Energy-efficient film coating machine for pharmaceutical tablets
Tablet coating involves applying a thin layer of coating material to pharmaceutical tablets, which requires controlled temperature, humidity, and air quality. This process typically consumes significant energy and contributes to high costs and environmental impact. To address this, an advanced energy monitoring system can be integrated into your coater for a more sustainable process. Additionally, by implementing heat recovery in the ventilation system, the excess heat generated can be captured and repurposed, reducing waste.
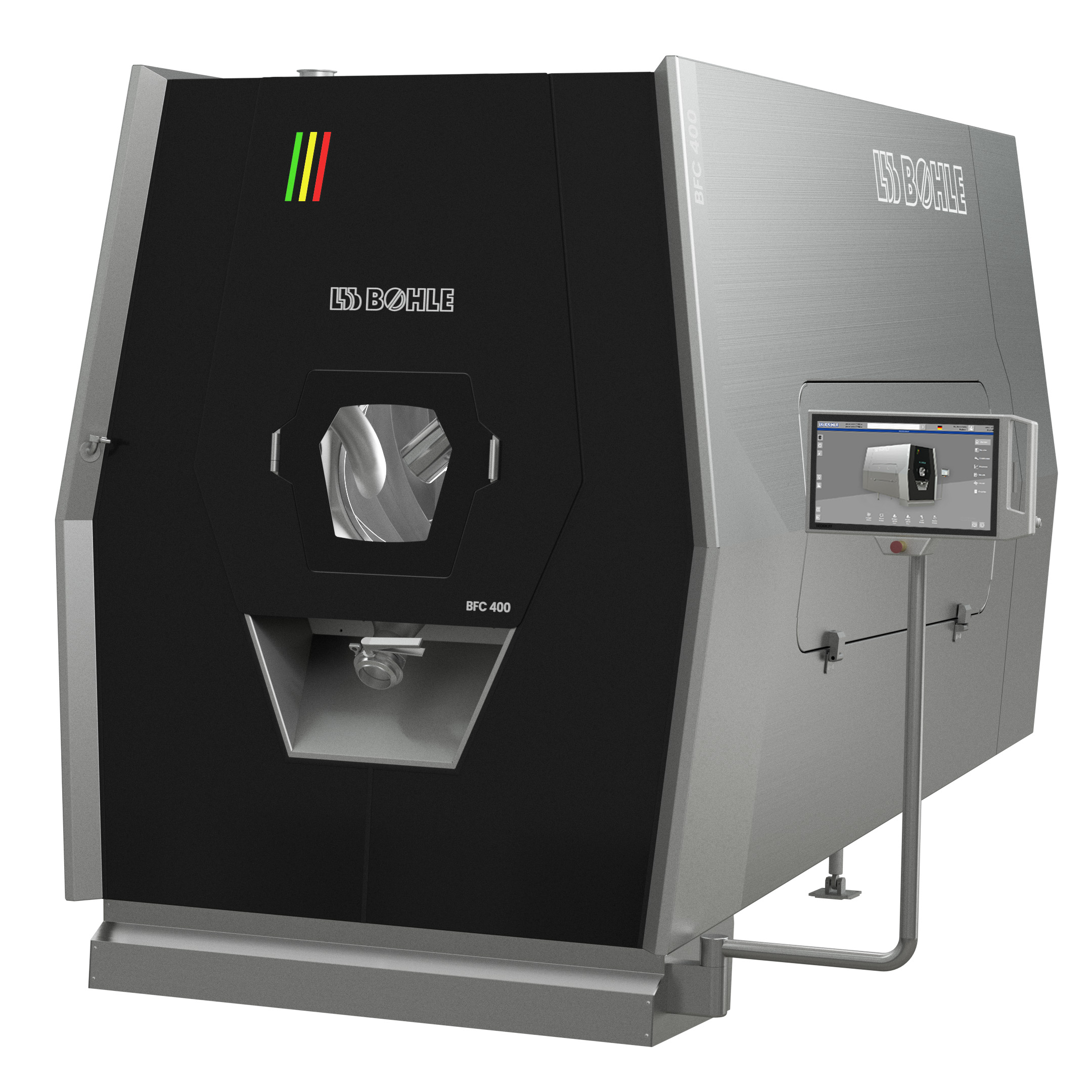
Evenly coat your tablets using automatic and adjustable spray nozzles
The BFC 400 from L.B. Bohle is a film coater equipped with 8 adjustable spray nozzles inside a long drum with patented helical baffles. The tablets are sprayed on a flat tablet bed while mixed gently and thoroughly by the helical baffles, which helps prevent the products from twinning. The system’s controlled air movement allows for improved coating structure of the tablets with minimal spray and suspension losses.
The system comes with an iFix control system featuring a large sight glass and a small nozzle arm for good visibility of the coating process. The machine allows fully automatic sampling and feeding even with the door closed for additional safety features. The system can be rapidly discharged by reversing the rotational direction of the pan and by tilting. The machine is also equipped with a CIP system for easy cleaning. A cleaning lance is provided at the bottom of the unit and an enlarged drain pipe allows quick draining of cleaning agents without leaving residues. Optional features include integrated energy control and heat recovery in the ventilation system for a more sustainable operation.
Benefits
- Capacity range from 65 to 650 liters per batch
- Reduced coating process time by up to 40% compared to conventional coating
- Integrated energy control and heat recovery provides sustainable operation
- Minimal spray losses - less than 5%
- Coating uniformity RSD of less than 3%