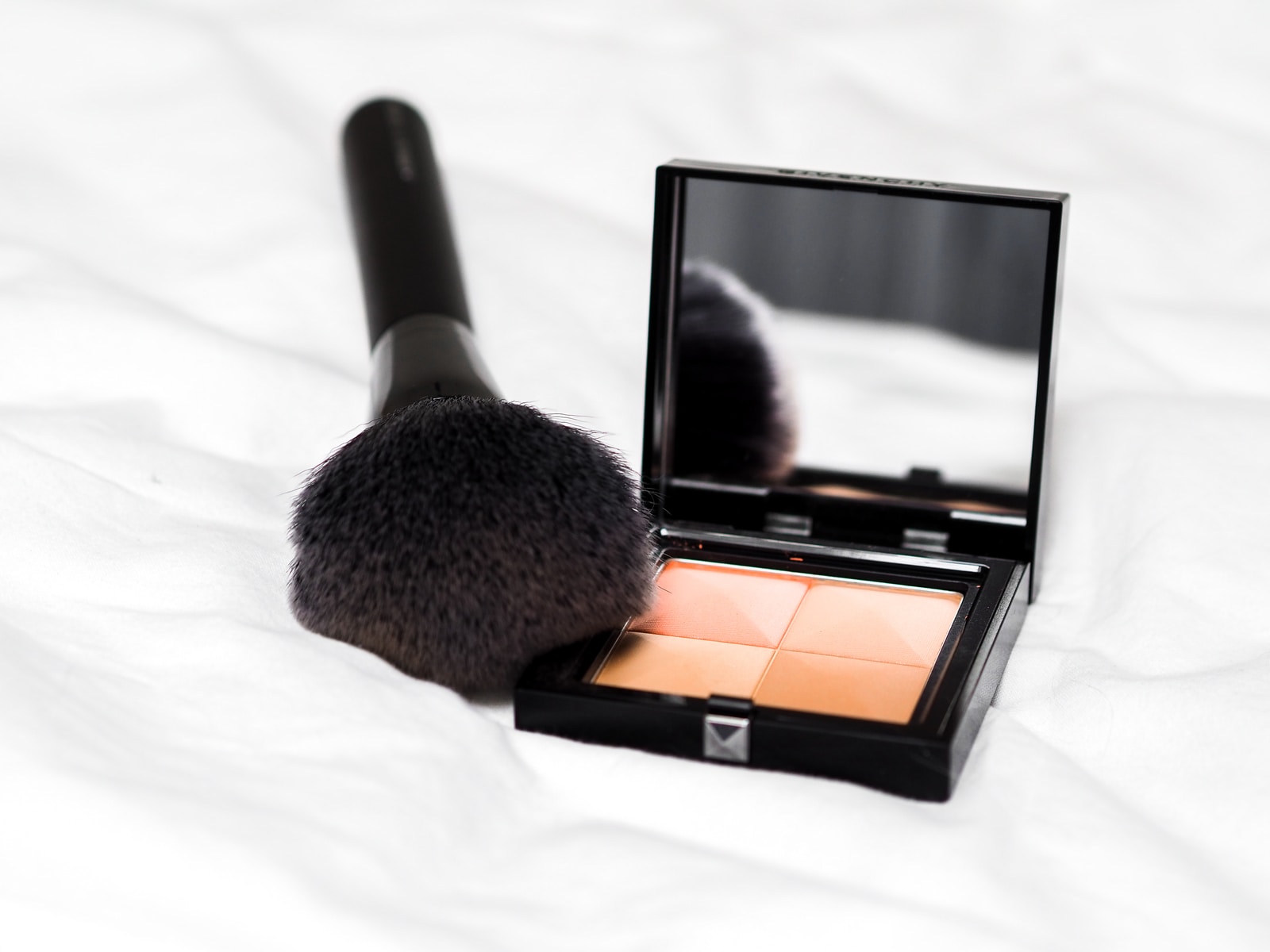
Making Face Powder
Find innovative production technology for making face powder and connect directly with world-leading specialists
Looking beautiful is hard work. Queen Elizabeth I knows this well. Just think she used so many cosmetics and makeup containing toxic materials, especially lead-based face powder, that she even died from them. Today fortunately, you no longer need lead to make face powder. Simply mix pigments, fillers, dry and wet binders, and compress the mixture using a powder compacting press. Then the face powder is ready to be applied using a powder puff.
Select your face powder process
Tell us about your production challenge
Face powder formulation – breaking it down to its ingredients
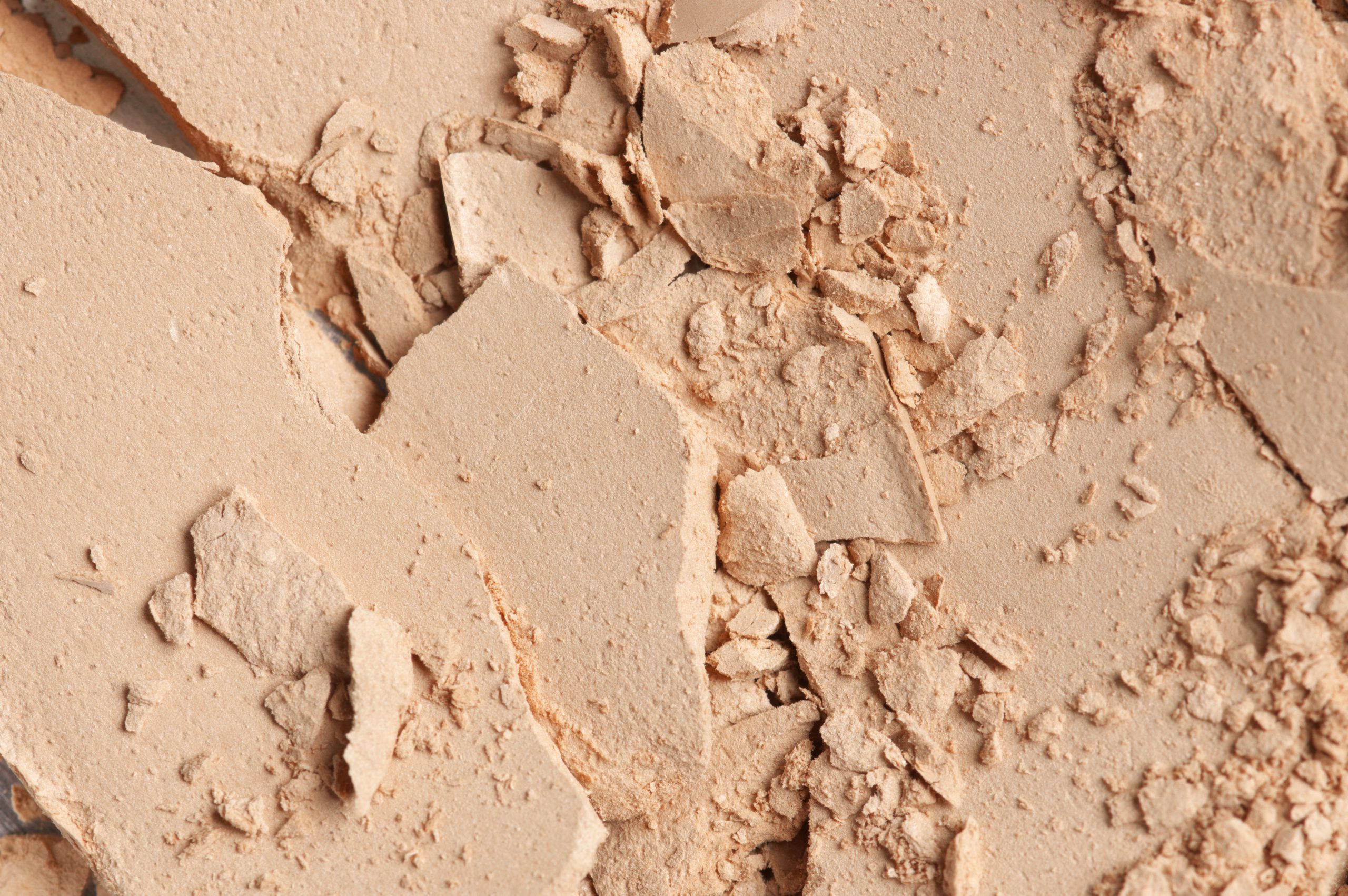
Face powder, like most makeup products, are used to mask minor imperfections visible on your skin (as Queen Elisabeth I did for smallpox scars – don’t follow her example) and to make the face skin glow. For the powder to do its job, it must have four properties: covering power, absorption, adhesiveness, and slip. Covering power can cover imperfections or blemishes and natural oil from the face. The amount of coverage needed varies from woman to woman; that’s why face powders are produced in different grades (light, medium, and heavy). Common ingredients used for it are zinc oxide, kaolin and magnesium oxide, but titanium dioxide is considered to have the best covering power.
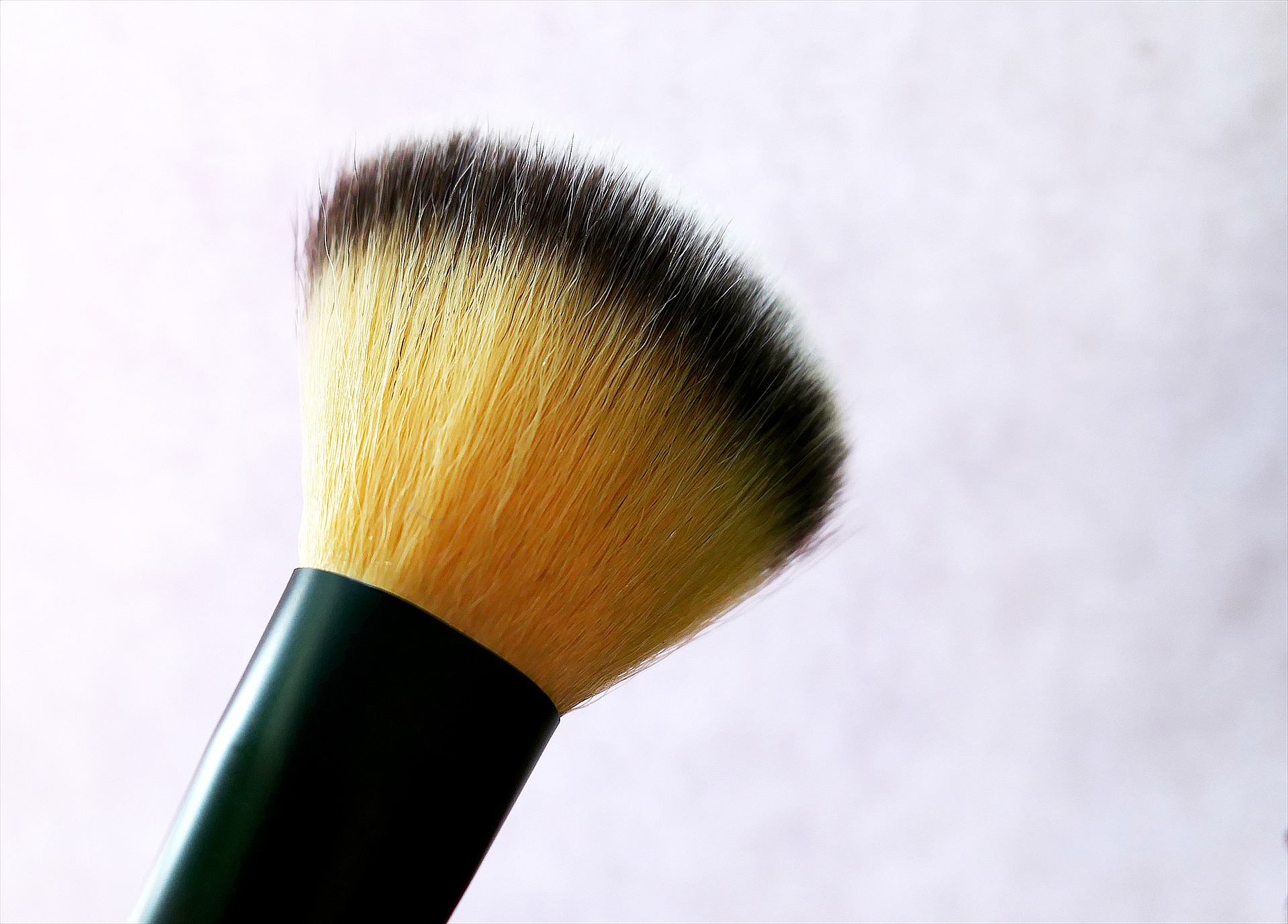
Absorption property refers to the capacity of the powder to absorb sweat and oil. Kaolin, magnesium carbonate, starch, and calcium carbonate are used for this property. Adhesiveness is about how well the powder sticks to the skin. Magnesium, zinc or aluminum stearates are commonly used to keep the powder in place. Slip is a property that enables a powder to be easily applied to the skin. Talc or magnesium silicate has excellent slip properties.
Loose powders or pressed powders?
First things first. Let’s talk about the main difference in the formula. Pressed face powders contain more binders than loose powders to hold the formula together in the compact. This also means that pressed powders adhere better to the skin so you can have better durability. During the process, though, pay attention to balancing the amount of binders you use to avoid glazing in your product or flaking out of the product.
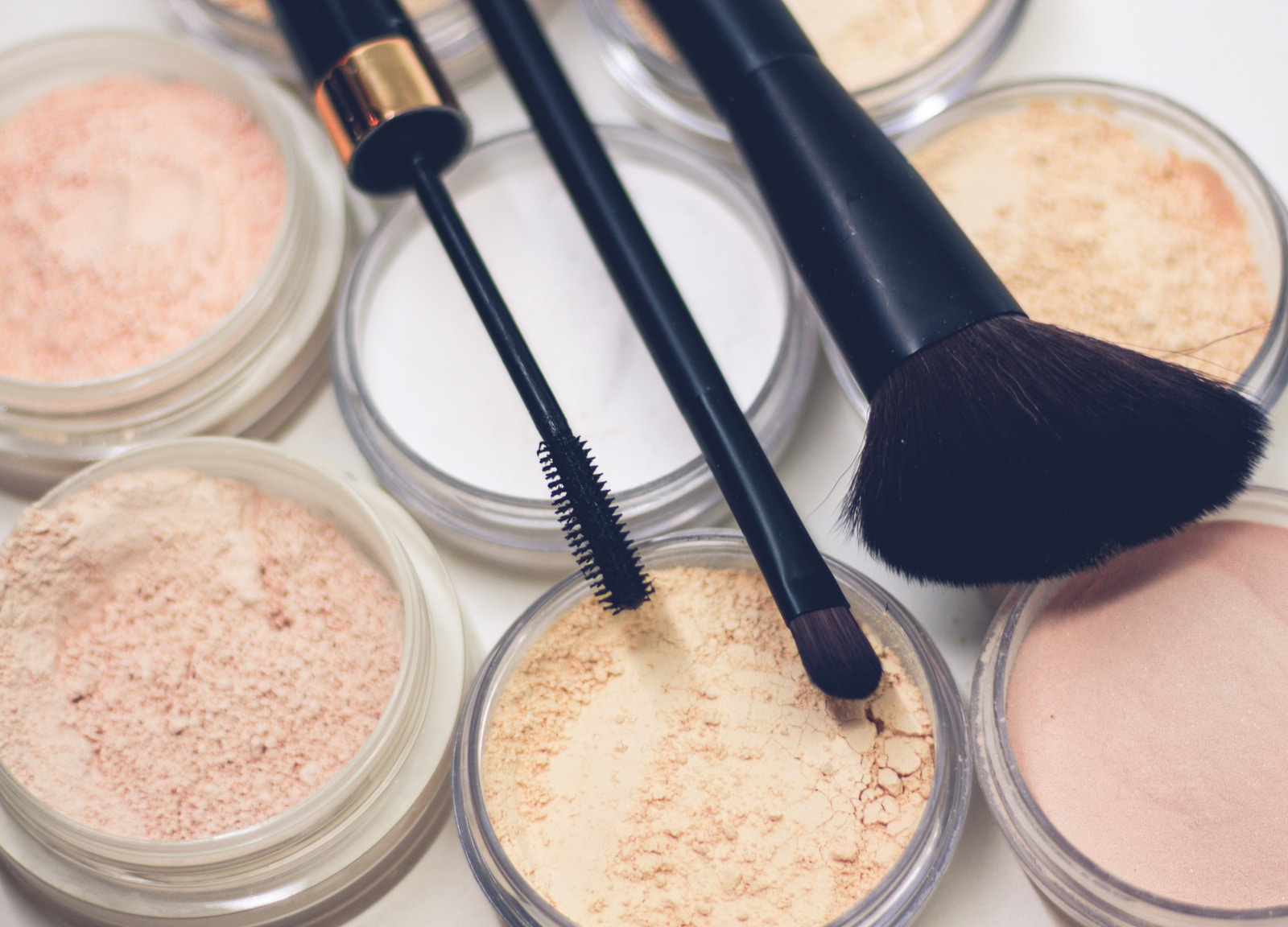
These problems can also recur if you don’t balance the amount of oil you use. The oil must also be mixed evenly using a ribbon blender; if you don’t mix it homogeneously, there is also a risk of having oily clumps in the final pressed powder.
The particles in pressed powders are larger than the ones in loose powders. With small particles, loose powders have a fine texture and can be made in translucent or colored form. Loose powders are usually packed in jars.
Powder compacting press for a compact packaging
Formula is not the only thing that matters when making pressed face powder. The pressure you use to press is also significant and needs to match with the size of the godet you are pressing into. The face powder is compressed by a powder compacting press and when the process is done right, it gives a durable compaction quality.
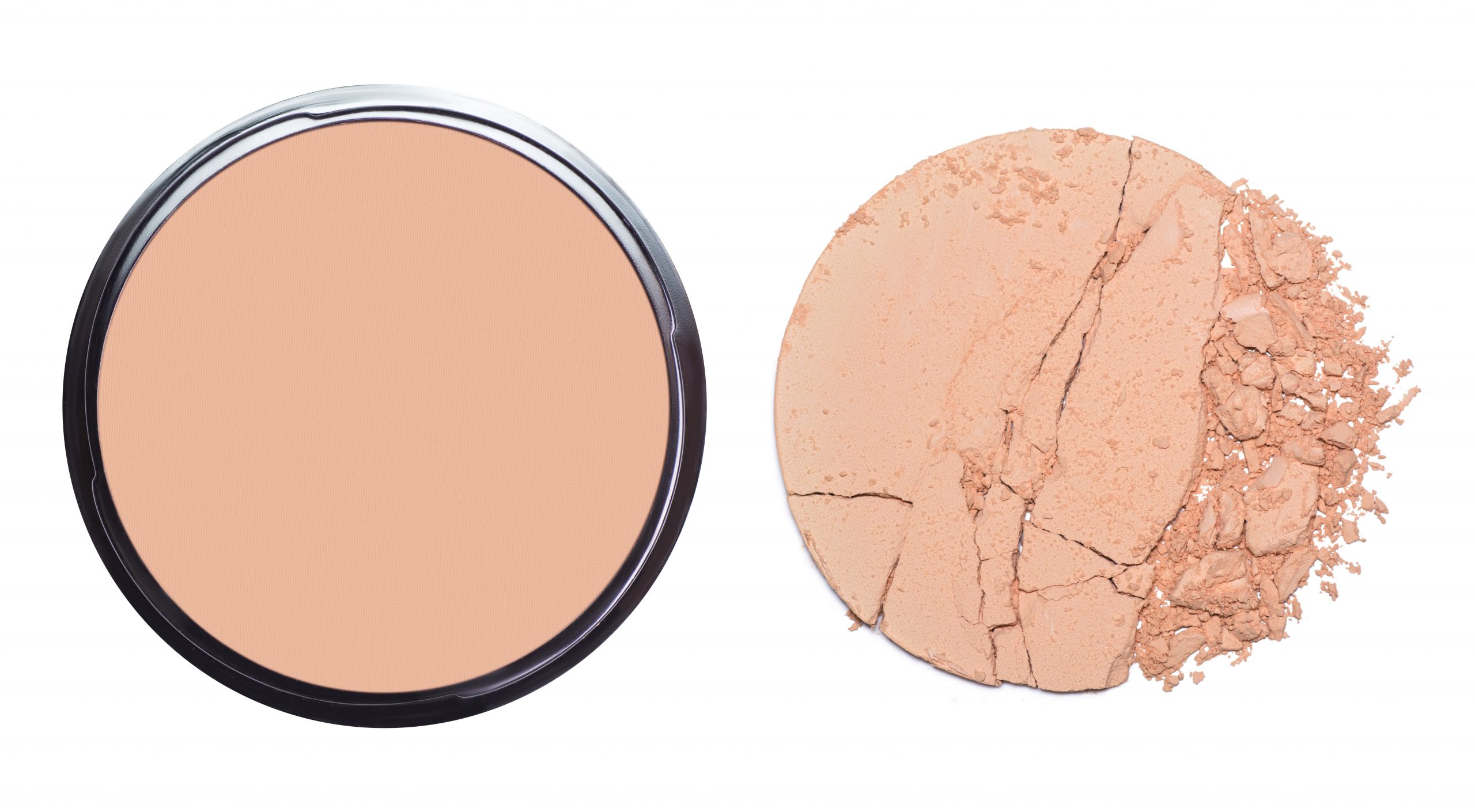
If formula and pressure don’t match the godet’s size, the product won’t fit properly into the godet or will come out during application. A drop test can be performed using a drop tester to check the compaction’s quality and make sure that the contents do not easily break during the transportation of the product.
Processing steps involved in face powder making
Which face powder technology do you need?
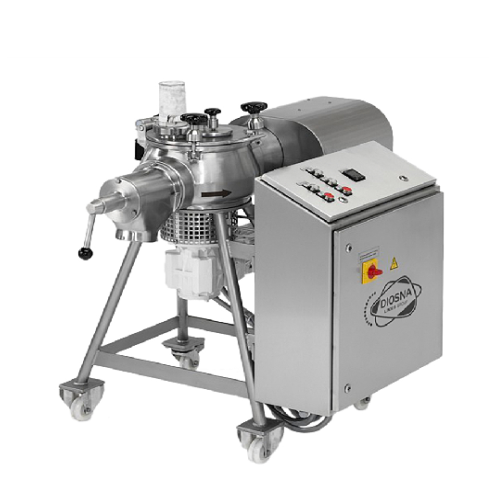
Versatile entry-level mixer granulator
Solve complex mixing and granulating challenges with this compact solution, offering...
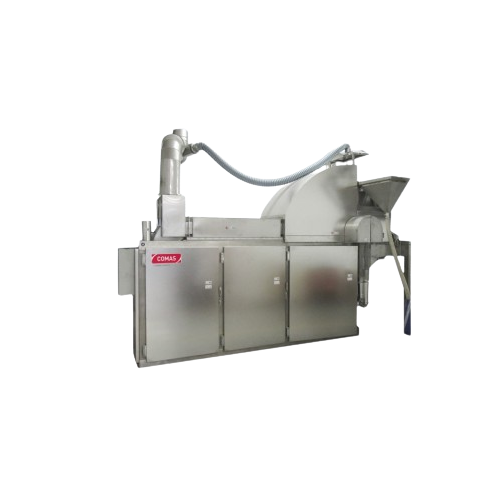
Drying solution for cosmetic slurries
Streamline the drying process of cosmetic slurries with precision control to achieve ...
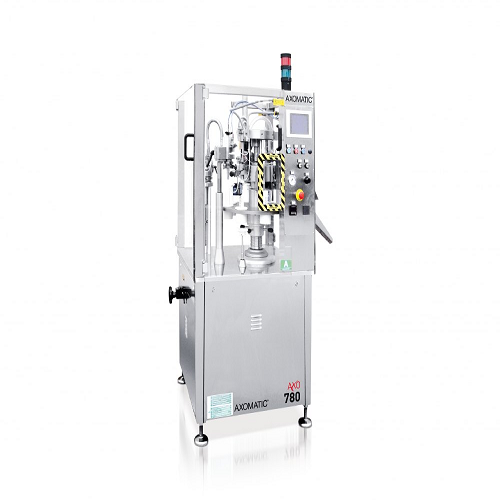
Semi-automatic tube filling and closing system
Achieve precise filling and secure closing for diverse tube types, optimizi...
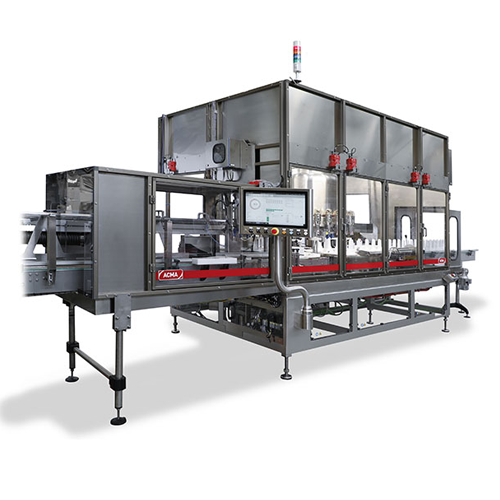
Rotary filler capper for personal care products
Ensure consistent filling and capping of liquid products with high-speed p...
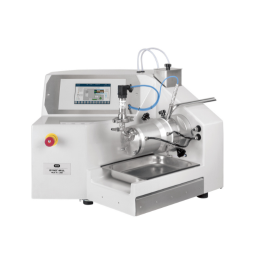
Flexible R&D wet agitator mill for cosmetics
Using nanoparticles in cosmetics requires precise control over material break...

Manual cosmetic powder press
The design, manufacture and testing of new cosmetic powder products require a small-scale press...
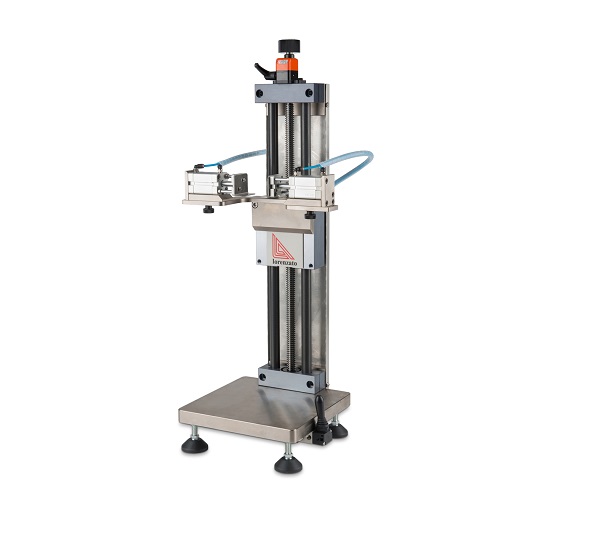
Drop tester for compacted powders
A key requirement for cosmetic compressed powder products is that they maintain their com...
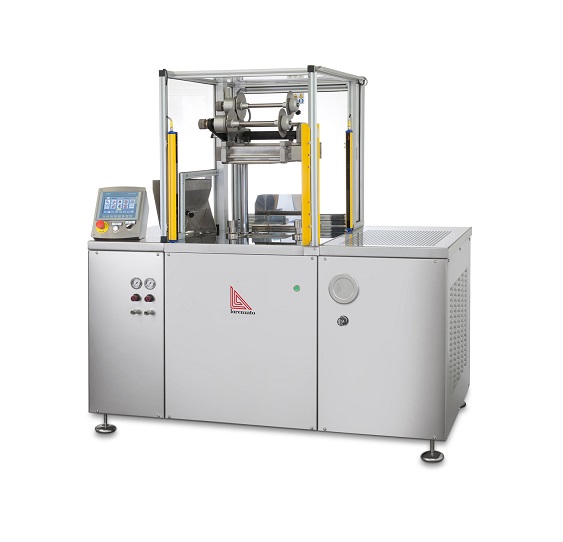
Makeup blusher compacting machine
When producing high-quality compressed powder cosmetics, control of the pressing process ...
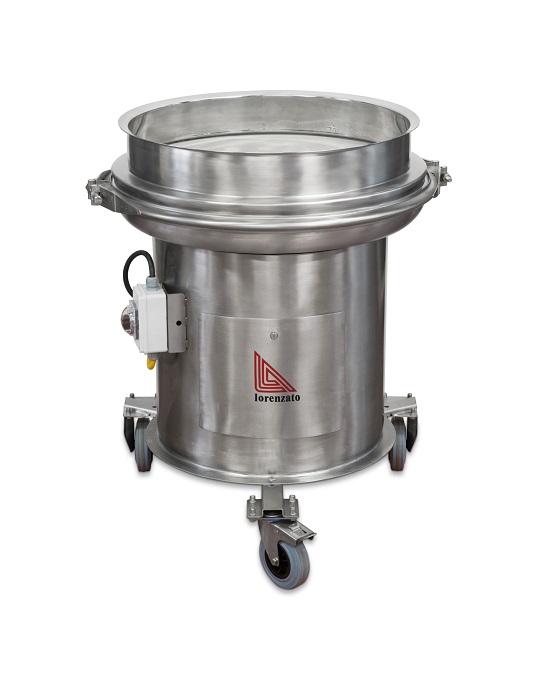
Vibrating screen for cosmetic powders
Dense or viscous compounds can be difficult to prepare for use in cosmetic products. ...
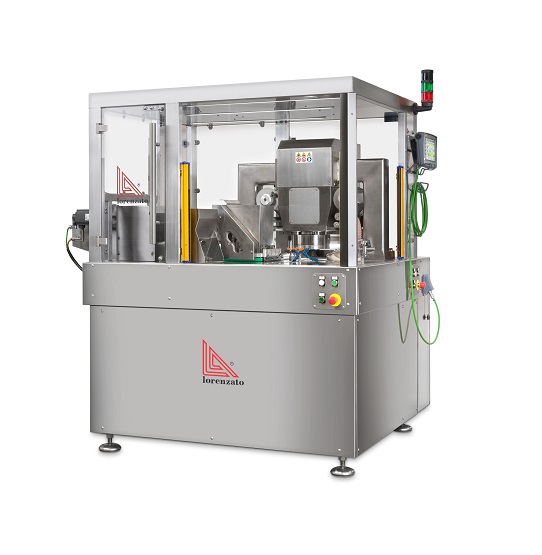
Cosmetic powder pressing machine
For the medium and large-scale production of compressed powder cosmetics, a fully-automatic...
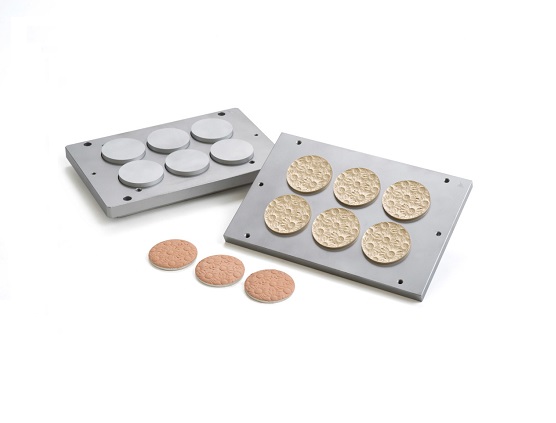
Powder pressing mould
Traditional powder pressing moulds are based on plain shapes or basic designs. In order to differentiat...
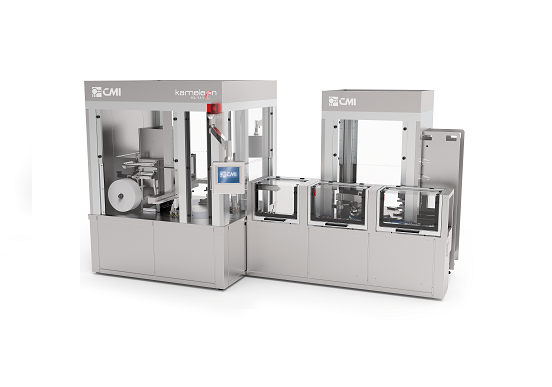
Compact powder pressing machine
Pressed powder products are extremely popular in cosmetics, but their production has challen...