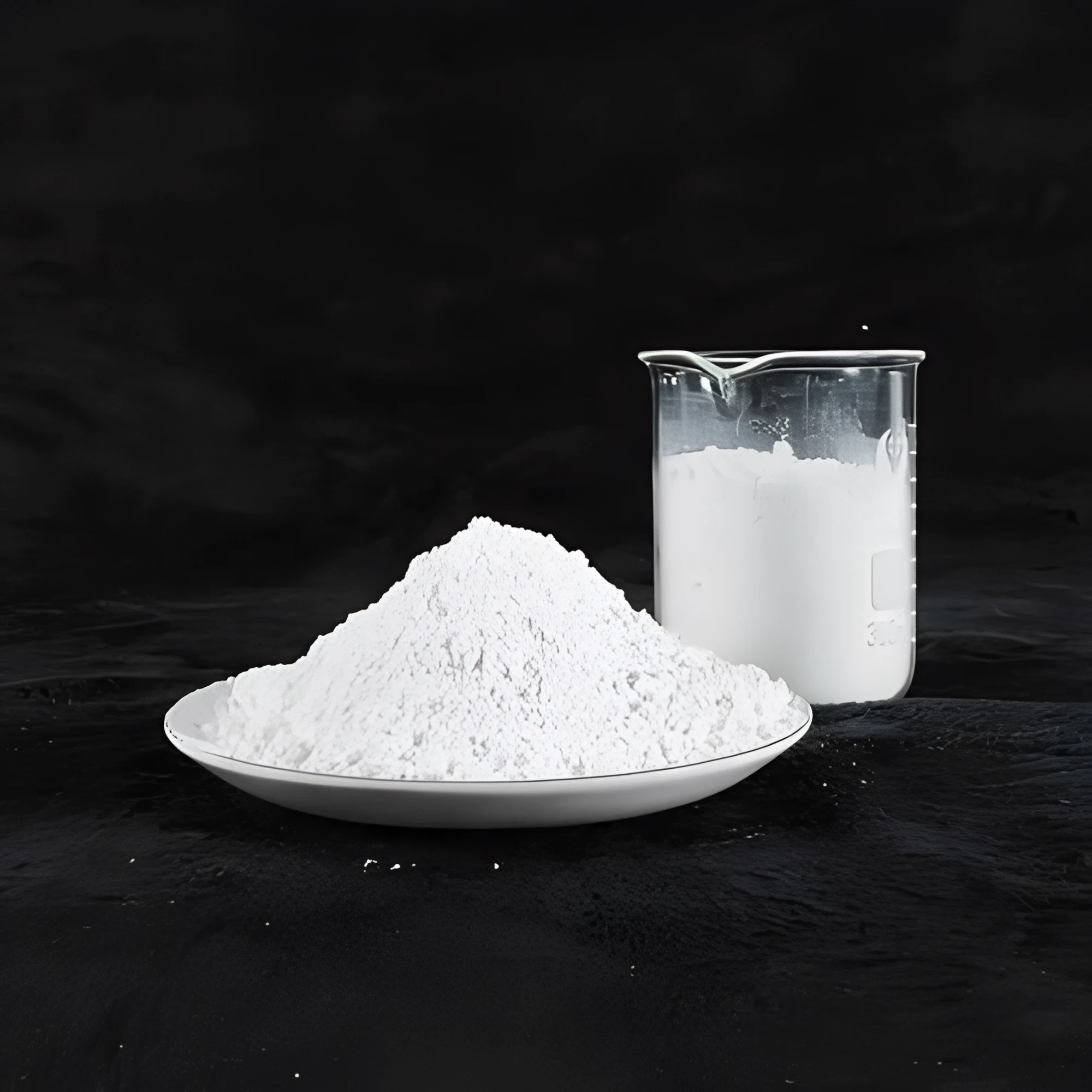
Calcium carbonate (gcc)
Find innovative production technology for making calcium carbonate (gcc) and connect directly with world-leading specialists
Let's navigate the complex world of engineered-to-order production technology together. Whether you're building a new process or optimizing an existing line, our platform connects you directly to the experts who can help. Use our curated catalogue to dive straight into the technologies that match your production goals. We continuously map out how production technology from suppliers around the world can help solve real production challenges. If you find something interesting, we introduce you directly to the specialists who know how to implement it. With more than 600 trusted machine manufacturers and over 20.000 technical experts in our network, you’re never far from the answers you need.
Tell us about your production challenge
Which calcium carbonate (gcc) technology do you need?
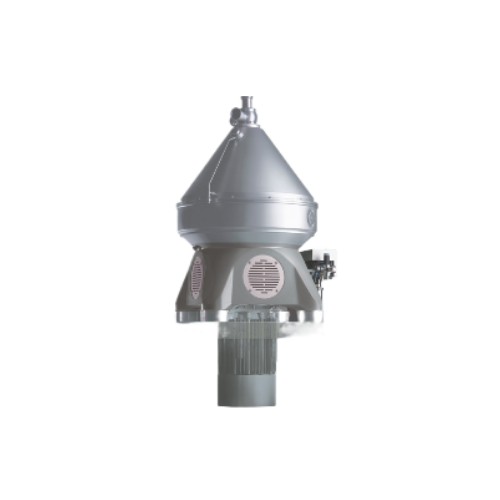
Centrifugal separator for chemicals and minerals
Achieve precise separation of liquids and slurries with this high-speed c...
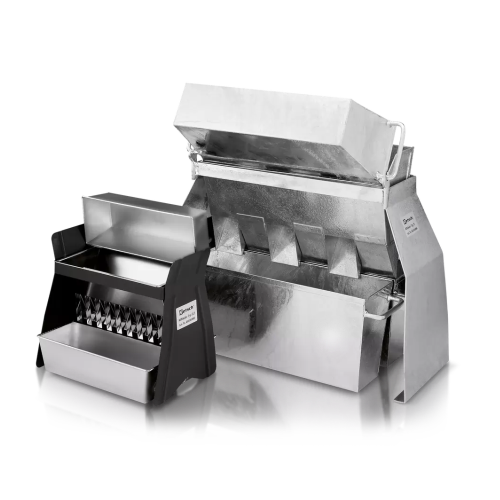
Sample divider for on-site reduction of bulk materials
Ensure consistent sample analysis with precise on-site material di...
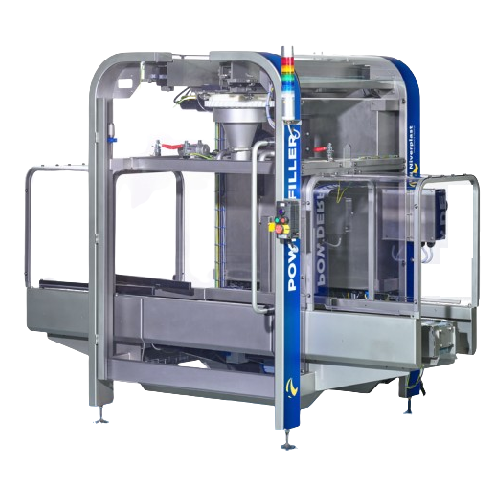
Accurate powder filling solution
When precision is paramount, this solution offers exceptional accuracy, filling powders up ...
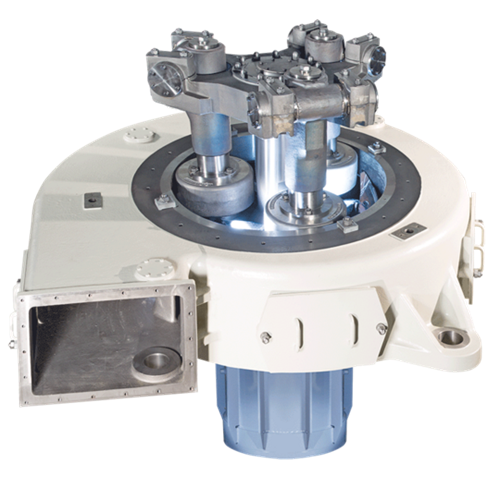
Pendulum mill for fine grinding and drying
Achieve efficient and precise grinding for soft to medium-hard materials while ...
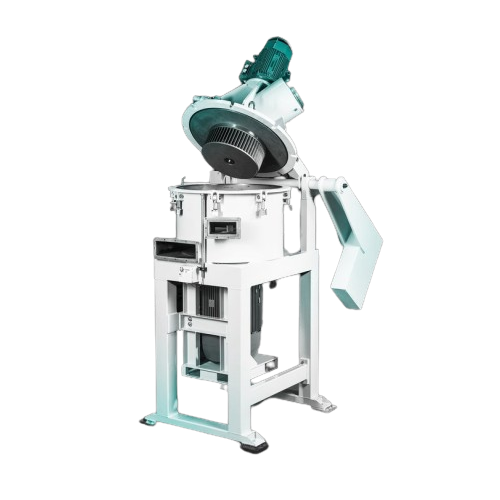
Energy-efficient impact classifier for superfine grinding
Achieve precise superfine grinding with energy efficiency, per...
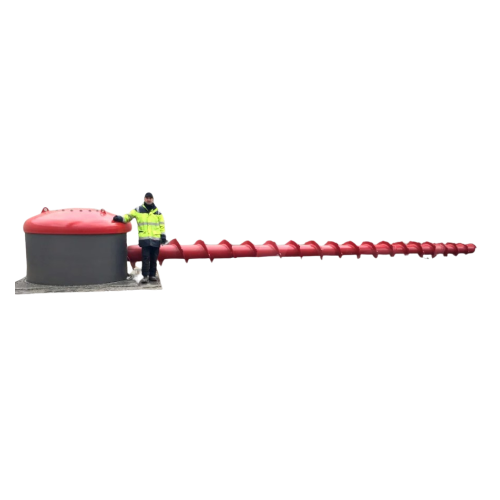
Unloader for non-free-flowing materials in flat bottom silos
Facing challenges unloading non-free-flowing materials? Thi...
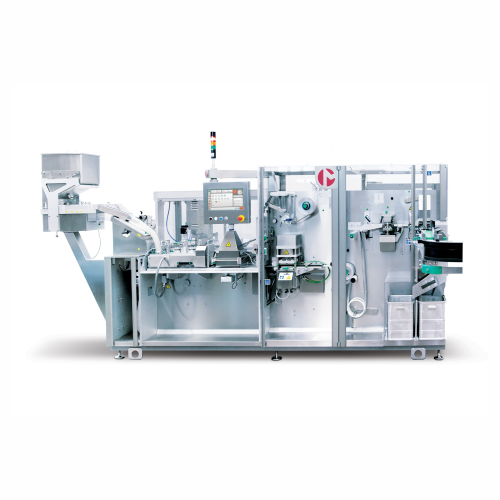
Blister thermoforming for Pvc/alu
Effortlessly mold and seal blister packs for a range of solid products, optimizing packag...
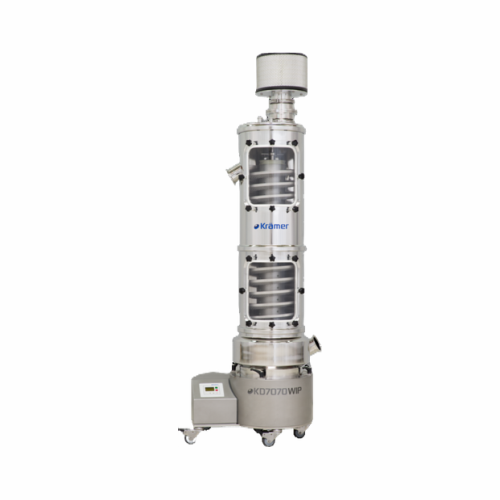
High-containment tablet dedusting solution
Ensure pharmaceutical tablets and capsules meet strict dust control and safety ...
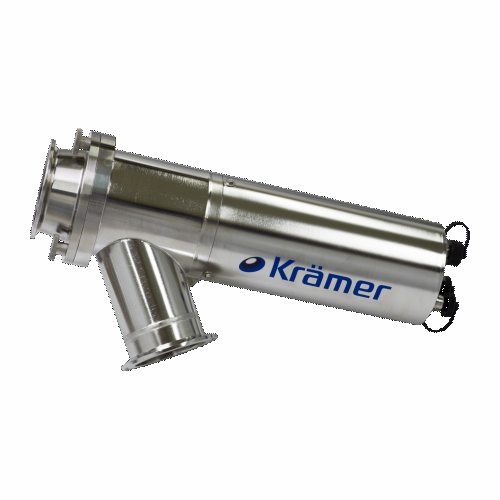
2-way diverter for tablet and capsule filling
Ensure precision in tablet and capsule filling with seamless batch switching...
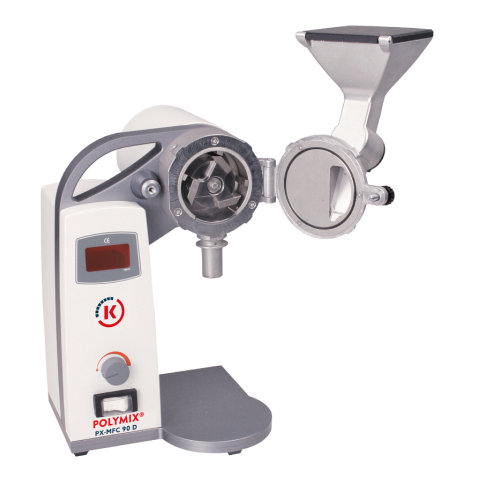
Dry sample preparation mil
Optimize your grinding processes with precision particle size reduction for various materials, en...
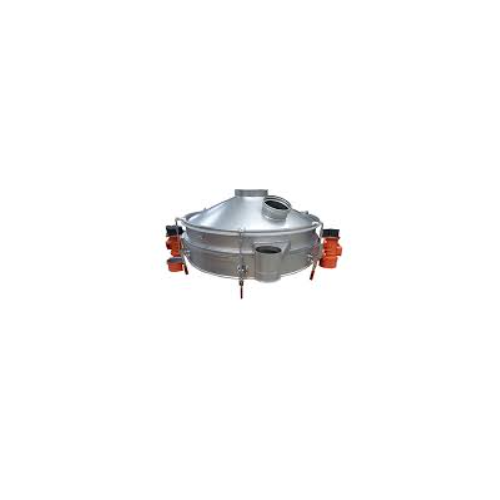
Vibrating control screeners for high volume screening and sifting
Ensure precise material separation with a solution de...
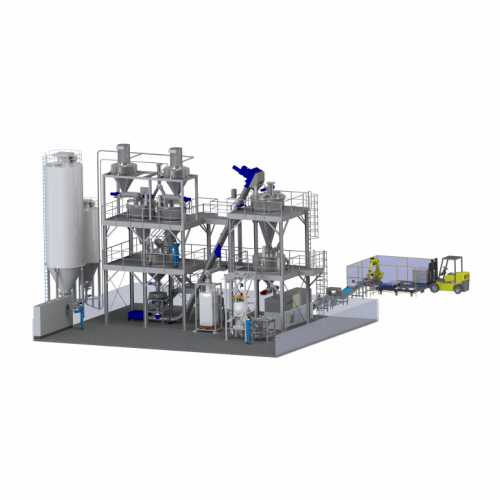
Powder mixing systems
Optimize your production line with precision powder mixing systems that ensure uniformity, enhance prod...
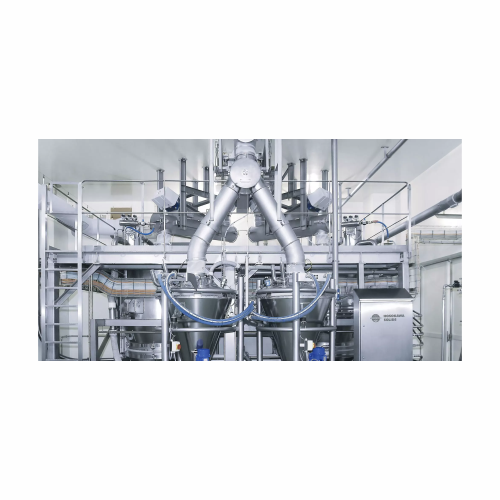
Pneumatic conveying system for bulk material handling
Efficiently transport bulk materials with precision through pneumat...

Table roller mills for mineral raw material comminution
Achieve precise mineral raw material comminution and energy-effic...
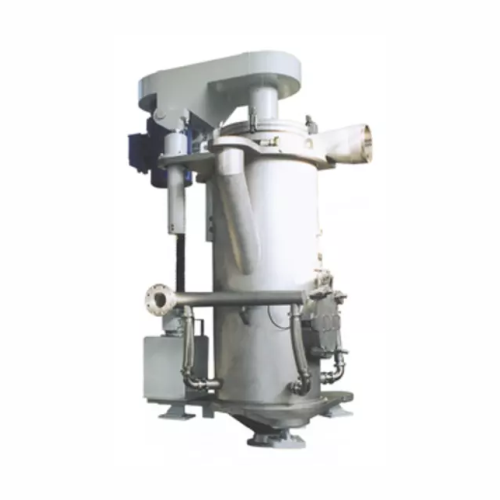
Jet mill for toner and pigment industries
Optimize particle size and distribution for high-demand applications with this h...
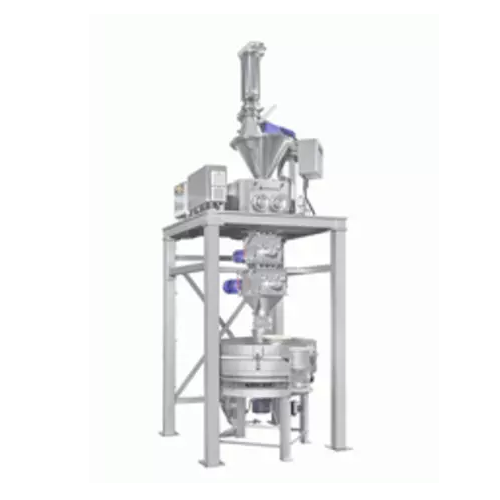
Roller press for fine-grained material compaction
Achieve optimal density and stability in your solid press agglomerates ...
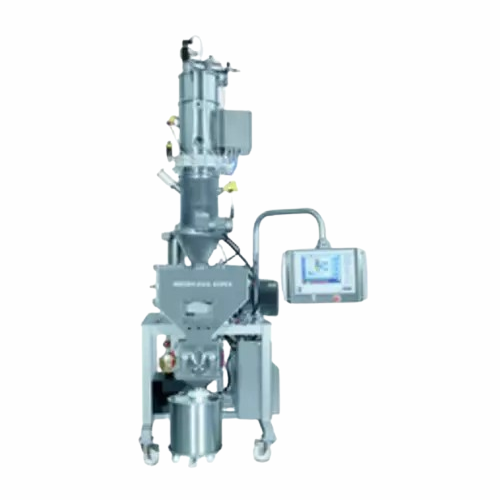
Compactor for powder processing
Designed for transforming powdered materials into uniform granules, this compactor enhances ...
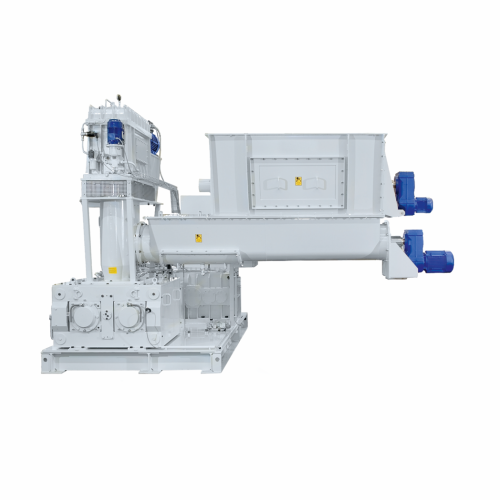
High-pressure roller compactors for chemical, food, and minerals industries
Achieve precise particle compaction and br...
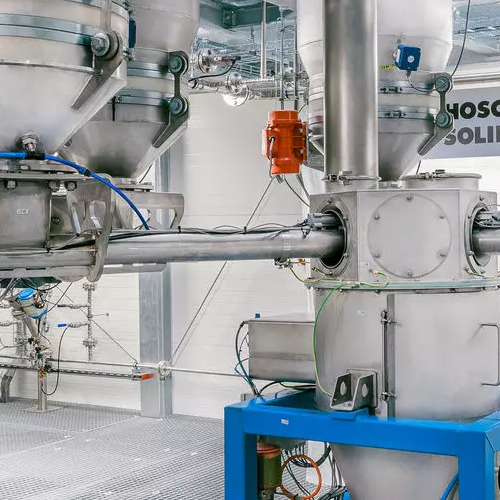
Mechanical conveying systems for bulk solids
Optimize your bulk material processes with advanced mechanical conveying syst...
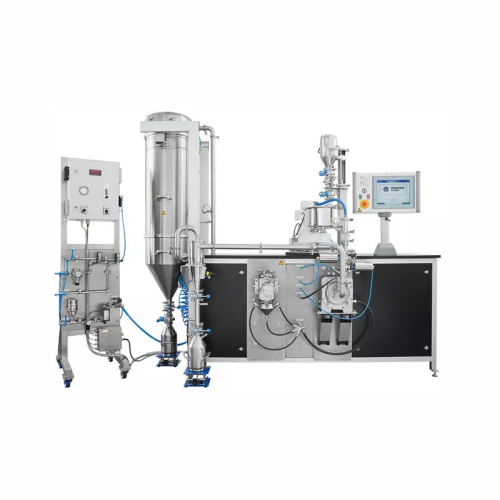
Multiprocessing system for flexible research and production
Optimize your process development with a versatile system th...

Pelleting and spheronizing equipment for chemical granulates
Optimize your production line with versatile pelleting and ...
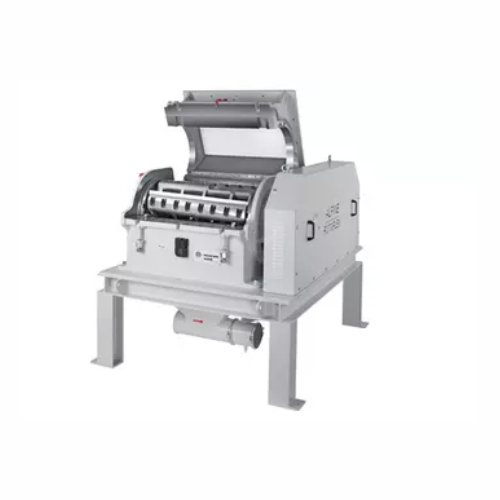
Industrial granulator for high-throughput plastic recycling
Facing challenges in efficiently recycling high-volume plast...
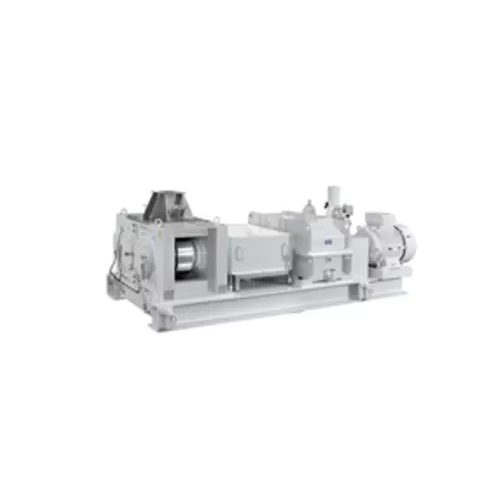
High pressure roller mill for medium-fine crushing
Achieve precision in particle size with high-pressure roller mills, id...
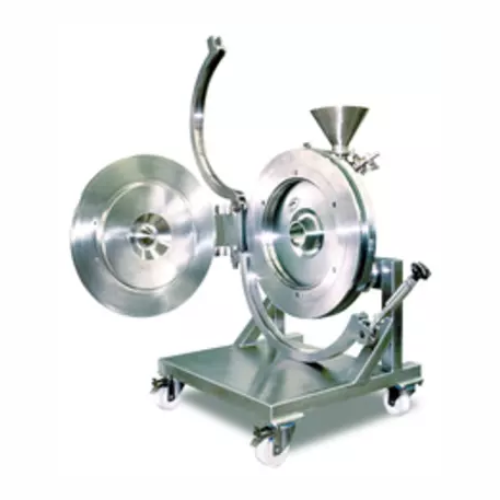
Spiral jet mill for superfine powder production
Achieve consistent ultra-fine powder with precise particle size control, c...
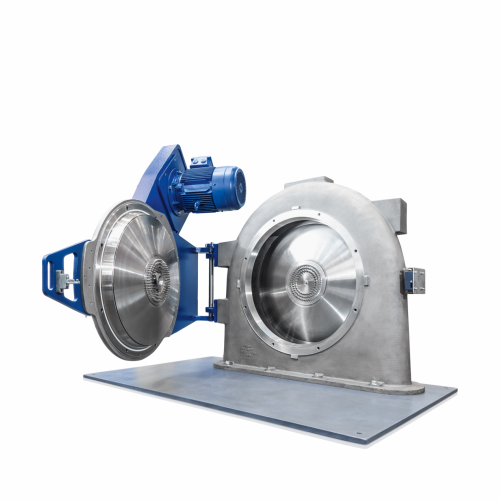
Pin mill for fine grinding of sticky materials
Achieve ultra-fine grinding of challenging materials with high speed and pr...
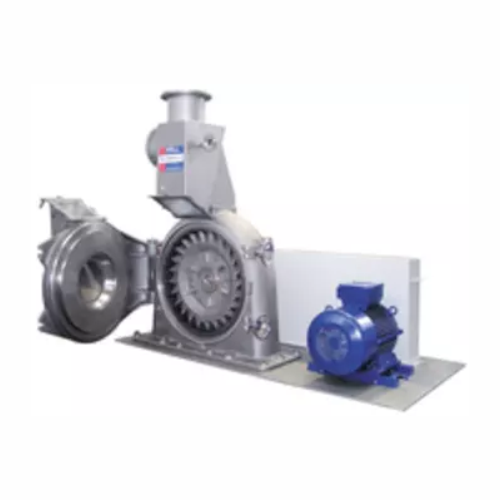
Versatile fine impact mill for soft materials
Achieve precision grinding with flexibility for a wide range of materials, e...
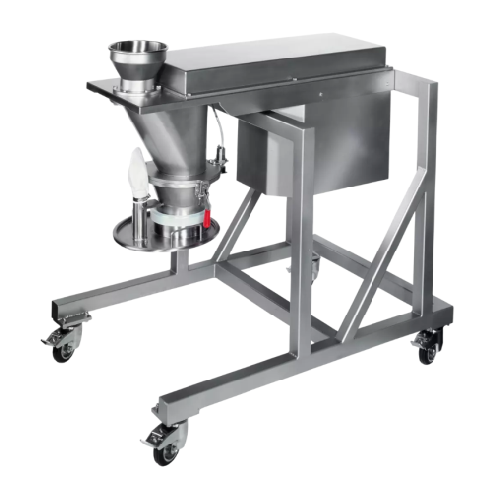
Flake crushers for gentle crushing of brittle materials
For processes needing precise granule control, our equipment ensu...
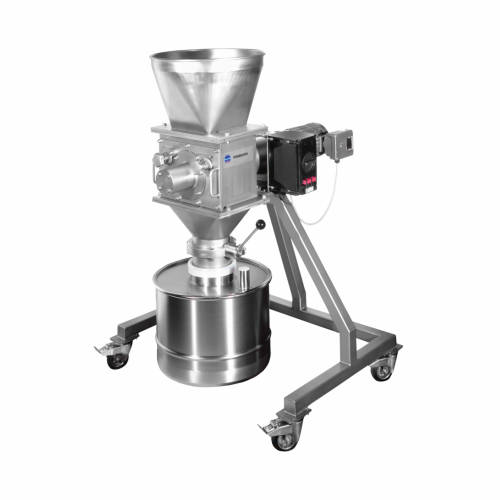
Flake crusher for hygroscopic substances and lumped salts
Efficiently turn fragile, aggregated materials into manageable...
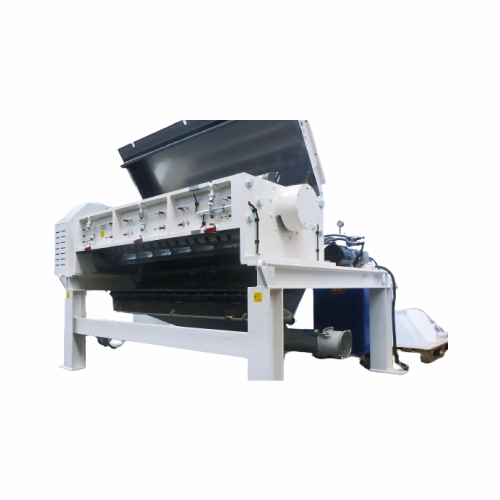
Industrial granulators for plastic recycling
Streamline your recycling operations with a solution that not only reduces en...
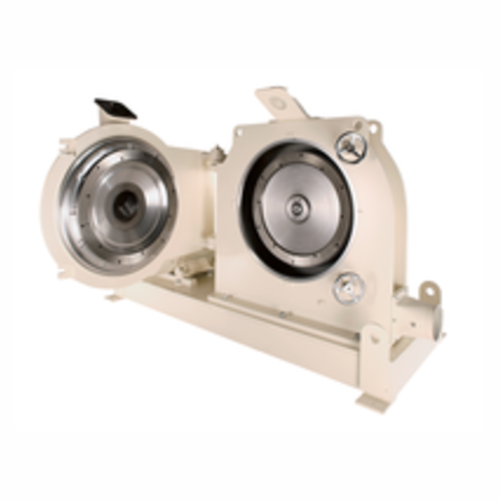
Fine cutting mill for soft to medium-hard plastics
Achieve precise size reduction and smooth particle shapes in plastic p...
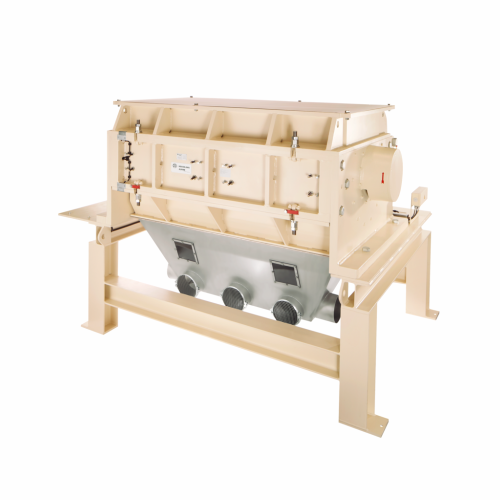
Compact granulator for plastic comminution
Optimize your plastic recycling operations with a compact granulator designed t...
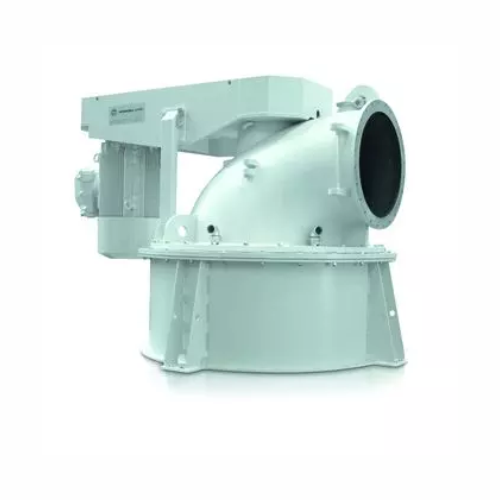
Air classifier for fine powder processing
Enhance your production line with precise particle size control and energy-effic...
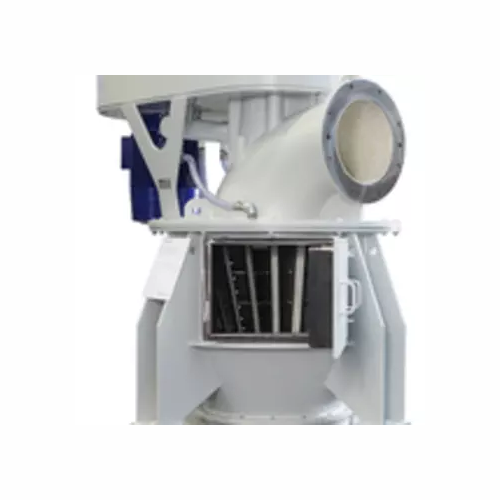
Ultrafine classifier for precise particle separation
Gain precise control over particle size with this ultrafine classifi...
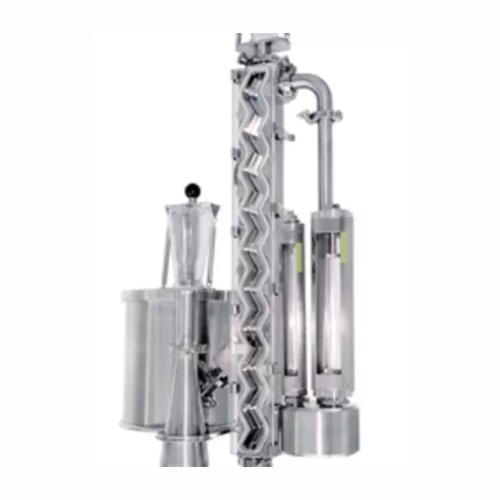
Gravity classifier for precise particle separation
Achieve sharp separations in particle processing with minimal maintena...

Ultrafine classifier for soft to medium-hard mineral processing
Achieve exceptional particle precision with an ultrafine...
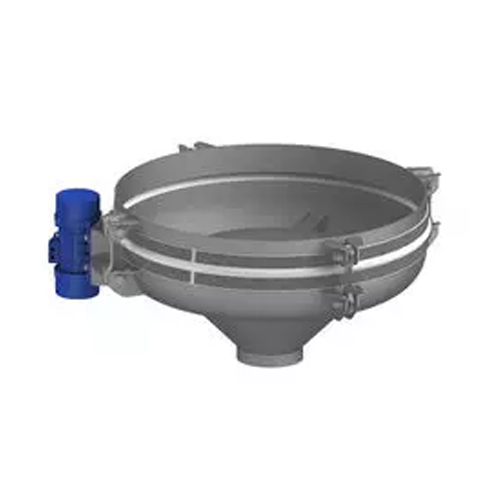
Discharge systems for difficult bulk materials
Achieve seamless bulk material discharge with our advanced systems that eff...
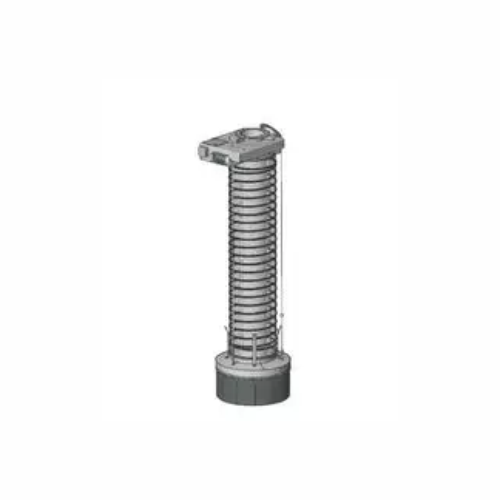
Automatic bulk material filling system
Ensure precise, contamination-free filling of various bulk materials with an advance...
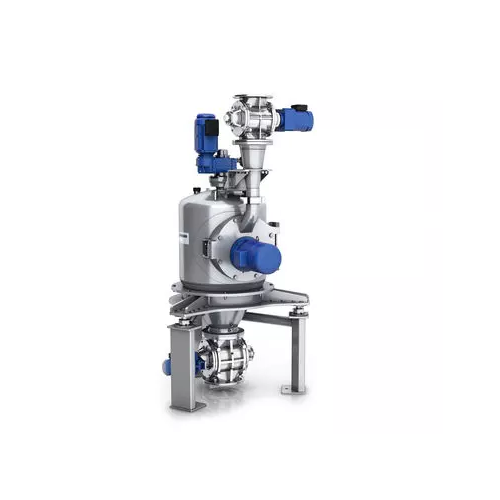
Fine impact mills for particle size reduction
Achieve precise particle size reduction with fine impact mills, essential fo...
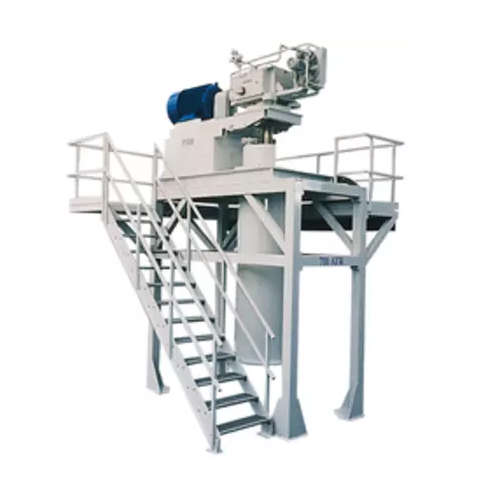
Ultra-fine grinding with ball mills and agitated media mills
Achieve precision in ultra-fine grinding for demanding mate...
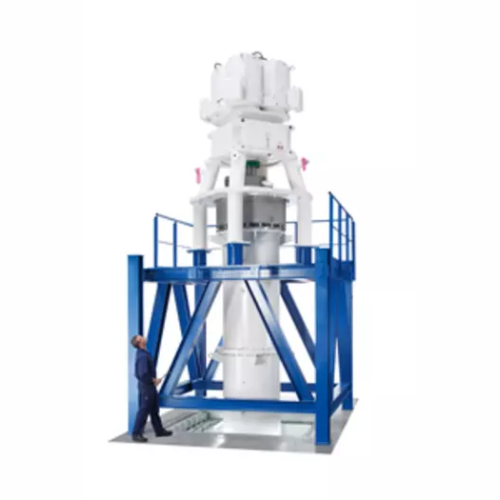
Ultrafine grinding mill for calcium carbonate slurries
Achieve precise particle size distribution in your mineral slurrie...

Ultra-fine dry grinding mill for glass and ceramics
Achieve ultra-fine particle sizes and energy savings with a dry grind...
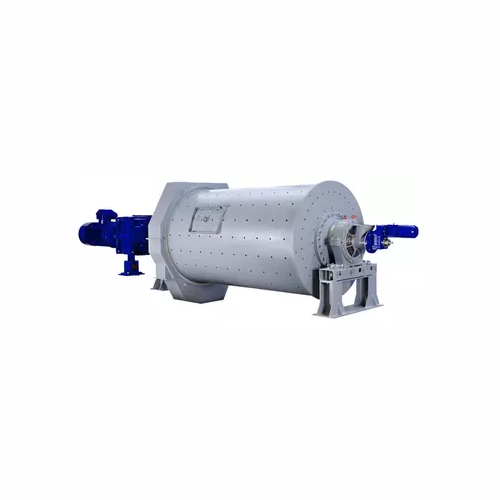
Ball mill for dry comminution of hard materials
Achieve ultrafine particle sizes and precise material breakdown with this ...
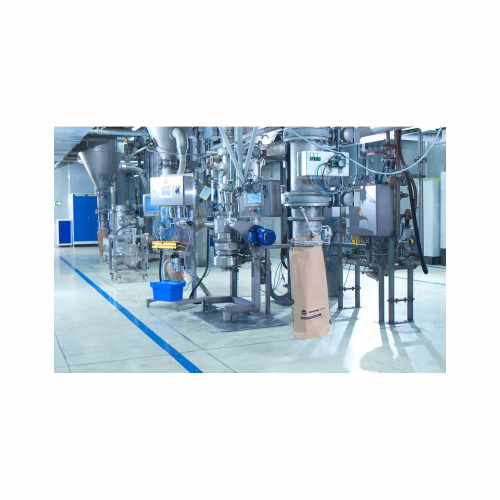
Air classifier for classifying industrial minerals
Achieve precise particle separation with advanced air classifiers, par...
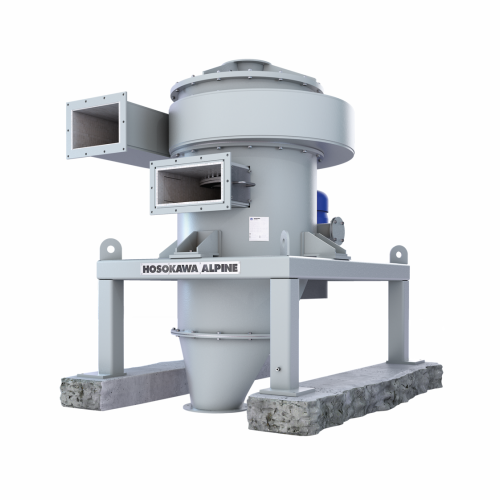
Air classifier for fine to medium-fine separation
Reduce energy consumption and wear while achieving high precision in th...
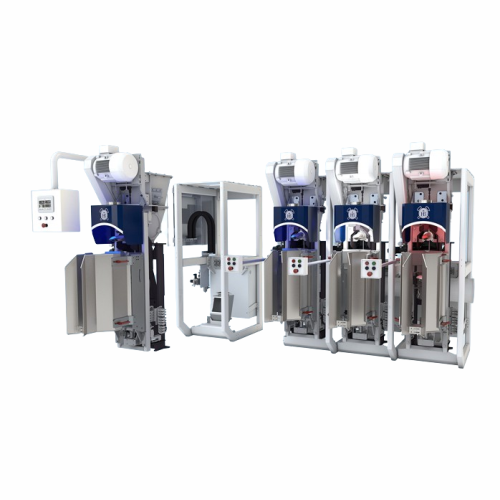
Valve bag filling system for cement and chemicals
Optimize your material handling with precision filling and sealing, ens...
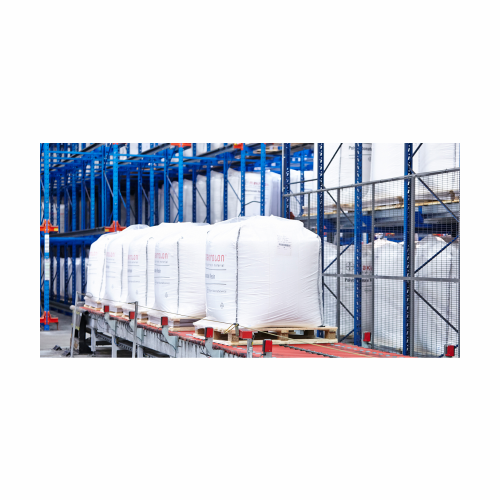
Stationary entry packaging system for valve bags
Optimize your packaging workflow with a high-speed, modular filling syste...
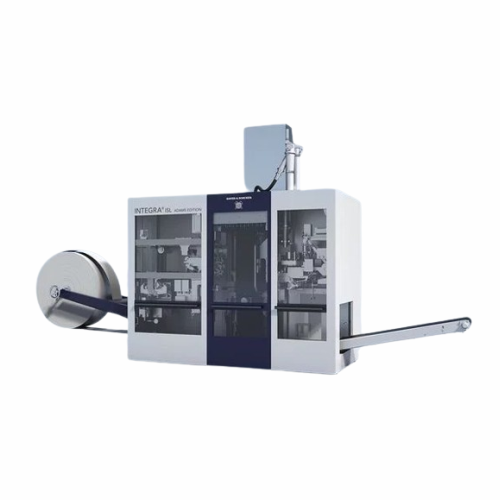
Integrated packaging system for cement and building materials
Streamline your packing operations with a fully enclosed s...
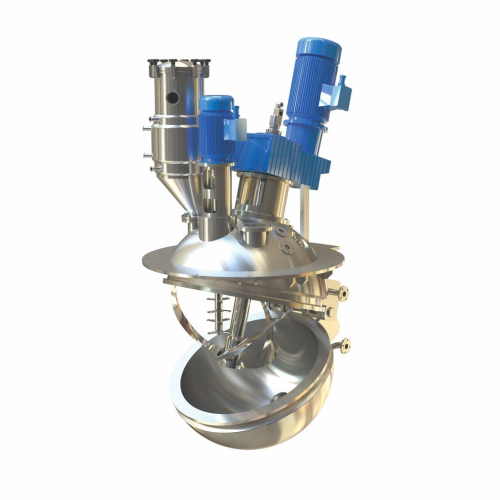
Spherical vacuum dryer for Apis and fine chemicals
Achieve precise moisture control and efficient drying for APIs and fin...
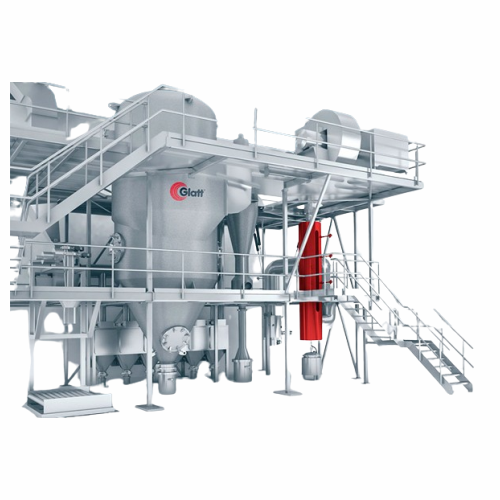
Powder synthesis reactors for nanometer and micrometer particles
Achieve precise particle control and enhance material p...
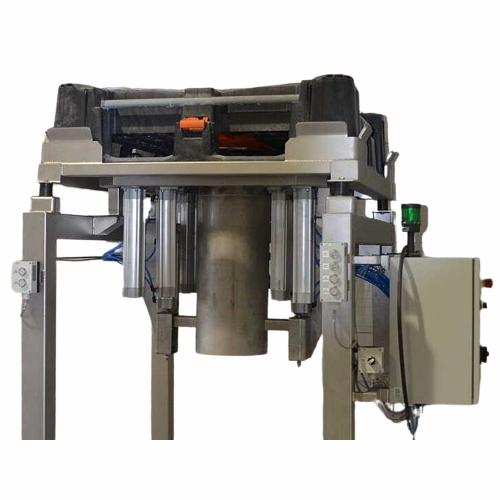
Big bag pallet unloader for bulk products
Efficient and reliable solution for unloading and transporting powders and bulk ...
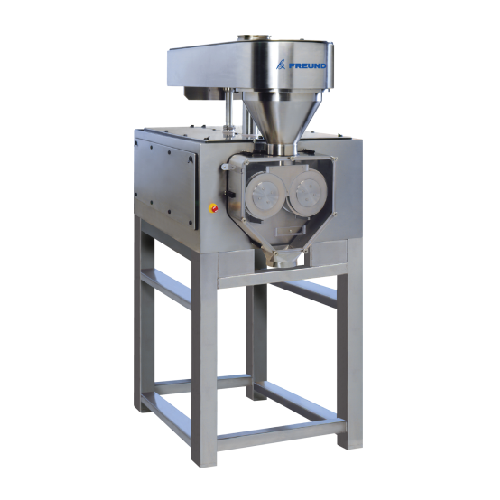
Dry granulation system for powder compaction
Achieve consistent sheet hardness and increased density in powdered materials...
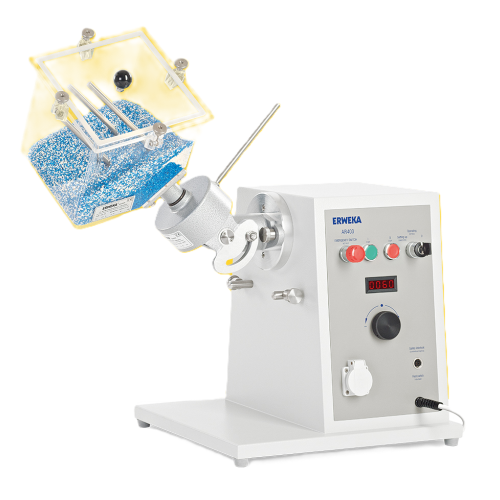
Tumbling cube mixer for homogeneous blending
Achieve uniform blending with precision using a cube mixer that enhances mixi...
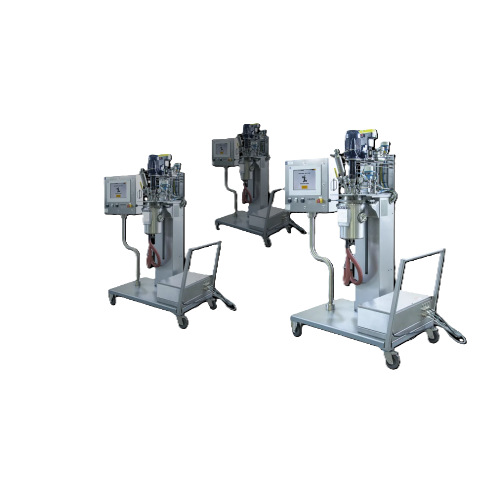
Portable process development unit for gas-liquid reactions
Optimize your gas-liquid reaction processes with a versatile,...
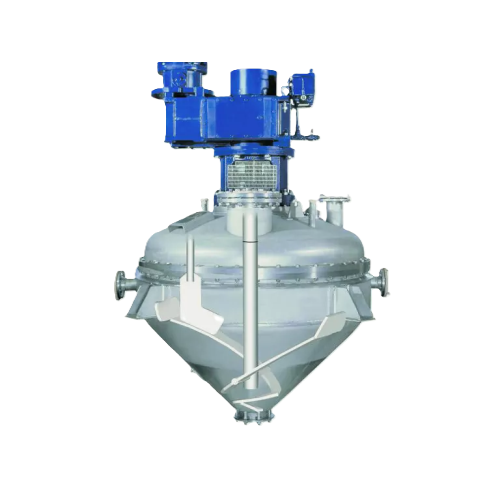
Vacuum dryer for free-flowing and pasty solids
Achieve precise drying and mixing with this vacuum dryer, optimizing heat t...
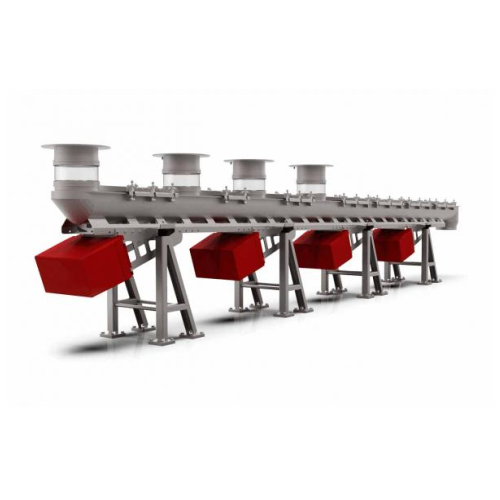
Vibration transport system for hygienic conveying of bulk goods
Optimize your production line with efficient and hygieni...
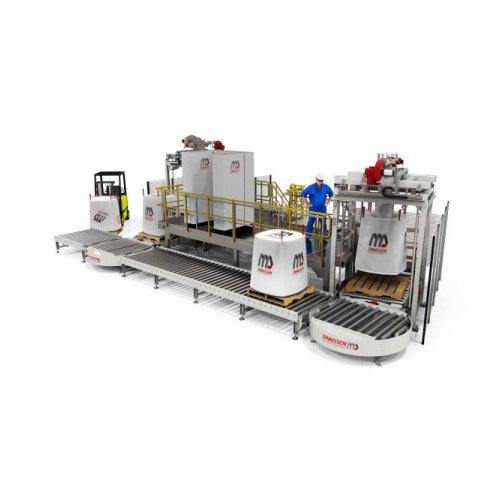
Product handling system for big bags and containers
Optimize your production line with a comprehensive system for transpo...
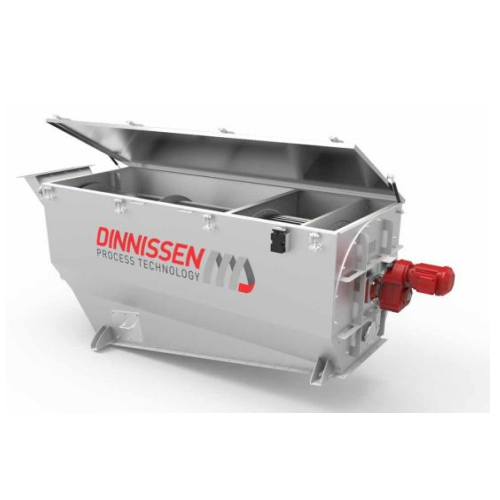
Rotary drum sifter for pellets and chunks
Achieve precise particle separation and minimize product loss with a rotary drum...
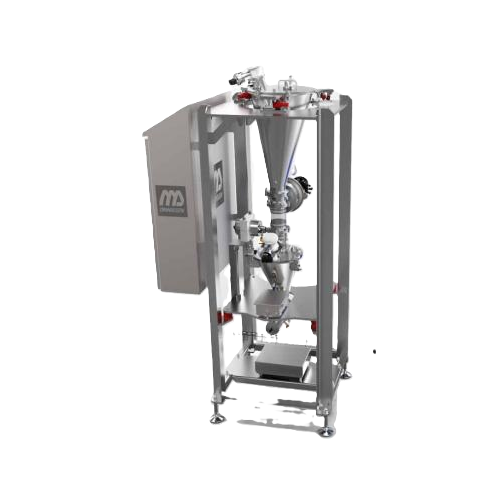
Micro dosing system for precise powder weighing
Achieve unparalleled dosing accuracy in your production line with a system...
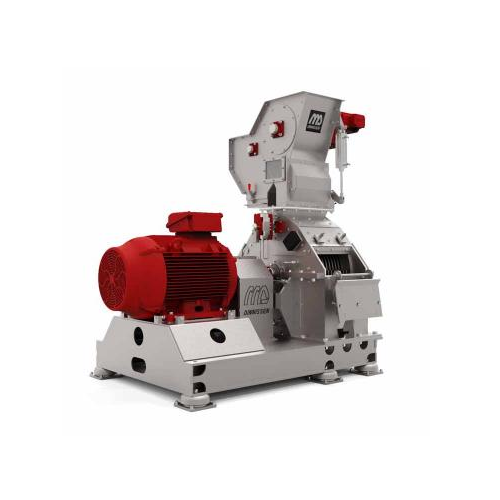
Industrial hammer mill for grinding and sifting
Ensure precise particle size reduction and consistent product quality with...
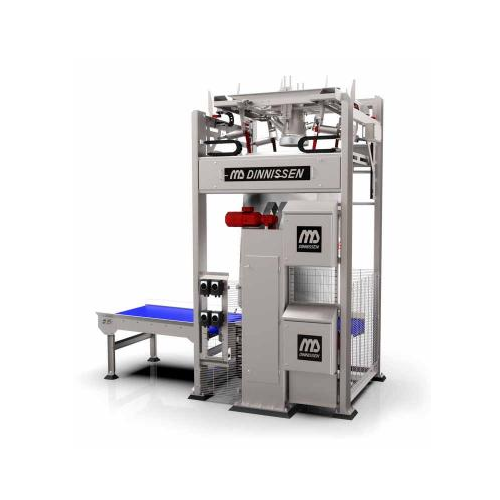
High-care big bag filling system for hygienic environments
Ensure precise hygienic filling of Big Bags in high-care envi...
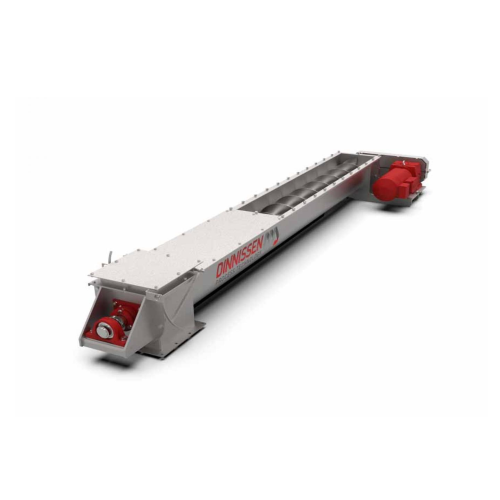
Vertical transport for bulk goods
Efficiently move bulk goods vertically with minimal energy usage, ensuring seamless integ...

Big bag conditioning system for compact materials
Struggling with clumped materials during unloading? This system expertl...
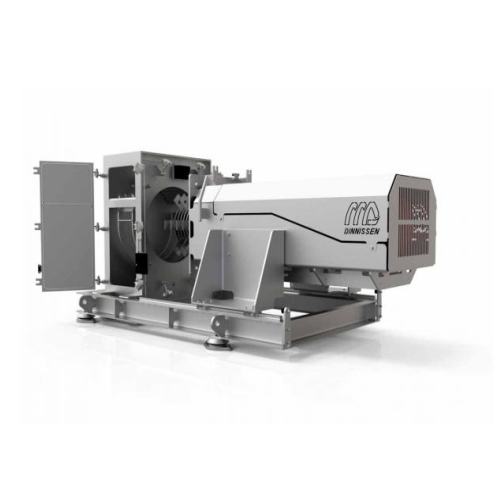
Hygienic industrial grinder for food and pharma applications
Achieve optimal hygiene and efficiency in your grinding pro...
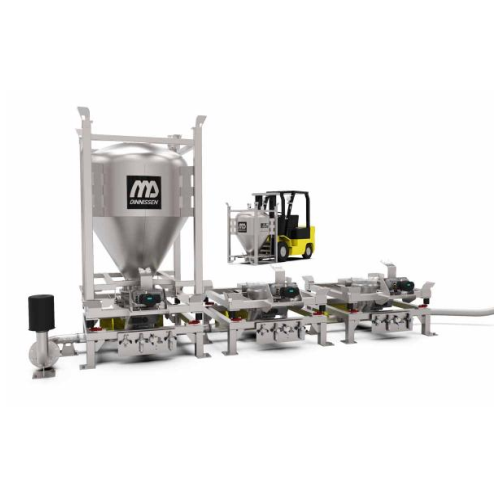
Drum and container emptying system
Ensure safety and efficiency when handling and emptying drums or containers, whether dea...
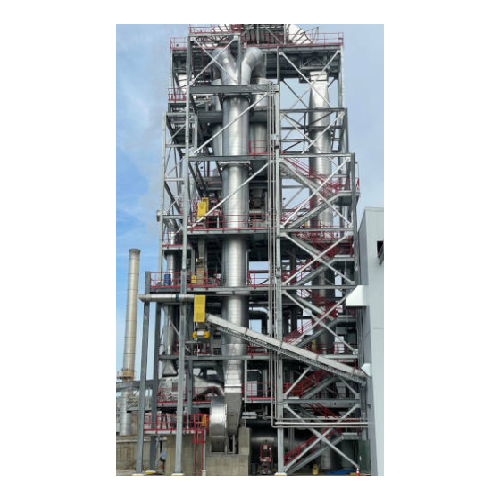
Industrial ring dryers for high-capacity drying applications
Maximize drying efficiency for diverse materials with ring ...
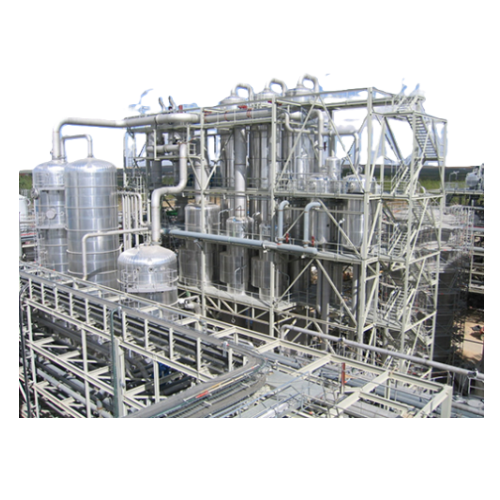
Industrial evaporators for diverse applications
Maximize energy efficiency and reduce operational costs with cutting-edge ...
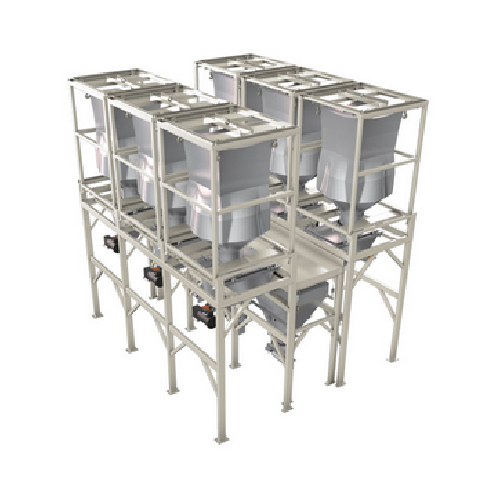
Bulk bag weighing system for batching operations
Streamline your batching process by accurately weighing minor ingredients...
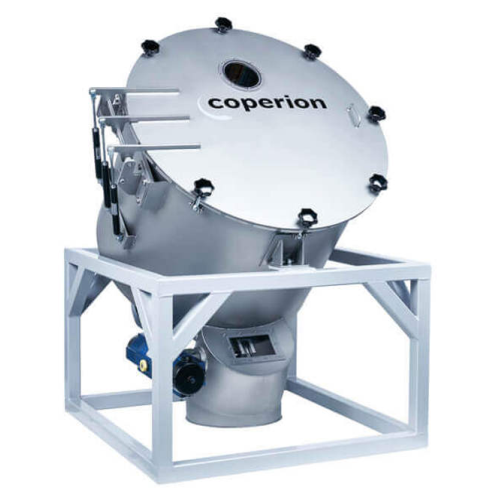
Bulk material mixer for high-speed homogenization
Achieve fast and gentle homogenization of bulk materials with a high-sp...

Precision feeders and mixers for plastics processing
Achieve precise blending and feeding for plastics processing with mo...
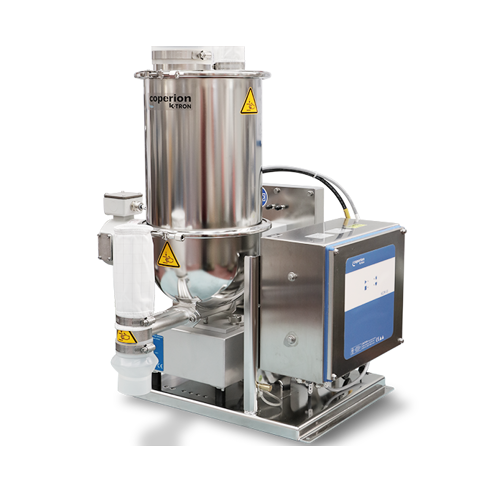
Twin screw feeders for difficult bulk materials
For manufacturers handling sticky or fine powders, twin screw feeders ensu...

Industrial vibratory feeder for bulk solids
Ensure precise and gentle handling of delicate bulk materials with a cutting-e...
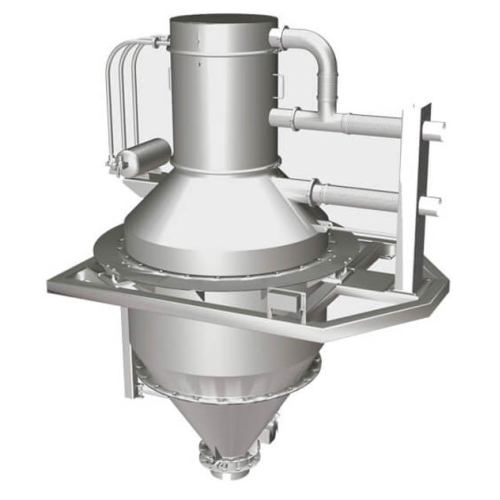
Batch weigh vacuum receiver
Optimize precision in ingredient batching and streamline your production line with advanced vacu...
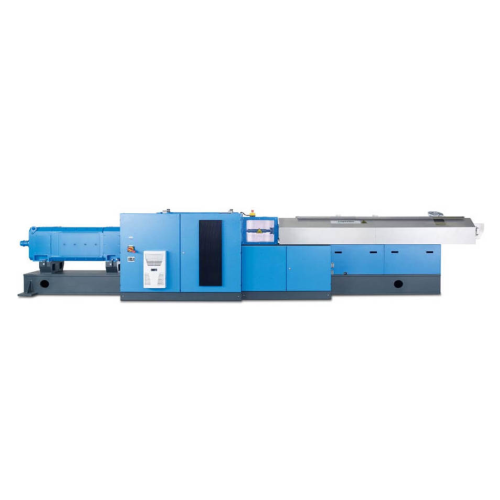
High throughput twin screw extruder for low bulk density products
When handling low bulk density materials, achieving m...
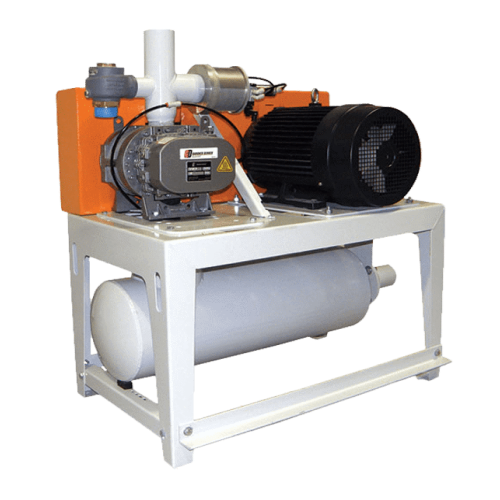
Industrial vacuum blower for continuous pressure conveying
Optimize your production line with reliable vacuum conveying,...
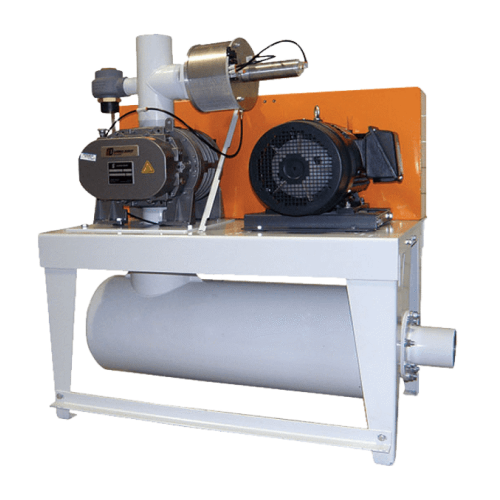
Vacuum sequencing blower for industrial conveying systems
For manufacturers handling bulk materials like powders and gra...
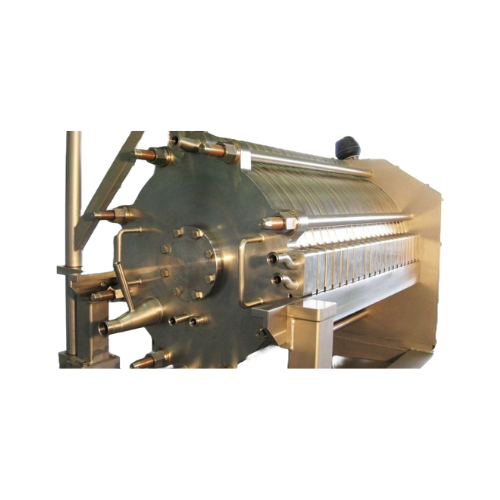
Crossflow filtration for microfine to nanoscale suspensions
Optimize your production line with advanced crossflow filtra...
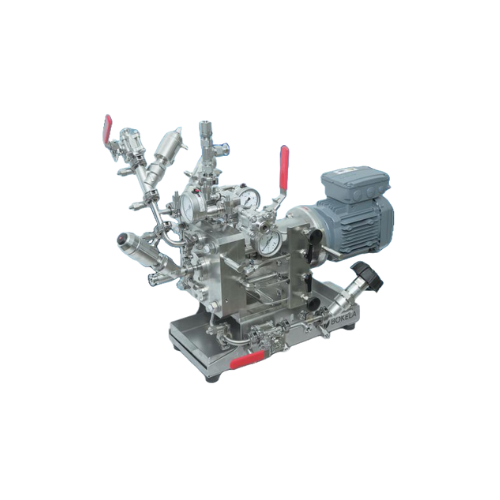
Laboratory crossflow filtration test system
Efficiently test and determine optimal filtration parameters with this portabl...
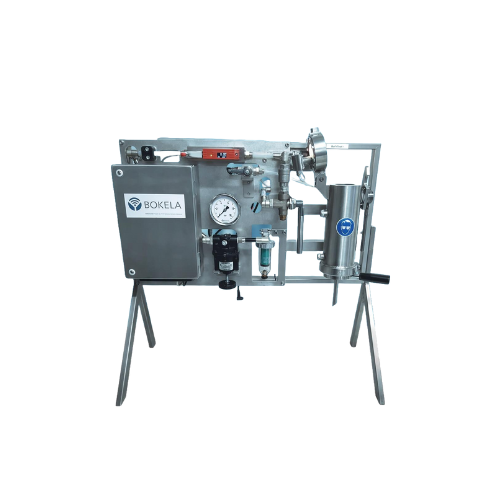
Compact filtration device for laboratory and field use
Achieve precise filtration with minimal sample sizes for rapid ana...
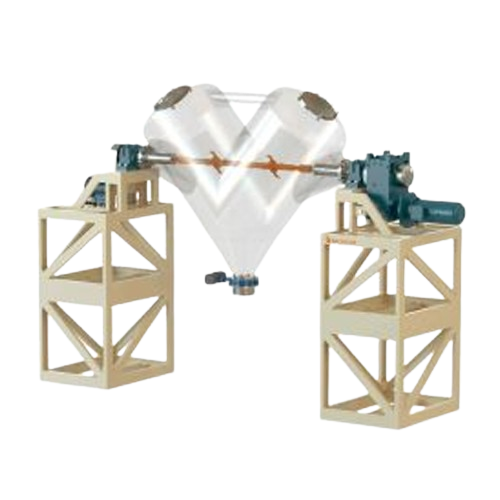
V shape mixer for solids and powders
Ideal for preserving the delicate structures of fragile materials, this mixer ensures ...
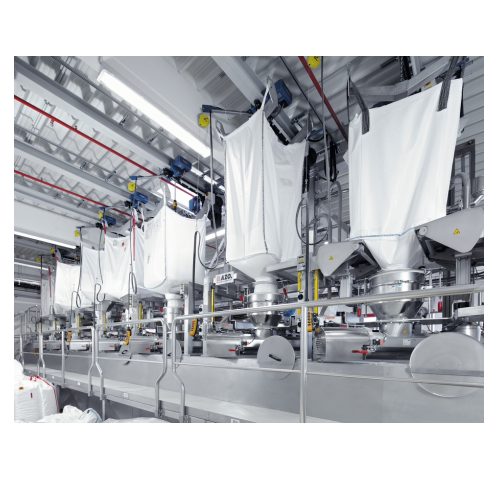
Big bag discharge station for bulk material handling
Ensure low-dust and efficient discharge of bulk materials with a sys...
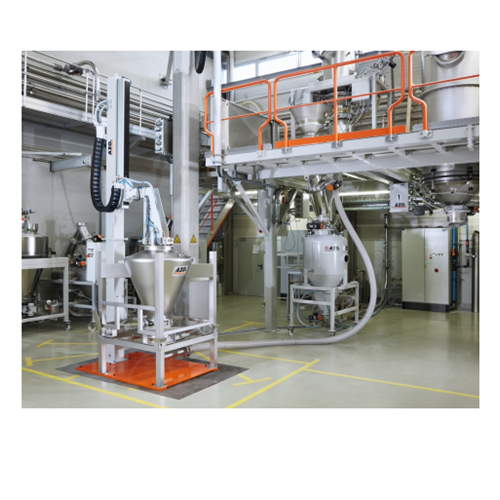
Dry cleaning container & hopper station
Effectively manage cleaning of rotation-symmetrical containers with minimal downtim...
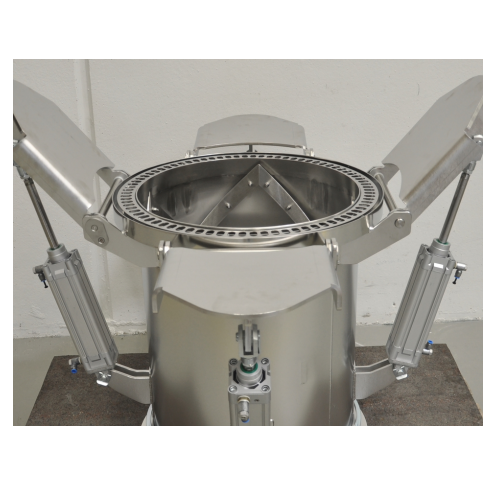
Dust-free big bag connection system for bulk solids
Eliminate dust and ensure reliable discharge with this vacuum docking...

Industrial filter press for dewatering and filtration
Optimize your dewatering and filtration needs with a highly adaptab...
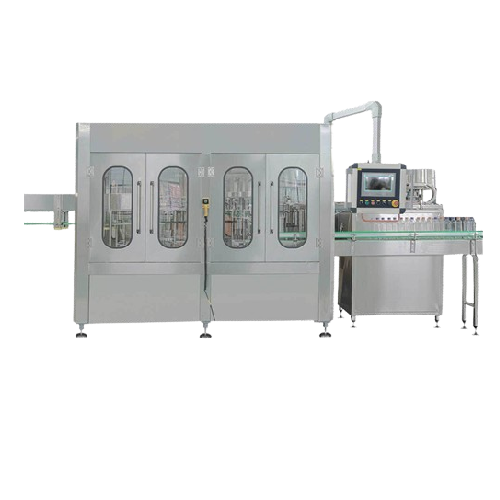
Drum blender for homogeneous powder mixing
Achieve precise powder homogenization directly in storage drums, minimizing han...
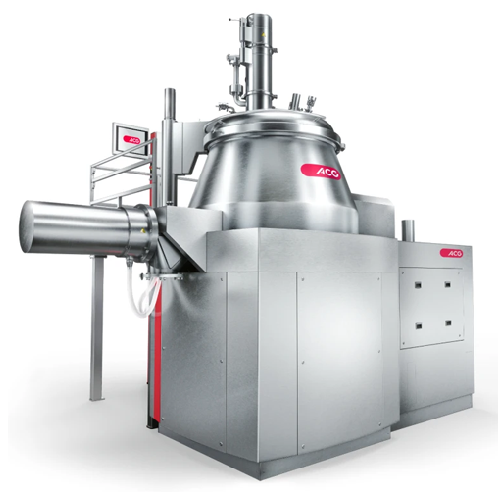
High-shear mixer granulator for small batches
Achieving consistent particle size and mix uniformity in pharmaceutical and ...
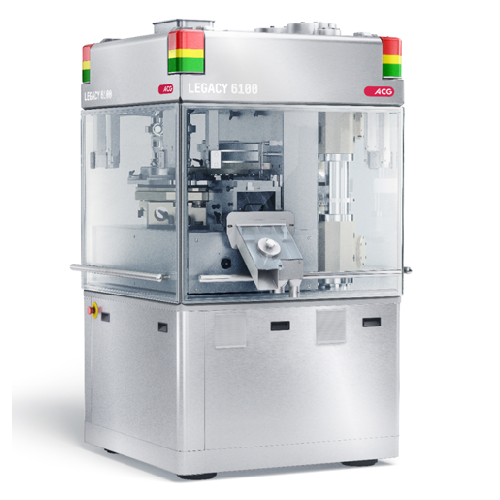
Single rotary tablet press
Streamline your tablet production with enhanced efficiency and precision, ensuring consistent tab...
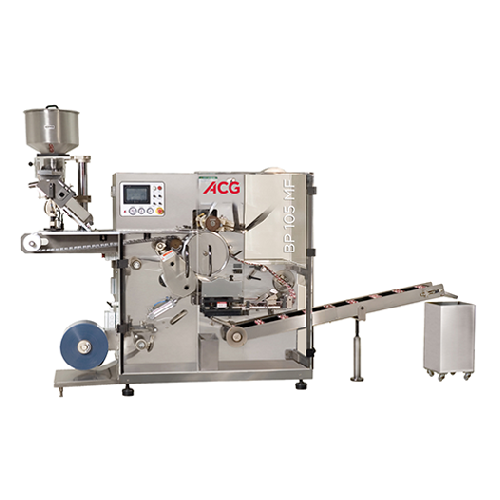
Rotary blister packaging for tablets and capsules
Optimize your blister packaging with high-performance rotary forming an...
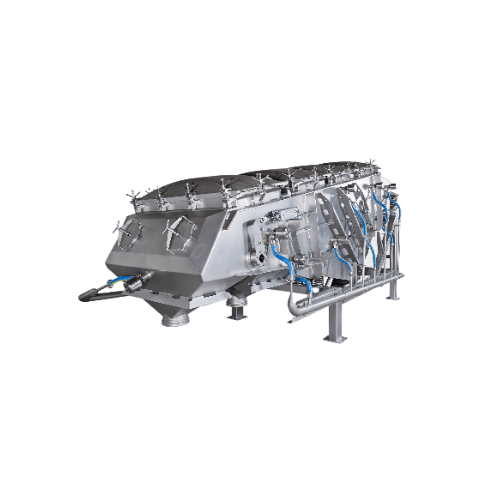
Industrial powder sifter with sanitary compliance
Optimize your powder processing with this versatile sifter, ensuring pr...
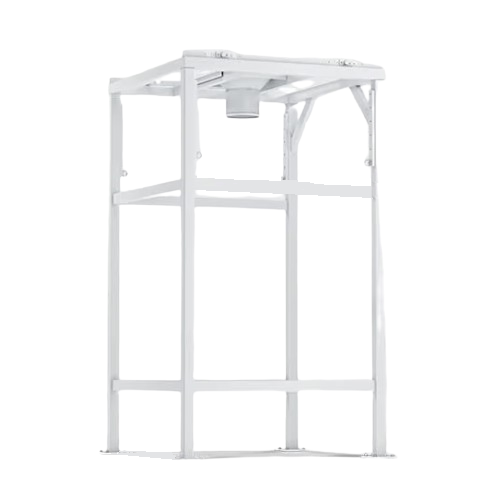
Big bag loading station for bulk product handling
Efficiently manage big bag handling with a system that combines hoistin...
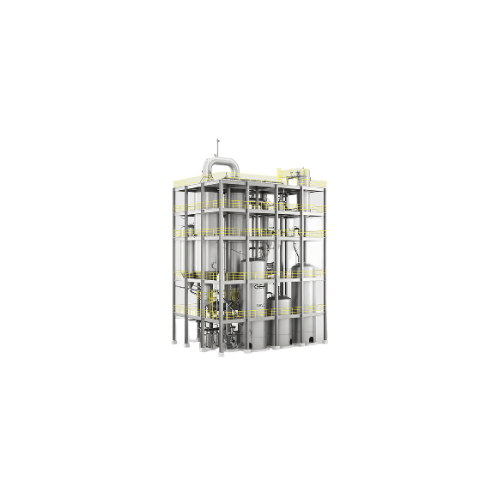
Co2 utilization and sequestration system
Optimize CO2 emissions management by converting captured CO2 into valuable product...
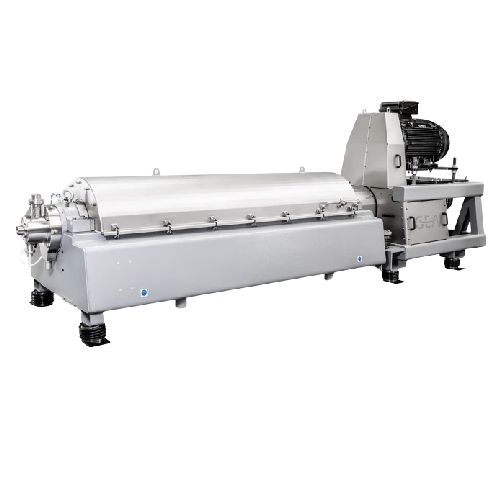
2-phase separating decanter for chemical and mineral processing
Ensure precise separation and optimal moisture control i...
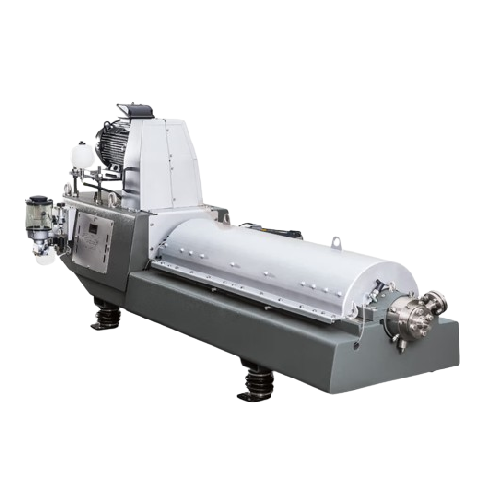
Decanter centrifuge for chemical and mineral processing
Optimize dewatering and clarification efficiencies in your proces...
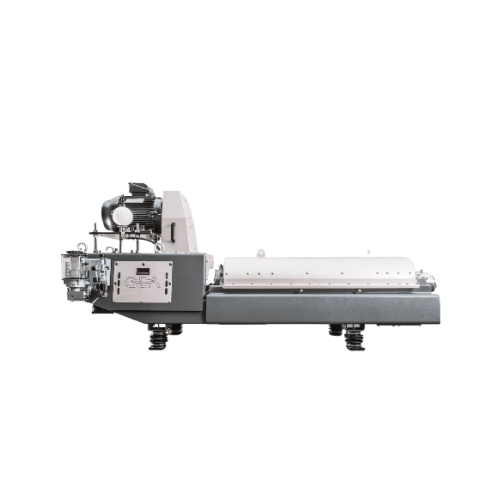
Chemical and mineral processing centrifuge
Optimize your chemical and mineral extraction processes with this high-performa...
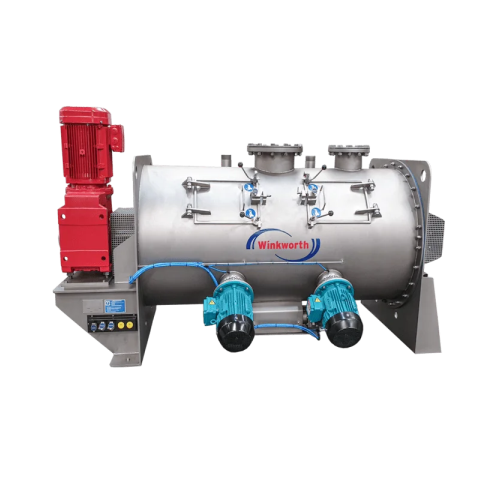
High-speed mixer for industrial mixing applications
Achieve rapid, consistent mixing and dispersion across diverse materi...
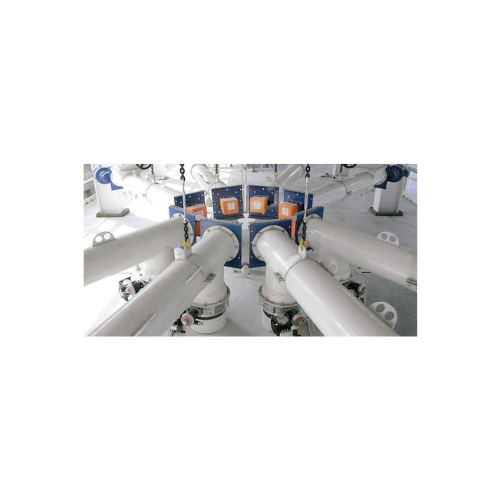
Heavy-duty tubular screw conveyor for bulk solids
Optimize your production line with a durable solution for uninterrupted...
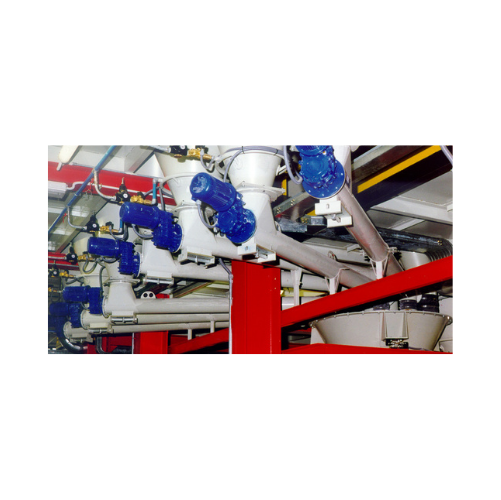
Tubular screw conveyor for concrete production
Optimize your production line with a versatile solution designed for effici...
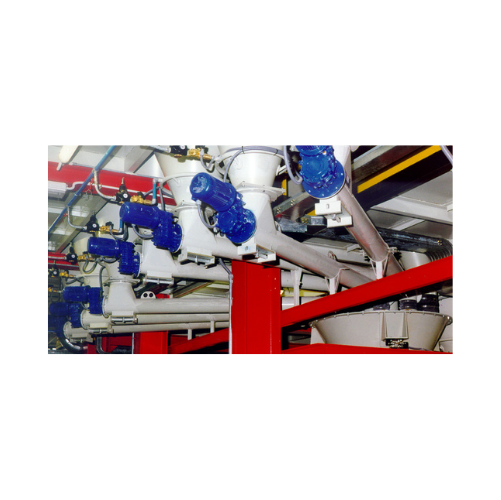
Tubular screw conveyor for powdery and granular materials
Optimize your material handling processes with a versatile sol...
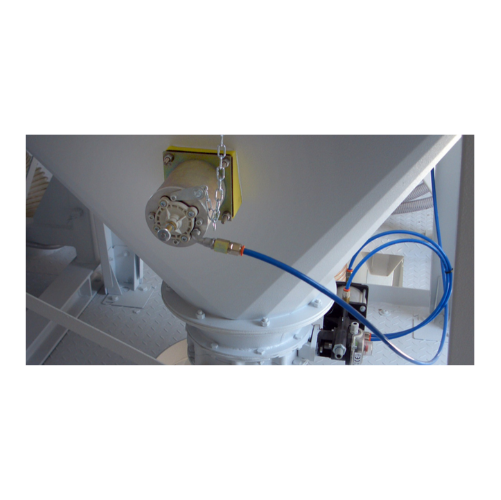
Combined hammer blaster for powder handling
Address powder flow issues with ease by preventing bridging and ratholing, ens...

High-temperature screw conveyors for bulk solids
Designed for extreme conditions, these conveyors handle high-temperature ...

External electric motovibrators for hazardous materials
Ensure safety and efficiency in hazardous environments with relia...
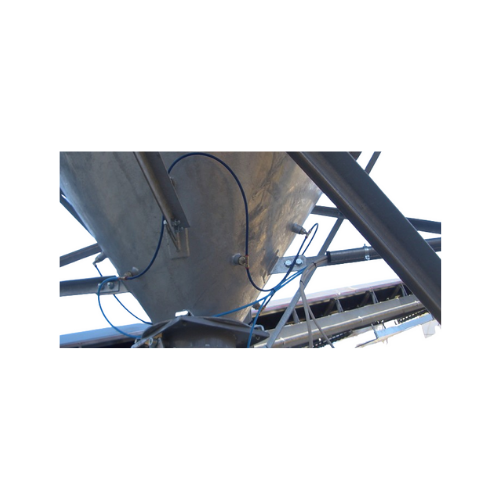
Aeration pads for powdery material flow in silos
Ensure consistent material flow in your silos and bins with a reliable ae...
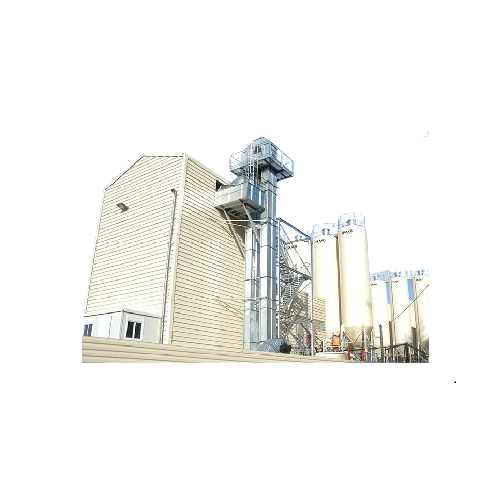
Heavy-duty vertical conveying for aggregates and minerals
Achieve efficient vertical transport of heavy bulk materials w...
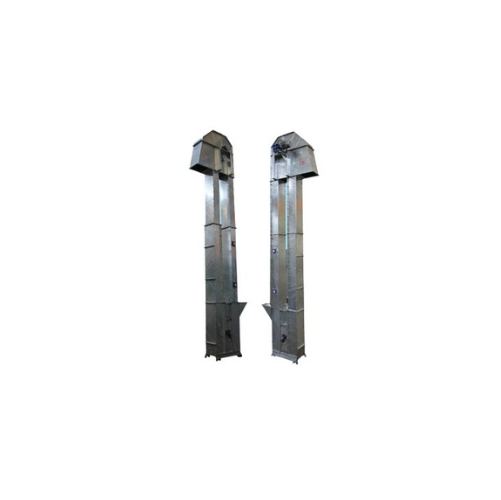
Vertical conveyor for fine aggregates and minerals
Optimize the handling of abrasive materials with a vertical conveying ...
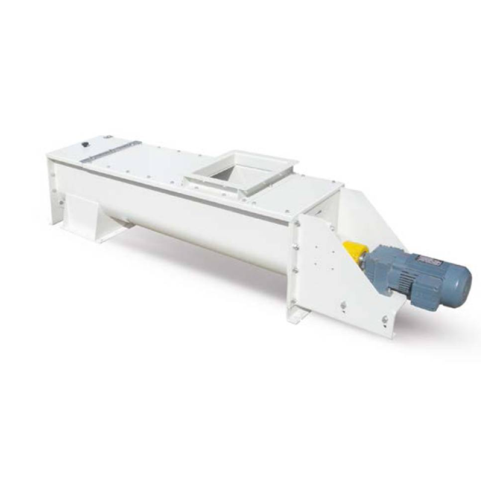
Screw conveyor for grain or finished products
Optimize your production line with a space-efficient screw conveyor designed...
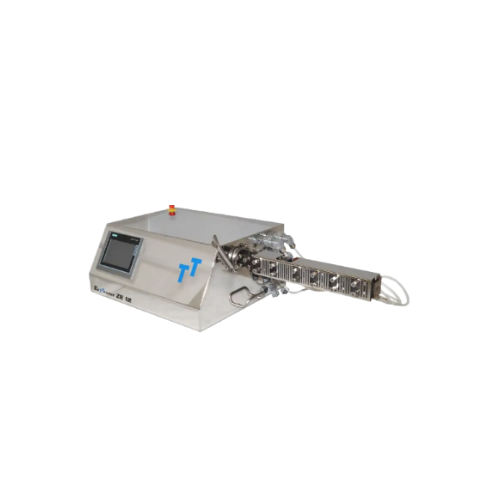
Table-top mini extruder for precision material processing
Achieve precise control over complex formulations with this fl...
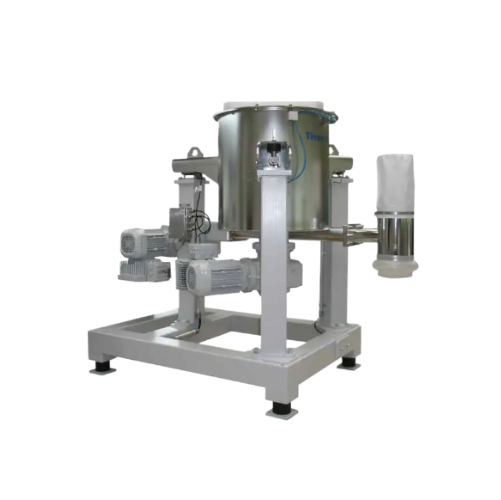
Twin screw feeder for poorly flowing powders
Optimize your process with precision feeding for powders that easily clump or...
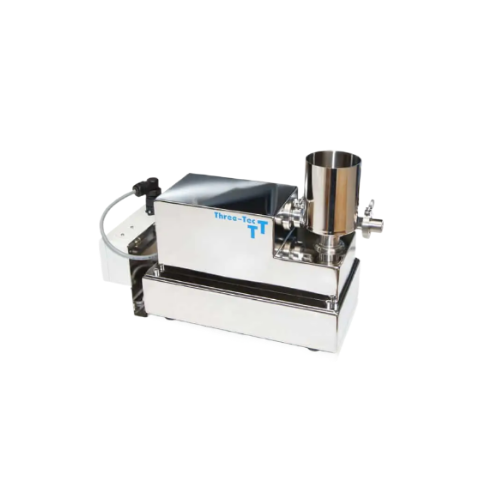
Precise volumetric or gravimetric powder feeder
For precise feeding of challenging powders prone to clumping and bridging,...
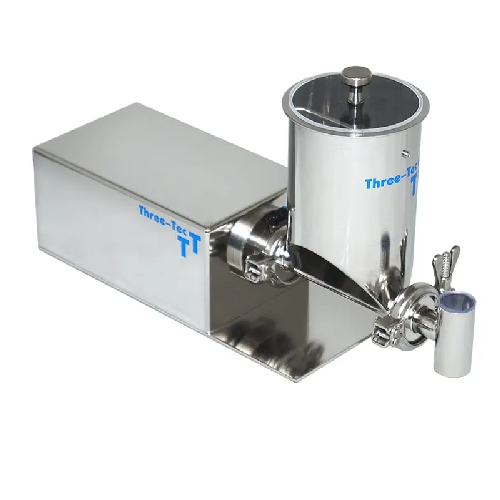
Volumetric single-screw feeder for fine dosing
Achieve precise and consistent dosing of fine powders and granules with a c...
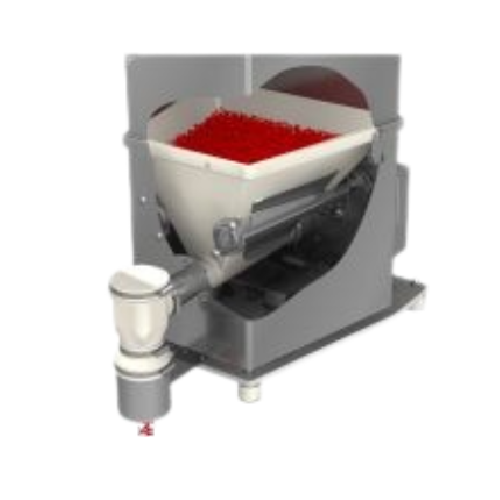
Volumetric feeder for consistent ingredient flow
Achieve precise and consistent ingredient dosing in your production line ...
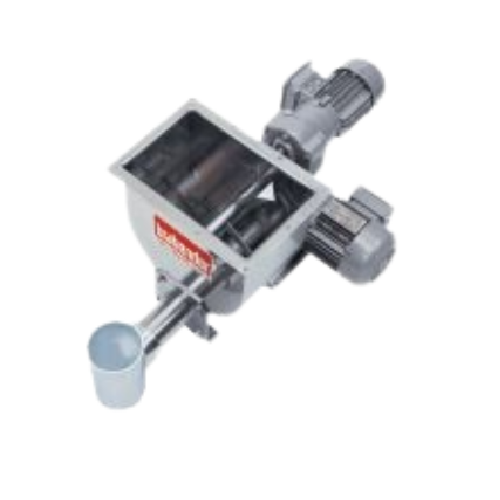
Single screw feeder with stirring agitator for powders and pellets
Ensure consistent mass flow and precise dosing with ...
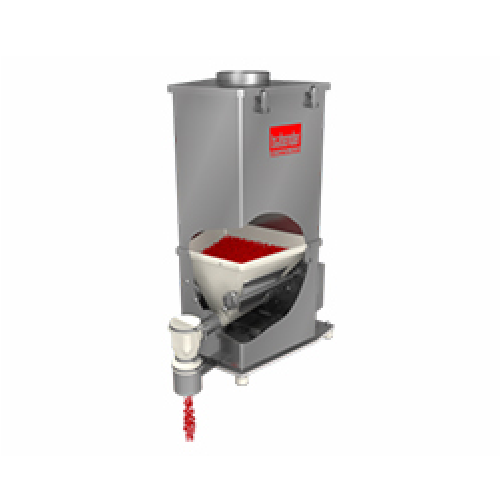
Loss-in-weight feeder for flowable ingredients
Achieve precise ingredient delivery with this feeder, designed to handle a ...
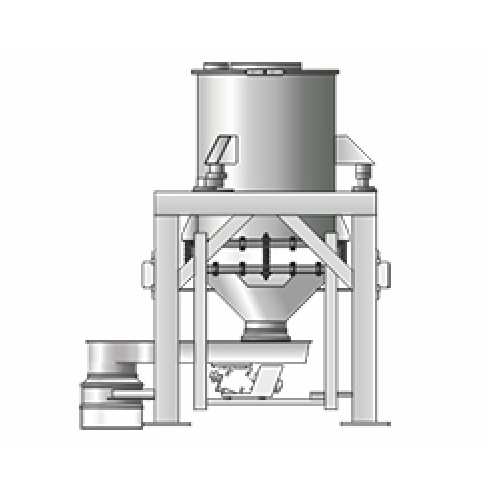
Loss-in-weight feeder for non-hygroscopic ingredients
Ensure precision in your dosing and weighing processes with this ad...
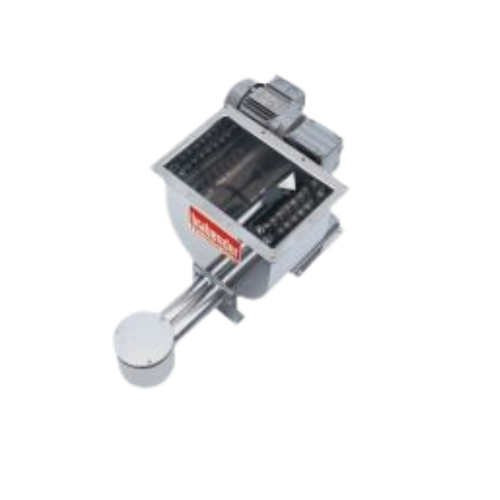
Twin screw volumetric feeder for poor flowing powders
Struggling with poor flowing or floodable powders? This twin screw ...
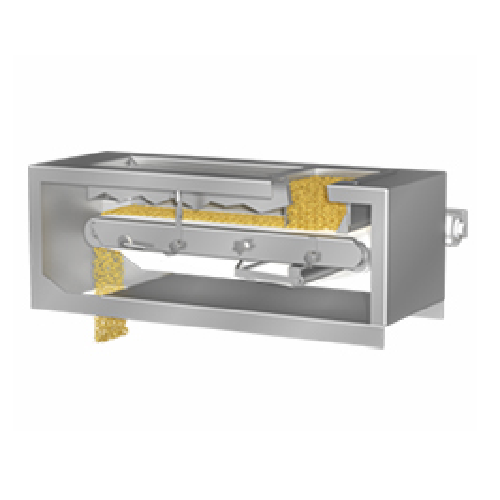
Weigh-belt feeder for industrial processes
Efficiently manage material flow and precision with a dependable weigh-belt fee...
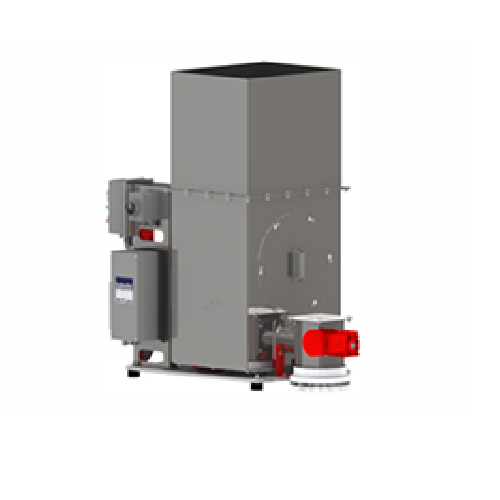
Loss-in-weight feeder for long and uneven fibers
Optimize feeding precision for challenging materials like long and uneven...
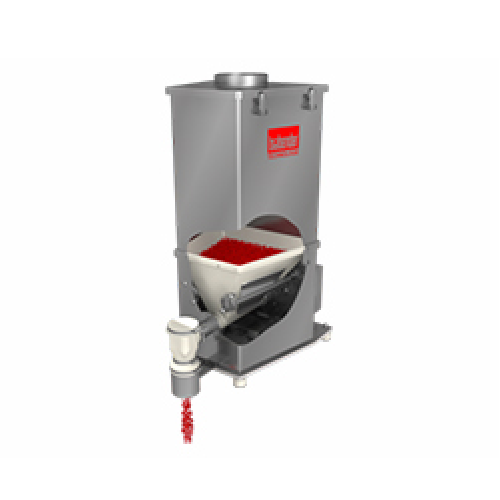
Precision batch feeder for flowable ingredients
Achieve precise ingredient control with a batch feeder designed for versat...
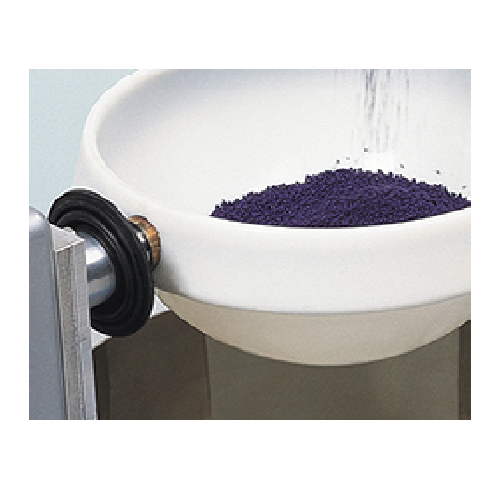
Microbatch dosing for precision ingredient measurement
Achieve precise ingredient dosing with our MicroBatch system, desi...
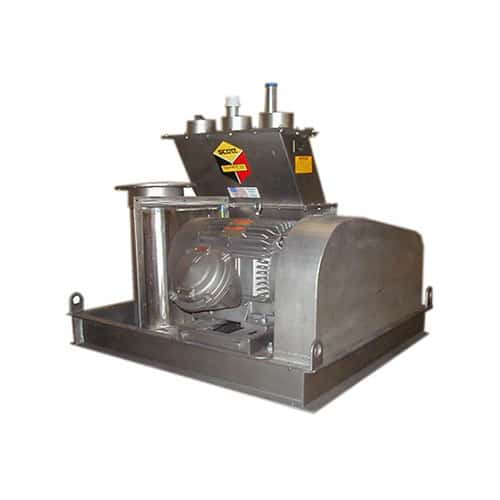
Shredder for fine particle size reduction
Optimize your production line with high-speed shredding technology designed for ...
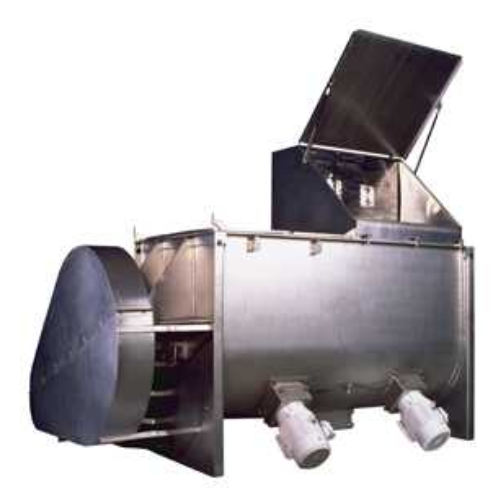
Single shaft horizontal batch mixer
Achieve consistent, high-quality blends with precise homogenization using a single shaf...

Efficient grinding and drying mill
Transform your production line with a versatile mill that simultaneously grinds, dries, ...
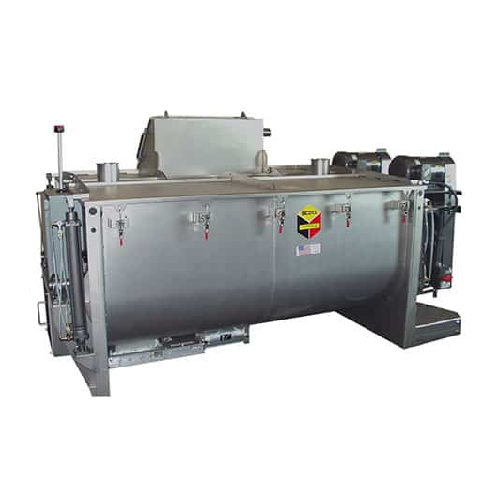
Twin shaft horizontal batch mixers for homogenous material mixing
Achieve consistent and rapid mixing of diverse materi...
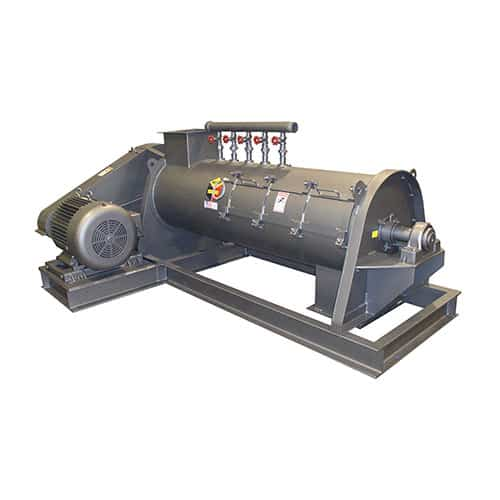
Industrial high-speed turbo blender
Achieve homogeneous blending with high-speed precision, ideal for creating fine product...
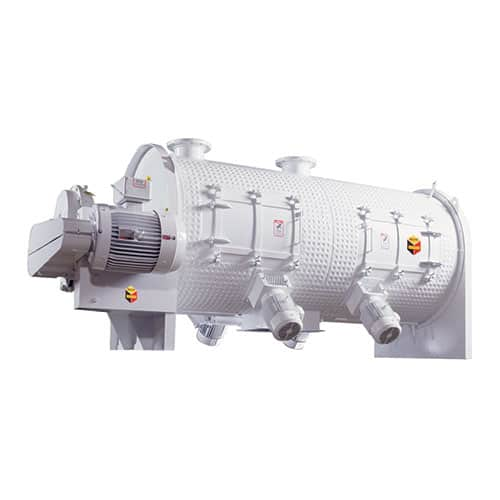
Industrial plow mixer for efficient solid and liquid mixing
Experience unparalleled mixing precision with high-speed plo...
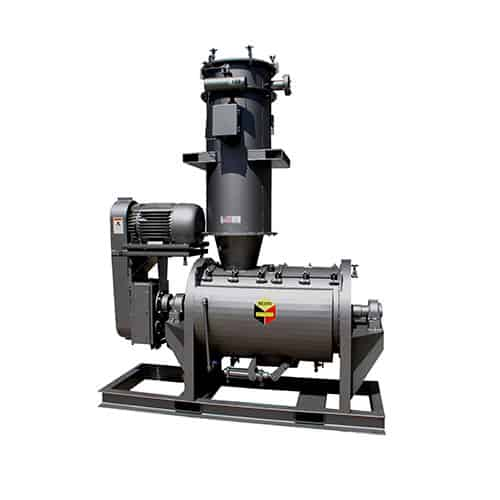
Industrial vacuum batch dryer for reducing moisture content
Achieve precise moisture control with a solution that handle...

Mechanical air separator for uniform fineness
Achieve precise material separation and de-dusting with our air separator, e...
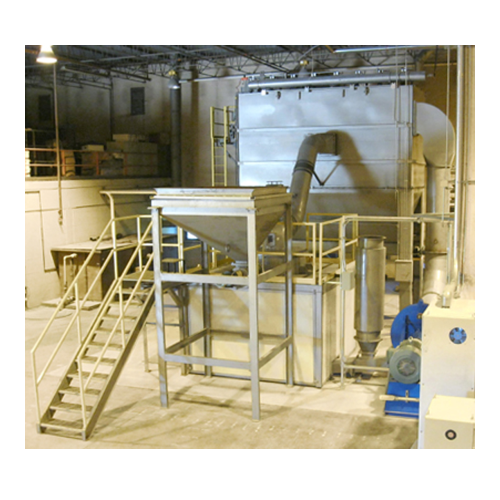
Ultrafine powder mill for coatings and pigments
Optimize your ultra-fine powder production with this precise grinding and ...
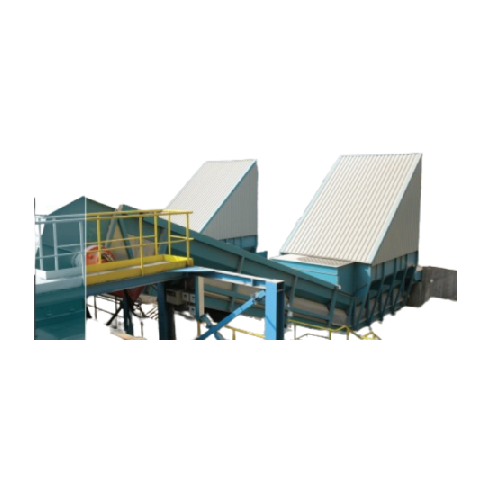
Bulk reception solution for industrial material handling
Optimize your operations with an above-ground bulk reception sys...
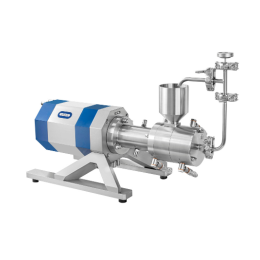
Agitator bead mill for flow chemistry
During the early stages of synthesis, generating only limited product quantities can ...
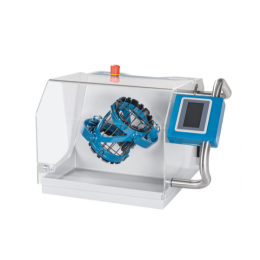
R&D shaker mixer for battery powders and chemicals
Material heterogeneity, agglomeration, and contamination are key param...
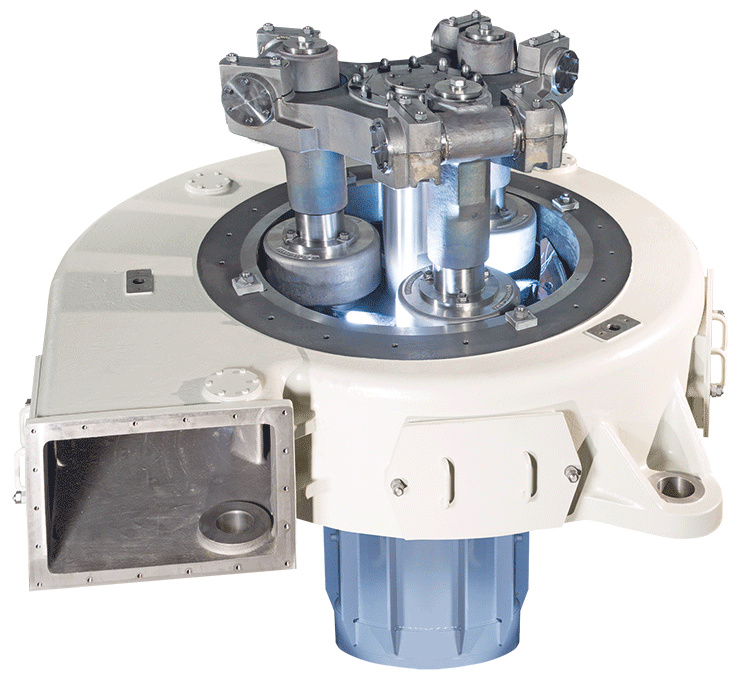
Grinding and drying of CaCO3
Widely used in the construction industry as filling materials, calcium carbonate is usually mad...
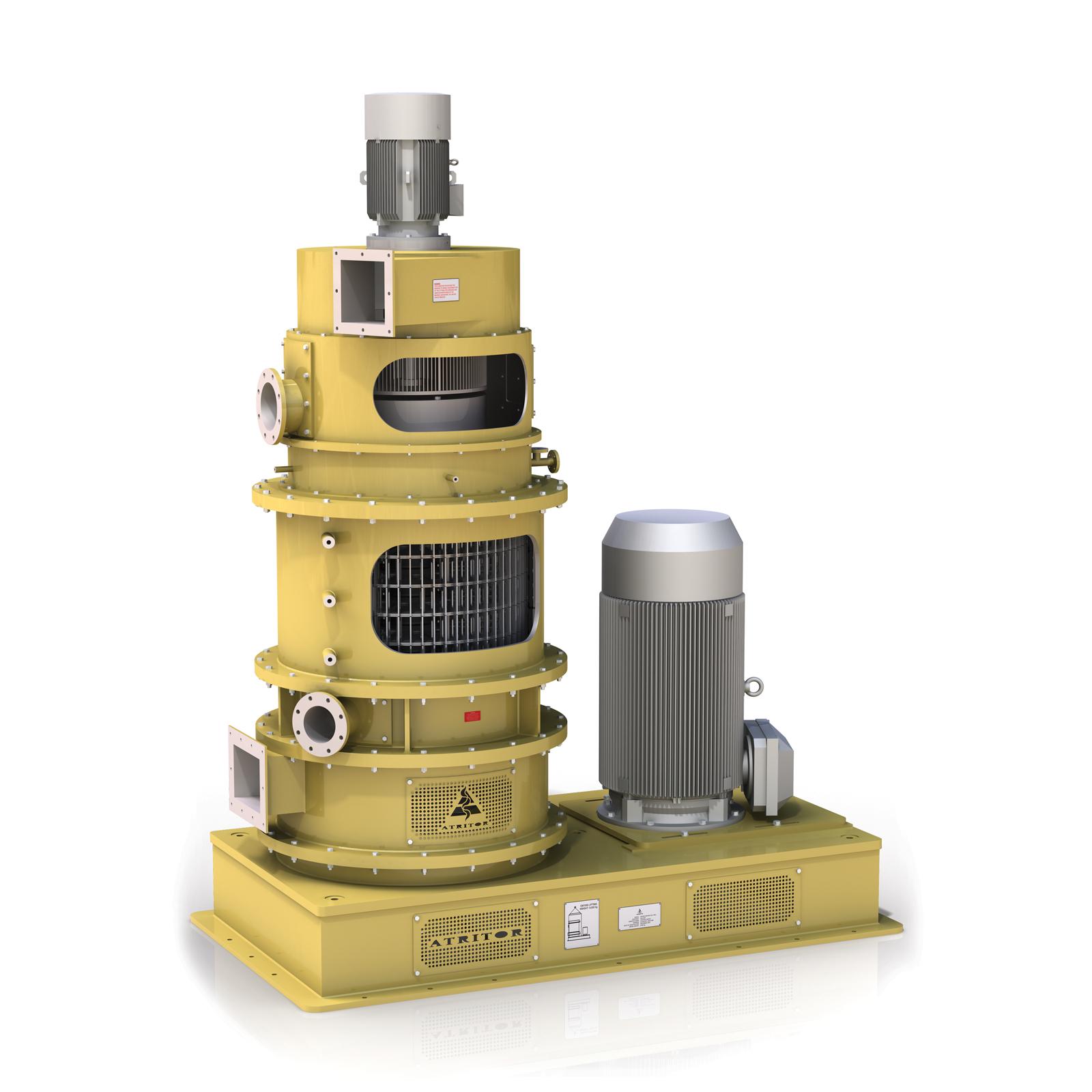
Milling and drying machine for fine powders
When you need to produce ultra-fine powders, the milling and drying process em...
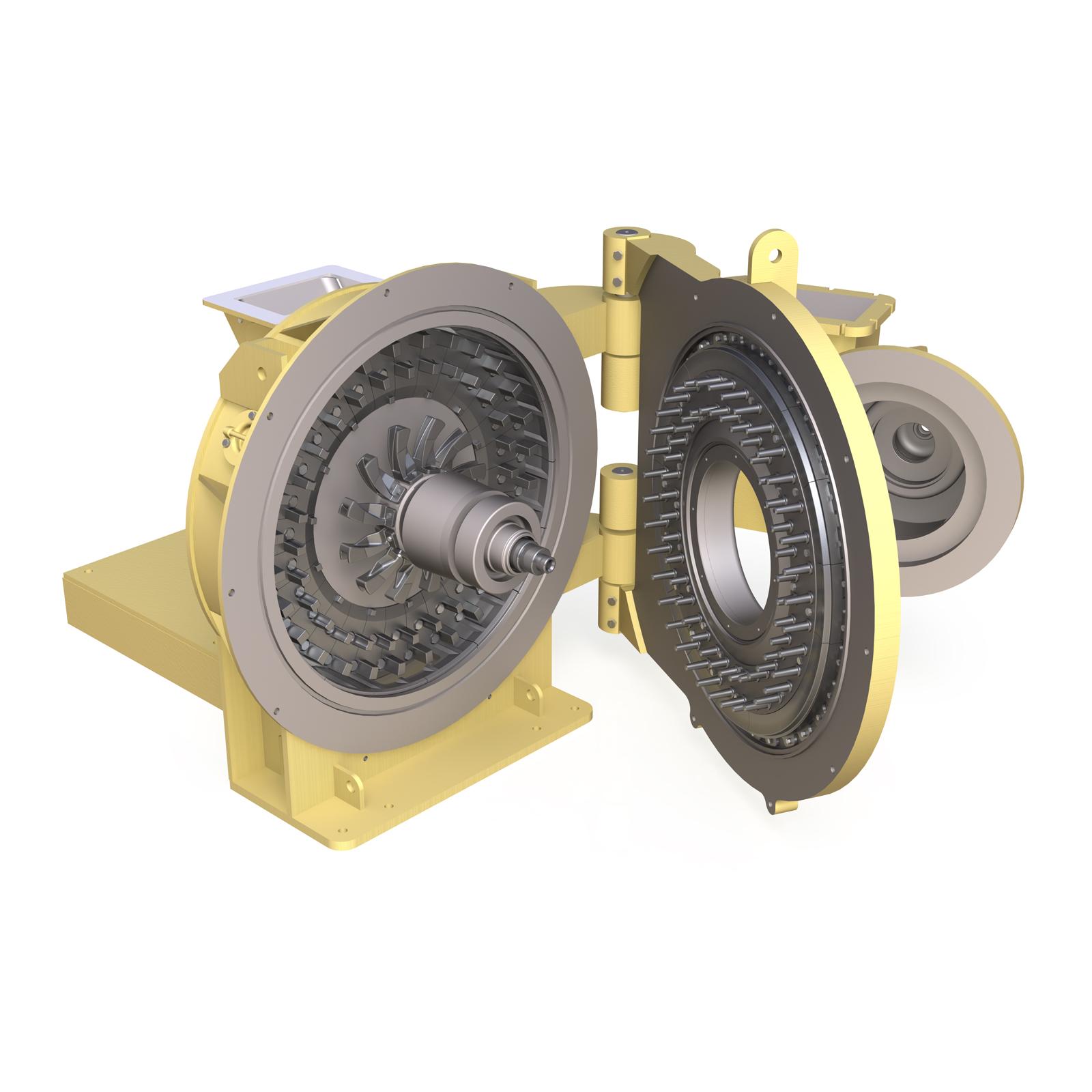
Flash drying grinder for powders
Drying and grinding can be an important feature when trying to process products such as raw...

Open mouth bag filling machine for powders
The packaging of powdery products such as flour can be challenging as it is cru...

Simple valve sack packer
Sometimes in the packing process, product leaks out of the top of a bag that has just been filled. A...
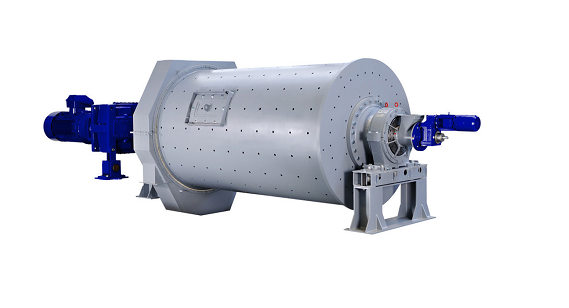
Horizontal rotary ball mill drum
A horizontal rotary ball mill drum can be used for grinding of dry hard materials, such as ...

High volume particles separation sieve
For large scale production processes in the chemicals or food industries that requir...
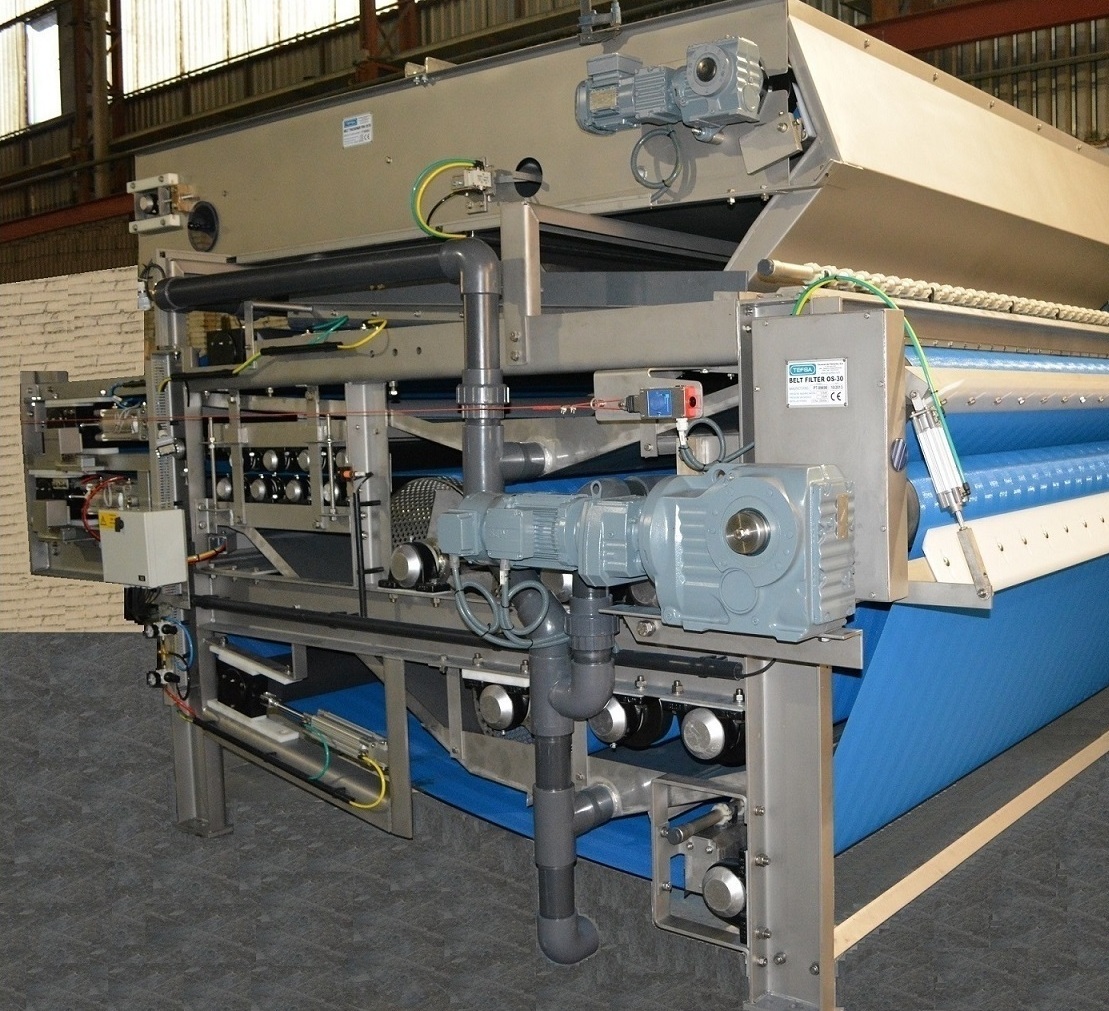
Belt filter press
When a saturated slurry or sludge must be dehydrated in a continuous process municipal waste water treatmen...
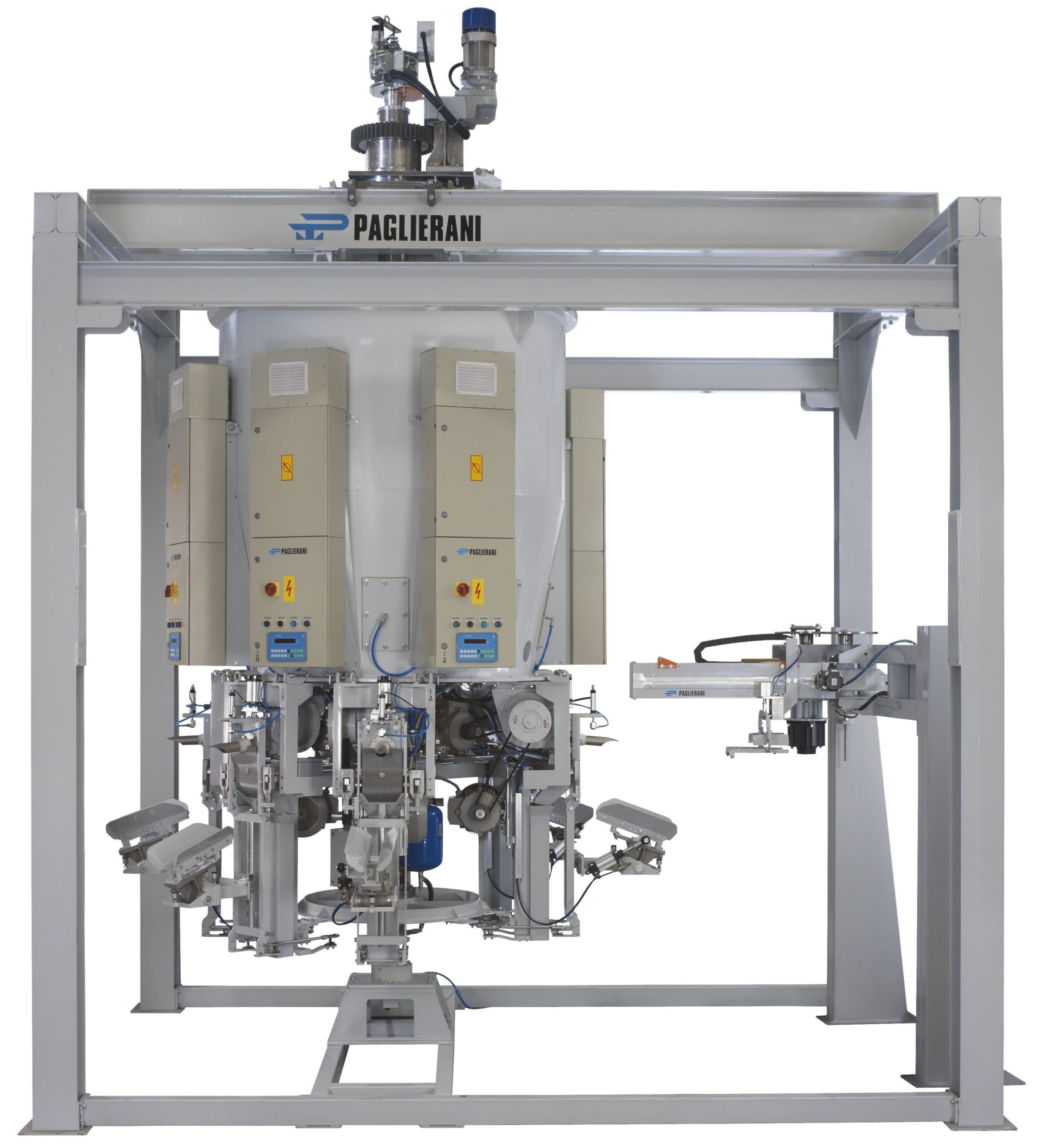
Rotary bag packers for valve bags
Quick filling of bags while avoiding leakage out of the top of a bag can be challenging o...
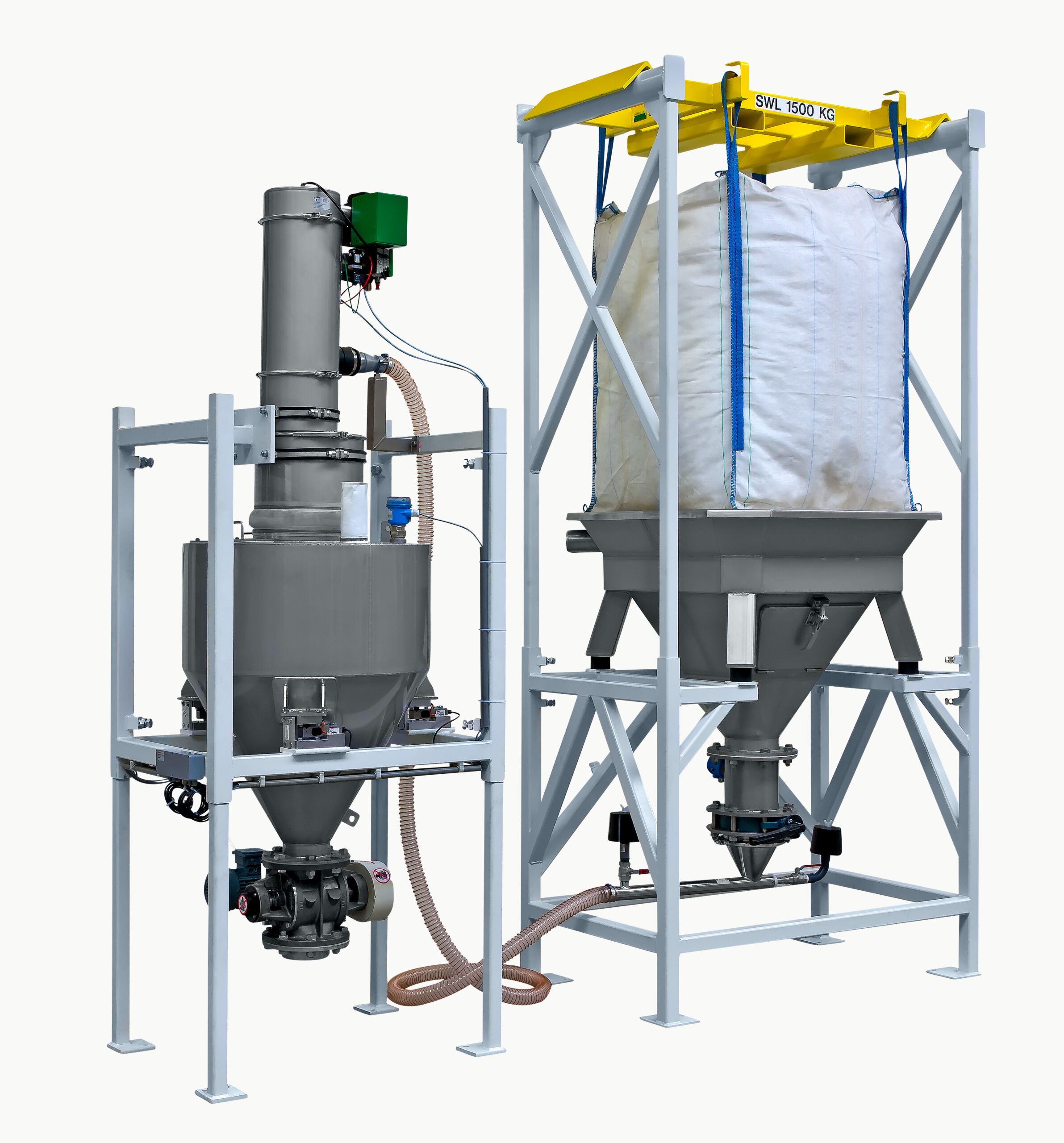
Big bag discharge system
Dust emissions, product loss and product contamination are the main risks when discharging products ...
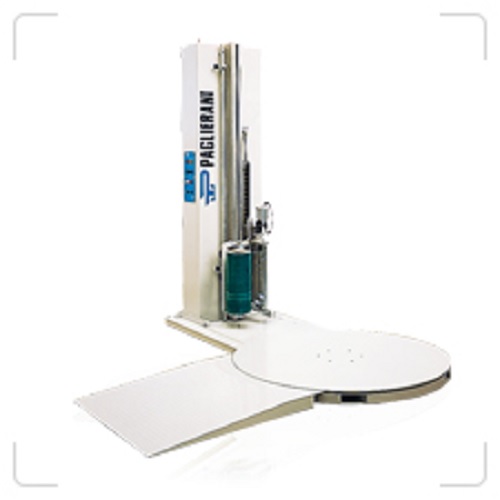
Semi-automatic stretch wrapping machine
At lower speeds, some level of automation is required to provide a cost-effective m...
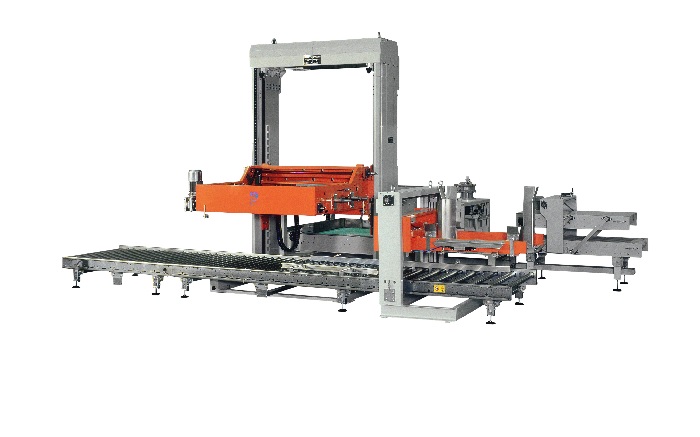
Traditional palletizer for bags
Packaging lines may require a single, flexible solution that can handle many different palle...
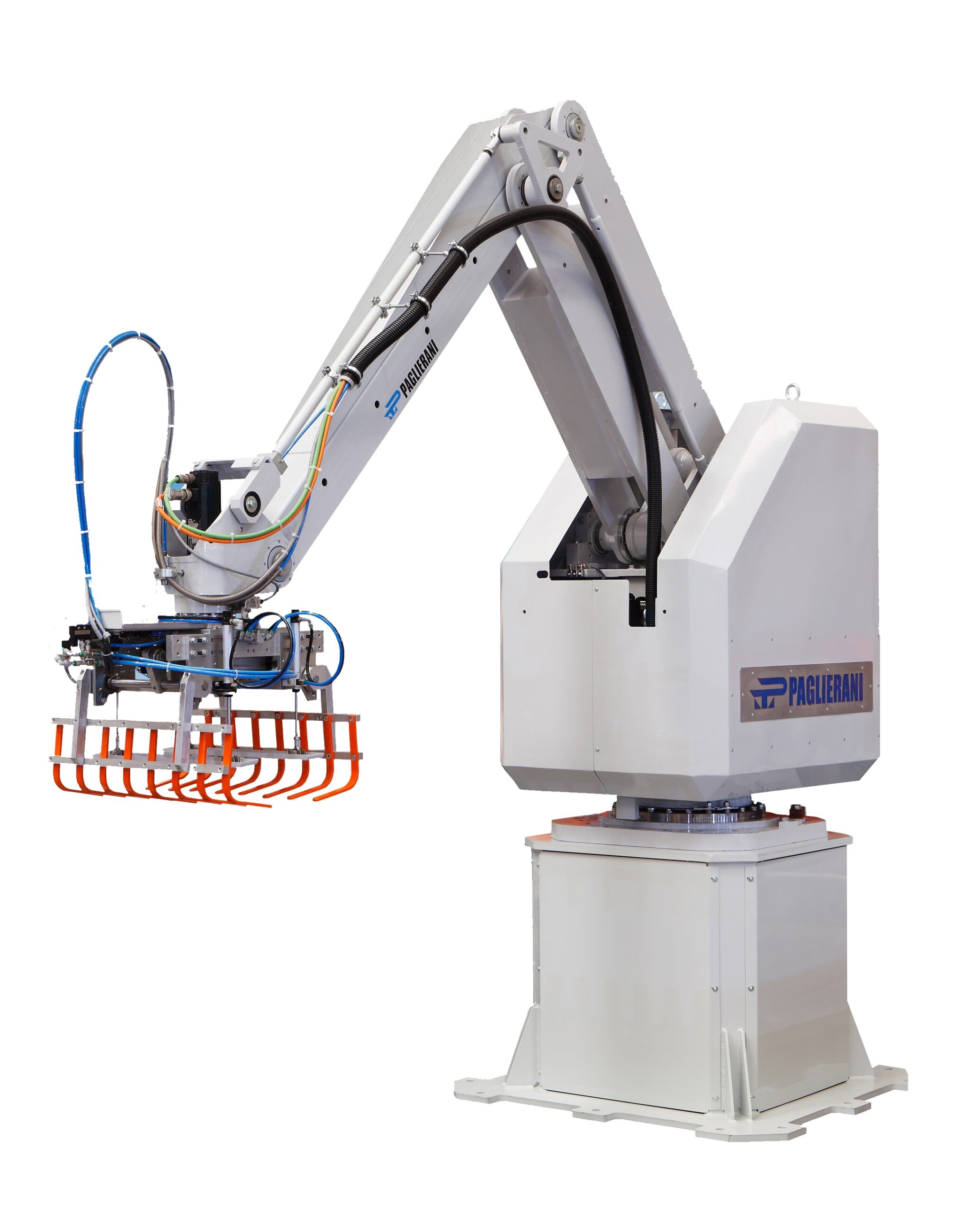
Palletizing robot arm
For high speed palletizing, palletizing high payloads, or just where greater flexibility is required, i...
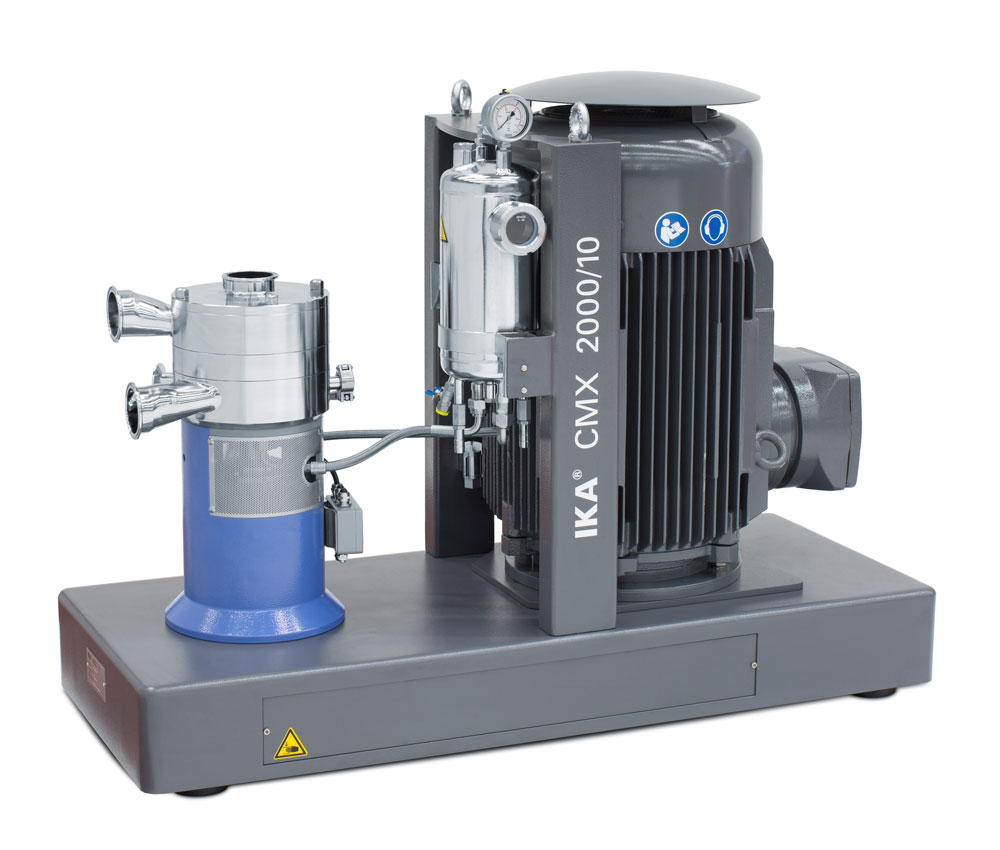
Inline batch mixer for solids and liquids
Several issues often arise when your process requires batch-wise mixing of powde...

Vertical agitated dry media mill
A vertical agitated media mill is used for grinding ultrafine particles, in an agitated (or...
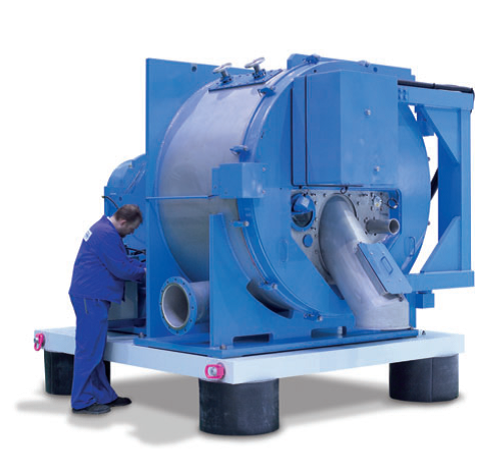
Horizontal chemical scraper centrifuge
For slurries difficult to discharge, a scraper can improve process reliability, effi...