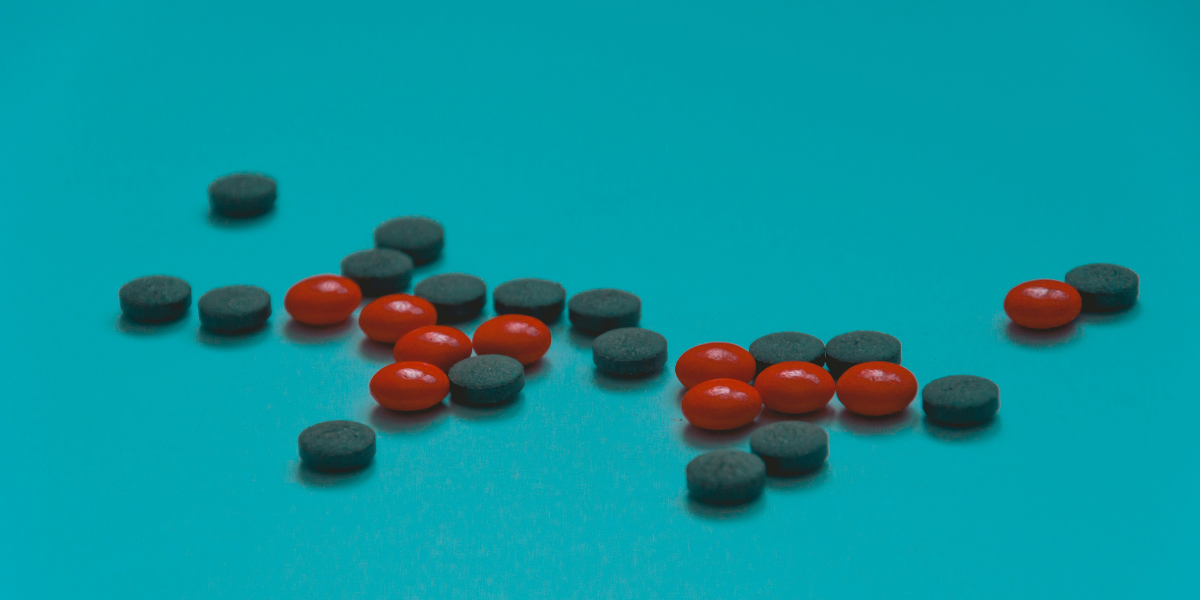
Scientifically tested continuous drying for your tablets
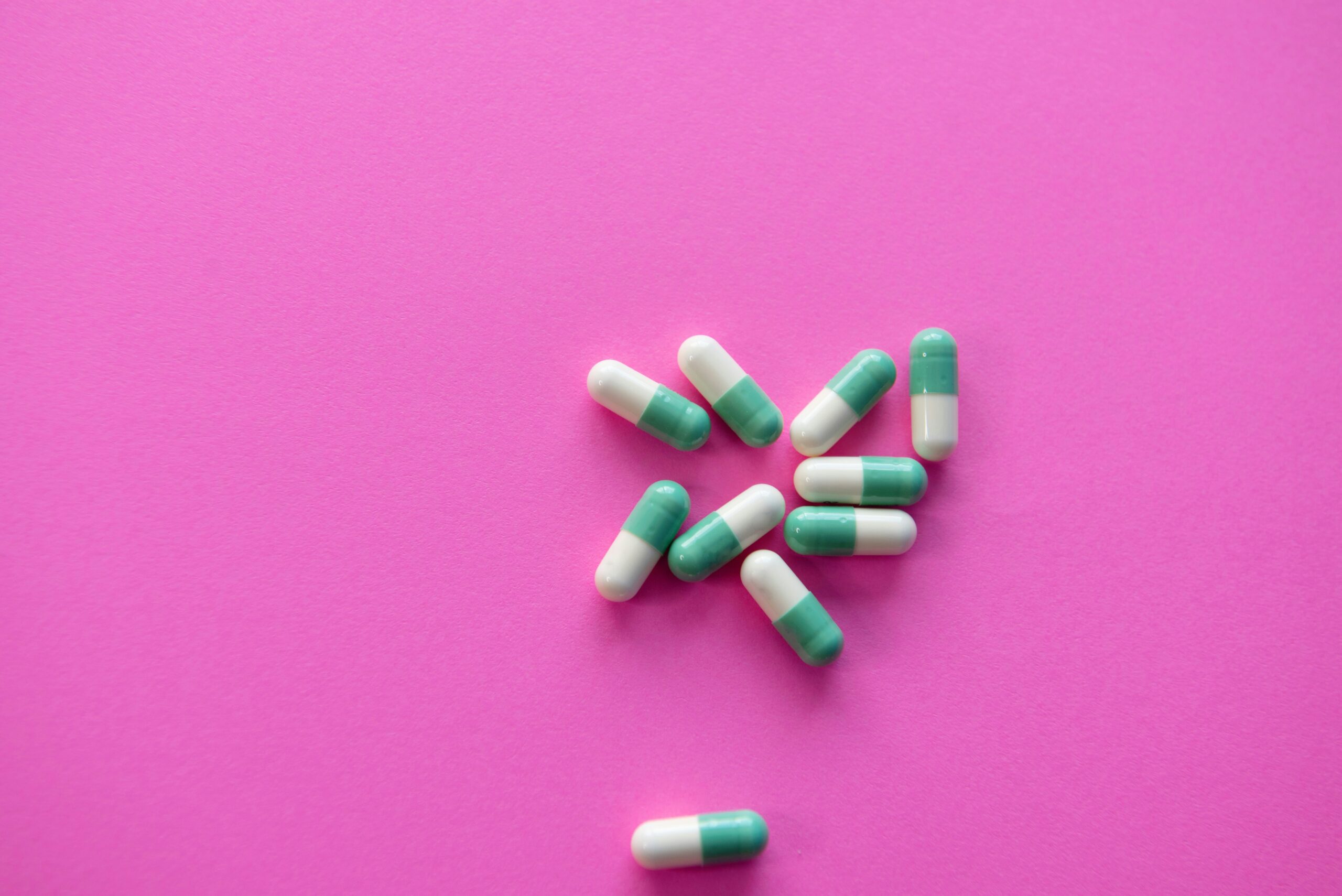
Aim your safety standards high, while granulating dry
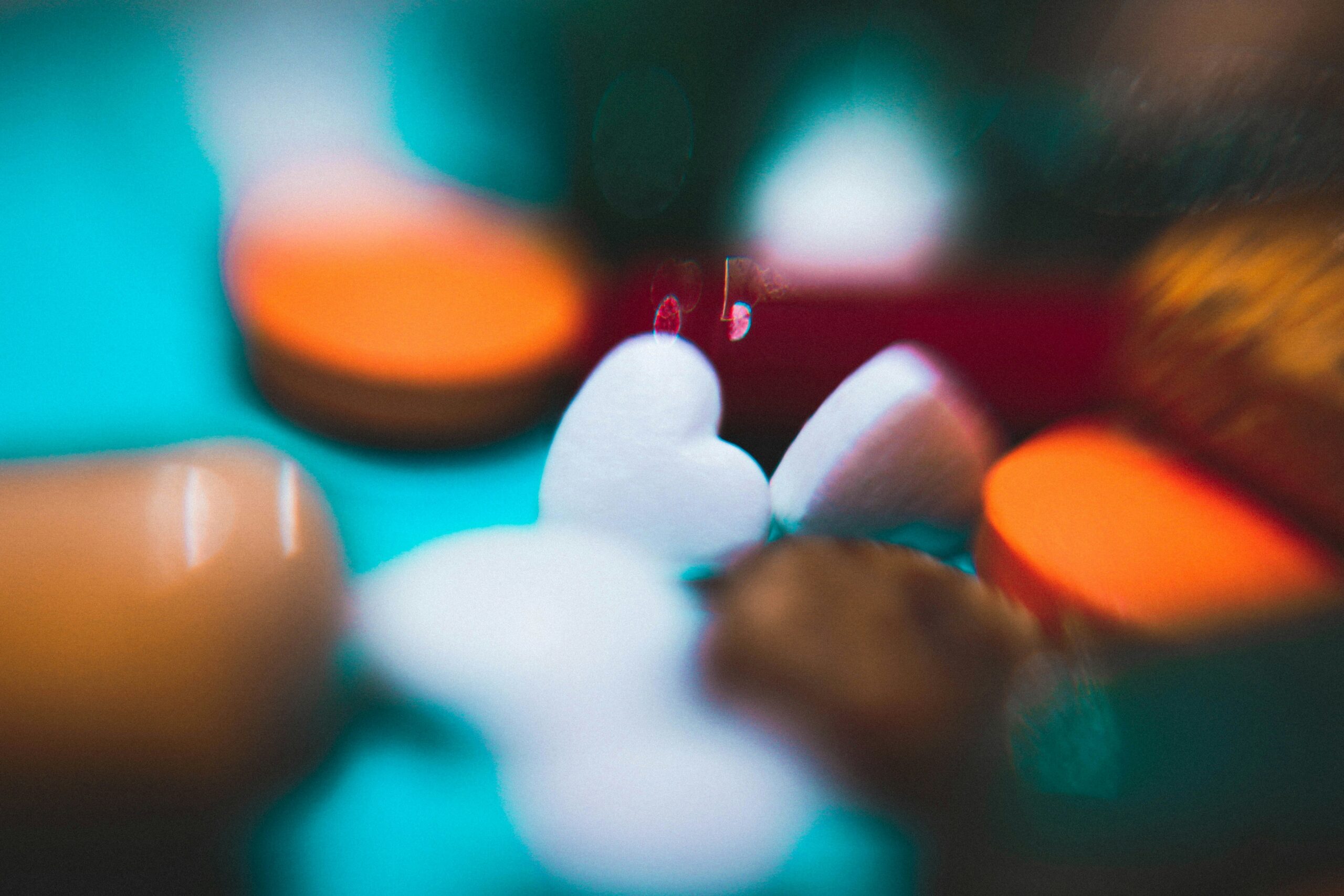
Discover the best mix for your blending application
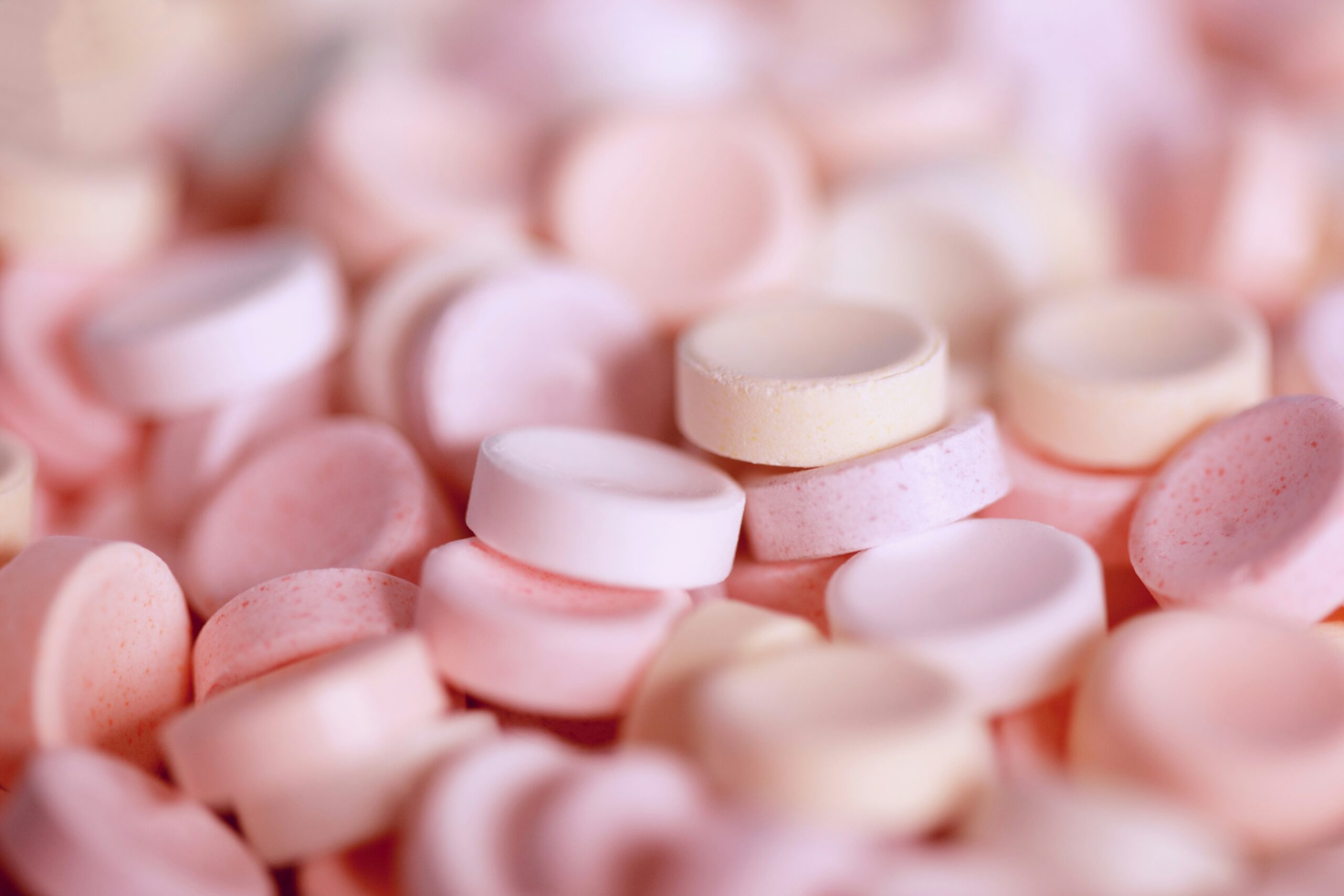
Coat-astrophe averted: a sprightly spin on tablet efficiency

Lean into efficiency with inclined tablet discharging
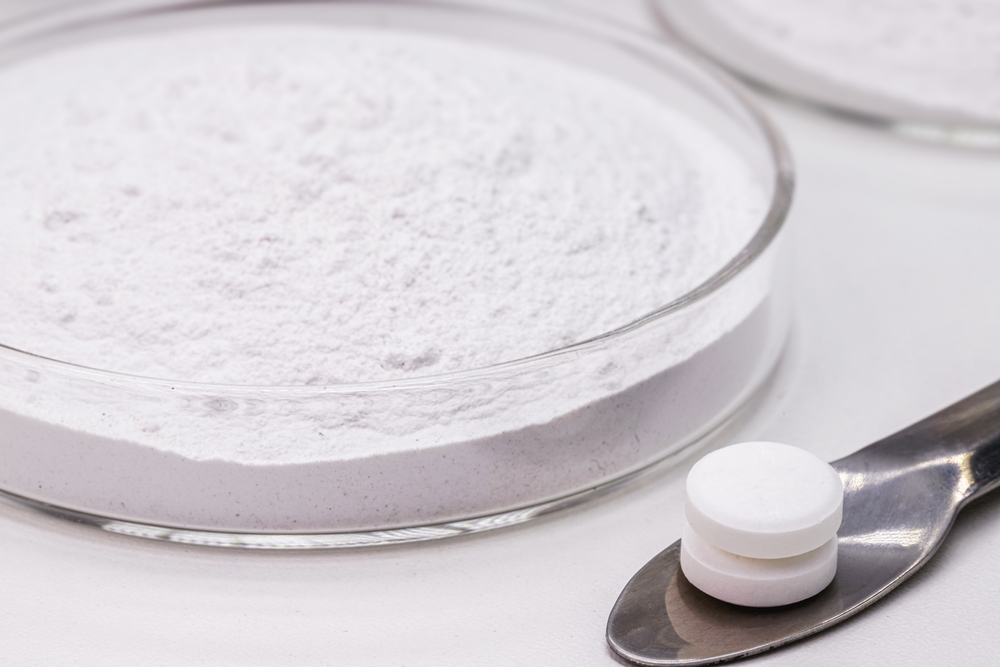
Wet milling: The revolution in the API production
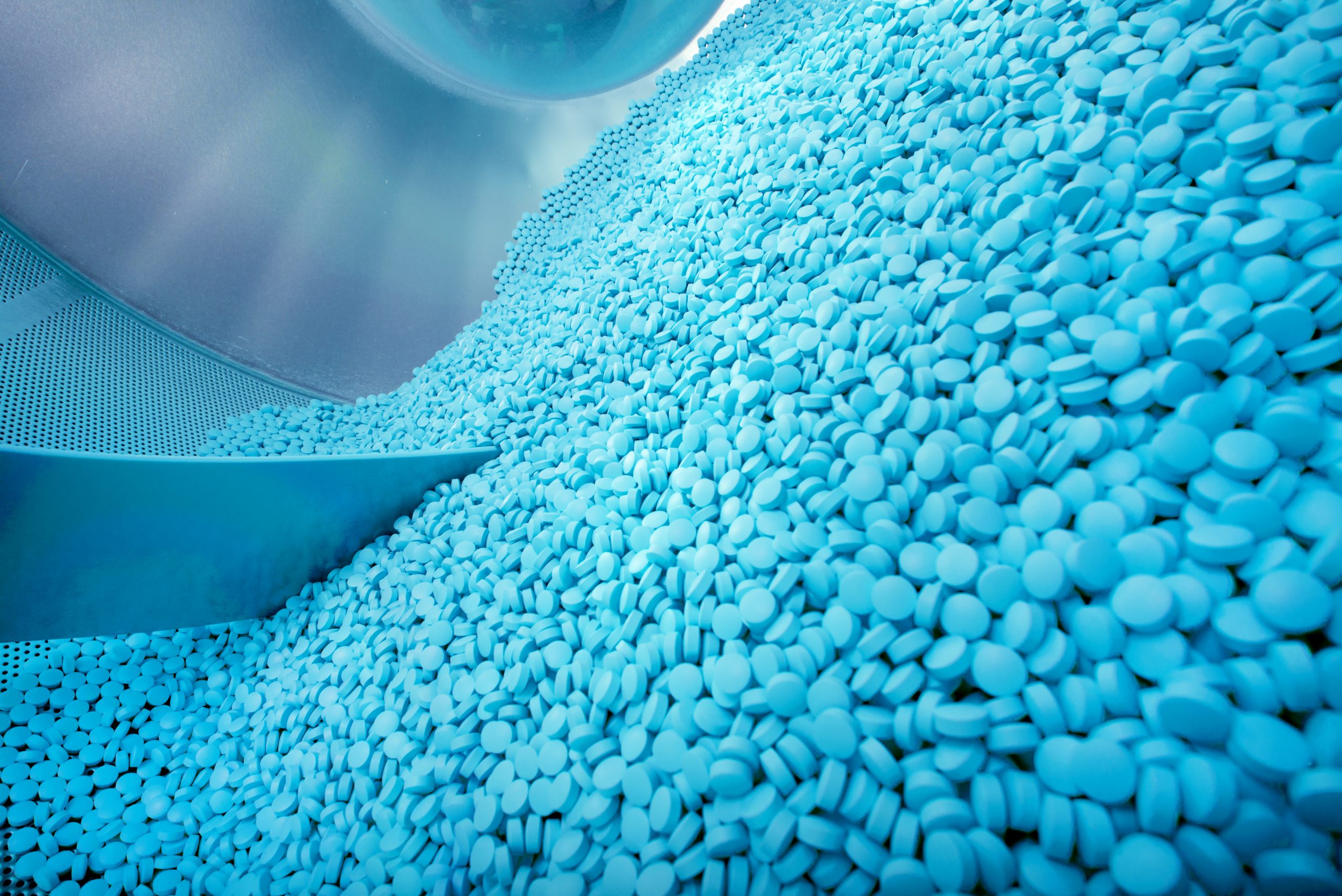
The sweet world of pharmaceutical tablets - The trifecta for achieving coating uniformity
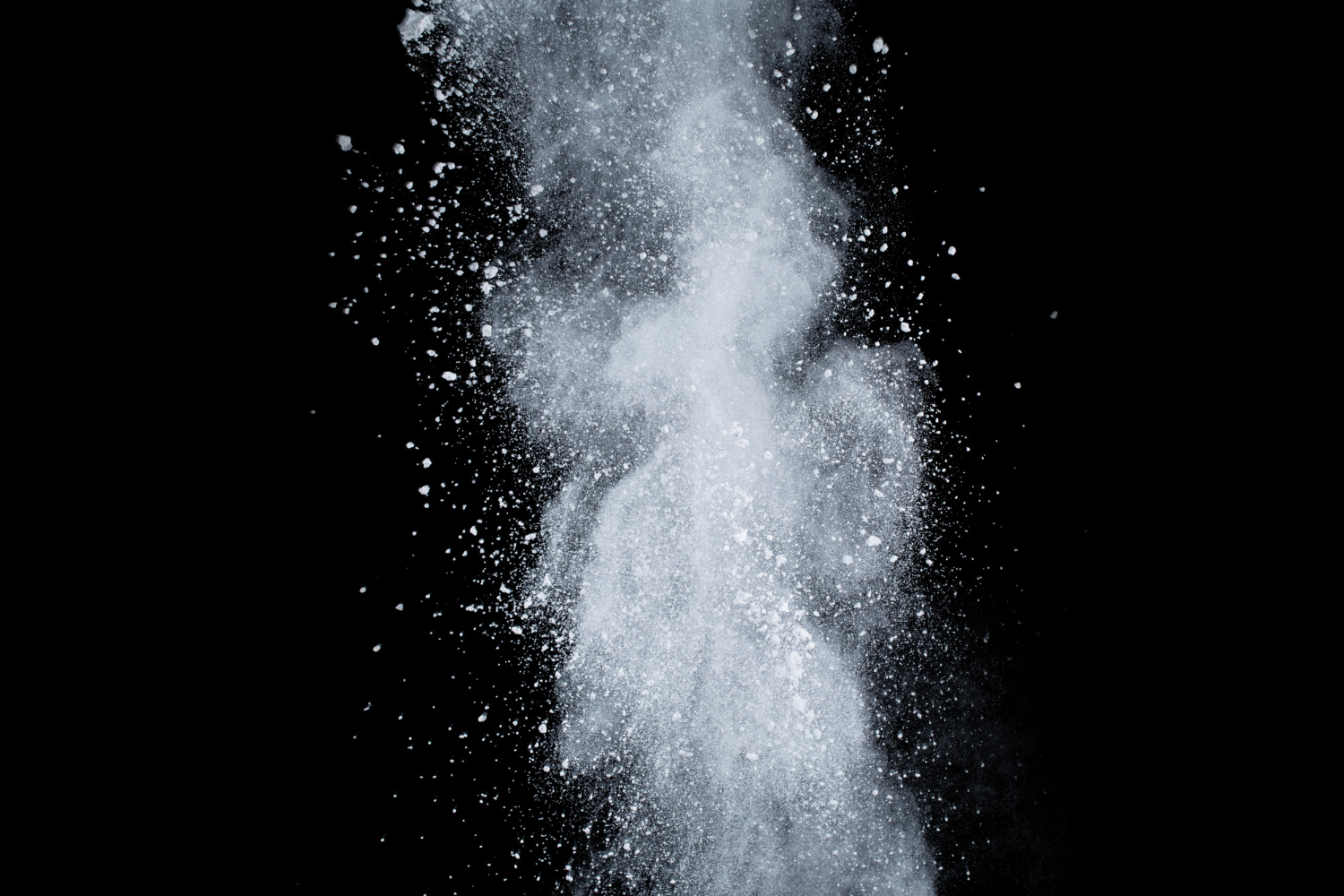
Closing the containment loop in HPAPI manufacturing
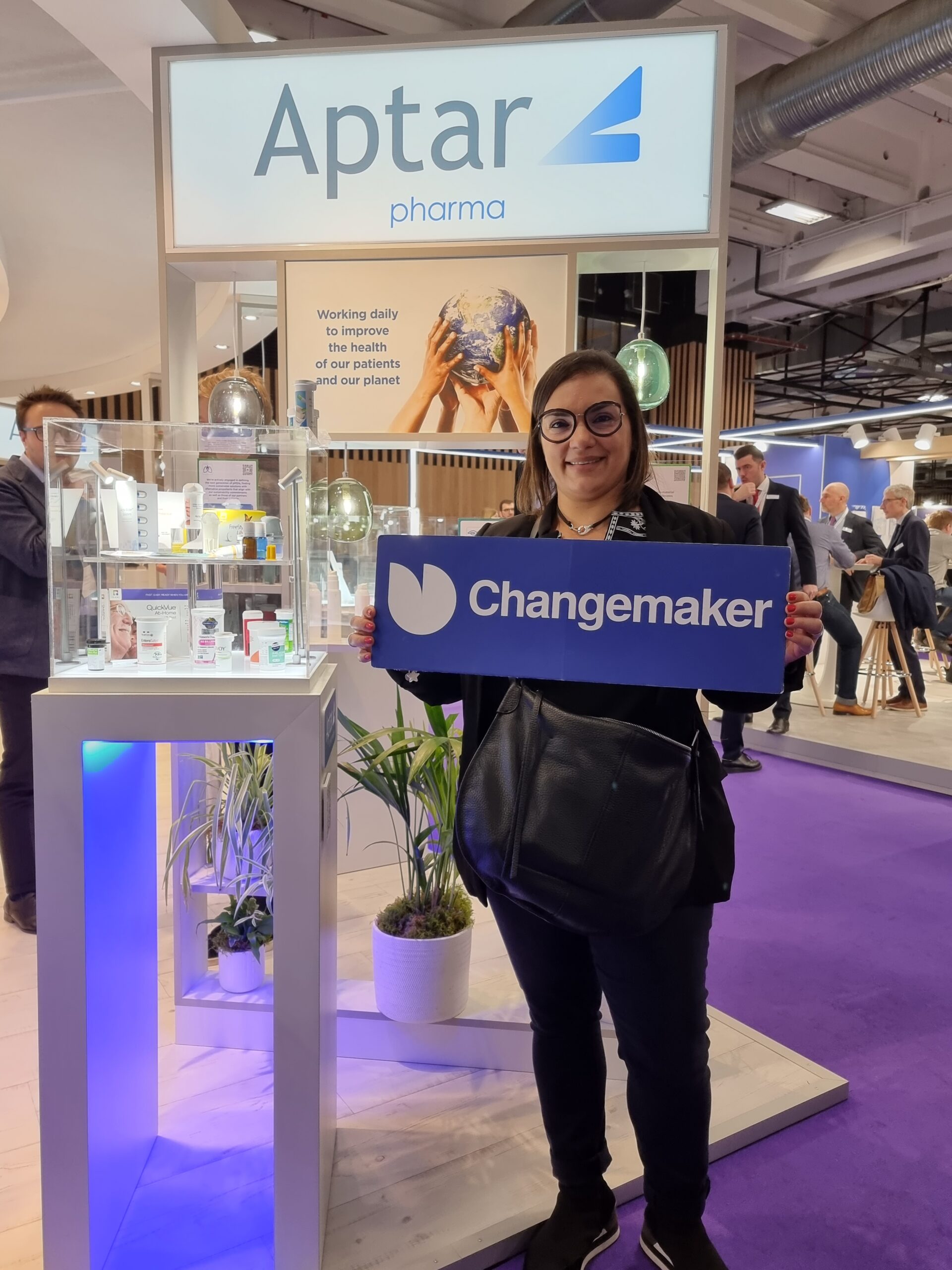
#Changemaker: Ready to protect your pharmaceutical products from moisture?
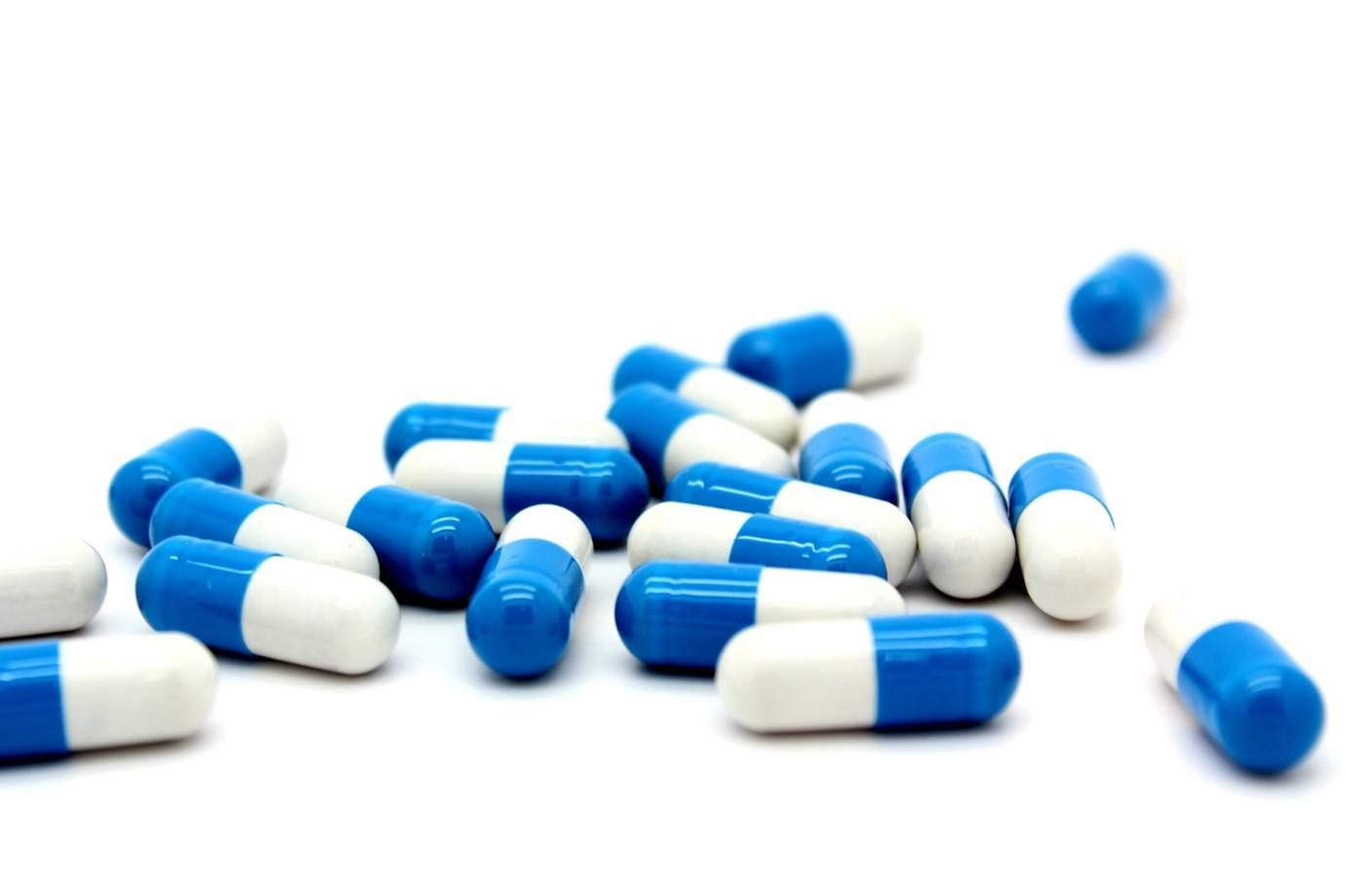
How reliable imaging plays an important role in capsule visual inspection
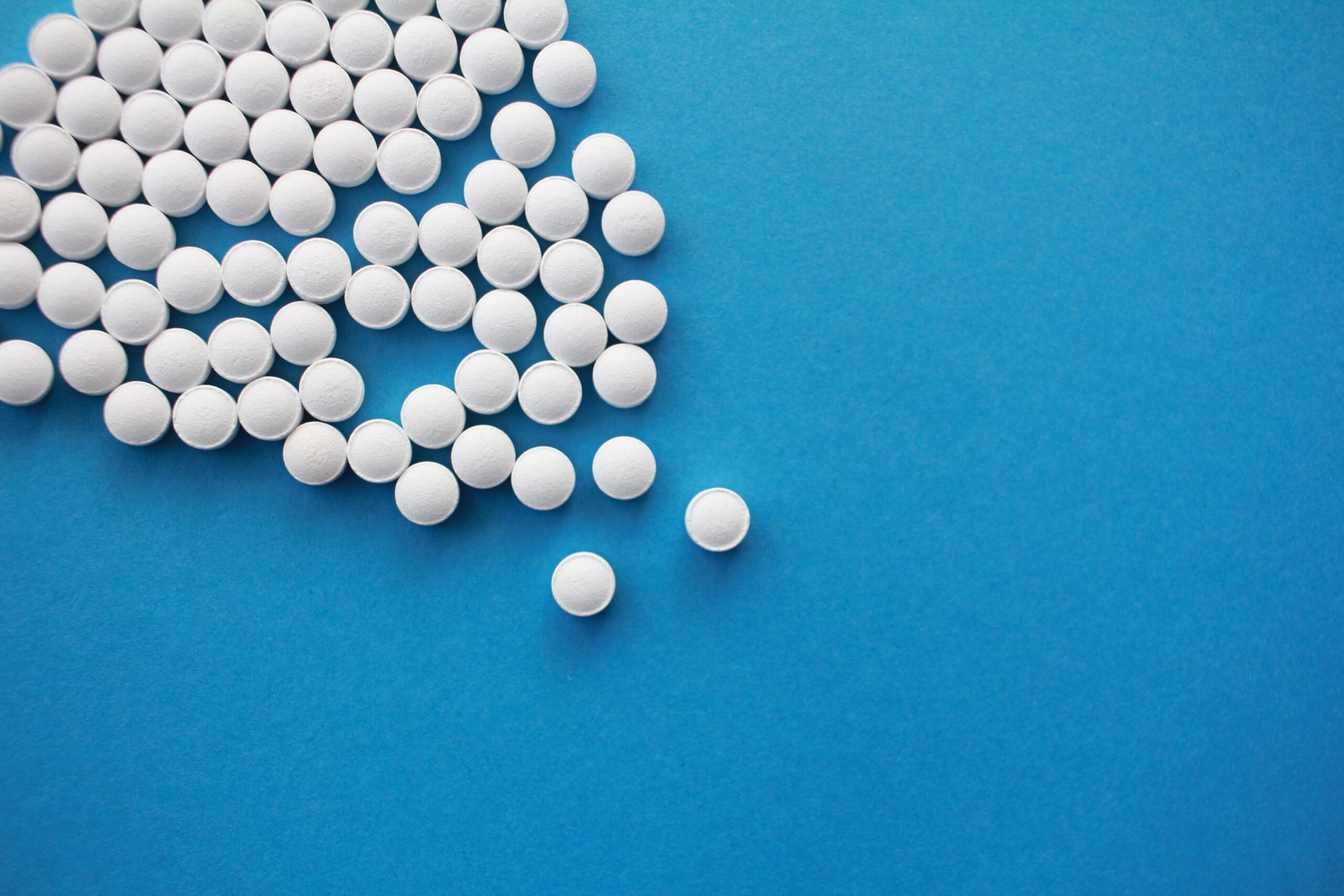
Chewable or regular aspirin: what is the difference?
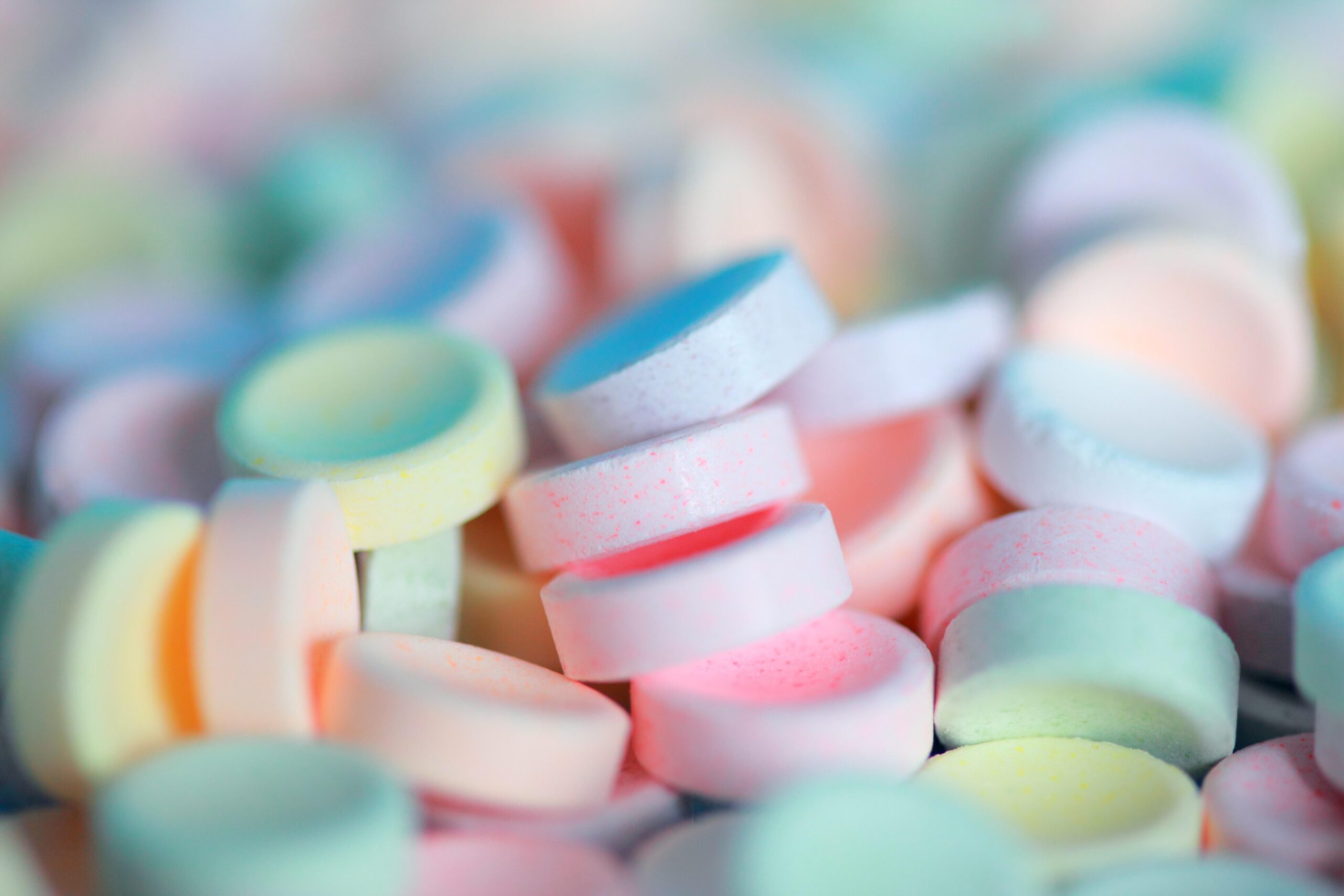
Making chewable multivitamin tablets for kids

Keeping pharmaceuticals moisture free
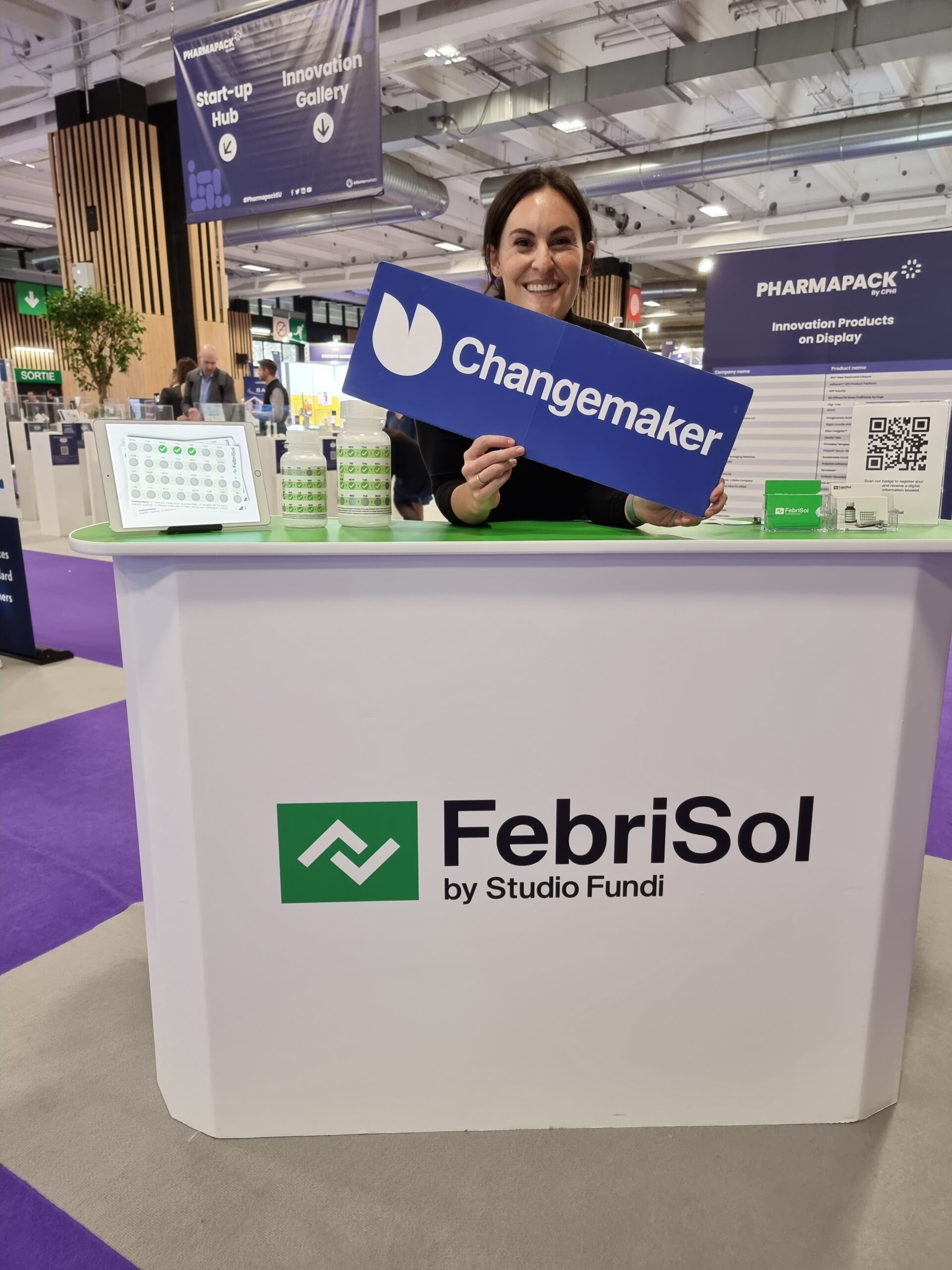
#Changemaker: Keep track of your medicine every day with FabriSol sticker
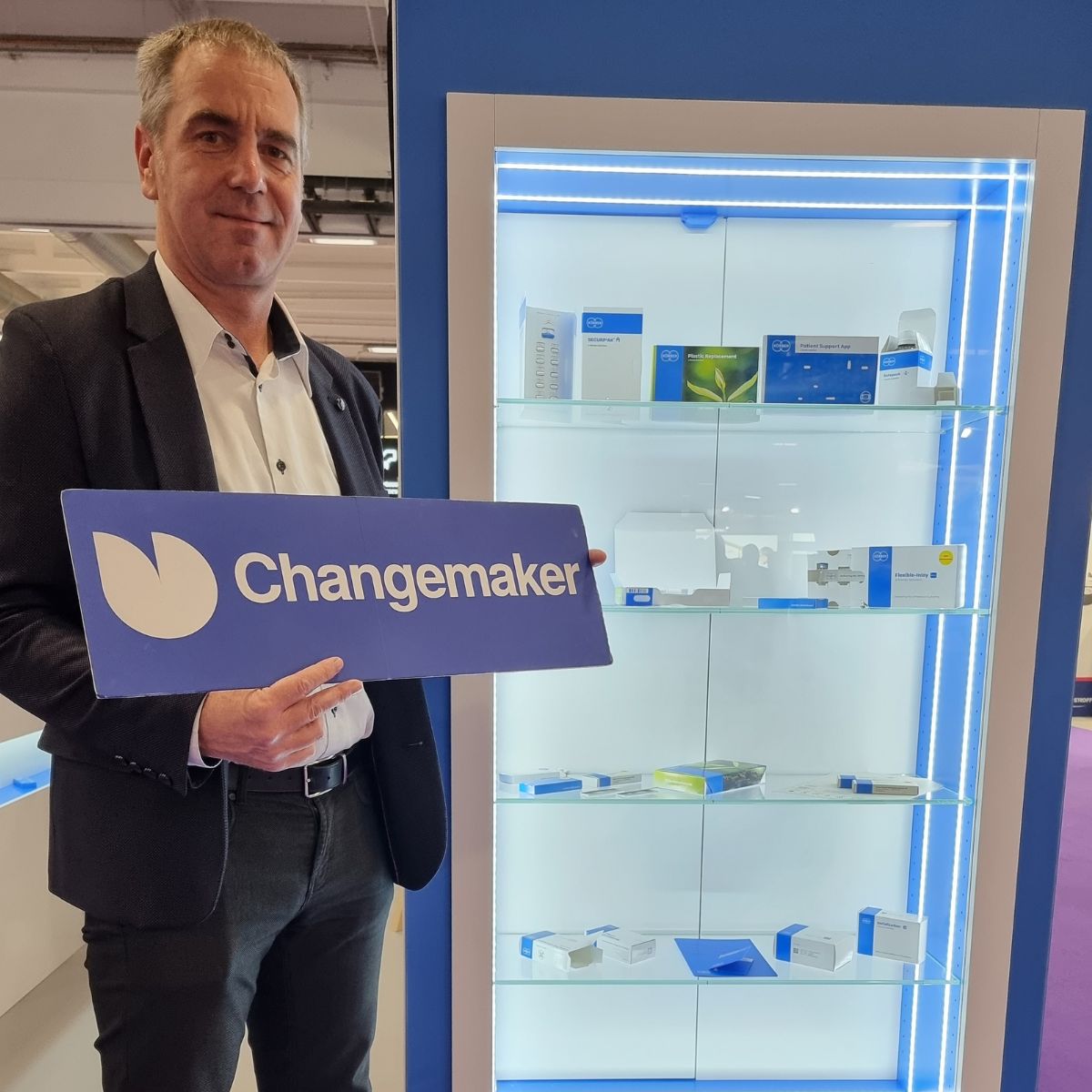
#Changemaker: Turning grass into pharmaceutical packaging
Select your tablets process
What are you making?
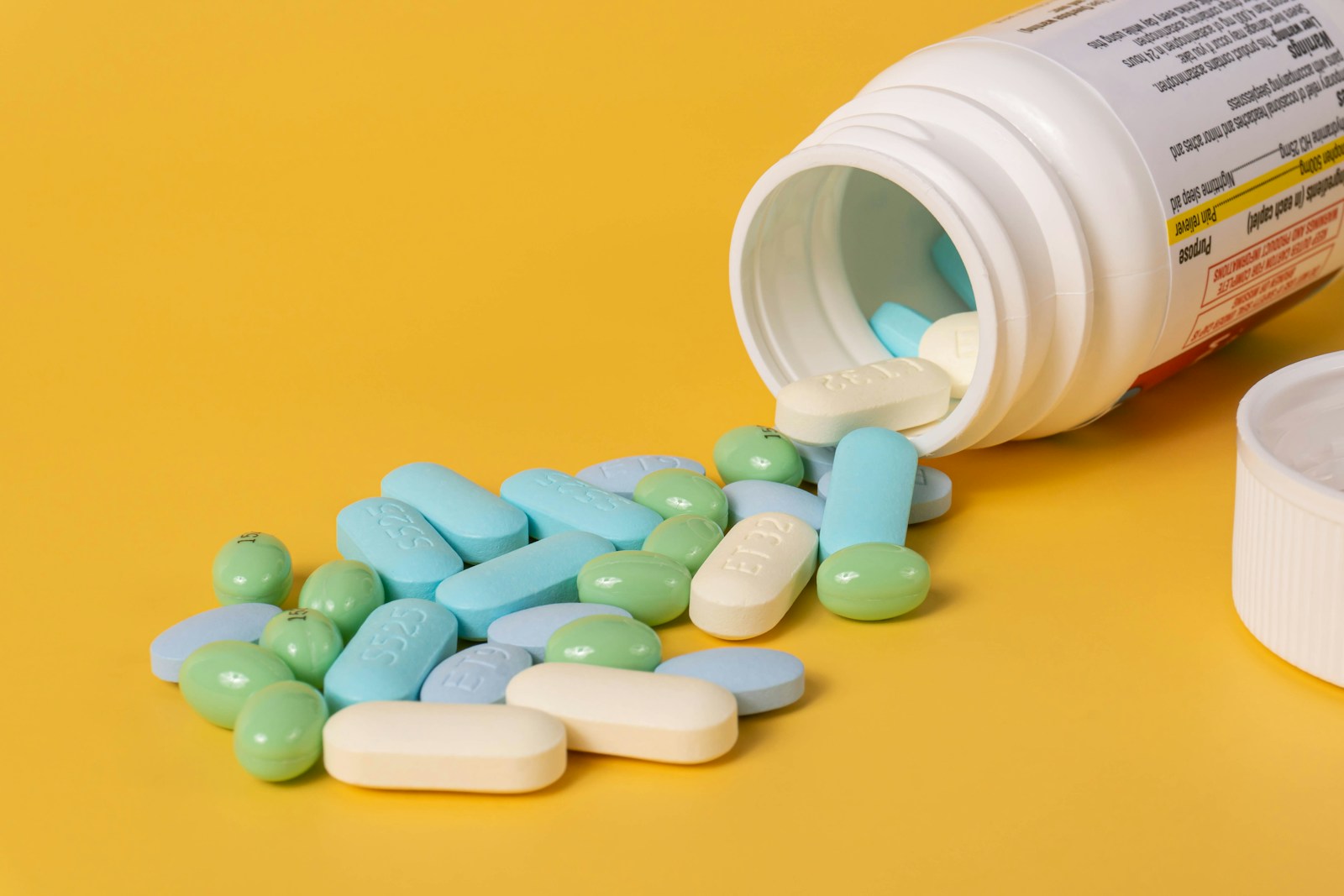
Antihistamine tablets
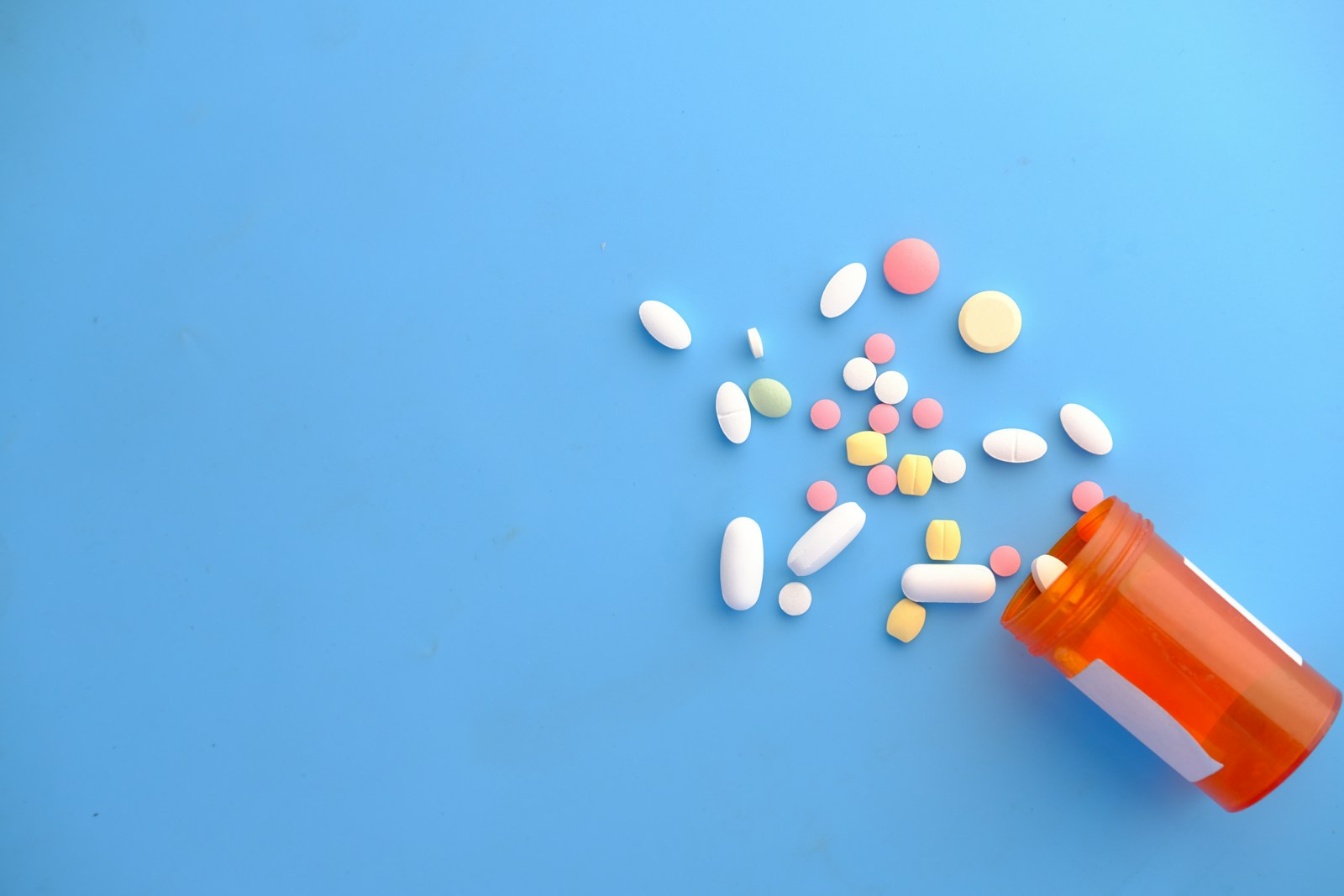
Antibiotic tablets
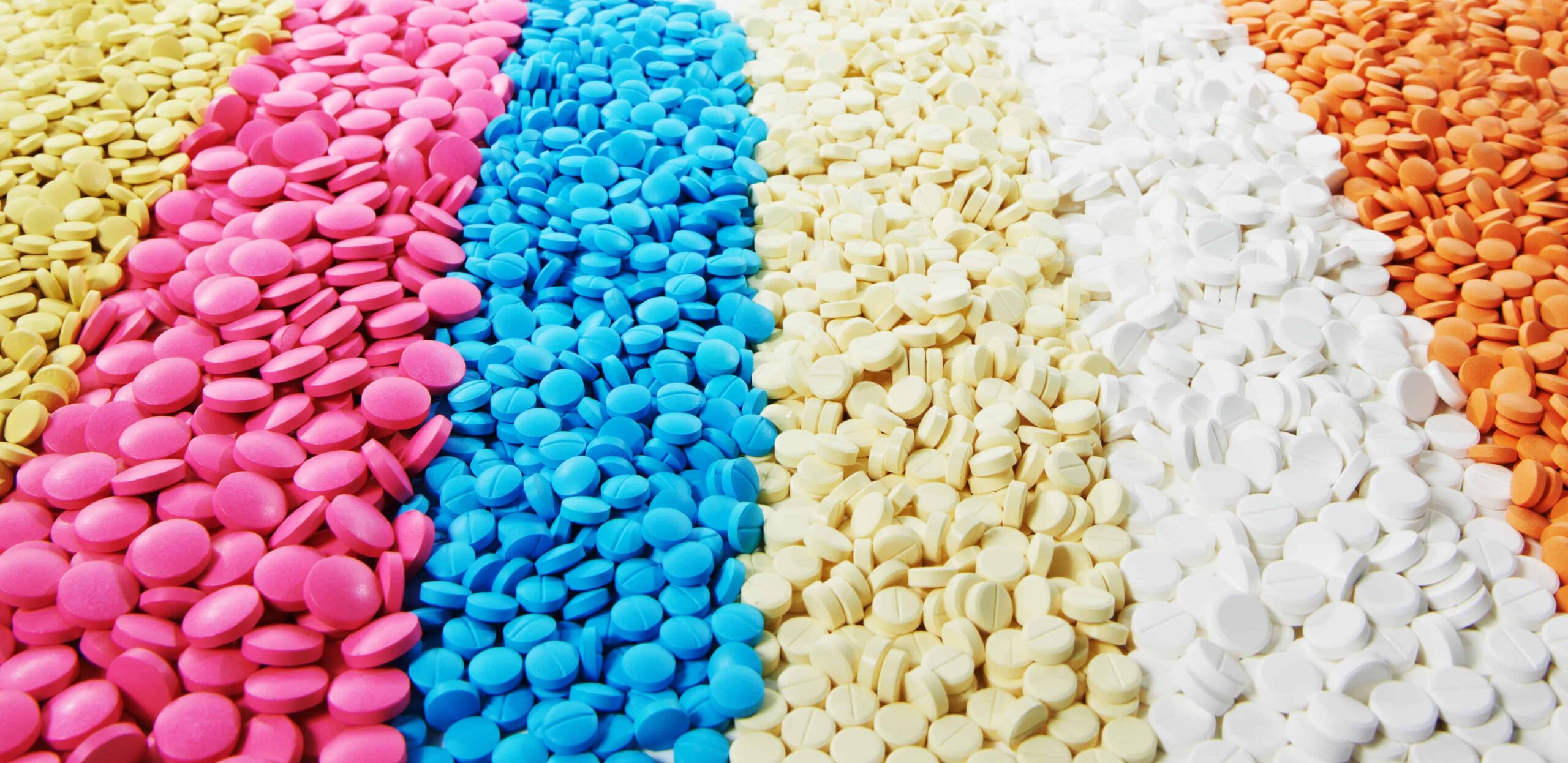
Sugar-coated tablets

Sustained-release tablets
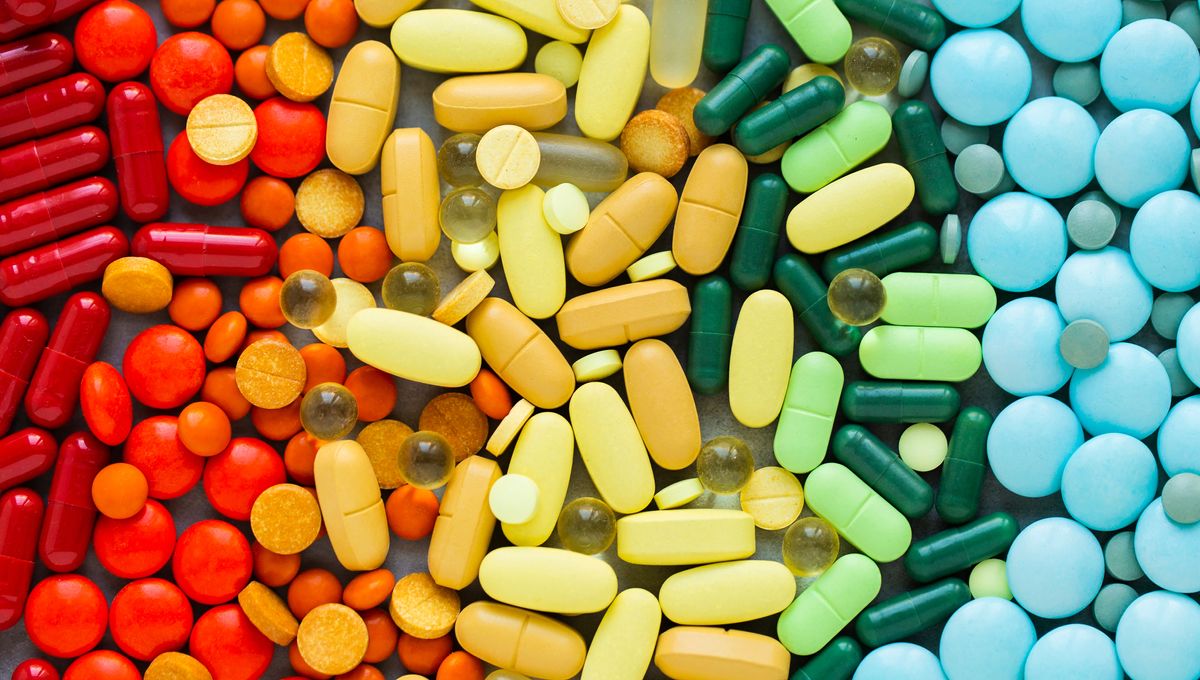
Pharmaceutical pills
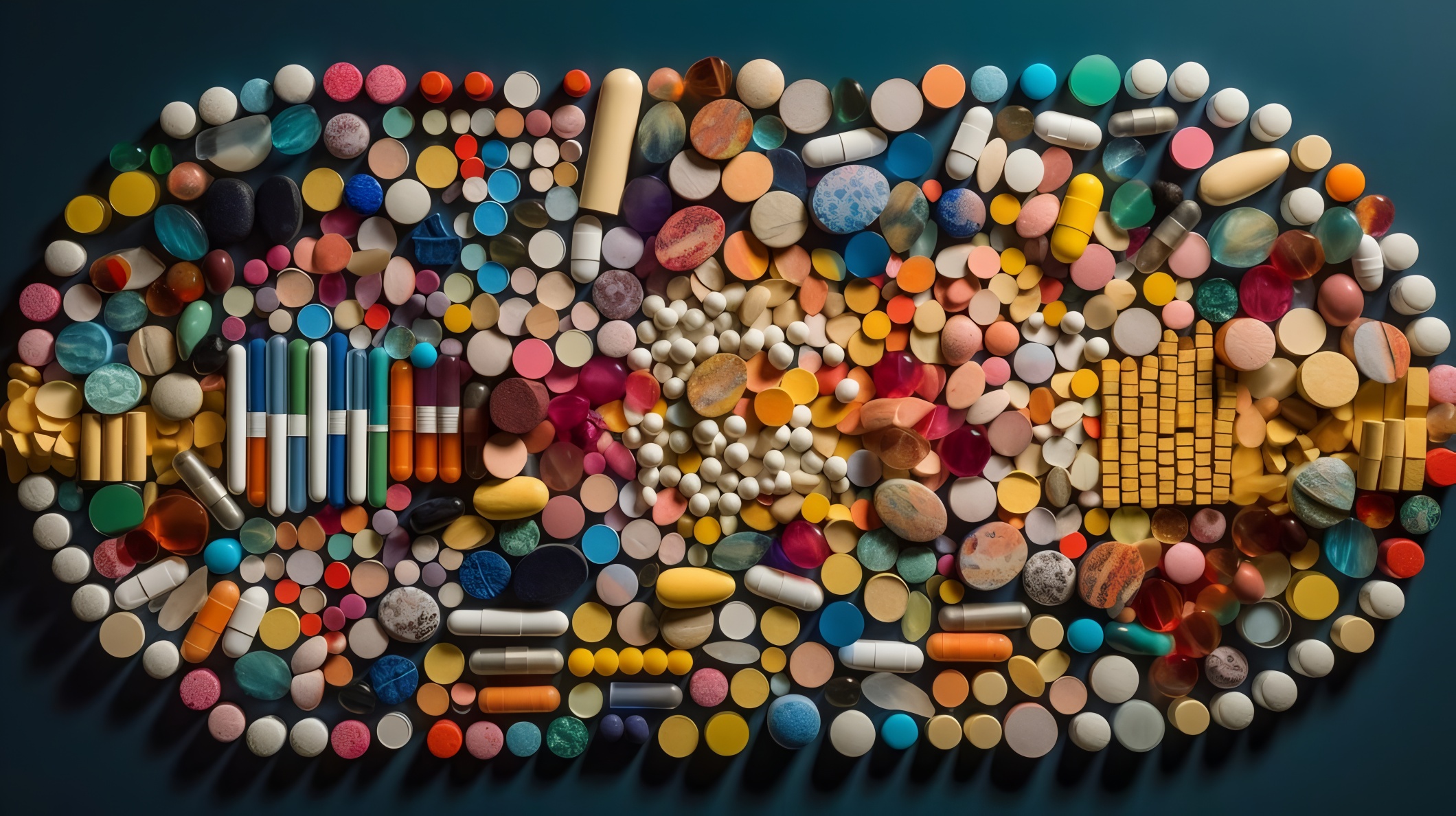
Micro-tablets
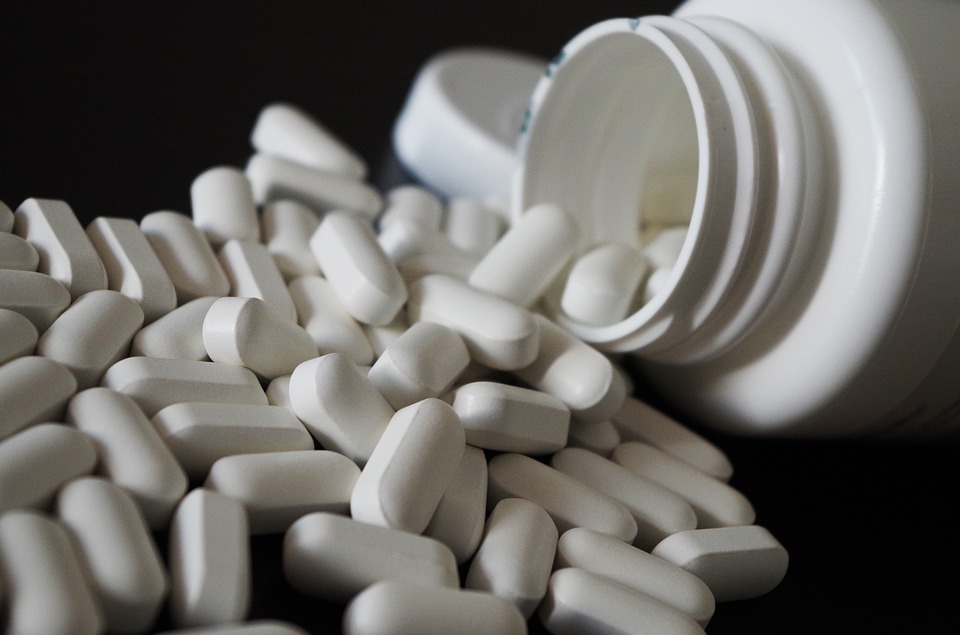
Immediate-release tablets
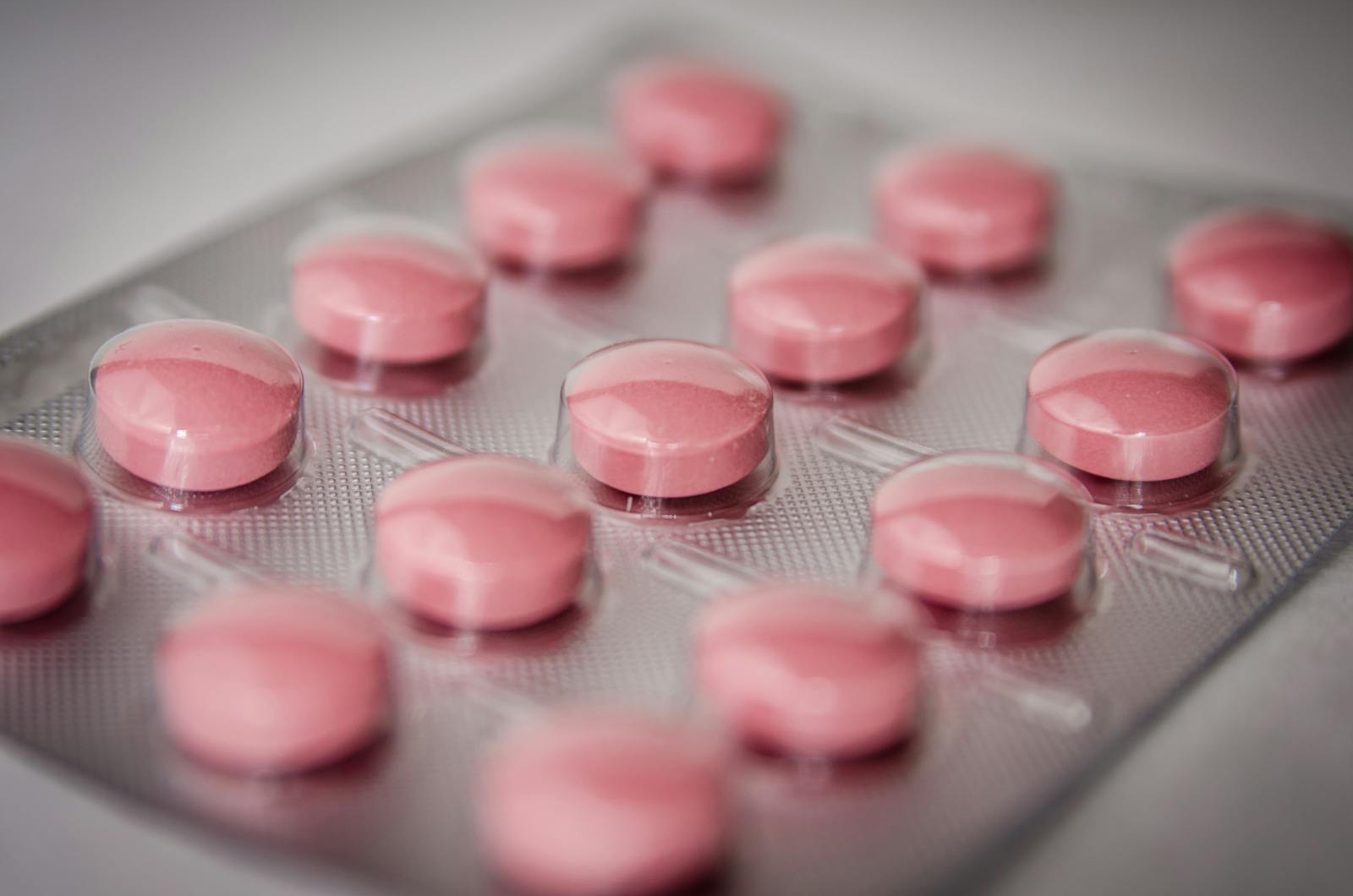
Er tablets
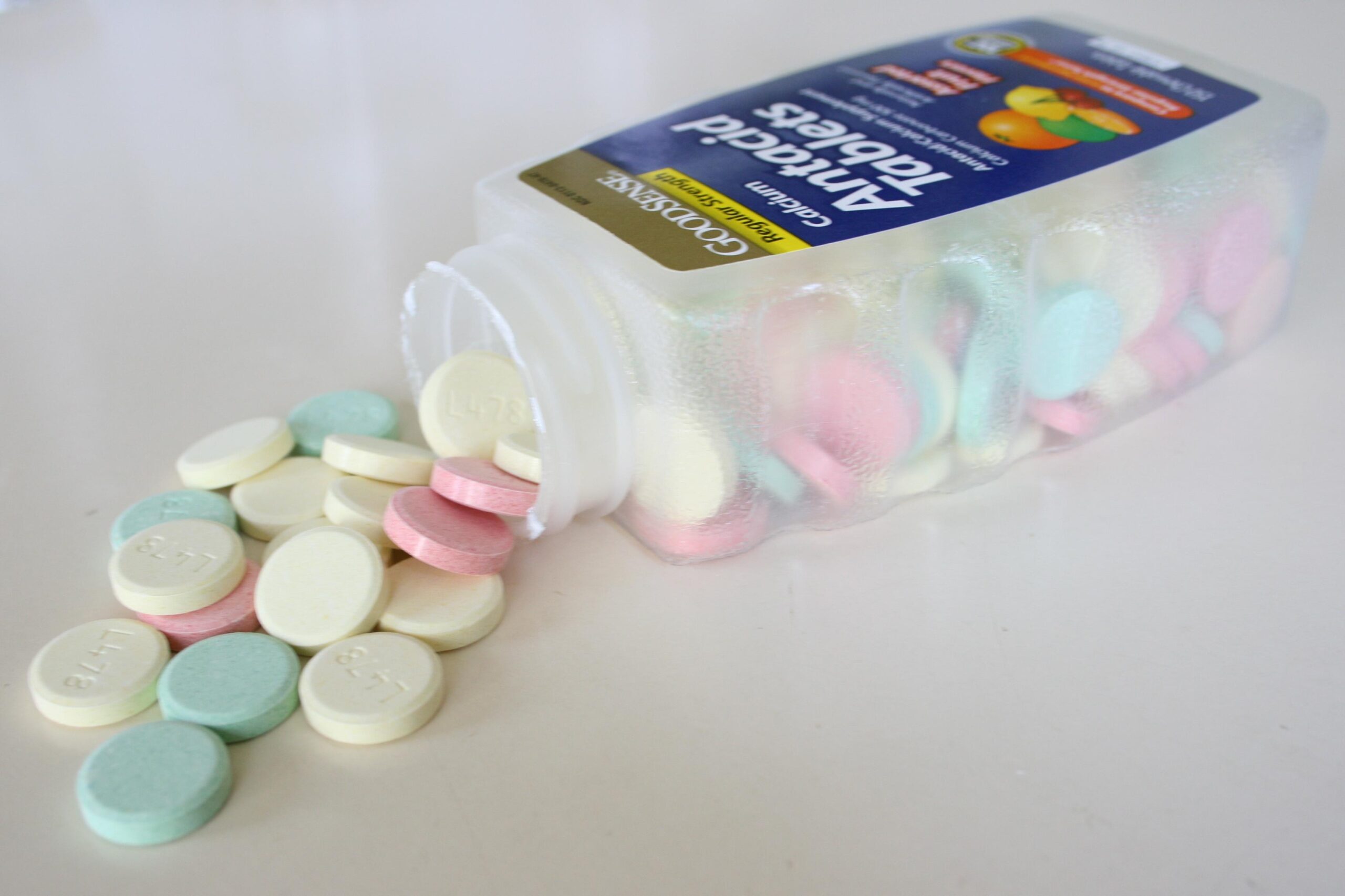
Antacid tablets
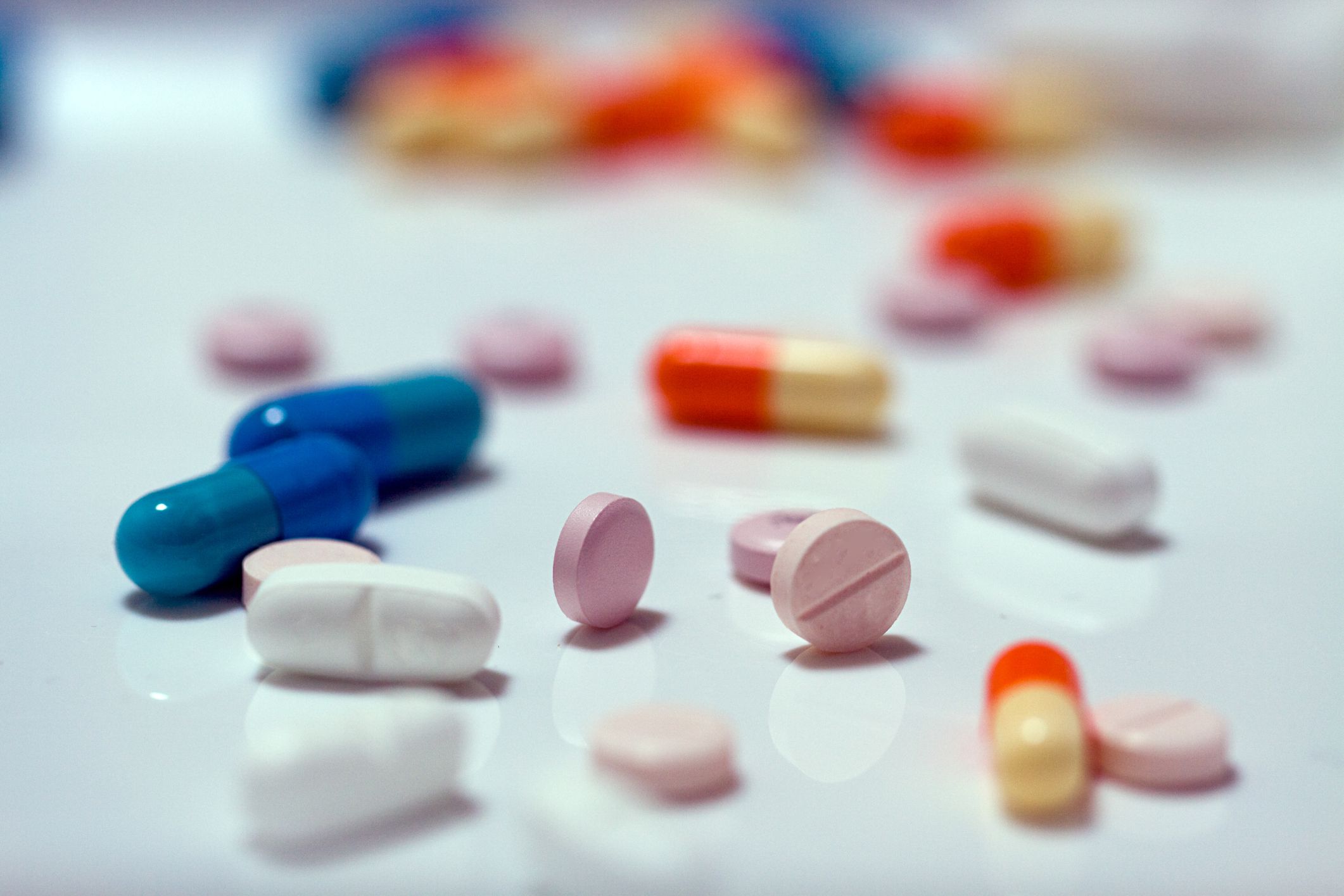
Analgesic tablets
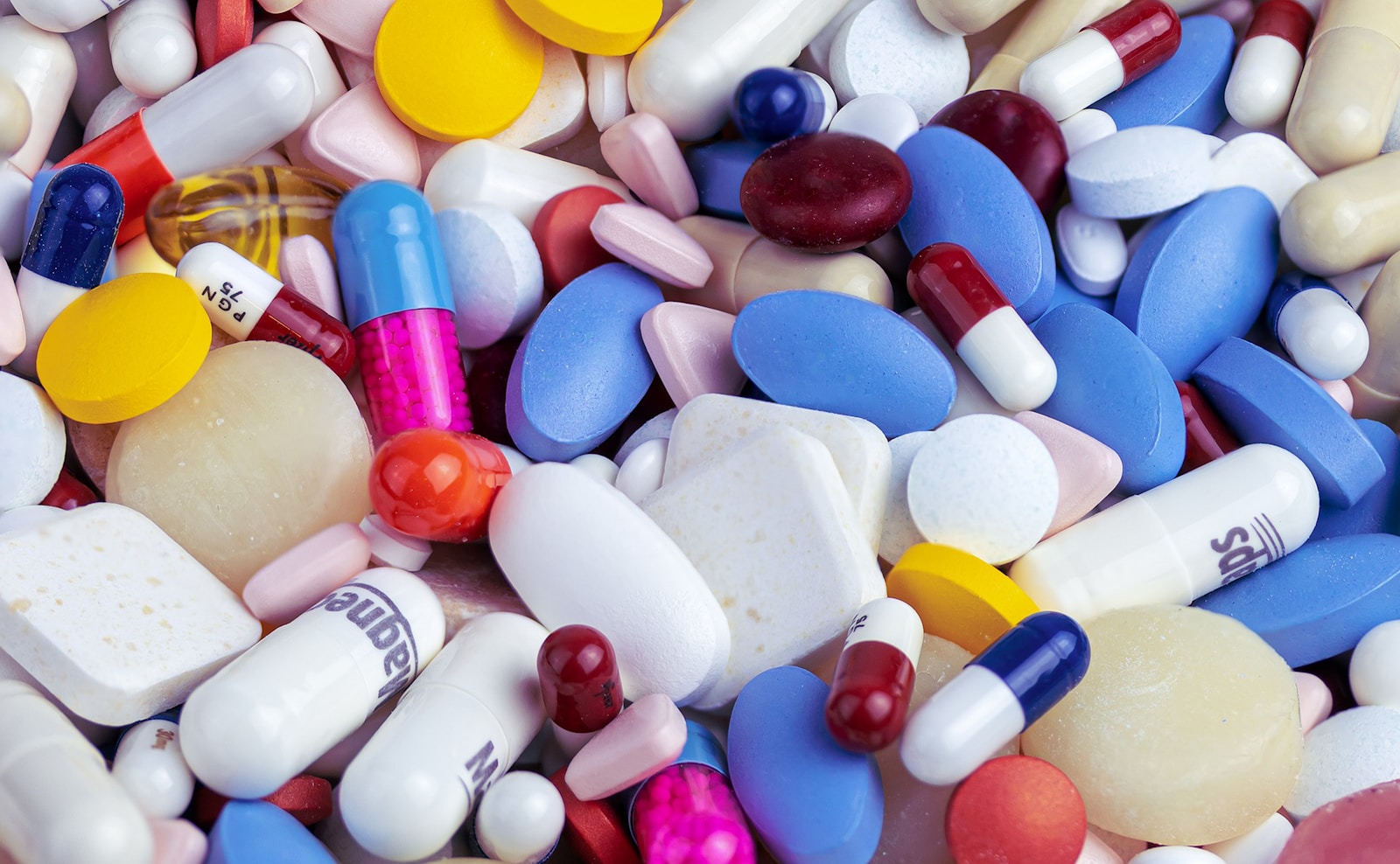
Coated tablets
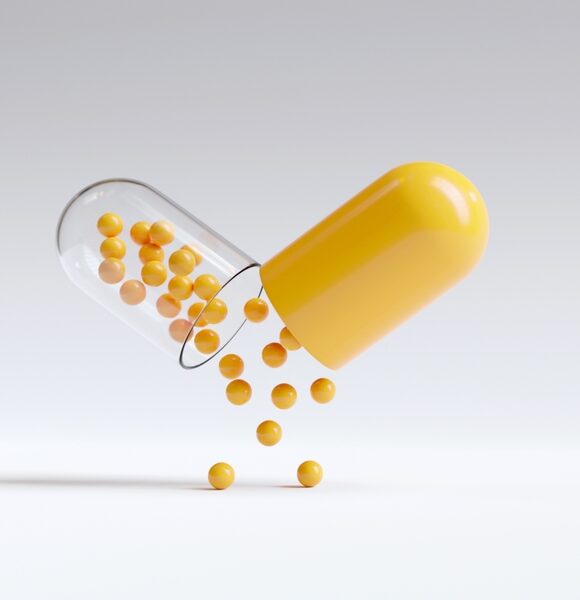
Pharmaceutical granules
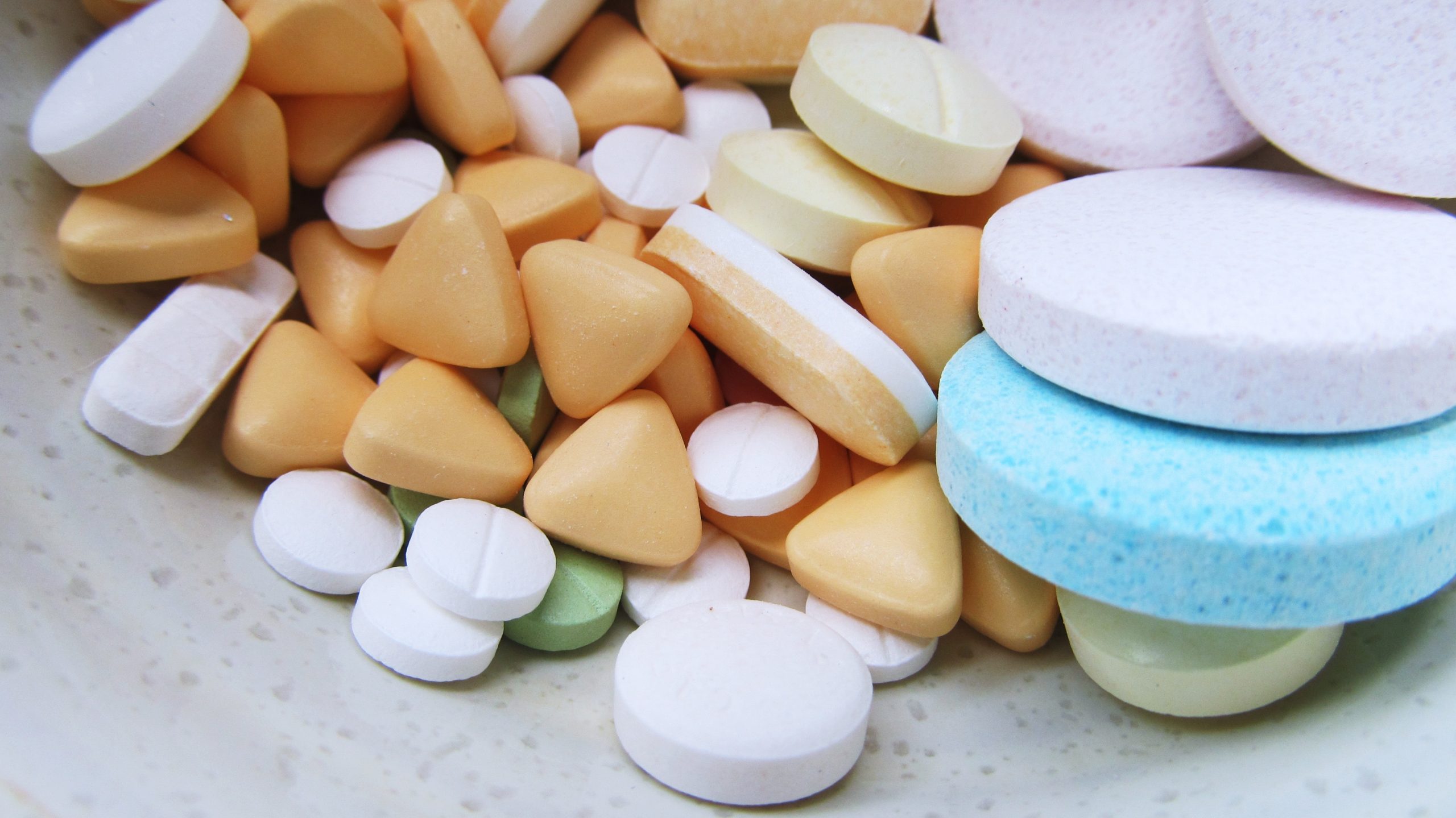
Multi-layer tablets
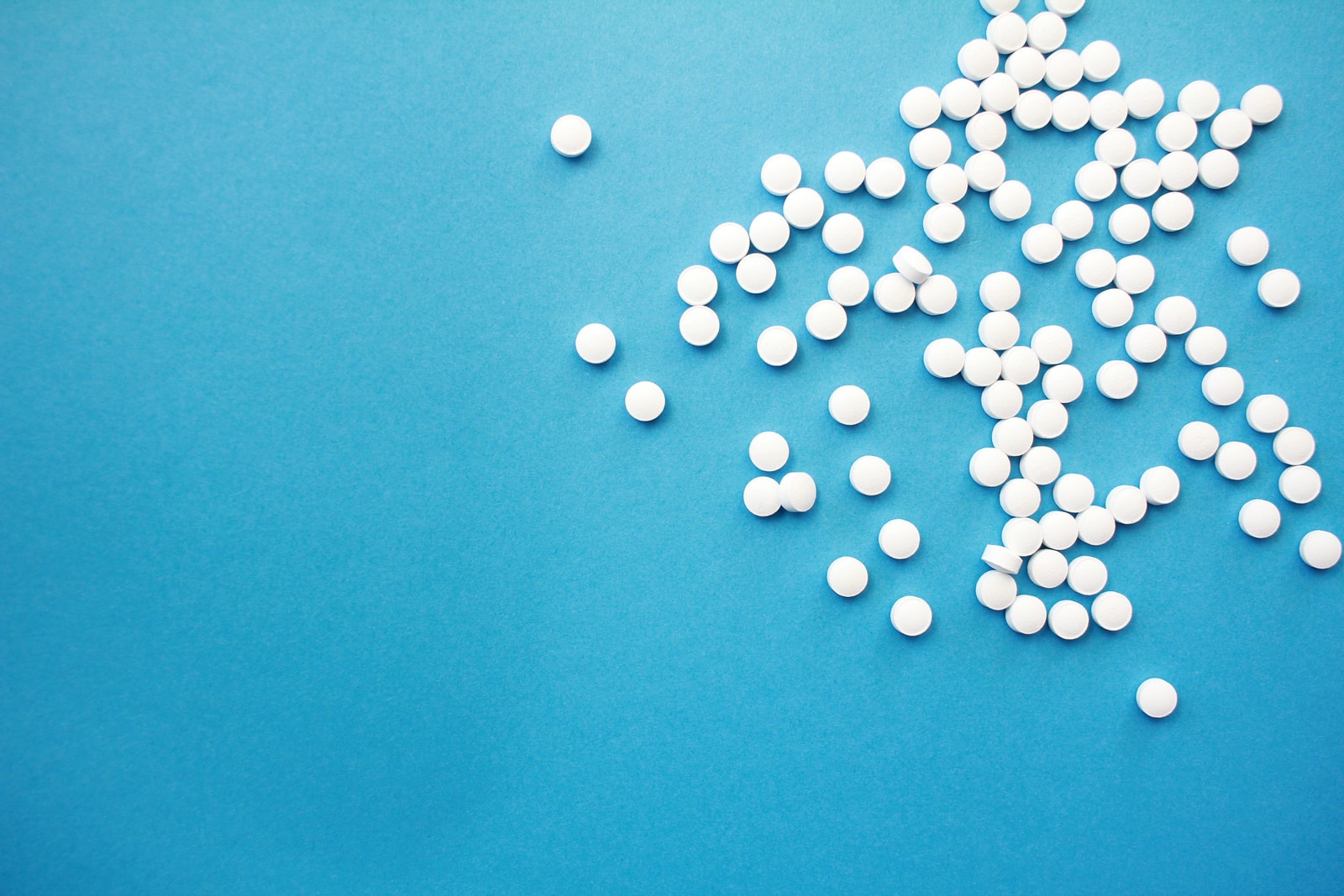
Microtablets

Uncoated tablets
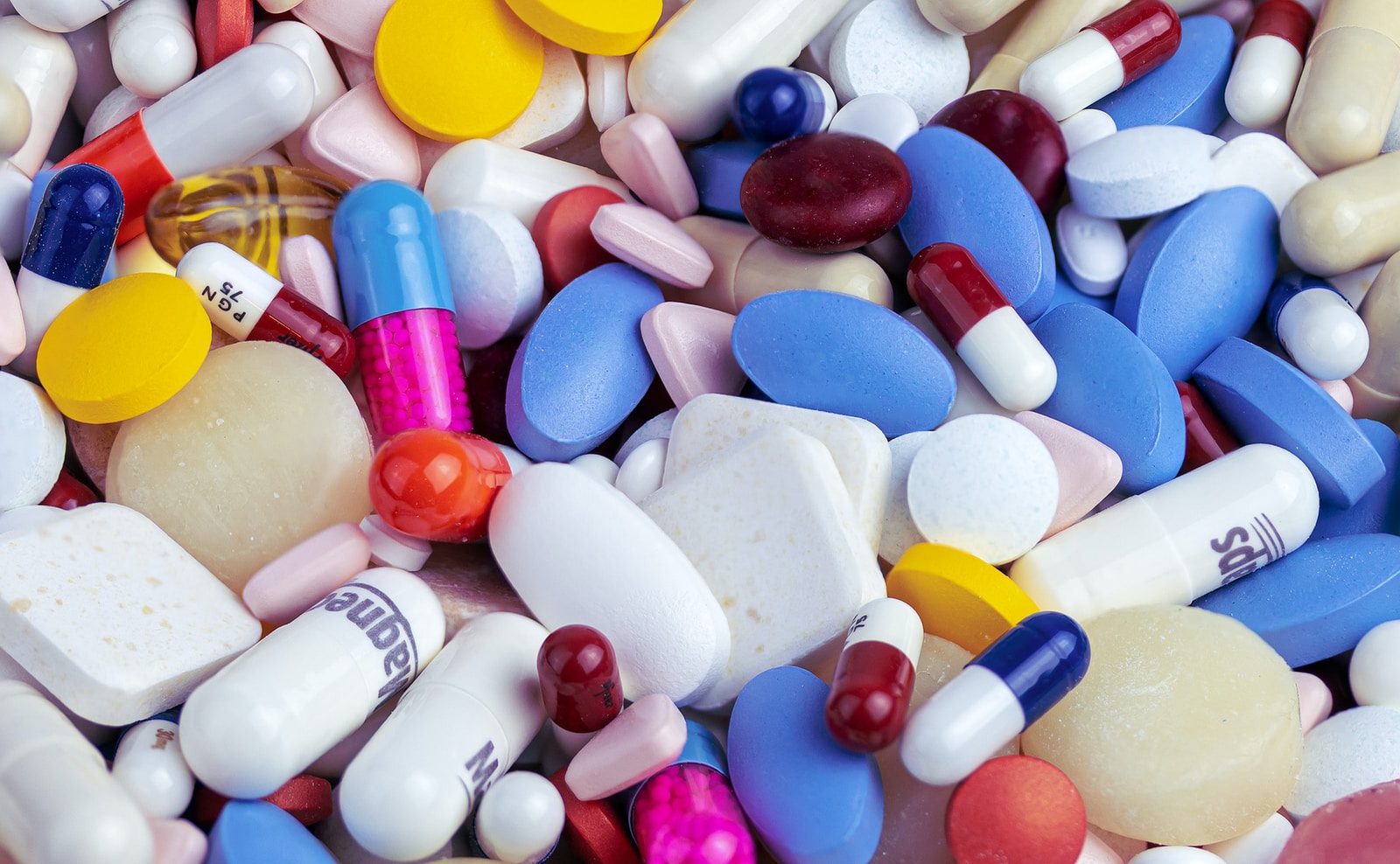
Enteric Coated Tablets
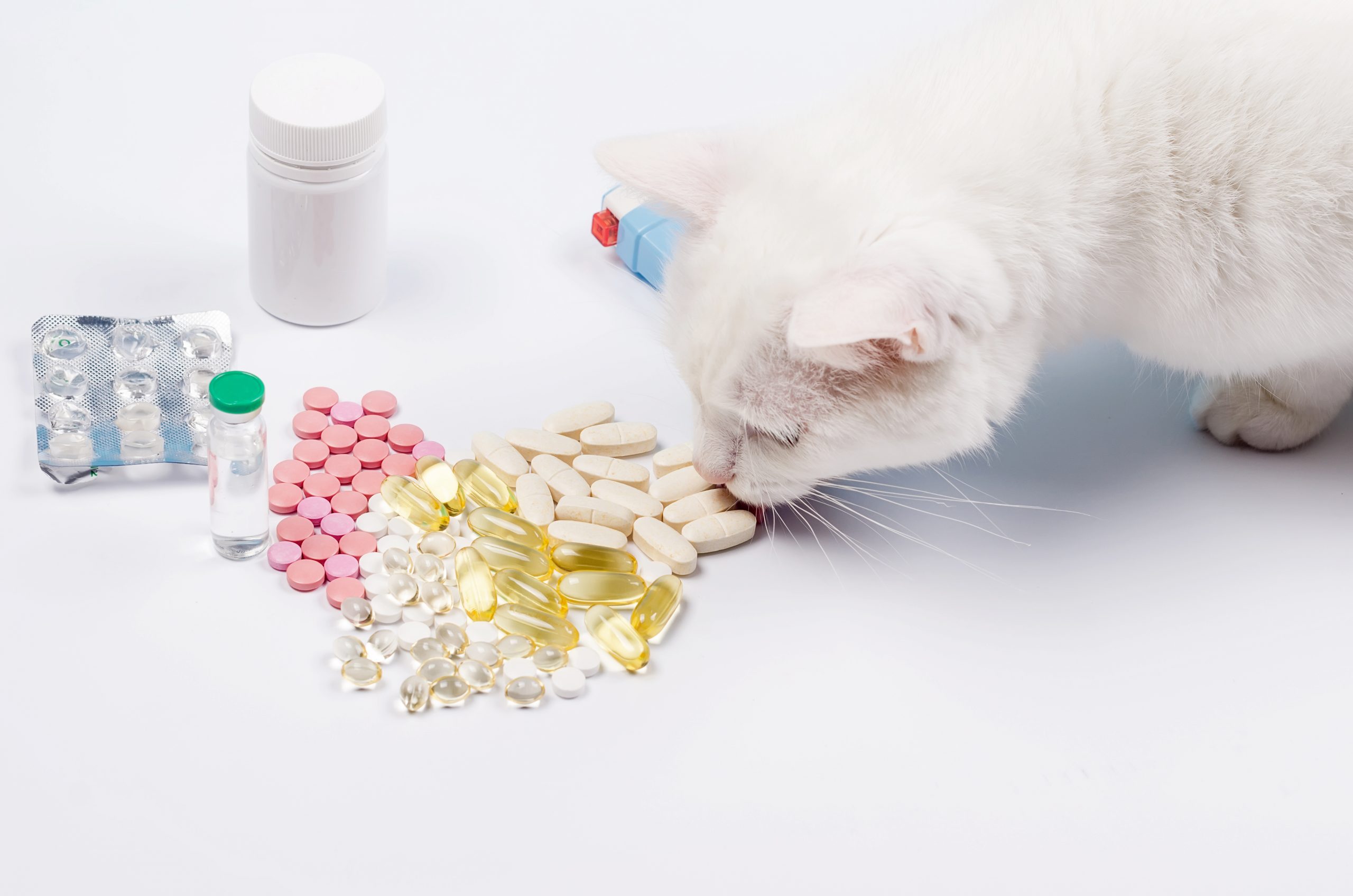
Veterinary tablets
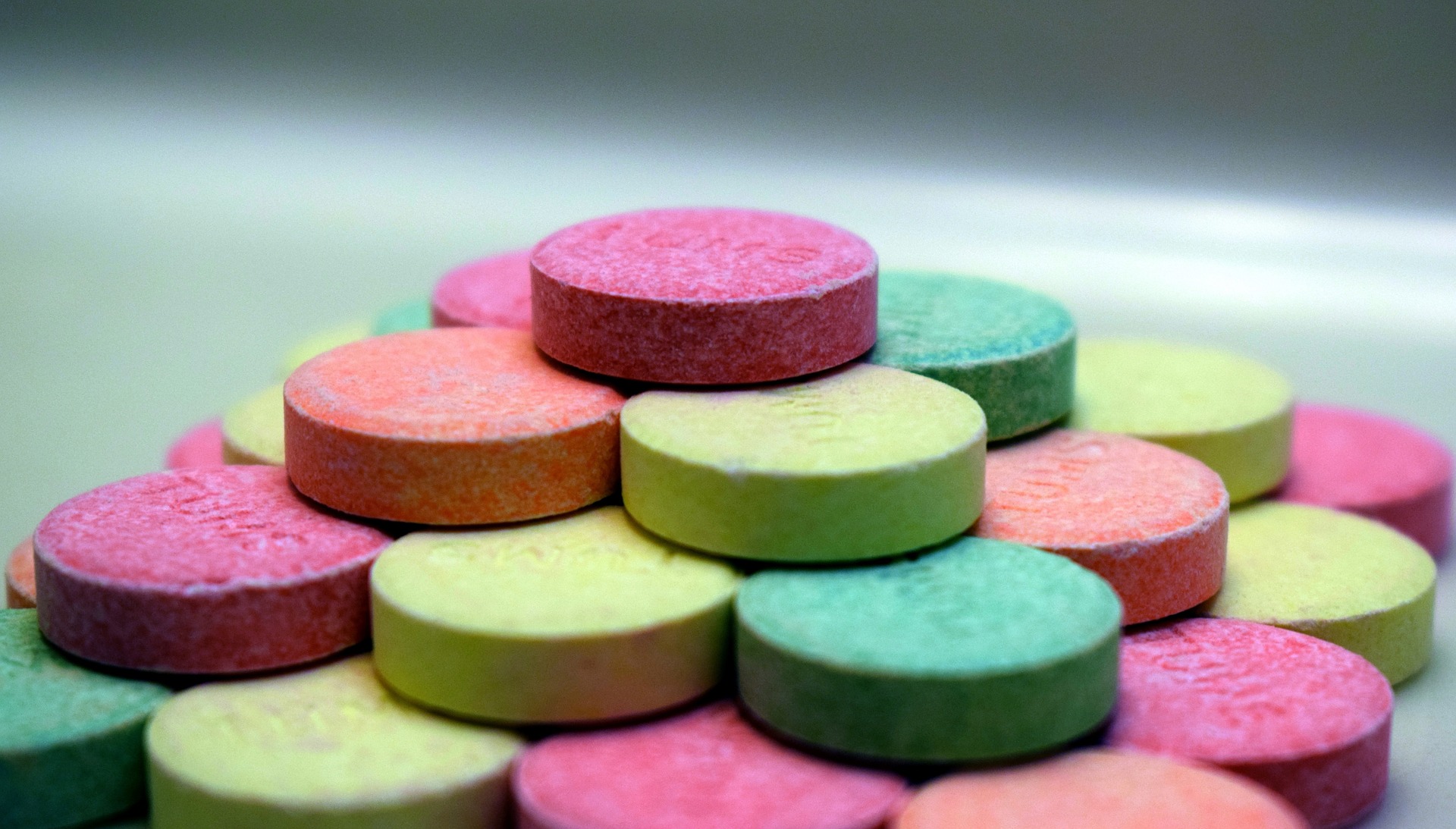
Chewable tablets
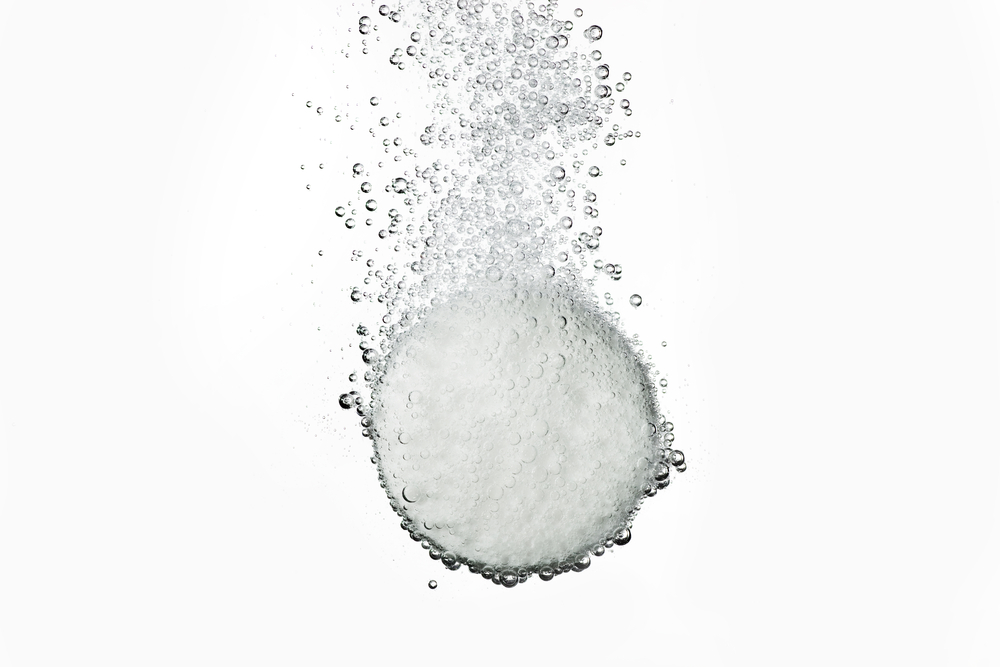
Effervescent tablets
Tell us about your production challenge
Originally only manufactured in discoid shape, tablet today also come in triangular, rectangular, round, oval, oblong, or cylindrical varieties. Colors can vary to distinguish different medicines, and tablets are often stamped with symbols, letters, and numbers, enabling them to be identified.
According to their route of administration and the method of manufacture, it is possible to classify tablets into chewable tablets, effervescent tablets and multi-layer tablets, to name a few. Still, the compressed tablet remains the most popular dosage form nowadays.
Production processes involved in making pharmaceutical tablets
In the pharmaceutical industry, the methods used for tablet making can be classified as granulation (wet granulation and dry granulation) and direct compression.
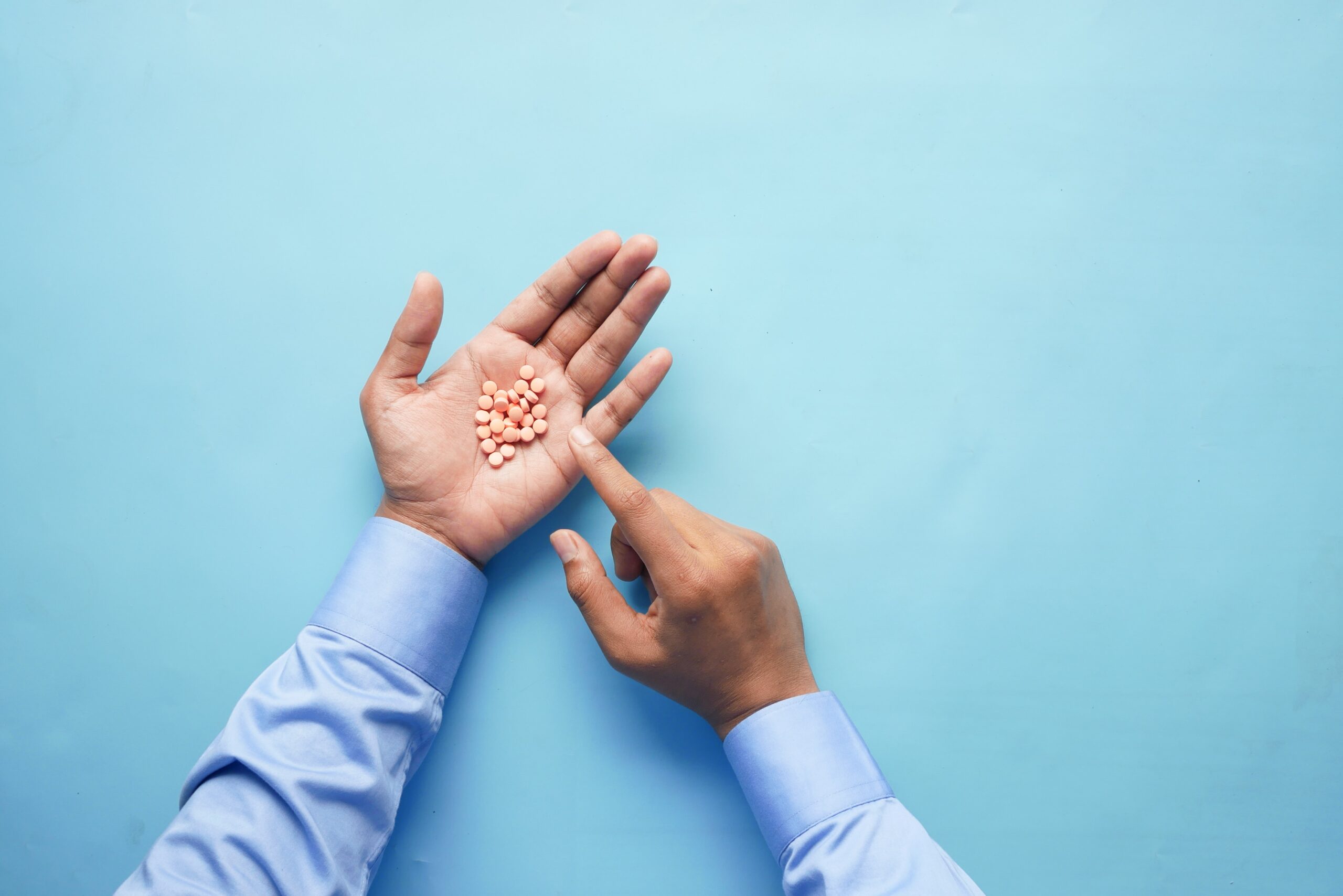
Wet granulation vs. dry granulation
Granulation is a complex multi-stage process in which small powder particles are combined together to form agglomerates called granules.
The main difference between wet granulation and dry granulation is that wet granulation involves a granulating fluid like water, isopropanol, ethanol, or mixtures thereof. In contrast, dry granulation is the formation of granules without using any liquid solution.
Dry granulation can be accomplished with two methods, slugging and roller compaction, and it is used above all for those tablet ingredients that are sensitive to moisture or are unable to withstand elevated temperatures.
In wet granulation, powder particles are bound together using liquid solutions to achieve particle enlargement. The granulating fluid should be volatile to be easily removed by drying and should be non-toxic.
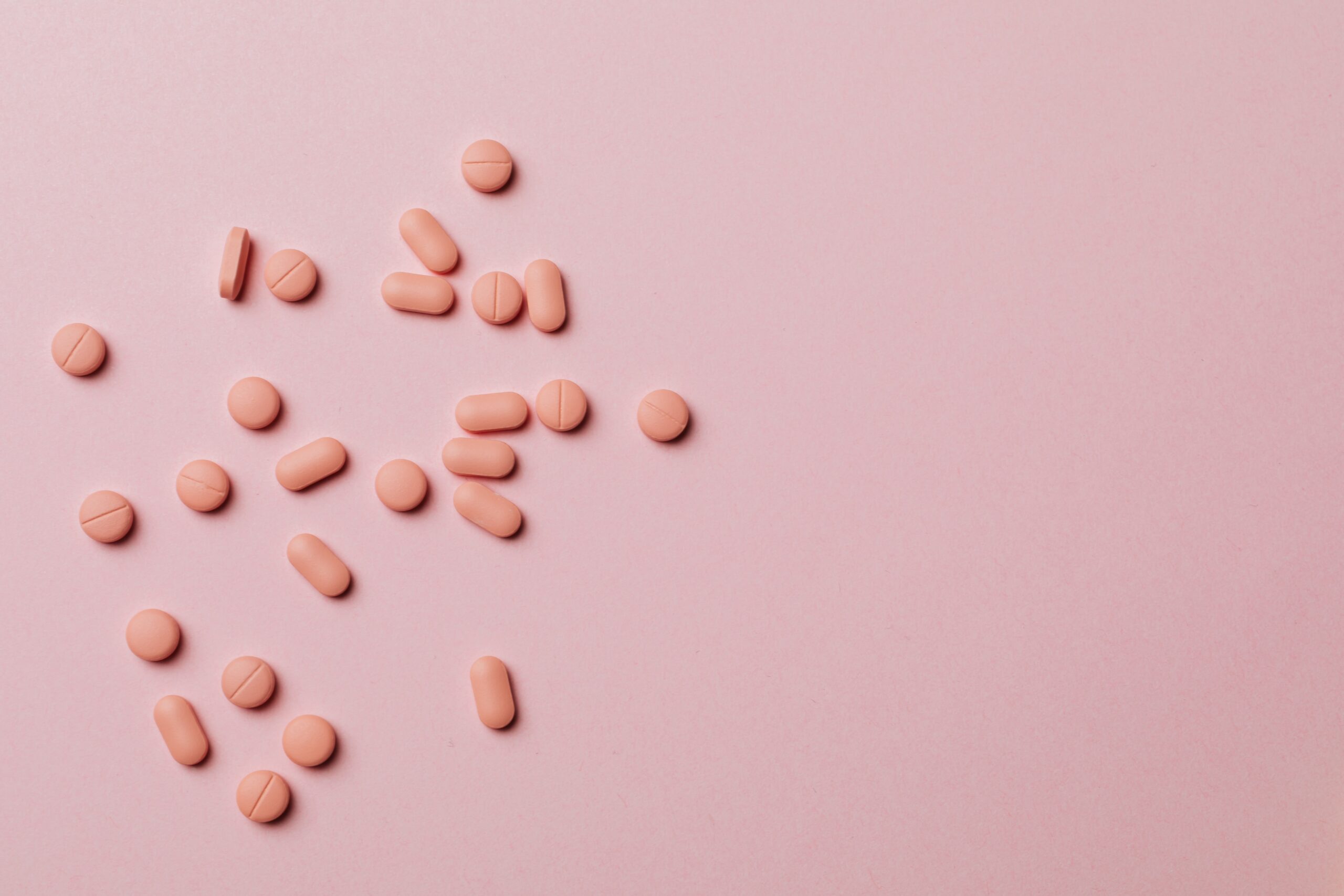
Tablet making equipment for direct compression
Direct compression refers to a process in which powdered APIs are mixed with excipients and lubricants without involving granulation steps. It has grown in popularity because it provides the shortest, cheapest, and most effective way to produce tablets while minimizing processing time, steps, and equipment required. This tablet production method is suitable for moisture and heat-sensitive API ingredients. Direct compression requires a tablet press in which the upper and lower punches are pressed together within the die hole and compress the tablet until it is formed.
The tablet equipment used for compression is the single punch tablet press and the rotary tablet press. The difference is that the single punch tablet press has two punches (upper and lower), but it uses only the upper one for compression. The rotary press has multiple punches and uses both the upper and the lower ones to compress the granules.
Uncoated tablets vs. coated tablets. When is a tablet coating machine needed?
Have you ever wondered why some tablets are coated and others are not?
Let’s start by understanding the difference, although the name already says it all. Uncoated tablets are simply made by compressing the granules with no coating added afterward. They don’t taste good and are harder to swallow, especially for children. This can be an excellent reason to use a coating; for instance, tablets are coated to mask an unpleasant taste.
An example of coated tablets is enteric coated tablets. The enteric coating is necessary when the tablet’s active ingredient is acid sensitive. Using tablet coating equipment that applies a polymer barrier to the tablet makes it possible to protect it from stomach acidity. This involves spraying the film-forming material onto the tablet surface as the tablets rotate in the pan.
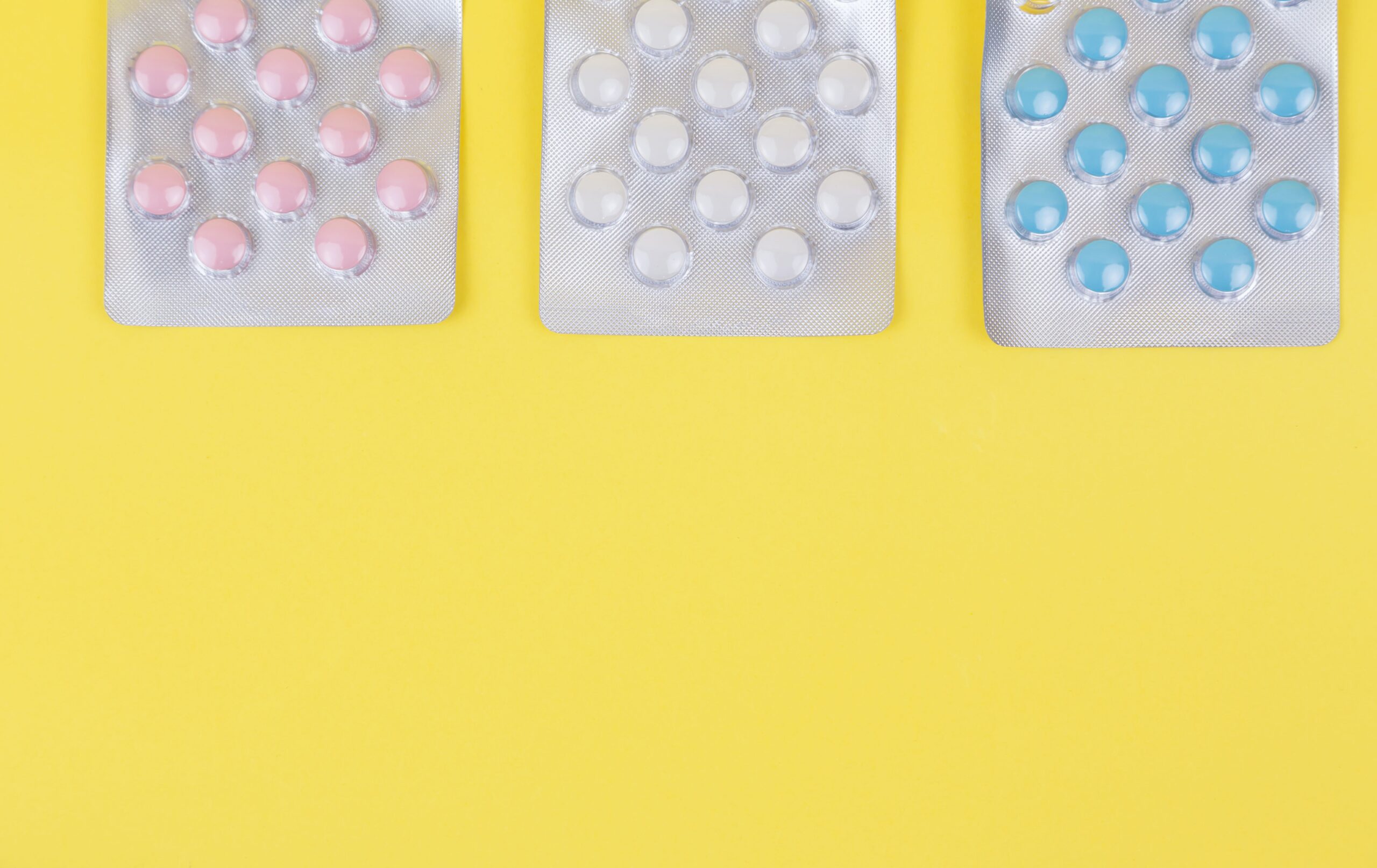
Keep your tablet safe by choosing suitable packaging
Solid dosage forms such as tablets are commonly packed in blister packs. This type of packaging assures the integrity of each dose since each cavity is separate, so if one of their seals is breached, this doesn’t compromise the quality of the whole product
The main aim of pharmaceutical packaging, like all others, is usually to protect products from any physical and biological damage and from external conditions that can alter the property of the product inside.
The importance of serialization in the pharmaceutical industry
When it comes to informing the buyer, medical packaging must provide correct information about product name, ingredients, use, and dose, to mention a few. This way, consumers are more aware of product origin or manufacture. To be able to access all this information, product traceability needs to be provided.
The most commonly used standard to facilitate traceability on drug units is serialization. A barcode needs to be printed on a different level of drug packaging (primary, secondary, and tertiary). With the help of this printed symbol, it is easier to track and trace the origin of a drug and reduce the chance of counterfeit products.
Tablet Making Equipment in Action
Tablet press - automated line
Tablet visual inspection
Which tablets technology do you need?
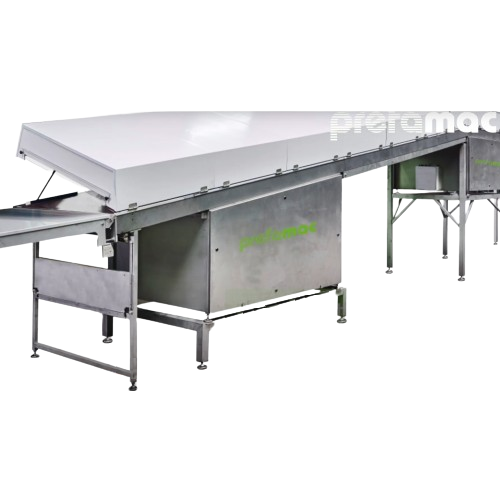
Dosing system for chocolate tablets
Enhance your confectionery production with a versatile solution for precise dosing and ...
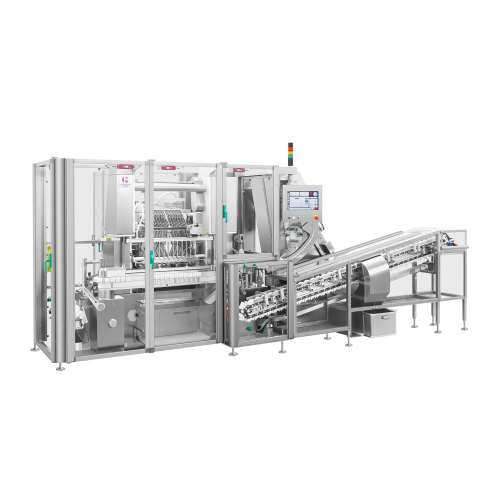
Rigid tube filling and capping system for tablets
Streamline your tablet production with an efficient solution that preci...
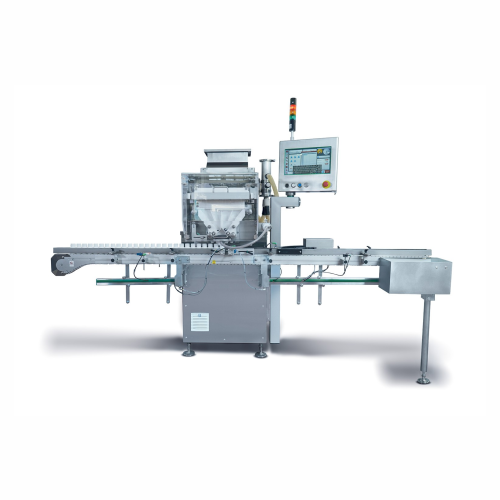
Tablet and capsule counting system
Need precise counting and filling of solid doses like tablets and capsules in your produ...
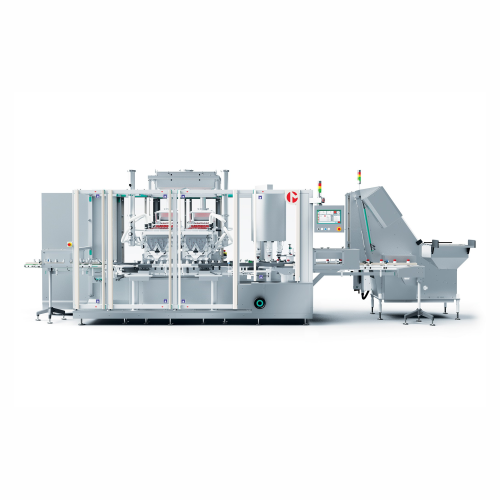
Counting and capping solution for tablets and capsules
Streamline your tablet and capsule production with a high-speed so...
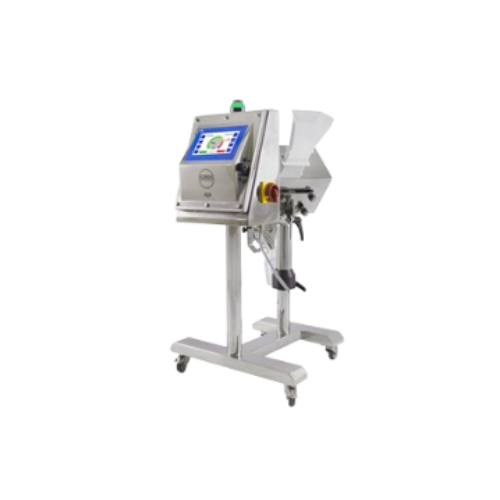
Pharmaceutical metal detector for tablets and capsules
Ensure contaminant-free tablets and capsules with advanced detecti...
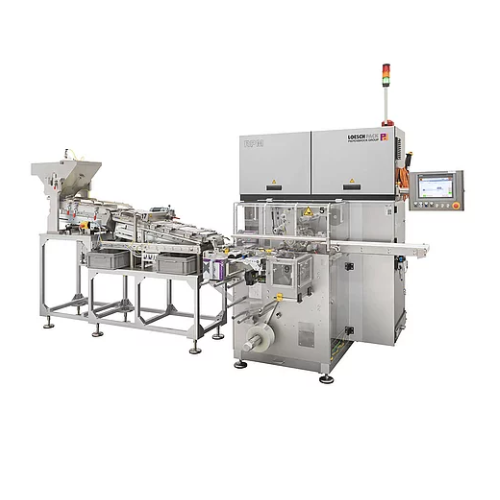
Fold wrapping solution for round pharma tablets
Ensure precise and gentle packaging of round tablets with our innovative f...
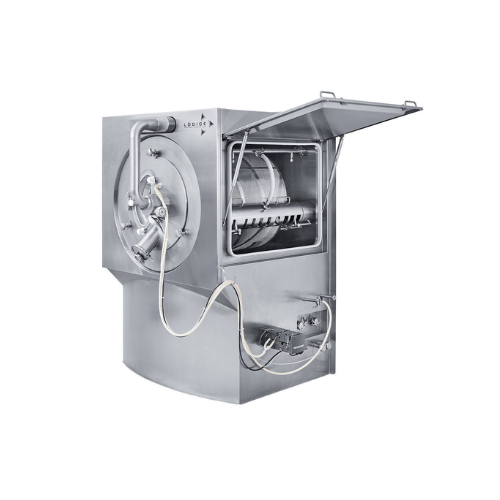
Tablet coater for pharmaceutical applications
Achieve uniform tablet coatings with exceptional efficiency and reduced proc...
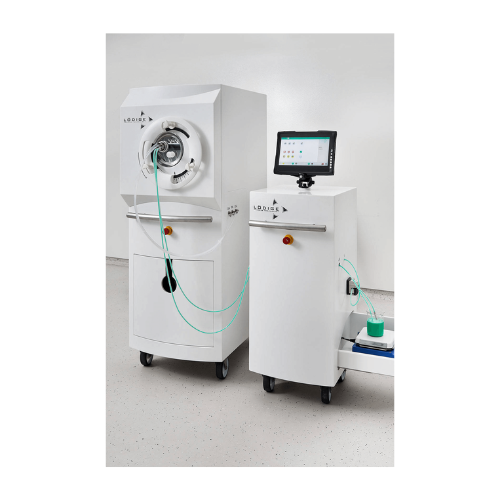
Laboratory tablet coater for pharmaceuticals
Achieve consistent and efficient coating of tablets with this innovative coat...
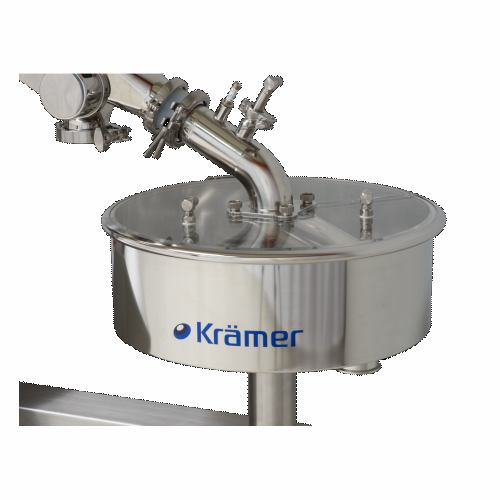
High-containment diverter for continuous tablet and capsule filling
Enhance your production line with a versatile solut...
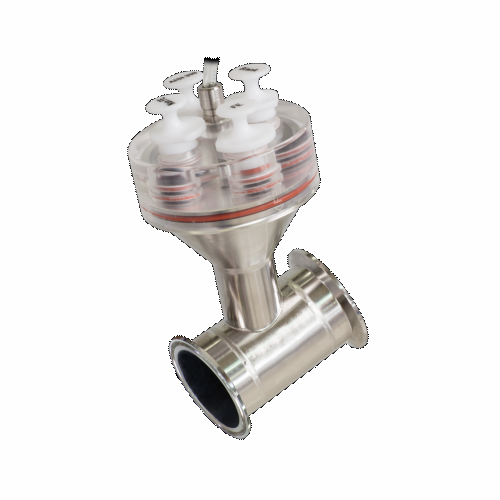
Dust-tight dispenser for metal detector test tablets
Ensure seamless integration of test tablets in high-containment envi...
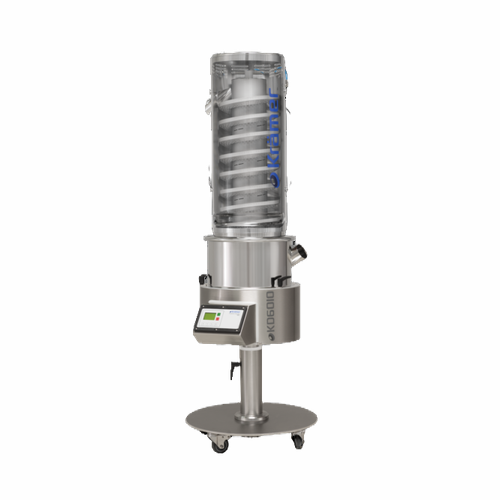
Vertical vibratory tablet deduster for pharmaceutical tablets
Ensure optimal cleanliness and quality assurance for table...
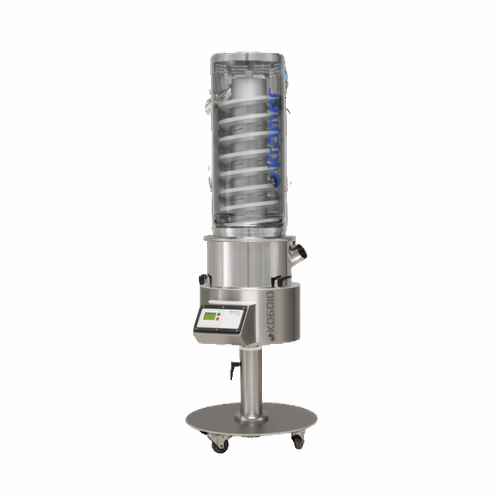
Tablet deduster with upward conveying
Ensure consistent dedusting and deburring of tablets and capsules while maintaining h...
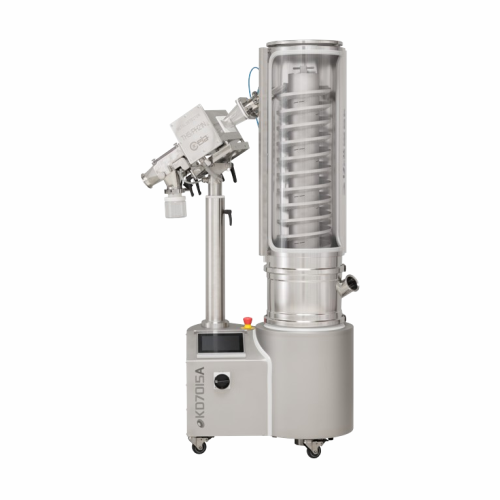
High performance tablet deduster with metal detection
Achieve precision dedusting and metal detection in tablet processin...
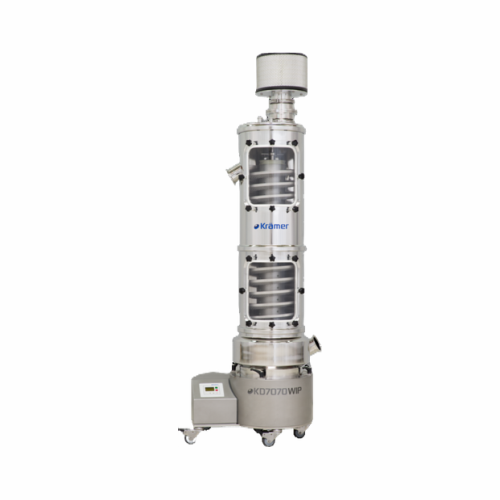
High-containment tablet dedusting solution
Ensure pharmaceutical tablets and capsules meet strict dust control and safety ...
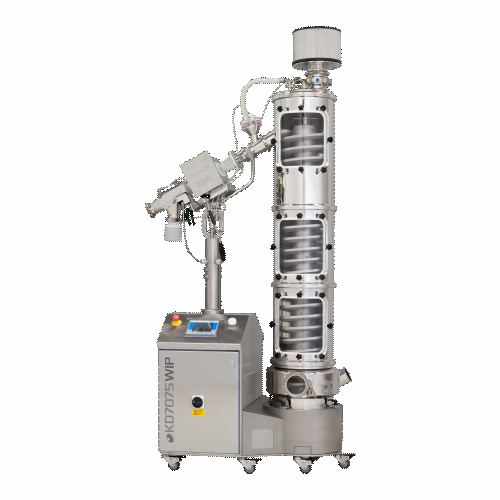
High-containment tablet deduster
Ensure optimal purity and safety in pharmaceutical production with high-containment dedusti...
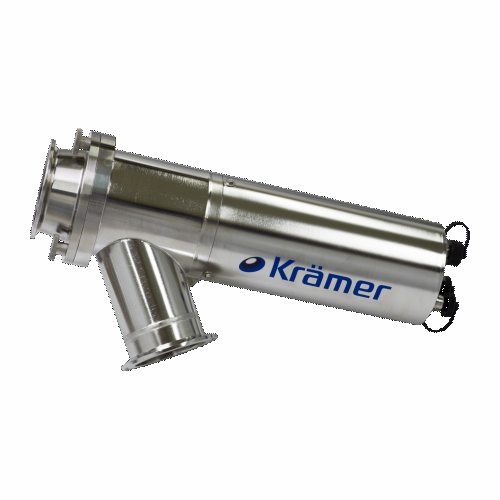
2-way diverter for tablet and capsule filling
Ensure precision in tablet and capsule filling with seamless batch switching...
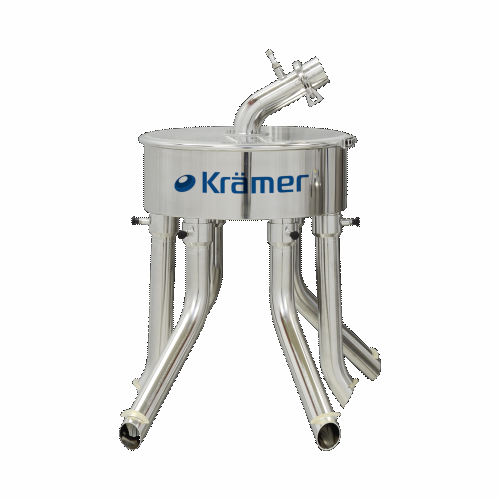
Tablet and capsule diverter
Streamline your tablet and capsule production with precise container filling and flexible config...
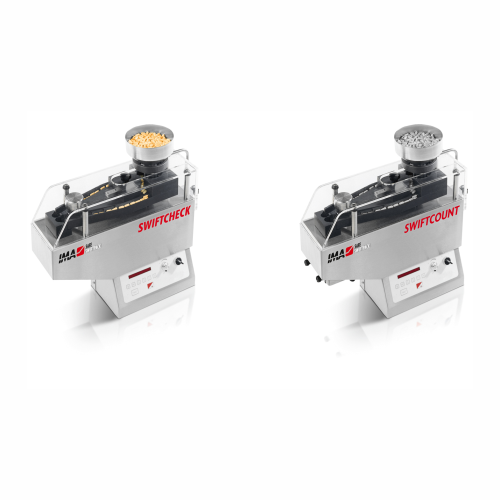
Table top tablet and capsule counter
Effortlessly ensure precise tablet and capsule counts with solutions that seamlessly i...
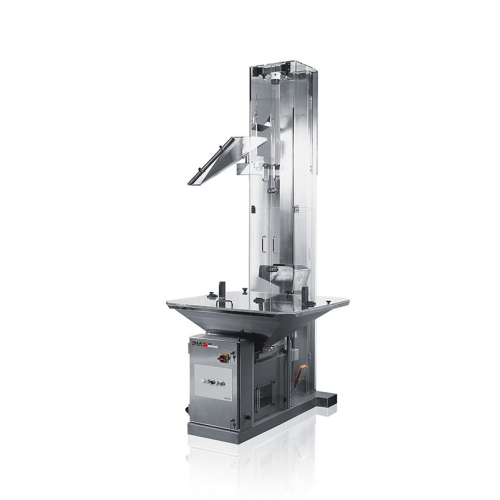
Tablet elevator for pharmaceutical applications
Ideal for efficient transport and elevation of delicate pharmaceutical tab...
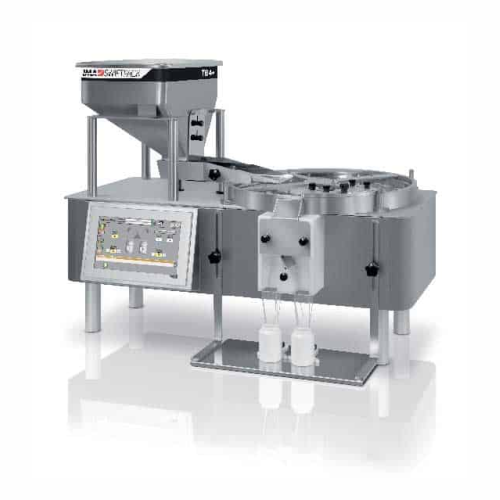
Electronic tablet counter for tablets and capsules
Optimize your production line with precise counting solutions for a wi...
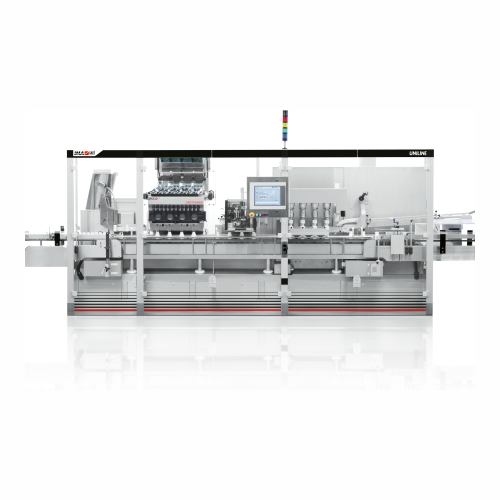
Integrated counting system for tablets and capsules
Streamline your packaging line with a highly versatile system that se...
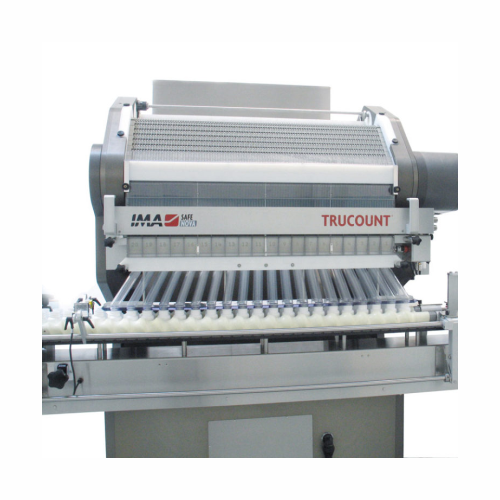
High-precision slat counter for tablet bottling
Optimize your tablet bottling with a low-energy, high-speed counter design...
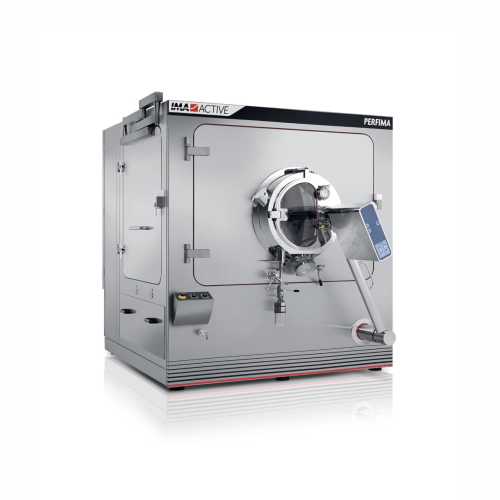
Industrial tablet coating solution
Achieve precise film and sugar coatings on a versatile range of tablet and pellet forms,...
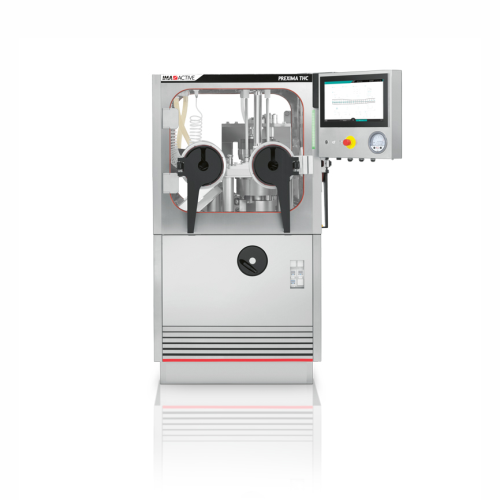
Tablet press for high containment environments
For handling potent compounds without compromising safety, a high-containme...
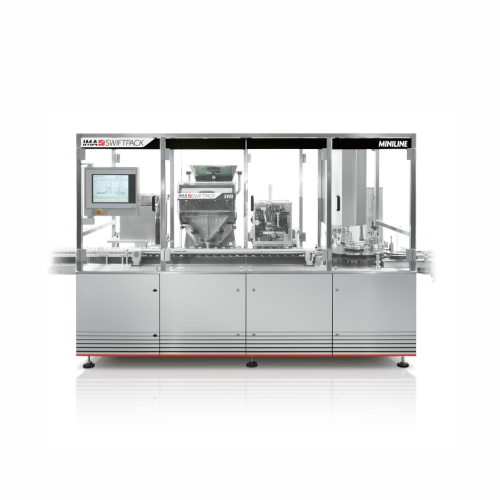
Integrated counting system for tablet and capsule bottling
Optimize your production line with a compact solution designe...
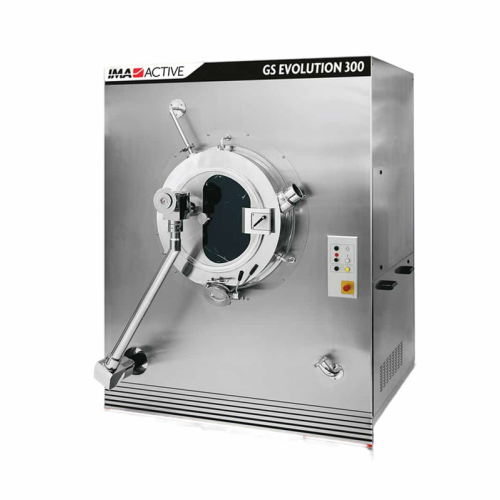
Tablet film and sugar coating pan
Achieve uniform coating while minimizing operator exposure to potent substances, ensuring...
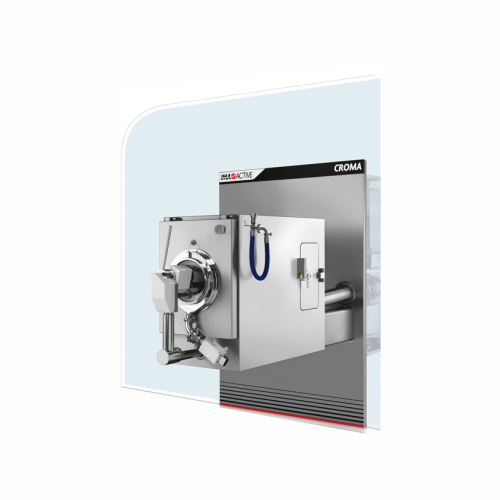
Continuous coater for tablet coating
Achieve seamless tablet coating with continuous processing, enhancing efficiency and r...
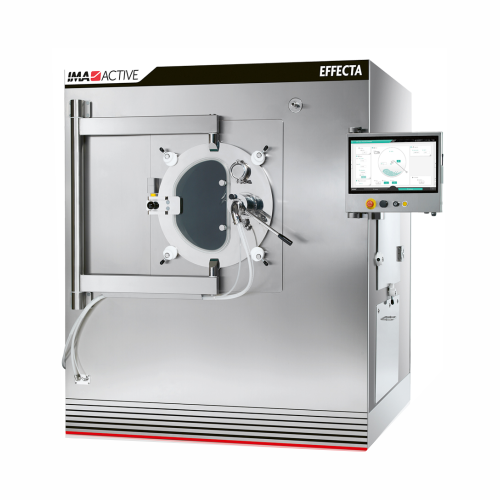
Tablet coating pan for pharmaceutical and nutraceutical industries
Enhance coating efficiency with a versatile solution...
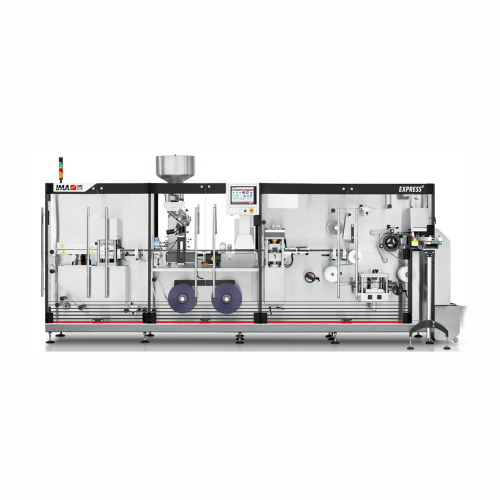
Blister packaging system for tablets and capsules
Designed for seamless 24/7 production, this blister packaging machine e...
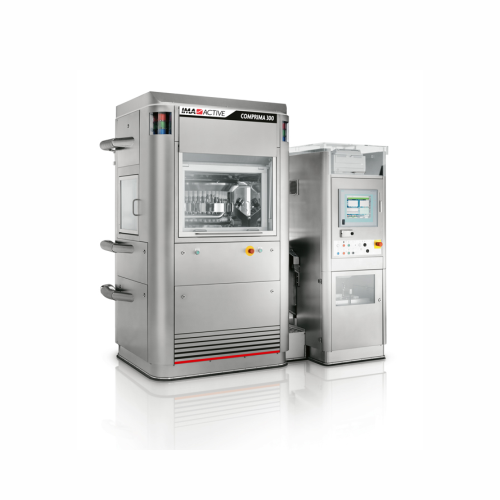
Tablet press for high-quality pharmaceutical tablets
Ensure optimal tablet quality and yield with an advanced compression...
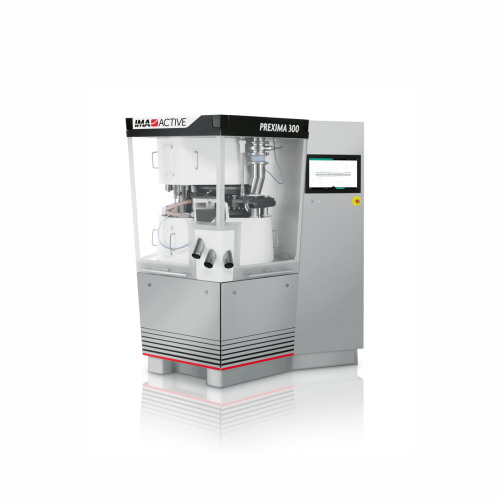
Tablet pressing system for solid chemicals and cosmetic products
Optimize your tableting process for diverse solid produ...
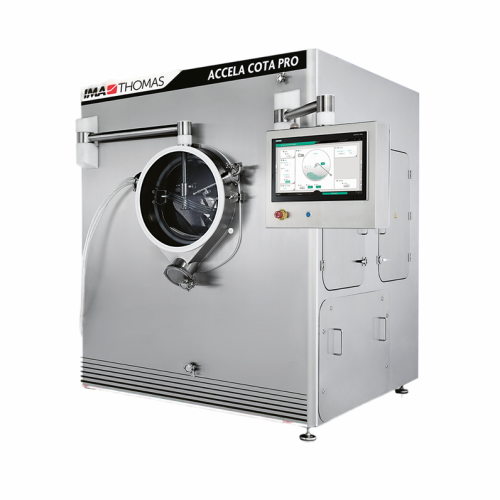
Automated coating pan for pharmaceutical tablets
Enhance your tablet production with a fully automated system that ensures...
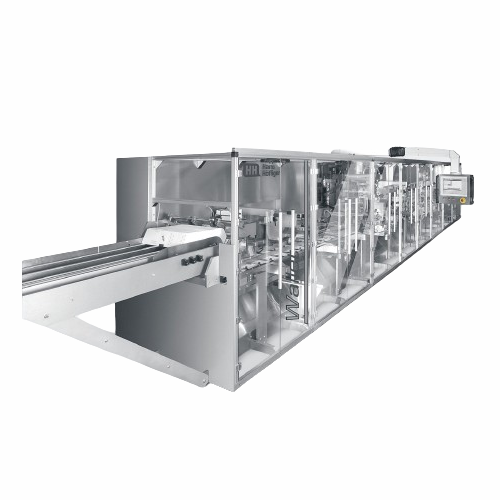
Tablet blister wallet packaging line
Enhance packaging efficiency with a high-speed line that integrates blister packaging ...

Weighing system for 100% inspection of capsules and tablets
Ensure precise quality control with a format-free system tha...
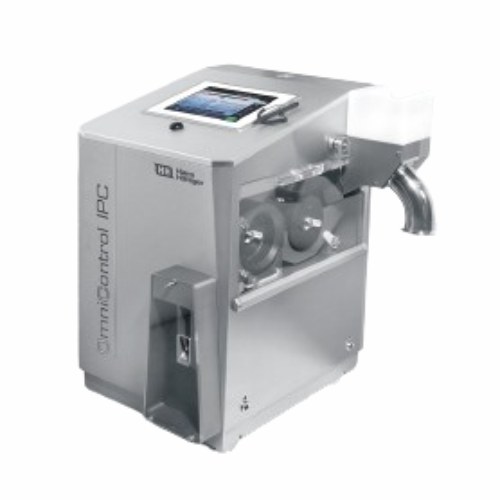
In-process weighing system for capsules and tablets
Ensure precise dosing and consistent quality with a format-free syste...

Capsule filling system for powder, pellets, and tablets
Optimize capsule production with rapid dosing changes, minimizing...
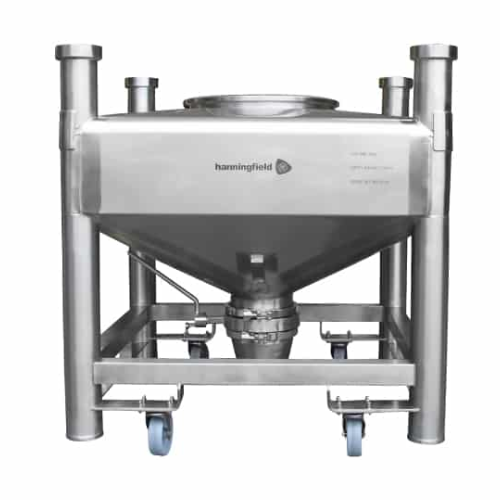
Tablet storage and transport containers
Ensure the safe and gentle handling of tablets during storage and transport, minimi...
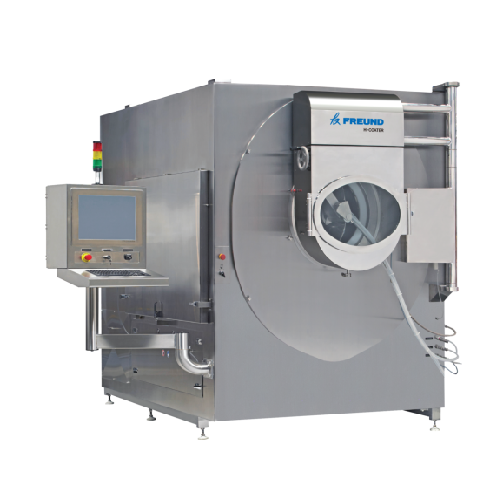
Tablet coater for precision pan coating
Achieve precise coating control for pharmaceuticals and nutraceuticals, accommodati...
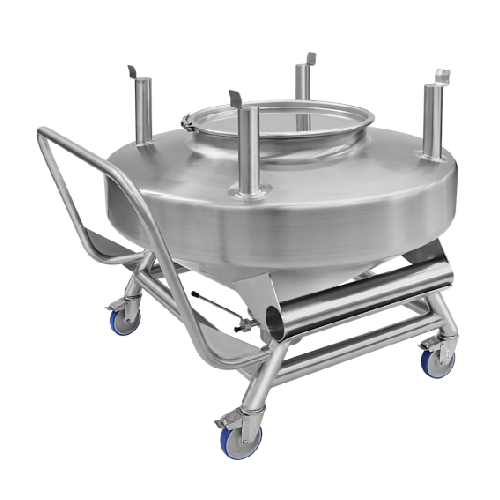
Ibc tablet bins for pharmaceutical storage and handling
Efficiently manage pharmaceutical tablet processes with adaptable...

Integrated plenum tablet coater
Achieve consistent and high-quality coatings on tablets with advanced airflow management, ef...
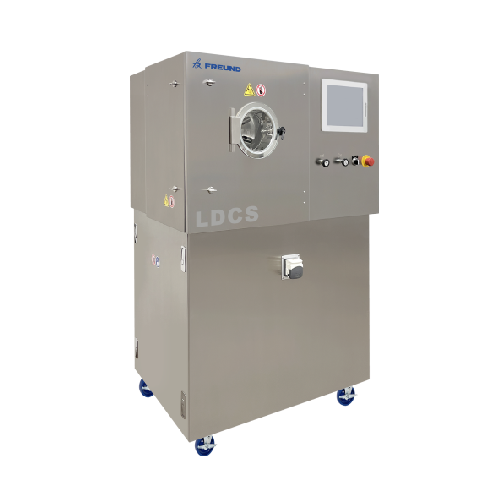
Tablet coating system for laboratory development
Optimize your tablet formulation development with a versatile coating sys...

Laboratory development coating system for tablet coating
Efficiently manage small-scale batch coating with versatile, ful...
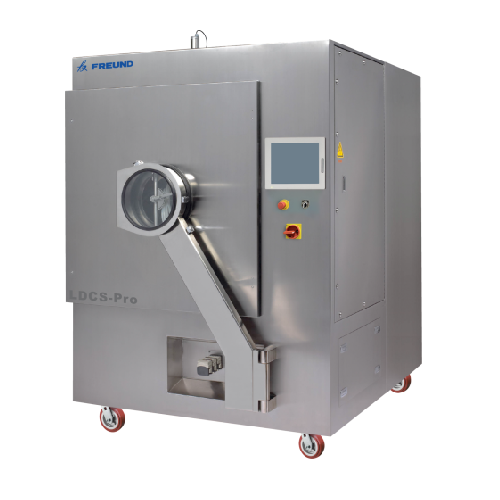
Portable pan coater for pilot scale tablet coating
Achieve uniform tablet coating with interchangeable pans and anti-mark...
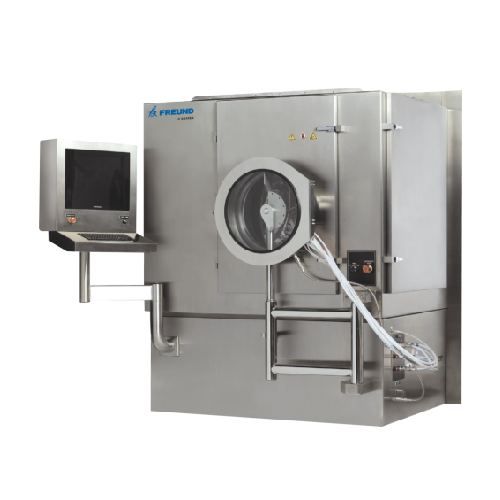
Tablet coating system for aqueous, solvent, and sugar films
Achieve precision coating with flexible application capabili...
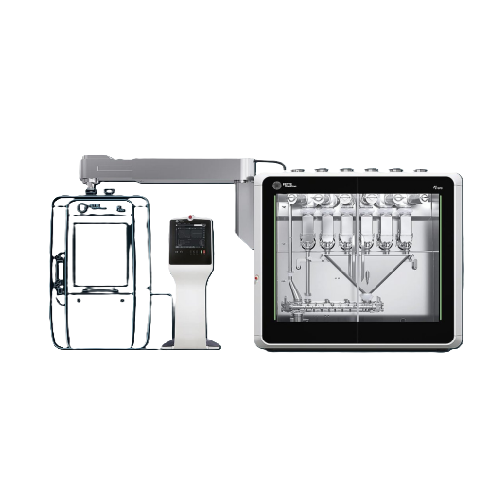
Continuous direct compression system for tablet production
Achieve seamless continuous direct compression by integrating...
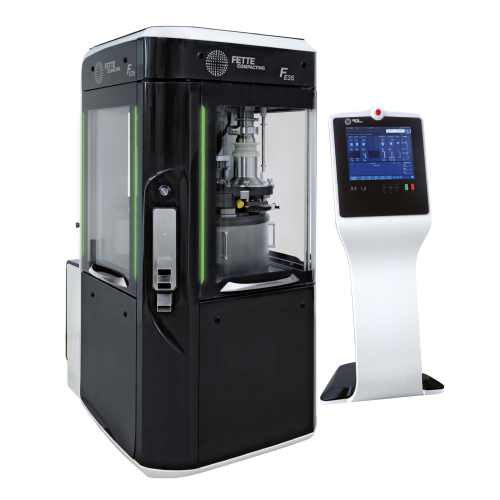
High-capacity tablet press for pharmaceutical production
Achieve precise compression and consistent tablet density with a...
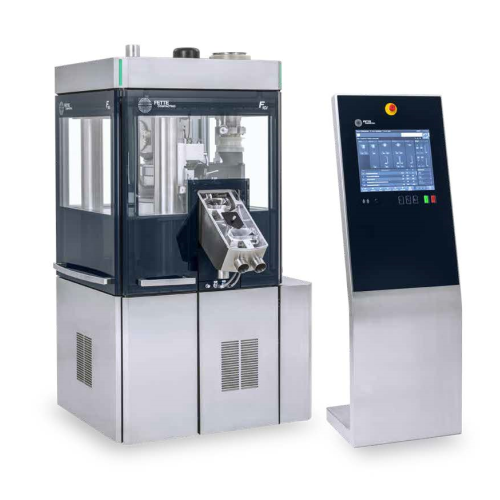
Industrial tablet press for high output production
Achieve precise control and efficient production with advanced rotary ...
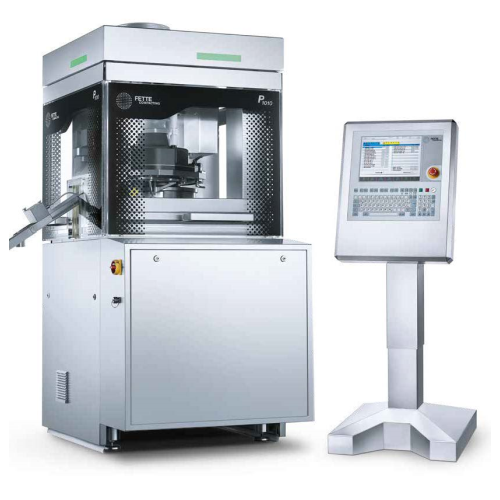
High performance tablet press for large batches
For manufacturers aiming to boost tablet production without sacrificing pr...
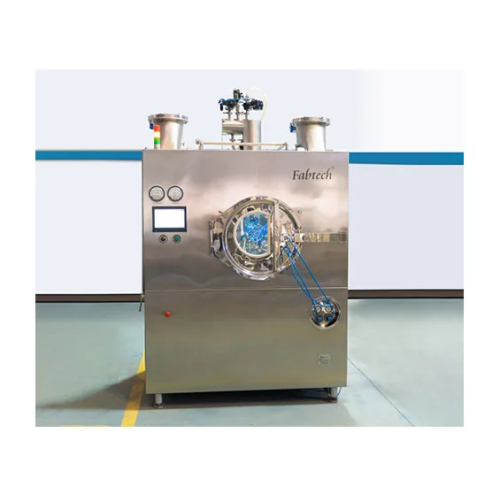
Tablet coating solution
Achieve precise tablet coating with uniformity and efficiency, tailored for diverse tablet types, ens...
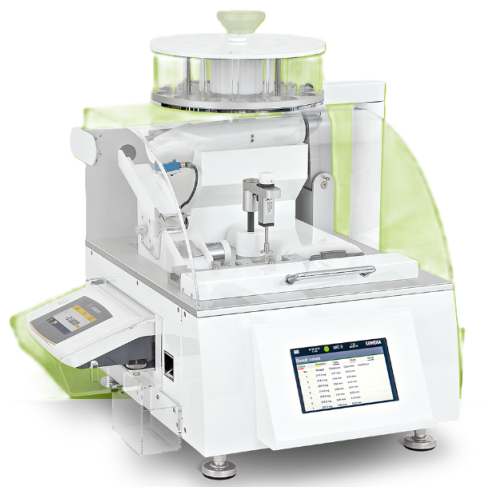
GMP automatic tablet hardness tester
Ensure precise control over tablet quality with a fully automated tester that seamless...
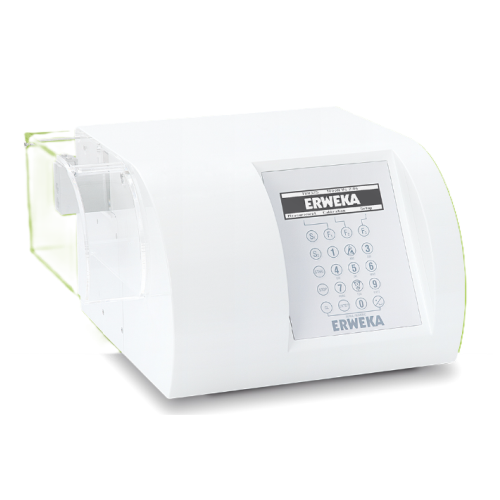
Tablet hardness tester
Ensure consistent tablet quality by precisely measuring hardness, thickness, diameter, and weight with...
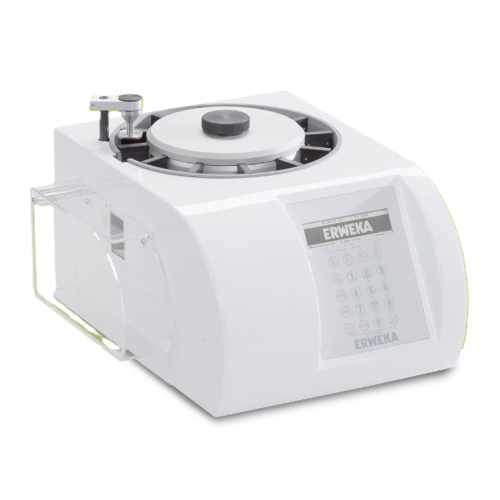
Tablet hardness and combination tester
Ensure consistent tablet hardness and precision across multiple parameters with this...
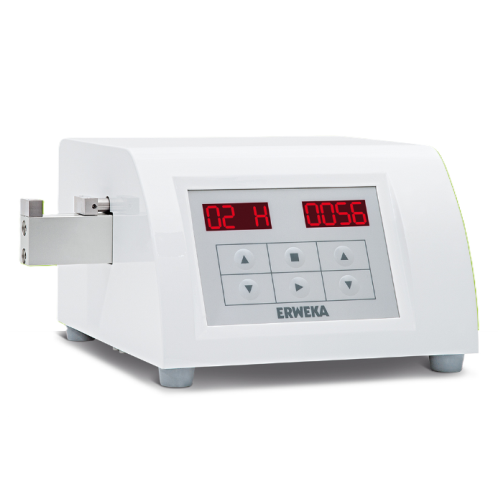
Tablet hardness tester for pharmaceutical quality control
Ensure precise tablet hardness measurement to enhance pharmace...
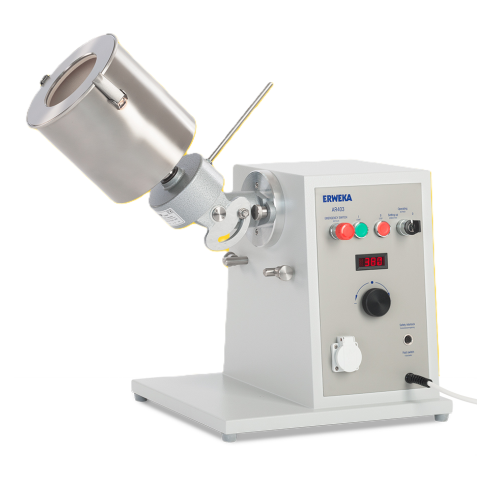
Polishing drum for coated tablets
Enhance the surface quality of coated tablets with this polishing drum, perfect for achie...
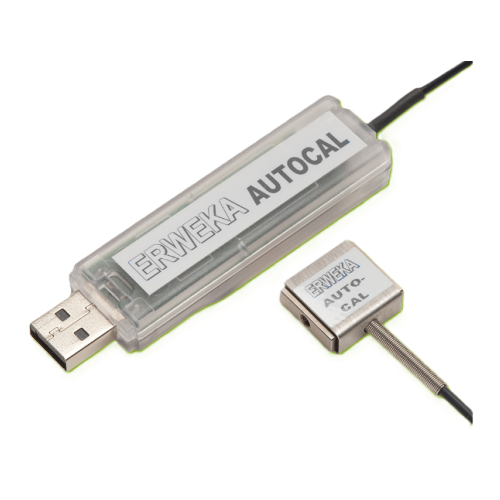
Automated calibration tool for tablet hardness testers
Streamline your tablet hardness testing with a tool that automates...
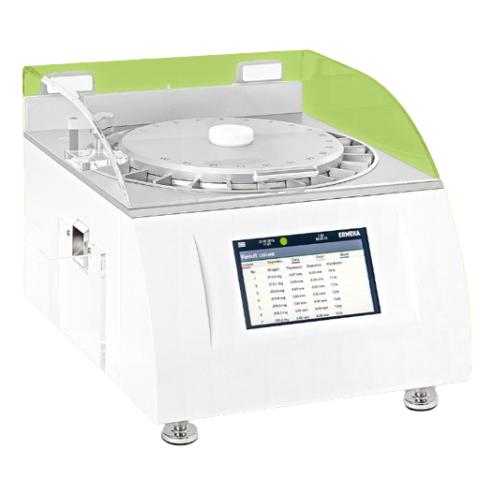
pharmaceutical-tablet hardness testing system
Ensure consistent tablet quality and compliance with pharmacopeia standards ...
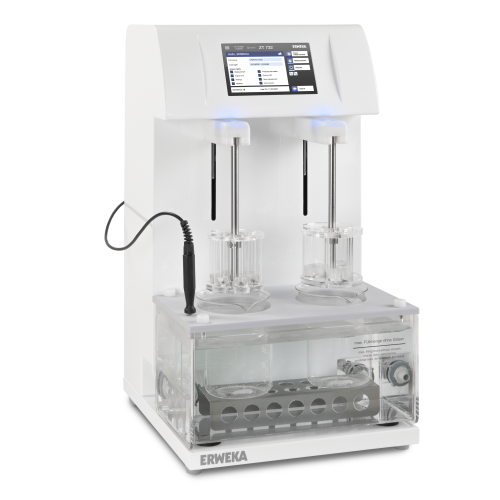
Automated disintegration tester for tablets
Efficiently determine tablet disintegration times with advanced waterbath tech...
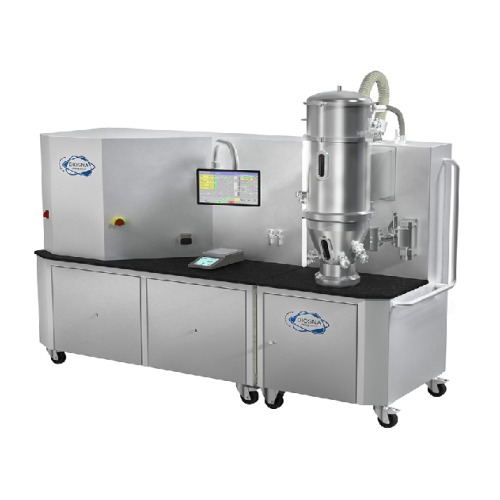
Laboratory fluid-bed dryer and tablet coater
Experience seamless transition from laboratory to production scale with a ver...
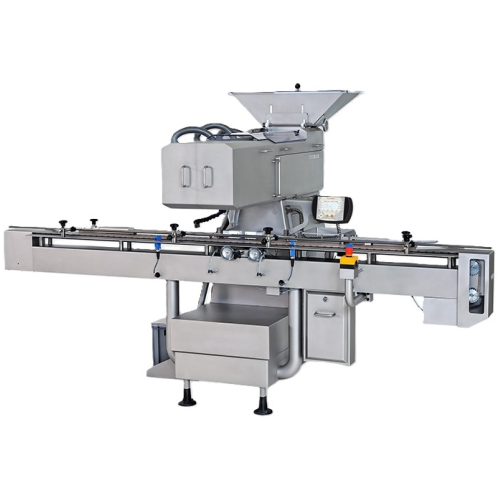
Linear tablet and capsule counter
Ensure precise and efficient bottle filling with a cutting-edge counting system that guar...
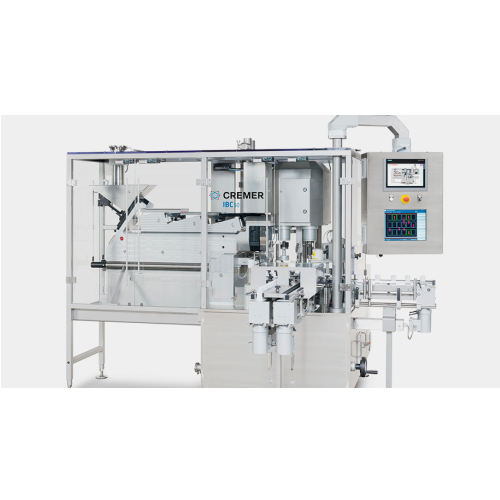
Integrated bottling center for pharmaceutical tablets and capsules
Enhance your production line with versatile bottling...

Mini laboratory mixer for tabletops
Optimize your lab’s mixing precision with this compact tabletop bin mixer, design...
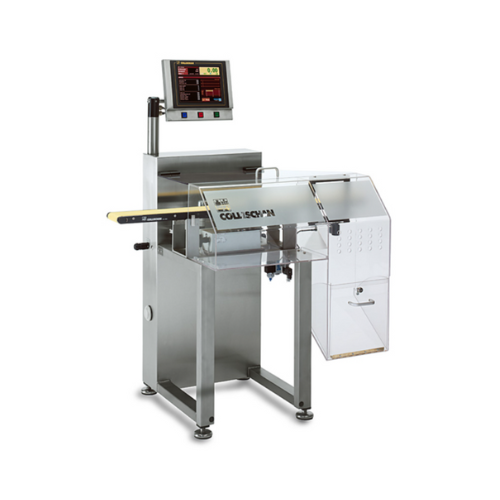
High-performance checkweigher for pharmaceutical tablet cartons
Achieve precision weighing at speeds up to 500 units per...
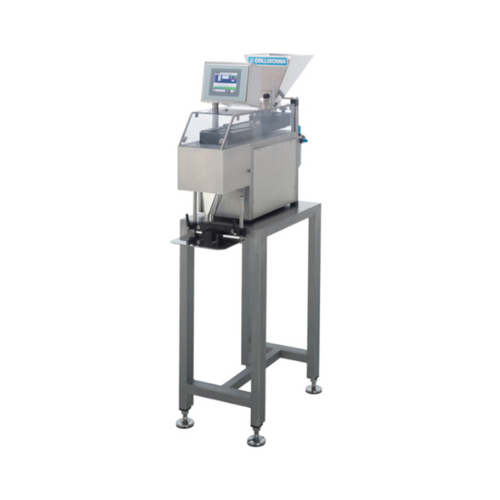
Counting system for tablets and capsules
Effortlessly count a variety of tablets, capsules, and dragées with precision, ens...
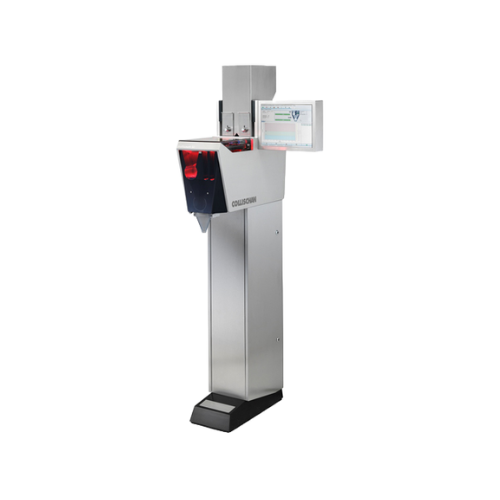
Tablet counting solution for pharmaceutical industry
Maximize dosing precision and reduce miscounts in high-speed pharmac...
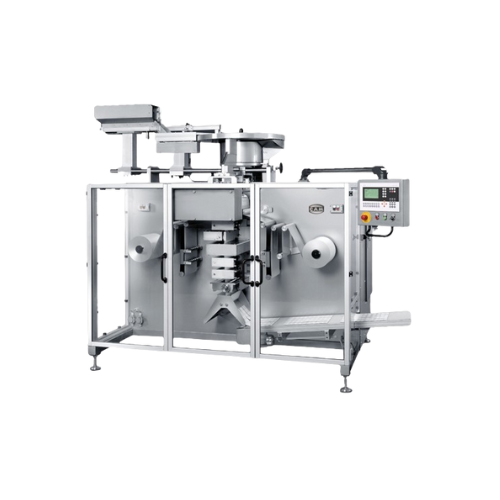
High-speed strip packaging for tablets and capsules
Optimize your high-speed pouching operations with precise four-side s...
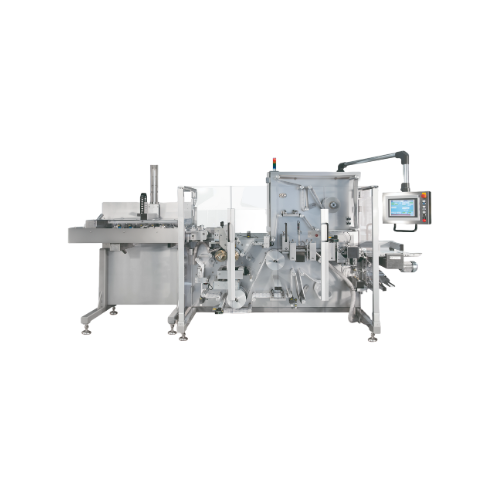
High speed strip packaging for tablets and capsules
Ensure precise packaging of pharmaceutical tablets and capsules with ...
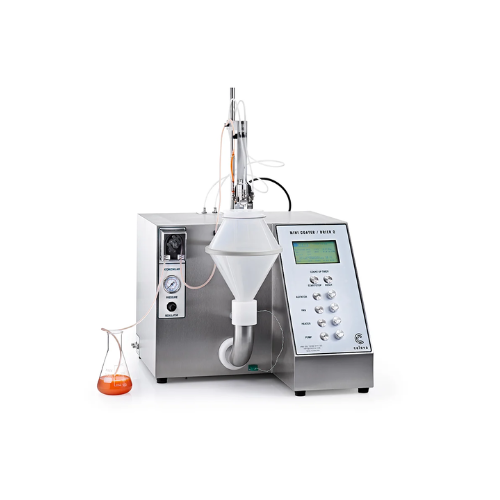
Small batch tablet and pellet coating solution
Optimize your small batch coating and drying processes with a versatile ben...
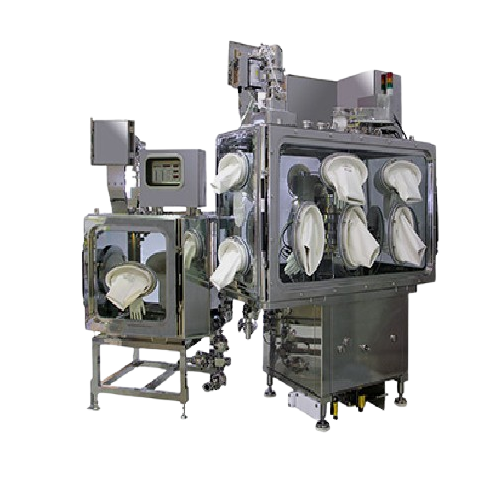
Tablet press for multi-layer and dry-coated tablets
Optimize your tablet production with high-speed multi-layer pressing ...
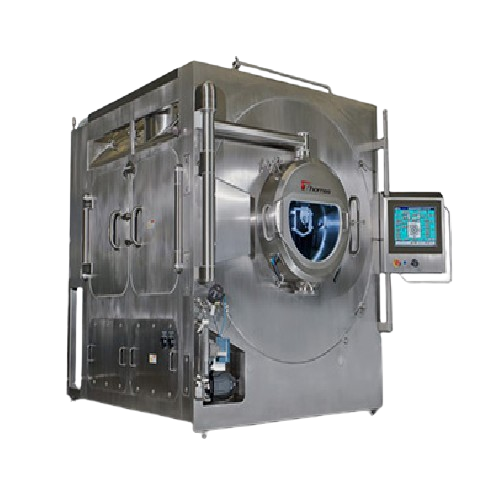
Tablet coating system for pharmaceuticals and supplements
Enhance tablet coating efficiency with flexible, replaceable p...
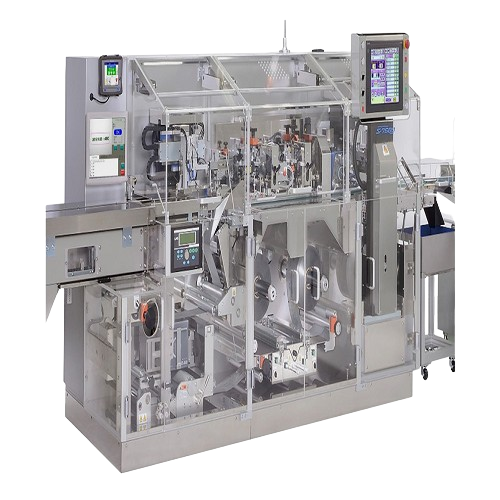
Efficient blister packing for pharmaceutical tablets
Streamline your production with a blister packing machine that enhan...
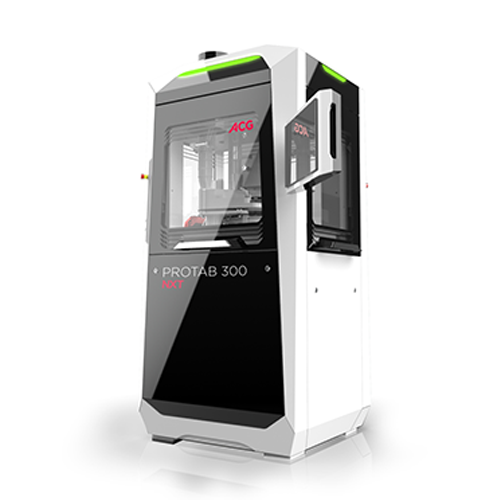
Single rotary tablet press for small and medium-batch production
Optimize your tablet production with precision compress...
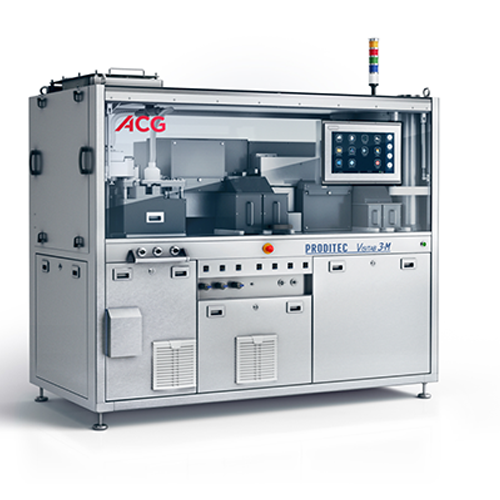
Tablet and capsule visual inspection system
Achieve unparalleled precision in tablet and capsule inspection with a high-sp...
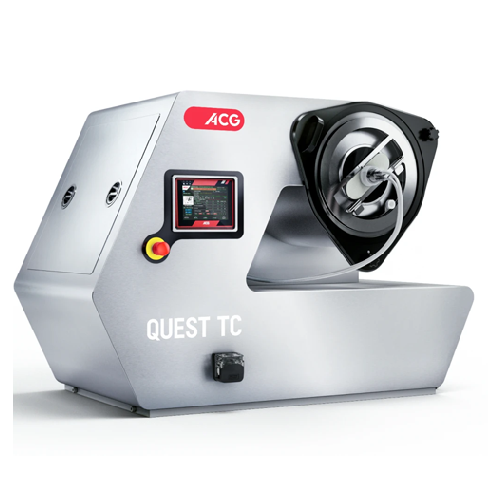
Tablet coating for r&d and small-scale production
Achieve precise, efficient tablet coating with a compact, versatile mac...
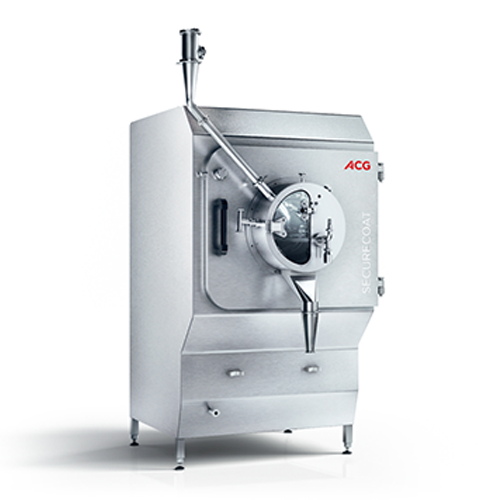
Containment tablet coater for high-potency drugs
Ensure operator safety while achieving precise tablet coating on high-pot...
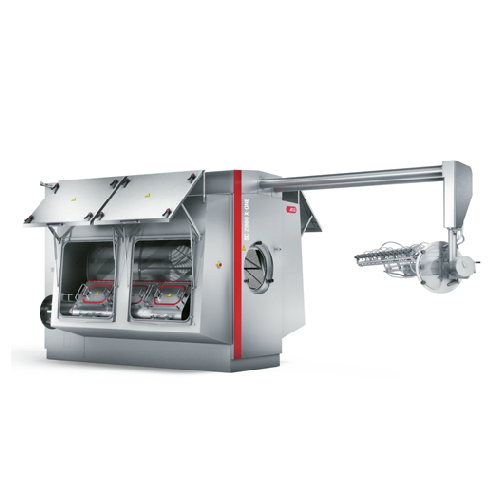
Tablet coating system for high-capacity operations
Streamline your tablet production with a coater that maximizes through...
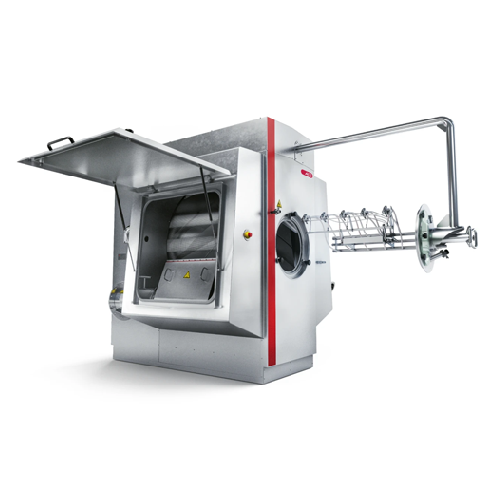
Tablet coater for batch sizes up to 250 liters
Enhance your tablet production process with high-speed coating solutions de...
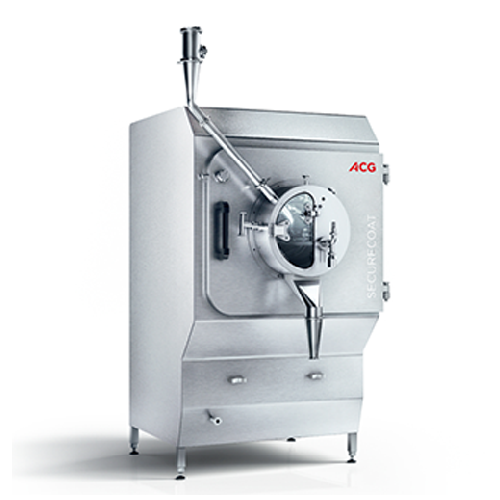
Containment tablet coater for high-potency pharmaceuticals
Ensure operator safety and maintain stringent OEB 4 complianc...
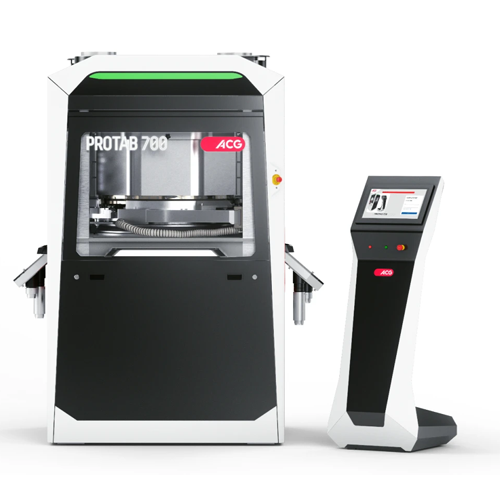
Double rotary press for high-volume tablet compression
Achieve high-speed, precision tablet compression with a machine th...
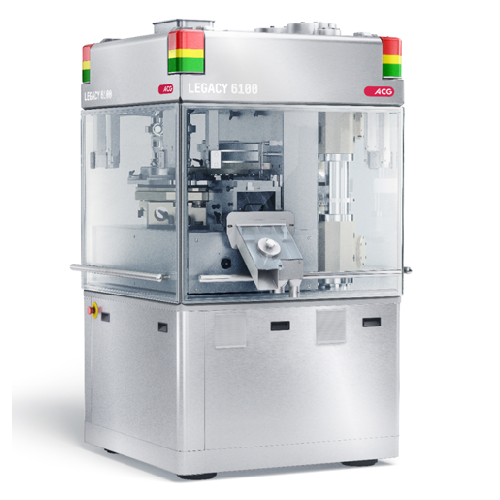
Single rotary tablet press
Streamline your tablet production with enhanced efficiency and precision, ensuring consistent tab...
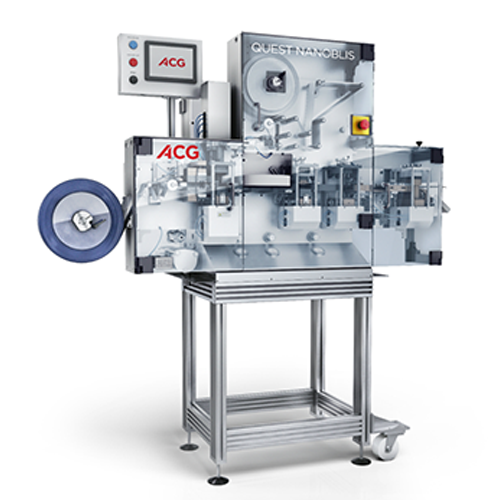
Tabletop blister packaging for clinical trials
For R&D facilities conducting clinical trials or feasibility studies, ...
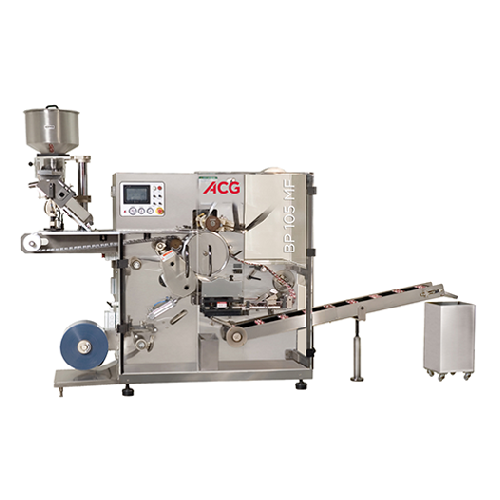
Rotary blister packaging for tablets and capsules
Optimize your blister packaging with high-performance rotary forming an...
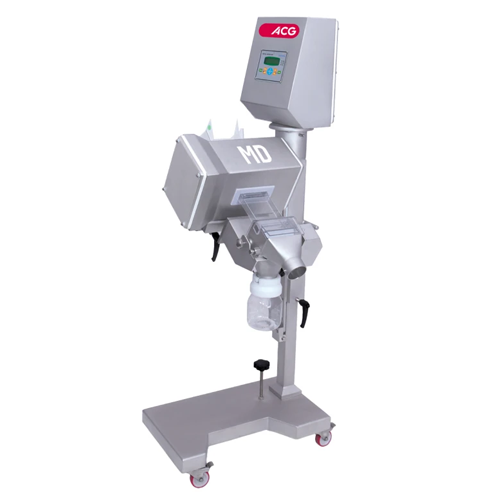
Metal contamination detection for tablets and capsules
Ensure product integrity by detecting and separating metal particl...
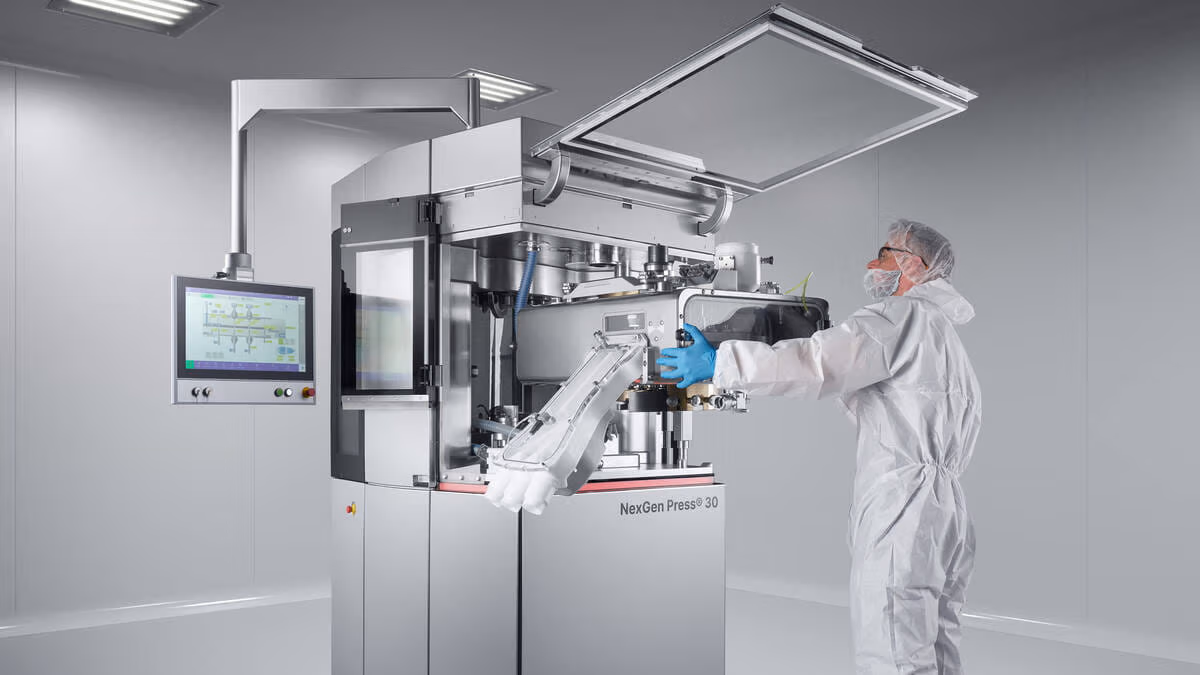
Next generation tablet compression unit
Meet the demands of modern tablet production with advanced modular design, ensuring...
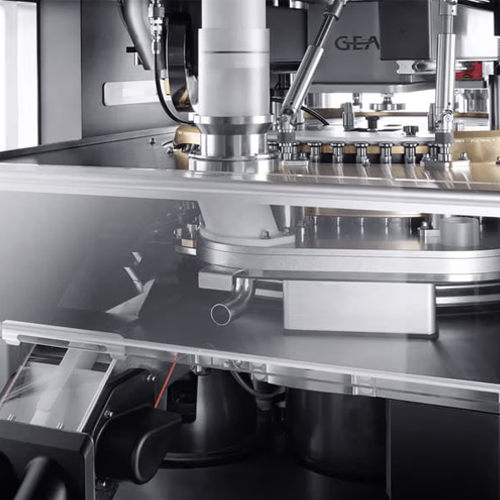
High-output tablet press for pharmaceutical production
Achieve high-speed, continuous production of precise and consisten...
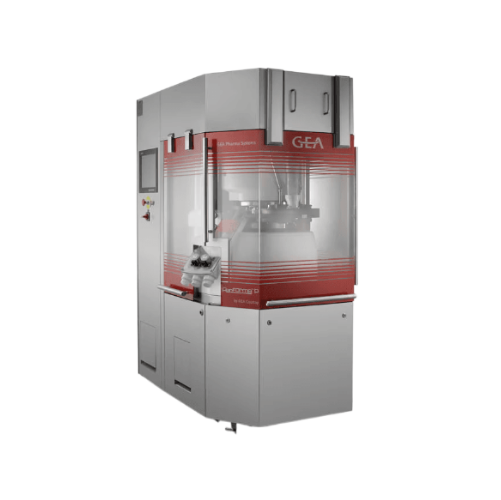
Rotary tablet press for pharmaceutical industries
Optimize your tablet production with swift format changeovers and bi-la...
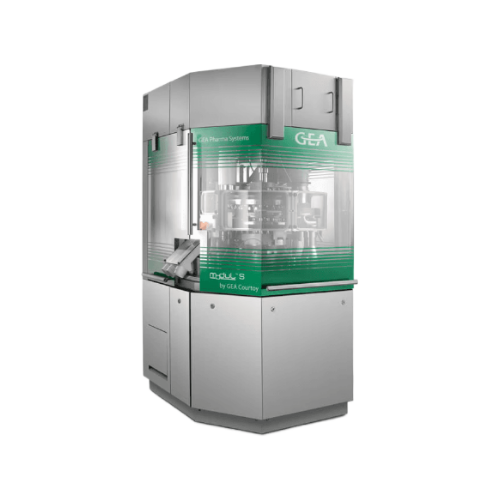
Rotary tablet press for small to medium scale production
Optimize your tablet production with a versatile rotary press, o...
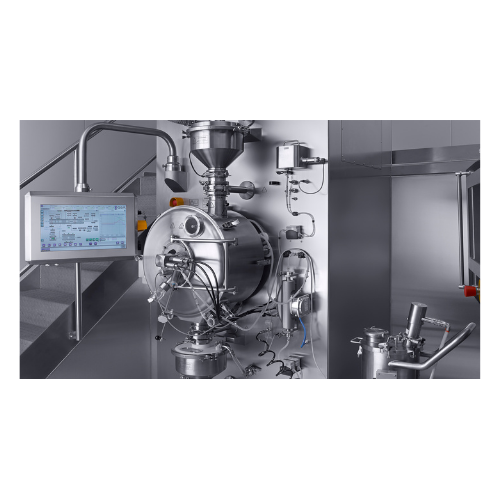
Pharmaceutical tablet coating system
Achieve precise and efficient coating of pharmaceutical tablets to enhance product sta...
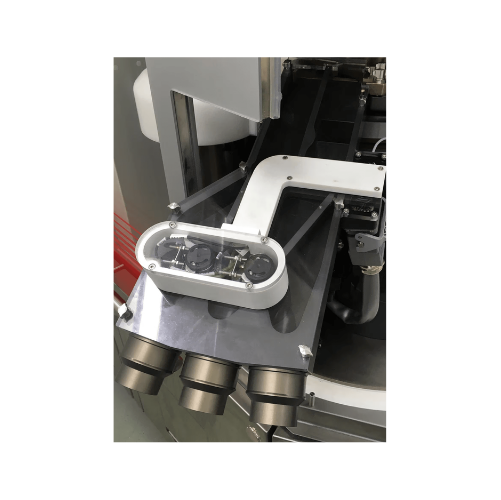
Rotary tablet press for abrasive powders
Achieve precise tablet sizing and bilayer production, even with abrasive powders, ...
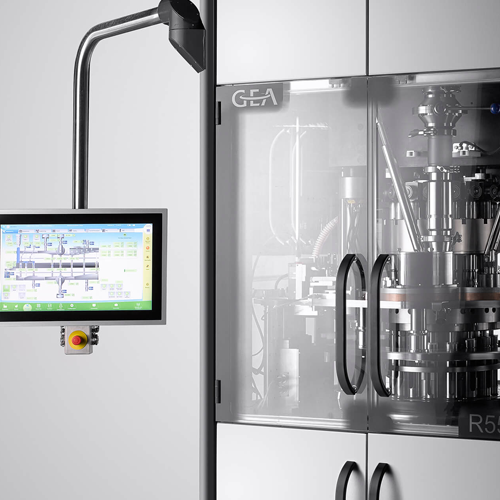
Heavy-duty tablet press for single & double-layer tablets
Maximize your tablet production with a high-speed solution cap...
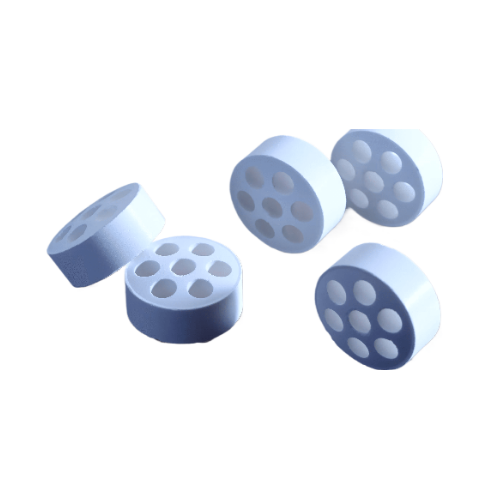
Rotary tablet press for large volume industrial tablets
Optimize your high-volume tablet production with a fully automati...
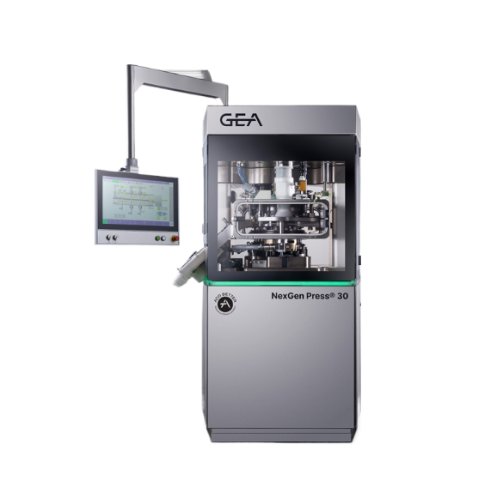
Double-sized bi-layer tablet press
Achieve high-volume production with precision using a double-sized bi-layer tablet press...
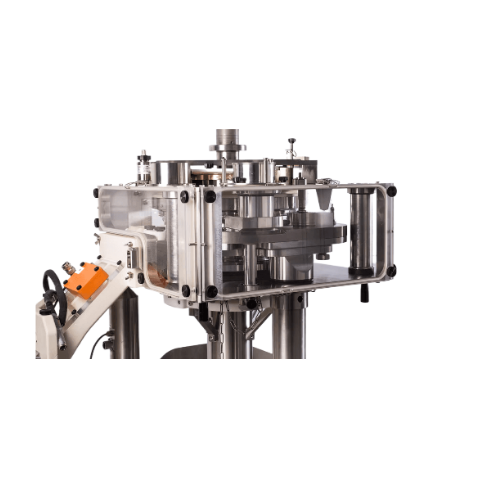
Tablet compression module for high containment applications
Quickly switch between tablet batches without compromising s...
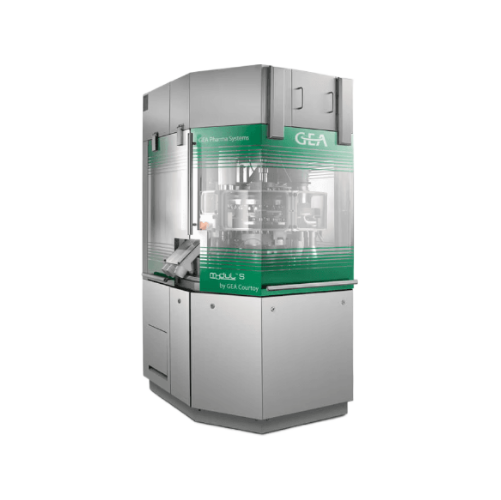
Medium-volume rotary tablet press for pharmaceuticals
Optimize tablet production with high-throughput and rapid changeove...
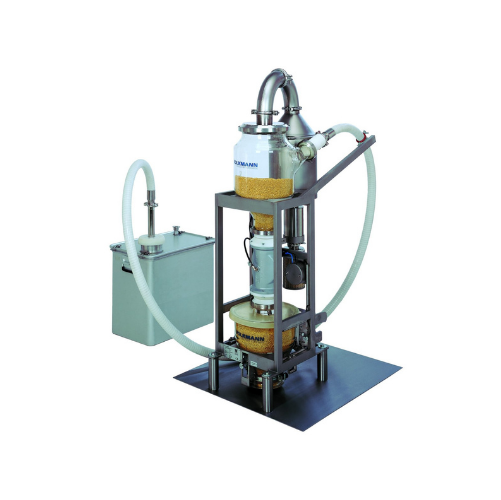
Vacuum conveyor for tablets and capsules
Ensure the integrity of your tablets and capsules with gentle vacuum conveying des...
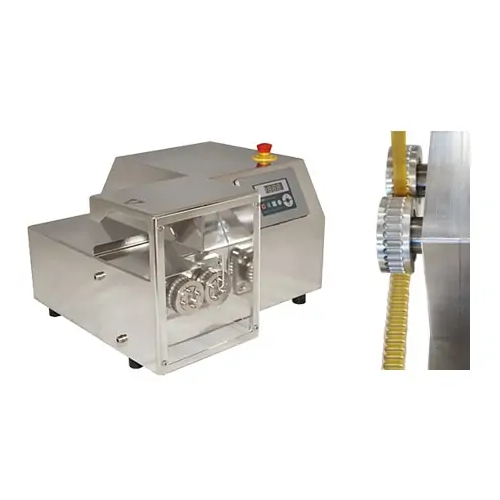
Calendering solution for laboratory production of films, tapes, and tablets
When rapid production of high-quality film...
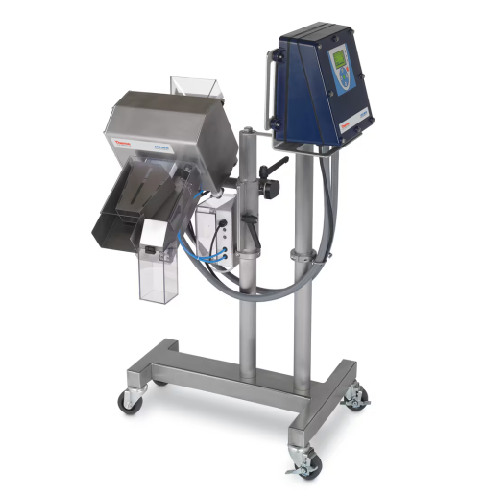
Pharmaceutical metal detector for tablet presses and capsule filling
Detect and eliminate metal contaminants in high-sp...
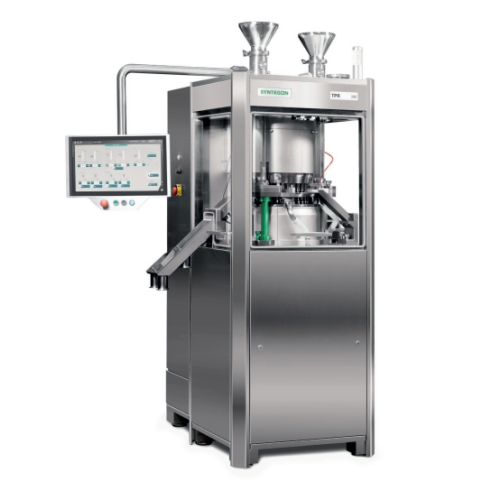
Tablet compression technology for pharmaceutical production
Enhance your production capabilities with advanced tablet co...
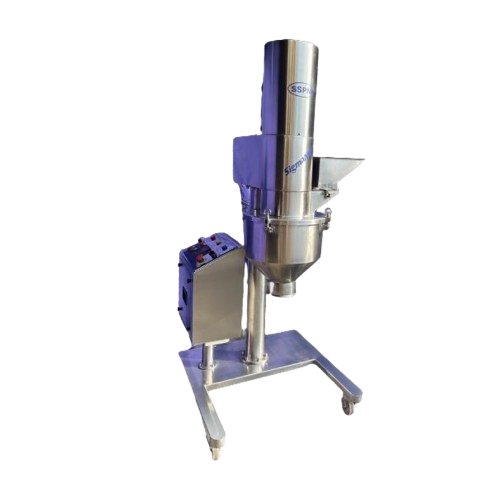
Wet granulation system for pharmaceutical tablets
Optimize your tablet production with precise particle size reduction an...
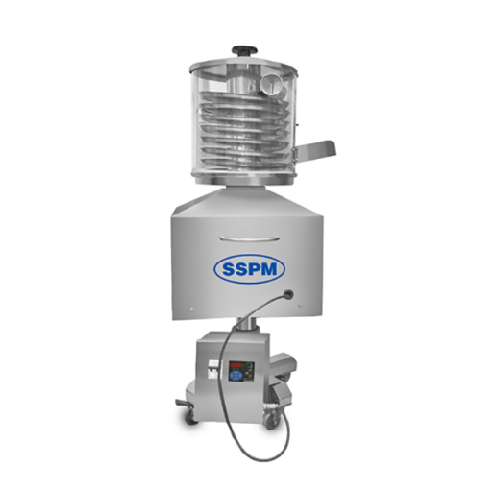
Tablet de-dusting system for pharmaceuticals
Ensure the highest quality of your tablets by effectively removing excess pow...
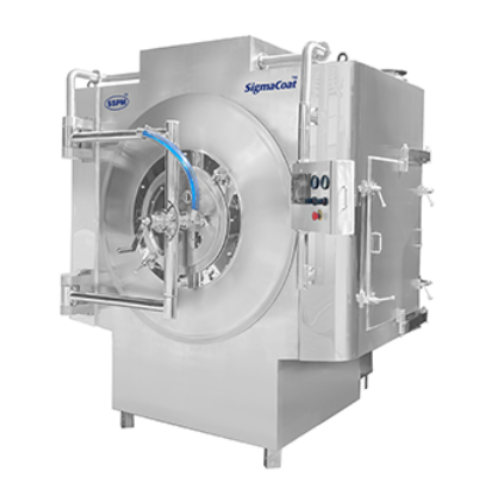
Tablet coating system
Achieve precise and uniform coating on pharmaceutical tablets with this scalable system, designed for o...
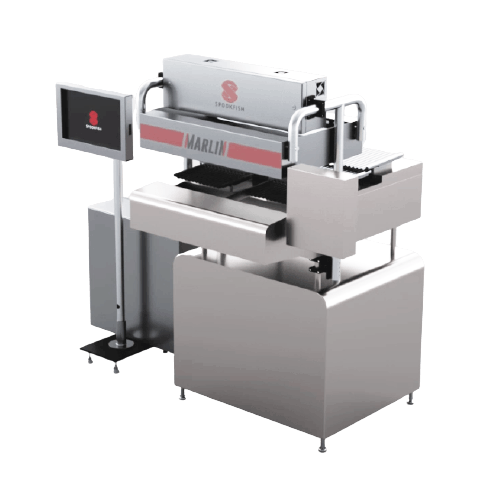
Online tablet counter inspection system
Ensure product integrity by precisely inspecting and rejecting defective tablets an...
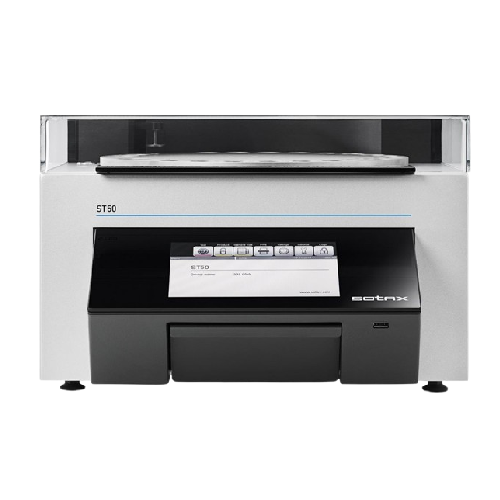
Semi-automatic tablet hardness tester
Optimize your tablet production with precise and reliable testing of hardness, dimens...
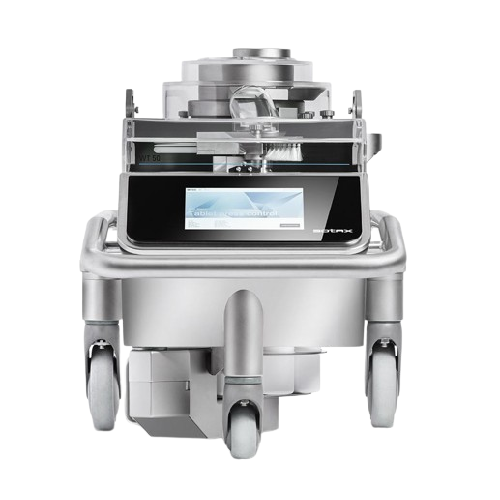
Automated weighing system for tablets
Ensure precision in pharmaceutical manufacturing by seamlessly integrating advanced w...

Bathless disintegration apparatus for tablet and capsule testing
Achieve rapid and precise disintegration testing of tab...

Manual tablet disintegration tester
Ensure precise and reliable disintegration testing of pharmaceutical tablets, capsules,...
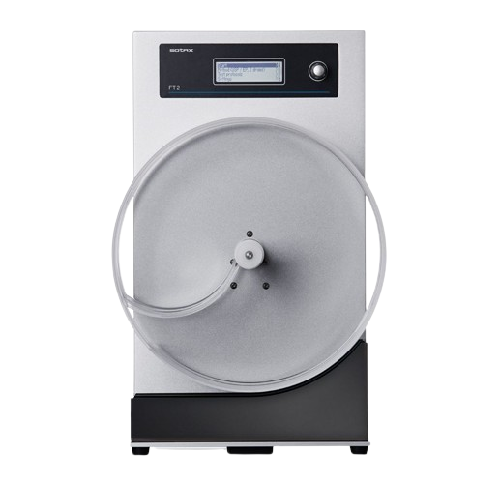
Tablet friability tester
Ensure your tablets meet rigorous quality standards by accurately measuring friability and abrasion,...
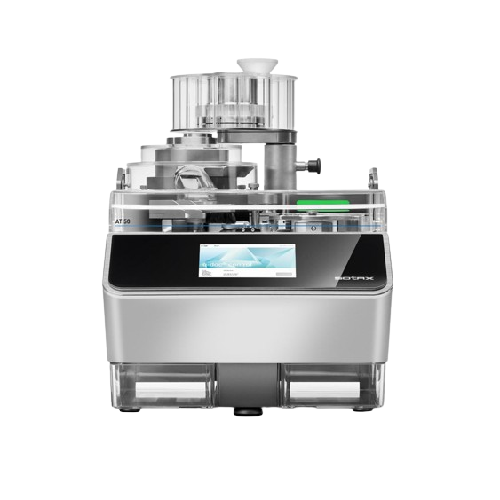
Multi-parameter tablet hardness tester for laboratories
Optimize your tablet production line with a versatile tester that...
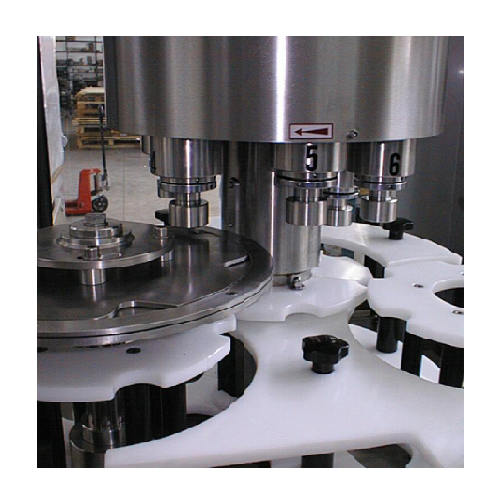
Automatic counting and capping system for tablets and capsules
Ensure precise tablet and capsule counting and seamless c...
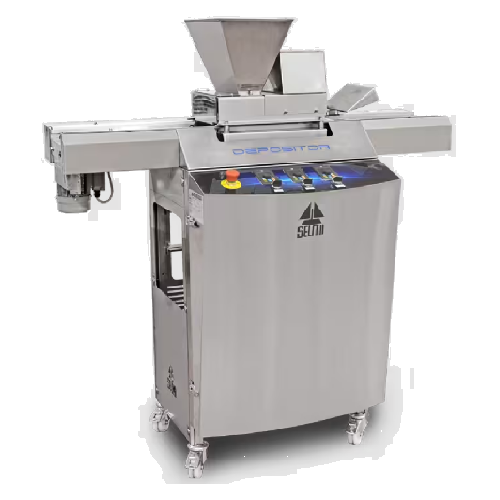
Grain dispenser for decoration of chocolate tablets
Elevate your confectionery with precise grain decoration, enhancing t...
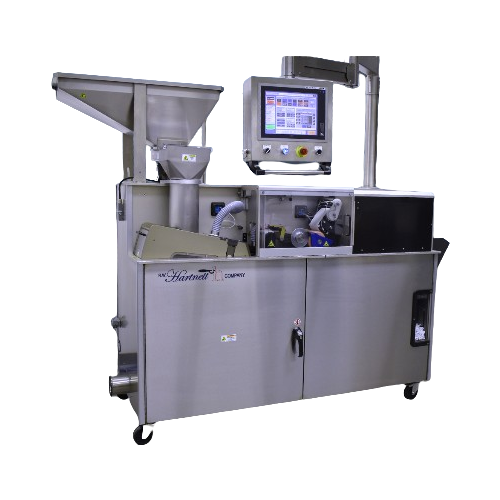
H-track ink printing solution for tablets and capsules
Ensure precise ink printing on tablets and capsules with high-spee...
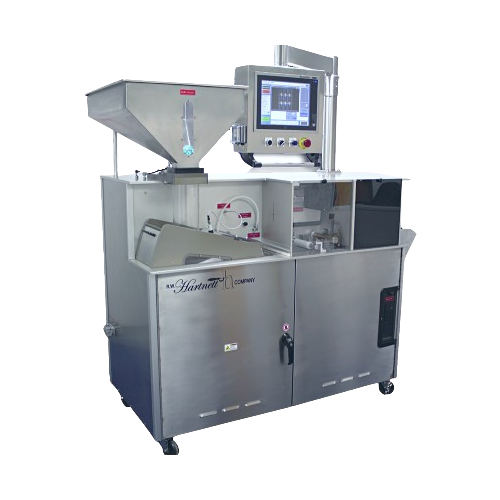
Flatbed laser drilling for tablet manufacturing
Optimize your tablet production with high-speed laser drilling, ensuring p...
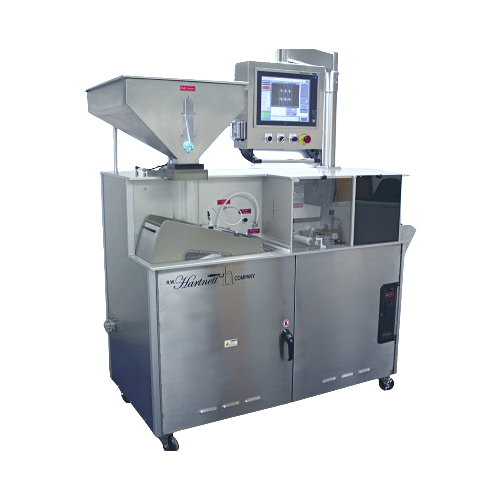
Uv laser writer for tablets and capsules
Achieve precise laser marking on tablets and capsules with high-speed production, ...
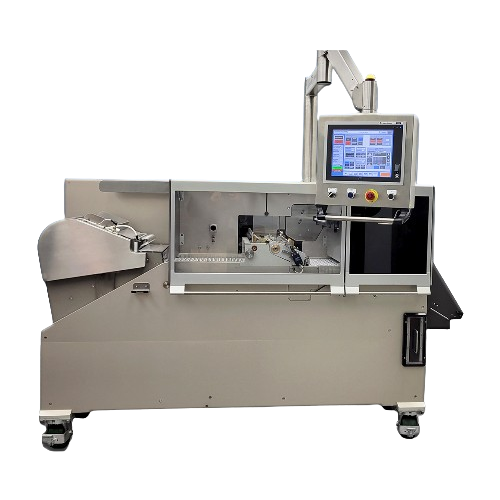
High-speed tablet ink printer
Achieve precise and high-speed printing on tablets and capsules for streamlined production and...
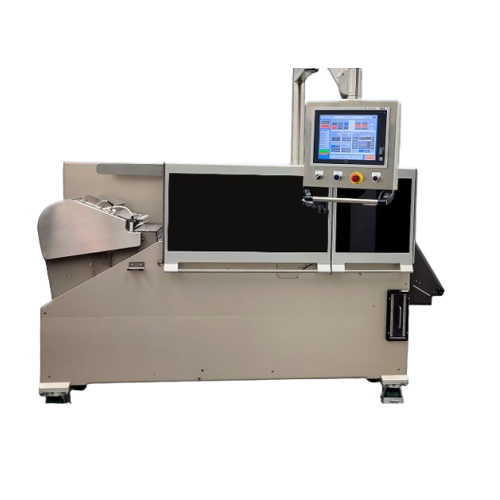
High-speed tablet laser drilling system
Achieve precise, high-speed drilling of solid dosage forms with a system capable of...
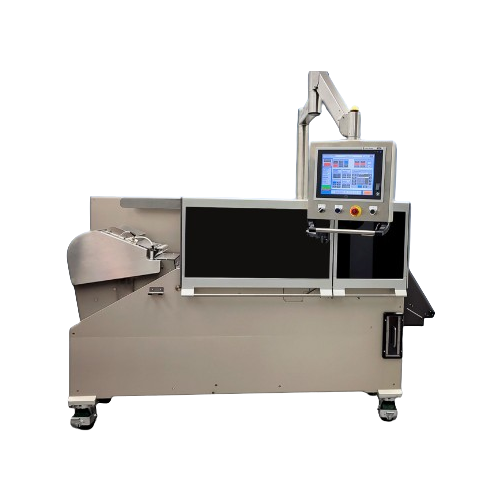
Uv laser writer for high-speed tablet marking
Achieve precise and rapid marking of pharmaceutical and nutraceutical tablet...
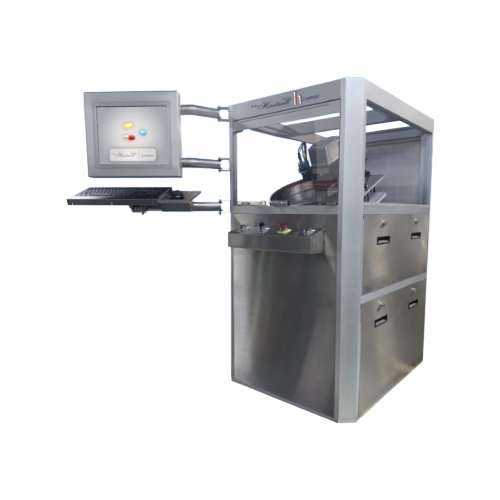
Lab laser drilling for tablet manufacturing
Achieve precise drilling in pharmaceutical tablets with advanced laser detecti...
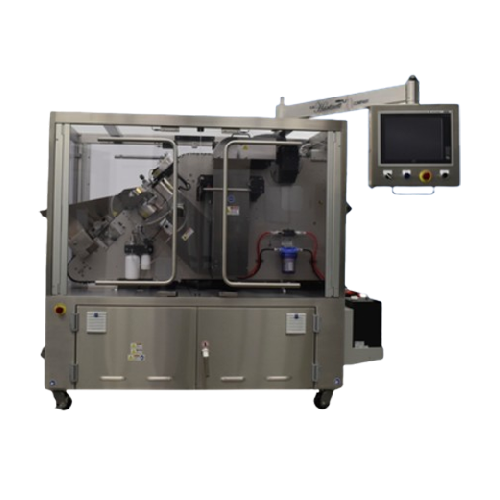
Tablet and capsule ink print and laser marking system
Streamline tablet and capsule identification with a high-speed syst...
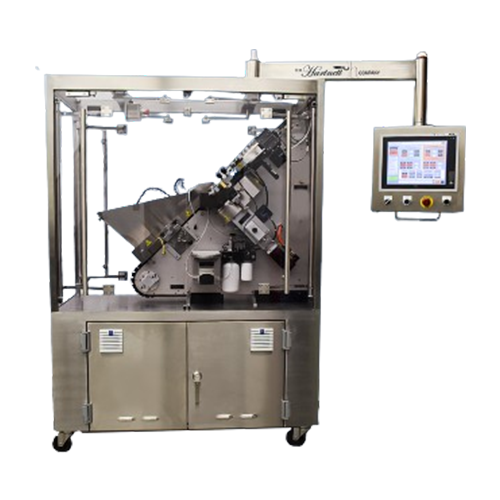
Tablet and capsule ink printer
Achieve precise and high-speed printing on tablets and capsules, ensuring clear product ident...
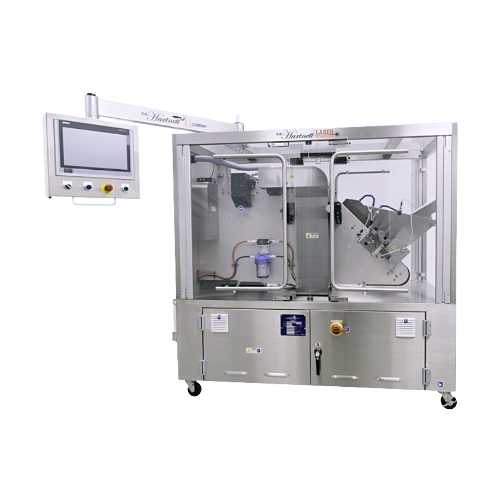
Precision laser drilling for osmotic controlled release tablets
Enhance tablet precision and control drug release with h...
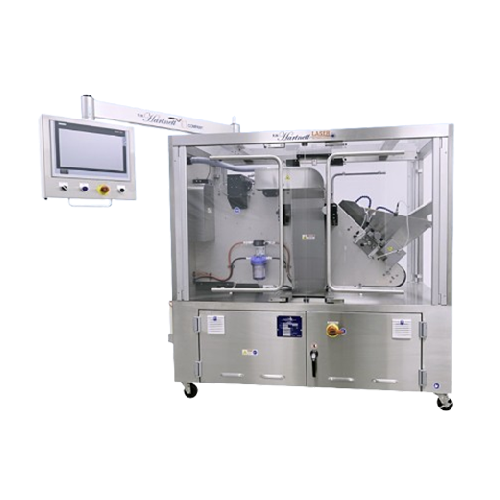
Uv laser marker for tablets and capsules
Achieve precise laser marking on tablets and capsules at high speeds while maintai...

Tablet and capsule ink printing and laser writing solution
Maximize efficiency in marking and coding with a high-speed s...
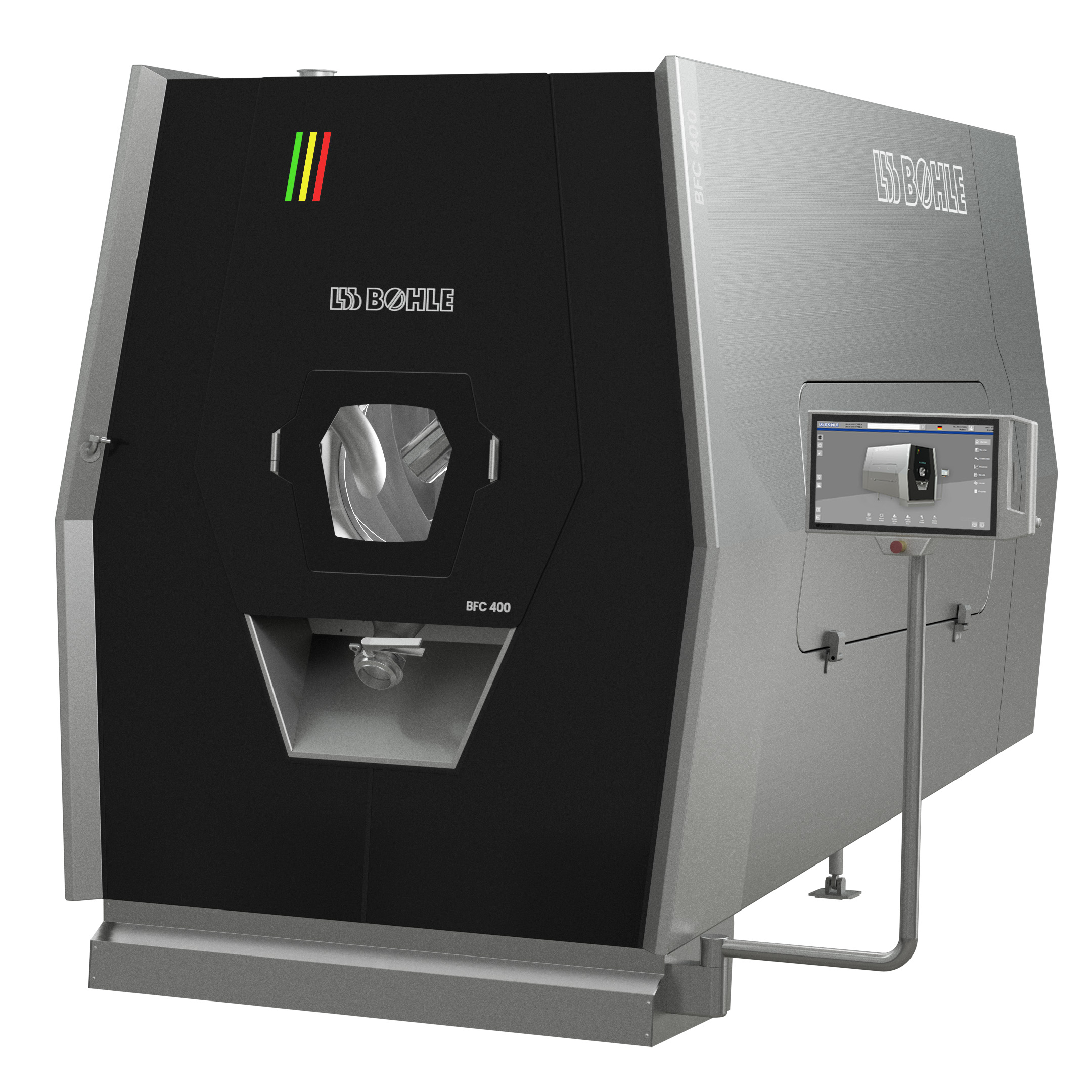
Energy-efficient film coating machine for pharmaceutical tablets
Tablet coating involves applying a thin layer of coatin...
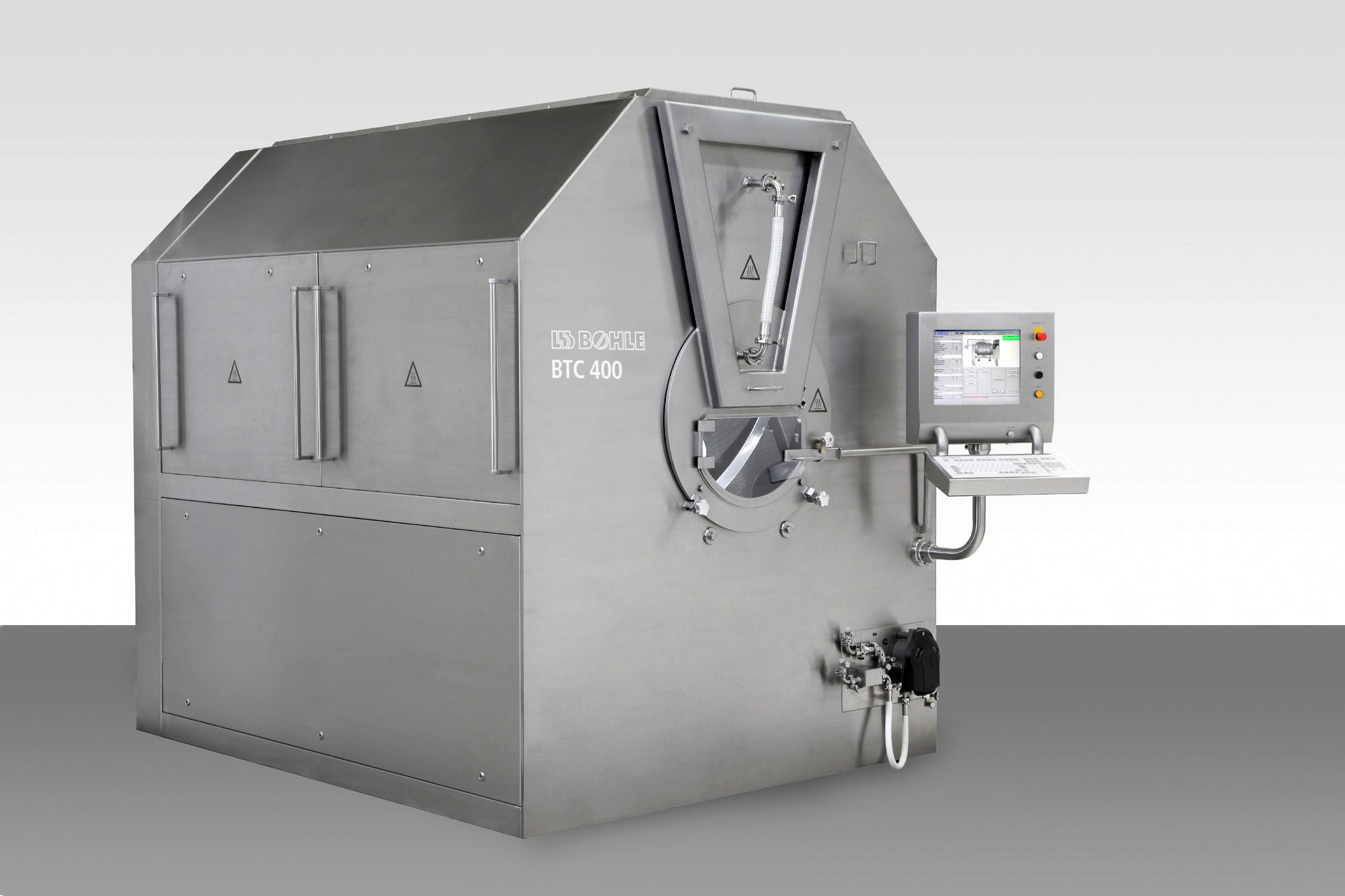
Pharmaceutical tablet coating machine
Tablet coating requires spraying, mixing, and drying procedures that must be carried ...
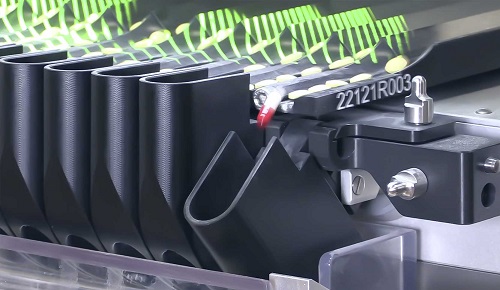
Vision inspection system for tablets and capsules
Pharmaceuticals and healthcare product manufacturers dealing with oral ...
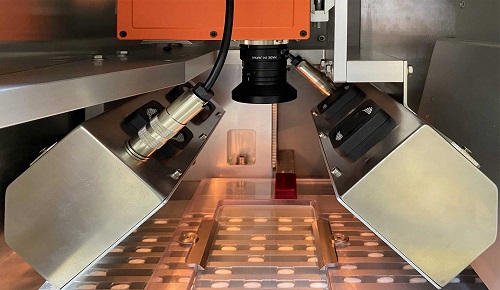
Inspection system for tablets chemical composition
The packaging of pharmaceuticals and oral solid products such as table...
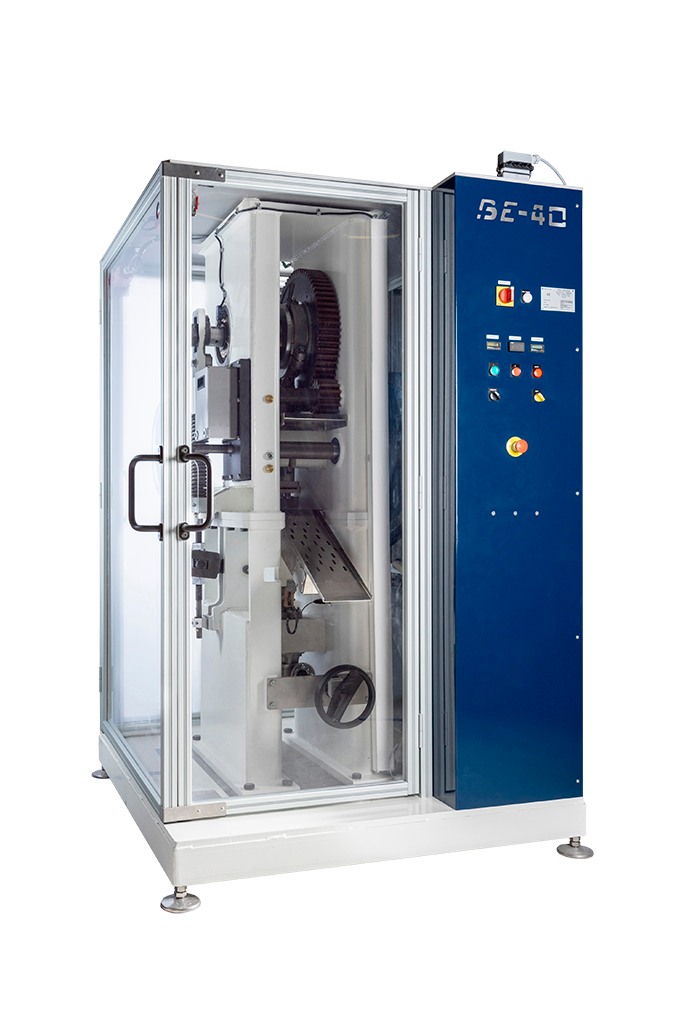
Eccentric press for refill tablets
Hundreds of different refill tablets, of various shapes or sizes, are on the market toda...
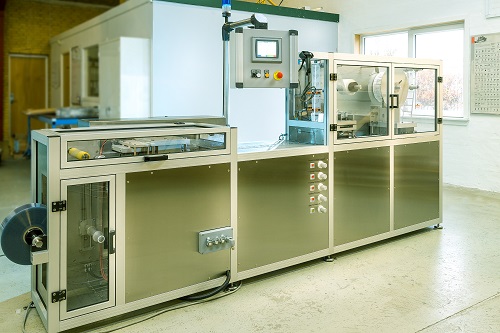
Automatic medical forming and sealing blister machine for packing capsules and tablets
Product safety is very importa...
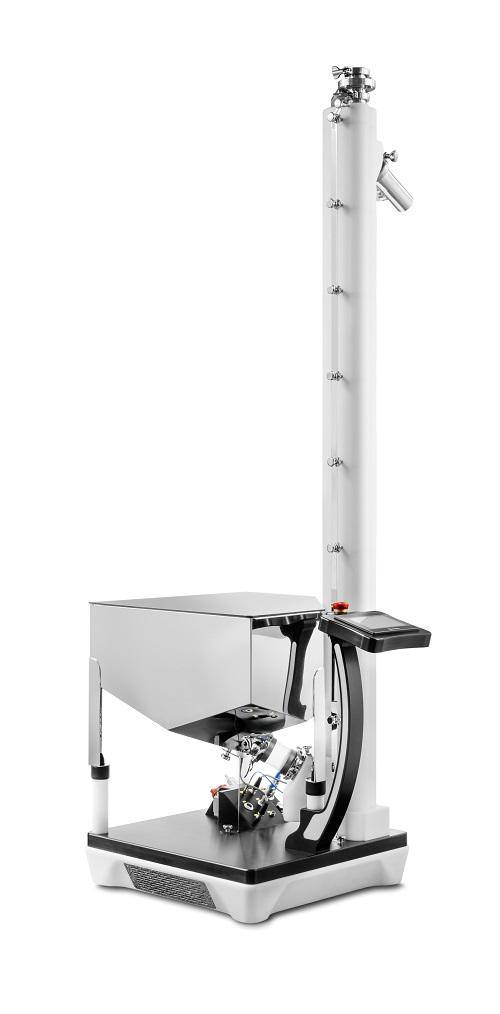
Lifter and De-duster for Tablets
The use of several different tools for lifting, de-dusting, and polishing in the pharmaceut...
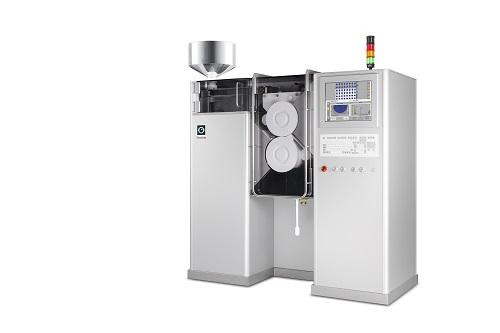
High Speed Visual Inspection System for Tablets
In order to ensure quality and standard specifications of tablets, capsule...
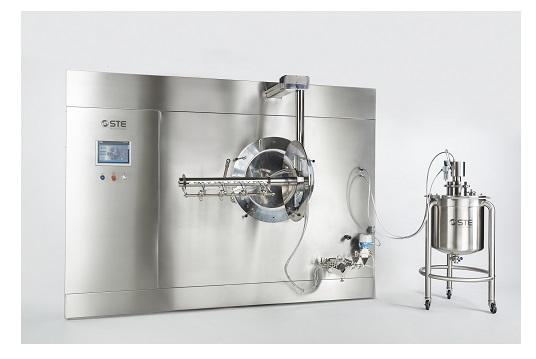
Industrial scale tablet coater
During the coating process, tablets pass many stages that can make them wet and sticky or cra...
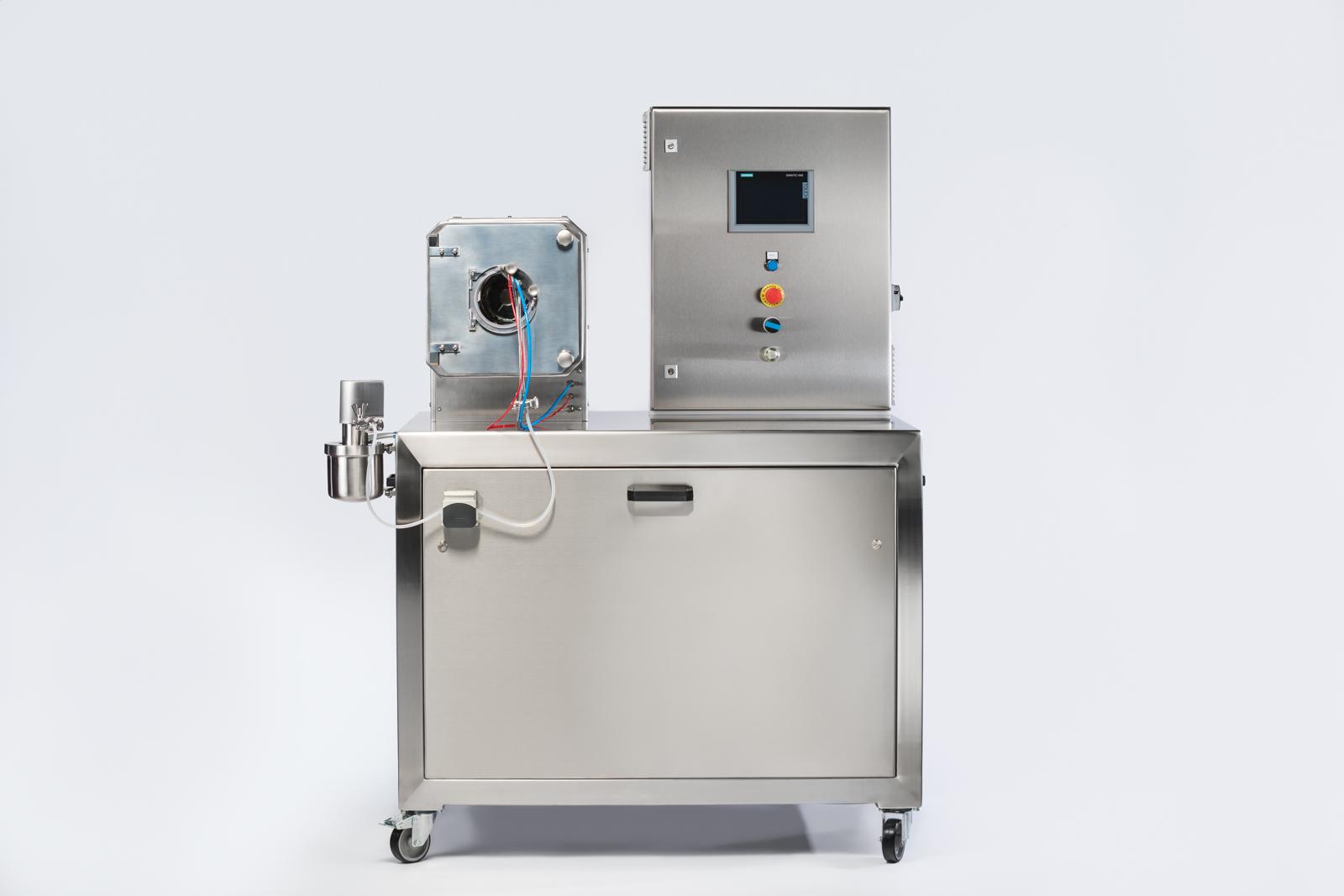
Tablet coater for laboratory scale
Tablet coating can be applied for adding colours or glosses, or based around sugar in or...
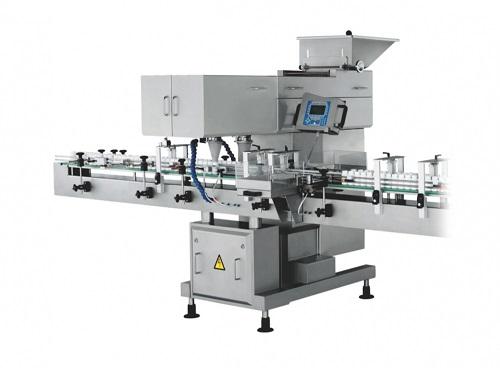
Tablet counting machine
Production of pharmaceutical solid dosage forms usually require complete accuracy, flexibility, and c...
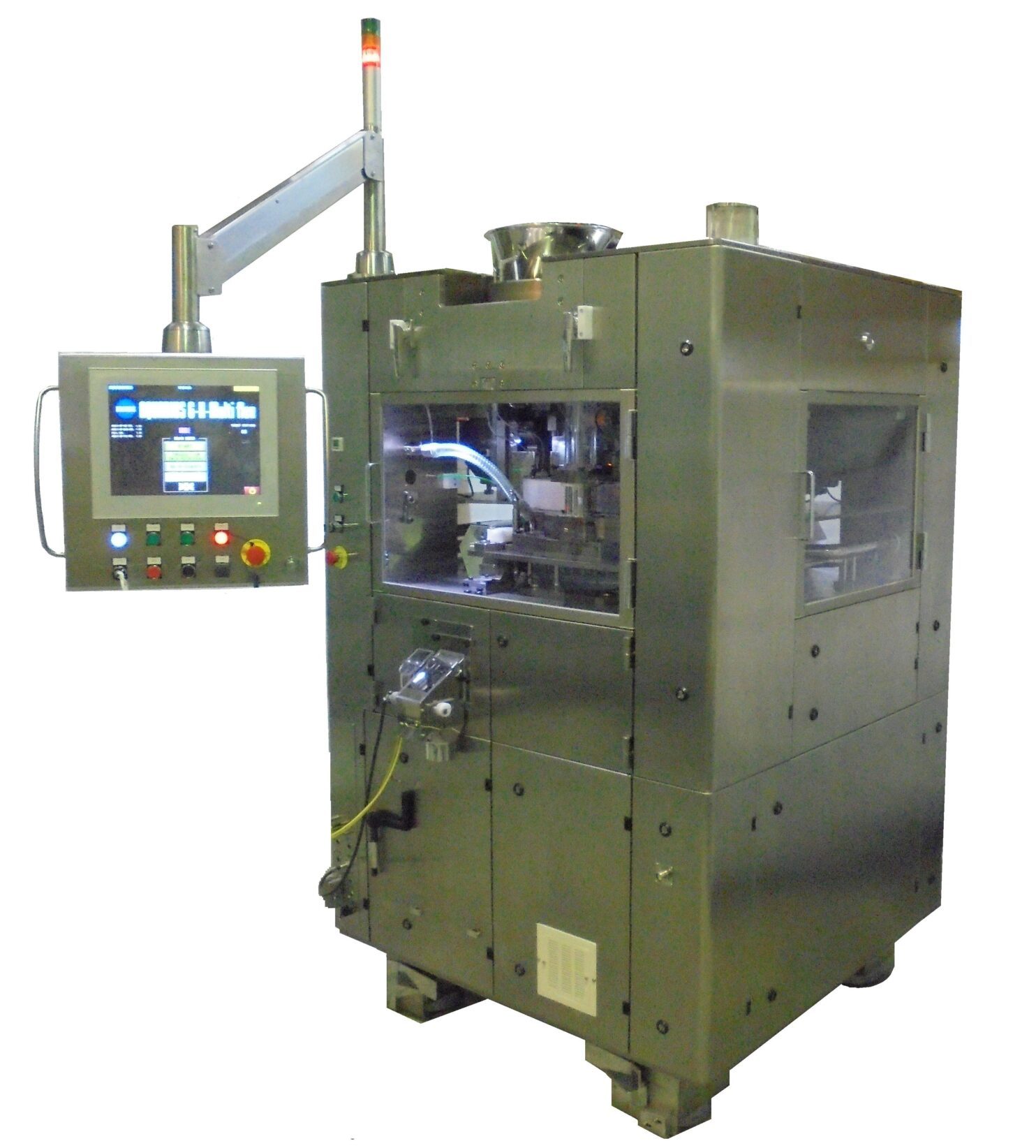
High Speed Double-Sided Tablet Press
To achieve as much as double the output of single-sided tablet press, the upper and lo...
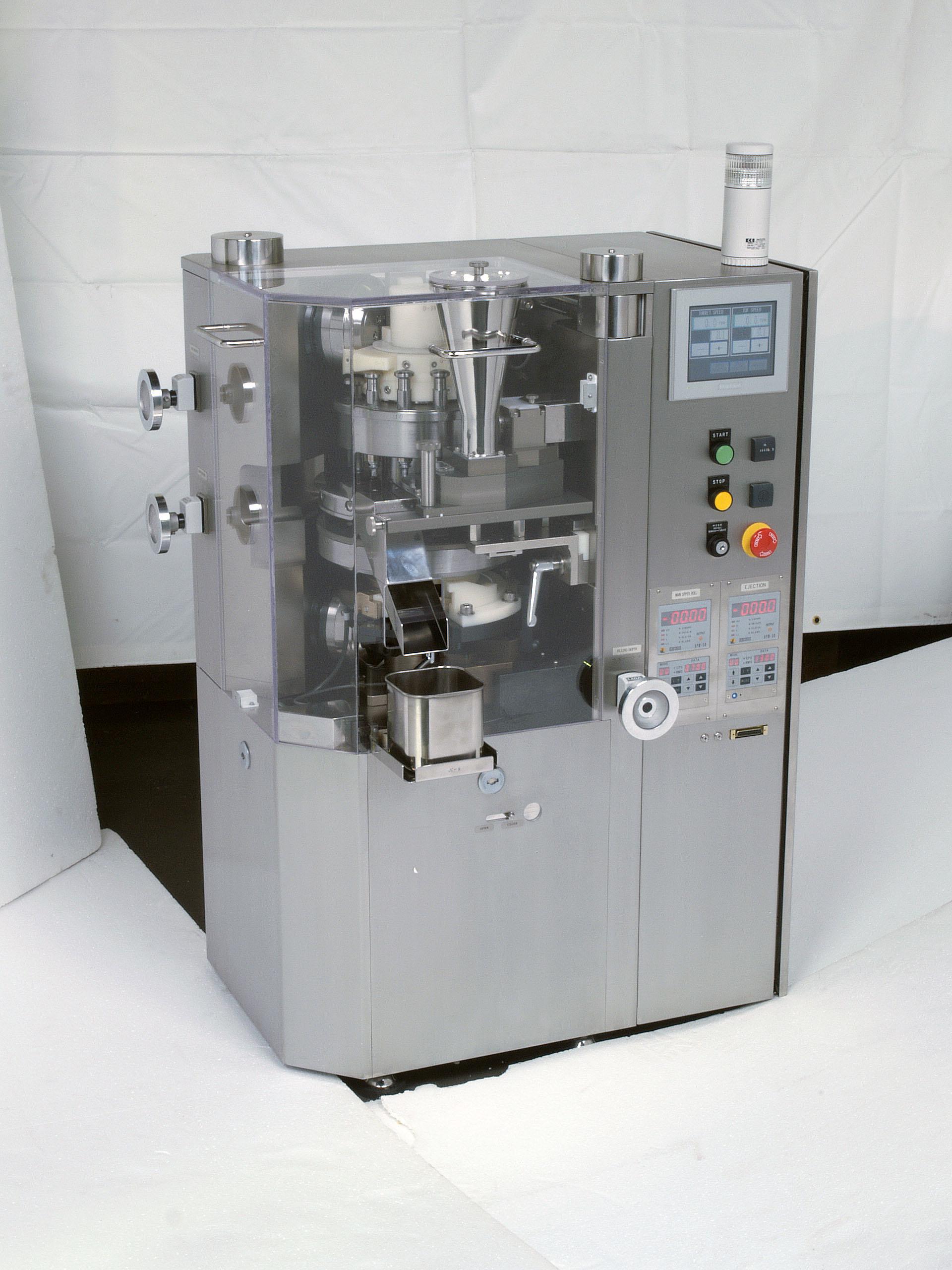
Laboratory Tablet Press
Pharmaceutical research and development projects may require small samples of high quality tablets fo...
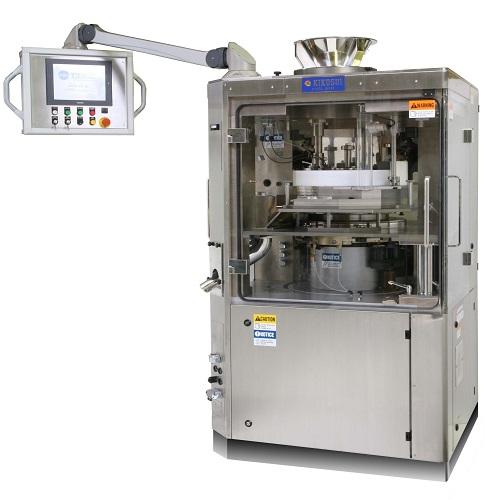
High Speed Tablet Press
High speed pharmaceutical tablet presses convert powder to tablets. The operations should be quick an...
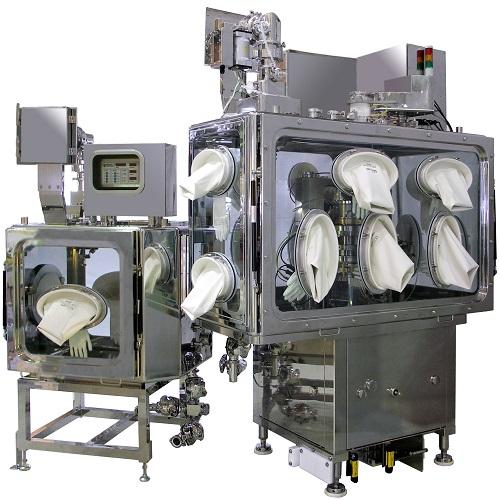
High Speed Containment Tablet Press
High speed containment presses make pharmaceutical tablets in closed environments with ...
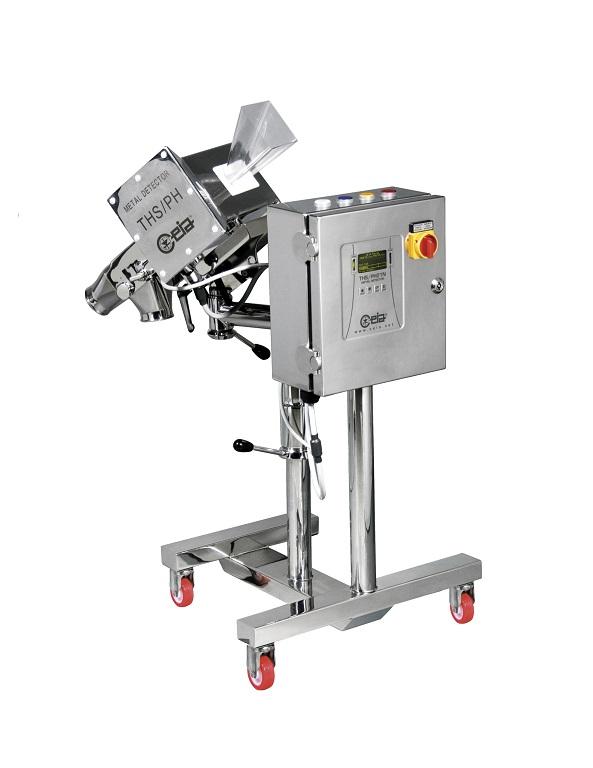
Metal detector for tablets and capsules
Identification of metallic contaminants is a vital part of pharmaceutical quality c...
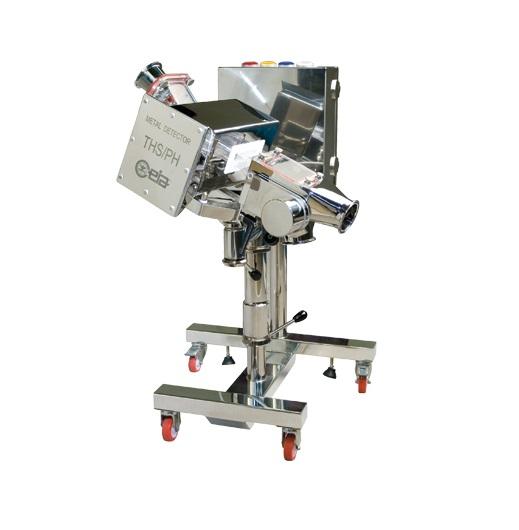
Dust-tight metal detector for tablets
For FDA-compliant production of tablets, the elimination of airborne dust containing ...
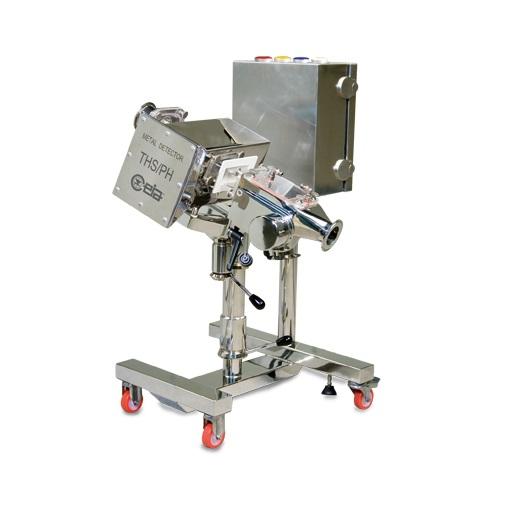
Wash-in-Place metal detector for tablets
Where hygiene and decontamination are vital, traditional pharmaceutical metal dete...
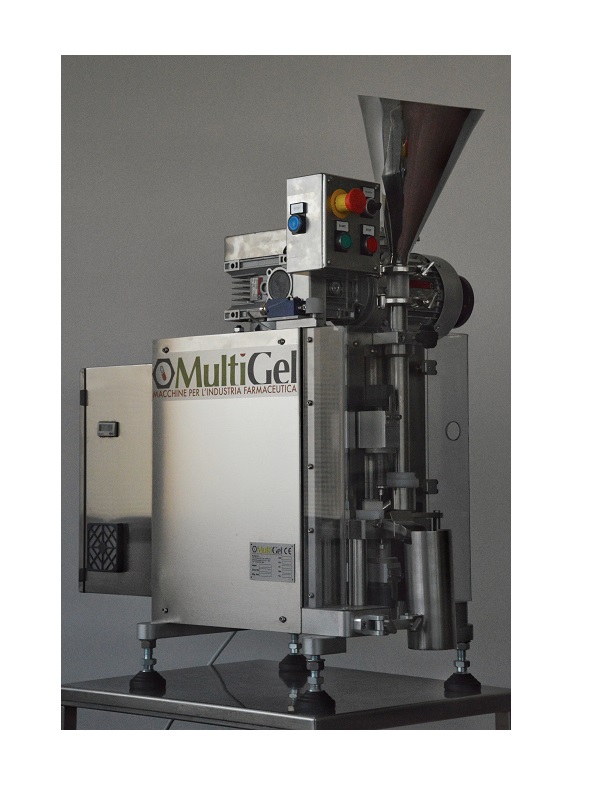
Benchtop tablet press
For lab work or small-scale production, a purpose-designed tablet press that meets your exact requireme...
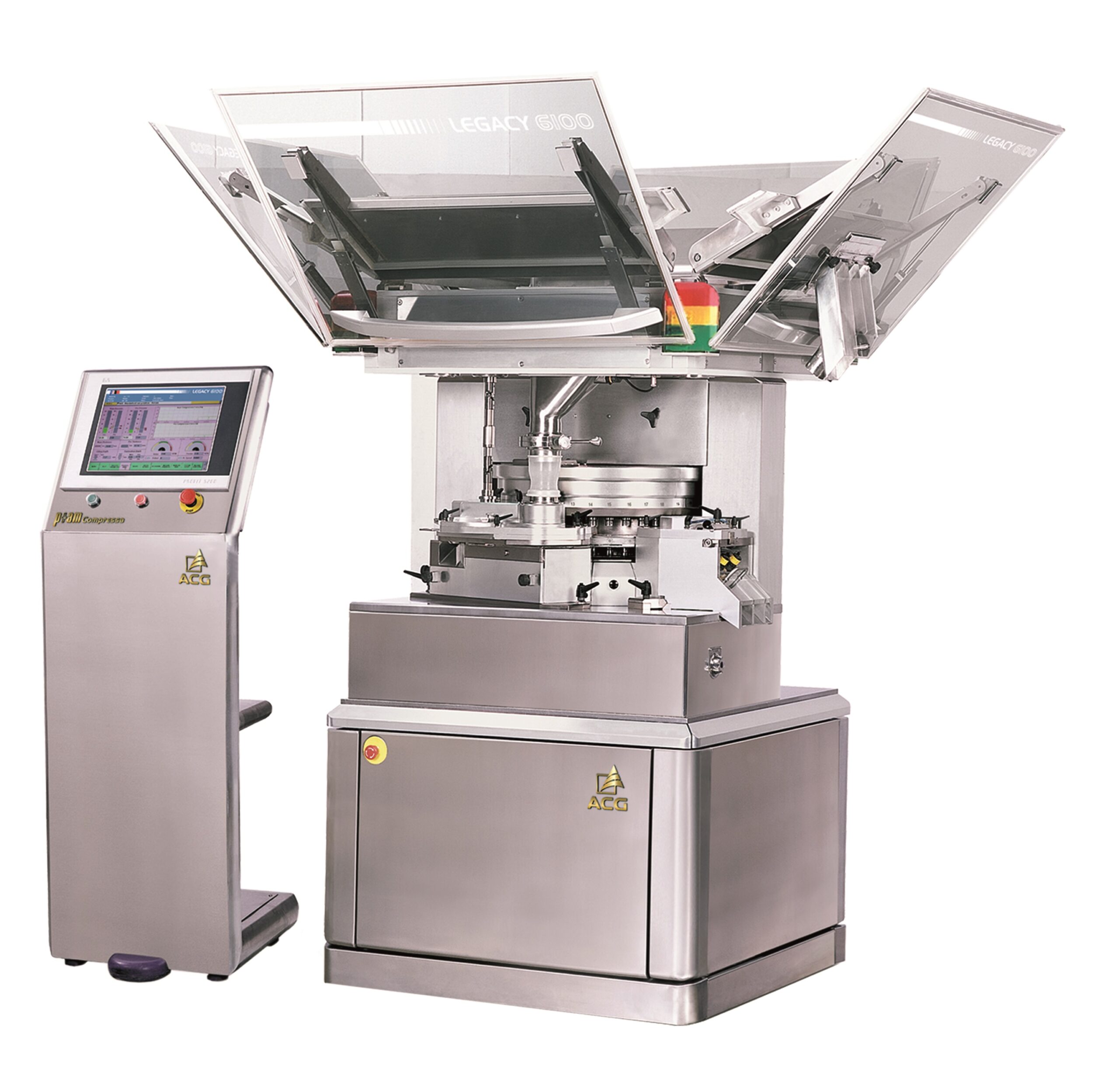
Economic tablet press
Successful pharmaceutical manufacturers know that high quality, reliable equipment is essential in orde...
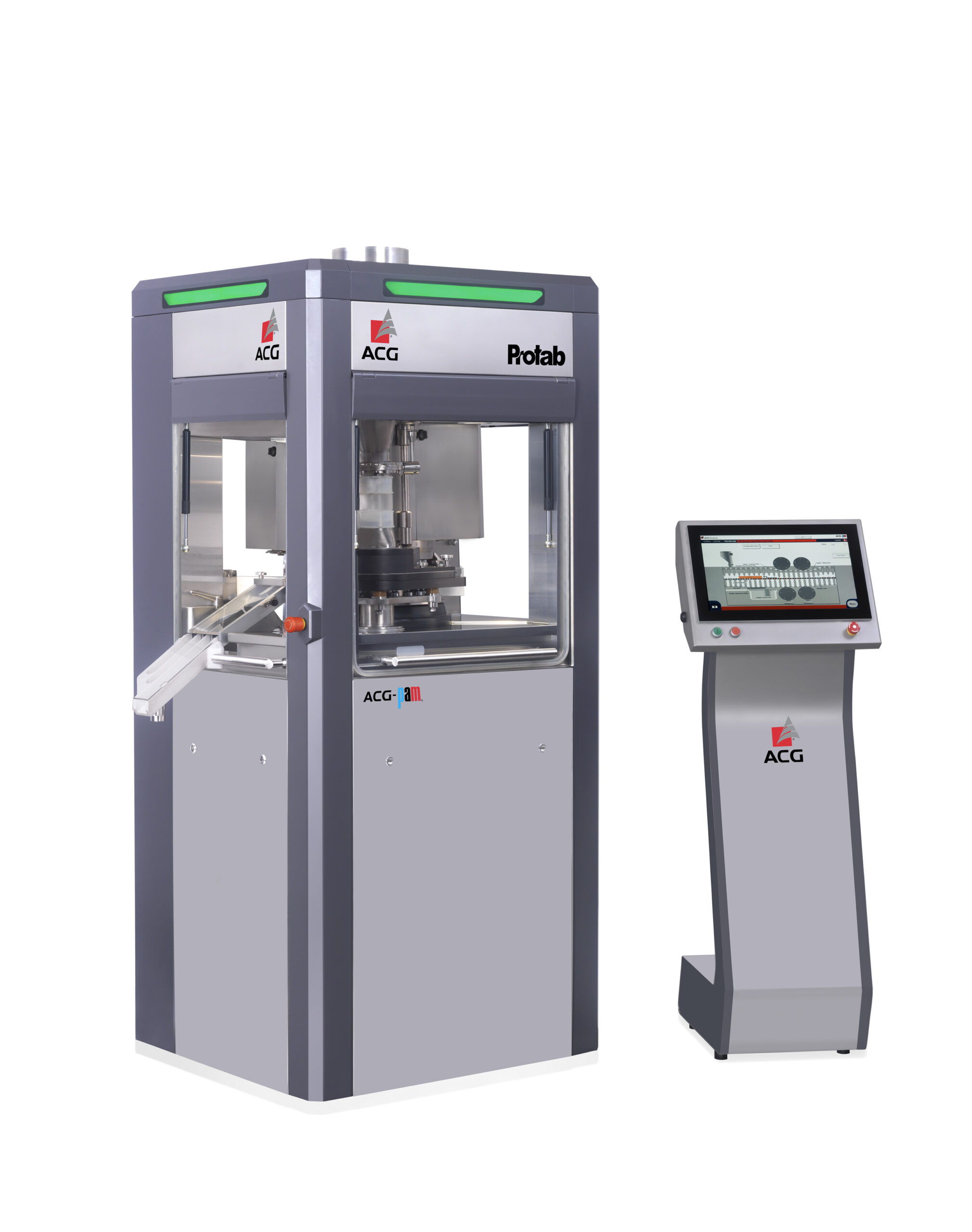
Single rotary tablet press
Creating batches of consistent high quality pharmaceutical grade tablets from your powdered ingre...
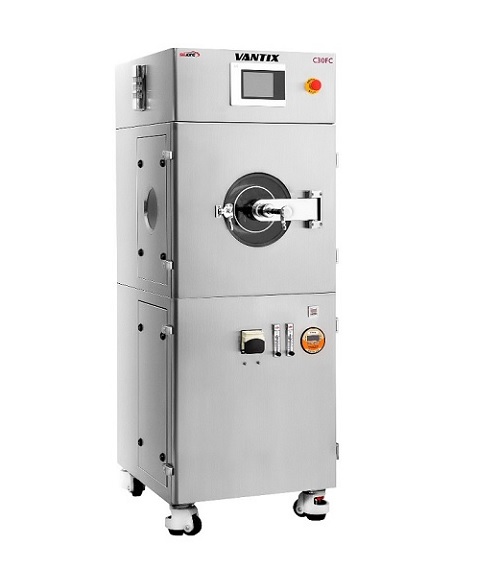
Automatic tablet coater for lab scale
The ability to coat tablets in an even and controlled way is an important stage in th...
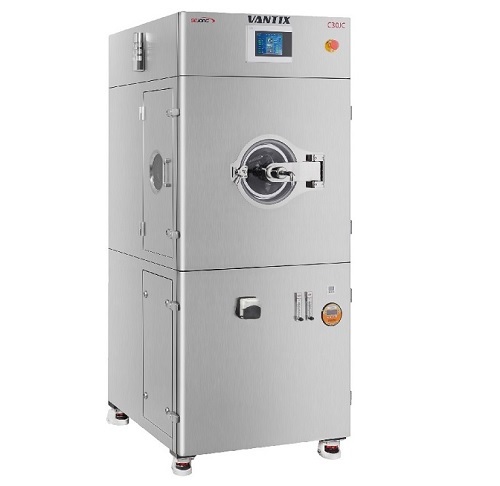
Tablet auto coater for lab scale
Many pharmaceutical doses in tablet form require a coating before they are ready for use. T...
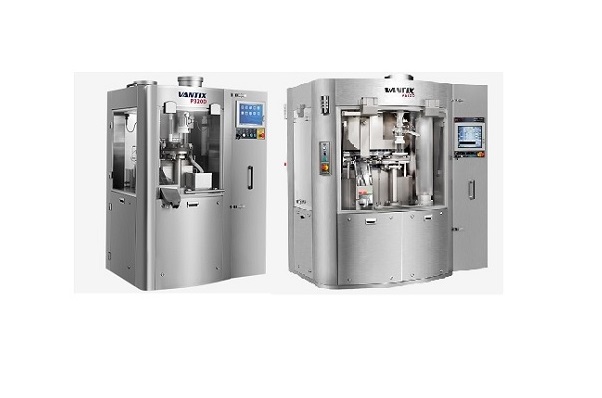
Single and double layer tablet press
High performance tablet presses that are capable of producing both single and double-l...
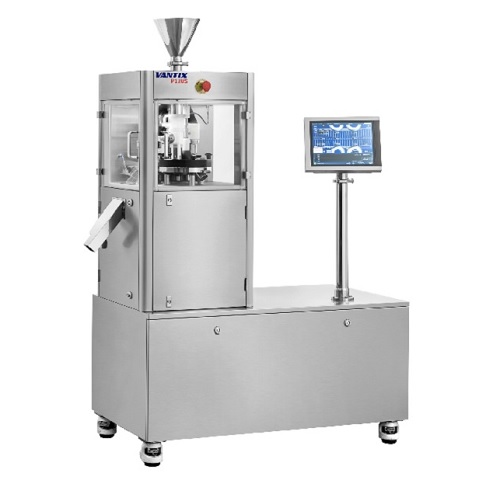
Lab scale single layer tablet press
Automated pressing of tablets saves time and improves quality. In R&D or laboratory...
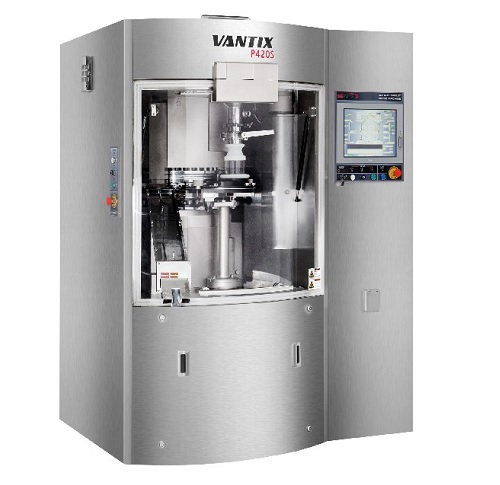
Single layer tablet press
High performance tablet presses for the modern production environment need to be fast, accurate an...
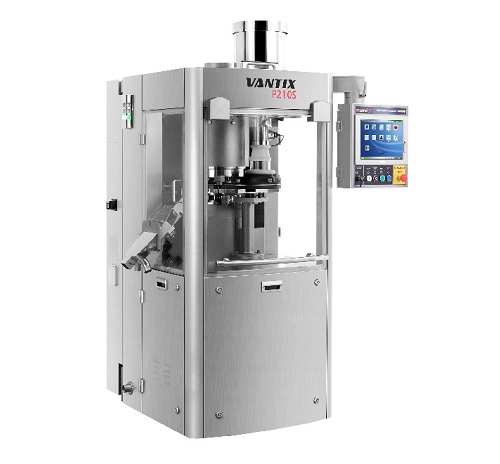
Rotary tablet press
For pharmaceutical tablet producers looking to reduce waste, costs and increase production volume, a hig...
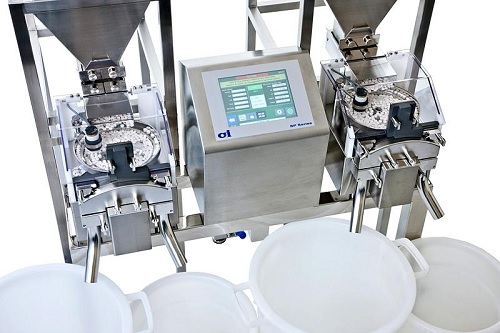
Waste minimization weight sorter for tablets & capsules
For medium scale production, you can improve line efficiency and ...

High capacity weight sorter for tablets & capsules
By employing a weight sorter that is fully flexible and able to ha...

Benchtop weight sorter for tablets & capsules
For laboratory pharmaceutical R&D work or use in clinical trials, a...
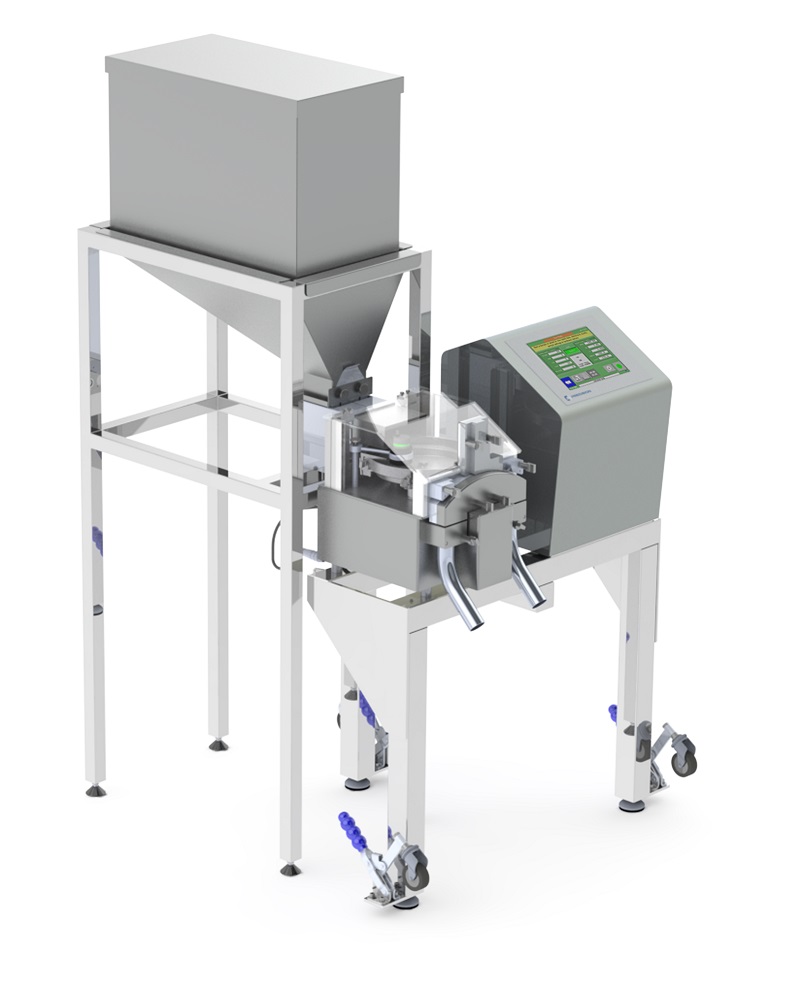
Versatile weight sorter for tablets & capsules
Saving costs and improved production efficiencies are possible by opti...
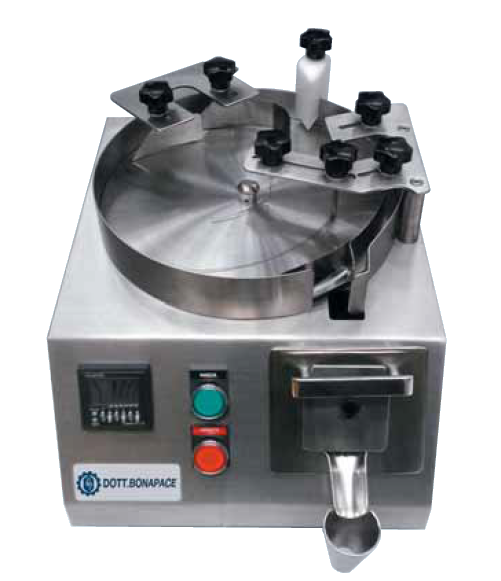
R&D electronic counter for capsules and tablets
This machine has been designed to offer an ever-precise and reliable count...
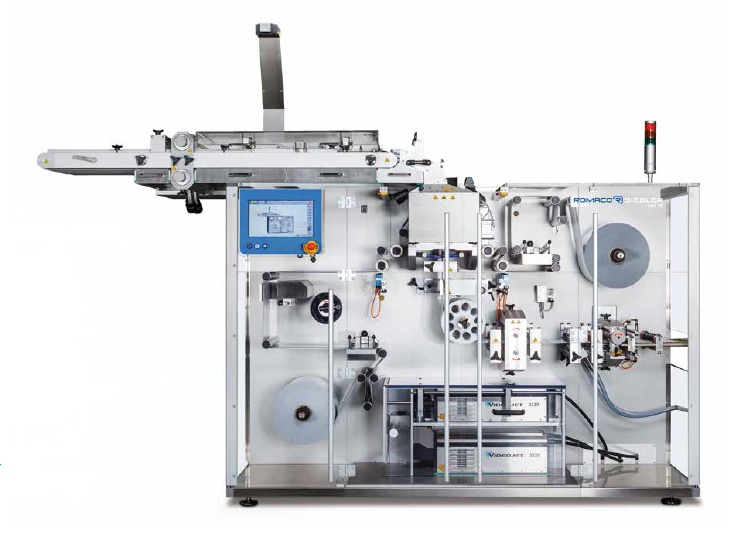
Strip packaging machine for effervescent tablets
Pack your effervescent tablets with extreme precision and care at a speed...
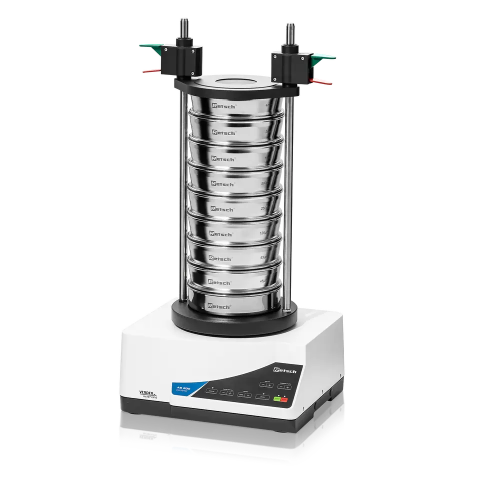
Vibratory sieve shaker for particle size determination
Achieve precise particle size analysis with rapid, reproducible re...
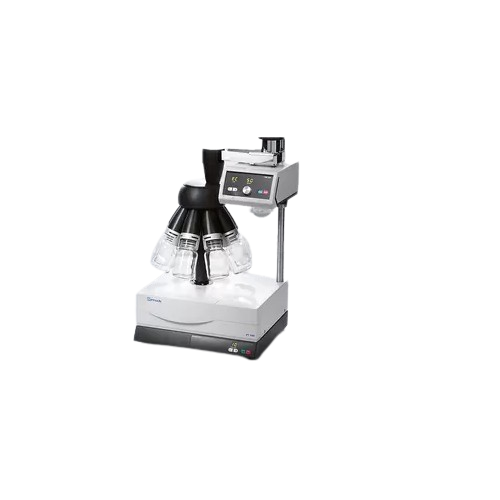
Sample dividing solutions for laboratory applications
Streamline your lab’s precision in sample preparation with so...
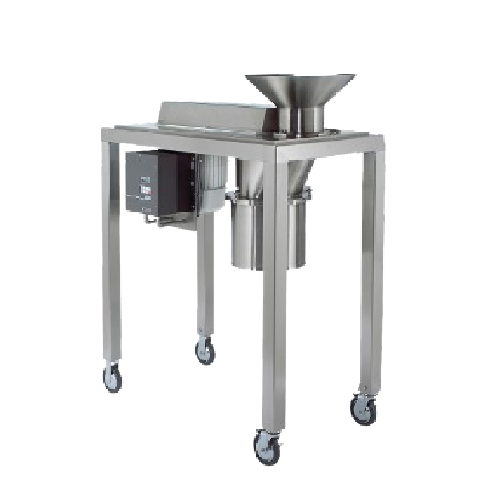
High efficiency milling solution for pharma and food industries
Achieve precise particle size control and enhance produc...
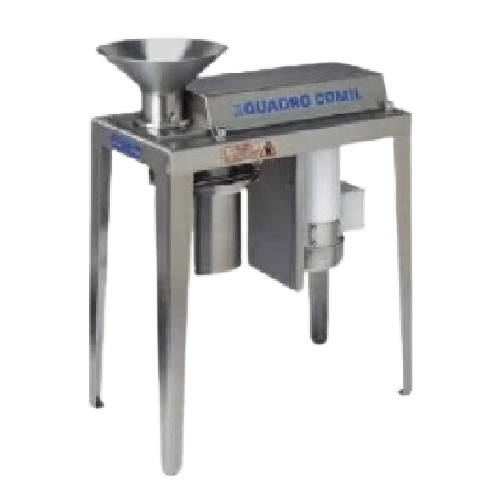
Conical milling for high-efficiency particle sizing
Maximize efficiency in your production line with conical milling tech...
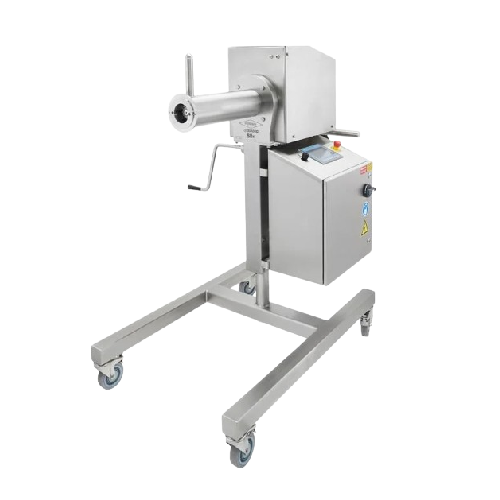
Mid-size milling platform for pilot-scale production
Achieve precise particle size control with this integrated milling s...

Atex compliant milling equipment for explosive atmospheres
Ensure operator safety and process integrity with milling equ...
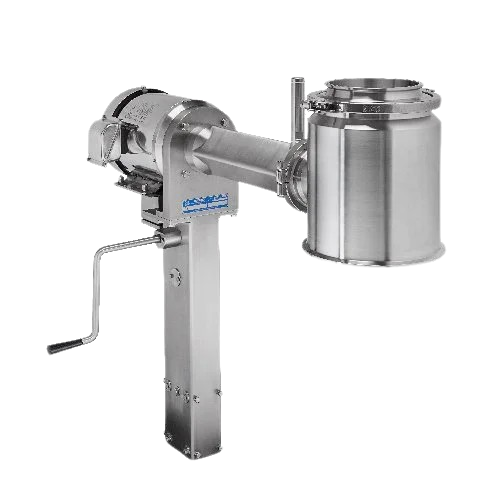
Cone mill for size reduction
Achieve precise particle size reduction and deagglomeration with minimal heat generation, ensur...
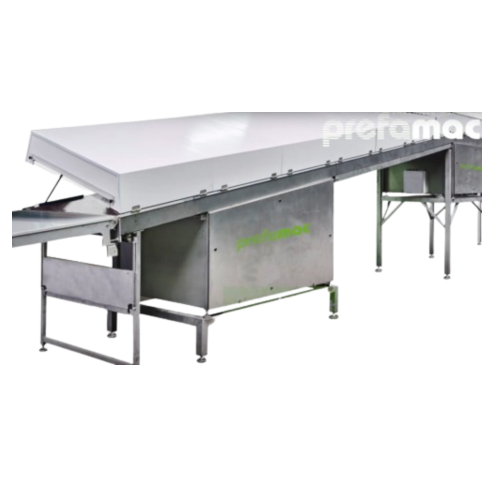
Precise dosing technology for praline and chocolate production
Streamline the production of pralines, chocolate bars, an...
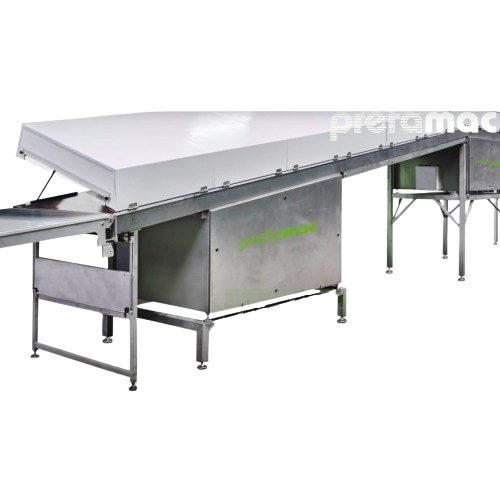
Buttercream filling applicator for chocolates
Enhance your confectionery process with precision dosing and moulding to cre...

Dosing system for kügel chocolate moulds
Automate your chocolate production with precision dosing, seamlessly integrating m...
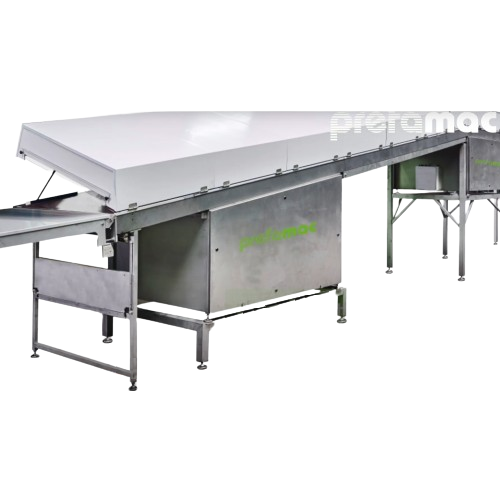
Chocolate filling application system for manons
Efficiently apply a variety of fillings, from delicate buttercream to rich...
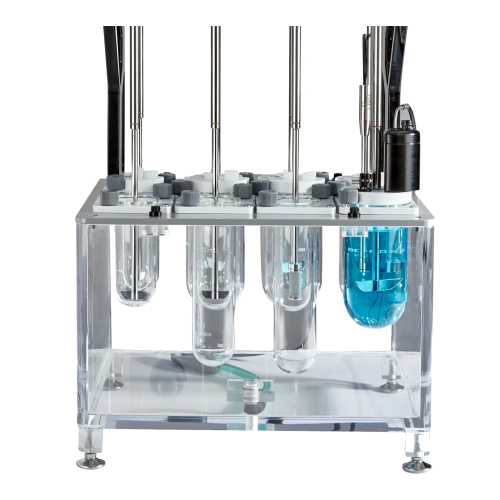
In vitro dissolution and flux measurement platform
Optimize drug formulation by accurately assessing dissolution, solubil...

Flow through dissolution system for drug products
Capture real-time dissolution behavior with high-resolution imaging, pr...
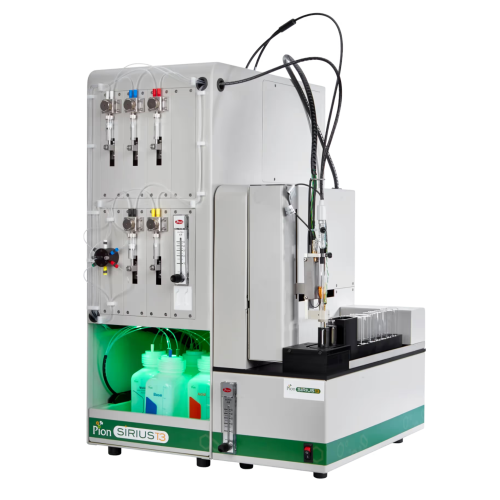
Automated platform for determination of physicochemical properties
Optimize your compound screening process with a full...
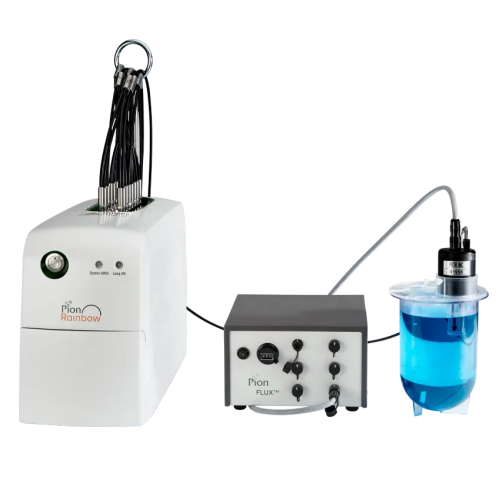
In-vitro dissolution-absorption assessment
Optimize drug formulation tests by combining dissolution and absorption measure...
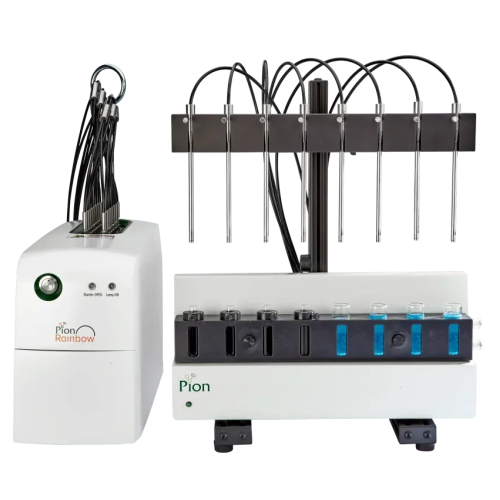
Uv monitoring system for small volume dissolution studies
Efficiently monitor small-volume dissolution processes in real...
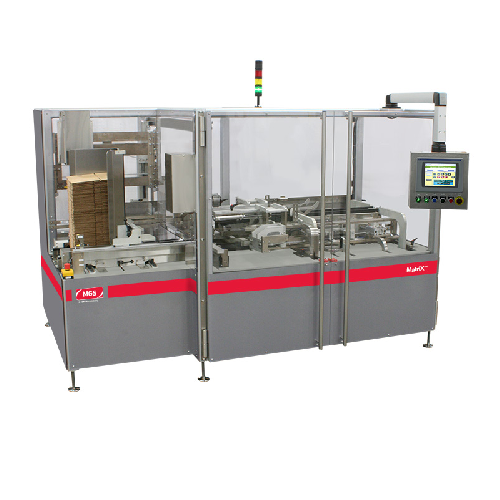
Case packer for pharmaceutical and healthcare products
Streamline your packaging line with a versatile case packer design...
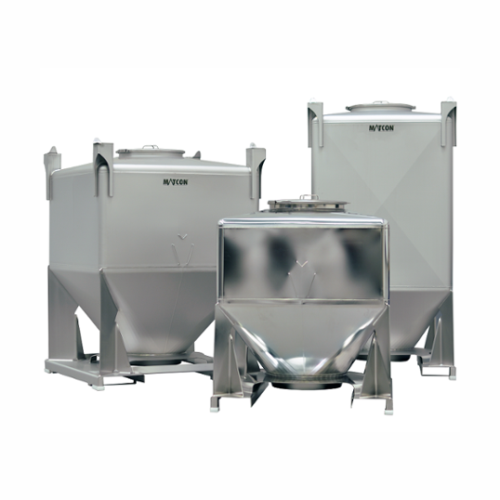
Intermediate bulk containers for powder and materials handling
Optimize your material handling processes with containers...
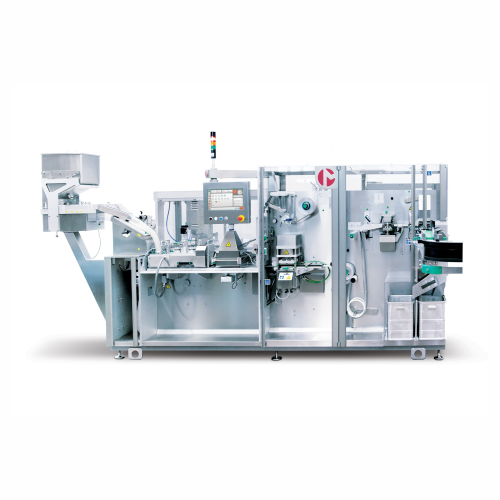
Blister thermoforming for Pvc/alu
Effortlessly mold and seal blister packs for a range of solid products, optimizing packag...
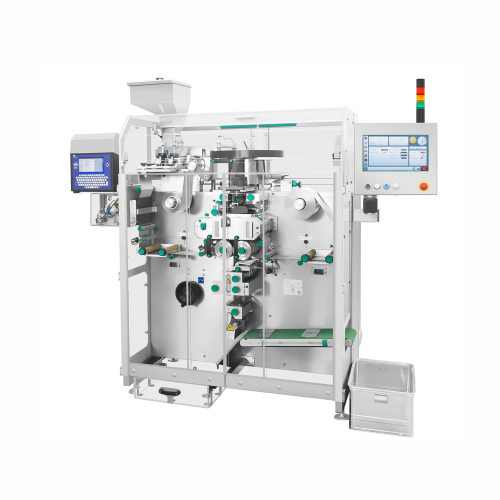
Compact strip packaging for solid products
Efficiently package a variety of solid pharmaceutical products with precision a...
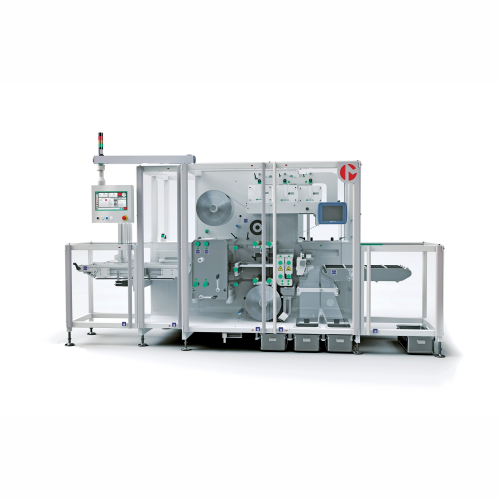
Strip packing for solid products
Ensure consistent quality and precision in packaging solid products with this advanced stri...
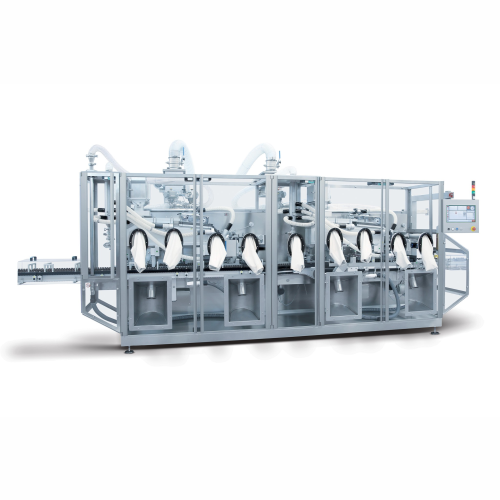
Electronic counting and filling system for vials
Efficiently streamline the packaging of solid dosage forms with a cutting...
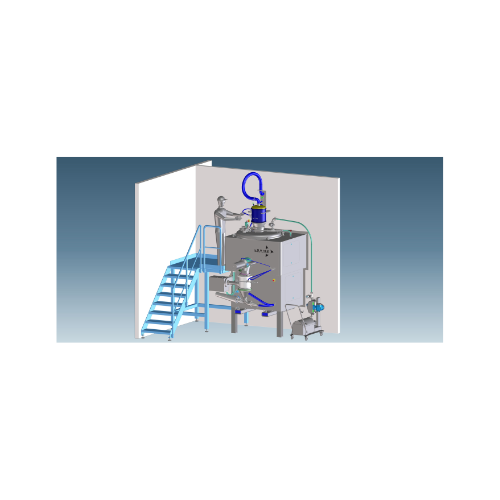
Mixing granulator for pharmaceutical and cosmetic industries
Achieve precise granulation and uniform mixing for high-qua...
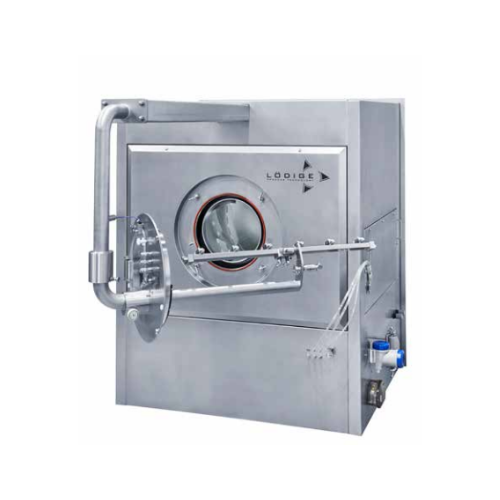
Film coater for Otc and food supplements
Achieve optimal film coating for tablets and capsules with precision-engineered so...
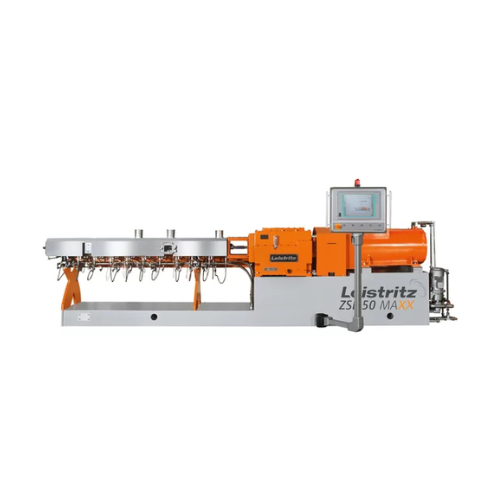
Industrial twin screw extruders for high torque and volume applications
Optimize your extrusion processes with high tor...
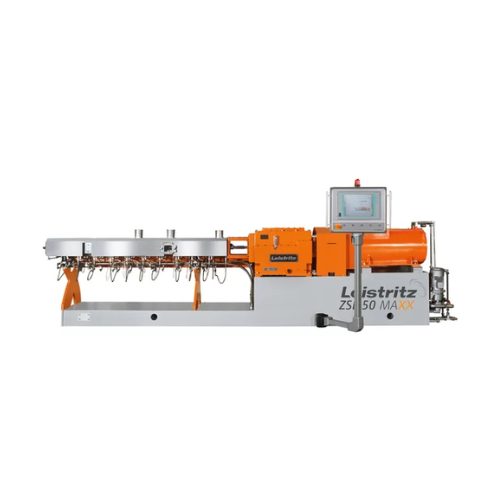
High torque and volume twin screw extruder
Maximize processing adaptability and efficiency across diverse applications wit...
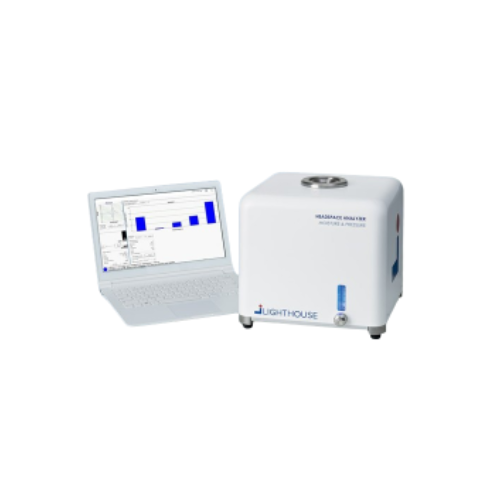
Water activity headspace analyzer for drug product samples
Ensure precise control of moisture levels across the entire p...
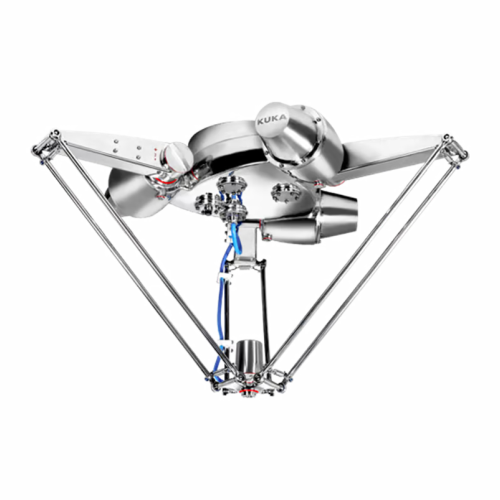
Hygienic design robot for food industry
Optimize your production line with a high-speed, hygienic design robot engineered f...

Capsule polisher for pharmaceutical production
Enhance capsule quality and safety by effectively polishing, dedusting, and...
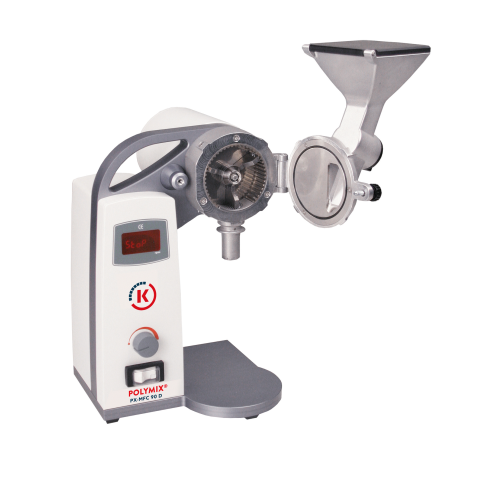
Laboratory mill for dry sample preparation
Achieve precise particle size reduction for pharmaceuticals and fine chemicals ...
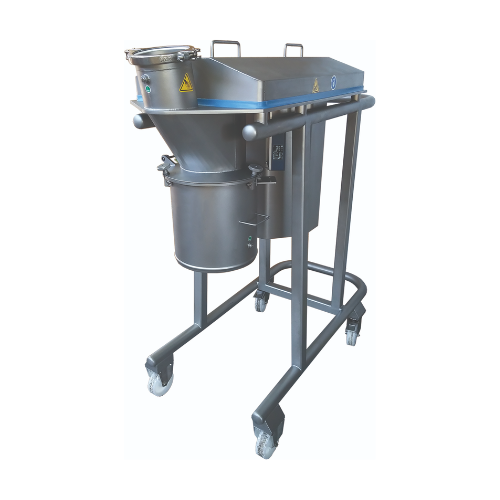
Versatile cone mill for uniform size reduction
Achieve precise particle size consistency and gentle deagglomeration across...
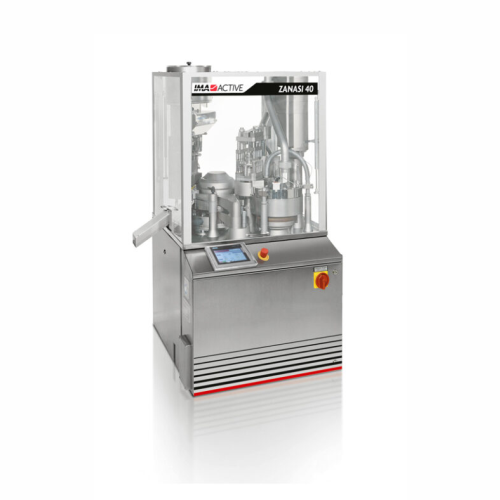
Automatic capsule filling machines
Efficiently fill capsules with precise doses of powders, liquids, and tablets to enhance...
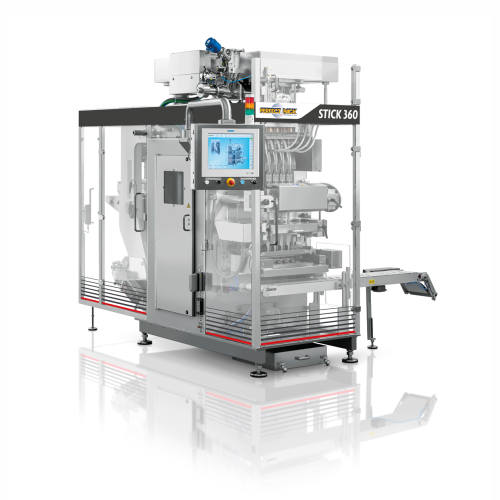
Vertical intermittent motion stick packaging
Experience seamless packing for diverse products, from powders to dense paste...
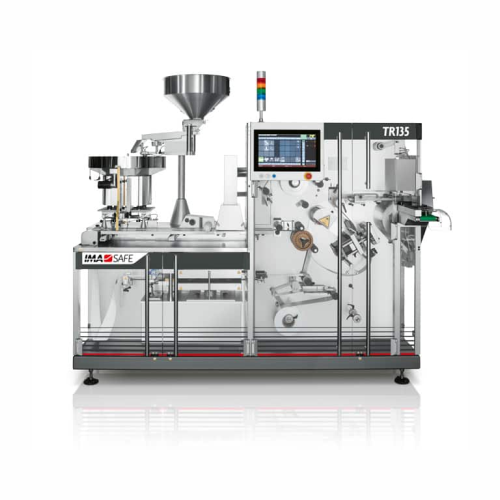
Medium speed blister packaging solution for pharmaceuticals
Optimize medium-speed tablet blister packaging with seamless...
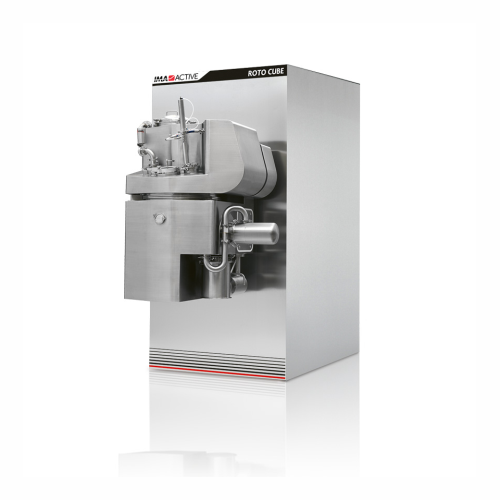
Single-pot granulation processor for pharmaceutical applications
For manufacturers needing precise granulation and dryin...
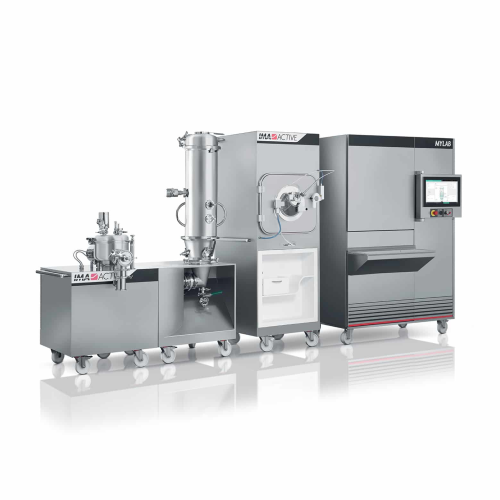
Fluid bed and coating system for small batch processing
Streamline your R&D process with a modular system that ensur...
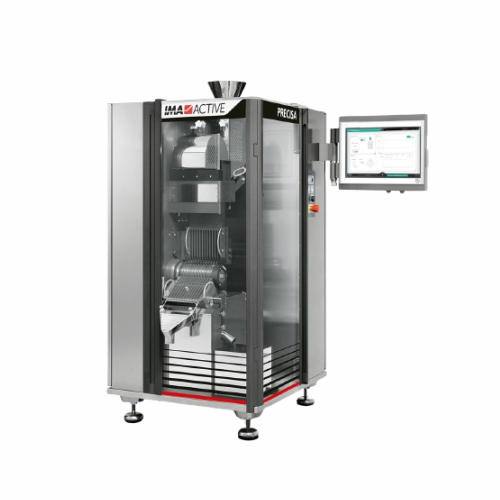
Precision weight-checking for pharmaceutical capsules
Ensure exact capsule and tablet dosage with high-speed precision we...
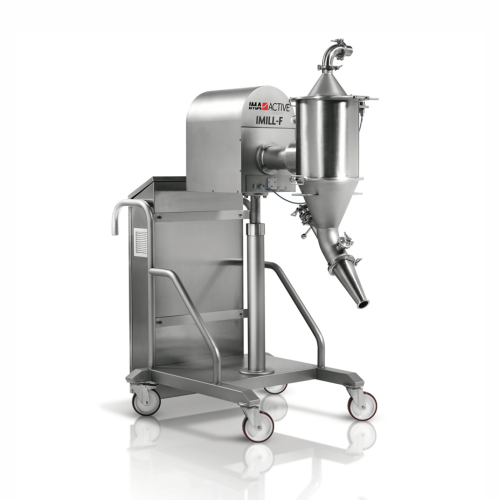
Cone mill for particle size reduction in pharmaceuticals
Achieve precise particle size control with this cone mill, desig...
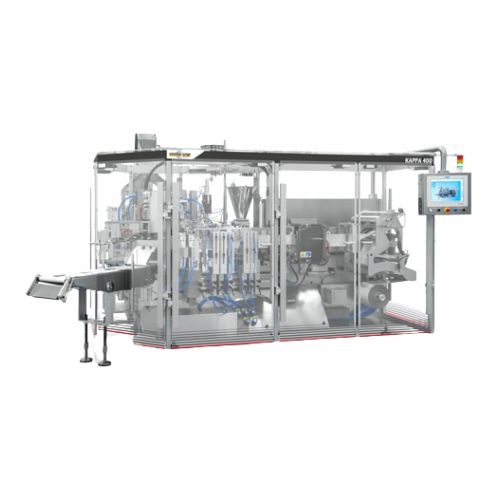
Horizontal intermittent motion sachet packaging solution
Optimize your packaging operations with a versatile sachet solut...
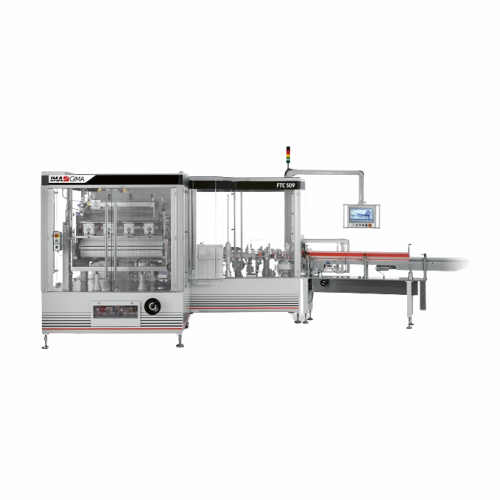
Vertical dosing and filling solution for confectionery packaging
Optimize your confectionery and nutraceutical packaging...
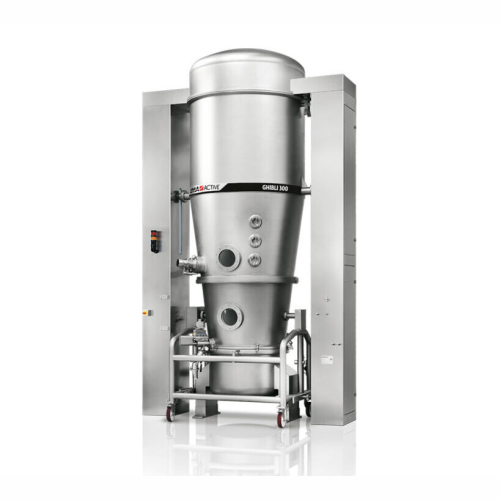
Fluid bed processor for pharmaceutical granulation and drying
Achieve precise drying, granulation, and coating of pharma...
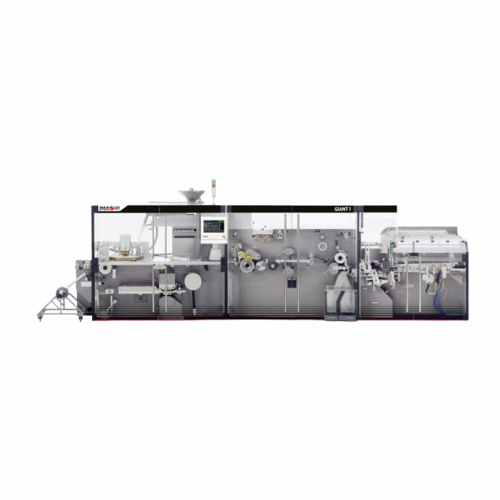
Blister packaging solution for small-medium batches
Achieve unparalleled versatility and efficiency in blister packaging ...
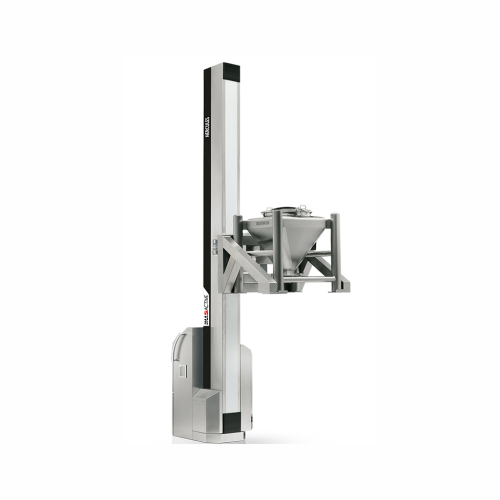
Lifting column for drums and containers
Streamline your production with lifting columns designed for precise handling, blen...

Blister packaging solution for small/medium batches
Achieve high production efficiency with frequent changeovers for your...
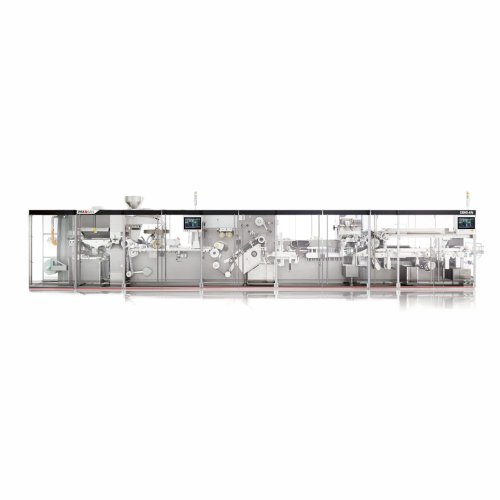
High-speed blister packaging with integrated cartoner
Optimize your blister packaging process with a solution that seamle...
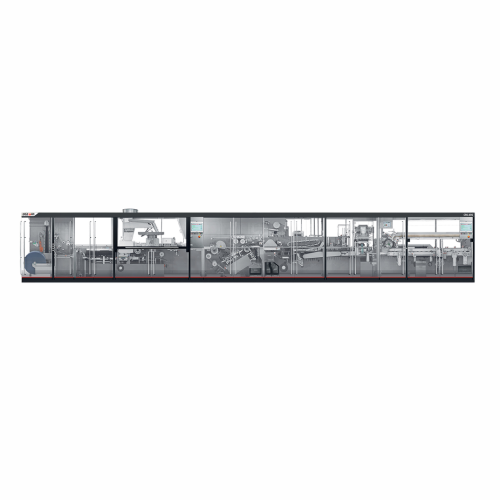
High-speed blister packaging with integrated cartoning
Achieve unmatched efficiency in blister packaging with seamless in...
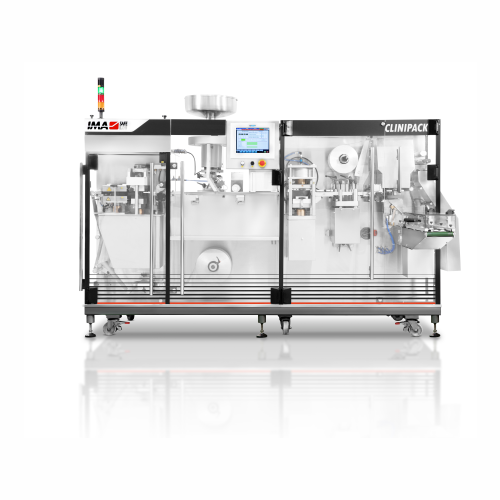
Thermoforming solution for clinical trials
Designed for precision and flexibility, this compact thermoforming machine stre...
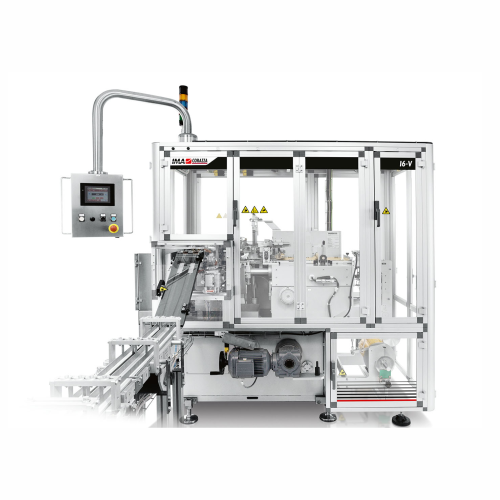
Pressed soup cube bottom fold wrapper
Optimize your packaging line with high-speed wrapping machines designed for precision...
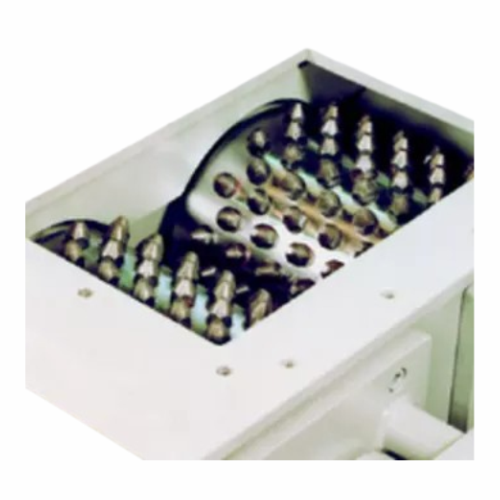
Industrial pre-crusher for coarse crushing
Optimize your production line by efficiently transforming clumped materials int...
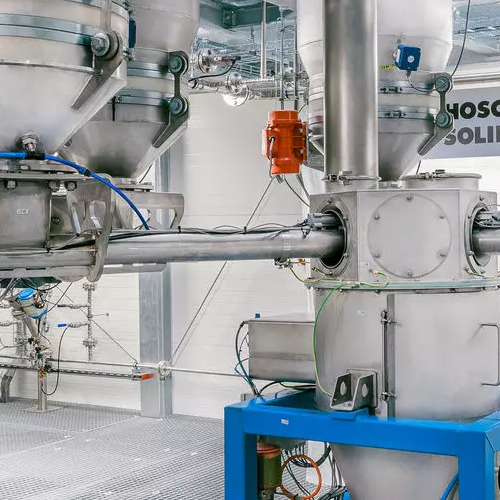
Mechanical conveying systems for bulk solids
Optimize your bulk material processes with advanced mechanical conveying syst...
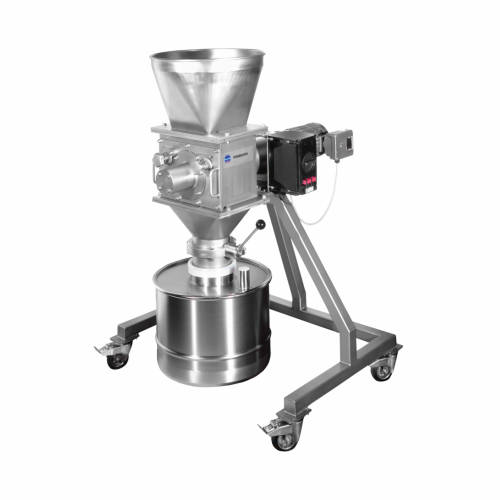
Flake crusher for hygroscopic substances and lumped salts
Efficiently turn fragile, aggregated materials into manageable...
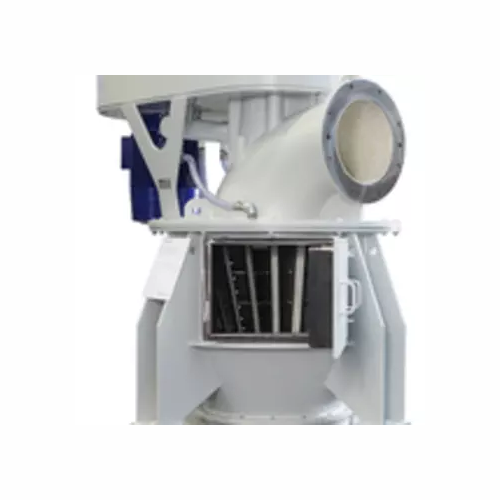
Ultrafine classifier for precise particle separation
Gain precise control over particle size with this ultrafine classifi...
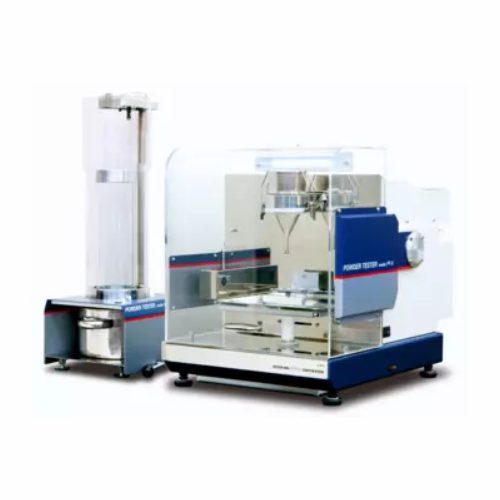
Powder flowability and compressibility analysis
Ensure accurate powder flowability and compressibility data with this adva...

Mid-capacity film coating solution
Enhance your seed coating and biofuel pellet production with a customizable turn-key sol...
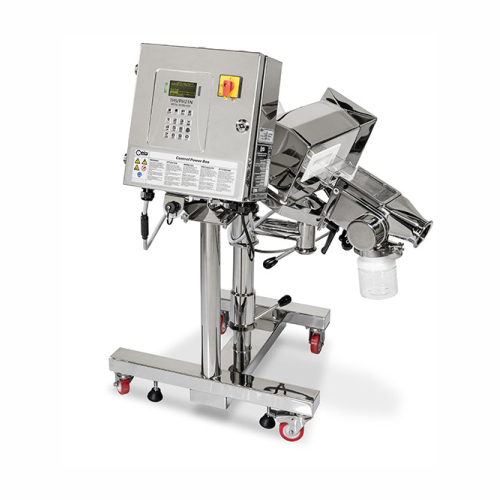
Pharmaceutical metal detectors
Ensure product purity by detecting and eliminating metal contaminants in pharmaceuticals, enh...
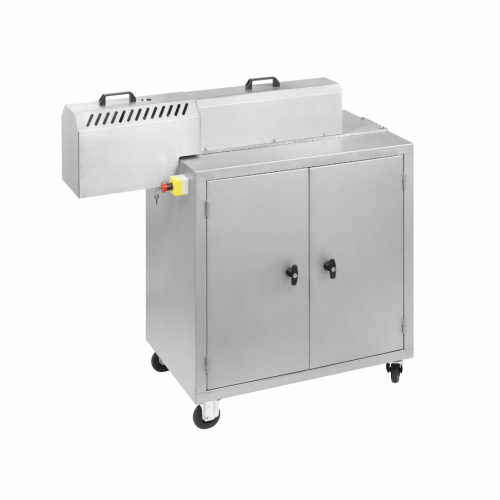
High-viscosity continuous industrial kneader for small volumes
Achieve consistent high-viscosity material processing wit...
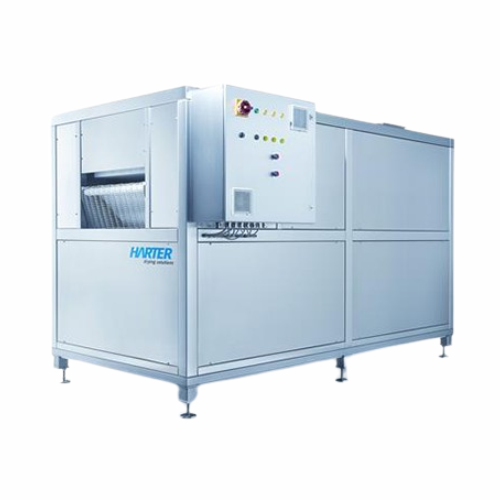
Continuous dryer for large production volumes
Achieve high-speed moisture removal with precision and minimal thermal impac...
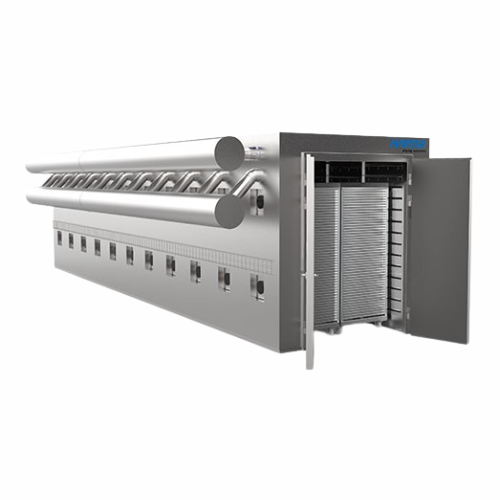
Batch drying system for food, pet feed, pharmaceuticals, and more
Optimize your drying needs with precision control for...
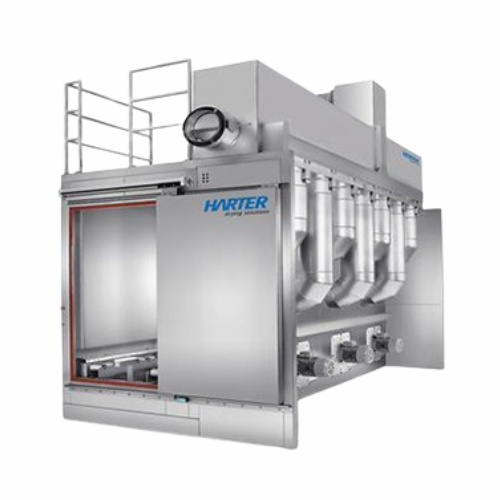
Continuous tunnel dryer for food products
Achieve precise moisture removal with adaptable drying technology, ensuring your...
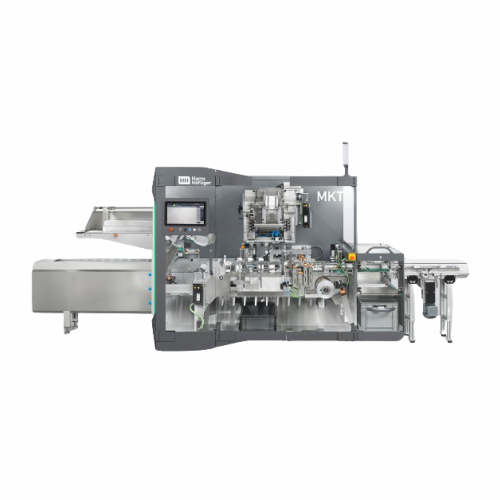
High-performance cartoning system for pharmaceutical products
Optimize your packaging line with a flexible cartoning sol...
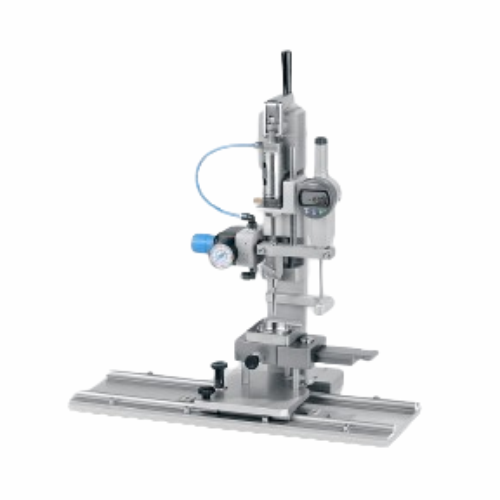
Powder dosing for lab and galenics
Ideal for precise dosing needs, this compact lab device streamlines powder filling proce...
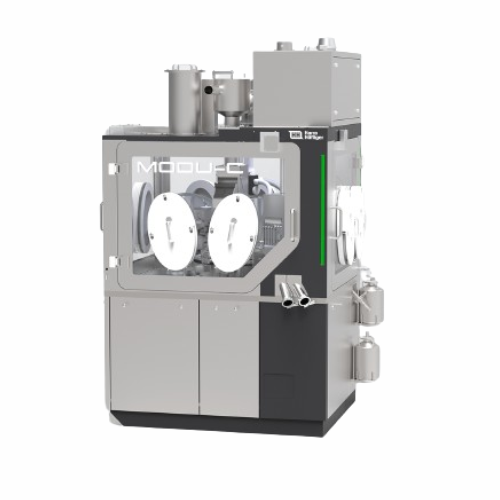
High-containment capsule dosing and filling system
Achieve precise dosing and optimal containment for pharmaceutical prod...
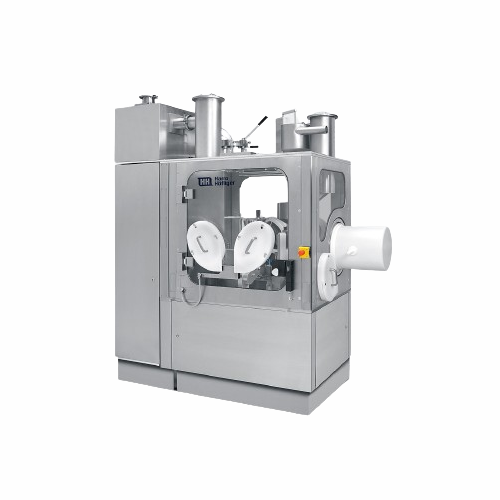
Containment capsule filling system for lab and small batch production
Designed to ensure maximum safety in pharmaceutic...
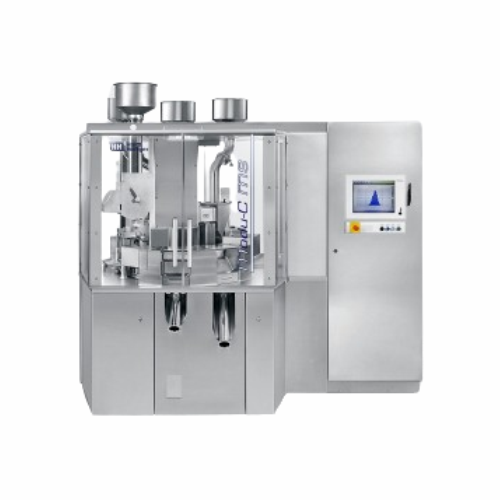
Versatile capsule filler for pharmaceuticals
Effortlessly switch between powder, pellet, and liquid dosing with this adapt...
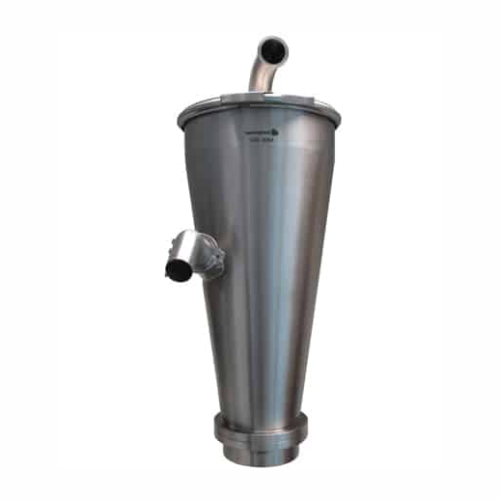
Ultra-hygienic vacuum conveyor for pharmaceutical industry
Optimize powder transfer with ultra-hygienic vacuum conveying...
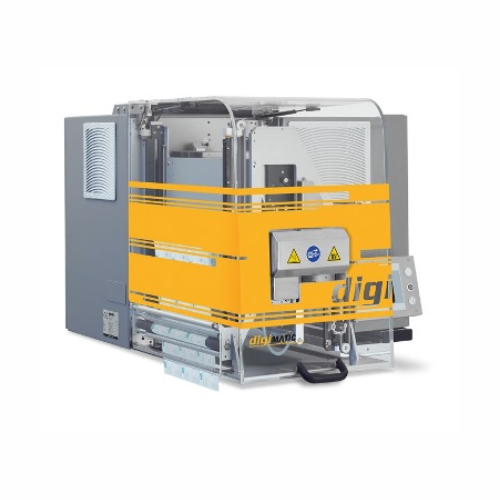
Single-color inline digital printer for blister-lidding foils
Streamline your pharmaceutical packaging with precision pr...
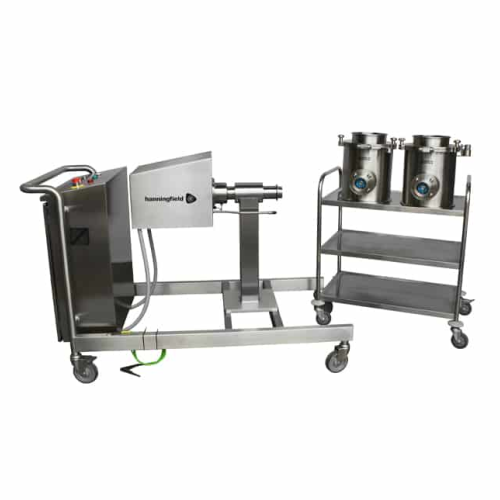
Particle sizing solution for milling and sifting
Streamline your milling and sifting processes with a flexible system desi...
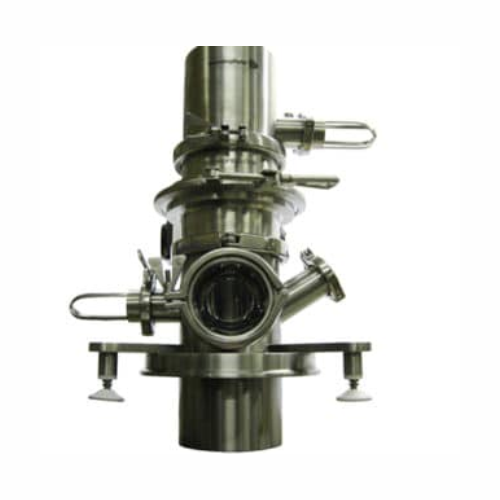
Powder flow control system for gravity transfer
Ensure precise dosing and prevent spillage during powder transfers in your...
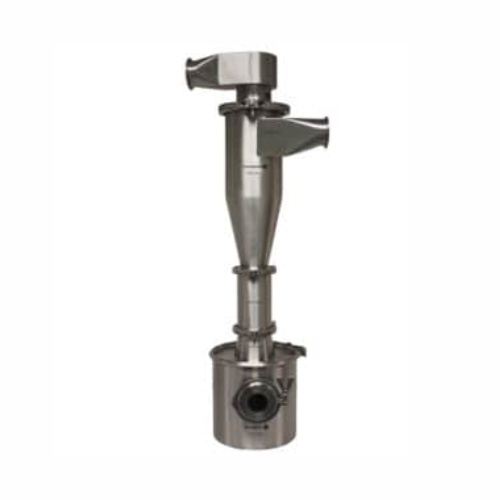
Waste powder recovery cyclone for pharmaceutical processes
Efficiently recover up to 99.9% of waste powder from oral sol...
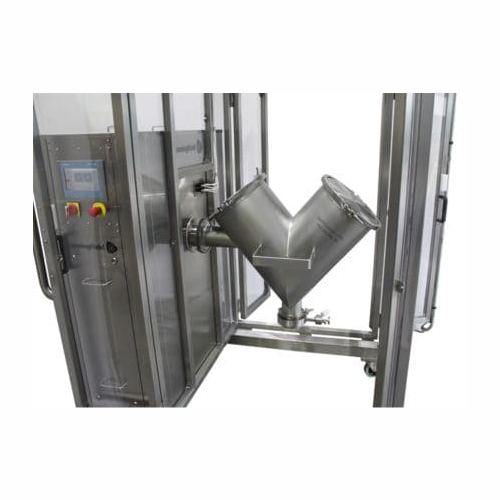
Laboratory and pilot scale blending module
Efficiently integrate multiple blending functions on a single drive for streaml...
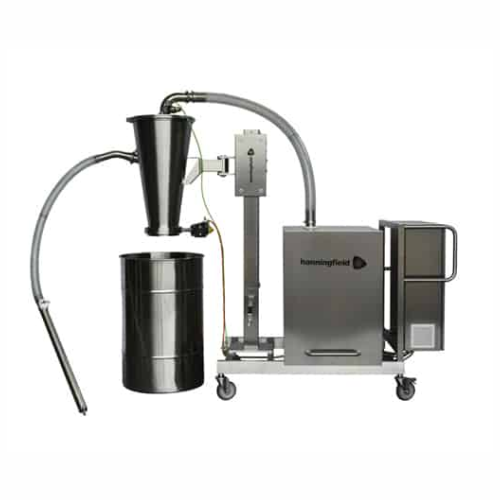
Hygienic vacuum conveyor for pharmaceutical and food industries
Optimize your material handling process with a vacuum co...
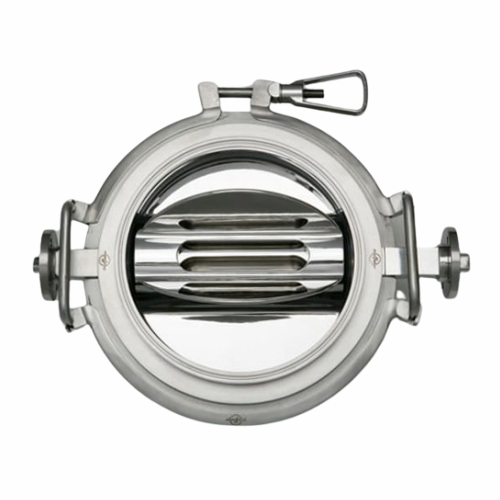
High-accuracy rotary dosing valve for fine material feeding
Ensure precise dosage of fine powders and granules, enhancin...
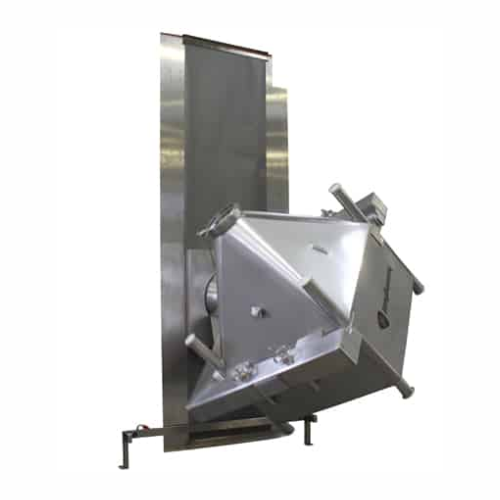
Industrial bin blenders for uniform batch production
Optimize your blending process by achieving uniform mixtures with in...
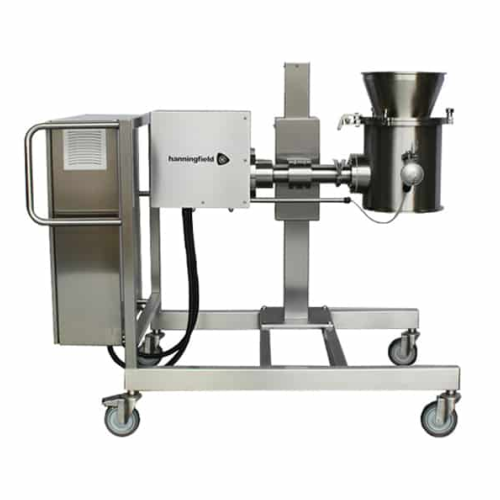
Conical mills for size reduction in pharmaceutical production
Achieve precise particle size control with an innovative m...
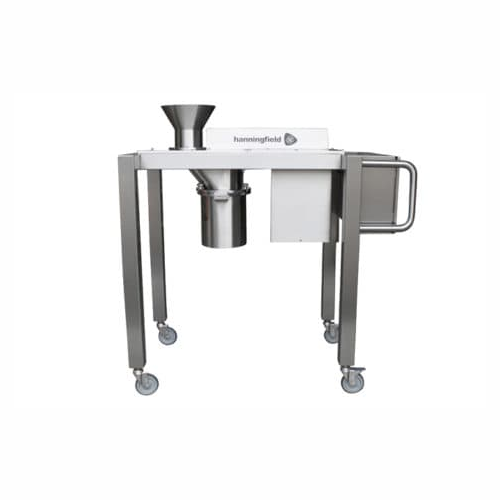
High capacity conical mill for powder processing
Optimize your milling process with a versatile solution that ensures prec...
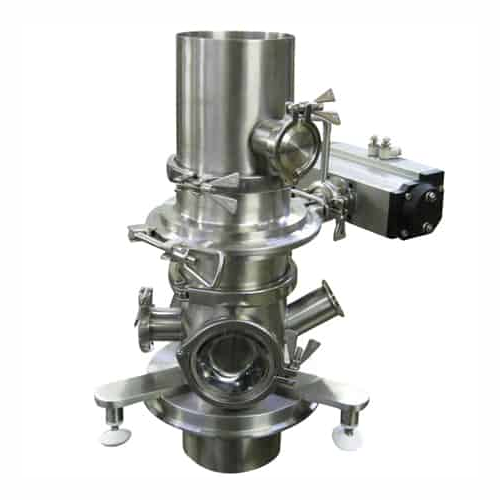
Powder flow control systems for precise gravity transfer
Achieve seamless powder flow control in your production line wit...
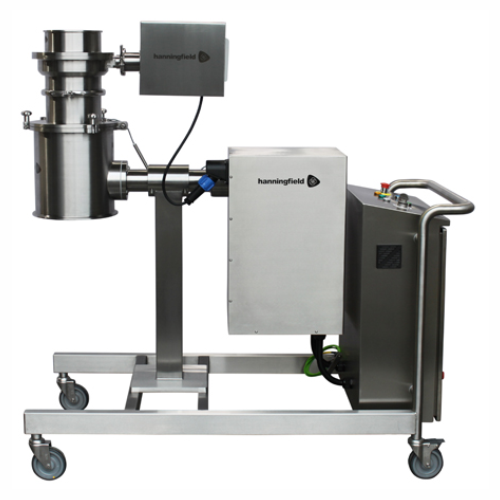
Pharmaceutical size reduction shredder
Achieve fast, efficient material size reduction with this shredder, enabling seamles...
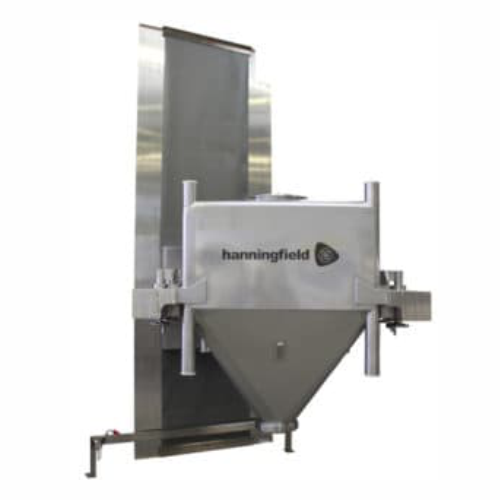
Ibc tumbler for uniform batch mixing
Achieve consistent and homogenous mixing of powders, granules, and solid products with...
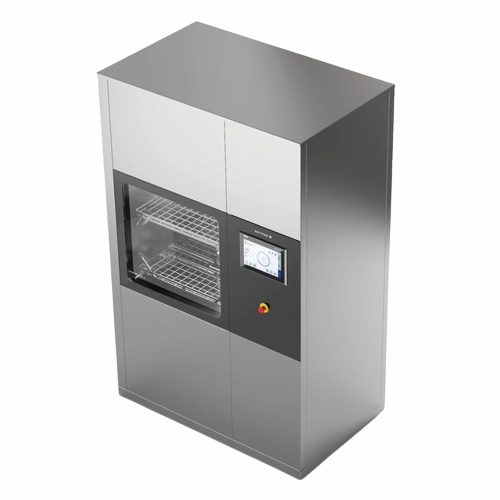
High-capacity cgmp washer/dryer for cleanrooms
Optimize your cleanroom operations with this compact washer/dryer, designed...
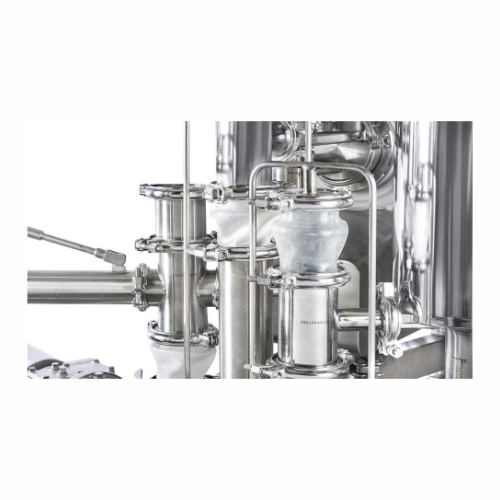
Gravimetric feeders for pharmaceutical applications
Ensure precise ingredient metering in continuous pharmaceutical proce...
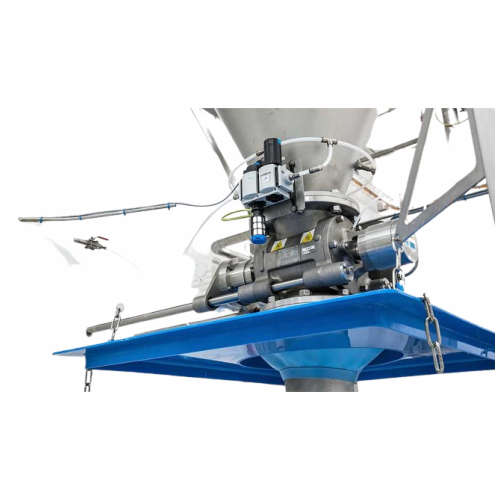
Heavy duty rotary valves for powder handling
Ensure precise material flow and safety in harsh processing environments with...
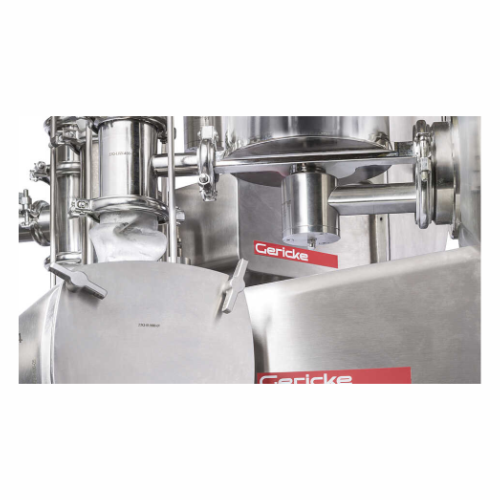
Continuous mixer for homogeneous blending
Achieve consistent product quality with precise mixing and blending, ideal for a...

Continuous powder mixer for industrial applications
Achieve precise and efficient integration of powders, granules, and l...
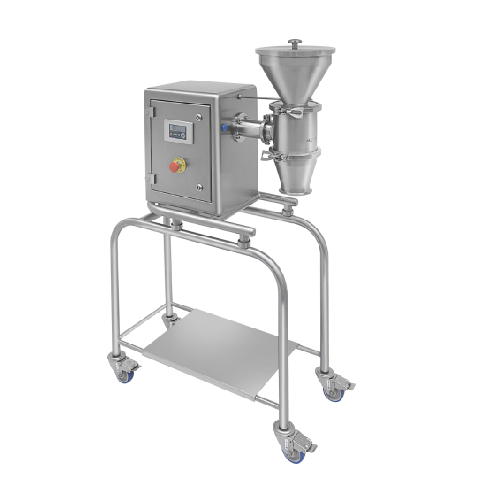
Laboratory conical screen mill for powder calibration
Achieve precise particle size control with this compact laboratory ...
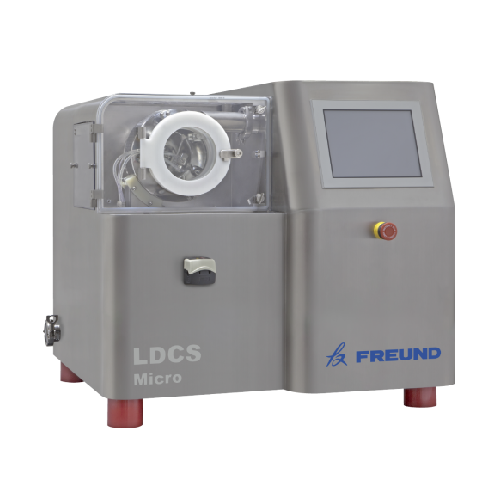
Laboratory film coating system for development and clinical batches
Achieve precision in tablet coating with a versatil...
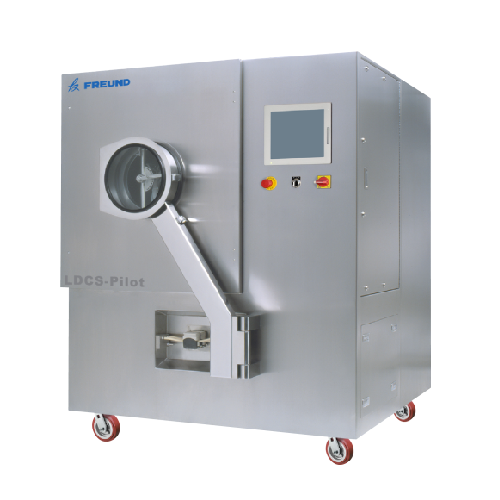
Laboratory and pilot scale pan coater
Maximize coating efficiency in tablet production with this advanced pan coater, offer...
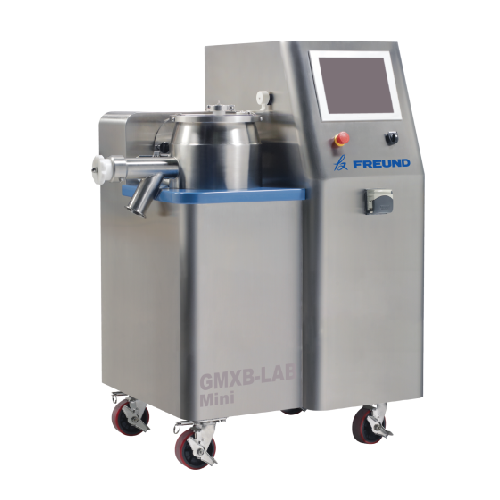
High shear granulator for wet granulation of powders
Achieve consistent granule density and size with a high shear granul...
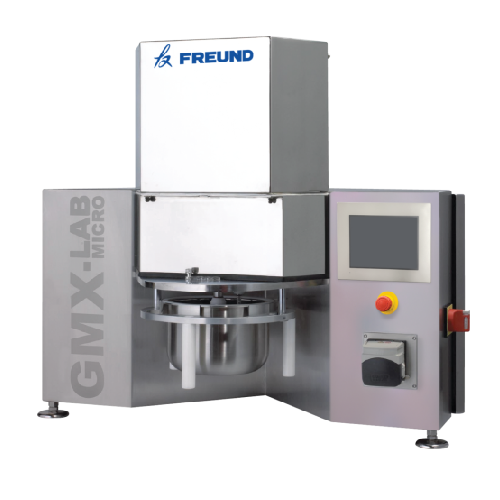
High shear lab granulation system for powder processing
Achieve precise granulation and consistent mixing of powders with...
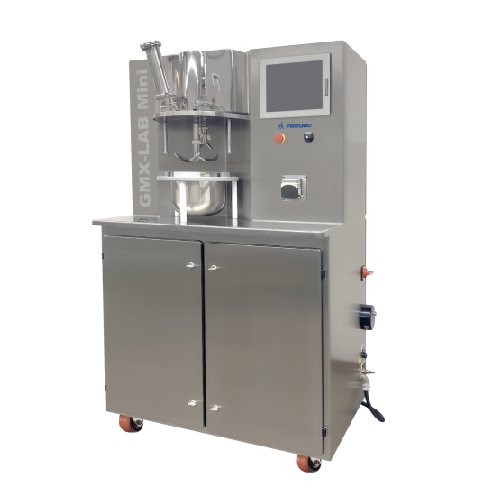
Mini High shear granulator for wet granulation
Optimize your powder granulation with precision and flexibility, ensuring c...
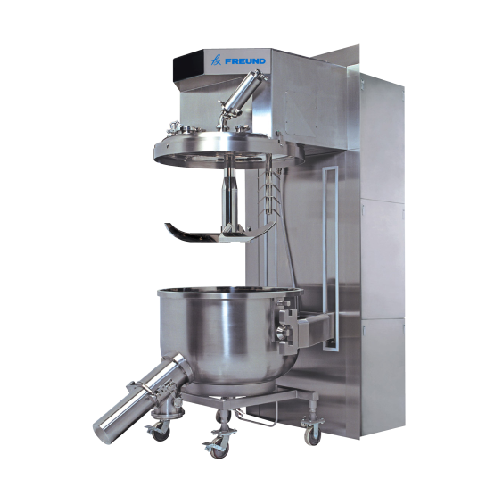
High shear wet granulation line
Achieve consistent and uniform granules with energy-efficient wet granulation designed to op...

Pilot Gmp spray dryer system for small-scale manufacturing
For precise control in spray drying, streamline your small-sc...
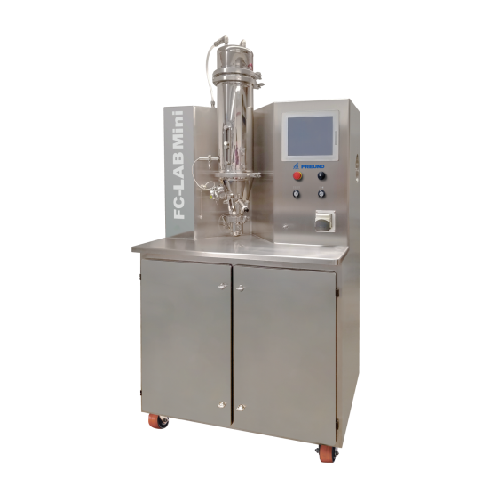
Laboratory fluid bed system for solvent processing
Optimize your laboratory scale operations with a versatile fluid bed s...
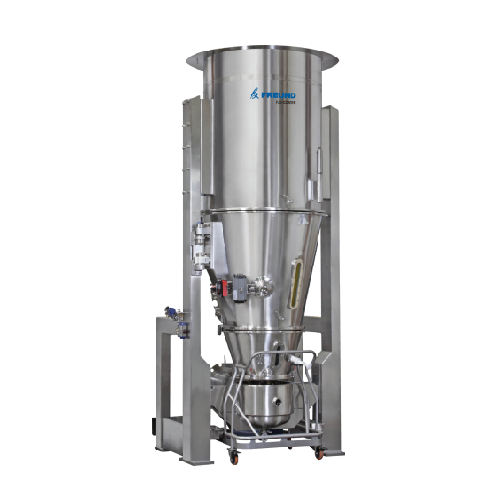
Fluid bed granulator for industrial granulation
Optimize your production efficiency with versatile fluid bed granulation, ...
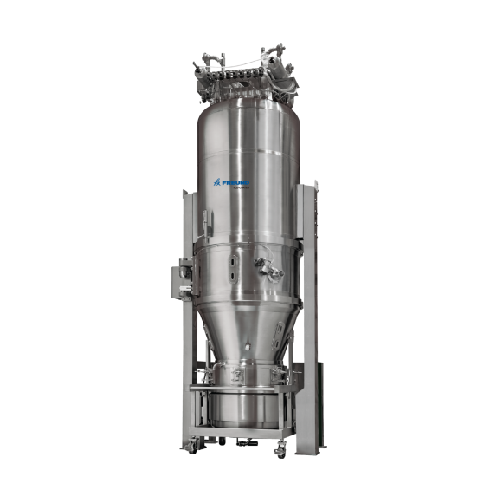
Fluid bed system for granulation and coating
Optimize your production with a multi-purpose fluid bed system designed for e...
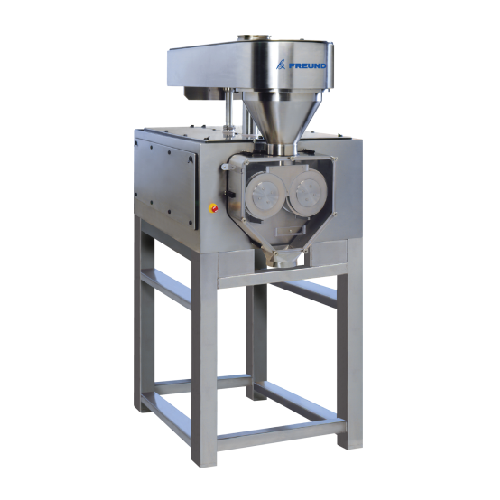
Dry granulation system for powder compaction
Achieve consistent sheet hardness and increased density in powdered materials...

High shear wet granulation system
Experience efficient wet granulation with precise control over granule density and moistu...
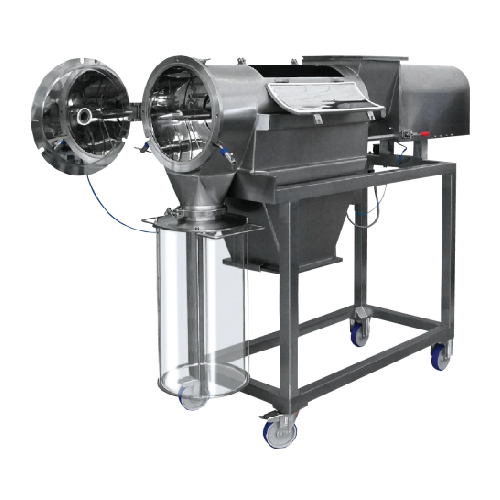
Centrifugal sifter for particle size classification
Achieve precise particle size control with high output efficiency, en...
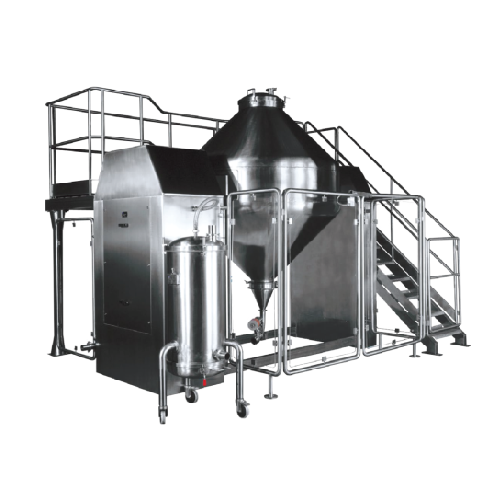
Pharmaceutical powders and granules dry blending
Achieve uniform blending of diverse powder and granule formulations with ...
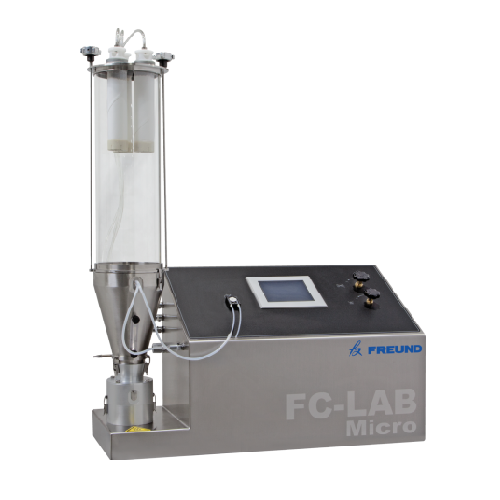
Development fluid bed system for feasibility studies
Explore precise granulation and coating capabilities for small batch...
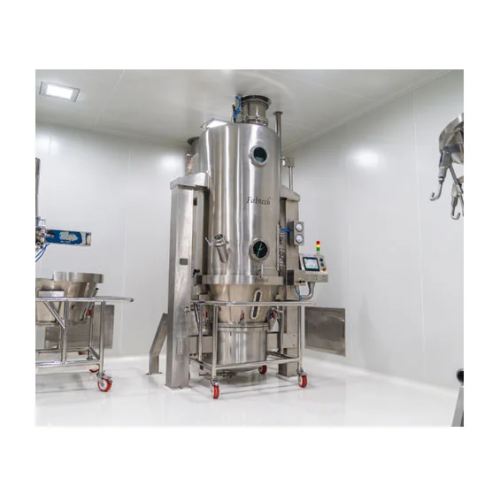
Fluid bed processor for granulation and coating
Fluid bed processors offer efficient granulation and coating, streamlining...
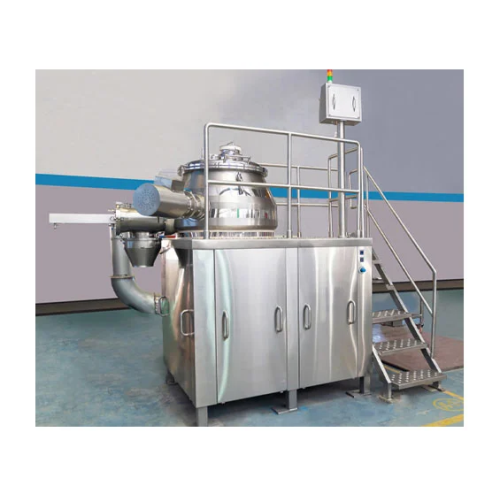
High shear mixer granulator for efficient wet granulation
Achieve consistent and precise granule formation with high she...
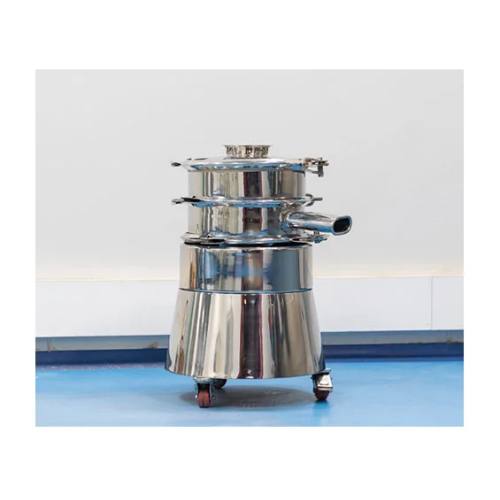
Particle sizer for precise sifting
Optimize your production line with high-speed particle sizing, ensuring precise control ...
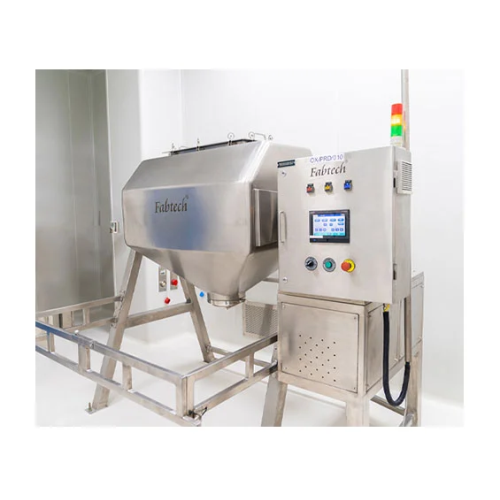
Pharmaceutical powder blender
Ensure uniform mixing of pharmaceutical powders and granules with advanced blenders designed f...
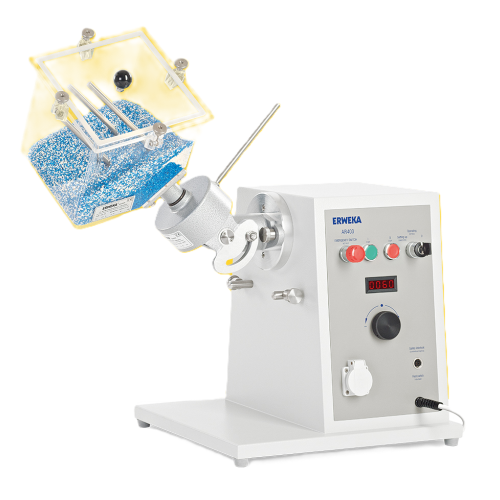
Tumbling cube mixer for homogeneous blending
Achieve uniform blending with precision using a cube mixer that enhances mixi...
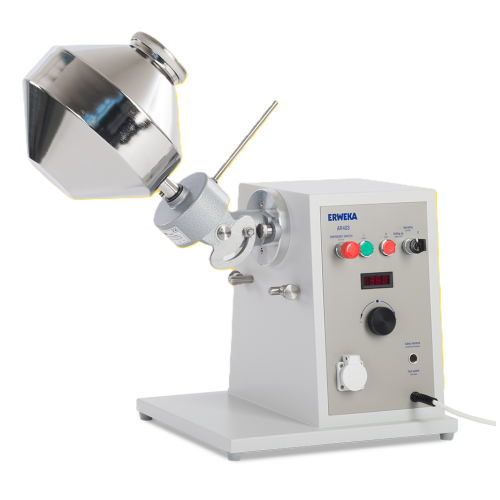
Double cone mixer for free flowing powders and granules
Achieve uniform blending of powders and granules with precision, ...
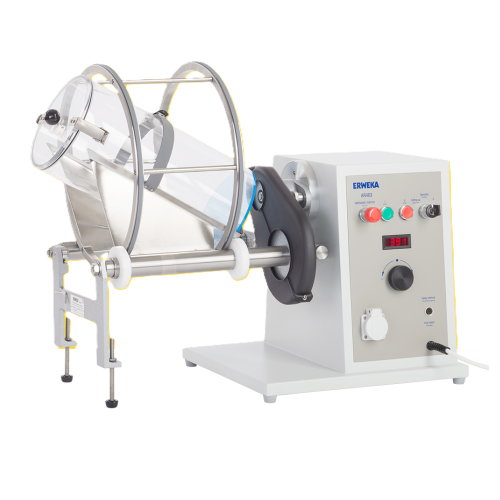
Drum hoop mixer for uniform three-dimensional mixing
Achieve consistent, homogenous mixing of powders and granules with a...
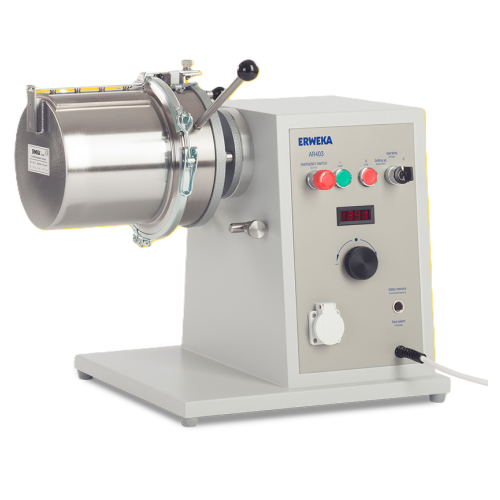
Laboratory high speed mixer for powders and granules
Achieve homogenous blending of powders and granules efficiently with...
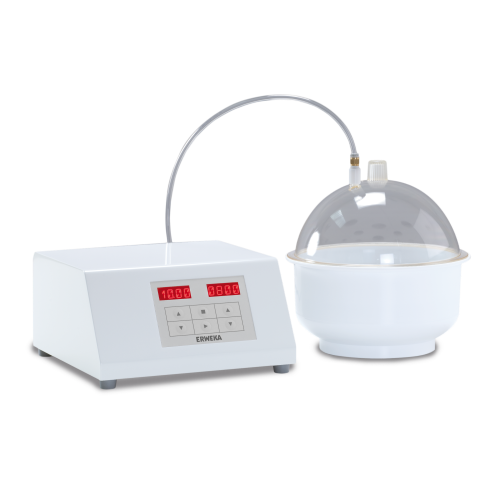
Blister packaging leak tester
Ensure airtight integrity in your blister packaging with precise vacuum and dye penetration te...
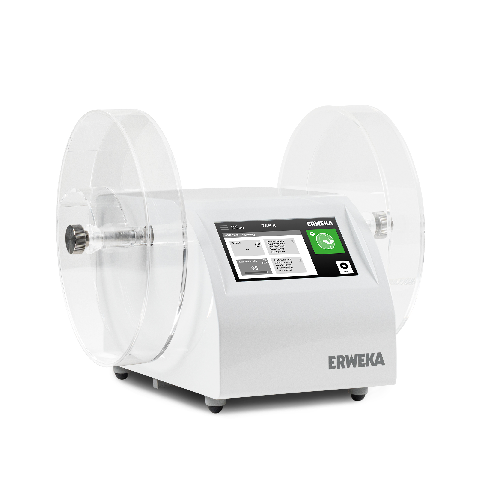
Advanced friability and abrasion testing solution
Ensure precise compliance in pharmaceutical tablet testing with this in...
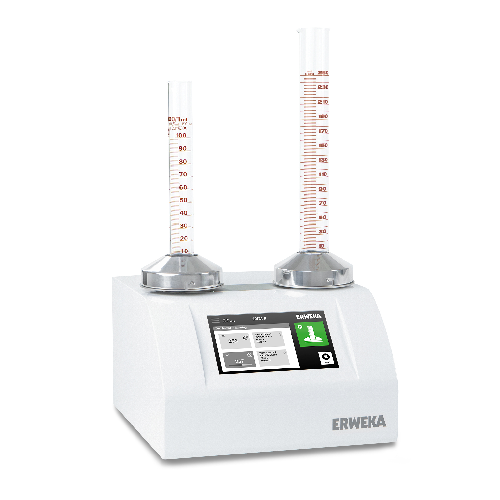
Tapped density tester for pharmaceutical and chemical powders
Ensure precise density measurements for pharmaceuticals an...
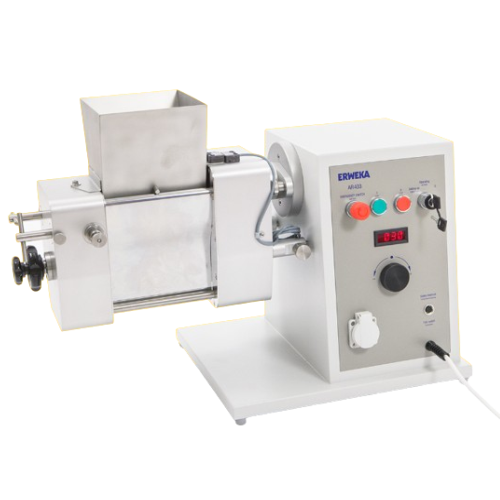
Wet granulator for pharmaceutical applications
Achieve precise granule consistency with advanced oscillating rotor technol...
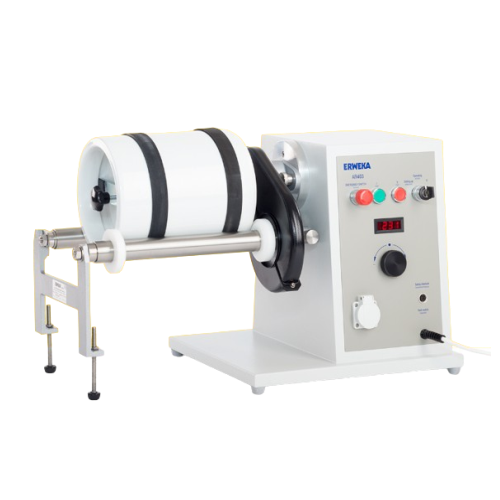
Lab-scale ball mill for crystalline material grinding
Effortlessly grind and mix crystalline materials into fine powders ...
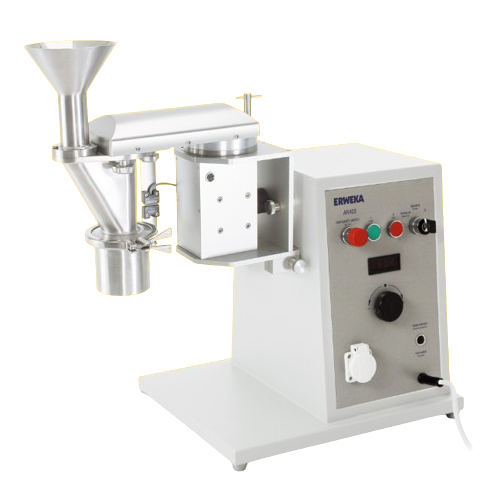
Conical mill for particle size reduction and homogenization
Achieve precise particle size reduction and homogenization w...
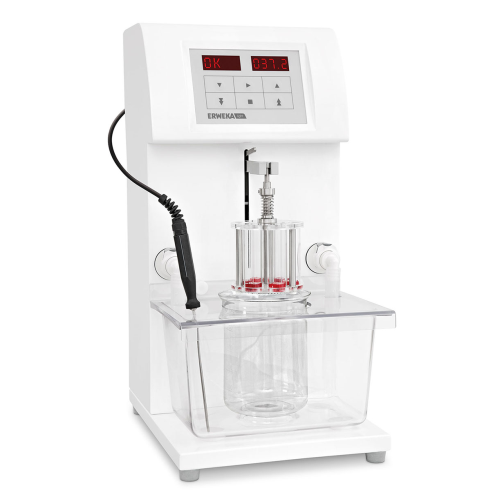
Manual disintegration testing for pharmaceuticals
Ensure precise disintegration testing of pharmaceuticals with a compact...
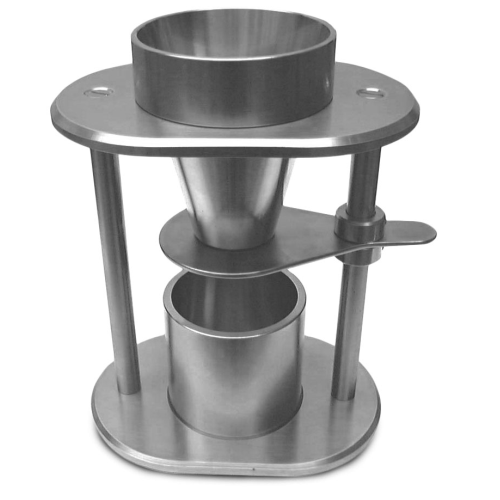
Apparent bulk density tester for granules and powders
Ensure accurate formulation by determining the apparent bulk densit...
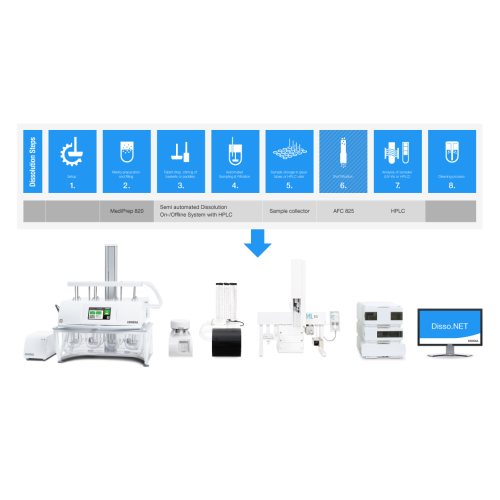
Dissolution testing system with Hplc analysis
Streamline your dissolution testing with integrated HPLC analysis, offering ...
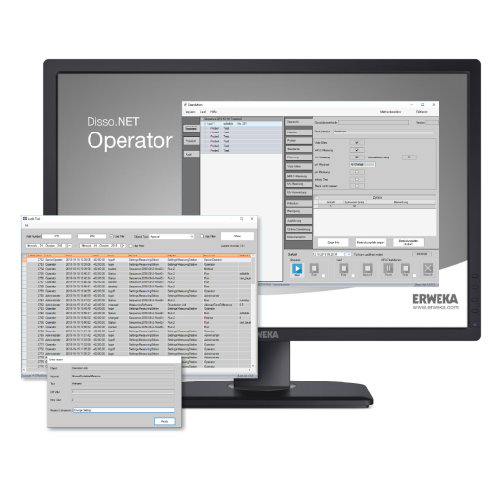
Dissolution testing software for compliance and efficiency
Ensure data integrity and streamline compliance with a robust...
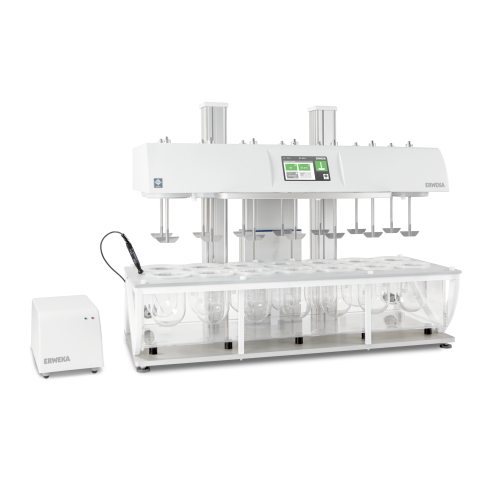
Digital dissolution tester for high volume testing
Optimize high-volume tablet and supplement testing with precise contro...
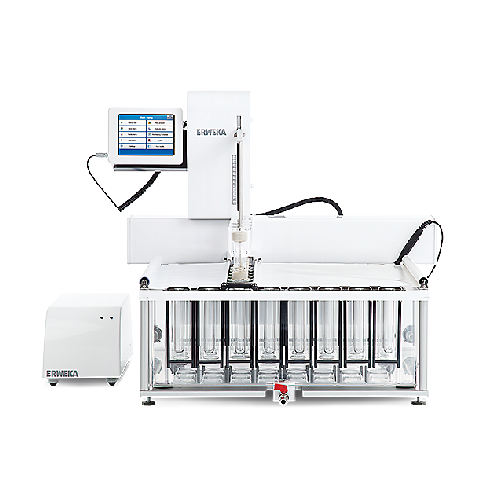
Automatic dissolution testing for sustained release dosage forms
Effortlessly simulate pH changes for accurate dissoluti...
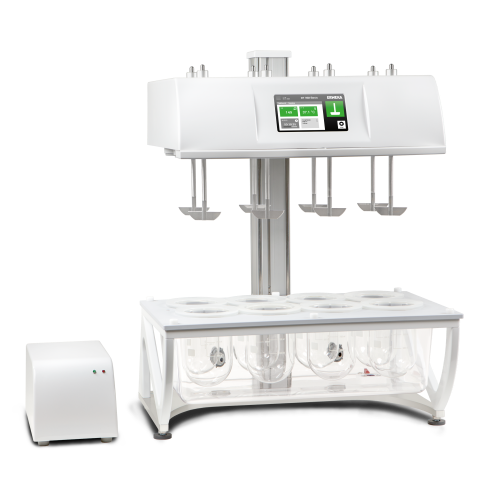
Dissolution online system for automated Uv-vis analysis
Ensure precise dissolution testing and seamless UV/VIS analysis w...
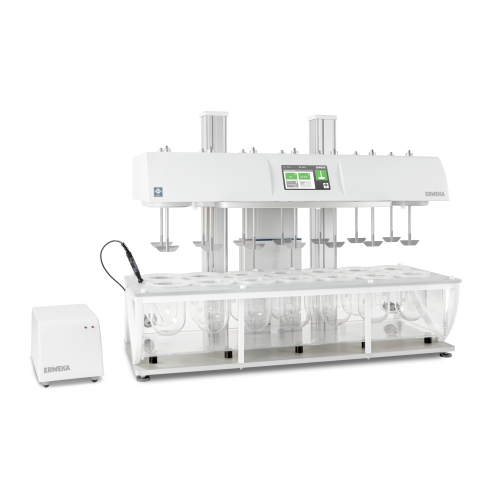
High volume dissolution tester for pharmaceutical research
Achieve precise dissolution testing of tablets across two bat...
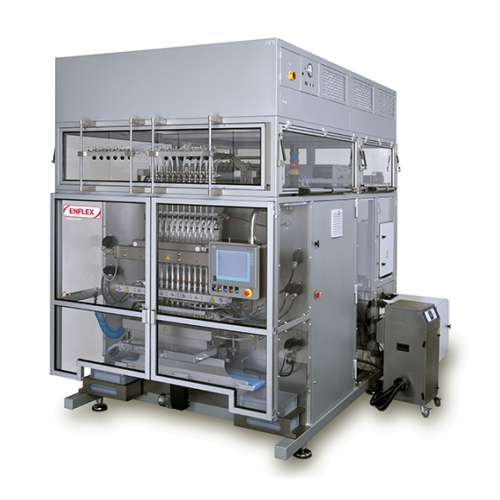
Intermittent stick pack machine for pharma and healthcare
Looking to streamline your packaging operations with high-spee...
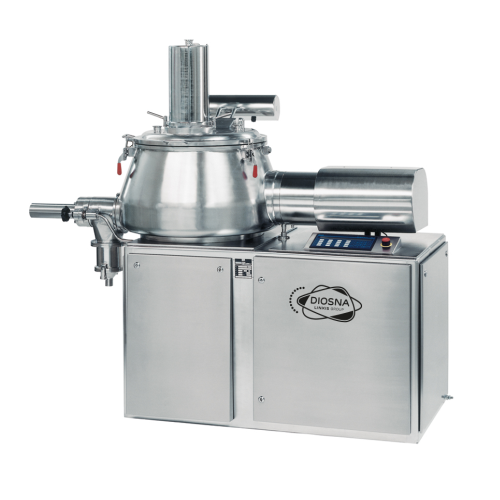
High-shear mixer granulator for pharmaceutical production start-up
Effortlessly achieve optimal granule consistency and...
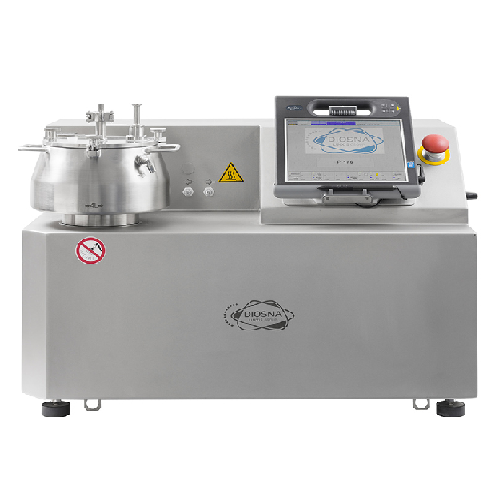
Compact laboratory mixer for high-shear granulation
Streamline your R&D processes with advanced mixing and granulati...
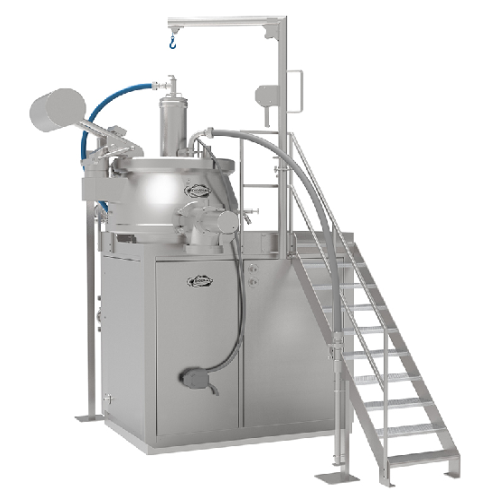
Pharmaceutical high-shear mixer granulator
Enhance your production efficiency with a high-shear mixer granulator, designed...
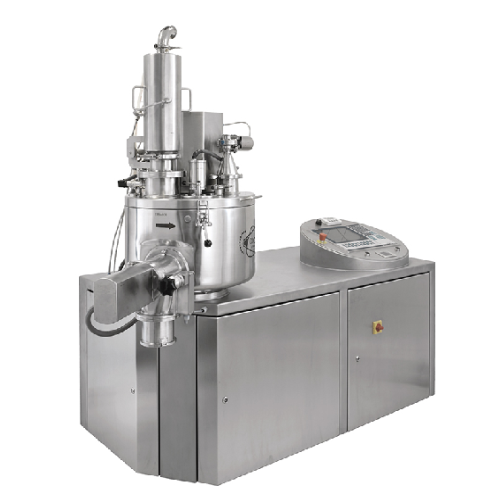
Pilot single-pot processor for granulation and drying
For efficient pilot production, streamline your mixing, granulating...
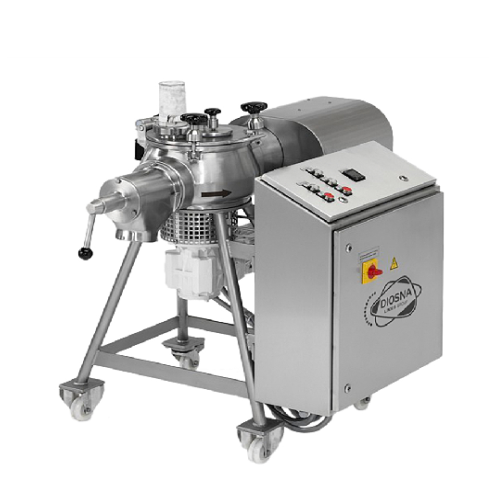
Versatile entry-level mixer granulator
Solve complex mixing and granulating challenges with this compact solution, offering...
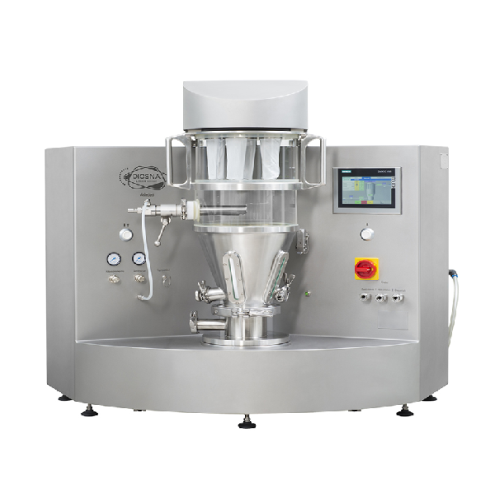
Laboratory granulator and coating system
Optimize your research with a versatile benchtop unit that combines fluid-bed proc...
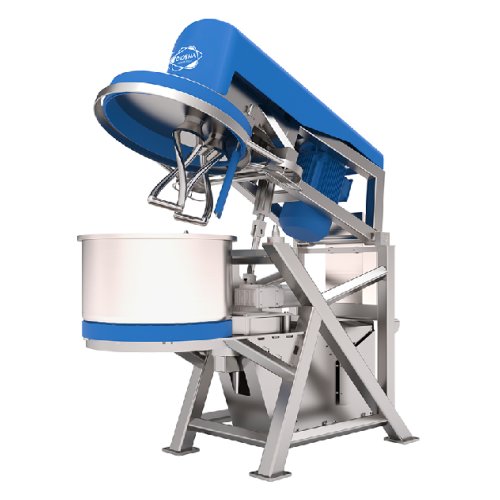
Hygienic design dough mixer
Achieve superior dough consistency and safety with our hygienic design mixer, ideal for reducing...
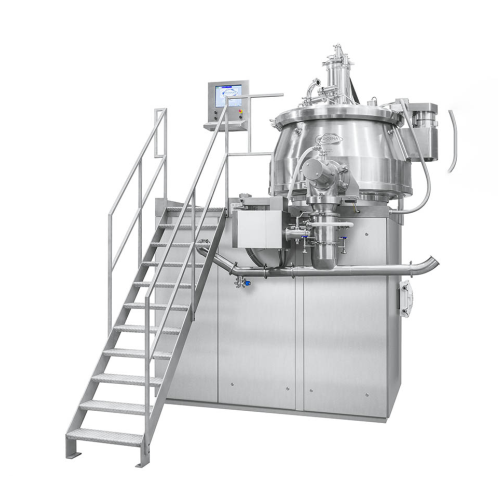
Granulation line for pharmaceutical manufacturing
Enhance your batch production with integrated mixer and fluid-bed techn...
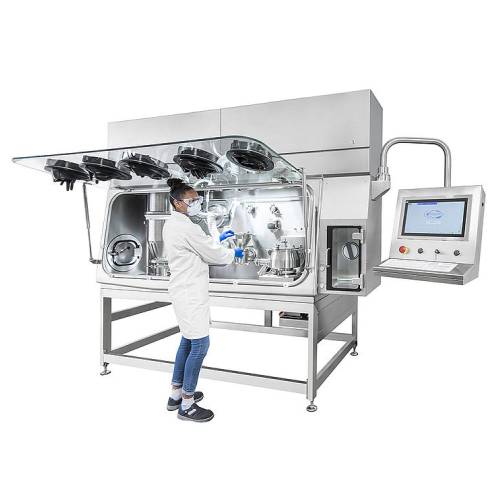
Containment solutions for pharmaceutical production
Enhance operator safety and product integrity with advanced containme...

Single-pot processor for wet granulation and vacuum drying
Achieve efficient mixing, granulation, and swift vacuum dryin...
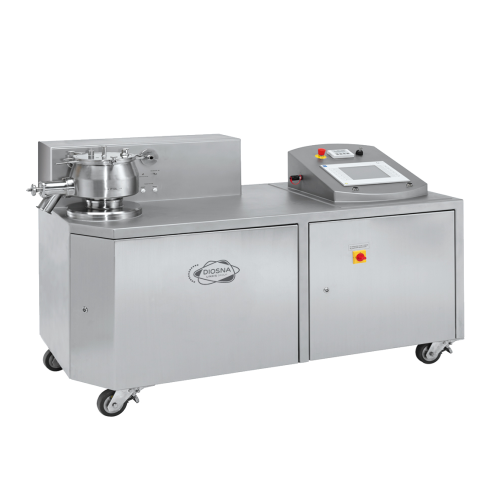
Laboratory unit for mixing, granulating, and vacuum drying
Achieve precise mixing, granulating, and drying in laboratory...
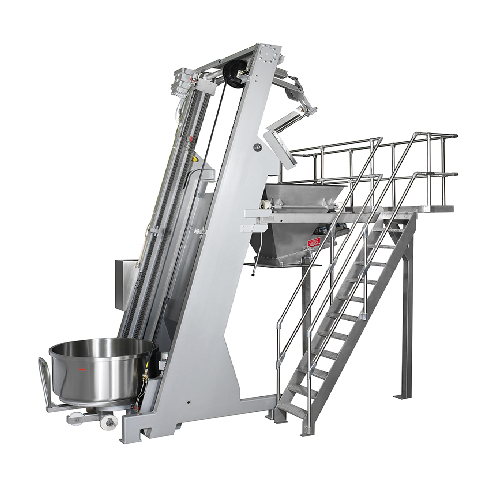
Industrial dough feeding elevator tipper
Optimize your dough handling process with a robust elevator tipper designed for se...
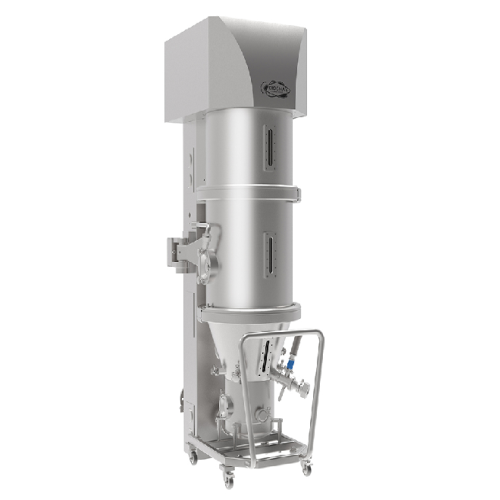
Fluid bed processor for granulating, drying, and coating in pilot scale
When scaling from laboratory to production, rel...
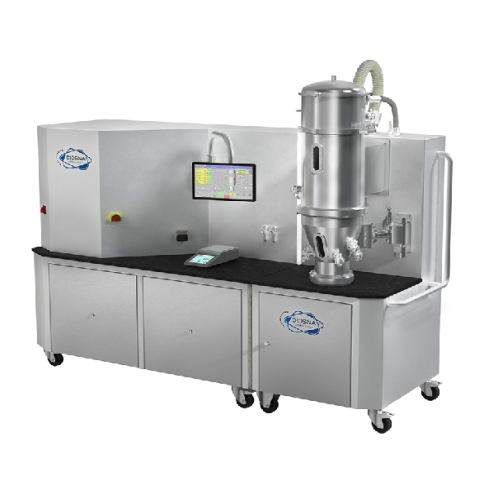
Midilab for efficient laboratory-scale product development
Streamline your laboratory and pilot-scale production process...
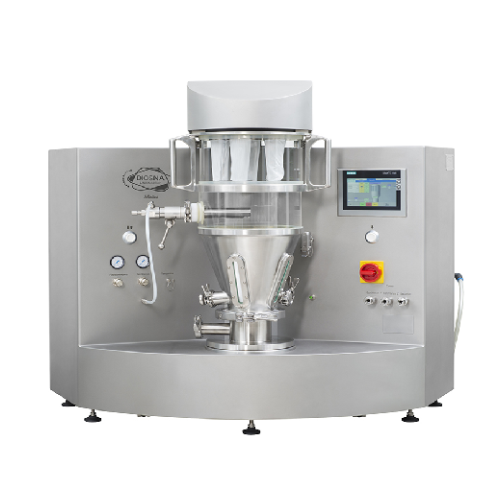
Laboratory coater and fluid bed processor
Optimize your research and development with a versatile benchtop unit that integ...
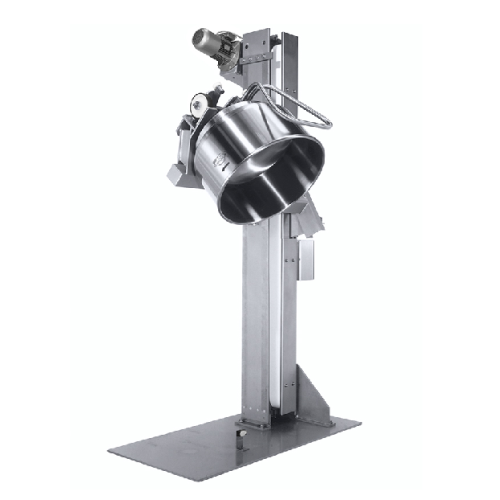
Industrial elevator tipper for efficient material handling
Optimize your material handling process with a high-performan...
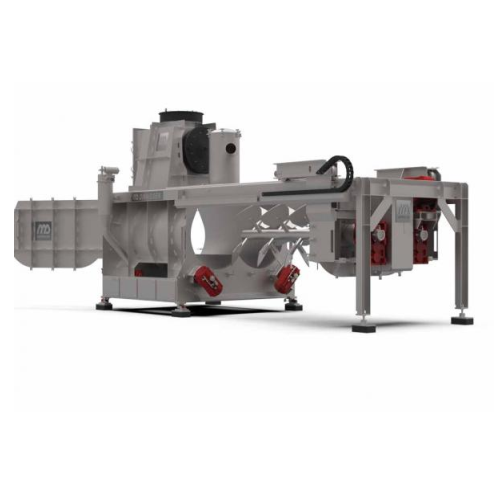
Industrial mixer for batch granules or grains
Achieve precise mixing with seamless integration of heating, sterilization, ...
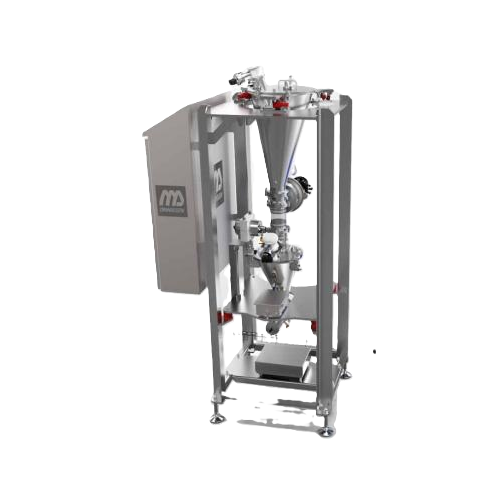
Micro dosing system for precise powder weighing
Achieve unparalleled dosing accuracy in your production line with a system...
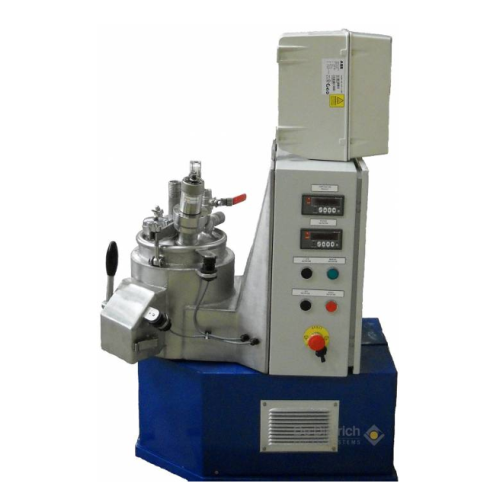
Powder blender for efficient mixing and discharge
Achieve precise mixing and efficient discharge with advanced powder ble...
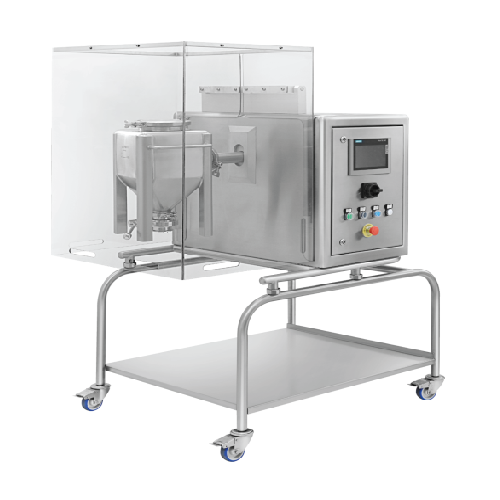
Benchtop laboratory powder blender
Perfect for R&D labs needing precise, small-batch powder blending and mixing, this ...
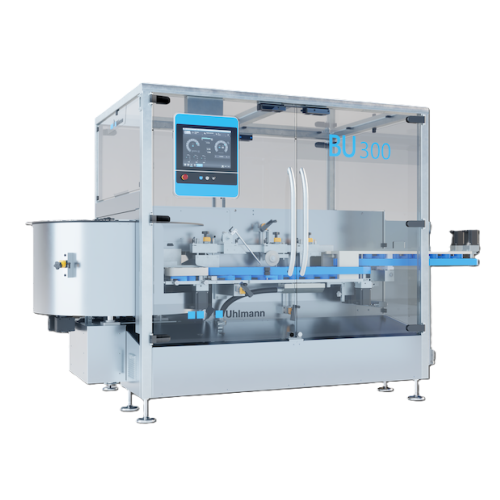
Pharmaceutical bottle unscrambler
Streamline your pharmaceutical packaging process by efficiently sorting and aligning bott...
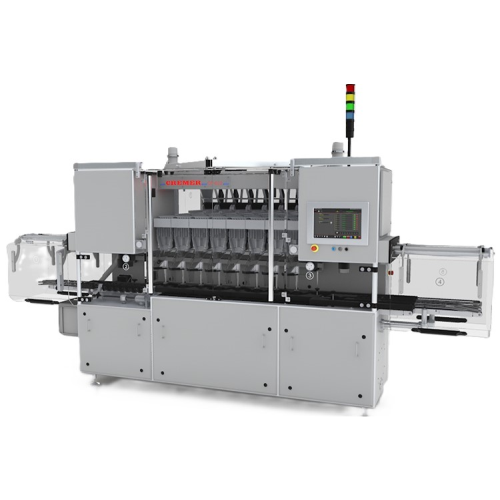
In-motion pharmaceutical bottle filler
Achieve up to 400 bottles per minute with this modular bottle filling solution, desi...
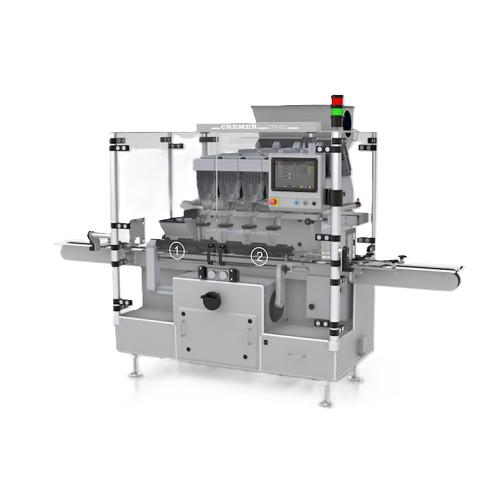
In-motion bottle filling system for pharmaceuticals
Boost your production efficiency with our high-speed bottle filling s...
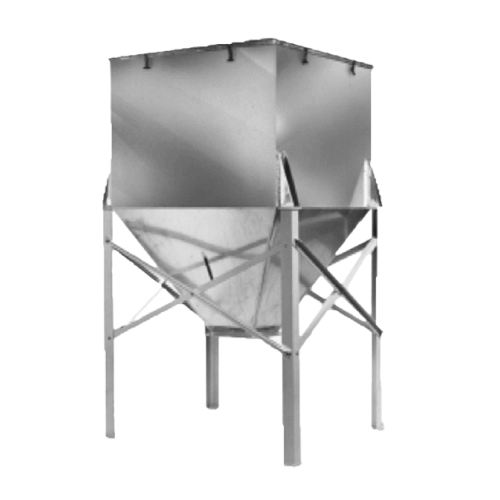
Surge bins for material handling
Ensure efficient material flow and storage in your production line with surge bins that fea...
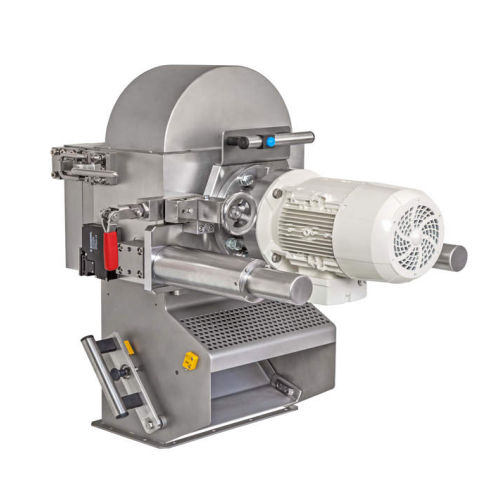
Centric pelletizer for direct extrusion
Effortlessly transform materials into uniform granules with our high-speed pelletiz...
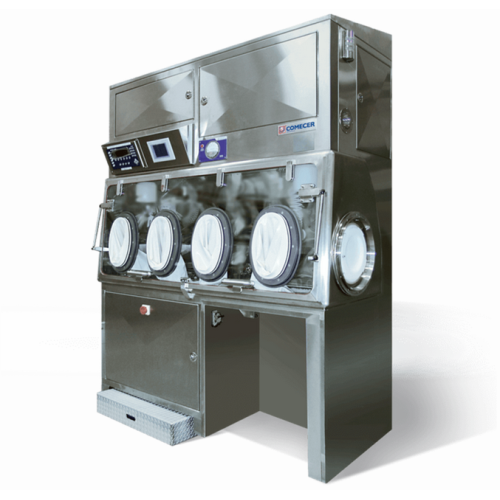
Atex compliant isolator for dispensing powder procedures
Ensure safe weighing and transfer of explosive and pharmaceutica...
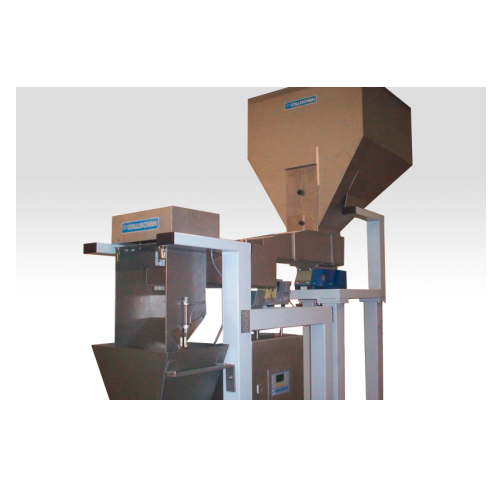
Weigh filler for bulk quantities 2-20kg
Optimizing your filling process with precision, this equipment handles bulk quantit...
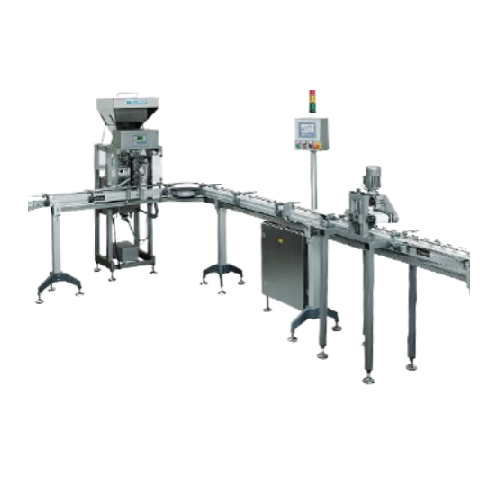
Precision weigh filler for food and pharma industries
Optimize precision in multi-component dosing with seamless integrat...
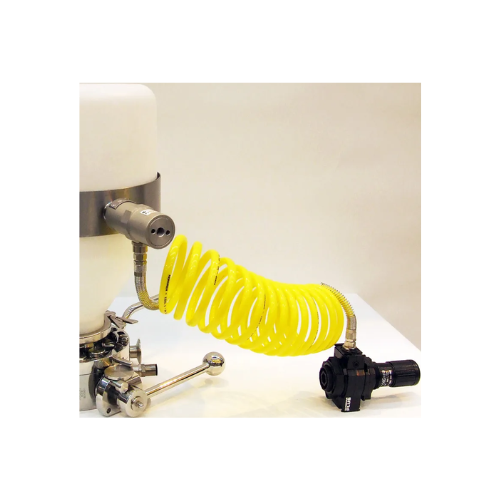
Vibratory collar for powder flow assistance
Struggling with sticky or poorly flowing powders during discharge? This vibrat...
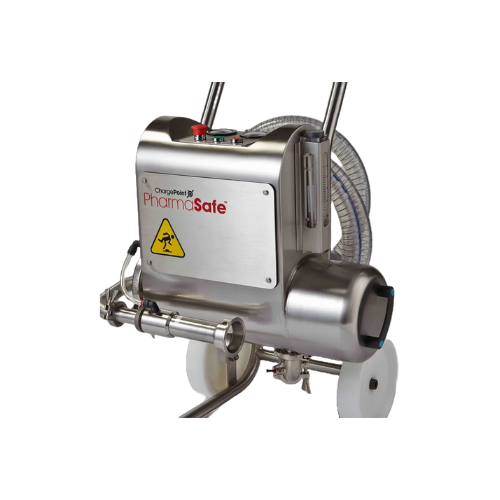
Dust particulate extraction system
Ensure safe containment and minimize airborne particulates in your production line with ...
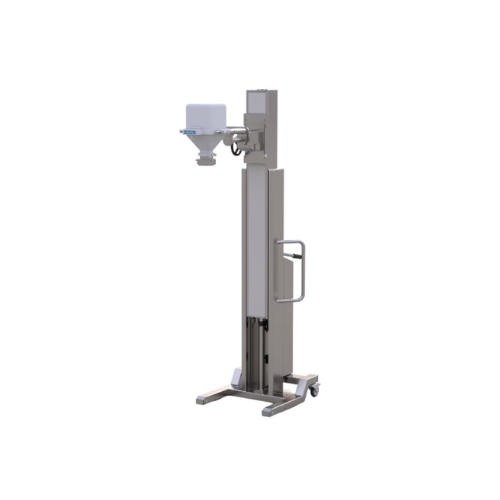
Mobile lifter solutions for pharmaceutical handling
Streamline your handling of sensitive materials with versatile mobile...
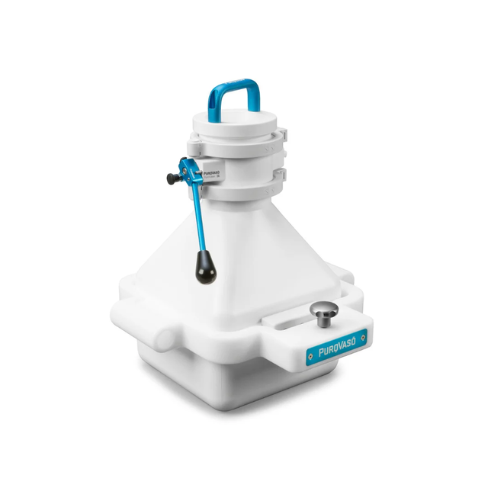
Lightweight plastic butterfly valve for industrial use
Achieve precise flow control and quick disassembly during pharmace...
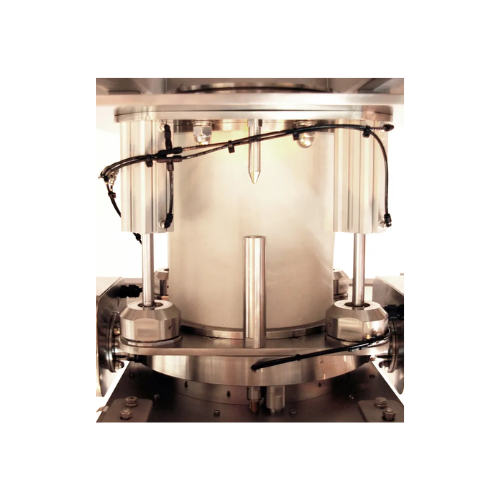
Automatic docking system for bulk powder handling
Optimize docking precision and ensure seamless alignment in bulk powder...
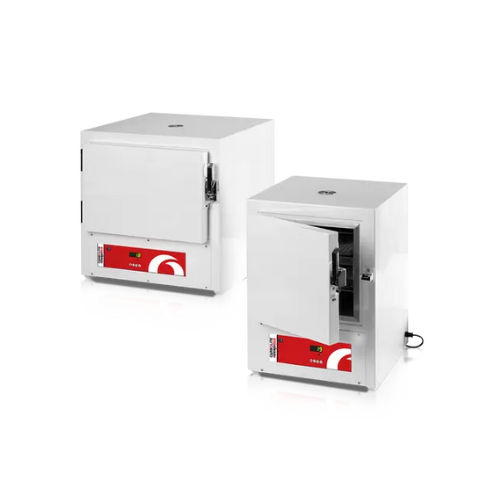
Clean room oven for class 100 environments
Achieve precise temperature control and maintain particle integrity in critical...
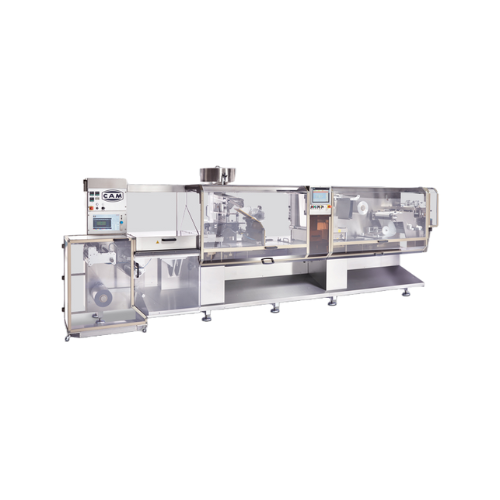
High speed blister packaging for pharmaceutical industry
Ensure precision and speed in pharmaceutical packaging with a hi...
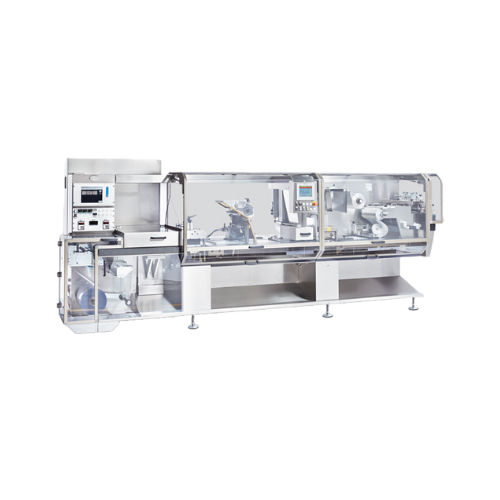
High speed blister packaging for pharmaceuticals
Need efficient packaging with quick format changeovers for various capsul...
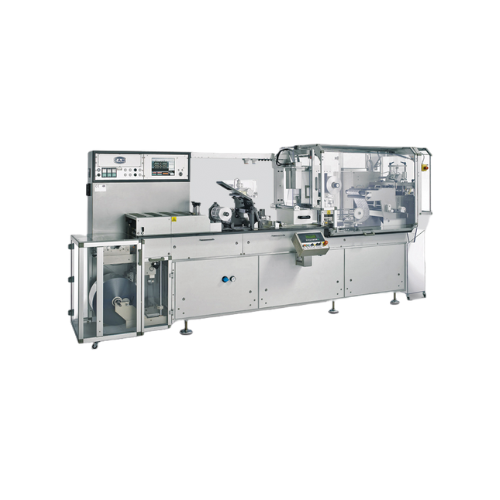
Blister packaging for pharmaceutical products
Facilitate seamless packaging of pharmaceuticals with a solution designed to...
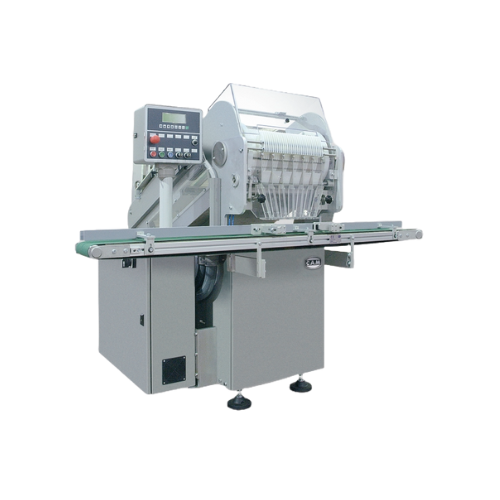
Slat-type counting solution for pharmaceutical applications
Ensure precise tablet counts and efficient packaging with th...
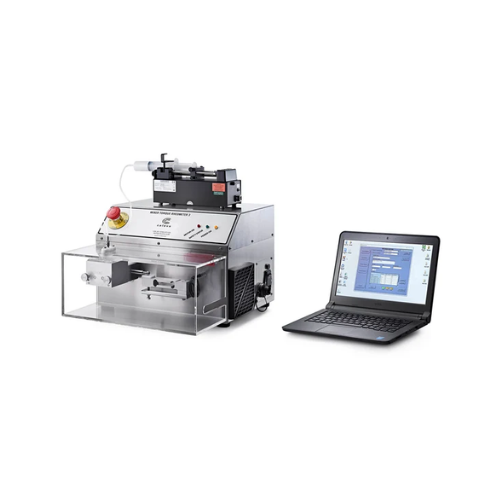
Analyze wet granulation properties for pharmaceutical formulation
Optimize your pharmaceutical and chemical formulation...
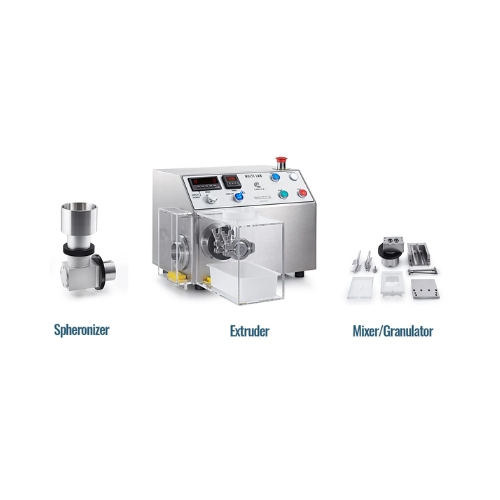
Lab scale mixer, extruder & spheronizer for r&d formulation
Optimize and streamline your research and development proces...
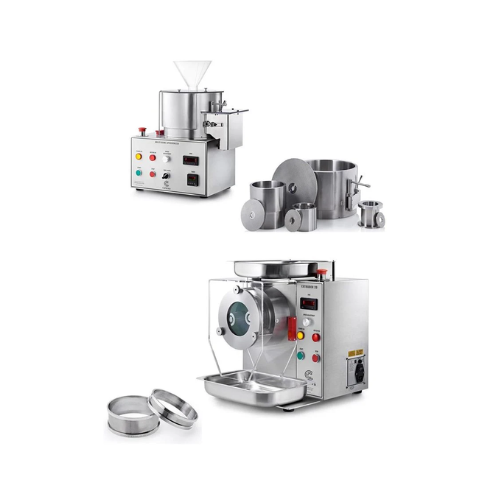
Flexible spheronization kit for wet granulation pellets
Achieve precise pellet and granule formation with a versatile ben...
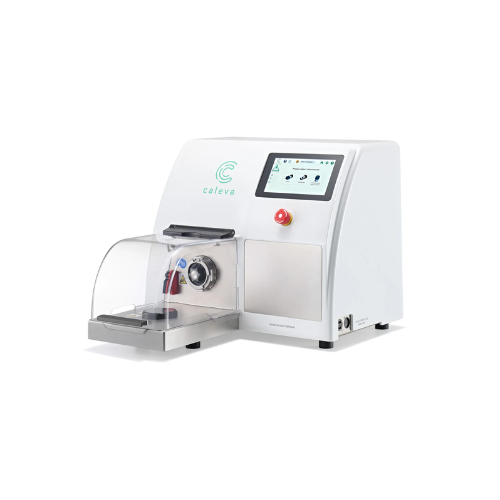
Bench-top mixer and spheronizer for formulation development
Accelerate R&D success by seamlessly integrating mixing...
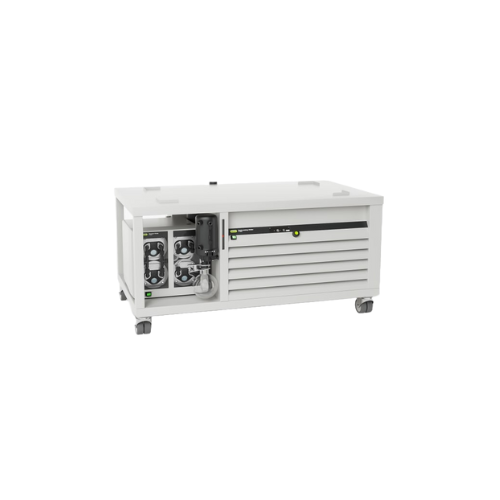
Industrial recirculating chiller for laboratory applications
For consistent distillation results, maintain accurate temp...
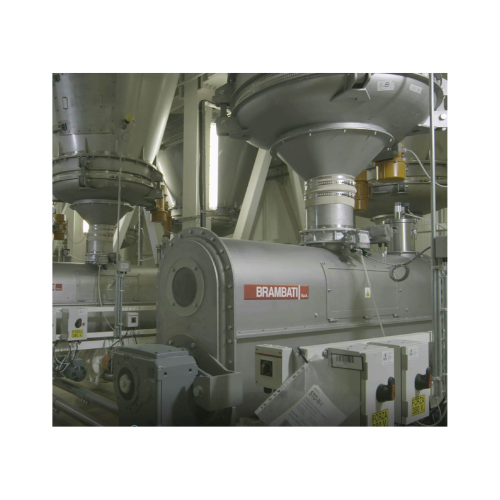
Flour handling plant for pasta production
Streamline your production with precision handling and processing of flour for p...
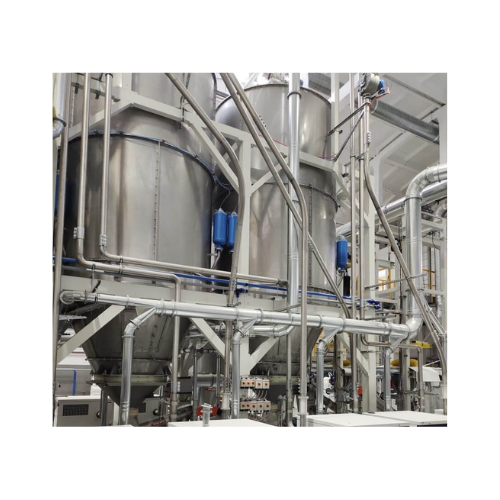
Raw material handling systems for plastic and pharmaceutical industries
Effortlessly manage and optimize the handling a...
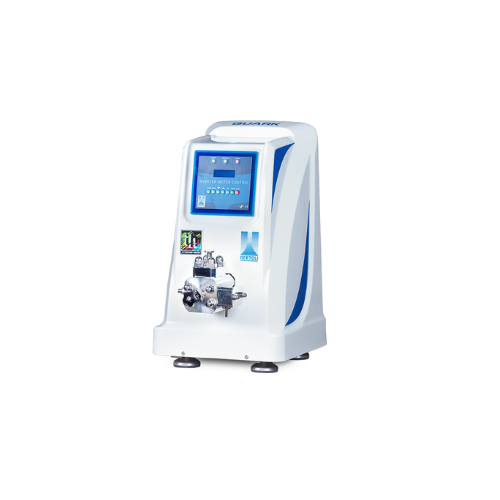
Laboratory homogenizer for pharmaceutical and biotech applications
Achieve precise homogenization for your laboratory n...

Sampling unit for continuous sampling in industrial processes
The PRS sampling unit ensures precise and uncontaminated s...
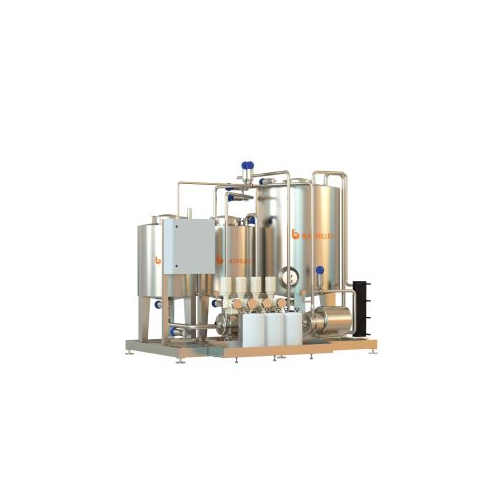
Cip system for process tanks
Ensure high-level cleanliness and compliance in your production line with an efficient in-place...
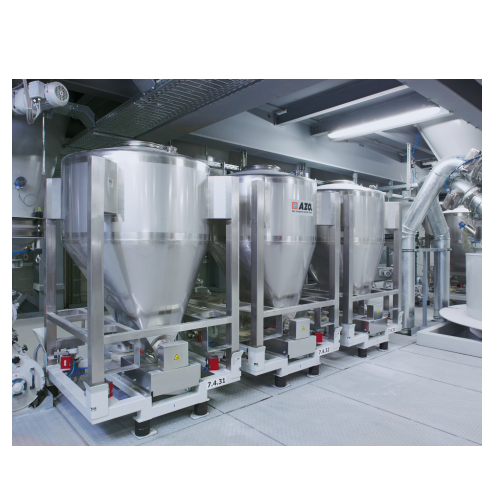
Precise dosing system for bulk materials
Ensure precise bulk material dosing with minimal dust, seamlessly switching betwee...
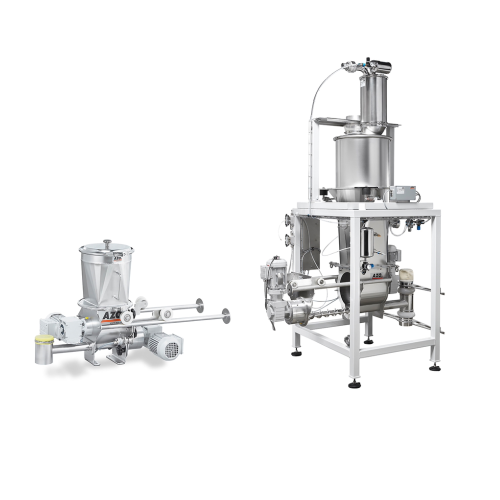
Accurate dosing for powder products
Ensure precise dosing and consistent flow of bulk powders in your production line to en...
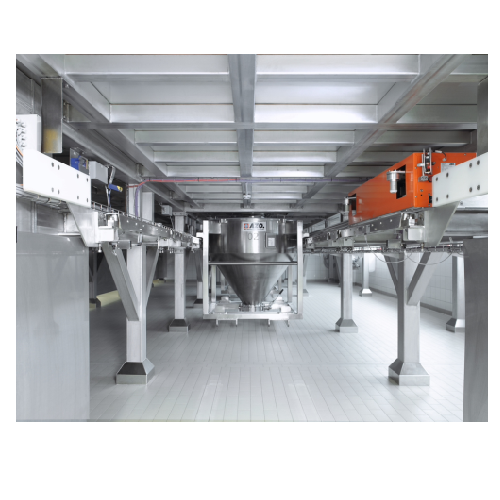
Batch automation system for fast and precise weighing
Achieve unmatched precision and speed in batch processing with this...
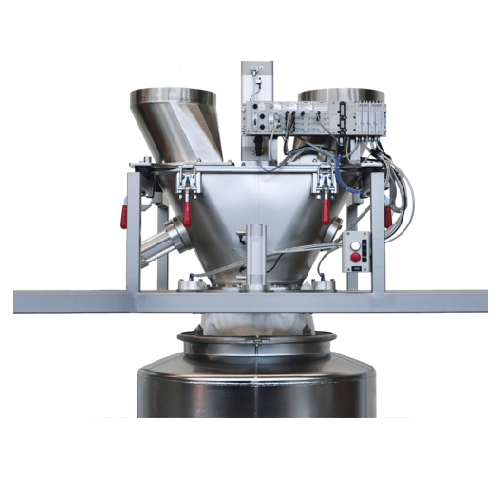
Contamination-free docking system for bulk solids
Achieve contamination-free transfer of bulk powders and granules while ...
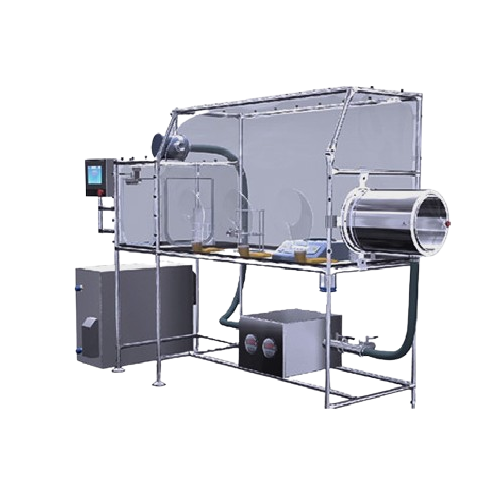
Flexible isolator for aseptic containment
Ensure sterility and safety with a flexible isolator designed for efficient cont...
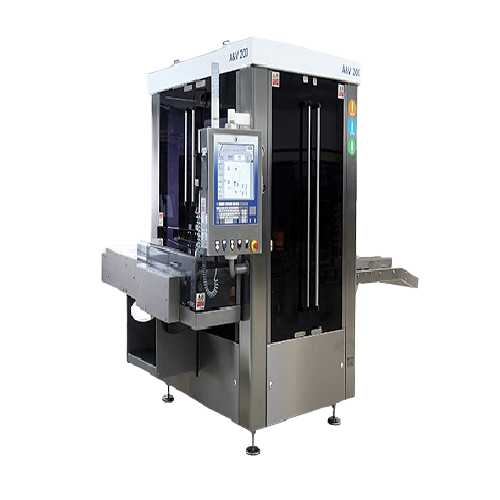
Automatic visual inspection for sterile preparations
Ensure the integrity of sterile products with precise visual inspect...
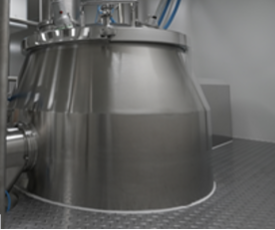
Continuous wet granulation equipment
Achieve optimal particle size and uniformity in pharmaceutical production with our con...
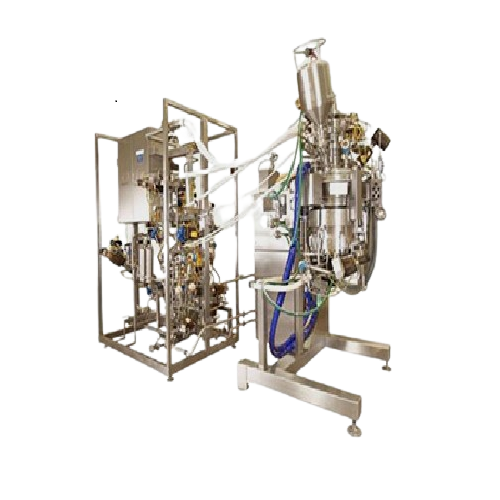
Microspheres process equipment for classification, washing, drying
Achieve high yield production of polymeric microsphe...
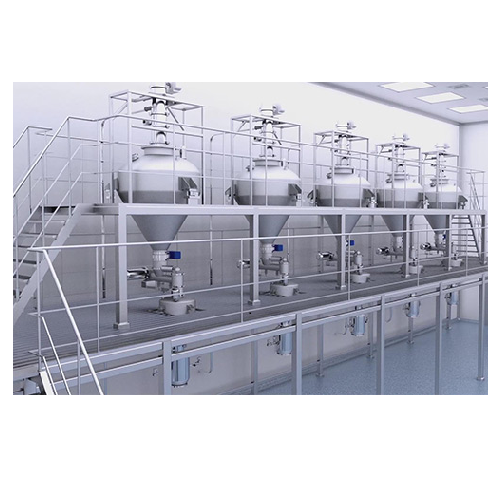
Integrated raw & auxiliary material pre-treatment system
Experience dust-free processing with an integrated system design...
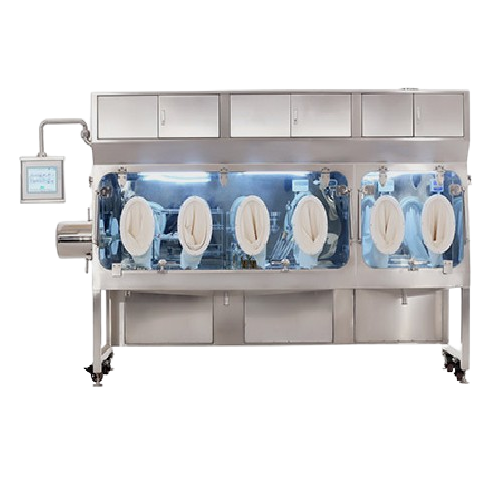
High containment isolator for toxic and active drug handling
Ensure safe handling and environmental protection while pro...
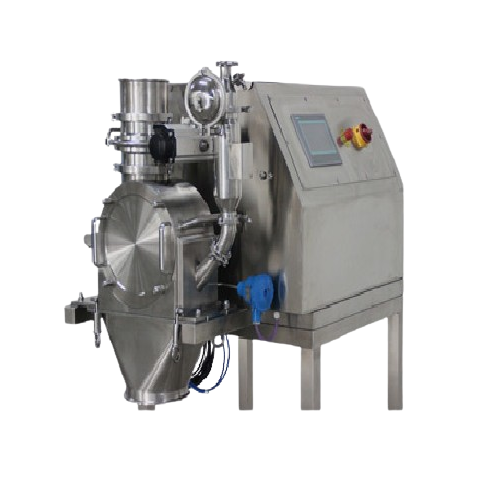
Particle size control equipment for pharmaceutical applications
Achieve precise particle size control for diverse materi...
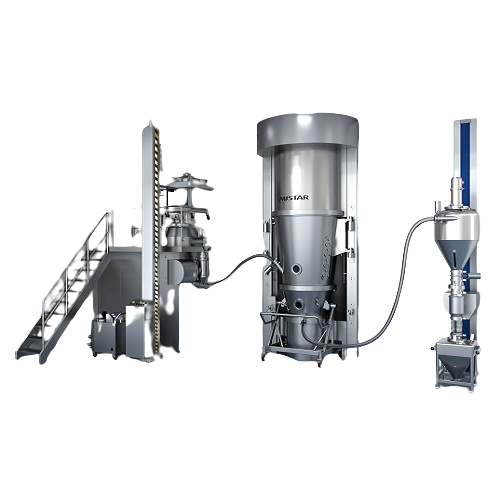
Wet granulating equipment for pharmaceutical industry
Enhance production efficiency and safety in high-potency pharmaceut...
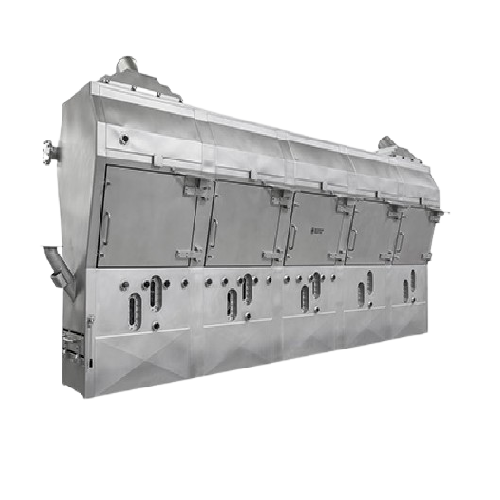
Continuous wet granulation equipment
Optimize your production line with continuous wet granulation, seamlessly transforming...
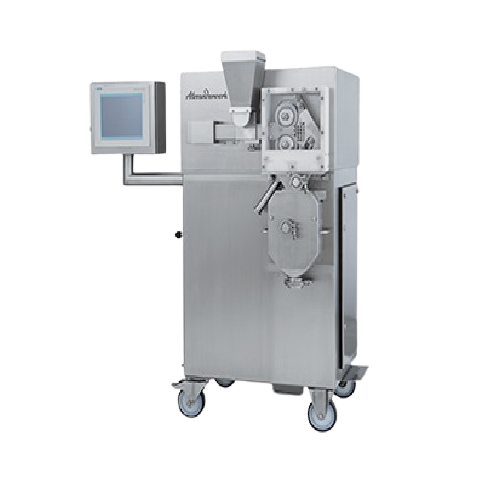
Roller compactor for pharmaceutical and chemical industries
Optimize your powder processing with precision compaction an...
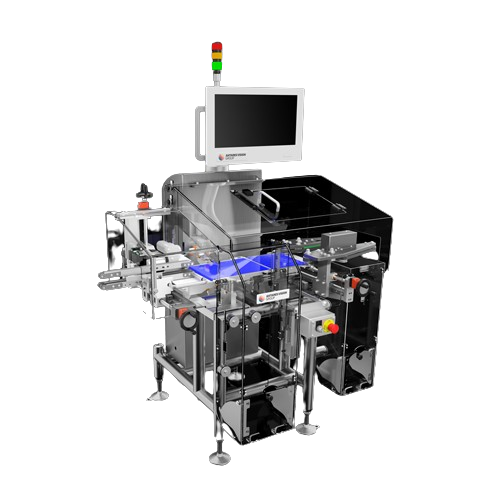
Pharmaceutical checkweigher for milligram-level accuracy
Ensure precision and compliance in your pharmaceutical packaging...
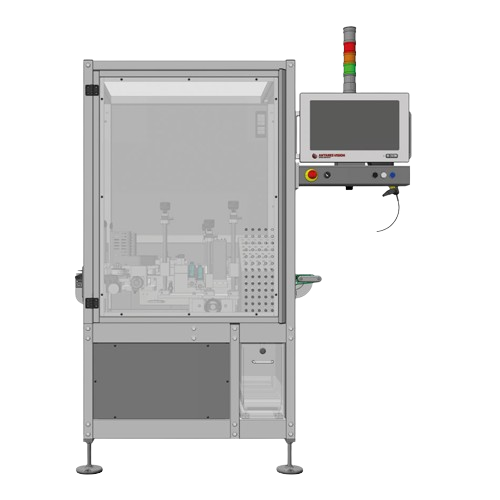
Serialization system for printing and verifying carton codes
Ensure accurate serialization with high-speed printing and ...
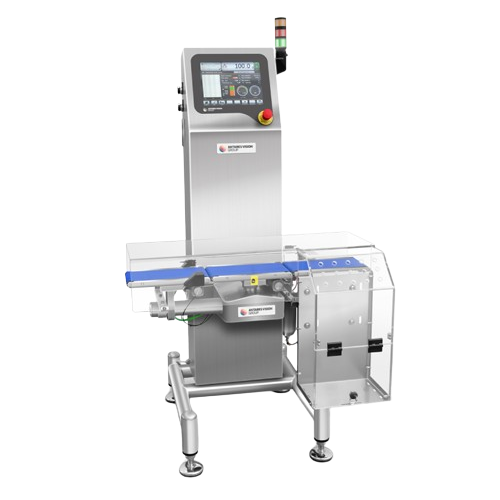
Checkweighers for medium and small products
Ensure precise weight control in high-speed production lines with advanced che...
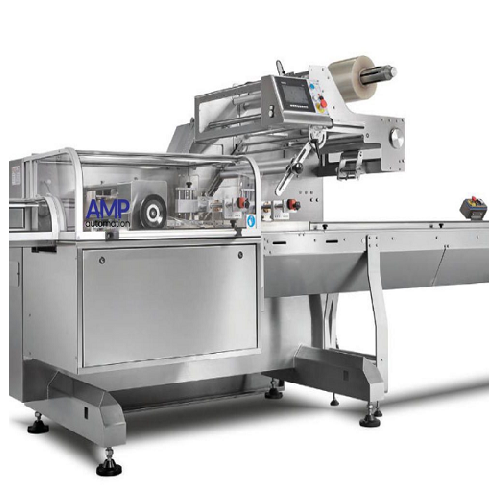
Pillow bag horizontal form-fill-seal solution
Optimize production efficiency with seamless integration of continuous, high...
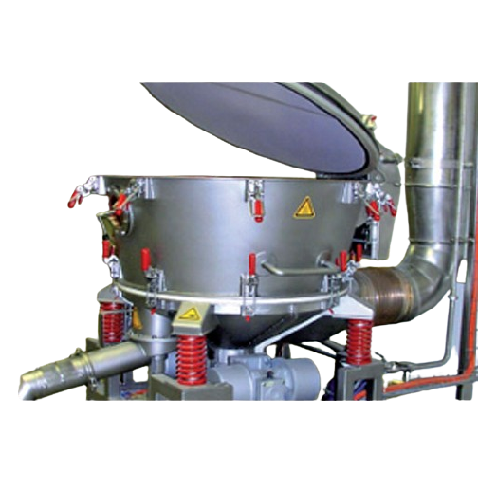
Vibration batch dryer for difficult solids
Ensure efficient drying of complex solids prone to sticking and shape irregular...
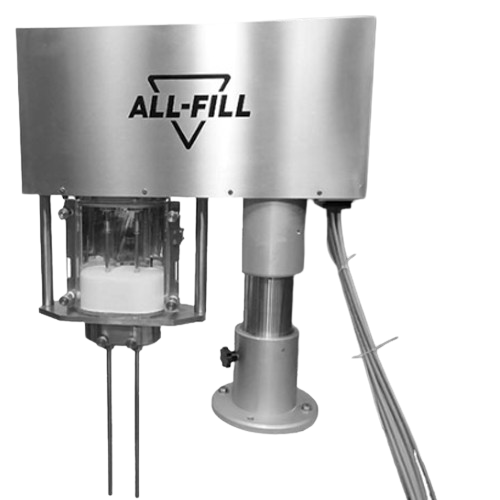
Multi-fill powder filling system
Achieve precise and consistent filling for your powdered and granulated products with a mod...
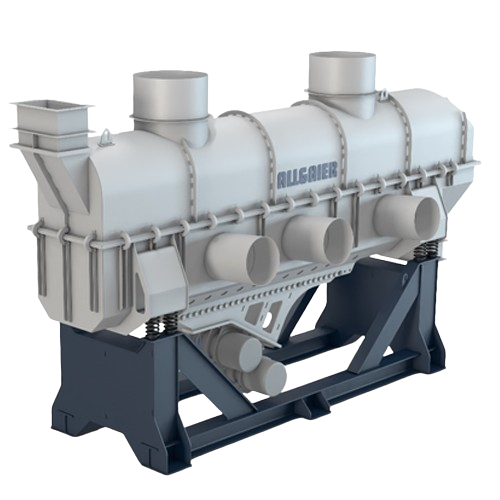
Fluidized bed dryer for industrial materials
Enhance product quality and energy efficiency with fluidized bed dryers, opti...

Pharmaceutical roller compactor for precise granulation
Achieve consistent and high-quality granulation with a solution t...
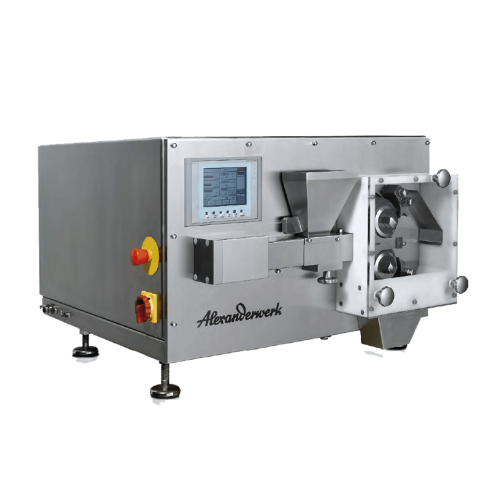
Pharmaceutical roller compactor for dry granulation
When precision and uniformity in tablet production are crucial, optim...
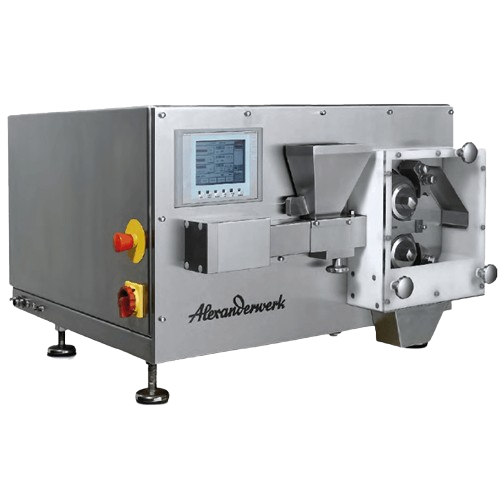
Dry granulation technology
Achieve precise control over particle size and density with our compacting and granulation soluti...
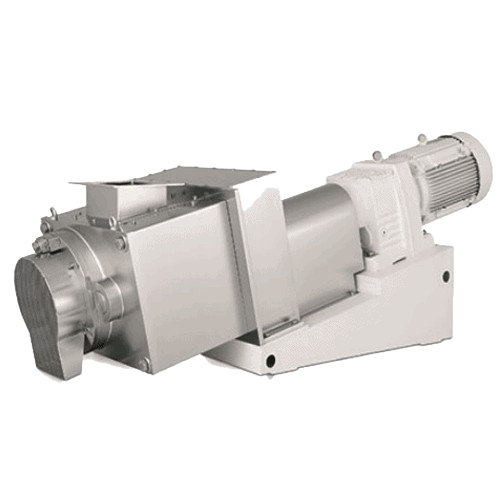
Moist granulation system for pharmaceutical and chemical industries
Transform powdered materials into uniform granules ...
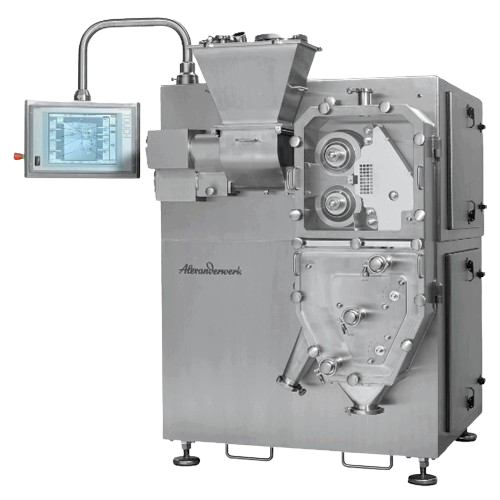
Pharmaceutical roller compaction solution
Optimize your pharmaceutical tablet production with precision granulation and co...
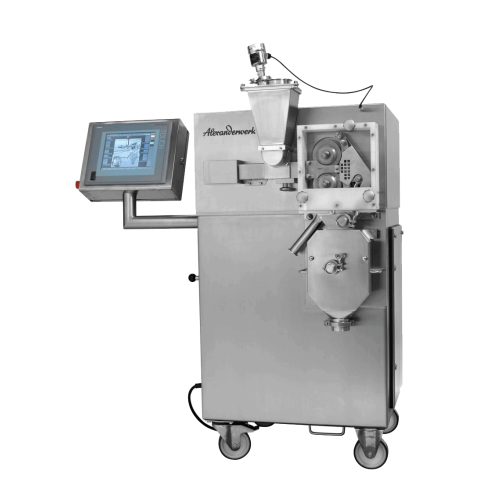
Pharmaceutical roller compactor
Achieve consistent granulate quality with optimized compacting processes, ideal for transfor...
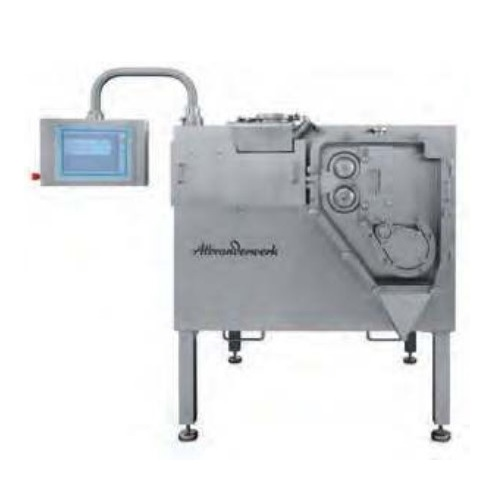
Pharmaceutical roller compactor for granulation
Achieve precise granulation with streamlined compaction, ensuring consiste...
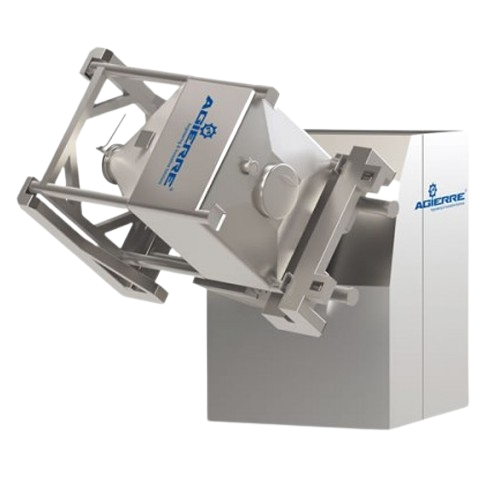
Bin blender for pharmaceutical powder mixing
Achieve uniform mixing and homogenization of dry powders directly in storage ...
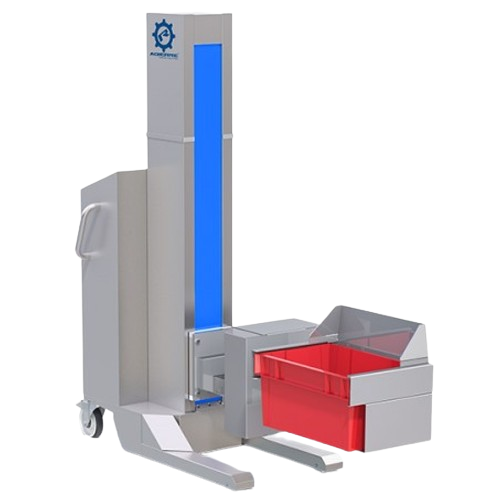
Lifting column for plastic boxes in pharmaceutical processing
Optimize your tablet and powder processing by seamlessly l...

Powder dosing and weighing system
Optimize precision in pharmaceutical processing with a system designed to ensure accurate...
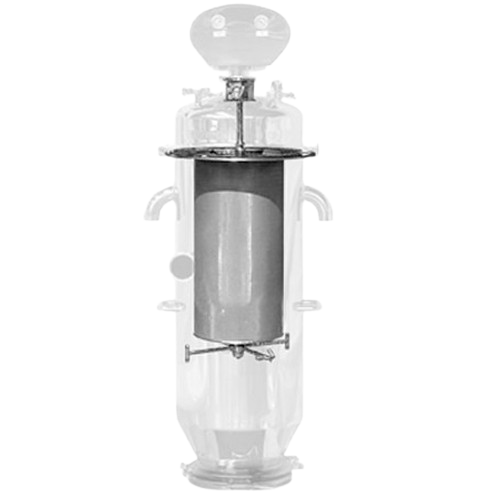
Vacuum transfer system with integrated cleaning
Ensure sterile powder handling and contamination-free production with vacu...
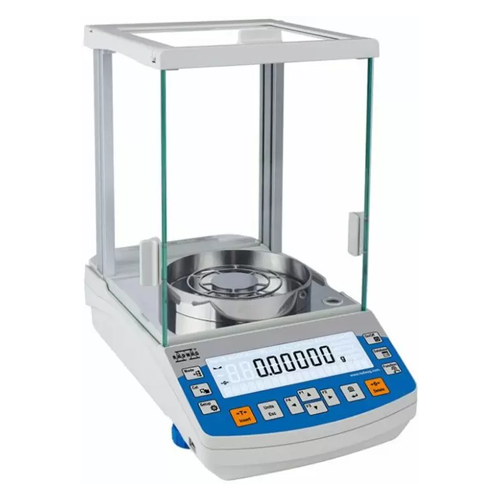
Analytical balance for precise laboratory measurements
Achieve unparalleled precision and reliability in your lab’s...
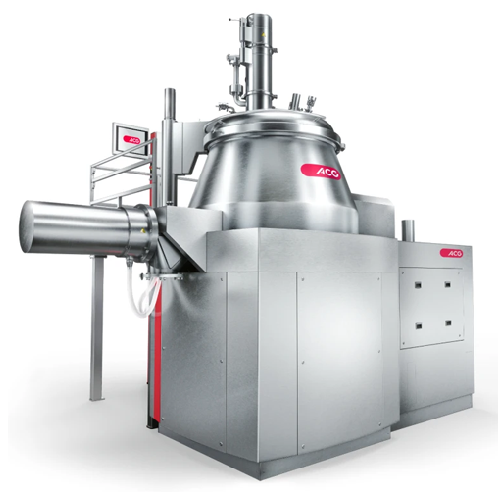
High-shear mixer granulator for small batches
Achieving consistent particle size and mix uniformity in pharmaceutical and ...

High-shear granulator for wet granulation
Achieve precise content uniformity with advanced high-shear granulation, designe...
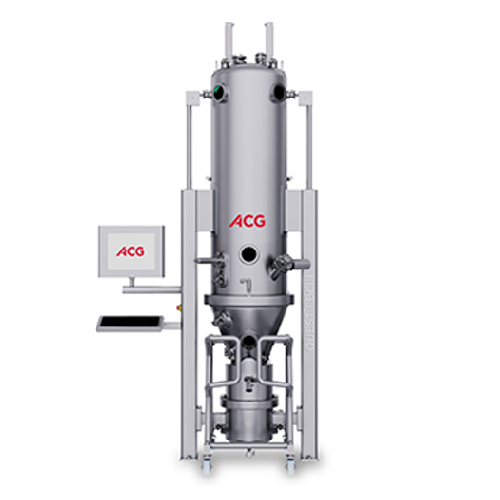
Intermediate-scale fluid bed system for drying and granulation
Achieve precise drying and granulation with this versatil...
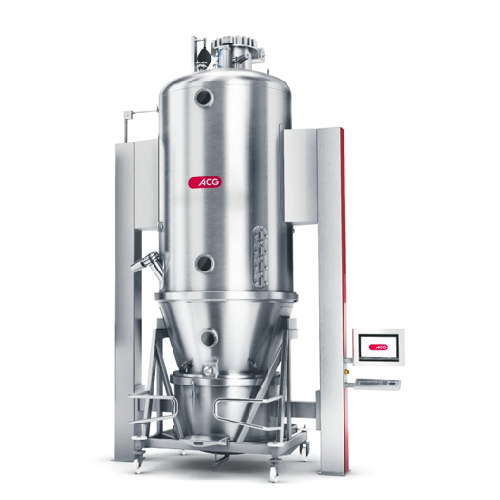
Fluid-bed granulator for top-spray applications
Need precise granulation and drying for sensitive materials? This fluid-be...
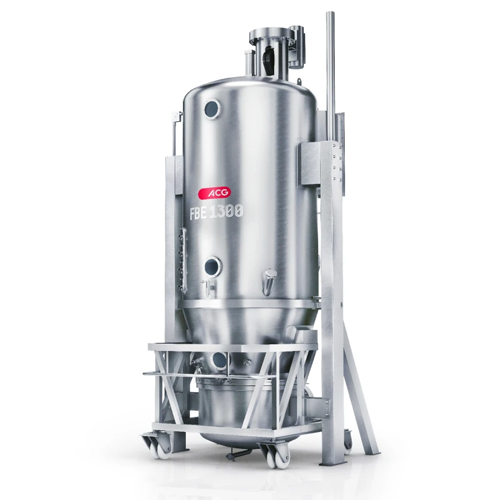
Fluid-bed drying and granulation system
Optimize your production line with high-speed batch processing for efficiently dryi...
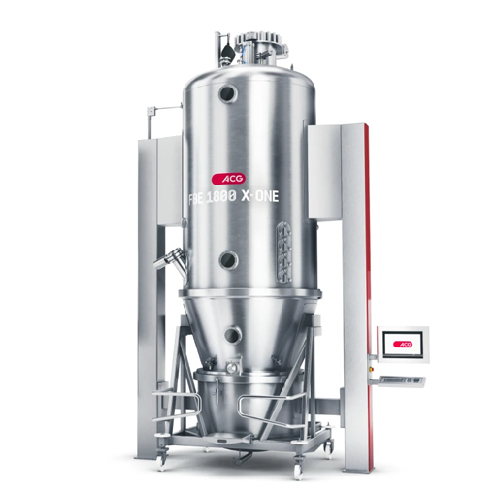
Fluid bed granulator for pharmaceutical applications
Optimize your granulation and drying processes with advanced fluid-b...
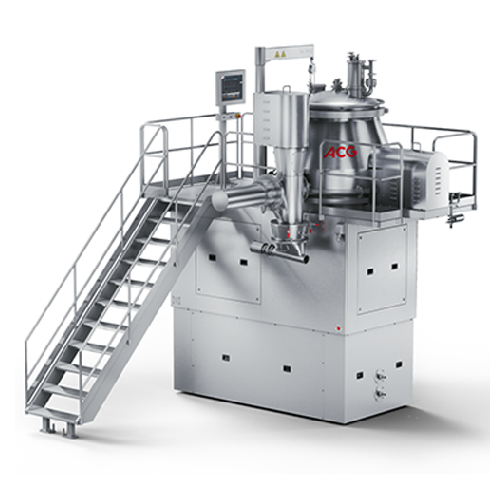
High-shear mixer for large-scale pharmaceutical production
Optimize your granulation process with an advanced high-shear...
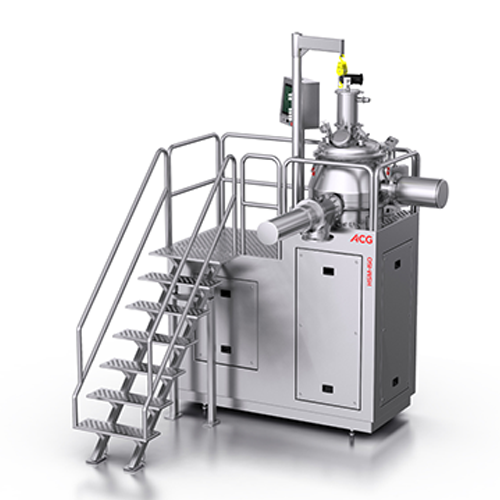
High-shear mixer for small batch granulation
Enhance your production efficiency with a high-shear mixer designed for preci...
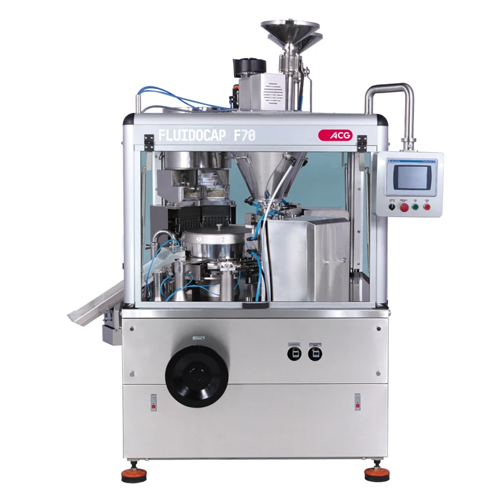
Liquid filling system for hard capsules
Easily fill two-piece hard capsules with liquids, pastes, and suspensions with prec...
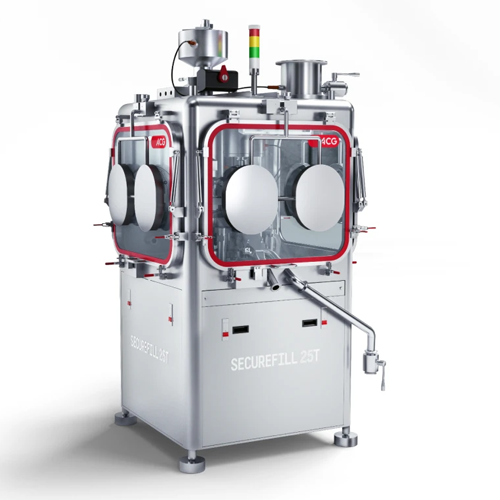
Containment capsule filler for highly potent drugs
Achieve complete operator safety while encapsulating potent pharmaceut...
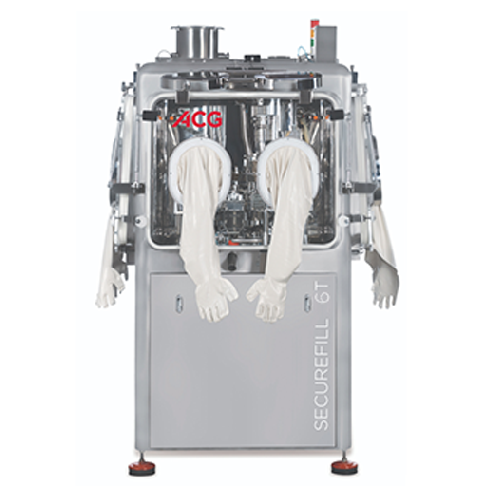
Containment capsule filling system for highly potent drugs
Ensure operator safety while filling capsules with high-poten...
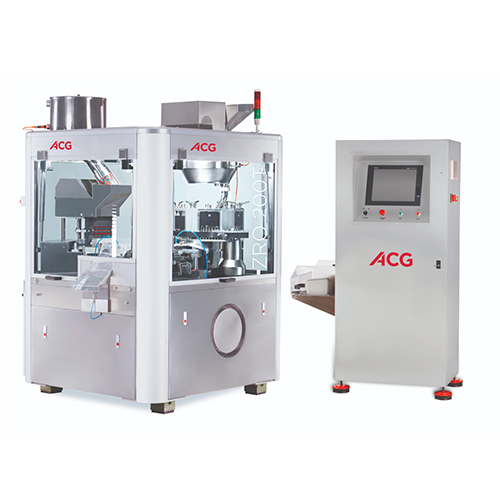
High-speed capsule filler for large batch production
Achieve higher yields and reduce powder waste with a capsule filling...
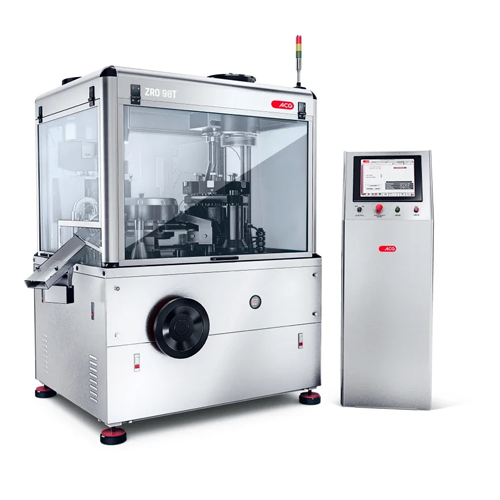
Capsule filler for high-speed, dust-free capsule production
Enhance your production efficiency with a solution designed ...
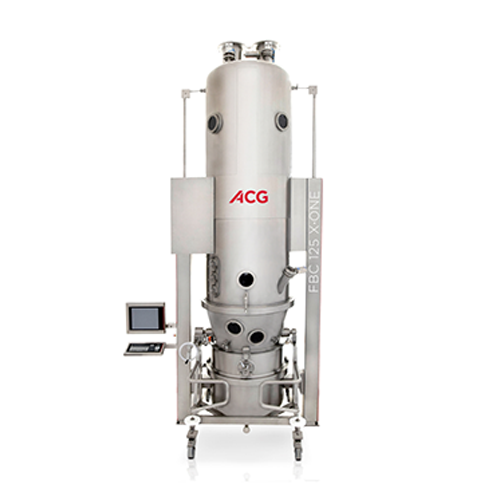
Fluid bed dryer with granulation and coating
Enhance your processing efficiency with a versatile system capable of combini...
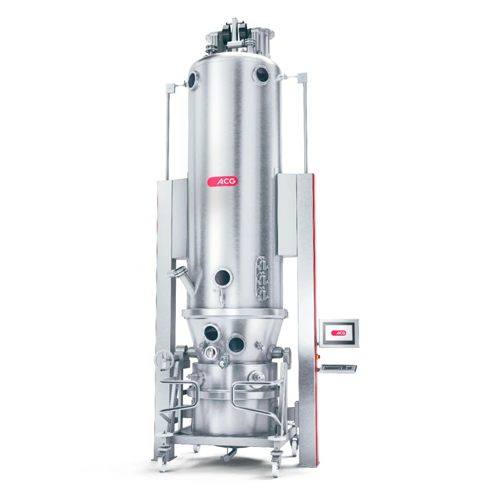
Fluid bed combo for granulation and coating
Achieve seamless granulation and coating with batch and high-speed operations,...
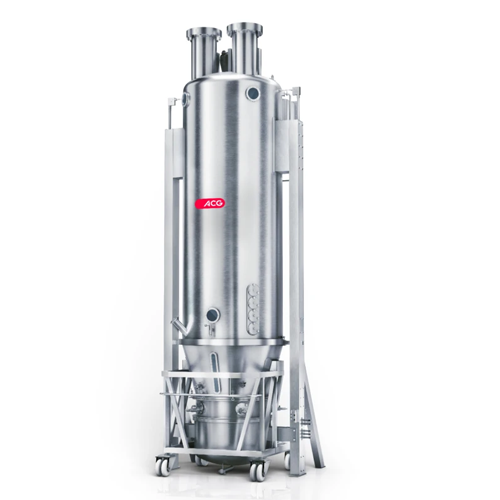
Fluid bed combo for top-spray granulation and wurster coating
Optimize your batch processing with a versatile system cap...
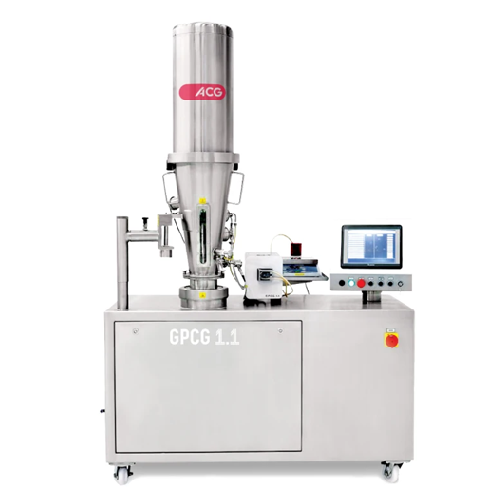
Fluid bed combo for granulation and coating
Streamline your manufacturing with a versatile fluid bed combo, integrating gr...
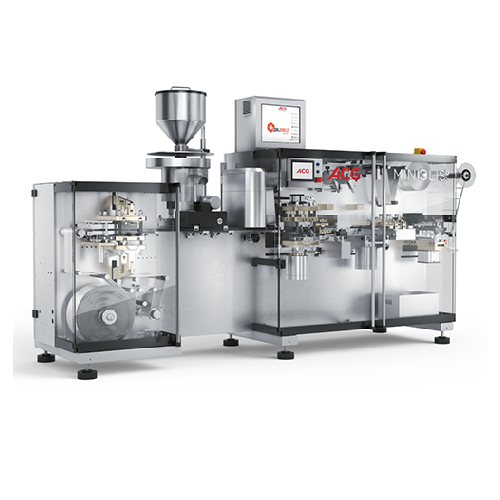
Flat-forming blister packager for small production batches
Ideal for pharmaceutical and nutraceutical firms seeking effi...
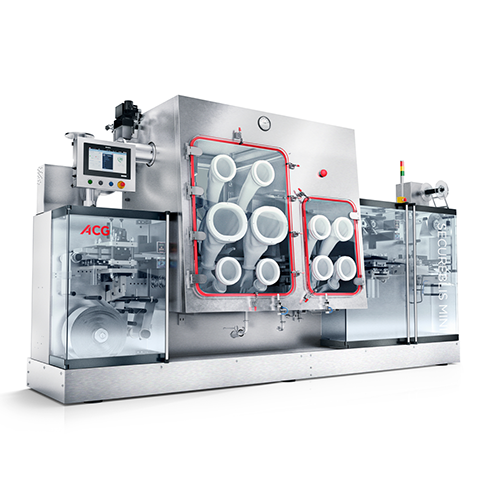
Containment blister packaging for highly potent Apis
Ensure operator safety during the blister packaging of highly potent...
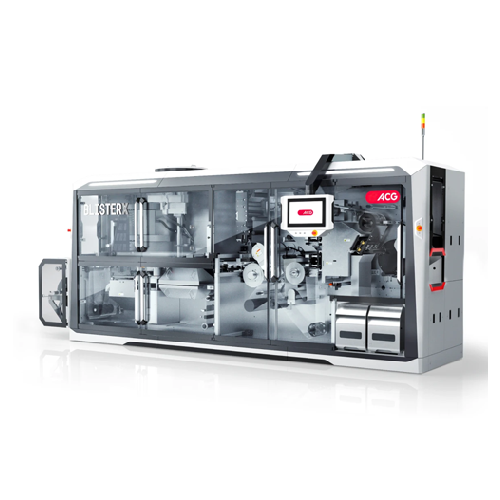
High-output blister packaging system
Maximize blister packaging efficiency with continuous-motion capabilities, ensuring su...
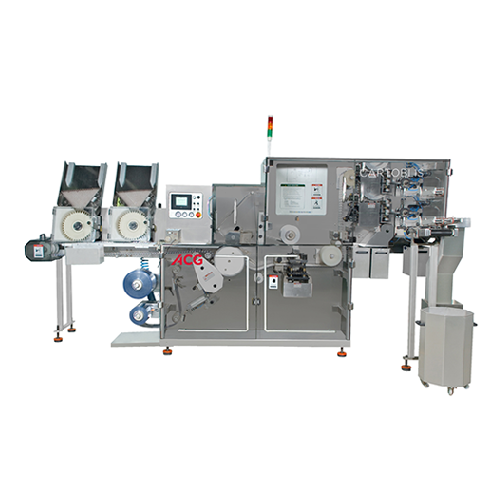
Blister packaging for solid dosage forms
Optimize your packaging line with high-speed, continuous blister packaging that en...
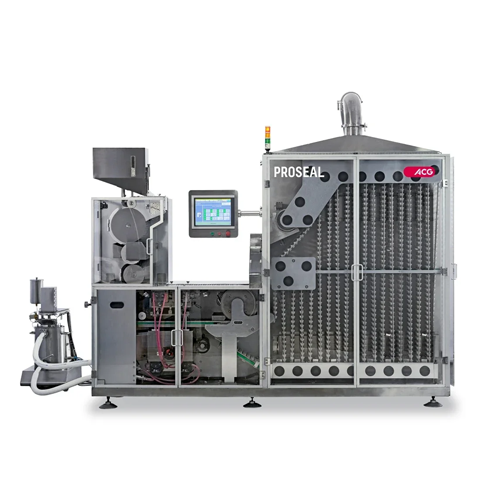
Capsule band sealer for liquid-filled hard capsules
Seamlessly seal liquid-filled hard capsules to enhance product integr...
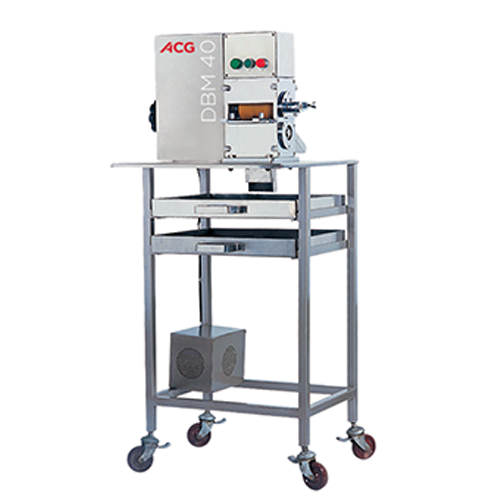
Semi-automatic de-blistering solution for Pvc and alu blister packs
Streamline your packaging operations by swiftly rec...
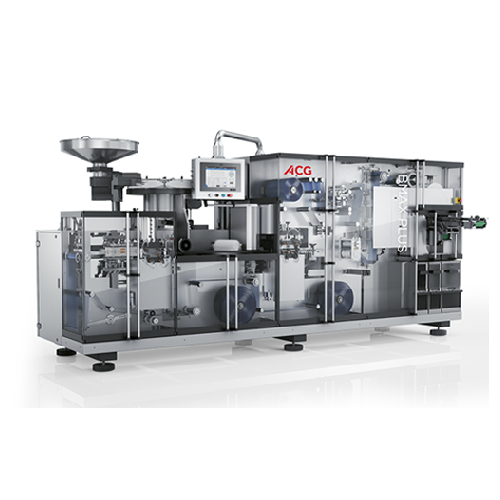
Flat forming and sealing blister packaging solution
Enhance your blister packaging process with a solution that ensures p...
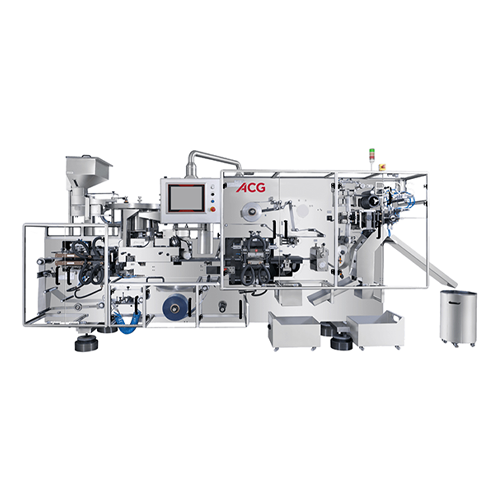
Flat-sealing continuous-motion blister packaging solution
Enhance your blister packaging with precise, high-speed sealin...

Desiccant inserter for pharmaceutical containers
Prevent product degradation by efficiently inserting desiccants into cont...
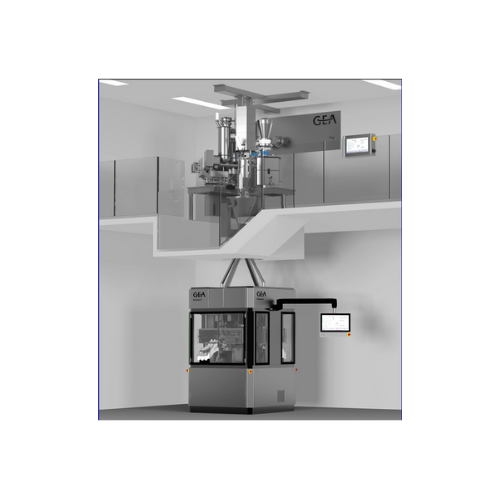
Continuous direct compression line for pharmaceuticals
Optimize tablet production with a seamless system combining contin...
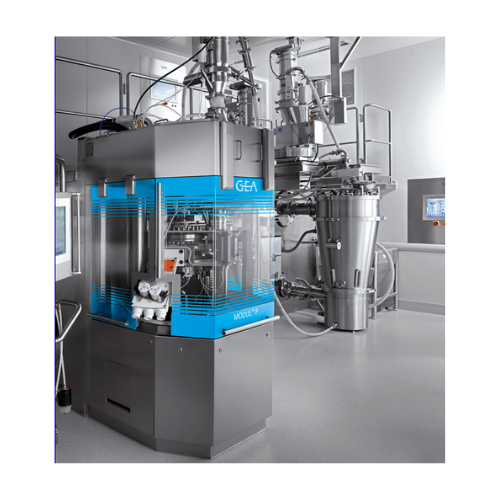
Continuous granulation and compression line for pharmaceuticals
Optimize your pharmaceutical production with a line that...
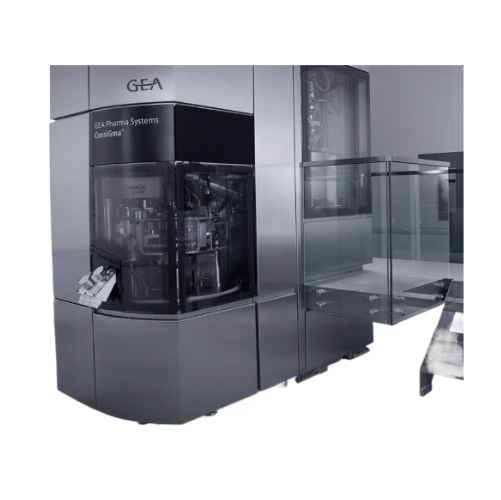
Pharmaceutical direct compression with linear blending
Streamline your pharmaceutical production with a continuous direct...
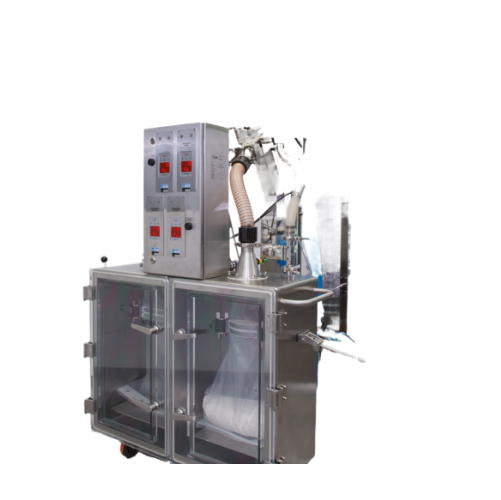
Disposable containment system for solid dosage material
Ensure safe and dust-free transfer of hazardous materials with ou...
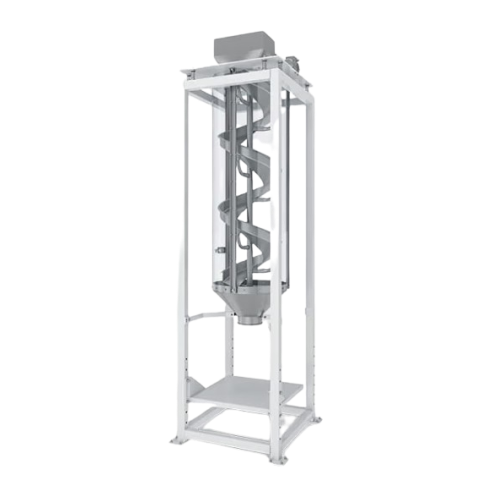
Direct discharge descender for product handling
Efficiently transport granulated materials without compromising their inte...
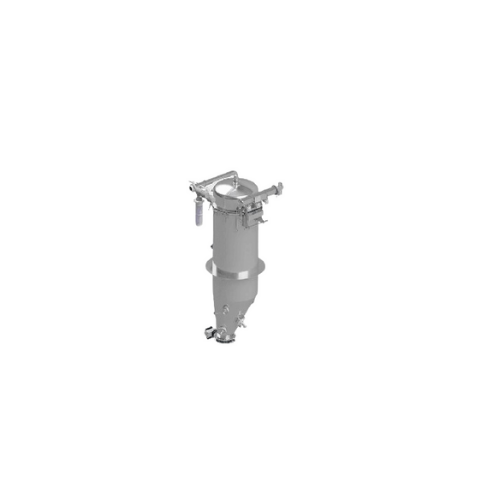
Dense phase vacuum conveying system for powder handling
Effortlessly transport delicate powders and fragile granules with...
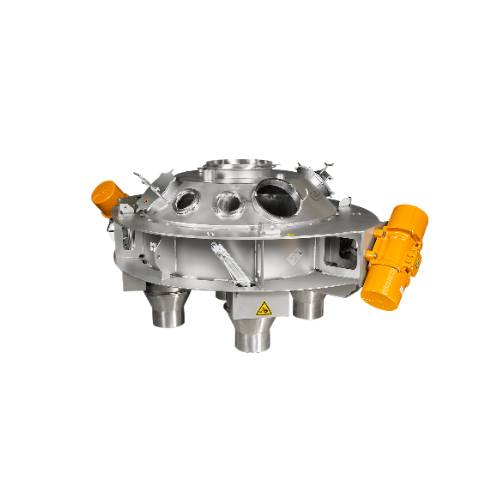
Circular distribution feeder for fragile product handling
Achieve precise dosing and reduced product damage with a versa...
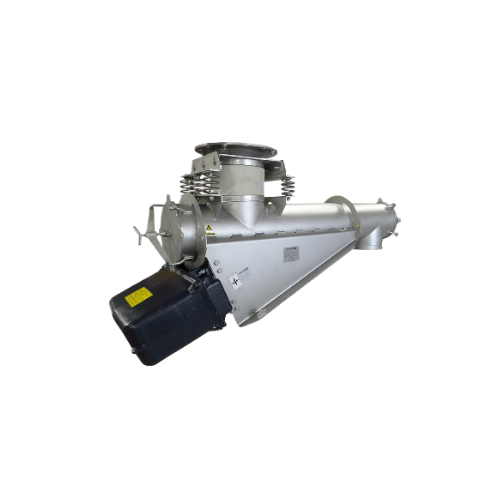
Vibrating feeder for food and pharmaceutical industries
Optimize your production line with precision dosing and gentle ma...
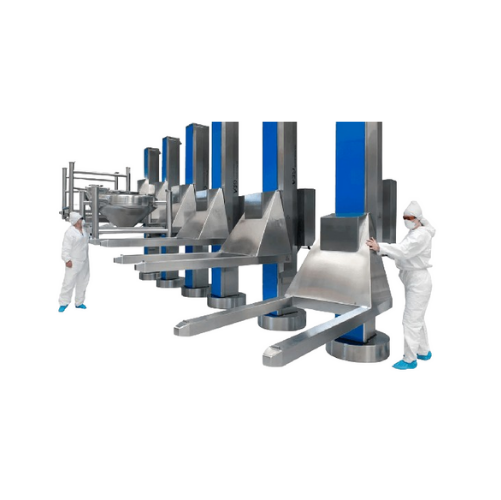
Ibc post hoists for pharmaceutical manufacturing
Ensure precise material handling with advanced lifting solutions designed...
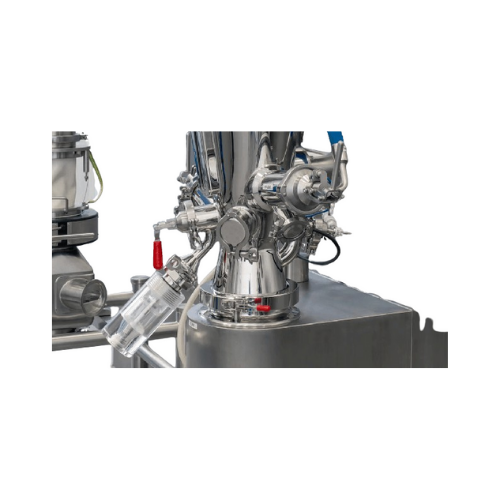
Contained powder sampling system
Ensure contamination-free sampling of active powders with fully contained system integratio...
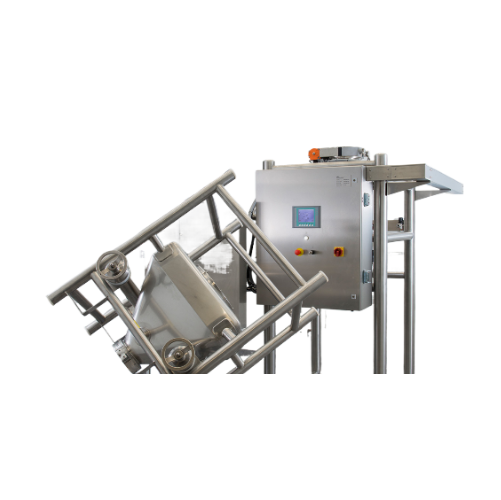
Intermediate bulk container (ibc) blending for pharmaceutical manufacturing
Streamline your pharmaceutical blending pr...
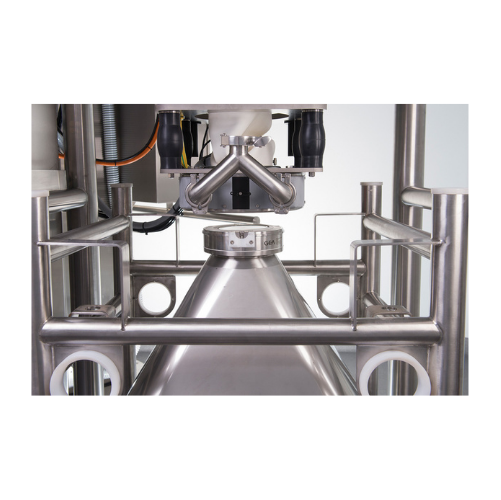
Pharmaceutical intermediate bulk containers (ibc)
Streamline pharmaceutical production with precise containment and trans...
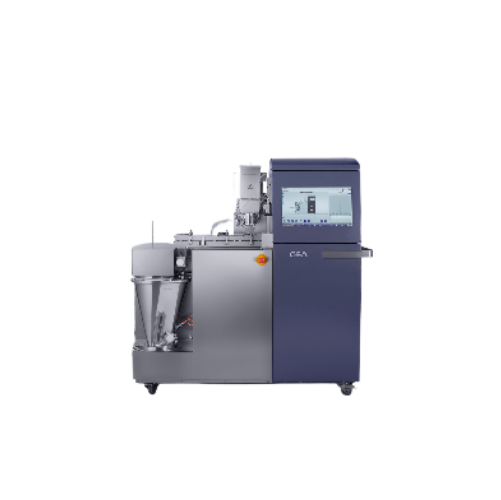
Continuous granulation and drying system for r&d
Develop precise pharmaceutical granules with this compact system, tailore...
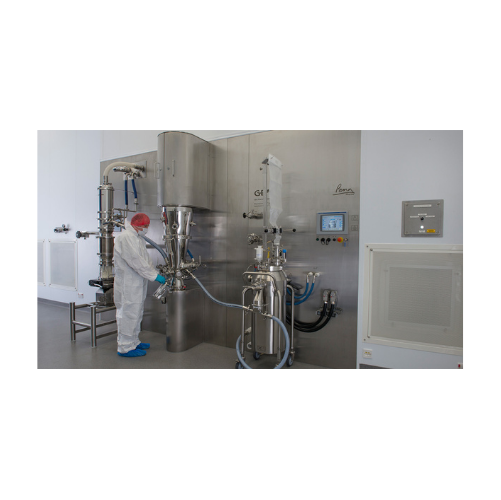
Pharmaceutical r&d granulation system
Optimize your pharmaceutical research with a versatile small-scale granulation system...
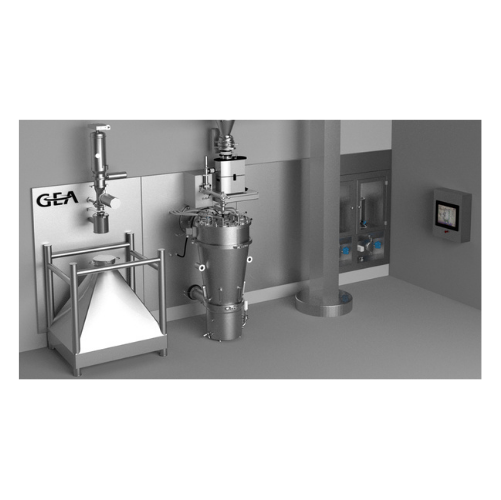
Continuous granulation and drying system for pharma production
Achieve precise control over granule quality with a conti...
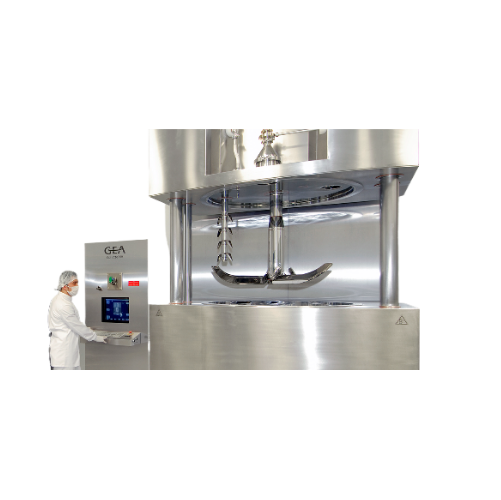
High shear granulator for pharmaceutical applications
Efficiently transform powders into uniform granules for consistent ...
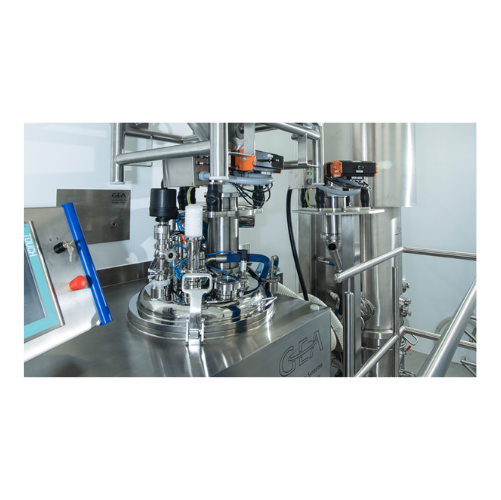
Pharmaceutical bottom-drive high shear granulator
Achieve optimal granule uniformity and precise control over moisture le...
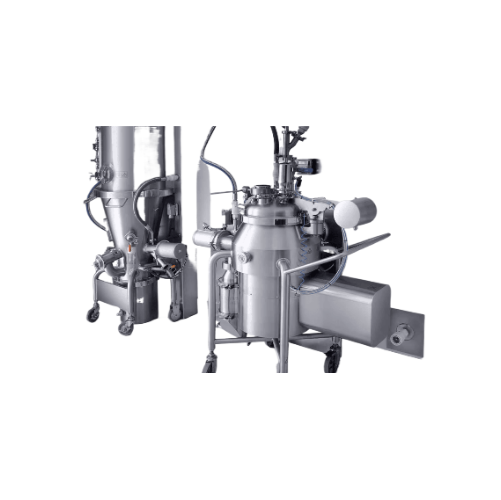
Integrated small-scale granulation and drying system
Ensure precise granule size and moisture control for enhanced tablet...
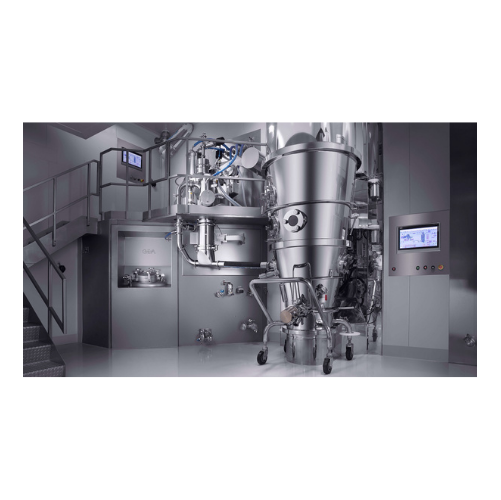
Integrated granulation and drying system for pharmaceuticals
Achieve seamless granulation and drying with our fully inte...
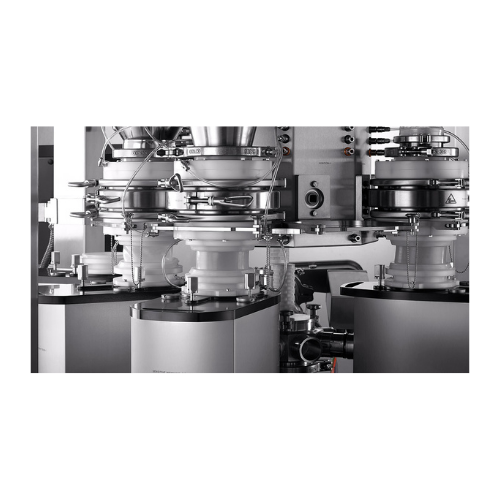
Powder feeding behavior characterization solution
Optimize your R&D with precise powder feeding behavior analysis, c...
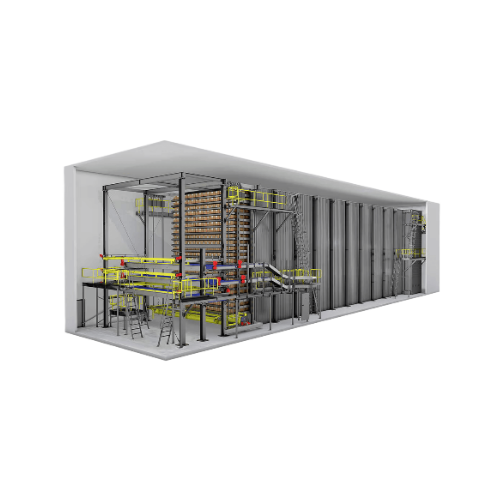
Variable retention time carton freezer
Optimize your production line with a flexible freezing solution that handles multipl...
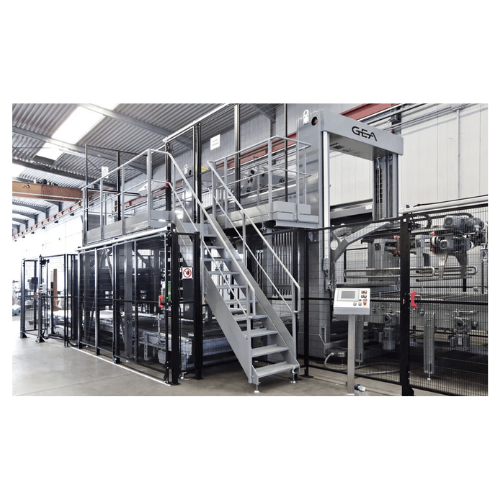
Palletizer for high-speed pallet loading
Achieve efficient, high-speed palletizing with a system designed for seamless inte...
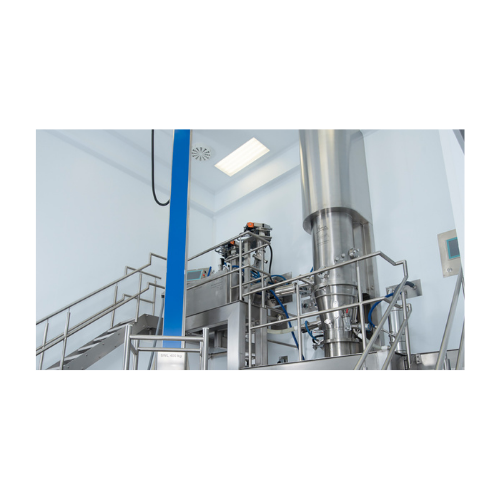
Fluid bed pellet coating solution
Achieve precise and uniform pellet coating with fluid bed technology for enhanced product...
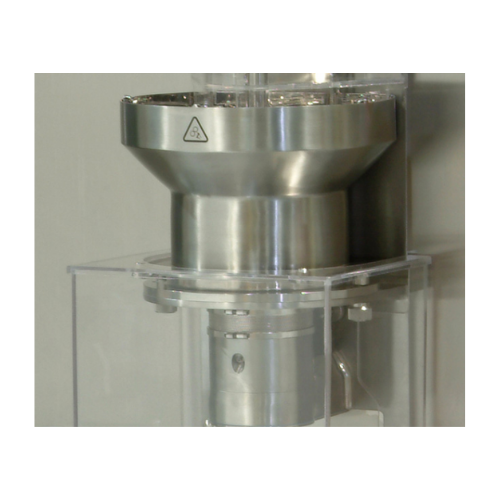
Pharmaceutical low shear extruder
Optimize your pharmaceutical pellet production with precision-controlled extrusion, ensur...
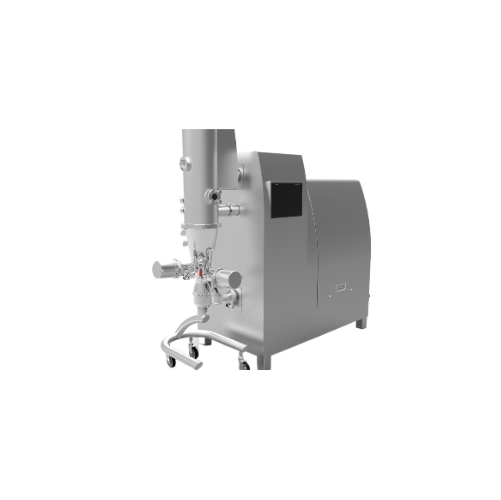
Pharmaceutical fluid bed processor for r&d
Optimize your pharmaceutical R&D with a versatile fluid bed processor desi...
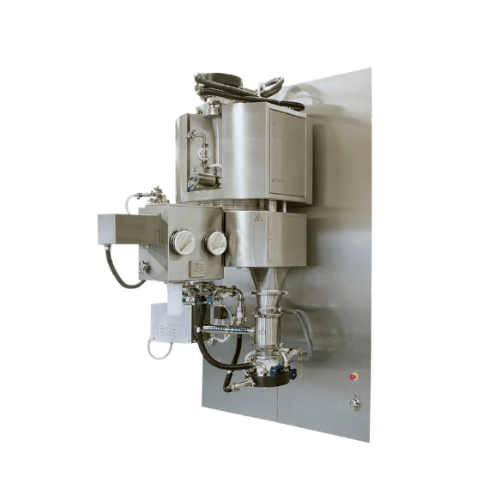
Single pot processor for granulation and drying
Streamline your pharmaceutical production with an integrated solution that...
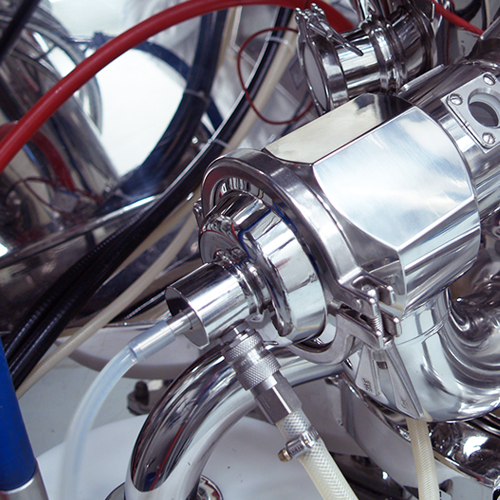
Flexstream fluid bed processor for pharmaceutical applications
Addressing the limitations of traditional fluid bed proce...
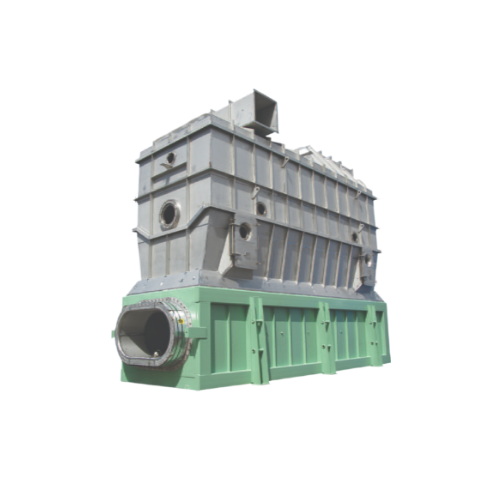
Static fluid bed dryer for powder and granular materials
Achieve optimal moisture control in powder and granular products...
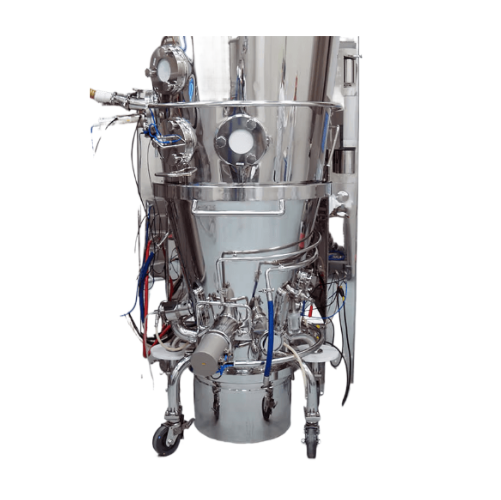
Fluid bed processing of pharmaceuticals
Enhance your pharmaceutical production with versatile fluid bed processors, enablin...
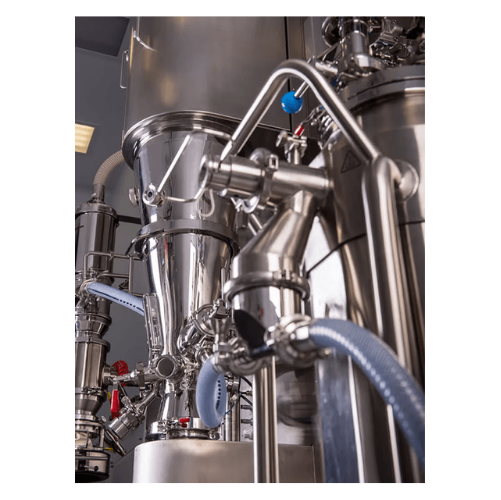
Pharmaceutical fluid bed r&d processing
Ensure precise formulation and consistency in pharmaceutical and nutraceutical tabl...
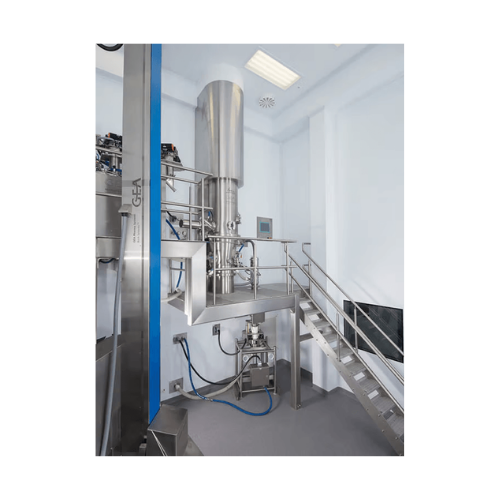
Cip for pharmaceutical process plants
Streamline your cleaning processes with integrated CIP systems to ensure precise and ...
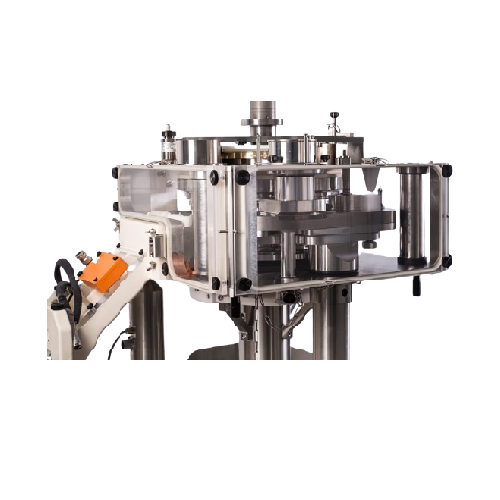
Wash-off-line system for pharmaceutical plants
Optimize your production with a versatile wash-off-line system, ensuring pr...
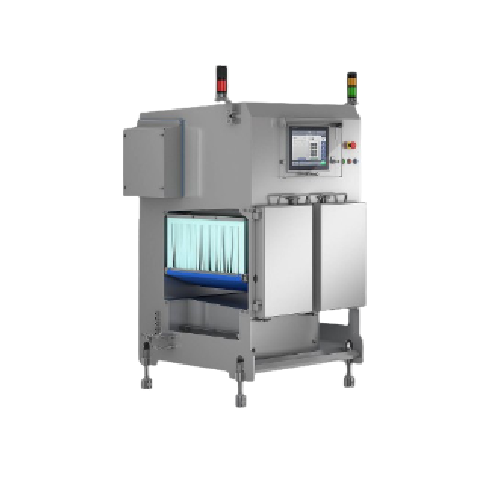
X-ray inspection system for wet environments
Ensure unparalleled product inspection under extreme cleaning conditions with...
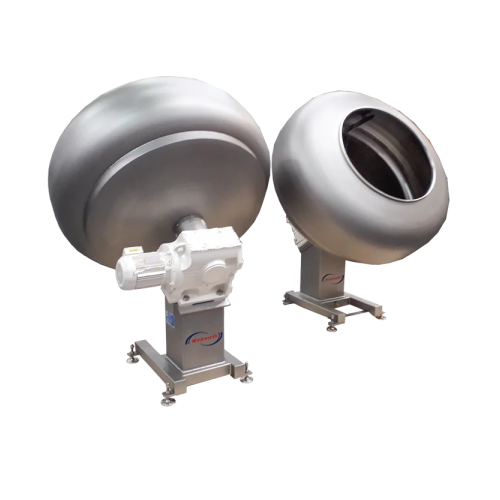
Industrial coating pans for sweets and confectionery
Ensure even and consistent coatings with high-capacity pans designed...
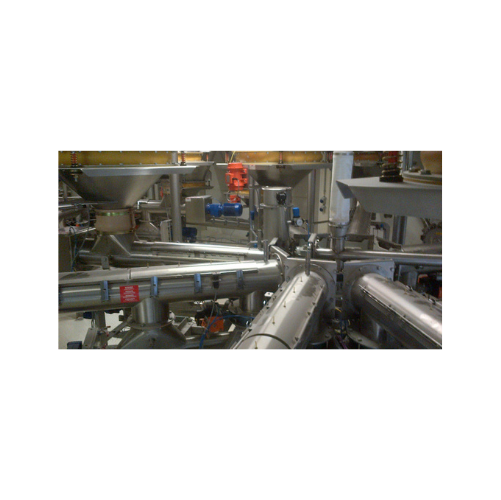
Stainless steel tubular screw conveyor for bulk solids handling
Ensure precise material handling with stainless steel tu...
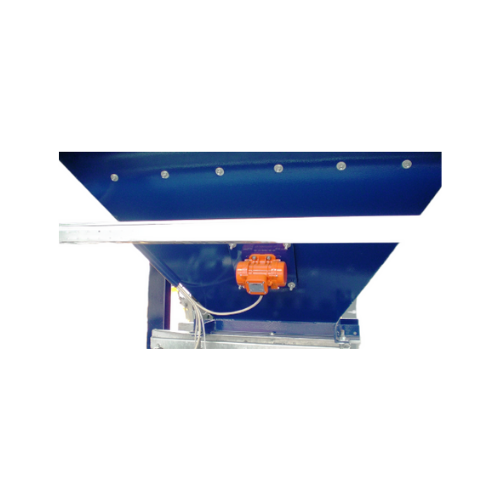
External electric motovibrators for industrial applications
Optimize material movement and improve discharge efficiency ...
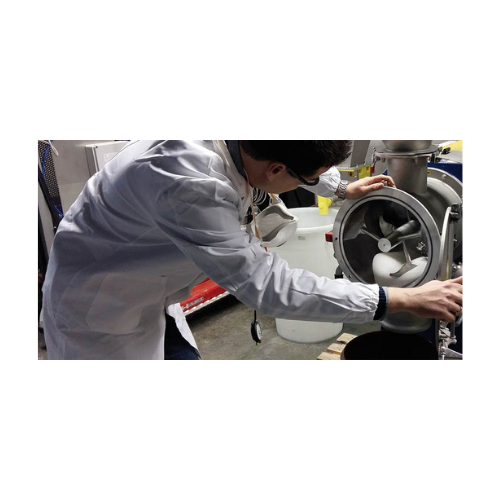
Laboratory batch mixer for small scale production
Achieve rapid and reproducible mixing results with this laboratory batc...
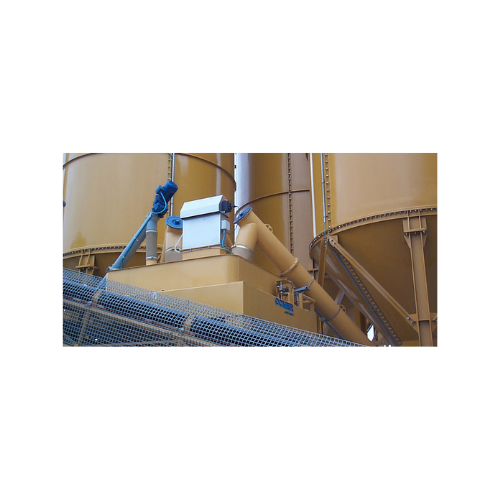
Hopper venting filter for efficient dust filtration
Achieve superior dust control and efficient material handling with a ...
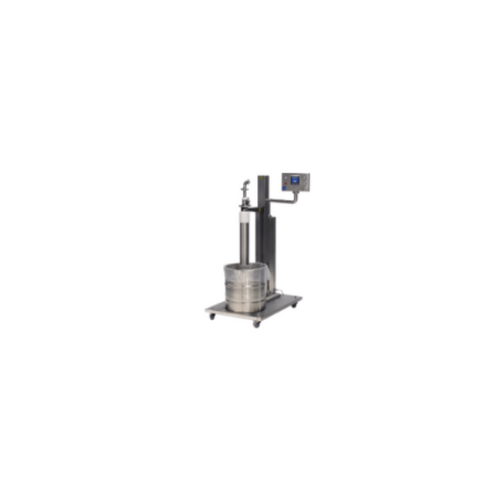
Drum discharge system for bulk material handling
Achieve precise, gentle transfer of sensitive pharmaceuticals and granula...
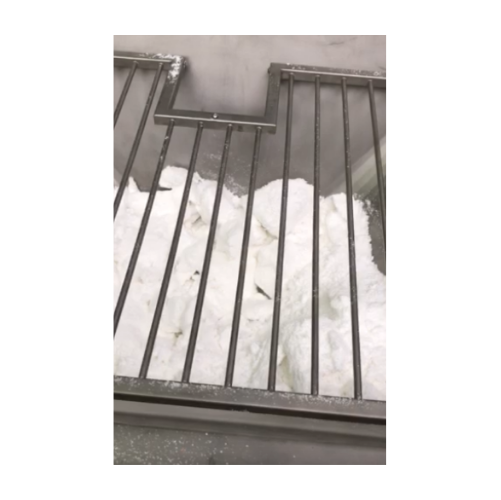
Lump breaker for breaking agglomerates and lumps
Effortlessly break down challenging agglomerates and clumps to ensure smo...
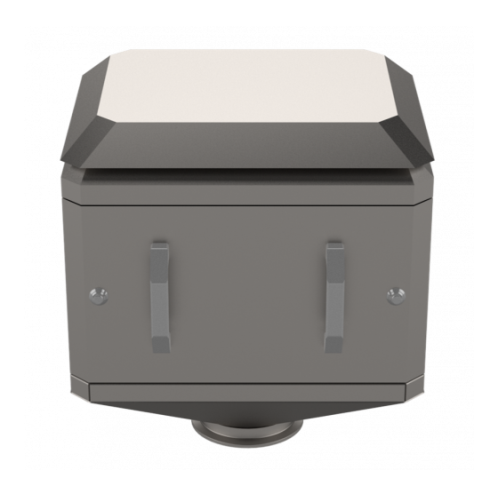
Laboratory dedusting systems
Designed for high-containment lab environments, this solution efficiently captures and manages ...
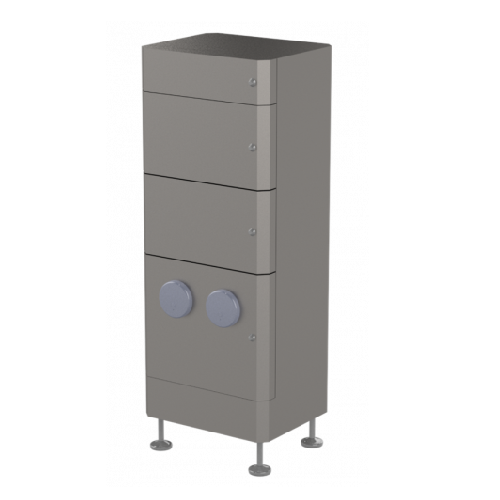
Supply air filter systems for industrial cleanrooms
Ensure critical air purity and operational safety in sensitive enviro...
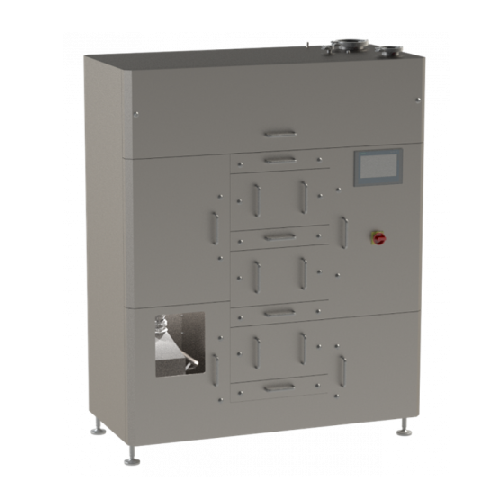
Compact dust extractors for cleanroom applications
Ensure safe and efficient dust extraction in cleanroom environments wi...
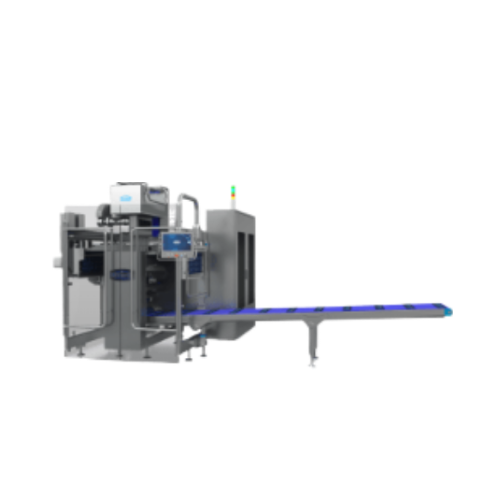
Sachet packaging for pharmaceuticals
Streamline your pharmaceutical packaging with high-precision sachet solutions, ensurin...
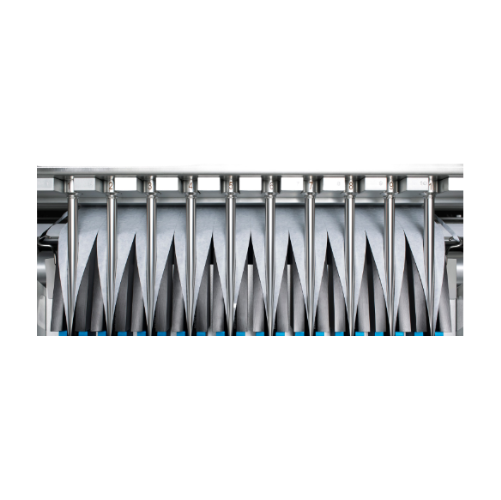
Stick pack packaging for pharmaceutical products
Enhance your production efficiency with compact stick pack solutions, off...
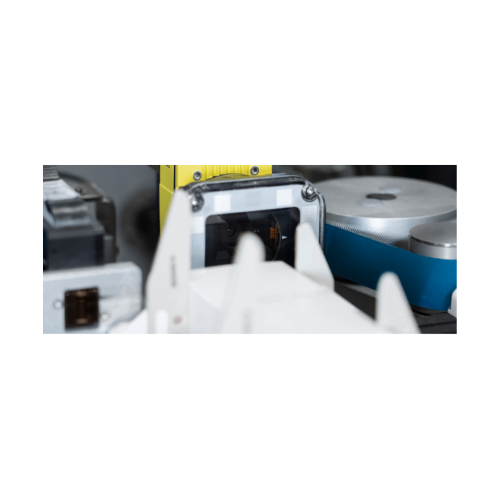
Sachet packaging lines for pharmaceuticals
Optimize your pharmaceutical production with high-speed sachet packaging lines ...
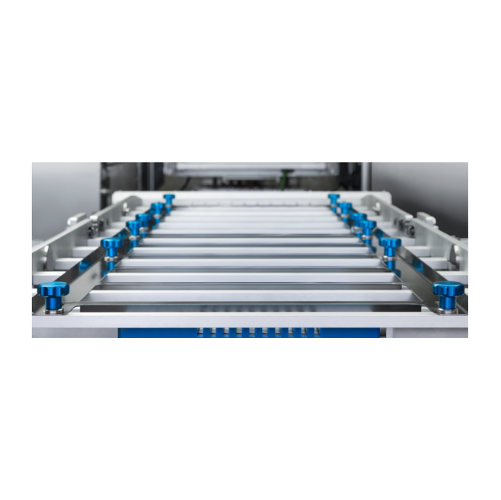
Stick pack packaging line for pharmaceuticals
Optimize your pharmaceutical production with stick pack packaging lines that...
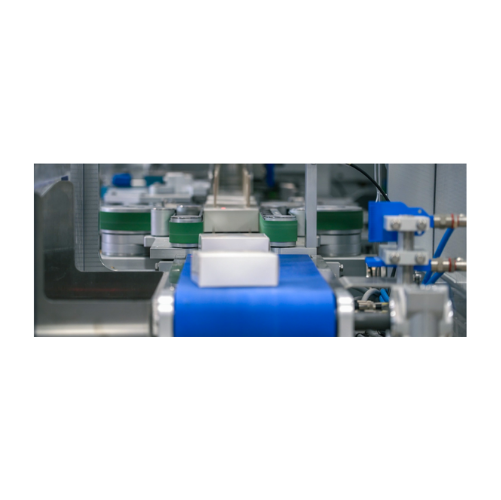
Cartoning solution for pharmaceutical products
Ensure accurate and efficient packaging of pharmaceutical products with pre...
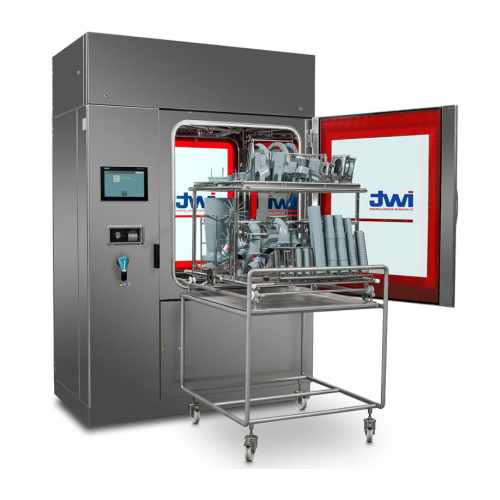
Gmp contact part washers for pharmaceutical industry
Ensure product integrity and hygiene with specialized washing system...
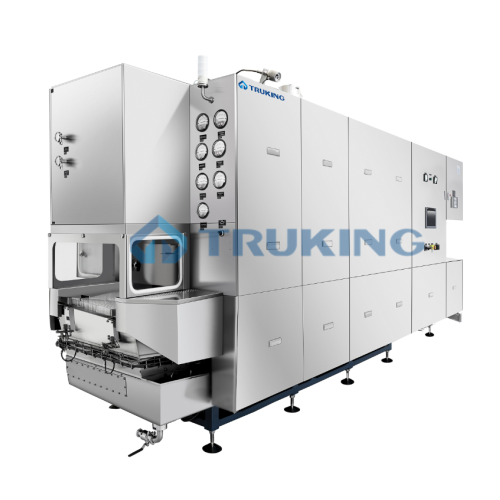
Sterilizing and depyrogenization tunnel for ampoules
Ensure sterile and pyrogen-free ampoules with precision control in d...
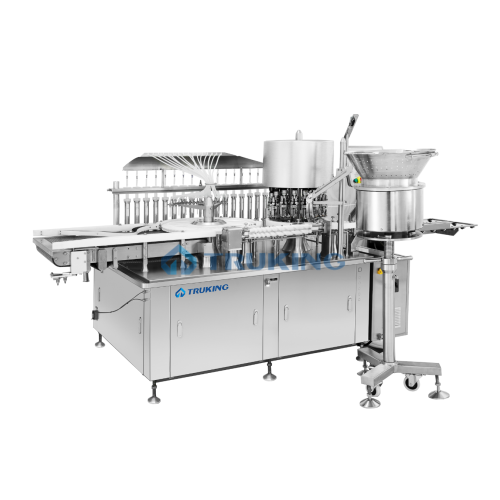
Oral liquid bottle filling & capping system
Streamline your liquid manufacturing processes with precise filling and secure...
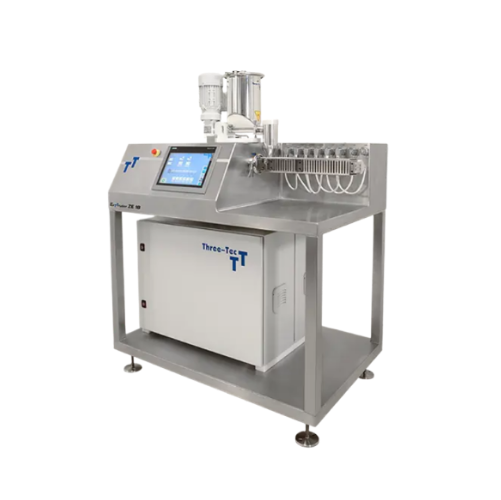
Twin-screw extruder for high containment applications
Achieve precise mixing of sensitive compounds with a twin-screw ext...
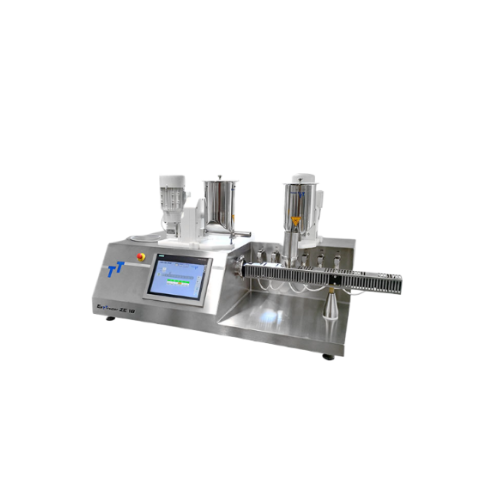
Table top extruder for customizable extrusion processes
Discover versatile extrusion capabilities for developing complex ...
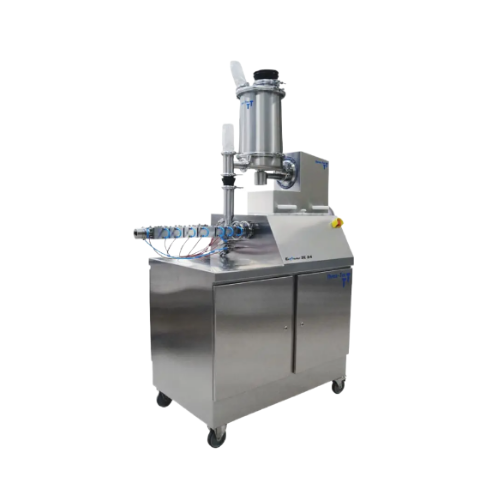
Compact high-torque extruder for customizable extrusion tasks
Ensure precise control over your extrusion processes with ...
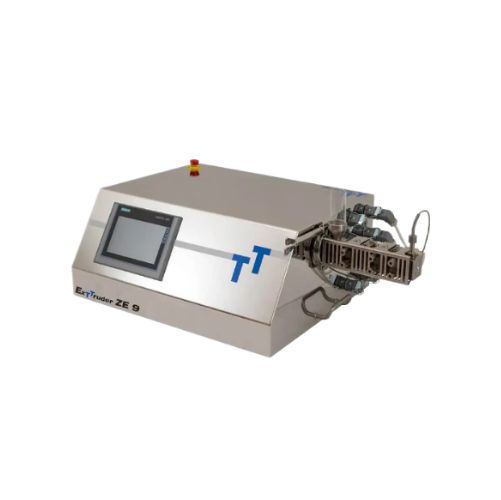
Mini extruder for small batch processing
Ideal for precise control in experimental formulations, this mini extruder streaml...
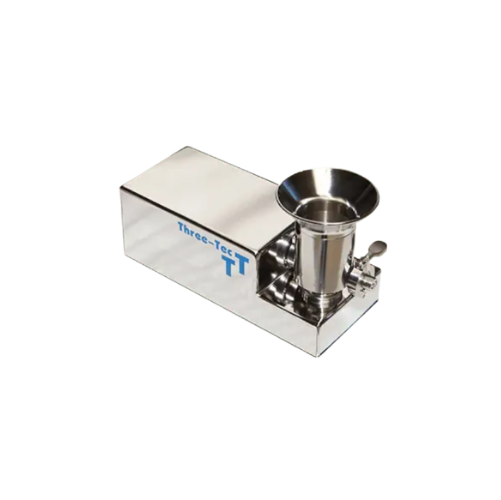
High-precision feeding system with load cell and weighing electronics
Achieve unparalleled accuracy in dispensing powde...
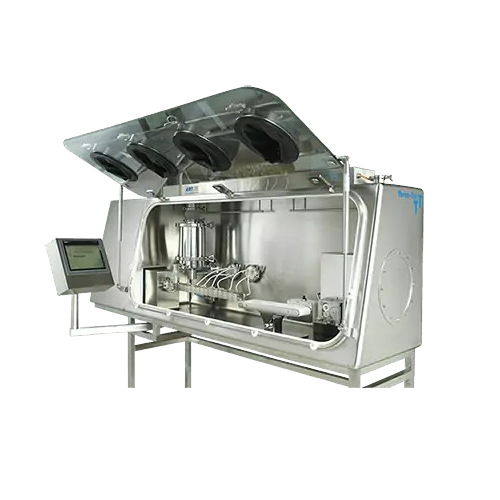
Isolator high containment for granule production
Ensure high-purity production in pharmaceuticals with controlled granulat...
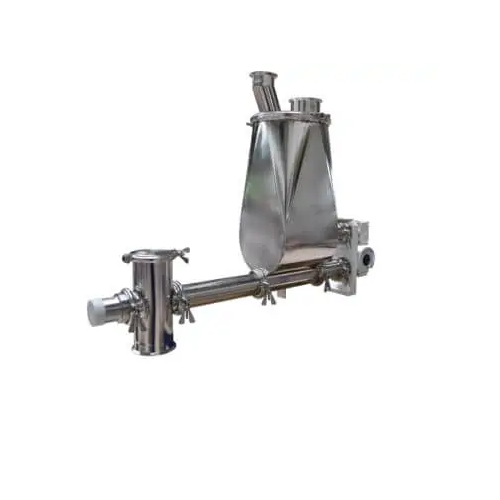
Quick change volumetric and gravimetric single-screw dosing device
Simplify your dosing process with a quick-change sin...
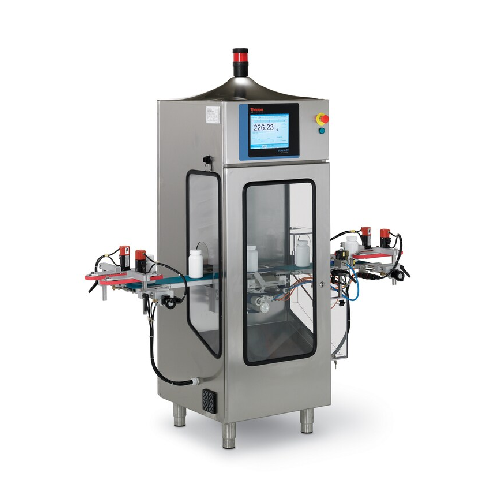
Checkweigher for pharmaceutical and food industries
Ensure precise weight measurement and reliable product rejection in h...
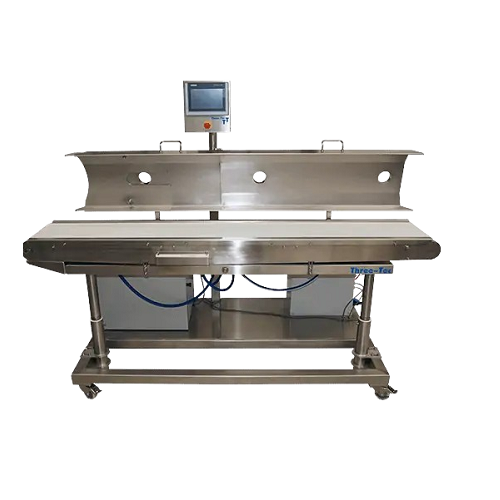
Cooling conveyor belt for extrudates and granules
Efficiently cool and convey extrudates and granules with precise temper...
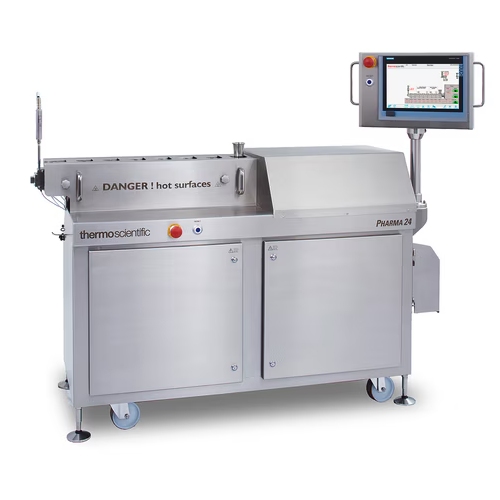
Pharmaceutical twin-screw extruder
Optimize your pharmaceutical production with high-speed continuous extrusion that ensure...
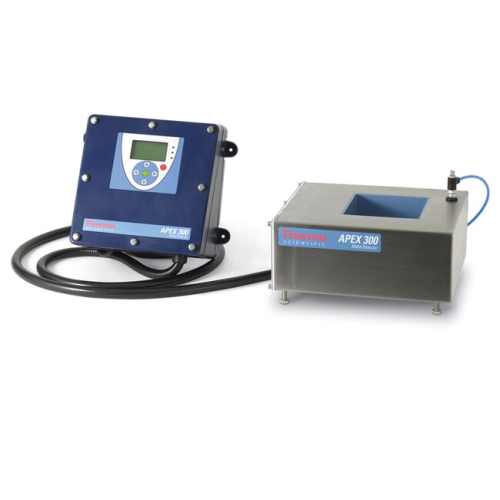
Industrial metal detector for food and beverage applications
Ensure your production line is free from metal contaminants...
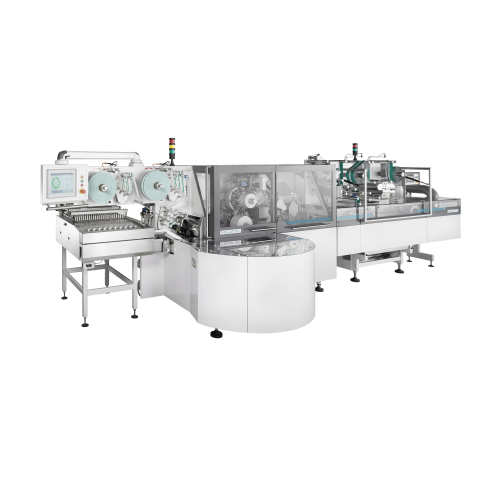
High speed wrapping solution for pre-formed products
Achieve seamless integration of primary and secondary packaging with...
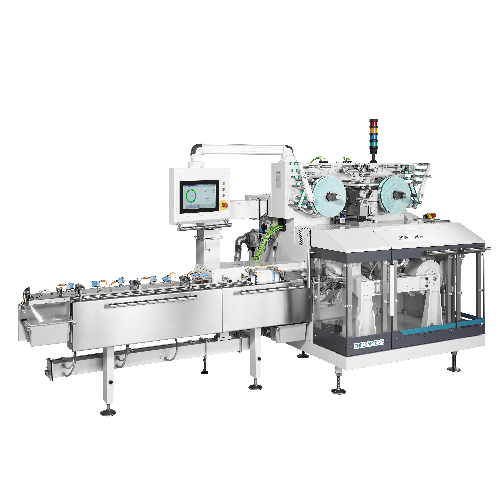
High-speed wrapping machine for chocolate or compressed powder products
For confectionery and pharmaceutical operations...
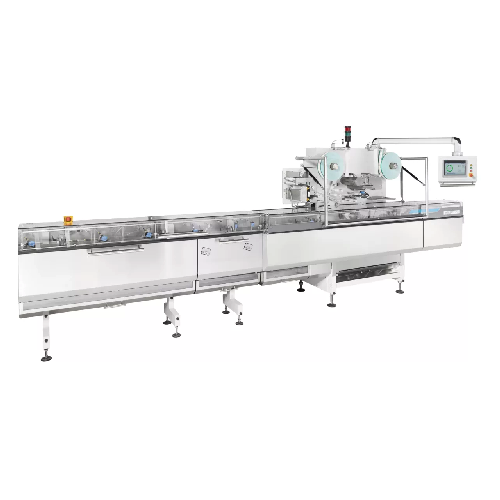
High-speed wrapping solution for compressed powder products
Efficiently wrap high-volume compressed powder products with...
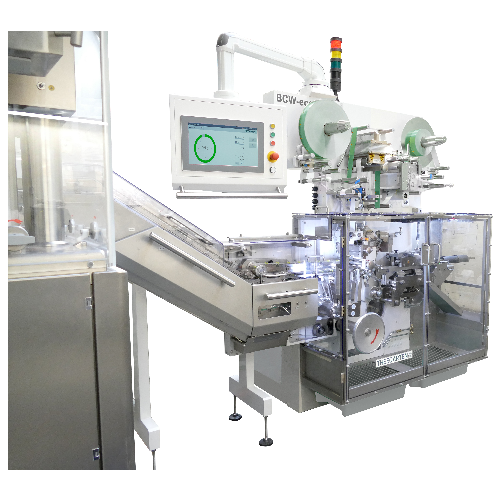
Bouillon cube wrapping system
Streamline your packaging line with a high-speed system tailored for compact, compressed produ...
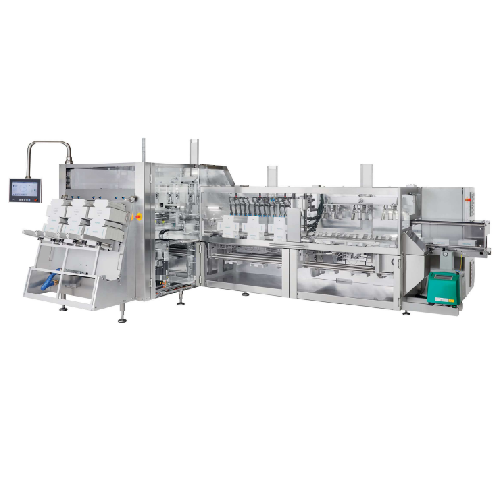
High-speed cartoning system for primary wrapped products
Optimize your packaging line with this high-speed cartoning syst...
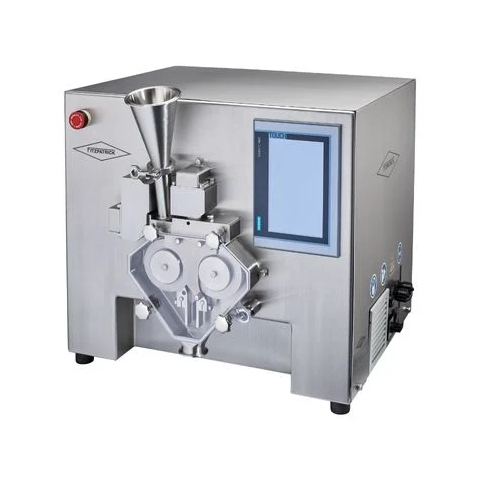
Lab scale roller compactor for dry granulation
Achieve seamless scale-up from lab development to full-scale production wit...
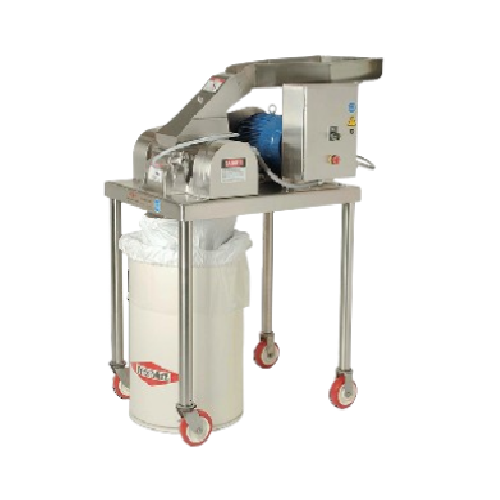
Atex approved hammer mills for high-capacity particle size reduction
Ensure precise and reliable particle size reductio...
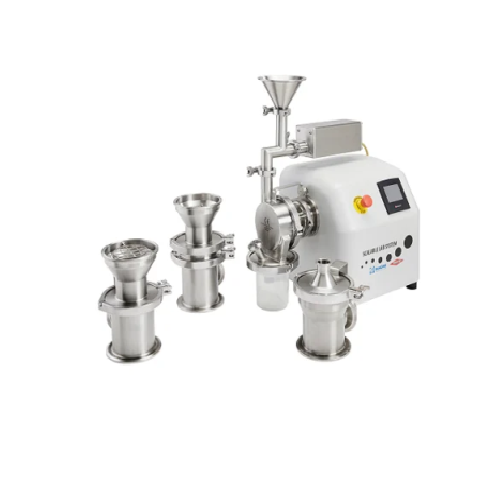
Lab scale hammer mills for fine particle size reduction
Optimize your R&D scaling efforts with versatile lab equipme...
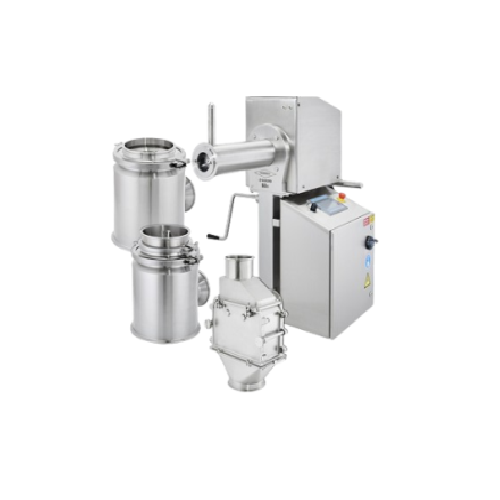
Pilot-scale milling and screening platform
Achieve precise powder consistency and integrity with flexible milling and scre...
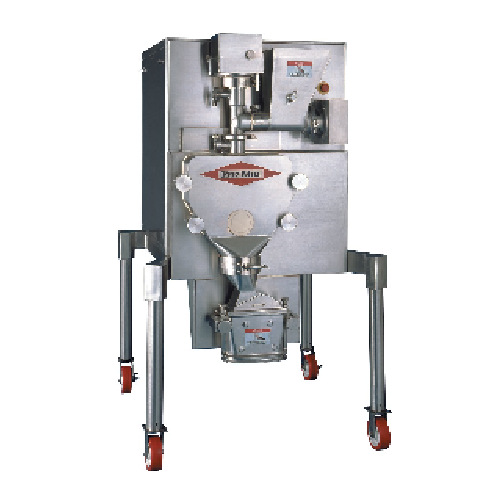
Pilot to full-scale roller compactor for dry granulation
Easily transition from pilot to full-scale production with this ...
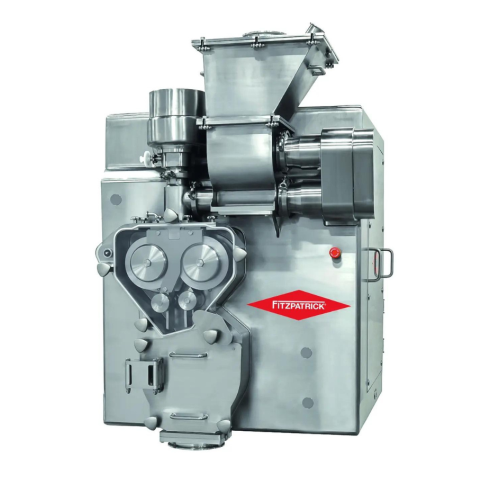
Dry granulation system for pharmaceutical powders
Streamline your powder processing with a dry granulation system that en...
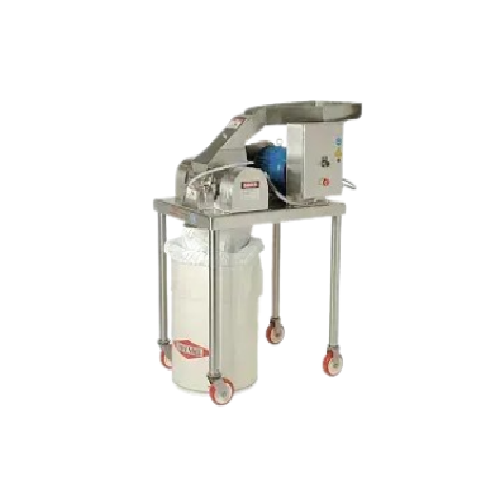
Industrial powder milling solution
Achieve precise particle size control and improve material flowability with this advance...

Modular high-speed flow pack wrapper for preformed products
Eliminate packaging line bottlenecks with a versatile high-s...
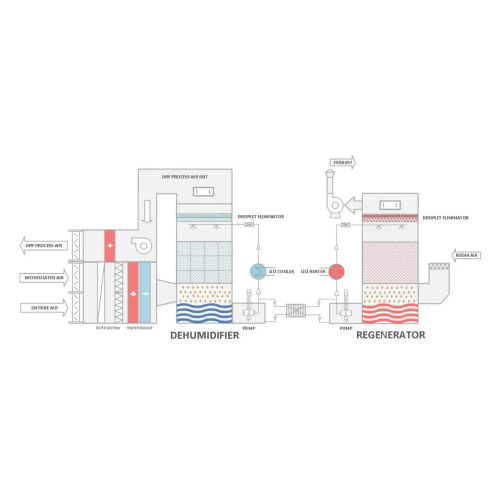
Industrial lithium chloride dehumidifier
Efficiently control air moisture and temperature with a solution that ensures prec...
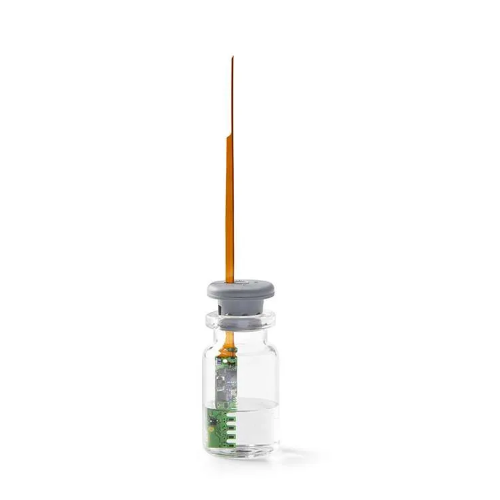
Sublimation front monitoring system for freeze drying
Ensure precise control over your freeze-drying process with real-ti...
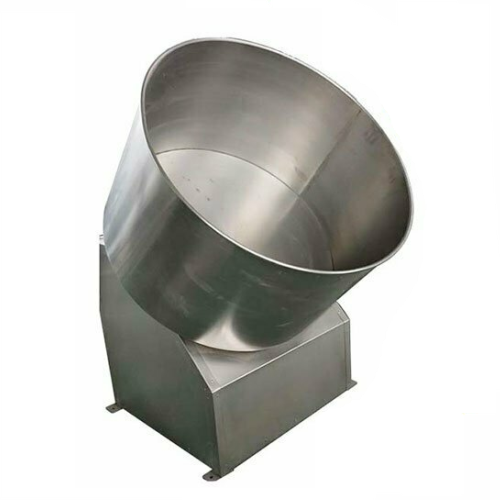
Nut coating machine for snack food processing
Enhance your snack and confectionery production with a nut coating machine t...
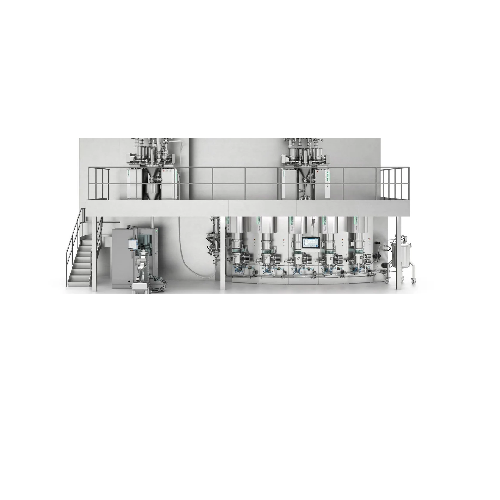
Continuous manufacturing for pharmaceuticals
Achieve precision in oral solid dosage production with seamless continuous pr...

Fluid bed processor for pharmaceutical granulation and coating
Achieve superior granulation and coating of pharmaceutica...
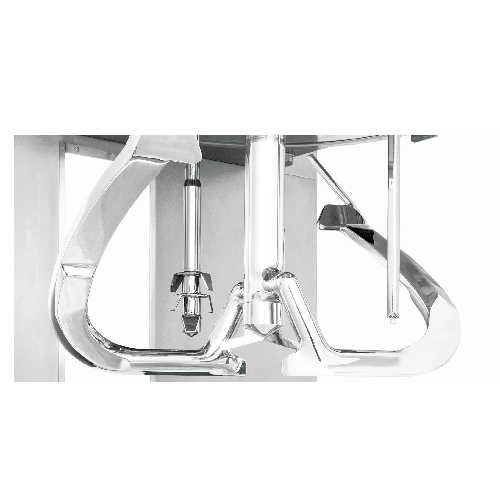
High-shear mixer granulator for pharmaceutical production
Achieve optimal granulation with enhanced mixing efficiency, r...
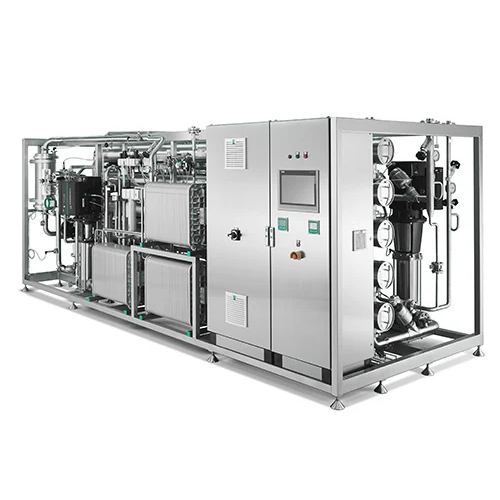
Pure water generation system for pharmaceutical manufacturing
Ensure high-purity water and steam production with precisi...
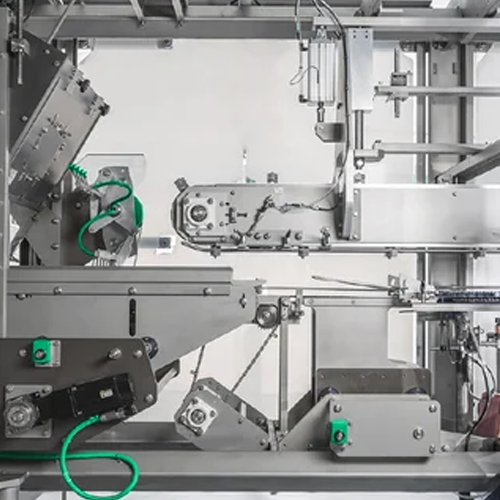
Nutraceutical products processing and packaging
Streamline your nutraceutical production with versatile equipment capable ...
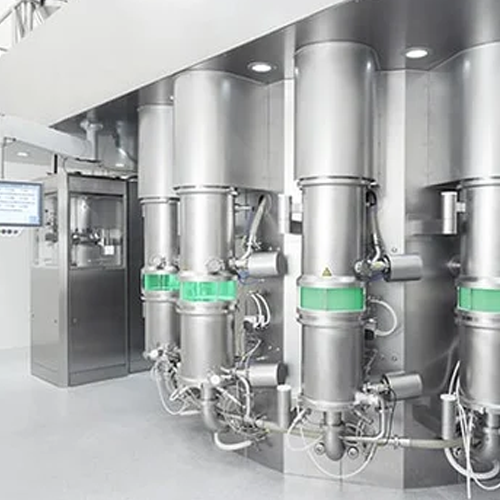
Pharma r&d equipment for solid dosage forms
Optimize your pharmaceutical production with cutting-edge equipment designed f...
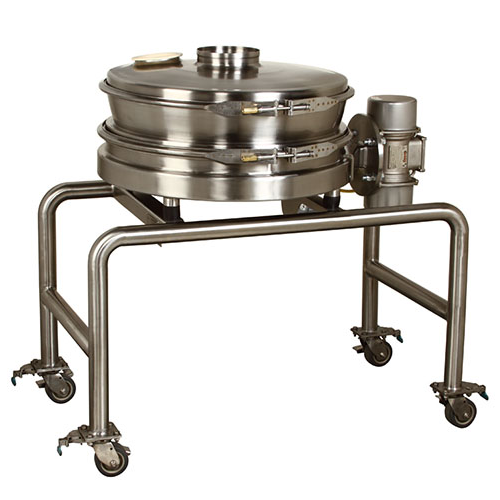
Sanitary separator for food processing applications
Ensure efficient separation and prevent contamination in food product...
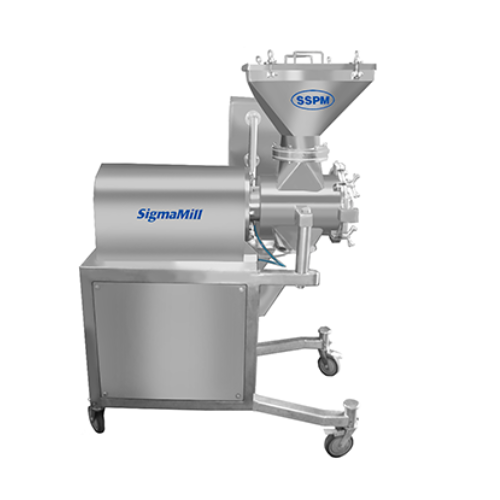
Wet granulation process for pharmaceutical applications
Achieve consistent granule size and uniform mixing with advanced ...
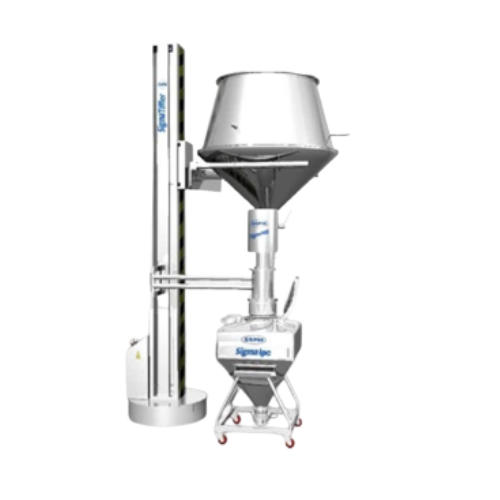
Material handling system for granules and powders
Optimize your production with seamless material handling specifically d...
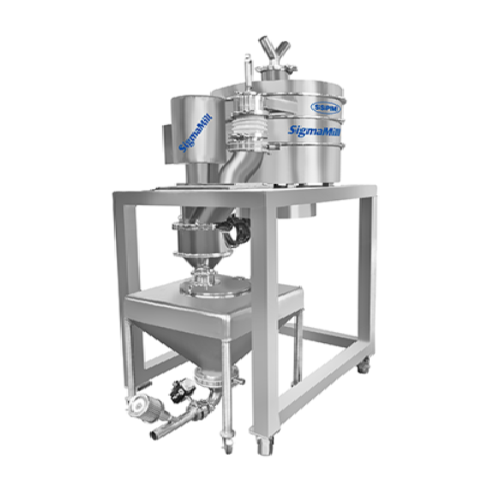
Wet granulation for pharmaceutical products
Achieve seamless integration of sifting and milling with precise powder handli...
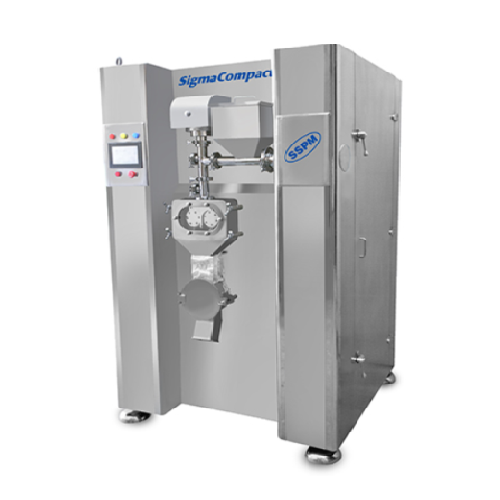
Dry granulation roll compactor
Optimize your tablet and capsule formulation by efficiently compacting and granulating powder...
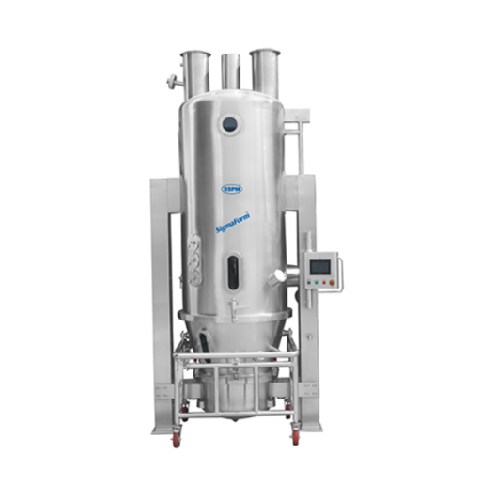
Fluid bed dryer for wet granulation in pharmaceutical industry
Streamline your production with fast, uniform drying and ...
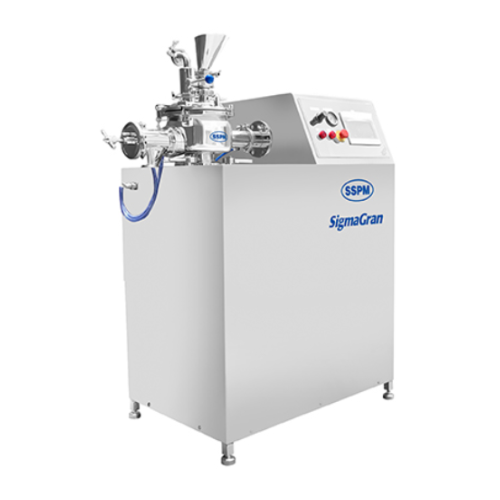
High shear granulator for uniform wet granules
Achieve uniform and homogeneous wet granules with high-speed mixing and aut...
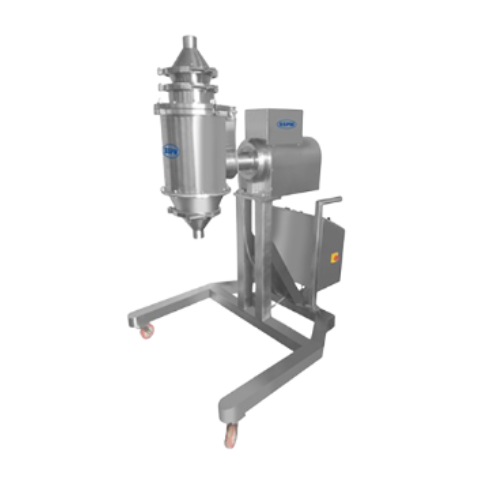
High-speed sifting for safety screening in pharmaceutical production
Achieve precise particle sizing with a high-speed ...
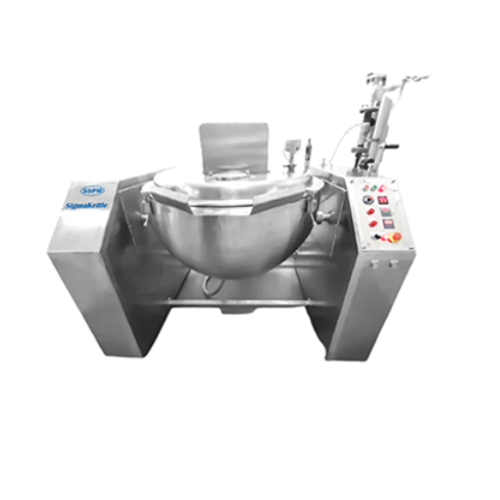
Steam/electrical kettle for wet granulation processes
Achieve precise moisture content and uniformity in your granulation...
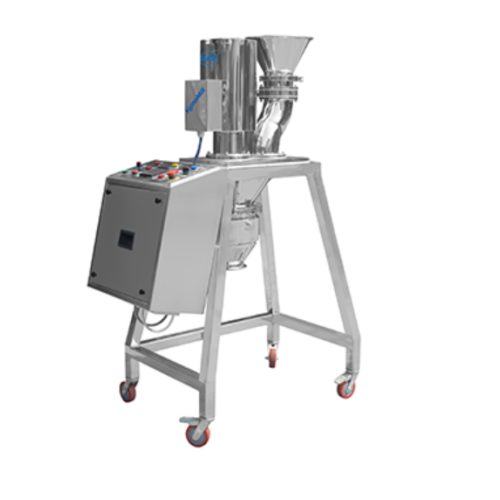
Wet granulation co mill for pharmaceutical formulations
Optimize your manufacturing process with precise particle size re...
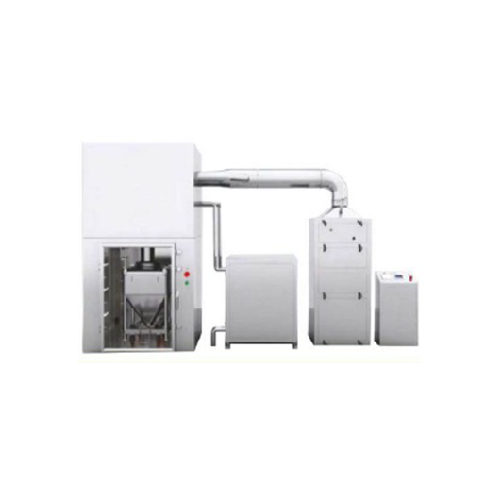
Bin washing station for pharmaceutical applications
Achieve reliable sanitation and enhanced efficiency with this tailore...
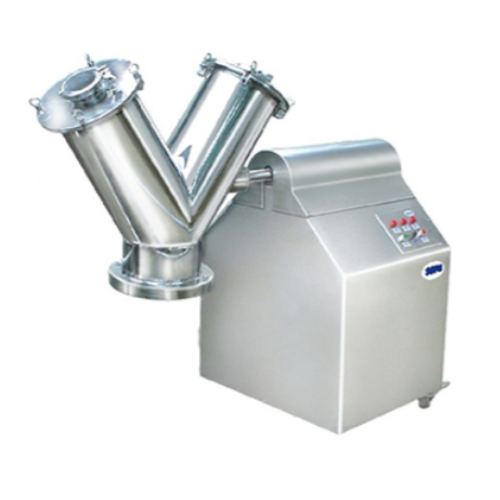
Industrial blender for uniform mixing
Optimize your process with precise mixing and consistent blending, ensuring uniformit...
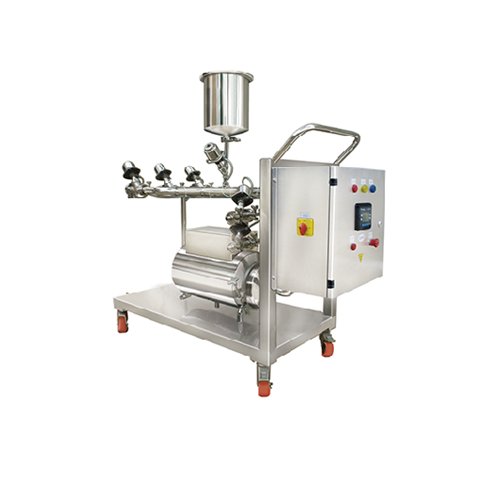
Wet granulation cleaning system
Ensure optimal cleaning and purification within your production line with a system designed ...
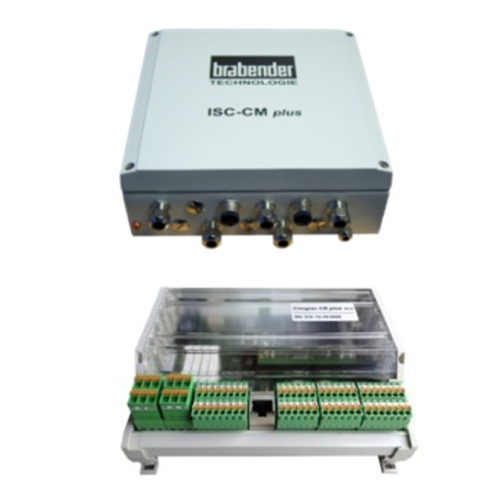
Feeder controller for gravimetric feeders
Optimize your dosing precision and monitoring accuracy with a versatile feeder c...
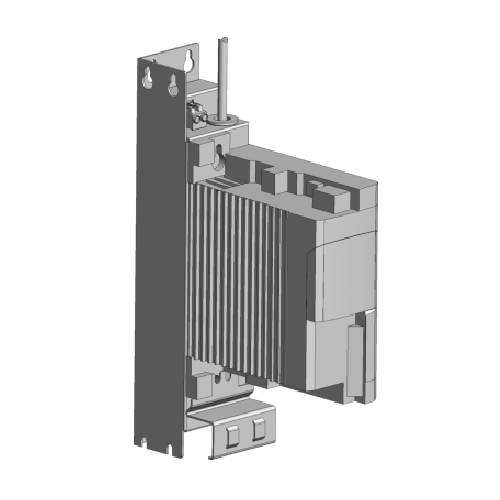
Speed controller for feeders
Ensure precise material flow by integrating this speed controller, ideal for managing both volu...
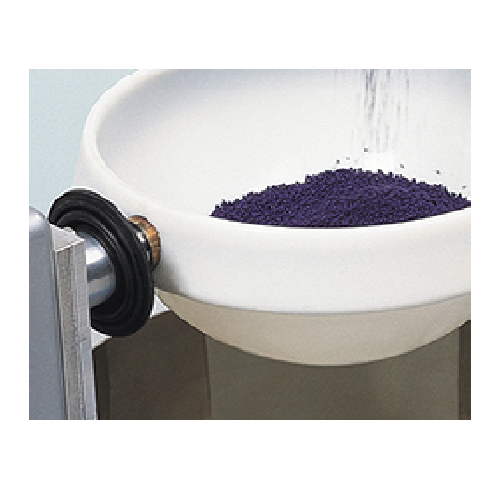
Microbatch dosing for precision ingredient measurement
Achieve precise ingredient dosing with our MicroBatch system, desi...
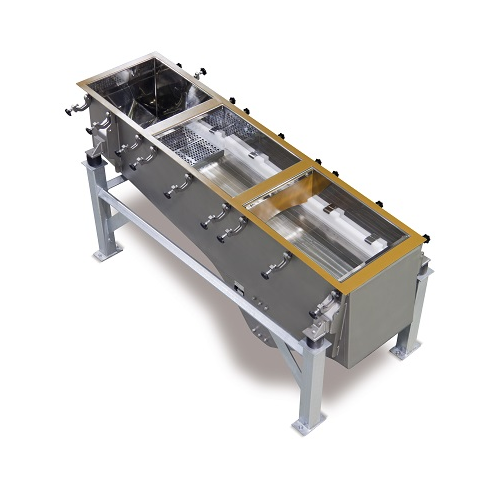
Pharmaceutical sieving equipment for high hygiene standards
Ensure the purity of pharmaceutical powders and granulates w...
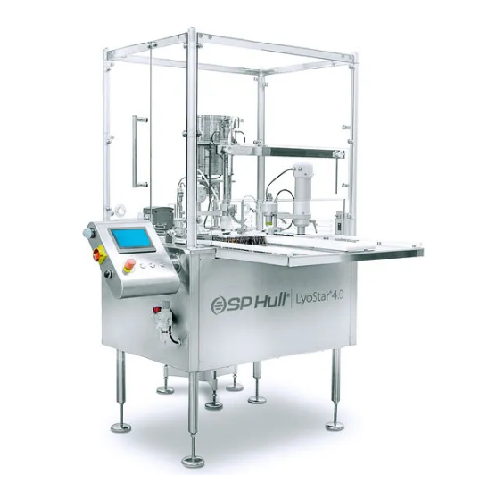
Small scale pharmaceutical filler and stoppering system
Optimize your R&D operations with a versatile filling and st...
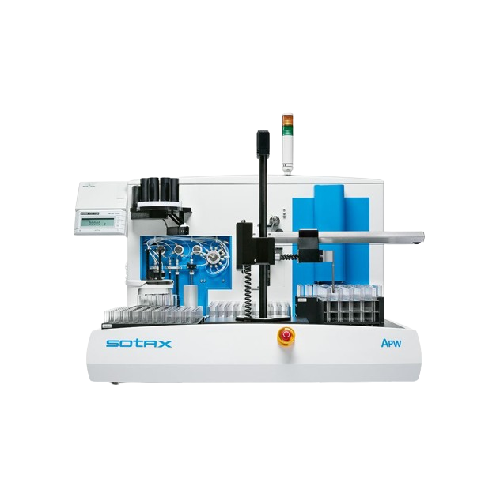
Automated sample preparation workstation for lab efficiency
Streamline laboratory operations by automating sample prepar...
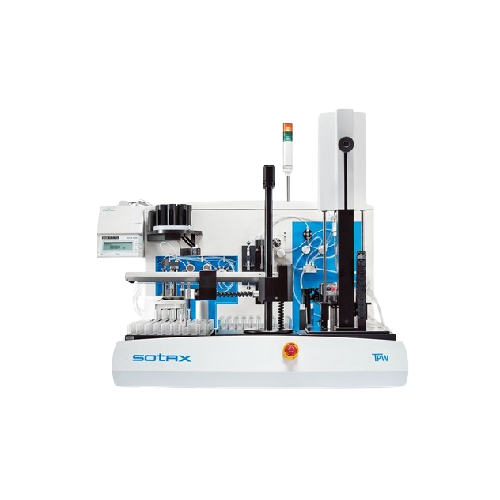
Automated sample preparation workstation for content uniformity testing
Streamline your laboratory workflows with autom...
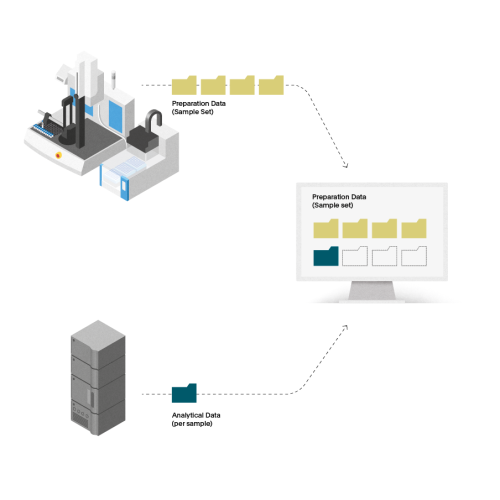
Automated sample preparation software for pharmaceutical testing
Streamline your laboratory’s sample preparation w...
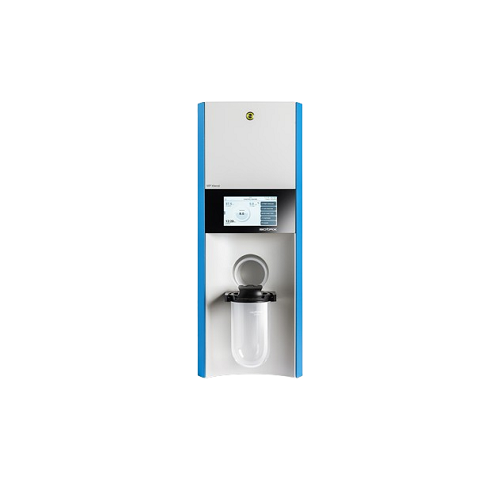
Dissolution medium preparation system
Streamline your laboratory workflows with a system that prepares and manages dissolut...
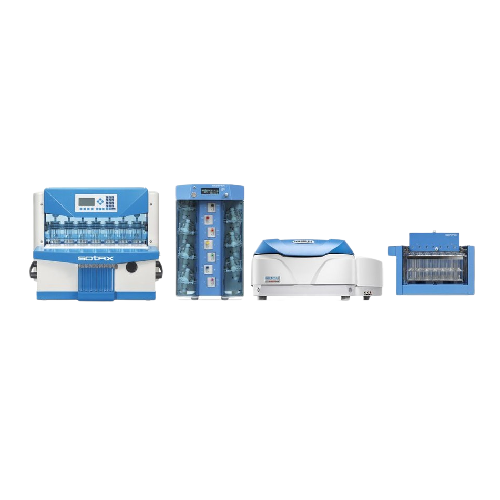
Automated flow-through cell dissolution testing system
Enhance precision in dissolution testing with real-time UV-Vis ana...
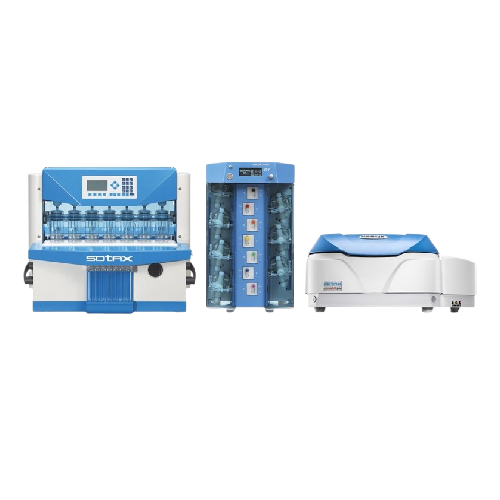
Flow-through cell dissolution testing with Uv analysis
Effortlessly monitor real-time dissolution with flow-through cell ...
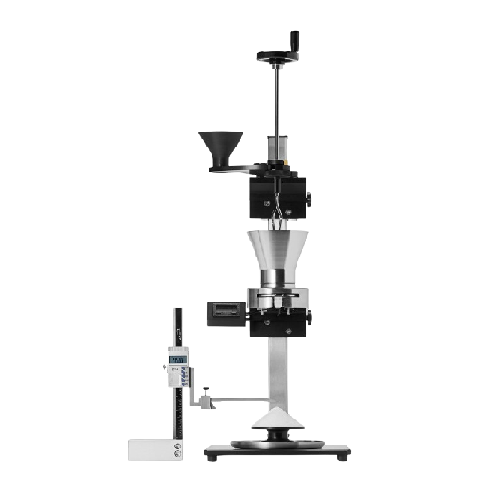
Powder flow tester for pharmaceutical powder flowability
Quickly assess powder flow characteristics to ensure consistent ...
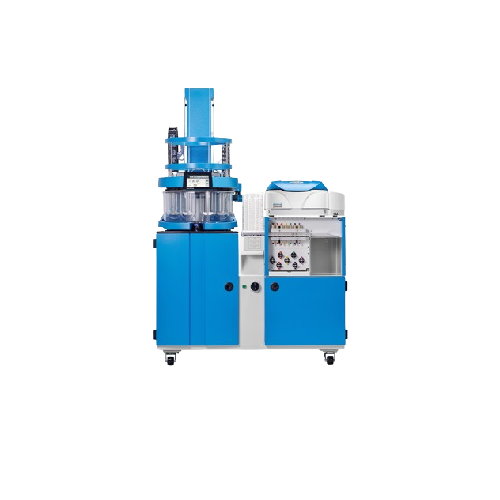
Advanced dissolution tester for pharmaceutical laboratories
Achieve consistent and reproducible dissolution results with...
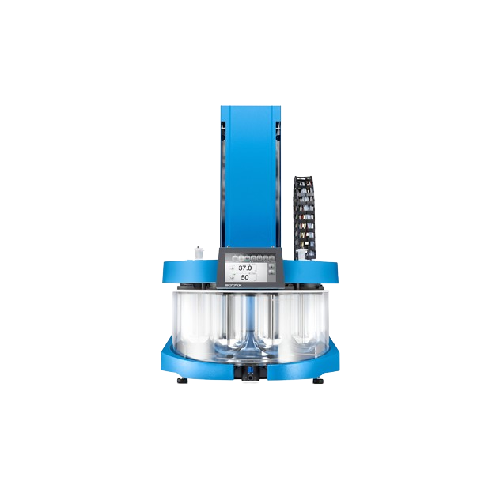
Manual dissolution tester for pharmaceutical applications
Achieve precise and repeatable sampling in pharmaceutical test...
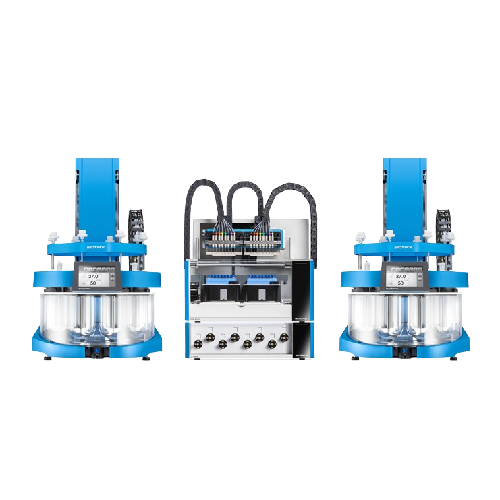
Automated dissolution sample collection system
Double your testing efficiency with parallel dissolution sampling, ensuring...

Automated dissolution testing with direct Hplc injection
Streamline your lab operations with precise and efficient direct...
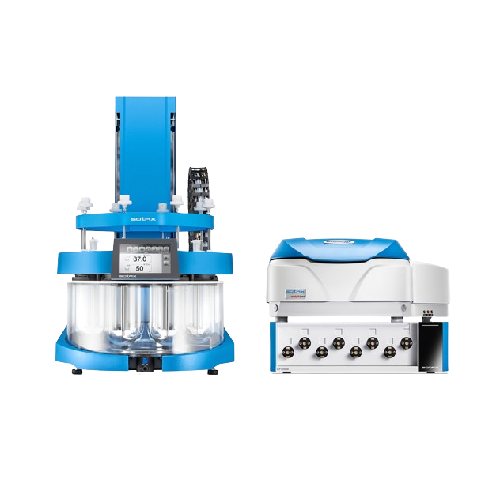
Integrated Uv-vis spectrophotometer for dissolution testing
Streamline your dissolution testing with real-time UV-Vis an...
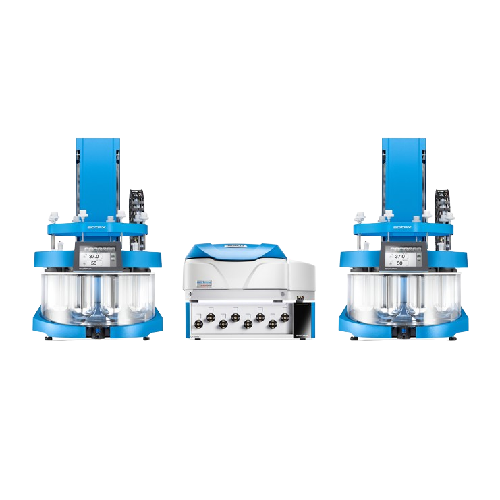
Real-time Uv-vis analysis for dissolution testing
Efficiently perform dual dissolution tests simultaneously, seamlessly i...
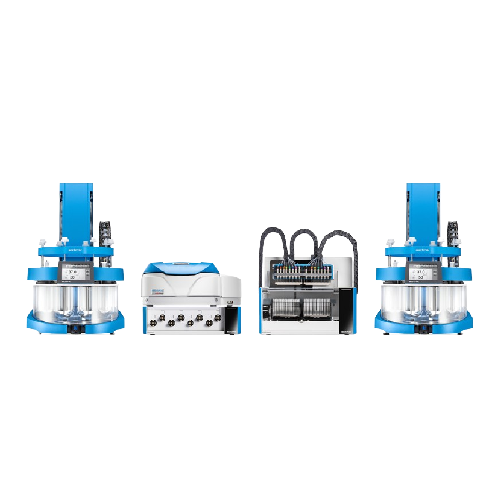
Automated dissolution testing system for 16 vessels
Maximize your laboratory throughput by conducting parallel dissolutio...

Dissolution testing software for automated analysis
Streamline your laboratory testing with seamless data capture and in-...
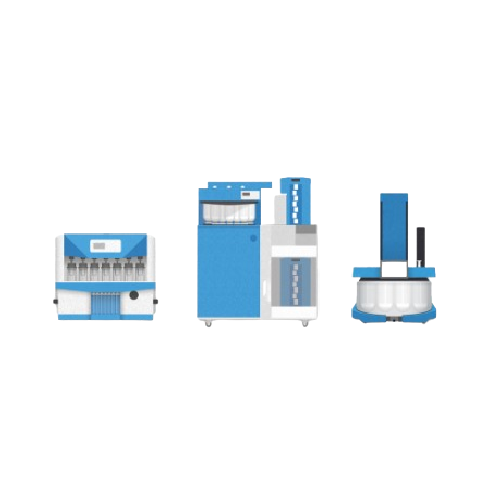
Dissolution testing software for pharmaceutical industry
Optimize dissolution testing with advanced software that manages...

Automated sample preparation software
Enhance your laboratory’s efficiency with a software solution that automates sa...
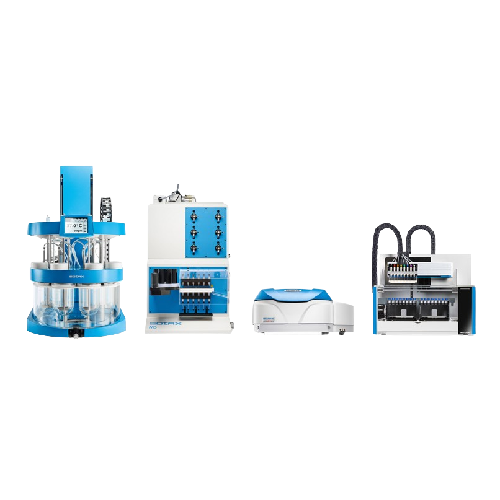
Benchtop dissolution tester for multiple test runs
Streamline your laboratory’s workflow with a fully automated ben...
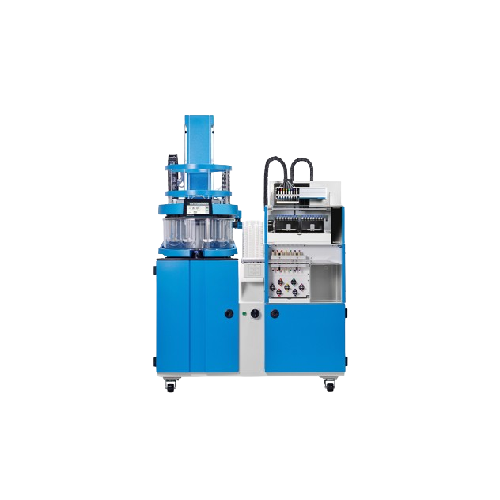
Self-cleaning dissolution tester for automated series testing
Achieve unparalleled precision in dissolution testing with...
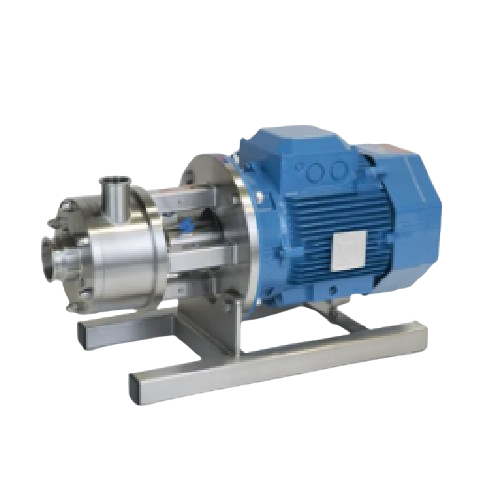
High shear mixer for efficient particle size reduction
Achieve rapid and precise blending and particle reduction in your ...
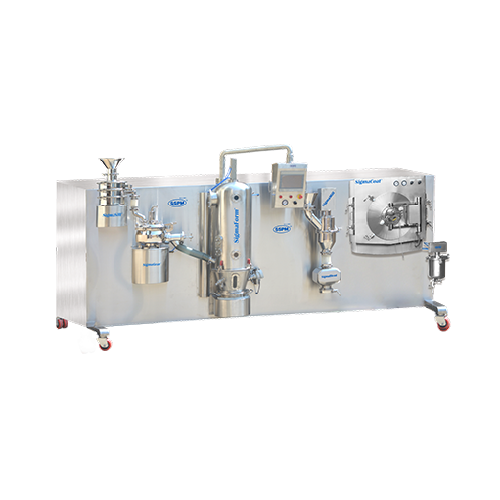
Compact wet granulation r&d system
Ensure precise formulation of pharmaceutical powders with a scalable, lab-friendly syste...
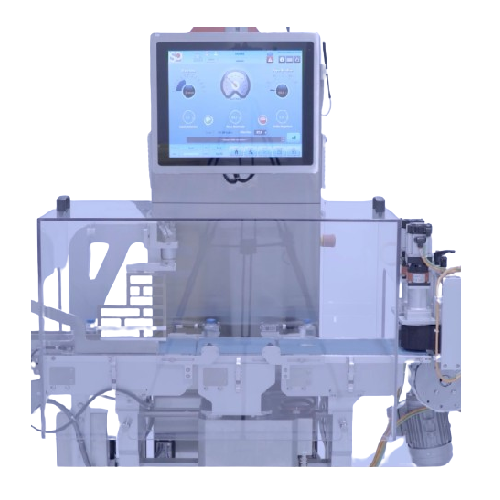
High precision pharmaceutical checkweigher
Ensure precise weight compliance in high-speed production lines with this advan...
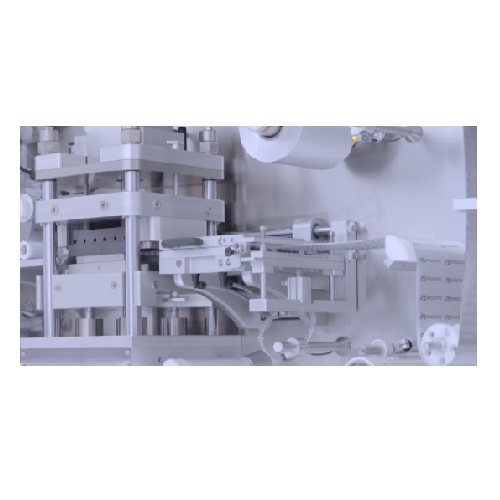
Automatic blister packaging for pharmaceuticals
Experience precise blister packaging that ensures product integrity and qu...

Pneumatic conveying system for dry bulk powders
Ensure seamless and contamination-free transfer of pharmaceutical powders ...
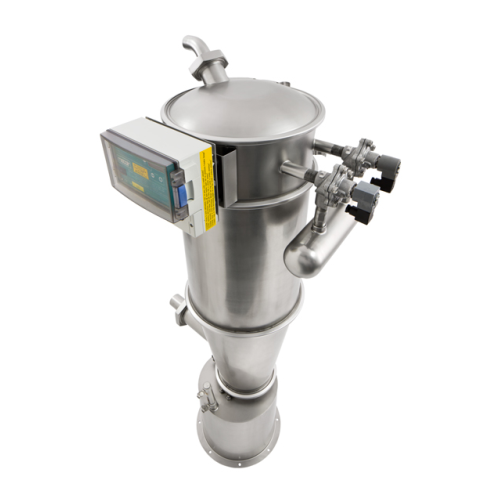
Industrial vacuum conveying system
Simplify bulk material movement and separation with a versatile vacuum conveying system,...
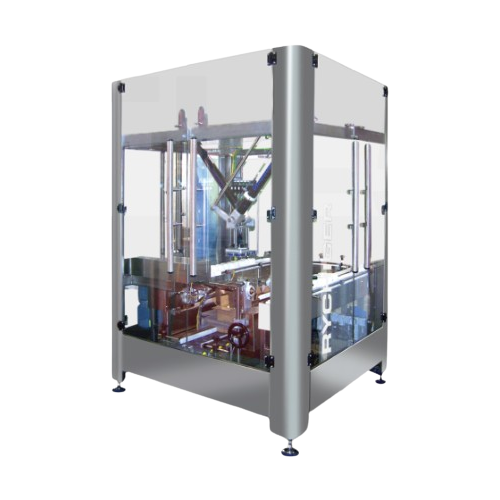
Top-loading delta robot automation solution
For high-speed operations requiring precise product handling, this top-loading...
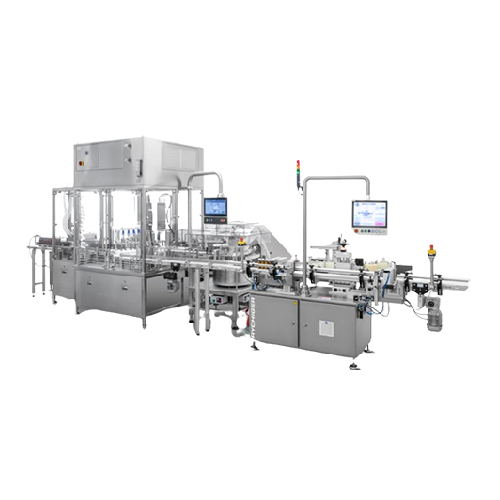
Rotary transfer system for pharmaceutical product filling
Ensure precise and hygienic filling of diverse pharmaceutical ...
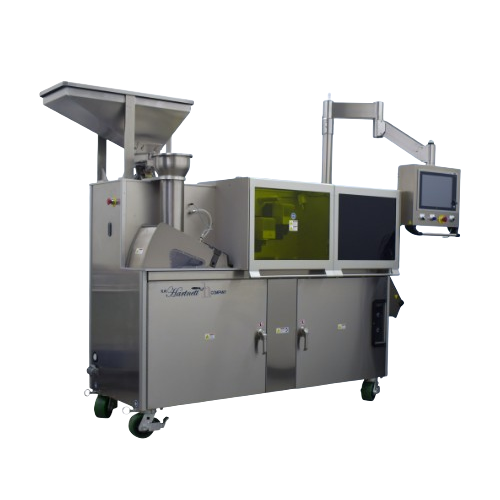
Dual laser capsule marking system
Ensure precise and rapid laser marking of tablets and capsules with a dual-laser system, ...
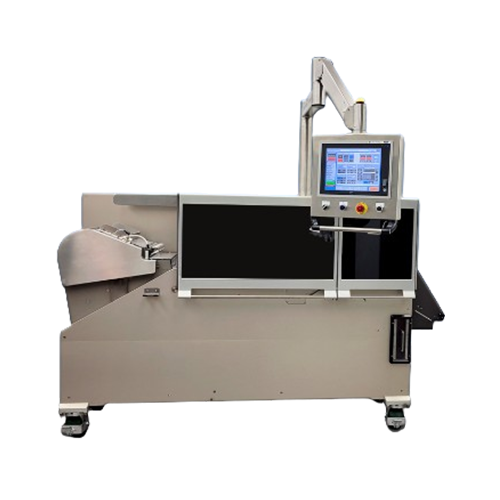
High-speed laser writer for soft gelatin capsules and caplets
Achieve precise laser marking on up to 300,000 tablets or ...
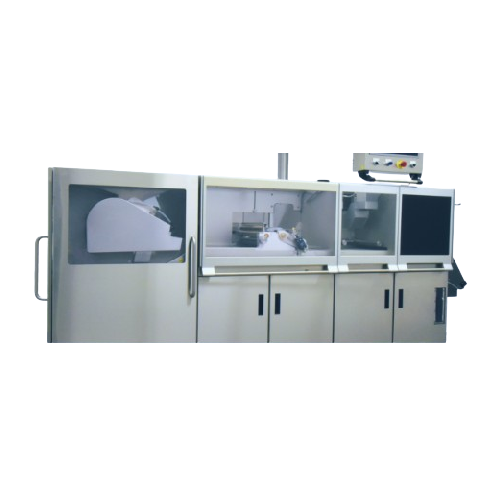
Combination ink printing and laser writing for high-speed production
Achieve precise ink printing and laser marking at ...
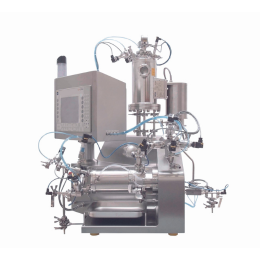
Agitator bead mill for API
To achieve precisely defined API properties and safe and reproducible production, rigorous implem...

Continuous roller compactor for dry granulation of pharmaceuticals
When making tablets, pharmaceutical manufacturers ne...

Container blender for pharmaceuticals
Manufacturing pharmaceutical solids like tablets requires using a proper blender to b...
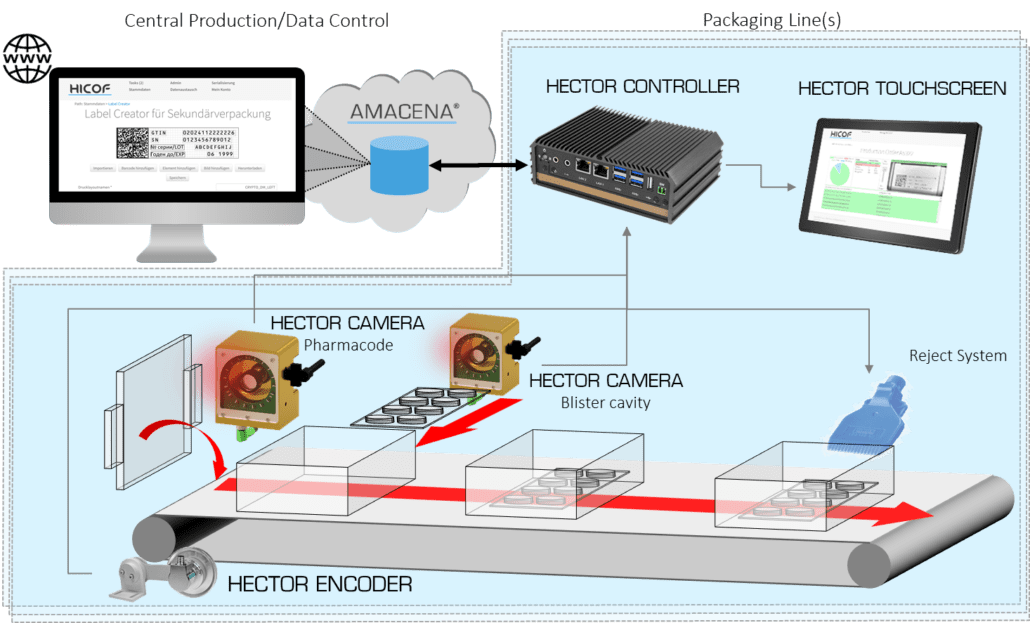
Serialization and aggregation inspection system
Including serialization and aggregation inspection systems to packaging li...

Blister inspection system
The pharma and healthcare industries widely use blister thermoforming machines to package a variet...

Semi-automatic forming and sealing blister machine
As a manufacturer of medical device, the packaging is a critical facto...
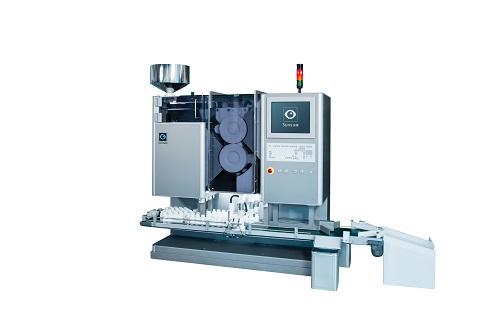
High speed bottle filler with inspection
Medicines in tablet, capsule, or soft gel forms undergo various processes before r...
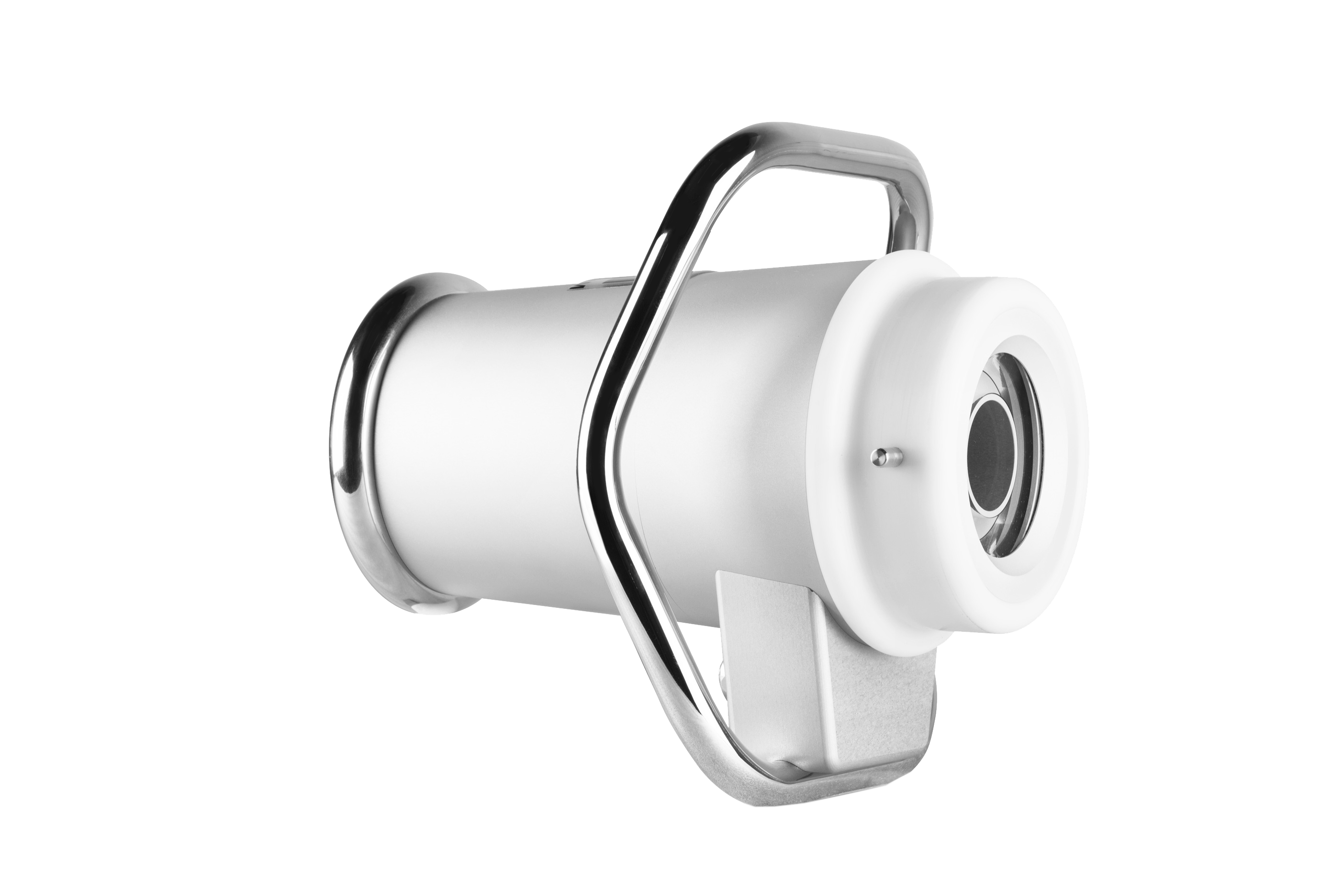
Particle analysation monitor
Products like granules, tablets and capsules require inspection at numerous steps in the produc...
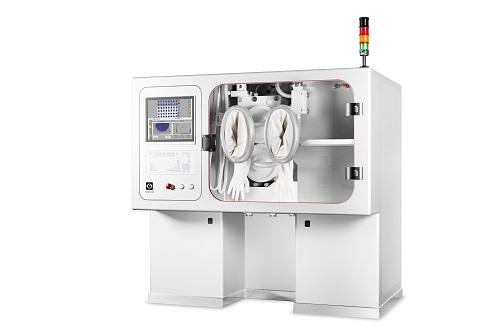
Contained Visual Inspection System
In the medicine industry, it is important to ensure there are no defects in tablets or c...
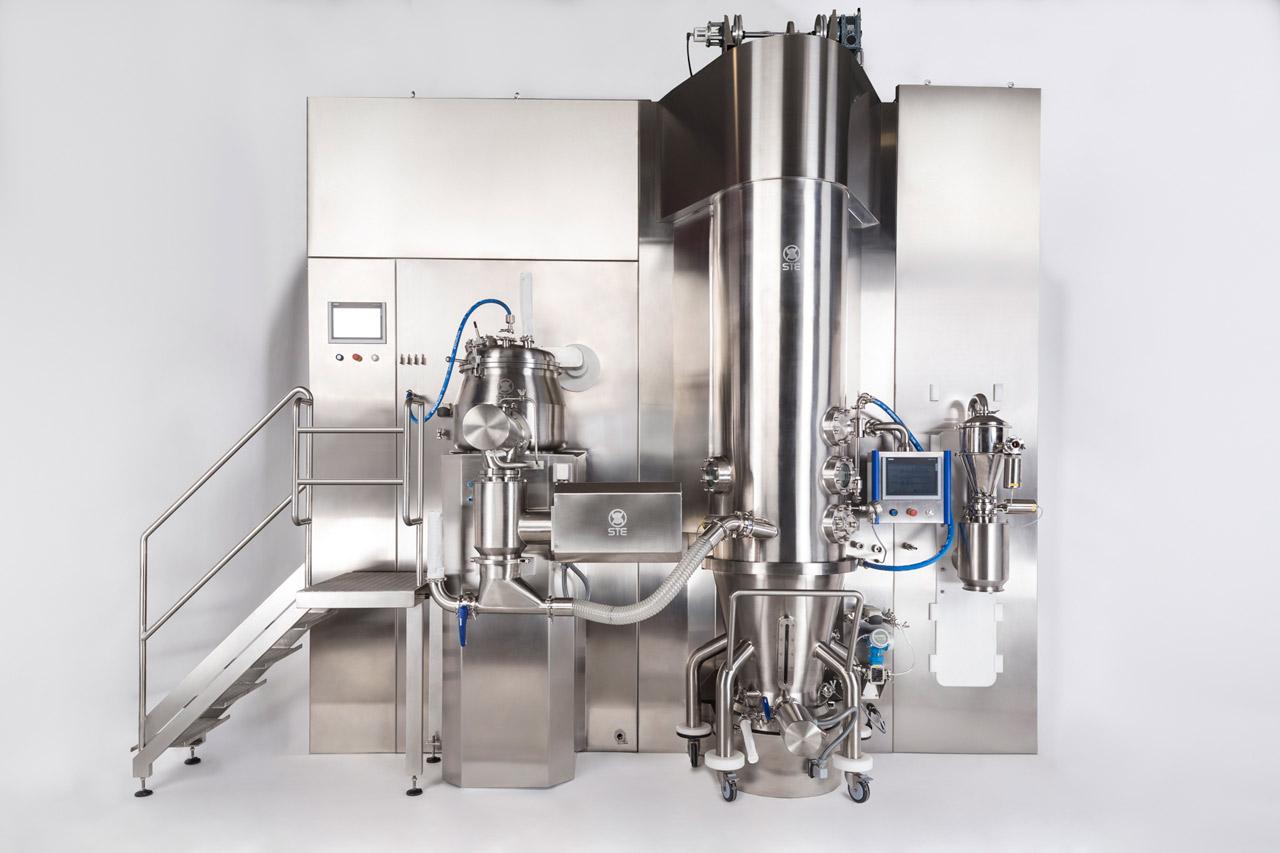
Granulation line for pharmaceutical solid dosage forms
Granulation is a common technique in production of pharmaceutical ...
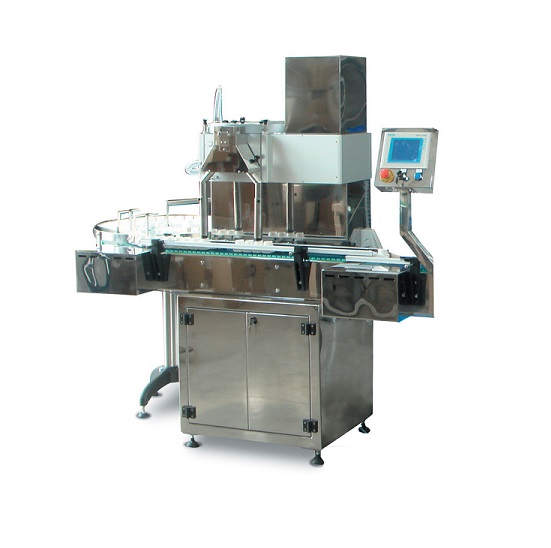
Automatic filling line for solid doses
For medium-scale production of solid doses such as tablets, capsules, and softgels t...
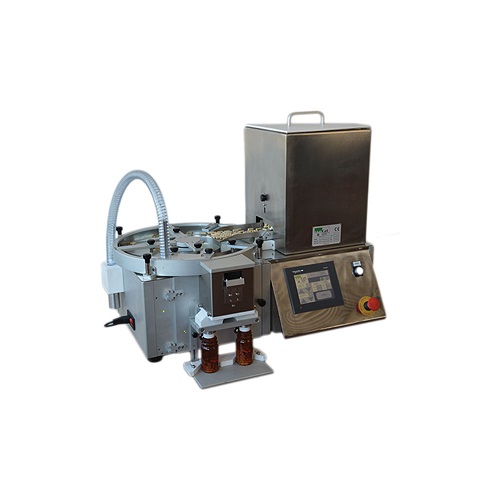
Electronic capsule counter
For lab work or small batch production, hand counting of solid doses into dispensing containers i...
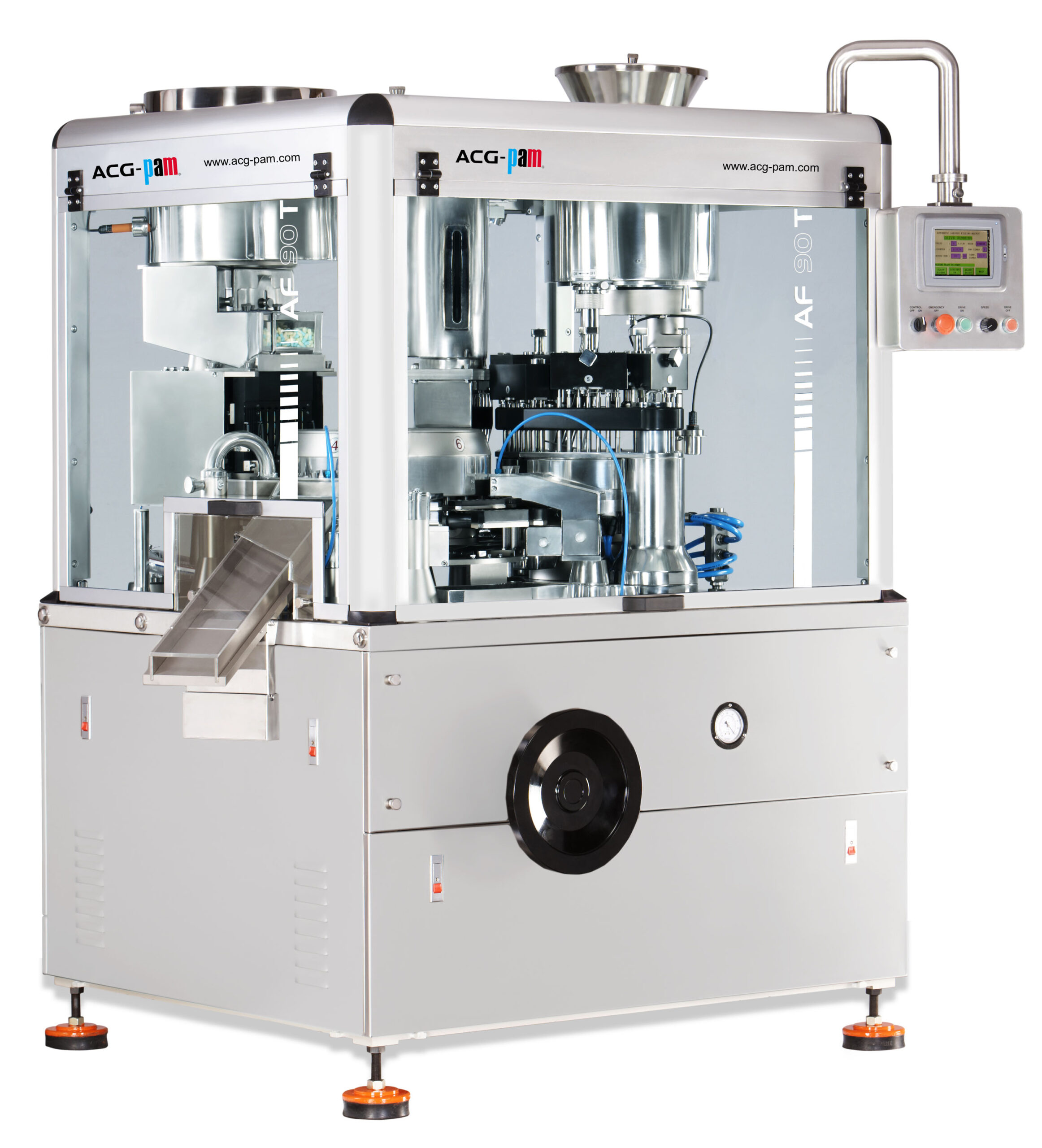
Automatic capsule filler
Capsule filling should be a worry-step in pharmaceutical and nutraceutical manufacturing. The right...
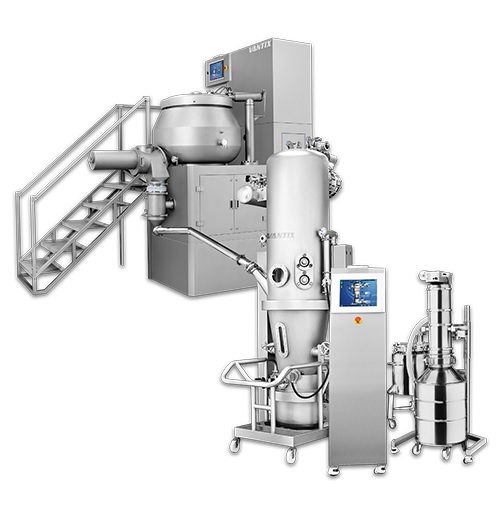
Granulation line of mixer and fluid bed dryer
A complete granulation line allows for the mixing and granulation of pharmac...
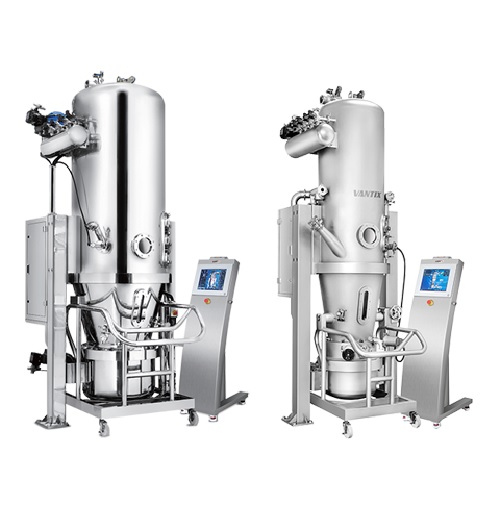
Fluid bed dryer for production scale
Fluidized bed drying (FBD) is a common process in the pharmaceutical industry for dryi...
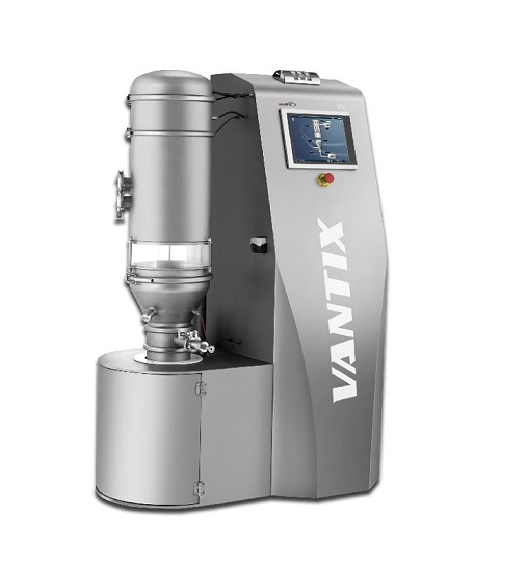
Fluid bed dryer for lab scale
Fluidised bed drying (FBD) is a common process in the pharmaceutical industry for drying compo...
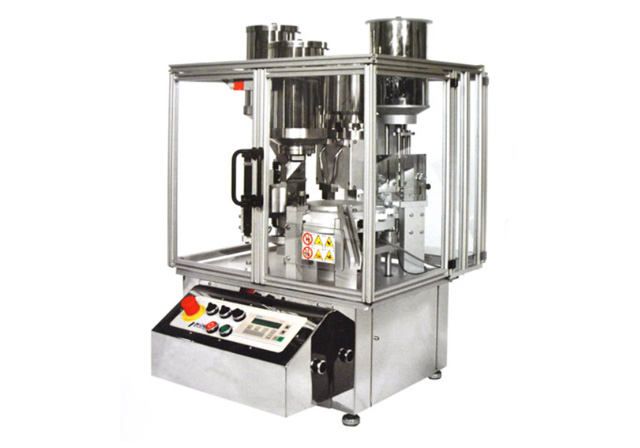
R&D automatic capsule filler
Automatic capsule filling machine for powders, pellets, tablets, mini-tablets, capsule in capsu...
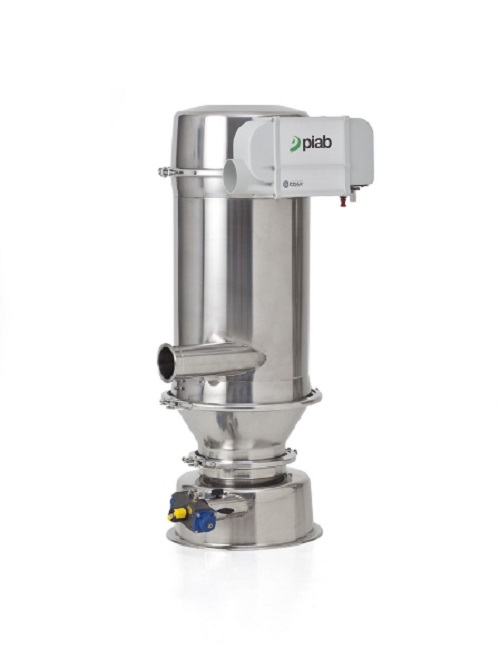
Premium vacuum conveyor
When you have a need to tailor make your conveyor and still have the high requirement on hygiene, e.g...
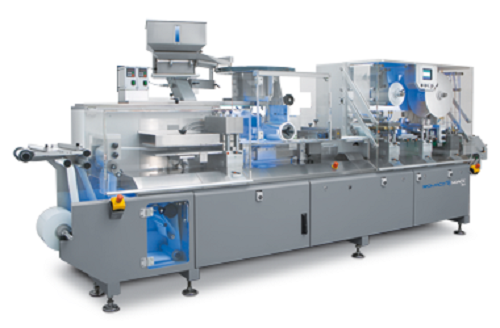
Compact blister machine
A compact blister machine ideal for packing tablets, capsules, ampoules and syringes and other applic...
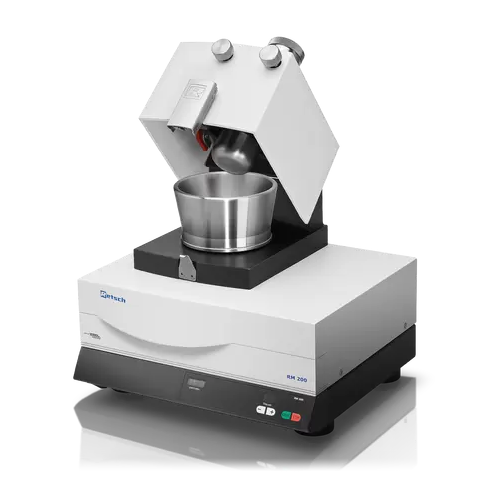
Mortar grinder for reproducible sample preparation
Achieve precise and consistent material preparation with this mortar g...
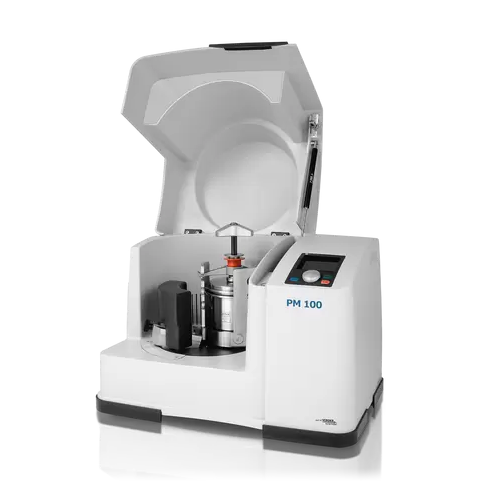
Planetary ball mills for fine grinding of materials
Optimize particle size and surface area in your samples with high-ene...
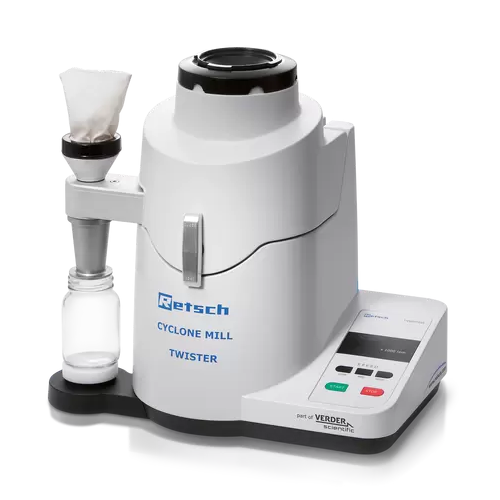
Cyclone mill for Nir analysis sample preparation
Ensure accurate NIR analysis by optimally preparing samples with efficien...
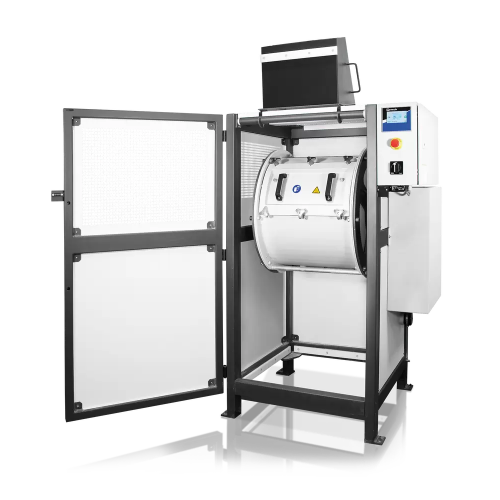
Laboratory drum mill for large sample volumes
Efficiently process large volumes of diverse materials into precise particle...
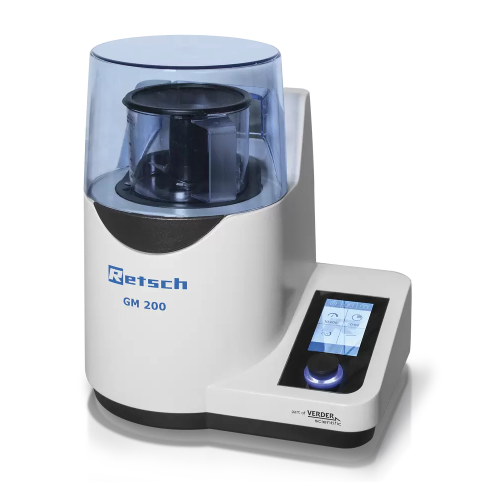
Knife mill for food and feed sample grinding and homogenization
Achieve consistent texture and precise size reduction of...
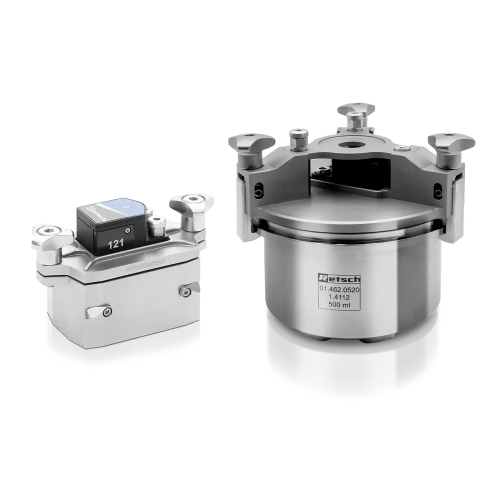
Pressure and temperature monitoring system for ball mills
Ensure optimal grinding conditions and enhance product quality...
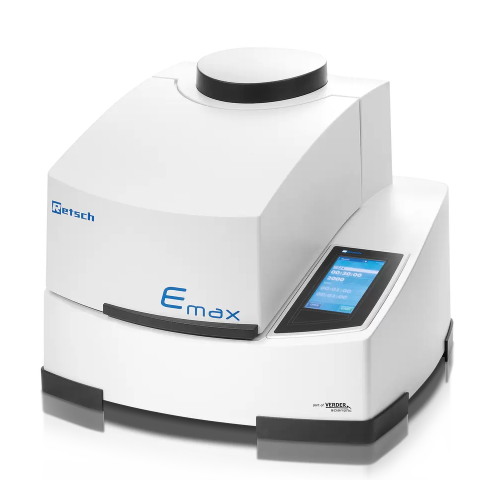
High energy untra fine ball mill
Achieve ultra-fine particle sizes rapidly with this high energy milling solution, designed ...
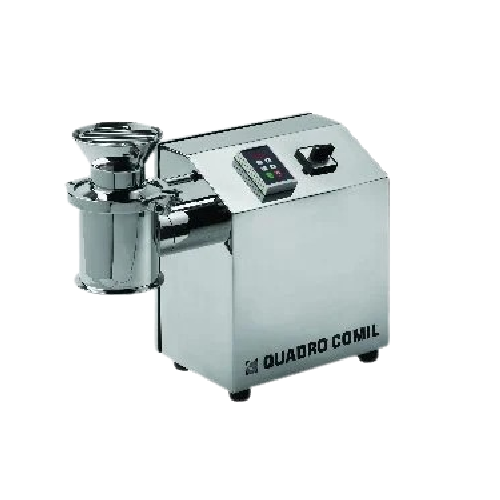
Conical mill for high-capacity powder milling
Optimize your powder milling process with efficient conical milling systems ...
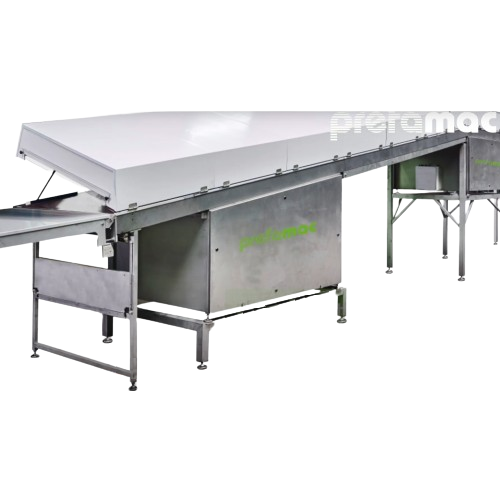
Filling system for chocolates and pralines
Efficiently dose, mold, and fill chocolates to create a variety of enticing con...
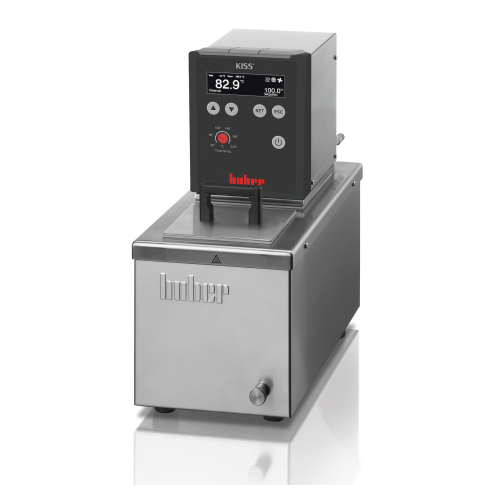
Heated circulator for laboratory temperature control
Achieve precise temperature control for demanding applications like ...
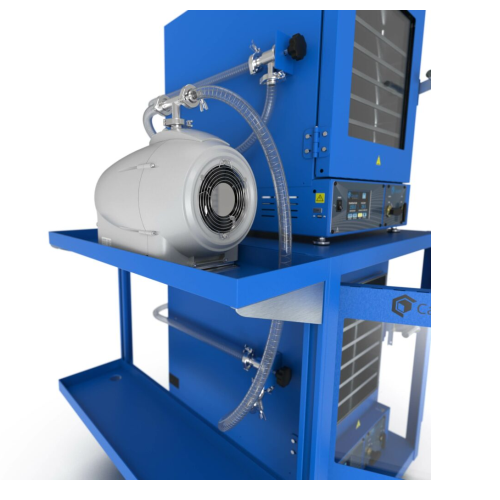
Dry scroll vacuum pumps for laboratories and manufacturing
Ensure a clean, oil-free environment with advanced dry scroll...
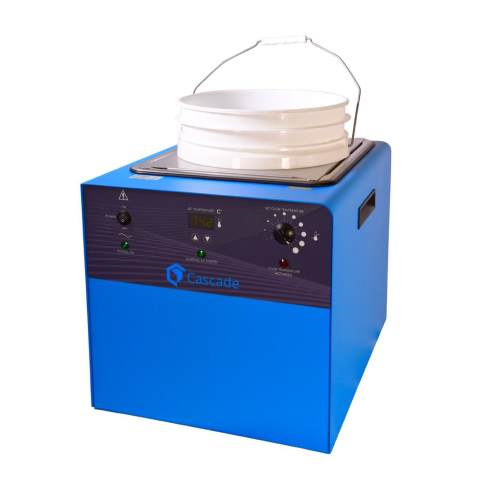
Deep water bucket bath for lab heating applications
Achieve precise temperature control and uniform heating for delicate ...

Digital stir controllers for laboratory applications
Achieve precise stirring and mixing control with this digital soluti...
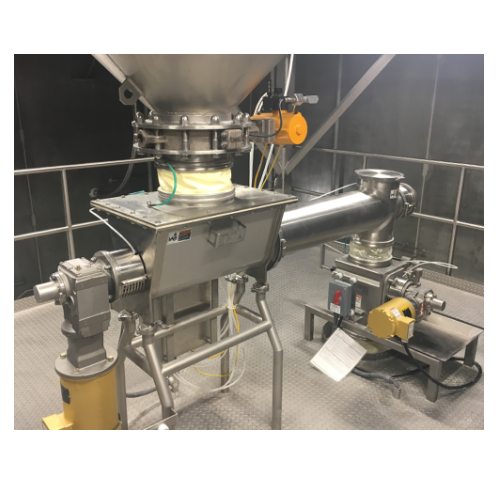
Mechanical conveyors for powder transport
Optimize your powder and granule handling with precise, customizable conveying s...
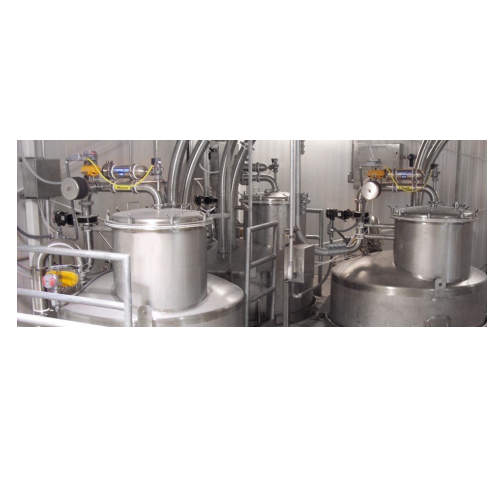
Air filtration system for dairy and food powder processing
Optimize powder processing with advanced air filtration, ensu...
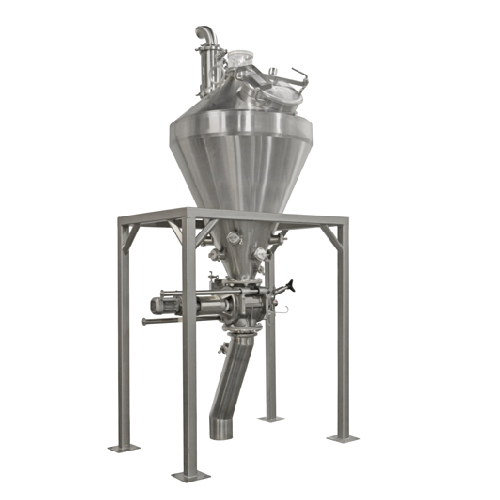
Storage silos and hoppers for food and dairy industries
Ensure optimal powder storage with solutions that enhance space e...
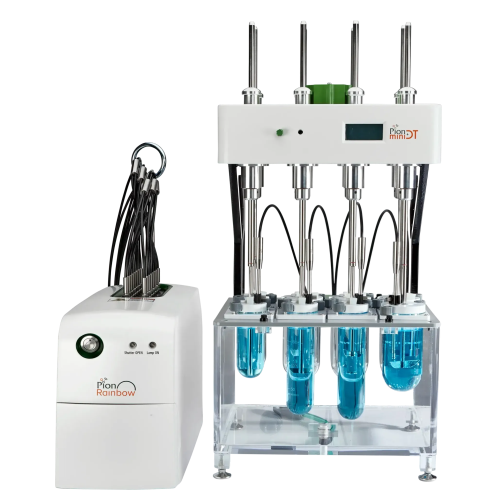
Dissolution profiling system for biorelevant media volumes
Optimize your lab’s efficiency by integrating this dissolutio...
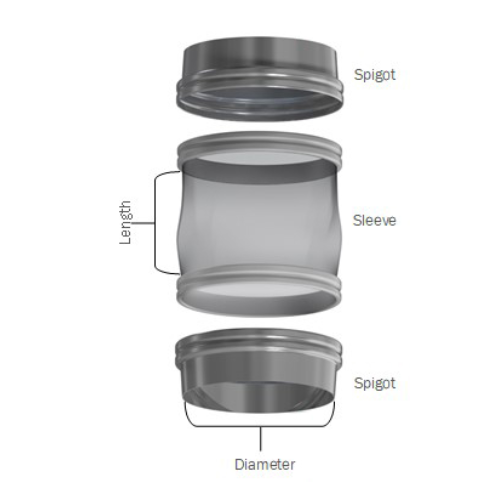
Flexible connector for bulk powder manufacturing
Eliminate leakage and enhance hygiene in your powder processing with a sn...
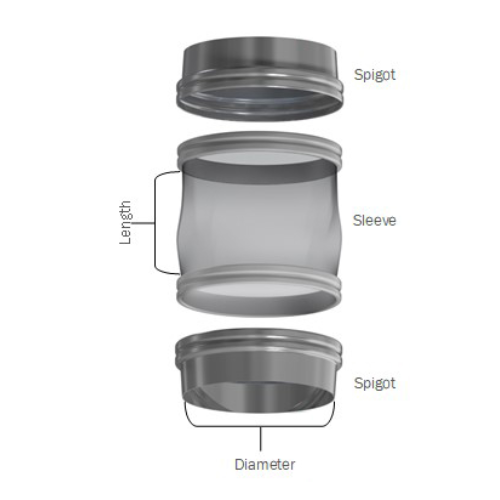
Flexible connector system for bulk powder processing
Eliminate leaks and enhance hygiene in your powder processing line w...
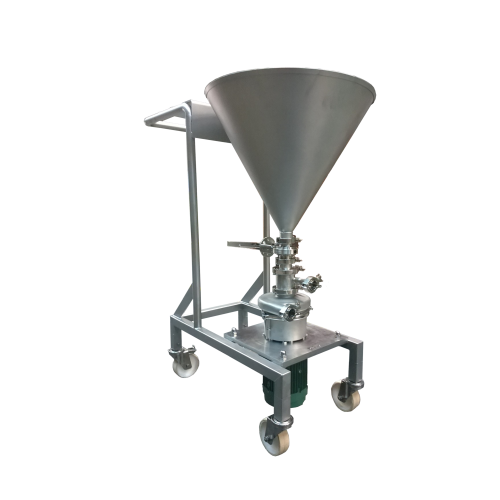
Powder and liquid mixing system for food and life sciences
Achieve rapid and homogeneous dissolution of large quantities...
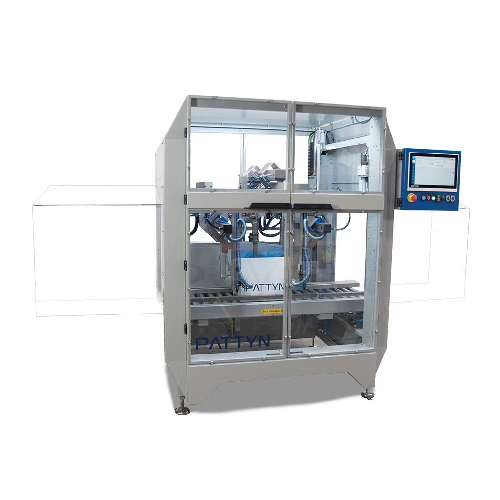
Automatic bag folding solution for bulk packaging
Enhance your production line efficiency and product protection by integ...
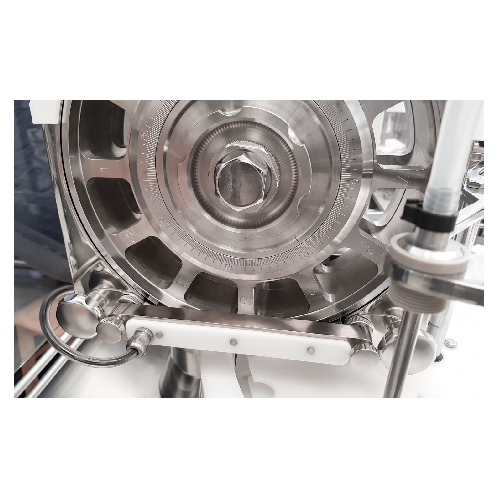
Micro-dosing system for pharmaceutical powders in vials
Ensure accurate aseptic dosing of sensitive pharmaceutical powder...
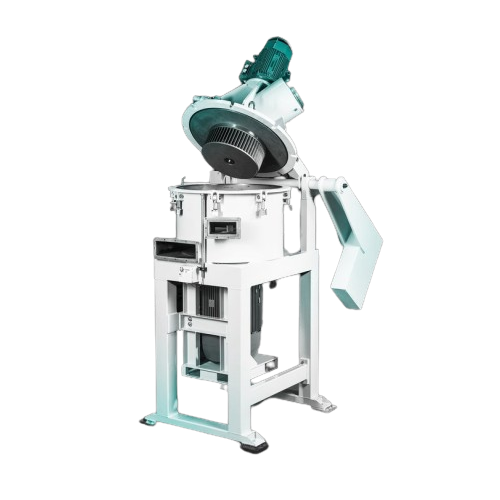
Energy-efficient impact classifier for superfine grinding
Achieve precise superfine grinding with energy efficiency, per...
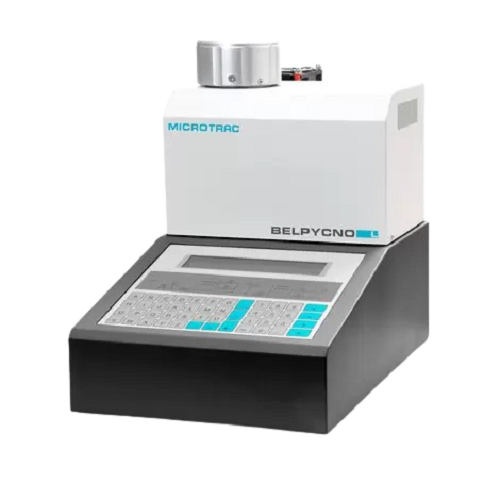
Gas pycnometer for precise density determination
Achieve accurate and reliable density measurements for a diverse range of...
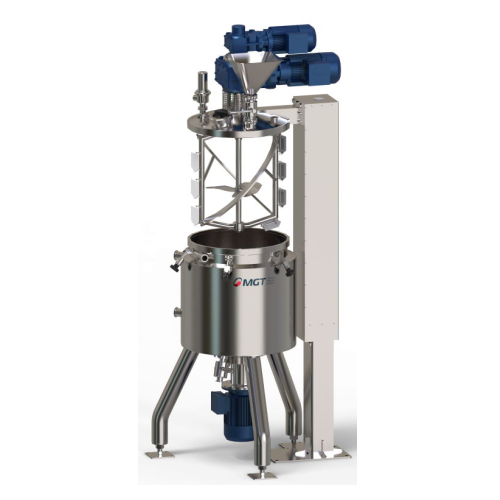
Vacuum mixing system for emulsion and homogenization
Achieve seamless emulsion and homogenization with precision: this sy...

Membrane filtration system for bioburden and water testing
Ensure accurate microbial detection and efficient filtration ...
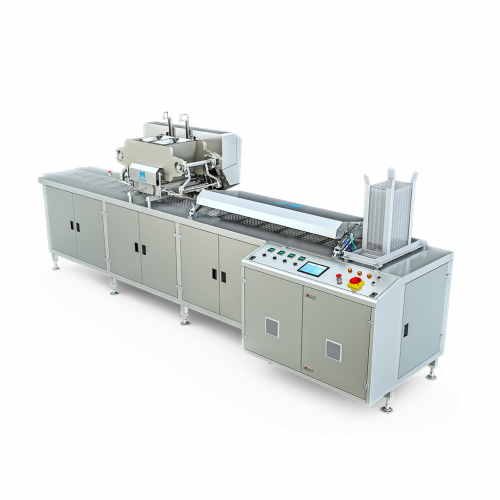
Chocolate one-shot moulding line
Streamline your chocolate production with a high-speed moulding line designed to simultaneo...
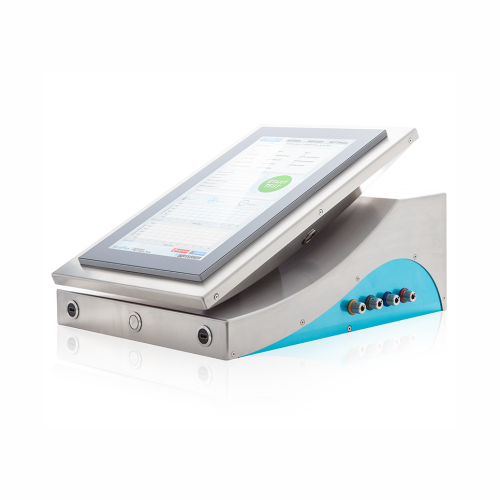
Integrity tester for filtration system validation
Ensure precise validation of your filtration systems with highly accura...
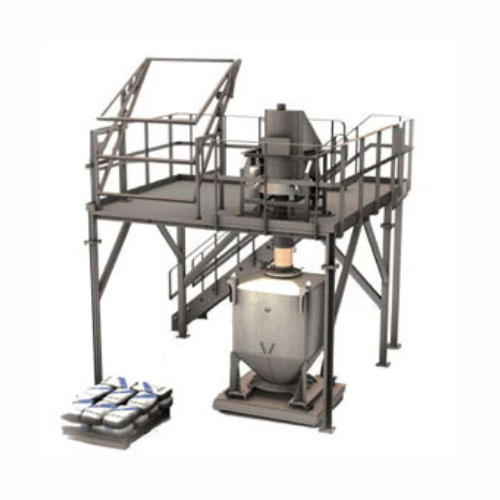
Small powder recipe formulation system
Streamline the formulation of diverse powder recipes with seamless integration into ...
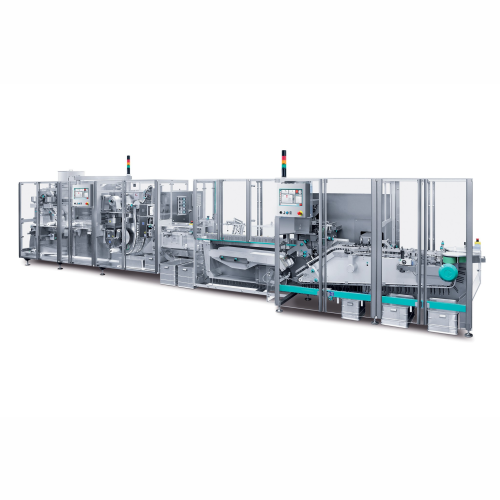
Blister thermoforming solution for pharmaceutical packaging
For high-speed blister packaging of solid dose pharmaceutica...
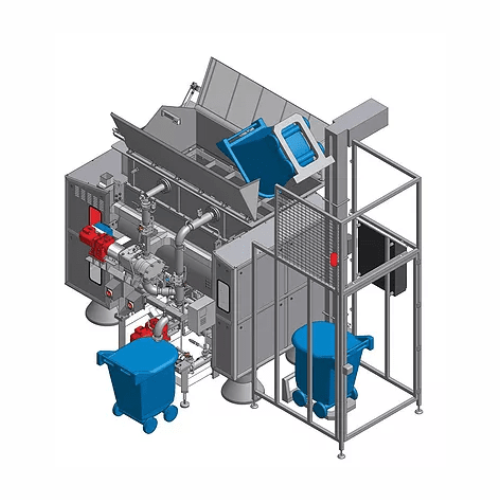
Industrial product rework system
Efficiently rework products while minimizing waste with a robust system designed for precis...
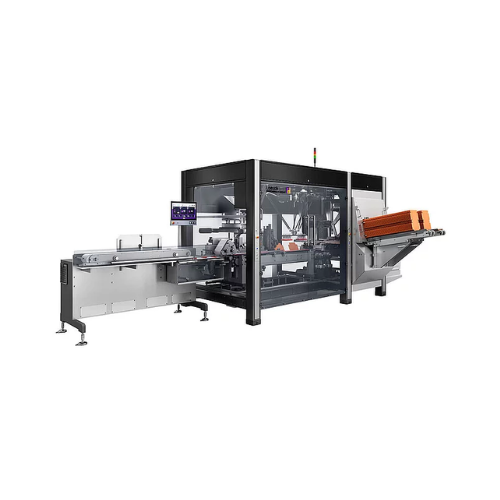
Top-loading cartoner for bar and confectionery packaging
Optimize your high-speed packaging operations with a flexible ca...

Hygienic mixer for batch operation
Achieve consistent and precise mix quality across diverse powders and granules with this...
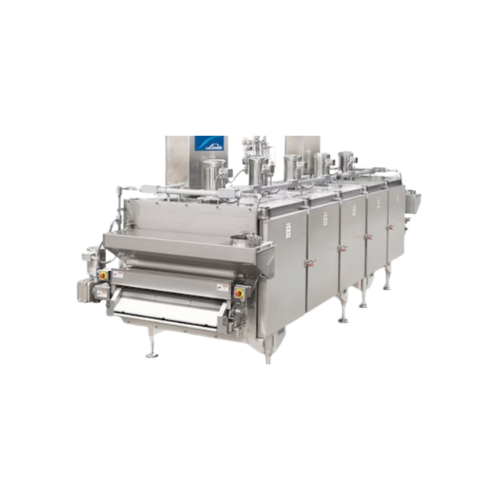
Cryogenic freezing systems for food processing
When you need precise and rapid freezing for diverse food products, these a...
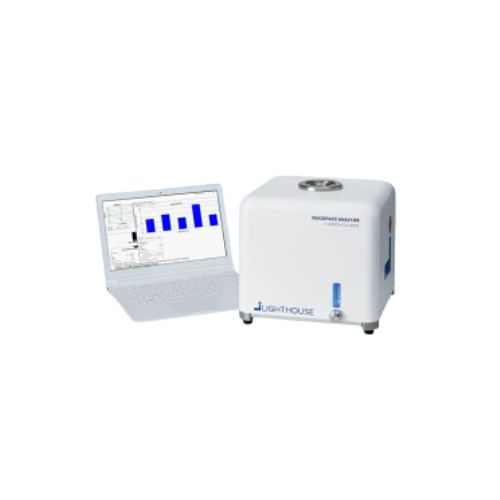
Carbon dioxide headspace analyzer for parenteral containers
Ensure accurate headspace gas analysis to maintain container...
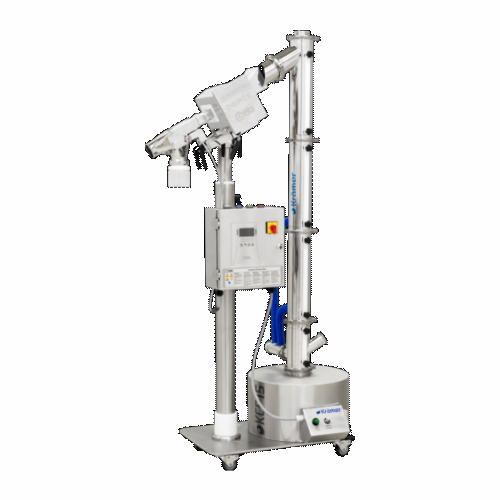
Capsule polisher for pharmaceutical capsules
Ensure your capsules are free from dust and perfectly polished with a solutio...
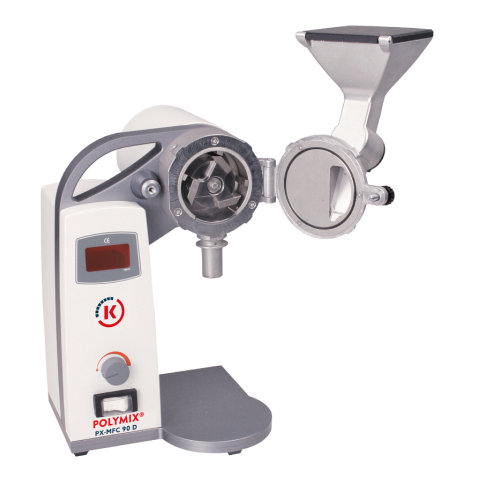
Dry sample preparation mil
Optimize your grinding processes with precision particle size reduction for various materials, en...
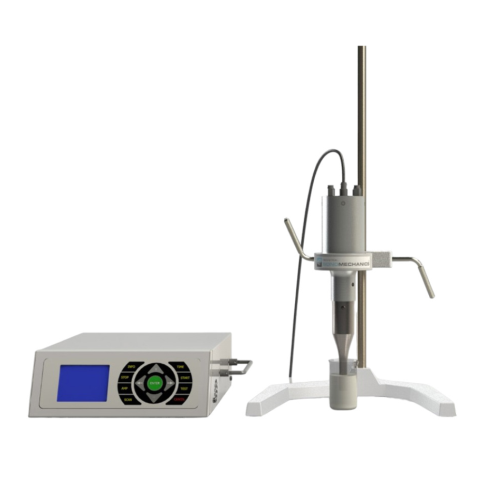
Ultrasonic liquid processor for feasibility testing and procedure optimization
Optimize your liquid formulations by en...
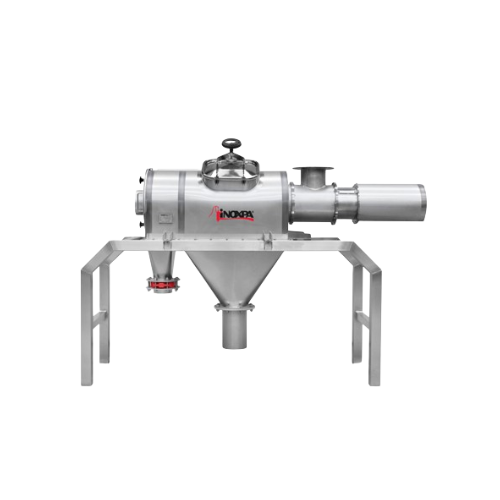
Industrial sieving solution for solid materials
Effortlessly separate impurities and adjust particle size for optimal prod...
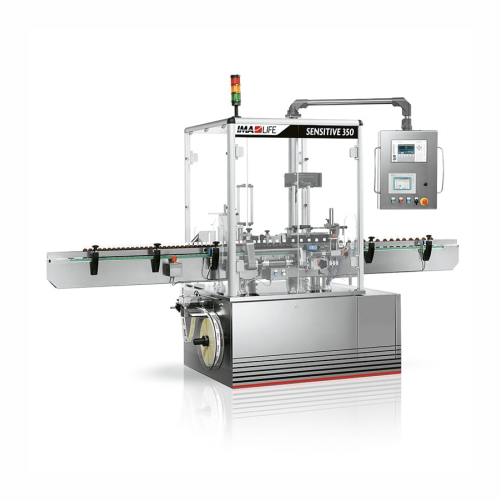
Labelling solution for cylindrical containers
Achieve precise and efficient labelling for cylindrical containers with a sy...
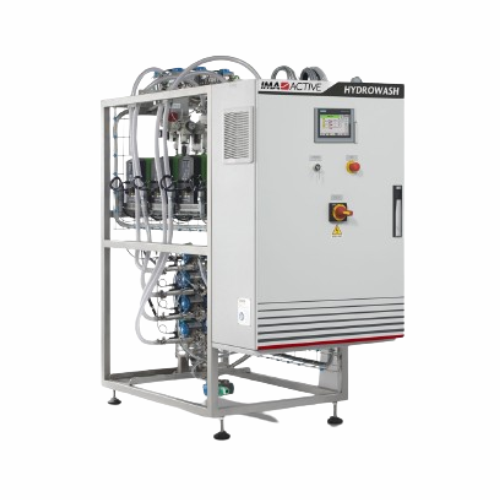
Industrial washing skid for pharmaceutical components
Ensure precise cleaning and drying of pharmaceutical components wit...
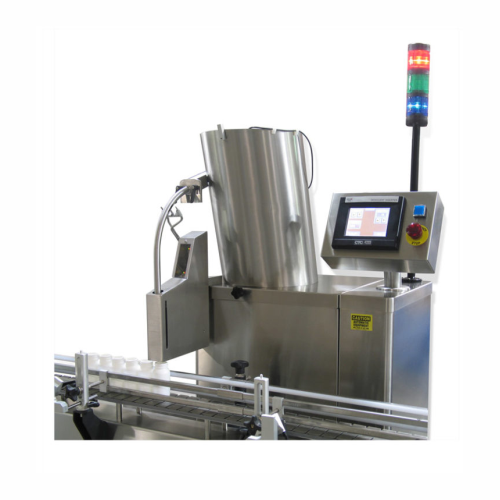
Desiccant inserter for pharmaceutical bottles
Ensure your products remain moisture-free and preserved by integrating this ...
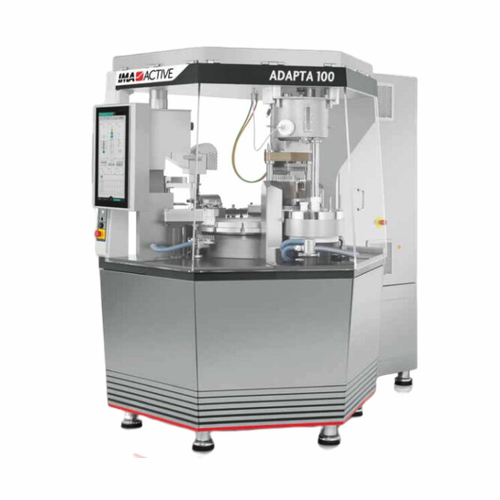
Capsule filler for multi-product dosing
Achieve precision and flexibility in capsule filling with a system designed for hig...
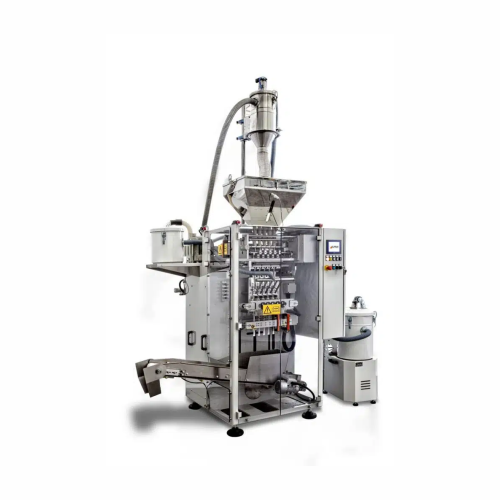
Vertical stick pack sachet packaging solution
Ideal for mid-scale operations, this vertical stick pack machine streamlines...
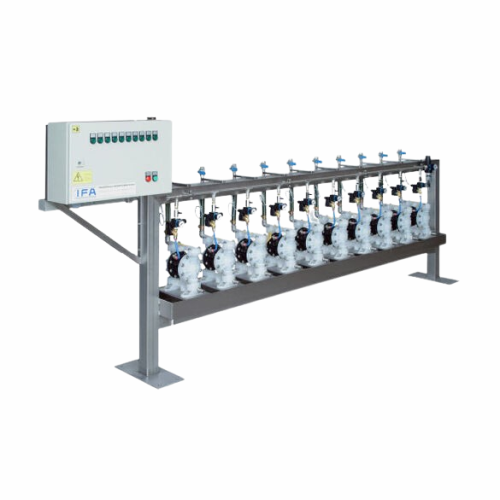
Pneumatic conveying systems for industrial applications
Efficiently transport bulk materials or liquids across your produ...

Pure steam sample cooler for pharmaceutical industry
Ensure sterile sampling of pure steam while maintaining precise cool...
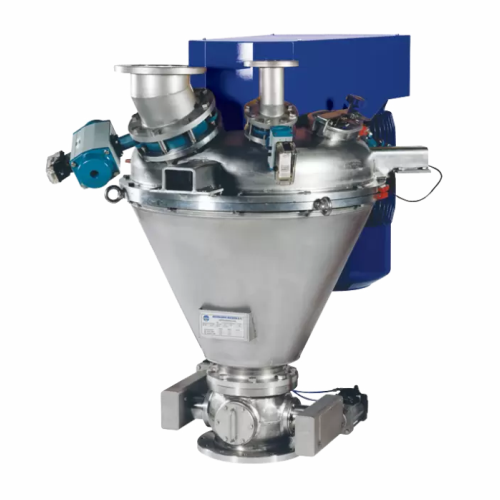
High shear impact mixer for agglomeration and dispersion
Achieve precise homogeneity and efficient agglomeration with a h...
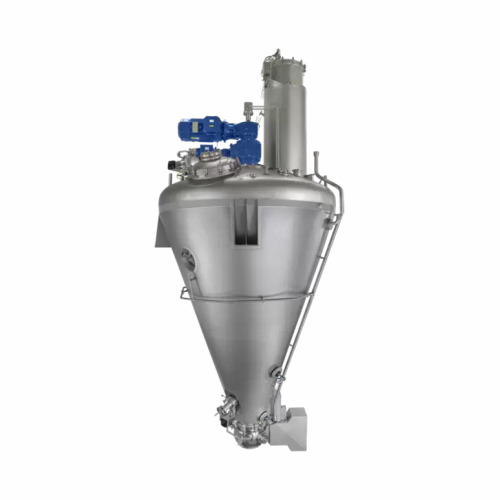
Vacuum dryer for powders and granules
Achieve precise moisture control for sensitive materials with a versatile vacuum dryi...
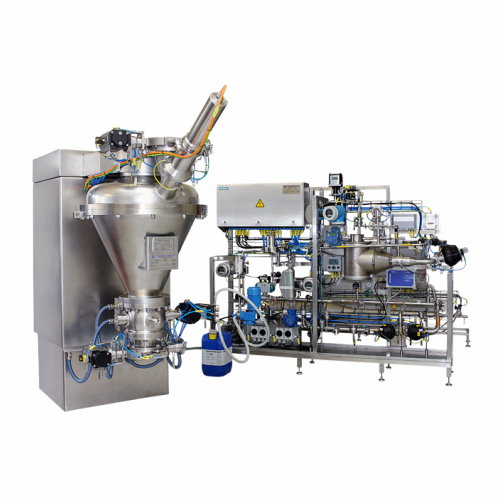
Cip/sip cleaning for solids processing systems
Ensure seamless transitions and maintain hygienic production environments w...
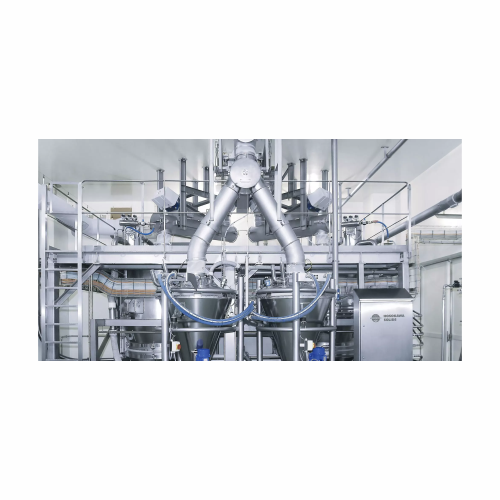
Pneumatic conveying system for bulk material handling
Efficiently transport bulk materials with precision through pneumat...

Table roller mills for mineral raw material comminution
Achieve precise mineral raw material comminution and energy-effic...
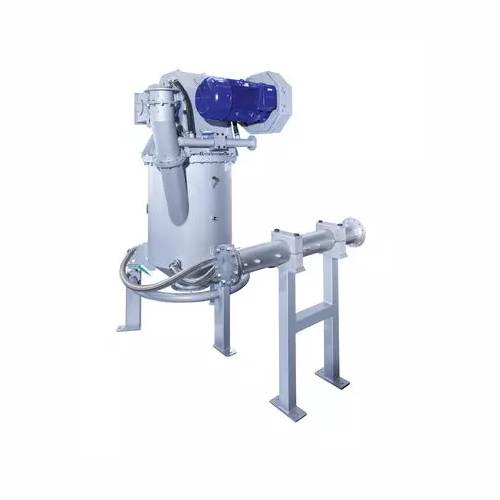
Fluidised bed opposed jet mill for fine particle processing
Achieve precise and consistent particle sizes with high-spee...
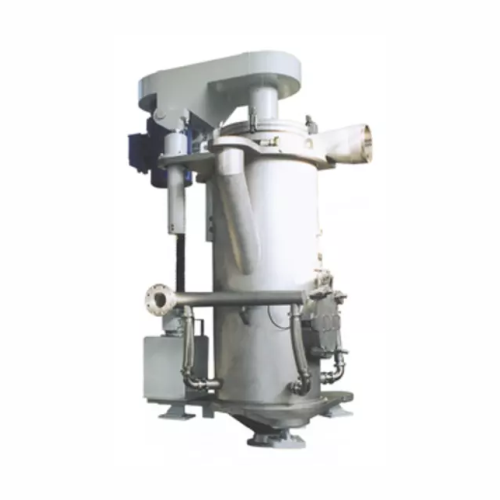
Jet mill for toner and pigment industries
Optimize particle size and distribution for high-demand applications with this h...
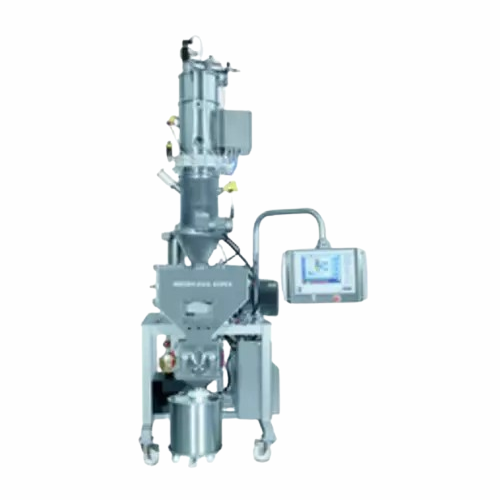
Compactor for powder processing
Designed for transforming powdered materials into uniform granules, this compactor enhances ...
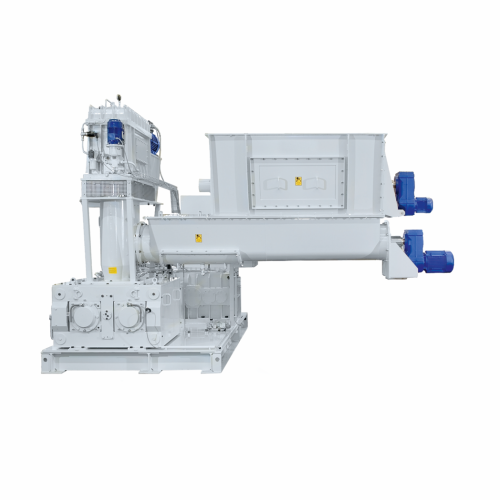
High-pressure roller compactors for chemical, food, and minerals industries
Achieve precise particle compaction and br...
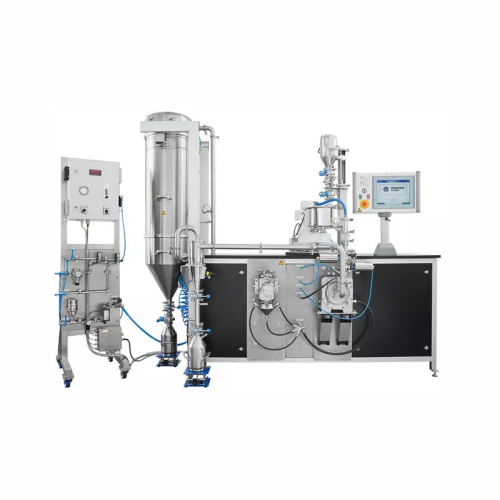
Multiprocessing system for flexible research and production
Optimize your process development with a versatile system th...

Pelleting and spheronizing equipment for chemical granulates
Optimize your production line with versatile pelleting and ...
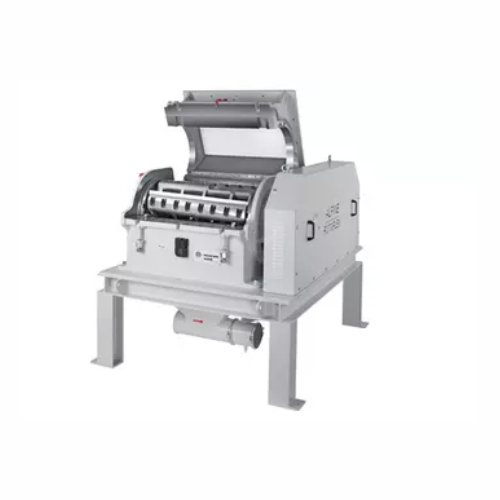
Industrial granulator for high-throughput plastic recycling
Facing challenges in efficiently recycling high-volume plast...

High-speed hammer mill for continuous operation
Achieve precise particle size reduction with high-speed hammer milling, id...
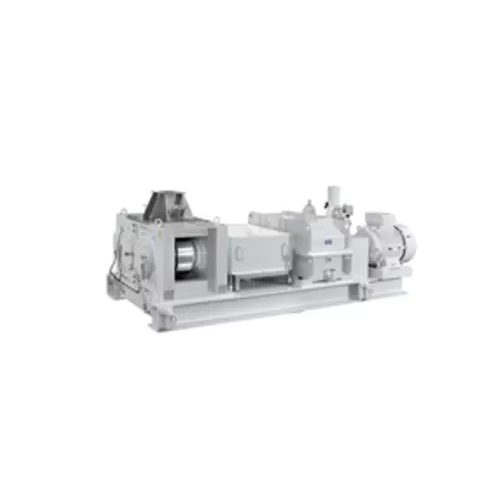
High pressure roller mill for medium-fine crushing
Achieve precision in particle size with high-pressure roller mills, id...
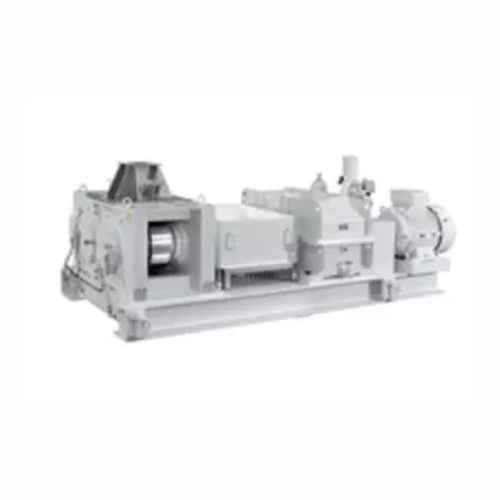
High-pressure roller mill for medium-fine crushing
Achieve precise granule distribution in medium-fine crushing applicati...
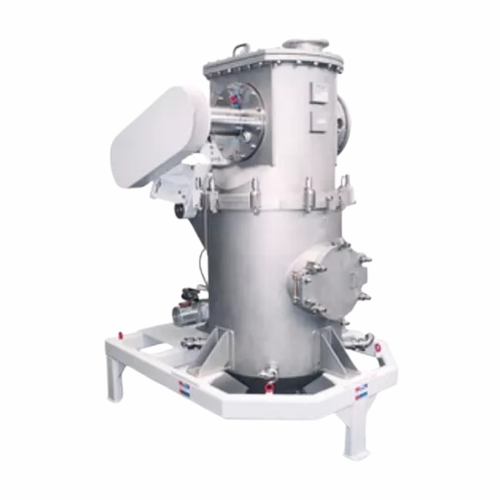
Fluidised bed opposed jet mill for ultrafine powder production
Achieve contamination-free ultrafine powder milling with ...
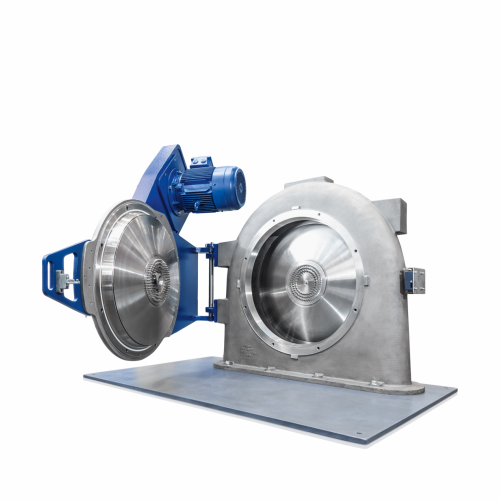
Pin mill for fine grinding of sticky materials
Achieve ultra-fine grinding of challenging materials with high speed and pr...

Sugar grinding and recrystallization system
Optimize your sugar production with a system that integrates grinding and recr...
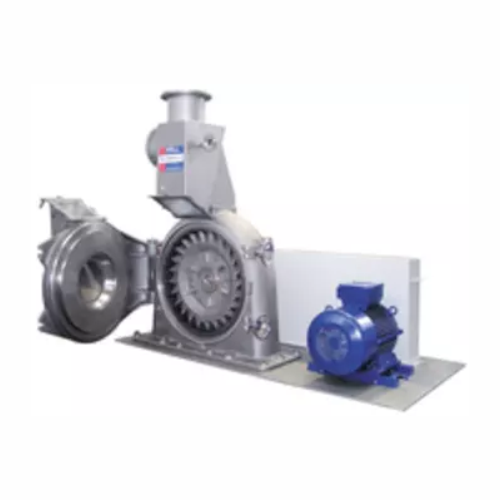
Versatile fine impact mill for soft materials
Achieve precision grinding with flexibility for a wide range of materials, e...
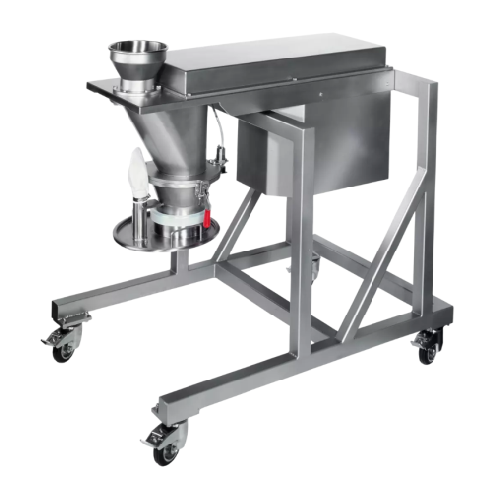
Flake crushers for gentle crushing of brittle materials
For processes needing precise granule control, our equipment ensu...
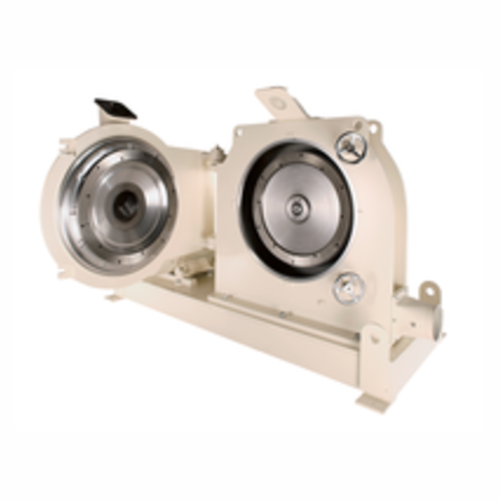
Fine cutting mill for soft to medium-hard plastics
Achieve precise size reduction and smooth particle shapes in plastic p...
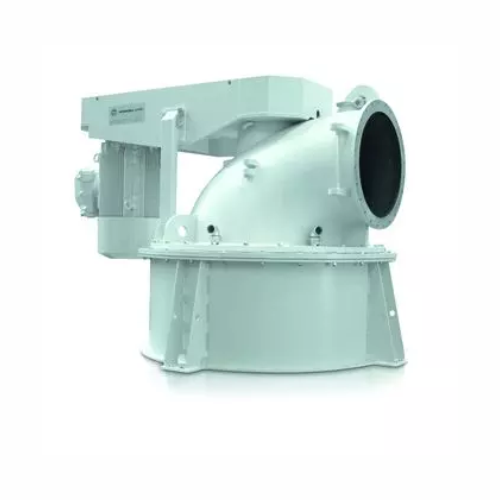
Air classifier for fine powder processing
Enhance your production line with precise particle size control and energy-effic...
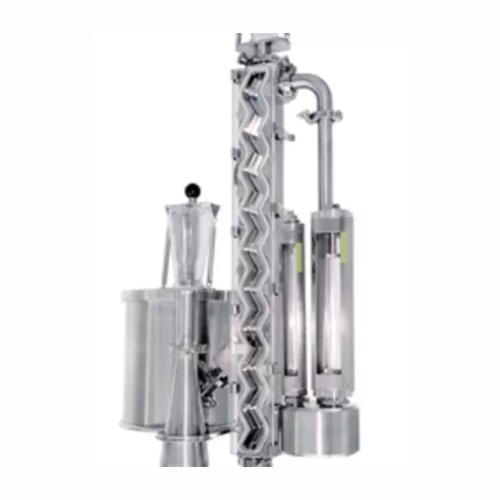
Gravity classifier for precise particle separation
Achieve sharp separations in particle processing with minimal maintena...
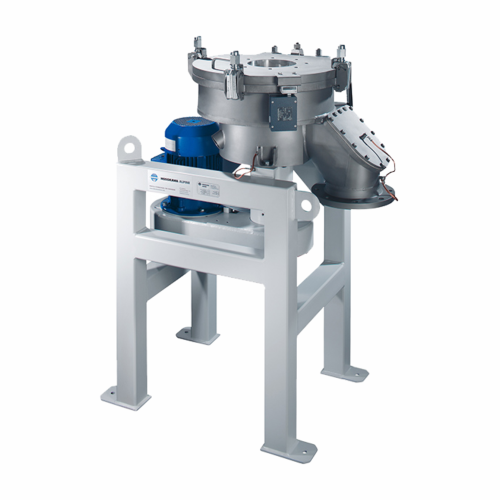
Ultrafine classifier for toner and pigments
Achieve unparalleled precision in classifying fine powders essential for high-...
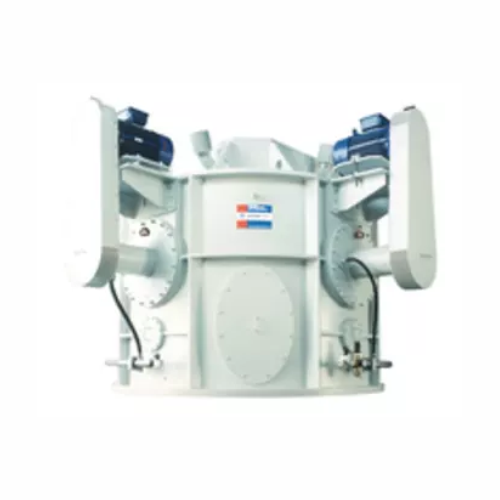
Ultrafine air classifier for powder separation
Achieve precise particle separation with technology designed to enhance you...
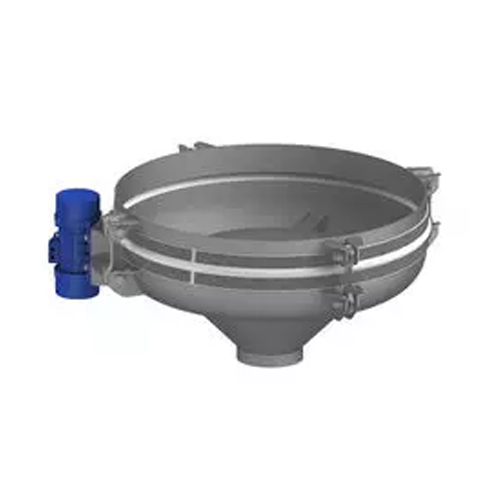
Discharge systems for difficult bulk materials
Achieve seamless bulk material discharge with our advanced systems that eff...
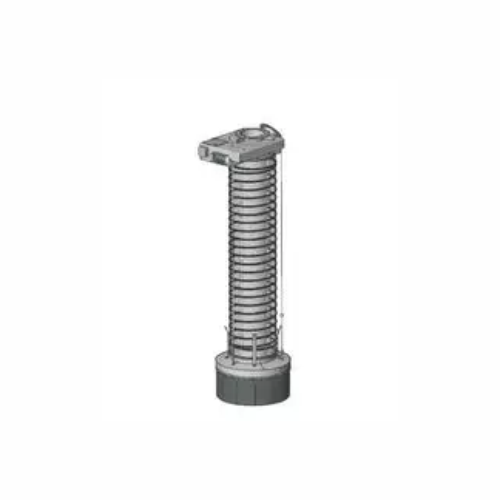
Automatic bulk material filling system
Ensure precise, contamination-free filling of various bulk materials with an advance...
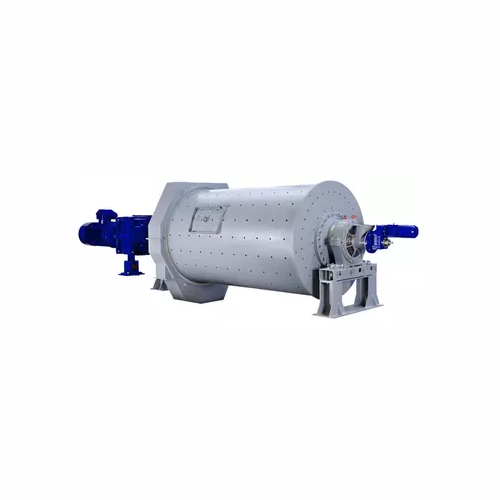
Ball mill for dry comminution of hard materials
Achieve ultrafine particle sizes and precise material breakdown with this ...
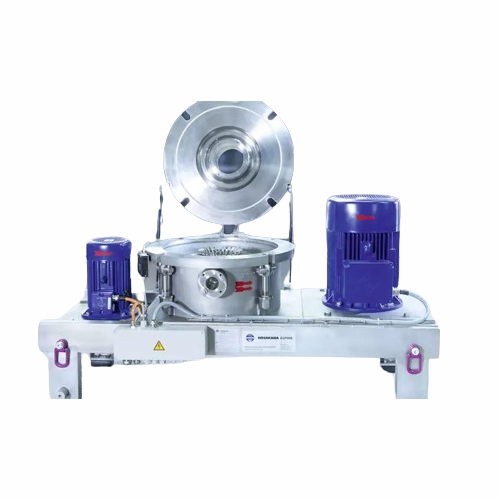
Classifier mill for ultrafine grinding
Achieve precise particle size distribution and contamination-free processing with th...
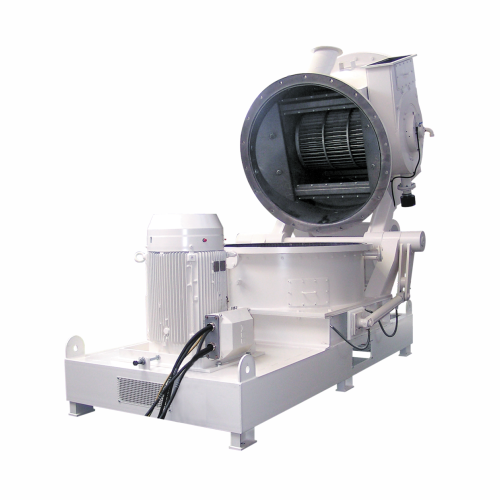
Classifier mill for ultra-fine grinding and precise particle size control
Achieve consistent ultra-fine particle distr...
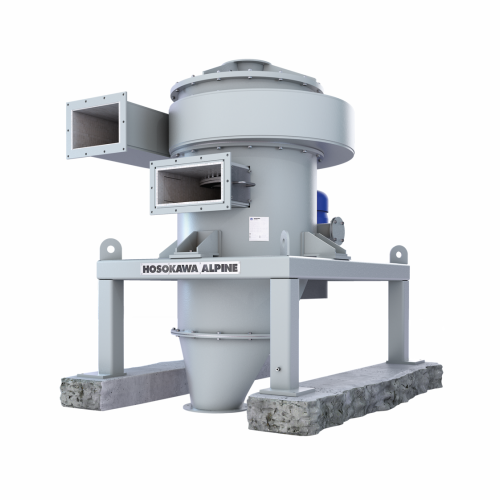
Air classifier for fine to medium-fine separation
Reduce energy consumption and wear while achieving high precision in th...
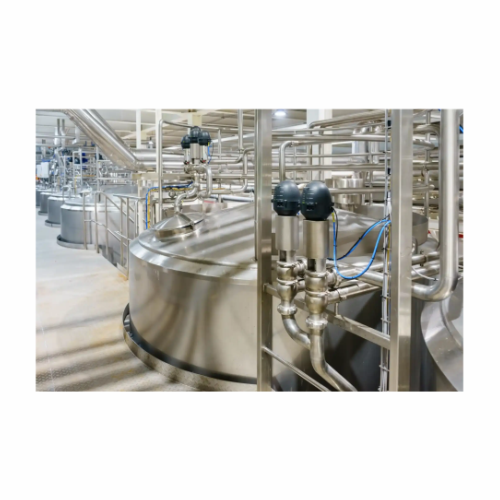
Filtration system for Cip cleaning in food production
Optimize your cleaning processes with a state-of-the-art filtration...
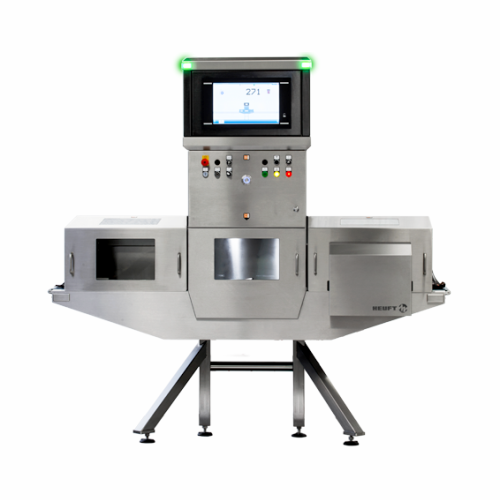
Top-down x-ray inspection for pharmaceutical packages
Ensure product safety by detecting minute foreign particles and pac...
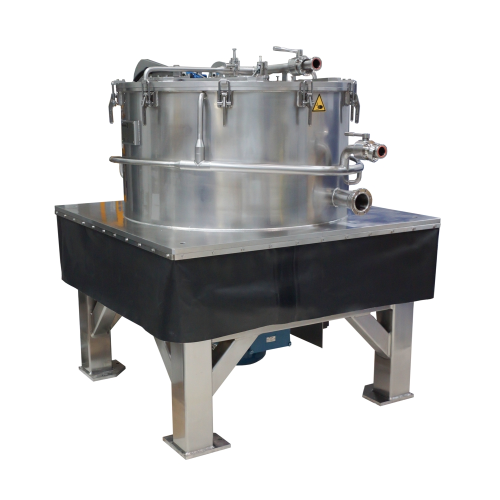
Top discharge centrifuge for pharmaceutical production
Optimize your product yield and quality with precise filtration an...

Side entry mixer for industrial fluid mixing
Optimize your fluid mixing processes with high-speed side entry mixers, desig...
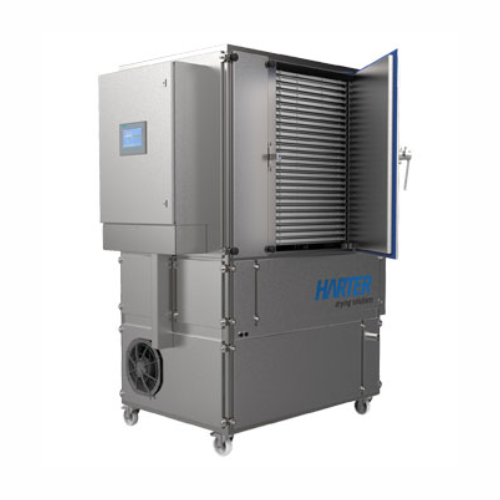
Pharmaceutical and laboratory product drying solution
Ensure precise moisture control for diverse products, from pharmace...
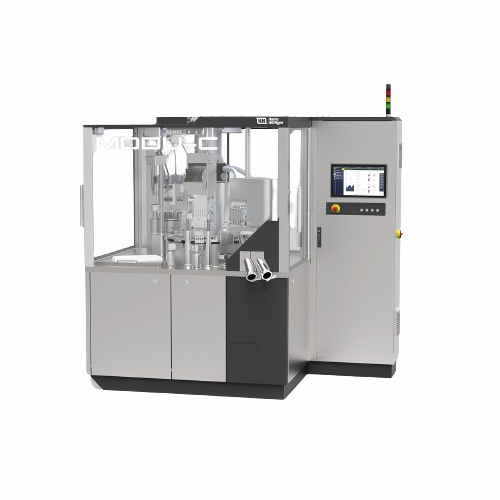
Commercial capsule filling for small scale production
Efficiently fill and dose capsules with precision, ensuring flawles...
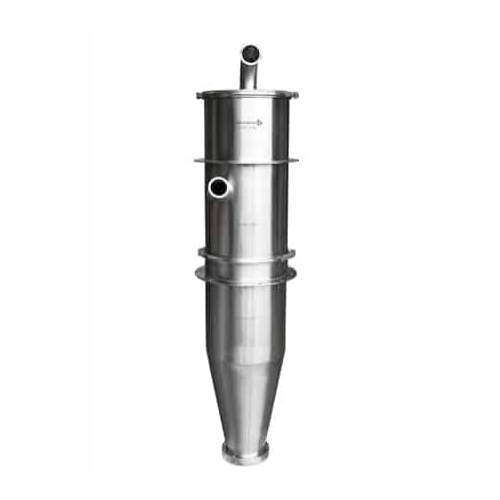
Ultra-hygienic vacuum conveyor for pharmaceutical and food industries
Streamline material handling with this ultra-hygi...
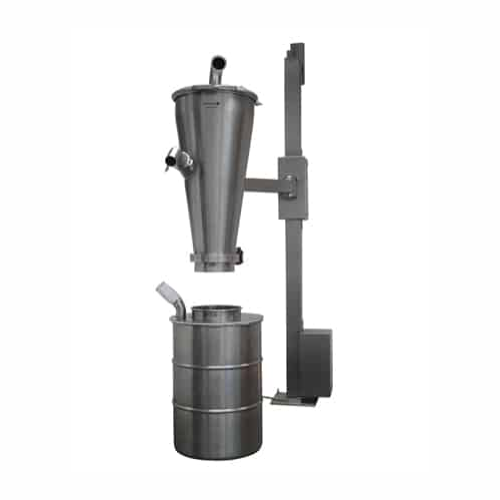
Vacuum conveyor for hygienic material transfer
For operations demanding swift, dust-free material handling, this solution ...

Pre-breaker for initial material size reduction
Efficiently prepare your bulk materials for further processing by swiftly ...
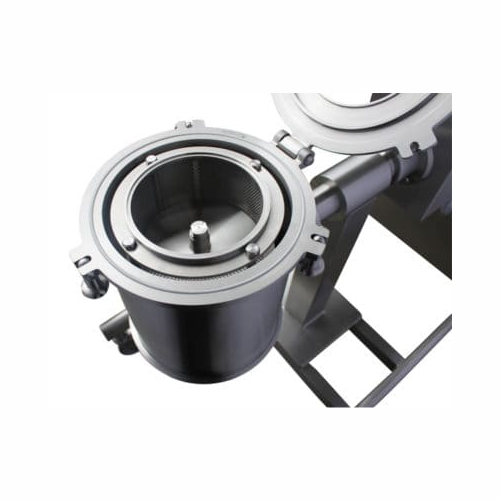
Centrifugal powder sifter for particle separation
Achieve consistent material quality with efficient powder sifting and d...
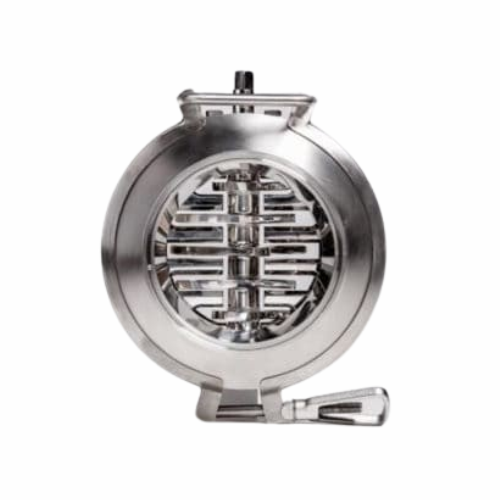
Rotary crushing valve for lump breaking
When handling bulk solids, effective pre-breaking and sizing are crucial to ensure ...
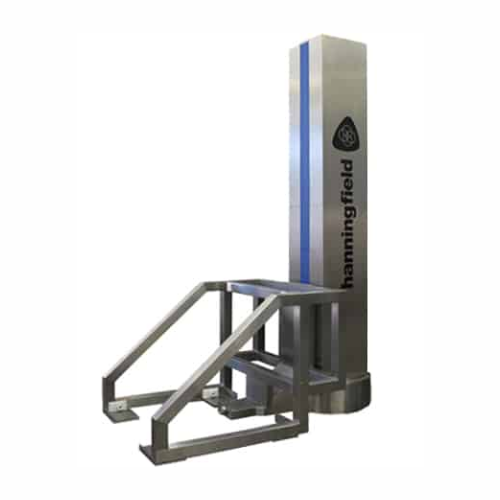
Industrial container and drum handling solution
Effortlessly maneuver and position heavy containers such as IBCs and drums...
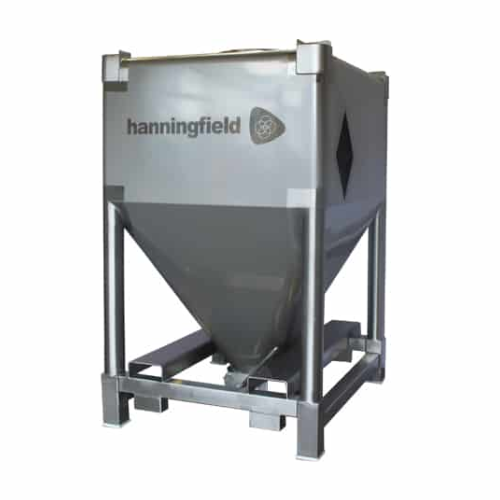
Stainless steel intermediate bulk containers for pharmaceutical use
Ensure safe, efficient transport and handling of po...
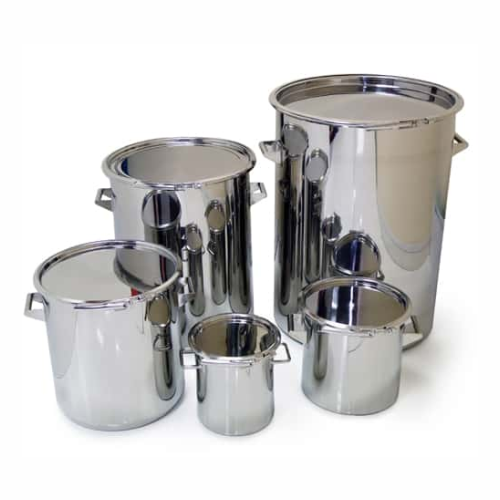
Stainless steel drums for powder storage
For high-value powder storage, these stainless steel drums offer reliable containm...
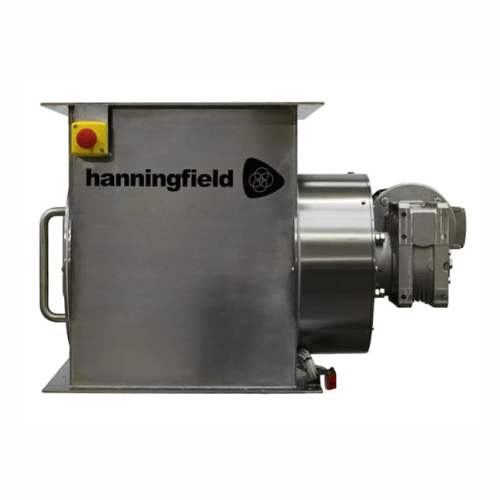
Industrial lump breaker for compact material deagglomeration
Efficiently deagglomerate compacted materials to enhance fl...
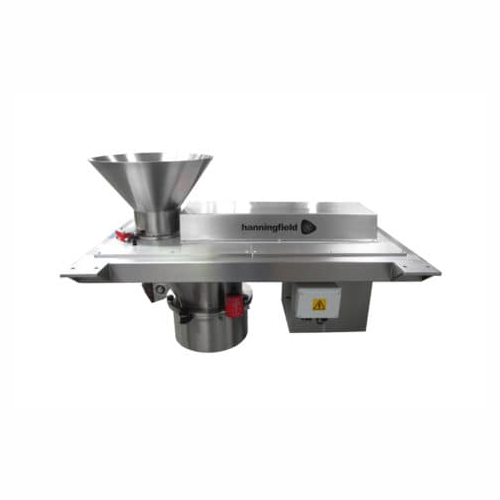
Over-driven conical mills for precise particle size reduction
Achieve consistent particle size reduction with minimal he...
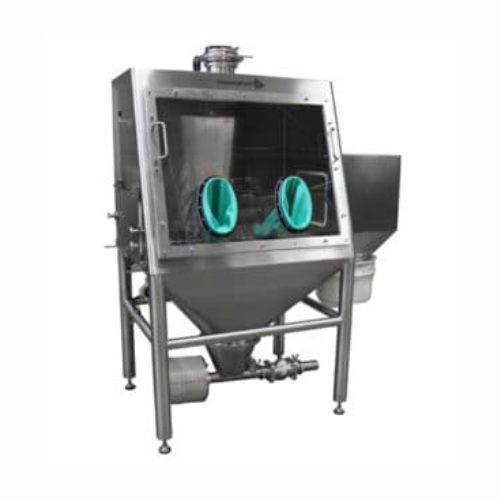
Dust-control sack tip station for industrial loading
Ensure seamless and safe unloading of powders with an integrated dus...
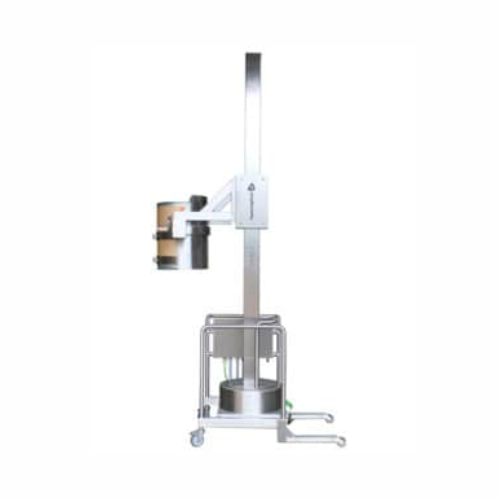
Drum tippers for precise and safe drum handling
Streamline your operations by eliminating manual lifting and aligning proc...
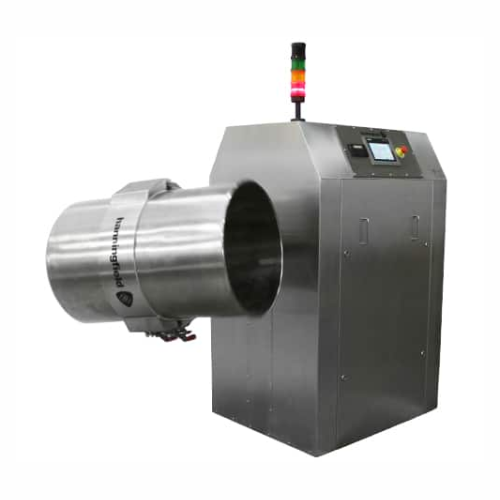
Industrial drum tumblers for uniform batch processing
Achieve precise mix uniformity in your batches with drum tumblers, ...
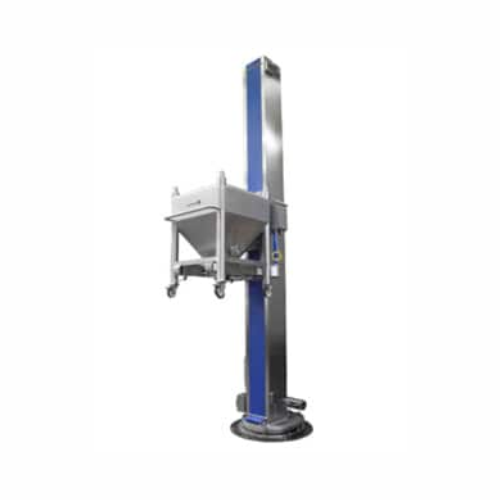
Industrial container lifting system
Optimize your production line with a versatile lifting solution designed to safely hand...
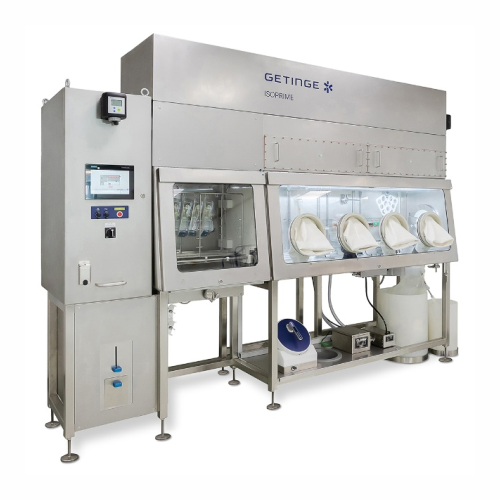
Cost-effective rigid-wall isolator for aseptic applications
Ensure sterility and safety with a versatile isolation and d...
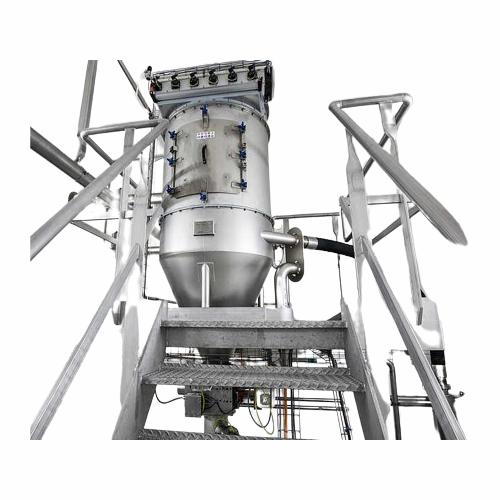
Vacuum pneumatic conveying for infant nutrition
Ensure efficient handling of delicate powders with a versatile vacuum pneu...
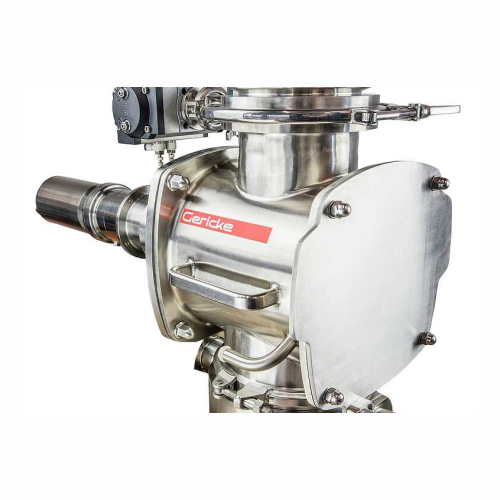
Mini batch blender for pharmaceutical solids
Achieve precise mixing homogeneity with the mini batch blender, perfect for l...
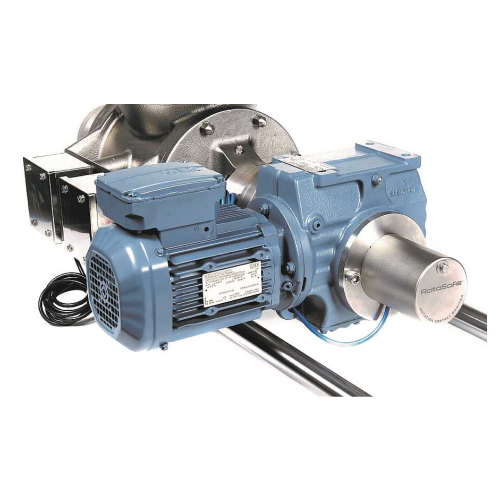
Contact detection system for rotary valves
Prevent product contamination and equipment damage with instant contact detecti...
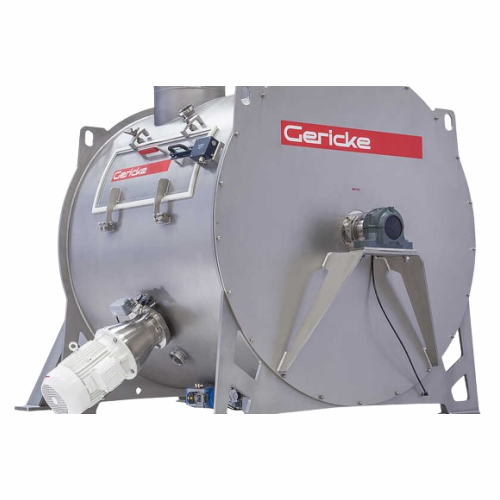
Single shaft batch mixer for chemical and pharmaceutical applications
Optimize mixing efficiency with rapid batch proce...
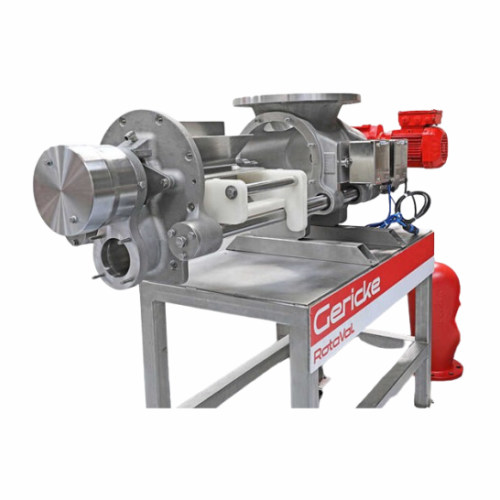
Quick-clean hygienic rotary valves
Ensure seamless cleaning and minimal downtime in your production line with rotary valves...
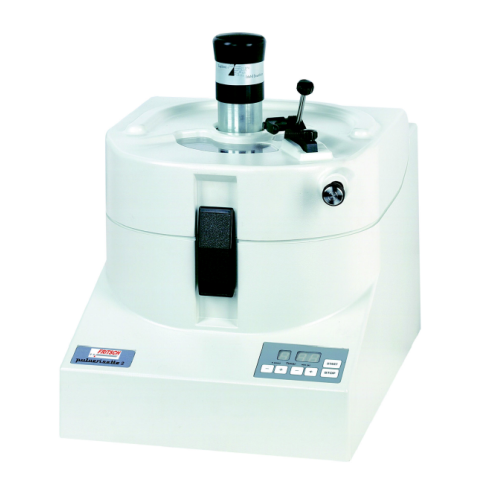
Laboratory mortar grinder for wet and dry grinding
Ensure precise blending of fine powders, pastes, and creams with contr...
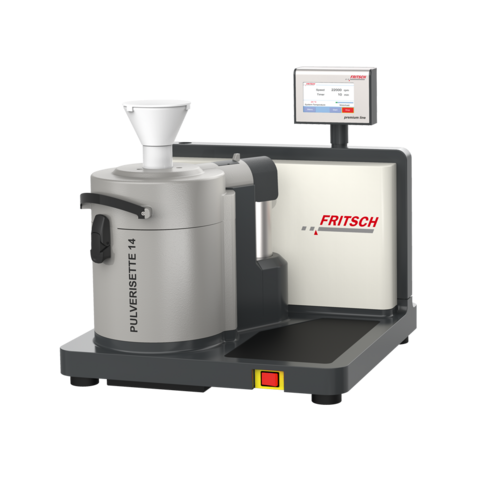
Variable speed rotor mill for sample preparation
Achieve rapid and precise grinding of various materials with a versatile ...
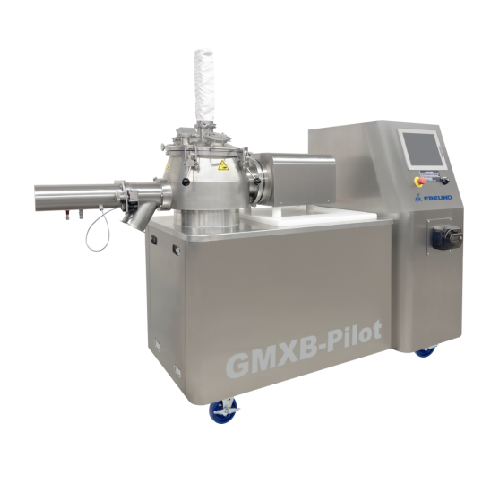
Pilot High shear granulator for wet granulation
Achieve consistent particle sizing and superior homogeneity in your powder...

Filter washing cabinet for industrial cartridge filters
Achieve hygienic standards with precision washing and drying of i...
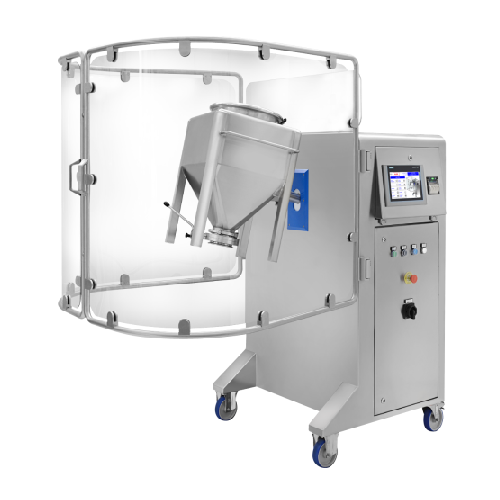
Pilot blender for small batch powder blending
Optimize your R&D processes with this versatile mobile blender, ideal f...
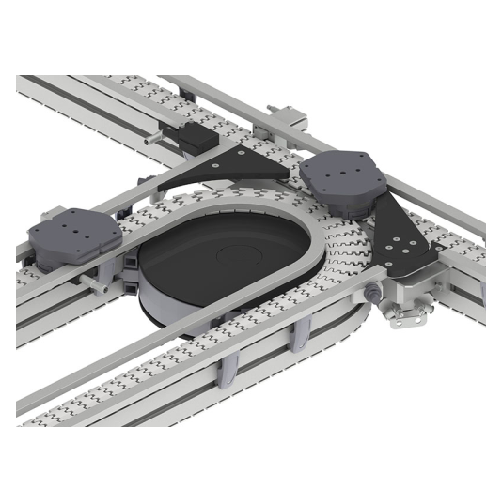
Single track pallet conveyors for electronics production
Efficiently manage single-piece flow with precise routing, balan...
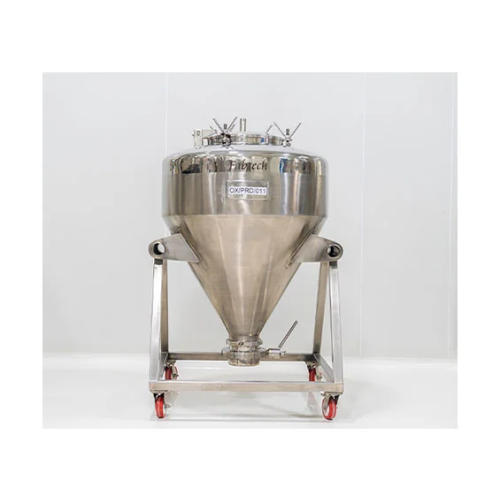
Vacuum transfer system for powders and granules
Effortlessly transfer and manage powders and granules with seamless integr...

Closed loop granulator for pharmaceutical production
Streamline your production with a fully automated closed-loop system...
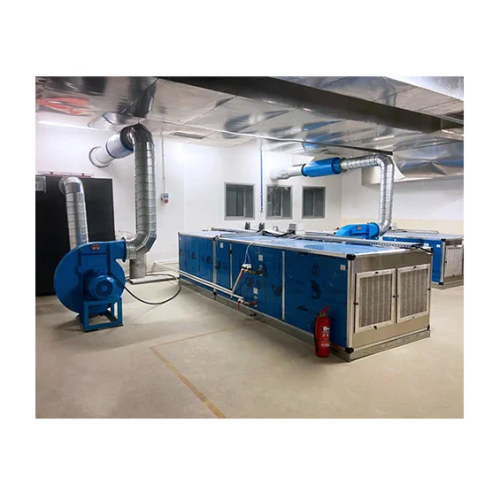
Cleanroom infrastructure for contaminant control
Ensure optimal contaminant control and regulatory compliance in cleanroom...
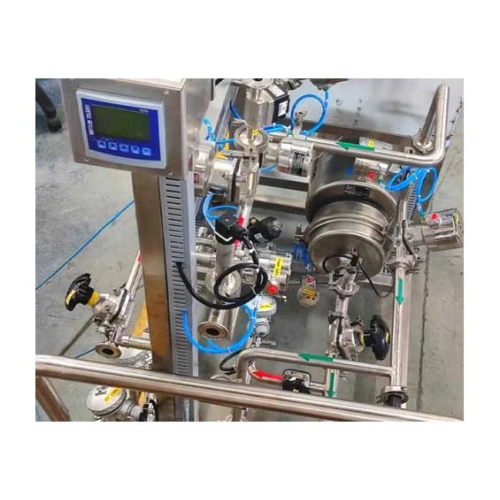
Cip & Sip systems for pharmaceutical cleaning
Ensure effective cleaning and sterilization in production lines with customi...
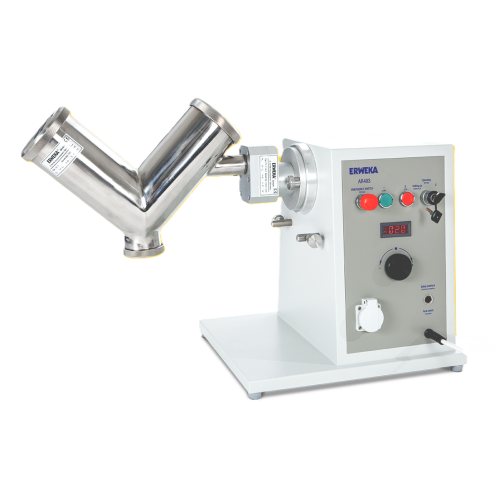
V-mixer for solid bulk material blending
Achieve precise and uniform mixing of sensitive powders with gentle treatment, ide...
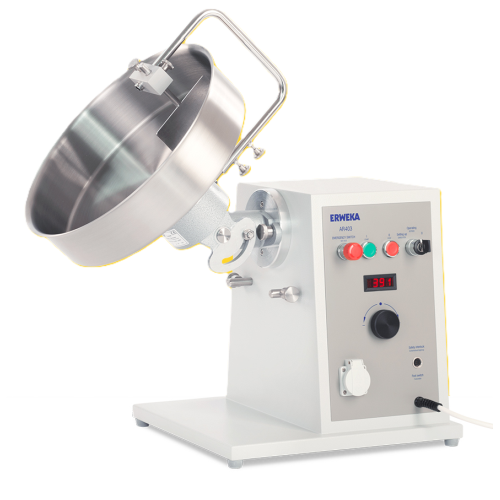
Pelletizer for pharmaceutical and biotech applications
Achieve precise pellet formation with adjustable pan angles and li...
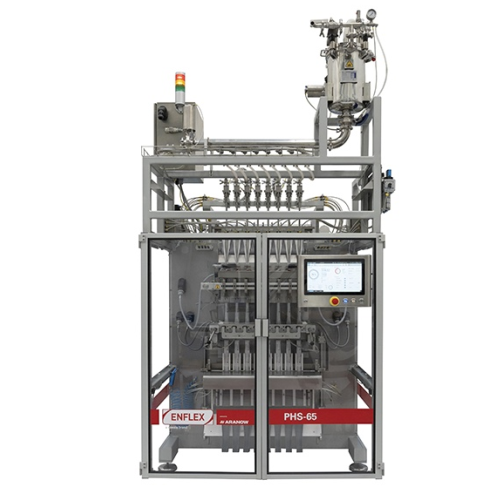
Intermittent stick pack system for pharmaceuticals
Effortlessly streamline your packaging process with a high-speed, mult...
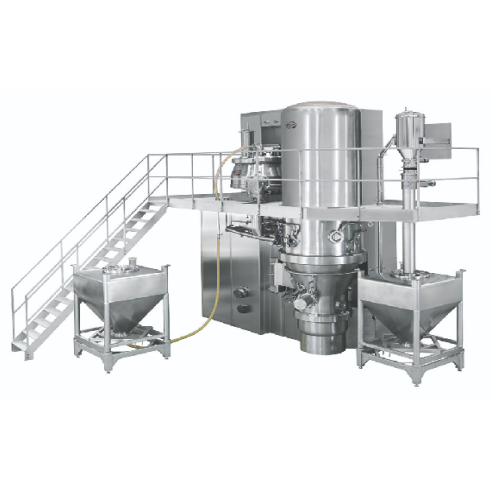
Pharmaceutical granulation line
Streamline your production with an integrated system that combines mixing, granulation, and ...
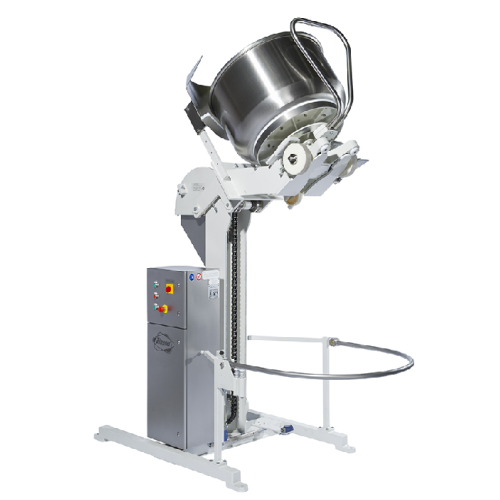
Compact elevator tipper for craft businesses
Optimize your production line with a versatile elevator tipper that ensures s...
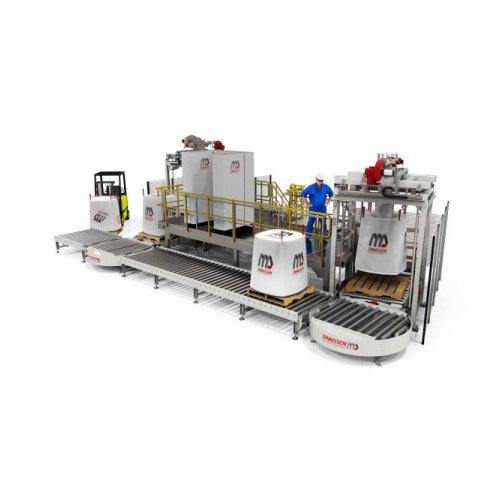
Product handling system for big bags and containers
Optimize your production line with a comprehensive system for transpo...
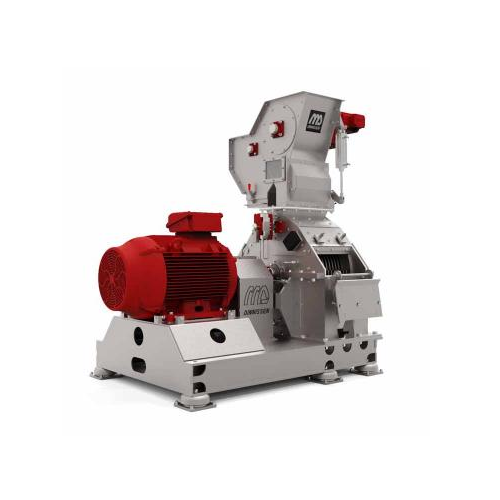
Industrial hammer mill for grinding and sifting
Ensure precise particle size reduction and consistent product quality with...
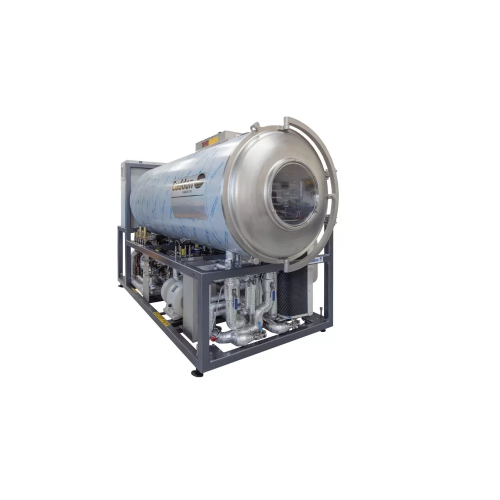
Freeze dryer for high sugar or acid content products
Achieve precise moisture control for challenging high sugar or acid ...
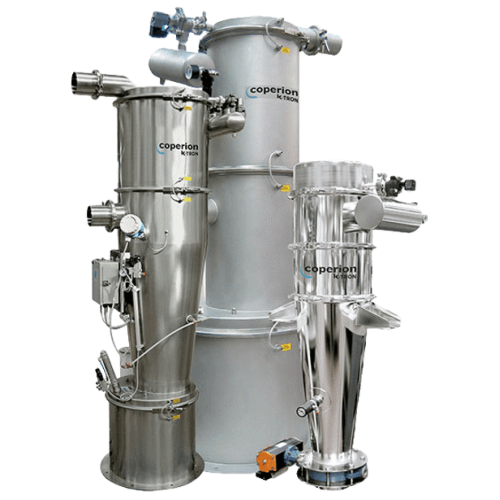
Sanitary bulk solids receiver for food and pharma
Ensure precise control over bulk solid transfer with a system designed ...
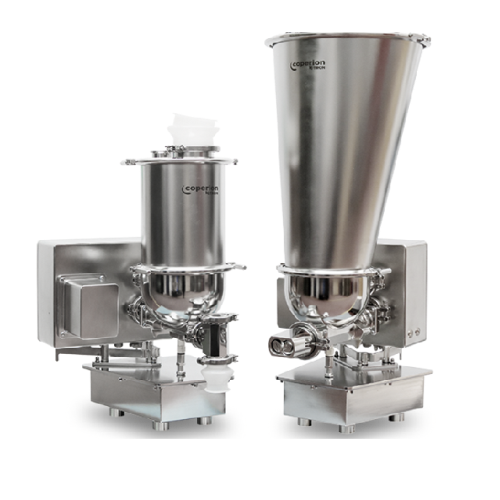
Pharmaceutical design feeders for precise ingredient handling
Achieve precise ingredient handling and seamless integrati...
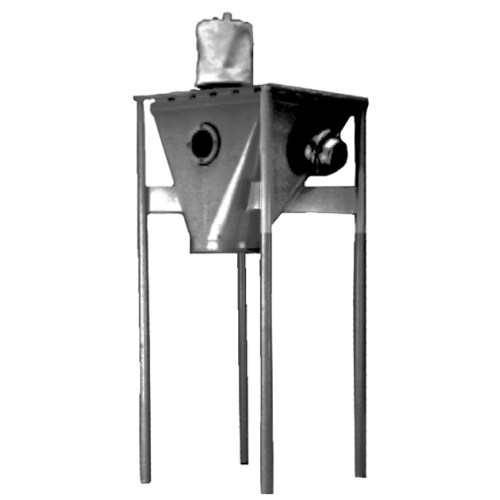
Aerolock surge hopper for precise bulk material management
Optimize your production with a surge hopper designed to ensu...
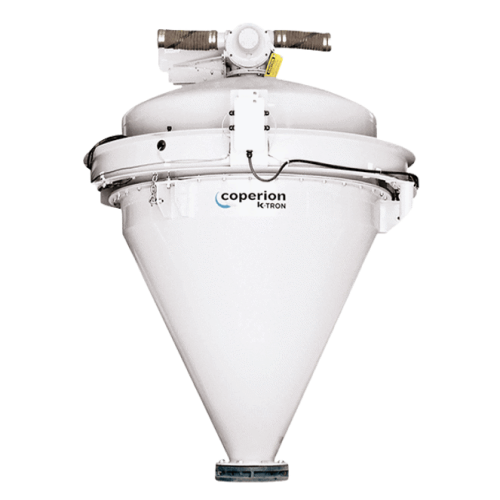
Scale hopper for bulk material processing
Optimize your bulk material handling with precise control in separation, filling...
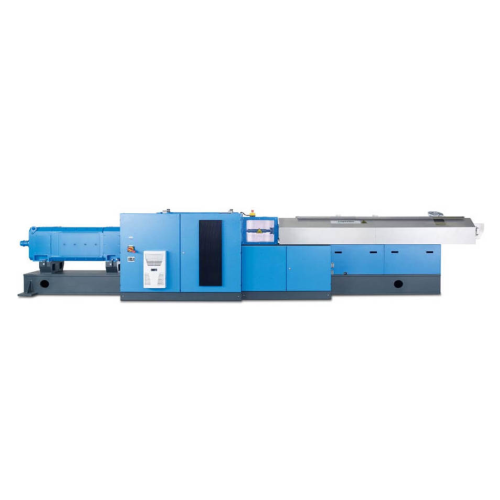
High throughput twin screw extruder for low bulk density products
When handling low bulk density materials, achieving m...
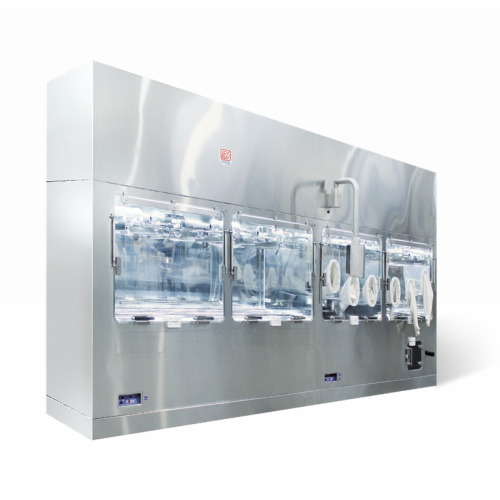
Custom automation for drug-device filling and assembly
Efficiently integrate precise filling and assembly for biopharmace...
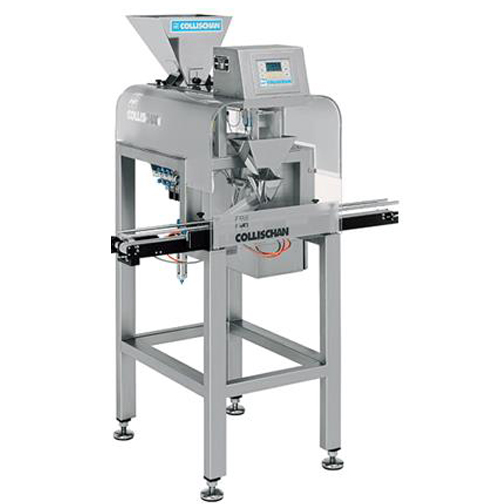
Weight filler for small batches in explosive areas
Efficiently handle and weigh small batch products with precision, even...
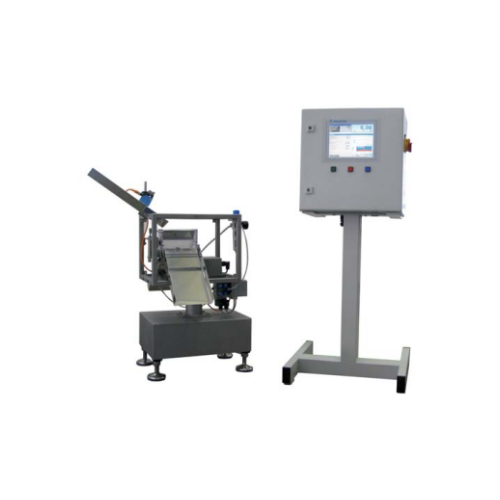
Static checkweigher for accurate measurement
For those needing unparalleled precision, this static checkweigher ensures ex...
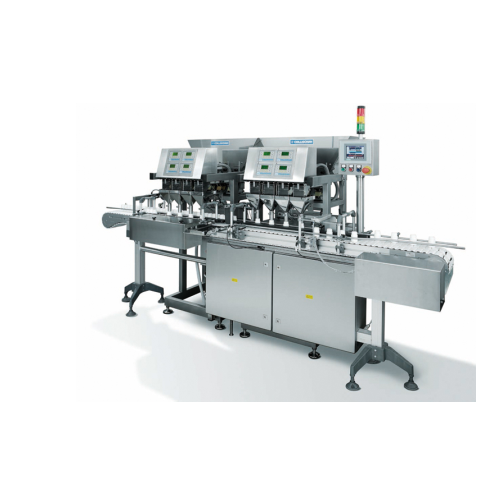
Complete packaging lines for various containers
Streamline your packaging process with versatile equipment capable of hand...
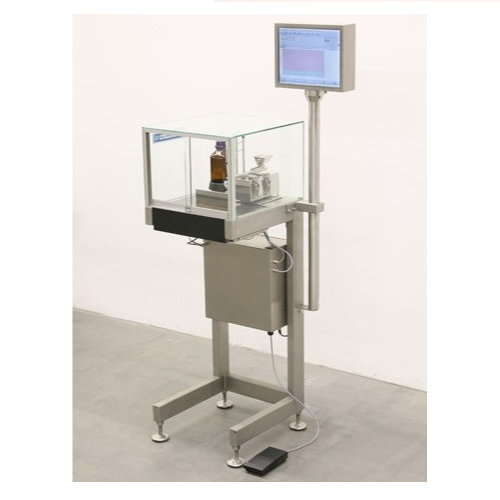
Microdosing system for granules and powder
Achieve precise dosing with minimal variance across all fills, ensuring consist...
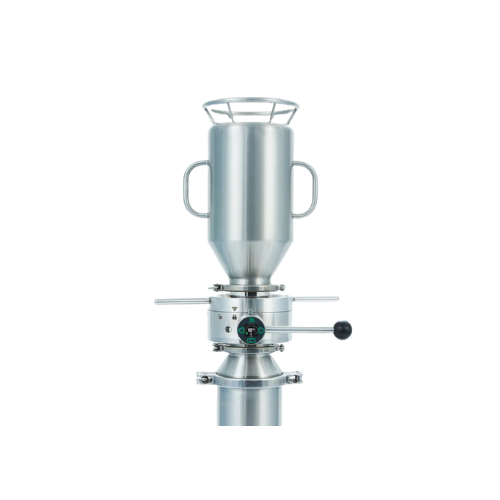
High containment powder transfer valve
Ensure high containment for potent powders in your production line, reducing contami...

High containment powder transfer valve for bulk material
Ensure operator safety and prevent cross-contamination with robu...
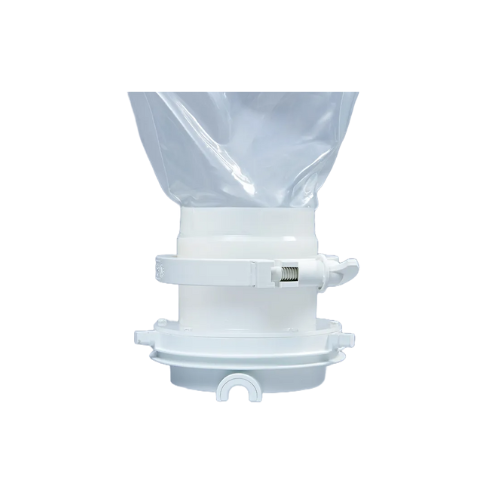
Single use valves for powder transfer
Efficiently transfer powder ingredients with a single-use containment solution, ensur...
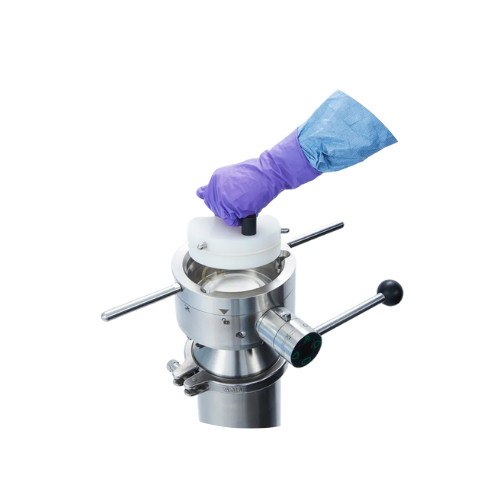
Active Gmp plug for valve containment
Ensure the integrity and safety of your valve system by preventing contamination and ...
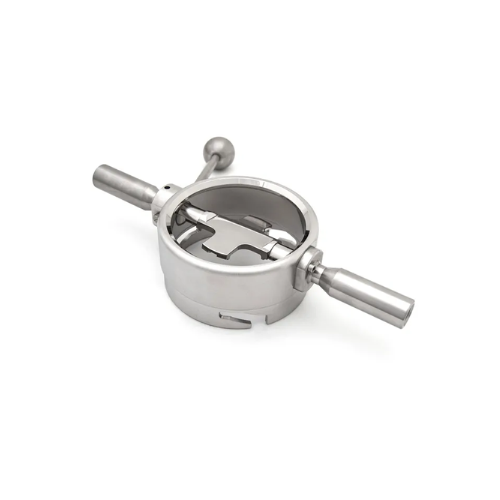
Autoclave passive opener for sterilisation of passive valves
When sterilising passive valves, ensuring maximum exposure ...
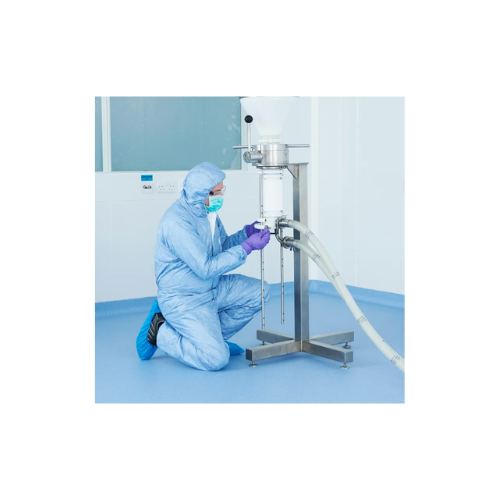
Bottle cleaning station for controlled environments
Ensure high-level decontamination of passive units and containers wit...
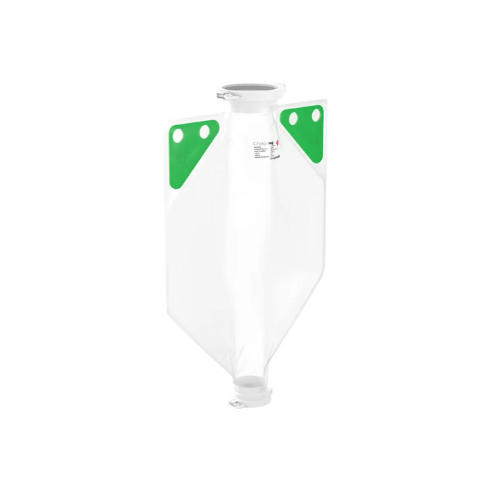
Single use powder handling bags for pharmaceutical ingredients
Achieve contamination-free powder transfers with ease, ma...
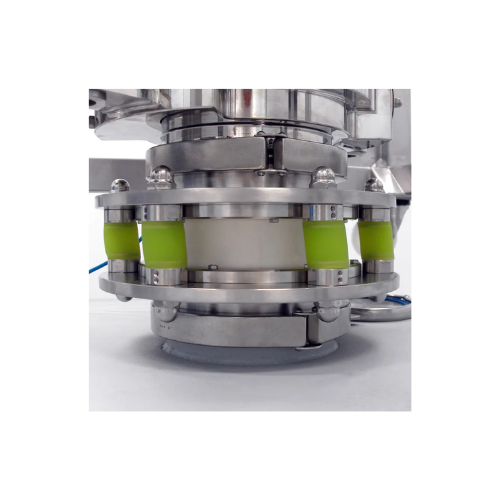
Bulk powder transfer safety device
Ensure stable and secure docking by minimizing equipment damage during powder transfer p...
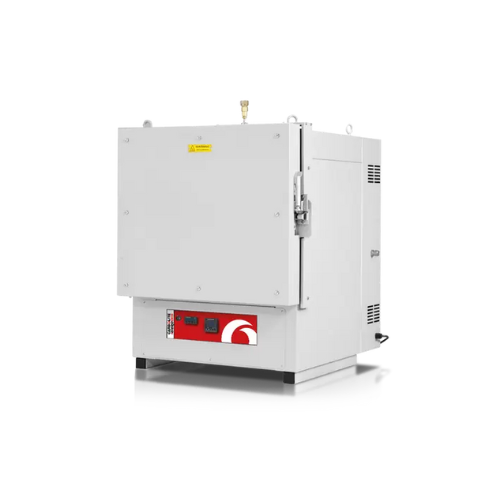
High temperature clean room ovens
Achieve precise environmental control for heating, drying, and sterilizing sensitive mate...
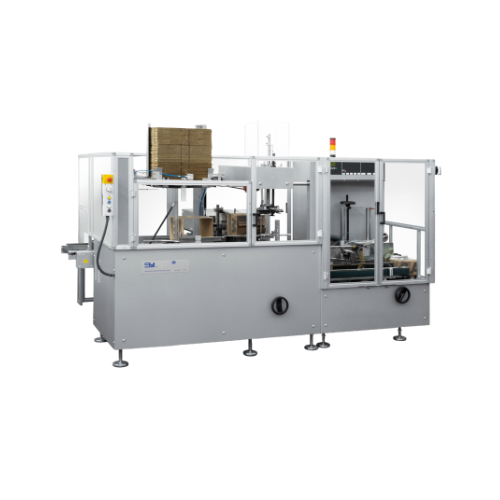
High-speed horizontal case packer for shipping cases
For high-demand production lines, this modular case packer streamlin...
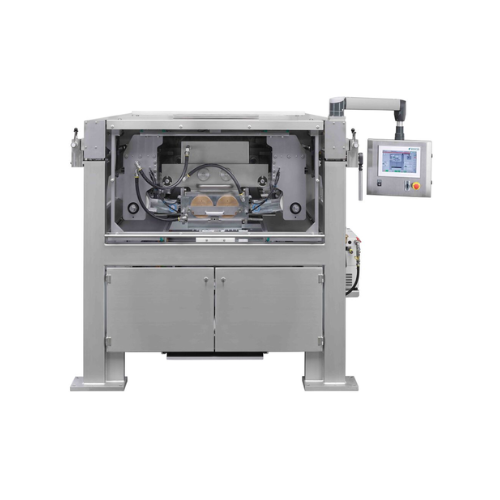
One-shot chocolate depositing system
Enhance your confectionery line with precise, high-speed depositing technology designe...
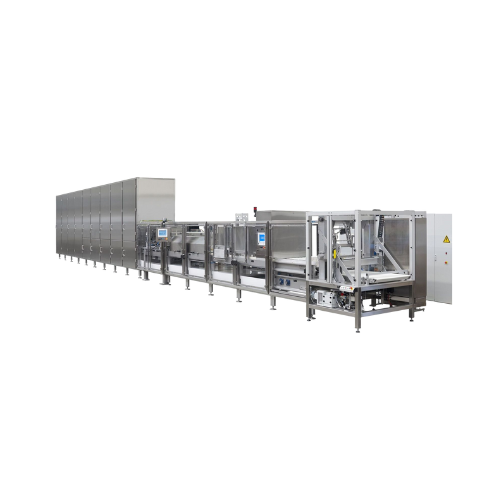
Continuous moulding line for chocolates
Achieve precise chocolate moulding with continuous operation, ensuring high-speed p...
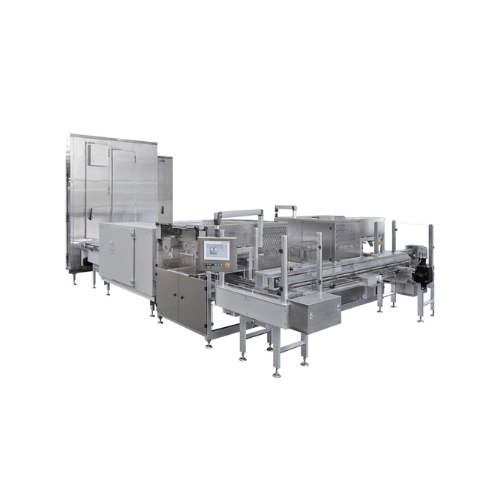
Loose mould line for chocolate production
Streamline your chocolate production with a high-throughput line that seamlessly...
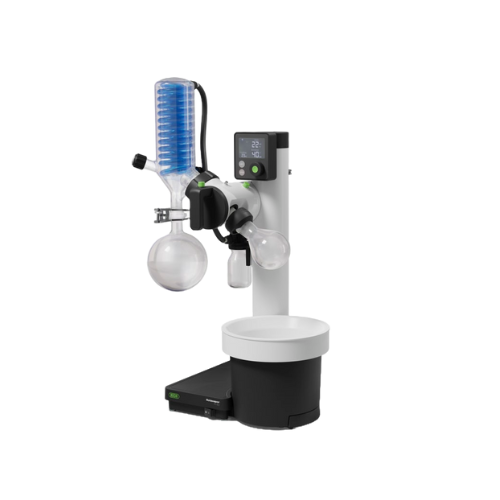
Compact rotary evaporator for laboratory distillation
Achieve efficient solvent removal and sample concentration with thi...
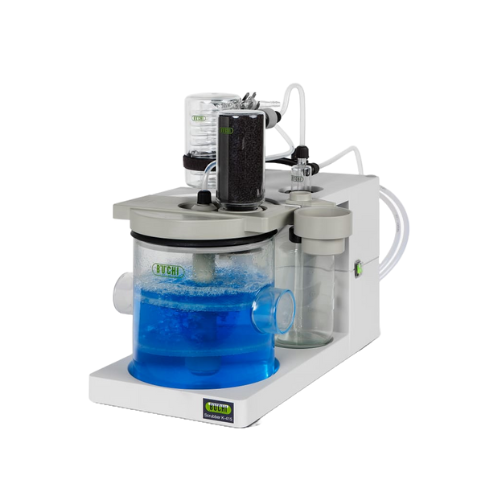
Industrial fume scrubber for safety compliance
Enhance workplace safety by efficiently neutralizing hazardous fumes and va...
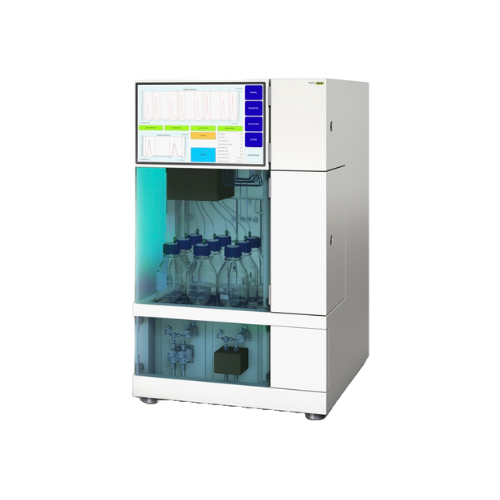
Supercritical fluid chromatography system for preparative separations
For complex substance formulations requiring rapi...
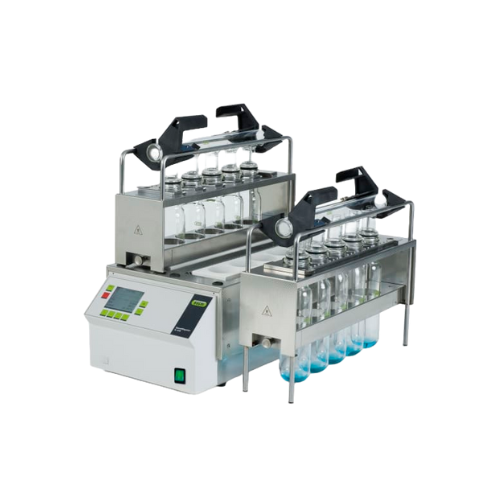
Infrared speeddigester for nitrogen determination and chemical oxygen demand
Effortlessly enhance your laboratory thro...
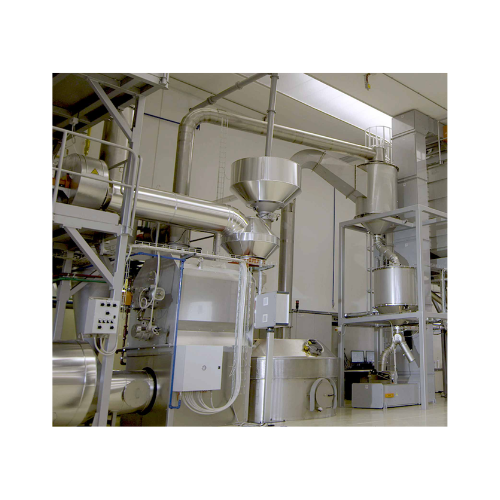
Coffee roasting system
Optimize your coffee production from green beans to finely ground espresso with this versatile system,...

Lab-scale extruders for material development
Optimize your lab and pilot-scale extrusion processes with advanced material ...
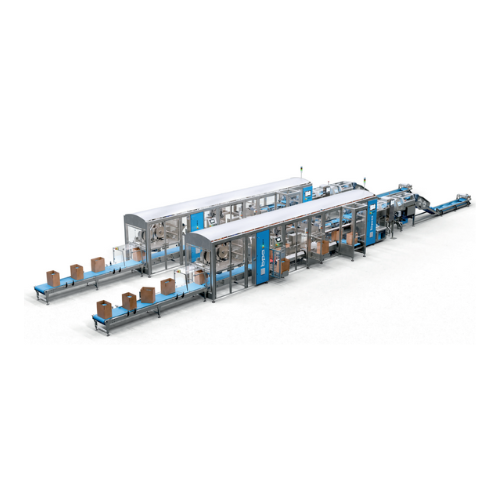
High-speed case packer for flexible bags
Streamline your packaging process with a solution designed for high-speed, error-f...
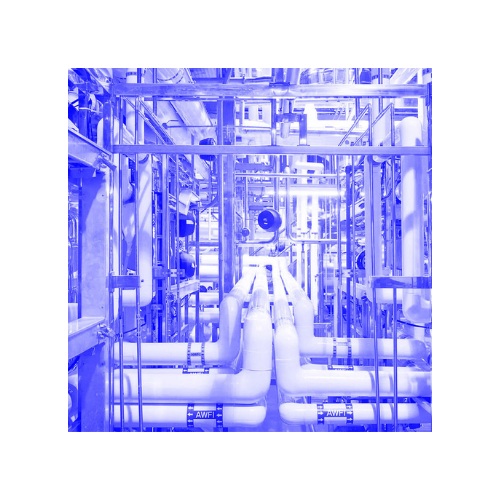
Cleaning in place systems for bioreactors
Ensure seamless sanitization with a mobile cleaning system designed to maintain ...
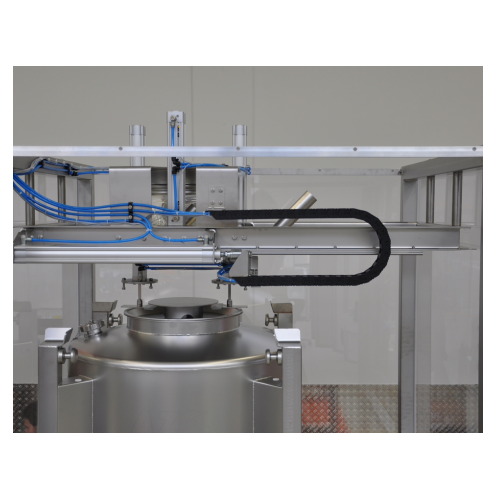
Dust-tight docking for dosing units to bulk solids containers
Ensure seamless, dust-free transfer and dosing of bulk sol...
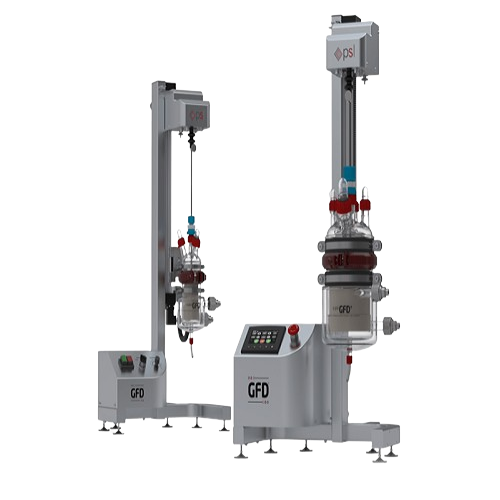
Automatable benchtop agitated nutsche filter-dryer
Effortlessly integrate seamless solid-liquid separation into your labo...
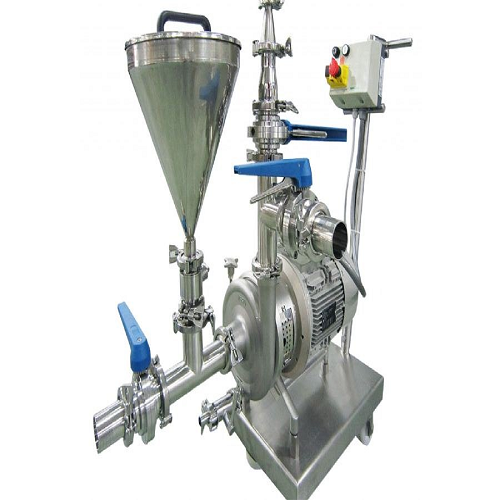
Cleaning system Cip for internal equipment maintenance
Ensure optimal hygiene and production efficiency with this portabl...
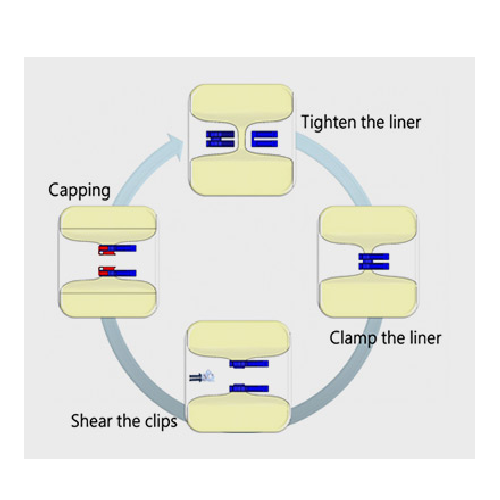
Closure system for aseptic containment
Achieve secure and verifiable seals for sterile pharmaceuticals with advanced closur...
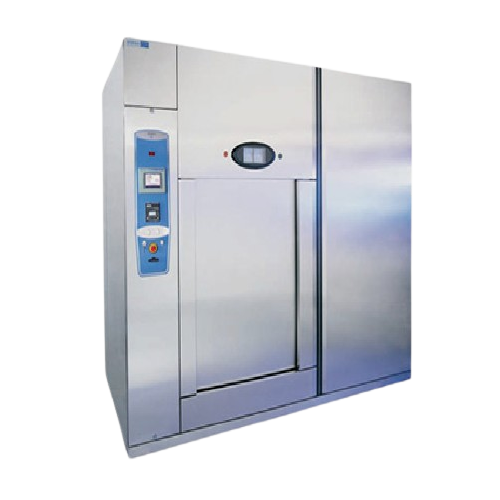
Gmp steam sterilizer for pharmaceutical applications
Ensure consistent sterilization and contamination control across you...
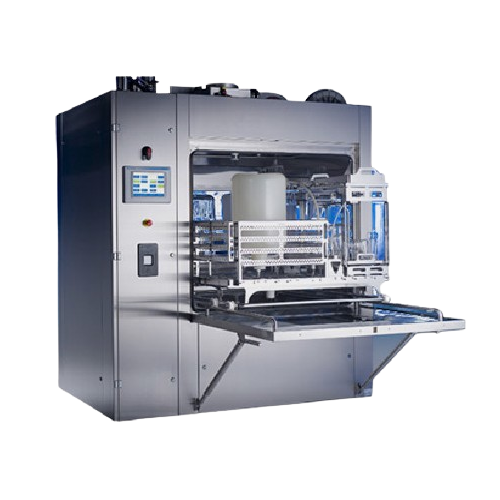
Gmp washer for pharmaceutical contamination control
Ensure verifiable cleaning and drying of critical components in bioph...
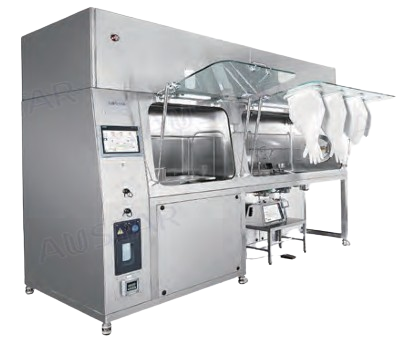
Sterilisable isolator workstation for aseptic containment
Ensure precise contamination control and sterile conditions du...
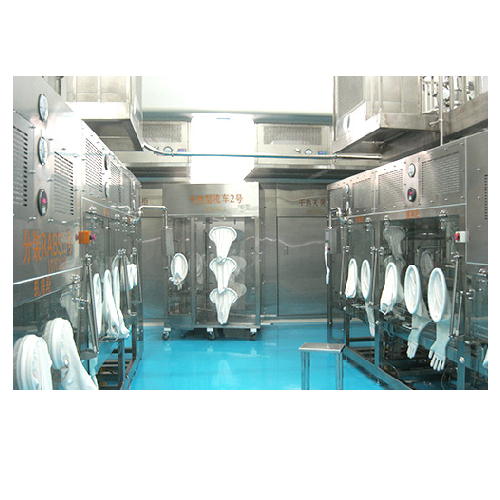
Sterile Api production line for powder treatment
Achieve seamless sterile API production by integrating precise weighing, ...
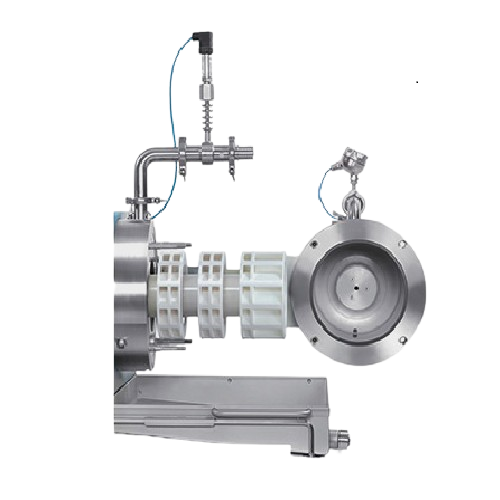
Bead mill for nano-preparation grinding
Achieve precise nano-processing and efficient wet grinding for pharmaceuticals and ...
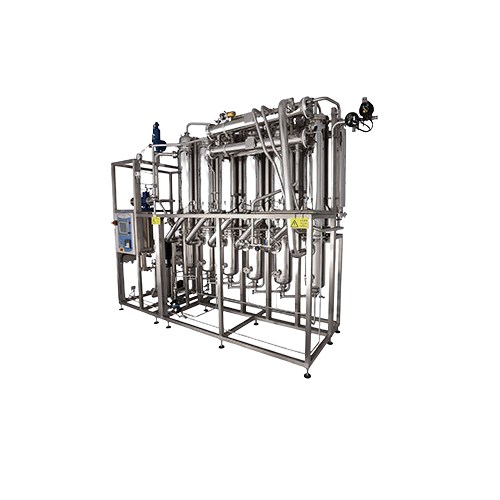
Multi-effect water distiller for pharmaceutical and biological applications
Achieve unmatched water purity for sterile...
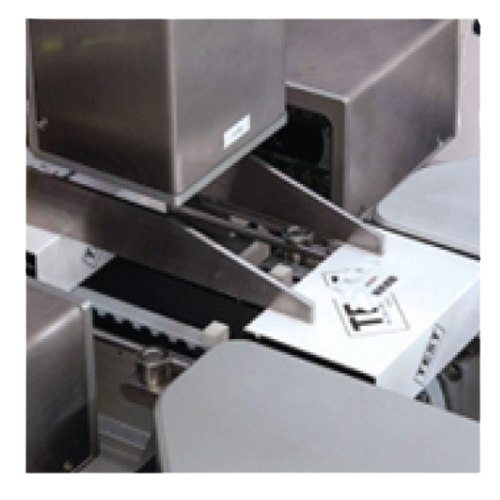
Serialization and inspection kit for packaging machines
Effortlessly enhance packaging integrity and compliance with high...
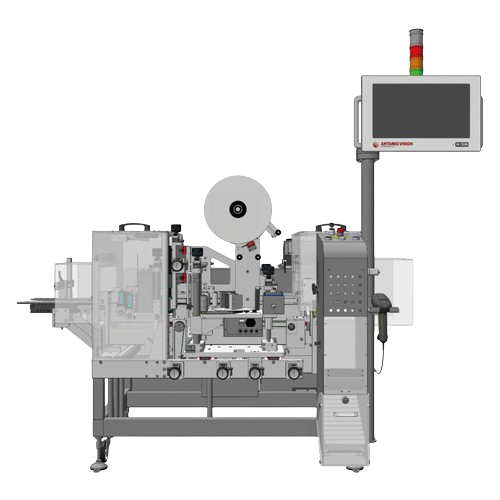
Automatic in-line serialization and tamper-evident sealing unit
Ensure seamless serialization and secure packaging with ...
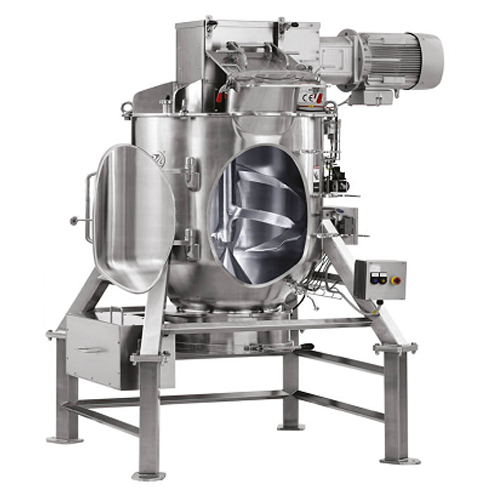
Precision powder mixer for baby formula
Achieve consistent texture and rapid homogenization for sensitive powder blends lik...
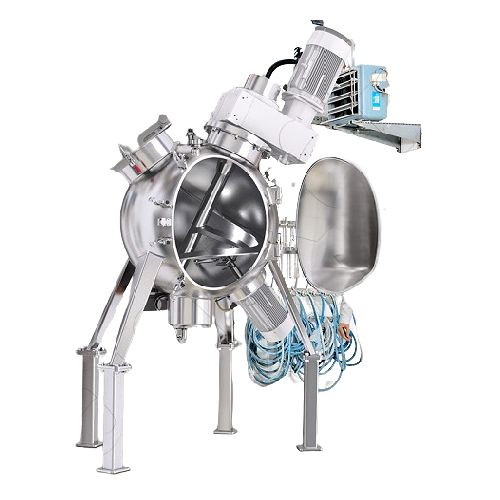
Spherical mixer for industrial mixing applications
Experience precise and efficient mixing with this hollow spherical mix...
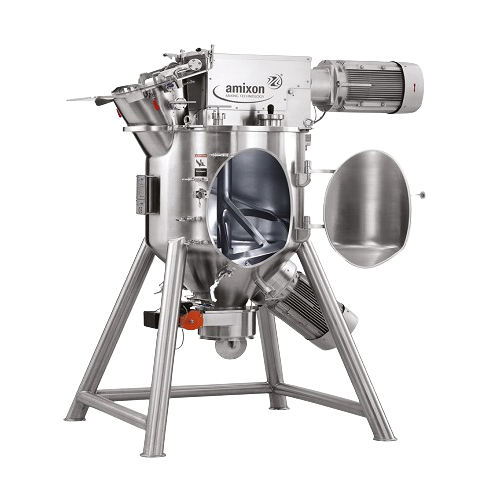
Conical mixer for dry, moist, and viscous materials
Achieve optimal mixing consistency and precision for diverse material...
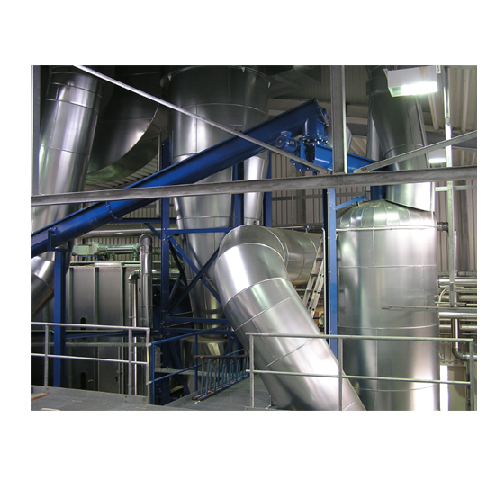
Flash dryer for high-moisture bulk materials
Tackle high-moisture challenges head-on with rapid drying solutions that effi...
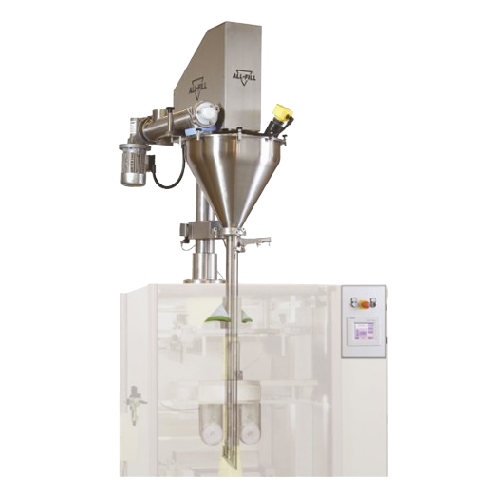
Vertical form fill seal filling system for auger applications
Effortlessly integrate precise powder and granule filling ...
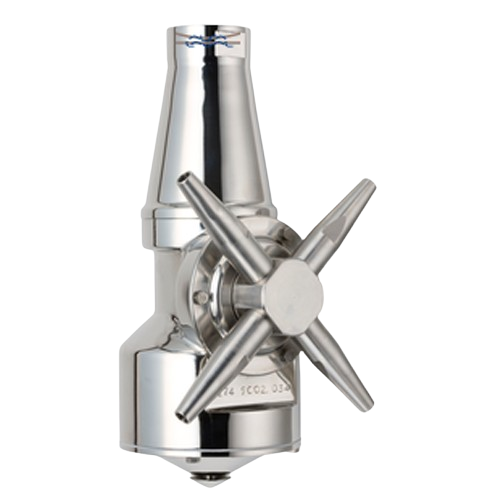
Rotary jet head for hygienic tank cleaning
Ensure efficient, hygienic cleaning with a rotary jet head designed to optimize...
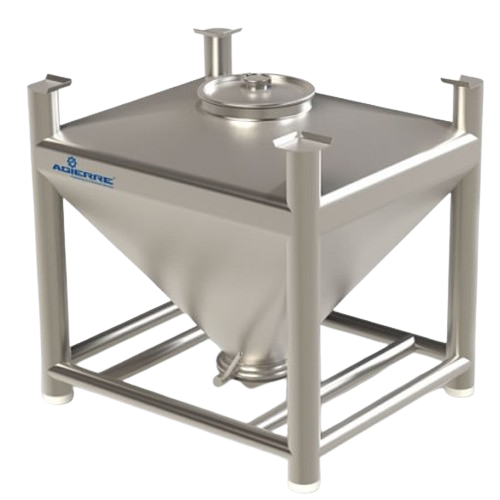
Stainless steel pharma bin for powder containment
Ensure precise powder handling and containment with this stainless stee...
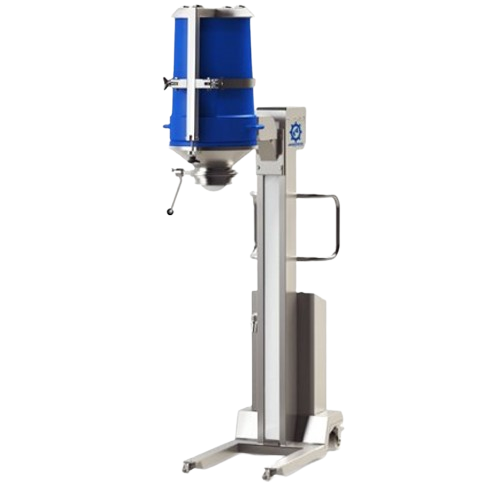
Mobile lifting column for drum handling
Streamline your powder and drum handling operations with this versatile mobile lift...
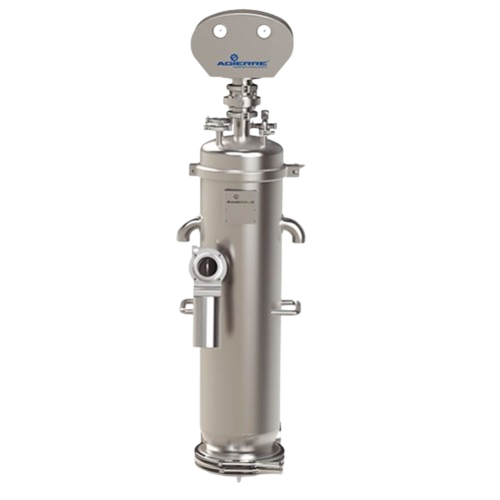
Vacuum conveyor for powder and granule transfer
Ensure efficient and contamination-free transfer of powders and granules w...
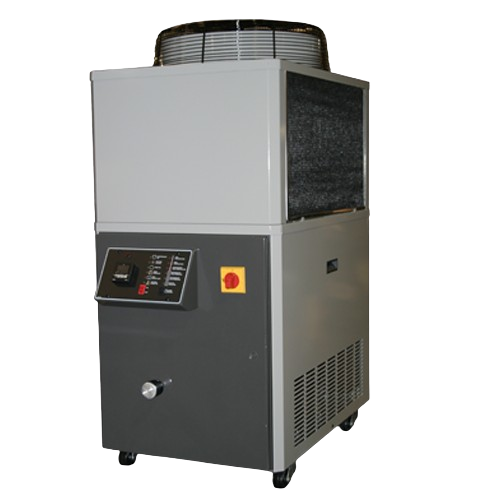
3.5 Hp air-cooled chiller for industrial cooling
Optimize your production with high-efficiency cooling, essential for main...
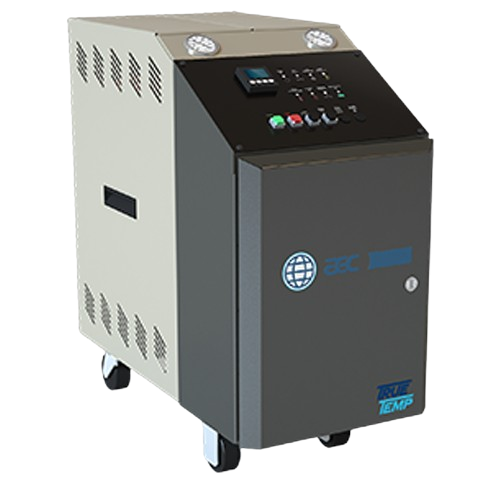
Water temperature control unit for production applications
Enhance your production efficiency by precisely managing wate...
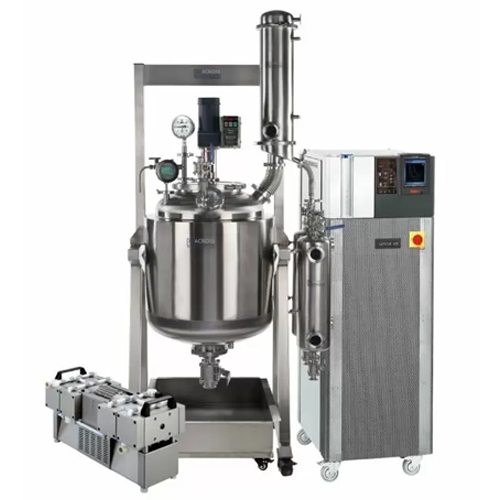
Winterization reactor for botanical extraction
Achieve precise temperature control and efficient separation during winteri...
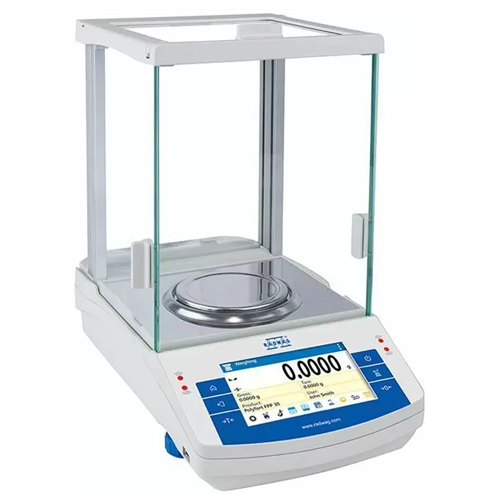
High precision analytical balance for laboratory use
Ensure precision and reliability in your laboratory measurements wit...
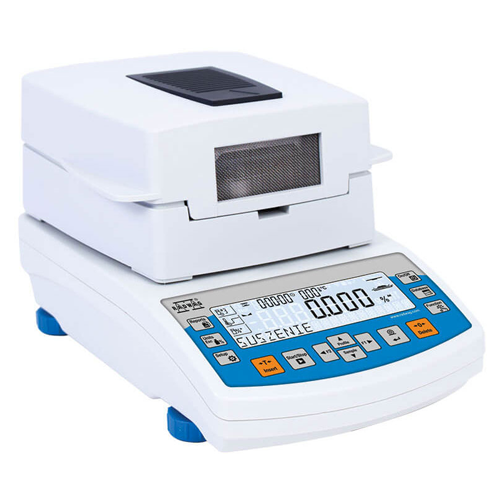
Moisture analyzer for laboratory samples
Accurate moisture analysis is crucial for ensuring product quality in pharmaceutic...
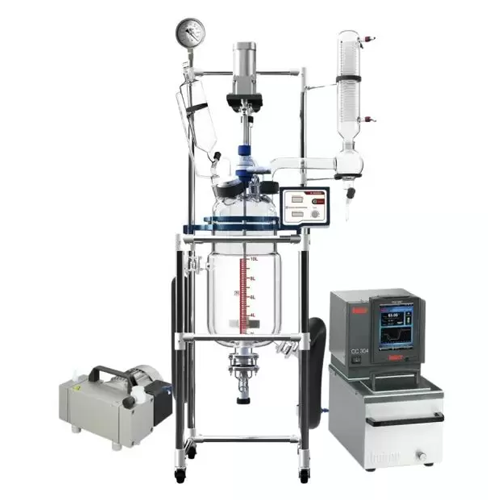
Decarboxylation package for botanical extraction
Optimize decarboxylation and reaction processes with precise temperature ...
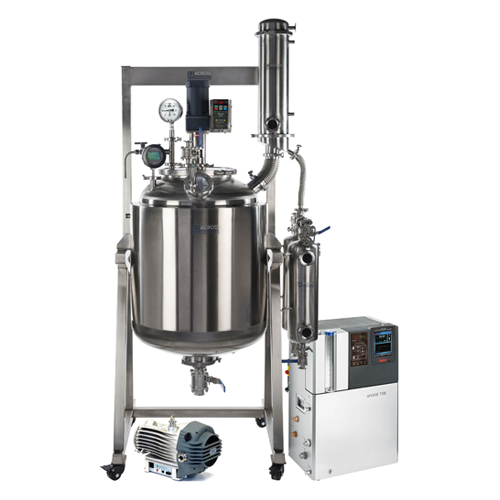
Dual-jacketed reactor for decarboxylation processes
Streamline your decarboxylation process with a dual-jacketed reactor ...
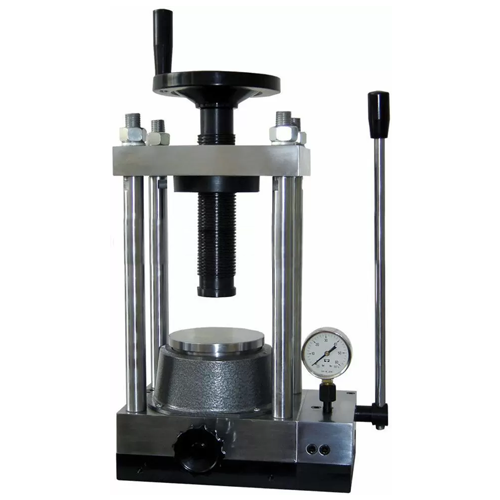
40-ton pellet press for laboratory applications
Achieve precise sample preparation with a 40-ton capacity, ideal for press...
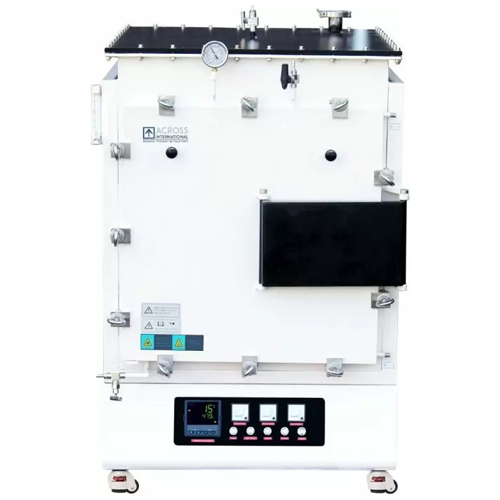
Controlled atmosphere muffle furnace
Achieve precise temperature and atmosphere control for critical processes like sinteri...
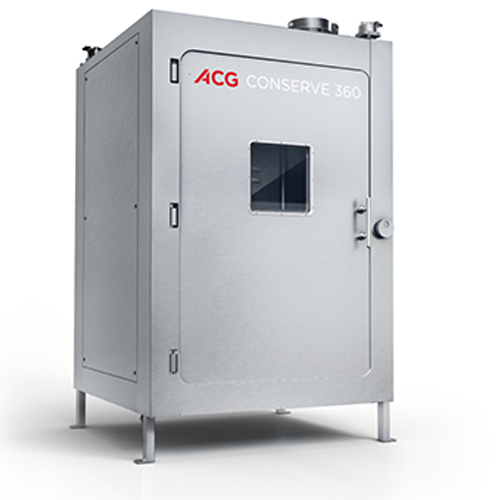
Industrial bin washer for Ibc cleaning
Ensure your Intermediate Bulk Containers are contamination-free and ready for reuse ...
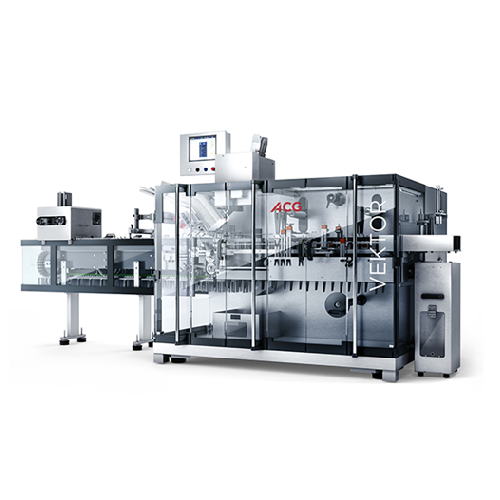
Intermittent motion cartoning machine for blister packs
Optimize your packaging line with a space-efficient cartoning mac...
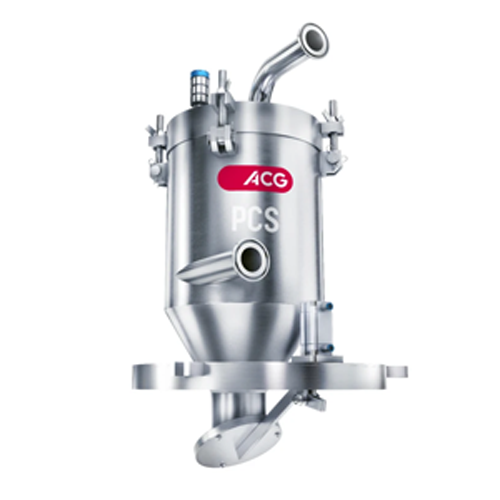
Automated powder and pellet product conveying system
Optimize your encapsulation process effortlessly with this fully aut...
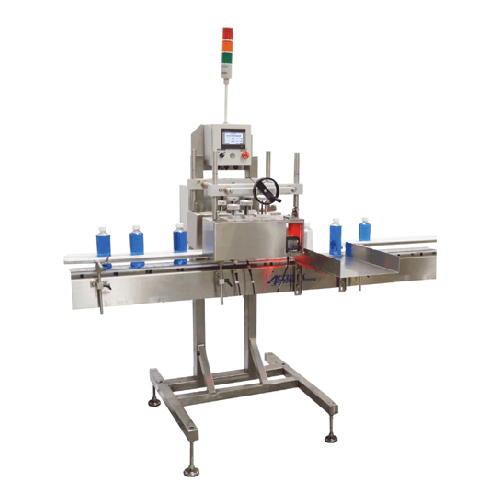
Inspection-rejection station for bottled products
Ensure your bottled and packaged products ship defect-free by automatic...
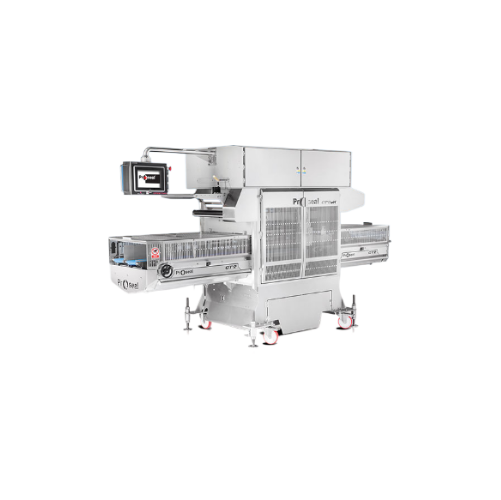
High-capacity tray sealer for vacuum gas packaging
Enhance your production efficiency with a versatile twin-lane tray sea...
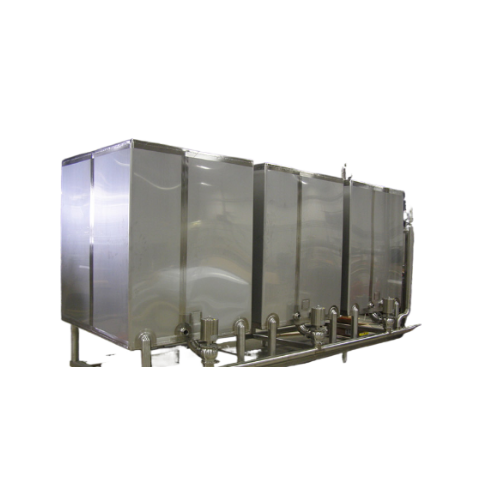
Clean-in-place tanks for industrial sanitation
Optimize your sanitation processes with clean-in-place tanks, designed to r...
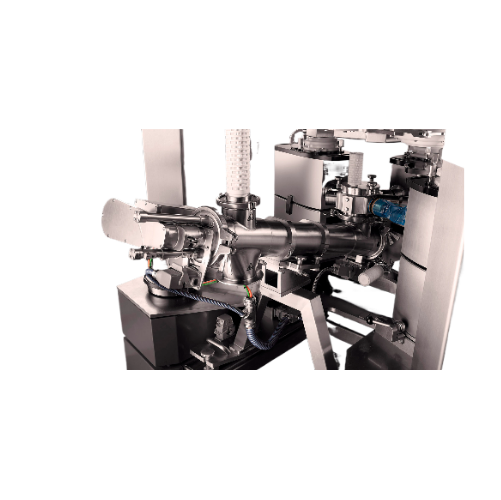
Continuous dosing and blending for pharmaceutical powders
Optimize your pharmaceutical production with precise dosing an...
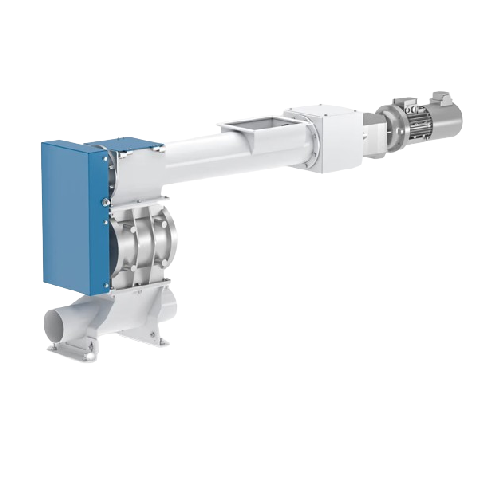
Continuous raw material distribution screw doser
Optimize your material flow with a screw doser designed for precise and c...
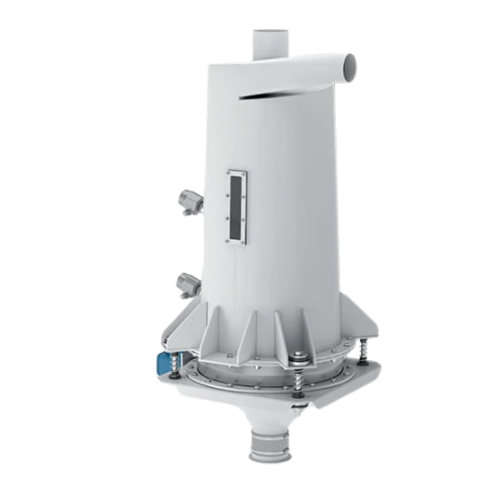
Cyclone tank for dust separation in production lines
Optimize your production line with efficient dust separation, ensuri...
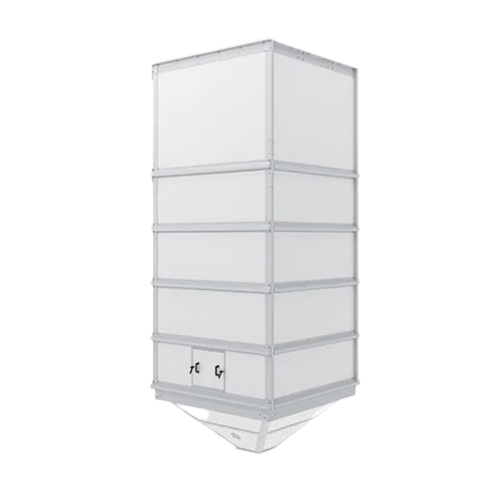
Finished product storage silos for industrial applications
Optimize your storage capabilities with silos that ensure saf...
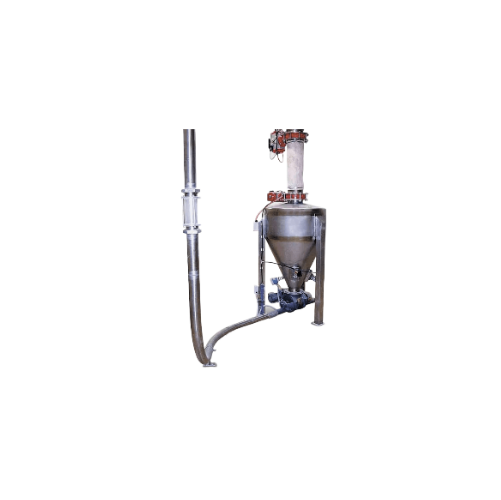
Lean phase vacuum conveying system for powder handling
Efficiently transport and separate powders and granules with preci...
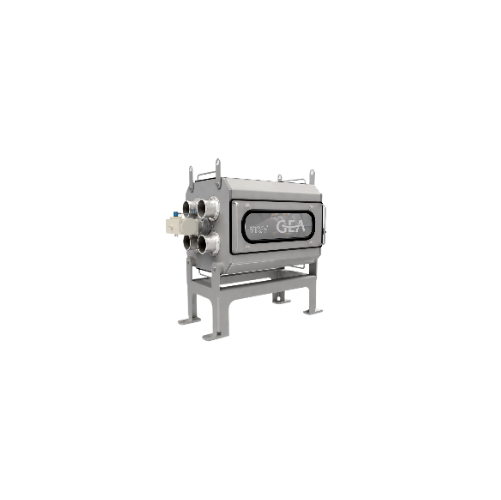
Rotary tube selector valve for powder conveying
Streamline your pneumatic transport system with a robust solution that div...
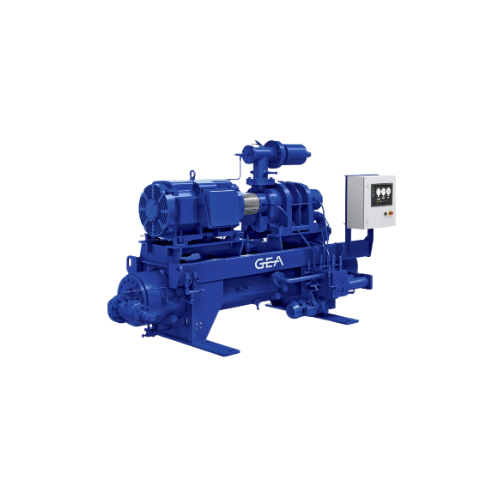
Sustainable packaged compressor system
Enhance your production with a scalable compressor system designed for high efficien...
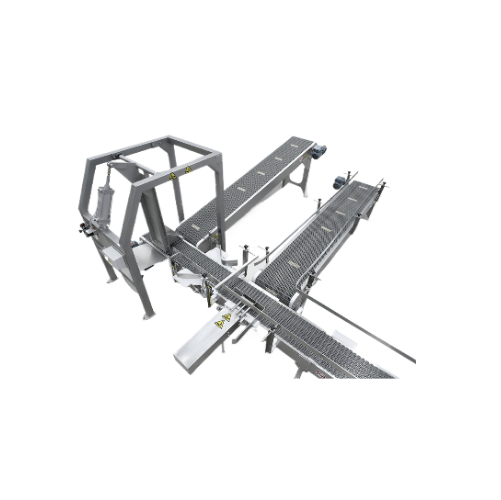
Bag, box, and drum container handling solutions for powder products
Optimize the flow and integrity of your powder pack...
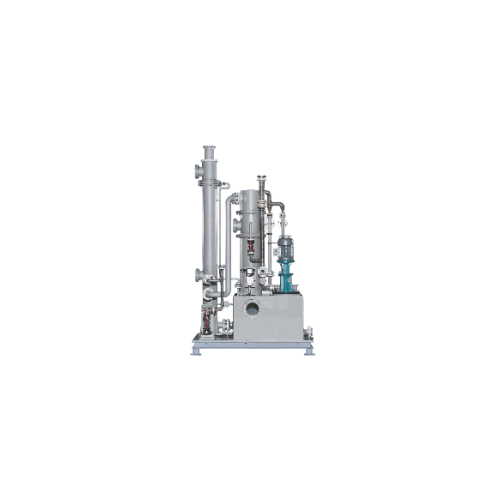
Aerosol separator system for industrial emission control
Enhance your emission control measures with our aerosol separato...
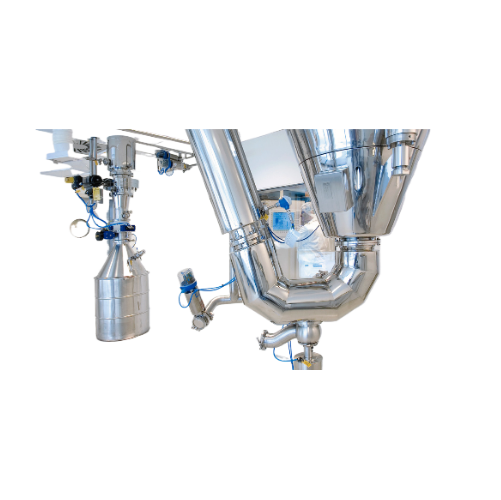
Pharmaceutical spray dryer
Unlock the potential of spray drying to enhance bioavailability, achieve controlled release, and ...
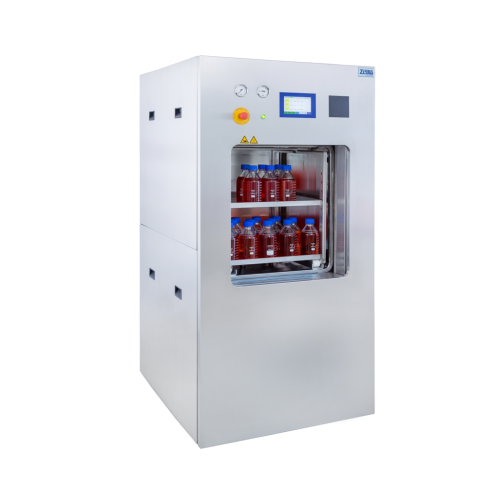
Autoclaves for laboratory and production with square chamber
Optimize your laboratory space with compact autoclaves that...
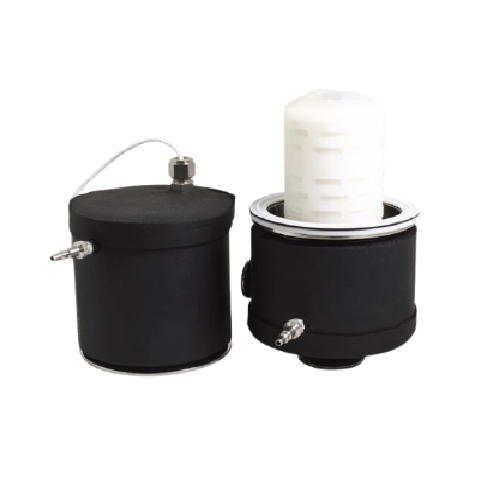
Large production autoclaves for laboratory and pharmaceutical use
Enhance your production line with our large autoclave...
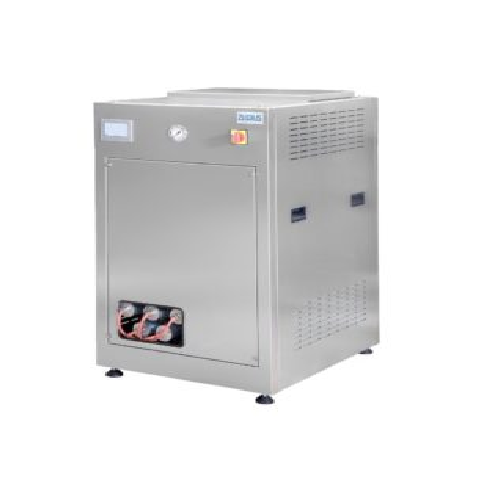
Pure steam generator for industrial applications
Ensure the highest levels of steam purity and precise pressure control fo...
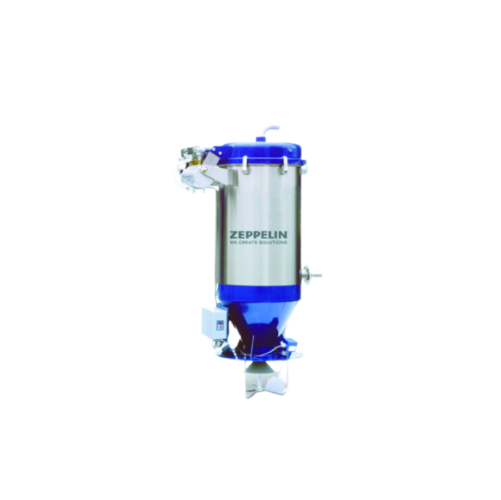
Vacuum hopper loader for automatic feeding of powders and pellets
Optimize your material handling with seamless automat...
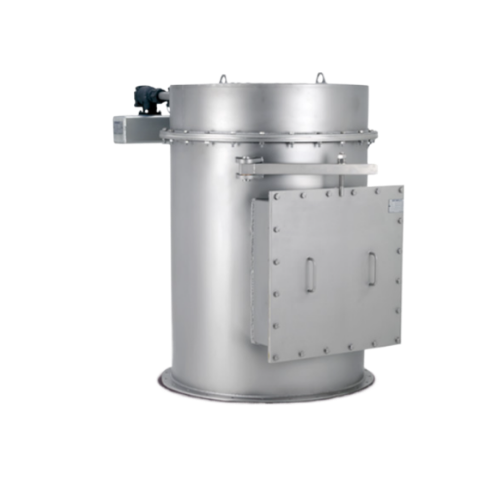
Bin vent filter for dust control in modular systems
Optimize your production line by efficiently controlling dust and fin...
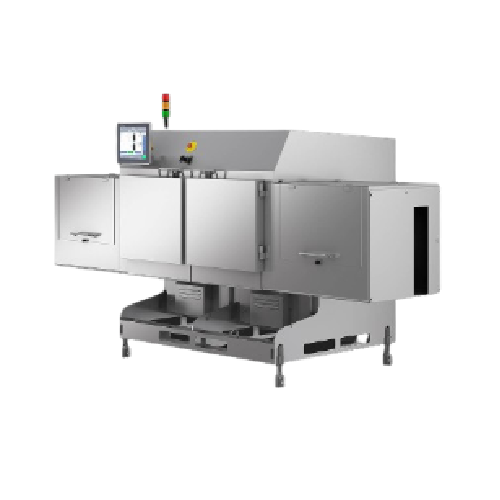
Dual view x-ray inspection for canned goods
Enhance your production line with advanced dual-view X-ray inspection, ensurin...
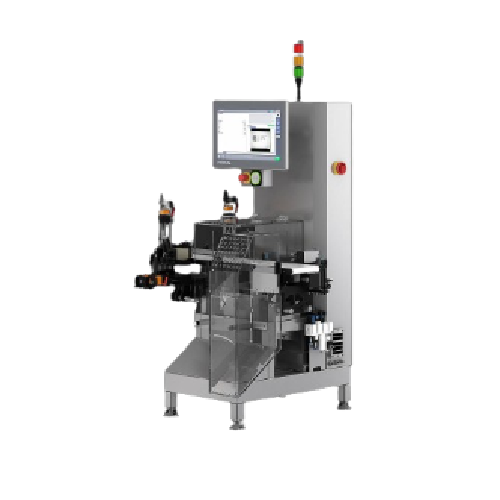
Batch coding system for product verification
Optimize your production line with an integrated system that accurately marks...
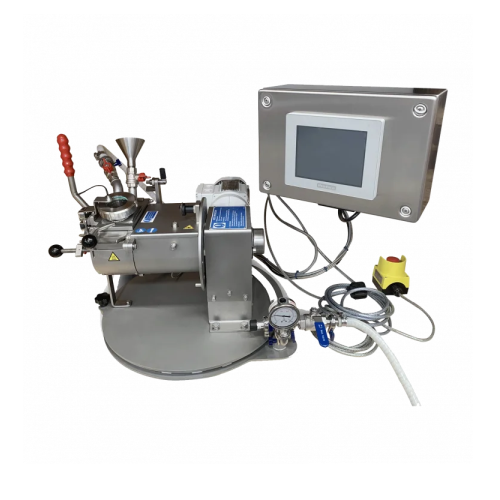
Laboratory mixers for product development and research
Optimize your R&D efforts with advanced mixing solutions desi...
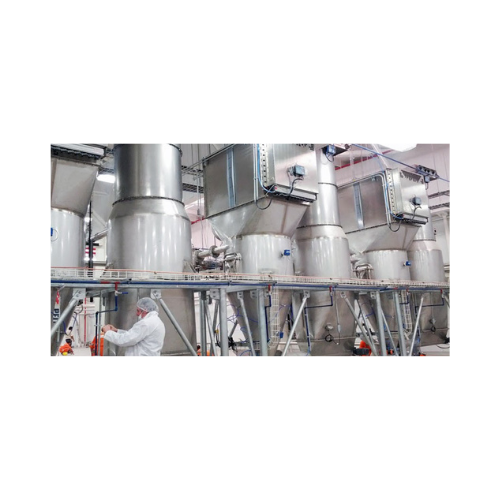
Industrial dust collection system for air filtration
Optimize air quality in your production line with this compact dust ...
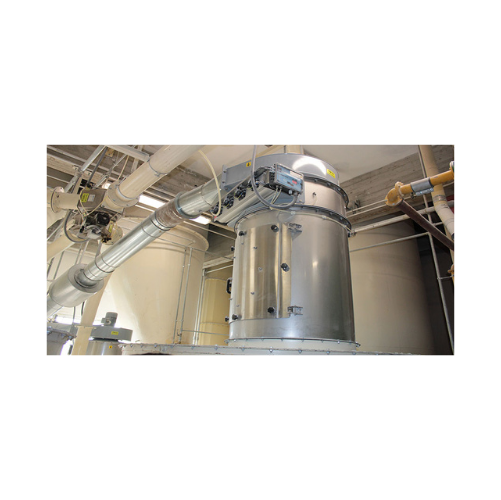
Food-grade round dust collectors
Maintain a clean production environment with this food-grade dust collector, designed to ma...
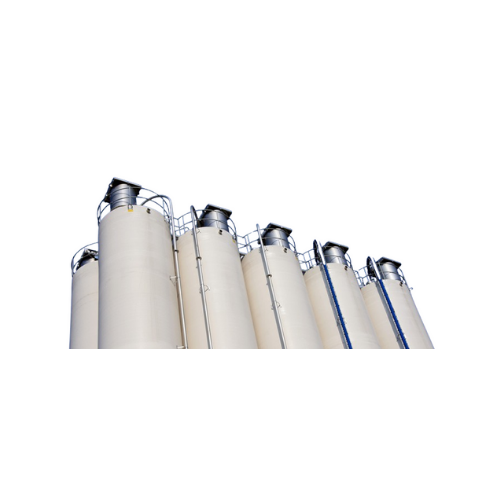
Flanged round dust collectors for industrial air filtration
Optimize your industrial processes with a dust collection sy...
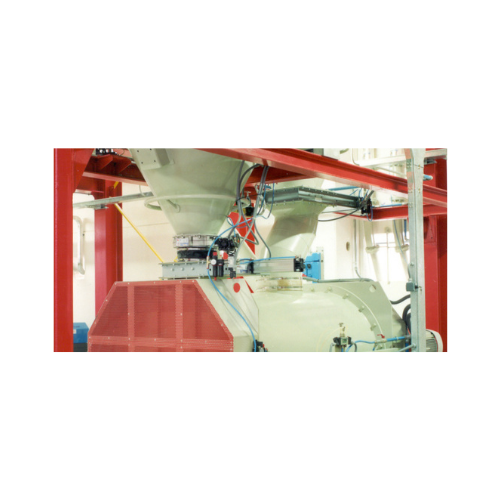
Butterfly valves for powders and granules
Ensure precise flow control and reliable sealing for gravity-fed or pneumatic sy...
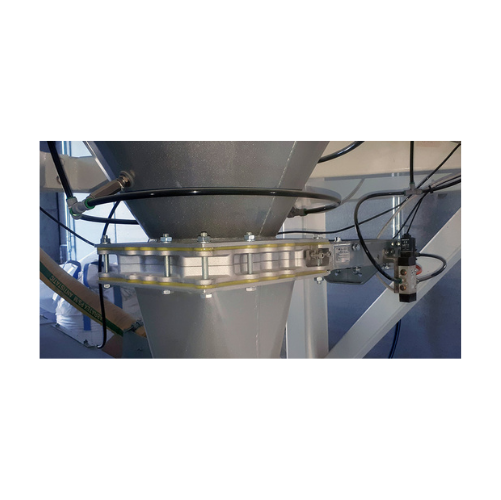
Slide valves for flow interception in powder and granular materials
Effectively manage the flow of powdery and granular...
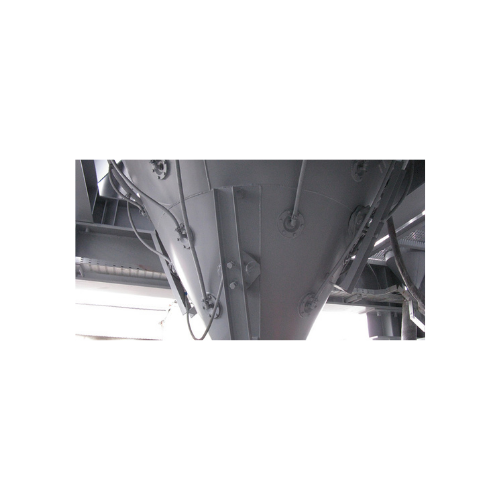
Vibro-aerators for bulk solids discharging
Optimize your powder flow and ensure consistent discharge with this advanced ae...
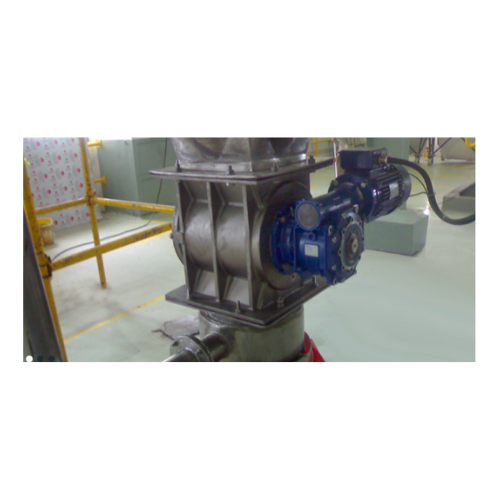
Drop-through rotary valve for powder and granular material feeding
Achieve precise control in discharging and feeding p...
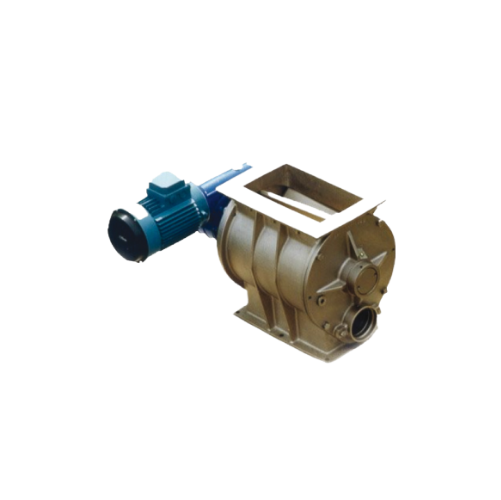
Blow-through rotary valves for pneumatic conveying
Optimize your pneumatic conveying systems with high-efficiency blow-th...
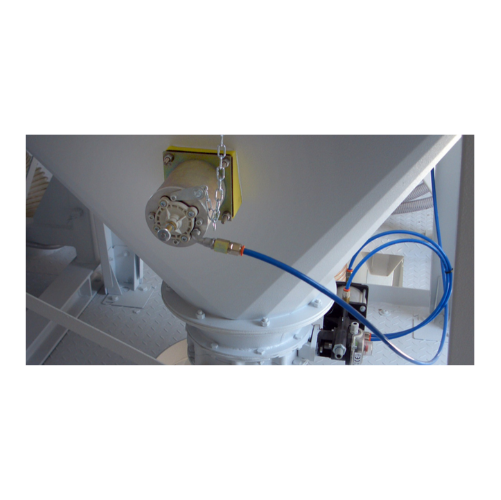
Combined hammer blaster for powder handling
Address powder flow issues with ease by preventing bridging and ratholing, ens...
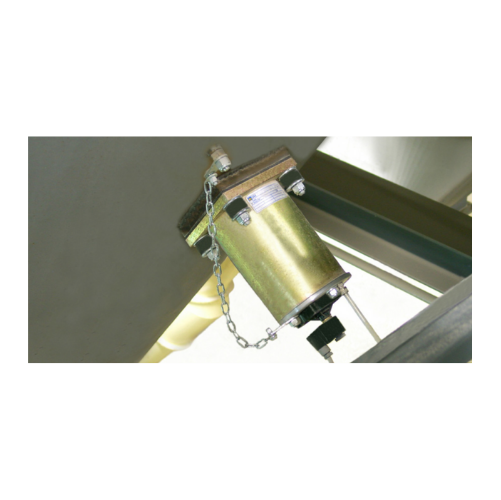
Pneumatic hammers for bulk solids discharging
Optimize your production efficiency and solve material flow challenges with ...
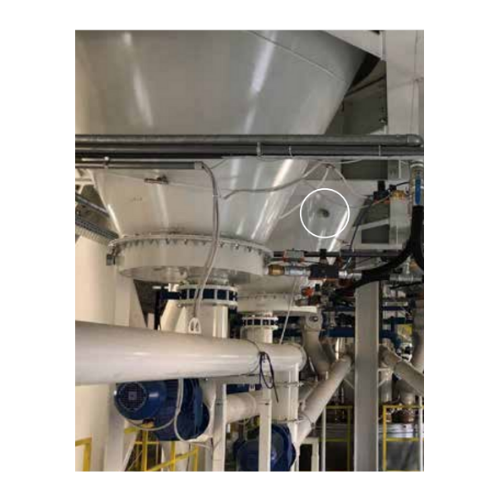
Continuous impact vibrators for bulk material removal
Combat material flow issues like bridging and rat-holing with our i...
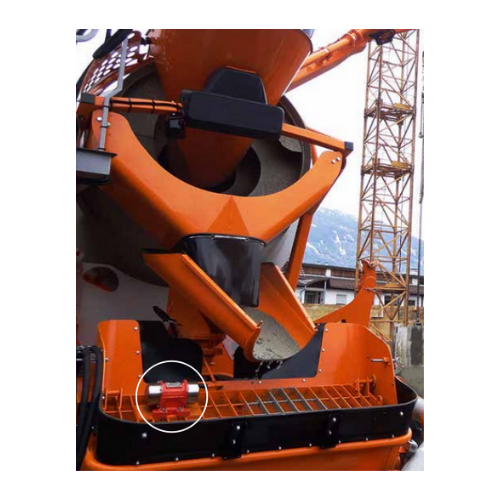
Continuous impact vibrator for aggregate reclaiming
Tackle material flow challenges head-on by preventing common issues l...

Continuous impact vibrators for bulk solids discharging
Optimize your discharging process with vibrators that effectively...
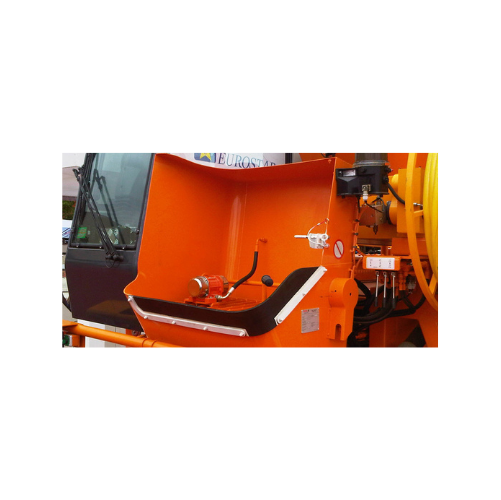
External electric motovibrators for hazardous environments
Ensure safety and efficiency in explosive environments with t...
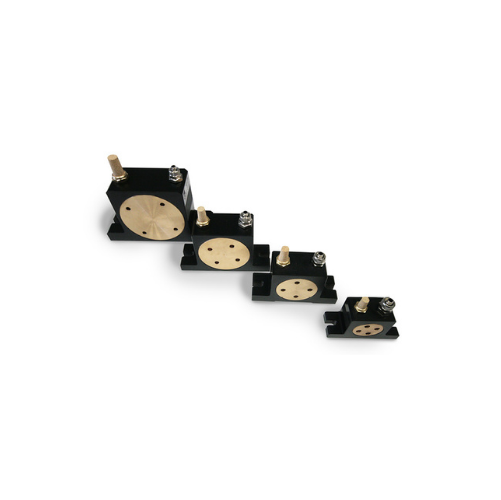
Rotary roller vibrators for concrete compacting and hopper emptying
Achieve higher compaction and efficient emptying wi...
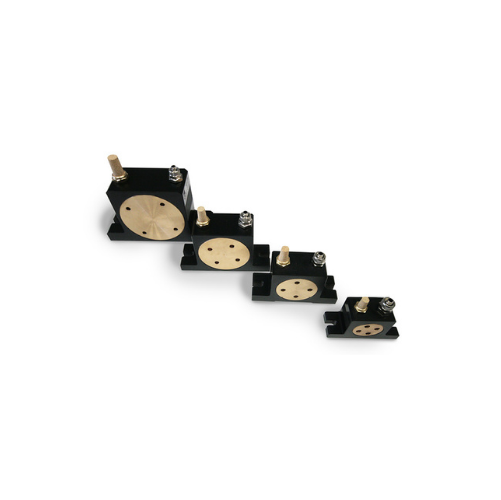
Rotary roller vibrators for material flow assistance
Enhance material flow efficiency in your production line with high-f...
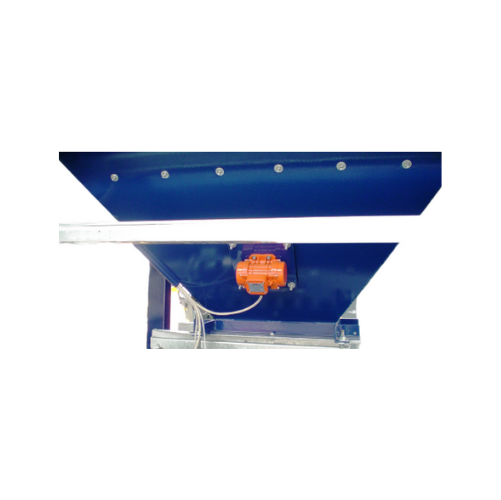
Industrial electric vibrator for bulk solids discharging
Enhance material flow efficiency and ensure consistent output ac...
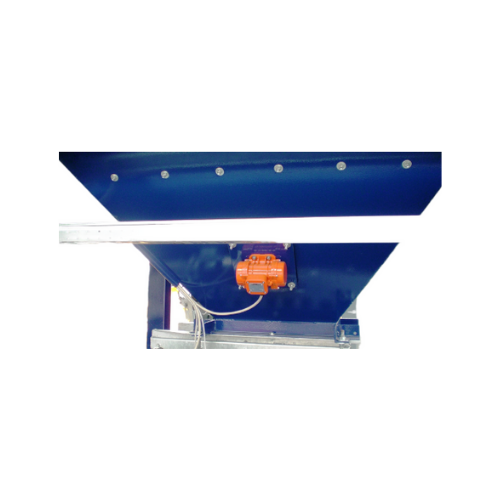
External electric motovibrators for industrial material flow
Experience enhanced material flow and precise material disc...
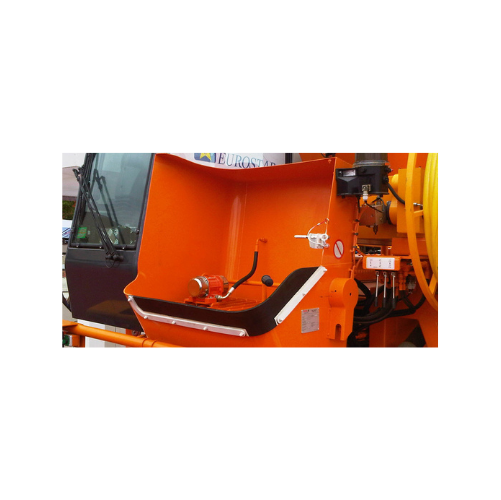
External electric motovibrator for increased safety in hazardous environments
Designed for environments with explosive...

External electric motovibrators for hazardous materials
Ensure safety and efficiency in hazardous environments with relia...
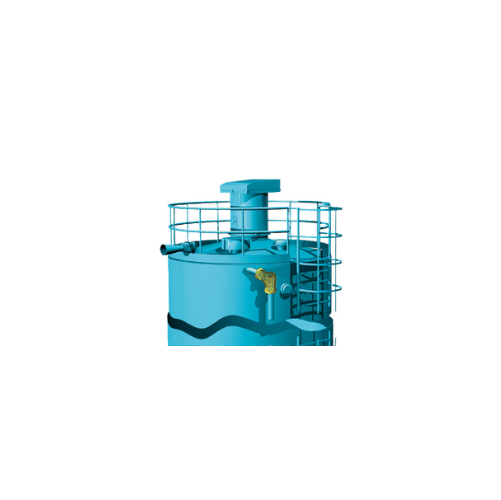
Silo overfilling safety system
Ensure safe silo filling with our system that prevents overfilling and excess pressurization,...
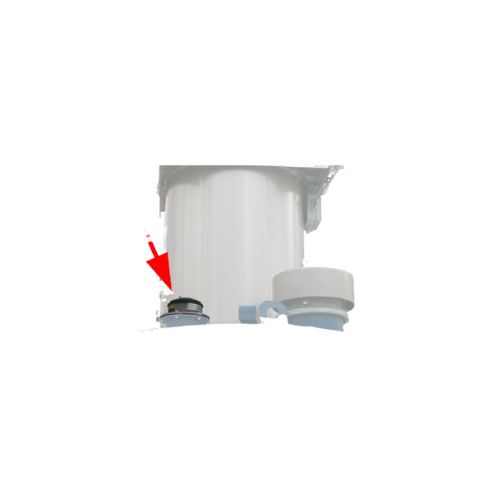
Electronic pressure meter for silo safety
Ensure the safety of your silos by efficiently monitoring internal pressure chan...
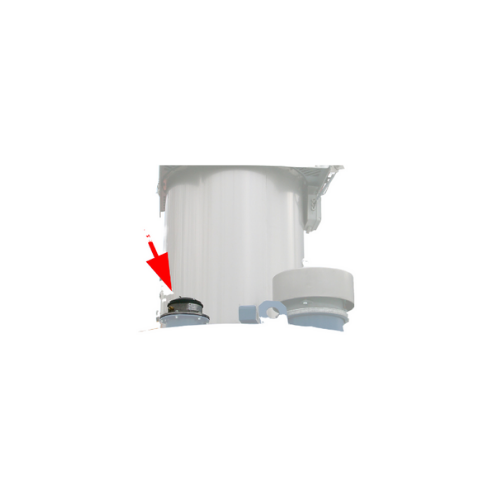
Electronic pressure meters for silo safety monitoring
Ensure precise pressure management in your systems with this advanc...
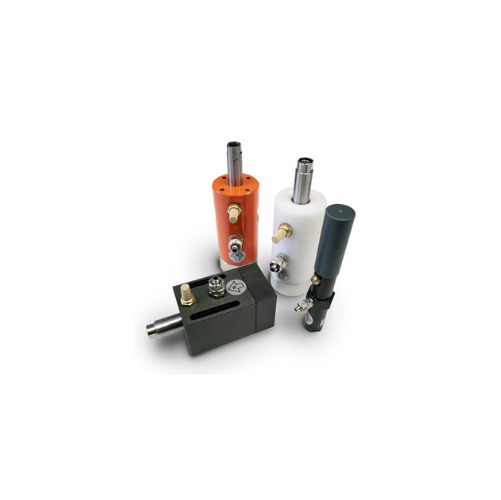
Cushioned pneumatic vibrators for coarse particle materials compaction
Enhance your material flow and compaction proces...
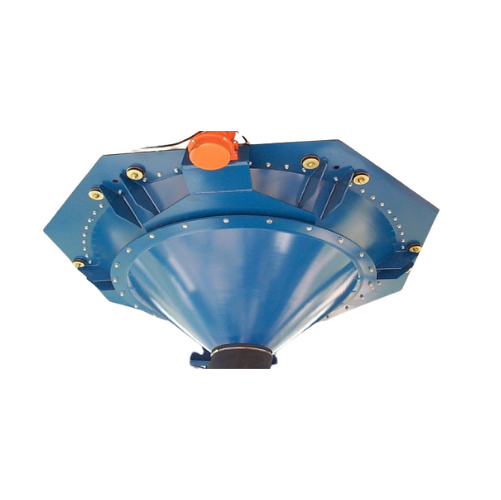
Vibratory outlet hopper for bulk solids discharge
Reduce material handling challenges with highly efficient vibration tec...
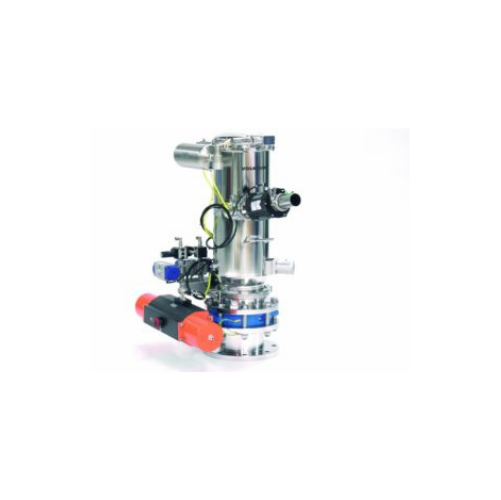
Vacuum conveyors for explosive and inert gas environments
Optimize the safe transfer of hybrid mixtures and fine powders...
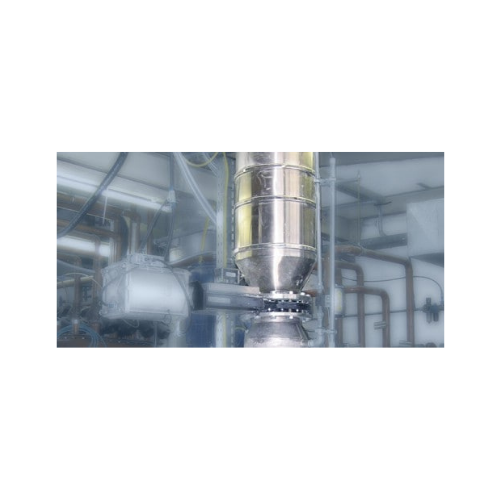
Powder locks for safe bulk material handling
Ensure containment and prevent contamination while processing sensitive bulk ...
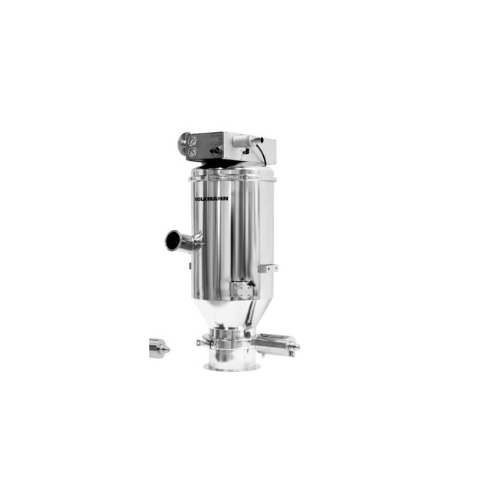
Pharmaceutical vacuum conveyors for hygienic transport
Ensure contamination-free transport of sensitive pharmaceuticals a...
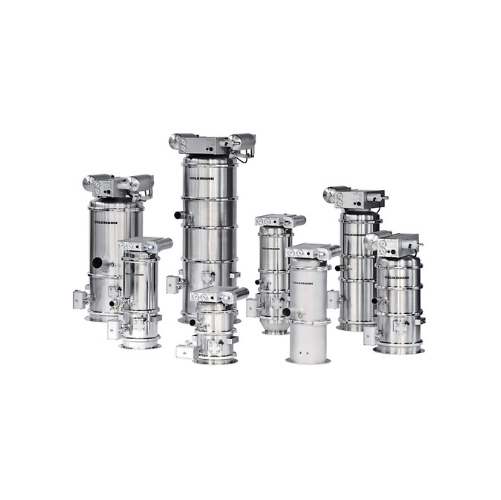
Powder handling vacuum conveyor system
Streamline your material transfer with a versatile vacuum conveyor system that ensur...
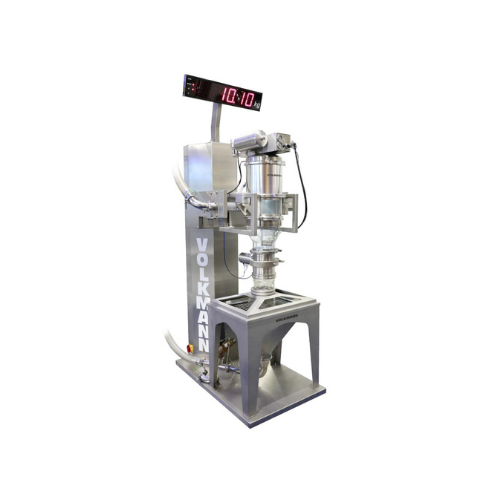
Integrated conveying and weighing system for bulk materials
Achieve precise material management with a solution that sea...
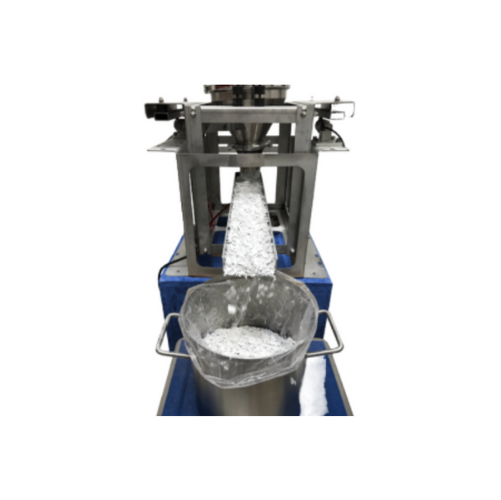
Vibratory feeder for dosing powders and bulks
Ensure precise feeding of powders and bulk materials with a system that inte...
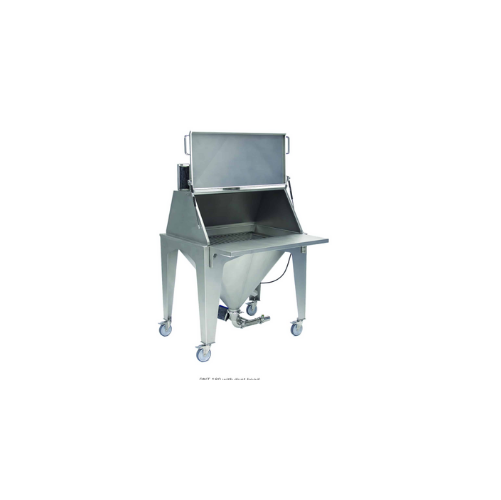
Bag rip-and-tip dump stations for bag emptying
Efficiently manage bag emptying operations with advanced dust containment a...
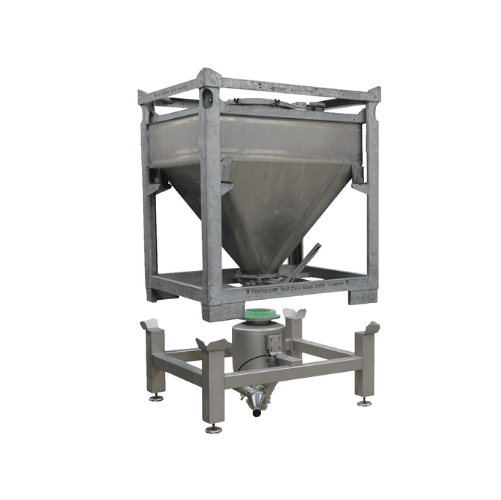
Ibc docking and discharge stations
Ensure seamless material transfer with dust-free docking and effective discharge, mainta...
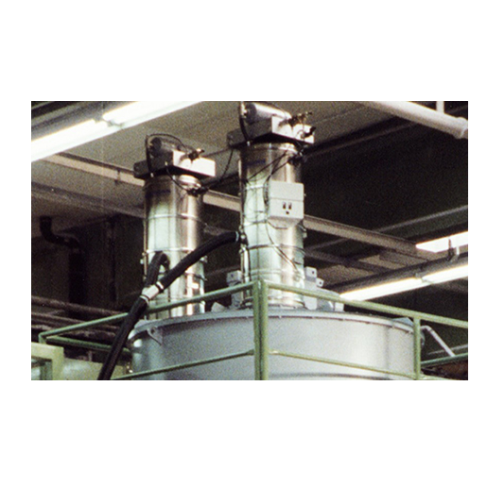
Continuous vacuum conveyors for material flow control
Ensure consistent material transfer and reduce downtime in your pro...
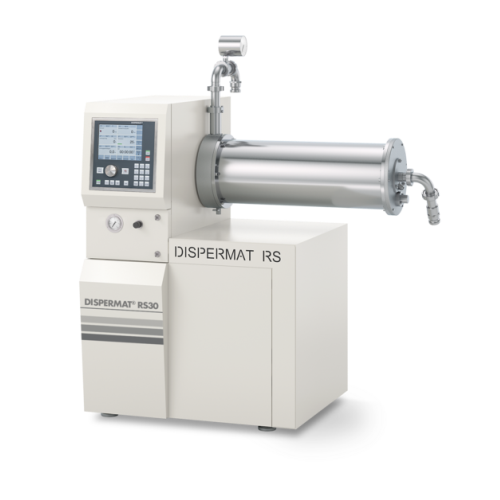
Horizontal bead mill for industrial nano grinding
Achieve precision in nano-scale grinding with this advanced bead mill, ...
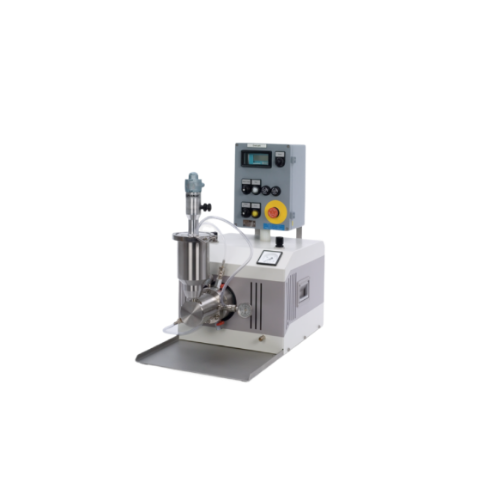
Atex horizontal bead mill
Ensure precision and safety in explosive environments with a robust solution that finely grinds an...
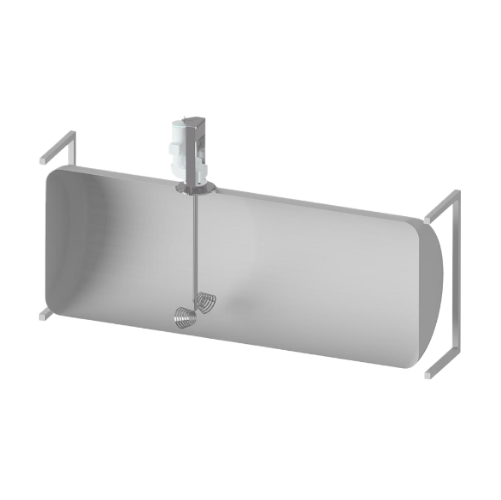
Agitator for horizontal storage tanks
Efficiently blend various viscosities in horizontal tanks, ensuring optimized flow pa...
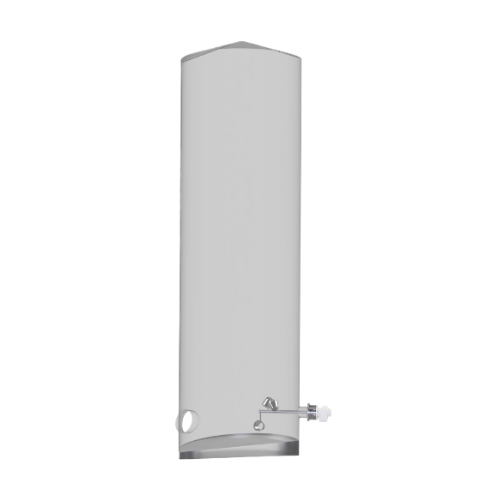
Industrial side-mounted agitator for efficient mixing
Enhance your production line with a side-entry agitator designed fo...
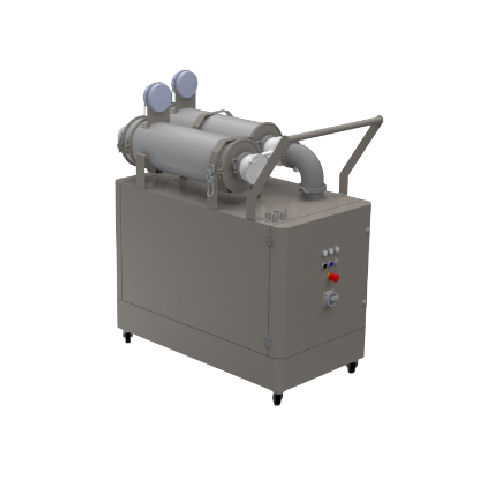
Containment single-use filter module
Ensure safe handling of high-potency substances and streamline filtration processes wi...
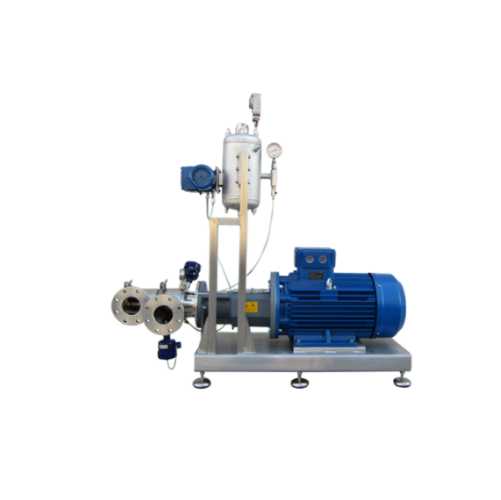
In-line mixer for liquid-liquid and solid-liquid processes
Optimize your mixing operations with an efficient solution th...
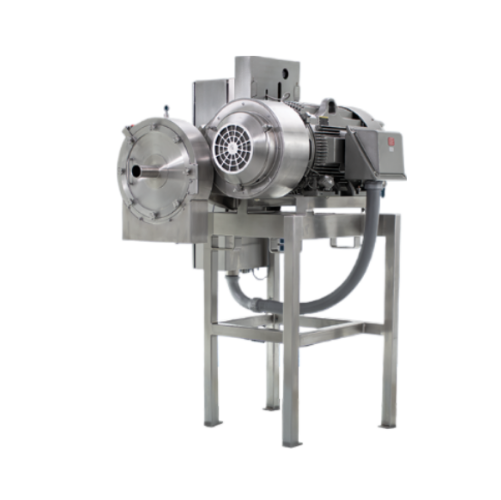
Industrial particle size reduction processor
Optimize your production line with high-capacity, continuous particle size re...
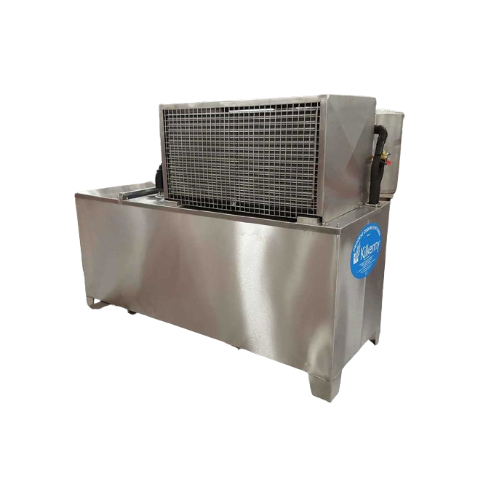
Industrial chiller systems for processing cooling
Optimize your production line with advanced chiller systems designed to...
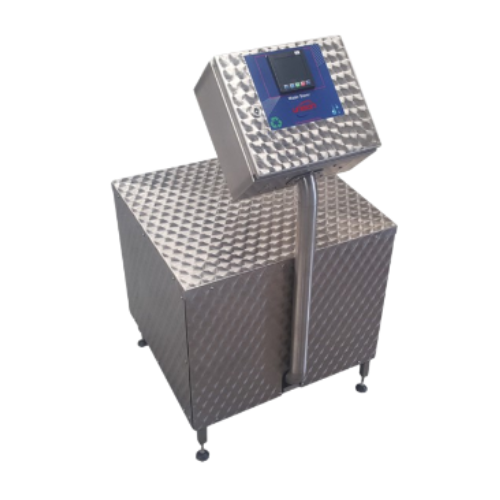
Industrial water recycling system
Reduce excess water consumption in your process line by recycling and reusing up to 96% o...
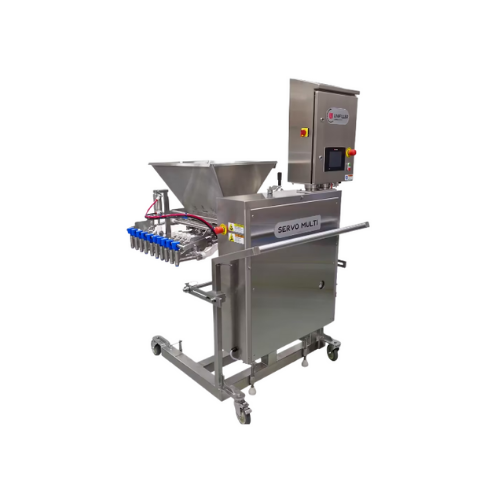
Servo multi depositor for food portioning
Achieve precise portion control and high-speed depositing with versatility acros...
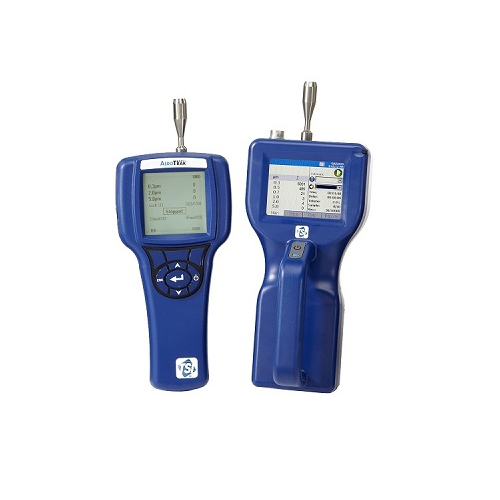
Handheld particle counters for cleanroom environment monitoring
Ensure precision in contamination monitoring and quality...
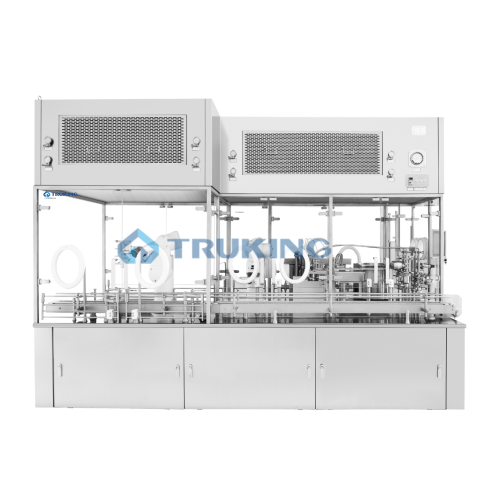
Nested fillers for vials, pre-filled syringes, and cartridges
Optimize your aseptic filling processes with precision dos...
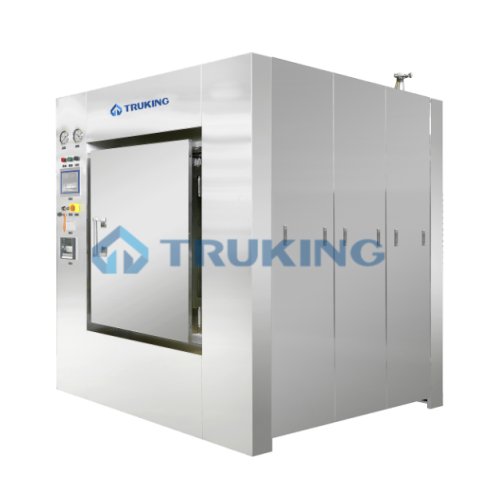
Pharmaceutical autoclave for terminal sterilization
Optimize your sterile production with high-precision terminal sterili...
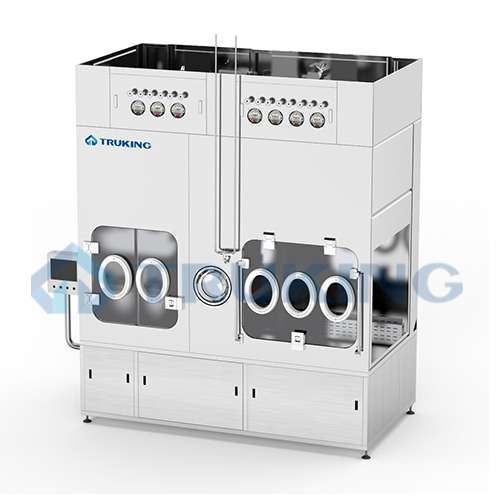
Autoclave unloading isolator for sterile assembly
Ensure aseptic conditions and prevent microbial contamination during th...
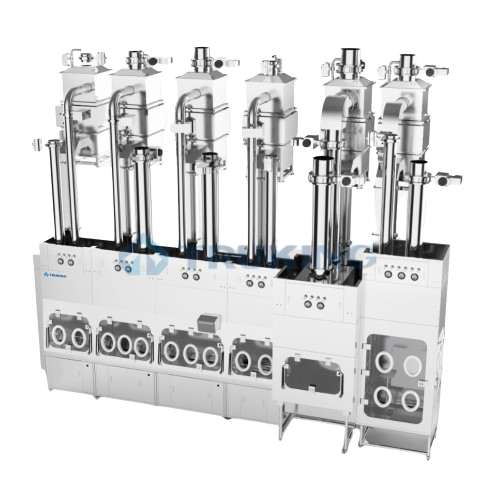
Active pharmaceutical ingredient isolation system
Ensure the aseptic production of pharmaceuticals while protecting perso...
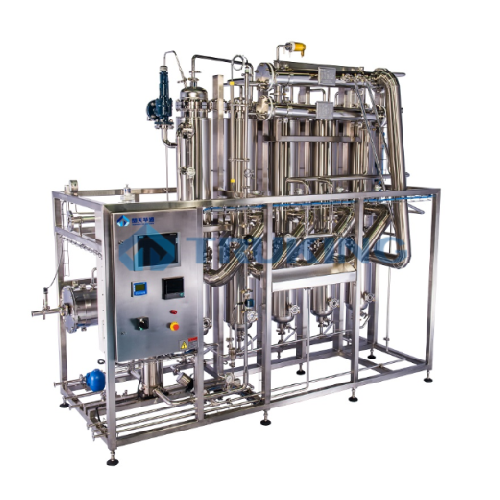
Multi-effect water distillator for pharmaceutical applications
Ensure your production line meets stringent regulatory st...
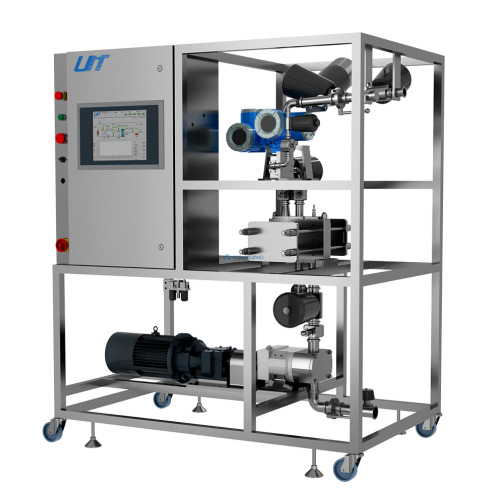
Production-level ultrafiltration system for industrial applications
Achieve precise concentration and separation of val...
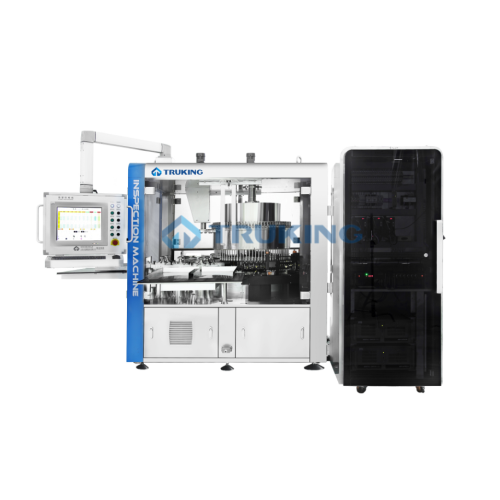
Automatic inspection system for ampoules and vials
Ensure precision in pharmaceutical production with a comprehensive ins...
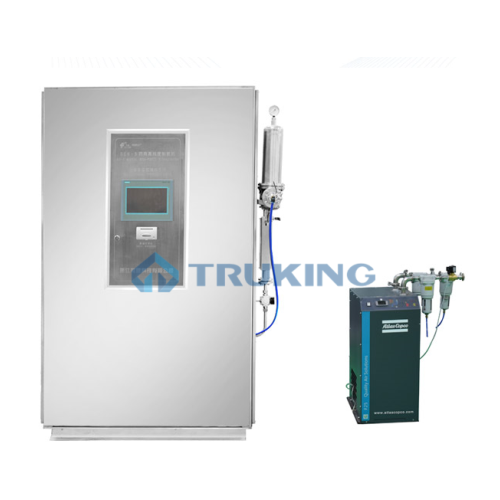
High-purity nitrogen generator for pharmaceutical and food industries
Achieve ultra-high purity levels in your producti...
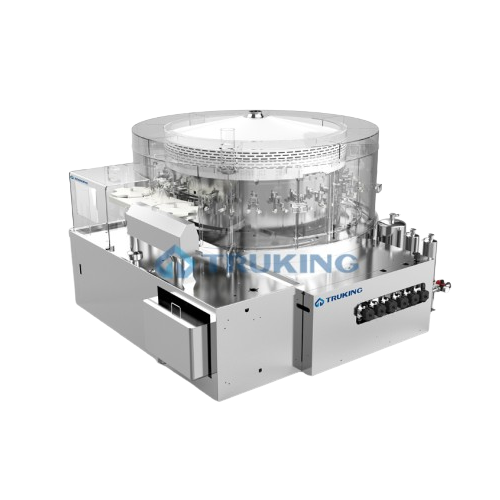
Industrial freeze dryer for pharmaceutical applications
Enhance your production line with precision cleaning solutions fo...
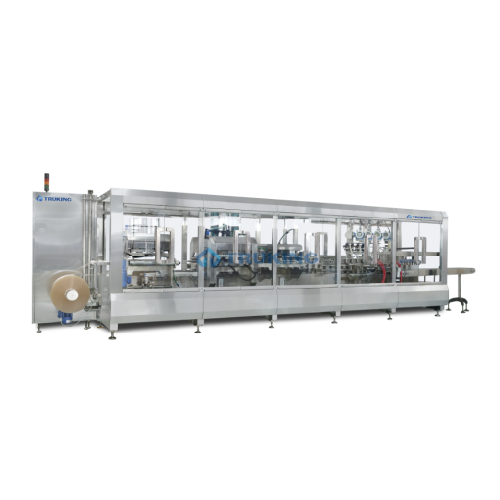
Non-pvc film large infusion compact line
Streamline your infusion production with a compact line designed for high-speed, p...

High capacity automatic blister packaging system
Streamline your production line with a high-speed blister packaging syste...
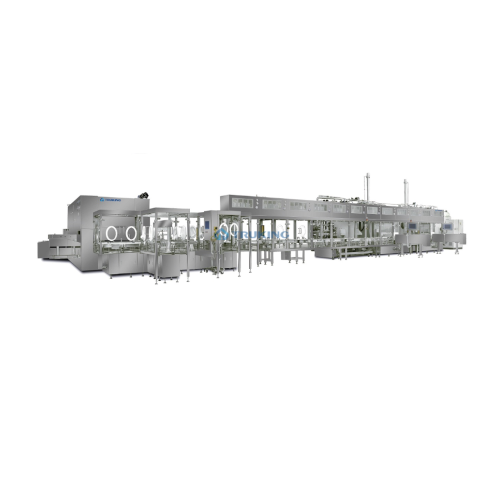
Auto loading & unloading system for freeze dryers
Efficiently manage vial handling in freeze-drying processes with automa...
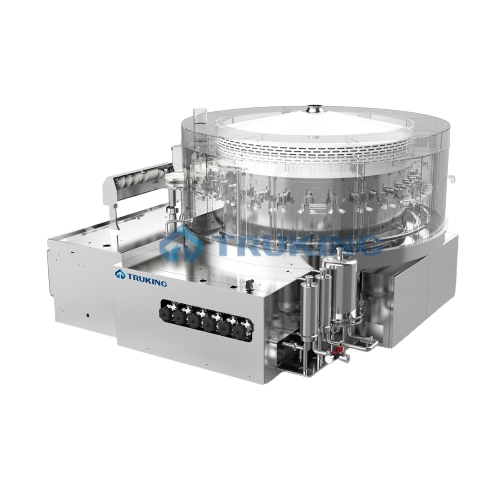
Ultrasonic pre-washing system for large infusion glass bottles
Optimize your cleaning process with an ultrasonic pre-was...
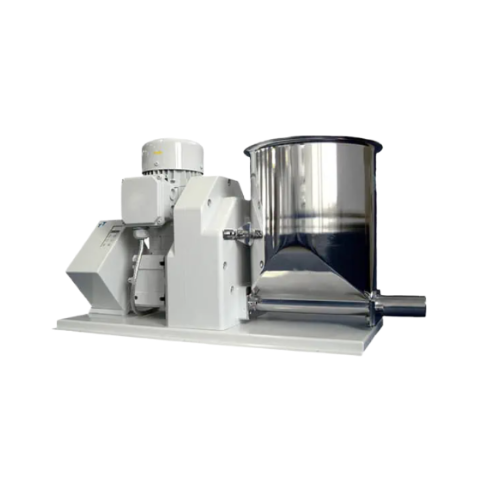
Volumetric twin screw feeder for powder and micro-granules
Optimize your production flow by ensuring consistent and prec...
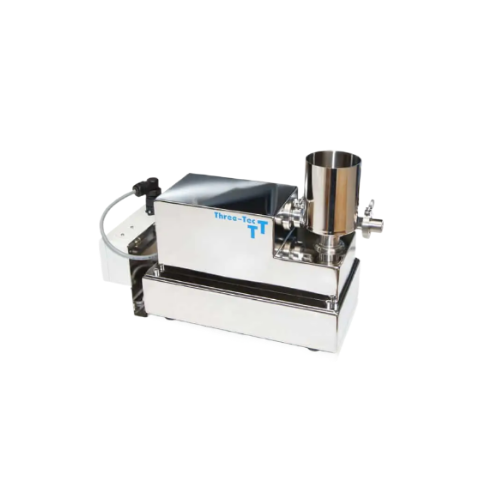
Precise volumetric or gravimetric powder feeder
For precise feeding of challenging powders prone to clumping and bridging,...

Spheronizer for extrudate strand reduction and rounding
Achieve precise pellet formation with a versatile system that cus...
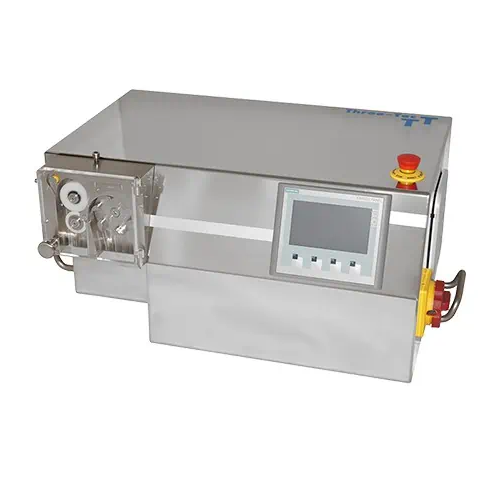
Granulator for processing strands into granulate
Optimize granule production with precise control over pellet size and ext...
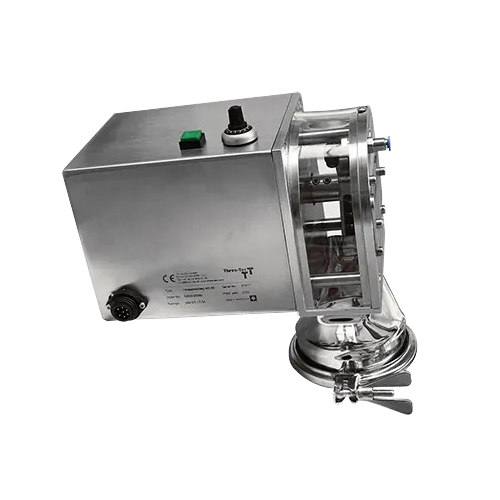
Hot cutter for processing extrudate into pellets
Efficiently transform extrudates into precise pellet sizes, enhancing you...
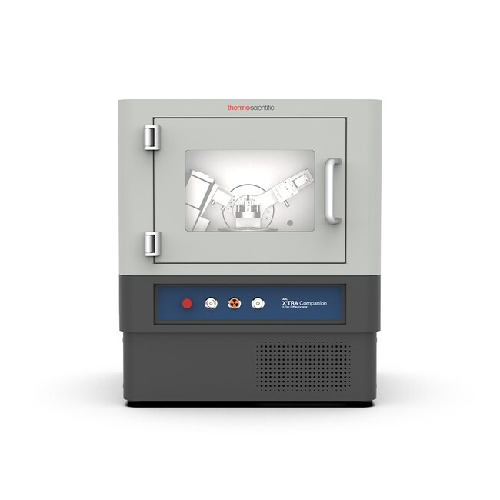
Benchtop x-ray diffractometer for routine analysis
Achieve high-precision phase analysis and crystalline characterization...
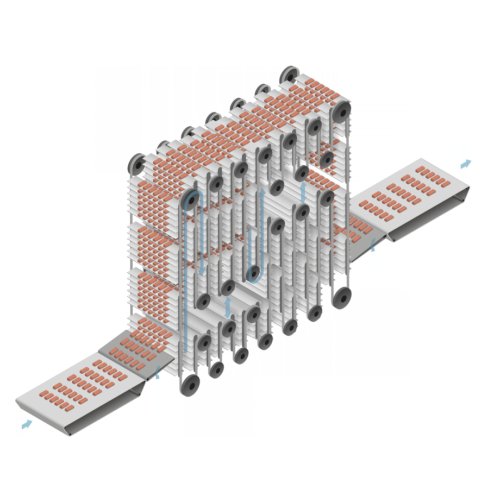
Gondola storage system for efficient product handling
Manage production line inconsistencies with precision by employing ...
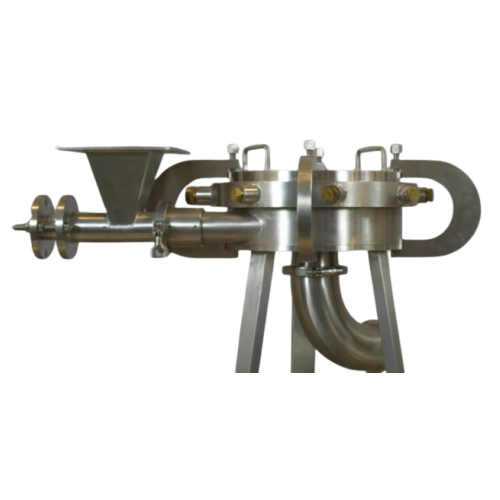
Jet milling system for super fine particle size reduction
Achieve ultra-fine particle sizes with precision milling techn...
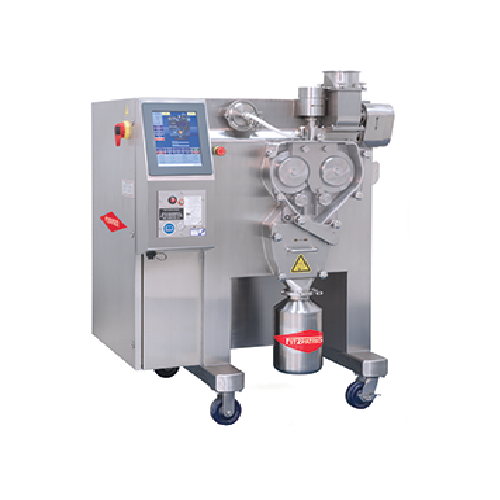
Roller compaction for dry granulation in pharmaceuticals
Ensure consistent granule size and density in your product line ...
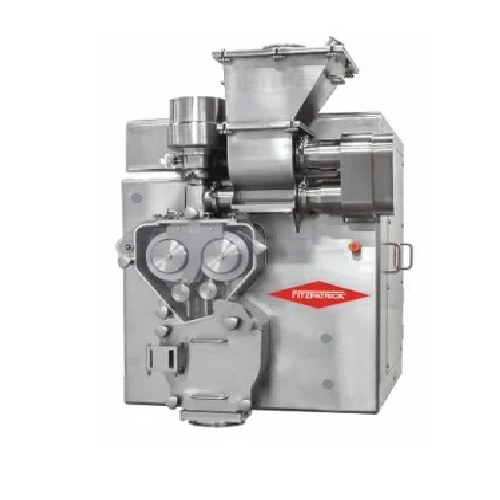
Roller compactors for dry granulation
Optimize your powder processing with advanced roller compaction, ensuring consistent ...
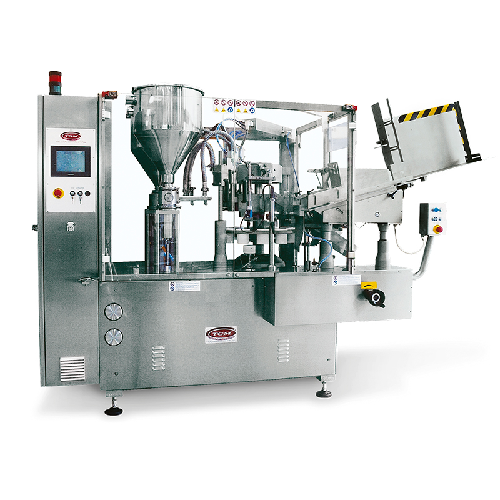
Automatic tube filler for multi-color coextruded products
Achieve precise dual- or tri-color product designs with except...
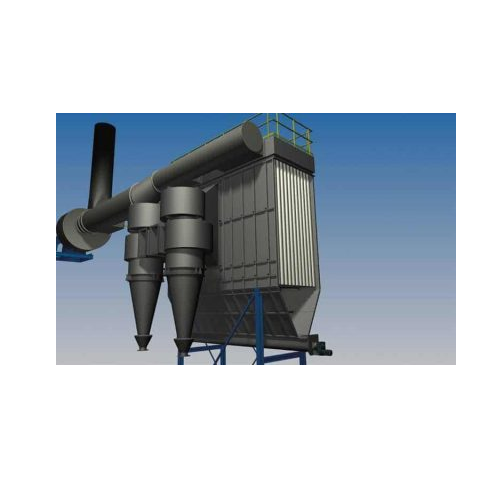
Industrial dust collection system
Optimize your process by efficiently capturing and removing airborne dust particles, ensu...
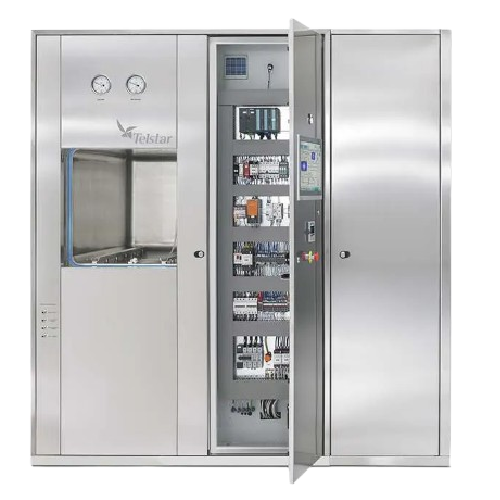
Saturated steam sterilizer for pharmaceutical production
Ensure sterility for a diverse range of pharmaceutical products ...
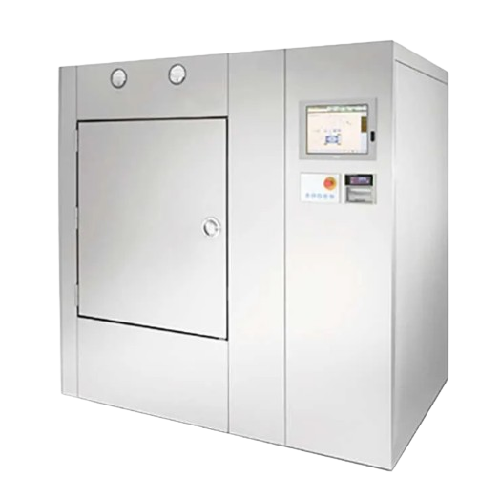
Dry heat sterilization and depyrogenation oven for glassware
Achieve precise sterilization and depyrogenation of glasswa...
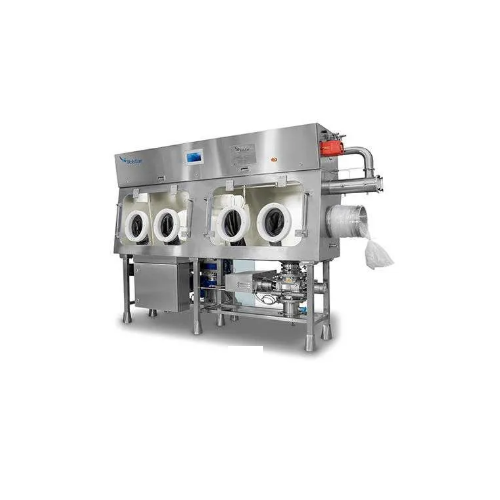
Sterile lyophilised filler
Achieve precise weighing and contamination-free lyophilisation with our cutting-edge sterile fill...
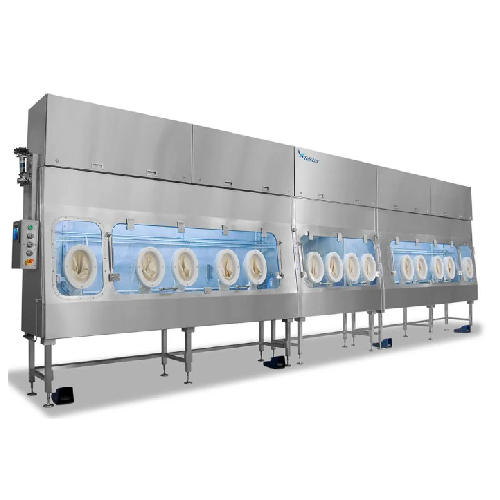
Aseptic barrier isolators for pharmaceutical applications
Enhance sterility and operator safety during aseptic processin...
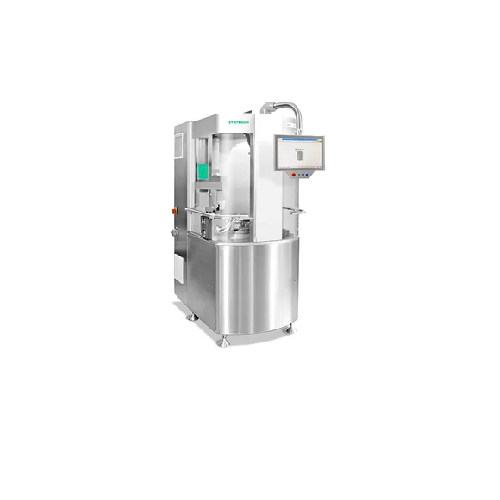
Capsule filling for pharmaceuticals and nutraceuticals
Enhance your capsule production capabilities with modular filling ...
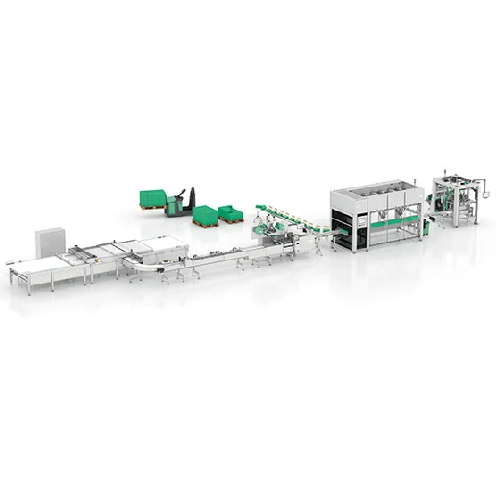
Automated visual inspection for pharmaceutical products
Ensure the integrity and safety of your parenteral products with ...
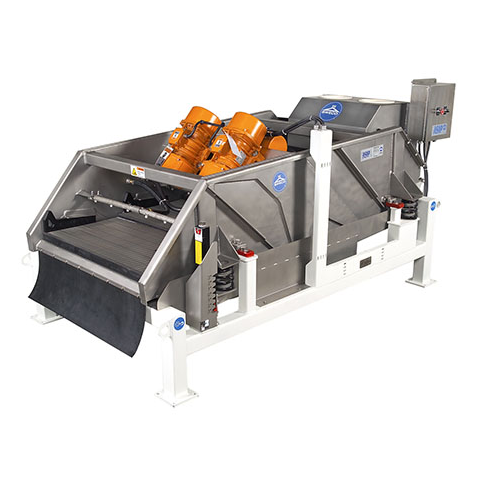
Multi-motion rectangular separator
Solve screen blinding effortlessly with an innovative system that combines elliptical an...
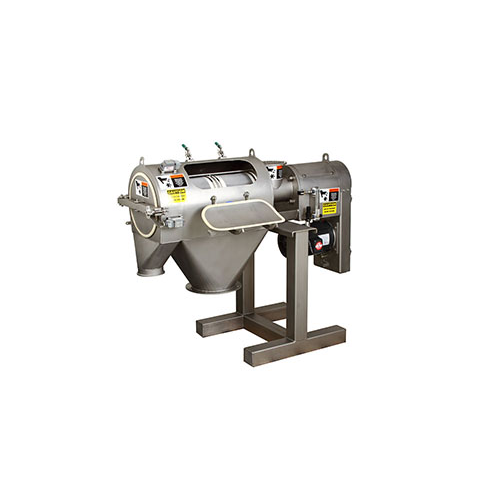
Centrifugal sifter for efficient particle separation
Enhance your material throughput by efficiently separating particles...
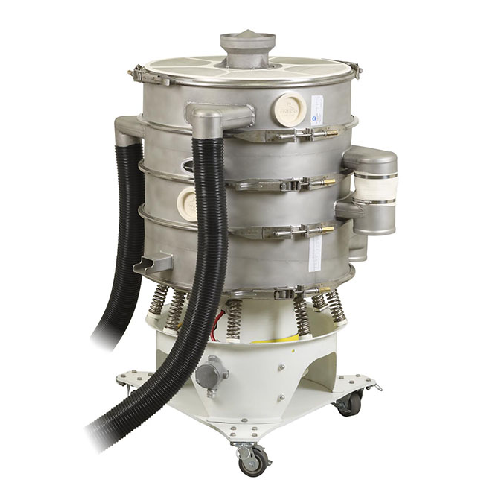
Drying and cooling classifier for plastic pellets
This solution enhances efficiency by combining drying, cooling, and cla...
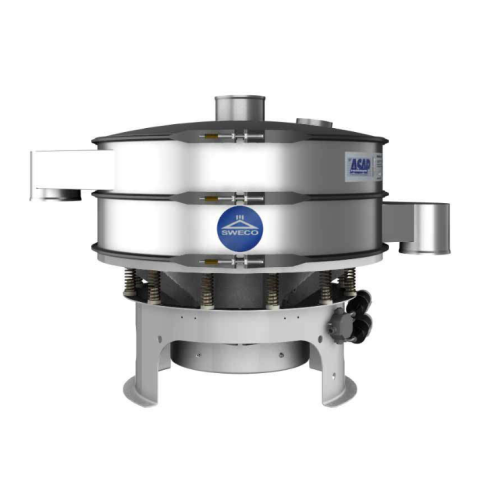
Vibratory separator for efficient solid-liquid separation
Maximize throughput and efficiency in your production line wit...
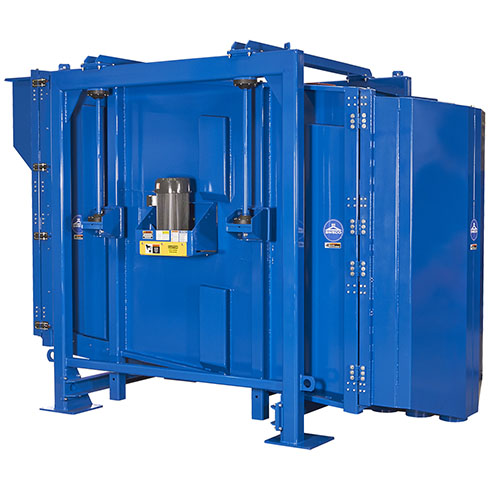
High-capacity industrial sifter for chemical and food processing
Achieve unparalleled screening precision and efficiency...
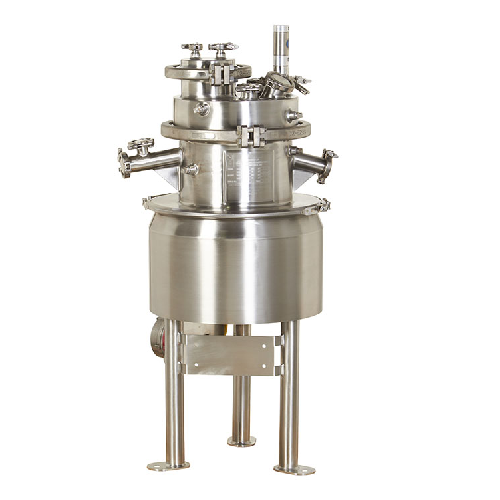
Lab Pharmaceutical aseptic separator
Achieve high-yield recovery and safe handling of potent pharmaceuticals with this asep...
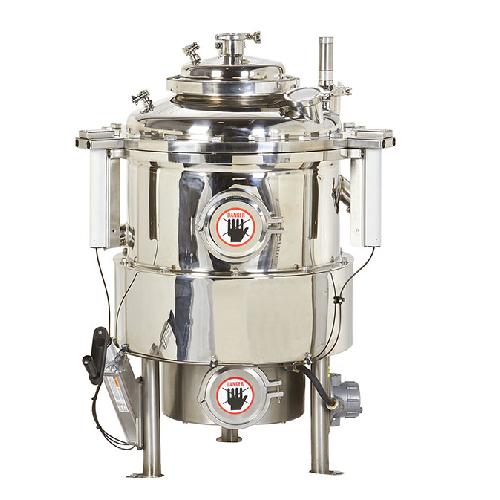
Pilot pharmaceutical aseptic separator and dryer
Achieve high-yield recovery of potent compounds with a separator that com...
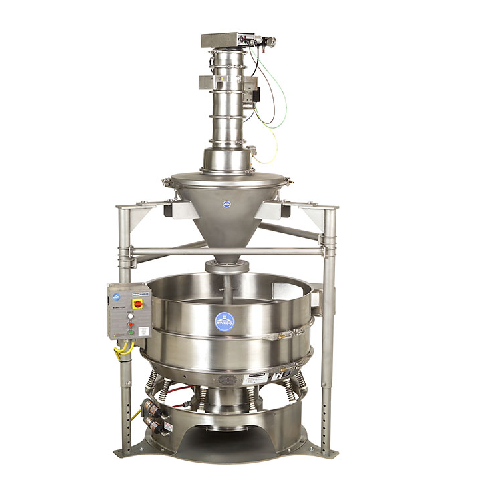
Accu-feed system for dry material separation
Boost efficiency by combining storage, feeding, and screening into one space-...
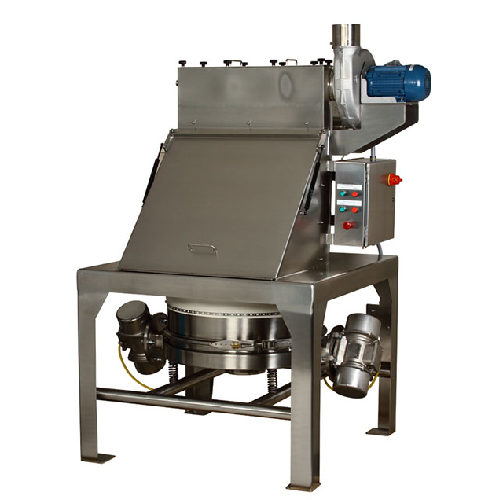
Round vibratory separation equipment - bag dump screener system
Enhance your material handling and safety by efficiently...
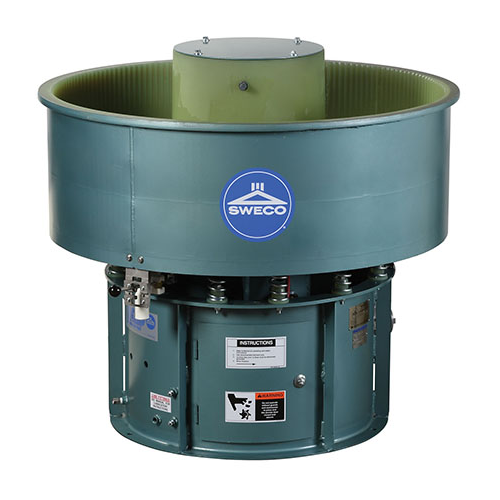
Vibratory finishing and deburring technology
Achieve precise surface finishing and deburring with advanced vibratory motio...

Multiple-effect water still for pharmaceutical applications
Optimize your pharmaceutical water production with a system ...
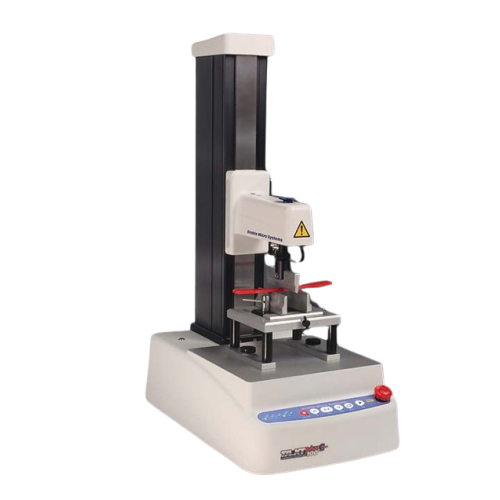
High-force texture analyser for precise measurement
Achieve unparalleled precision in texture analysis for high-force app...
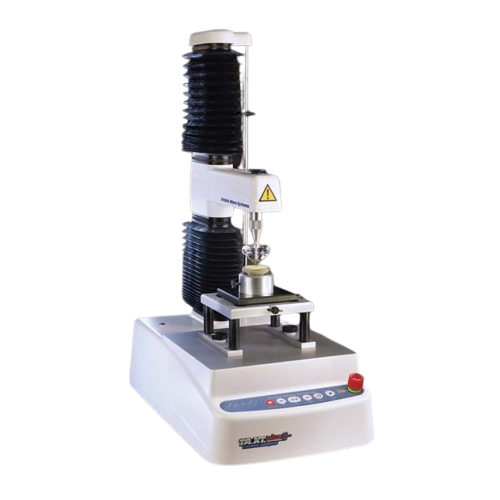
Texture analyser for food and cosmetics testing
Ensuring consistent product quality across diverse food and cosmetic appli...
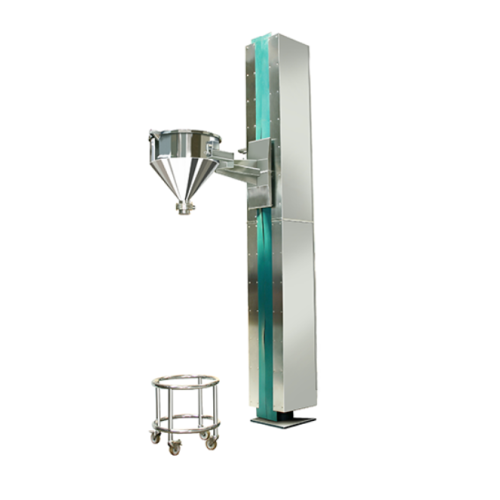
Material lifting system for dust-free transfer in pharma plants
Achieve seamless material transfer with reduced manual h...
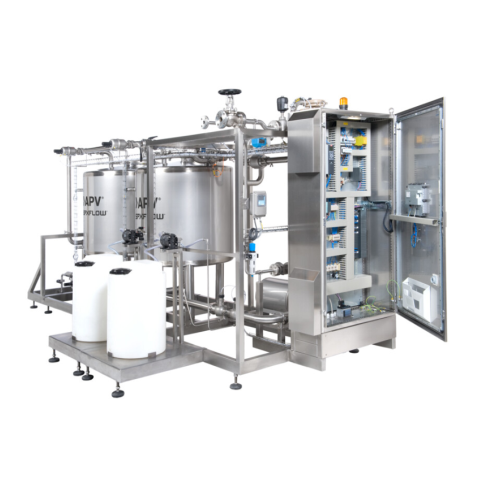
Clean in place (cip) system for industrial cleaning
Ensure optimal hygiene and production efficiency with a system that s...
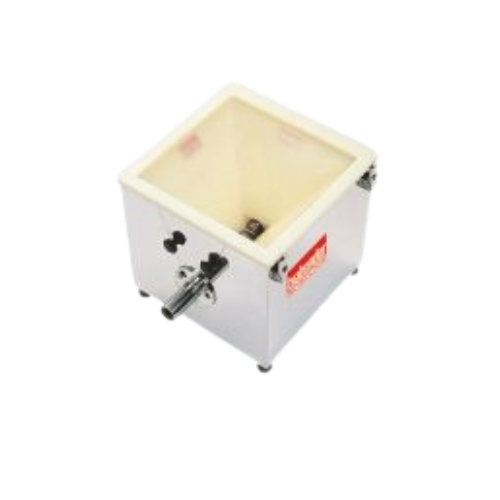
Volumetric feeder for flowable ingredients
Ensure consistent and precise dosing of diverse materials in your production li...
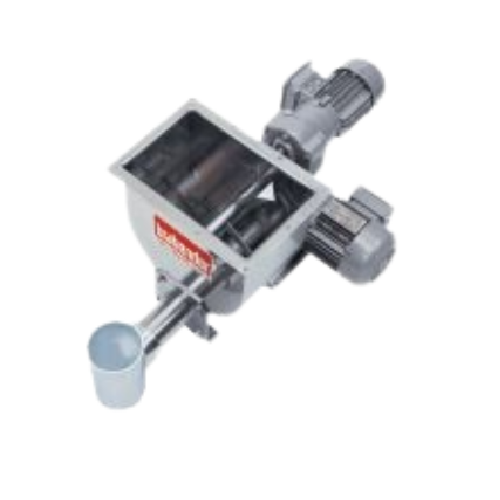
Single screw feeder with stirring agitator for powders and pellets
Ensure consistent mass flow and precise dosing with ...
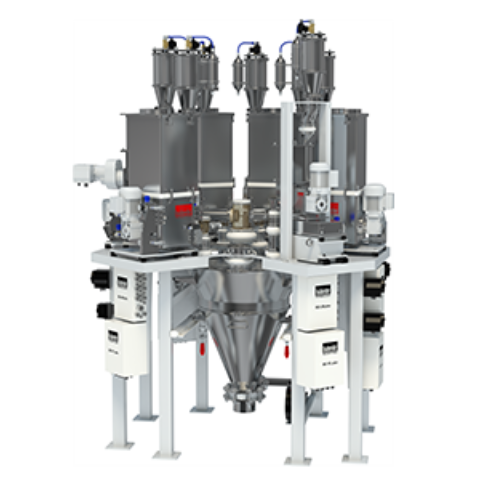
Hopper scale for precision batching
Achieve high batch accuracy with a central weighing hopper engineered for seamless inte...
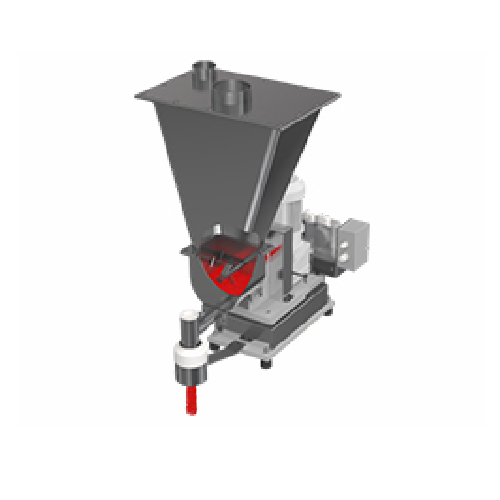
Single screw batch feeder with stirring agitator for powders and pellets
Ensure precise ingredient control and consiste...
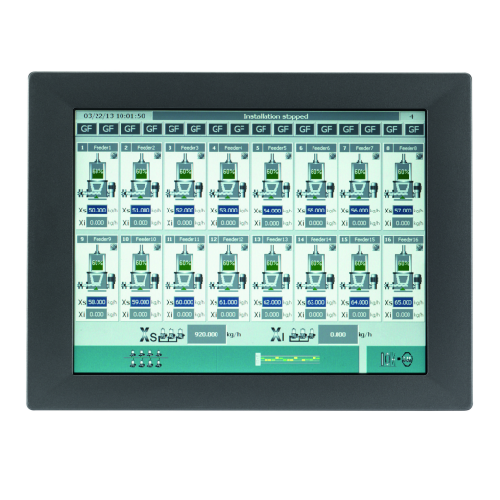
Gravimetric feeder operator interface
Efficiently manage up to 16 gravimetric feeders with a user-friendly interface, enabl...
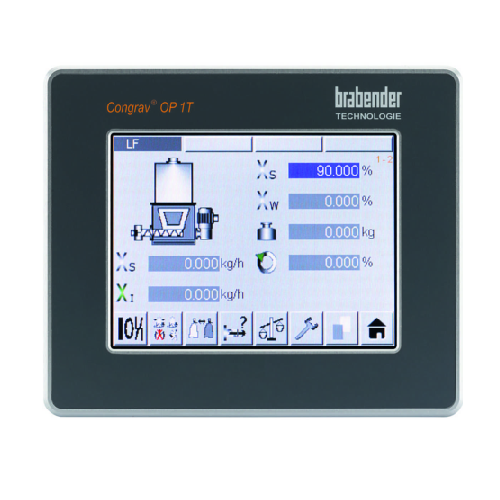
Single feeder operator interface for gravimetric feeders
Enhance precision in your dosing operations with an intuitive to...
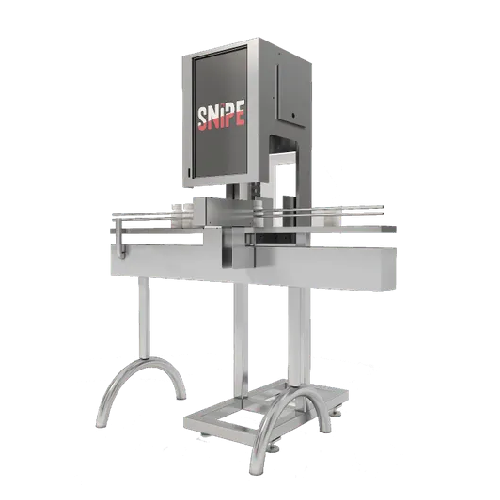
Bottle induction seal integrity inspection
Ensure uncompromised product quality by accurately inspecting and verifying the...
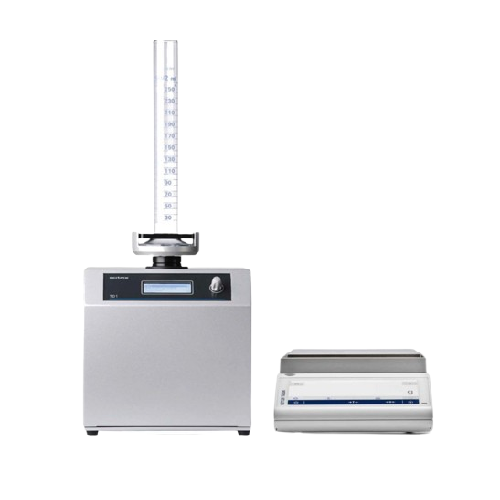
Tapped density tester for pharmaceutical powders
Ensure precise quality control in pharmaceuticals by accurately measuring...
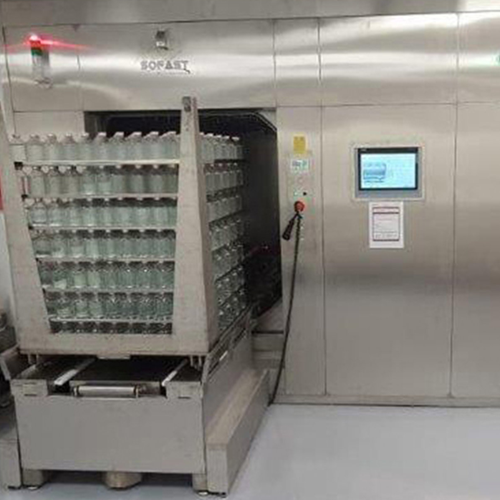
Medical lab sterilization autoclave
Ensure product sterility with high-performance ventilated autoclaves designed to optimi...
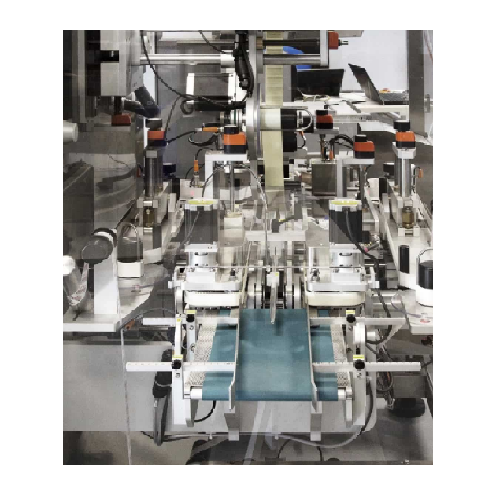
Automatic tamper-evident seal applicator
Ensure your product integrity and traceability in packaging lines with this soluti...
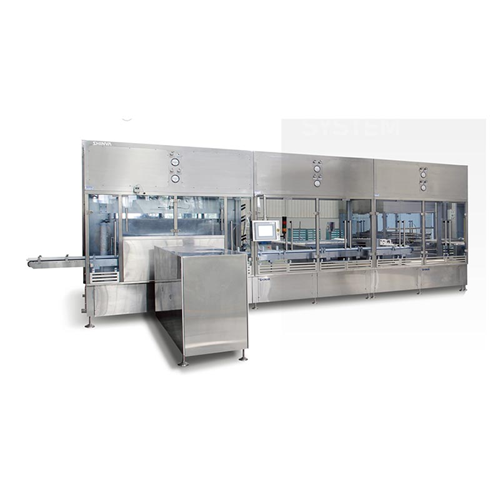
Automatic loading and unloading system for freeze-drying
Eliminate contamination risks and improve operational efficiency...
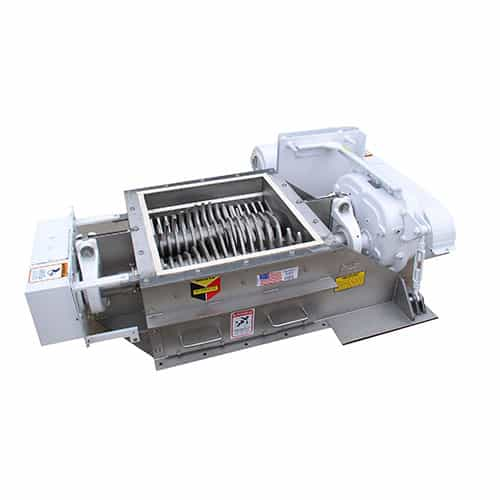
Industrial crusher for size reduction and waste recycling
Optimize your production line with versatile and robust crushi...
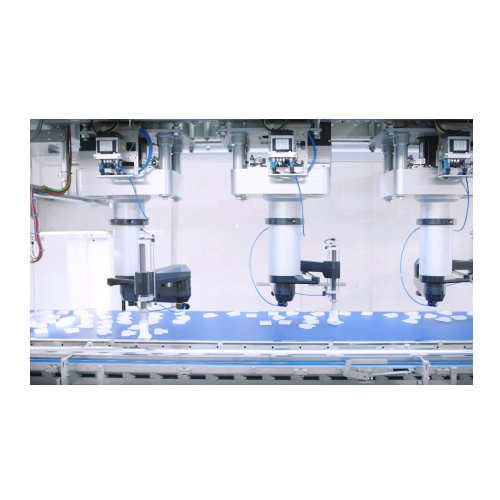
Compact carton packing solution for standardized tasks
Streamline your packaging workflow with a preconfigured solution d...
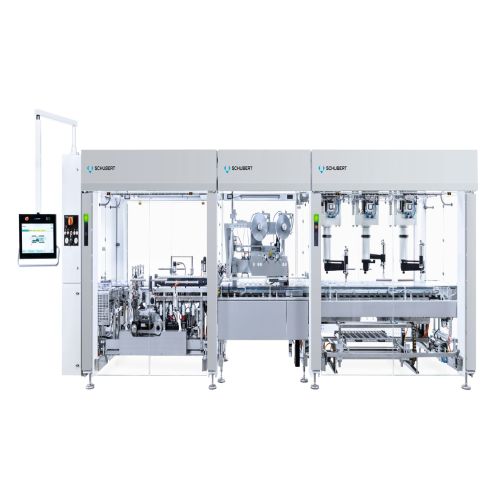
Flowpacker for packaging products in flowpacks
Optimize your flowpack packaging line with a preconfigured solution that ac...
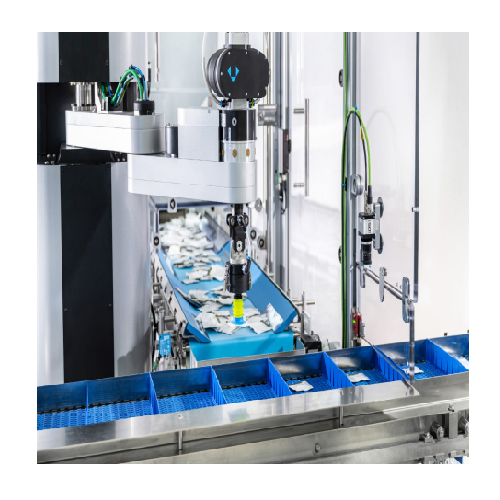
Automated pick and place cobot for packaging
Overcome packaging bottlenecks with an advanced cobot designed for high-speed...
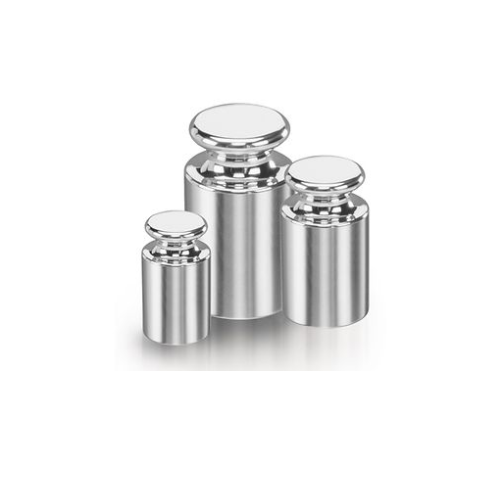
Metrological weights and weight sets for precise measurements
Ensure accuracy in your laboratory weighing processes with...
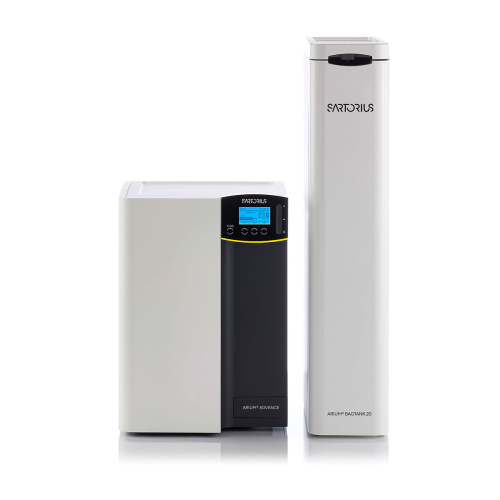
Reverse osmosis water purification system
Efficiently purify and maintain high-quality laboratory-grade water crucial for ...
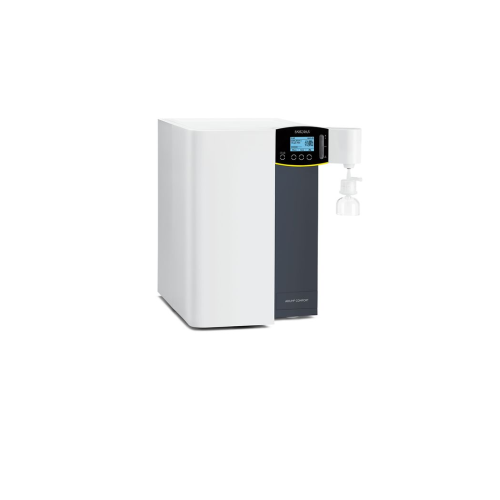
Combined lab water purification system
Optimize lab efficiency with a streamlined system delivering ultrapure and pure wate...
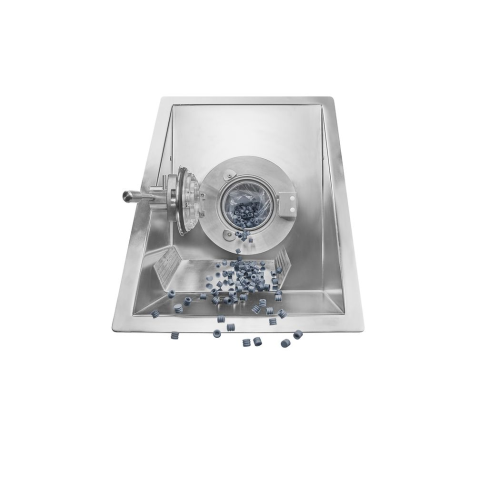
Single-use transfer and filling solutions in barrier isolated filling lines
Ensure sterile, high-volume liquid transfe...
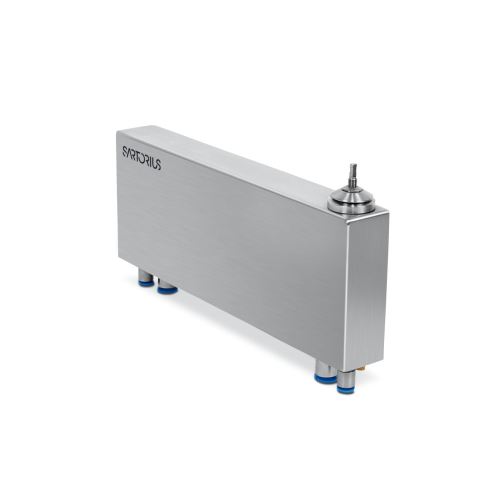
Semi micro and micro weighing cells for lab weighing
Achieve unparalleled precision in your laboratory measurements with ...
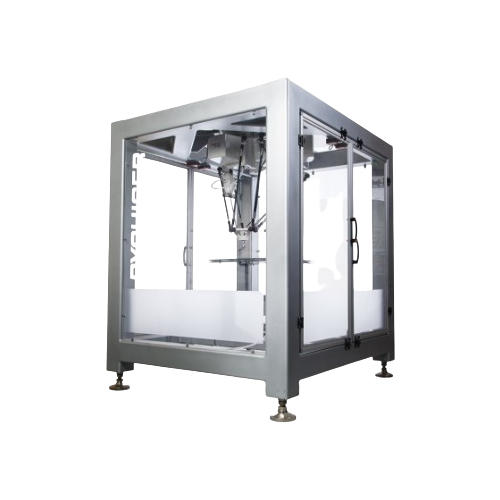
Top loader robots for precision packaging
Optimize packaging operations with versatile robotic top loaders that achieve hi...
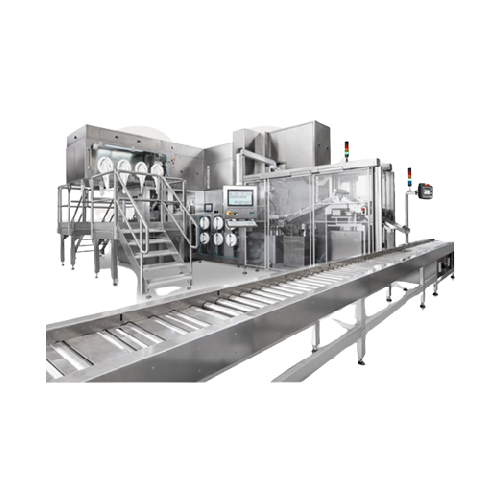
Filling solution for powders and liquids in diagnostics
Simplify precision filling of diverse products, from freeze-dried...
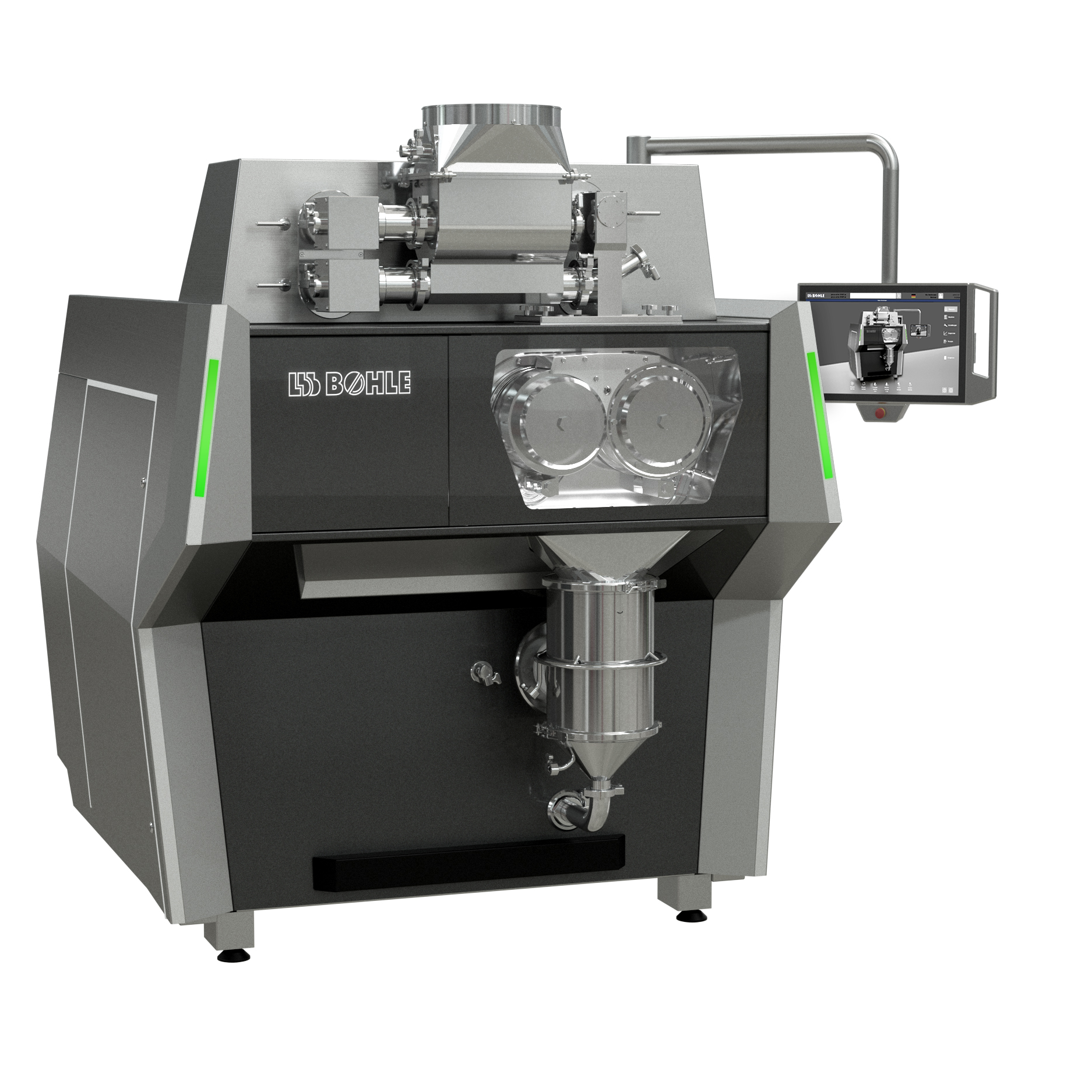
Dry granulator for pharmaceutical powders
In pharmaceutical industries, where large-volume production is the norm, compact...
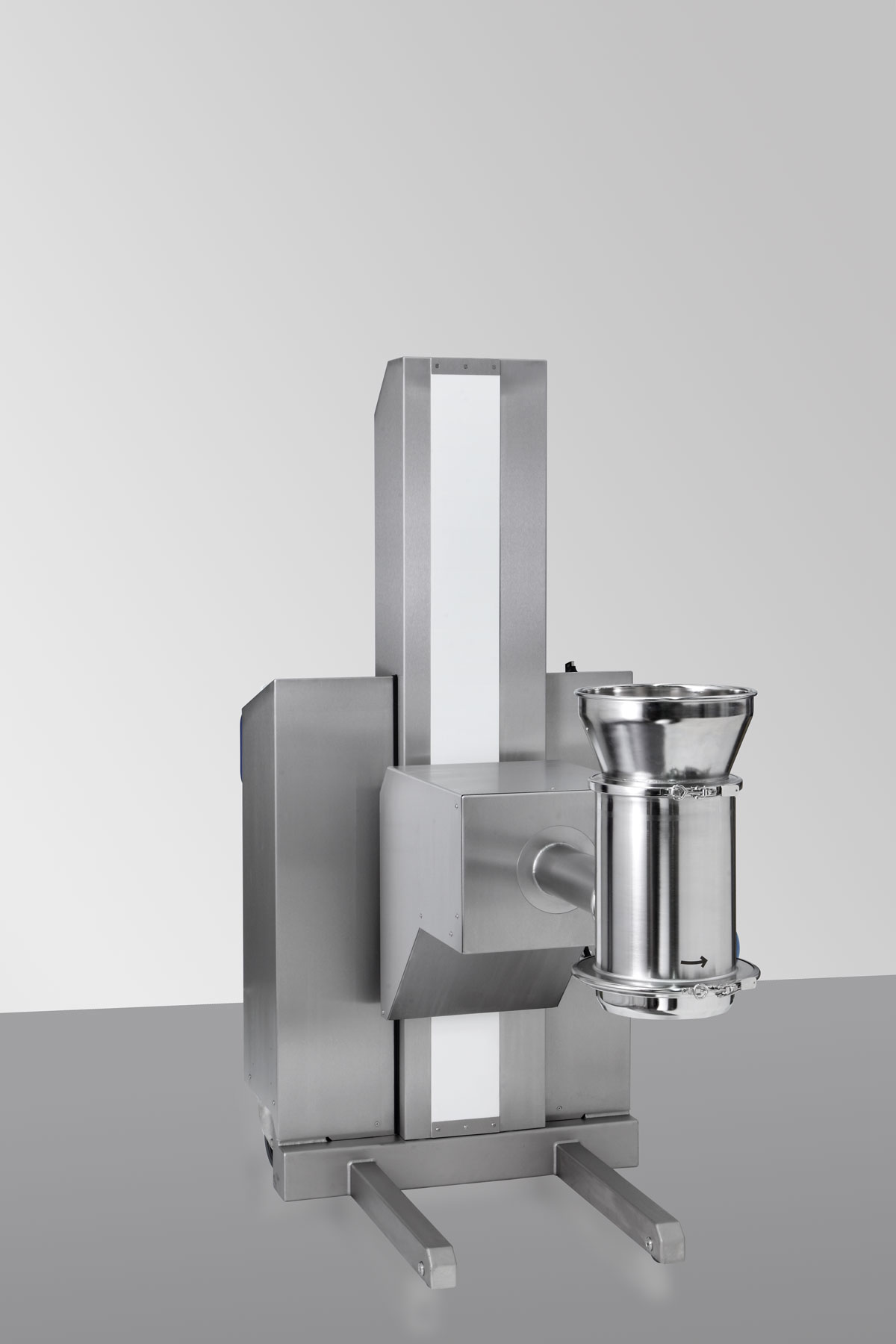
Industrial sieving machine for pharmaceuticals
One of the physical attributes that granular pharmaceutical products must h...
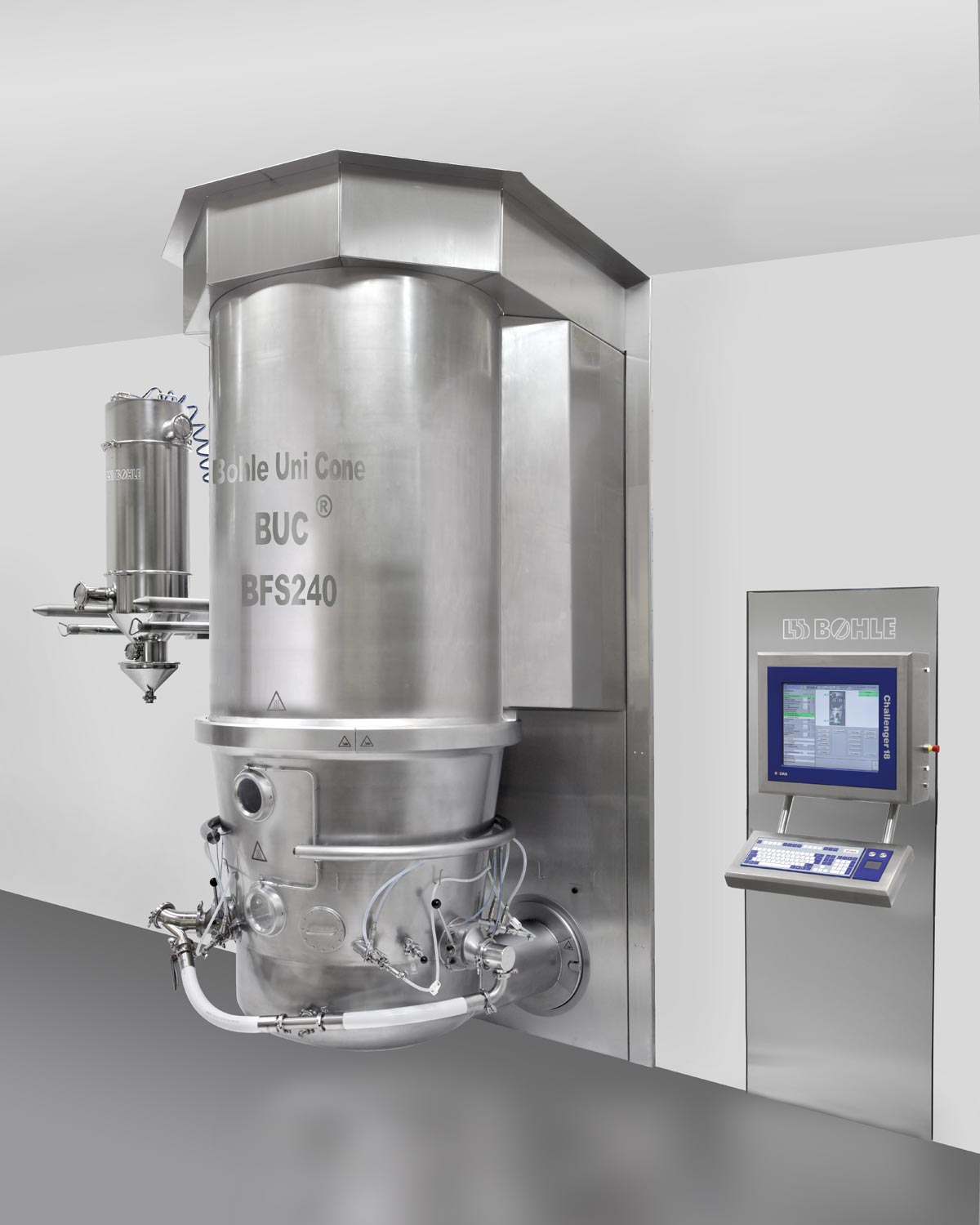
Fluidized bed system for the granulation and drying of pharmaceuticals
Pharmaceutical industries employ several process...
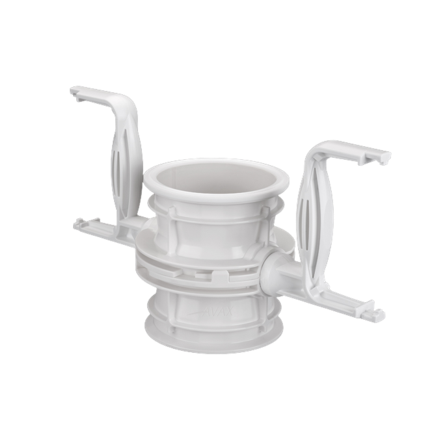
Single-use containment valves
From GMP and HSE perspective material transfer is critical for chemical and pharmaceutical for...
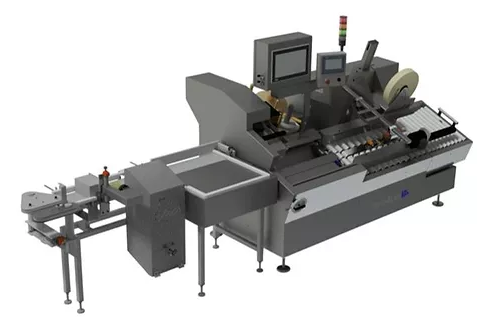
Serialization equipment for cases
Serialization is a multi-stage process that includes printing, inspection, and labeling. ...
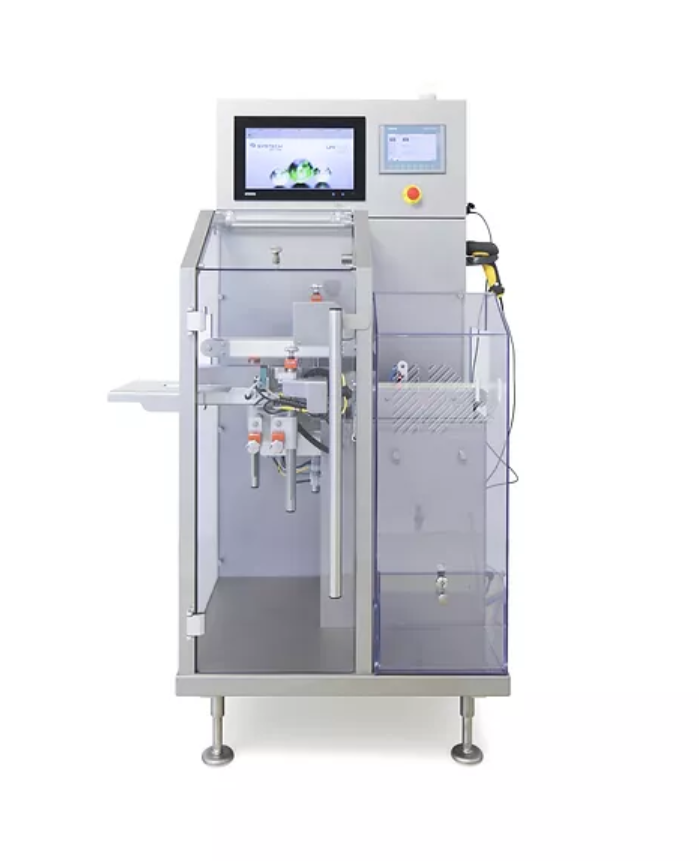
Individual item serialization equipment
Traceability is critical to quality assurance in the pharmaceutical sector. But ser...
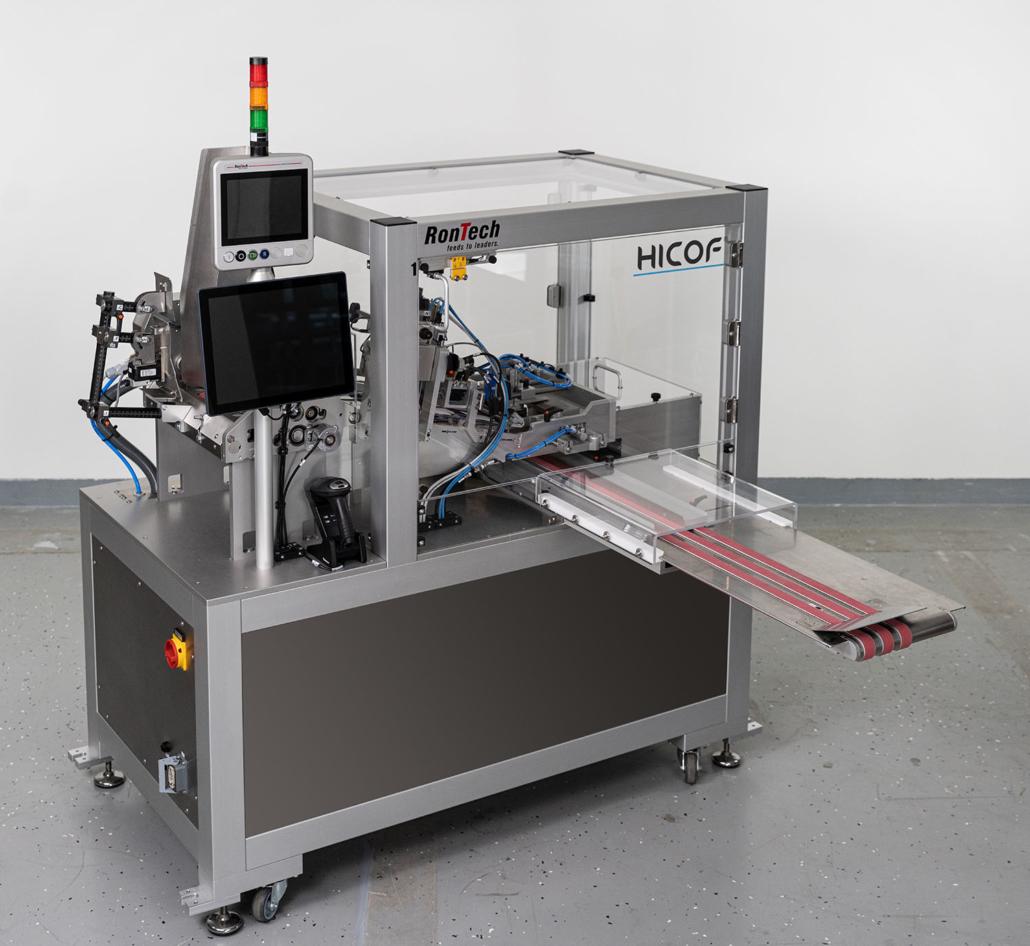
Flat carton coding machine
The coding process is an essential step in the production line as it can provide trusted supply c...
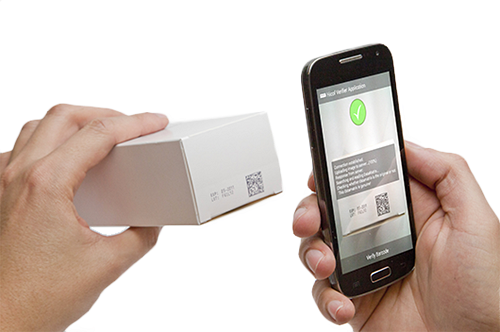
Software to differentiate between the original pharmaceutical barcode and a reprint
Counterfeit products pose a serio...
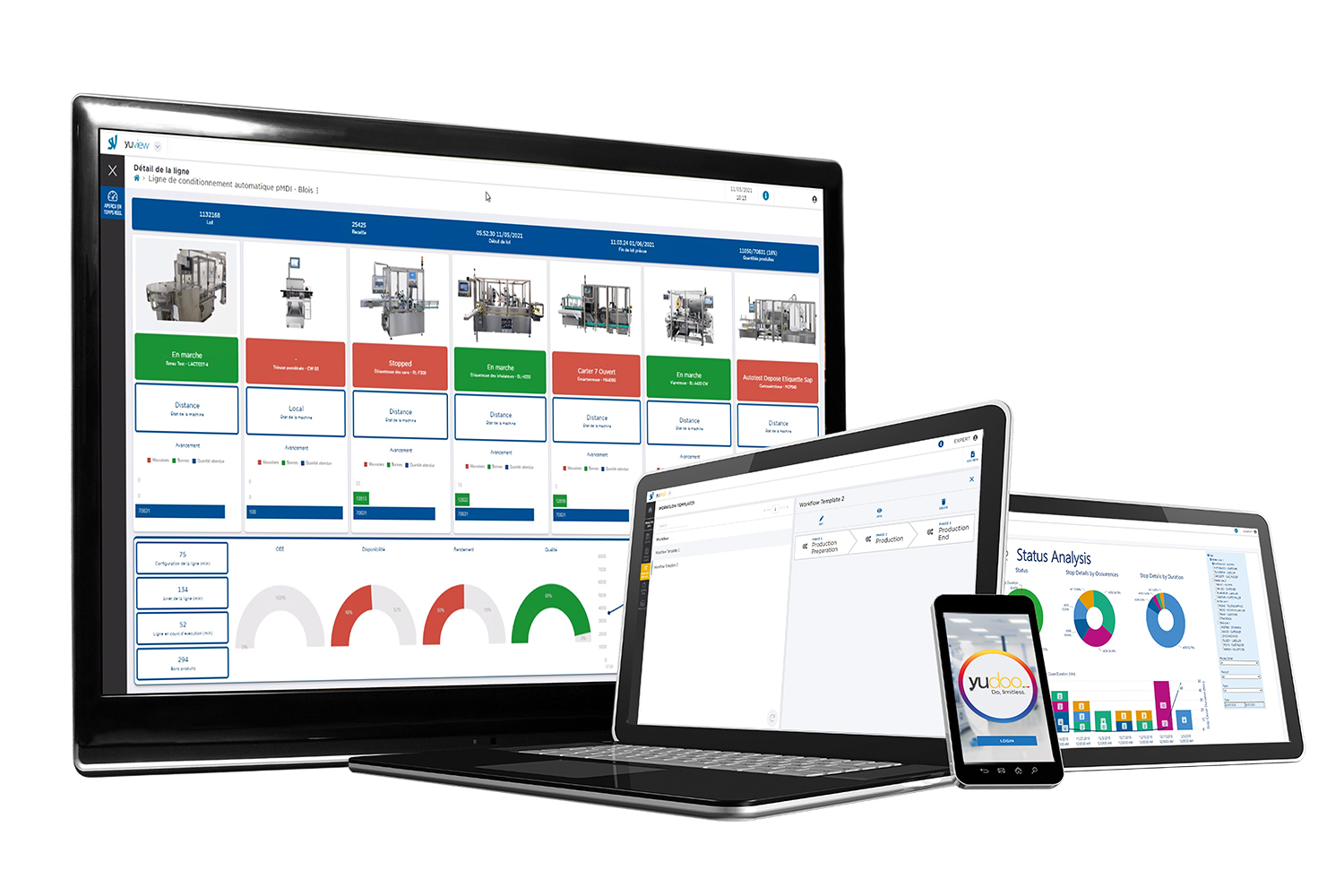
Pharmaceutical data management software
A typical pharmaceutical production handles numerous work flow activities like mana...
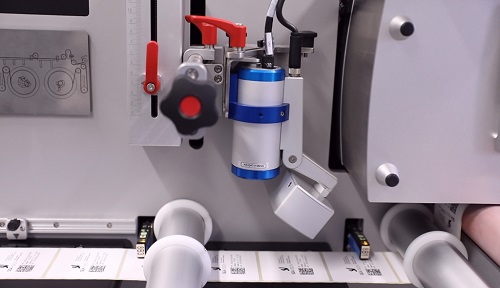
Serialized labels inspection and printing station
Labels are a key component in pharmaceutical packaging lines as they in...
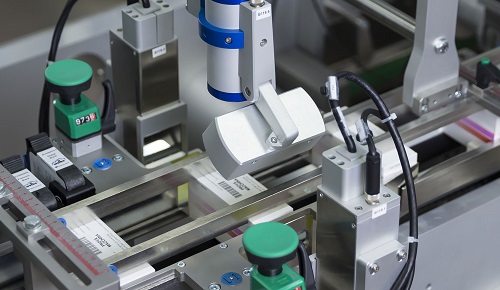
Serialization tracking system
To accommodate different products of varied sizes, the pharmaceutical industry requires handli...
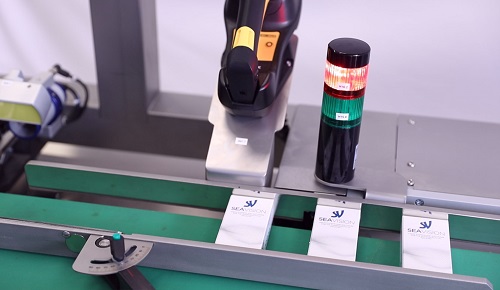
Serialization and aggregation system
Manufacturers from the pharmaceutical industry require a variety of cartons, cases and...
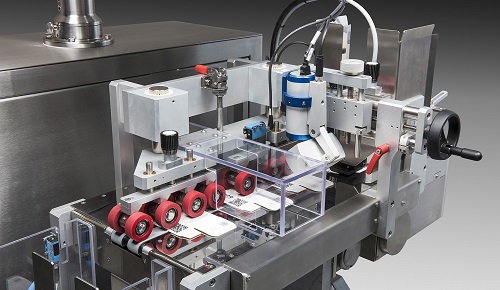
Flat carton serialization station
The packaging lines in the pharmaceutical industry handle several flat cartons. Manual pa...
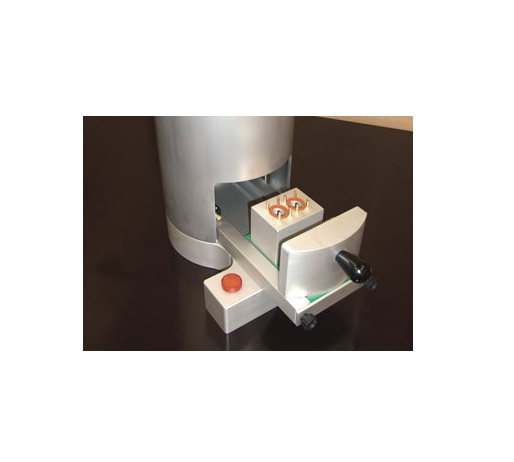
Clinical trial lab sealer for a laminar airflow bench
When running small production for clinical trials, stability studie...
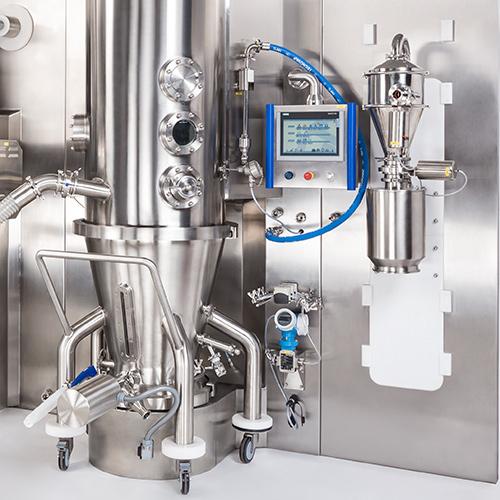
Fluid bed dryer for pharmaceutical solid dosage form
Fluid bed drying is a pharmaceutical process carried out to reduce t...

Industrial high shear mixer granulator for drug formation
It is rather difficult to successfully produce a pharmaceutica...
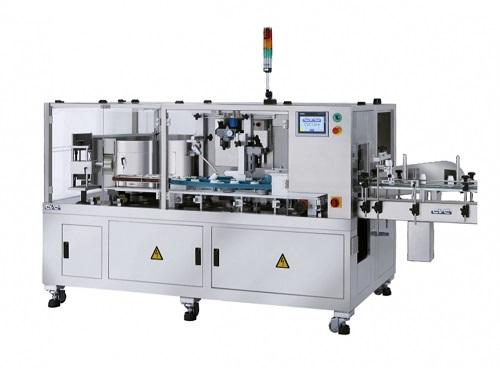
Pharmaceutical bottle unscrambler
Pharmaceutical packaging industry requires the ability to quickly manage the process yet ...
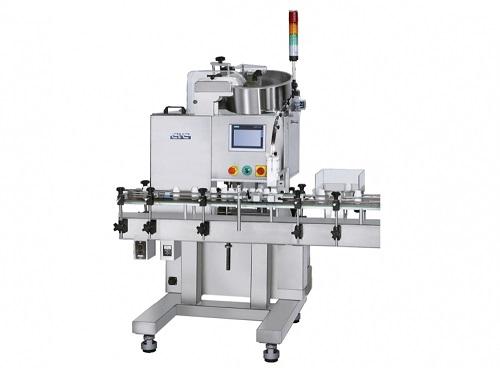
Dessicant inserting machine
Desiccant canisters play an important role in the pharmaceutical and nutraceutical industries. T...
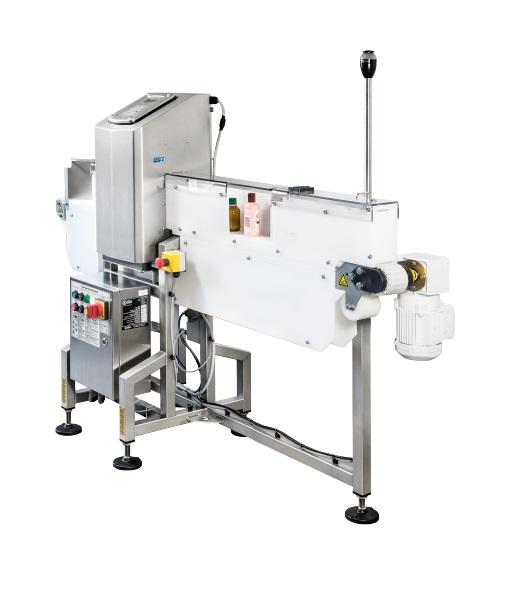
Metal detector for bottles
For metal contamination detection in finished products that are bottled, traditional solutions re...
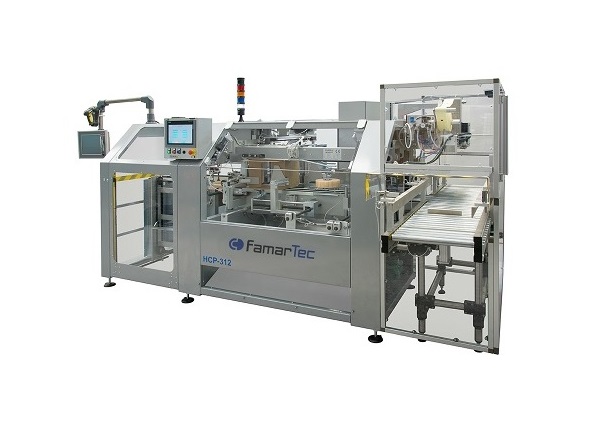
Side-load case packer
As the final stage in the packaging process, an automated case-packing solution can ensure that your co...
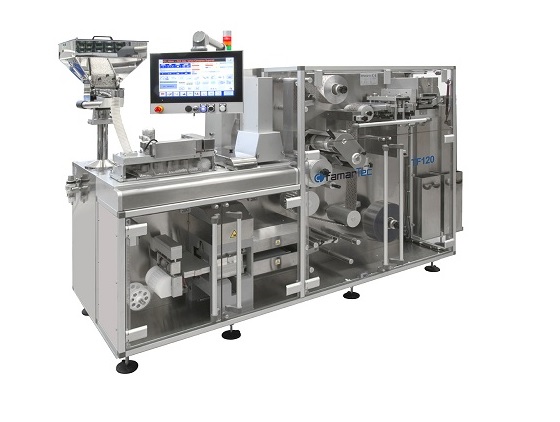
Entry-level blister packaging machine
Blister packaging is a popular packing method in the pharmaceutical industry thanks t...
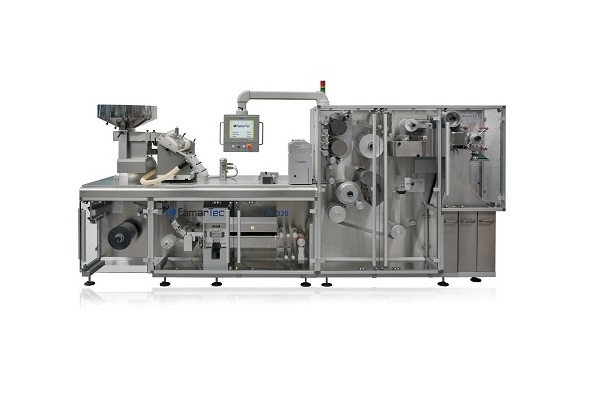
Industrial blister packaging machine
High-volume, fully-automated blister packaging is the perfect choice for large scale p...

Plate sealing blister machine
Blister packaging is the preferred choice for most large-scale pharmaceutical lines, and a pla...
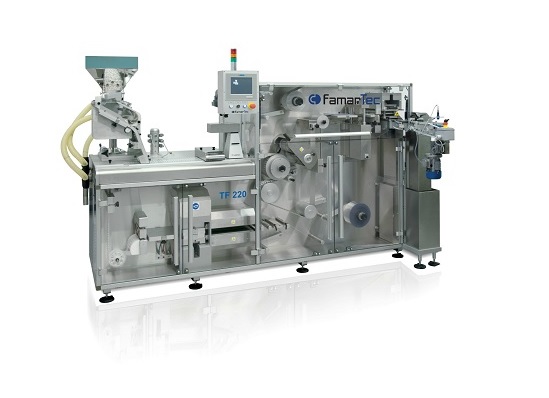
Automatic blister packaging machine
Automated blister packaging is a popular choice for pharmaceutical production thanks to...
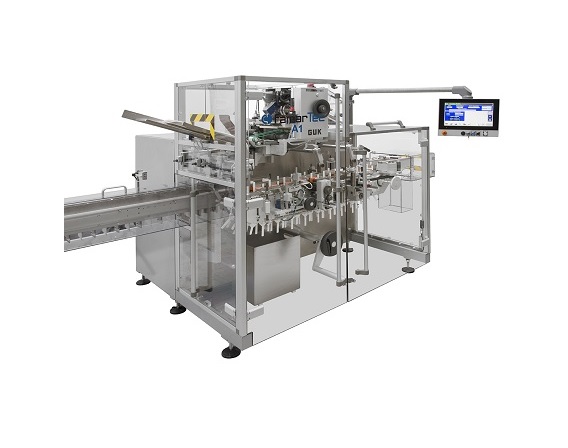
Horizontal cartoner for pharmaceutical applications
Automatic cartoning for cosmetic or pharmaceutical products is a requ...
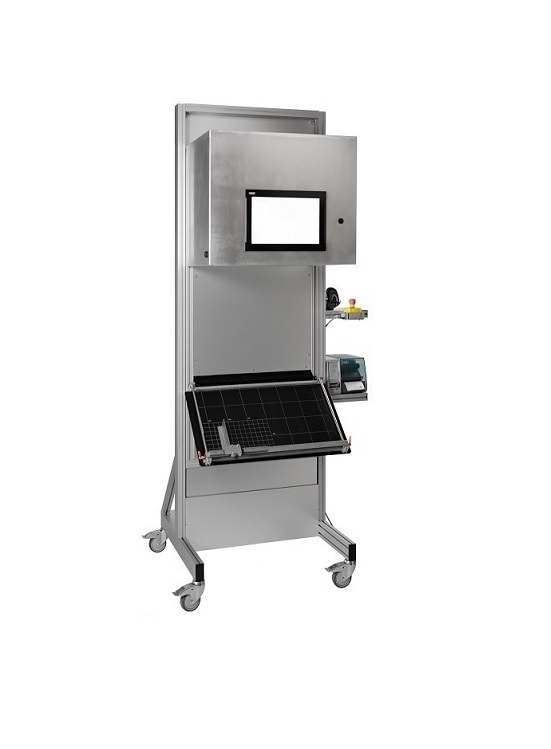
Stand-alone aggregation station
The aggregation of pharmaceutical products for tracking purposes is already compulsory in ma...
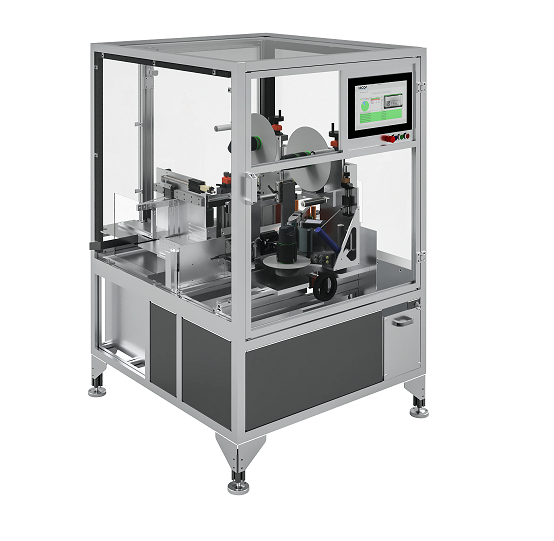
Serialization coding and labeling equipment
In the pharmaceutical industry, product serialization is the cornerstone of al...
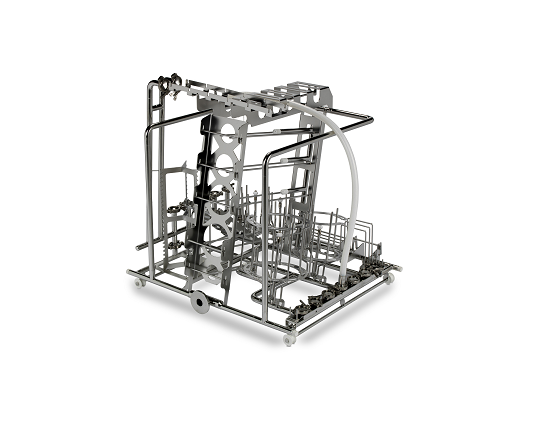
Loading basket for GMP washer
To ensure perfect cleaning of contact parts they must be placed in the GMP washer in such a wa...
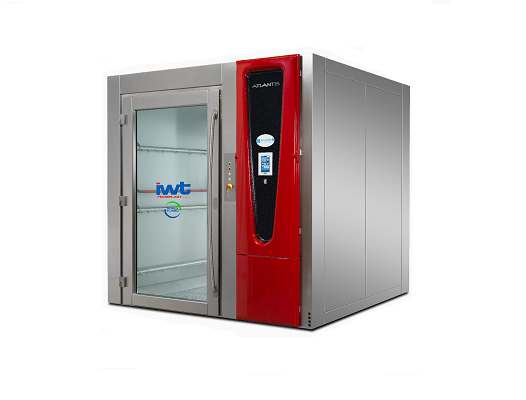
Bulk chamber washer
The production of cosmetics, nutraceuticals or unregulated pharmaceuticals often requires the cleaning an...
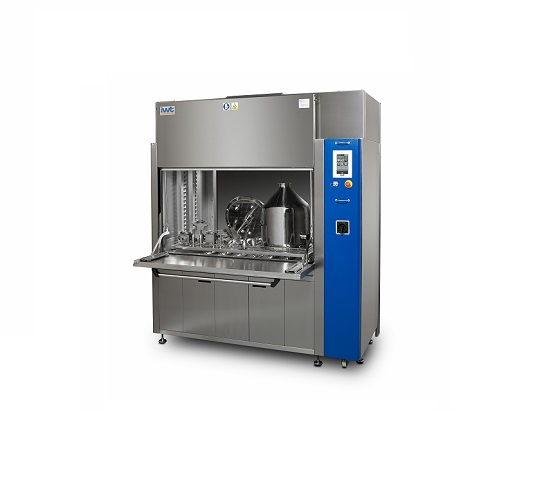
Entry-level chamber washer
When cleaning smaller products contacting filling or compressing components used in the productio...
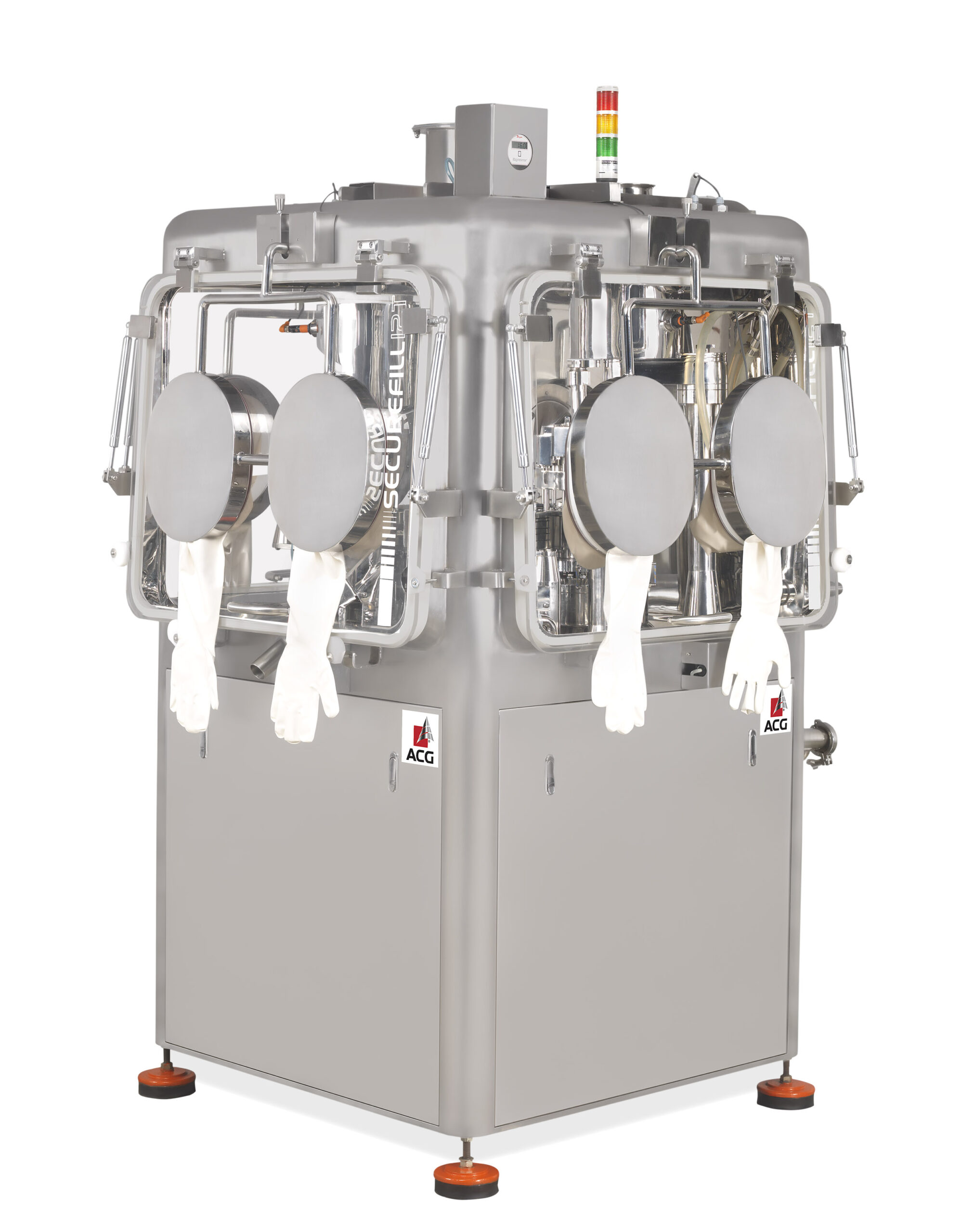
Contained capsule filler
For pharmaceutical formulations that are highly active specialized capsule filling equipment is ofte...
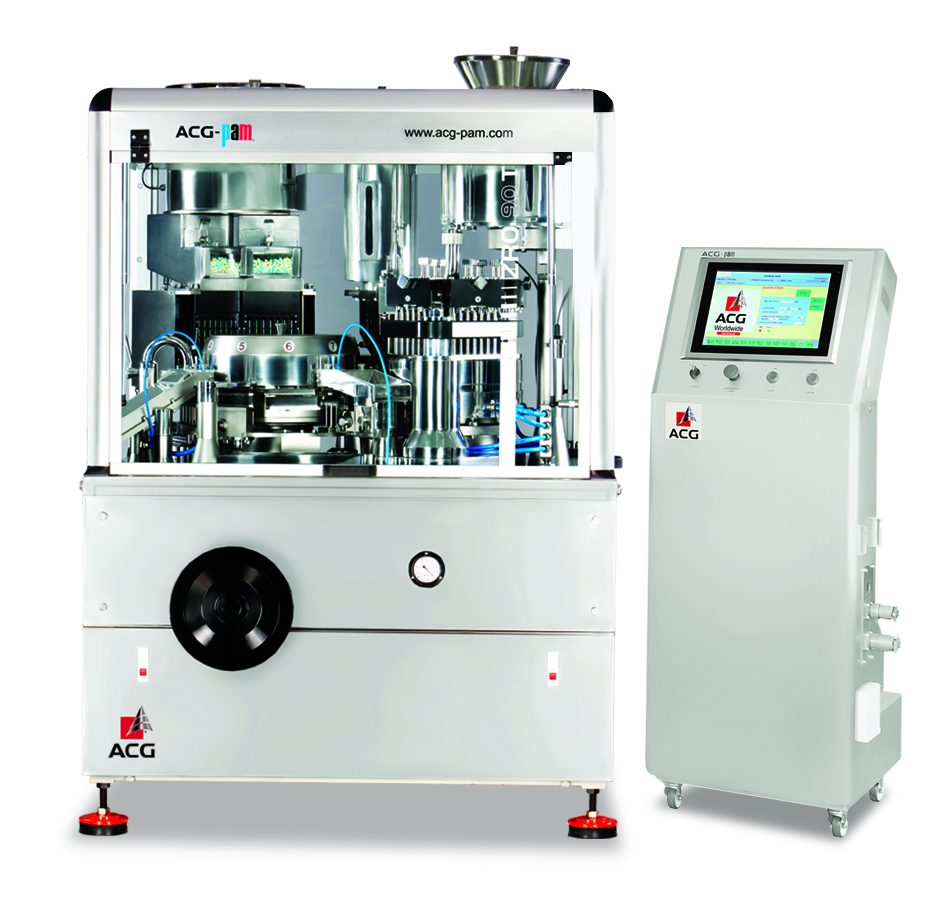
High-yield capsule filler
Pharmaceutical manufacturers require maximum yield from their encapsulation process for efficient ...
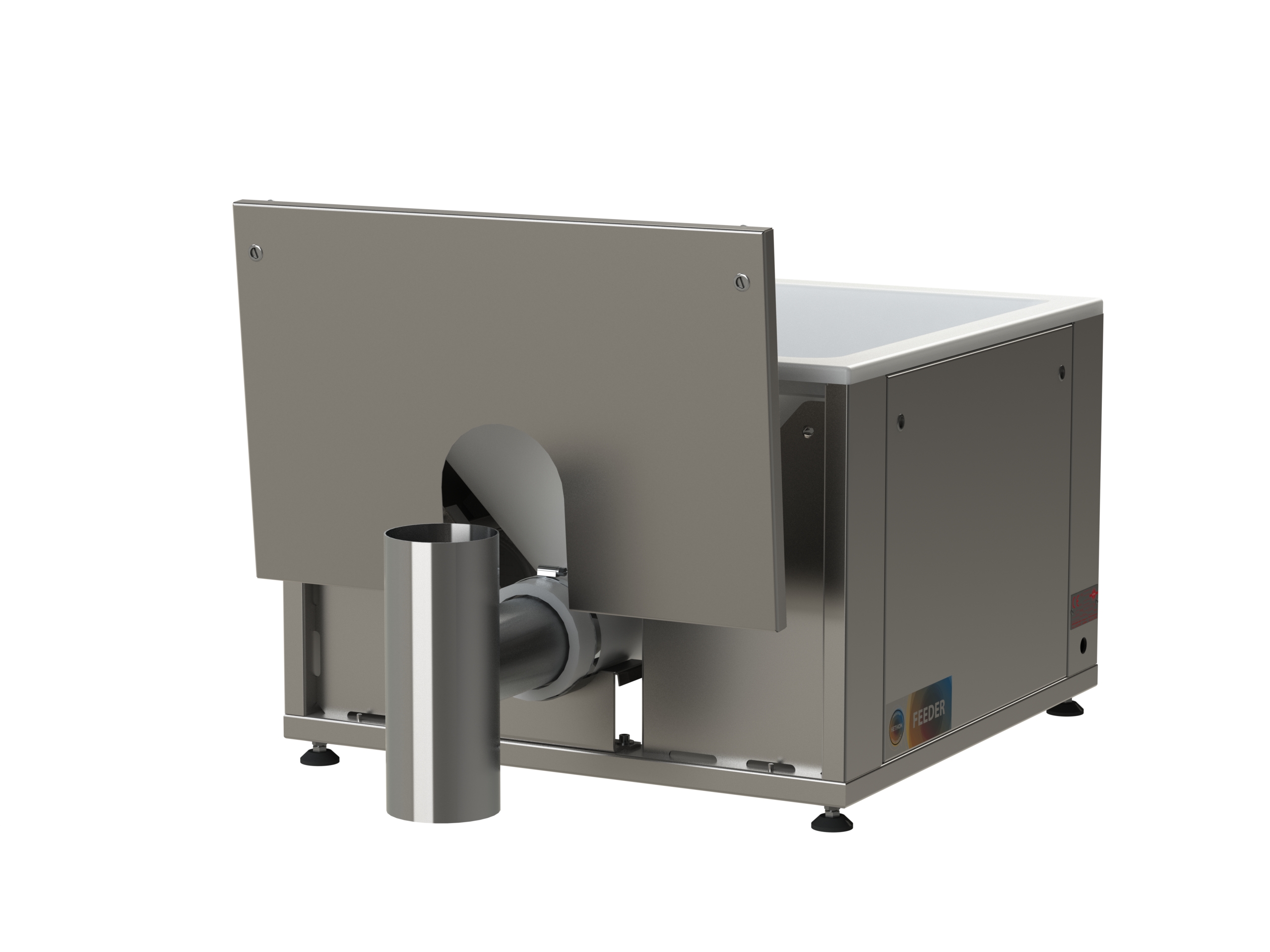
Feeder with flexible wall hopper
The varying properties of dry powder products mean that specialized feeders are required fo...
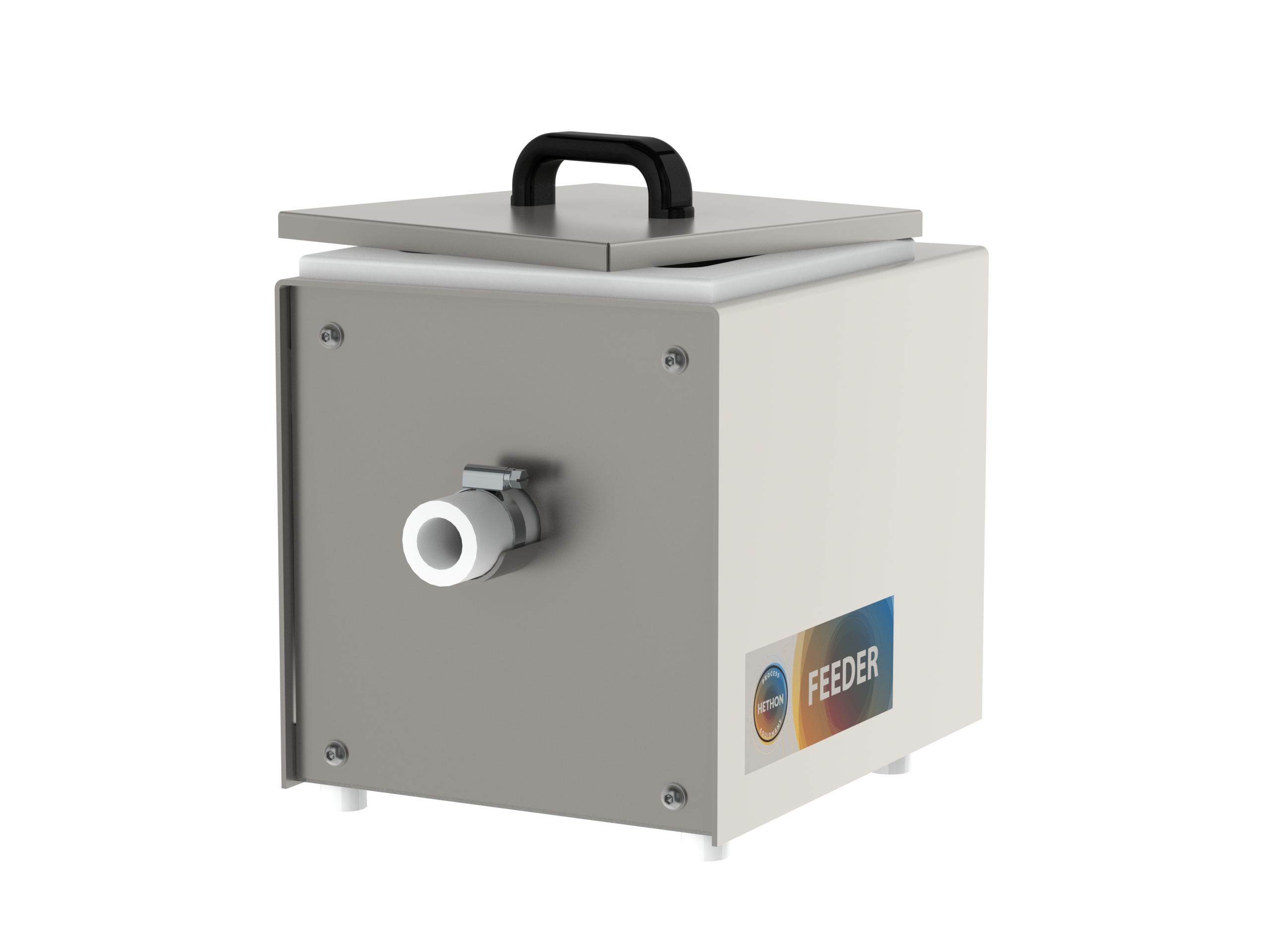
Small feeder with flexible wall hopper
In many laboratory applications and production processes, smaller quantities of powd...
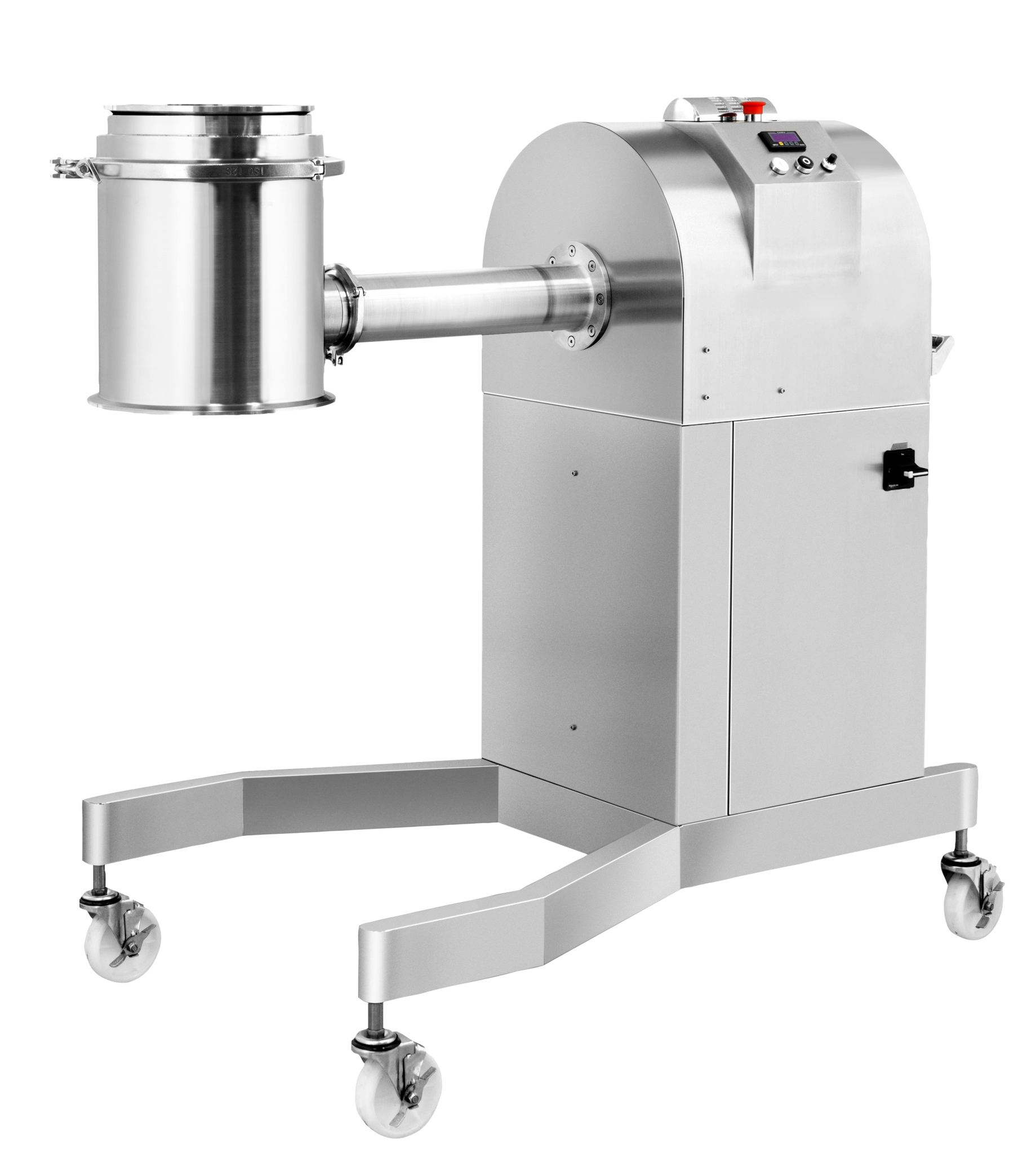
Conical mill for drug formulation
The efficient size reduction of granular powders is a key step in many pharmaceutical pro...
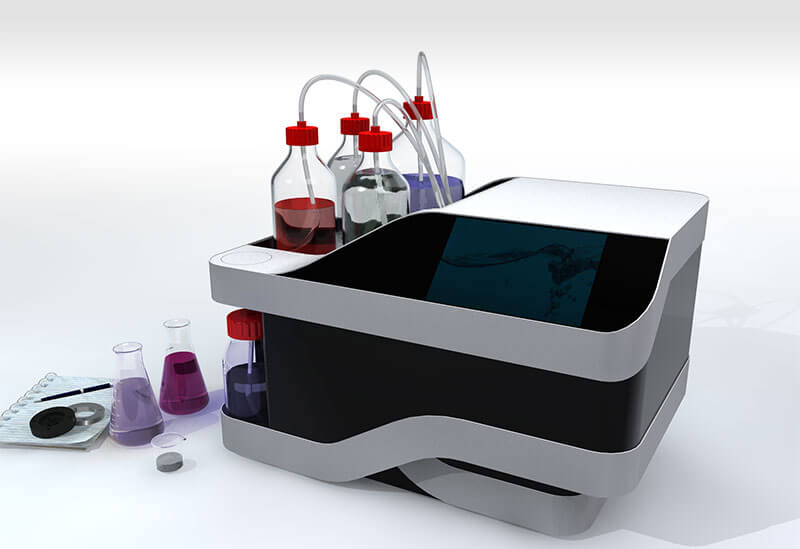
Microencapsulation system for your drug delivery system
Whether you want to improve the stability of nutrients, protect a...
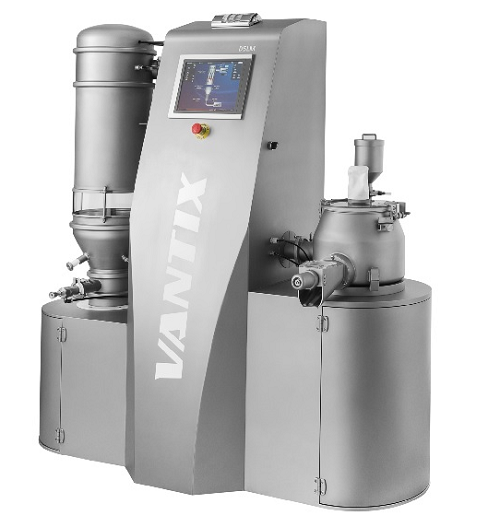
Fluid bed dryer and mixer for lab scale
Designed for pharmaceutical R&D, a lab-scale fluid bed dryer and mixer/granulat...
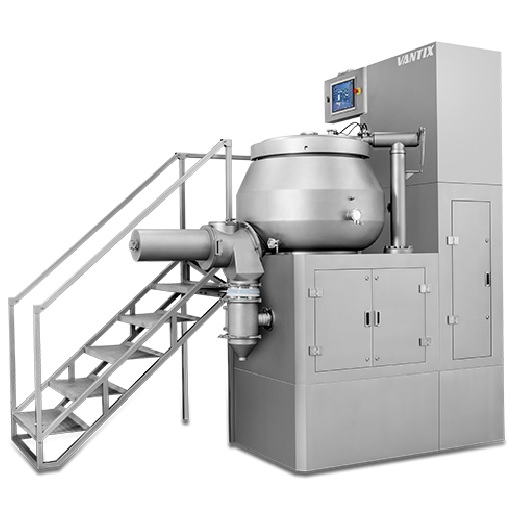
High-shear mixer
For the efficient mixing of larger batches of pharmaceutical compounds and high-shear mixer provides the opti...
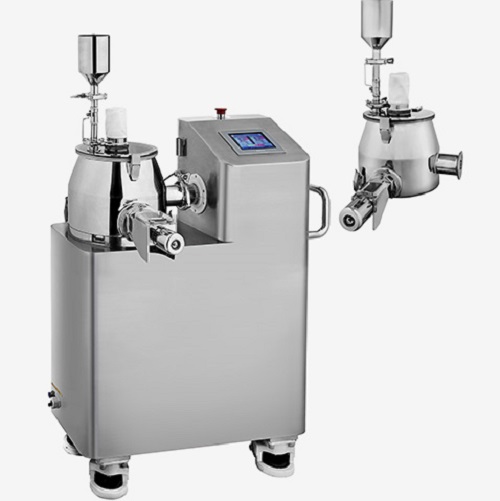
Entry-level high-shear mixer for drug formulation
For pilot and lab-scale pharmaceutical formulations, a high-shear granu...
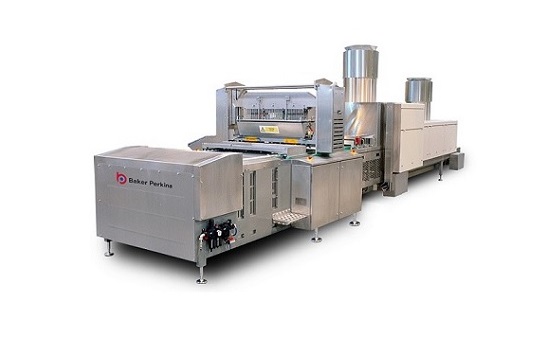
Starch-free depositor for hard candy
Forming hard candies requires careful handling of syrups in order to avoid quality iss...
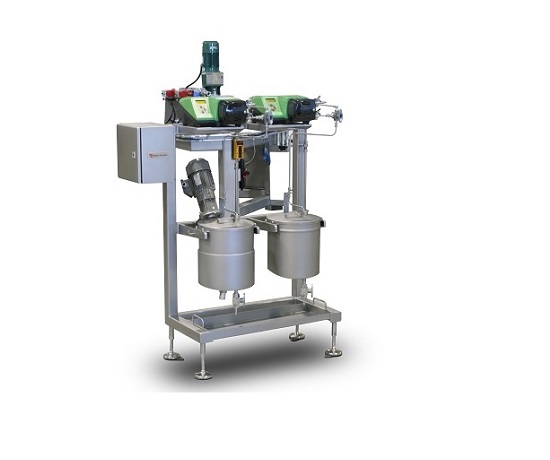
In-line colour or flavour addition for confectionery
The addition of colourings and flavourings increases value and quali...
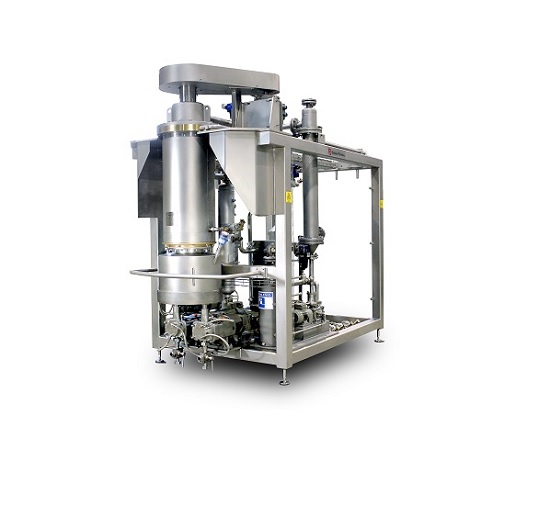
Thin-film cooker for confectionery products
Producing excellent confectionery products requires high quality cooking. Trad...
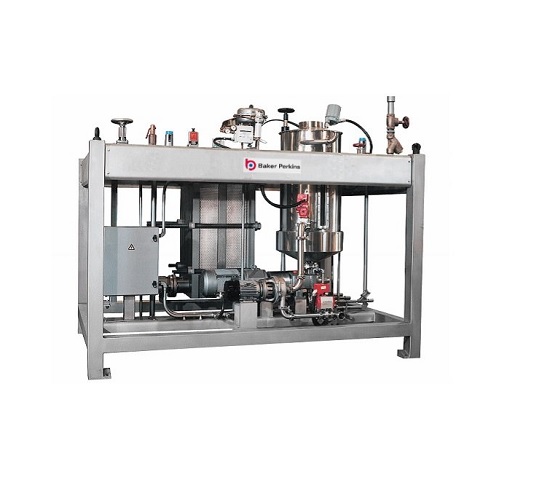
Dissolver of confectionery syrups
Many high quality confectionery products require a dissolved syrup as their starting poin...
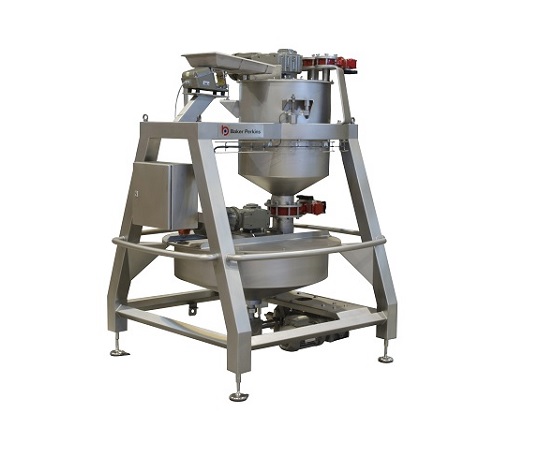
Automatic weigher and mixer of confectionery ingredients
The production of accurately proportioned and homogenous slurrie...

Half-suit tester
Designed to allow operators to perform sterility testing in an aseptic environment providing assurance of mat...
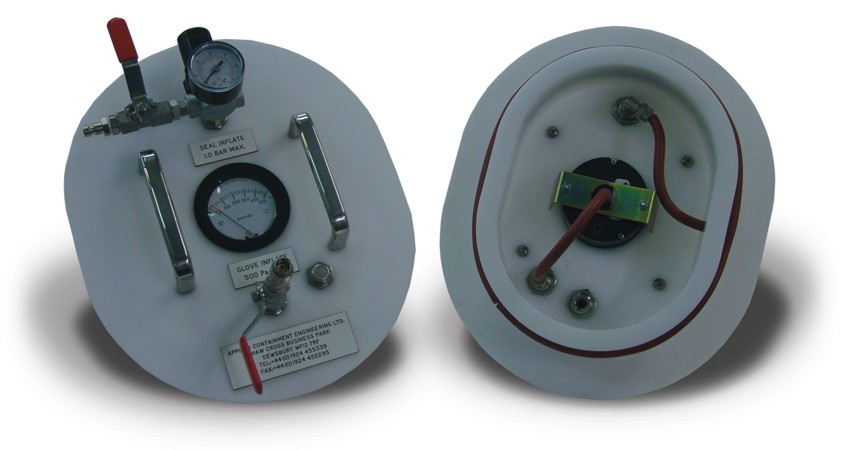
Glove tester
Testing device of the containment capability of gloves, which is as important as the other parts of the integrate...
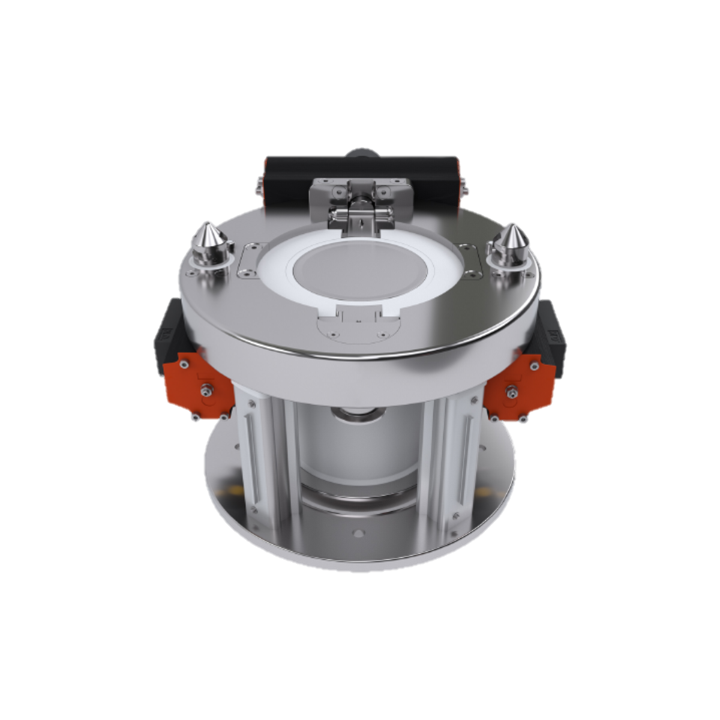
High containment split butterfly valve
Powder containment is the cornerstone of chemical and pharmaceutical manufacturing. ...
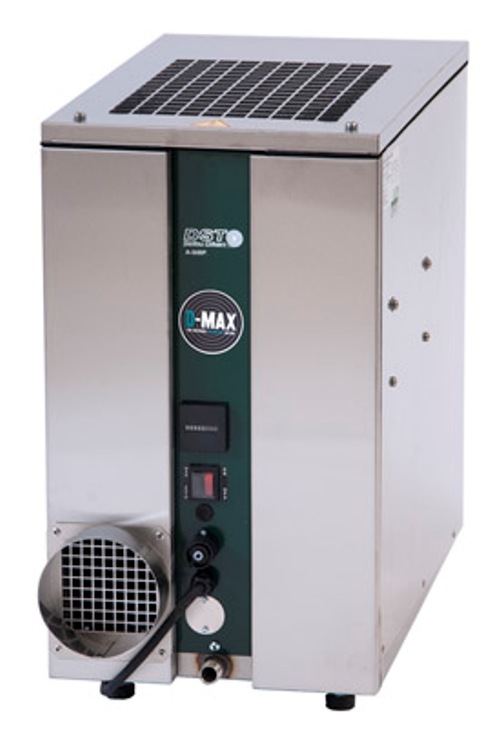
Sorption dehumidifier with air-chilled condenser
It is not always possible to duct out the wet air from a dehumidifier ser...
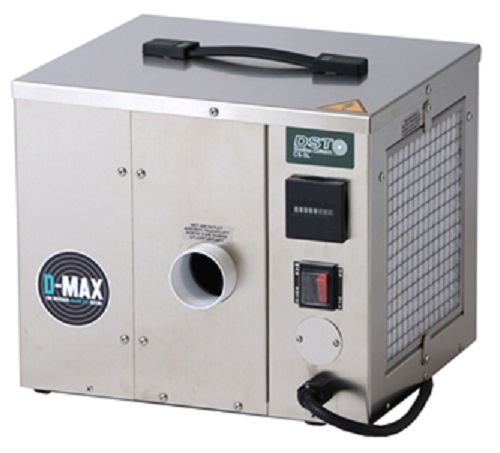
Small portable dehumidifier
Water damaged areas require dehumidification to limit the damage and prepare the area for restor...
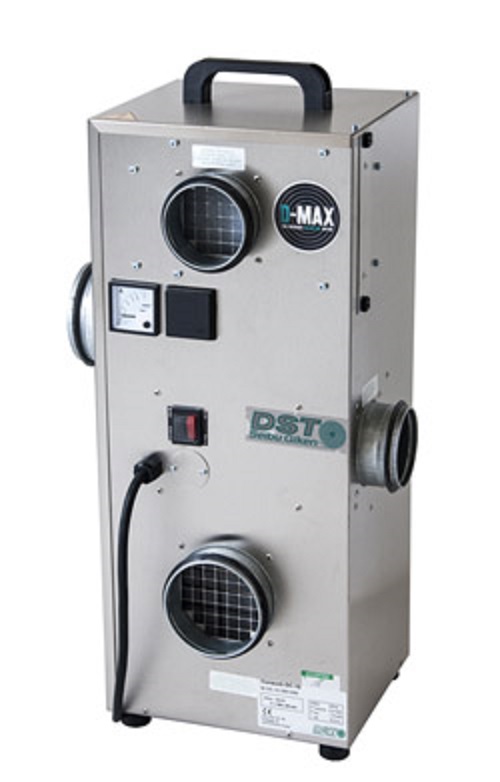
Sorption dehumidifier for large temperature differences
Small, humid areas can be difficult to dehumidify in humid ambien...
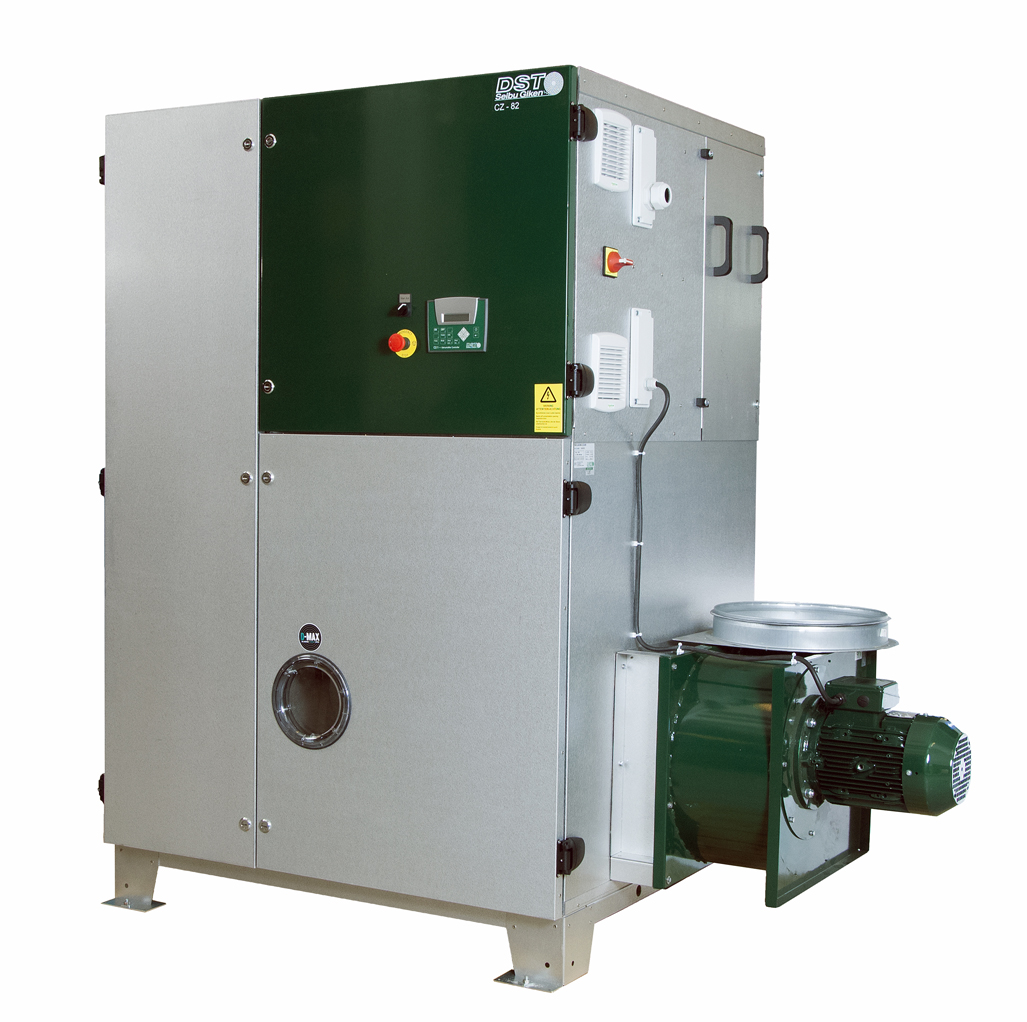
Sorption dehumidifier for deep drying
Humid ambient conditions such as those in tropical climates make dehumidification mor...
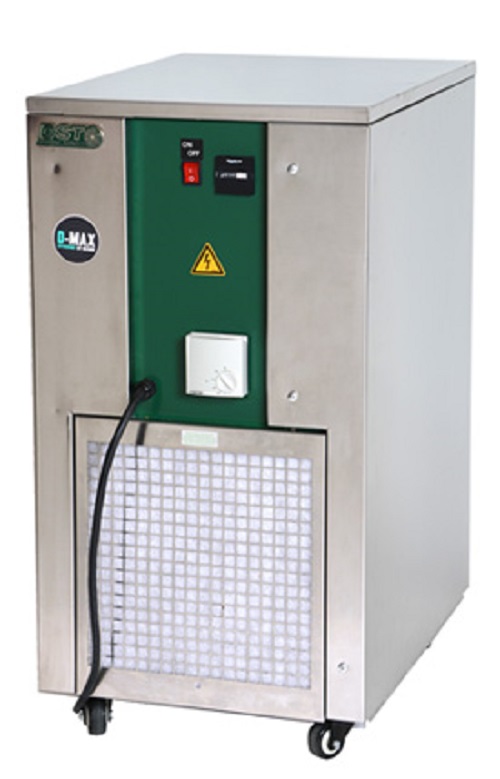
Dehumidifier for difficult wet airflows
Sealed rooms can be challenging to dehumidify with ordinary dehumidifiers. The wet ...
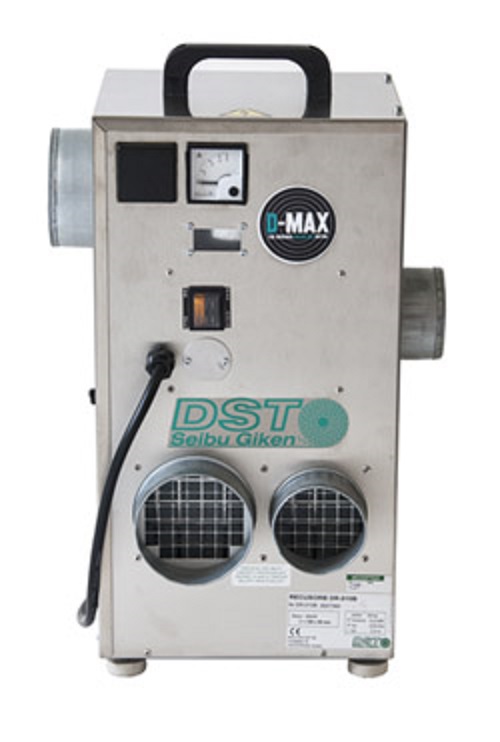
Sorption dehumidifier for overpressured rooms
Small humid spaces, used for processing or storage, often need a simple dehu...
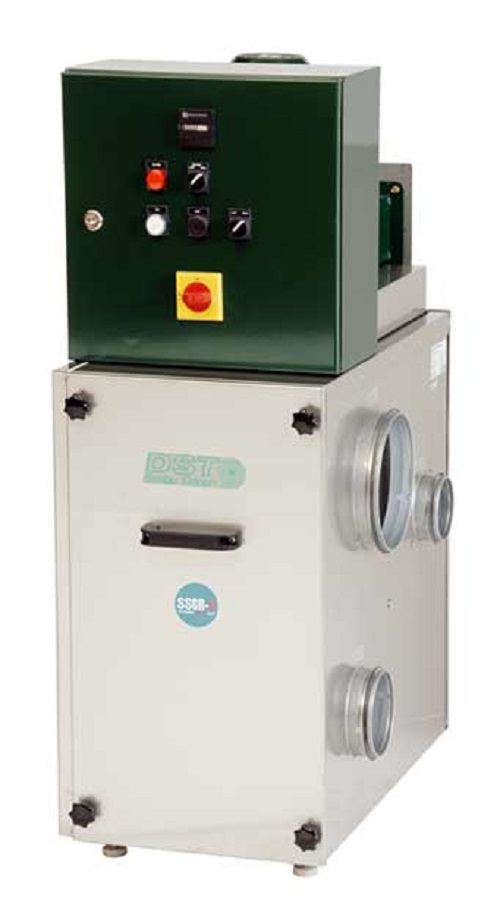
Heat recycling sorption dehumidifier
Facilities that handle large amounts of water can become very humid. High humidity may...
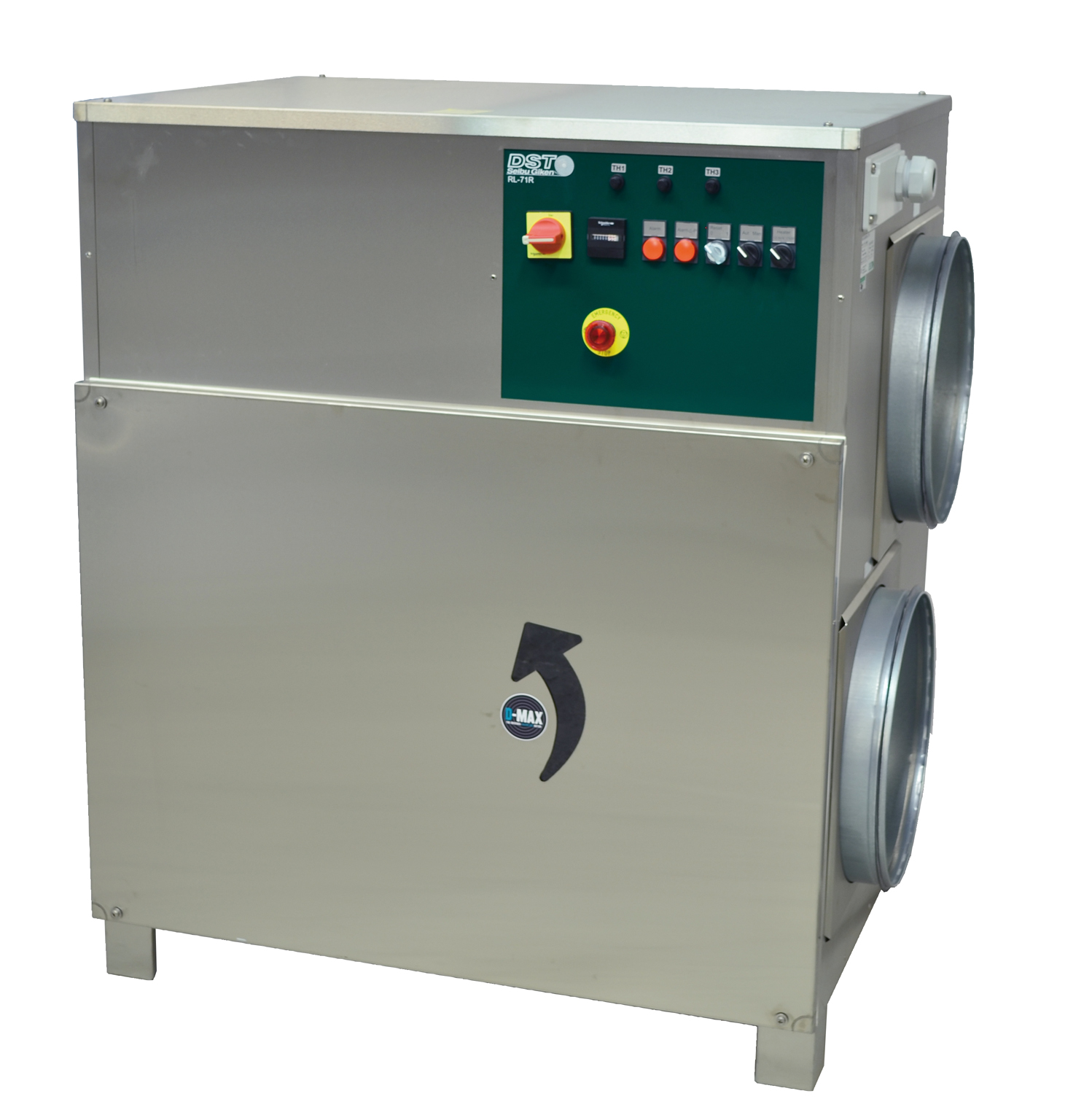
Industrial desiccant dehumidifier
Dehumidification of medium sized manufacturing and processing facilities can be a dauntin...
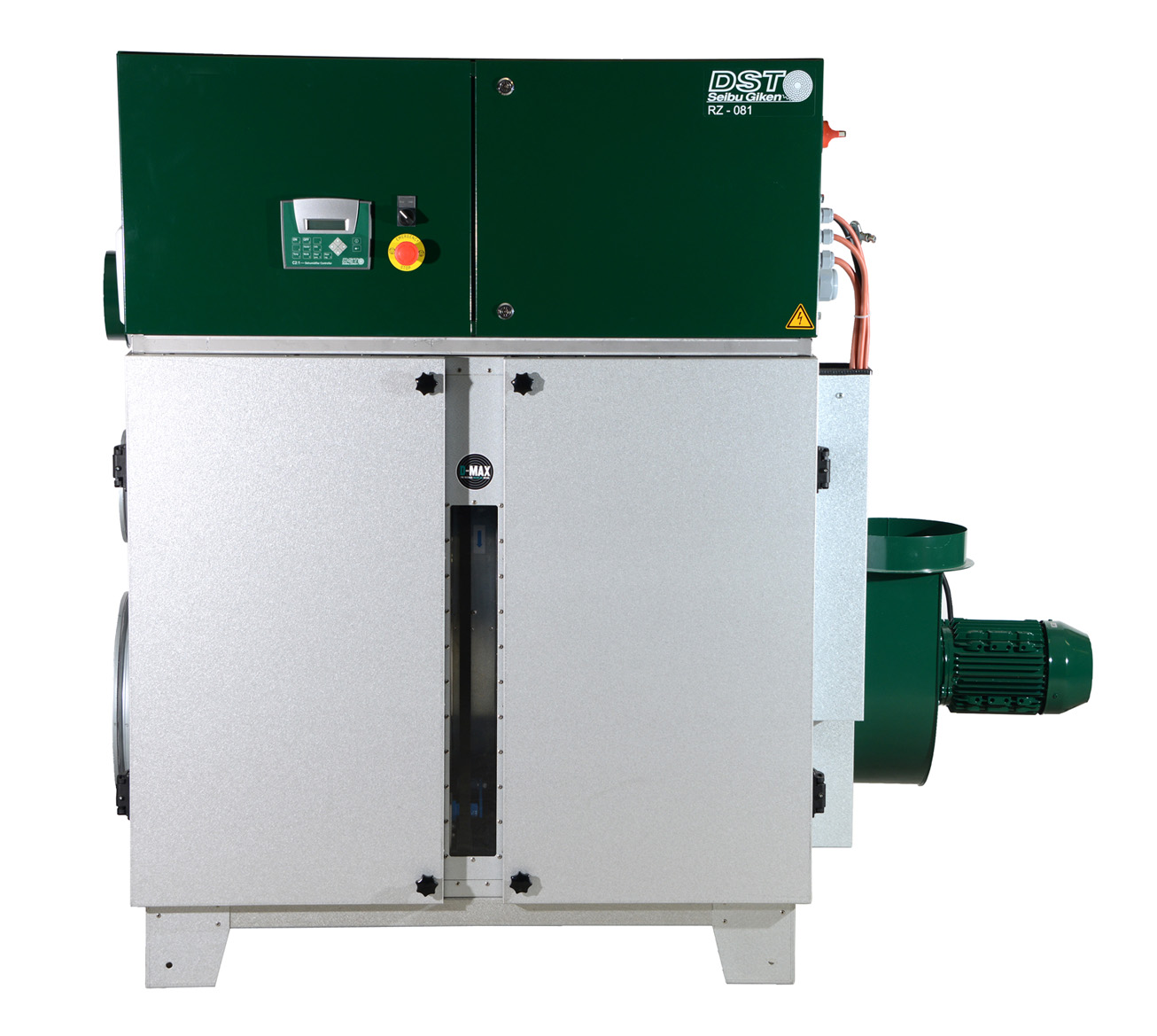
Large scale desiccant dehumidifier
Moisture sensitive processing and storage facilities need low humidity environments to s...
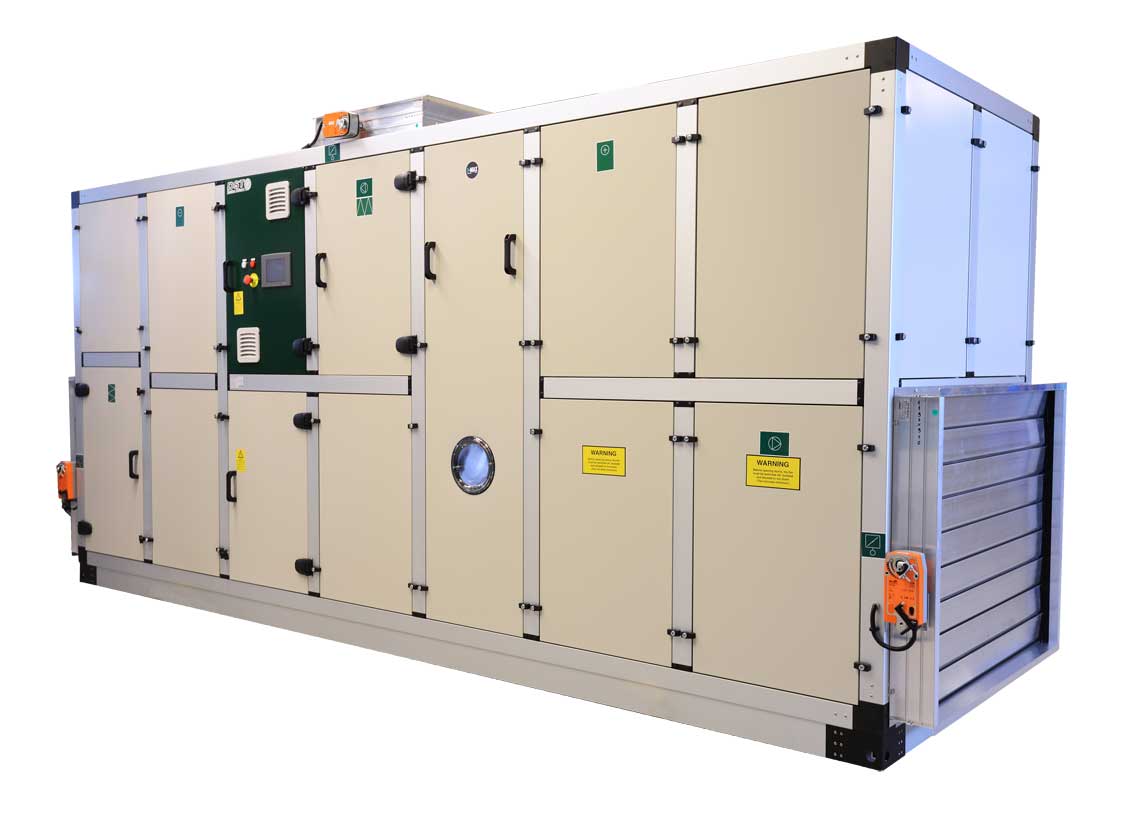
Customizable dehumidifier
Dehumidification needs can vary significantly from one project to another. Dehumidifiers with a fi...
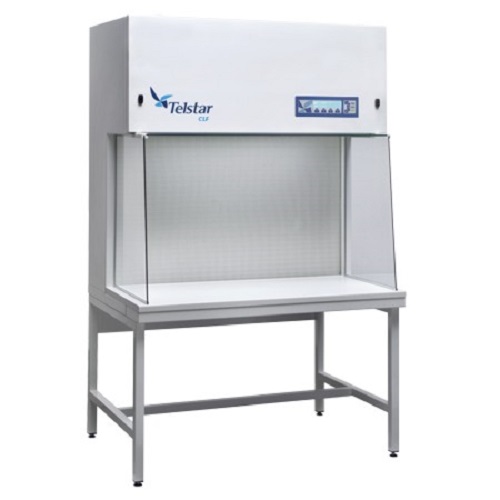
Horizontal laminar flow benches
HEPA filtered horizontal laminar airflow (crossflow) creates an ISO 14644-1 (Class 5) work a...
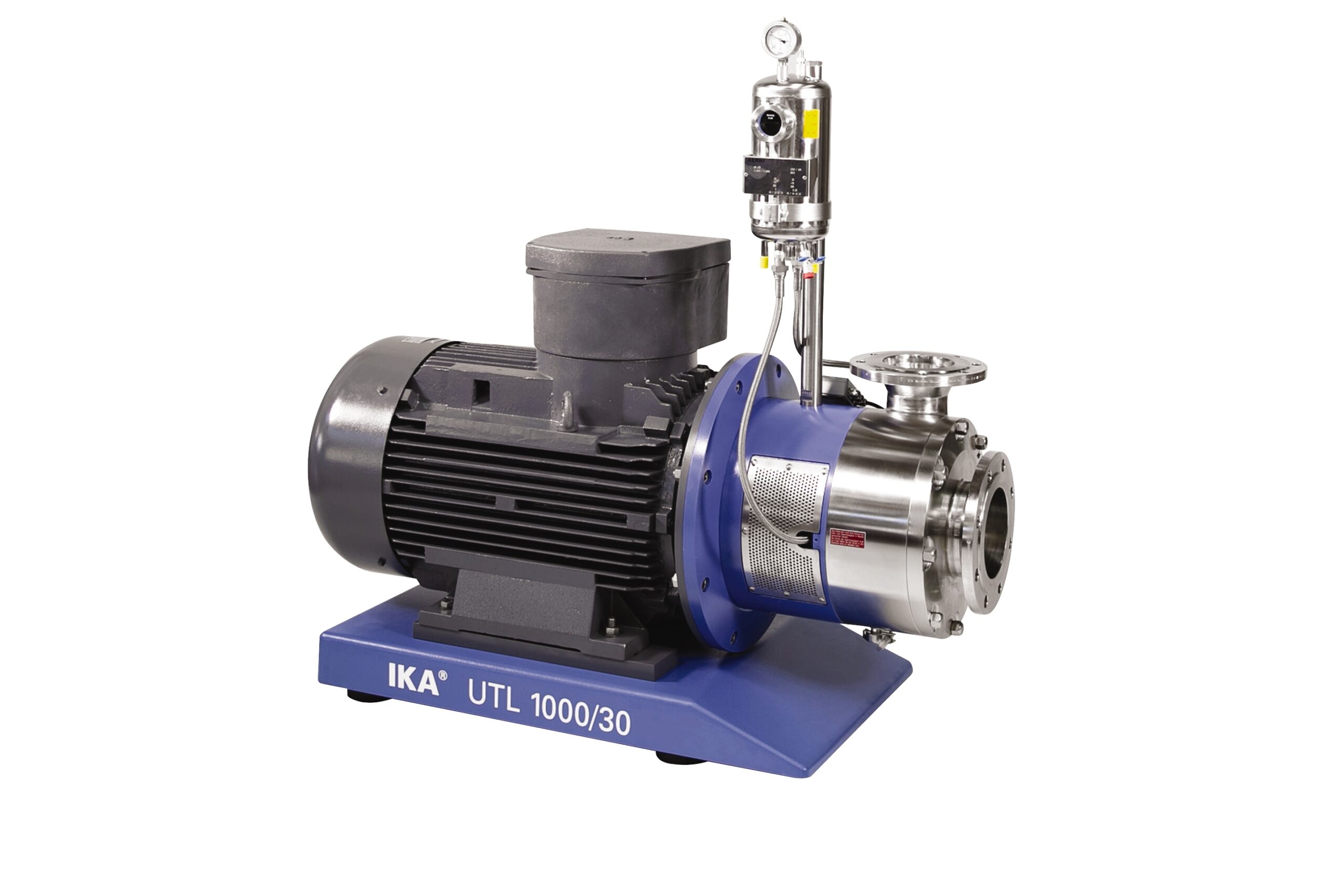
Economic dispersing machine for emulsions and suspensions
For products of medium viscosity and relatively consistent par...
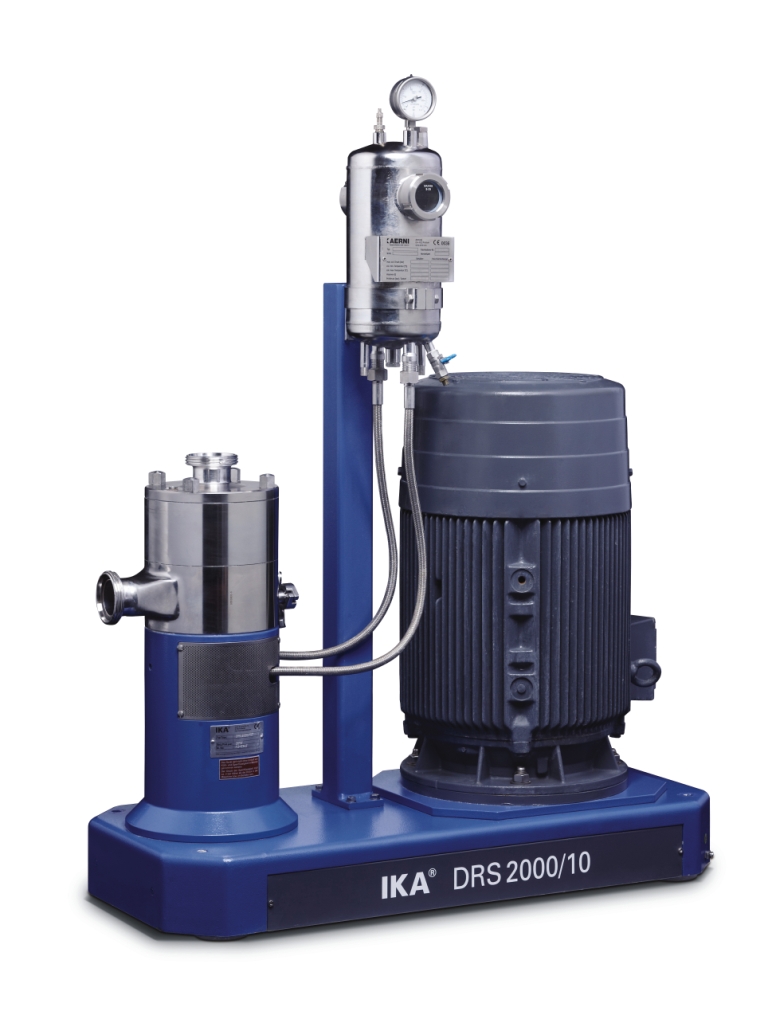
Ultra-fine dispersing machine for emulsions and suspensions
Producing the finest micro-emulsions and suspensions require...
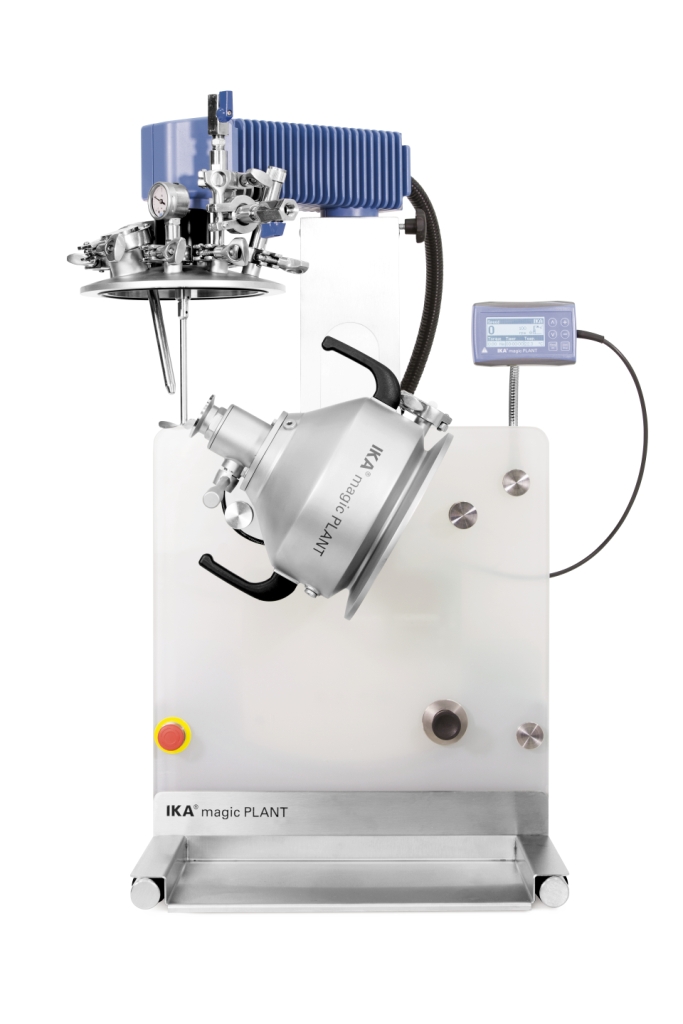
Laboratory dispersing machine for low-viscous masses
Laboratory mixers have not always been easy to work with. Getting a...
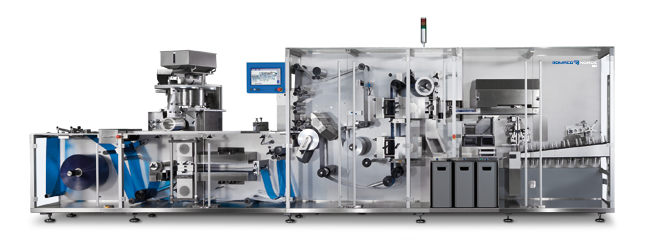
High-speed blister machine
If you are looking for a compact machine that produces blisters with an output of up to 700 blist...

Horizontal intermittent motion cartoner
User-friendly cartooning solution with an intermittent motion for a wide range of p...
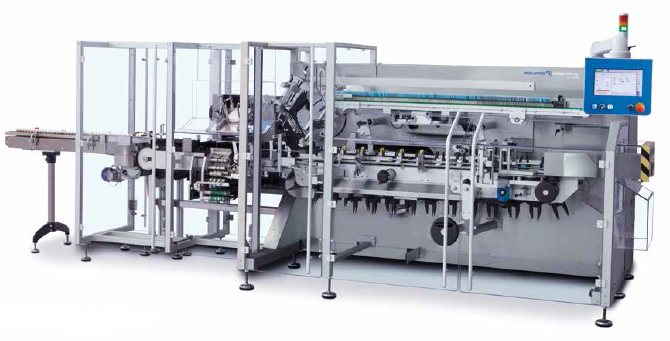
Horizontal continuous motion cartoner
An automatic cartoning machine designed for both high-speed operations and medium pac...
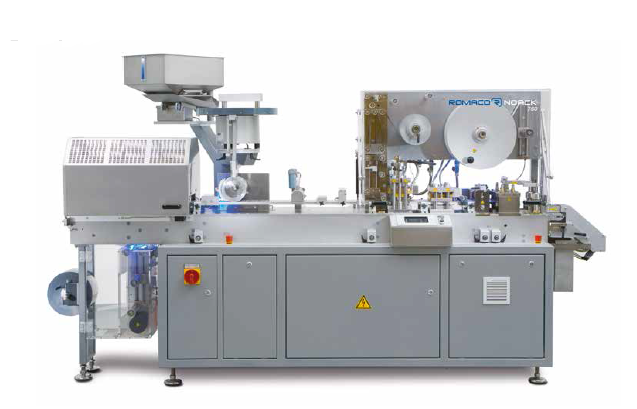
Entry-level blister machine
A start-up solution for contract packing and generics manufacturing with an easy-to-get upgrade ...
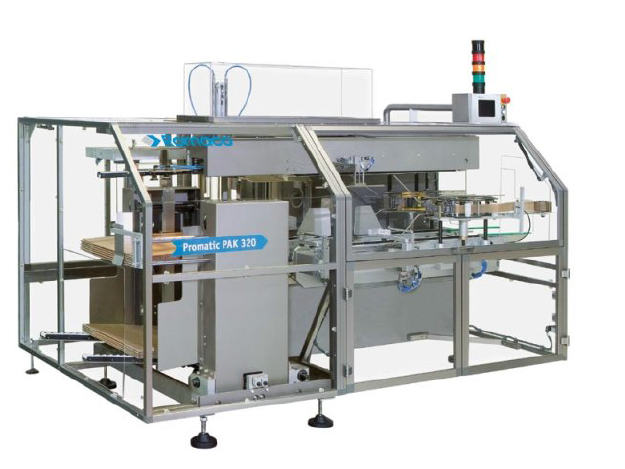
Case packer for cartons and bundles
Pack cartons and bundles into RSC (Regular Slotted Case) cases and perform functions li...
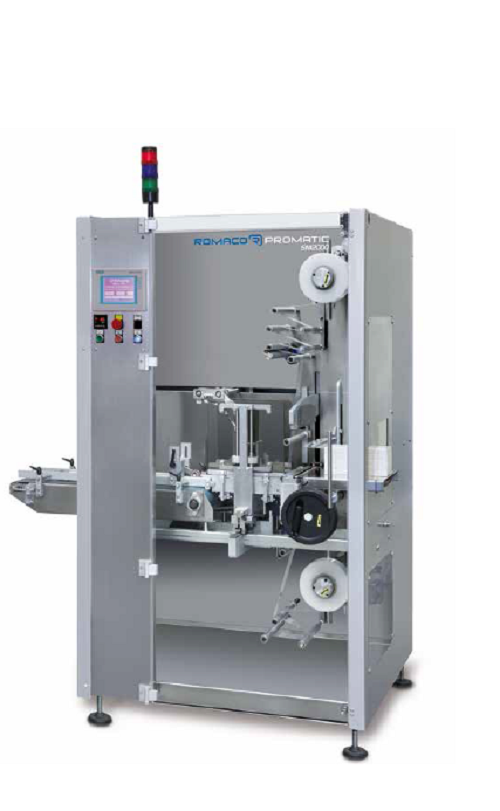
Stretch bander
A compact wrapping machine to seal your boxes with a max speed of 50 packs per minute.
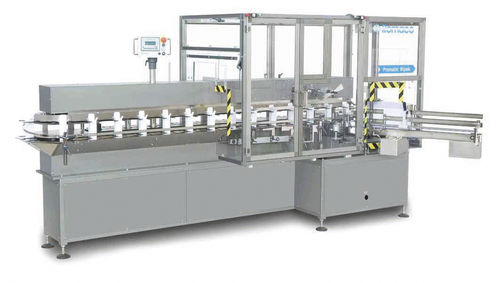
Vertical cartoner
A cartoning solution that can be operated in either continuous or intermittent mode depending on the carton...
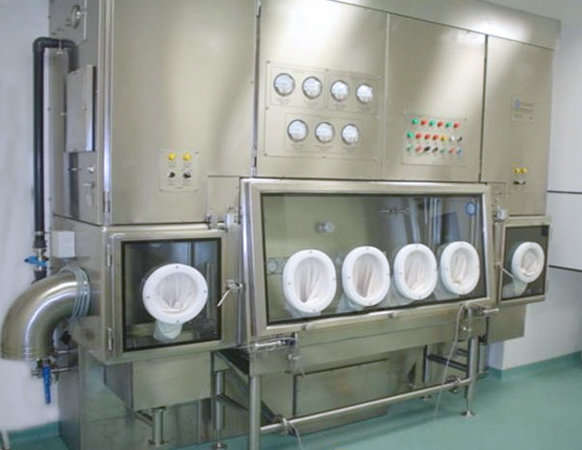
Aseptic barrier systems
Designed for sterile product and Potent API’s either with low or high OEL requirements.
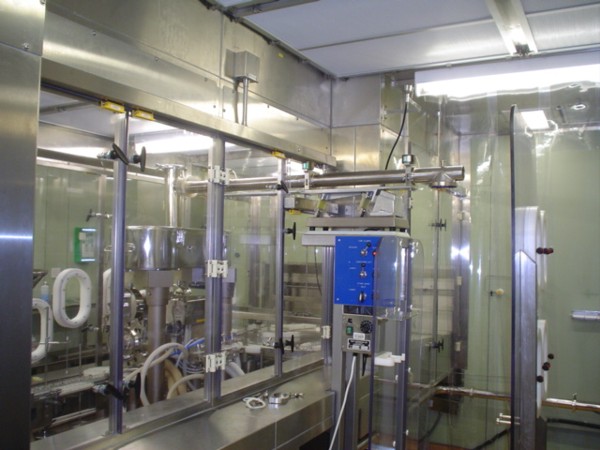
Restricted-access barrier systems
Create a physical barrier between the operator and the product. More flexible than an iso...
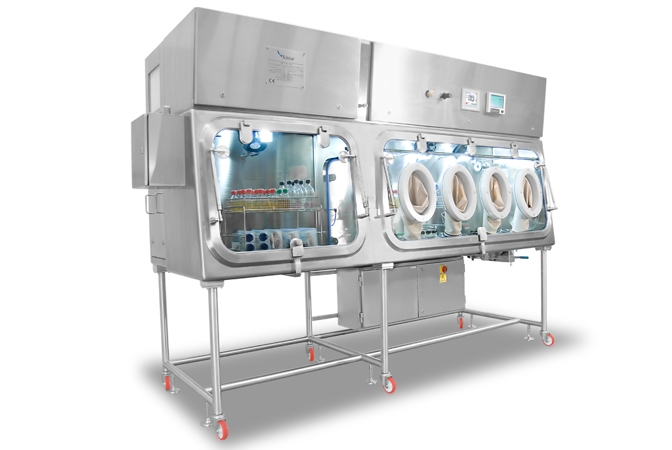
Sterility test isolators
Designed to avoid this risk and protect the product from both the process and externally generated f...