2-phase separating decanter for chemical and mineral processing
Ensure precise separation and optimal moisture control in your chemical and mineral processes with this robust decanter centrifuge, designed to efficiently handle complex slurry compositions and enhance product consistency.
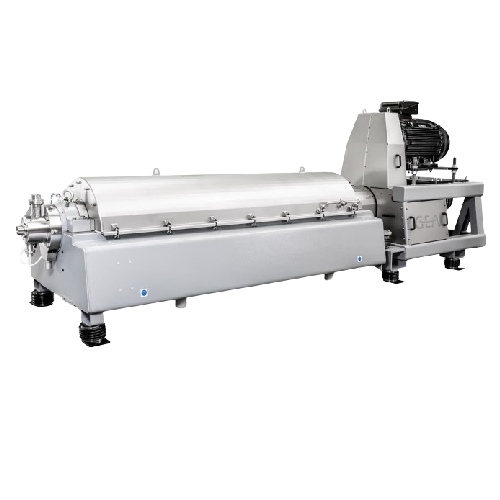
Separates and Classifies Chemical and Mineral Slurries
The 2-Phase Separating Decanter cutMaster from GEA is a robust industrial centrifuge meticulously engineered for dewatering and classification in chemical and mineral processing industries. This equipment distinguishes itself with a solid-wall bowl design featuring a cylindrical section for efficient liquid clarification and a conical section for drying solids. With its adaptable GEA summationdrive, the centifuge excels in processing high solid capacities through dynamic differential speed and torque adjustments.
Capable of operating in continuous and automated settings, this decanter is integral to the separation and classification of materials such as titanium dioxide pigments, sodium carbonate, and kaolin. It effectively handles a diverse range of solid, liquid, slurry, and cake product types, offering customizable throughput options aligned with specific production needs.
Built to withstand rigorous industrial conditions, the equipment incorporates high-alloyed duplex and super duplex steels or Hastelloy C276, ensuring superior corrosion resistance. The decanter is CIP-compatible for seamless cleaning, reducing downtime significantly. GEA’s unit meets stringent ATEX standards, offering explosion protection with inert gas blanketing, and is suitable for use in temperatures up to 130°C. Integration into existing production lines is streamlined with its frequency-controlled motor and energy-efficient design, saving up to 20% on energy consumption.
Benefits
- Enhances process efficiency by delivering precise separation and classification.
- Supports high solid capacities, reducing production bottlenecks.
- Minimizes energy consumption with variable-speed motor optimization.
- Ensures safety in hazardous environments with ATEX-certified explosion protection.
- Streamlines maintenance with integrated CIP system for quick cleaning.
- Applications
- Mineral products, Chemical products
- End products
- Lime, Gypsum, Silica gel, Titanium dioxide pigments, Kaolin, Bentonite, Alumina, Zeolites, Sodium carbonate, Talc, Calcium carbonate, Barite
- Steps before
- Mixing, Precipitation, Chemical Reaction
- Steps after
- Clarification, Solid Drying, Filtration
- Input ingredients
- chemical products, mineral products
- Output ingredients
- clarified liquid, dried solids
- Market info
- GEA is known for its expertise in engineering innovative and sustainable equipment and solutions, focusing on sectors such as food, beverages, pharmaceuticals, and energy, with a reputation for quality, efficiency, and advanced technological applications in industrial processing.
- Phase separation
- 2-Phase
- Type
- Deep-pond decanter centrifuge
- Bowl type
- Solid-wall
- Bowl sections
- Cylindrical for clarification, conical for drying
- Centrifugal force
- Used for solids flinging
- Discharge method
- Gravity flow into liquid catcher
- Drive system
- GEA summationdrive with intelligent kinematics
- Differential speed
- Automatic adaptation via frequency-controlled motor
- Material
- High-alloyed duplex steels, super duplex steels, Hastelloy C276
- Gaskets
- NBR, FKM, FFKM, EPDM
- Temperature compatibility
- Up to 130 °C
- Cleaning method
- CIP-compatible
- Working mechanism
- Centrifugal force via decanter centrifuge
- Integrated steps
- Dewatering, classification, drying of solids
- Batch vs. continuous operation
- Continuous
- Cleaning method
- CIP-compatible
- Automation level
- Automatic adaptation of differential speed
- Drive efficiency
- High efficiency with variable speed motor
- Energy input principle
- Energy feeding via variable speed motor
- Solids discharge method
- Transported by scroll
- Abrasion resistance
- High
- Cleanability
- CIP-compatible
- Corrosive resistance (e.g. acids)
- Hastelloy C276, Duplex Steels
- Explosion protection
- Gas-tight decanters, Inert atmosphere
- Machine footprint
- Compact
- Bowl shape
- Solid-wall with cylindrical and conical sections
- Discharge method
- Scroll transport to solids discharge, free discharge of clarified liquid into a catcher
- Material of construction
- Stainless steel, high-alloyed duplex or super duplex steels
- Temperature range
- Available up to 130 °C
- Control panel type
- HMI / Touchscreen / PLC
- Integration possibilities
- Process automation / SCADA integration
- Discharge method
- Gravity / Pump assisted
- Drive type
- GEA summationdrive with intelligent kinematics
- Torque adjustment
- High differential speeds and torques
- Variable speed motor
- Frequency-controlled motor
- Material of construction
- High-alloyed duplex steels, super duplex steels or Hastelloy C276
- Explosion protection
- ATEX certification / Gas-tight decanters
- Temperature resistance
- Up to 130 °C