Fs closing devices for industrial packaging solutions
Streamline your packaging process with versatile closing devices, designed to seamlessly integrate into your production line and accommodate a variety of container types, ensuring optimal sealing for enhanced product quality and shelf-life.
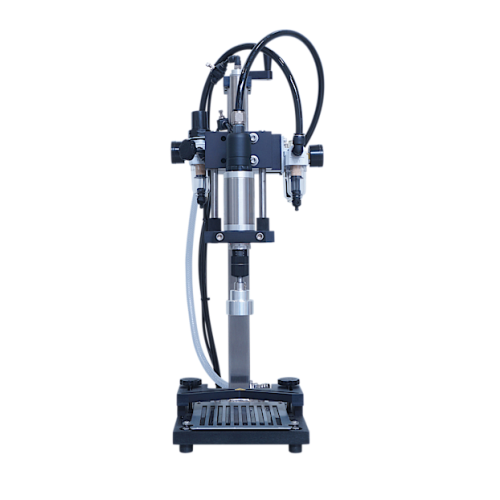
Secures Packaging with Versatile Closing Solutions
OMVE’s FS-Series Closing and Sealing Equipment offers a comprehensive line of packaging solutions designed for the food and beverage industry, accommodating everything from small-scale operations to pilot plant settings. This equipment series excels in performing precise closing and sealing, utilizing a flexible system that integrates seamlessly within a production line. It features options such as the FS107 can seamer, FS105 screw cap sealer, FS108 heat sealer, and FS104 crown cork capper, each tailored for specific packaging formats such as beverage cans, PET bottles, HDPE cups, and glass bottles.
The equipment is designed with hygiene in mind, integrating seamlessly into clean-fill systems and counter-pressure fillers. With a focus on energy efficiency, these units offer PLC control for effortless operation and integration, meeting stringent industry standards with CE certification. Built with robust materials to withstand high demands, each unit offers easy cleaning solutions, ideal for maintaining production line efficiency. OMVE supports customization needs, offering engineering support to adjust specifications according to your unique operational requirements.
Benefits
- Enhances packaging security with versatile sealing options for multiple container types.
- Integrates seamlessly into existing production lines to boost efficiency.
- Reduces energy consumption through optimized control systems.
- Complies with CE standards, ensuring safety and reliability.
- Simplifies maintenance with easy-to-clean design and robust materials.
- Applications
- Soups, Alcoholic drinks, Sauces, Nutraceuticals, Fats, Still drinks, Oils, Plant-based, Carbonated drinks, Ice creams, Dairy
- End products
- Beer bottles, Almond milk bottles, Soda cans, Fruit juice cartons, Sparkling water bottles, Olive oil bottles, Ice cream tubs, Herbal tonic vials, Wine bottles, Soup cans, Protein shake bottles, Yogurt cups, Ketchup bottles, Cheese spread jars, Soy milk cartons, Avocado oil sachets
- Steps before
- Filling, Carbonation, Homogenizing, Deaeration, Fermenting
- Steps after
- Packaging, Shelf-life Testing
- Input ingredients
- beverage cans, PET bottles, HPDE cups, HPDE bottles, glass bottles, ingredients, yogurts, still drinks, soft drinks, margarine, liquid products
- Output ingredients
- cans with lids, sealed PET bottles with screw caps, sealed HPDE cups, sealed HPDE bottles, corked glass bottles
- Market info
- OMVE is known for manufacturing pilot and small-scale processing equipment for the food and beverage industry, specializing in pasteurization, carbonation, fermentation, and homogenization systems, with a strong reputation for innovation and quality in engineered-to-order solutions.
- Cap type
- Screw / Crown / Aluminum seal
- Container type
- Can / PET bottle / Glass bottle / HPDE cups
- Automation
- Manual / Integrated
- Compatibility
- FS107, FS105, FS108, FS104
- Mounting option
- Standalone / Table-mounted / Integrated within fillers
- Filling,Closing System
- Clean-Fill, Counter-pressure fill
- Sealing method
- Heat sealing / Screw cap sealing
- Applications
- Packaging for dairy, alternative dairy, beverages
- Closure sizes
- 200 and 202 lids
- Pressure Compatibility
- Counter Pressure Fillers
- Working mechanism
- Crowning, sealing, and capping
- Integrated steps
- Closing, sealing
- Automation level
- Manual / Standalone / Integrated in system
- CIP/SIP
- Manual
- Batch vs. continuous operation
- Batch
- Cleaning method
- Manual
- Changeover time
- Quick for different closures
- Density/particle size
- 0.5–2.5 g/cm³ / 50–1000 µm
- Container Type
- Beverage cans, PET bottles, HPDE cups, Glass bottles
- Discharge method
- Stand-alone or integrated
- Container type
- Glass / PET / HPDE
- Control panel type
- HMI / Touch screen
- Integration possibilities
- Standalone / Integrated with Clean-Fill or Counter Pressure Fillers
- Mounting option
- Table / Inside filler units