Industrial sigma mixer extruder for homogeneous mixing and extrusion
Achieve precise mixing and seamless extrusion of diverse materials with a robust tool designed for high-shear processes, enabling consistent product quality while integrating efficiently into both batch and continuous production lines.
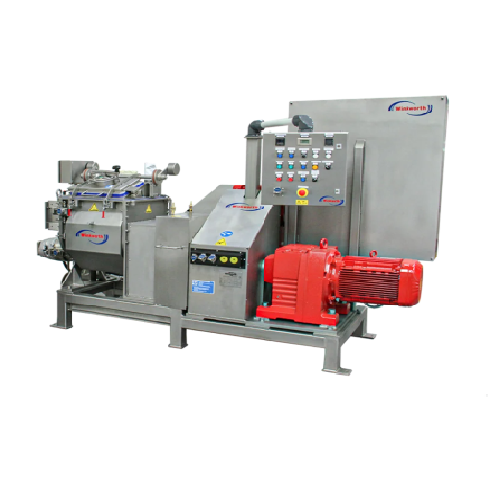
Mixes, Extrudes, and Homogenizes Industrial Materials
The ZX Sigma Mixer Extruder from Winkworth is engineered to elevate your production capabilities. It features twin Z-sigma blades and an extrusion screw at the heart of its mixing process, designed for optimal shearing and extrusion, making it a standout choice for complex materials and processes. With applications spanning adhesives, confectionery, pharmaceuticals, and ceramics, it can handle everything from epoxy adhesives to protein powders. Offering flexible volumes from 2 to 1800 liters, it seamlessly fits into batch or continuous operations with ease.
Equipped with options like a heating/cooling jacket and vacuum models for drying or de-aerating, this mixer ensures consistent quality through precise thermal management. Energy efficiency is highlighted by its energy-efficient drives, which minimize consumption through enhanced motor control. Constructed from robust stainless steel with customizable coating and finish options, it’s built to resist high-wear applications.
Automation is facilitated via a user-friendly HMI control panel, supporting recipe control and machine data storage for streamlined operations. Compliance with ATEX certification and options for GMP standards make this equipment adaptable across various regulatory environments. Maintenance is simplified with features like split gland shaft packing and easy-clean hinged endplates, reducing downtime and maximizing productivity. With customization options for rotor speeds and chamber configurations, Winkworth offers tailored engineering support to suit your specific production line needs.
Benefits
- Enhances production efficiency with reliable mixing and extrusion for consistent product quality.
- Lowers energy costs through optimized motor control and energy-efficient design.
- Versatile material compatibility ensures suitability across multiple industries, including food, pharmaceuticals, and plastics.
- User-friendly HMI controls reduce training cost and effort, simplifying operation and oversight.
- Customizable configurations allow seamless integration into existing production lines, enhancing flexibility.
- Applications
- Vitamins, Sealants, Biscuit dough, Sauces, Plastic injection moulding, Metal injection moulding, Ceramic injection moulding, Sports nutrition, Minerals, Chocolate, Chemicals, Dyes, Soups, Batteries, Chewing gum, Rubber, Ceramics, Ready meals, Protein powders, Inks, Animal feeds, Household products, Pet foods, Pharmaceutical products, Paints, Creams, Biofuels, Medical ointments, Nutraceuticals, Confectionery, Food and beverages, Adhesives
- End products
- Silicone sealant, Hydrocortisone ointment, Black printer ink, Neoprene gaskets, Polyethylene containers, Lasagna sheets, Mushroom soup, Dishwasher detergent, Multivitamin tablets, Whey protein isolate, Liquorice candies, Shortbread dough, Detergent chemicals, Dog kibbles, Metal valve bodies, Porcelain tiles, Watercolor paints, Red textile dye, Ceramic phone parts, Calcium supplements, Cat treats, Moisturizing cream, Milk chocolate bars, Biodiesel blend, Bubblegum base, Cough syrup, Fish oil capsules, Lithium-ion cell paste, Epoxy adhesive, Energy bars, Tomato ketchup
- Steps before
- Mixing, Formulation, Material Selection, Grinding
- Steps after
- Extrusion, Pelletizing, Drying, Packing, Integration into Production Line
- Input ingredients
- adhesives, sealants, biscuit dough, cake mix, chewing gum, chocolate, ceramics, ceramic injection moulding, metal injection moulding, insulators, agrichemicals, paints, inks, dyes, household products, waxes, carbon, metal powders, explosives, lubricants, biofuels, chalk, crayons, animal feeds, pet foods, tea, coffee, cream, milk, yogurt, cheese, cereals, butter, margarine, fats, lards, granules, herbs, spices, powders, jams, preserves, seasonings, sauces, chutneys, ready meals, soups, stews, baby food, meat analogue, edible oils, snack foods, dental products, shampoo, conditioner, nail varnish, creams, lotions, deodorants, fragrances, biotechnology, medical ointments, plastic injection moulding, plastics, rubber, urethanes, vitamins, minerals, protein powders, probiotics, nutritional energy bars, sports nutrition
- Output ingredients
- pelletized products, extruded products, dried products, homogeneously mixed products
- Market info
- Winkworth is known for manufacturing high-quality, engineered-to-order industrial mixing equipment, including mixers and blenders, renowned for their reliability and innovation in the pharmaceutical, food, and chemical industries.
- Material of construction
- 304/316 grade stainless steel
- Size
- Working volumes ranging from 2 to 1800 litres
- Mixing mechanism
- Twin Z-sigma blades
- Extrusion mechanism
- Extrusion screw
- Automation
- HMI control panel
- Shear capability
- Highest shear forces
- Die plate arrangement
- Customizable
- Heating/cooling jacket
- Optional
- Construction type
- Fully welded
- Outlet valve
- Flush fitting (bomb door) optional
- Operation mode
- Manual push-button control
- Vacuum capability
- Optional for drying or de-aerating
- ATEX certification
- Available
- Surface finish
- Polished/bead blasted/mill finish
- Automation level
- Manual / Push-button Control / HMI Touchscreen
- Batch vs. continuous operation
- Batch / Inline Continuous
- Cleaning method
- Manual / Option for Cleanability Enhancements
- Energy efficiency
- Energy-efficient Drives with Heater Control
- Integration capability
- Inlet and Outlet Options for Production Line Integration
- Mixing mechanism
- Twin Z-sigma Blades and Extrusion Screw
- Process flexibility
- Reverse Operation for Homogeneous Mixing / Ram Extrusion System
- Product handling
- Special Hardened Steels and Coatings for High-Wear Applications
- Product sensitivity accommodation
- Option for Vacuum Models for Drying or De-aerating
- Abrasion resistance
- High
- Biological compatibility
- Yes
- Cleanability
- Easy clean
- Corrosive resistance (e.g. acids)
- Yes
- Density/particle size
- Customizable
- Tank Shape
- Z-sigma blades configuration
- Feed/Discharge Method
- Inlet and outlet options for line integration
- Construction Material
- Stainless steel
- Special Finishes
- Polished, bead blasted, or mill finish
- Control Panel Type
- Push-button or HMI touchscreen
- Die Plate Arrangement
- Customizable for pelletizing, drying, extrusion
- Blade Type
- Curved masticator blades available
- Discharge Method
- Flush fitting outlet valve (bomb door) optional
- Screw Configuration
- Extrusion screw at mixing chamber base
- Container Size
- Working volumes 2 to 1800 liters
- Split gland shaft packing
- Yes
- Energy efficient drives
- Available