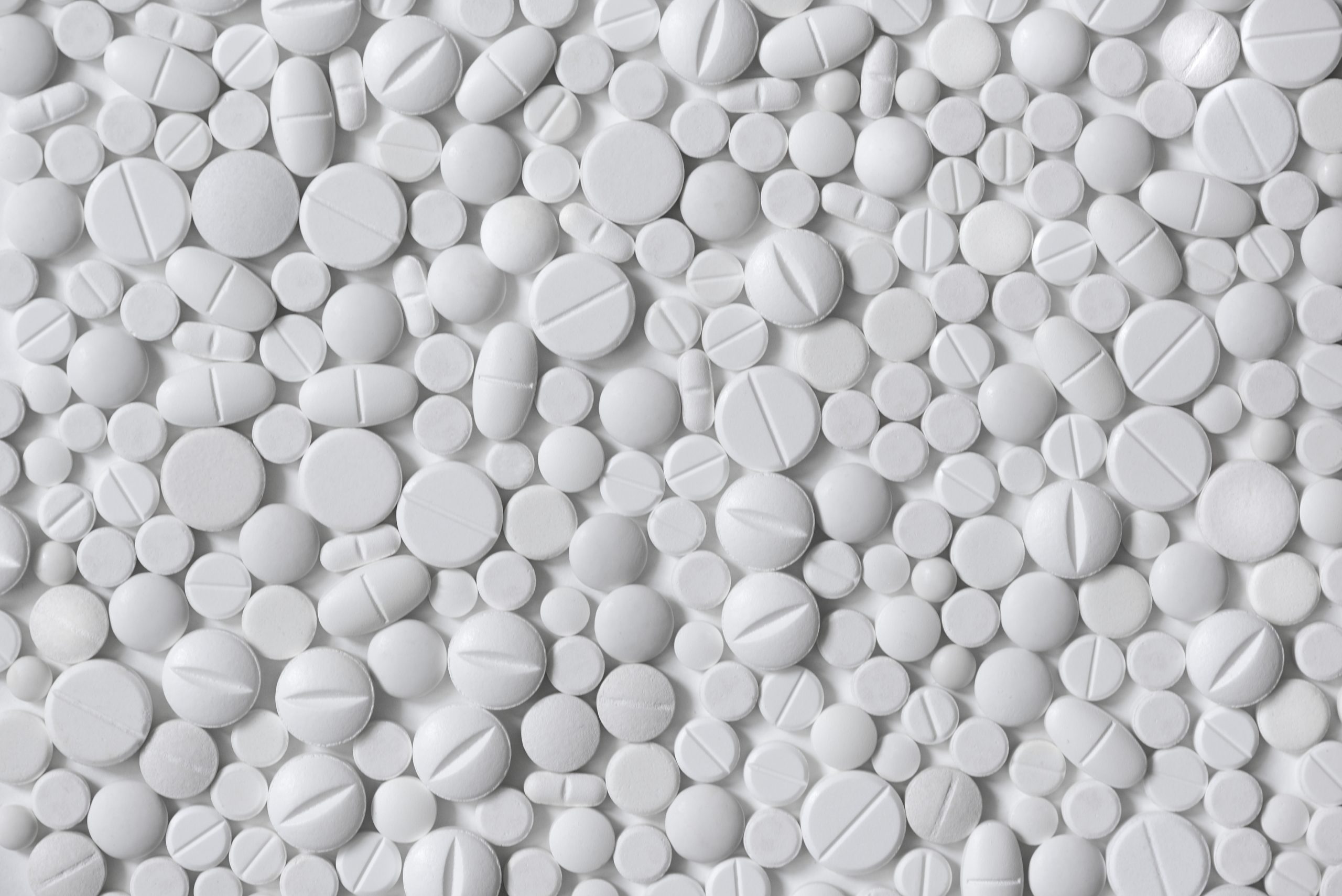
Tablet Coating Equipment
Find production technology for coating tablets, and connect directly with leading machine manufacturers worldwide.
The process of coating tablets occurs for many reasons; to improve patient compliance, to mask an unpleasant taste and odor, to protect the drug from the gastric environment of the stomach (enteric-coated tablets), or to control the release of the drug. As the name suggests, tablet coating equipment applies coating material to the external surfaces of tablets. Regardless of the type of coating you want to apply (sugar coating, film coating or enteric coating), various types of tablet coating technology differ in structure, air capacity, or coating composition.
Difference Between Coated Tablets and Uncoated Tablets
Depending on the application, coated and uncoated tablets have their own advantages and disadvantages. Since coated tablets have an additional coating process, manufacturing costs are higher than uncoated tablets. In applications where the medication must be released slowly or move further beyond the stomach to the intestines, a tablet with an enteric coating becomes essential. Its purpose is to shield the tablet from rapid degradation caused by stomach acid exposure.
Uncoated tablets have exposed active ingredients and excipients, which allow the medication to break down quickly and be absorbed easily by the body, which is suitable for applications that require immediate action. Uncoated tablets are also cheaper to manufacture since they do not have an additional coating process. Coating alters tablet properties like taste, odor, texture, and how the tablet is dissolved in the patient’s body. Enteric-coated tablets allow delayed drug release for the medication to get past the stomach acid and dissolve where intended, making the medicine more effective.
Different Types of Coated Tablets
In most cases, pharmaceutical tablets don’t taste well but are necessary for medicinal or supplementary purposes like vitamins for kids. Sugar-coated tablets are a good option to improve the taste and aroma of the tablet, making it easy for patients, especially children, to take. Film-coated tablets reign as the predominant tablet variety in the pharmaceutical industry, boasting a plethora of benefits. These advantages include masking the taste and odor, allowing the application of colors for easy product identification, and maintaining a stable tablet with longer life and better resistance from exposure to light and moisture.
In cases where two incompatible active pharmaceutical ingredients need to be combined in a single tablet, also known as a combination tablet, compression coating or dry coating method is used. This method allows one active ingredient to be contained in the tablet core while the other in the coating. Sustained-release or extended-release tablets use polymer coating similar to an enteric coating that slowly dissolves over a sustained period in the body, eliminating abrupt bursts of drug release.
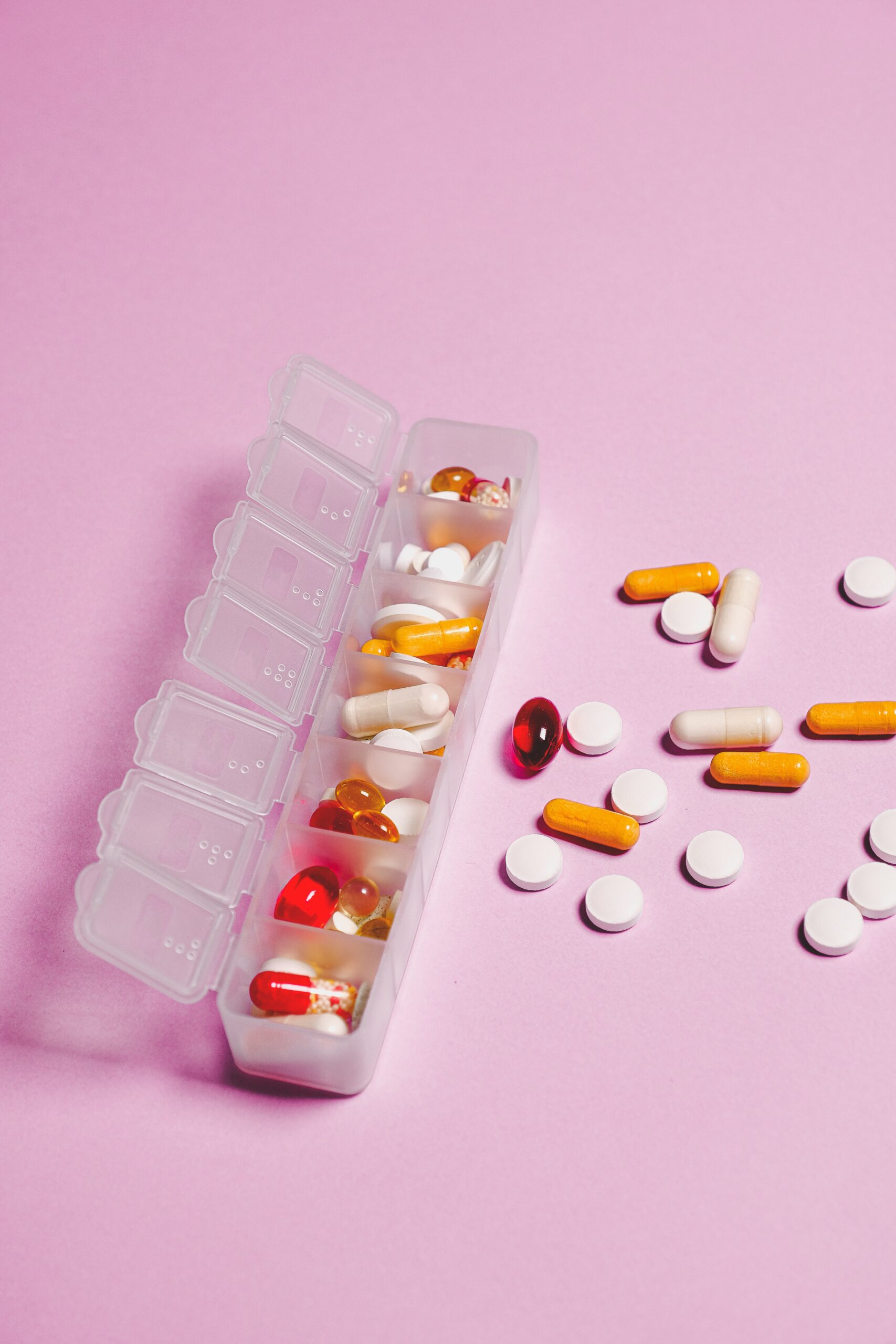
From tablet core to coated tablet
The tablet coating process initiates with the formulation of a coating solution, achieved by blending essential components. The coating solution must have the correct solvent compatible with the core tablet. Subsequently, tablets are placed within a rotating pan, the speed of which is meticulously controlled. The coating solution is continuously sprayed through a nozzle until the tablets are fully coated. Post-coating, the tablets undergo rapid drying via precisely regulated airflow at a specific temperature. Finally, the tablets are extracted from the pan and inspected for uniformity in coating and the absence of defects.
Film coating solutions for pharmaceutical tablets
Film-coated tablets are the pharmaceutical industry’s prevailing choice for a wide array of solid oral medications, primarily due to their numerous advantages. Like other coated tablets, they enhance stability and visual appeal while concurrently concealing taste and facilitating controlled drug release, all are made possible through the selection of purpose-specific film-coating materials.
The film coating process starts with the tablets loaded into the coating pan, forming a tablet bed. The tablet bed tumbles slowly while a controlled airflow is introduced. When the desired temperature is reached, the coating solution is sprayed onto the bed until the tablets are fully coated. The controlled temperature and airflow operate simultaneously to allow the tablets to quickly dry and form a thin film all over the tablet. Various coating solutions are available depending on your product application.
Organic film coating is a solution made up of polymers, colorants, and excipients dissolved in organic solvents. Polymers like ethyl cellulose and hydroxypropyl methylcellulose (HPMC) are widely used in film coating to form flexible films that adhere strongly to the tablet’s surfaces while being highly soluble in organic solvents. Another coating option is aqueous film coating, which employs water as the coating solvent. This choice is considered safer due to its lower flammability and reduced toxicity, making it both cost-effective and environmentally friendly when contrasted with organic solvents.
Enteric coating for modified-release tablets
Enteric-coated tablets are tablets coated with pH-sensitive polymers such as acrylate polymers and hydroxypropyl methylcellulose phthalate (HPMCP). These polymers prevent the tablet core from disintegrating in the stomach, where pH levels are acidic. The coating is only soluble when it reaches the small intestines, with basic pH levels. Examples of common polymers used for enteric coating formulations are Cellulose acetate phthalate (CAP), which has a high hydrolysis potential when exposed to high temperature and humidity, and Hydroxypropyl methylcellulose acetate succinate (HPMCAS), which has a low hydrolysis potential under elevated temperature and humidity. Although both are used for the same purpose, we must consider the compatibility of the tablet core’s chemical composition with the enteric coating applied.
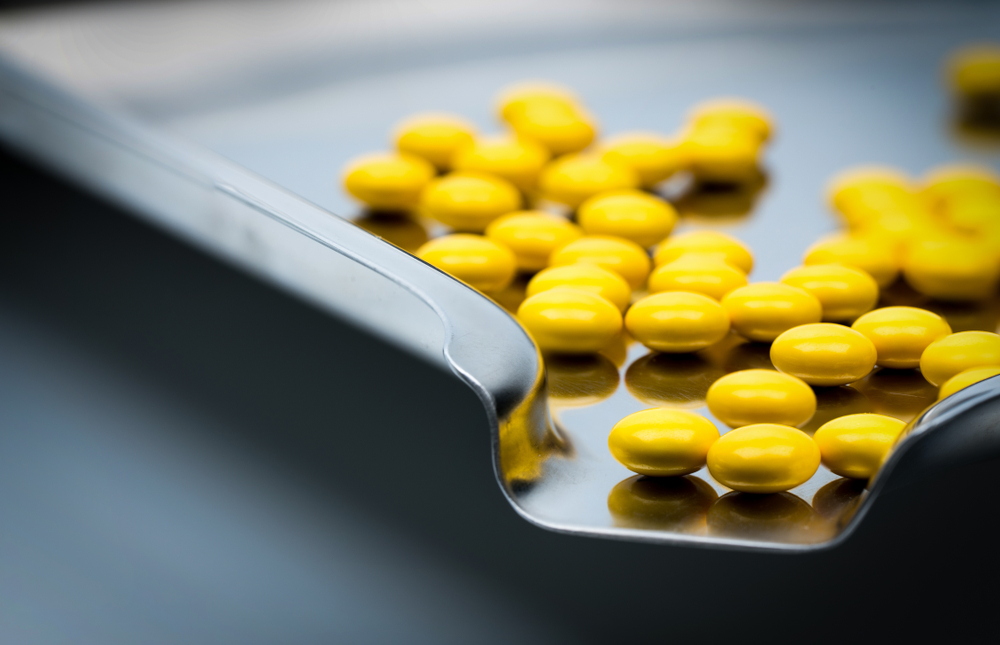
Coating of enteric-coating tablets starts with loading tablet cores into the coating pan, where they tumble slowly, and controlled airflow is introduced. The enteric-coating solution is sprayed onto the tablet cores as soon as the desired temperature is reached. The simultaneous operation of spraying coating solution and maintaining controlled airflow and temperature allows the tablets to dry quickly and produce a tablet with a thin film coating.
Coating in laboratory scale to industrial scale
Tablet coating between industrial scale and small-scale production are similar in process but differ in loading capacity and equipment performance.
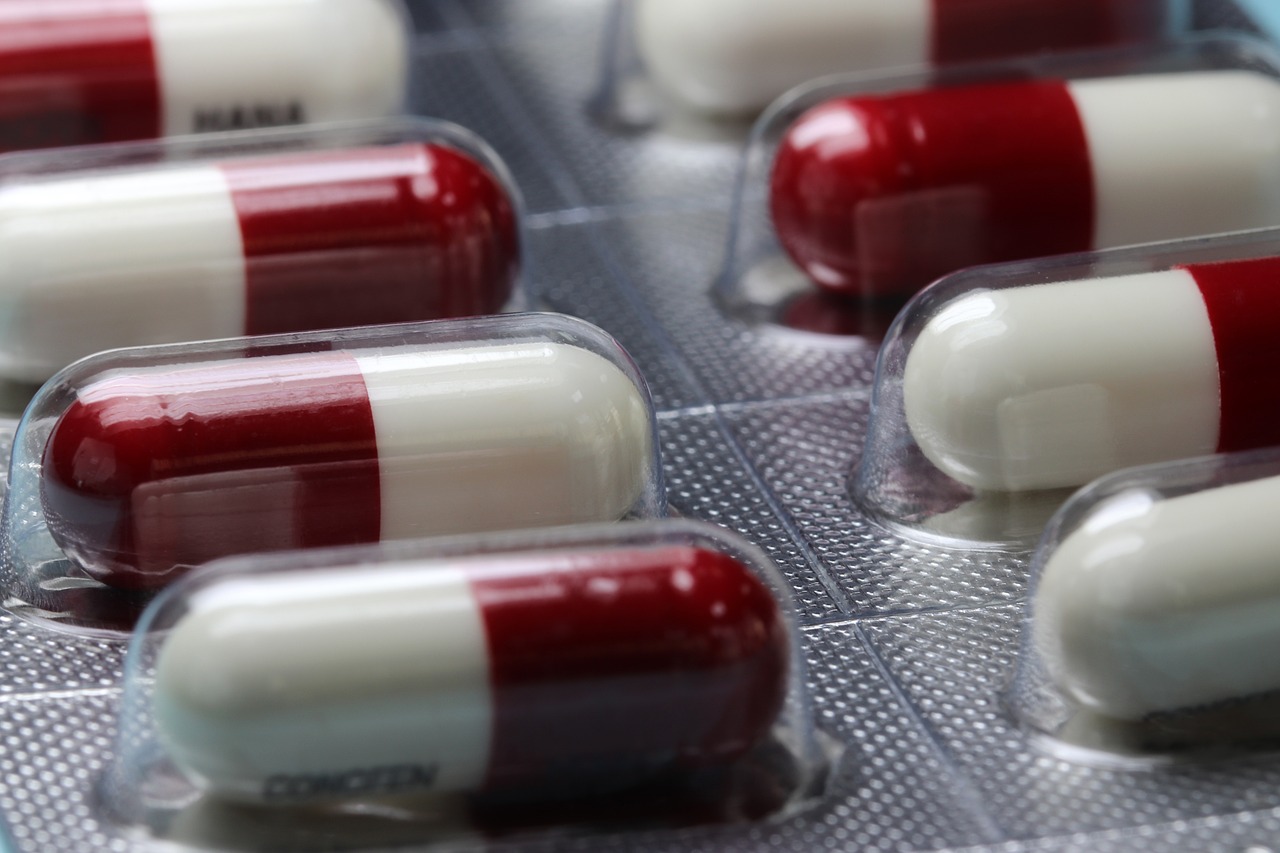
On an industrial scale, the process is highly automated and operates with precision and efficiency. Massive coating machines with advanced controls can coat thousands to millions of tablets in a single batch. This level of production ensures consistent quality and allows for cost-effective mass production of medications. The residence time of the tablets for industrial-scale systems tends to be longer due to the size of the pan and the time required to reach the correct operating temperature within the system.
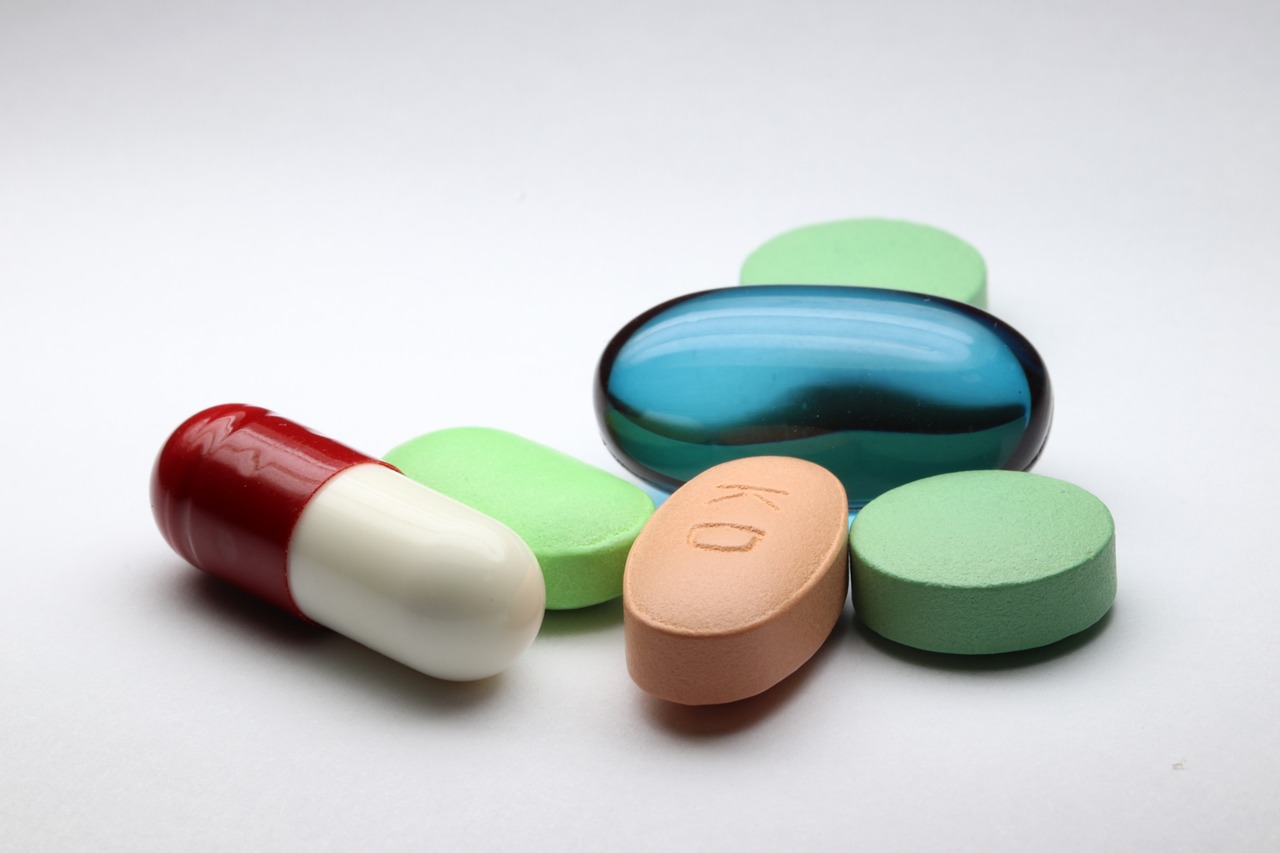
On the other hand, small-scale tablet coating is typically carried out in laboratories or smaller manufacturing facilities. While less automated, it offers greater flexibility for research and development purposes, allowing for the creation of prototype formulations and specialized coatings for niche drug delivery requirements. Laboratory scale systems have quicker process times since the parameters of the operating conditions can be reached quickly due to smaller dimensions.
Other notable differences between industrial scale and laboratory scale systems are the pan perforations where controlled air passes; the ideal drum spin rate for providing adequate mixing without breaking the tablets; inlet air flow rate for drying; the number of spray nozzles and their volume flow rate; the number of baffles to avoid twinning of tablets; and the ideal temperature and humidity for during operation to achieve uniformity. Both approaches are essential in the pharmaceutical industry, catering to diverse needs, from mass production to customized drug delivery systems.
Tablet Coating Technologies
In the pharmaceutical industry, several prevalent coating technologies include sugar coating, film coating, compression coating, and enteric coating. Sugar coating, in particular, encompasses a multi-step process that includes sealing, subcoating, syrup coating, coloring, and polishing. This method results in a thicker coating layer due to the application of multiple coating layers.
Film coating uses a rotating pan with baffles and an efficient spraying system for the coating solution. A controlled airflow and temperature allow the film coating to dry quickly. Enteric coating follows the same principle as film coating but utilizes enteric coating polymers, which are resistant to stomach acid to coat the external surfaces of the tablet core. At basic pH levels, the enteric coating disintegrates and exposes the tablet core.
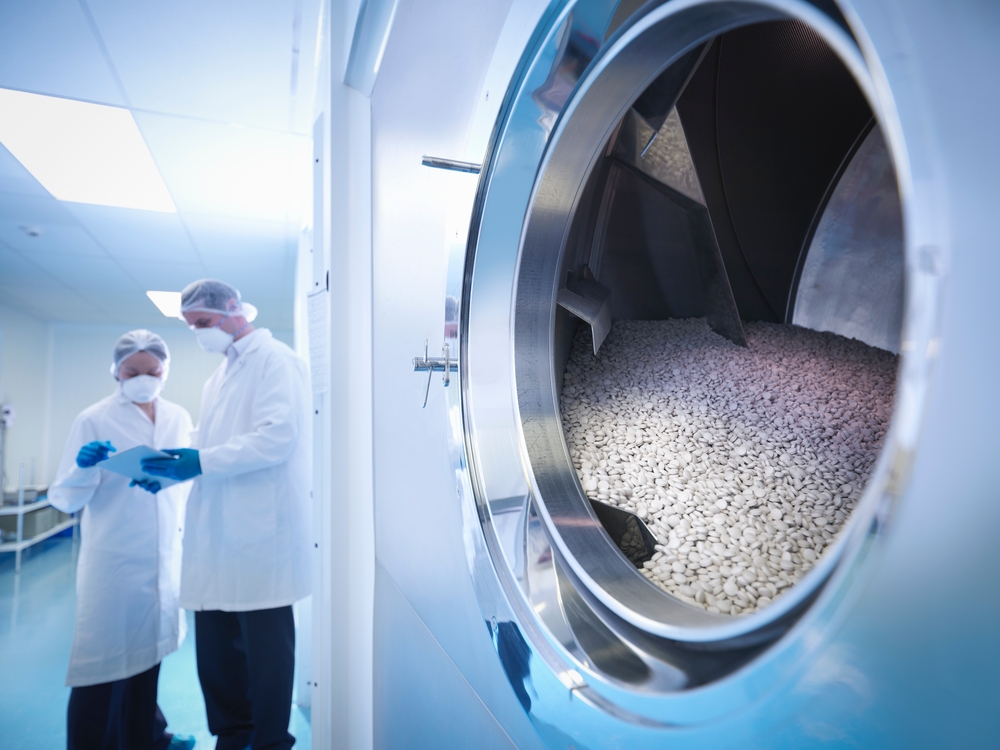
Compression coating or dry coating simply requires the coating to be pressed on the surfaces of the tablet core using a specially designed tablet press. This coating process applies to tablets with two incompatible active ingredients where one ingredient is contained in the tablet core and the other is contained in the coating. The modified-release coating uses polymer coating solutions like enteric coating that dissolve slowly over time to release small doses of medicine inside the body.
Testing for quality and regulation compliance
Based on the International Council for Harmonisation (ICH) guidelines, organic solvents must be avoided in the formulation of pharmaceutical dosage forms due to safety issues regarding health and environmental risks. Because of this, manufacturers are shifting to the aqueous film coating method, which uses water-based coating solutions that are less toxic to health and the environment. Coated tablets’ assessment and quality testing involve a comprehensive set of evaluations.
These encompass visual appearance inspections, disintegration tests where tablets are submerged in 37°C water to replicate stomach conditions with recorded disintegration times, dissolution tests, and scrutiny of drug content. Advanced analytical instruments like near-infrared and Raman spectroscopy are employed for precision, uniformity of content, and weight assessments. Furthermore, tablets undergo hardness assessments and friability tests, which are weighed before and after being subjected to a rotating drum to determine any weight loss percentage due to chipping or breakage. Additional evaluations include adhesion tests and assessments of water vapor stability.
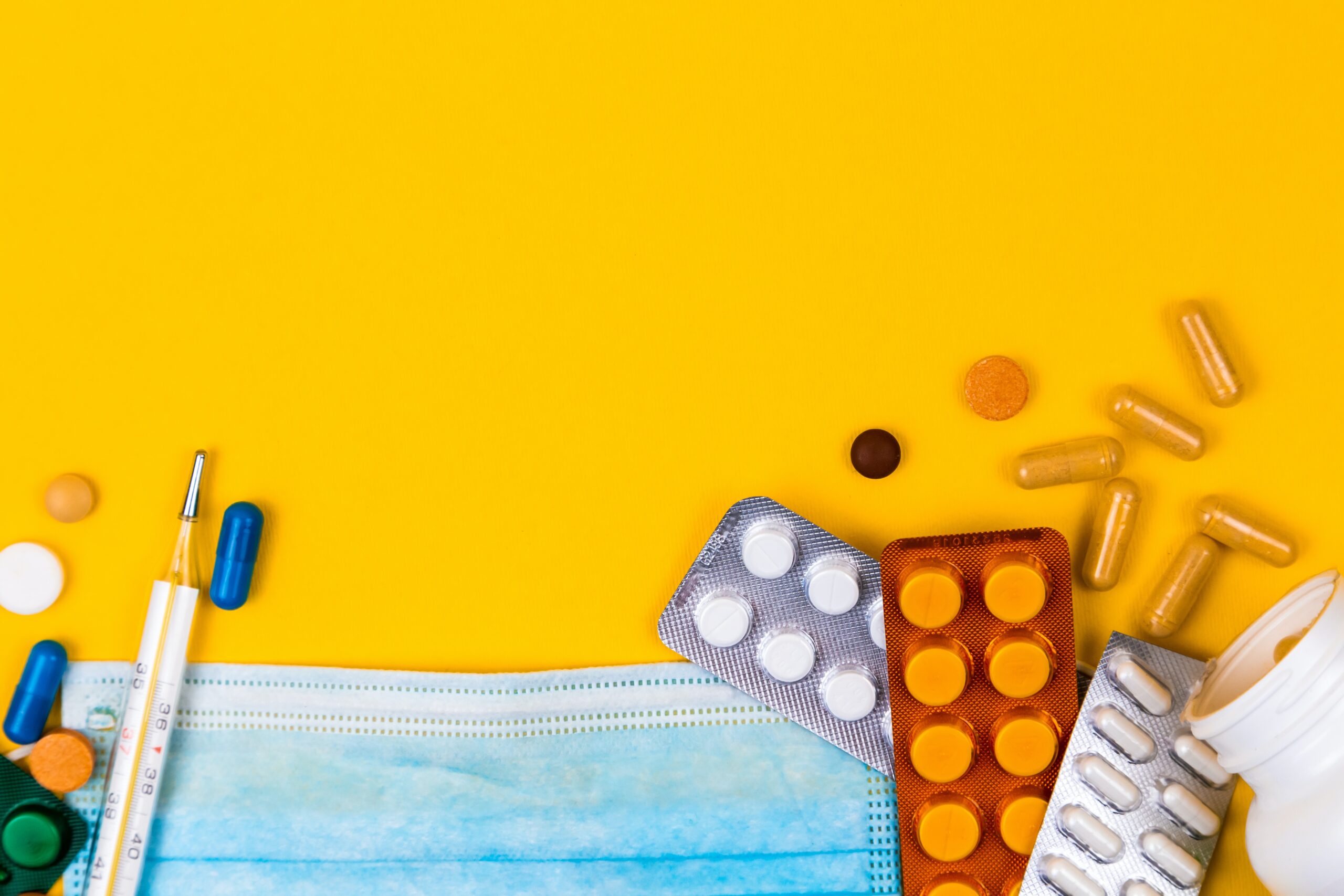
Technological innovations for tablet coating
New methods are being developed for coating technology to improve production processes, safety, product quality, and environmental impact. Electrostatic coating is an effective coating method for conductive substances. An electrostatic charge is applied to the substrate while the coating material is made up of conductive ionic species of the opposite charge and is sprayed on the substrate. Another dry coating method when dealing with powders that are sensitive to temperature is using magnetically assisted impaction coating (MAIC). MAIC is a soft coating method where the coating material and the particles to be coated can be attached with minimum changes to the particle shape and size. This is due to less heat buildup compared to compression coating.
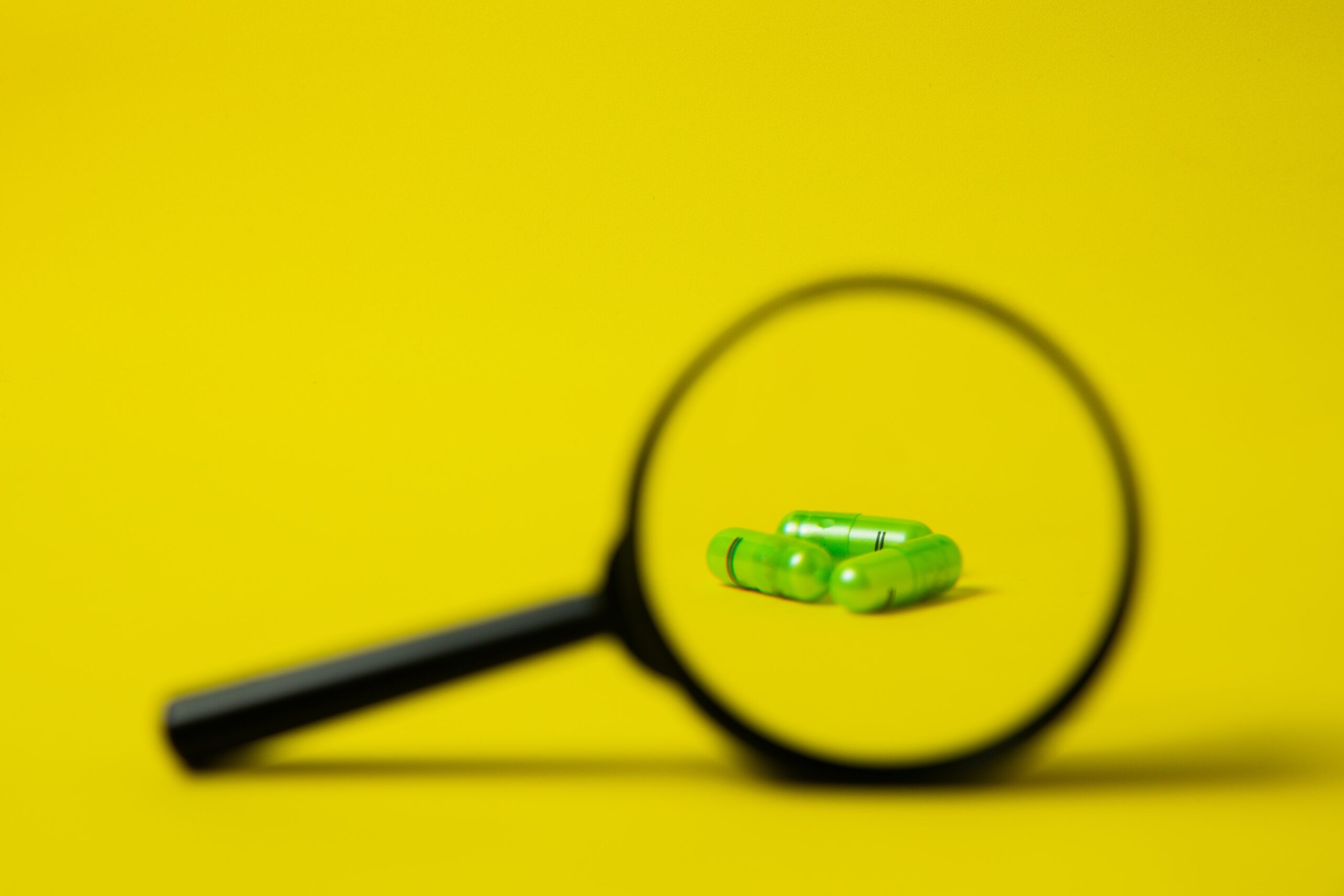
Sustainability and environmental impact of materials
There is an effort to decrease the use of Volatile Organic Compounds (VOC) emissions as this is considered harmful to health and the atmosphere. In the pharmaceutical industry, many tablet producers use organic solvents in their coating process. However, some manufacturers are shifting to an aqueous film coating process that uses water-based solutions as coating materials to minimize harmful emissions. Aqueous film coating solutions are preferably devoid of plasticizers and contain about 6% hydroxypropyl methylcellulose (HPMC) and less than 1% combination of sodium hexametaphosphate and lecithin, by weight, in water.
Tablet coating process challanges
It is necessary for manufacturers to understand the properties of various excipients and the formulation of the coating materials to select the most compatible coating application for the tablet core. Coating adhesion problems may require changes to the polymer mixtures for coating by using Hypromellose and copovidone as the primary polymer. Other challenges include the blistering of tablets, where the film coating detaches from the core due to high-temperature application during the drying process. The drying process must apply mild drying conditions, such as moderate temperatures, during the coating process. Chipping and erosion can happen for reasons like the tablet profile has sharp edges or due to alterations to the coating process like slow pan rotation, low spray rate, or even poor coating formulation. By adjusting the proportion of the plasticizer or selecting a polymer with high molecular weight for the coating solution, the hardness of the coating can be increased. Manufacturers must understand the limits and the specific ideal conditions necessary for coating their products to minimize defects and waste in production.
Which tablet coating technology do you need?
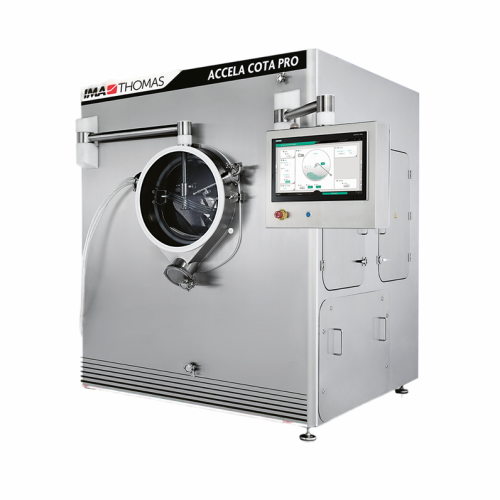
Automated coating pan for pharmaceutical tablets
Enhance your tablet production with a fully automated system that ensures...
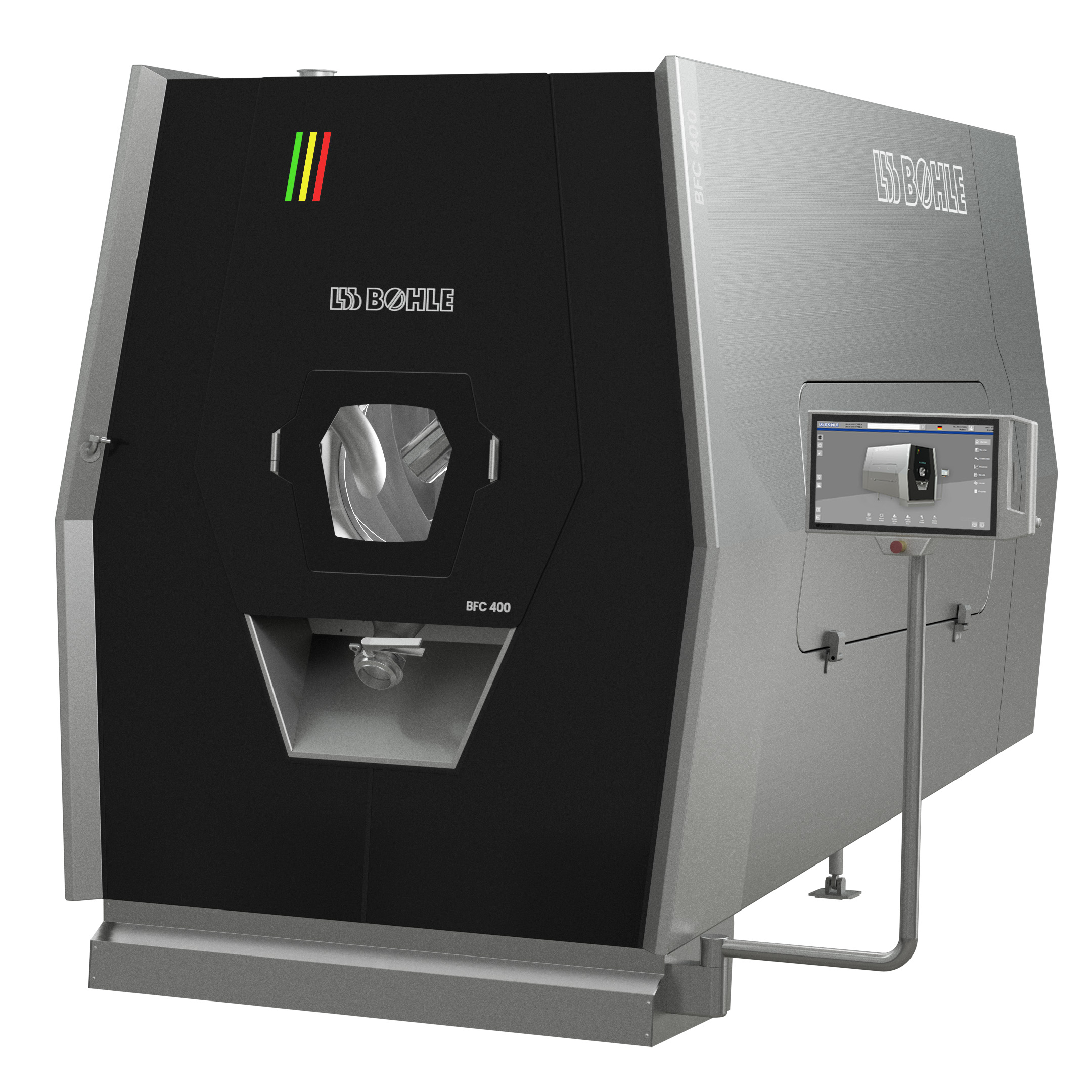
Energy-efficient film coating machine for pharmaceutical tablets
Tablet coating involves applying a thin layer of coatin...
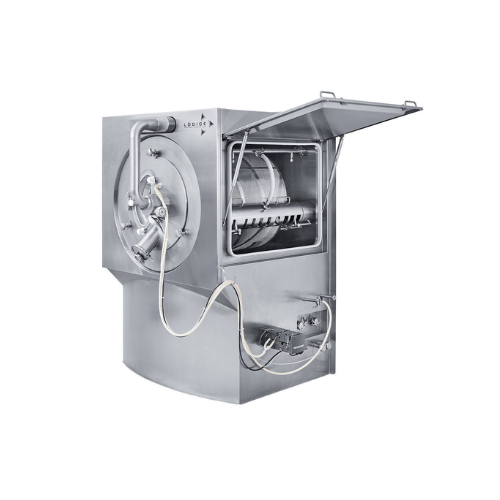
Tablet coater for pharmaceutical applications
Achieve uniform tablet coatings with exceptional efficiency and reduced proc...
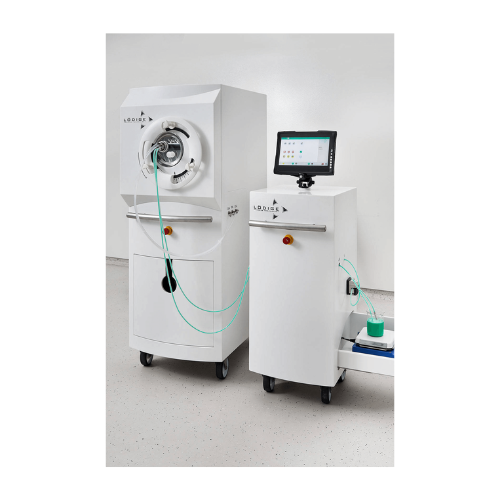
Laboratory tablet coater for pharmaceuticals
Achieve consistent and efficient coating of tablets with this innovative coat...
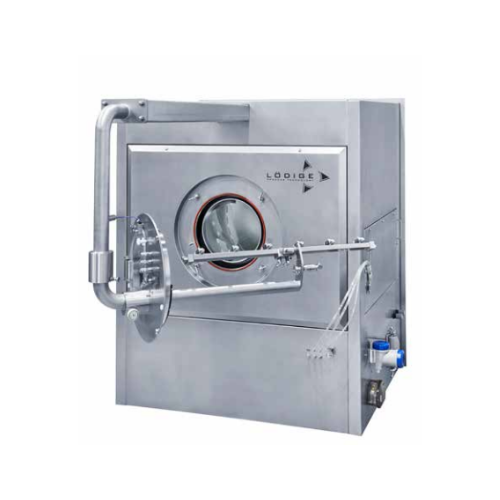
Film coater for Otc and food supplements
Achieve optimal film coating for tablets and capsules with precision-engineered so...
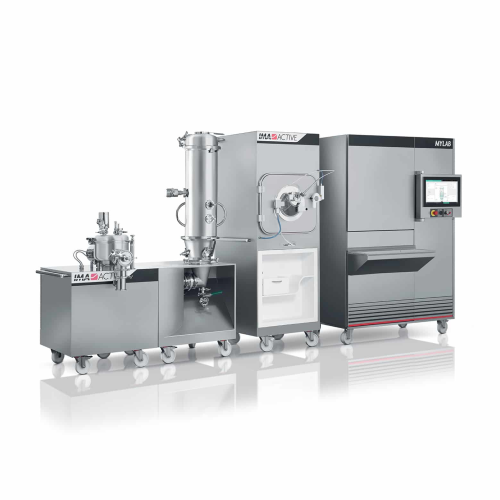
Fluid bed and coating system for small batch processing
Streamline your R&D process with a modular system that ensur...
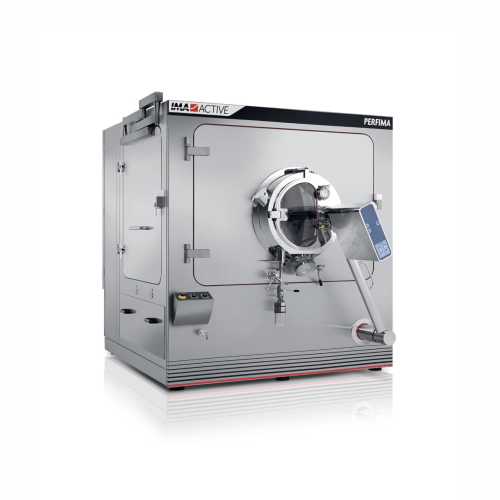
Industrial tablet coating solution
Achieve precise film and sugar coatings on a versatile range of tablet and pellet forms,...
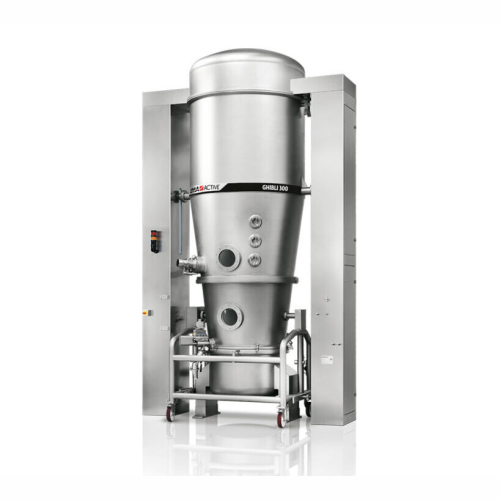
Fluid bed processor for pharmaceutical granulation and drying
Achieve precise drying, granulation, and coating of pharma...
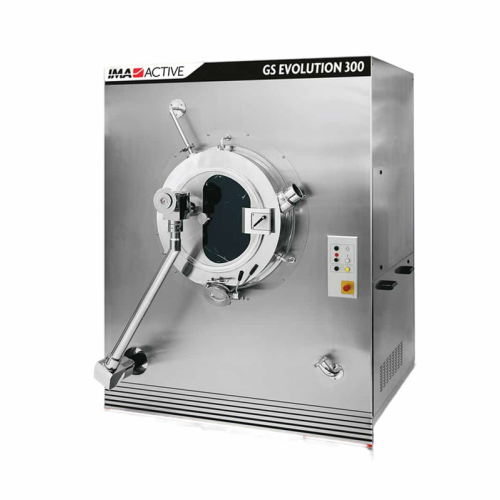
Tablet film and sugar coating pan
Achieve uniform coating while minimizing operator exposure to potent substances, ensuring...
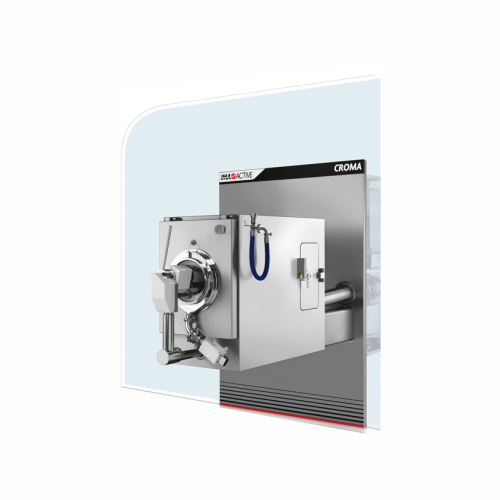
Continuous coater for tablet coating
Achieve seamless tablet coating with continuous processing, enhancing efficiency and r...
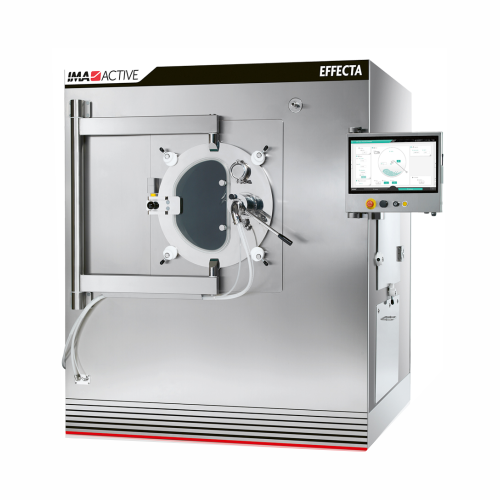
Tablet coating pan for pharmaceutical and nutraceutical industries
Enhance coating efficiency with a versatile solution...

Mid-capacity film coating solution
Enhance your seed coating and biofuel pellet production with a customizable turn-key sol...
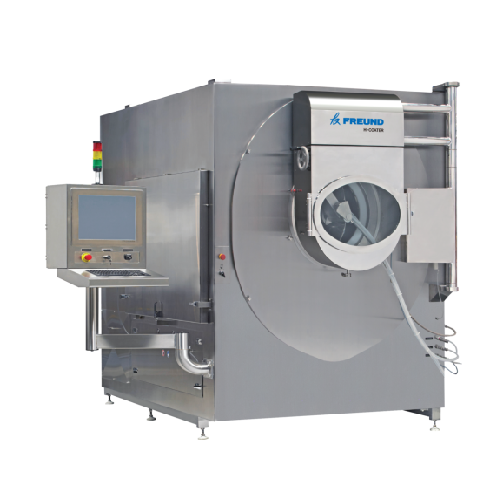
Tablet coater for precision pan coating
Achieve precise coating control for pharmaceuticals and nutraceuticals, accommodati...

Integrated plenum tablet coater
Achieve consistent and high-quality coatings on tablets with advanced airflow management, ef...
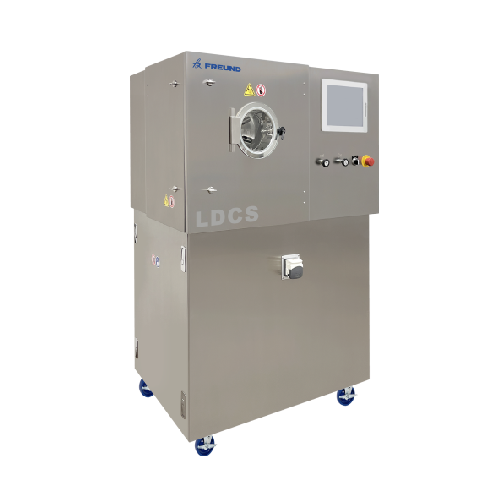
Tablet coating system for laboratory development
Optimize your tablet formulation development with a versatile coating sys...
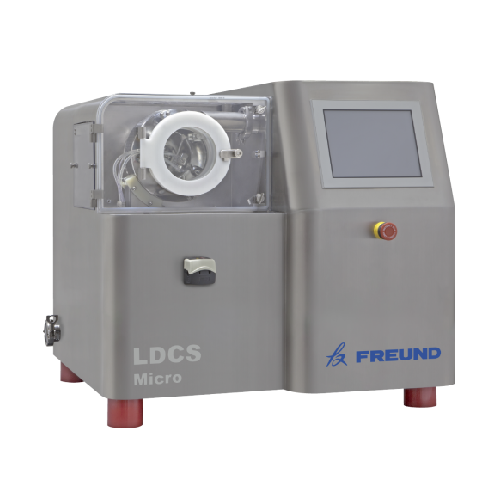
Laboratory film coating system for development and clinical batches
Achieve precision in tablet coating with a versatil...
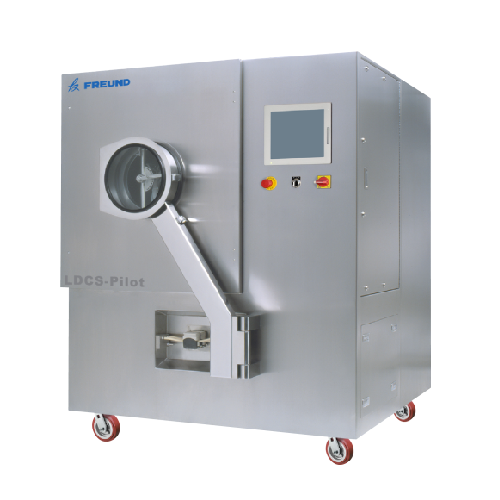
Laboratory and pilot scale pan coater
Maximize coating efficiency in tablet production with this advanced pan coater, offer...

Laboratory development coating system for tablet coating
Efficiently manage small-scale batch coating with versatile, ful...
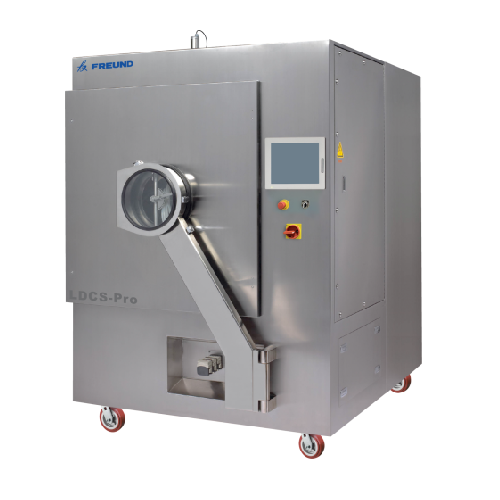
Portable pan coater for pilot scale tablet coating
Achieve uniform tablet coating with interchangeable pans and anti-mark...
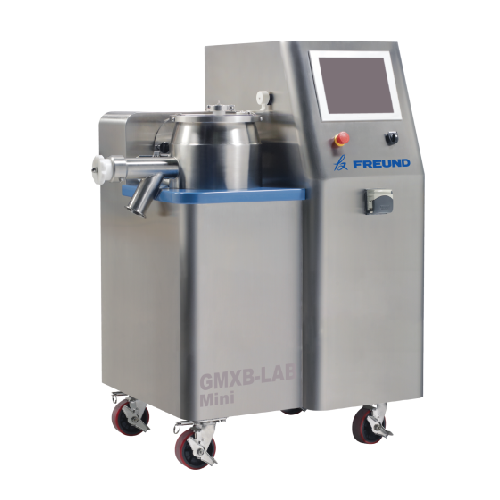
High shear granulator for wet granulation of powders
Achieve consistent granule density and size with a high shear granul...

Pilot Gmp spray dryer system for small-scale manufacturing
For precise control in spray drying, streamline your small-sc...
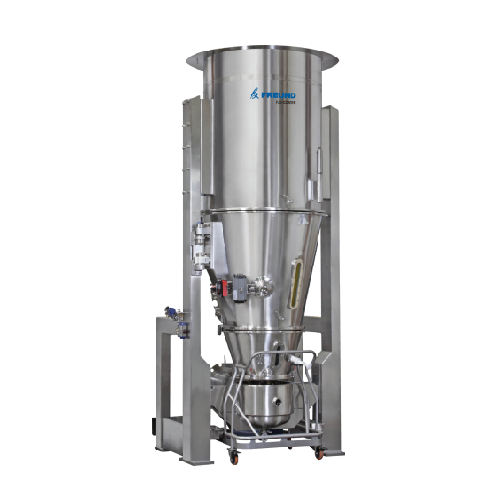
Fluid bed granulator for industrial granulation
Optimize your production efficiency with versatile fluid bed granulation, ...
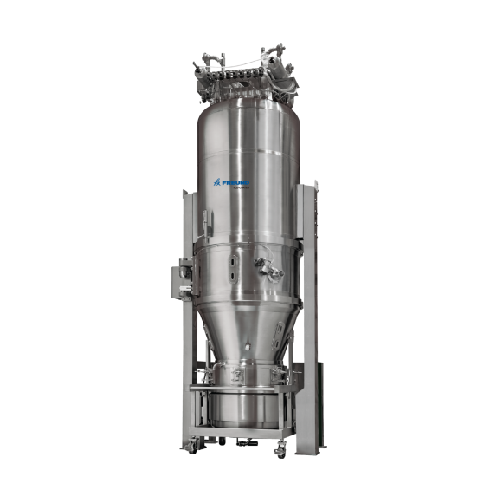
Fluid bed system for granulation and coating
Optimize your production with a multi-purpose fluid bed system designed for e...
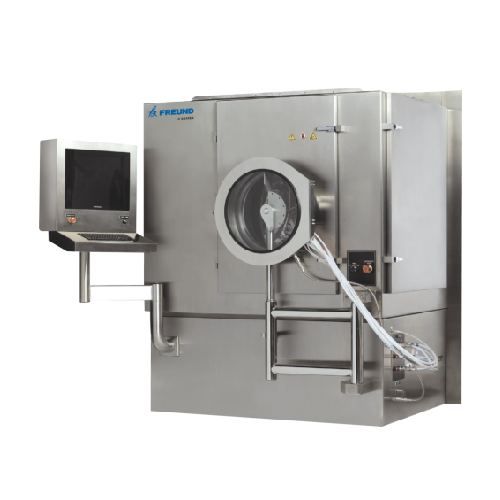
Tablet coating system for aqueous, solvent, and sugar films
Achieve precision coating with flexible application capabili...
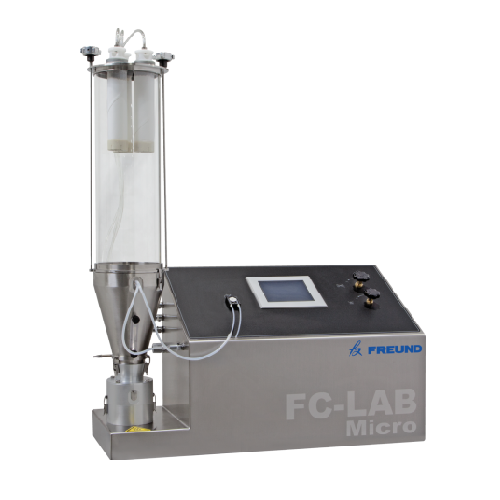
Development fluid bed system for feasibility studies
Explore precise granulation and coating capabilities for small batch...
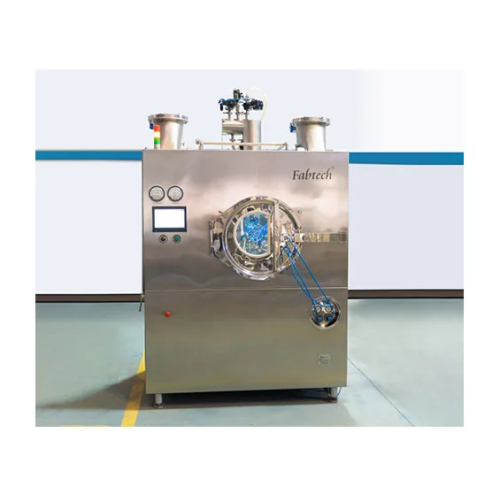
Tablet coating solution
Achieve precise tablet coating with uniformity and efficiency, tailored for diverse tablet types, ens...
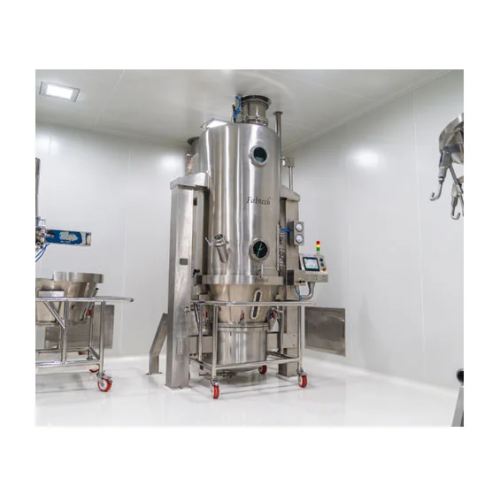
Fluid bed processor for granulation and coating
Fluid bed processors offer efficient granulation and coating, streamlining...
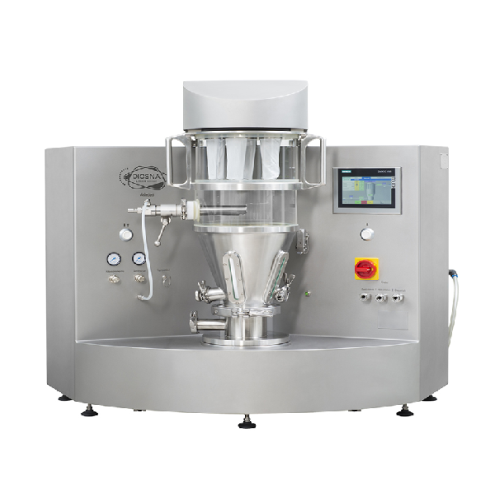
Laboratory granulator and coating system
Optimize your research with a versatile benchtop unit that combines fluid-bed proc...
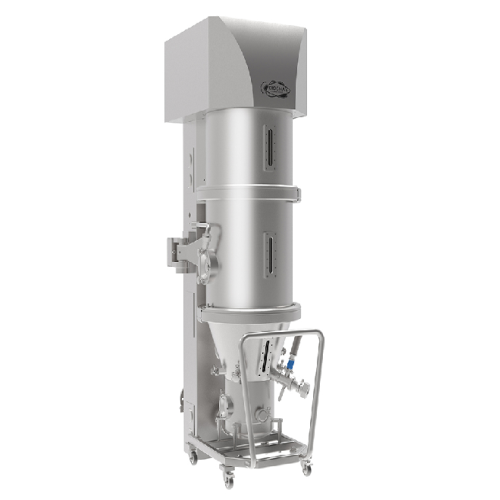
Fluid bed processor for granulating, drying, and coating in pilot scale
When scaling from laboratory to production, rel...
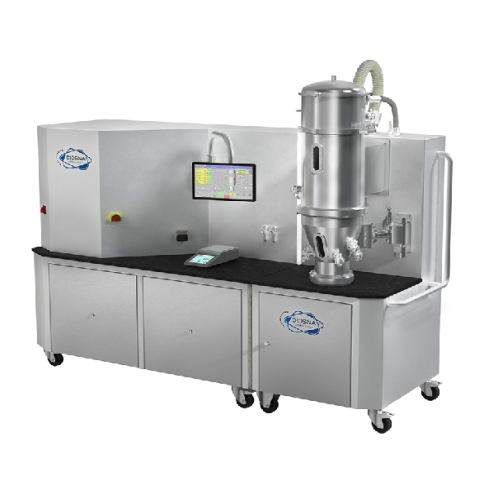
Midilab for efficient laboratory-scale product development
Streamline your laboratory and pilot-scale production process...
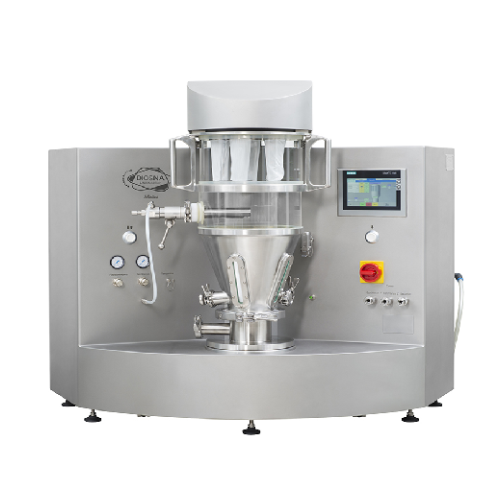
Laboratory coater and fluid bed processor
Optimize your research and development with a versatile benchtop unit that integ...
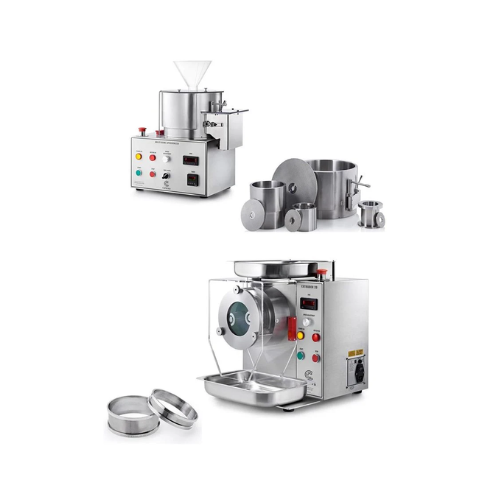
Flexible spheronization kit for wet granulation pellets
Achieve precise pellet and granule formation with a versatile ben...
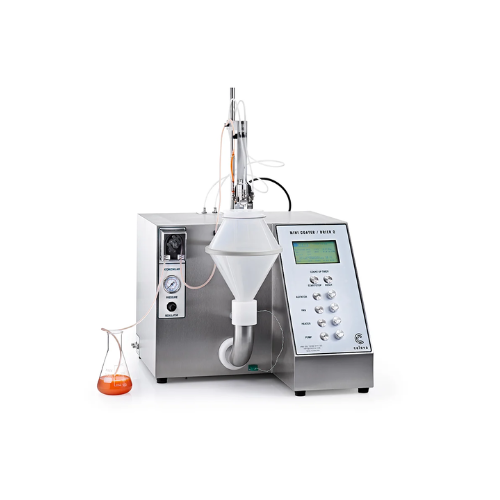
Small batch tablet and pellet coating solution
Optimize your small batch coating and drying processes with a versatile ben...
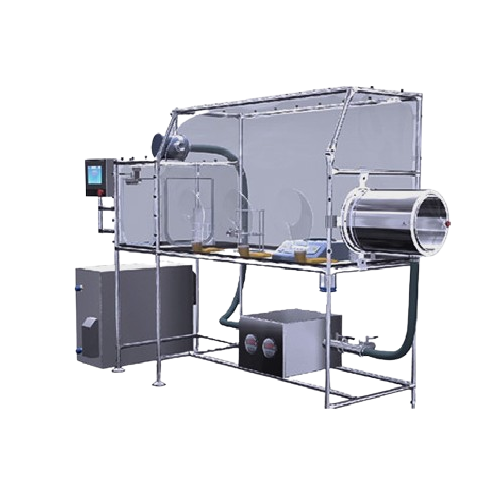
Flexible isolator for aseptic containment
Ensure sterility and safety with a flexible isolator designed for efficient cont...
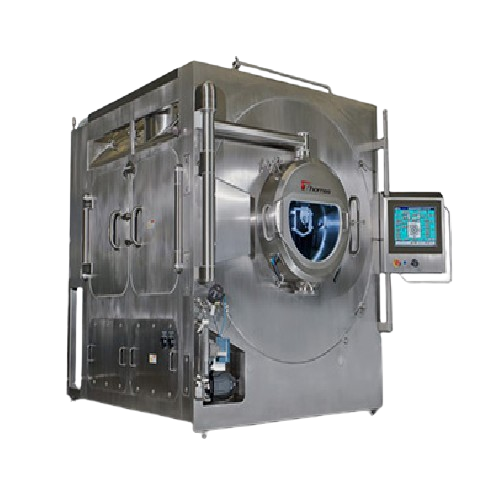
Tablet coating system for pharmaceuticals and supplements
Enhance tablet coating efficiency with flexible, replaceable p...
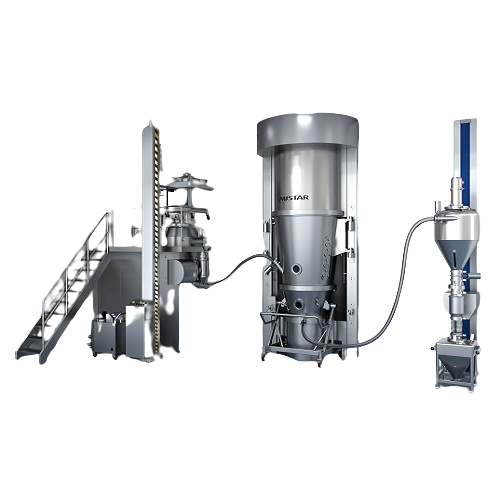
Wet granulating equipment for pharmaceutical industry
Enhance production efficiency and safety in high-potency pharmaceut...
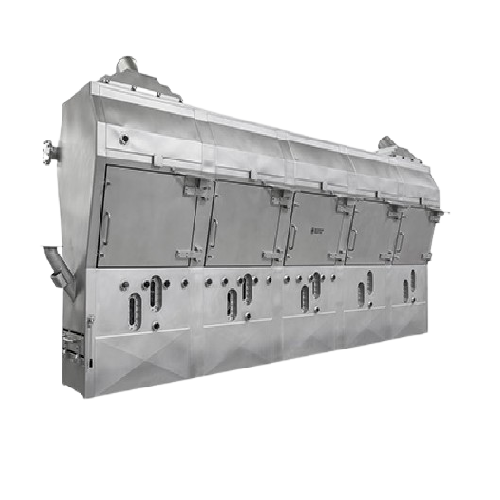
Continuous wet granulation equipment
Optimize your production line with continuous wet granulation, seamlessly transforming...
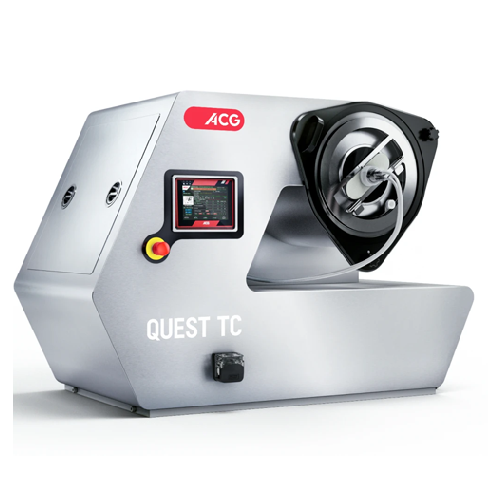
Tablet coating for r&d and small-scale production
Achieve precise, efficient tablet coating with a compact, versatile mac...
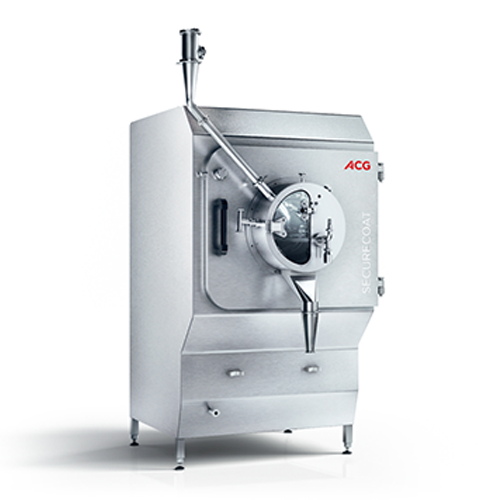
Containment tablet coater for high-potency drugs
Ensure operator safety while achieving precise tablet coating on high-pot...
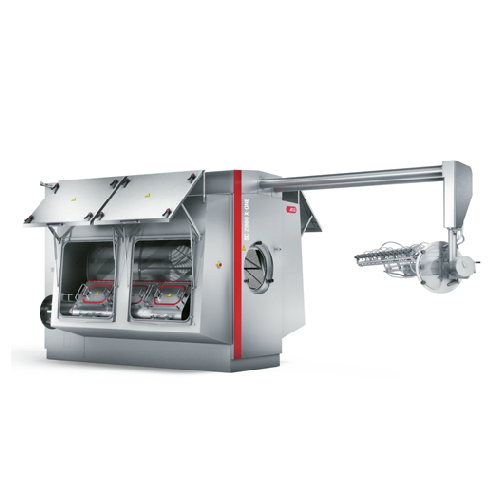
Tablet coating system for high-capacity operations
Streamline your tablet production with a coater that maximizes through...
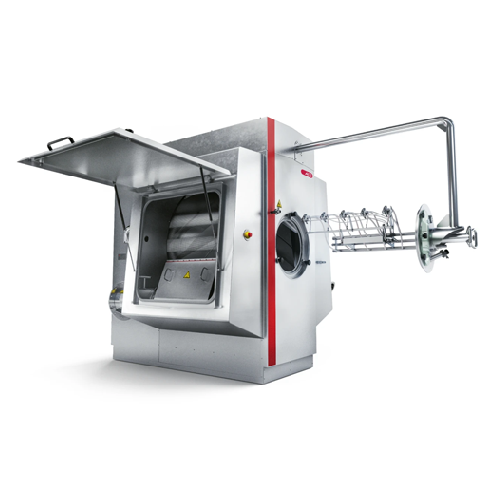
Tablet coater for batch sizes up to 250 liters
Enhance your tablet production process with high-speed coating solutions de...
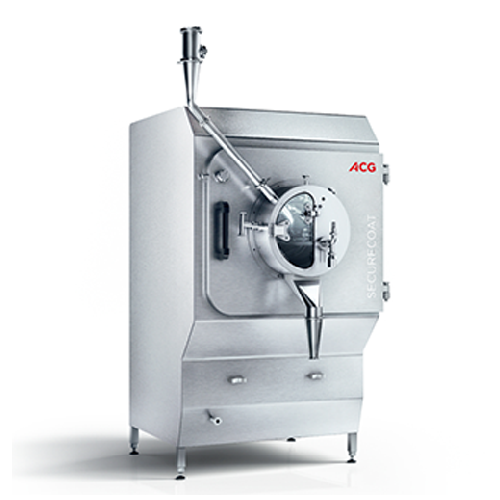
Containment tablet coater for high-potency pharmaceuticals
Ensure operator safety and maintain stringent OEB 4 complianc...
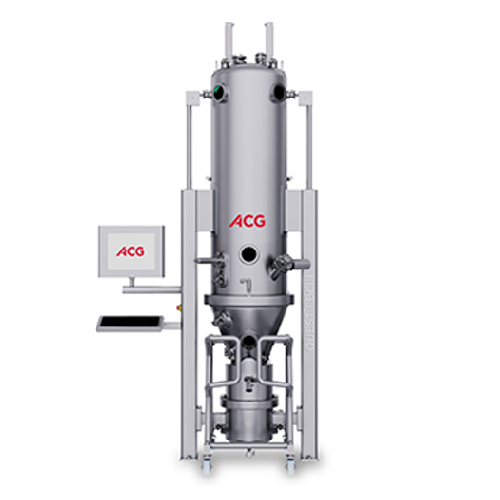
Intermediate-scale fluid bed system for drying and granulation
Achieve precise drying and granulation with this versatil...
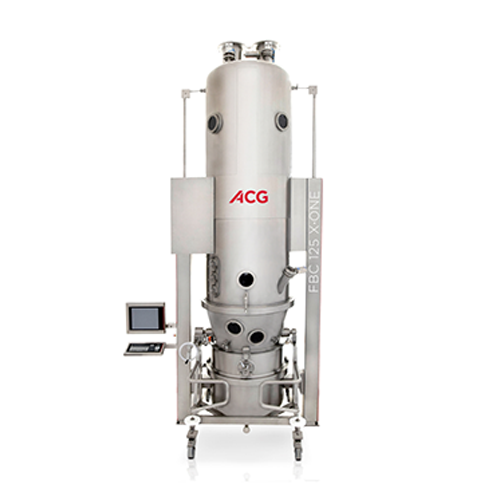
Fluid bed dryer with granulation and coating
Enhance your processing efficiency with a versatile system capable of combini...
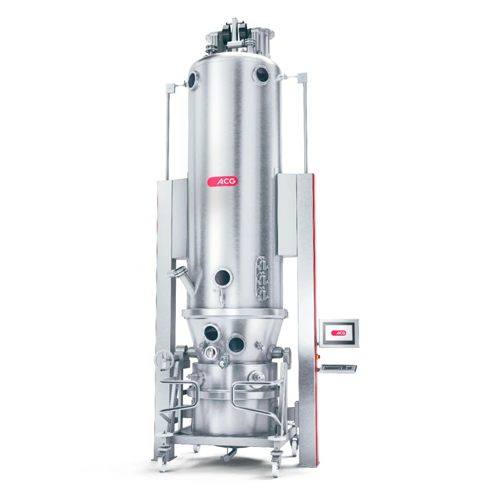
Fluid bed combo for granulation and coating
Achieve seamless granulation and coating with batch and high-speed operations,...
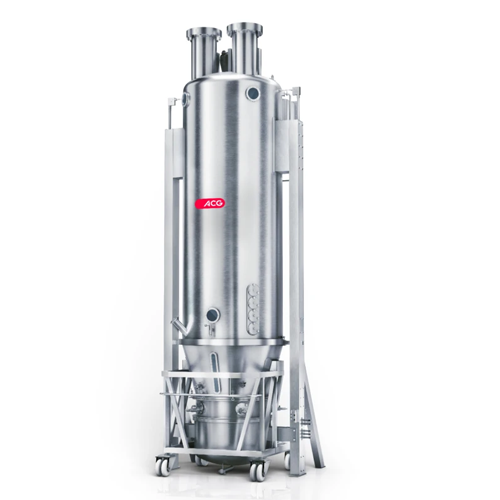
Fluid bed combo for top-spray granulation and wurster coating
Optimize your batch processing with a versatile system cap...
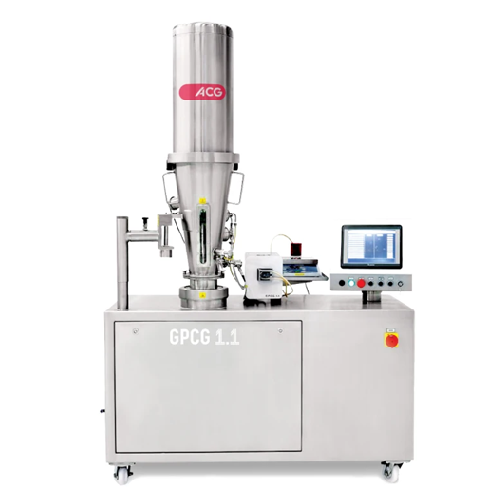
Fluid bed combo for granulation and coating
Streamline your manufacturing with a versatile fluid bed combo, integrating gr...
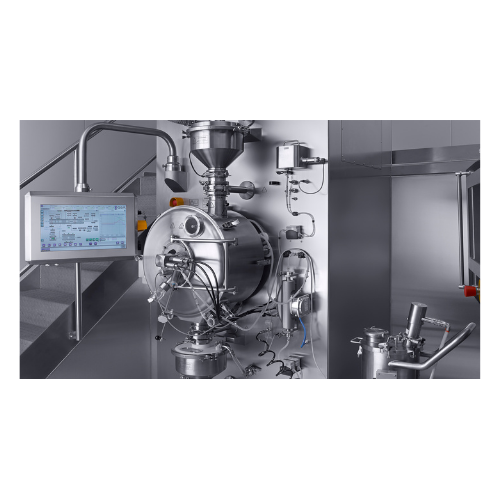
Pharmaceutical tablet coating system
Achieve precise and efficient coating of pharmaceutical tablets to enhance product sta...
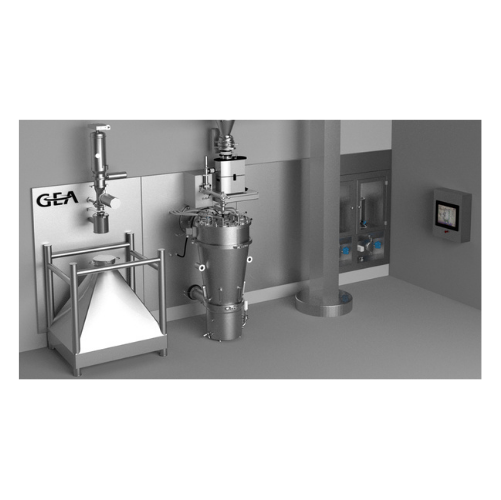
Continuous granulation and drying system for pharma production
Achieve precise control over granule quality with a conti...
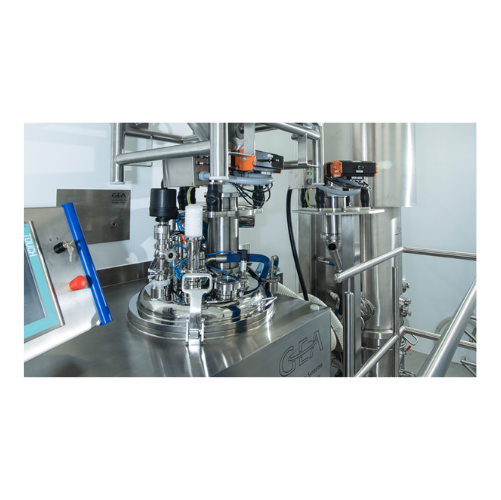
Pharmaceutical bottom-drive high shear granulator
Achieve optimal granule uniformity and precise control over moisture le...
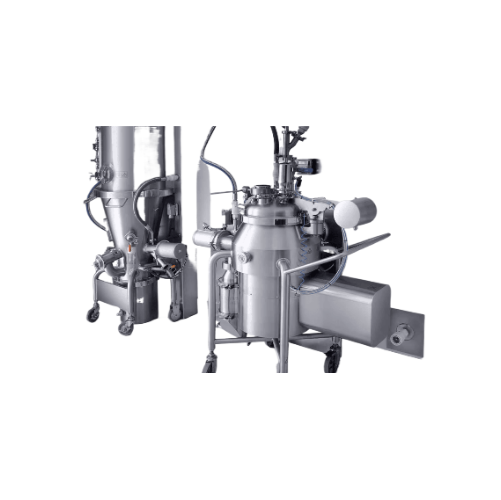
Integrated small-scale granulation and drying system
Ensure precise granule size and moisture control for enhanced tablet...
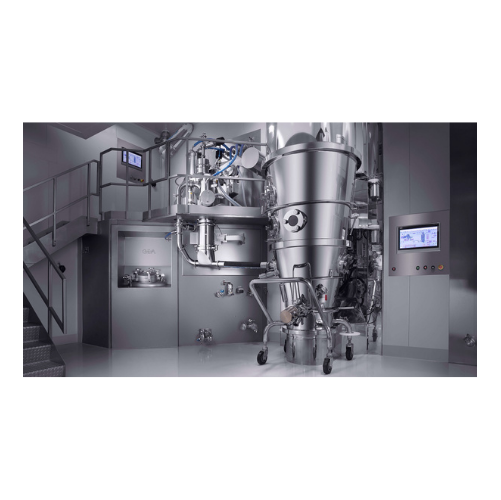
Integrated granulation and drying system for pharmaceuticals
Achieve seamless granulation and drying with our fully inte...
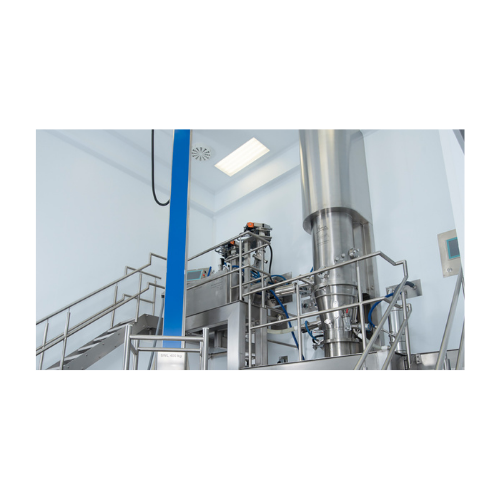
Fluid bed pellet coating solution
Achieve precise and uniform pellet coating with fluid bed technology for enhanced product...
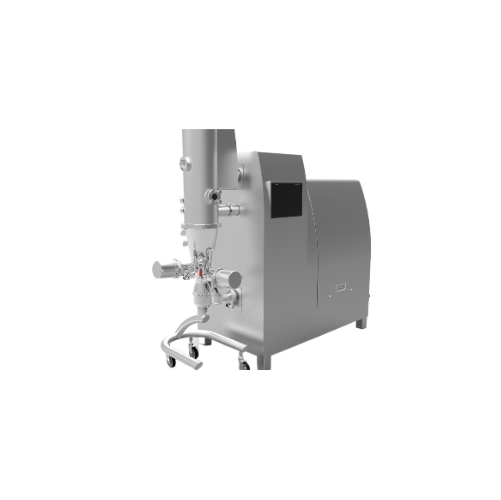
Pharmaceutical fluid bed processor for r&d
Optimize your pharmaceutical R&D with a versatile fluid bed processor desi...
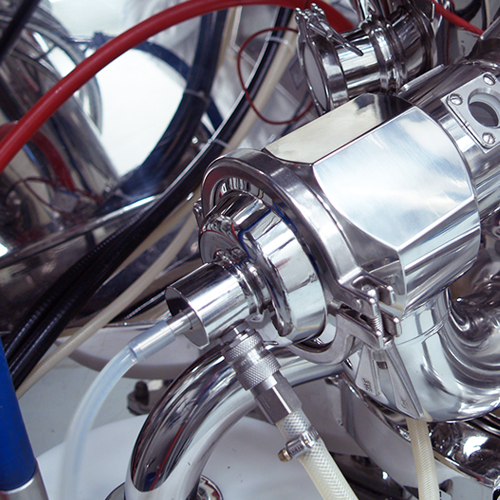
Flexstream fluid bed processor for pharmaceutical applications
Addressing the limitations of traditional fluid bed proce...
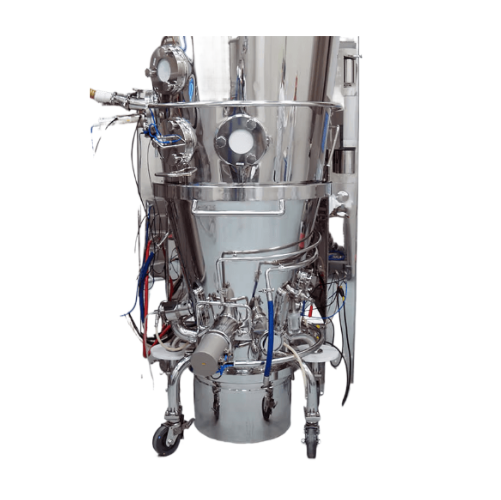
Fluid bed processing of pharmaceuticals
Enhance your pharmaceutical production with versatile fluid bed processors, enablin...
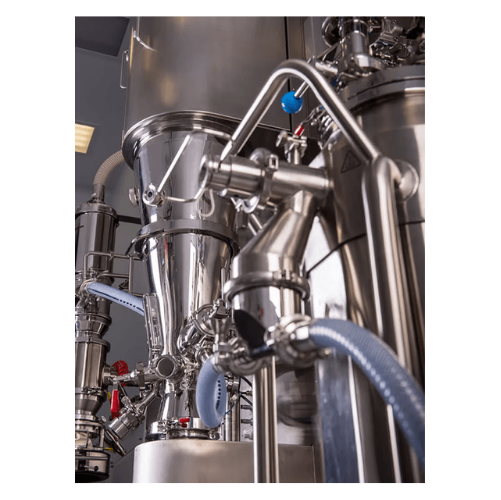
Pharmaceutical fluid bed r&d processing
Ensure precise formulation and consistency in pharmaceutical and nutraceutical tabl...
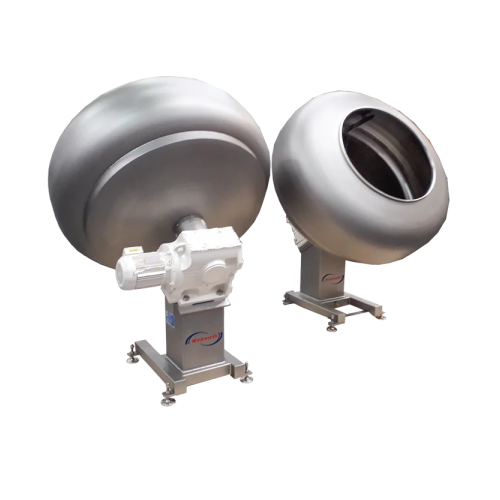
Industrial coating pans for sweets and confectionery
Ensure even and consistent coatings with high-capacity pans designed...
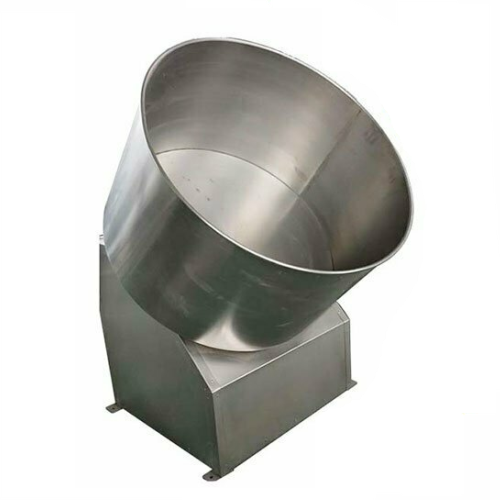
Nut coating machine for snack food processing
Enhance your snack and confectionery production with a nut coating machine t...
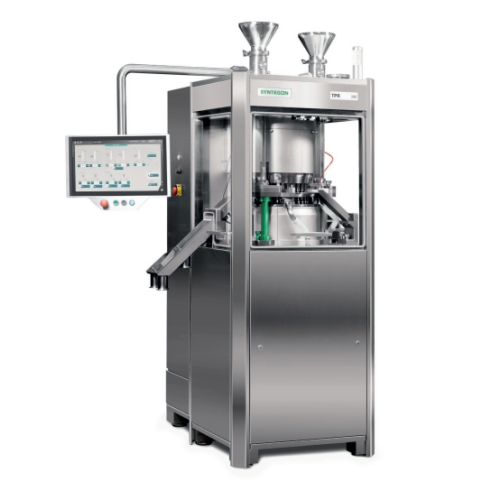
Tablet compression technology for pharmaceutical production
Enhance your production capabilities with advanced tablet co...
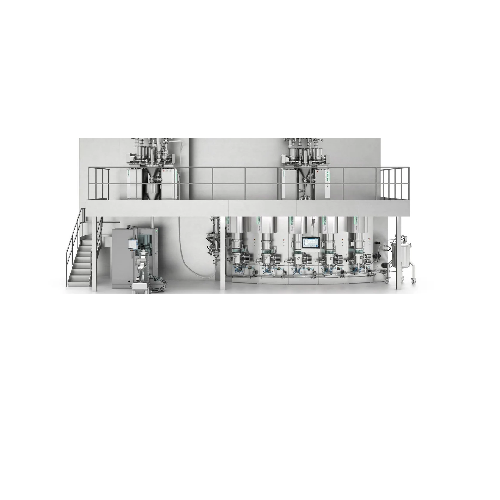
Continuous manufacturing for pharmaceuticals
Achieve precision in oral solid dosage production with seamless continuous pr...

Fluid bed processor for pharmaceutical granulation and coating
Achieve superior granulation and coating of pharmaceutica...
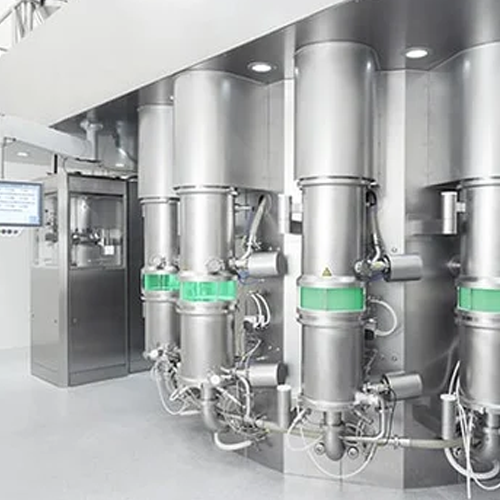
Pharma r&d equipment for solid dosage forms
Optimize your pharmaceutical production with cutting-edge equipment designed f...
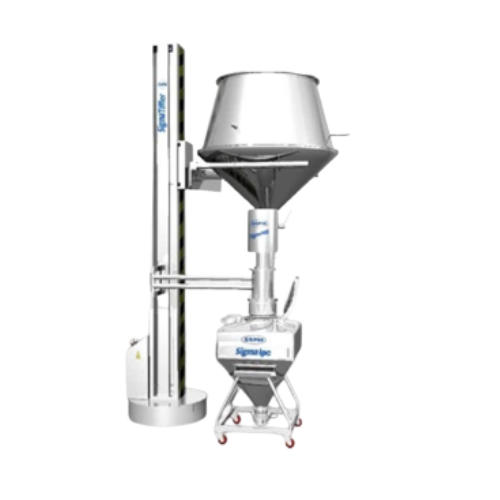
Material handling system for granules and powders
Optimize your production with seamless material handling specifically d...
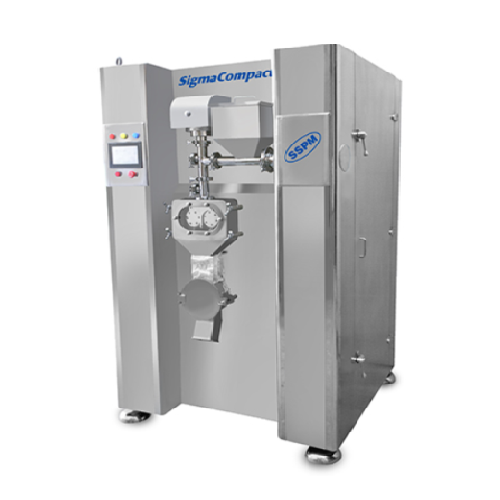
Dry granulation roll compactor
Optimize your tablet and capsule formulation by efficiently compacting and granulating powder...
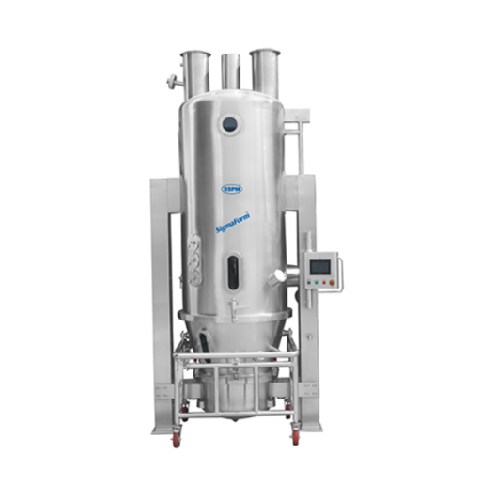
Fluid bed dryer for wet granulation in pharmaceutical industry
Streamline your production with fast, uniform drying and ...
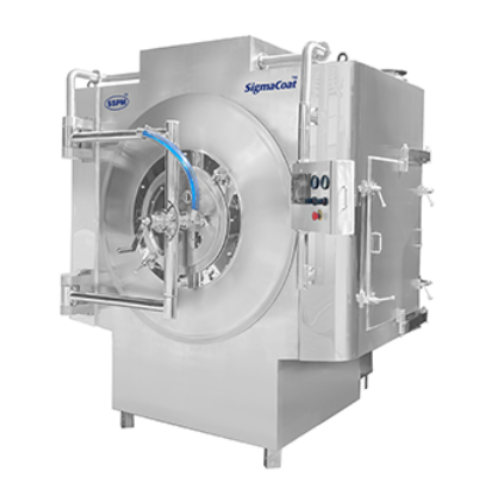
Tablet coating system
Achieve precise and uniform coating on pharmaceutical tablets with this scalable system, designed for o...
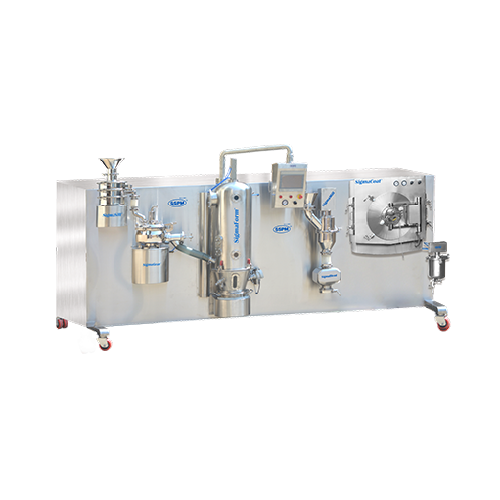
Compact wet granulation r&d system
Ensure precise formulation of pharmaceutical powders with a scalable, lab-friendly syste...
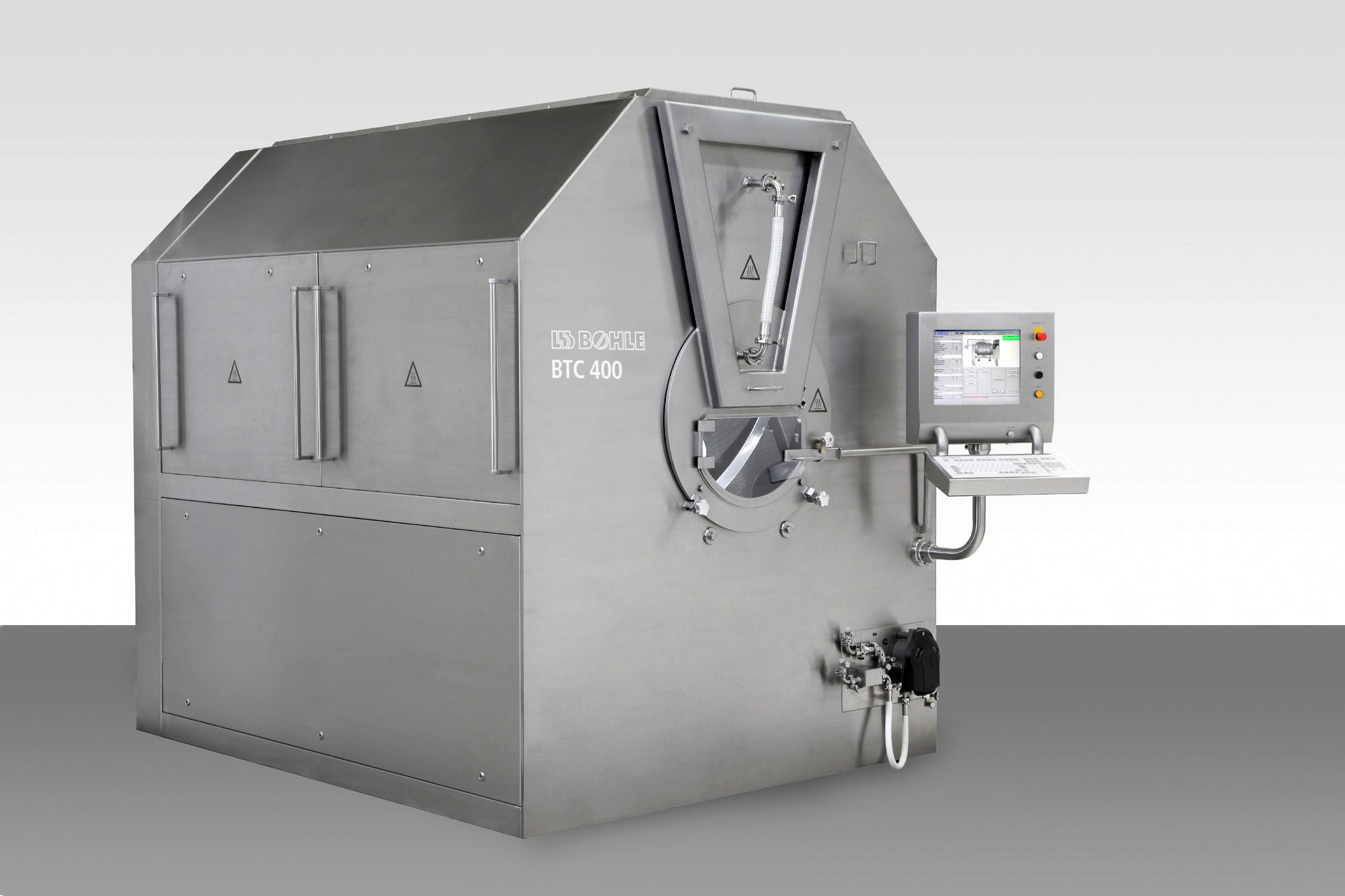
Pharmaceutical tablet coating machine
Tablet coating requires spraying, mixing, and drying procedures that must be carried ...
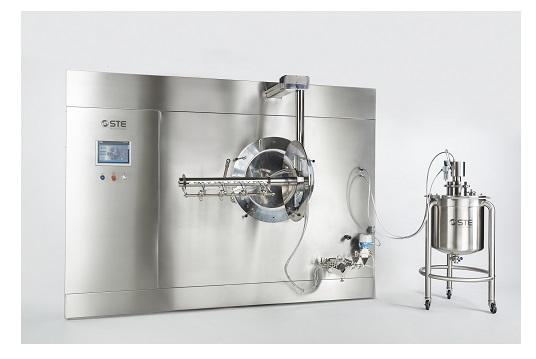
Industrial scale tablet coater
During the coating process, tablets pass many stages that can make them wet and sticky or cra...
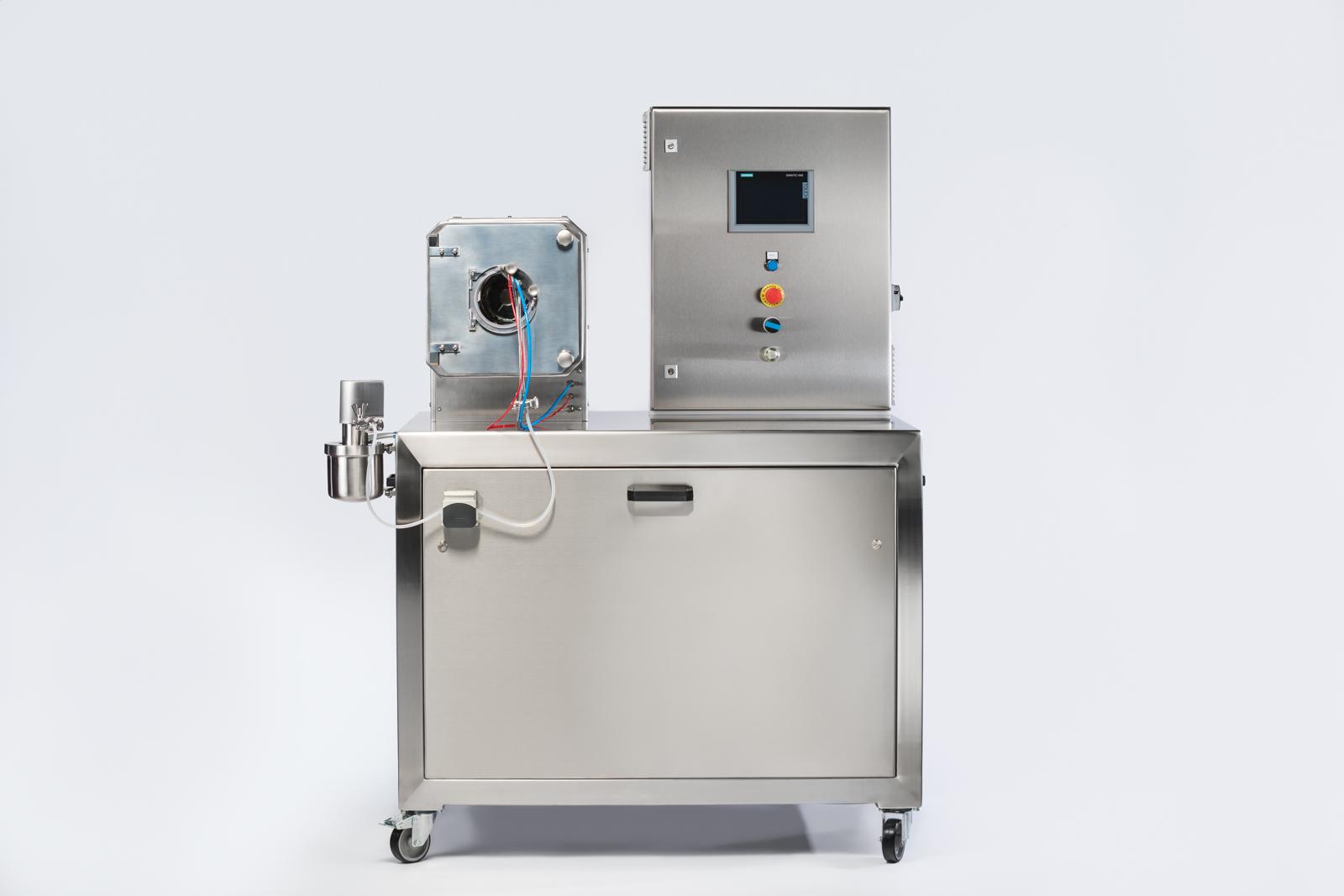
Tablet coater for laboratory scale
Tablet coating can be applied for adding colours or glosses, or based around sugar in or...
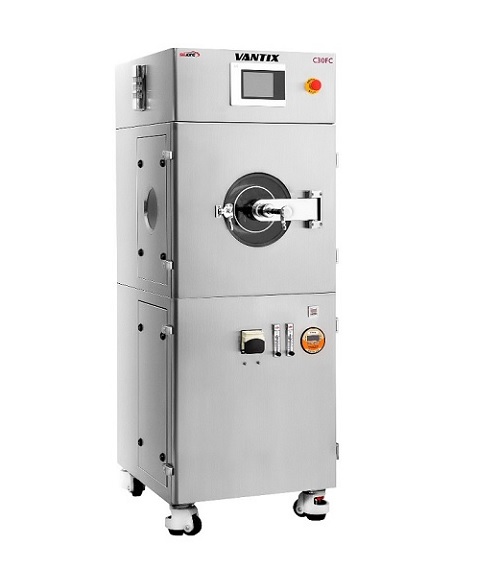
Automatic tablet coater for lab scale
The ability to coat tablets in an even and controlled way is an important stage in th...
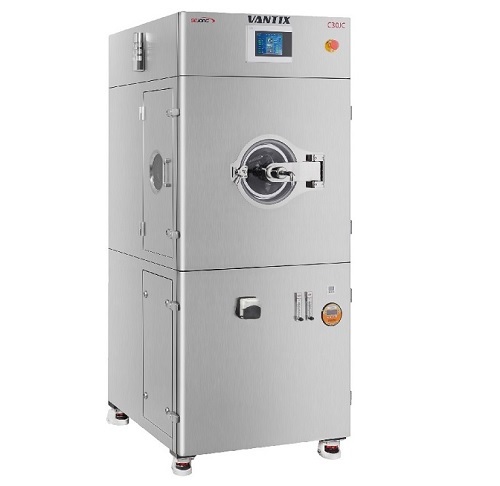
Tablet auto coater for lab scale
Many pharmaceutical doses in tablet form require a coating before they are ready for use. T...

Hygienic mixer for batch operation
Achieve consistent and precise mix quality across diverse powders and granules with this...
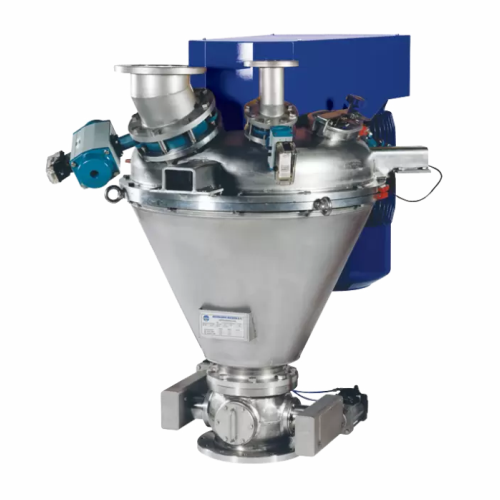
High shear impact mixer for agglomeration and dispersion
Achieve precise homogeneity and efficient agglomeration with a h...
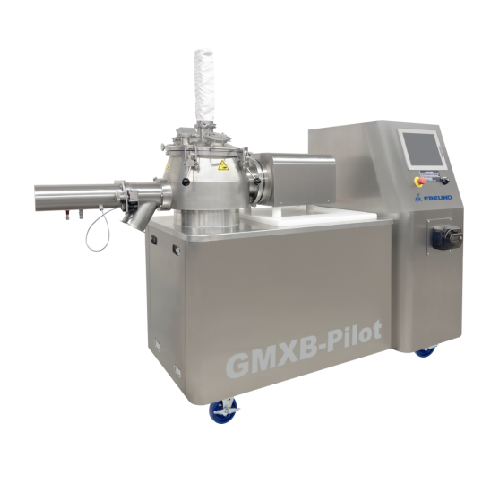
Pilot High shear granulator for wet granulation
Achieve consistent particle sizing and superior homogeneity in your powder...
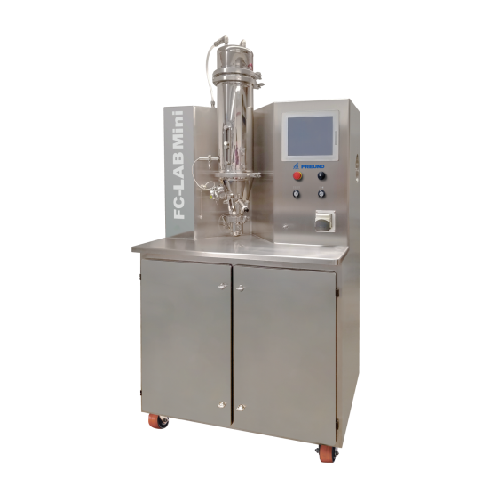
Laboratory fluid bed system for solvent processing
Optimize your laboratory scale operations with a versatile fluid bed s...
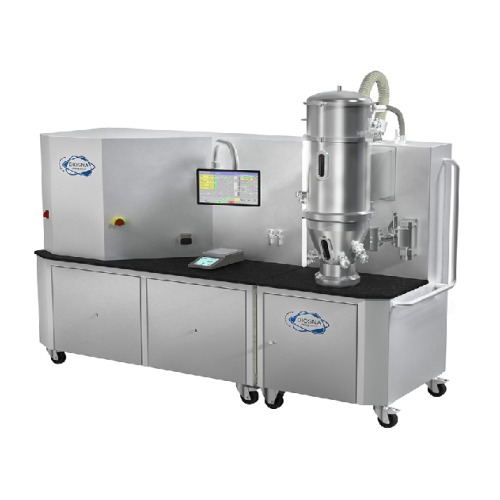
Laboratory fluid-bed dryer and tablet coater
Experience seamless transition from laboratory to production scale with a ver...
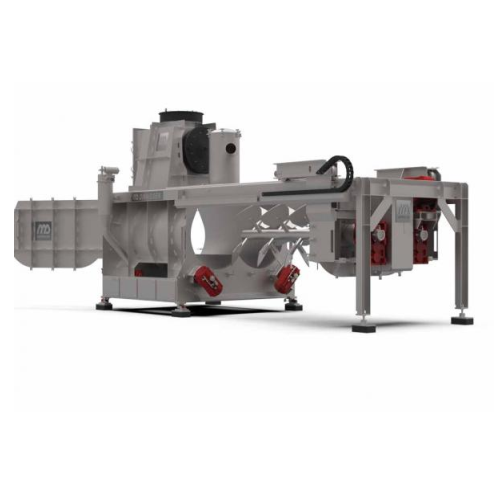
Industrial mixer for batch granules or grains
Achieve precise mixing with seamless integration of heating, sterilization, ...
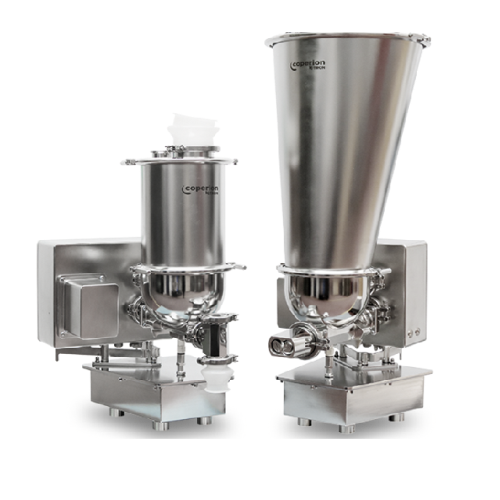
Pharmaceutical design feeders for precise ingredient handling
Achieve precise ingredient handling and seamless integrati...
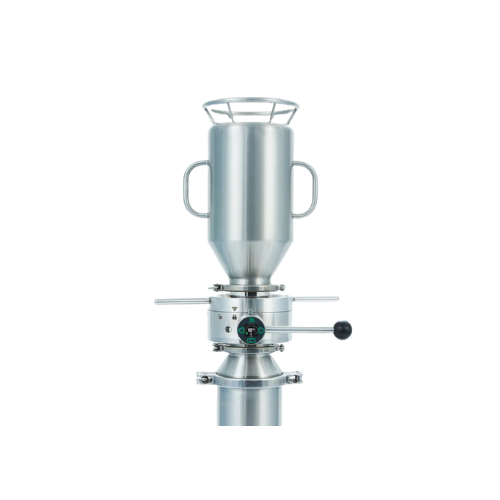
High containment powder transfer valve
Ensure high containment for potent powders in your production line, reducing contami...

High containment powder transfer valve for bulk material
Ensure operator safety and prevent cross-contamination with robu...
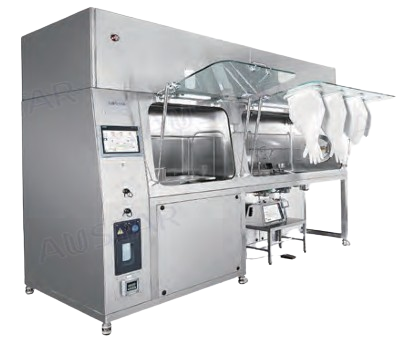
Sterilisable isolator workstation for aseptic containment
Ensure precise contamination control and sterile conditions du...
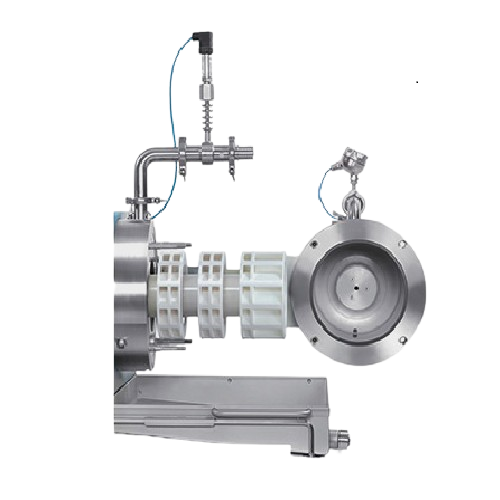
Bead mill for nano-preparation grinding
Achieve precise nano-processing and efficient wet grinding for pharmaceuticals and ...
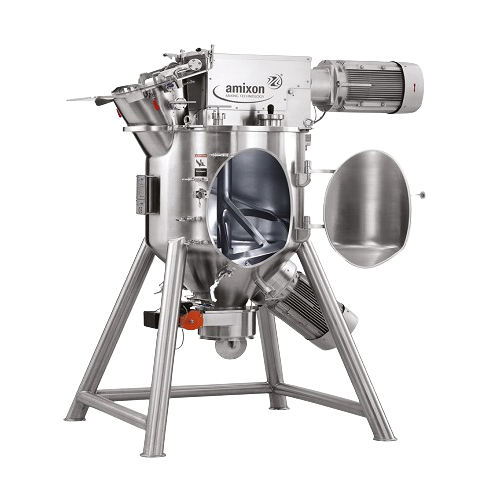
Conical mixer for dry, moist, and viscous materials
Achieve optimal mixing consistency and precision for diverse material...