Fluid bed processing of pharmaceuticals
Enhance your pharmaceutical production with versatile fluid bed processors, enabling precise blending, granulating, drying, and coating to support complex formulations and meet stringent quality standards.
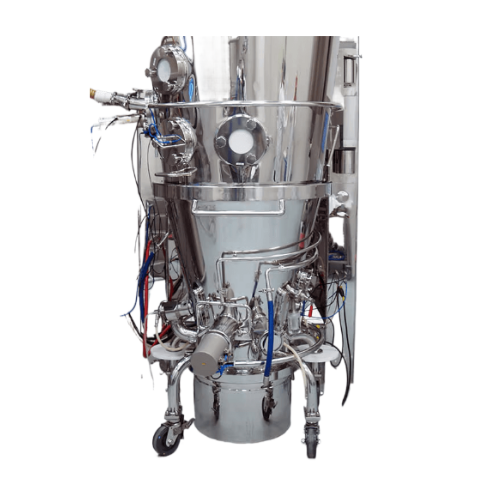
Processes and Coats Pharmaceutical Powders and Granules
The FlexStream Fluid Bed Processor from GEA combines granulation, drying, and coating in a single, versatile system designed specifically for pharmaceutical applications. Known for its precision and efficiency, it performs multi-step processing from a single unit, enhancing production flexibility and reducing equipment footprint. This processor is particularly suited for creating effervescent tablets, vitamin granules, and enteric-coated pellets. It operates in batch, continuous, pilot, and industrial-size modes, accommodating a range of production scales. The FlexStream integrates easily into existing systems, featuring PLC control with options for automated FDA-compliant monitoring. The unique nozzle design eliminates over-wetting without needing compressed air, boosting yield and lowering energy use. Available in various material options, it meets cGMP conditions while offering easy cleaning and maintenance solutions, including CIP. Its modular construction allows customization, ensuring it fits specific needs for pharmaceutical manufacturers, R&D departments, and CMOs.
Benefits
- Enhances production flexibility by integrating multiple processes in one unit.
- Minimizes operational costs with efficient energy use and reduced need for compressed air.
- Achieves consistent product quality with in-line particle growth measurement and PAT compliance.
- Streamlines cleaning and maintenance with integrated CIP system.
- Ensures compliance with cGMP and FDA standards for pharmaceutical manufacturing.
- Applications
- Pharmaceutical tablets, Nutraceuticals, Pharmaceutical powder, Coating materials, Pharmaceuticals
- End products
- Ibuprofen tablets, Gelatin capsules, Vitamin c granules, Enteric-coated pellets, Herbal extract capsules, Coated aspirin tablets, Multivitamin powder blend, Effervescent tablets, Nutritional supplement tablets, Anti-caking powder for tablets
- Steps before
- Mixing, Blending, Purification
- Steps after
- Coating, Tablet Pressing, Packing
- Input ingredients
- pharmaceutical compounds, liquid droplets, suspensions, solutions, inert core, active material
- Output ingredients
- blended materials, granules, pellets, coated particles, free-flowing granulates, dry granules
- Market info
- GEA is known for its expertise in engineering innovative and sustainable equipment and solutions, focusing on sectors such as food, beverages, pharmaceuticals, and energy, with a reputation for quality, efficiency, and advanced technological applications in industrial processing.
- Air Speed
- 1–20 m/s
- Automation
- PLC-controlled
- Batch size
- 25-1800 L
- Capacity
- Small to industrial-size
- Cycle Time
- Very short processing times
- Drying Time
- Rapid
- Granulation process
- High velocity air stream
- Humidity
- Low in holding area
- Inlet Air Preparation
- Filter and conditioning units
- Process Control
- FDA-compliant
- Product container
- Single for all operations
- Spray Nozzle Position
- Side walls
- Temperature control
- Granulation and drying
- Type
- Fluid Bed Processor
- Working Mechanism
- Fluid bed technology
- Integrated Steps
- Granulation, drying, pellet coating
- Batch vs. Continuous Operation
- Batch production
- Automation Level
- PLC / SCADA
- CIP/SIP
- CIP 121°C / SIP 135°C
- Energy Efficiency
- High, comparative
- Process Monitoring
- Online (PAT) analyzers
- Changeover Time
- Reduced downtime
- Containment Level
- High containment, GMP compliant
- Density/particle size
- 0.5–2.5 g/cm³ / 50–1000 µm
- Granulation type
- Fluid Bed Granulation
- Coating method
- Top Spray / Precision Coating
- Pelletizing method
- Precision Layering
- Drying method
- Fluid Bed Drying
- Batch production conditions
- cGMP
- Blending method
- Fluid Bed Blending
- Containment level
- High Containment
- Process flexibility
- Single Unit Operations
- Formulation stage
- Clinical Development and Full-Scale Manufacture
- Spraying system
- Spray Dryer Granulator
- GMP Compliance
- Yes
- FDA Compliance
- Yes
- FDA Materials
- Yes
- CGMP Conditions
- Yes
- CE marking
- Yes
- Machine footprint
- Compact
- Configuration
- Modular
- Height
- Reduced
- Width
- Reduced
- Design
- Single product container
- Process integration
- Granulation, drying, coating in one
- Nozzle Position
- Side wall mounted
- Air flow design
- Pneumatic particle control
- Control panel type
- PLC and PC-based
- Process monitoring integration
- Online PAT analyzers
- Dryer configuration
- Standardized modular design
- Spray nozzle position
- Mounted in side walls
- Inlet air preparation unit
- Multiple filter options
- Spraying systems
- Nozzles and pumps per process needs
- Product discharge method
- Pneumatic or gravity-based
- Containment techniques
- Buck® MC Valve and Hicoflex® interfaces