High-capacity dissolvers for industrial mixing
Enhance your production line with precision mixing, achieving consistent dispersions and reducing processing time for challenging formulations.
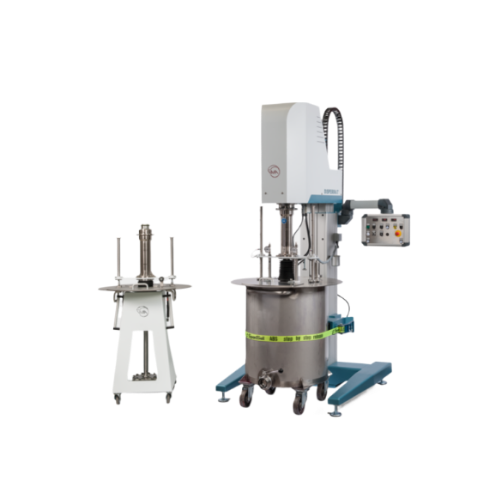
Dispersion and Mixing for High-Viscosity Products
VMA-GETZMANN’s DISPERMAT® SC4 Production Dissolver is engineered to deliver precise dispersion and mixing for high-viscosity products across various industries. Utilizing an advanced multi-stage dispersion process, it efficiently handles challenging applications like battery slurries and automotive coatings. The dissolver is capable of processing batches from 30 to 600 liters, ensuring excellent product uniformity through its PLC-controlled system, allowing seamless integration into your production line. Its energy-efficient design reduces power consumption by 15% with optimized motor speeds, while material options in stainless steel ensure corrosion resistance and durability. Easy-to-maintain with a quick cleaning feature, the DISPERMAT® SC4 aligns with industry standards, offering customization and engineering support for tailored solutions.
Benefits
- Boosts production efficiency with precise mixing for high-viscosity products.
- Minimizes energy usage by 15% with optimized motor control.
- Seamlessly integrates into existing production lines with PLC automation.
- Ensures longevity in corrosive settings with stainless steel construction.
- Simplifies maintenance with rapid and contamination-free cleaning features.
- Applications
- Biotechnology, Liquid formulations, Metal powders, Printing inks, Nanomaterials, Agrochemicals, Polishing agents, Building and paints, Carbon materials, Cosmetics, Fuel cells, Adhesives and sealants, Foods, Automotive coatings, Ceramics and glass, Batteries, Pharmaceuticals
- End products
- Liquid fertilizers, Spice pastes, Active pharmaceutical ingredients, Lip gloss, Hygienic fermentation systems, Carbon nanotube dispersion, Base coats, Catalyst inks, Carbon black pigment, Exterior wall paint, Aluminium powders, Lithium-ion battery slurry, Metal polishing paste, Herbicides, Epoxy adhesives, Ceramic tile glazes, Digital printing inks
- Steps before
- Pre-dispersion, Mixing, Slurry Preparation
- Steps after
- Fine Grinding, Product Circulation, Cleaning, Packaging
- Input ingredients
- paint ingredients, slurries, active ingredients, raw materials, spices, color pigments, adhesives, silicones, filler, anode materials, cathode materials, conductive additives, separator films, ceramic pigments, wood putties, spice mixtures, food dyes, food additives, pharmaceutical excipients, nano materials
- Output ingredients
- dispersed paints, uniform slurries, homogeneous products, fine suspensions, dispersed inks, blended adhesives, uniform silicones, mixed fillers, anode slurries, cathode slurries, battery compounds, processed ceramic pigments, homogeneous wood putties, ground spice pastes, color stable food products, finely processed pharmaceuticals, nano-dispersions
- Market info
- VMA-Getzmann is renowned for manufacturing high-quality dispersing, mixing, and milling equipment, particularly for the chemical, coatings, and inks industries, specializing in engineered-to-order solutions that emphasize innovation, reliability, and technical excellence.
- Power
- 0.3 - 55 kW
- Product Capacity
- 0.05 - 2000 litres
- Control Type
- CN / C / SC / PLC
- Milling Chamber Volume
- 4 - 10 litres
- Product Volume
- 0.25 - 1000 litres
- Vacuum Option
- Available / Optional
- Explosion Protection
- ATEX certified
- Batch vs. Continuous
- Batch
- Milling Bead Size
- 0.6 mm and up
- Cooling System
- Double-walled for cooling
- Sieve Type
- Retains milling beads
- Cleaning Method
- Simple and quick
- Milling Tool Material
- SiSiC / ZrO2
- Working mechanism
- Immersion milling
- Automation level
- Manual / PLC / SCADA
- Changeover time
- Quick-change system
- Cleaning method
- Simple cleaning
- Batch vs. continuous operation
- Batch
- Energy efficiency
- Low energy requirement
- Air incorporation control
- Closed system to prevent air incorporation
- Abrasion resistance
- High
- Biological compatibility
- Yes
- Cleanability
- Easy to clean
- Corrosive resistance (e.g. acids)
- Excellent
- Density/particle size
- 0.5–2.5 g/cm³
- Container capacity
- 75 – 750 litres
- Milling chamber volume
- 4 – 10 litres
- Control Panel Type
- CN / C / SC / PLC
- Integration Options
- Modular quick-change systems
- Design Options
- Standard / Vacuum / ATEX / Ceramic
- Milling Chamber Material
- SiSiC / ZrO2
- Explosion Protection
- ZONE 0/1/2
- Cooling System
- Double-walled