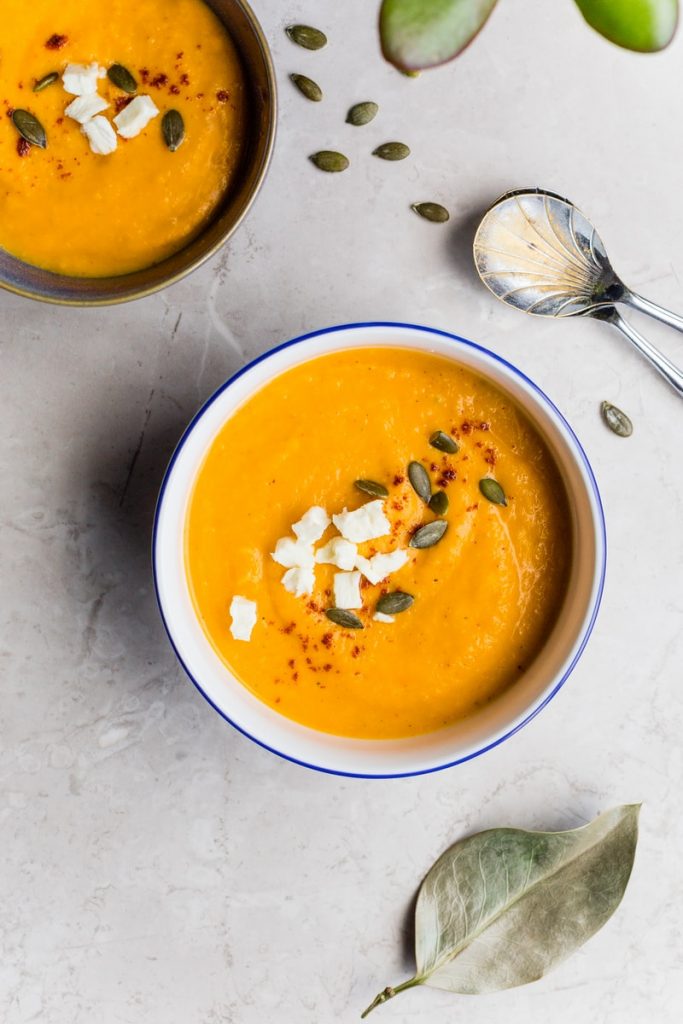
Soup Manufacturing Equipment
Find innovative soup equipment and connect directly with world-leading technology suppliers
Industrially manufactured soups gained traction in the 19th century when canning was invented and they have been warming us ever since. Whether it’s a classic ready-to-eat canned soup, condensed soup or a dry soup mix, soup manufacturing equipment for mixing, cooking, boiling, or sterilizing caters to every manufacturer’s production requirements.
Innovative solutions for making soup
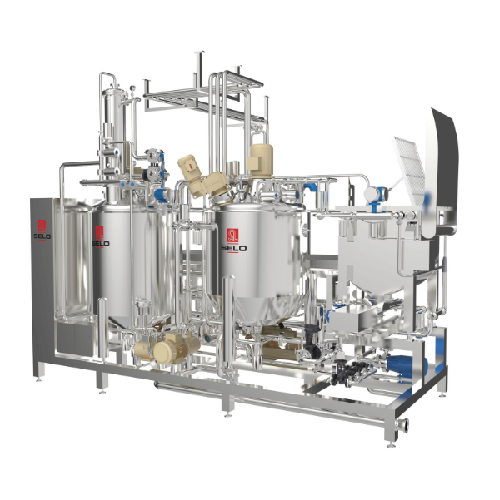
Automated soup production line
Transform your soup production with a high-efficiency, fully automated line, seamlessly integ...
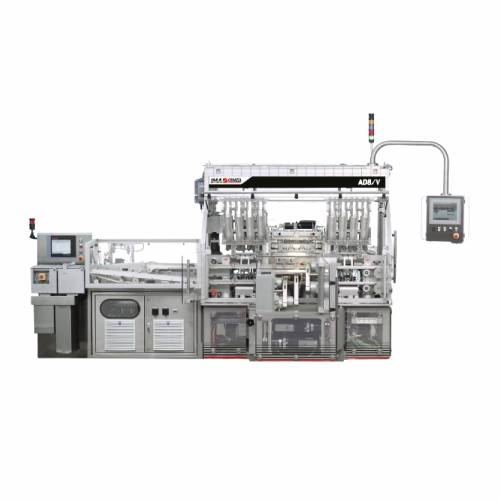
Cartoning solution for soup cubes
Optimize your soup cube packaging process with a compact, high-speed wrap-around solution...
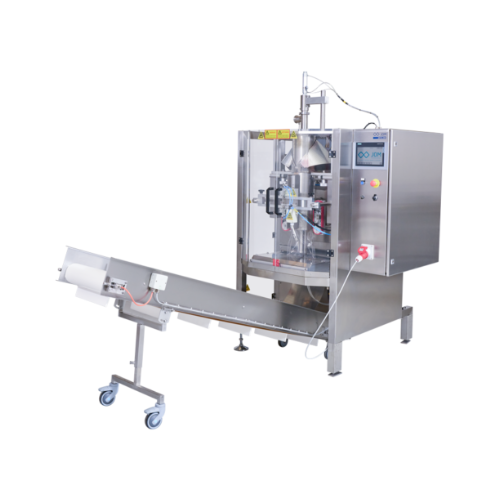
Automatic hot-fill dosing system for soups and sauces
Ensure consistent portioning and minimize occupational risks when h...
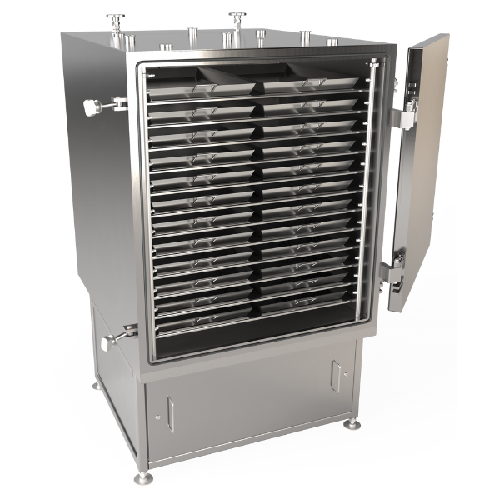
Continuous heat exchanger for soups and sauces
Optimize your soup and sauce production with a continuous heat exchanger th...
Select your soup process
Tell us about your production challenge
Different soups – different soup making equipment
Soups consist of various vegetables- potatoes, tomatoes, pumpkins, mushrooms, carrots and sometimes even dairy – all of which require different steps. In order to make soup, all ingredients must be properly cleaned, peeled, chopped and sliced into smaller pieces for optimal food processing.
As different vegetables are used and different soup recipes are formulated, changes must be made in the soup production line to include different equipment for pre-treating the vegetables. Potatoes and carrots must be peeled, while tomatoes are blanched to remove their bitter flavonols-rich skins.
After the ingredients are prepared, manufacturers can use different cooking techniques and soup making equipment like blanchers, steamers, stockpots immersion blenders and slow cookers, among others.
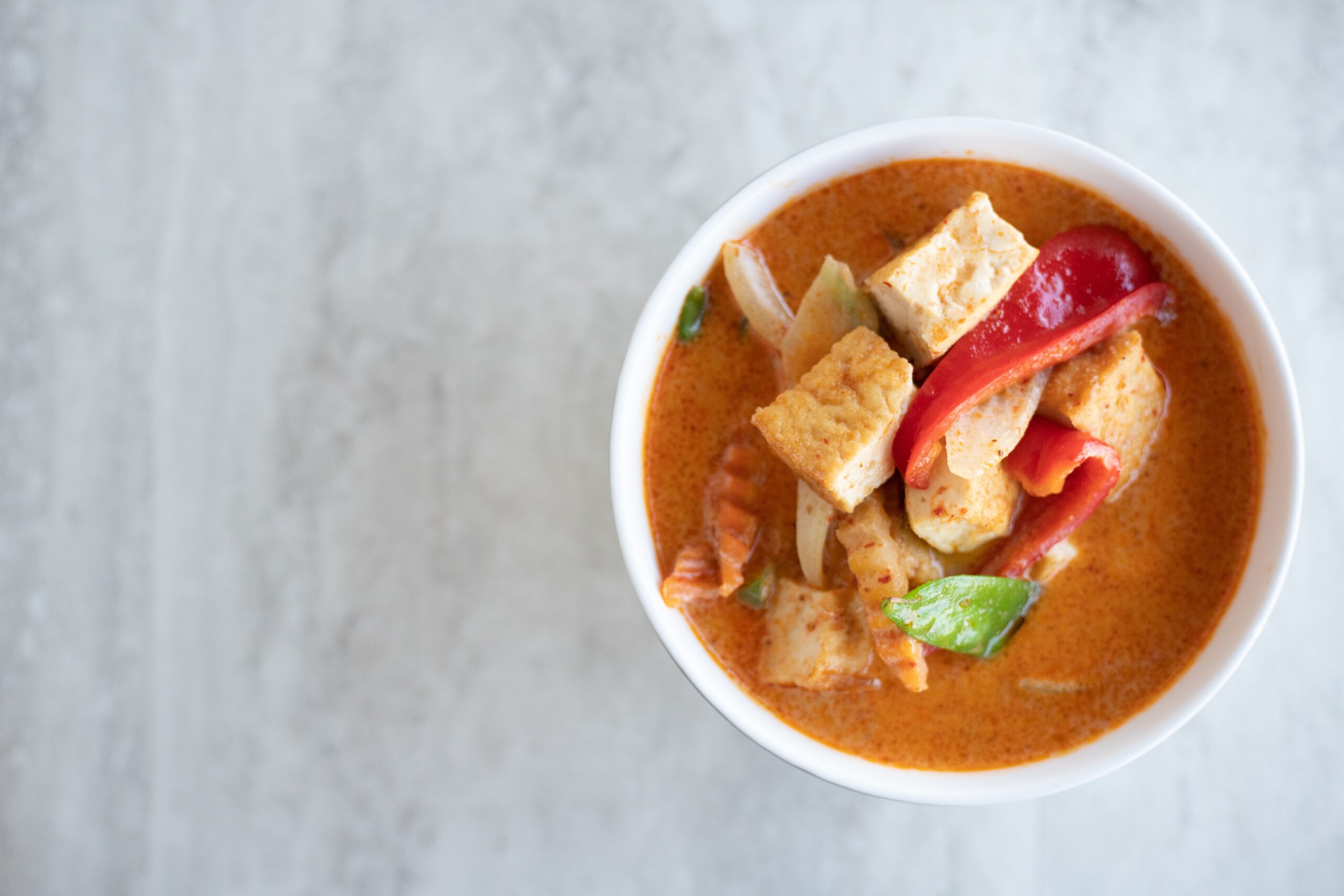
During blanching, vegetables are immersed in boiling water or steam before enzymes are deactivated. Some vegetables like eggplants need particular attention because they are sensitive to post-cooking browning. The problem can be avoided by adding antioxidants during blanching.
Soup can be further processed, depending on whether you are making ready-to-eat or dry mix soup. Ready-to-eat soup is deaerated to prevent oxidation and changes in color, while dry mix soup’s ingredients are dehydrated so they can be reconstituted with boiling water at a later date.
How does thermal processing affect vegetables?
Vegetables must undergo an industrial thermal process before being consumed. Heat treatment definitely brings benefits such as increased protective compounds, but it can also cause color degradation and losses of nutritional and soluble compounds (sugars and soluble fibers). Whether these conditions occur or not depends both on the characteristics of the vegetable to be processed such as enzymes or oxygen concentration and on the severity of the heat treatment.
For example, it has been determined that steaming reduces the loss of fat-soluble nutrients better than boiling. Instead, a study conducted by the Institute of Nutrition at Mahidol University in Thailand showed low losses in the vegetable’s β-carotene content when blanching, only 7-11%, while steaming, frying and boiling showed greater losses, 15, 18 and 43%.
To pasteurize or to sterilize?
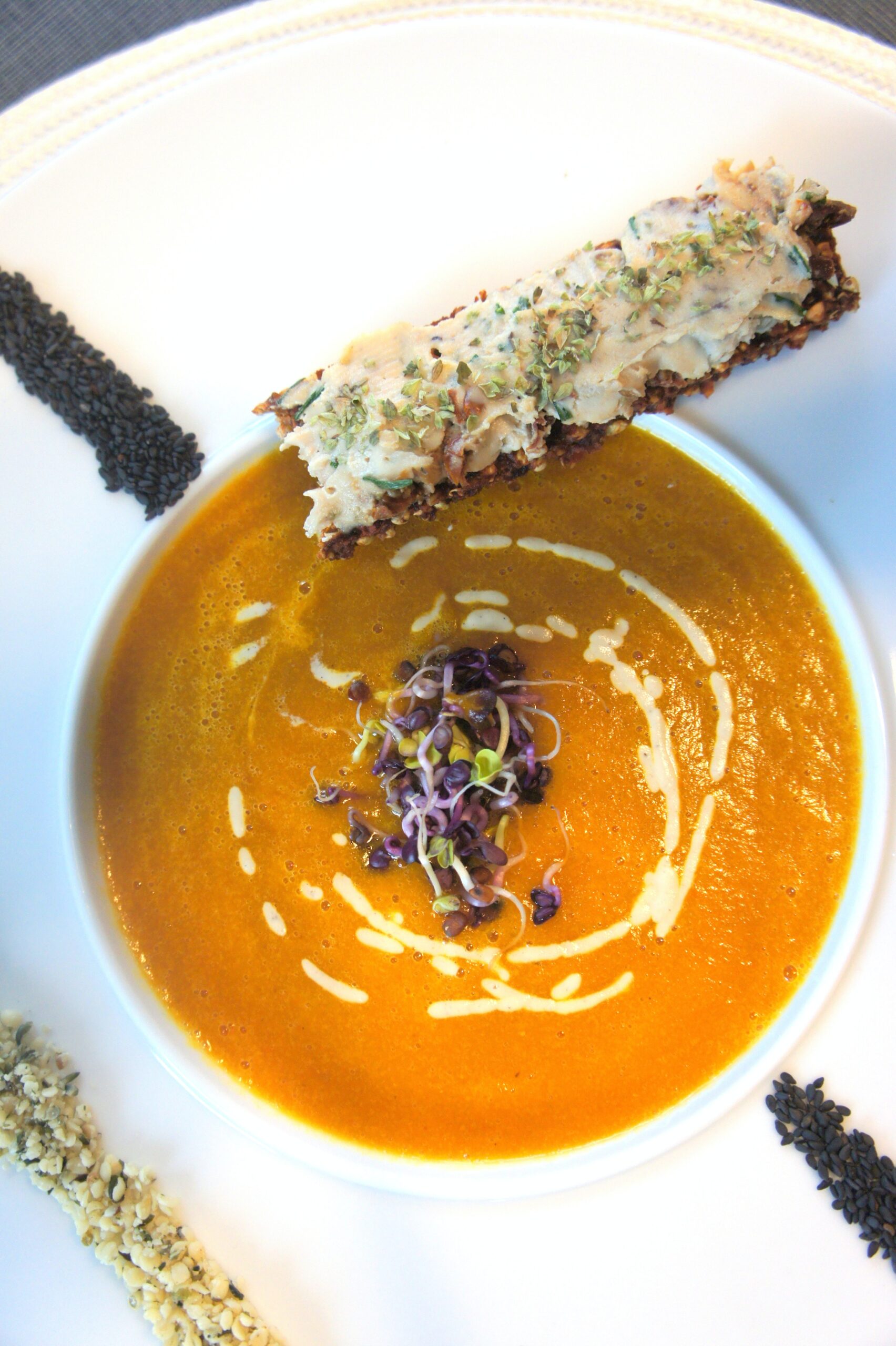
There are two methods of removing microorganisms in the soup manufacturing process: pasteurization and sterilization. The choice between the two depends on the pH of the soup– most meat and vegetable-based soups have low acidity and manufacturers can fully sterilize them. In this case, sterilization temperature are above 100 °C and the product is then cooled down and transferred into previously sterilized packaging.
If the soup’s pH is in the acid range, pasteurization is recommended. Different temperatures for pasteurization are required to complement the pH range, for example if the pH range is between 3.4 and 4.0, the recommended temperature is 85°C. If it falls between 4.3 and 4.5, the recommended temperature for pasteurization is 99°C.
Soup in cans, pouches and trays
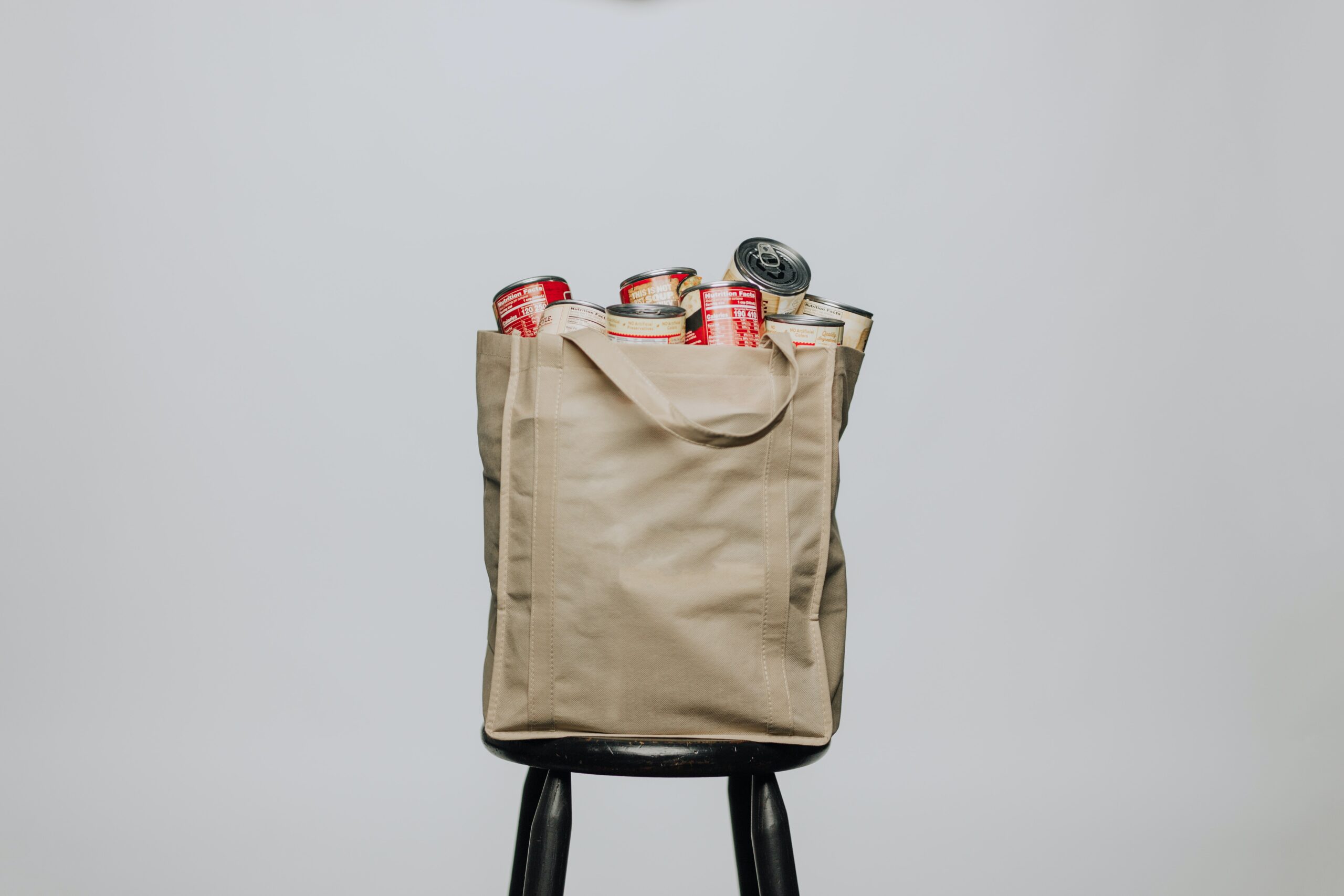
Canned soup is immensely popular owing to its versatile and recyclable packaging. After transferring the ready-to-eat soup into cans, can seamers ensure the product is sealed properly to prevent spoiling and spilling.
Since the invention of canning, soup’s packaging has evolved to plastic pouches that are re-sealable easy to use. High-speed stainless steel pouch packaging machines rapidly package liquid products into flexible pouches with great precision.
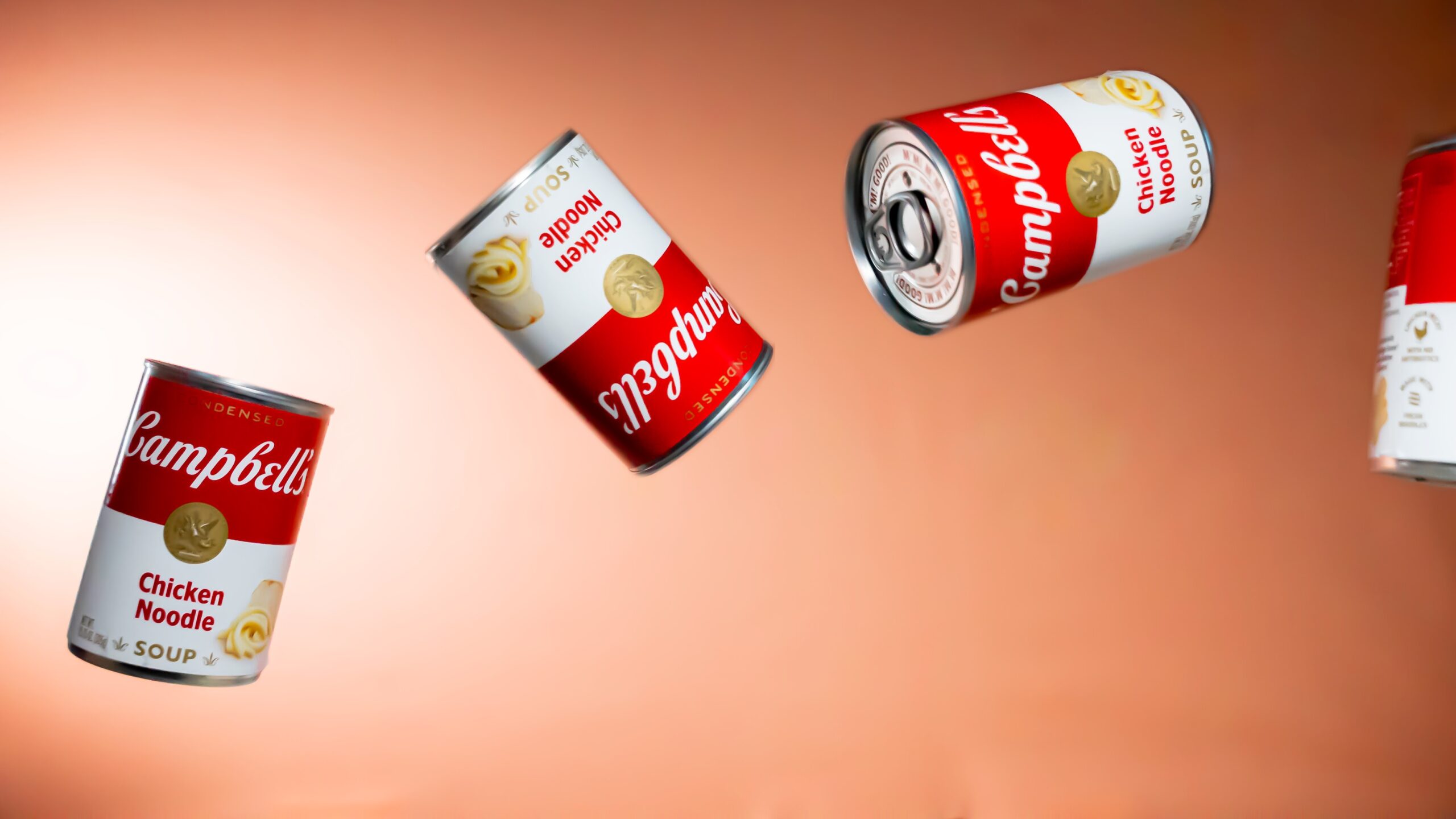
Soup trays are also gaining popularity because they can be frozen and microwaved, providing a single serving of soup. During the manufacturing process, trays are filled with soup and then sealed with tray sealers which secure the contents and prevent spillage.
Which soup technology do you need?
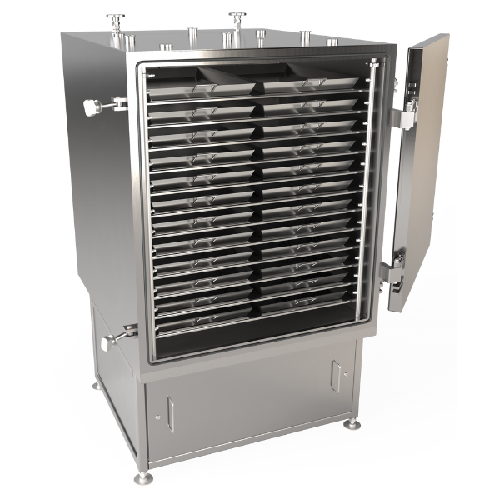
Continuous heat exchanger for soups and sauces
Optimize your soup and sauce production with a continuous heat exchanger th...
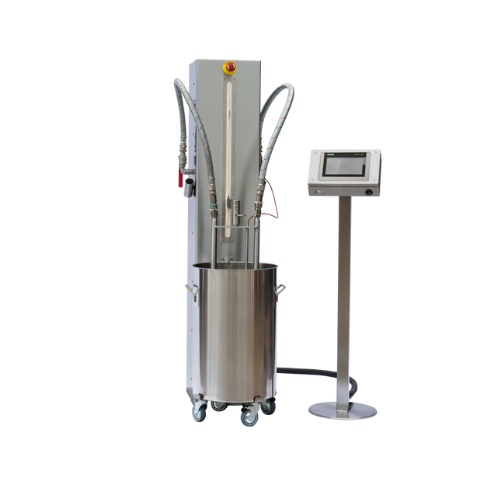
Soup and sauce chiller for rapid cooling
Reduce cooling time drastically and maintain quality with a chilling solution that...

Hot-fill dosing system for soups and sauces
Efficiently dose hot soups, sauces, and porridges while ensuring workplace saf...
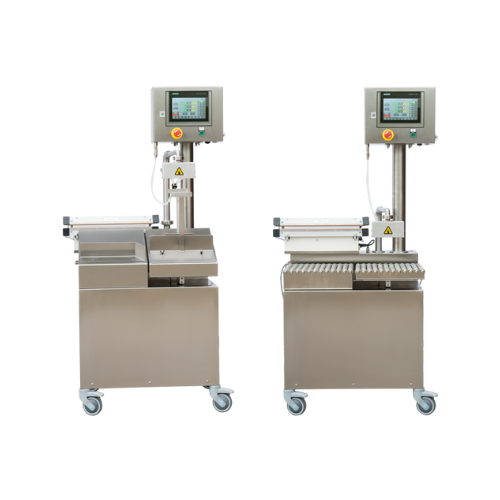
Hot-fill dosing system for soups and sauces
Ensure precise and efficient dosing of hot and cold liquid foods with integrat...
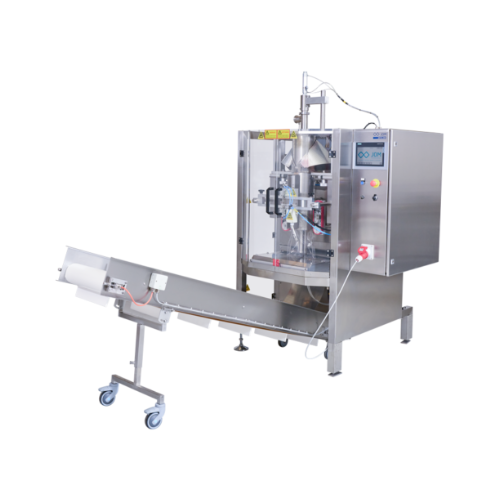
Automatic hot-fill dosing system for soups and sauces
Ensure consistent portioning and minimize occupational risks when h...
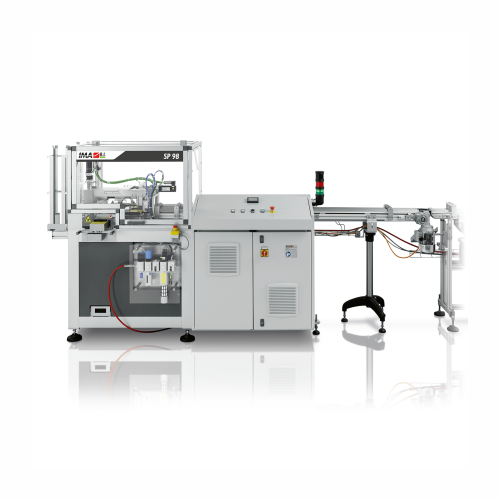
Semi-automatic tray packing for soup cubes
Effortlessly package soup cubes into organized, stratified layers, optimizing y...
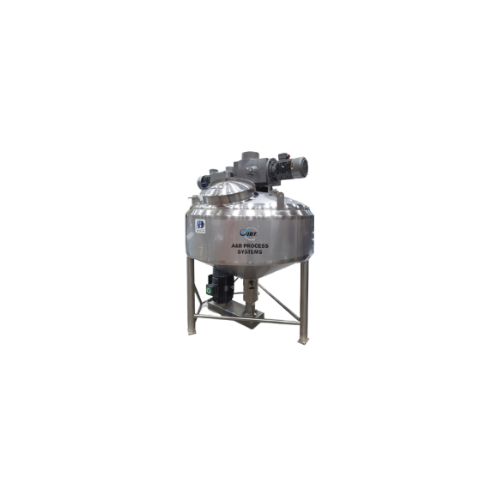
Mixing tank for soups, sauces, and dressings
Streamline your soup and sauce production with advanced mixing technology des...
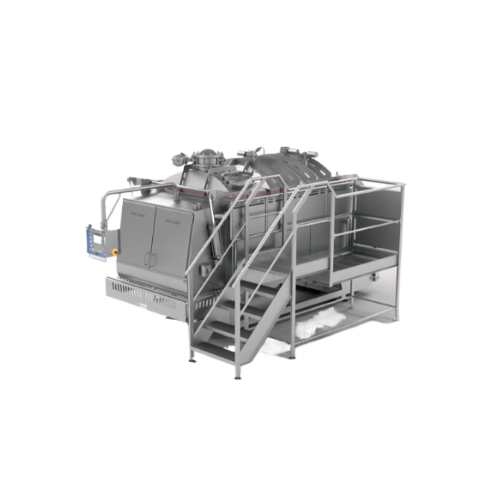
Industrial cooker for soups and ready meals
Streamline your cooking operations with a versatile system capable of mixing, ...
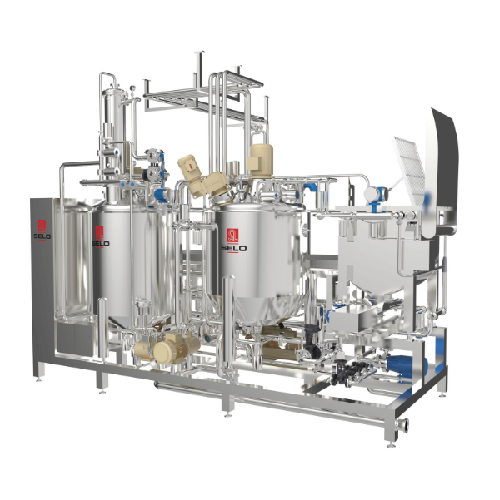
Automated soup production line
Transform your soup production with a high-efficiency, fully automated line, seamlessly integ...

Heat exchangers for efficient heat transfer in industry
Achieve precise temperature control across diverse viscosities wi...
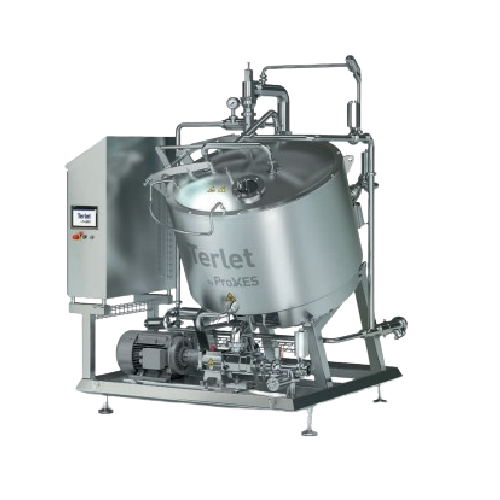
Precise liquid cooling solution for food processing
Ensure high-quality preservation of flavors and textures in liquid fo...
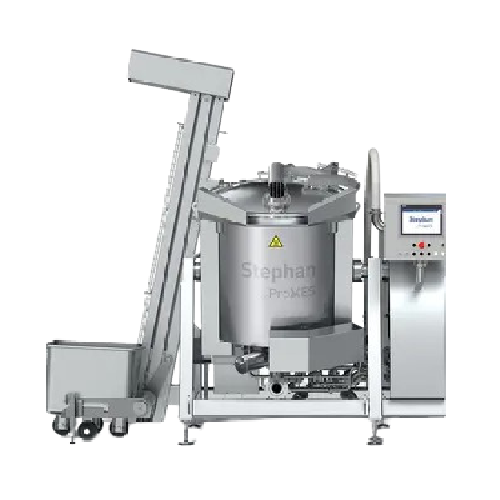
Industrial cooker for sauces and stews
When producing diverse culinary delights such as sauces and stews, achieving even he...
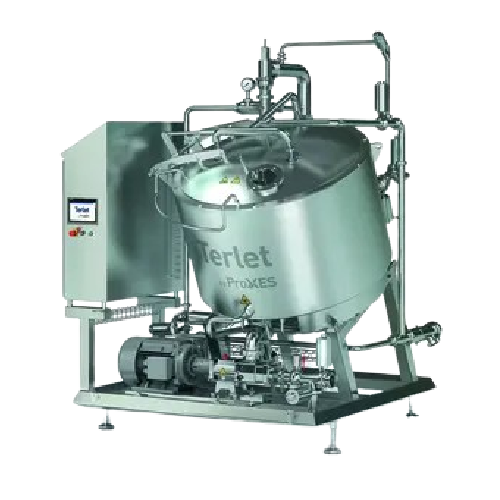
Efficient cooling and cooking systems for food processing
Streamline your production with integrated cooling and cooking...

Continuous tahina production line
Streamline your tahina production with precise grinding and controlled cooling, ensuring ...
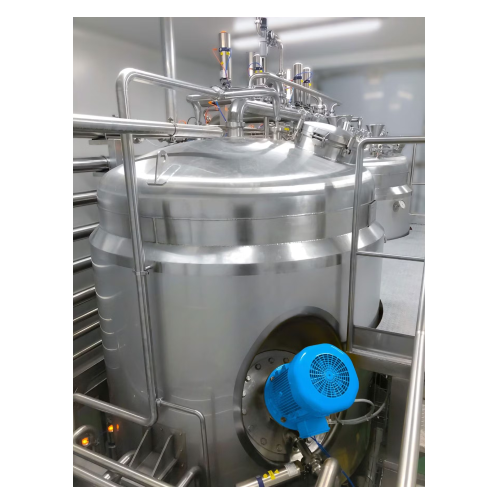
Industrial cooling vessel for ready meal components
Enhance your production with precise cooling and gentle handling of t...
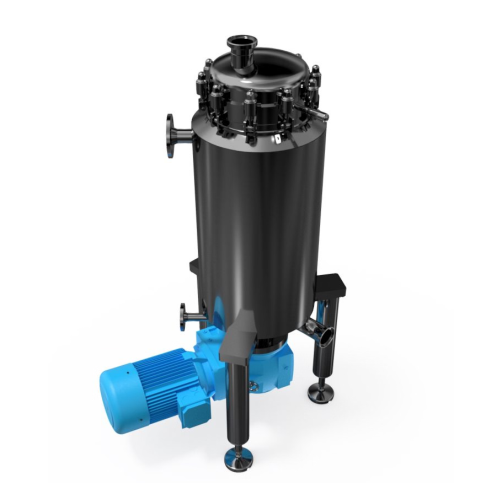
Scraped surface heat exchanger for food processing
Efficiently handle temperature-sensitive food products with a compact ...
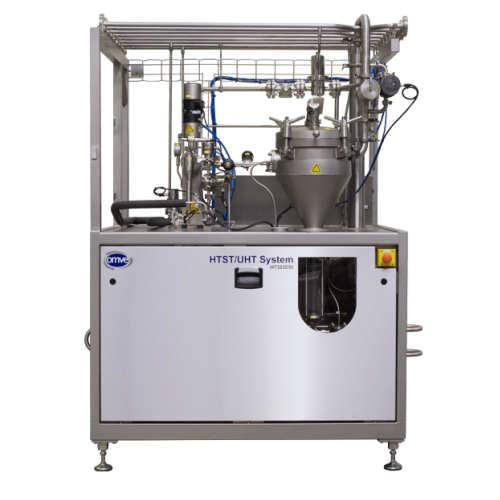
Laboratory in-line sterilization system
Ensure precise temperature control and rapid cooling for diverse liquid application...
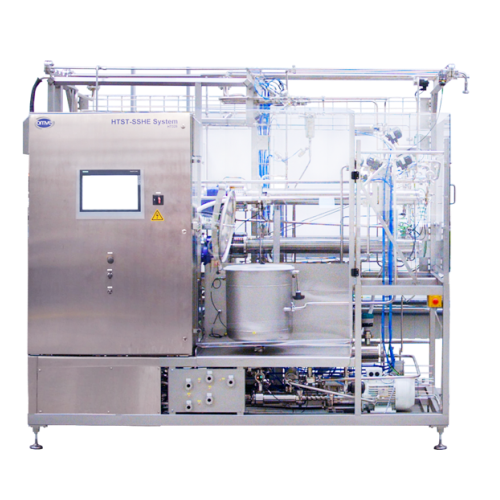
Pilot system for high-viscosity product processing
Efficiently handle high-viscosity or large particle products with this...
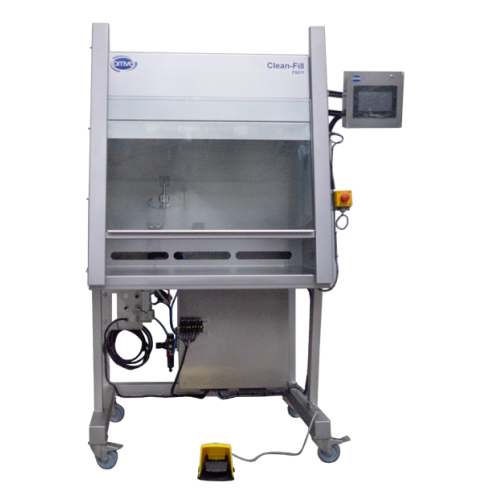
Sterile filling and closing bench for bottles and cups
Ensure precise and sterile filling for liquid products with a hygi...
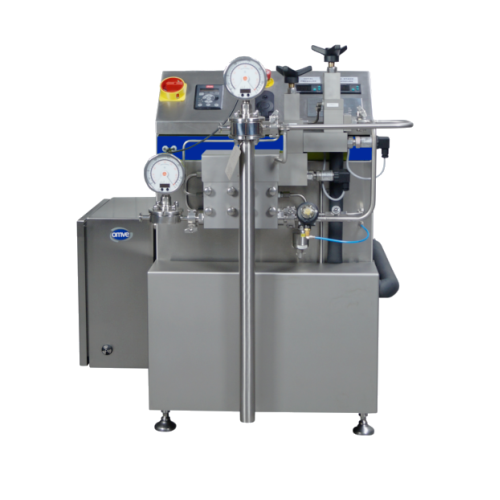
Pilot homogenizer for high-pressure inline homogenization
Achieve precise homogenization and emulsification across vario...
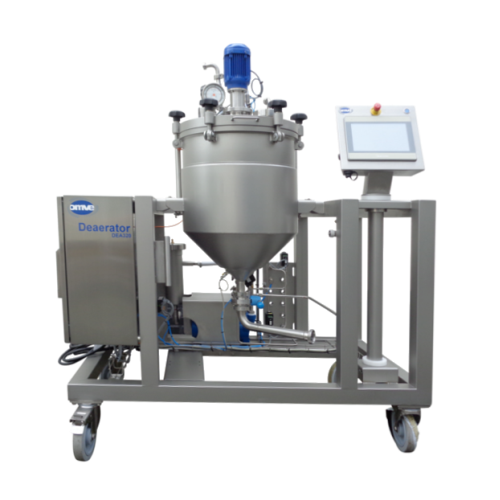
Batch deaerator for reduced oxidation in liquid processing
Optimize product shelf life and quality by efficiently removi...
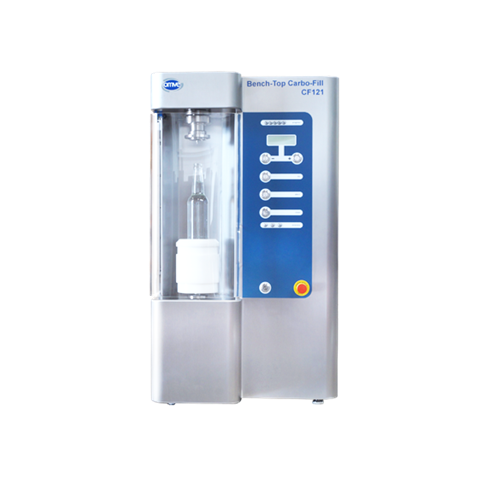
Bench-top carbonation system for postmix drink production
Achieve precise carbonation in small batches with a reliable b...
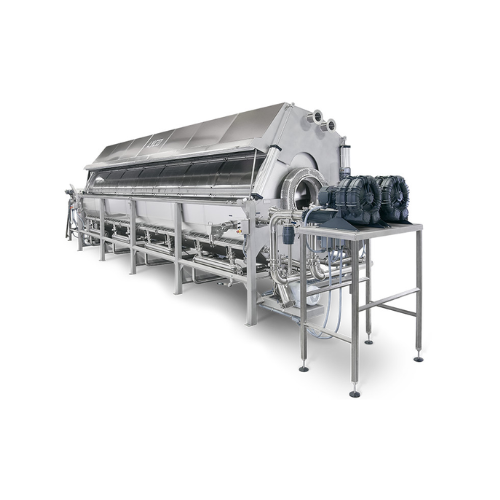
Pouch cooling system for food processing
Experience rapid cooling for your pouched food products, minimizing time in the ba...
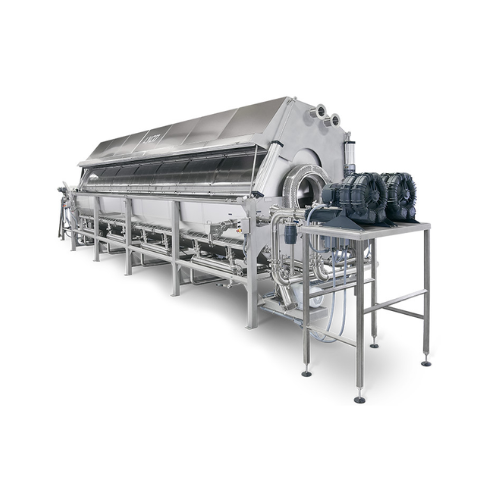
High-capacity pouch cooling system
Move pouched foods swiftly through critical temperature zones, ensuring rapid cooling fo...
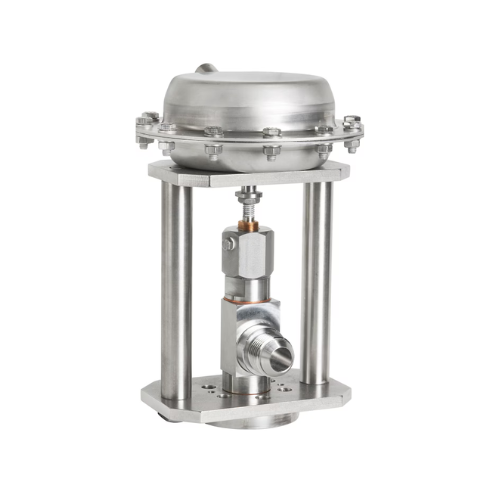
Cryogenic chilling systems for bulk food processing
Maintain optimal temperatures during high-volume food processing with...
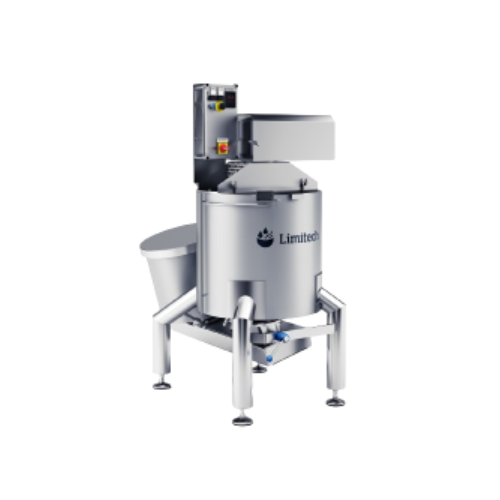
Industrial mixer for baby food and dairy production
Optimize your production line efficiency with a versatile mixing solu...
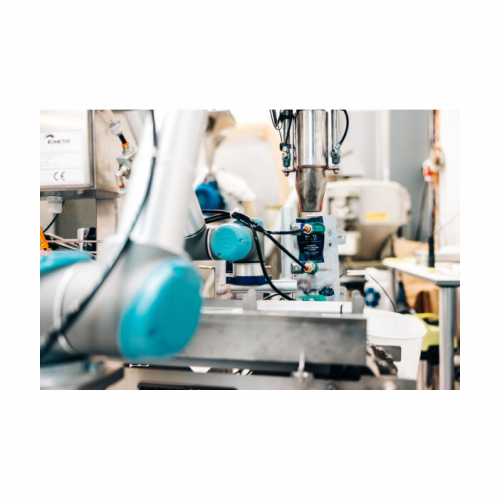
Dosing and tray handling lines for ready meals
Ensure precise dosing and seamless tray handling for a variety of ready mea...
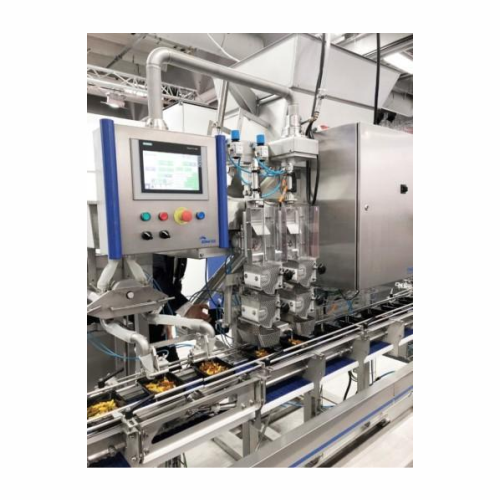
Food dosing systems for industrial applications
Optimize your food production efficiency by minimizing waste with precisio...
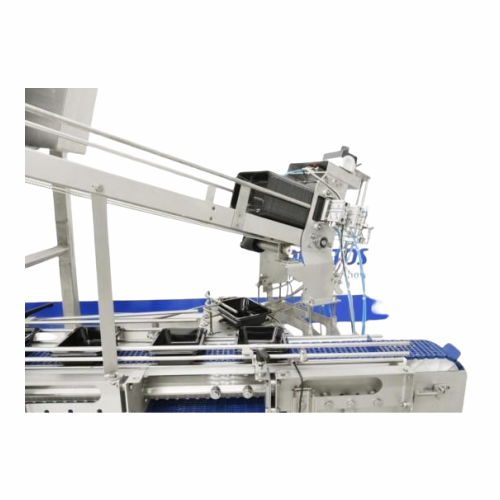
Tray handling equipment for food packaging
Optimize your food production with adaptable tray handling units that streamlin...
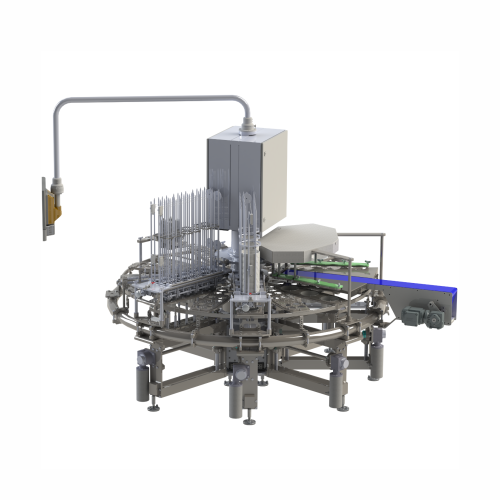
Rotary filling and sealing for liquid to pasty products
Boost production efficiency with a flexible rotary solution that ...
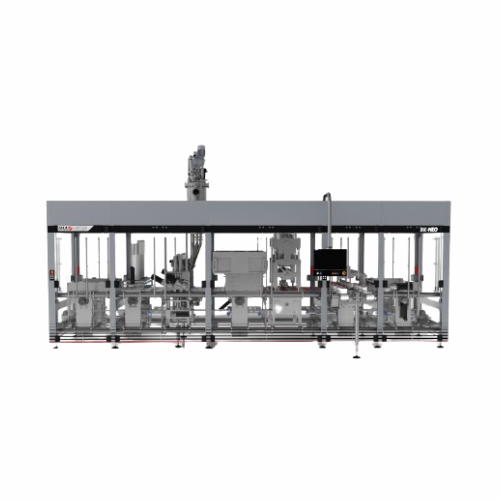
Filling and sealing system for pre-formed cups
Experience seamless integration of hygienic filling and sealing with adapta...
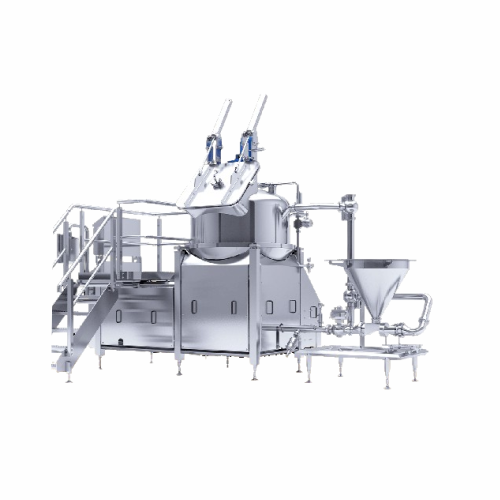
Lump-free emulsifier and steam batch cooker for processed cheese
Achieve consistent, lump-free processed cheese and crea...
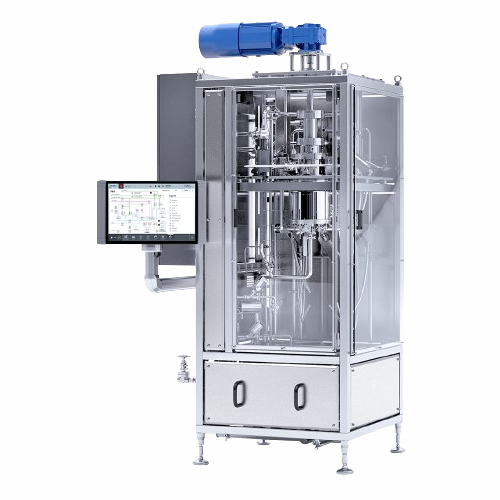
R&d scale steam cooker for small batch processing
Optimize your R&D with a steam cooker that replicates large-scale ...
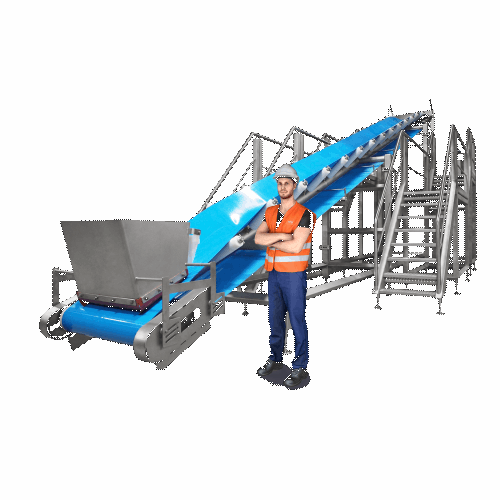
Hygienic conveyor belts for food manufacturing
Ensure bacteriological safety and boost productivity with hygienic conveyor...
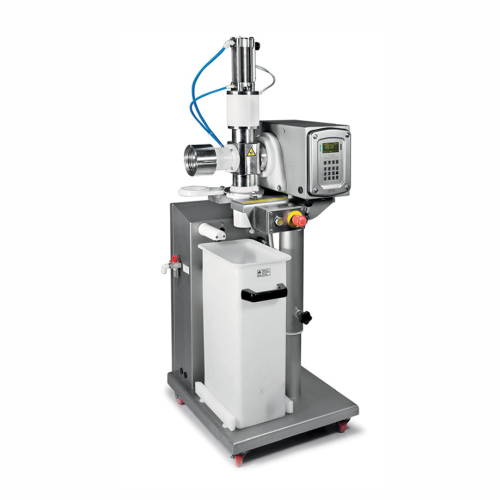
Pipeline metal detection for pumpable products
Ensure safety and quality by detecting and rejecting metal contaminants in ...
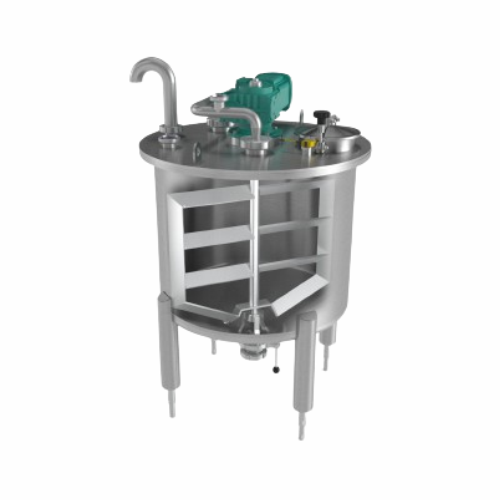
Stainless steel buffer tanks for food, pharma, and cosmetics
Ideal for maintaining process fluidity, these stainless ste...
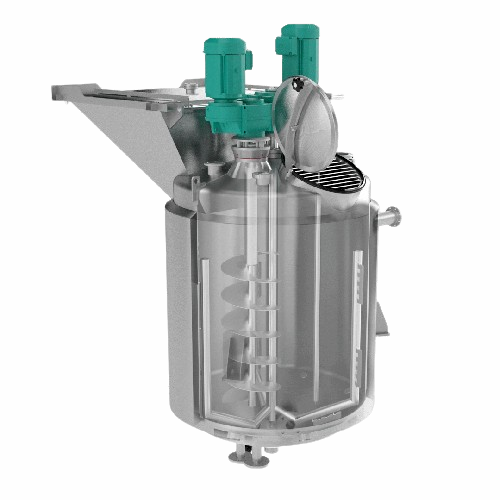
Stainless steel cooking kettle for food, pharma, and cosmetics
Efficiently streamline your production with versatile sta...
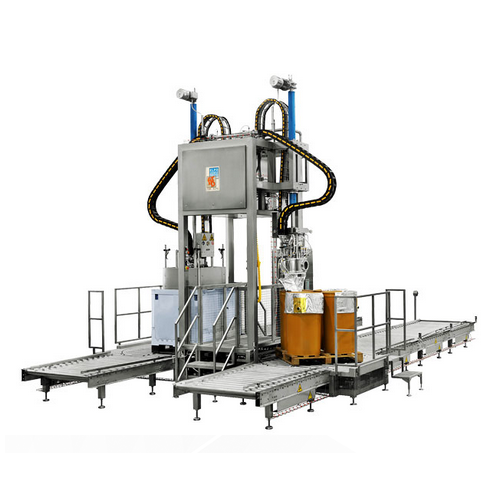
Aseptic filler for large bags
Ensure safe and sterile packaging of liquid and slurry products in large formats with this ase...
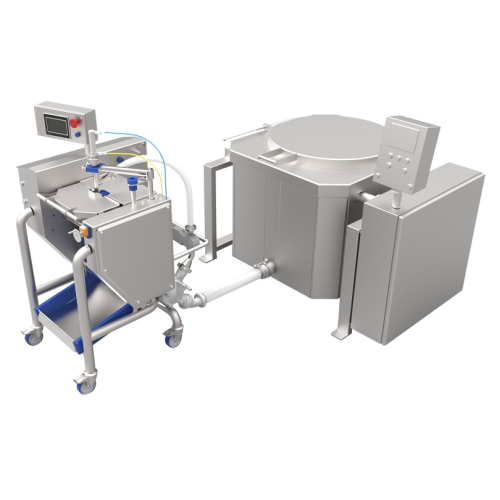
Production solutions for convenience foods
Effortlessly transform your innovative recipe ideas into consistent, high-quali...
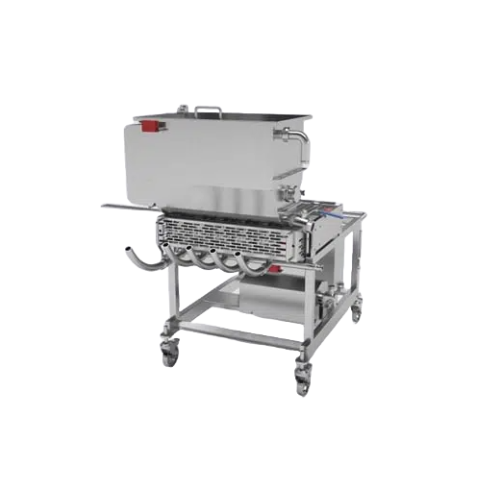
Automatic piston fillers for liquid products
Optimize your liquid filling process with high-precision piston fillers, engi...
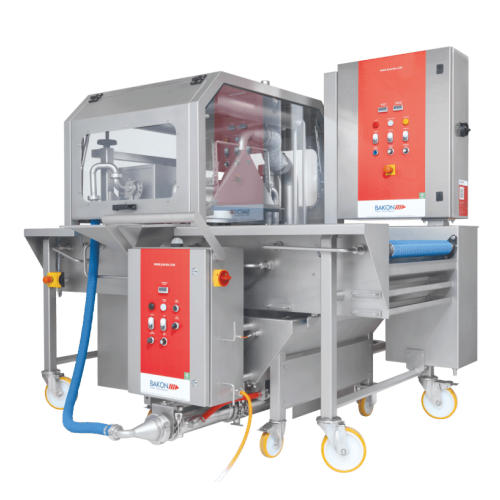
Ultrasonic cutter for pastry and bakery products
Achieve precise, high-quality cuts for your bakery and confectionery prod...
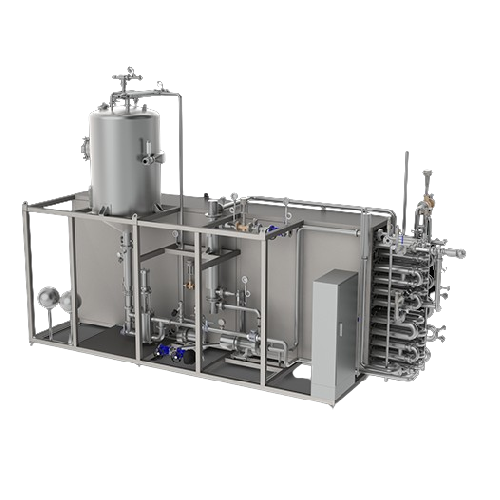
Sterilization for food and pharmaceutical processing lines
Ensure your liquid product’s sterility before productio...
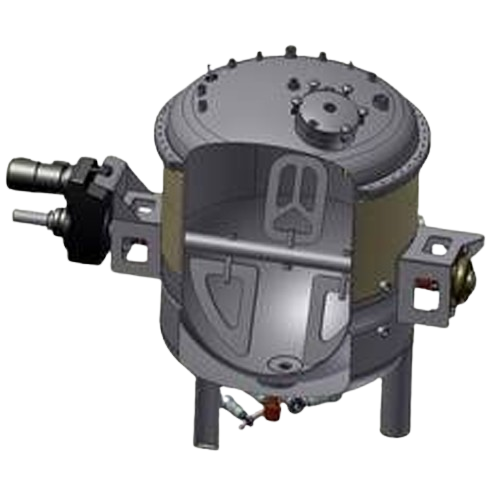
Vacuum cooker-cooler for jams and sauces
Optimize your food production with a vacuum cooker-cooler that enhances flavor whi...
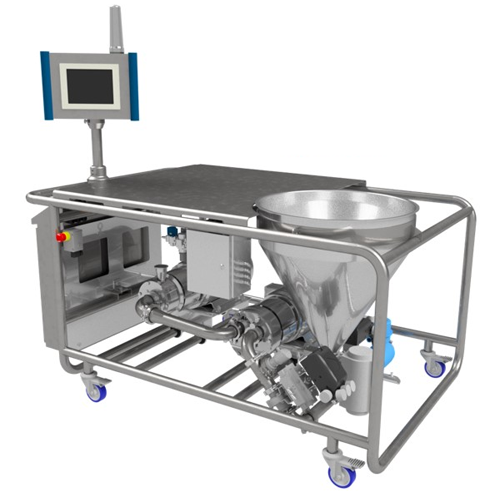
Automated powder induction and dispersion system for industrial mixing
Achieve rapid and efficient incorporation of pow...
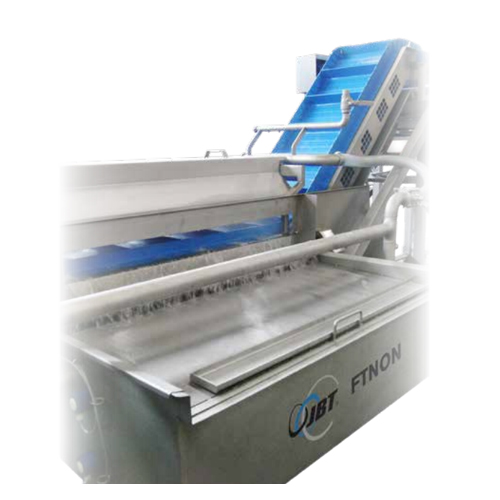
Multifunctional washer for fruits and vegetables
Achieve impeccable cleanliness in your food processing line with a versat...
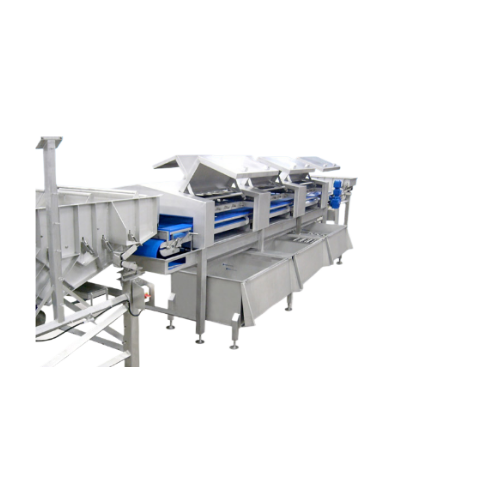
Industrial water belt cooler for fresh produce
Ensure consistent cooling for various food products with a system designed ...
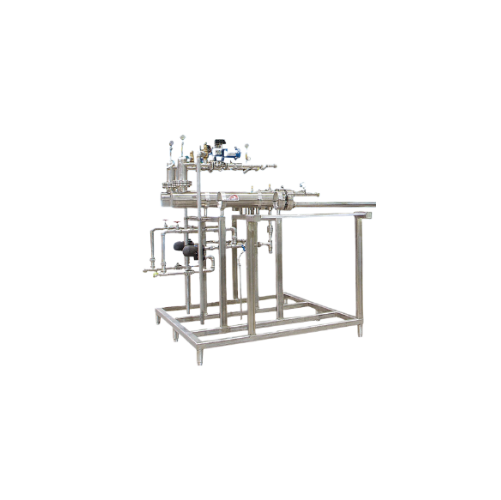
Industrial hot water heating system
Optimize your production line’s efficiency with precise water temperature control...
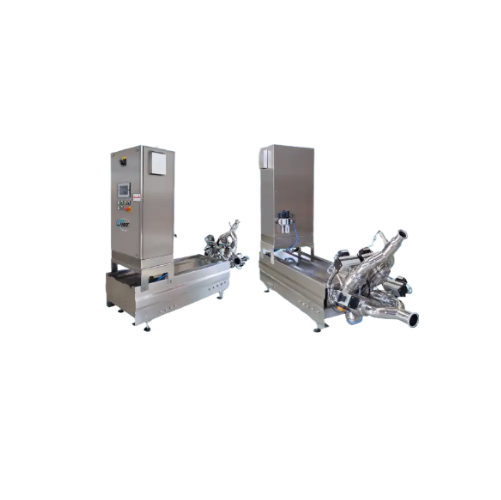
Pump for products with large particulates
When handling products with large particulates, maintaining integrity is paramou...
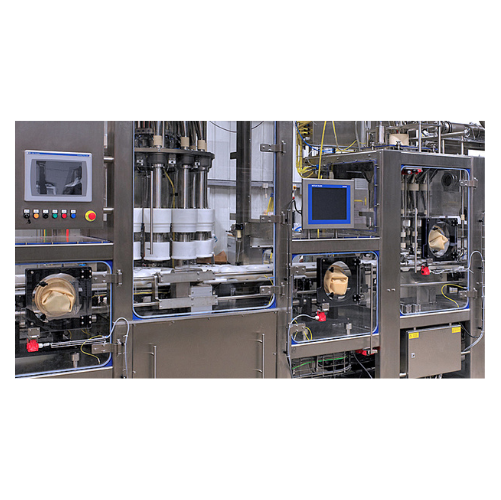
Vacuum powder filler for dairy and pharmaceutical products
Achieve precision and maintain product integrity with a versa...
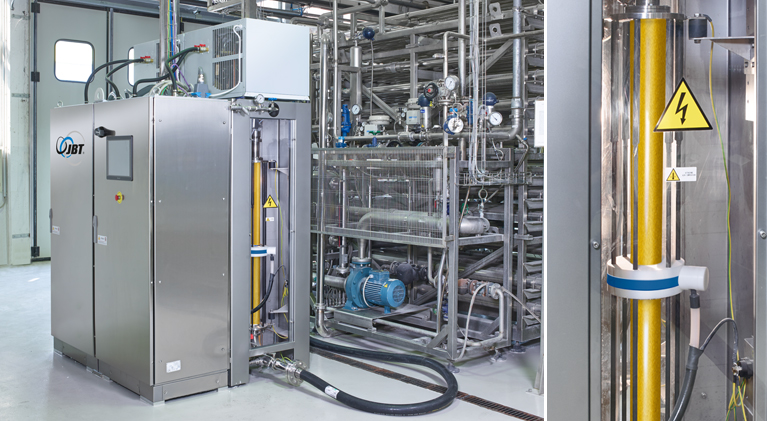
Ohmic heat exchanger for high viscosity foods
Optimize the thermal processing of heat-sensitive foods with precise ohmic h...
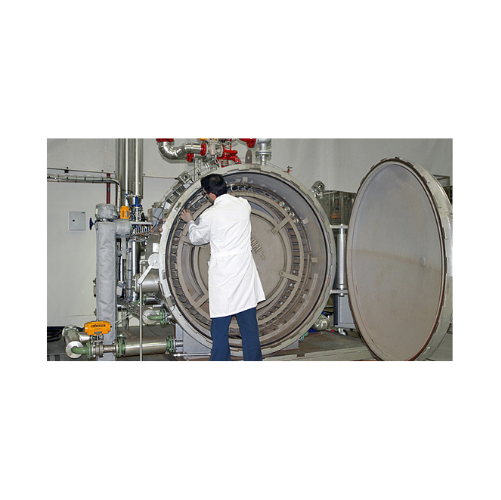
Pilot rotary retorts for laboratory sterilization
Optimize your prototype testing with precision thermal simulations to p...
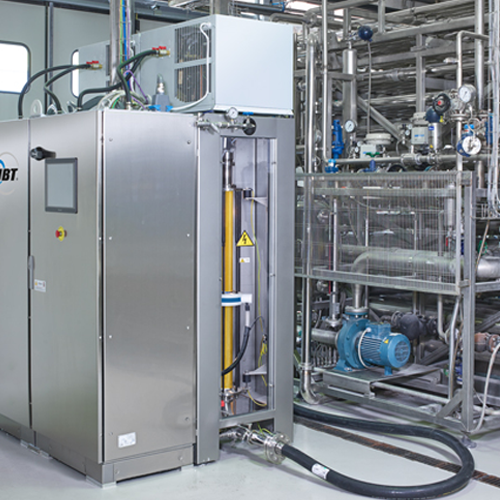
Heat exchanger for liquid and semi-liquid foods
Optimize your heating and cooling processes with superior heat transfer ef...
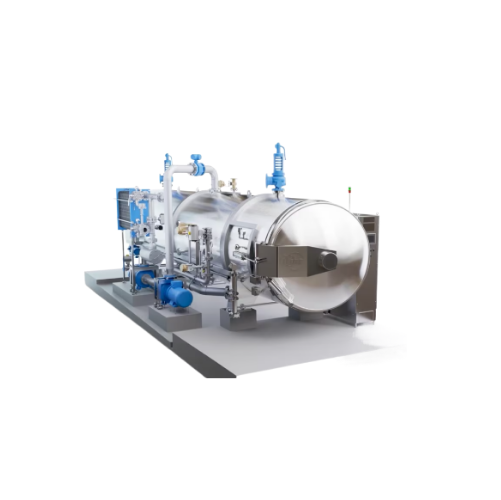
Industrial retort for food sterilization
Achieve uniform sterilization and cooling in your batch production processes while...
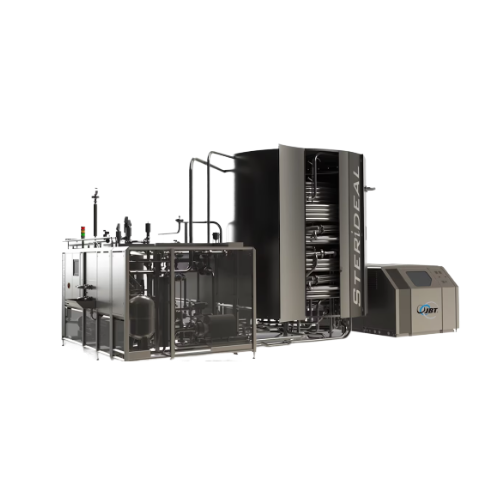
Coil heat exchanger for dairy and beverage processing
Quickly sterilize and retain product quality with this coil heat ex...
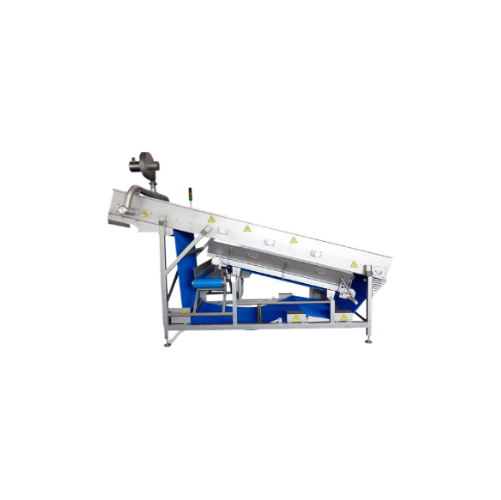
Knocker conveyor for fresh produce processing
For processors dealing with mixed produce, this conveyor effectively separat...
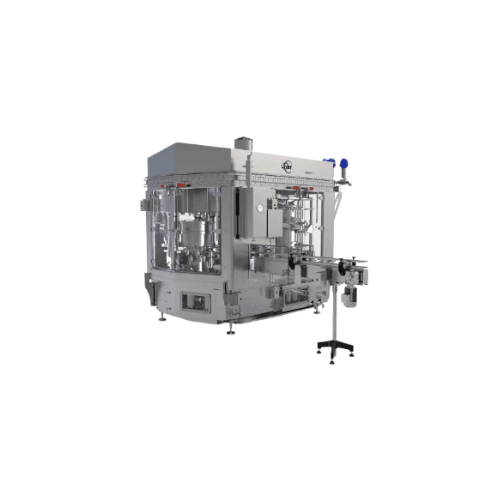
Rotary can filler and closer for metal cans
Achieve seamless integration in your production line with a solution that sinc...
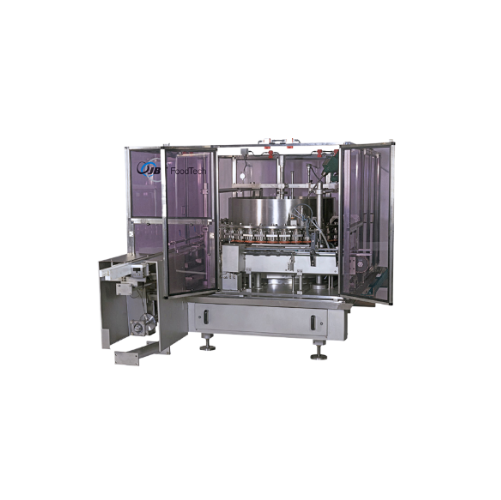
Vacuum filler for low viscous products
Achieve precise vacuum filling for liquid and granule products while effectively eli...
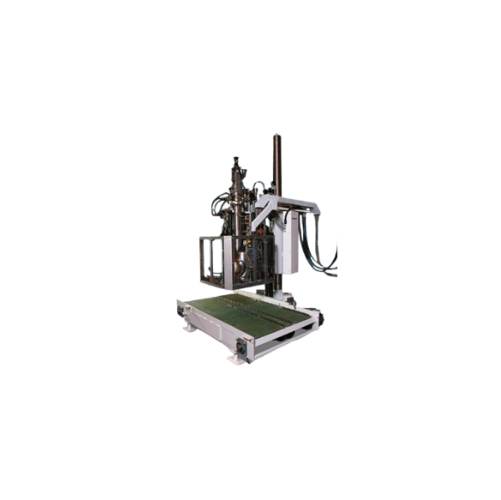
Aseptic bag filler for bulk containers
Eliminate spoilage events and ensure sterility in high-speed filling of bulk aseptic...
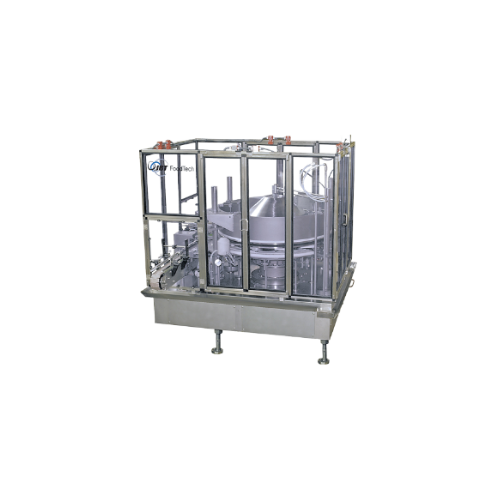
Granular filler for wide mouth containers
Ensure precise filling and minimize product loss with this granular filler, expe...
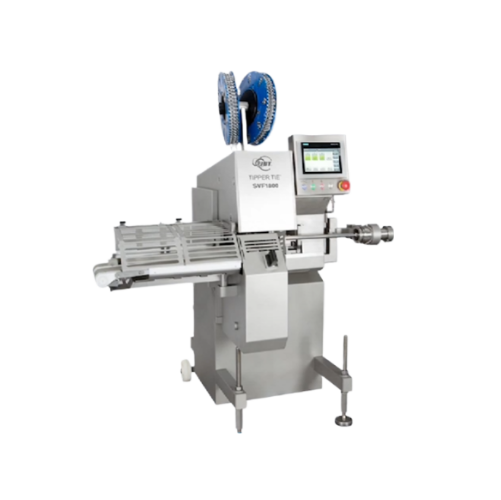
Automatic double clipper for sausage production
Optimize your production line with a high-speed double clipper that secure...
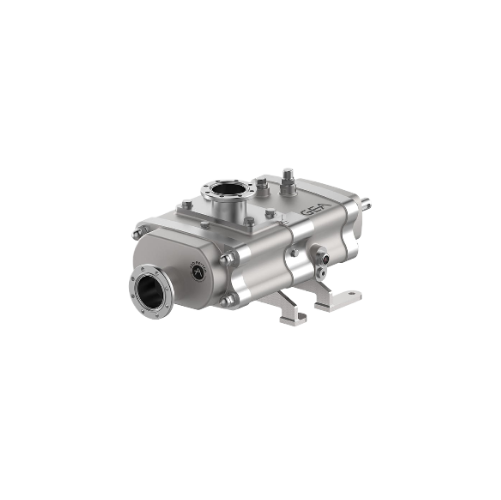
Twin screw pump for viscous media
Streamline your production with a twin screw pump that effortlessly handles viscous media...
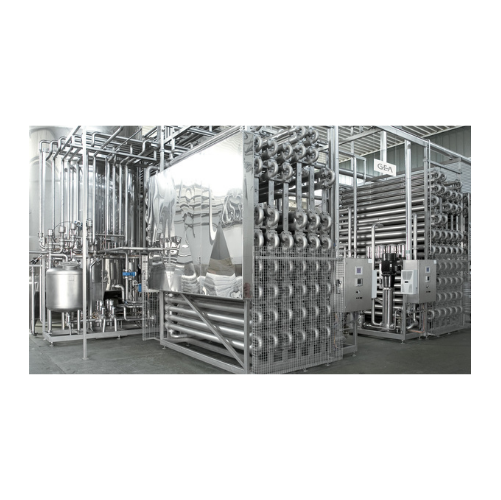
Uht plant for aseptic product treatment
Ensure optimal product quality and production safety with versatile UHT solutions f...
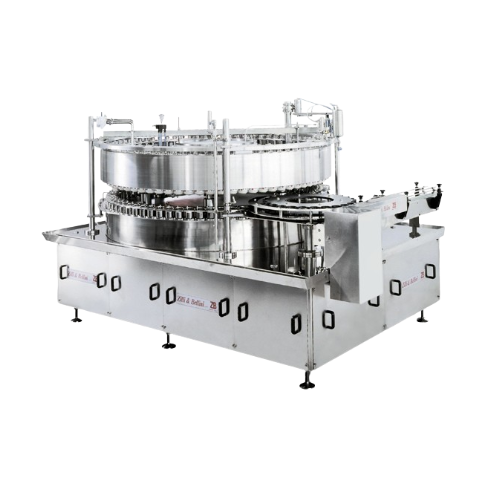
Rotary vacuum fillers for liquid and semi-liquid food products
Achieve precise filling of a wide range of liquid and sem...
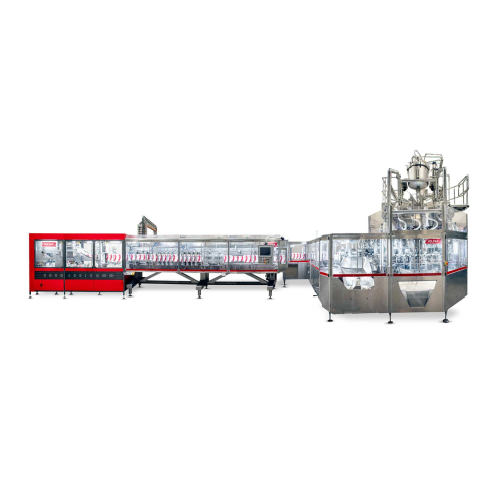
Continuous stand-up pouching solution for up to 1000ml
Maximize efficiency in high-speed production lines with precise st...
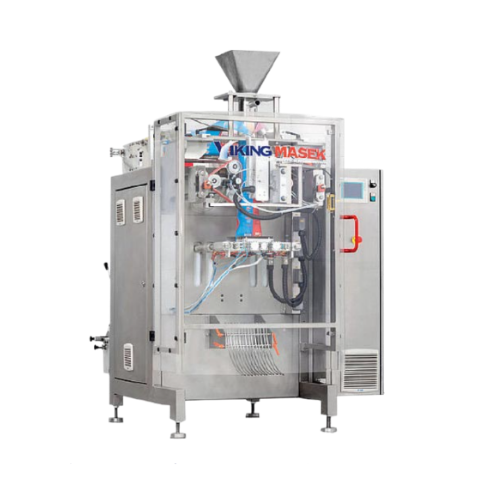
Continuous motion liquid packaging system
Achieve precise and clean liquid packaging with advanced servo-driven squeegee s...
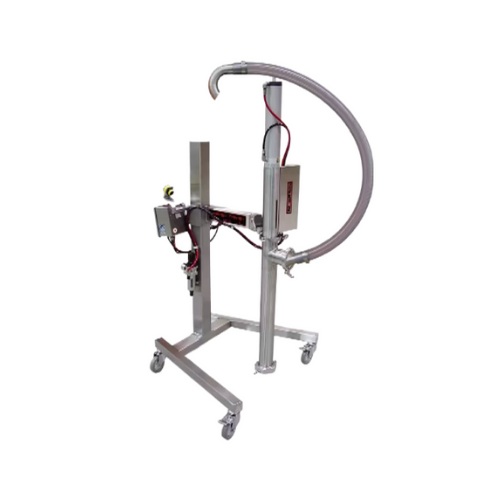
Food grade transfer pump for semi-solid products
Streamline your production with a high-speed transfer pump designed for s...
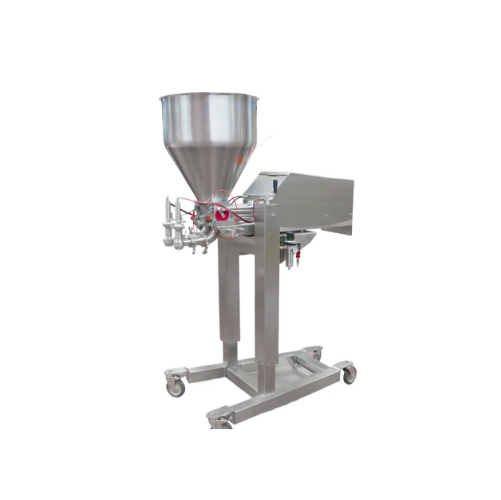
Dual or triple lane food depositor
Enhance your production efficiency with a depositor that seamlessly handles a variety of...
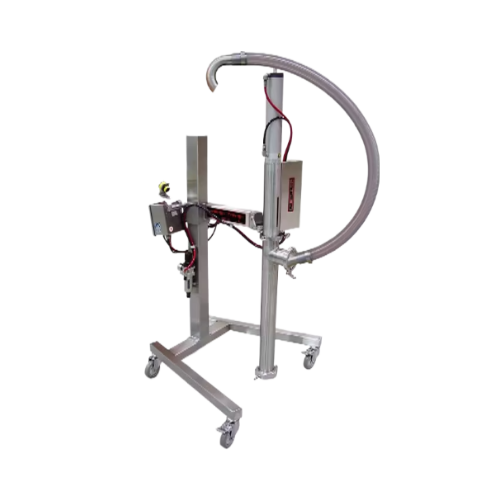
Hopper transfer pump for bakery production
Effectively transfer and maintain the integrity of various food products, from ...
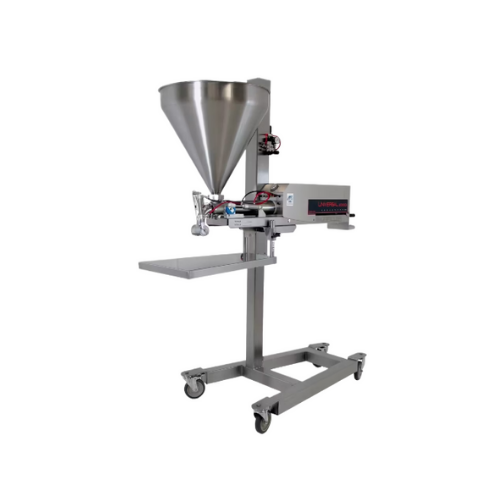
Single piston food depositor
Achieve precise portion control for diverse food products, from soups to chunky fillings, with ...
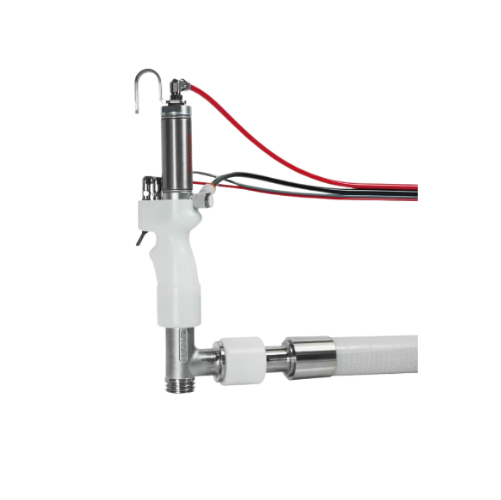
Semi-automated depositor with handheld nozzle
Maintain portion precision and reduce ingredient waste with a versatile depo...
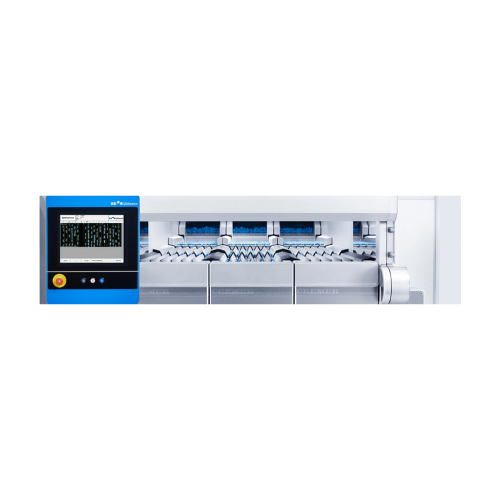
High-speed vacuum blender for commercial use
Achieve optimal blending with cutting-edge vacuum technology, ensuring vibran...
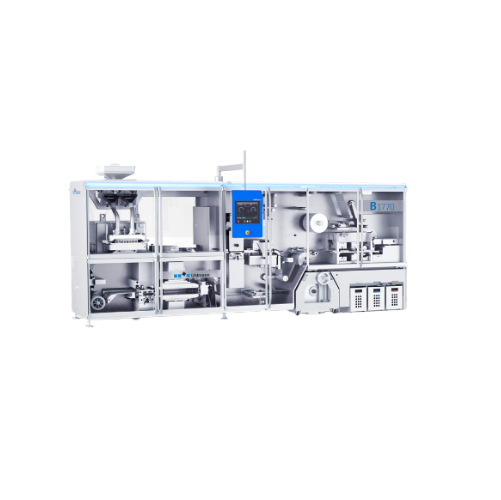
High-speed blender for commercial use
Designed for high-performance blending tasks, this solution integrates vacuum technol...
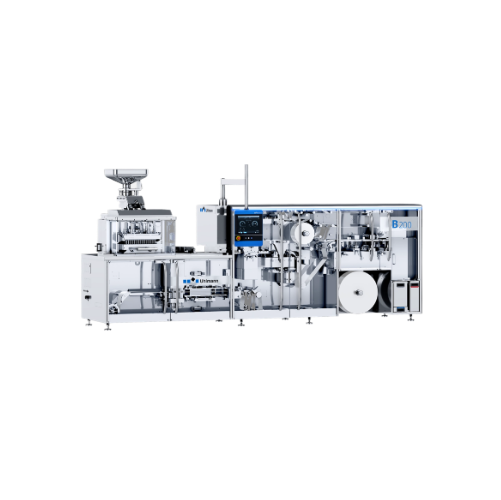
Single-serving blender for home use
Create smooth, nutrient-rich beverages and culinary delights effortlessly, whether you&...
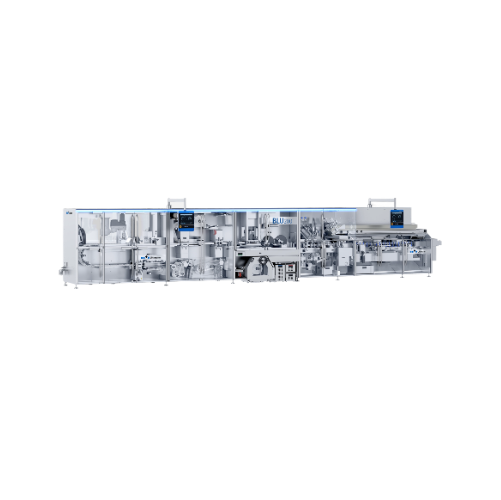
Single-serving blender for quick personal blends
Transform your favorite ingredients into nutritious smoothies, soups, and...
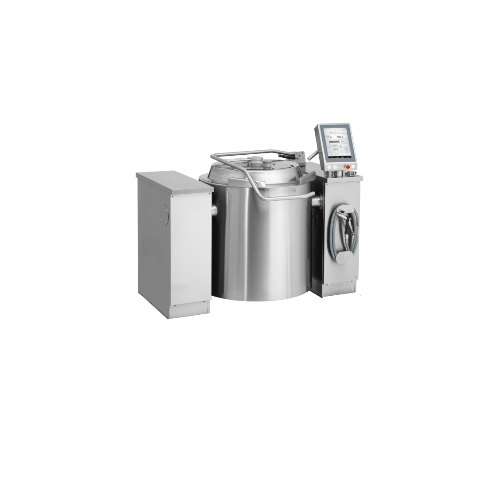
Commercial cooking kettles for cook-and-chill food production
Transform your cook-and-chill processes with kettles that ...
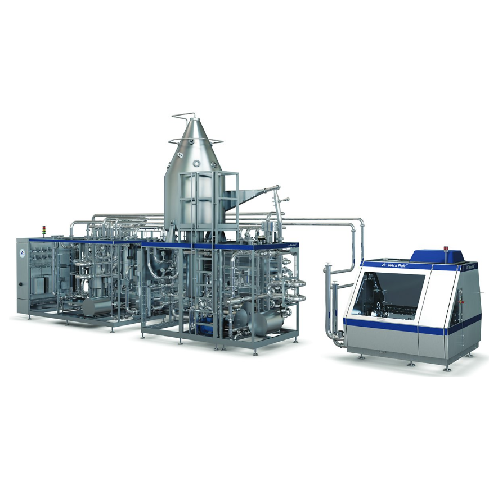
Direct Uht processing for heat-sensitive liquid products
Achieve optimal taste and nutritional value in liquid foods thro...

Evaporator for dairy products
Need efficient moisture removal in diverse dairy and food applications? This falling film evap...
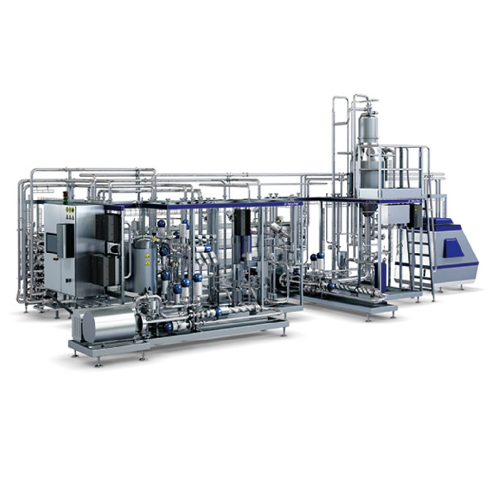
Continuous ultra-high temperature treatment for prepared food products
Optimize your prepared food production with cont...
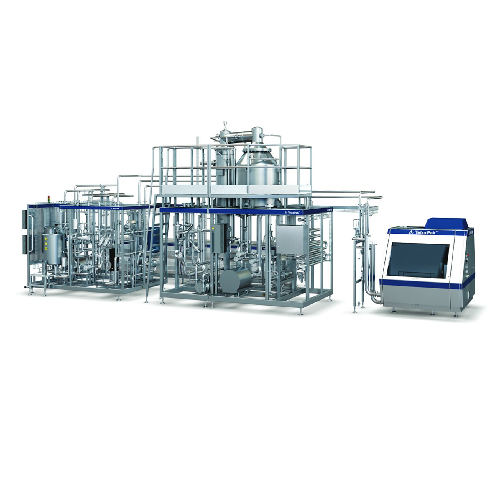
Ultra-high temperature processor for premium liquid foods
Achieve superior product quality and flexibility with advanced...
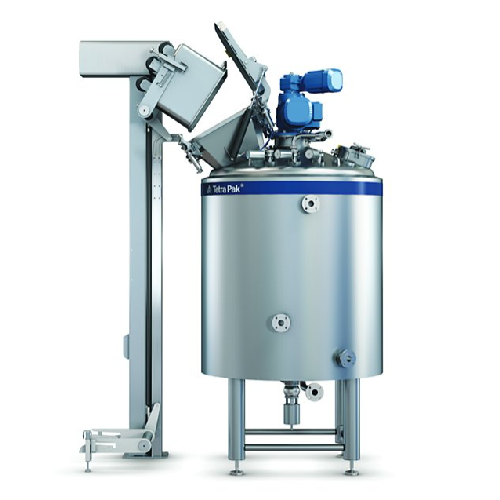
Food processor for high and low viscosity products
Achieve consistent recipe results and streamline your operations with ...
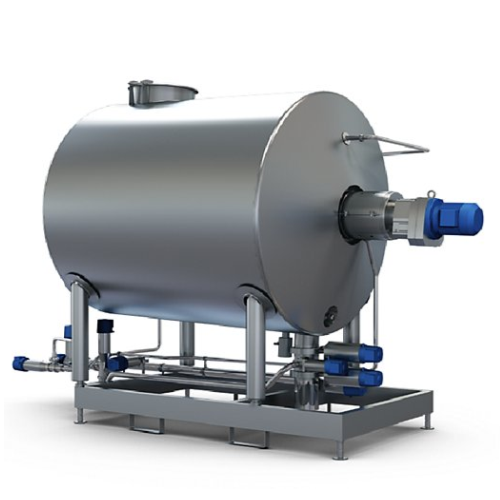
Blending tank for food preparations
Optimize your production line with a tank designed for efficient blending and storage o...
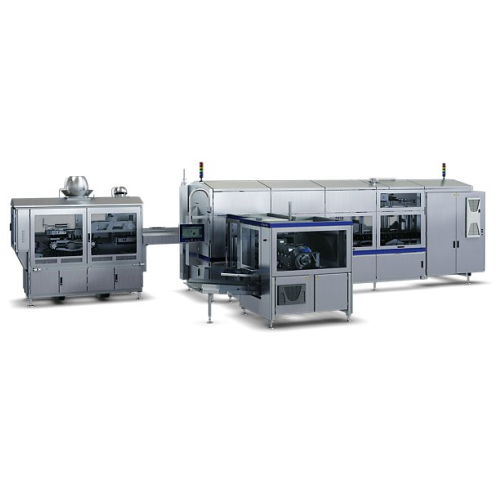
High-speed form and seal machine for retortable food packages
Streamline your production with a machine engineered for h...
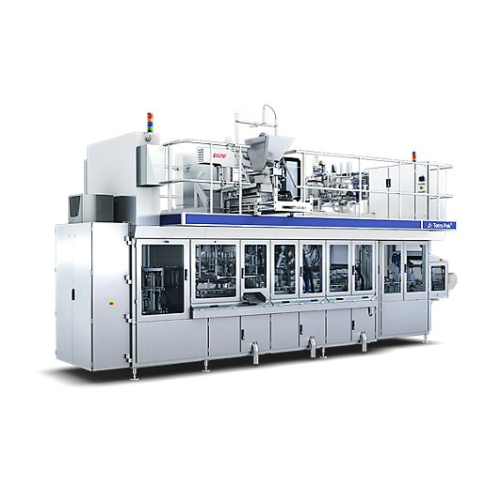
Compact filling system for retortable carton packages
Simplify your production of ready meals and soups with a space-savi...
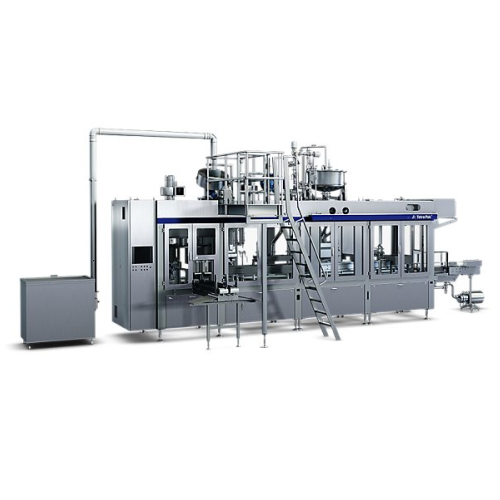
Filling system for gable top packages
Achieve precise, cost-effective filling with reduced energy consumption for chilled l...
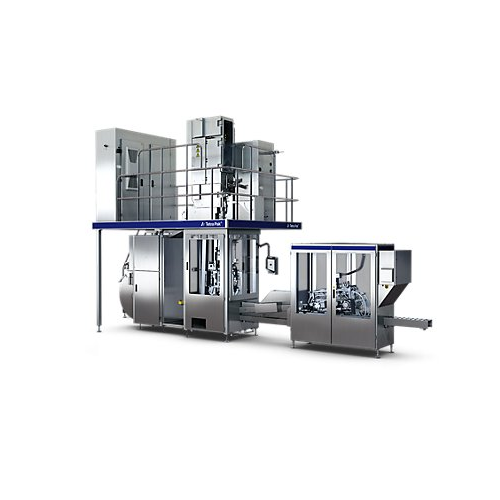
Filling system for tetra wedge aseptic packages
Optimize your production line with a reliable filling system designed to e...
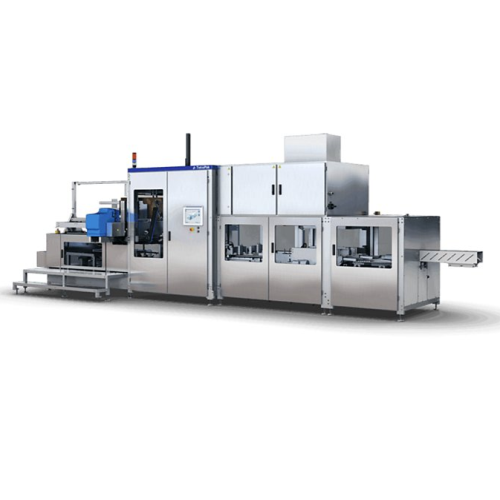
Cardboard packer for secondary packaging
Streamline your packaging process with a high-speed, automated cardboard packer th...
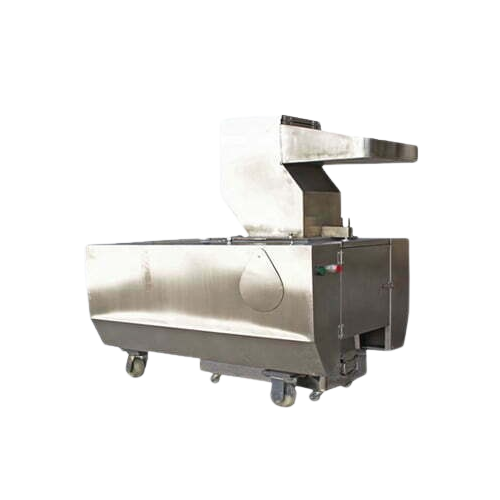
Industrial animal bone crushing solution
Efficiently transform hard animal bones into fine granular materials, enhancing nu...
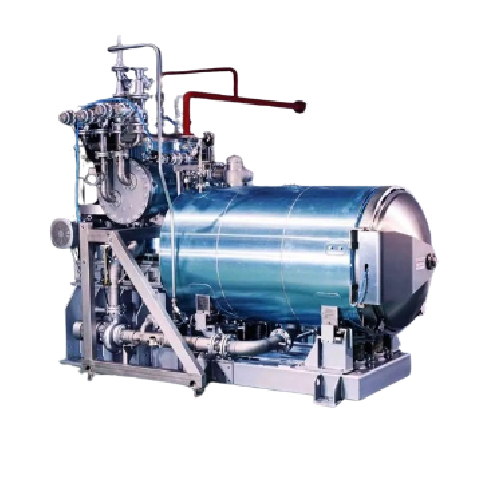
Cascading water sterilizer for optimized food preservation
Reduce sterilization times significantly while preserving foo...
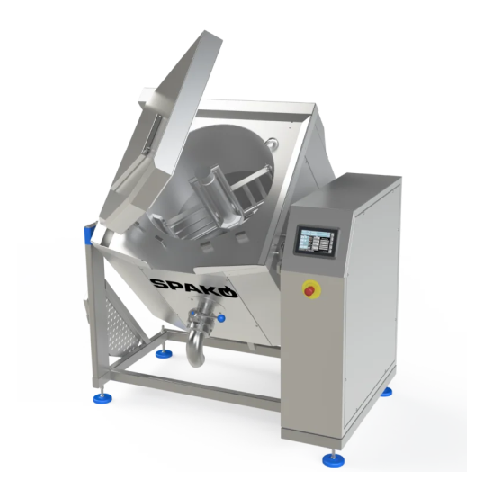
Industrial cooking kettle for diverse food processing needs
Optimize your food processing with a versatile kettle design...
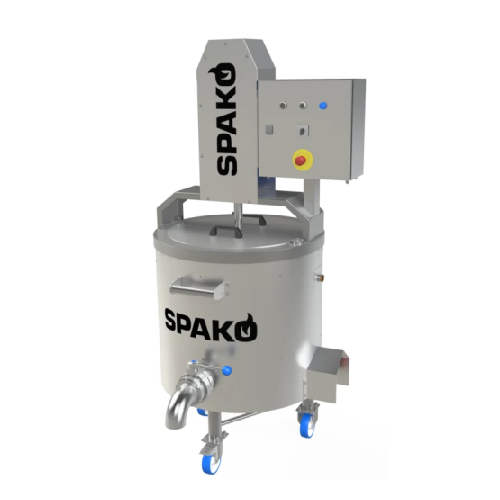
Electric double-walled cooking kettle with agitator for thick products
Tackle diverse cooking challenges with a double-...
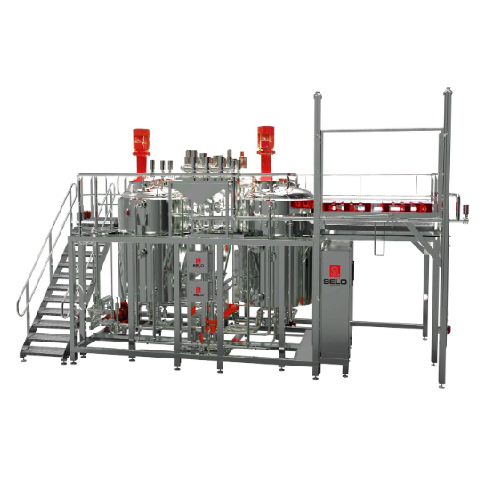
Automated sauce production lines
Streamline your sauce production with flexible lines designed for rapid recipe changeovers,...
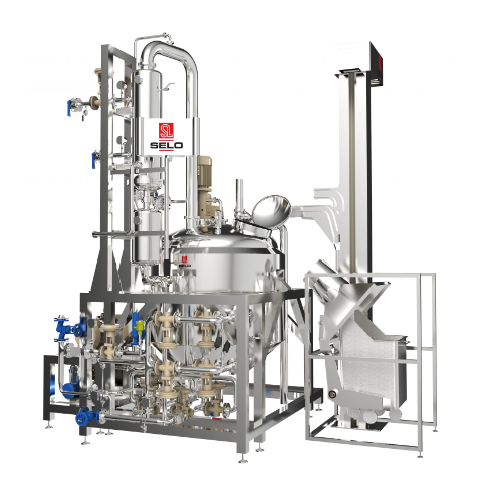
Ketchup manufacturing line
Streamline your sauce production with precision-engineered efficiency, allowing for seamless reci...

Batch cooker and mixer for food and pet food production
Streamline your cooking and mixing processes with a versatile bat...
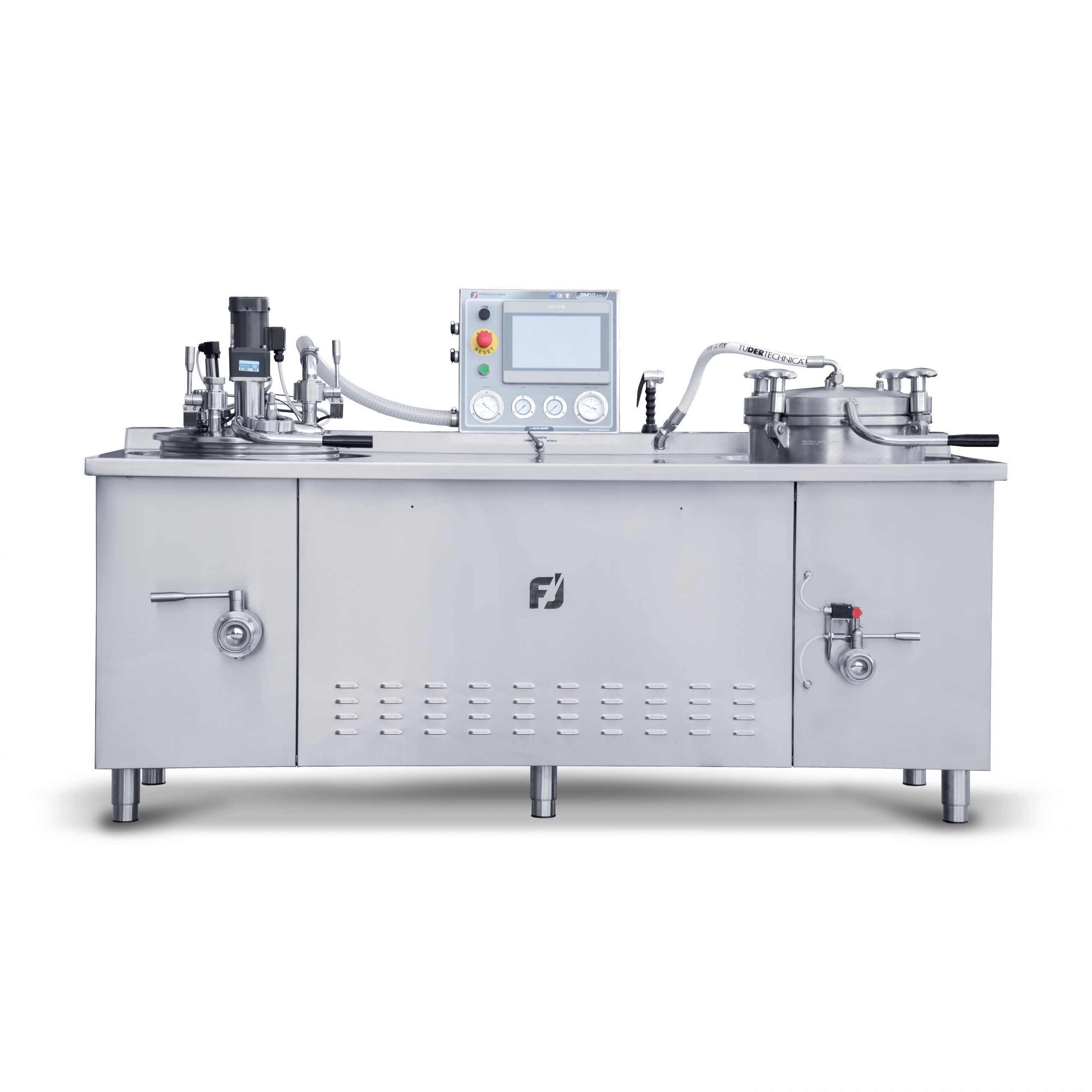
Marmalade and Jam Processing Machine
When producing jams and marmalades, preserving the natural flavours, aromas and colors...
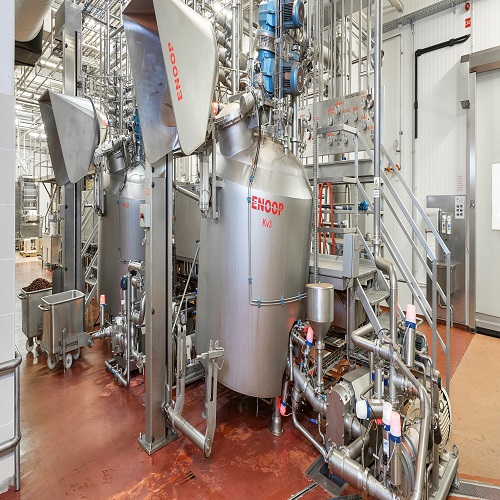
Industrial vacuum cooker
Batch cookers can be highly inflexible and inefficient, relying on maximum fill levels to operate we...
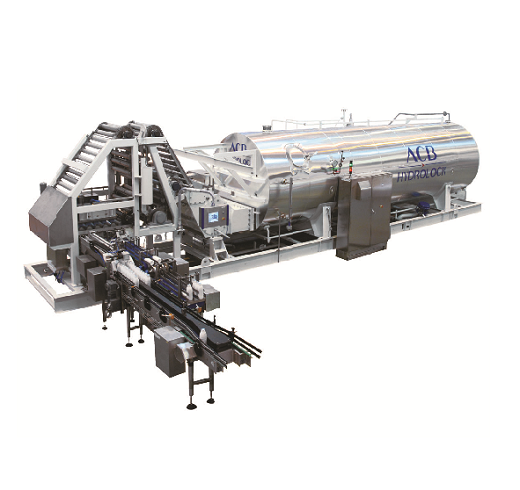
Continuous sterilizer for milk beverages
An important goal of heat processing in the manufacturing of milk beverages is to ...
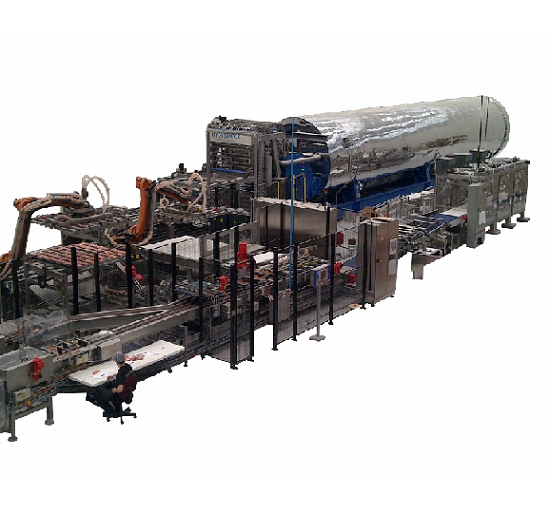
Continuous sterilizer for pet food
Sterilization is a critical operation in the manufacturing of wet pet foods. An importan...

Pipeline metal detector for sauces
Ensuring liquid and viscous products such as sauces, soups, juices and meat are contamin...
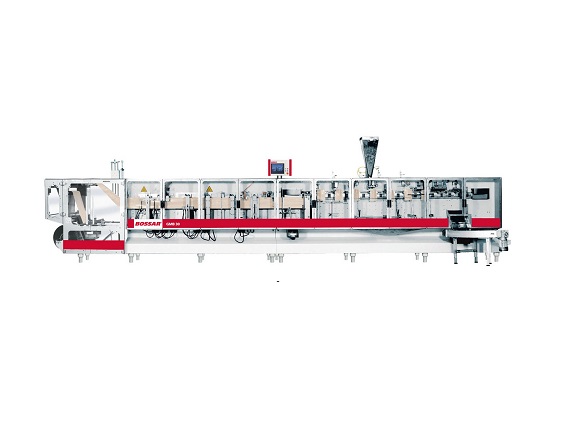
HFFS Machine for Large or Heavy Pouches
Traditional pouch-forming machines can struggle to maintain the position of the pac...
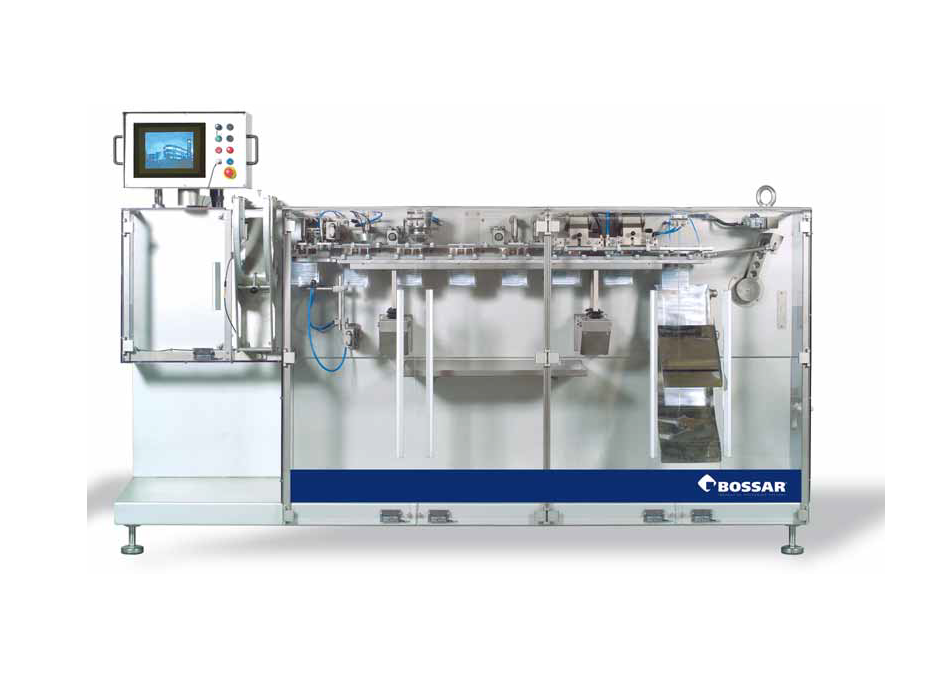
Retort Pouch Packaging Machine
A wide variety of products that were previously canned are now able to be more economically p...
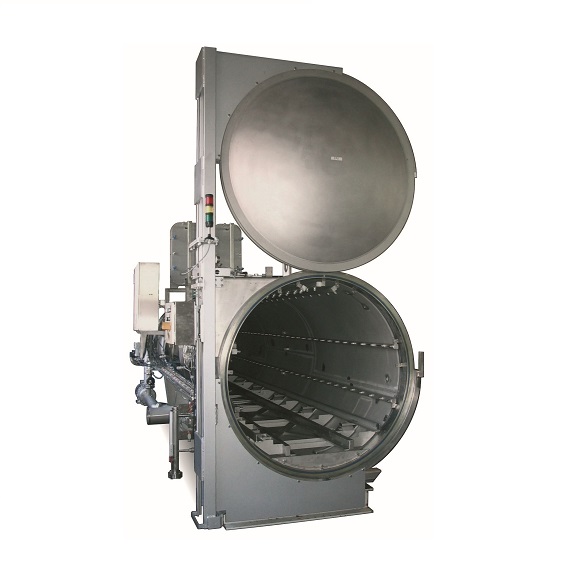
Autoclave for doypack pouches
The self-standing Doypack and other similar pouch products are a very popular method of packag...
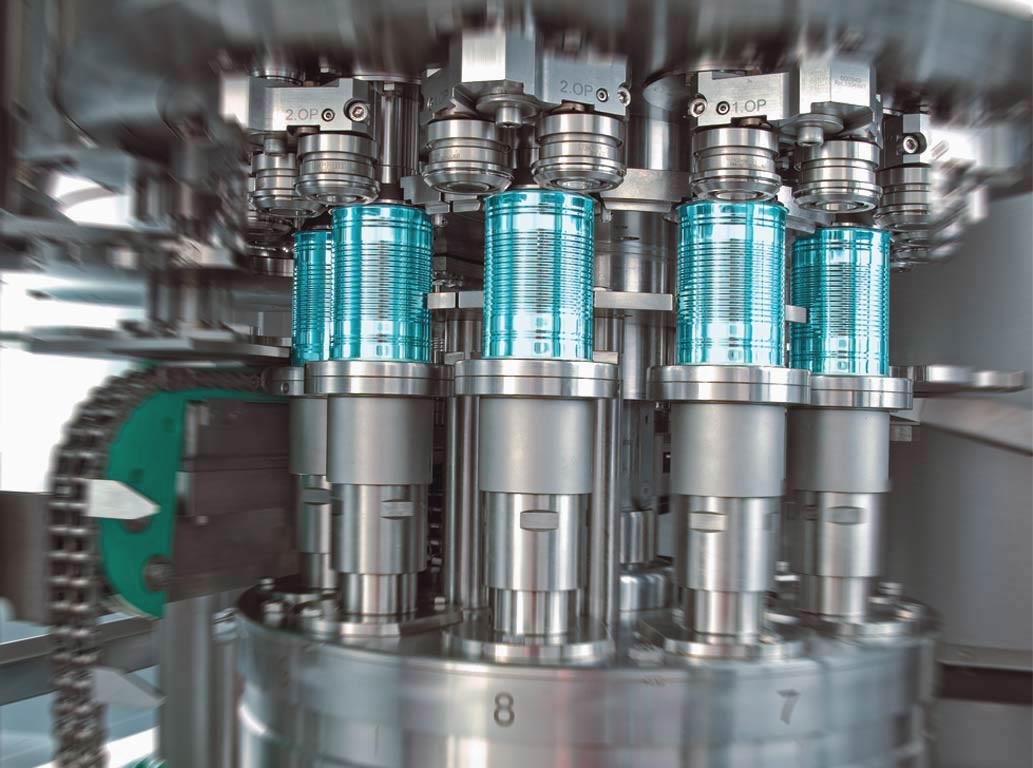
Can seamer for food products
Flexible can seaming equipment is required to adapt for product-specific variations in food can...
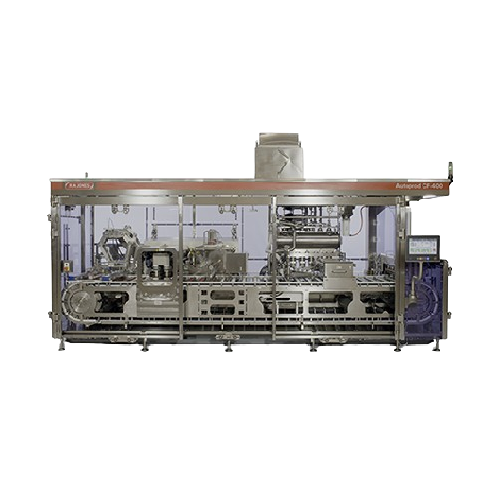
Cup filling and sealing system for dairy products
Optimize your production line with versatile cup filling and sealing ca...
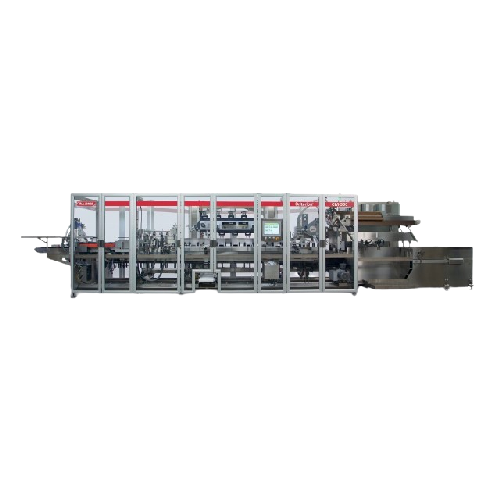
Medium-speed end load cartoner for food and beverage packaging
Streamline your packaging line with versatile cartoning c...
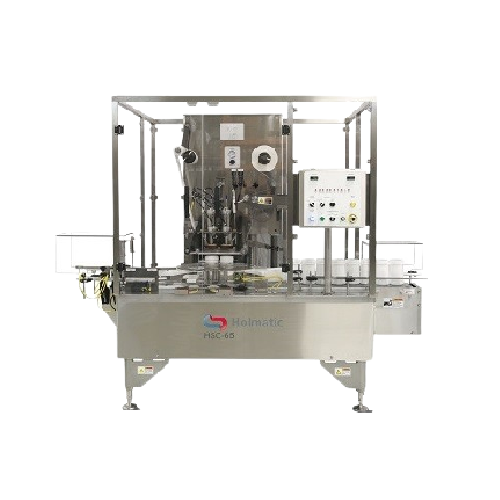
Rotary indexing sealer for cup filling
Streamline your production line with precise cup filling and sealing, ideal for a wi...
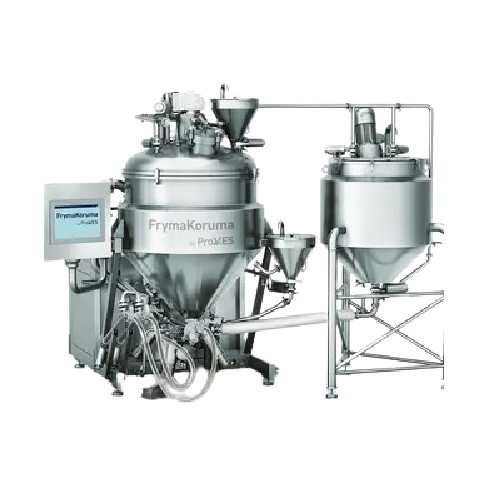
High shear emulsifier for mayonnaise production
Streamline your production of high-quality emulsions with this high-capaci...
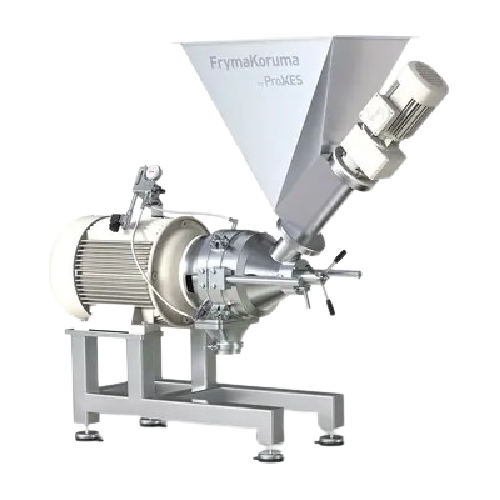
High shear emulsifier for food and pharmaceutical products
Optimize your production line with precise emulsification, ho...
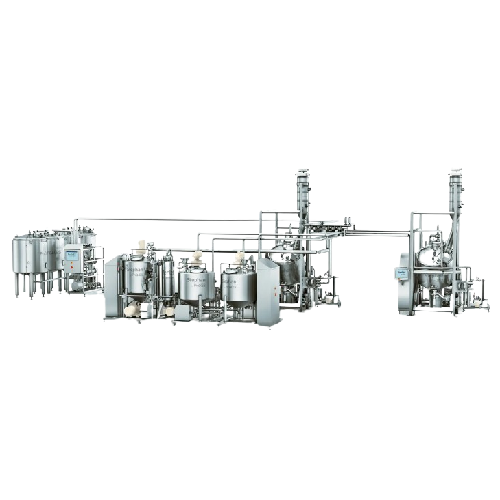
Continuous nut paste production line
Elevate your production efficiency with a versatile preparation line designed to seaml...
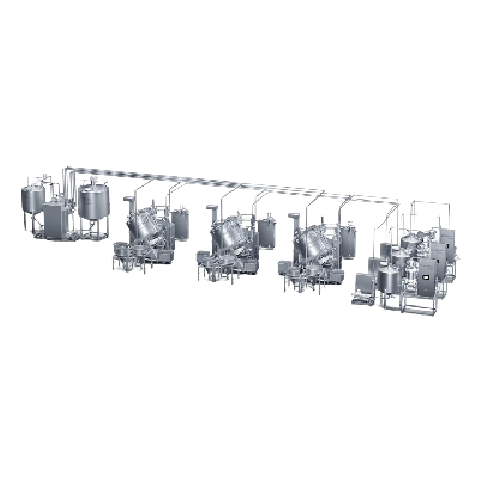
Continuous mustard production line
Optimize your condiment production with precision-engineered systems capable of transfor...
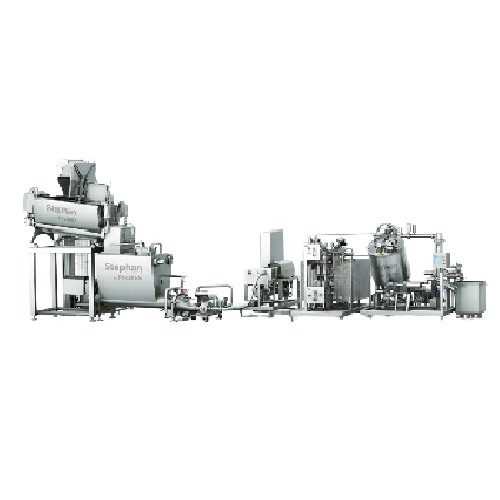
Cheese blending and heating line for processed cheese
Optimize your processed cheese production with a solution that seam...
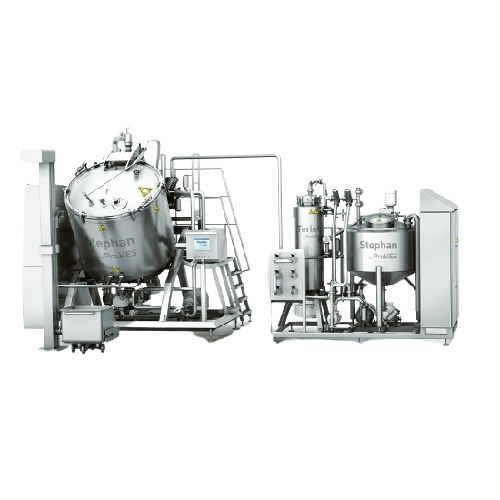
Continuous caramel production line
Optimize your caramel production with seamless integration, achieving precise fat meltin...
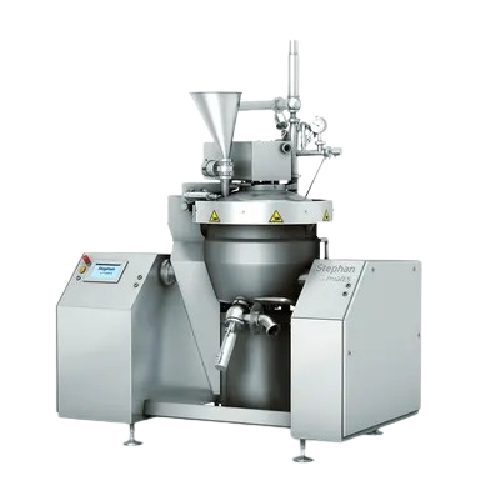
Industrial cutting system for fine emulsions
Optimize your production line with precision cutting and emulsifying, ensurin...
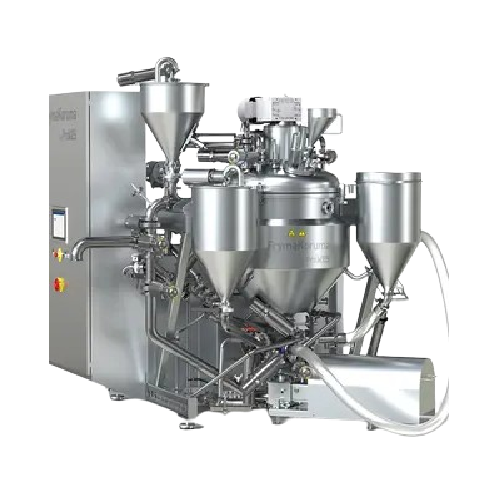
Vacuum deaeration system for mustard and liquid detergents
Ensure optimal product quality by effectively removing air fr...
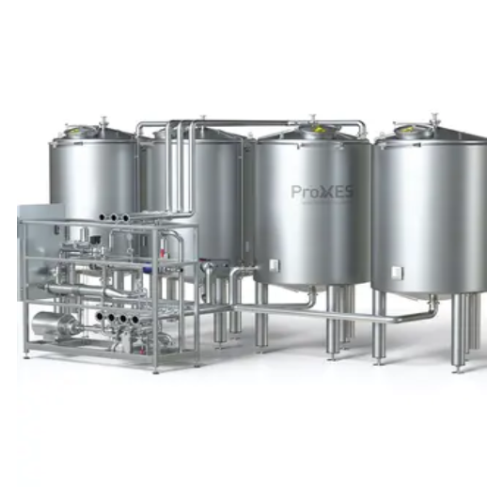
Cleaning systems for food, pharmaceuticals, and cosmetics
Ensure optimal hygiene and safety with advanced cleaning syste...
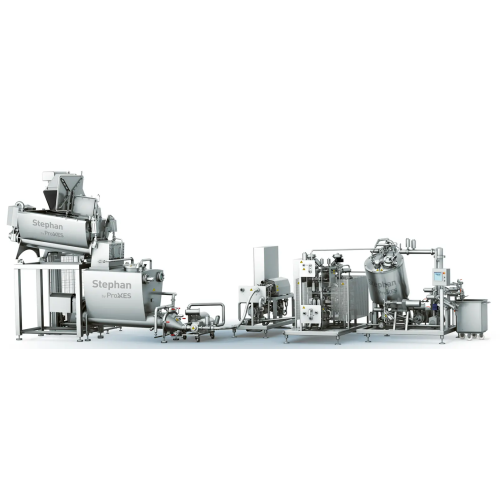
Continuous caramel process line
Optimize your continuous food processing with an engineered-to-order line tailored for preci...
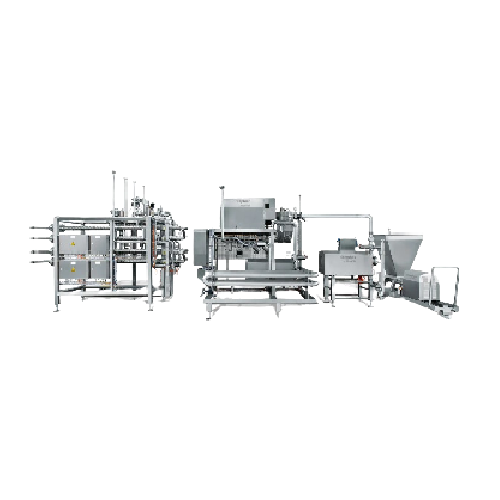
Continuous cheese line
Achieve precise temperature control and seamless product transitions with this equipment, ideal for en...
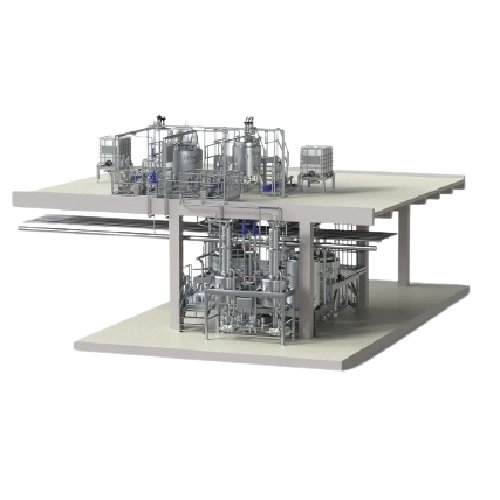
Continuous mustard line
Streamline mustard production with high-capacity continuous processing that reduces air pockets and e...
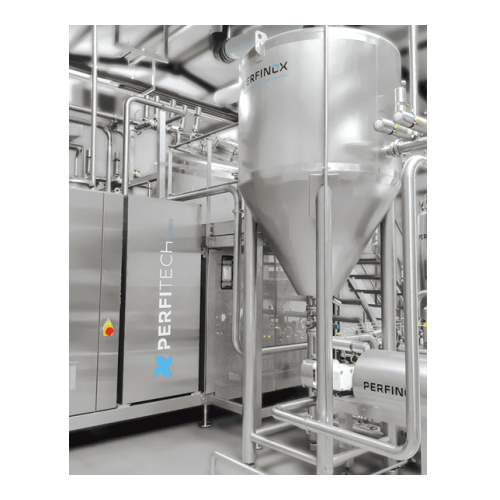
Industrial premixing system for batch and inline processing
Streamline your production with advanced premixing systems d...
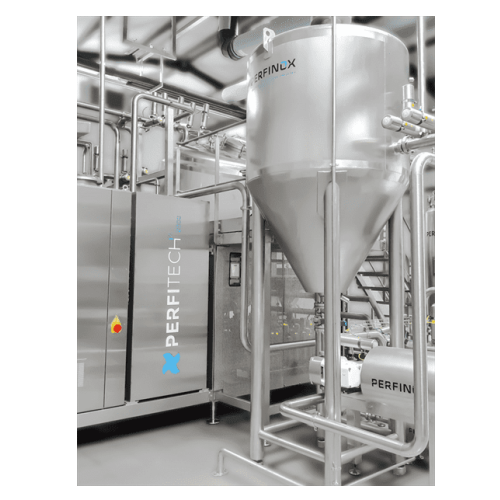
Compact production unit for liquid food products with varied viscosities
Streamline your batch production with this ver...
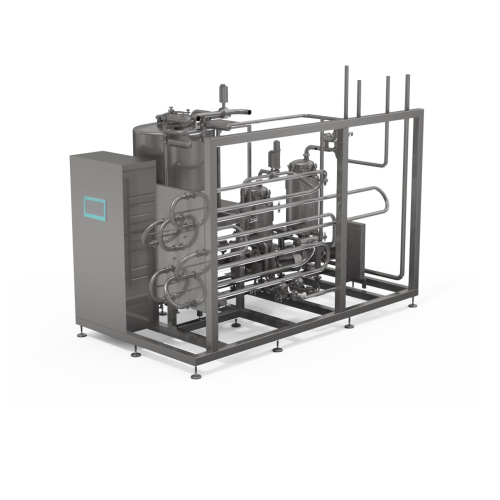
Aseptic thermal processor for high viscosity products
Optimize your processing of high viscosity products with precise te...
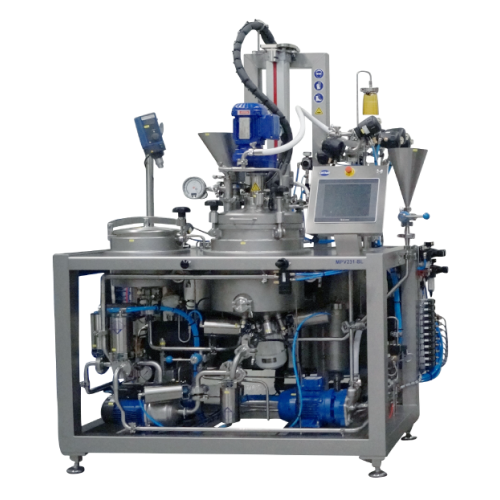
In-line production of fine emulsions
Achieve homogenous emulsions with precise control, reducing the risk of lump formation...
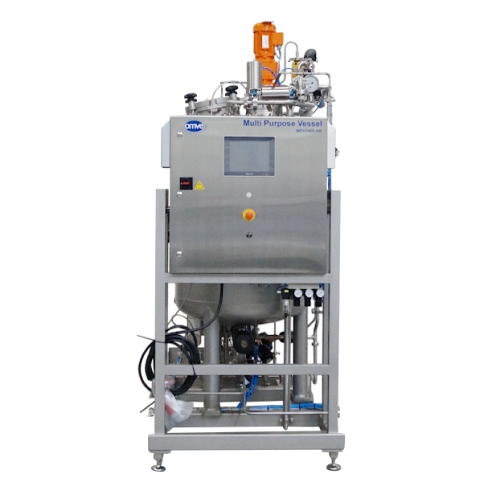
Aseptic buffer tanks for pilot scale process lines
Ensure seamless production flow and quality control in sterile environ...
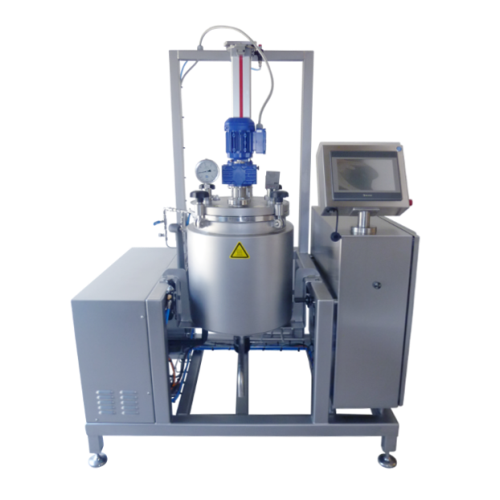
Batch food processing cookers
Achieve precise temperature and pressure control for small-scale food production with modular ...
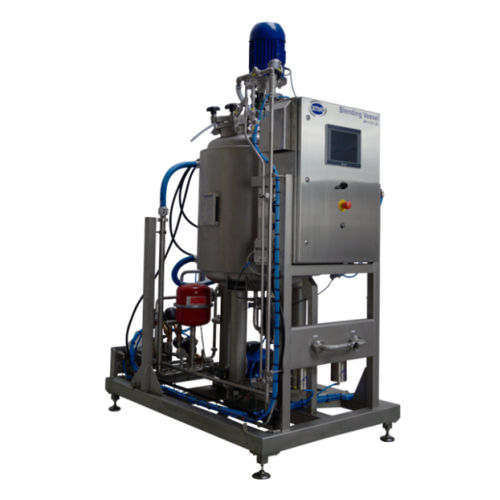
Advanced closed blending vessels for liquid food products
Enhance your production line with advanced closed blending ves...
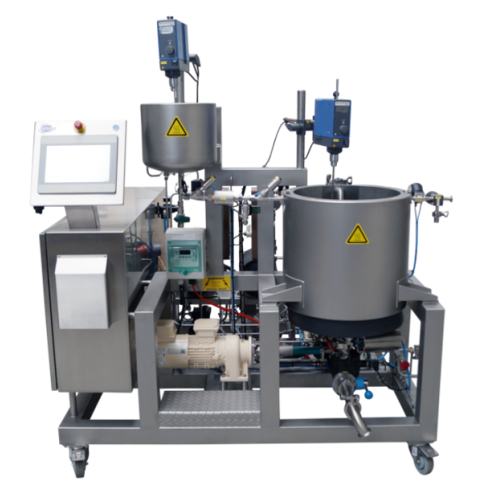
Atmospheric blending vessel for r&d activities
Optimize your liquid blending processes with this versatile vessel, designe...
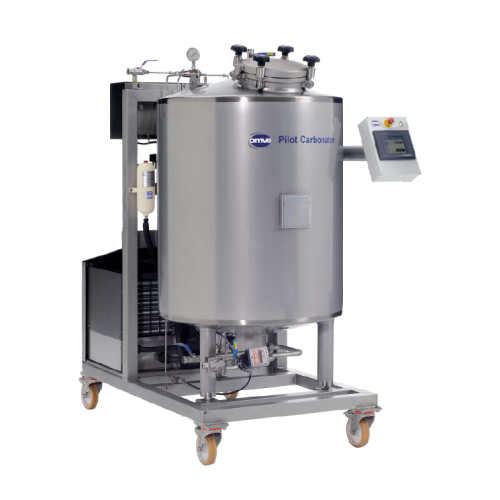
Hygienic buffer tanks for process optimization
Enhance your production flow with hygienic buffer tanks that ensure consist...
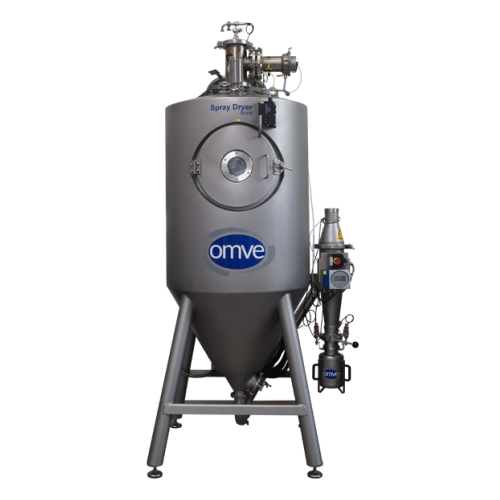
Pilot scale spray dryer for product development
Achieve precise moisture levels and product consistency in development env...
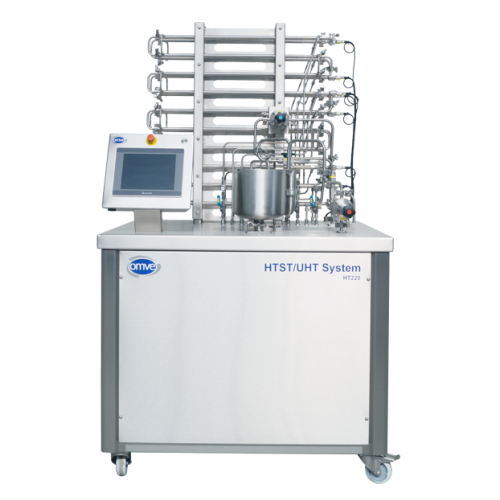
Lab Uht/htst system for r&d activities
Optimize your R&D with a versatile, modular system allowing precise control ove...

Small-scale scraped surface heat exchanger for high-viscosity products
For R&D teams tackling complex formulations...
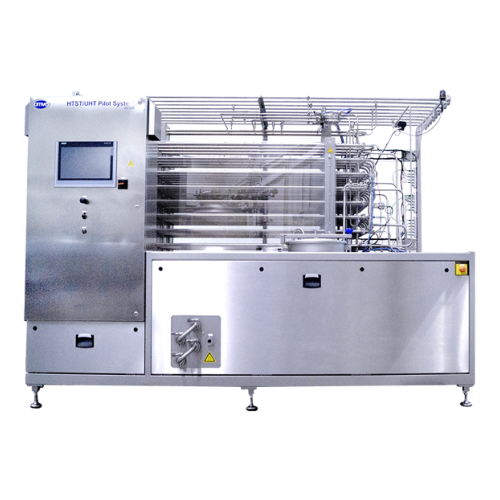
Uht/htst aseptic processor for pilot plants
Achieve precise heat treatment and aseptic processing with flexible pilot syst...
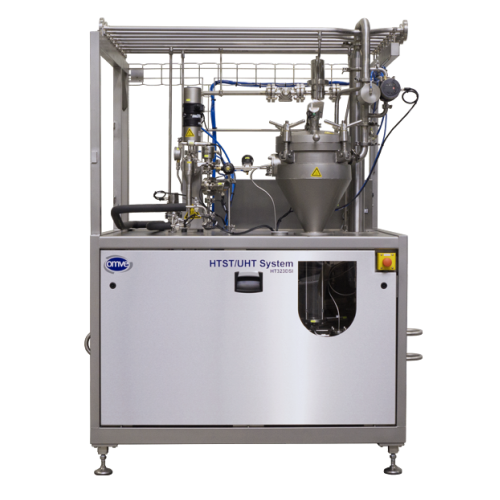
Direct steam injection Uht pilot system
Elevate your production capabilities with a sanitary UHT pilot system designed for ...
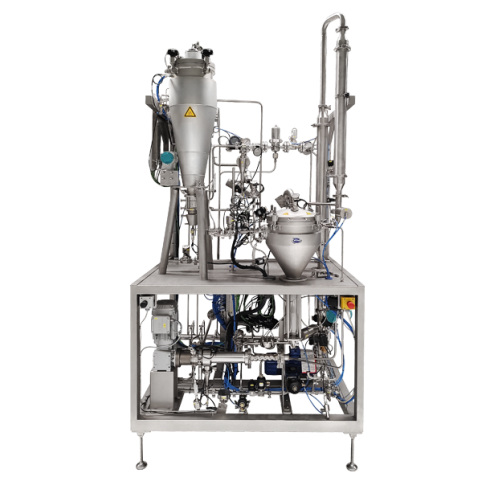
Direct steam infusion for high spore kill rate in sensitive food products
Achieve rapid, efficient sterilization and m...
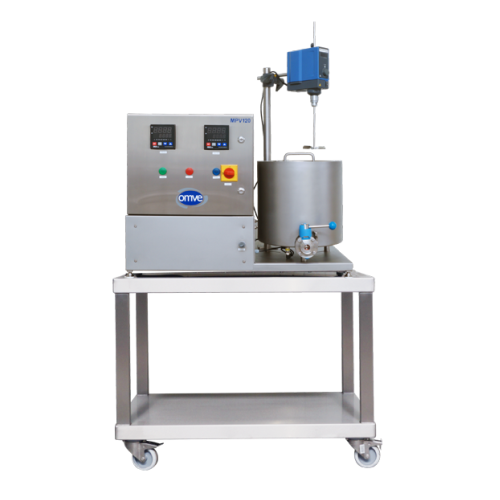
Bench-top blending vessel for small batch preparation
For small-batch liquid products, achieve precise mixing, heating, a...
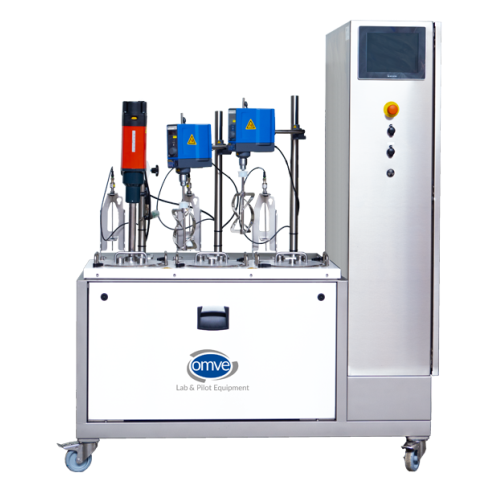
Lab-scale water bath blending vessel for product preparation
Ensure consistent flavor and quality across diverse small-s...
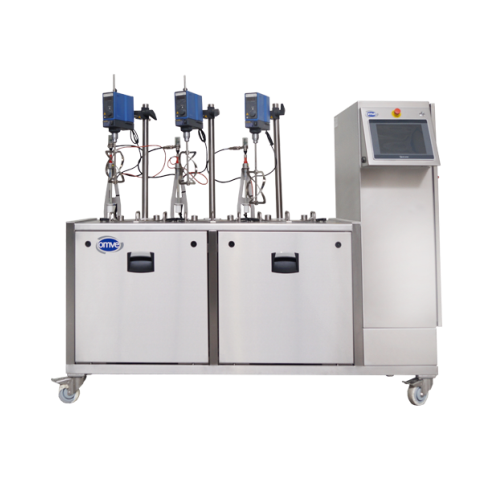
Lab-scale fermenter for simultaneous batch processing
Optimize your lab-scale fermentation process with a versatile solut...
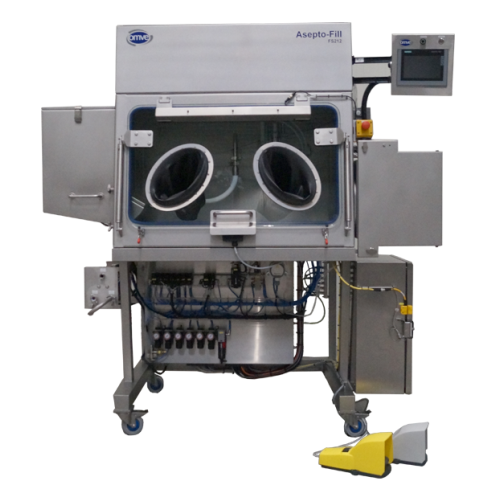
Cold aseptic filling solution for Uht samples
Ensure aseptic integrity and extend shelf life by securely filling and closi...
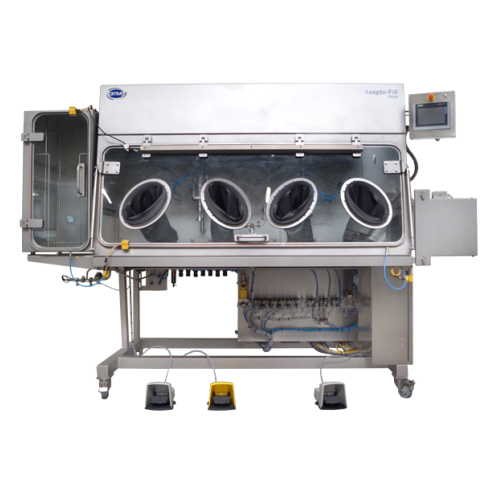
Aseptic filler for nutraceuticals
Ensure the sterility of your liquid nutraceuticals and beverages with a versatile solutio...
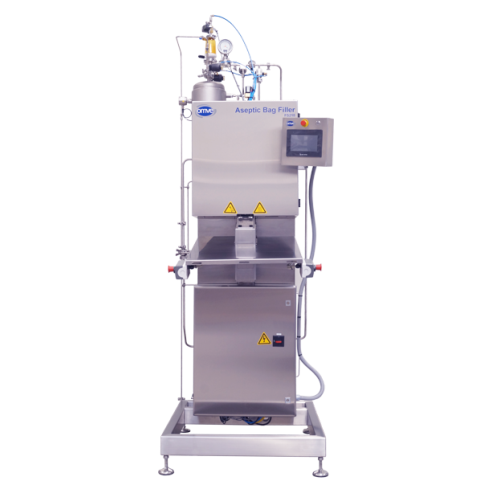
Aseptic bag-in-box filler for laboratory use
Achieve aseptic filling precision on a lab-scale with a compact solution that...
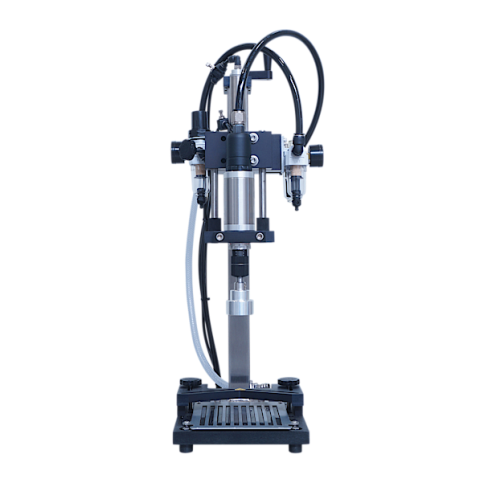
Fs closing devices for industrial packaging solutions
Streamline your packaging process with versatile closing devices, d...
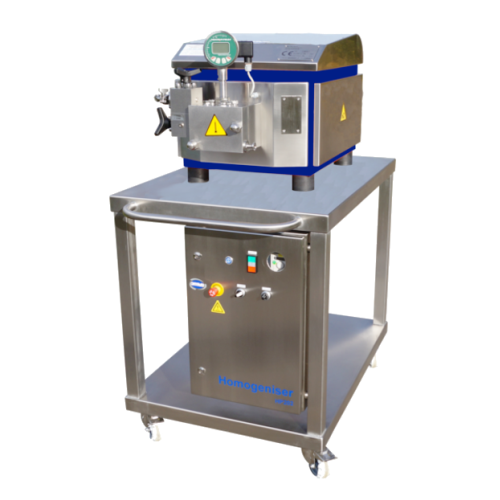
Lab-scale high-pressure homogenization solution
Optimize your lab-scale production with precision homogenization, ensuring...
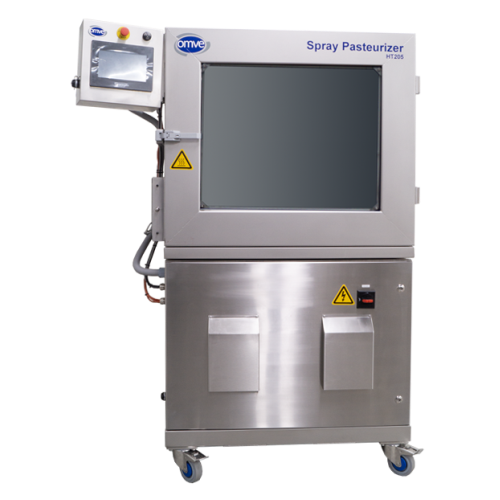
Small-scale in-container spray pasteurizer for laboratory use
Optimize your R&D processes with precise control over...
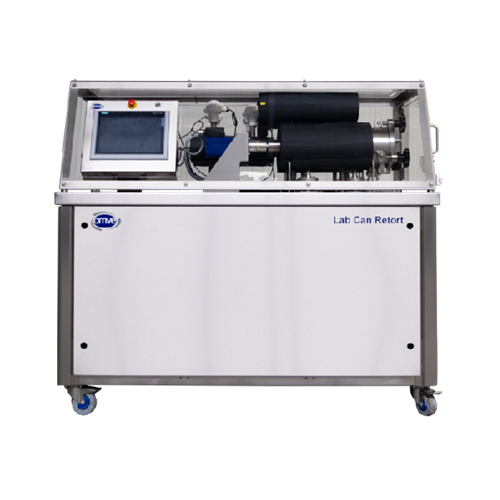
Lab can retort for precise temperature and pressure control
Achieve precision in recipe validation and packaging testing...
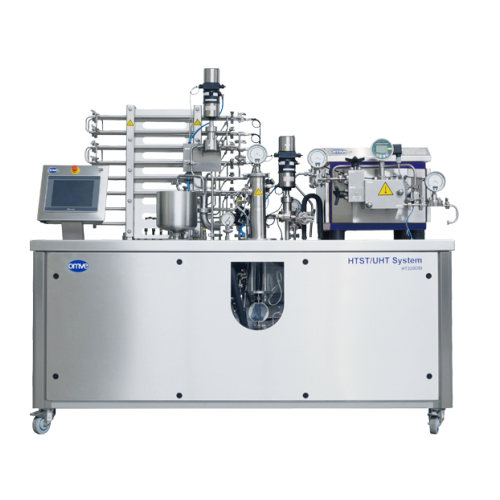
Direct steam injection system for heat treatment
Achieve precise thermal processing and enhance product quality for comple...
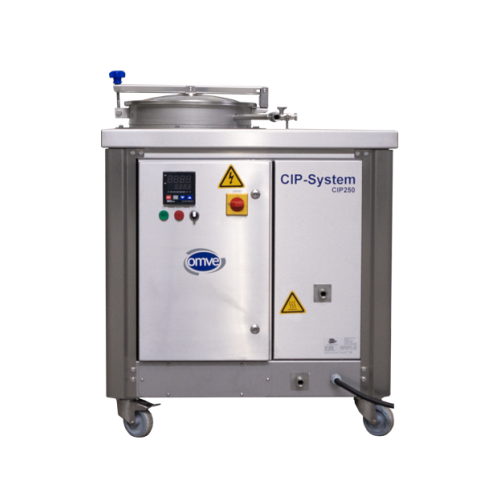
Manual Cip unit for lab and pilot plant cleaning
Need thorough cleaning without disassembling your pilot plant? This compa...

Cleaning in place unit for lab and pilot equipment
Streamline your lab and pilot-scale cleaning processes with a mobile, ...
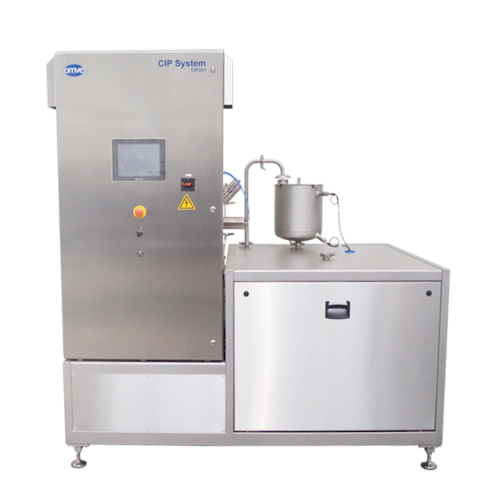
Fully automated cleaning in place unit for food processing plants
Enhance food safety and streamline operations with a ...
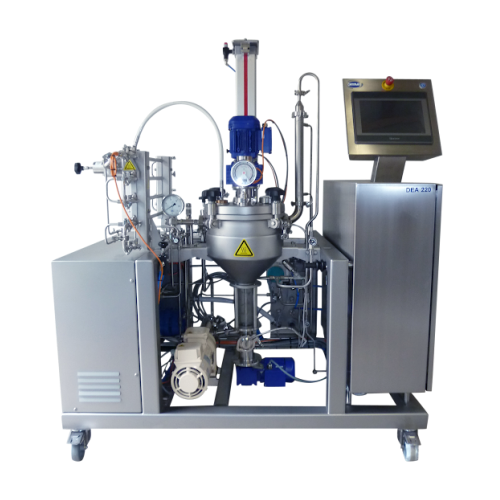
Continuous deaeration solution for laboratory and pilot systems
Achieve superior product stability and minimize foaming ...
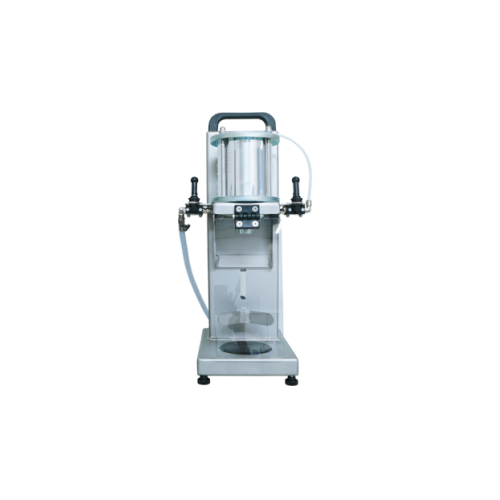
Crown cork sealer for liquid food packaging
Ensure reliable sealing for bottled beverages and dairy with a compact, table-...
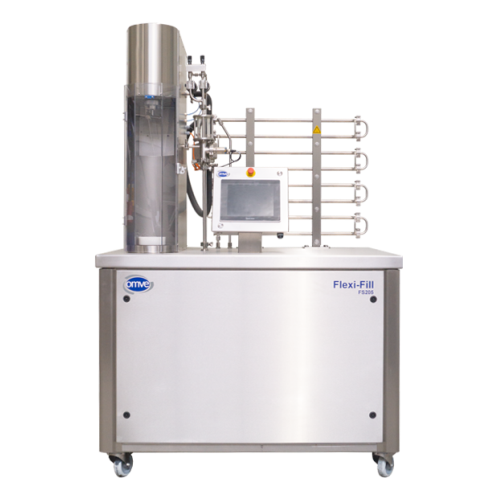
Counter-pressure filler for carbonated drinks
Enhance your carbonated beverage production with advanced counter-pressure f...
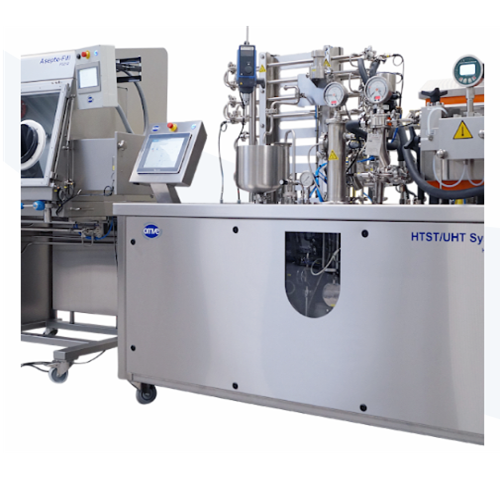
Customized process plants for plant-based beverages
Efficiently scale your production of plant-based beverages with modul...

Lab-scale carbonation system for beverage filling
Streamline your beverage development with precision carbonation and ver...
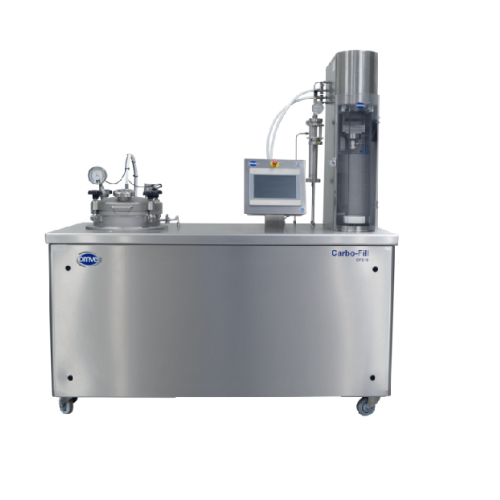
Carbonation and filling system for Pet and glass bottles
Optimize your beverage production with precise carbonation, fill...
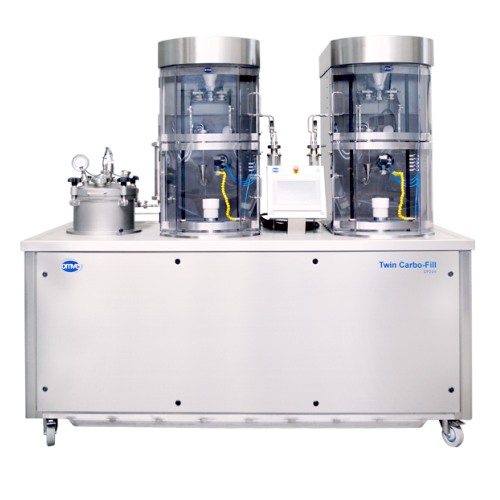
Carbonation and can seaming solution for beverages
Optimize your beverage production with a seamless integration that sim...
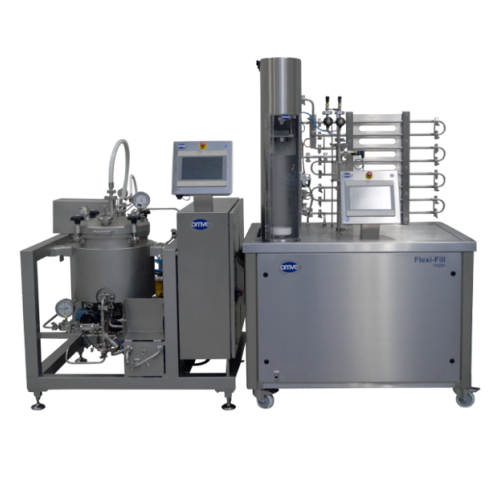
Sterile carbonation system for beverages
Achieve precise carbonation for both common and specialty beverages with this vers...
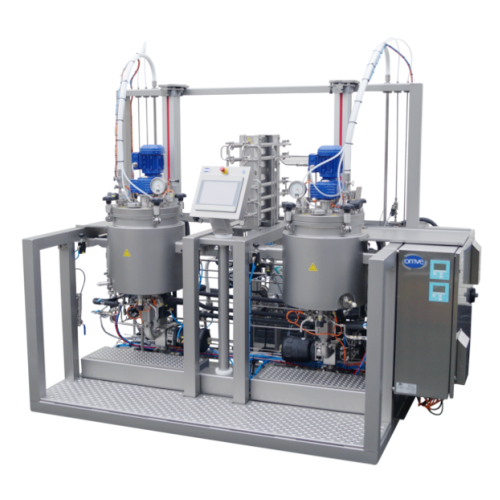
Pressurized fermenter for lab-scale fermentation
Achieve precise and controlled fermentation with this advanced pressurize...
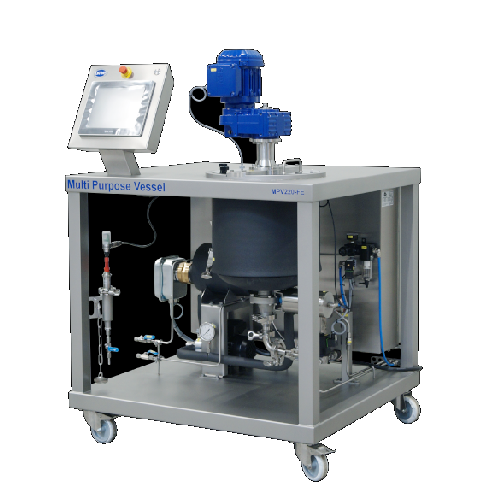
Atmospheric fermenter for lab and pilot scale projects
Streamline your fermentation process with precise control over tem...
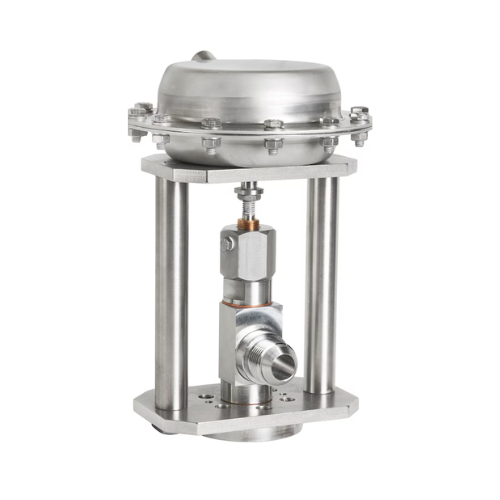
Cryogenic chilling system for meat processing
Ensure uniform temperature control in meat production lines to maintain prod...
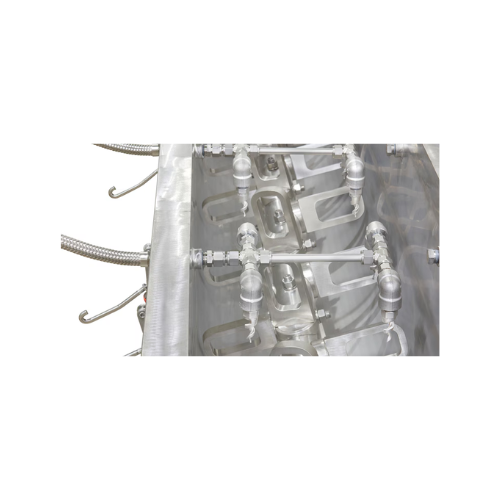
Cryogenic chilling systems for food processing
Efficiently maintain precise temperatures to enhance product quality and sa...
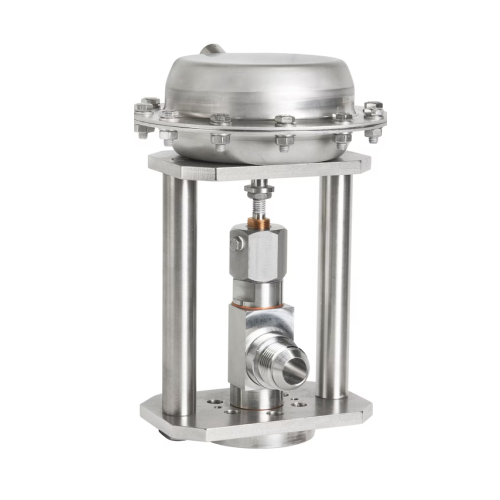
Cryogenic chilling for meat mixing and blending
Ensure precise temperature control during mixing and blending to prevent b...
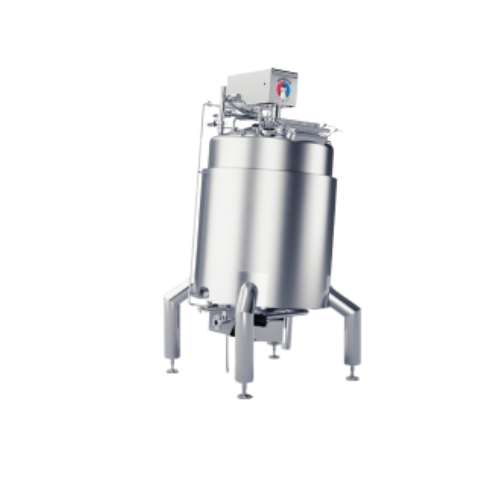
Heating and cooling system for food and dairy products
Achieve precise temperature control and efficient processing with ...
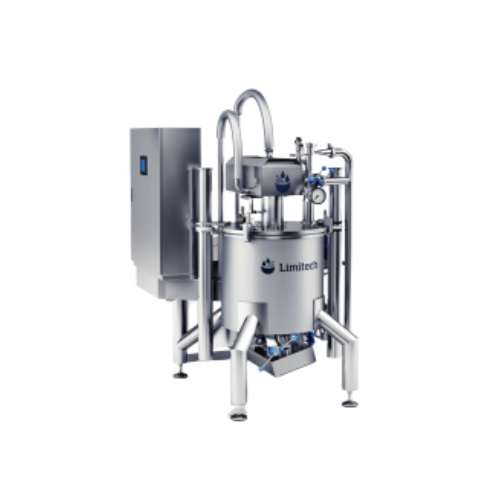
Multifunctional mixer for high volume batches
Efficiently handle complex mixing, emulsifying, and homogenizing tasks with ...
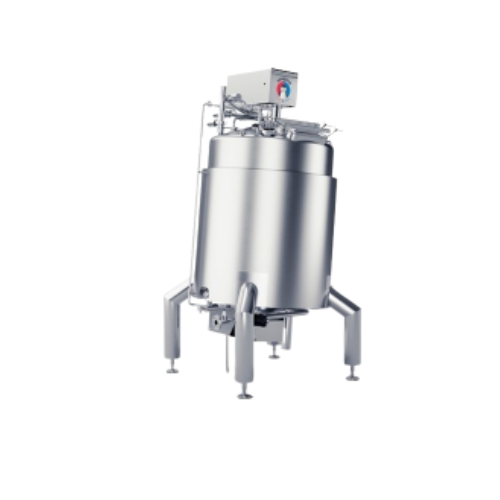
Heating solution for vegetable and meat products
Achieve efficient heating and optimal heat transfer for sauces and dairy ...
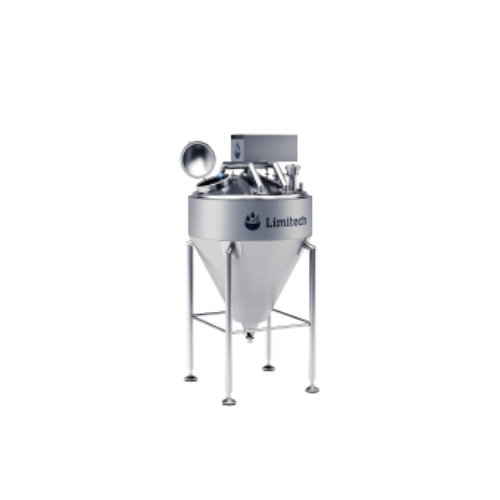
Conical buffer tank for hygienic dairy and food processing
Achieve efficient processing of high-viscosity products with ...
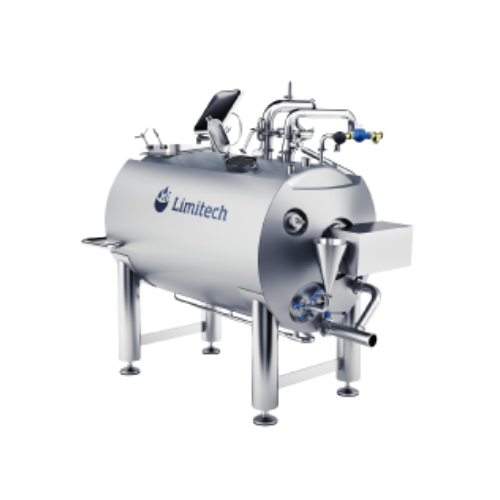
Emulsifying and blending system for liquid and semi-liquid food products
Efficiently emulsify and blend liquid and semi...
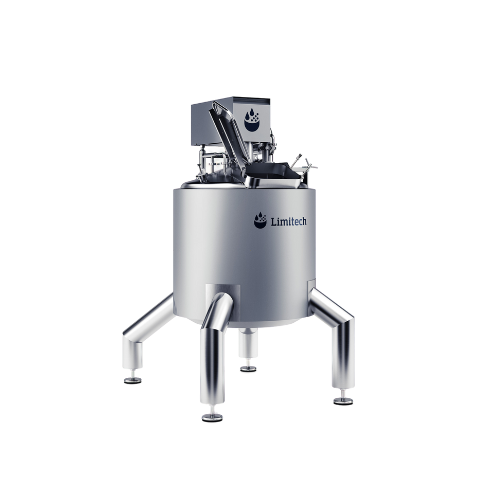
Powder dissolver for large liquid quantities
Achieve uniform powder blending swiftly with a vacuum-assisted system that pr...
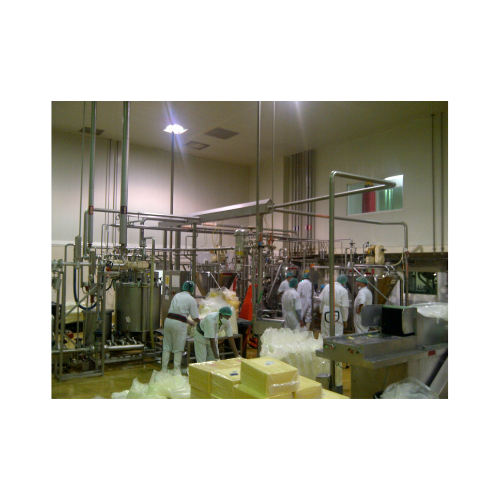
Ultra high temperature treatment system
Achieve extended shelf life and product stability with ultra high temperature treat...
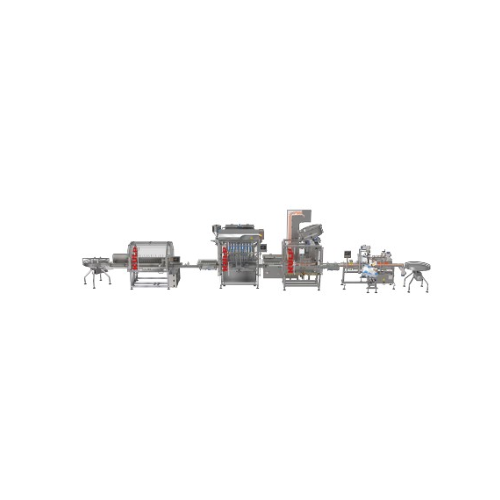
High capacity filling line for jars and bottles
Need to streamline your packaging line? This high-capacity solution proces...
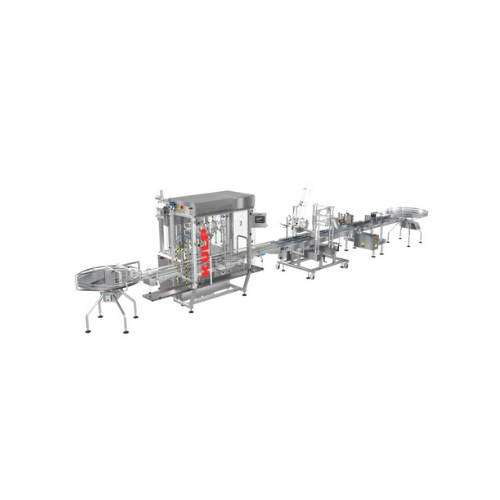
Large container filling line
Optimize your production line with a seamless solution for efficiently filling large containers...
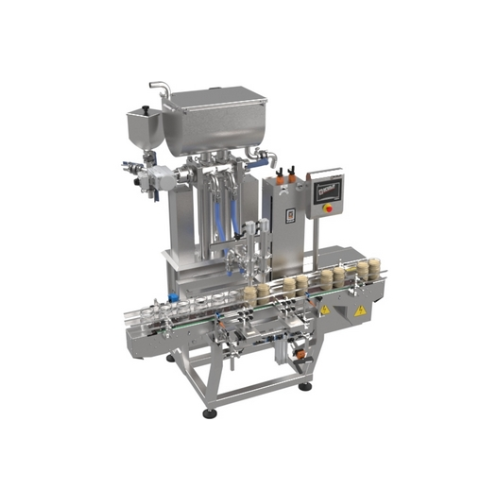
2-head liquid and viscous product filling system
Streamline your filling operations with precision and versatility designe...
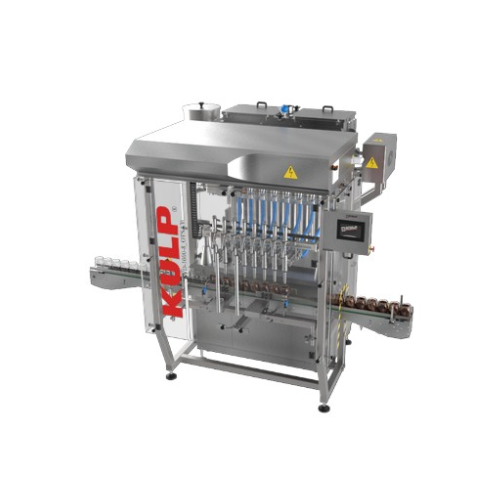
8 head liquid and viscous product filling system
When precision and speed are crucial, this 8 head filling machine ensures...
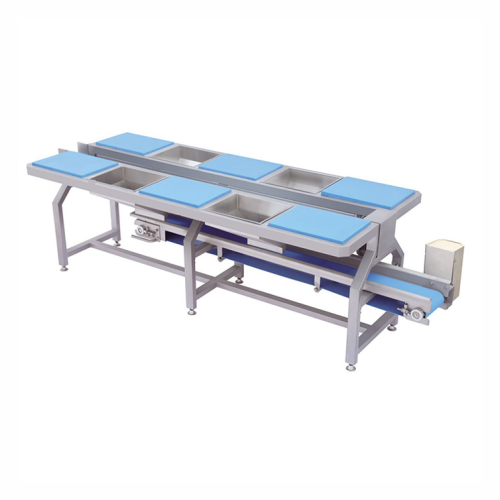
Vegetable and fruit preparation table
Optimize your food processing line with a versatile preparation table designed for ef...
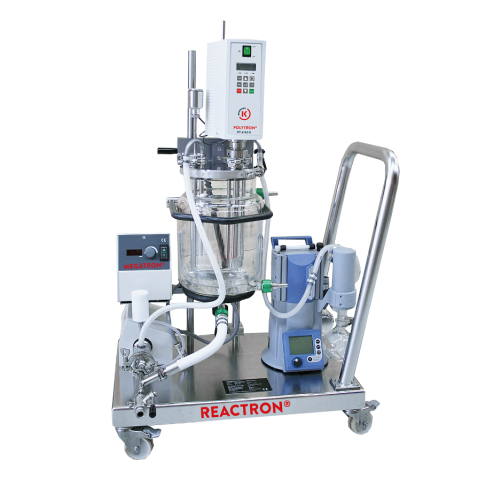
Highly scalable reactors for chemical synthesis
Optimize your production line with versatile reactors designed for seamles...
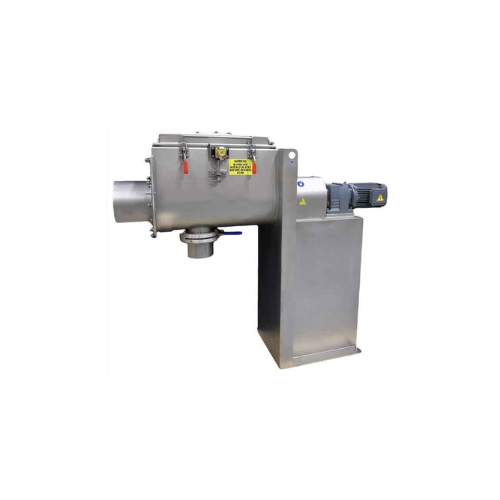
Homogenous blending solution for powders and granules
Achieve precise, homogenous blending of challenging materials like ...
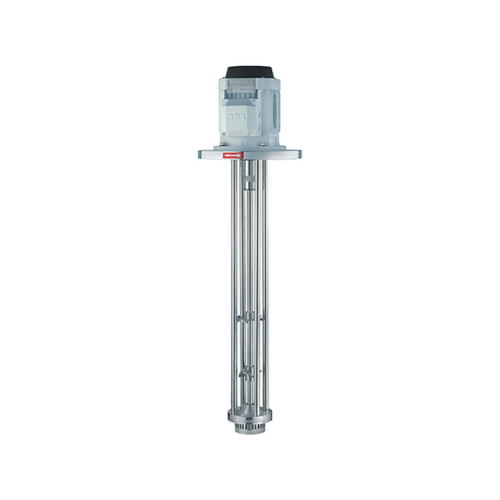
High shear vertical mixer for dispersion and emulsification
Achieve seamless emulsification and homogenization in divers...
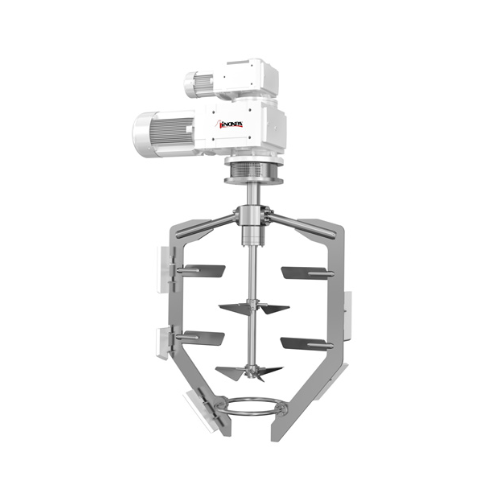
Counter-rotating agitator for high viscosity products
Achieve seamless heat transfer and precise mixing with a counter-ro...
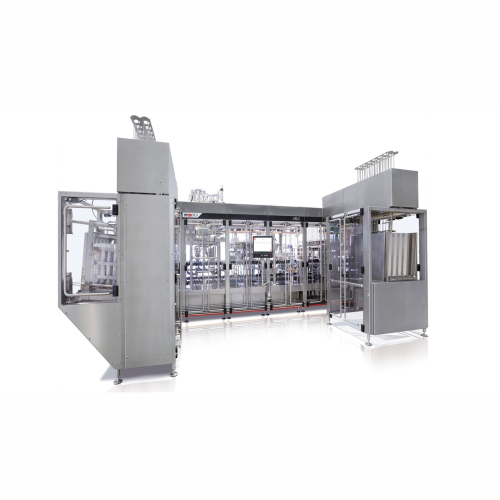
Flexible filling and sealing system for pre-formed cups
Achieve precise portioning and consistent quality in your product...
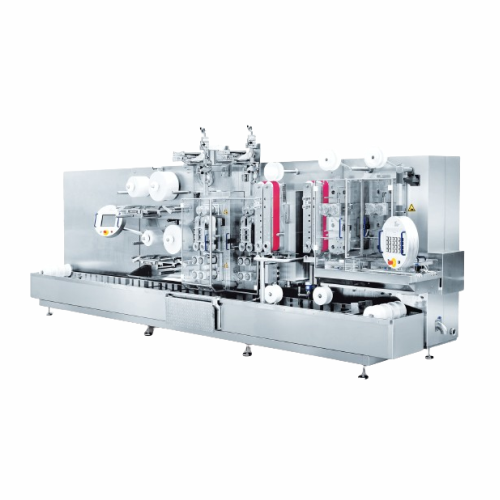
High-speed cheese slice wrapper
Achieve unparalleled efficiency with the high-speed wrapping machine that securely packages ...
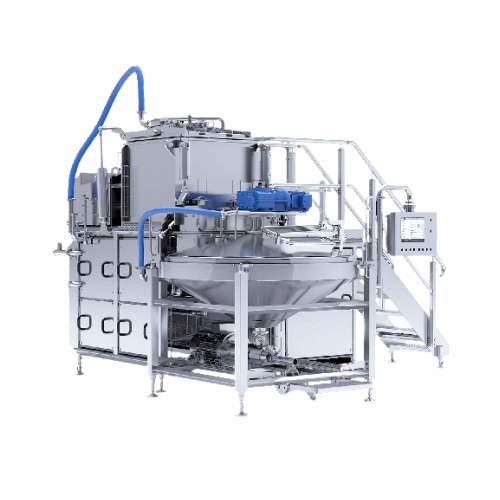
Multifunctional batch cooker for various food products
Optimize your production line with a versatile batch cooker design...
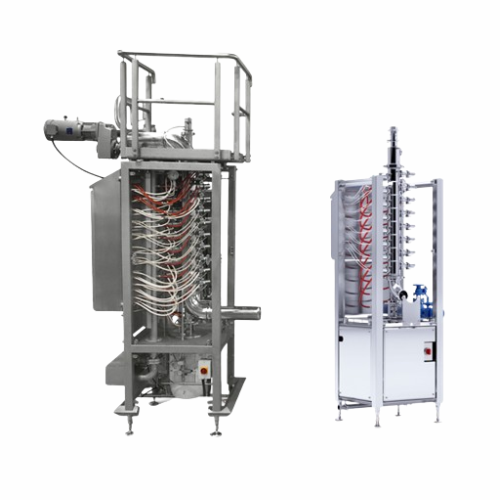
Continuous cooker for high-volume food processing
Elevate your production efficiency with a continuous cooker that ensure...
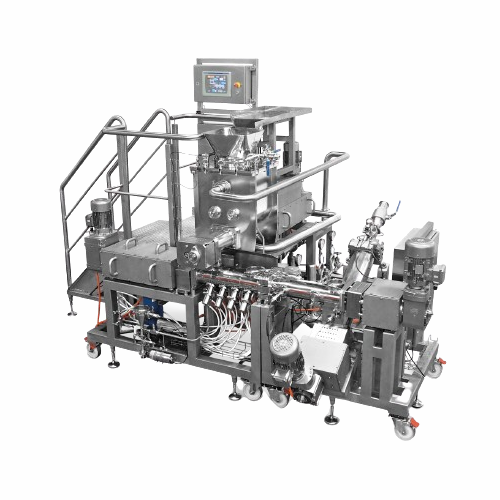
Mozzarella cooker stretcher for continuous production
Experience continuous mozzarella production with steam injection te...
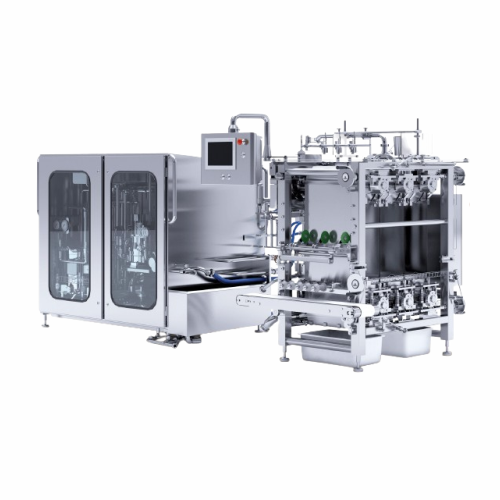
Pilot unit for processed cheese slices
Perfect for R&D and small-scale production, this adaptable unit offers high fle...
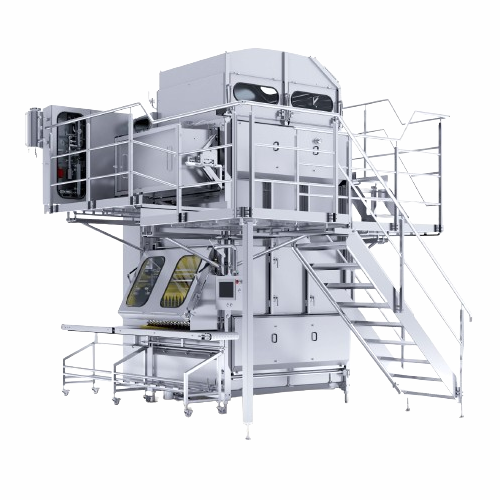
Processed cheese slice production system
Reduce recontamination risks in cheese production with a system designed for high-...
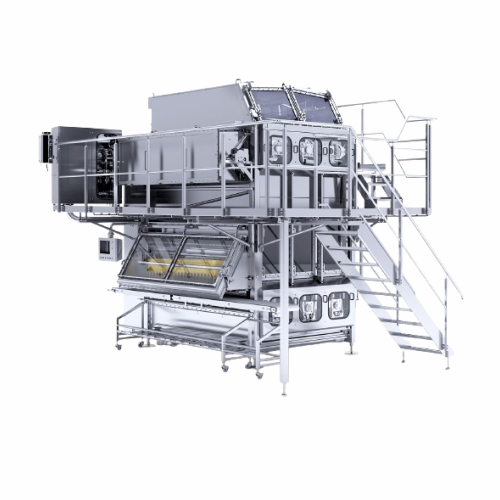
Cheese forming and slicing system
Optimize your cheese production with high-speed, precision forming and slicing, ensuring ...
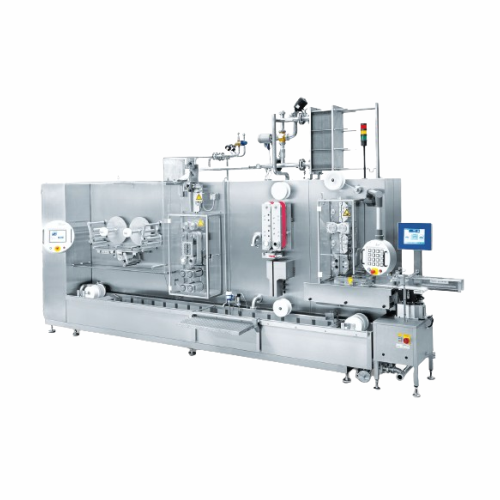
Individually wrapped processed cheese slice production line
Efficiently produce consistent, individually-wrapped cheese ...

Separating packed cheese products from packaging
Efficiently separate individual cheese portions from packaging, reducing ...
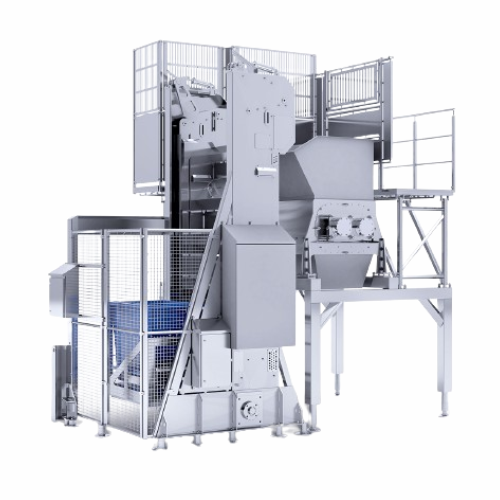
Cheese and butter block grinder
Efficiently transform frozen cheese and butter blocks into manageable sizes for continuous p...
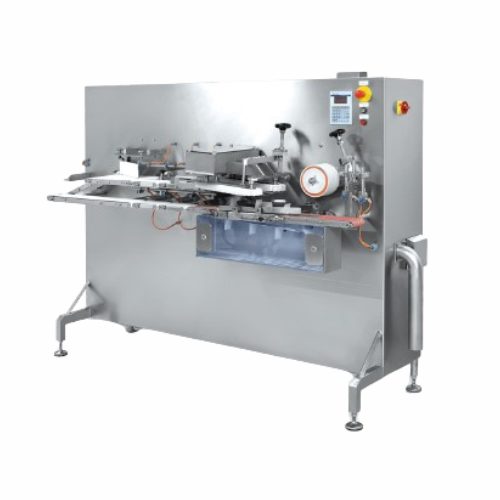
Cheese packaging system for mixed cheese types
Optimize your cheese production line by seamlessly integrating a system des...
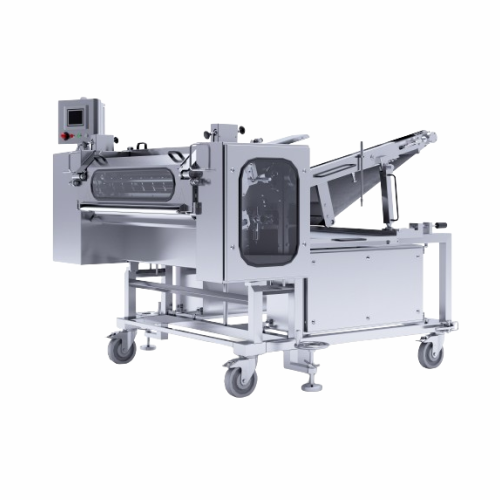
Processed cheese stick cutter
Achieve precise and consistent cheese stick production with a machine designed to streamline f...

Cheese ribbon cutting solution
Achieve precise and efficient cheese ribbon cutting with high-speed operations, ensuring perf...
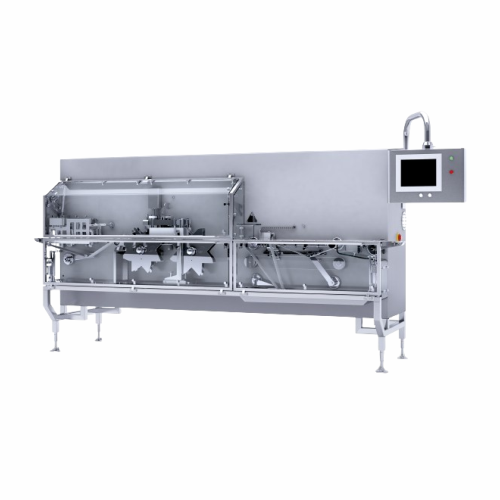
Automatic cheese stack and grouping system
Efficiently stack and group cheese slices to streamline your production line an...
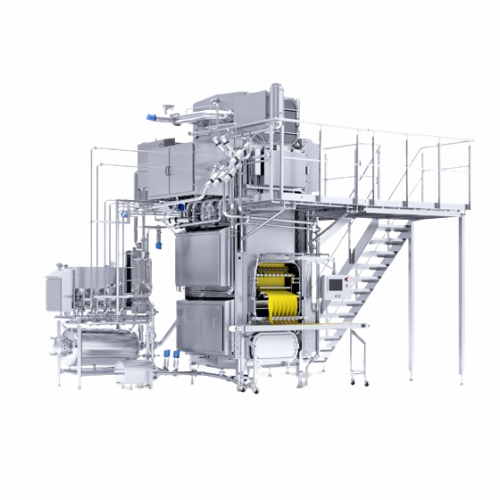
Processed cheese slice forming system
Effortlessly produce high-quality Slice-on-Slice cheese slices, cubes, shreds, and st...
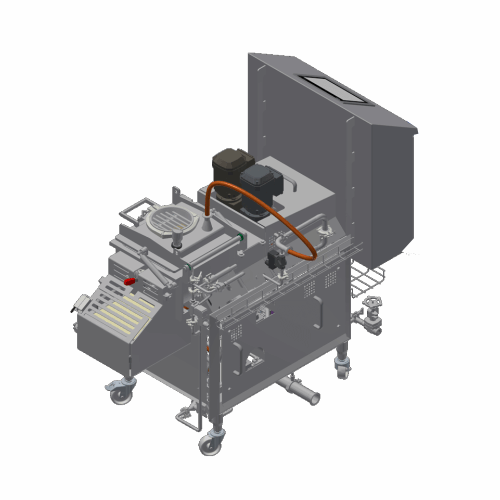
Multifunctional batch processing system for processed cheese
Enhance your production line with a sophisticated batch pro...
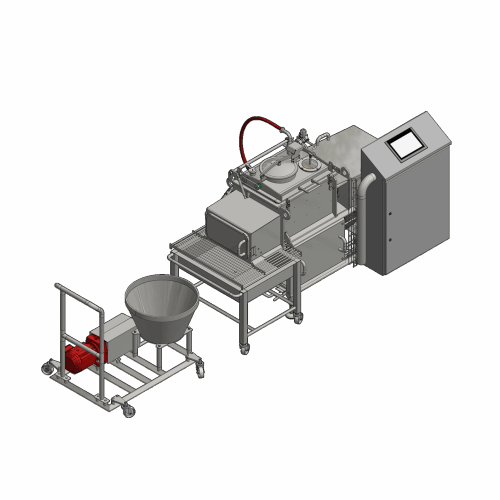
Batch processing system for processed cheese and sauces
Optimize your food processing line with a versatile batch process...
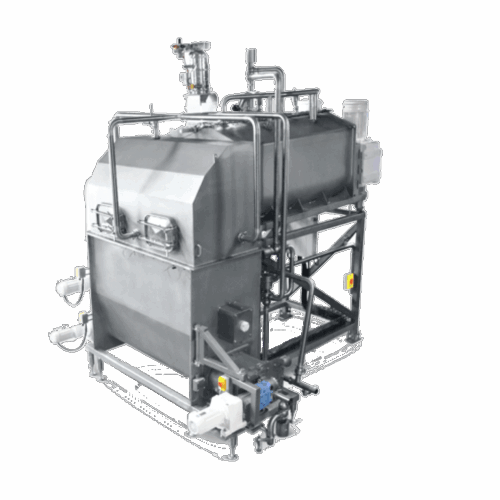
Twin ribbon blender for processed cheese and meat products
Achieve seamless blending and consistent feeding for large-sc...
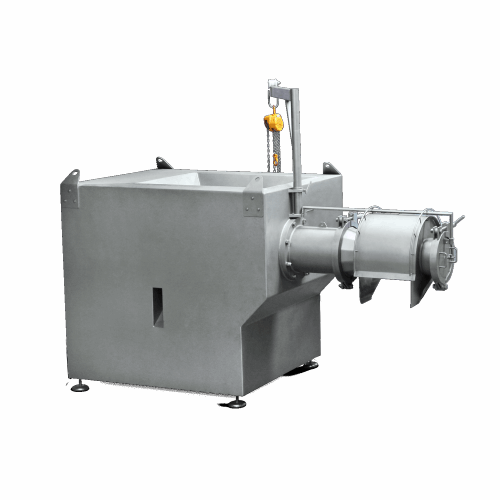
Cheese grinder for fine cheese grinding
Achieve optimal protein emulsification and minimize waste with this high-capacity g...
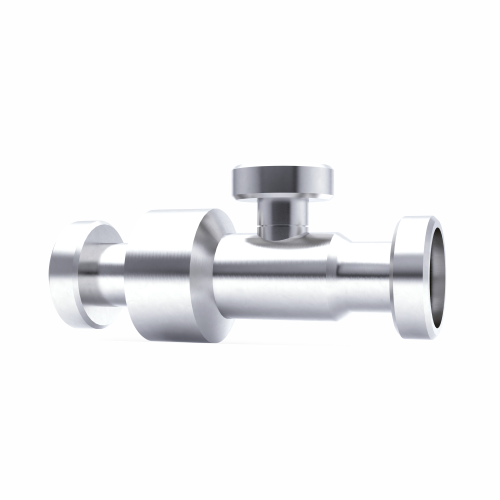
Magnet for emulsion technology for lump-free blends
Achieve perfectly smooth and stable emulsions in a single pass with a...
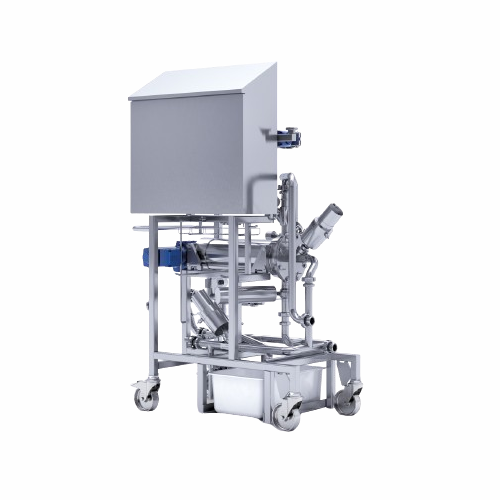
Automated filter cleaning system for food production lines
Eliminate frequent production interruptions by utilizing an a...
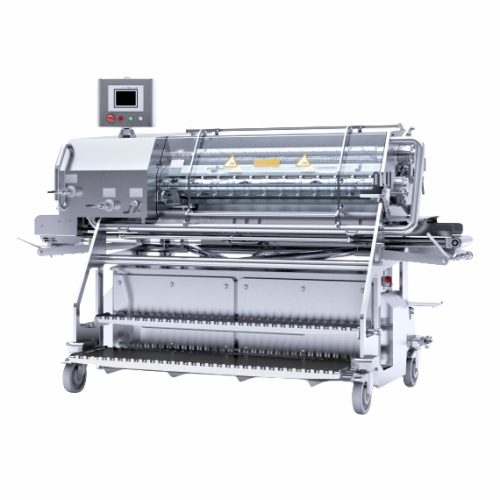
Cheese cube and shreds production line
Achieve precision cutting for cheese products while seamlessly integrating forming a...

Beer production filtration system
Enhance your beverage production with cutting-edge filtration systems designed to maintai...
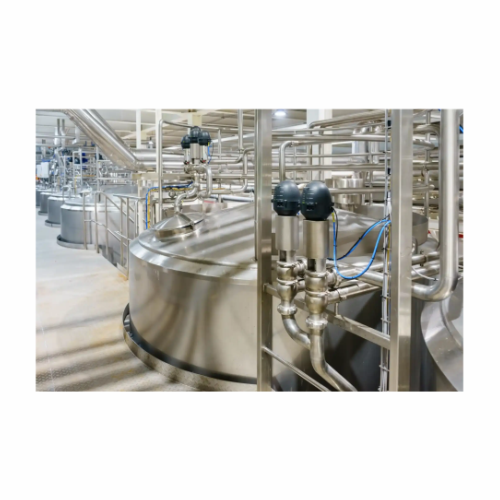
Filtration system for Cip cleaning in food production
Optimize your cleaning processes with a state-of-the-art filtration...
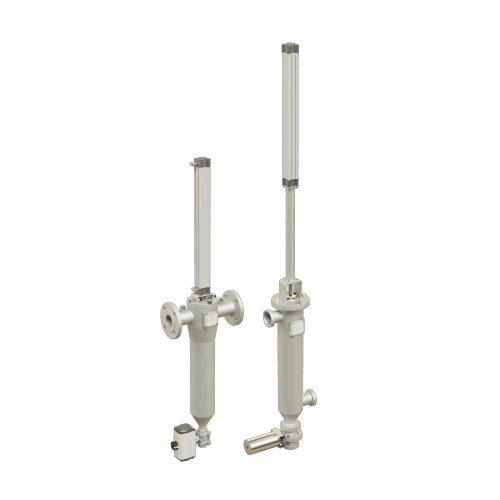
Self-cleaning automatic filters for industrial liquids
Ensure reliable filtration of high-contamination liquids while min...
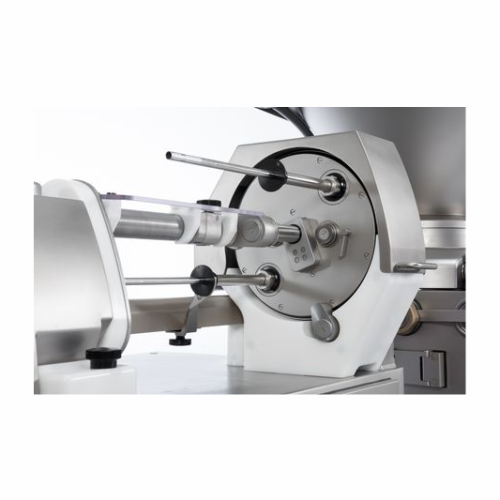
Sausage filling line for natural, collagen, and peel-off casings
Streamline your sausage production with rapid casing ch...
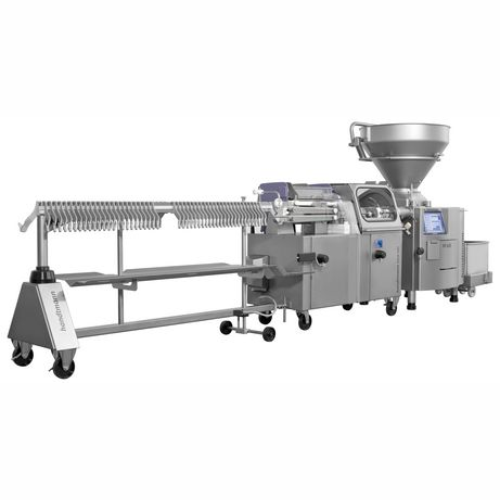
Automatic sausage filling and hanging system
Streamline sausage production with precise portioning and seamless integratio...
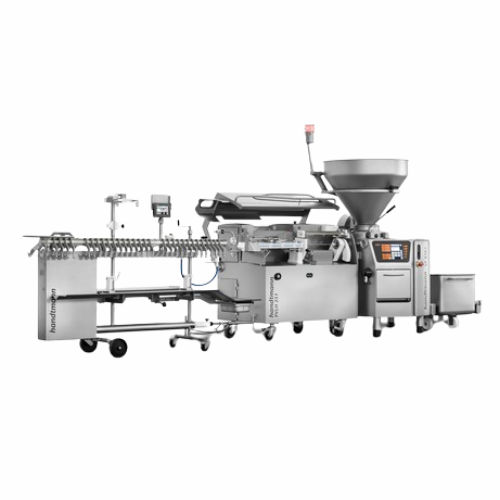
High-performance sausage linking and hanging line
Boost your production efficiency with a high-speed line designed for se...
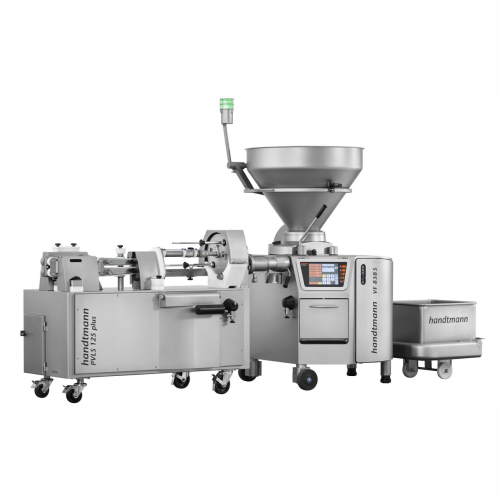
Sausage filling line for adjustable portions
Achieve precision in high-speed sausage production with rapid casing changes ...
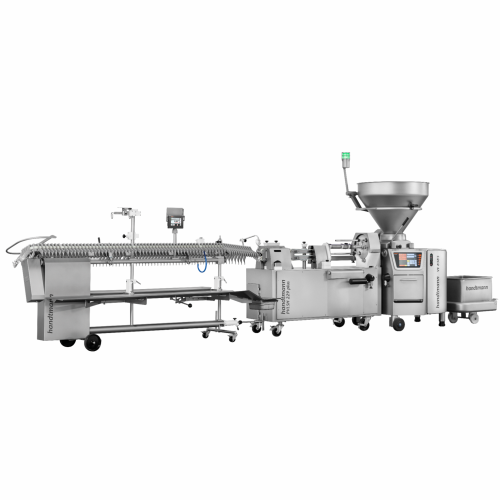
Automated sausage filling and portioning line
Boost your production efficiency with a versatile solution that seamlessly h...
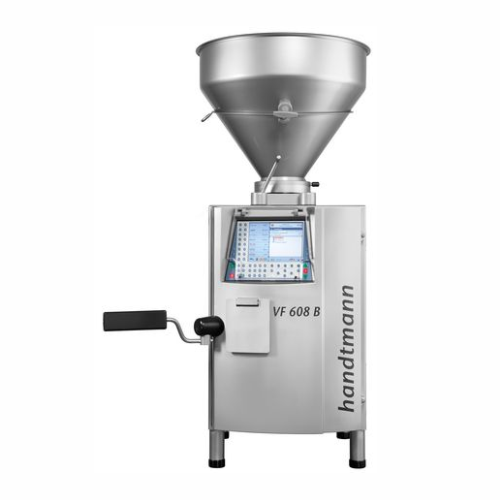
Dough portioning system for bakery operations
Achieve precise dough portioning with minimal waste using our advanced syste...
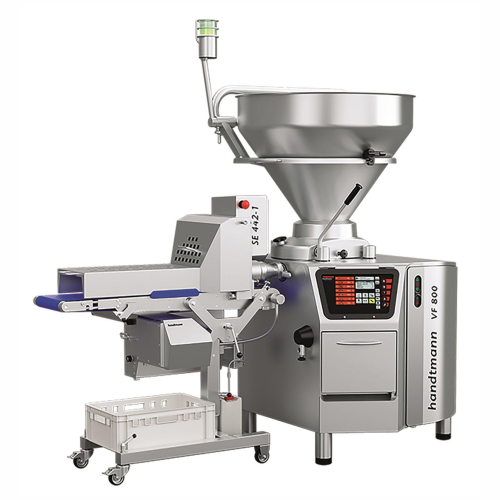
Continuous dough dividing and portioning system
Achieve precise dough portions and enhance product quality with high-speed...
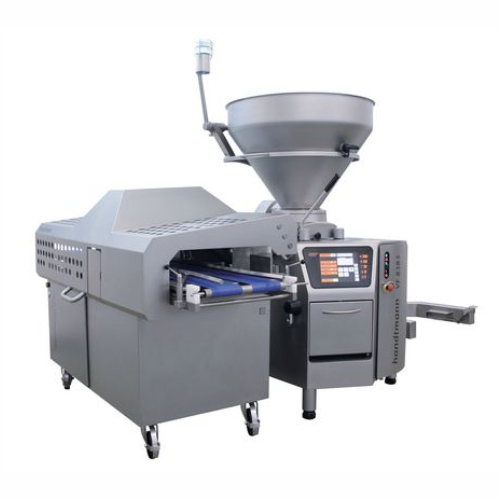
Cutting unit for high-yield tin loaves
Experience precision and efficiency in dough portioning with our high-capacity cutti...
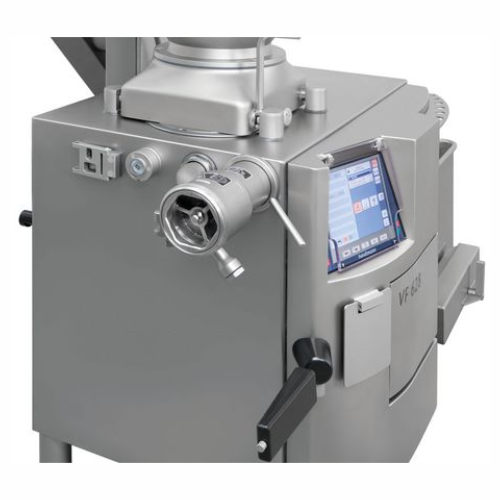
Inline grinding system for sausage and minced meat production
Streamline your production line by simultaneously grinding...
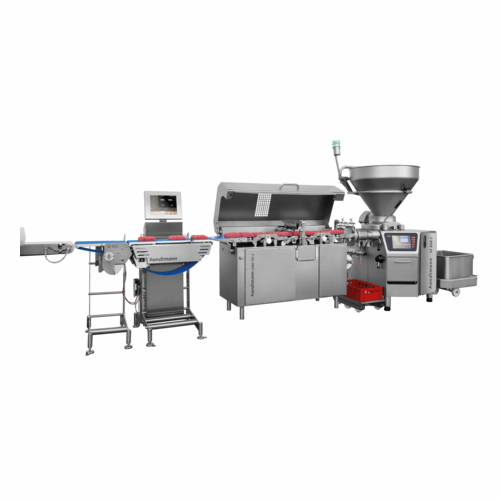
Minced meat portioning line
Optimize your production line with precise portioning and packaging of minced meat, enhancing ef...

Industrial grinder for ultra-fine grinding and homogenizing
Enhance your production line with versatile grinding technol...
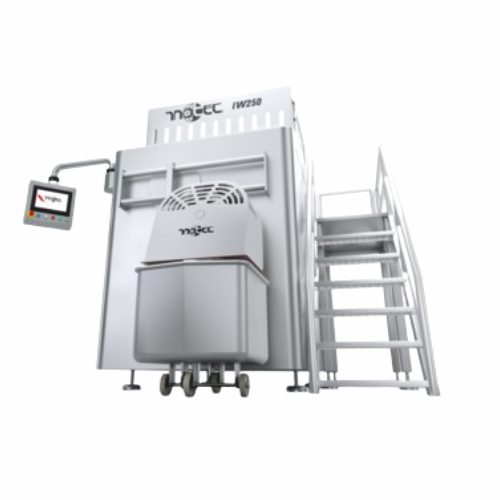
High-capacity industrial grinder for frozen and fresh raw materials
Effortlessly grind both deep-frozen blocks and fres...
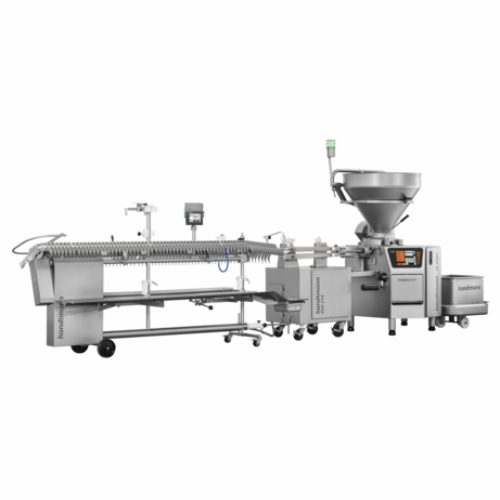
Automated sausage filling and portioning system
Streamline your sausage production with precision filling and versatile po...
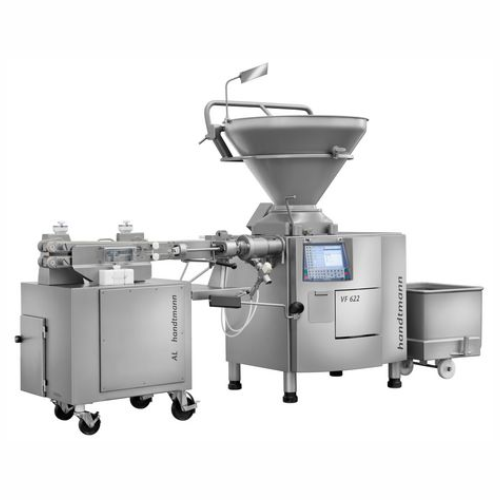
Automatic sausage filling and separating system
Achieve precise portioning with exact weights and lengths for sausages, st...
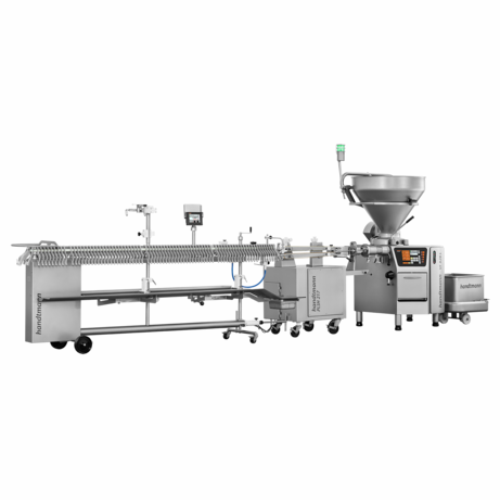
Sausage filling and portioning line
Streamline your sausage production with versatile equipment designed to seamlessly inte...
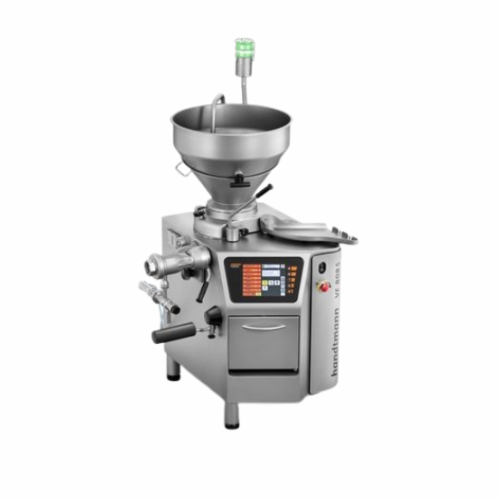
Compact vacuum filler for small to industrial scale food processors
Achieve precise portioning and high-speed productio...
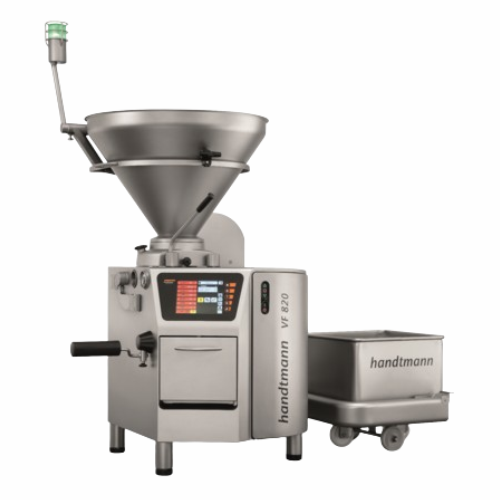
Vacuum filler for medium-scale sausage production
Achieve precise portion control and optimal hygiene with a versatile fi...
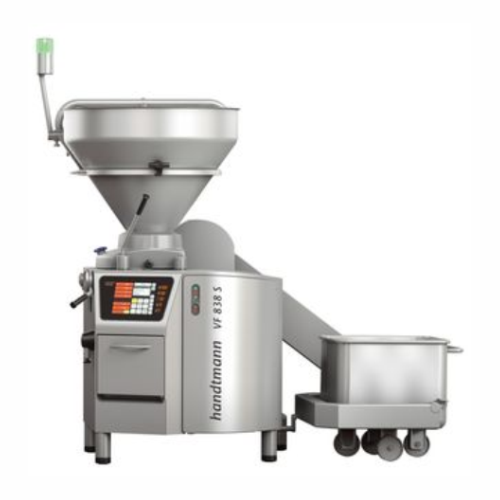
High-pressure vacuum filler for industrial sausage production
Effortlessly tackle high-pressure demands in sausage produ...

Vacuum filler for sausage and ham production
Achieve precision in filling and portioning pasty and fluid products with a s...
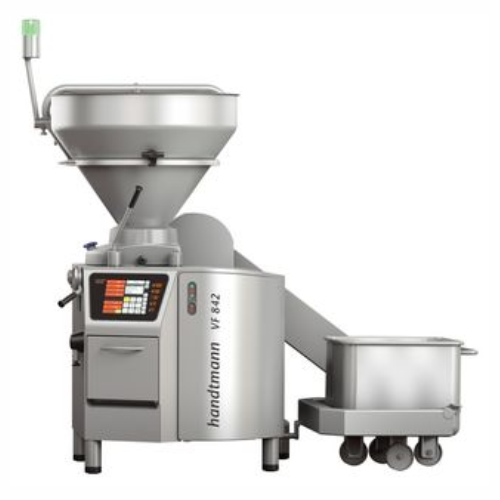
Industrial sausage and ham vacuum filler
Achieve unmatched precision in filling and portioning with high-capacity vacuum te...
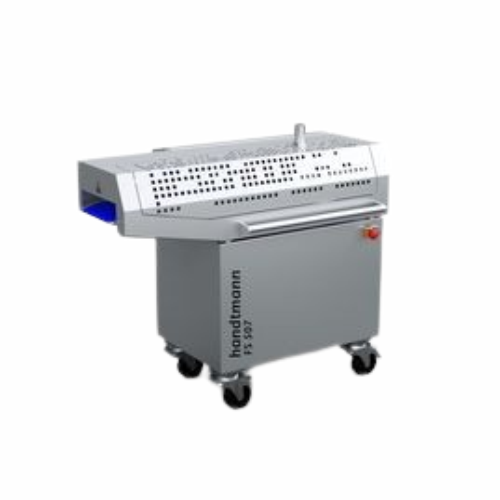
Forming system for minced meat products
Achieve high-quality formed meat and plant-based patties with precision and flexibi...
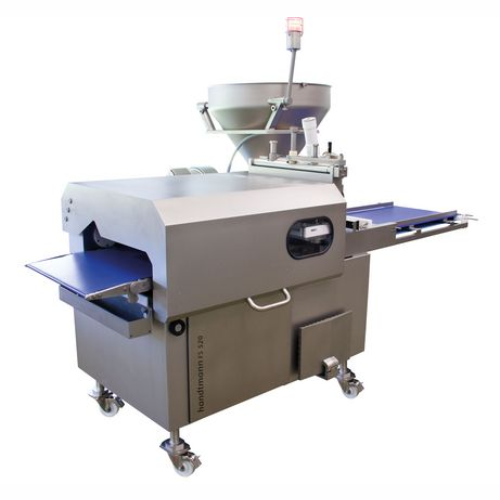
Multi-lane forming system for 3d food product shapes
Achieve precise weight accuracy and high-speed production of diverse...
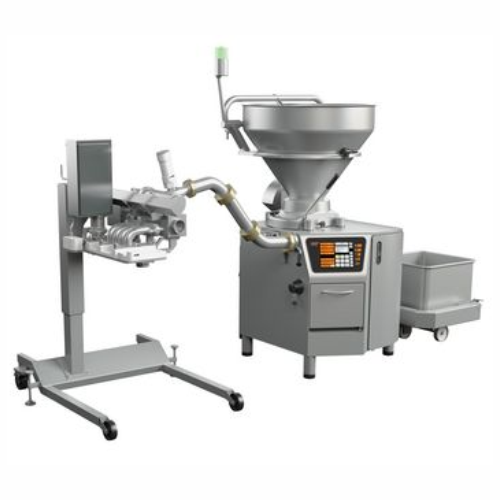
Forming system for multi-lane production of shaped foods
Streamline your production of uniform shaped foods with a multi-...
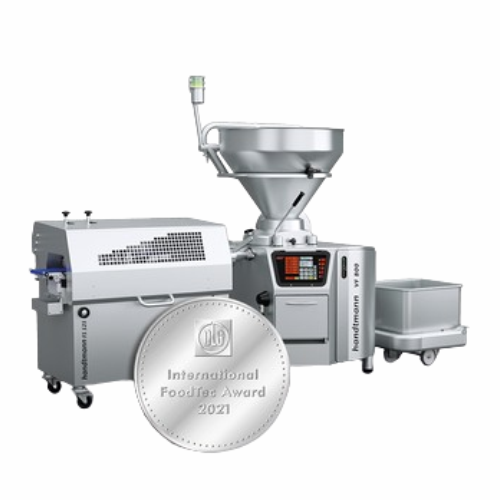
Industrial forming and cutting system for diverse products
Maximize product versatility with a system that effortlessly ...
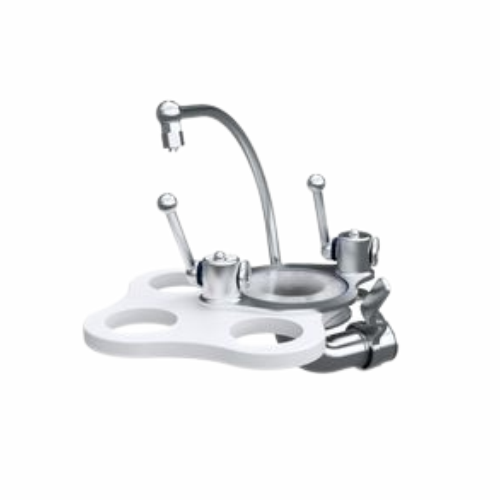
Manual forming unit for burger patties
Produce up to 30 perfectly shaped burger patties per minute with consistent quality ...
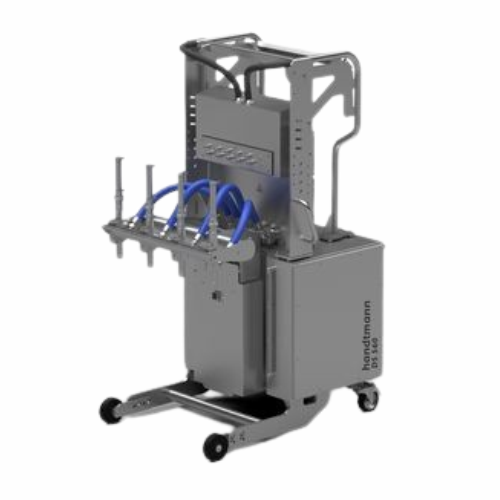
Depositing system for multi-lane dosing with vertical traversing
Achieve precision dosing and flexible portioning with t...
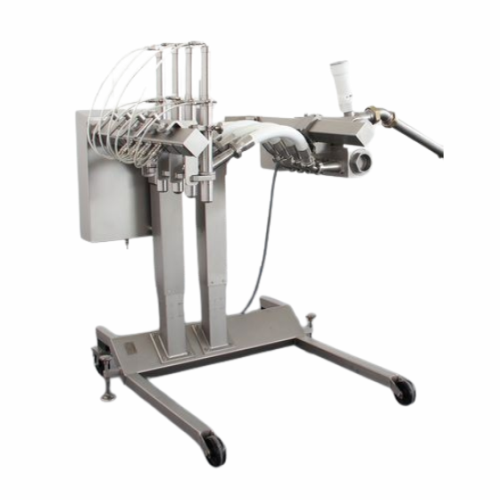
Filling flow divider for food and pet food applications
Optimize your production line with precision filling flow divider...
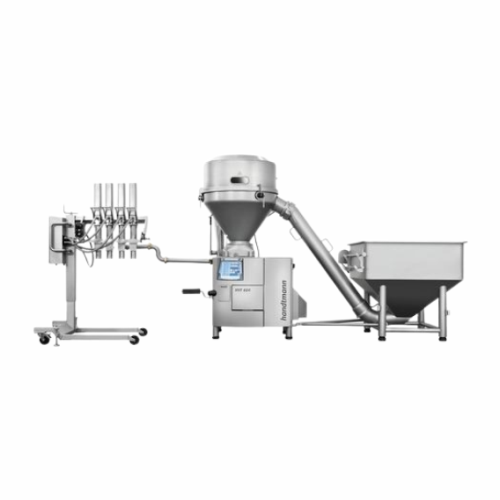
Cutting valve for chunky food portioning
Achieve precise portioning of chunky products, reducing waste and increasing effic...
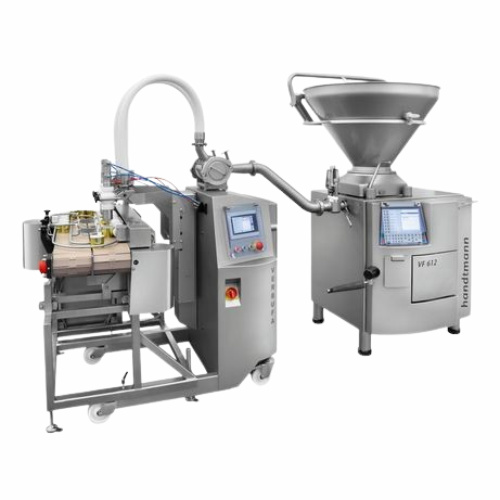
Automatic multi-lane dosing system for fluid to pasty products
Streamline your production with precise multi-lane dosing...
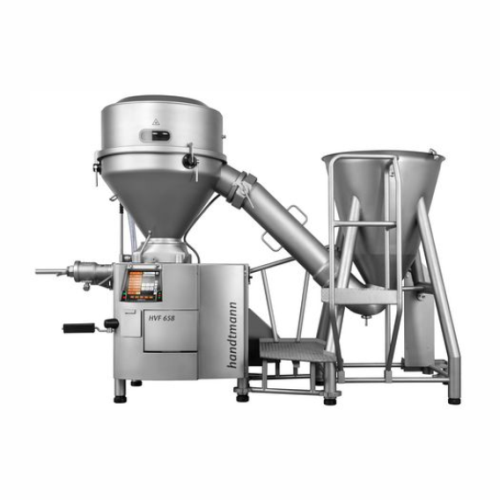
High vacuum filler for dry sausage products
Achieve pore-free, compact dry sausage products with superior evacuation perfo...
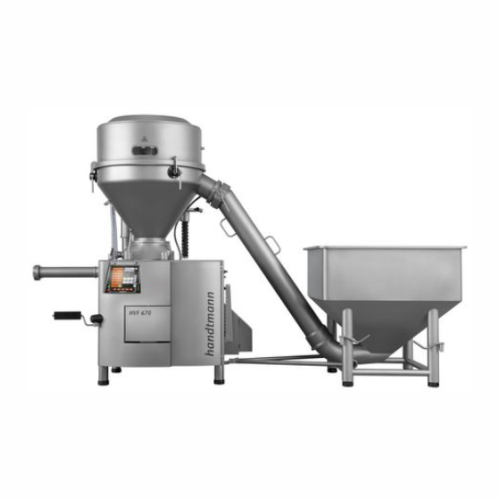
High vacuum filler for ham and ground material
Achieve unrivaled product quality and precision with high vacuum technology...
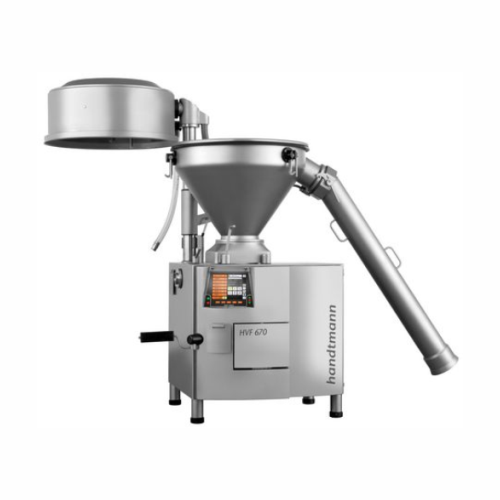
High vacuum filler for cooked ham with whole muscle pieces
Ensure precision and quality in cooked ham production with hi...
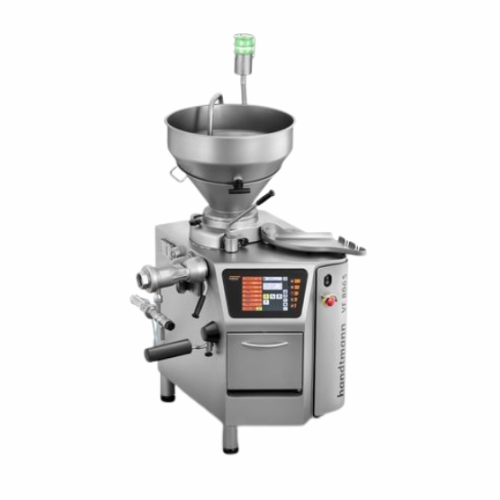
Vacuum filler for small and medium-scale meat producers
Achieve precise portioning with high-speed filling and grinding c...
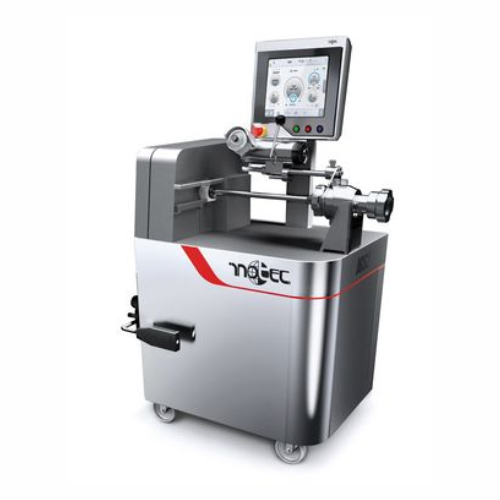
Tying solution for sausage products in natural and collagen casings
Efficiently portion and tie sausage products to per...
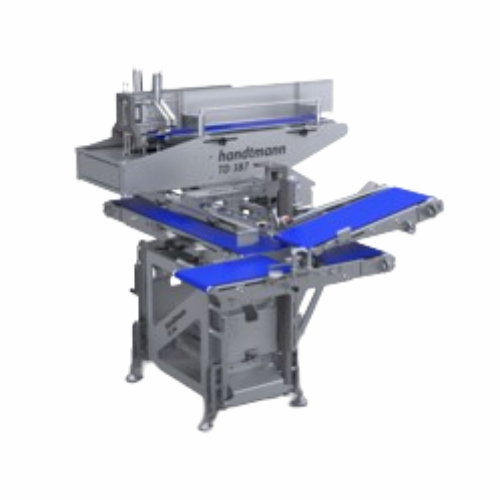
Automatic tray loader for minced meat portions
Streamline your tray loading process by integrating a flexible and fully au...
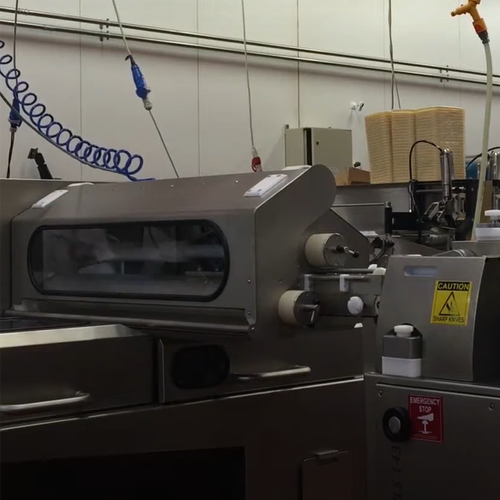
Collating system for fresh sausage automation
Maximize production efficiency by seamlessly integrating automated collating...
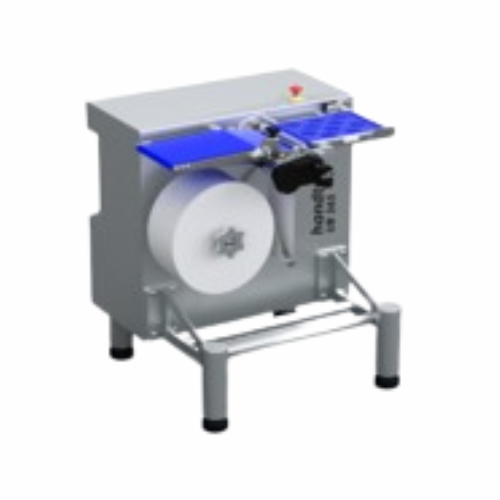
Product aligning and stacking solution
Enhance process stability and resource efficiency by integrating precise product ali...
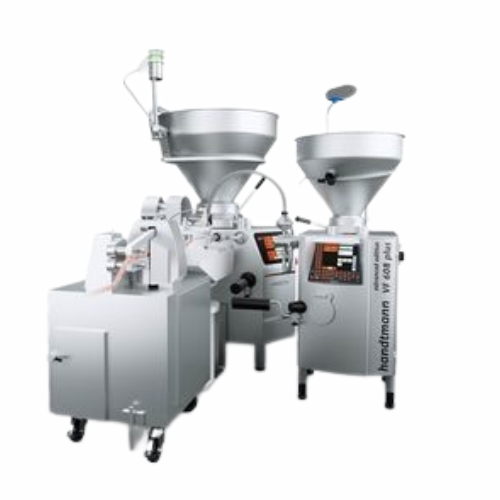
Industrial co-extrusion system for sausages with alginate casing
Eliminate the need for traditional sausage casings with...
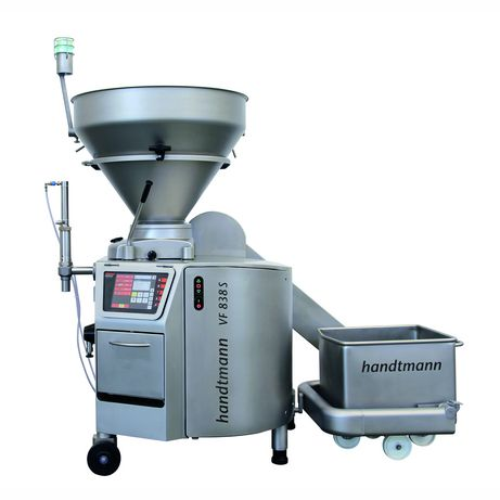
Precise dosing valve for pasty products
Achieve precise, gram-accurate dosing for a wide array of pasty and semi-viscous pr...

Ribbon blender for homogeneous blending of solids
Achieve perfectly consistent blends with a ribbon blender that ensures ...
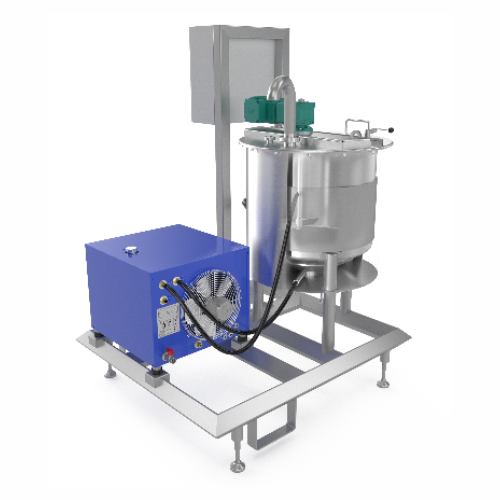
Stainless steel skids for food process integration
Optimize your production process with compact stainless steel skids th...

Stainless steel agitators for pharmaceutical and food applications
Optimize your production line with tailored agitator...
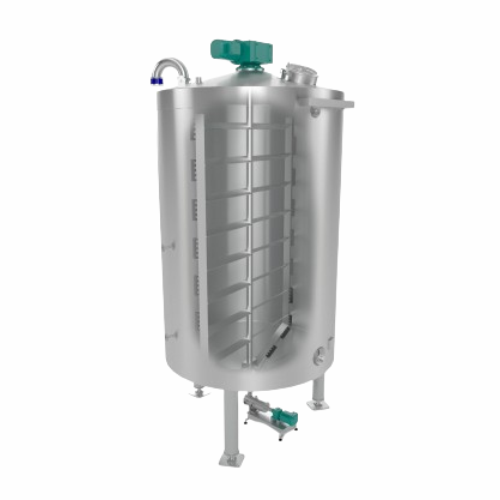
Stainless steel chocolate tank for storage and processing
Efficiently control temperature and consistency for chocolate ...
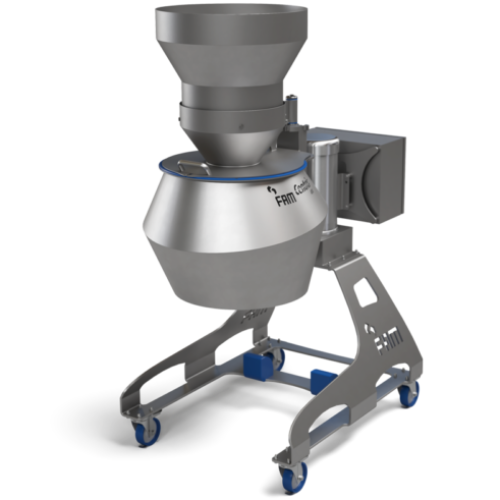
Vegetable and fruit centrifugal slicer and shredder
Enhance your food processing with high-capacity slicing and shredding...
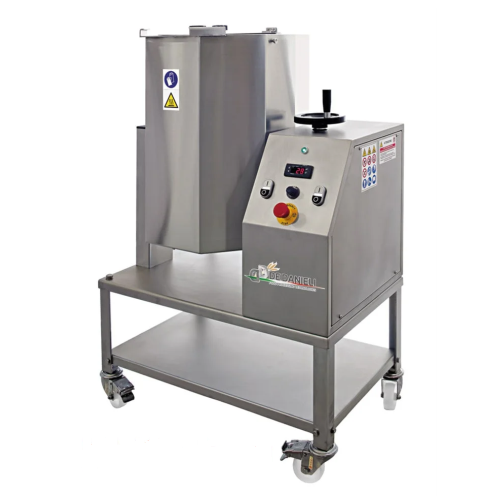
Compact cooker for confectionery and catering
Effortlessly prepare diverse culinary and cosmetic creations, from sauces to...
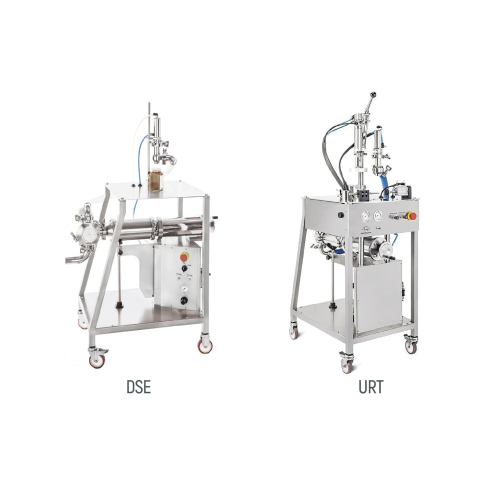
Pneumatic dosers for variable density products
Achieve precise dosing for liquid to dense products with versatile pneumati...
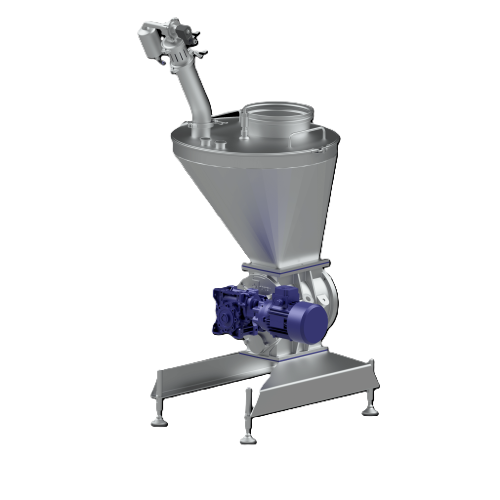
Dilute-phase conveying solution for powder handling
Efficiently transfer powders and granules with robust leak containmen...
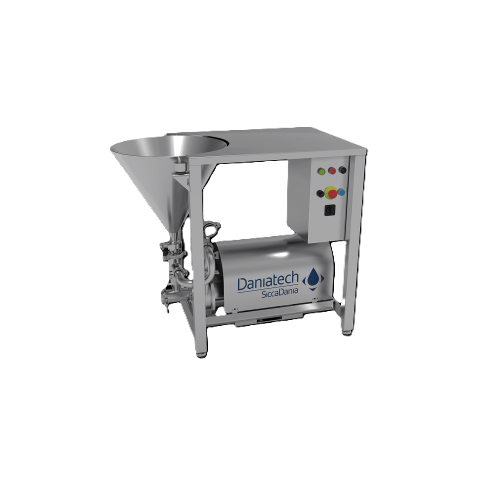
Inline high-shear mixer for powders and liquids
Achieve efficient mixing and homogenization in your production line with a...
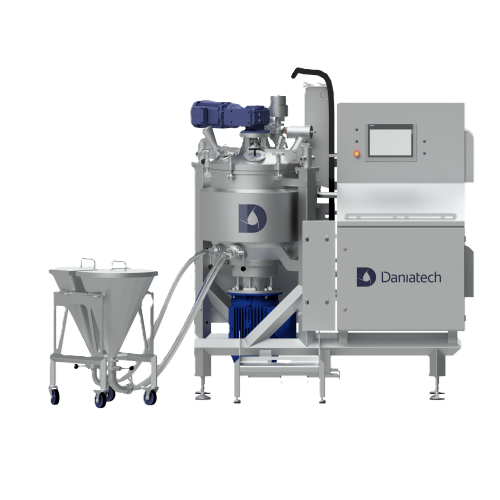
Lab-scale high-shear mixer for recipe development
Optimize your recipe development process with precise mixing, homogeniz...
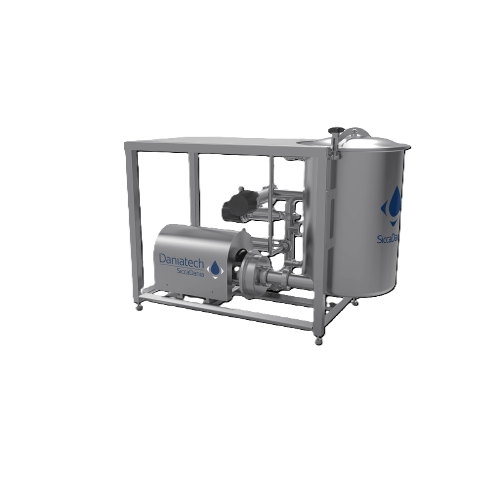
Mixer for low to medium viscosity products
Optimize your mixing, dosing, and homogenization processes with a versatile mix...
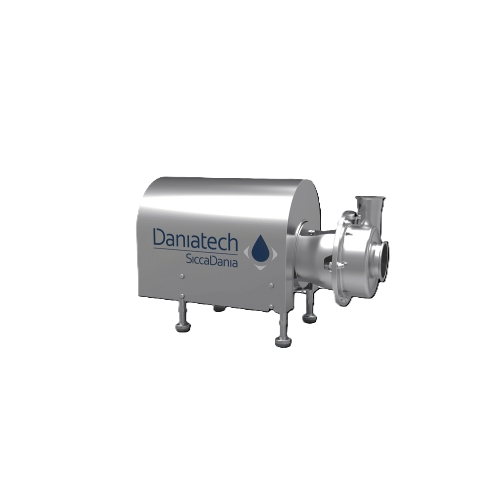
Inline high shear mixing unit for low to medium viscosity products
Achieve precise emulsification and size-reduction wi...
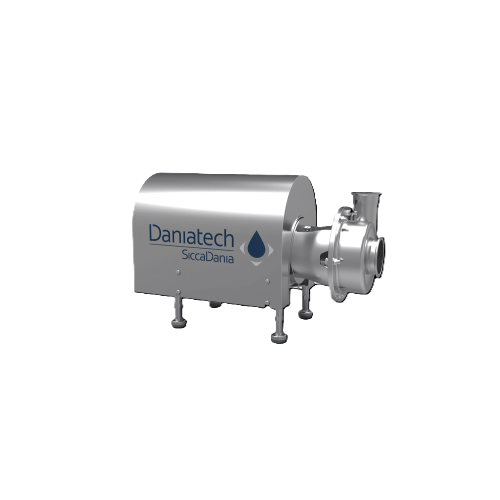
Ultra-high shear mixer for emulsification and homogenization
Optimize your production with ultra-high shear mixing, acce...

Vacuum high shear mixer for medium to high viscosity products
Achieve flawless blending and air-free consistency in visc...
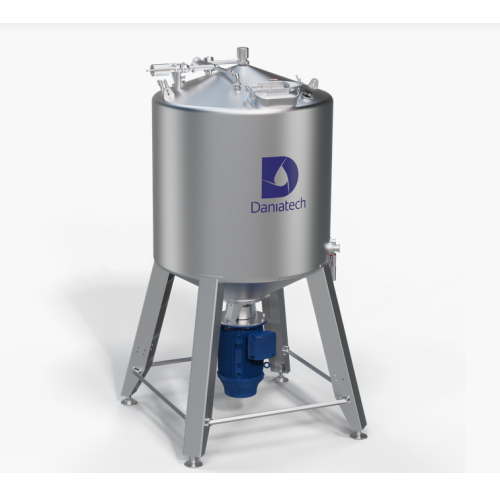
High-capacity manual mixer for industrial applications
Optimize your mixing process with a highly efficient, manually ope...
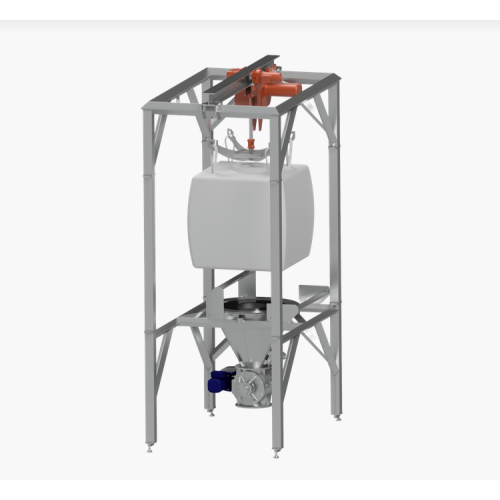
Bigbag discharge system for food, chemical, and pharmaceutical industries
Ensure precise and dust-free handling of bul...
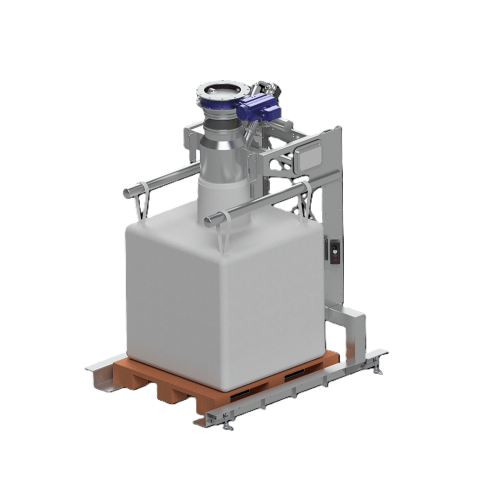
Bigbag filling system for powder and bulk materials
Ensure precise and dust-free bigbag filling with this versatile syste...
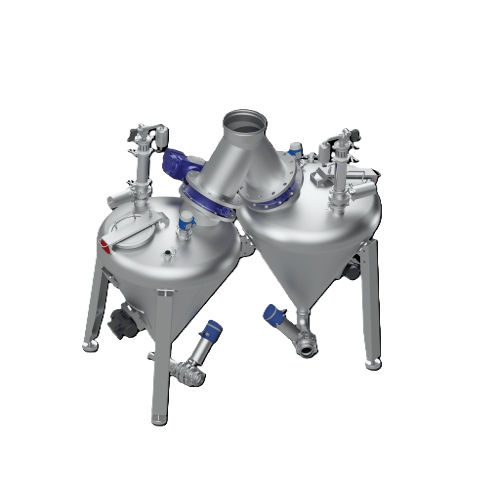
Dense-phase powder conveying system
Optimize your powder processing with a system designed to handle abrasive and fragile m...
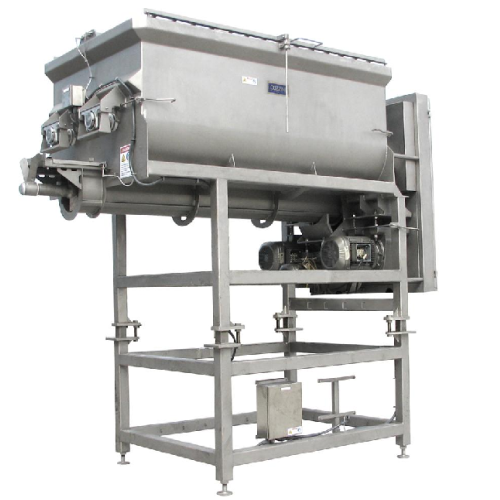
Overlapping paddle mixer for precise food processing
For precise and thorough mixing in food processing, this solution en...
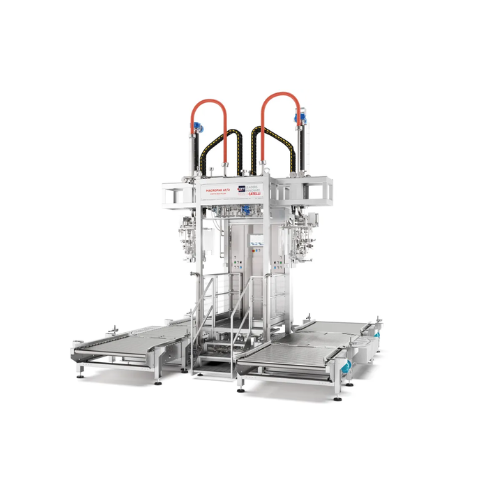
Aseptic fillers for liquid and viscous products
Ensure sterile and precise filling of liquid and viscous foods with adapta...
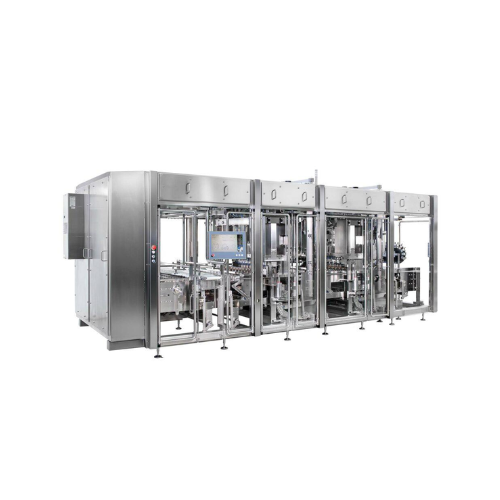
High-capacity filler and closer for pumpable products
Efficiently handle pumpable, flowable, and pasty products with this...
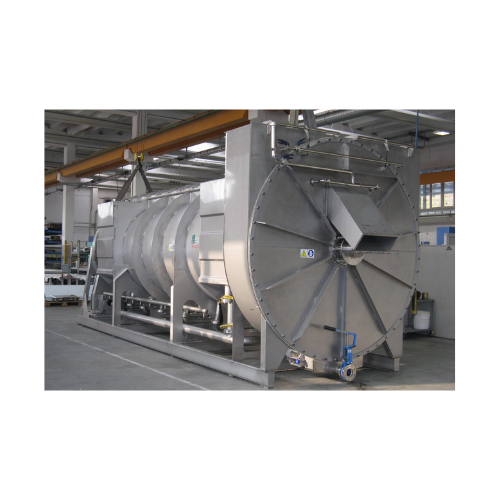
Drum blancher for continuous cooking and blanching
Optimize your production line with a continuous drum blancher, designe...
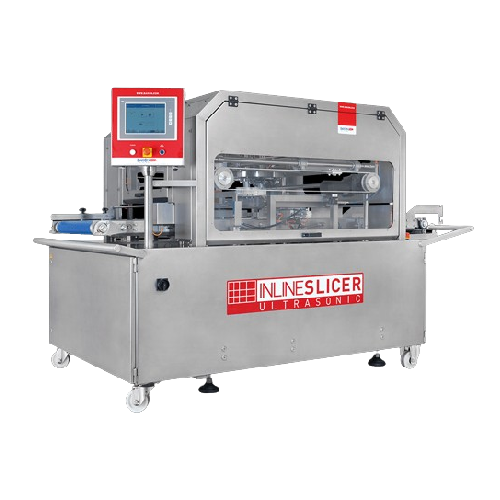
Inline ultrasonic slicer for bakeries
Achieve consistent precision in high-speed food portioning with this cutting-edge sli...
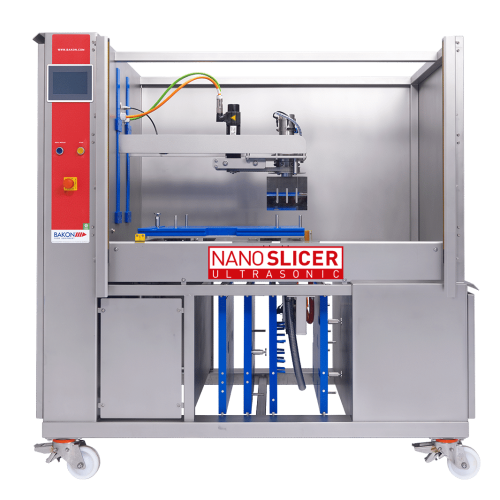
Ultrasonic slicer for precise food cutting
Achieve perfectly portioned bakery and food products with precision ultrasonic ...
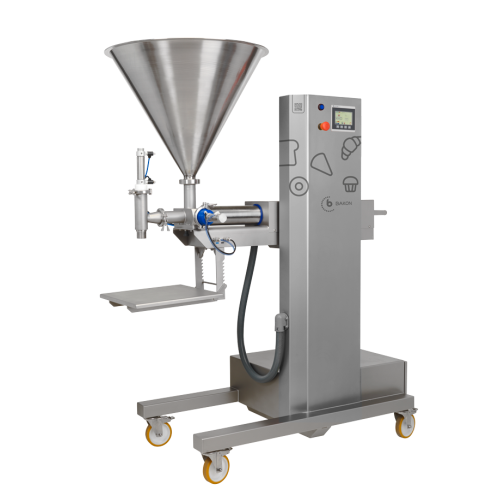
Depositing solutions for liquid and semi-liquid foods
Ensure consistent portioning and minimize waste with advanced depos...

Depositing line for cake production with paper cup denester
Optimize your cake production by seamlessly depositing marbl...
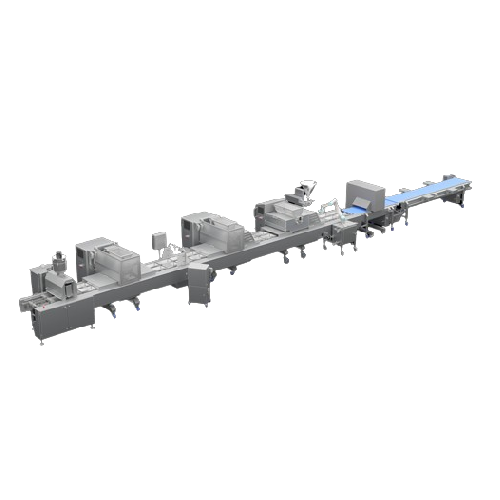
Multifunctional depositing line for bakery production
Optimize your bakery and food production with a modular depositing ...
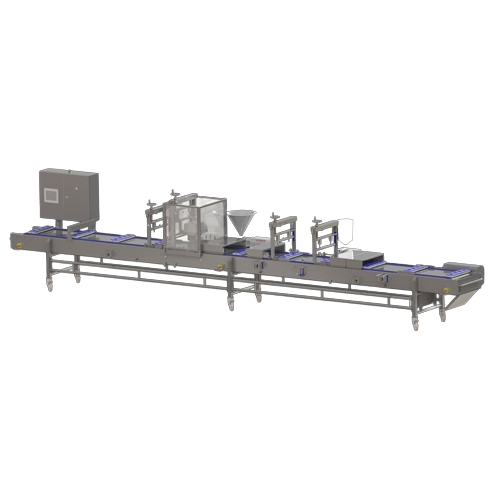
Multifunctional dessert line for layered dessert production
Effortlessly create complex, multi-layer desserts or meal co...
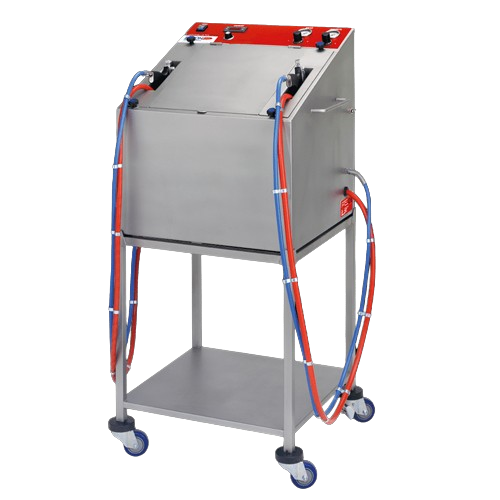
Chocolate spraying system for bakery decoration
Achieve precision chocolate coatings and intricate dessert decorations eff...
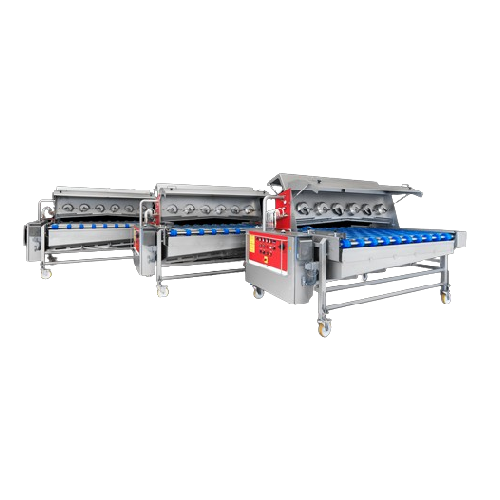
Egg wash disc sprayer for bakery finishing
Achieve precise liquid application with minimal waste using this disc sprayer, ...
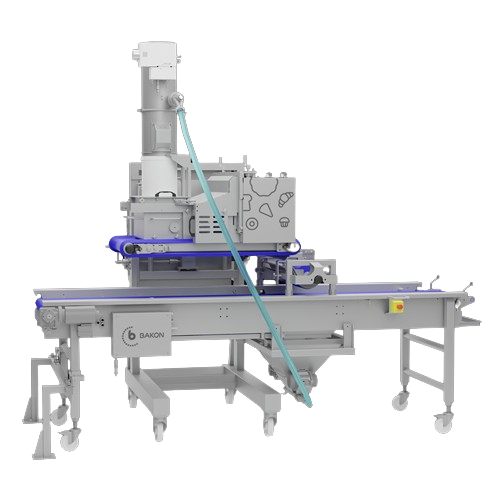
Efficient topping strewer for bakery production lines
Enhance your product’s appeal and streamline topping applicat...
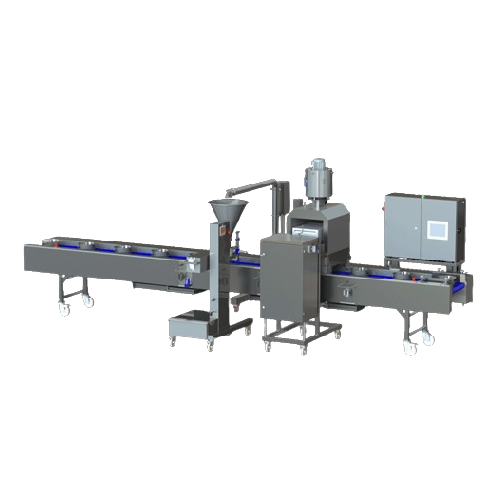
Cake batter depositing line
Streamline your production with precise batter depositing and greasing, minimizing waste and opt...
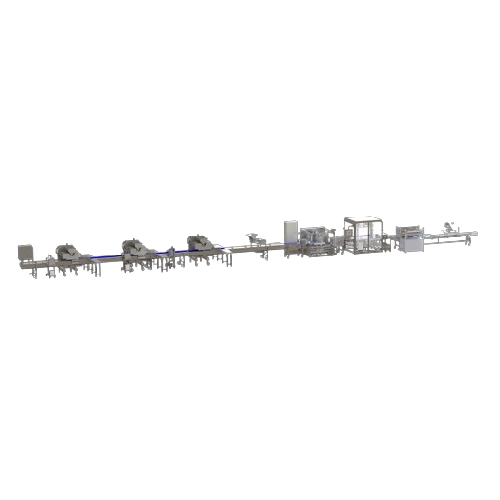
Full production line with depositing and ultrasonic cutting
Streamline your baked goods and dessert production with this...
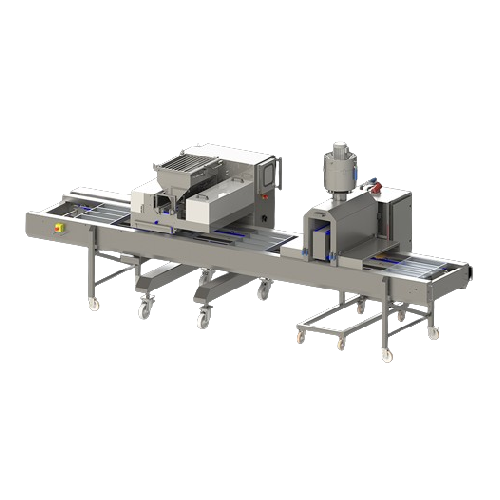
Full production greasing and depositing line for bakery products
Elevate your production process with a greasing and dep...
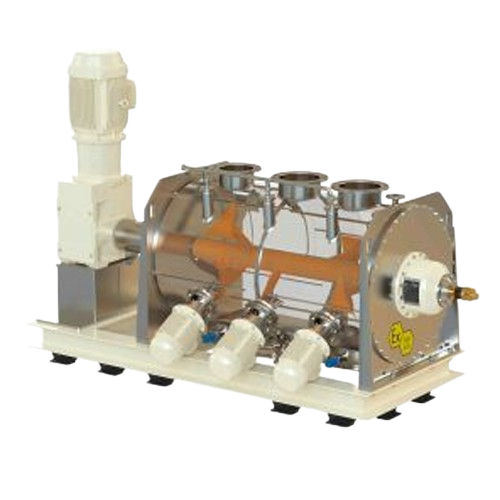
Horizontal ploughshare mixer for solids and powders
Achieve uniform blends of diverse solids and powders with precision a...
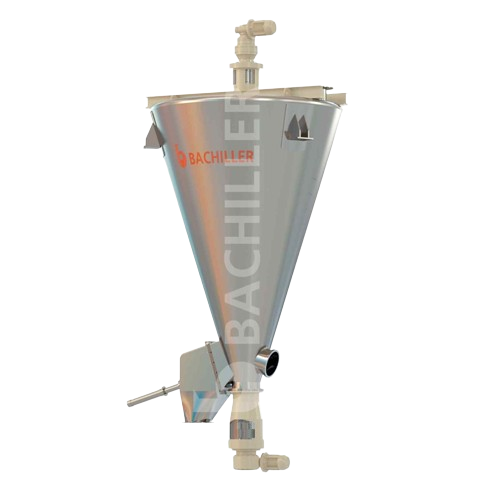
Conical screw mixer for solids and powders
Achieve precise homogenization of your solid and powder mixtures with minimal e...
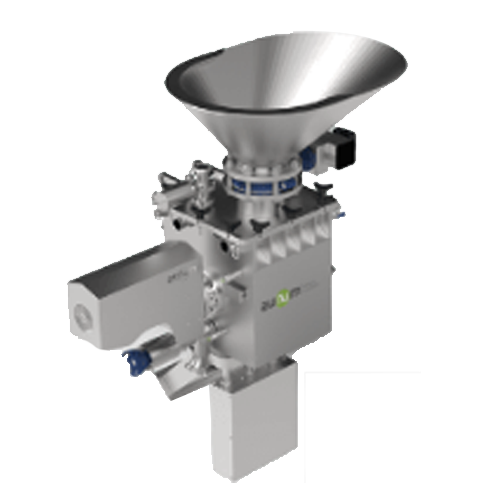
High-efficiency high-capacity reactor for industrial processing
Enhance production efficiency with a reactor system desi...
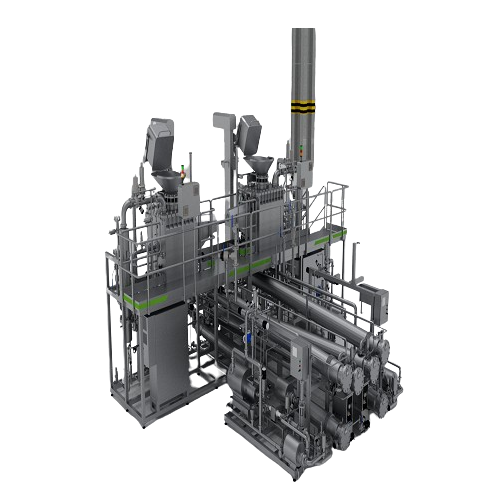
Aseptic cooking line for plant-based products
Enhance your production efficiency and product quality with an advanced doub...
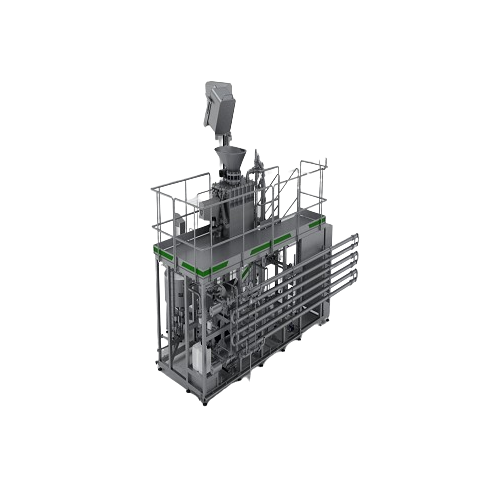
Aseptic cooking line for industrial food processing
Achieve seamless aseptic cooking and filling for diverse food product...
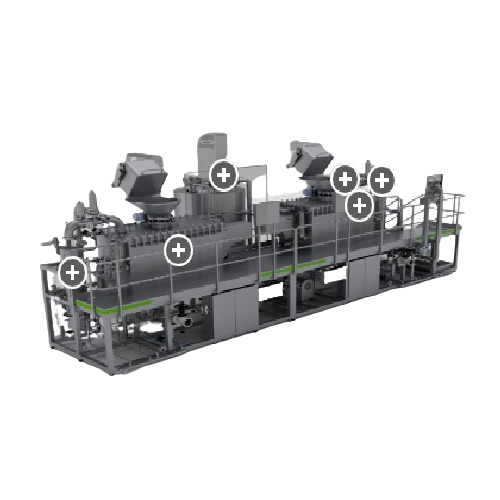
Aseptic cooking and filling line with two reactors
Streamline your production with a versatile line that combines high-ef...
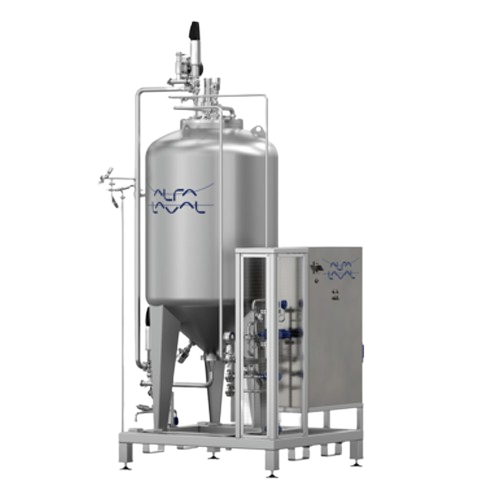
Aseptic tank module for liquid food storage
Ensure safe storage of sterilized liquid foods with a customizable tank module...
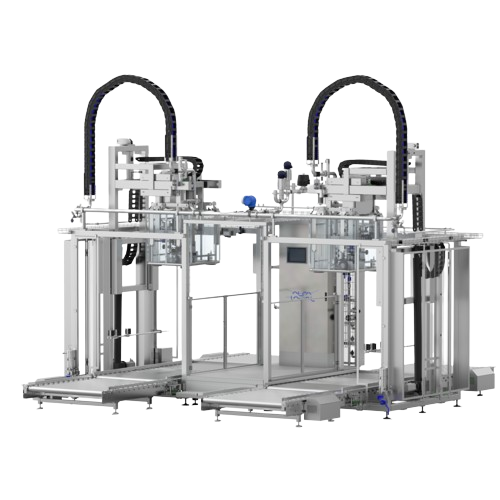
Thousand-litre aseptic filler
Ensure the aseptic filling of bulk liquid and viscous food products, reducing contamination ri...

Double seat valve for hygienic processing
Eliminate cross-contamination risks and enhance efficiency with a modular valve ...

Rotary jet head tank cleaning system for food and beverage industry
Reduce your tank cleaning costs by up to 70% with a...
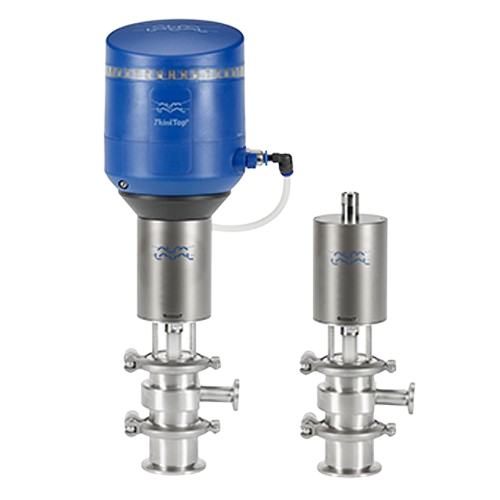
Vacuum breaker valve for Htst pasteurization systems
Prevent vacuum conditions in high-temperature pasteurization systems...
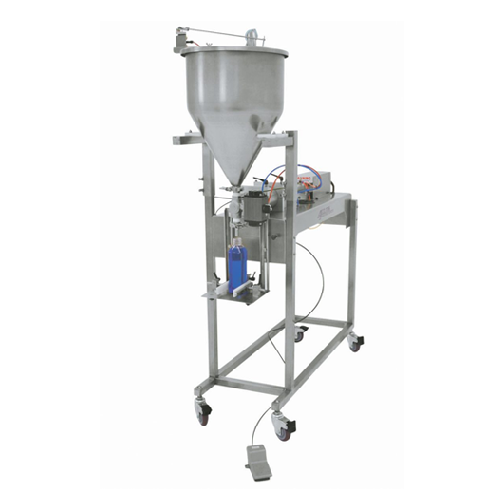
Semi-automatic volumetric piston filler
Achieve precise filling of diverse liquids and viscous products while minimizing wa...

Product in tote/crate washer for fresh produce
Enhance the cleanliness of your production line by ensuring that crates and...
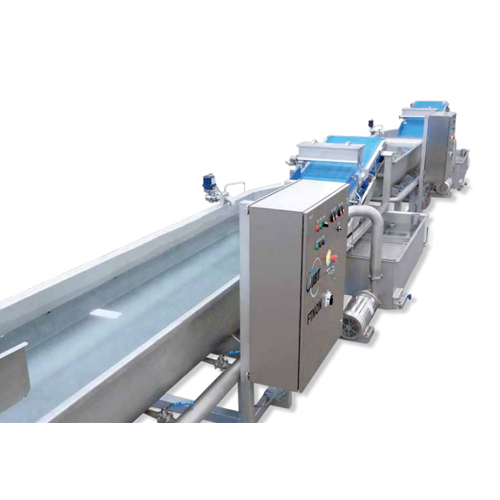
Industrial swirl bath washer for sliced vegetables
Achieve optimal cleanliness with a delicate touch—this advanced swirl ...
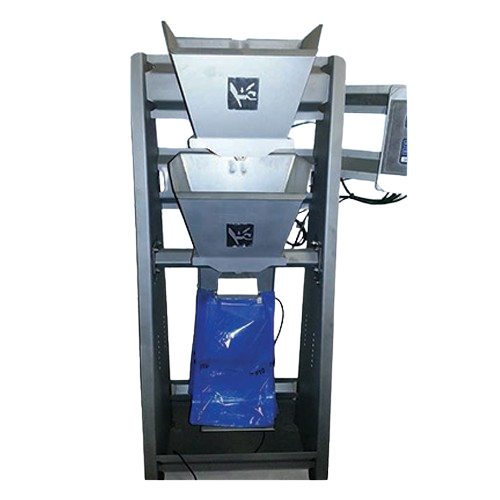
Industrial bagging system for high-speed processing
Optimize your packaging line with this engineered-to-order bagging sy...
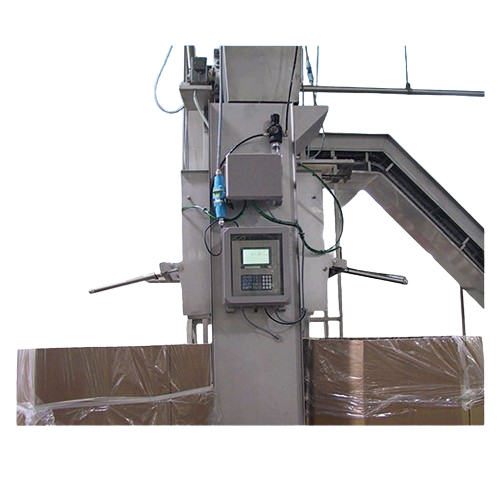
Bi-directional frame scale for industrial weighing
Achieve precise product accumulation and streamlined batch processing ...
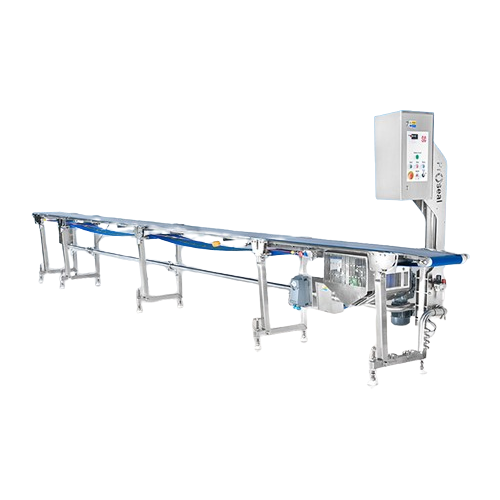
Flat belt product transfer conveyor for food processing
Efficiently streamline your production line with a hygienically d...
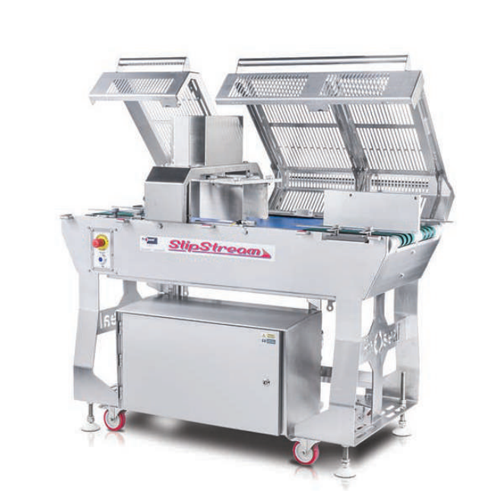
Twin lane separator for automated tray sealing
Optimize your production line with this conveyor system designed to effortl...
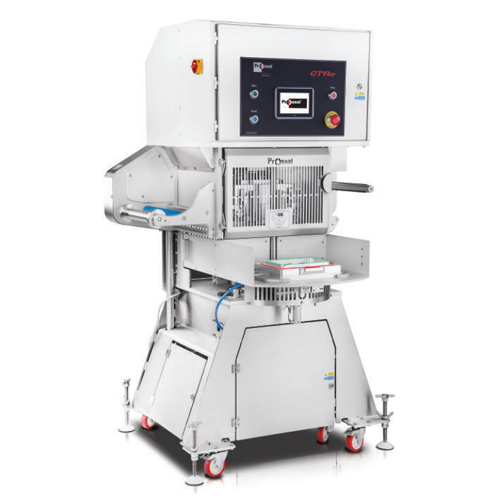
Semi-automatic tray sealing for ready meals
Achieve versatile packaging with a semi-automatic tray sealing solution design...
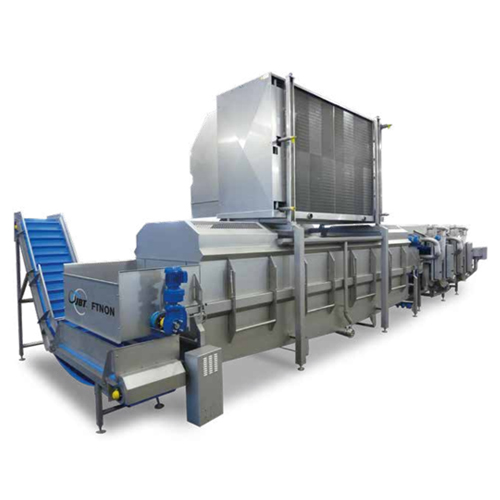
Air and suction dryers for fresh salads and vegetables
Ensure longer shelf life and optimal quality for your fresh produc...
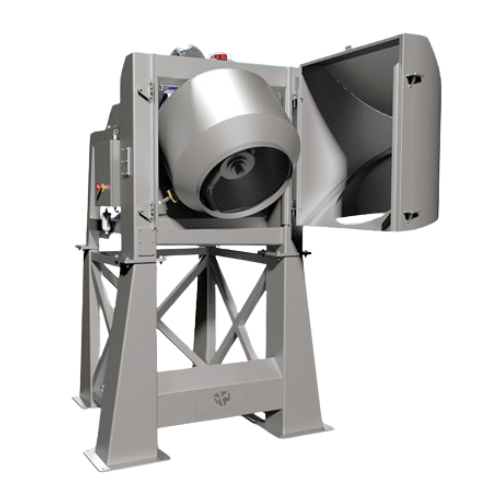
Centrifuge for drying fresh-cut vegetables
Enhance your production line with reliable surface water removal from fresh pro...

Automatic tray sealer for high-speed food packaging
Optimize your production line with a high-capacity tray sealing solut...
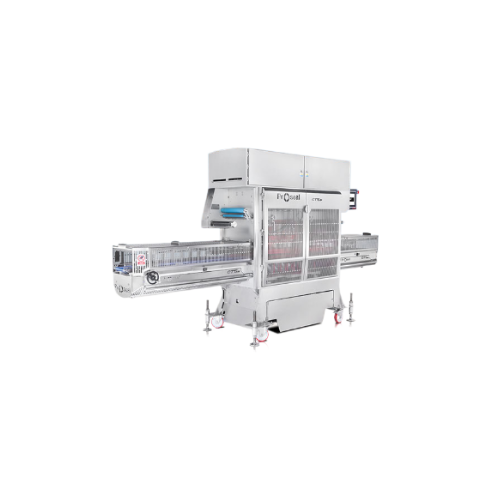
High-speed tray sealer for food packaging
Streamline your packaging process with high-speed tray sealing, reducing labor c...
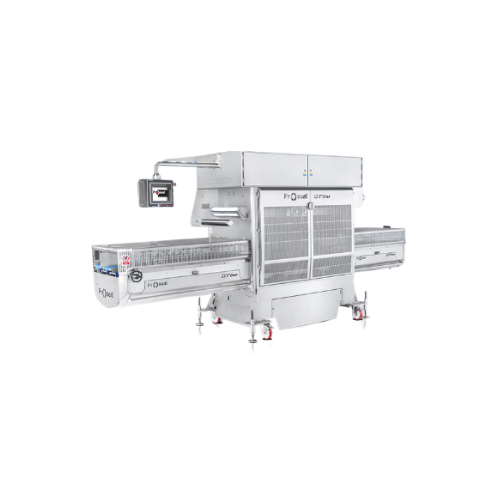
Automatic tray sealer for high-speed production
Ensure your product packaging stays fresh and secure with this high-capaci...
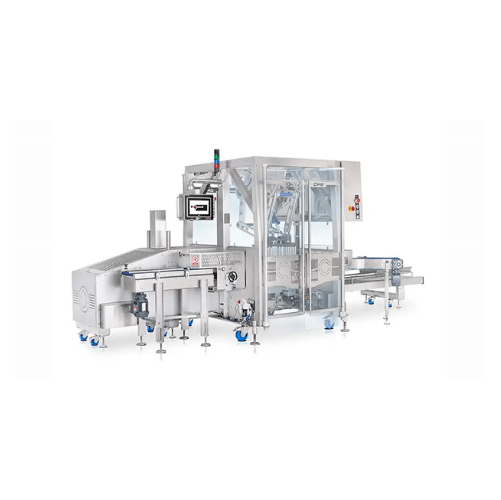
Industrial case packing solution for high-speed operations
Optimize your production line with a compact, efficient case ...
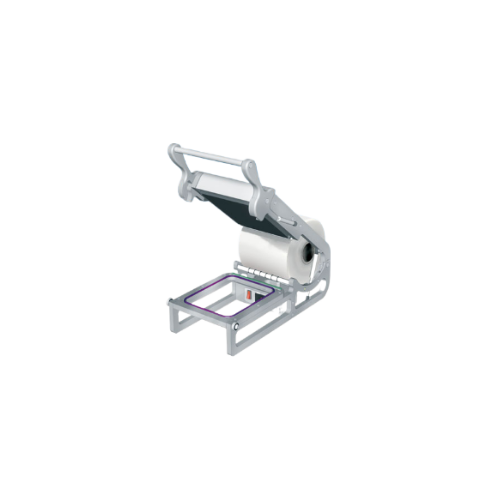
Hand operated tray sealer for small-scale food production
Optimize your packaging process with this compact tray sealing...
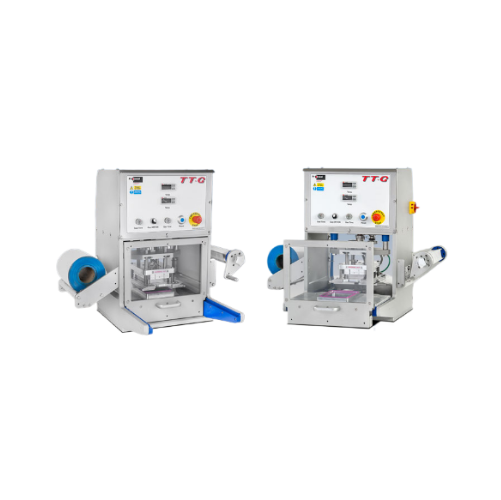
Bench mounted tray sealer with gas flush
Optimize your production line with a compact tray-sealing machine designed for pre...

Linear conveyor tray sealing
Experience unparalleled flexibility and efficiency in tray sealing with high-speed integration,...
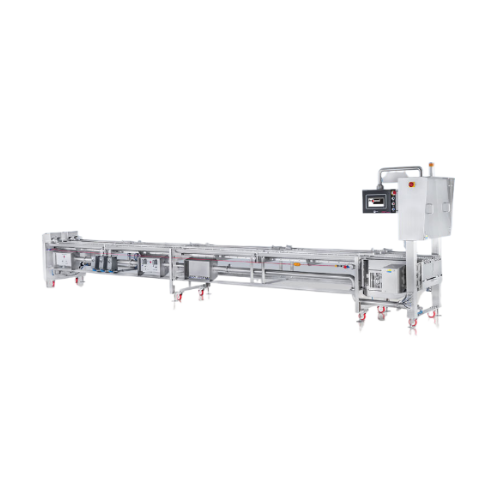
High throughput tray conveyor system
Looking to streamline your tray sealing process? This modular conveyor system integrat...
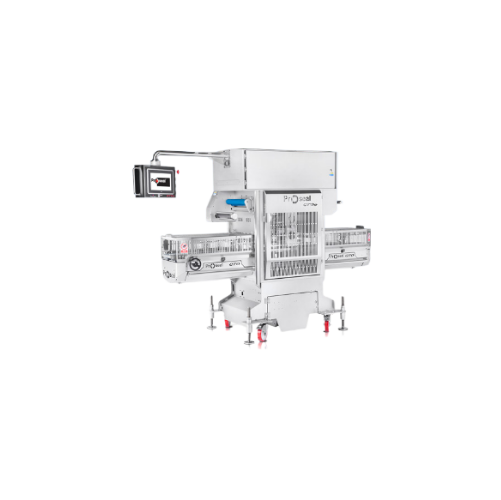
High-speed tray sealer for food
Enhance your packaging line’s efficiency with a high-speed, in-line tray sealer design...

Industrial high speed tray sealer
Enhance your production line efficiency with precision sealing capabilities, accommodatin...
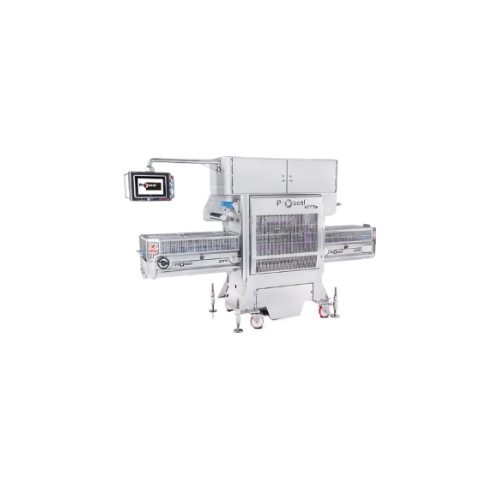
Automatic tray sealer
Maximize throughput and shelf life with our high-speed inline tray sealing solution, ideal for diverse ...
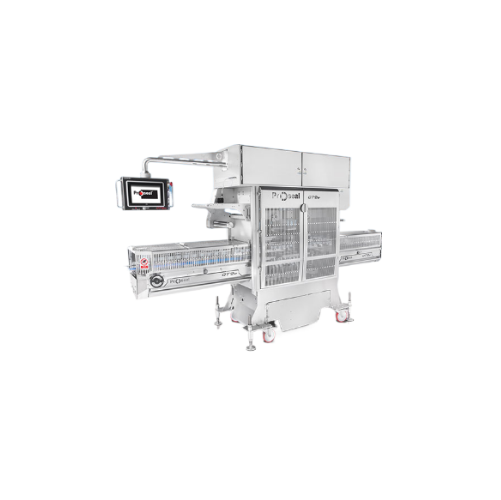
In-line tray sealer for high-speed packaging
Optimize your packaging line with a high-speed solution that accommodates mul...
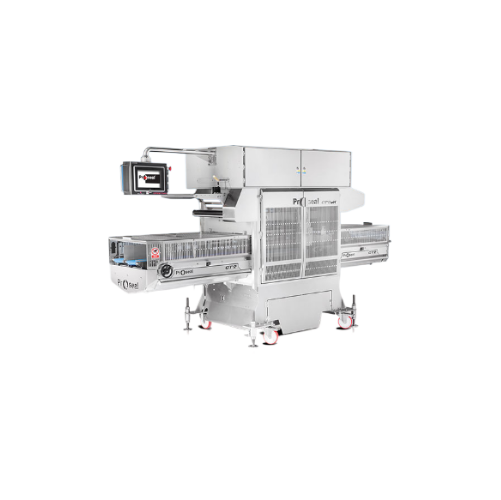
High-capacity tray sealer for vacuum gas packaging
Enhance your production efficiency with a versatile twin-lane tray sea...
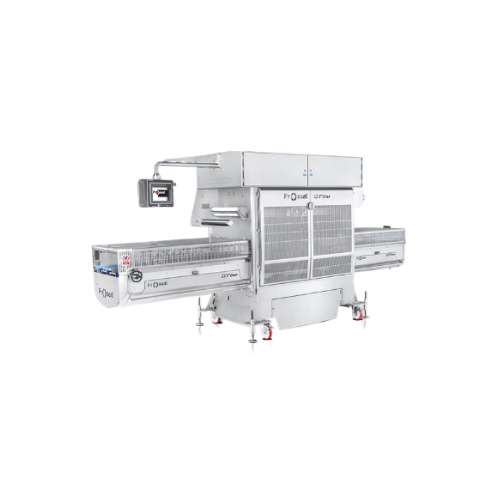
In-line tray sealing system
Streamline your packaging line by implementing a high-speed, in-line tray sealing system designe...
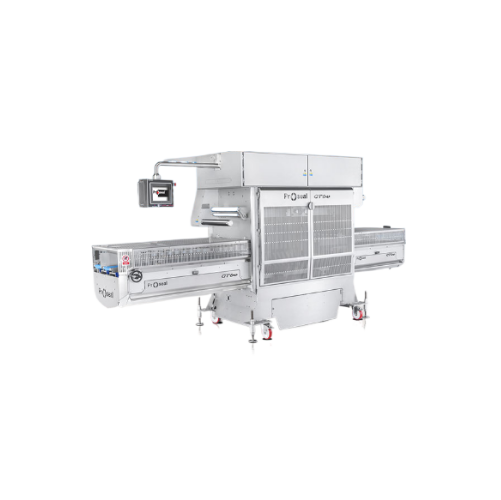
High-capacity tray sealer for poultry, meat & seafood
Optimize your high-speed packaging line with this large-capacity tr...
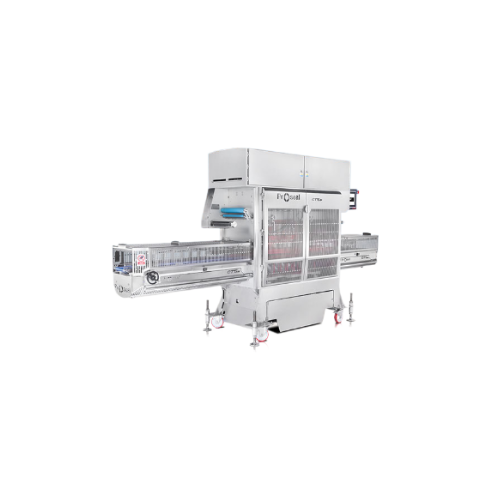
Automatic tray sealer for high-speed packaging
Streamline your packaging line with an in-line tray sealer that adapts to t...
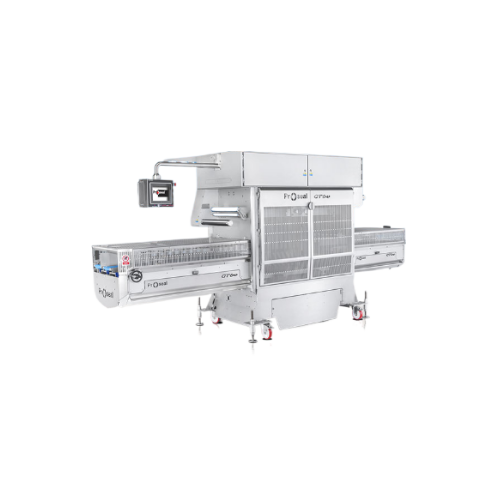
Large-capacity automatic tray sealer
Optimize your production line with this tray sealer, designed for high-speed sealing a...
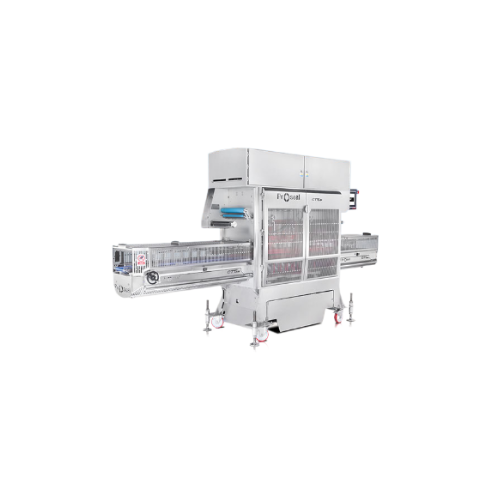
Automatic inline tray sealer for food packaging
Streamline your packaging process with high-speed, reliable tray sealing t...
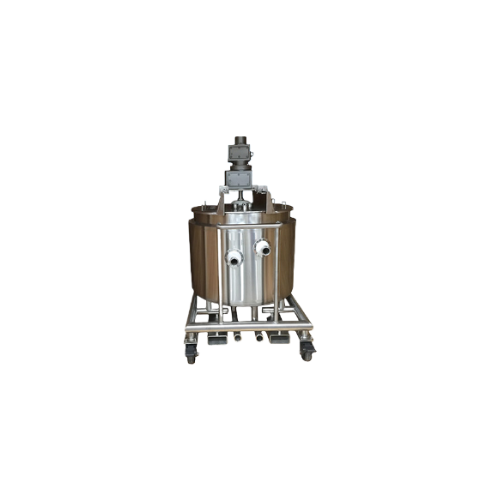
R&d vessels for research and development centers
Optimize your R&D operations with versatile vessels designed to hand...
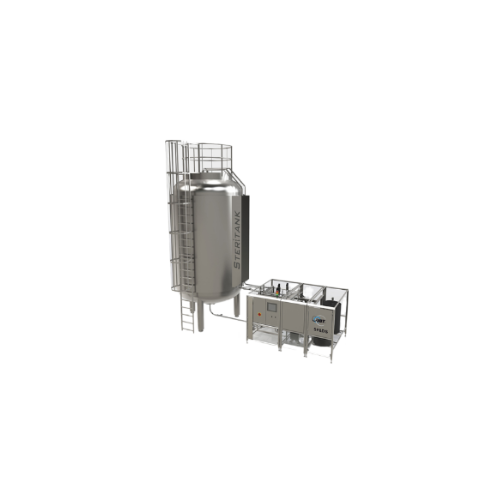
Aseptic storage tank for sterile liquid products
Ensure the sterile safety of your liquid products with a reliable storage...
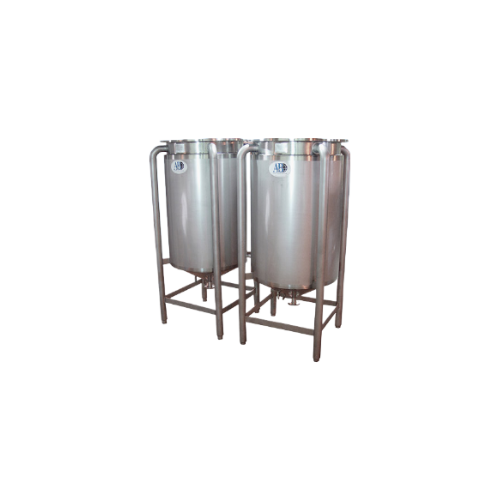
Customizable storage tanks for industrial use
Optimize your production with versatile storage tanks designed for precise c...
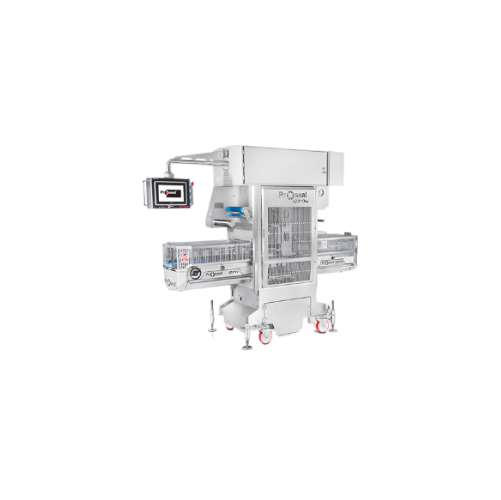
Automatic tray sealing system
Optimize your packaging line with versatile tray sealing technology that accommodates various ...
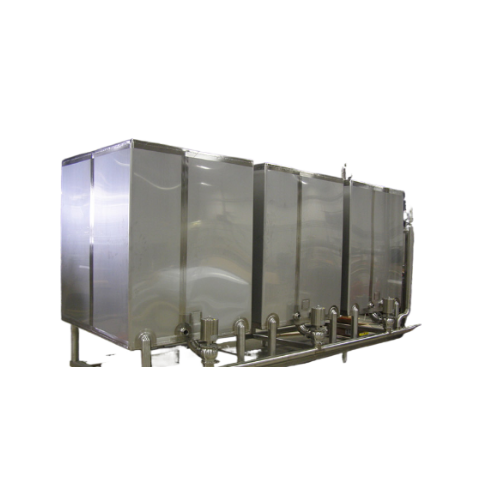
Clean-in-place tanks for industrial sanitation
Optimize your sanitation processes with clean-in-place tanks, designed to r...
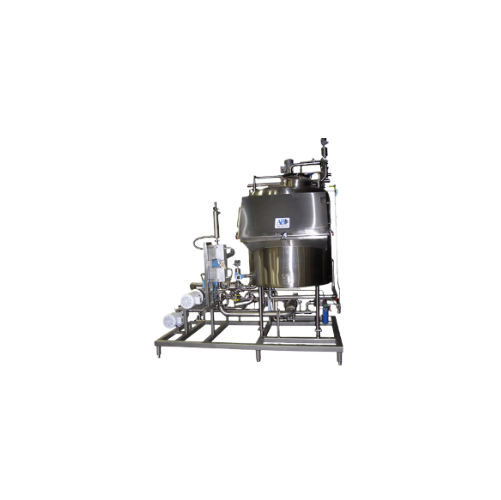
Industrial melt tanks for butter and chocolate
Reduce manual labor and elevate safety in your production line with a melt ...
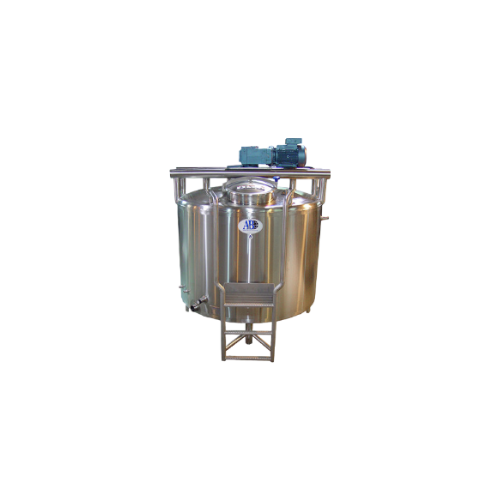
Industrial mixing tanks for liquid, slurry, and gas dosing
Optimize your production with versatile mix tanks, designed t...
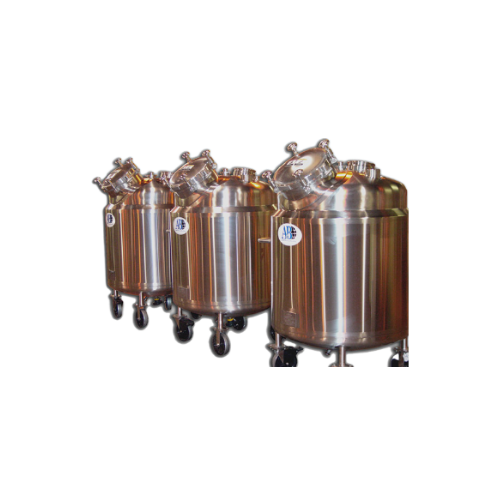
Industrial pressure vessels
Ensure product integrity and regulatory compliance with engineered-to-order pressure vessels, de...
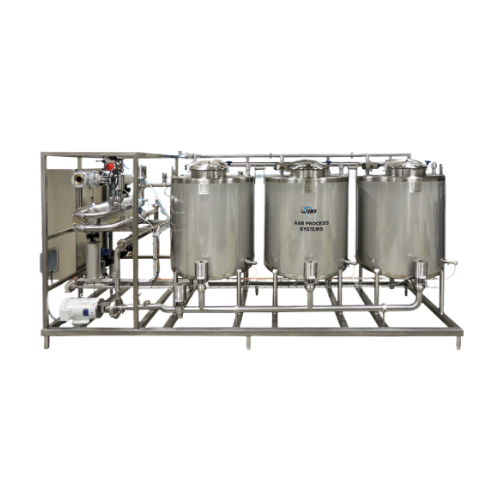
Clean-in-place system for diverse processing needs
Ensure the precision and consistency of your cleaning cycles with a ro...
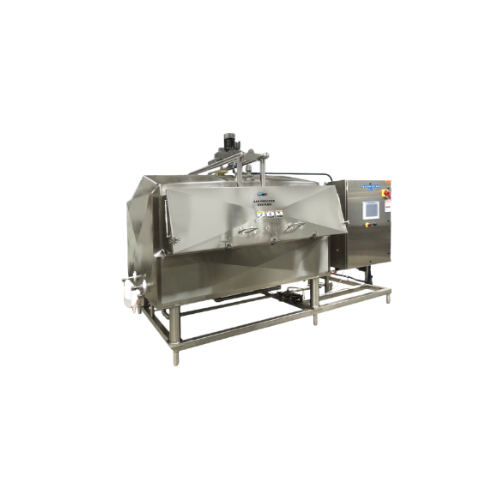
Industrial block melt system for butter and chocolate
Efficiently transition solid blocks of butter, chocolate, or waxes ...
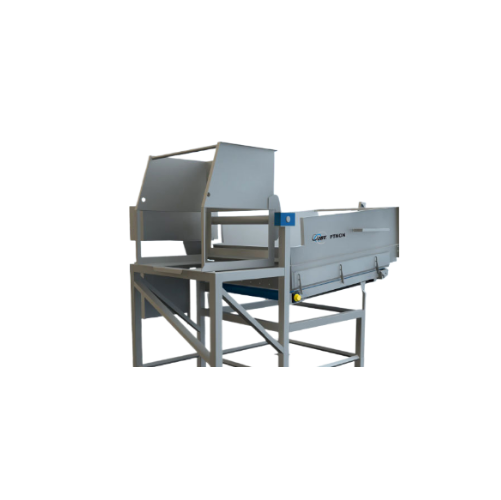
Electric bin tipper system for food processing
Achieve consistent product flow and minimize manual handling with this adva...
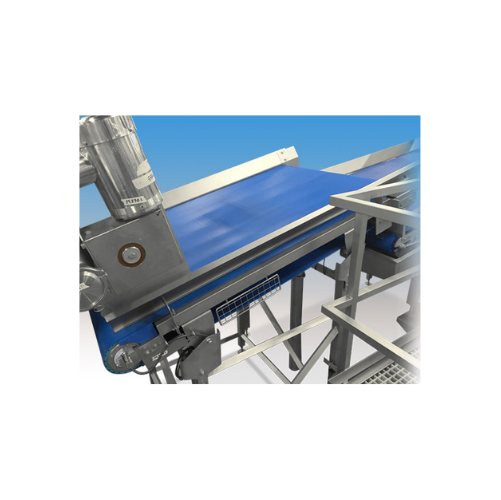
Weighing conveyor for consistent product flow in food processing
Ensure uniform product distribution and precise weight ...

Basket tracking system for automated batch retort systems
Efficiently manage and monitor your batch processing with a sy...
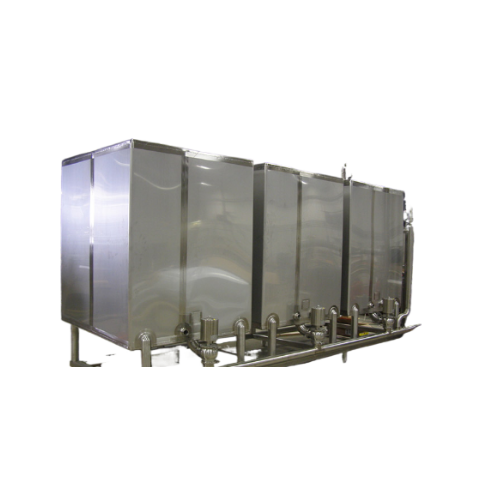
Industrial clean-in-place (cip) system
Ensure seamless cleaning and sanitation in your production line with innovative CIP ...
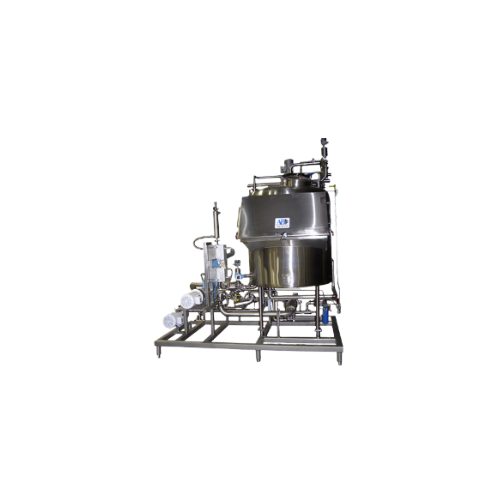
Ergonomic melt systems for solid food and personal care products
Eliminate manual lifting and enhance safety by integrat...
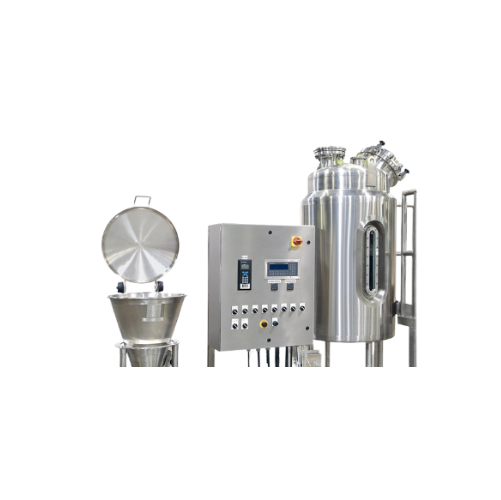
Powder induction system for efficient liquid powder mixing
Achieve precise and dust-free powder incorporation into liqui...
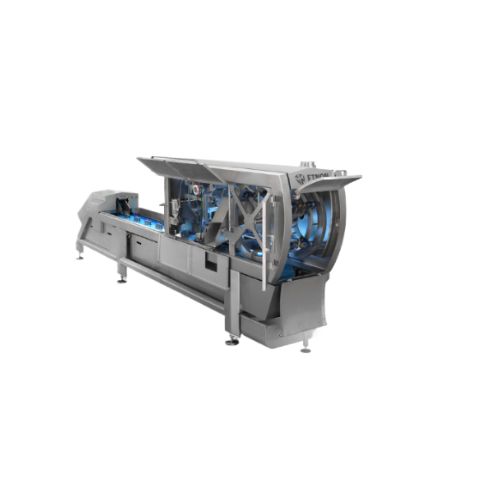
Magnetic onion peeler for high-yield production
Achieve high yields and superior hygiene in onion processing while seamles...
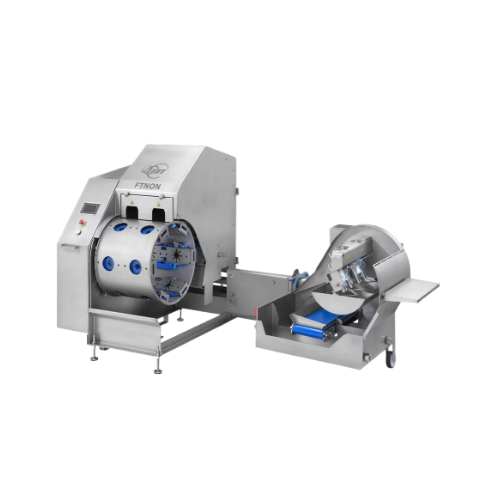
Sweet pepper decorer
Streamline your sweet pepper processing with a high-speed solution that efficiently removes cores, clean...
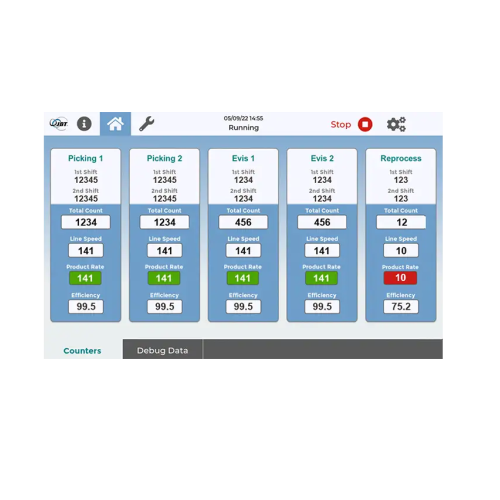
Poultry processing efficiency monitoring system
Maximize production efficiency with real-time monitoring and precise track...
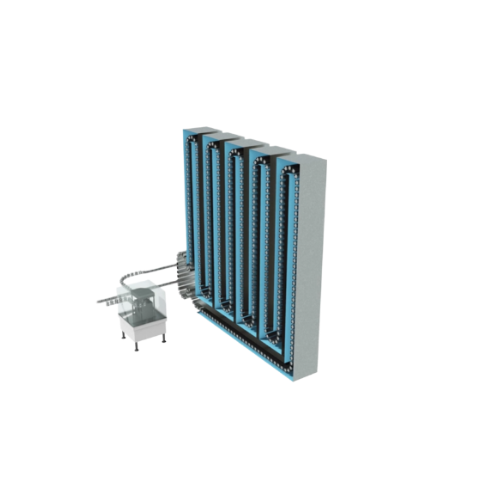
Hydrostatic sterilizer for continuous food processing
Maximize your production line’s efficiency with a continuous ...
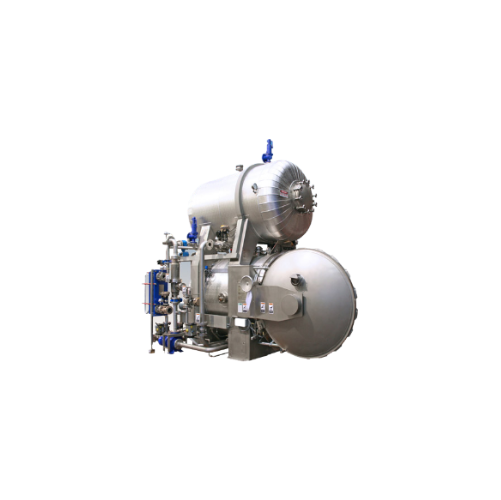
Multi-purpose laboratory sterilizer for food processing
Achieve precise thermal process design and flexibility with a ste...
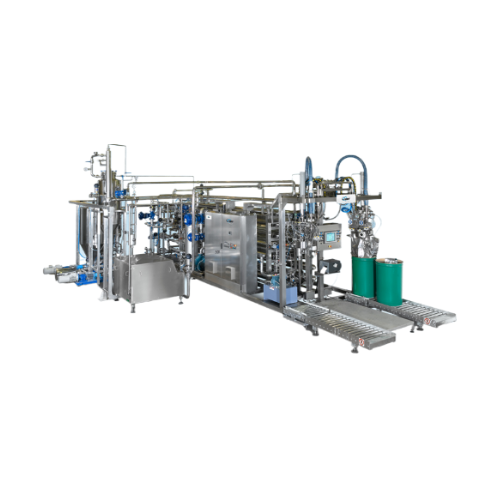
Aseptic processing system for food products
Streamline your food processing line with an efficient aseptic processing syst...
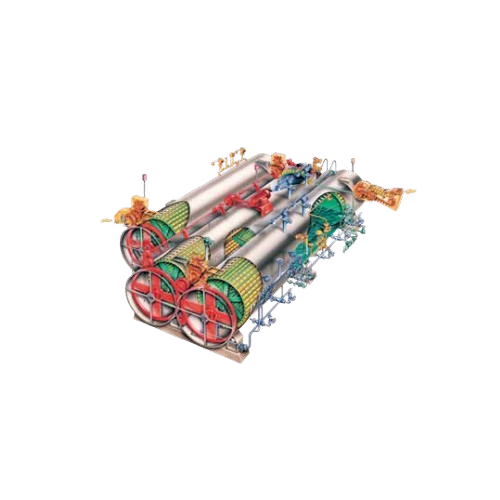
Gentle can handling ejector for rotary cooker
Achieve seamless can transfer and sterilization with reduced damage during h...
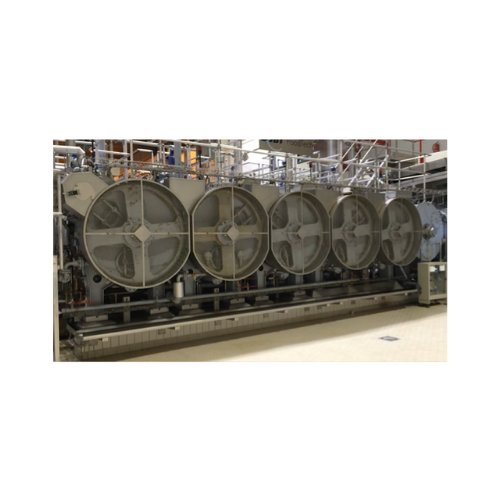
Rotary pressure sterilizer for canned food products
Streamline your canning operations with continuous high-speed sterili...
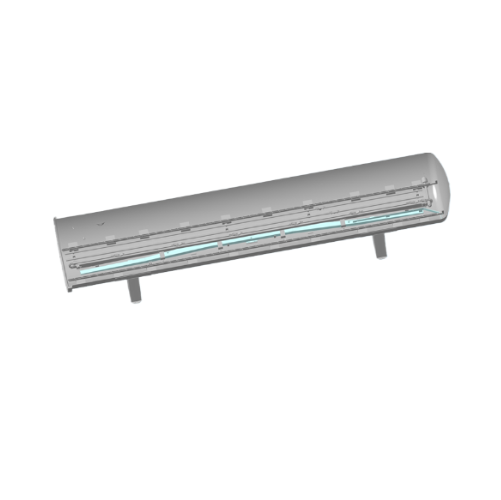
Low energy suction system for food processing retorts
Optimize your sterilization process with innovative suction technol...

Steam water spray retort for shelf-stable food processing
Ensure uniform heat distribution and precision control in ster...
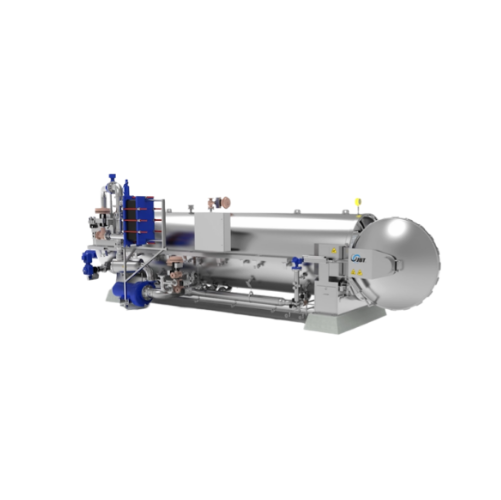
Agitating batch retort for food sterilization
Ensure superior heat distribution and precise control in your sterilization ...
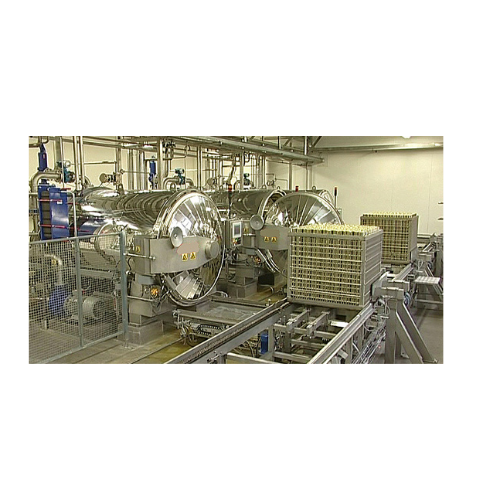
Automated batch retort system for food sterilization
Optimize your sterilization process with seamless transportation fro...
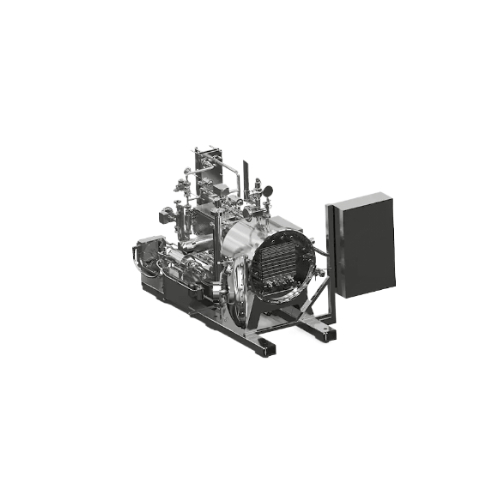
Efficient agitation system for retort packages
Enhance product quality and reduce processing time with this advanced agita...
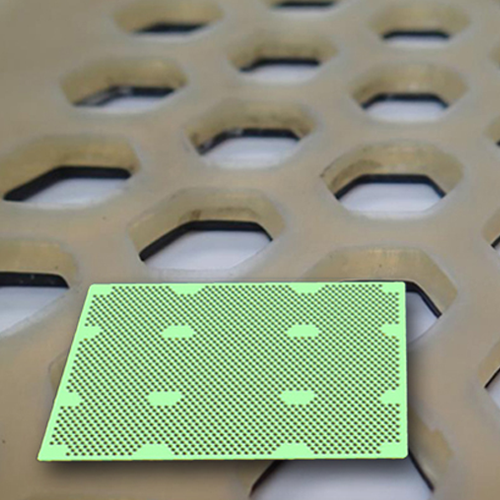
Layer pad for agitating retorts in food processing
Efficiently secure and process irregularly shaped containers in retort...
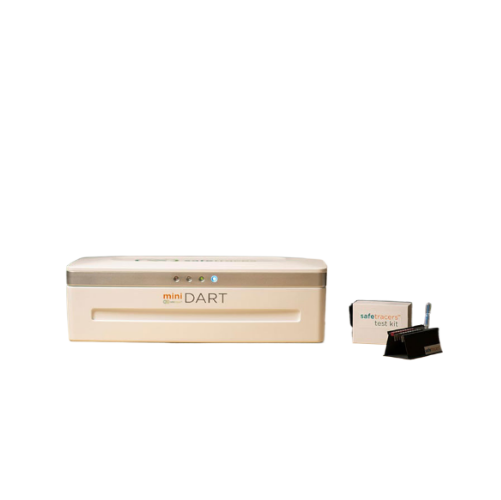
On-food traceability technology for produce
Enhance your product authenticity with a revolutionary traceability technology...
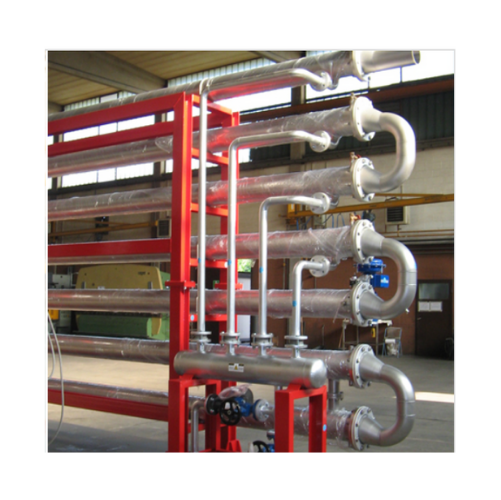
Cold break system for tomato processing
Enhance product quality and consistency in liquid processing by utilizing precise t...
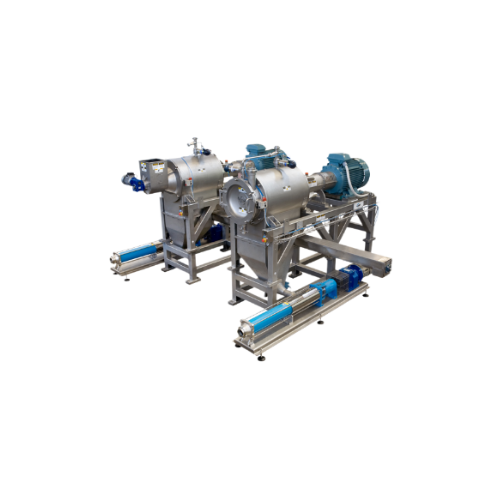
Juice extractors for variety of fruits and vegetables
Streamline your juice and puree production with advanced extraction...
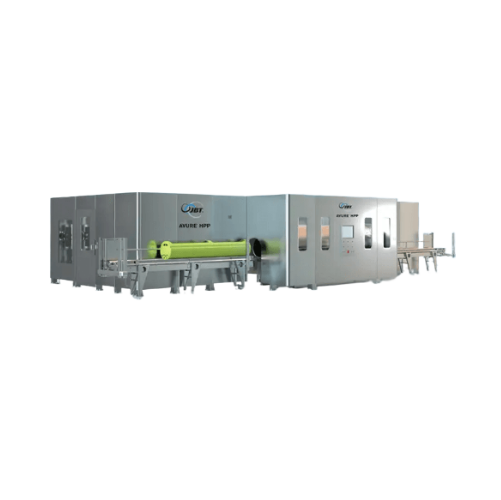
Expandable high pressure processing system
Optimize your production line with an expandable high-pressure processing syste...

High pressure processing water filtration system
Ensure super clear water after high pressure processing to protect your s...
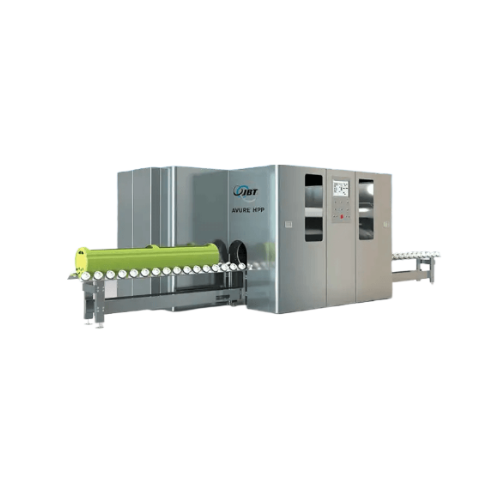
High pressure food processing solution for medium-scale producers
Achieve reduced operational costs with high-pressure ...
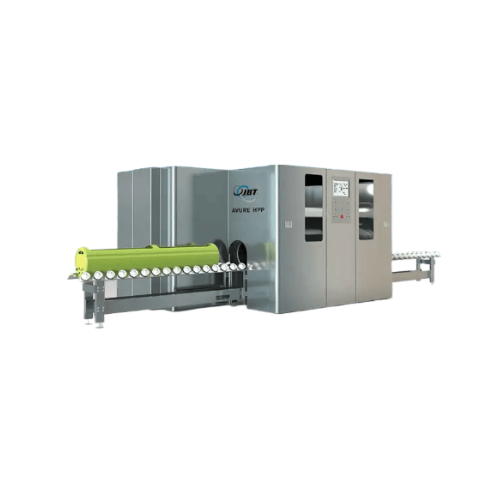
High pressure processing for diverse food products
Maximize production versatility and ensure product safety with a high-...
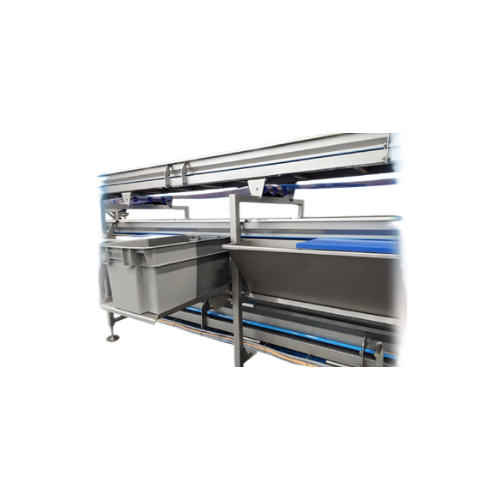
Preparation line for fresh produce
Streamline your fresh-cut processing with this efficient preparation line, facilitating ...
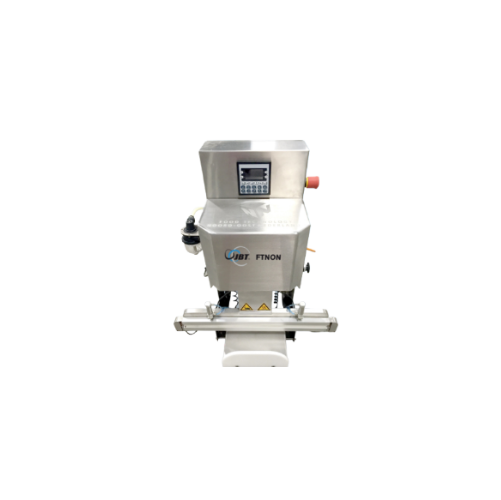
Fresh cut produce tray sealer
Ensure freshness and extend product shelf life with a flexible sealer designed for varied pack...
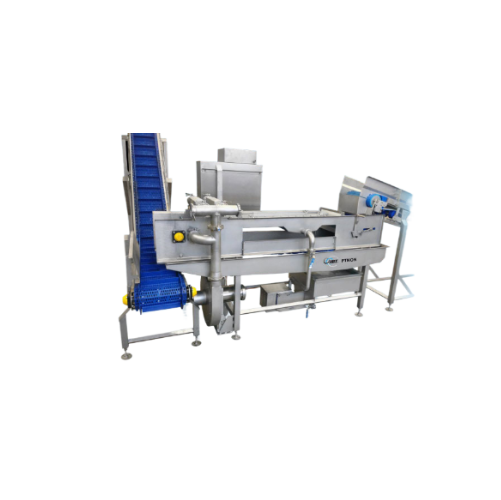
Fruit and vegetable shelf life extender
Extend the freshness and appeal of your produce with our innovative dipping solutio...
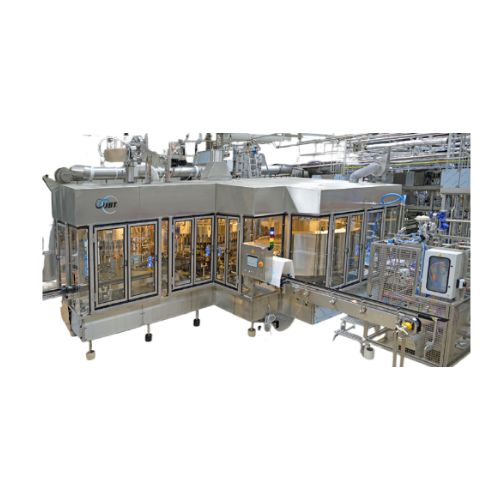
Rotary level filler for low to high viscosity liquid products
Ensure precise fill levels and enhance production efficien...
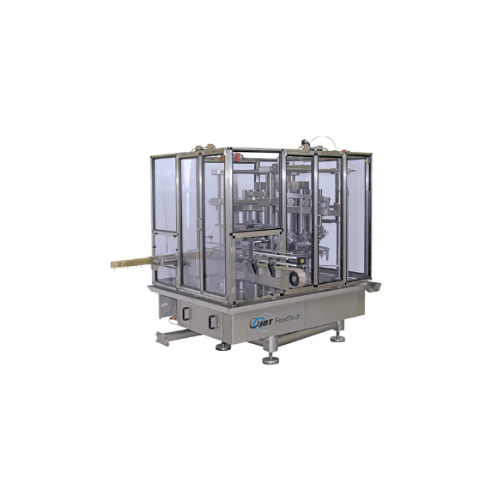
Volumetric piston filler for liquid and viscous products
Achieve precise volume control and enhance product integrity wit...
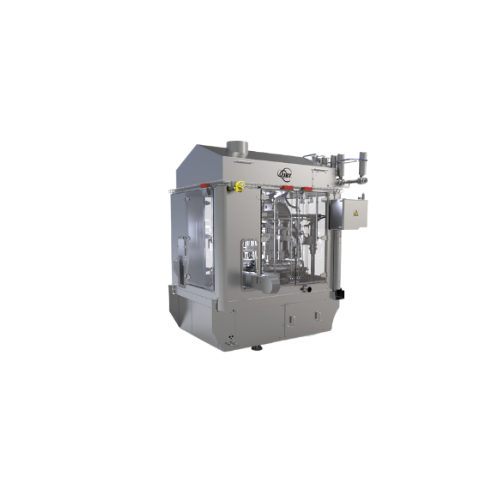
Volumetric filler for various food products
Achieve high precision and flexibility in your filling processes with a volume...
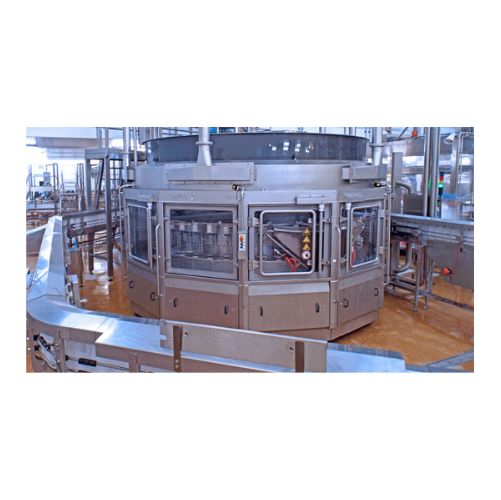
Industrial weight filler for bottles and jars
Achieve precise product filling with our weight filler system, expertly desi...
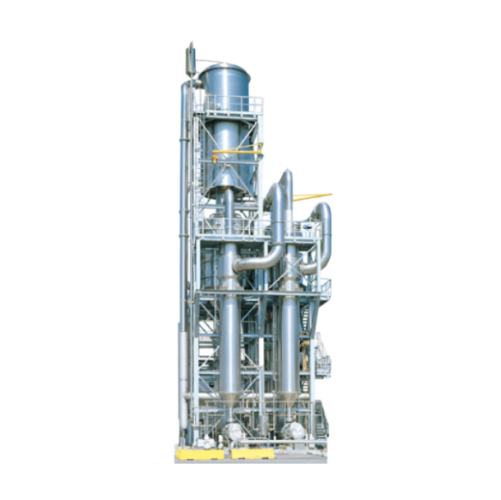
Forced circulation evaporator for tomato and fruit paste
Optimize your high-viscosity tomato and fruit paste production w...
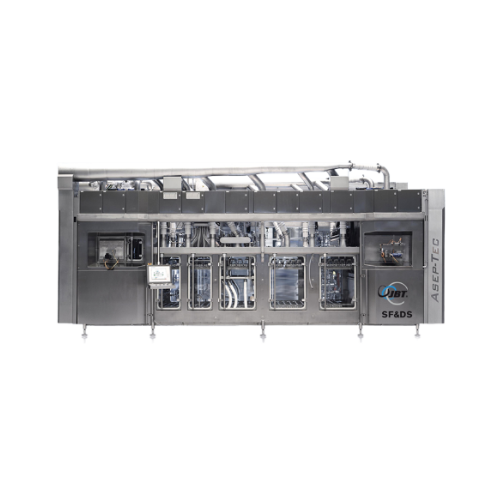
Aseptic filler for packaged dairy and beverages
Ensure product sterility and extend shelf life efficiently with high-speed...
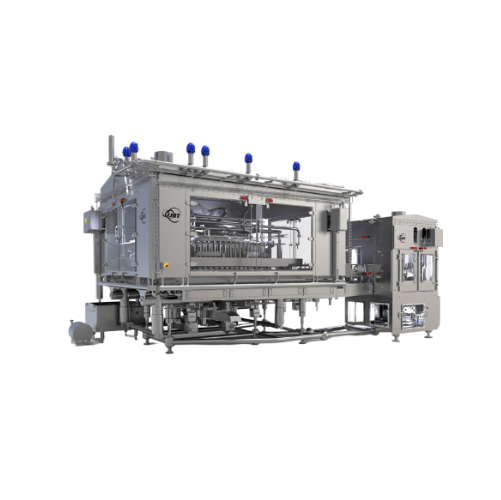
High capacity volumetric filler for pumpable products
When you need high-speed, precise filling for diverse liquid and sl...
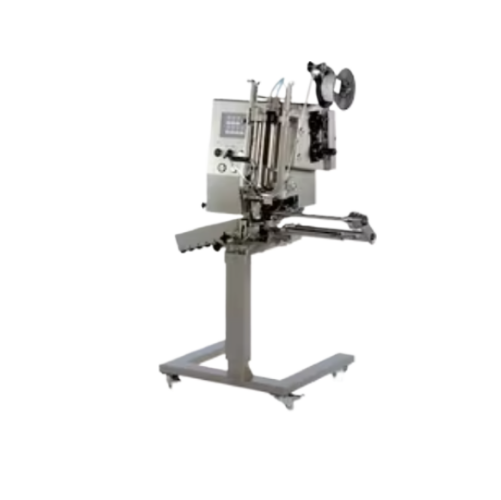
Semi-automatic clipper for sausage and meat packaging
Optimize your packaging operations with a modular solution that ens...
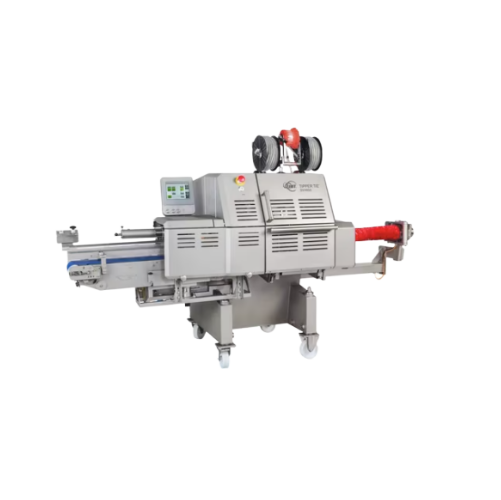
Automatic double clipper for sausage and deli meats production
Optimize your meat and deli production line with seamless...
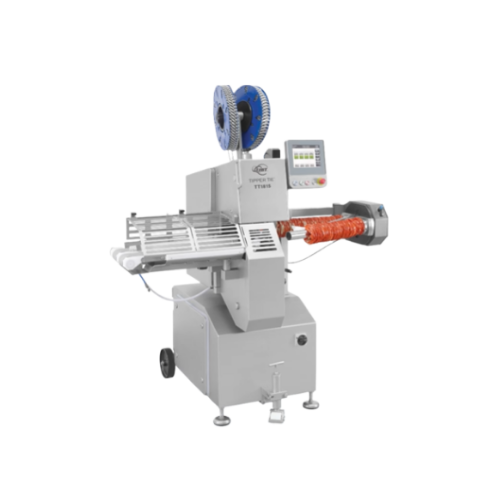
Automatic double clipper for sausage and food packaging
Streamline your packaging process with precision clipping technol...

Heat-seal and clip system for packaging pumpable products
Enhance your packaging efficiency with a system that seamlessl...
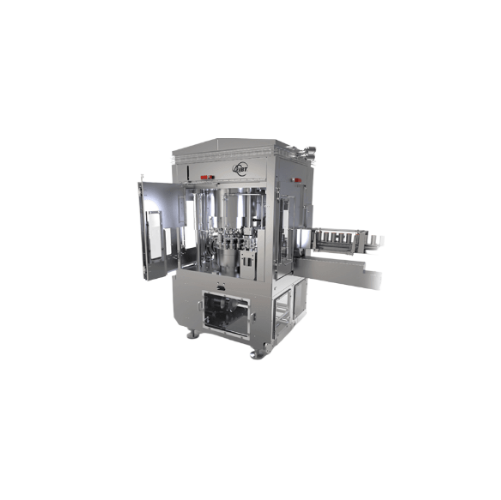
Can seamer for high-speed liquid applications
Ensure consistent seal integrity and maximize throughput with this advanced ...
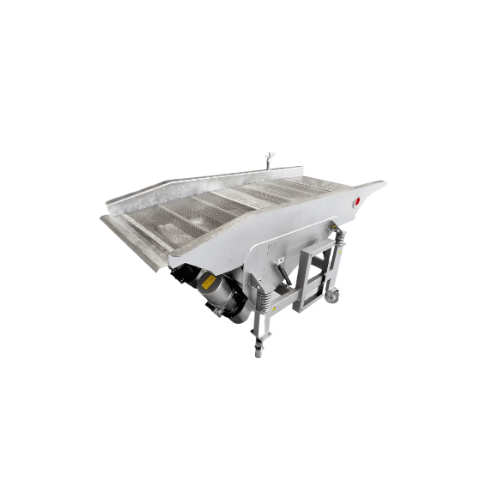
Food product sifter
Ensure precise separation with vibratory sifters designed for continuous operation, delivering gentle han...
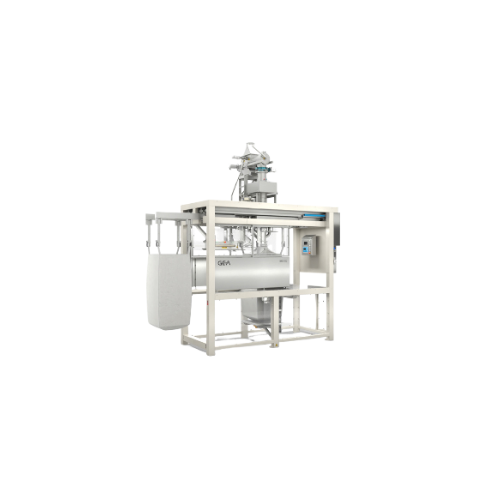
High care bulk powder fillers
Ensure hygienic packaging for your bulk powders with a system designed to enhance filling accu...
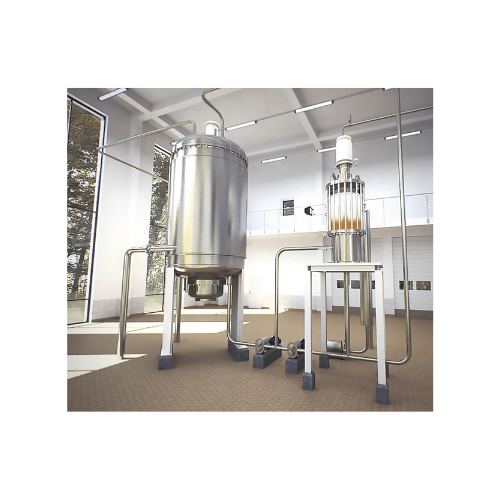
Freeze concentration system for liquid food products
Achieve precise concentration while preserving volatile components a...
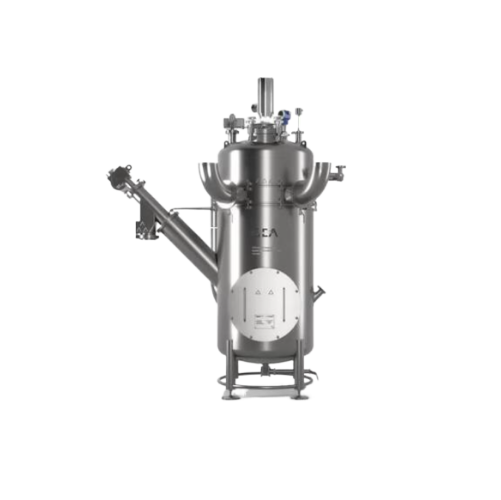
Liquid nitrogen freezer for sensitive food and fermentation ingredients
Achieve rapid, uniform freezing of sensitive fo...
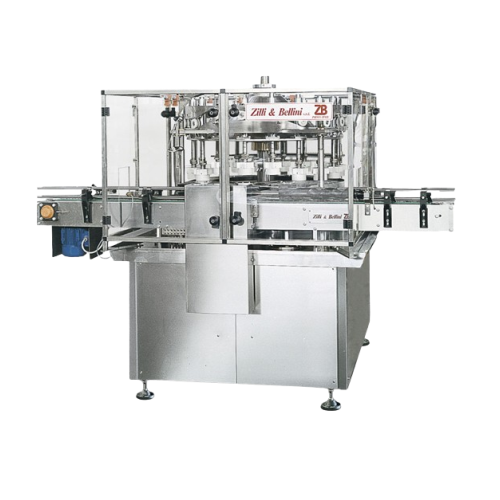
Rotary tampers for metal and glass containers
Optimize your food production line with high-speed rotary tampers, designed ...
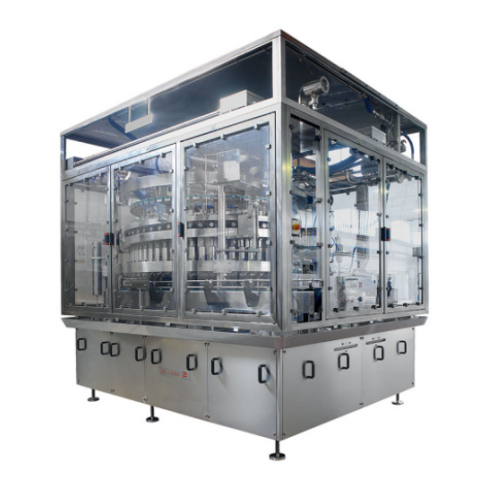
Rotary piston fillers for pumpable products
Optimize high-speed production lines with precision filling for diverse liquid...
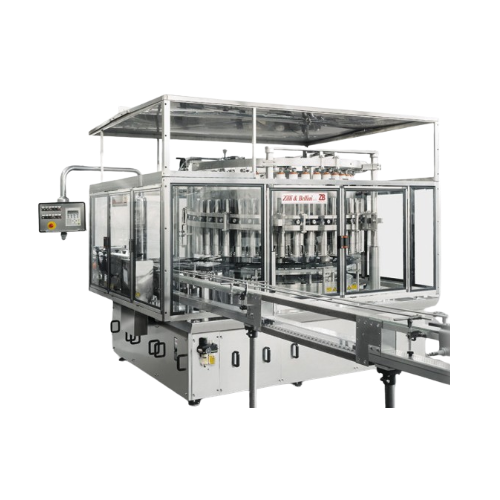
Rotary piston fillers with plunger for viscous products
Optimize your filling process with high-speed, rotary piston fill...
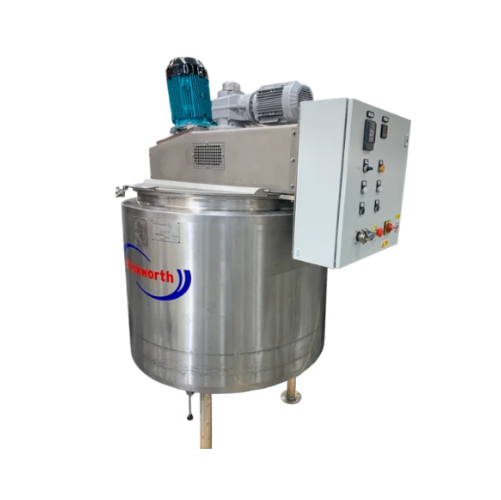
Pv processing vessels for liquid and cream mixing
Optimize your mixing operations with versatile processing vessels desig...
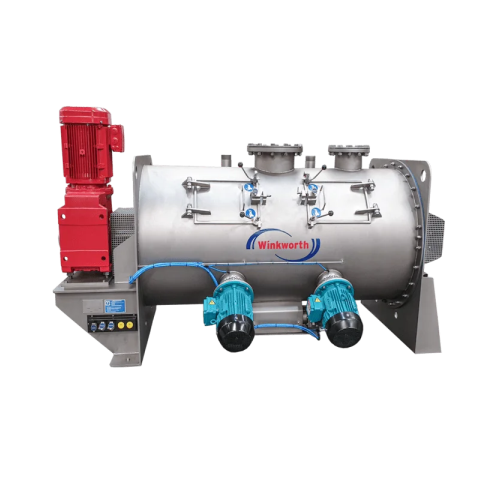
High-speed mixer for industrial mixing applications
Achieve rapid, consistent mixing and dispersion across diverse materi...
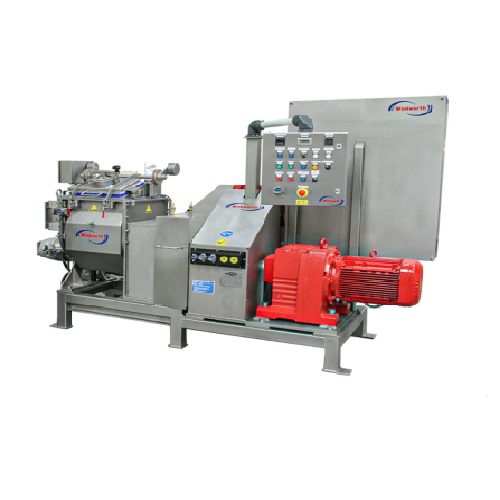
Industrial sigma mixer extruder for homogeneous mixing and extrusion
Achieve precise mixing and seamless extrusion of d...
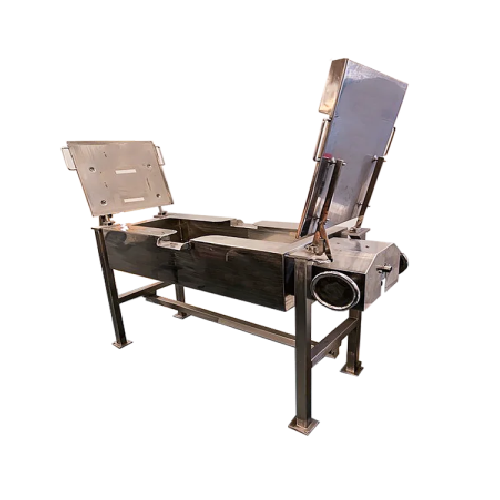
Industrial brat pan for ethnic food manufacturing
Enhance your culinary production with a versatile brat pan designed for...
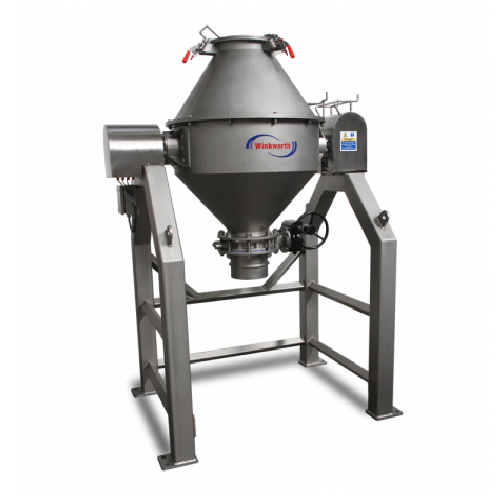
Double cone mixer for free-flowing material blending
Optimize your production with precision blending and gentle drying o...
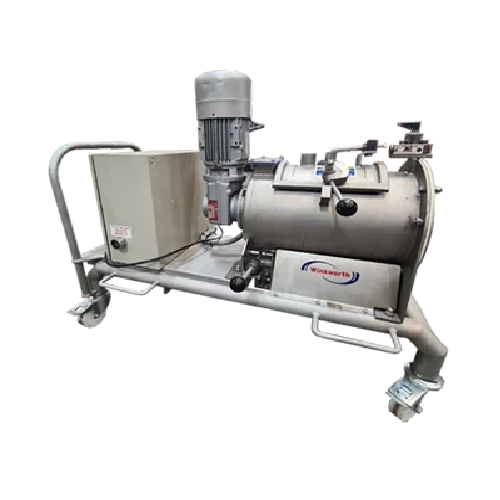
Industrial mixers for hire
Optimize your production line with versatile mixers designed for precision blending, heating, and...
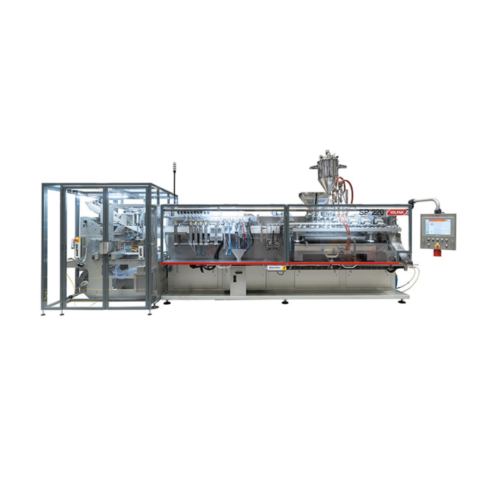
Stand-up pouch packaging for various industries
Elevate your packaging capabilities with a high-speed horizontal pouching ...
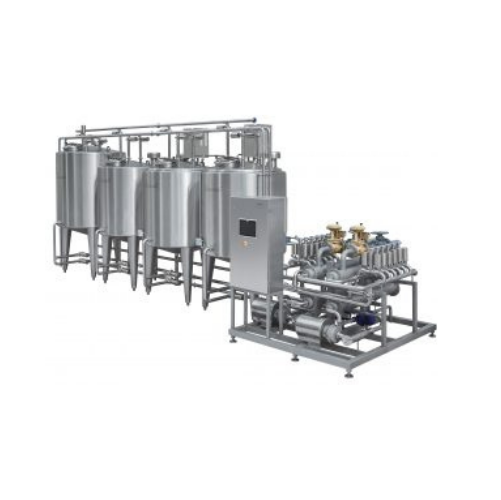
Clean-in-place (cip) system for sanitation processes
Ensure thorough sanitation in your production line with a streamline...
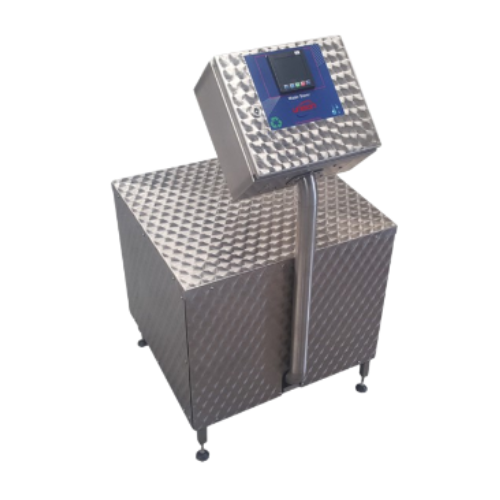
Industrial water recycling system
Reduce excess water consumption in your process line by recycling and reusing up to 96% o...
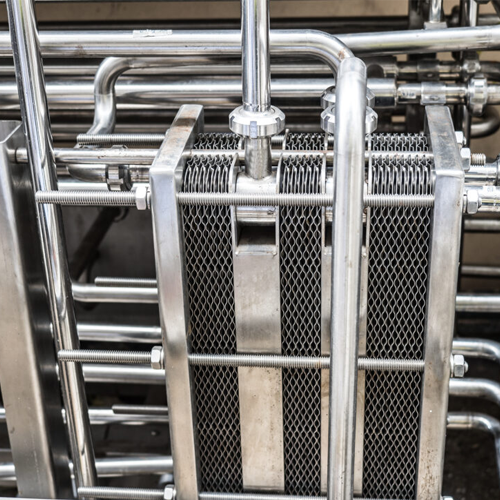
Hygienic plate heat exchanger
Optimize temperature control for liquid processing with precision-engineered heat exchangers, ...
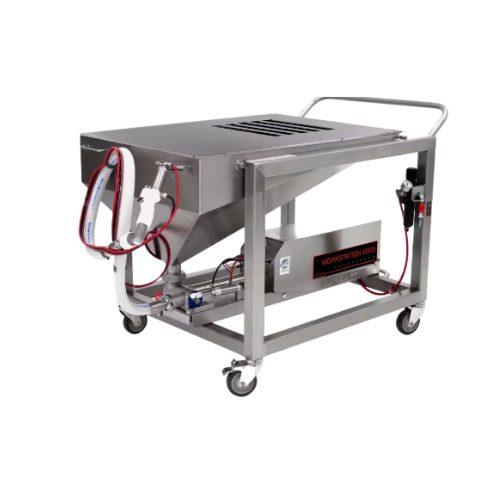
Industrial food depositor for large volume applications
Efficiently handle diverse food textures with precise portion con...
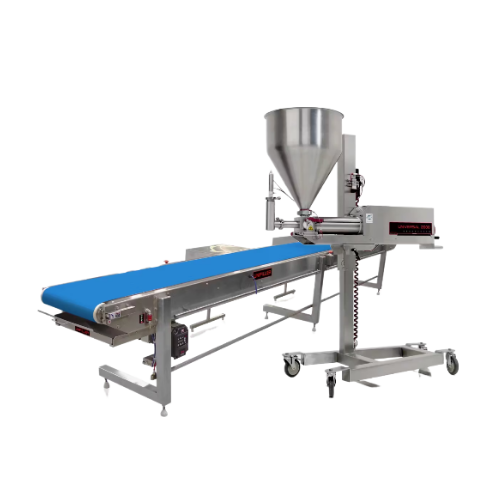
Industrial food portioning system
Optimize your production flow with precision portioning equipment designed to handle a di...
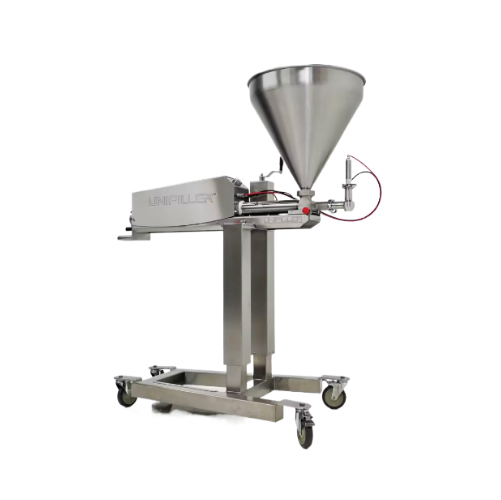
Food depositor for large chunk applications
Need precise depositing of chunky food products like stew or salsa? This versa...
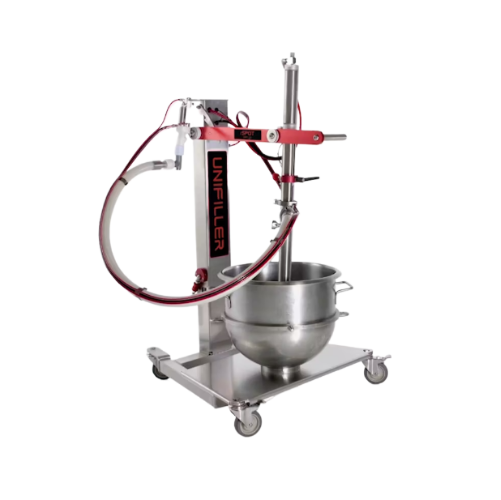
Compact food depositor for direct container use
Streamline your depositing process with a versatile solution that handles ...
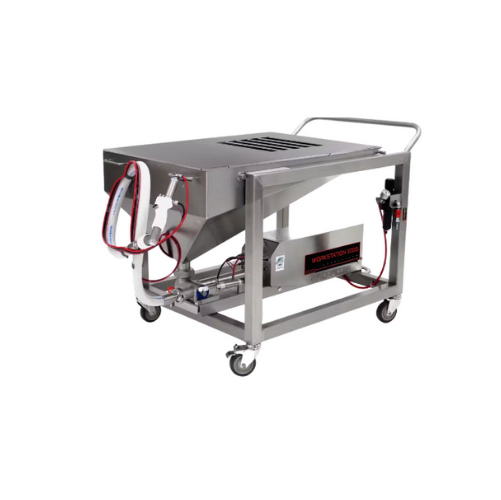
Industrial food portioning depositor
Optimize portioning precision and streamline your production with this advanced deposi...
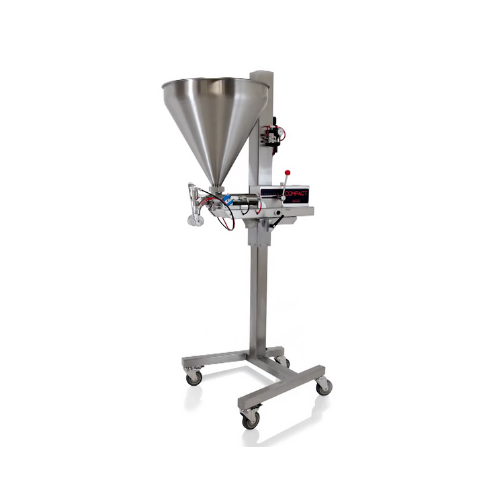
Compact food filling and portioning solution
Ideal for facilities needing precise portioning, this versatile filling machi...
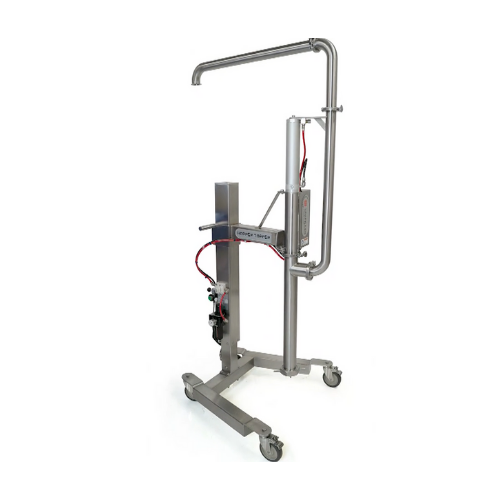
Bakery transfer pump for smooth and chunky products
Ensure consistent product quality with this transfer pump that gently...
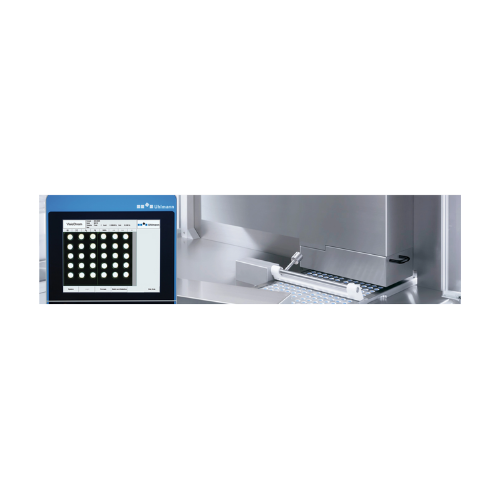
Glass personal blender for nutrient preservation
Experience enhanced flavors and nutrient retention with advanced vacuum b...
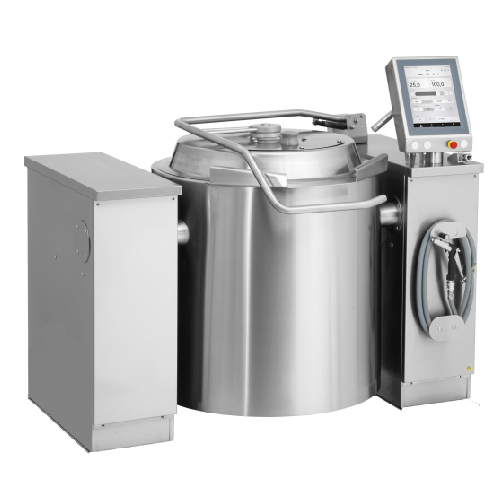
Multifunctional cooking kettle for commercial kitchens
Optimize your batch cooking processes with an all-in-one solution ...
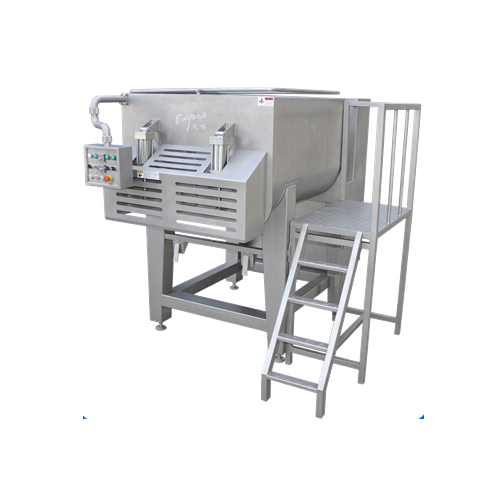
Commercial food mixers for versatile culinary applications
Streamline your food production with mixers and kneaders desi...
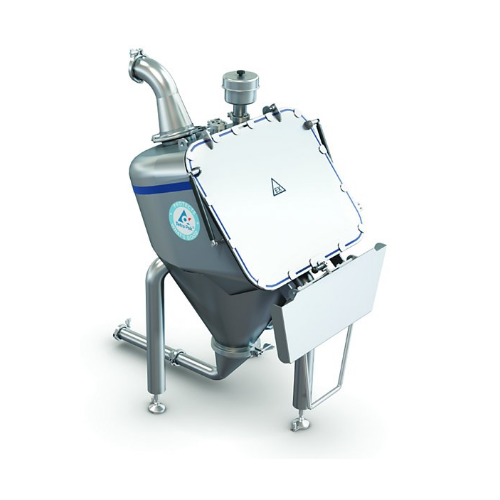
Bag tipping unit for Cip processes in powder handling
Ensure seamless powder handling and high hygiene standards in your ...
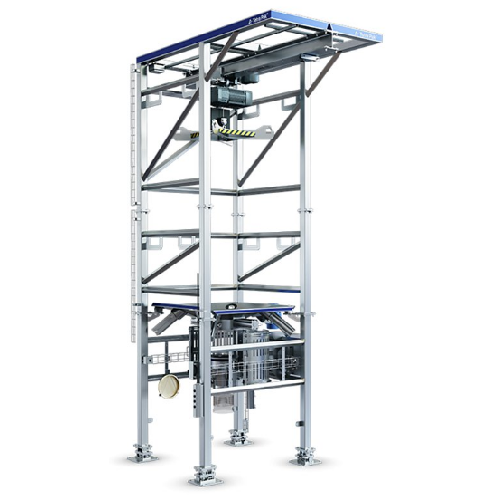
Big bag discharger for powder handling
Effortlessly discharge large bags of powdered ingredients with a modular, safe syste...
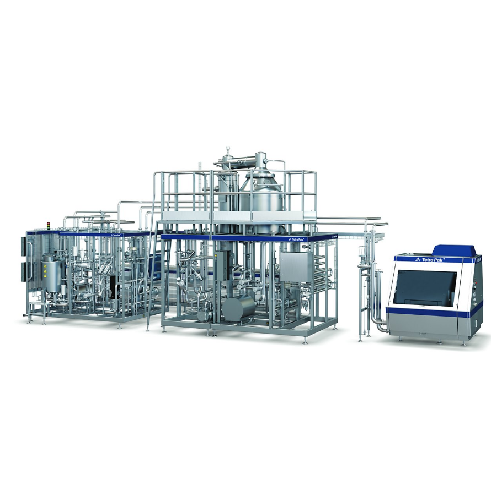
Direct Uht treatment for liquid foods
Optimize aseptic production with advanced UHT technology to preserve nutritional valu...
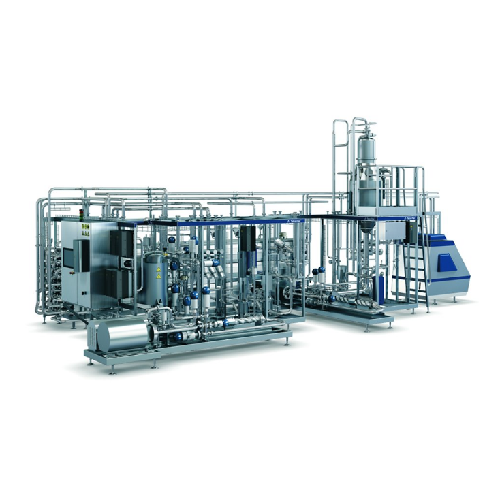
Food pasteurizer for prepared foods
Optimize your prepared food production with precise temperature control and automated o...
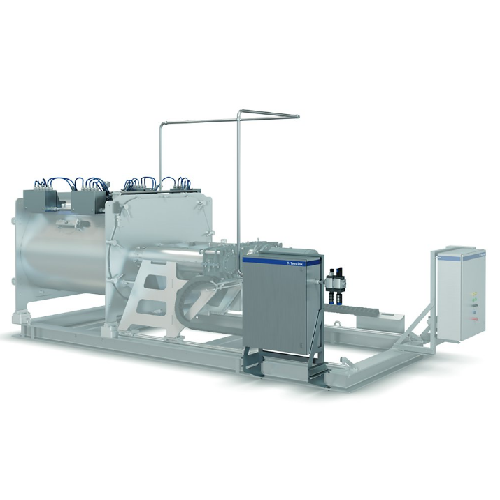
Air jet cleaning system for powder production
Eliminate water and chemical use while maximizing production efficiency with...
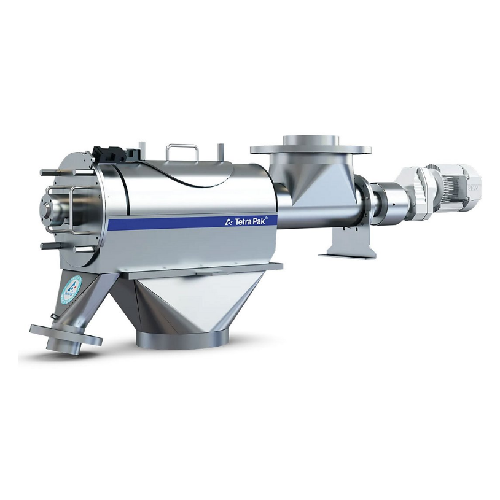
Centrifugal sifter for food and pharmaceutical powders
Ensure consistent particle size and remove contaminants in high-sp...
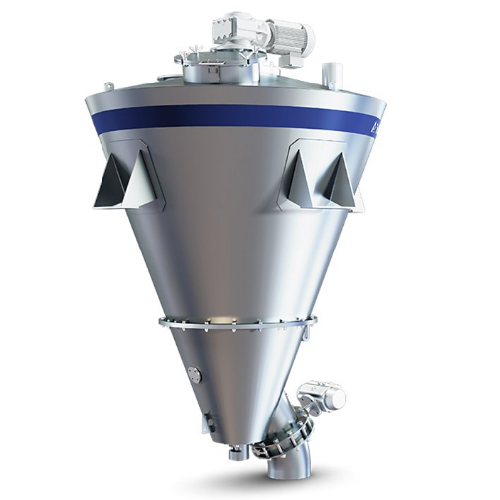
Conical homogenizer for powder and granulated products
Achieve seamless homogenization of diverse powders and granulated ...
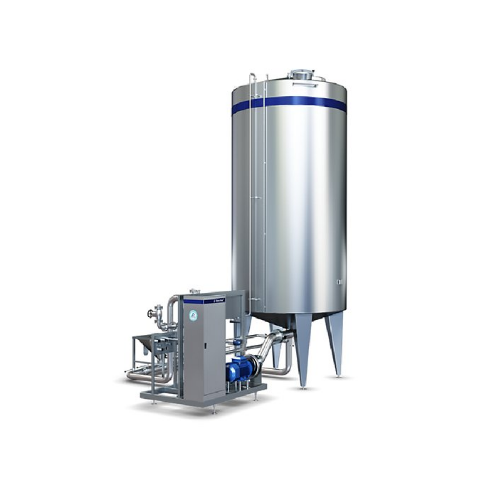
Batch dissolver for crystalline sugar and dextrose
Streamline your ingredient preparation with high-capacity batch dissol...
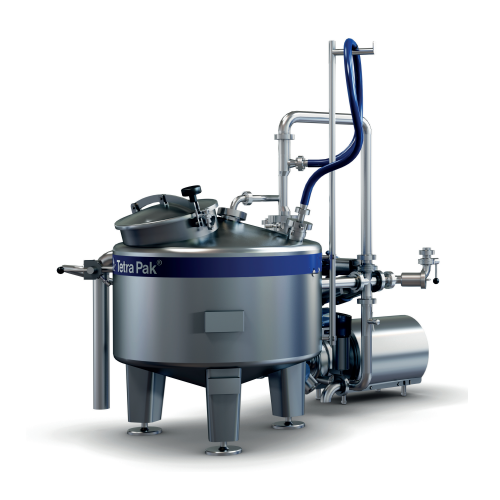
Ingredient dissolver for small batch processing
Optimize your mixing processes with a versatile dissolver designed for eff...
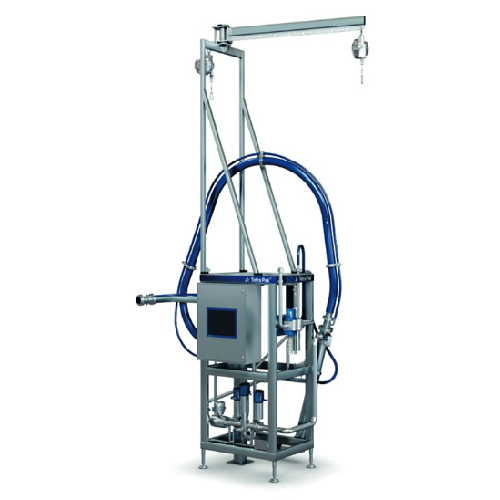
Drum unloader for liquid ingredients
Streamline the unloading of viscous liquid ingredients with advanced water injection t...
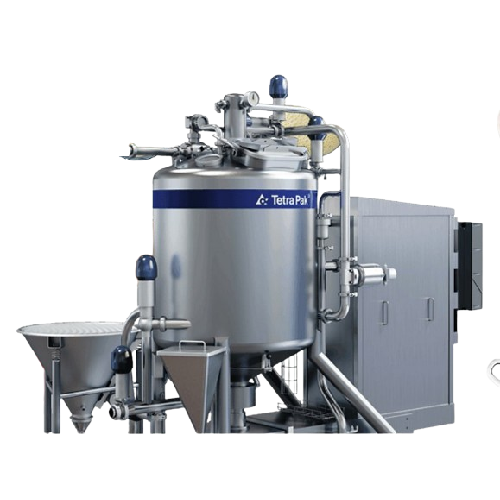
High shear mixer for emulsions and dispersions
Achieve precise emulsification and dispersion with advanced high-speed mixi...
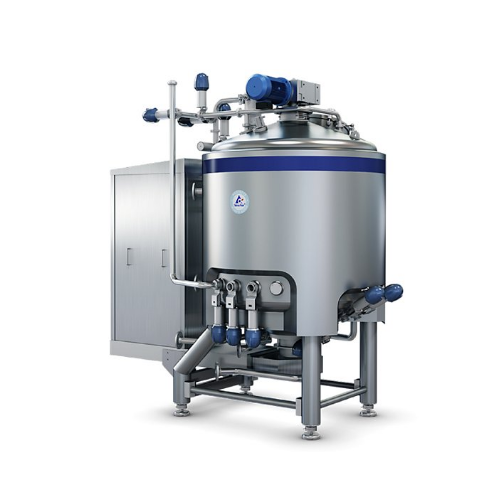
High shear mixer for dairy and beverage applications
When creating complex formulations like sauces or dairy spreads, ach...
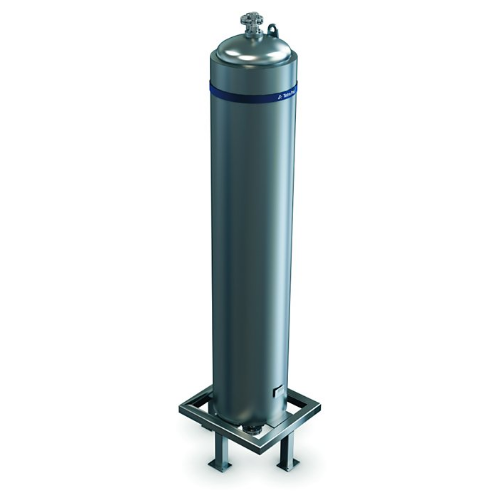
Coiled heat exchanger for high viscosity products
Efficiently handle high-pressure, viscous product heating and cooling w...
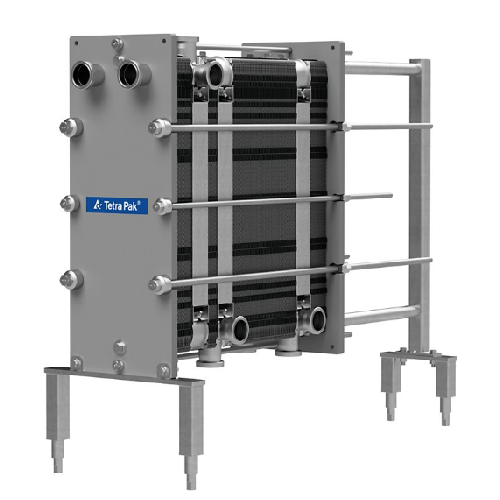
Plate heat exchanger for food products
Achieve precise temperature control in your processing line with this plate heat exc...
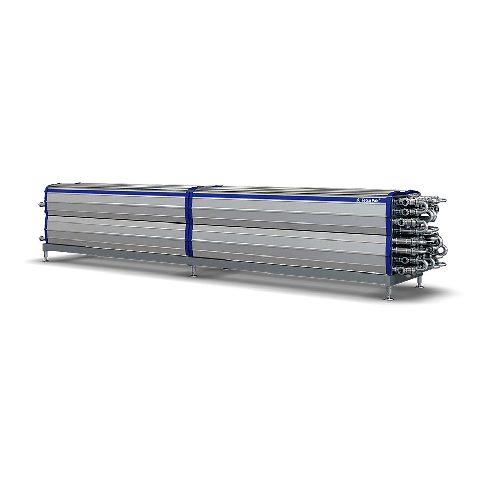
Tubular heat exchanger for food processing
Optimize energy consumption and ensure unparalleled food safety during heat tre...
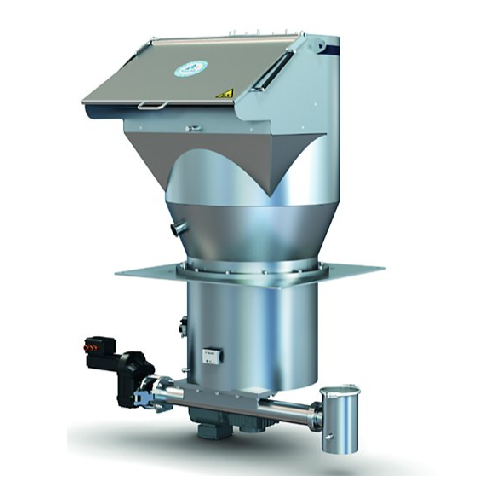
Powder feeder for consistent and accurate dosing
Ensure precise powder dosing with high hygiene standards to maintain prod...
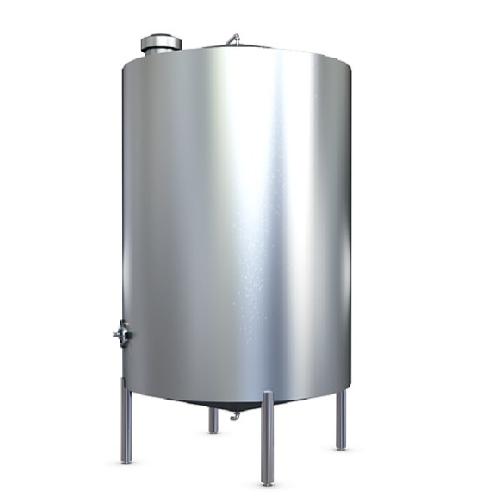
Liquid ingredient reception tank
Optimize your liquid processing with versatile tanks designed for efficient storage and han...
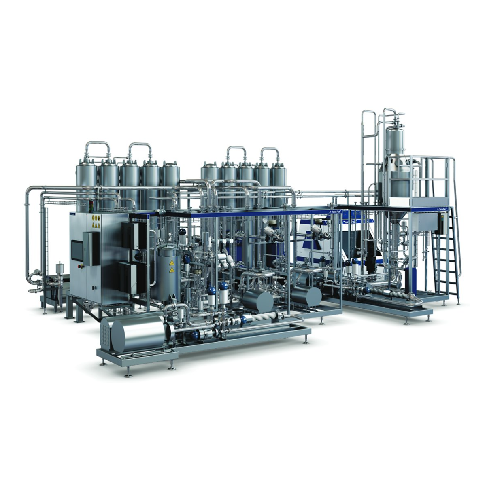
Indirect Uht treatment for high viscous products with particles
Optimize your production line with a unit that ensures h...
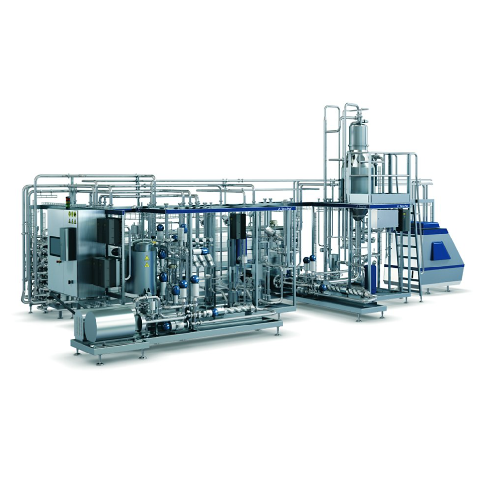
Efficient pasteurizer for prepared foods
Achieve precise heat treatment and reduce product waste with a modular pasteurizat...
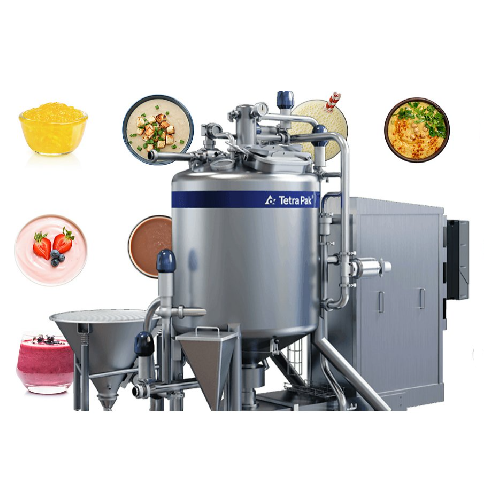
High shear mixer for dairy and beverage industry
Achieve consistent product quality with a high shear mixer, enabling seam...
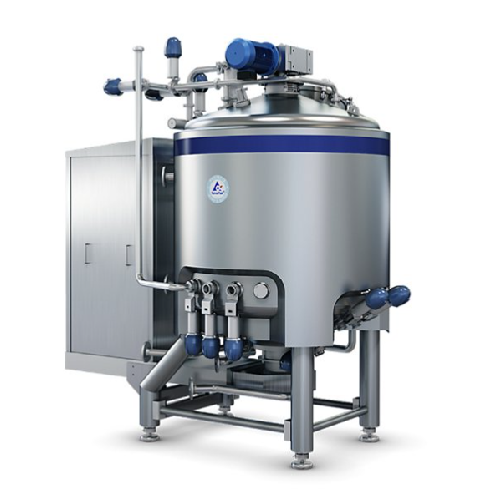
High shear mixer for emulsification and powder dissolving
Achieve seamless mixing and emulsification for high and low vi...
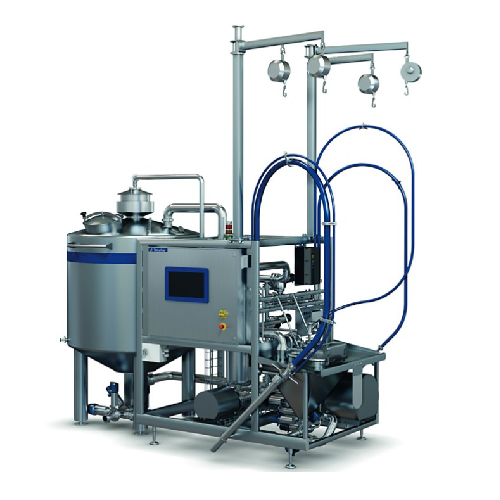
Batch mixer for soft drinks ingredients
Effectively manage diverse ingredient formats with a high-performance mixing system...
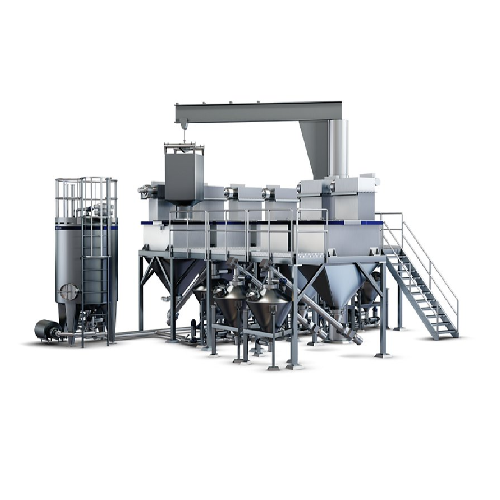
Autonomous ingredient dissolver for high volume dry ingredient mixing
Streamline your production by seamlessly mixing d...
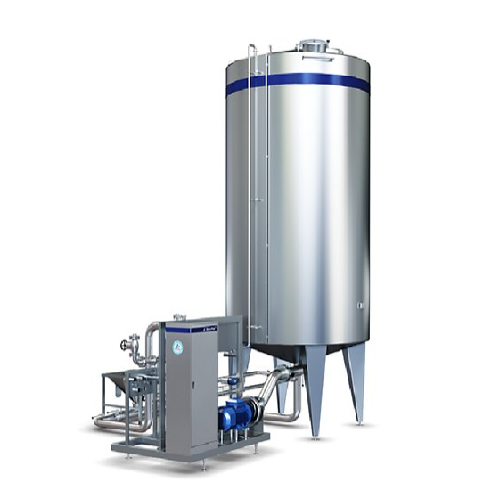
Batch dissolver for sugar or dextrose
Efficiently dissolve crystalline substances like sugar and dextrose with precision, e...
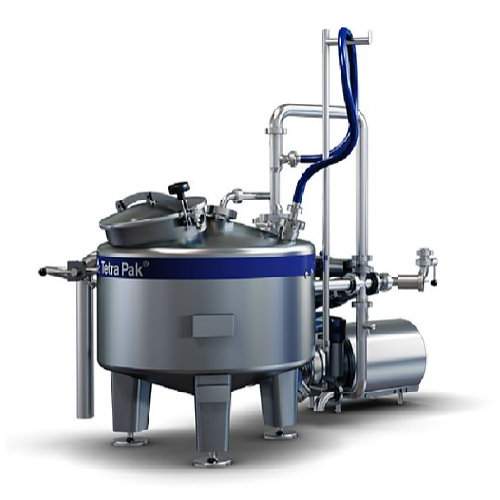
Ingredient dissolver for small batches
Efficiently dissolve water-soluble powders and concentrates up to 200 cP with precis...
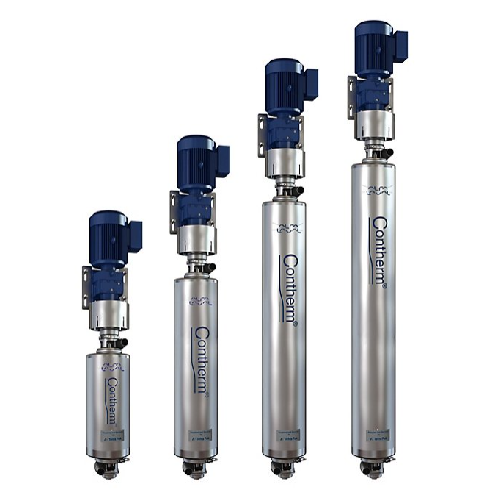
Contherm scraped-surface heat exchanger for viscous food products
Optimize your heating and cooling processes for stick...
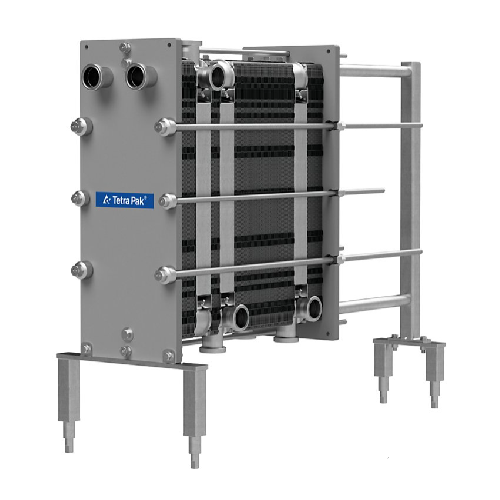
Industrial plate heat exchanger for food processing
Ensure consistent product quality with precise temperature control an...
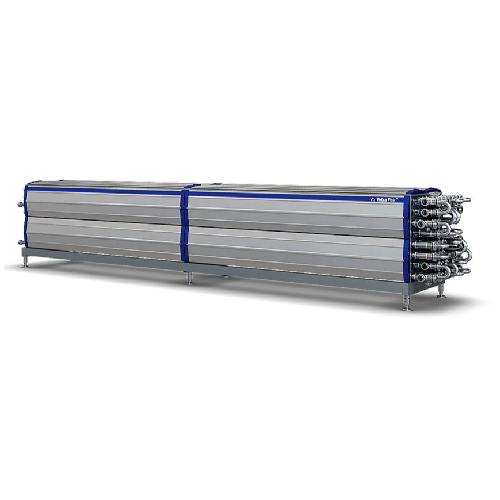
Tubular heat exchanger for food products
Achieve precise temperature control and energy efficiency with this innovative tub...
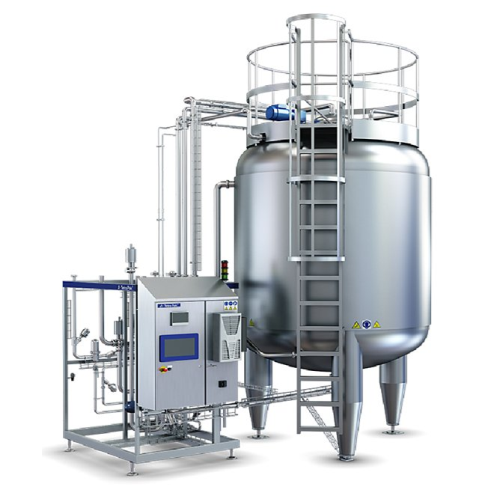
Aseptic tank for blending and buffering
Optimize your production line with a secure aseptic tank that ensures precise in-li...
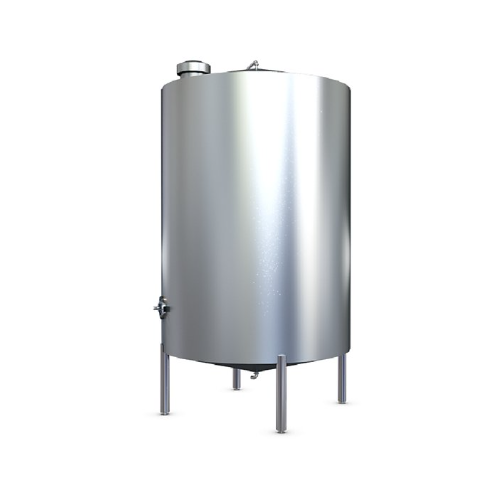
Liquid sugar storage tank
Ensure seamless liquid sugar management in your production line with advanced storage solutions de...
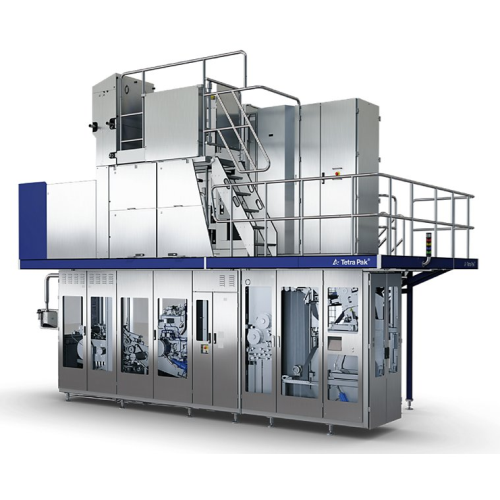
High-speed aseptic carton filling solution
Maximize production efficiency and meet growing demand with this high-output fi...
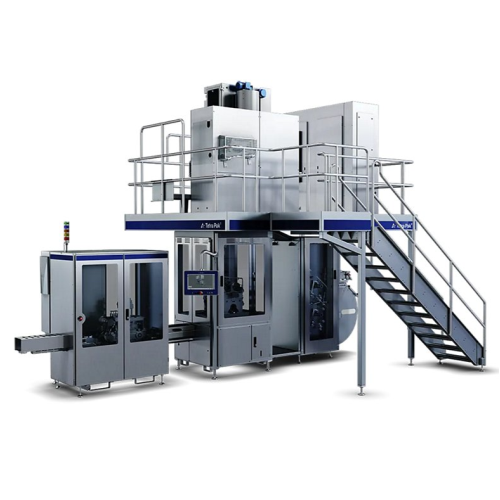
Filling system for tetra brik 100 slim packages
Optimize your chilled product packaging with a high-speed filling system d...
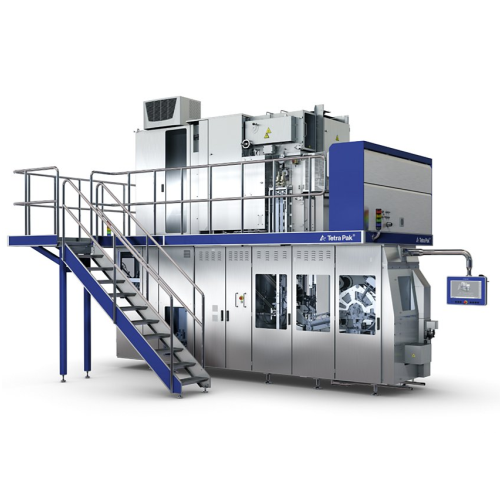
Compact aseptic filling solution for versatile production
Maximize production line efficiency with a compact filling sys...
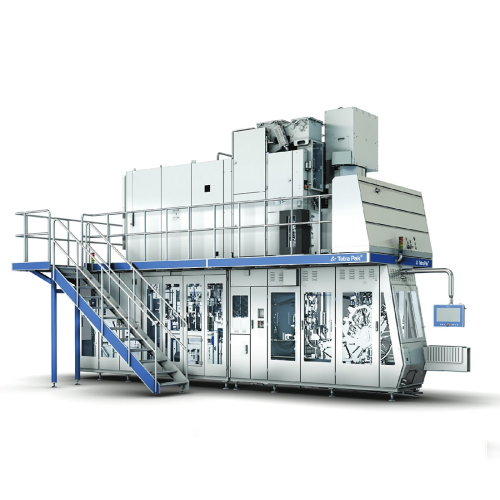
Versatile filling system for aseptic packaging
Achieve seamless integration in high-speed aseptic packaging with this flex...
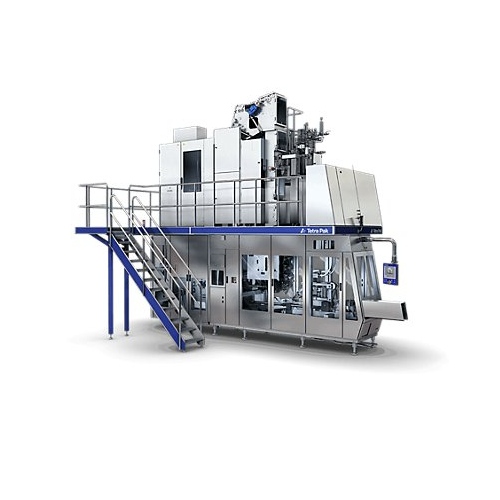
High-speed carton filler for aseptic packaging
Maximize production efficiency with this high-speed filling solution that e...
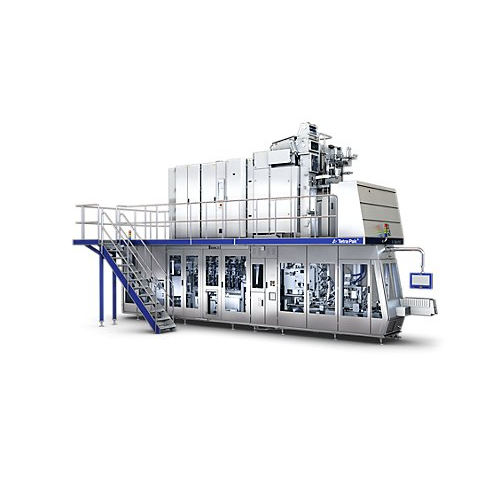
Aseptic filling solution for liquid food packaging
Optimize liquid food production with advanced aseptic filling, ensurin...
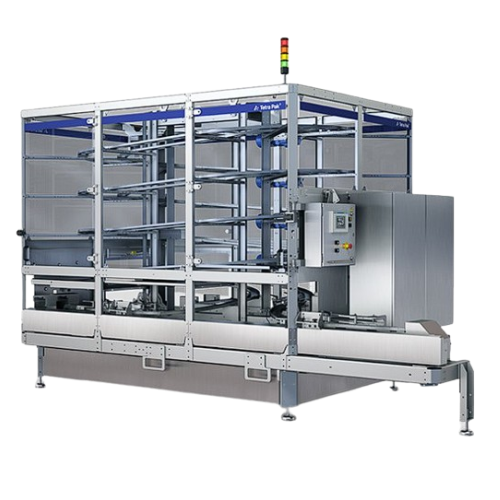
Vertical package accumulator for food and beverage production
Ensure seamless flow and precise order tracking of package...
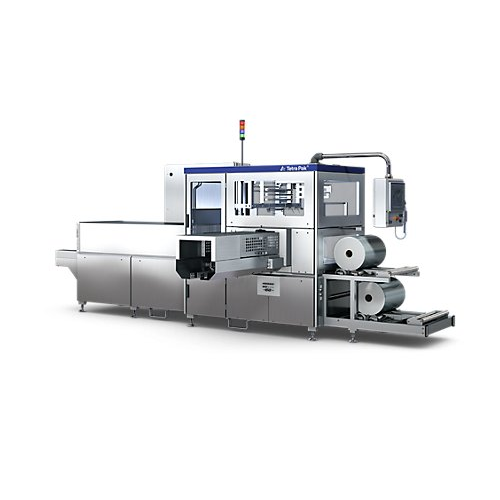
Industrial tray shrink wrapper
Optimize your packaging line with rapid, resource-efficient shrink wrapping, accommodating di...
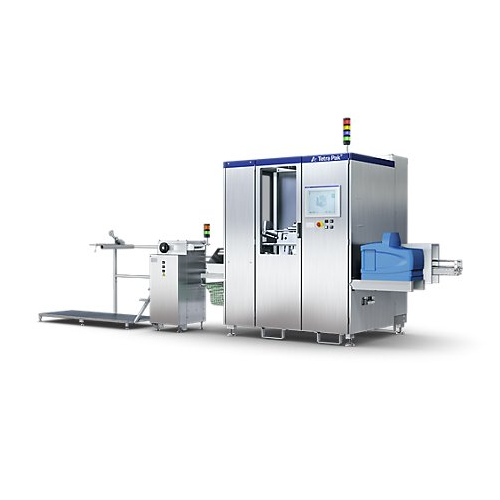
Straw applicator for tetra pak packages
Enhance your packaging efficiency with a high-speed solution that seamlessly attach...
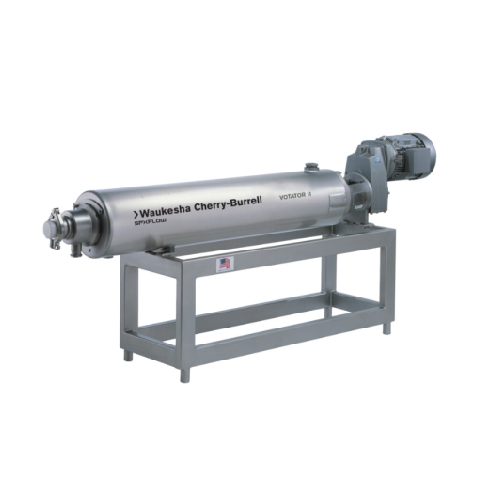
Food processing scraped surface heat exchanger
Enhance your production line with precise temperature control and continuou...
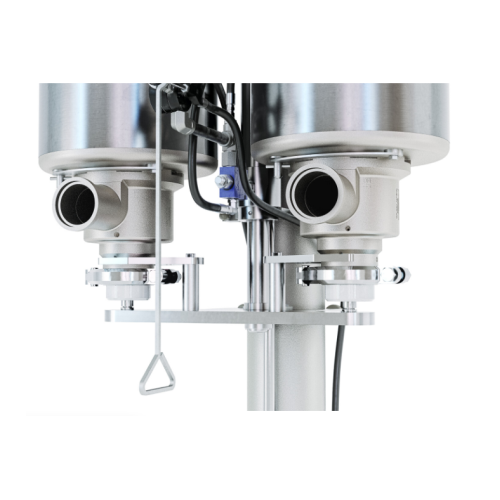
Vertical scraped surface heat exchanger for food processing
For continuous production that demands consistent texture an...
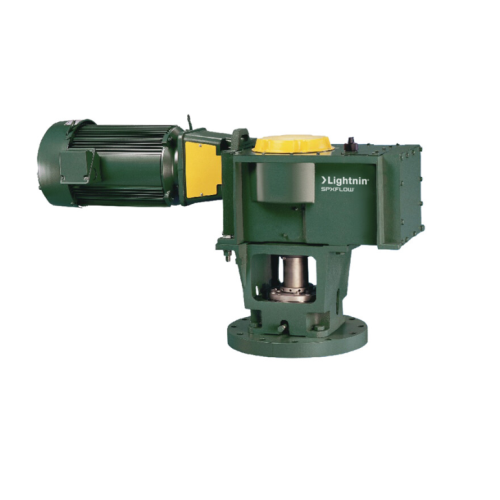
Medium torque top entering mixer for complex mixing tasks
Optimize your production line with a versatile mixing solution...
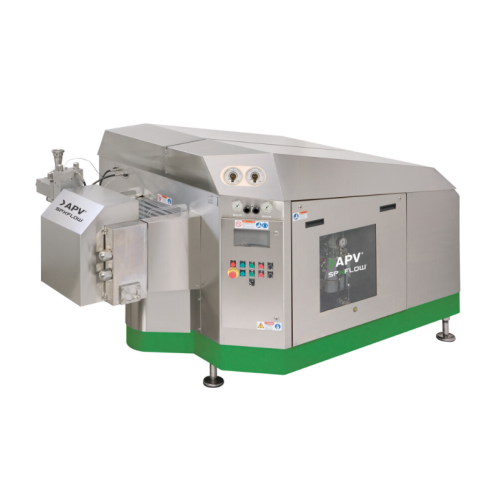
High pressure homogenization system for dairy and creams
Optimize your high-speed homogenization processes with precise c...
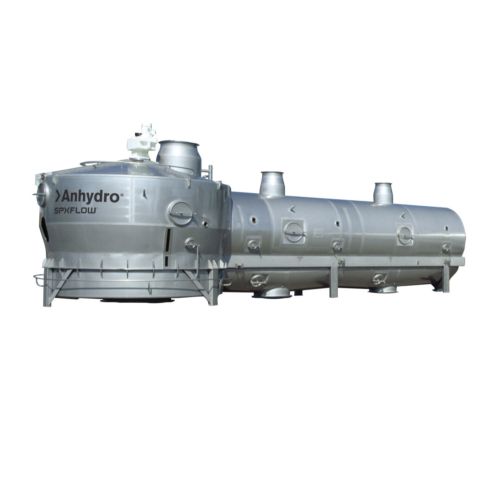
Industrial fluid bed dryers for powder processing
Enhance moisture control and uniformity in powder products with dynamic...
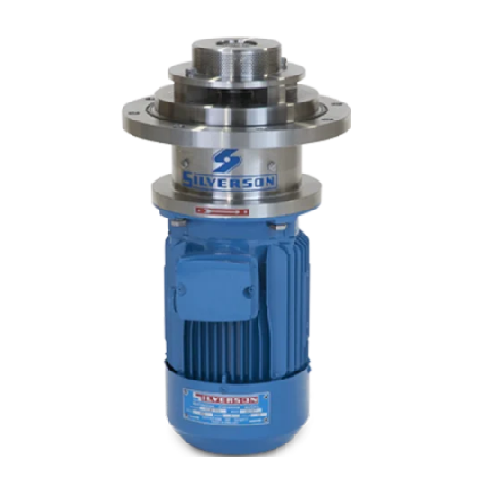
Bottom entry mixers for high viscosity products
Optimize your production line with mixers designed to handle both high and...
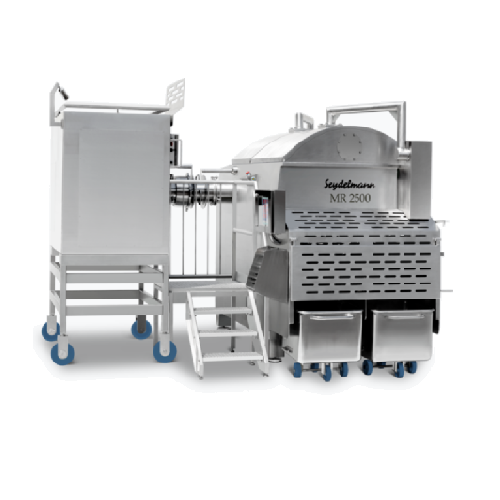
Automated production line for ground meat products
Enhance your meat processing efficiency by seamlessly integrating grin...
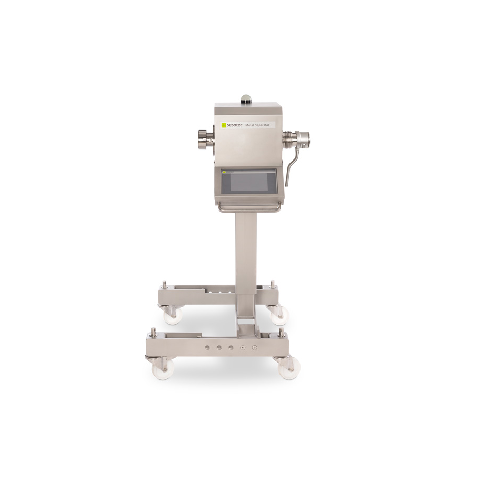
In-line metal detector for liquids & pastes
Ensure product safety by seamlessly integrating a metal detection system into ...

Mayonnaise production line
Streamline your high-capacity mayonnaise production with precise mixing, emulsifying, and pasteur...
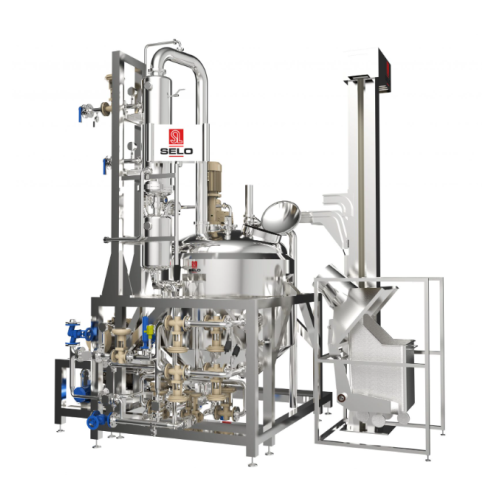
Automated mayonnaise and dressing production line
Ensure the consistent quality of your mayonnaise, dressings, and sauces...
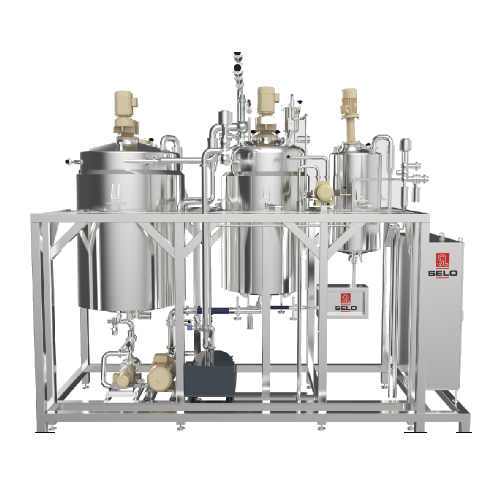
Baby food production line
Ensure optimal safety and precision with this production line, designed for processing delicate ba...
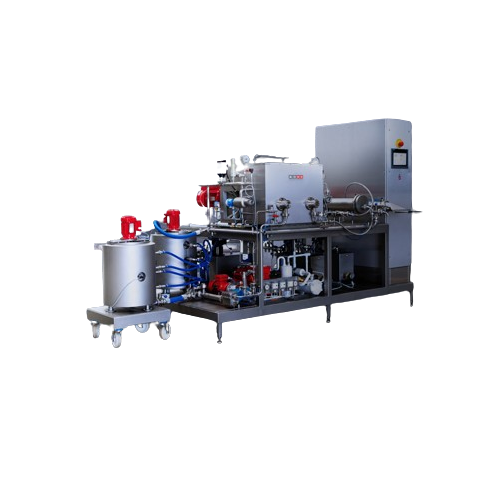
High pressure plunger pump for continuous food processing
Achieve consistent texture and quality in spreads and sauces w...
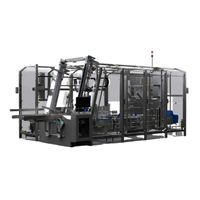
Side Load Case Packer For Packaged Food
Accuracy is a primary concern for case-packing pre-packaged foods such as milk or p...
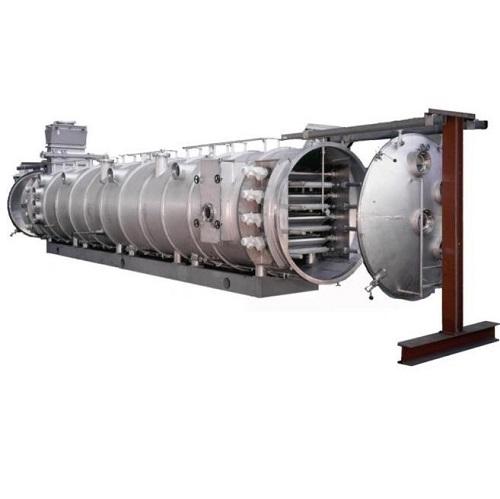
Vacuum belt dryer for fruit, vegetable and herbal extracts
Organic volatile compounds from fruits, vegetables and herbs ...
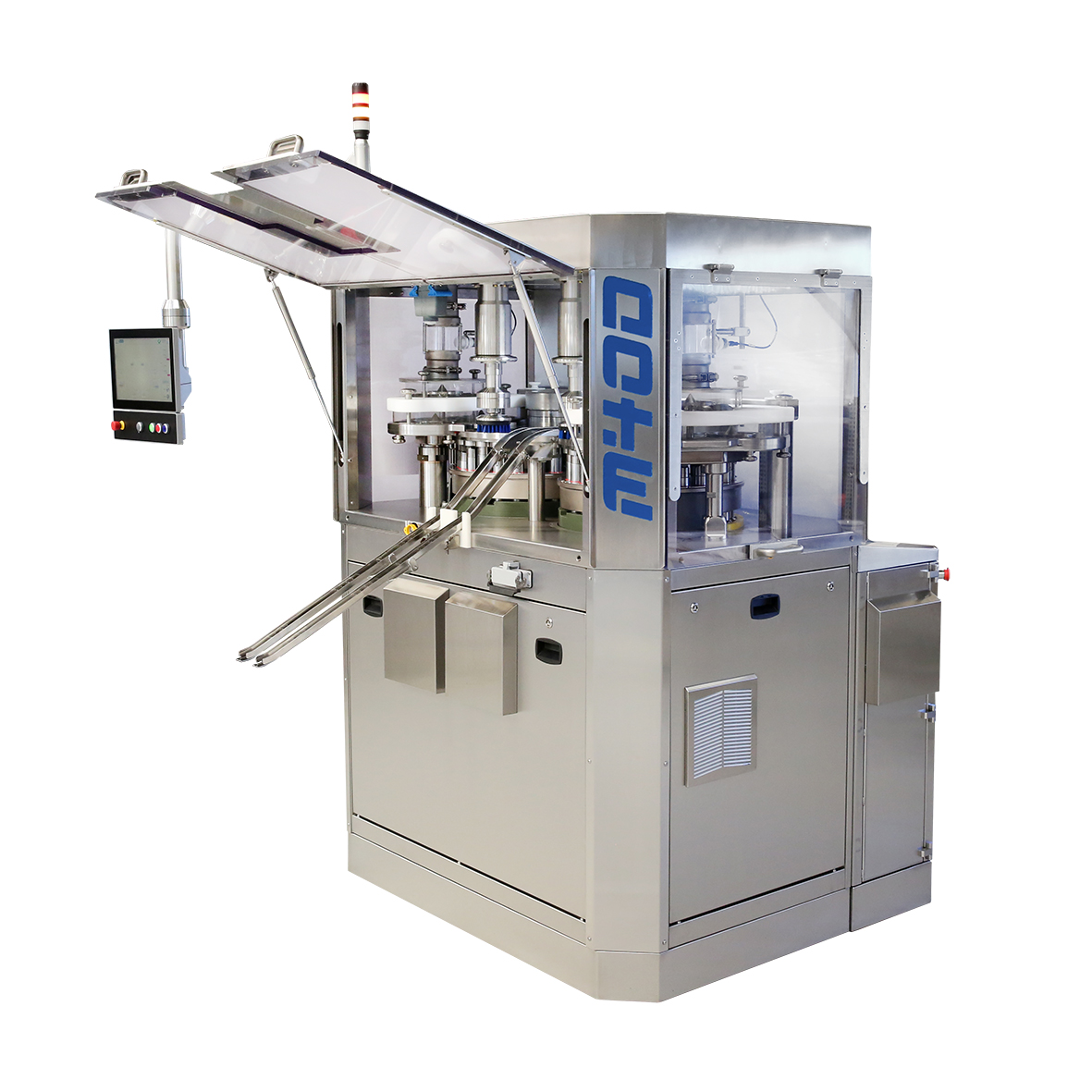
High-speed bouillon cube press machine
Mass production of bouillon cubes and tablets with very high output requires higher ...
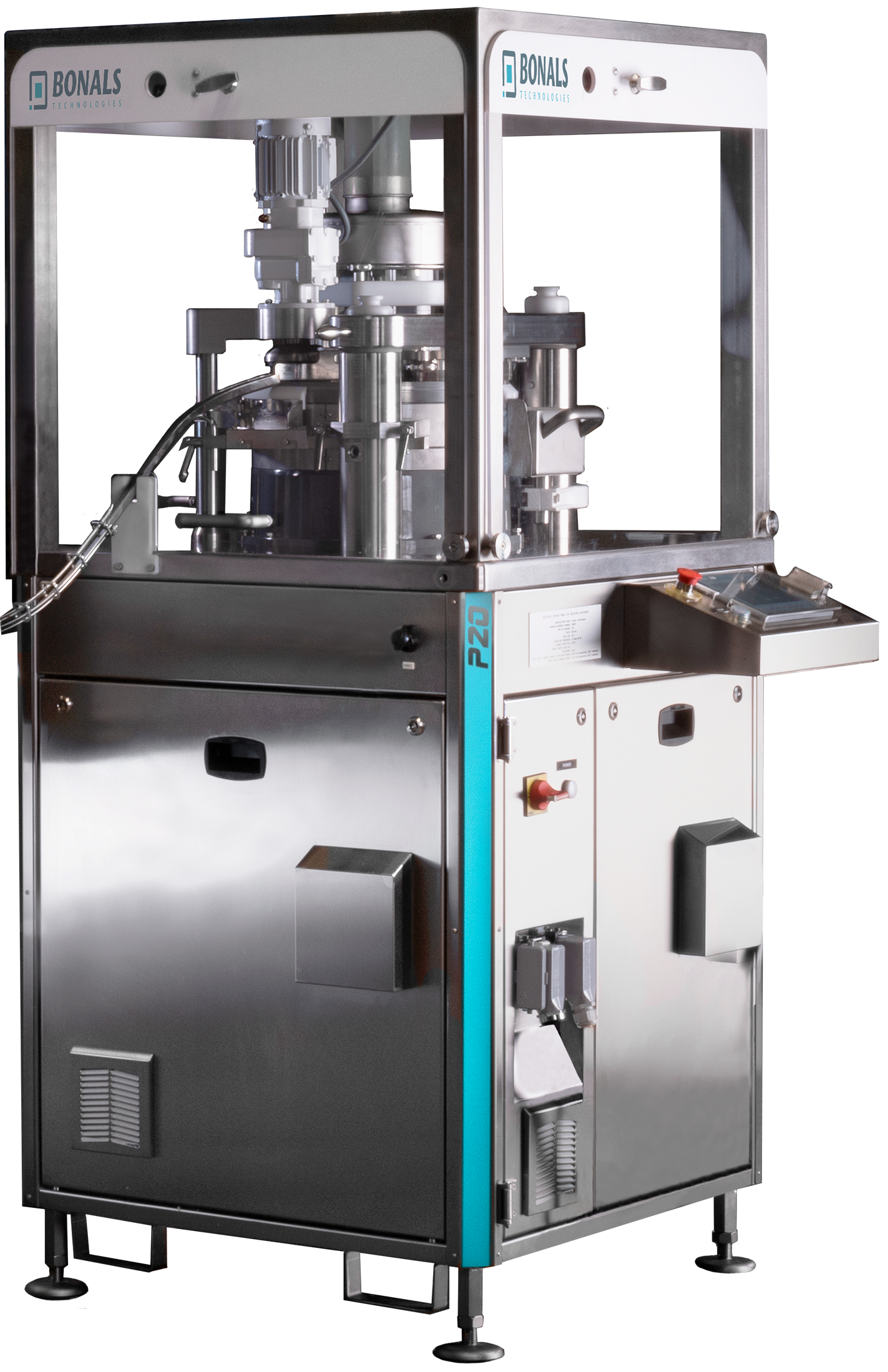
Bouillon cube press machine for medium-range batches
The pressing stage during the production of bouillon cubes or tablet...
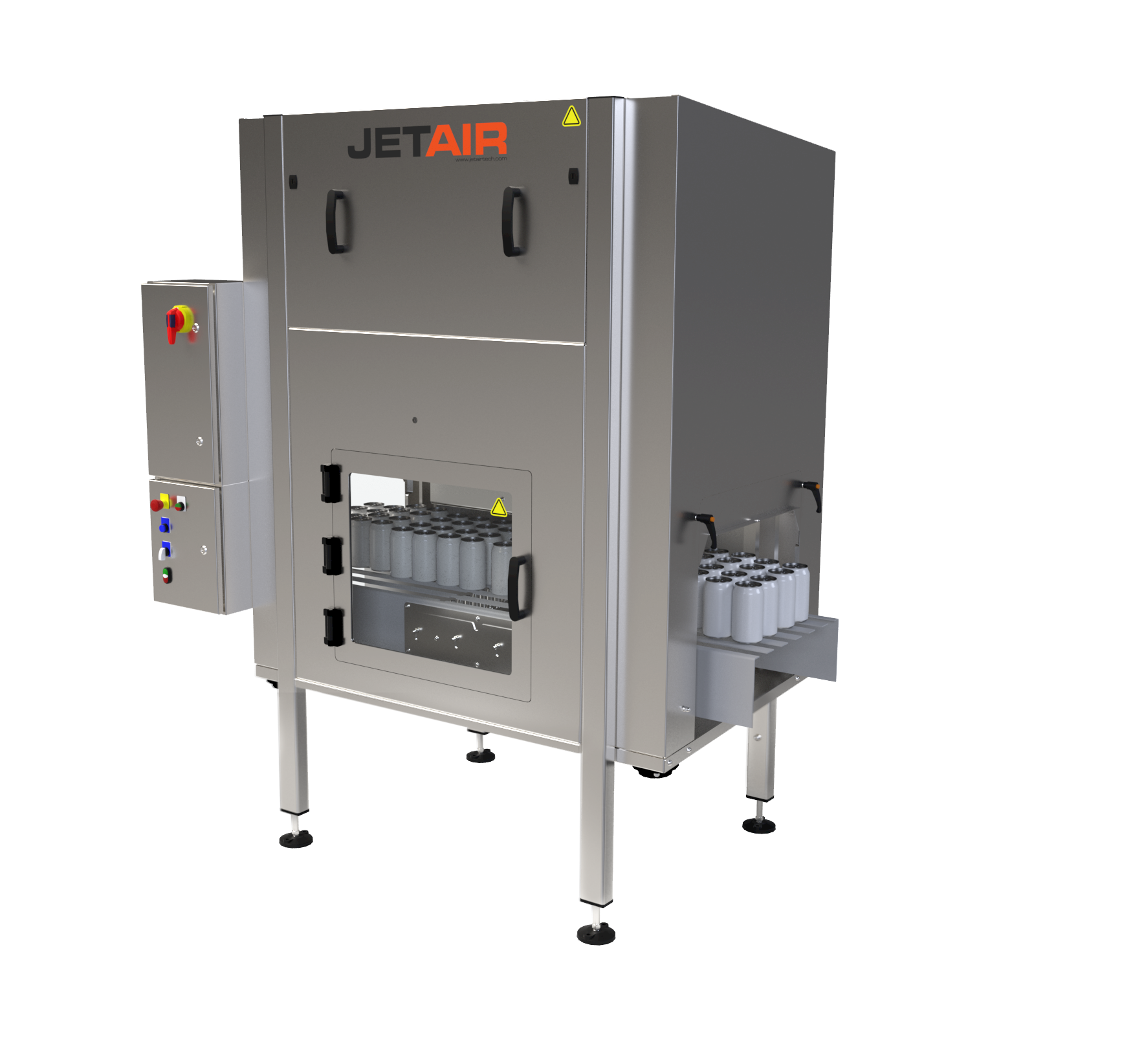
Mass flow air knife drying system for cans
For large-scale production of canned beverages, line throughput and efficiency ...
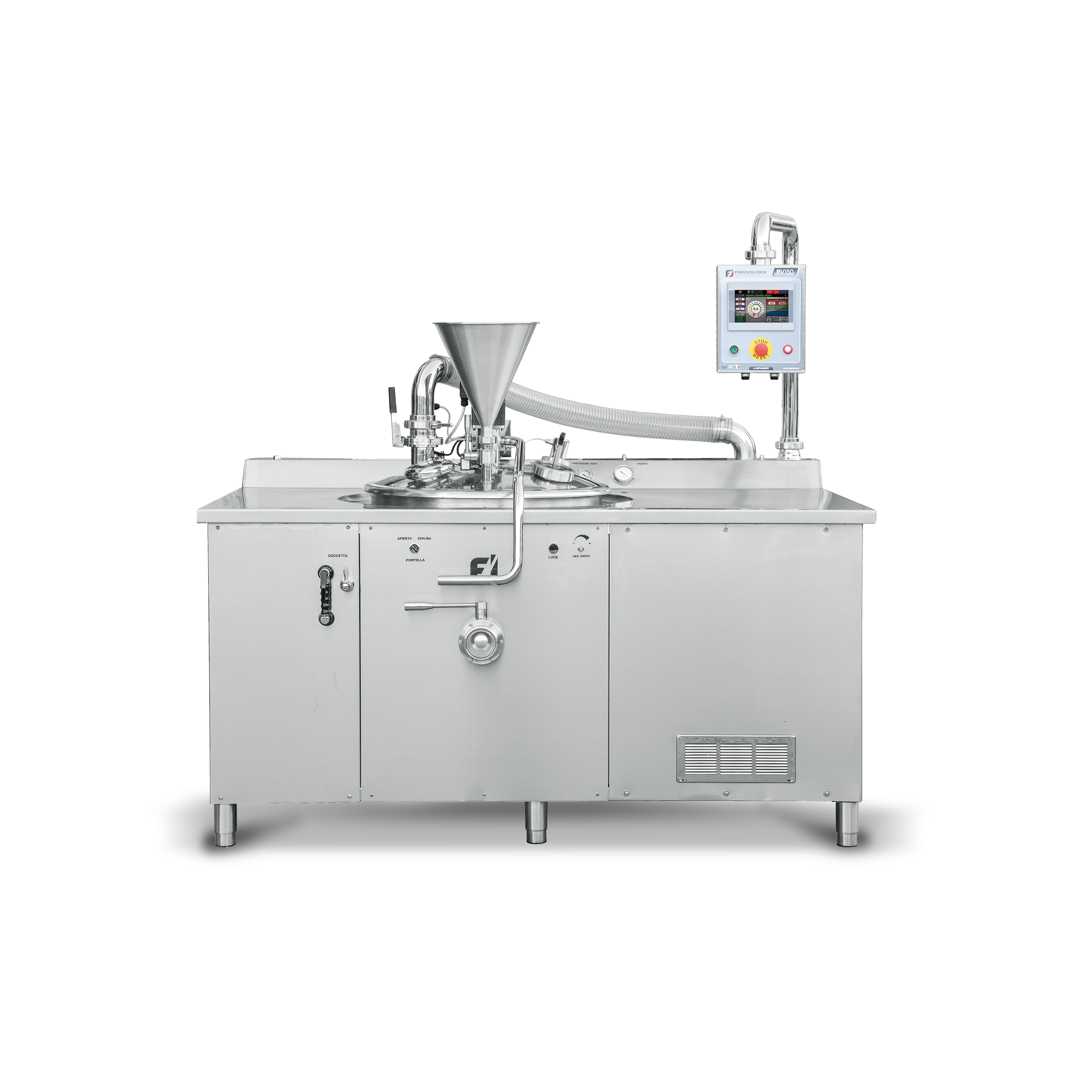
Industrial jam vacuum cooker
In a production setup of agri-food preserves, sauces, and other condiments, vacuum cooking at 5...
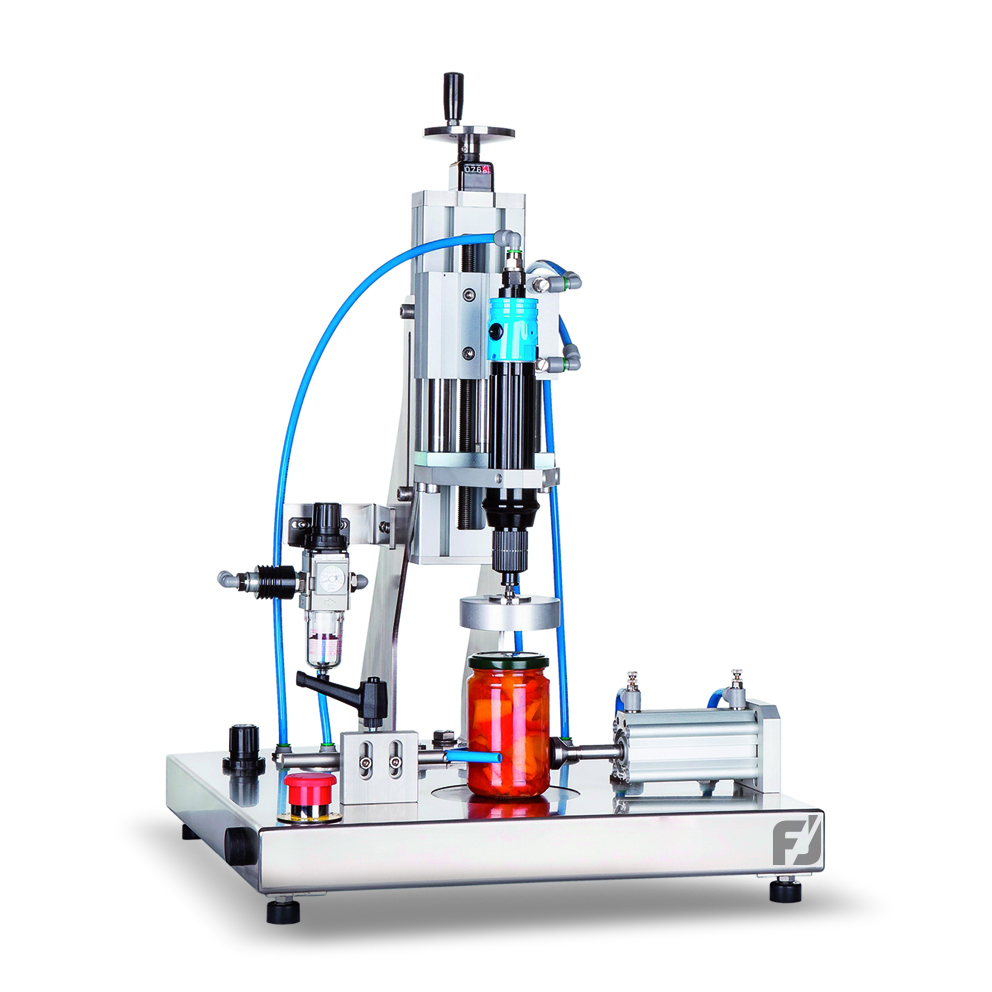
Capping Machine for Jars
In production lines that involve sterilization processes, jars that are not properly capped may expl...
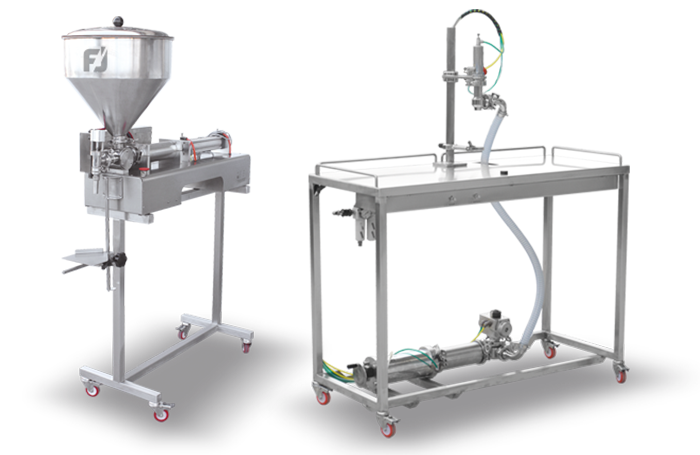
Semi-Automatic Volumetric Liquid Filling Machine
Filling containers manually with liquid and viscous products is the metho...
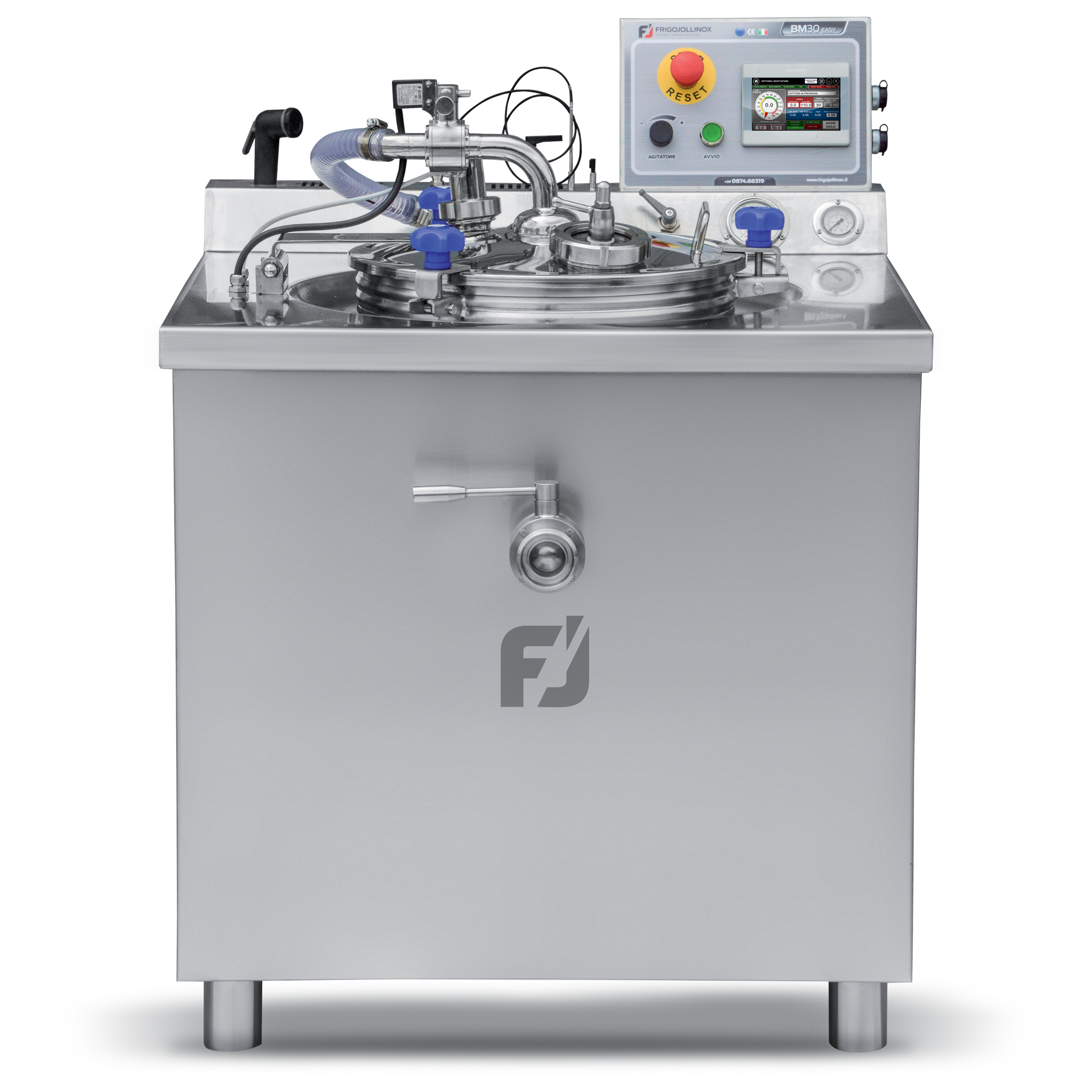
Small Scale Industrial Jam Cooker
Production of marmalades, jams, fruit concentrates, and sauces requires multiple steps. T...
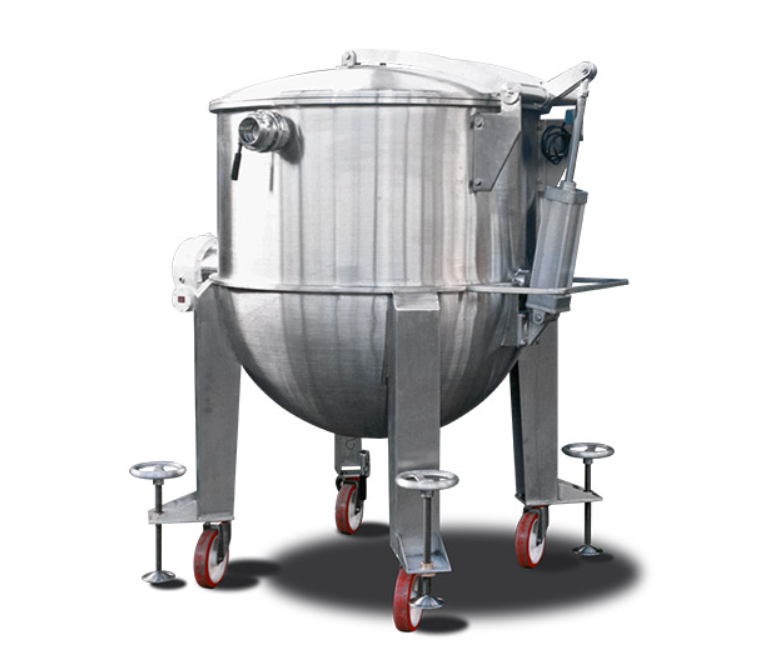
Batch cooker for fruit puree
The fruit pulp is used in many different bakery products, especially as a filling. Since fruit ...
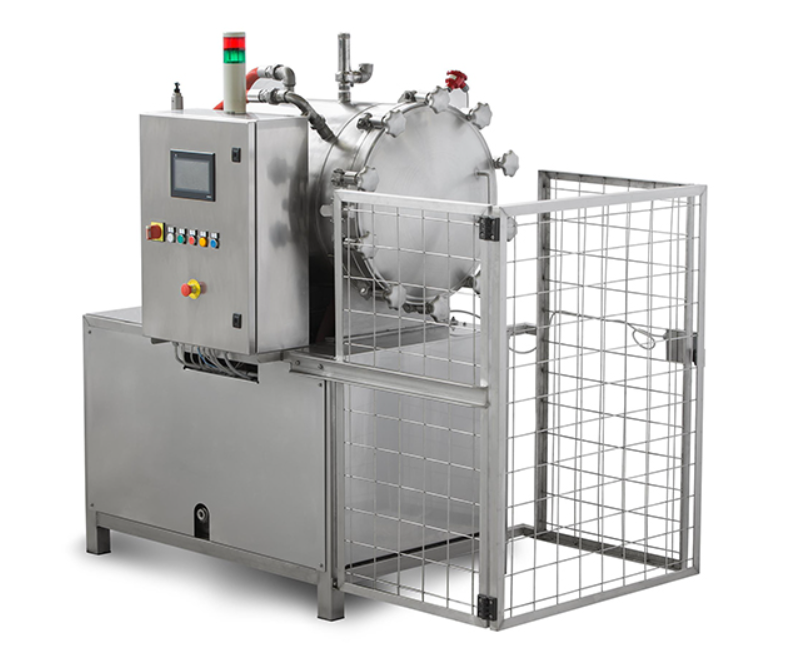
Autoclave sterilizer for food cans and jars
An autoclave is a must-have machine for canned food production lines. It perfo...
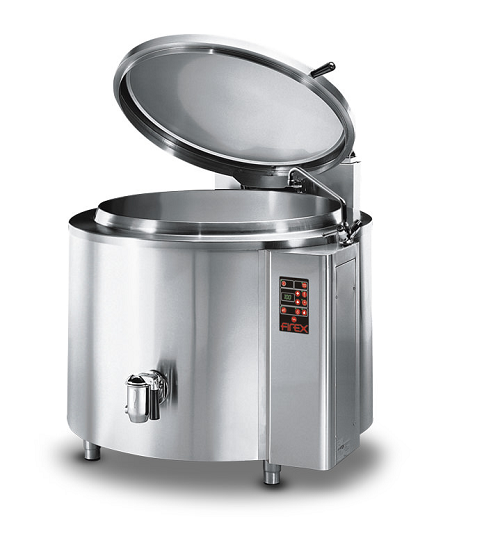
Jam pasteurizer with temperature control
Microorganisms and pathogenic forms in fresh fruit jams can shorten storage time. ...
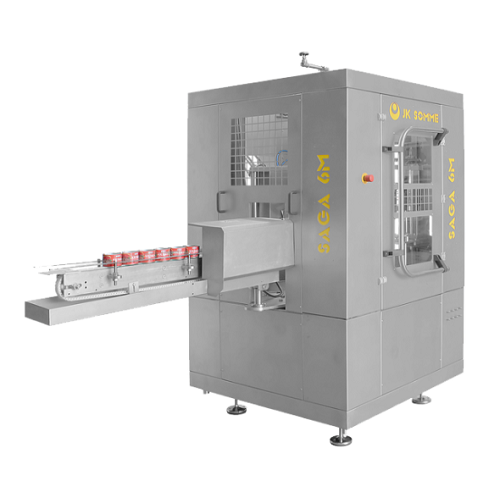
High speed can seamer
Tin plate thickness for cans has gradually reduced over the years, which makes it a hassle to use new c...
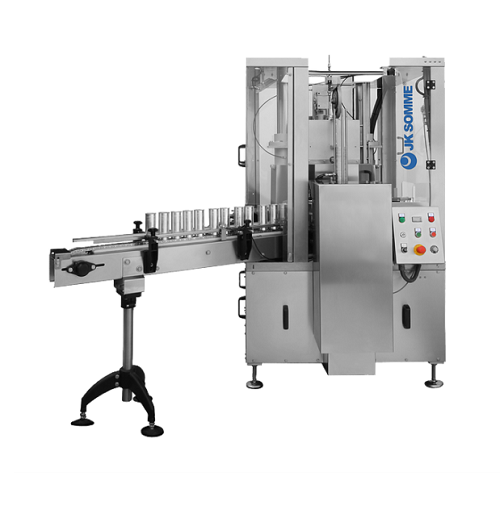
Medium scale round can seamer
Automatic seaming of cans of craft bear can be quite the hassle with the movement from the cen...
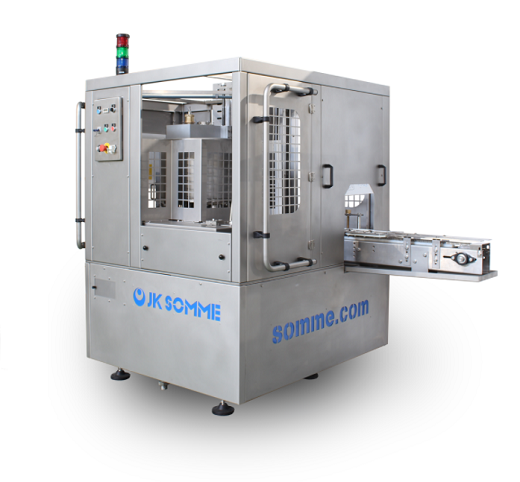
Irregular can seamer
Quite some time can be lost adjusting the seaming process to different can sizes when orders keep follow...
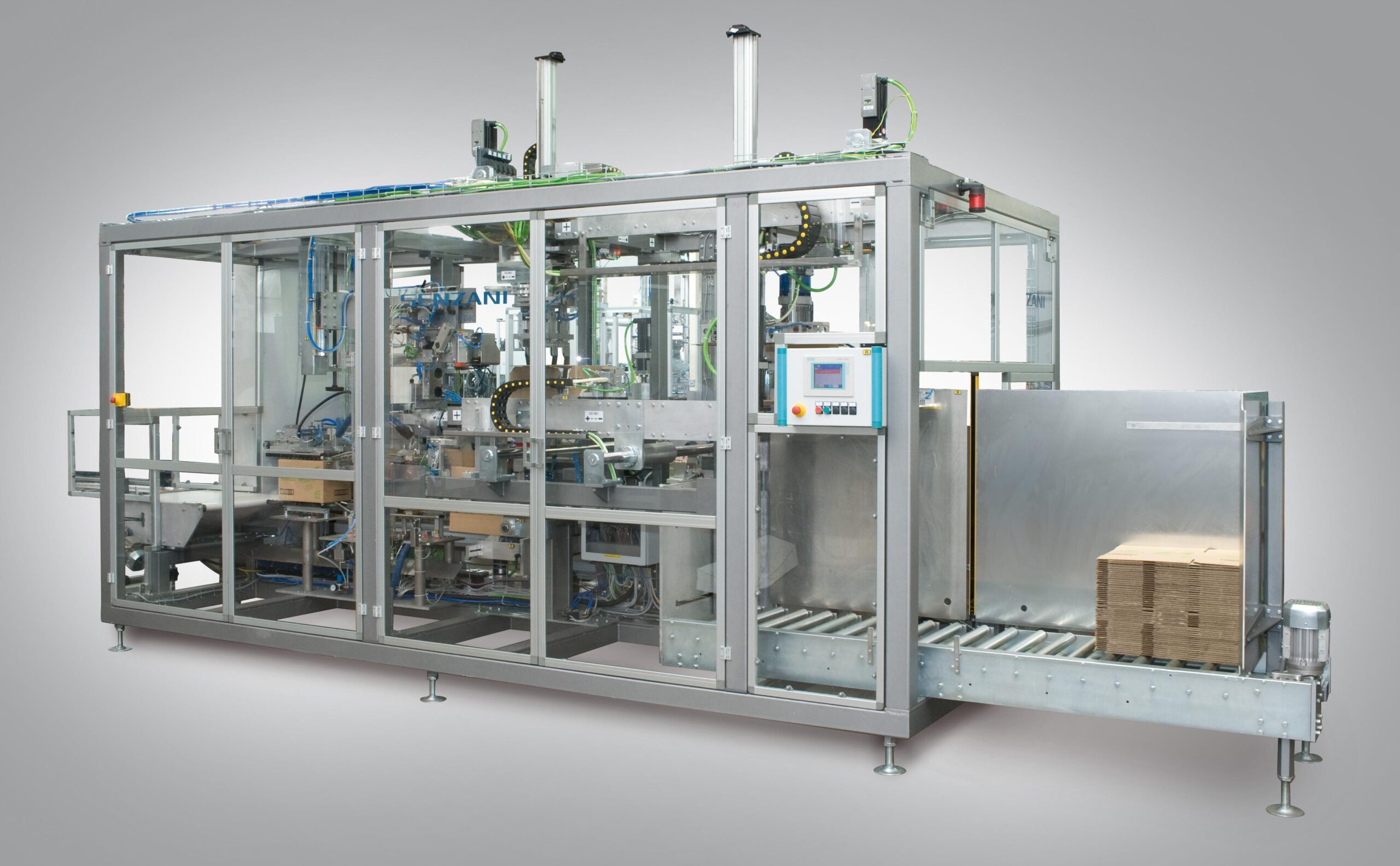
Case packer machine for pouches
Automated case packer machines are a good solution to achieve reliability and to increase th...
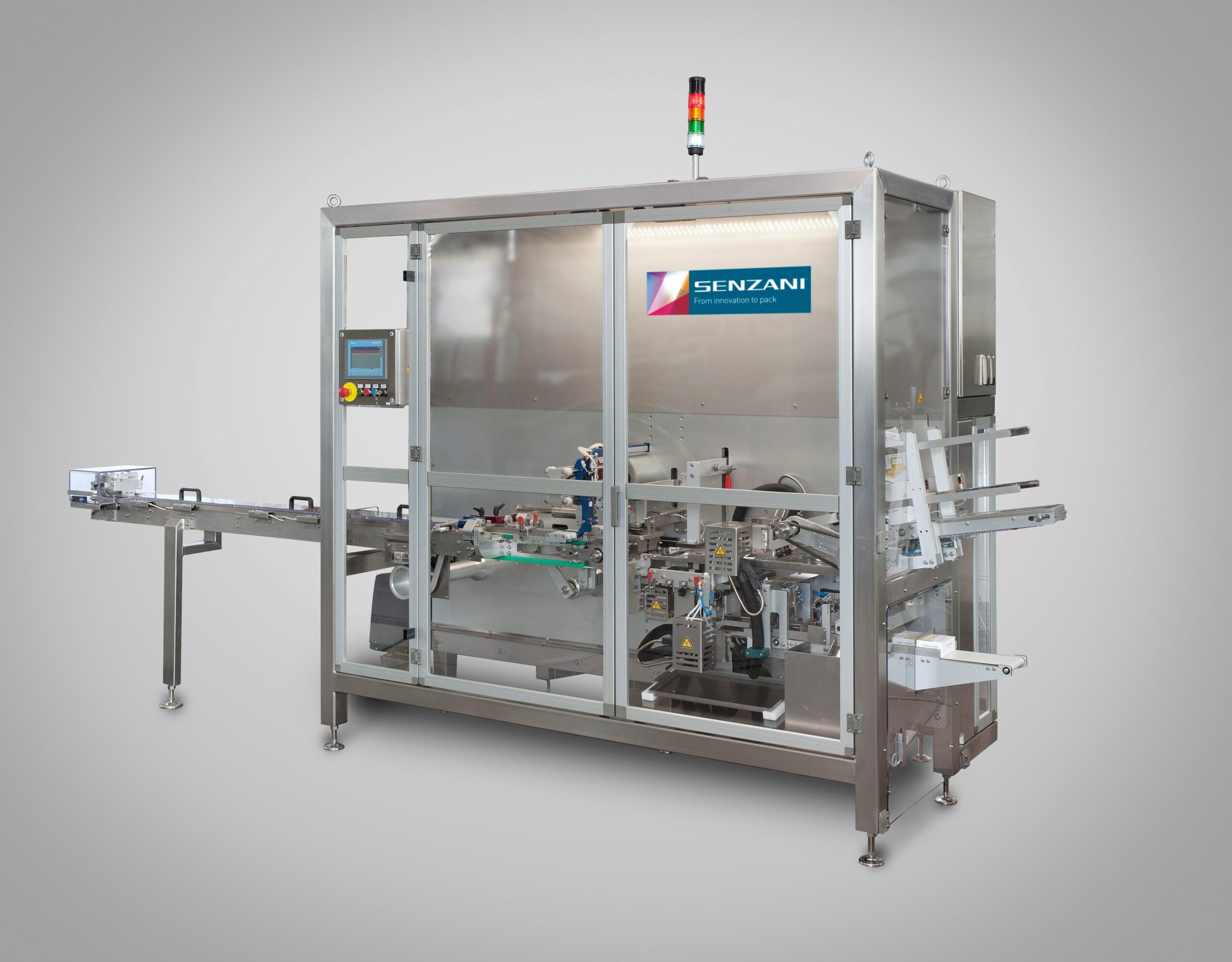
Display tray cartoner machine
Packaging products usually require a great deal of flexibility to comply with demand from mark...
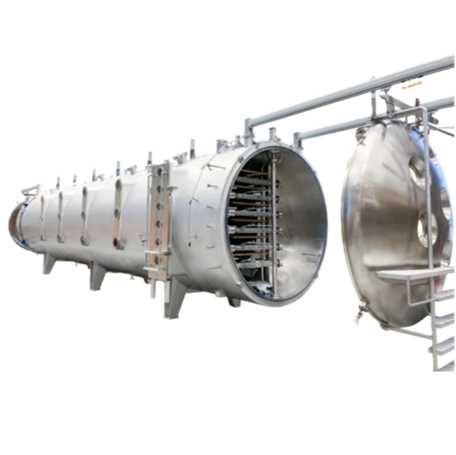
Vacuum belt dryer for instant drink powders
Extracting the essential acids and compounds from fruits and plants is a compl...
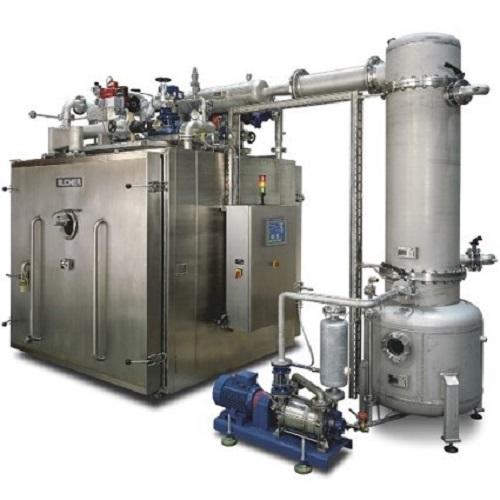
Vacuum cabinet dryer for plant extracts and functional foods
Plant extracts are vital to functional food preparations. B...
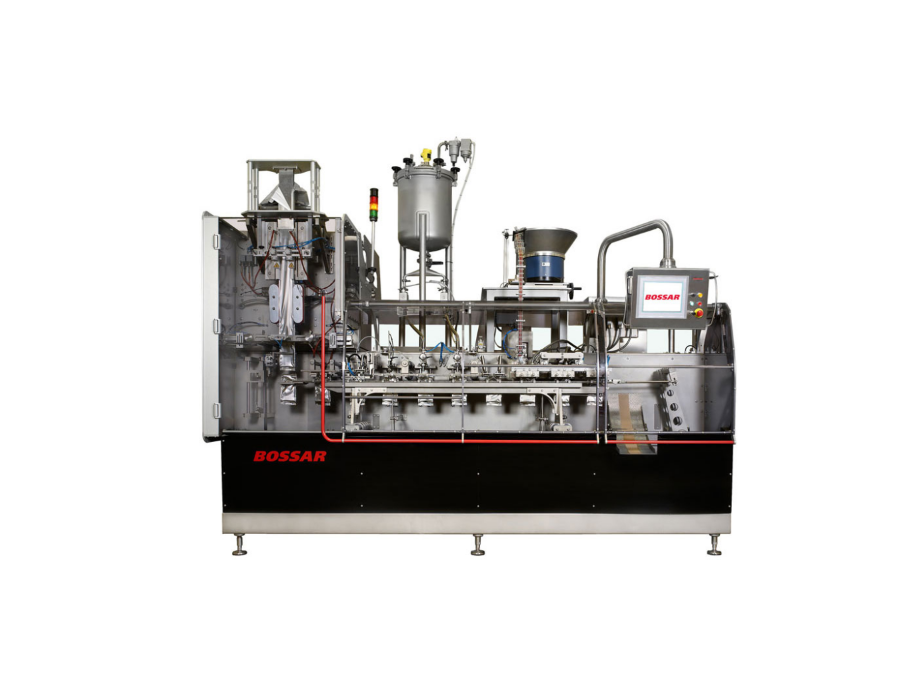
Economical Pouch Packaging Machine
The side gusset pouch is a popular packaging solution for medium formats, particularly f...
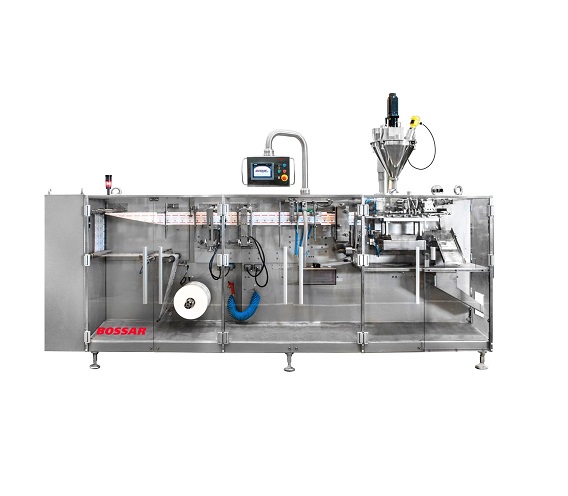
Entry level HFFS Machine for flat sachets
Traditional horizontal form fill and seal sachet machines for lower volume lines...

High-Speed Pouch Packaging Machine
For large scale production of powders and liquids in a wide range of industry sectors, a...
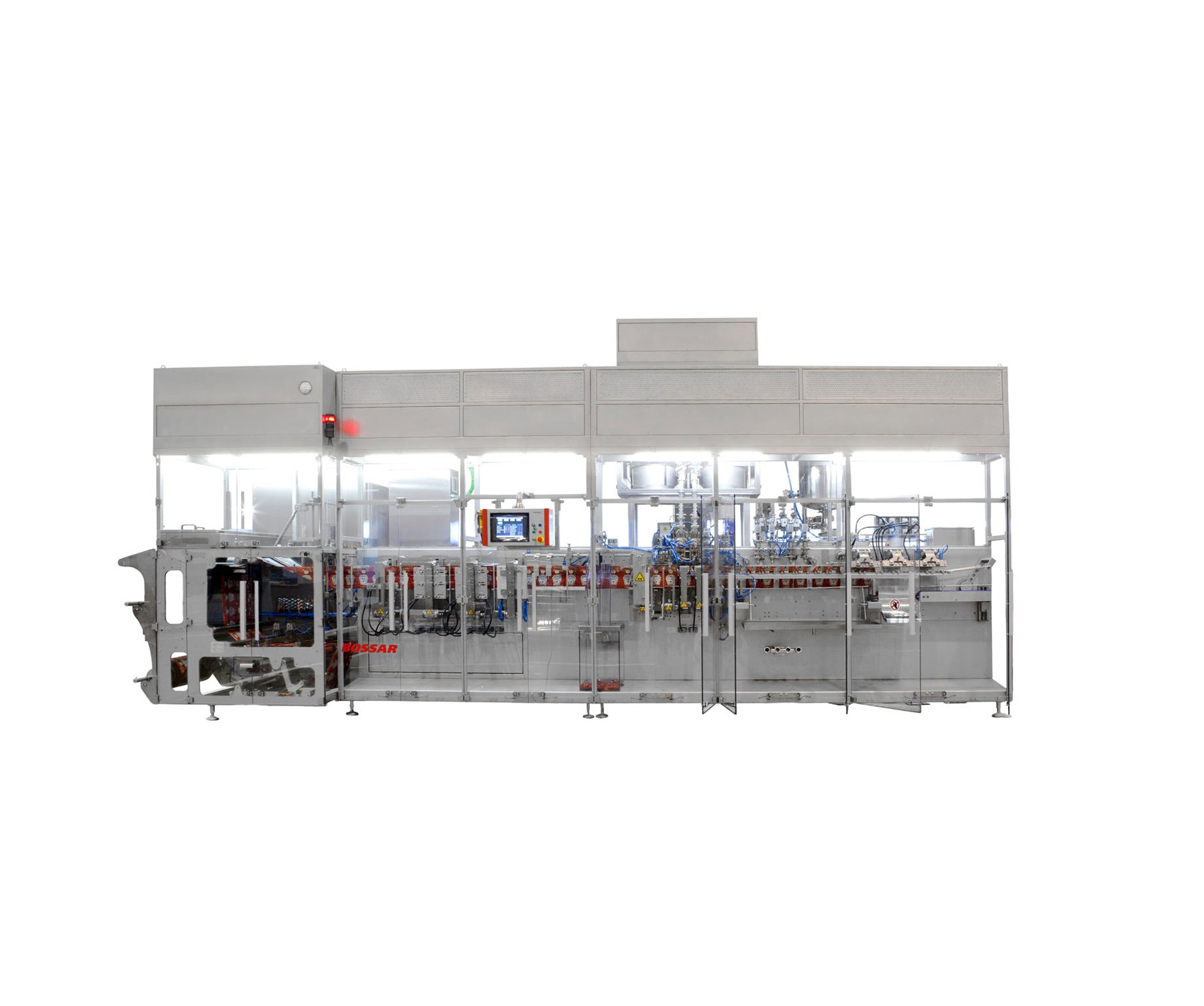
Modular HFFS Machine
A large range of sizes and types is available, with traditional horizontal form fill and seal machines b...
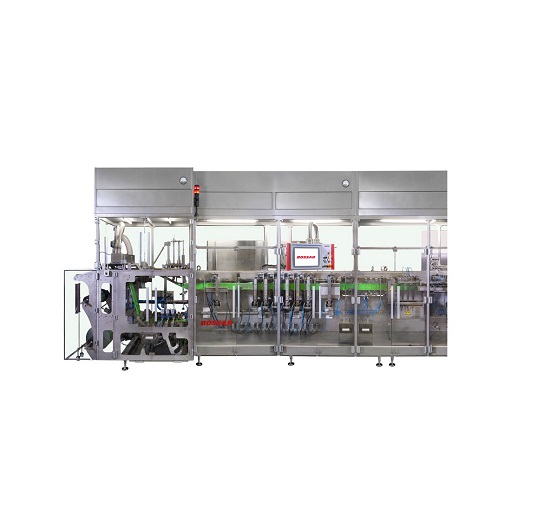
HFFS machine with servo-control system
Traditional HFFS machines use mechanical cams to drive the production path through t...
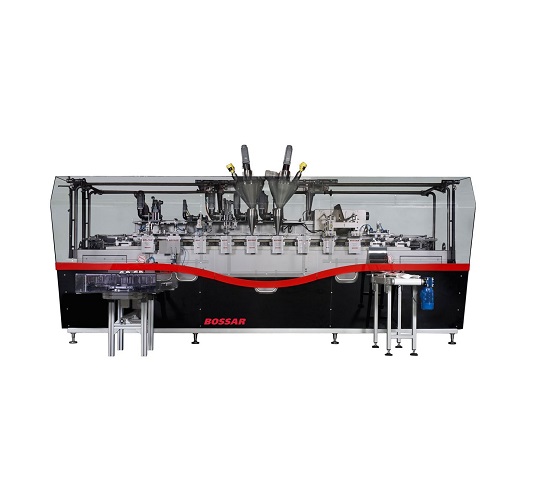
High Speed Premade Pouch Packaging Machine
Pre-made pouches can be problematic for traditional cam-driven mechanical HFS m...
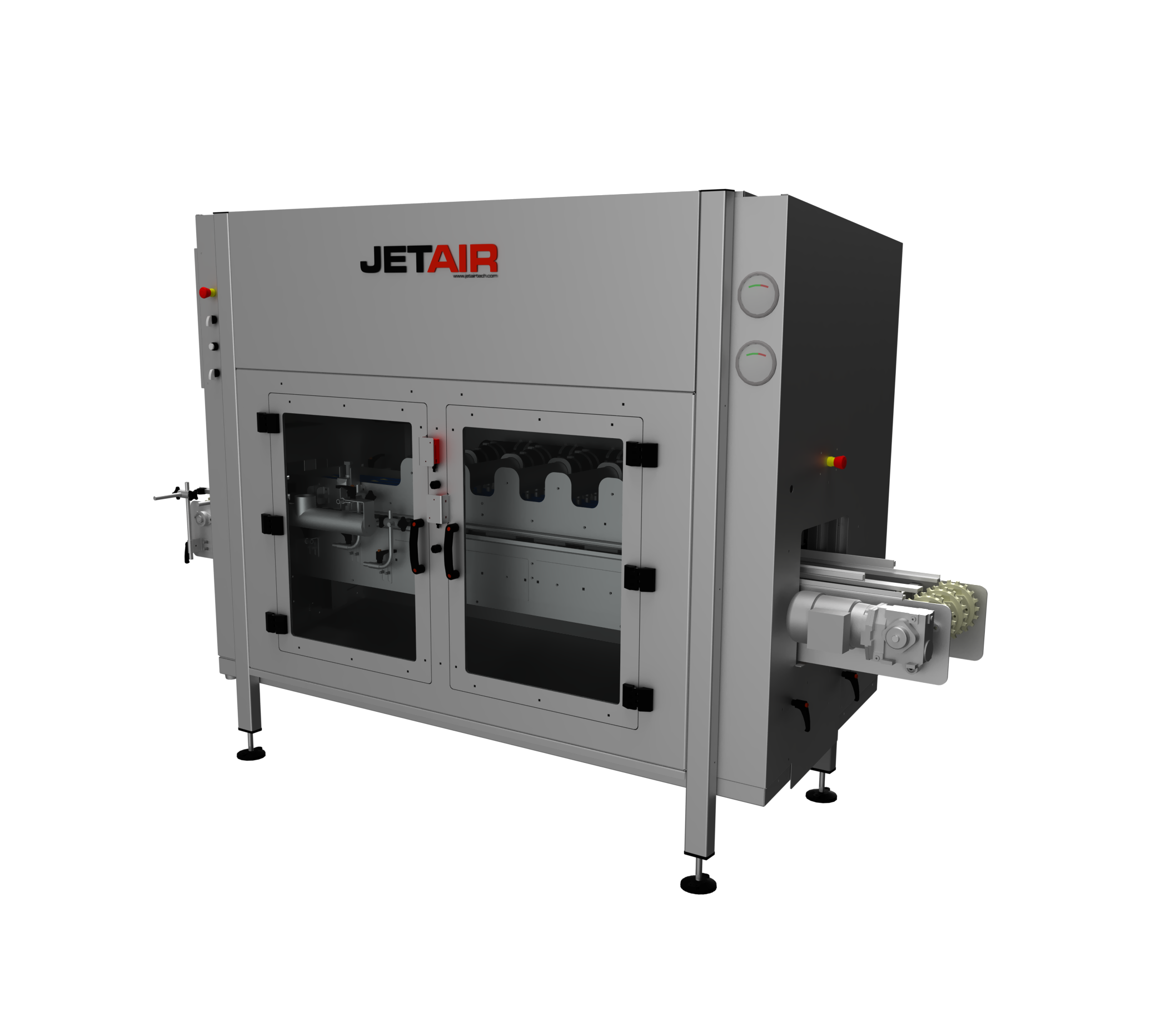
Air knife dryer for pouches
Flexible pouch packaging is a popular choice for many consumer food products. Before final print...
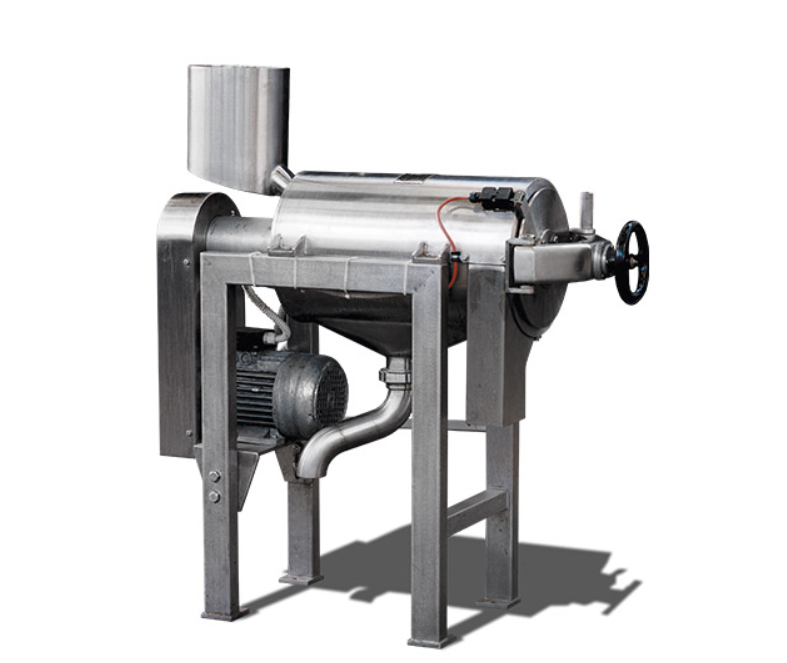
Fruit pulping machine
When making fruit pulp, a pulping machine helps you remove seeds, stems, and skins from your fruit. How...
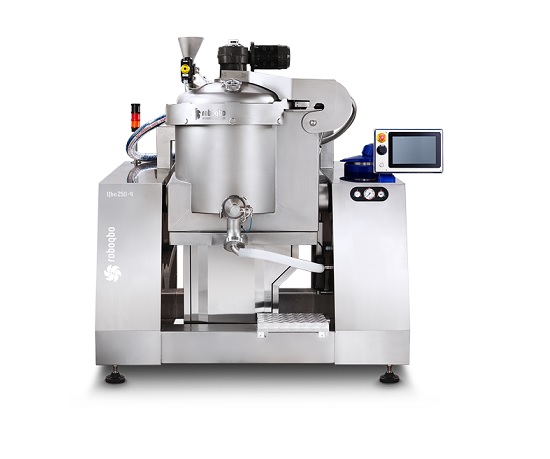
Industrial food processor for cooking ready meals in different consistencies
In food industry production, the developm...

Easy to use food processor for gastronomy sauces and pastes
For the development and production of high quality gastronom...
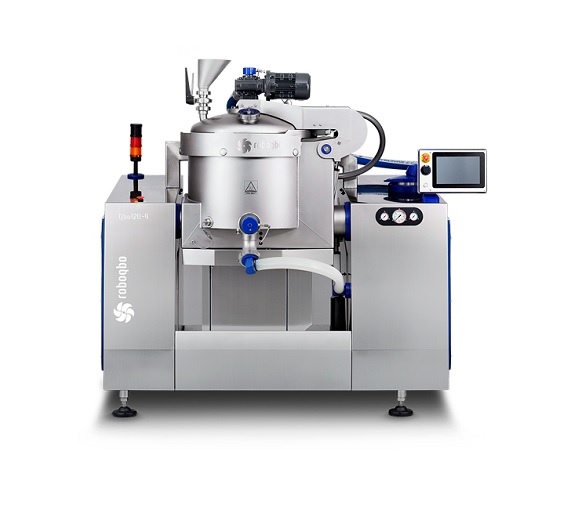
Food processor for making fruit jams for pastries
In a bakery environment fruit jams are often used for the decoration or...
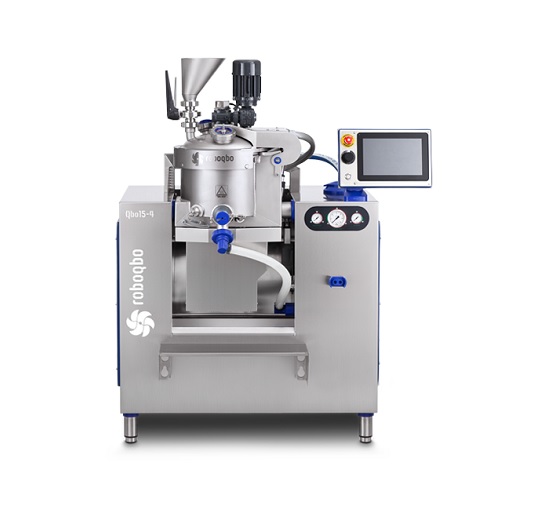
Multi-functional food processor for a high sugar percentage pastes production
For the development and production of hi...
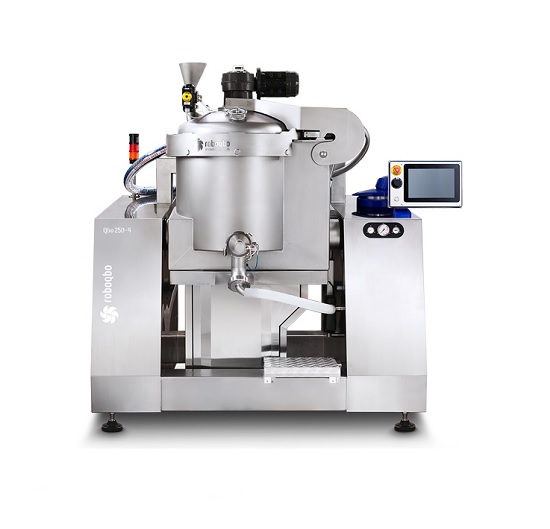
Vacuum cooker for concentrating sauces and purees
When producing high quality prepared food, concentrating products for s...
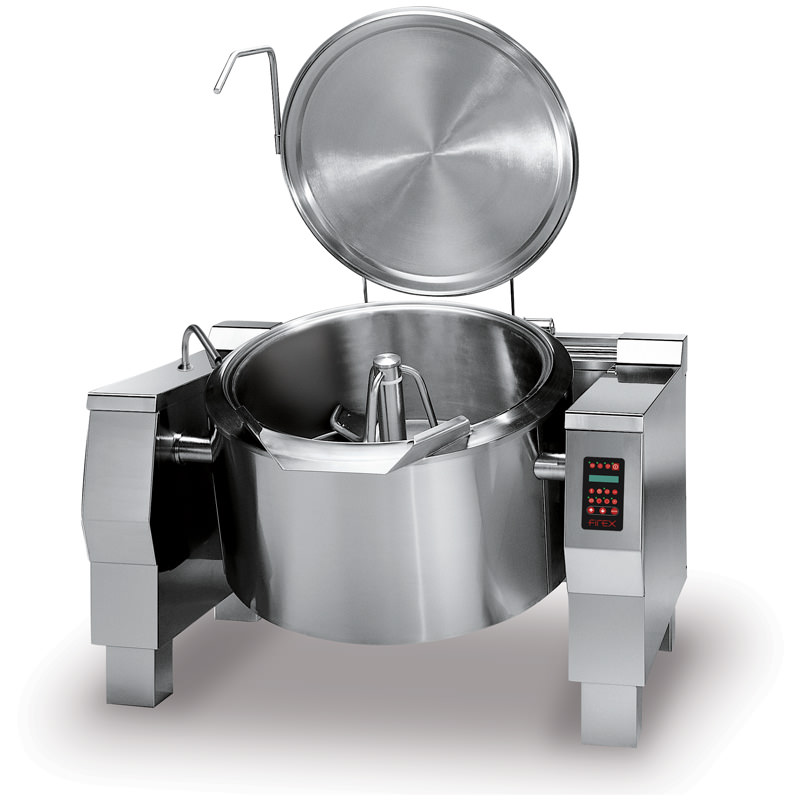
Industrial tilting pan with cooling system
Raw materials need to be processed into finished, cooked products most quickly ...

Compact industrial sauce pan
Safe, reliable cookers that operate unobtrusively are required in any kitchen where space and t...
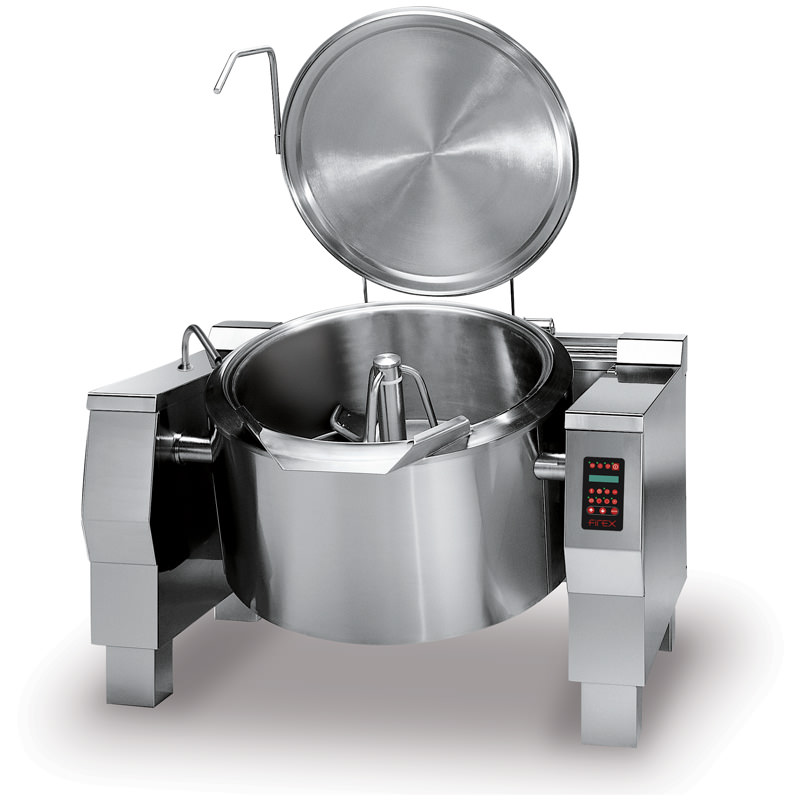
Industrial pressure cooker
Optimizing production processes and human resources to reduce energy consumption and save time an...
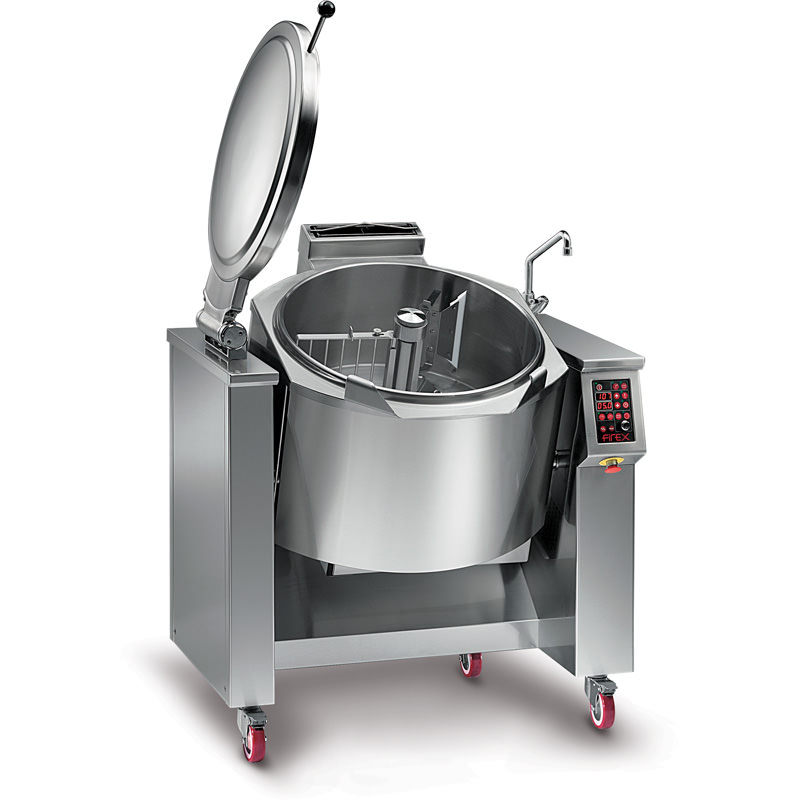
Industrial sauce pan
For the small and medium food industry, economical use of time, space and human resources is critical wh...
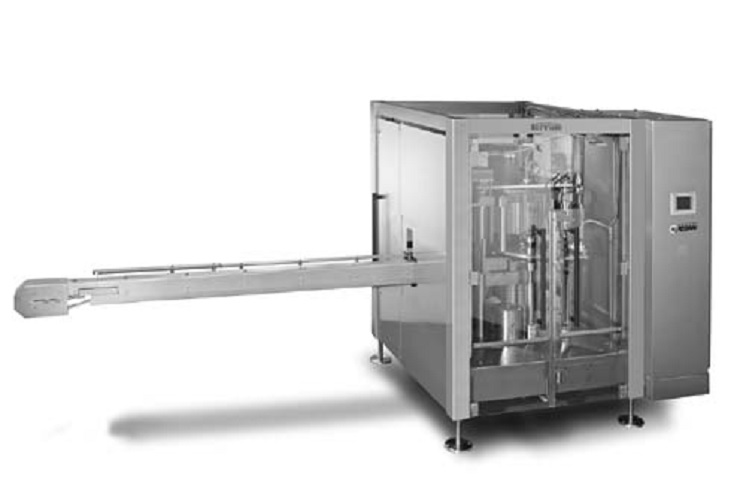
High performance can seamers for the food industry
The wide variation of materials and dimensions used in the food cannin...
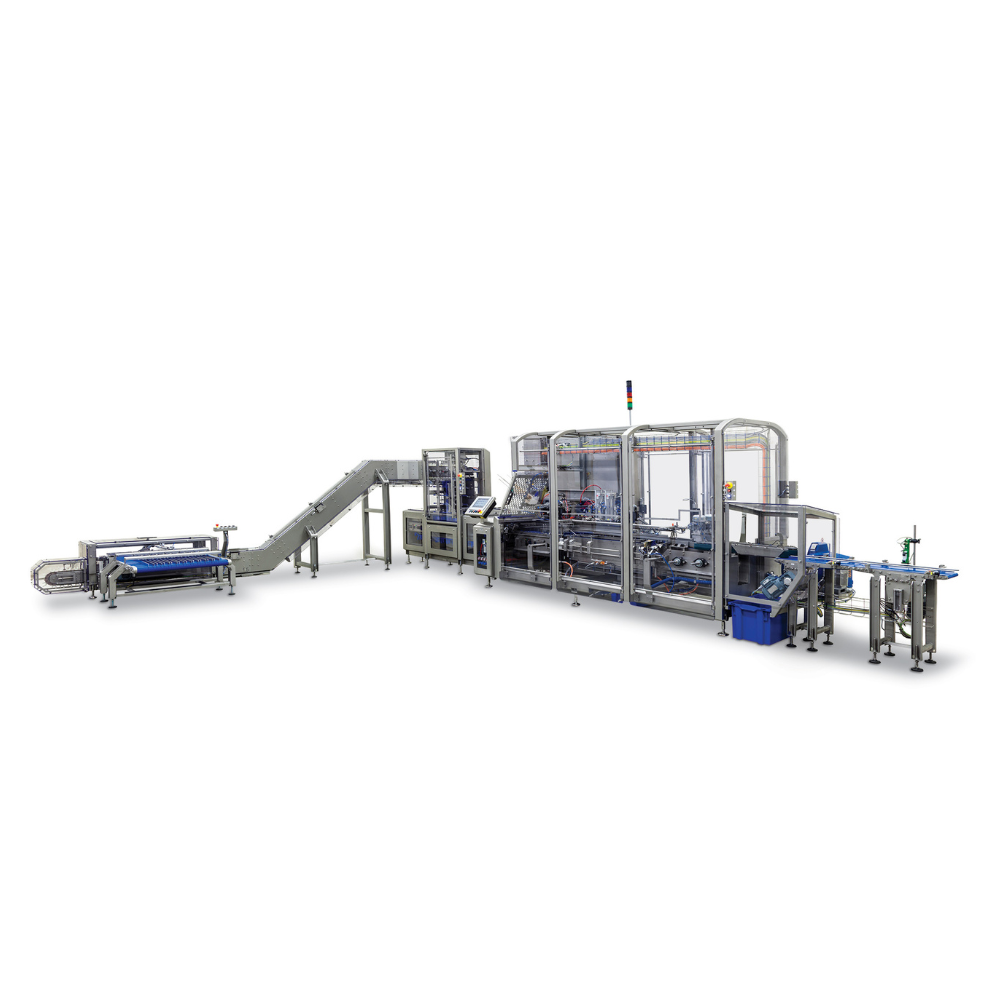
Smart Industrial Sauce Cartoning System
Large volume producers of sauces and ready meals continuously pack different produc...
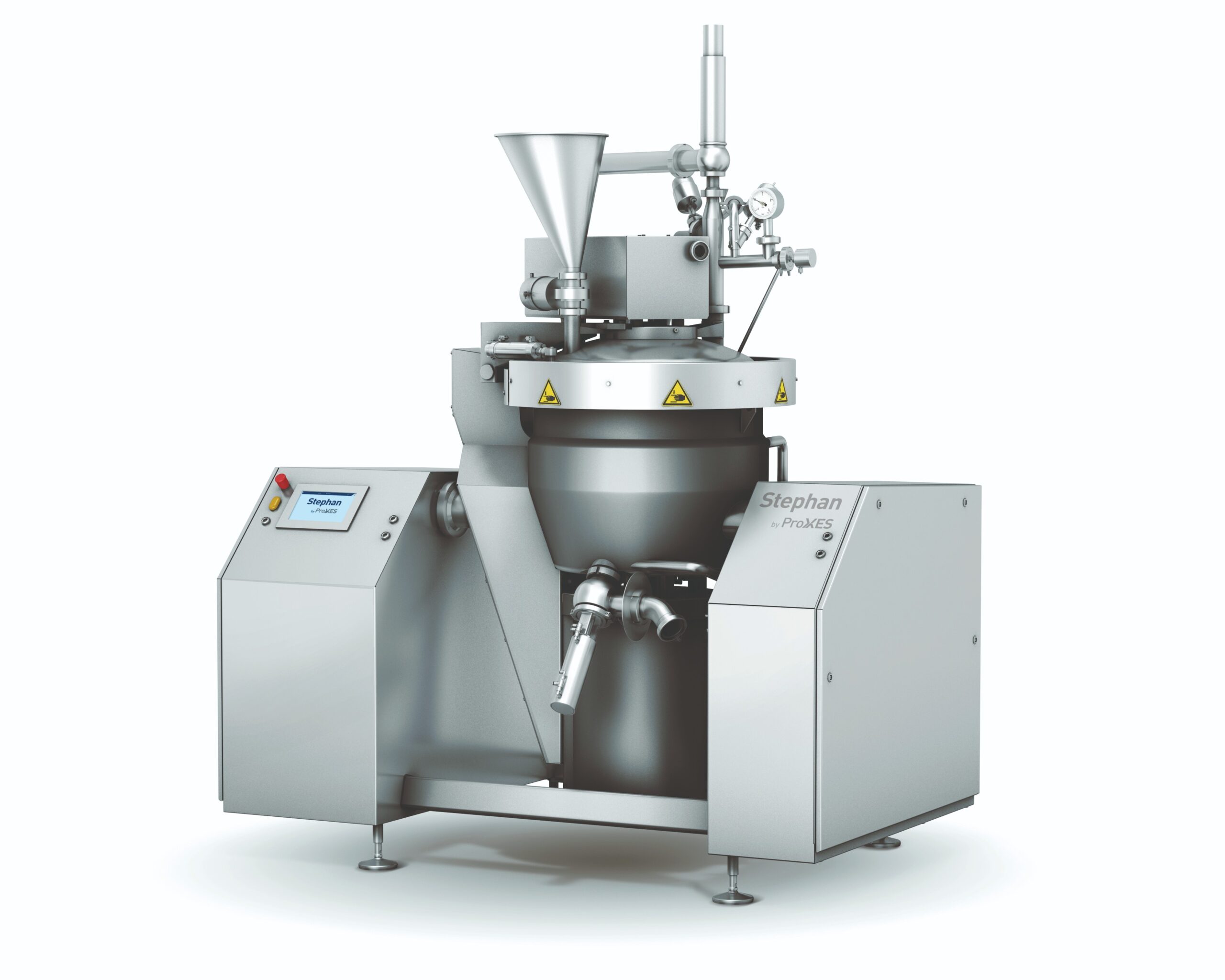
Complete cutting, mixing, emulsifying and heating system
From laboratory scale to large volume food or cosmetic productio...