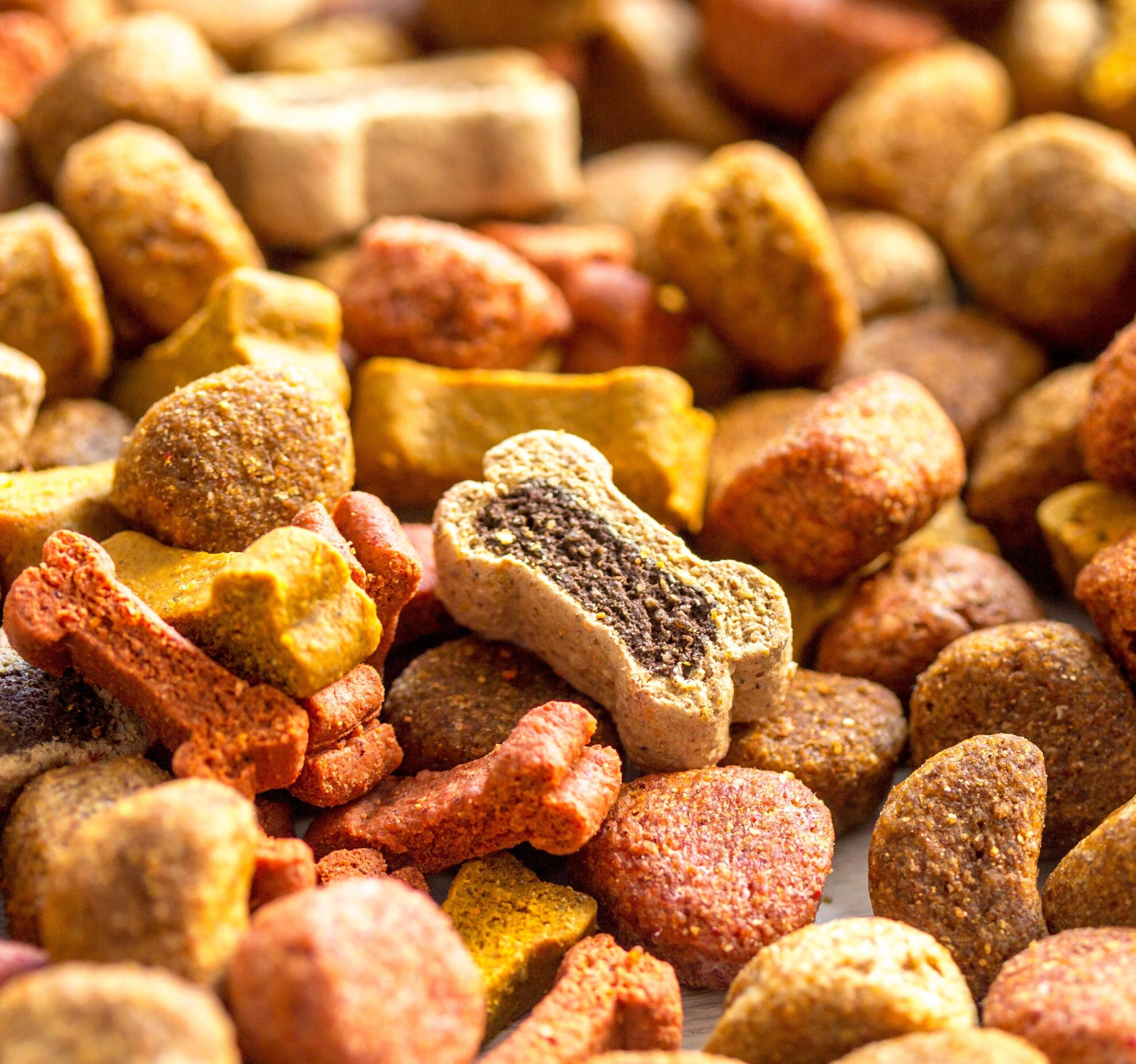
Pet Food Processing Equipment
Find innovative pet food equipment and connect directly with world-leading technology suppliers
Pet food is a specialty food mostly based on formulated ingredients for various nutritional and dietary requirements. Pet food formulas are becoming more diverse and complex, considering the special health conditions and needs of young and aging pets that live in cities. The production of pet food is similar to processing food in general when it comes to fresh feedstock and flesh products.
Innovative pet food equipment
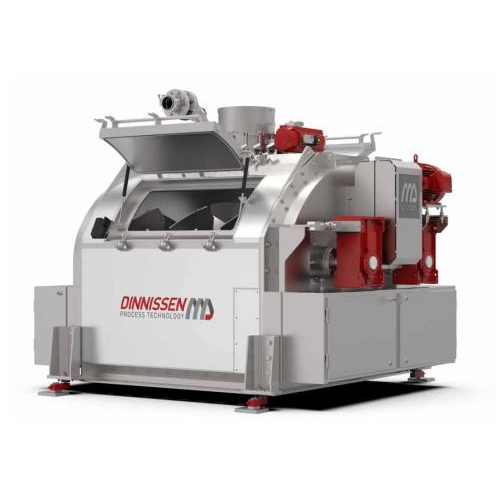
Advanced vacuum coating system for pet food and feed
Achieve uniform saturation in pellets and granules with precise liqu...

Batch cooker and mixer for food and pet food production
Streamline your cooking and mixing processes with a versatile bat...
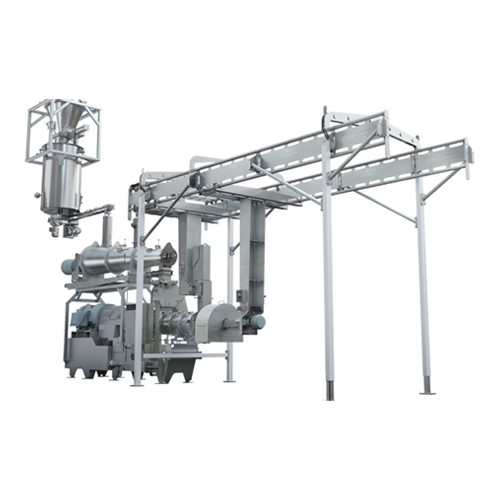
Conical twin screw extruder for pet food and aquatic feed
Precision-engineered for high-speed extrusion and drying proce...
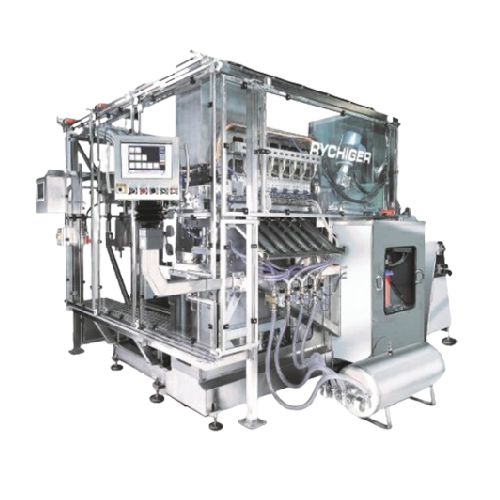
Convenience and pet food filling solution
Optimize your production line with high-speed, hygienic filling of diverse food ...
Stories about pet food
Select your pet food process
What are you making?
Tell us about your production challenge
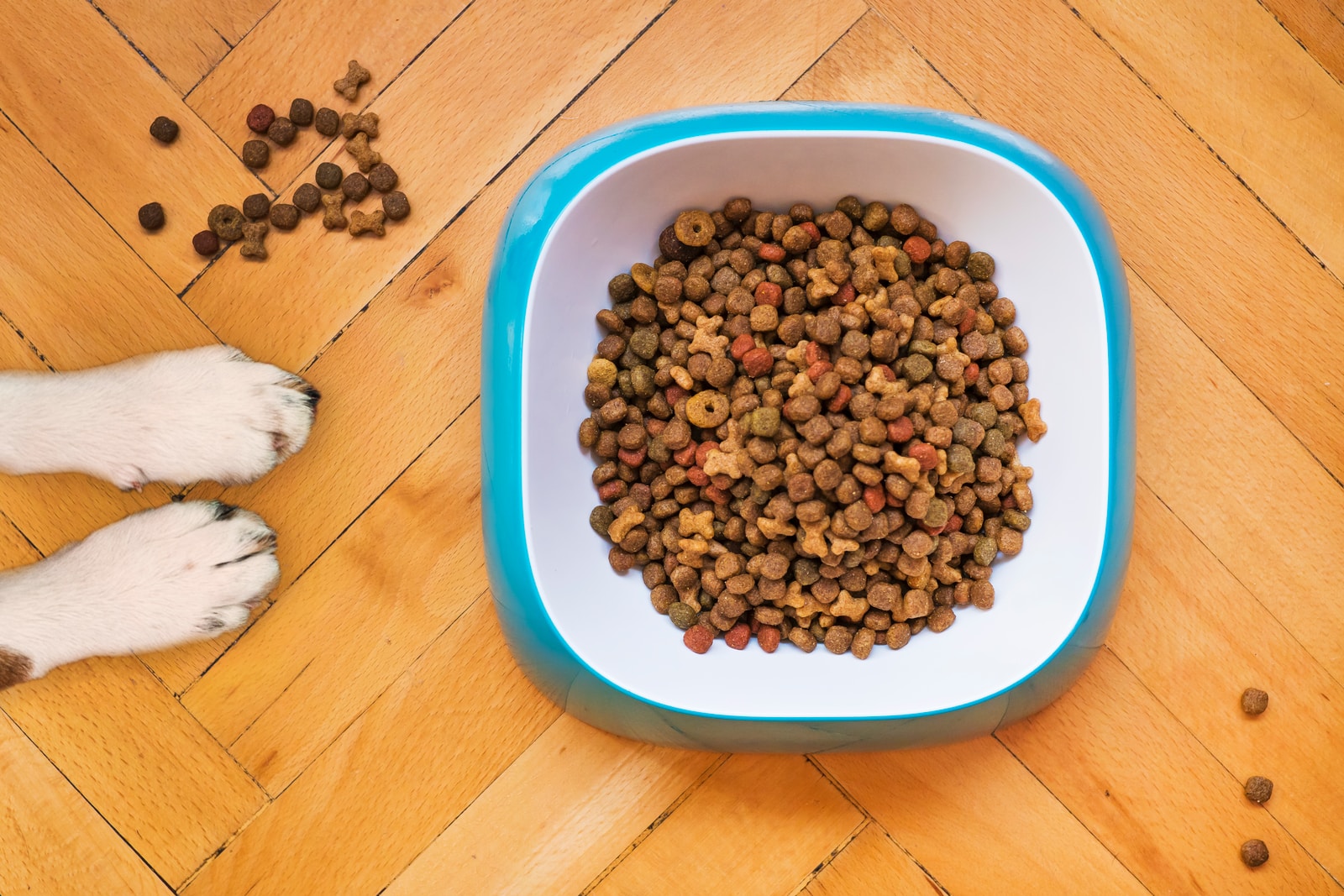
Pet food usually comes in the form of pellets and kibbles that are extruded or baked from dry compound feed. Dry pet foods contain grains and cereals, meat meal and fat, vegetables and proteins and functional ingredients. Wet pet food has similar dry ingredients to dry pet food, but is usually produced in the form of single-serve tin cans or pouches filled with high moisture level. Meat pieces and gravy or jelly are commonly seen in wet pet food mixed with vitamins and minerals.
Pet food making process
Following the increasing demand for nutrition and regulatory compliance, pet food formulation needs to take factors such as fat tissue content, protein quality, the moisture level of raw materials into consideration. Pet foods oftentimes are made from dry ingredients such as feed grain and soybean meal, byproducts of meat and seafood, and liquid ingredients such as water and meat broth. Also, coatings and coloring and flavoring agents are needed in pet food formulas to appeal to different pet groups.
The broad range of available ingredients for pet food production requires precise weighing and dosing in the handling of raw materials. Another crucial step in processing pet food ingredients is grinding and mixing, ensuring the required particle size and consistency of the mixture. Before going into extrusion, the grinded and mixed ingredients need to be (pre-) conditioned. The addition of moisture and fat with pre-heating conditions makes sure that the mixture to be extruded reach the desired nutritional quality, bulk density and consistency. Finally, extruded and pelleted pet foods proceed to the coating and cooling section of the entire production before packaging.
For canned pet food, the production process centers around the handling of meat and flesh products from defrosting and rendering to grinding, cooking and mixing with other ingredients such as vitamins, minerals and preservatives. After packaging and sealing in cans (and labeled), wet pet food needs to go through a crucial step, sterilization.
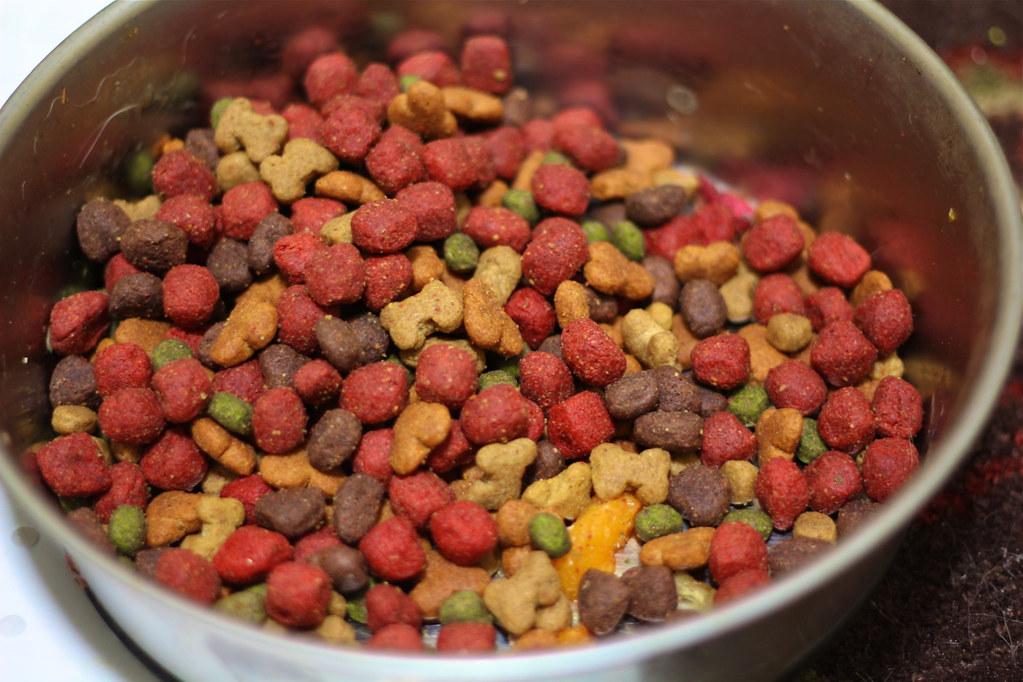
Extruded or baked pet food?
For producing dry pet foods, there are two main cooking methods: extrusion (the most common) and baking. Nowadays about 95% of pet foods is made by extrusion.
In the extrusion process, a mixture of wet and dry ingredients called dough enters the expander which cooks the doughy mixture at high pressure and high temperature. Then, the dough is forced through the dies that create ribbons of the desired shapes that are cut with a rotary cutter afterwards. Instead, when baked, the dough is cut by rotary moulders into the desired shapes and sizes. Then, the final moulded products are placed into the oven and baked.
Weighing and dosing of pet food
Dosing and weighing process – from the intake of raw material to the distribution of finished product – is the key factor to ensure the balanced mixture of ingredients based on what animal needs.
To provide zero contamination and avoid human error, for example KSE supplies fully automatic dosing and weighing systems, thus eliminating hand dosing. Plus, for a quick and a zero-contamination dosing , KSE supplies a new type of technology called “dosingtainers”, which reduces the number of dosing steps. If bulk ingredients stay for too long in a silo, they can get spoilt. Therefore, using these dosing containers instead of traditional silos saves time because ingredients can also be dosed inside them.
Packaging and sterilization of pet food
The basic difference between wet and dry pet food is the water content, which affects the shelf life of the product – 3-5 years for wet pet food and 10-12 months for dry pet food. The most common forms of dry pet food include kibbles, biscuits and snacks, which after processing are transferred to bags, boxes or pouches to pack the right amount of weight.
Instead, ingredients in wet pet food are measured and mixed together and put into cans, trays or pouches. The selected container is sealed and cooked at certain temperatures. To guarantee the microbiological safety of the food, sterilization is a critical part of wet pet food manufacturing process. Sterilization takes place in a retort where steam is pumped under high pressure.
Pet food making videos
How pet food is made?
Dry pet food packaging
Which pet food technology do you need?
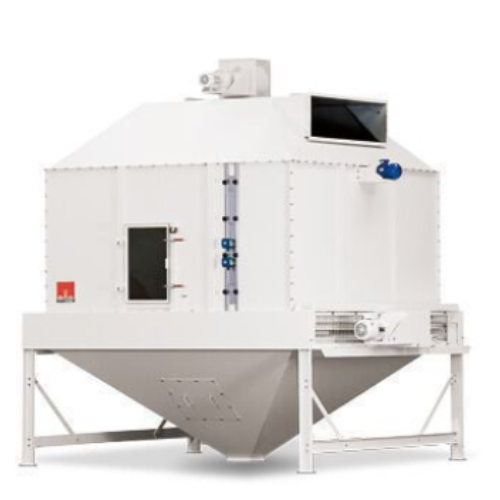
Counterflow dryer for pet food and fish feed
Optimize moisture control and enhance feed quality with efficient drying, cru...
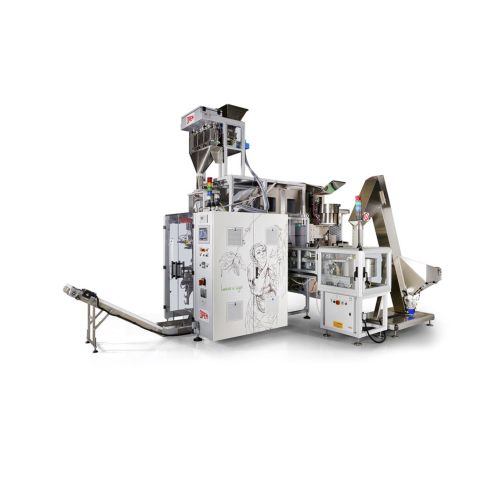
Vertical packaging system for pet food
Streamline your production line with high-speed packaging capabilities, handling var...
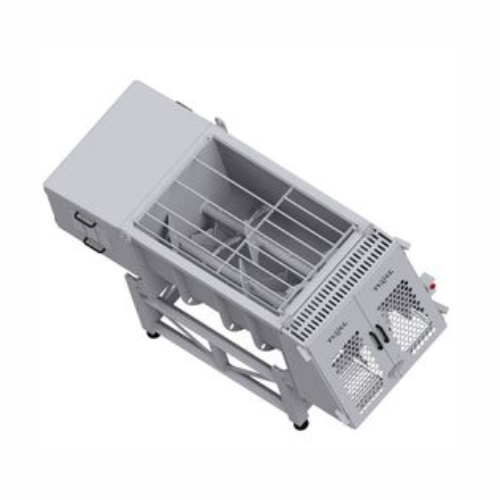
Industrial mixer for food and pet food production
Achieve precise and efficient mixing of viscous to highly viscous produ...
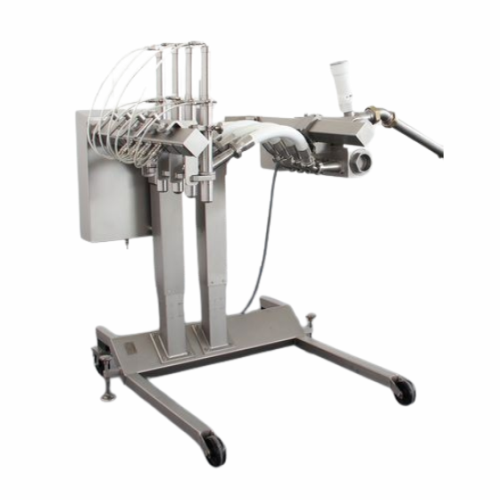
Filling flow divider for food and pet food applications
Optimize your production line with precision filling flow divider...
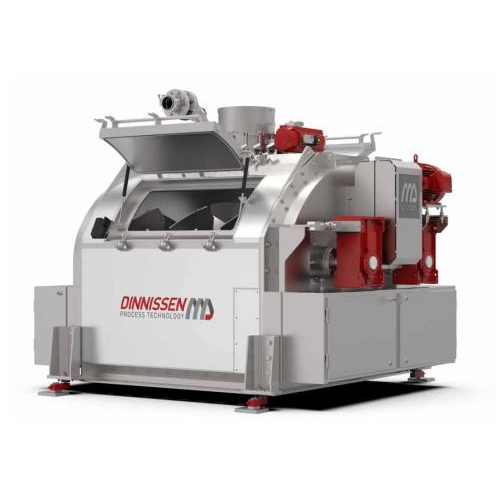
Advanced vacuum coating system for pet food and feed
Achieve uniform saturation in pellets and granules with precise liqu...
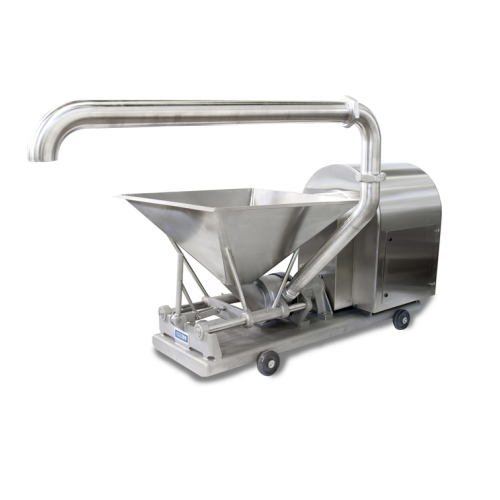
Gravity-fed emulsion system for meat and pet food processing
Achieve optimal particle size reduction and seamless integr...
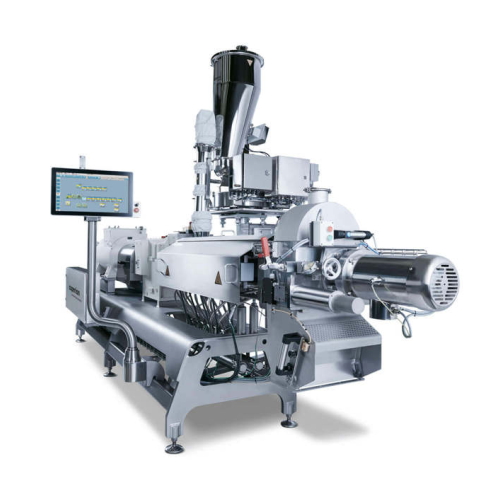
Food extruders for pet food production
Achieve precise control in food production with advanced twin screw extruders, desig...
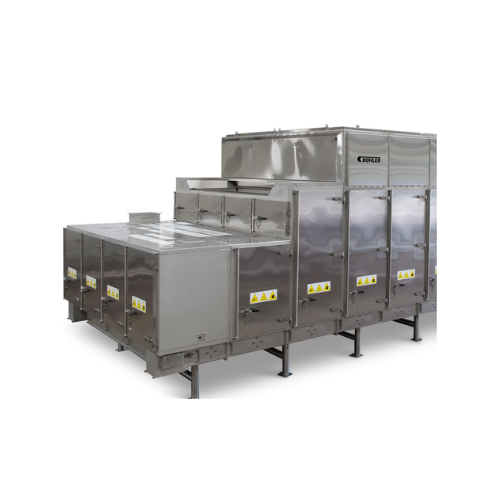
Multi-pass pet food dryer for consistent moisture content
Achieve precise moisture control and enhanced product quality ...
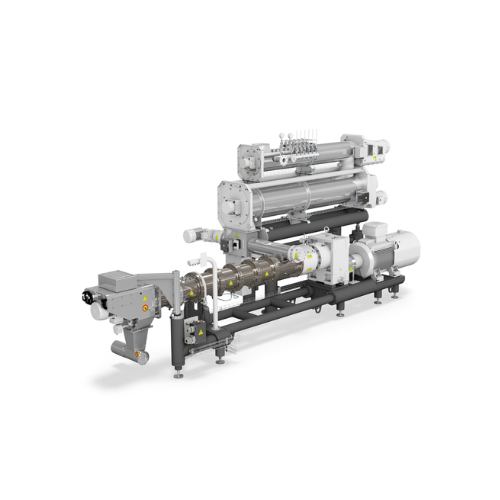
Single-screw extruder for pet food and aqua feed
For producers aiming to diversify their offerings, this single-screw extr...

Ultra-fine pulverizer for aqua feed and pet food
Achieve precise granulation with high efficiency for your feed and food p...
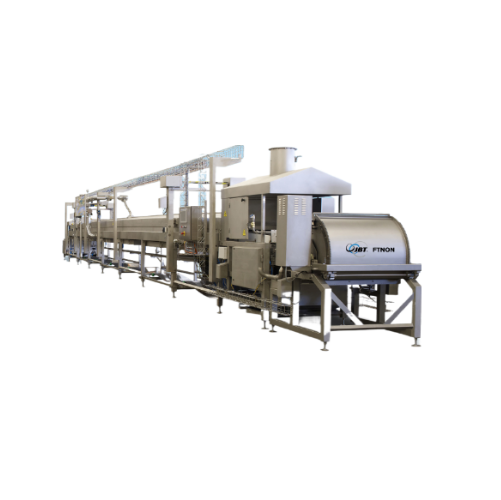
Wet pet food processing system
Optimize your wet pet food production with a system that integrates steaming, cooling, mixing...
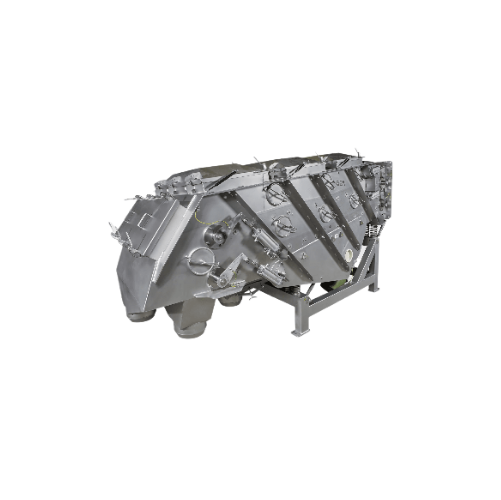
Sifter for pet food, fish feed, and animal feed
Achieve precise particle separation and enhance feed quality with this vib...
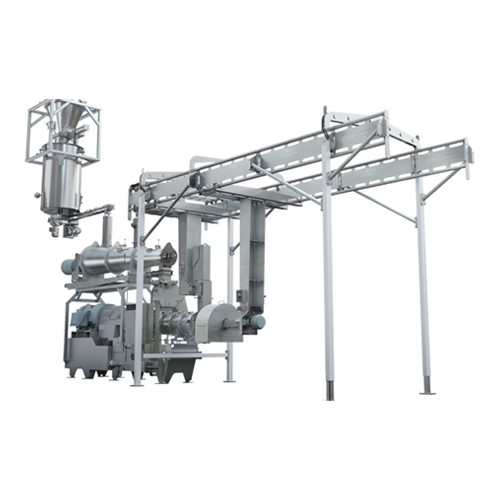
Conical twin screw extruder for pet food and aquatic feed
Precision-engineered for high-speed extrusion and drying proce...
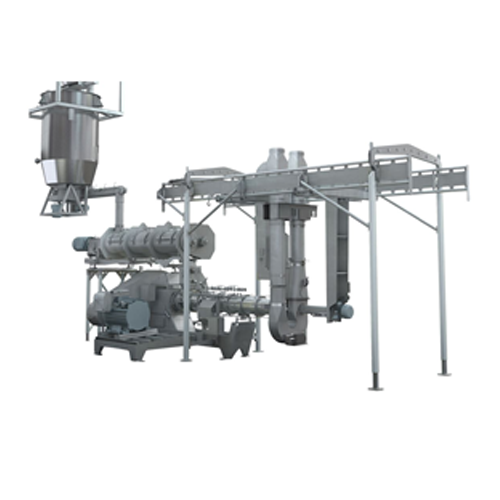
Single screw extruder for pet food and aquatic feed
Maximize production capacity and optimize product quality with advanc...
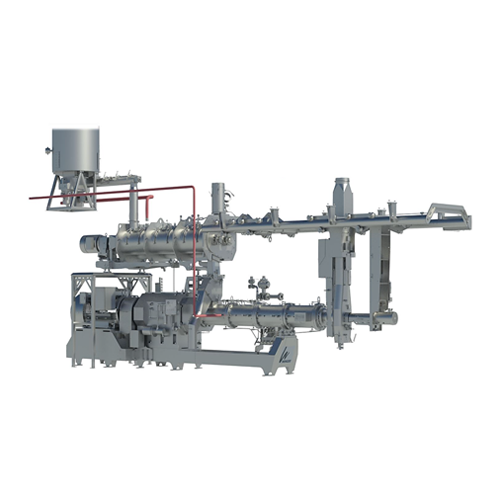
Extruder for high-volume pet food production
Maximize production efficiency with an advanced extrusion system designed for...
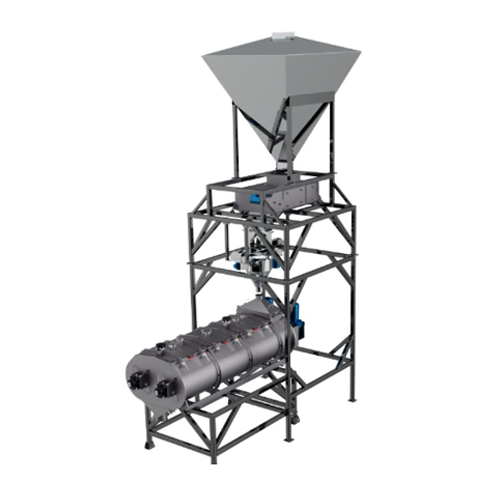
Coating and enrobing system for pet foods and treats
Achieve precise coating and flavoring of various food and feed produ...
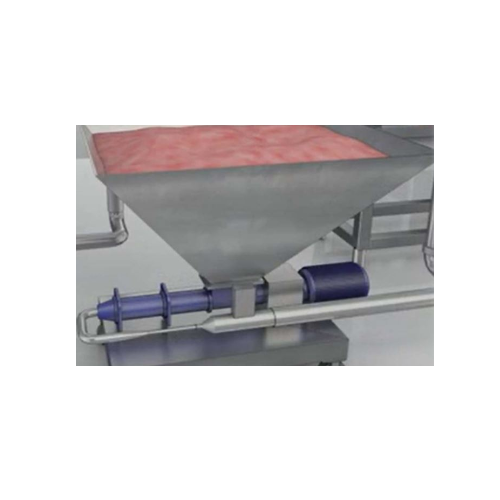
Meat injection system for pet food production
Integrate fresh meat seamlessly into your pet food production line, enhancin...
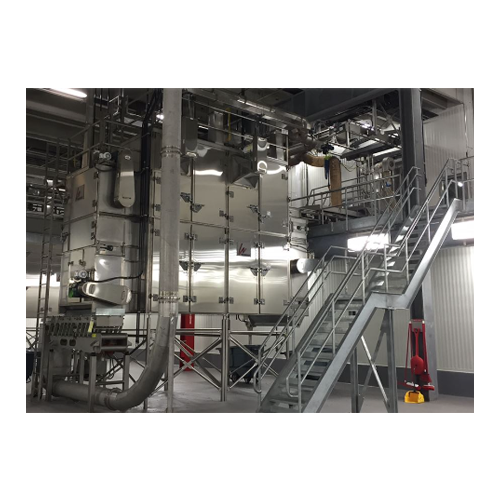
Convection roaster for pet food and delicate food products
Achieve optimal texture and moisture control in delicate food...
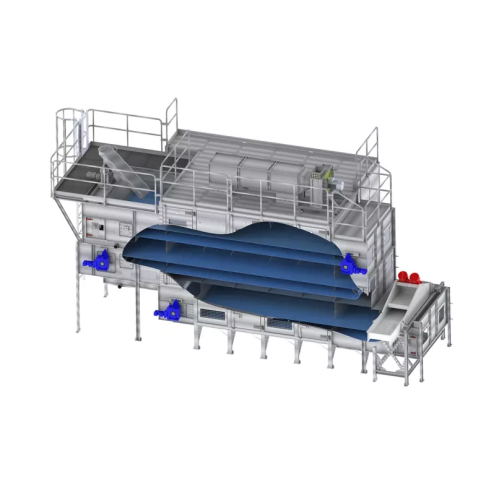
Layer dryer for food and pet food applications
Optimize drying efficiency with multi-layer technology that minimizes space...
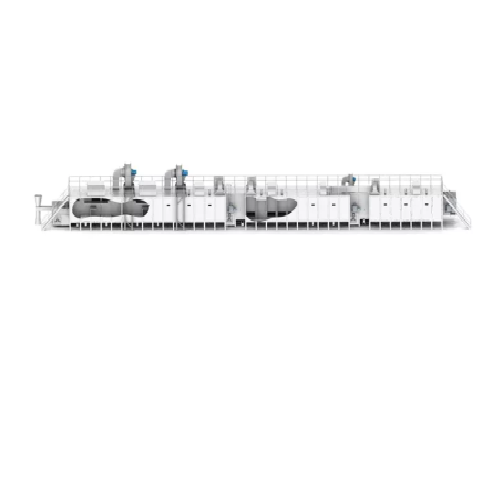
Belt dryer for food and pet food products
Optimize drying processes with customizable belt dryers, engineered to handle ro...
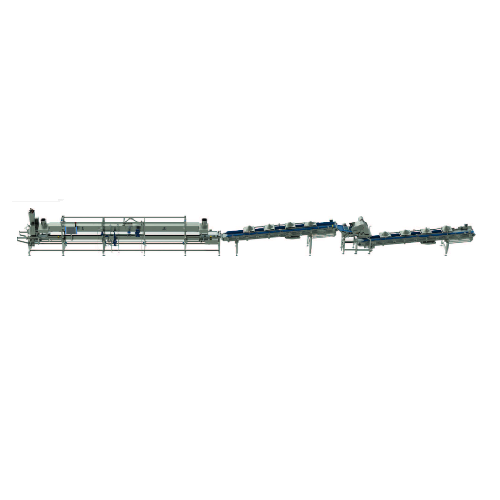
Pet food production line
Enhance your pet food production with a seamless, efficient system that emulsifies, extrudes, and pa...
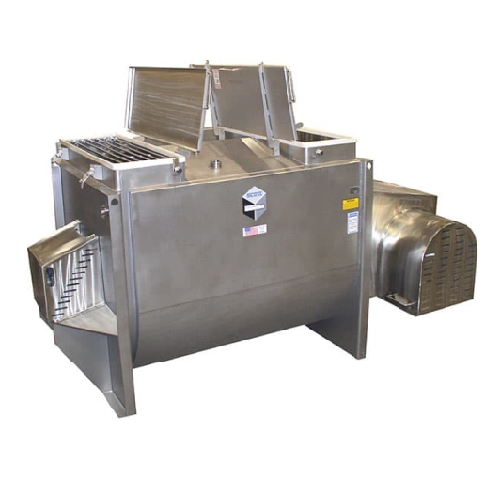
Industrial batch mixers for pet food
Achieve homogenous mixing of complex multi-ingredient formulations with precision and ...
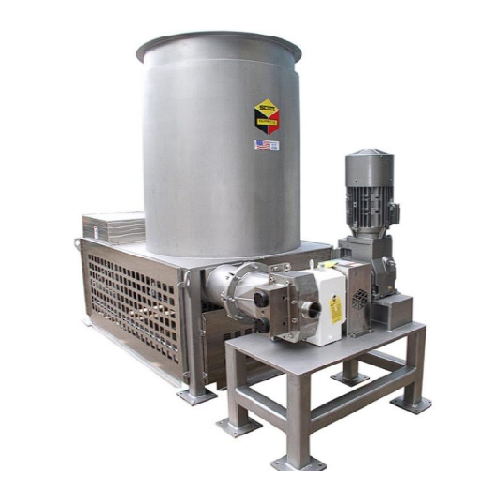
Feeding system for filter cake and wet pet food
Achieve seamless material handling and agitation for solid shortening and ...
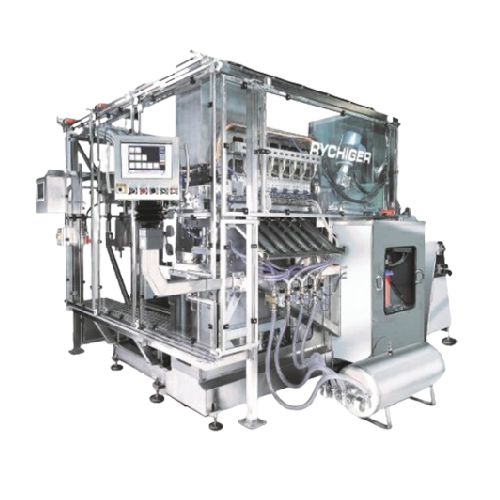
Convenience and pet food filling solution
Optimize your production line with high-speed, hygienic filling of diverse food ...
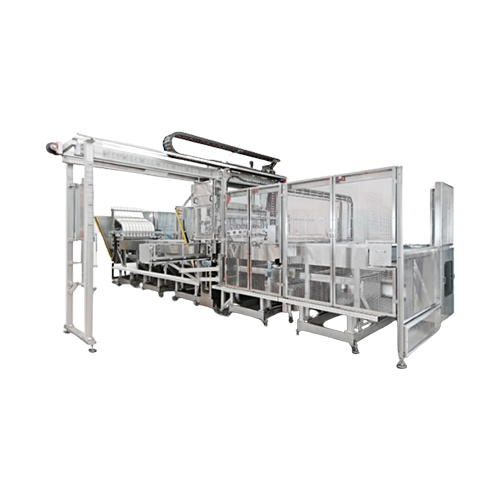
Precision filler for convenience and pet food
Achieve unparalleled precision and efficiency in filling solids, powders, li...

Batch cooker and mixer for food and pet food production
Streamline your cooking and mixing processes with a versatile bat...
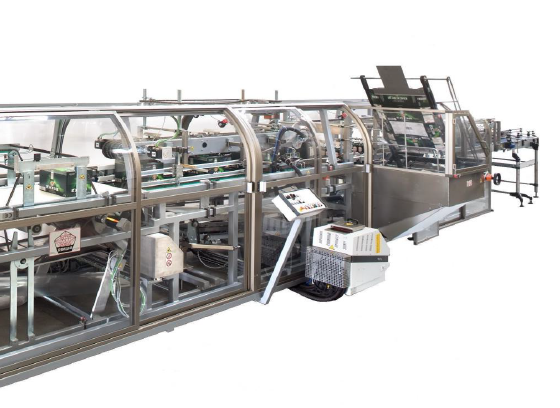
Machine for packing canned pet food
Most packaging applications require different types of packaging machines, some need wr...
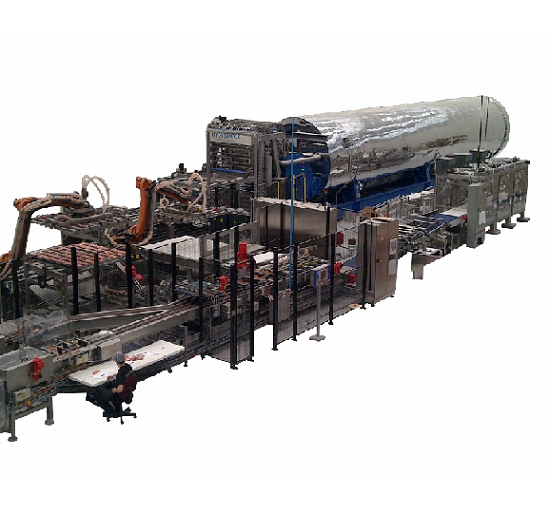
Continuous sterilizer for pet food
Sterilization is a critical operation in the manufacturing of wet pet foods. An importan...
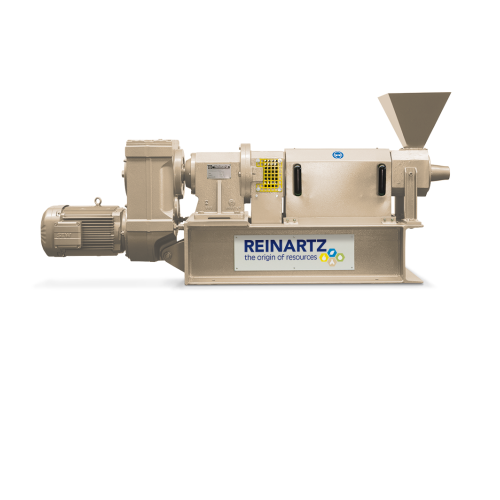
Screw press for insect protein extraction
Address the rising protein demand with our screw press, designed to efficiently ...
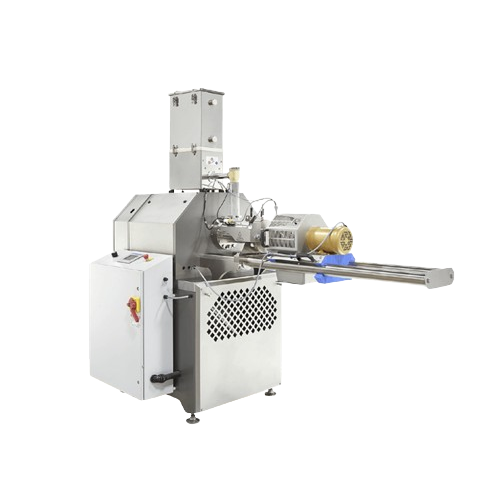
High pressure extruder for expanded snacks
Enhance your snack production with precise control over texture and shape throu...
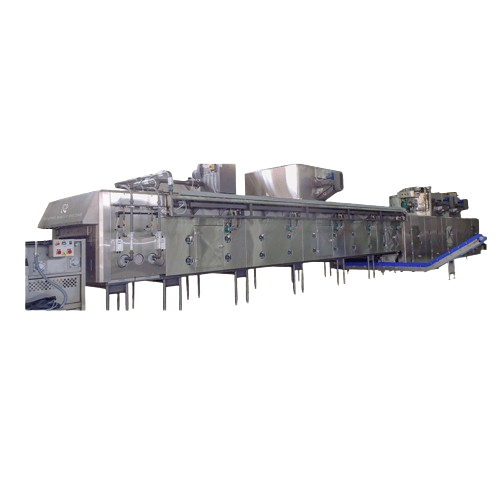
Smart bakery oven zone for flexible heating
Optimize your production with flexible heat transfer options that enhance cont...
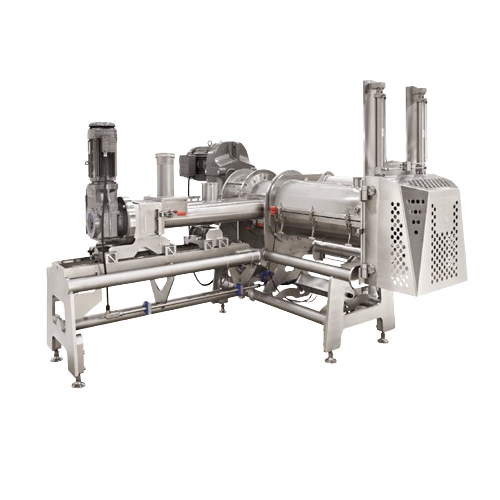
Continuous mixer for wheat-based products
Achieve consistent dough quality with minimal variation using a continuous mixer...
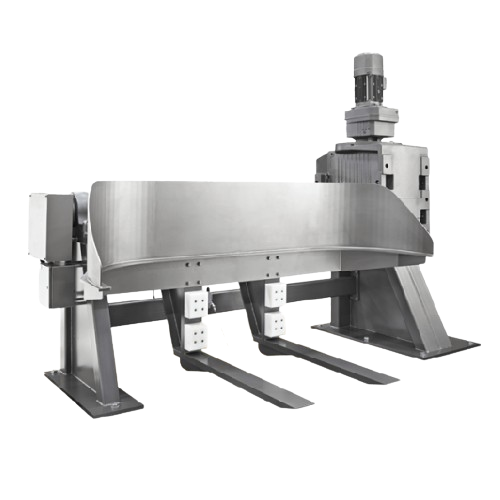
Efficient dough dump station for bakery systems
Streamline your dough handling process with this advanced dumping station,...
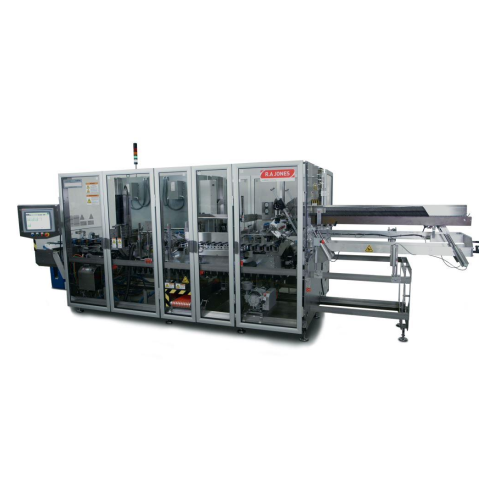
Intermittent end load cartoner for baked goods and snacks
Optimize your packaging line with an efficient, space-saving c...
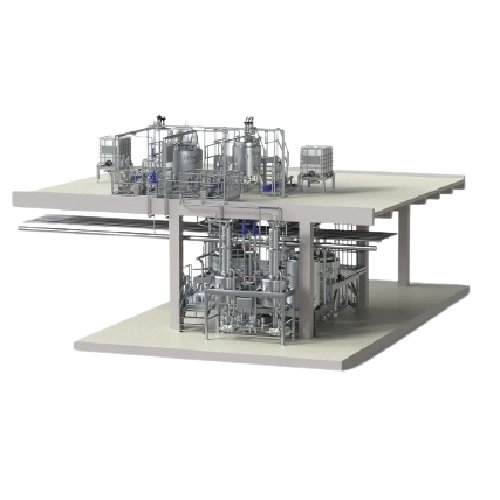
Continuous mustard line
Streamline mustard production with high-capacity continuous processing that reduces air pockets and e...
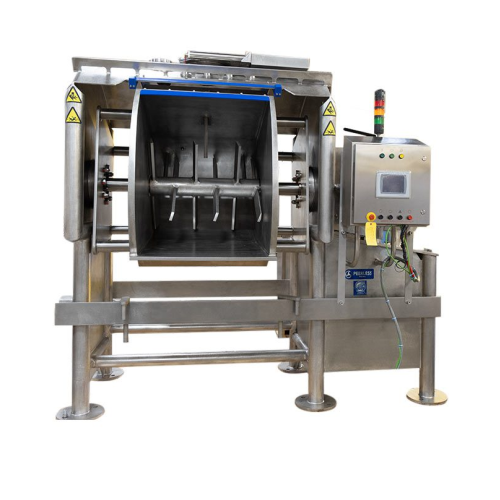
Open frame mixer for bread and dough applications
Enhance baking productivity with a versatile mixer designed for efficie...
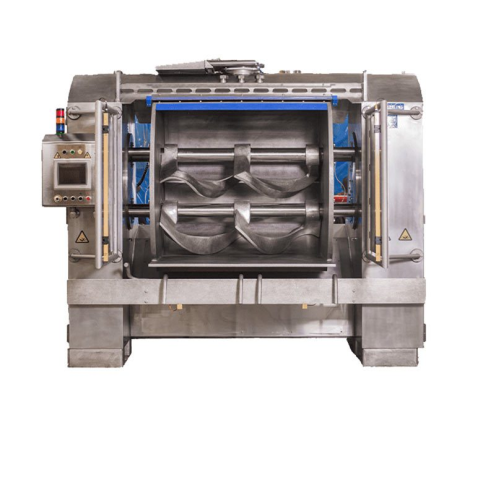
Traditional enclosed frame mixer for dough and batter preparation
Optimize your production with high-capacity mixing, e...
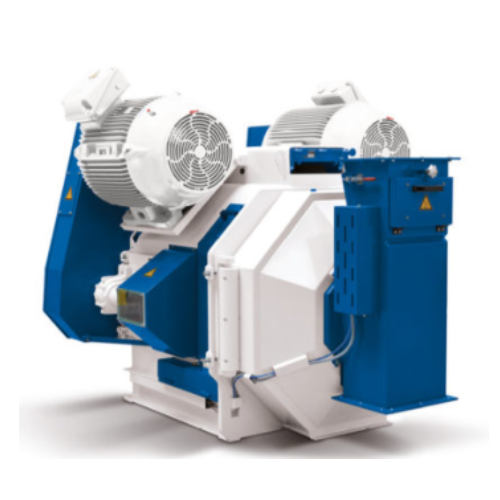
Pellet mill for high efficiency animal feed production
Achieve stable, vibration-free pellet production with enhanced ene...
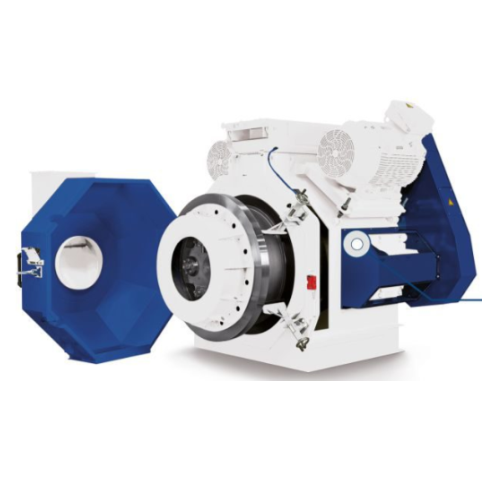
Pellet mill for animal feed production
Optimize your feed production with a robust pellet mill designed to enhance the dura...
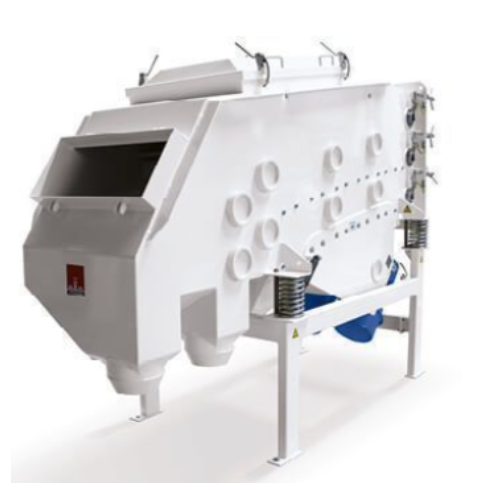
Industrial vibrating sieves for pellets and fine particles
Optimize feed quality and material flow in your production li...
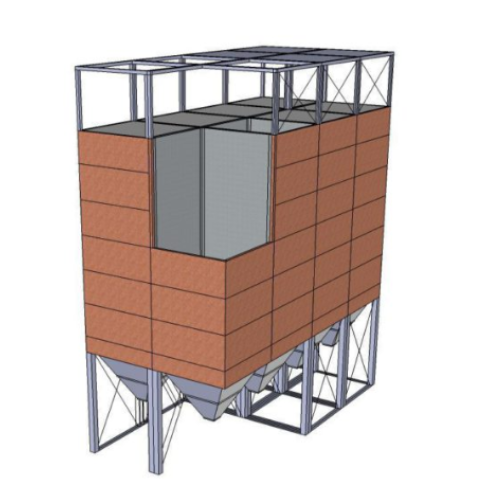
Square silo for bulk goods storage
Maximize your storage efficiency by 25% with square silos, uniquely designed for effecti...
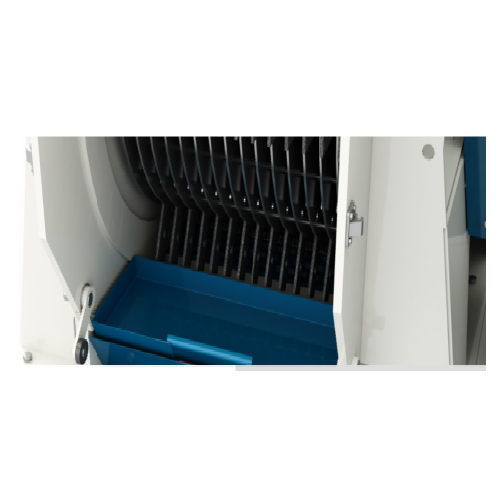
Quick hammer exchange system for hammer mills
Streamline hammer replacement in your milling process with a system designed...
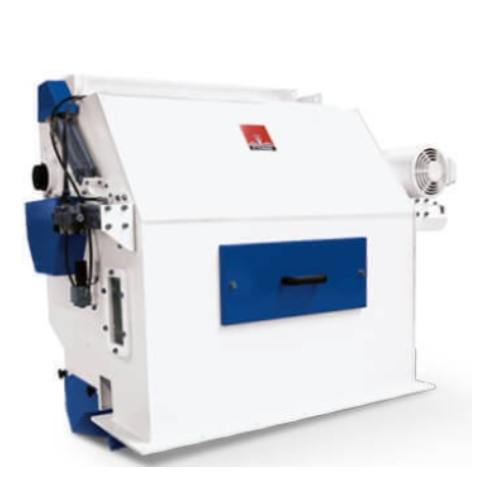
Roll feeders for consistent hammer mill supply
Ensure precise and controlled feedstock delivery to your hammer mill, effec...
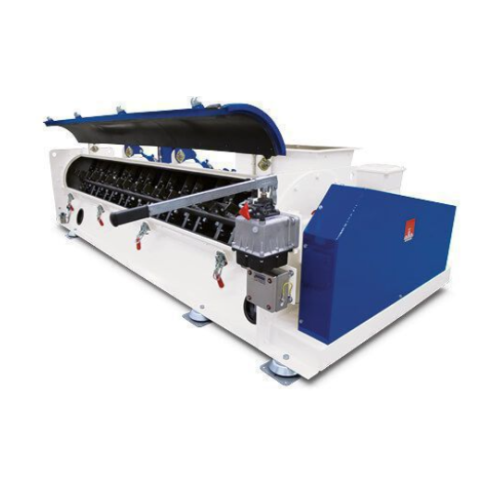
Continuous mixers for feed mill applications
Optimize your liquid incorporation process with continuous mixers that ensure...
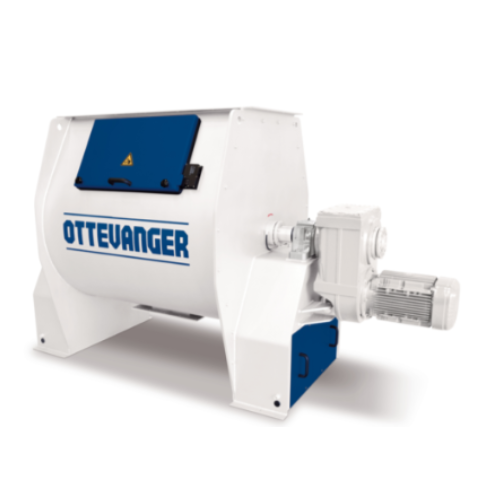
Horizontal ribbon mixers for animal feed production
Experience precise and efficient mixing with low energy consumption f...
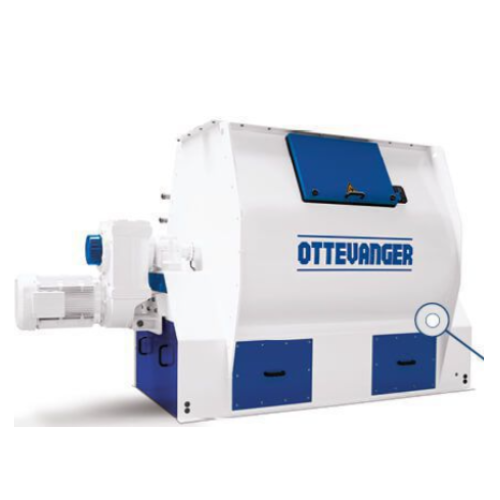
Single shaft paddle mixers for dry powders and granulates
Achieve uniform and precise mixing for your batch processing n...
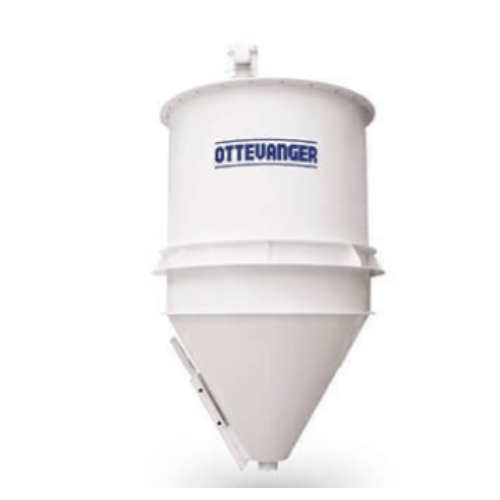
Vertical mixers for animal feed industry
Efficiently combine a variety of powdered and raw materials with precision, ensuri...
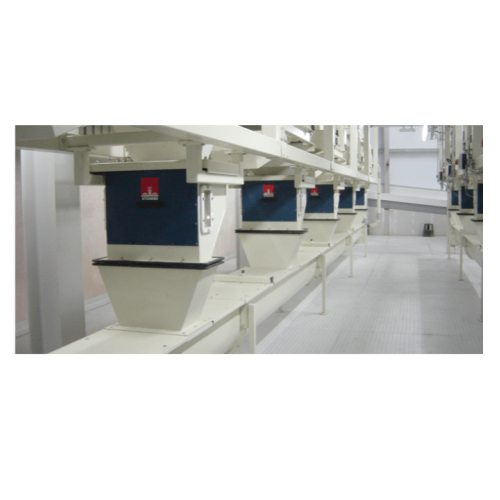
Inline and continuous weighers for accurate product flow management
Maintain precision and efficiency in your productio...
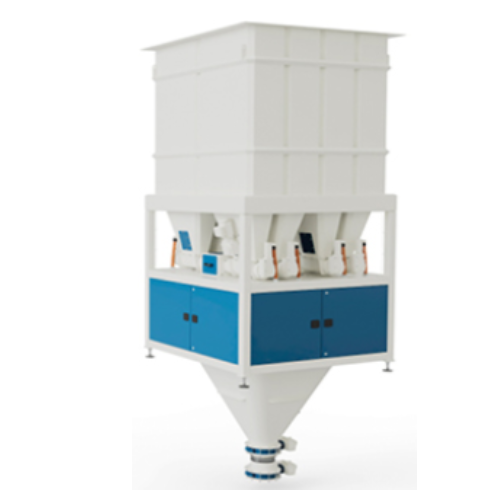
High accuracy micro dosing system
When handling diverse ingredients, precise dosing is crucial to ensuring consistent produ...
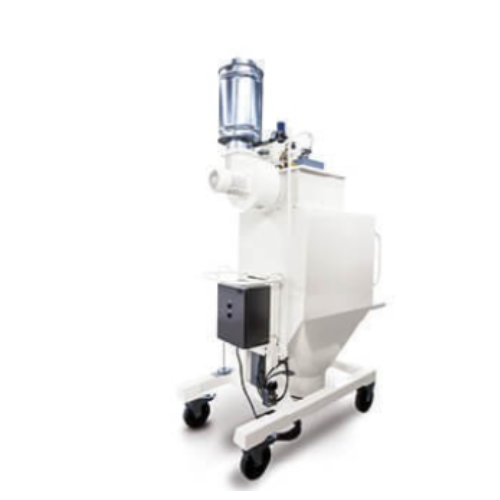
Micro-ingredient dosing system for animal feed production
Optimize your feed formulation accuracy with precision dosing,...
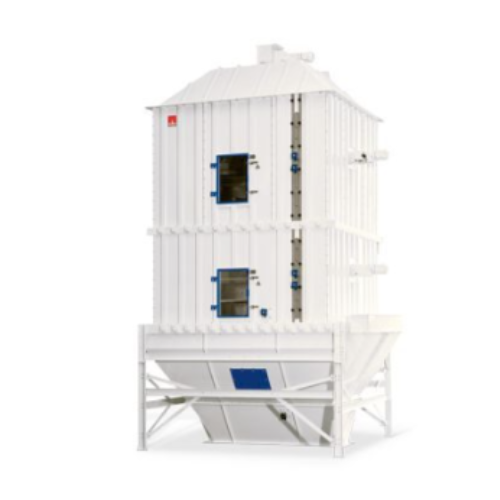
Counterflow pellet coolers
Optimize temperature control and enhance product integrity in your feed production line with prec...
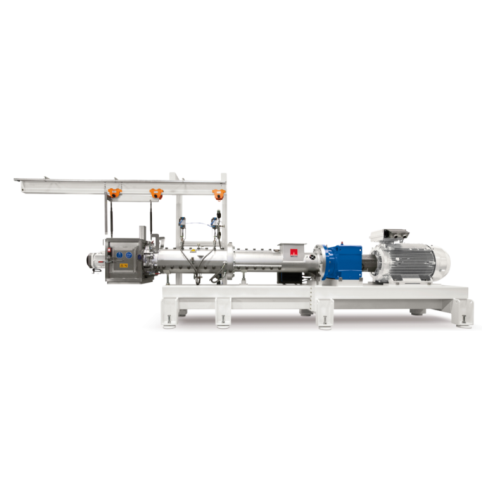
Extruders for animal feed production
Optimize nutritional value and ensure efficient processing of animal and aqua feeds wi...
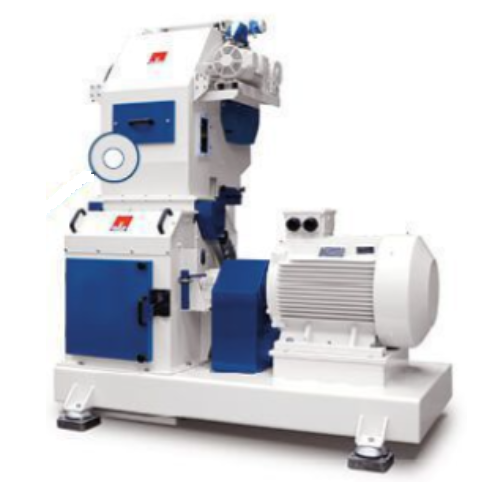
Industrial hammer mill for granulate grinding
Optimize the grinding process in feed production with a high-efficiency solu...
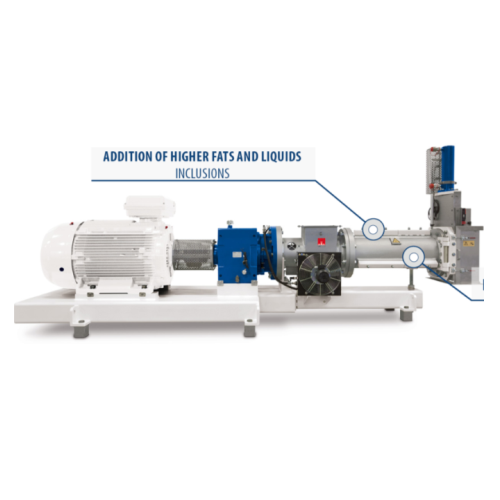
Feed expander for improved pellet mill output
Enhance your feed quality and production efficiency with a robust expander d...
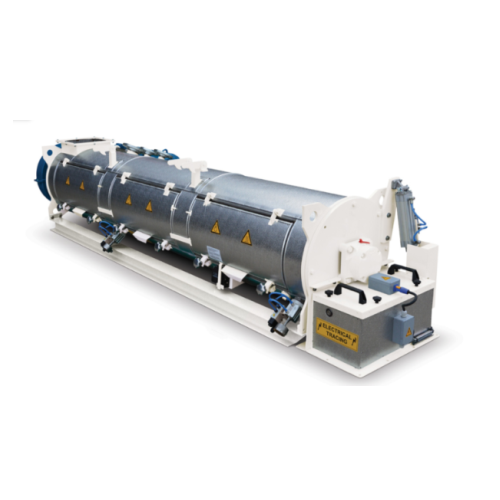
Hot start conditioner for feed and food processing
Enhance your production process with a high-efficiency thermal heating...
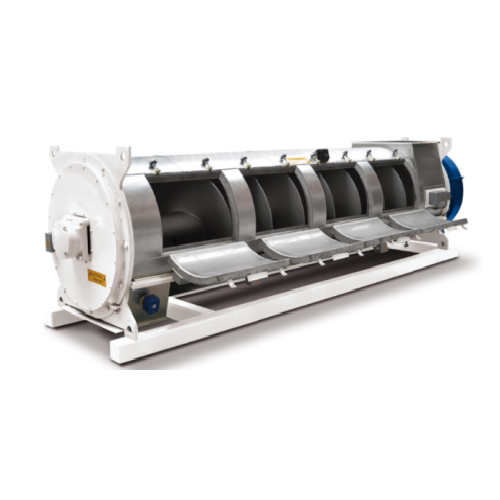
Retention time barrel for feed pelleting
Enhance your feed processing efficiency with a specialized retention time barrel, ...
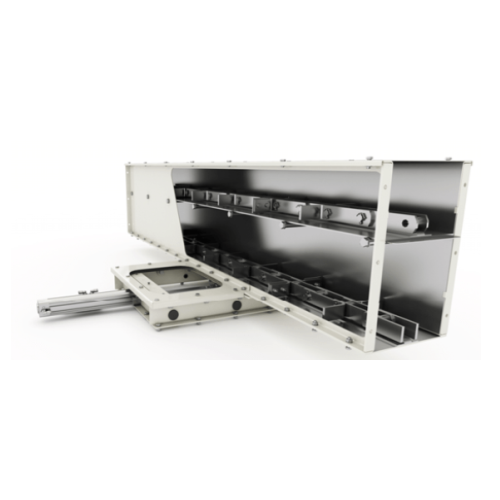
Chain conveyors for long-distance bulk material transport
Efficiently transport challenging bulk materials across long d...
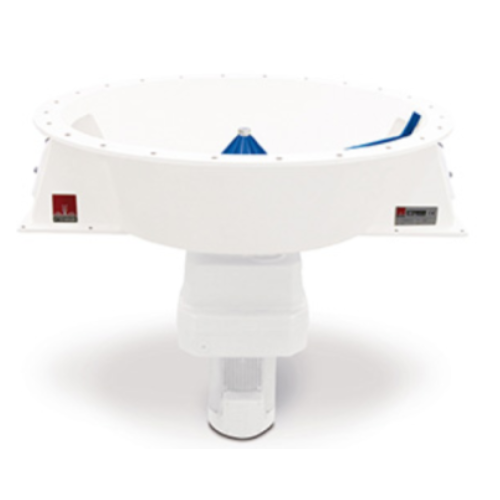
Rotary dischargers for powders and granules
Prevent production halts with this solution designed for efficient discharge o...
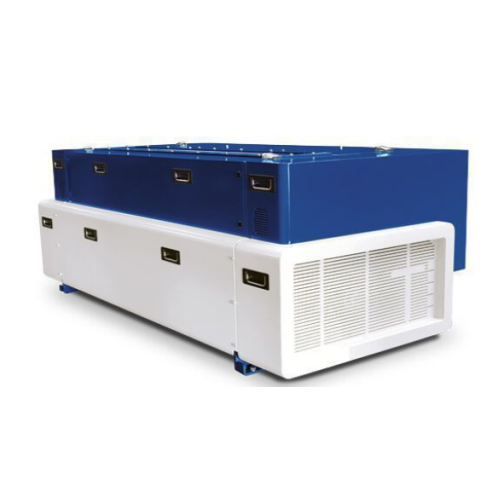
Feed pellet crumbler
Achieve precise size reduction of feed pellets with high efficiency and minimal fines, optimizing your p...
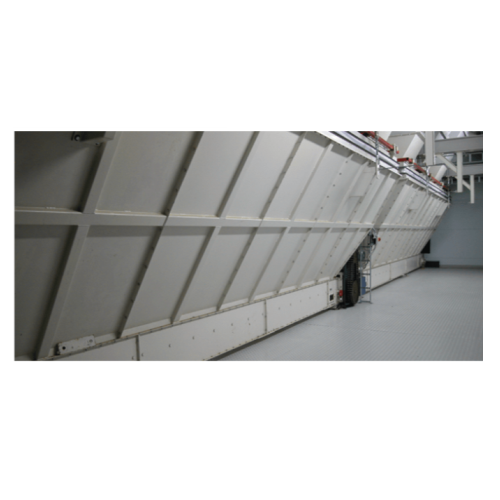
Batch weighers for large-volume powder and granulate weighing
Ensure precise ingredient dosing and streamline your produ...
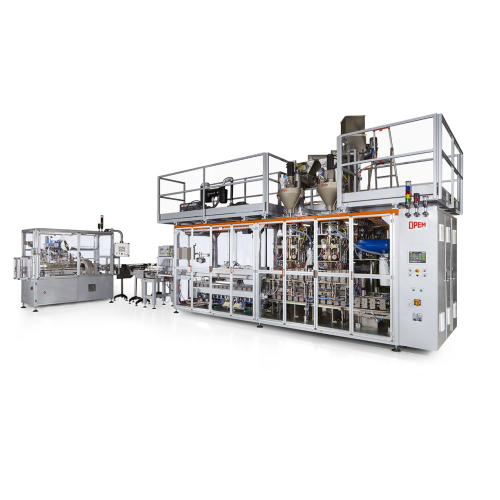
Vacuum packaging system for high-volume operations
Optimize your packaging line with high-speed vacuum sealing for divers...
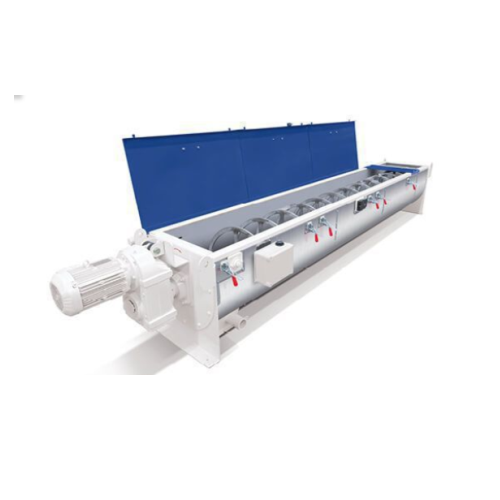
Continuous coater for pellet and extrudate liquid addition
Efficiently enhance your feed products by uniformly adding li...
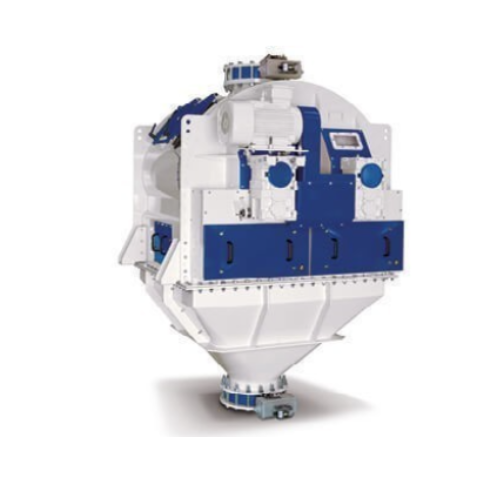
Vacuum coaters for high liquid addition in feed production
Enhance your feed production with precision liquid coating, s...
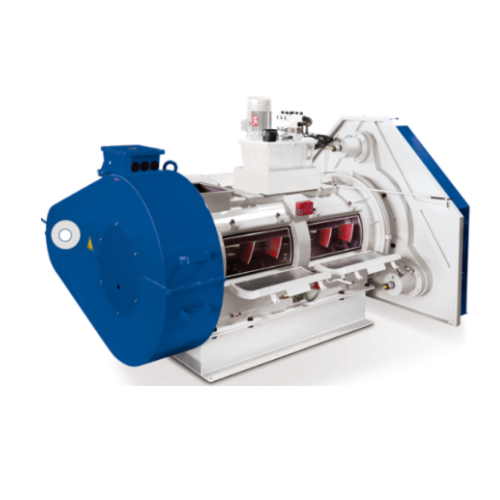
Feed mill compactor for improved pellet quality
Optimize your feed production with a compactor designed to enhance pellet ...
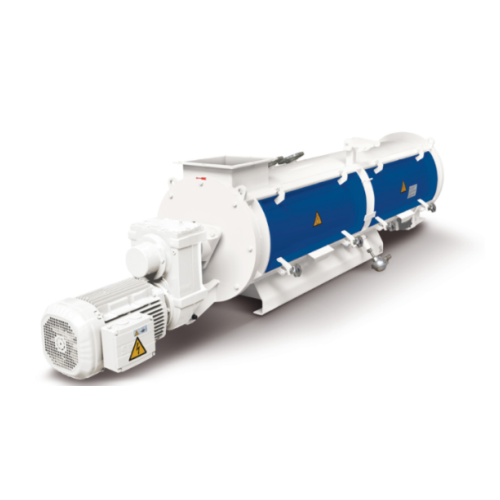
Single conditioner for feed mills
Achieve homogeneous mixing and enhanced hygiene in feed production with adjustable paddle...
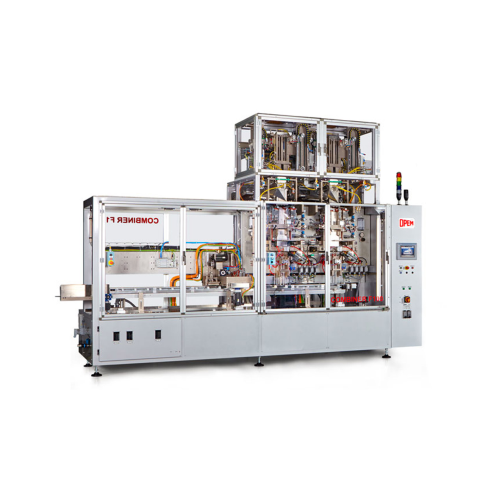
System for packaging stacked coffee pods in filter paper
Streamline your pod production with precision bagging and sealin...

Vacuum packaging system for food products
Optimize your packaging process with high-speed vacuum technology designed to pr...

Roasting and pasteurization system for nuts and seeds
Ensure optimal pasteurization and roasting of nuts, seeds, and drie...
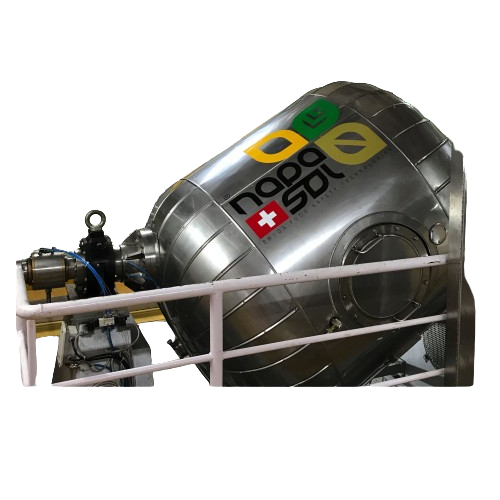
Roasting and pasteurization solution for nuts and seeds
Optimize your product line with seamless blending and pasteurizat...
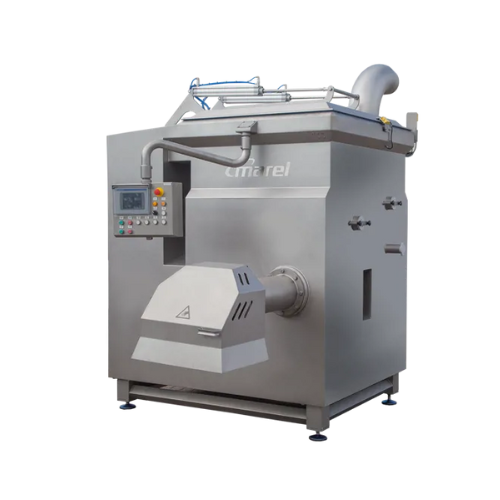
Industrial mixer-grinder for food processing
Streamline your processing line with a robust mixer-grinder that combines eff...
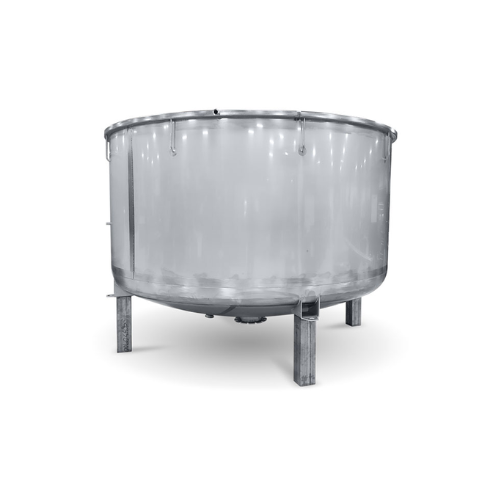
Heavy duty soak tanks for dry bean processing
Optimize your pre-processing with heavy duty soak tanks designed to ensure u...

Intermediate snipper for green bean processing
Optimize your green bean processing with a high-efficiency snipping solutio...
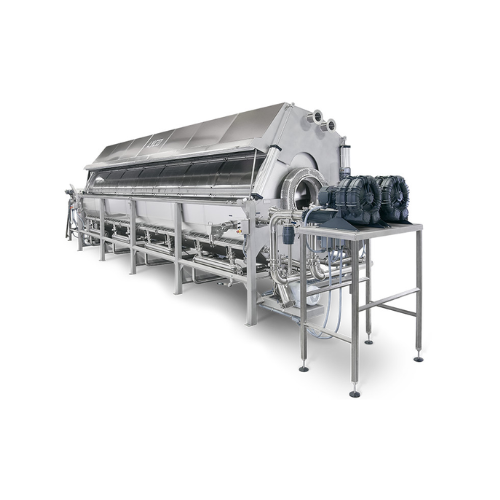
Pouch cooling system for food processing
Experience rapid cooling for your pouched food products, minimizing time in the ba...
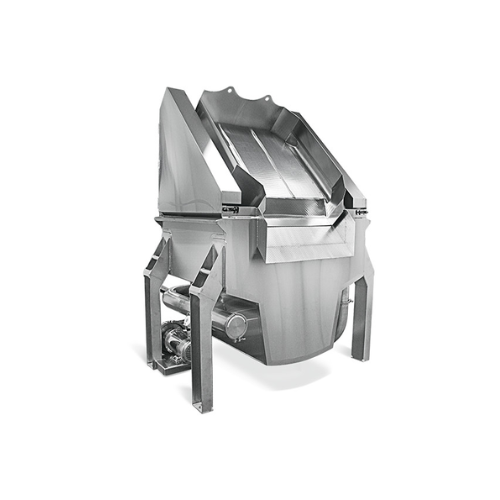
Rapid food cooling solution for vegetables and pasta
Efficiently reduce the temperature of particulate foods with rapid p...

Efficient pouch cooling solution
Designed to cut cooling times in half, this solution efficiently reduces the bacterial dang...
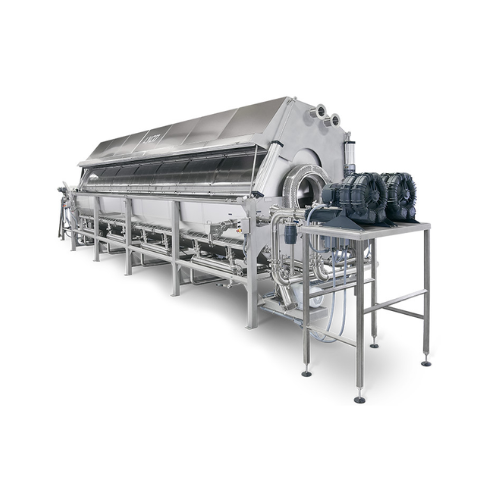
High-capacity pouch cooling system
Move pouched foods swiftly through critical temperature zones, ensuring rapid cooling fo...
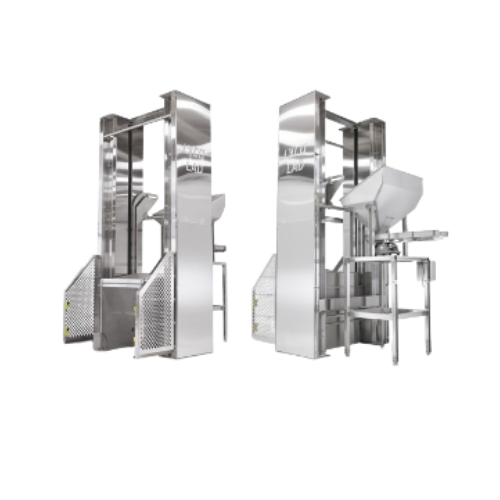
Lift and dump system for blanchers and cookers
Enhance precision in your food processing line by seamlessly integrating a ...
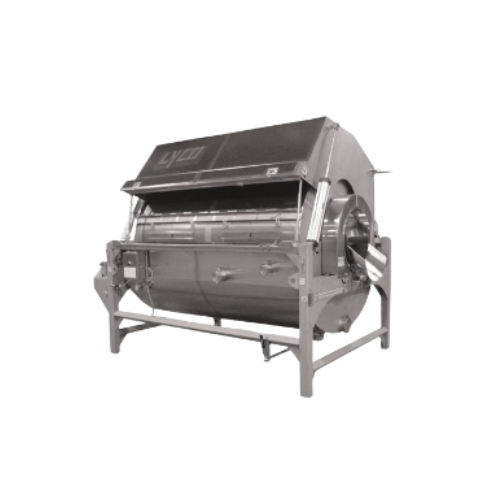
Rotary drum blancher for vegetables
Streamline your processing line with this rotary drum solution, ensuring precise blanch...
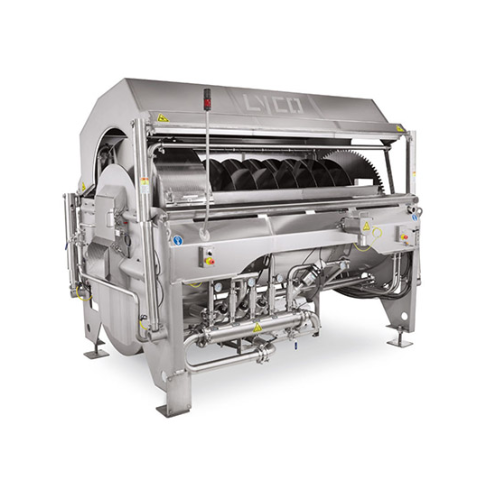
Sanitary cooker and cooler for pasta and rice
Effortlessly tackle the challenges of undercooked or overcooked pasta and ri...
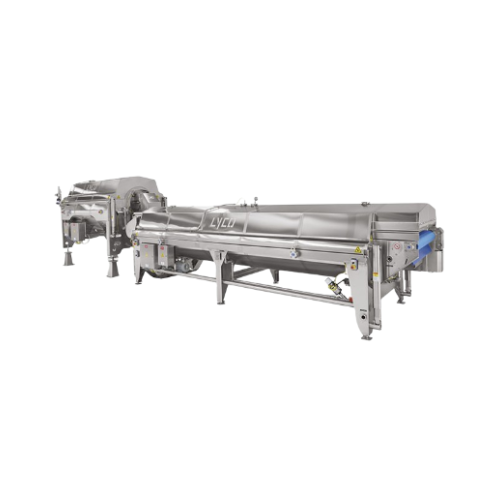
Rice cooking system for low-moisture processing
Achieve fully cooked, low-moisture rice with precise control over absorpti...
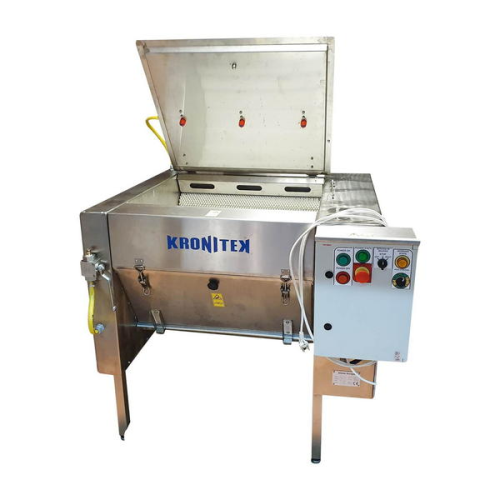
Vegetable and fruit peeling and washing
Efficiently wash and peel a wide range of fruits and root vegetables in one seamles...
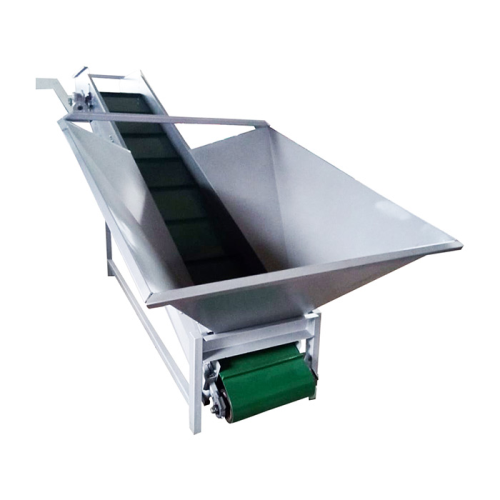
Receiving hopper for jumbo boxes
Efficiently unload and handle bulk agricultural products with ease, streamlining your pre-p...

Industrial food dehydrator for fruit and vegetables
Optimize your drying process with a high-temperature food dehydrator ...
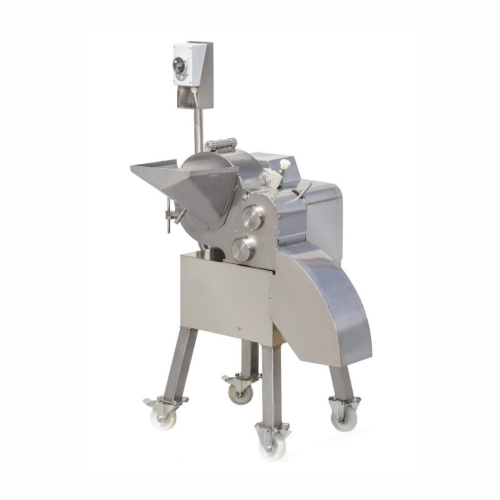
Commercial dicing machine for fruit and vegetables
Effortlessly transform your raw vegetables and fruits into uniform dic...
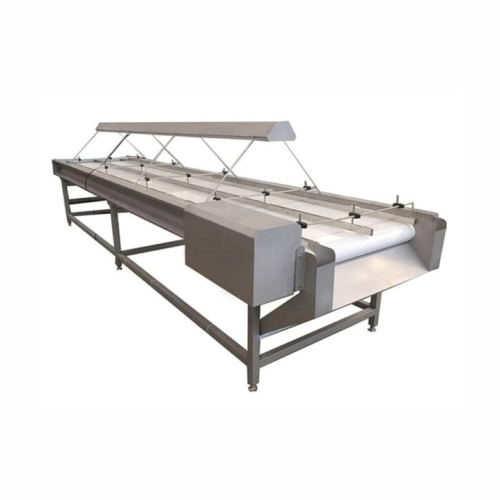
Inspection table for vegetables and fruits
Streamline your quality control with an efficient inspection table designed for...
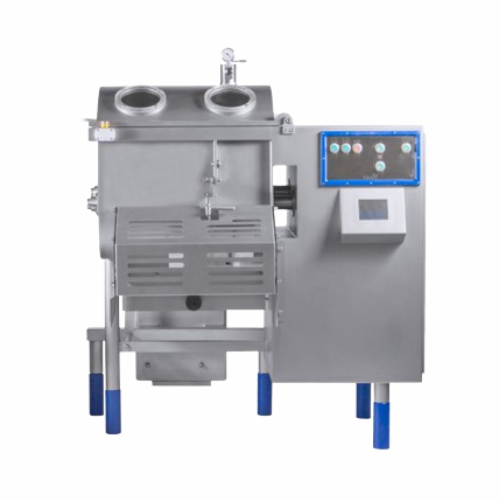
Industrial salad and delicatessen mixer
Achieve consistent and gentle mixing for diverse food applications with a solution ...
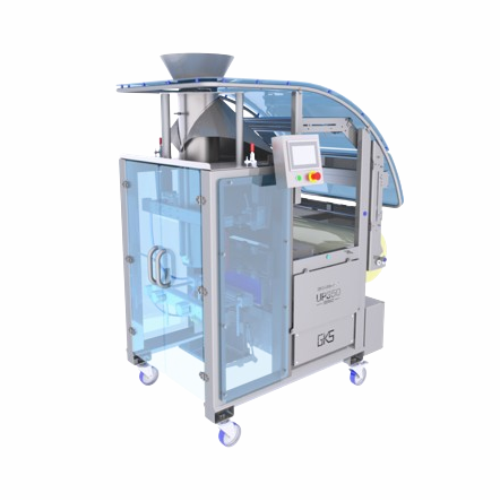
Continuous packaging solution for free-flowing food products
Streamline your production with a high-speed packaging mach...
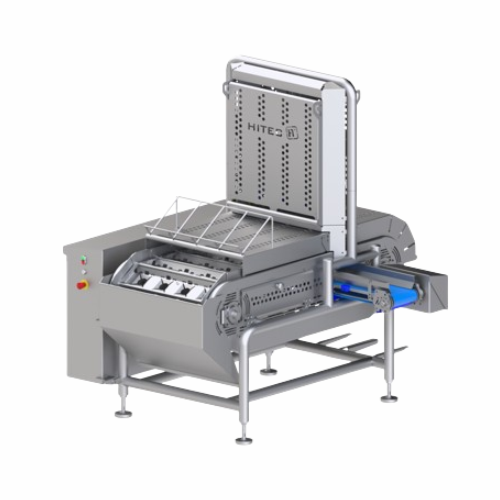
Pepper coring and dividing system
Effortlessly core and segment bell peppers, slashing labor costs while ensuring consisten...
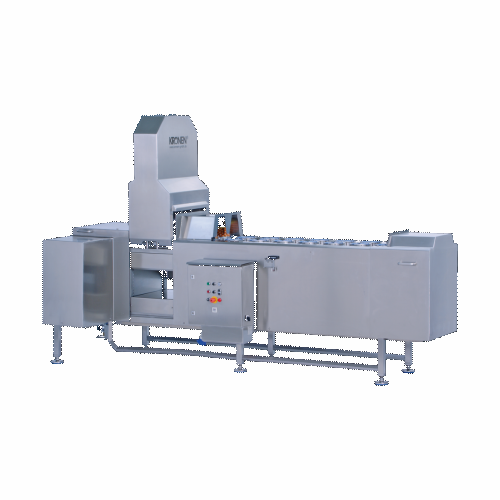
Cutting solution for large fruits and vegetables
Optimize your food processing operations with a semi-automatic solution d...
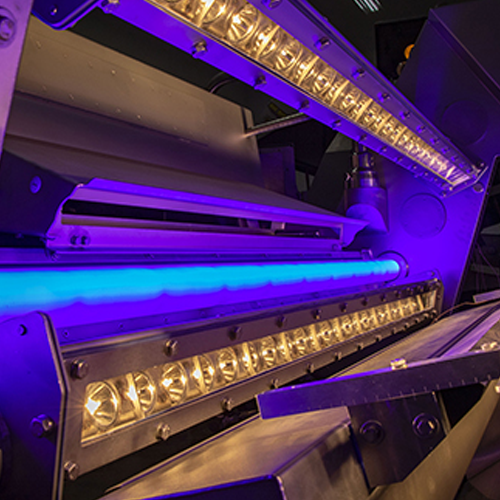
Optical sorter for blueberries
Enhance product quality and yield by precisely sorting blueberries, ensuring only optimal fru...
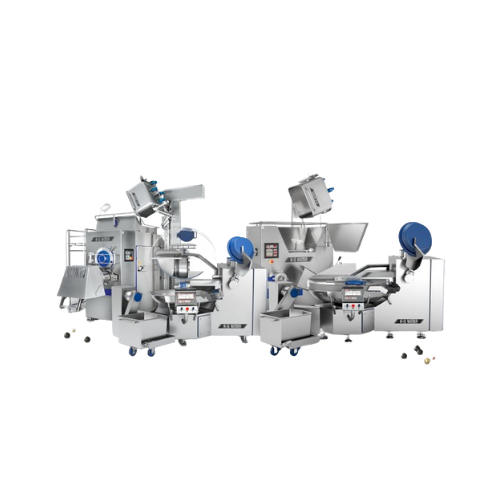
Industrial mixer grinder for fresh and frozen meat processing
Efficiently process diverse meat products for fresh and fr...

Industrial cooking kettle for food processing
Achieve seamless integration of cutting, mixing, and cooking processes to cr...

Rotary doypack packaging system for various materials
Enhance your packaging line with versatile doypack machines designe...
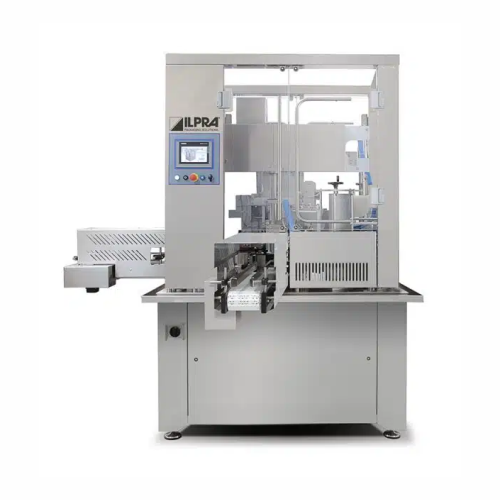
Packaging solution for small bottles and jars
Effortlessly seal and fill non-stackable containers, ensuring precision for ...
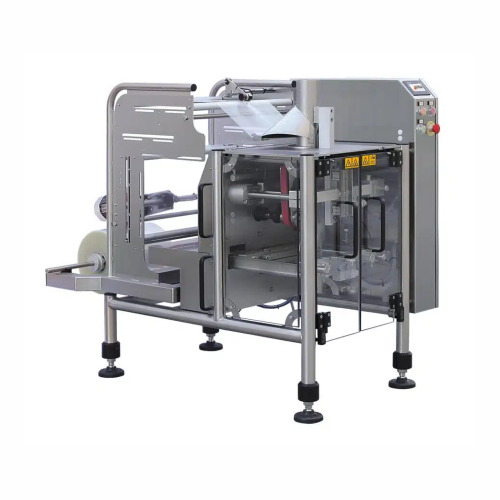
Vertical form fill seal for small to medium production runs
Ideal for scaling production, this compact packaging solutio...
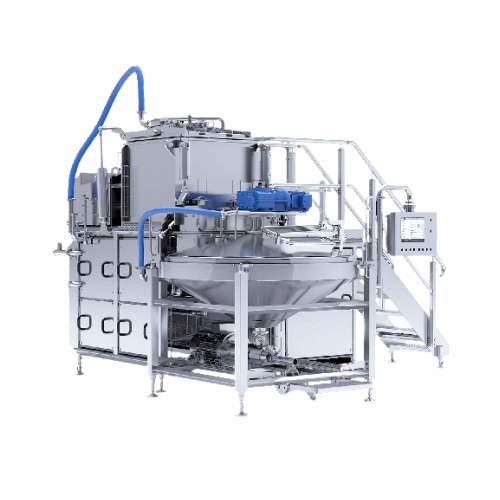
Multifunctional batch cooker for various food products
Optimize your production line with a versatile batch cooker design...
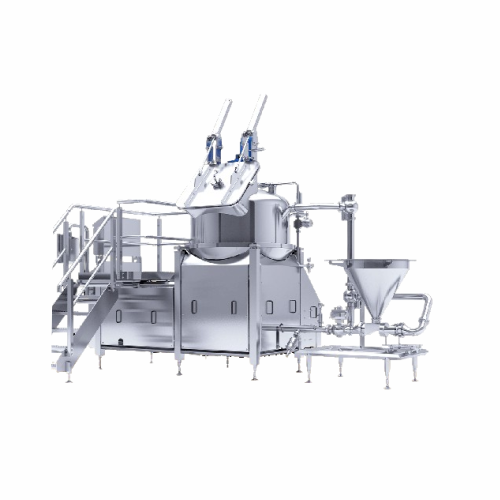
Lump-free emulsifier and steam batch cooker for processed cheese
Achieve consistent, lump-free processed cheese and crea...
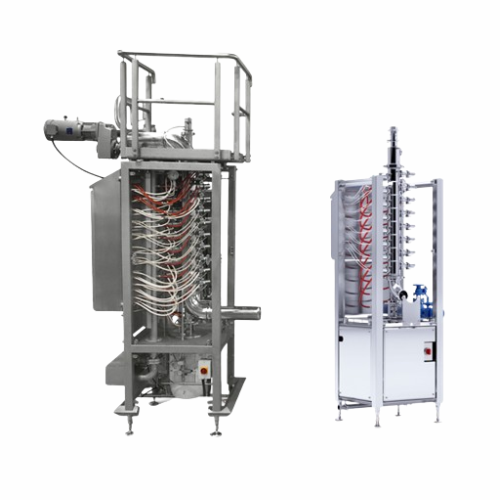
Continuous cooker for high-volume food processing
Elevate your production efficiency with a continuous cooker that ensure...
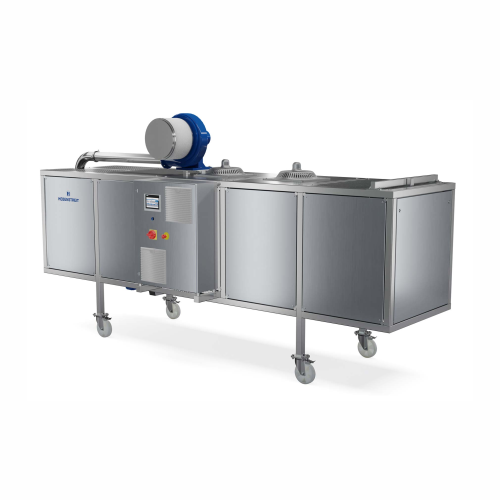
Cooling drum for seasoned extrudates
Ensure consistent texture and quality in your extruded snacks by effectively cooling s...
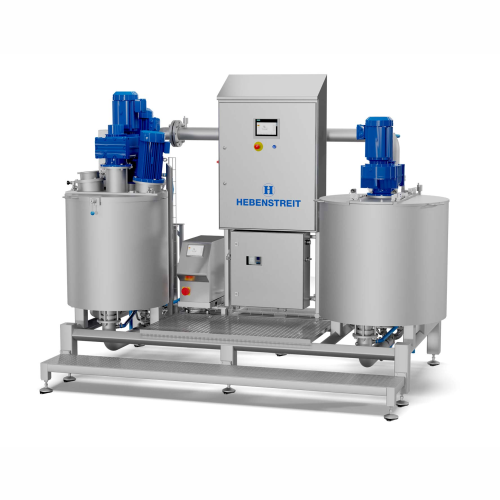
Cream preparation plant for homogeneous mixing
Optimize your snack production with precise mixing technology, ensuring con...

Seasoning drum for extruded snack products
Achieve consistent seasoning and mixing for extruded snacks with precision and ...
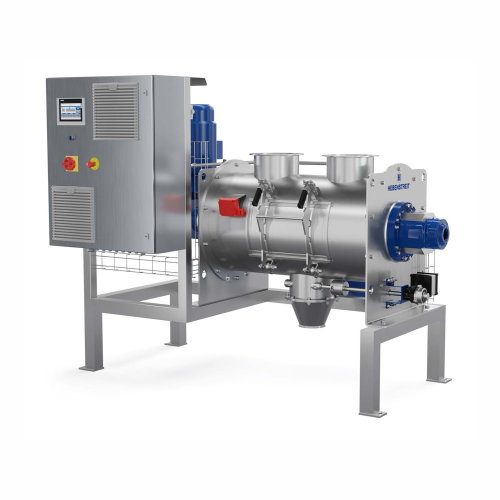
Industrial raw material mixer for complex recipes
Struggling with complex raw material mixtures? This advanced mixing sol...
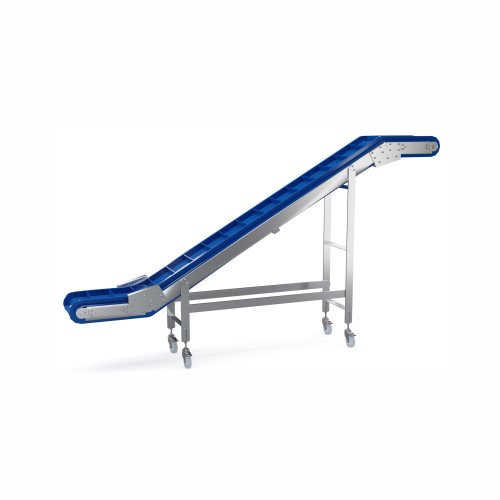
Conveyor systems for snack production
Streamline your snack production with advanced conveyor systems designed for seamless...
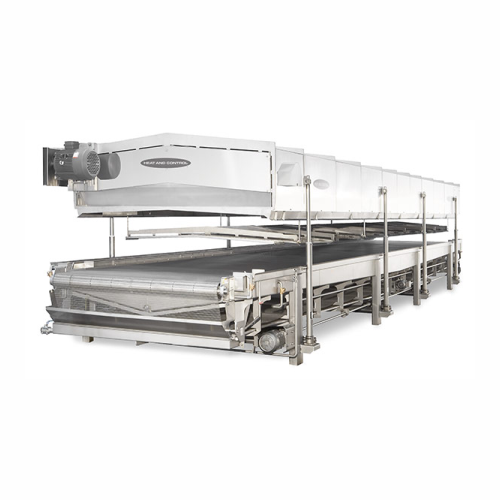
Multi-purpose oven for prepared foods
Ensure consistent cooking precision with this multi-purpose oven, designed to optimiz...
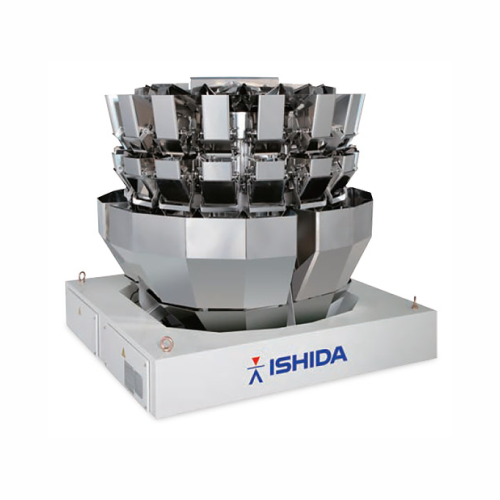
Blending multihead weigher for accurate component mixing
Achieve precise blending in high-speed operations with individua...
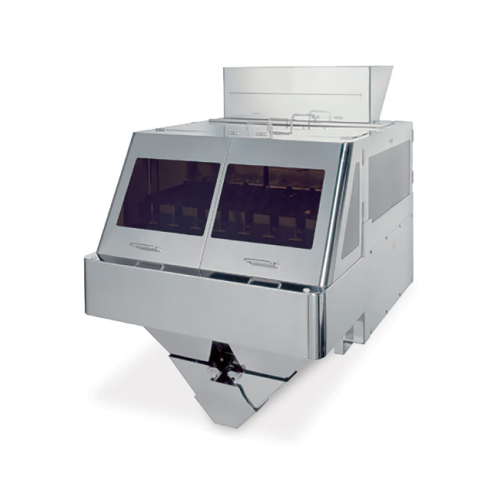
Linear weigher for dry or frozen free-flowing products
Optimize precision in high-speed weighing tasks with a compact sol...
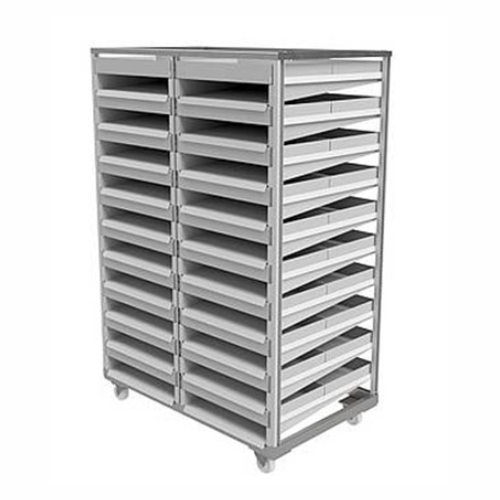
Flexible drying system for various industrial applications
Achieve precise moisture control across diverse materials wit...
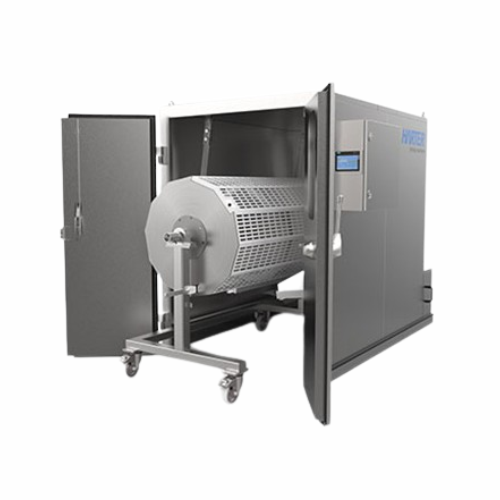
Drum dryer for animal feed
Achieve efficient and uniform drying for a variety of products, from nuts to medicinal cannabis, ...
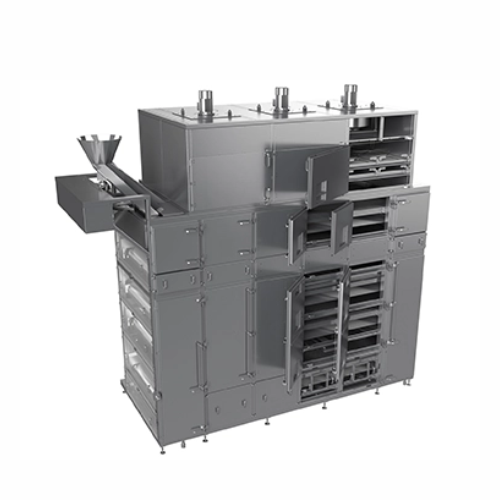
Continuous belt dryer for industrial production
For operations requiring precise moisture control, this continuous belt dr...
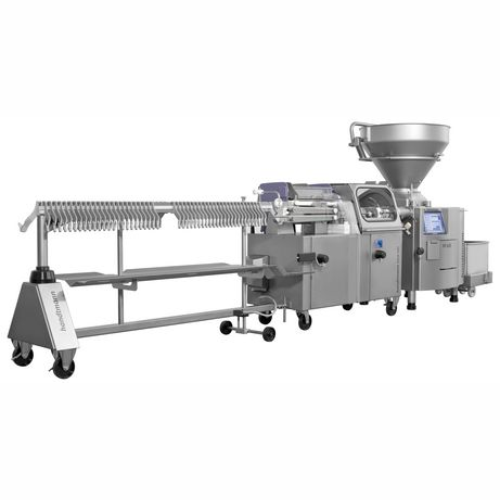
Automatic sausage filling and hanging system
Streamline sausage production with precise portioning and seamless integratio...
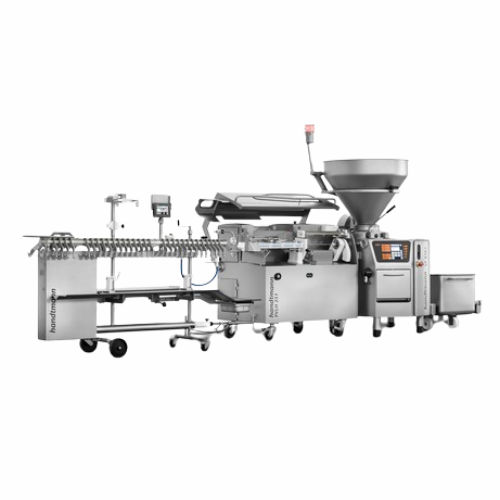
High-performance sausage linking and hanging line
Boost your production efficiency with a high-speed line designed for se...
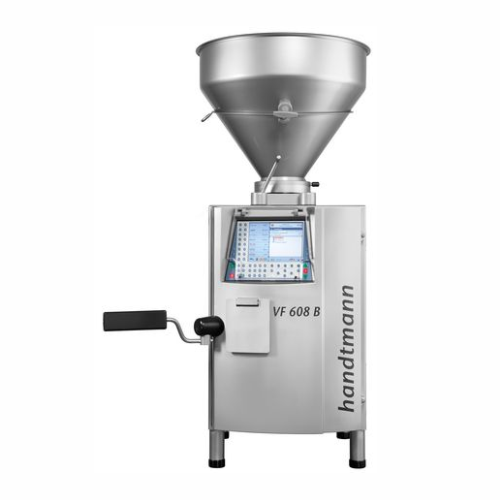
Dough portioning system for bakery operations
Achieve precise dough portioning with minimal waste using our advanced syste...
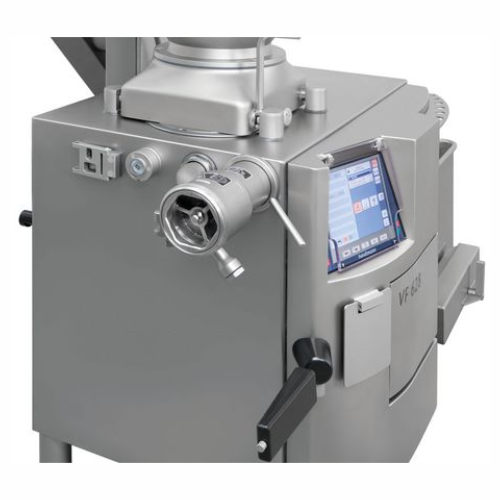
Inline grinding system for sausage and minced meat production
Streamline your production line by simultaneously grinding...
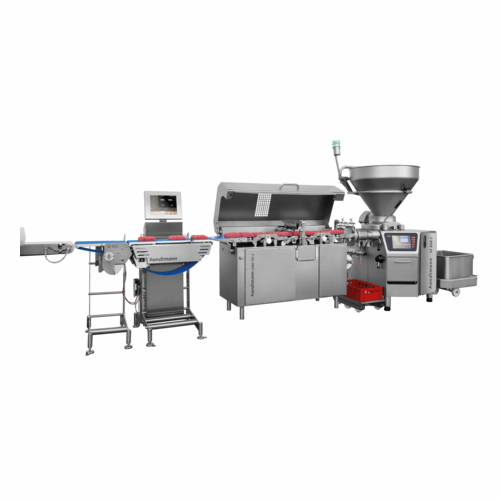
Minced meat portioning line
Optimize your production line with precise portioning and packaging of minced meat, enhancing ef...
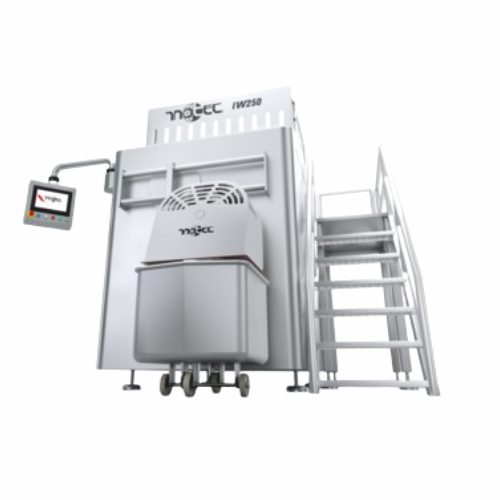
High-capacity industrial grinder for frozen and fresh raw materials
Effortlessly grind both deep-frozen blocks and fres...
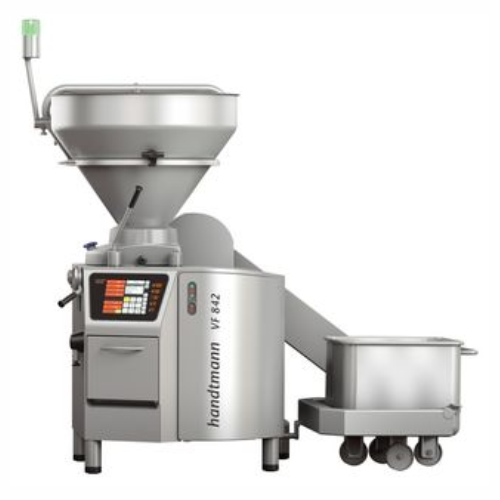
Industrial sausage and ham vacuum filler
Achieve unmatched precision in filling and portioning with high-capacity vacuum te...
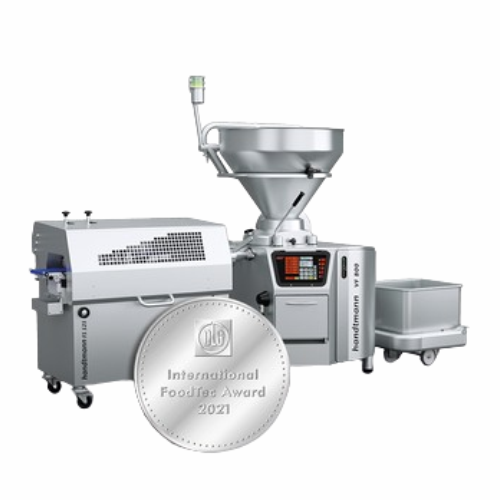
Industrial forming and cutting system for diverse products
Maximize product versatility with a system that effortlessly ...
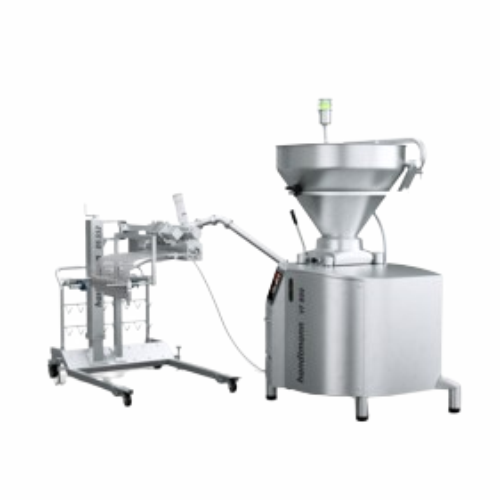
High-precision depositing system for fluid and viscous fillings
Achieve precise and efficient dosing for diverse food pr...
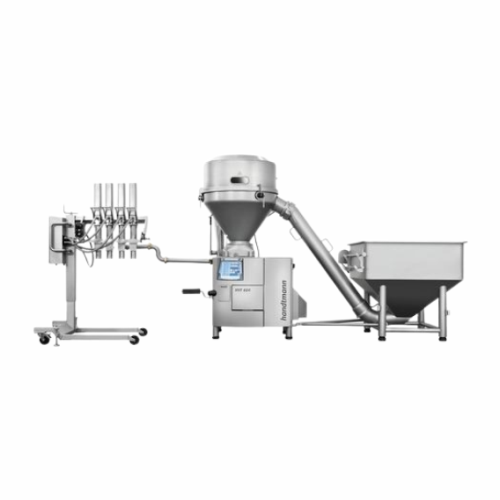
Cutting valve for chunky food portioning
Achieve precise portioning of chunky products, reducing waste and increasing effic...
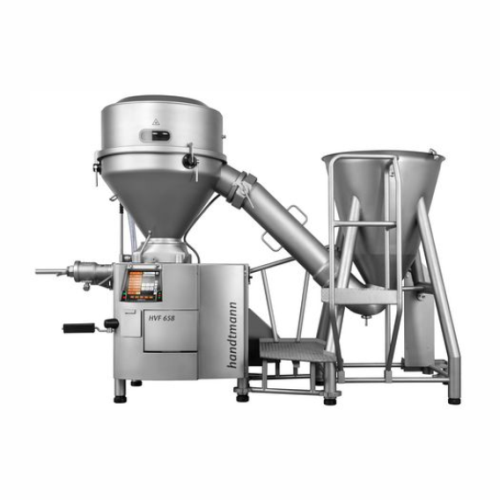
High vacuum filler for dry sausage products
Achieve pore-free, compact dry sausage products with superior evacuation perfo...
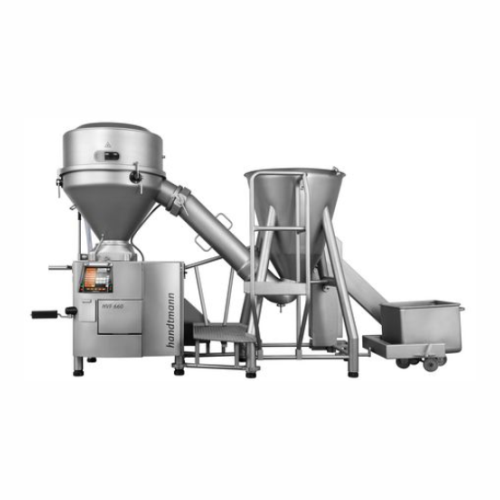
High vacuum filler for large-calibre sausages
Achieve pore-free, high-quality products with optimal portioning accuracy an...

High-capacity piston stuffer for industrial filling and portioning
Streamline your production with high-speed, fully el...
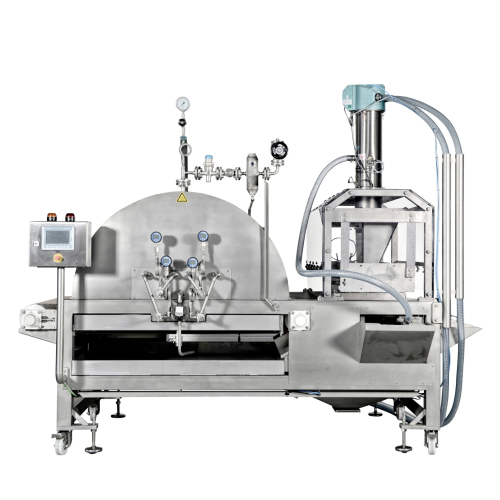
Industrial sugar sander for confectionery coating
Enhance product appeal and longevity with a sugar sander designed to un...
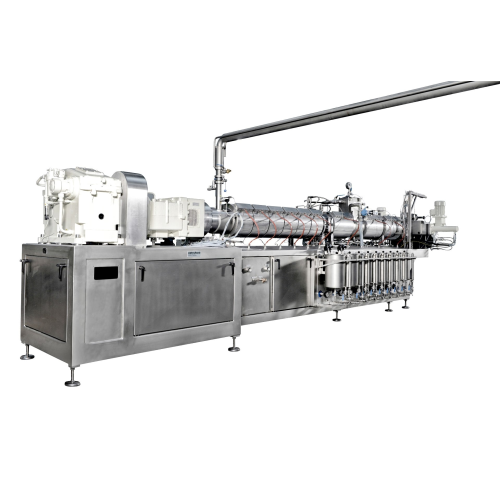
Cooking extruders for low shear confectionery production
For producers looking to create high-quality confectionery, this...
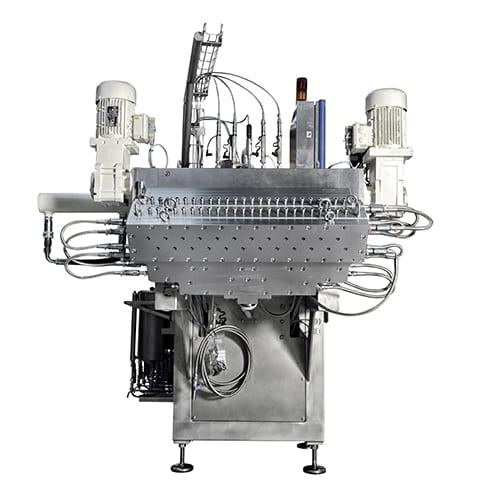
Multi-color and flavor confectionery production system
Maximize production flexibility with a single extruder that seamle...
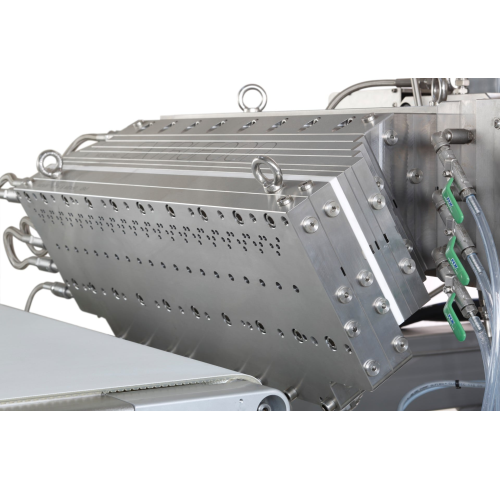
Extrusion system for color changing confectionery strands
Easily switch colors in confectionery strands mid-production, ...
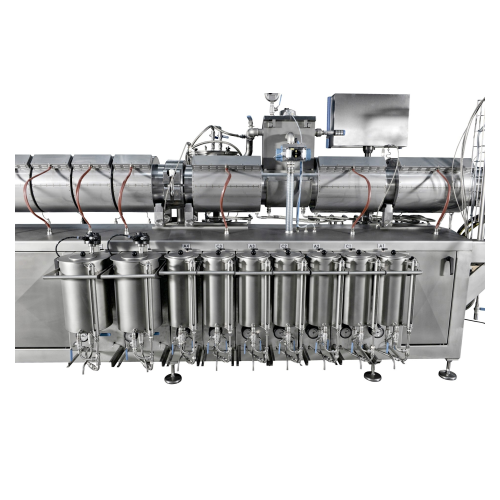
High precision dosing system for color, flavor, and acid
Achieve precision and reliability in dosing color, flavor, and a...
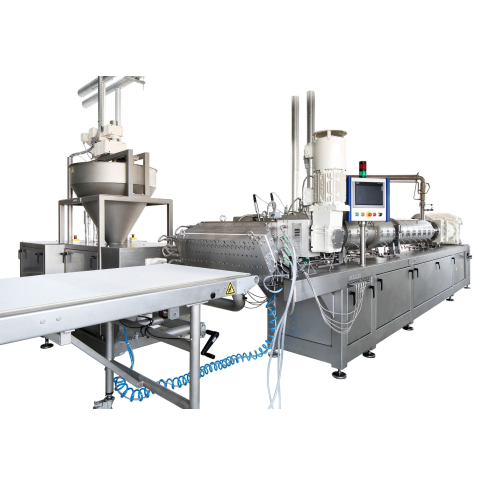
Screen changer for extrusion lines
Prevent clogs and maintain quality with this screen changer, designed to filter out soli...
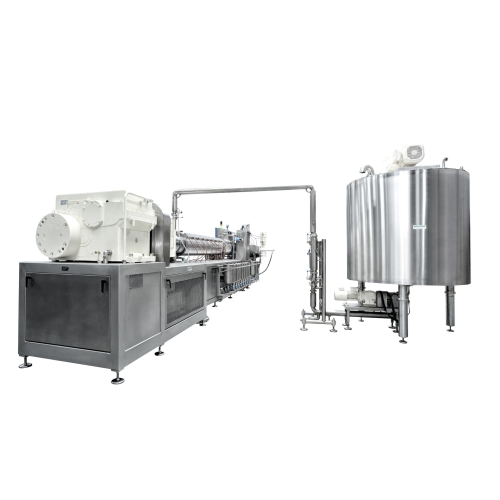
Slurry preparation for licorice production
Ensure a continuous and homogeneous feed of licorice slurry to your extruder, o...
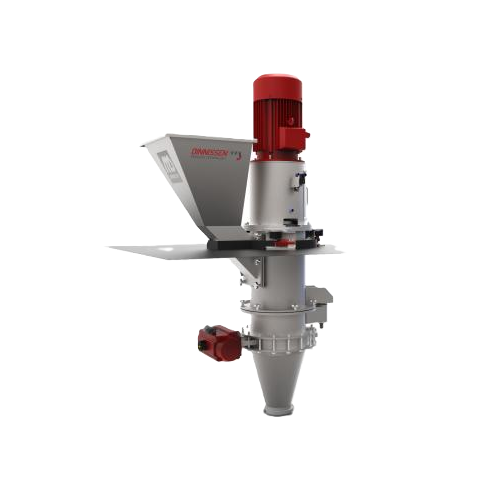
Industrial shredder for diverse material reduction
Achieve precise and efficient material resizing for diverse applicatio...
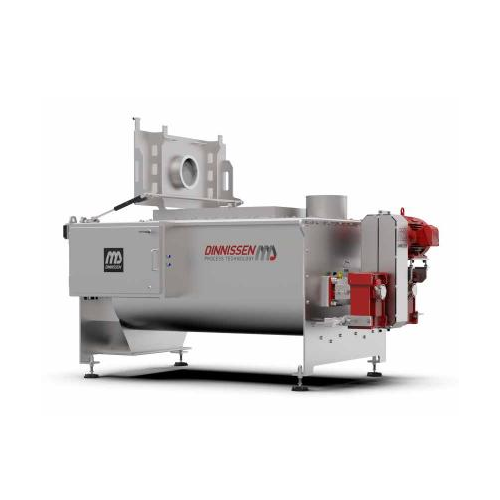
Continuous mixer for industrial powders and liquids
Achieve precise and efficient mixing of solids and liquids with minim...
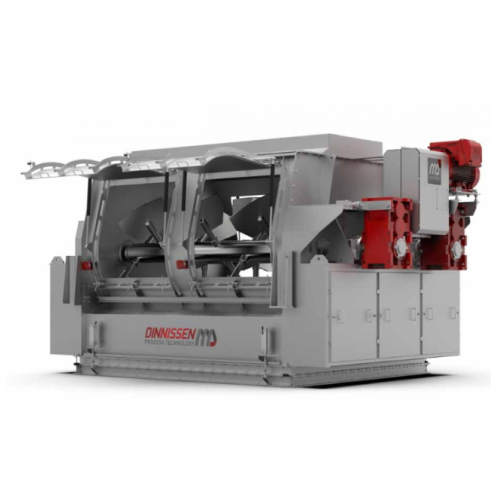
Batch mixer for powder and grain processing
Achieve ultra-fast, homogenous mixing in just 20 to 50 seconds with this versa...
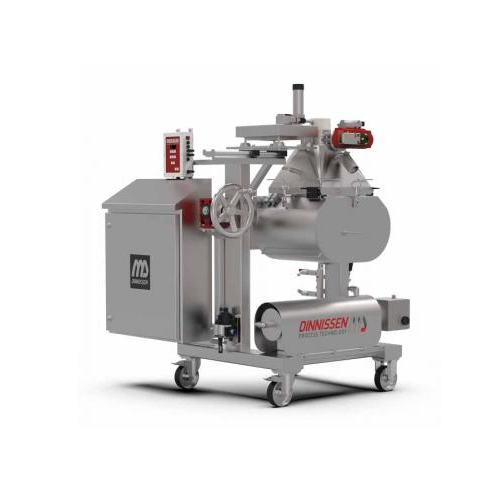
R&d mixer for small batch experimentation
Perfect your mixing techniques swiftly with precision-controlled small batch exp...
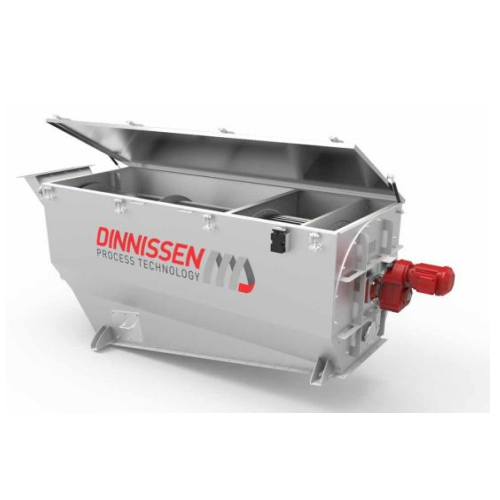
Rotary drum sifter for pellets and chunks
Achieve precise particle separation and minimize product loss with a rotary drum...
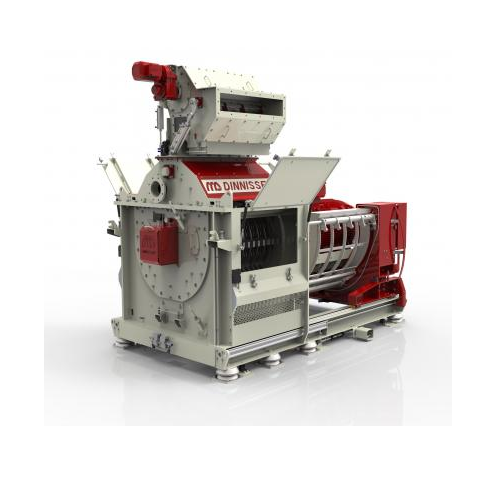
Fast screen exchange grinding solution for medium-hard products
Maximize your milling efficiency with a solution that al...
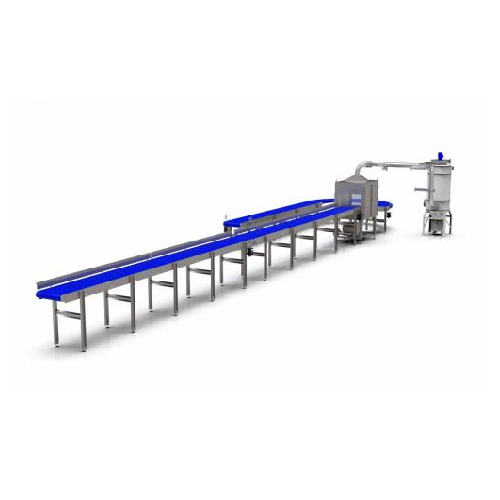
Mechanical horizontal conveyor for powders and granulates
Efficiently handle and transport your delicate powders and gra...
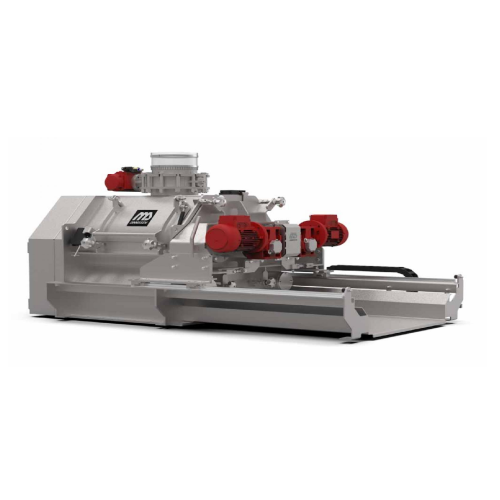
5-in-1 industrial mixer for food and chemical industries
Streamline your production with a multifunctional system that ef...
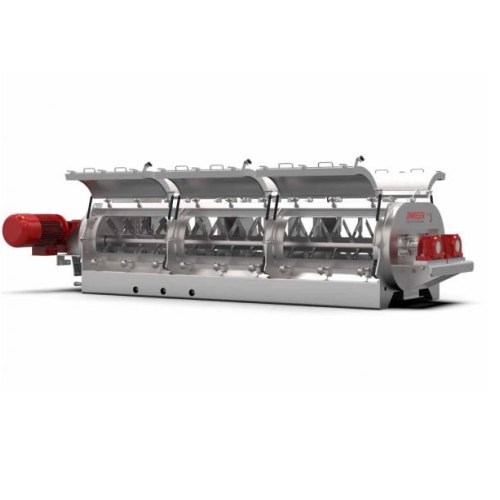
Industrial mixer for moisture conditioning
Ensure precise moisture levels and homogeneous mixtures for complex extrusion p...
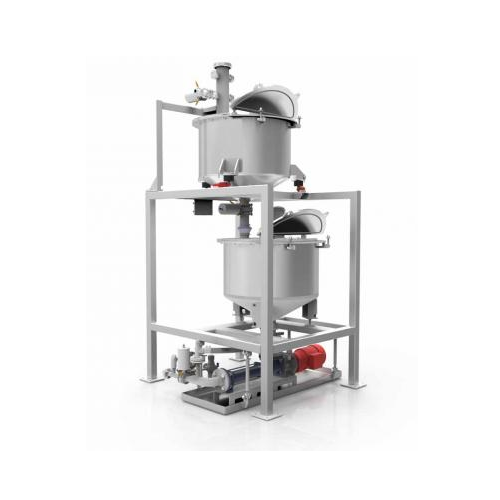
Liquid dosing system for powders and granulates
Achieve precise liquid addition with this dosing system, ideal for integra...
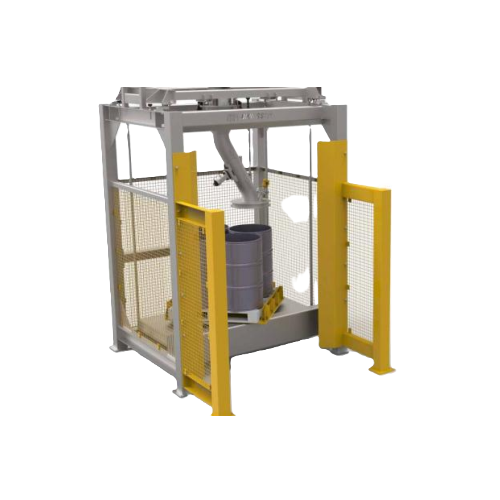
Ibc and drum filling system for chemical substances
Ensure safe and efficient handling of sensitive materials with a modu...
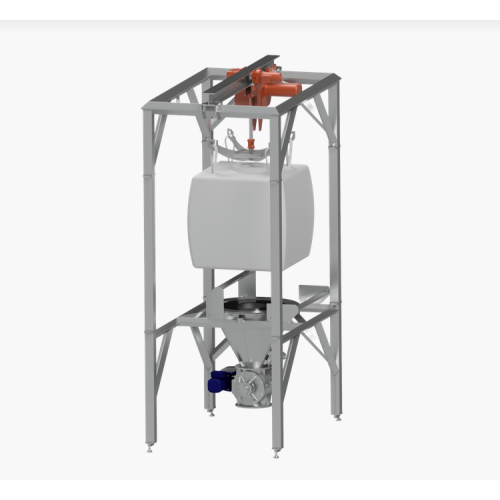
Bigbag discharge system for food, chemical, and pharmaceutical industries
Ensure precise and dust-free handling of bul...
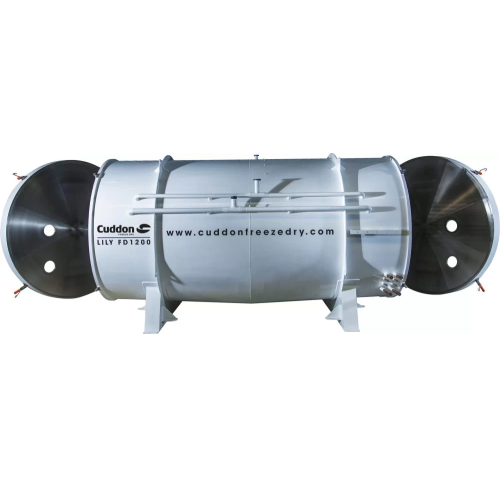
Industrial freeze dryer for large scale food processing
Optimize moisture removal for high-quality food preservation and ...
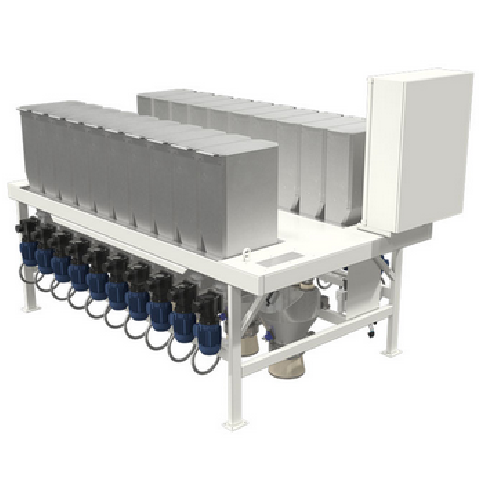
Accurate weighing system for micro ingredients
Ensure precise micro-ingredient dosing for batch operations with this versa...
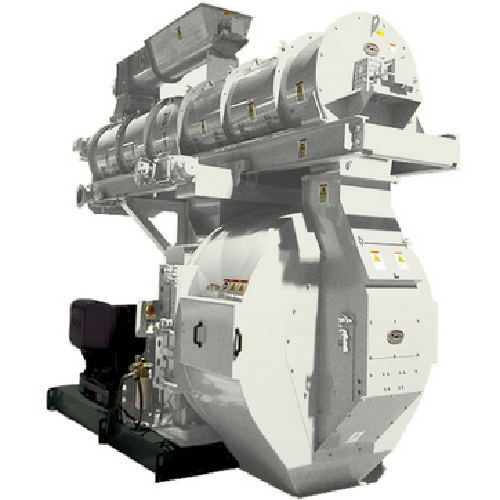
High-capacity ring-die pellet mill for animal feed production
Optimize your high-capacity feed production with this pell...
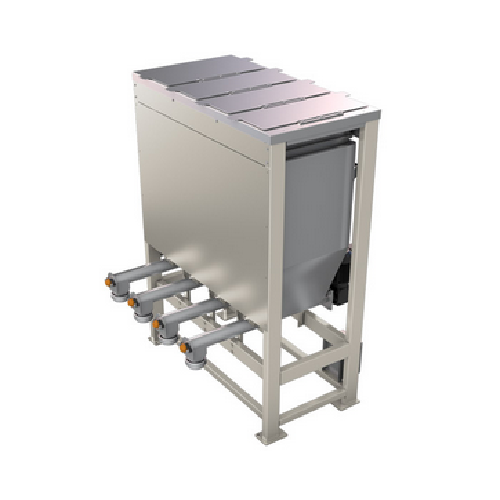
Loss-in-weight scale for micro ingredient batching
Enhance precision in your production line with advanced micro ingredie...
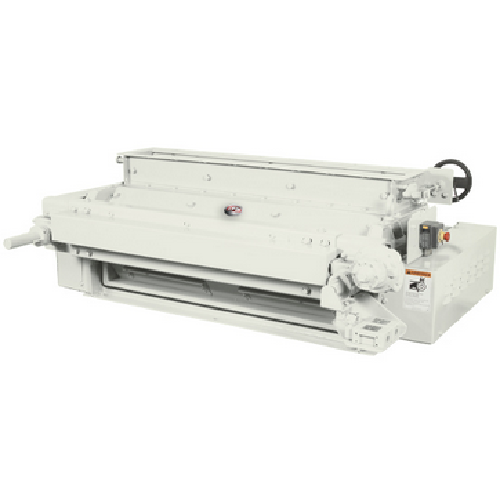
Pellet crumbler for animal feed pelleting
Optimize pellet size reduction with precise control and high efficiency, ensurin...
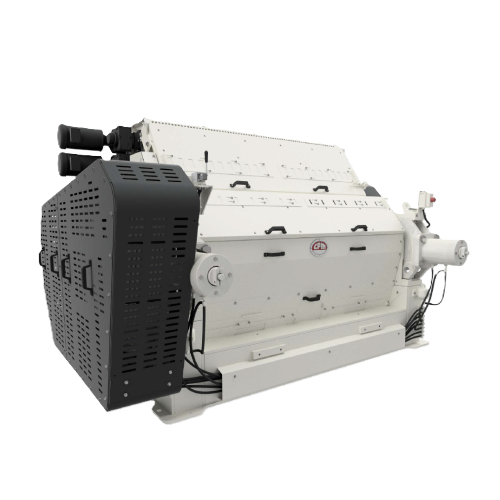
Oilseed flaking mill
Enhance flake consistency and output efficiency with advanced roll technology designed to optimize your ...
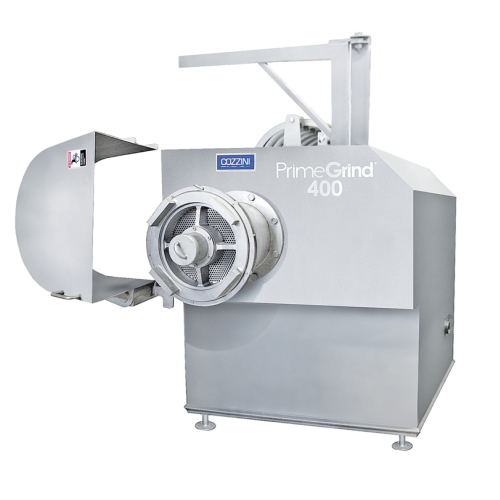
Frozen meat grinder
Streamline your protein processing with a solution designed to efficiently grind frozen meats, ensuring c...
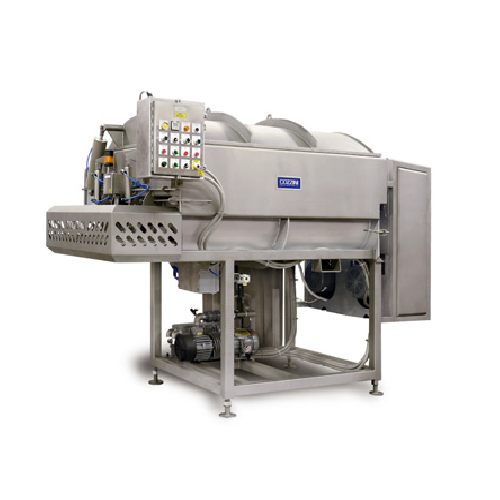
Vacuum mixer/blender for food processing
Achieve precise mixing and blending with air removal for consistent quality across...
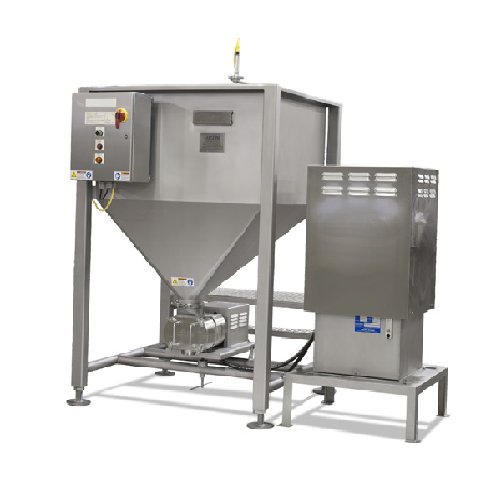
Stuffing hopper with stainless positive displacement pump
Enhance your high-volume processing line with a seamless integ...
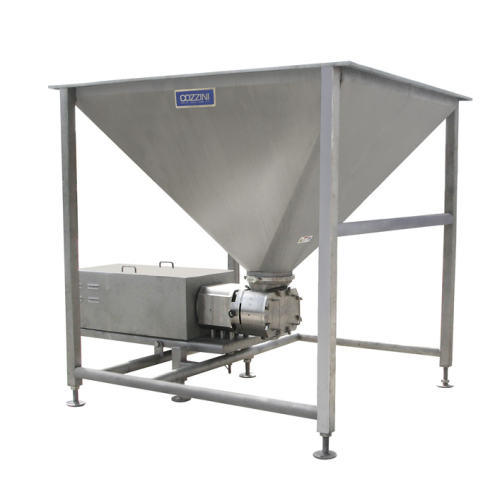
Transfer hopper with stainless Pd pump for food processing
Eliminate spillage and maintain continuous flow with a positi...
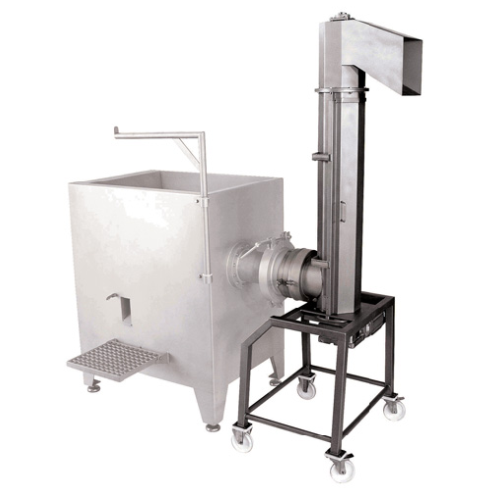
Vertical screw conveyor for ground materials
Optimize floor space in food processing with this vertical solution, ensuring...
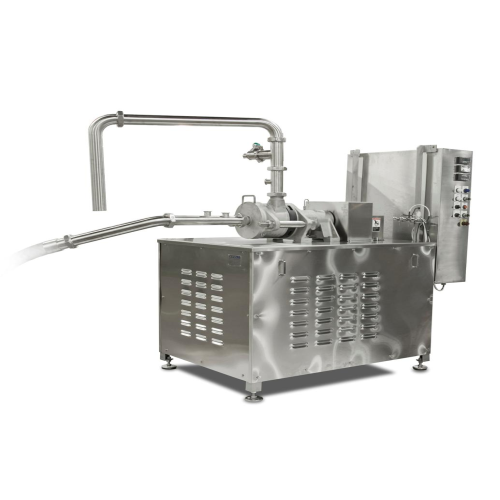
Emulsion and reduction system for meat processing
Achieve precise particle consistency and texture control in food proces...
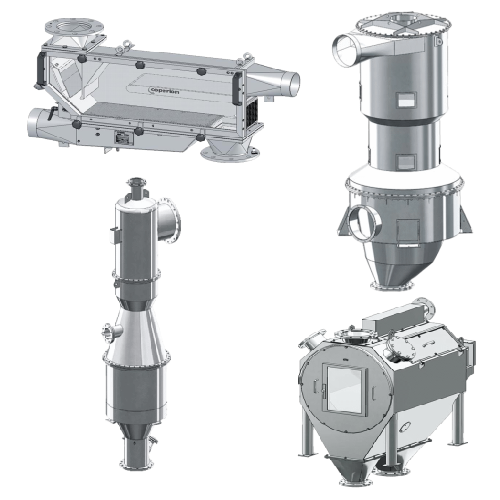
Pellet dedusting elutriators
Achieve superior purity in your production line by effectively removing dust and streamers with...
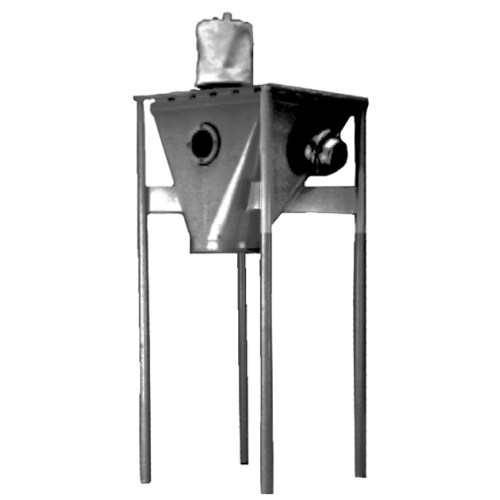
Aerolock surge hopper for precise bulk material management
Optimize your production with a surge hopper designed to ensu...
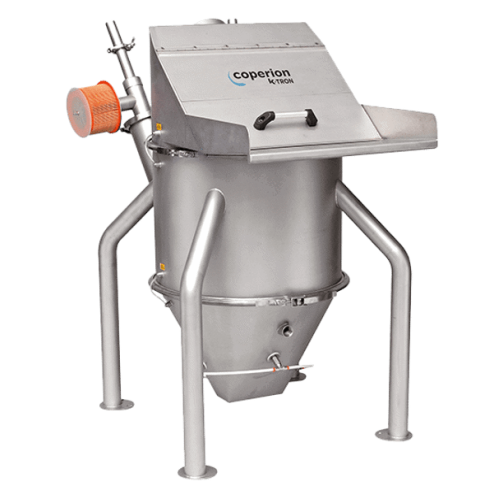
Feed bins for pre-conditioning materials
Optimize your material flow by pre-conditioning bulk solids for efficient vacuum c...
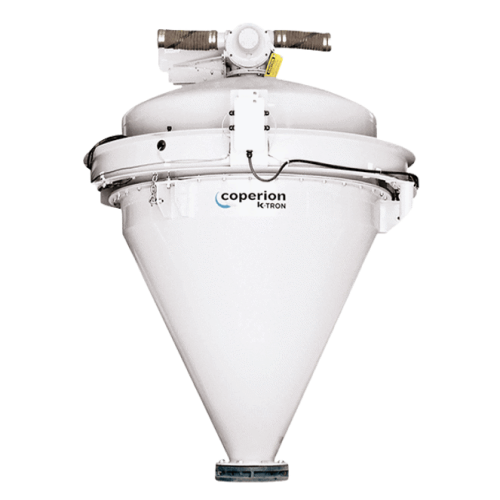
Scale hopper for bulk material processing
Optimize your bulk material handling with precise control in separation, filling...

Laboratory twin screw extruder for small batch processing
Efficiently develop formulations and conduct precise research ...
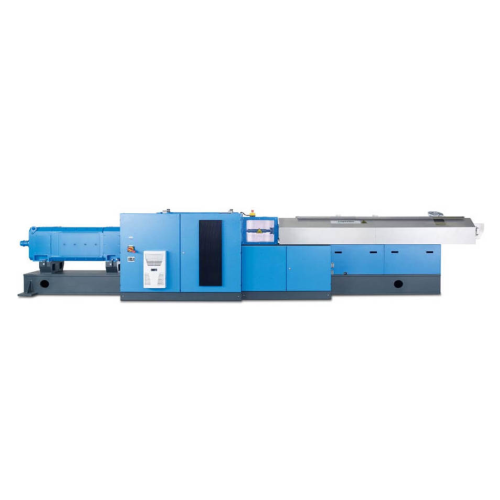
High throughput twin screw extruder for low bulk density products
When handling low bulk density materials, achieving m...
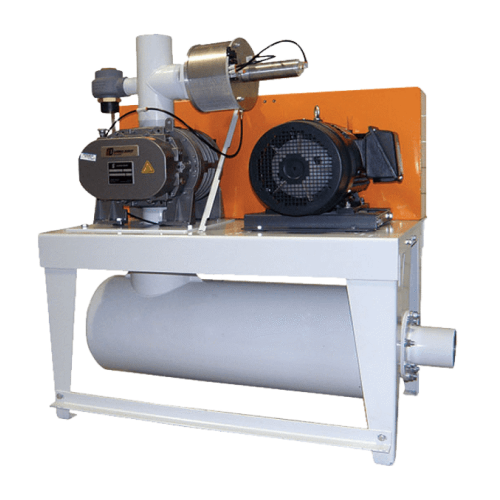
Vacuum sequencing blower for industrial conveying systems
For manufacturers handling bulk materials like powders and gra...
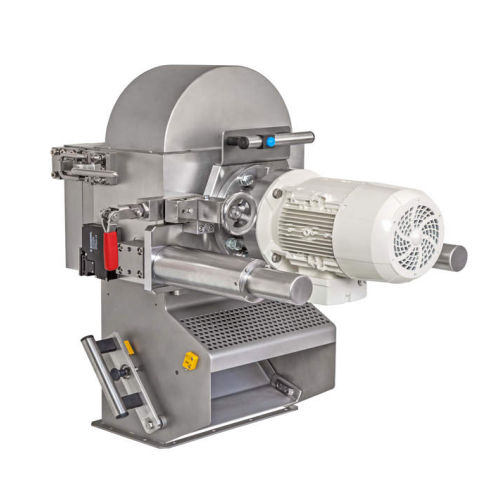
Centric pelletizer for direct extrusion
Effortlessly transform materials into uniform granules with our high-speed pelletiz...
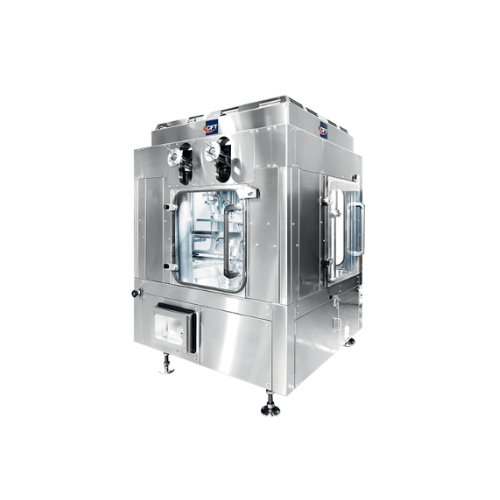
Industrial can seamers for food and beverage packaging
Streamline your canning process with precision seaming solutions d...

Industrial rice cooker
Enhance rice processing with an engineered solution that ensures precise cooking and cooling, optimizi...
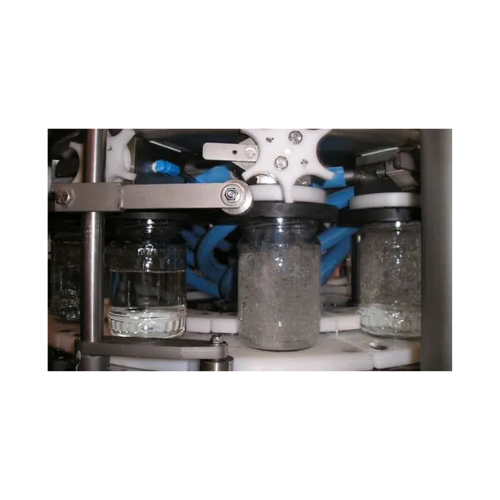
Vacuum filler for glass jars and cans
Ensure precise filling and equal headspace for your products with this vacuum filler,...

Marinating line for meat and poultry
Streamline your marinating process with reduced spillage and cleaning time by incorpor...
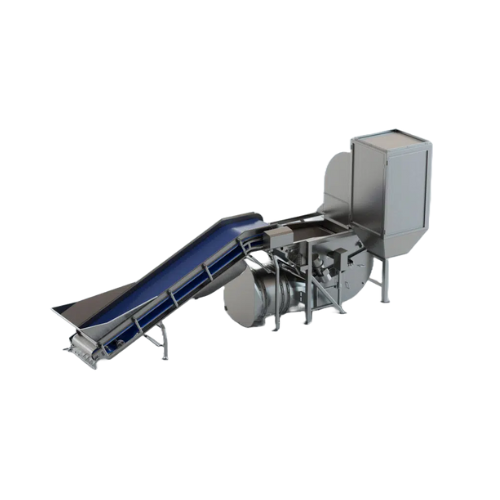
Air-cleaning system for fragile berries
Ensure the pristine quality of your delicate berries with a system designed for gen...

Continuous belt thawing unit for frozen seafood
Quickly defrost block-frozen products with minimal water usage, enhancing ...
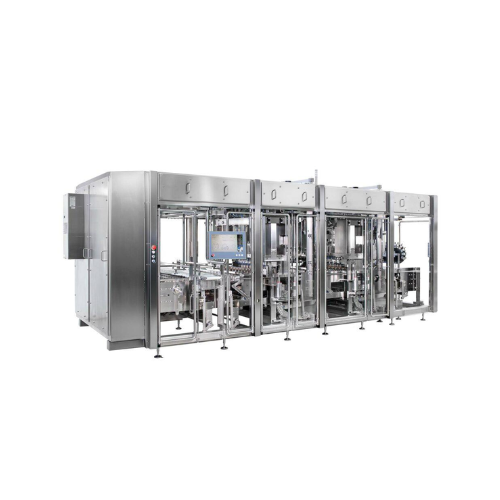
High-capacity filler and closer for pumpable products
Efficiently handle pumpable, flowable, and pasty products with this...
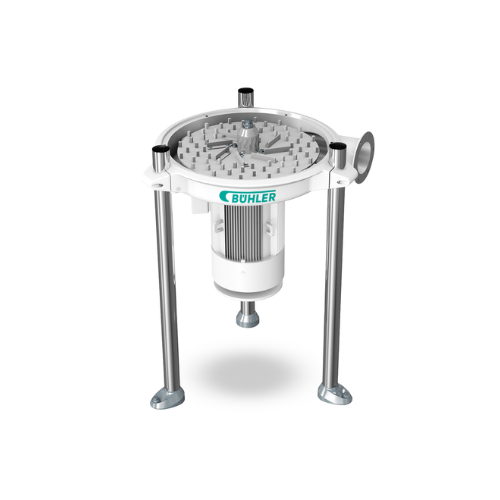
Impact machine for milling applications
Optimize your grain processing with this versatile impact machine, designed to refi...
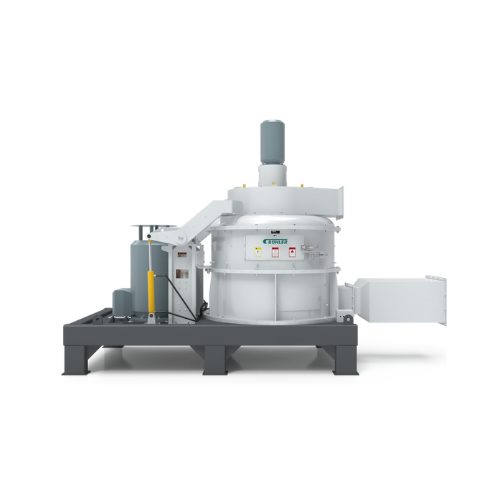
High-efficiency pulverizer for ultra-fine applications
Optimize your production of animal and aqua feed with this high-sp...

Twin-screw extruder for breakfast cereals production
Enhance your product range with flexible twin-screw extrusion techno...
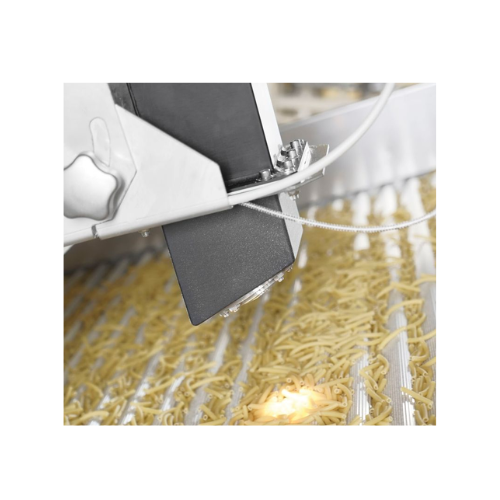
Digital process service for regulating water in dough preparation
Achieve consistent dough moisture levels with this di...
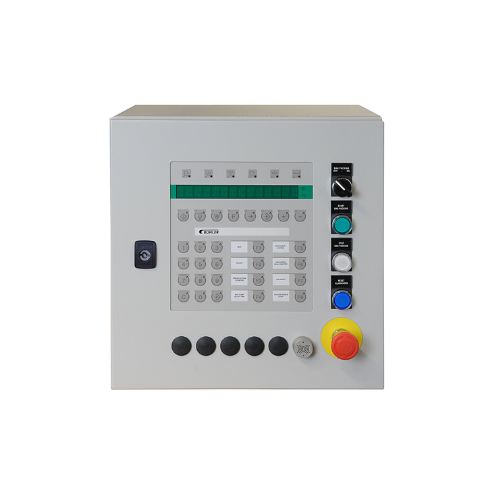
Bagging control system for centralized operations
Streamline your bagging operations with a centralized control system, d...

Twin-screw extruder for breakfast cereal
Optimize your production with a robust twin-screw extruder that accommodates high ...
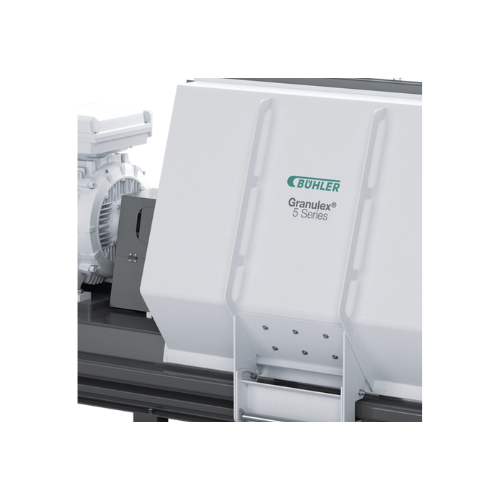
Hammer mill for animal feed grinding
Achieve precise granulation with high throughput and energy efficiency, while reducing...
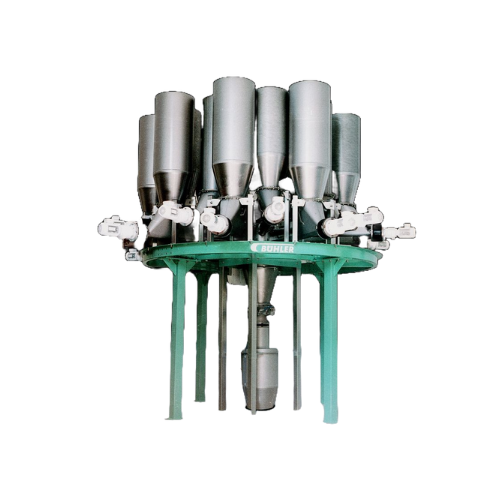
Micro-dosing system for animal feed additives
Achieve precise and consistent feed formulation with high-precision micro-do...
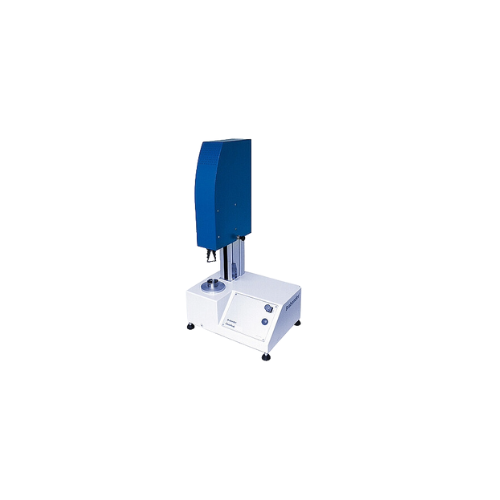
Gluten quality testing solution
Ensure optimal flour quality by rapidly assessing gluten properties, allowing you to refine ...
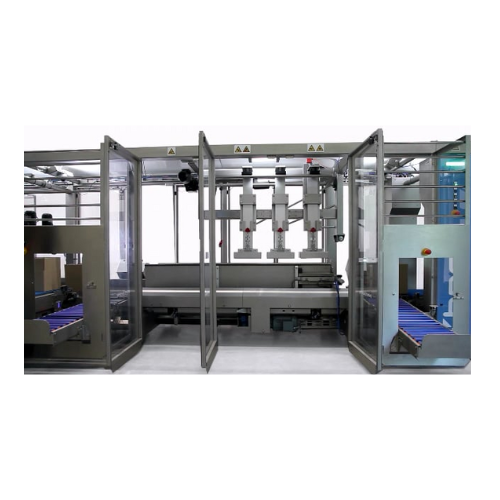
Full Rsc case shaker-compactor-sealer
Streamline your packaging line with a solution that compacts and seals cases to elimi...
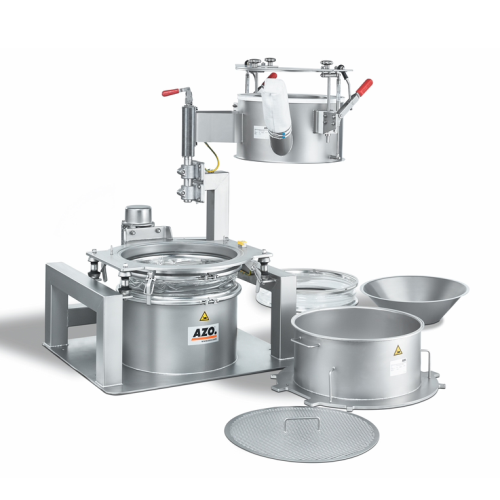
Big bag connection system for dust-free docking
Achieve dust-free docking and seamless discharging of bulk solids with an ...
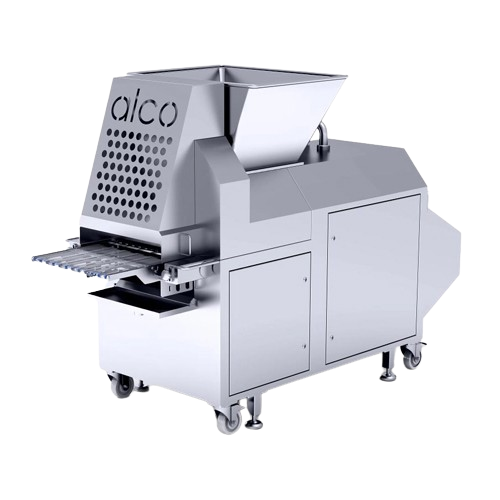
Food forming solution for poultry and plant-based products
Optimize your production line with high-pressure forming that...
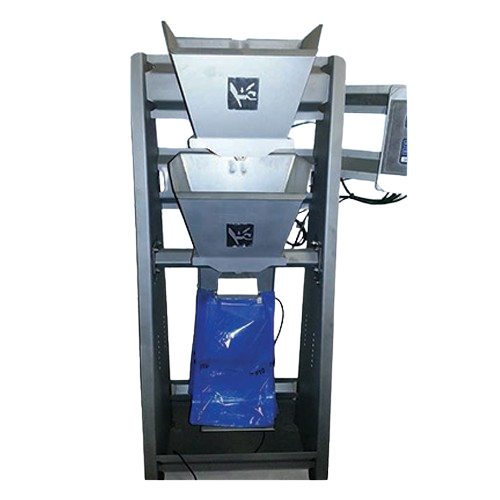
Industrial bagging system for high-speed processing
Optimize your packaging line with this engineered-to-order bagging sy...
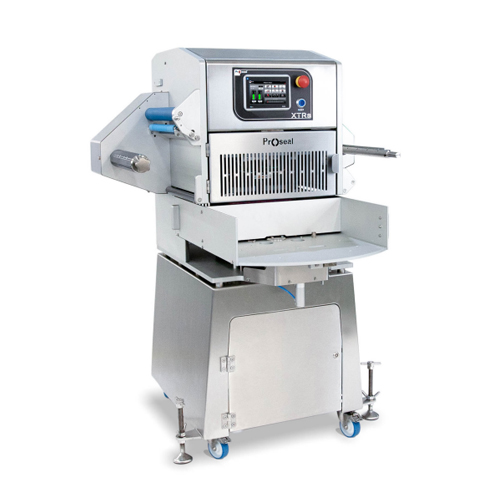
Semi-automatic tray sealer for ready meals
Achieve optimal freshness with consistent sealing, maximizing shelf life for va...
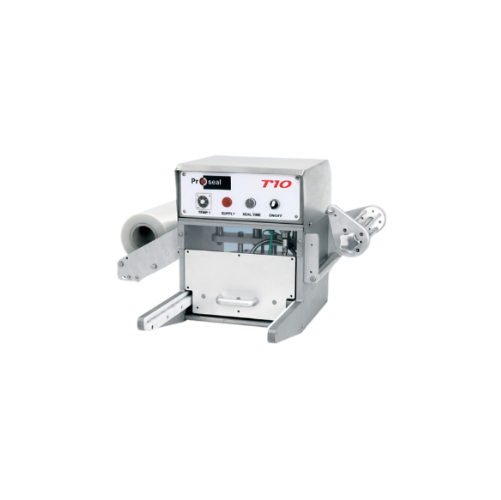
Bench mounted tray sealer for small-scale production
Perfect for pilot runs and small batches, this compact tray sealer e...
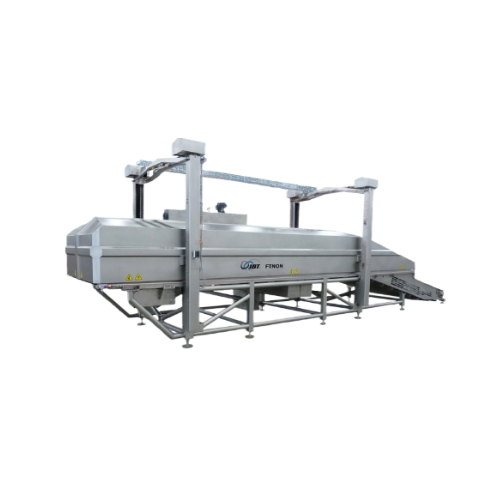
Energy efficient steaming for fresh produce
Achieve exceptional product quality while minimizing energy use by up to 90% w...
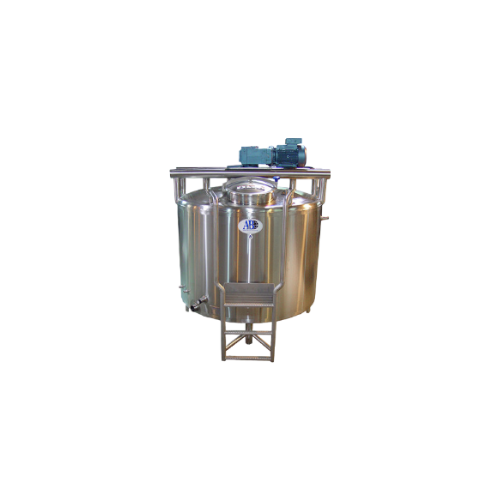
Industrial mixing tanks for liquid, slurry, and gas dosing
Optimize your production with versatile mix tanks, designed t...
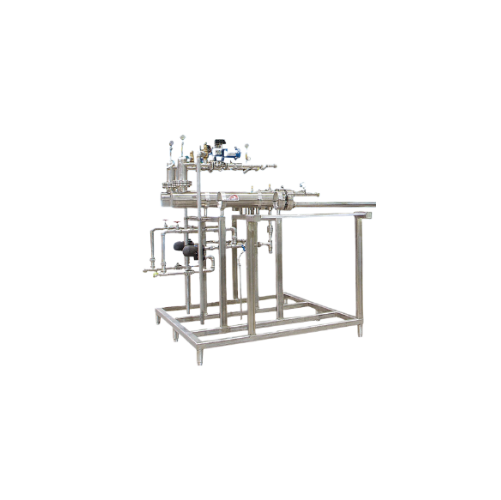
Industrial hot water heating system
Optimize your production line’s efficiency with precise water temperature control...
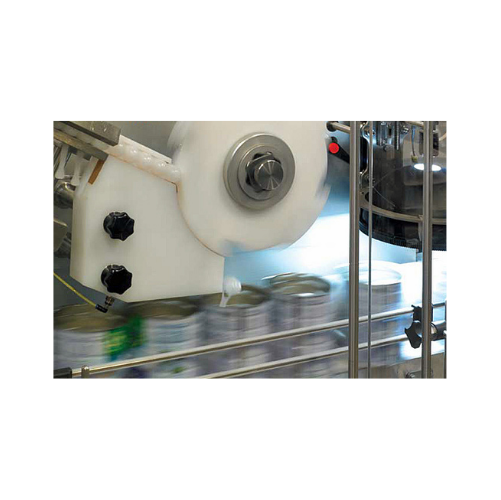
Automated scoop insertion system for powder containers
Streamline your container filling operations by ensuring precise s...
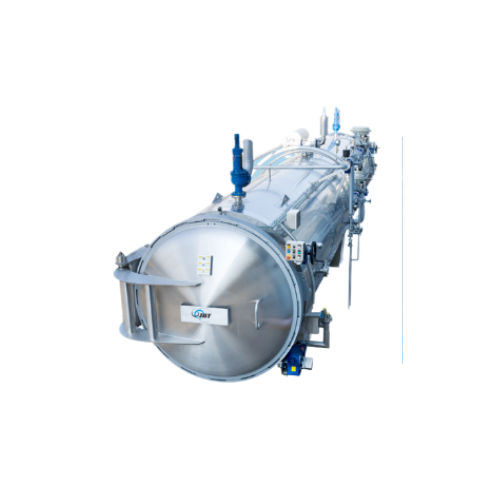
Tuna vacuum pre-cooker cooler
Optimize your tuna and seafood processing with precise thawing, cooking, and cooling under vac...
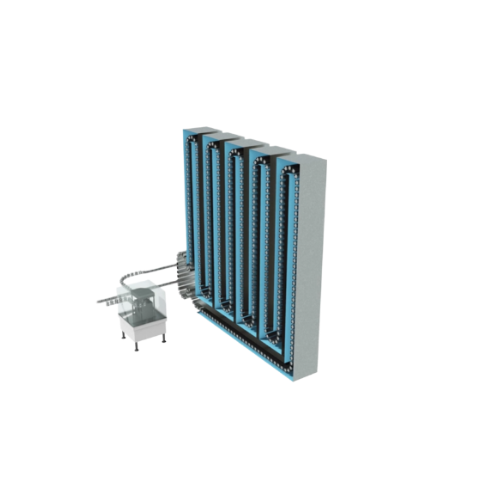
Hydrostatic sterilizer for continuous food processing
Maximize your production line’s efficiency with a continuous ...
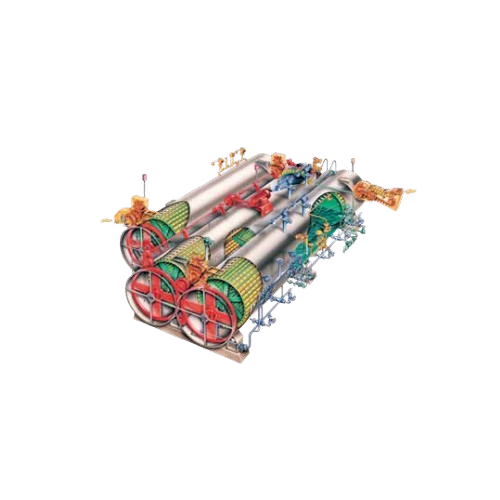
Gentle can handling ejector for rotary cooker
Achieve seamless can transfer and sterilization with reduced damage during h...

Steam water spray retort for shelf-stable food processing
Ensure uniform heat distribution and precision control in ster...
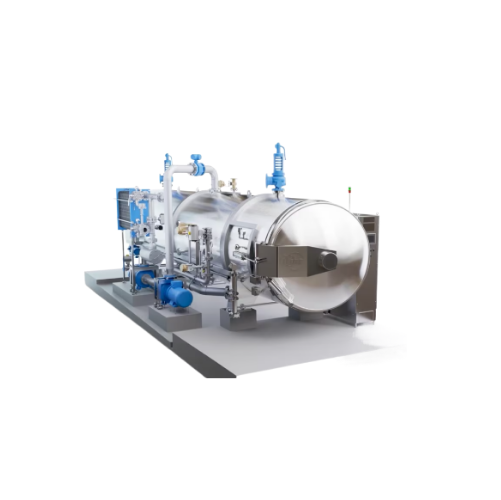
Industrial retort for food sterilization
Achieve uniform sterilization and cooling in your batch production processes while...
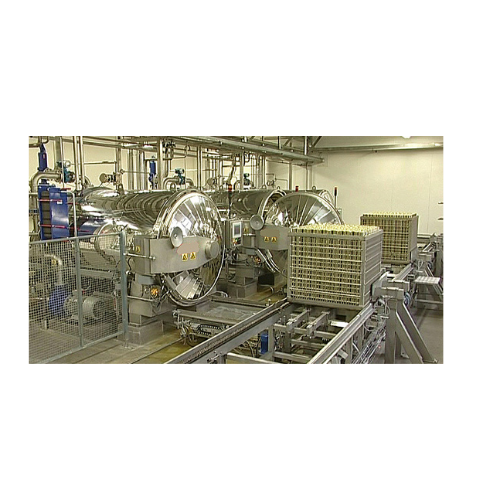
Automated batch retort system for food sterilization
Optimize your sterilization process with seamless transportation fro...
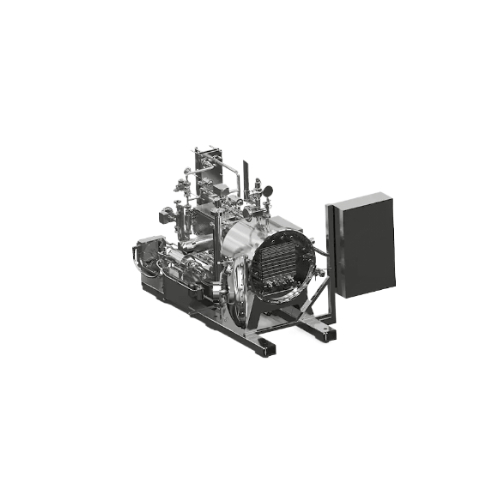
Efficient agitation system for retort packages
Enhance product quality and reduce processing time with this advanced agita...
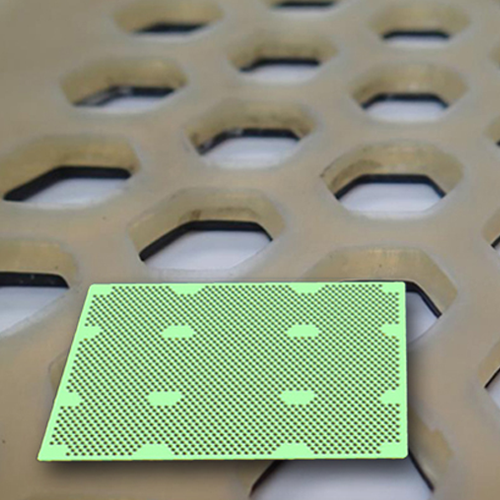
Layer pad for agitating retorts in food processing
Efficiently secure and process irregularly shaped containers in retort...
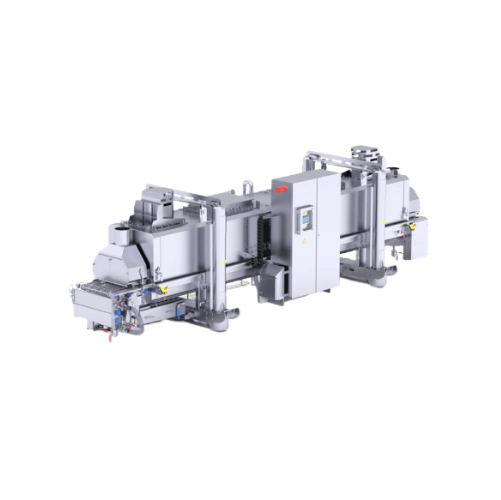
Linear convection oven for food processing
Achieve precise cooking and browning of diverse food products simultaneously wh...
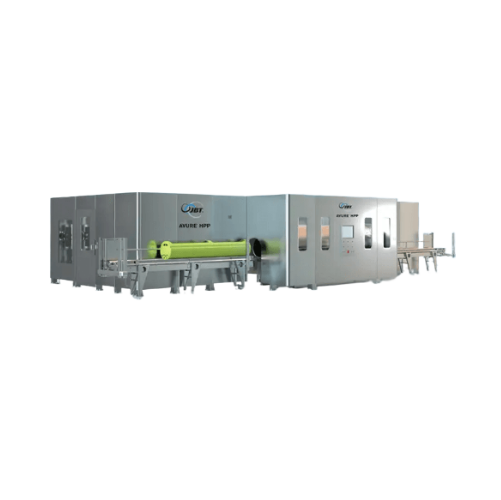
Expandable high pressure processing system
Optimize your production line with an expandable high-pressure processing syste...
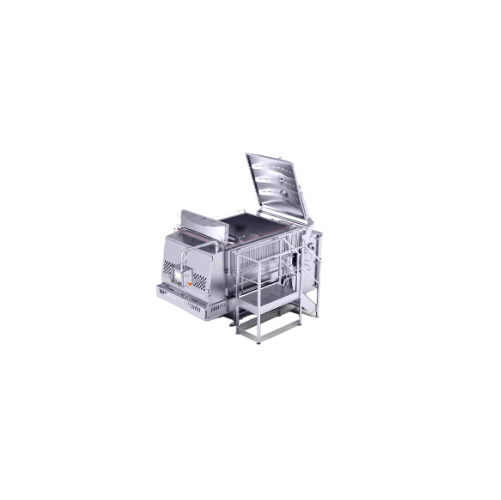
Double-shaft paddle mixer for homogeneous raw masses
Optimize your mixing efficiency with a dual-shaft system designed fo...
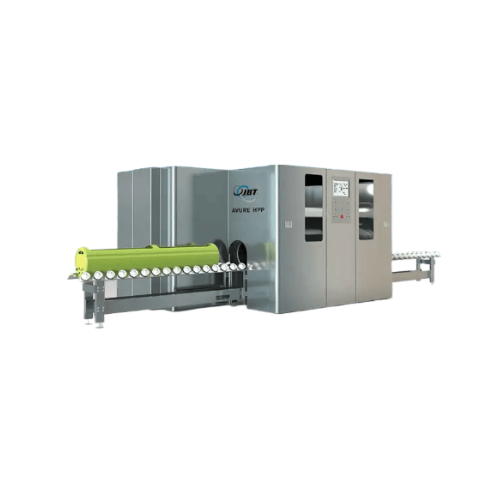
High pressure processing for diverse food products
Maximize production versatility and ensure product safety with a high-...
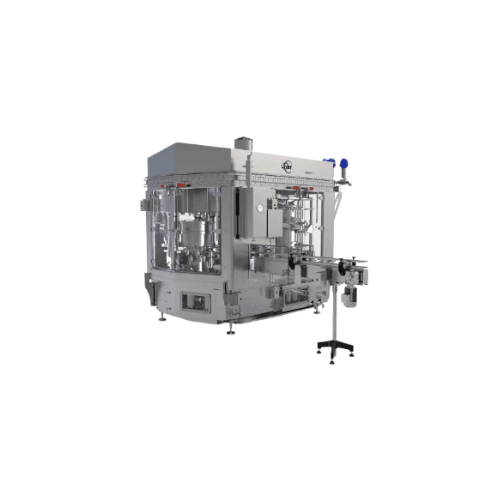
Rotary can filler and closer for metal cans
Achieve seamless integration in your production line with a solution that sinc...
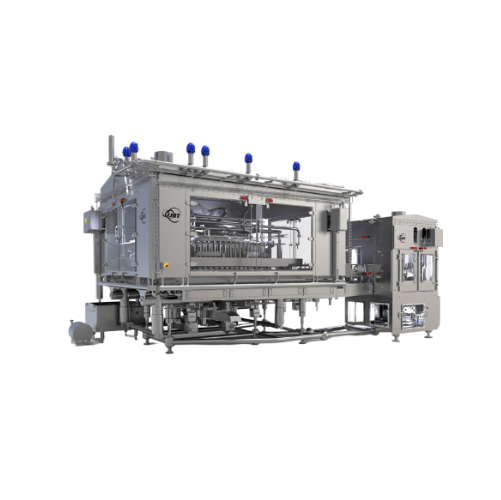
High capacity volumetric filler for pumpable products
When you need high-speed, precise filling for diverse liquid and sl...
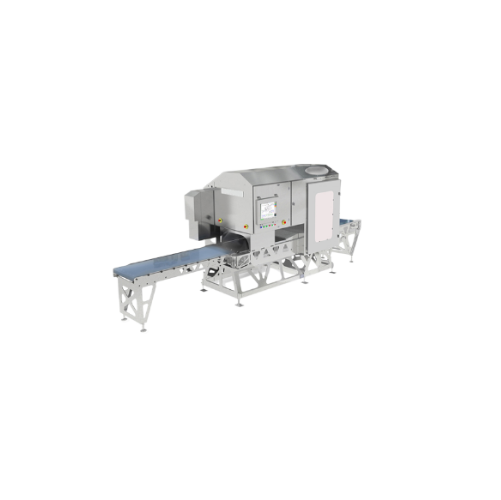
Portioning system for poultry, meat, and seafood
Achieve precise cuts and maximize yield with high-speed waterjet technolo...
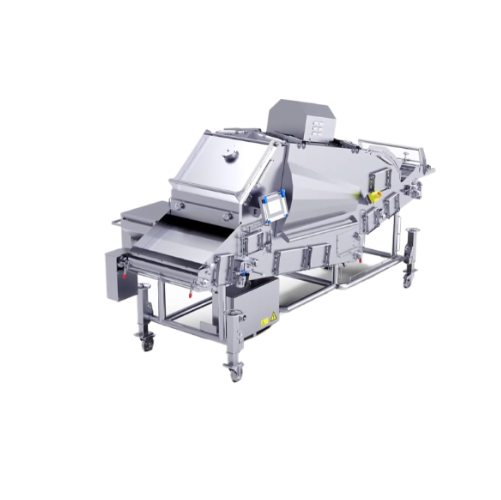
Home style drum breader for meat and poultry
Achieve consistent, high-quality breading on diverse food products with this ...

Preduster for fine-grain coating in food processing
Ensure your products receive a perfect, consistent fine-grain coating...

Automatic clipper for pre-tied casings
Streamline your casing process with a solution designed for efficient stuffing and c...
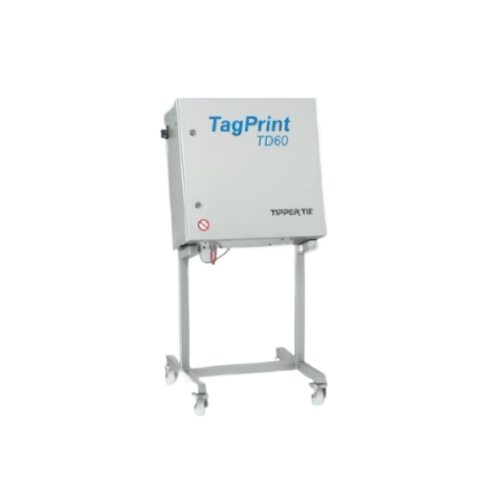
Industrial labeling system for precise product traceability
Enhance your production line with a state-of-the-art system ...
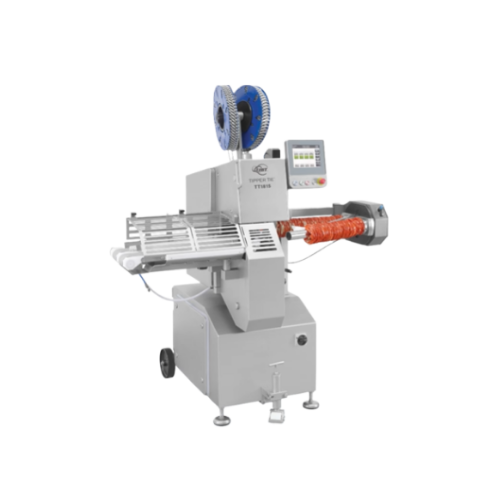
Automatic double clipper for sausage and food packaging
Streamline your packaging process with precision clipping technol...
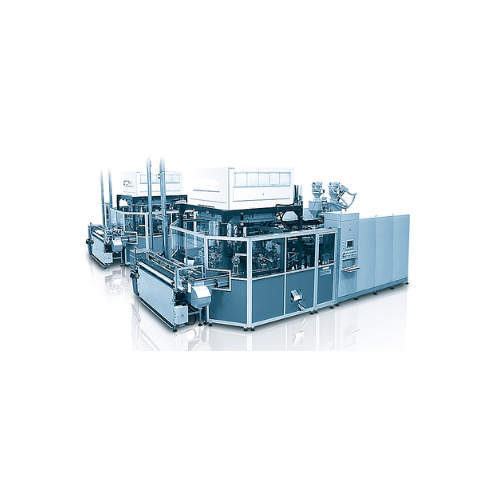
Extrusion blow molder for custom bottles
Enhance your production line by creating versatile and customized bottles with sea...
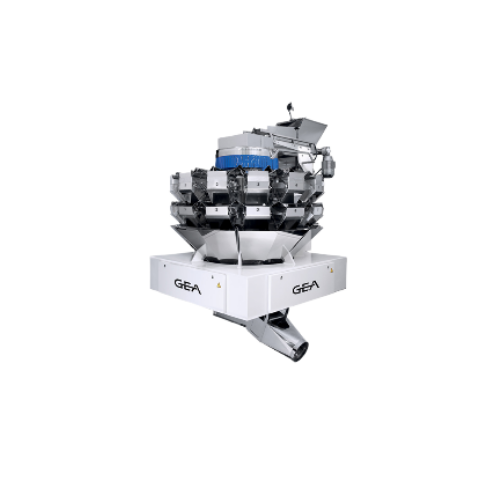
High precision multihead weigher for dry pasta
Enhance your production line’s efficiency with precise weighment and ...
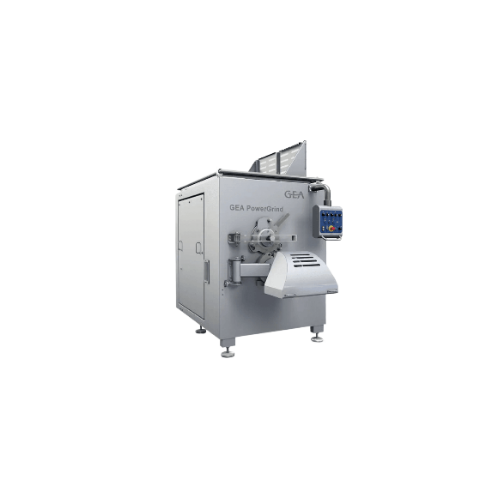
Industrial food grinder for meat and vegetables
Enhance your grinding process with a robust solution designed to efficient...
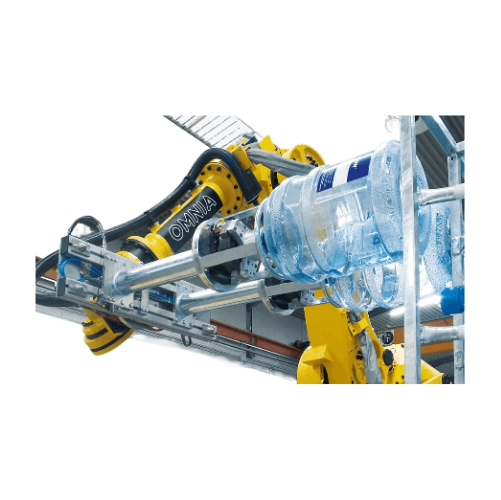
Robotic palletizer for food and beverage industries
Enhance your production line’s efficiency with a flexible robot...
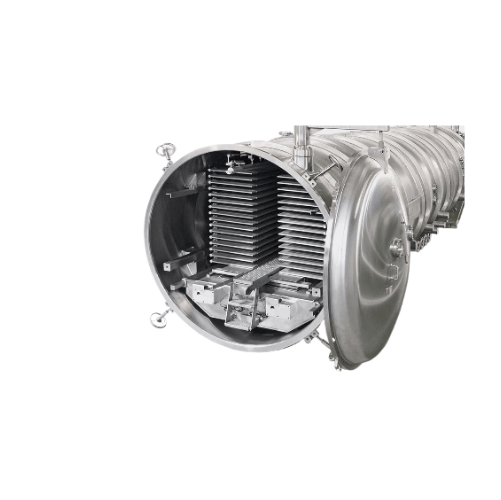
Batch freeze drying system for food and beverage preservation
Achieve precise and efficient preservation of your food an...
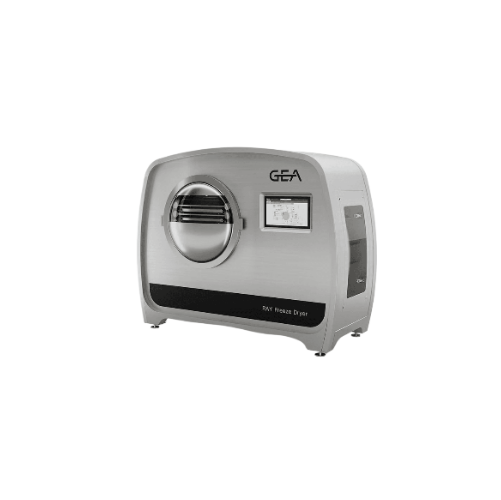
Pilot plant freeze dryer for sensitive products
Achieve precise moisture control and nutrient preservation in food and pha...
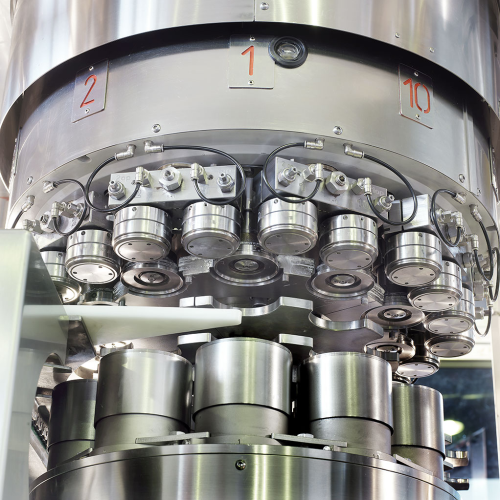
Automatic can seamers for food and beverage industry
Ensure airtight sealing of canned goods with precision seamers desig...
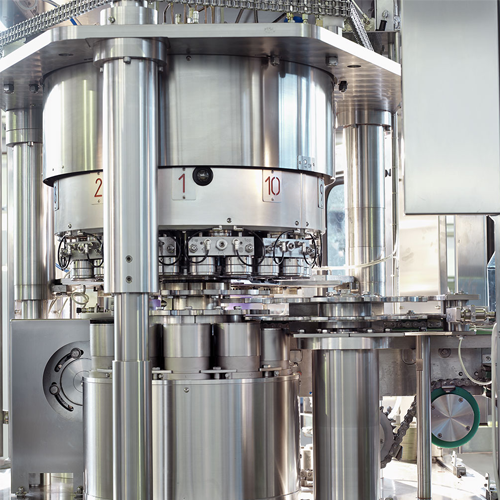
Seamers for round food containers
Ensure airtight sealing for food products with high-speed seamers designed for precision ...
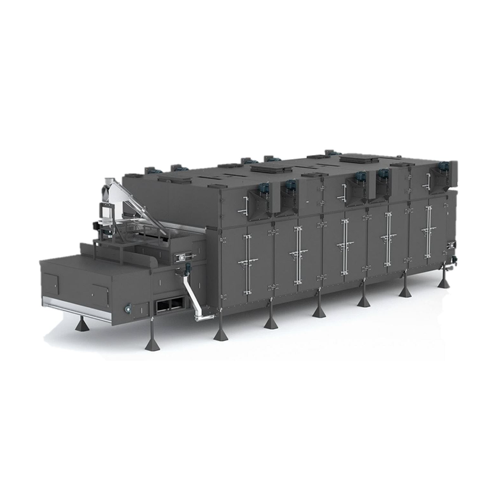
High capacity horizontal dryers and coolers for industrial applications
Achieve consistent moisture levels and uniformi...
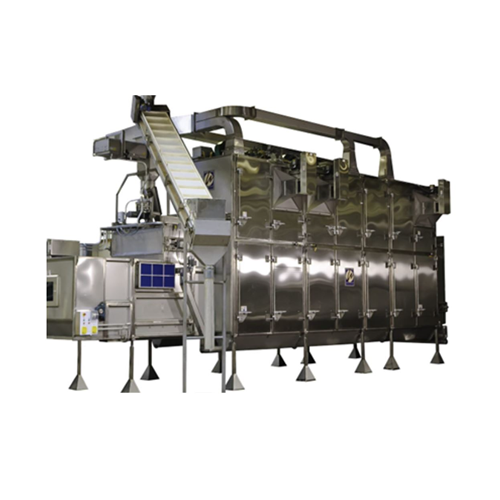
Sanitary dryers for textured vegetable proteins
Optimize drying and sanitation for textured vegetable proteins and pet foo...
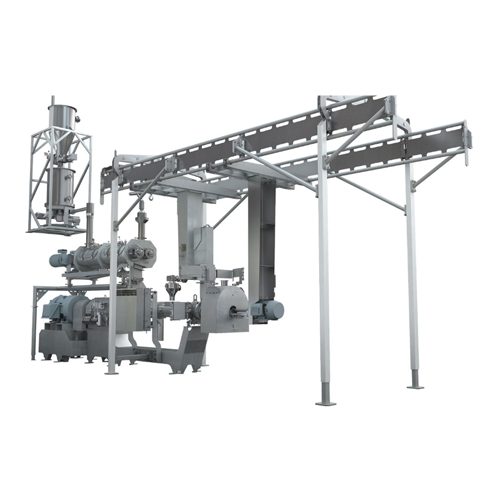
High-sme extruder for structured meat analogs
Enhance production versatility with precise extrusion control, accommodating...
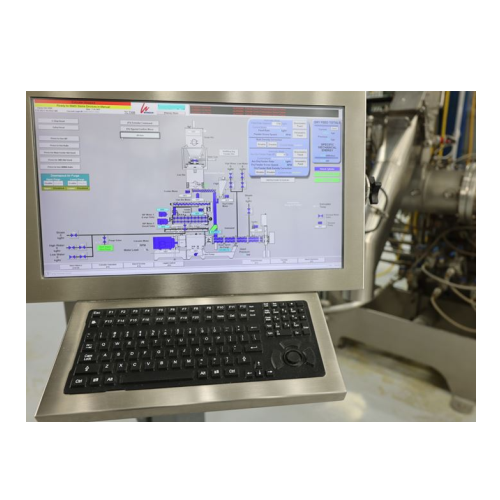
Automated process management system for industrial extrusion
Optimize your production line with precise control and moni...

High intensity preconditioner for textured vegetable proteins
Optimizing your production with precise moisture control a...
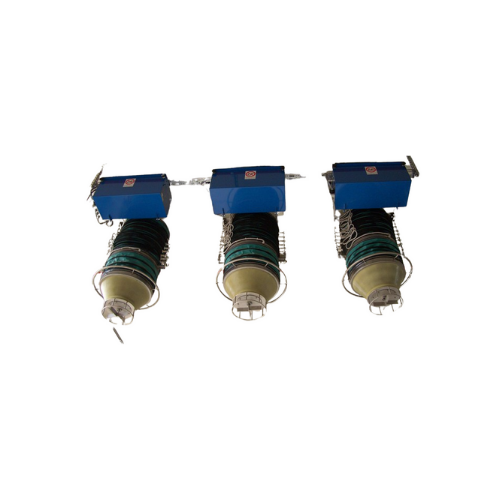
Tanker loading bellow for dust-free bulk solids loading
Optimize tanker loading while minimizing dust emissions with this...
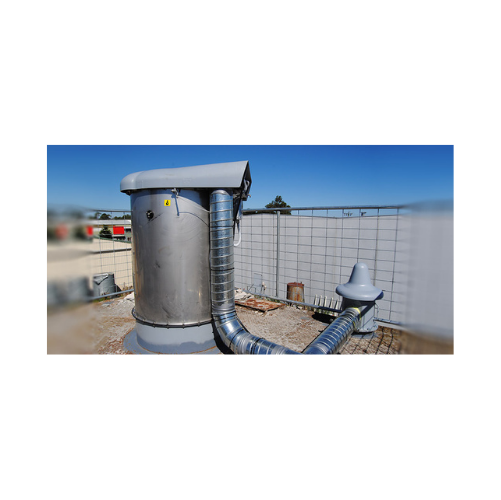
Low profile slide valve for controlling powder flow
Optimize your powder and granule flow management with precision-engin...
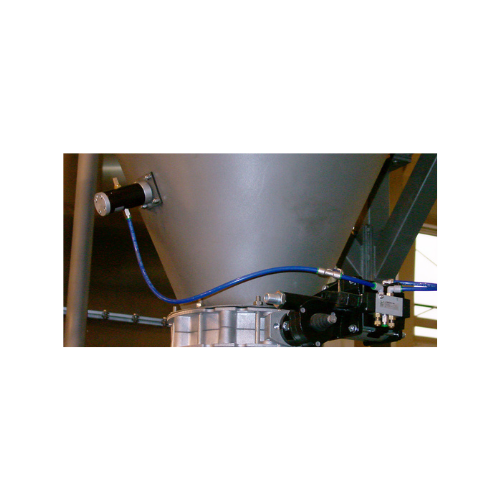
Cushioned pneumatic linear vibrators for bulk solids
Combat material bridging and rat-holing with silent vibratory techno...

Tapered twin shaft screw feeders for bulk solids
Ensure consistent flow and avoid material bridging challenges with a solu...
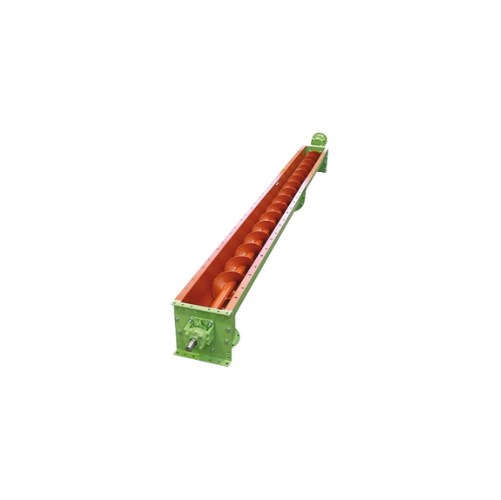
Trough screw conveyors for powdery and granular materials
Optimize your material handling process with a flexible screw ...
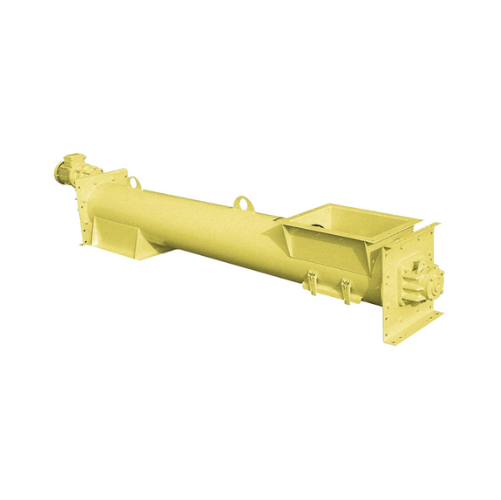
Tubular trough screw conveyors for gentle powder and granular material handling
Achieve precise powder and granular ma...
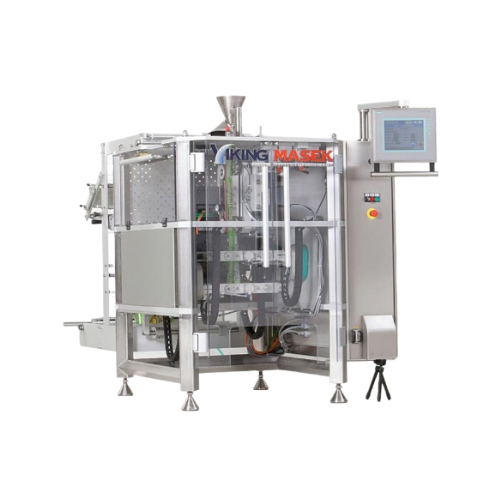
High-speed vertical form fill seal packaging machine
Optimize your packaging line with this high-speed vertical form fill...
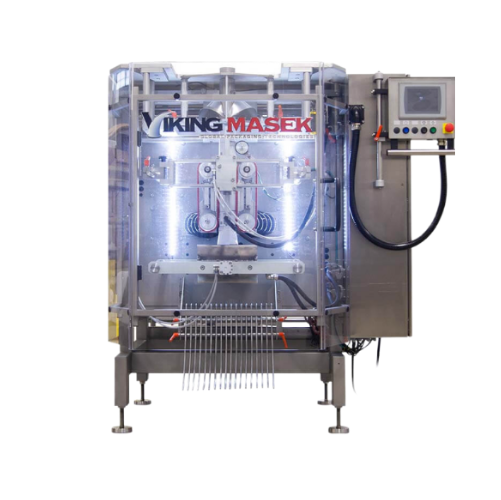
Vertical form fill seal for dusty and liquid products
Optimize your packaging line with a versatile solution designed to ...
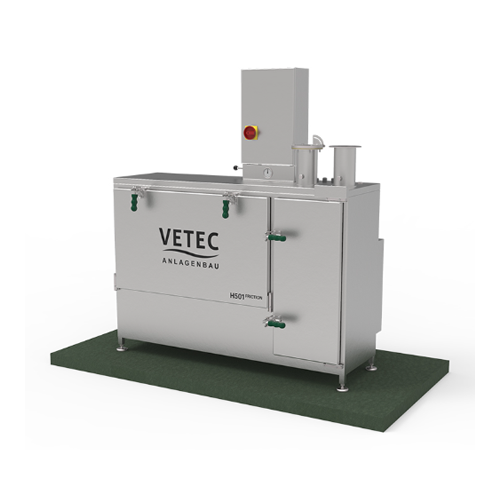
Friction smoke generator for hot smoking and climatic maturing
Optimize your production with a friction smoke generator ...
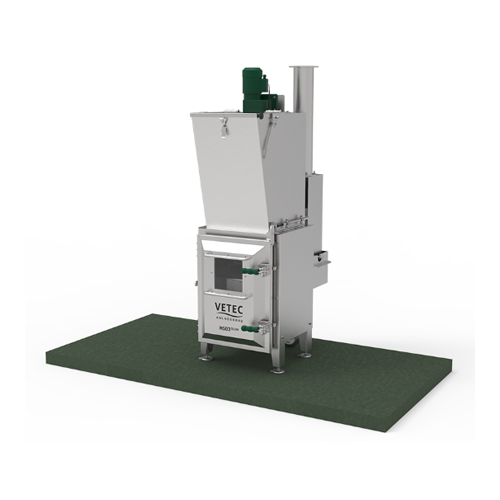
Closed glow smoke generator for hot smoking installations
Enhance your smoking process with efficient energy use and sea...
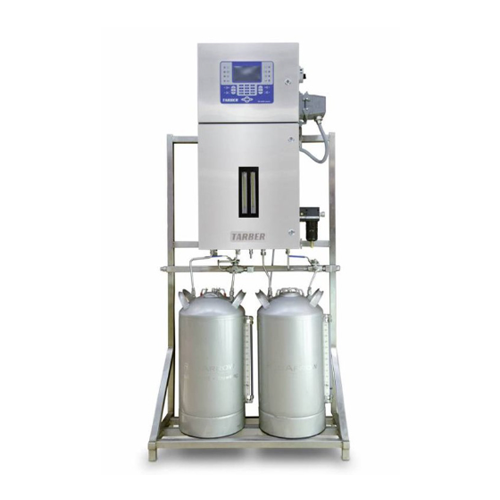
Liquid smoke system for meat and seafood processing
Achieve uniform smoking results across diverse products by employing ...
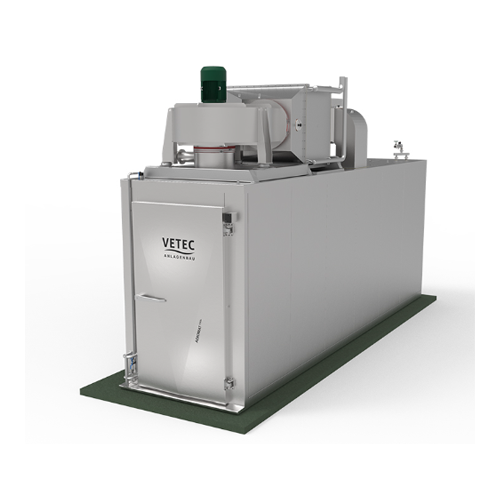
Dual-method cooling system for sausage and meat products
Achieve optimal freshness, flavor, and shelf life for your meat ...
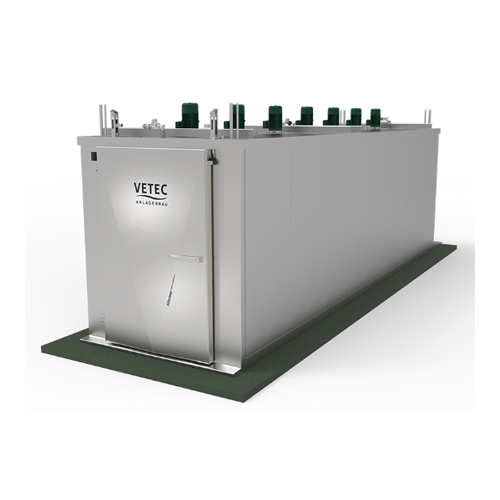
Industrial food cooling system
Achieve precise core temperatures and optimized shelf life with rapid cooling for diverse foo...

Horizontal air flow drying and smoking system for meat products
Achieve superior drying and smoking efficiency with hori...
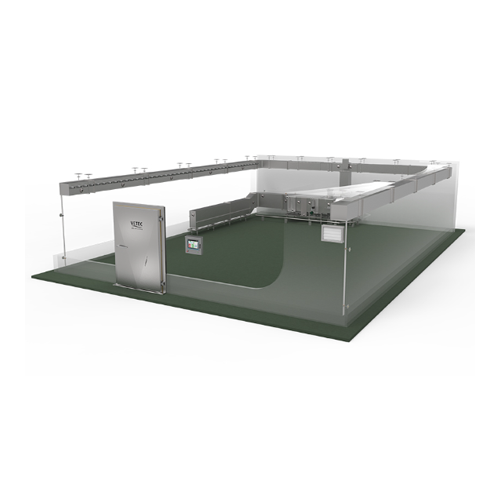
Air-conditioned storage chambers for post-curing
Ensure consistent product quality with precise humidity control, essentia...
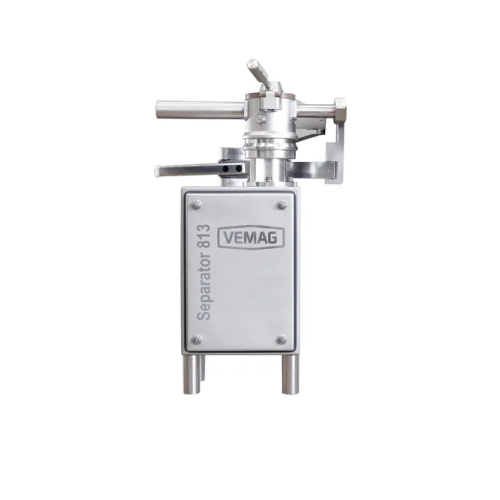
Grinding and separating solution for meat processing
Optimize your meat and plant-based production lines by integrating a...
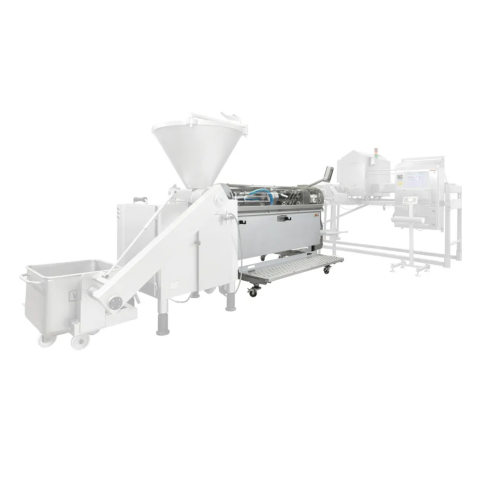
Linking, hanging, and cutting system for sausage production
Streamline your sausage production process with precision-en...
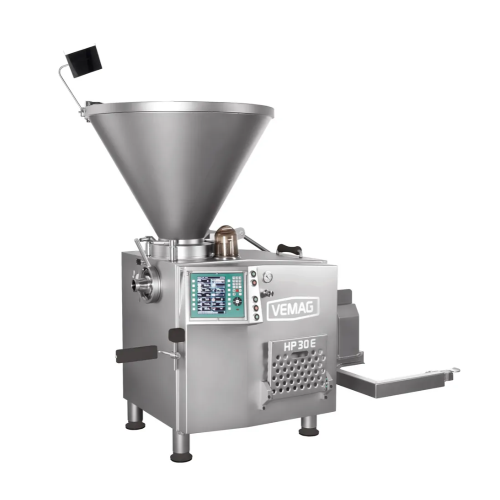
Vacuum filling machines for cooked ham & sausages
Achieve precise portioning and enhanced product quality with this advan...
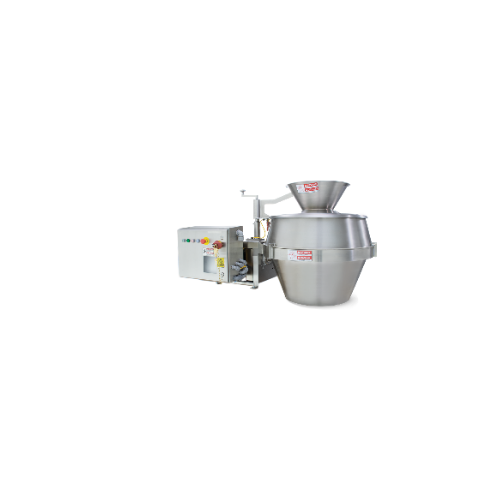
High capacity shredder, slicer, and strip cutter
Optimize your production line with advanced cutting versatility, handling...
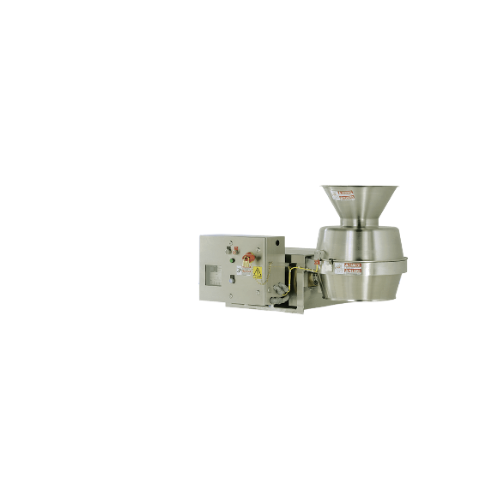
Industrial cheese shredder
Optimize continuous food processing with a machine that handles high-speed shredding, slicing, cu...
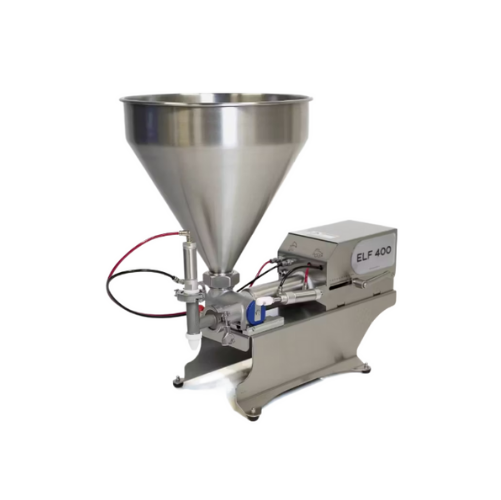
Single piston food filler
Achieve precise portioning and consistent product flow with a versatile solution perfect for handl...
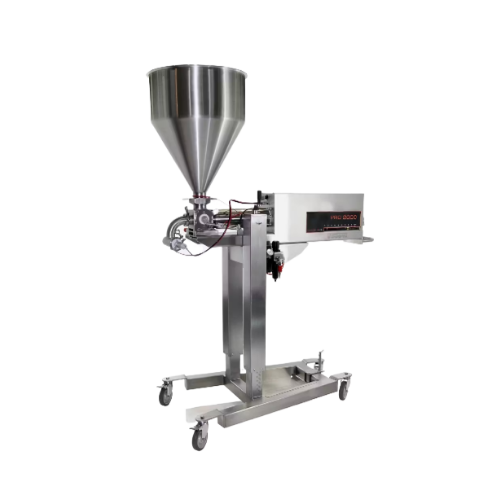
Single piston depositors for bakery and food production
Optimize your depositing and filling processes with versatile equ...
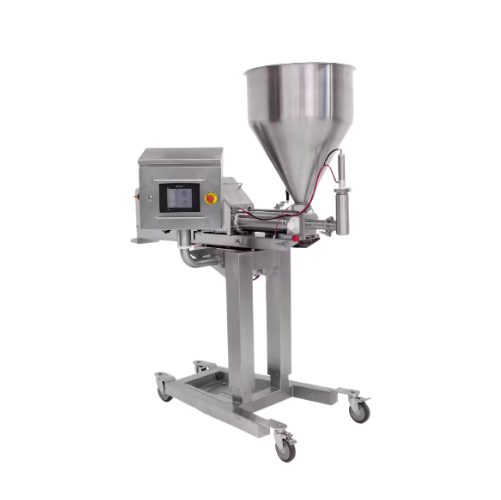
Industrial depositor for automated recipe management
Effortlessly streamline your production with precise depositing cont...
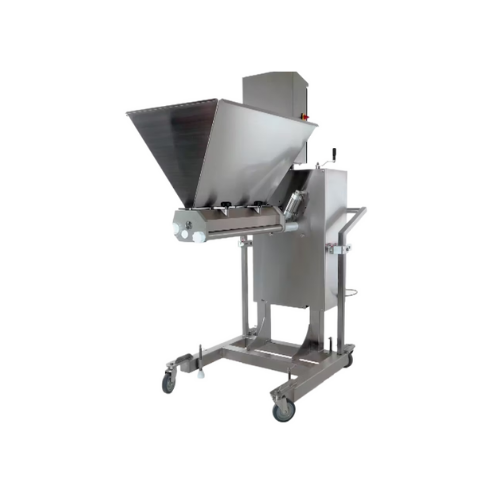
High speed pneumatic depositor for bakery applications
When depositing batters, creams, and sauces, achieving consistent ...
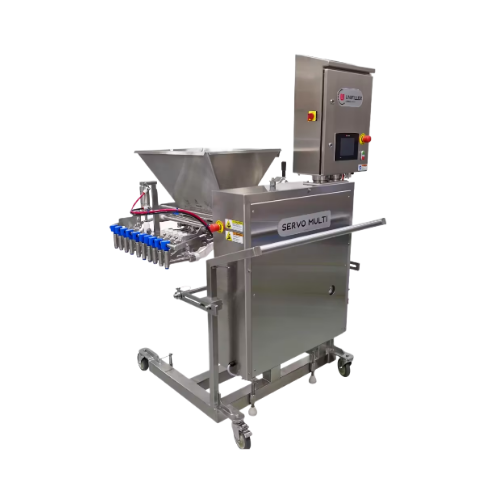
Servo multi food portioner
Achieve precise portion control and high-speed depositing for diverse applications with this adva...
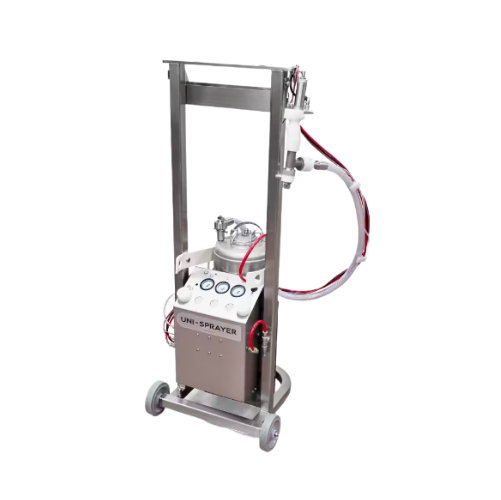
Food spraying and flocking system for bakery applications
Enhance your production line with precision spraying and flock...
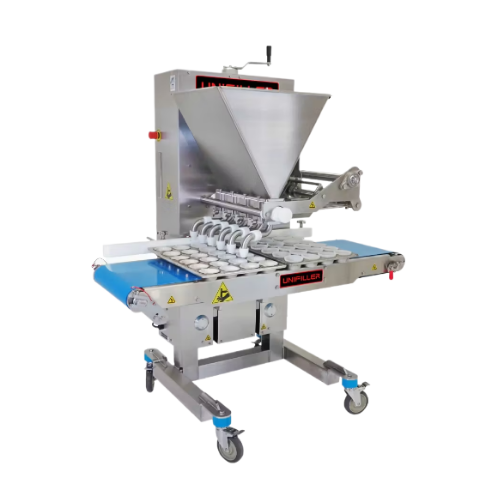
Multi piston depositors for bakery production
For bakeries seeking precision in depositing and filling, these multi piston...

Multi piston depositors for high-volume baking production
Optimize your high-speed production line with precision deposi...
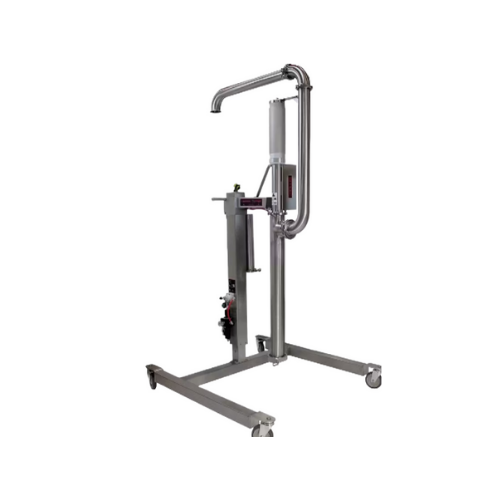
Food transfer and dosing pumps for bakeries
Enhance efficiency in food processing with pumps designed for precise transfer...
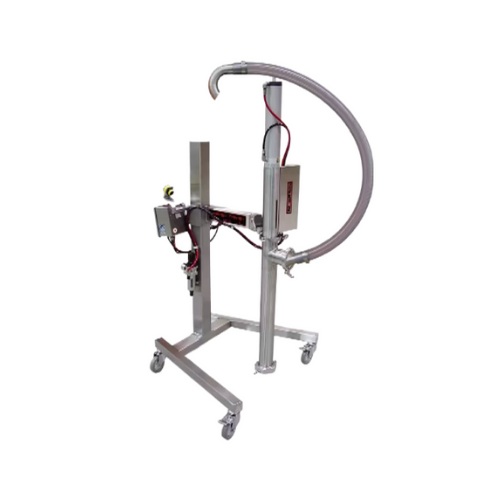
Food grade transfer pump for semi-solid products
Streamline your production with a high-speed transfer pump designed for s...
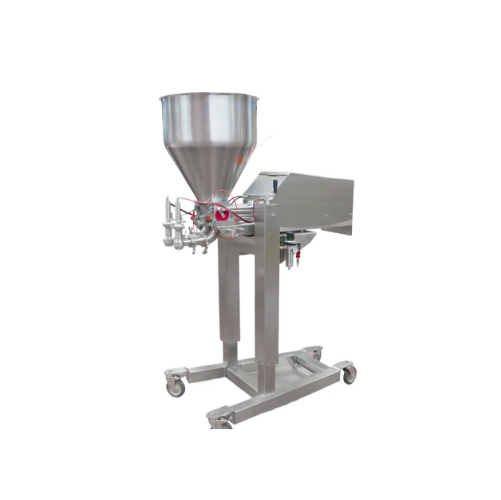
Dual or triple lane food depositor
Enhance your production efficiency with a depositor that seamlessly handles a variety of...
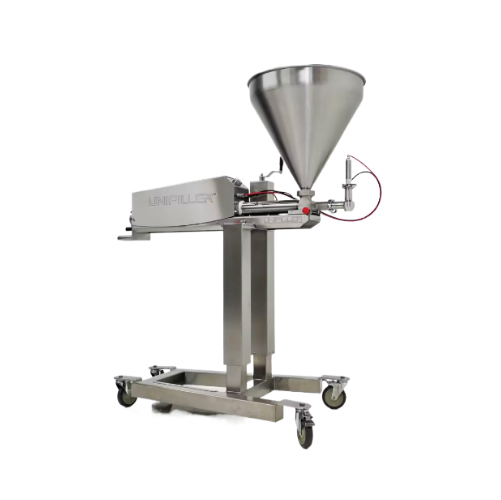
Food depositor for large chunk applications
Need precise depositing of chunky food products like stew or salsa? This versa...
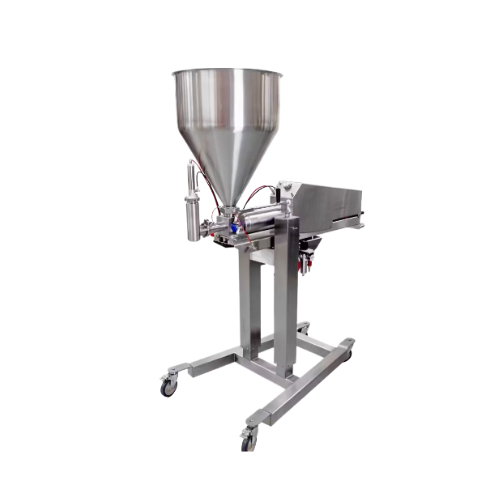
Large portion depositor for food production
Achieve precision and efficiency in depositing large portions with versatile s...
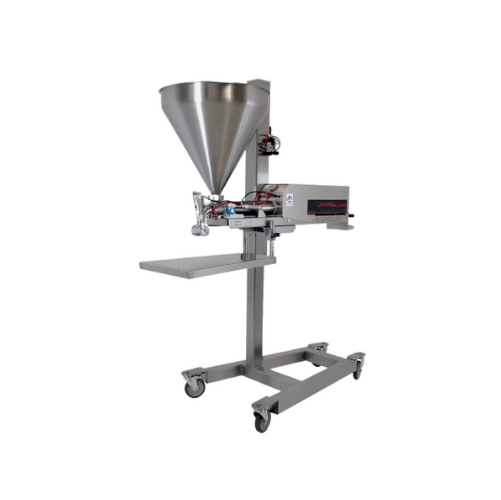
Bakery batter depositor for efficient, consistent depositing
Enhance your bakery production with precision depositing fo...
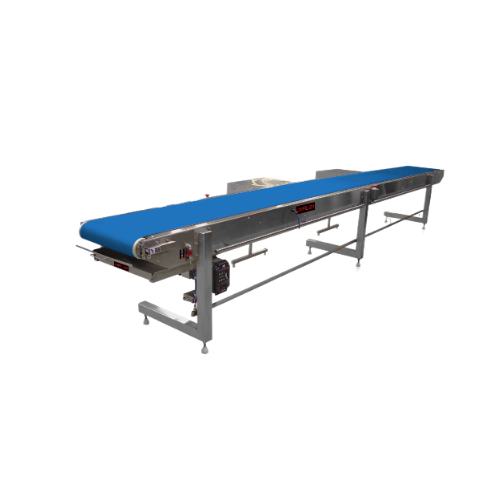
Bakery and food grade conveyor systems
Optimize your bakery and food production with versatile conveyors designed for seaml...
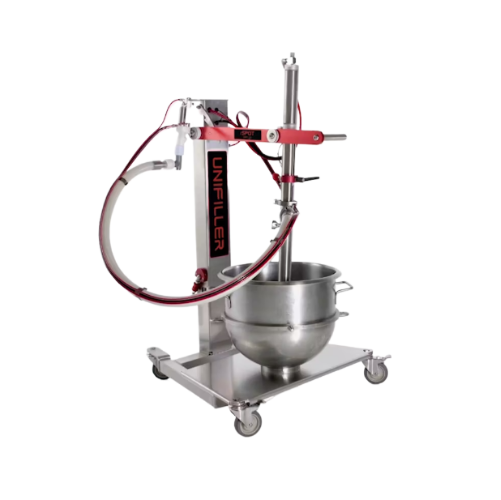
Compact food depositor for direct container use
Streamline your depositing process with a versatile solution that handles ...
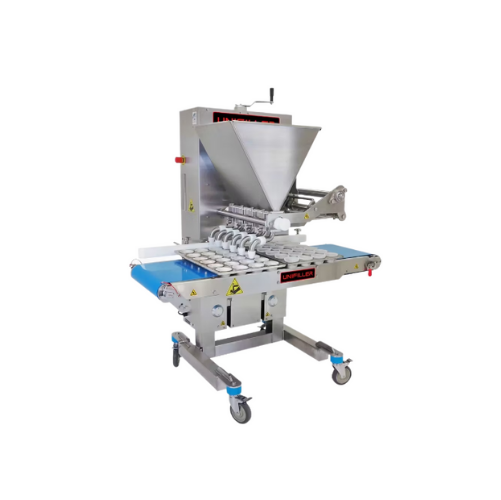
High-speed piston depositor for food applications
Achieve precise portioning and rapid depositing of diverse food product...
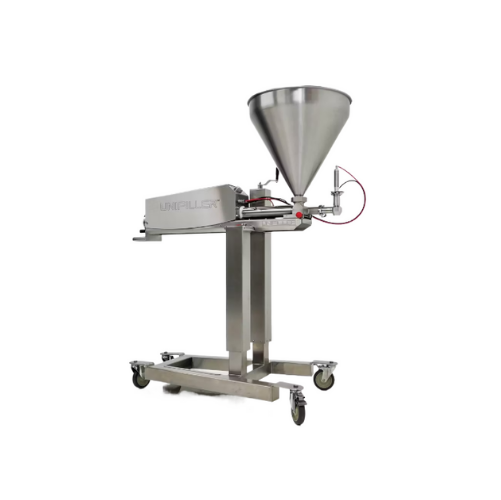
Industrial food filler for precise depositing over conveyors
Optimize your food production line with a versatile filler ...
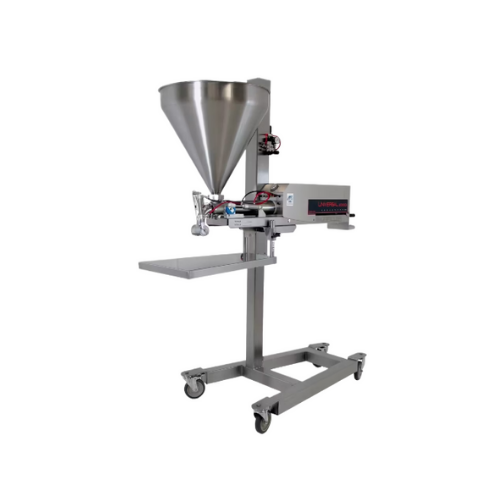
Single piston food depositor
Achieve precise portion control for diverse food products, from soups to chunky fillings, with ...
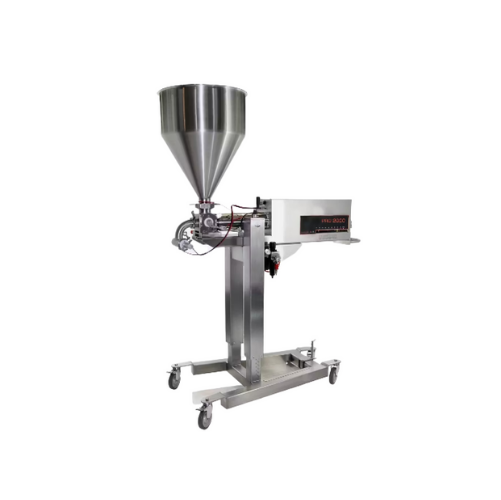
Automated production lines for cakes and cupcakes
Streamline your bakery’s production line with a versatile automat...
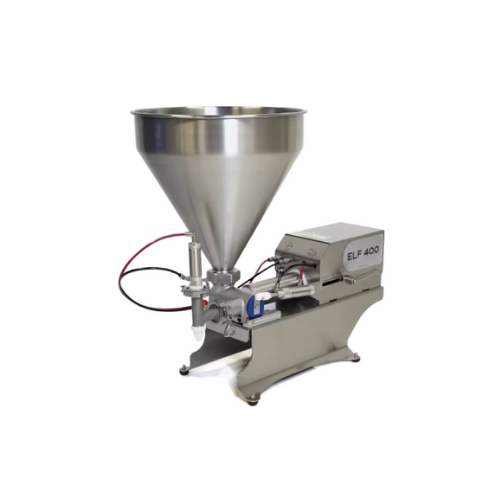
Tabletop food depositor for portion control
Streamline your food production with precise portion control, reducing waste a...
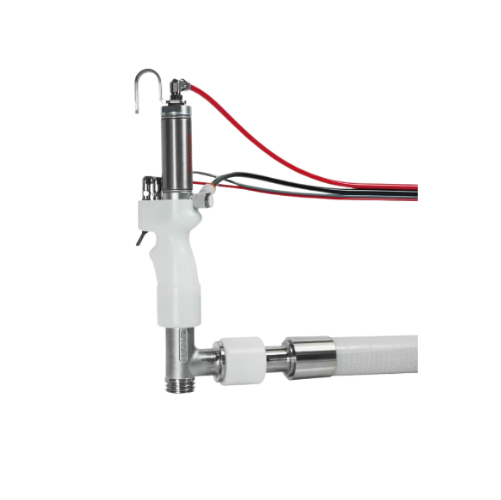
Semi-automated depositor with handheld nozzle
Maintain portion precision and reduce ingredient waste with a versatile depo...
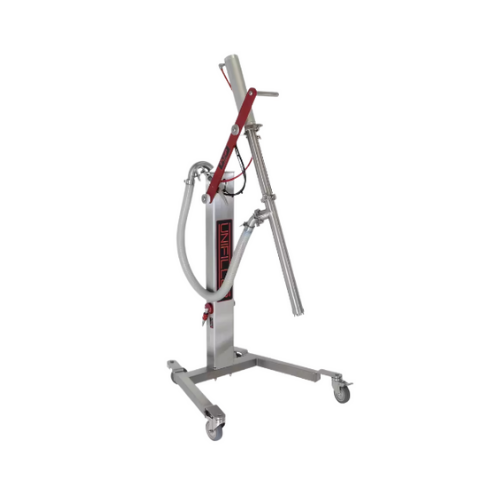
Compact food transfer pump
Effortlessly maintain your production flow with a compact transfer pump designed to handle a wide...
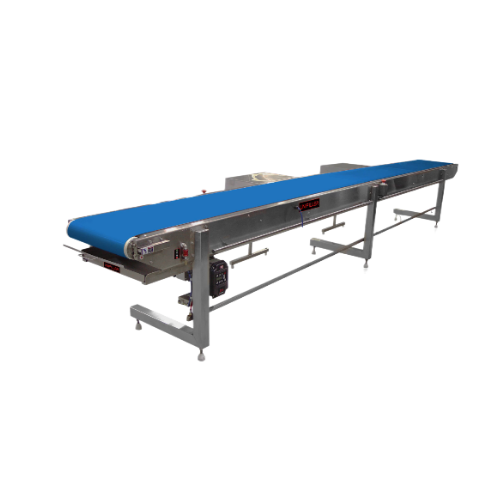
Bakery and food grade conveyors
Enhance your bakery and food production with conveyors designed to seamlessly transport and ...
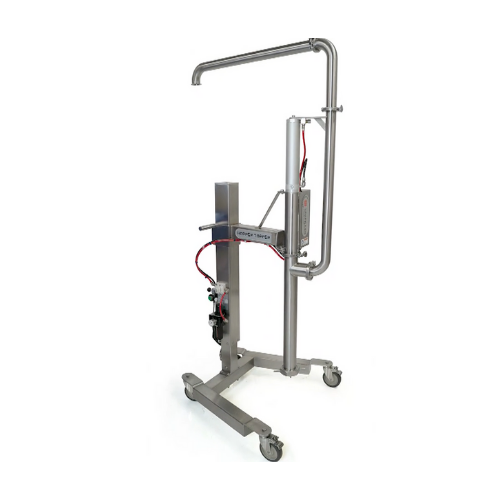
Bakery transfer pump for smooth and chunky products
Ensure consistent product quality with this transfer pump that gently...
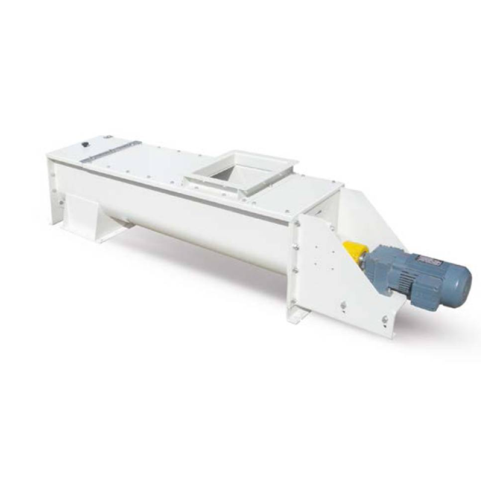
Screw conveyor for grain or finished products
Optimize your production line with a space-efficient screw conveyor designed...
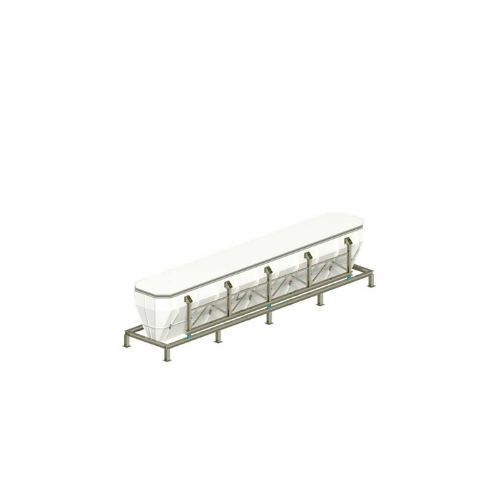
Dosing scale for accurate raw material weighing in feed recipes
Ensure precise feed formulation by weighing raw material...
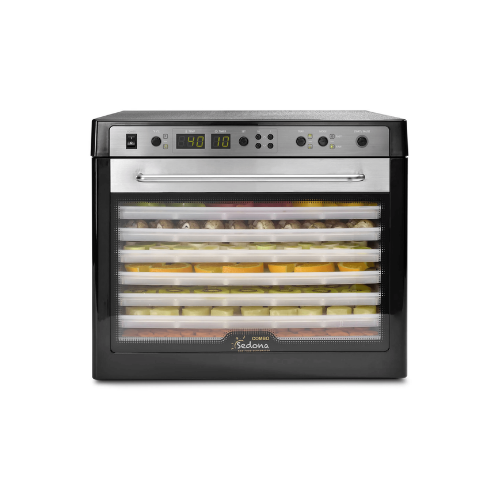
Food dehydrator with Bpa-free plastic trays
Achieve precise dehydration for fruits, vegetables, and snacks with advanced t...
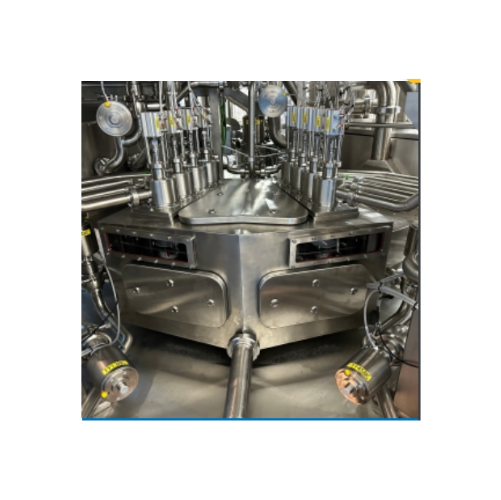
In-line filling and closing system for pre-formed containers
Looking to enhance production efficiency with a solution th...

Aseptic rotary cup filling and closing solution
Maximize your production capacity with this cutting-edge aseptic solution,...
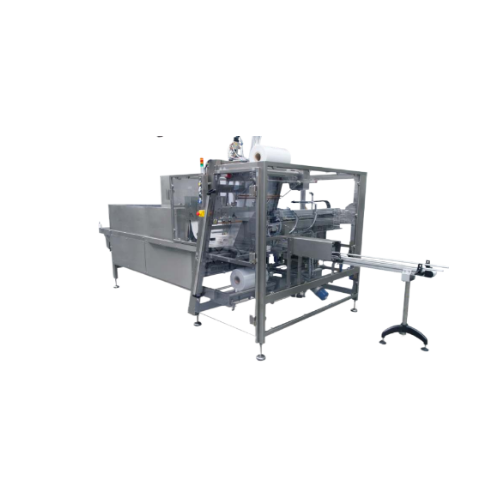
Industrial shrink wrapping solution
Optimize your packaging line with a robust shrink wrapping solution, efficiently accomm...
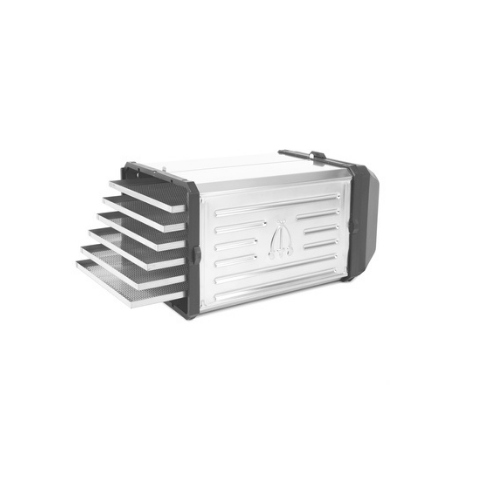
Professional food dehydrator for fruits and vegetables
Enhance your culinary creations with precise dehydration technolog...
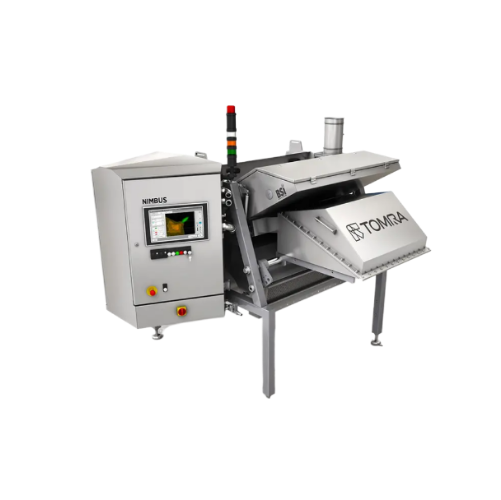
Food sorting system for nuts and dried fruit
Streamline sorting processes by removing visual irregularities, defects, and ...
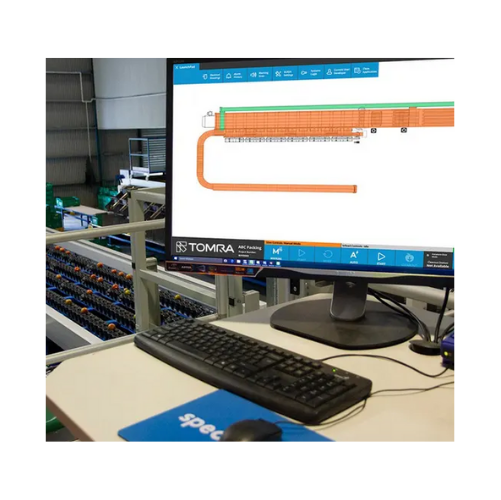
Line control and product tracking systems for post-harvesting
Optimize your production line with precision control and r...
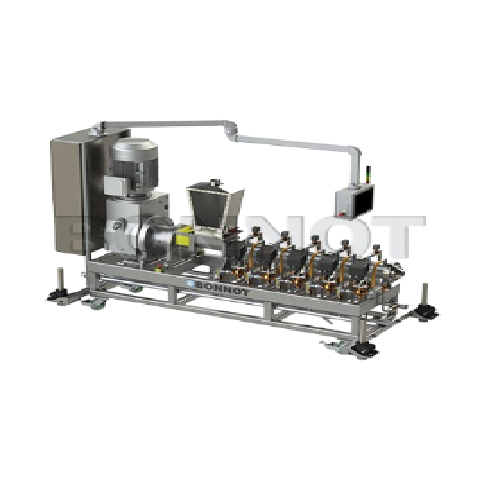
Cooking extruders for continuous food processing
Optimize your extrusion processes with cooking extruders designed for con...
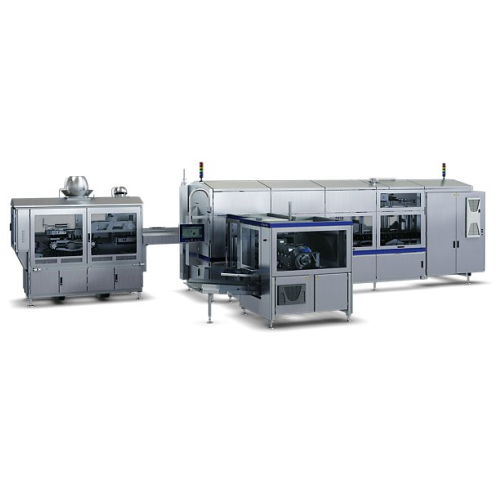
High-speed form and seal machine for retortable food packages
Streamline your production with a machine engineered for h...
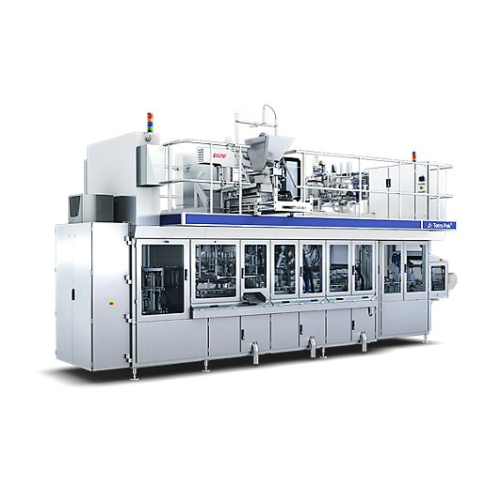
Compact filling system for retortable carton packages
Simplify your production of ready meals and soups with a space-savi...

Volumetric piston fillers for dense liquid products
Ensure precise filling of liquids and dense products with versatile i...
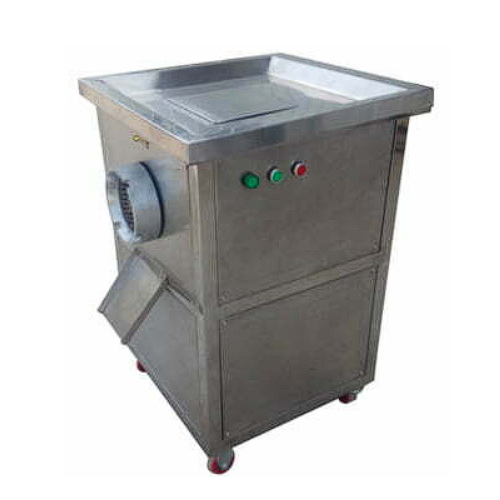
Commercial meat bone grinder for whole chicken & fish
Effortlessly transform whole chickens and fish into finely minced p...
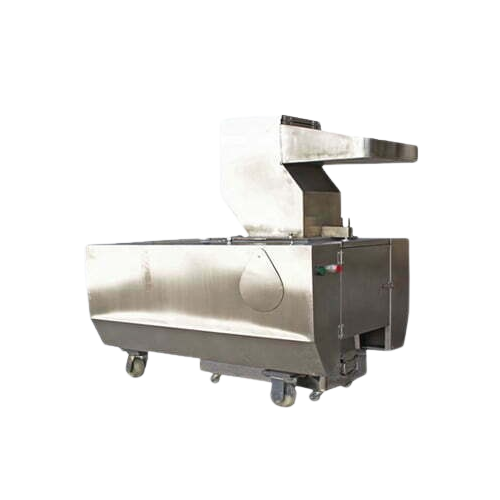
Industrial animal bone crushing solution
Efficiently transform hard animal bones into fine granular materials, enhancing nu...
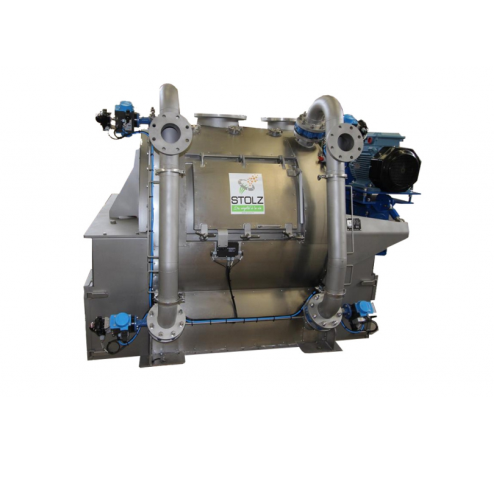
Vacuum coater for petfood and livestock feed
Enhance nutritional value and product quality with precision liquid incorpora...
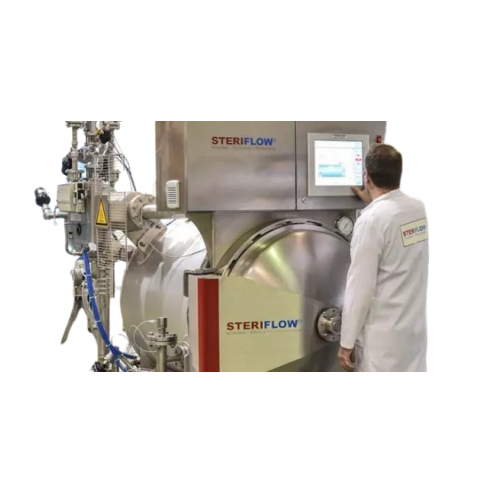
Laboratory pilot sterilizers for food packaging
Optimize your R&D with precise sterilization and heat treatment capab...
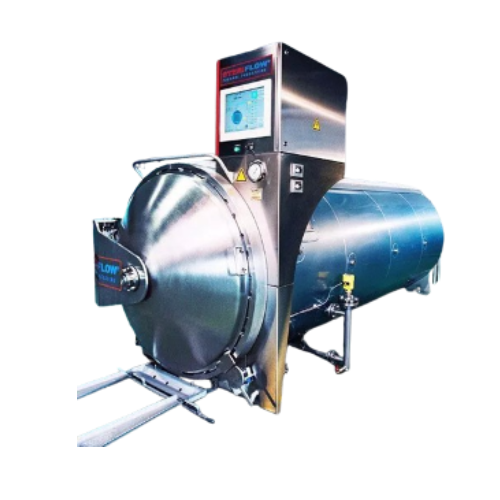
Cascading water autoclave for food sterilization
Streamline your food sterilization process with an energy-efficient autoc...
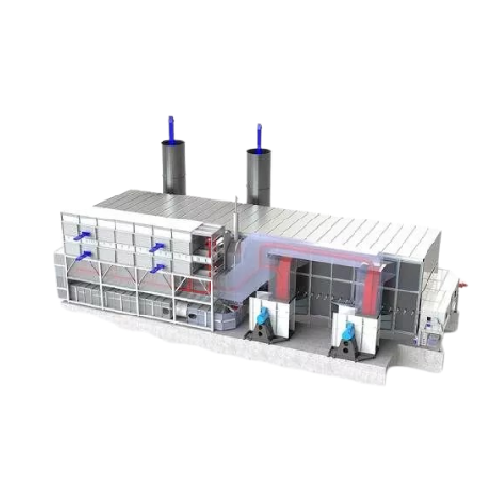
Low-emission belt dryer for timber industry
Achieve maximum drying efficiency and significant energy savings in your proce...
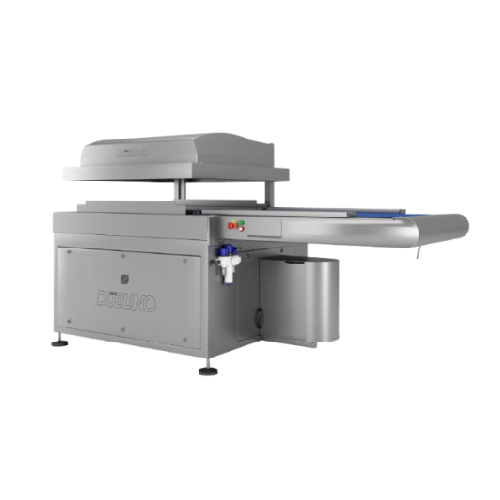
Mid-size belt-chamber vacuum packaging for smallgoods and seafoods
Optimize your packaging line with efficient mid-spee...

Scraped surface heat exchangers for high viscosity products
Ideal for continuous processing, these heat exchangers effic...
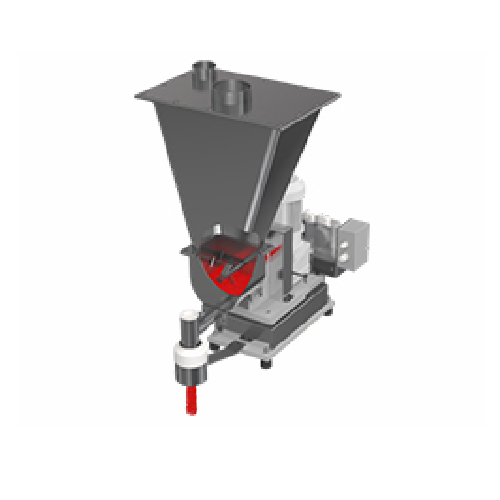
Single screw batch feeder with stirring agitator for powders and pellets
Ensure precise ingredient control and consiste...
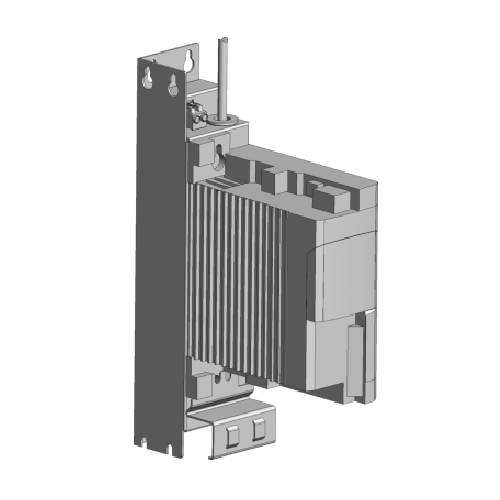
Speed controller for feeders
Ensure precise material flow by integrating this speed controller, ideal for managing both volu...
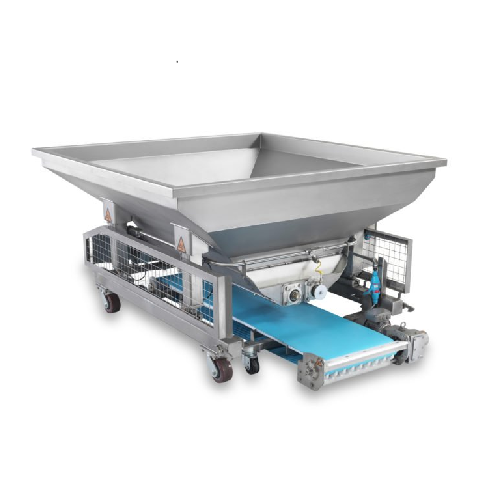
Dough chunkers for bakery production
Optimize dough processing by efficiently feeding and dividing dough portions, ensuring...
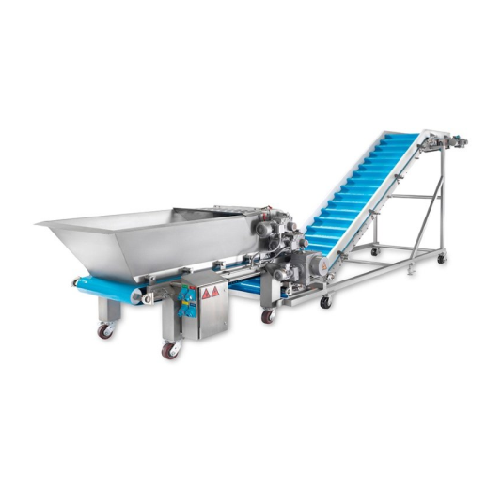
Dough kibbler for bakery production
Effortlessly transform large batches of dense dough into uniform, manageable pieces wit...
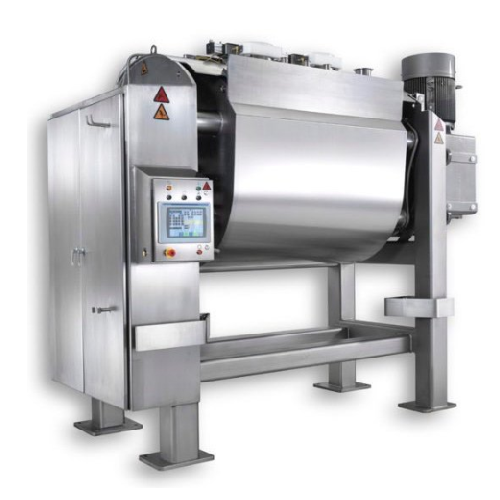
Single sigma arm bakery mixer
Streamline complex mixing tasks with precision using a mixer designed for optimal batch contro...
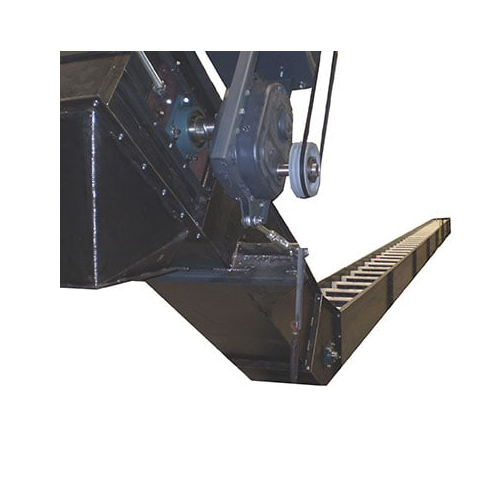
Grain unloading conveyor for ground level use
Efficiently unload bulk materials at ground level while minimizing dust and ...
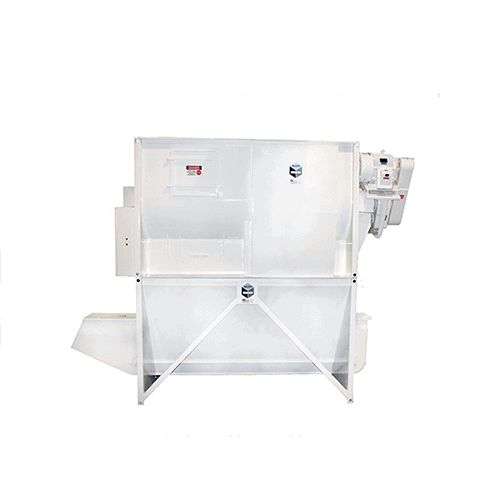
Surge hoppers for efficient batch mixing
Streamline your production with surge hoppers engineered to reduce batch cycle tim...
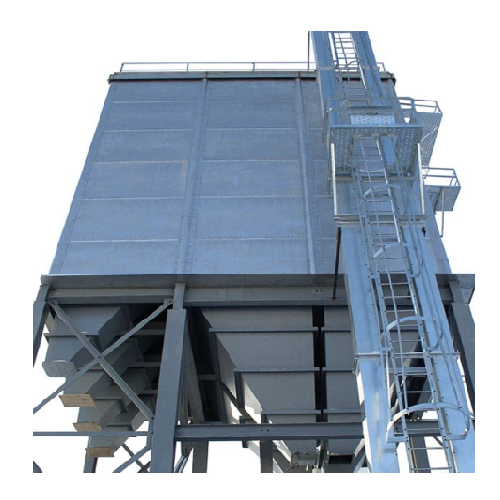
Modular bulk storage bins for efficient material handling
Maximize your storage efficiency with bolt-together solutions ...
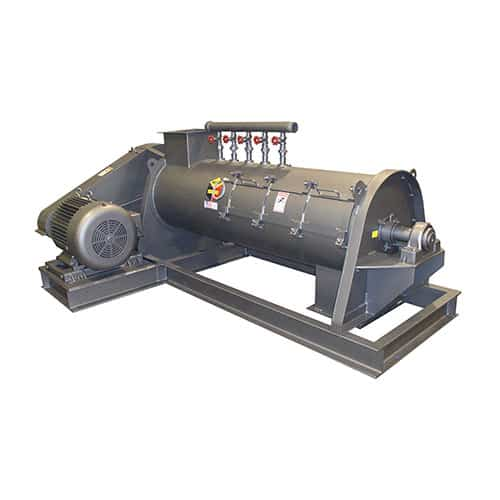
Industrial high-speed turbo blender
Achieve homogeneous blending with high-speed precision, ideal for creating fine product...
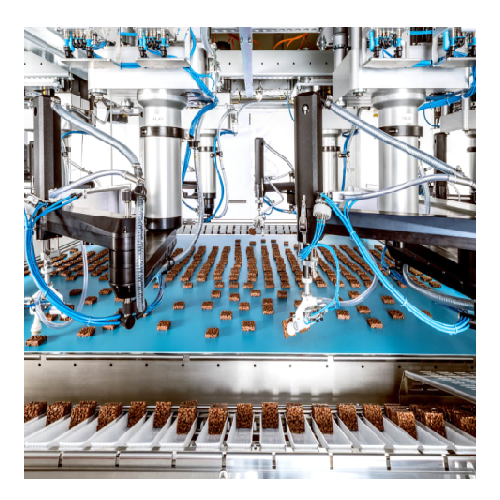
Pick and place robots for efficient product handling
Enhance your production line with high-speed pick and place robots c...
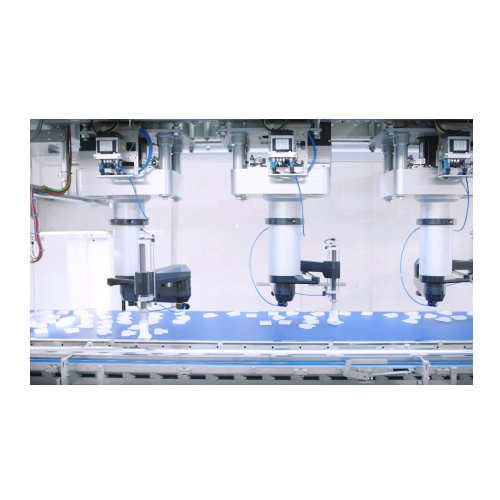
Compact carton packing solution for standardized tasks
Streamline your packaging workflow with a preconfigured solution d...
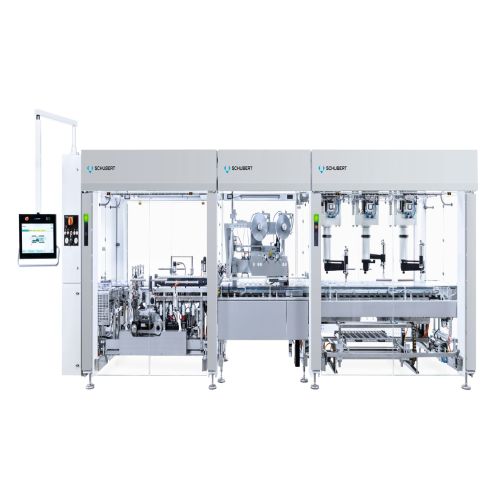
Flowpacker for packaging products in flowpacks
Optimize your flowpack packaging line with a preconfigured solution that ac...
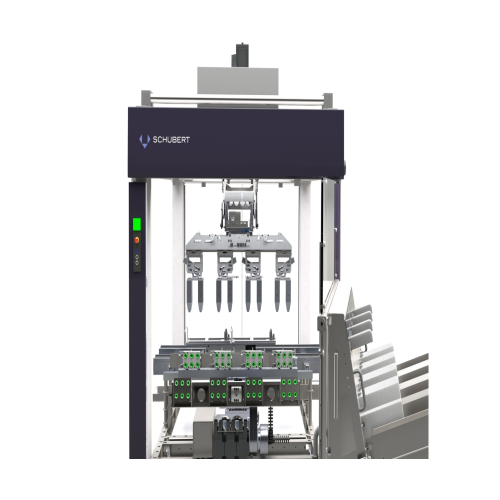
Modular packaging systems for diverse industries
Effortlessly adapt to market demands with versatile packaging systems, de...
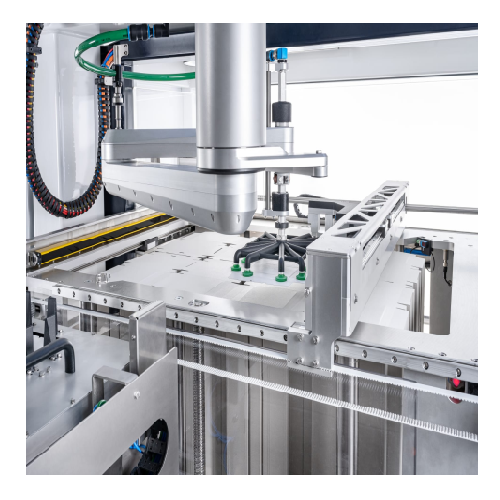
Compact carton blank feeding system
Maximize your production efficiency with a solution designed to streamline carton blank...
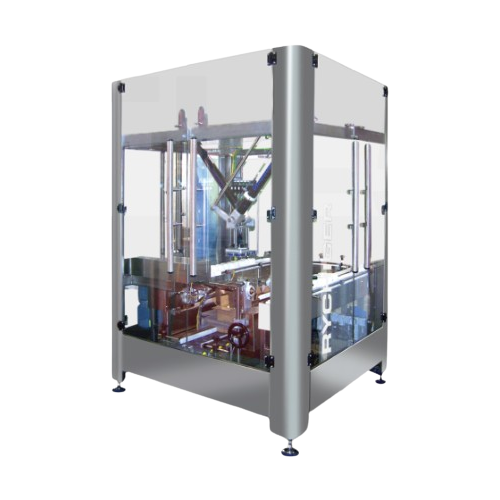
Top-loading delta robot automation solution
For high-speed operations requiring precise product handling, this top-loading...
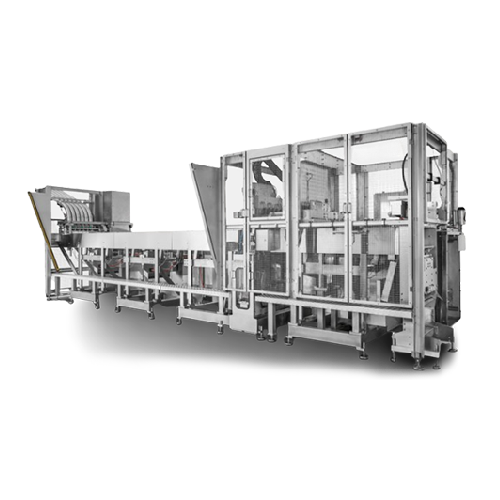
Filling system for solids, pastes, and liquids
Eliminate contamination risks while achieving high-speed, precise filling o...
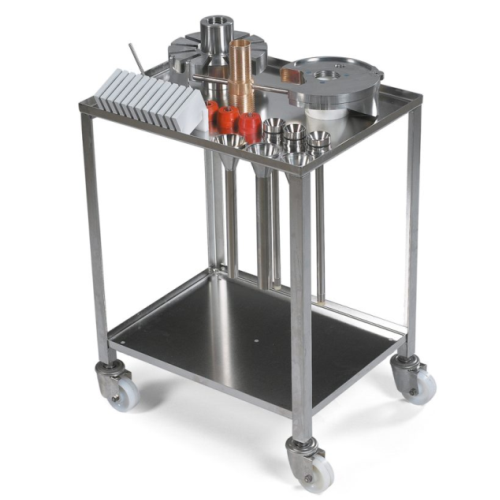
Organized component storage for vacuum fillers
Prevent equipment damage and streamline cleaning operations with a storage ...
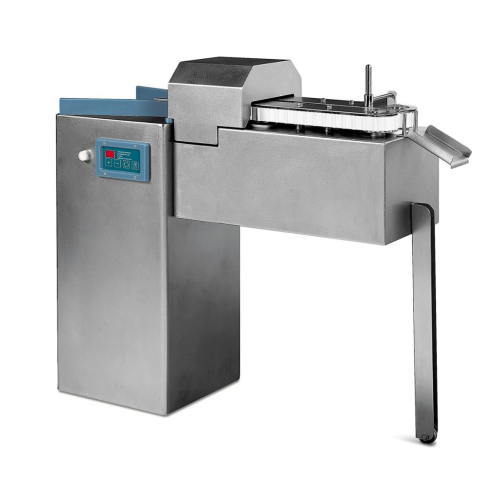
Automatic tying system for fresh sausages
Streamline your sausage production process with high-speed tying, ensuring consi...
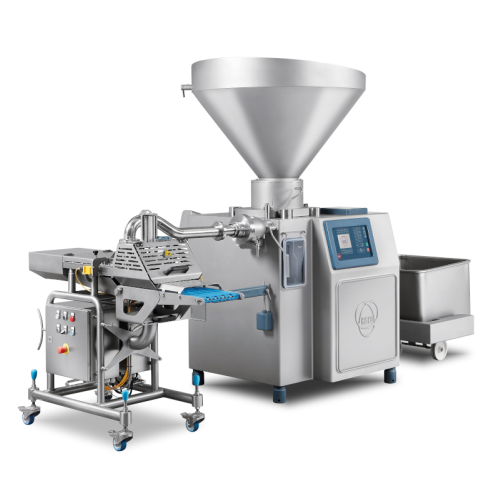
Double head forming system for burger production
Streamline your burger production with a high-speed forming system that e...
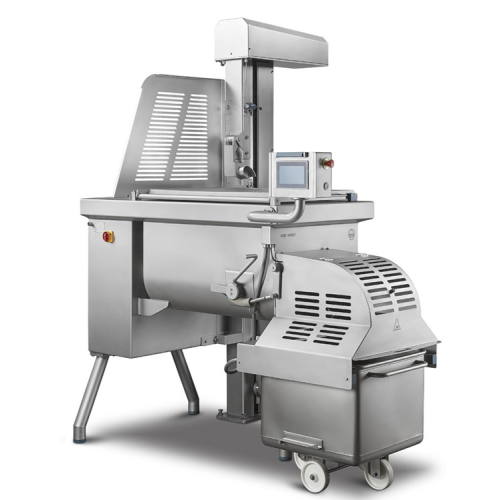
Frontal discharge mixer for meat processing
Enhance your mixing process with an efficient solution that seamlessly combine...
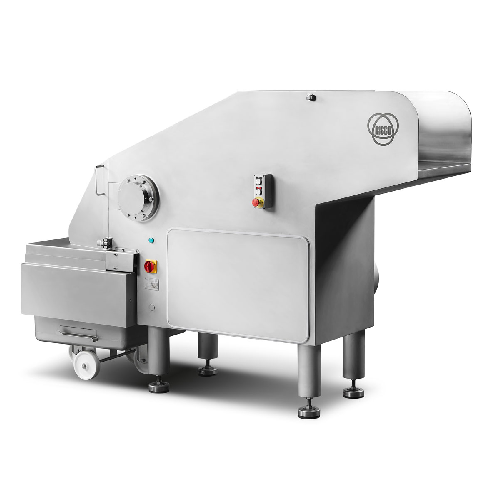
Flaker for frozen meat and food blocks
Efficiently transform solid blocks of frozen foodstuffs into precise cuts and flakes...
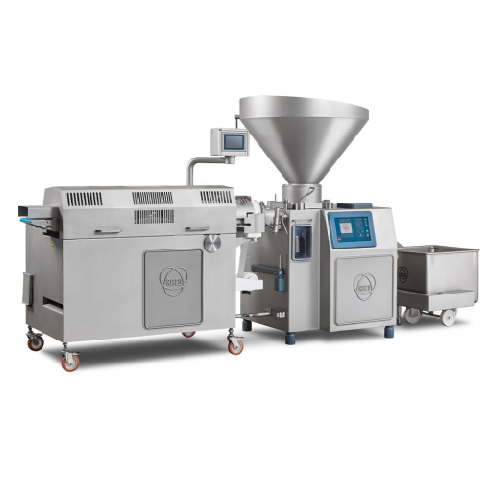
High speed portioner for minced meat and burgers
Optimize your production speed and portioning precision with this high-pe...
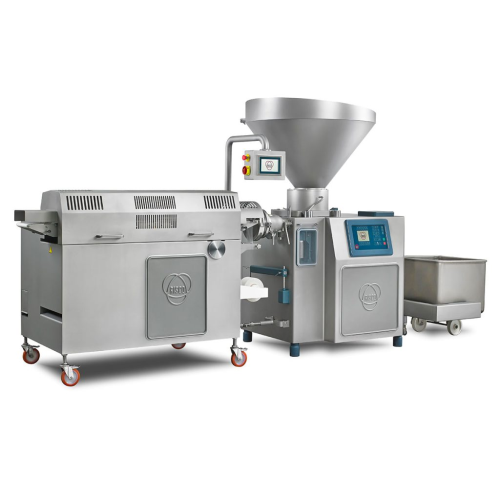
High performance minced meat portioner
Achieve consistent and precise minced meat portions with advanced grinding and porti...
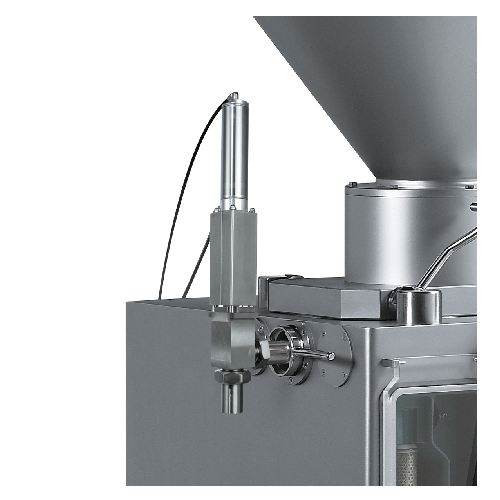
Vertical dosing valve for accurate food portioning
Ensure precision in portioning liquid and semi-liquid food products wi...
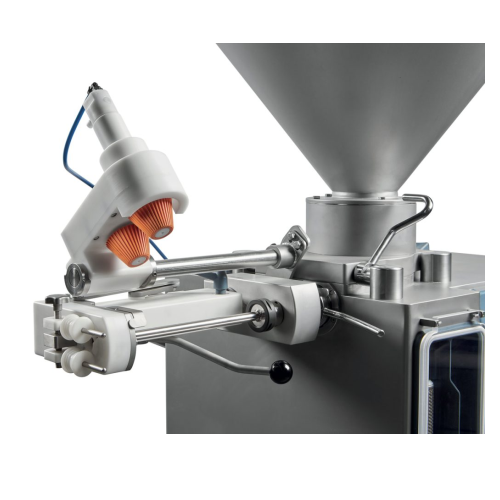
Casing spinner for natural sausage casings
Improve efficiency in your sausage production by seamlessly integrating natural...
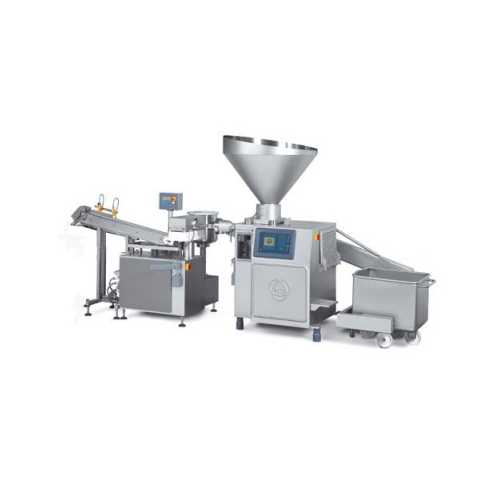
Innovative sausage production with vegetable coating
Optimize sausage production with a vegetable-based alginate coating,...
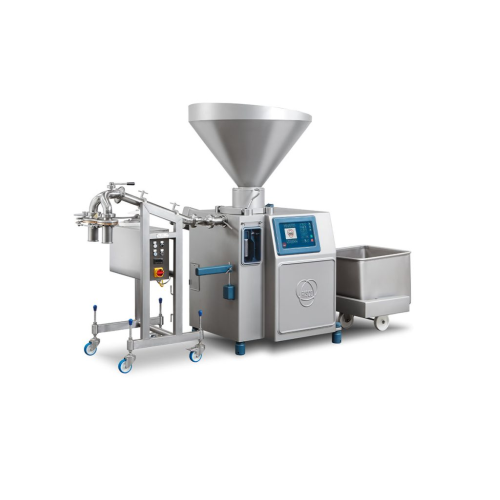
Forming system for meatballs
Achieve precise portioning and consistent shapes for various food balls and dumplings, enhancin...
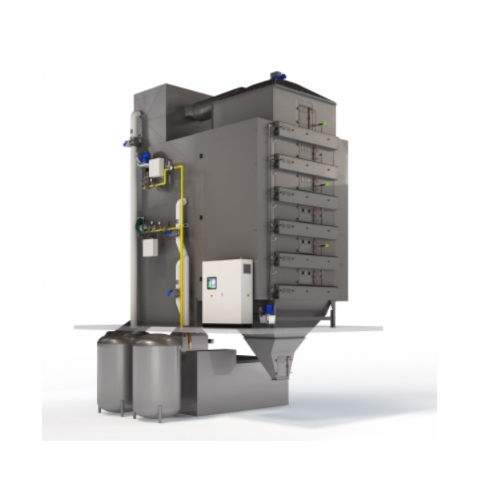
Industrial heat pump dryer
The drying of extruded products is highly energy-demanding in traditional belt dryers that use ga...
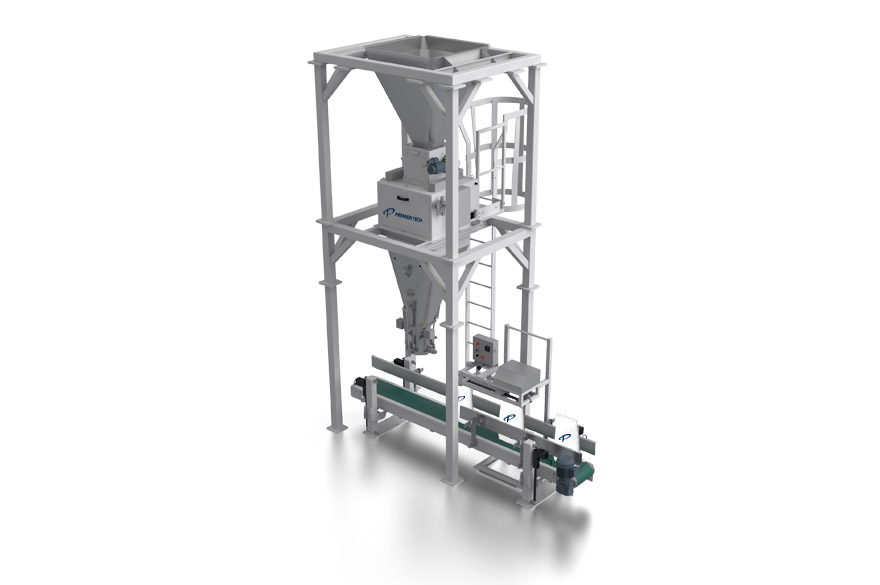
Manual bagger with net weigher
If you are looking for a weigher that is manually controlled for bagging, here it is. It has ...
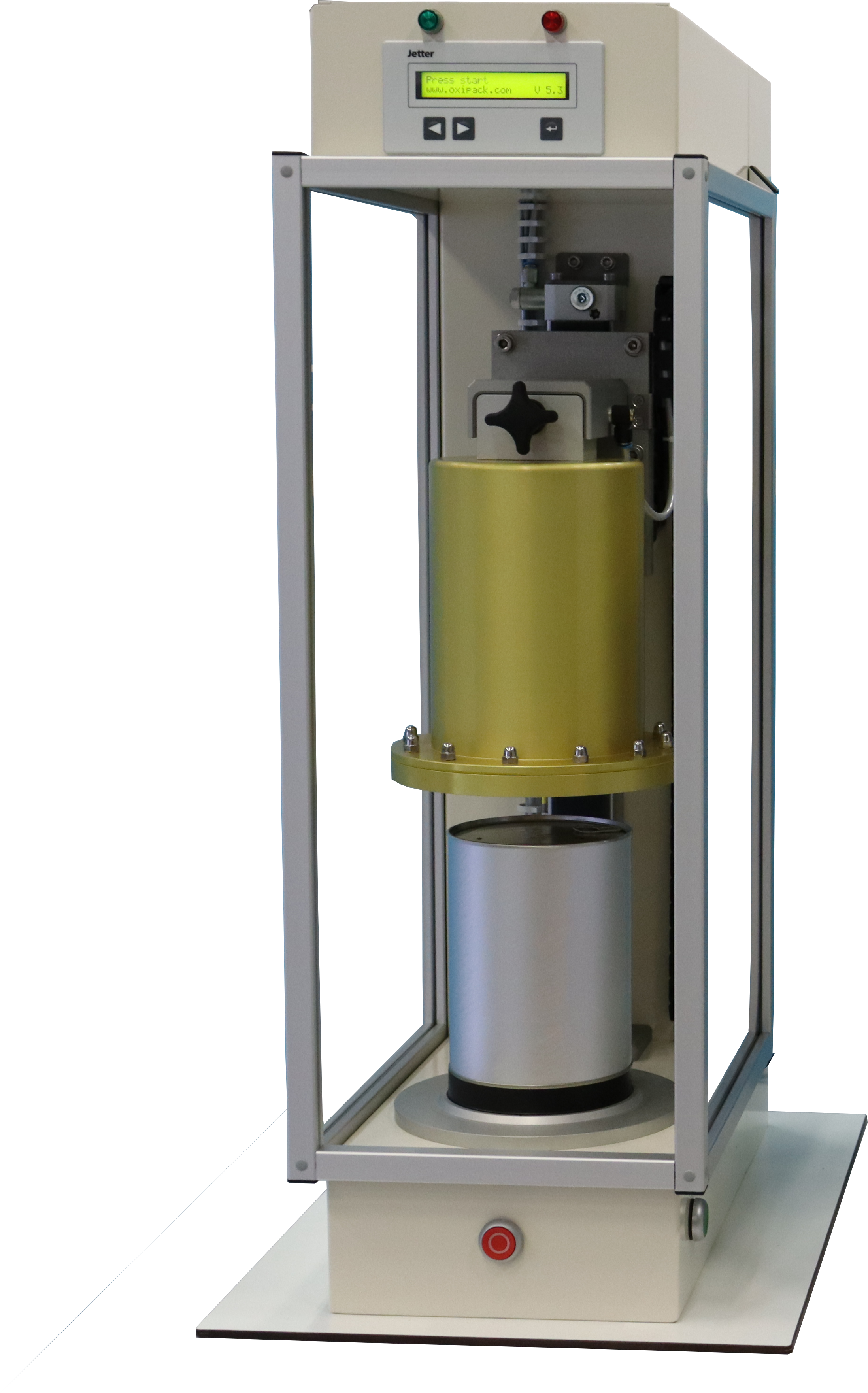
Can leak tester
Every canned pet food producer knows that their product should avoid the growth of microorganisms that could s...
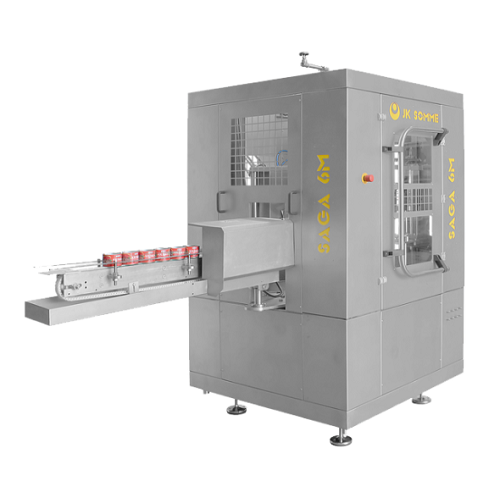
High speed can seamer
Tin plate thickness for cans has gradually reduced over the years, which makes it a hassle to use new c...

Macro ingredient dosing system
Traditional dosing systems do not have a very long operational life and are hard and expensiv...
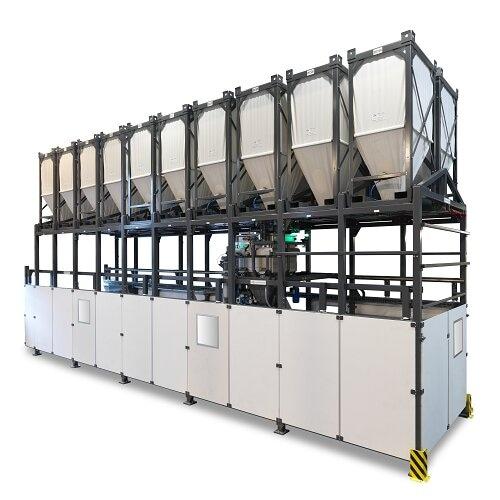
Exchangeable silo dosing system
Rarely used bulk ingredients, like grains, agricultural feed or silage, can get spoilt if th...
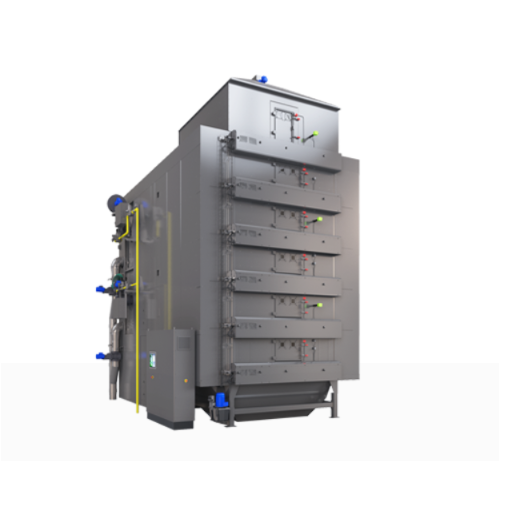
Recirculating batch dryer
Drying can be the most energy and time-consuming process in the food industry. This can have an ef...
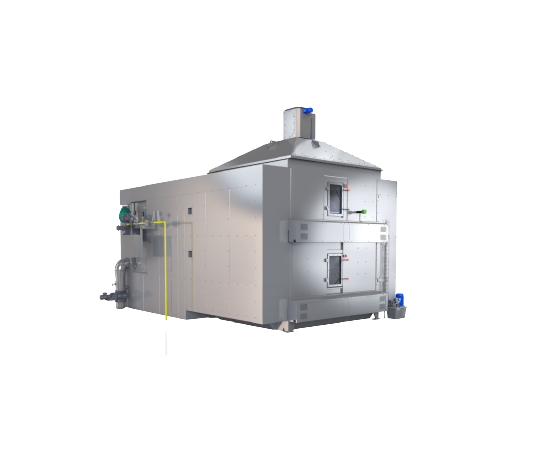
Continuous dryer machine
Traditional drying methods in the pet food, aquafeed, and extruded food industry can be the most ene...
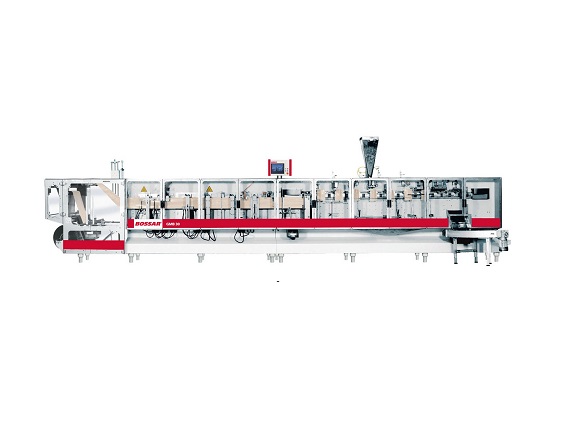
HFFS Machine for Large or Heavy Pouches
Traditional pouch-forming machines can struggle to maintain the position of the pac...
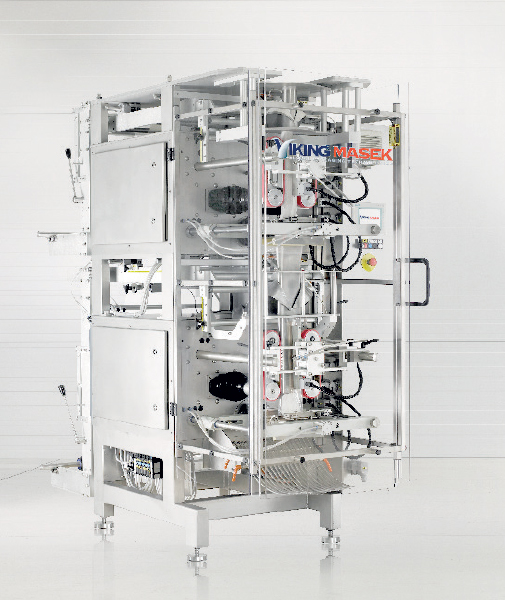
Bag-in-Bag machine
If you are looking for a compact packing machine that packs multiple smaller packs in one master bag; this...
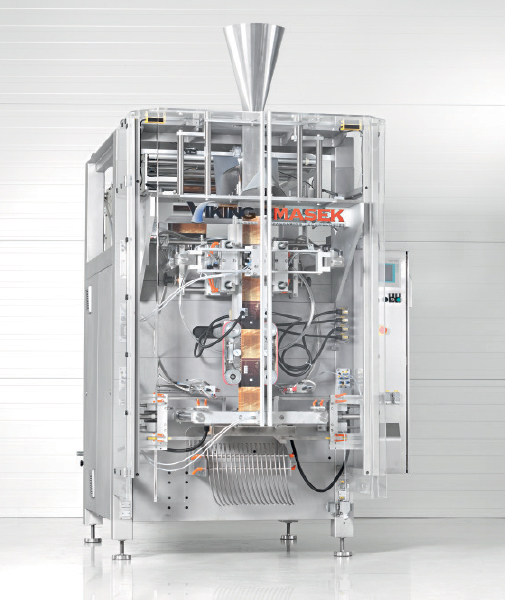
Bagger with servo driven jaw actuation
If you want to accommodate multiple bag designs and dimensions with fast speed and a...
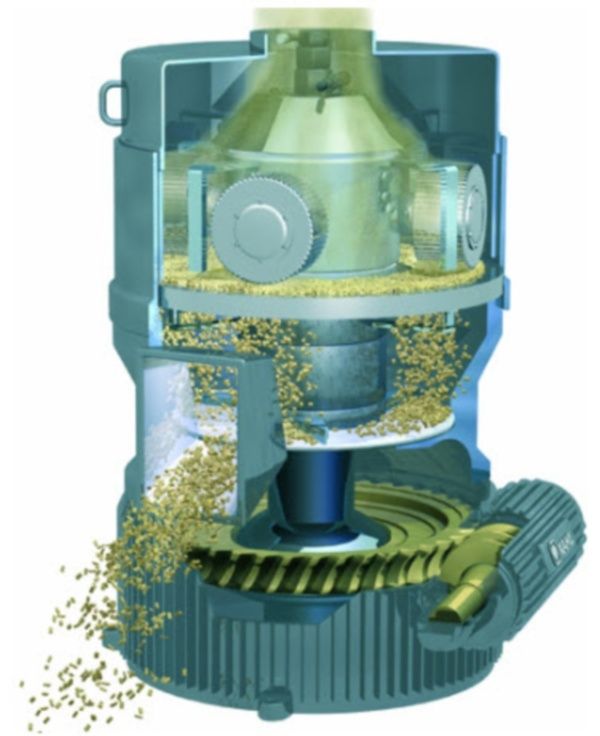
Pelleting press for feed and petfood
The production of agricultural feed and pet food products requires machines and plants...
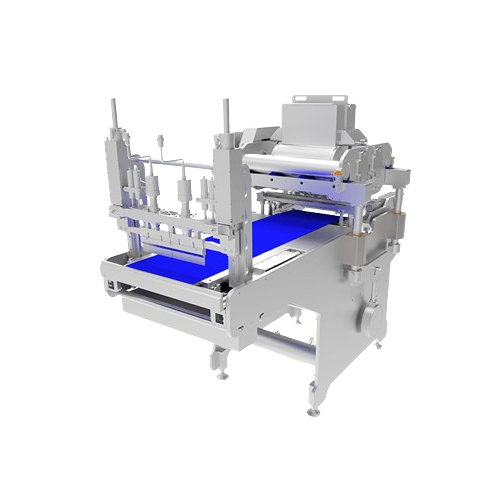
Cookie dough wirecut machine
Achieve precise control and flexibility in shaping a wide variety of cookies and bars with this...
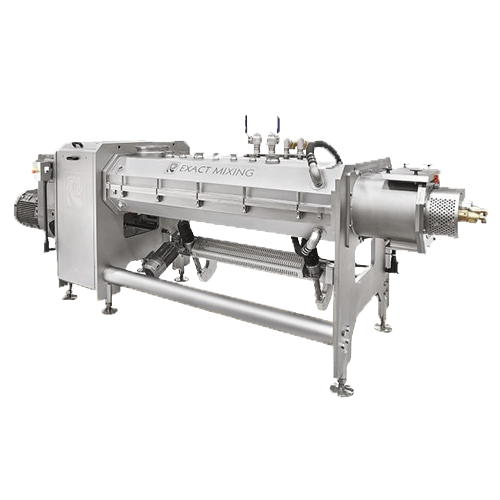
Continuous mixer for cookie and snack dough
Achieve uniform and consistent mixing of cookie and snack dough with seamless ...
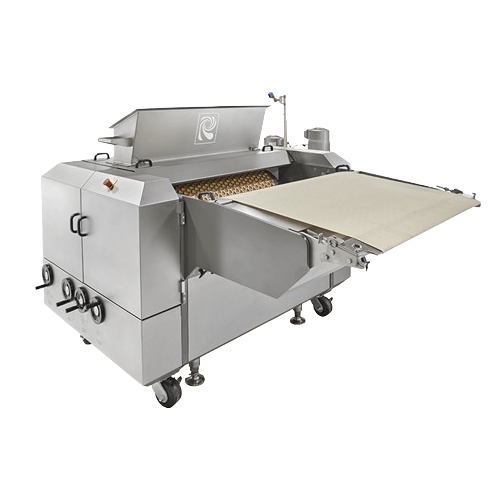
Rotary moulder for high-definition cookie dough shapes
Efficiently shape intricate dough designs with precision, ensuring...
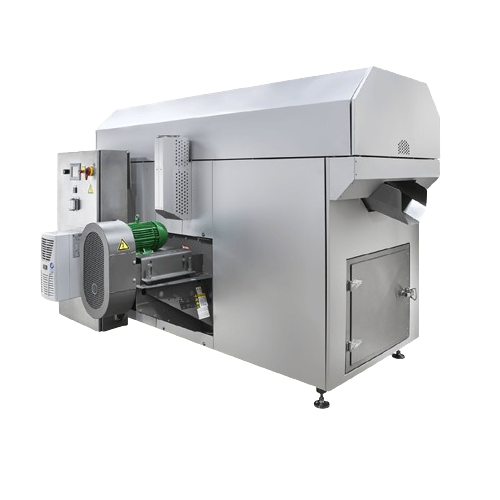
Industrial tumble dryer for moisture control in snack production
Ensure precise moisture reduction and optimal air circu...
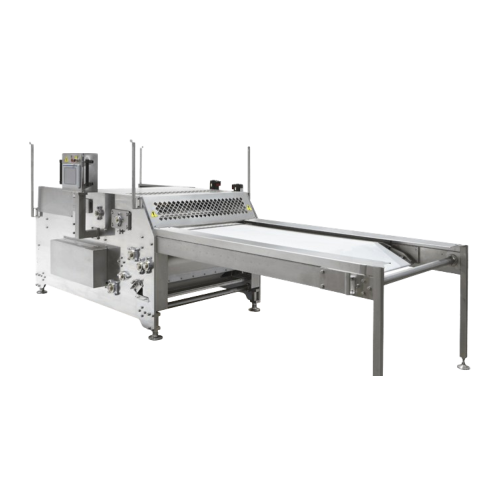
Servo in-line dough laminator for industrial bakeries
Optimize your snack production with precise dough sheet cutting, st...
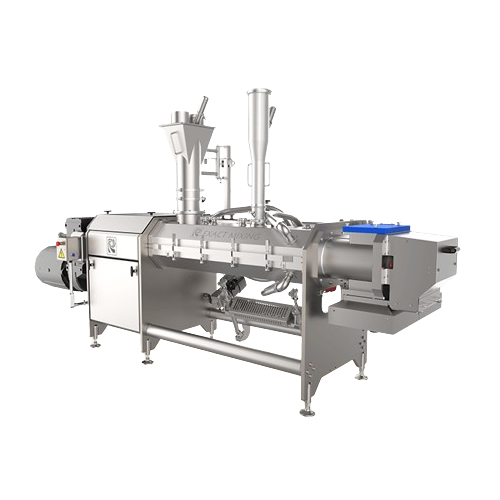
Continuous mixer for cookie dough
Achieve consistent dough quality and streamline your production with a continuous mixing ...
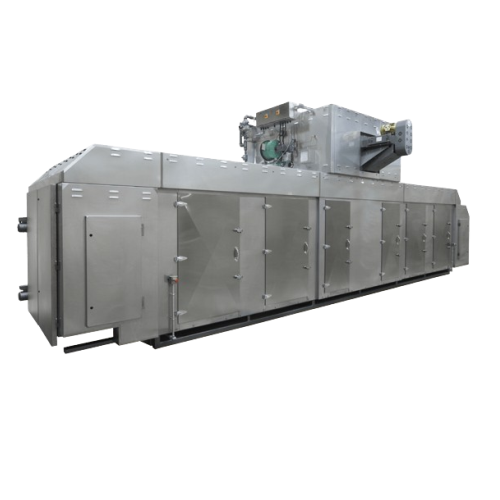
Industrial multi-pass dryer for bakery products
Ensure consistent moisture reduction and quality enhancement in your baker...
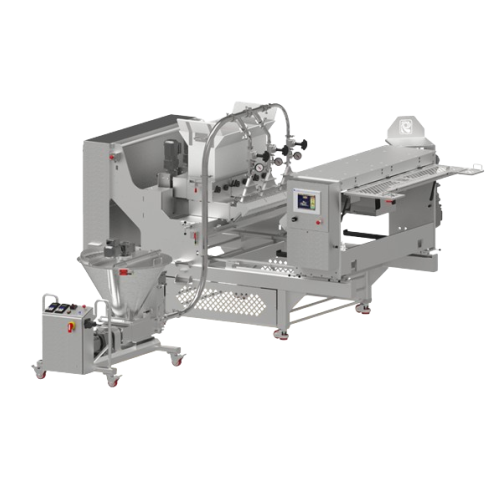
Filled stick extruder for bakery products
Streamline your snack production line with a versatile extruder capable of creat...
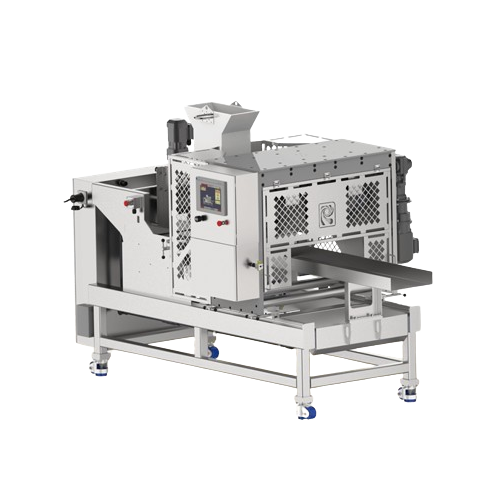
Fried snack extruder for potato rings
Efficiently produce a variety of fried snacks, from potato rings to ethnic noodles, w...
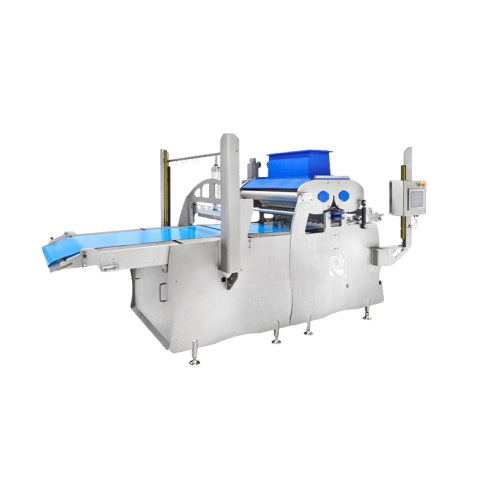
Automated frozen dough production solution
Maximize your frozen dough production with precision control and streamlined ma...
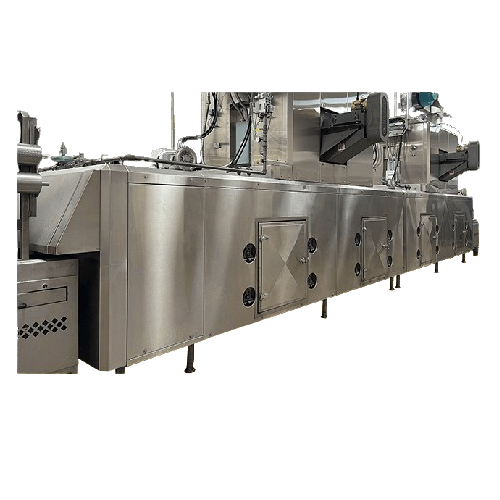
Electric oven zones for snack and cookie baking
Optimize your baking line with electric oven zones designed to eliminate e...
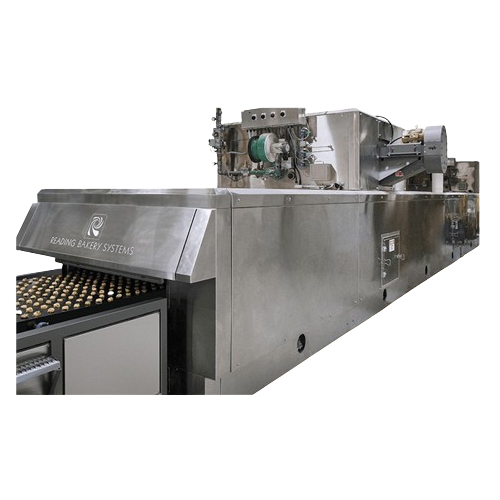
Emithermic zone for baking biscuits and cookies
Enhance your baking efficiency and precision with a flexible heat transfer...
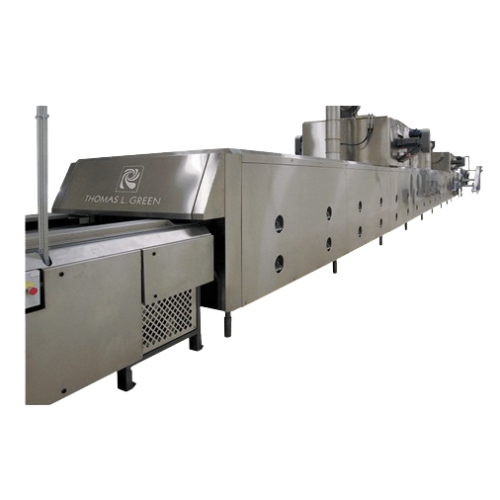
Emithermic Xe zone for baking biscuits and crackers
Achieve precise baking and drying for your bakery products with a sys...
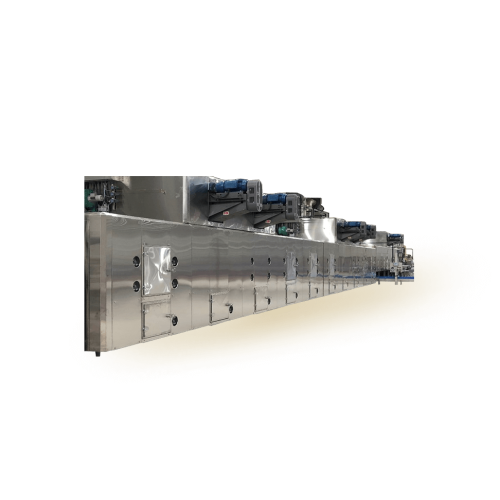
Convection oven with integrated dryer for large scale baking
Optimize your baking process with a convection oven that ef...
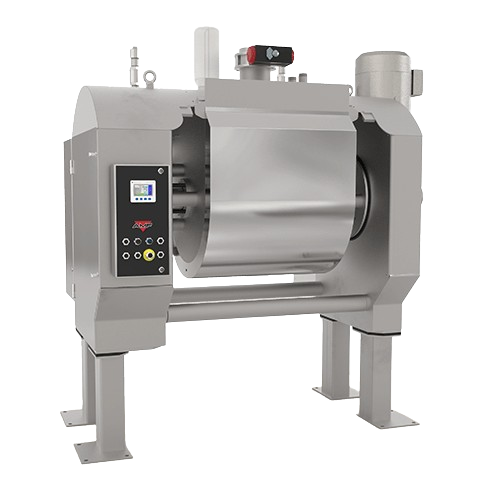
Industrial direct drive mixer for dough preparation
Optimize your production line with a robust mixer designed for seamle...
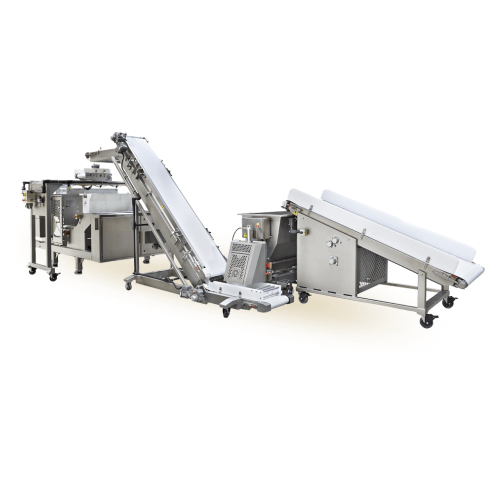
Automated dough handling system for pretzel production
Streamline your dough processing with a system that precisely port...

Vertically feeding system for cookie dough
Optimize your dough handling with a system that ensures seamless and efficient ...
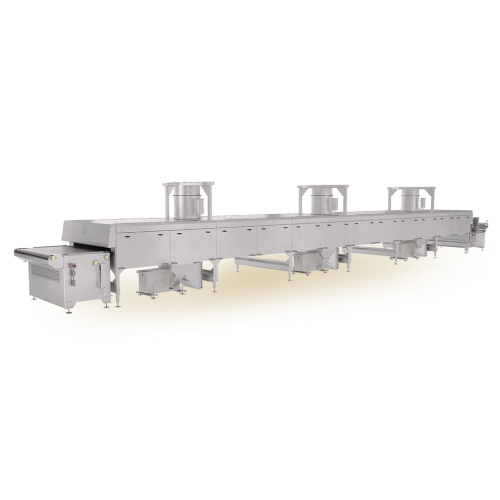
Ambient air cooler for bakery products
Efficiently cool fragile baked goods without causing distortion, using ambient air t...
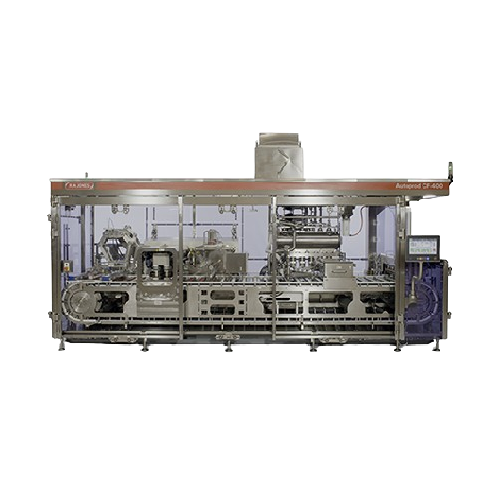
Cup filling and sealing system for dairy products
Optimize your production line with versatile cup filling and sealing ca...
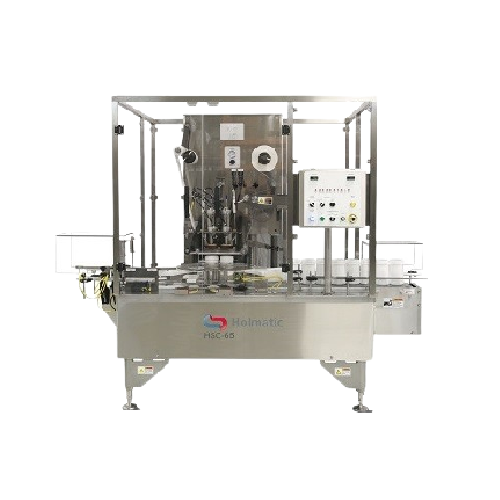
Rotary indexing sealer for cup filling
Streamline your production line with precise cup filling and sealing, ideal for a wi...
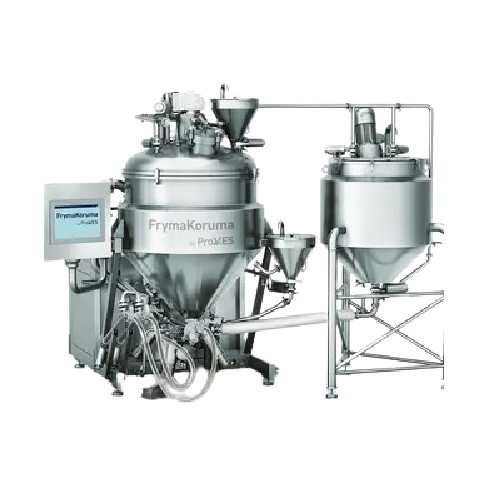
High shear emulsifier for mayonnaise production
Streamline your production of high-quality emulsions with this high-capaci...
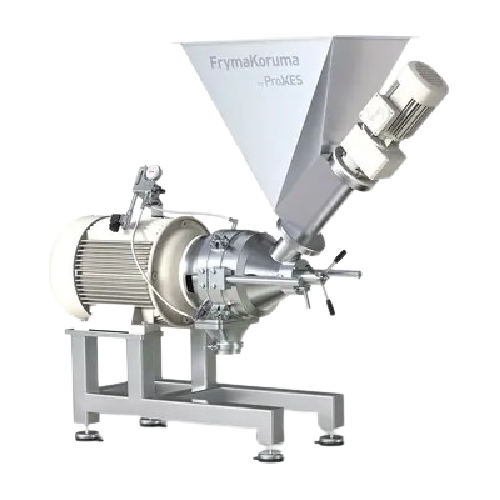
High shear emulsifier for food and pharmaceutical products
Optimize your production line with precise emulsification, ho...

Heat exchangers for efficient heat transfer in industry
Achieve precise temperature control across diverse viscosities wi...
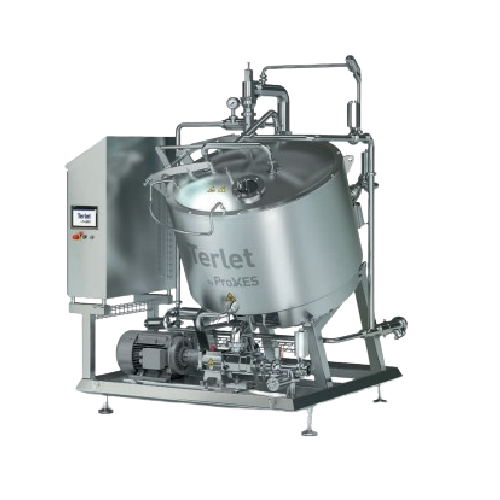
Precise liquid cooling solution for food processing
Ensure high-quality preservation of flavors and textures in liquid fo...
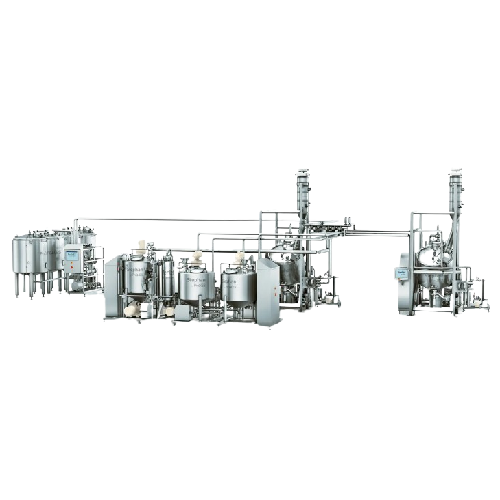
Continuous nut paste production line
Elevate your production efficiency with a versatile preparation line designed to seaml...
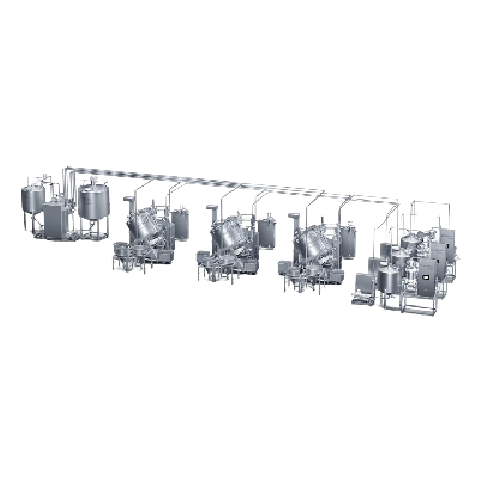
Continuous mustard production line
Optimize your condiment production with precision-engineered systems capable of transfor...
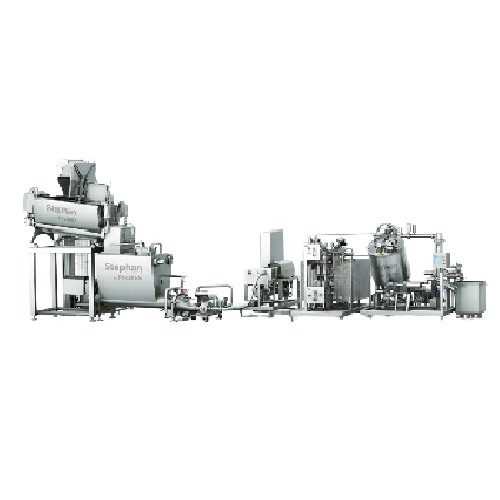
Cheese blending and heating line for processed cheese
Optimize your processed cheese production with a solution that seam...
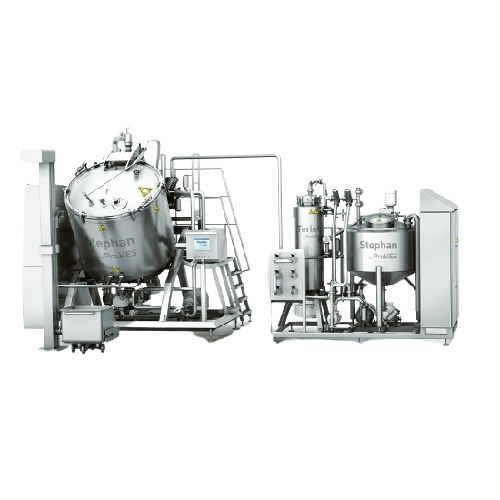
Continuous caramel production line
Optimize your caramel production with seamless integration, achieving precise fat meltin...
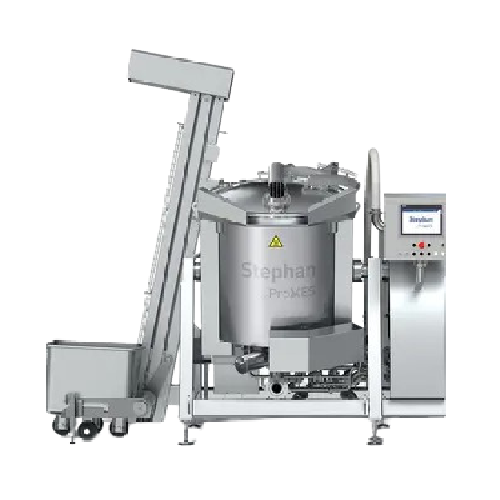
Industrial cooker for sauces and stews
When producing diverse culinary delights such as sauces and stews, achieving even he...
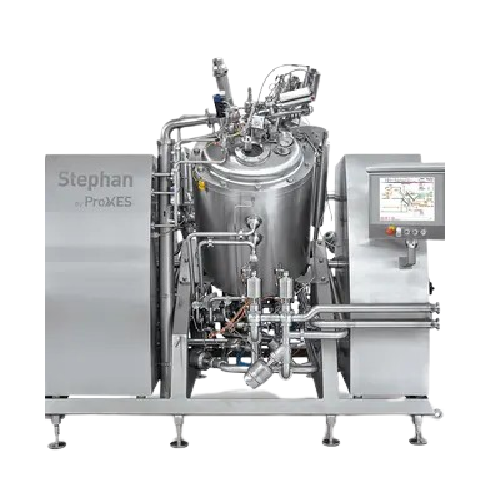
Continuous ultra-high temperature processor for processed cheese
Ensure precise thermal treatment and enhanced flavor re...
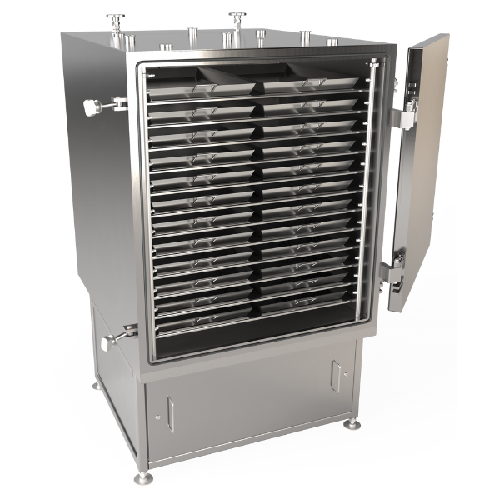
Continuous heat exchanger for soups and sauces
Optimize your soup and sauce production with a continuous heat exchanger th...
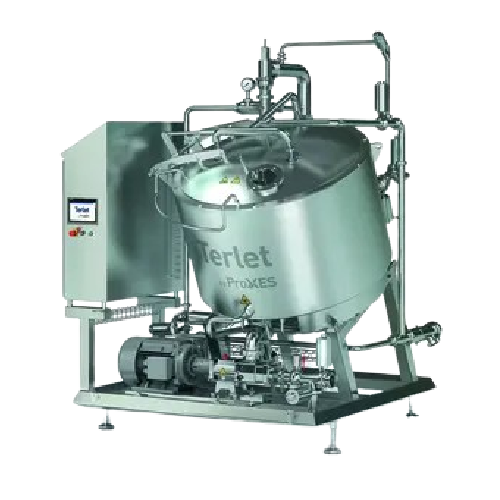
Efficient cooling and cooking systems for food processing
Streamline your production with integrated cooling and cooking...
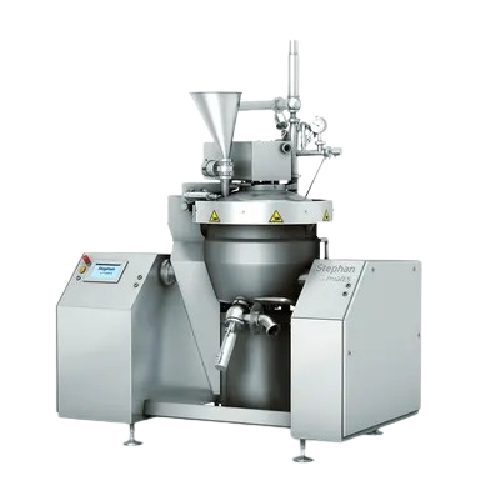
Industrial cutting system for fine emulsions
Optimize your production line with precision cutting and emulsifying, ensurin...
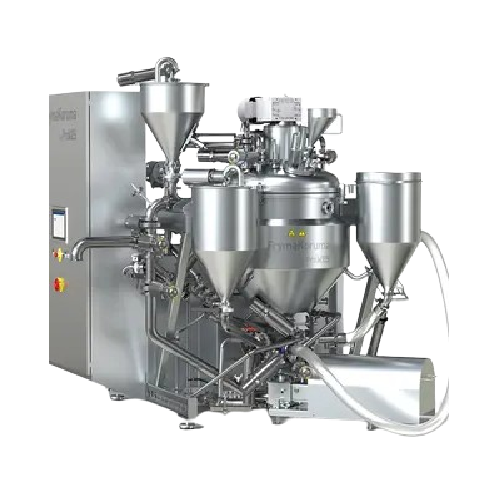
Vacuum deaeration system for mustard and liquid detergents
Ensure optimal product quality by effectively removing air fr...
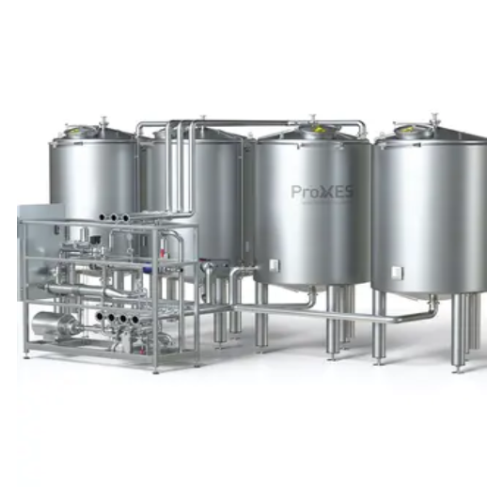
Cleaning systems for food, pharmaceuticals, and cosmetics
Ensure optimal hygiene and safety with advanced cleaning syste...
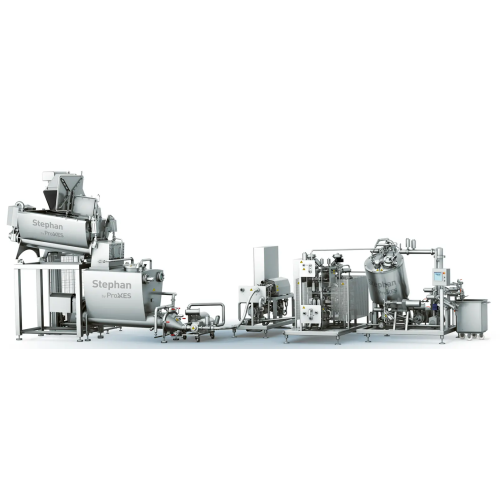
Continuous caramel process line
Optimize your continuous food processing with an engineered-to-order line tailored for preci...
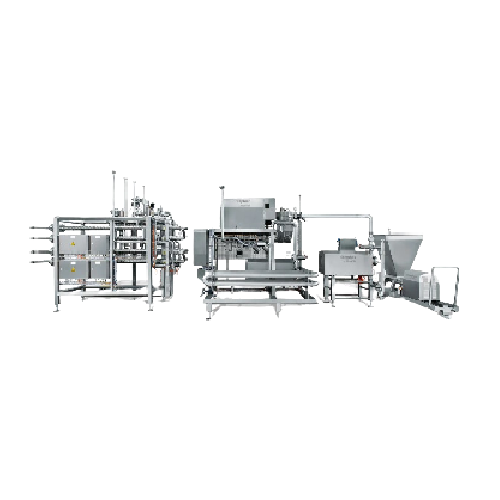
Continuous cheese line
Achieve precise temperature control and seamless product transitions with this equipment, ideal for en...

Continuous tahina production line
Streamline your tahina production with precise grinding and controlled cooling, ensuring ...
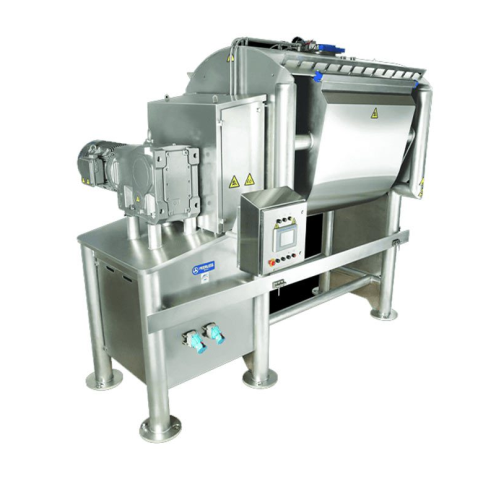
Open frame mixer for bread and pastry dough
Enhance your dough consistency and reduce production downtime with a robust, h...
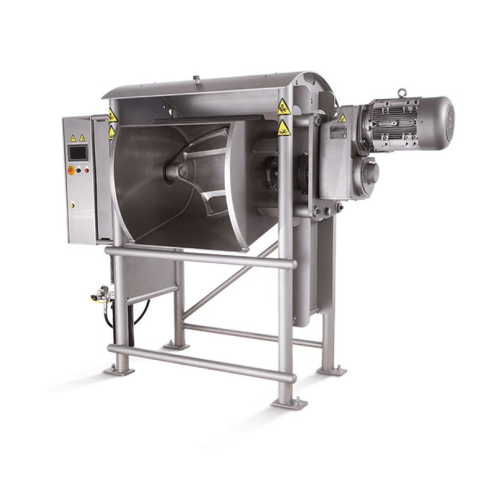
Medium duty mixer for breads and pastries
Achieve consistent dough development and uniform mixing for a wide variety of ba...
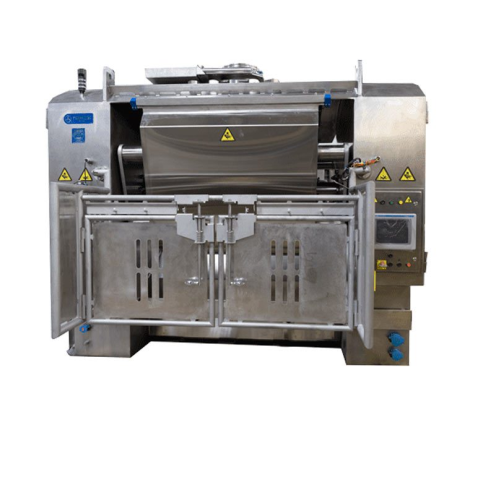
Industrial enclosed frame mixer for high-capacity dough mixing
Optimize your bakery’s output with a mixer designed...
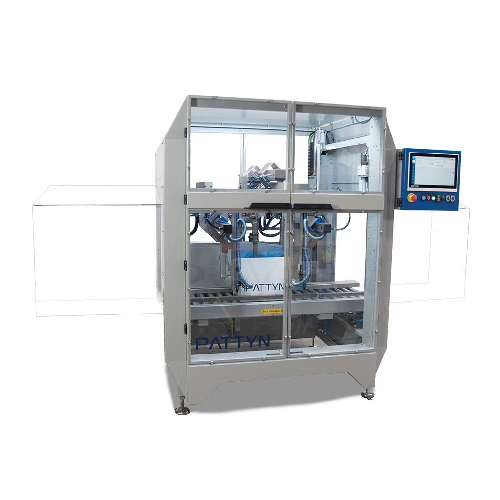
Automatic bag folding solution for bulk packaging
Enhance your production line efficiency and product protection by integ...
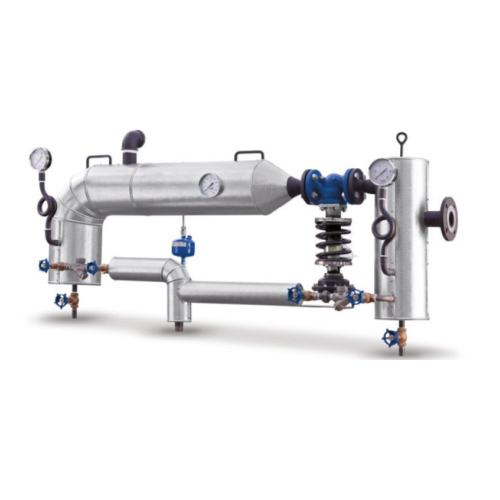
Steam injection systems for animal feed production
Enhance product quality in animal feed production with steam injection...
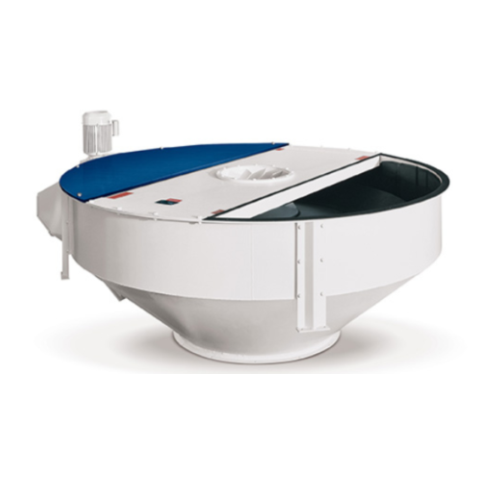
Cryloc rotary screens for grain processing
Efficiently sort and separate fine particles with high precision to enhance pro...
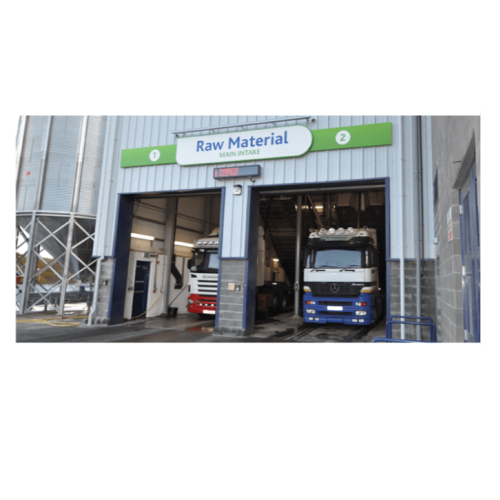
Product intake solutions for feed processing
Optimize your feed production with efficient material intake systems, ensurin...
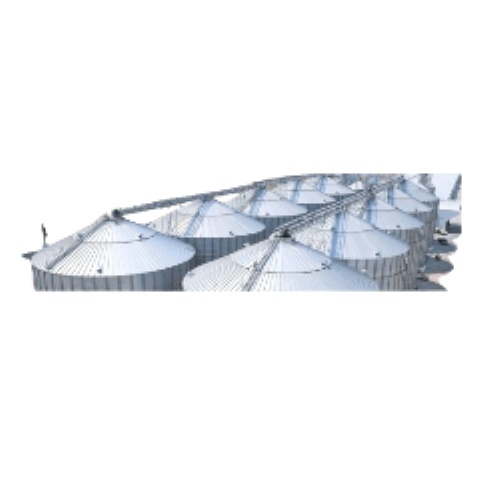
Cylindrical storage silos for long-term raw material storage
Efficiently store bulk raw materials for extended periods w...
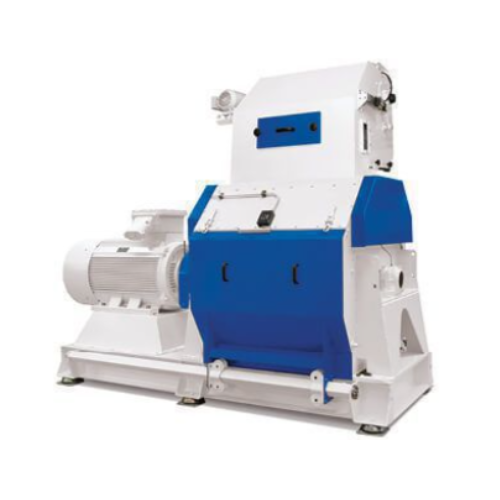
Hammer mills for high-efficiency grinding in feed production
Optimize your feed production with high-efficiency grinding...
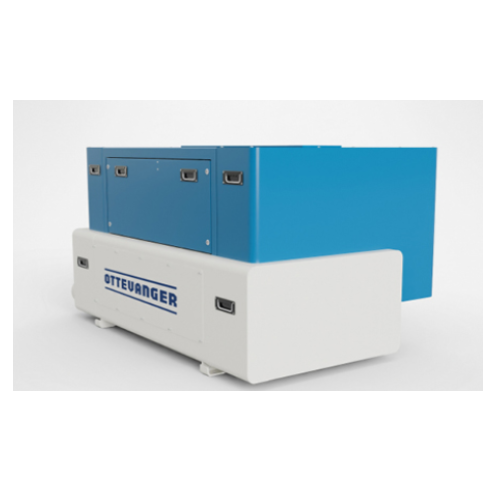
Grain flow regulator for roller mills
Achieve consistent grain distribution and safeguard your roller mills from wear and c...
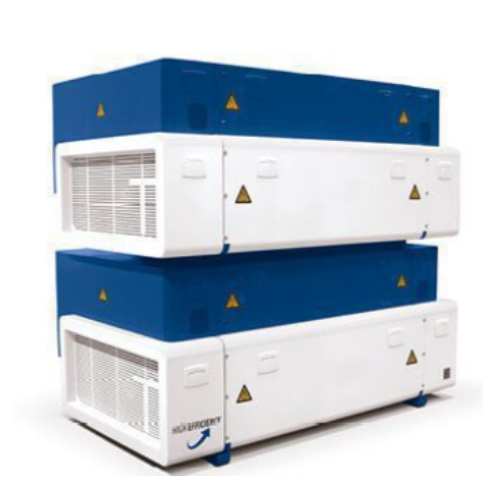
High efficiency roller mill for grain and oilseeds
Optimize your crushing and grinding processes with a versatile roller ...
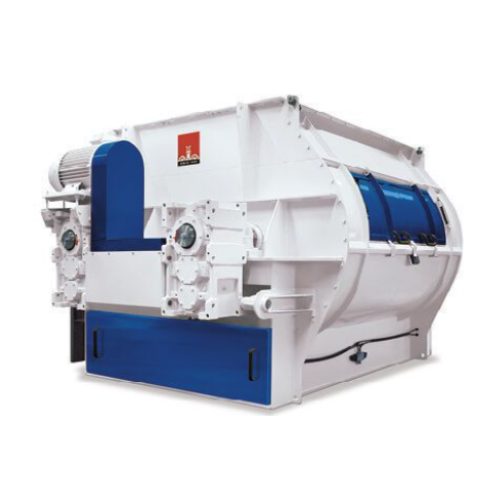
Double shaft paddle mixers for industrial powders and granulates
Achieve precise mixing and homogenization of dry powder...
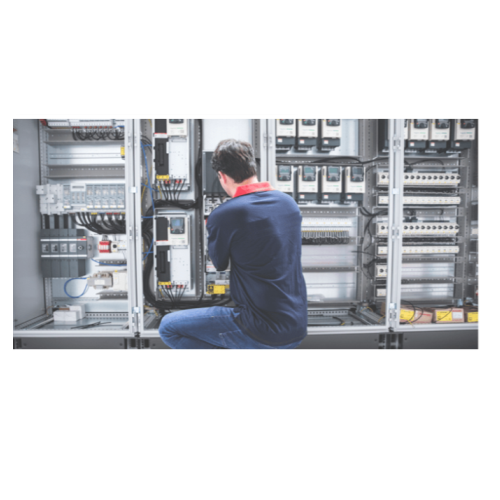
Industrial control panel construction
Streamline your production line with advanced panel building solutions that enhance a...
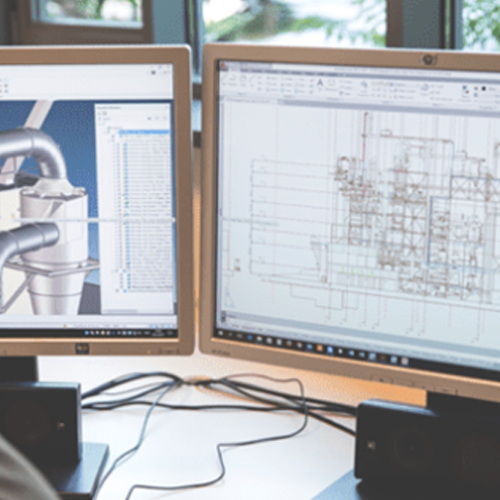
Process automation for feed mills
Optimize your feed production line by seamlessly integrating advanced process automation ...

Hammer mill for efficient particle size reduction in feed mills
Optimize your feed milling operations with this hammer m...

Bucket elevators for bulk material handling
Efficiently transport and discharge granular and powdered materials with preci...
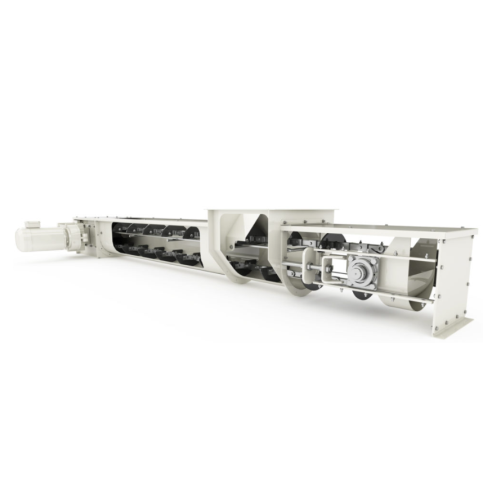
Efficient powder and granulate flight conveyors
Elevate your production efficiency with our cutting-edge flight conveyors,...
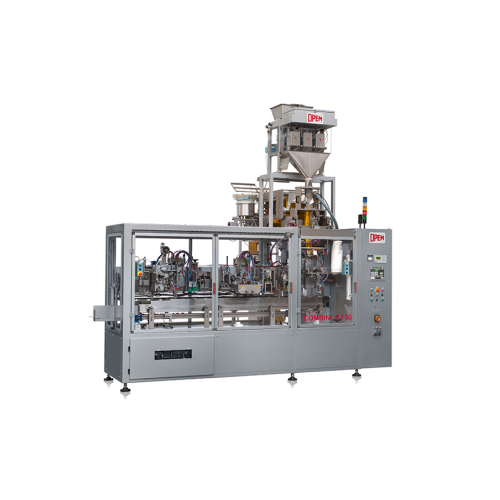
Vertical bagging system for four corner seal bags
Optimize your coffee pod and capsule production with a high-speed, cont...
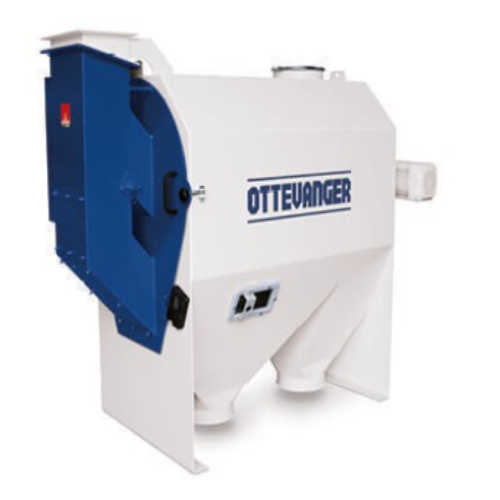
Industrial pre-cleaners for raw material safeguarding
Effectively eliminate foreign objects from your raw materials with ...
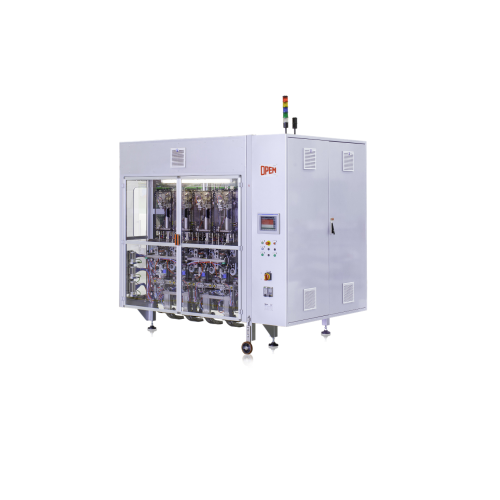
Automated capsule packaging system
Streamline your high-speed packaging operations with a system designed for precision fil...
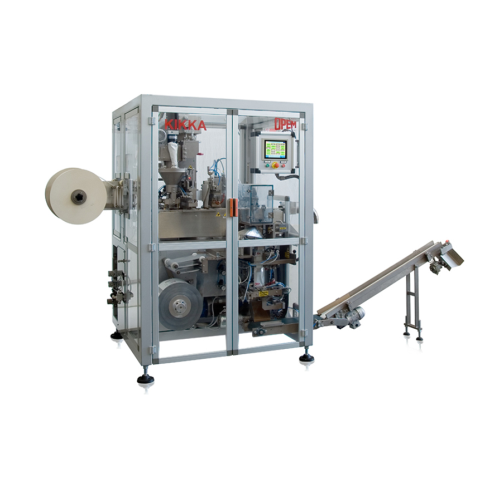
Filter paper pod production system
Streamline your production of single-serve beverages with precise weight control and sea...
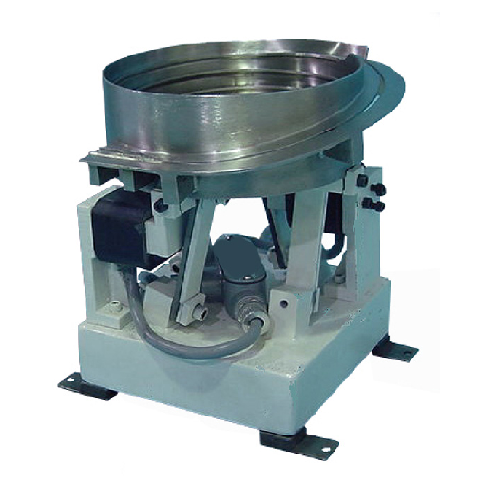
Vibratory bowl feeder for bulk items
When precision and speed are crucial, ensure your production line efficiently handles ...
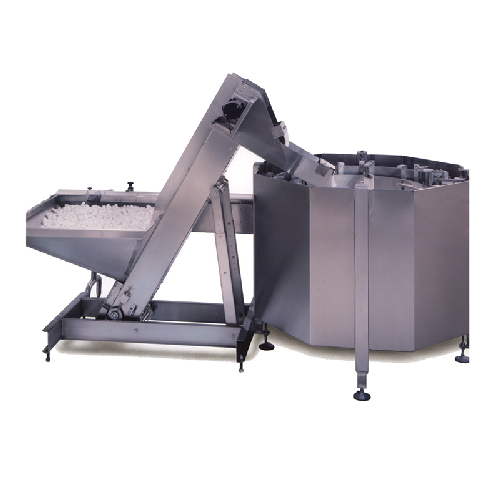
Centrifugal bowl feeder for high-speed bulk item feeding
Optimize your production line with high-speed feeding of diverse...
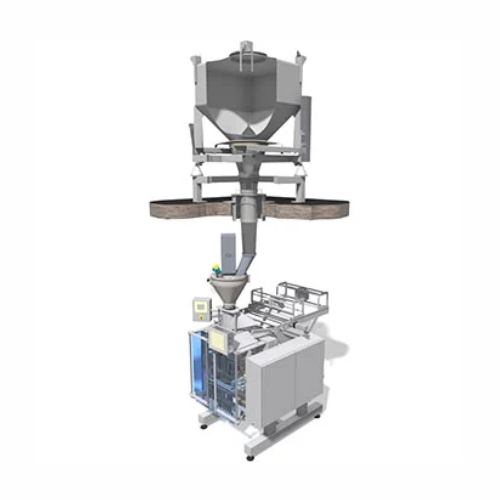
Powder packing module for consistent flow
Enhance your production efficiency with streamlined powder packing that ensures ...
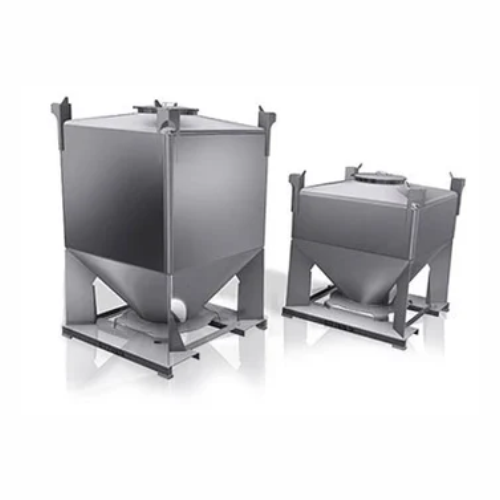
Powder handling system for industrial applications
Overcome powder flow issues and enhance production efficiency with adv...
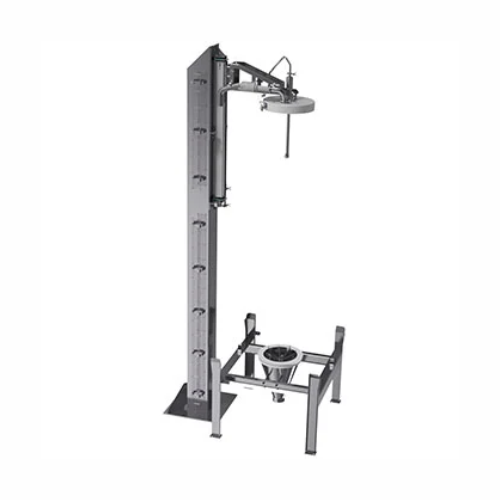
Ibc cleaning equipment for hygienic powder handling
Optimize cleaning efficiency and maintain hygiene standards with a ve...
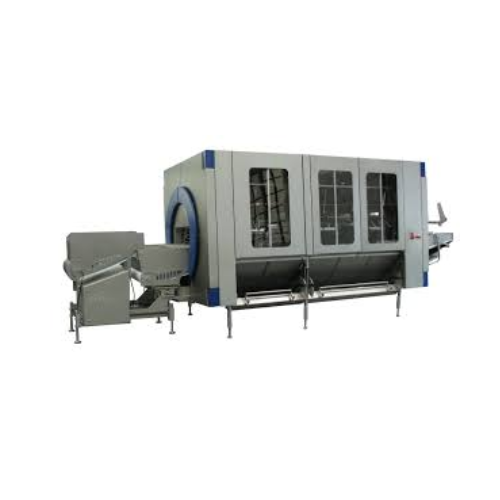
Inline marinating and coating for meat and poultry
Enhance product quality and consistency with an inline tumbler that si...
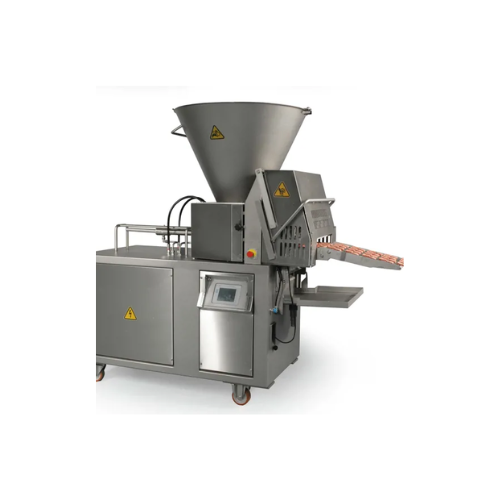
High-pressure forming solution for plant-based and meat products
Experience precision forming with versatile application...
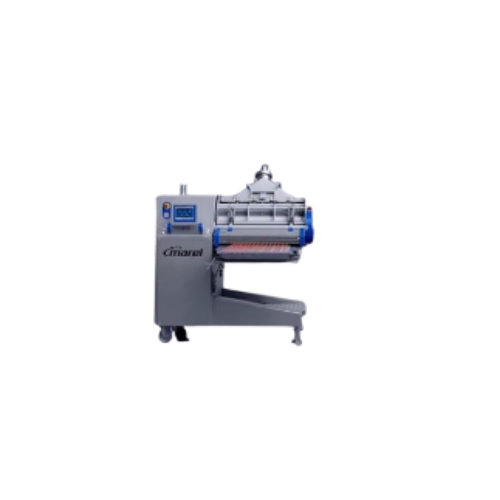
Low pressure forming for plant-based products
Achieve precise shape and weight consistency in plant-based products with lo...
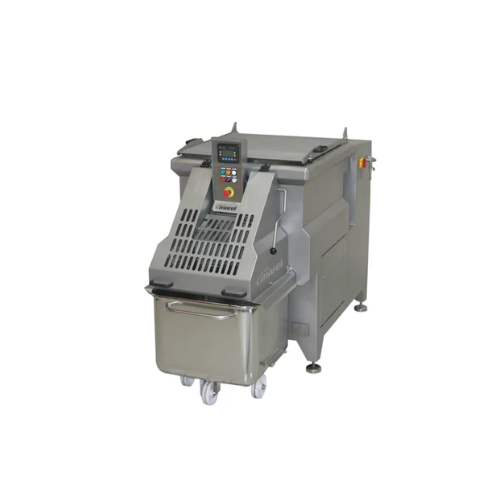
Industrial double shaft mixer for food processing
Ensure precise mixing in industrial food production with this double sh...
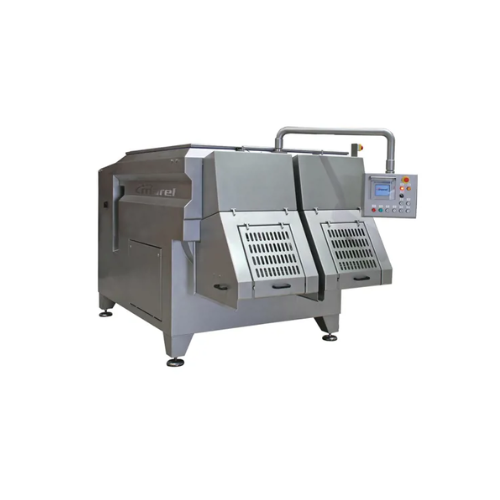
Industrial double shaft mixer for homogeneous blending
Achieve quick, gentle, and homogeneous mixing for diverse food mat...
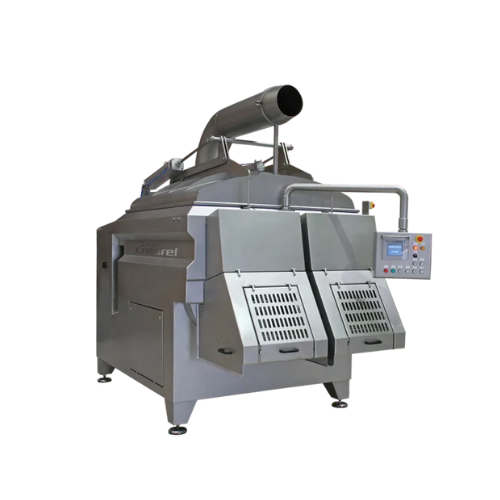
Vacuum mixer for fresh and frozen ground meat
Achieve precise homogeneity with this vacuum mixer, designed to handle high-...
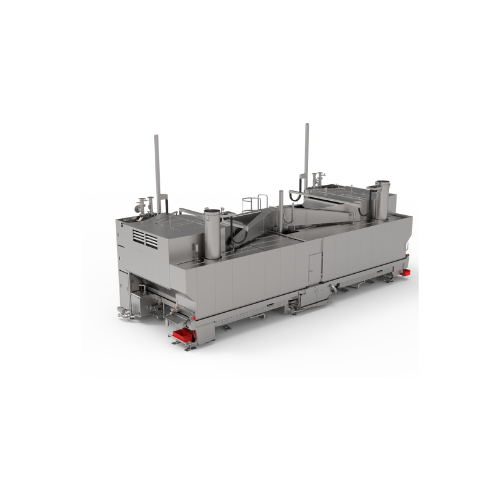
Spiral oven for cooking plant-based and conventional products
Achieve perfectly cooked products every time with advanced...

Flake ice producer for food-safe ice
Enhance your production line with hygienic flake ice, optimized for energy efficiency ...
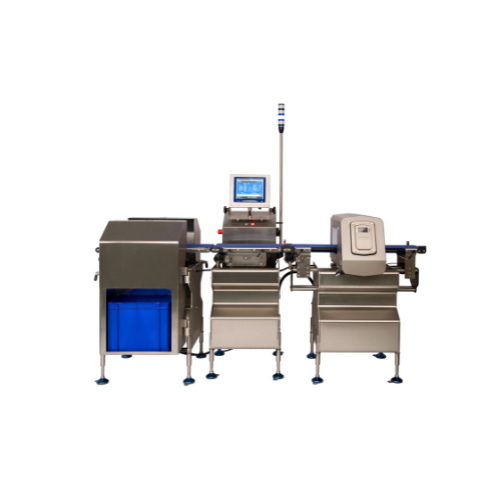
Checkweigher for food processing compliance
Ensure accurate package weights while preventing underweight or overweight pro...
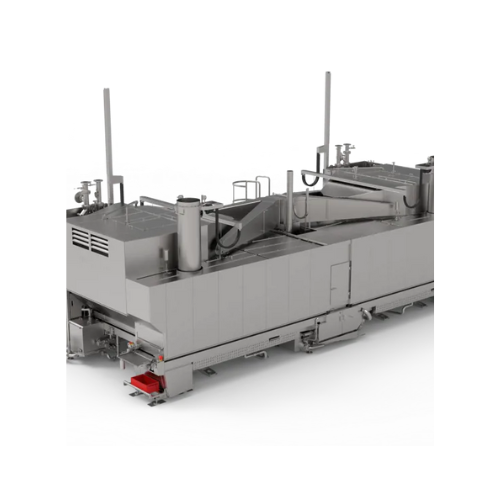
Oven for high-yield cooking of prepared foods
Achieve unparalleled consistency and enhanced yield in food production with ...
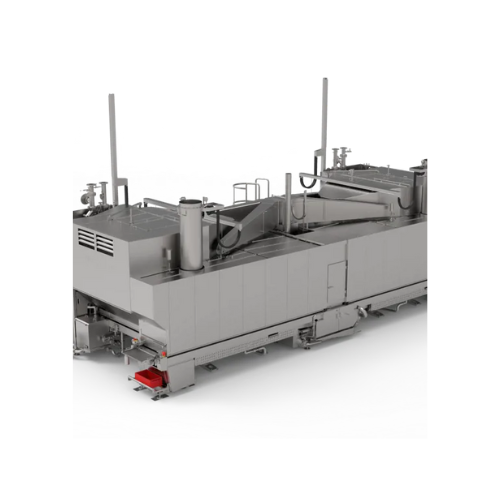
Modular industrial oven for high-yield food processing
Need a solution that offers high-yield roasting and precision cook...
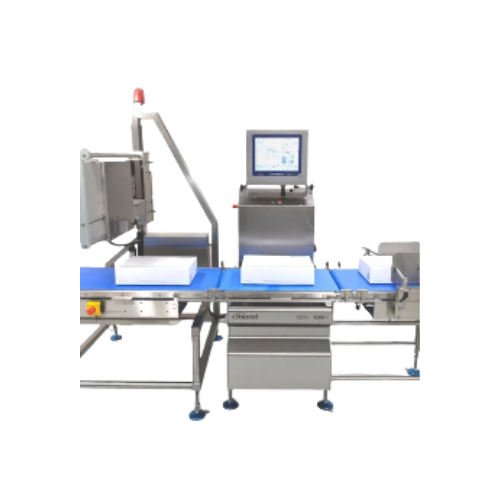
Automatic box and crate labeler
Achieve precise, high-speed labeling and weighing for various packaging needs, ensuring cons...
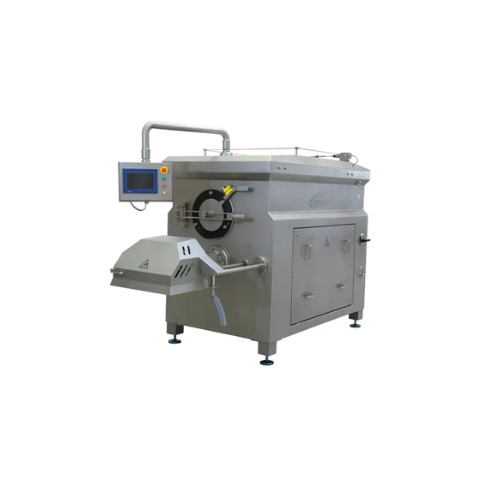
Industrial grinder for fresh and frozen meat
Optimize your production line with high-performance grinding capabilities for...
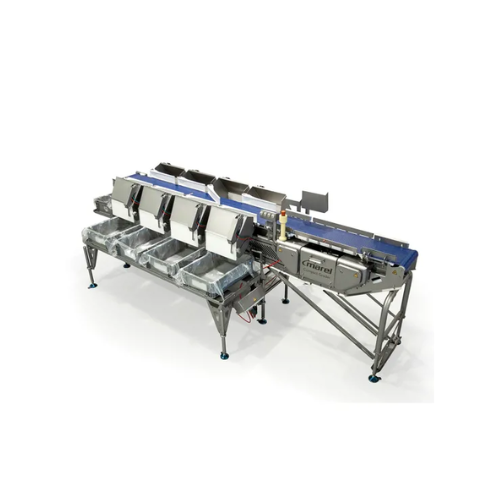
Compact grader for poultry and meat processing
Streamline your production line with this precise grading solution, designe...
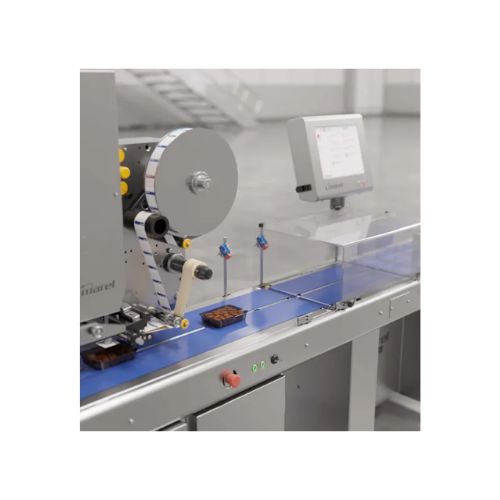
Weigh price labeler for retail food products
Achieve consistent, high-speed labeling and pricing with precision—streamlini...
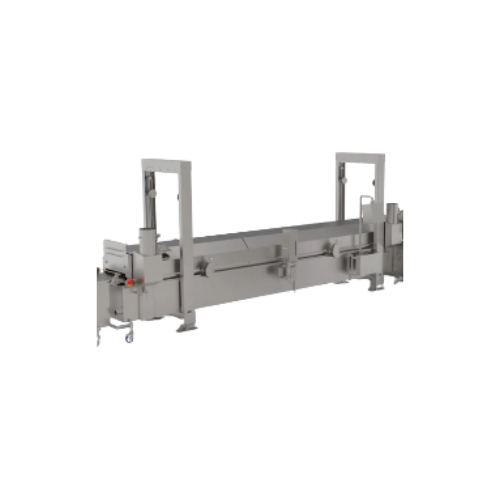
Industrial fryer for uniformly cooked convenience foods
Ensure perfectly fried textures and flavors with cutting-edge oil...
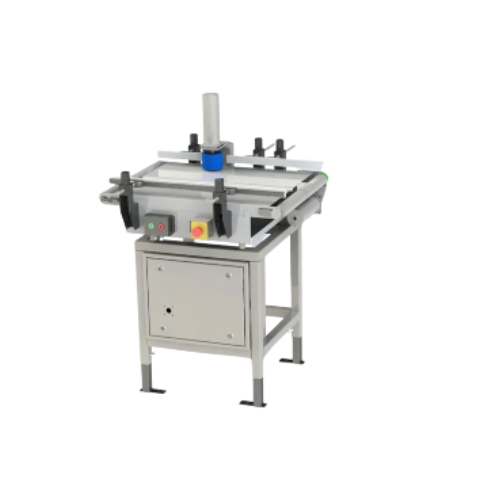
Pack turner for efficient label presentation
Optimize your packaging line efficiency and accuracy by ensuring precise labe...
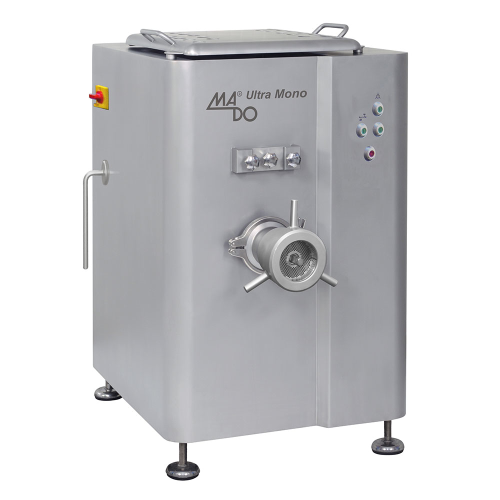
Industrial automatic mixer grinder for meat processing
Effortlessly process and mix large quantities of meat and frozen m...
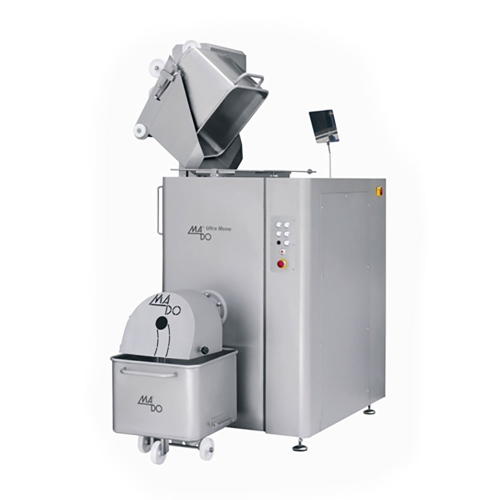
Industrial meat mixing solution
Streamline your meat processing operations with a high-capacity mixer designed for effortles...
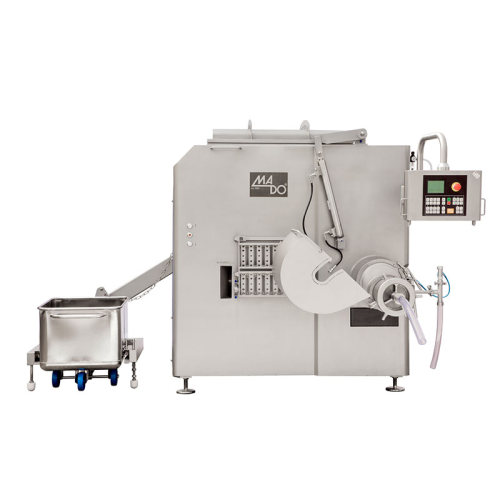
High-capacity extrusion grinder for industrial applications
Achieve seamless integration of grinding, mixing, and extrud...
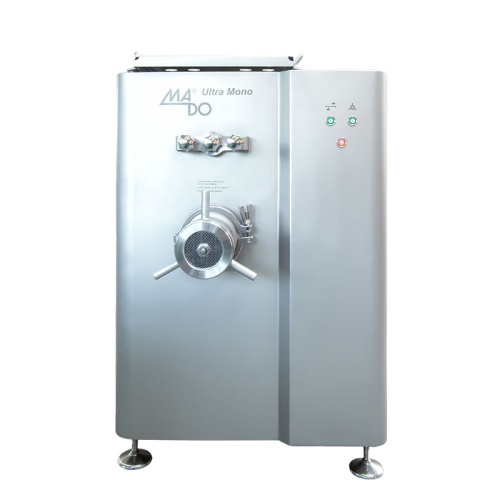
Industrial meat ginder and mixer
Streamline your large-scale meat production with a machine that seamlessly mixes, grinds, a...
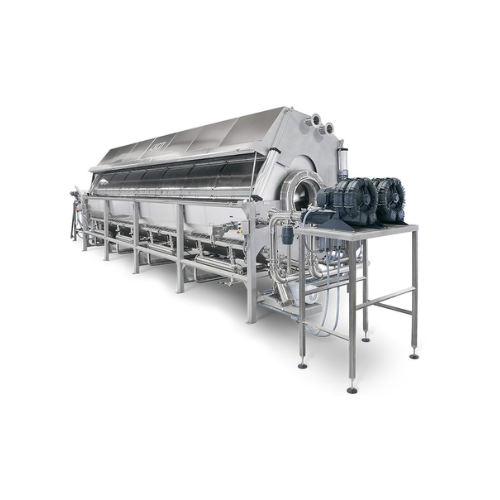
Rotary drum pasteurizer for pouches
Efficiently pasteurize delicate pouch contents like meats, vegetables, and grains with ...
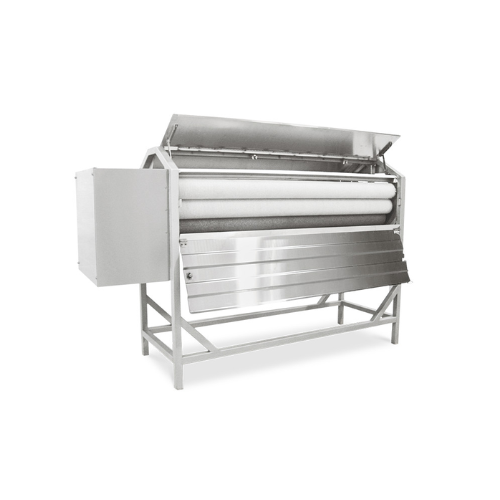
Root crop peeler and scrubber
Achieve efficient peeling and scrubbing of root crops while maximizing product recovery, makin...
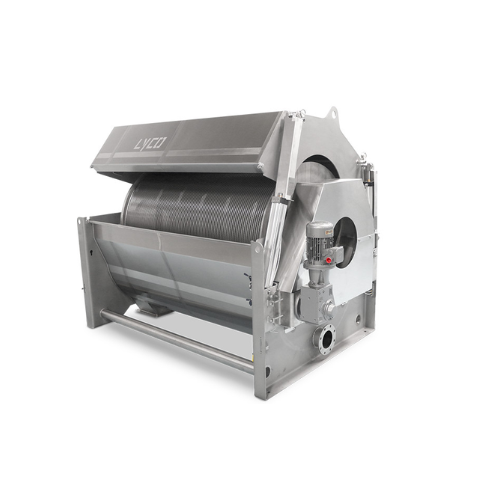
Sealed drum separator for rendering operations
Efficiently recover liquids and manage odors with a robust solution designe...
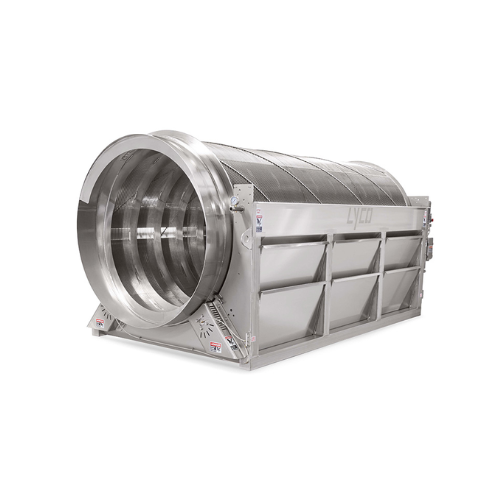
Single drum wastewater screen for liquid-solid separation
Optimize your liquid-solid separation process and reduce indus...
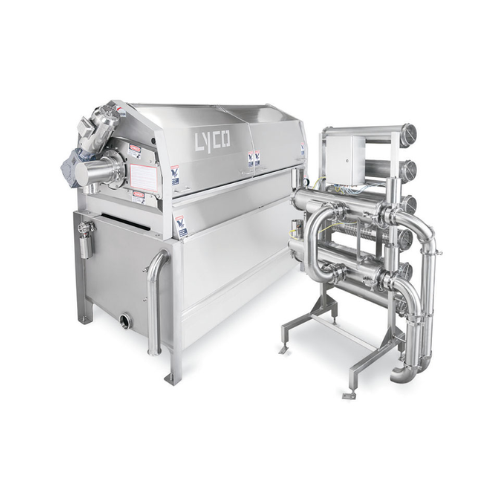
Water reuse system for poultry plants
Optimize your water usage and reduce operating costs with an efficient system that re...
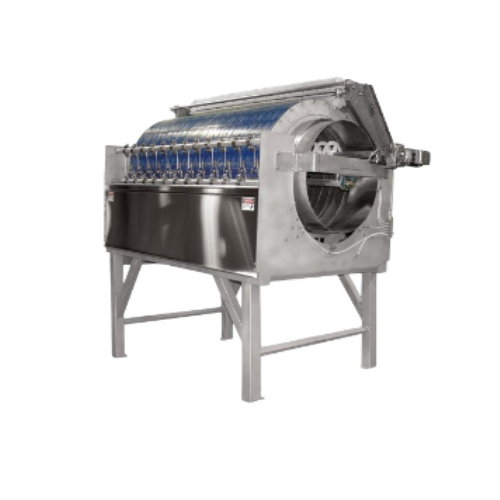
Cluster cutter for green bean processing
Efficiently streamline your green bean and vegetable processing with advanced snip...
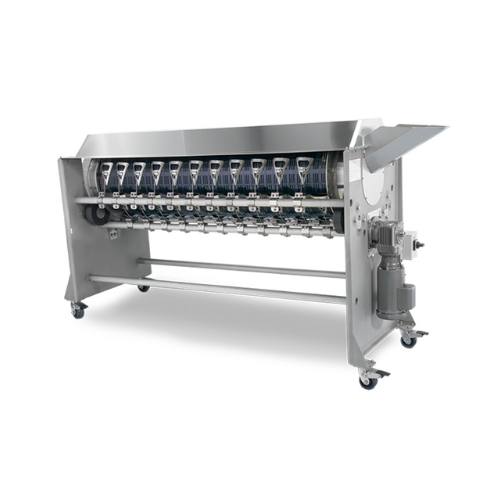
Green bean snipper for minimizing bruising
Efficiently snip and process green beans with reduced bruising while integratin...
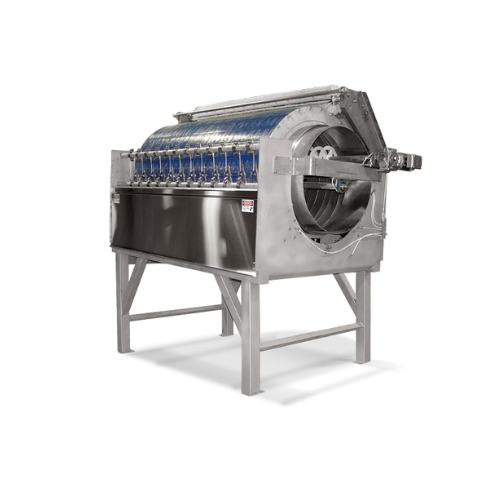
Green bean snipper for snap bean processing
Achieve precision in green bean processing with a specialized snipping solutio...
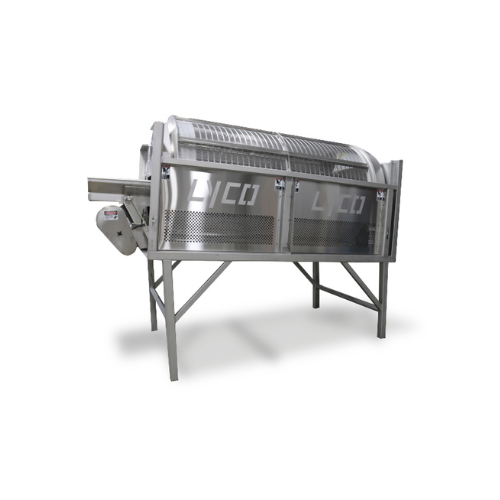
Unsnipped bean remover for green bean processing
Enhance your green bean processing line by seamlessly removing unsnipped ...
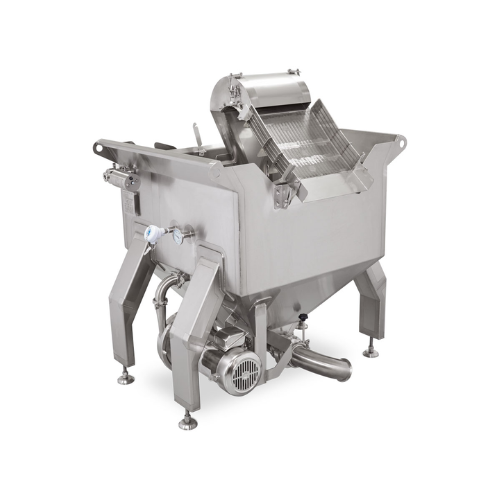
Industrial food cooler for pasta, rice, and vegetables
Rapidly reduce temperatures to halt cooking and preserve quality i...
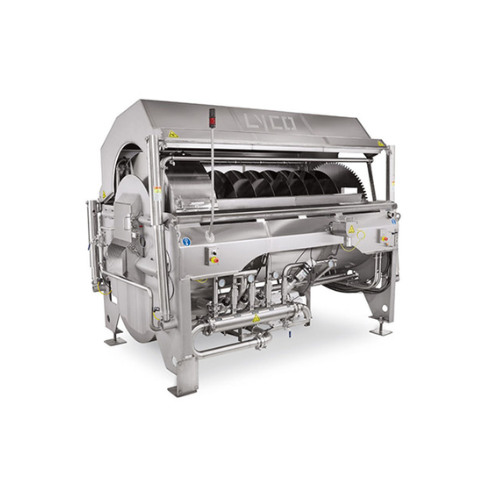
Blanching solution for pasta and rice
Eliminate clumping and overcooking with a high-capacity continuous system designed fo...
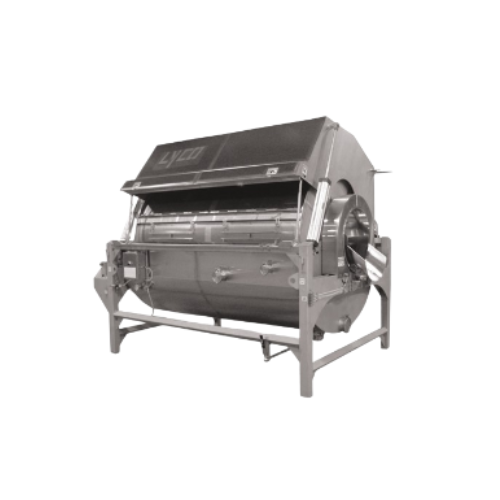
Rotary drum blancher for high volume food processing
Optimize your food production line with a versatile rotary drum blan...
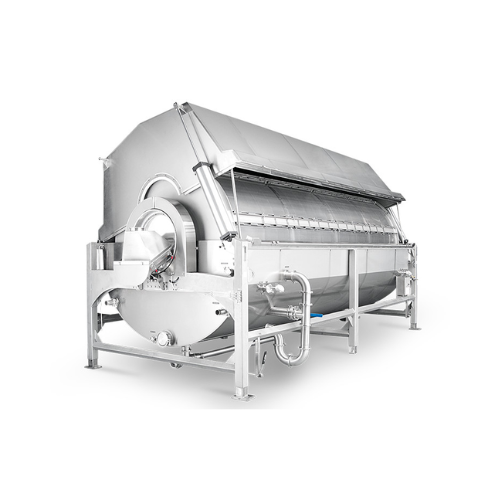
Continuous steam blancher for vegetables
Efficiently reduce water and energy usage while ensuring uniform blanching and coo...
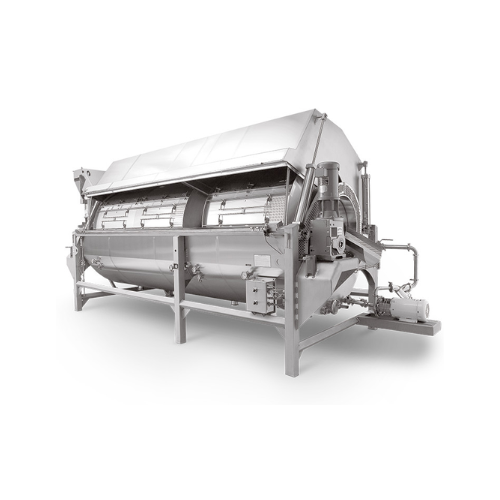
Combination cooker-cooler for pasta production
Streamline your production with a machine that efficiently cooks and cools ...
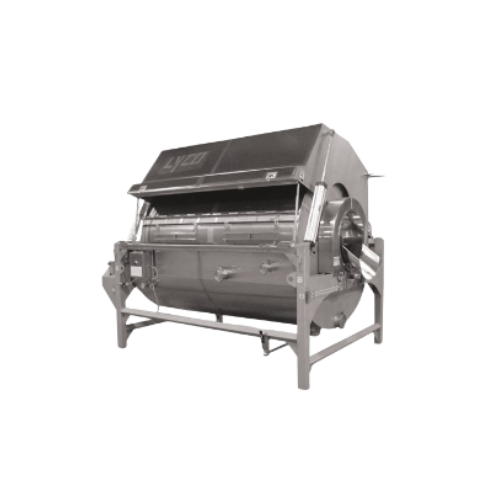
Rotary drum blancher for industrial food processing
Optimize your food processing line with a robust solution that ensure...
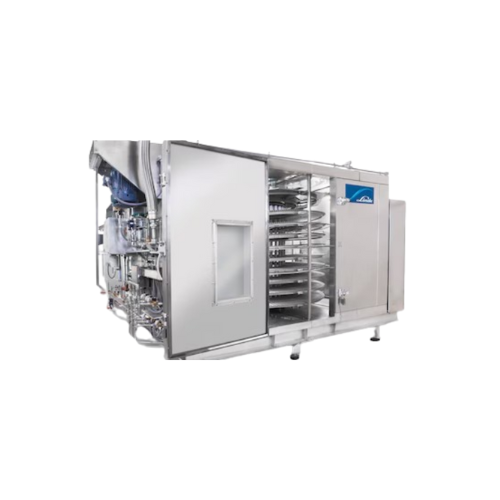
Cryogenic tunnel freezer for continuous food processing
Optimize product quality and retention with advanced cryogenic fr...
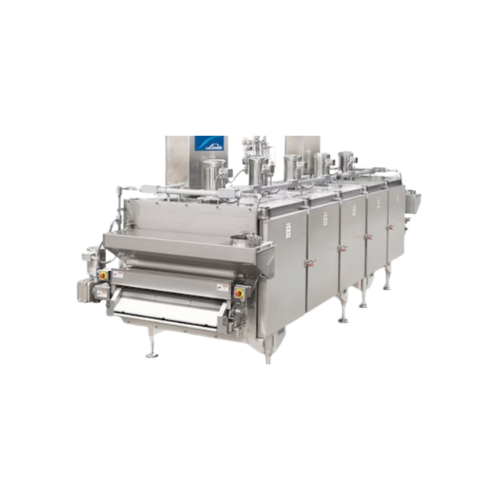
Cryogenic freezing systems for food processing
When you need precise and rapid freezing for diverse food products, these a...
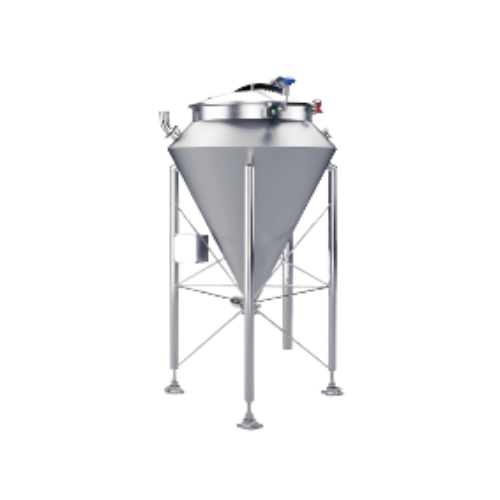
Precision weighing tank for liquid and dry ingredient blending
Enhance your production line with precision control over ...
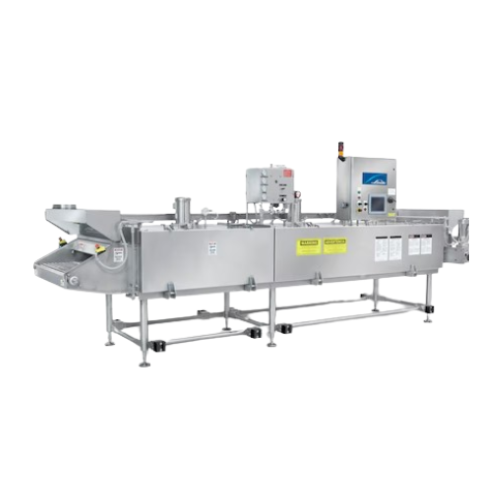
Cryogenic food freezer
Achieve rapid and precise freezing for diverse food products, ensuring optimal texture and moisture re...
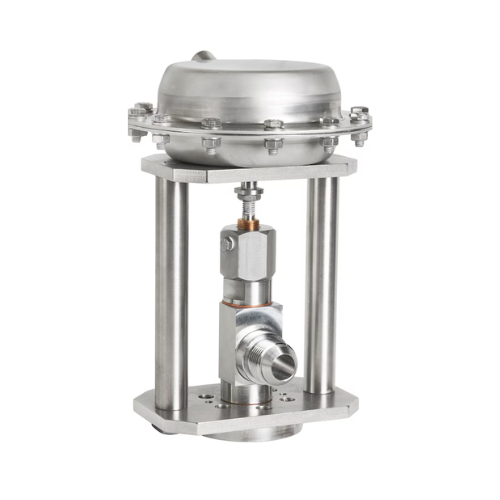
Cryogenic chilling system for meat processing
Ensure uniform temperature control in meat production lines to maintain prod...
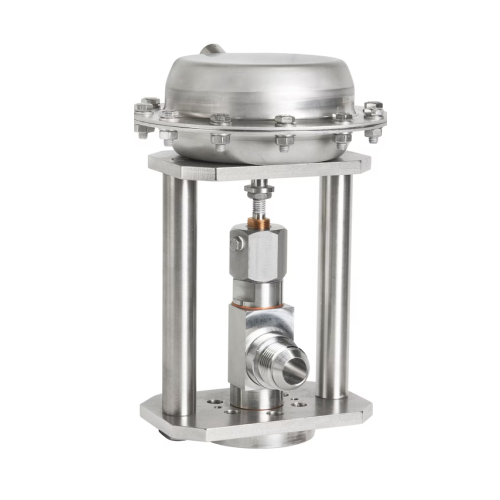
Cryogenic chilling for meat mixing and blending
Ensure precise temperature control during mixing and blending to prevent b...
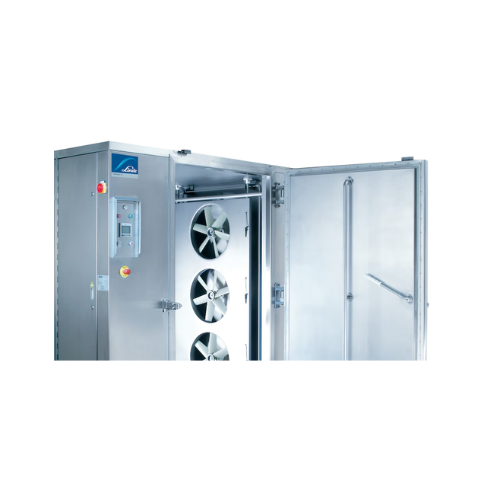
Cryogenic freezer for food industry applications
Efficiently tackle high-speed freezing and chilling challenges with a ver...
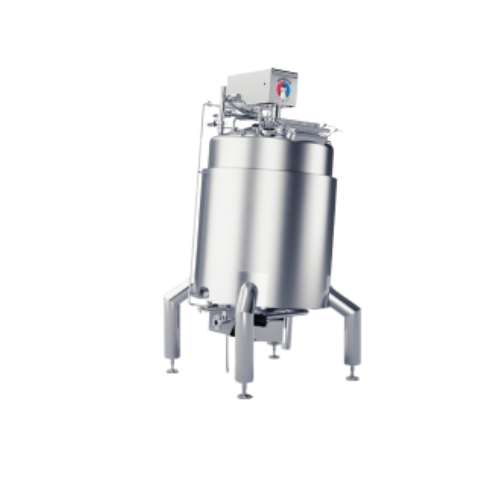
Heating and cooling system for food and dairy products
Achieve precise temperature control and efficient processing with ...
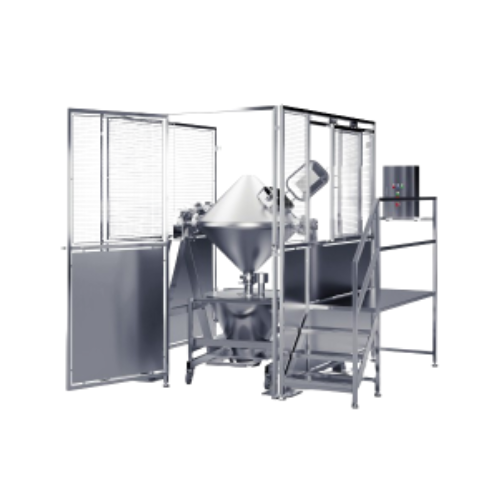
Industrial powder blender
Optimize your production with precise dry blending, ensuring efficient mixing processes and seamle...
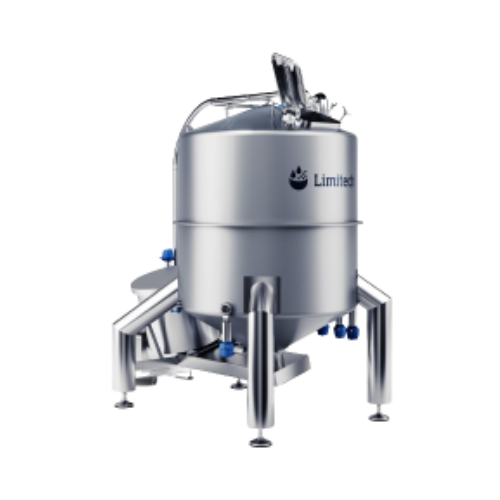
High shear mixer for viscous powder dissolution
Need consistent, homogeneous blending of high-viscosity liquids and powder...
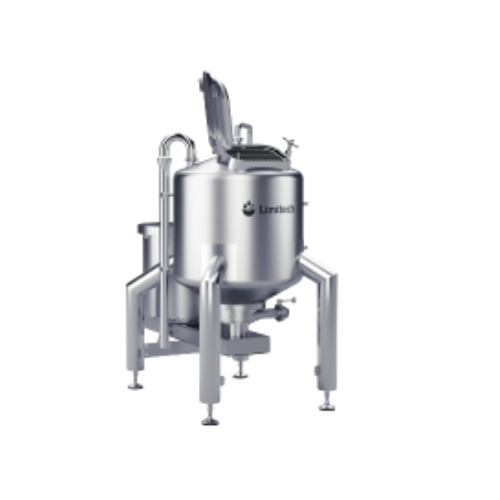
Inline high shear mixer for low to medium viscosity liquids
Efficiently dissolve large quantities of powders into liquid...
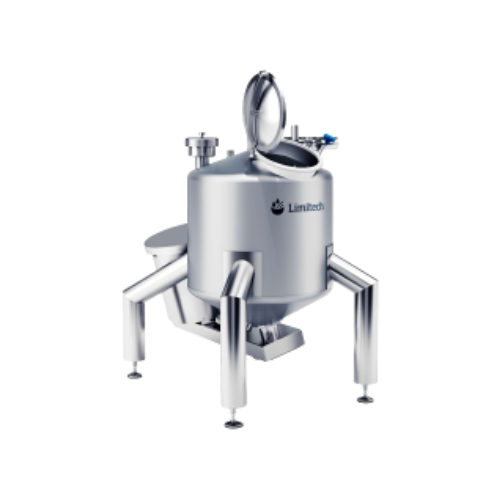
Industrial mixer for high shear mixing and emulsifying
Enhance your production line efficiency with versatile high shear ...
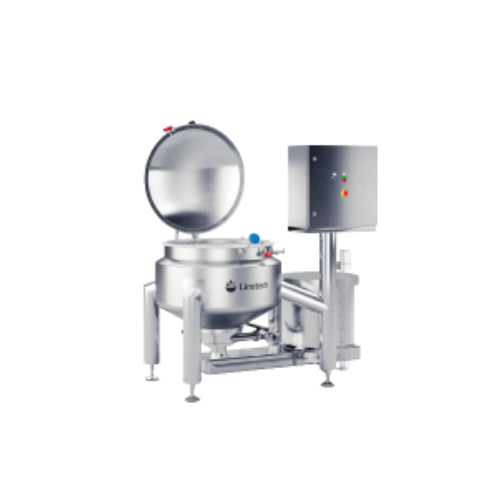
Inline high shear mixing for dairy and condiments
Streamline your production line with innovative inline high shear mixin...
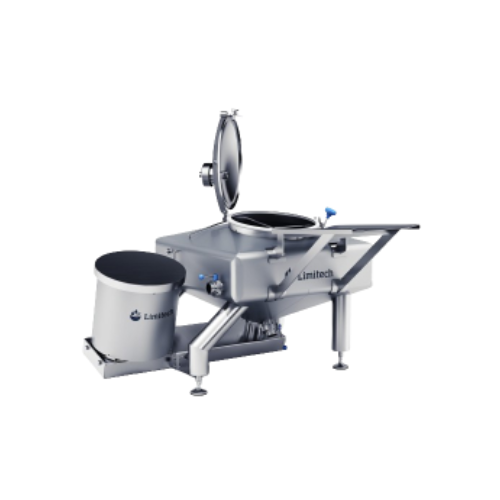
Batch mixer for dry and liquid ingredients
Achieve efficient blending of diverse ingredients with high shear mixing to str...

Pre-mixer for dissolving powders fast
Quickly dissolve powders without lumps or “fisheyes,” ensuring a smooth a...
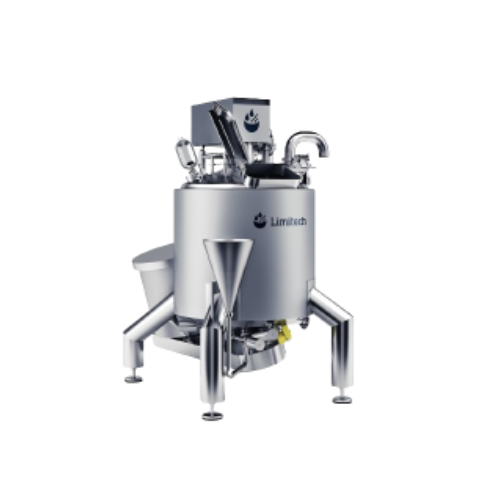
Process mixer for food production
Optimize your production line with a versatile and adaptable process mixer that offers se...
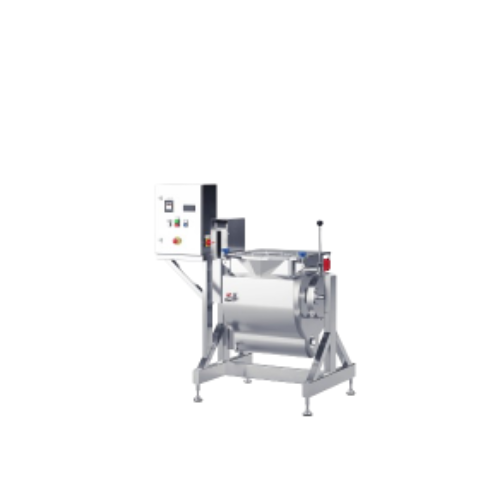
Industrial melting tank for diverse manufacturing applications
Optimize your production with this versatile melting tank...
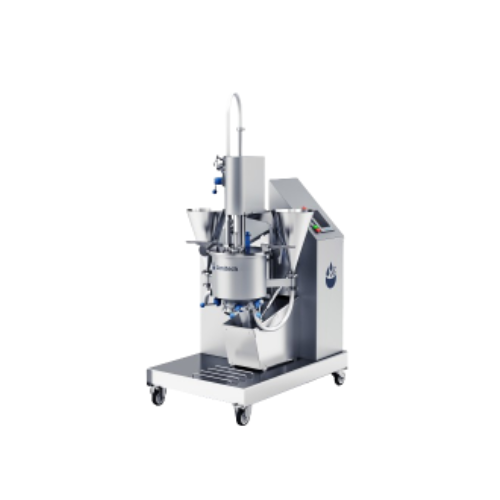
Blender for high viscous products
Tackle high-viscosity challenges with an advanced blending solution designed for efficien...
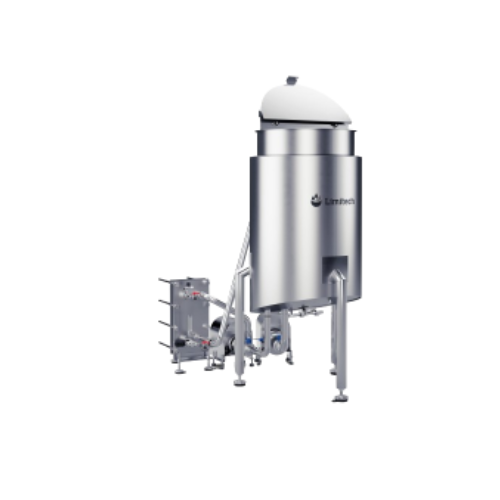
Oil cooling tank for fast product cooling
Accelerate your cooling process efficiently with an advanced oil cooling tank fe...

Customized oil storage tank for industrial use
Enhance production efficiency and ensure seamless integration with customiz...
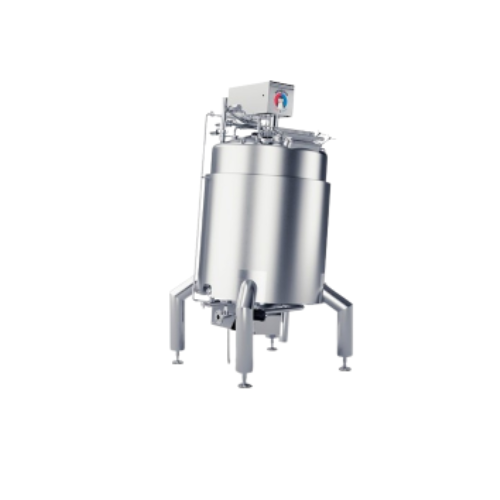
Cooling system for vegetables and meat
Optimize cooling efficiency with dual counterrotating agitators and expansive surfac...
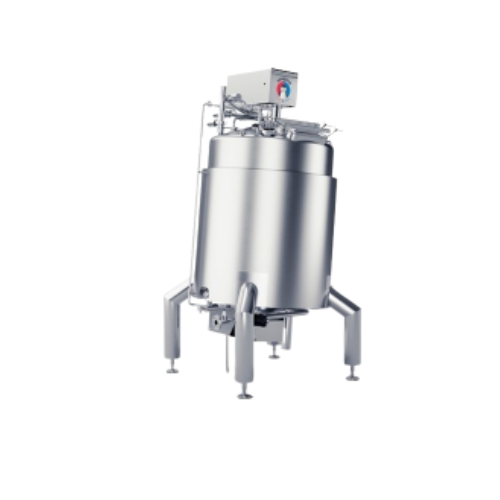
Heating solution for vegetable and meat products
Achieve efficient heating and optimal heat transfer for sauces and dairy ...
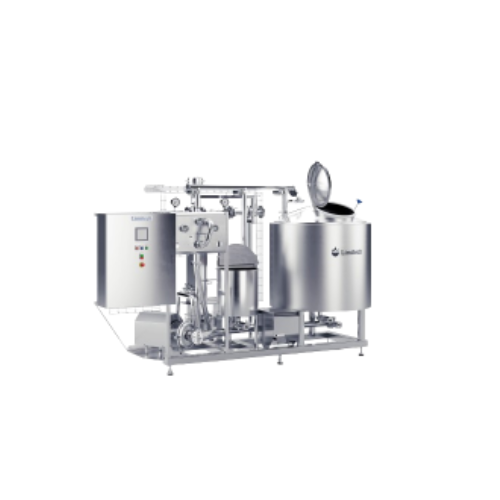
Cip dosing and water unit for industrial cleaning
Elevate your plant’s hygiene with this system, designed for seaml...
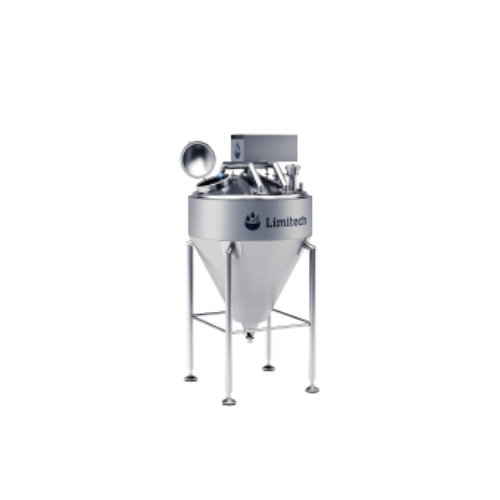
Conical buffer tank for hygienic dairy and food processing
Achieve efficient processing of high-viscosity products with ...
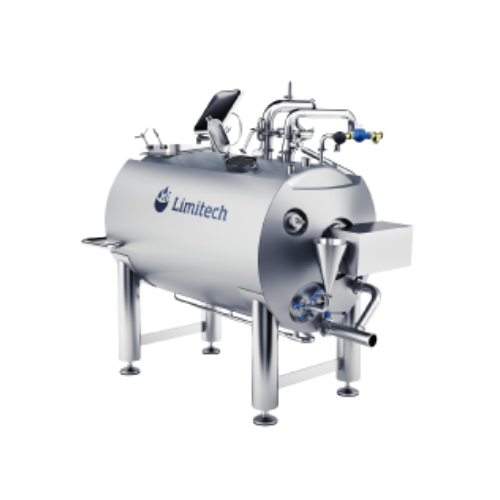
Emulsifying and blending system for liquid and semi-liquid food products
Efficiently emulsify and blend liquid and semi...
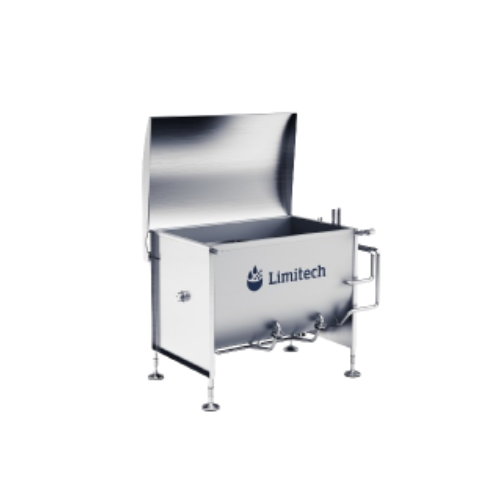
Food mixing and blending system
Enhance your production line with a versatile system designed for gentle processing needs, o...
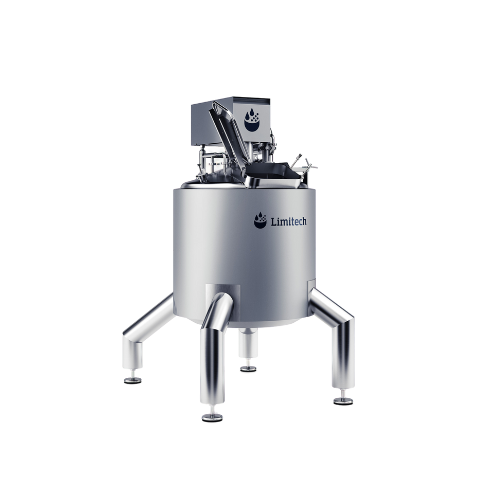
Powder dissolver for large liquid quantities
Achieve uniform powder blending swiftly with a vacuum-assisted system that pr...
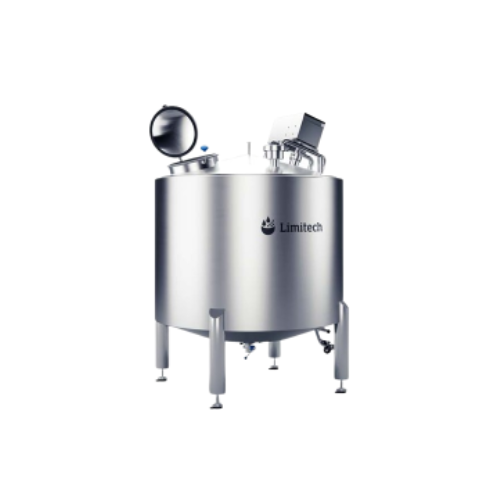
Cylindrical buffer tank for processing lightly liquid products
Optimize production continuity with this cylindrical buff...
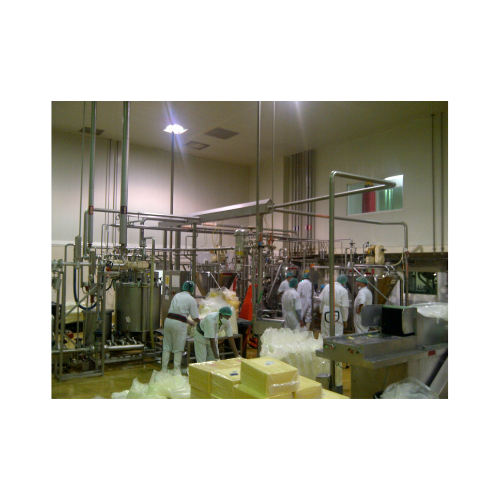
Ultra high temperature treatment system
Achieve extended shelf life and product stability with ultra high temperature treat...
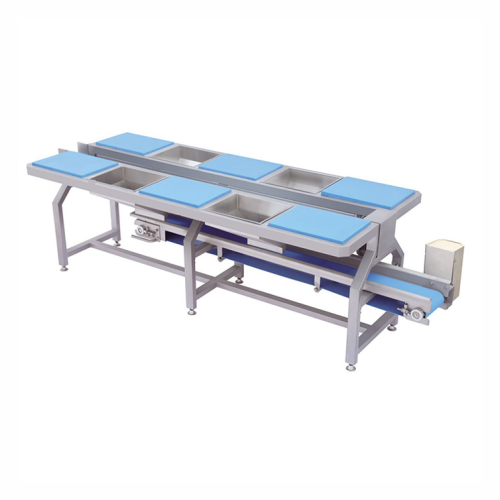
Vegetable and fruit preparation table
Optimize your food processing line with a versatile preparation table designed for ef...
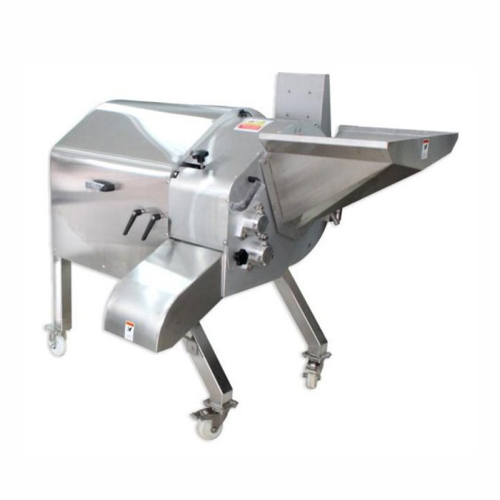
Vegetable and fruit dicer for commercial use
Efficiently transform a variety of produce into precise cubes, slices, or shr...
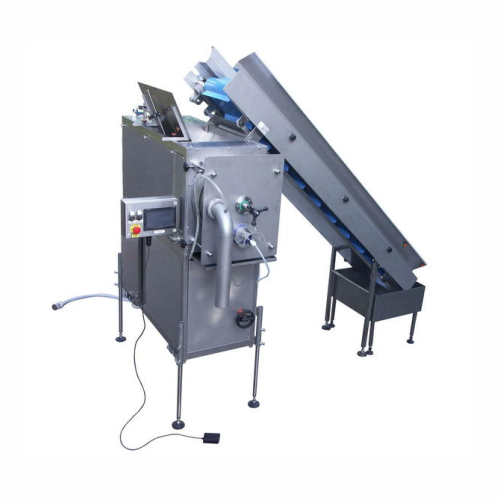
Automatic dosing and packing system for cabbage and sauerkraut
Streamline your vegetable processing line with a robust, ...
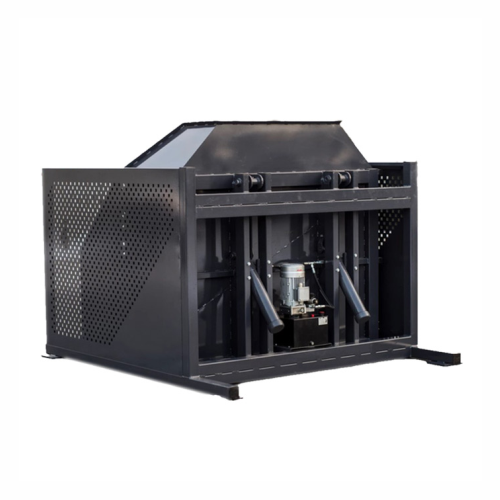
Hydraulic box tipper for pallets
Streamline your material handling with precision and safety by integrating this hydraulic t...
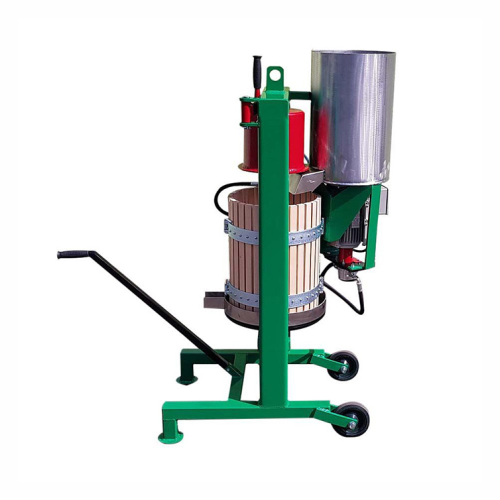
Hydraulic juice press for fruit and vegetables
Streamline your juicing operations with this hydraulic solution, expertly d...
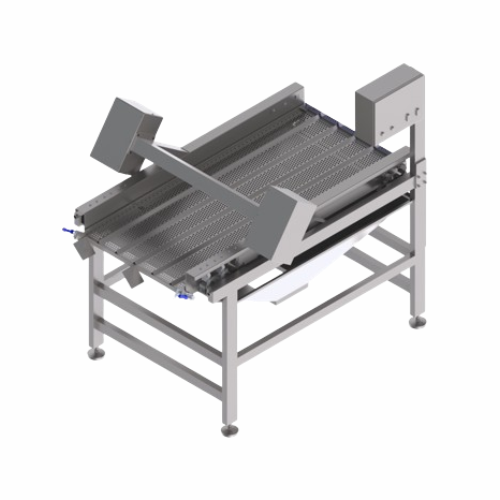
Vibrating sorting table for pre-dewatering
Efficiently streamline your production with a versatile vibrating sorting table...
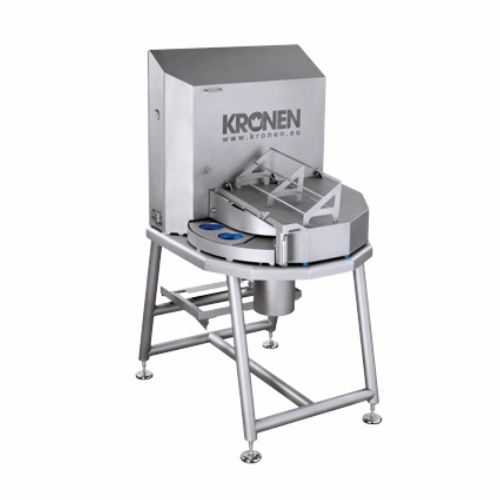
Vegetable and fruit cutting solution for slices, segments, and sticks
Streamline your pre-processing with a versatile c...
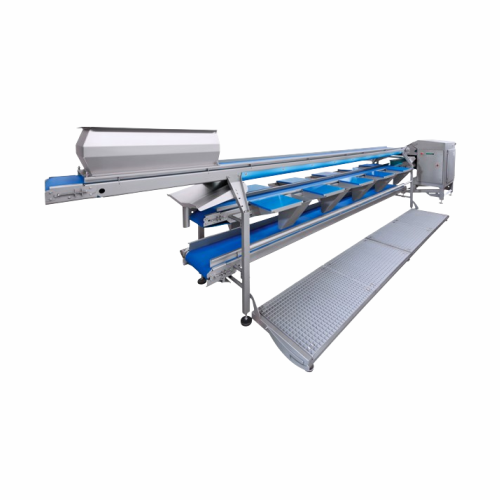
Trimming table for fruit and vegetables
Streamline your pre-processing phase with this trimming table, helping you efficien...
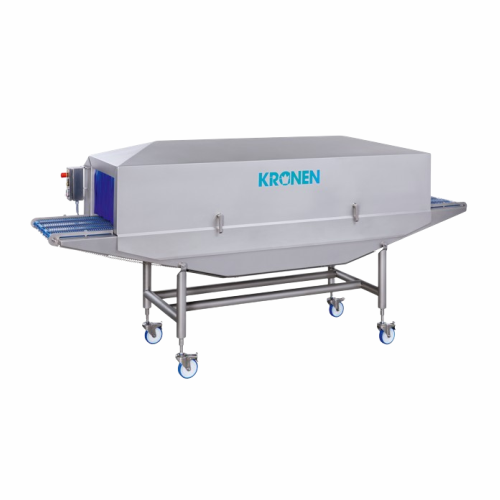
Uvc surface disinfection for food packaging and tools
Achieve fast and effective UVC disinfection of food products and pa...
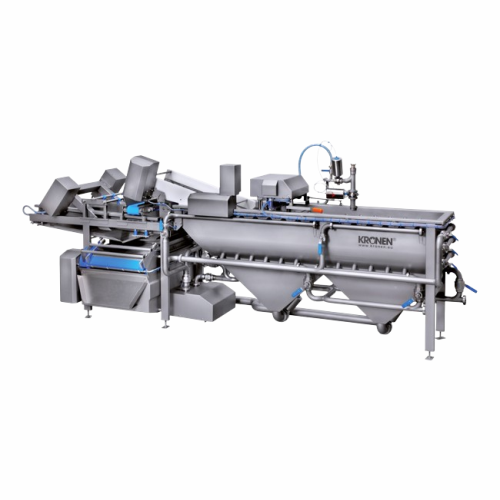
Industrial washing and sorting for bell peppers
Efficiently sort, trim, and wash your peppers with a single system, ensuri...
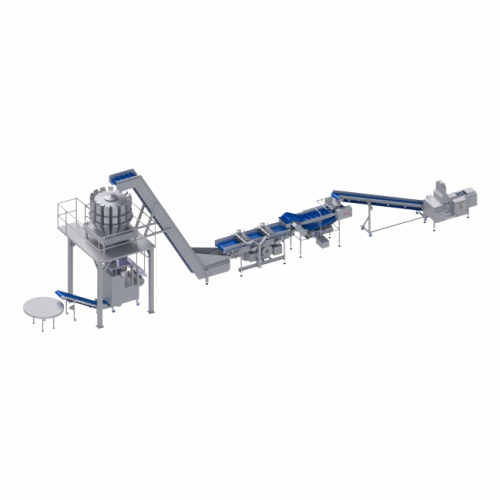
Fruit processing and packaging line
Streamline your fruit and vegetable processing with this semi-automatic system designed...
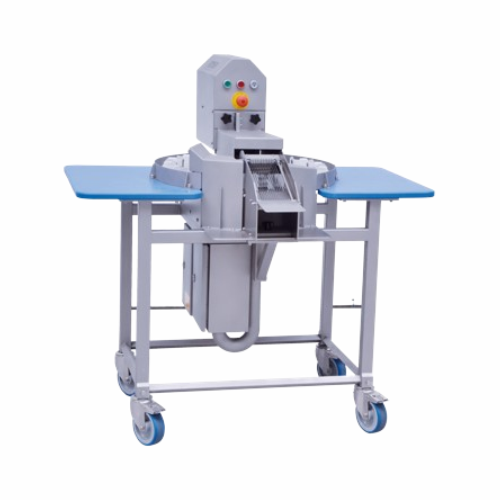
Vegetable and fruit slicer
Achieve uniform, precise slices for your fruits and vegetables with a state-of-the-art cutting so...
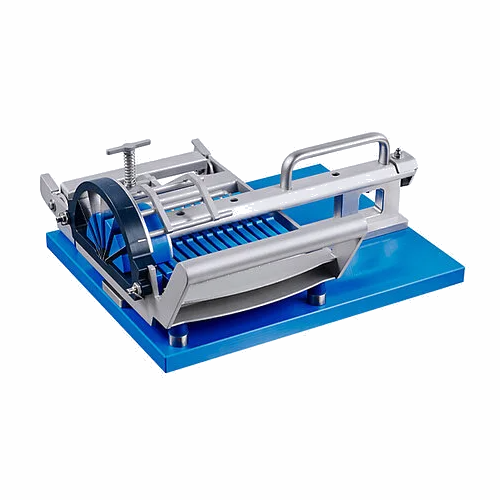
Manual melon chunk cutter
Transform your melon processing with a compact tabletop cutter, designed for efficient chunking an...
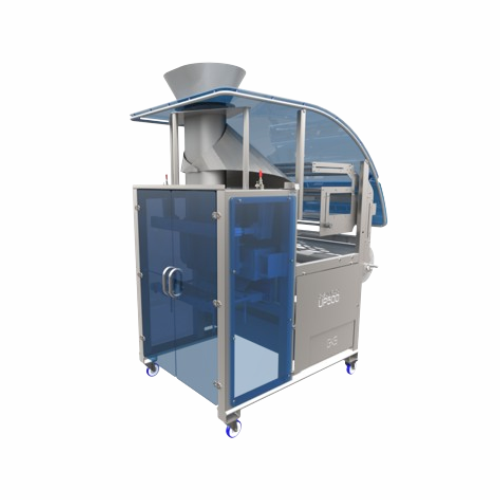
Flexible packaging solution for large food volumes
For high-volume food packaging, achieving consistent bag sizes and red...

Decontamination system for whole fruits and vegetables
Enhance hygiene and extend shelf life by effectively reducing micr...
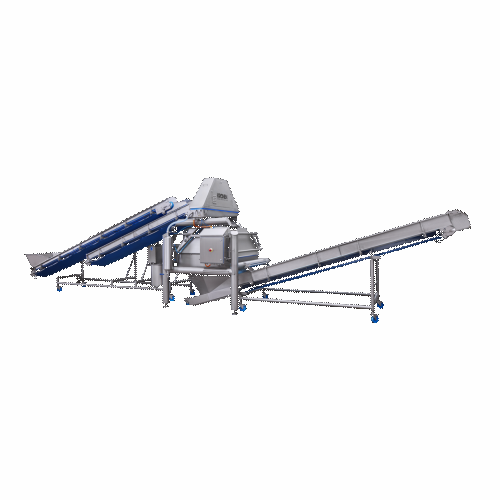
Centrifugal drying system for lettuce and vegetables
Enhance your production line’s efficiency with this high-capac...
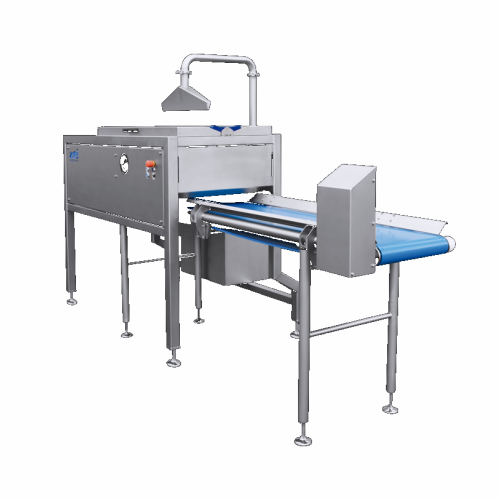
Grape destemming solution for efficient fruit processing
Streamline your fruit preparation process with a versatile machi...

Manual vegetable and fruit grid cutter
Effortlessly transform small-sized fruits and vegetables into decorative and functio...
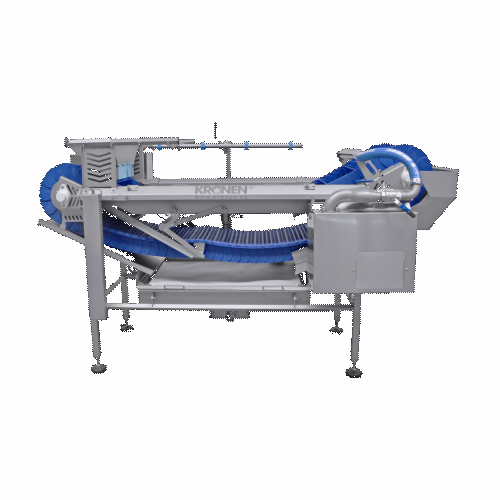
Industrial dipping bath for prolonging shelf life of cut fruits and vegetables
Enhance the shelf life and hygiene of y...
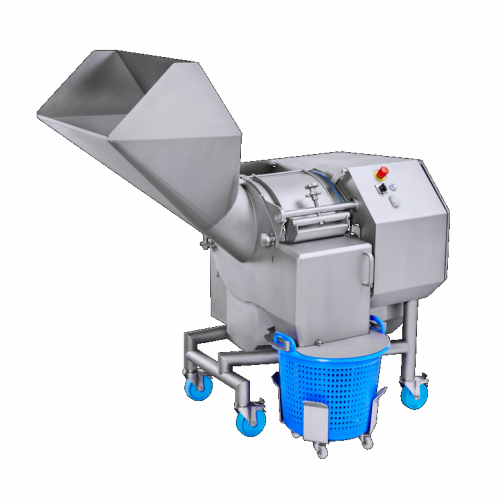
High-capacity cutting solution for fruits and vegetables
Efficiently transform large volumes of food products into cubes,...
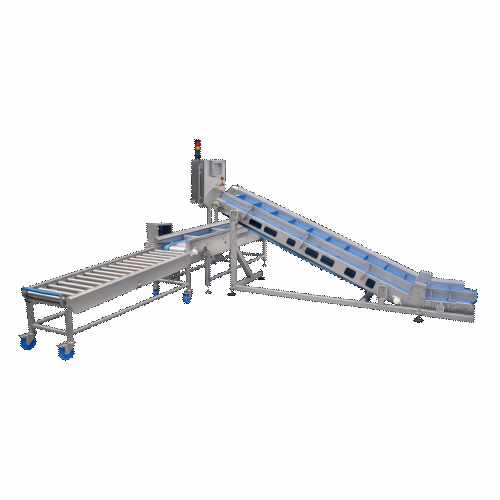
Automatic crate weighing system for fresh produce
Streamline your fresh produce processing by precisely weighing and fill...
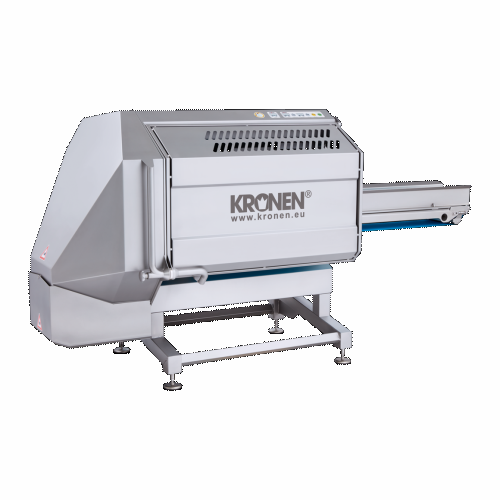
Industrial belt cutting system for vegetables and fruits
Achieve precise and high-capacity cutting for various food produ...
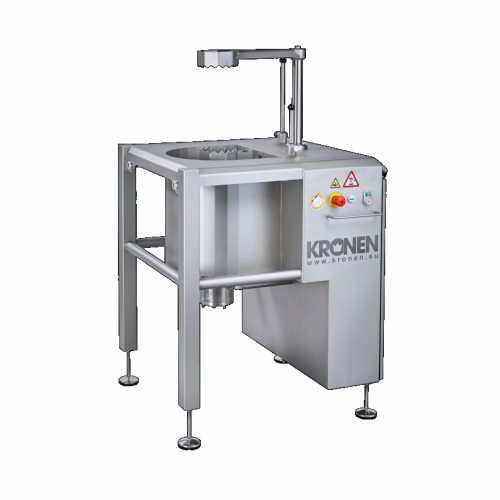
Cabbage coring solution for high throughput
Streamline your high-volume cabbage processing with a precise and efficient co...
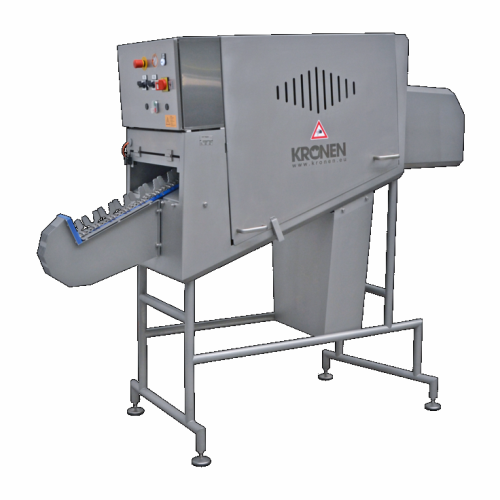
Automated chicory root cutter
Streamline your chicory processing with precise root removal, reducing waste and enhancing yie...
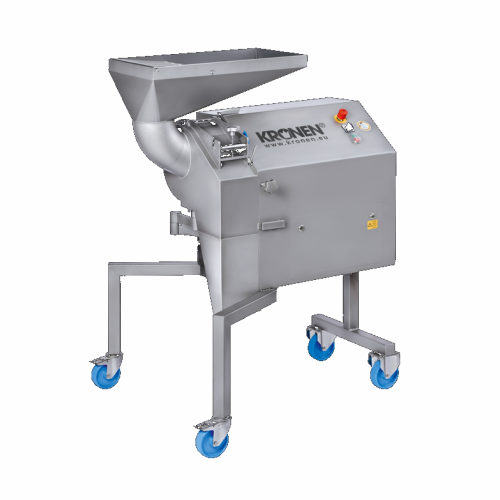
High-performance cube, strip & slice cutting solution
Achieve precision in high-volume food processing with a cutting sol...
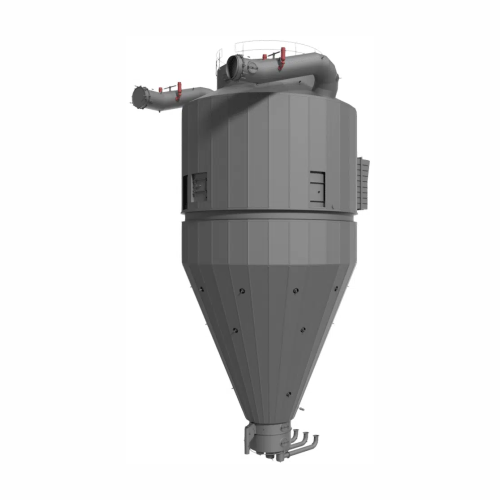
Wide body dryer for dairy and food products
Achieve precise moisture control and optimal powder agglomeration for dairy an...
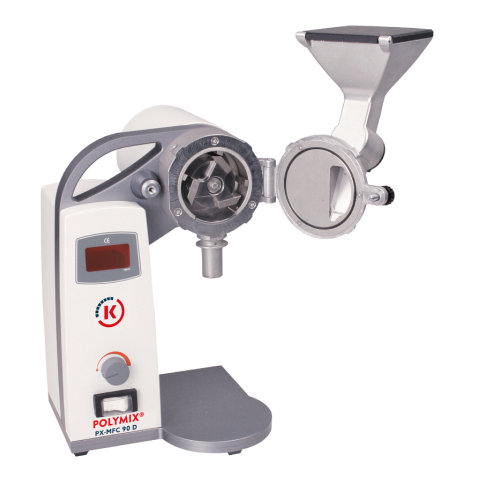
Dry sample preparation mil
Optimize your grinding processes with precision particle size reduction for various materials, en...
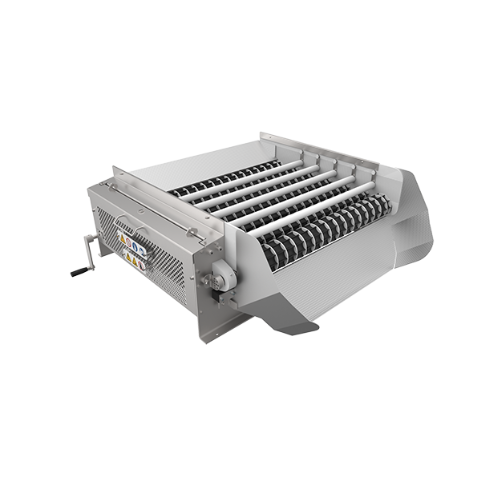
Rotary size grader for food processing
Enhance your production line by efficiently sorting and classifying produce to ensur...
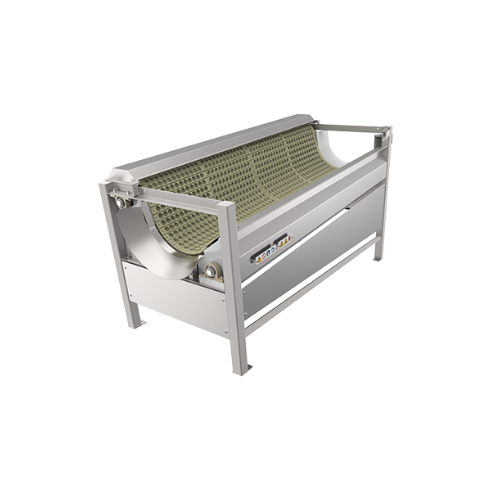
Small piece remover for food processors
When handling diverse food products, ensuring consistent product sizing is vital. T...
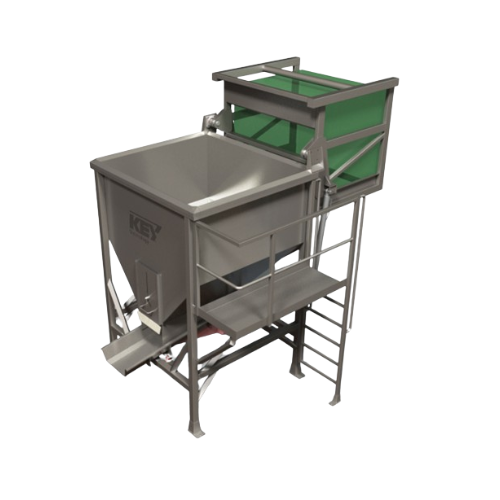
Tote bin dumper for bulk product transfer
Streamline your bulk product handling with a solution that efficiently transfers...
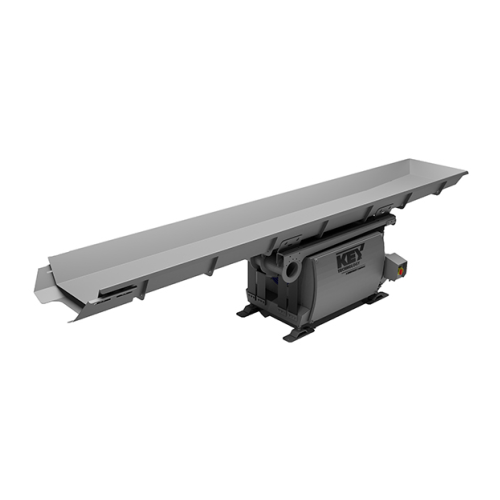
Industrial transfer conveyor system
Efficiently transport and sort diverse food products with precision, ensuring seamless ...
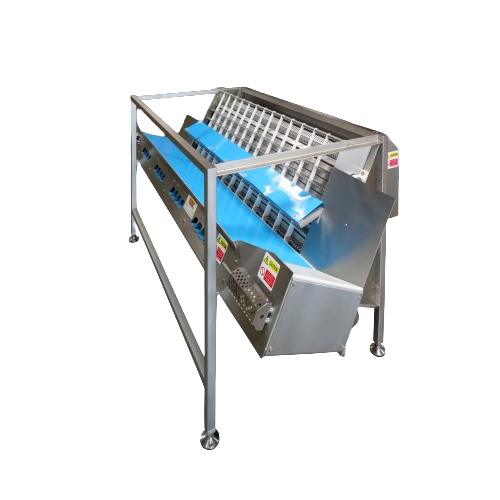
High-performance food processing and sorting solutions
Optimize your production line with integrated processing, conveyin...
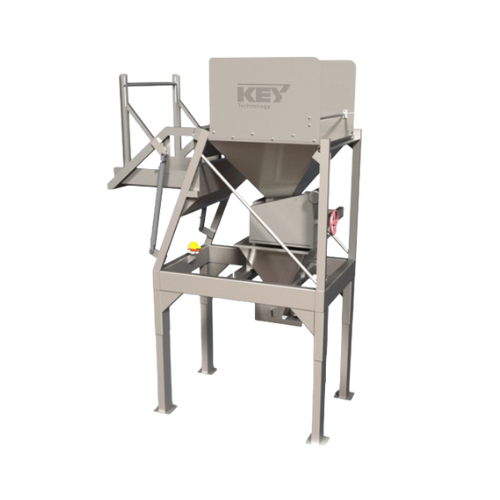
Food processing mixing system for vegetables
Tackle complex product mixing challenges with a system that seamlessly integr...
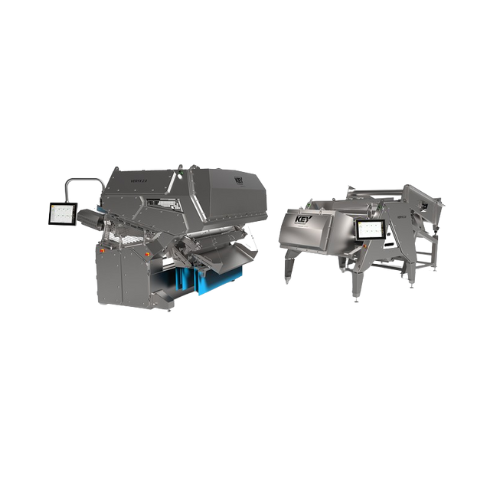
Optical sorting platform for food processing
For manufacturers aiming to enhance quality control, this platform offers pre...
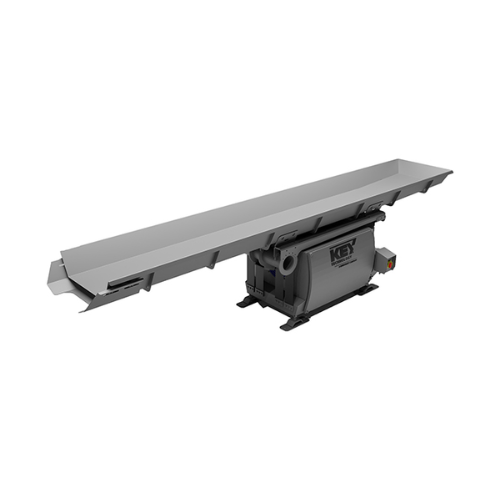
Large capacity horizontal motion conveyor for fragile products
Achieve gentle handling and minimize product damage with ...
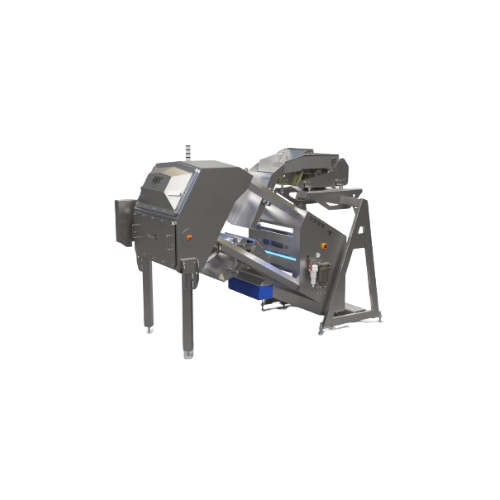
Optical sorter for food processing
Enhance your production line with advanced sorting technology that meticulously inspects...
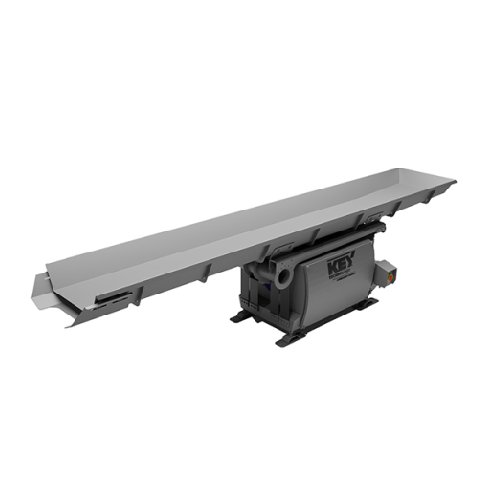
Distribution conveyor systems for food processing
Streamline your food processing pipeline with precision-engineered dist...
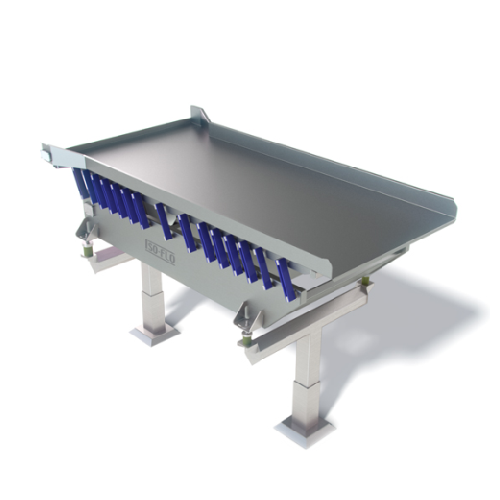
Feed conveyors for efficient product presentation
Optimize your production line with feed conveyors designed to streamlin...
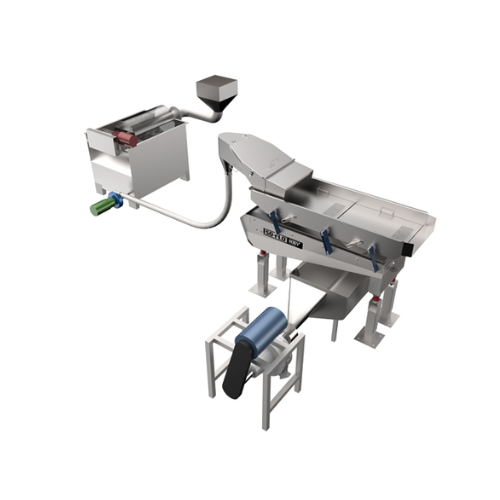
Hydro-flo food processing pump for vegetable transfer
Optimize food handling with a gentle, space-saving pump that protec...

Industrial food grading system for vegetables
Optimize your production line with a versatile food grading system, ensuring...
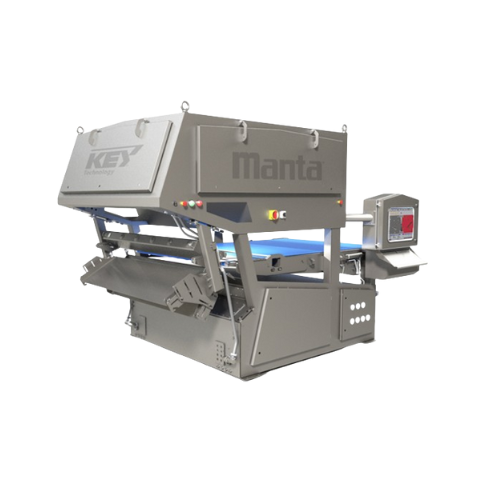
High-capacity optical sorter for food processing
Optimize your production line with precise sorting and separation, enhanc...
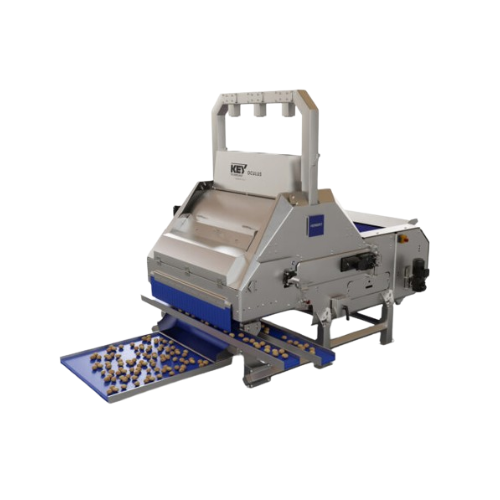
Optical potato sorter
Ensure precise sorting with advanced optical technology that identifies and separates defects in a wide...
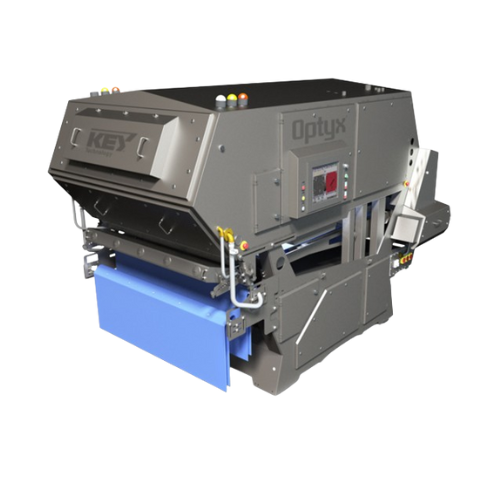
Optical sorting solution for food processing
Achieve precise sorting and maximize yield with a cutting-edge optical soluti...
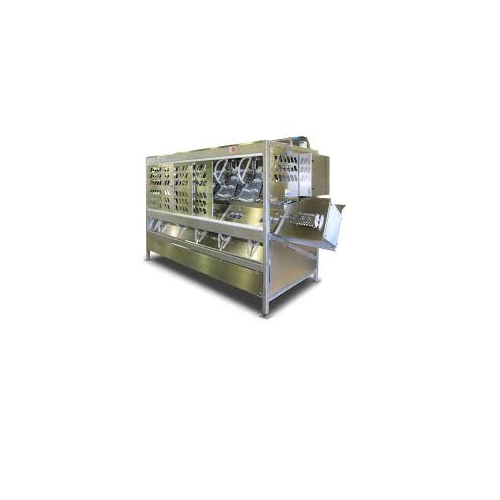
Sorting system for blueberries
Streamline diverse food processing tasks by efficiently conveying, processing, and sorting pr...
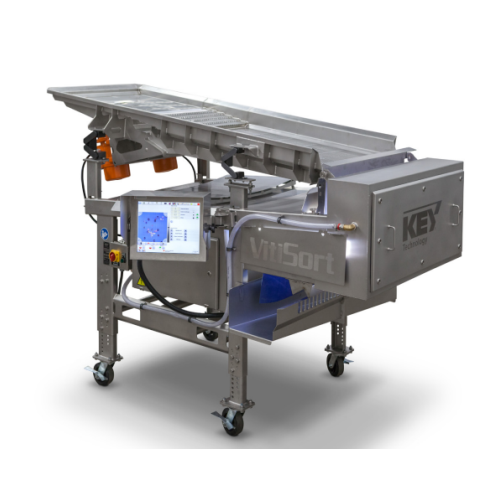
Vibratory conveyor for efficient bulk material transportation
Optimize your processing line with robust vibratory convey...
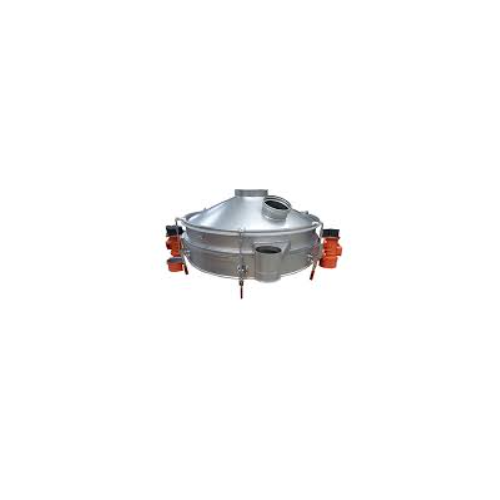
Vibrating control screeners for high volume screening and sifting
Ensure precise material separation with a solution de...
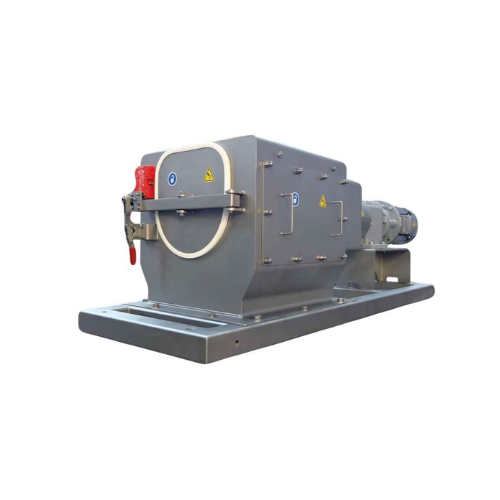
Heavy duty lump breaker for coarse and pre-grinding
Achieve consistent particle size reduction with this heavy-duty solut...
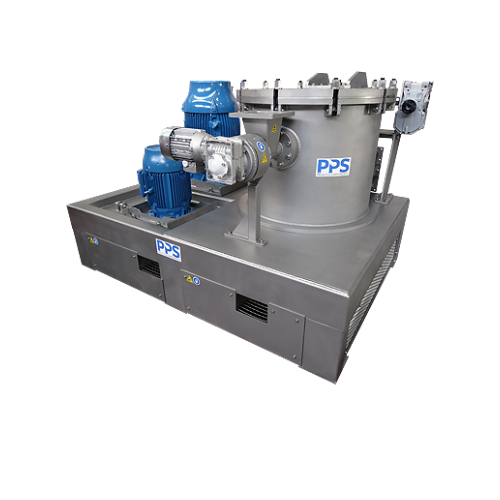
Air classifier mill for ultra-fine powder grinding
Optimize your milling operations with precision particle size control ...
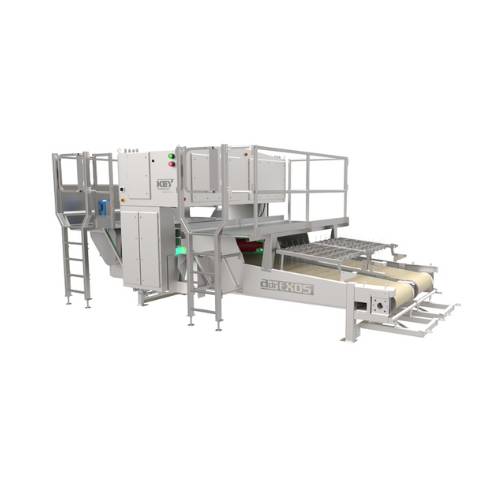
Automatic defect removal for french fries
Maximize yield and enhance quality in potato strip production with precision cut...
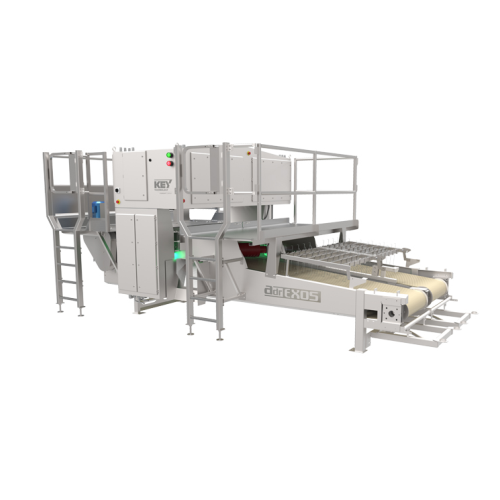
Inspection systems for poultry and seafood processing
Enhance the quality control of your food production with cutting-ed...
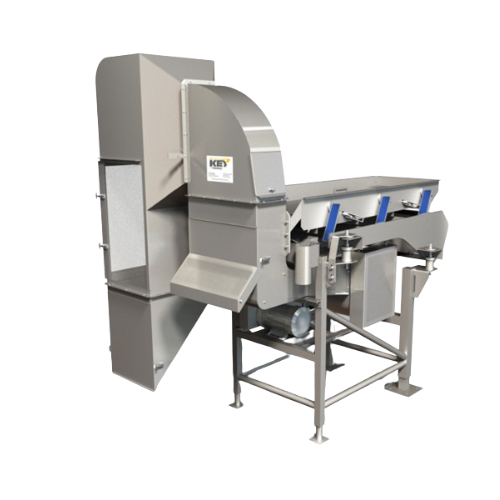
Industrial air cleaner for food processors
Optimize your production line with high-speed air separation, effectively remov...
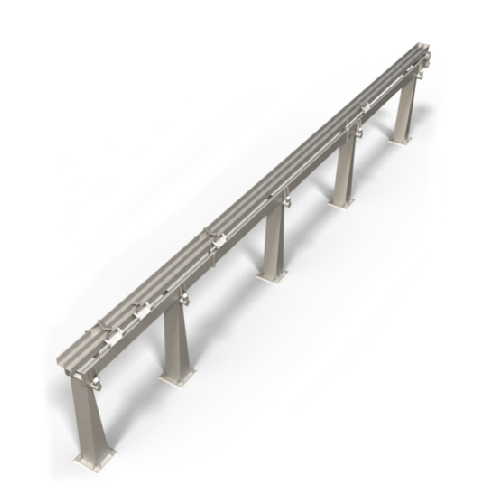
Collection conveyors for food processing
Optimize your production line by efficiently collecting and conveying solid produc...
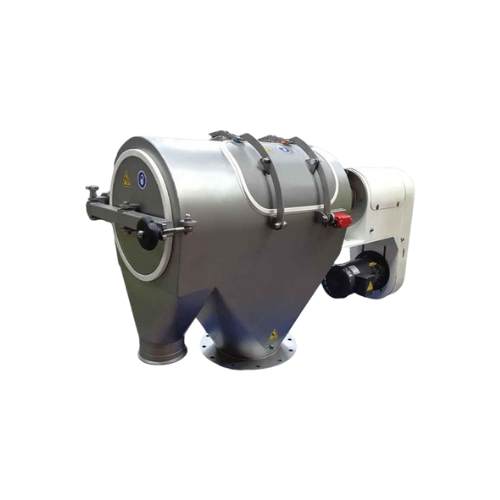
High-speed centrifugal sifter for food and pharma applications
Optimize your powder processing with a high-speed centrif...
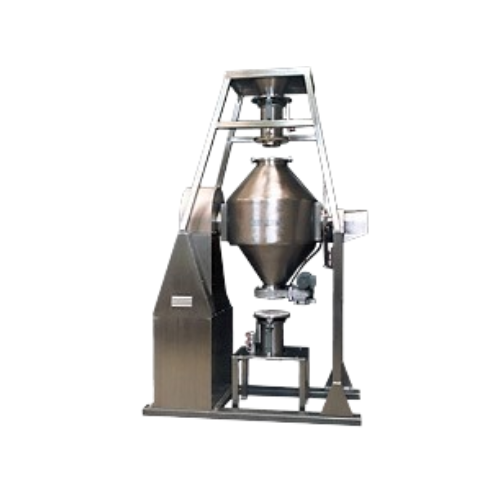
Double cone blender for fragile and abrasive material
Achieve homogeneous blends of fragile materials while minimizing da...
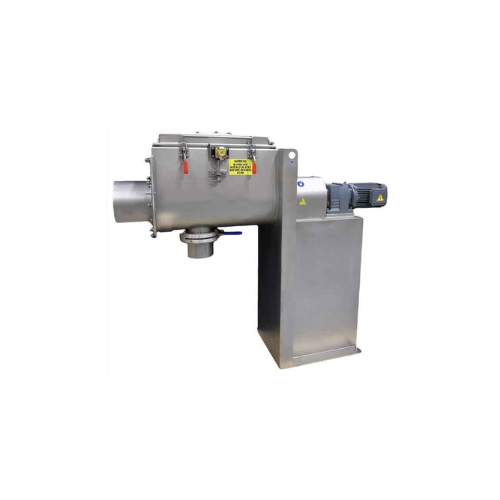
Homogenous blending solution for powders and granules
Achieve precise, homogenous blending of challenging materials like ...

Vertical bagging system for heat sealing films and Lpde
Achieve unparalleled flexibility with a versatile vertical baggin...
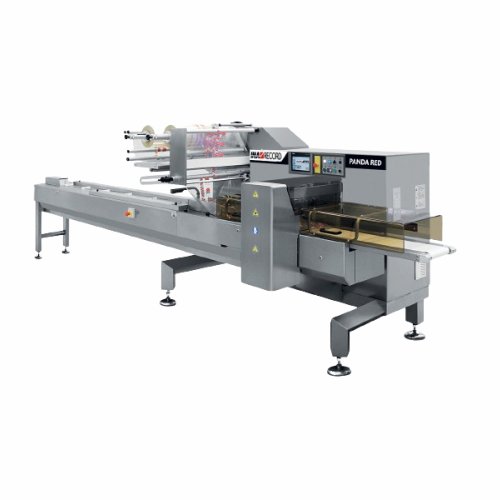
Horizontal flow wrapper for medium performance level
Offering high-speed, continuous flow wrapping, this versatile machin...
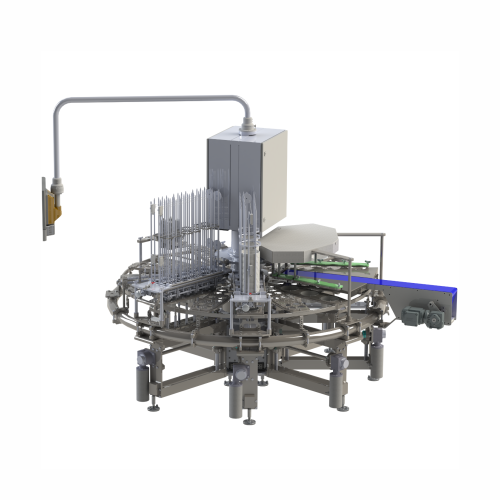
Rotary filling and sealing for liquid to pasty products
Boost production efficiency with a flexible rotary solution that ...
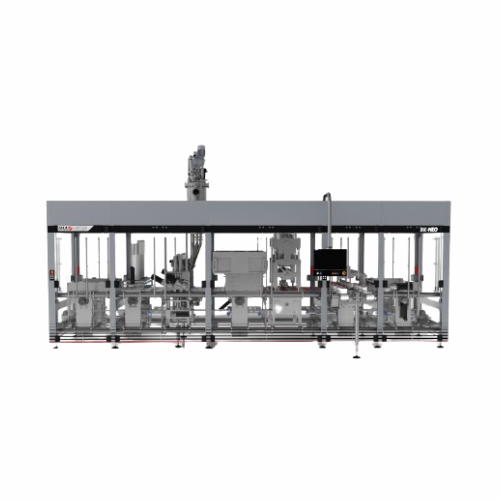
Filling and sealing system for pre-formed cups
Experience seamless integration of hygienic filling and sealing with adapta...
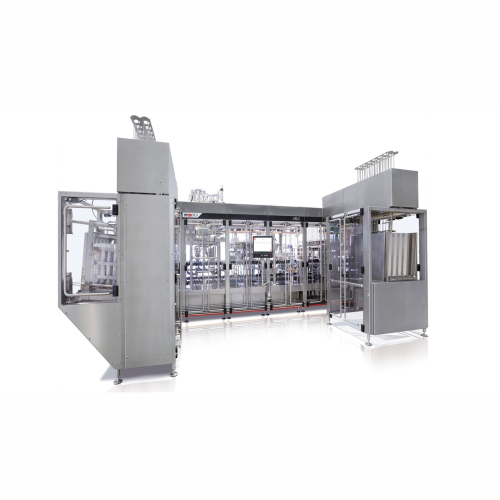
Flexible filling and sealing system for pre-formed cups
Achieve precise portioning and consistent quality in your product...
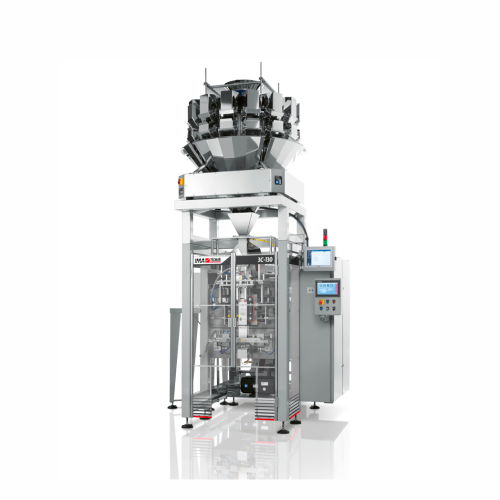
Vertical baggers for confectionery packaging
Streamline your packaging operations with high-performance vertical baggers d...
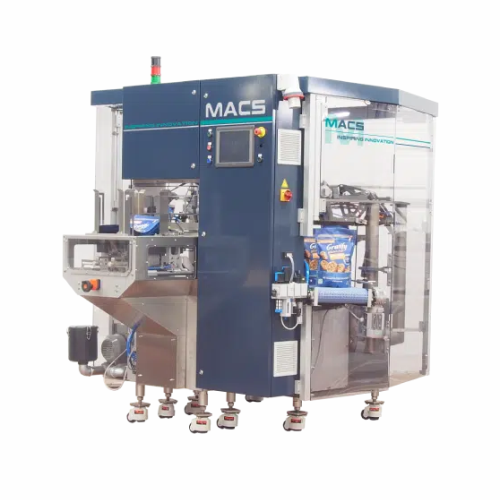
Rotary doypack for granules, liquids, and powders
Enhance your packaging line with a rotary doypack system designed to ef...
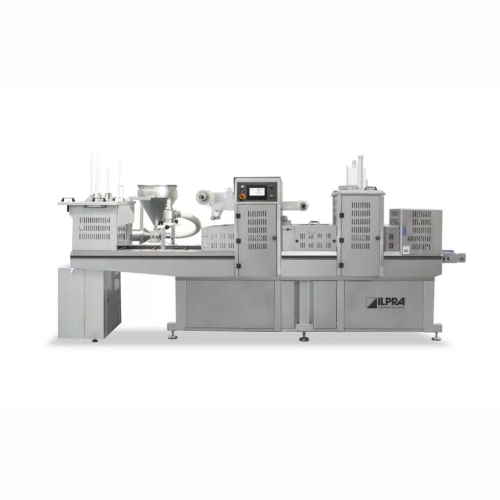
Tray sealing machine for buckets
Ensure efficient sealing and preservation with high-speed tray sealing for various food pro...
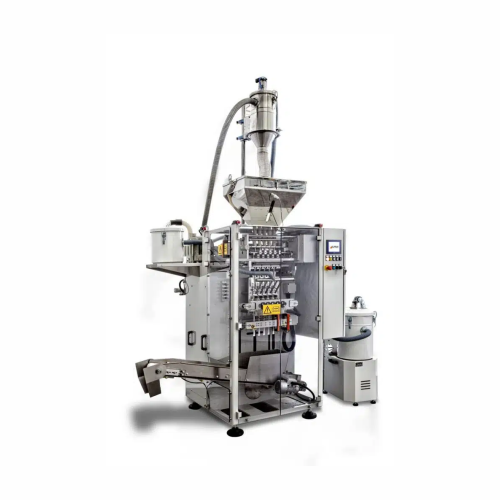
Vertical stick pack sachet packaging solution
Ideal for mid-scale operations, this vertical stick pack machine streamlines...
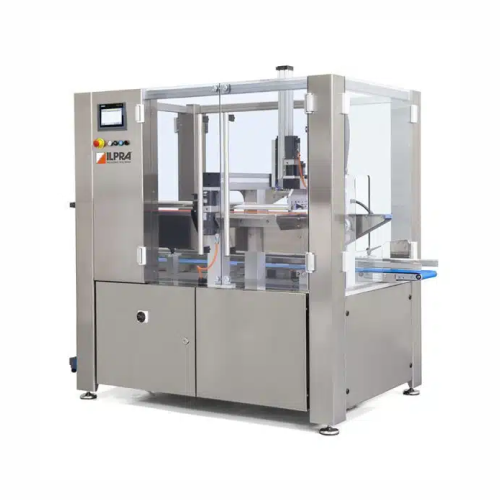
Automatic vertical casepacker for efficient packaging integration
Streamline your packaging process with a vertical cas...
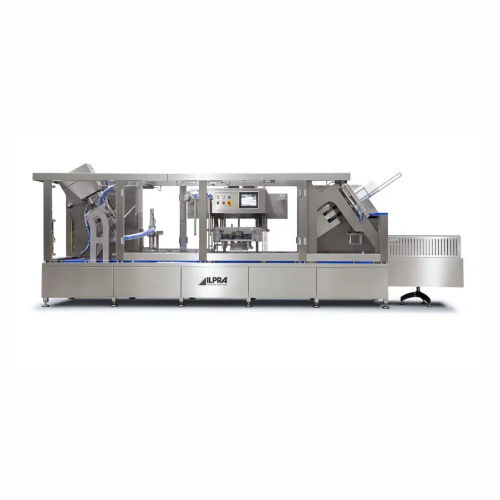
Tray sealer for food packaging buckets
Enhance your packaging efficiency with a highly adaptable tray sealer, designed for ...
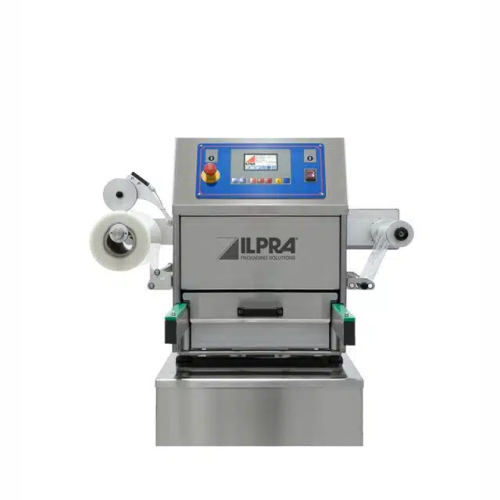
Tray sealer for packaged food products
Optimize your food packaging with precise sealing and advanced Modified Atmosphere P...
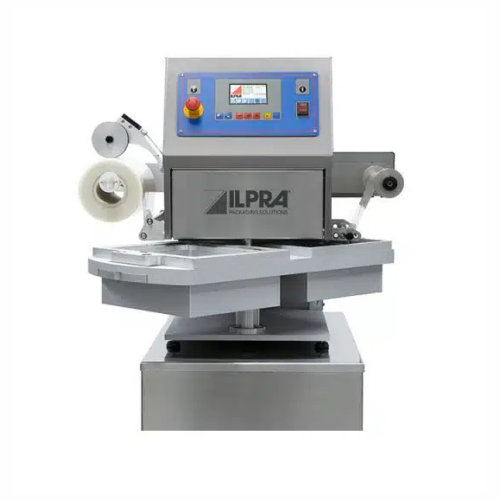
Traysealer for modified atmosphere packaging - food products
Optimize your packaging line with this semi-automatic trays...
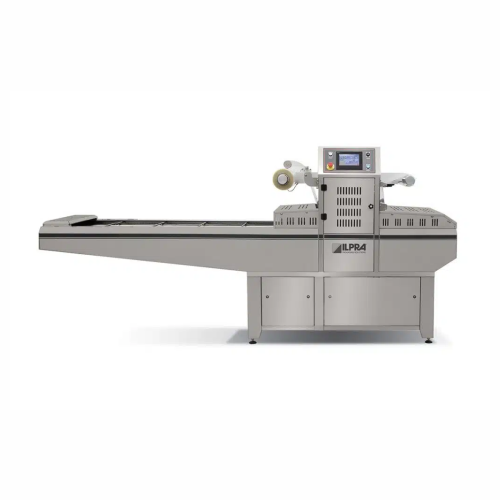
Traysealer for medium production
Streamline your packaging process with high-speed traysealing, ensuring freshness and exten...
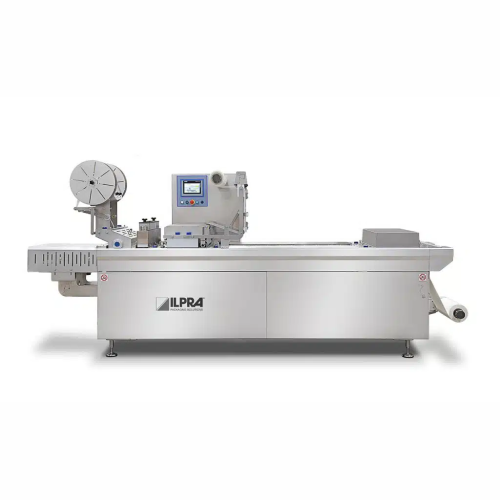
Thermoforming packaging solution for food and medical applications
Enhance your packaging line with a solution designed...
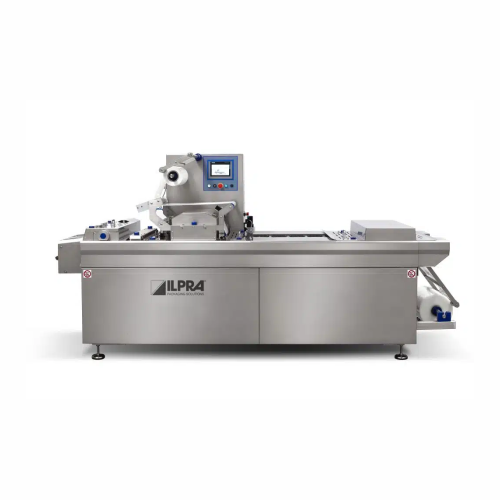
Compact thermoforming packaging system for food industry
Revolutionize your packaging line with a space-saving solution t...
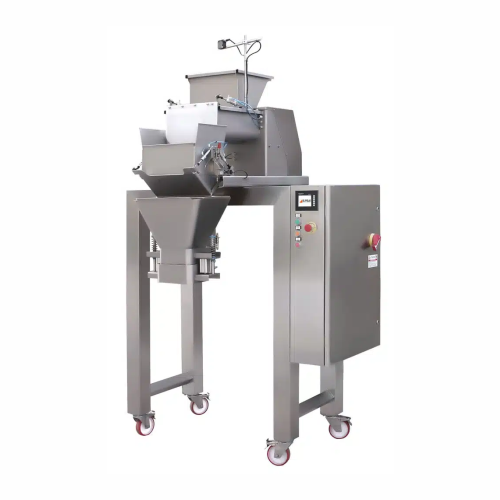
Linear and auger weighing systems for non-free-flowing products
Optimize your production line with precise weighing and ...
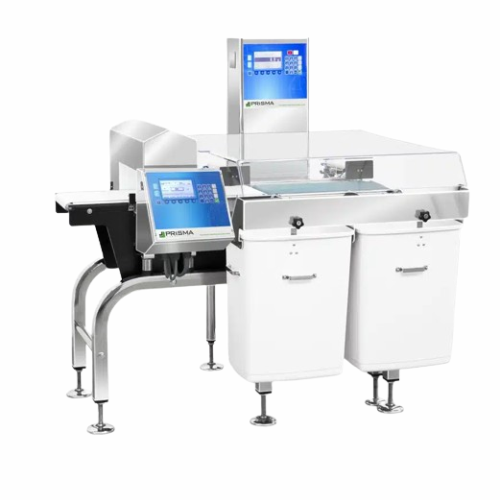
Metal detector for small to medium-sized products
Ensure product integrity and compliance by seamlessly integrating metal...
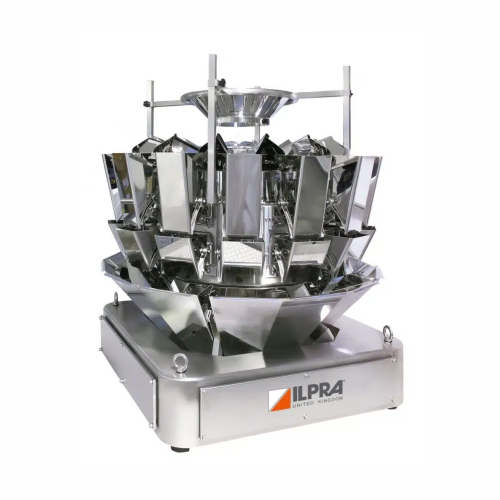
Multi head weigher for precise portioning
Ensure consistent product portions with our multi head weigher, ideal for high-s...
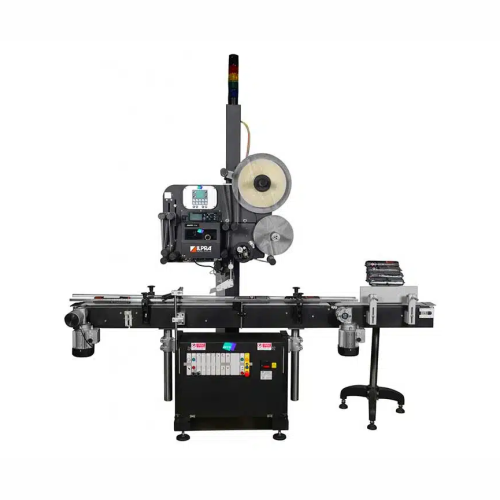
Automatic c-wrap labelling for packaged products
Enhance your production line with precise C-wrap labelling, seamlessly in...
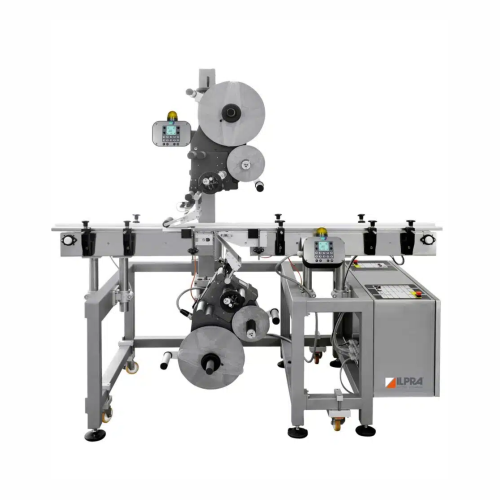
Automatic top & bottom labelling system
Enhance your packaging line efficiency by applying precise top and bottom labels to...
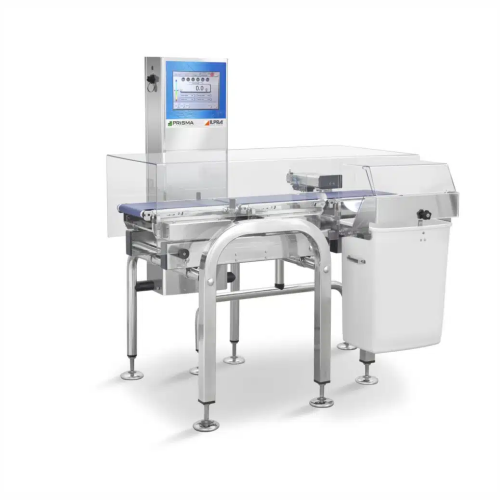
Industrial check-weigher for accurate product weight verification
Ensure precise weight compliance and reduce waste wit...
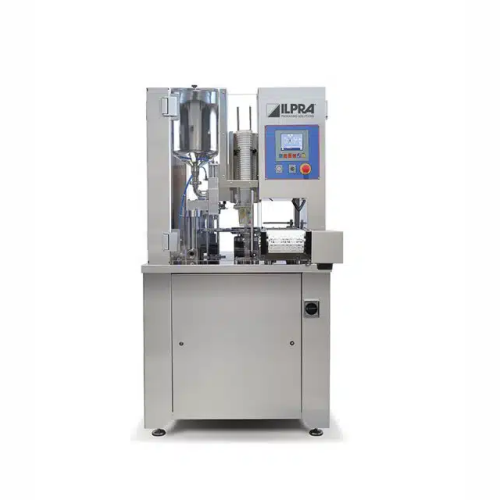
Rotary filler and sealer for dairy products
Optimize your filling and sealing needs with a compact solution designed for c...
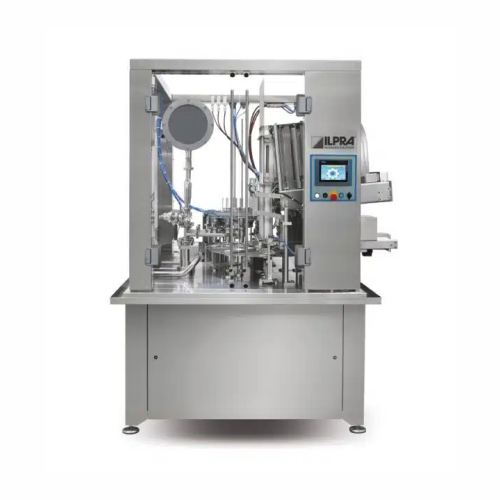
Automatic filling and sealing solution for medium to large production
Streamline your high-capacity filling and sealing...
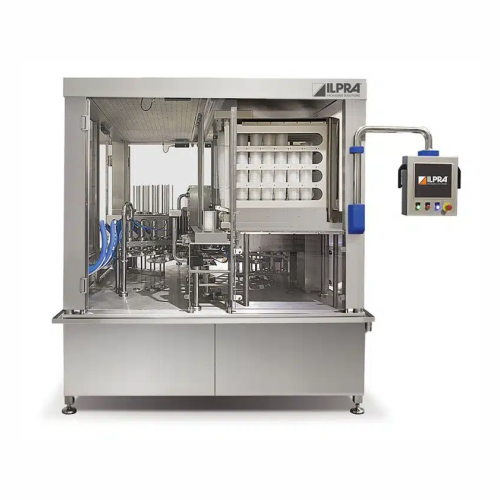
Rotary filler for optimized production processes
Streamline your fill and seal process with precise timing control and enh...
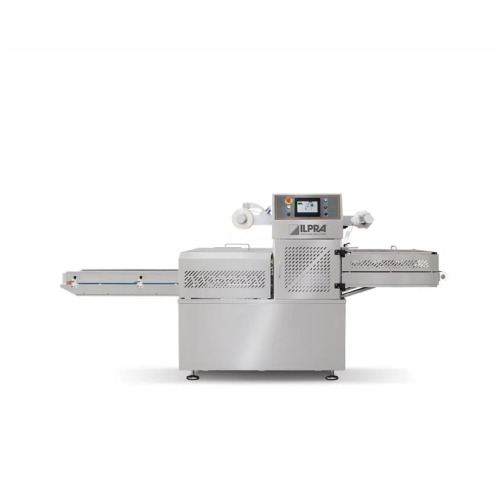
Entry-level in-line traysealer for ready-to-eat meals
Streamline your ready meal packaging with a compact traysealer that...
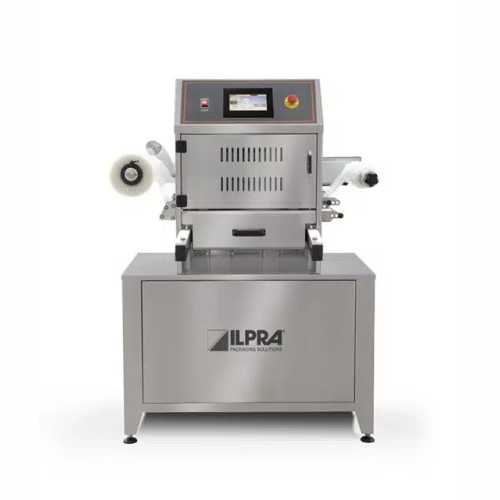
Semi-automatic tray sealer for skin packaging
Optimize your small-scale food packaging with a compact tray sealer designed...
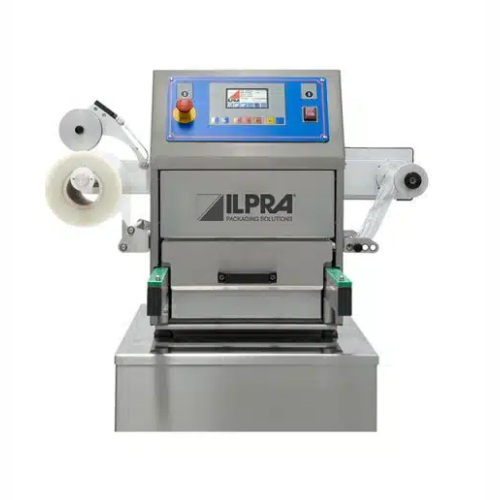
Traysealer for small scale food packaging
Improve your production efficiency with a compact traysealer designed for versat...
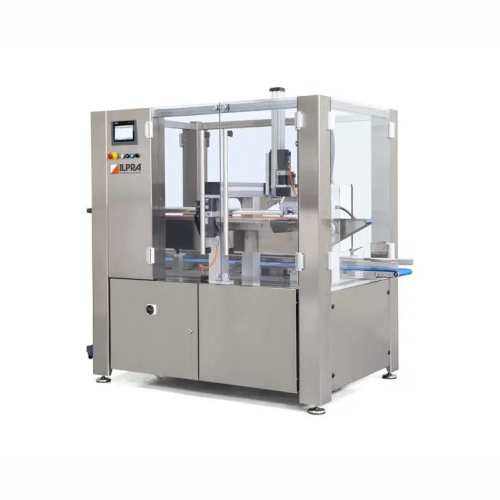
Industrial pick and place system for packaging
Streamline your packaging line with precise robotic pick and place operatio...
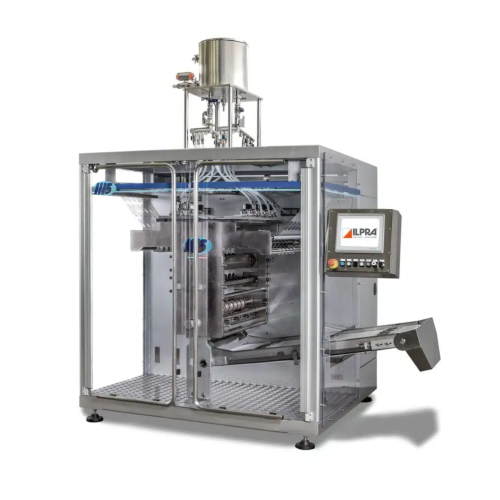
High-speed continuous rotating packaging solution
Transform your packaging efficiency with versatile operations, accommod...
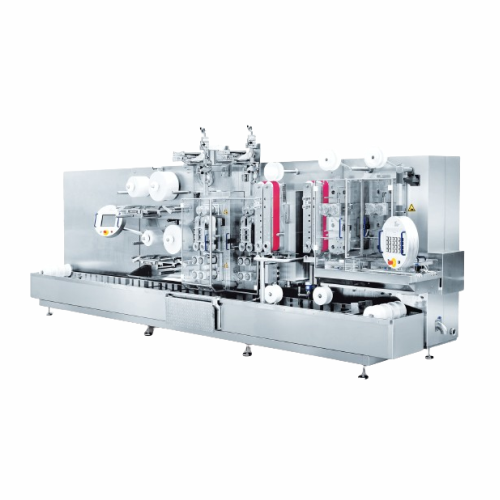
High-speed cheese slice wrapper
Achieve unparalleled efficiency with the high-speed wrapping machine that securely packages ...
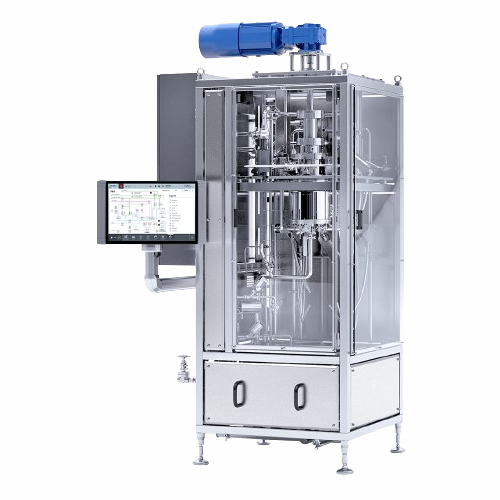
R&d scale steam cooker for small batch processing
Optimize your R&D with a steam cooker that replicates large-scale ...
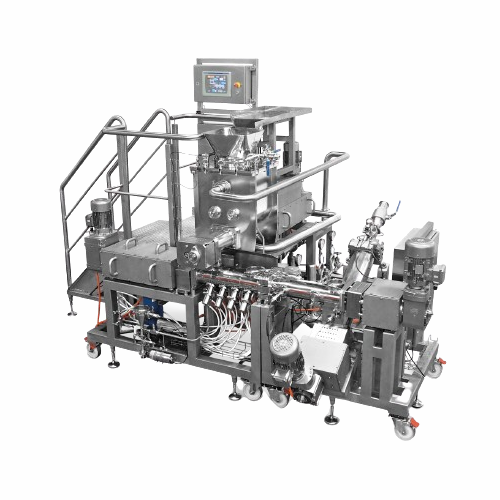
Mozzarella cooker stretcher for continuous production
Experience continuous mozzarella production with steam injection te...
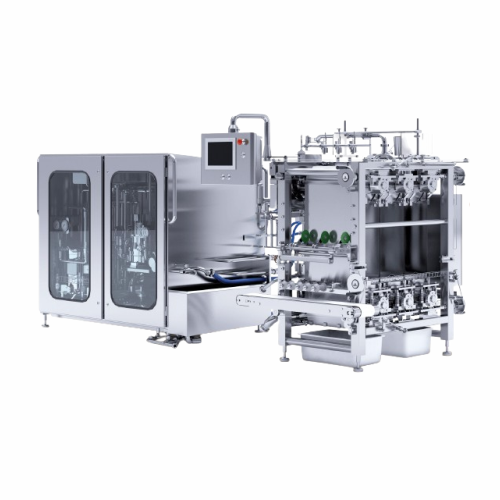
Pilot unit for processed cheese slices
Perfect for R&D and small-scale production, this adaptable unit offers high fle...
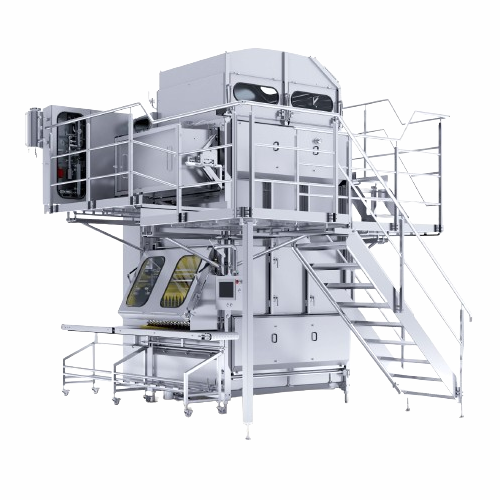
Processed cheese slice production system
Reduce recontamination risks in cheese production with a system designed for high-...
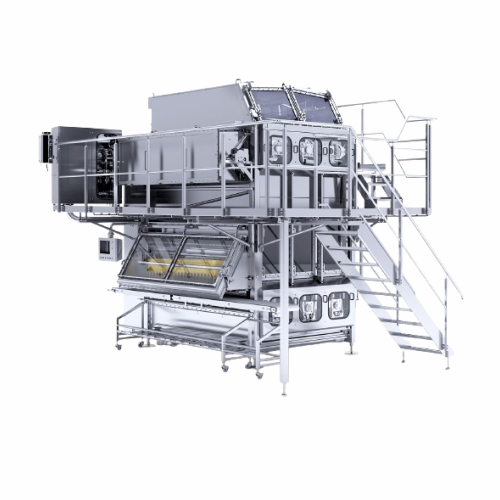
Cheese forming and slicing system
Optimize your cheese production with high-speed, precision forming and slicing, ensuring ...
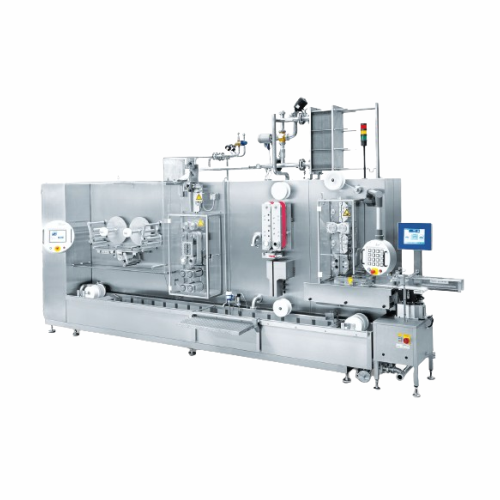
Individually wrapped processed cheese slice production line
Efficiently produce consistent, individually-wrapped cheese ...

Separating packed cheese products from packaging
Efficiently separate individual cheese portions from packaging, reducing ...
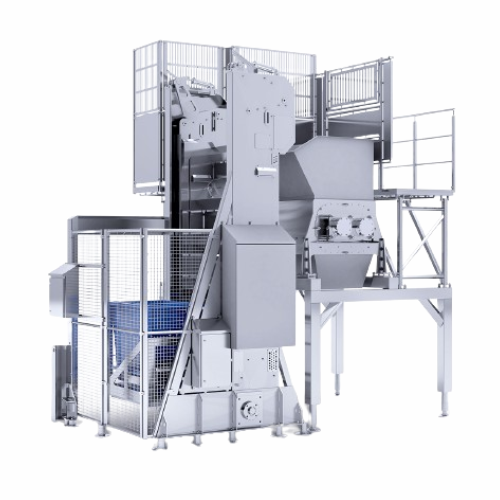
Cheese and butter block grinder
Efficiently transform frozen cheese and butter blocks into manageable sizes for continuous p...
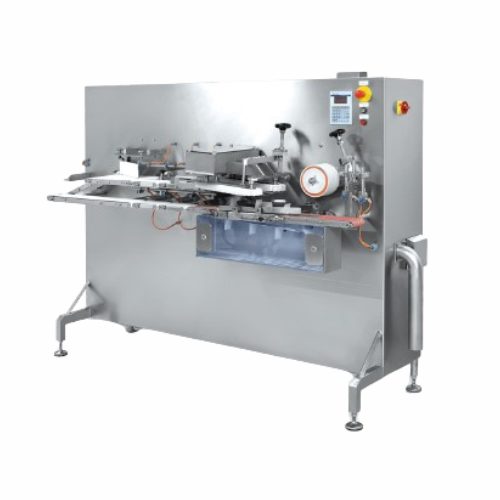
Cheese packaging system for mixed cheese types
Optimize your cheese production line by seamlessly integrating a system des...
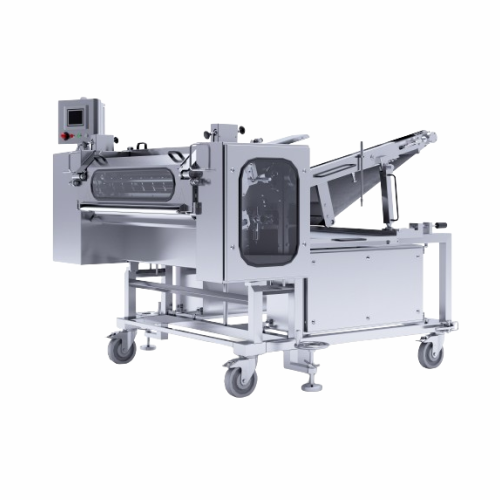
Processed cheese stick cutter
Achieve precise and consistent cheese stick production with a machine designed to streamline f...

Cheese ribbon cutting solution
Achieve precise and efficient cheese ribbon cutting with high-speed operations, ensuring perf...
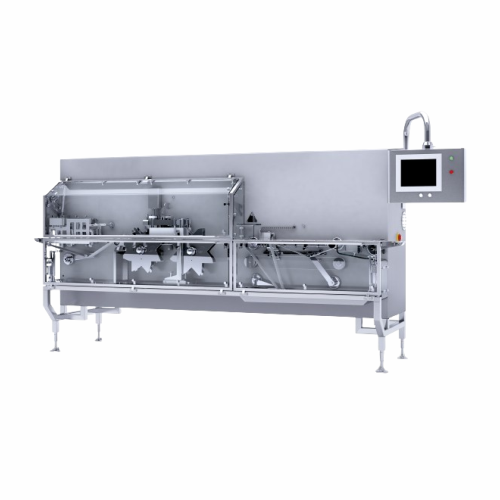
Automatic cheese stack and grouping system
Efficiently stack and group cheese slices to streamline your production line an...
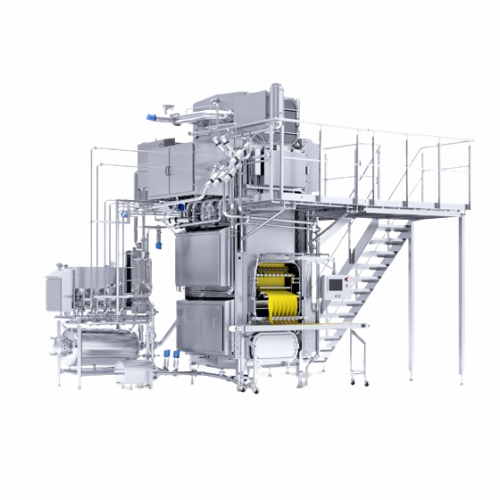
Processed cheese slice forming system
Effortlessly produce high-quality Slice-on-Slice cheese slices, cubes, shreds, and st...
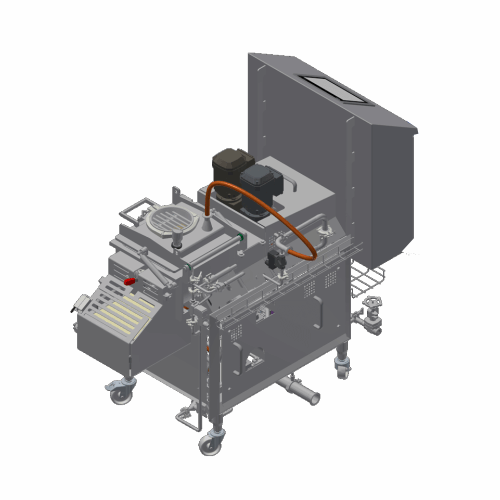
Multifunctional batch processing system for processed cheese
Enhance your production line with a sophisticated batch pro...
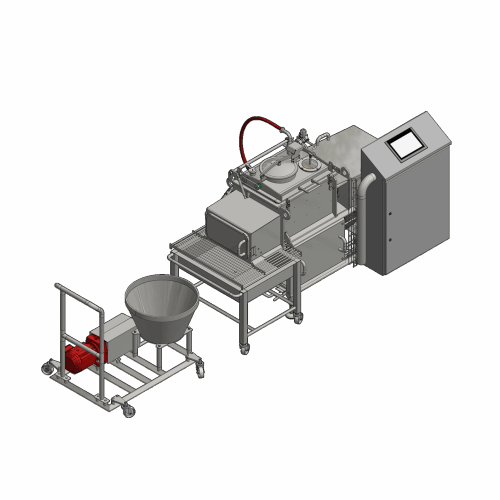
Batch processing system for processed cheese and sauces
Optimize your food processing line with a versatile batch process...
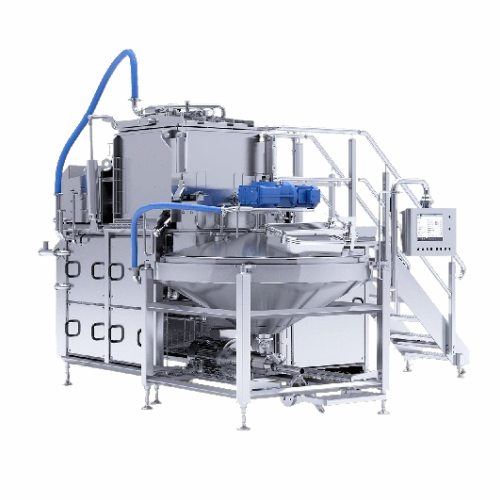
Batch processing system for processed cheese and various food products
Optimize your food production line with a multif...
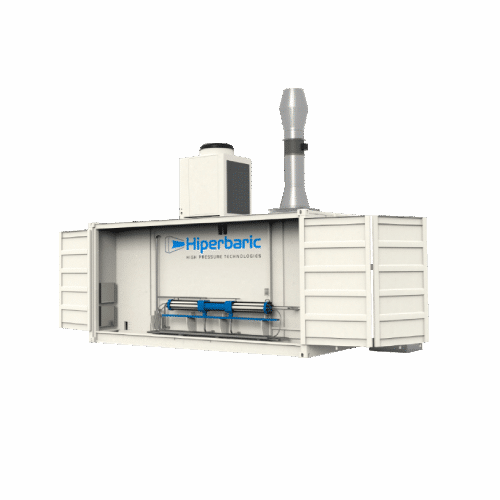
Hydrogen compression solution for refueling stations
For operations demanding efficient hydrogen compression, this modula...
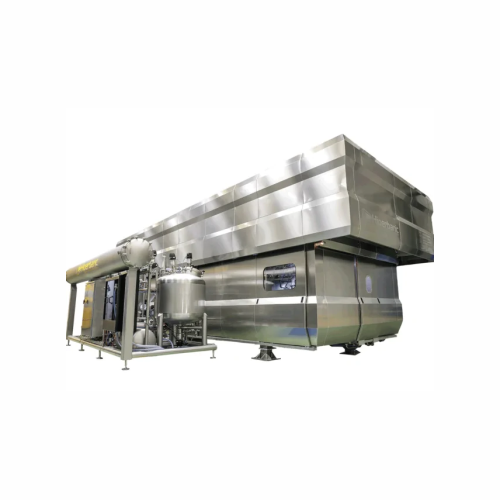
High pressure processing for bulk liquid beverages
Streamline your liquid processing with high-pressure in-bulk technolog...
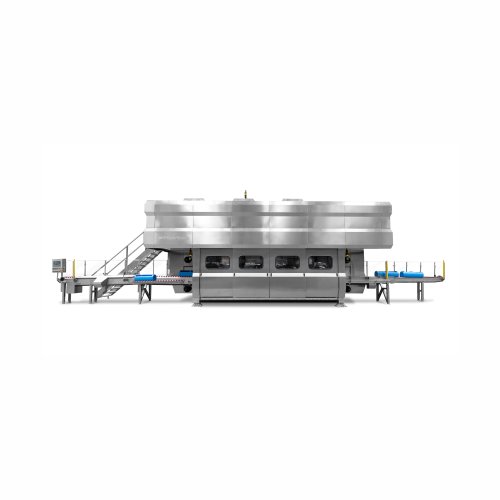
High pressure food processing system
Achieve extended shelf life and enhanced food safety with a cutting-edge high-pressure...
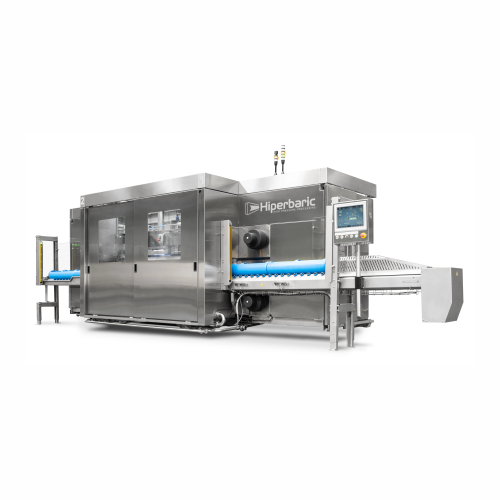
Hpp system for small-scale food production
Enhance food safety and prolong shelf life with this compact high pressure proc...
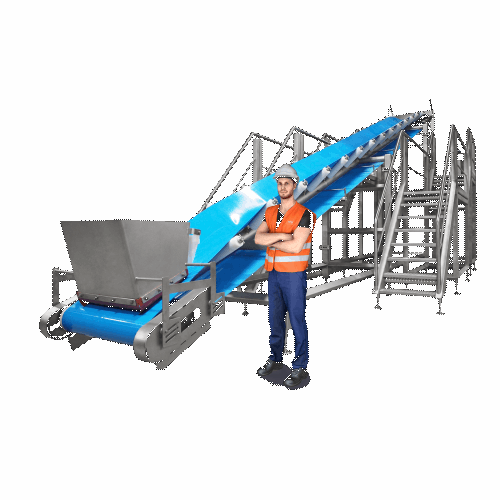
Hygienic conveyor belts for food manufacturing
Ensure bacteriological safety and boost productivity with hygienic conveyor...
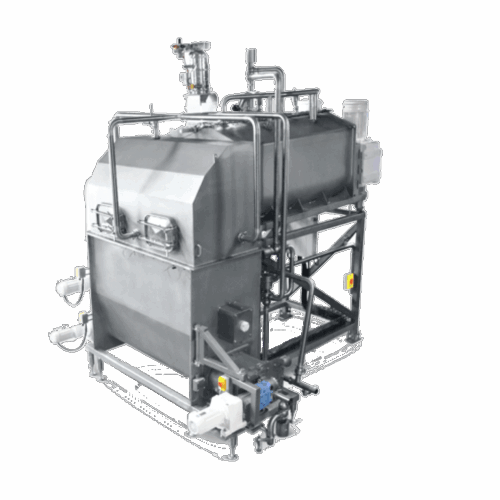
Twin ribbon blender for processed cheese and meat products
Achieve seamless blending and consistent feeding for large-sc...
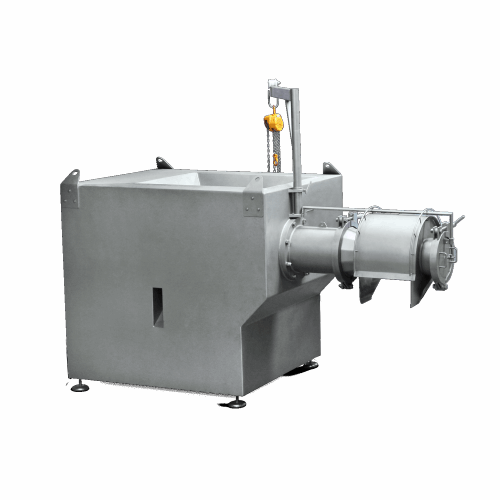
Cheese grinder for fine cheese grinding
Achieve optimal protein emulsification and minimize waste with this high-capacity g...
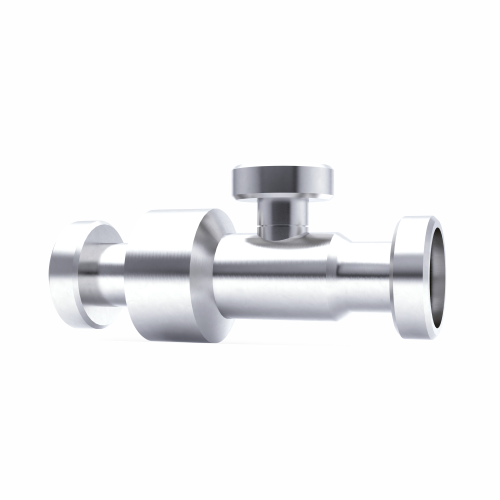
Magnet for emulsion technology for lump-free blends
Achieve perfectly smooth and stable emulsions in a single pass with a...
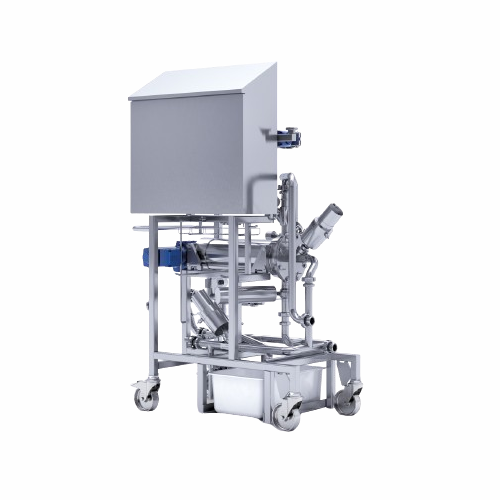
Automated filter cleaning system for food production lines
Eliminate frequent production interruptions by utilizing an a...
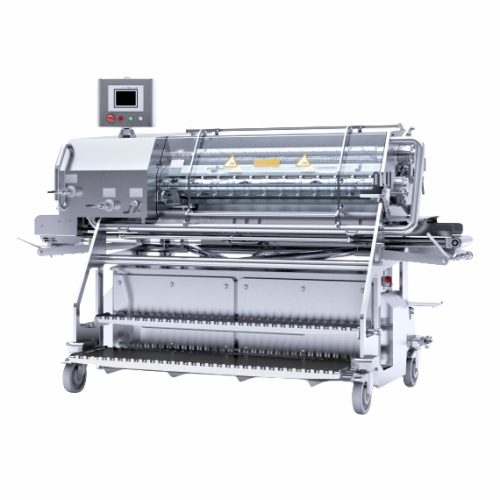
Cheese cube and shreds production line
Achieve precision cutting for cheese products while seamlessly integrating forming a...
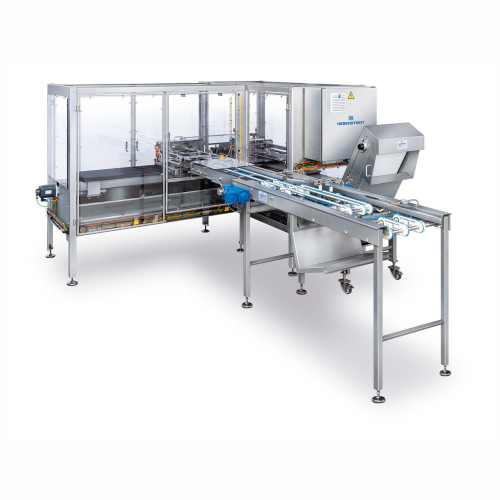
Wafer cutting system for cream-filled wafers
Achieve precise cuts on filled and coated wafer products with high-speed effi...

Wafer row discharge device for feeding packing machines
Efficiently automate wafer row feeding to improve packaging throu...
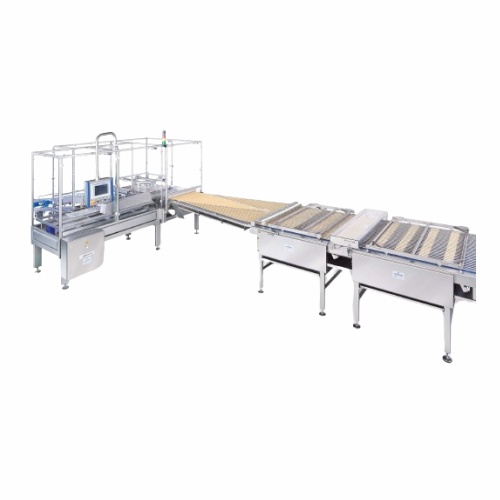
Wafer distribution device for chocolate coating plants
Enhance your chocolate coating operations with precision wafer dis...
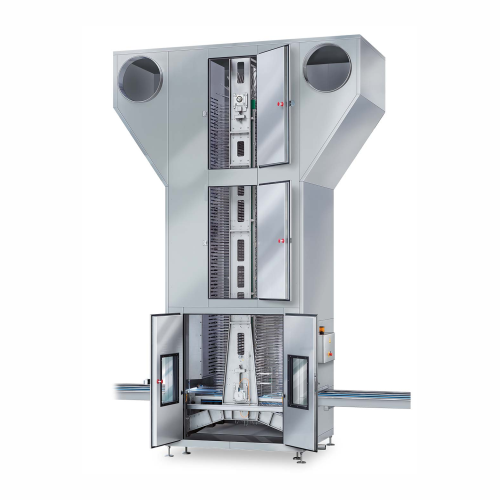
Wafer sandwich cooling systems
Efficiently setting cream fillings for clean cuts, this cooling system ensures your wafer san...
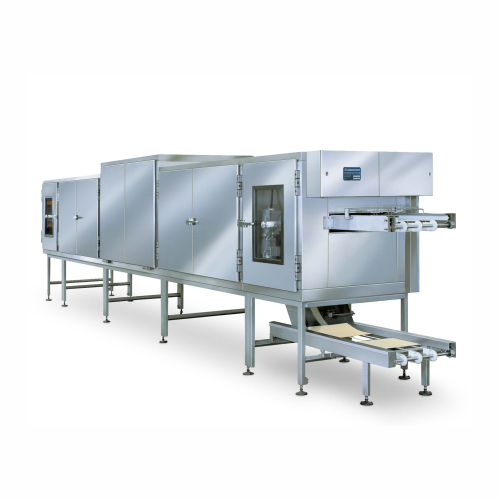
Wafer sheet conditioning tunnel for chocolate coating
Optimize your chocolate-coated wafer production by ensuring precise...

Wafer sheet cooling system
Ensure optimal cooling and conditioning of baked wafer sheets with a system designed to maintain ...
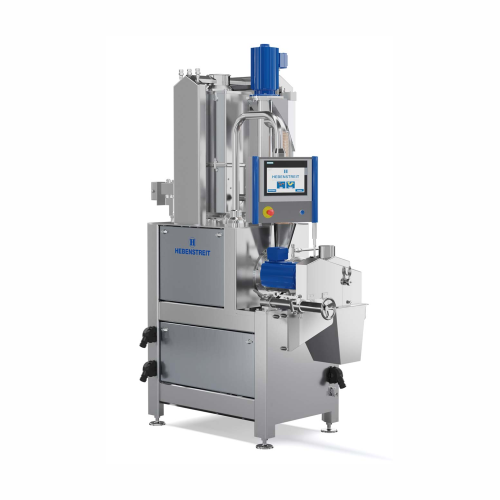
Single-screw cooking extruder for snack production
Optimize your snack production with a versatile extruder designed to h...
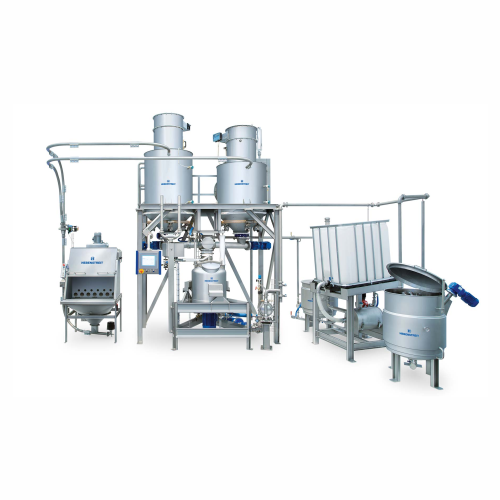
Automatic wafer batter preparation system
Optimize wafer production with precision dosing and homogeneous mixing, ensuring...
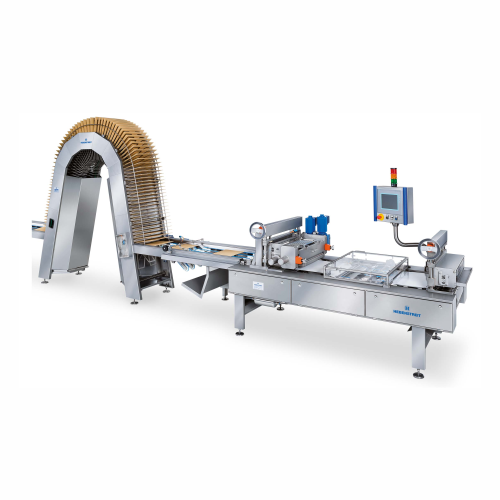
Contact spreading machine for cream application on wafer sheets
Ensure precise cream application with our specialized co...
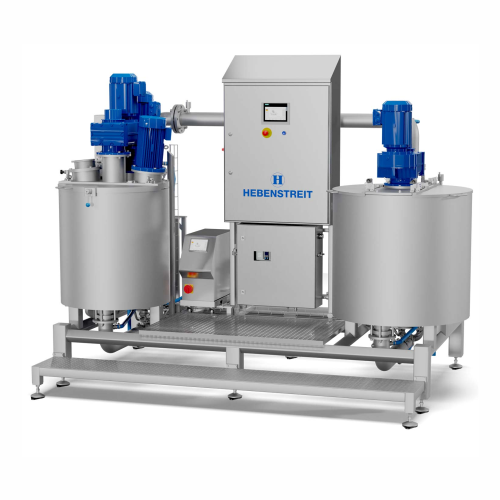
Cream preparation plant for wafer production
Achieve consistent cream texture and optimal weight for perfect wafer product...
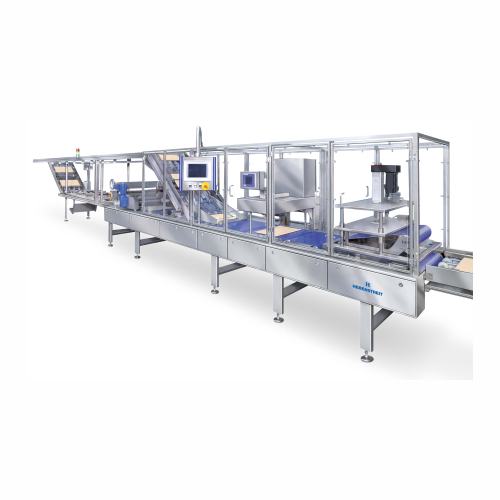
Wafer sheet cream application system
Achieve precision in cream application with high-capacity, continuous film spreading, ...
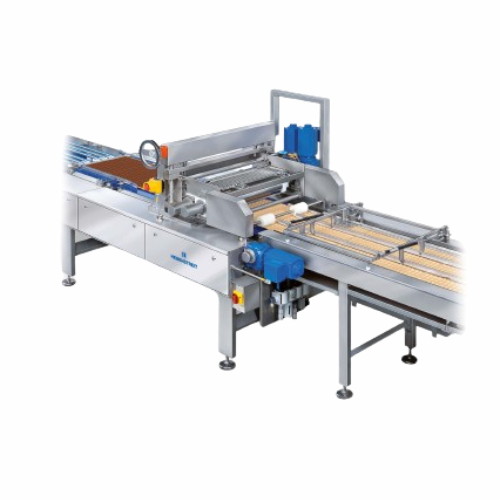
Hollow wafer spreading machine for consistent coating
Optimize your snack production with precise spreading—achieve unifo...
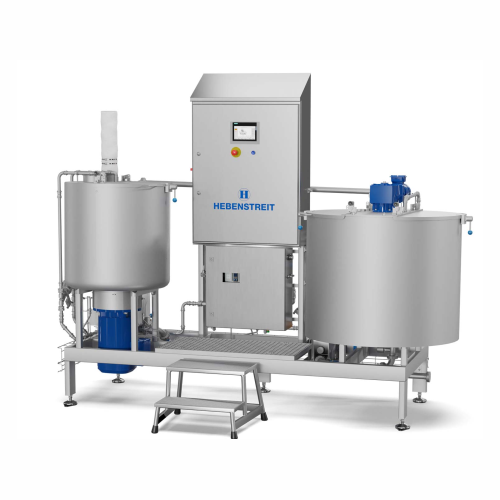
Semi-automatic batter preparation plant for wafer production
Enhance your wafer production with a versatile system desig...
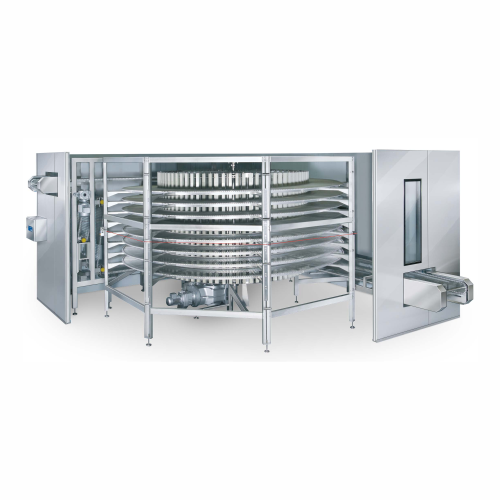
Spiral wafer sandwich cooler for consistent cooling
Ensure precise temperature control and optimal firmness for wafer san...
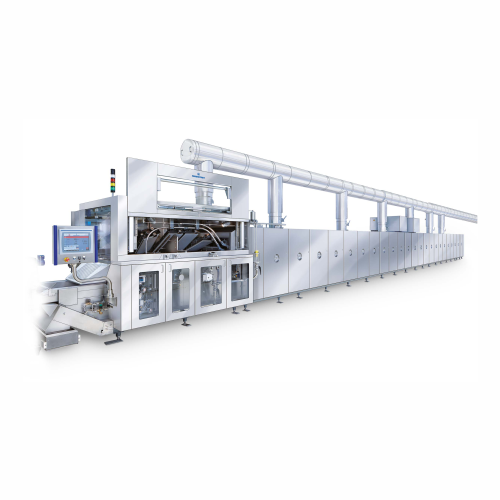
Automatic wafer baking machine for high-capacity production
Streamline your wafer and snack production with a high-speed...
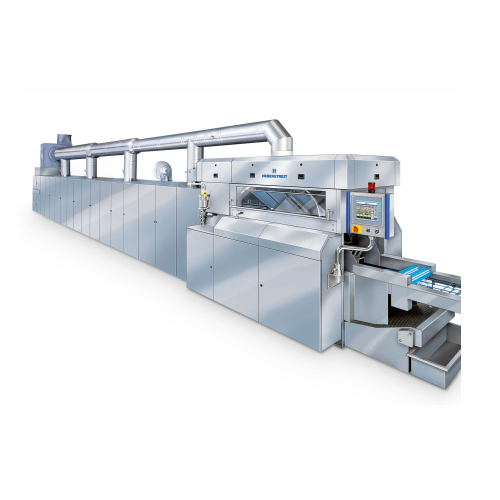
Wafer baking machine for flat and hollow wafer sheets
Effortlessly produce high-quality flat and hollow wafer sheets with...
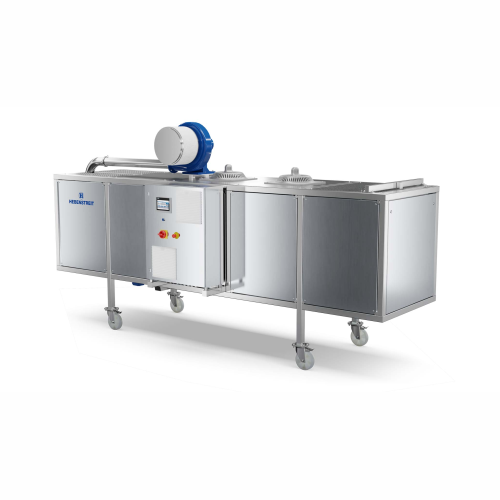
Industrial drum dryer for extruded snacks
For snack producers aiming to achieve precise moisture control, this rotating dr...
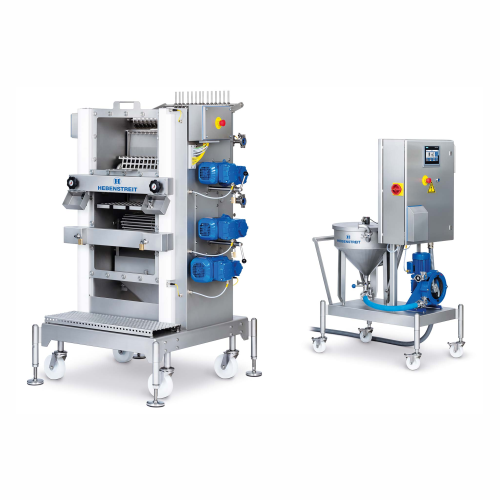
Continuous extruded snack dyeing system
Enhance the aesthetics of your extruded snacks with precise and continuous dyeing, ...
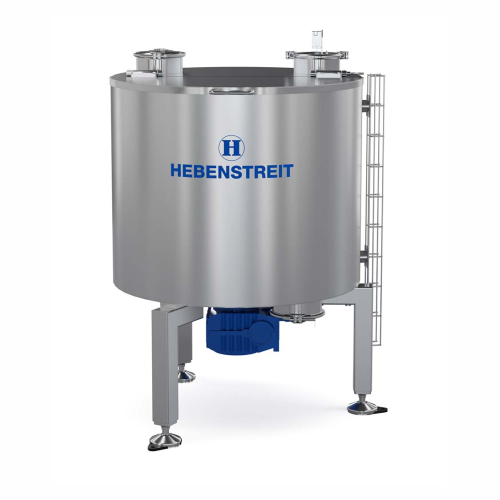
Intermediate container for raw material preparation
Streamline your snack and cereal production with this solution that e...
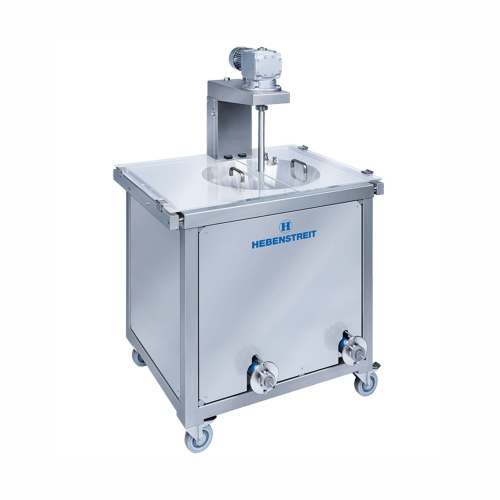
Intermediate cream container for snack production
Ensure consistent cream texture before extrusion with a solution design...
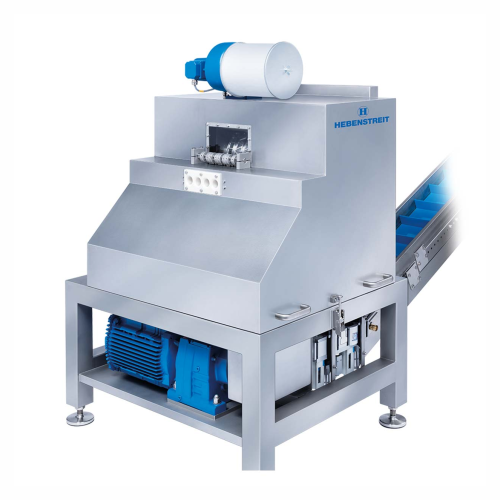
Roller embossing system for snack production
Effortlessly shape and press multiple product strands into diverse, precise f...
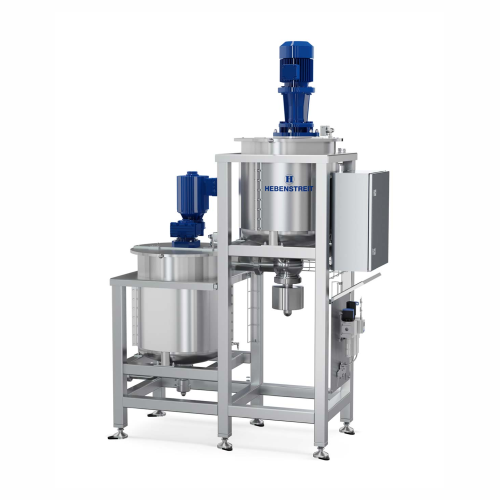
Seasoning mixing system for extruded snacks
Achieve consistent flavor profiles in your extruded snacks with this high-spee...
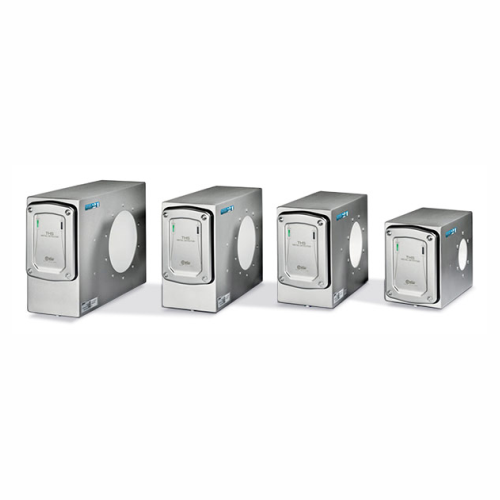
Industrial metal detector for gravity feed applications
Ensure the purity of your products by detecting and removing both...
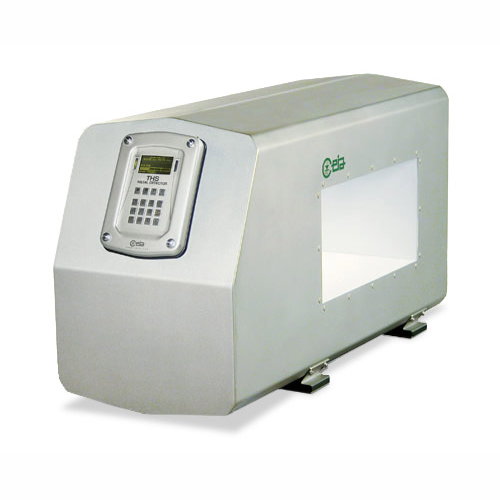
Ferrous-in-foil metal detection system
Enhance quality control for foil-packaged goods with precise ferrous metal detection...
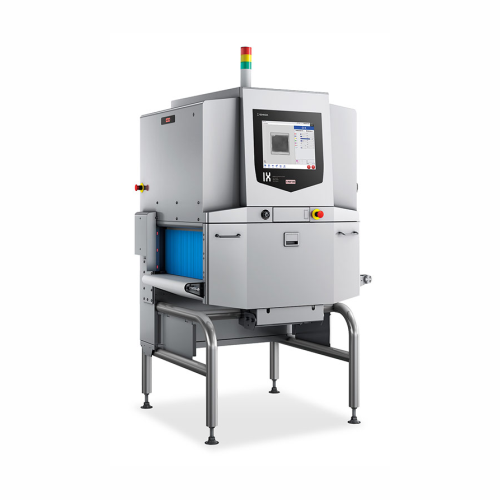
X-ray inspection system for contaminant detection
Detect and eliminate foreign contaminants in a wide range of food produ...
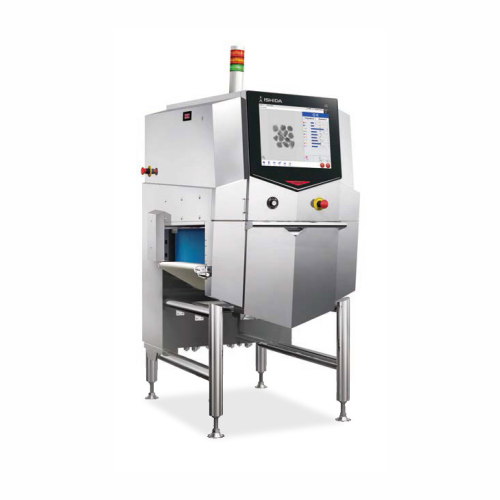
X-ray inspection system for low-density foreign objects
Enhance your inspection capabilities with advanced X-ray technolo...
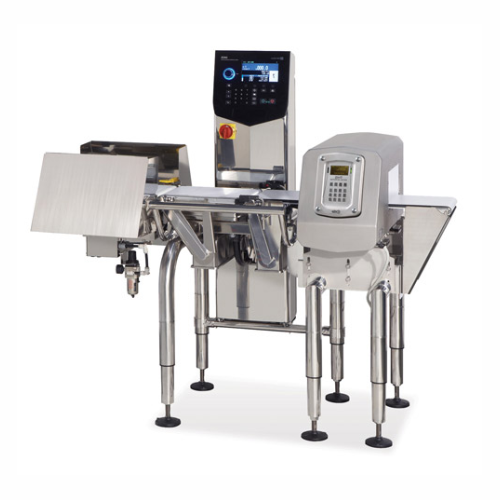
Metal detection and weight verification system
Optimize space and boost inspection accuracy by combining metal detection a...
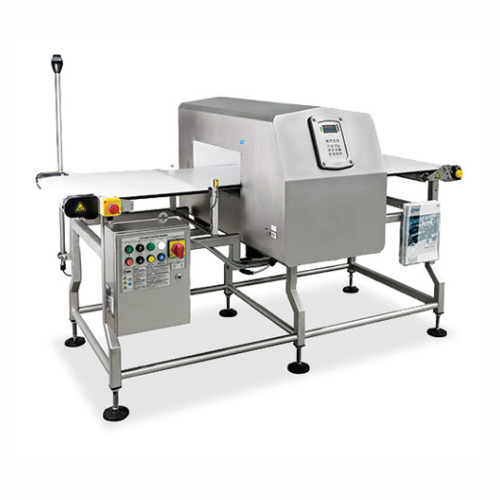
Conveyor belt metal detection system for food processing
Enhance product safety and ensure compliance with the most strin...
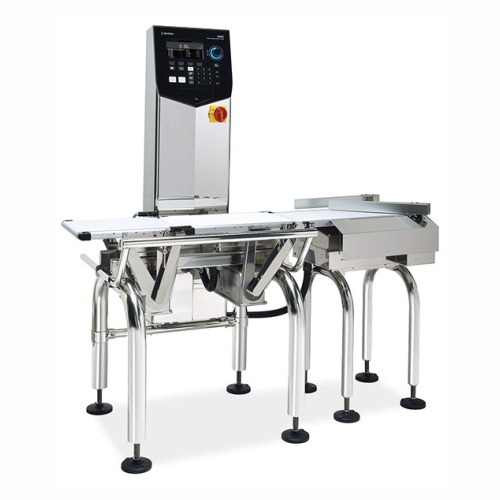
Checkweigher for packaged goods inspection
Ensure precision and compliance with this high-speed checkweigher, perfect for ...
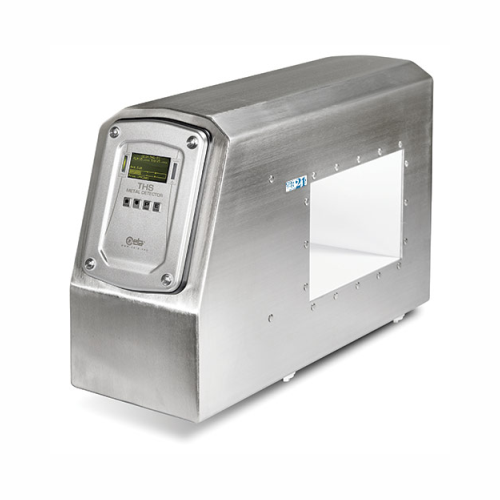
Advanced metal detection for food processing
Maximize your production line’s safety and efficiency with a cutting-ed...
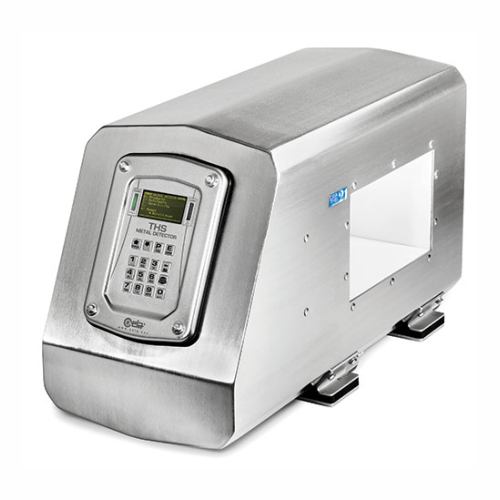
Multi-spectrum metal detector for food industry
Achieve unmatched detection accuracy in your food processing line with thi...
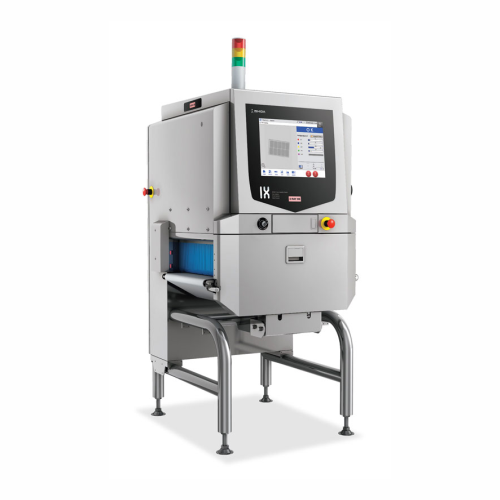
X-ray inspection system for identifying foreign bodies in food products
Ensure precise detection of foreign materials i...
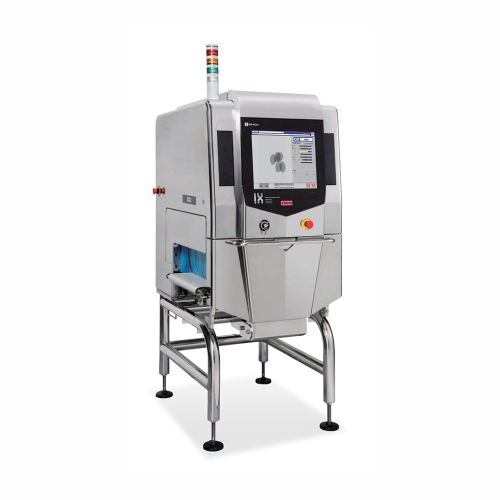
X-ray inspection system for detecting foreign objects in food products
Ensure product safety and quality by detecting e...
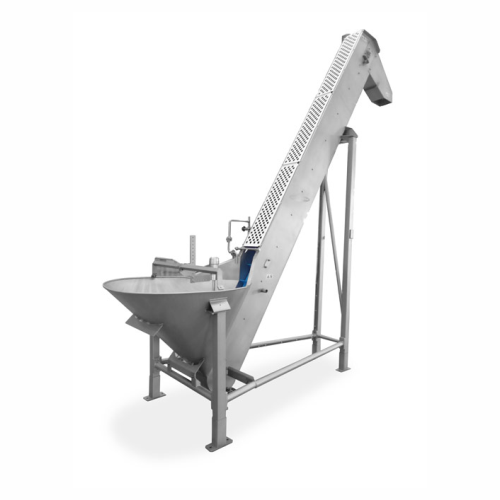
Potato chip production slicer feeder
Ensure optimal slicing and consistent chip quality with a feeder that delivers a stead...

Spiral oven for meat and poultry cooking
Experience even cooking and reduced processing times with a high-speed spiral oven...
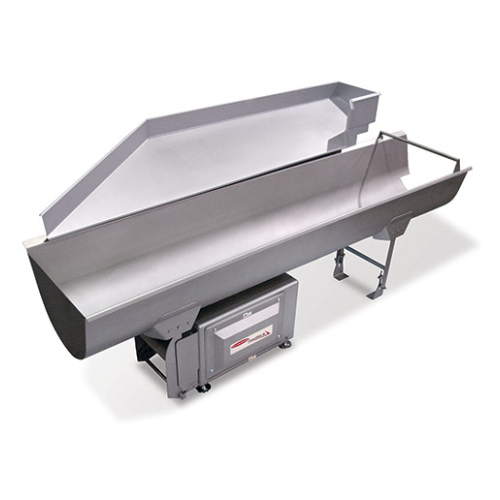
Accumulation conveyor for snacking industry
Optimize your production line with a space-saving accumulation conveyor that r...
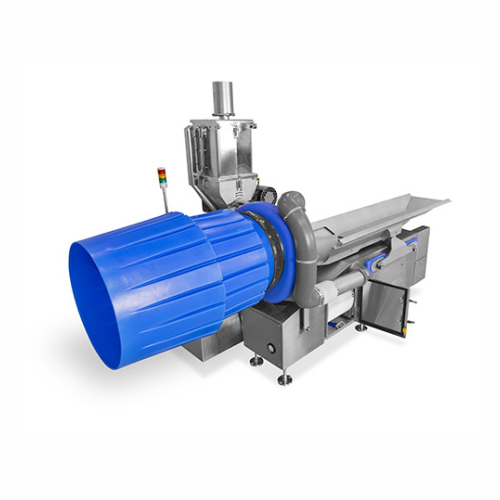
On-machine seasoning system for potato chips
Achieve uniform seasoning coverage for various snack foods with minimal wasta...
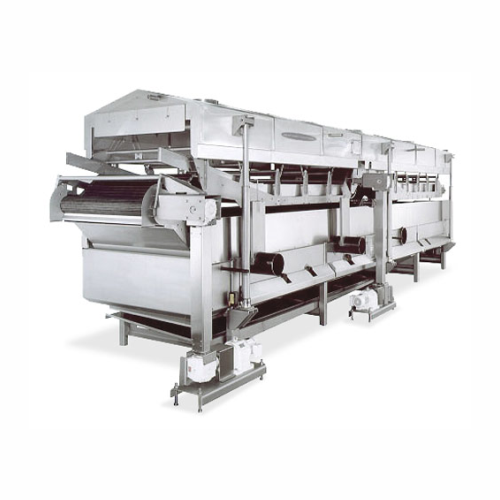
Continuous french fry fryer
Achieve optimal frying conditions with precise temperature control and rapid load adjustments, e...
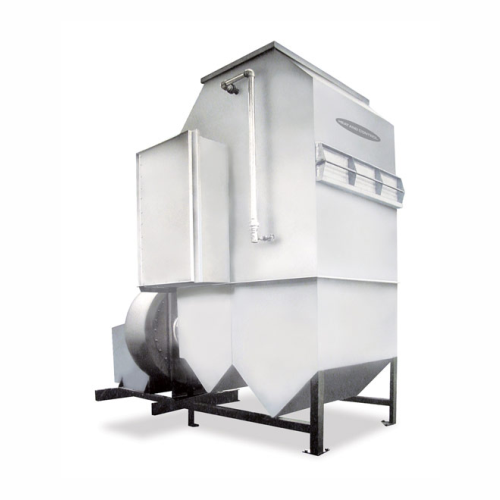
Industrial heat recovery system
Transform exhaust heat from fryers into usable energy, reducing operational costs and boosti...
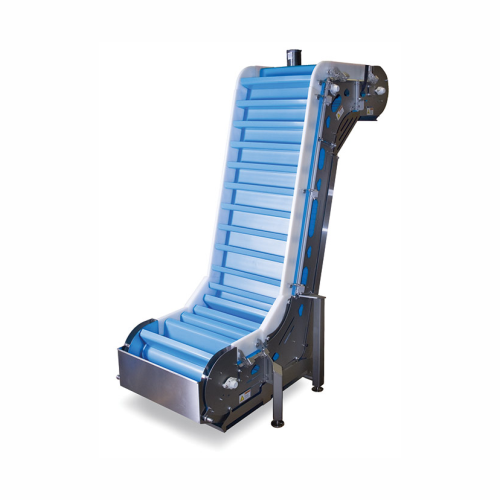
Incline transfer conveyors for dry, fresh, and frozen food products
Efficiently transfer a variety of solid and granule...
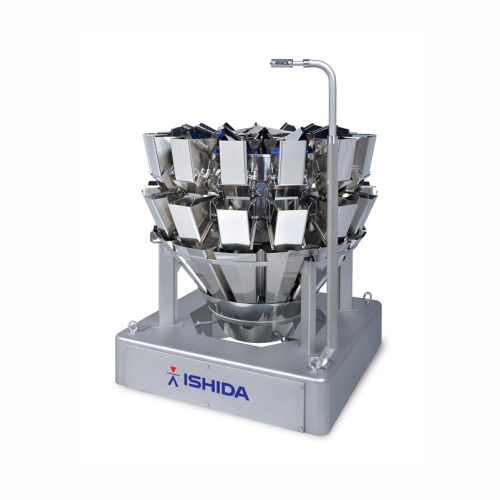
Multihead weigher for precise bulk product weighing
Optimize your weighing operations with highly accurate multihead tech...
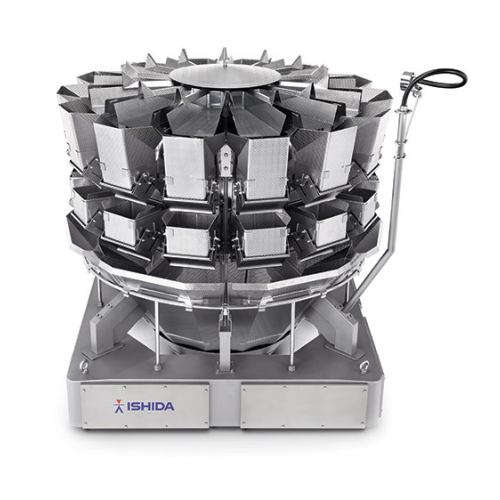
Multihead weigher for food processing
Enhance production efficiency and accuracy with multihead weighing technology, offeri...
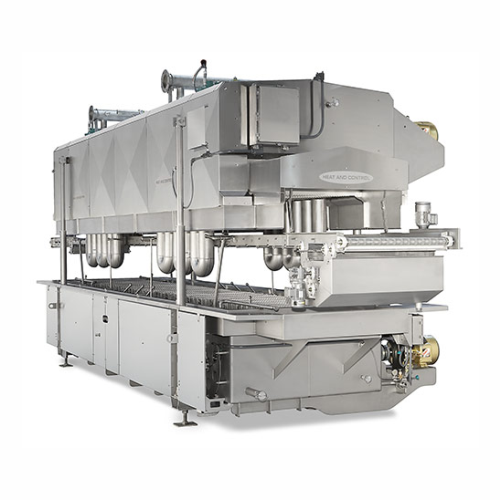
Impingement oven for meat and baked products
Achieve faster cooking and greater uniformity with advanced airflow technolog...
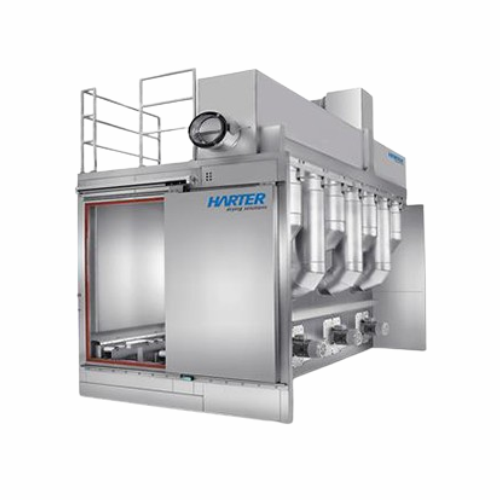
Industrial tunnel dryer
Optimize drying efficiency and maintain product quality with continuous tunnel drying, ideal for prec...
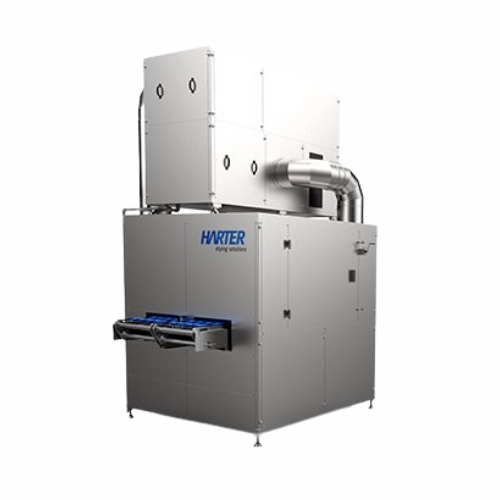
Large continuous tunnel dryer
Optimize your production with advanced drying and dehumidification technologies, ensuring prec...
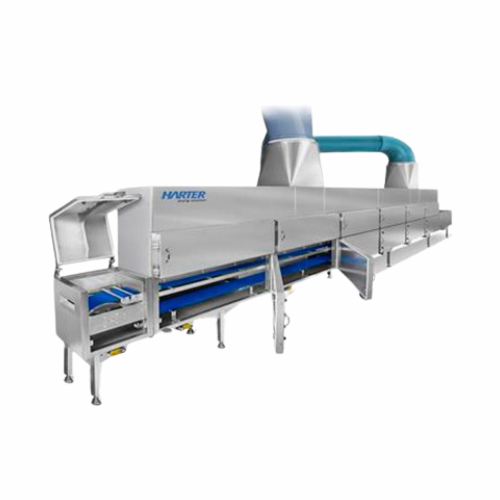
Continuous drying system for viscous substances
When handling viscous substances, ensure precise moisture control with con...
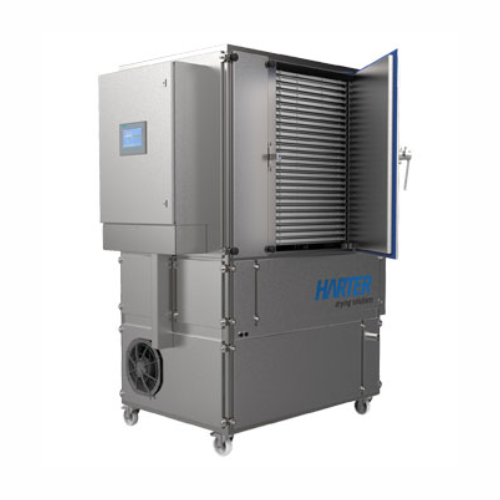
Pharmaceutical and laboratory product drying solution
Ensure precise moisture control for diverse products, from pharmace...
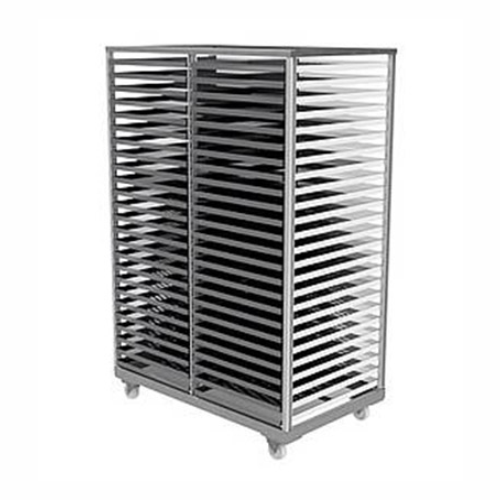
Pharmaceutical and med-tech drying solution
Achieve precise moisture control and adaptability across diverse products with...
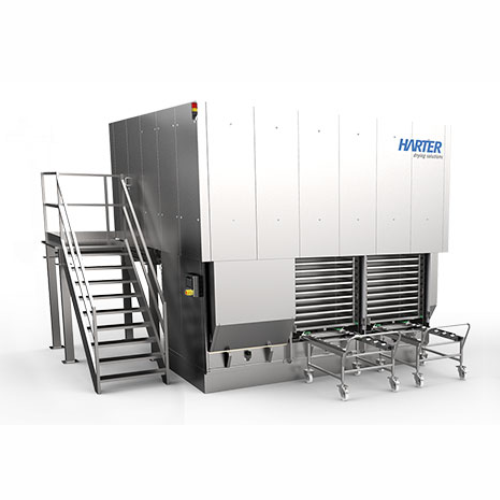
Batch-operated chamber dryer for surface drying
Enhance production efficiency with precise, low-temperature drying and coo...
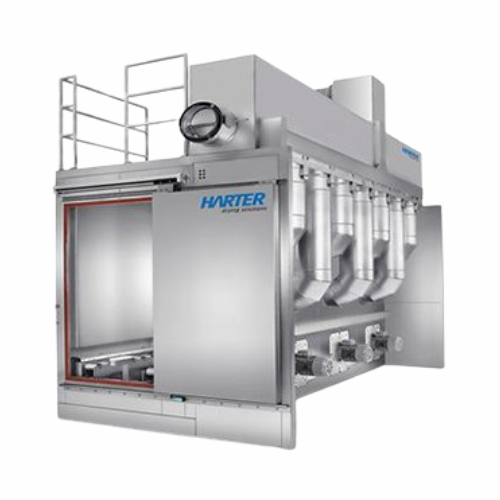
Continuous tunneling drying system for industrial applications
Streamline your drying process with precision-controlled ...
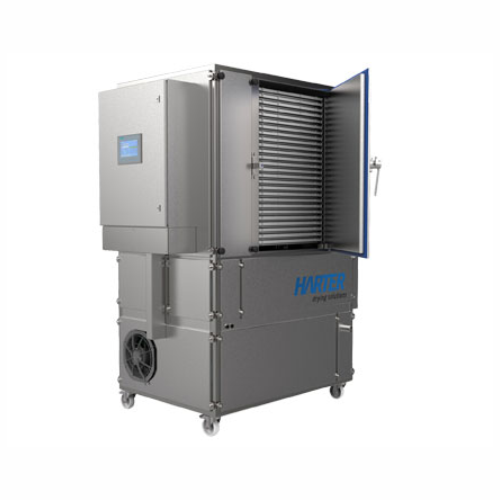
Compact dryer for product and process development
Optimize your testing and product development with a compact drying sol...
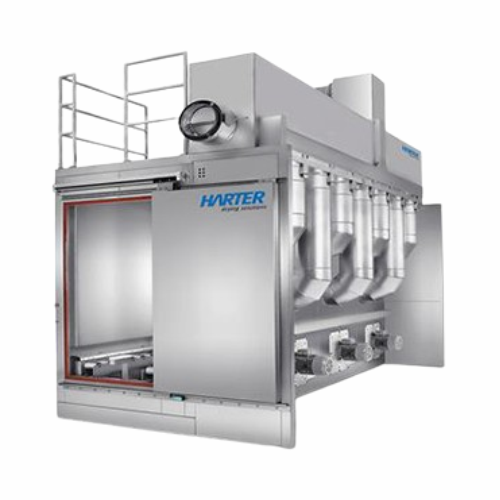
Continuous tunnel dryer for tray carts
Efficiently dry diverse products with precision temperature control, ensuring gentle...
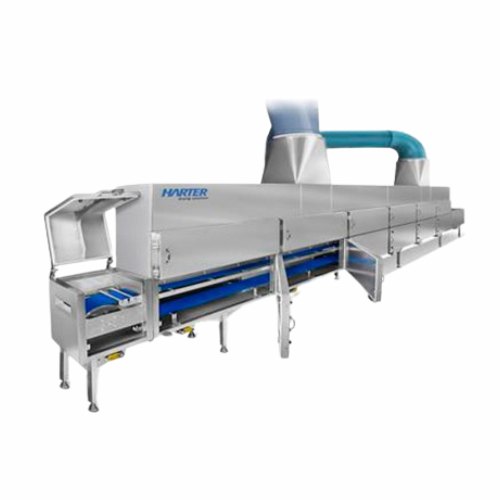
Continuous conveyor belt dryer for endless products
Optimize your continuous production line with a high-speed drying sol...
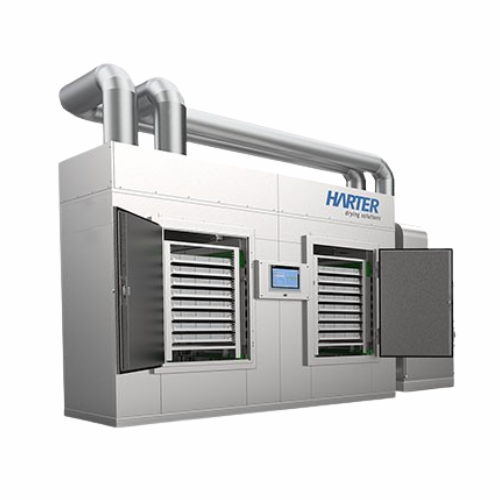
Batch drying solutions for industrial applications
Ensure precise moisture control across diverse materials with our vers...

Compact food drying system
Achieve precise moisture control for product development and testing with this versatile compact ...
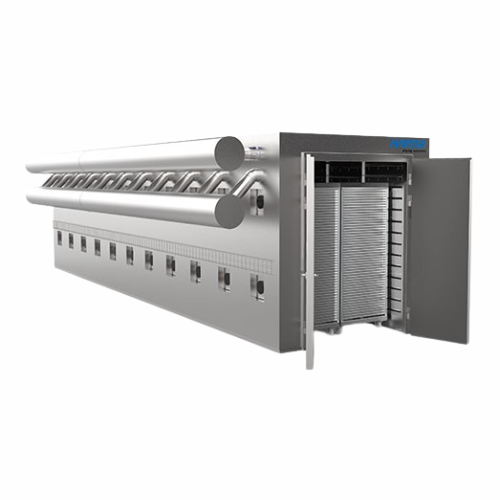
Batch drying system for food, pet feed, pharmaceuticals, and more
Optimize your drying needs with precision control for...
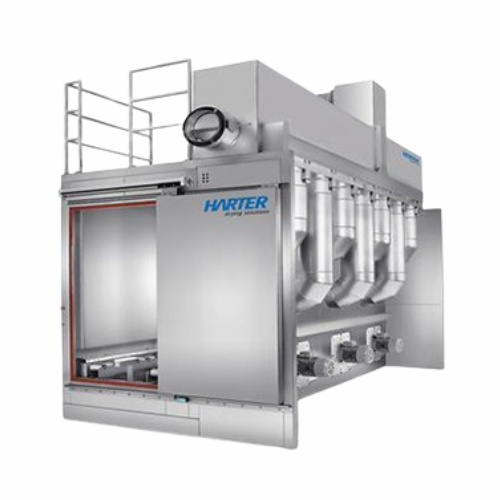
Continuous tunnel dryer for food products
Achieve precise moisture removal with adaptable drying technology, ensuring your...
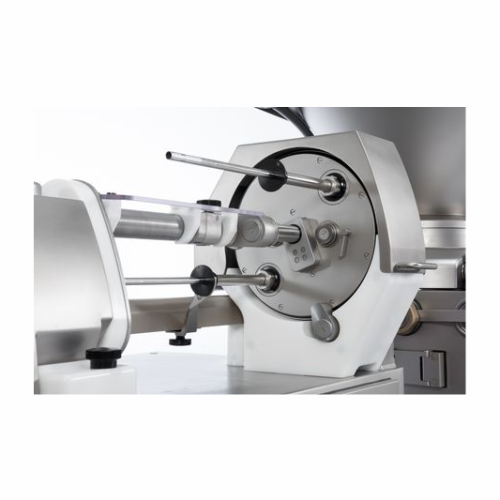
Sausage filling line for natural, collagen, and peel-off casings
Streamline your sausage production with rapid casing ch...
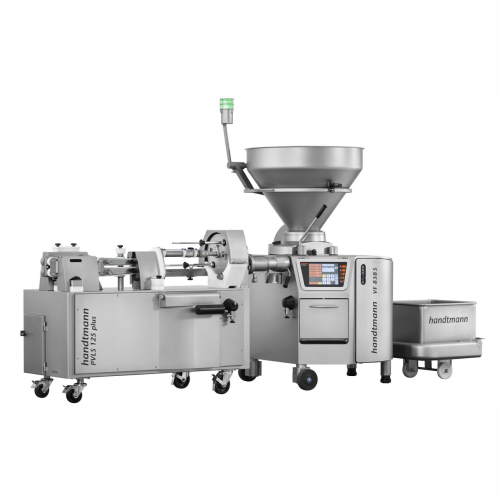
Sausage filling line for adjustable portions
Achieve precision in high-speed sausage production with rapid casing changes ...
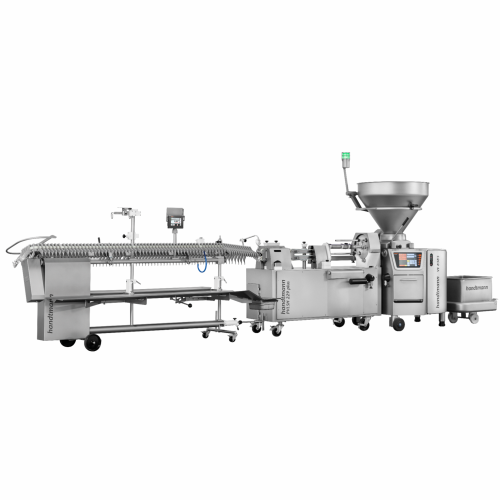
Automated sausage filling and portioning line
Boost your production efficiency with a versatile solution that seamlessly h...
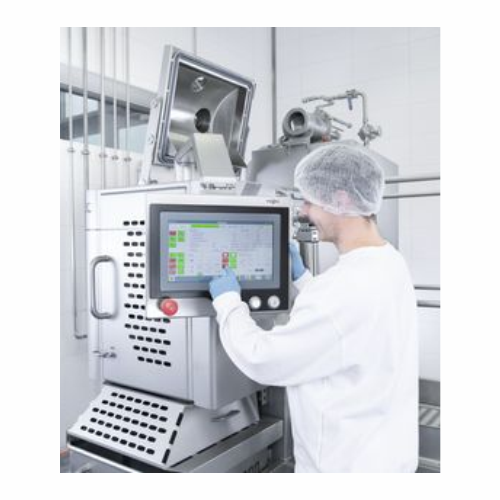
Flexible mixing system for meat and dairy products
This versatile mixing system delivers precise control over temperature...
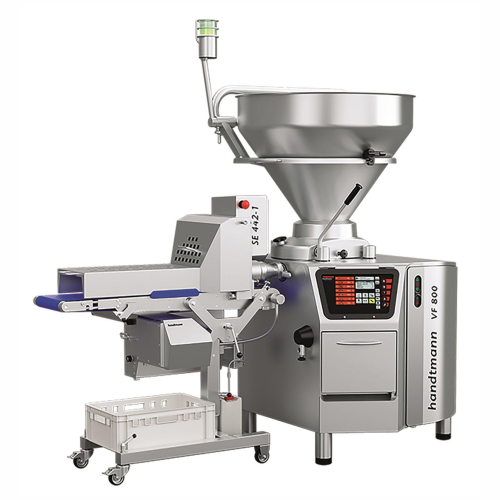
Continuous dough dividing and portioning system
Achieve precise dough portions and enhance product quality with high-speed...
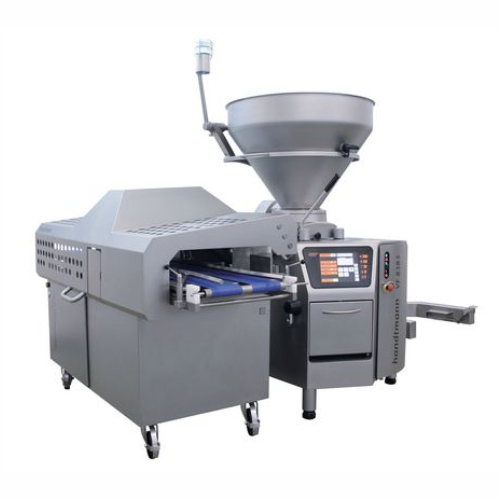
Cutting unit for high-yield tin loaves
Experience precision and efficiency in dough portioning with our high-capacity cutti...

Industrial grinder for ultra-fine grinding and homogenizing
Enhance your production line with versatile grinding technol...
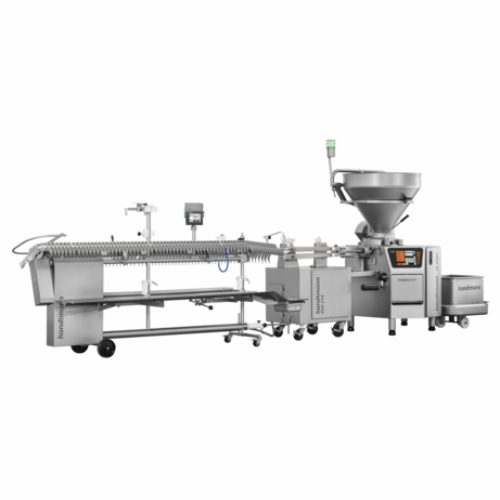
Automated sausage filling and portioning system
Streamline your sausage production with precision filling and versatile po...
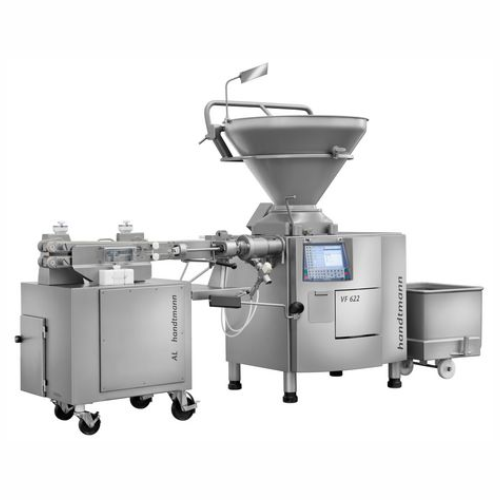
Automatic sausage filling and separating system
Achieve precise portioning with exact weights and lengths for sausages, st...
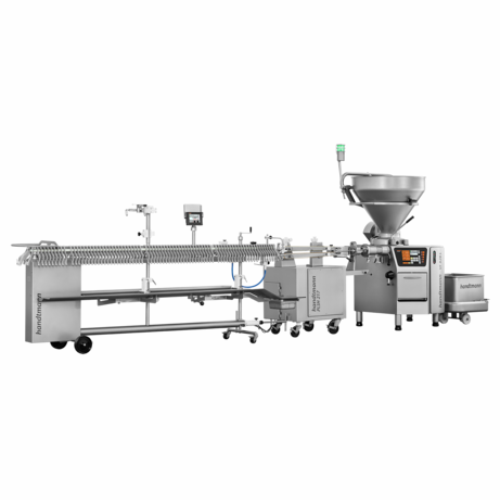
Sausage filling and portioning line
Streamline your sausage production with versatile equipment designed to seamlessly inte...
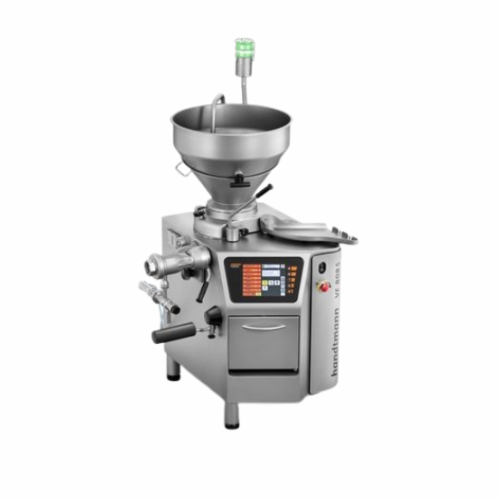
Compact vacuum filler for small to industrial scale food processors
Achieve precise portioning and high-speed productio...
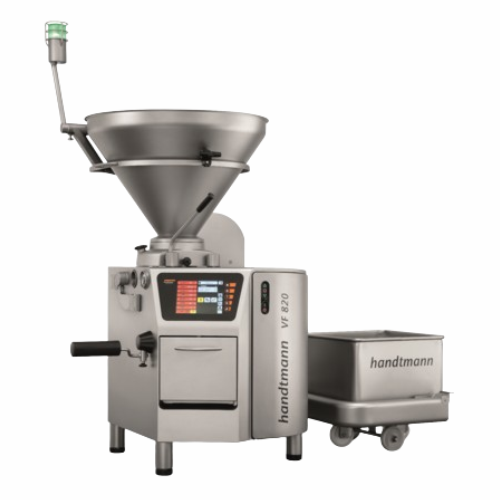
Vacuum filler for medium-scale sausage production
Achieve precise portion control and optimal hygiene with a versatile fi...
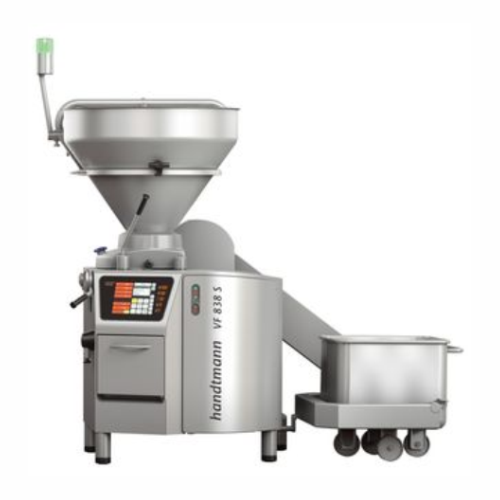
High-pressure vacuum filler for industrial sausage production
Effortlessly tackle high-pressure demands in sausage produ...

Vacuum filler for sausage and ham production
Achieve precision in filling and portioning pasty and fluid products with a s...
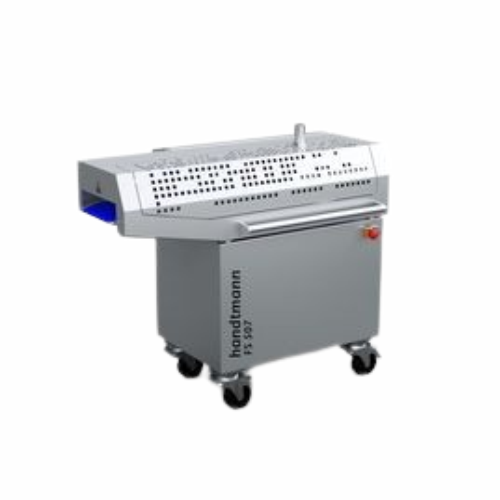
Forming system for minced meat products
Achieve high-quality formed meat and plant-based patties with precision and flexibi...
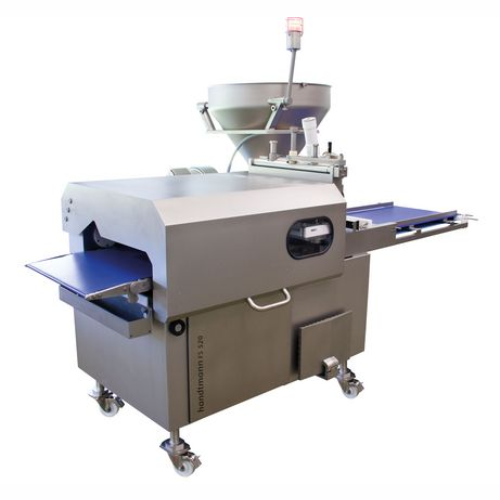
Multi-lane forming system for 3d food product shapes
Achieve precise weight accuracy and high-speed production of diverse...
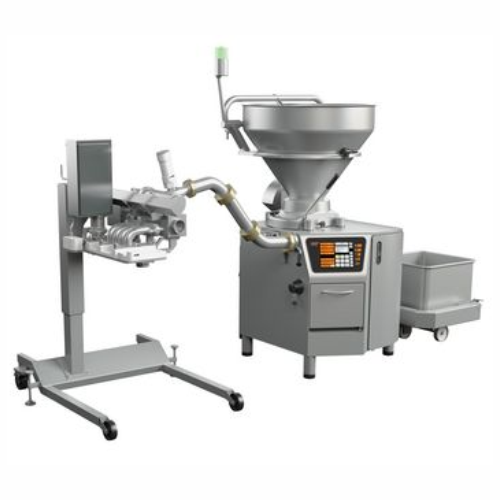
Forming system for multi-lane production of shaped foods
Streamline your production of uniform shaped foods with a multi-...
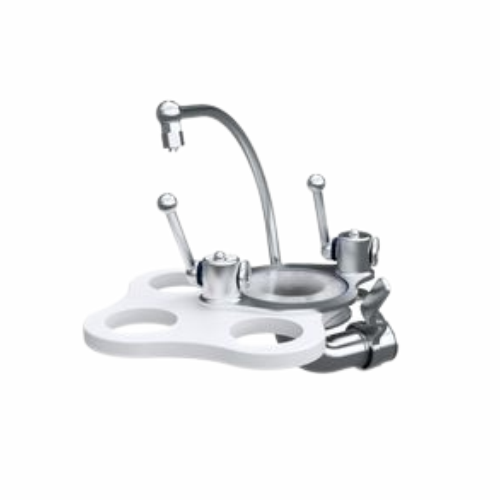
Manual forming unit for burger patties
Produce up to 30 perfectly shaped burger patties per minute with consistent quality ...
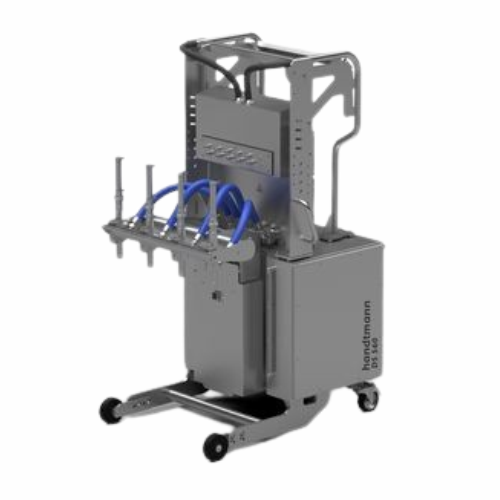
Depositing system for multi-lane dosing with vertical traversing
Achieve precision dosing and flexible portioning with t...
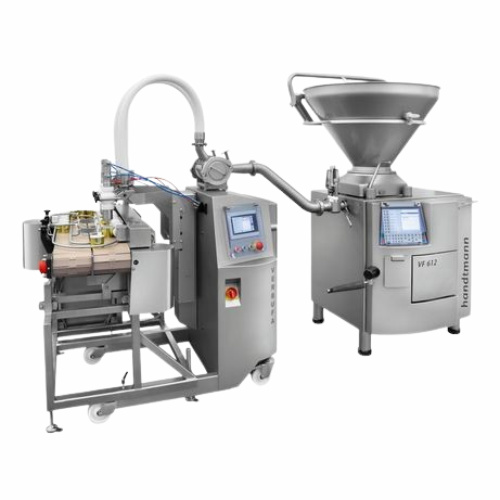
Automatic multi-lane dosing system for fluid to pasty products
Streamline your production with precise multi-lane dosing...
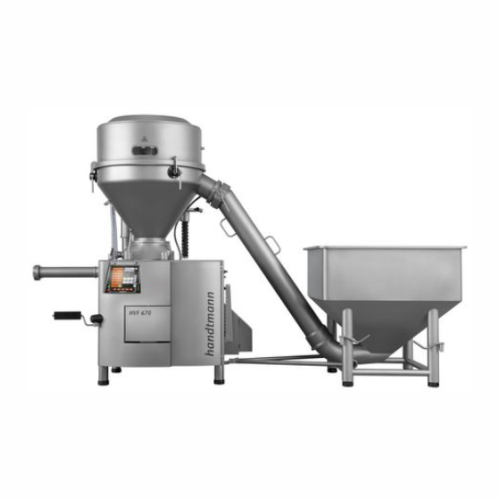
High vacuum filler for ham and ground material
Achieve unrivaled product quality and precision with high vacuum technology...
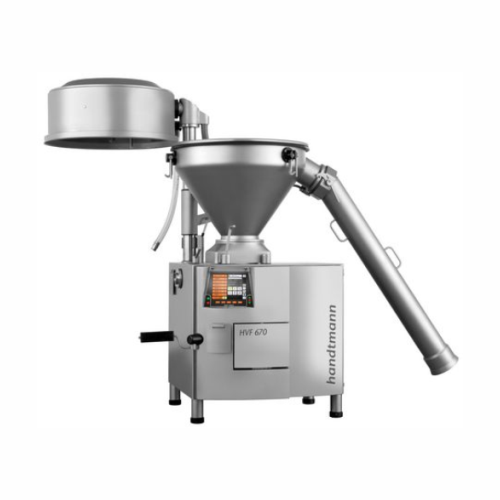
High vacuum filler for cooked ham with whole muscle pieces
Ensure precision and quality in cooked ham production with hi...
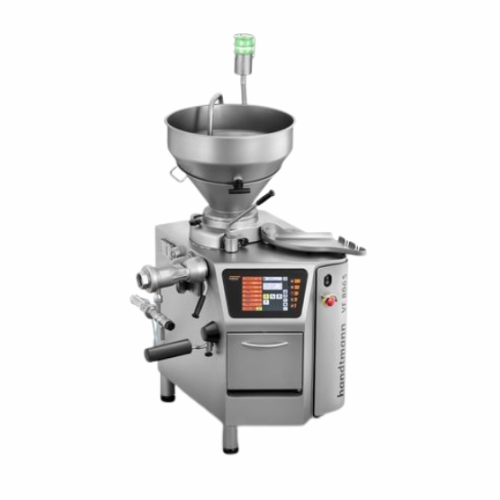
Vacuum filler for small and medium-scale meat producers
Achieve precise portioning with high-speed filling and grinding c...
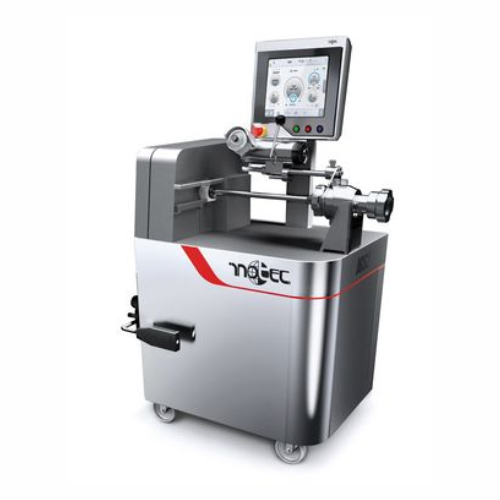
Tying solution for sausage products in natural and collagen casings
Efficiently portion and tie sausage products to per...
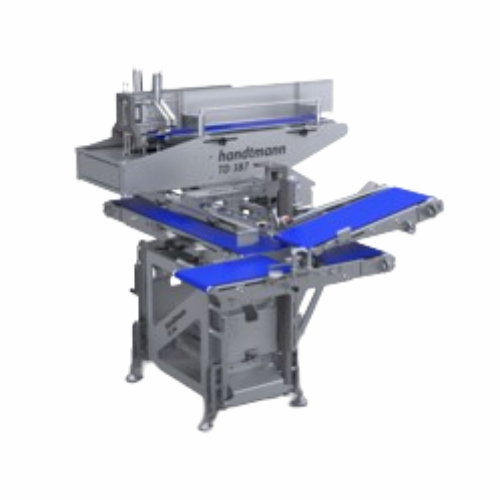
Automatic tray loader for minced meat portions
Streamline your tray loading process by integrating a flexible and fully au...
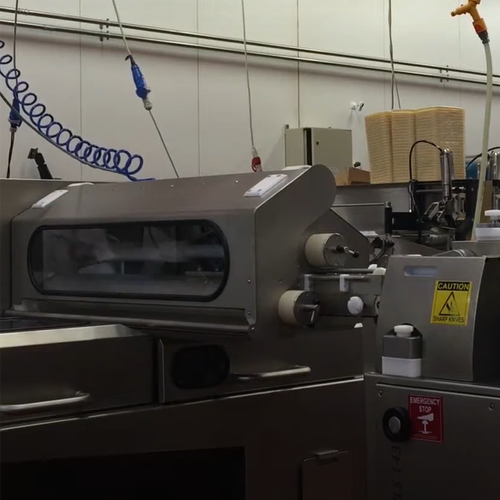
Collating system for fresh sausage automation
Maximize production efficiency by seamlessly integrating automated collating...
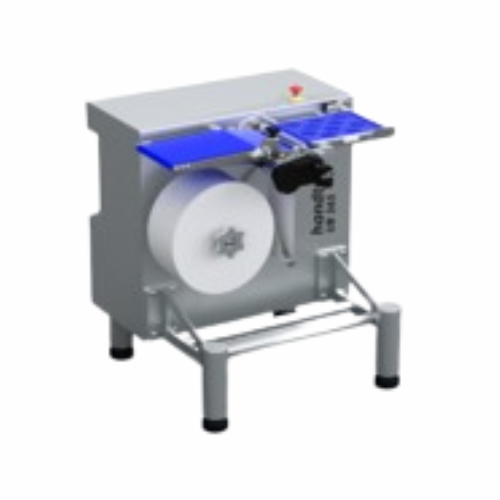
Product aligning and stacking solution
Enhance process stability and resource efficiency by integrating precise product ali...
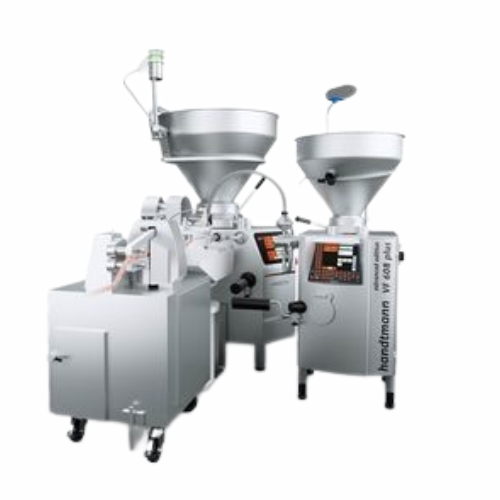
Industrial co-extrusion system for sausages with alginate casing
Eliminate the need for traditional sausage casings with...
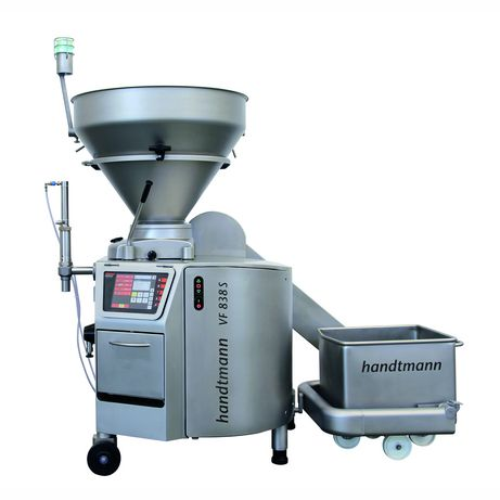
Precise dosing valve for pasty products
Achieve precise, gram-accurate dosing for a wide array of pasty and semi-viscous pr...
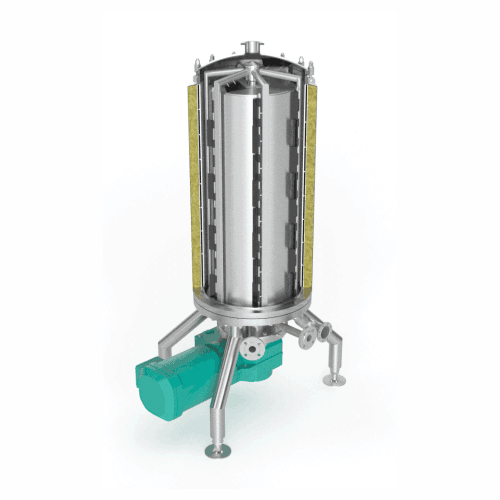
Scraped surface heat exchanger for high viscous products
Efficiently handle the cooling and heating of high viscous produ...
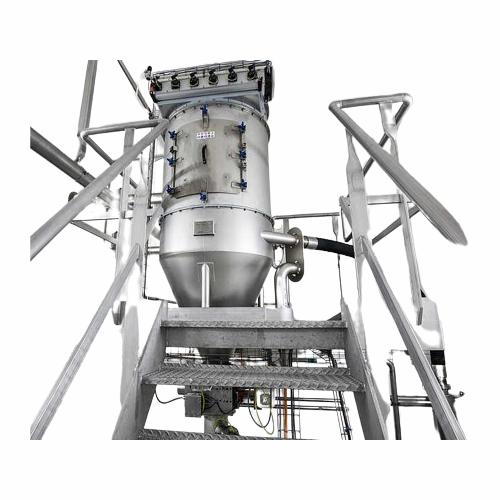
Vacuum pneumatic conveying for infant nutrition
Ensure efficient handling of delicate powders with a versatile vacuum pneu...
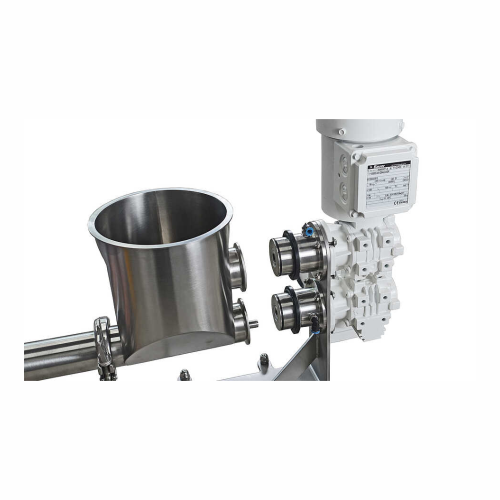
High-precision volumetric feeder for bulk materials
Achieve precise bulk material flow with a solution that ensures consi...
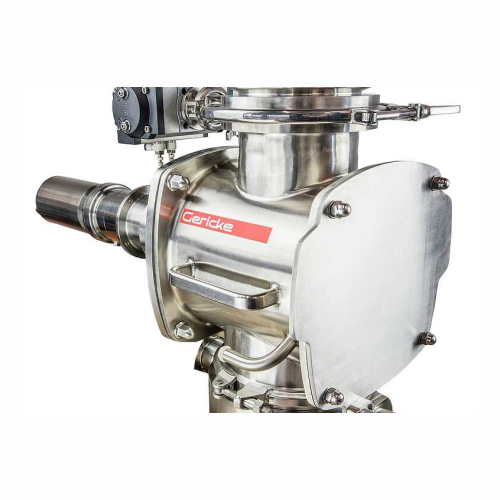
Mini batch blender for pharmaceutical solids
Achieve precise mixing homogeneity with the mini batch blender, perfect for l...
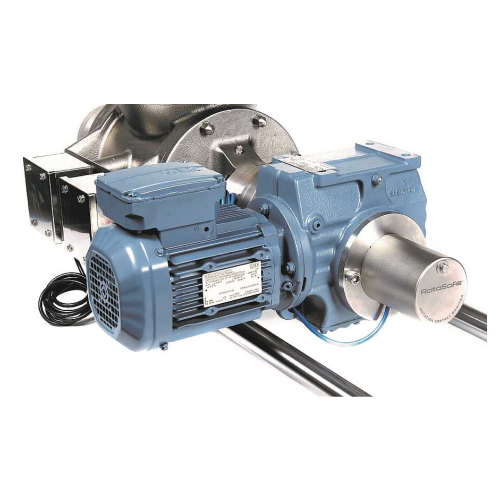
Contact detection system for rotary valves
Prevent product contamination and equipment damage with instant contact detecti...
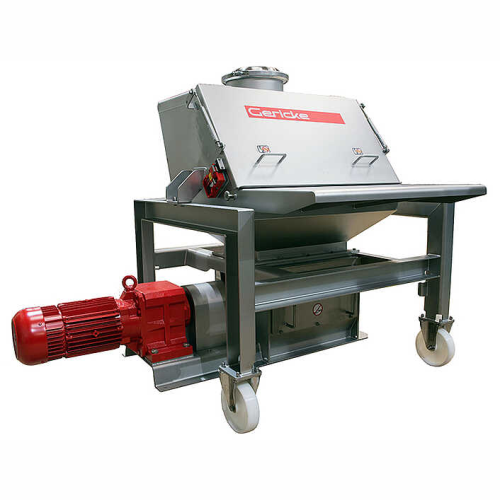
Sack tipping station for dust-free bulk material handling
Efficiently manage bulk materials while minimizing dust exposu...
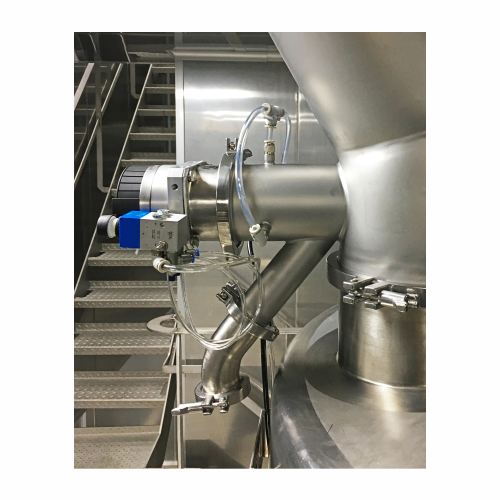
Sampling valve for secure sample extraction
Ensure product quality by safely extracting representative samples without hal...
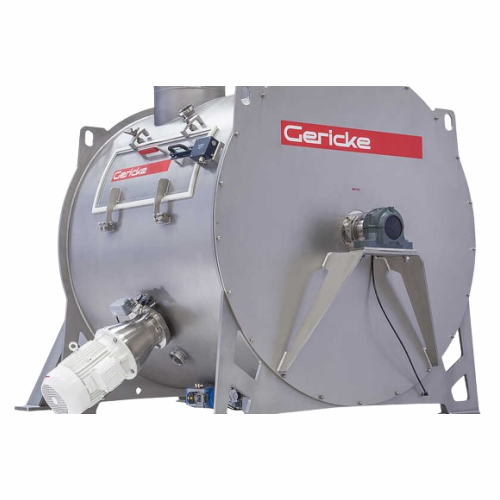
Single shaft batch mixer for chemical and pharmaceutical applications
Optimize mixing efficiency with rapid batch proce...
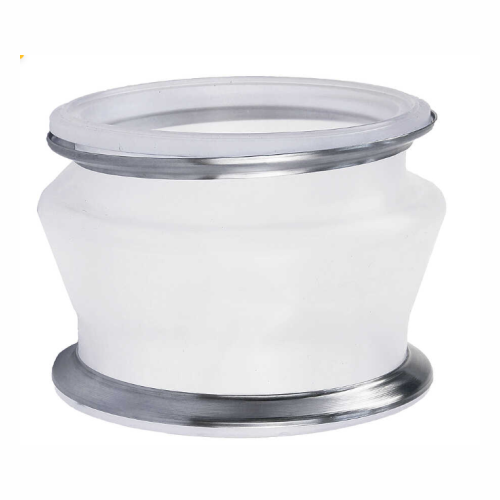
Hygienic flexible sleeves for tri-clamp connections
Ensure seamless, contamination-free transitions between processing st...
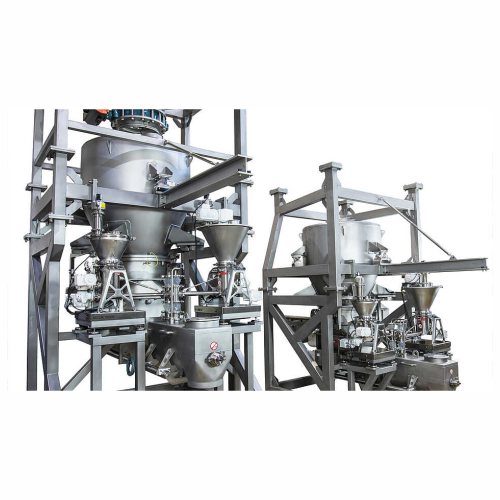
Continuous inline mixing for late product differentiation
Achieve seamless product differentiation with compact inline m...
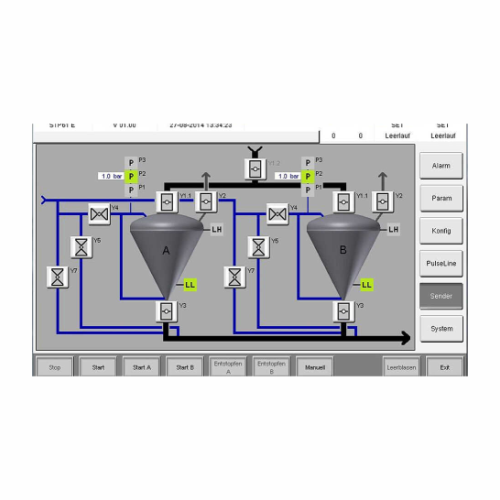
Conveying controller for dense phase conveying
Streamline your dense phase conveying operations with precise control and m...
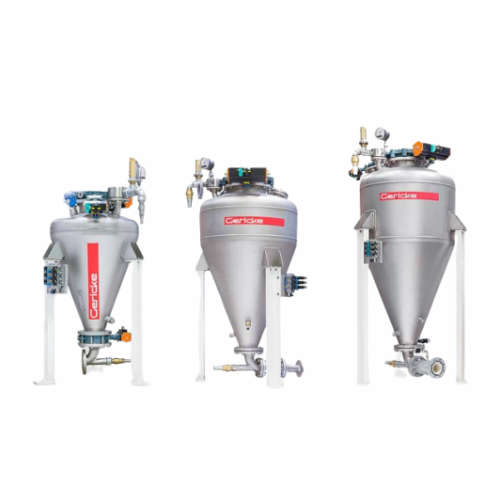
Dense phase pneumatic conveying system for powder transfer
Ensure gentle and efficient material transport with minimal m...
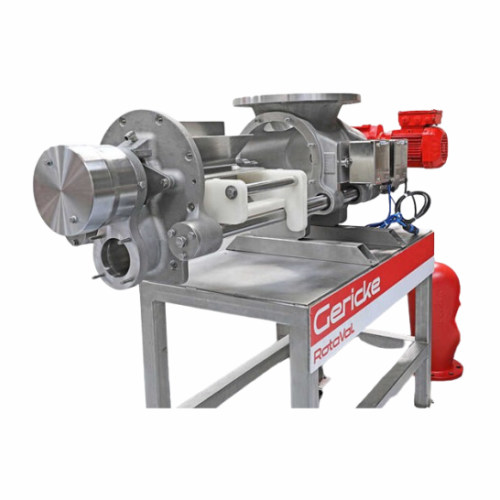
Quick-clean hygienic rotary valves
Ensure seamless cleaning and minimal downtime in your production line with rotary valves...
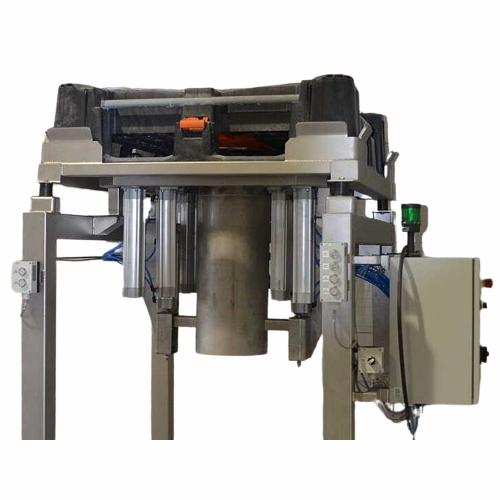
Big bag pallet unloader for bulk products
Efficient and reliable solution for unloading and transporting powders and bulk ...
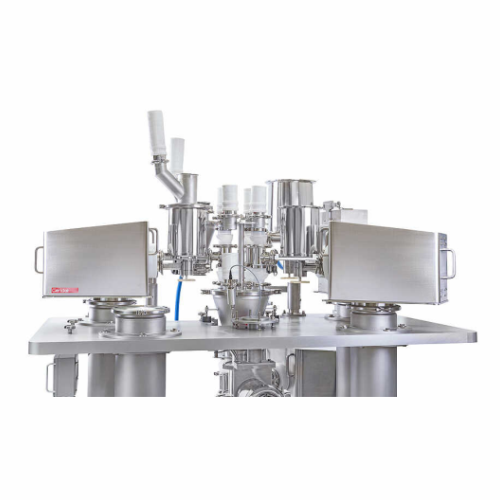
High-precision gravimetric feeders for industrial bulk solids
Achieve unparalleled accuracy in your production line with...
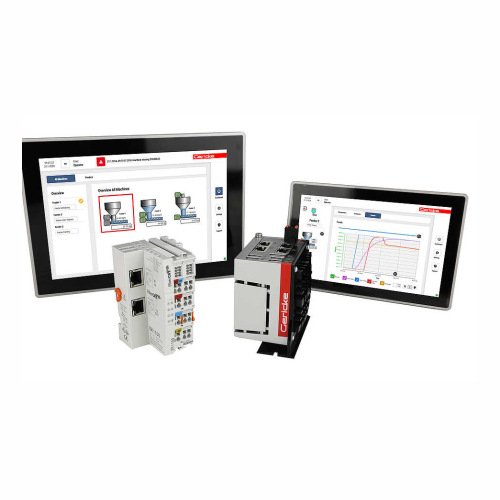
Universal controller for feeders in powder handling applications
Simplify and enhance your powder handling with precise ...
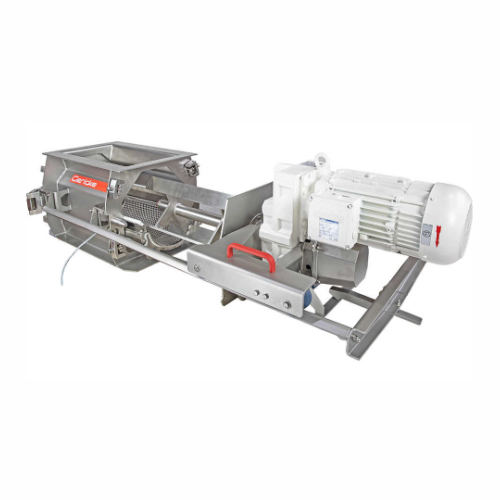
Deagglomerator for consistent particle size reduction
Struggling with inconsistent particle sizes or unwanted lumps in yo...
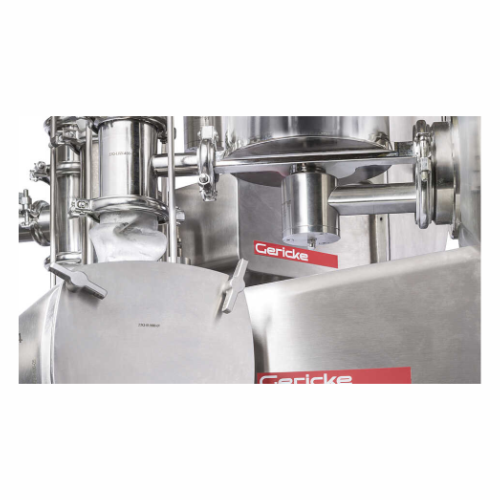
Continuous mixer for homogeneous blending
Achieve consistent product quality with precise mixing and blending, ideal for a...
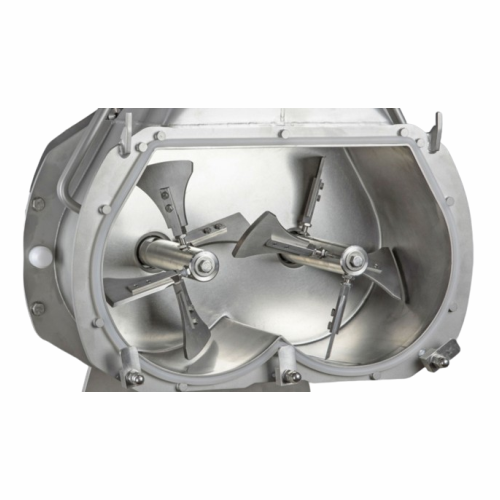
Laboratory mixer for r&d and small batch production
Achieve superior mixing precision for R&D and pilot production w...
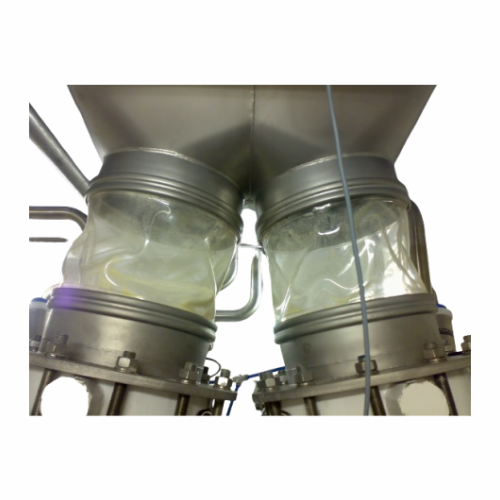
Hygienic flexible sleeves for food and pharmaceutical use
Say goodbye to contamination risks with this tool-free, quick-...
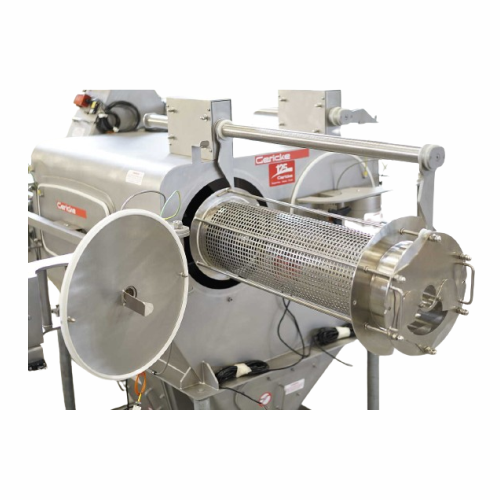
Centrifugal sifter for bulk solids and powders
Achieve precise particle separation and enhance product quality with a solu...

Continuous powder mixer for industrial applications
Achieve precise and efficient integration of powders, granules, and l...
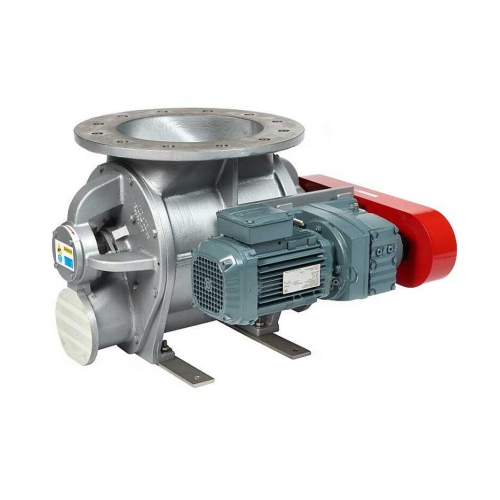
Heavy duty blowing seals for abrasive products
For operations dealing with abrasive materials under high pressure, these r...
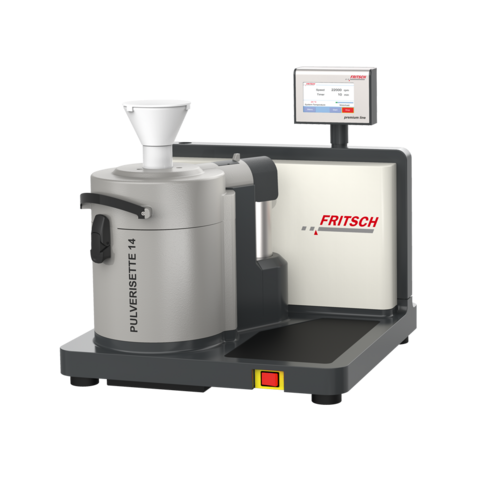
Variable speed rotor mill for sample preparation
Achieve rapid and precise grinding of various materials with a versatile ...
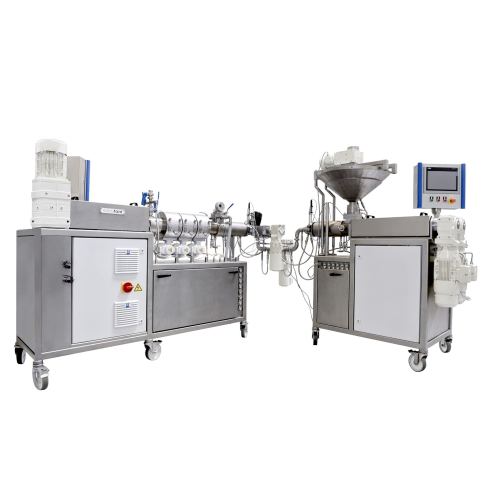
Lab cooking and forming extruders for r&d
Optimize your R&D processes by testing new recipes and improving formulatio...
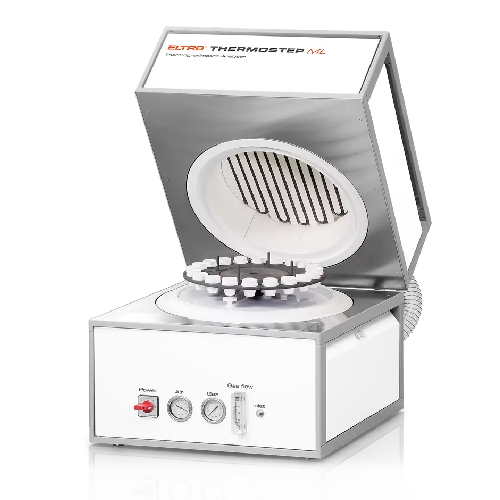
Thermogravimetric analyzer for ash and moisture content analysis
Optimize your production with precise weight loss analy...
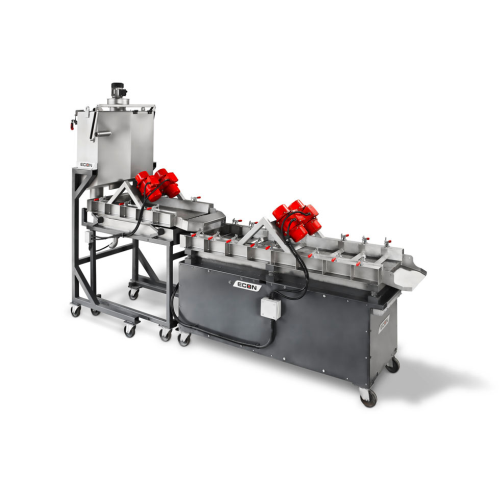
Vibration drying system for pellets
Achieve precise moisture control for pellets with high filler content, enhancing final ...
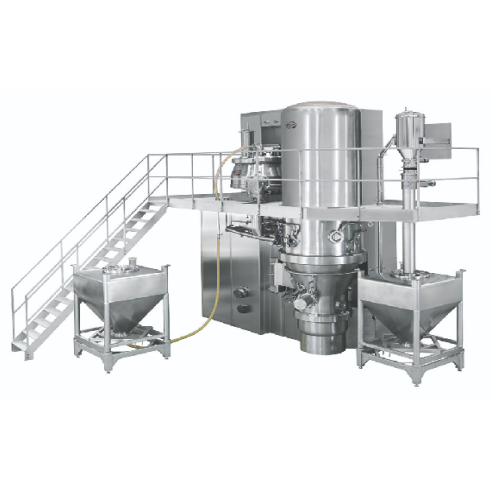
Pharmaceutical granulation line
Streamline your production with an integrated system that combines mixing, granulation, and ...
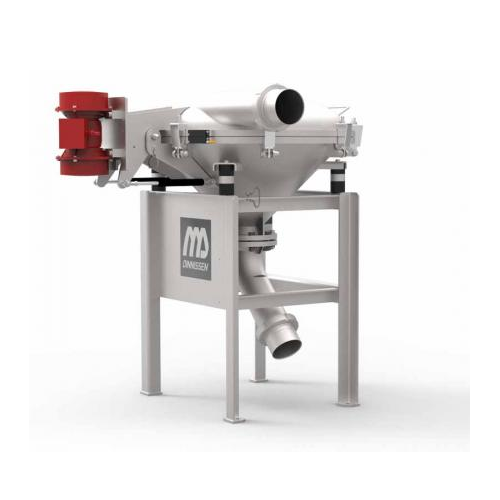
Industrial vibrating sifters for granular material separation
Achieve precise particle separation and ensure product pur...
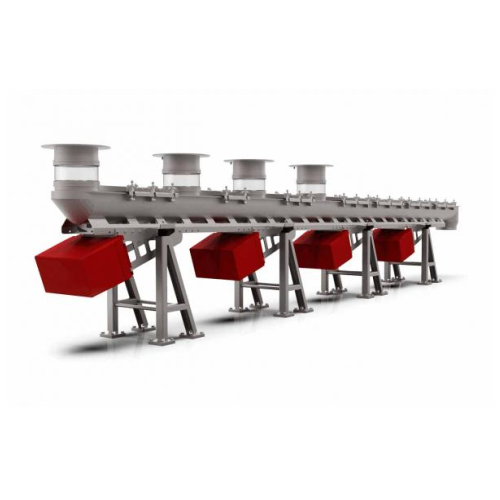
Vibration transport system for hygienic conveying of bulk goods
Optimize your production line with efficient and hygieni...
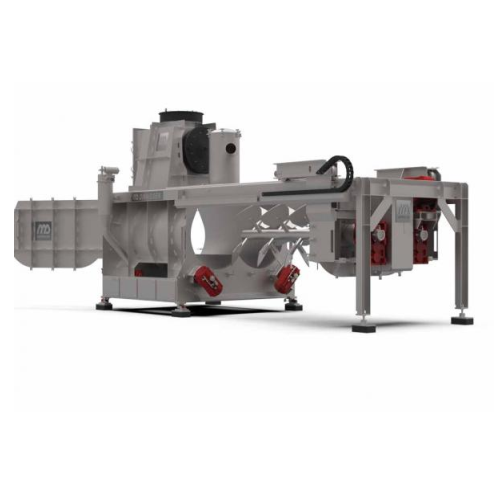
Industrial mixer for batch granules or grains
Achieve precise mixing with seamless integration of heating, sterilization, ...

Industrial pneumatic conveying system for powders and granulates
Achieve hygienic and dust-free transport of powders and...
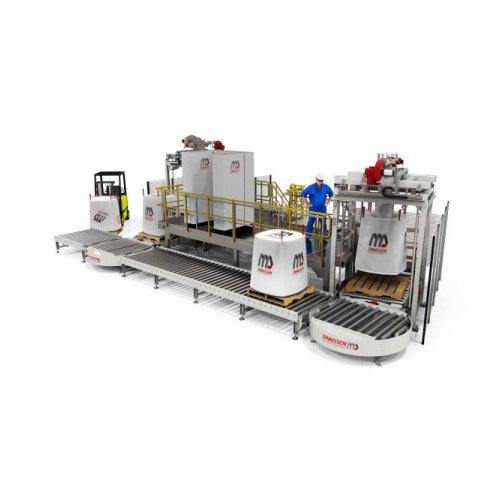
Product handling system for big bags and containers
Optimize your production line with a comprehensive system for transpo...
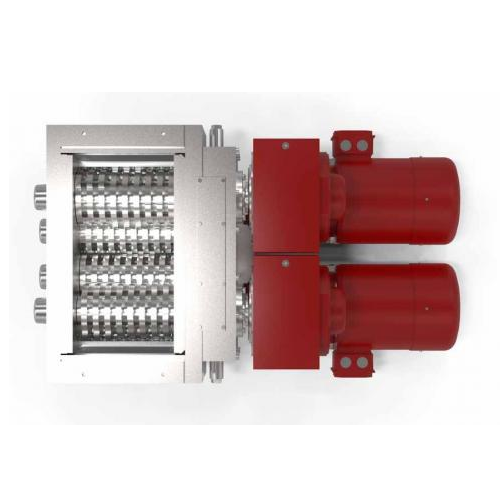
Industrial roller mill for grain size reduction
Achieve precise grain size reduction with minimal heat generation and opti...
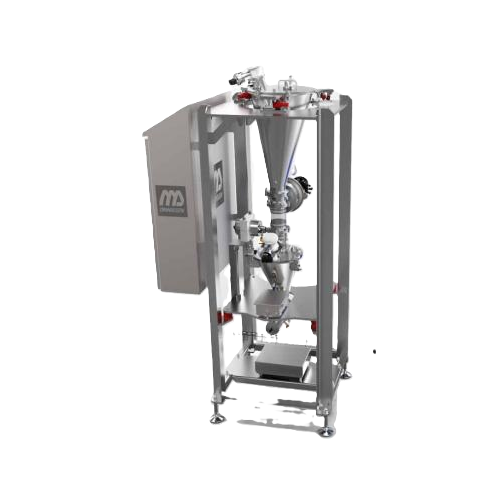
Micro dosing system for precise powder weighing
Achieve unparalleled dosing accuracy in your production line with a system...
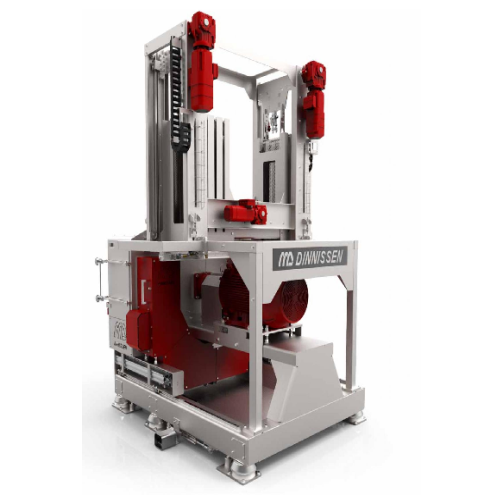
Hammer mill with automatic screen exchange
Optimize your milling operations with a high-speed solution that ensures seamle...
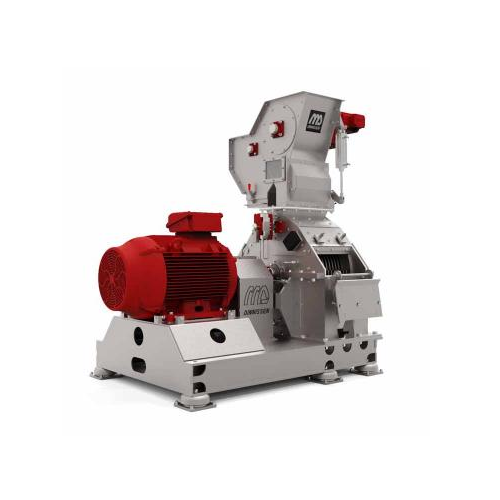
Industrial hammer mill for grinding and sifting
Ensure precise particle size reduction and consistent product quality with...
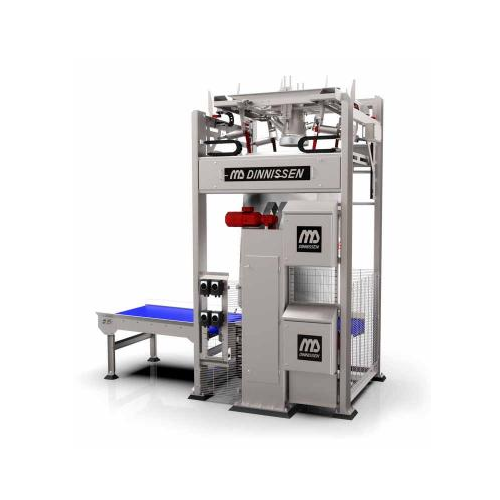
High-care big bag filling system for hygienic environments
Ensure precise hygienic filling of Big Bags in high-care envi...
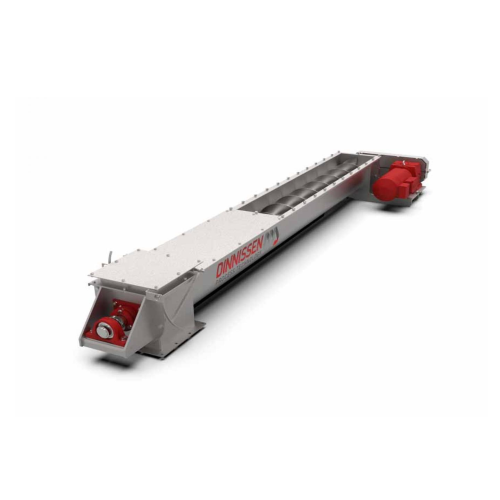
Vertical transport for bulk goods
Efficiently move bulk goods vertically with minimal energy usage, ensuring seamless integ...
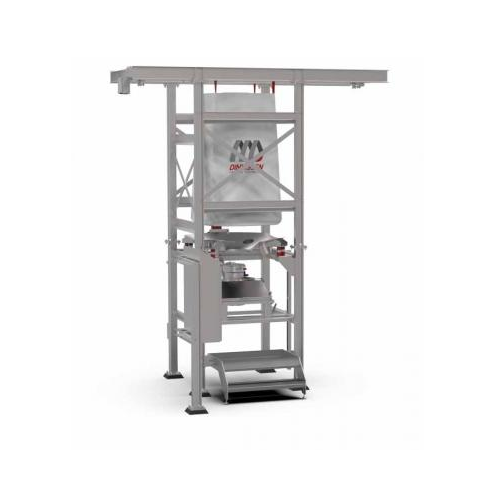
Modular big bag unloading station for various materials
For hassle-free handling of bulk materials, this modular solution...

Big bag conditioning system for compact materials
Struggling with clumped materials during unloading? This system expertl...
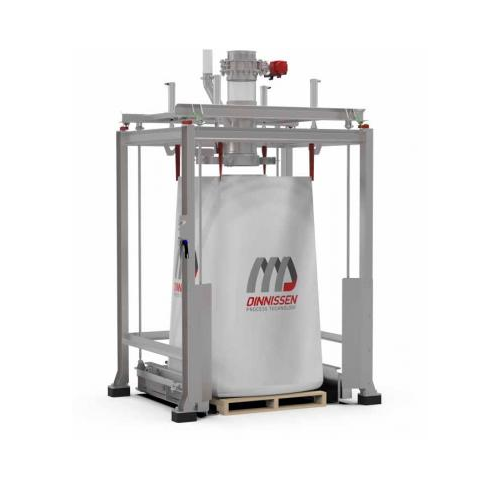
Calibratable big bag filling station for dust-free operations
Ensure precise, dust-free filling of bulk bags with ergono...
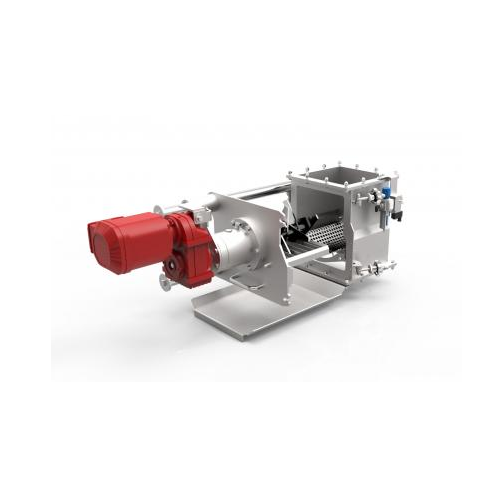
Industrial breaker for reducing large lumps and agglomerates
Efficiently break down challenging materials with a robust ...
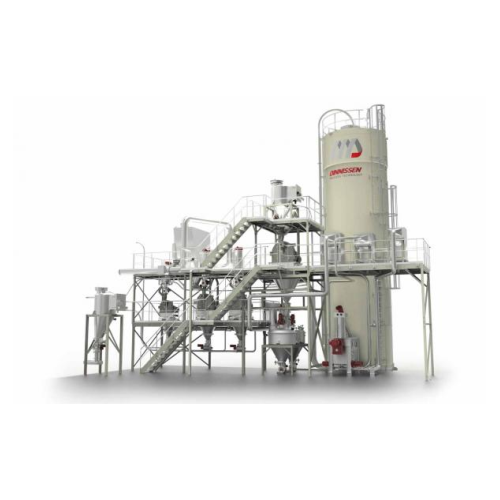
Centrifugal mill for fine grinding in industrial processes
Achieve exceptional fineness without overheating your materia...
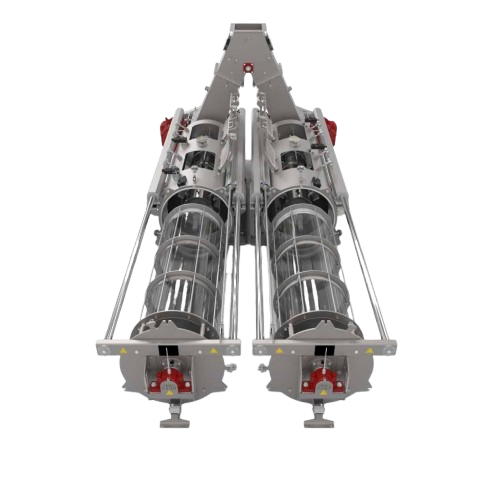
Industrial centrifugal sifter for solid particulate materials
Quickly and accurately sift a wide range of powders and gr...
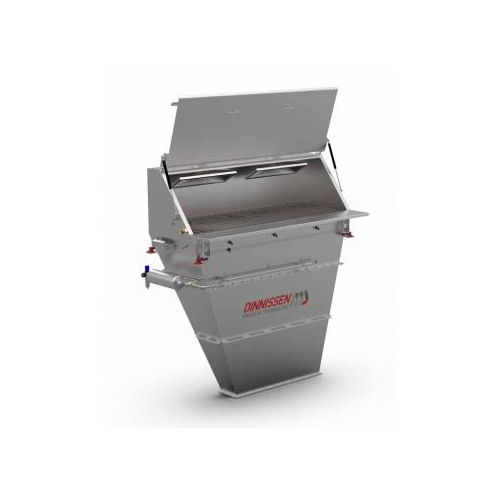
Bag emptying system for bulk material handling
Streamline your material processing operations with a versatile solution de...
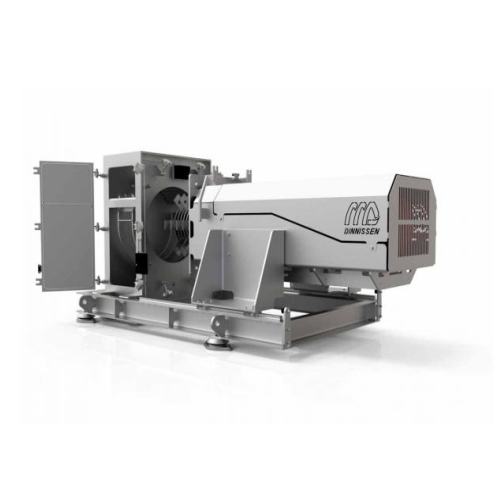
Hygienic industrial grinder for food and pharma applications
Achieve optimal hygiene and efficiency in your grinding pro...
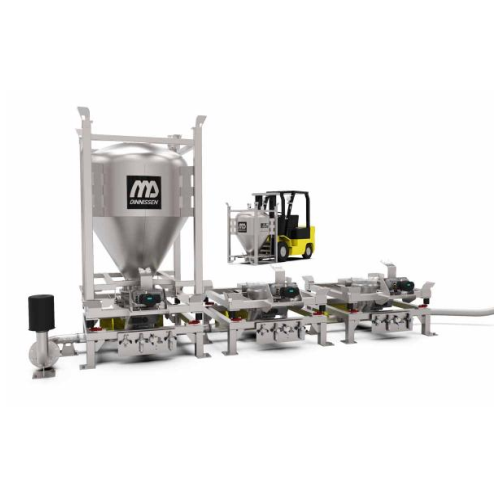
Drum and container emptying system
Ensure safety and efficiency when handling and emptying drums or containers, whether dea...

Bag-in-box filling system for packaging efficiency
Streamline your packaging process by integrating filling and boxing in...
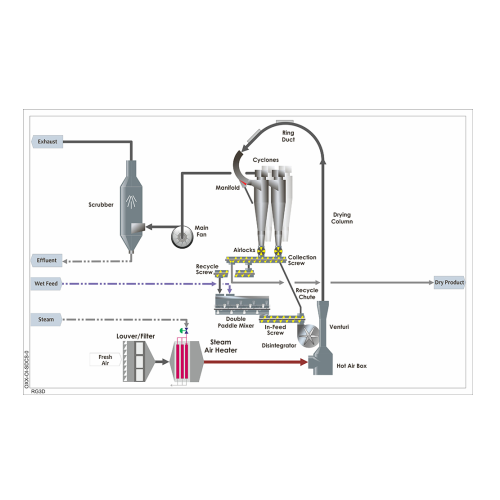
Pea fiber drying solutions for food or feed applications
Ensure top-tier product quality with precise drying of pea fiber...
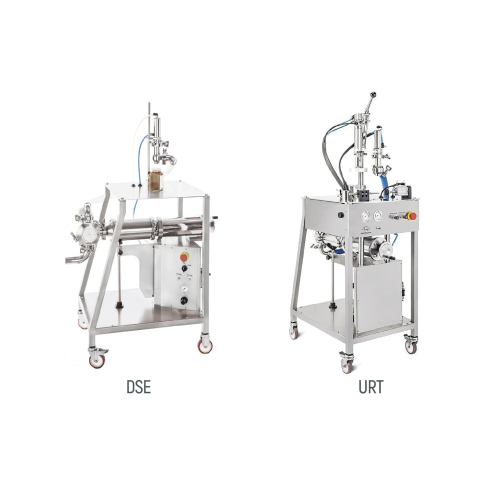
Pneumatic dosers for variable density products
Achieve precise dosing for liquid to dense products with versatile pneumati...
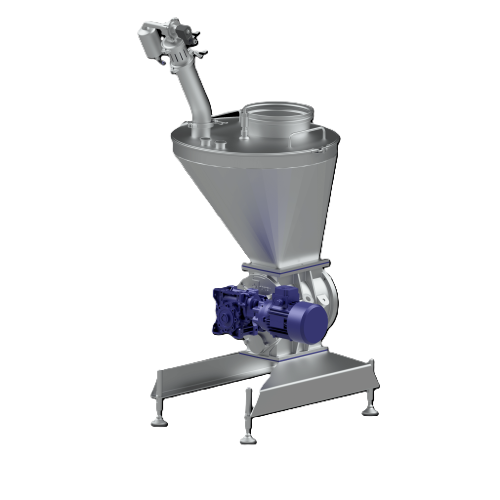
Dilute-phase conveying solution for powder handling
Efficiently transfer powders and granules with robust leak containmen...
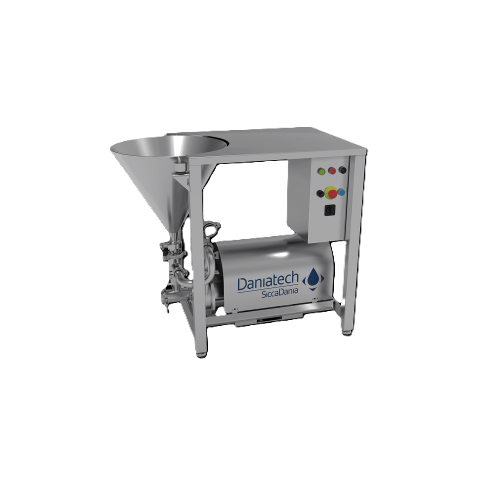
Inline high-shear mixer for powders and liquids
Achieve efficient mixing and homogenization in your production line with a...
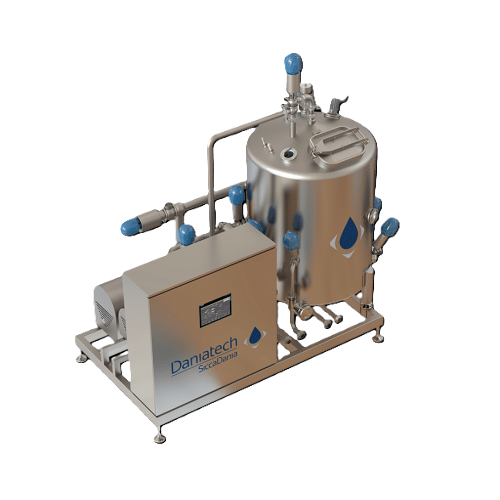
High-capacity inline mixer for dairy and beverages production
Achieve a rapid and homogeneous mix in high-capacity produ...
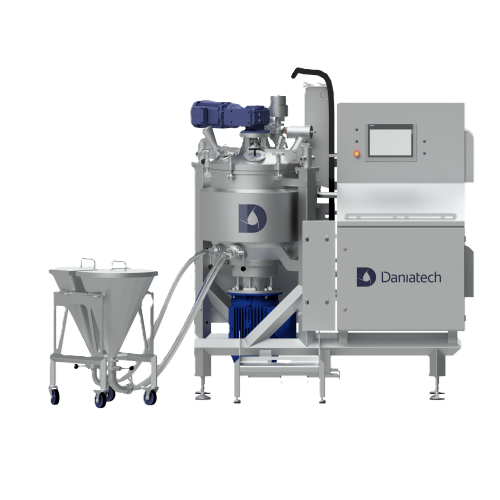
Lab-scale high-shear mixer for recipe development
Optimize your recipe development process with precise mixing, homogeniz...
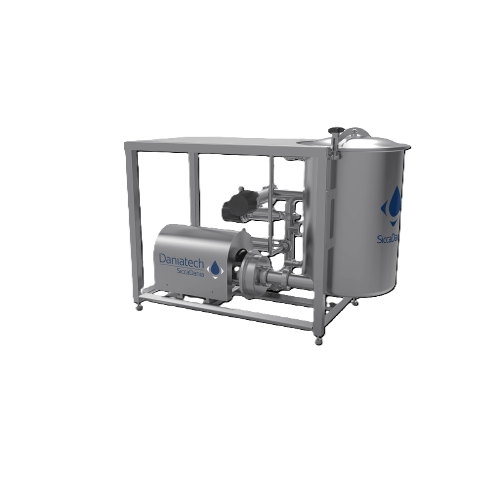
Mixer for low to medium viscosity products
Optimize your mixing, dosing, and homogenization processes with a versatile mix...
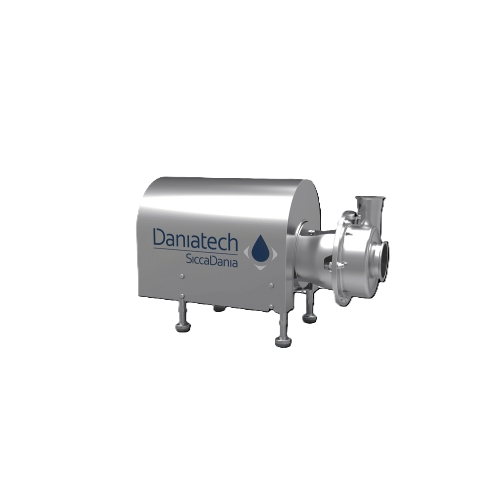
Inline high shear mixing unit for low to medium viscosity products
Achieve precise emulsification and size-reduction wi...
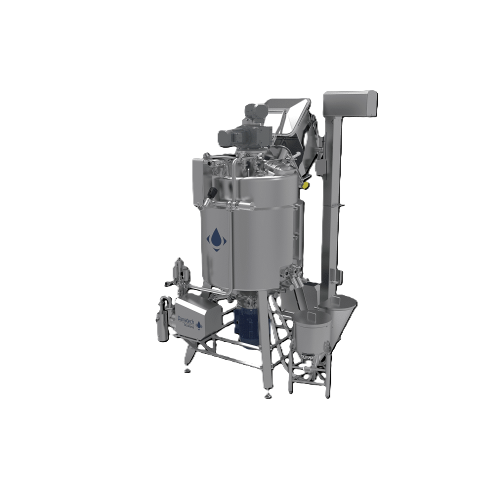
High-shear mixer for high viscosity products
Achieve consistent, homogeneous mixtures of high-viscosity products with a ve...
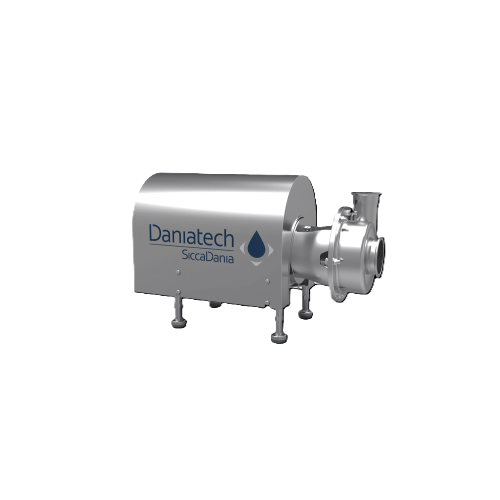
Ultra-high shear mixer for emulsification and homogenization
Optimize your production with ultra-high shear mixing, acce...

Vacuum high shear mixer for medium to high viscosity products
Achieve flawless blending and air-free consistency in visc...
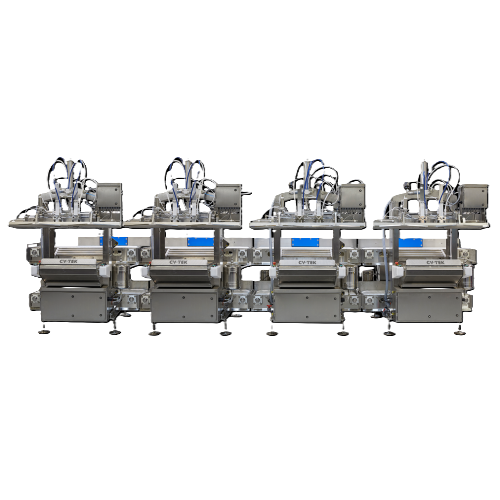
Multi-station modified atmosphere packaging system for bulk products
Optimize your packaging efficiency with a system d...
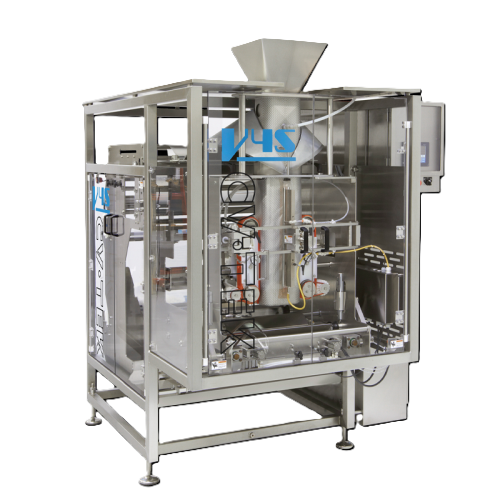
Vertical form fill seal packaging for high washdown environments
Ensure optimal packaging in demanding environments with...
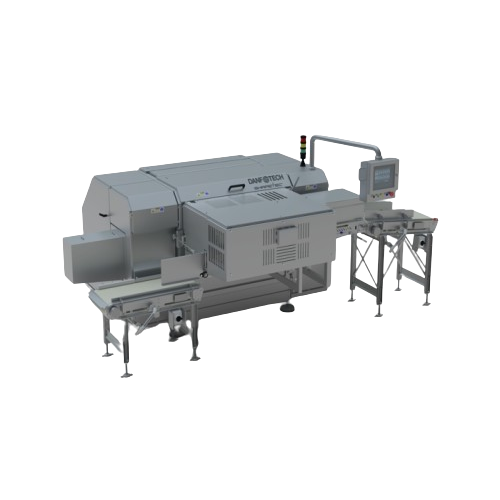
Servo press for optimal shaping of bacon and meat loins
Achieve precise shaping and consistent slice yield for bacon and ...
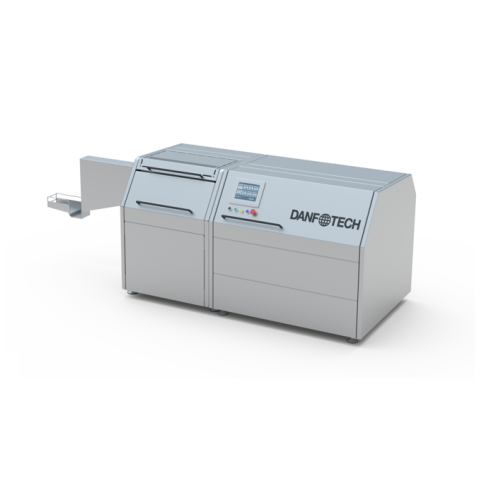
Hydraulic press for frozen meat and bacon
Achieve consistent shaping and high-quality output for frozen meat and bacon pro...
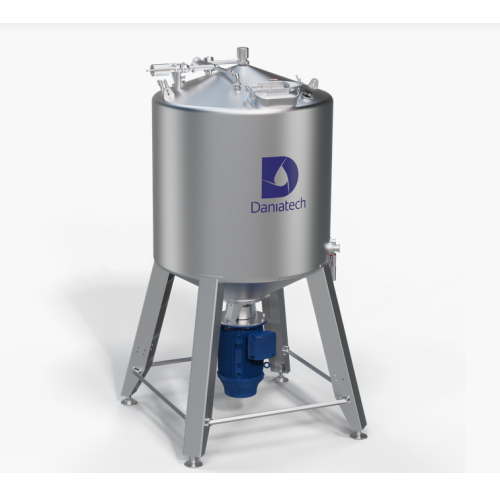
High-capacity manual mixer for industrial applications
Optimize your mixing process with a highly efficient, manually ope...
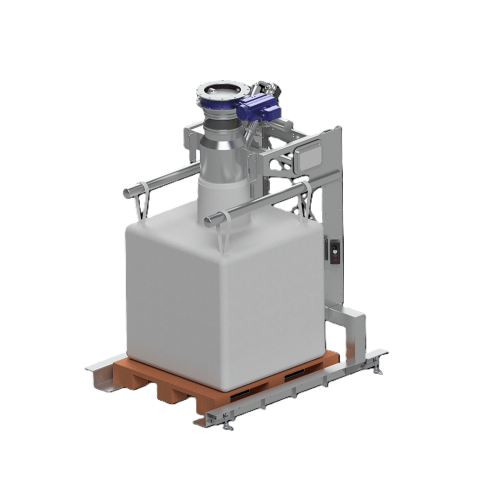
Bigbag filling system for powder and bulk materials
Ensure precise and dust-free bigbag filling with this versatile syste...
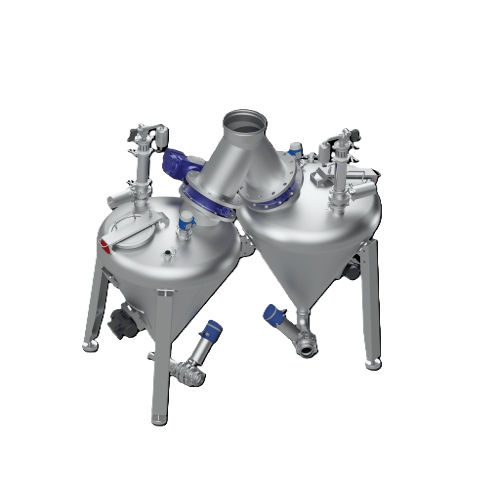
Dense-phase powder conveying system
Optimize your powder processing with a system designed to handle abrasive and fragile m...
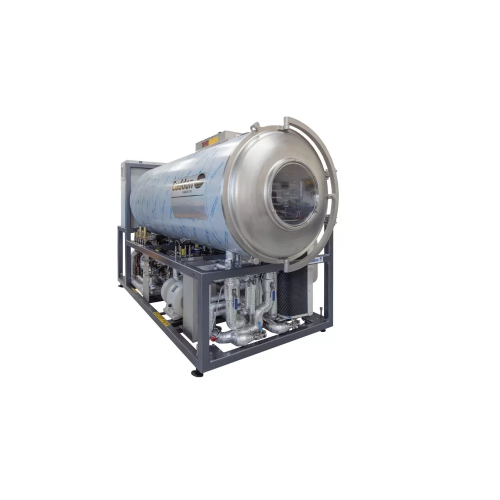
Freeze dryer for high sugar or acid content products
Achieve precise moisture control for challenging high sugar or acid ...
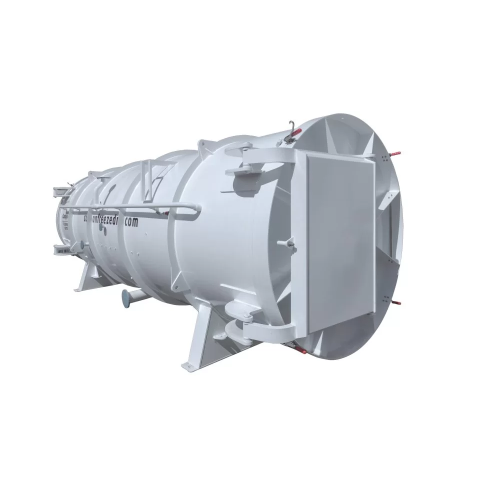
Large-scale industrial freeze dryer
Achieve precise moisture control and preserve product integrity with a large-scale free...
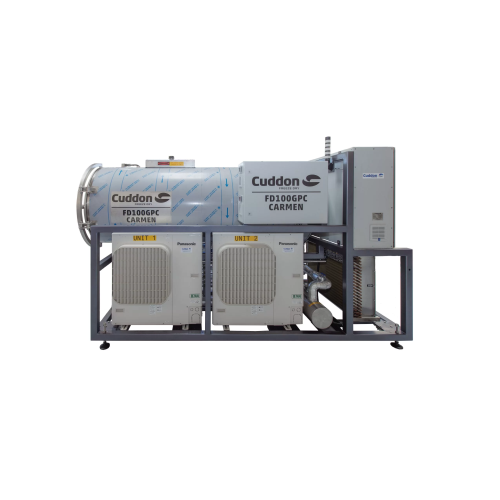
General purpose freeze dryer for small commercial batches
Maximize your production line’s flexibility with this ve...
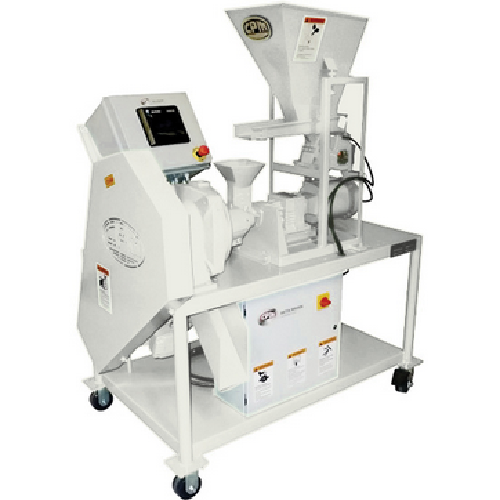
Laboratory pellet press for testing and formulation
Achieve precise pellet formulation and performance testing with versa...
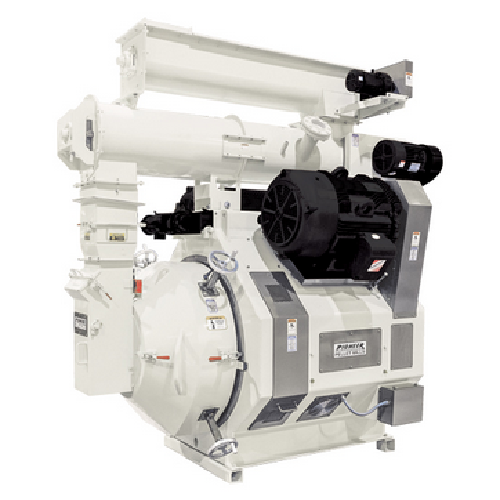
Pellet mill for noise-reduced pelleting
Optimize production with a pellet mill designed to minimize noise and enhance lubri...
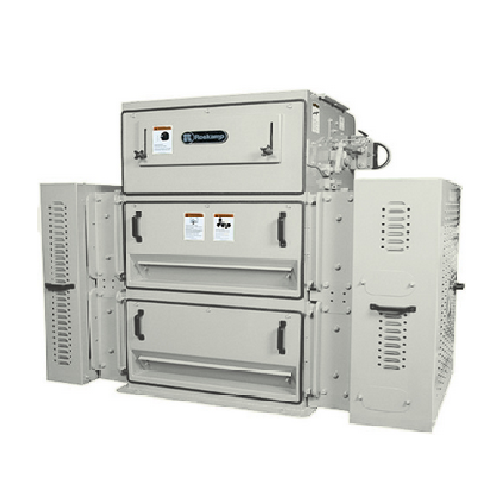
Roller mills for high-demand crushing applications
Optimize your production line with versatile roller mills designed to ...
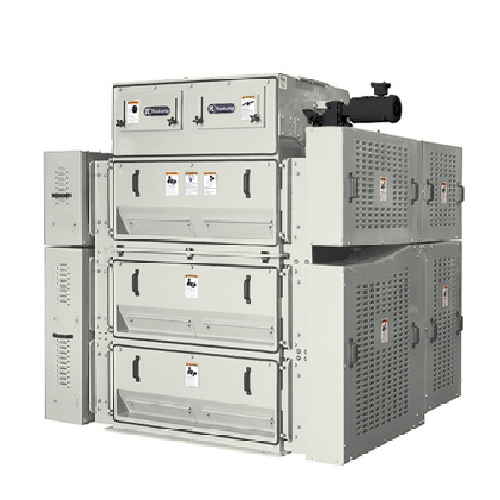
Heavy-duty roll crushers for crushing applications
Optimize your crushing and grinding processes with robust roll crusher...
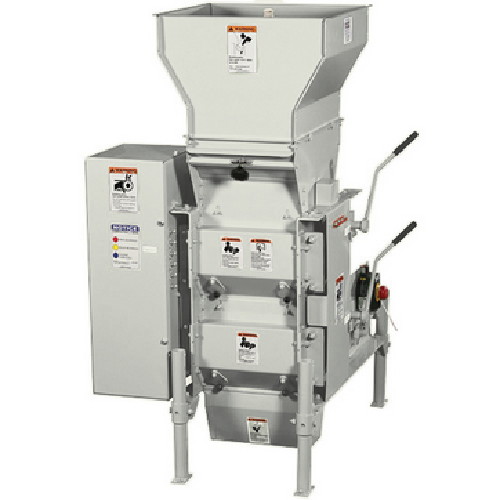
Efficient barley malt crushing with roller mills
Achieve precise particle size control in your processing line with a robu...
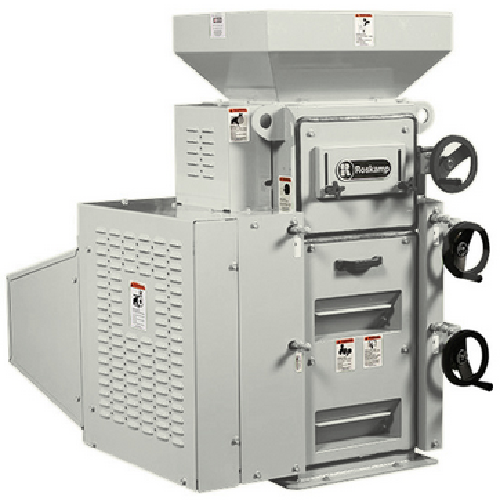
Industrial roller mill for barley malt crushing
Ensure precise barley malt crushing with minimized maintenance for enhance...
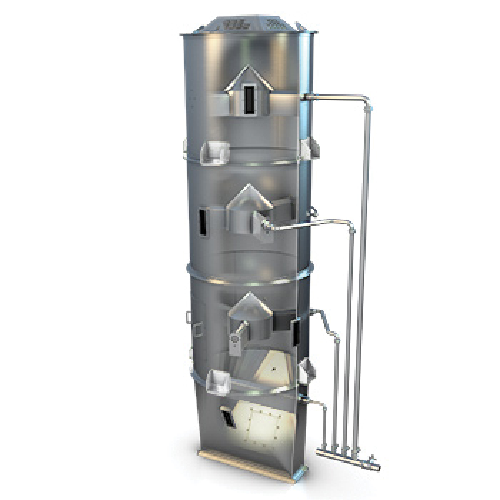
Steam chambers for grain expansion in steam-flaking
Ensure precise grain expansion with steam chambers, designed for unif...
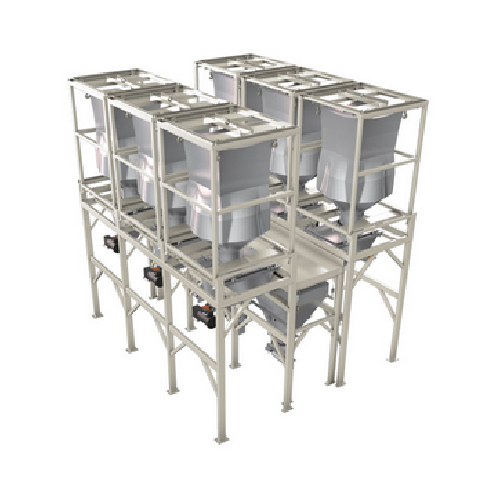
Bulk bag weighing system for batching operations
Streamline your batching process by accurately weighing minor ingredients...
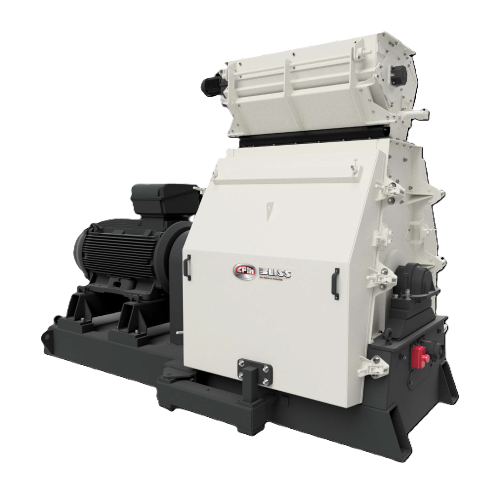
Industrial hammermill for size reduction
Optimize your production line with high-efficiency size reduction, designed to han...
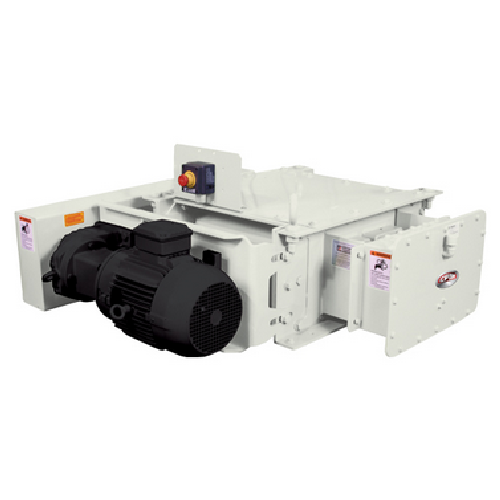
Industrial lump breaker for particle size reduction
Optimize your production line with an advanced solution for efficient...
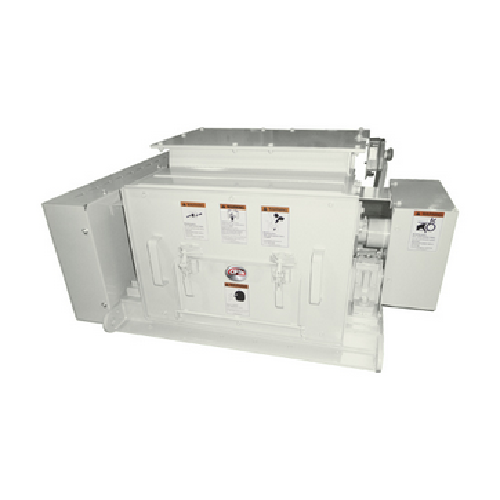
Heavy-duty crusher for 6-inch material
Efficiently tackle challenging crushing tasks with our solution designed to process ...
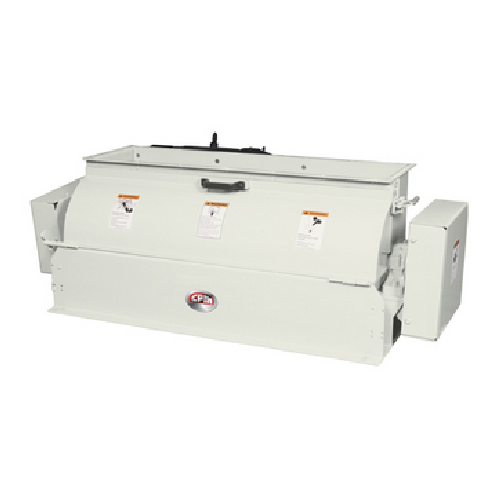
Industrial shredder for high-capacity shredding and delumping
Optimize production with precision shredding and delumping...
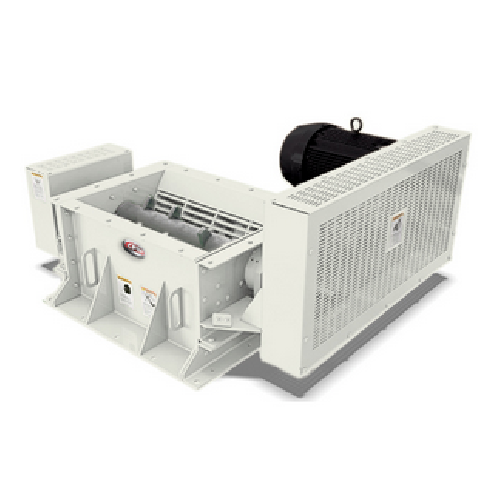
Industrial crusher for medium- to heavy-duty applications
Enhance efficiency in material size reduction operations with ...
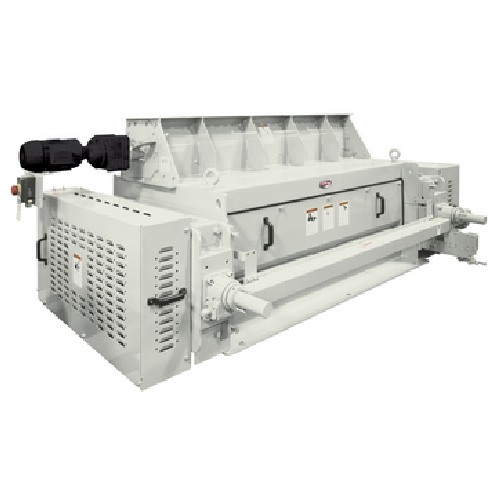
High-capacity pellet crumbler
Achieve precise pellet size reduction with this high-capacity solution, designed for effortles...
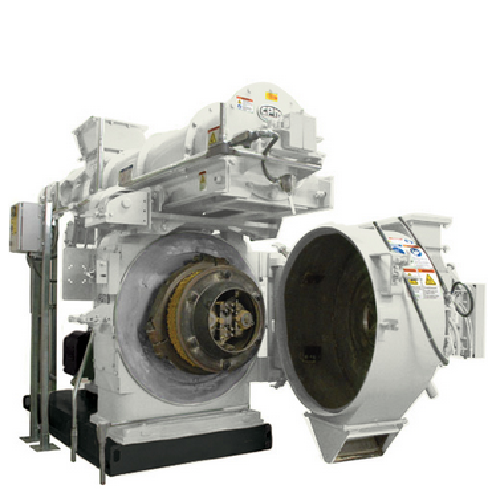
Small-scale pellet mill for animal feed production
Achieve precise pellet formulation for diverse feedstocks with an effi...

Pellet mills for feed, plastics, and industrial products
Optimize pelleting output across diverse materials with precisio...
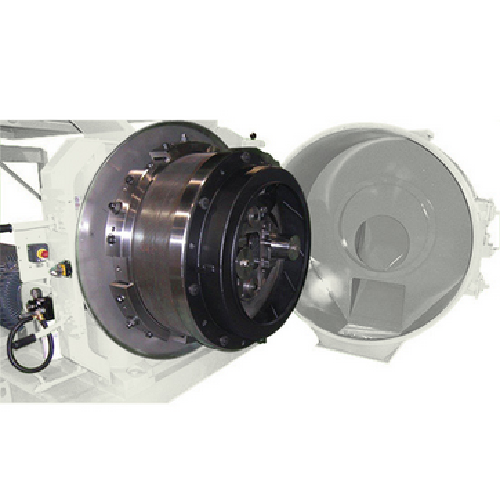
High-capacity pelletizer for oilseed meal processing
Maximize throughput and ensure consistency in your pelleting process...
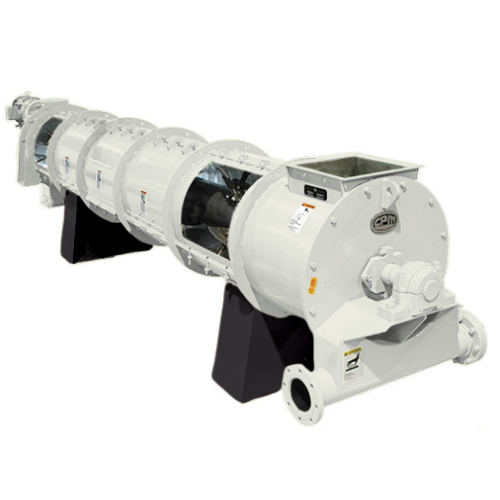
Industrial feed conditioner for optimal moisture absorption
Achieve precise control of moisture and temperature to enhan...
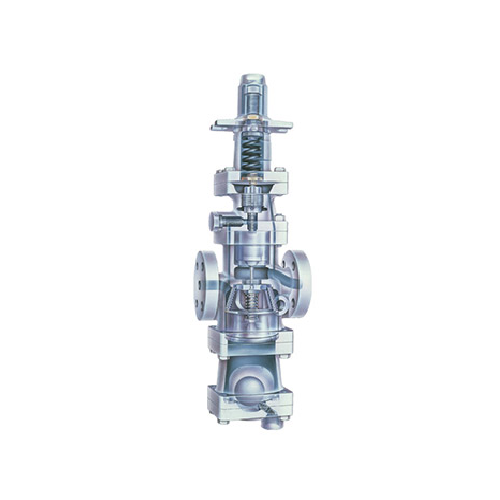
Industrial steam systems for conditioning
Efficiently deliver optimal steam conditioning for diverse feedstock, enhancing ...
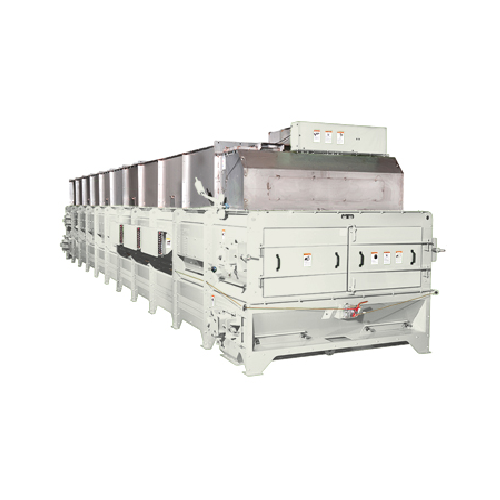
Heavy-duty horizontal dryer/cooler for pellets and meal
Optimize your production line with continuous high-speed drying a...

Industrial circular coolers for uniform product cooling
Achieve consistent cooling across your product range with circula...
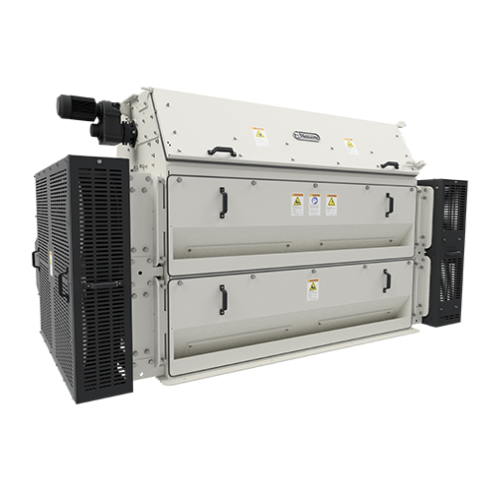
Oilseed cracking solution
Maximize throughput with precision cracking, ensuring optimal downstream processing for oilseed pr...
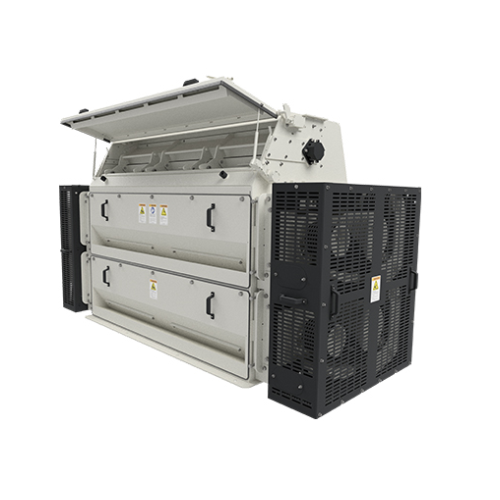
Oilseed cracking mill for efficient processing
Designed for high-capacity oilseed processing, this cracking mill enhances ...
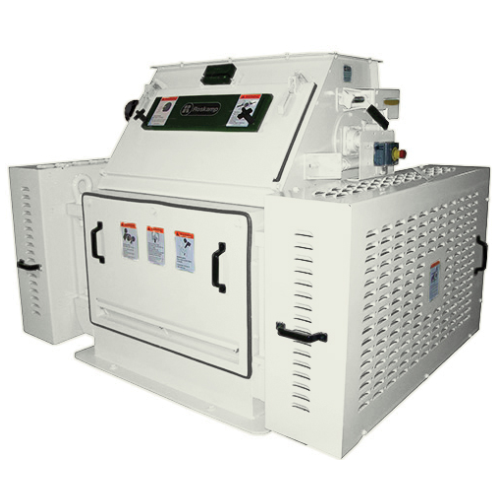
Industrial grain flaking solution
Enhance grain processing efficiency with precision-engineered flaking solutions, designed...
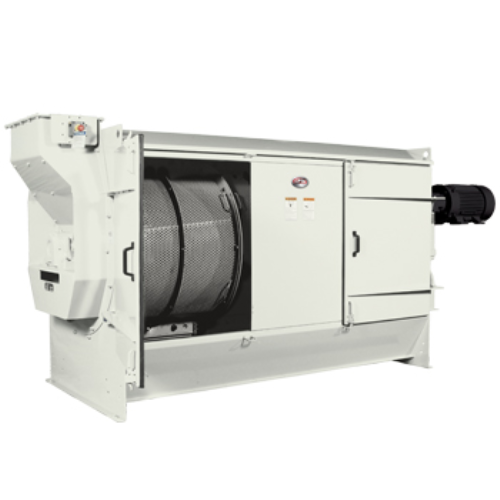
Gyro sifter for feed cleaning
Eliminate contamination and optimize product quality with high-speed screening and cleaning te...
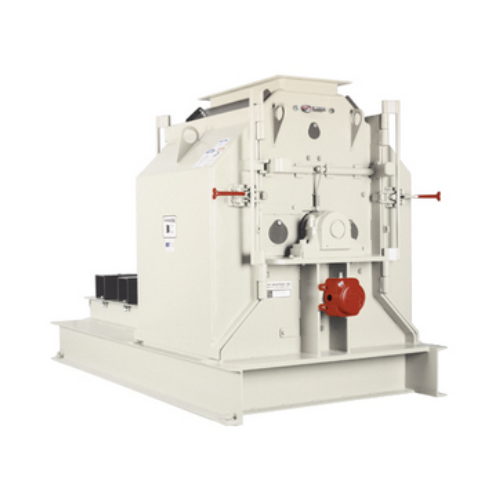
Hammermills for grinding tough products
Optimize particle size reduction with precision-designed hammermills that efficient...
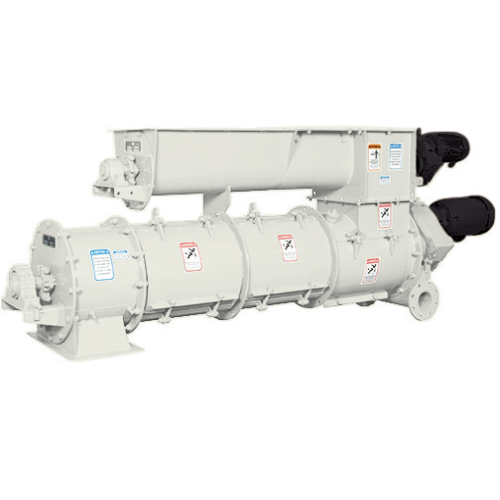
Industrial moisture and temperature control conditioner
Optimizing moisture absorption and temperature management, this c...
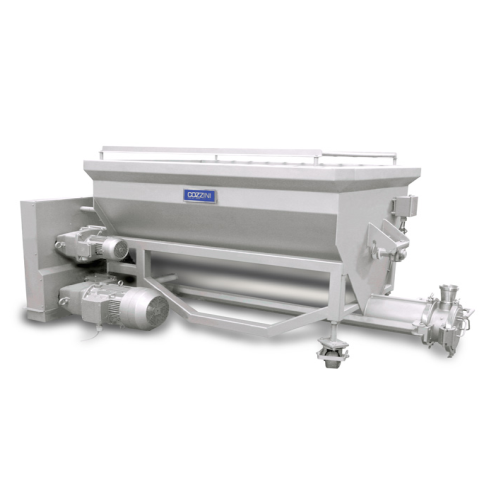
Horizontal screw loader for food processing
Optimize your production flow with a smooth-loading solution designed to effic...
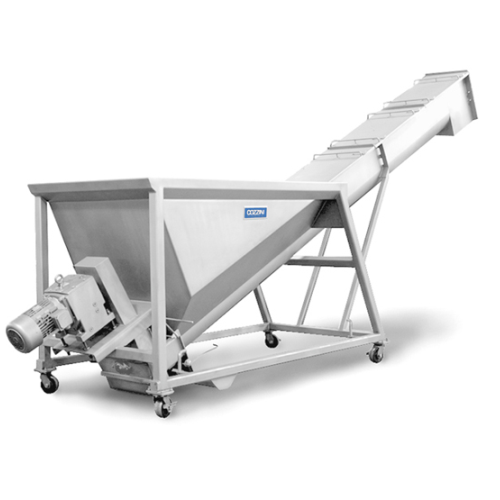
Inclined screw loader for food processing
Optimize your food processing line with an inclined screw loader, designed for e...
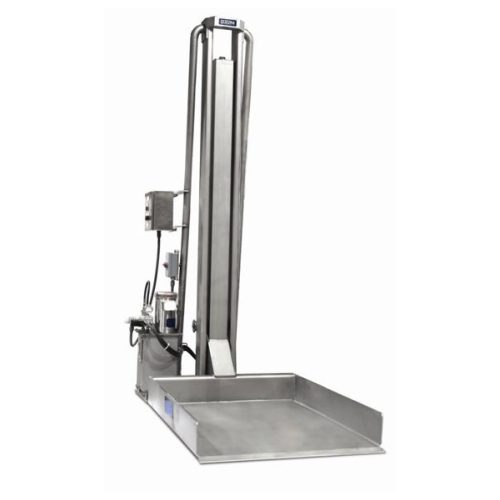
Pallet lift for food processing handling
Enhance your food processing efficiency with a robust pallet lift designed for sea...
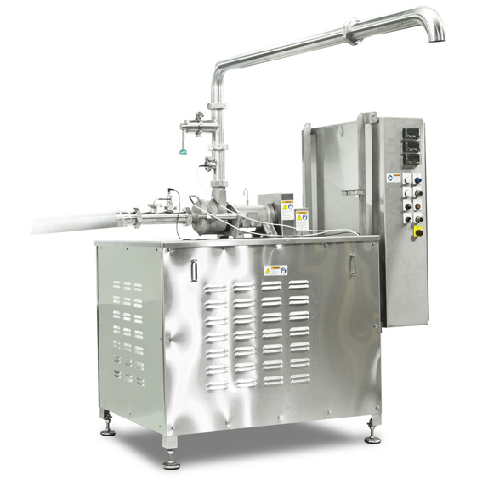
Emulsion reduction system for meat processing
Achieve precise control over particle size and consistency with a state-of-t...
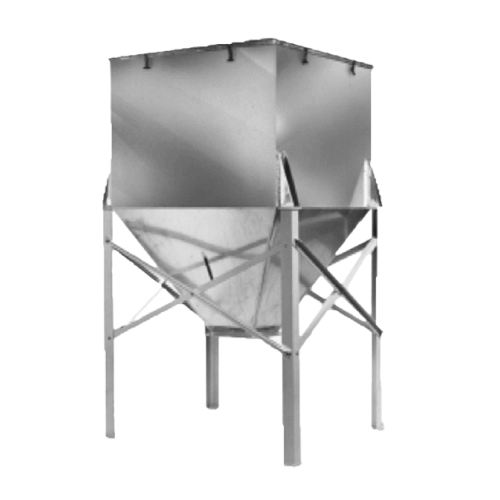
Surge bins for material handling
Ensure efficient material flow and storage in your production line with surge bins that fea...
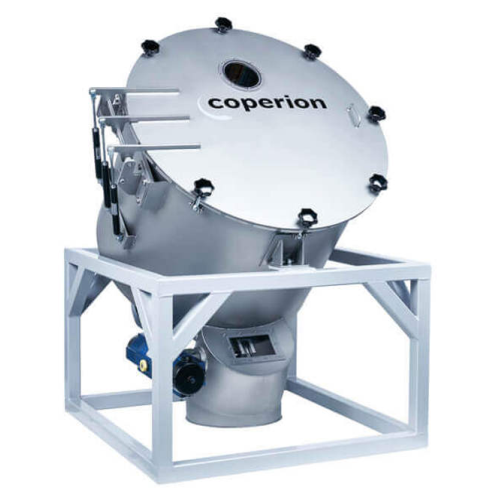
Bulk material mixer for high-speed homogenization
Achieve fast and gentle homogenization of bulk materials with a high-sp...

Precision feeders and mixers for plastics processing
Achieve precise blending and feeding for plastics processing with mo...
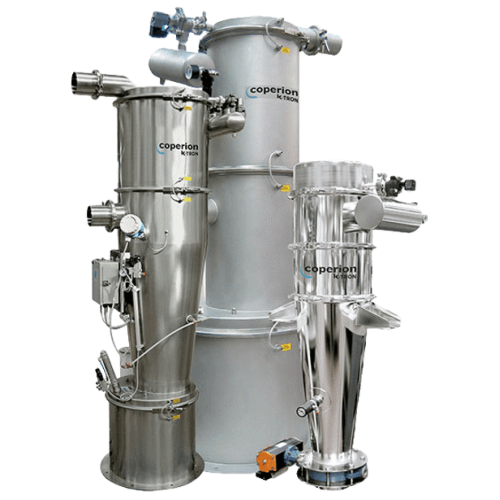
Sanitary bulk solids receiver for food and pharma
Ensure precise control over bulk solid transfer with a system designed ...
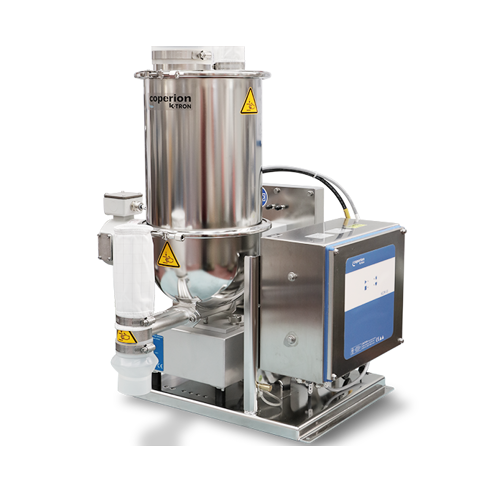
Twin screw feeders for difficult bulk materials
For manufacturers handling sticky or fine powders, twin screw feeders ensu...

Industrial vibratory feeder for bulk solids
Ensure precise and gentle handling of delicate bulk materials with a cutting-e...
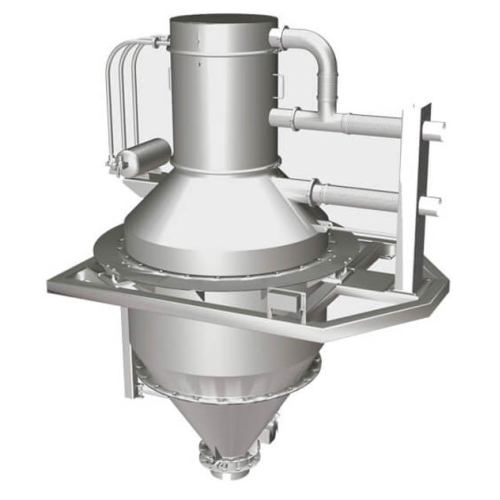
Batch weigh vacuum receiver
Optimize precision in ingredient batching and streamline your production line with advanced vacu...
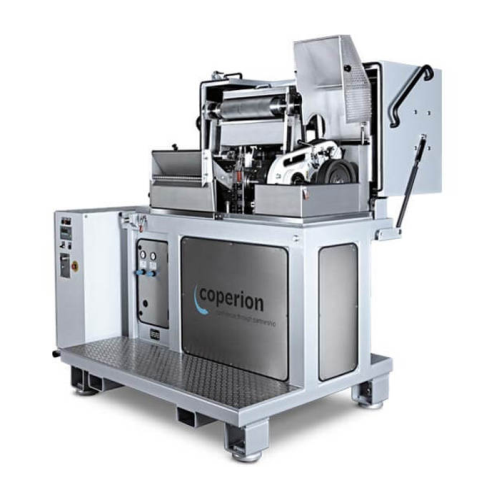
Industrial strand pelletizer for polymer processing
Optimize polymer pellet production with precision engineering, ensuri...
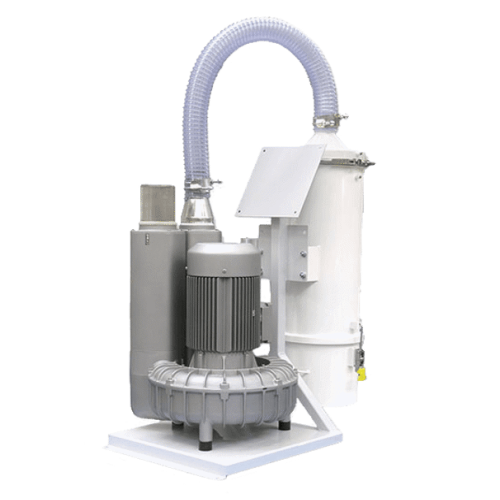
Regenerative vacuum blower for pneumatic conveying
Optimize your material handling with a compact regenerative vacuum blo...
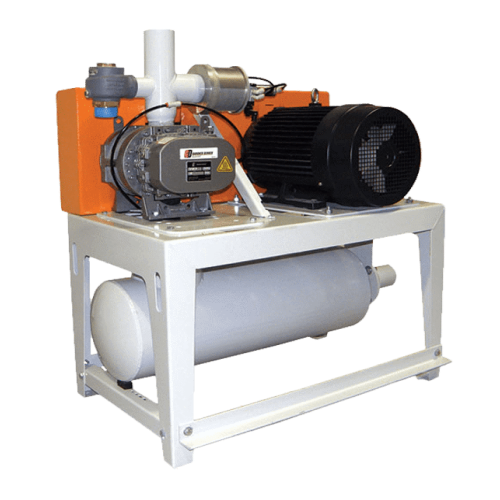
Industrial vacuum blower for continuous pressure conveying
Optimize your production line with reliable vacuum conveying,...
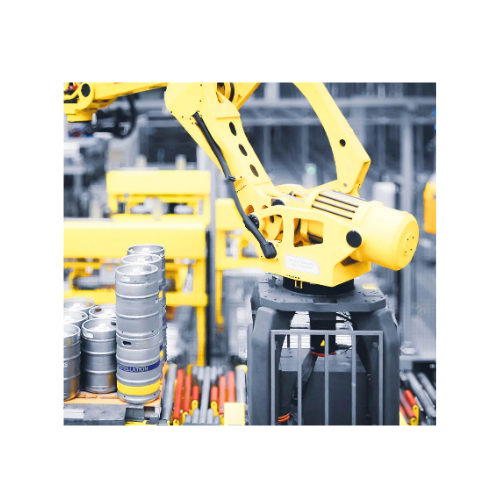
Robotic handling systems for beverage containers and bins
Streamline your container handling with precision-engineered r...
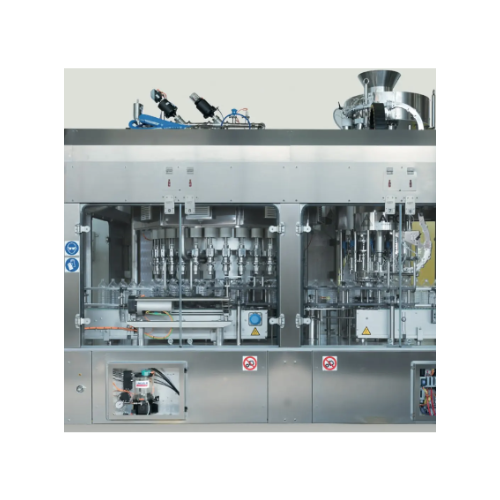
High-precision rotary weight filler for edible oils and sauces
Achieve exceptional filling precision with solutions desi...
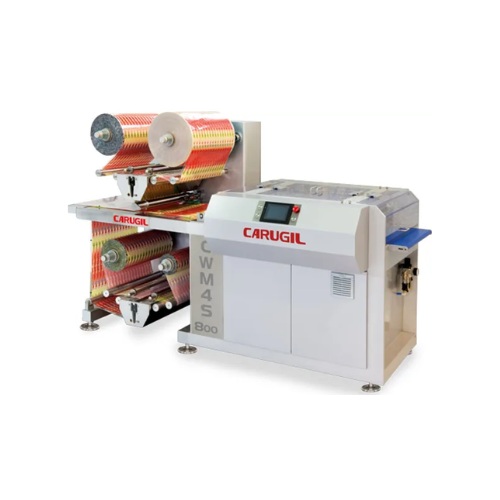
Multilane wrapping solution for food and confectionery products
Enhance your packaging line efficiency with high-speed m...
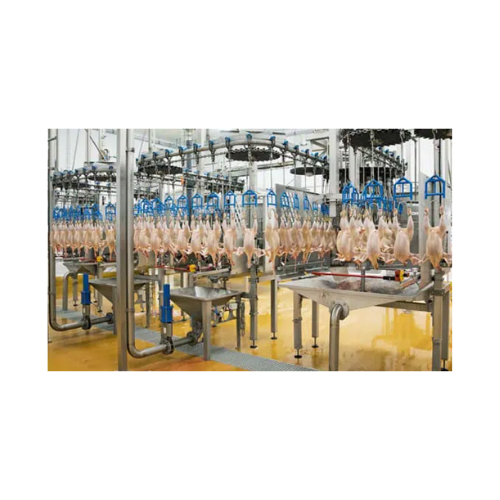
Vacuum waste handling system for food processing
Optimize waste management with a vacuum system that enhances hygiene, red...
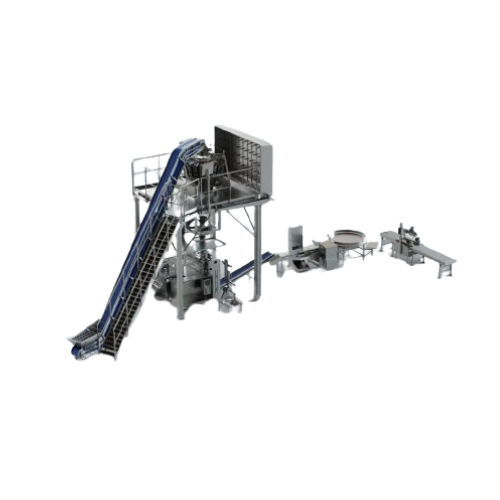
Retail packing solution for Iqf products
Streamline your IQF product packaging with a compact system designed to cut manual...
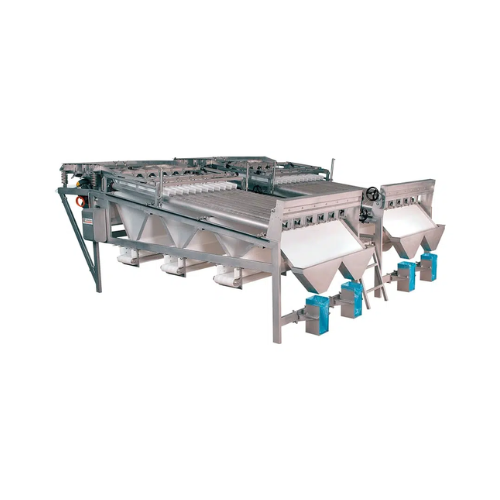
Axial roller grader for gentle size grading
Optimize your grading process with this precision axial roller grader, designe...

Automatic sausage depositor
Streamline your production by precisely depositing and aligning sausage portions into trays, ens...
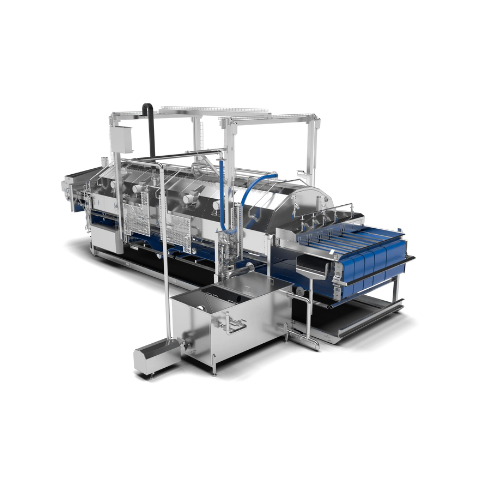
Seafood cooker for brown crabs
Optimize your crab processing line with a high-speed seafood cooker designed for precision he...
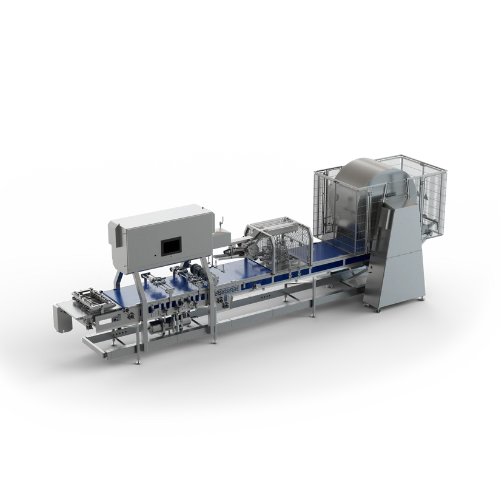
Processing line for spring rolls
Streamline your spring roll production with a compact machine designed to minimize downtime...
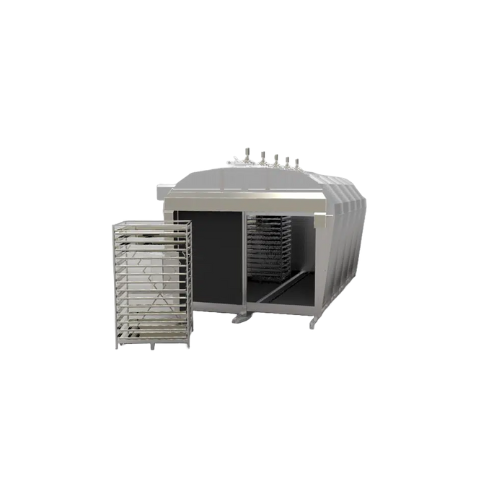
Thawing chamber for block frozen products
Optimize your production line with a thawing chamber that ensures uniform defros...
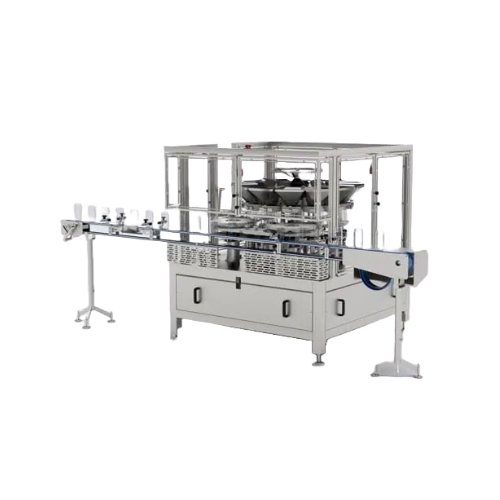
Vibratory rotary filler for accurate filling in food packaging
Achieve precise and efficient filling of diverse solid pr...

Precise glazing system for Iqf products
Ensure consistent product quality and cost savings with a glazing system designed t...
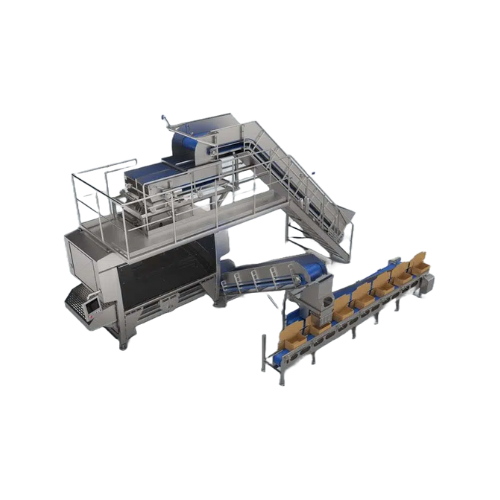
High-speed weighing system for large batch sizes
Maximize yield and minimize waste with a high-speed batching solution des...
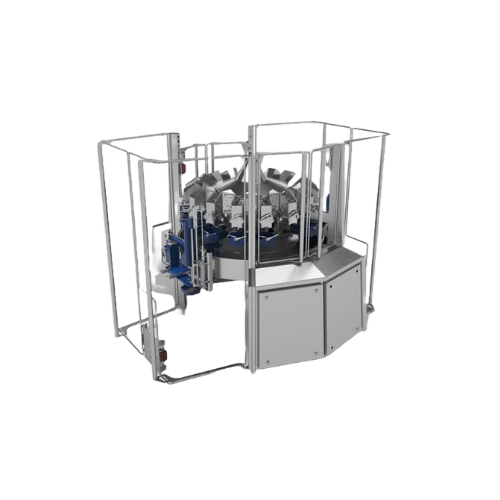
Multihead weigher for sticky products
Efficiently tackle the challenge of weighing extremely sticky products like mixed sal...
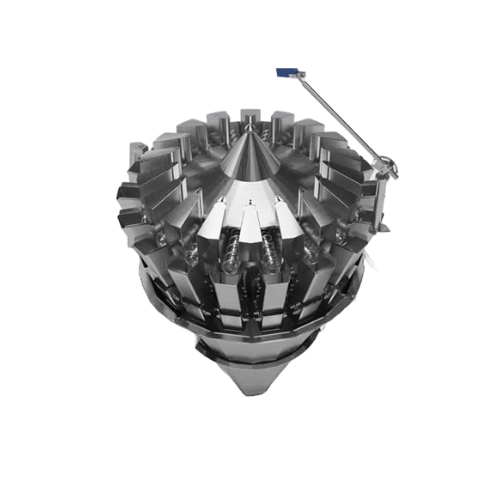
Multihead weigher with screw feeding for sticky products
Achieve exceptional precision and reduce giveaway costs in handl...
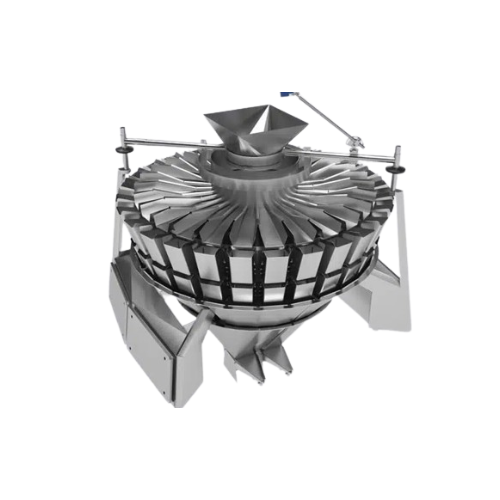
Multihead weigher with vibratory feeding
Experience precise and efficient weighing with a multihead system designed for com...
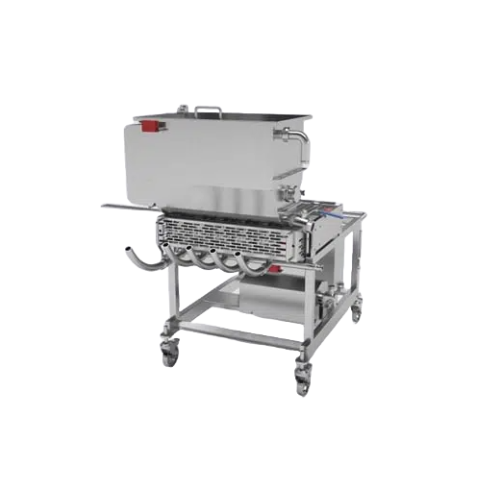
Automatic piston fillers for liquid products
Optimize your liquid filling process with high-precision piston fillers, engi...
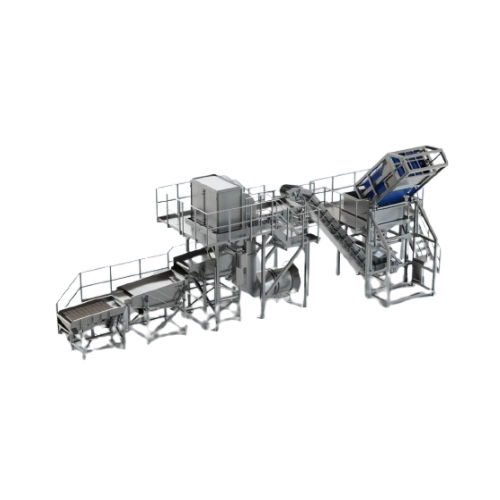
Pre-cleaning system for Iqf berries
Ensure the purity of your IQF berries with advanced pre-cleaning technology that expert...
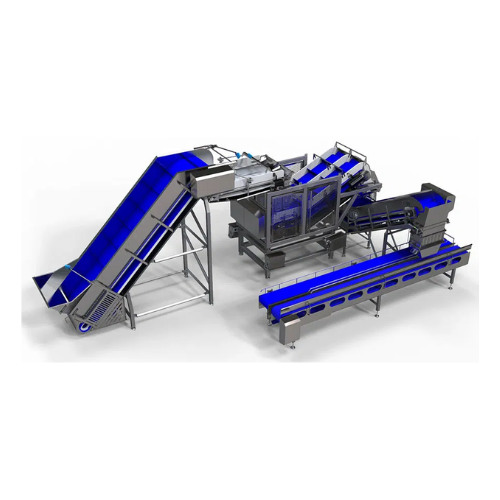
Industrial weighing and batching system for meat, poultry and seafood
Optimize your production line with a high-precisi...
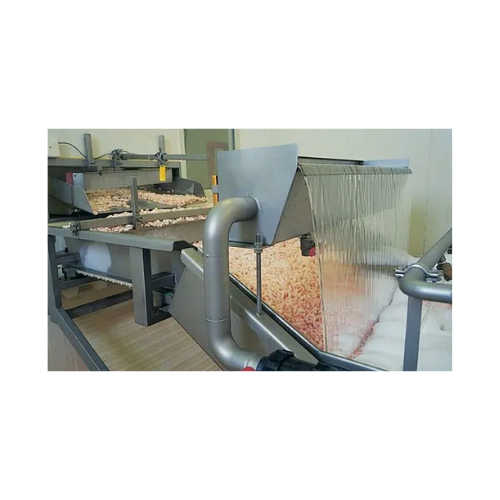
Belt thawing unit for seafood and meat
Efficiently thaw block-frozen products with a continuous submersion belt system, ens...
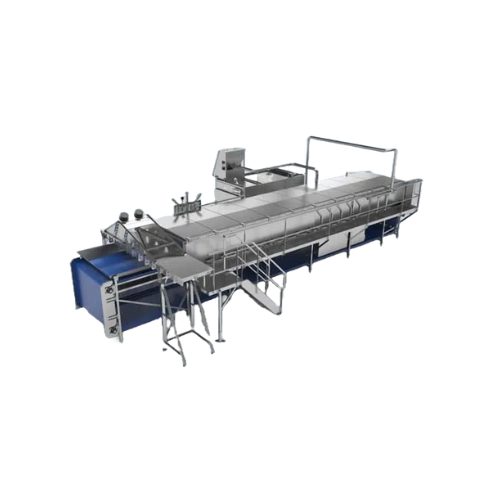
Industrial vegetable blanching solution
Achieve unparalleled efficiency and precision in food processing with this advanced...

Evaporative blancher for fruits and vegetables
Achieve significant water savings and reduce wastewater generation in your ...
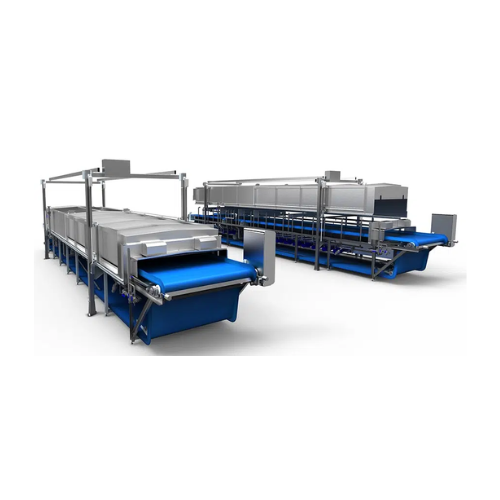
Ibc blancher with forced steam for vegetables
Optimize your blanching process with advanced steam control, reducing steam ...
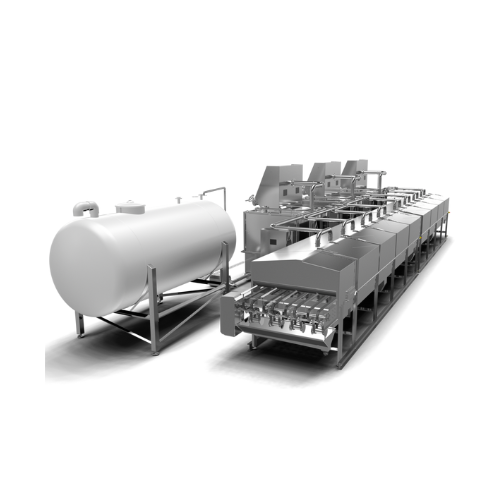
Brine freezer for shrimp processing
Achieve rapid and uniform freezing for shrimp while preserving their delicate texture a...
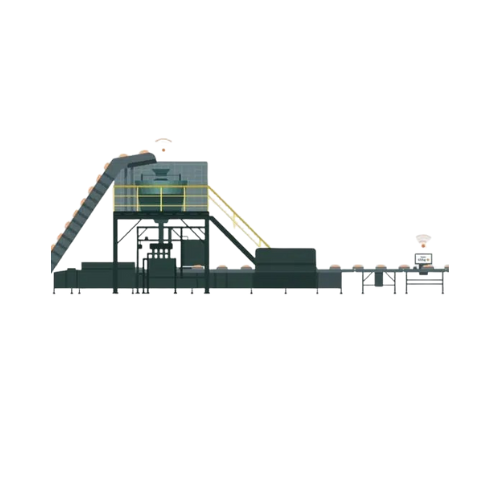
Optimization solution for weighing processes
Achieve precise weight compliance with minimal give-away using advanced monit...
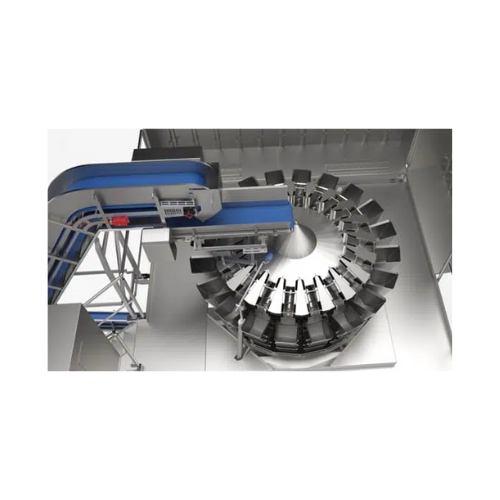
Weighing optimization with sensorfeed
Optimize your production by enhancing weighing accuracy and reducing material waste t...
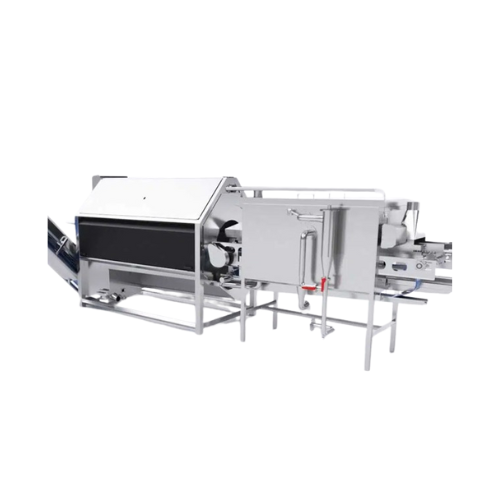
Mackerel deskinning system
Eliminate chemical use and reduce product loss to just 5% with our continuous mackerel deskinning...
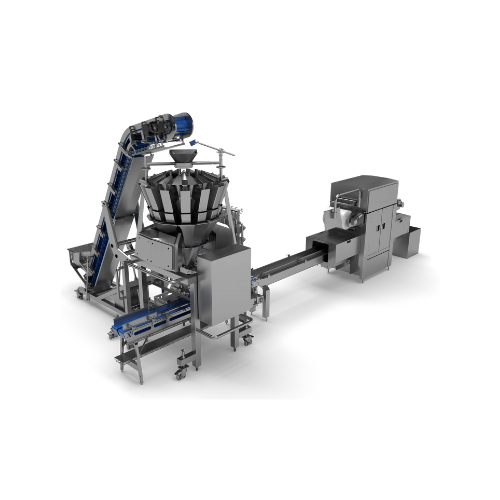
Flexible weighing and packaging solution for small batch producers
Streamline your packaging line with a mobile solutio...
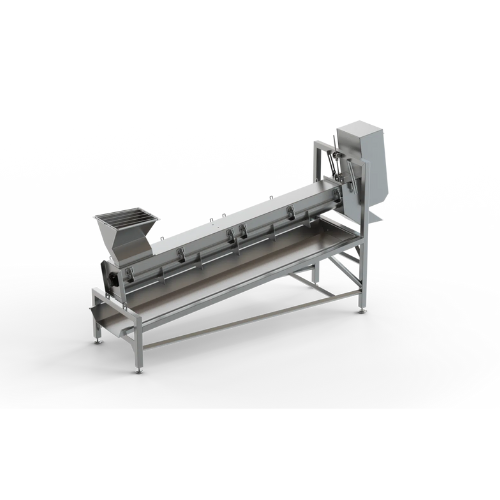
Fruit strigger for Iqf berries
When processing IQF berries, achieving precise stem and flower removal ensures superior quali...
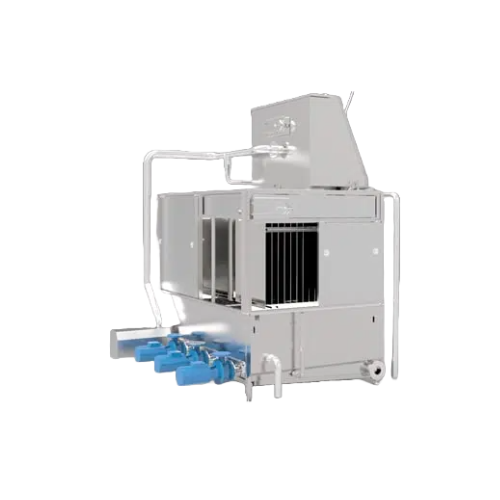
Industrial water chiller for efficient cooling
Achieve precise temperature control and efficient heat transfer with this w...
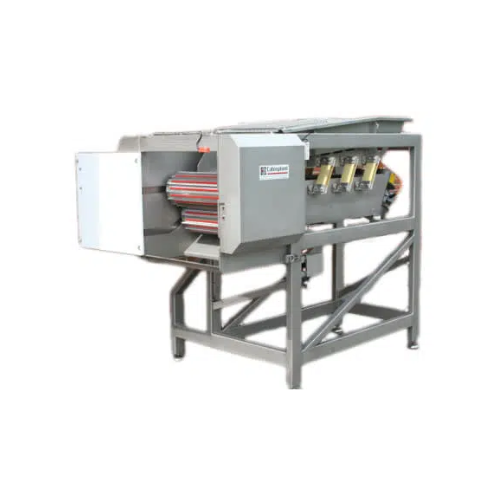
Green bean cutting solution
Optimize your processing line with precise green bean cutting, ensuring uniform lengths and perf...
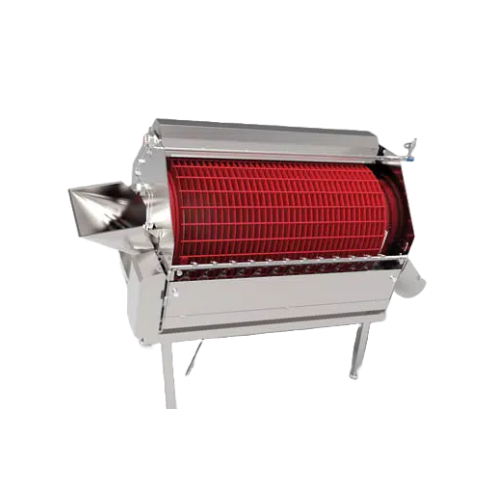
Automatic green bean snipping system
Enhance your vegetable processing line with a high-capacity solution that automaticall...
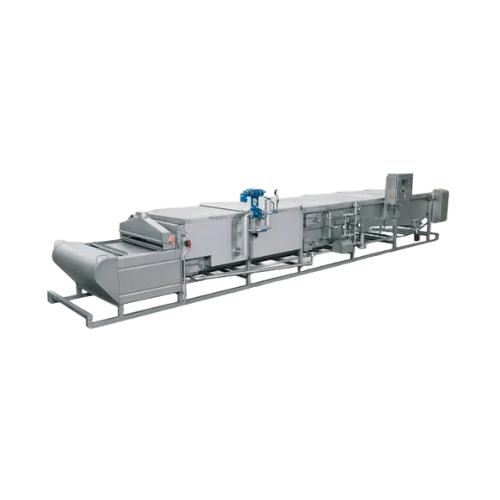
Continuous belt cooker for vegetables and fish
Enhance product quality and reduce energy costs with a continuous belt cook...
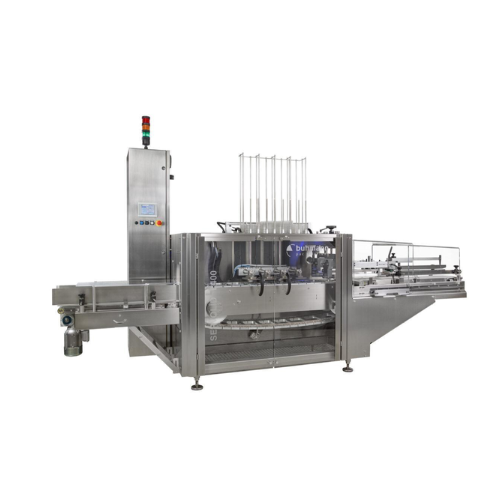
Lidding system for cups and trays
Enhance your packaging line with precise, space-saving lidding technology, ideal for seal...
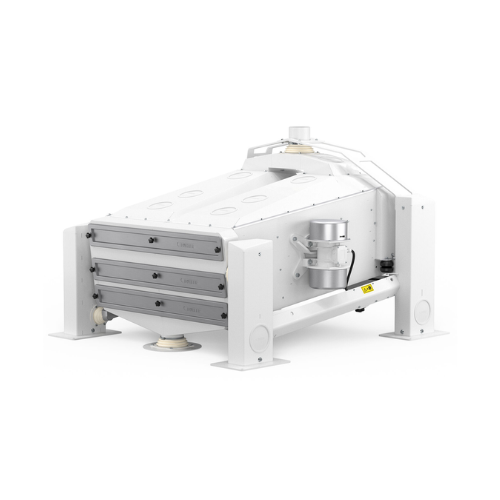
Grain separator for impurity removal in milling
Optimize grain cleaning with a high-performance separator designed to effi...
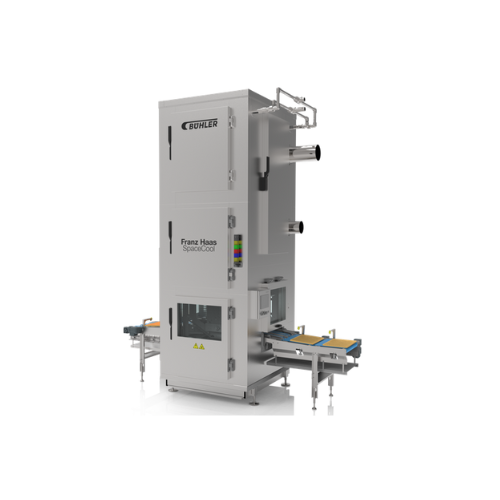
Wafer block cooling tower
Optimize your confectionery production with seamless wafer cooling, ensuring precise temperature c...
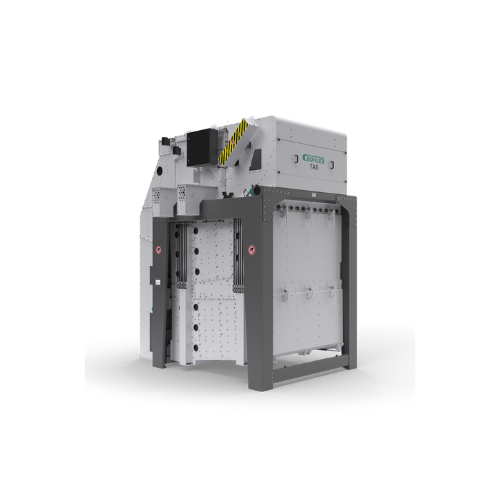
Grain cleaning system for high-quality processing
Optimize your grain processing with a versatile cleaning system designe...
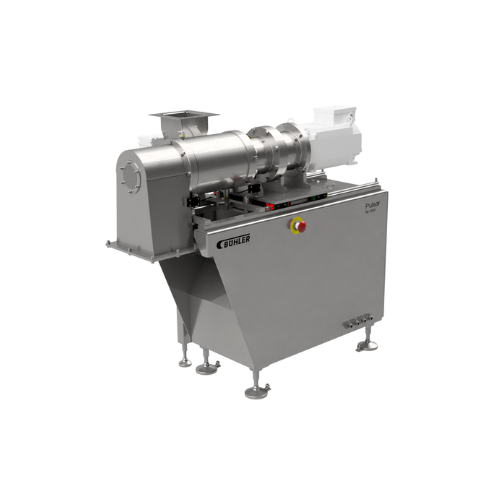
Universal mill for grinding nuts and seeds
Optimize your nut paste production with a high-speed, versatile milling solutio...
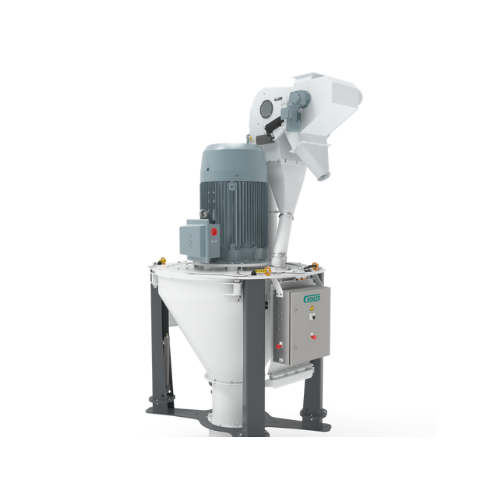
Vertical hammer mill for feed and grain processing
Optimize your milling operations and improve energy efficiency with th...
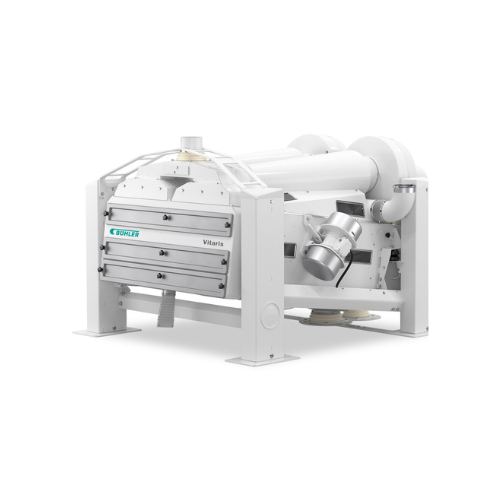
Efficient grain destoning and concentrating system
Optimize your grain processing with a solution that ensures precise se...
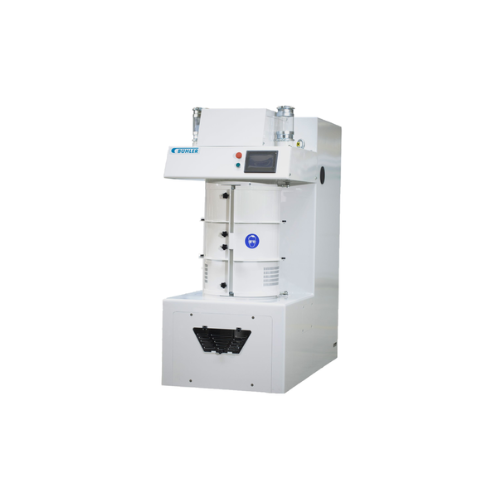
Automatic rice whitening solution
Need consistent rice whiteness and bran removal without manual intervention? This high-sp...
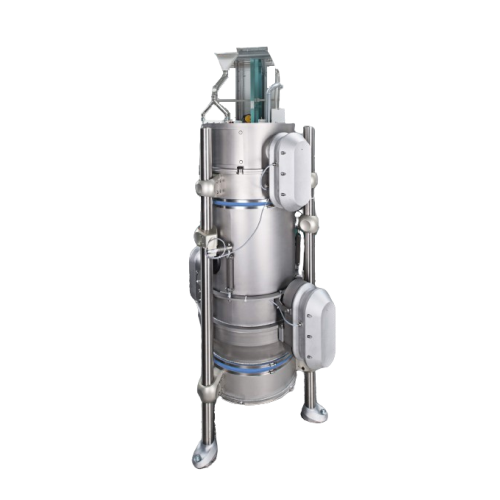
Advanced superheated steam drying solution
Harness the power of consistent drying technology to achieve optimal moisture c...
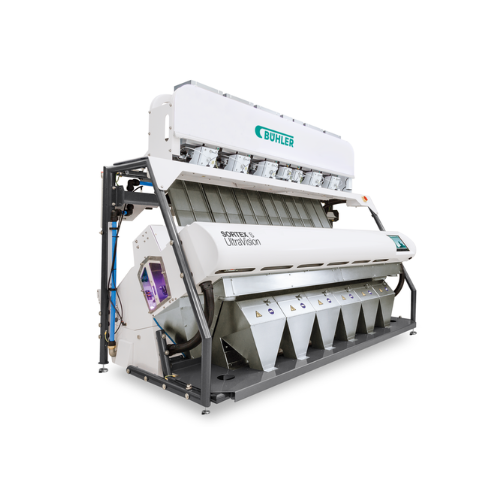
Optical sorter for rice
Enhance your product quality by efficiently sorting and removing color defects and foreign materials ...
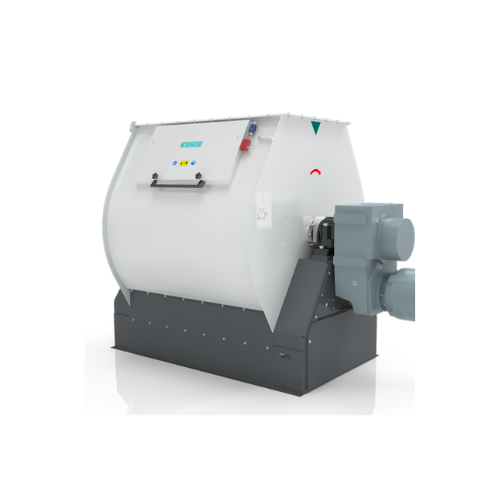
Batch mixer for animal feed
Streamline your mixing process with a high-speed batch mixer that delivers up to 20 mixing cycle...
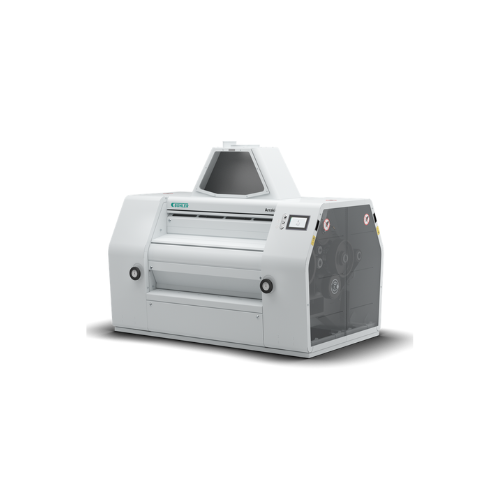
Four-roller and eight-roller mill for wheat and grain grinding
Optimize your grinding operations with this versatile rol...
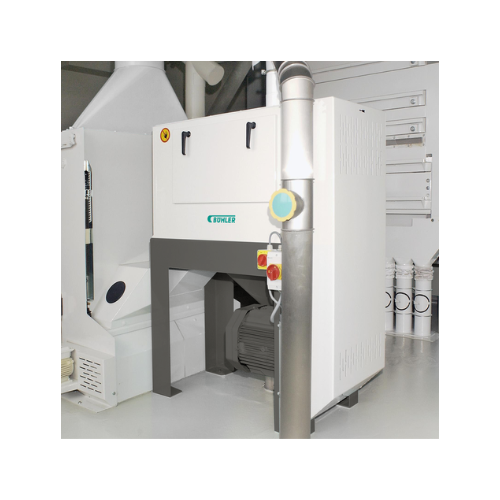
Grain scourer for wheat, durum, and rye
Enhance grain processing by efficiently removing impurities like dust, sand, and so...
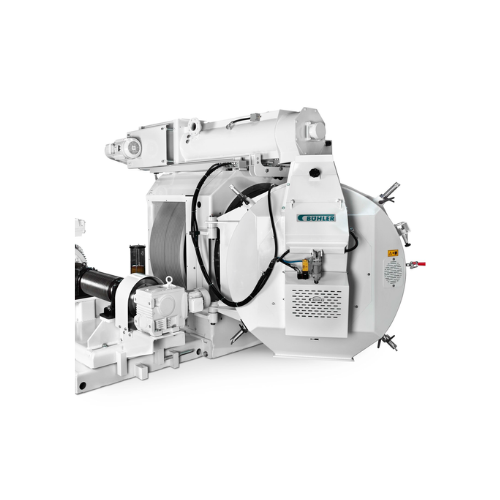
Pellet mill for biomass and sunflower hulls
Achieve high-speed, continuous production of durable pellets from varied mater...
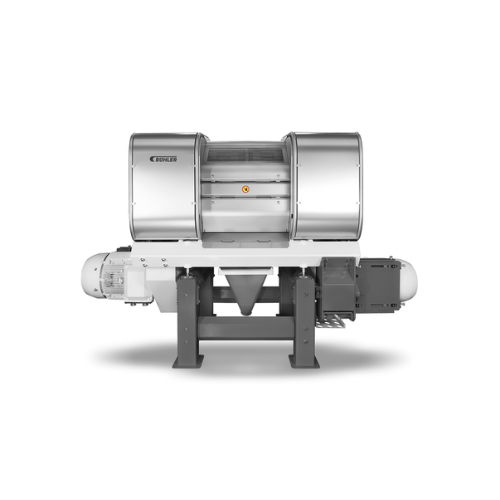
Flaking mill for grain and cereal production
Achieve consistent flake thickness and high throughput with advanced roller t...
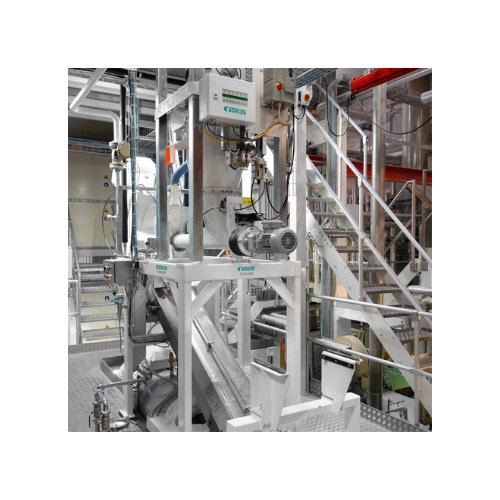
Commercial pasta press for diverse ingredients
Optimize your pasta production with a flexible solution capable of handling...
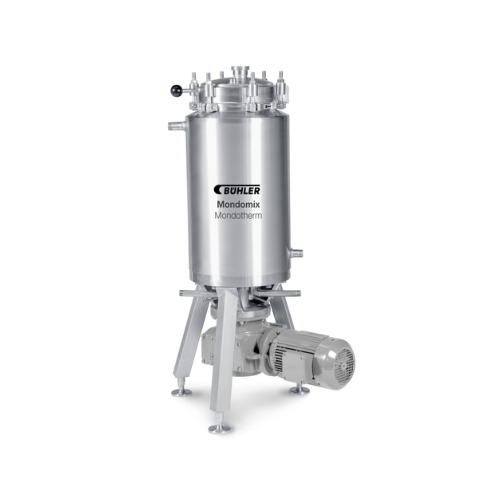
Scraped surface heat exchanger for viscous liquids
Optimize heating and cooling of viscous liquids efficiently with conti...
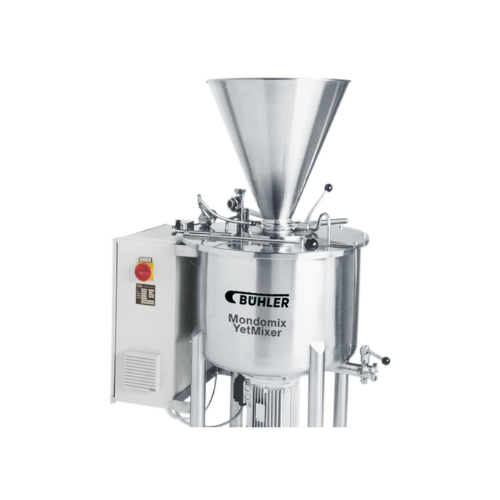
Premixer for confectionery masses
Achieve consistent ingredient blending with precision-premixing for candy and baked goods...
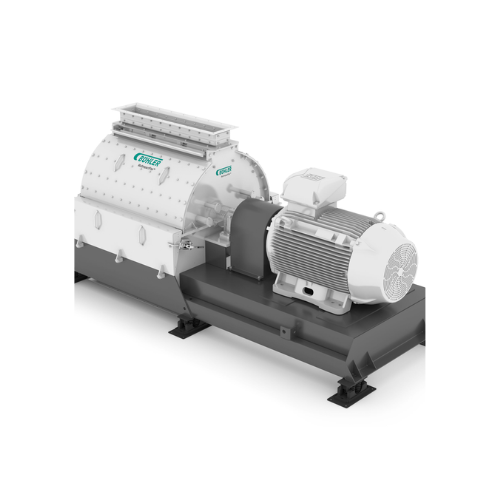
Hammer mill for fine grinding in food and feed industries
Achieve exceptionally fine particle-size distribution with a h...
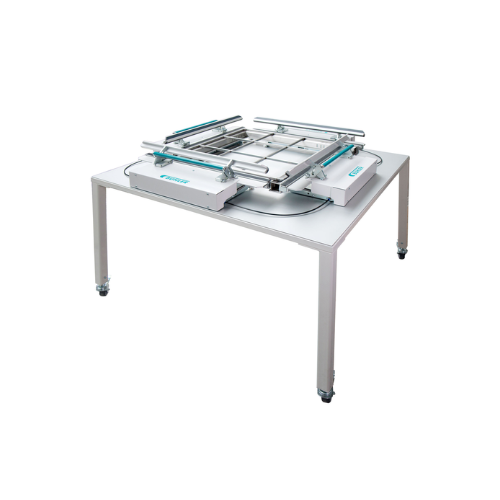
Sieve tensioning device for milling applications
Achieve precise and consistent tensioning across various sieve frames wit...
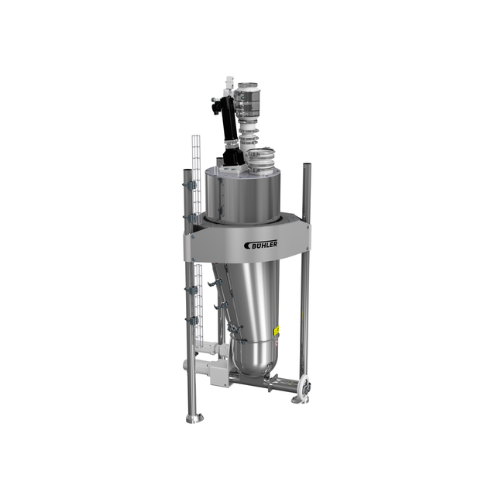
Micro loss-in-weight scale for precise dosing
For precise control over micro-component addition, this technology ensures c...
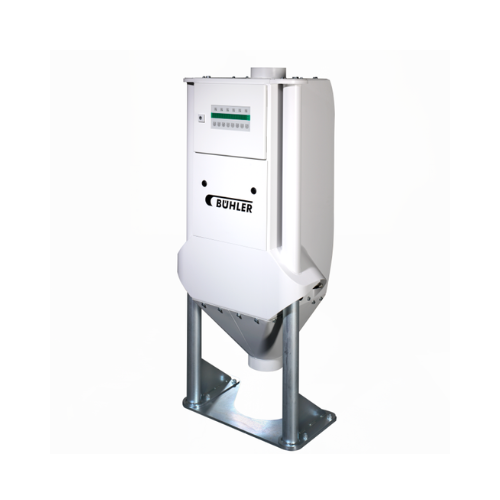
Moisture control system for grain milling
Optimize moisture levels precisely within your grain milling process, ensuring c...
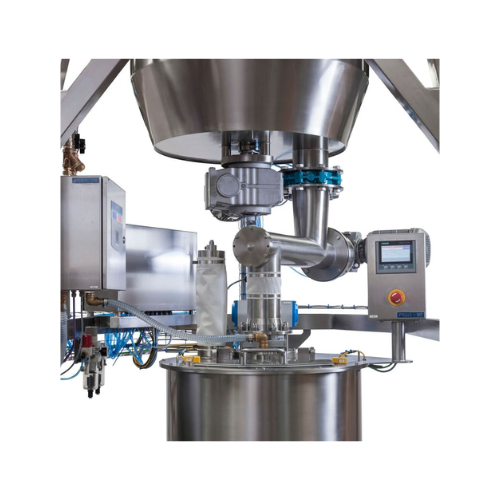
Compact batter mixing system
For food producers aiming to ensure consistent batter quality, this modular system streamlines ...
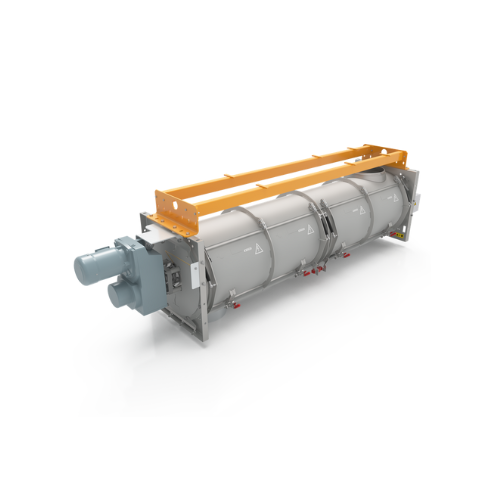
Retentioner for animal feed safety enhancement
Enhance your feed production line with a retention system designed for unif...
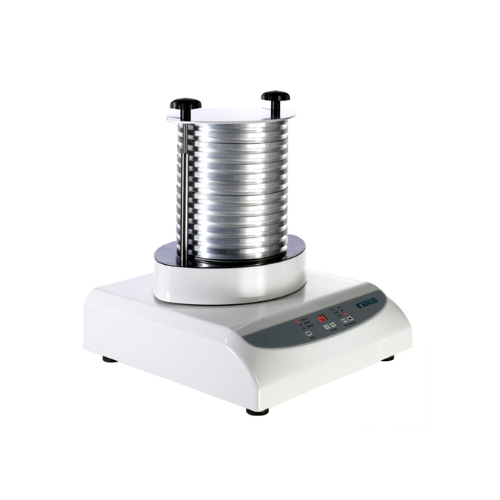
Laboratory plansifter for particle-size distribution
Optimize your grain milling and brewing operations with precise part...
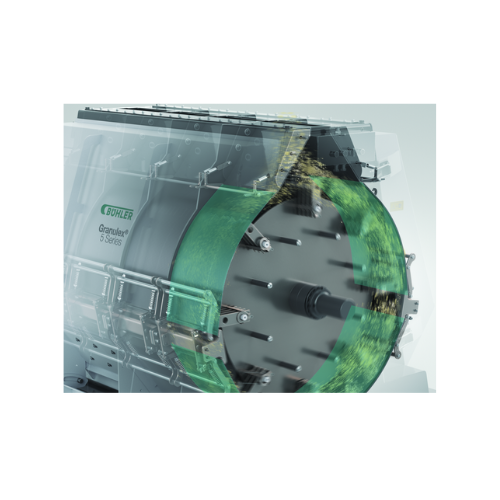
Horizontal hammer mill for grain processing
Optimize your grinding processes with our horizontal hammer mill, designed to ...
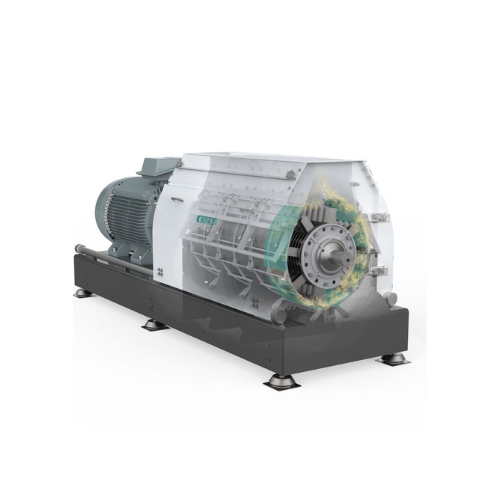
Industrial hammer mill for size reduction in food and feed processing
Achieve precise grinding and milling for diverse ...
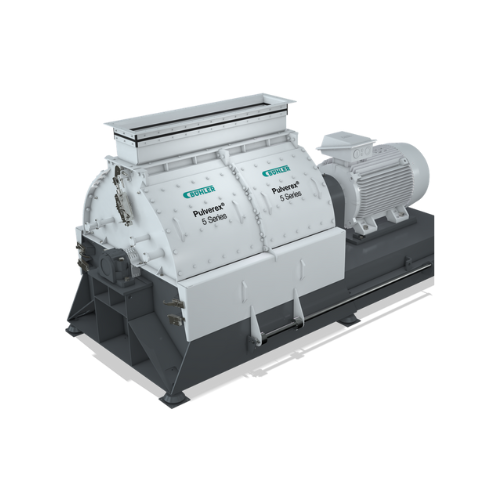
Pulverizer for fine grinding applications
Achieve optimal particle size distribution and enhance throughput with this adva...
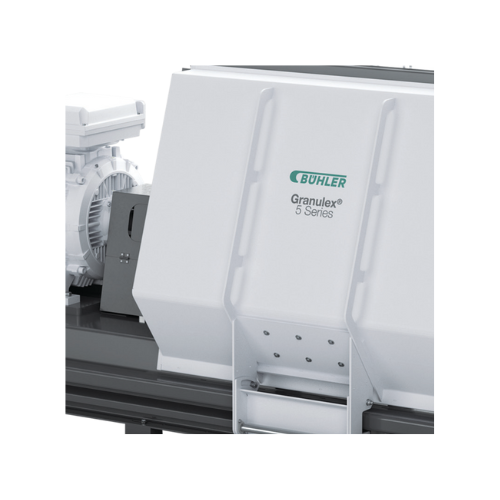
High-throughput hammer mill for animal feed production
Ideal for high-throughput operations, this hammer mill ensures pre...
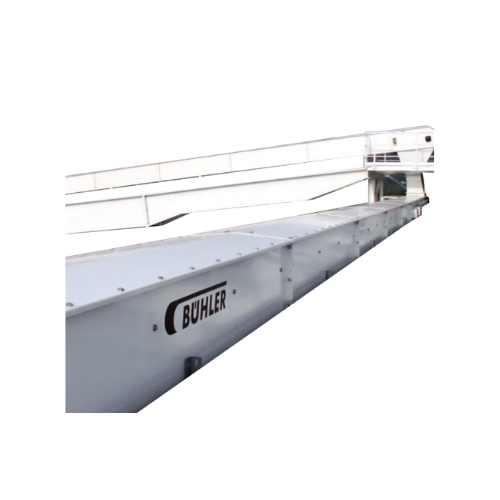
Heavy-duty trough chain conveyor for high throughput applications
Optimized for high-capacity operations, this robust c...
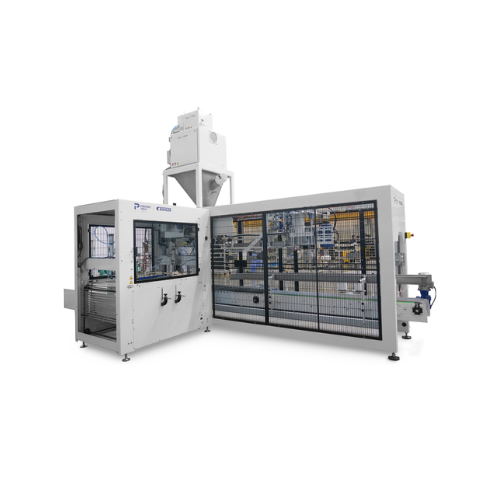
Fully automatic bagging station for granular products
Streamline your packaging line with a high-speed solution designed ...

Hydrothermal kiln for oats and sorghum
Optimize your grain production with advanced enzyme inactivation and hydrothermal tr...
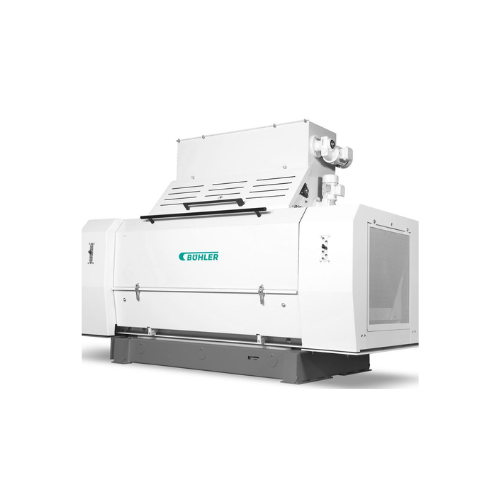
Oilseed flaking and milling system
Optimize your oilseed processing with a flaking system that enhances extraction efficien...
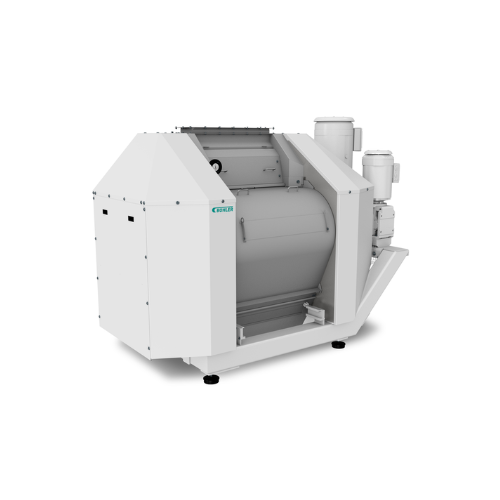
Industrial grain flaking mill
For efficient grain processing, achieve uniform flake quality with advanced temperature-contro...
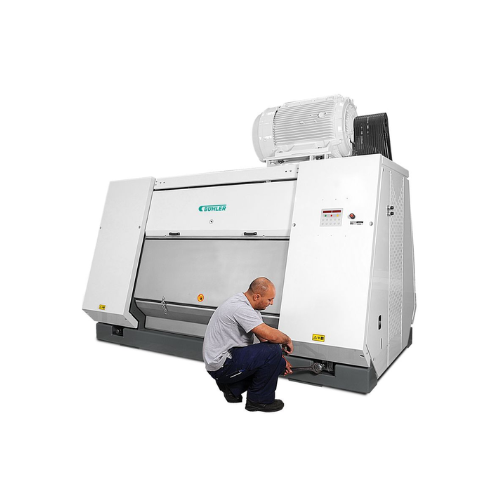
Flaking mill for oilseeds
Achieve consistent, high-throughput flake production with precise thickness control, ideal for enh...

Four-roller and eight-roller mill for grains
Optimize your grain processing with precise roller configurations, ensuring c...

Discharge station for bags and big bags
Ensure consistent material flow and hygiene in your production line with a versatil...

Malt conditioner for optimal brewing efficiency
Enhance your milling process with precise moisture control, ensuring optim...

Control systems for wet grinding industry
Enhance precision and efficiency in your production line with advanced control s...
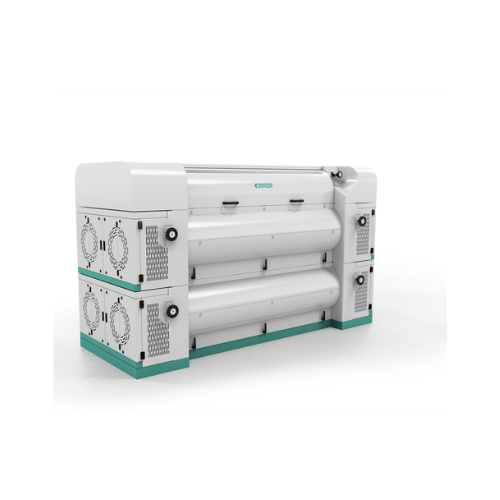
Cracking mill for oilseeds and feed
Enhance your production efficiency with a cracking mill that optimizes throughput and m...
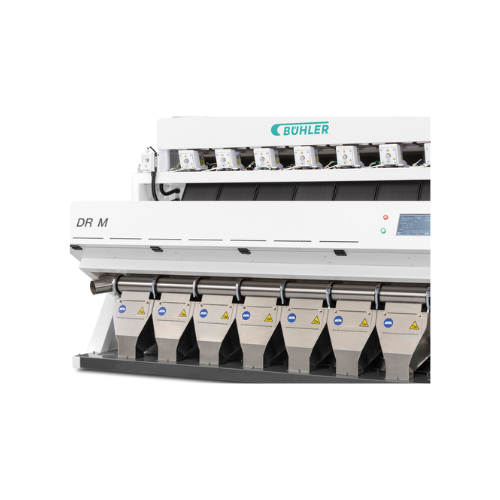
Optical sorter for wheat applications
Effortlessly enhance product purity by eliminating color defects and foreign material...
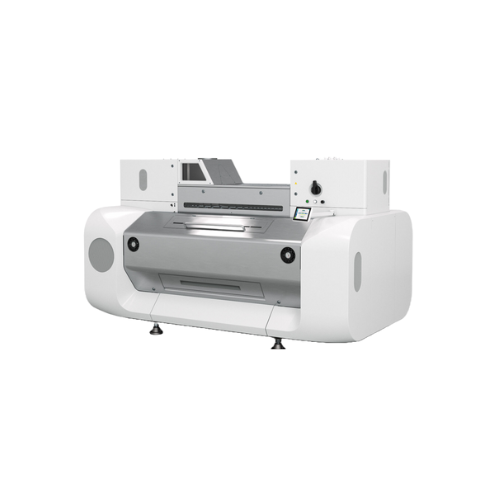
Integrated grinding system for wheat and grain
Optimize your grinding process with a system that delivers consistent parti...
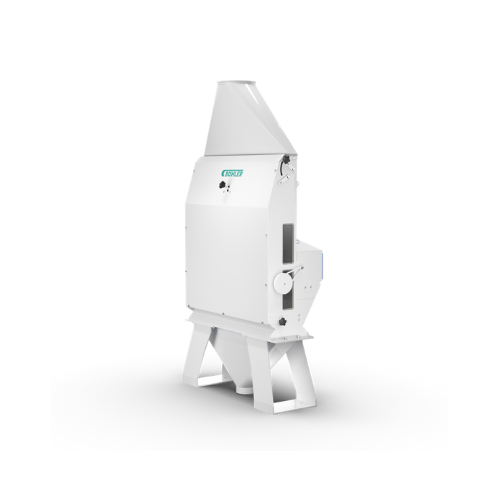
Aspiration channel for grain cleaning
Achieve superior product quality by efficiently removing light impurities from granul...
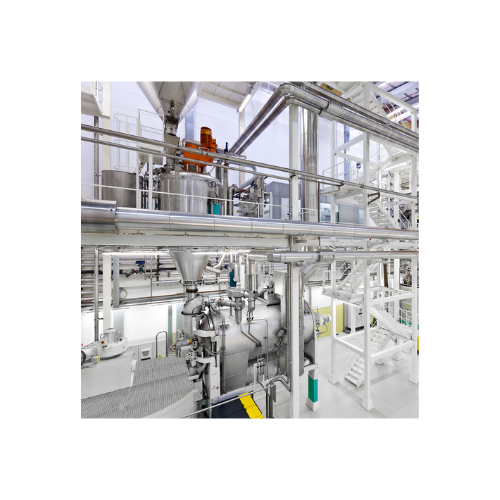
Alkalizing system for cocoa powder coloring
Achieve precise cocoa powder coloration and enhanced flavor development with a...
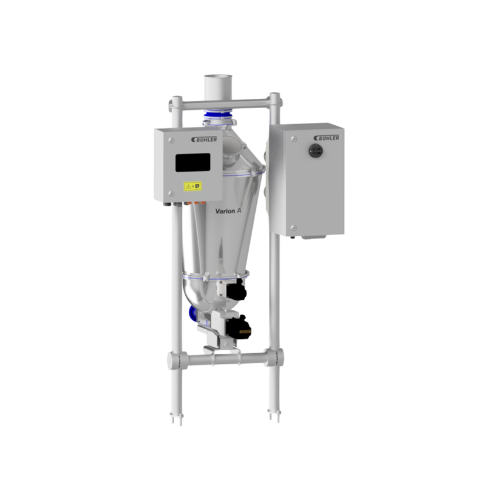
Batch scale for high accuracy weighing of powdery products
Achieve unparalleled precision in powder dosing with our batc...
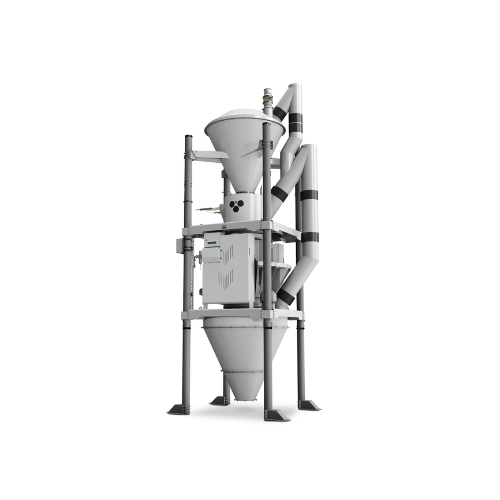
Fully automatic batch scale for powdery and granular products
Achieve precise and repeatable dosing for powdery and gran...

Industrial cooling die for wet textured proteins
Maximize production efficiency by creating diverse, high-quality protein ...
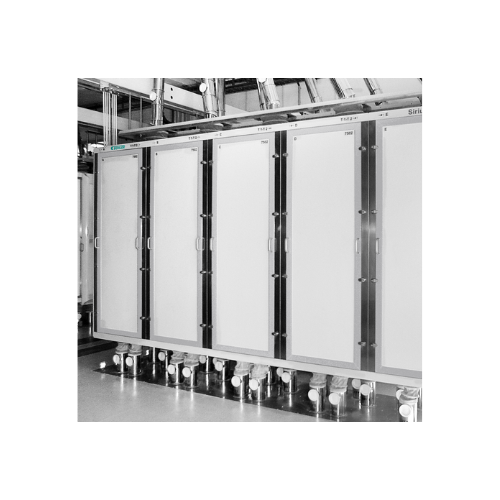
Industrial plansifter for grain sifting and grading
Optimize your production line with precision grain separation, mainta...
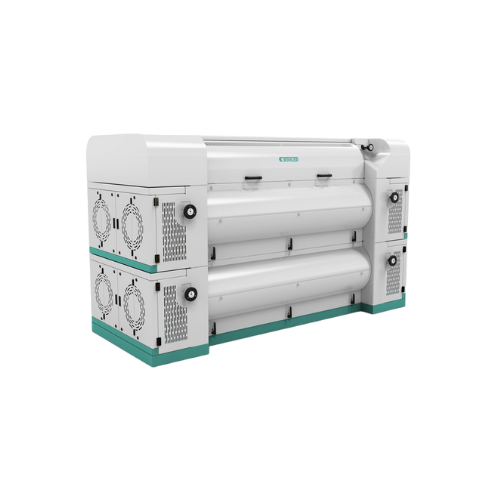
Cracking mill for oilseeds and feed processing
Maximize your production efficiency with advanced cracking and milling solu...

Hammer mill for size reduction in food and feed processing
Efficiently tackle size reduction challenges with a versatile...
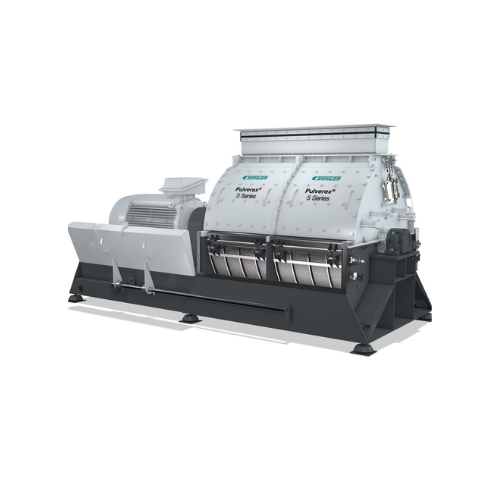
Industrial fine grinding pulverizer
Achieve consistent fine granulation at high capacity with reduced energy consumption, u...
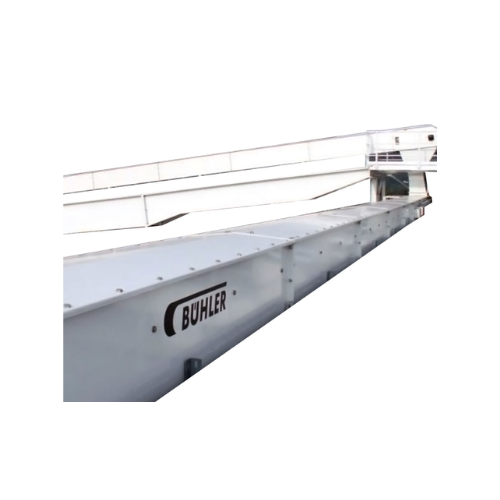
High-capacity horizontal conveyor for bulk storage
Optimize your high-speed bulk material handling with a durable and eff...

Laboratory plansifter for grain milling and brewing
Achieve precise particle-size distribution and quality control across...
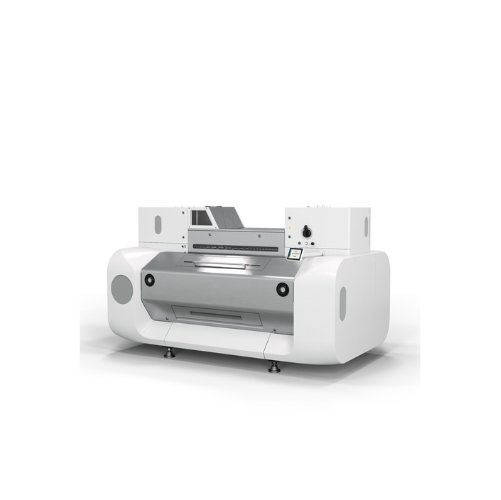
Integrated grinder for wheat and grain
Achieve superior grinding performance and energy efficiency with this fully integrat...
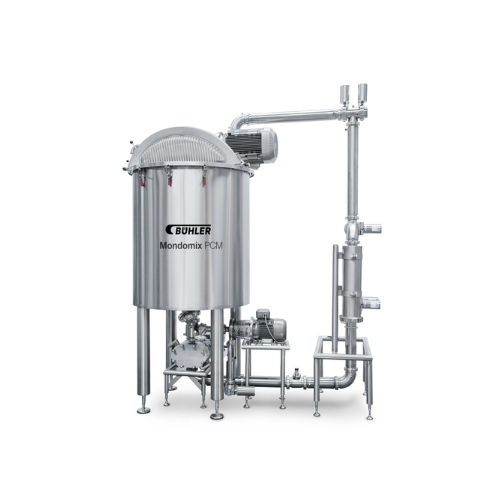
Premixer for cream production
Achieve precise mixing of liquid and solid fats for diverse cream formulations with insulated ...

Air cleaners for grain dust removal
Enhance safety and operational efficiency by effectively removing dust and light partic...
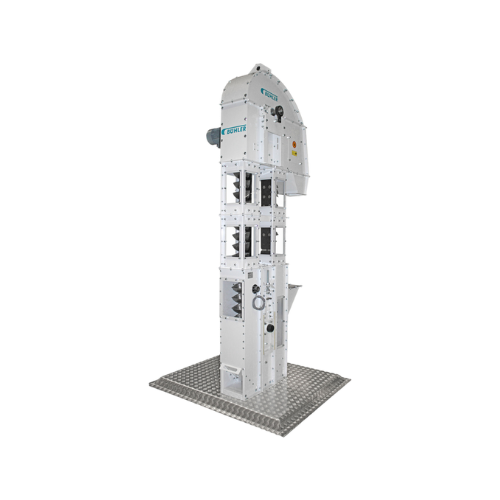
Vertical grain conveying solution for animal feed and bulk materials
Efficiently transport and elevate various bulk mat...
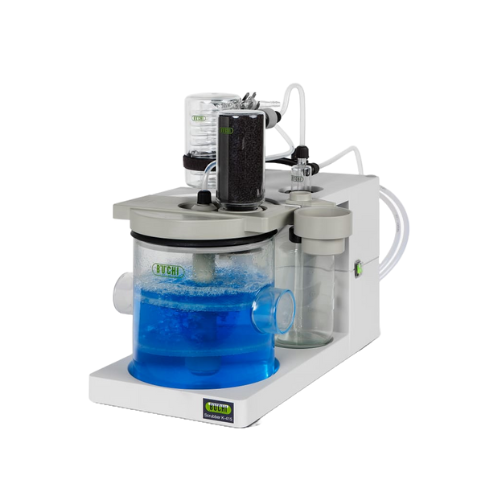
Industrial fume scrubber for safety compliance
Enhance workplace safety by efficiently neutralizing hazardous fumes and va...
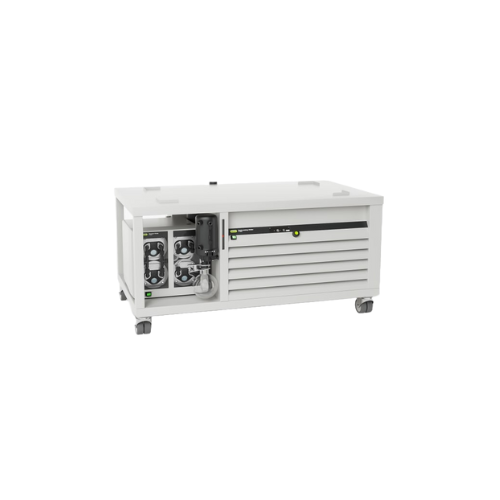
Industrial recirculating chiller for laboratory applications
For consistent distillation results, maintain accurate temp...
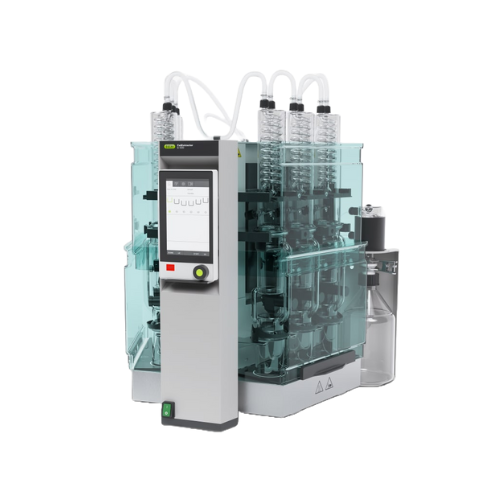
Industrial fat extraction system for food and feed analysis
Optimize your laboratory workflow with a versatile fat extra...
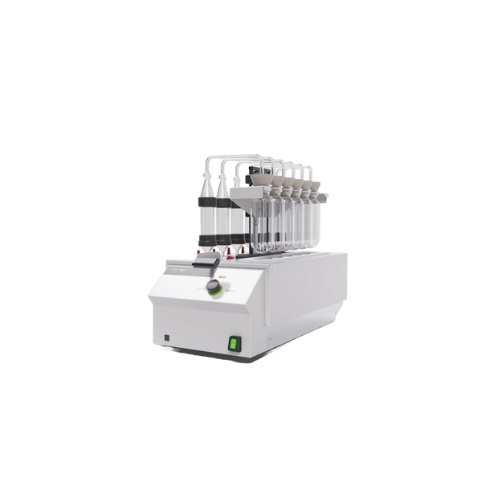
Acid hydrolysis system for total fat determination
Streamline your laboratory workflow with a powerful hydrolysis system ...

Lab-scale extruders for material development
Optimize your lab and pilot-scale extrusion processes with advanced material ...
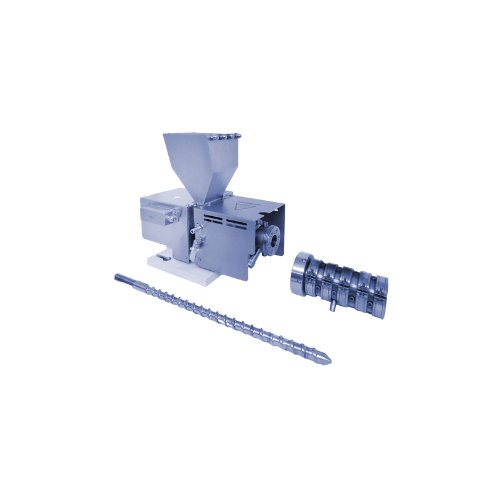
Lab extruder for elastomer extrudability testing
Optimize your small-scale testing with an innovative extruder designed to...
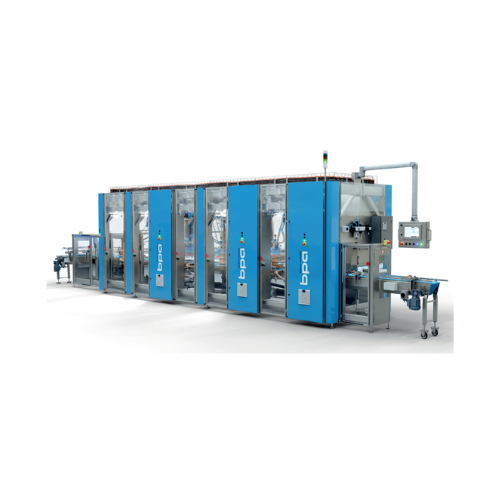
Top load and side load case packer with vision guided robotics
Optimize packing efficiency and flexibility with a versat...
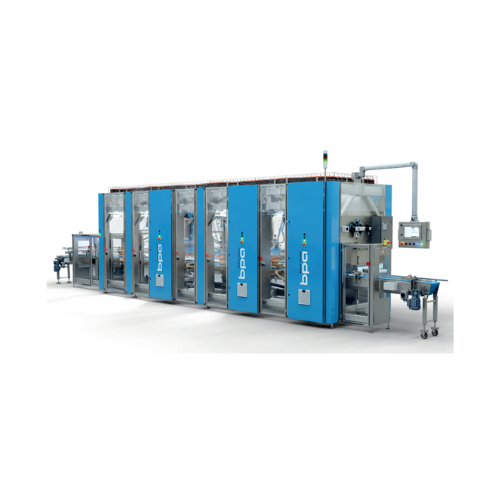
Case packing system for bags and cases
Streamline your secondary packaging process with a compact, fully integrated system ...
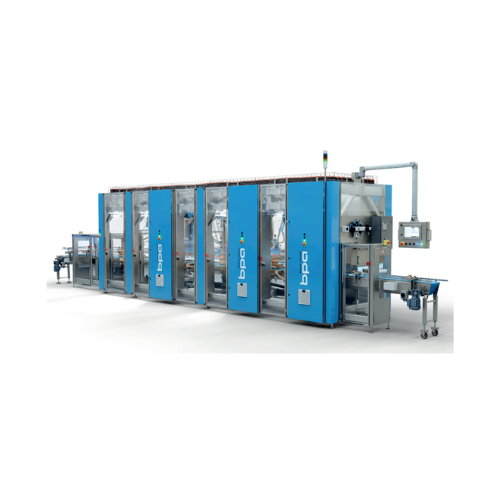
Vision guided robotics case packer
Maximize efficiency with vision-guided robotics for versatile case and tray loading, red...
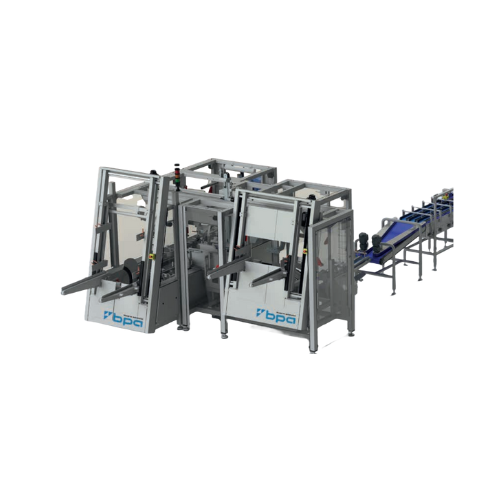
Vertical packing pattern case packer
Optimize your packaging efficiency with this high-speed case packer designed for seaml...
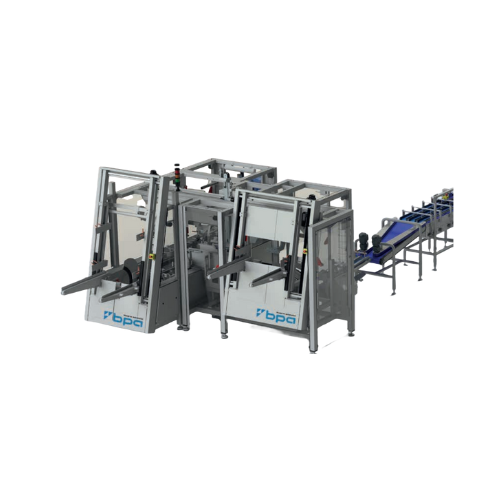
Wrap around case packer for horizontal and vertical packing patterns
Optimize your palletizing and distribution with a ...
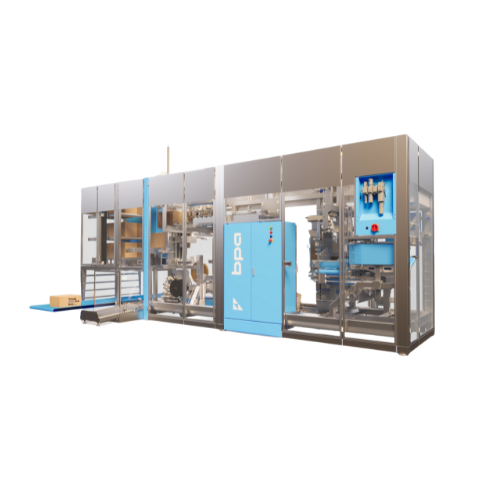
High-speed case packer for snack bags
Optimize your packaging efficiency with a compact solution designed for seamless vert...
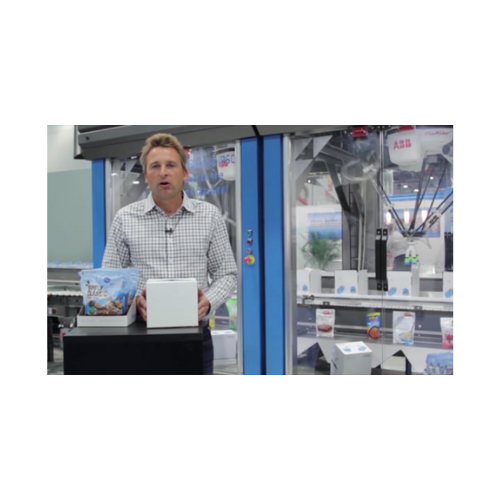
Automated retail ready case closer
Optimize your retail packaging process with a solution that seamlessly seals and closes ...
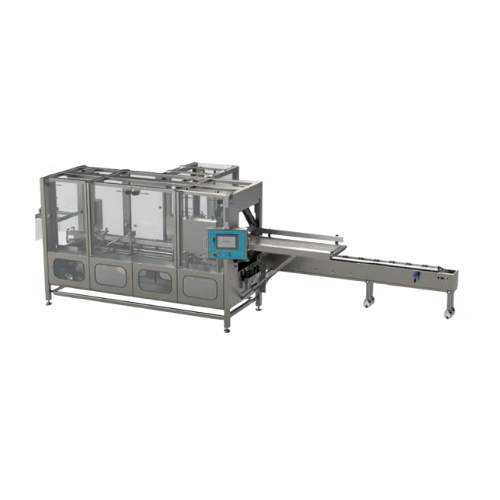
Horizontal load carton erector for food production
Enhance your production line with precise carton erecting, loading, an...

Semi-auto case packer for flexible bag collation
Enhance your manual packing speed and flexibility with a semi-automatic s...
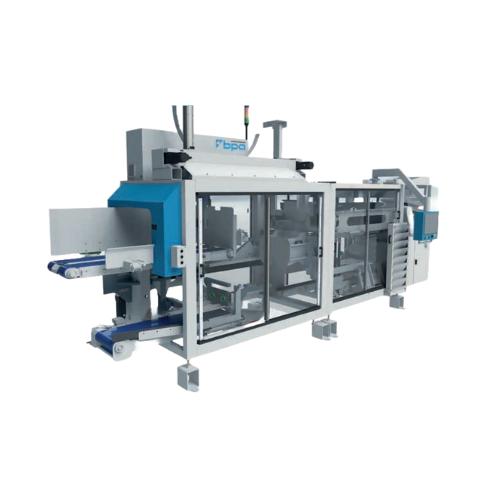
Automatic case packer for frozen potato products
Efficiently pack frozen and delicate products with precision side-loading...
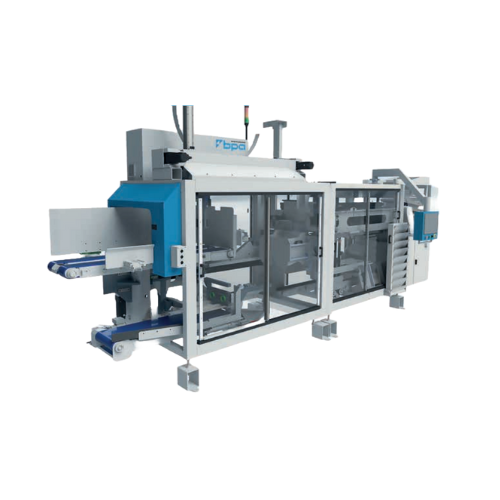
Flexible bag case packer with integrated case erector
Streamline your secondary packaging process with an efficient solut...
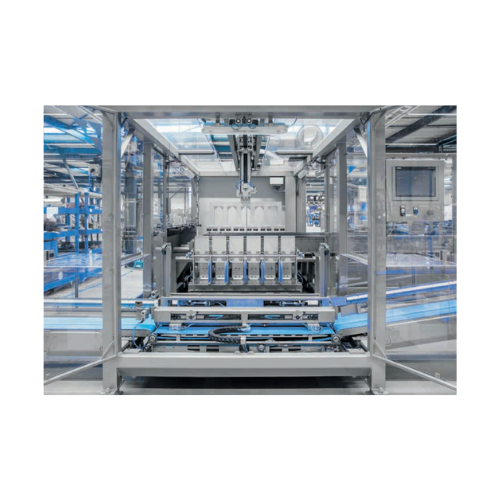
High-speed vertical and horizontal case packer
Enhance your packaging line efficiency with a versatile case packing soluti...
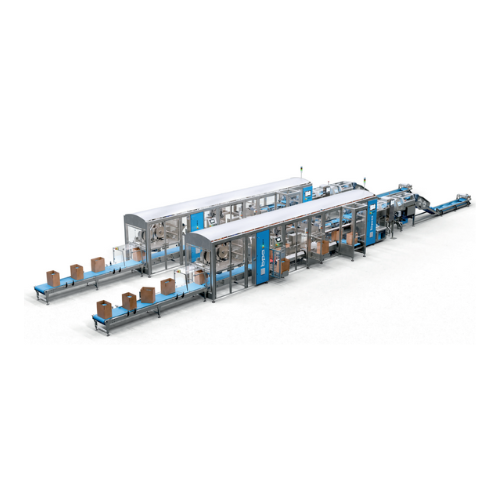
High-speed case packer for flexible bags
Streamline your packaging process with a solution designed for high-speed, error-f...
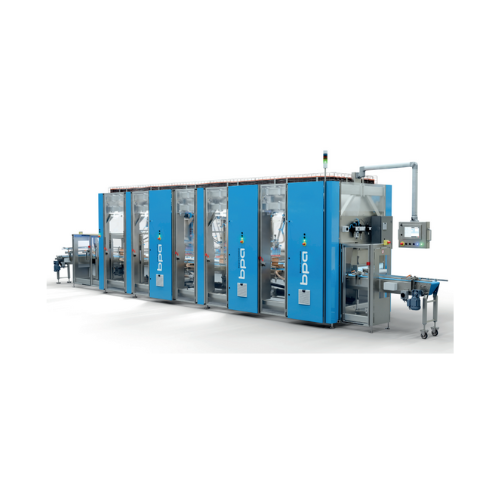
Horizontal case packing and tray loading
Enhance your packaging line efficiency with a highly adaptive system that seamless...

Vertical case packer for reusable and Rsc cases
Streamline your packaging line with versatile, high-speed case packing tha...
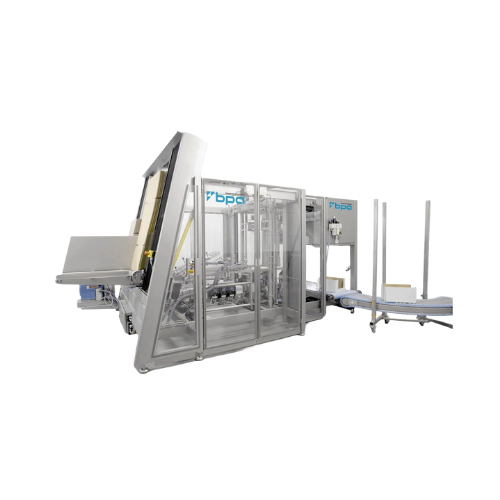
Tray erecting system for various tray styles
Effortlessly configure diverse tray styles with an efficient system designed ...
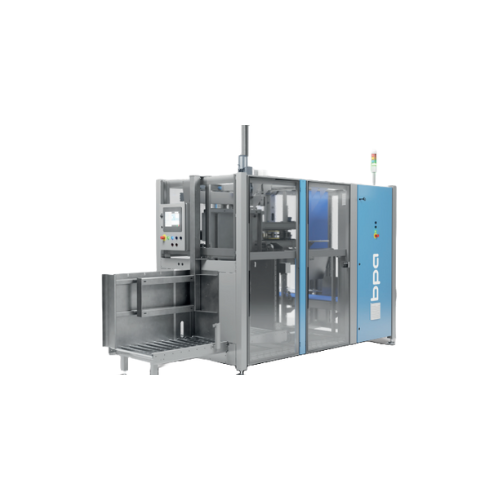
Automatic case forming and sealing solution
Streamline your end-of-line packaging with a solution that forms, folds, and s...
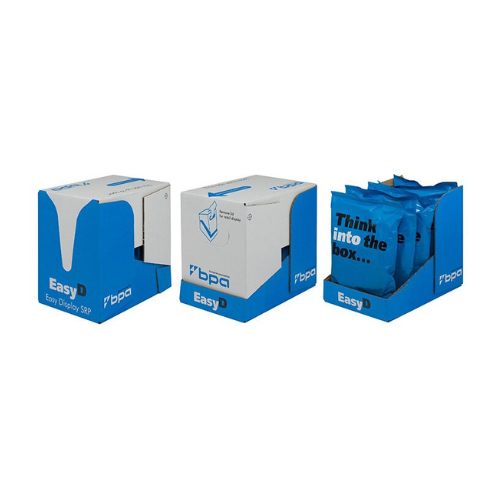
Retail ready packaging system for easy store stocking
Simplify shelf stocking with a sturdily designed packaging system t...
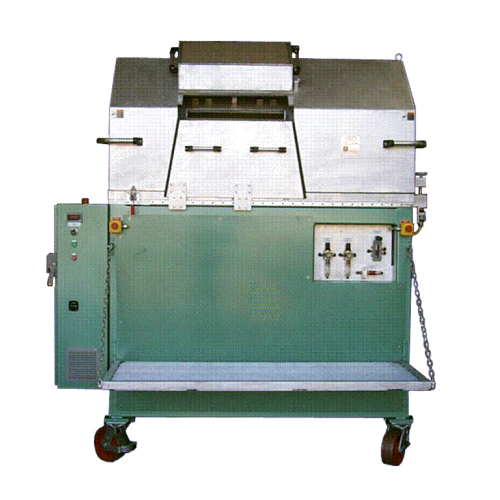
Dx strand pelletizer for plastic pellet production
Reduce operational noise while precision-cutting a wide array of therm...
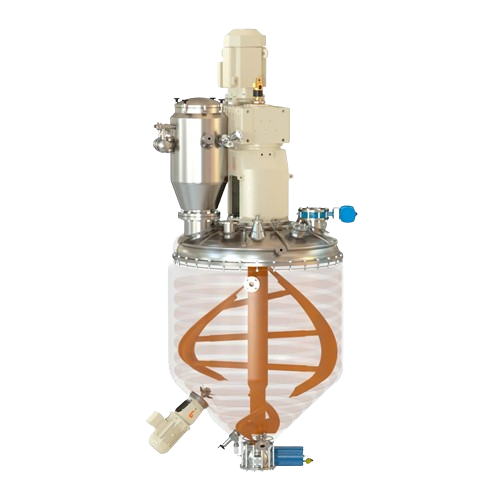
Vertical ribbon vacuum dryer for thermosensitive products
Achieve optimal drying of thermo-sensitive materials like powd...
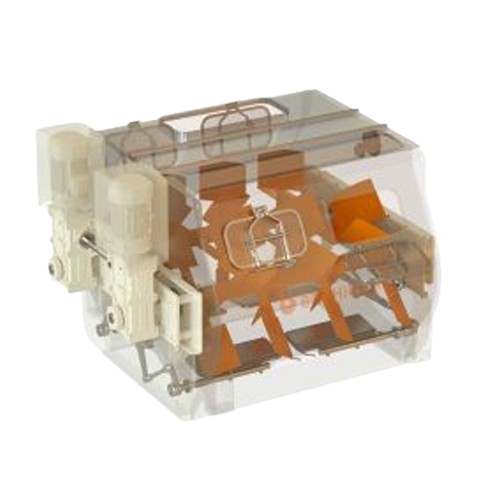
Double shaft paddle mixer for solids and powders
Achieve unparalleled mixing precision for fragile and diverse materials w...
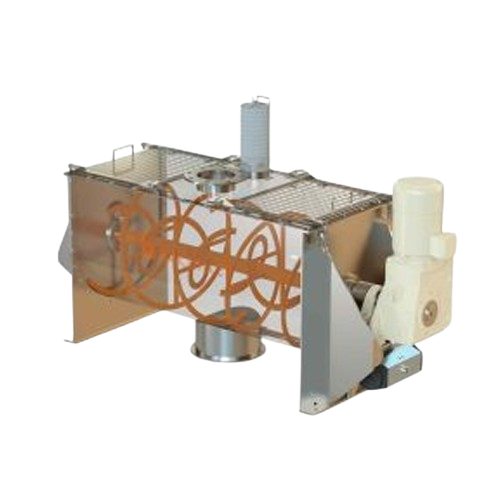
Horizontal ribbon blender for solids and powders
Efficiently achieve uniform blending of bulk solids and powders, ensuring...
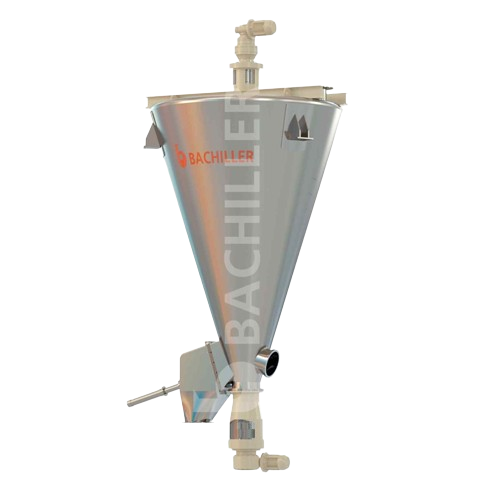
Conical screw mixer for solids and powders
Achieve precise homogenization of your solid and powder mixtures with minimal e...
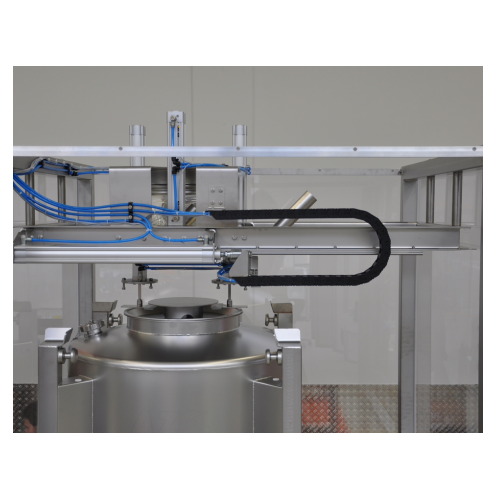
Dust-tight docking for dosing units to bulk solids containers
Ensure seamless, dust-free transfer and dosing of bulk sol...
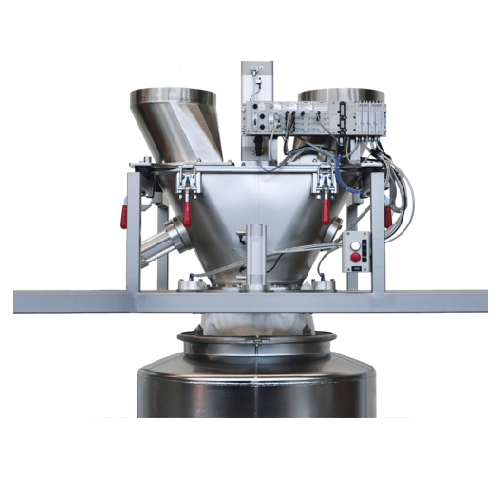
Contamination-free docking system for bulk solids
Achieve contamination-free transfer of bulk powders and granules while ...
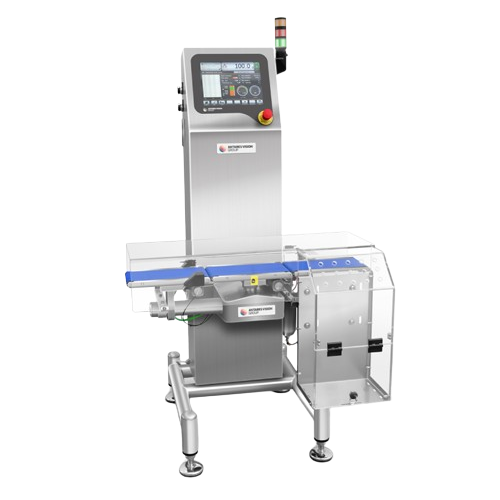
Checkweighers for medium and small products
Ensure precise weight control in high-speed production lines with advanced che...
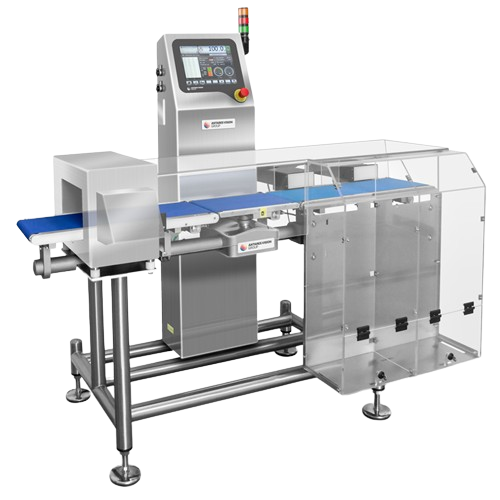
Integrated metal detector and checkweigher for small/medium formats
Ensure precise quality control and contaminant-free...
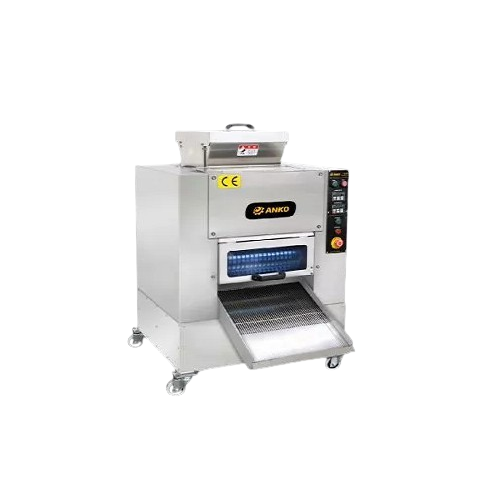
Automatic cutting and rounding solution for tapioca products
Optimize your production of tapioca pearls, tang yuan, and ...
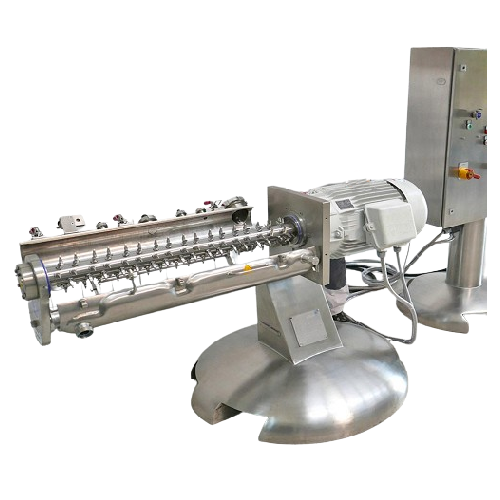
Continuous granulator for powdery goods
Achieve uniform particle size and structure with a continuous granulation process t...
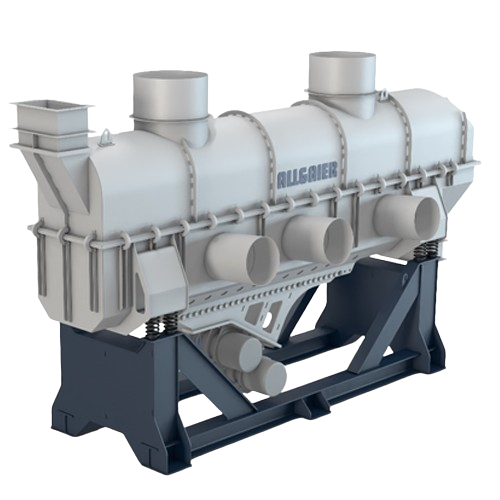
Fluidized bed dryer for industrial materials
Enhance product quality and energy efficiency with fluidized bed dryers, opti...
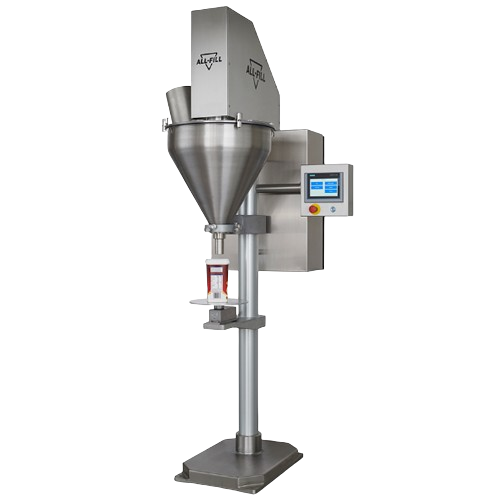
Gravimetric filling solution for inconsistent density products
Achieve precise weight accuracy in your filling processes...
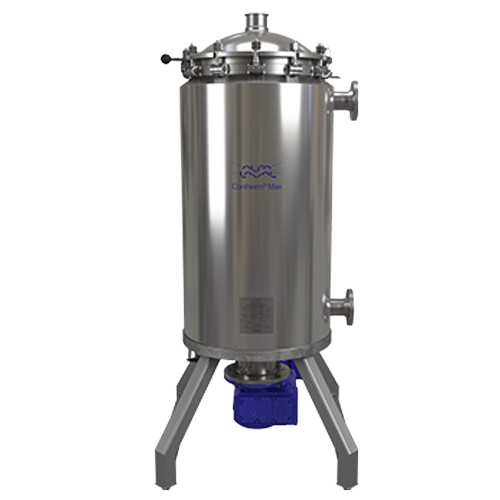
Double-wall scraped surface heat exchanger
Achieve high-capacity processing with gentle handling for shear-sensitive produ...
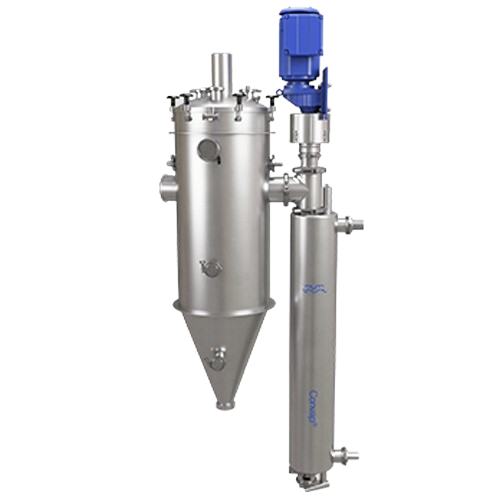
Scraped surface evaporator for high-viscosity materials
Efficiently concentrate high-viscosity and hard-to-handle materia...
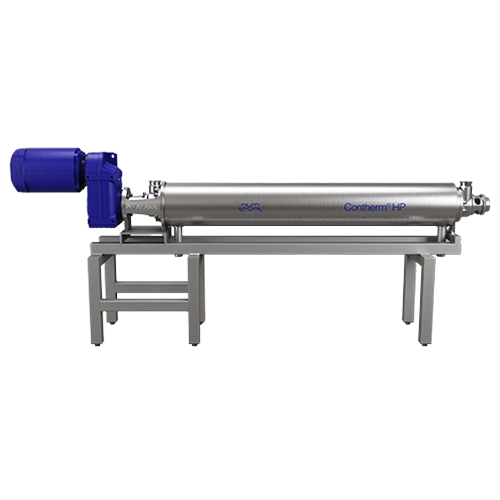
Scraped surface heat exchanger for high-pressure applications
Handle high-viscosity and particulate-rich products with p...
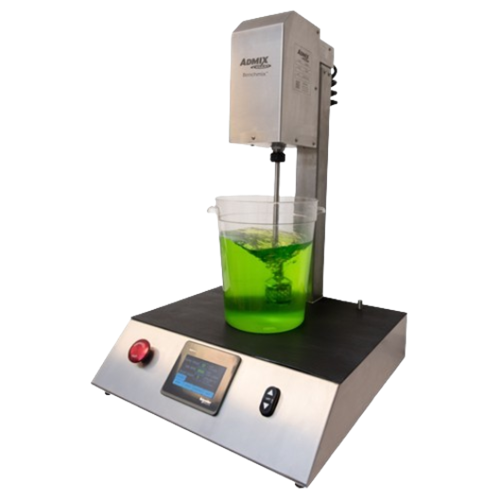
Benchtop mixer for lab-scale product development
Easily scale up your formulations with precise and repeatable lab-scale m...

Inline continuous mixer for dairy and beverage processing
Achieve precise emulsification and particle size reduction for...
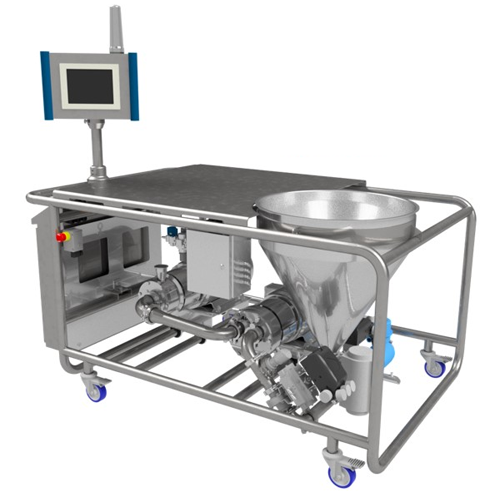
Automated powder induction and dispersion system for industrial mixing
Achieve rapid and efficient incorporation of pow...
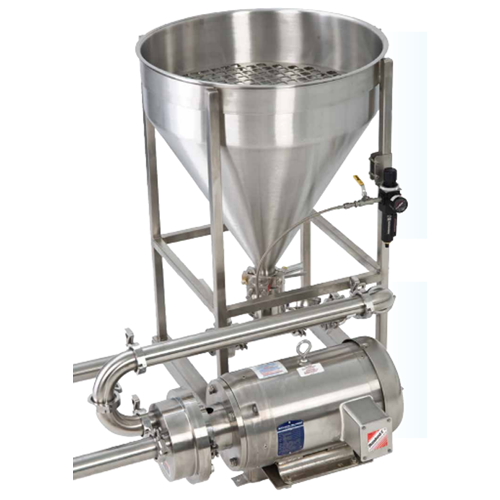
Atmospheric powder induction system
Enhance your mixing efficiency with a system designed for rapid powder induction and th...
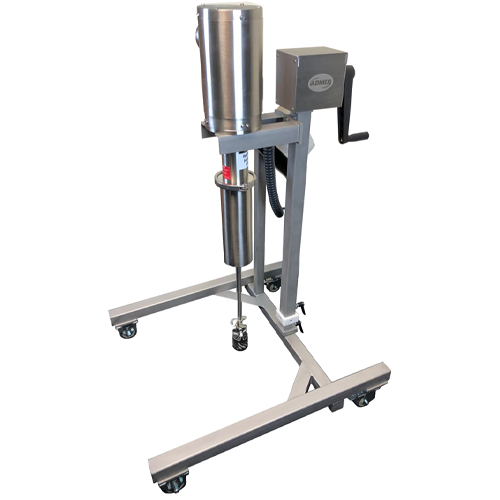
Pilot scale mixers for product development and small production runs
Optimize your mixing processes with precision cont...
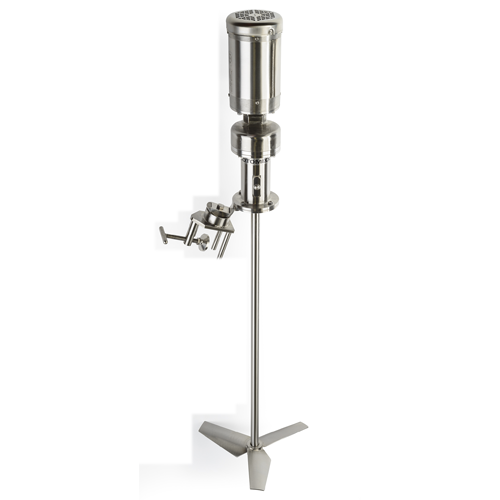
Low-shear portable mixer
For processes demanding strict hygiene, this mixer eliminates rust and chipped coatings by offering ...

High shear emulsifier for hygienic applications
Achieve precise emulsification and consistent mixture quality with enhance...
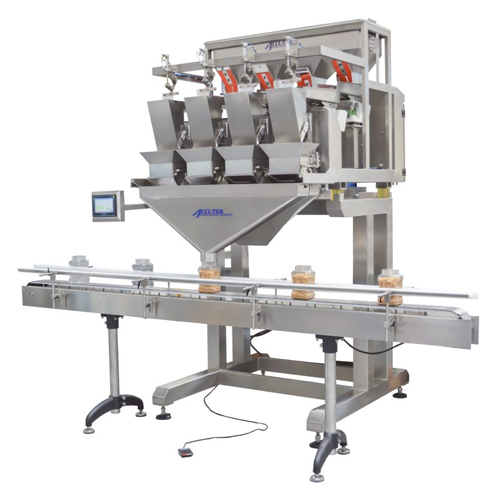
Automatic granular product weighing system
Effortlessly achieve precise fills for dry granular products and powders while ...
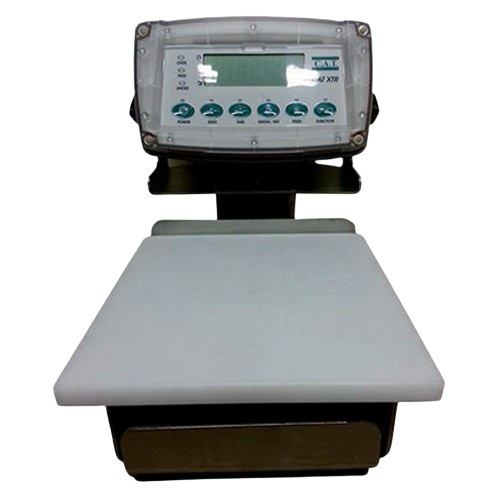
Industrial bench scale for Qa processes
Ensure precise weight measurements and maintain quality control with this bench-top...
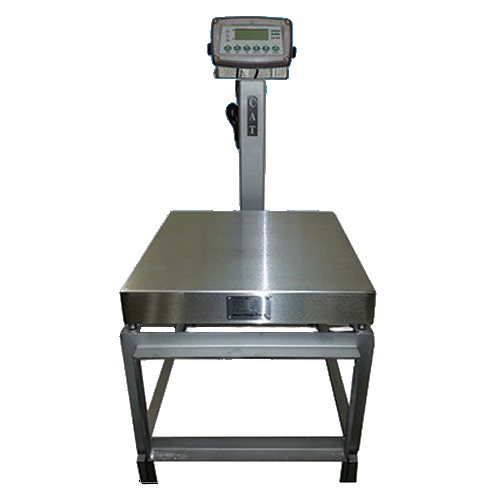
Compact digital bench weighing scale for food processing
Ensure precise portioning with this compact and durable digital ...
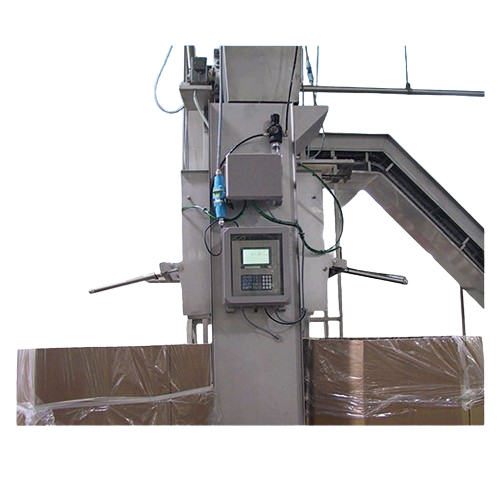
Bi-directional frame scale for industrial weighing
Achieve precise product accumulation and streamlined batch processing ...
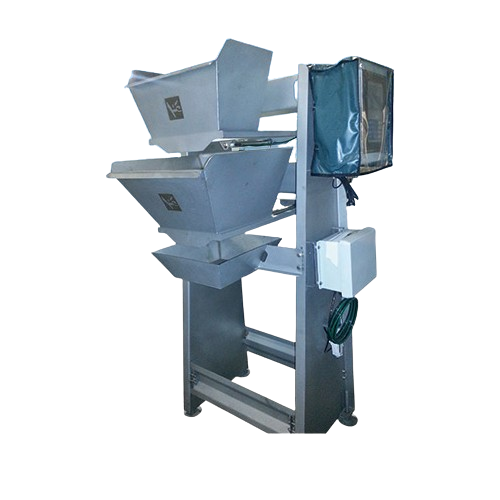
Indexing scale for precise weighing in packaging lines
Ensure accurate product portioning and streamline your packaging p...

Industrial weight tracking system for injected products
Optimize your production line by accurately tracking product weig...
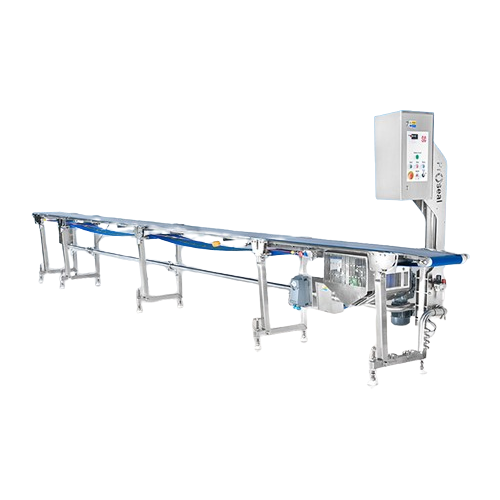
Flat belt product transfer conveyor for food processing
Efficiently streamline your production line with a hygienically d...
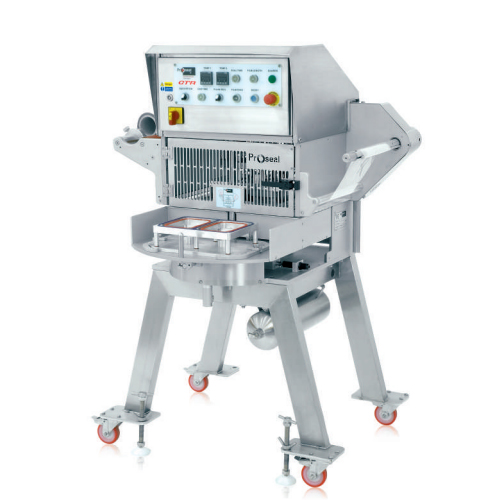
Semi-automatic tray sealing solution
Streamline your production line with a versatile tray sealing solution that enhances p...
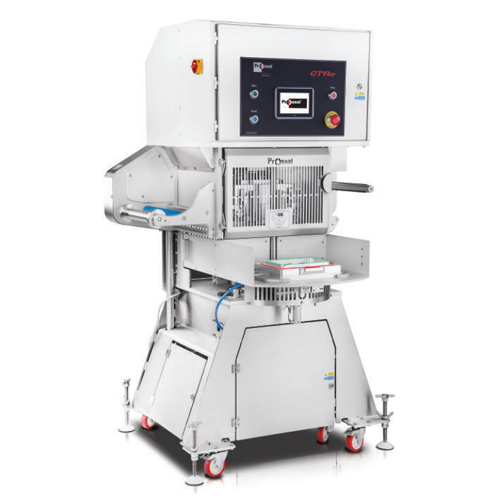
Semi-automatic tray sealing for ready meals
Achieve versatile packaging with a semi-automatic tray sealing solution design...

Automatic tray sealer for high-speed food packaging
Optimize your production line with a high-capacity tray sealing solut...
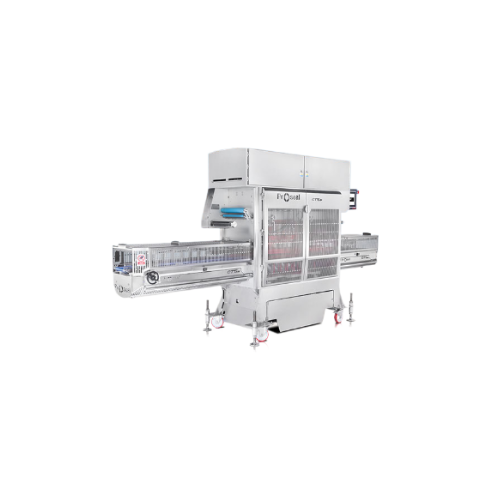
High-speed tray sealer for food packaging
Streamline your packaging process with high-speed tray sealing, reducing labor c...

Automatic tray sealing system for high-speed packaging
Experience seamless high-speed packaging with this versatile tray ...
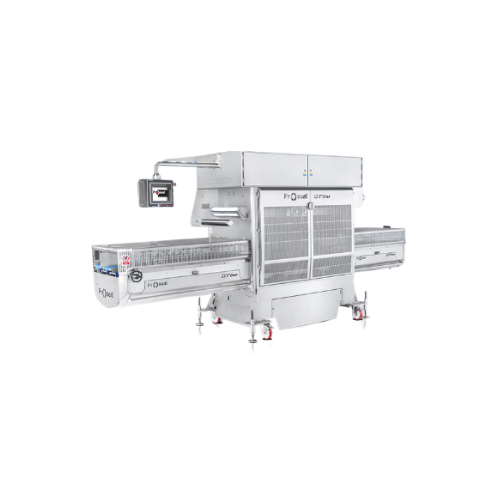
Automatic tray sealer for high-speed production
Ensure your product packaging stays fresh and secure with this high-capaci...
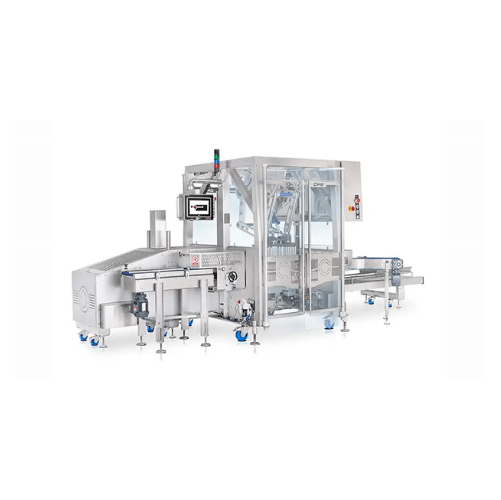
Industrial case packing solution for high-speed operations
Optimize your production line with a compact, efficient case ...
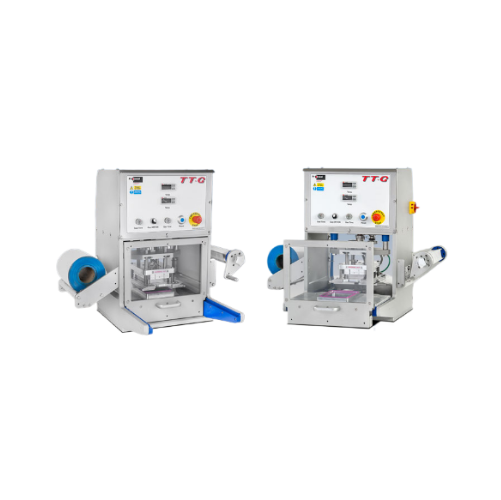
Bench mounted tray sealer with gas flush
Optimize your production line with a compact tray-sealing machine designed for pre...

Linear conveyor tray sealing
Experience unparalleled flexibility and efficiency in tray sealing with high-speed integration,...
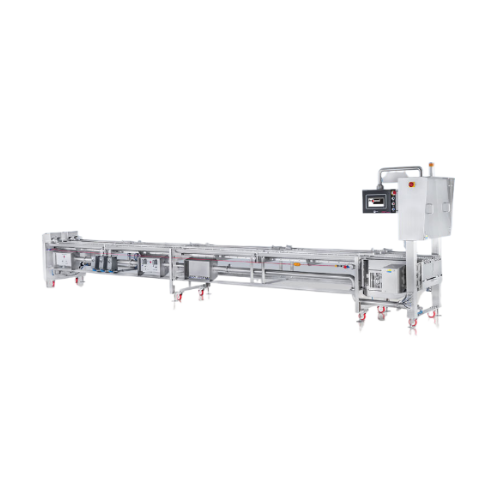
High throughput tray conveyor system
Looking to streamline your tray sealing process? This modular conveyor system integrat...
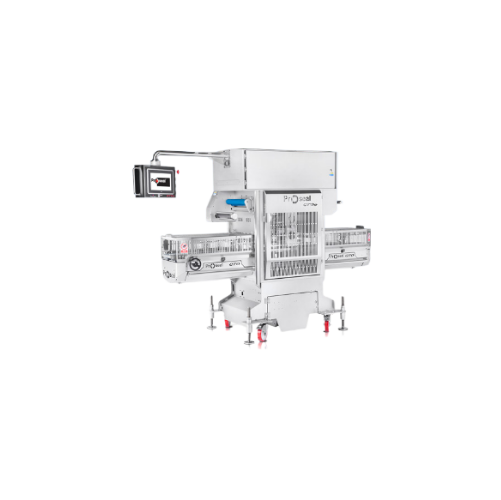
High-speed tray sealer for food
Enhance your packaging line’s efficiency with a high-speed, in-line tray sealer design...

Industrial high speed tray sealer
Enhance your production line efficiency with precision sealing capabilities, accommodatin...
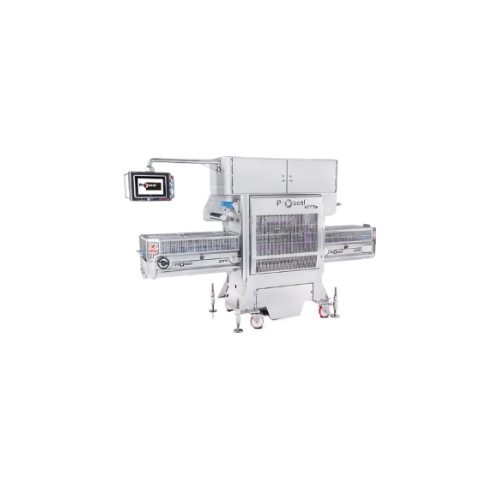
Automatic tray sealer
Maximize throughput and shelf life with our high-speed inline tray sealing solution, ideal for diverse ...
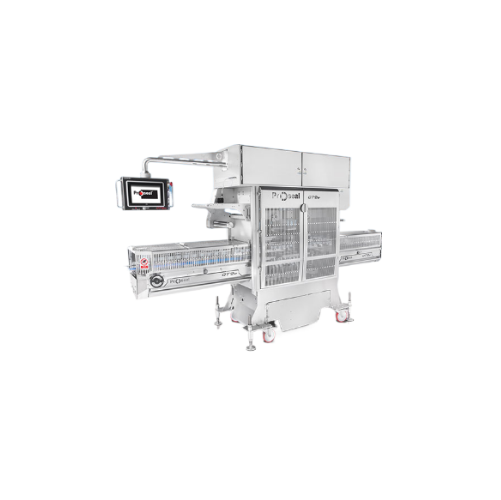
In-line tray sealer for high-speed packaging
Optimize your packaging line with a high-speed solution that accommodates mul...
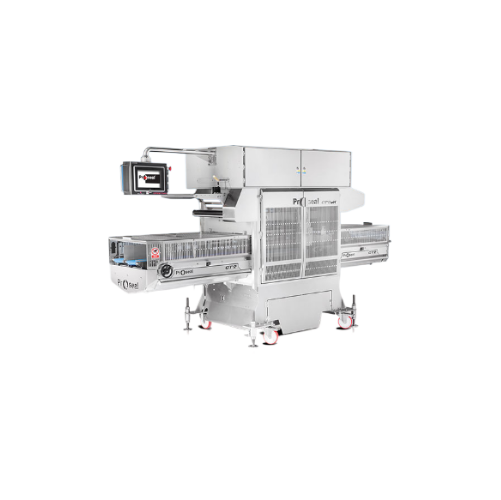
High-capacity tray sealer for vacuum gas packaging
Enhance your production efficiency with a versatile twin-lane tray sea...
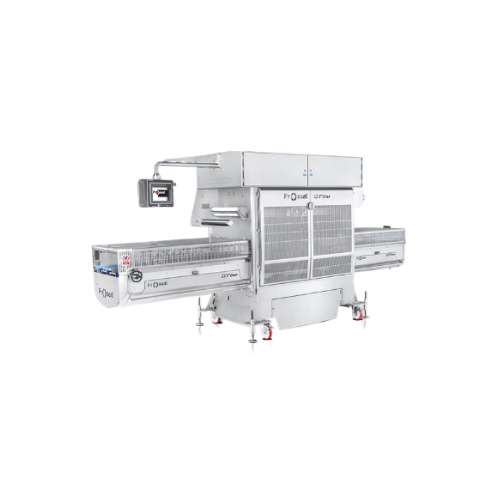
In-line tray sealing system
Streamline your packaging line by implementing a high-speed, in-line tray sealing system designe...
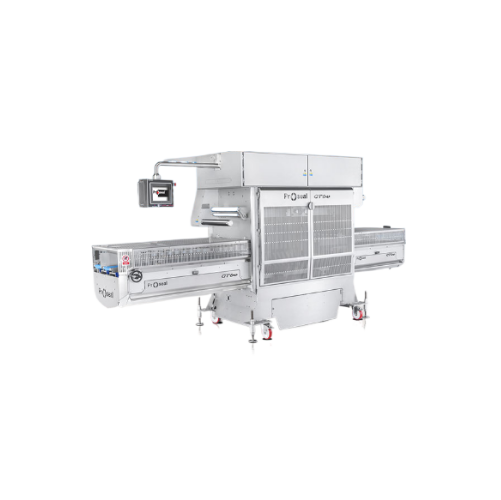
High-capacity tray sealer for poultry, meat & seafood
Optimize your high-speed packaging line with this large-capacity tr...
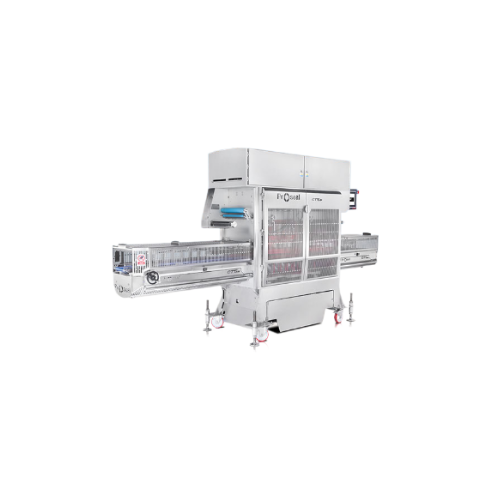
Automatic tray sealer for high-speed packaging
Streamline your packaging line with an in-line tray sealer that adapts to t...
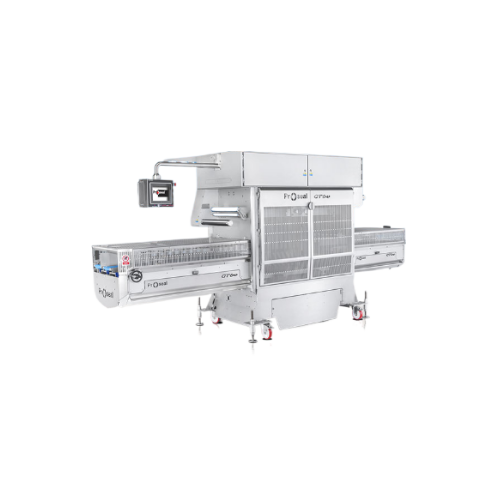
Large-capacity automatic tray sealer
Optimize your production line with this tray sealer, designed for high-speed sealing a...
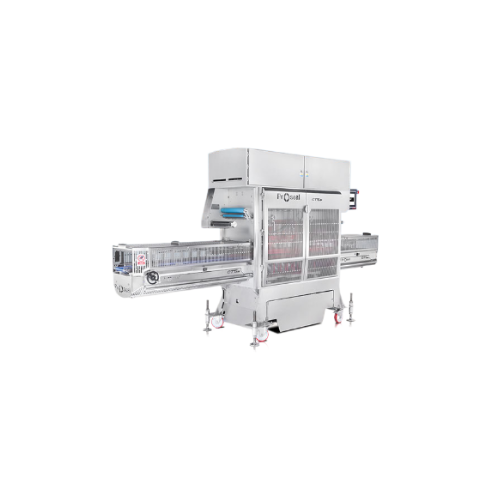
Automatic inline tray sealer for food packaging
Streamline your packaging process with high-speed, reliable tray sealing t...
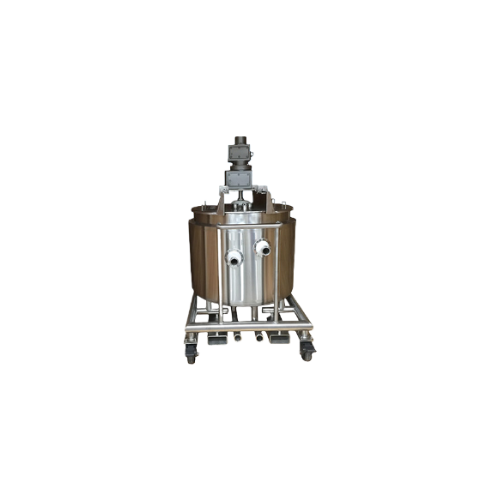
R&d vessels for research and development centers
Optimize your R&D operations with versatile vessels designed to hand...
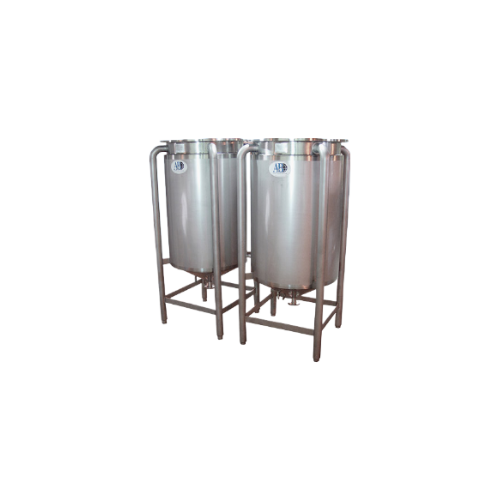
Customizable storage tanks for industrial use
Optimize your production with versatile storage tanks designed for precise c...
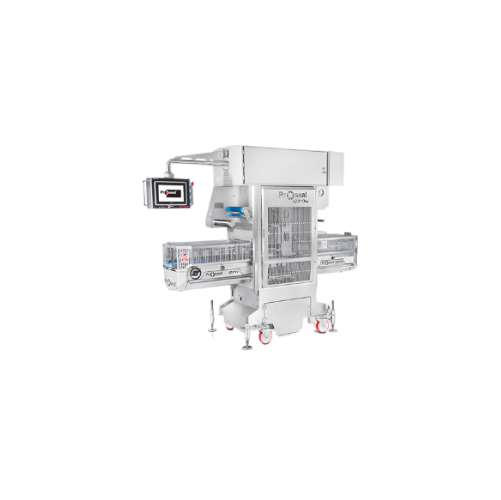
Automatic tray sealing system
Optimize your packaging line with versatile tray sealing technology that accommodates various ...
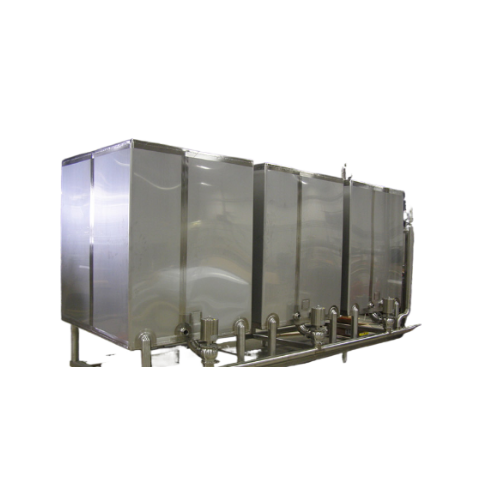
Clean-in-place tanks for industrial sanitation
Optimize your sanitation processes with clean-in-place tanks, designed to r...
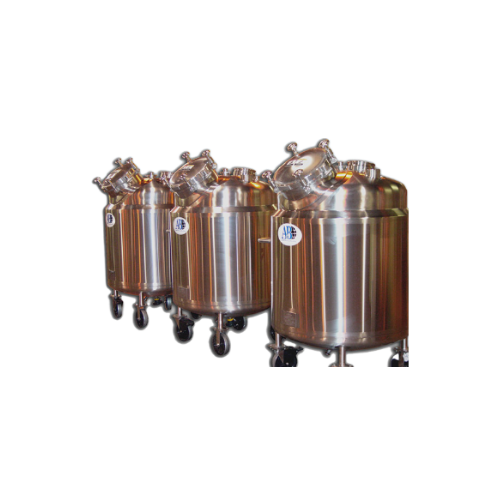
Industrial pressure vessels
Ensure product integrity and regulatory compliance with engineered-to-order pressure vessels, de...
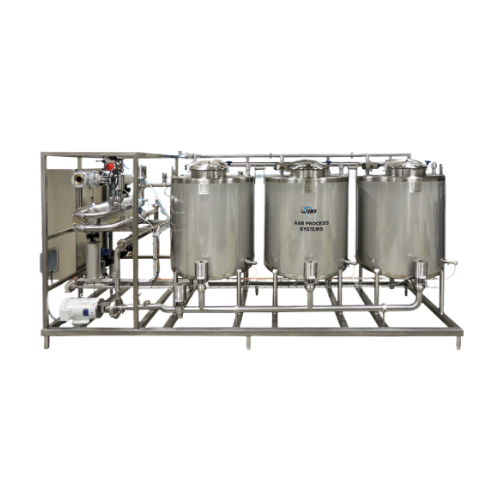
Clean-in-place system for diverse processing needs
Ensure the precision and consistency of your cleaning cycles with a ro...

Basket tracking system for automated batch retort systems
Efficiently manage and monitor your batch processing with a sy...
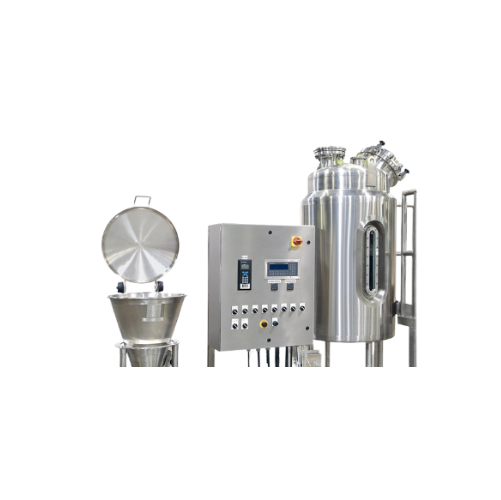
Powder induction system for efficient liquid powder mixing
Achieve precise and dust-free powder incorporation into liqui...
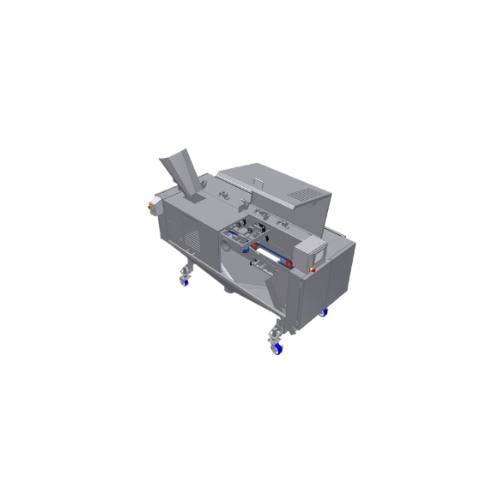
Turkey gizzard processor
Enhance efficiency in your poultry processing line by automatically splitting and rinsing turkey giz...
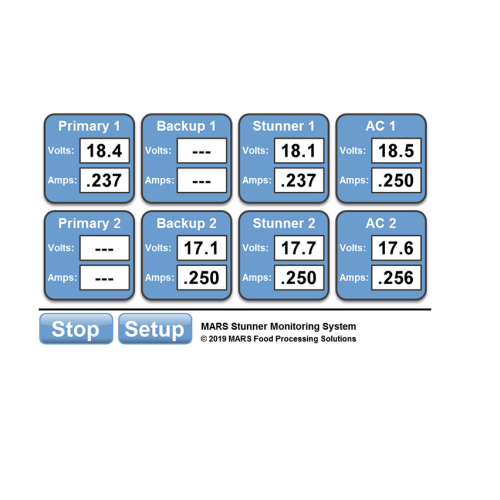
Stunner monitoring and reporting system for poultry processing
Optimize your stunner performance by accessing real-time ...
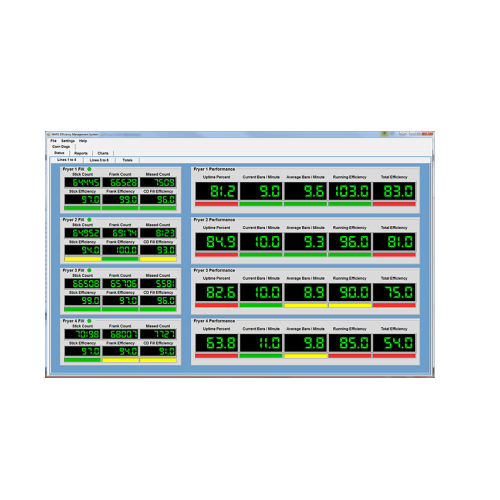
Custom efficiency solutions for poultry processing
Enhance your production line efficiency with cutting-edge solutions th...
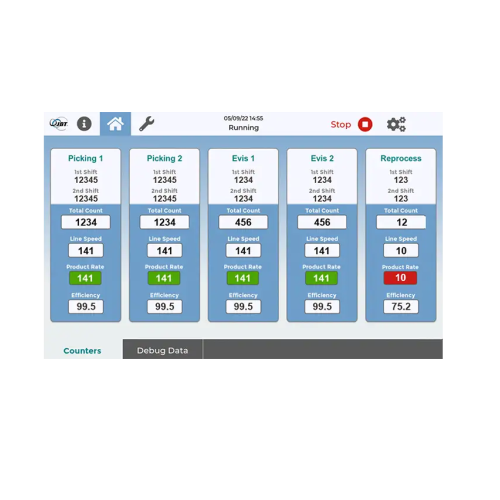
Poultry processing efficiency monitoring system
Maximize production efficiency with real-time monitoring and precise track...
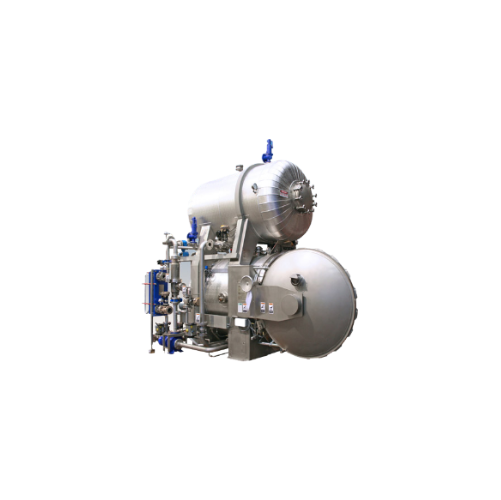
Multi-purpose laboratory sterilizer for food processing
Achieve precise thermal process design and flexibility with a ste...
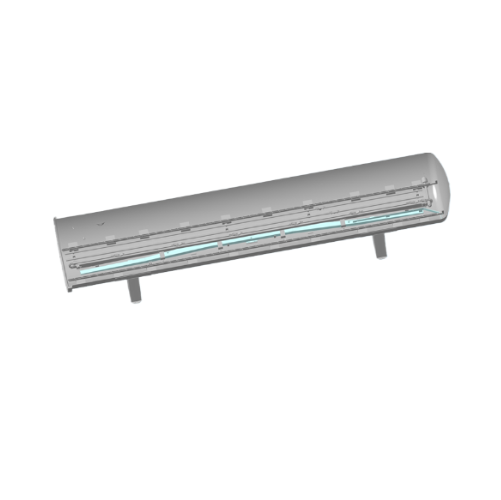
Low energy suction system for food processing retorts
Optimize your sterilization process with innovative suction technol...
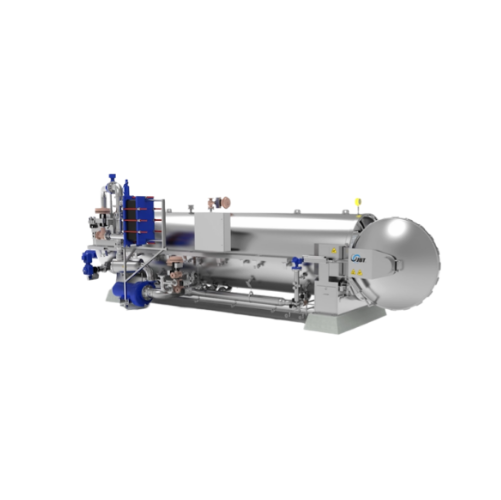
Agitating batch retort for food sterilization
Ensure superior heat distribution and precise control in your sterilization ...
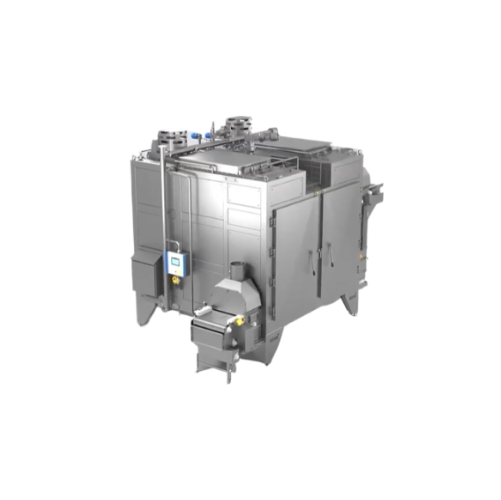
Spiral oven for cooking and browning products with steam and hot air
Optimize your cooking line with a compact spiral o...
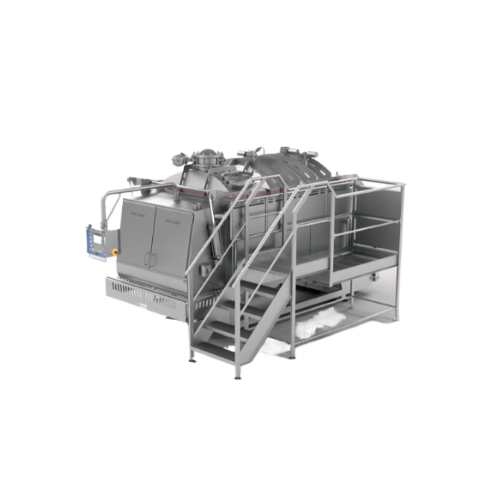
Industrial cooker for soups and ready meals
Streamline your cooking operations with a versatile system capable of mixing, ...

High pressure processing water filtration system
Ensure super clear water after high pressure processing to protect your s...
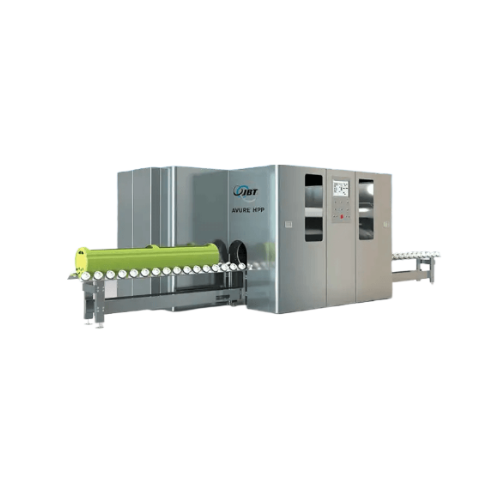
High pressure food processing solution for medium-scale producers
Achieve reduced operational costs with high-pressure ...
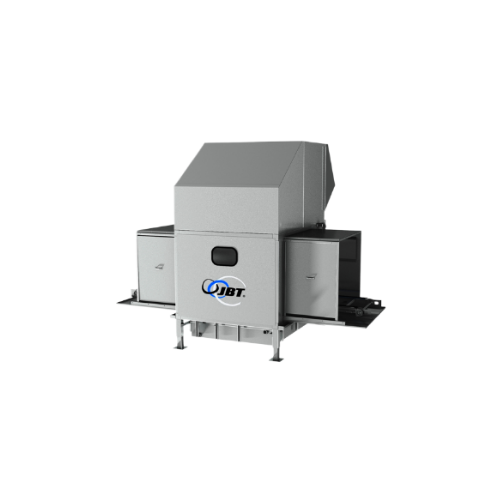
Industrial bin scrubbing system for fresh produce
Enhance food safety and operational efficiency with a bin scrubbing sys...
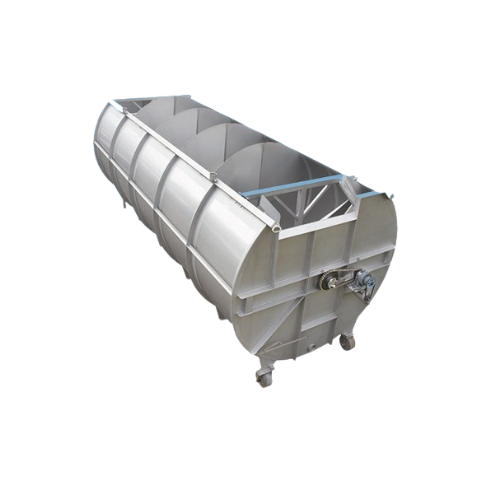
Industrial poultry chillers
Optimize temperature control with advanced chilling technology designed to maintain product inte...
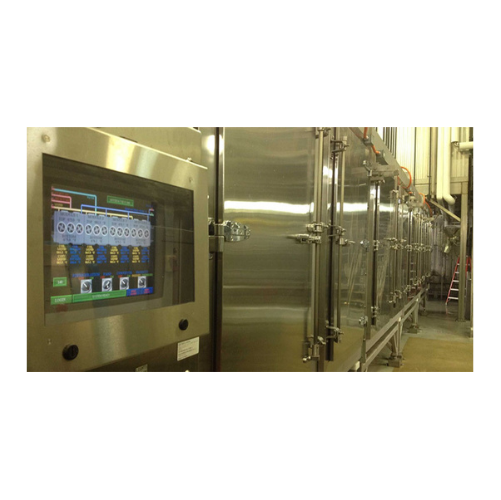
Fast crusting freezer for poultry products
Ensure optimal product integrity by rapidly sealing moisture in seconds, preven...
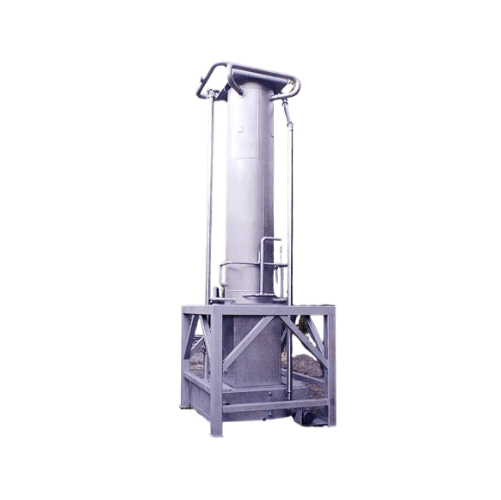
Industrial ice maker for high-volume production
Achieving precise temperature control and maximizing product quality, this...
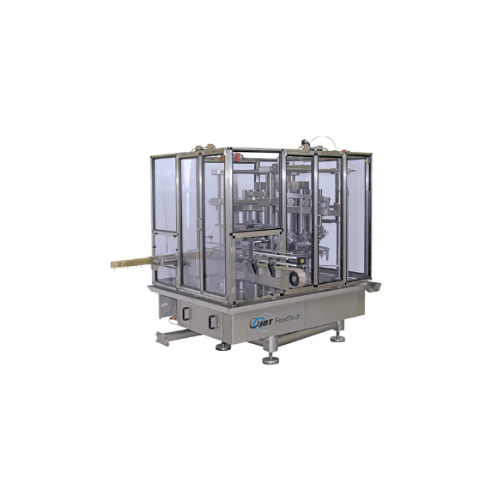
Volumetric piston filler for liquid and viscous products
Achieve precise volume control and enhance product integrity wit...
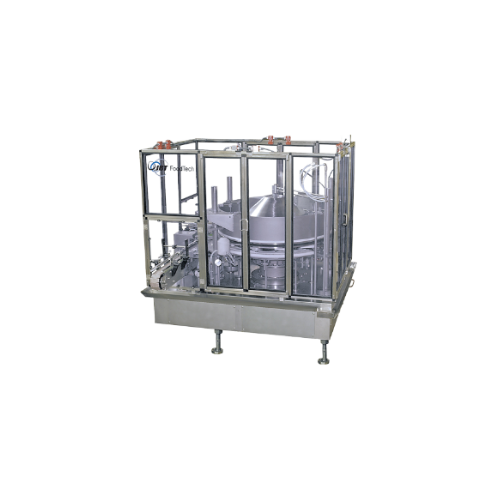
Granular filler for wide mouth containers
Ensure precise filling and minimize product loss with this granular filler, expe...
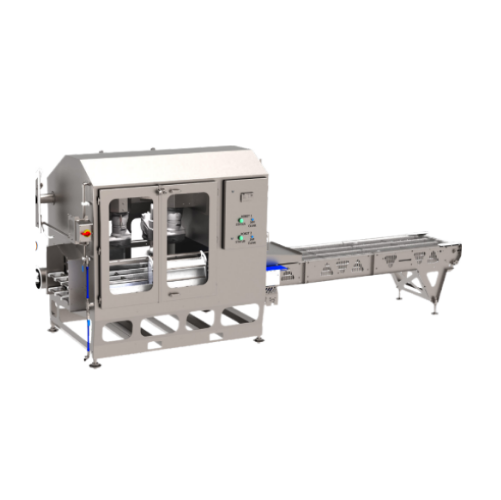
Automated meat portioning and trimming solution
Enhance your production line efficiency with a robotic system that automat...

Breading line for poultry and seafood products
Elevate your production with high-speed breading lines designed for uniform...
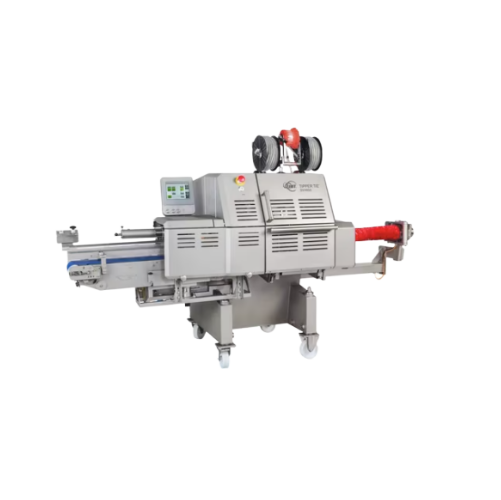
Automatic double clipper for sausage and deli meats production
Optimize your meat and deli production line with seamless...
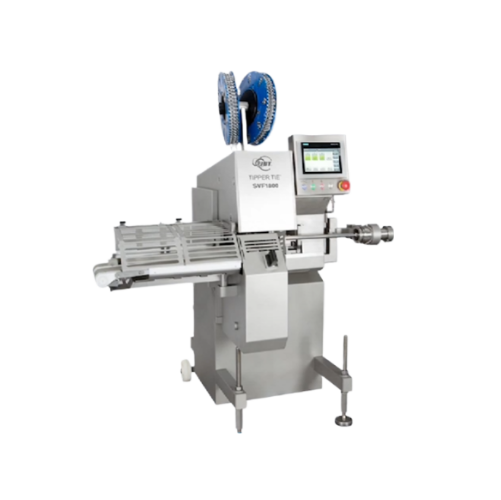
Automatic double clipper for sausage production
Optimize your production line with a high-speed double clipper that secure...
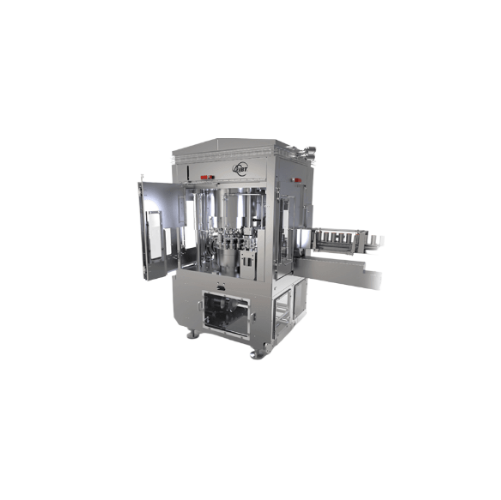
Can seamer for high-speed liquid applications
Ensure consistent seal integrity and maximize throughput with this advanced ...
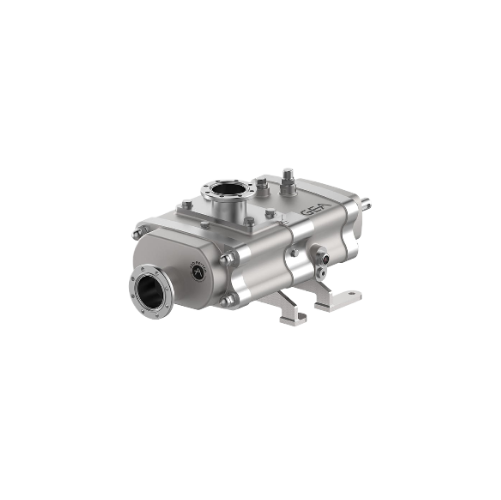
Twin screw pump for viscous media
Streamline your production with a twin screw pump that effortlessly handles viscous media...
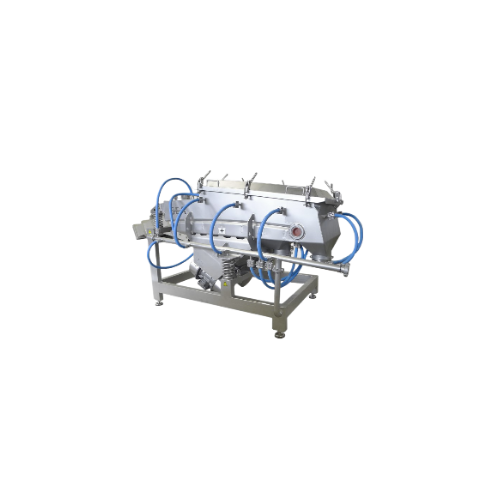
Industrial sifters for beverage processing
Optimize your beverage production with precisely engineered sifters that ensure...
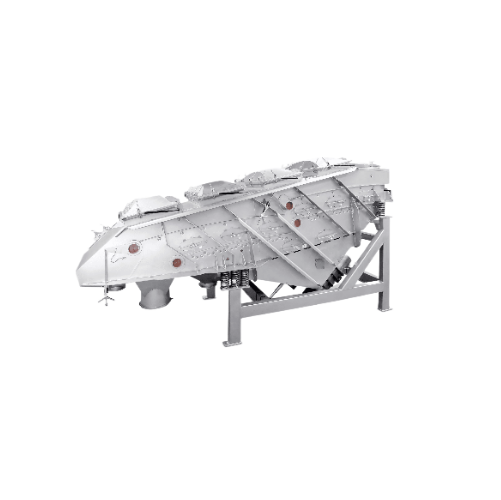
Vibrating sifter for chemical applications
Achieve precise particle separation with this vibrating sifter, ensuring optima...
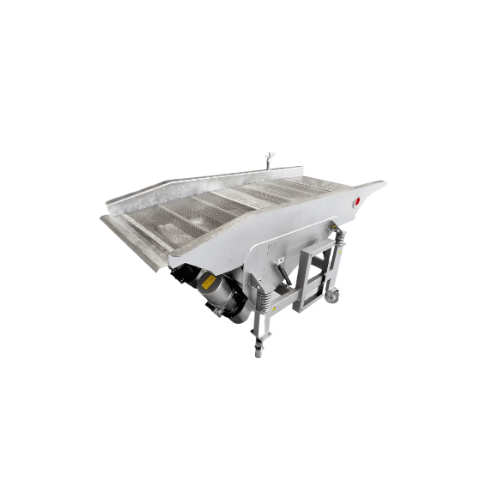
Food product sifter
Ensure precise separation with vibratory sifters designed for continuous operation, delivering gentle han...
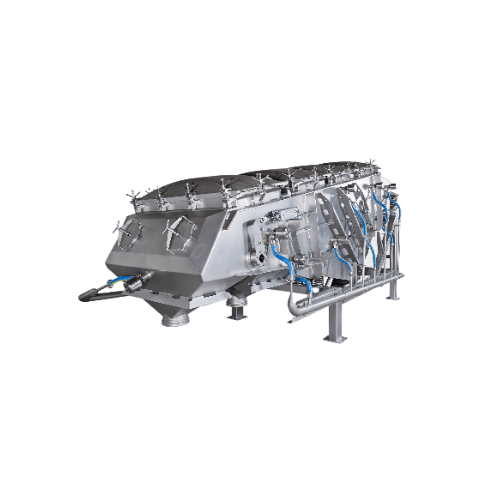
Industrial powder sifter with sanitary compliance
Optimize your powder processing with this versatile sifter, ensuring pr...
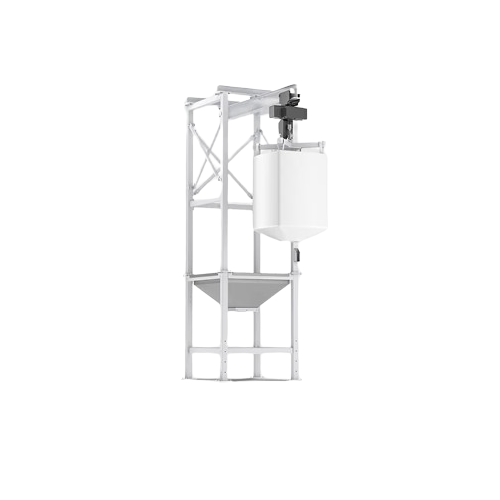
Big bag emptying station for bulk product handling
Streamline your bulk material handling with a station designed to effi...
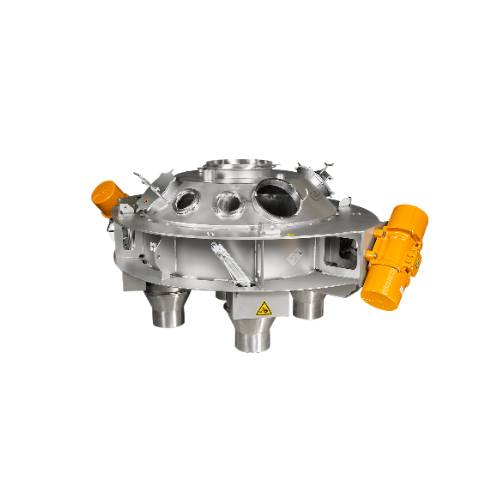
Circular distribution feeder for fragile product handling
Achieve precise dosing and reduced product damage with a versa...
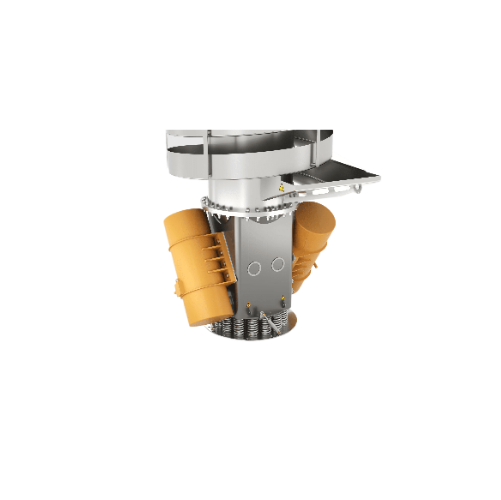
Vibratory spiral elevator for vertical transport
Achieve efficient vertical transport with precise temperature control, su...
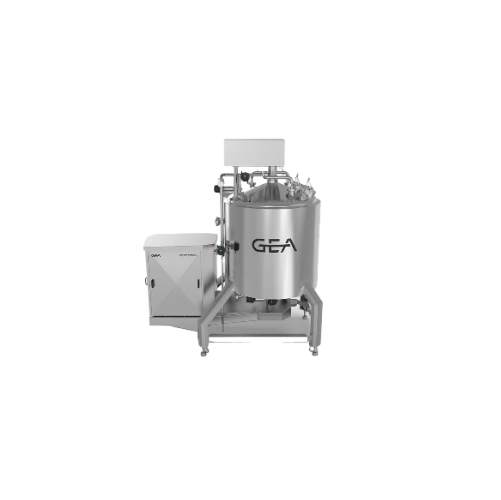
High shear mixer for dairy and personal care products
Achieve consistent emulsification and stable homogeneity with high ...
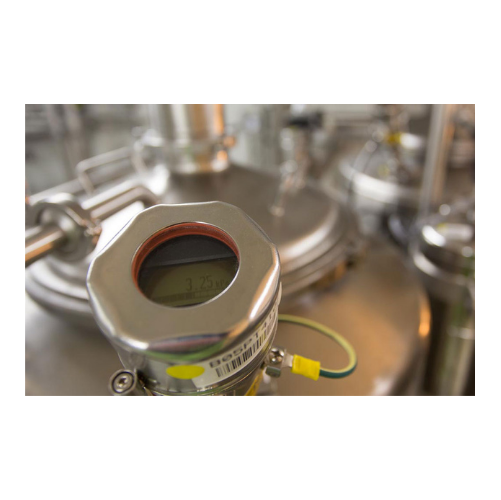
Powdered product shelf-life enhancement through inert gas packing
Extend the shelf life of sensitive powder products by...

Continuous leveler and sealer for powder packing
Enhance efficiency in powder packaging with a system that ensures precise...
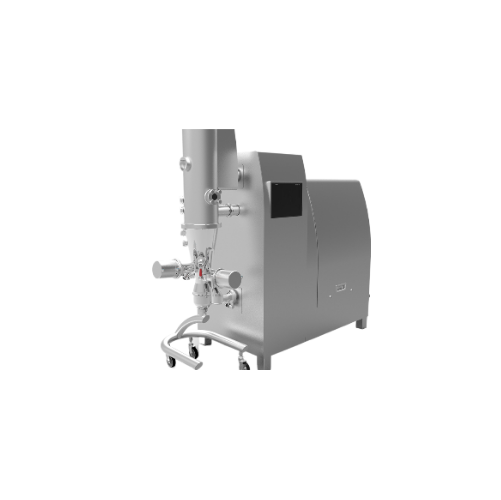
Screw press for vital wheat gluten dewatering
Optimize your production line with efficient moisture reduction for vital wh...
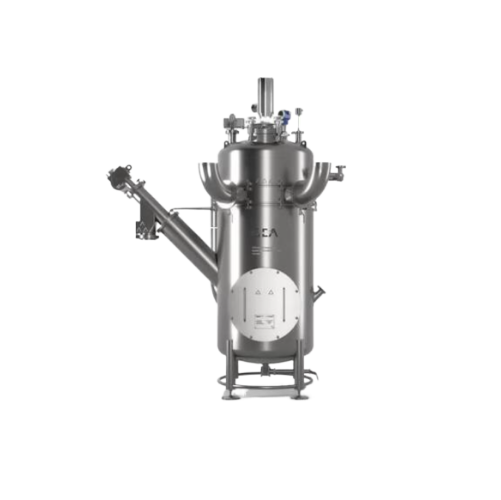
Liquid nitrogen freezer for sensitive food and fermentation ingredients
Achieve rapid, uniform freezing of sensitive fo...
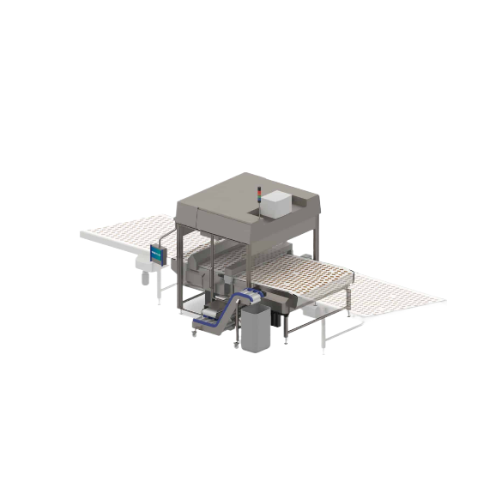
Vision-based product inspection system for rejecting defective items
Enhance your production line efficiency by ensurin...
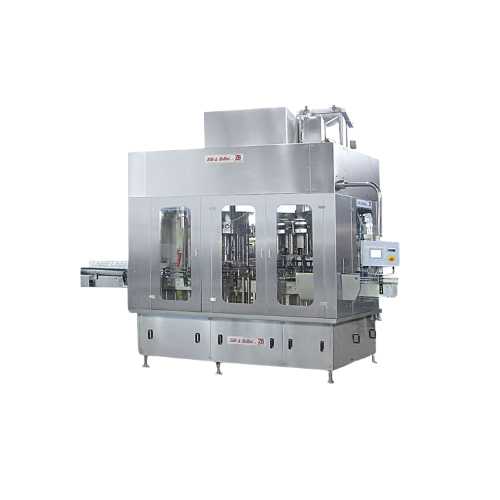
Ultraclean filling monoblocks for food industry
Enhance product safety and quality with monoblocks designed for ultraclean...
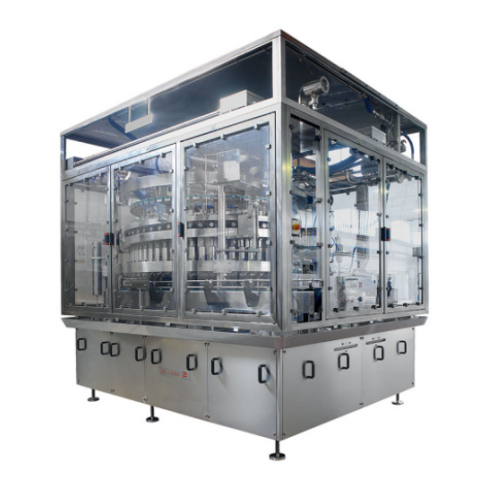
Rotary piston fillers for pumpable products
Optimize high-speed production lines with precision filling for diverse liquid...
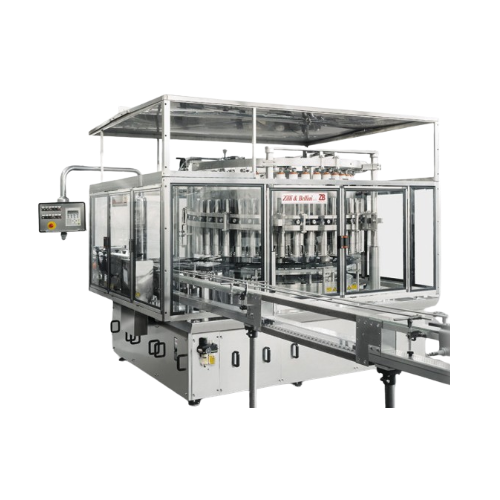
Rotary piston fillers with plunger for viscous products
Optimize your filling process with high-speed, rotary piston fill...
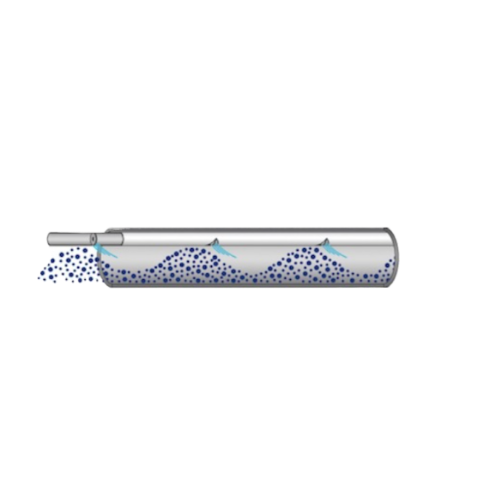
Pta and Pet production systems
Maximize throughput while minimizing dust fines in your production of PTA and PET pellets wit...
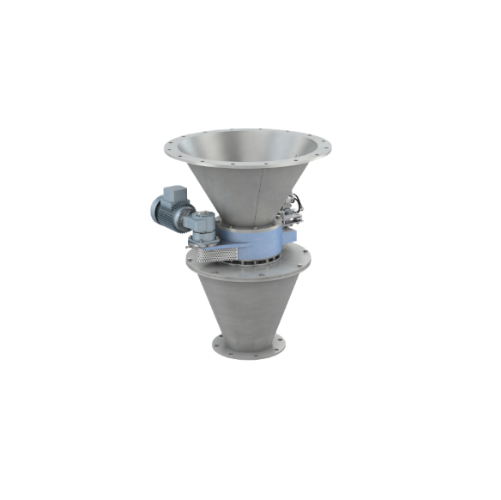
Precise discharge and dosing module for silos and containers
Ensure seamless material flow and accurate dosing with adva...
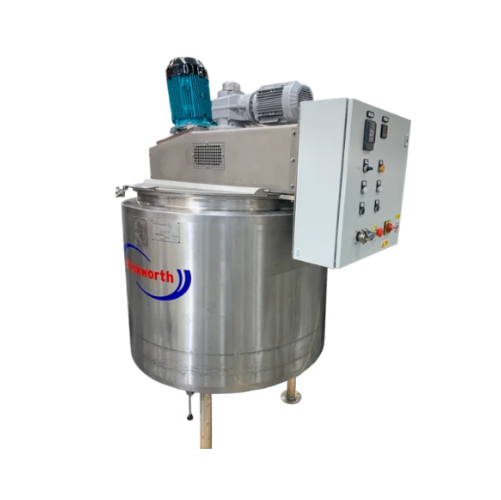
Pv processing vessels for liquid and cream mixing
Optimize your mixing operations with versatile processing vessels desig...
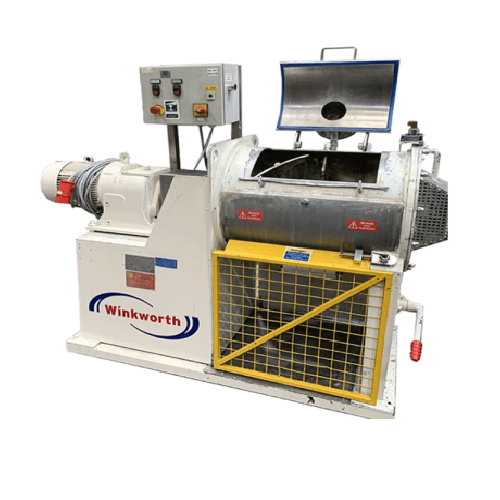
Industrial rapid turbulent mixer for homogeneous mixing
Achieve unparalleled homogeneity with rapid turbulent mixing, ess...
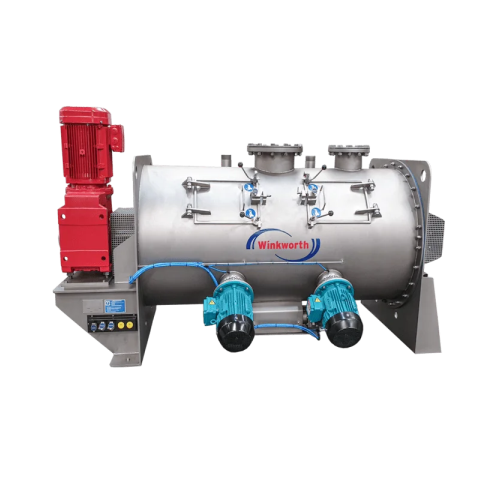
High-speed mixer for industrial mixing applications
Achieve rapid, consistent mixing and dispersion across diverse materi...
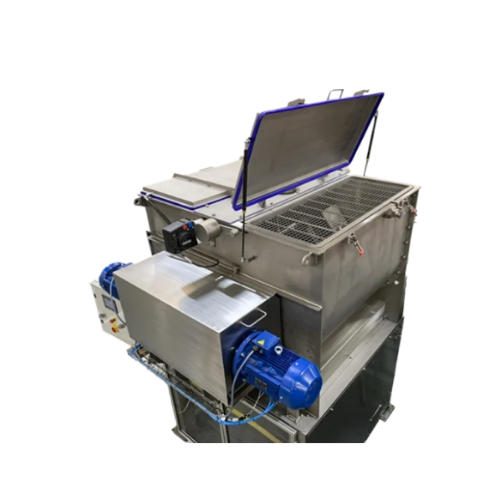
Twin shaft mixers for fragile and high throughput applications
Maximize mixing efficiency and protect delicate materials...
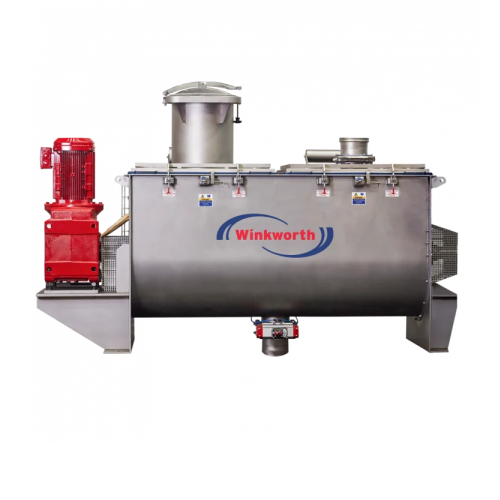
Efficient ribbon mixers for precise powder blending
Achieve consistent and uniform blending with this advanced U-Trough m...
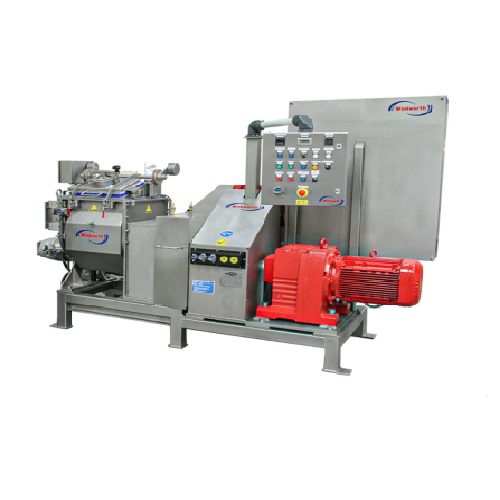
Industrial sigma mixer extruder for homogeneous mixing and extrusion
Achieve precise mixing and seamless extrusion of d...
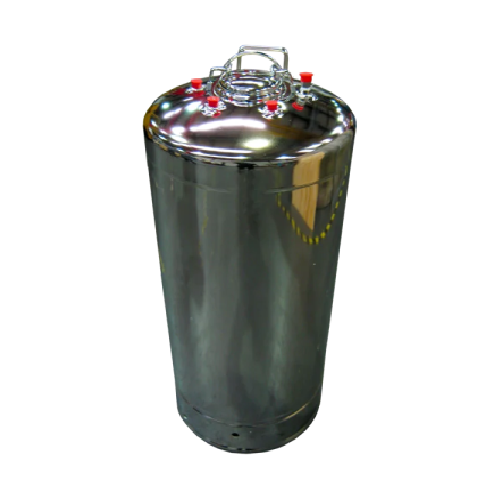
Pressure vessel for hazardous and non-hazardous liquids and gases
Ensure safety and compliance when handling hazardous ...
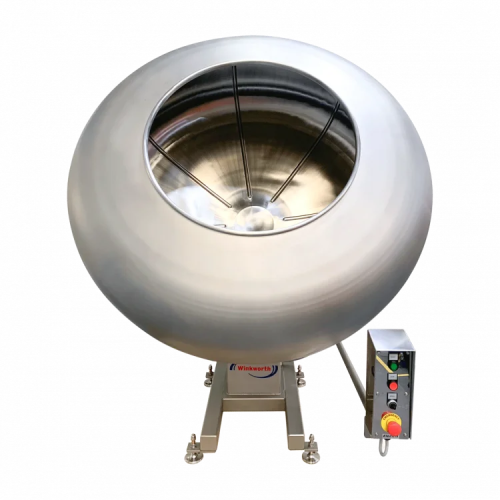
Coating pans for precision culinary coatings
Achieve consistent, high-quality coatings on a diverse range of products, fro...
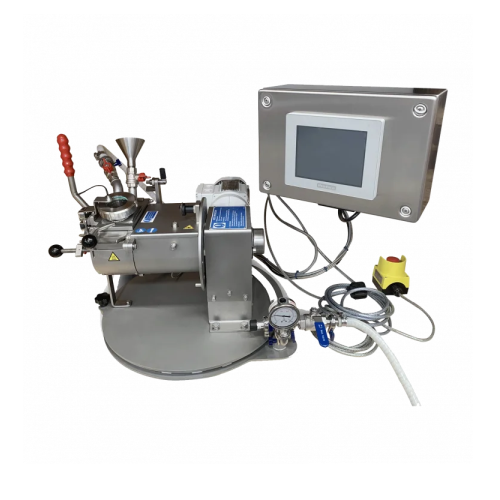
Laboratory mixers for product development and research
Optimize your R&D efforts with advanced mixing solutions desi...
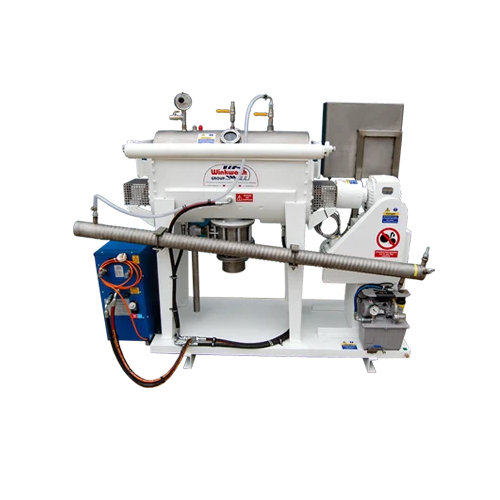
Industrial blenders for powder and granule mixing
Optimize your production line with advanced mixing solutions designed f...
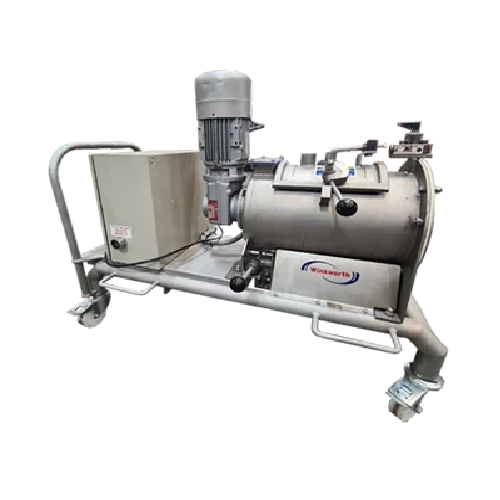
Industrial mixers for hire
Optimize your production line with versatile mixers designed for precision blending, heating, and...
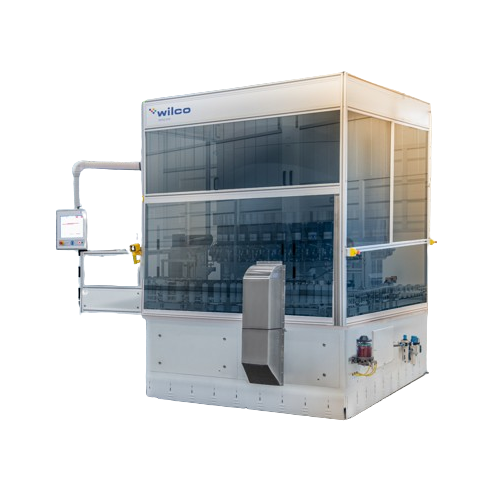
Leak testing system for aerosol cans
Ensure the integrity of your aerosol and metal packaging with a high-speed leak testin...
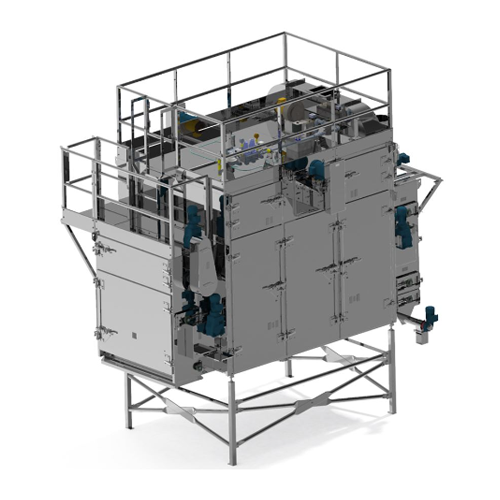
Light duty oven for snacks and light density foods
Maximize efficiency with precision-controlled drying and heating of sn...
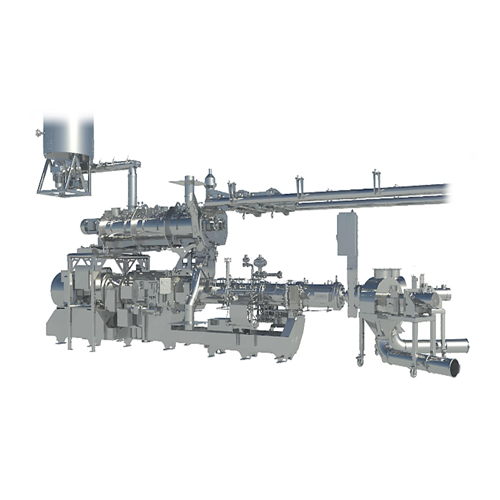
Extruder for aquatic feed production
Efficiently produce a wide range of aquatic and pet feed with precise control over pel...
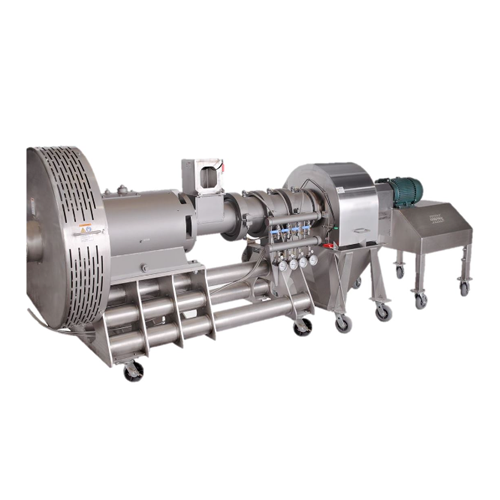
Forming extruders for flaked cereals
Optimize your production line with versatile forming extruders designed for precision ...
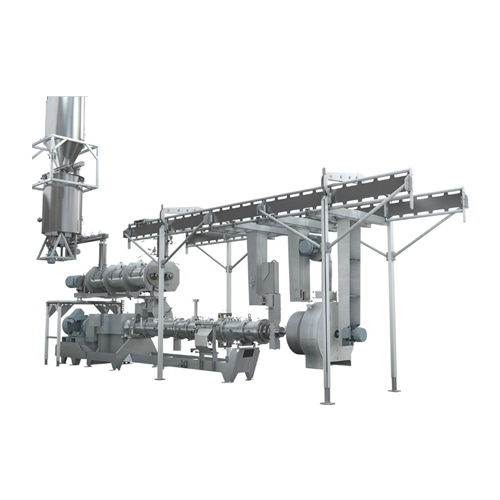
Twin screw extruder for pet and aquatic feed
Achieve exceptional cooking precision with our twin screw extruder, designed ...

High-performance slicer for food processing
Achieve precise and consistent slices for your diverse range of food products ...
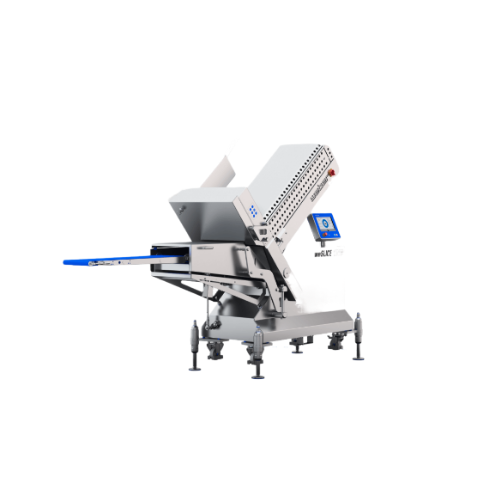
Circular blade slicer for cheese and deli products
Optimize your slicing operations with precise portion control and vers...
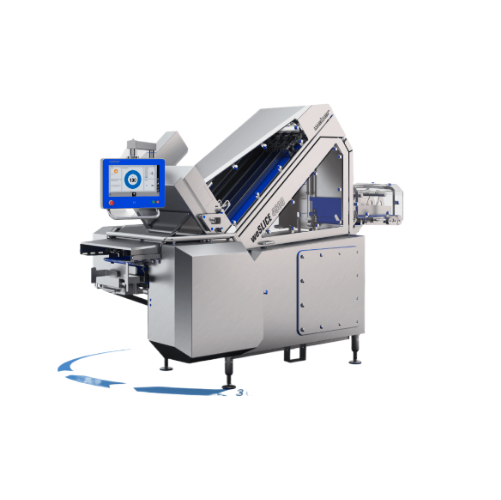
High-performance slicer for variety of meat products
Elevate your slicing precision with a high-speed system designed for...
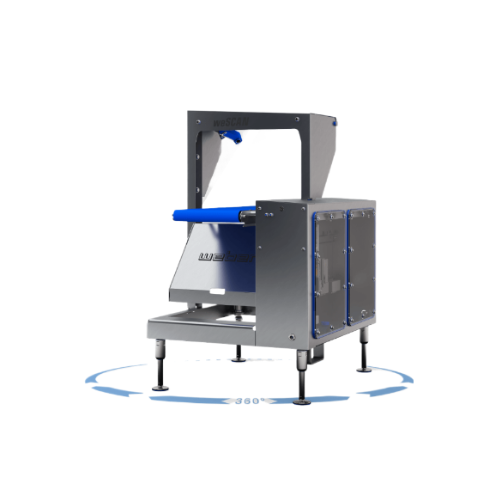
Involute blade slicer for diverse product range
Maximize throughput and efficiency with this advanced slicing solution, id...
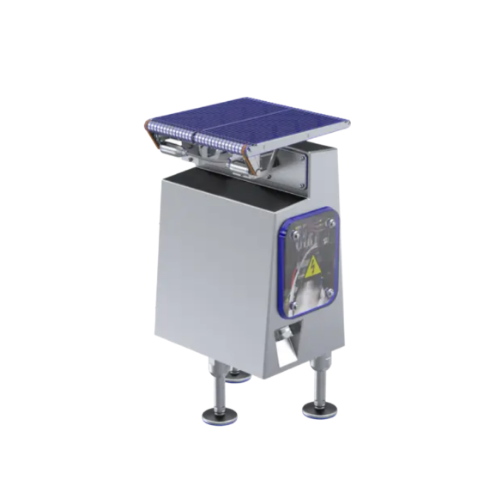
Circular blade slicer for caliber-consistent meat products
Achieve precise, high-speed slicing for diverse food products...
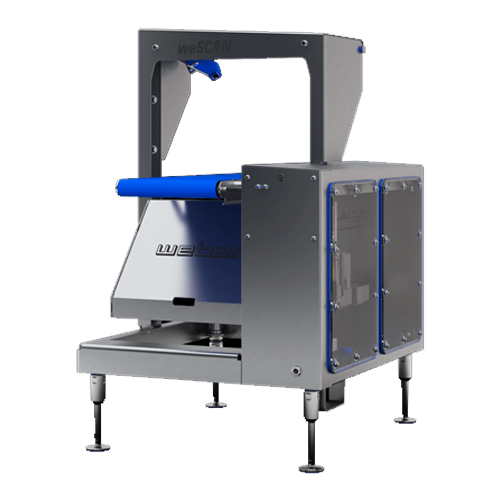
Laser scanner for precise slicing results
Achieve unparalleled slicing accuracy and enhanced yield with laser scanning tec...
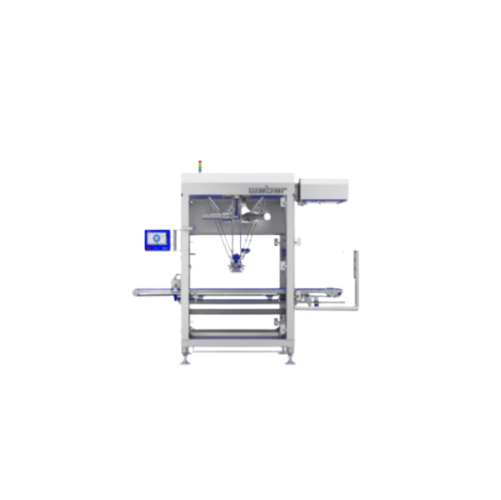
Automated cold cuts loading system
Optimize your production line with a flexible side loading solution designed for precise...
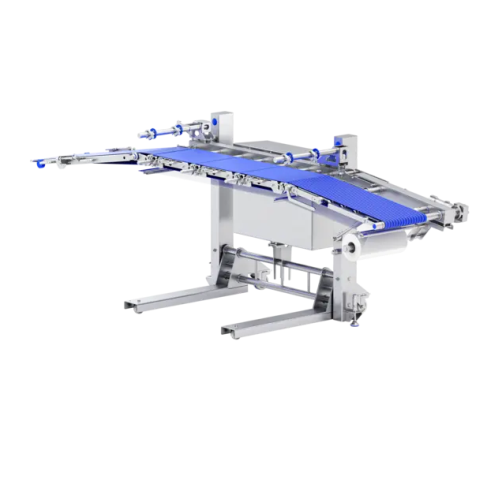
Automatic infeeder for cold cuts
Ensure seamless integration of portioned products into your packaging line with this compac...
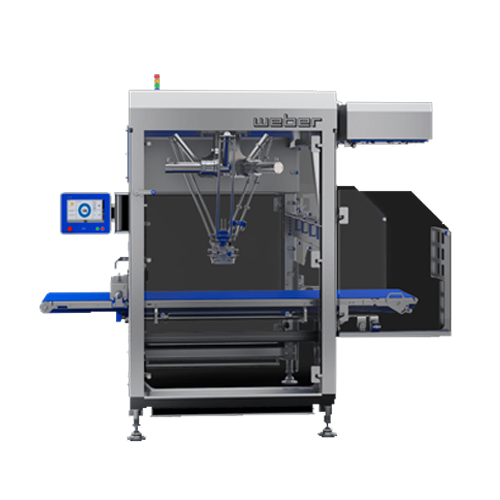
Automated picking and placing system for cold-cuts
Optimize your food production line by implementing a high-speed roboti...
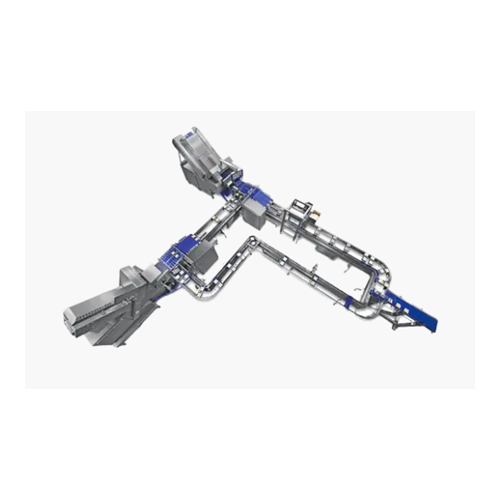
Automated transport system for cold-cuts in confined spaces
Optimize your production flow by conveying cold cuts efficie...
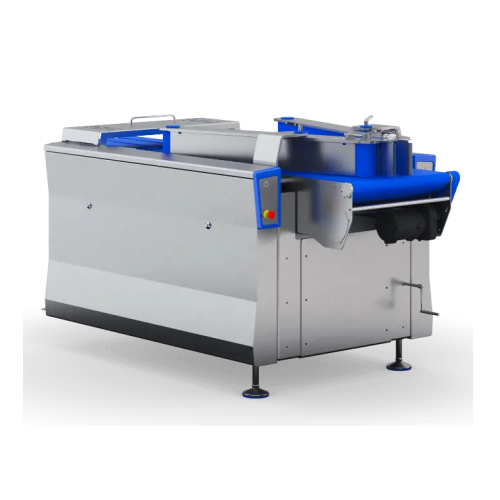
End-of-line converging solution for food packaging
Streamline your food packaging line with compact converging robots tha...
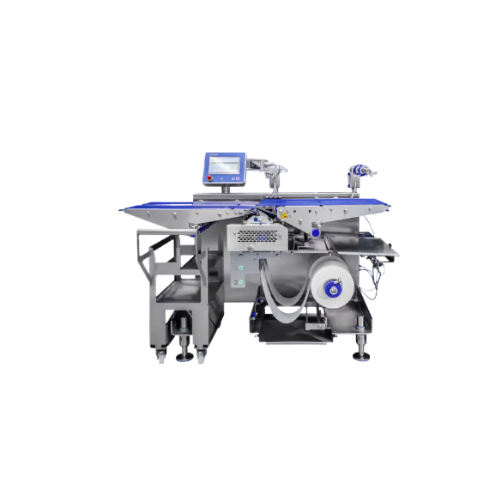
Compact belt separator for food packaging lines
Streamline your packaging line by efficiently merging up to six packing la...
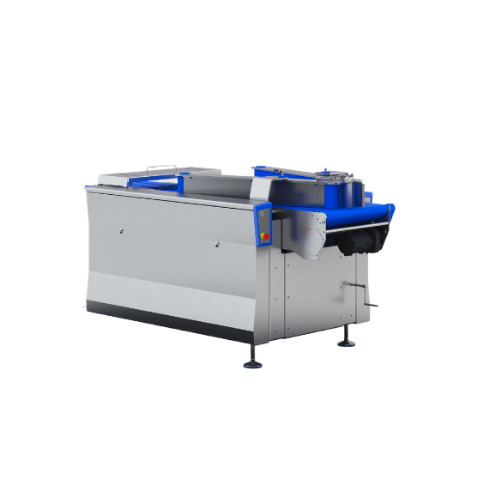
Thermoforming packaging system for medium production volumes
Optimize your food packaging with high-speed, continuous op...
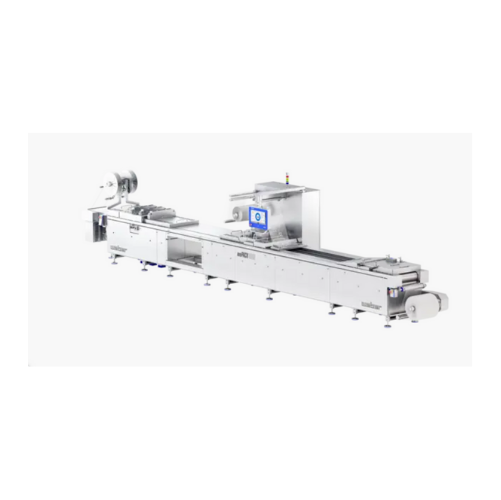
Thermoforming packaging solution for medium production volumes
Optimize your medium-volume packing with a compact thermo...
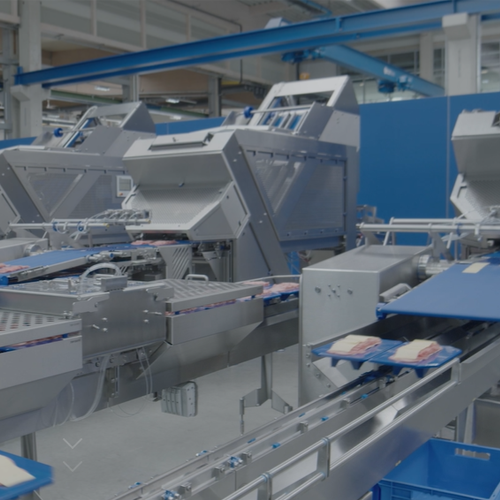
Automated insertion system for food processing
Streamline your food processing line with this versatile solution, designed...
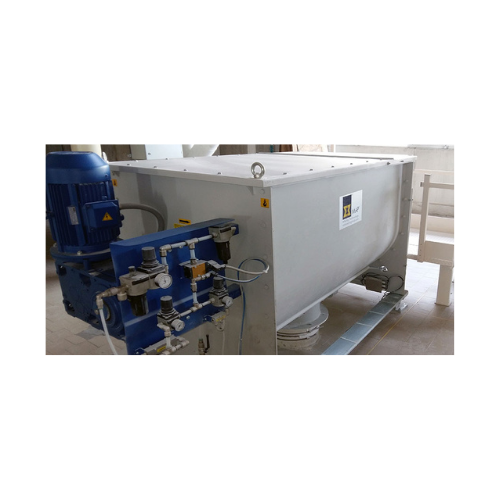
Single-shaft ribbon blender for homogeneous mixing
Achieve high-quality, precise blending of delicate and temperature-sen...
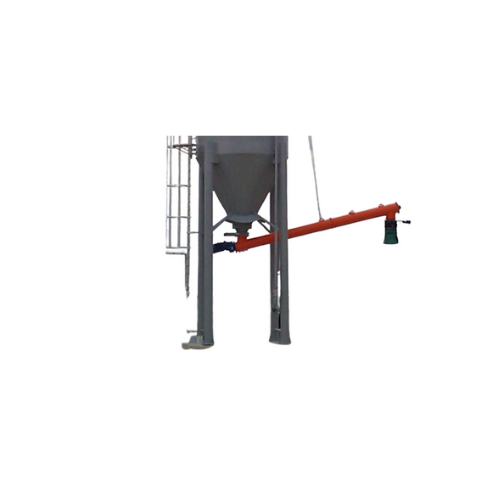
Bulk solids tanker loading bellows
For industries looking to efficiently load dry, non-dusty bulk solids into tankers, thes...
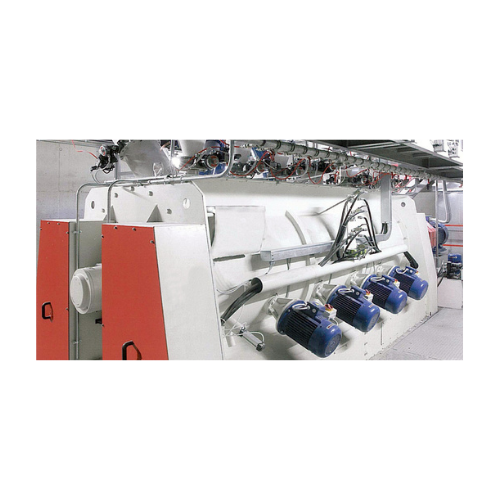
Batch-type single shaft mixers with bomb-bay discharge
When you need rapid, residue-free discharge in your batch mixing p...
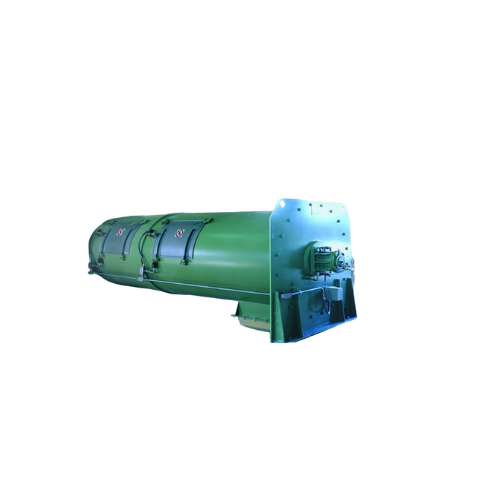
Continuous single shaft mixer for waste treatment
Achieve consistent mixing homogeneity and prevent dead spots in your pr...
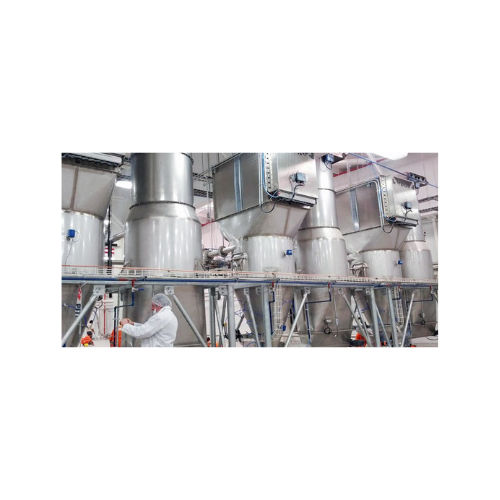
Atex-certified flanged polygonal dust collectors
Ensure dust control and compliance in explosive environments with our com...
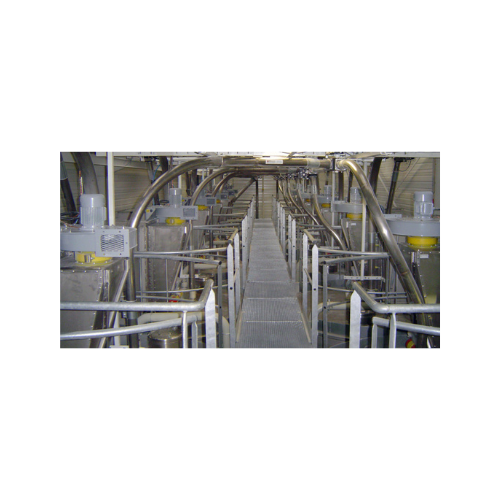
Atex certified flanged round dust collectors
Designed for potentially explosive environments, these flanged round dust col...
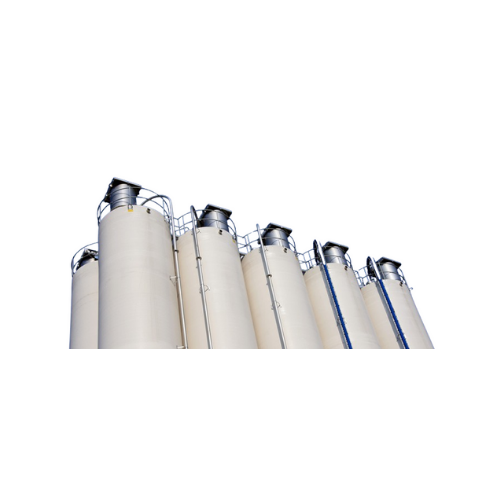
Flanged round dust collectors for industrial air filtration
Optimize your industrial processes with a dust collection sy...
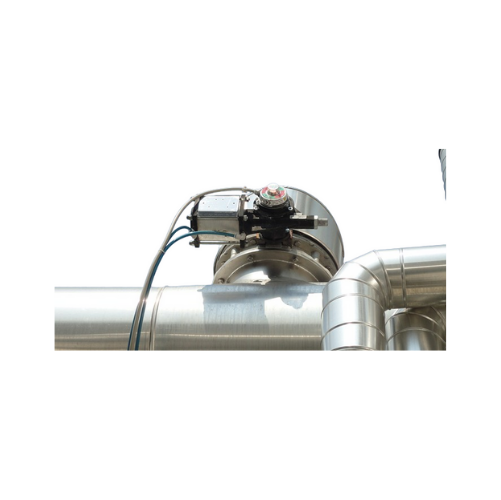
Fit-frame butterfly valves for dry bulk solids
Achieve precise control and minimize contamination in your dry bulk materia...
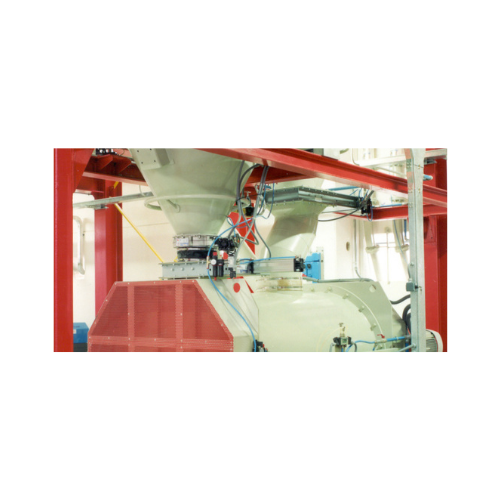
Butterfly valves for powders and granules
Ensure precise flow control and reliable sealing for gravity-fed or pneumatic sy...
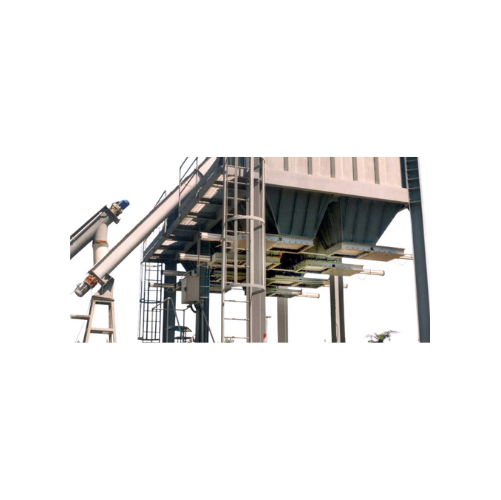
Industrial slide valve for heavy-duty applications
When managing gravity material flow in abrasive environments, achievin...
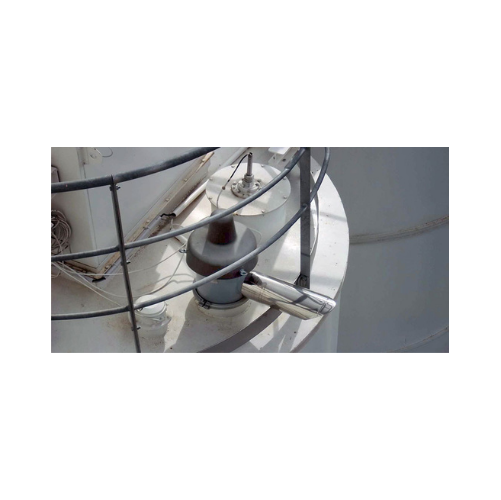
Membrane pressure relief valve for silos and bins
Ensure silo safety with our valve that instantly balances internal pres...
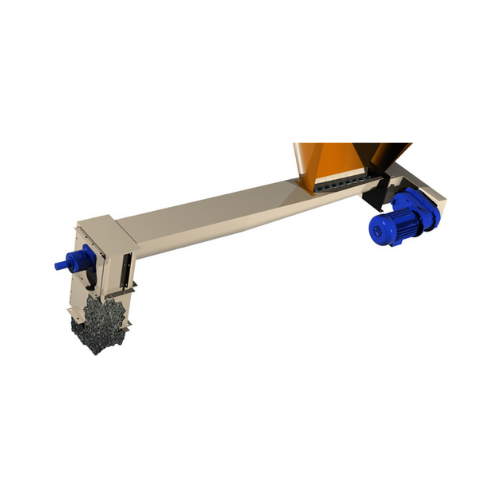
Tapered single shaft screw feeder for flour mills
Ensure consistent material flow and minimal residue with this precise s...
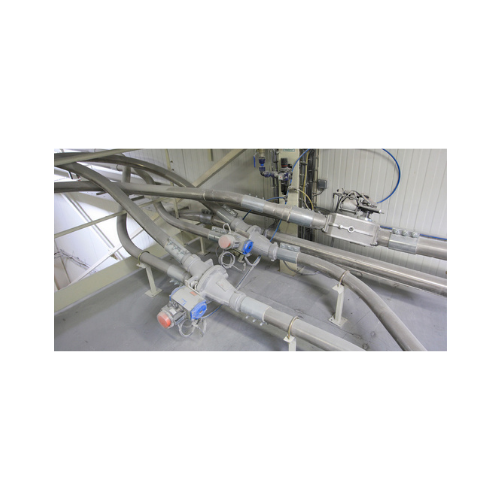
Flap diverter valves for pneumatic conveying
Streamline material flow in your pneumatic conveying system by effortlessly r...
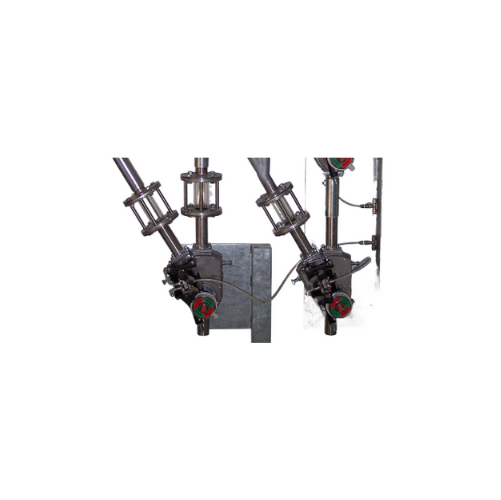
Diverter valves for pneumatic conveying lines
Experience precise flow control in pneumatic conveying with diverter valves ...
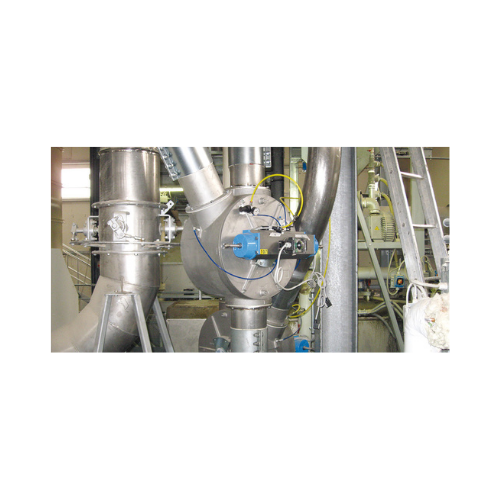
Drum-type diverter valves for pneumatic conveying
Optimize your pneumatic conveying system by effortlessly controlling th...
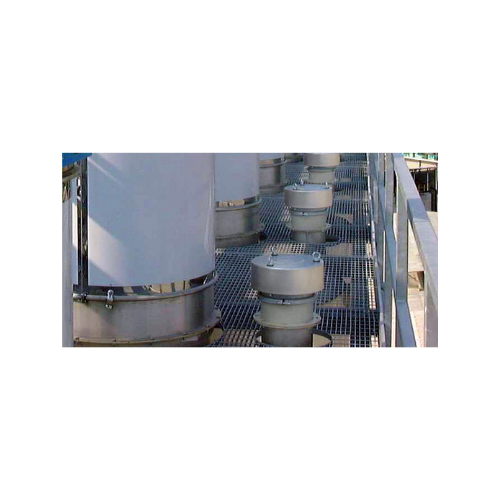
Spring-loaded pressure relief valves for silo overfill protection
Ensure safety and prevent costly overfills with press...

Single shaft screw feeders for consistent material feeding
Tackle challenging materials with poor flow characteristics b...
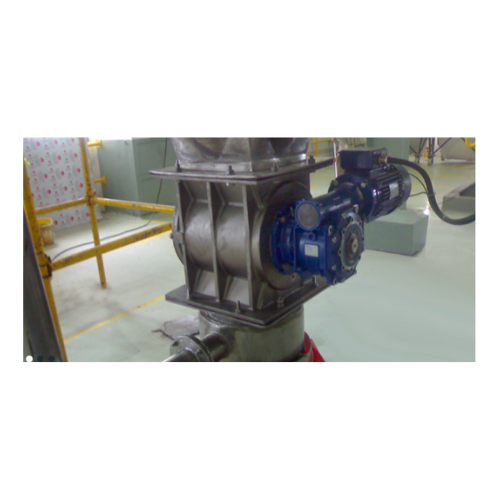
Drop-through rotary valve for powder and granular material feeding
Achieve precise control in discharging and feeding p...
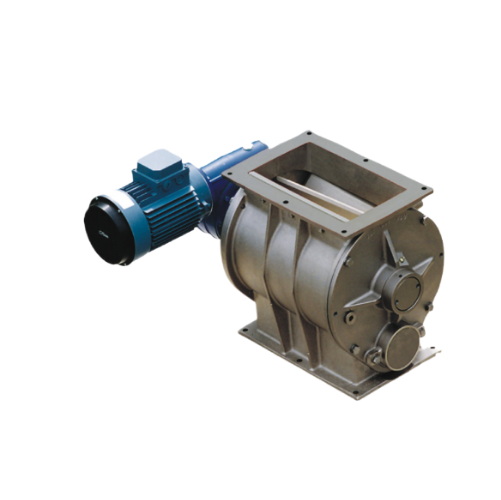
Drop-through rotary valve for precise powder and granule feeding
Ensure precise material handling with this drop-through...
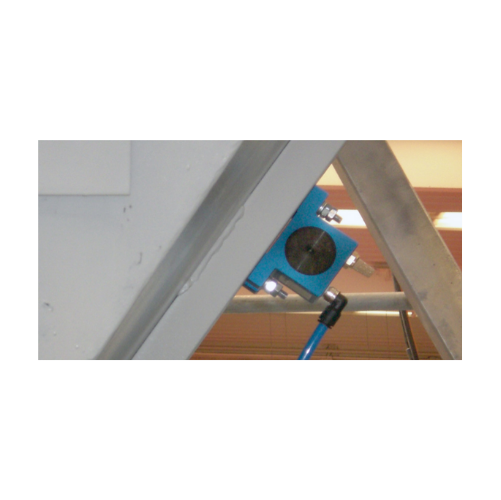
Rotary ball vibrators for fine powders and granular materials
Ideal for preventing material build-up and blockages, thes...
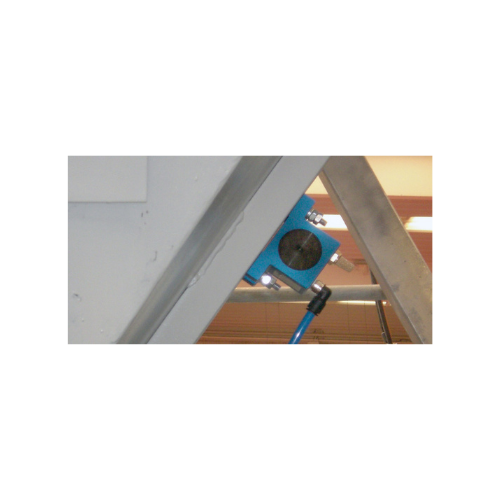
Rotary ball vibrators for aggregate reclaiming
Enhance efficiency in your production line with a solution that optimizes t...
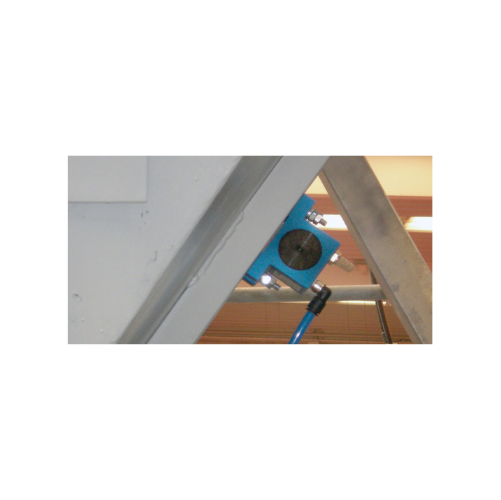
Rotary ball vibrators for bulk solids discharging
Ideal for enhancing material flow, this equipment efficiently handles f...
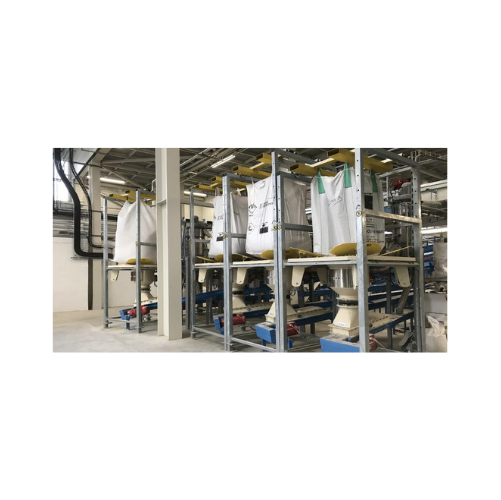
High flow rate Fibc discharger
Optimize your bulk material handling with a system designed for efficient and dust-free FIBC ...
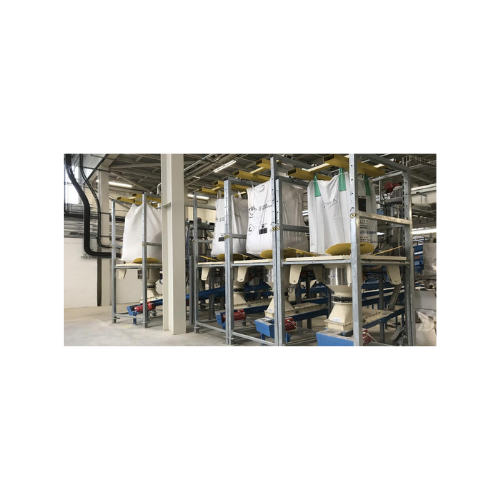
High flow rate Fibc dischargers for wastewater treatment
Optimize your material handling with efficient, dust-proof disch...
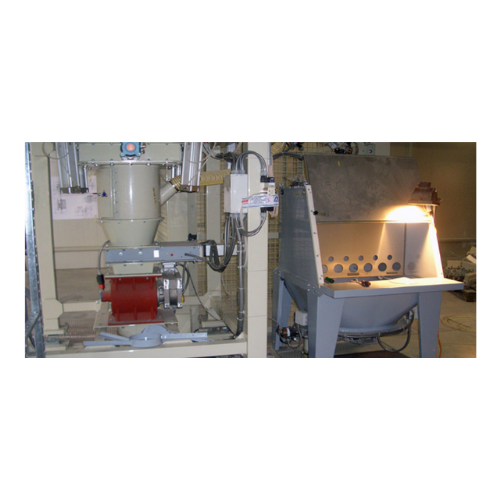
Manual bag opener for bulk solids discharging
Effortlessly open and empty bags while containing dust emissions, ensuring a...
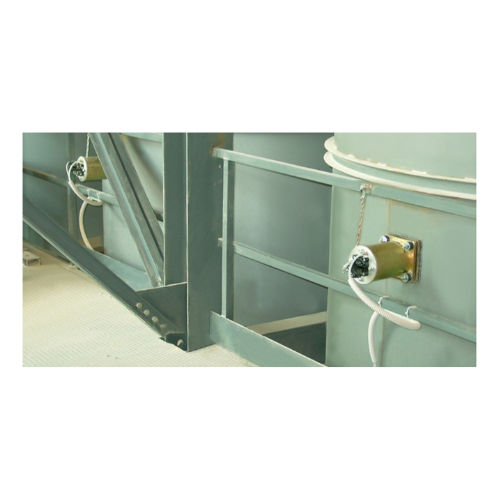
Air cannons for resolving bulk material flow issues
Solve bridging and rat-holing issues in bulk material storage with po...
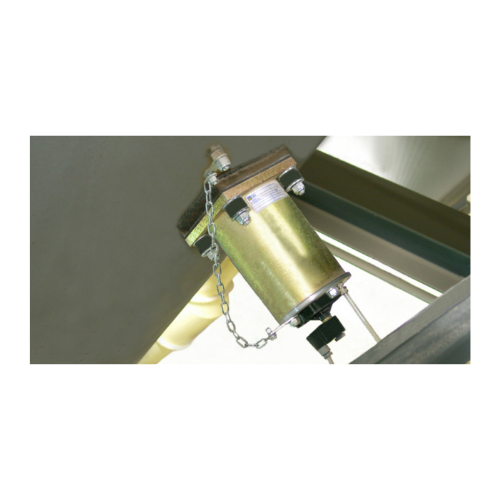
Single impact pneumatic hammers for flow aids
Combat material clogs and ensure smooth flow in your production line with pn...
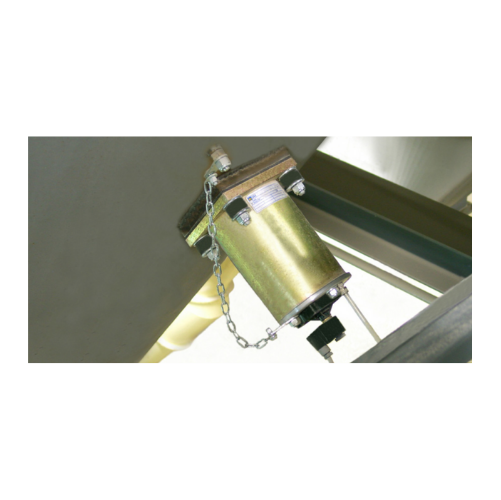
Pneumatic hammers for bulk solids discharging
Optimize your production efficiency and solve material flow challenges with ...

Pneumatic hammers for aiding material flow
Optimize material flow and eliminate blockages in your processing line with pne...
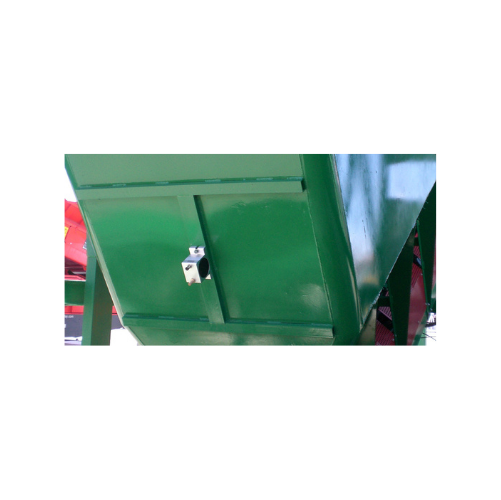
Industrial vibrator for high-frequency vibration
Achieve efficient material flow and compaction across various production ...
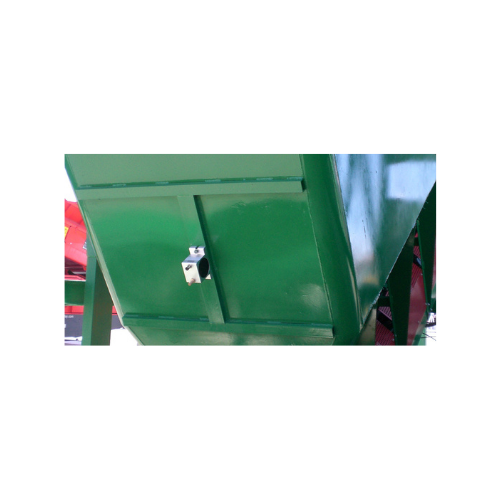
Rotary turbine vibrators for bulk solids discharging
Enhance the efficiency of material handling with high-speed, low-noi...
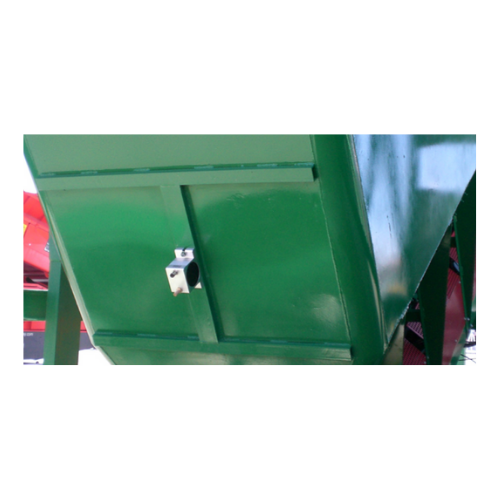
Rotary turbine vibrators for material flow aid
Optimize your production efficiency with high-speed, silent operation vibra...
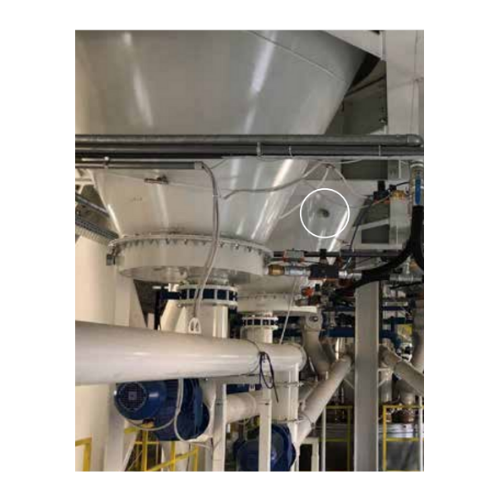
Continuous impact vibrators for bulk material removal
Combat material flow issues like bridging and rat-holing with our i...
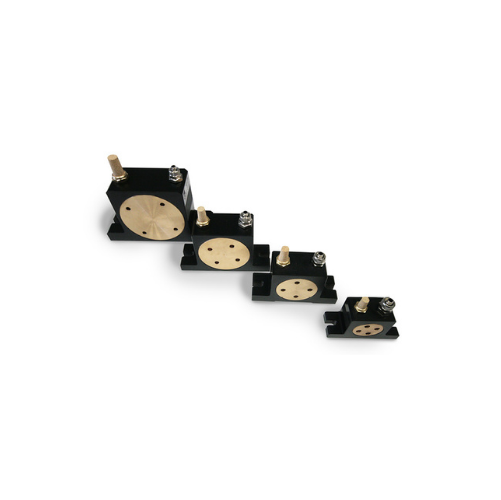
Rotary roller vibrators for concrete compacting and hopper emptying
Achieve higher compaction and efficient emptying wi...
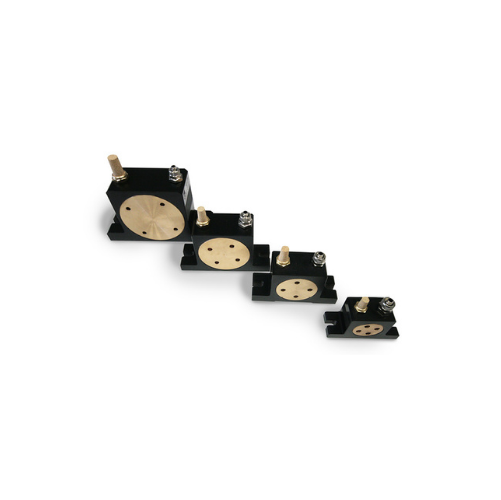
Rotary roller vibrators for material flow assistance
Enhance material flow efficiency in your production line with high-f...
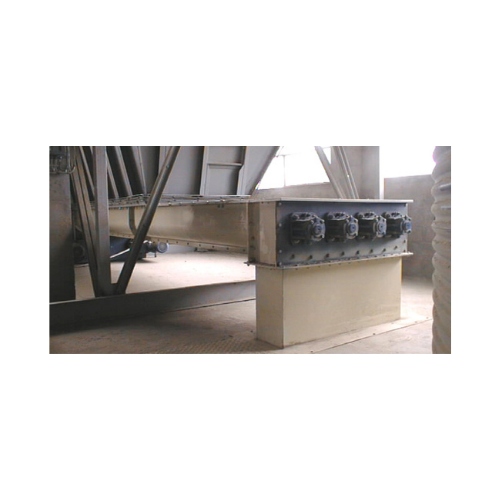
Live bin bottom for difficult material discharge
Efficiently manage the discharge of challenging materials like biological...
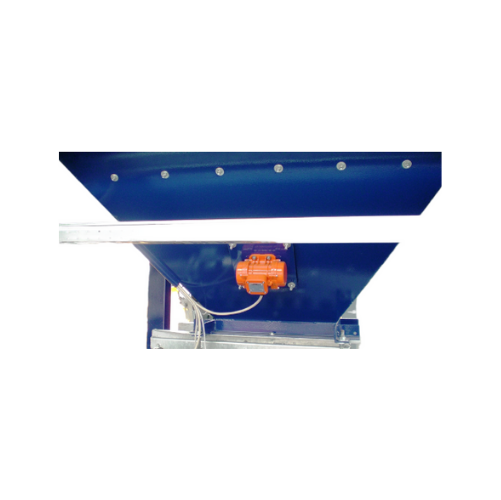
External electric motovibrators for bulk solids conveying
Enhance material flow efficiency and solve challenging dischar...
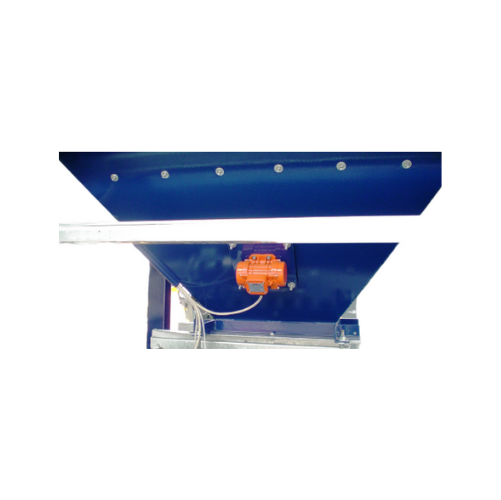
Industrial electric vibrator for bulk solids discharging
Enhance material flow efficiency and ensure consistent output ac...
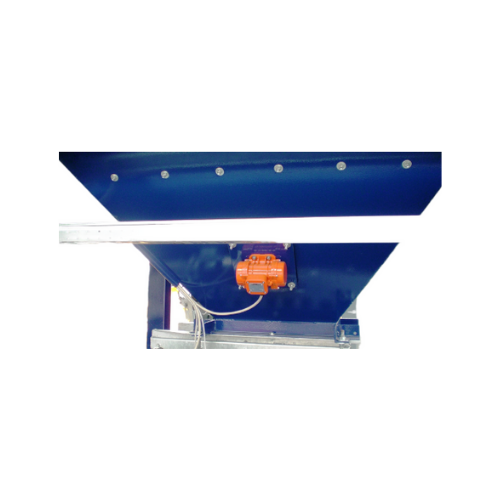
External electric motovibrators for industrial material flow
Experience enhanced material flow and precise material disc...
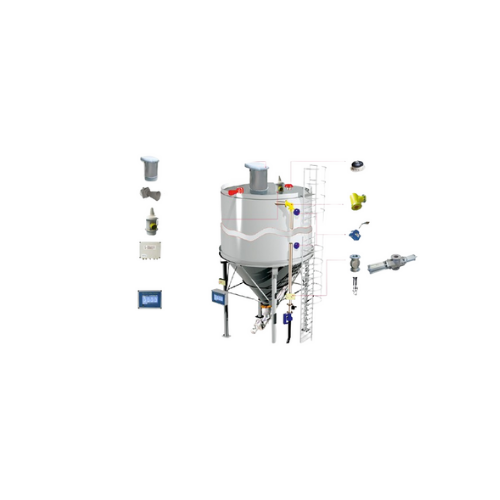
Silo overfill protection system
Prevent silo overfilling and excess pressurization with a system designed to safeguard silos...
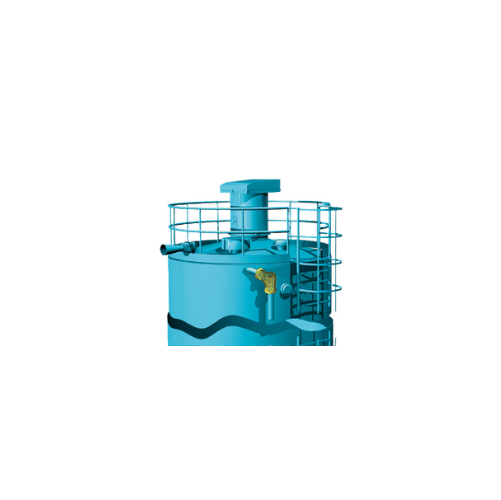
Silo overfilling safety system
Ensure safe silo filling with our system that prevents overfilling and excess pressurization,...
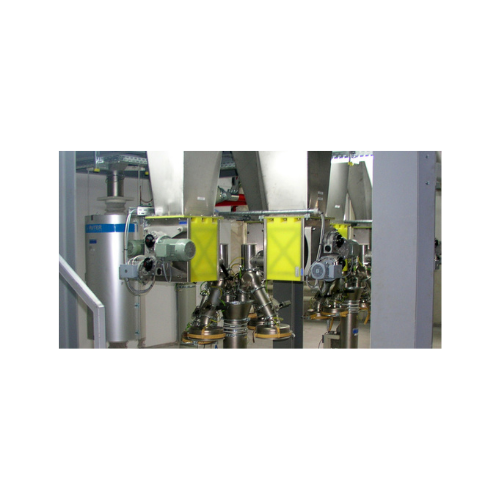
Micro-batch feeders for powder and granular material
Struggling with clog-prone powders? Gain precise control and consist...
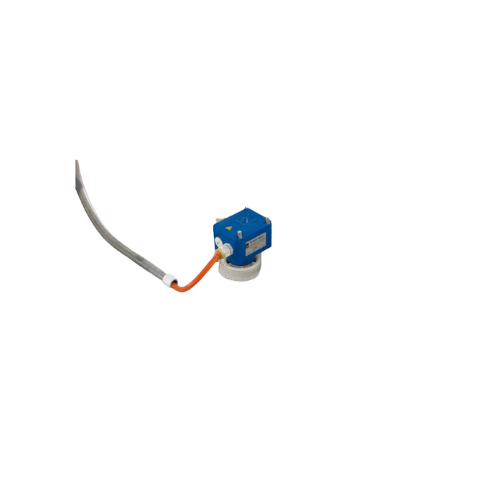
Bin level indicator for bulk solids
Ensure precise material level detection across your production processes, minimizing th...
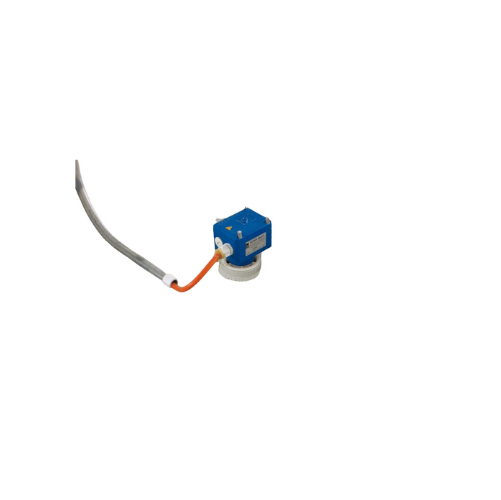
Bin level indicators for wastewater treatment
Ensure reliable material level monitoring in your silos and hoppers with ILT...
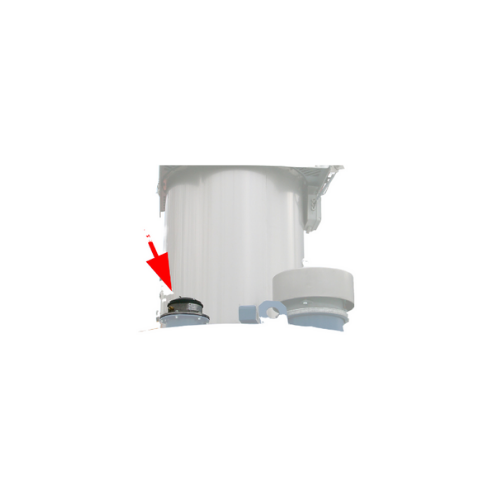
Electronic pressure meters for silo safety monitoring
Ensure precise pressure management in your systems with this advanc...
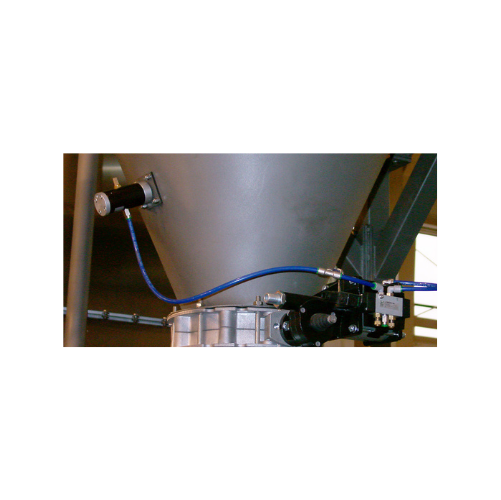
Pneumatic linear vibrators for bulk material flow
Prevent bridging and rat-holing in your production process with silent,...
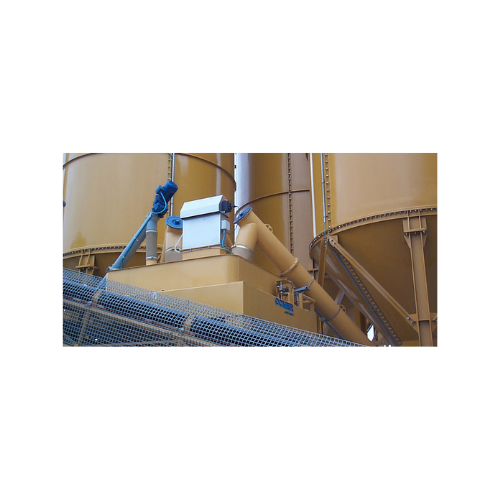
Hopper venting filter for efficient dust filtration
Achieve superior dust control and efficient material handling with a ...
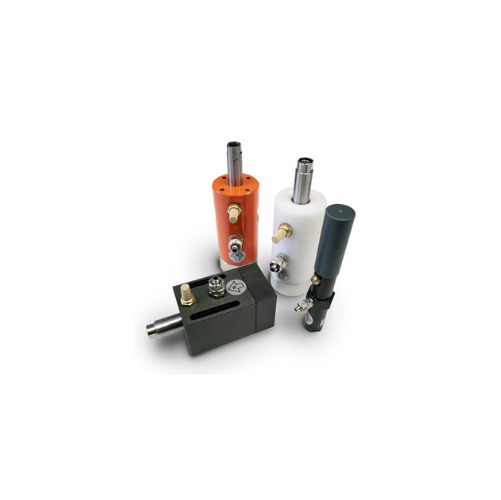
Cushioned pneumatic vibrators for coarse particle materials compaction
Enhance your material flow and compaction proces...
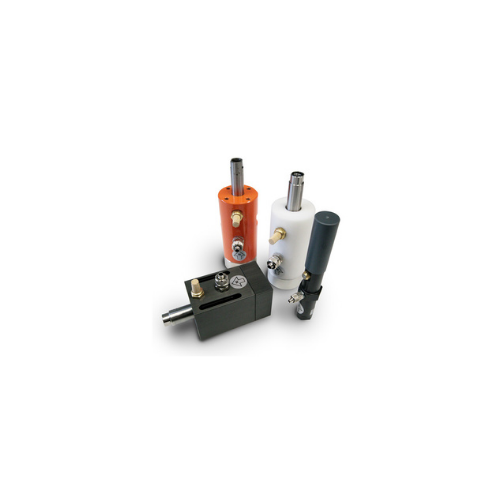
Cushioned pneumatic vibrators for bulk solids conveying
Streamline your material handling with precision vibration contro...
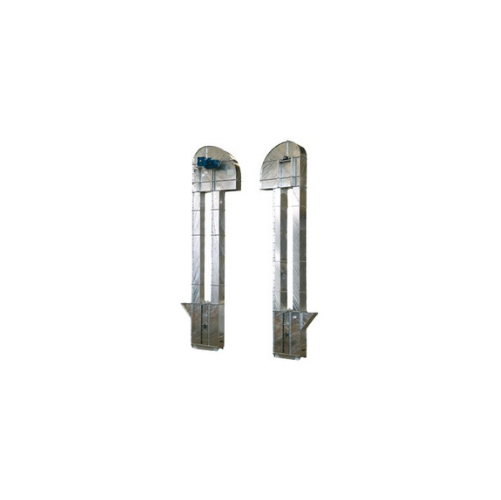
High capacity vertical conveying for flour
For consistent, high-speed handling of delicate and powdery materials, this eng...
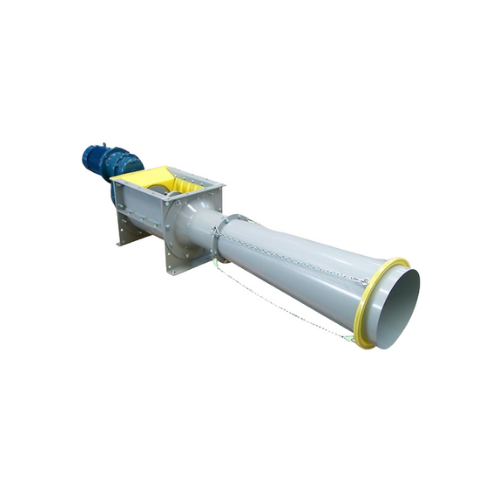
Waste bag compactor for bulk solids
Efficiently compact waste bags to a fraction of their volume, streamlining disposal whi...

Open truck loading bellows with dust collector
Achieve efficient, dust-free loading of dry bulk solids into open trucks, m...
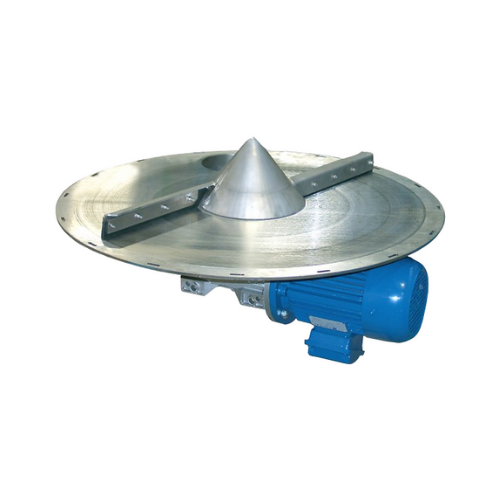
Rotary bin discharger for bulk solids
Efficiently manage bulk solids with a rotary bin discharger that minimizes residue an...
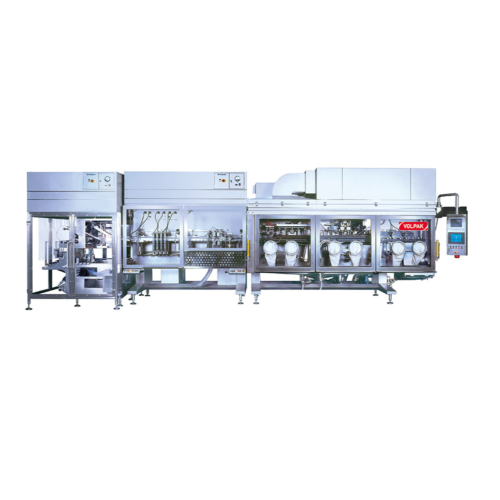
Horizontal stand-up pouching for beverages, dairy, and pet care
Optimize your liquid product packaging with rapid, high-...
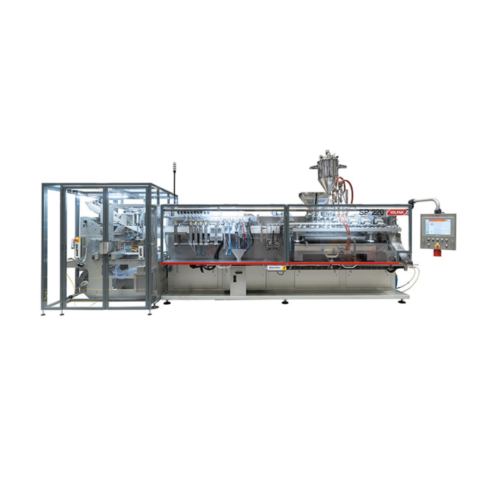
Stand-up pouch packaging for various industries
Elevate your packaging capabilities with a high-speed horizontal pouching ...
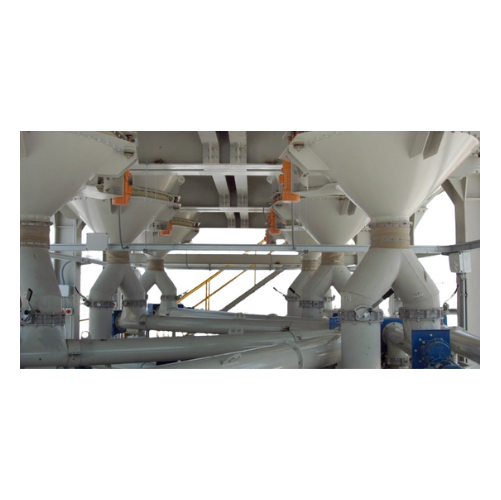
Bin activator for silo and hopper discharge
Ensure optimal material flow and prevent blockages in your storage systems wit...
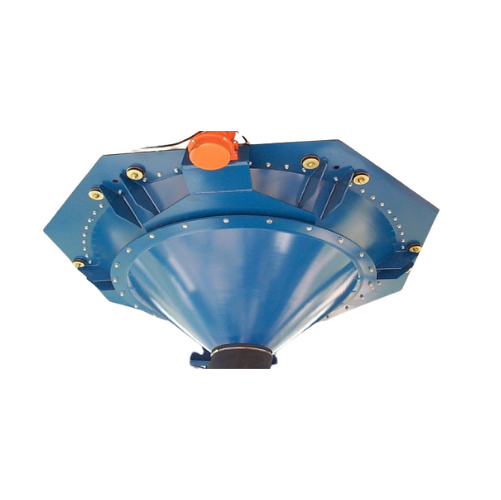
Vibratory outlet hopper for bulk solids discharge
Reduce material handling challenges with highly efficient vibration tec...
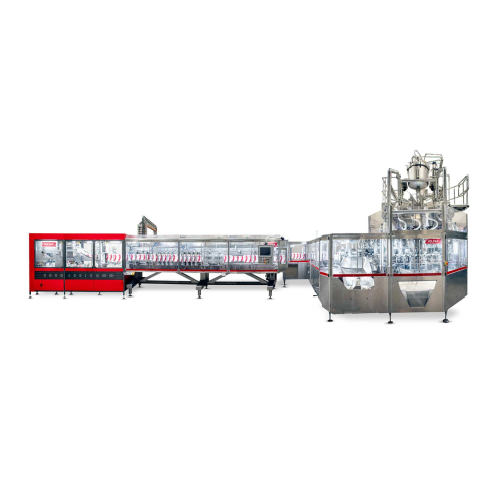
Continuous stand-up pouching solution for up to 1000ml
Maximize efficiency in high-speed production lines with precise st...
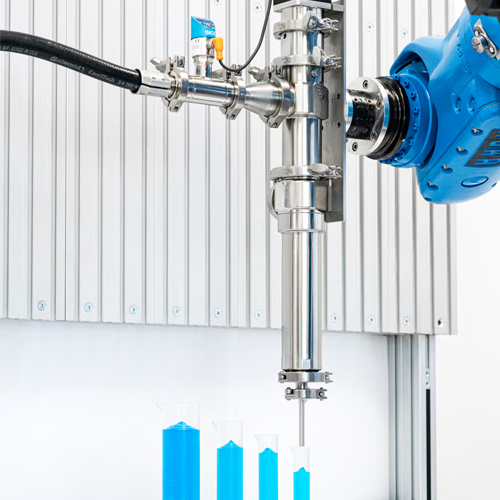
Dosing pump for liquids and pastes
Achieve precise dosing and filling of liquids and pastes with flexibility in dosing volu...

Dosing and filling pump for liquids and pastes
Achieve precise dosing and filling of liquids and pastes with compact, hygi...
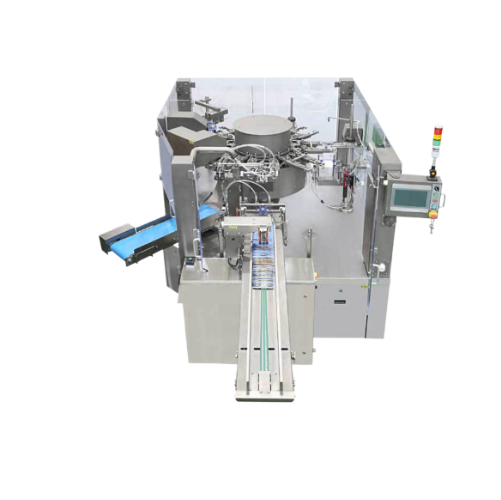
Rotary pouch packaging system for food and powder products
Streamline your packaging process with a rotary system that e...
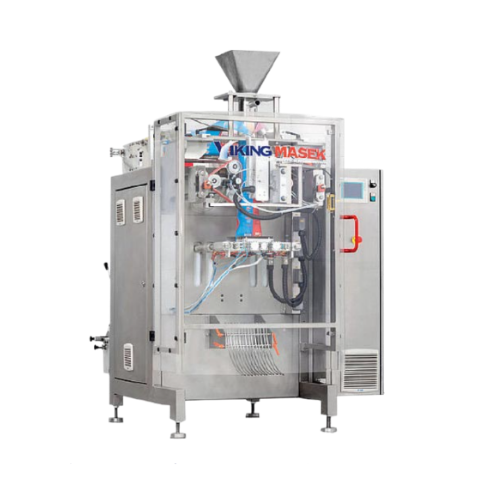
Continuous motion liquid packaging system
Achieve precise and clean liquid packaging with advanced servo-driven squeegee s...
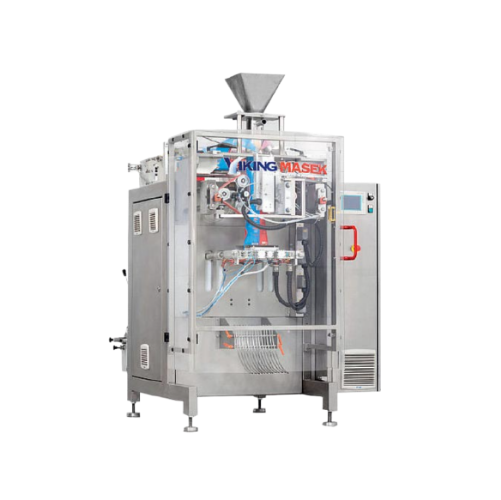
Continuous motion vertical form fill seal packaging system
Achieve high-speed, consistent packaging for diverse products...
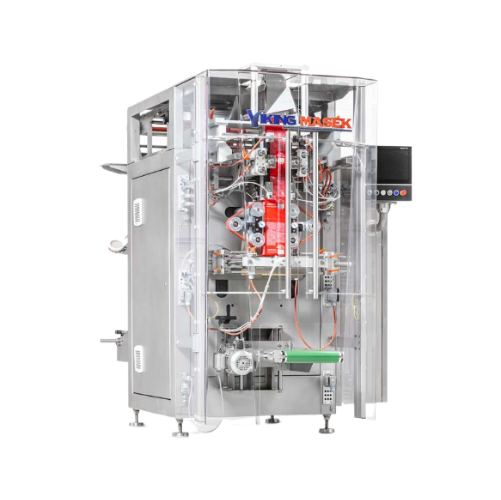
High-speed vertical form fill seal for various packaging needs
Streamline your packaging process with an advanced vertic...

Vertical form fill seal for large bag packaging
For operations requiring precise, large bag packaging, this equipment ensu...
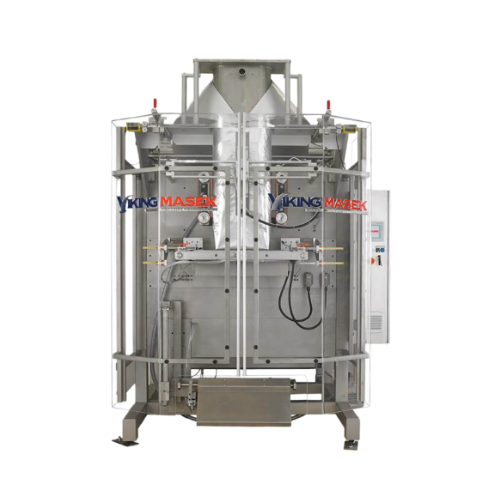
Vertical form fill seal for bulk bag packaging
Streamline your bulk bag packaging with efficiency and precision, ideal for...
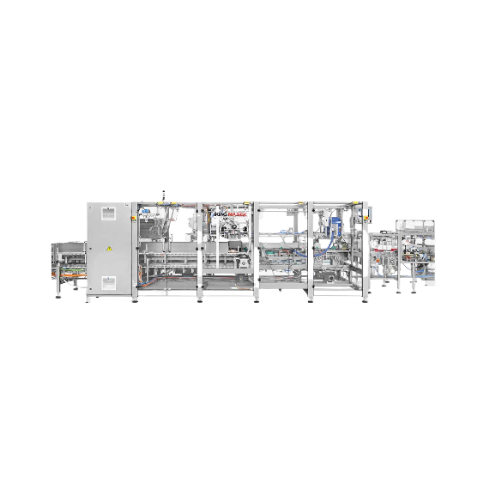
Endload automatic cartoning solution
Streamline your packaging line with this versatile cartoning solution, perfect for eff...
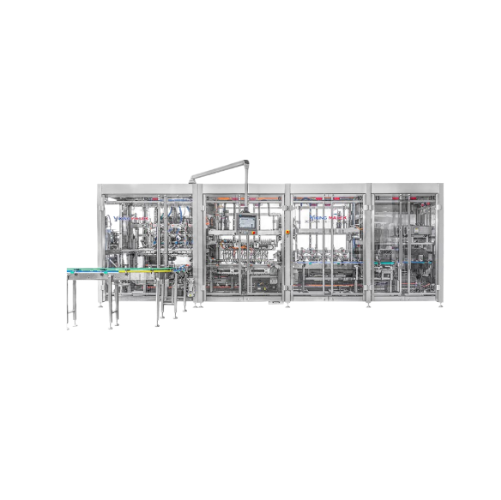
Topload cartoning system for efficient product packaging
Streamline your packaging line with this compact system that com...
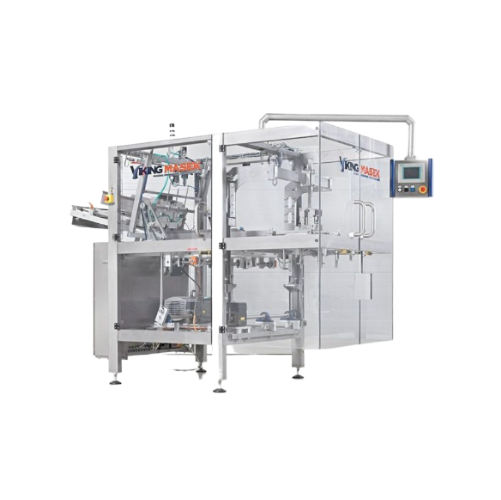
Top load cartoner for various carton shapes
Optimize your production line with a versatile cartoning solution, perfect for...
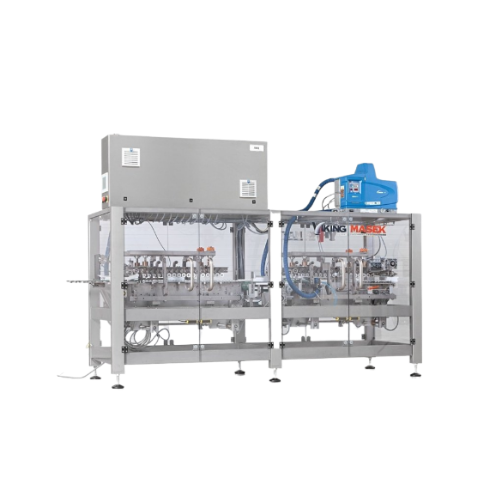
Topload cartoner for packaging cartons
Efficient flap closing for diverse carton sizes, ensuring gentle handling of sensiti...
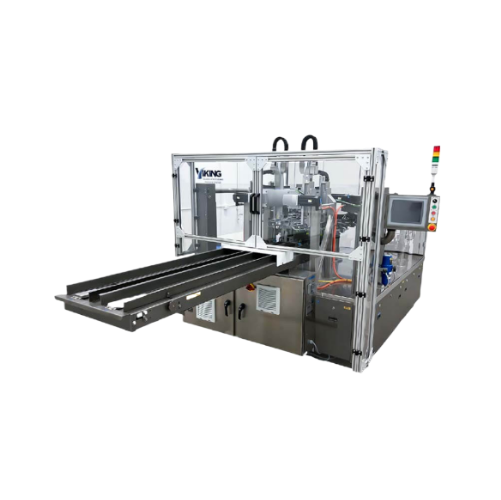
Rotary premade pouch filler and sealer
Maximize production efficiency by seamlessly filling and sealing diverse pouch sizes...
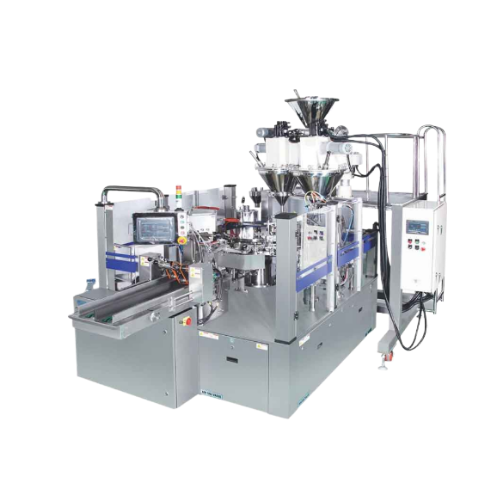
Automatic rotary filler and sealer for premade pouches
Enhance your production line efficiency with a dual-lane system th...
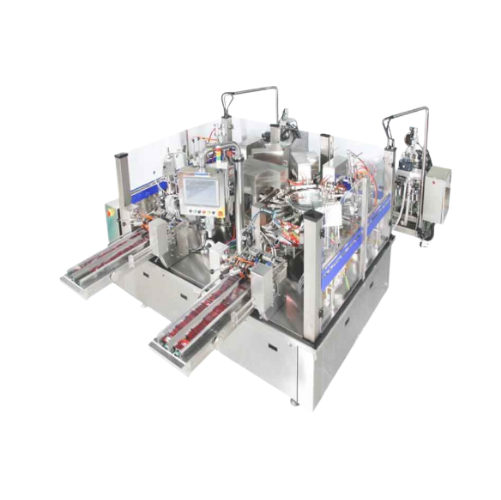
Automatic rotary premade pouch filler and sealer
Optimize your production line with high-speed pouch filling and sealing, ...
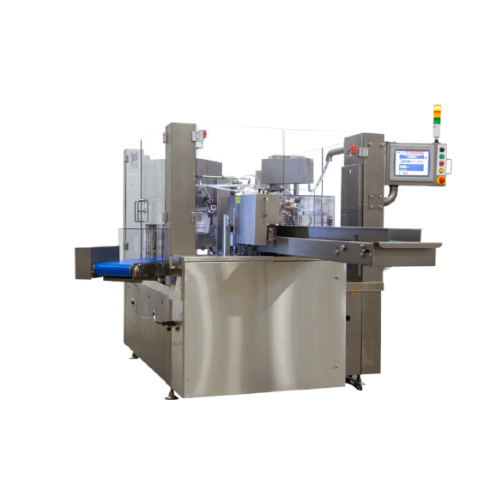
Automatic rotary premade pouch filler for various industries
Streamline your pouch packaging process with precision fill...
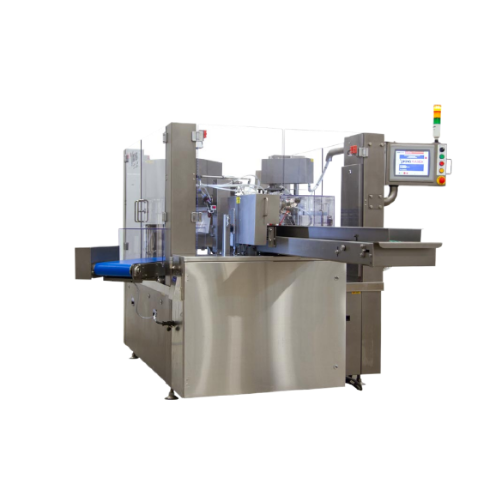
Premade pouch fill and seal solution
Effortlessly fill and seal various pouch sizes for streamlined packaging in diverse fo...
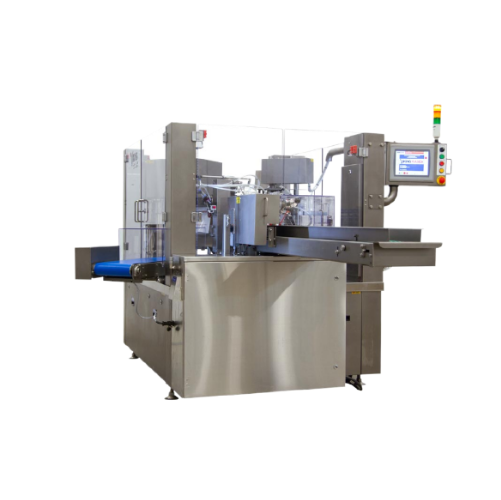
Automatic rotary premade pouch filler for food products
Enhance your packaging line with a high-speed solution designed t...
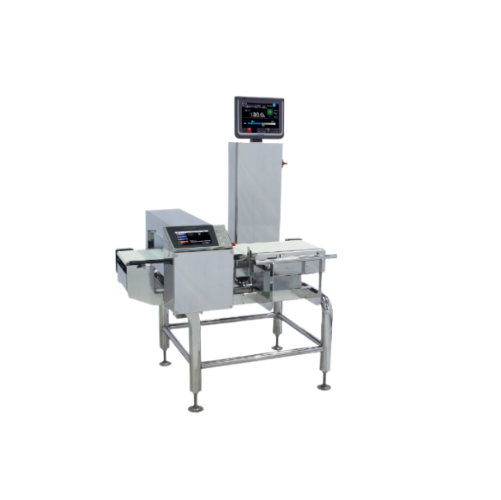
Product inspection systems for contamination control
Ensure product safety and compliance with precision inspection techn...
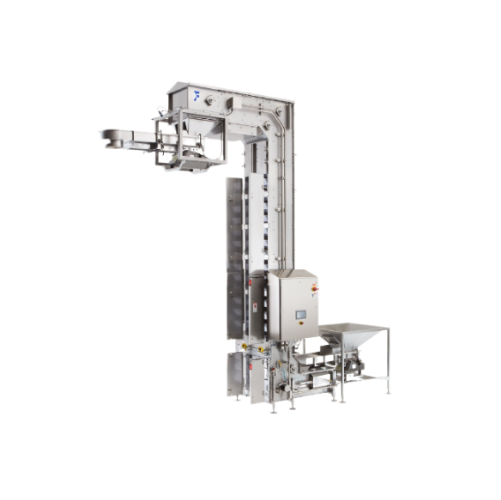
Automated infeed and outfeed systems for packaging lines
Streamline your production line by integrating reliable infeed a...
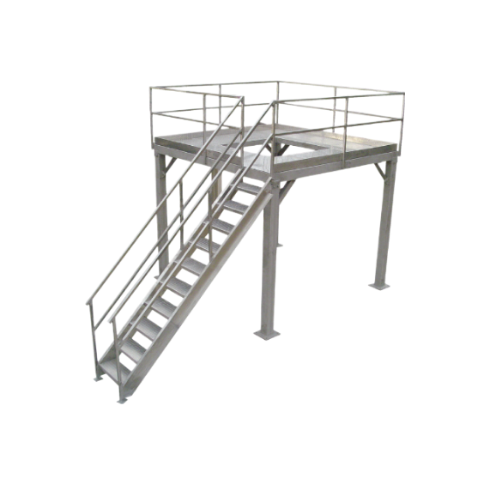
Support structures for packaging lines
Enhance safety and efficiency in your production line with robust support structures...
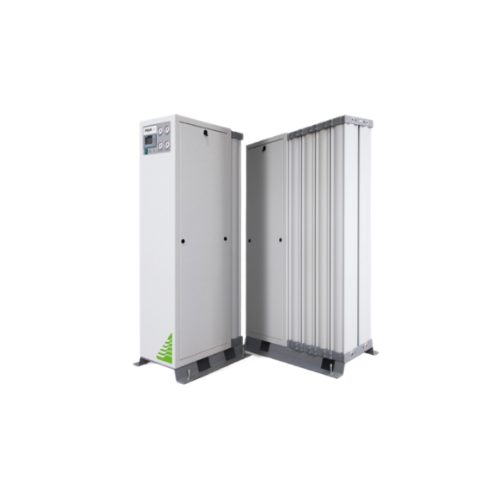
Modified atmosphere packaging solutions for perishables
Extend the freshness and shelf life of perishable goods with prec...
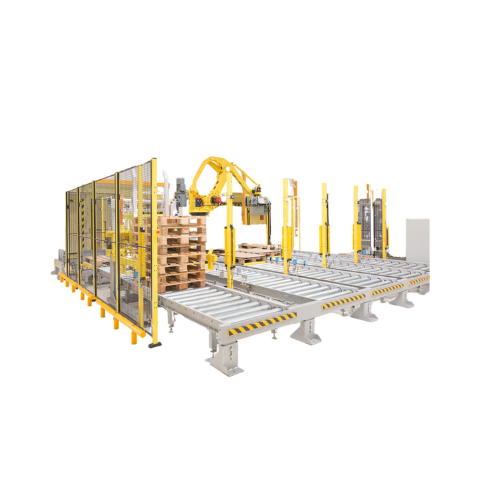
Robotic palletizing and depalletizing systems
Enhance your production efficiency by automating the repetitive and labor-in...
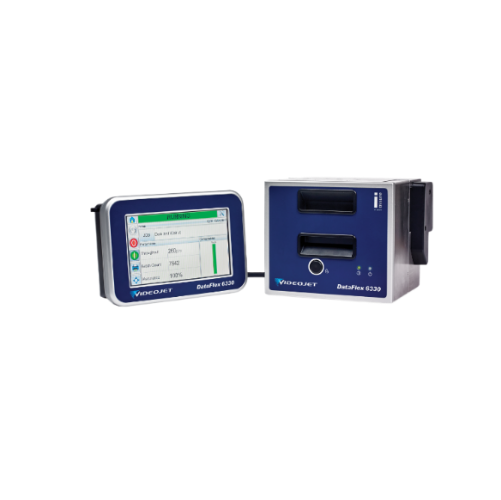
Industrial printers and labelers for packaging
Ensure precise package identification and traceability with robust printing...
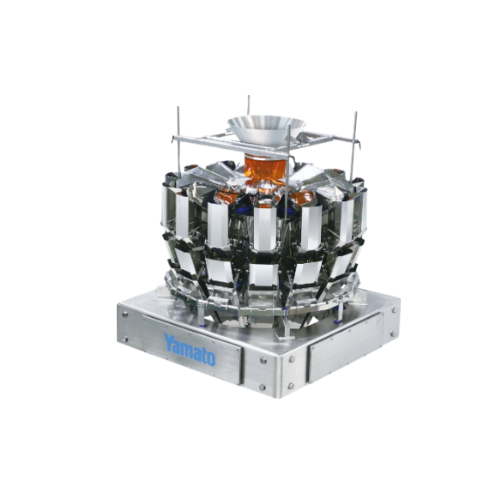
Industrial product fillers for precise packaging
Achieve consistent package weights and volumes with precision filling sol...

Robotic packaging integration for automated systems
Enhance your production line efficiency with seamless robotics integr...
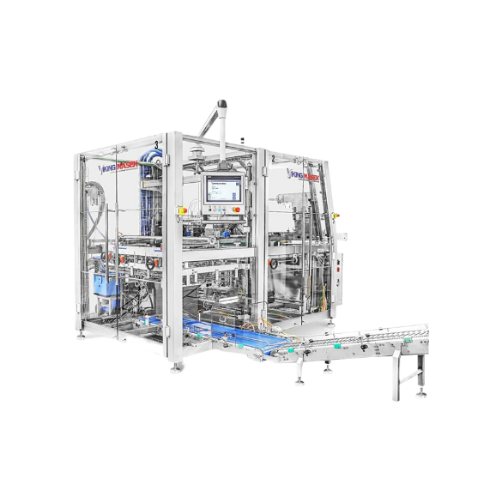
High-performance tray erector for packaging
Streamline your packaging process with a versatile tray erecting machine that ...
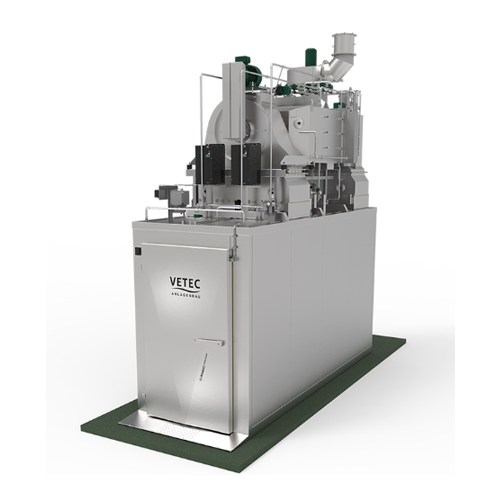
Drying and smoking solution for meat, fish, and cheese
Optimize your production with precise climate control, ensuring co...
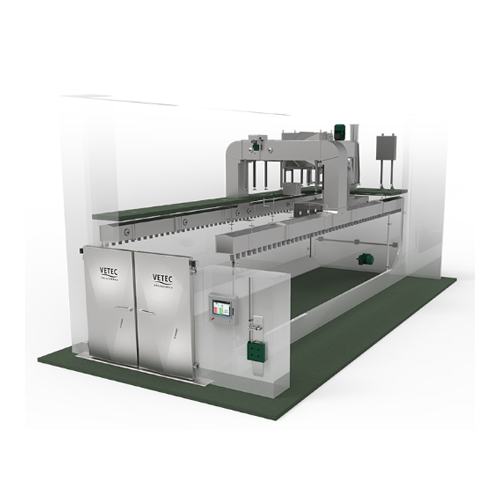
Hygienic thawing system for meat, fish, and poultry
Achieve optimal thawing with precise control of humidity and temperat...
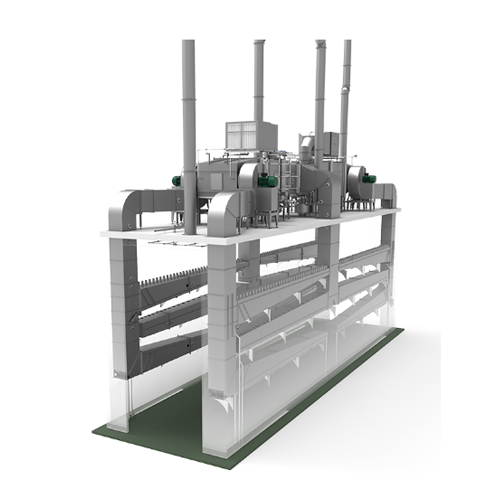
High-capacity industrial smoking and drying system
Maximize your production volume without expanding your facility footpr...
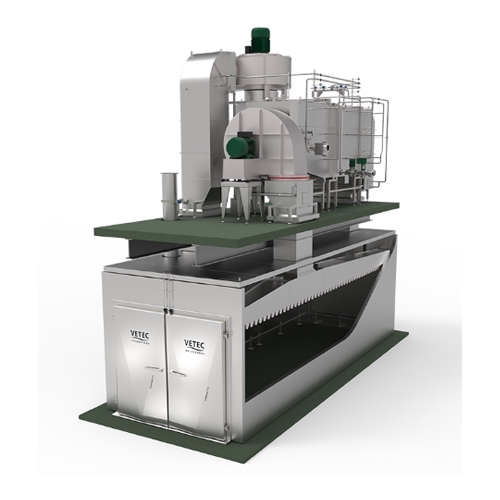
Advanced drying system for salami sticks
Achieve rapid drying and smoking of small-caliber products with up to 80% moisture...
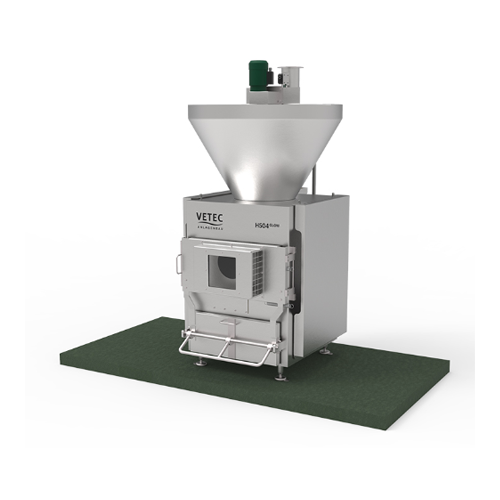
Glowing smoke generator for hot smoking installations
Enhance your production line with dense, aromatic smoke that ensure...
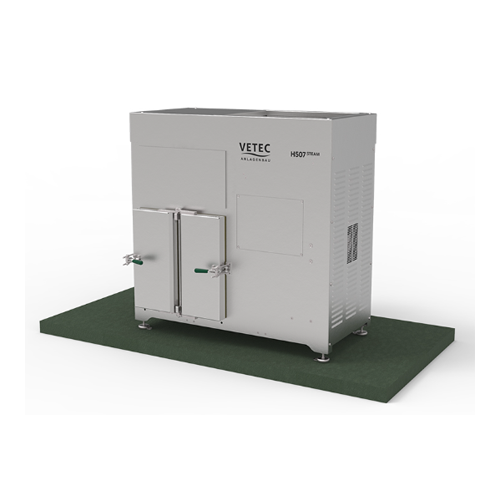
Steam smoke generator for hot smoking processes
Achieve consistent, high-quality smoked products with minimal weight loss ...

Thermal processing system for various meat products
Optimize your thermal processing with a versatile system that ensures...
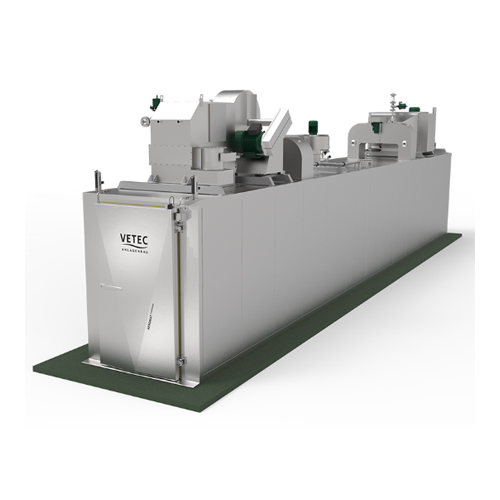
Advanced processing unit for meat and fish products
Transition seamlessly from hot to cold processing with a system that ...
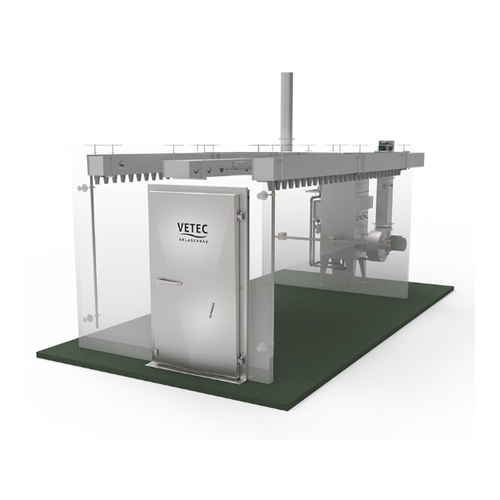
Air-conditioning curing for raw sausage production
Enhance your meat processing line with precise climate management for ...
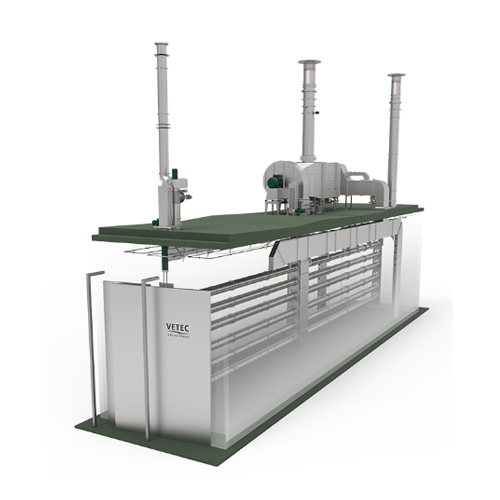
Cross-flow smoking and fermentation system for raw sausage
Enhance yield and ensure consistent quality in sausage and fi...
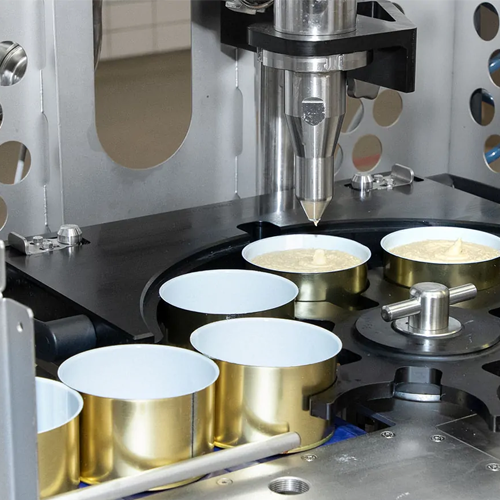
Container filling system for pasty and chunky products
Achieve precise, drip-free filling of diverse pasty and chunky pro...
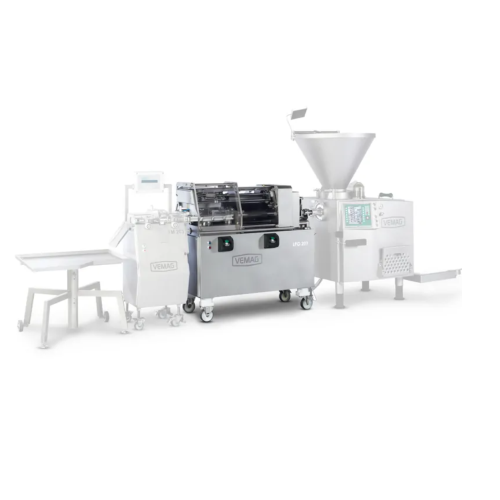
Sausage linking and portioning solution
Optimize your sausage production with precise linking, hanging, and cutting technol...
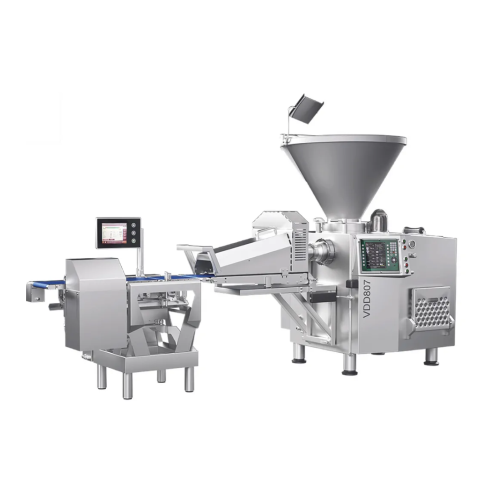
Dough portioner for baked goods applications
Achieve precise and gentle portioning with advanced dough portioning technolo...
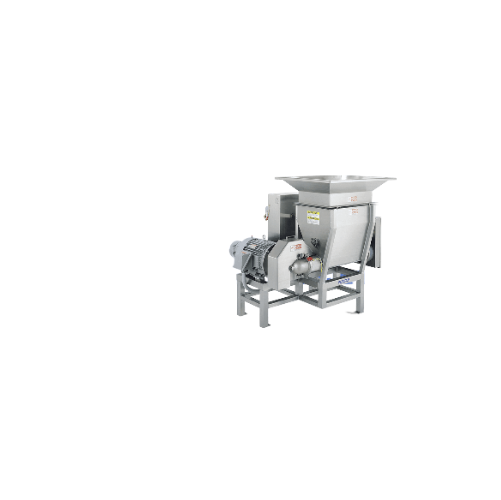
Industrial milling systems for food processing
Streamline your food production line with robust milling and cutting soluti...
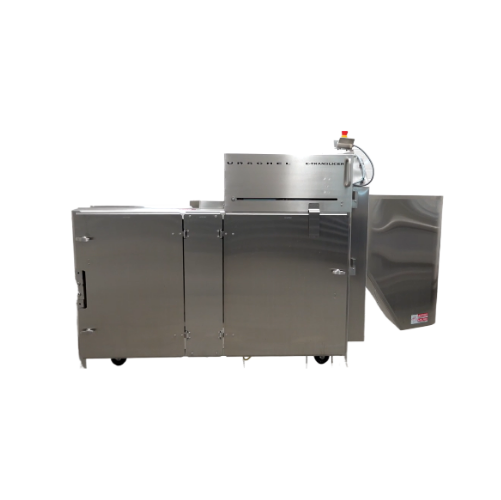
Slicer for food processing applications
Efficiently achieve precise cuts and textures for a variety of food products, enhan...
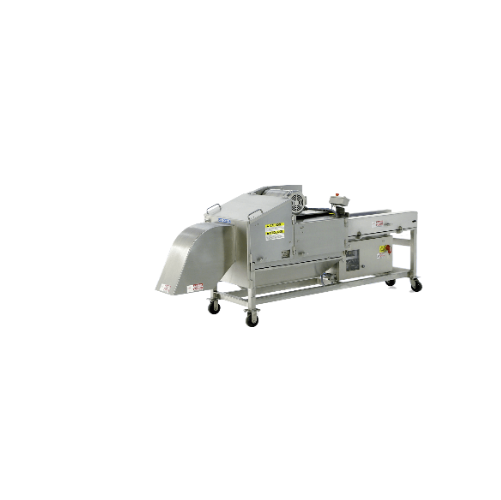
Industrial dicer for meat and bakery products
Streamline the dicing of meat, bakery items, and snacks with a versatile sol...
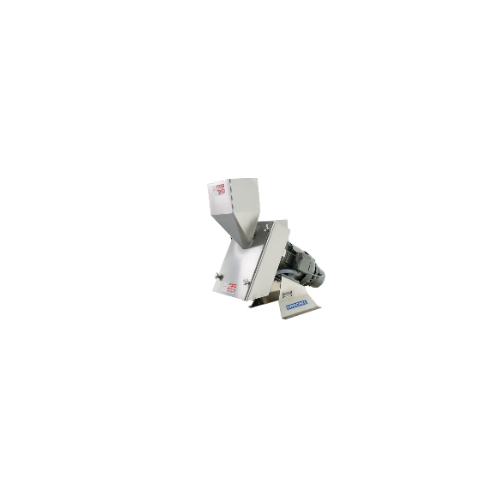
Industrial food processor for diverse applications
Optimize your production line with a versatile processor capable of ch...
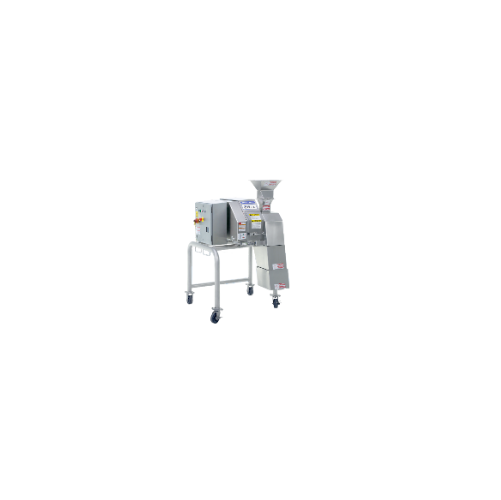
High-capacity industrial dicer for vegetables and fruits
Streamline your food processing line with a high-capacity soluti...
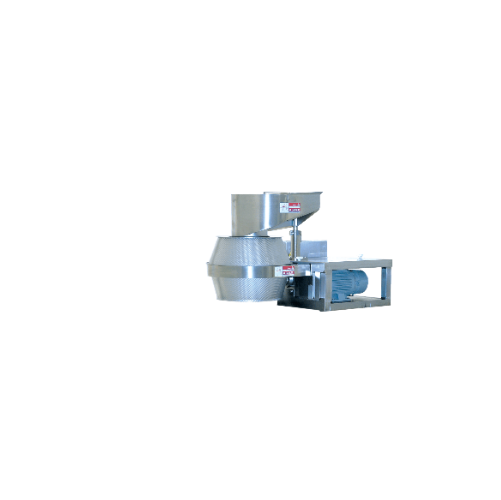
Industrial slicer for precise food cuts
Maximize your food processing efficiency with an industrial slicer that offers unpa...
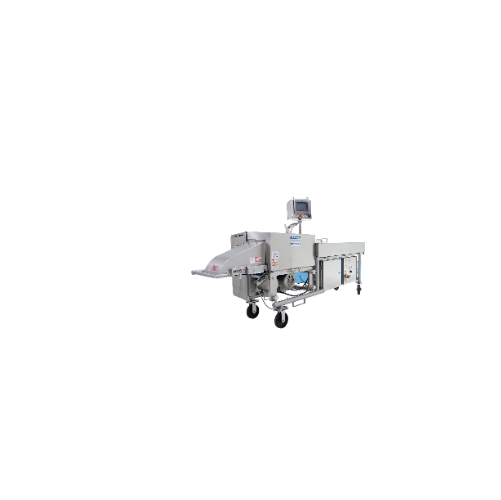
Industrial dicing solution for food products
Enhance processing efficiency with high-speed dicing and slicing solutions, e...
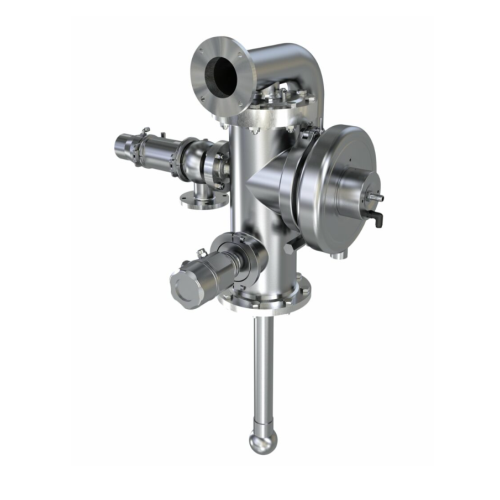
Vessel dome fittings for tank protection
Ensure seamless production by preventing tank damage due to overpressure or vacuum...

Automated sandwich production line
Optimize your sandwich production with high-speed automation that effortlessly handles d...
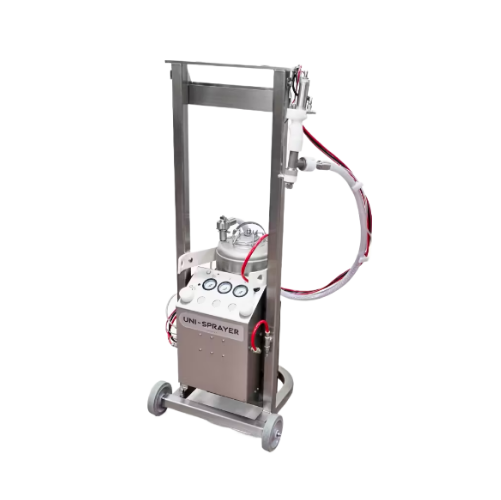
Food spraying solution for various products
Streamline your food processing with a versatile sprayer that handles everythi...
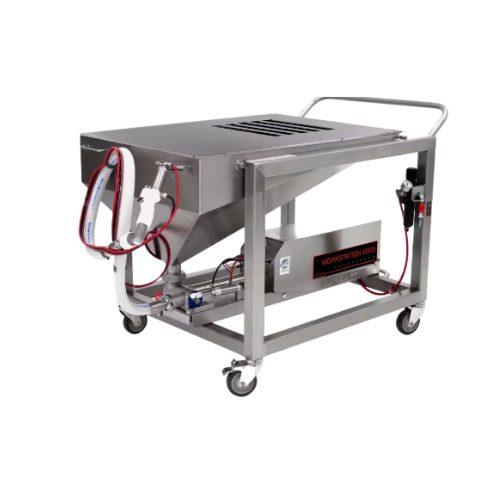
Industrial food depositor for large volume applications
Efficiently handle diverse food textures with precise portion con...
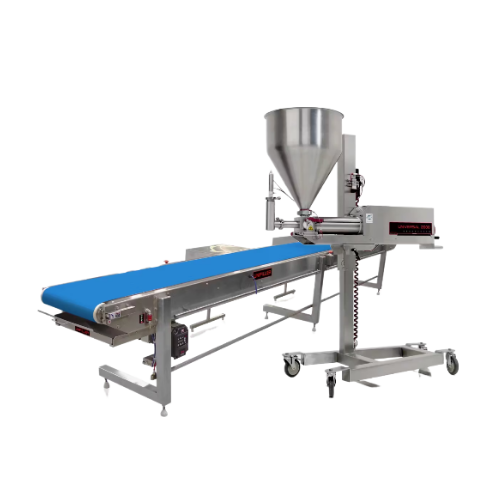
Industrial food portioning system
Optimize your production flow with precision portioning equipment designed to handle a di...
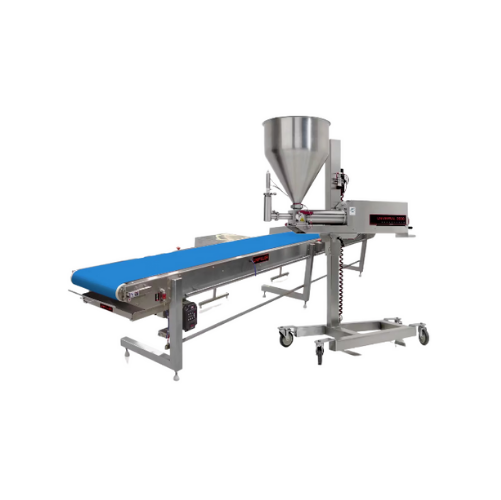
Industrial food filling and depositing equipment
Optimize your production line with precise, gentle depositing and filling...
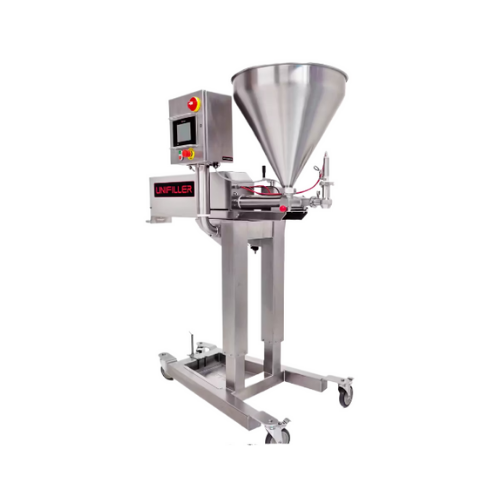
Industrial servo-based depositor for cake production
Effortlessly manage diverse depositing tasks across high-speed baker...
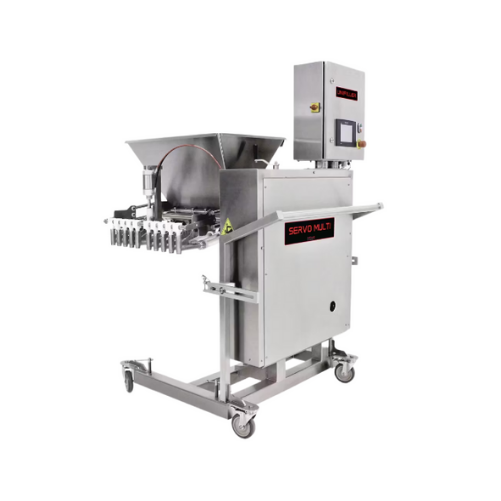
Servo multi piston depositor for bakery production
Streamline your bakery production with precise portion control and hig...
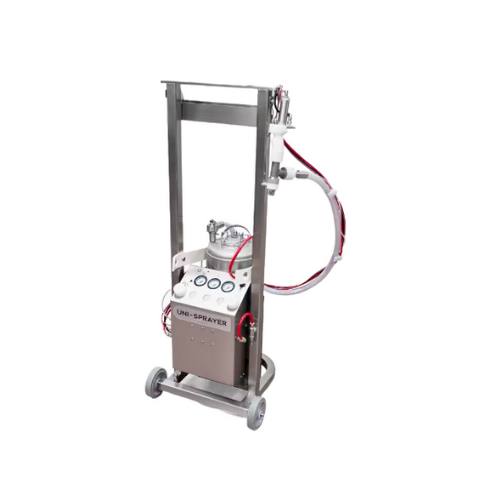
Industrial food spraying and flocking system
Reduce waste from single-use canisters in food production while achieving pre...
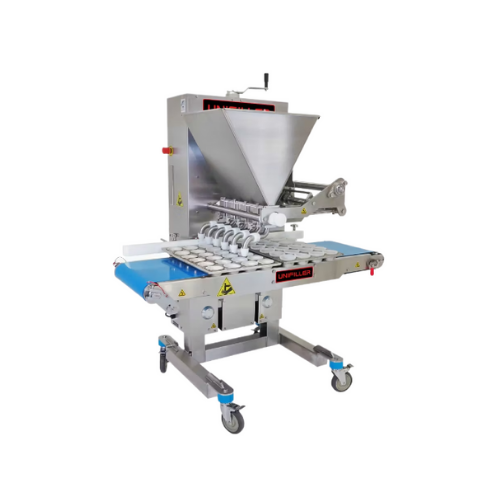
Servo driven multi-piston depositor for batters and fillings
Ensure precise portion control and maintain product integri...
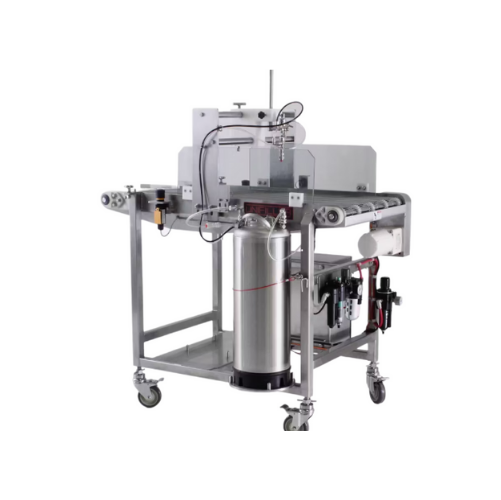
Automated syrup sprayer for bakery products
Achieve uniform coating and infusion with precision spraying systems designed ...
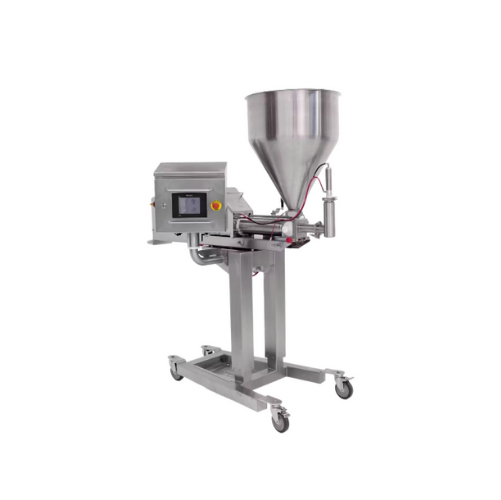
Industrial depositors for flowable food products
Enhance your production line’s efficiency with precision depositing...
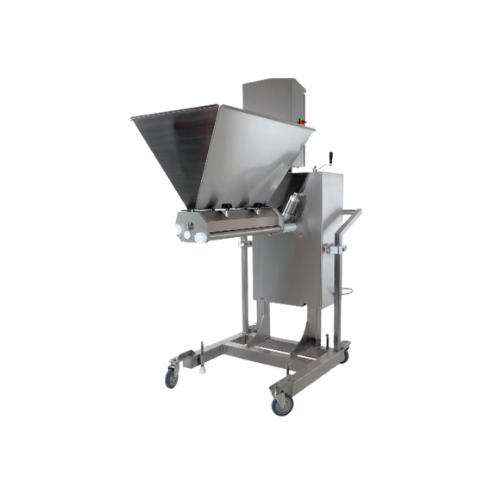
Pneumatic Rp depositor for bakery and food plants
Optimize your production line with a high-speed depositor designed to d...
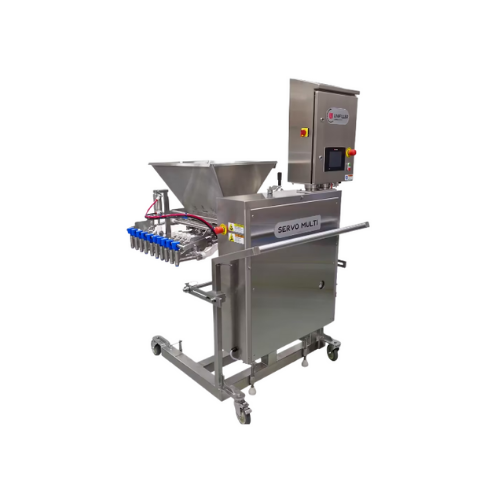
Servo multi depositor for food portioning
Achieve precise portion control and high-speed depositing with versatility acros...
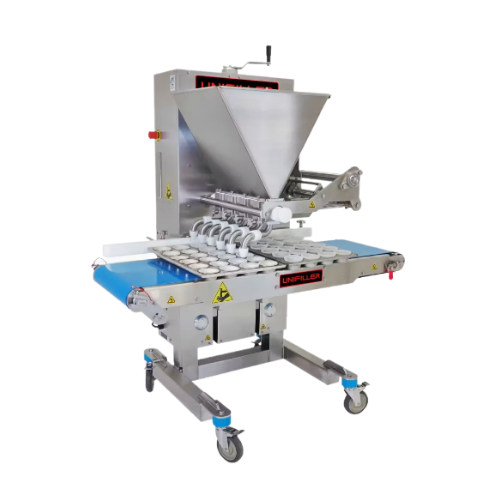
Servo driven multi-piston depositor
Experience precise control and high-speed depositing with the latest servo-driven techn...
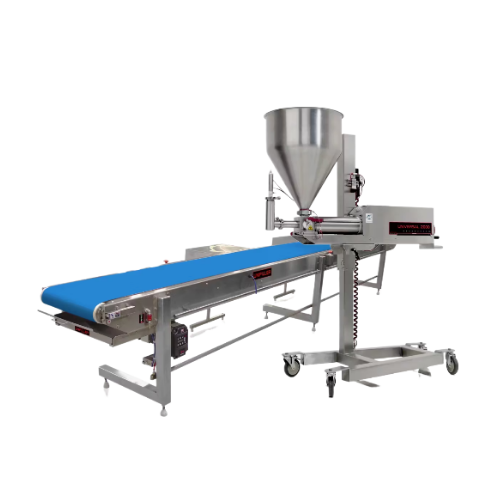
Single piston food depositor for temperature-sensitive environments
Optimize your production with a versatile depositor...
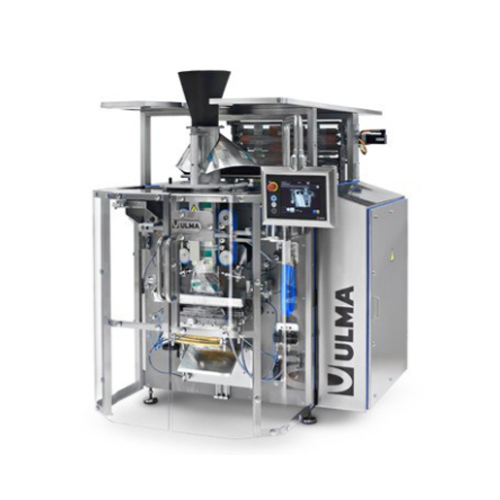
Vertical packaging system for medium-high speed applications
Optimize your packaging line with a system that delivers pr...
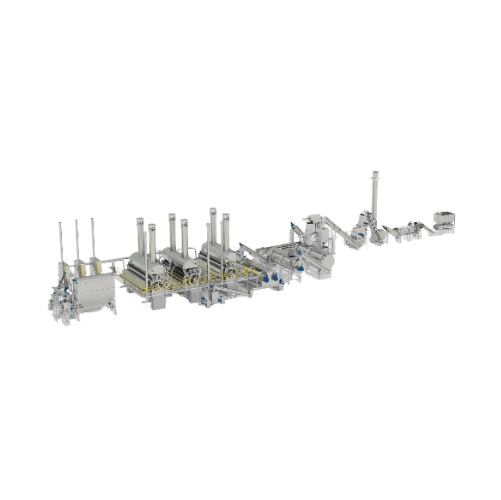
Turnkey potato flake processing line
Effortlessly transform raw potatoes into high-quality flakes with this integrated line...

Cabinet Food dehydrator
Achieve precise drying control with dual fan technology, ensuring even airflow and optimal nutrient p...
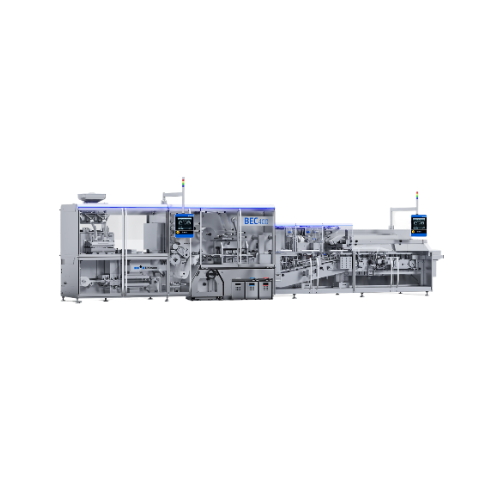
Fully automated packaging lines
Streamline your production with versatile packaging lines designed to handle a range of good...
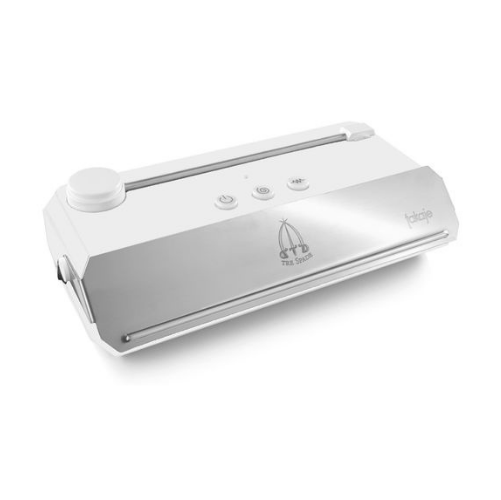
Vacuum sealing system for glass jars with metal lids
Efficiently vacuum seal glass jars with metal lids to transform pres...
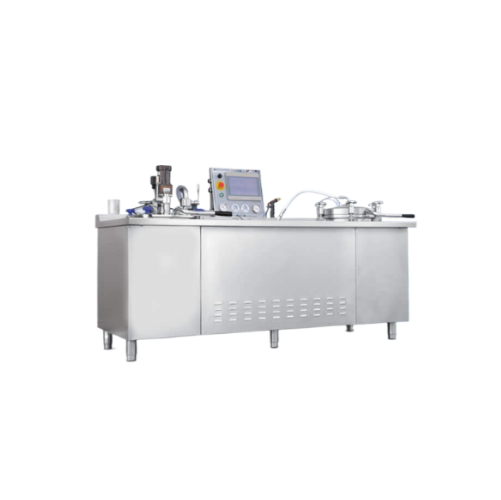
Low temperature food dehydration system for fruit and vegetables
Optimize your food processing with advanced low-tempera...
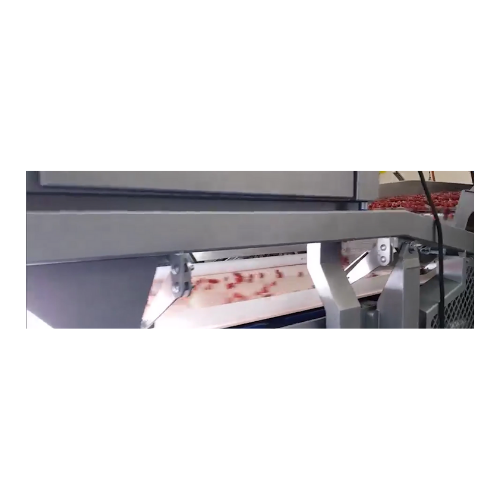
Belt sorter for potatoes and leafy vegetables
Enhance the precision and efficiency of your sorting process with a system d...
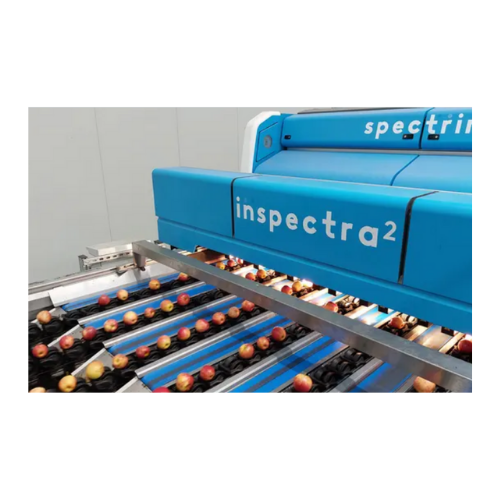
Advanced fruit sorting platform
Optimize your operations with a cutting-edge sorting solution designed to enhance product in...
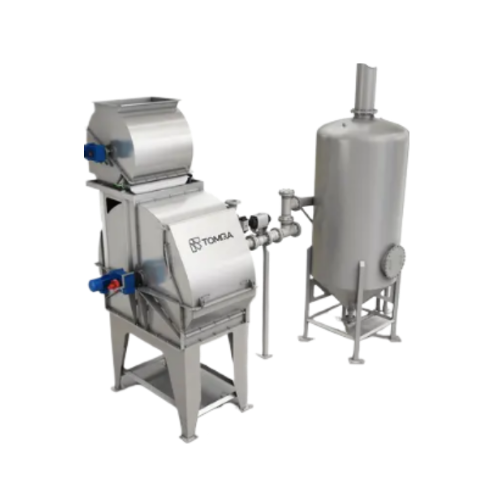
Steam peeler for vegetables and fruits
Optimize your food processing with a versatile steam peeling solution that efficient...
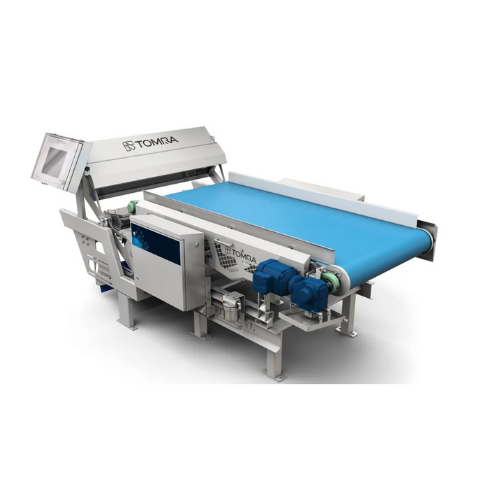
Advanced food sorter for tomatoes and peaches
Achieve precise sorting and defect removal for a variety of food products, e...
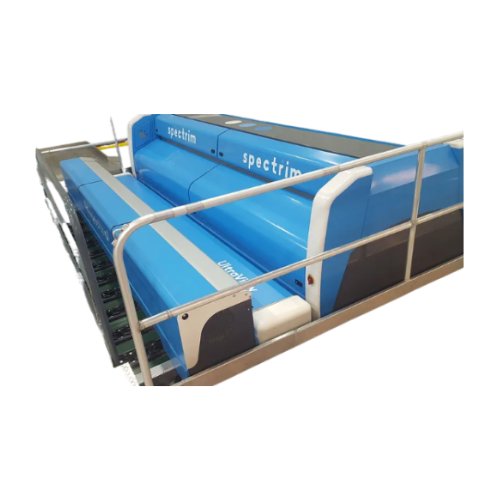
Single and dual lane sorters for fresh produce
Optimize your food processing line with precision defect detection and vers...
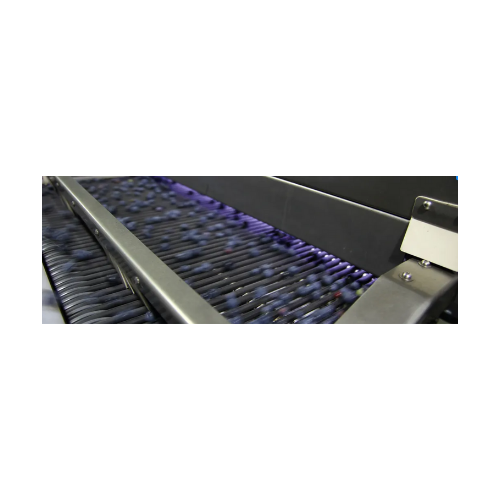
Color sorter for small fruits
Optimize your production line with a high-speed color sorting solution that enhances quality c...

Industrial steam peeler for potatoes
Optimize peeling efficiency while minimizing waste and energy usage with this high-spe...
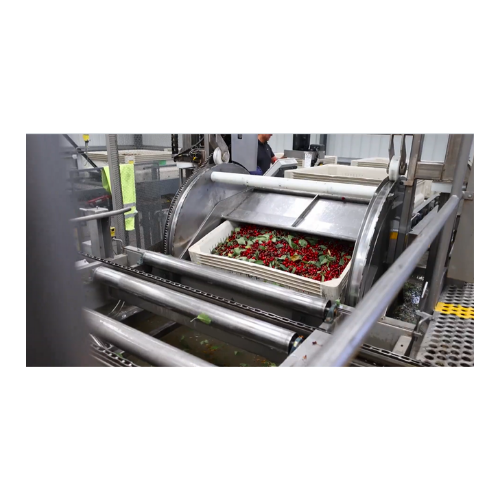
Cherry sorting system with deep learning technology
Boost your fruit processing efficiency by utilizing advanced deep lea...
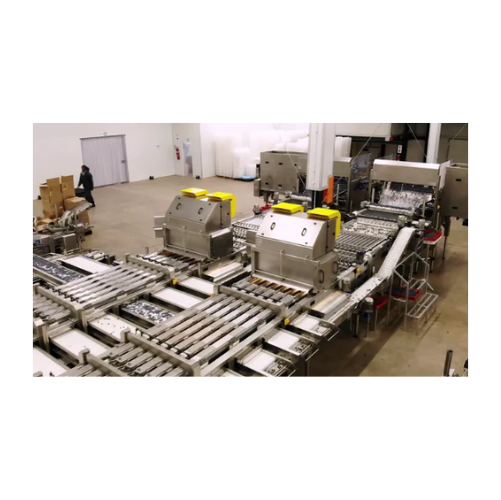
Blueberry sorting and grading system
Enhance your fruit processing line with a cutting-edge system designed for precision s...
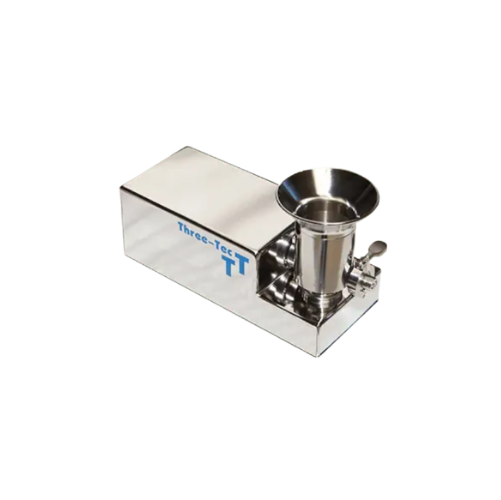
High-precision feeding system with load cell and weighing electronics
Achieve unparalleled accuracy in dispensing powde...
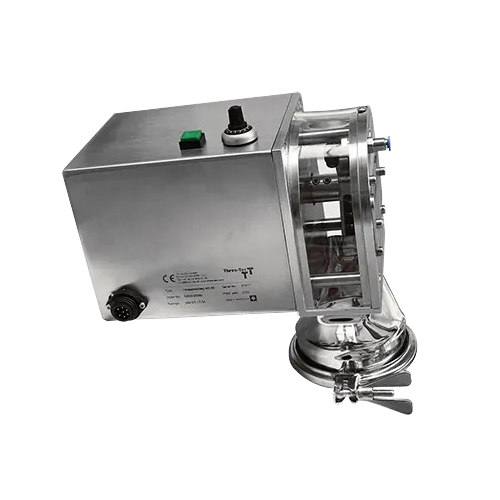
Hot cutter for processing extrudate into pellets
Efficiently transform extrudates into precise pellet sizes, enhancing you...
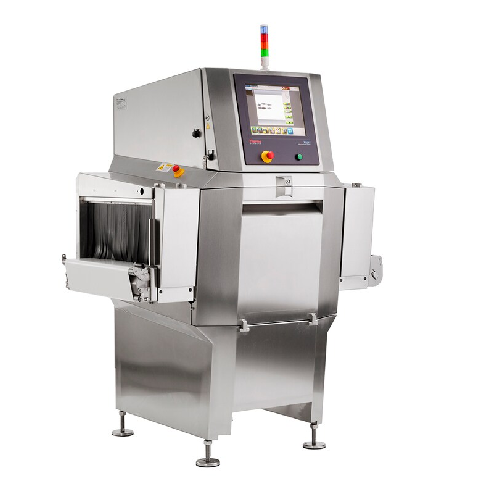
Conveyor x-ray inspection for large food packaging
Ensure the safety and quality of your packaged food products by detect...
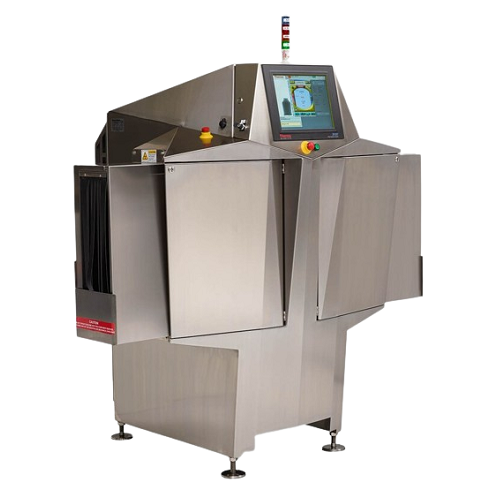
X-ray inspection for tall packages in cans and bottles
Ensure your production line detects foreign objects in tall packag...
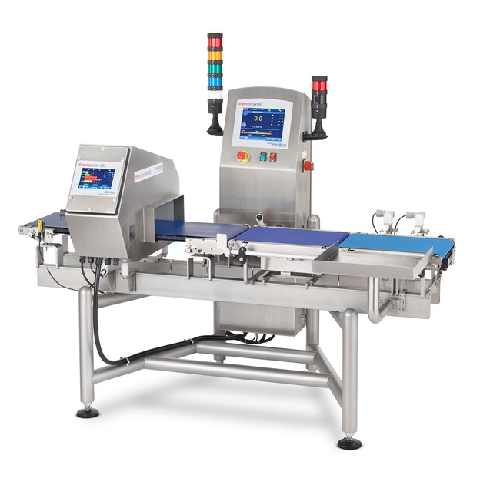
High sensitivity metal detectors for food products
Ensure food safety and product quality by effectively detecting and re...
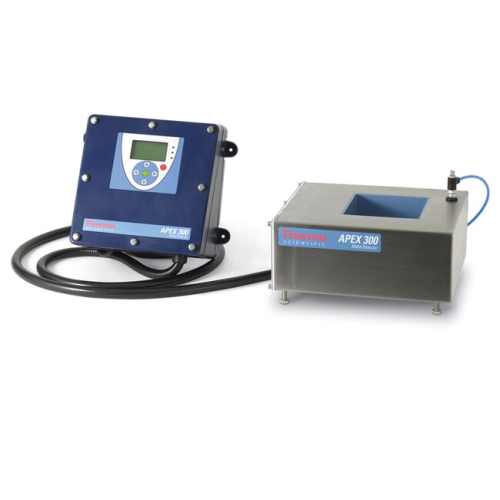
Industrial metal detector for food and beverage applications
Ensure your production line is free from metal contaminants...
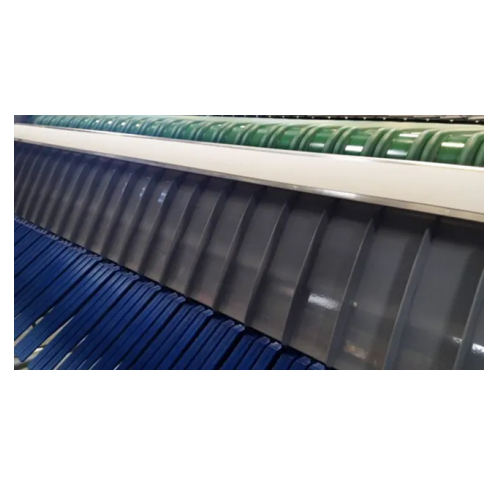
Corn seed sorting solution
Ensure precision in sorting and grading corn with optical and infrared technologies, enhancing pr...
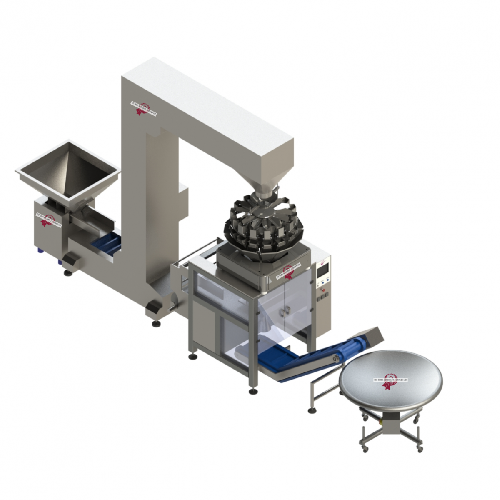
Modular packing system for multihead weighing
Streamline your production with a versatile multihead system designed for pr...
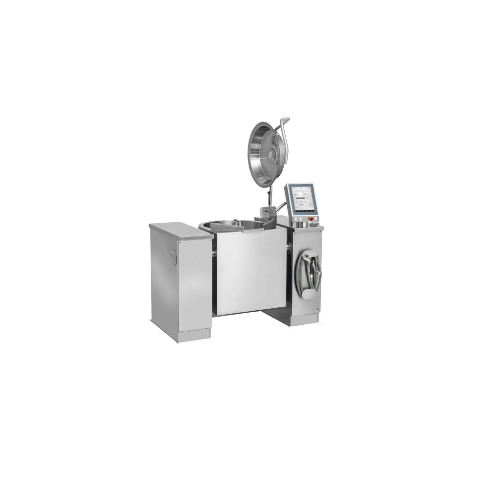
Integrated stirring cooking kettles for commercial kitchens
Streamline your culinary operations with innovative cooking ...
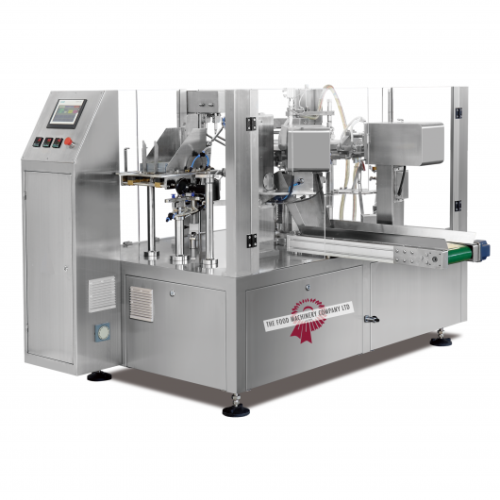
Rotary pouch filling system
Looking to efficiently manage pouch filling for diverse products? This rotary system seamlessly ...
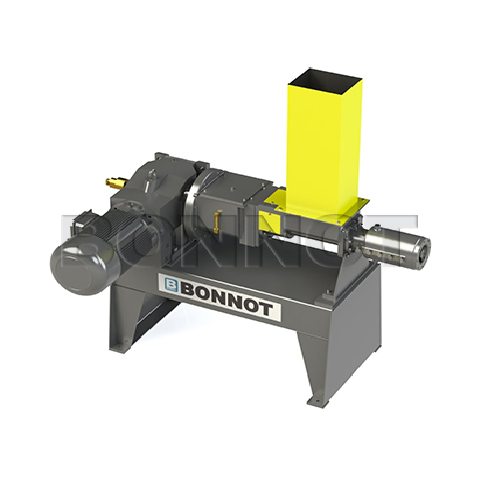
Single screw extruder for chemical catalysts and sealants
Optimize material ingestion and processing with a versatile si...
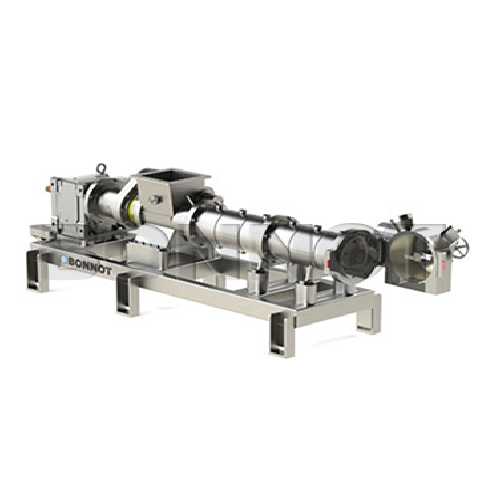
Cold forming extruder for food manufacturing
Achieve precise shape and density control in cereal and snack production by i...
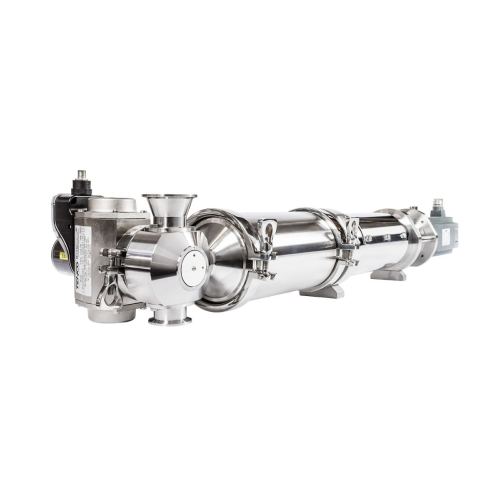
Volumetric piston fillers for liquid and dense products
Perfect for diverse packaging needs, these volumetric piston fill...
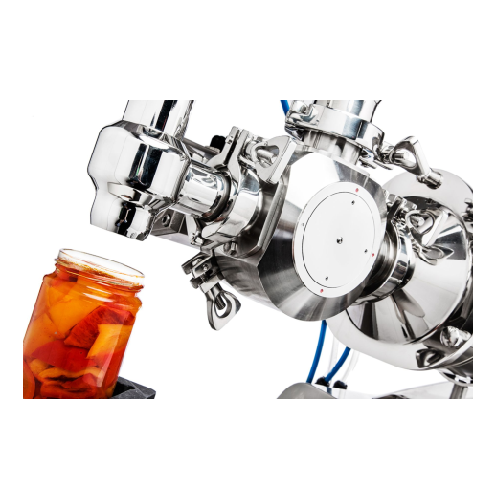
Filling solution for various container types
This versatile filling solution optimizes liquid packaging by accommodating a...
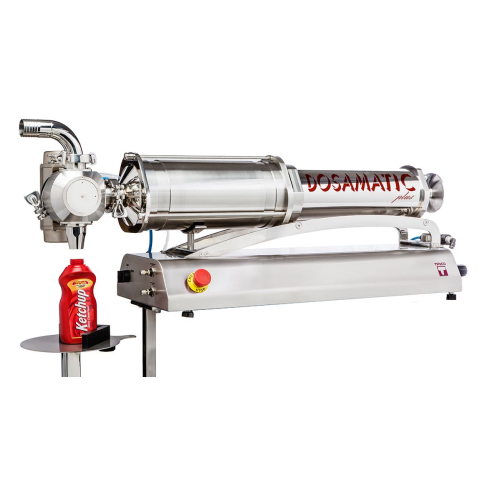
Accurate volumetric filler for liquid and semi-dense products
Achieve precise dosing and filling of various liquid and s...
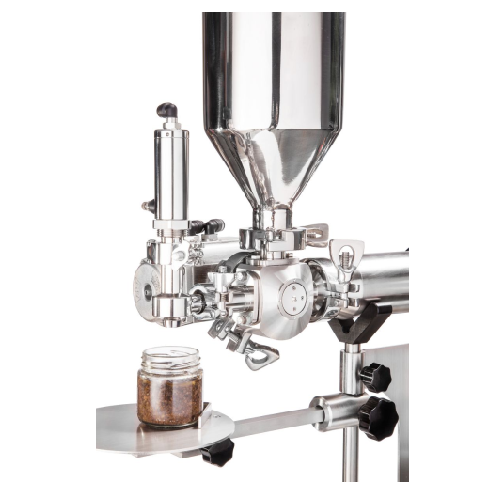
Bench-top piston filler for liquid and semi-dense products
Optimize your filling precision with a versatile piston fille...
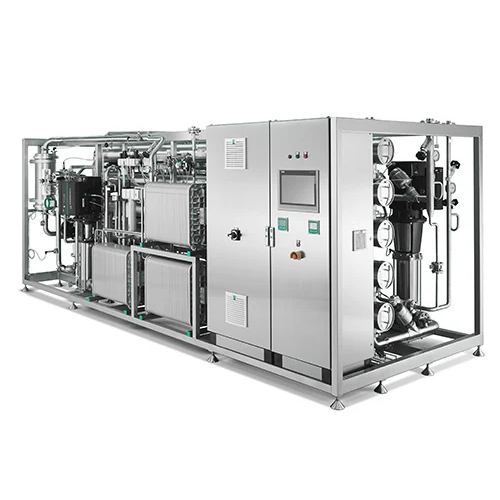
Pure water generation system for pharmaceutical manufacturing
Ensure high-purity water and steam production with precisi...
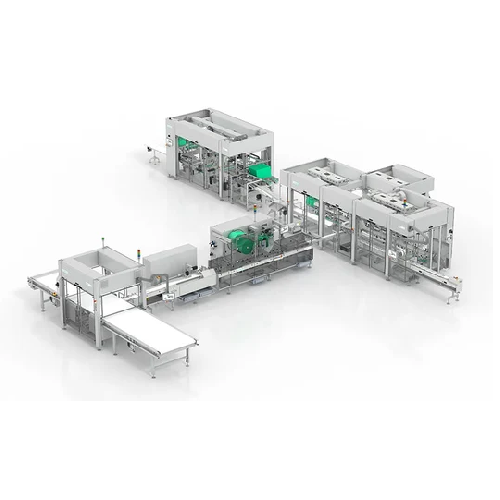
Horizontal flow wrapper for food packaging
Simplify your packaging process with our high-speed horizontal flow wrapper tha...
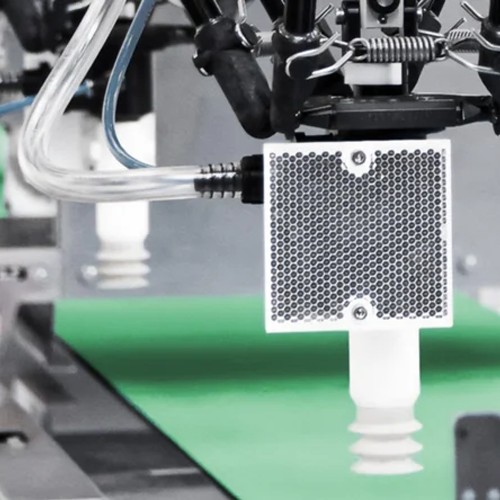
Robotic pick and place platform for food packaging
Enhance your packaging efficiency and product quality with a scalable ...
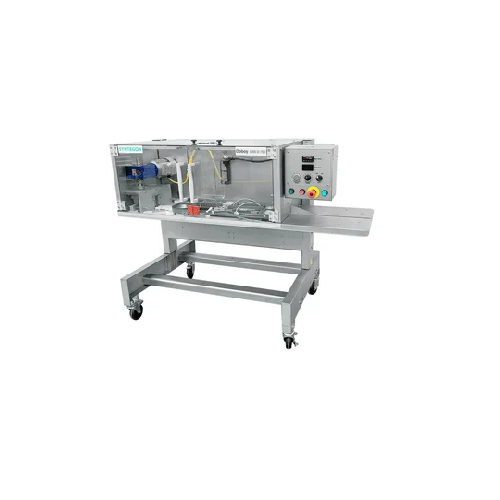
Industrial bag sealing solution for medical and food applications
Enhance your packaging line with reliable and versati...
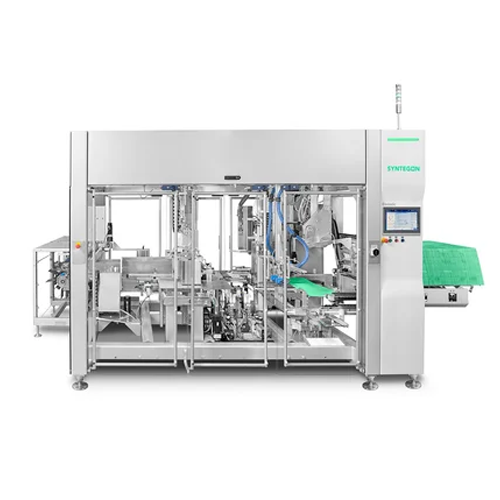
Case packer for diverse food products
Optimize your packaging line with this versatile case packer, capable of handling a w...
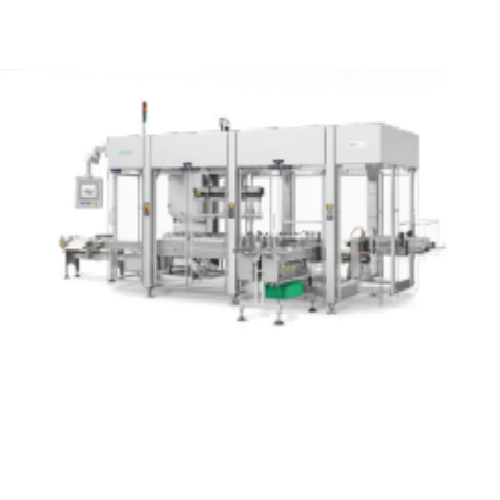
Reliable cartoning solution for food and non-food products
Achieve seamless product packaging with a cartoning solution ...
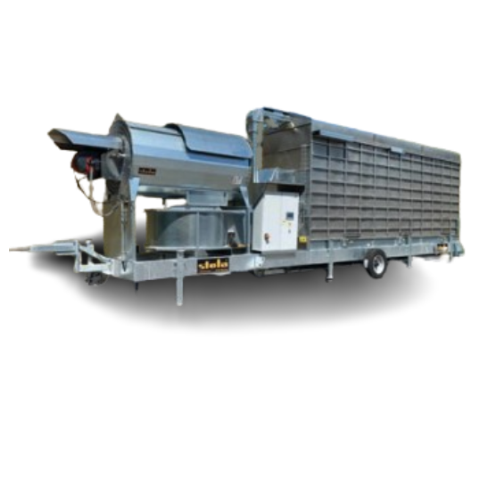
Mobile circulating dryer for agricultural products
Optimize your drying processes with a mobile circulating dryer, design...
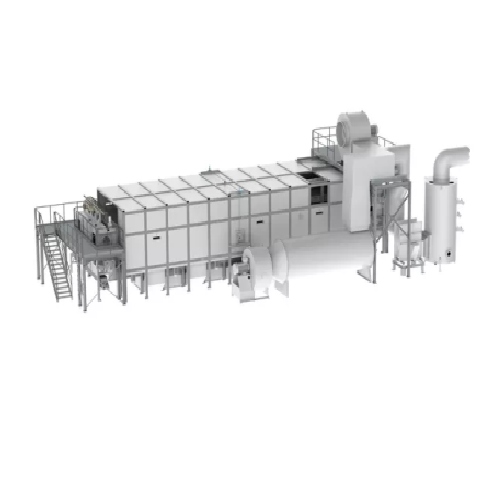
Slat conveyor dryer for industrial drying processes
Optimize your drying process with a robust slat conveyor system that ...
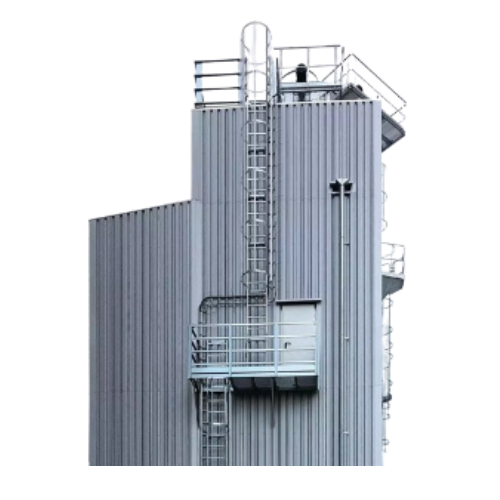
Stationary drying system for agricultural products
Optimize moisture control and energy efficiency in your drying process...
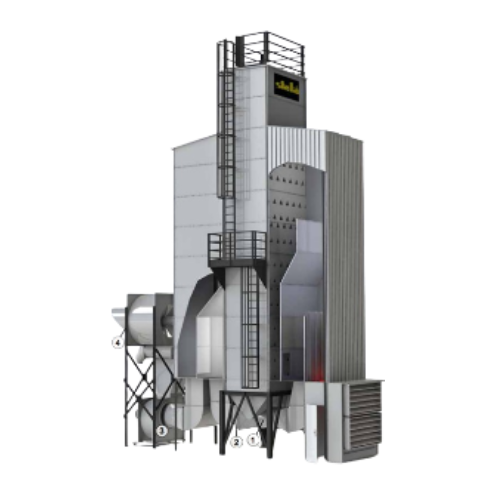
Stationary grain dryer with exhaust air system
Optimize your drying process with a system designed to handle diverse mater...
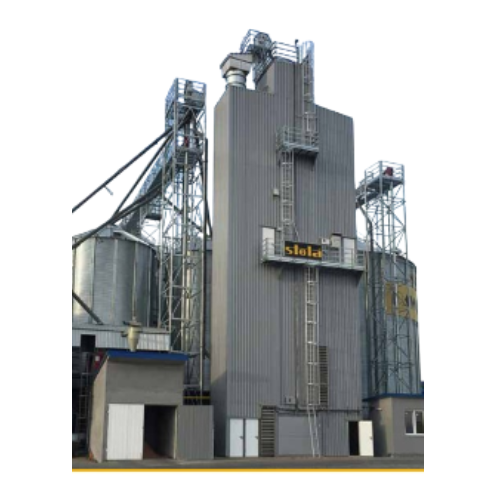
Grain dryer with air circulation system
Enhance efficiency and product quality with our versatile grain dryer, designed to ...
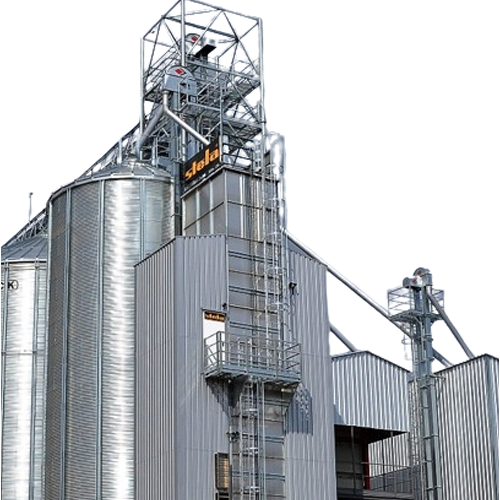
Stationary grain dryer with biturbo system
Optimize your drying processes with a system that efficiently manages air flow ...
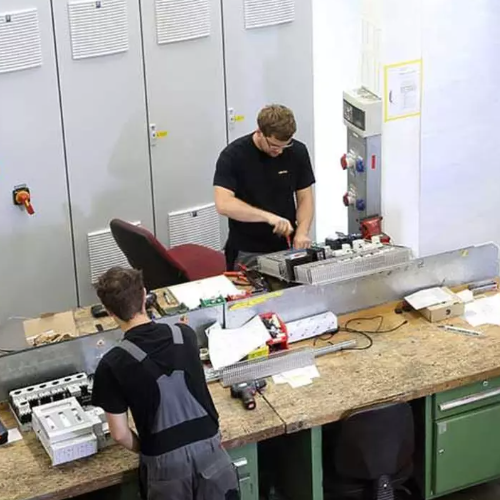
Low-emission belt drying systems for timber industry
Optimize moisture control and energy efficiency in drying processes ...
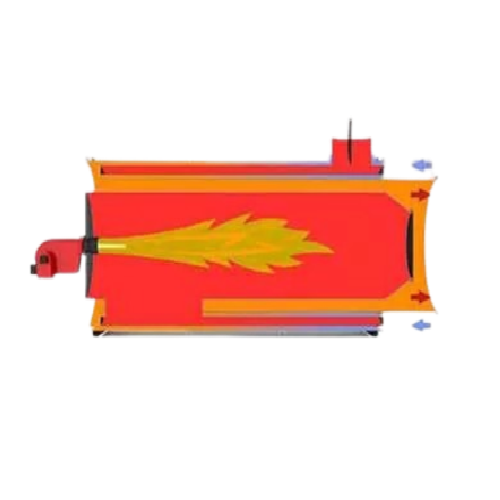
Industrial air heater for agriculture and industry
Optimize energy efficiency and maintain high air quality in your produ...
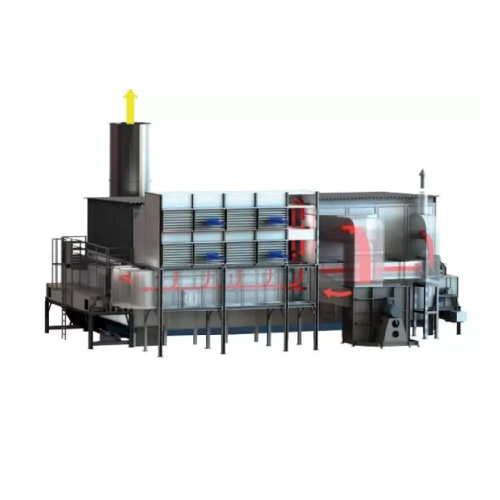
Belt dryer for timber industry
Optimize moisture removal and ensure consistent drying in your production line with advanced ...
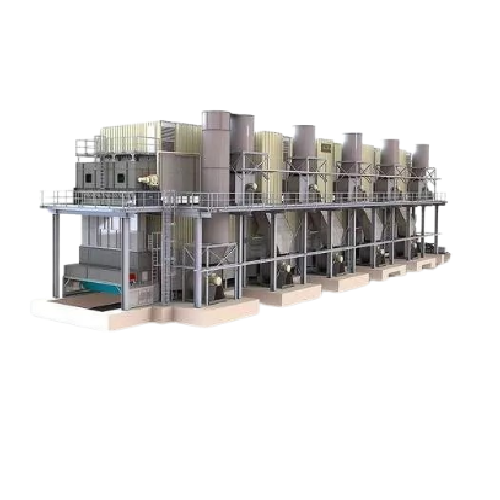
Belt dryer for sawdust
Optimize your drying process with advanced technology engineered for precise moisture reduction in div...
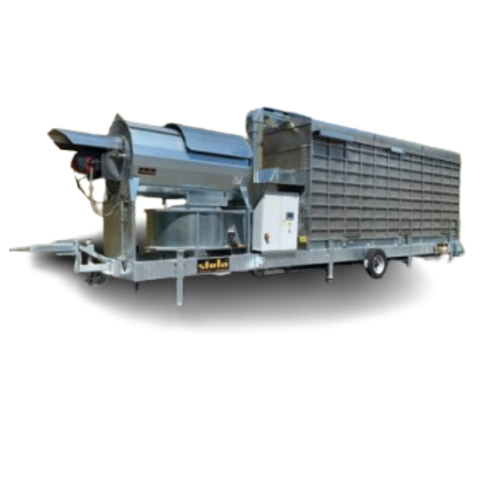
Hybrid dryer for agriculture and industrial applications
Achieve efficient moisture reduction in varied materials, from f...
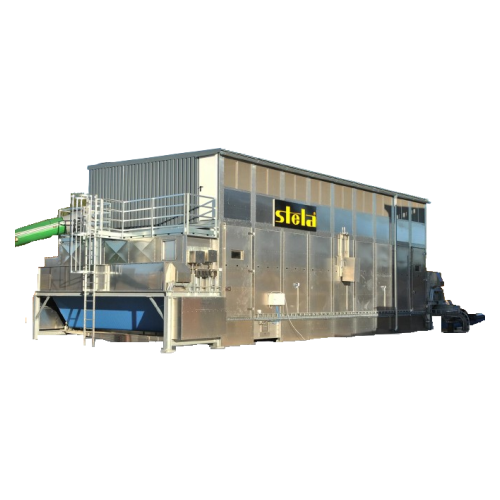
Mobile belt dryer for sawdust and biomass
Efficiently reduce moisture in a variety of materials, from sawdust to cereal sn...
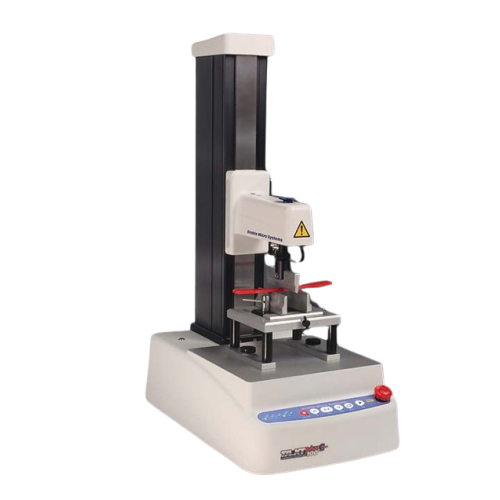
High-force texture analyser for precise measurement
Achieve unparalleled precision in texture analysis for high-force app...
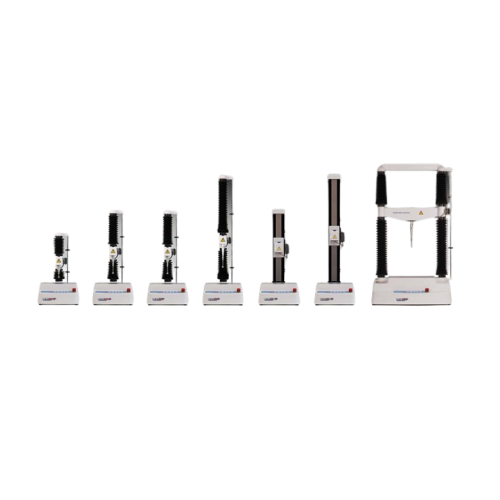
Portable texture analysis for low force applications
Easily perform precision texture measurements on low-force applicati...
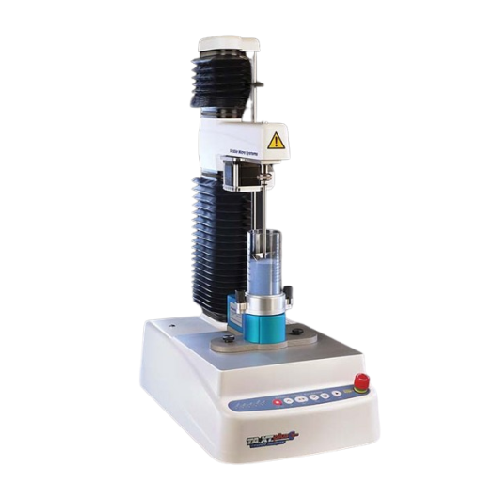
Powder flow measurement system
Achieve precise control over powder consistency and prevent process disruptions by assessing ...
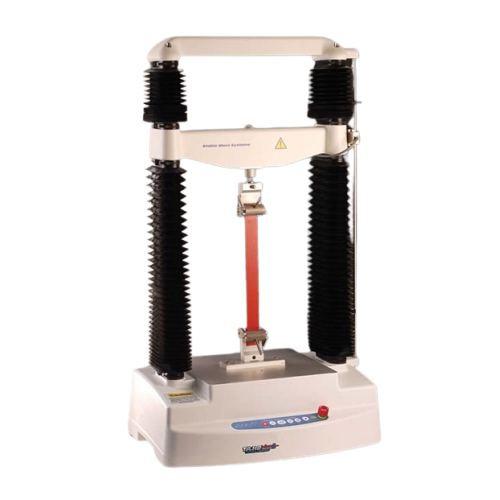
Texture analyzer for high force applications
Achieve precise texture measurement across a vast array of products with a so...
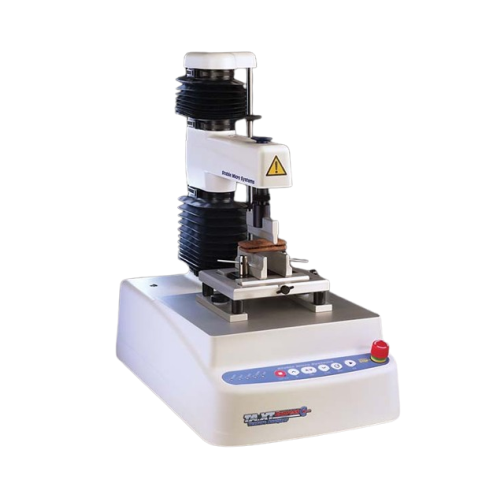
Entry-level texture analysis system for Qc applications
Perfect for quality control labs, this portable system streamline...
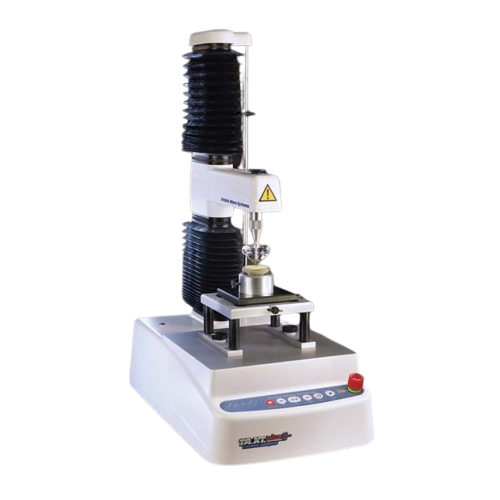
Texture analyser for food and cosmetics testing
Ensuring consistent product quality across diverse food and cosmetic appli...
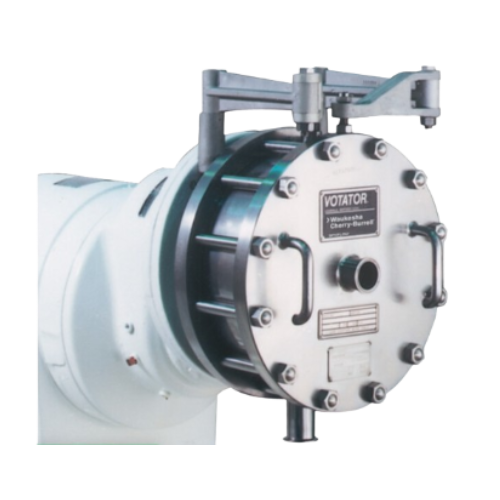
High-shear mixer for emulsions, dispersions, and foams
Achieve precise emulsions and dispersions effortlessly with high-s...
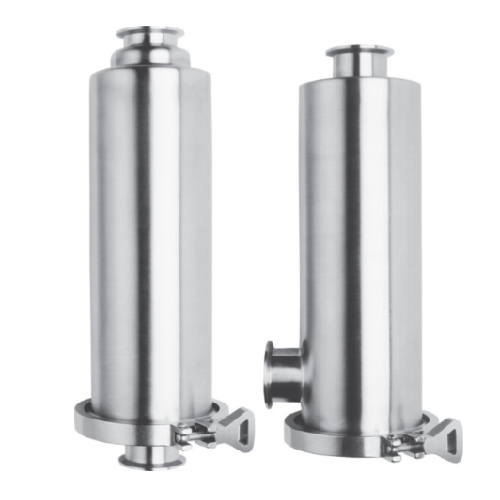
Industrial stainless steel filters and strainers
Optimize your liquid processing with precision filtration and straining, ...
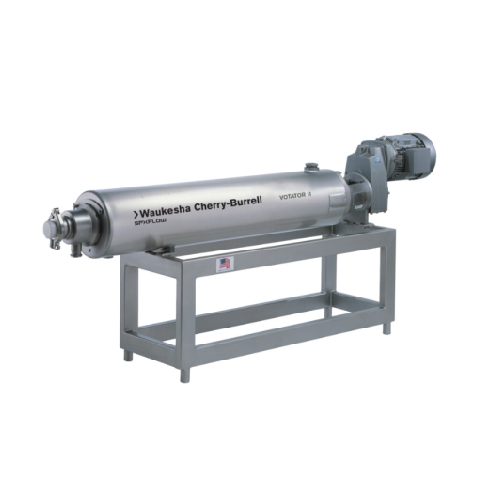
Food processing scraped surface heat exchanger
Enhance your production line with precise temperature control and continuou...
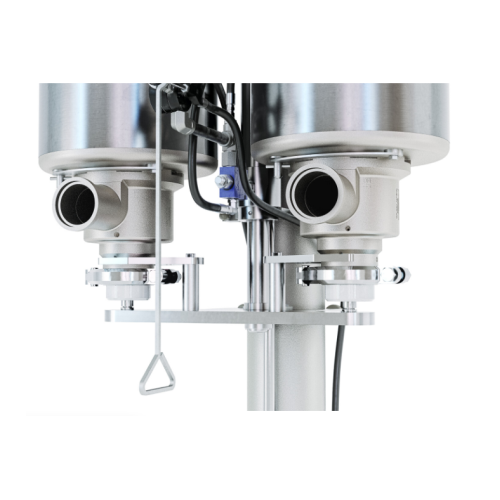
Vertical scraped surface heat exchanger for food processing
For continuous production that demands consistent texture an...
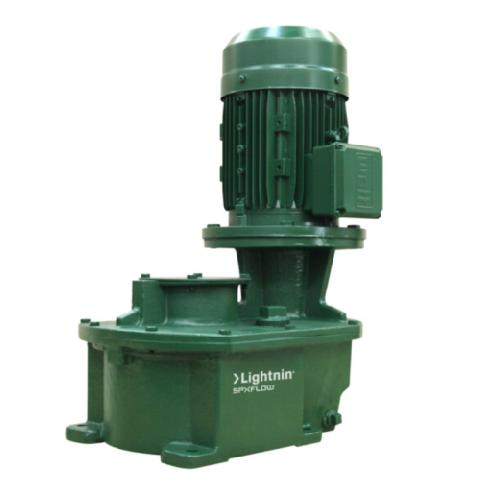
Medium torque mixer for chemical processing
Achieve optimal mixing efficiency and process consistency in demanding applica...
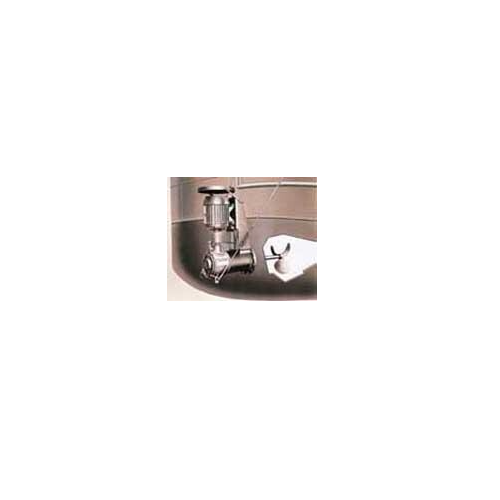
Side entry mixer for industrial tank applications
Ensure optimal mixing and blending of liquids and slurries with high ef...
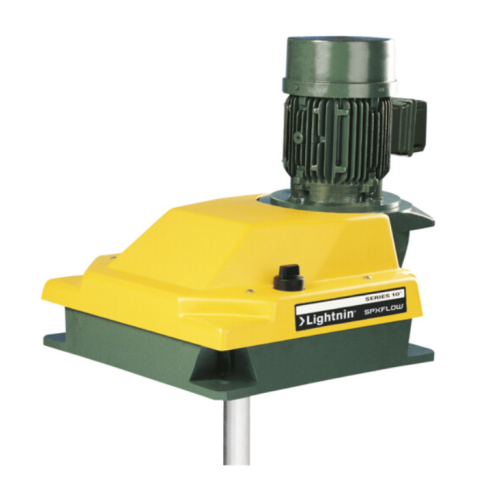
Medium torque top entering mixer for chemical processing
Achieve consistent mixing results with a versatile, high-torque ...

Self-cleaning clarifiers for liquid-solid separation
Optimize your production line with high-performance self-cleaning cl...
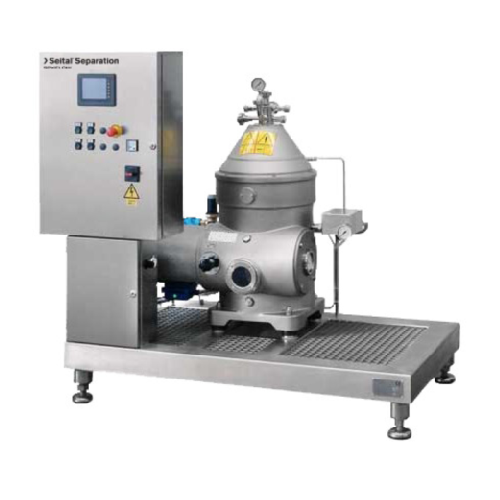
Self-cleaning separator for industrial liquid/solid separation
Optimize your production line with self-cleaning separato...
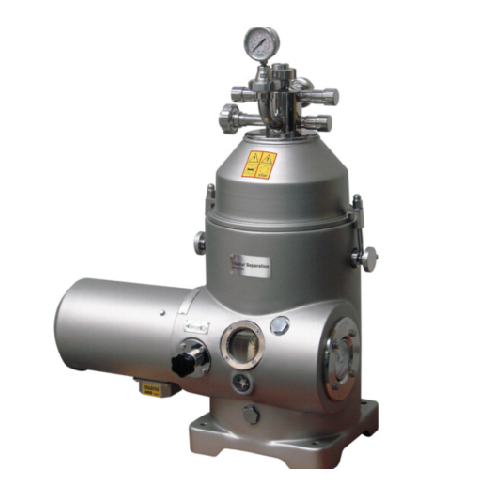
Solids retaining separator for liquid/liquid/solid separation
Achieve precise liquid-liquid-solid separation even with l...
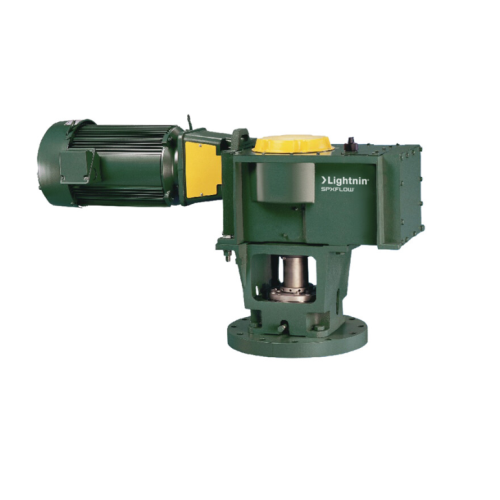
Medium torque top entering mixer for complex mixing tasks
Optimize your production line with a versatile mixing solution...
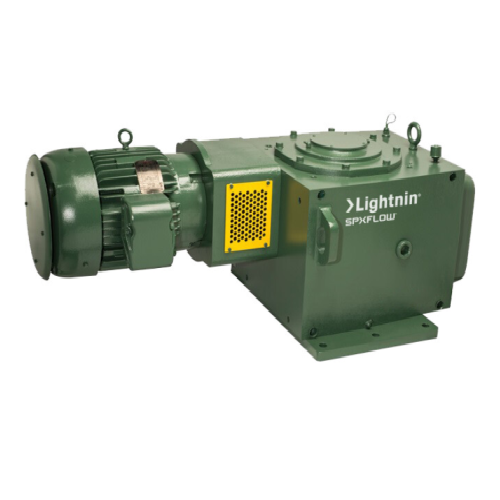
Medium torque top entering mixer for industrial applications
Optimize your mixing and blending operations with precise t...
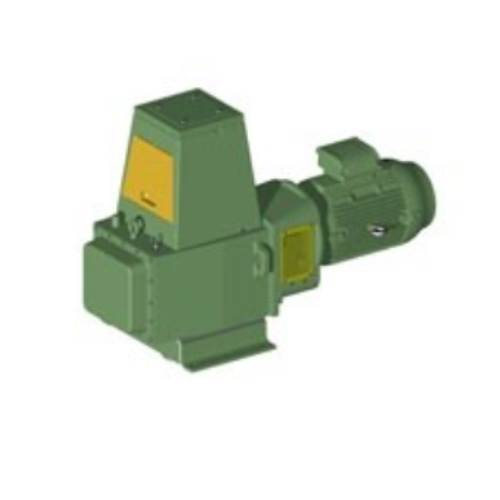
Medium torque top entering mixer for high fluid forces
Equip your production line with a robust mixer that transforms cha...
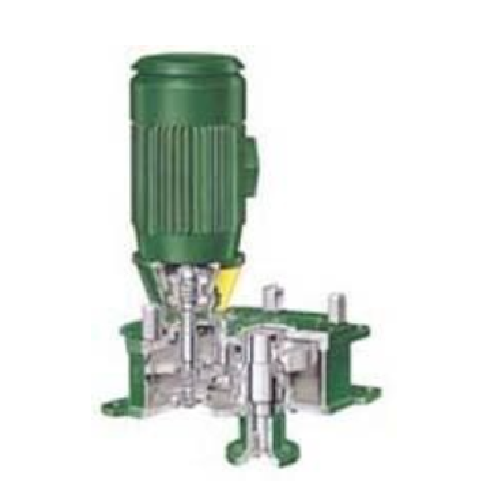
High torque top entering mixer
Ensure consistent high-torque mixing for various industrial applications with this robust top...
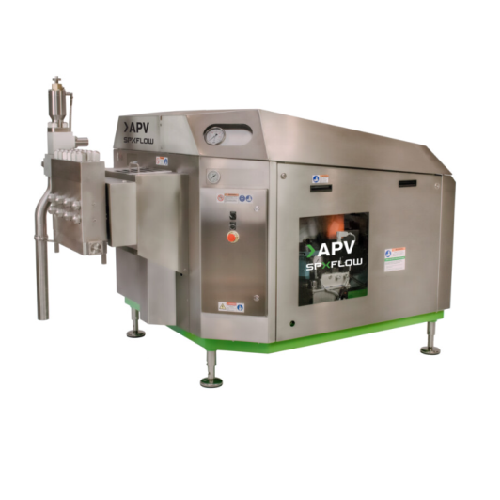
High pressure homogenizer for dairy and pharmaceutical industries
When uniform texture and stable emulsions are critica...
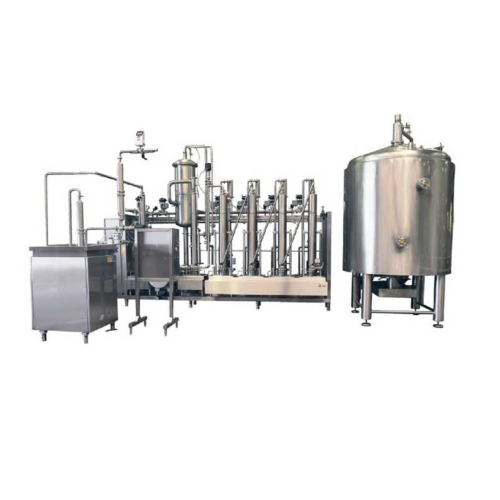
Scraped surface heat exchanger for high-viscosity products
Designed for handling high-viscosity products, this system en...
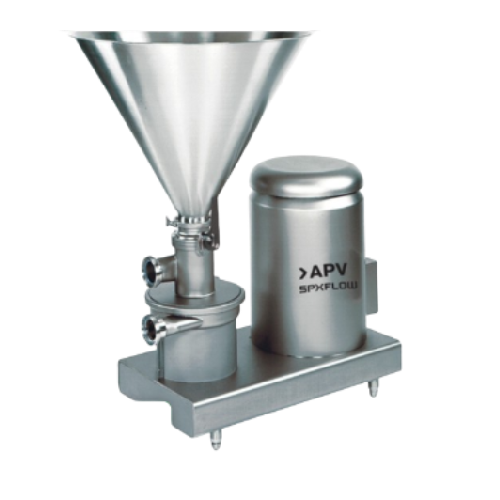
Batch powder mixer for circulatory dispersion
Optimize your batch production with a powder mixer designed for efficient di...
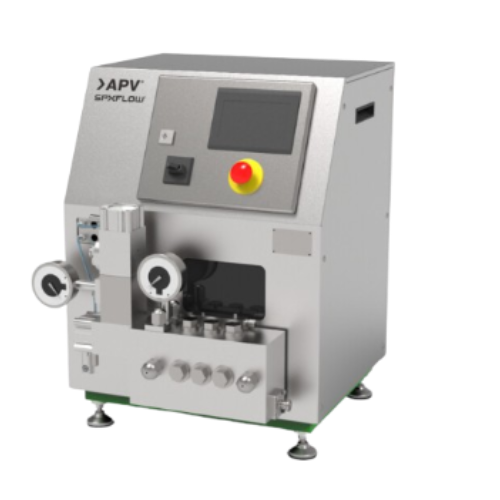
Pilot plant homogenizer for immiscible liquids
Streamline your R&D with precise homogenization, allowing you to test ...

High pressure homogenizer for food and beverage processing
Optimize your production line with a versatile high-pressure ...
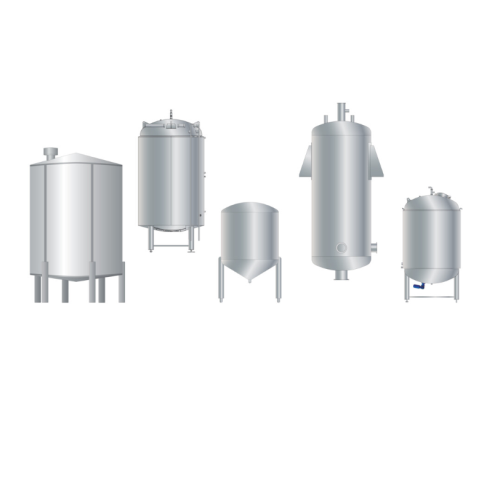
Hygienic tanks for various processing needs
Achieve optimal processing and storage with customizable hygienic tanks, desig...
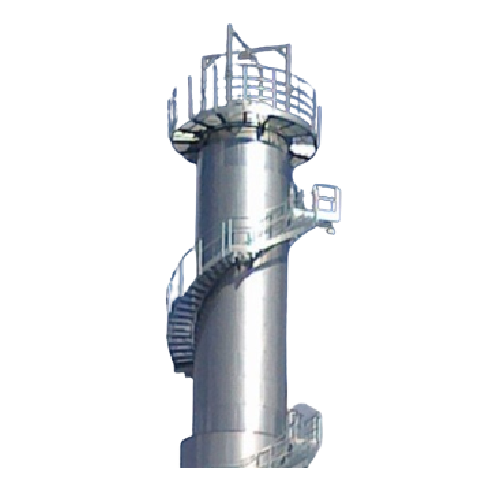
Mechanical vapor recompression evaporator for pre-concentration in food industry
Achieve efficient energy use by utili...
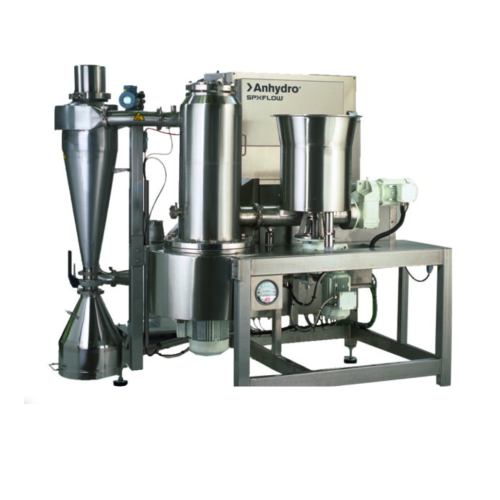
Small scale spin flash dryers for high-viscosity liquids
Optimize moisture control with cutting-edge spin flash dryers de...
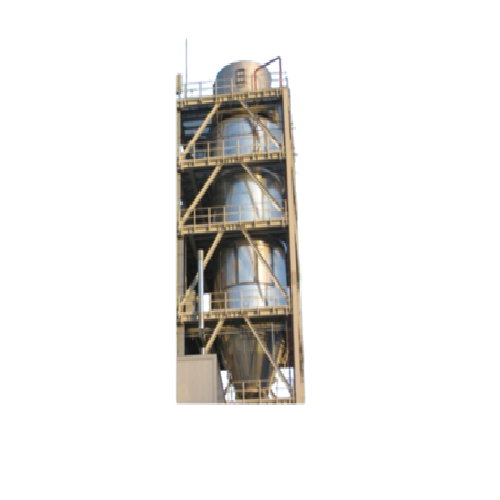
Tall form dryer for producing large non-agglomerated particles
Achieve precise particle size control and optimal moistur...
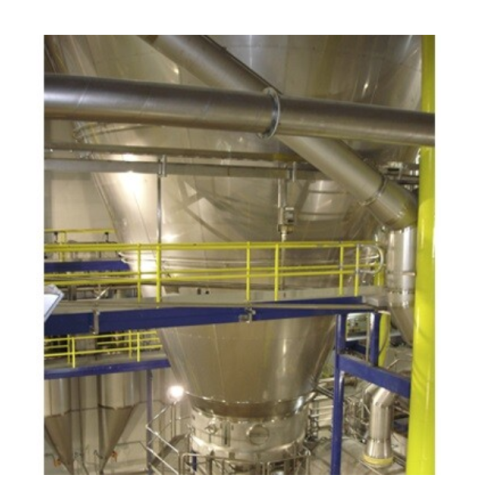
Spray dryers for producing free-flowing dustless powders
Achieve consistent product quality with customizable spray dryer...
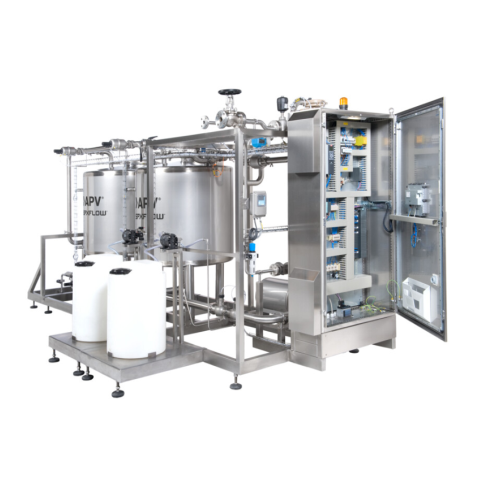
Clean in place (cip) system for industrial cleaning
Ensure optimal hygiene and production efficiency with a system that s...
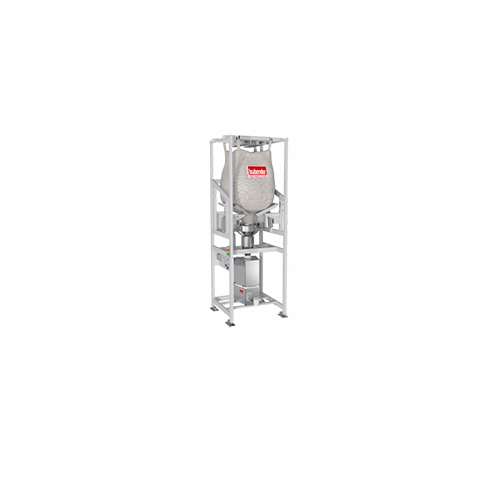
Bigbag discharge station with dust-free docking system
Streamline your production line with an efficient solution for man...
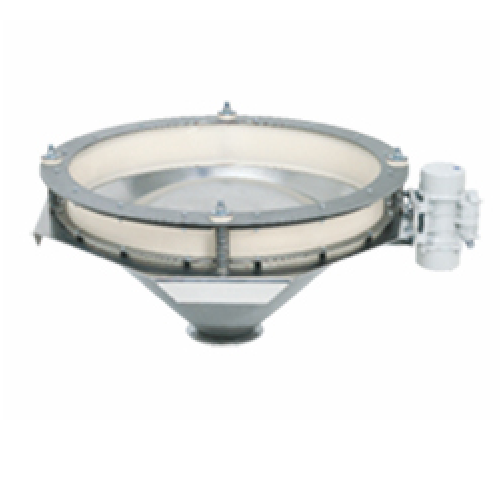
Bin activator for reliable bulk solids discharge
Ensure reliable flow and prevent compaction in your production line with ...
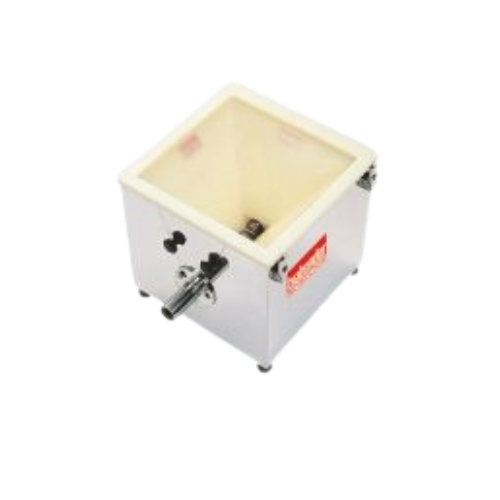
Volumetric feeder for flowable ingredients
Ensure consistent and precise dosing of diverse materials in your production li...
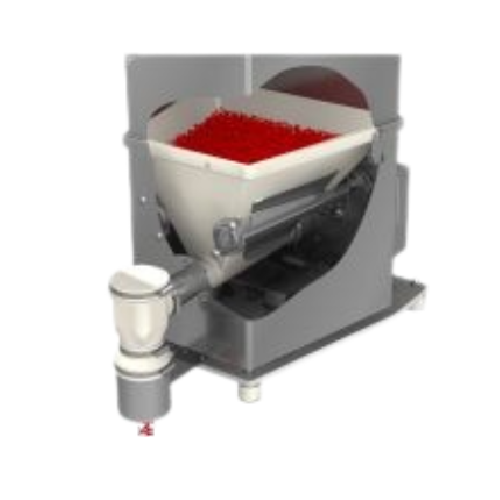
Volumetric feeder for consistent ingredient flow
Achieve precise and consistent ingredient dosing in your production line ...
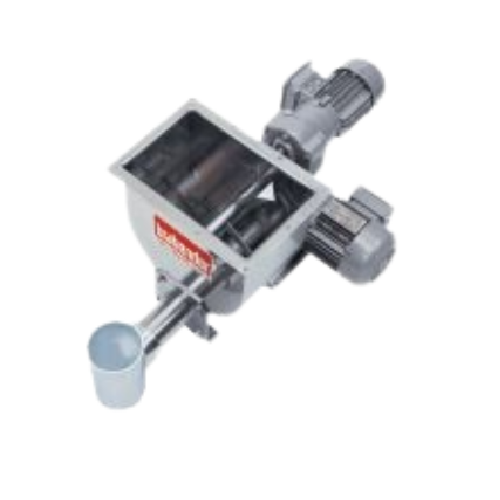
Single screw feeder with stirring agitator for powders and pellets
Ensure consistent mass flow and precise dosing with ...
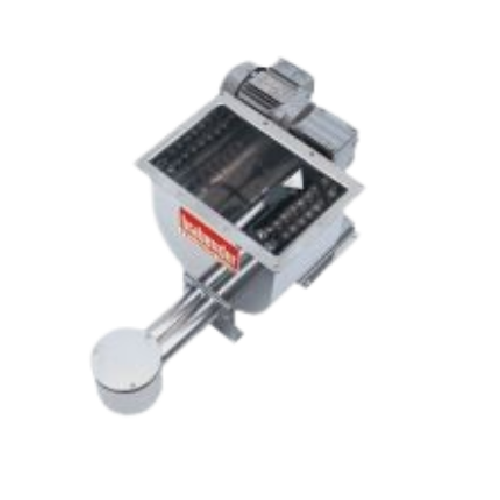
Twin screw feeder with stirring agitator for poor flowing powders
Optimize your processing line with a highly adaptable...
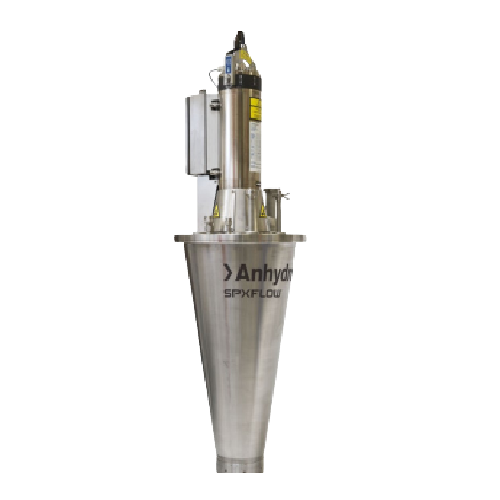
Centrifugal atomizer for precise spray drying
Achieve precise control over particle size and moisture content with centrif...
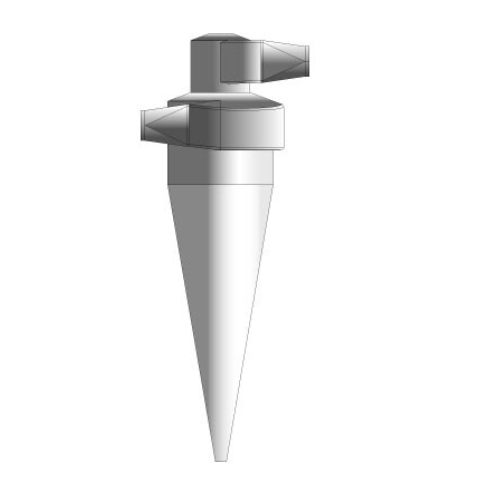
Industrial cyclone separators for air particulate removal
Optimize particulate removal in air streams with cyclone separ...
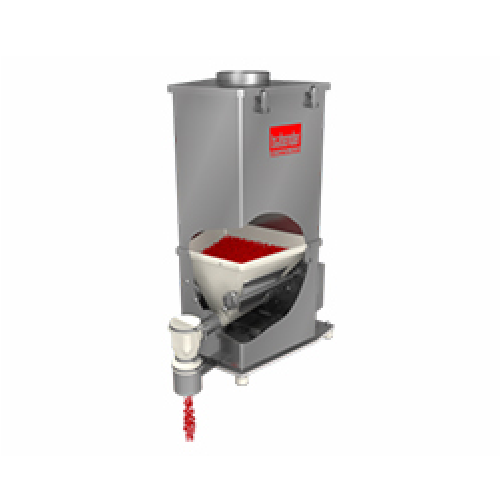
Loss-in-weight feeder for flowable ingredients
Achieve precise ingredient delivery with this feeder, designed to handle a ...
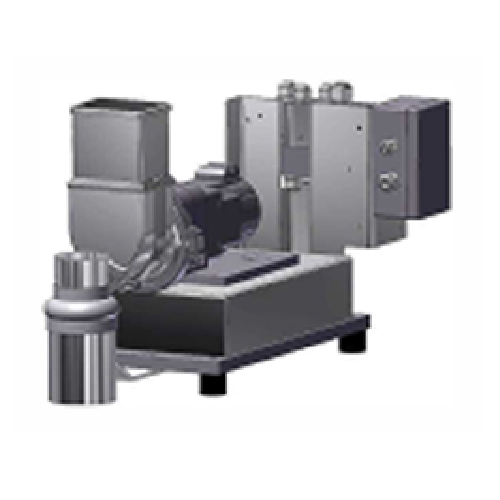
Laboratory loss-in-weight feeder for powders or pellets
Achieve precise dosing for lab-scale trials with this versatile f...
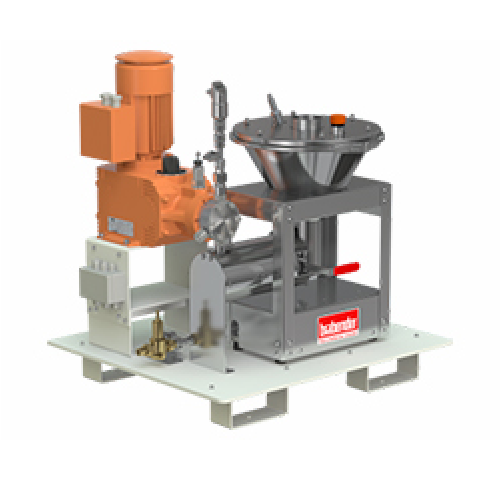
Loss-in-weight feeder for liquids
Achieve precise and continuous liquid dosing with high accuracy, adapting seamlessly to y...
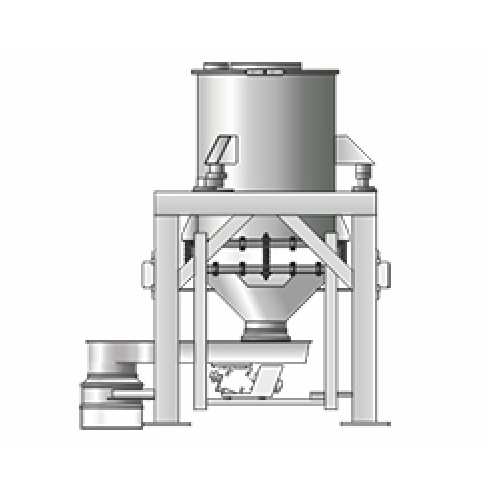
Loss-in-weight feeder for non-hygroscopic ingredients
Ensure precision in your dosing and weighing processes with this ad...
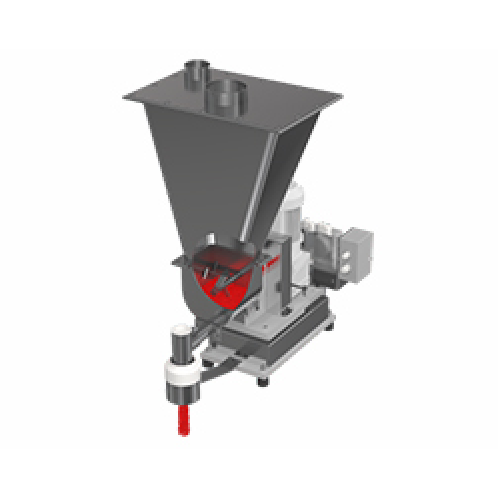
Single screw loss-in-weight feeder for powders and pellets
Ensure precise dosing and mixing in continuous automated oper...
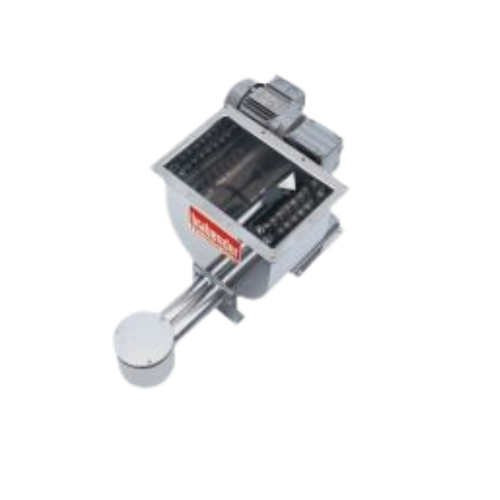
Twin screw volumetric feeder for poor flowing powders
Struggling with poor flowing or floodable powders? This twin screw ...
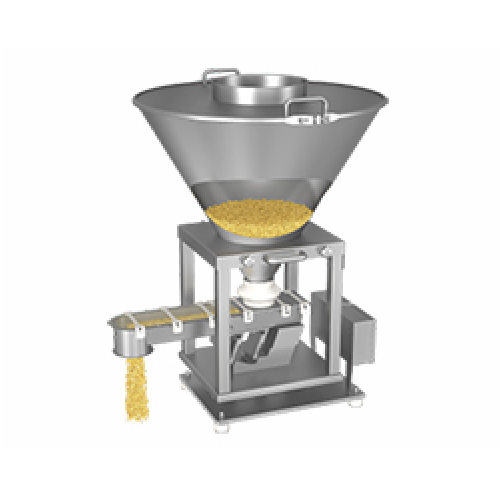
Vibrating tray loss-in-weight feeder for grained ingredients
Achieve precise and continuous dosing of free-flowing solid...
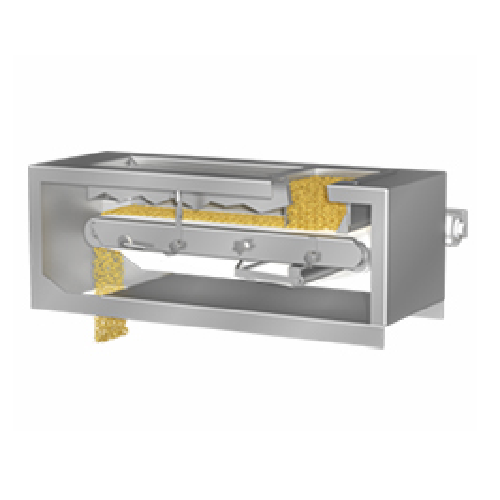
Weigh-belt feeder for industrial processes
Efficiently manage material flow and precision with a dependable weigh-belt fee...
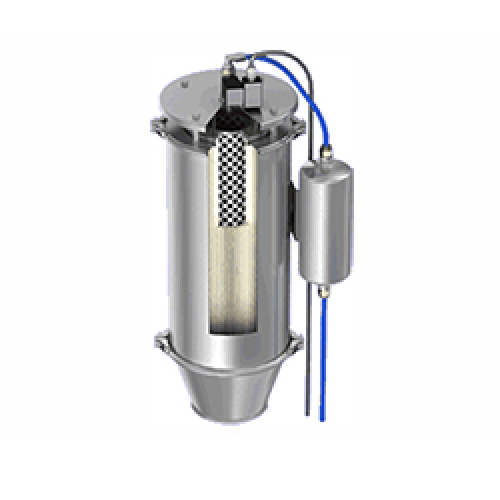
Dust filter for loss-in-weight feeder refill
Optimize your feeder operations by effectively filtering displaced air and mi...
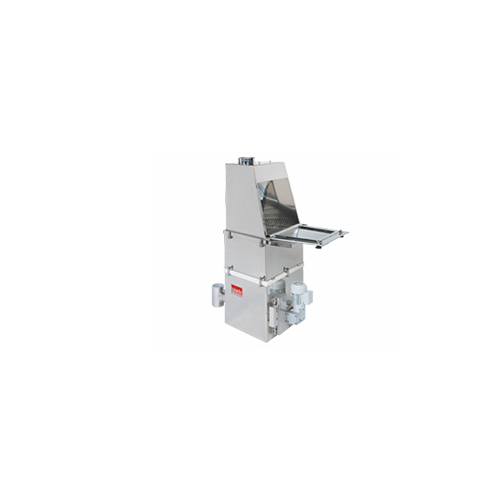
Bigbag discharge station
Efficiently manage bulk material unloading with this solution, which facilitates seamless dischargin...
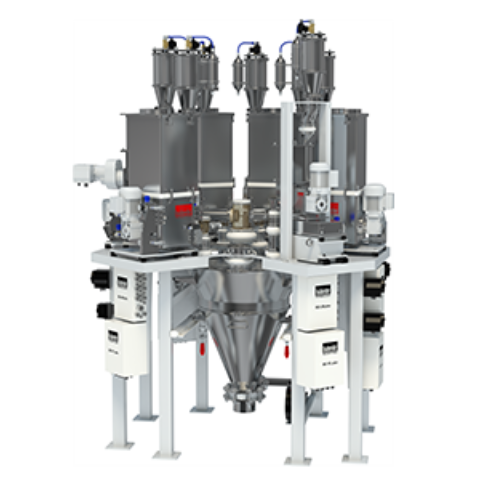
Hopper scale for precision batching
Achieve high batch accuracy with a central weighing hopper engineered for seamless inte...

Batch ingredient dosing system for high-accuracy weight control
Achieve precise weight measurement for multi-ingredient ...
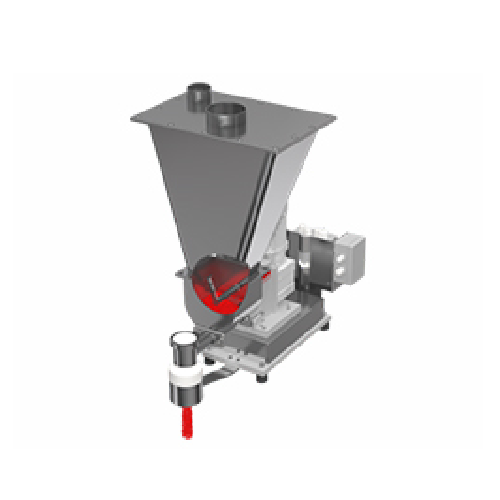
Double screw batch feeder for poorly flowing powders
Effectively manage challenging powders with precise batch dosing and...
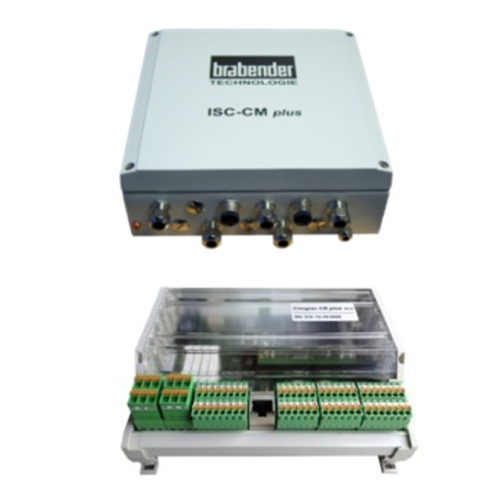
Feeder controller for gravimetric feeders
Optimize your dosing precision and monitoring accuracy with a versatile feeder c...
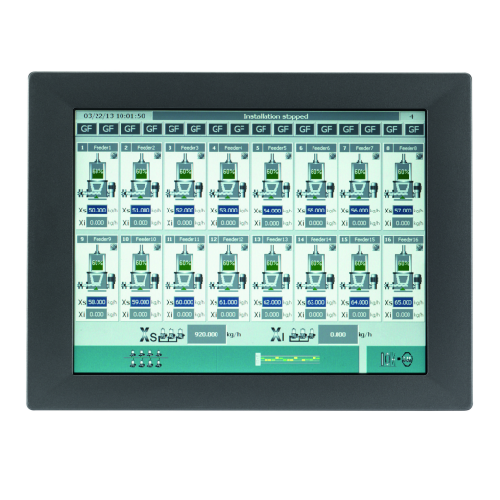
Gravimetric feeder operator interface
Efficiently manage up to 16 gravimetric feeders with a user-friendly interface, enabl...
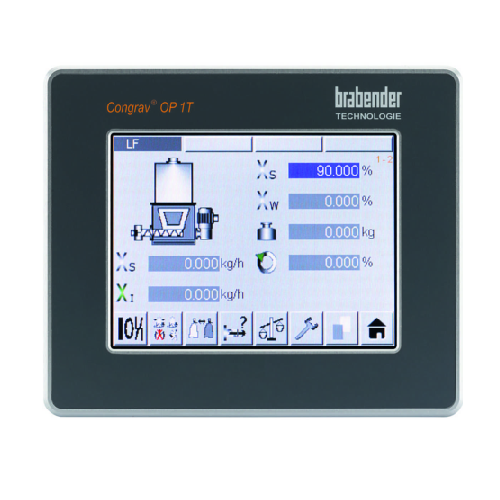
Single feeder operator interface for gravimetric feeders
Enhance precision in your dosing operations with an intuitive to...
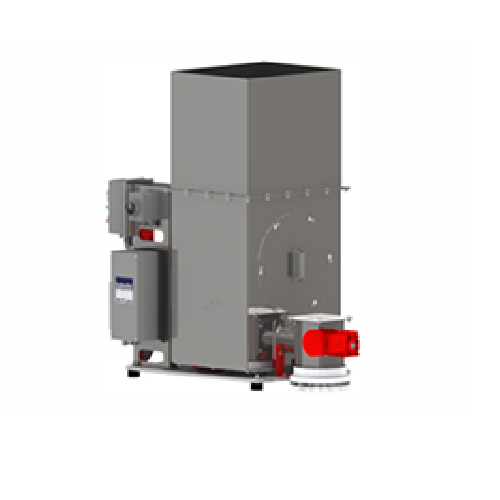
Loss-in-weight feeder for long and uneven fibers
Optimize feeding precision for challenging materials like long and uneven...
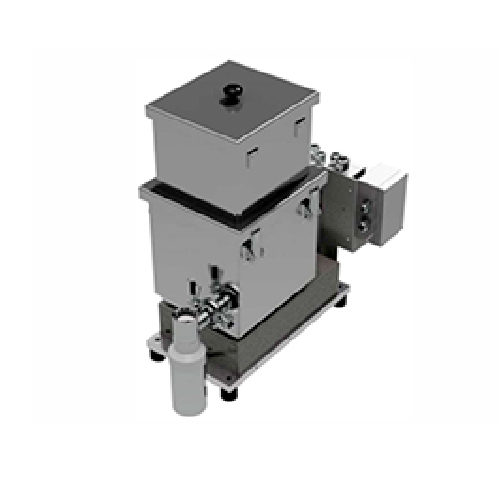
Loss-in-weight feeder for flowable particles
Ensure precise ingredient delivery with a feeder designed for high accuracy a...
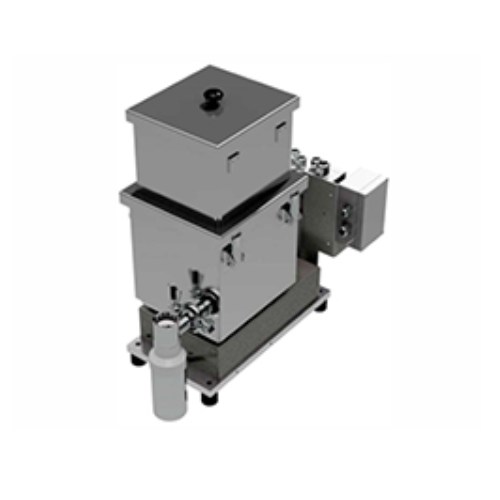
Batch feeder for bulk solids processing
Achieve precise batch dosing with this advanced feeder, designed to handle a variet...
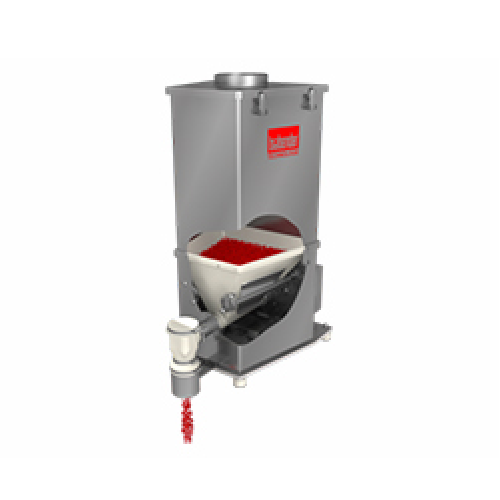
Precision batch feeder for flowable ingredients
Achieve precise ingredient control with a batch feeder designed for versat...
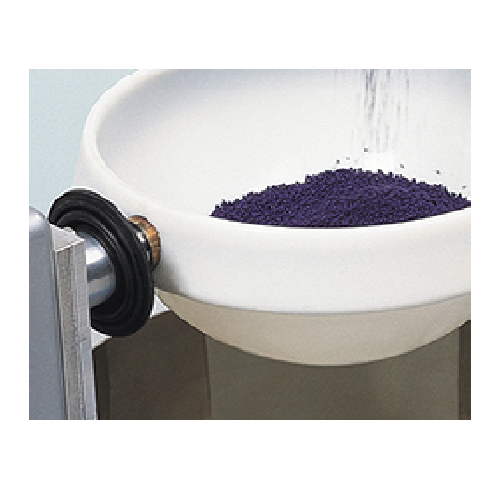
Microbatch dosing for precision ingredient measurement
Achieve precise ingredient dosing with our MicroBatch system, desi...
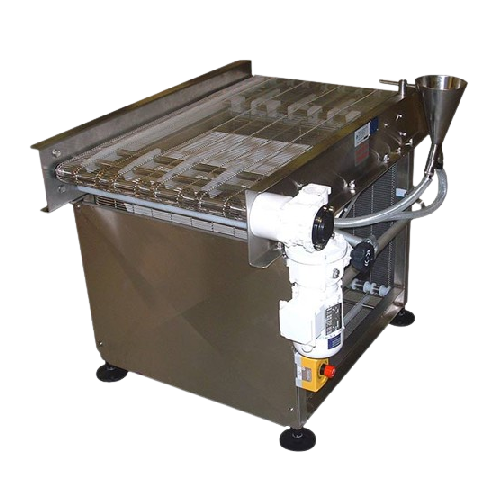
Electrostatic drum flavouring for uniform coating
Achieve precise and uniform flavor distribution on snack products with ...
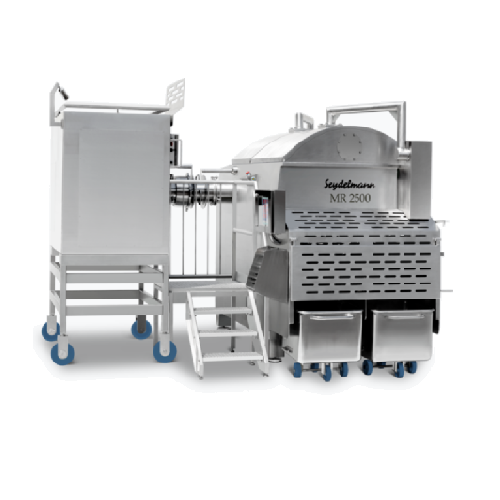
Automated production line for ground meat products
Enhance your meat processing efficiency by seamlessly integrating grin...
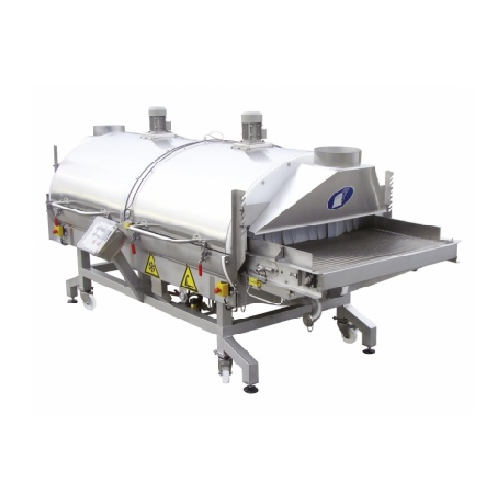
Cryogenic cooling tunnel for industrial freezing
Achieve precise temperature control and rapid freezing with a compact sol...

Mayonnaise production line
Streamline your high-capacity mayonnaise production with precise mixing, emulsifying, and pasteur...
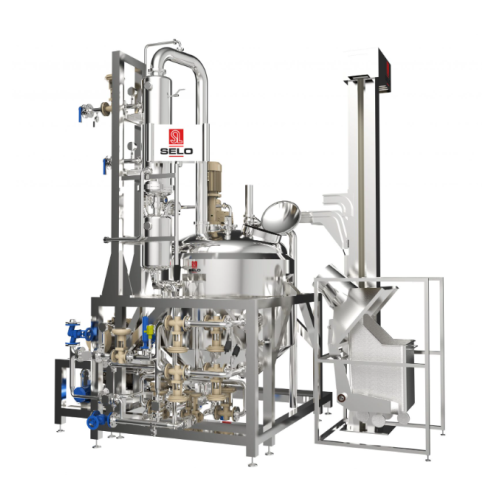
Automated mayonnaise and dressing production line
Ensure the consistent quality of your mayonnaise, dressings, and sauces...
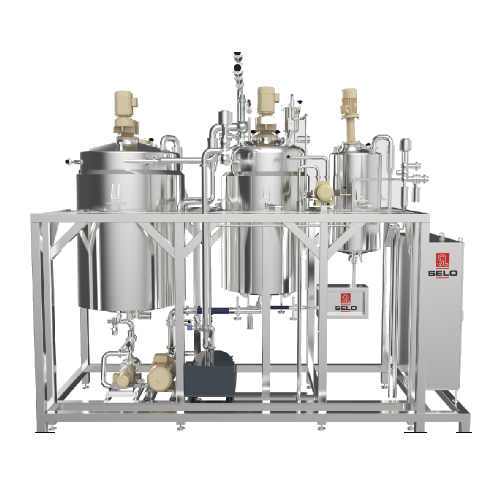
Baby food production line
Ensure optimal safety and precision with this production line, designed for processing delicate ba...
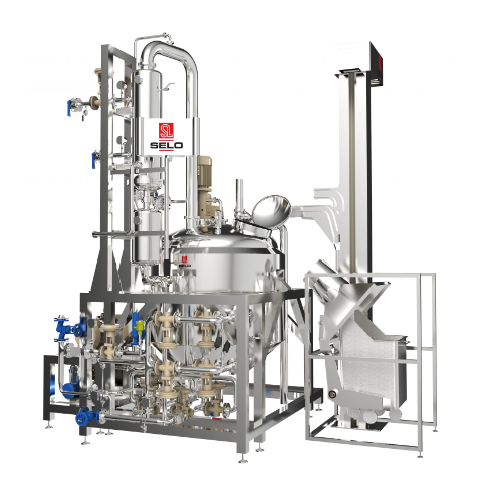
Ketchup manufacturing line
Streamline your sauce production with precision-engineered efficiency, allowing for seamless reci...
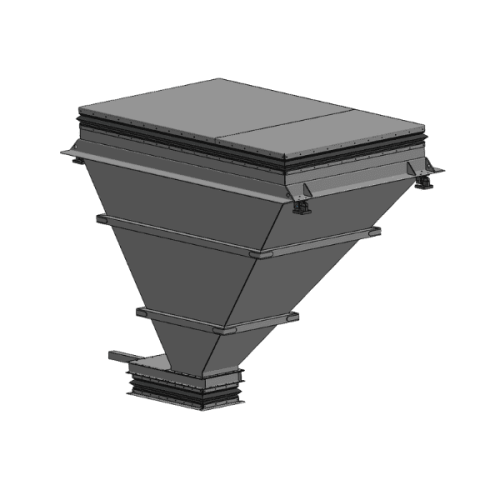
Scale hopper for industrial batch weighing
Optimize your production line with precise batch weighing and mixing, ensuring ...
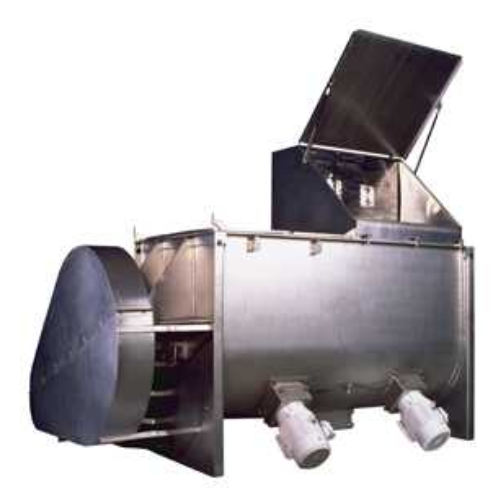
Single shaft horizontal batch mixer
Achieve consistent, high-quality blends with precise homogenization using a single shaf...
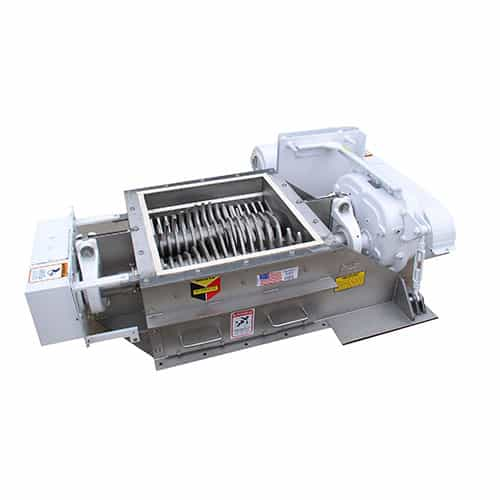
Industrial crusher for size reduction and waste recycling
Optimize your production line with versatile and robust crushi...
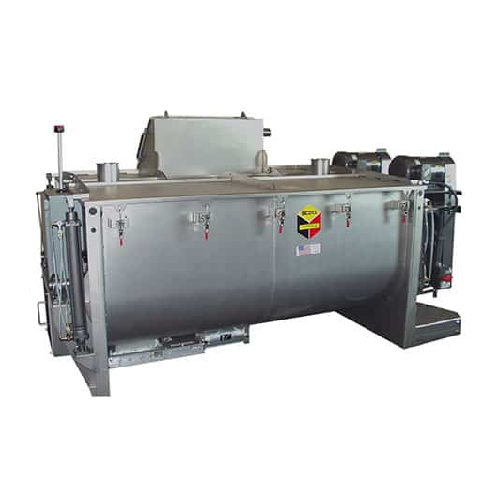
Twin shaft horizontal batch mixers for homogenous material mixing
Achieve consistent and rapid mixing of diverse materi...
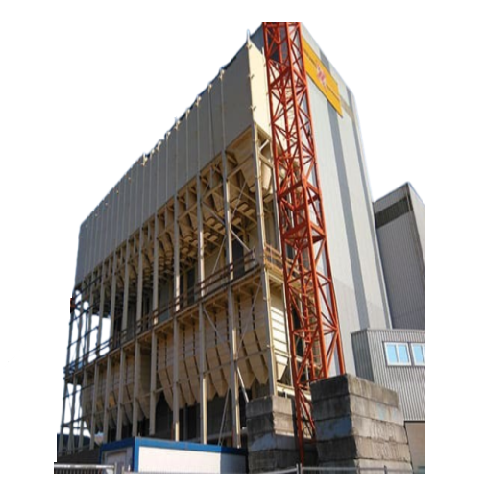
Sanitary modular bulk silos for efficient storage
Maximize your storage capacity and streamline assembly with a modular s...
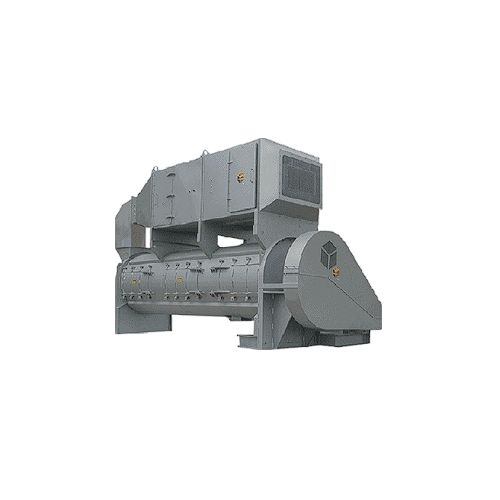
Pneumatic drying system for industrial slurries
Efficiently transform high-moisture slurries into dry solids in a single p...

Industrial batch mixer agitators
Achieve precise and efficient mixing of diverse materials with industrial batch mixer agita...
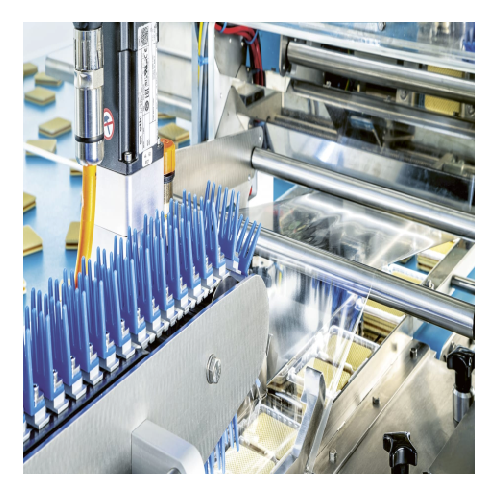
Flow-wrapping solution for varied packaging needs
Gain unmatched flexibility and sustainability with a cutting-edge flow-...
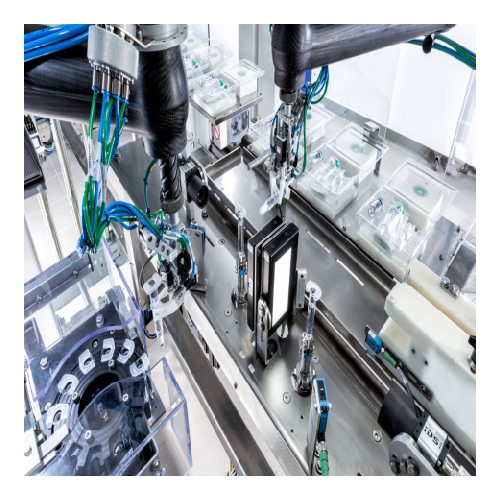
Process integration for pharma industry
Enhance your production line with seamless process integration, ensuring accurate l...
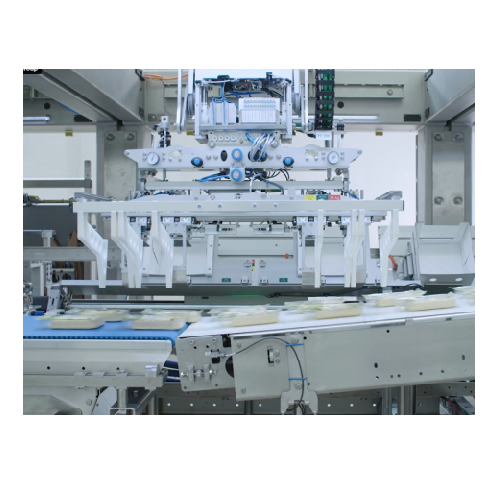
Case packer for diverse packaging needs
Optimize your production line with this modular case packer, designed to handle div...
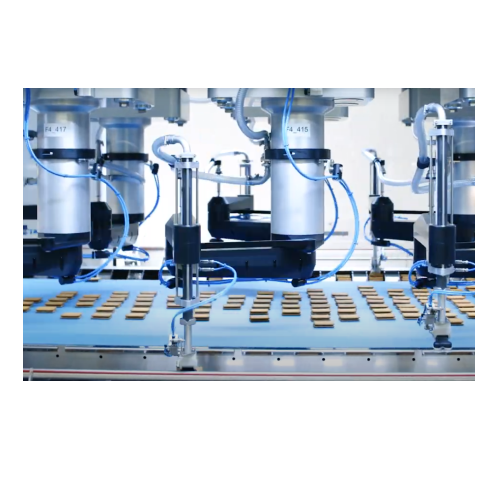
Pick & place robots for industrial packaging
Elevate your production line with advanced automation that ensures precise pa...
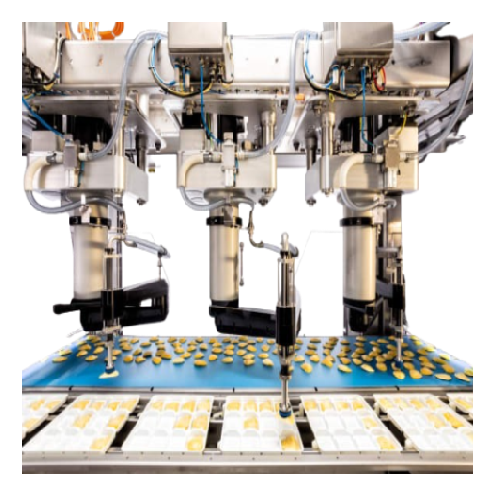
Pick & place vision system for packaging quality control
Ensure flawless product packaging with a vision system that enha...
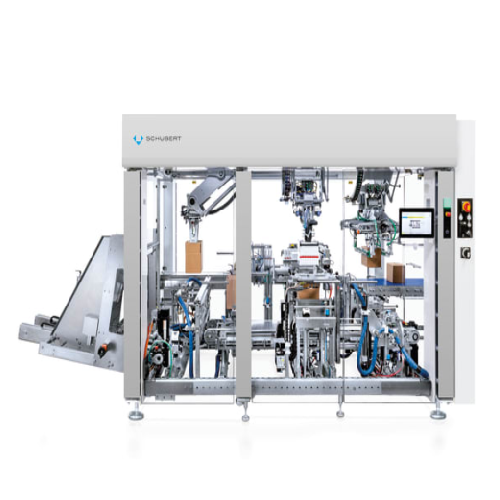
Ultra-compact case packer for consumer goods
Maximize efficiency on your production floor with a compact case packer desig...
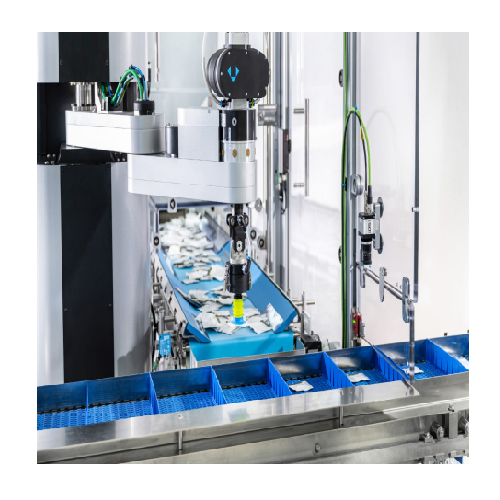
Automated pick and place cobot for packaging
Overcome packaging bottlenecks with an advanced cobot designed for high-speed...
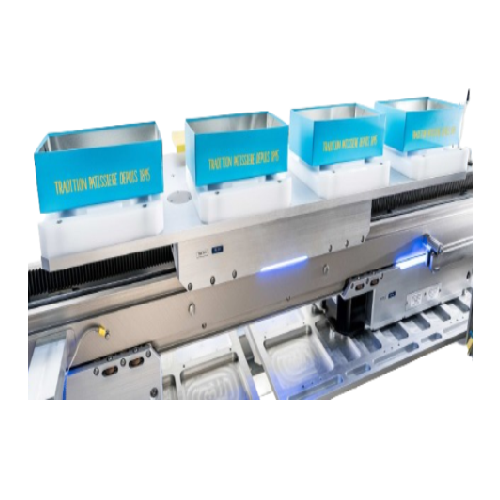
Flexible transport robot for packaging lines
Enhance your packaging efficiency with a transport robot engineered to seamle...
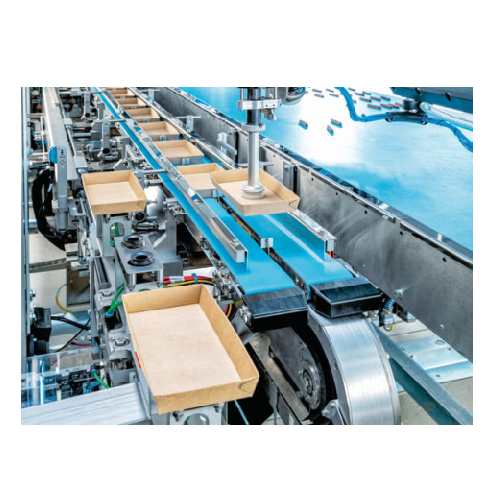
Flow wrapper with quick format change
Streamline your packaging operations with a machine that offers rapid format changeov...
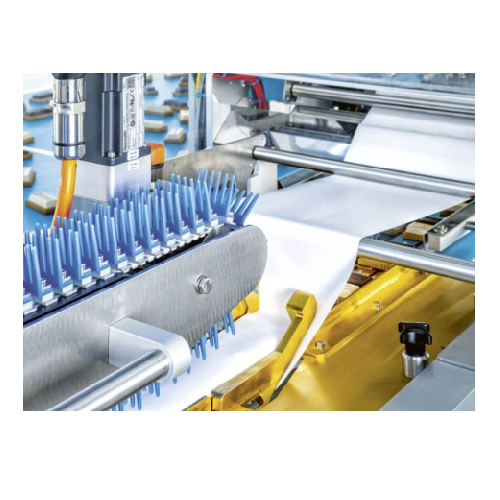
Flow-wrapping machine with quick format changeovers
Optimize your packaging flexibility with a flow-wrapping machine desi...
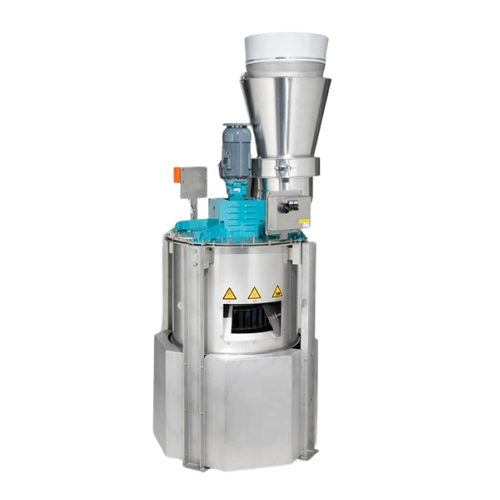
Mass flow rate feeder for bulk powders
Achieve precise control and consistent material flow in high-speed manufacturing env...
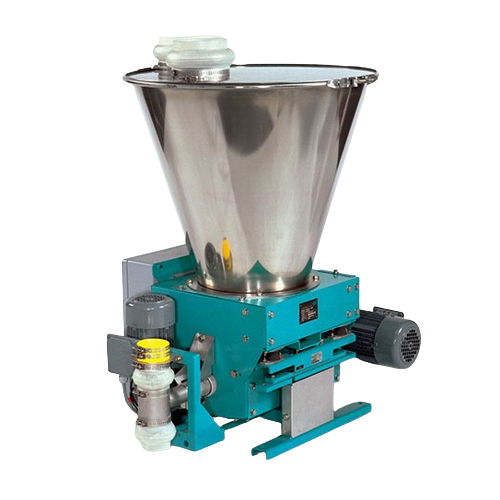
Loss-in-weight feeder for bulk solids
Ensure precise and reliable dosing of bulk solids with a compact feeder that eliminat...
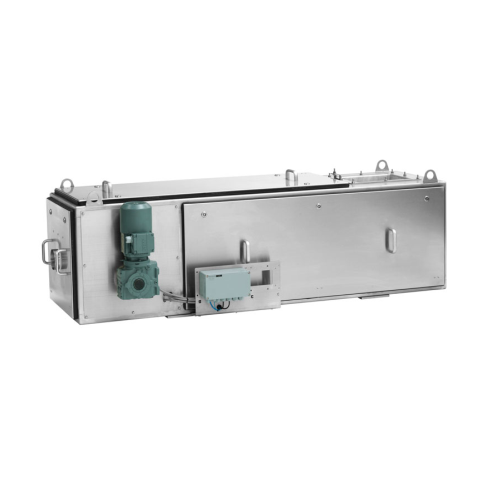
Continuous and batch feeding system for bulk materials
Achieve precise bulk material feeding with seamless integration in...
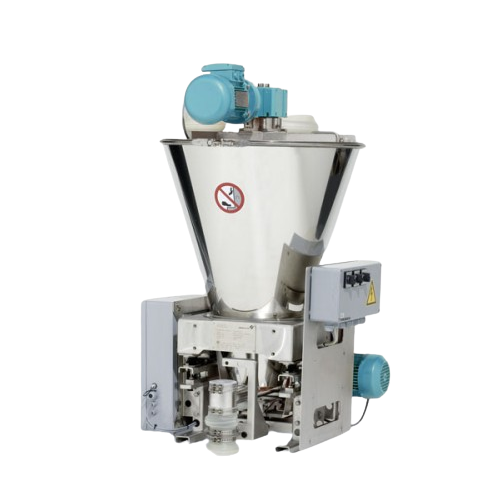
Loss-in-weight feeder for poor flowing bulk solids
Efficiently handle poorly flowing bulk solids with unparalleled precis...
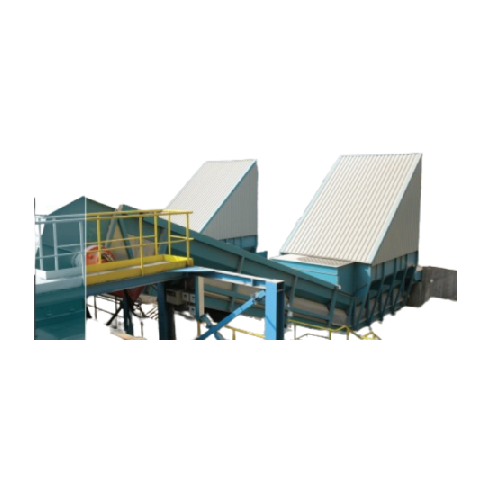
Bulk reception solution for industrial material handling
Optimize your operations with an above-ground bulk reception sys...
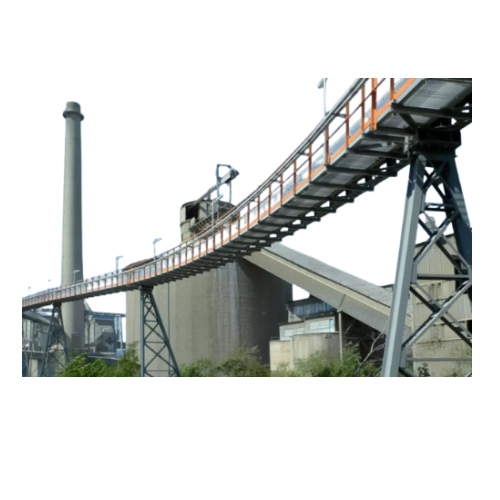
Tube belt conveyor for long-distance material handling
Ensure seamless and protective transport of bulk materials across ...
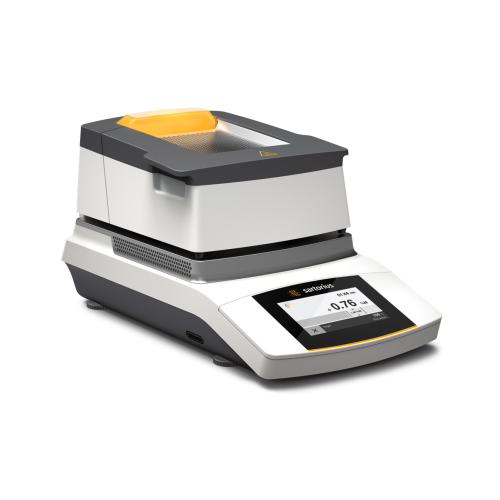
Basic moisture analyzer for laboratory weighing
Optimize moisture analysis tasks with precision and efficiency. Designed f...
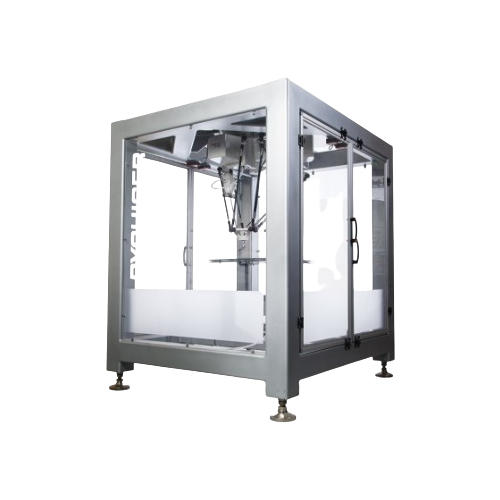
Top loader robots for precision packaging
Optimize packaging operations with versatile robotic top loaders that achieve hi...
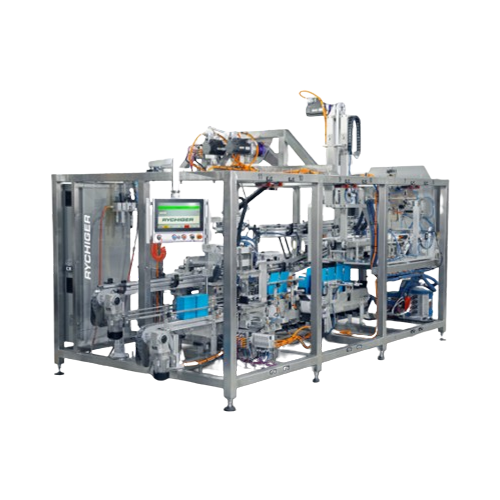
Tray packer for forming, loading, and sealing
Optimize your production line with a versatile tray packer designed to seaml...
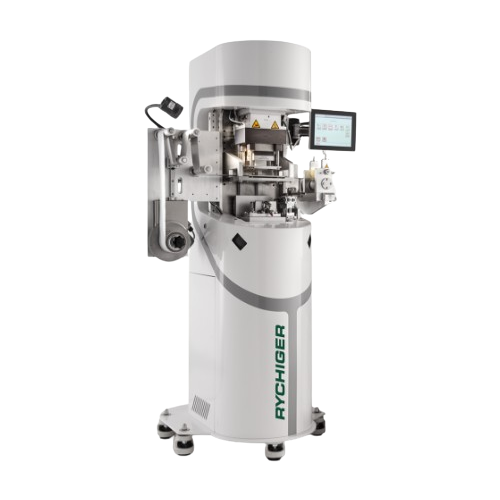
Lab punching and sealing system for cleanroom conditions
Test and refine your packaging processes with precision, ensurin...
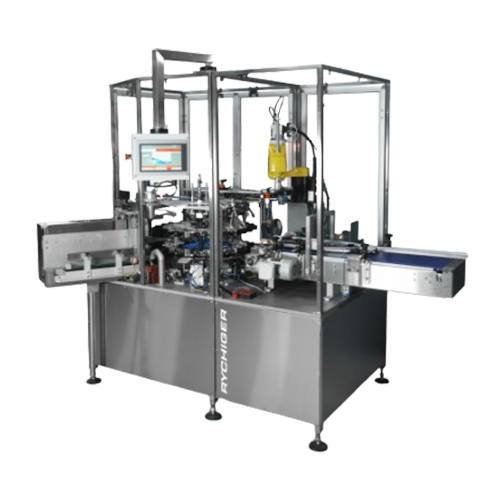
Cartoner for pharmaceutical products
Effortlessly streamline your packaging line with compact cartoning capabilities, ensur...
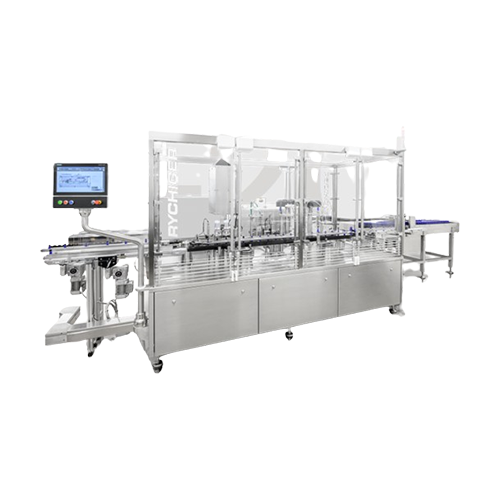
Sterile filling platform for pharmaceuticals
Achieve precise, high-speed aseptic filling and packaging with advanced compl...
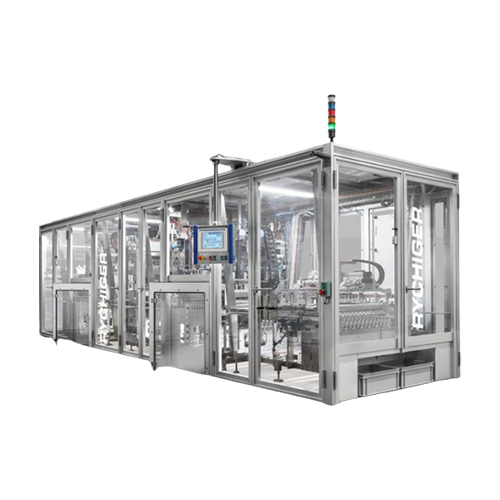
Coffee capsule filling and sealing solution
Optimize your production with a high-speed solution designed to fill and seal ...
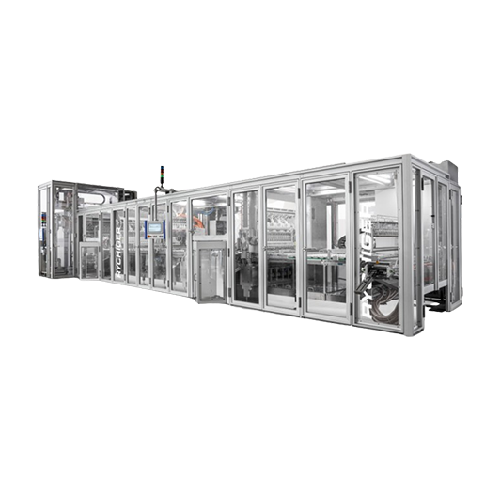
Coffee capsule filling and sealing system
Boost capsule production efficiency and reduce downtime with a high-speed system...
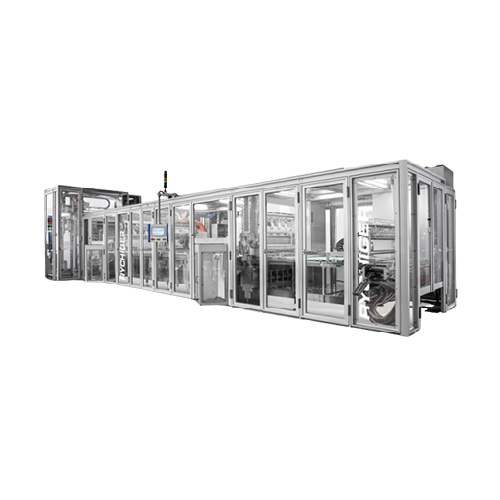
Coffee capsule filling and sealing line
Elevate your capsule production with a high-speed filling and sealing solution that...
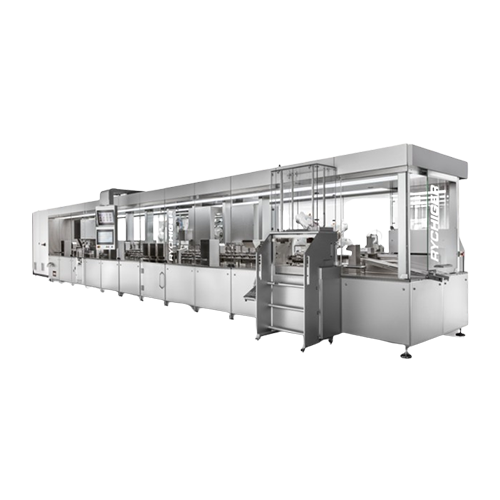
Production system for molecular diagnostics
Eliminate bottlenecks in molecular diagnostics production with a versatile sys...
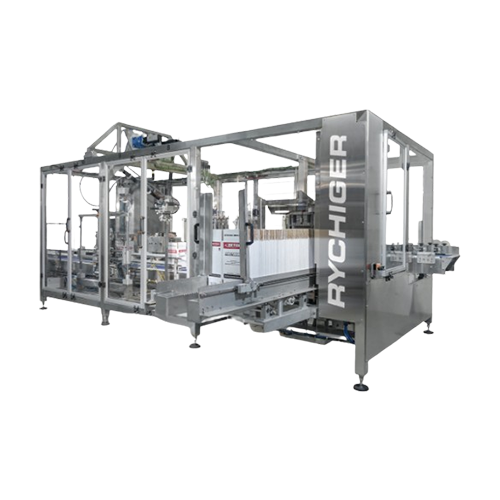
Compact case packer for secondary packaging
Optimize your secondary packaging process with a case packer that operates cle...
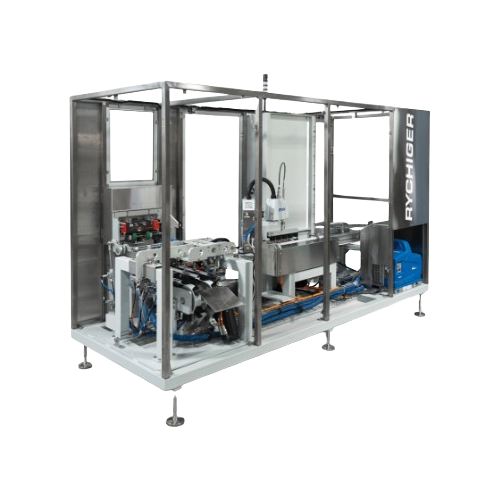
Horizontal cartoning system for coffee pods
Enhance your packaging line efficiency with a system designed for gentle handl...
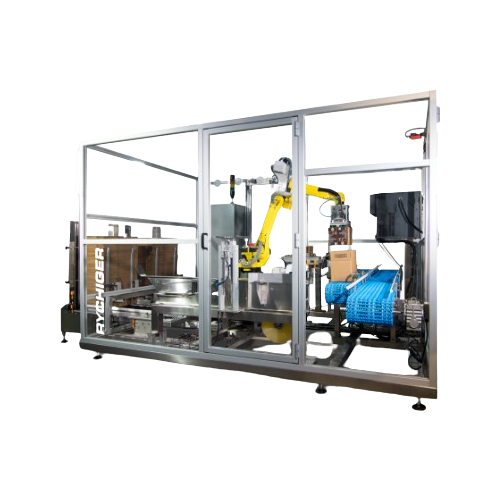
Sequentially automated case packer for small products
Efficiently pack diverse small products into large cases with preci...
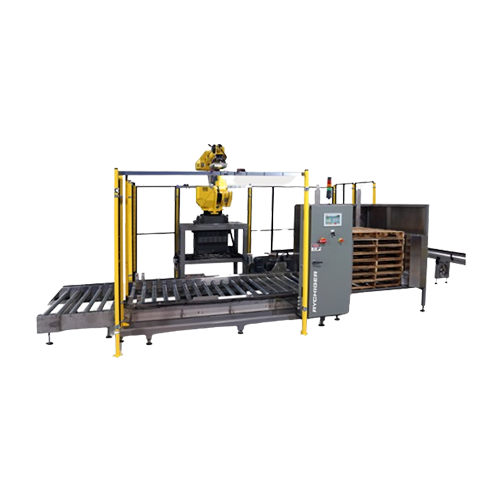
Compact palletizer for food and beverage products
Optimize your end-of-line operations with a space-saving palletizer tha...
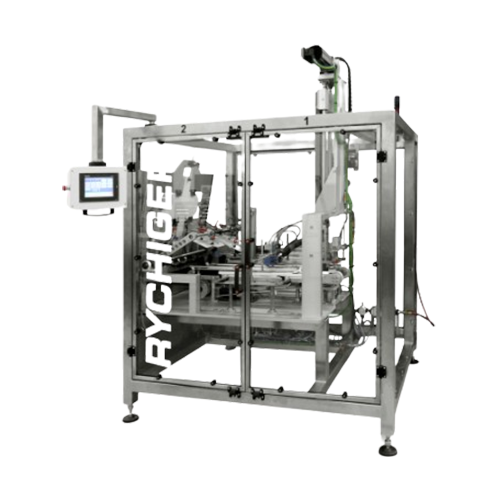
Standardized modular tray former for secondary packaging
Optimize your packaging line efficiency with this modular tray f...
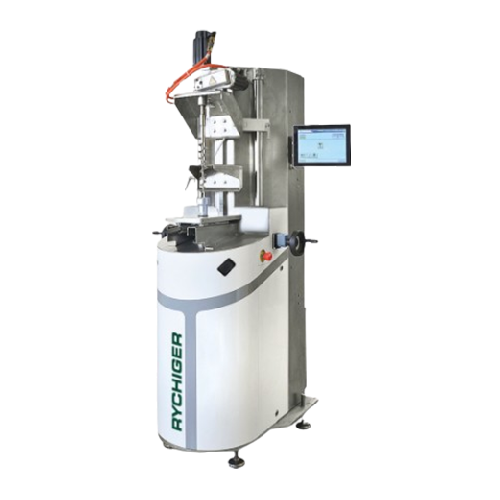
Lab device for testing coffee capsules
Achieve precise testing and reproducibility of coffee capsule parameters crucial for...
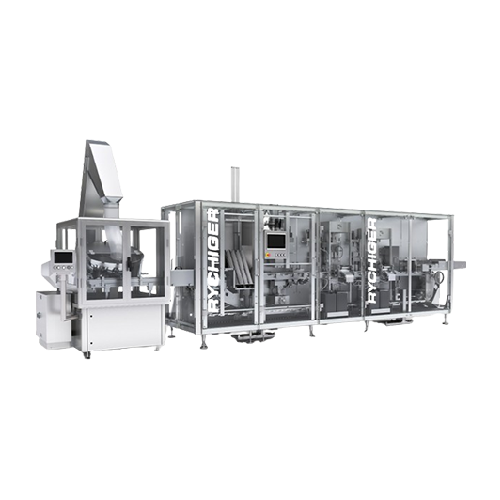
Filling and sealing solution for beverage capsules
Optimize your production with a modular capsule filling and sealing so...
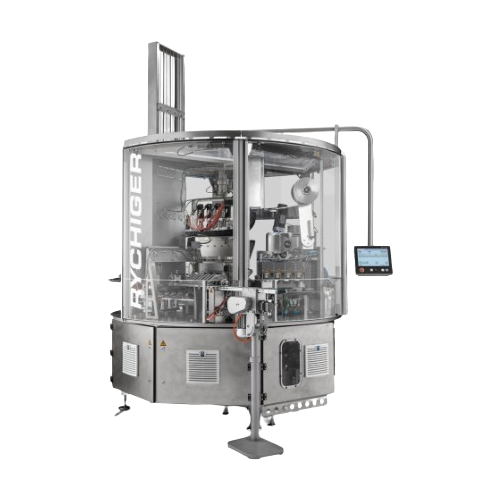
Coffee capsule filling and sealing machine
For producers seeking a compact yet powerful machine, this system efficiently f...
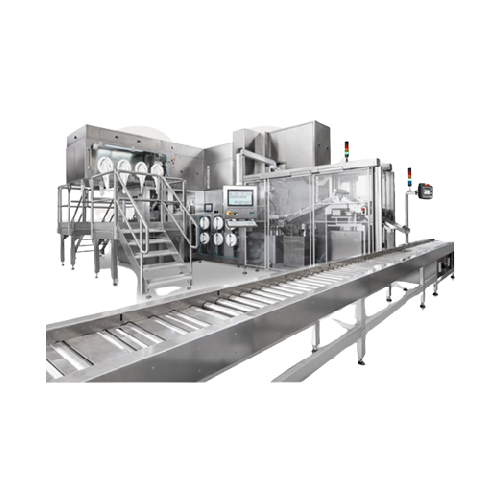
Filling solution for powders and liquids in diagnostics
Simplify precision filling of diverse products, from freeze-dried...
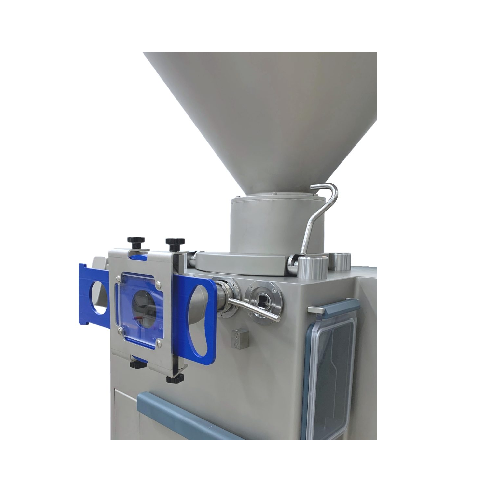
Manual burger former for food production
Streamline your food product shaping process with manual precision, ensuring unifo...
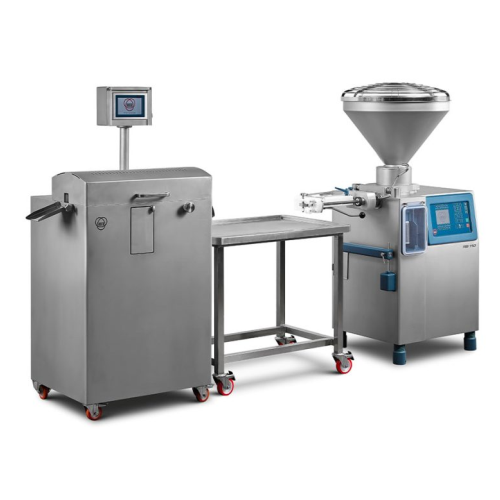
Sausage cutting solution for natural and artificial casings
Achieve precise sausage cuts at high speeds with solutions f...
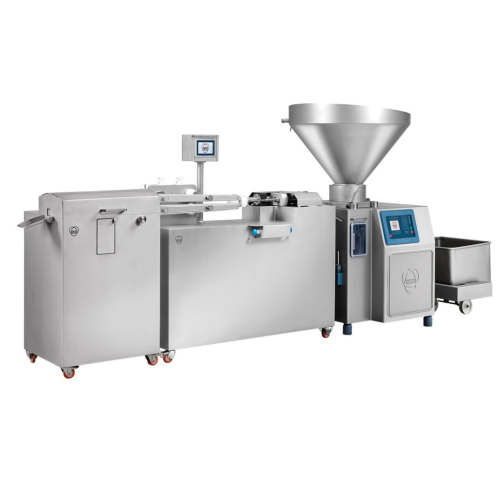
Sausage production line with in-line cutting system
Efficiently achieve precise portion control and separation in sausage...
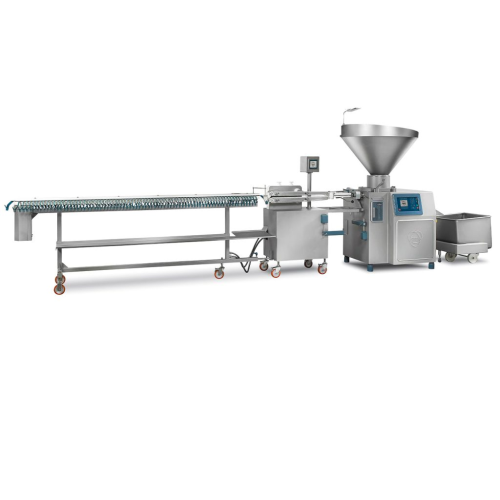
High-speed sausage production system with synchronized hanging
Enhance your high-speed sausage production with precision...

Vacuum filler for coarse and dry sausage products
Optimize your sausage production with a machine that ensures consistent...
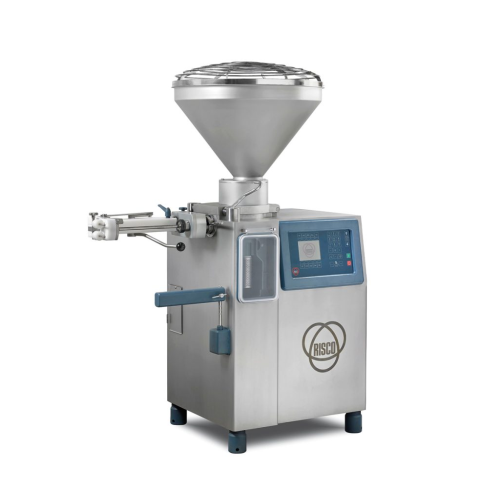
Portioning and filling system for sausage production
Achieve precise portioning and efficient filling for a diverse range...
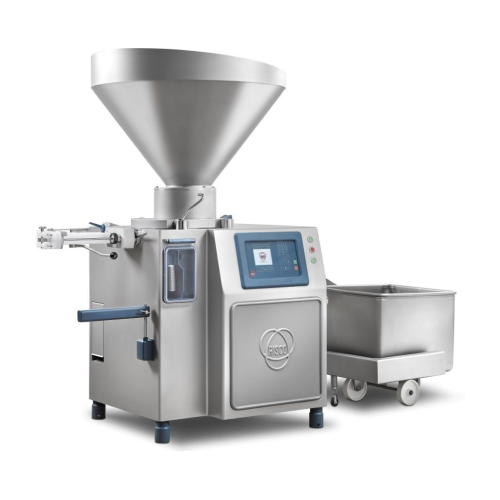
Industrial vacuum filler for large-scale food production
Enhance your production efficiency by integrating a vacuum fille...
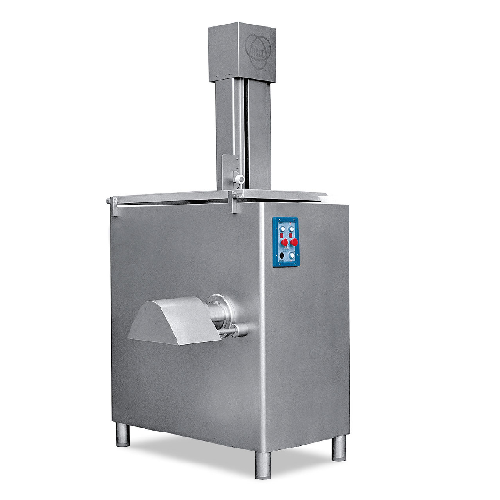
Industrial grinder for fresh meat and food products
Optimize your fresh food processing with a versatile grinding solutio...
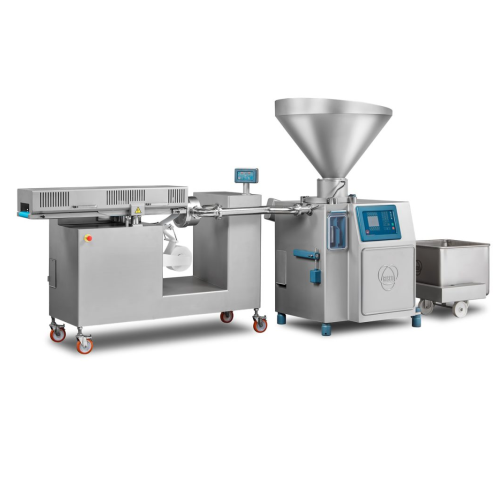
Portioner for ground meat production
Effortlessly streamline your high-volume meat processing with a versatile system desig...
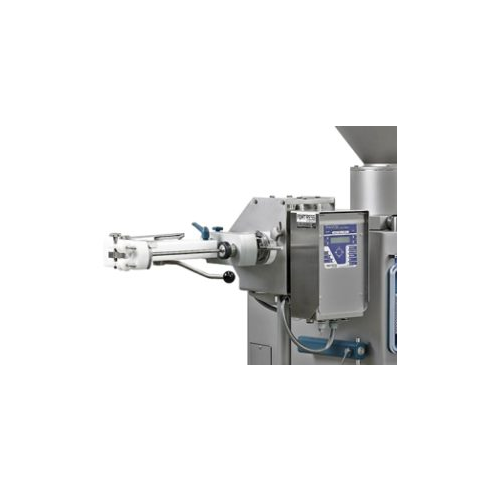
Metal detection system for twisted sausages production
Ensure the safety of your twisted sausage production line by detec...
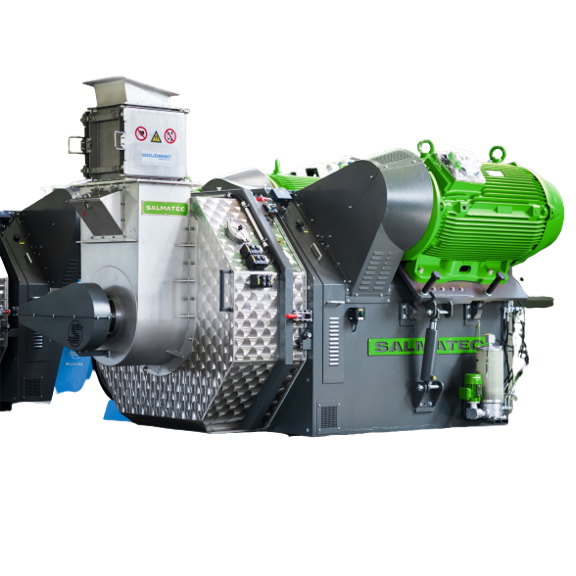
Complete pellet line
Large industries are shifting towards more environment-friendly technology, such as recycling wastes and...
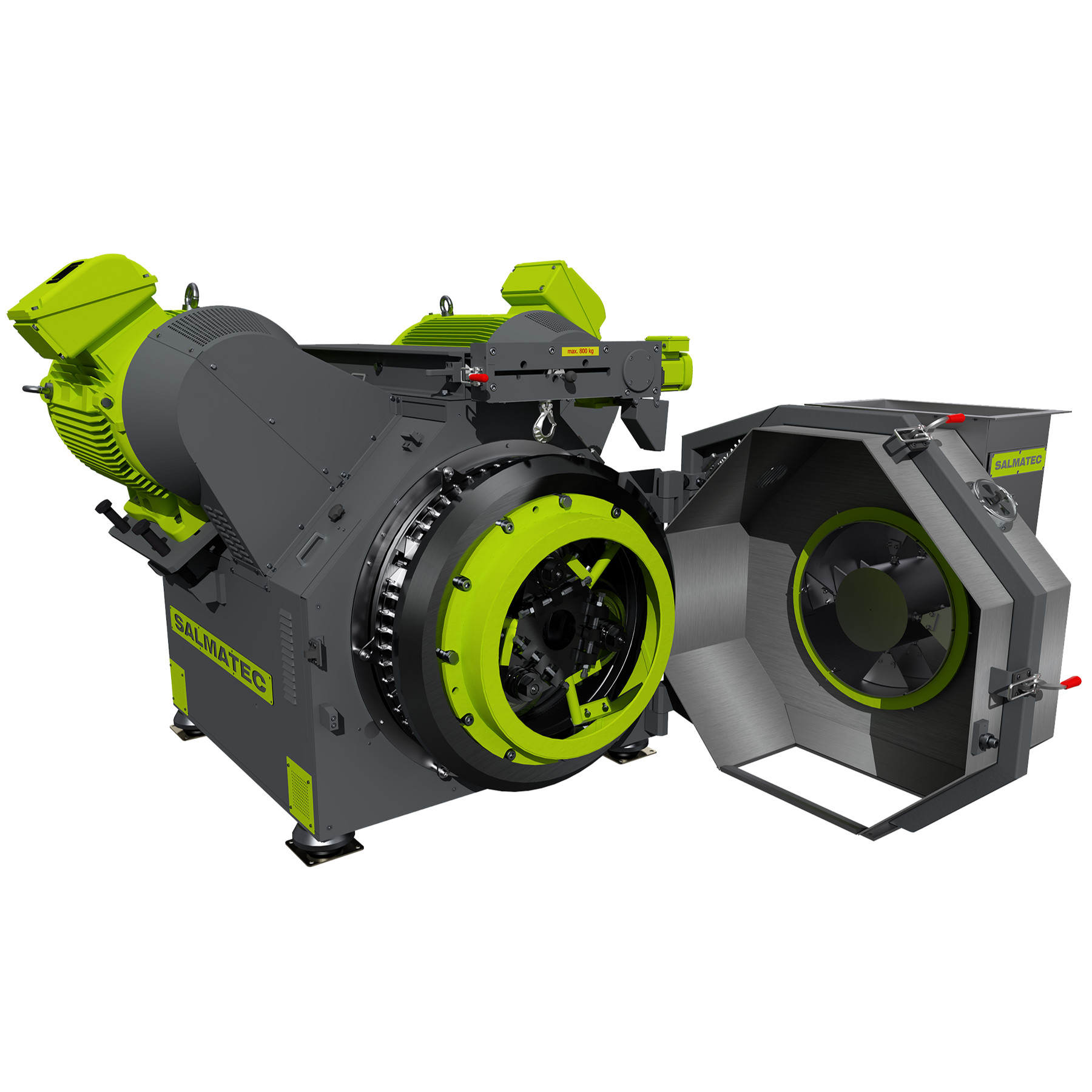
Industrial pellet mill
At the industrial level, the application areas of pellets range widely in fields such as feeds, biomas...

Energy saving cabinet dryer for food
Traditional drying systems use a lot of energy and take a long time to dry the product...
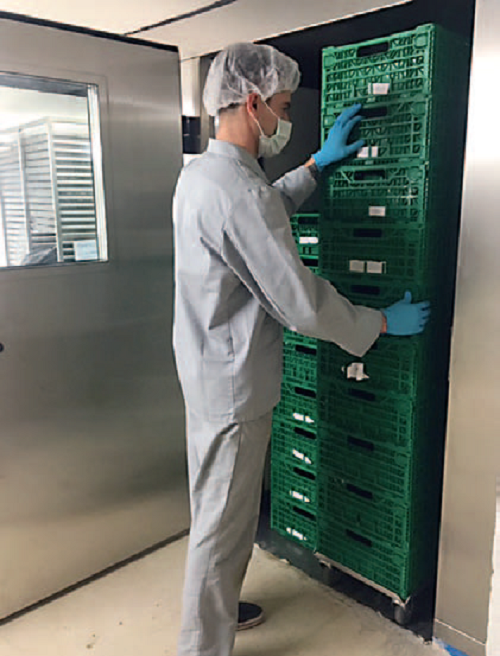
Cabinet dryer for cannabis
If you need careful drying for products like pharmaceutical-grade cannabis buds then traditional ...
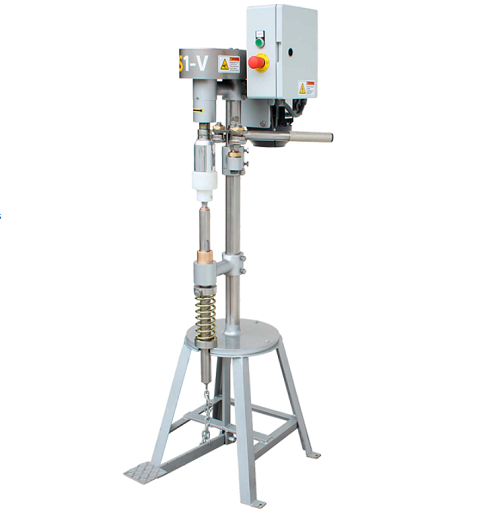
Semi-manual can sealer
When starting out in the canned product business, you do not necessary want to invest in industrial sc...
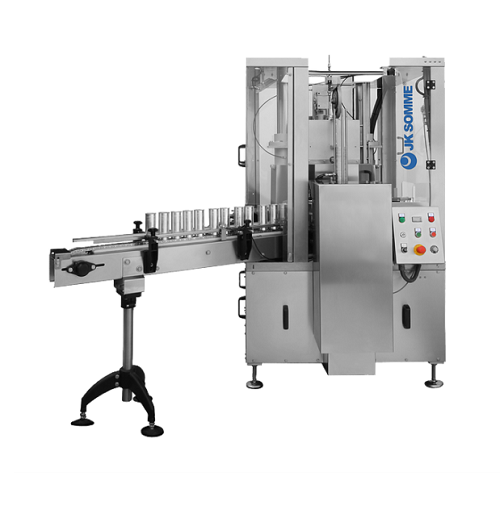
Medium scale round can seamer
Automatic seaming of cans of craft bear can be quite the hassle with the movement from the cen...
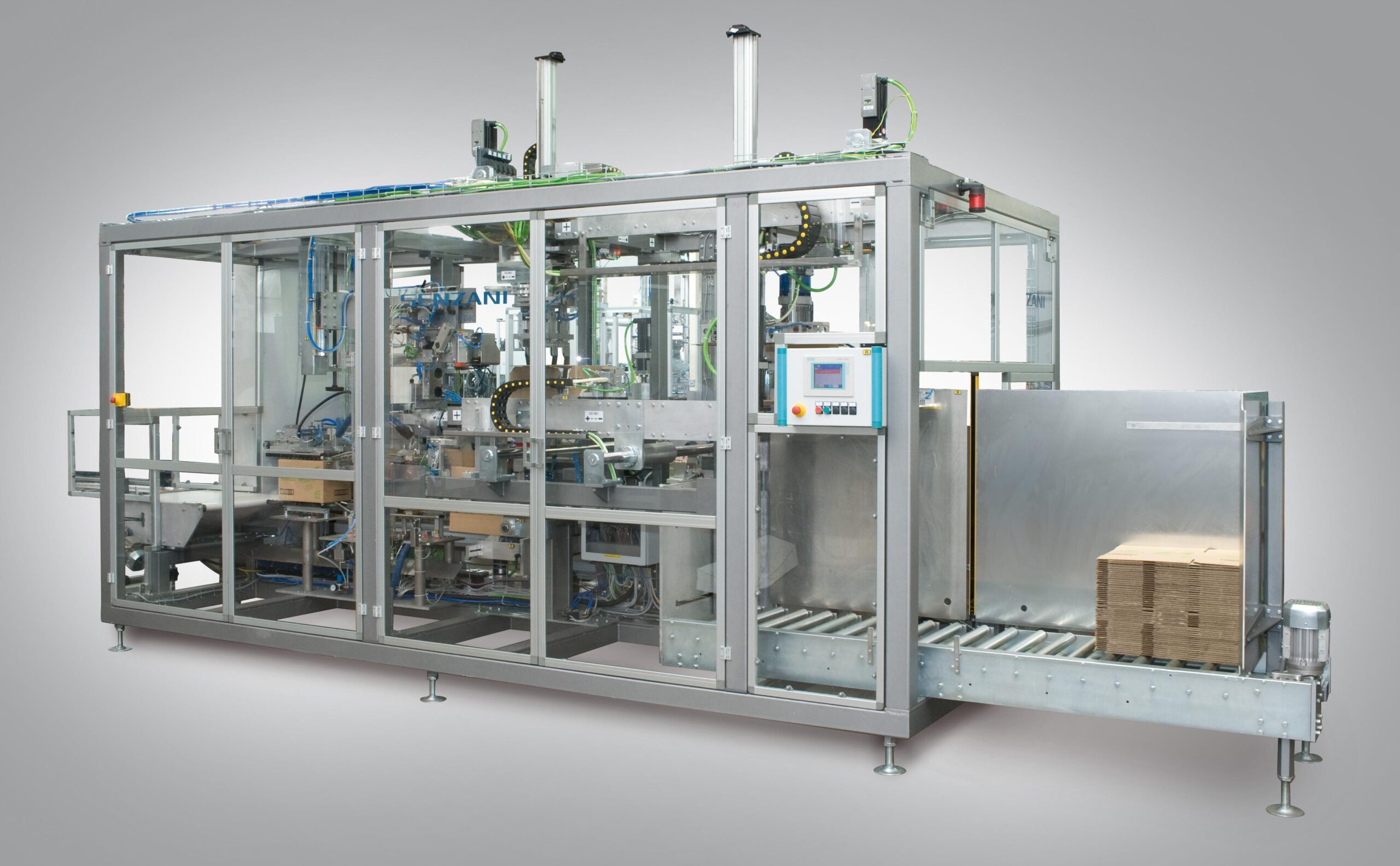
Case packer machine for pouches
Automated case packer machines are a good solution to achieve reliability and to increase th...
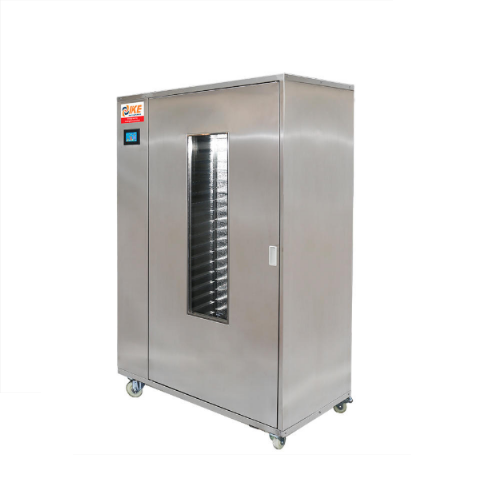
Industrial drying cabinet
The production of high-quality biltong and similar dried meat products can pose problems with main...
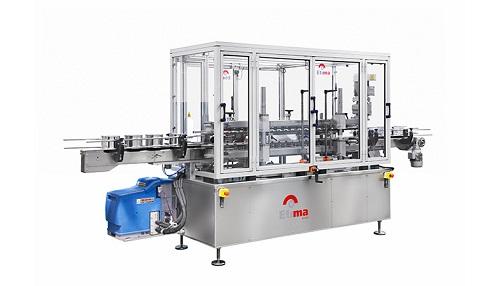
Linear machine for wraparound label
Wraparound labels allow you to offer detailed information using a small space or fit ex...
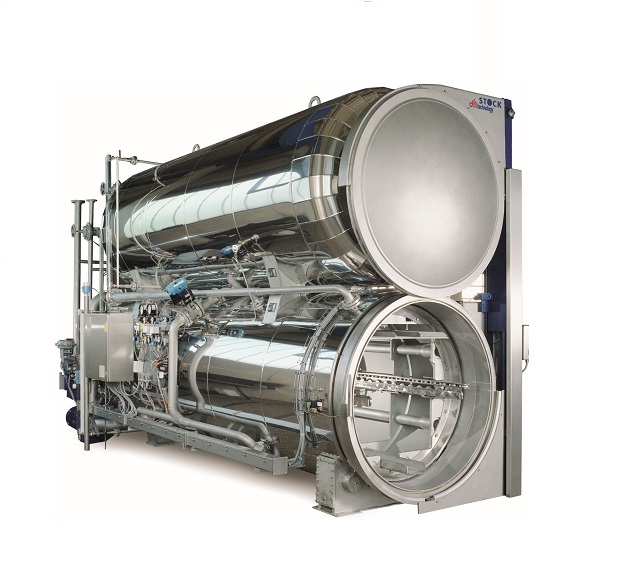
Autoclave for canned food
Sealing and cooking products in cans, pouches or other containers is a very popular method of pres...
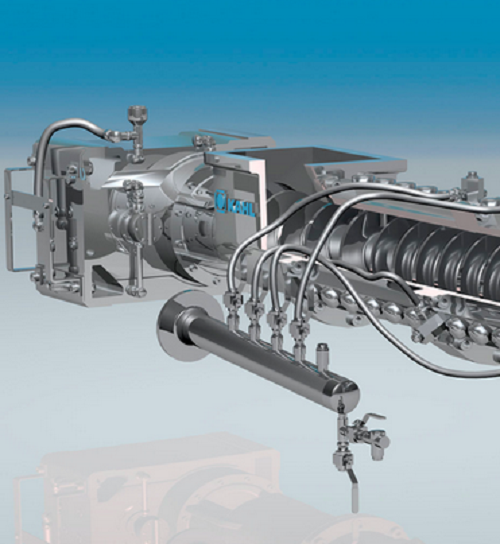
Extruder with annular gap expander
Products can be extruded with various shapes and characteristics by controlling the nozz...
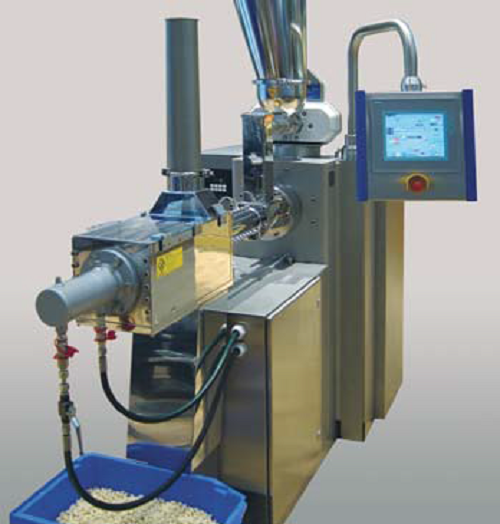
Laboratory extruder
Products can be extruded with a variety of shapes and characteristics by controlling the nozzle geometry ...