Highly scalable reactors for chemical synthesis
Optimize your production line with versatile reactors designed for seamless integration of mixing, dispersing, and homogenizing processes, ensuring precise control of chemical reactions and consistency in product quality for demanding industrial applications.
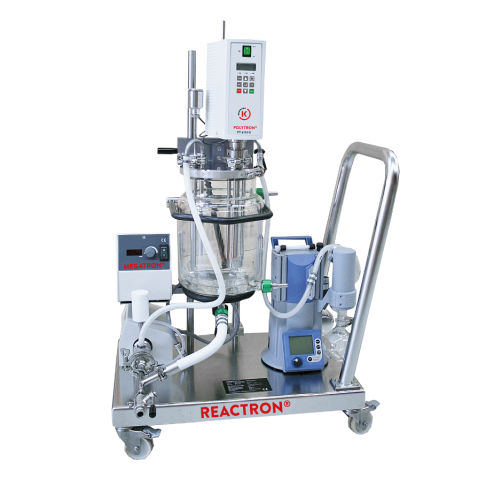
Processes Chemical Reactions and Mixes for Diverse Industries
The REACTRON® RT series from Kinematica AG offers highly scalable dispersion reactors tailored for challenging industrial applications across pharmaceuticals, chemicals, and food processing industries. These reactors excel in handling chemical reactions and complex mixing processes with operational volumes from 5 to 1,000 liters. The integration of POLYTRON® batch dispersers and POLYMIX® mixers creates a complete system capable of supporting diverse processes including heating, cooling, and homogenizing. They are designed to meet CIP/SIP and clean room standards, and can operate under various pressures, complying with ATEX guidelines for explosive environments. The adaptable design supports up to 1000 liters, making it ideal for producing synthetic polymers, emulsions, APIs, and more. Each system can be outfitted with additional components such as heat exchangers or process controllers to enhance performance. Available in corrosion-resistant materials, the reactors ensure reliability and long lifespan in harsh chemical environments. The systems accommodate full customization, including automation capabilities and remote monitoring, meeting the specific needs of R&D, processing, and purification departments.
Benefits
- Enhances scalability with flexible volume handling up to 1,000 liters.
- Ensures safety and compliance with ATEX guidelines for explosive atmospheres.
- Minimizes contamination risk through CIP/SIP-ready configurations.
- Customizable integration allows for tailored process control and efficiency.
- Supports diverse production needs from pharmaceuticals to food processing.
- Applications
- Fine chemicals, Pharmaceuticals, Nutraceuticals, Cosmetics, Life science applications, Chemical reactions, Biopharmaceuticals, Food processing, Mixing processes
- End products
- Cosmetic creams, Sauces, Soups, Synthetic polymers, Active pharmaceutical ingredients (apis), Protein shakes, Peptide solutions, Cell culture media, Liposome dispersions, Emulsions, Enzyme supplements, Lotions, Diagnostic reagents
- Steps before
- Heating, Cooling, Ingredient Preparation
- Steps after
- Clean In Place (CIP), Sterilization In Place (SIP), Packaging
- Input ingredients
- water, chemical reaction ingredients, mixing processes ingredients
- Output ingredients
- mixed chemical solutions, dispersed solutions, processed materials
- Market info
- Operating Volume
- Up to 1000 liters
- Application Volume (RT 5)
- 5 liters
- Application Volume (RT 10)
- 10 liters
- Application Volume (RT 15)
- 15 liters
- Application Volume (RT 40)
- 40 liters
- Application Volume (RT 50)
- 50 liters
- Application Volume (RT 100)
- 100 liters
- Application Volume (RT 500)
- 500 liters
- Application Volume (RT 1000)
- 1000 liters
- Compliance
- CIP / SIP operation
- Pressure Options
- Different Operating Pressures Available
- ATEX Guidelines
- Compliance Available
- Minimum Volume
- 5000 ml
- Maximum Volume
- 1000000 ml
- Working mechanism
- Batch and Inline
- Integrated steps
- Dispersing, Heating/Cooling, Mixing
- CIP/SIP Principles
- Available for CIP/SIP operation
- Batch vs. continuous operation
- Batch / Inline Continuous
- Automation level
- Integration with POLYTRON®, POLYMIX® Systems
- Cleaning method
- CIP / Manual
- Compliance with guidelines
- ATEX guidelines
- Density/particle size
- 0.5–2.5 g/cm³ / 50–1000 µm
- Machine footprint
- Customized based on volume
- Tank shape and size
- Varies from RT 5 to RT 1000
- Feed/Discharge method
- Inline/Batched
- Operating volume
- 5l to 1000l
- Control panel type
- Integrated system with process controls
- Compact footprint
- Varies according to specifications
- Variant Flexibility
- CIP/SIP, Cleanroom