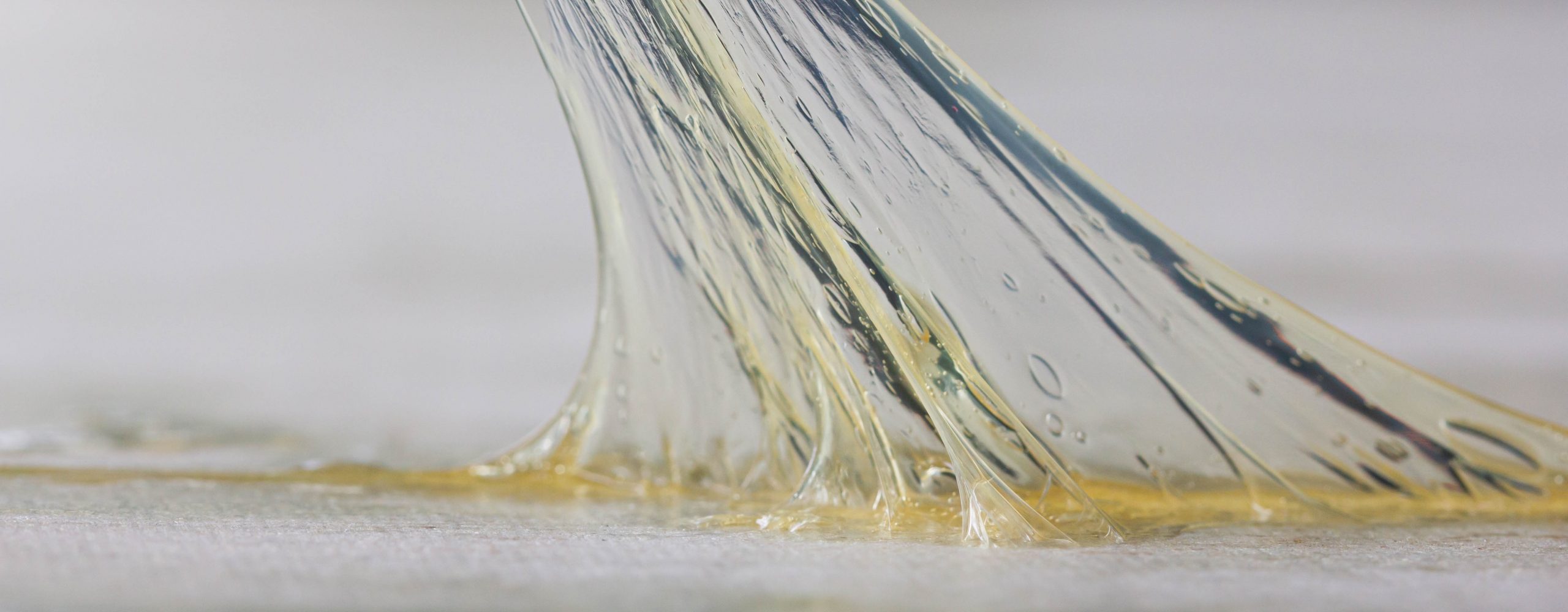
Adhesives Manufacturing Equipment
Find innovative adhesives equipment and connect directly with world-leading technology suppliers
Adhesives are grouped according to their form, origin - natural or synthetic - and their material joining method. You can make natural adhesives from plant and animal sources such as bones, hide and skin, agar, dextrin. Manufacturers count with adhesive making equipment to produce synthetic adhesives from organic compounds. They include epoxy adhesives, cyanoacrylates (or super glue), acrylic adhesives and so on.
Stories about adhesives
Select your adhesives process
Tell us about your production challenge
Reactiveness: when adhesives need special conditions for bonding
Further classification of adhesives involves their method of reaction. This implies that they may or may not need chemical reactions to harden. Reactive adhesives bond in the presence of a reactive catalyst like heat, moisture and absence of oxygen to solidify. Non-reactive adhesives harden by drying. Acrylic adhesive is reactive and you can produce it by the reaction of acrylic and methacrylic acids in the presence of a special activator, which initiates bonding. An acrylic reactor for helps get a better yield. Hot glue making can happen with batch processing, using a kettle mixer, for instance, or continuous extrusion. Adhesive making equipment automates large scale production.
Industrial production: how the adhesive making equipment design helps make quality adhesive
Solvent-based adhesives are suitable for different kinds of substrate, which explains their vast application in the manufacturing industry. You can use it in the medical industry, the packaging industry and for automobiles. Solvent- and water-based adhesives are both beneficial to manufacturers depending on their application. The former dries very quickly because they are made with hydrocarbon solvent such as acetone and toluene.
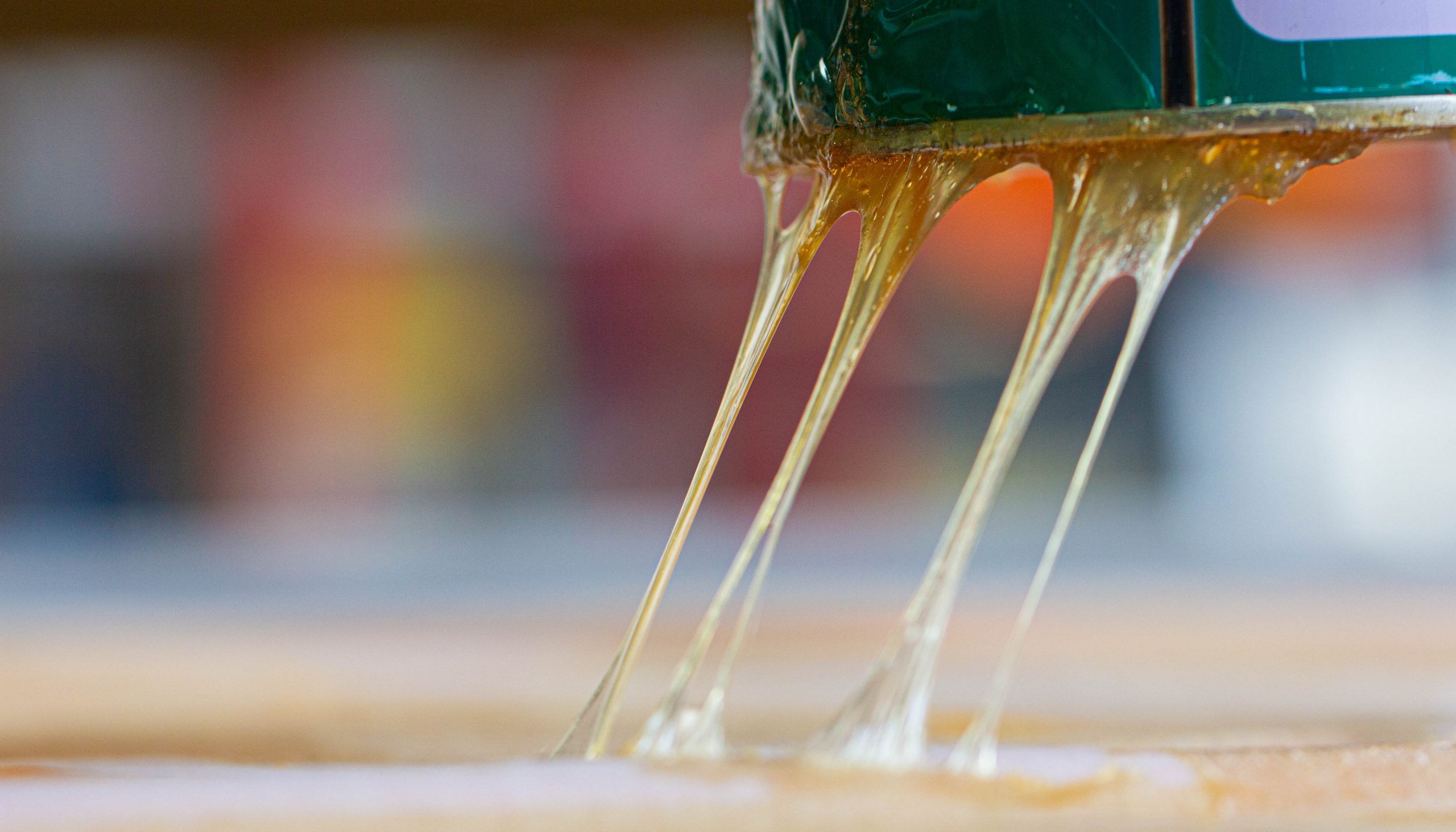
Asides from prolong drying time of water-based adhesives, they are safe and cheaper than the solvent-based. You can produce water based adhesives by combining water, polymers and additives. For solvent-based adhesives, mix solvents and thermoplastics such as acrylic or silicone. Use a high shear mixer to help you with that. It subjects the ingredients to intense high energy to make a stable and fine emulsion.
How do adhesives impact the environment – and are there alternatives?
The biodegradability of solvent-based adhesives is significantly low. The chemical wastes are not eco friendly and, as such ,affect the soil, water and air. A good number of manufacturing industries produce solvent-based adhesives because of their high substrate affinity.
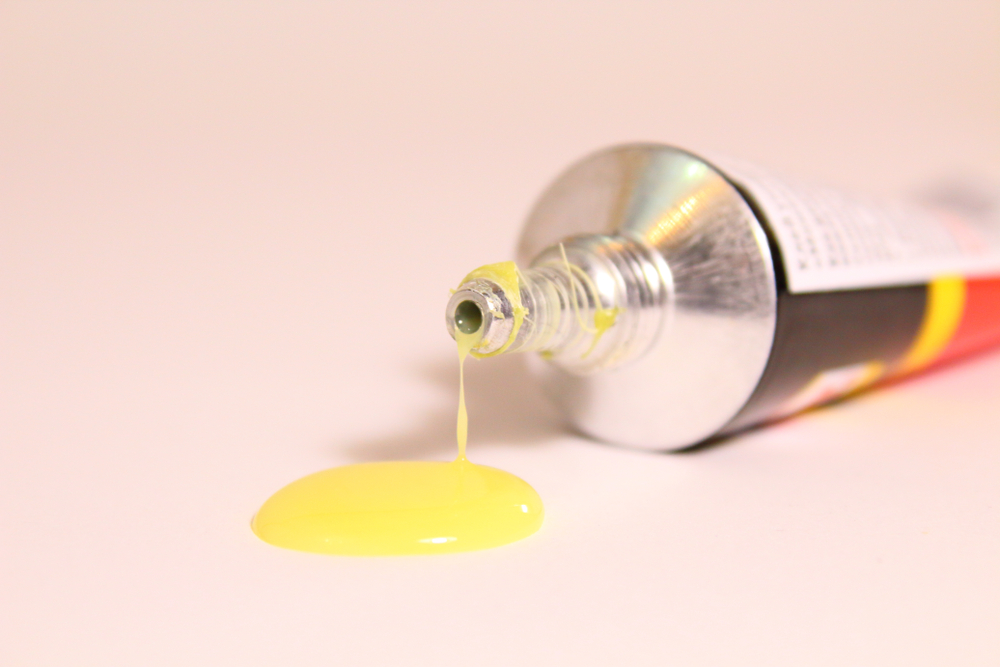
Consider sustainable options like beeswax or gum arabic in place of non-renewable adhesives. Gelatin, an animal collagen, is biodegradable, but involves different manufacturing process and equipment other than adhesive making machine. It usually involves pre-treatment with acid (hydrochloric acid) or alkaline (sodium carbonate) to remove minerals and impurities. The extraction kettle can help you with that. Countries like the United States do not allow the use of solvents like toluene and methylene chloride when producing adhesives due to their negative environmental impact.
From ceramics to packaging – trends in the adhesive market
The global hot melt adhesive market reached a value of US$ 6.75 billion in 2020. Looking forward, the market is expected to grow at a CAGR of 4.5% during 2021-2026. The packaging sector is growing and steadily driving the demand for hot melt adhesives. Asides from sealing purposes, the automobile industry uses it for car seat covers. Other rising demand includes flooring materials and ceramics. Apart from looking for better adhesive processing equipment, producers also regard the cost-effectiveness of making adhesives. Also, instead of oven drying or ultraviolet curing, manufacturers are opting for the Ebeam technology, which doesn’t produce volatile organic compounds (VOCs).
Which adhesives technology do you need?
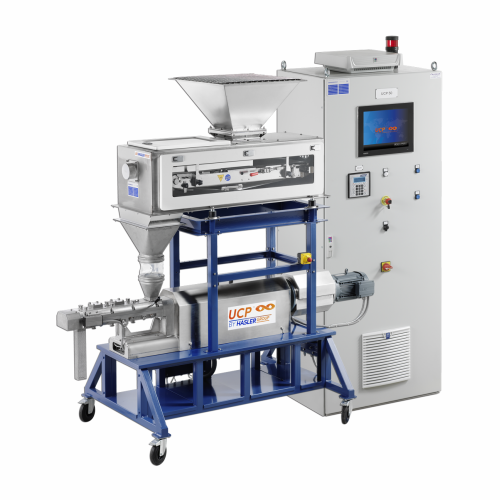
Continuous kneader for viscous applications
For engineers tackling high-viscosity challenges, this continuous kneader stre...
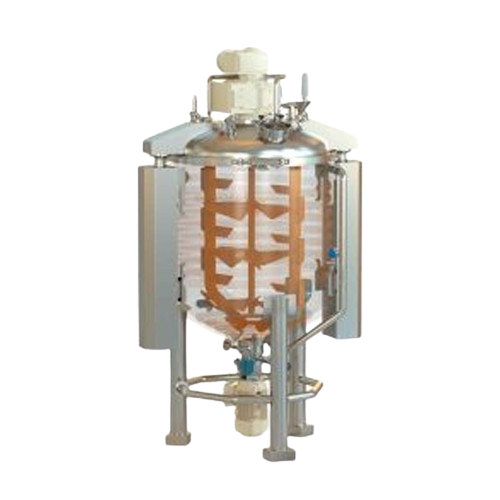
Industrial mixer for liquid and viscous products
Achieve precise mixing and homogenization of high-viscosity liquids and s...
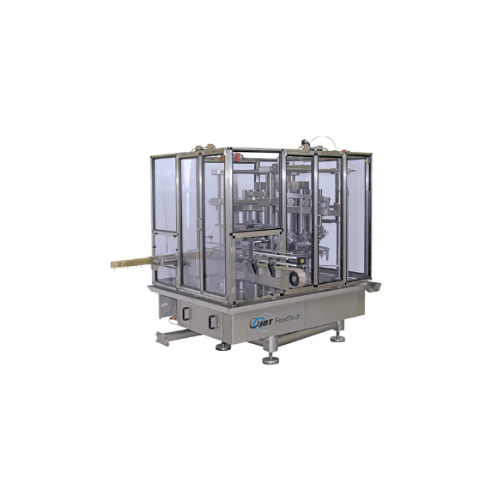
Volumetric piston filler for liquid and viscous products
Achieve precise volume control and enhance product integrity wit...
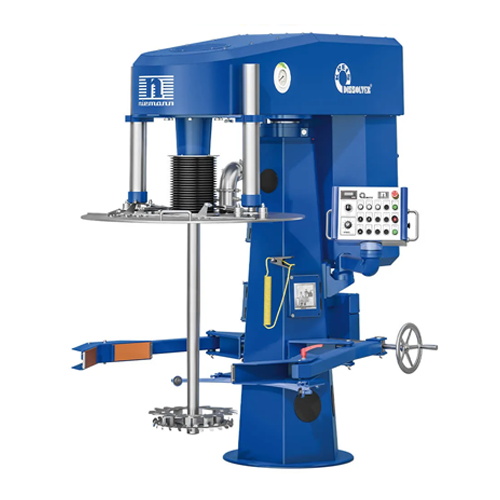
Dispersing system for high-viscous products
Achieve precise mixing and dispersing of high-viscous products with advanced f...
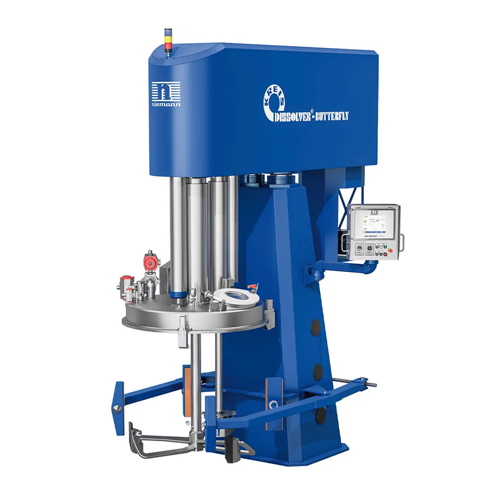
Mixing and dispersing solution for ultra high-viscous products
Efficiently process ultra high-viscous and thixotropic ma...
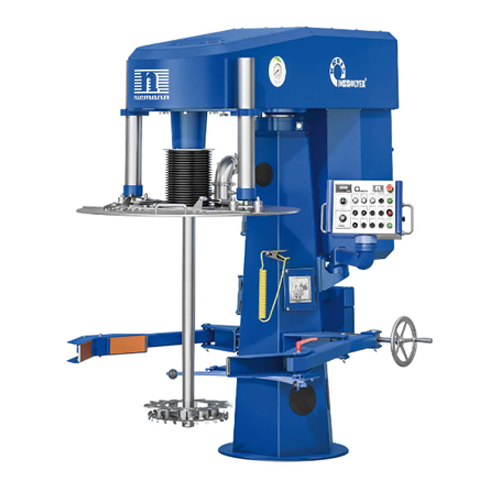
High-efficiency disperser for viscous products
Achieve precise control over the mixing and dispersing of high-viscosity ma...
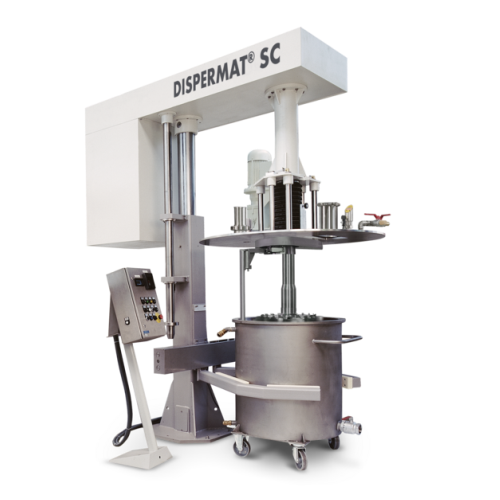
Explosion-proof production vacuum disperser for viscous products
Achieve precise and reliable dispersion of high-viscosi...
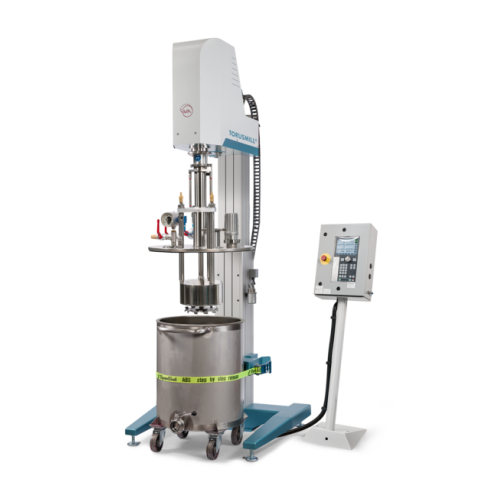
Vacuum basket mill for highly viscous products
Achieve precision in fine milling under vacuum to prevent air inclusions in...
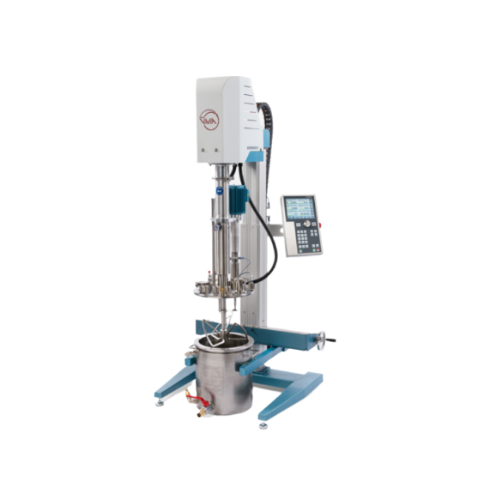
Vacuum dissolver for highly viscous products
Efficiently mix and disperse high-viscosity substances under vacuum to ensure...
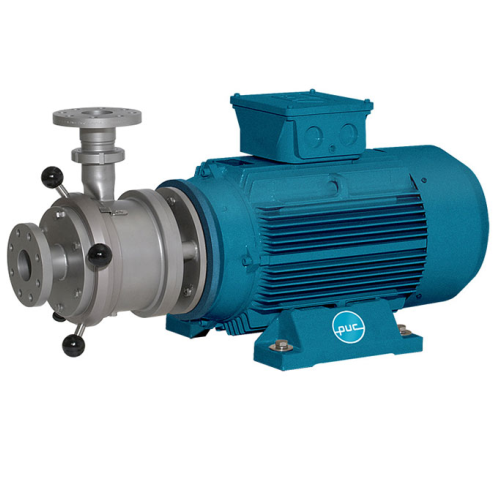
Colloid mill for emulsifying and wet milling applications
Achieve precise mixing and grinding with our colloid mill, des...
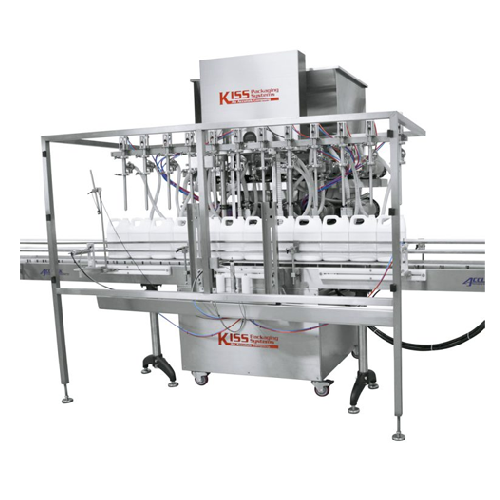
Automatic positive displacement filler for various liquids
Achieve precision and versatility in liquid filling operation...
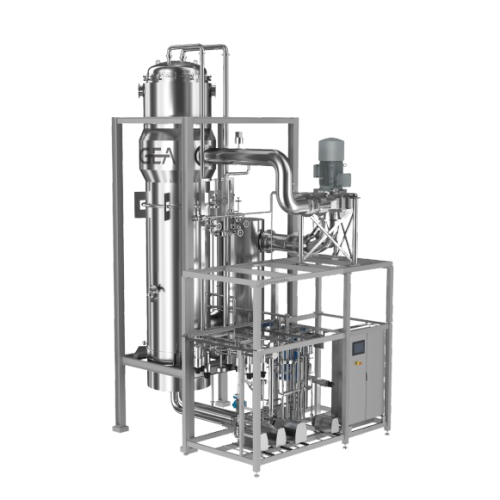
Compact plate evaporator for temperature-sensitive products
Ensure optimal heat transfer and minimal space usage with th...
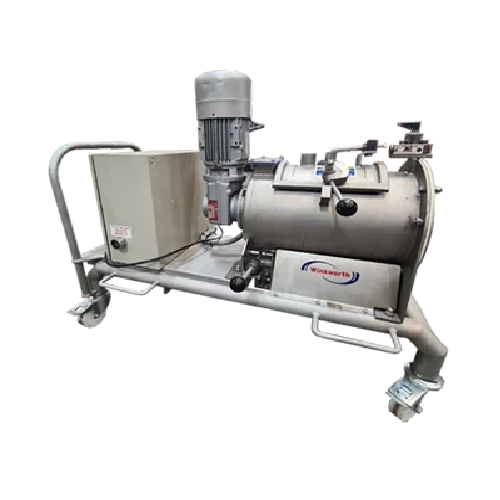
Industrial mixers for hire
Optimize your production line with versatile mixers designed for precision blending, heating, and...
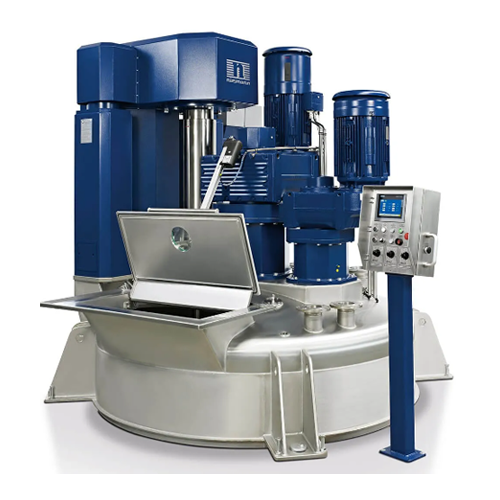
Triple shaft mixer for high-viscosity products
Achieve precision mixing and dispersing of high-viscosity products with a p...
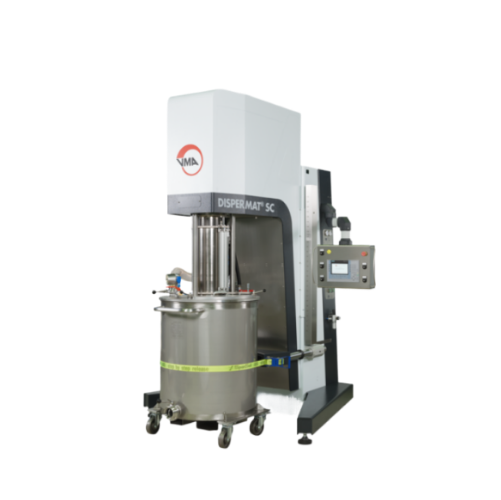
Modular basket mill for industrial dispersion
Effortlessly enhance your production efficiency with this versatile solution...
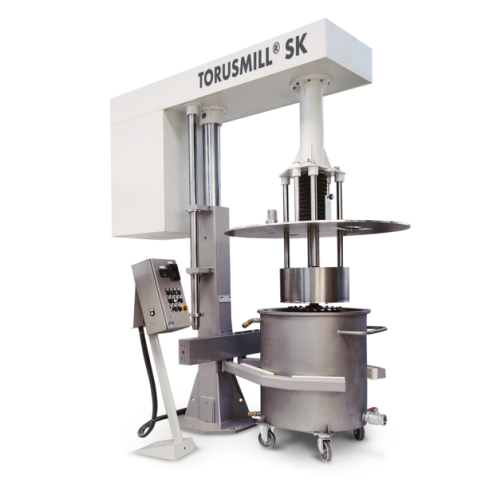
Explosion-proof basket mill for large scale production
Enhance your production line with an explosion-proof basket mill t...
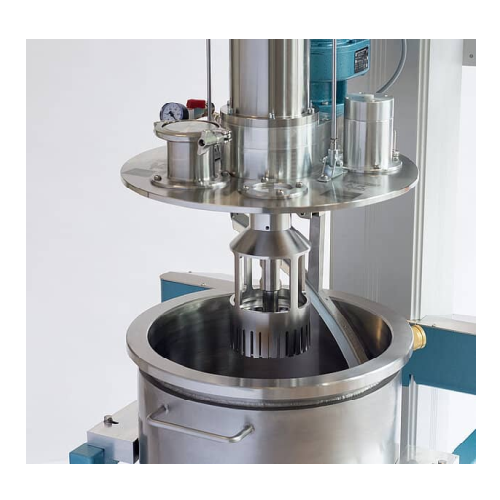
Efficient high-volume dissolver with scraper
For high-viscosity formulations, this advanced dissolver with integrated scra...
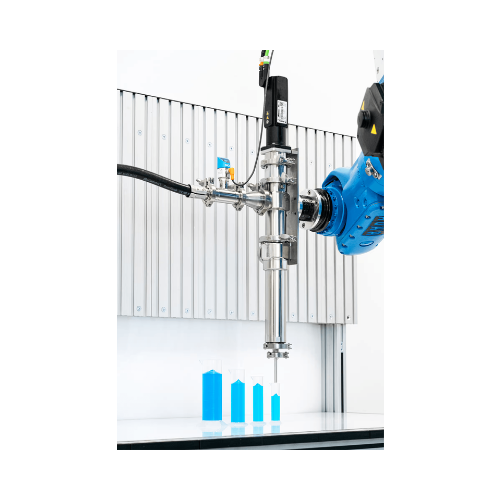
High-precision material coating for bore holes and internal threads
Achieve consistent, high-precision coating in bore ...
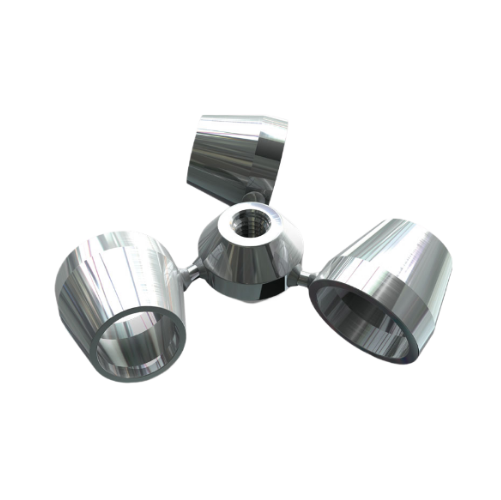
Homogenizer for low to medium viscosity media
Achieve uniform mixing and prevent air entrapment in low to medium viscosity...
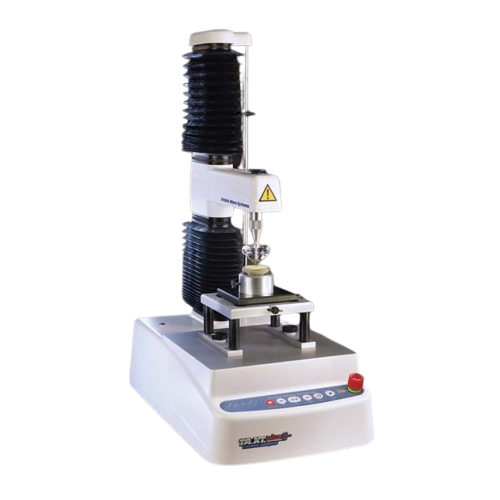
Texture analyser for food and cosmetics testing
Ensuring consistent product quality across diverse food and cosmetic appli...
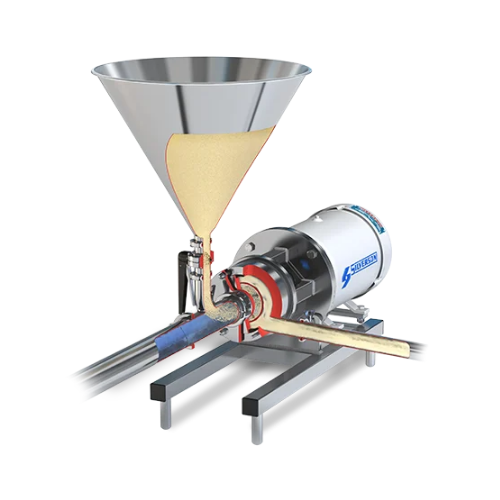
High shear powder mixing solution
Achieve agglomerate-free, homogeneous mixing of powders and liquids with high shear effic...
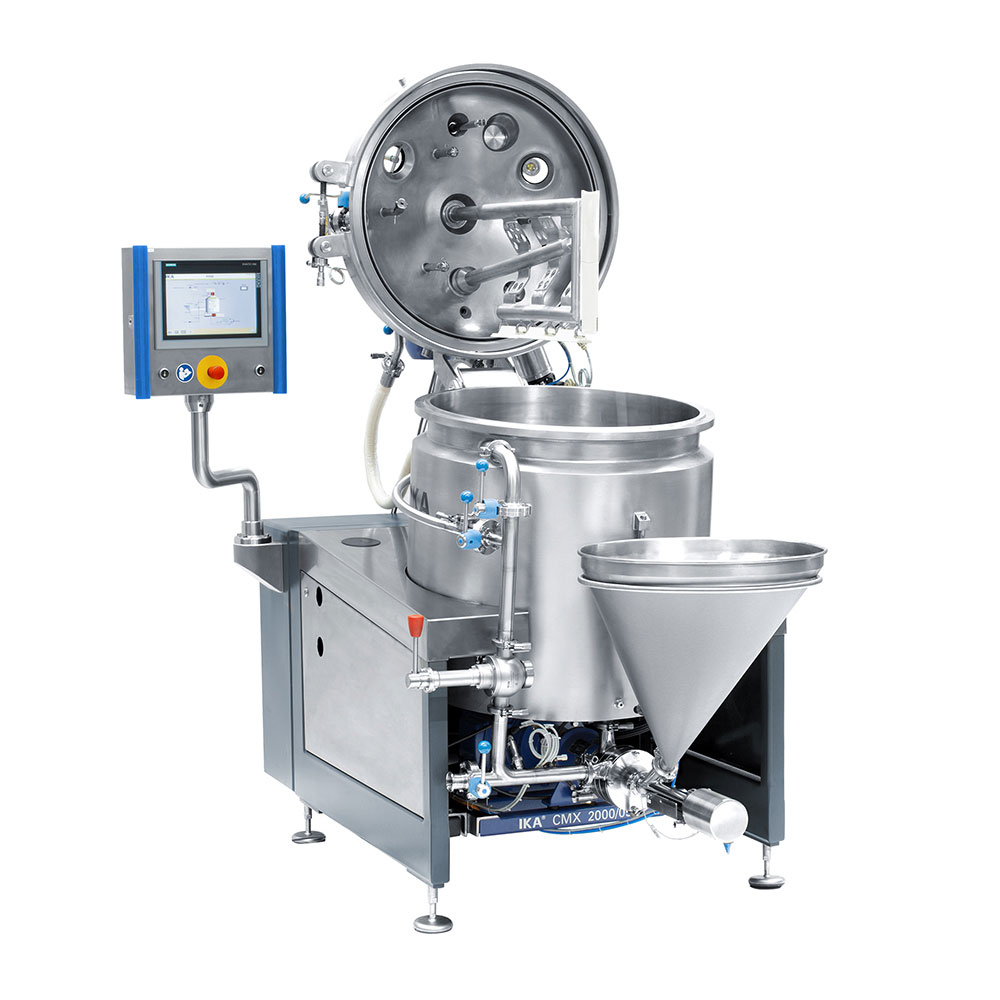
Compact Mixing Plant for Paints and Coatings
A smooth finish in paints and coatings depends on the grade of dispersal duri...
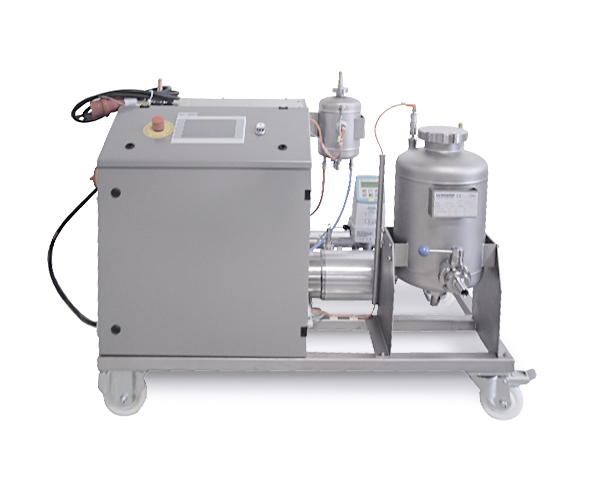
Aerator for high-viscosity media
Highly viscous ingredients in both the food and chemical processing industries require spec...
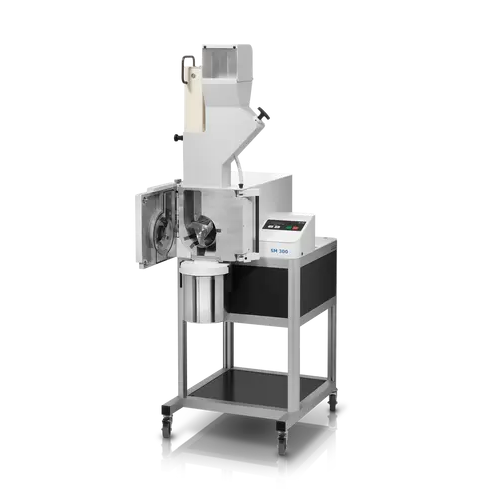
High-torque cutting mill for tough and fibrous materials
Tackle the toughest materials and ensure consistent particle siz...
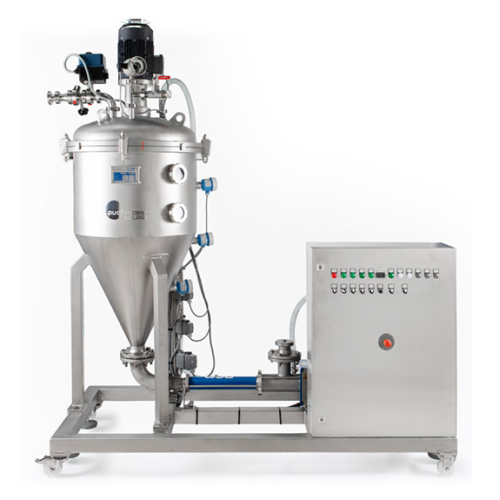
Vacuum de-aeration unit for liquid to pasty products
Optimize your product consistency and stability with continuous de-a...
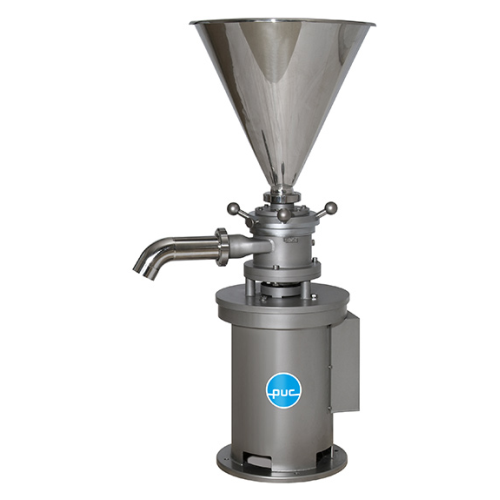
Vertical colloid mill for emulsifying and homogenizing
Optimize your production line with precise particle size reduction...
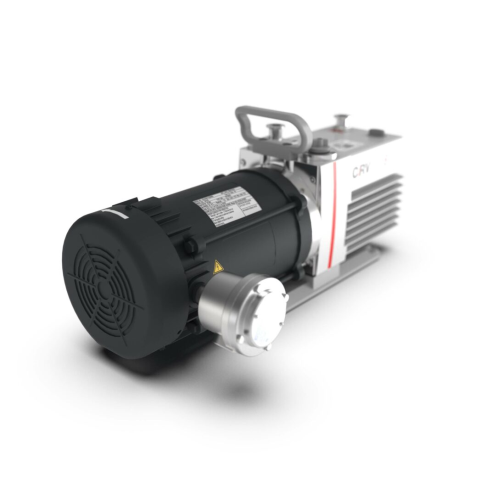
Explosion-proof rotary vane vacuum pump
Ensure safety and efficiency in flammable environments with this explosion-proof va...
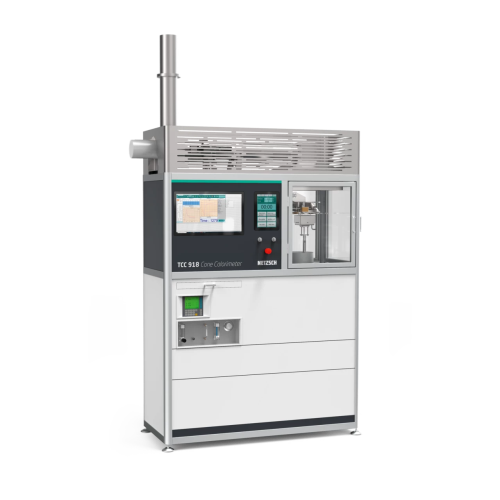
Cone calorimeter for fire testing and safety engineering
Ensure safety in your materials by precisely measuring combustio...
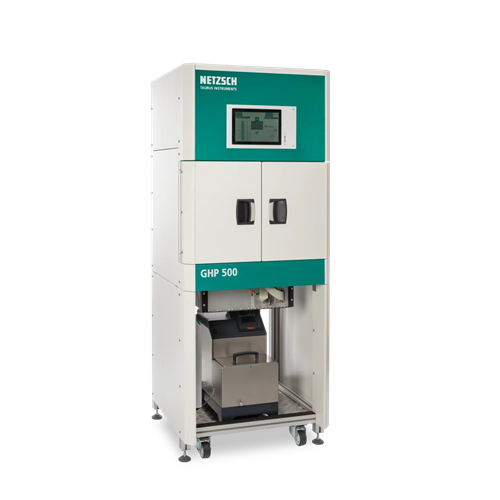
Guarded hot plate for thermal conductivity testing
Ensure optimal insulation performance with precise thermal conductivit...
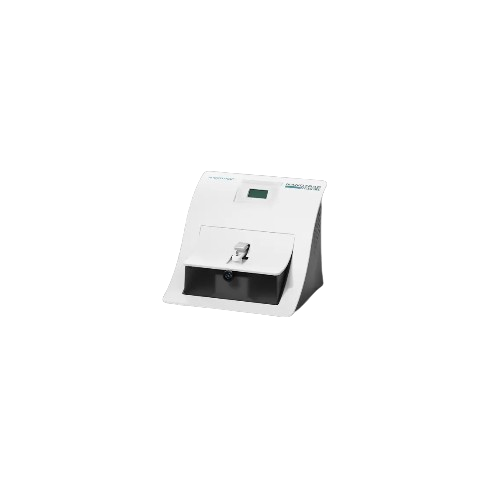
Nanoparticle size analyzer
Master precise nanoparticle and zeta potential analysis with dynamic light scattering technology,...
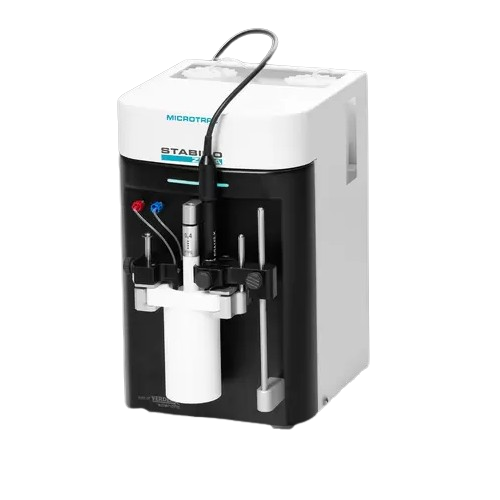
Zeta potential analyzer for colloidal stability
Achieve precise control over colloidal stability and particle interactions...
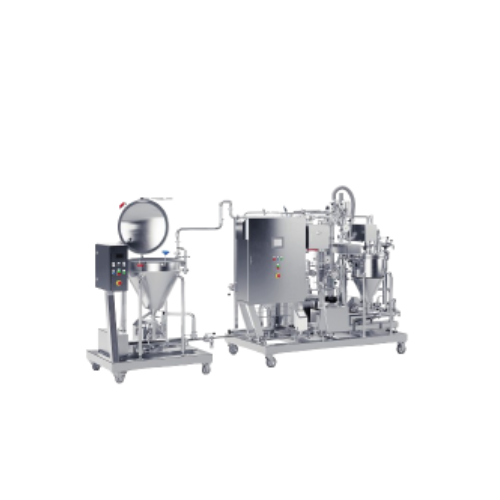
Ultra high temperature treatment for small-scale production
Achieve extended shelf life and uniform product quality with...
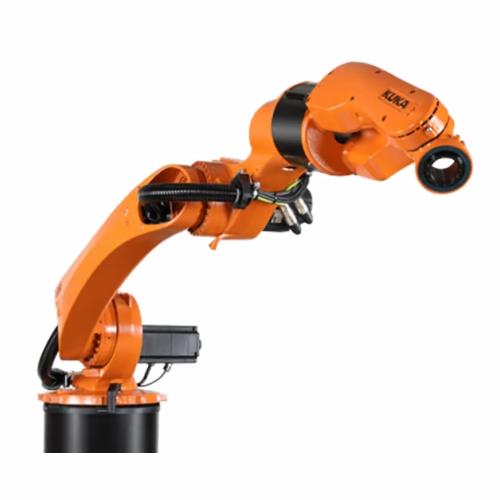
Industrial robot for arc welding and adhesive applications
Optimize your production line with precise and high-speed rob...
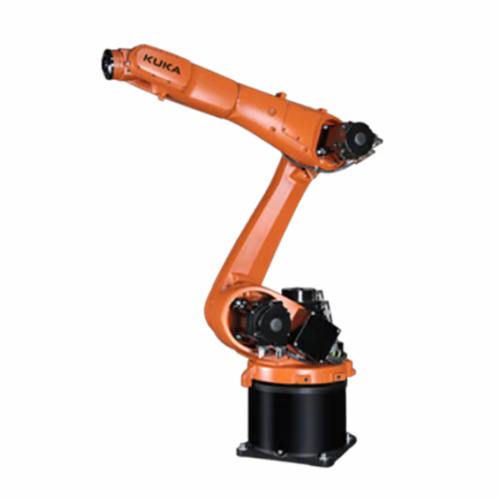
Robotic arm for small component handling
Streamline your production with a versatile robotic arm designed for small compone...
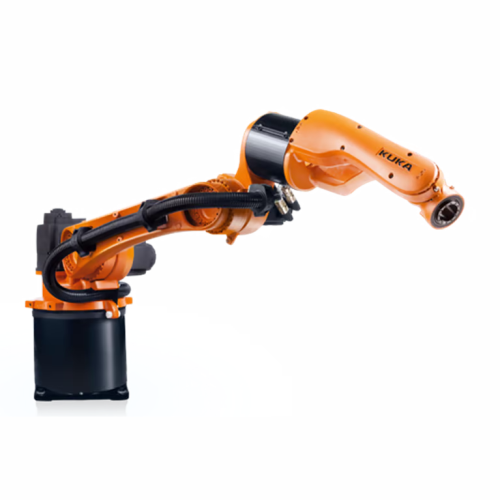
Continuous-path arc welding robot
Optimize your production line with high-speed, precision arc welding using our advanced h...
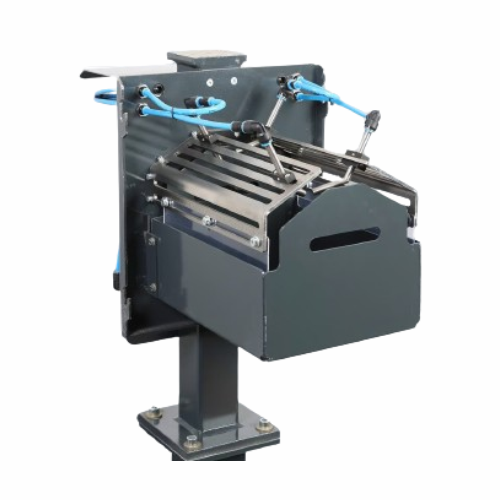
Adhesive nozzle cleaning system for automotive production
Ensure consistent adhesive application and seamless quality by...
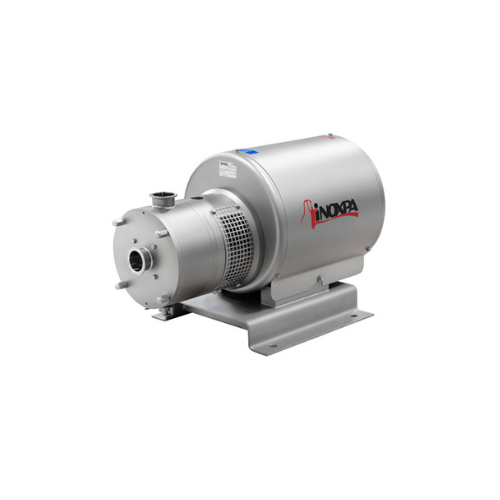
In-line high shear mixing solution
Achieve precise emulsification and particle size reduction with high shear capabilities,...
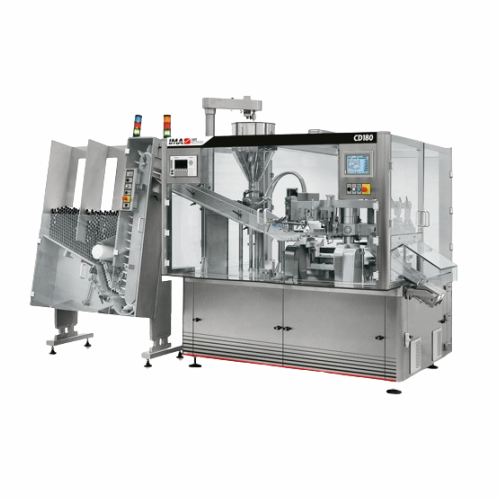
Automatic tubefiller for food and dairy products
Achieve precise dosing and seamless tube filling with high-speed efficien...
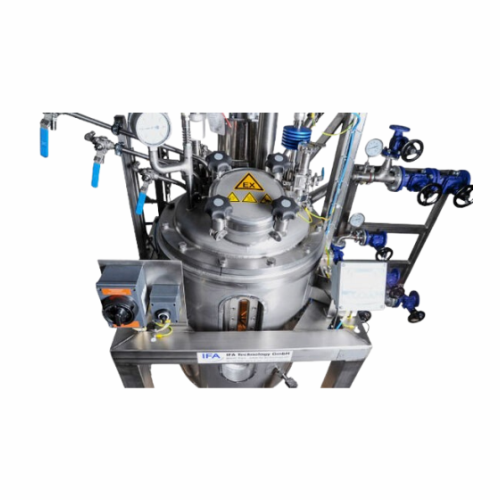
Wastewater treatment system for industrial applications
Optimize resource management and environmental impact by integrat...
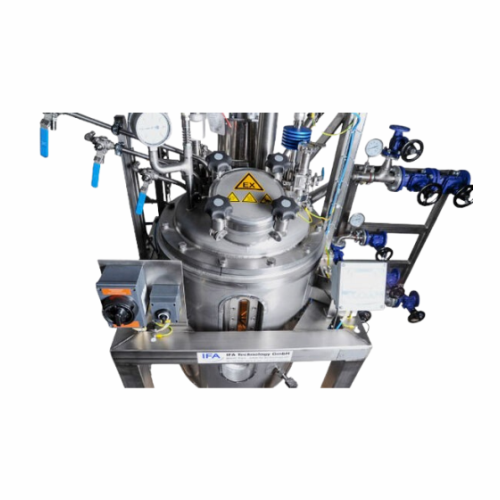
Turnkey resin synthesis plant system
Streamline resin production with a comprehensive turnkey system designed to efficientl...
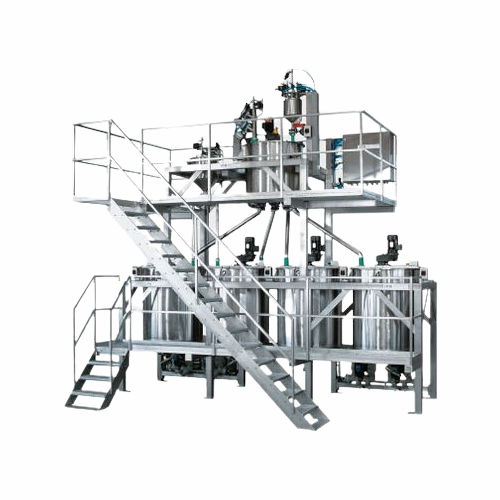
Gravimetric dosing systems for precise material measurement
Achieve precise material measurement with gravimetric dosing...
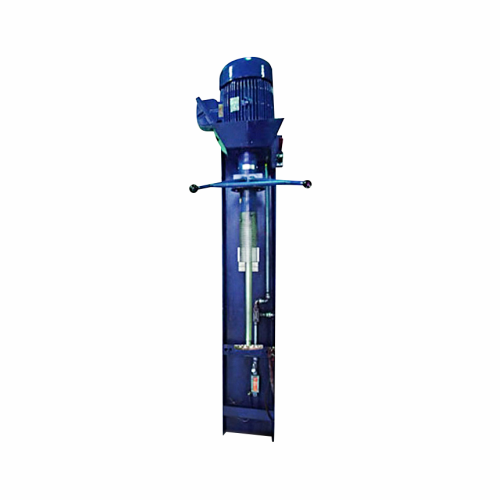
Drum mixer for dispersions & agitations
Achieve seamless fluid formulation and agitation with a compact, high-speed drum mi...
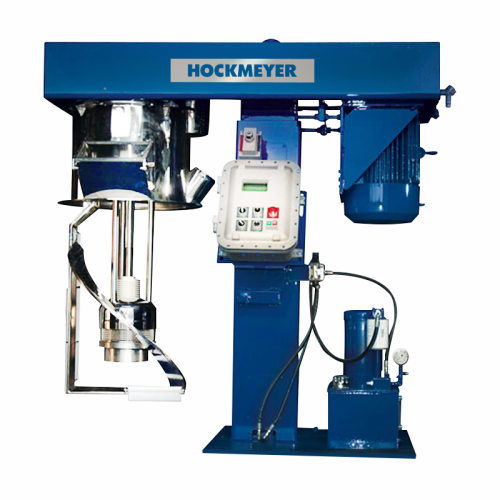
Immersion mill with sweep blade for high-viscosity products
Optimize your production line with this immersion mill desig...
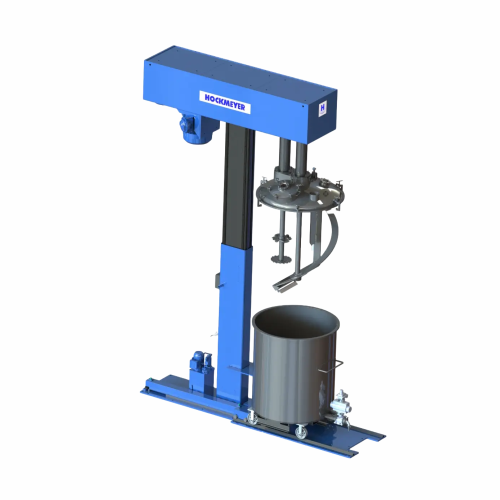
Dual shaft mixer for high viscosity products
Achieve uniform dispersions in high-viscosity processes with a dual-shaft mix...
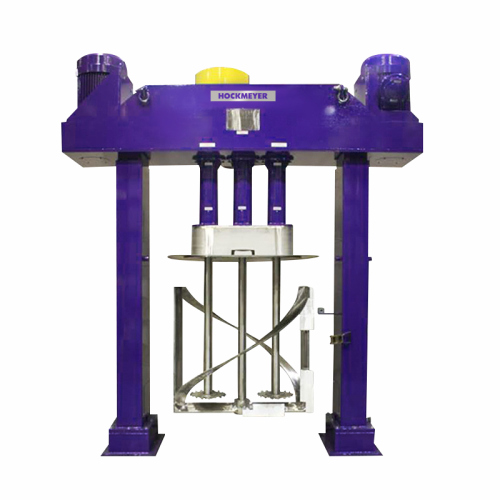
Triple shaft mixer for high viscosity products
Achieve uniform mixing and dispersion for high-viscosity materials with tri...
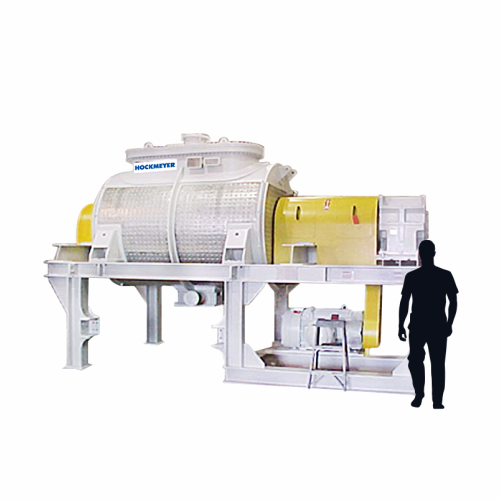
Horizontal paste mixer for high-viscosity materials
Efficiently transform high-viscosity and challenging materials into u...

Conical screw vacuum dryer for hazardous and temperature-sensitive products
When you need precise moisture control for...
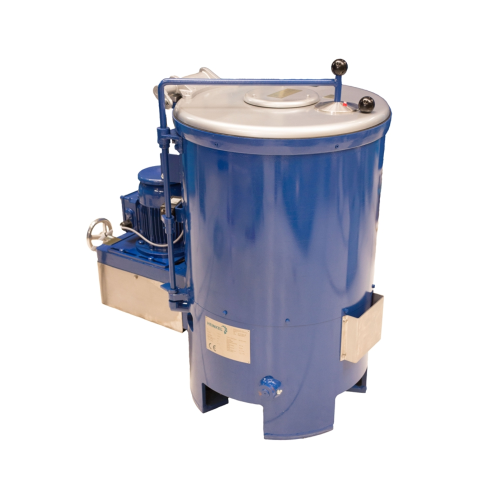
Coating centrifuge for small parts with oil and adhesives
Optimize your coating processes with a centrifuge designed to ...
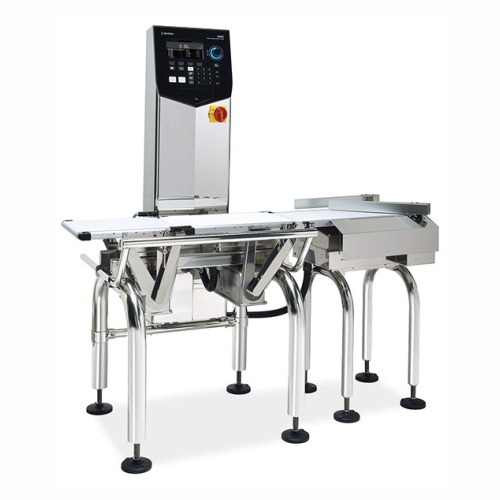
Checkweigher for packaged goods inspection
Ensure precision and compliance with this high-speed checkweigher, perfect for ...
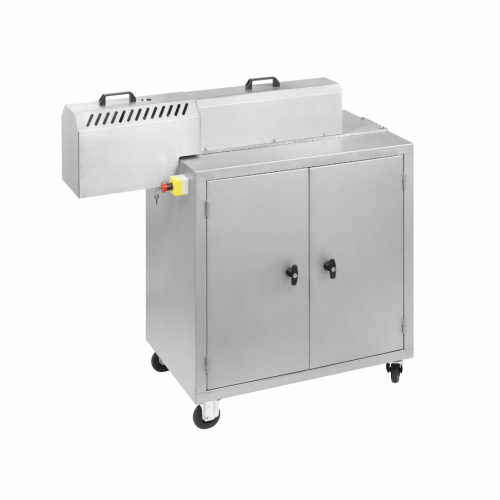
High-viscosity continuous industrial kneader for small volumes
Achieve consistent high-viscosity material processing wit...

Side entry mixer for industrial fluid mixing
Optimize your fluid mixing processes with high-speed side entry mixers, desig...
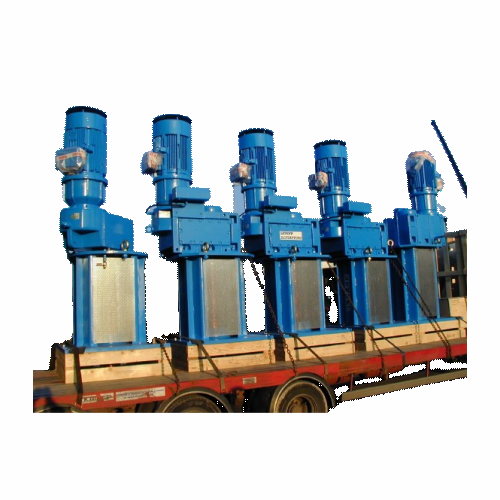
Universal industrial agitator for various fluid mixing needs
Optimize your production with an industrial agitator design...
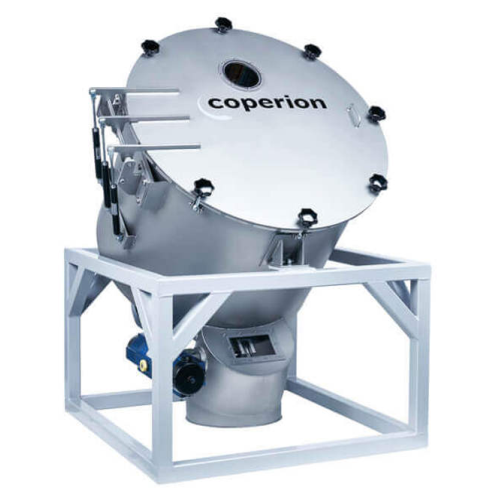
Bulk material mixer for high-speed homogenization
Achieve fast and gentle homogenization of bulk materials with a high-sp...
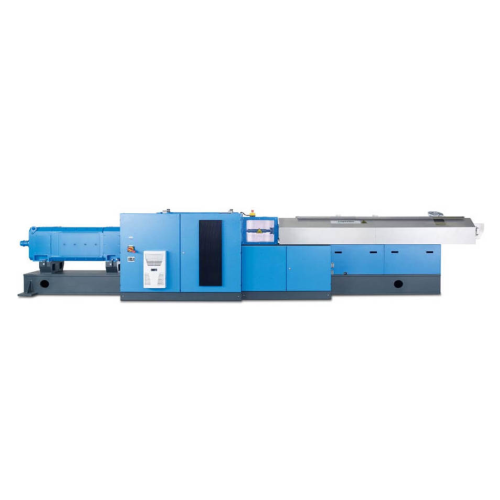
High throughput twin screw extruder for low bulk density products
When handling low bulk density materials, achieving m...
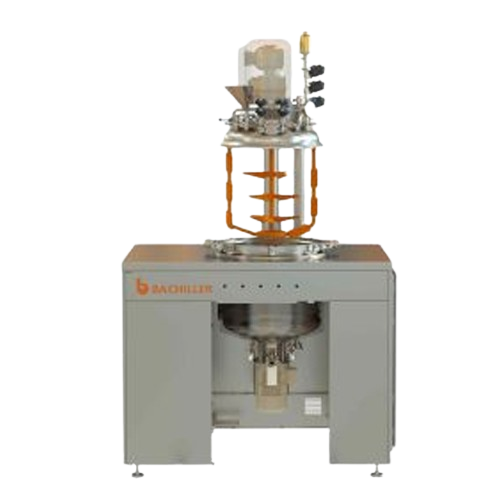
Laboratory vacuum mixer reactor for liquids and semi-solids
Achieve precise emulsification and mixing for high-viscosity...
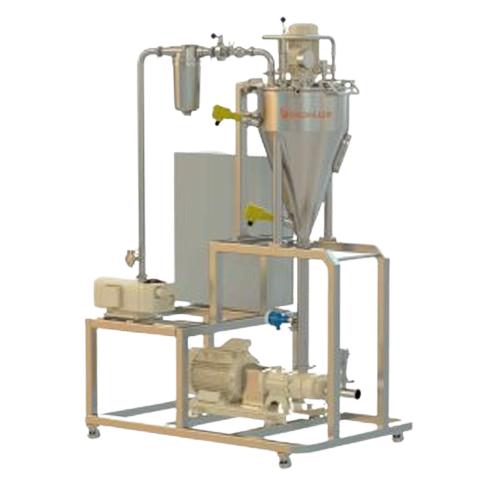
Vacuum deaerator for elimination of gases
Optimize your product quality by eliminating occlusive gases with this advanced ...
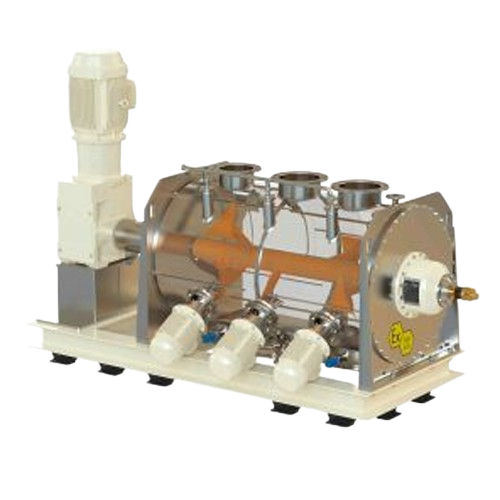
Horizontal ploughshare mixer for solids and powders
Achieve uniform blends of diverse solids and powders with precision a...
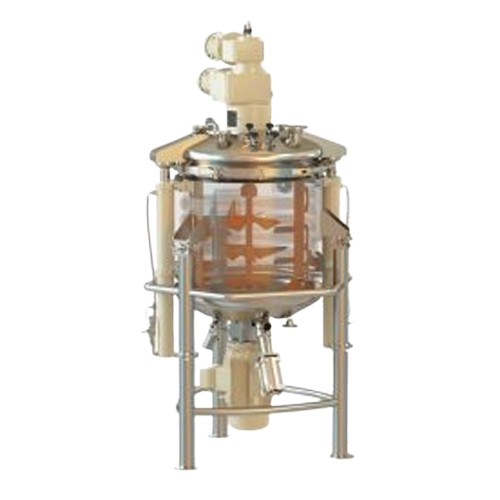
Industrial vacuum mixer and reactor for liquids
For manufacturers needing precise blending and stability, this advanced va...
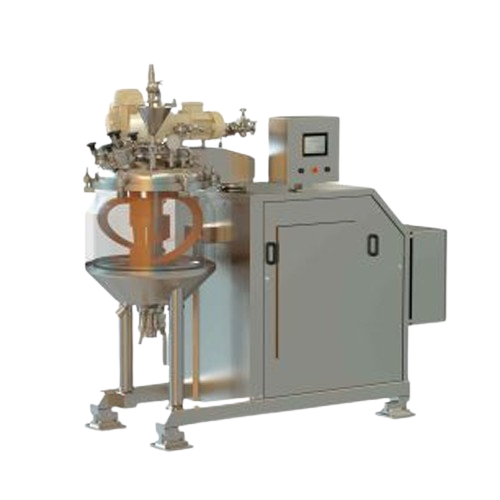
Vacuum mixer for liquids and semi-solids
Achieve precise mixing and homogenization of liquid and semi-solid formulations wi...
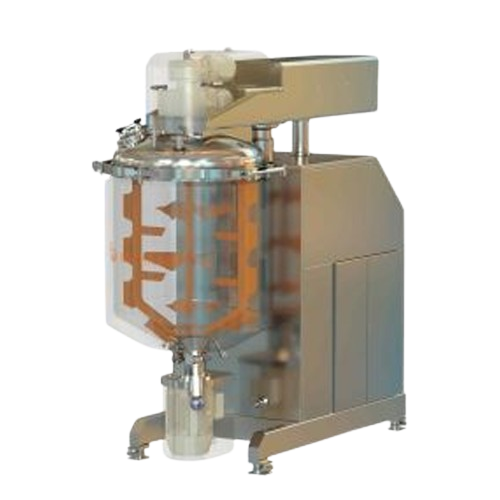
Vacuum mixer reactor for liquids and semi-solids
Achieve precise mixing and emulsification of complex liquid formulations ...
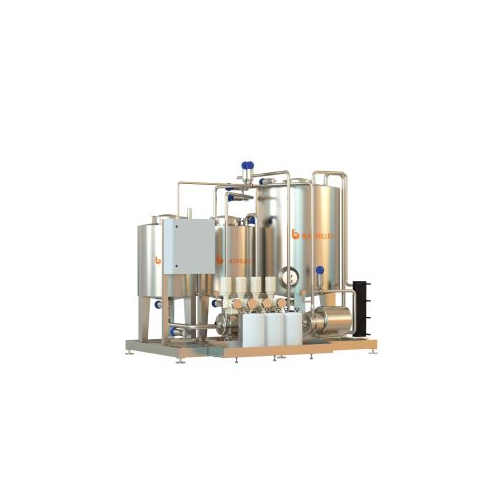
Cip system for process tanks
Ensure high-level cleanliness and compliance in your production line with an efficient in-place...
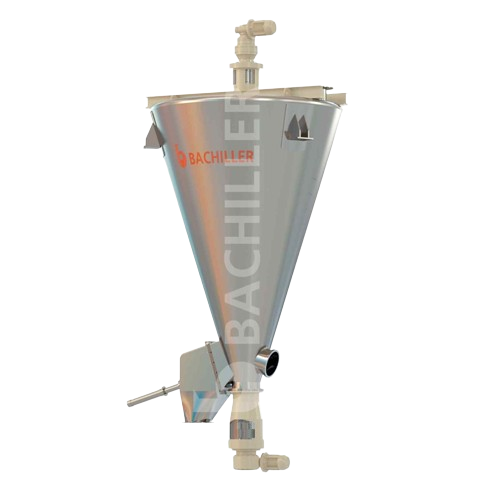
Conical screw mixer for solids and powders
Achieve precise homogenization of your solid and powder mixtures with minimal e...
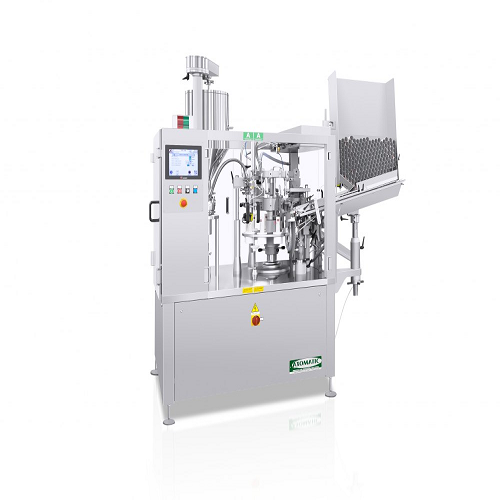
Automatic tube filling and closing solution
Optimize your production line with a high-speed machine for precise tube filli...
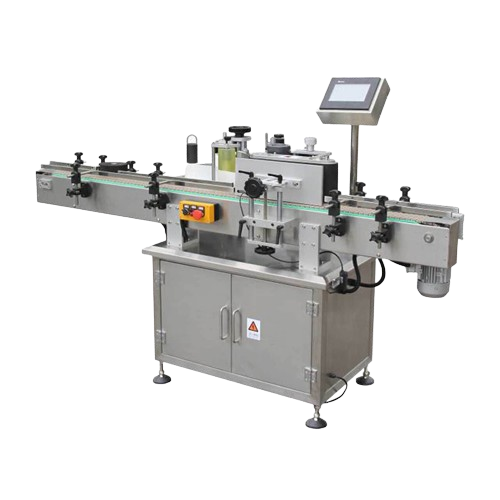
Automatic single side adhesive labeling solution
Streamline your packaging line with precision; this solution offers effic...
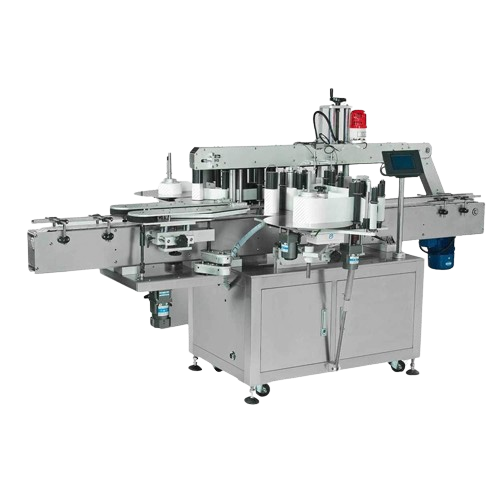
Double sides adhesive sticker labeling solution
Achieve seamless and precise double-sided labeling on bottles and containe...
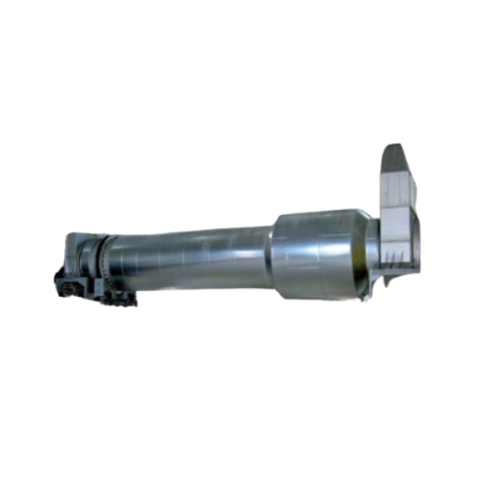
Indirect drying drums for solvent-based products
Optimize energy use and safety with our indirect drying drums, ideal for ...
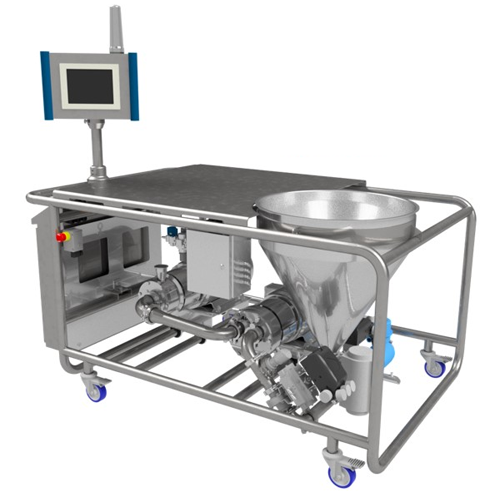
Automated powder induction and dispersion system for industrial mixing
Achieve rapid and efficient incorporation of pow...
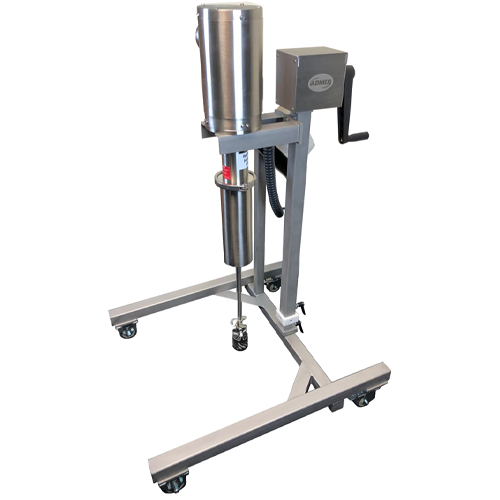
Pilot scale mixers for product development and small production runs
Optimize your mixing processes with precision cont...
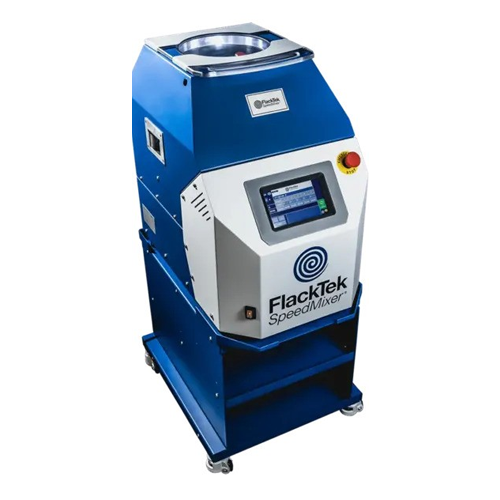
Dual asymmetric centrifugal mixer for epoxy and slurry mixing
Achieve precise mixing and consistency in your formulation...
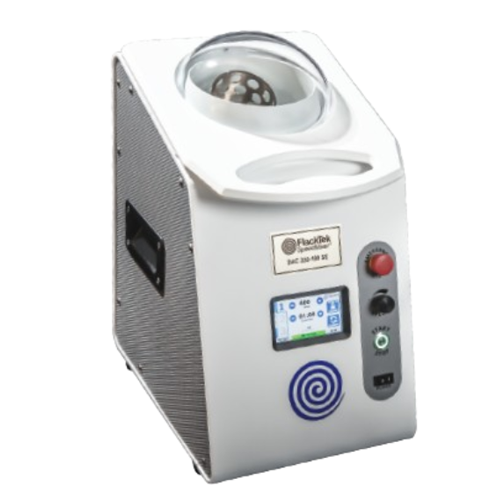
Dual asymmetric centrifugal processing system for epoxies and slurries
Streamline complex formulations with a system th...
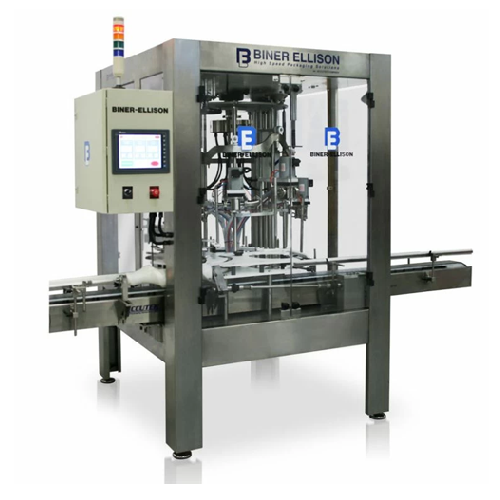
Automatic positive displacement bottle filler
Streamline your liquid filling operations with precision and flexibility, id...
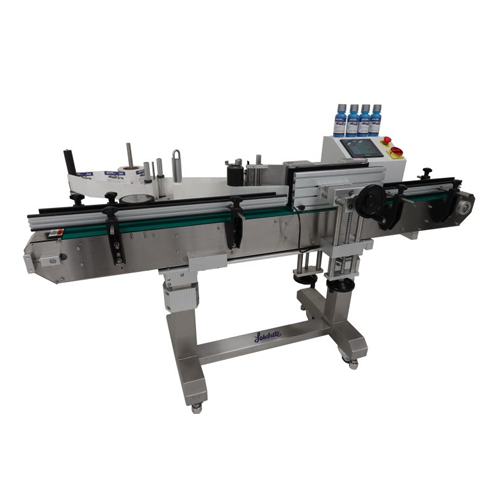
Automatic labeler for low profile containers
Optimize container labeling with precision and efficiency, addressing the cha...
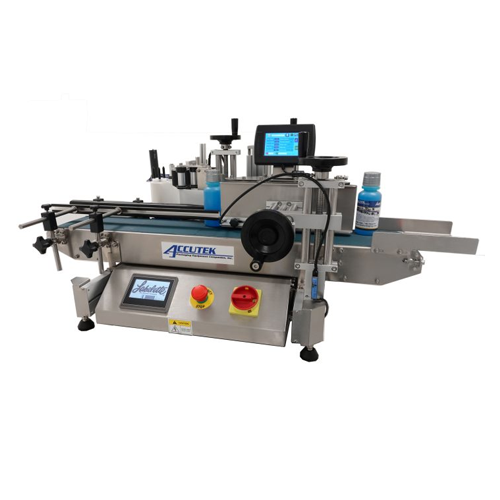
Tabletop labeler with integrated thermal printer for round containers
Efficiently label and print variable data on roun...
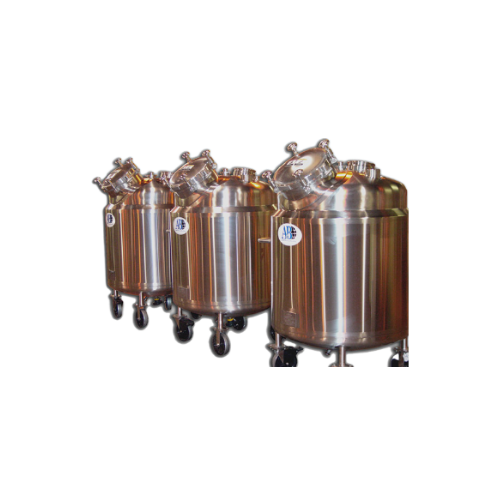
Industrial pressure vessels
Ensure product integrity and regulatory compliance with engineered-to-order pressure vessels, de...
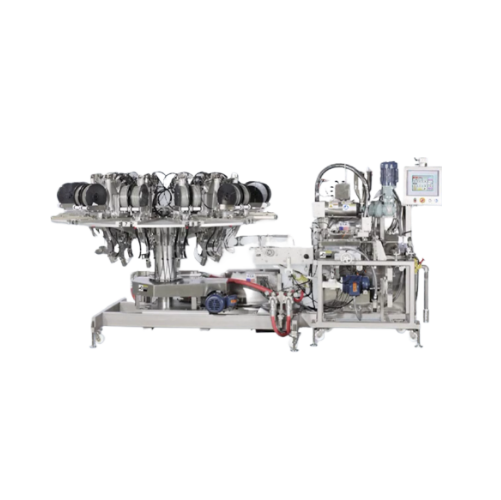
Automated clipping system for flexible packaging
Achieve precise volume control and reduce material waste with this high-s...
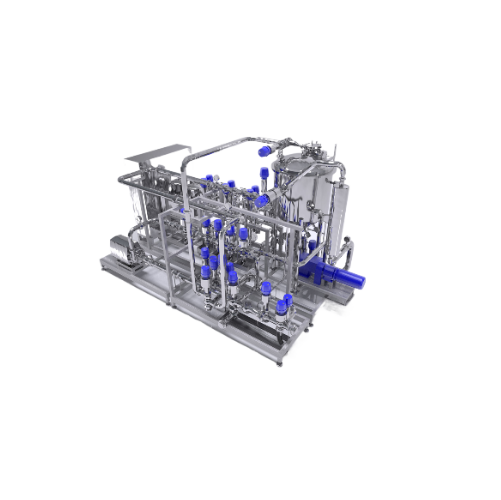
Tailor made mixing systems for personal and home care products
Achieve precise mixing for liquid formulations with conti...
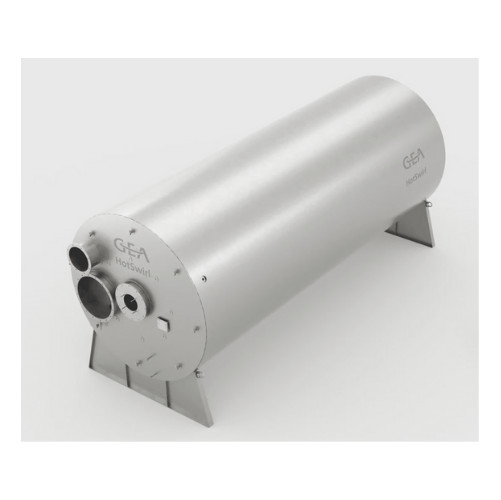
Industrial hot air system for spray dryers
Ensure consistent hot air delivery for critical drying processes, enhancing ene...
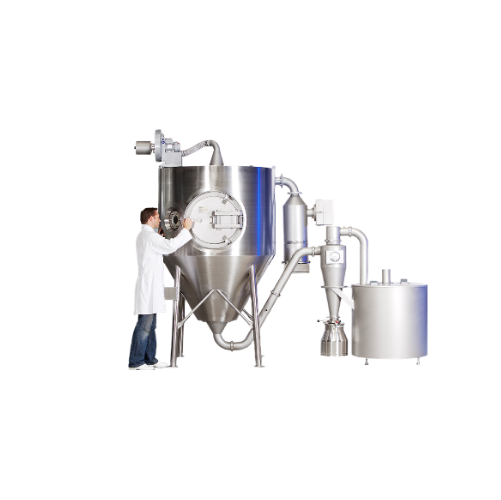
R&d spray drying solution for small batch production
Efficiently convert liquid solutions into precise, uniform powders f...
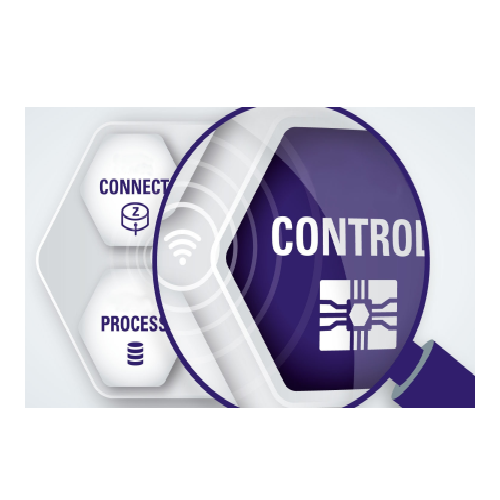
Automated process controllers for industrial plants
Enhance your production line’s efficiency and adaptability with...
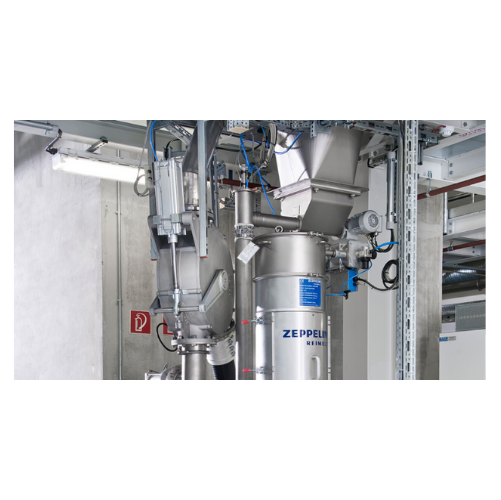
Special chemical plant safety systems
Ensure operational safety and regulatory compliance in chemical processing with advan...
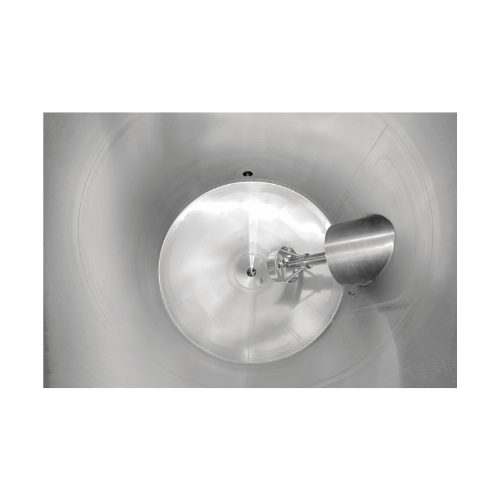
Industrial jetstream mixer for homogeneous mixing
Achieve consistent product quality with precise micro and macro mixing ...
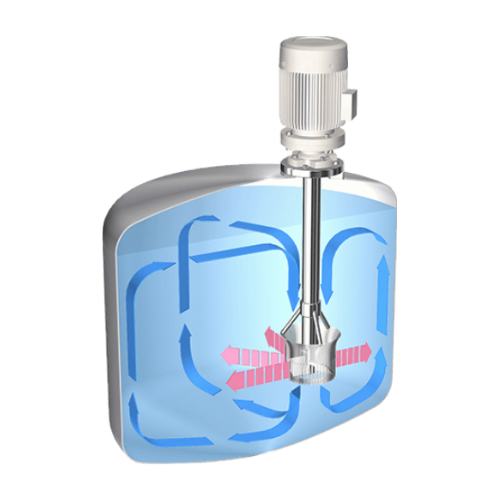
High-performance dispersing and mixing solutions
Enhance your mixing and dispersing processes with advanced fluid stream t...
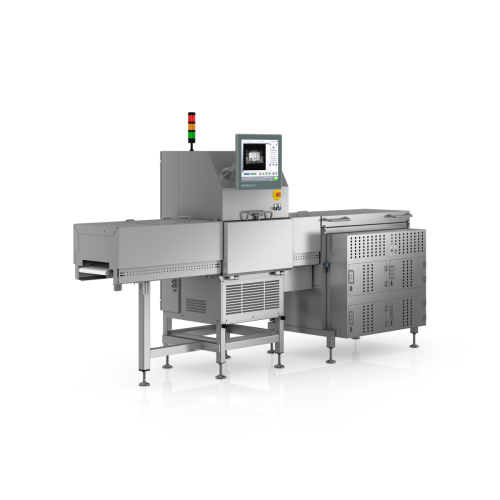
Integrated x-ray, checkweighing, and vision inspection unit
Ensure product safety and compliance by seamlessly detecting...
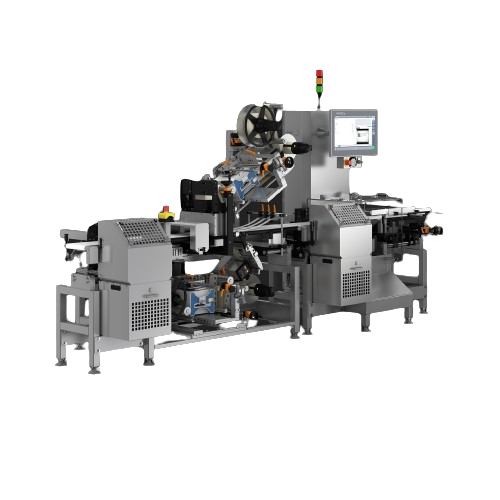
Modular end-of-line system for quality control
Streamline your end-of-line operations with seamless integration of weighin...
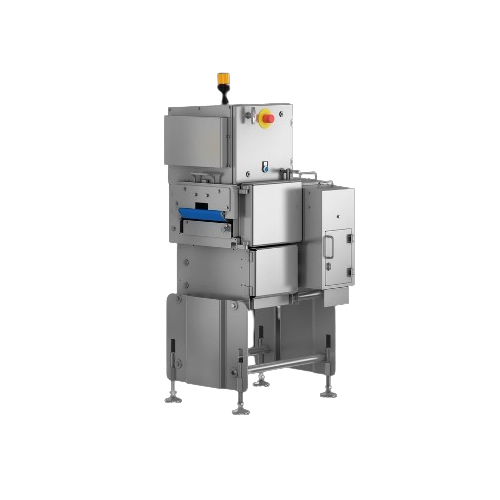
Compact x-ray scanner for foreign body detection
Ensure product quality with a space-saving x-ray scanner designed for hig...

Checkweighers for accurate weight control in production
Ensure precise weight compliance and complete data acquisition th...
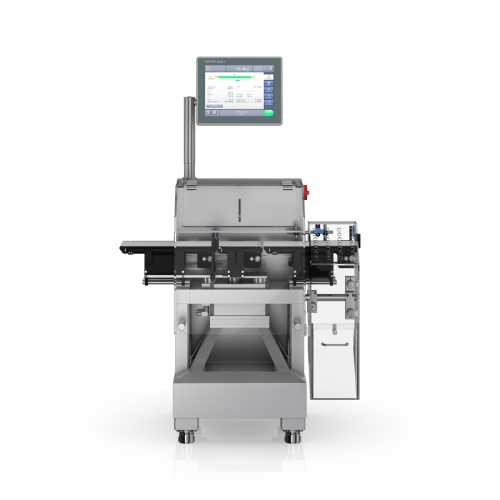
High-speed checkweigher for dynamic weighing
Achieve precision and consistency in high-speed production environments with ...
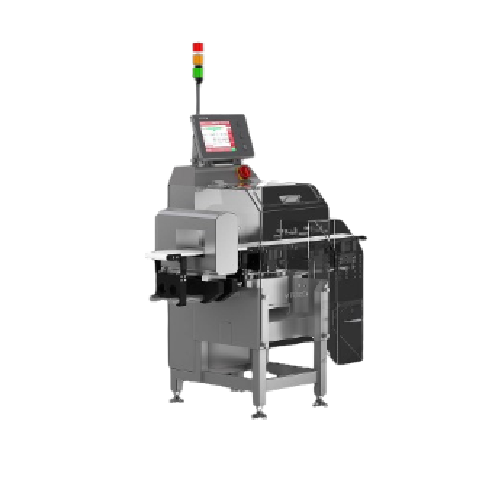
Checkweigher with integrated metal detector for food industry
Ensure comprehensive quality control in your production li...
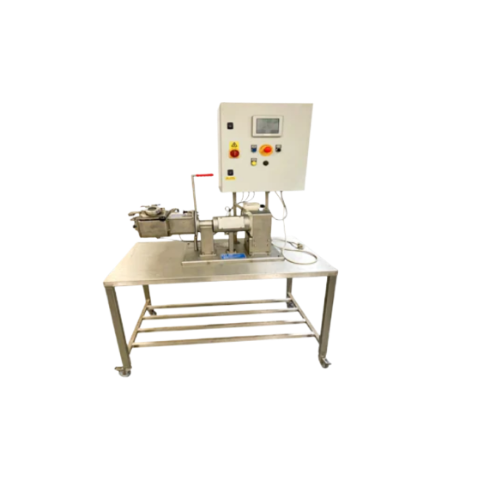
Processing vessel for liquid, sauce, or cream products
Efficiently mix and integrate liquid, cream, or slurry products wi...
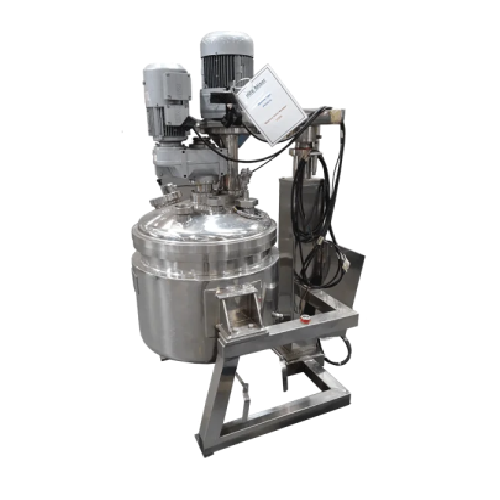
Mixing vessel for liquid, sauce, and cream products
Maximize efficiency in your production line with a versatile solution...
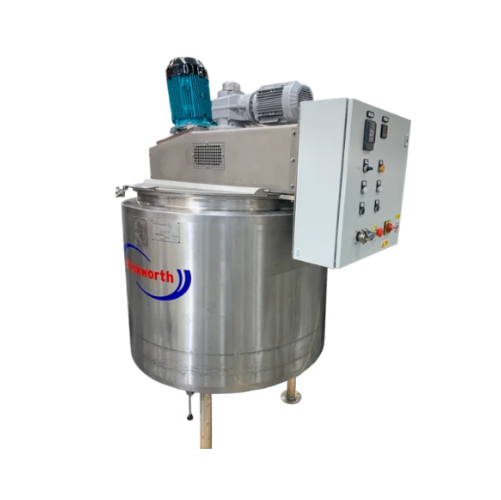
Pv processing vessels for liquid and cream mixing
Optimize your mixing operations with versatile processing vessels desig...
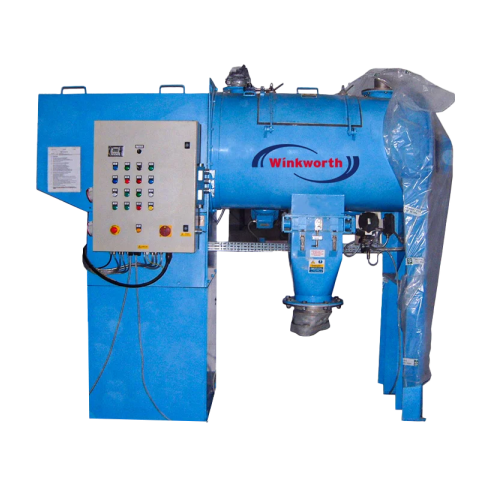
High-speed mixer for homogenous mixing of powders and pastes
Achieve rapid and precise mixing with high-speed dispersion...
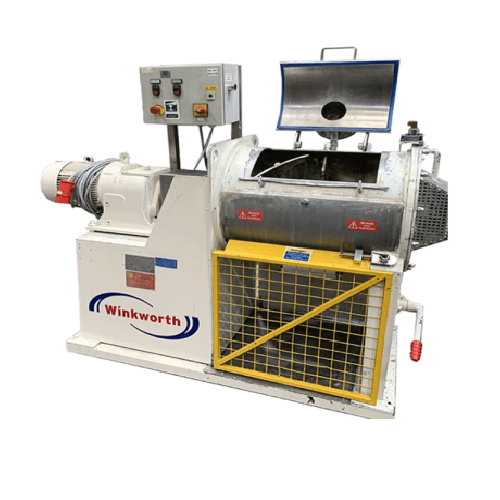
Industrial rapid turbulent mixer for homogeneous mixing
Achieve unparalleled homogeneity with rapid turbulent mixing, ess...
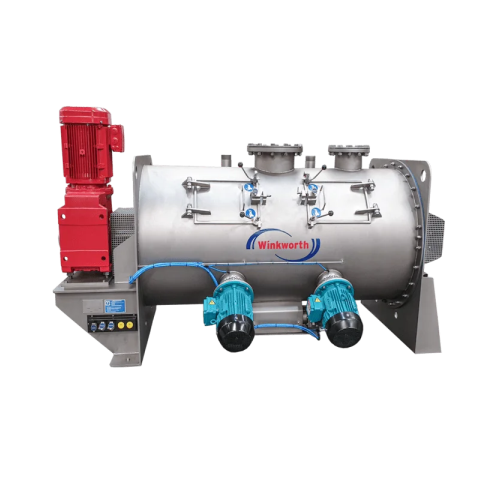
High-speed mixer for industrial mixing applications
Achieve rapid, consistent mixing and dispersion across diverse materi...
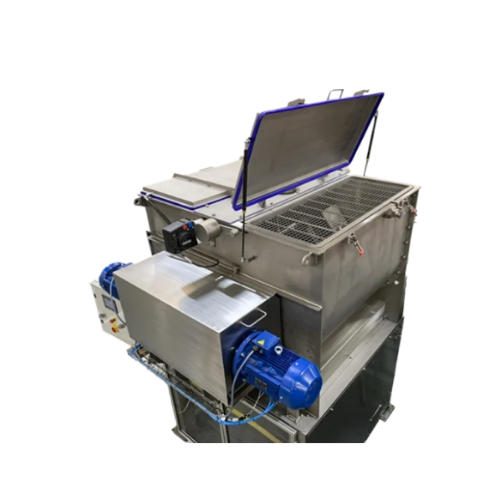
Twin shaft mixers for fragile and high throughput applications
Maximize mixing efficiency and protect delicate materials...
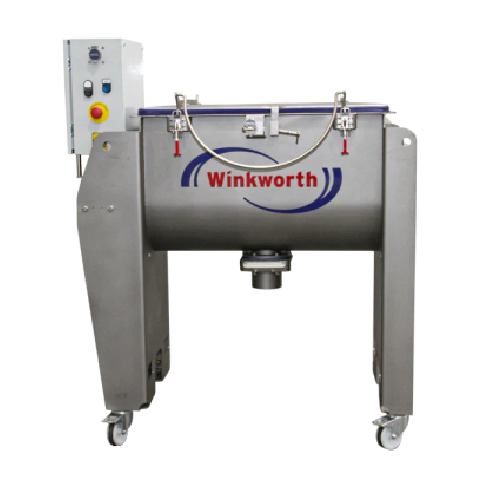
Horizontal shaft mixer for free-flowing materials
Achieve consistent mixing of diverse free-flowing materials with a reli...
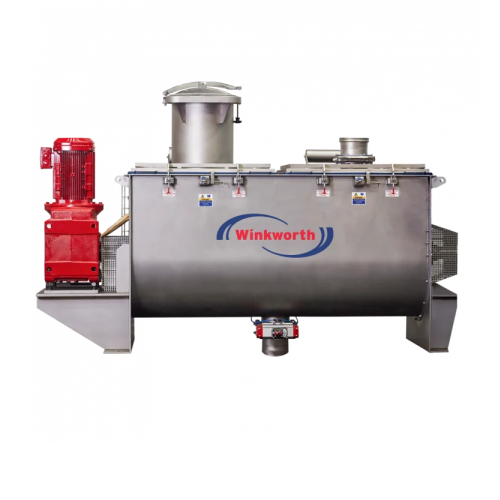
Efficient ribbon mixers for precise powder blending
Achieve consistent and uniform blending with this advanced U-Trough m...
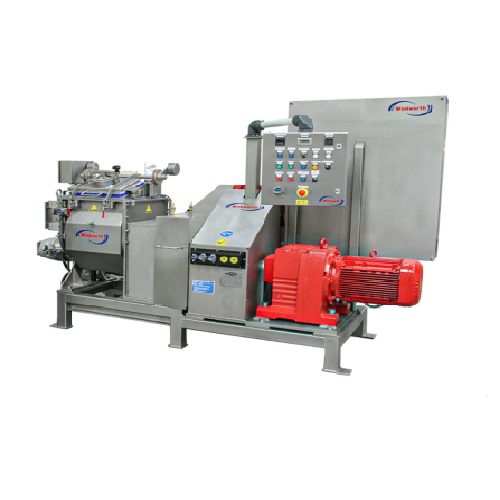
Industrial sigma mixer extruder for homogeneous mixing and extrusion
Achieve precise mixing and seamless extrusion of d...
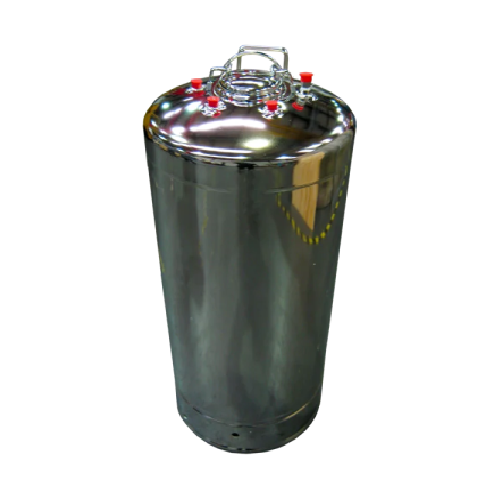
Pressure vessel for hazardous and non-hazardous liquids and gases
Ensure safety and compliance when handling hazardous ...
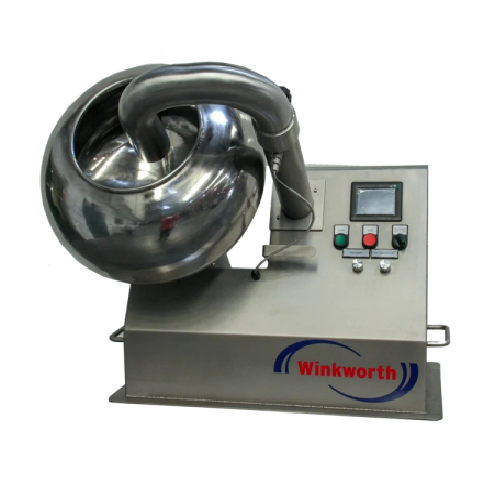
Industrial coating pan for food and pharmaceutical products
Optimize your production with precision mixing and coating, ...
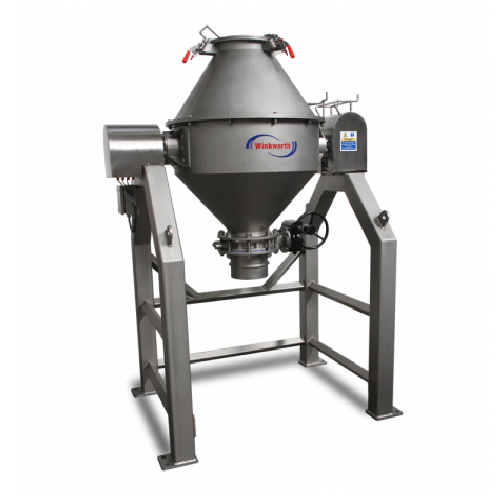
Double cone mixer for free-flowing material blending
Optimize your production with precision blending and gentle drying o...
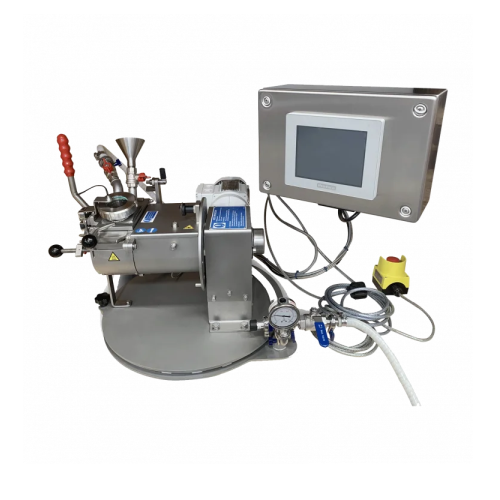
Laboratory mixers for product development and research
Optimize your R&D efforts with advanced mixing solutions desi...
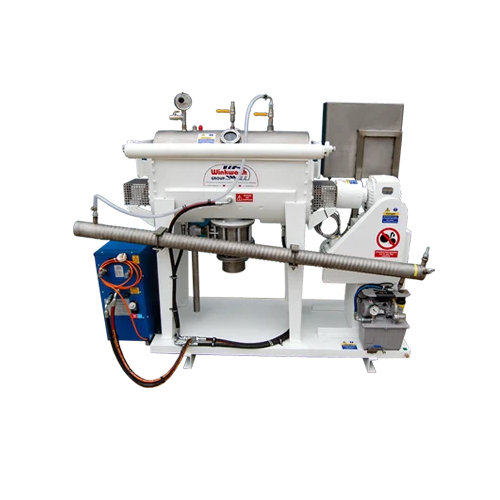
Industrial blenders for powder and granule mixing
Optimize your production line with advanced mixing solutions designed f...
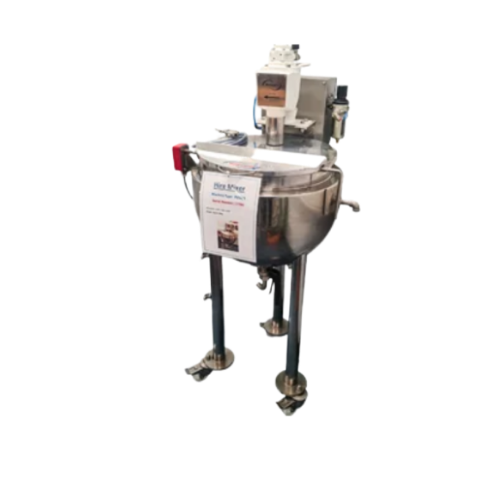
Pv mixing vessels for industrial hire
Optimize your production mix with vessels that ensure precise blending, heating, and ...
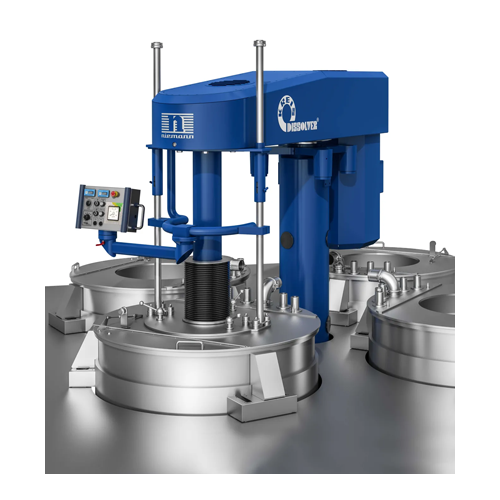
Dissolver for high-viscosity products through floor installation
Optimize production of ultra-high viscosity products wi...

Laboratory disperser for high-viscosity products
Optimize your laboratory processes with precise mixing and dispersing of ...
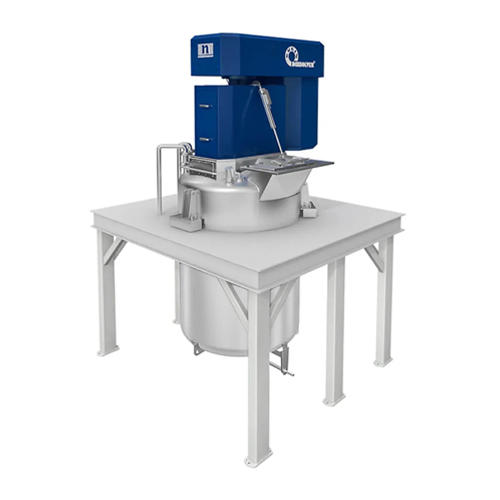
Top-mounted disperser for high-viscosity products
Achieve rapid, uniform dispersion of ultra-high viscosity materials wit...
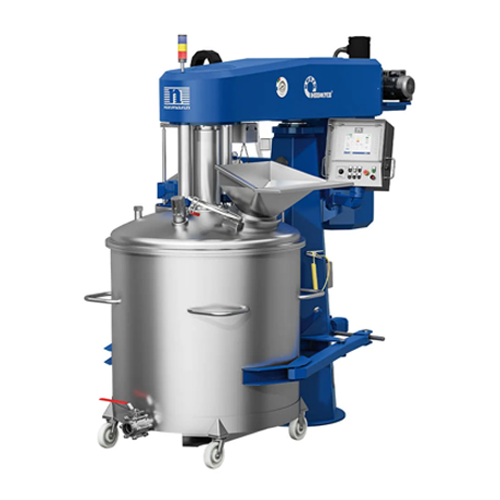
Vacuum dissolver for high-viscosity products
Elevate your production with precision mixing and deaeration, ideal for tackl...
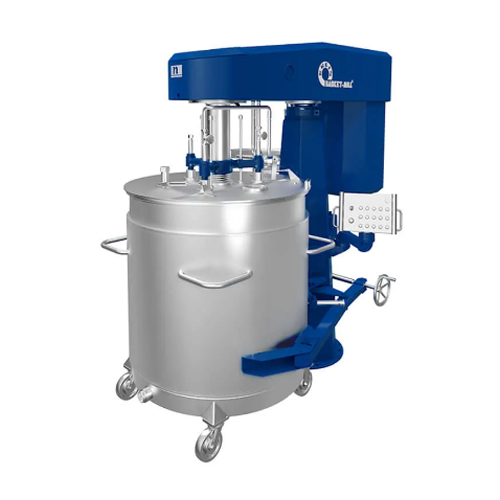
High-performance mill for paint and varnish industry
Achieve superior fine dispersing and grinding efficiency for liquid ...
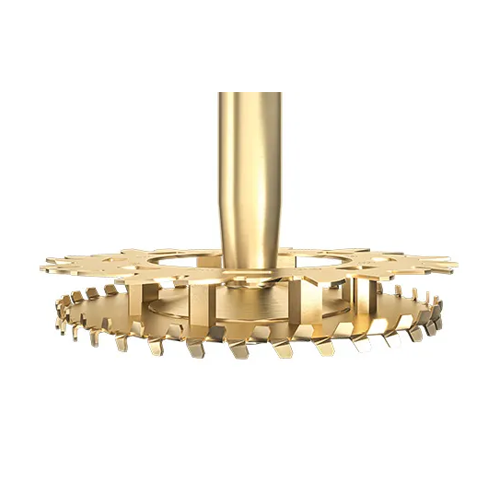
Mixer for high viscosity products
Enhance your production line with a versatile solution designed for precise mixing and di...
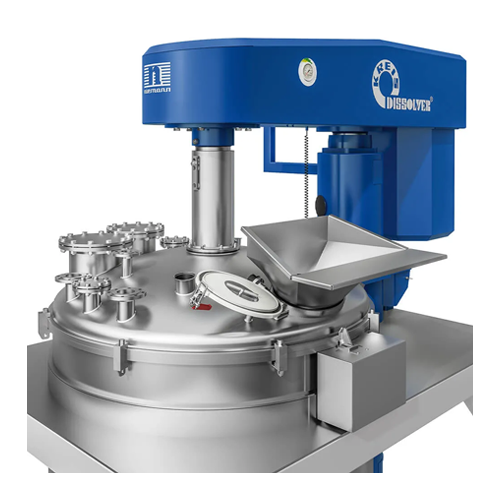
Advanced dissolver for high-viscosity products
Handle ultra-high viscosity mixing challenges effortlessly with this advanc...
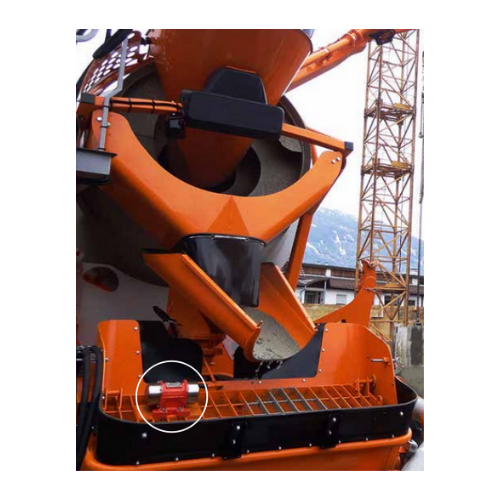
Continuous impact vibrator for aggregate reclaiming
Tackle material flow challenges head-on by preventing common issues l...
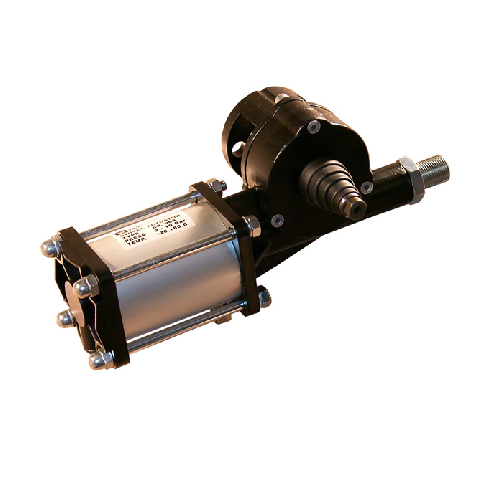
Pneumatic actuators for industrial valves
Optimize valve control in your production line with precision-engineered actuato...
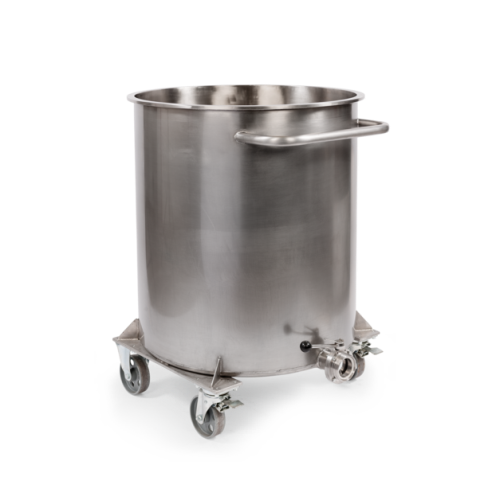
Industrial mixing dissolver for medium to large batches
Achieve precise mixing and dispersion of medium to large batch fo...
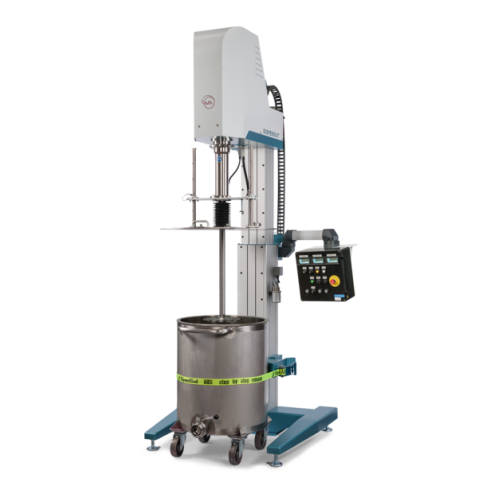
Explosion-proof dissolver for production applications
Ensure safety and efficiency in volatile environments with a robust...
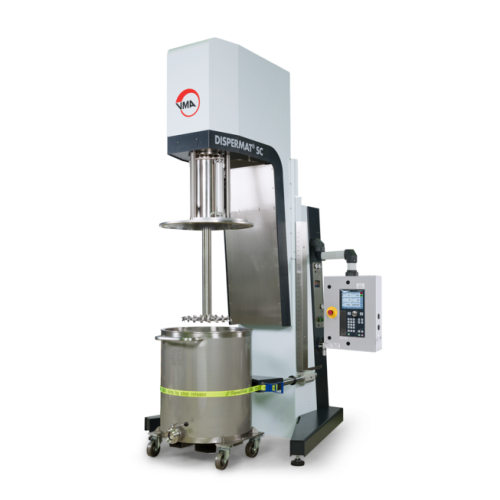
Explosion-proof production disperser for paint manufacturing
Ensure safe and efficient dispersion in volatile environmen...
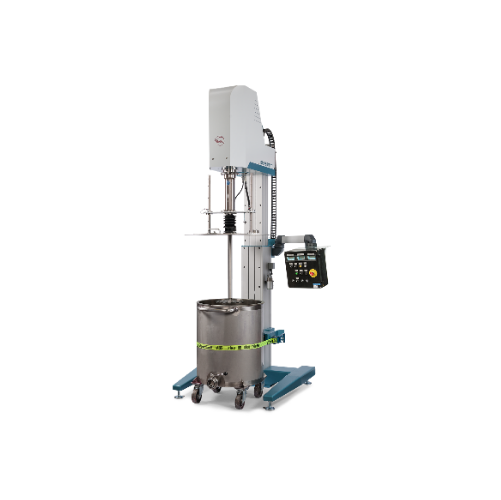
High-performance dissolver for large-scale production
Optimize your production line with precision-controlled dispersion ...
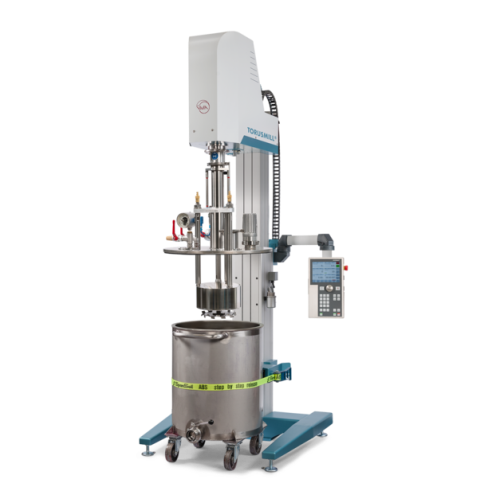
Vacuum basket mill for high-viscosity product processing
Achieve exceptional fine milling results while preventing air in...
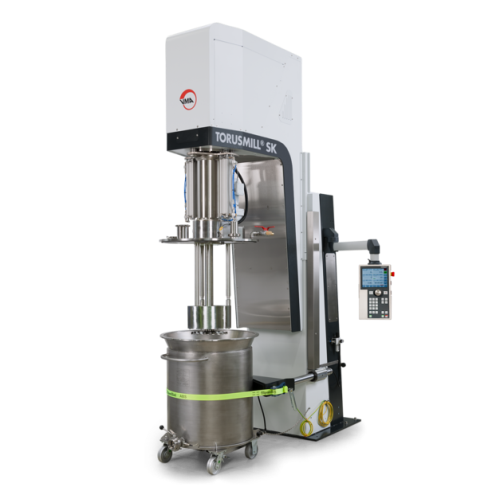
Vacuum basket mill for high viscosity products
Achieve efficient fine grinding of high-viscosity products while minimizing...
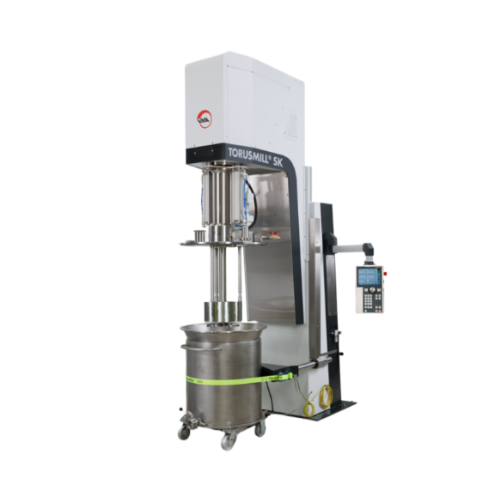
Vacuum dissolver for high viscosity products
Optimize your production with a vacuum dissolver designed to efficiently prev...
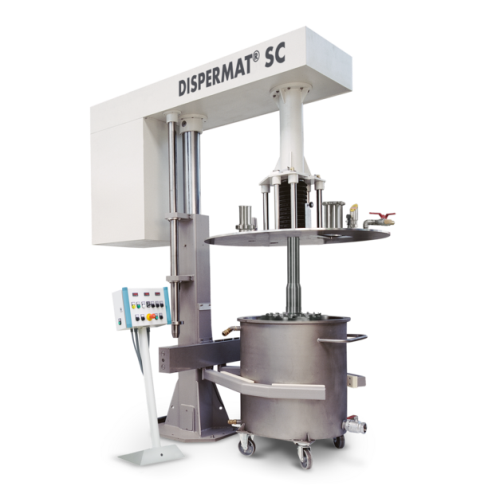
Vacuum disperser for high-viscosity products
Optimize high-viscosity product dispersion and prevent air inclusions with a ...

Vacuum dissolving system for high-viscosity products
Achieve flawless dispersion of high-viscosity substances under vacuu...
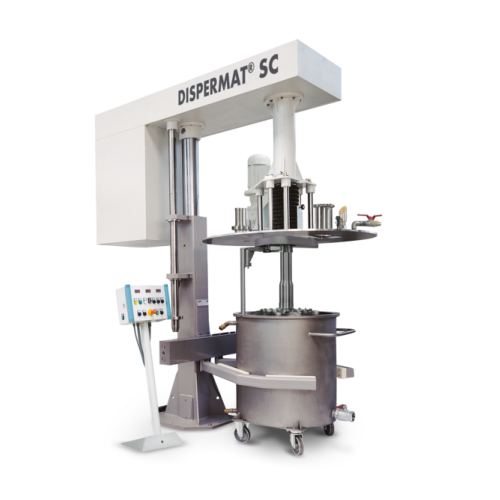
Production dissolver for high-viscosity products
Achieve optimal dispersion and grinding of high-viscosity substances with...
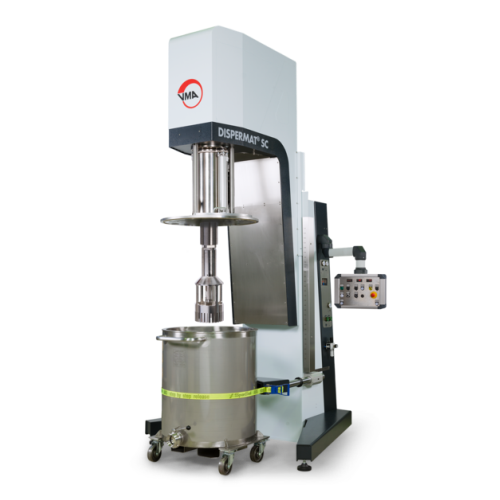
Rotary homogenizer for high shear mixing
Achieve precise homogenization of various viscosities with advanced rotor-stator t...
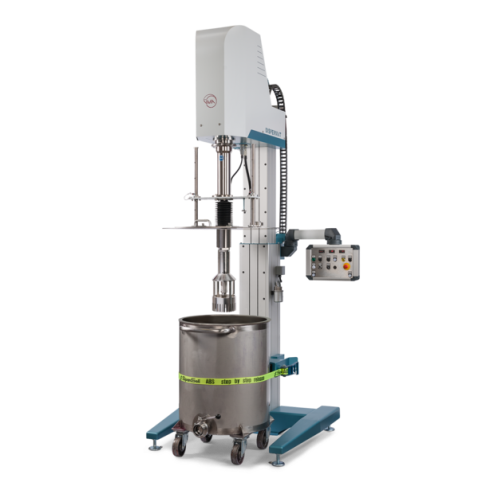
Rotor-stator homogenizer for high shear batch processing
Achieve ultra-fine particle distribution and stable emulsions wi...
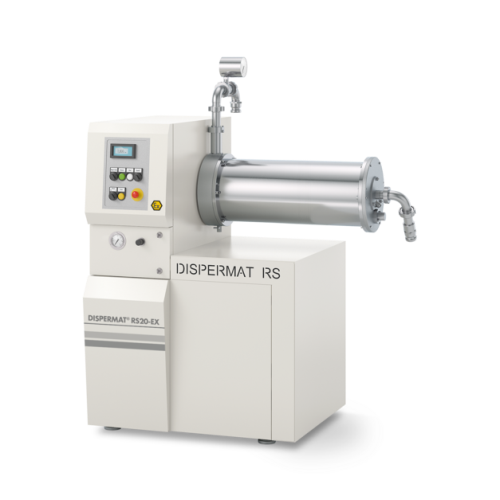
Explosion-proof horizontal bead mill for paint production
Ensure ultra-fine particle size and consistent quality with an...
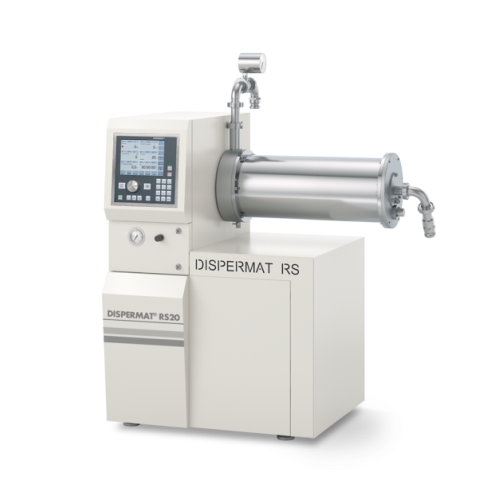
Horizontal bead mill for fine grinding in continuous process
Achieve ultrafine particle dispersion and consistent mixing...
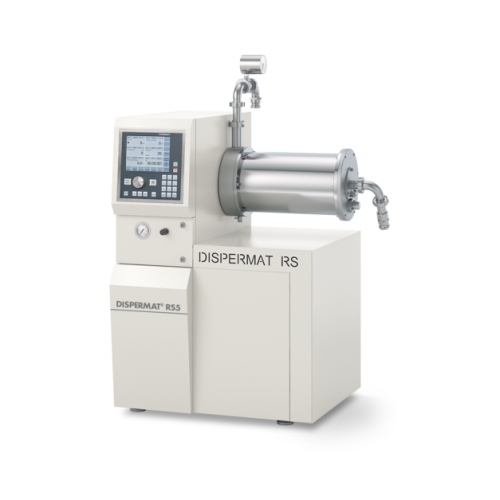
Horizontal bead mill for ultrafine particle grinding
Achieve precision in ultrafine grinding with a system that allows fo...
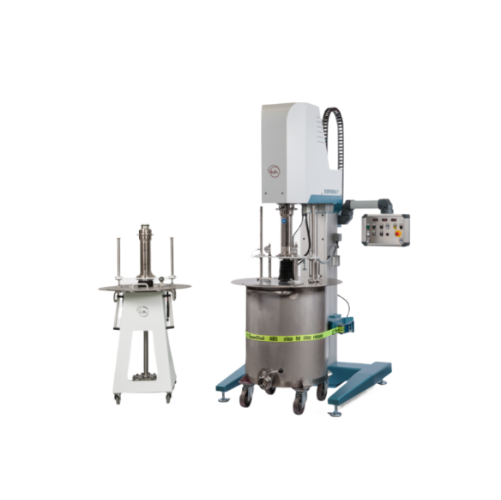
High-capacity dissolvers for industrial mixing
Enhance your production line with precision mixing, achieving consistent di...
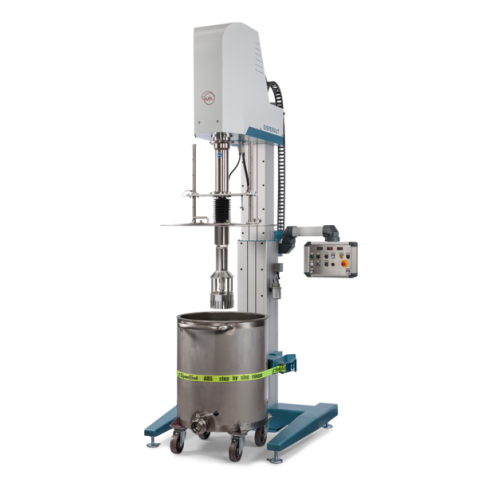
High shear batch process homogenizer for production
Achieve efficient emulsifying, homogenizing, and dispersing with prec...

Industrial basket mill for medium viscosity products
Achieve precise particle size reduction and rapid pigment dispersion...
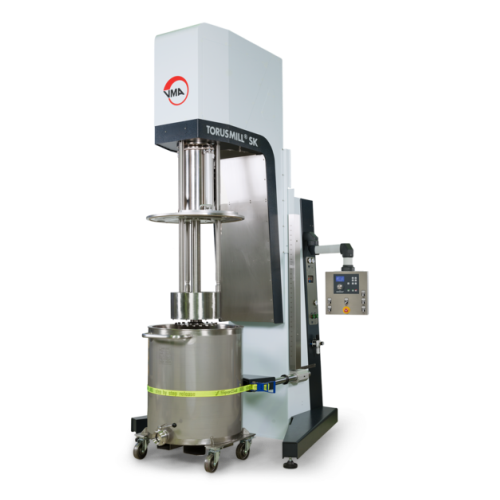
High-efficiency immersion mill for medium viscosity products
Achieve precise particle size reduction and superior disper...

High-efficient industrial immersion mill
Achieve rapid, efficient dispersion and fine grinding in demanding production envi...
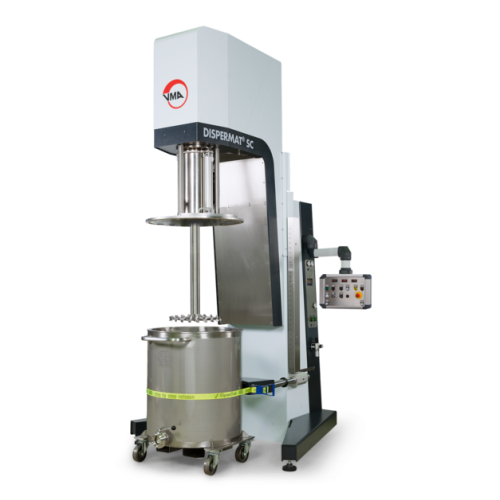
High-performance dissolver for industrial dispersion processes
Optimize your dispersion processes with this advanced dis...
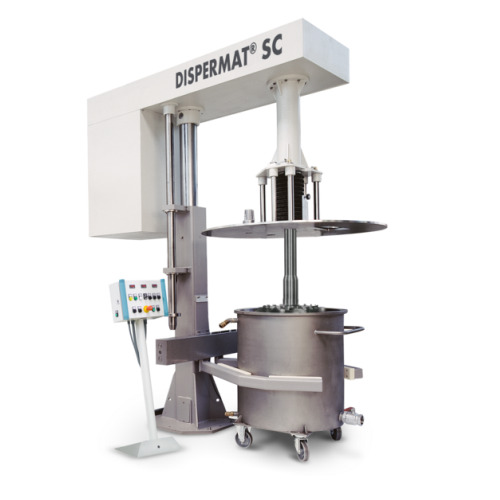
High-performance production dissolver for large batches
Achieve precise and repeatable dispersion for complex formulation...
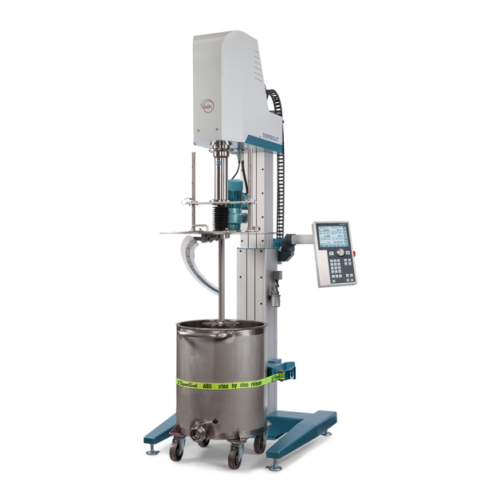
Dissolving system for high-viscosity products
Optimize the dispersion of high-viscosity liquids and pastes with this versa...
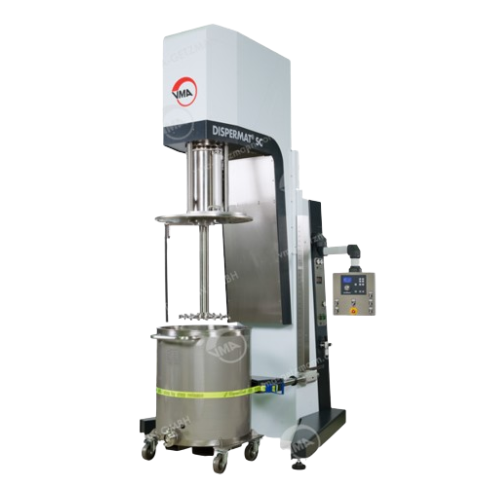
Production dissolver with scraper for high-viscosity products
Efficiently tackle high-viscosity material processing with...
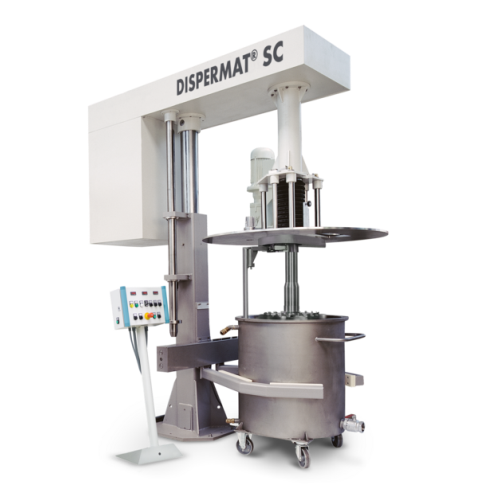
Industrial dissolver for high viscosity products
Optimize high-viscosity product dispersion with a robust dissolver design...
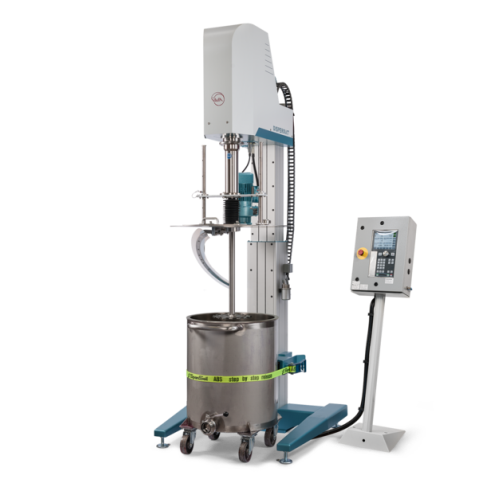
Explosion-proof dissolver with scraper for high viscosity substances
Ensure flawless dispersion with enhanced safety, d...

Explosion-proof dissolver for high-viscosity products
Optimized for safely processing high-viscosity products, this explo...
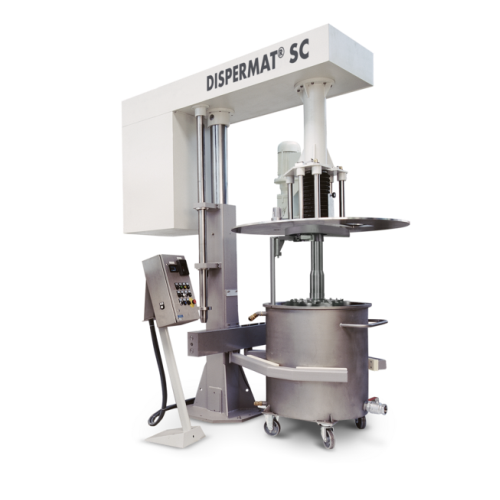
Explosion-proof dissolver for high viscosity products
Optimize your high-viscosity material processing with an explosion-...
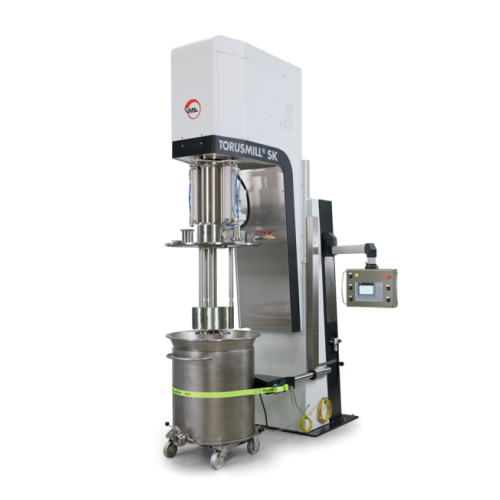
Vacuum basket mill for high-viscosity product milling
Achieve refined particle size and smooth texture in your high-visco...
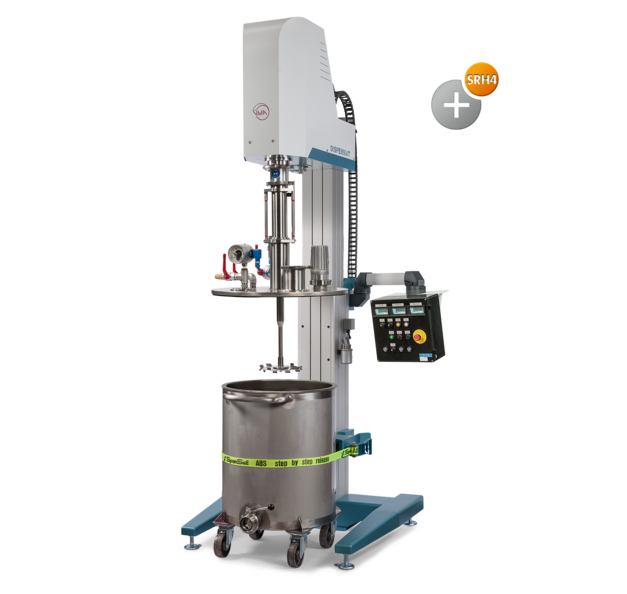
ATEX vacuum dissolver for high viscosity products
Ensure safe and efficient dispersion of high-viscosity materials under...
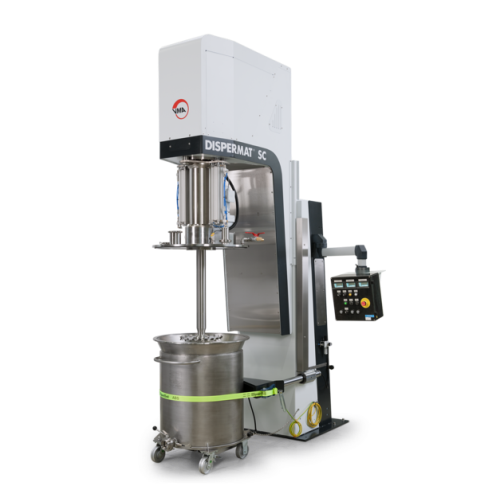
Explosion-proof vacuum dissolver for high-viscosity products
Optimize your production by eliminating air inclusions and ...
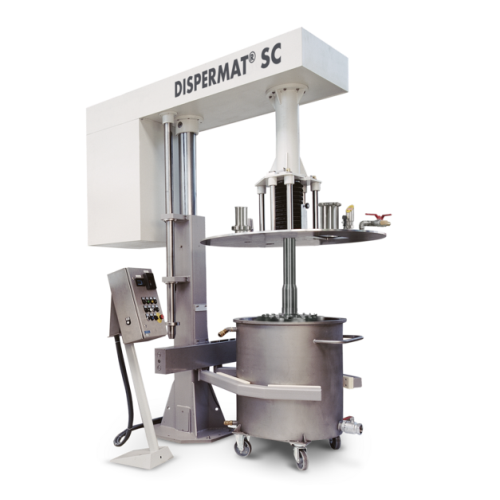
Explosion-proof vacuum dissolver for high viscosity products
Achieve precise dispersion of high-viscosity products under...
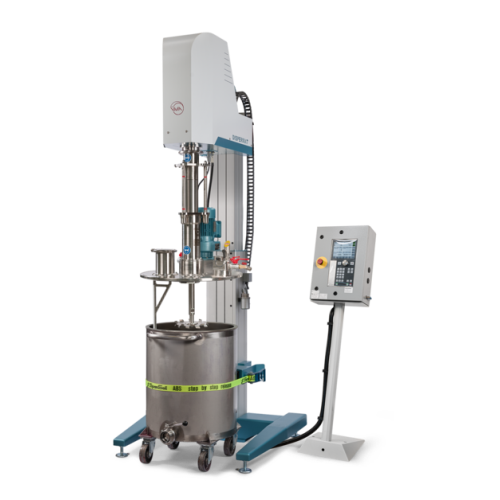
Explosion-proof vacuum dissolver for high viscosity applications
For operations requiring precise control in high-viscos...
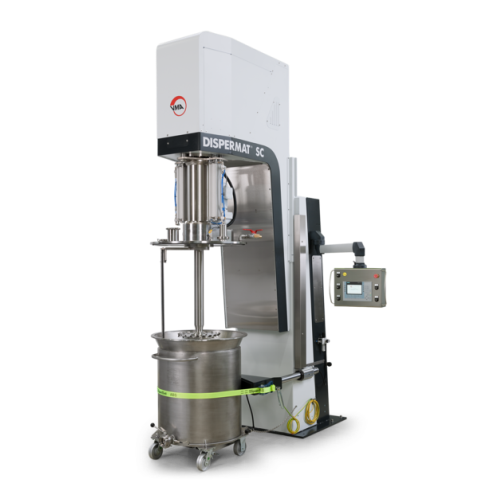
Explosion-proof vacuum disperser for high-viscosity substances
Achieve precise dispersion and eliminate air inclusions w...
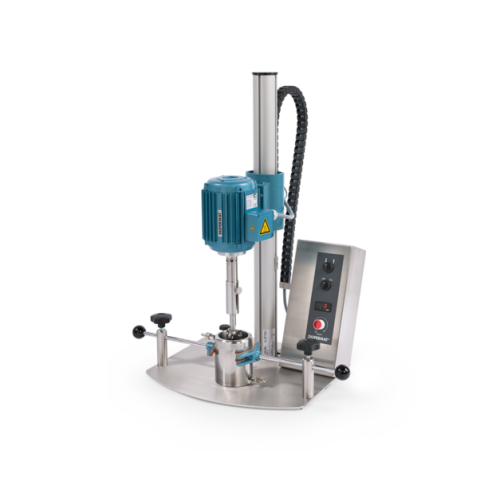
Laboratory stirrers for high viscosity materials
Efficiently mix and stir high-viscosity materials with ease, enabling pre...
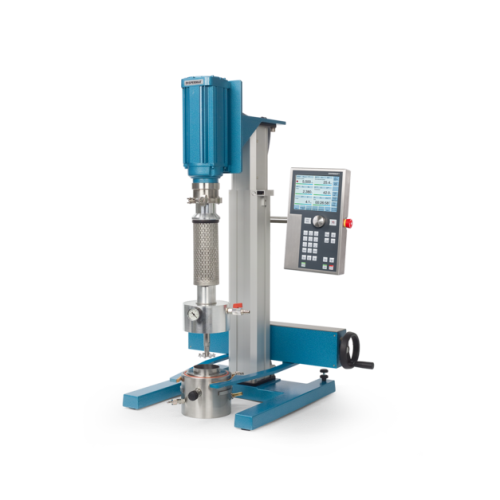
Vacuum dispersion system for laboratory applications
Achieve precise mixing and homogenization under vacuum conditions, e...
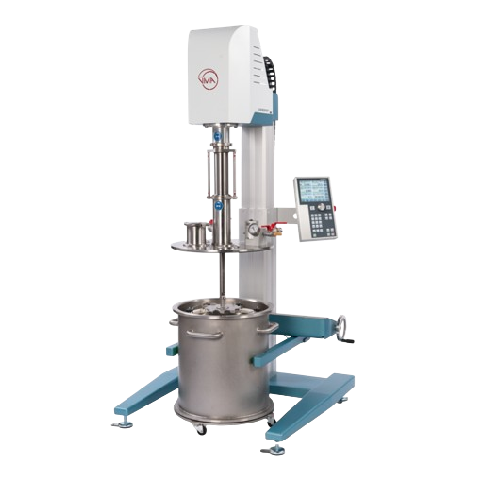
Vacuum dispersion system for single-walled containers
Optimize your production line with an adaptable vacuum dispersion s...
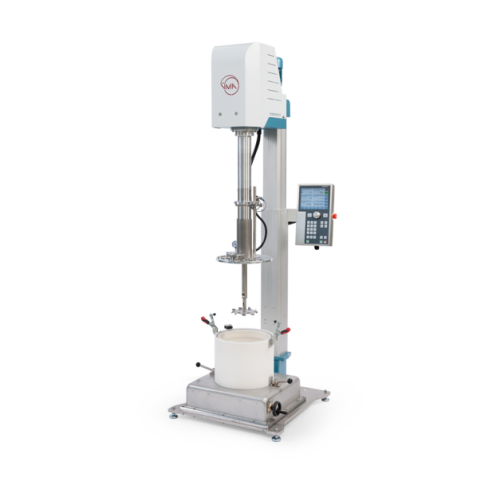
Laboratory vacuum dissolver
Experience precision vacuum processing for your high-viscosity formulations, ensuring optimal di...
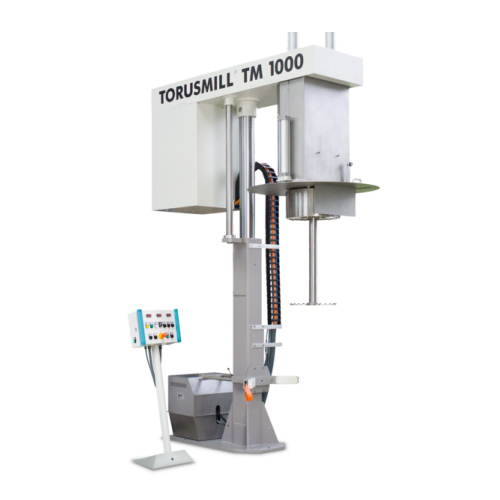
Basket mill with integrated dissolver for high viscosity products
Optimize your production efficiency by combining disp...
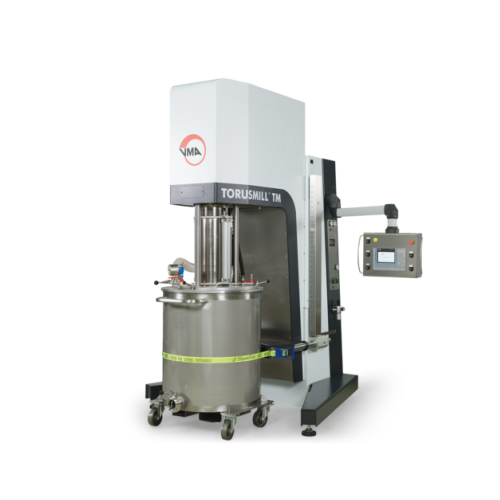
Dissolver for high-volume industrial dispersion
Achieve precise and efficient mixing with this dissolver, designed for sea...
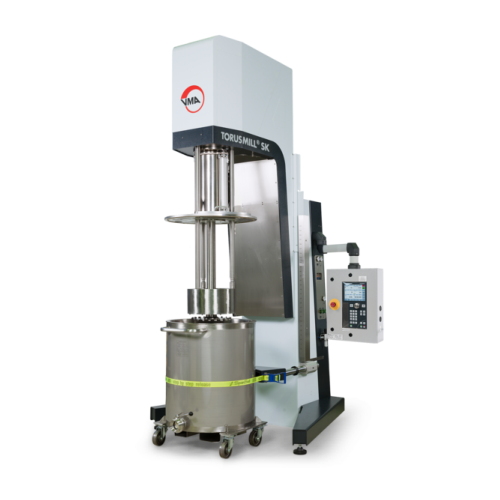
Explosion-proof immersion mill for paints and varnishes
Optimize high-performance coatings production with an explosion-p...
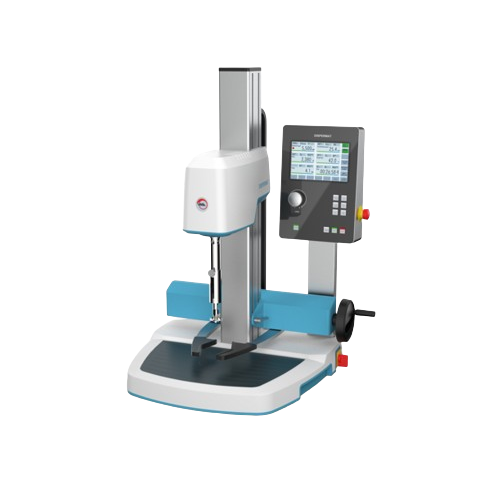
Laboratory dissolver for multiple applications
Efficiently streamline your laboratory processes with this versatile dissol...
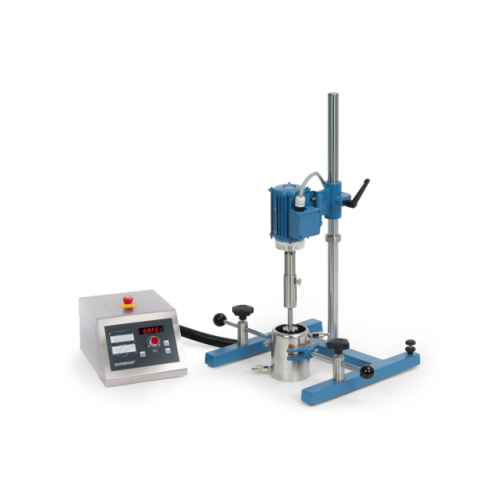
Lab and pilot plant dissolver for dispersion and fine grinding
Achieve efficient dispersion and fine grinding in laborat...
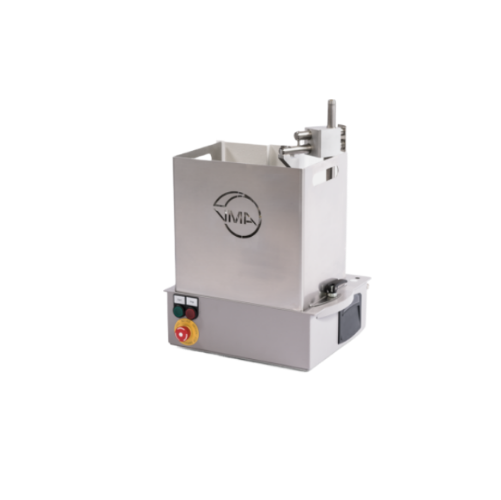
Industrial dissolver for high-viscosity materials
Efficiently disperse and mix high-viscosity materials with precision, e...
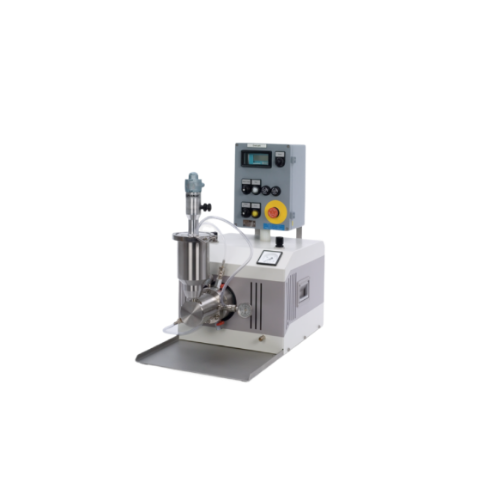
Atex horizontal bead mill
Ensure precision and safety in explosive environments with a robust solution that finely grinds an...
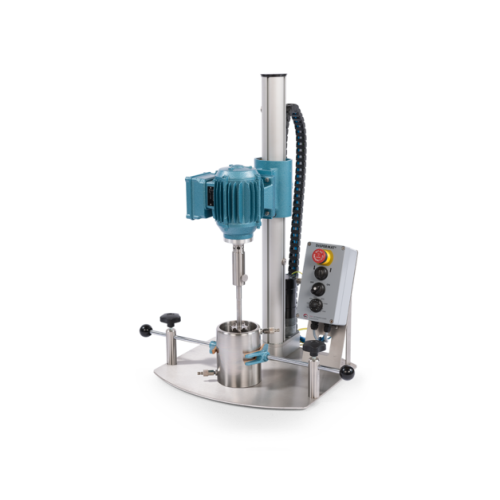
Explosion-proof dissolvers for laboratory use
Ideal for safely dispersing and mixing chemical substances in potentially ex...
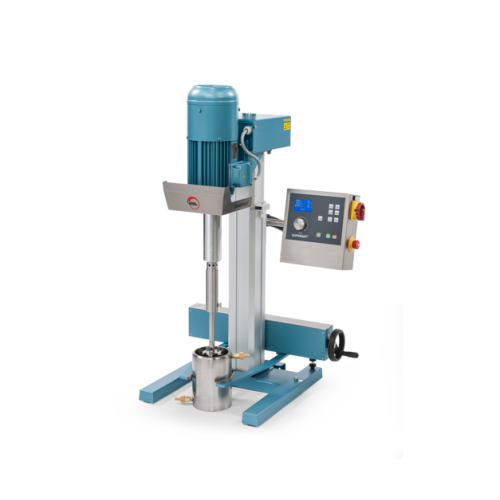
Lab stirrer for high-viscosity substances
Need precise, high-torque stirring for your complex formulations? This lab stirr...
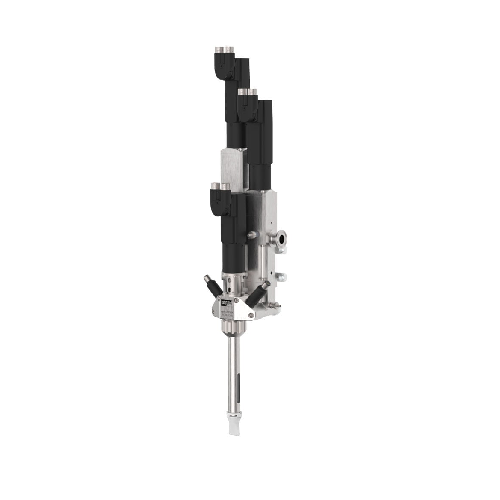
Two-component static-dynamic mixer for high-viscosity materials
Simplify the challenging task of mixing two-component ma...
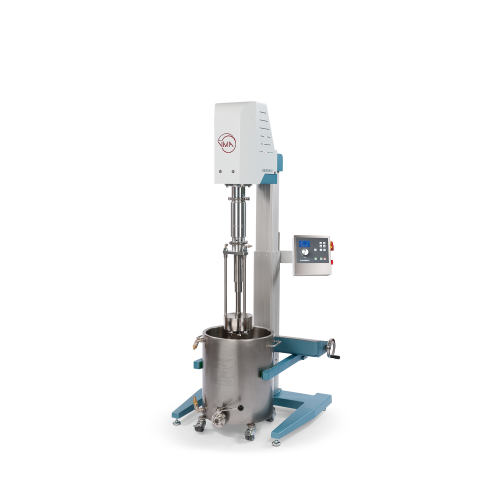
Entry-level vacuum dispersion system for laboratory applications
Achieve precise dispersion and milling with this versat...
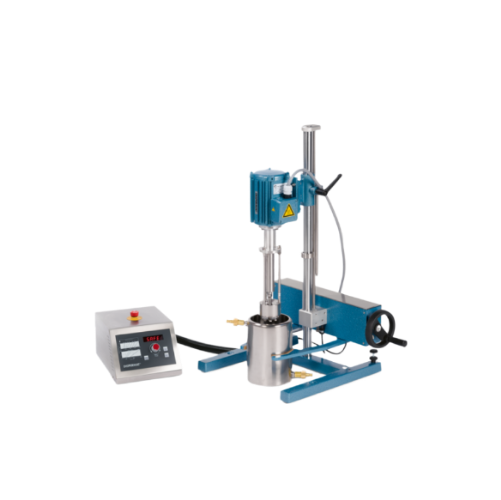
Laboratory bead mill for sample dispersion
Ensure precise particle size reduction with versatility and ease, enabling effi...

Laboratory and pilot plant horizontal bead mill
Achieve precision milling with minimal product waste, ensuring consistent ...
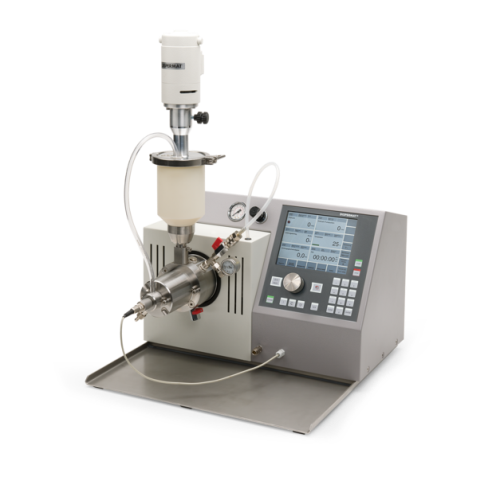
Nano bead mill for laboratory wet grinding
Achieve ultra-fine particle dispersion and consistent milling results with this...
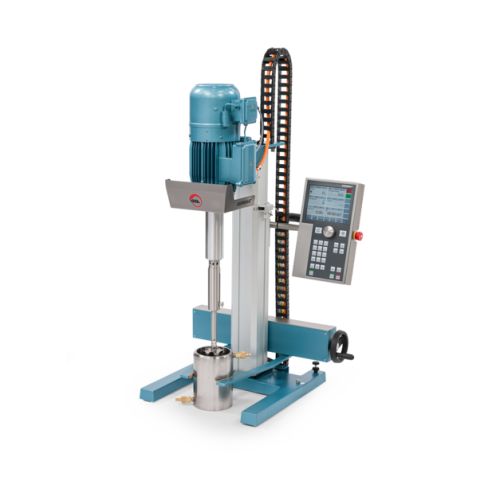
Rotary homogenizer for laboratory and pilot plant
For achieving optimal dispersion in complex formulations, this solution...
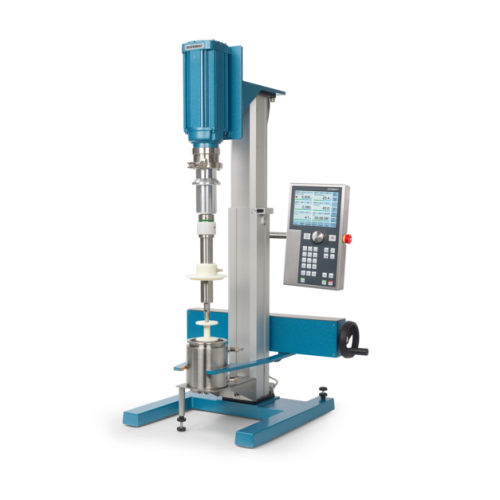
Laboratory disperser for small batch processing
Achieve precise dispersion and homogenization of high-viscosity mixtures w...

Modular dispenser for dosing adhesives and abrasive media
Streamline your production line with a modular dispenser desig...
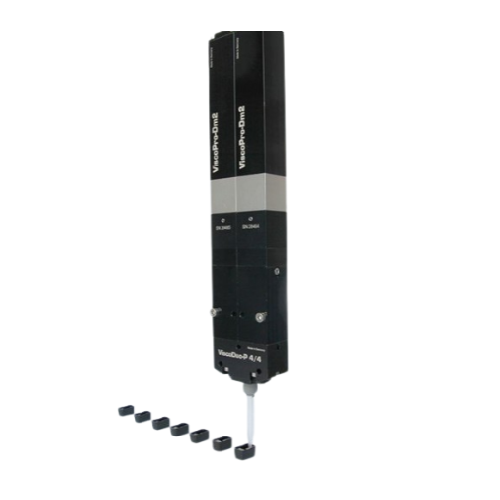
Precision 2k dispenser for automated systems
Achieve precise mixing and dispensing of two-component materials with minimal...
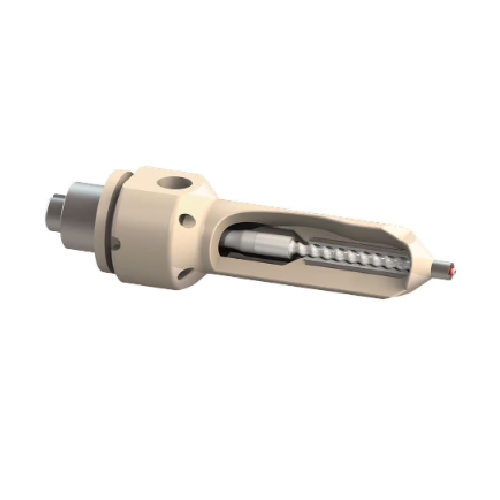
Dispenser for reactive material applications
Ensure precise dispensing of reactive materials without metal contamination, ...
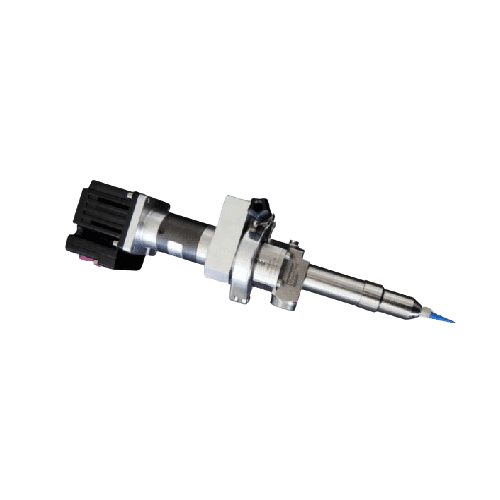
Precision dispenser for high-viscosity fluids
Achieve unparalleled precision in dosing and application with a dispenser de...
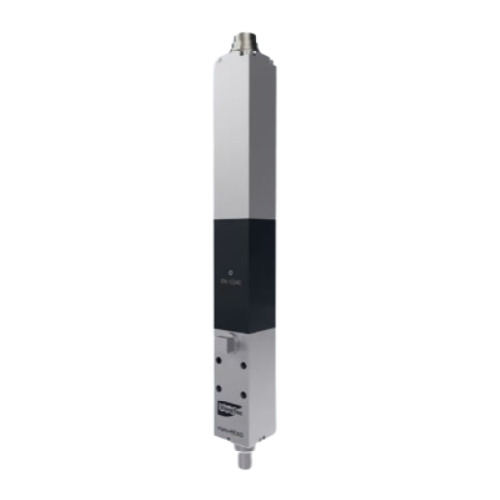
3d print head for high-viscosity fluids and pastes
Enhance your 3D printing capabilities by reliably handling high-viscos...
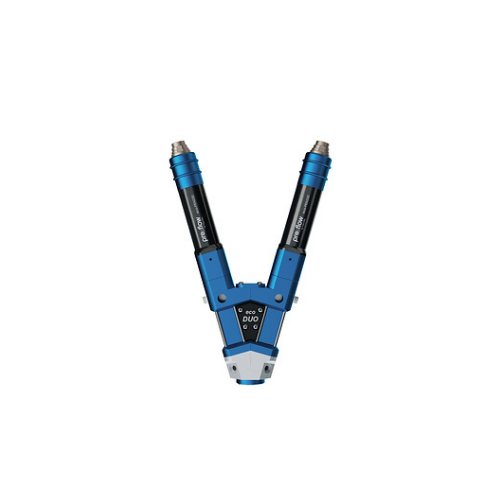
Two component dispensing and meter mixing system for small quantities
Achieve precision and consistency in microdispens...
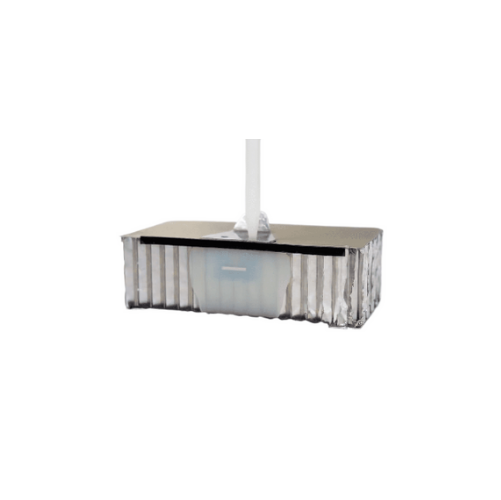
High-precision dosing systems for aerospace applications
Achieve unmatched precision and reliability when dosing complex ...
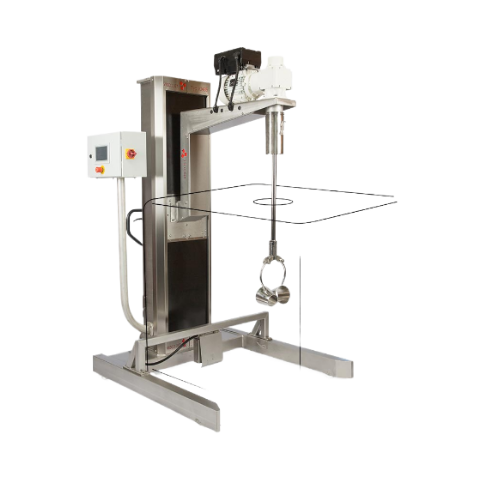
Industrial stativ mixer with adjustable height
Achieve precise mixing and stirring across diverse batches with a mobile, a...
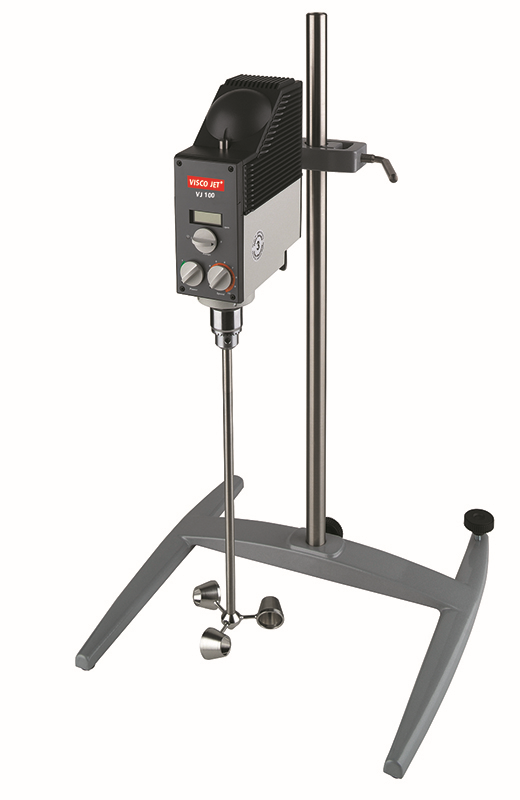
Laboratory stirrer for high-viscosity materials
Streamline your laboratory mixing processes with a powerful stirrer design...
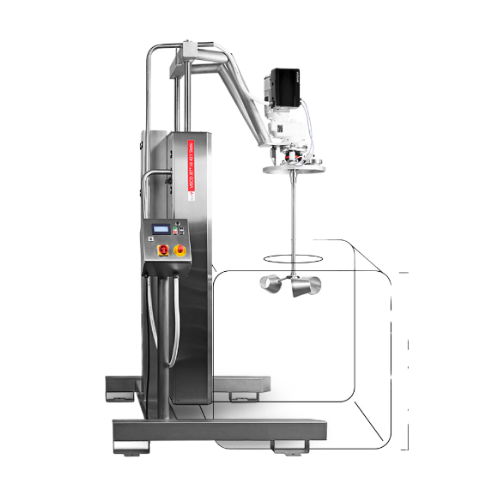
Industrial mixer for product-critical processes
When dealing with high-hygiene requirements and complex mixing tasks acros...
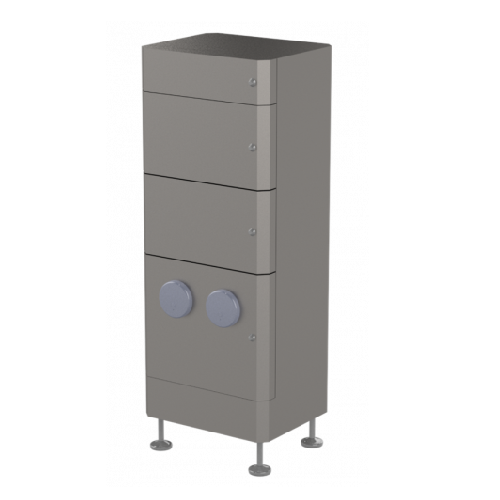
Supply air filter systems for industrial cleanrooms
Ensure critical air purity and operational safety in sensitive enviro...
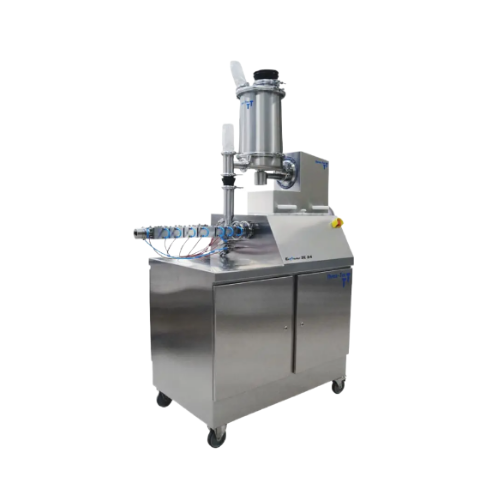
Compact high-torque extruder for customizable extrusion tasks
Ensure precise control over your extrusion processes with ...
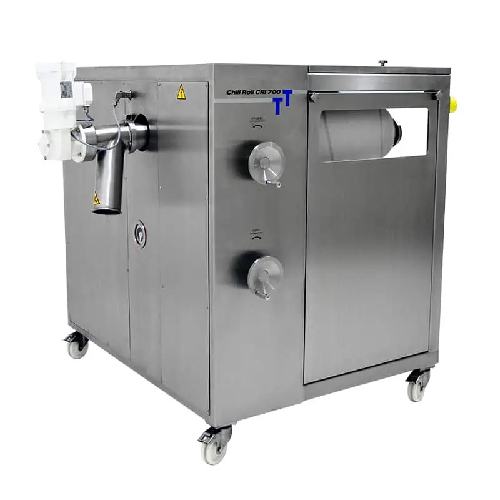
Continuous cooling roller for extrudates
Ensure rapid and efficient cooling of high-heat capacity extrudates with a compact...
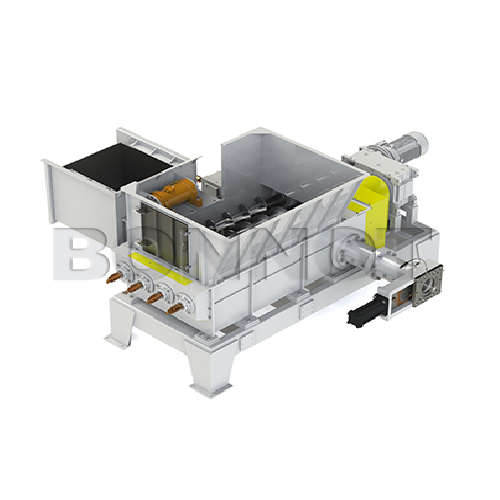
Live bottom extruder for processing sealants and mastics
Efficiently integrate entire material batches into your producti...
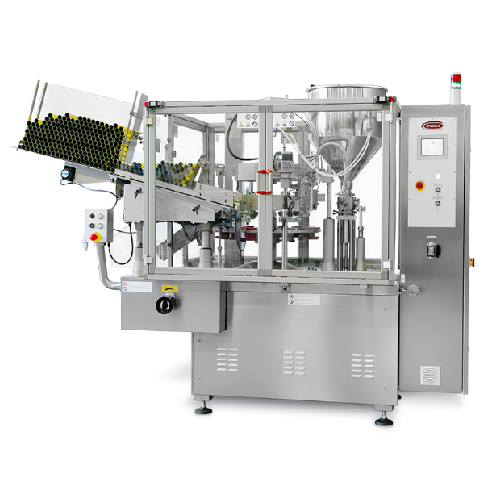
Automatic tube filling solution for medium to high volume production
Boost your production line efficiency with a robus...
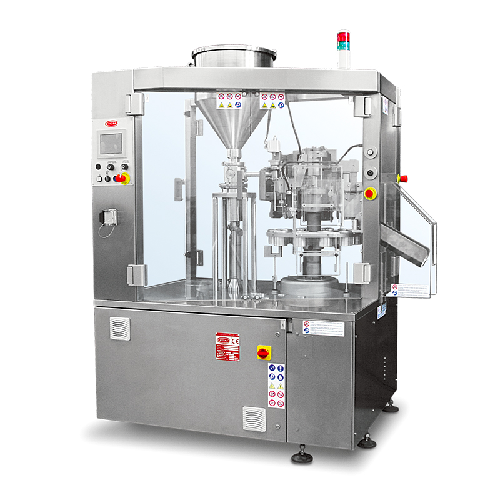
Small batch tube filling system for metal and plastic tubes
Optimize your small-batch production with precise tube filli...
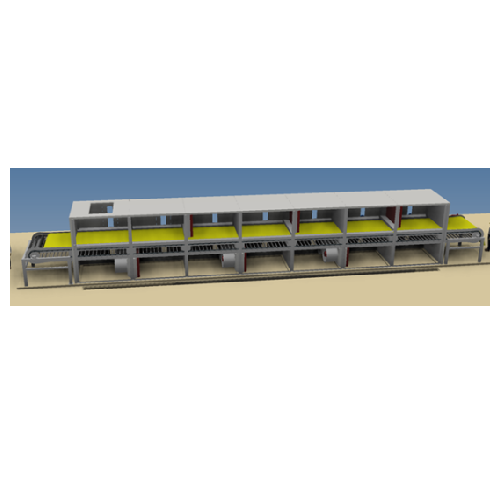
Belt dryers for gelatin processing
Efficiently transform liquid gelatin into high-quality solids with precise moisture cont...

Real-time trace gas analyzer for Voc detection
Achieve real-time, multi-analyte detection of volatile organic compounds an...
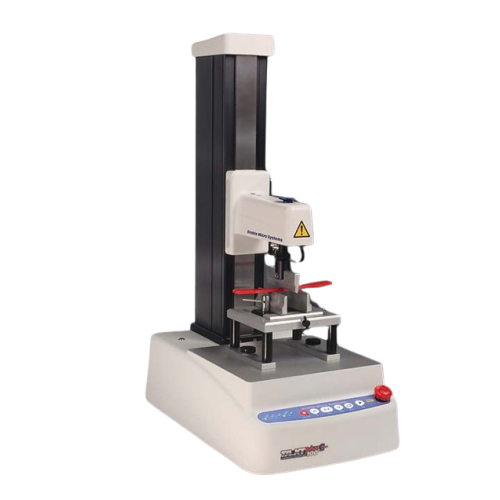
High-force texture analyser for precise measurement
Achieve unparalleled precision in texture analysis for high-force app...
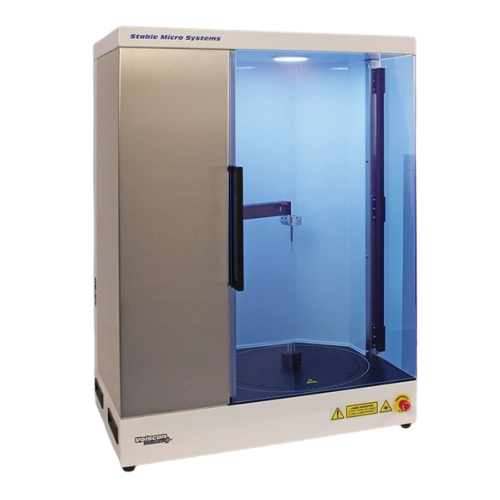
Laser-based volume measurement for bakery and solid products
For precision in product quality control, this laser-based ...
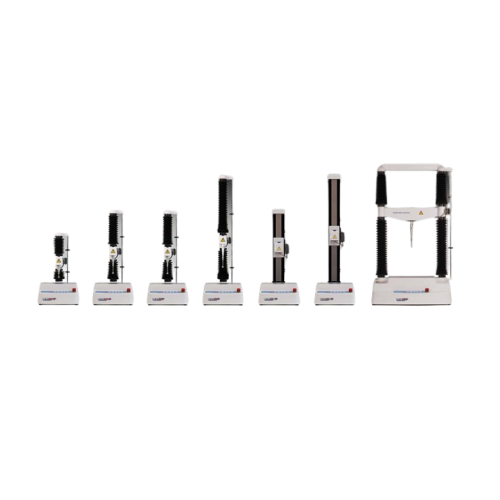
Portable texture analysis for low force applications
Easily perform precision texture measurements on low-force applicati...
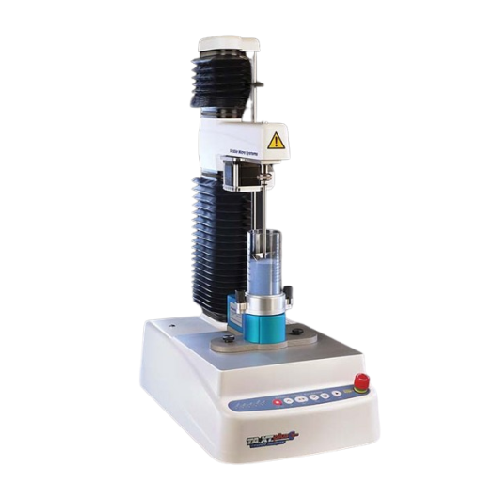
Powder flow measurement system
Achieve precise control over powder consistency and prevent process disruptions by assessing ...
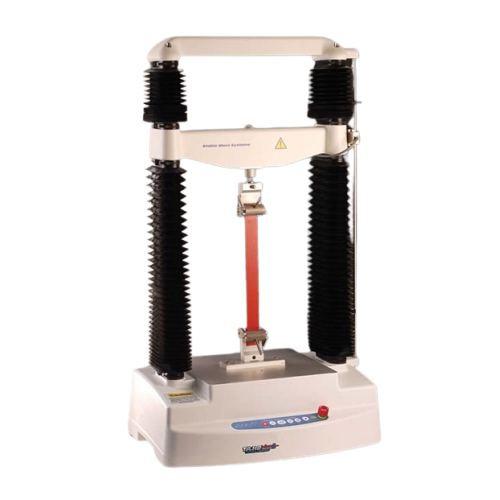
Texture analyzer for high force applications
Achieve precise texture measurement across a vast array of products with a so...
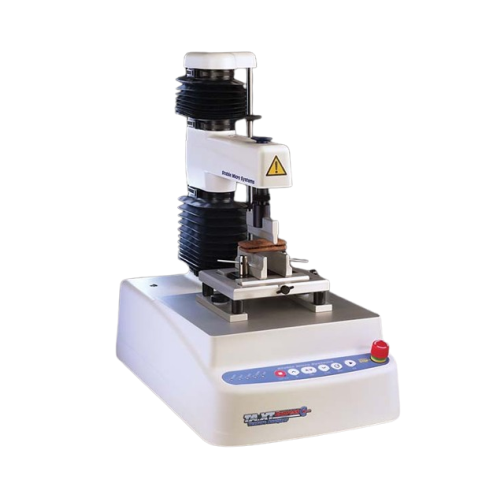
Entry-level texture analysis system for Qc applications
Perfect for quality control labs, this portable system streamline...
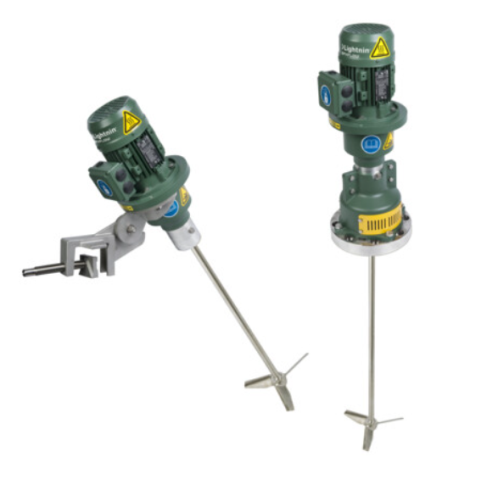
Portable and fixed mount mixing system
Optimize your mixing operations with a versatile system that adapts seamlessly betwe...
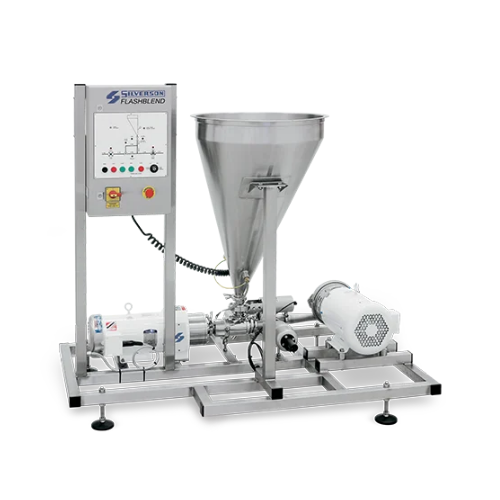
Powder/liquid mixing system for homogeneous dispersions
Struggling to integrate challenging powders into liquid formulati...
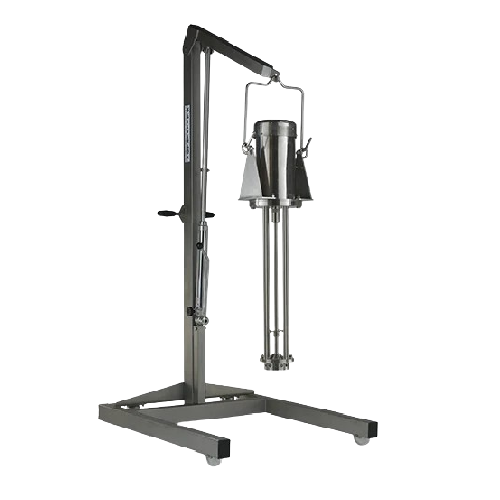
High shear batch mixer for industrial mixing
Optimize your production cycle with this high shear batch mixer, designed to ...
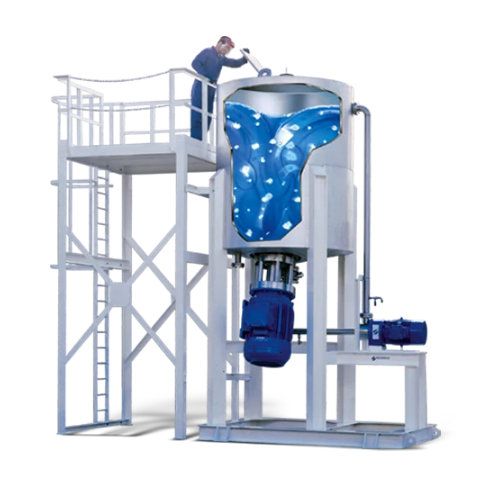
Disintegrator/dissolver mixing system for large solids
Streamline your process by transforming large, challenging solids ...
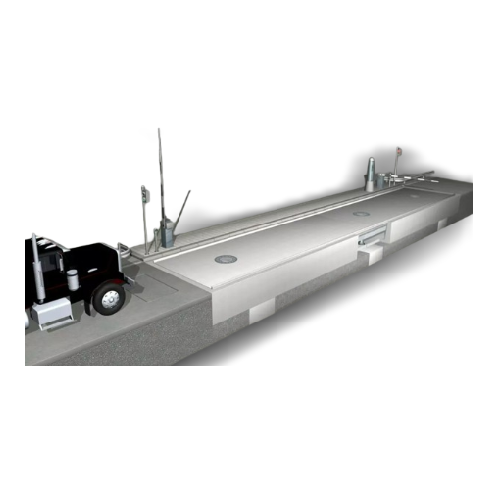
Pit scales for industrial weighing
Optimize material flow and ensure precise load determination with a robust pit scale sol...
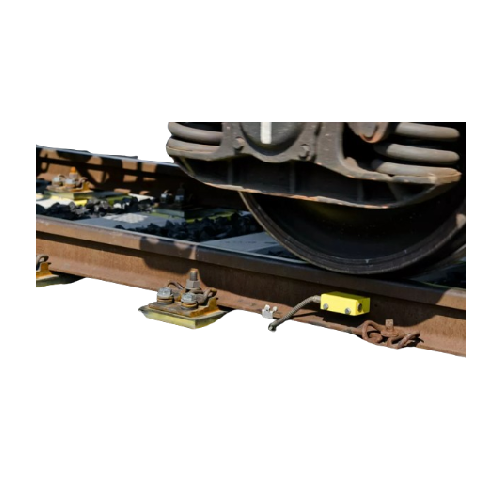
Dynamic weighing for solids and liquids
Ensure precision in rail transport with innovative dynamic scales that provide lega...
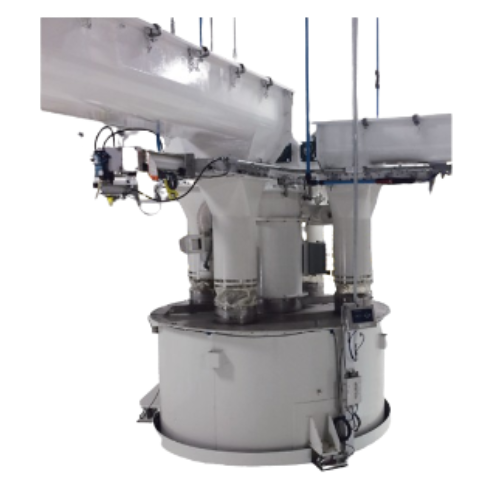
Scale hopper for bulk solid material handling
Ensure precise measurement and efficient transport of bulk solid materials w...
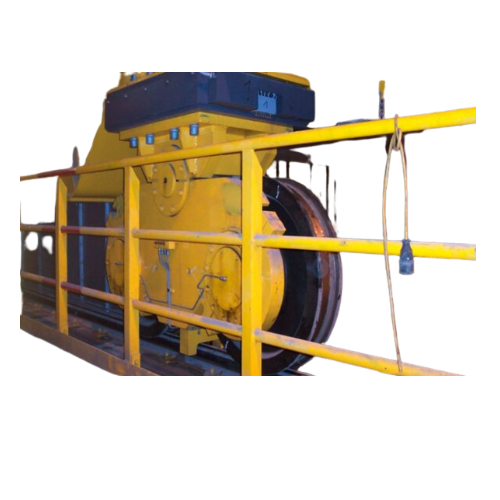
Crane scales for precise weighing in chassis
Optimize space with low-profile crane scales, ensuring accurate weight measur...
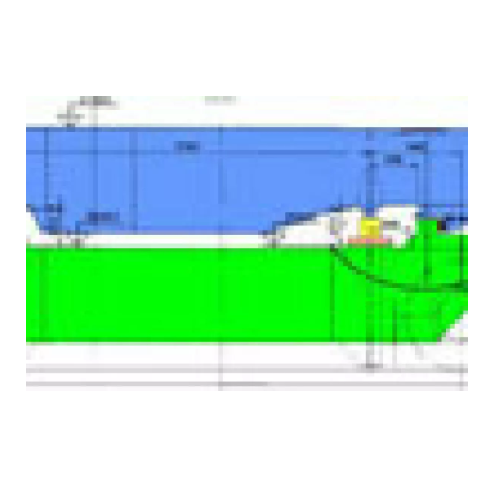
Crane weighing system for precision measurement
Ensure precise and temperature-resistant weighing during high-demand opera...
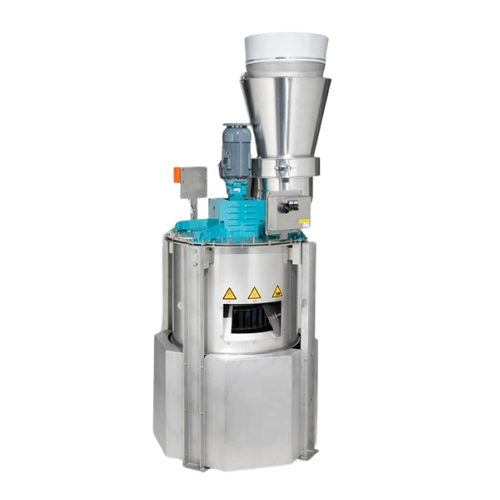
Mass flow rate feeder for bulk powders
Achieve precise control and consistent material flow in high-speed manufacturing env...
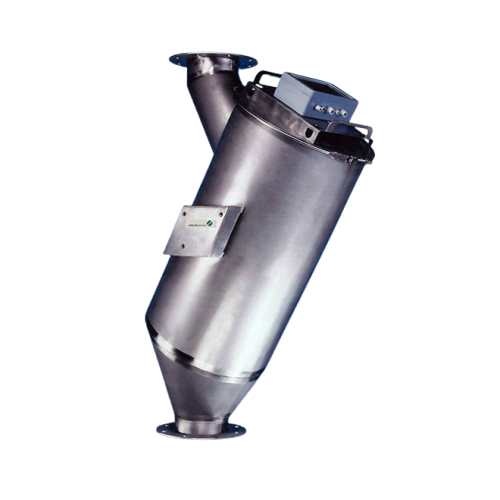
Solid flow meter for granular and powdered bulk materials
Ensure accurate mass flow measurement and seamless integration...
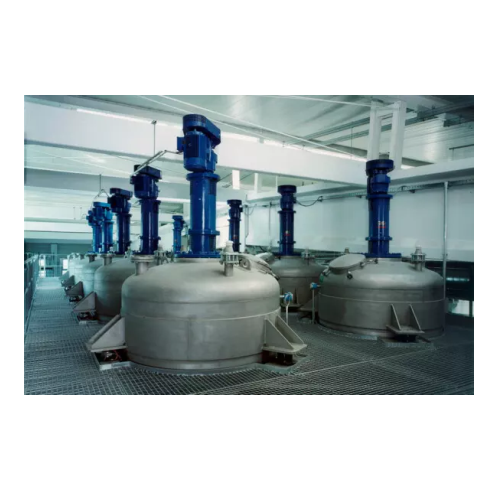
Bin weighing system kits for precise weight control
Ensure accurate material measurement in challenging environments with...
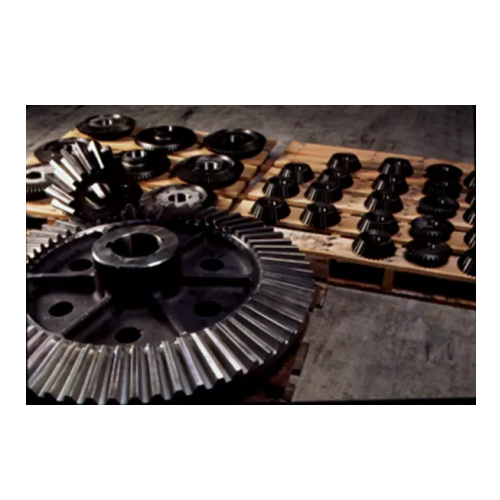
Industrial grinding mill replacement parts service
Optimize production efficiency with high-precision grinding solutions ...
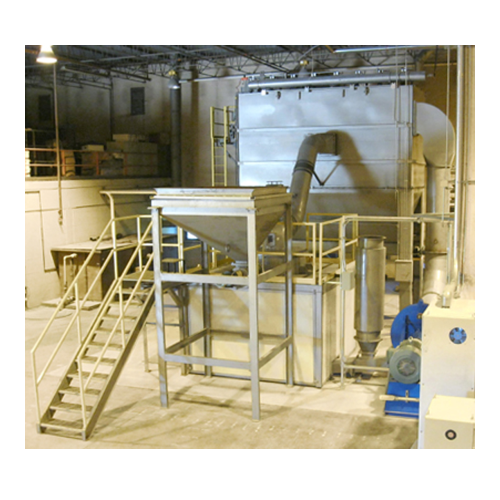
Ultrafine powder mill for coatings and pigments
Optimize your ultra-fine powder production with this precise grinding and ...
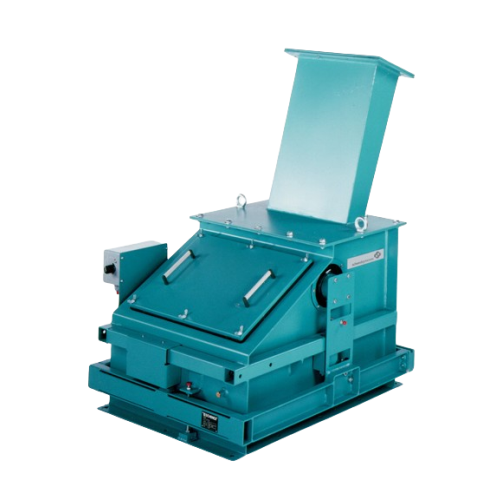
Solids flow meter for bulk solid streams
Ensure precise bulk material measurement with a system designed for accuracy and r...
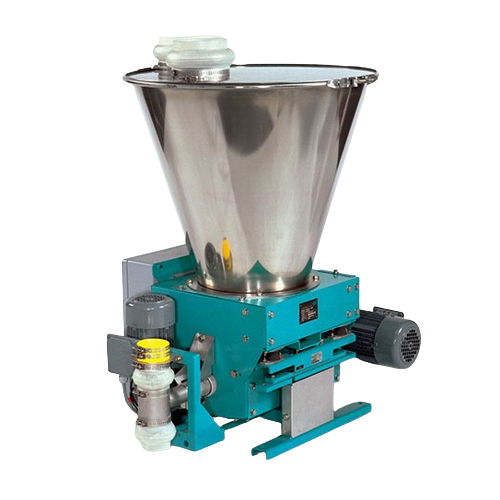
Loss-in-weight feeder for bulk solids
Ensure precise and reliable dosing of bulk solids with a compact feeder that eliminat...
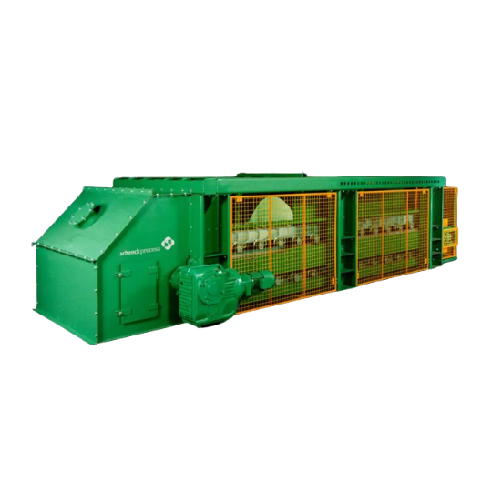
Apron weighfeeder for sticky bulk materials
Optimally handle challenging, sticky materials with precision and consistency ...
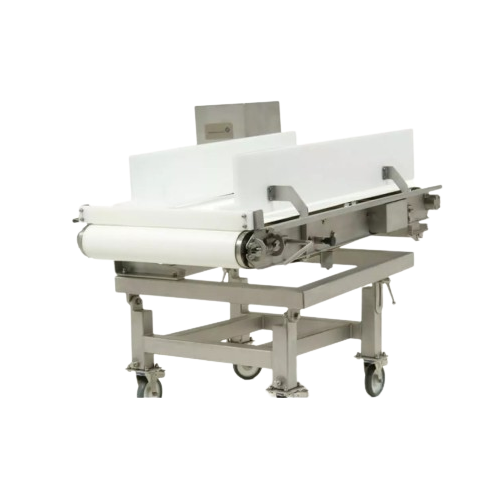
Industrial weighfeeder for hygienic applications
Achieve precise mass flow control with a hygienic design, ideal for appli...
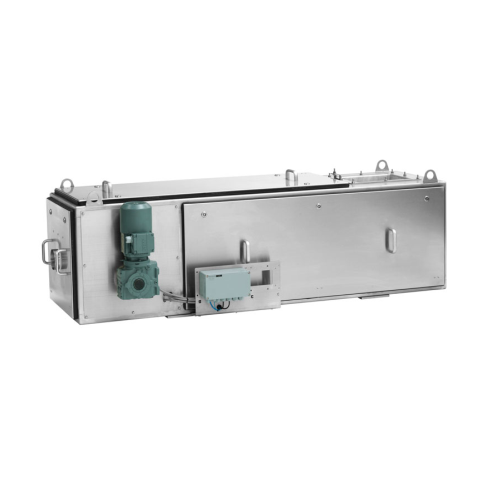
Continuous and batch feeding system for bulk materials
Achieve precise bulk material feeding with seamless integration in...
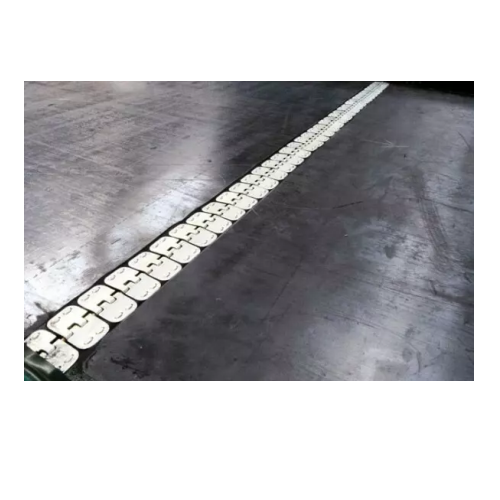
Optimal maintenance solution for industrial weighfeeders
Streamline your processing operations with a solution that minim...
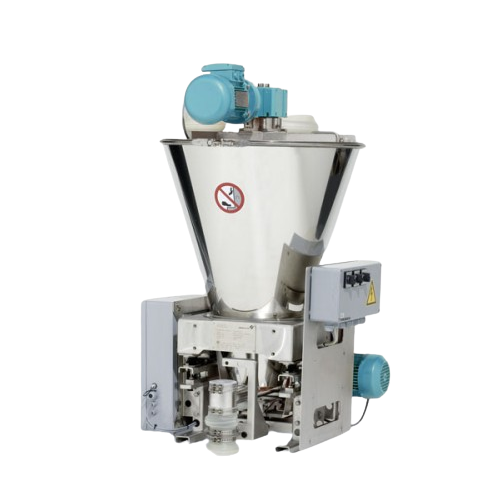
Loss-in-weight feeder for poor flowing bulk solids
Efficiently handle poorly flowing bulk solids with unparalleled precis...
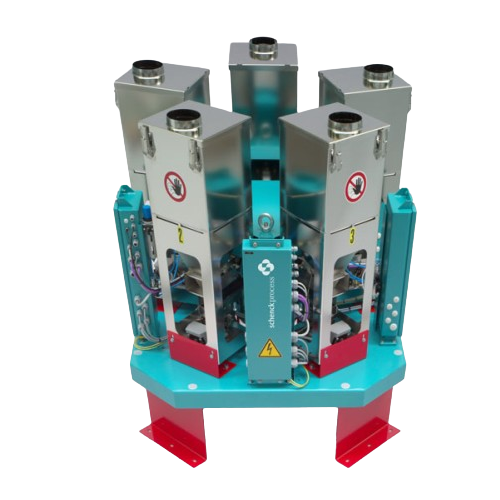
Multipurpose feed station for bulk solids
Optimize your production line with a versatile feeding station designed for simu...
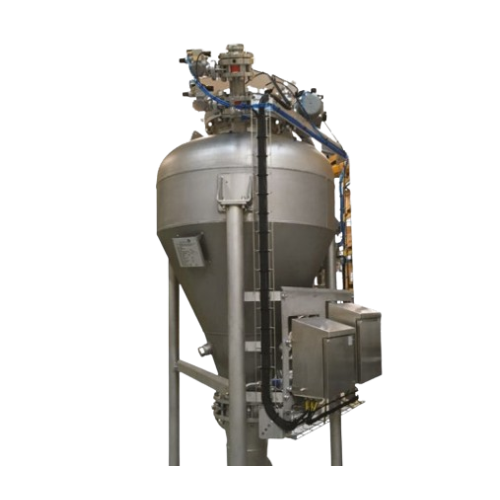
Dense phase pneumatic conveying accessories
Optimize material flow and reduce power consumption with dense phase pneumatic...
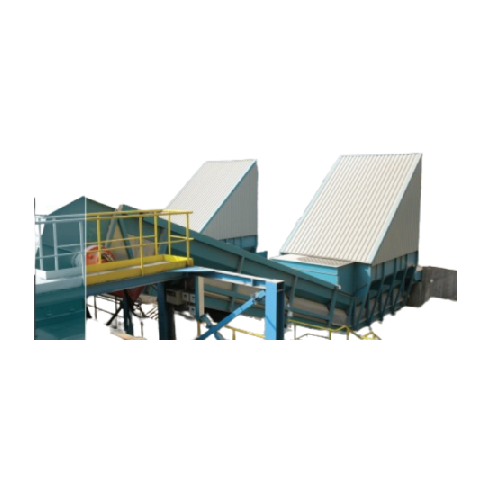
Bulk reception solution for industrial material handling
Optimize your operations with an above-ground bulk reception sys...
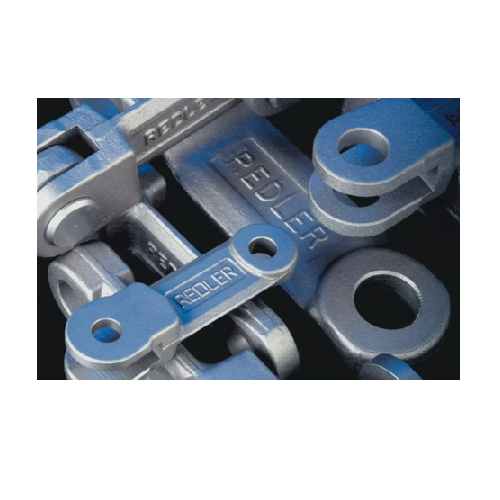
Drop forged chain for drag chain conveyors
Enhance your material flow efficiency with a robust drop forged chain designed ...
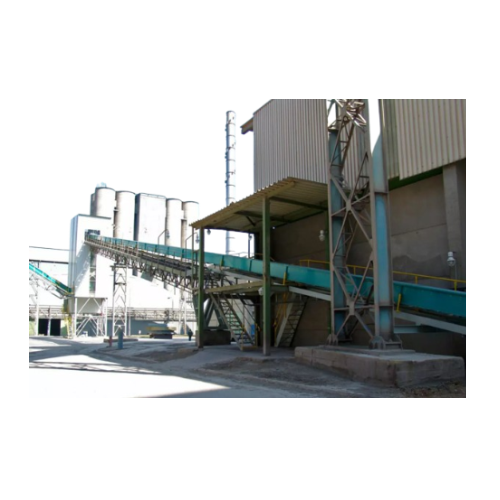
En-masse chain conveyor for bulk material handling
Streamline your bulk material handling with a gentle, efficient system...
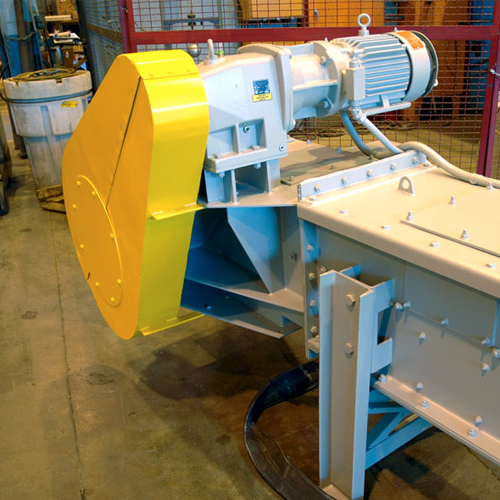
Bulk material handling with chain conveyor
Optimize your material transport with a solution designed for reliability in de...
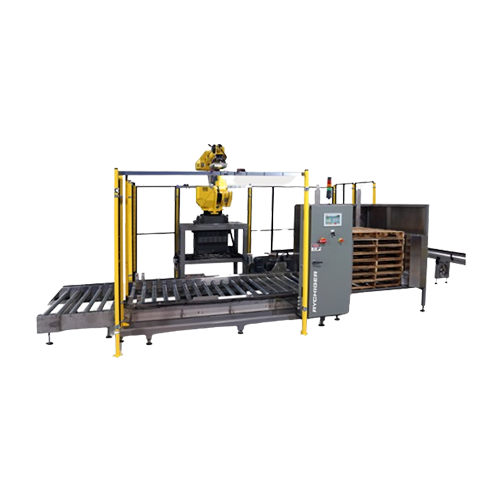
Compact palletizer for food and beverage products
Optimize your end-of-line operations with a space-saving palletizer tha...
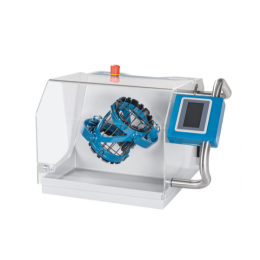
R&D shaker mixer for battery powders and chemicals
Material heterogeneity, agglomeration, and contamination are key param...
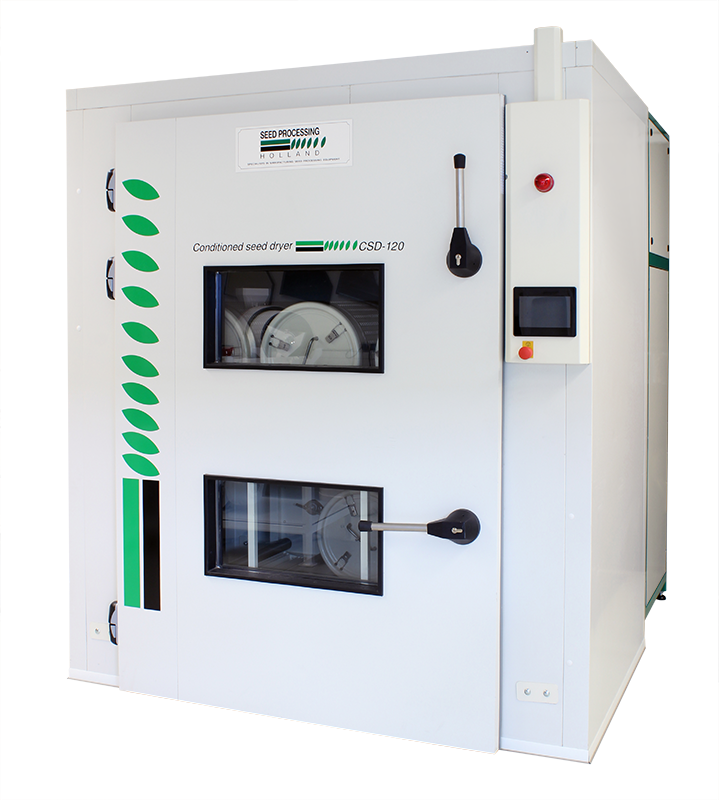
Conditioned seed drying machine
It’s essential to dry moist seeds before you process and store them. Seeds with too high or ...
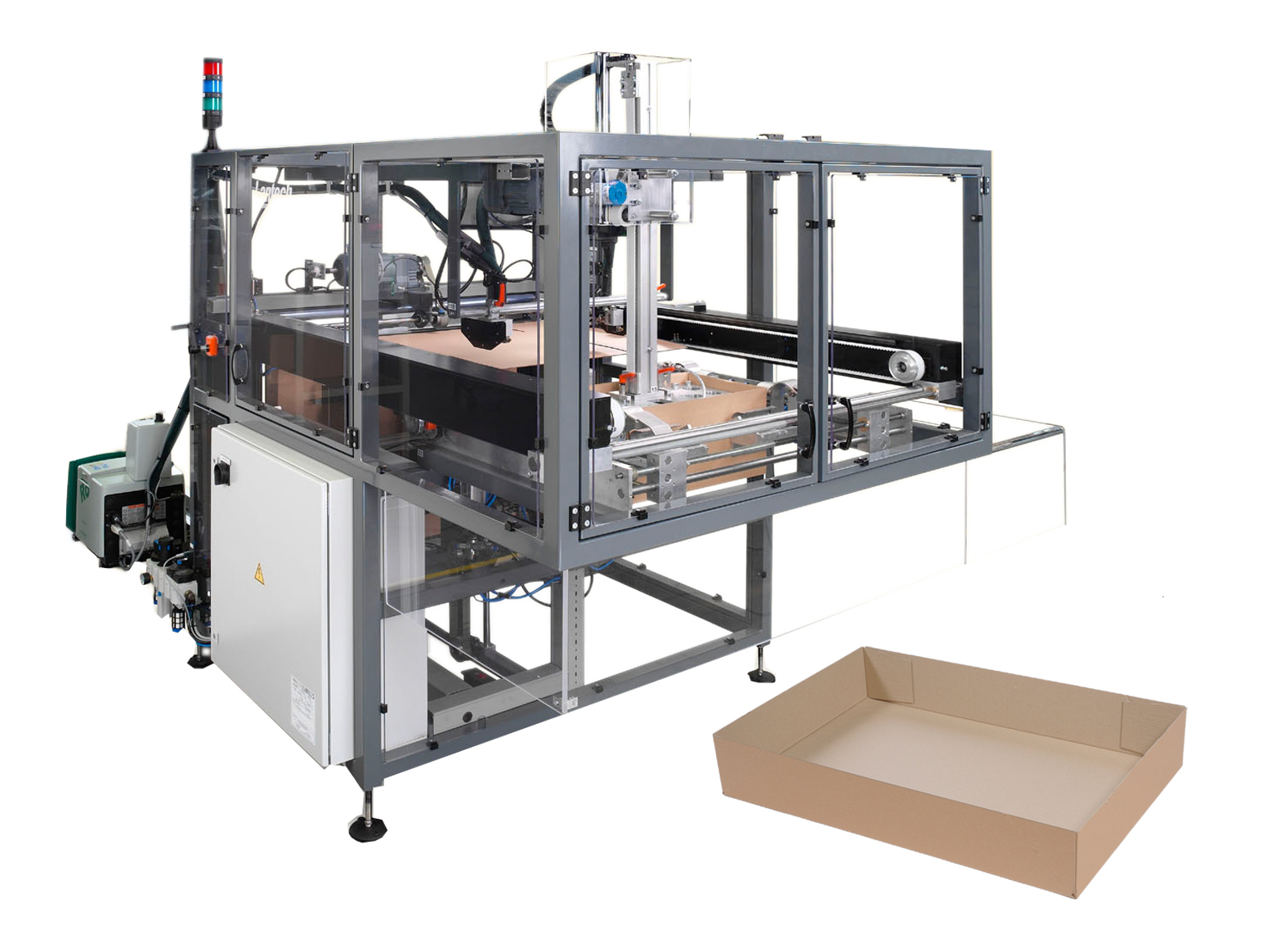
Tray erector
Corrugated trays come in many forms and sizes. Automate the process of erecting the trays to ensure consistent q...
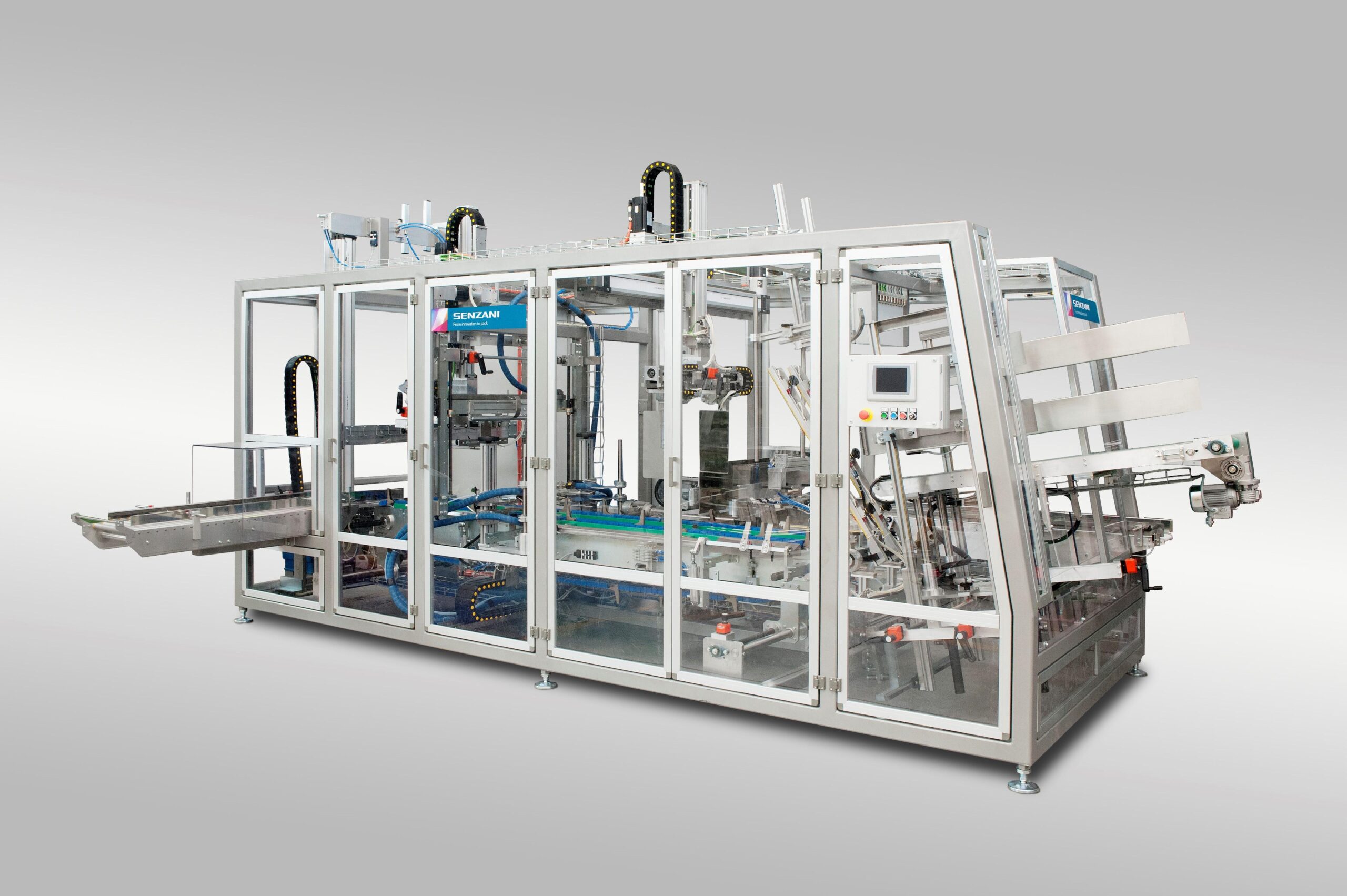
Wraparound case packer
Packaging companies need to pay attention to personalization in shape and design in addition to the at...
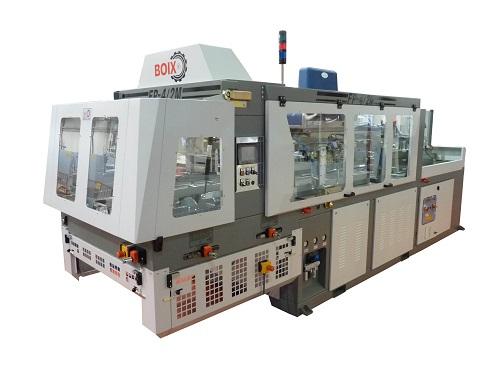
Tray former for various tray formats including trays with corner constructions
If you are looking to increase your sup...
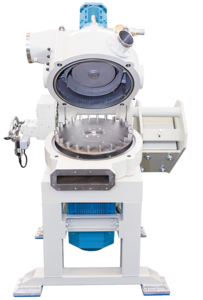
Classifier mill for powder coating
High-quality powder coatings are often required to manufacture equipment, appliances, an...
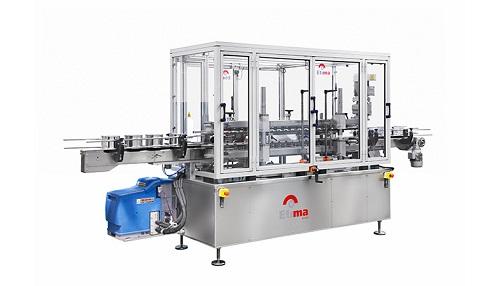
Linear machine for wraparound label
Wraparound labels allow you to offer detailed information using a small space or fit ex...
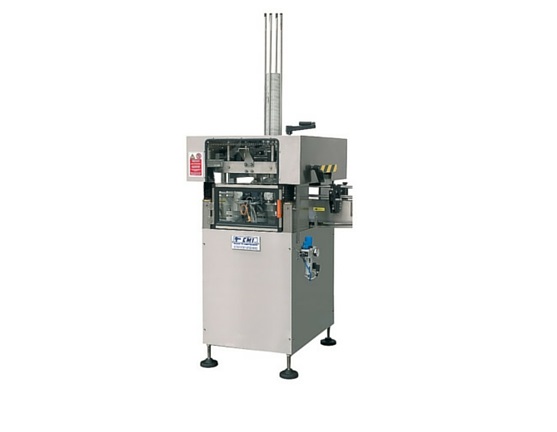
Automatic can sealer
If you need to cap paint, glues, and solvents containers and are currently manually placing the lids, yo...
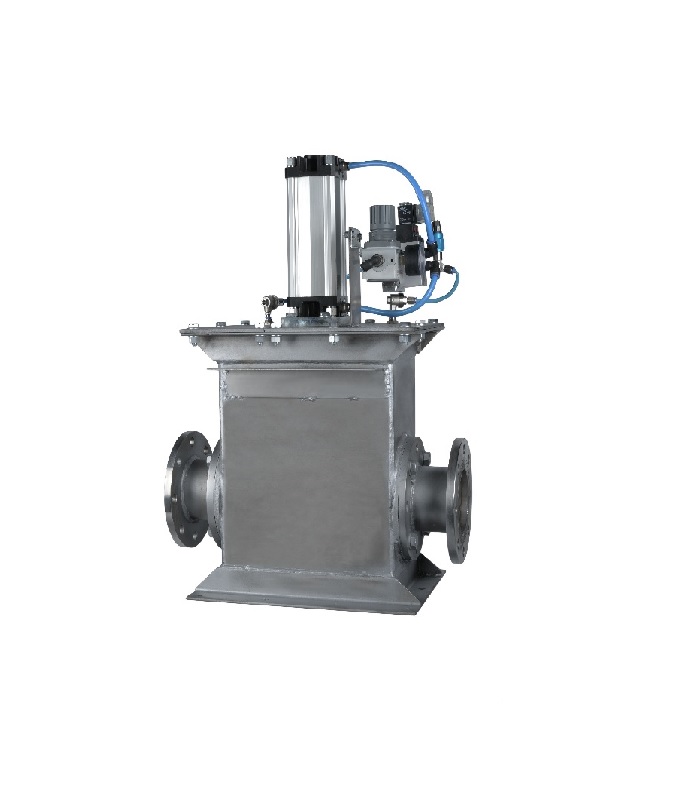
2-way diverter valves for pneumatic conveying
Products conveyed through pneumatic conveyor lines often need to be diverted...
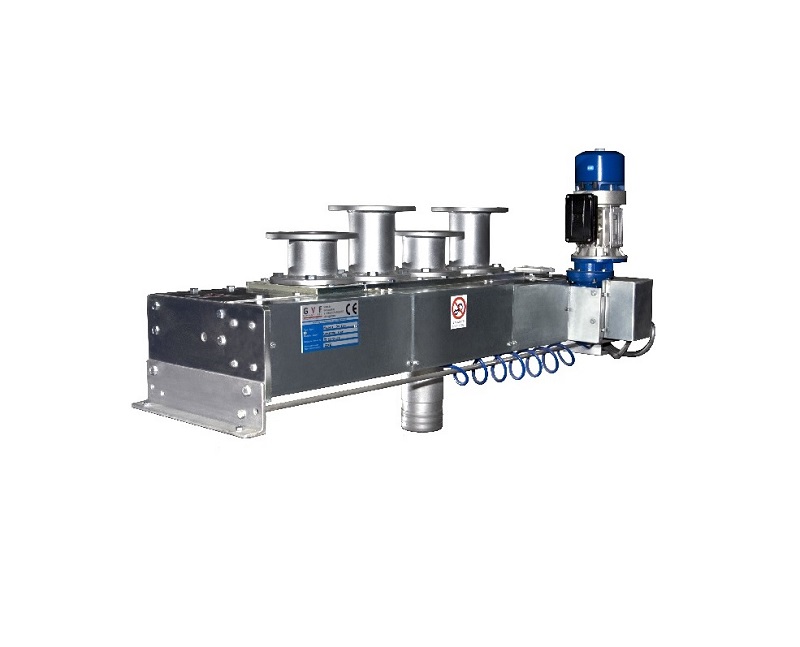
Multi-way diverter valve for pneumatic conveying
Products conveyed through pneumatic conveyor lines often need to be diver...
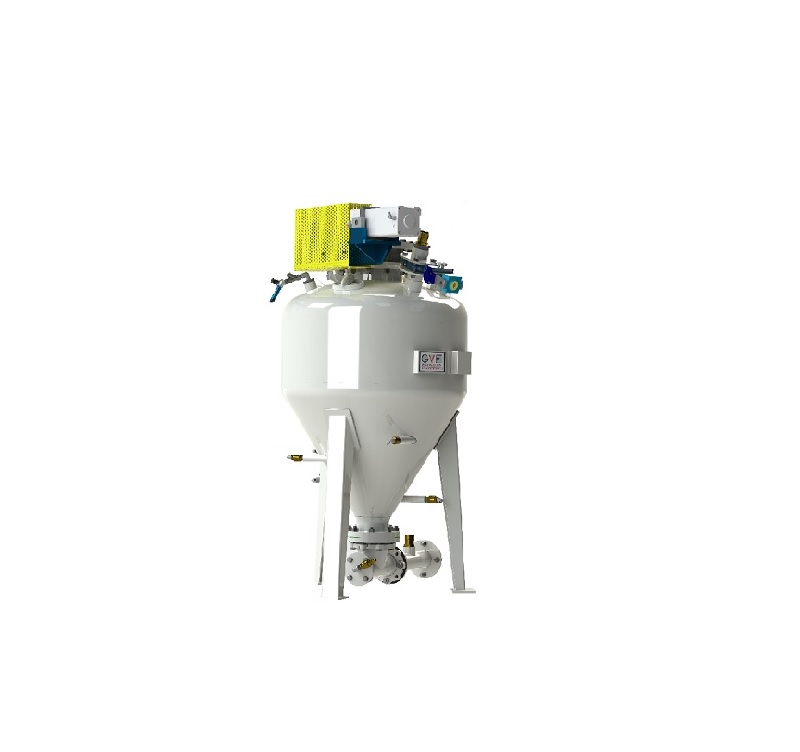
Dense phase conveyor for normal wearing materials
Dense phase pneumatic conveying is used for powders, granules, and grai...
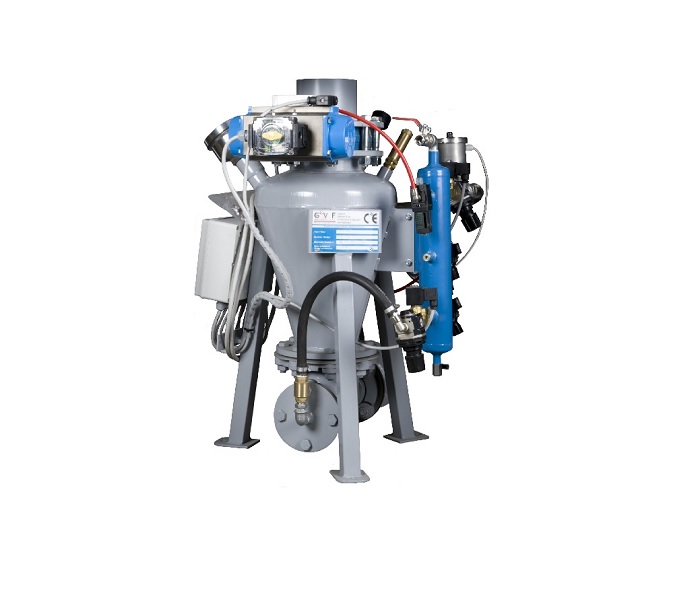
Dense phase conveyor for powders and granules
Some manufacturing and filling operations require a smaller pneumatic transp...
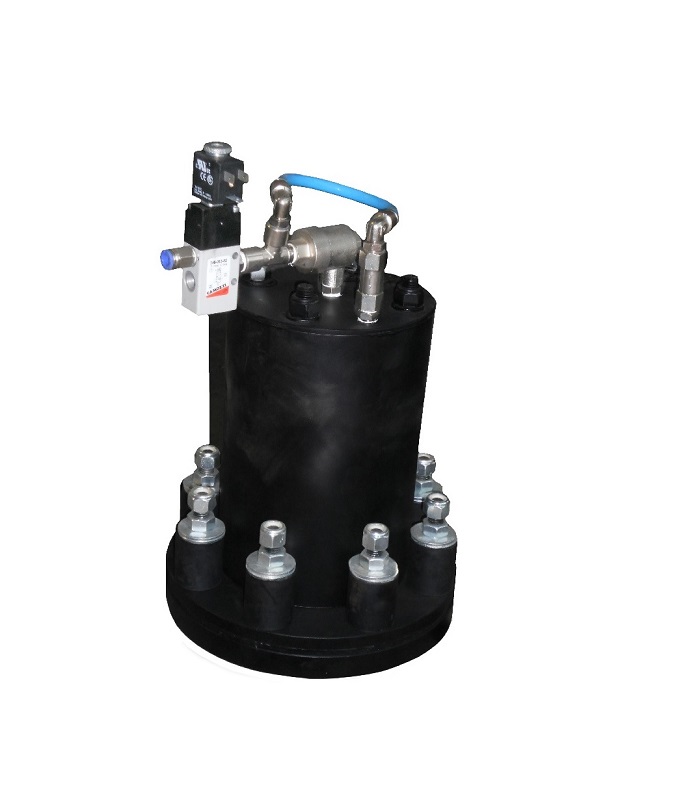
Airshocking hammer
Silos, hoppers, bins, and other containers can build up a layer of powdered product on the internal walls....
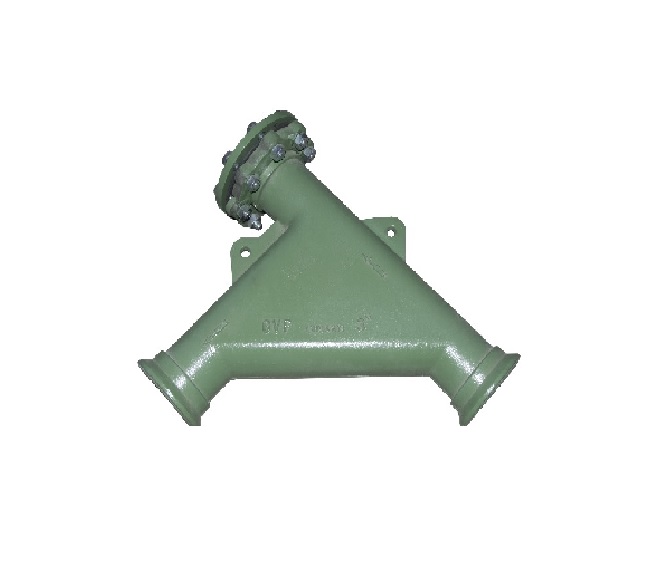
Wear resistant bends for pneumatic conveying
Bends in pneumatic conveyor lines cause load loss leading to lower flow rates...
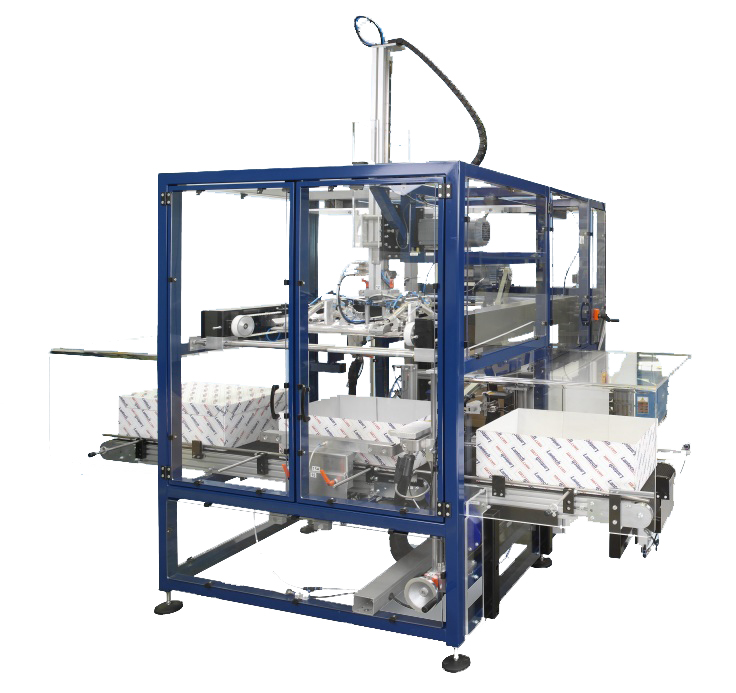
Lid applicator for corrugated cases
For your secondary packaging, you may be considering packing into boxes that require a ...
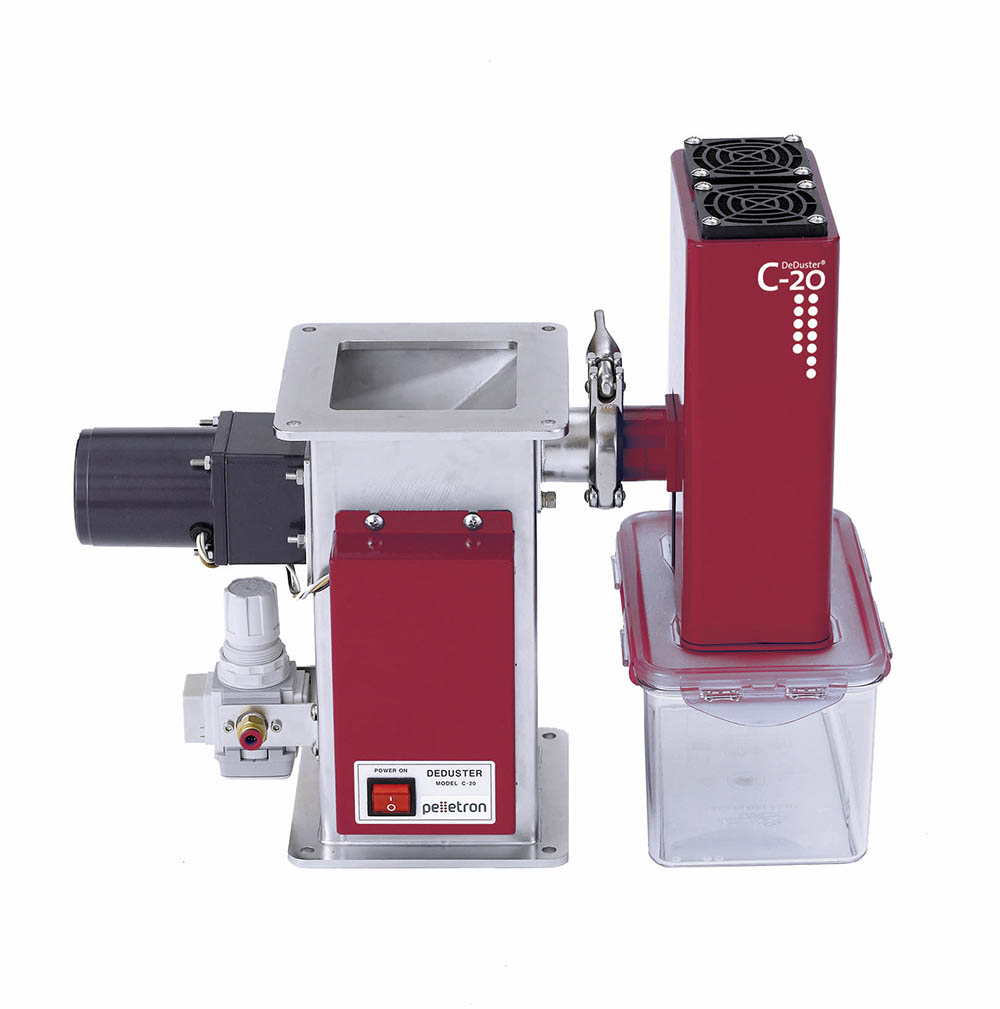
Deduster for injection moulding
High quality injection molded plastic parts require clean bulk resins free of dust and strea...