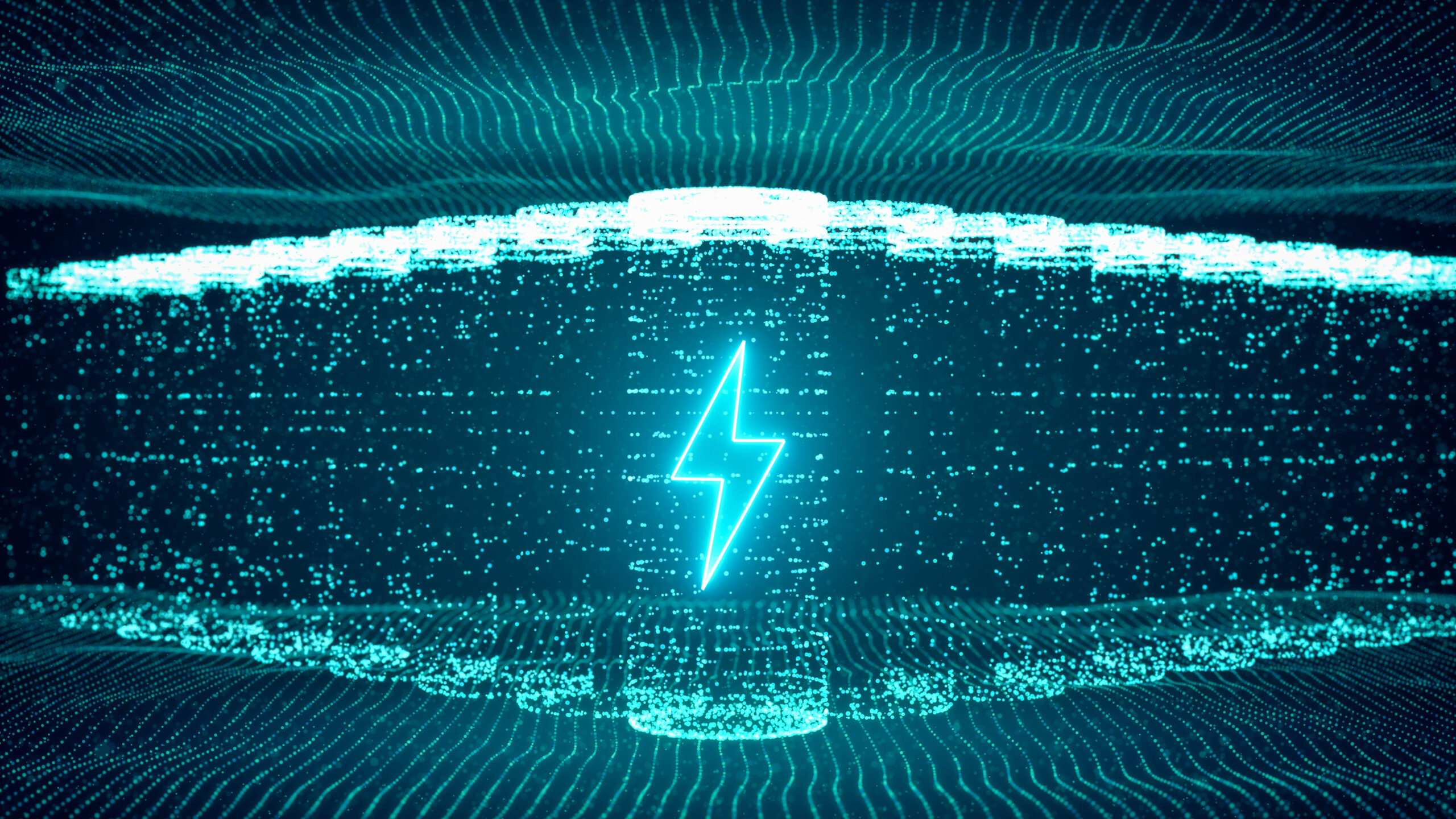
Battery Making Equipment
Find innovative batteries equipment and connect directly with world-leading technology suppliers
The battery revolution is as old as the industrial revolution. But batteries only emerged as a viable power source with lithium-ion solutions in the last quarter of the 20th century. Today, anything from power tools to automobiles runs on batteries, but advances in battery making equipment are eyeing more ambitious undertakings. Will we ever see battery-powered container ships? Will Battery Energy Storage Systems grow grid-scale successfully? Production technology is steadily moving towards this vision.
Technology picks for battery making
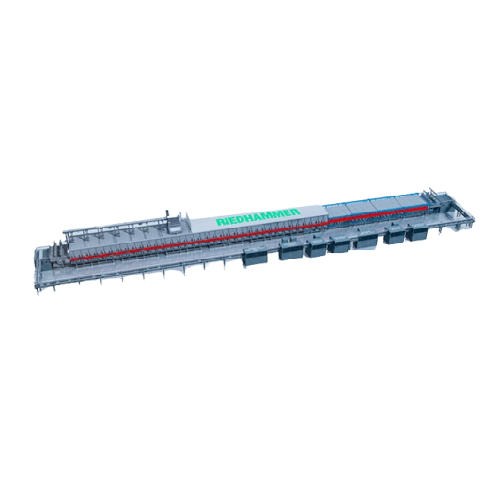
Lithium-ion battery powder processing solution
Optimize your lithium-ion battery manufacturing with advanced powder treatm...
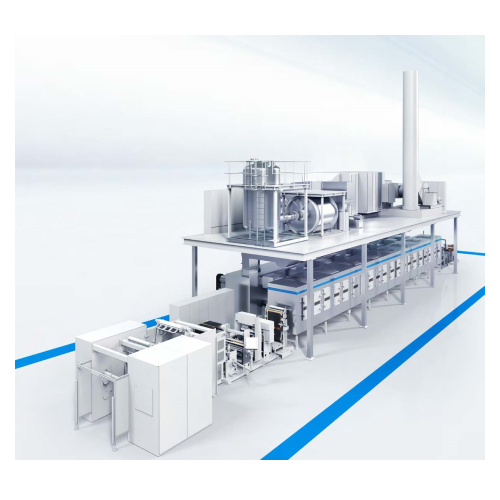
Electrode coating system for lithium-ion batteries
Achieve high-volume, precision electrode coating for lithium-ion batte...
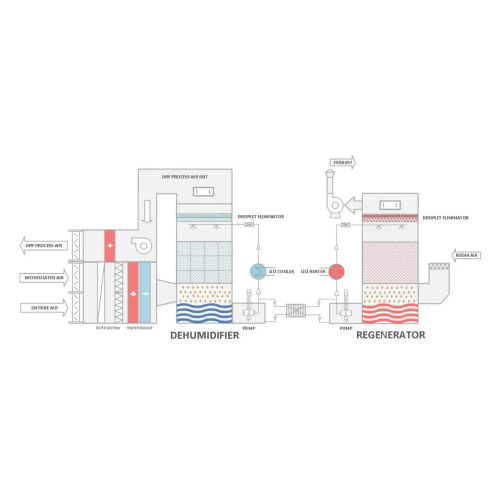
Industrial lithium chloride dehumidifier
Efficiently control air moisture and temperature with a solution that ensures prec...
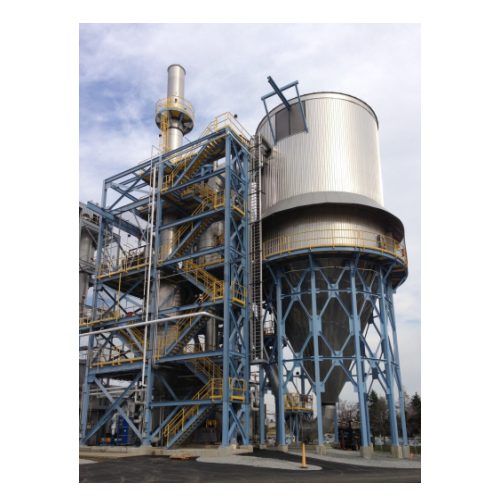
Spray dryers for lithium iron phosphate powder production
Optimize your lithium battery and electric vehicle production ...
Tell us about your production challenge
Reduce the surface area of materials with ultra-fine milling solutions
The battery chemistry determines the performance of the lithium-ion exchange. But the treatment of the materials significantly impacts the energy storage parameters of the final battery cells.
Battery manufacturing technology includes specialized mills to reduce the particle size of materials and increase their surface area. Grinding your chemicals into ultra-fine powders expands a battery pack’s overall capacity and recharge speed.
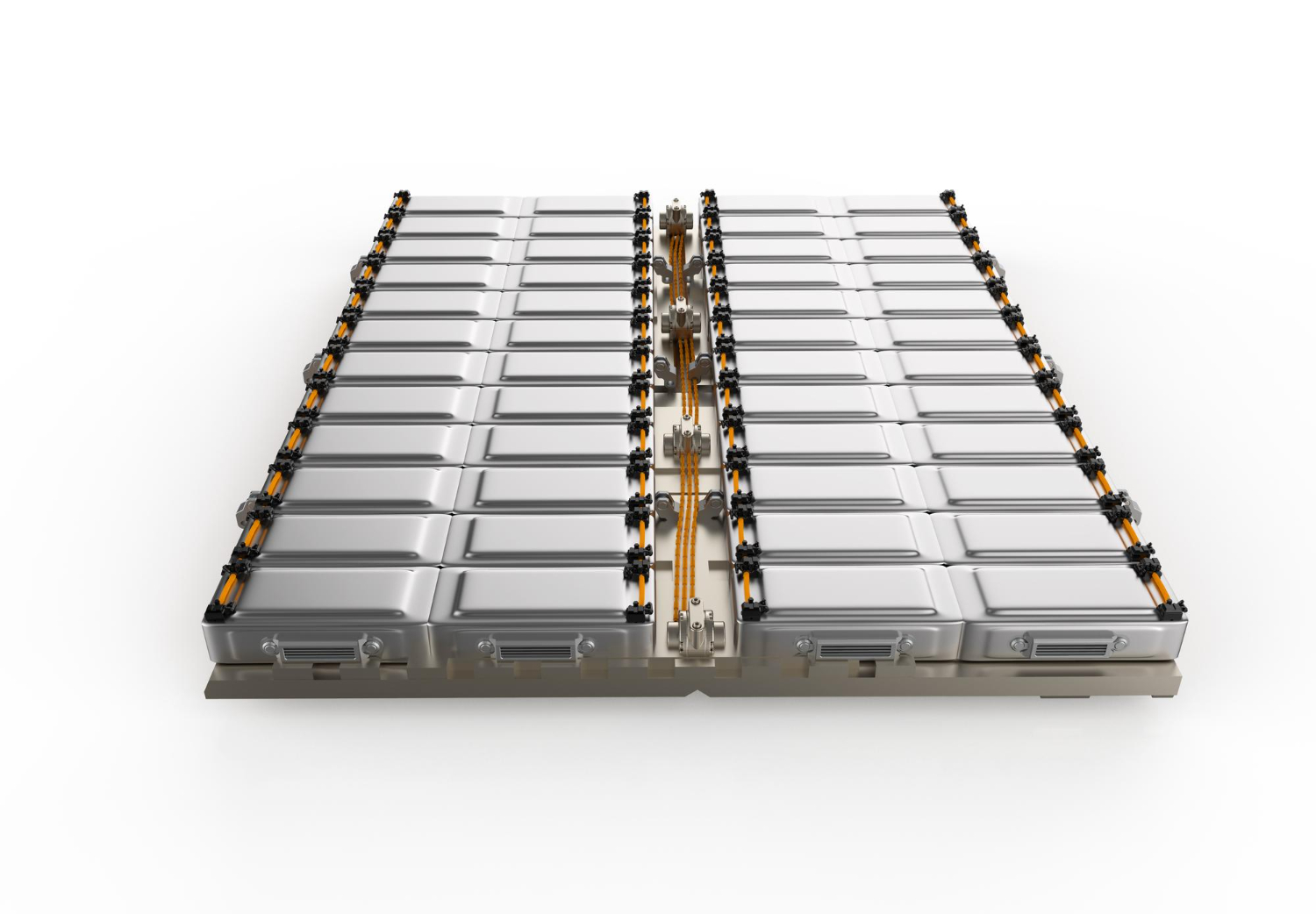
Distribute particles evenly with specially-designed battery making equipment
Lithium-ion batteries involve more than lithium, and the cornerstone of the manufacturing process is distributing materials homogeneously.
Milling equipment for ion battery production facilitates uniform dispersal by downsizing the minerals into ultra-fine powders. But particle size is only one-half of the effort. The materials must be mixed thoroughly but gently to achieve a consistent base for the electrodes.
Combat lithium dendrite with solid-state battery types
The early wave of electrolytes for lithium-ion batteries were liquid solutions enriched with dissolved salts, acids, or alkalis. But elevating temperatures, particularly while charging the battery, generates internal pressure and produces dendrites.
Solid-state batteries reduce this problem by replacing the liquid electrolyte with a ceramic plate that acts as a physical barrier. Repeated charging cycles still cause dendrite growth, but the solid-state technique offers further advantages. Batteries are lighter, charge faster, and are simpler to recycle.
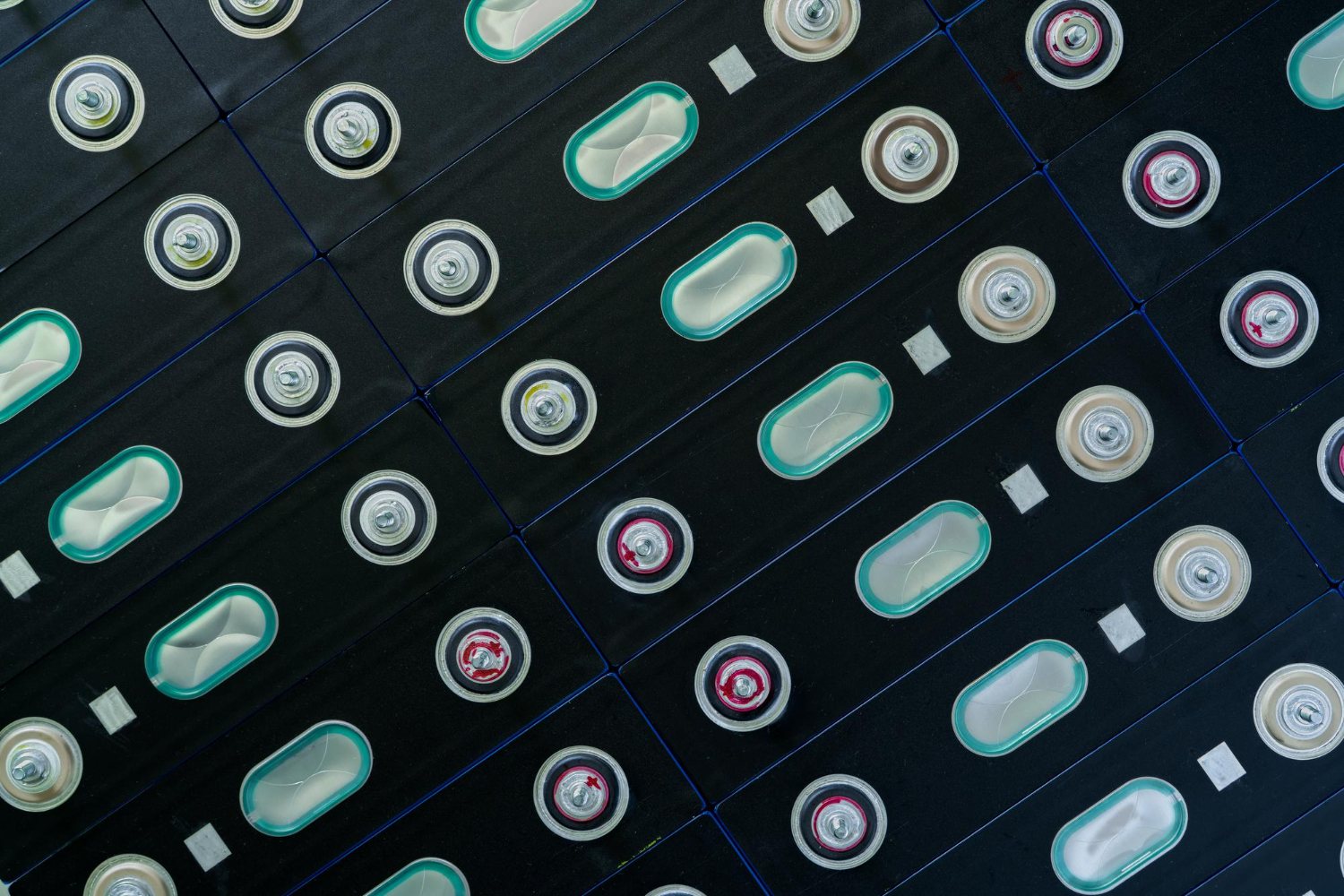
Round the graphite off to manufacture high-performance anodes
Graphite is the material of choice for most battery anodes as it is sourced relatively easily. But its effectiveness and storage capacity can be enhanced by rounding the particles.
Dedicated battery making equipment, such as classifier mills, apply mild pressure to achieve precise spheroidization. Natural graphite is usually highly irregular in shape, but the synthetic alternative still needs to be rounded.
Finish cathode production with a protective layer
The electrolyte transports the ions between the electrodes but also causes surface erosion of the materials. One strategy to minimize the wear is to coat the cathode and anode with a passivation layer.
Manufacturers apply various coating materials such as carbon black, zirconium dioxide, or magnesium oxide. Use high-shear mixing technology to coat the electrode material entirely and homogeneously.
Which batteries technology do you need?
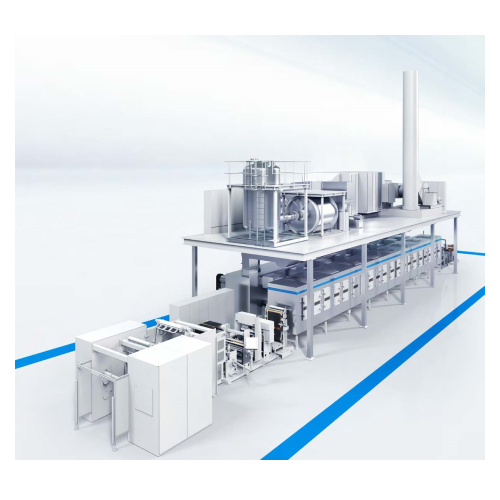
Electrode coating system for lithium-ion batteries
Achieve high-volume, precision electrode coating for lithium-ion batte...
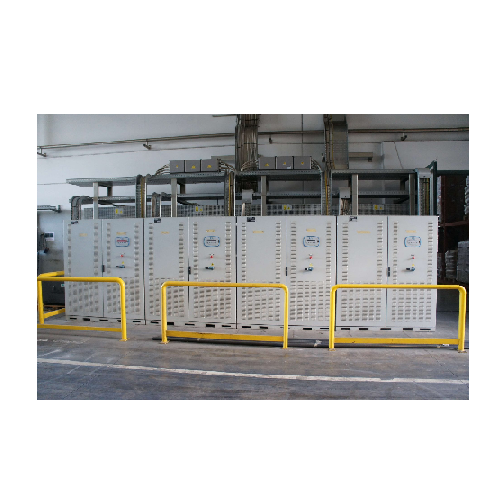
End of line testing for industrial batteries
Ensure battery reliability and safety in your production line with advanced t...
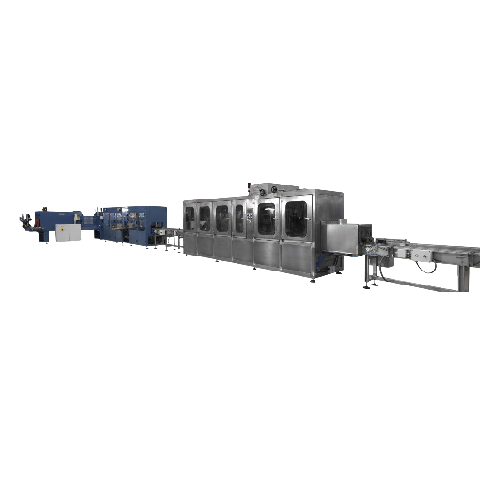
Battery plate finishing line for lead-acid batteries
Ensure your lead-acid battery plates achieve optimal thickness and u...
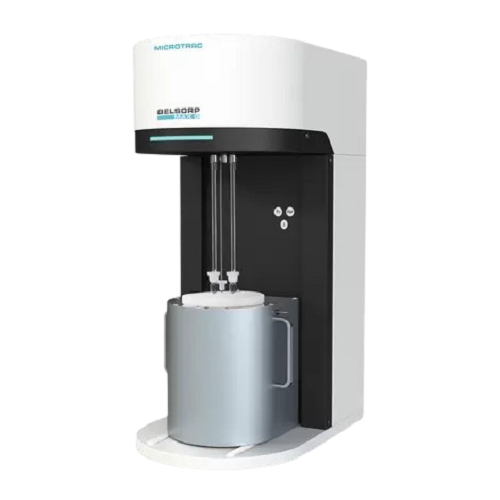
Specific surface area & pore size analyzer for materials
Achieve unparalleled precision in material characterization by m...
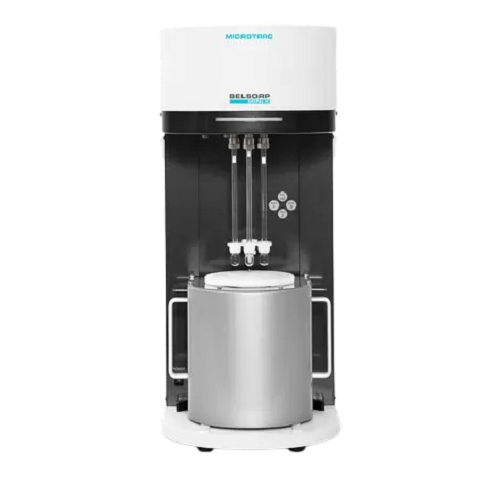
Pore size distribution analyzer
Optimize your material analysis with a system that delivers precise pore size distribution a...
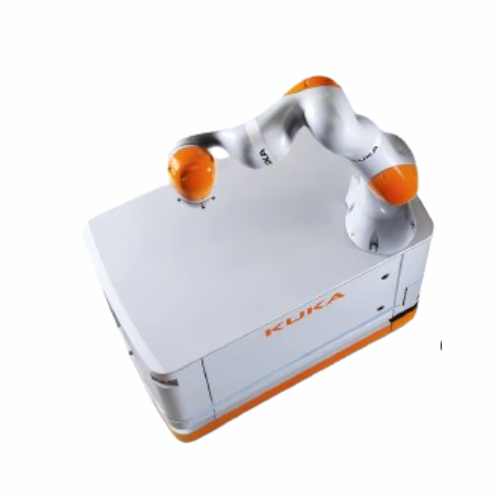
Autonomous mobile robot for flexible production
Enhance your production line with mobile precision; navigate and adapt to ...
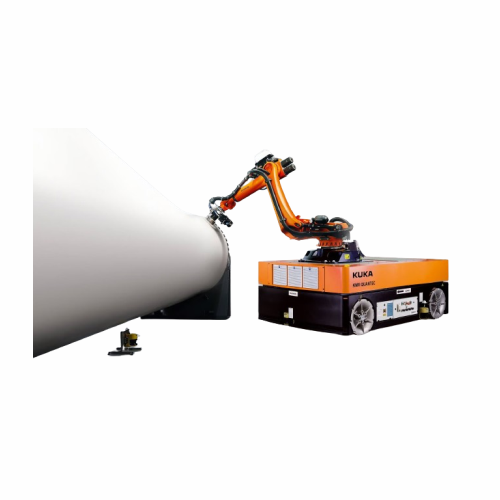
Autonomous mobile robot for precise positioning
Easily maneuver heavy machinery parts and large structural components with...
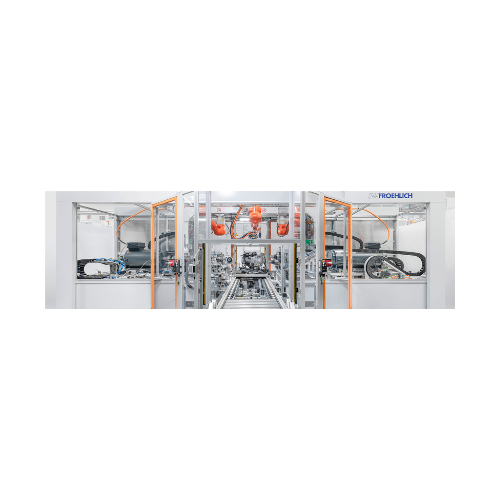
Automotive assembly and leak testing systems
Optimize your production line with versatile assembly and testing systems, en...
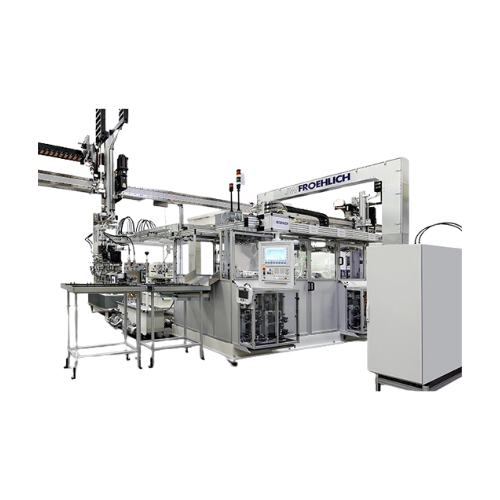
Function test for electro-hydraulic control units (ehs)
Ensure precise functionality and reliability in your production l...
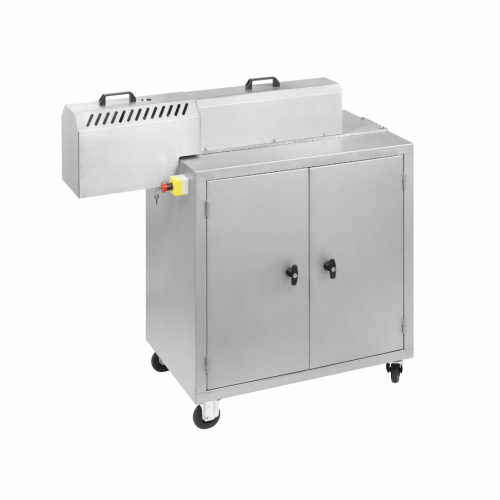
High-viscosity continuous industrial kneader for small volumes
Achieve consistent high-viscosity material processing wit...
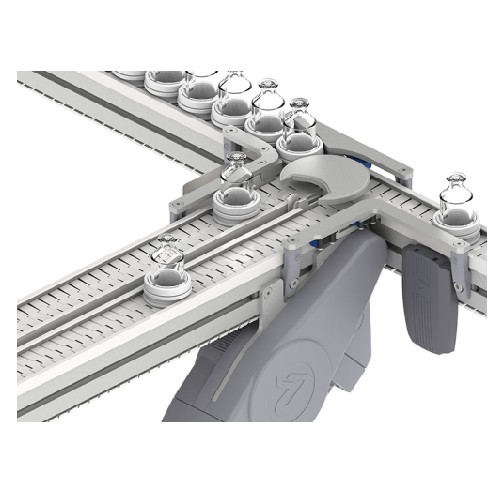
Conveying system for small, fragile products
Optimize your production line with high-capacity conveyors designed for effic...
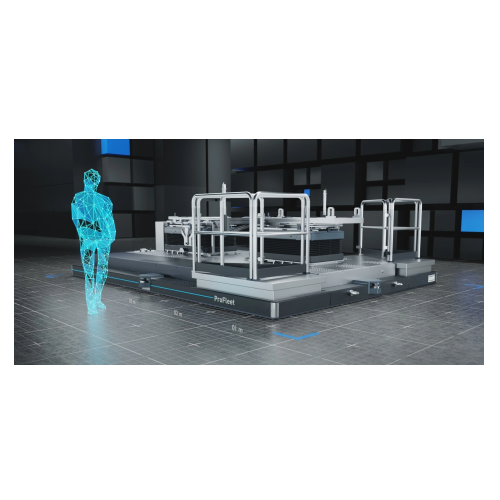
Compact Agv for trolley towing and load transport
Streamline your intralogistics operations with agile load transporters ...
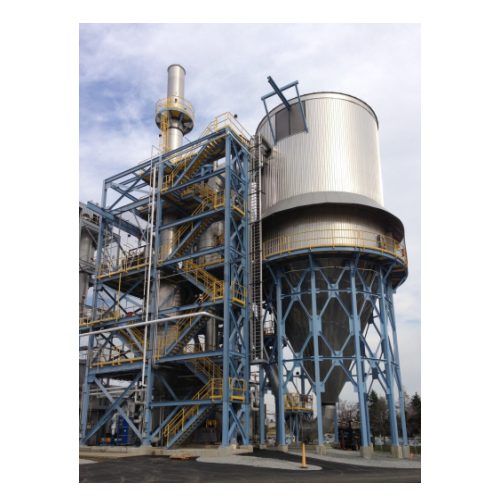
Spray dryers for lithium iron phosphate powder production
Optimize your lithium battery and electric vehicle production ...

Control systems for wet grinding industry
Enhance precision and efficiency in your production line with advanced control s...
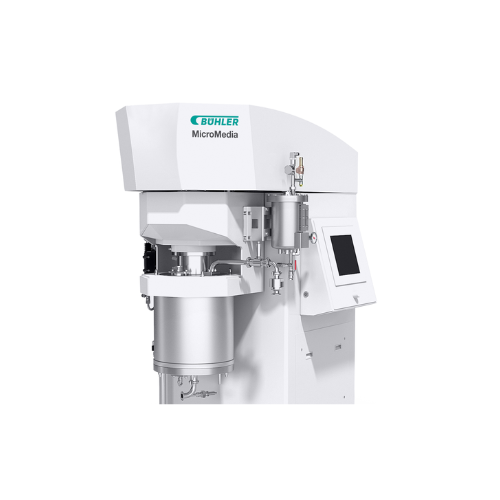
High-performance bead mill for wet grinding and dispersing
Optimize your production line with a bead mill designed for e...
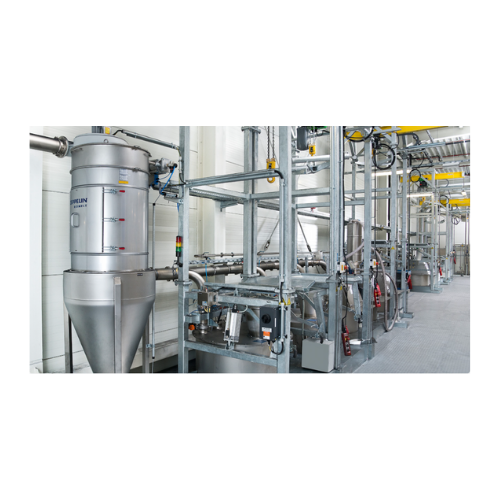
Battery production facilities with precision weighing
Achieve maximum product purity and precision in your production pro...
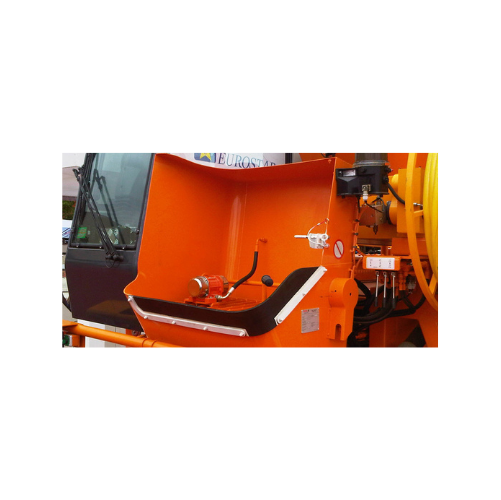
External electric motovibrators for hazardous environments
Ensure safety and efficiency in explosive environments with t...
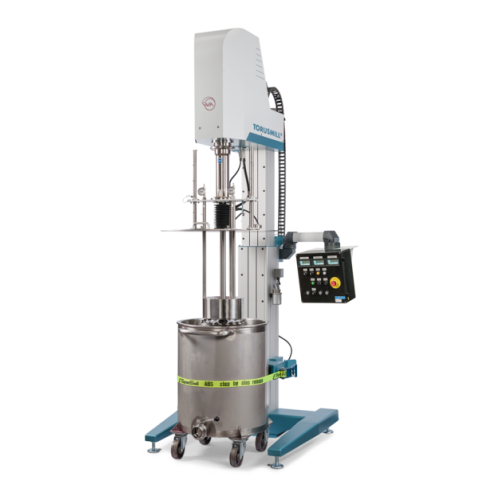
Explosion-proof basket mill for fine grinding
Achieve efficient and safe fine grinding with this innovative explosion-proo...
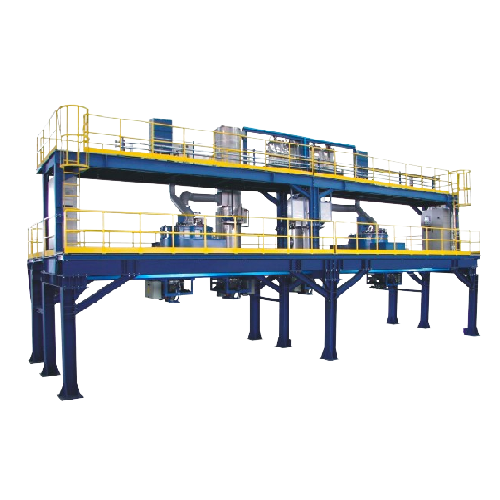
Paste mixer for battery manufacturing
Efficiently blend battery pastes to achieve precise consistency essential for manufac...
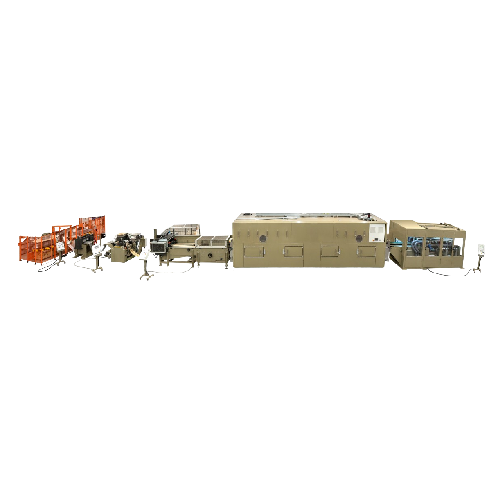
Pasting line for high-thickness plates
Optimize your battery production with precision control using a pasting line designe...
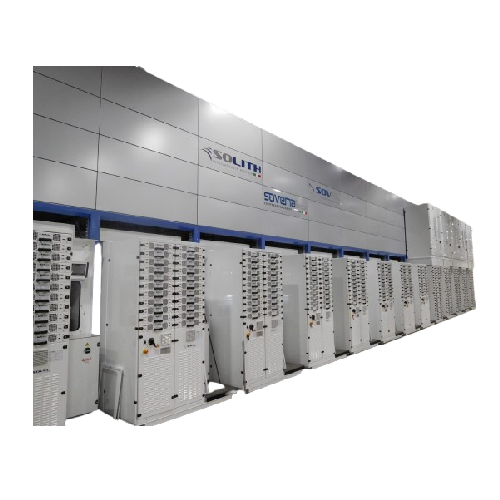
Battery chargers for industrial applications
Ensure optimal power management by integrating robust battery charging system...
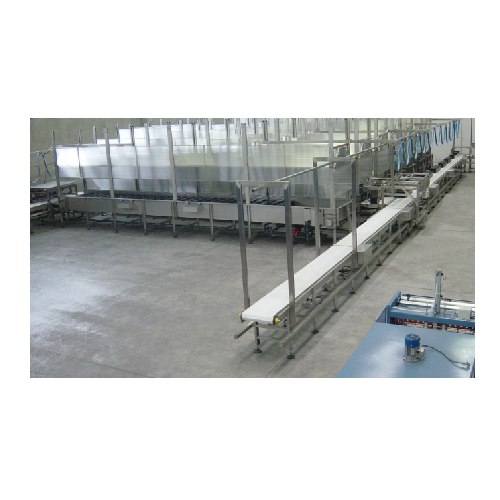
Water bath formation system
Enhance battery performance with precise temperature control, ensuring consistent formation and ...
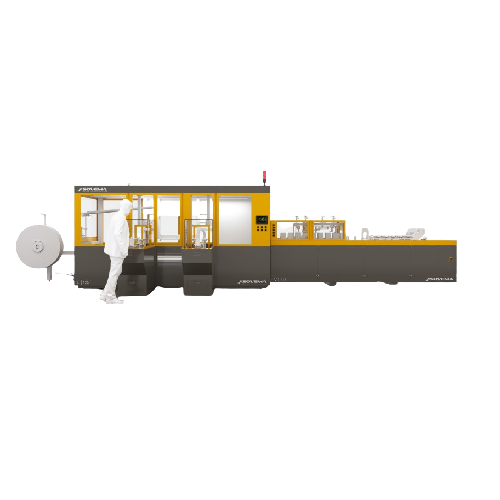
Enveloping and stacking solution for battery manufacturing
Streamline your battery production line with precision techno...
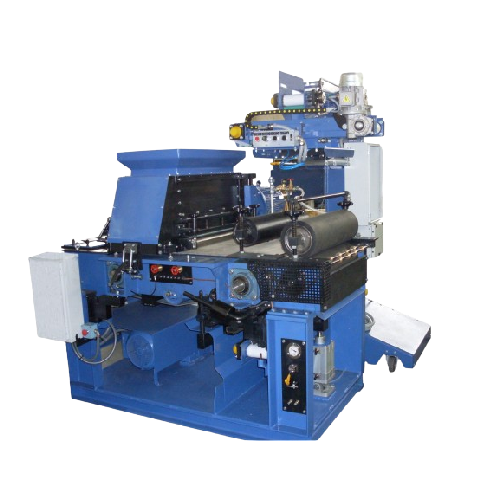
Industrial belt paster for battery manufacturing
Enhance battery production efficiency by precisely applying pastes to bat...
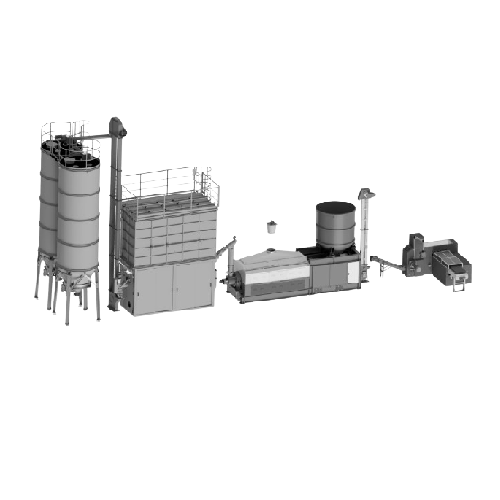
Lead oxide mill for battery production
Optimize your lead-acid battery production with chainless technology, ensuring consi...
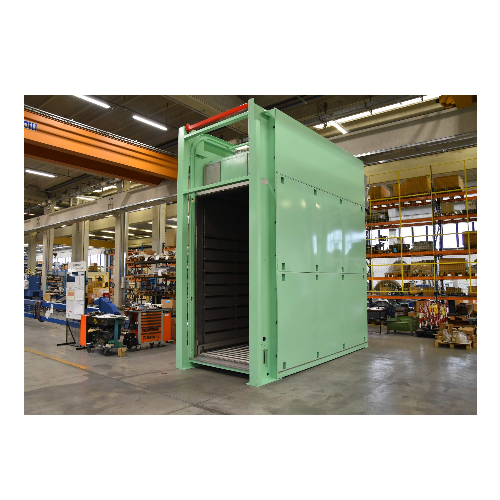
Industrial battery curing chamber
Achieve optimal battery performance with precise environmental control, ensuring the stab...
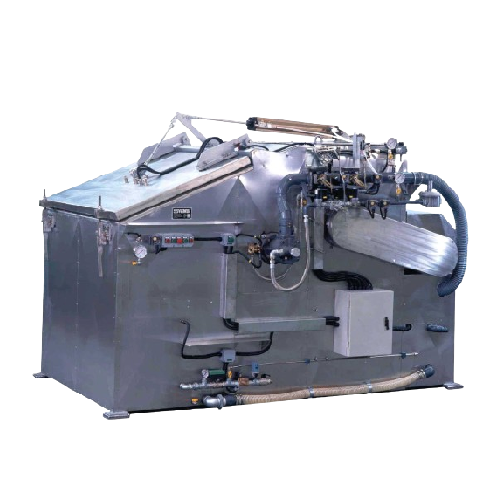
Eft chargers for industrial applications
Ensure optimal performance and longevity of lead-acid batteries with precise dry c...
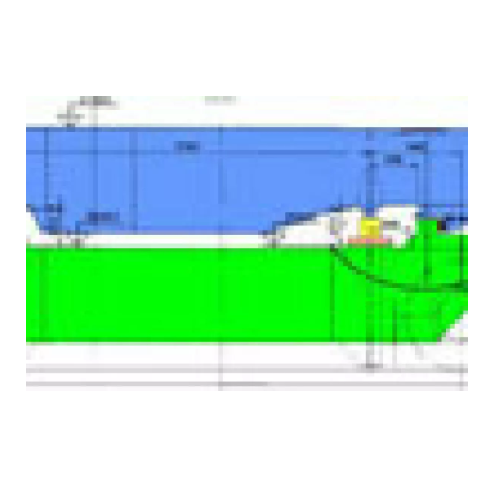
Crane weighing system for precision measurement
Ensure precise and temperature-resistant weighing during high-demand opera...
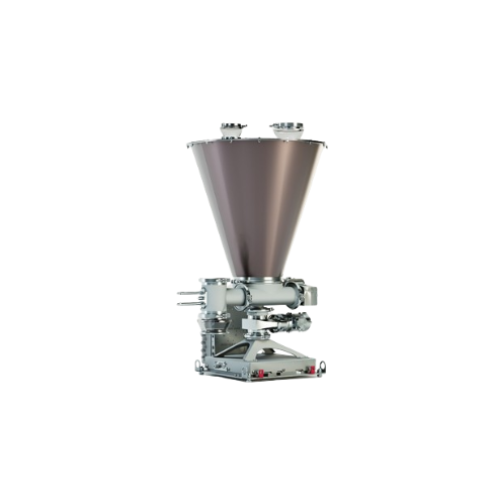
Loss-in-weight feeder for battery cell production
In battery cell production, achieving precise dosing and safe handling ...
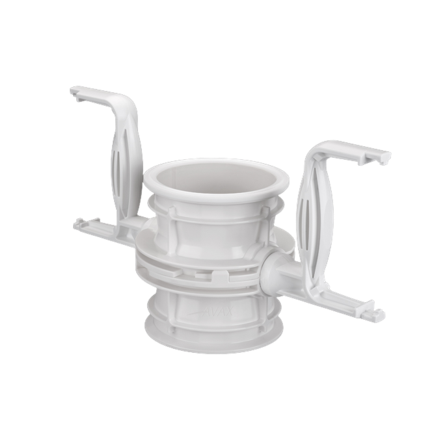
Single-use containment valves
From GMP and HSE perspective material transfer is critical for chemical and pharmaceutical for...
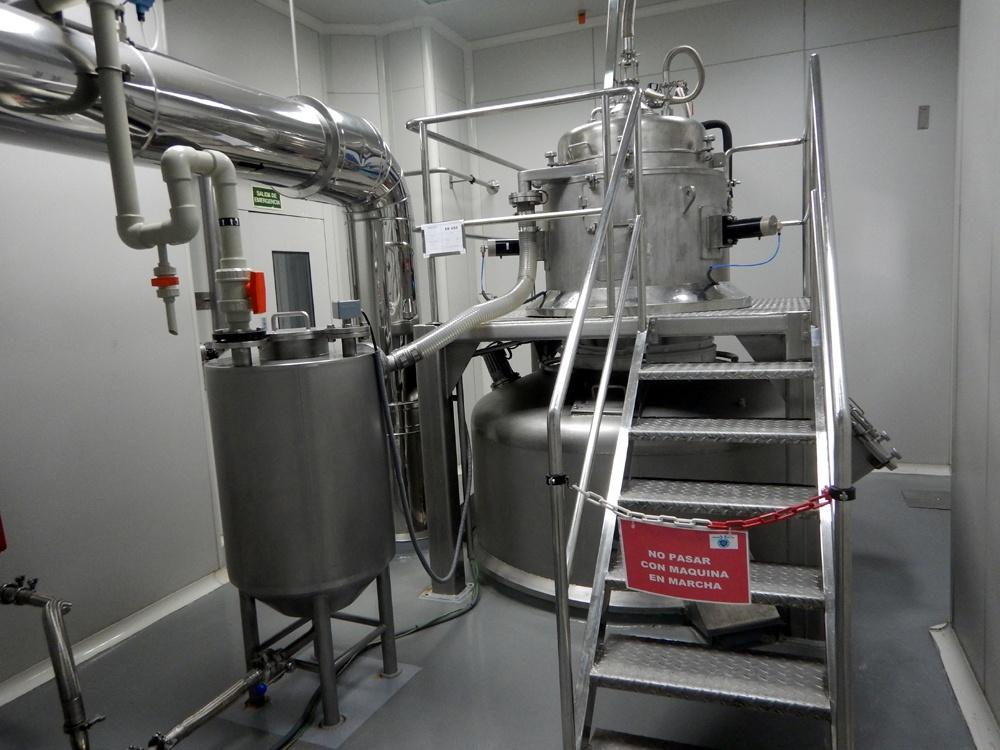
Continuous centrifuge for lithium hydroxide
Lithium hydroxide, a lithium compound used in making lithium batteries, is ind...

Automatic blister sealing machine for retail products
Blister packages for retail are usually designed with a paperboard ...
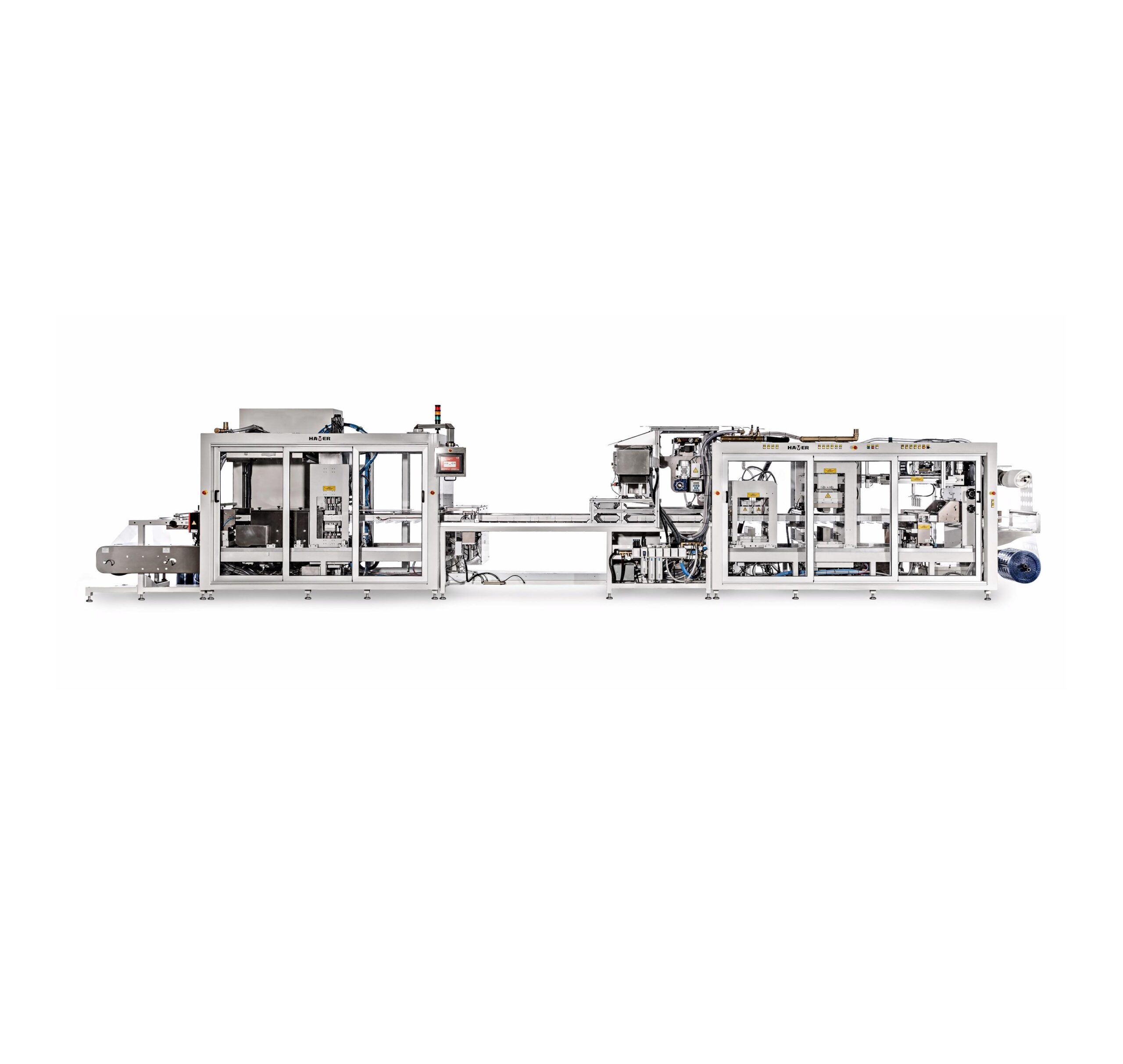
Industrial blister packaging machine for retail products
A blister can be simply defined as a type of packaging that cons...
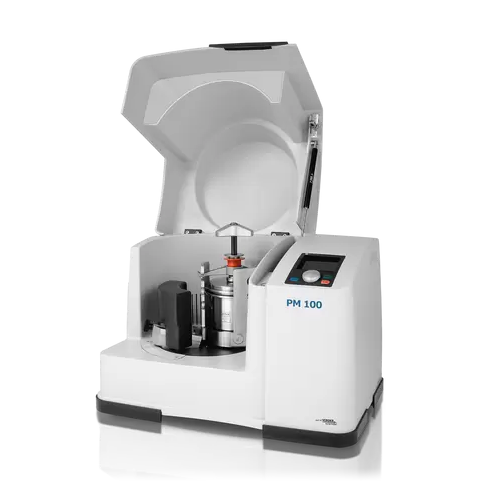
Planetary ball mills for fine grinding of materials
Optimize particle size and surface area in your samples with high-ene...
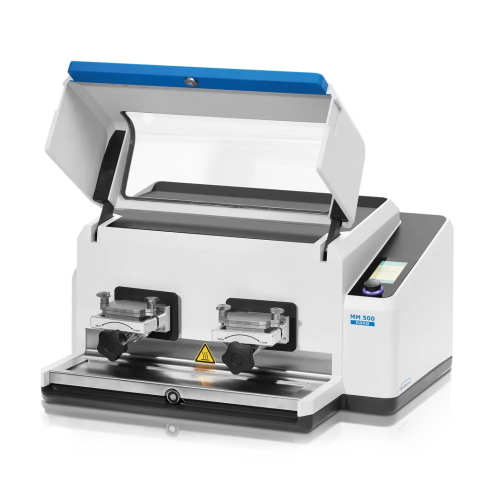
Ultrafine grinding solution for nanoparticles
Achieve ultrafine particle sizes with high-speed precision, ideal for labora...
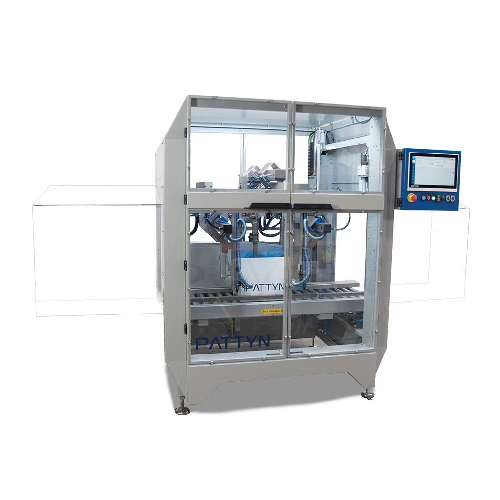
Automatic bag folding solution for bulk packaging
Enhance your production line efficiency and product protection by integ...
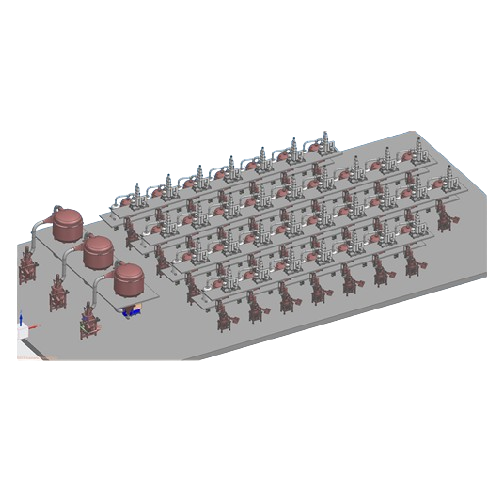
Graphite spheronization system for battery production
Enhance battery performance with precision spheronization of graphi...
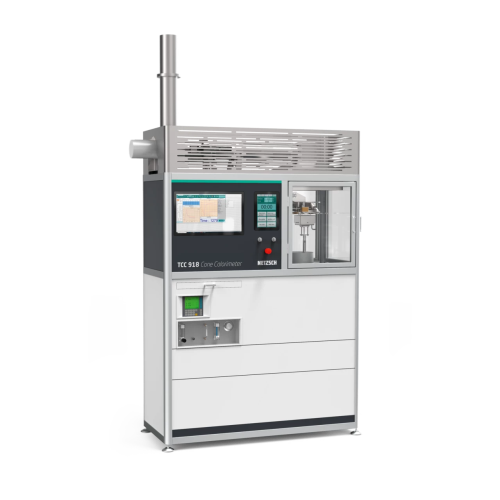
Cone calorimeter for fire testing and safety engineering
Ensure safety in your materials by precisely measuring combustio...
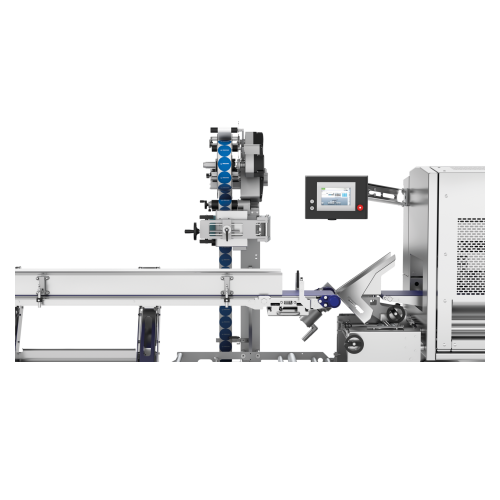
Label dispenser integration for packaging lines
Streamline labeling operations with precision and flexibility, ensuring yo...
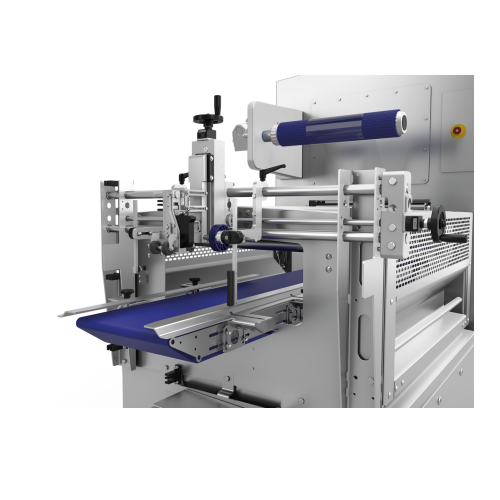
Marking solutions for traysealers
Ensure precise labeling and data printing on tray-sealed packages with integrated solutio...
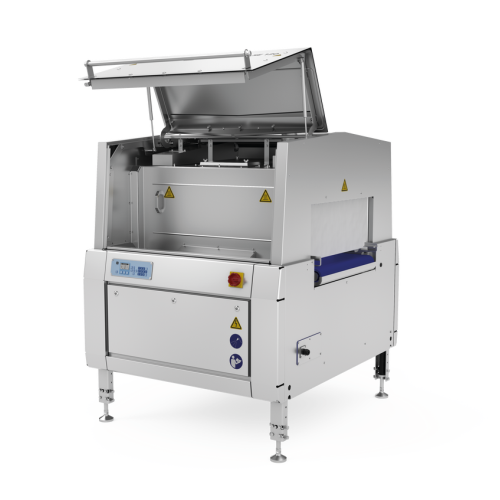
Industrial shrink and drying units for food products
Ensure optimal product integrity and extended shelf life by seamless...

Laser diffraction particle size analyzer
Achieve precise particle size analysis with laser diffraction technology, ensuring...
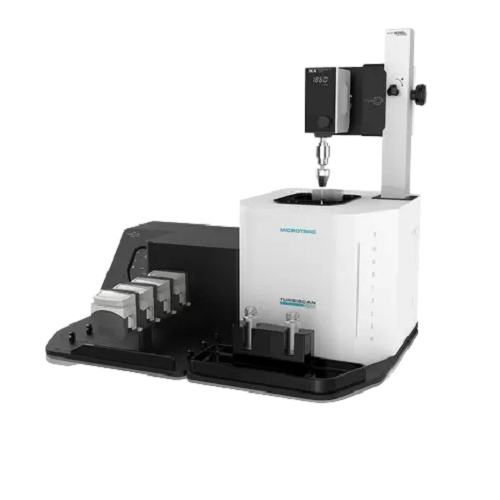
Stability analyzer for emulsions, suspensions, and foams
Accurately detect and quantify changes in dispersibility and sta...
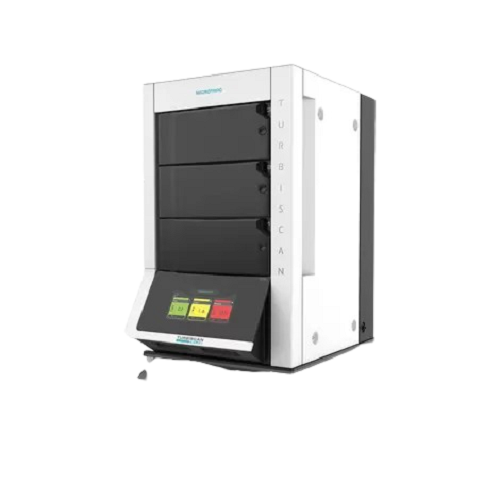
Multi-sample stability analyzer for emulsions and suspensions
Achieve precise, non-destructive stability analysis of emu...
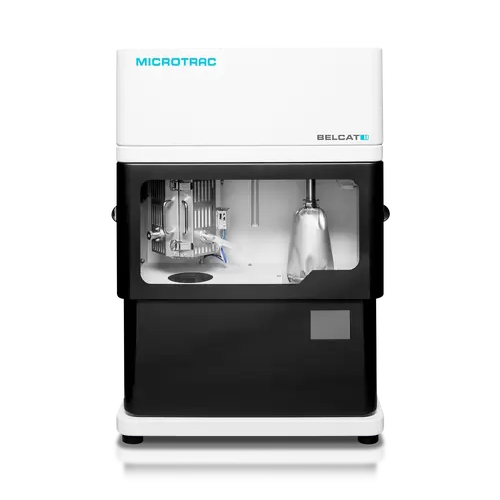
Catalyst characterization analyzer
Achieve precise catalyst characterization and optimization with advanced techniques like...
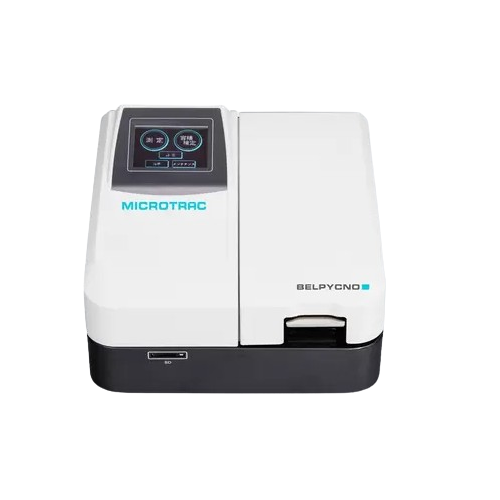
Gas pycnometer for true density measurement of solids and powders
Achieve highly precise density measurements of solid ...
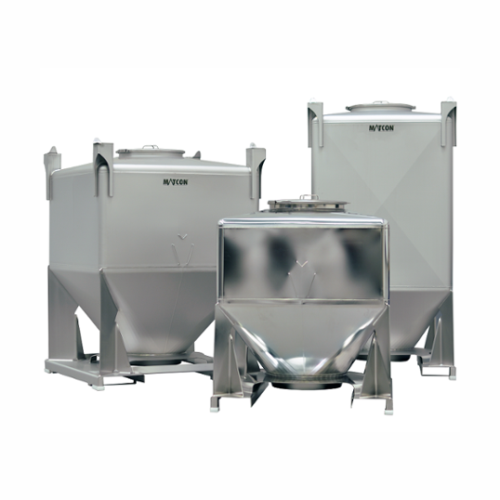
Intermediate bulk containers for powder and materials handling
Optimize your material handling processes with containers...
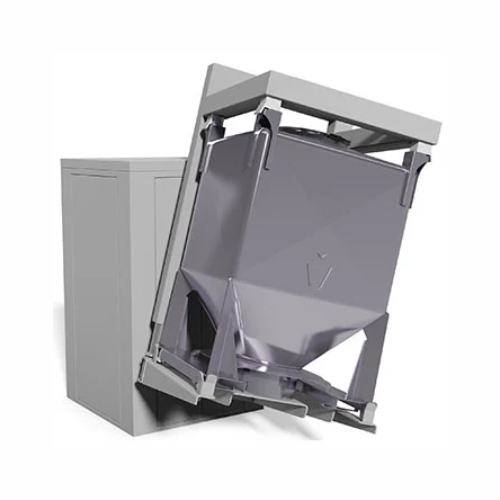
Ibc blender for industrial powder mixing
Streamline your powder mixing with rapid batch changeovers and reduced cleaning do...
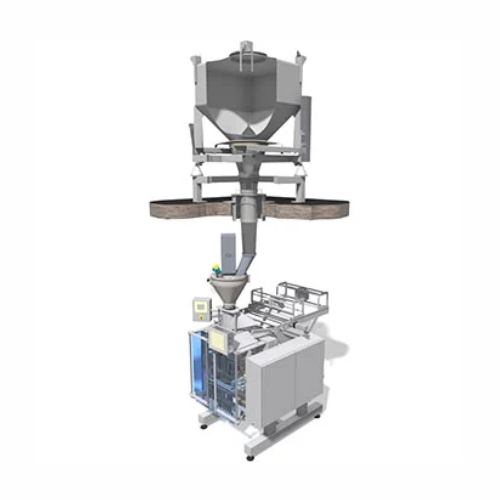
Powder packing module for consistent flow
Enhance your production efficiency with streamlined powder packing that ensures ...
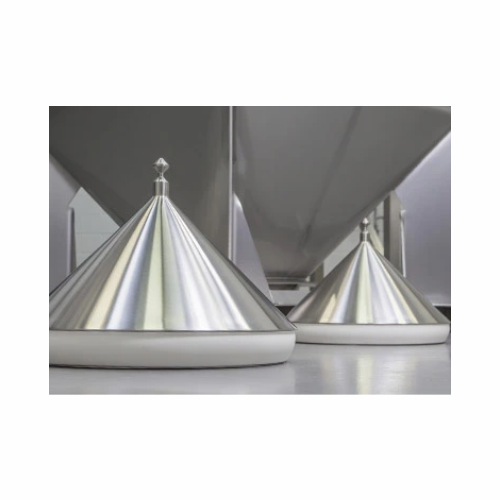
Valves for bulk powder flow control
Ensure efficient and controlled discharge of diverse powder forms while minimizing flow...
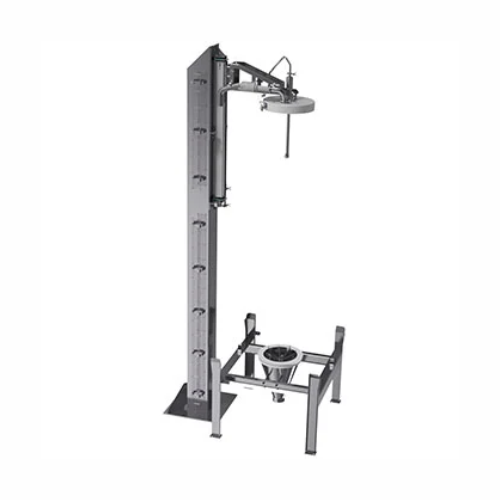
Ibc cleaning equipment for hygienic powder handling
Optimize cleaning efficiency and maintain hygiene standards with a ve...
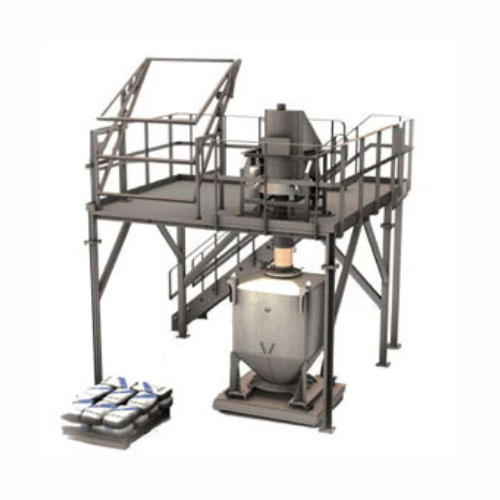
Small powder recipe formulation system
Streamline the formulation of diverse powder recipes with seamless integration into ...
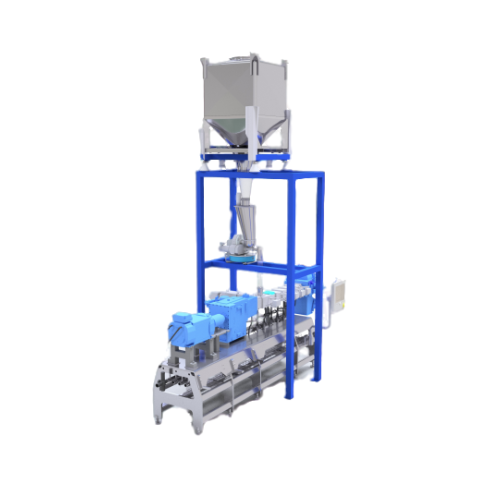
Powder handling systems for battery production
Optimize your battery production with a versatile powder handling system th...
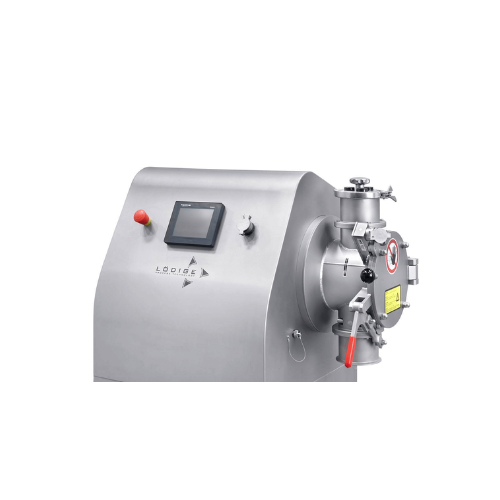
Laboratory ploughshare mixer for small-scale production
Achieve precise mixing and granulation for R&D and small-bat...
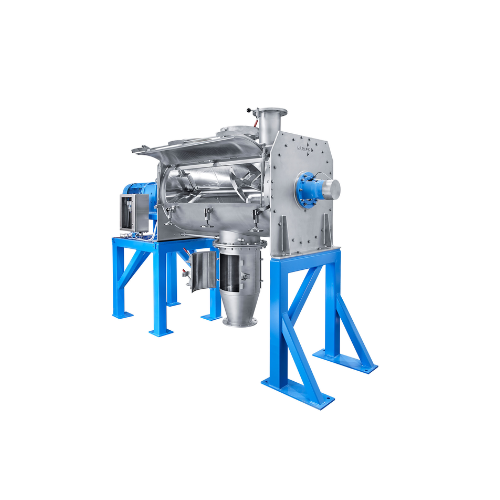
Ploughshare mixer for batch operation
Achieve superior mixing quality with a system designed for rapid batch operations. Ex...
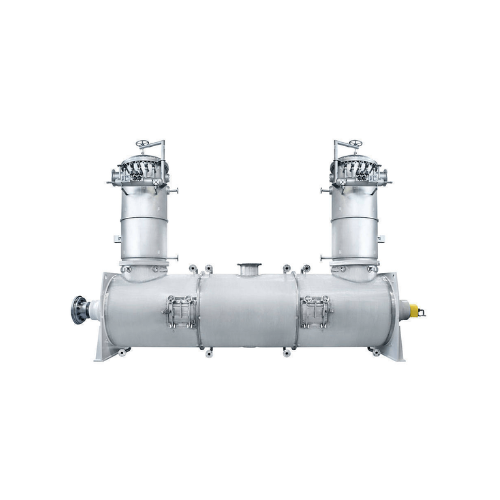
Vacuum paddle dryer for chemical and pharmaceutical applications
Achieve precise moisture control and efficient drying i...
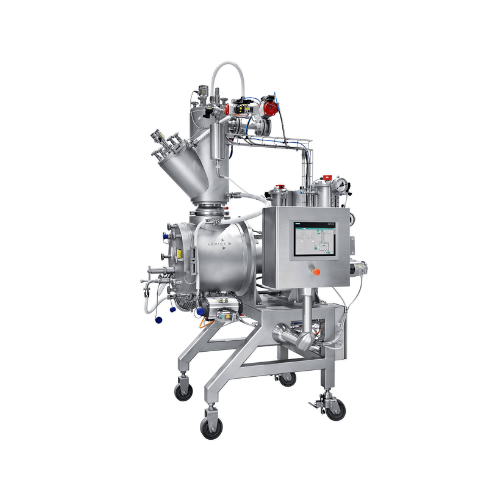
Vacuum paddle dryer for laboratory use
Achieve precise temperature and moisture control in your batches with this vacuum sh...
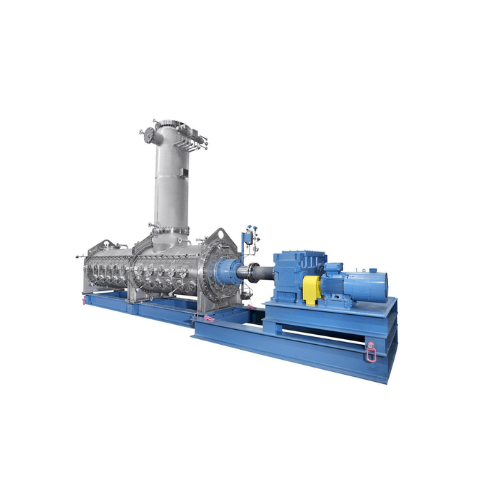
Continuous granulation dryer for chemical and polysaccharide applications
Enhance your production with precise drying ...
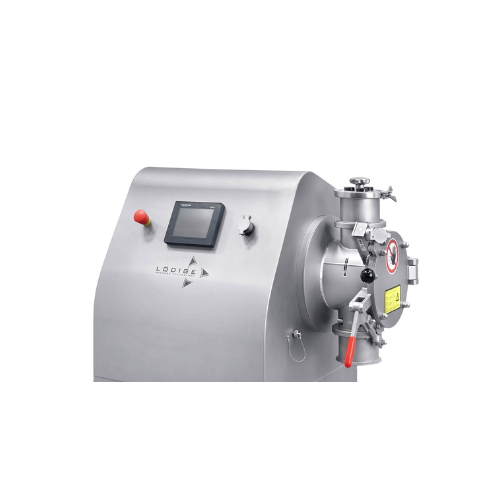
Laboratory mixer granulator
Achieve high-quality mixtures in R&D and small-batch production with versatile laboratory m...
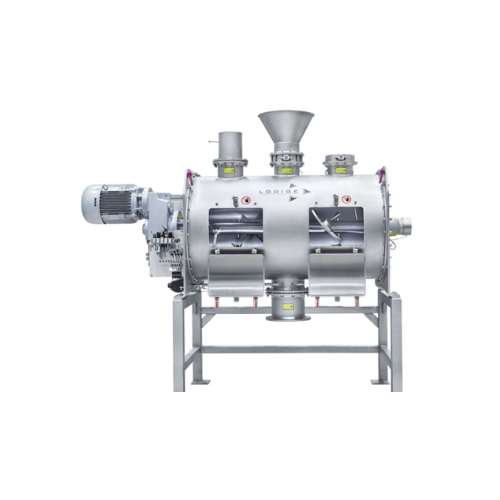
Batch mixer for powdery, granular, and fibrous materials
Achieve precise consistency and high batch reproducibility in yo...
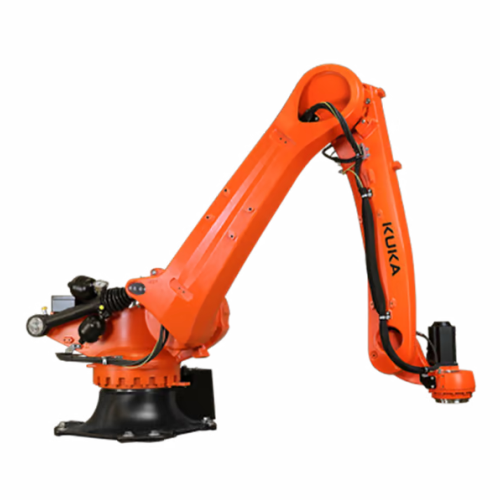
High-precision palletizing robot for industrial applications
Maximize efficiency and reduce floor space in your producti...
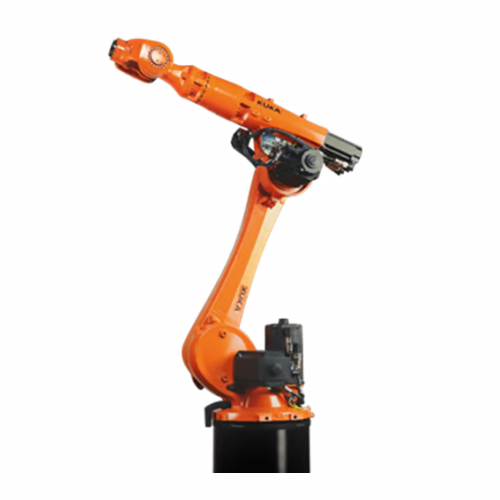
Industrial robot for low-payload applications
Optimize your production line with versatile automation solutions that enhan...
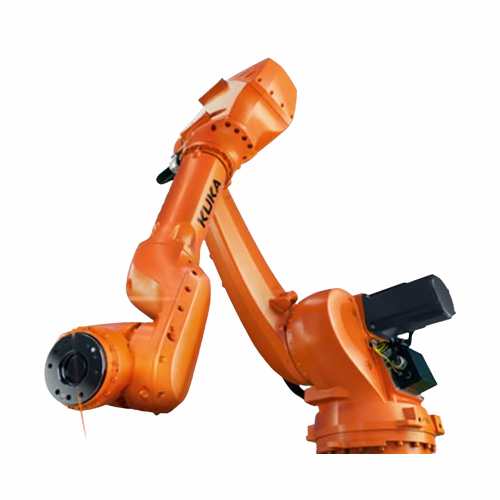
Flexible industrial robot for medium payloads
Optimize your production line with a versatile robotic solution that adapts ...

High payload industrial robot
Optimize your production with high payload robots designed to enhance flexibility and reduce o...
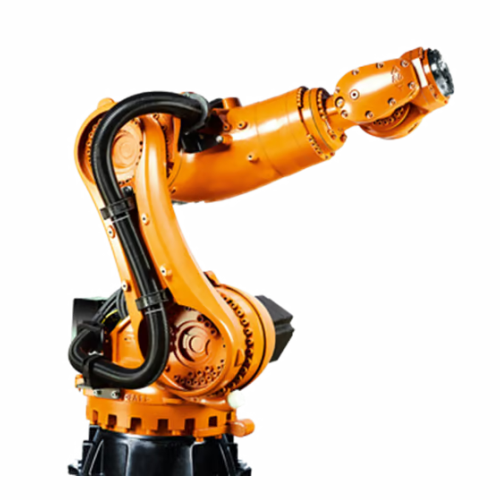
Spot welding robot for confined spaces
Optimize spot welding efficiency in tight manufacturing spaces with a compact robot ...

Intralogistics mobile platform for industrial automation
Streamline your material handling processes with this cutting-ed...
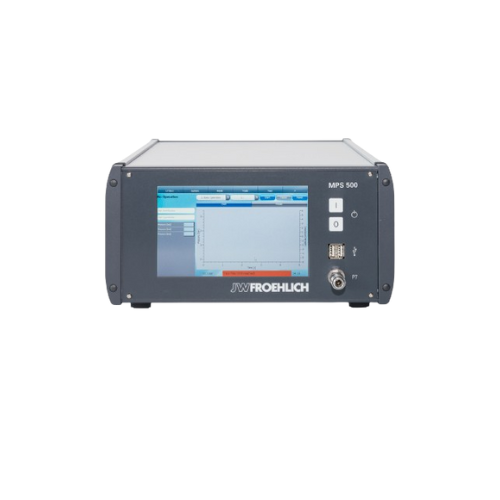
Leak test panels for industrial applications
Ensure the integrity of your critical components with precision leak testing ...
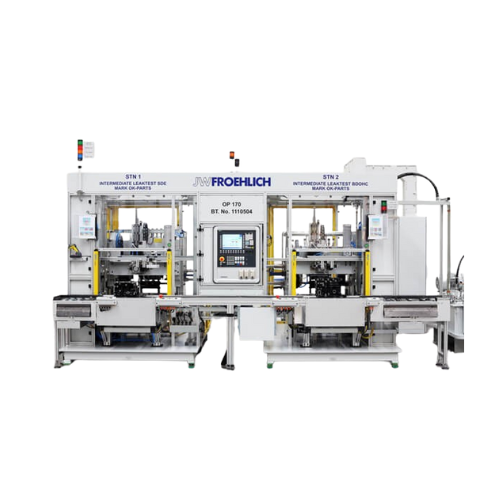
Cylinder block leak testing system
Ensure reliability and quality by detecting and addressing leaks in cylinder blocks with...
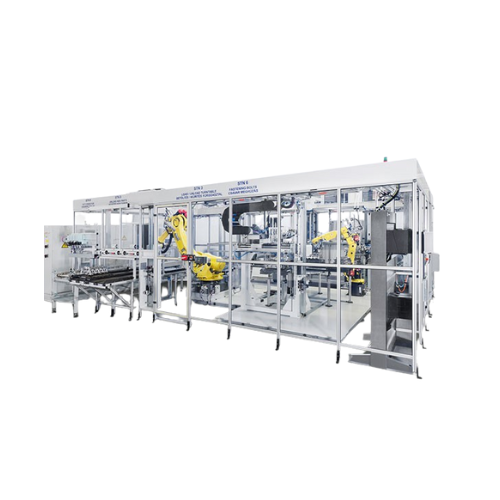
Cylinder head leak testing systems
Ensure critical sealing integrity with advanced leak testing systems designed to accurat...
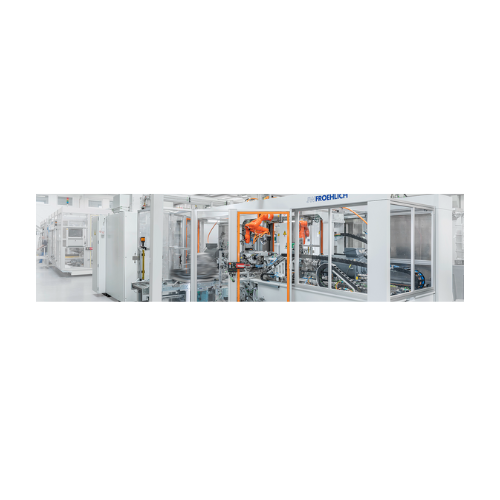
Electric drive unit testing systems
Optimize your electric vehicle production with comprehensive testing systems designed t...
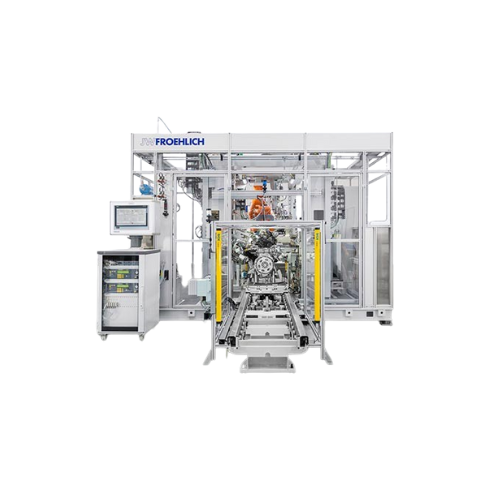
Leak test system for engine components
Ensure the integrity of engine components with precise and efficient leak detection,...
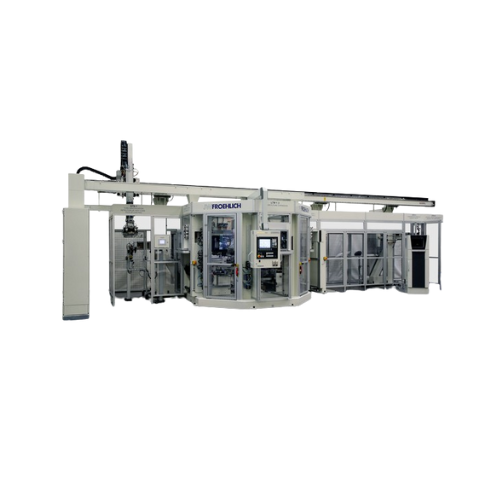
Leak testing system for automatic transmissions
Ensure the integrity and functionality of your automatic transmissions wit...
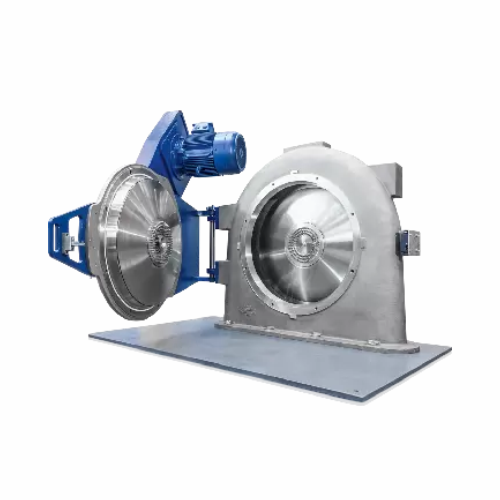
Industrial powder grinder
Achieve precise particle size reduction and classification with advanced equipment designed for co...
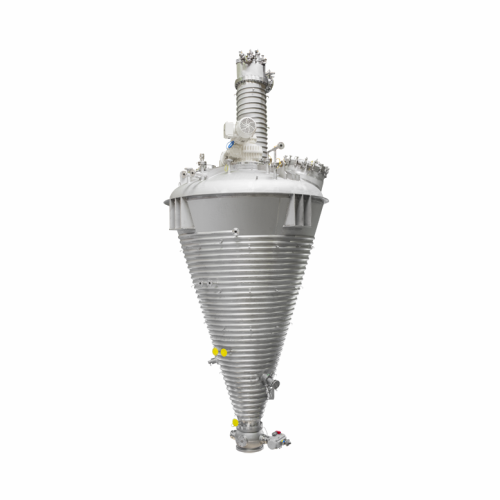
Vacuum dryers for powders and bulk solids
Achieve precise drying and mixing of sensitive materials with advanced vacuum te...
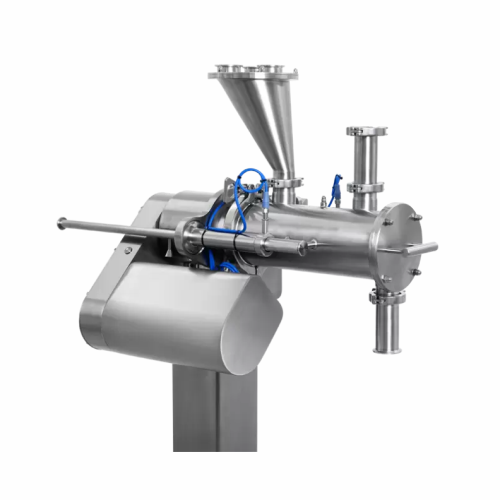
Continuous mixing for fine and cohesive powders
Achieve unparalleled mixing precision for cohesive powders while reducing ...
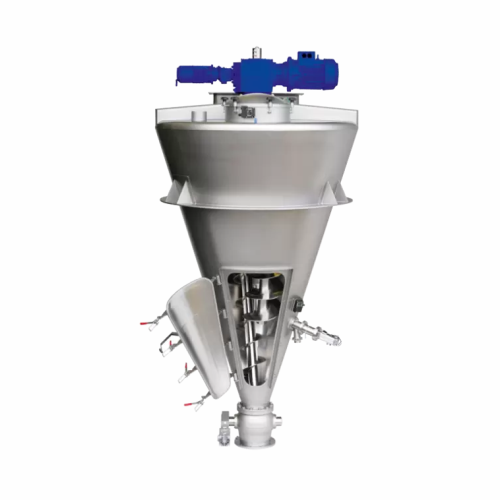
Batch mixer for segregative, free-flowing powders and pastes
Achieve precise and gentle batch mixing for delicate produc...
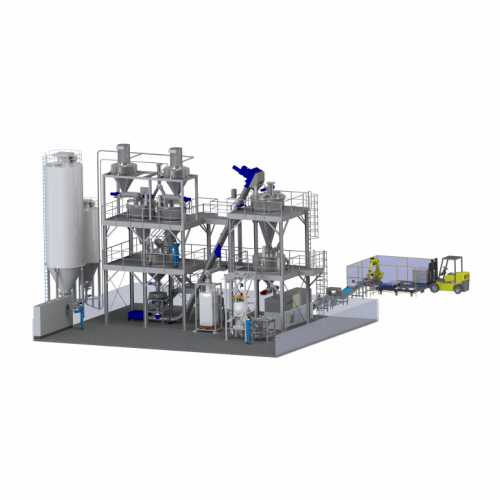
Powder mixing systems
Optimize your production line with precision powder mixing systems that ensure uniformity, enhance prod...
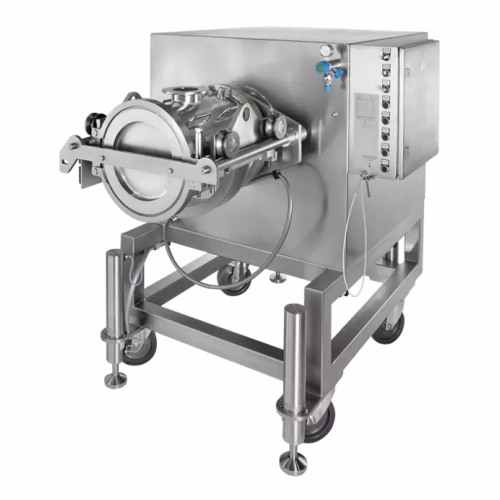
Super high shear mixer for nano to micron powders
Achieve high-precision mixing and surface treatment of nano to micron-s...
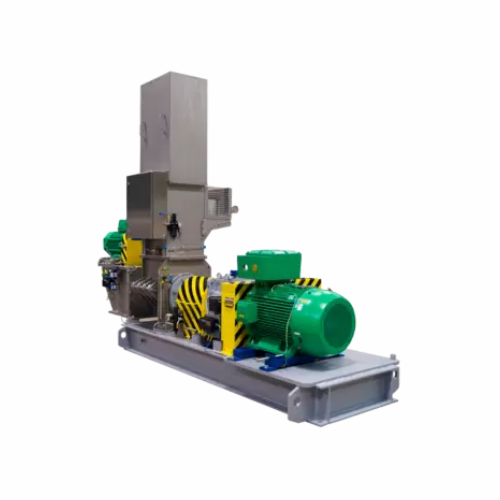
Choppers and disintegrators for industrial size reduction
Enhance your production efficiency by mastering size reduction...
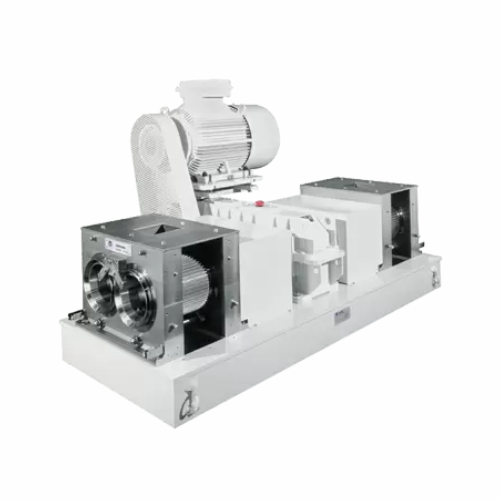
Compactors and granulators for powdery products
Transform loose powders into dense, free-flowing granules that enhance han...
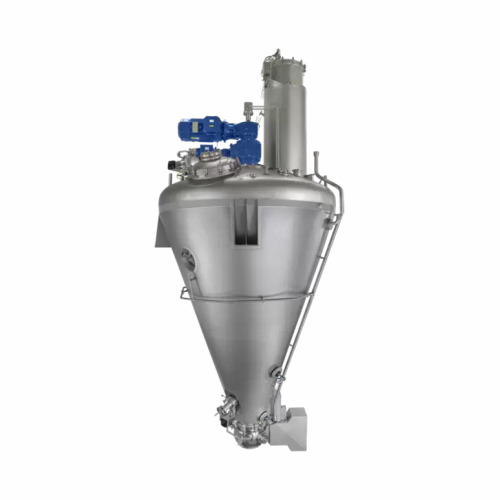
Vacuum dryer for powders and granules
Achieve precise moisture control for sensitive materials with a versatile vacuum dryi...
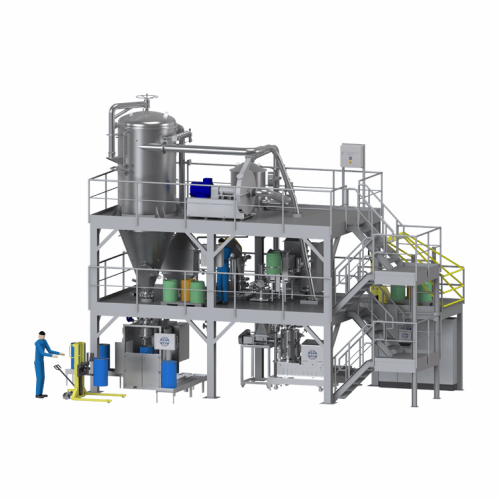
Drying systems for powders and bulk solids
Enhance your production line with precise control of moisture content in powder...
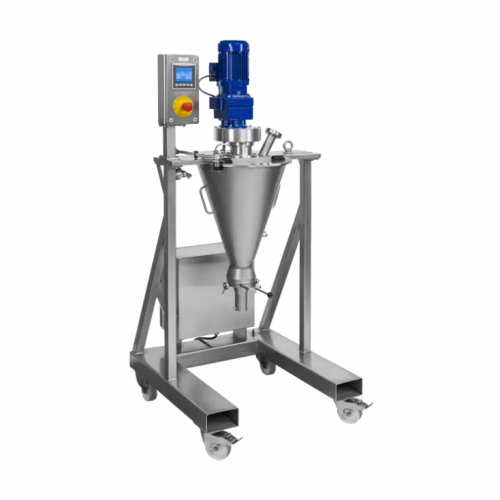
Lab mixer for high-accuracy powder and paste mixing
Achieve precise mixing of powders and pastes with a gentle convective...
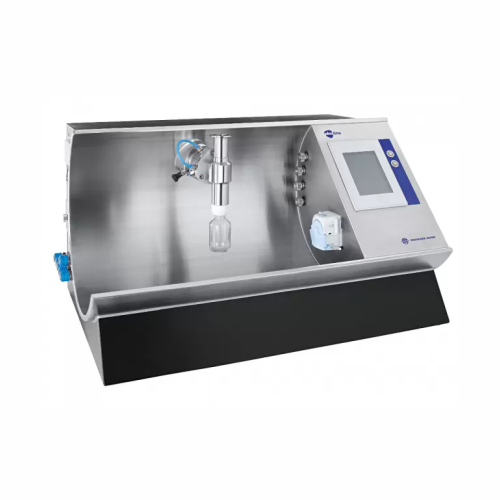
Lab-scale powder processing system
Achieve precise control in ultra-small batch processing with a versatile modular system,...
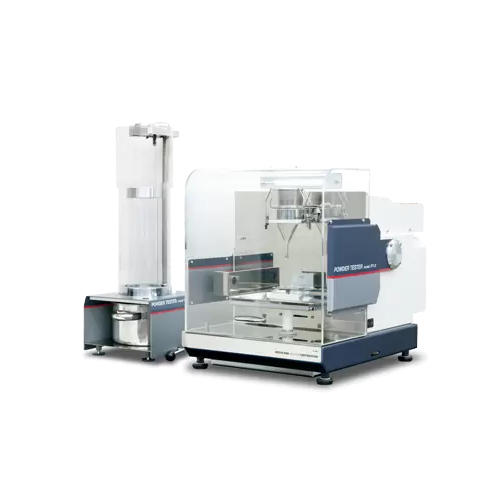
Powder characteristic evaluation
Ensure precise powder analysis and testing in your laboratory to optimize production qualit...
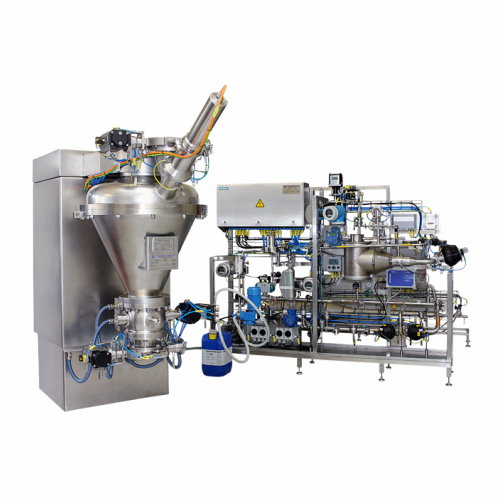
Cip/sip cleaning for solids processing systems
Ensure seamless transitions and maintain hygienic production environments w...
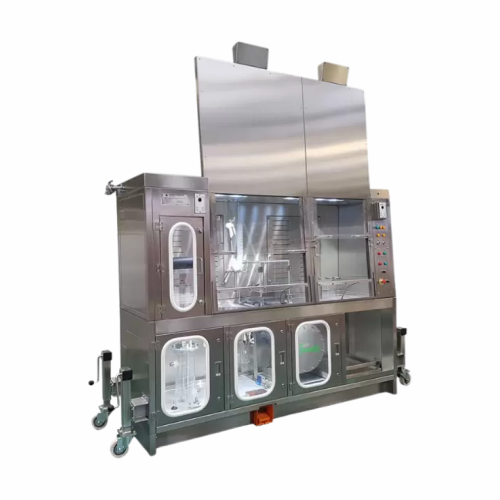
Containment solutions for hazardous material processing
Ensure safe and efficient processing of hazardous materials with ...

Table roller mills for mineral raw material comminution
Achieve precise mineral raw material comminution and energy-effic...
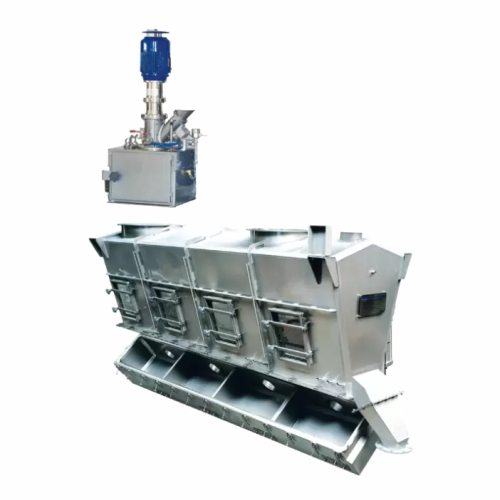
Continuous powder agglomeration system
Enhance product solubility and flowability while minimizing energy consumption with ...
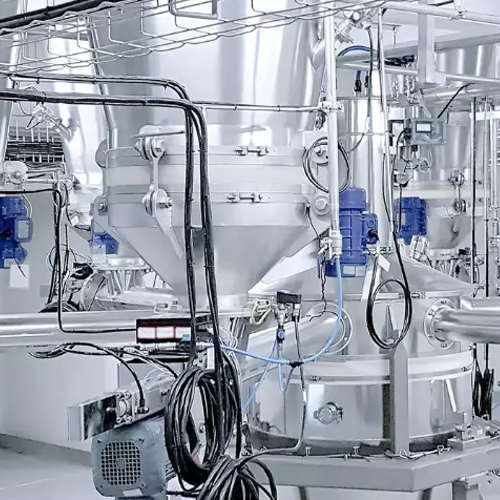
Conical screw mixer for powder blending
Achieve precise and homogeneous blending with the conical screw mixer, ensuring uni...
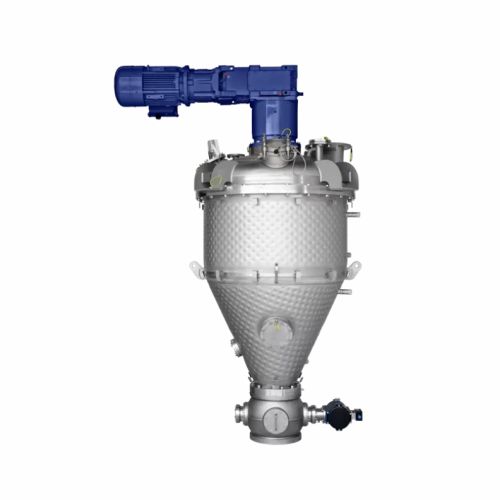
Conical paddle vacuum dryer for powders and granules
Achieve efficient drying of sensitive materials with this versatile ...
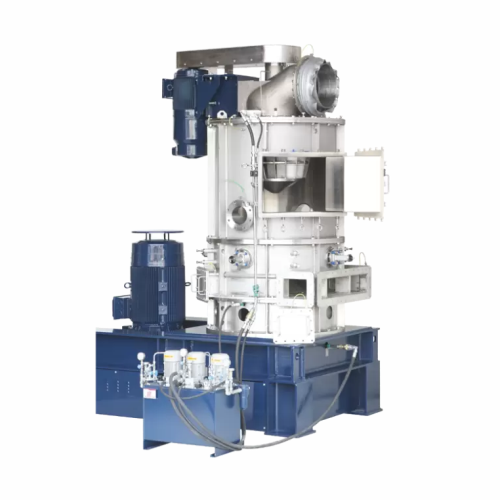
Ultra-fine powder flash drying system
Achieve rapid moisture removal and particle refinement with this integrated system, d...

Ultra-fine dry grinding mill for glass and ceramics
Achieve ultra-fine particle sizes and energy savings with a dry grind...
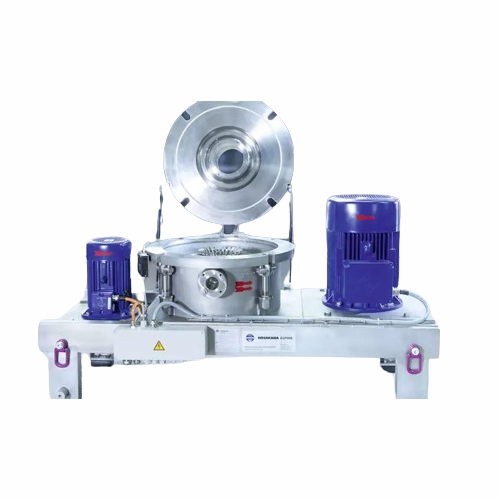
Classifier mill for ultrafine grinding
Achieve precise particle size distribution and contamination-free processing with th...
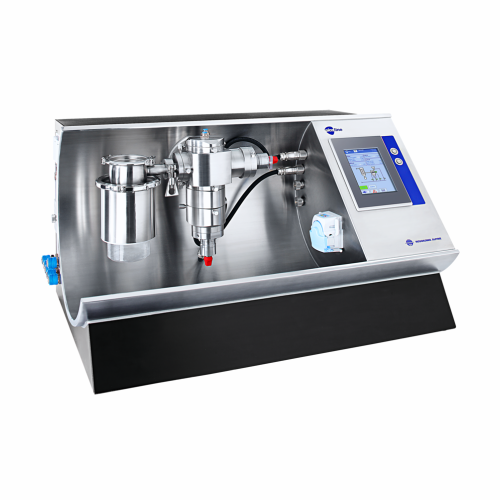
Laboratory system for powder and particle processing
When precision in powder processing is crucial, this versatile labor...
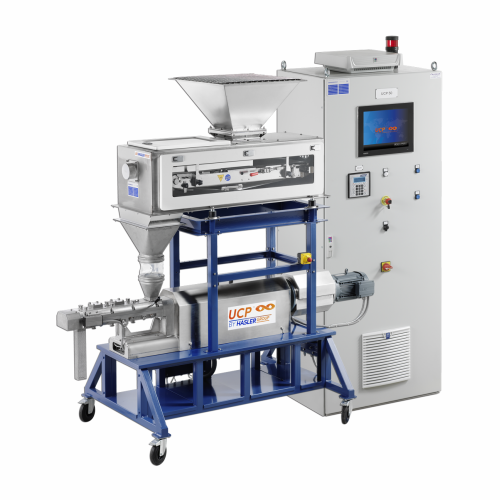
Continuous kneader for viscous applications
For engineers tackling high-viscosity challenges, this continuous kneader stre...
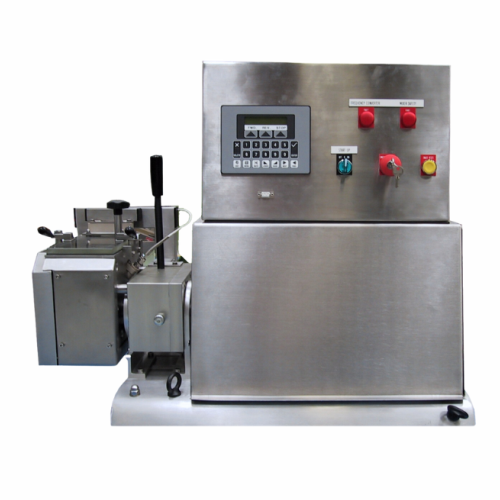
Laboratory z-arm kneader for high-viscosity materials
Ideal for R&D, this advanced Z-arm kneader efficiently handles...
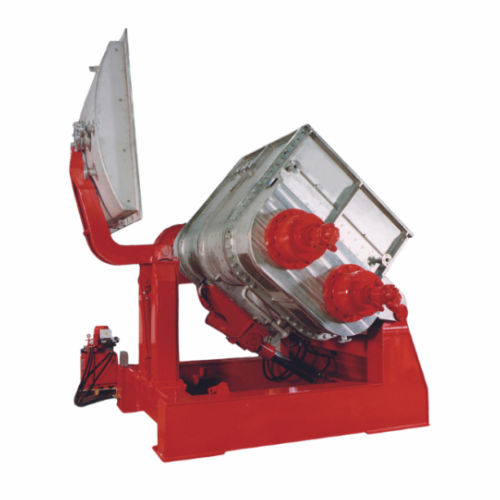
Double z-arm industrial extrusion kneader for high-viscosity processes
Optimize high-viscosity material processing with...
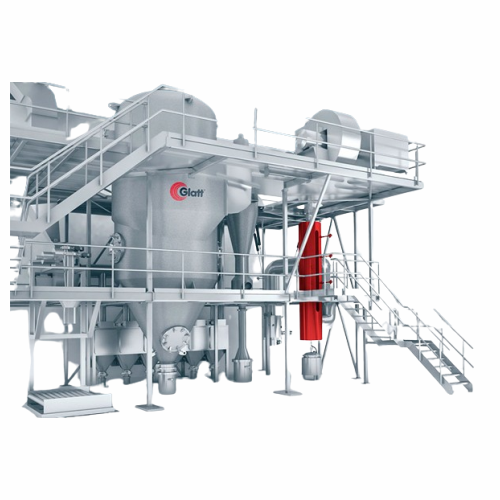
Powder synthesis reactors for nanometer and micrometer particles
Achieve precise particle control and enhance material p...
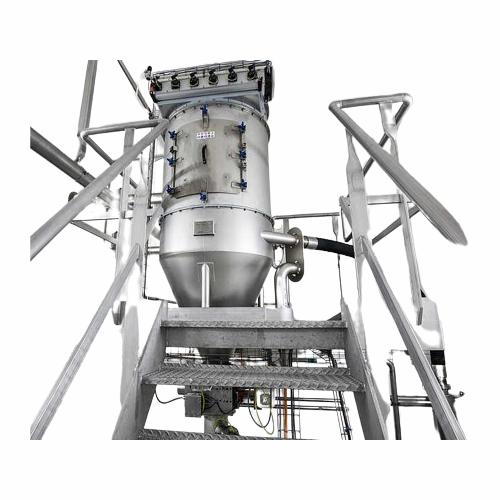
Vacuum pneumatic conveying for infant nutrition
Ensure efficient handling of delicate powders with a versatile vacuum pneu...
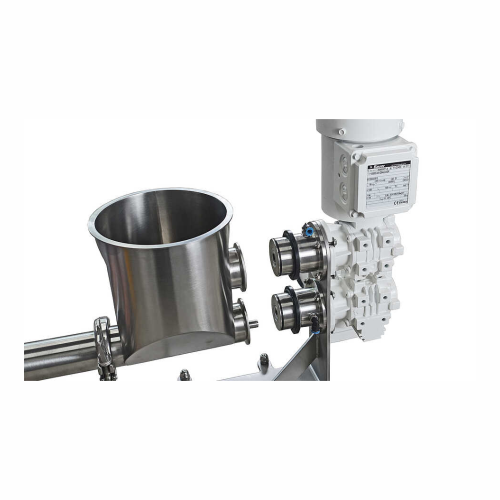
High-precision volumetric feeder for bulk materials
Achieve precise bulk material flow with a solution that ensures consi...
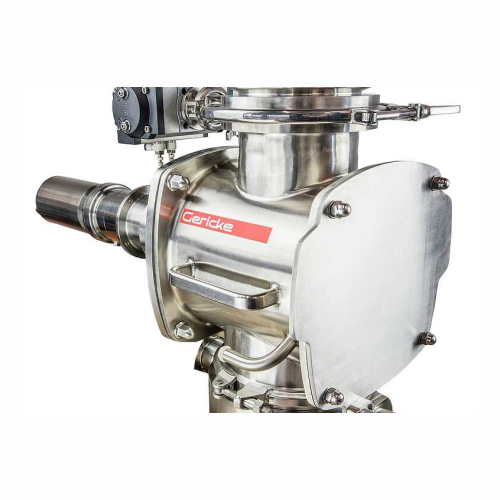
Mini batch blender for pharmaceutical solids
Achieve precise mixing homogeneity with the mini batch blender, perfect for l...

Pneumatic truck unloading for bulk tankers
Efficiently unload bulk materials from trucks with minimal dust emissions while...
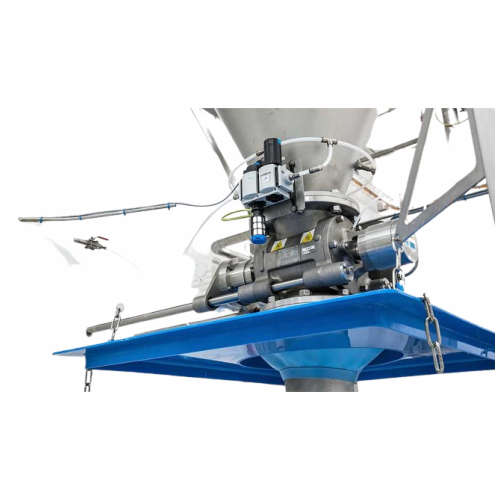
Heavy duty rotary valves for powder handling
Ensure precise material flow and safety in harsh processing environments with...
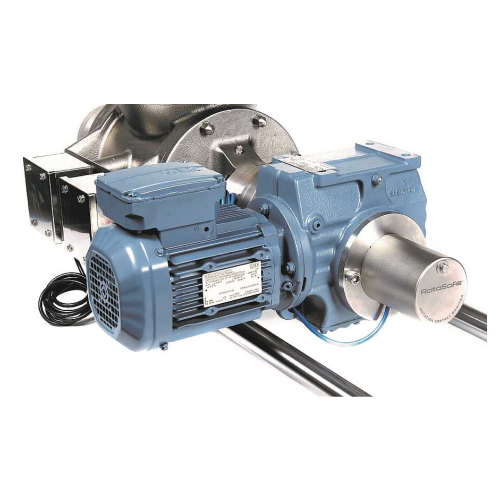
Contact detection system for rotary valves
Prevent product contamination and equipment damage with instant contact detecti...
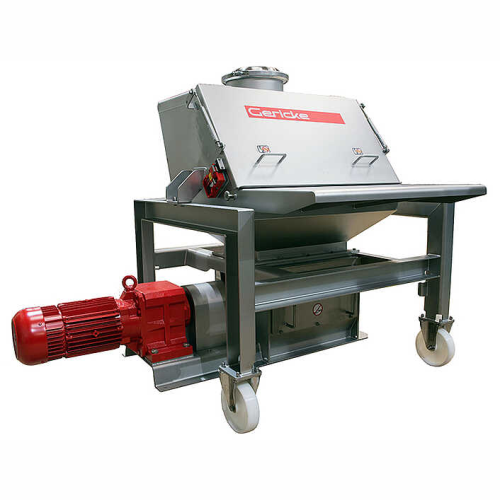
Sack tipping station for dust-free bulk material handling
Efficiently manage bulk materials while minimizing dust exposu...
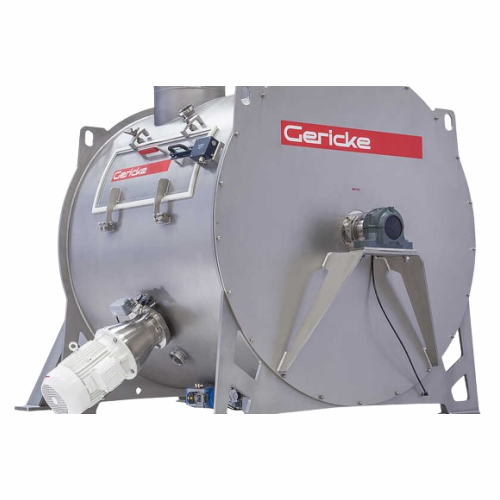
Single shaft batch mixer for chemical and pharmaceutical applications
Optimize mixing efficiency with rapid batch proce...
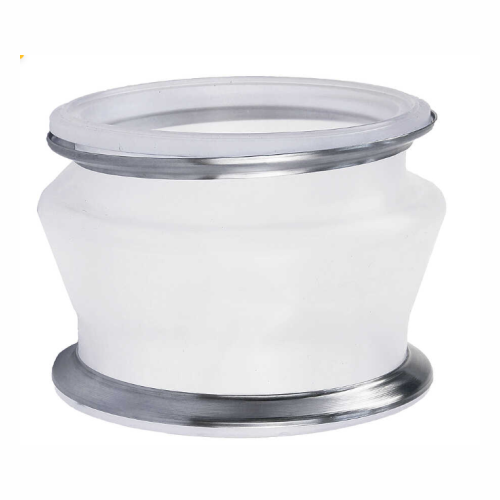
Hygienic flexible sleeves for tri-clamp connections
Ensure seamless, contamination-free transitions between processing st...
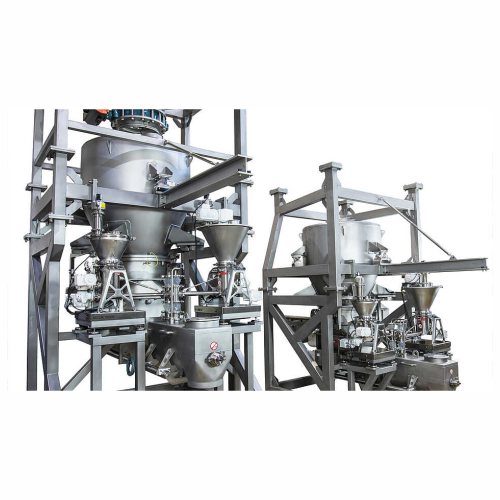
Continuous inline mixing for late product differentiation
Achieve seamless product differentiation with compact inline m...
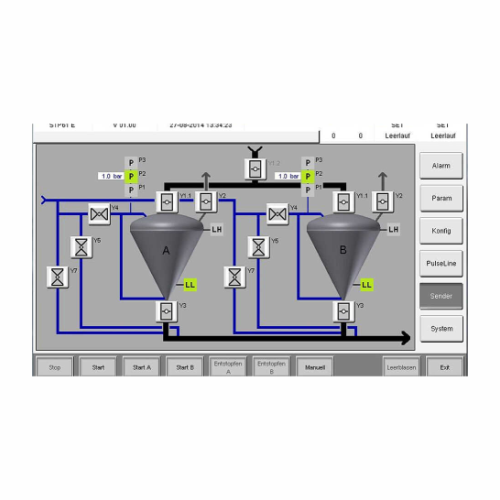
Conveying controller for dense phase conveying
Streamline your dense phase conveying operations with precise control and m...
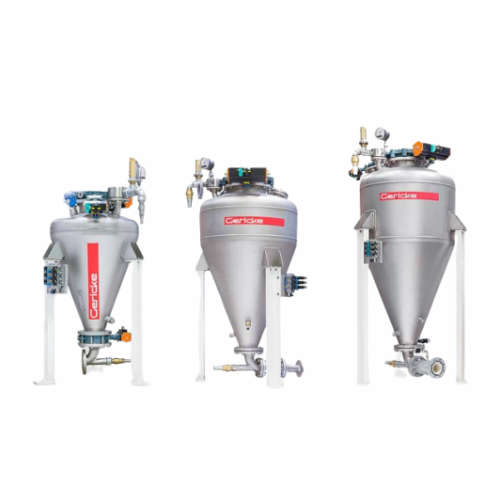
Dense phase pneumatic conveying system for powder transfer
Ensure gentle and efficient material transport with minimal m...
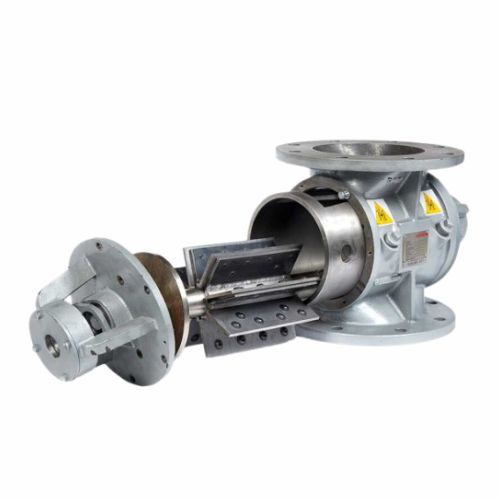
Pneumatic dilute phase conveying system for powders and bulk materials
Optimize your production line’s efficiency...
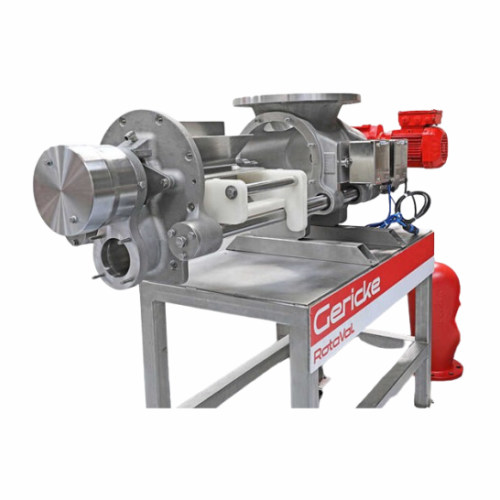
Quick-clean hygienic rotary valves
Ensure seamless cleaning and minimal downtime in your production line with rotary valves...
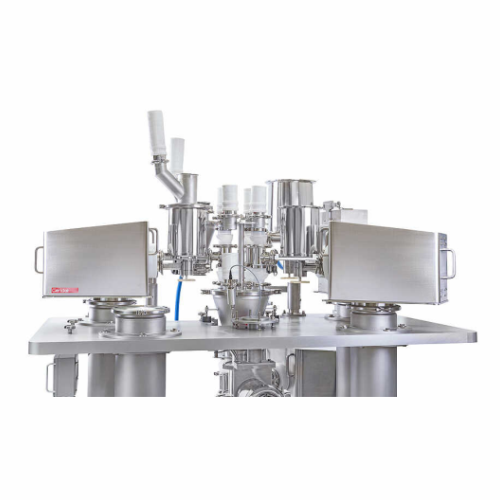
High-precision gravimetric feeders for industrial bulk solids
Achieve unparalleled accuracy in your production line with...
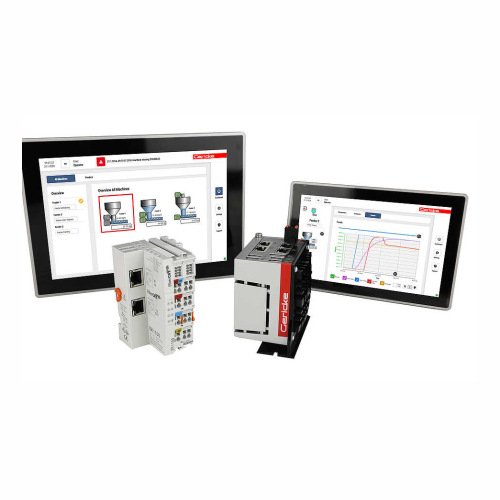
Universal controller for feeders in powder handling applications
Simplify and enhance your powder handling with precise ...
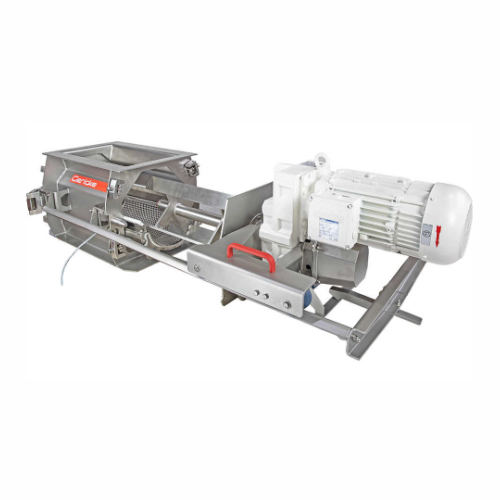
Deagglomerator for consistent particle size reduction
Struggling with inconsistent particle sizes or unwanted lumps in yo...
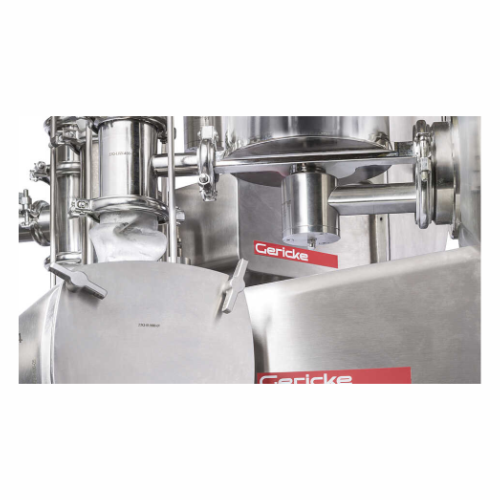
Continuous mixer for homogeneous blending
Achieve consistent product quality with precise mixing and blending, ideal for a...
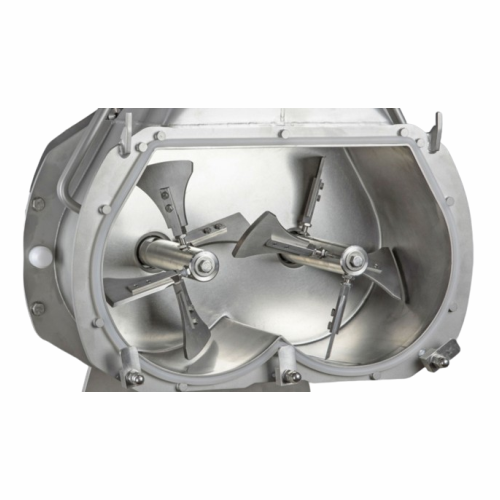
Laboratory mixer for r&d and small batch production
Achieve superior mixing precision for R&D and pilot production w...
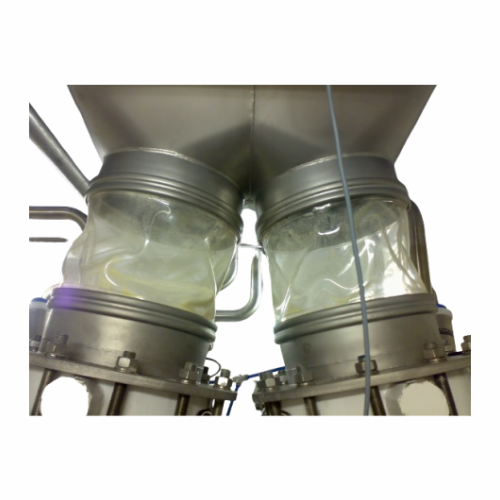
Hygienic flexible sleeves for food and pharmaceutical use
Say goodbye to contamination risks with this tool-free, quick-...

Big bag unloader for industrial bulk materials
Efficiently handle bulk materials with this modular unloading system, desig...
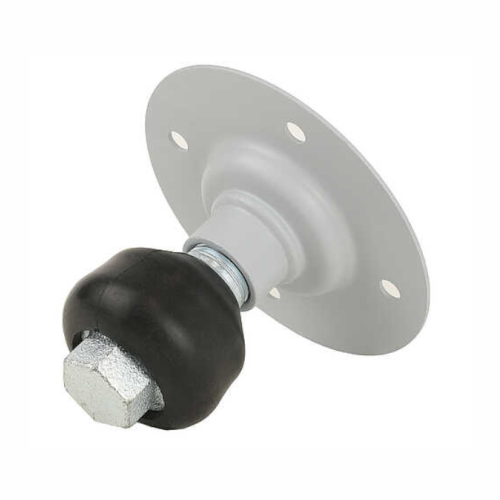
Bin aeration system for silo and hopper material flow
Optimize the flow of your stored powders and granules with an effic...
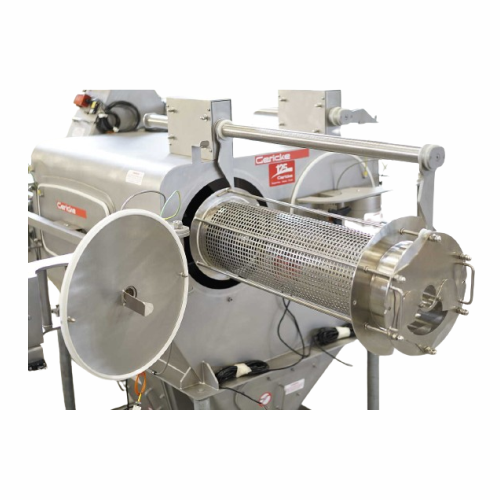
Centrifugal sifter for bulk solids and powders
Achieve precise particle separation and enhance product quality with a solu...

Continuous powder mixer for industrial applications
Achieve precise and efficient integration of powders, granules, and l...
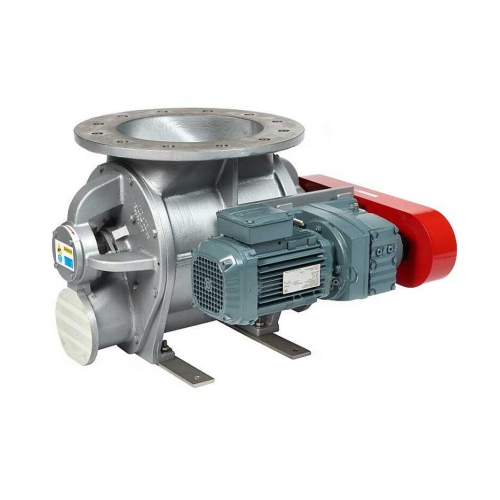
Heavy duty blowing seals for abrasive products
For operations dealing with abrasive materials under high pressure, these r...
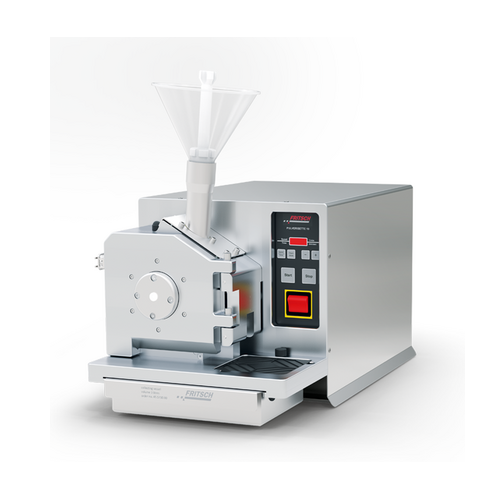
High-speed cutting mill for versatile material comminution
Efficiently transform diverse materials like plastics, textil...
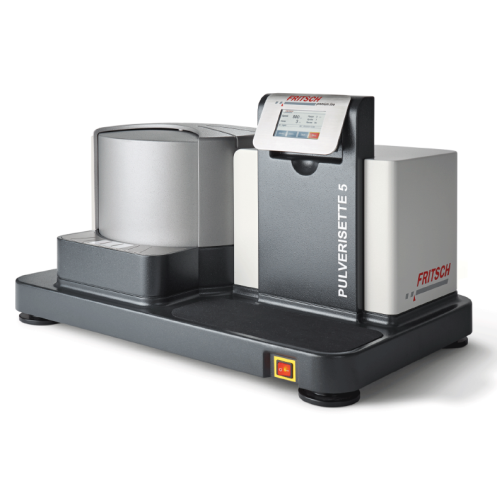
Planetary mill for nano grinding
Achieve precise nano-scale particle production and uniformity for demanding research enviro...
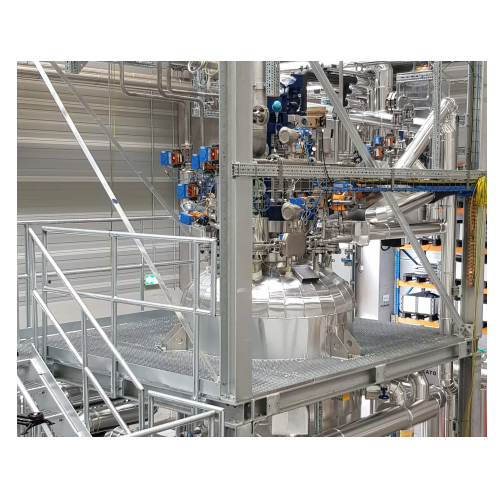
Industrial hydrogenation plant for pharmaceutical raw materials
Optimize your hydrogenation processes with a modular pla...
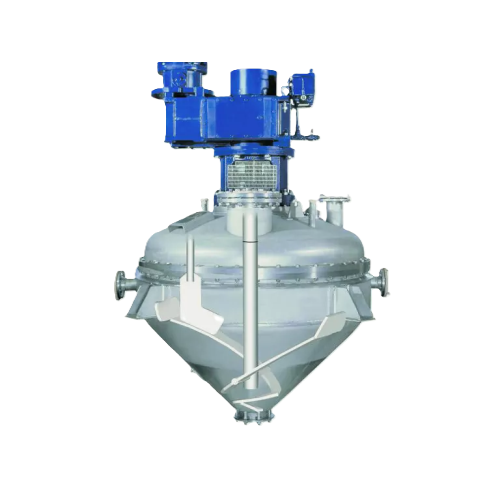
Vacuum dryer for free-flowing and pasty solids
Achieve precise drying and mixing with this vacuum dryer, optimizing heat t...
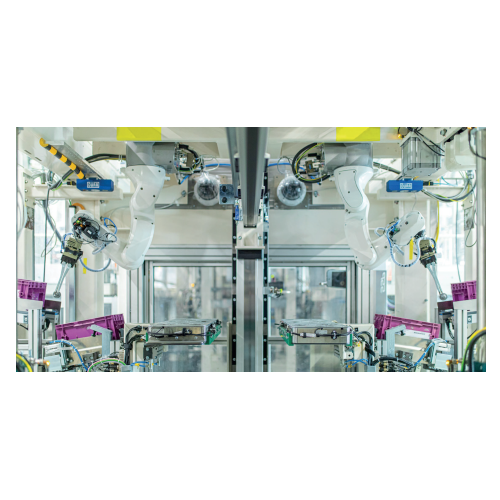
Automated bolting system for electric vehicle production
Enhance your production line with a multi-direct bolting system ...
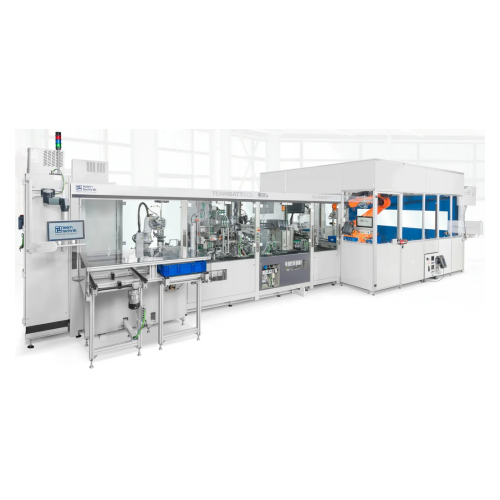
Production systems for battery cells with end-of-line testing
Optimize battery cell production with a flexible system of...
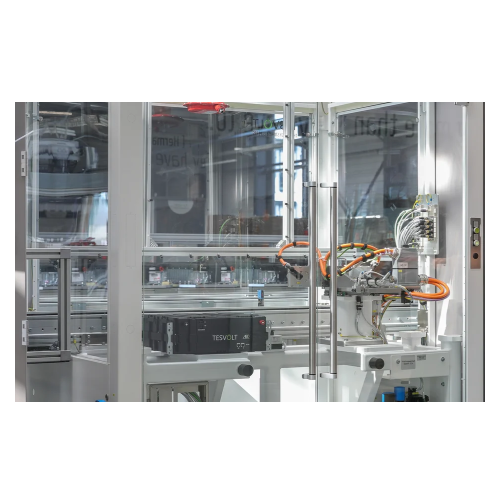
End-of-line battery pack testing system
Ensure the quality and reliability of your battery packs with comprehensive end-of-...
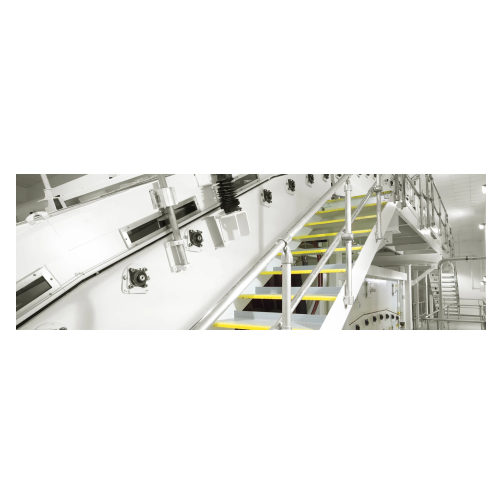
Roll support dryers for web transportation
Eliminate web curl issues and enhance drying precision for diverse materials wi...
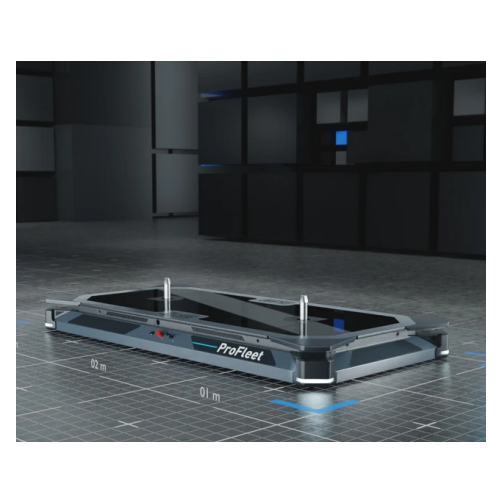
Compact automated guided vehicles for intralogistics
Optimize your facility’s logistics with versatile automated guided v...
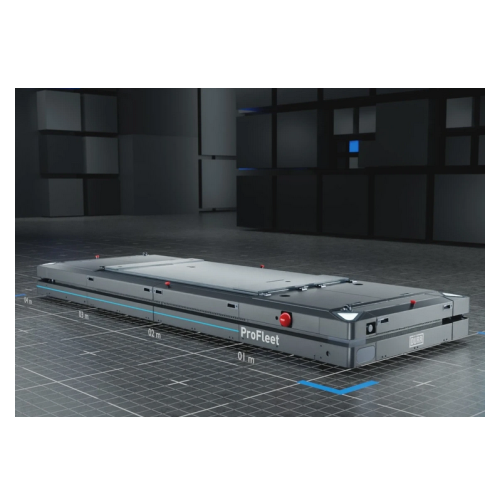
Automated guided vehicle for heavy load transport
Optimize your production flow with a robust solution for efficiently tr...
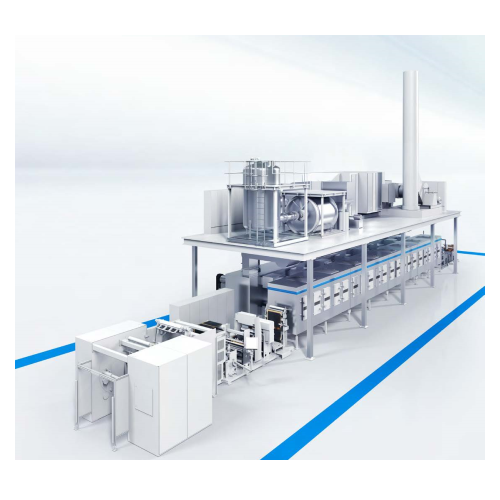
Battery electrode coating line
Optimize your battery production with a comprehensive coating line that enhances throughput a...
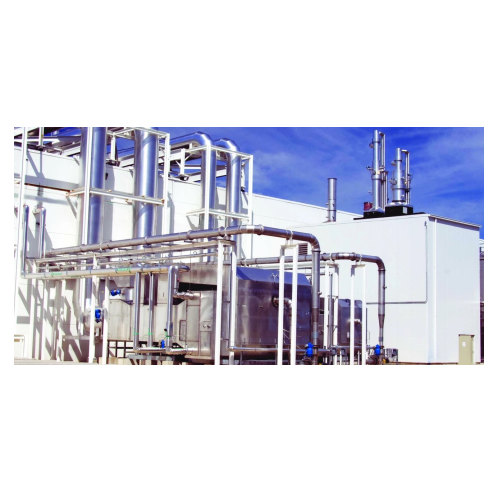
Solvent recovery systems for battery electrode manufacturing
Efficiently recover and purify solvents in battery electrod...
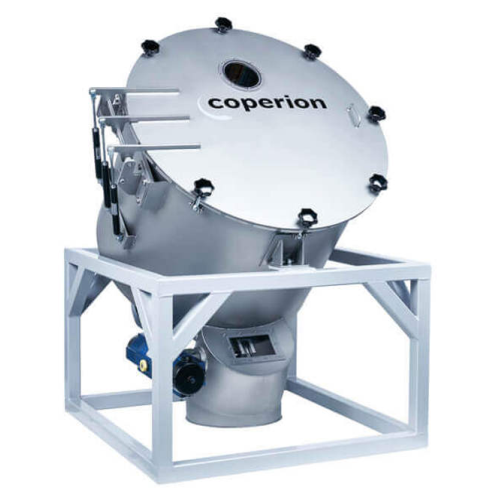
Bulk material mixer for high-speed homogenization
Achieve fast and gentle homogenization of bulk materials with a high-sp...

Precision feeders and mixers for plastics processing
Achieve precise blending and feeding for plastics processing with mo...
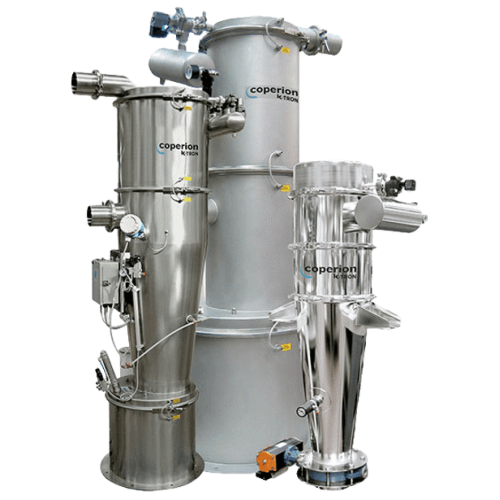
Sanitary bulk solids receiver for food and pharma
Ensure precise control over bulk solid transfer with a system designed ...
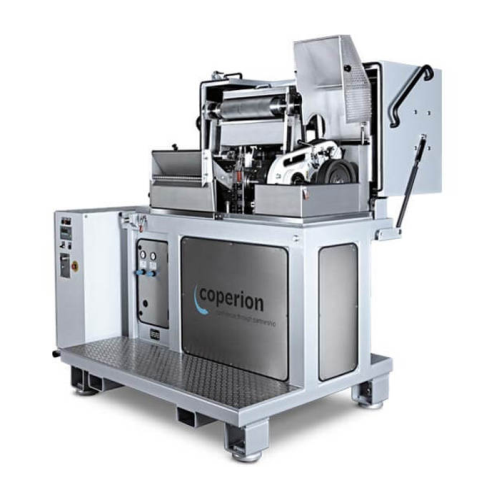
Industrial strand pelletizer for polymer processing
Optimize polymer pellet production with precision engineering, ensuri...
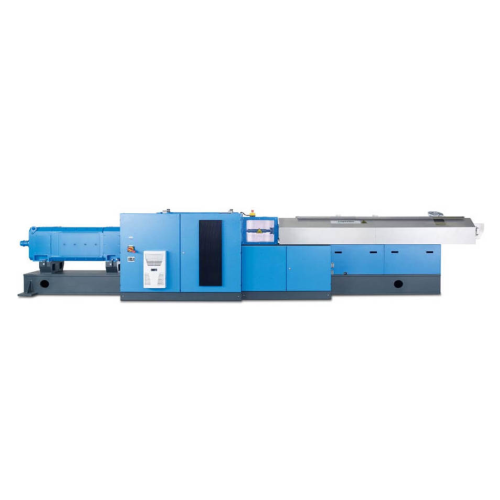
High throughput twin screw extruder for low bulk density products
When handling low bulk density materials, achieving m...
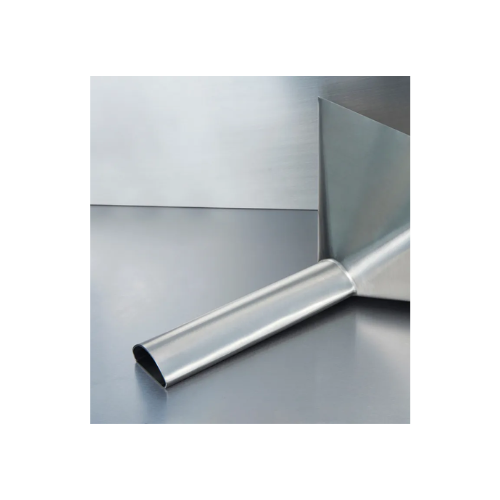
Powder dispensing funnel
Enhance powder handling accuracy while minimizing product loss with a precision-engineered dispensin...
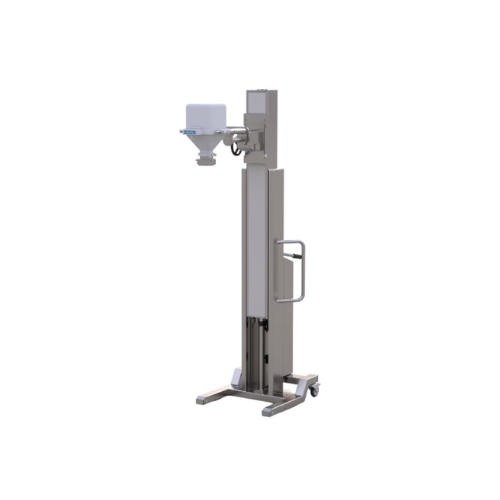
Mobile lifter solutions for pharmaceutical handling
Streamline your handling of sensitive materials with versatile mobile...
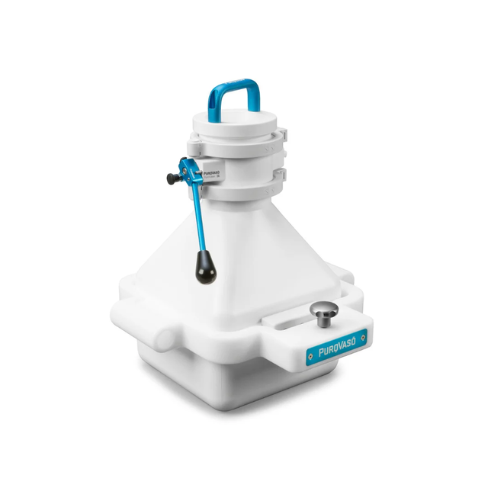
Lightweight plastic butterfly valve for industrial use
Achieve precise flow control and quick disassembly during pharmace...
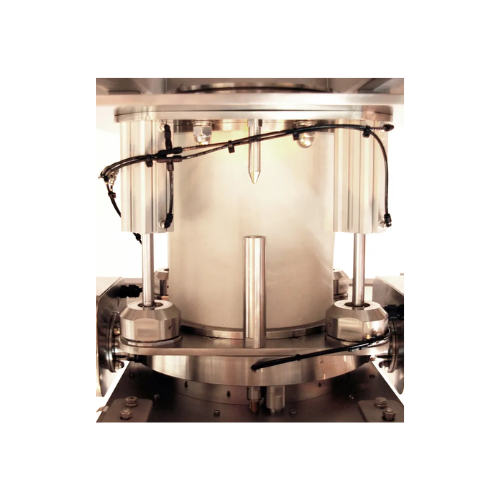
Automatic docking system for bulk powder handling
Optimize docking precision and ensure seamless alignment in bulk powder...
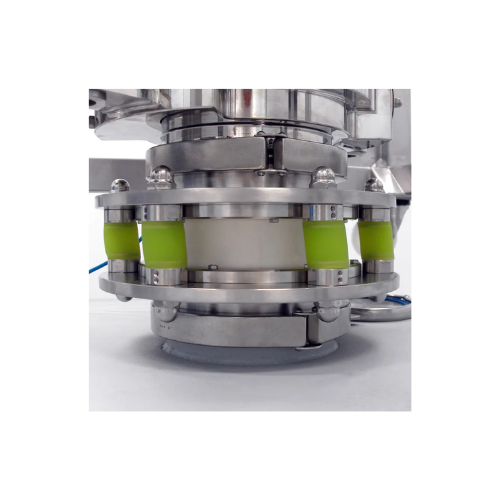
Bulk powder transfer safety device
Ensure stable and secure docking by minimizing equipment damage during powder transfer p...
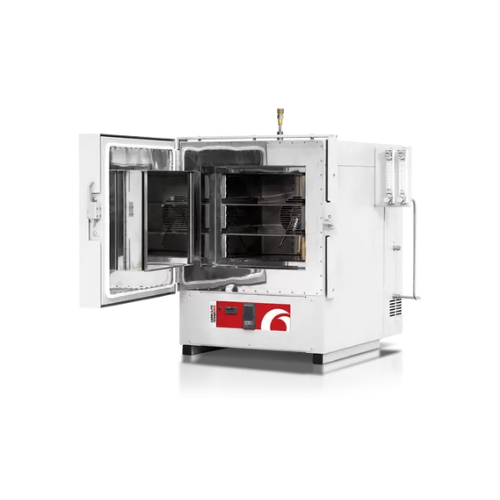
Controlled atmosphere oven for high-temperature applications
Achieve precise atmosphere control and uniform heating for ...
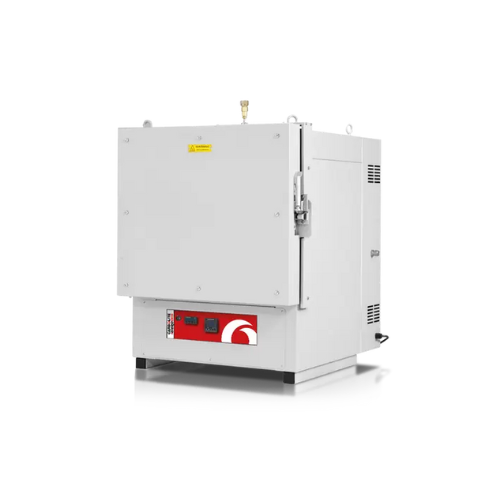
High temperature clean room ovens
Achieve precise environmental control for heating, drying, and sterilizing sensitive mate...
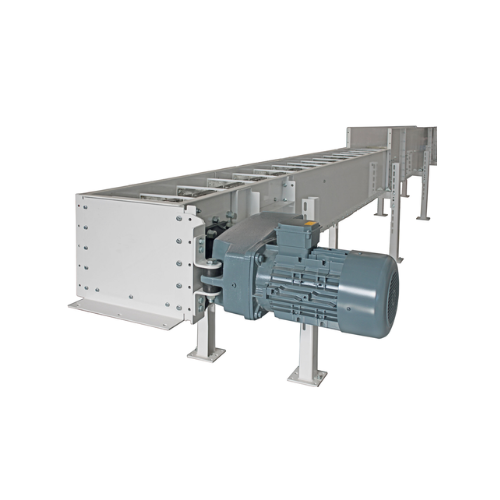
Chain conveyor for grain and floury products
Ensure seamless material handling with a versatile chain conveyor designed fo...
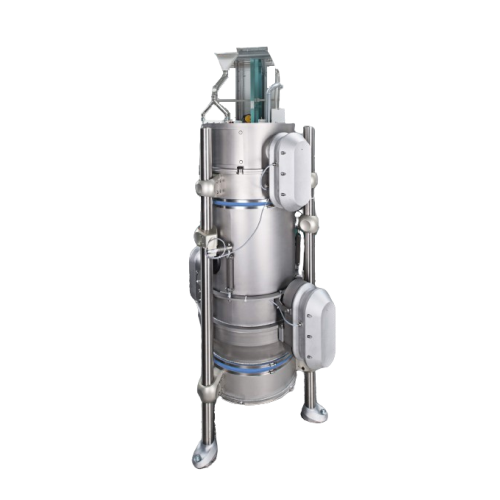
Advanced superheated steam drying solution
Harness the power of consistent drying technology to achieve optimal moisture c...
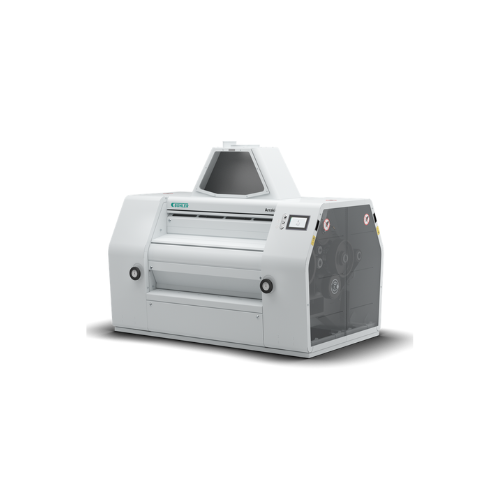
Four-roller and eight-roller mill for wheat and grain grinding
Optimize your grinding operations with this versatile rol...
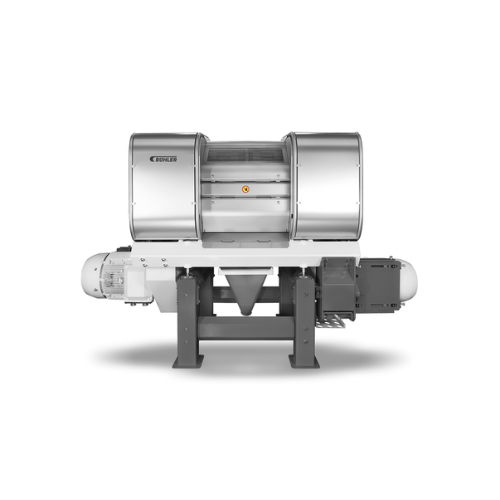
Flaking mill for grain and cereal production
Achieve consistent flake thickness and high throughput with advanced roller t...
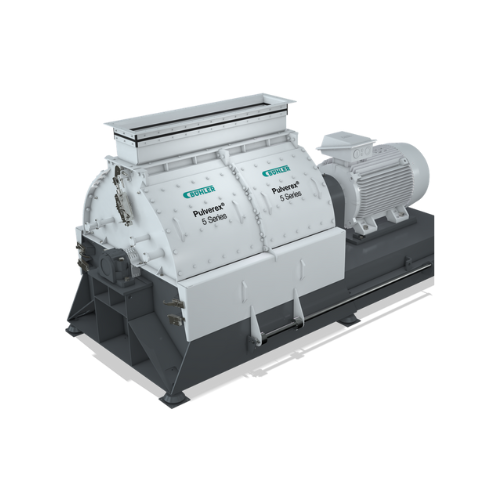
Pulverizer for fine grinding applications
Achieve optimal particle size distribution and enhance throughput with this adva...
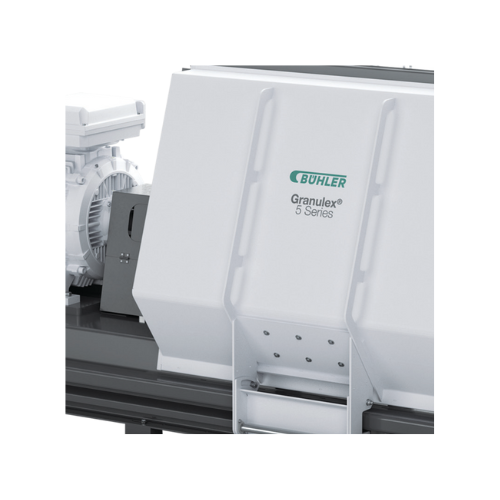
High-throughput hammer mill for animal feed production
Ideal for high-throughput operations, this hammer mill ensures pre...
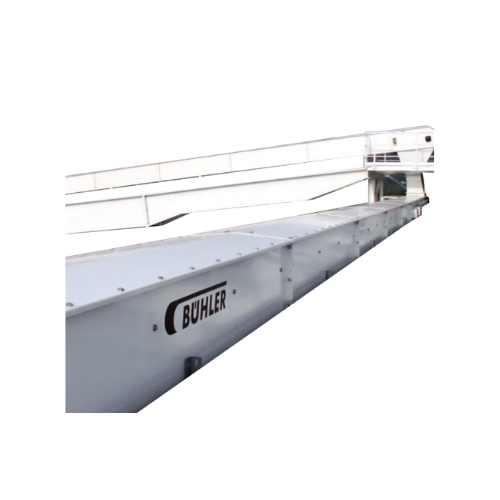
Heavy-duty trough chain conveyor for high throughput applications
Optimized for high-capacity operations, this robust c...

Twin-screw extruder for breakfast cereals production
Enhance your product range with flexible twin-screw extrusion techno...

Four-roller and eight-roller mill for grains
Optimize your grain processing with precise roller configurations, ensuring c...

Discharge station for bags and big bags
Ensure consistent material flow and hygiene in your production line with a versatil...
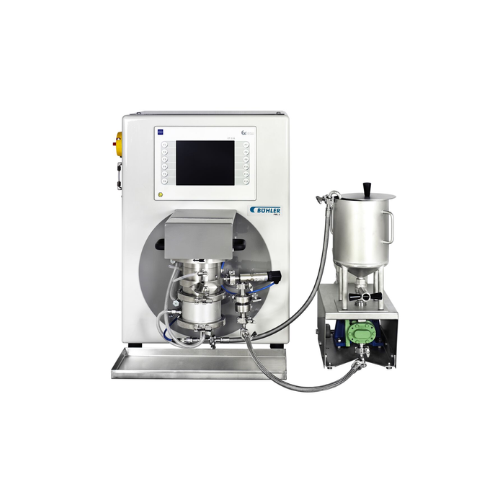
Laboratory bead mill for research and development
Optimize your laboratory processes with this flexible and modular bead ...
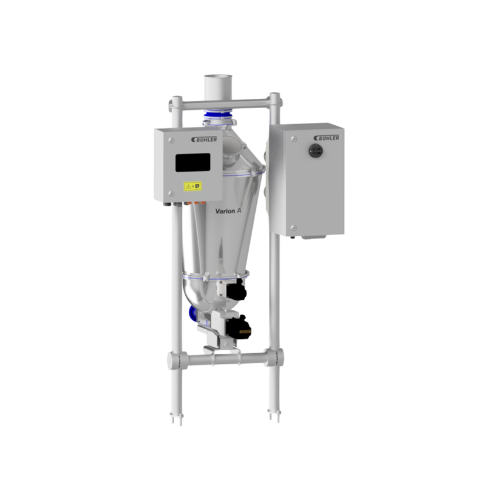
Batch scale for high accuracy weighing of powdery products
Achieve unparalleled precision in powder dosing with our batc...
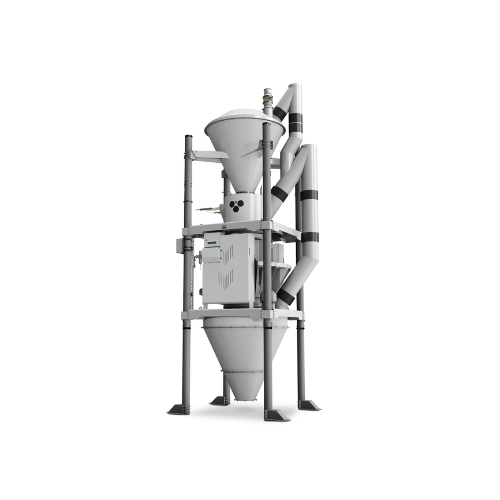
Fully automatic batch scale for powdery and granular products
Achieve precise and repeatable dosing for powdery and gran...

Twin-screw extruder for breakfast cereal
Optimize your production with a robust twin-screw extruder that accommodates high ...

Ultra-fine pulverizer for aqua feed and pet food
Achieve precise granulation with high efficiency for your feed and food p...
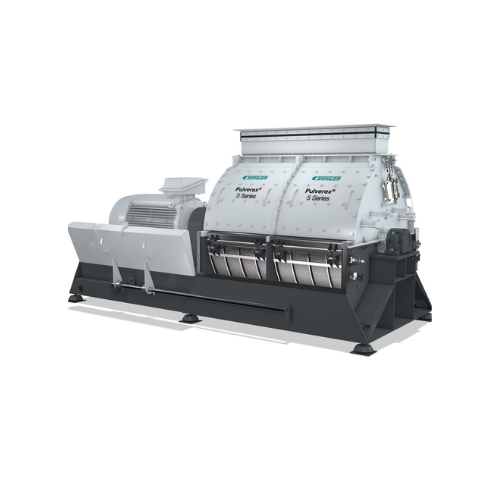
Industrial fine grinding pulverizer
Achieve consistent fine granulation at high capacity with reduced energy consumption, u...
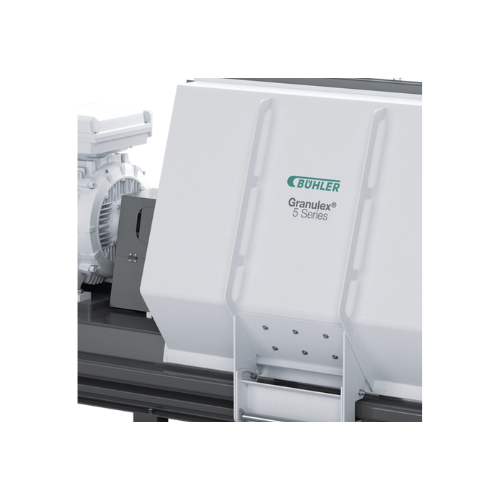
Hammer mill for animal feed grinding
Achieve precise granulation with high throughput and energy efficiency, while reducing...
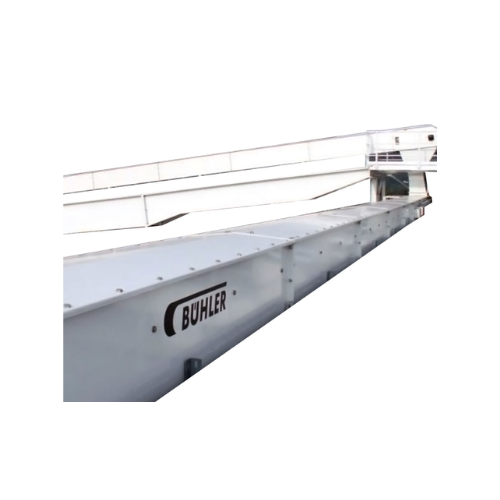
High-capacity horizontal conveyor for bulk storage
Optimize your high-speed bulk material handling with a durable and eff...
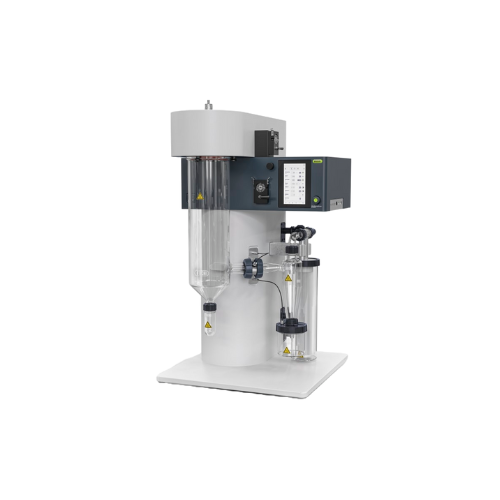
Laboratory spray dryer for organic solvent samples
Experience precise particle control and enhanced safety when convertin...
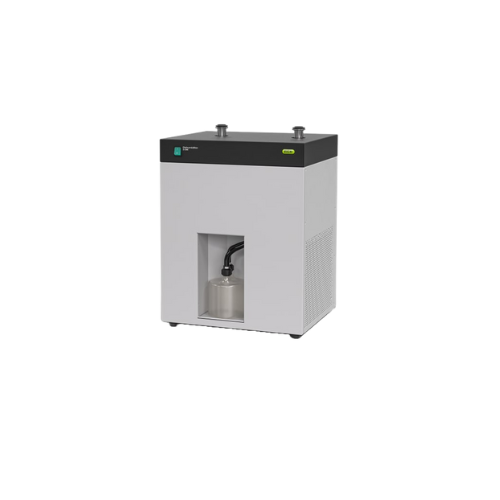
Industrial dehumidifier for continuous spray drying
Ensure stable spray drying conditions with precise humidity control, ...
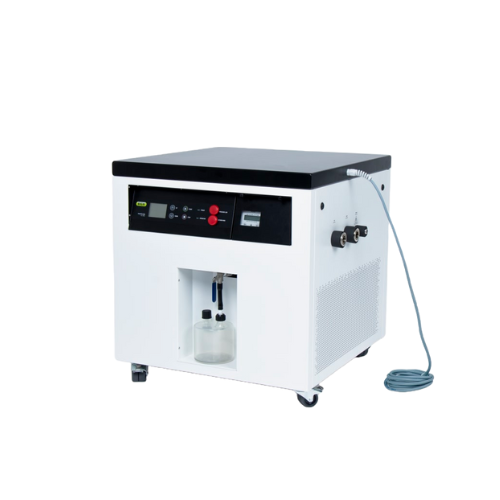
Inert loop for safe organic solvent spray drying
Ensure safe handling and efficient recovery of organic solvents in spray ...
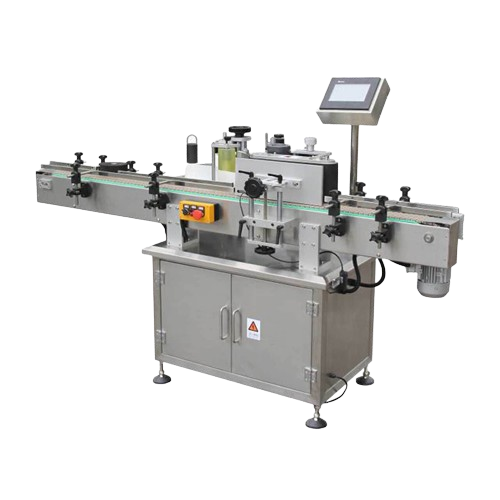
Automatic single side adhesive labeling solution
Streamline your packaging line with precision; this solution offers effic...
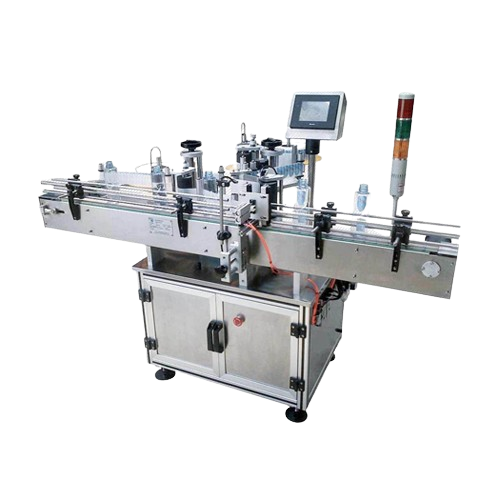
Automatic bottle self adhesive labeling solution
Enhance your production line with precision labeling for diverse containe...
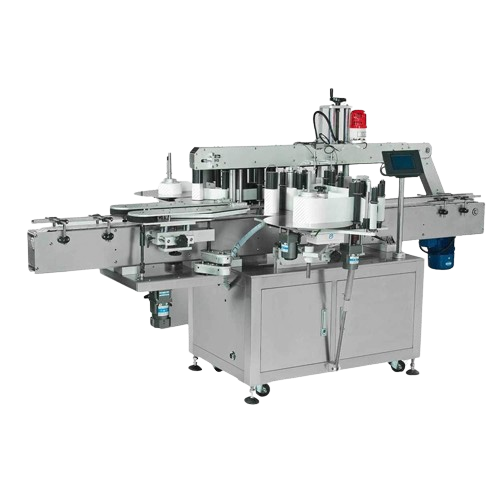
Double sides adhesive sticker labeling solution
Achieve seamless and precise double-sided labeling on bottles and containe...
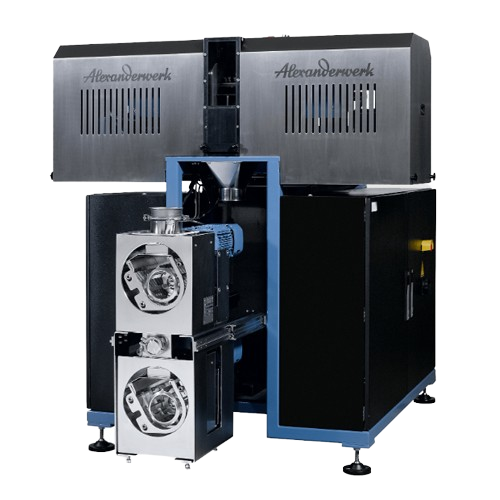
Industrial roller compaction for chemical applications
Enhance material flow and density with advanced roller compaction ...
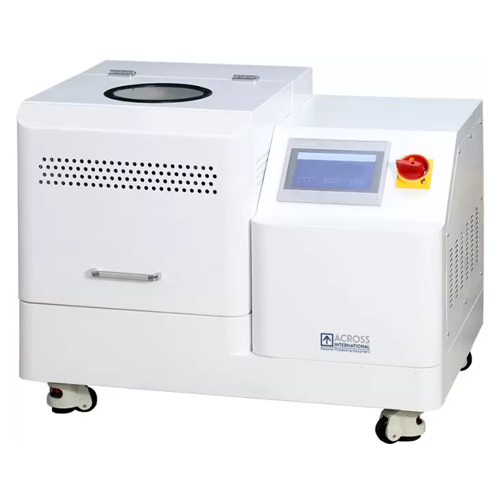
Planetary ball mill for powder material mixing and alloying
Achieve precise control in particle size reduction and homog...
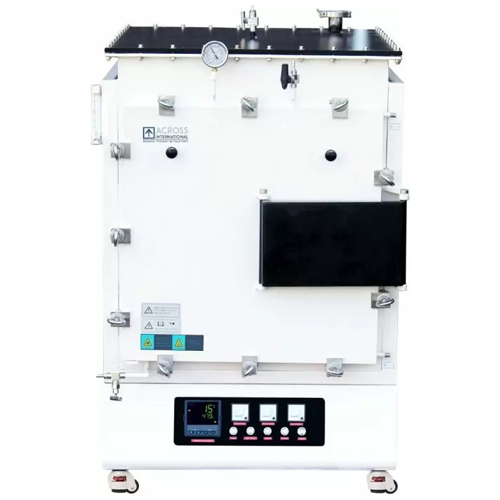
Controlled atmosphere muffle furnace
Achieve precise temperature and atmosphere control for critical processes like sinteri...
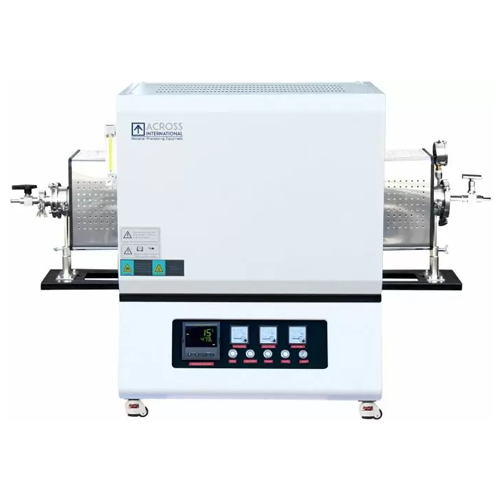
High-temperature tube furnace for laboratory applications
Achieve precise thermal treatment with this high-temperature t...
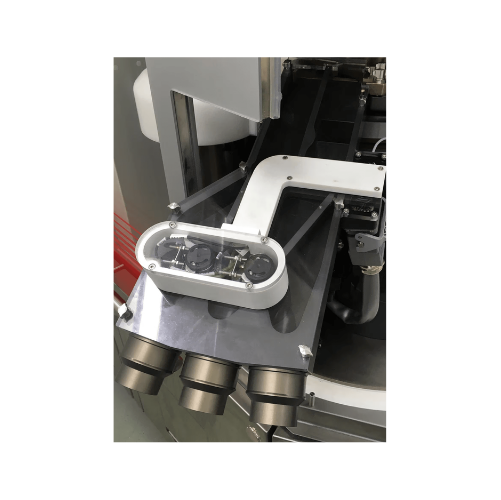
Rotary tablet press for abrasive powders
Achieve precise tablet sizing and bilayer production, even with abrasive powders, ...
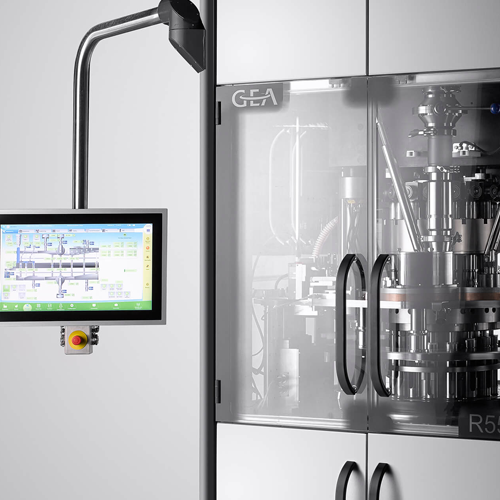
Heavy-duty tablet press for single & double-layer tablets
Maximize your tablet production with a high-speed solution cap...
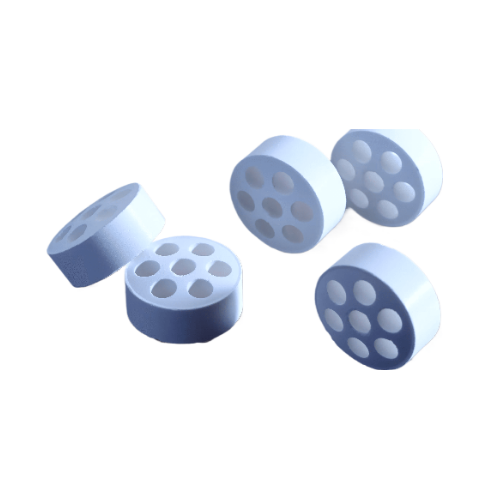
Rotary tablet press for large volume industrial tablets
Optimize your high-volume tablet production with a fully automati...
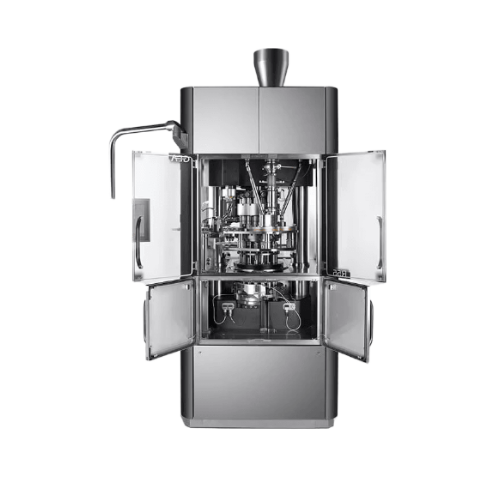
Industrial rotary press for single-layer tablet production
Optimize your tablet production with precision-engineered rot...
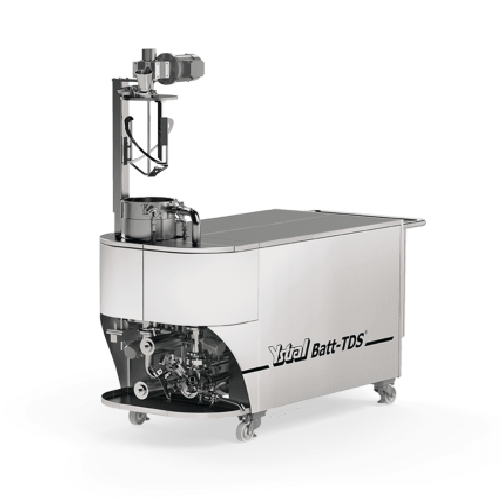
Inline disperser for lithium-ion electrode slurry mixing
Achieve highly efficient dispersion and homogeneity for battery ...
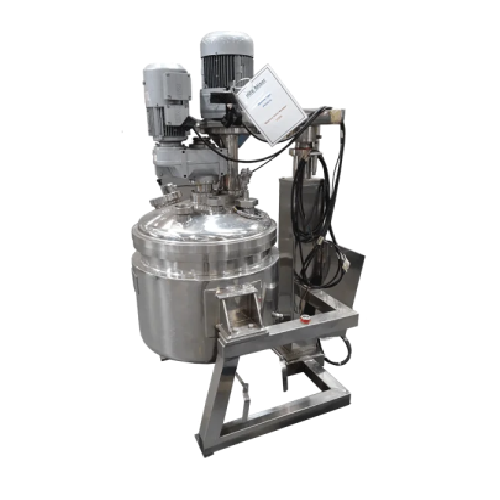
Mixing vessel for liquid, sauce, and cream products
Maximize efficiency in your production line with a versatile solution...
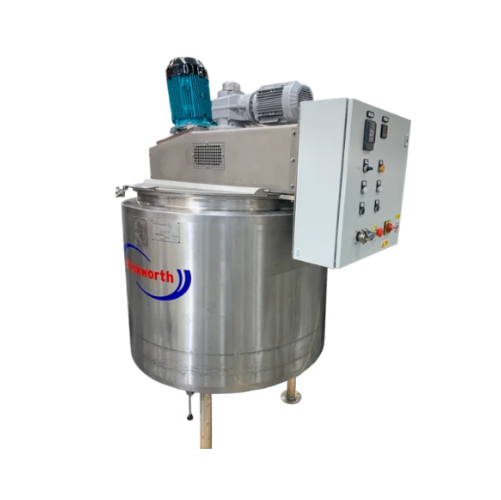
Pv processing vessels for liquid and cream mixing
Optimize your mixing operations with versatile processing vessels desig...
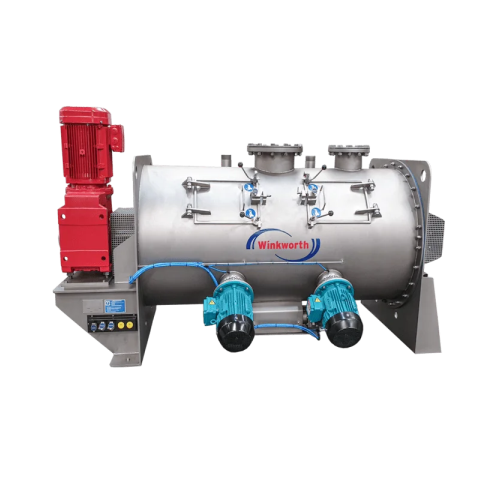
High-speed mixer for industrial mixing applications
Achieve rapid, consistent mixing and dispersion across diverse materi...
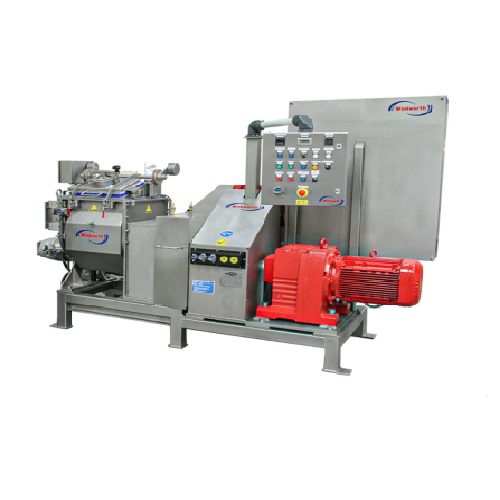
Industrial sigma mixer extruder for homogeneous mixing and extrusion
Achieve precise mixing and seamless extrusion of d...
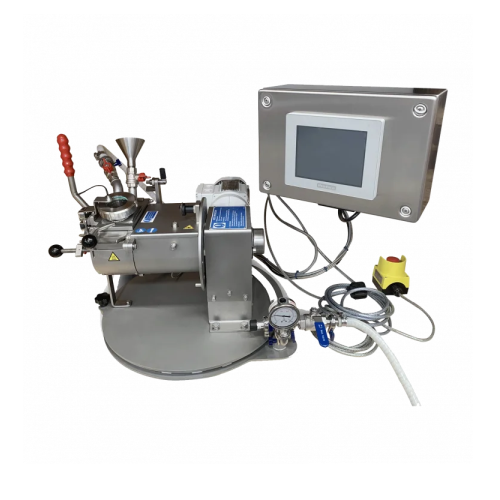
Laboratory mixers for product development and research
Optimize your R&D efforts with advanced mixing solutions desi...
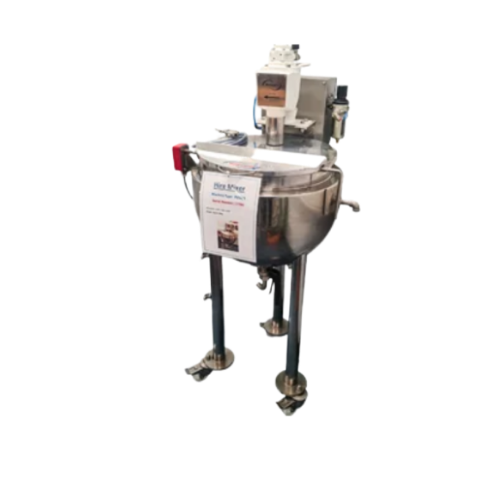
Pv mixing vessels for industrial hire
Optimize your production mix with vessels that ensure precise blending, heating, and ...
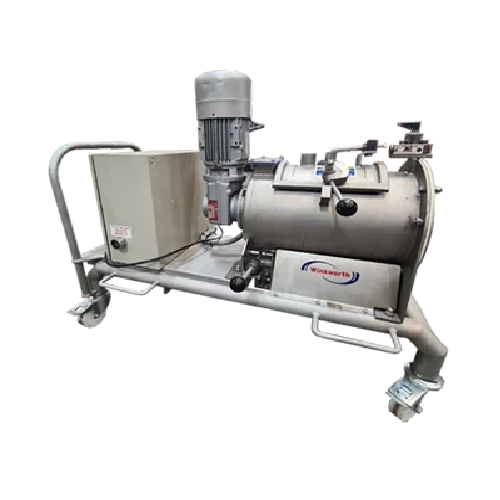
Industrial mixers for hire
Optimize your production line with versatile mixers designed for precision blending, heating, and...
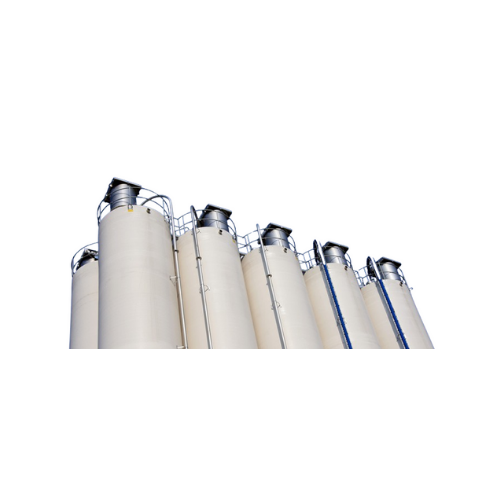
Flanged round dust collectors for industrial air filtration
Optimize your industrial processes with a dust collection sy...
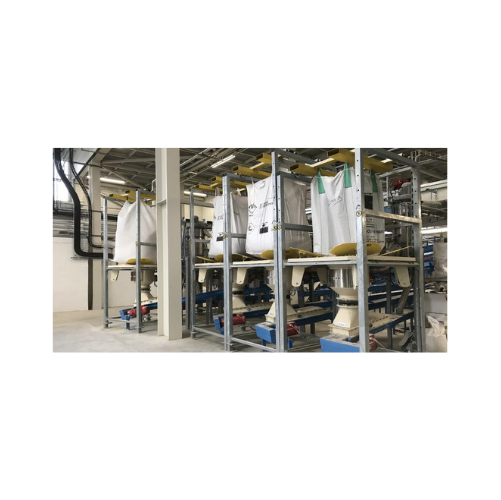
High flow rate Fibc discharger
Optimize your bulk material handling with a system designed for efficient and dust-free FIBC ...
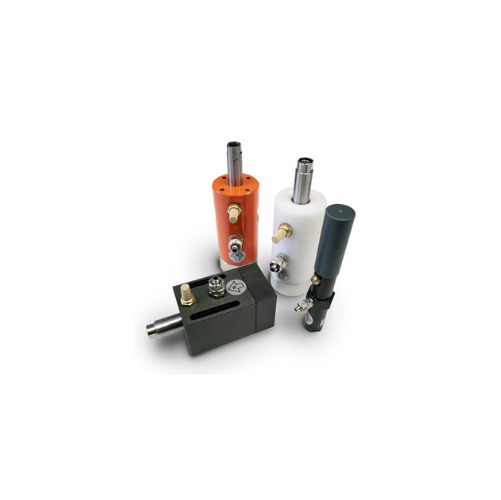
Cushioned pneumatic vibrators for coarse particle materials compaction
Enhance your material flow and compaction proces...
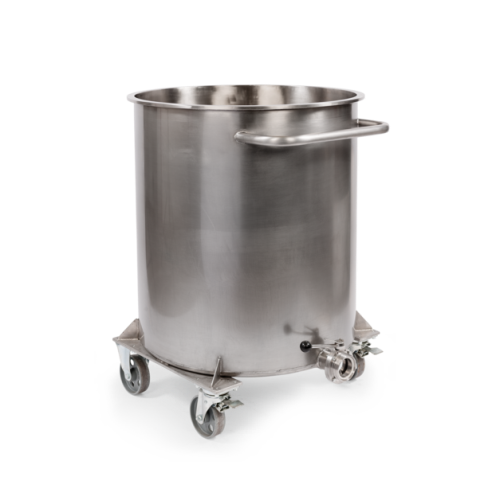
Industrial mixing dissolver for medium to large batches
Achieve precise mixing and dispersion of medium to large batch fo...
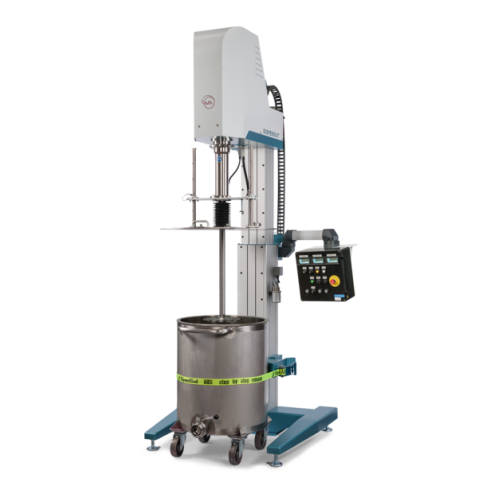
Explosion-proof dissolver for production applications
Ensure safety and efficiency in volatile environments with a robust...
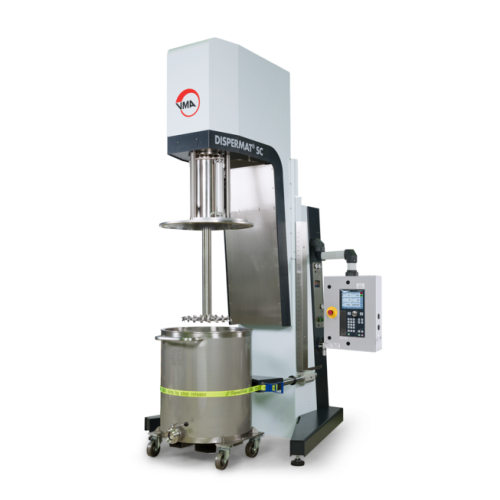
Explosion-proof production disperser for paint manufacturing
Ensure safe and efficient dispersion in volatile environmen...
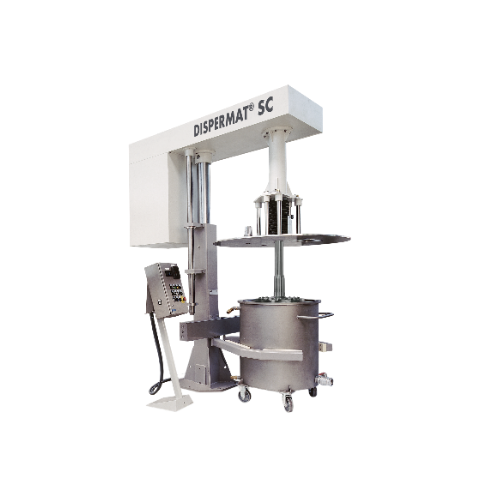
Explosion-proof dissolver for chemical processing
Ensure safe and efficient dispersion in volatile environments with this...
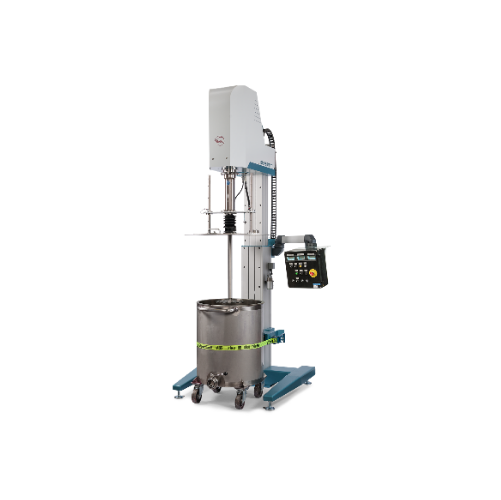
High-performance dissolver for large-scale production
Optimize your production line with precision-controlled dispersion ...
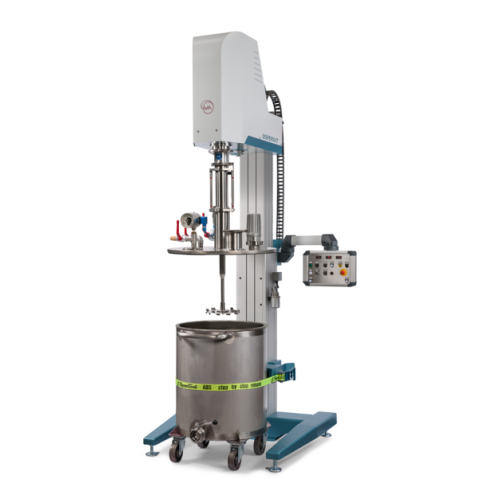
Vacuum dispersion system for high-viscosity products
Eliminate air inclusions during production with a modular vacuum sys...
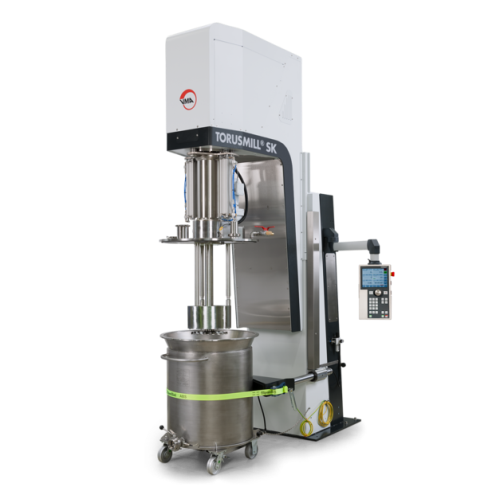
Vacuum basket mill for high viscosity products
Achieve efficient fine grinding of high-viscosity products while minimizing...
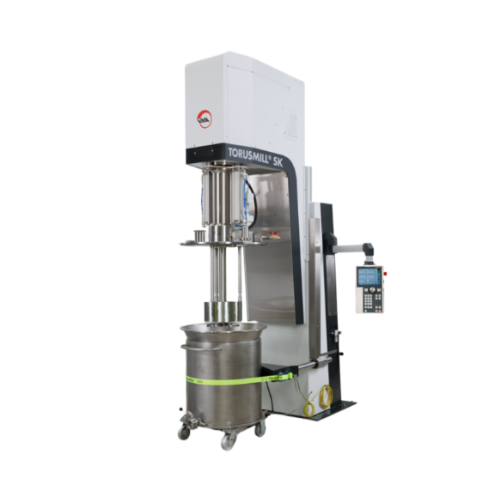
Vacuum dissolver for high viscosity products
Optimize your production with a vacuum dissolver designed to efficiently prev...
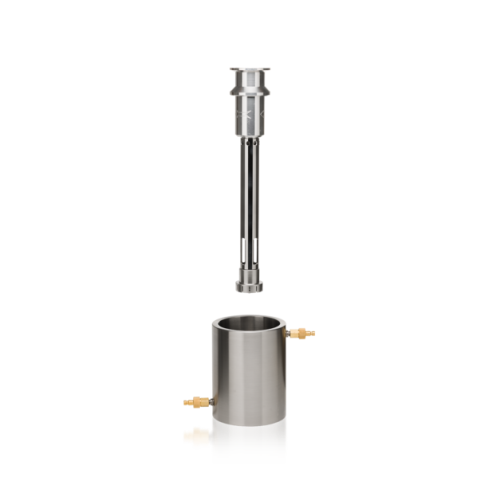
Vacuum dissolver for large batch production
Optimize your mixing processes with a versatile vacuum dissolver designed for ...
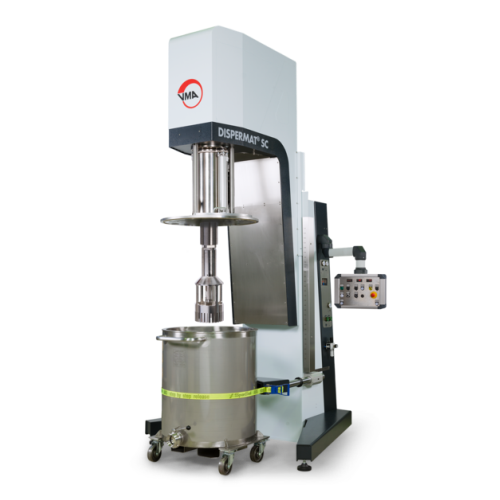
Rotary homogenizer for high shear mixing
Achieve precise homogenization of various viscosities with advanced rotor-stator t...
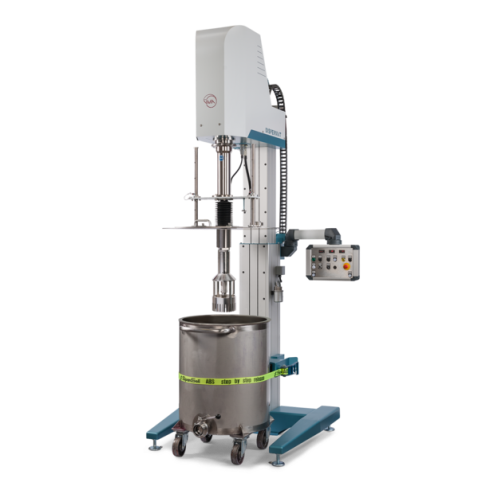
Rotor-stator homogenizer for high shear batch processing
Achieve ultra-fine particle distribution and stable emulsions wi...
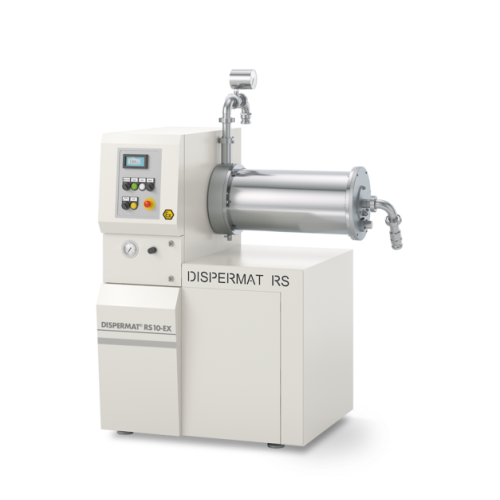
Explosion-proof bead mill for industrial grinding applications
For manufacturers seeking precise particle size control, ...
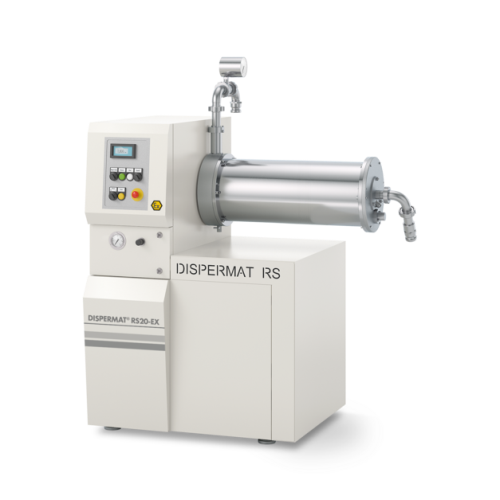
Explosion-proof horizontal bead mill for paint production
Ensure ultra-fine particle size and consistent quality with an...
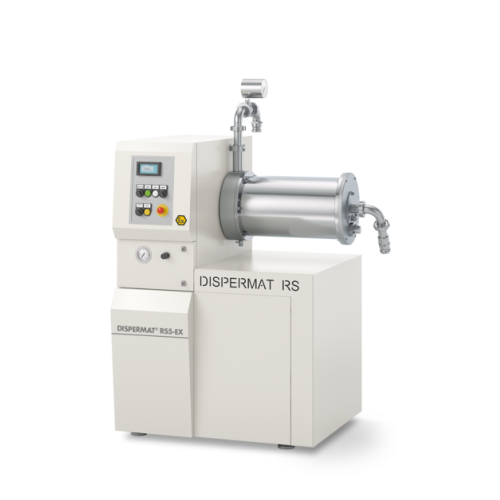
Explosion-proof horizontal bead mill
For manufacturers seeking precise particle sizing, this explosion-proof bead mill ensu...
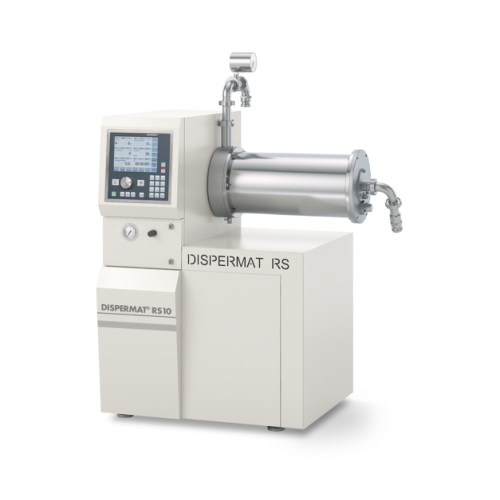
Horizontal bead mill for industrial production
Ensure ultra-fine particle size reduction in high-demand processes with thi...
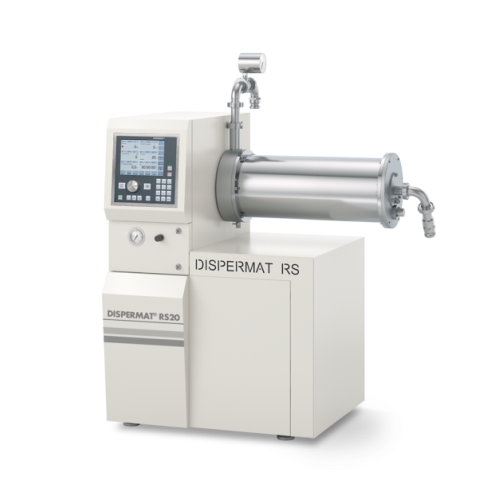
Horizontal bead mill for fine grinding in continuous process
Achieve ultrafine particle dispersion and consistent mixing...
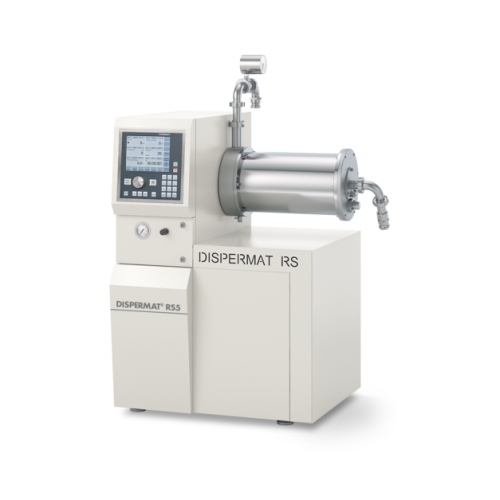
Horizontal bead mill for ultrafine particle grinding
Achieve precision in ultrafine grinding with a system that allows fo...
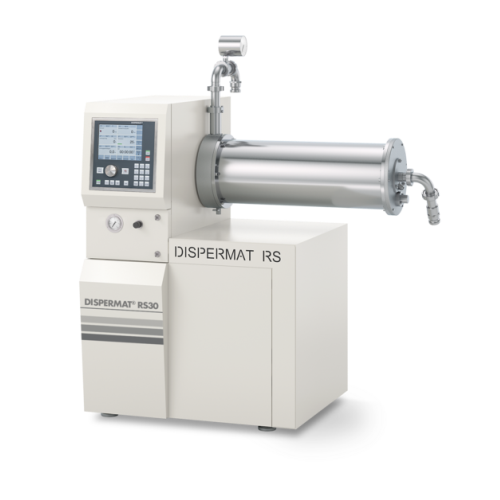
Horizontal bead mill for industrial nano grinding
Achieve precision in nano-scale grinding with this advanced bead mill, ...
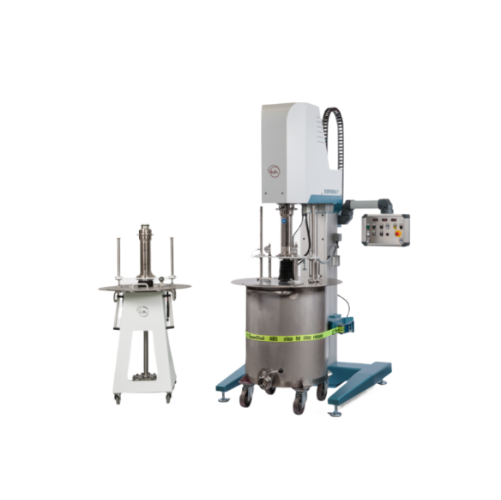
High-capacity dissolvers for industrial mixing
Enhance your production line with precision mixing, achieving consistent di...
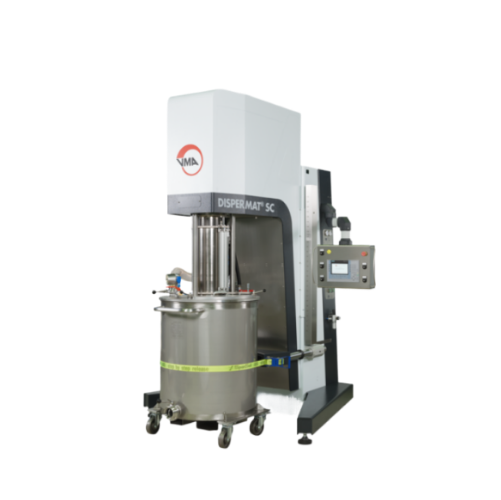
Modular basket mill for industrial dispersion
Effortlessly enhance your production efficiency with this versatile solution...
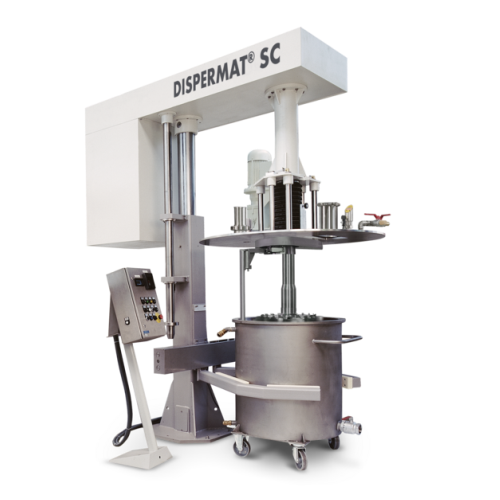
Explosion-proof production vacuum disperser for viscous products
Achieve precise and reliable dispersion of high-viscosi...

Industrial basket mill for medium viscosity products
Achieve precise particle size reduction and rapid pigment dispersion...
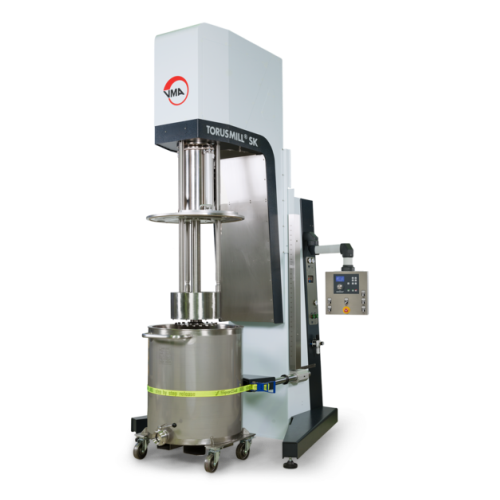
High-efficiency immersion mill for medium viscosity products
Achieve precise particle size reduction and superior disper...

High-efficient industrial immersion mill
Achieve rapid, efficient dispersion and fine grinding in demanding production envi...
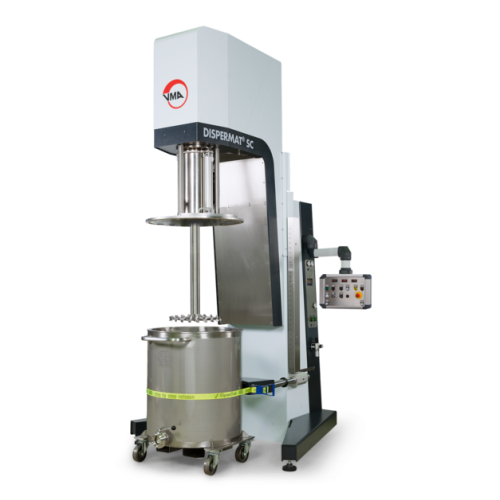
High-performance dissolver for industrial dispersion processes
Optimize your dispersion processes with this advanced dis...
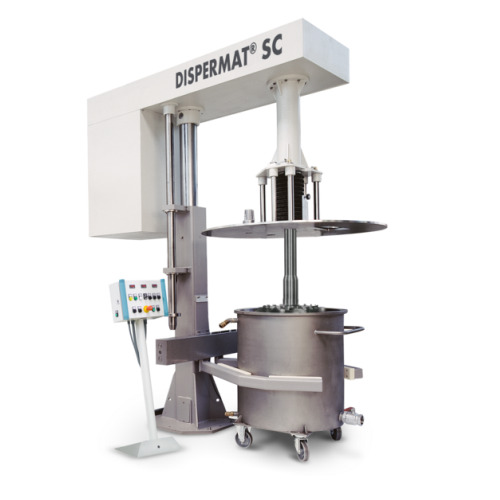
High-performance production dissolver for large batches
Achieve precise and repeatable dispersion for complex formulation...
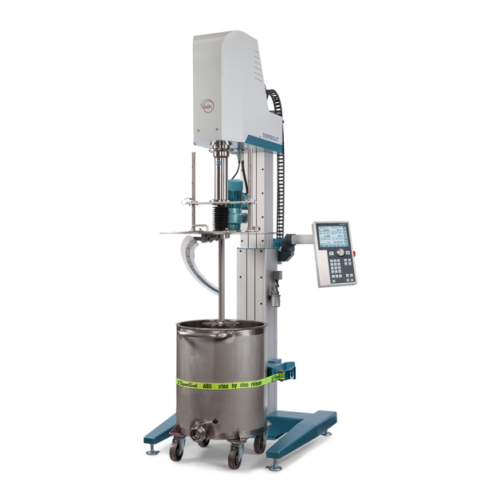
Dissolving system for high-viscosity products
Optimize the dispersion of high-viscosity liquids and pastes with this versa...
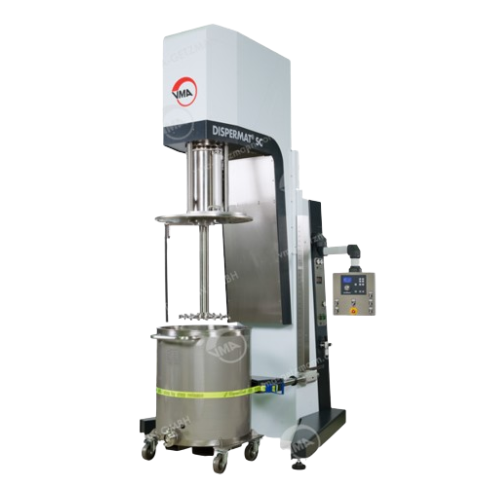
Production dissolver with scraper for high-viscosity products
Efficiently tackle high-viscosity material processing with...
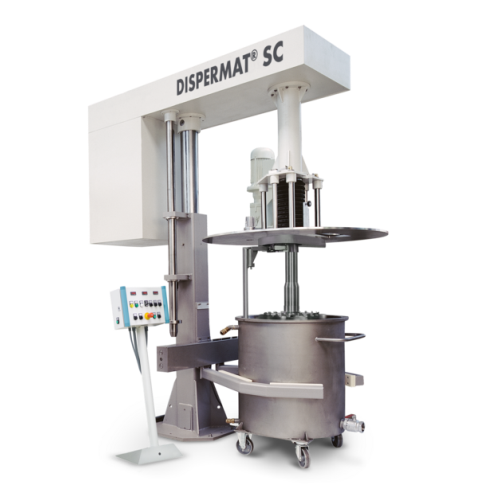
Industrial dissolver for high viscosity products
Optimize high-viscosity product dispersion with a robust dissolver design...

Explosion-proof dissolver for high-viscosity products
Optimized for safely processing high-viscosity products, this explo...
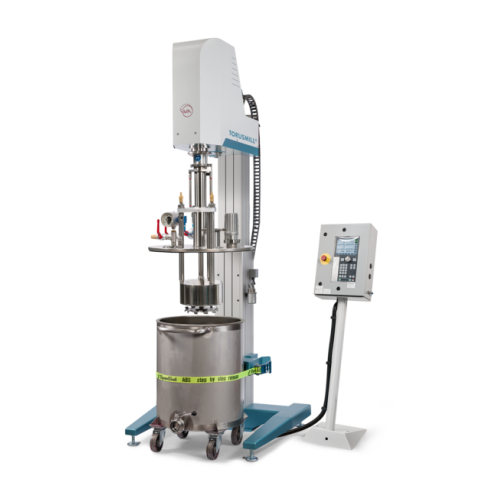
Vacuum basket mill for highly viscous products
Achieve precision in fine milling under vacuum to prevent air inclusions in...
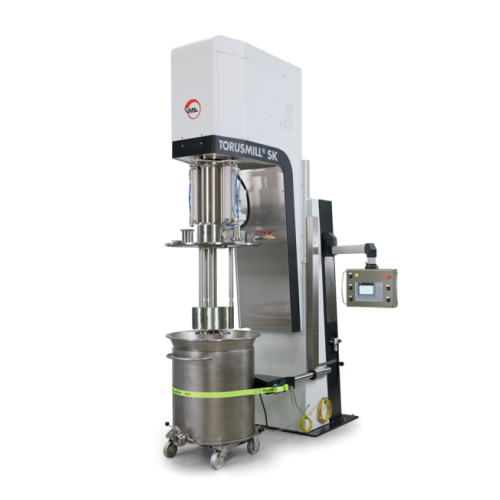
Vacuum basket mill for high-viscosity product milling
Achieve refined particle size and smooth texture in your high-visco...
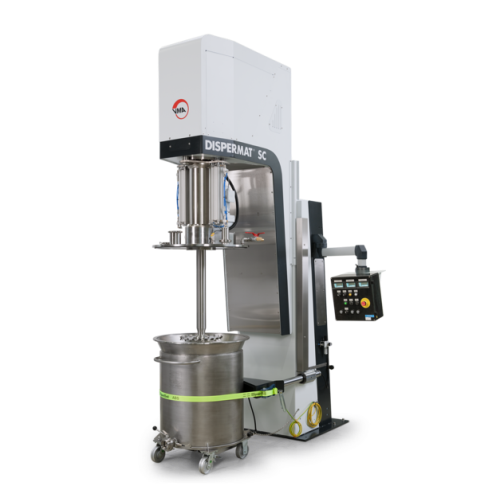
Explosion-proof vacuum dissolver for high-viscosity products
Optimize your production by eliminating air inclusions and ...
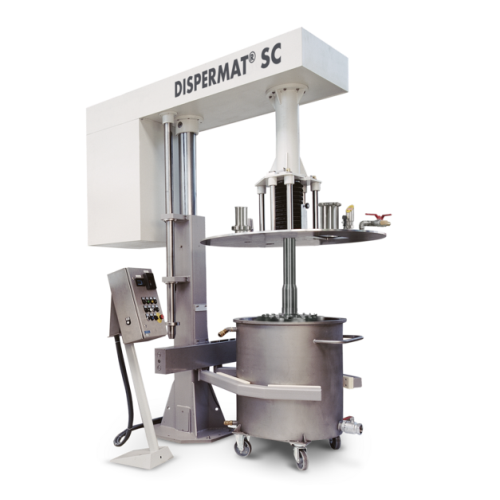
Explosion-proof vacuum dissolver for high viscosity products
Achieve precise dispersion of high-viscosity products under...
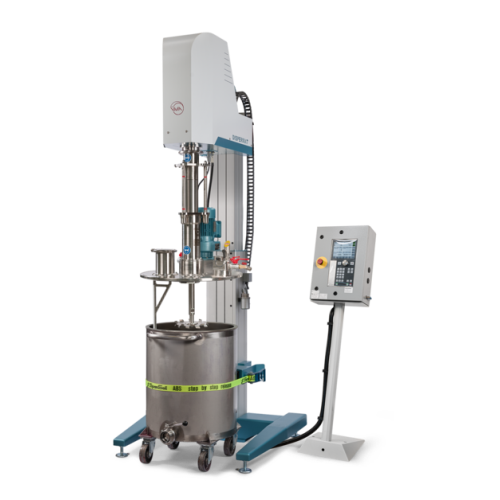
Explosion-proof vacuum dissolver for high viscosity applications
For operations requiring precise control in high-viscos...
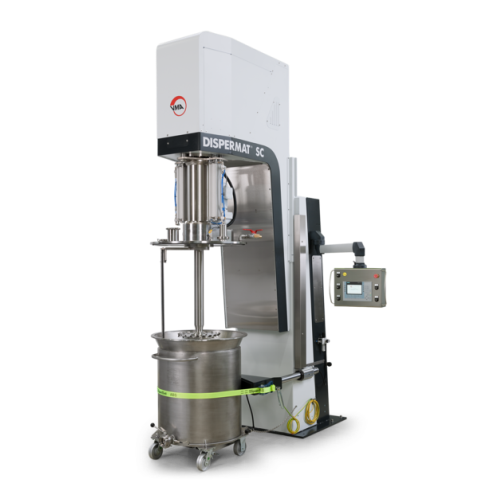
Explosion-proof vacuum disperser for high-viscosity substances
Achieve precise dispersion and eliminate air inclusions w...
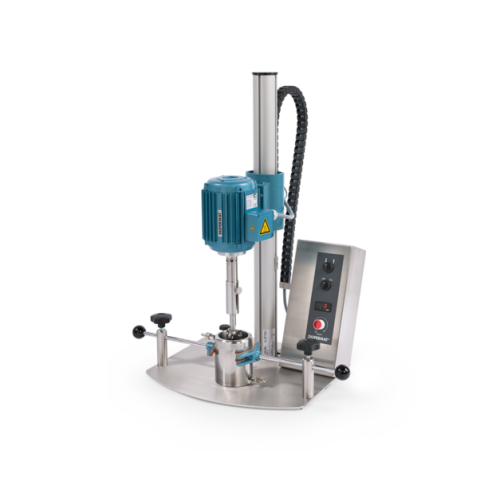
Laboratory stirrers for high viscosity materials
Efficiently mix and stir high-viscosity materials with ease, enabling pre...
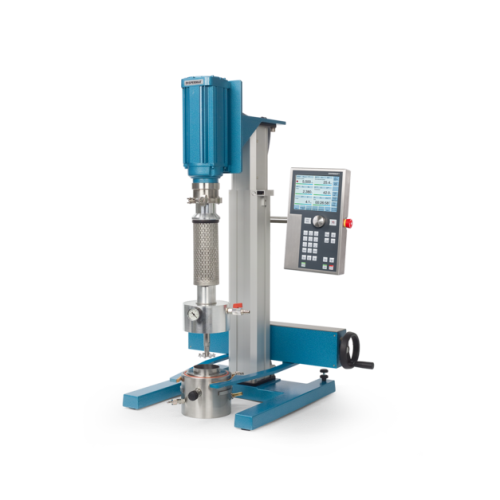
Vacuum dispersion system for laboratory applications
Achieve precise mixing and homogenization under vacuum conditions, e...
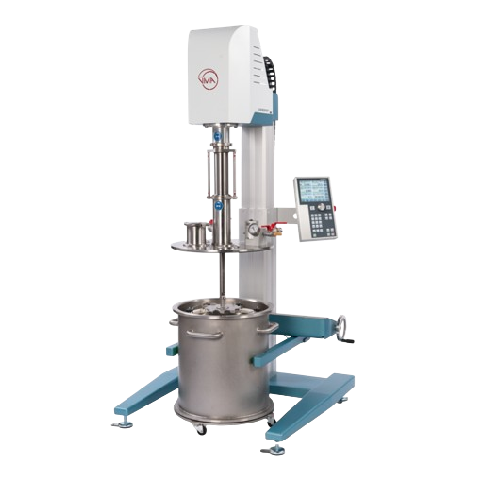
Vacuum dispersion system for single-walled containers
Optimize your production line with an adaptable vacuum dispersion s...
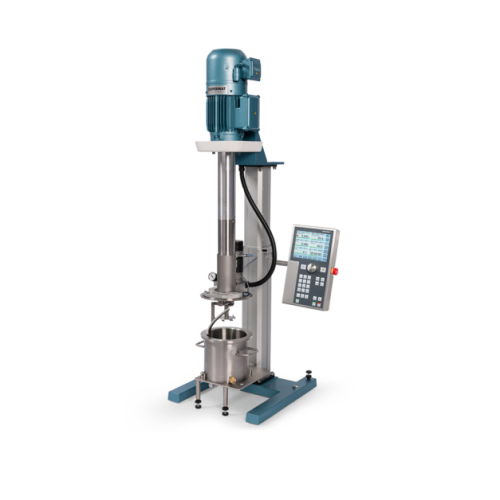
Vacuum dissolver for laboratory and pilot plant operations
Perfect for developing intricate formulations, this vacuum di...
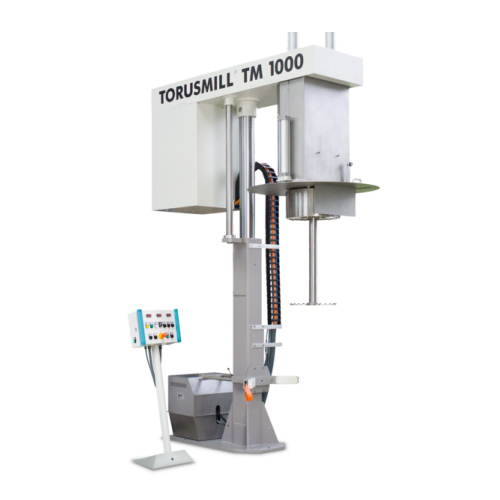
Basket mill with integrated dissolver for high viscosity products
Optimize your production efficiency by combining disp...
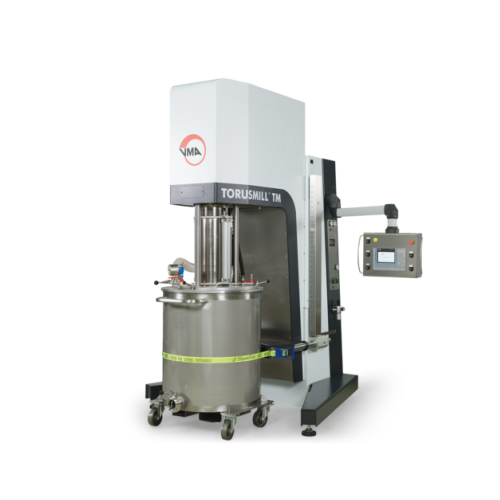
Dissolver for high-volume industrial dispersion
Achieve precise and efficient mixing with this dissolver, designed for sea...
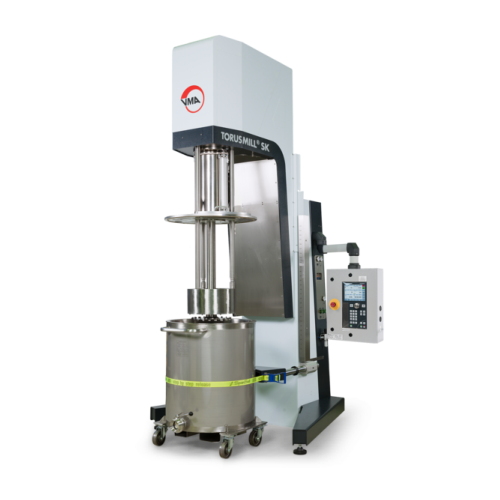
Explosion-proof immersion mill for paints and varnishes
Optimize high-performance coatings production with an explosion-p...
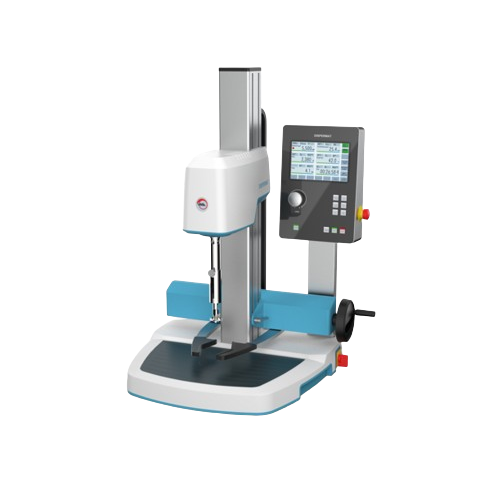
Laboratory dissolver for multiple applications
Efficiently streamline your laboratory processes with this versatile dissol...
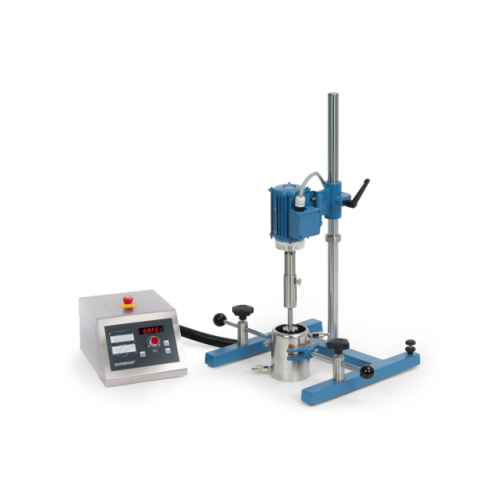
Lab and pilot plant dissolver for dispersion and fine grinding
Achieve efficient dispersion and fine grinding in laborat...
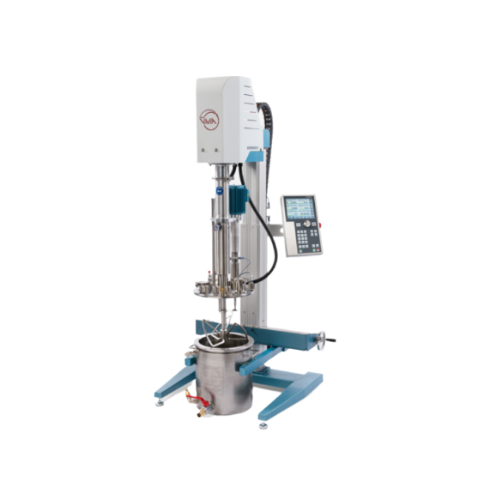
Vacuum dissolver for highly viscous products
Efficiently mix and disperse high-viscosity substances under vacuum to ensure...
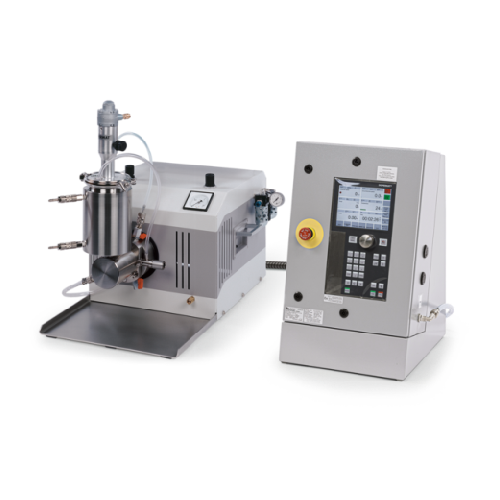
Explosion-proof horizontal bead mill for fine grinding
Ensure precise, explosion-proof grinding in hazardous environments...
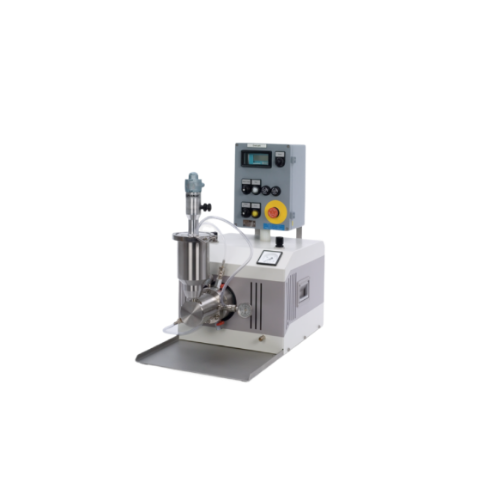
Atex horizontal bead mill
Ensure precision and safety in explosive environments with a robust solution that finely grinds an...
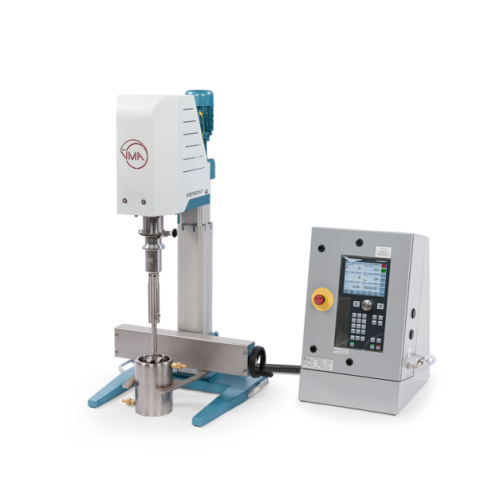
Explosion-proof dissolver for hazardous area mixing
When operating in hazardous environments, maintaining consistent and ...
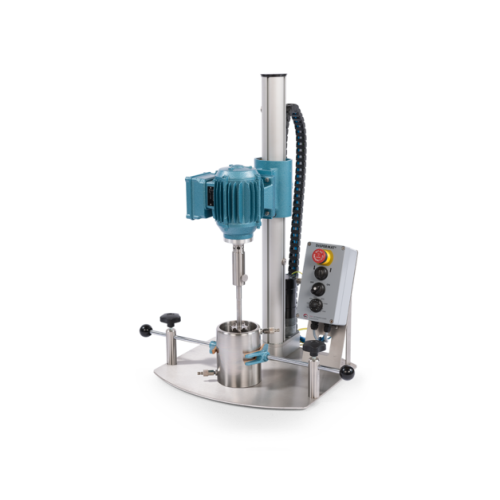
Explosion-proof dissolvers for laboratory use
Ideal for safely dispersing and mixing chemical substances in potentially ex...
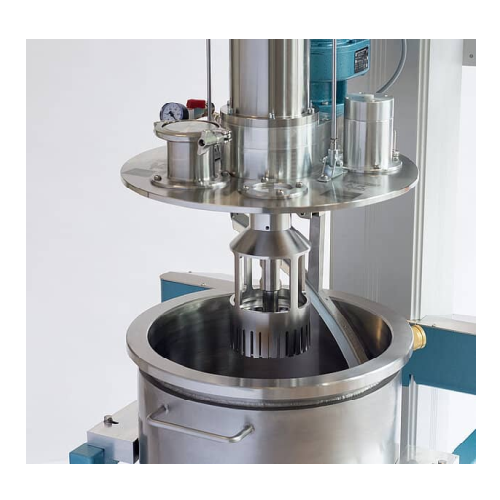
Efficient high-volume dissolver with scraper
For high-viscosity formulations, this advanced dissolver with integrated scra...
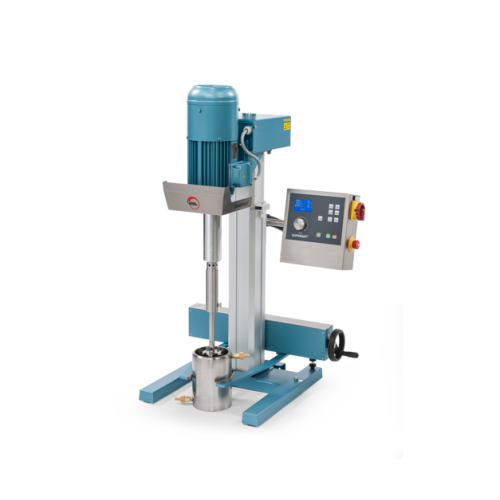
Lab stirrer for high-viscosity substances
Need precise, high-torque stirring for your complex formulations? This lab stirr...
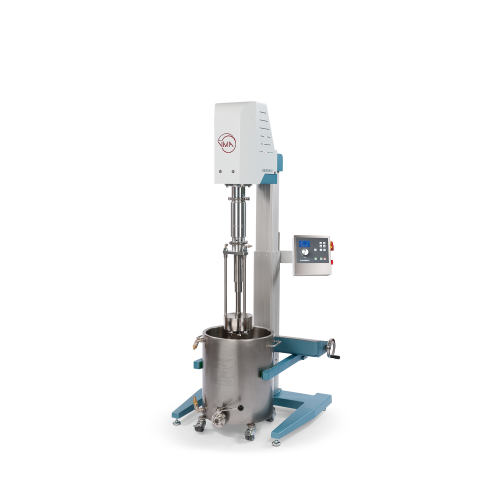
Entry-level vacuum dispersion system for laboratory applications
Achieve precise dispersion and milling with this versat...
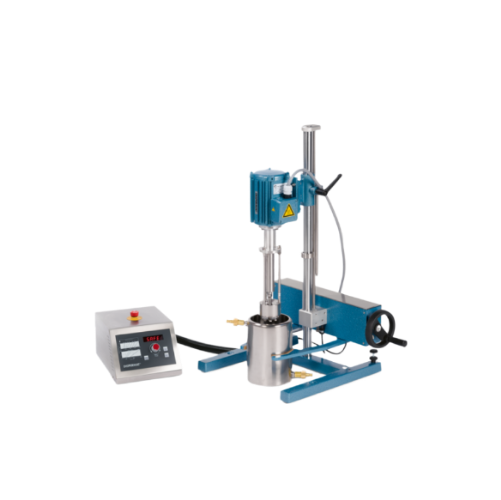
Laboratory bead mill for sample dispersion
Ensure precise particle size reduction with versatility and ease, enabling effi...

Laboratory and pilot plant horizontal bead mill
Achieve precision milling with minimal product waste, ensuring consistent ...
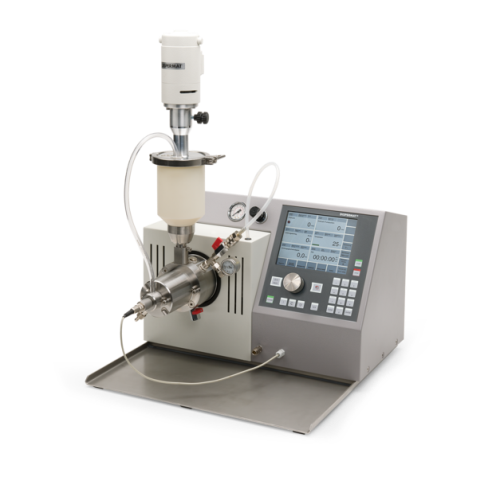
Nano bead mill for laboratory wet grinding
Achieve ultra-fine particle dispersion and consistent milling results with this...
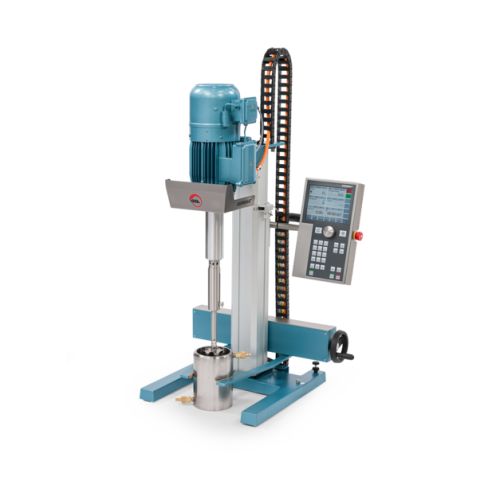
Rotary homogenizer for laboratory and pilot plant
For achieving optimal dispersion in complex formulations, this solution...
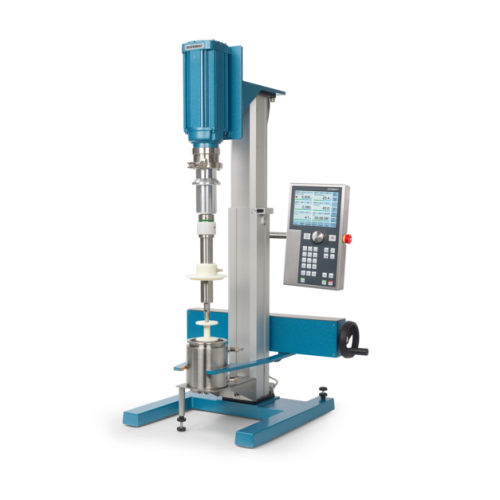
Laboratory disperser for small batch processing
Achieve precise dispersion and homogenization of high-viscosity mixtures w...
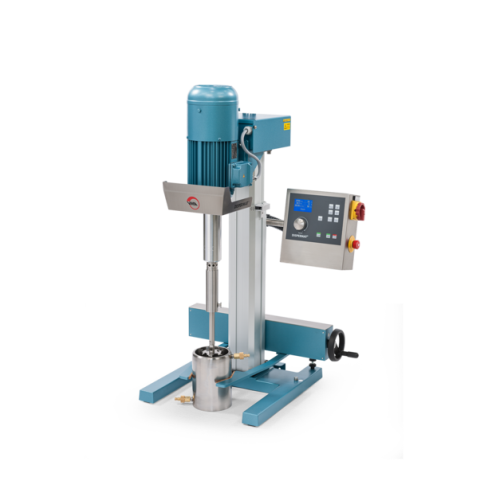
Dissolver for mixing and processing in lab and pilot plant
Optimize your material dispersion and homogenization processe...

Modular dispenser for dosing adhesives and abrasive media
Streamline your production line with a modular dispenser desig...
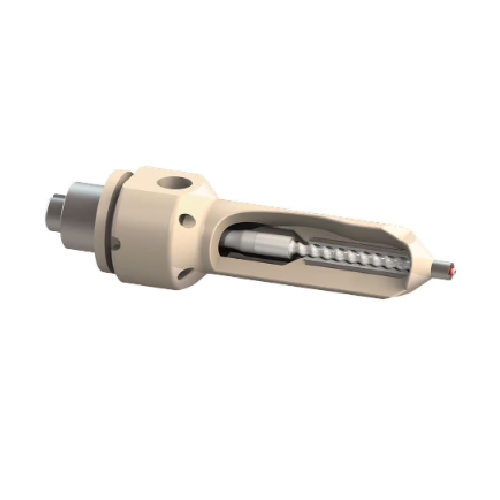
Dispenser for reactive material applications
Ensure precise dispensing of reactive materials without metal contamination, ...
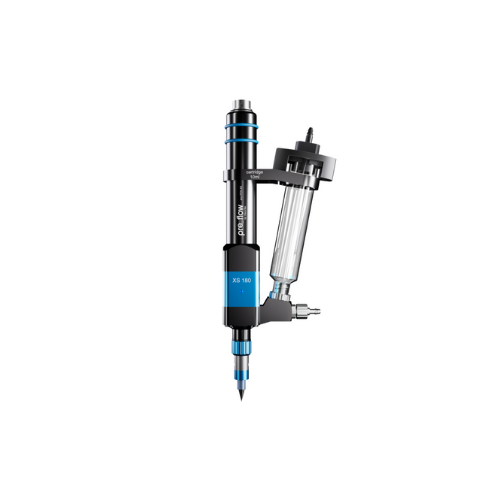
1-component industrial dispenser for precision dosing
Achieve unparalleled precision in microdispensing across diverse ap...
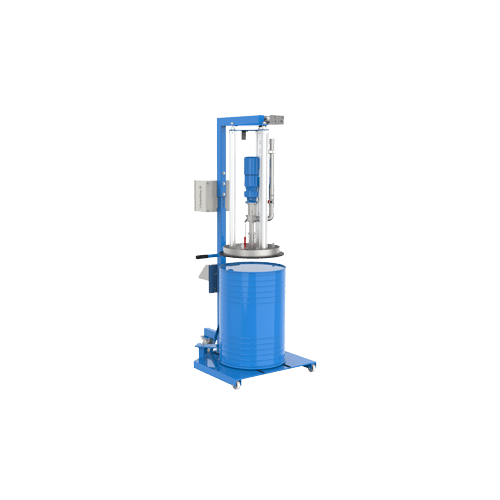
High-volume dispensing for single-component fluids and pastes
Enhance your production line with a pump that delivers lar...
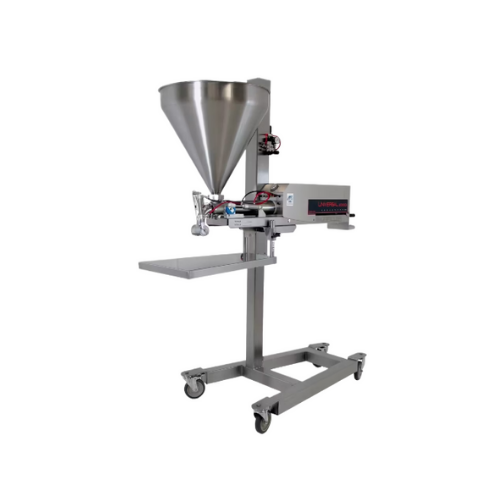
Single piston food depositor
Achieve precise portion control for diverse food products, from soups to chunky fillings, with ...
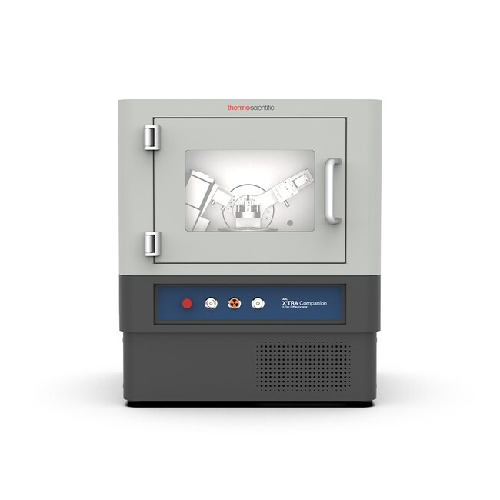
Benchtop x-ray diffractometer for routine analysis
Achieve high-precision phase analysis and crystalline characterization...
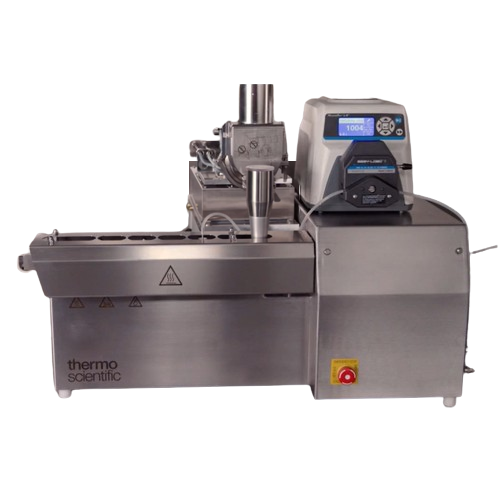
Glovebox for lithium-ion battery material processing
Ensure optimum material integrity with a solution designed to mainta...
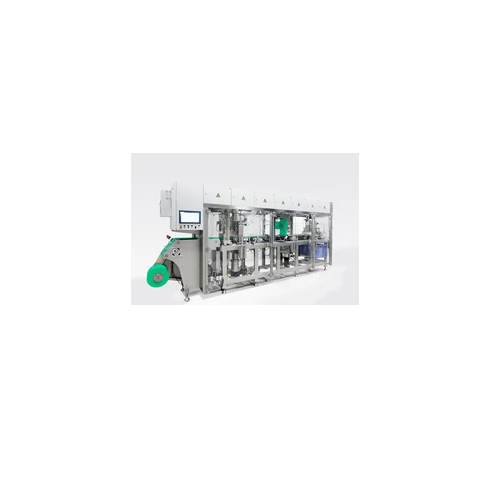
Paper forming technology for sustainable packaging
Elevate your product’s sustainability with advanced paper formin...
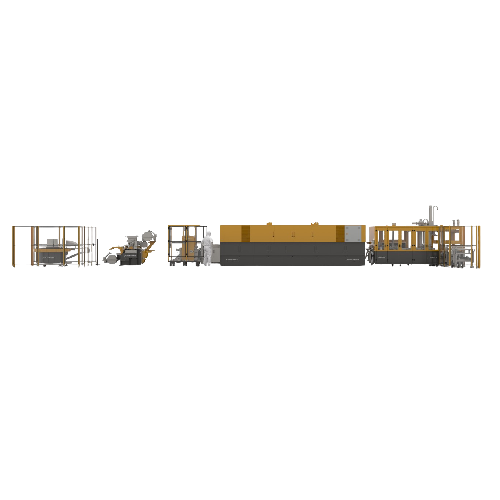
Pasting line for e-bike plates
Ideal for ensuring precision and consistency, this pasting line enhances the efficiency of ba...
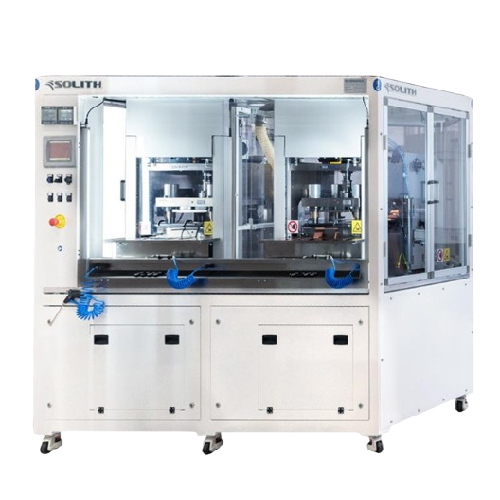
Pouch li-ion cell assembly line
Efficiently assemble high-performance lithium-ion pouch cells crucial for powering electric ...
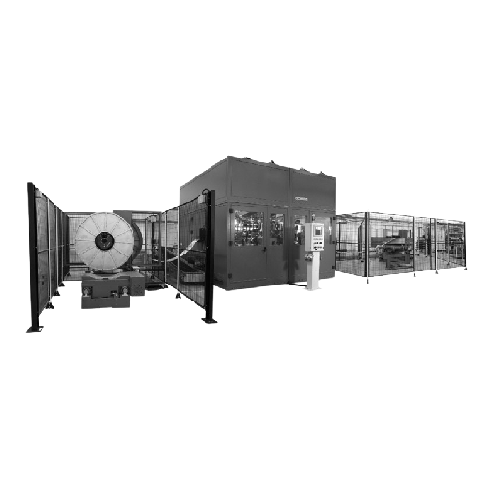
Punching machine for battery manufacturing
In the battery manufacturing industry, precision is paramount to ensure the lon...
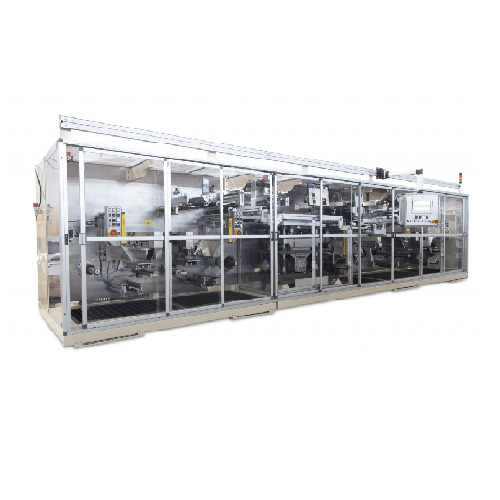
Roll to roll notching equipment for battery production
Optimize battery component production with precision notching, ens...
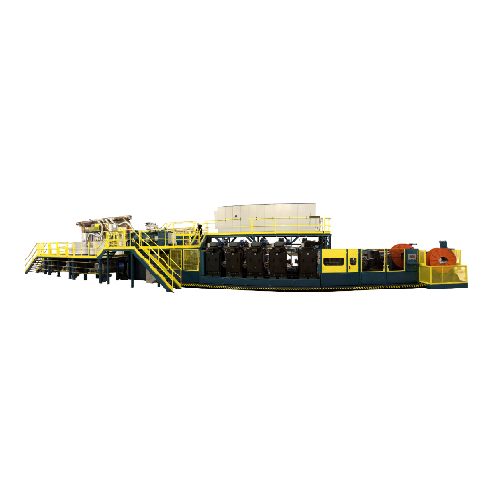
Wide strip casting and rolling lines
Optimize your metal processing line with continuous, high-speed wide strip casting and...
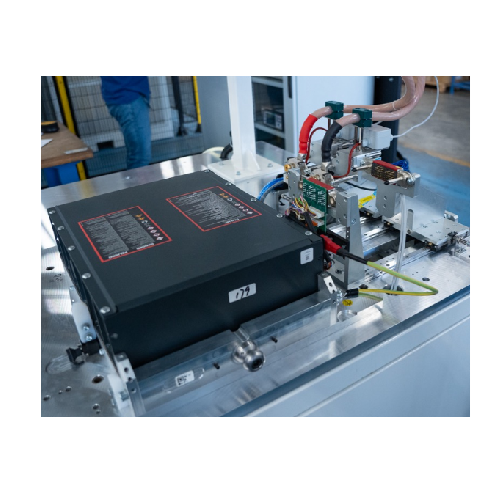
Enveloping and stacking solution for industrial applications
Ensure battery performance reliability with precise end-of-...
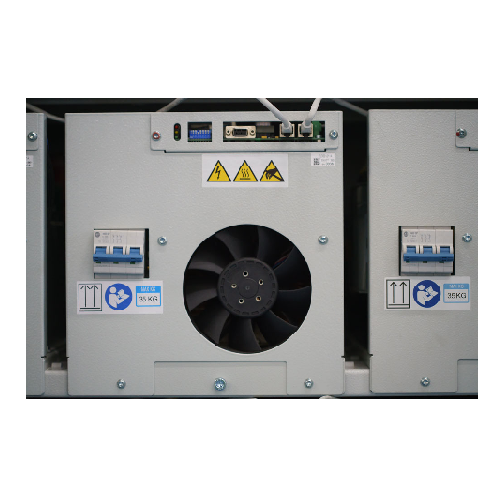
High-density battery chargers
Ensure your battery production line maintains optimal charge levels with precision and efficie...
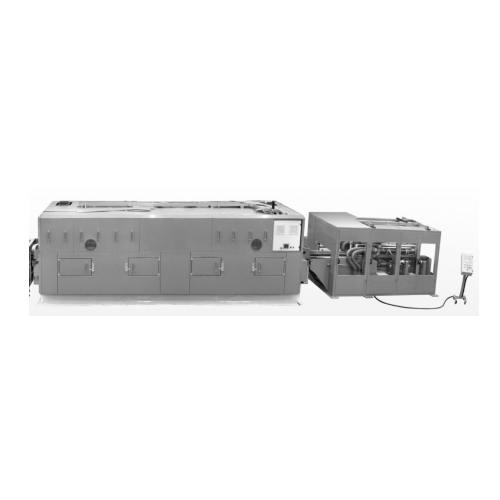
Industrial grid gravity casting system
For manufacturers seeking precise metal casting, this equipment ensures consistent q...
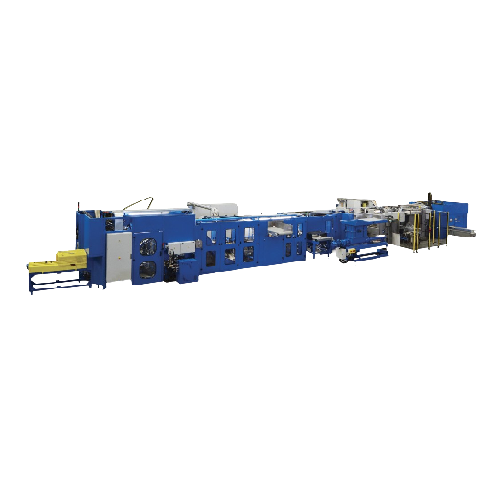
Industrial plate production line for battery manufacturing
Streamline your plate production workflow with a compact, eff...
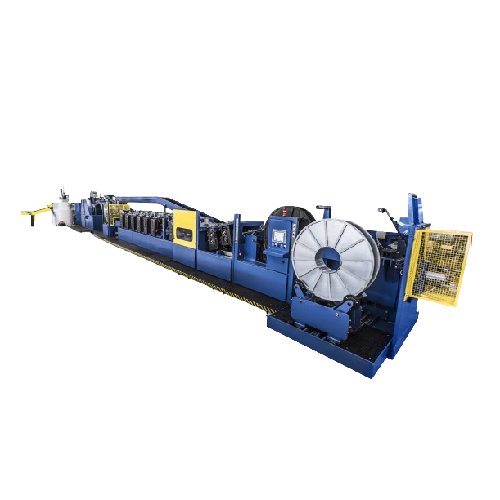
Lead strip manufacturing line
Enhance your battery production efficiency with a complete solution for precise lead strip man...
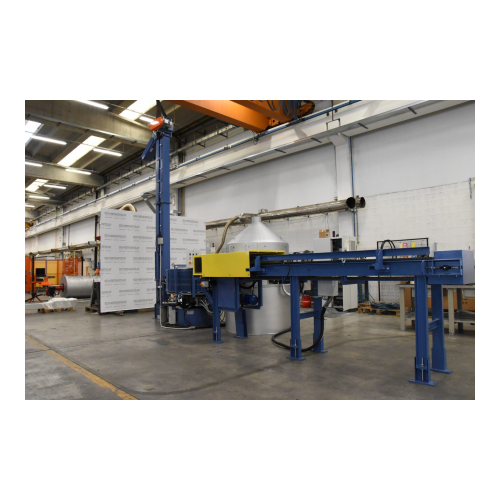
Lead cylinder casting solution
Optimize battery production by casting precise lead cylinders, essential for creating uniform...
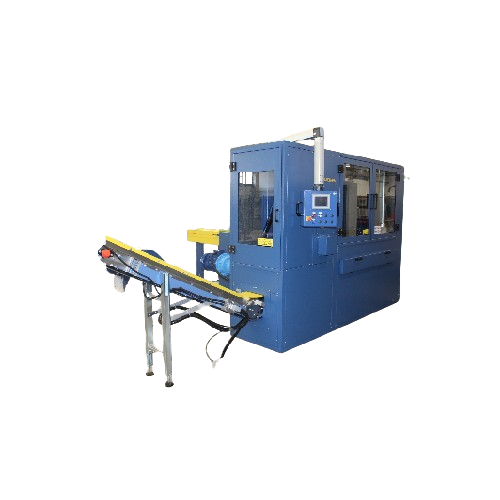
Cold lead cubing process
Optimize your production line efficiency by transforming lead into uniform cubes, ideal for streamli...
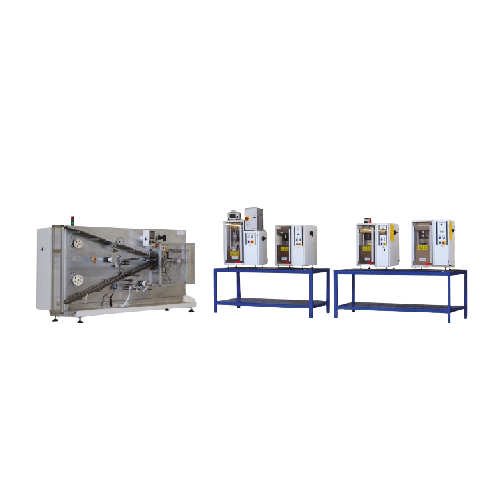
Industrial dry charge oven for battery manufacturing
Optimize your battery production with precision-engineered assembly ...
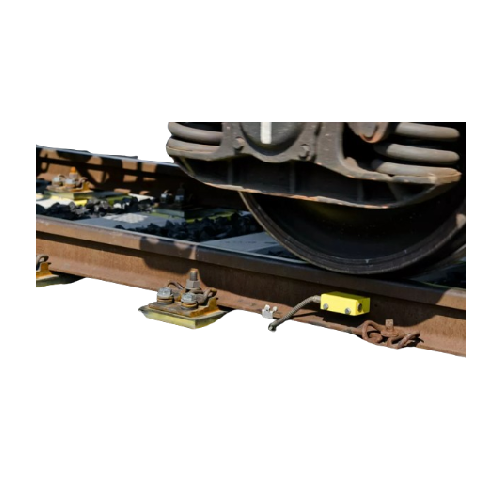
Dynamic weighing for solids and liquids
Ensure precision in rail transport with innovative dynamic scales that provide lega...
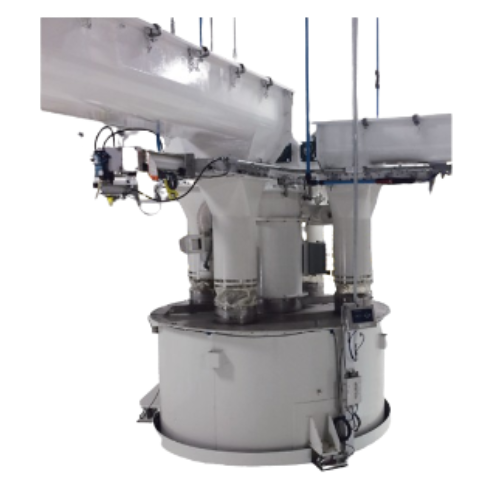
Scale hopper for bulk solid material handling
Ensure precise measurement and efficient transport of bulk solid materials w...
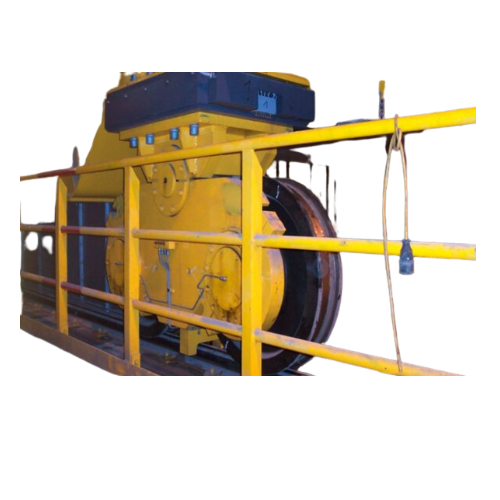
Crane scales for precise weighing in chassis
Optimize space with low-profile crane scales, ensuring accurate weight measur...
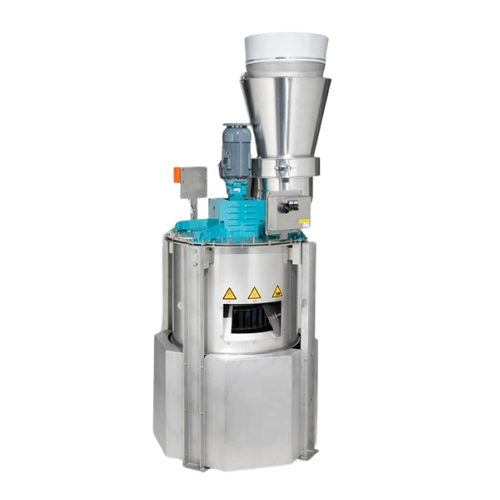
Mass flow rate feeder for bulk powders
Achieve precise control and consistent material flow in high-speed manufacturing env...
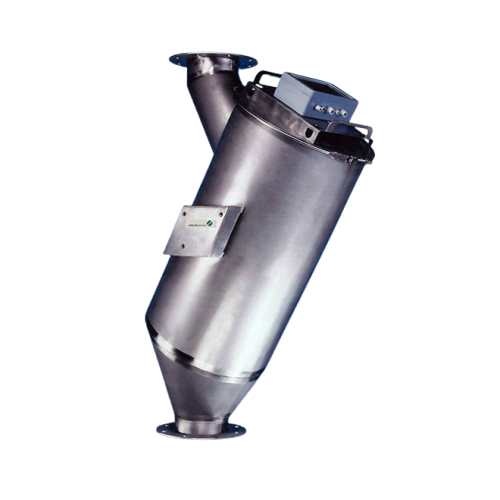
Solid flow meter for granular and powdered bulk materials
Ensure accurate mass flow measurement and seamless integration...
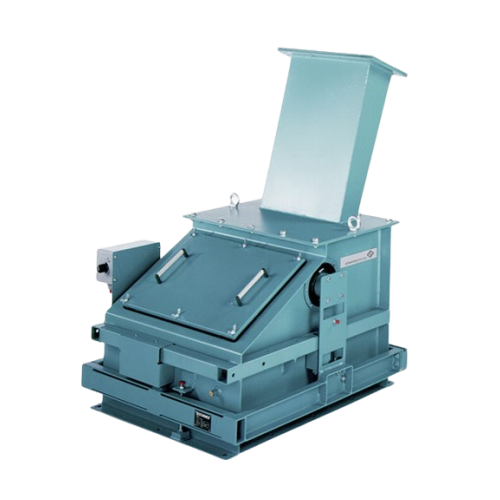
Solid flow meter for continuous bulk material measurement
Ensure consistent and accurate measurement of bulk solid mater...
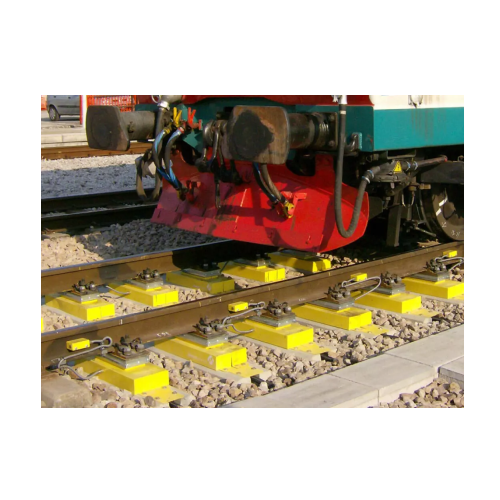
Dynamic high-speed railway weighing system
Prevent track damage and ensure safety by accurately weighing trains at speeds ...

Coal pulverization grinding mill
Maximize efficiency in pulverizing coal with continuous operation and low maintenance, idea...
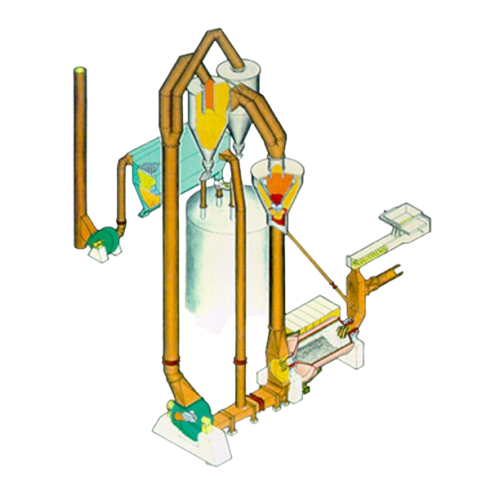
Industrial grinding solution for hard and abrasive materials
Efficiently grind and mill a spectrum of materials from coa...
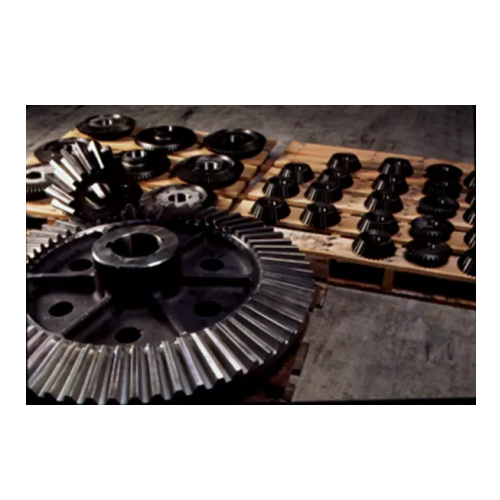
Industrial grinding mill replacement parts service
Optimize production efficiency with high-precision grinding solutions ...
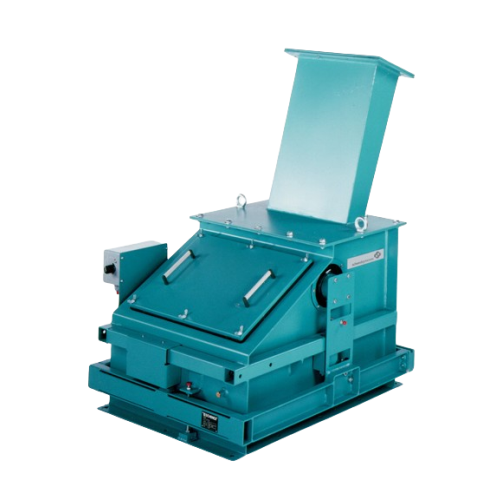
Solids flow meter for bulk solid streams
Ensure precise bulk material measurement with a system designed for accuracy and r...
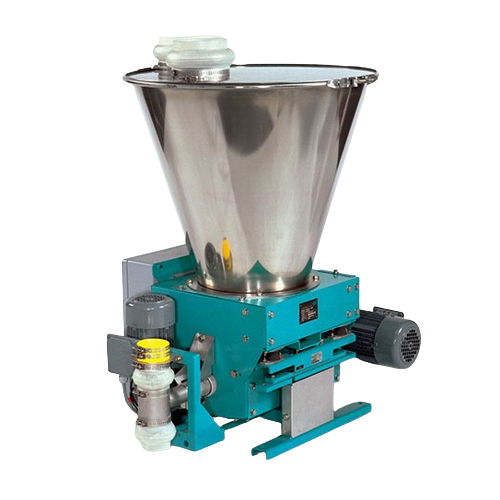
Loss-in-weight feeder for bulk solids
Ensure precise and reliable dosing of bulk solids with a compact feeder that eliminat...
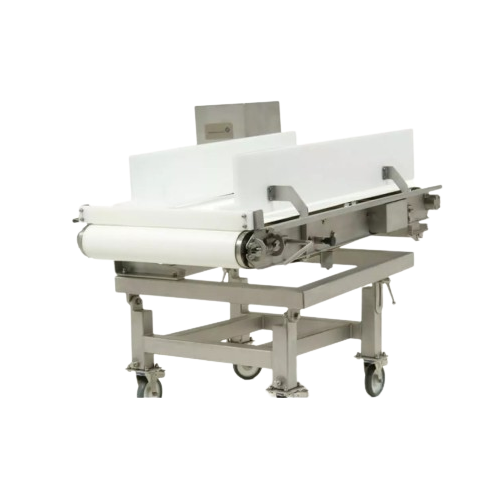
Industrial weighfeeder for hygienic applications
Achieve precise mass flow control with a hygienic design, ideal for appli...
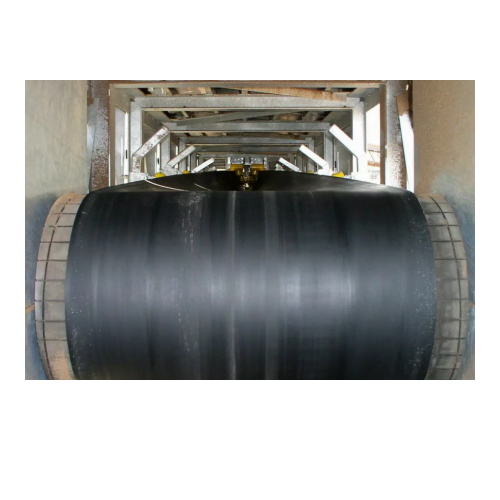
U-belt conveyor for bulk material transport
Optimize your high-speed bulk material transport with this space-saving convey...
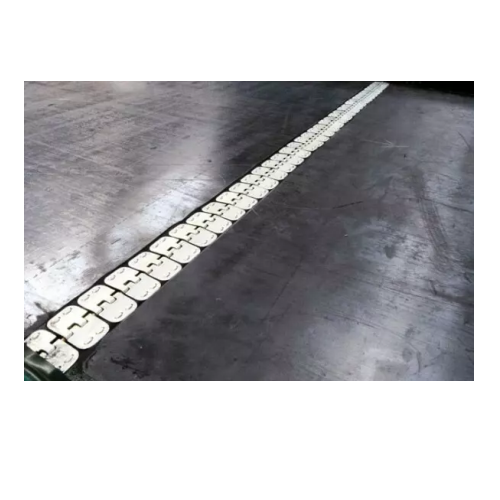
Optimal maintenance solution for industrial weighfeeders
Streamline your processing operations with a solution that minim...
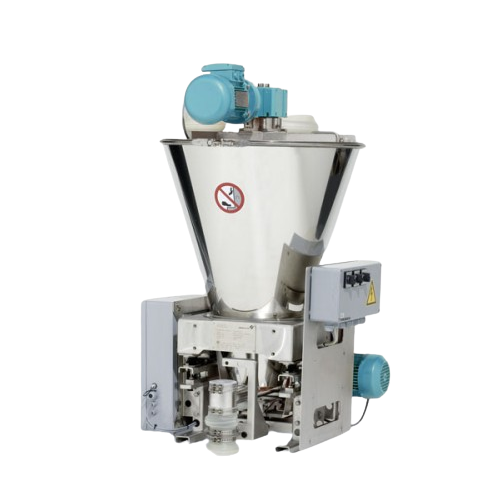
Loss-in-weight feeder for poor flowing bulk solids
Efficiently handle poorly flowing bulk solids with unparalleled precis...
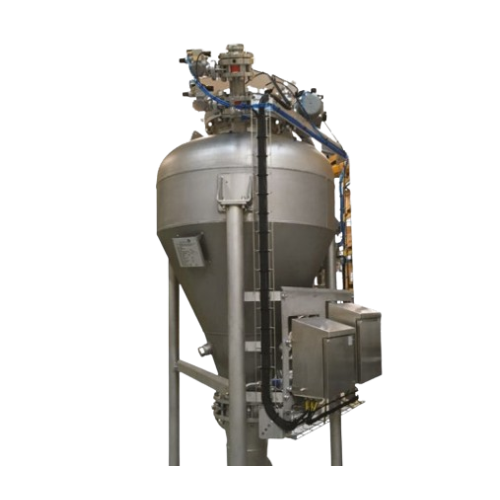
Dense phase pneumatic conveying accessories
Optimize material flow and reduce power consumption with dense phase pneumatic...
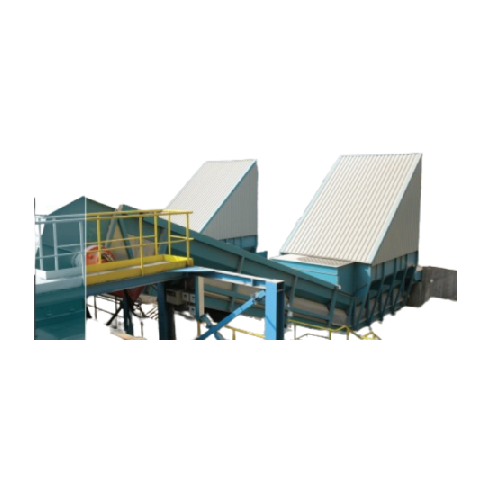
Bulk reception solution for industrial material handling
Optimize your operations with an above-ground bulk reception sys...
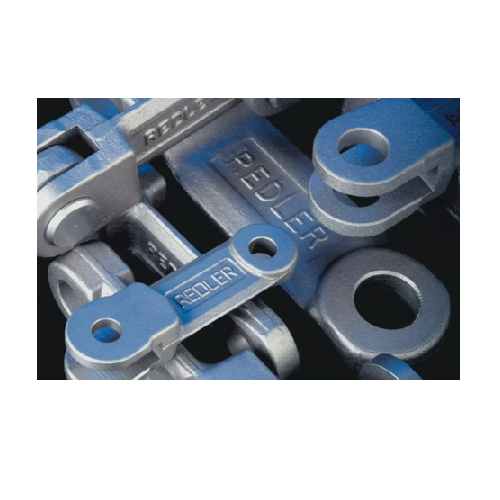
Drop forged chain for drag chain conveyors
Enhance your material flow efficiency with a robust drop forged chain designed ...
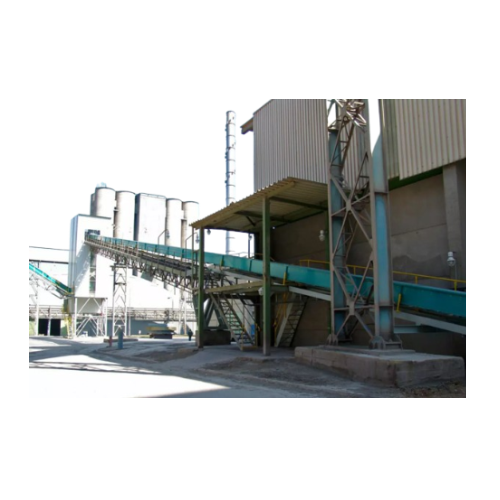
En-masse chain conveyor for bulk material handling
Streamline your bulk material handling with a gentle, efficient system...
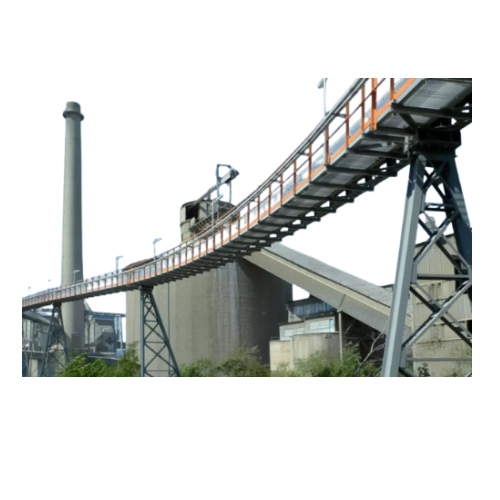
Tube belt conveyor for long-distance material handling
Ensure seamless and protective transport of bulk materials across ...
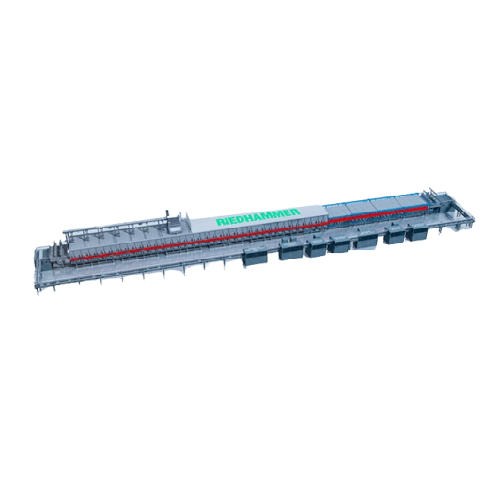
Lithium-ion battery powder processing solution
Optimize your lithium-ion battery manufacturing with advanced powder treatm...
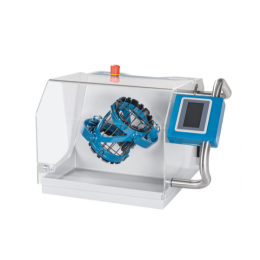
R&D shaker mixer for battery powders and chemicals
Material heterogeneity, agglomeration, and contamination are key param...
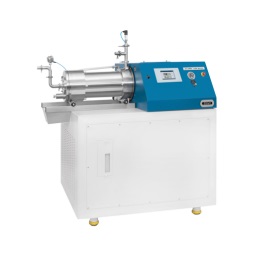
Ultrafine bead mill for battery materials
To facilitate the attainment of ultrafine particles and enhance electrode proper...
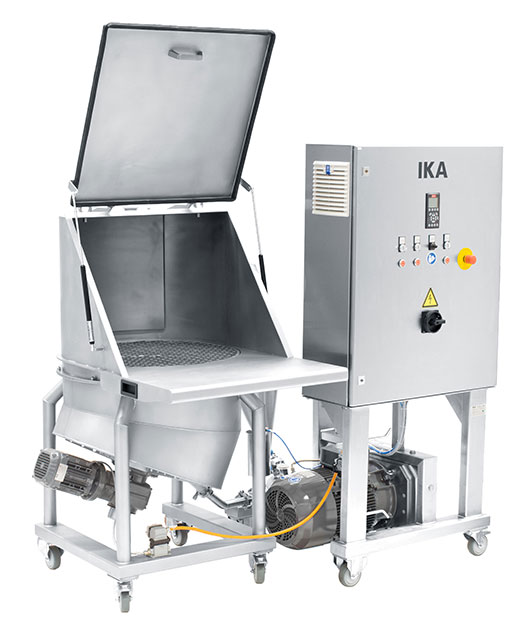
Inline solid-liquid mixer for battery production
In battery production, a critical phase entails mixing solids with liquid...
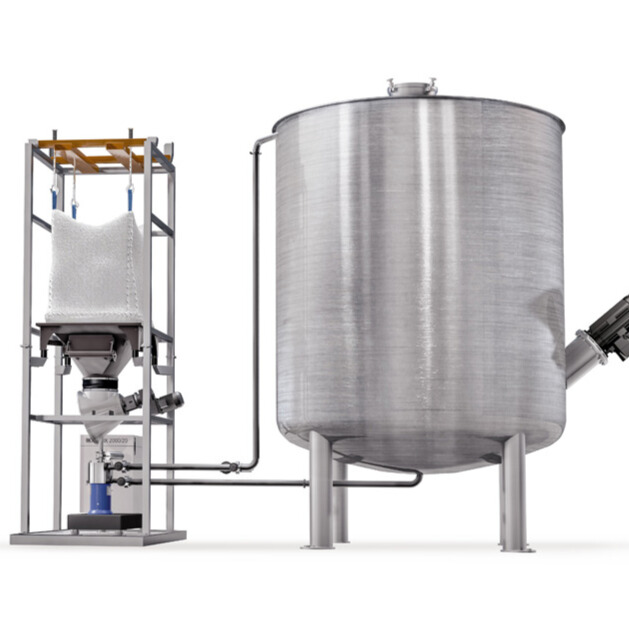
Inline solid-liquid mixer for chemicals and paints
Incorporating solids into liquids is a critical process in producing p...
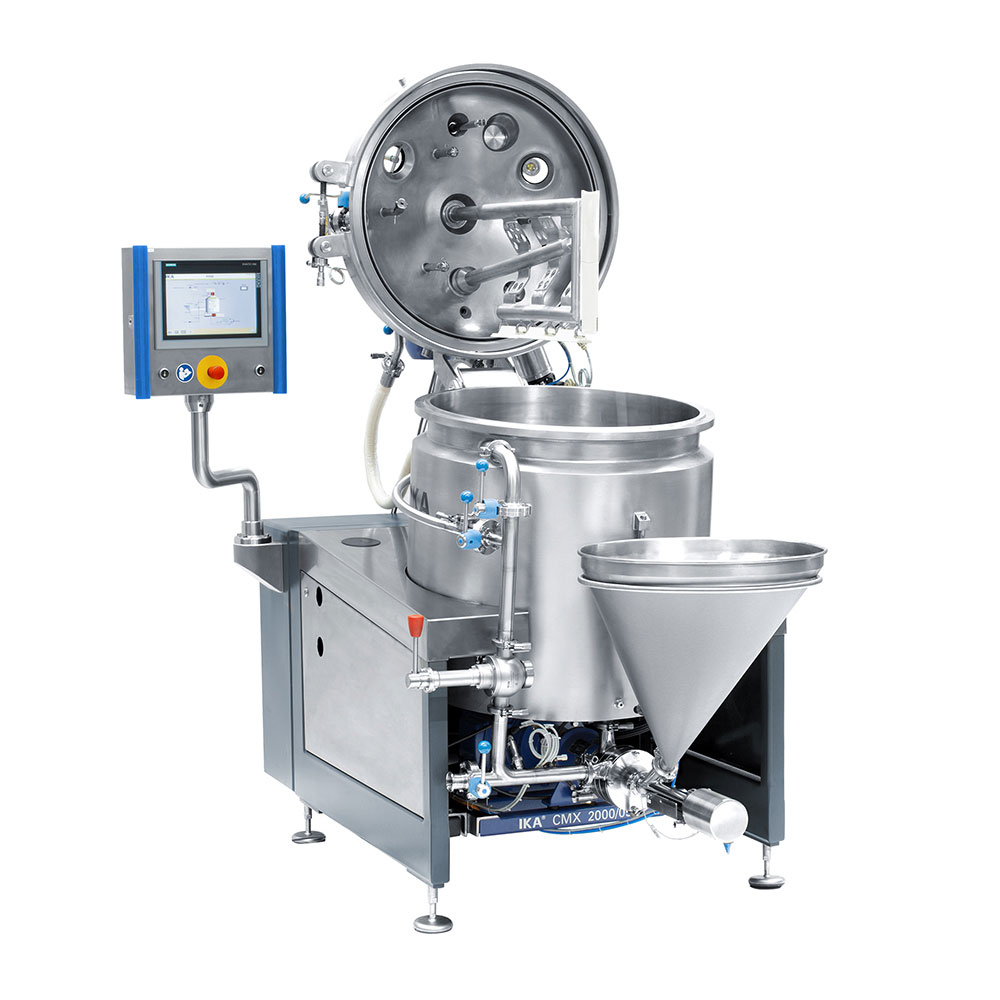
Compact Mixing Plant for Paints and Coatings
A smooth finish in paints and coatings depends on the grade of dispersal duri...
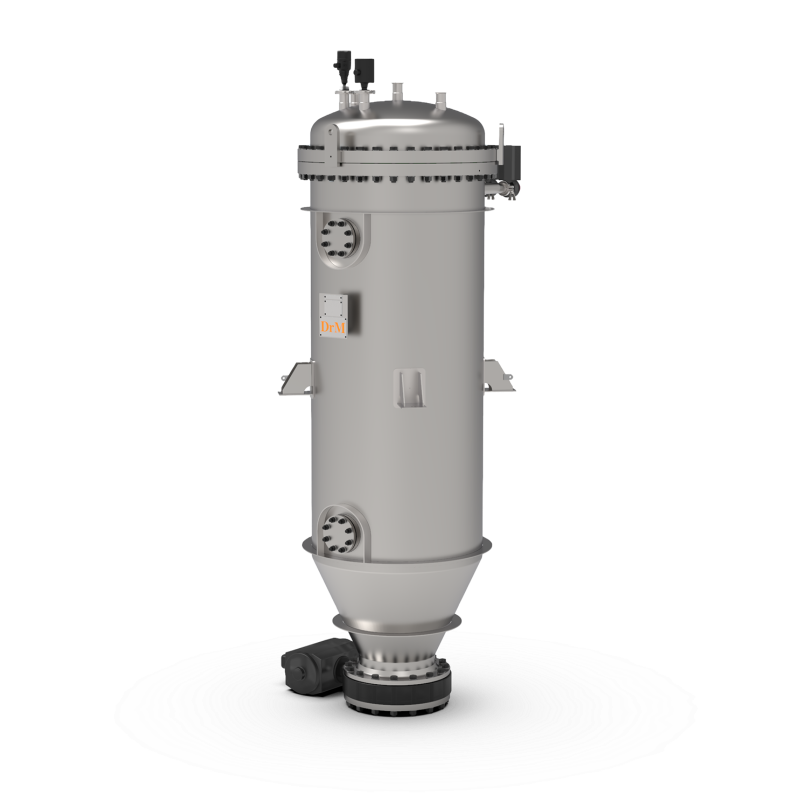
Self-cleaning candle filtration system
Separating solids from liquids by filtration requires frequent cleaning or replaceme...
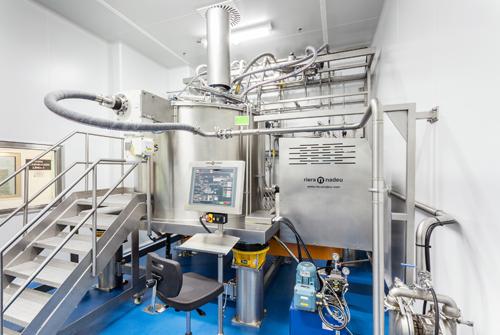
Automatic centrifuge for lithium carbonate
The battery industry requires high purity components. To obtain more than 99.5%...
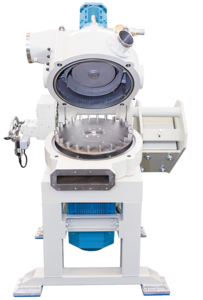
Classifier mill for powder coating
High-quality powder coatings are often required to manufacture equipment, appliances, an...

Open mouth bag filling machine for powders
The packaging of powdery products such as flour can be challenging as it is cru...
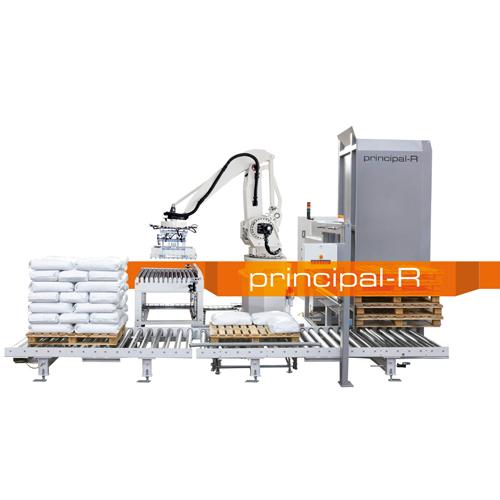
Robot palletizing system
If you are a relatively large-scale producer, packing and transporting large quantities of products ...
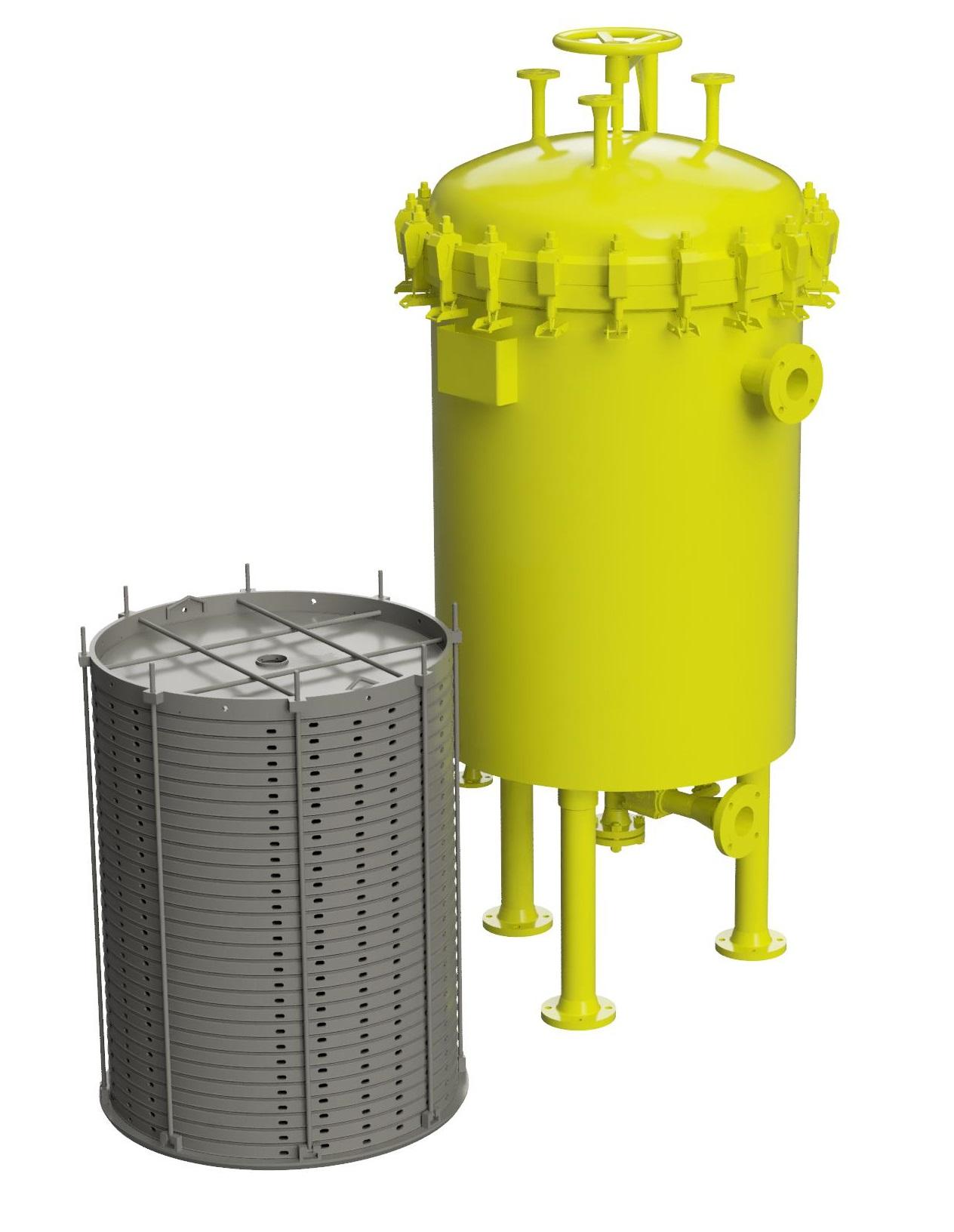
Industrial liquid filtration system
Systems for the filtration of liquids with suspended solid contents can be challenging ...
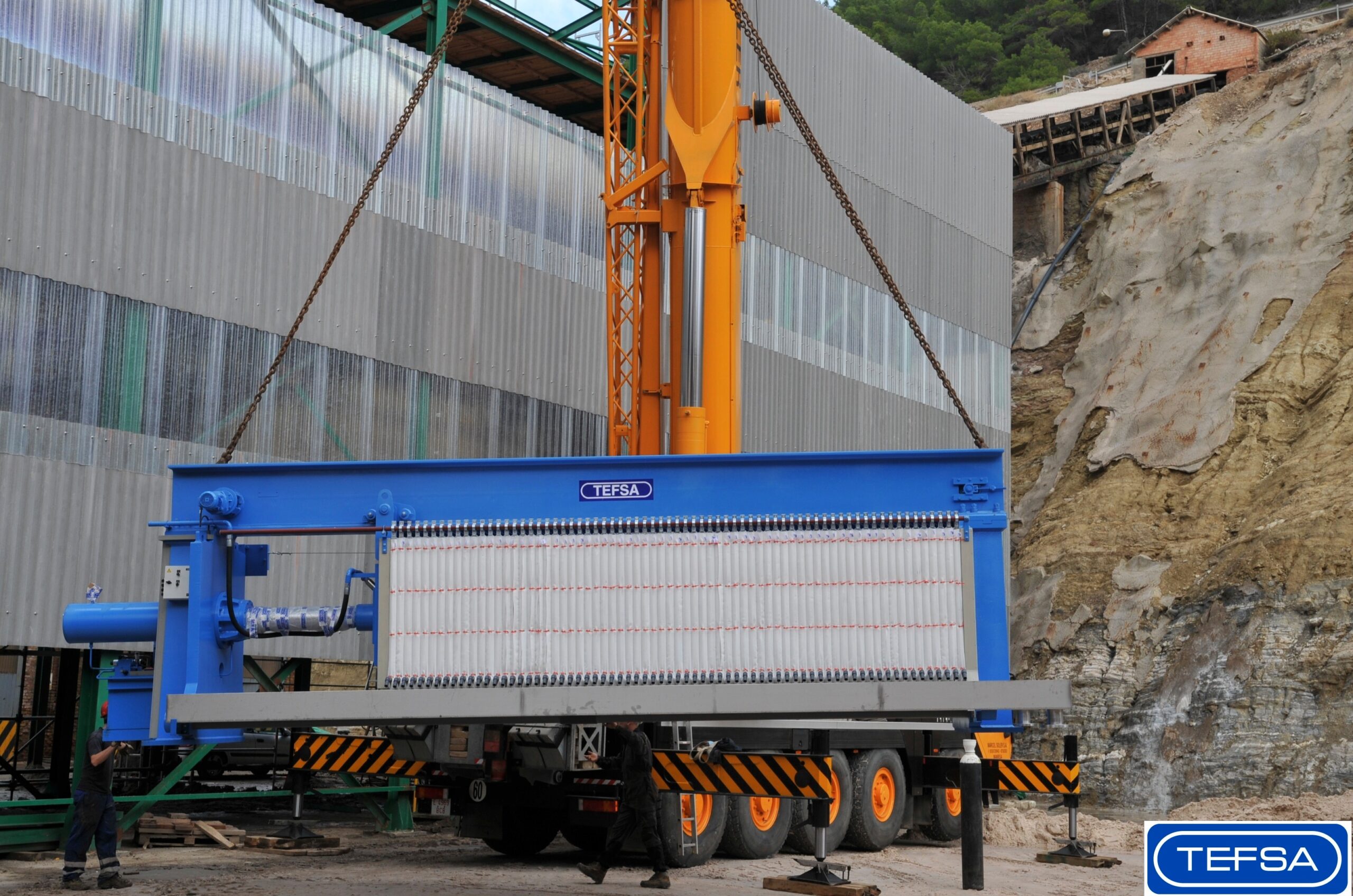
High yield filter press
When a saturated slurry or sludge must be dehydrated with high yield results mining and other heavy i...
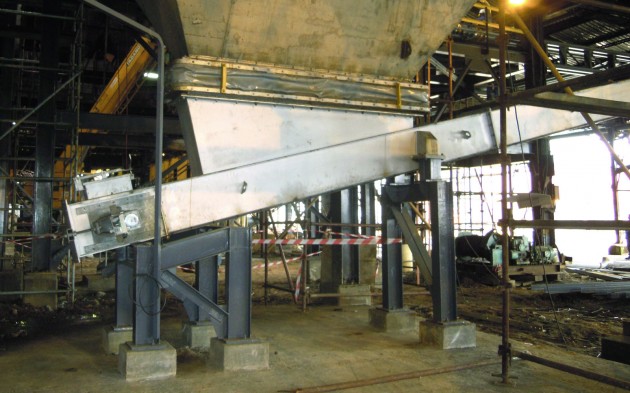
Dust and concentrate handling in smelting plants
Modern metal smelting operations involve extremely harsh conditions that ...

Circuit-air classifier
For high throughputs, with a fineness range of approx. d97 = 32 µm – 200 µm. Ideal for use in th...
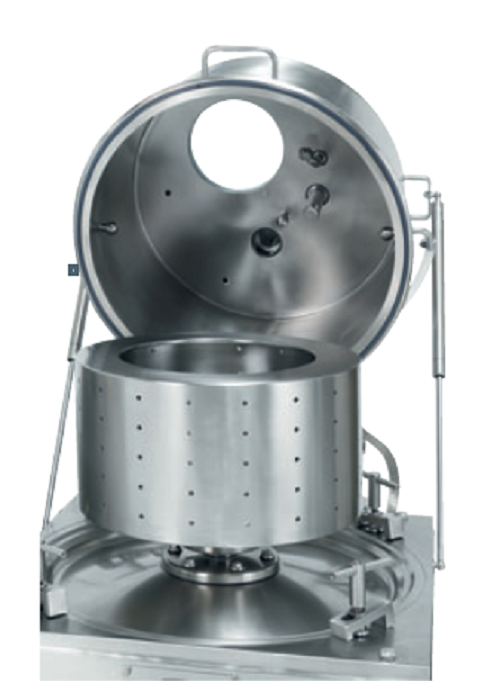
Isolator centrifuge
For transferring highly active pharmaceutical ingredients (HAPI) without contamination from the isolator ...