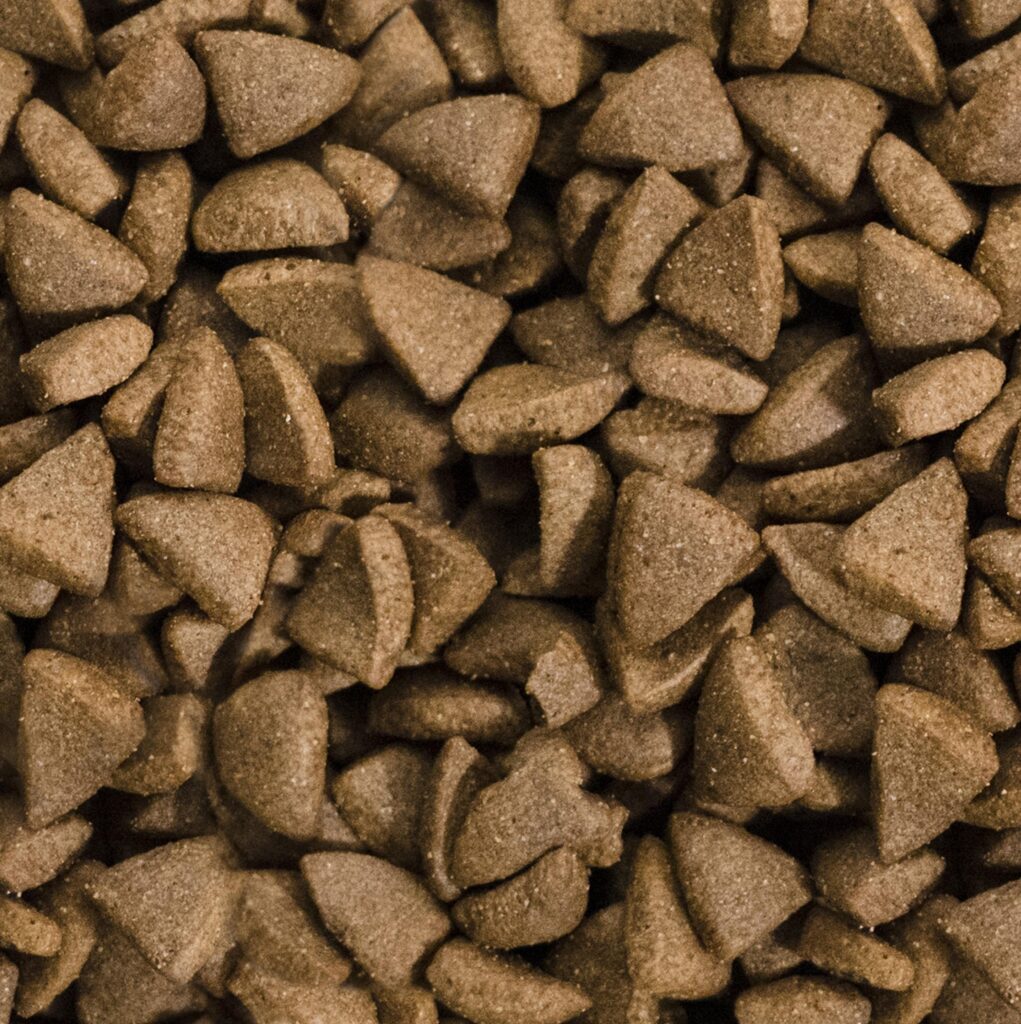
Making Dry Pet Food
Find innovative production technology for making dry pet food and connect directly with world-leading specialists
Around 1860, American businessman James Spratt made dog biscuits by mixing vegetables, flour, beetroot, and meat. His novel idea came after he noticed dogs eating leftover biscuits from ships in England. Following the commercial success in Britain, he started production in America, and it didn’t take long before others developed their own baked pet food formulas. But the need for more palatability led to experiments beyond the oven. In 1956, extruded dry pet food production made its splash on the market.
Stories about dry pet food
Select your dry pet food process
Tell us about your production challenge
Dry pet food production is not all about extrusion
About 95% of dry pet food production uses the extrusion technique. Pet food manufacturers choose this process not only for its convenience and low cost but also for its flexibility and efficiency.
The extrusion method gives you better control of processing parameters such as pasteurization and density. At the same time, however, the high temperature and pressure used in extrusion reduce the overall nutrient content. Consequently, this pet food type requires further coating with oil, vitamins, and other additives.
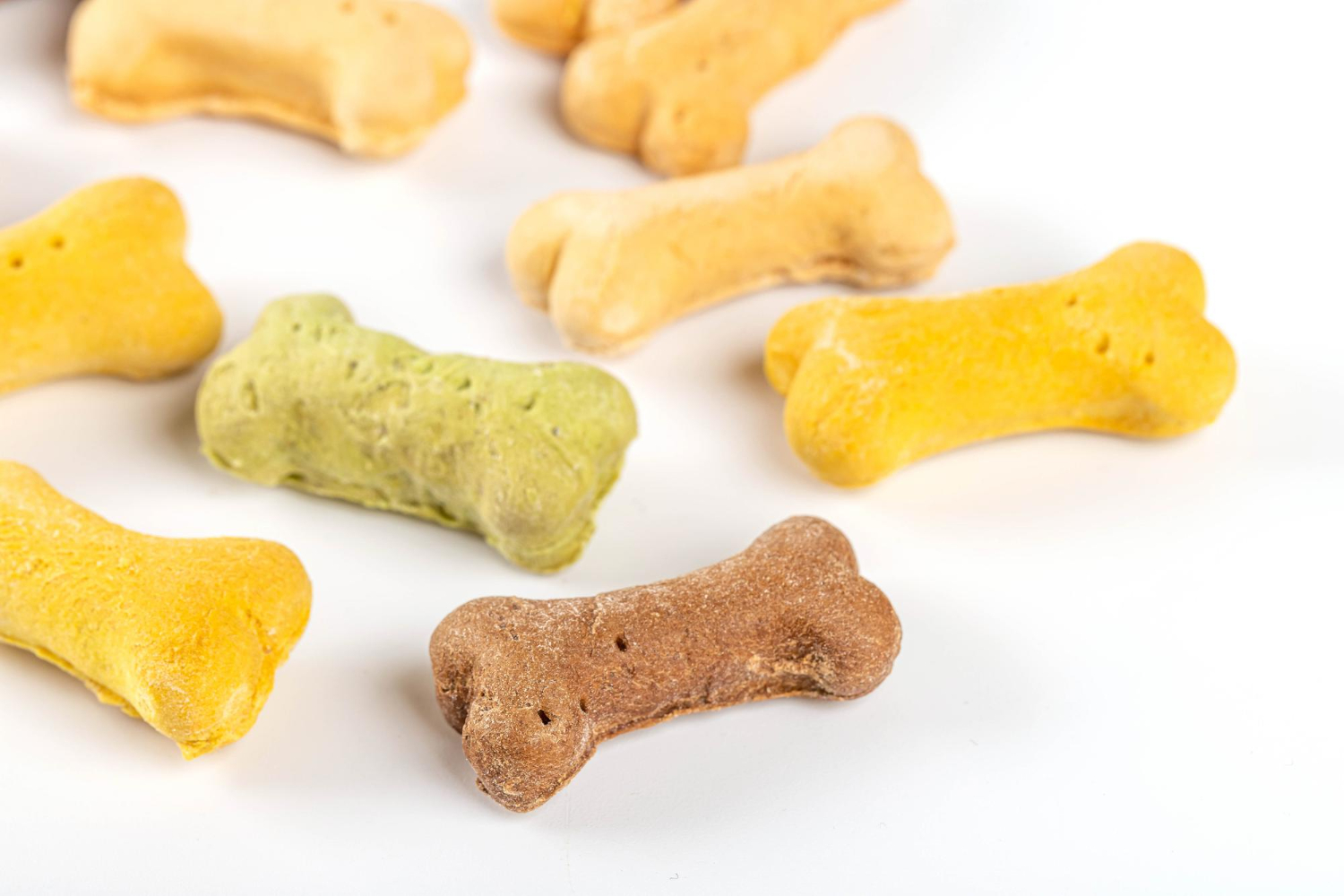
Baking retains higher nutritional values of ingredients
The versatility of extrusion allows you to make a range of pet foods, including kibbles, treats, snacks, and semi-moist foods. But you can use alternative methods such as baking, air-drying, freeze-drying, cold pressing, and cold extrusion. However, most of these methods are expensive compared with extrusion and are rarely applied. But baking is trying to find its way into the market.
Baking involves a milder process for nutrients, similar to baking human food. The lower temperatures and longer residence time help preserve tastes and nutritional values better than extrusion. However, the process takes about 10 times longer, making it a more expensive production option.
Alternative protein in dry pet food production
Producers and customers are increasingly turning to sustainable products, and the pet food sector is no stranger to this change. Manufacturers are adapting their methods to align with the UN’s sustainable development goals (SDGs).
One method of achieving SDGs is replacing fishmeal and soybean meal protein with black soldier fly protein. Insects have always been part of the animal food chain. Insect proteins present an alternative to integrating dry pet food production into the circular economy.
Processing steps involved in dry pet food making
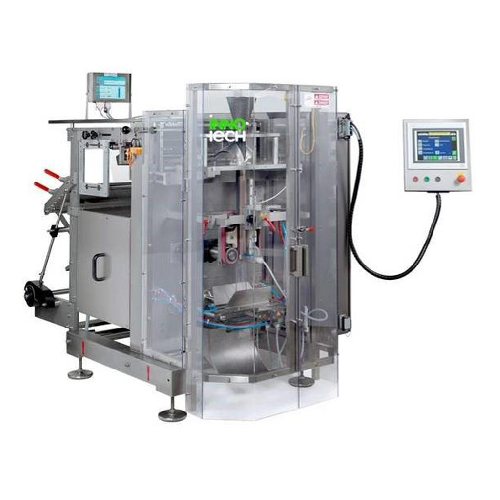
Bagging
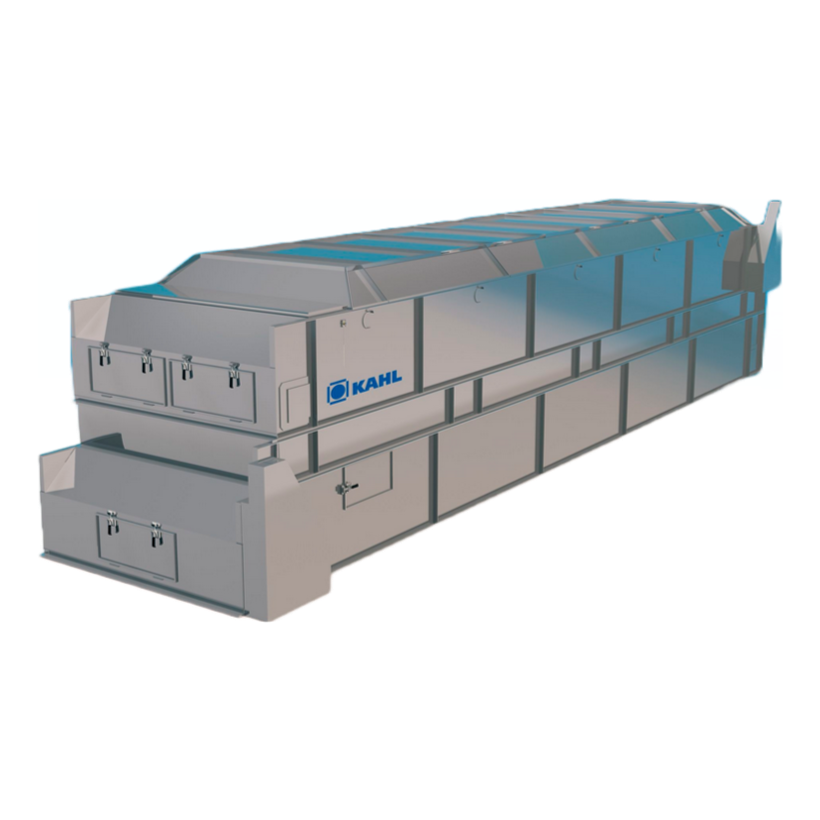
Belt dryers
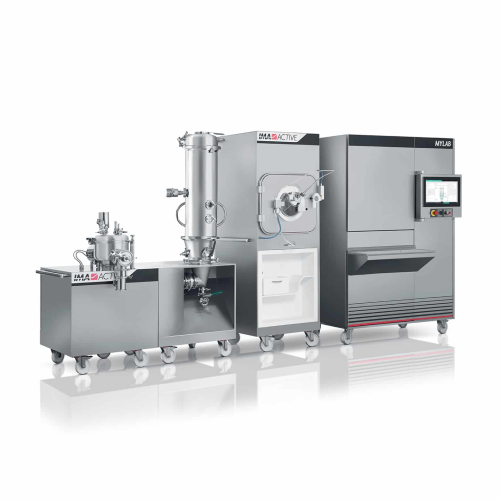
Coating

Conical screw mixers
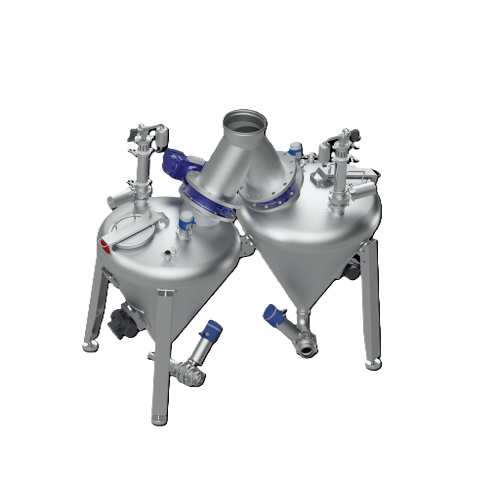
Conveying
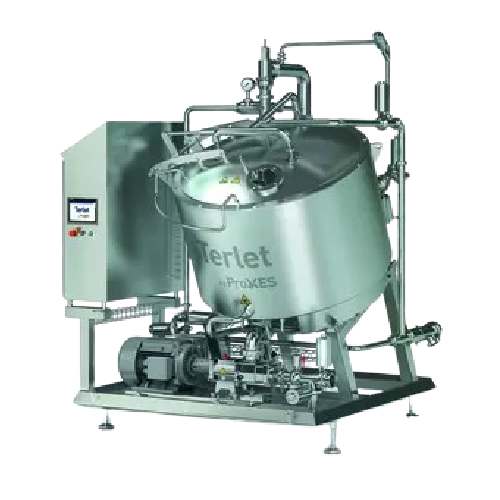
Cooking
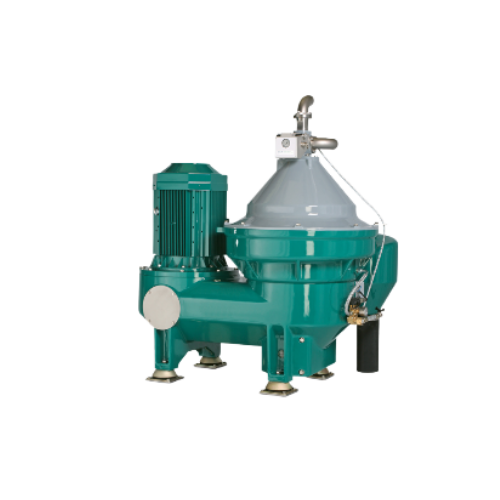
Cooling
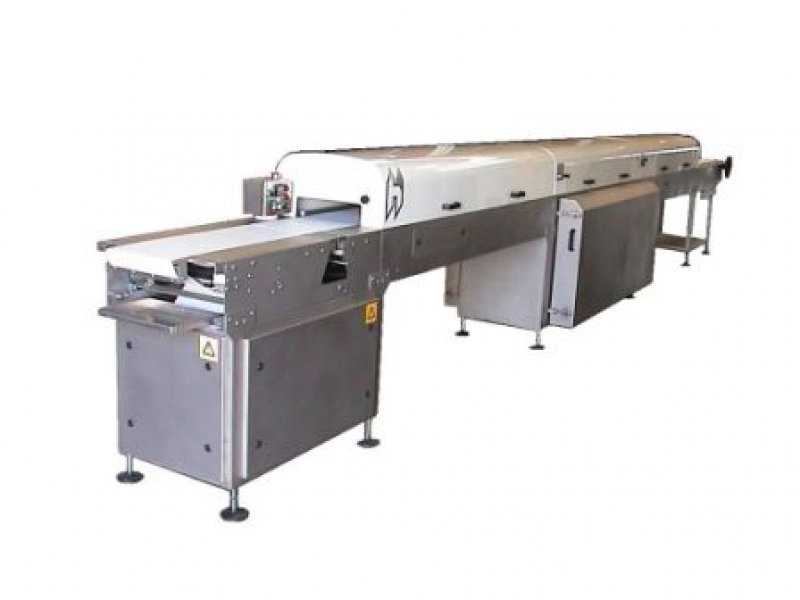
Cooling tunnels
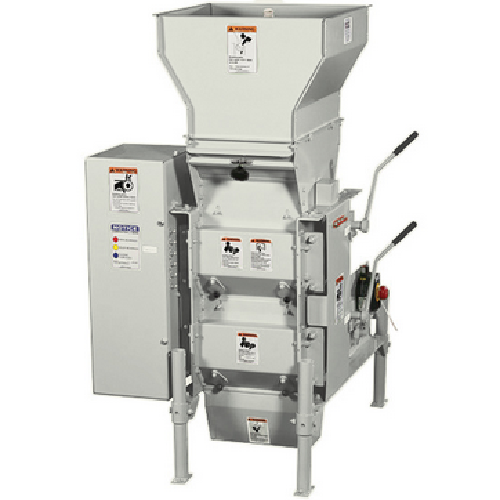
Crushing
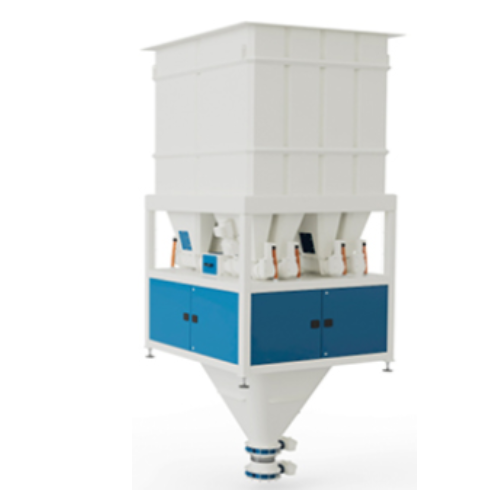
Dosing
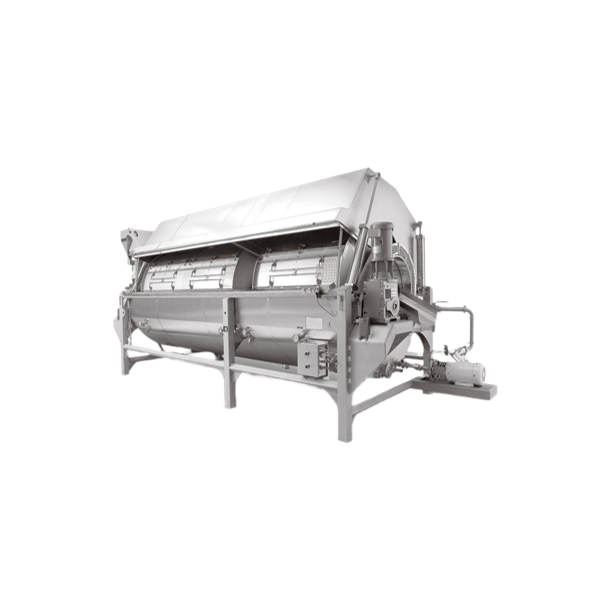
Drum coolers
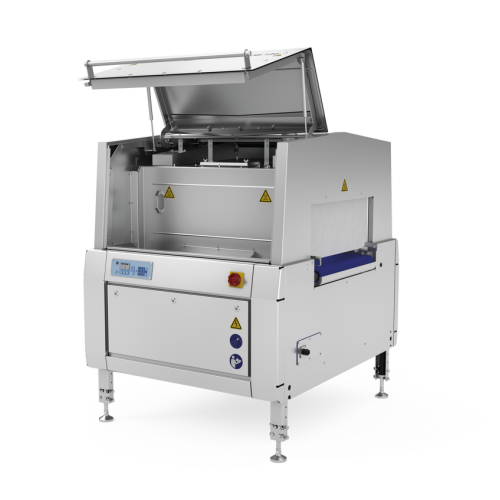
Drying
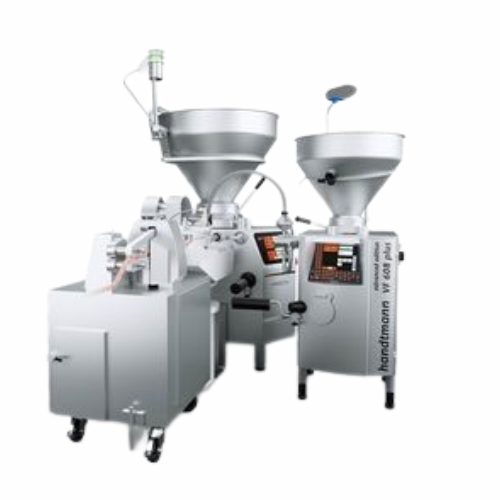
Extrusion
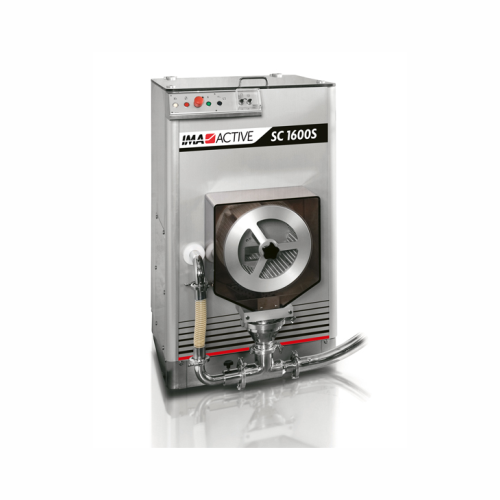
Feeding
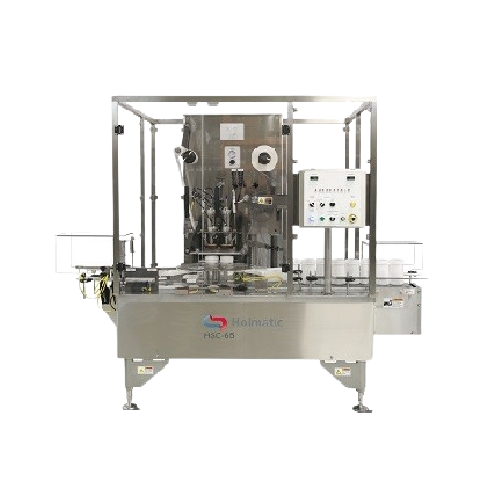
Filling
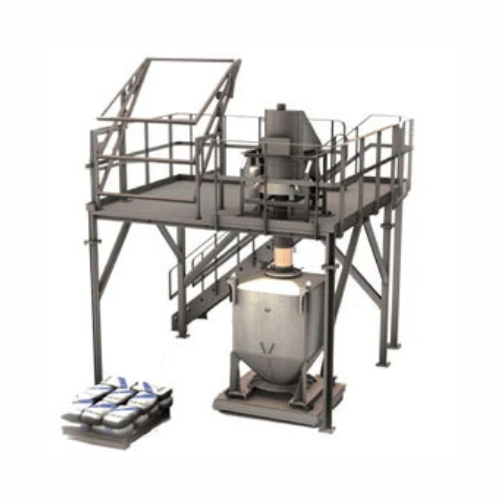
Formulation
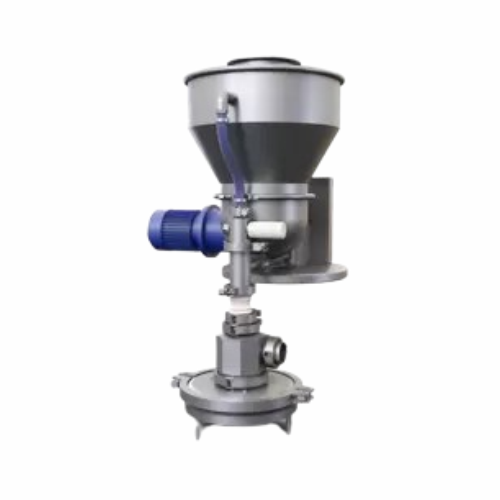
Grinding
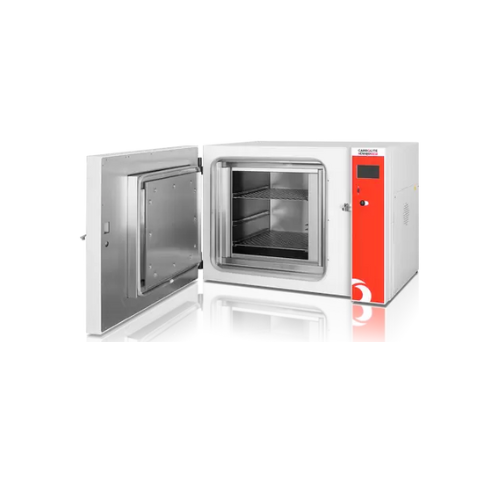
Heating
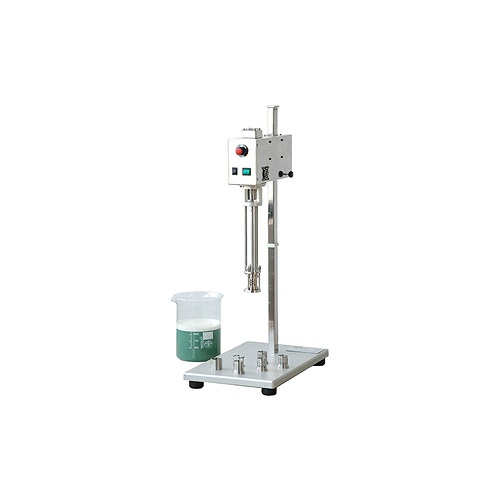
High-shear mixers
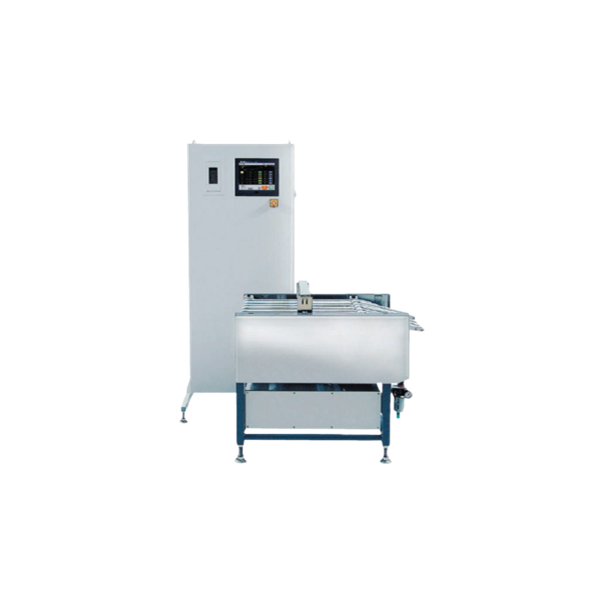
Industrial checkweighers
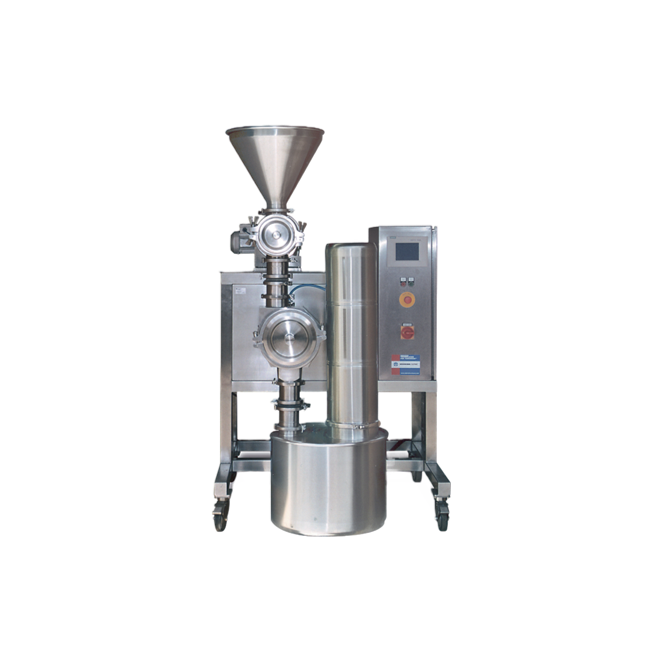
Industrial hammer mills
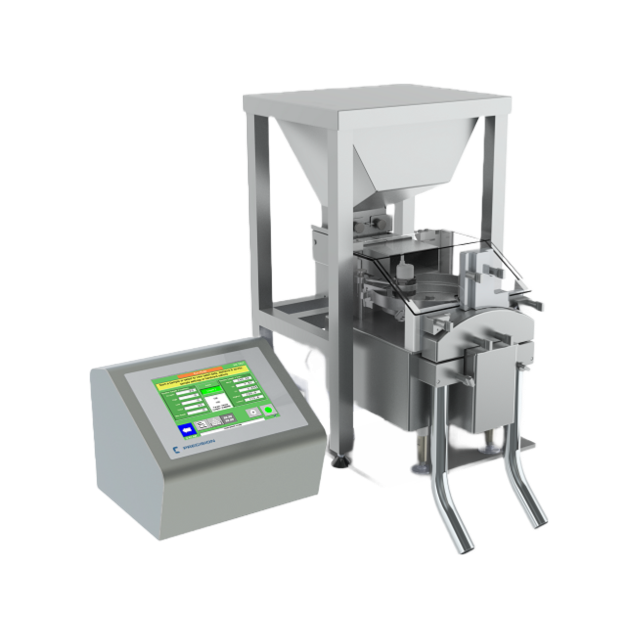
Industrial hoppers
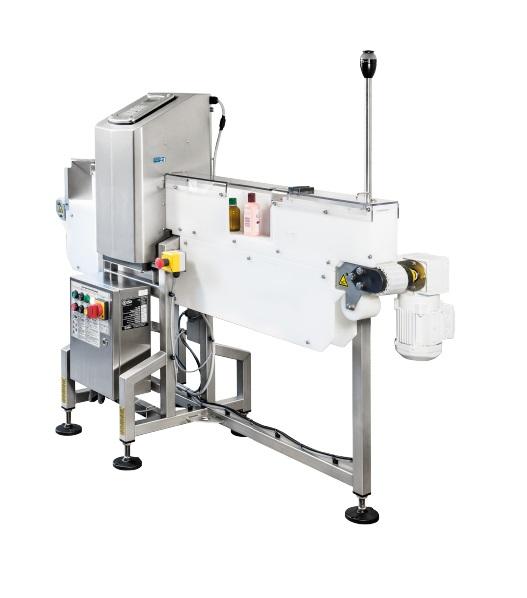
Industrial metal detectors
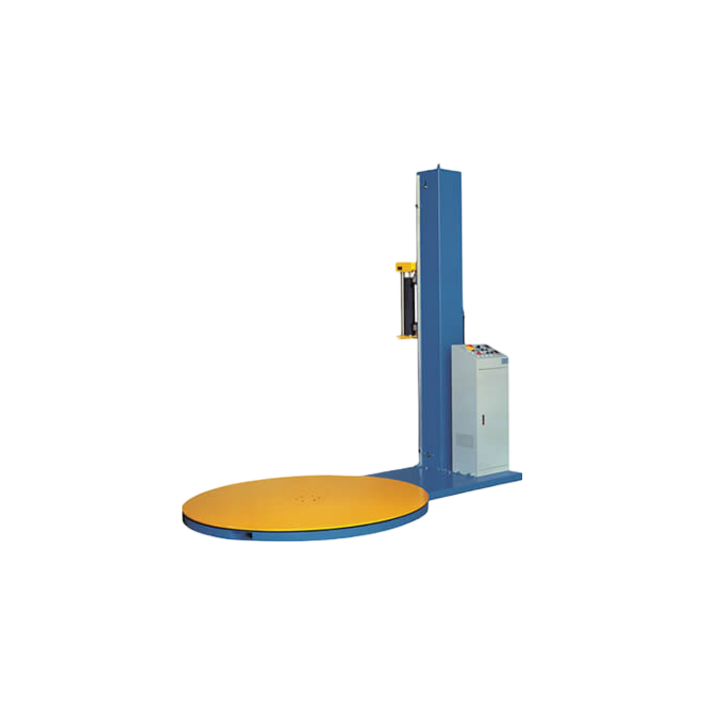
Industrial stretch wrappers
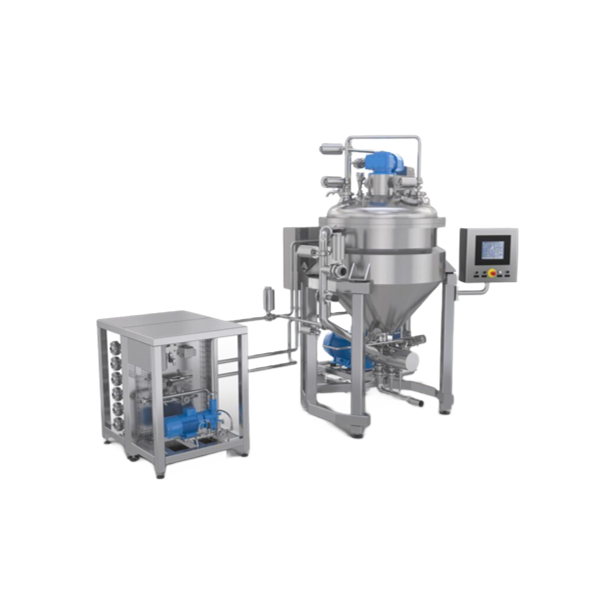
Industrial vacuum mixers
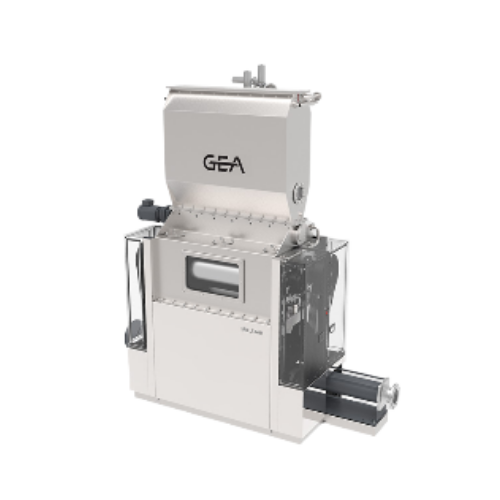
Milling
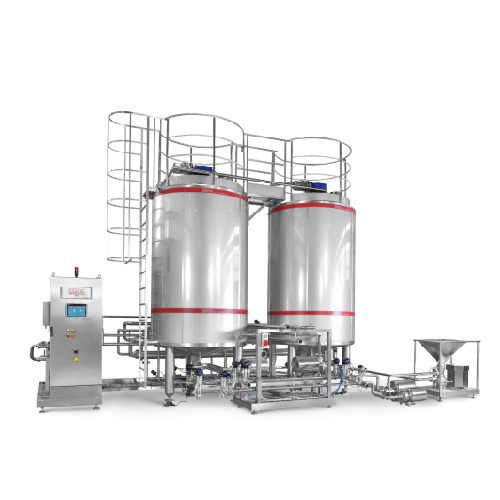
Mixing
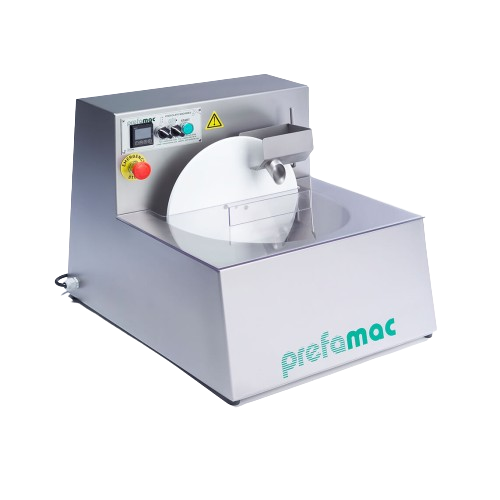
Moulding
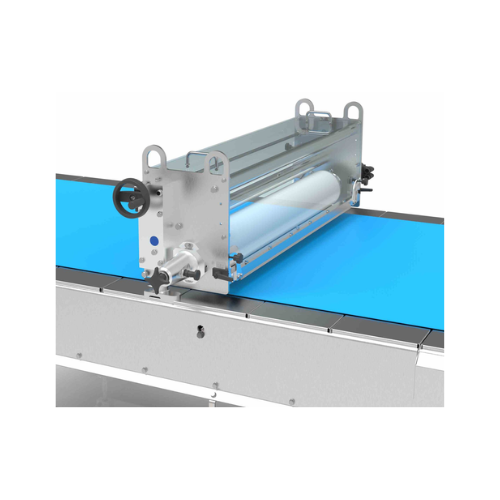
Pressing
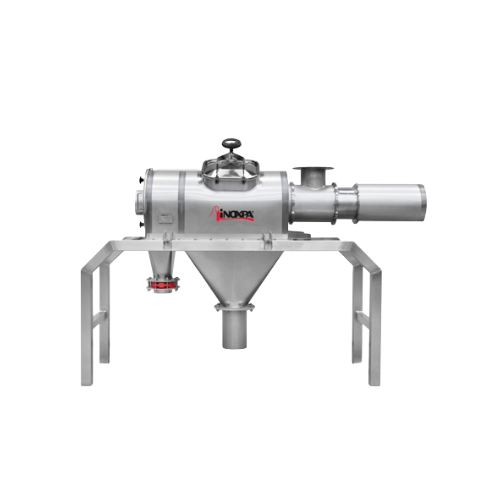
Sieving
Which dry pet food technology do you need?
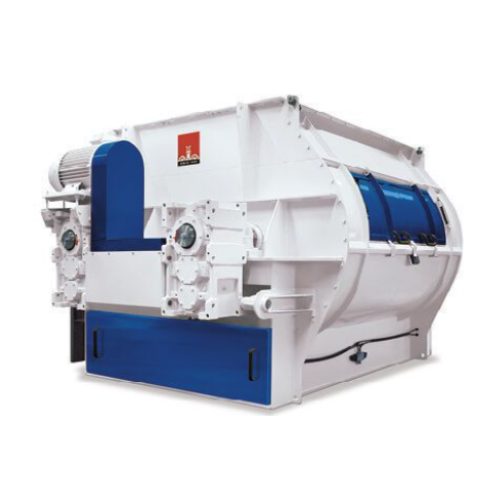
Double shaft paddle mixers for industrial powders and granulates
Achieve precise mixing and homogenization of dry powder...
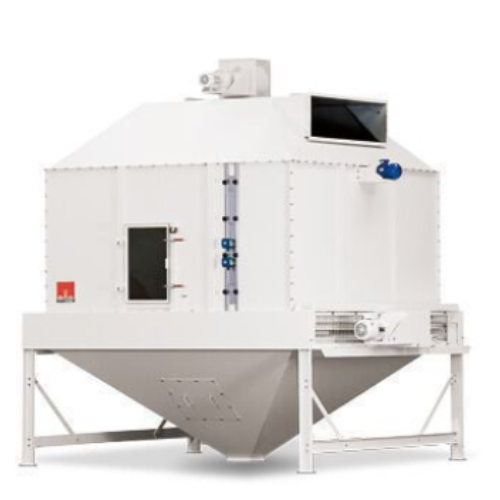
Counterflow dryer for pet food and fish feed
Optimize moisture control and enhance feed quality with efficient drying, cru...
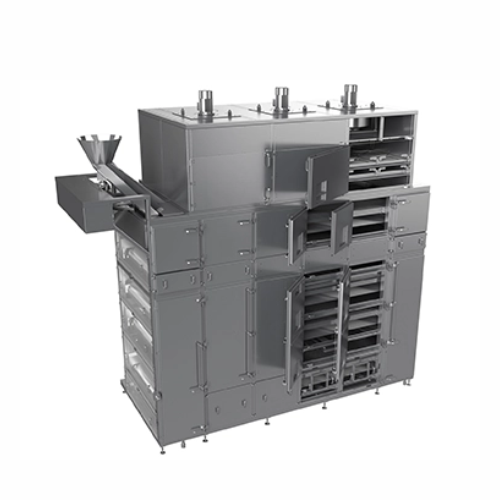
Continuous belt dryer for industrial production
For operations requiring precise moisture control, this continuous belt dr...
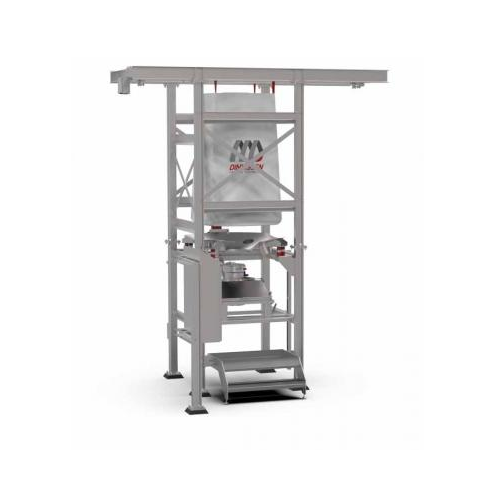
Modular big bag unloading station for various materials
For hassle-free handling of bulk materials, this modular solution...
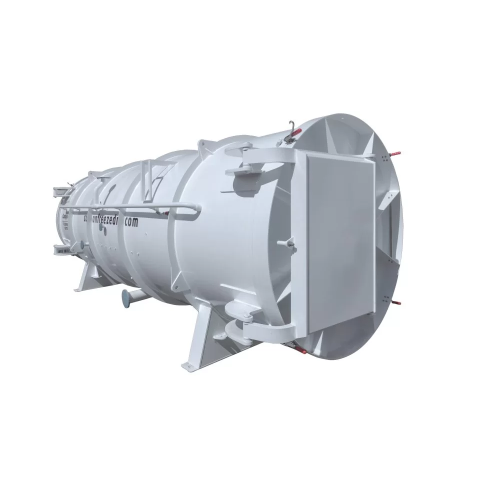
Large-scale industrial freeze dryer
Achieve precise moisture control and preserve product integrity with a large-scale free...
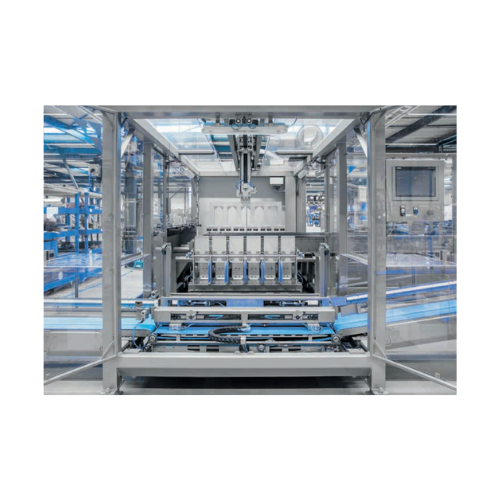
High-speed vertical and horizontal case packer
Enhance your packaging line efficiency with a versatile case packing soluti...
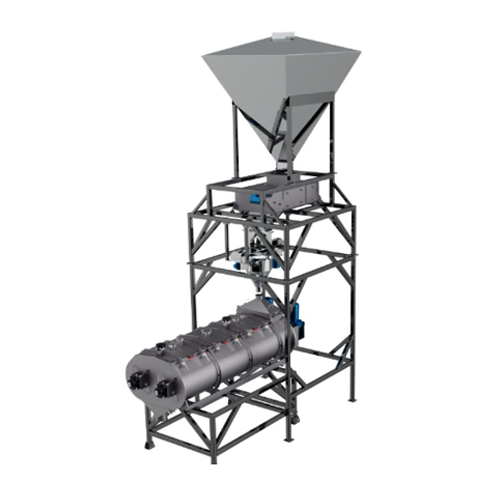
Coating and enrobing system for pet foods and treats
Achieve precise coating and flavoring of various food and feed produ...
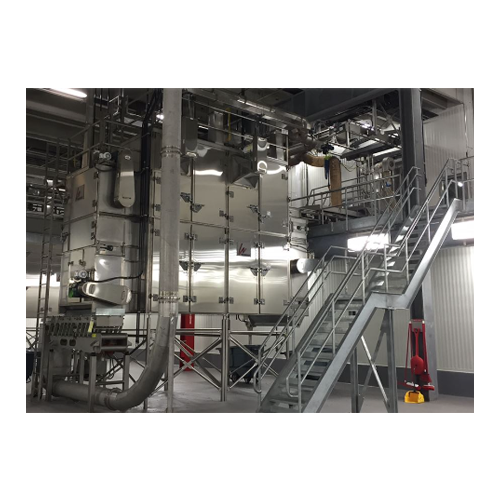
Convection roaster for pet food and delicate food products
Achieve optimal texture and moisture control in delicate food...
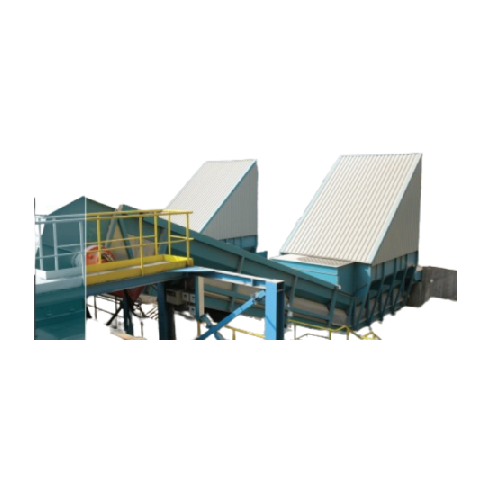
Bulk reception solution for industrial material handling
Optimize your operations with an above-ground bulk reception sys...
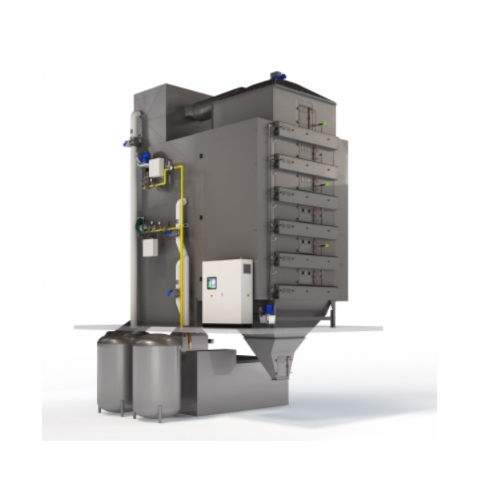
Industrial heat pump dryer
The drying of extruded products is highly energy-demanding in traditional belt dryers that use ga...
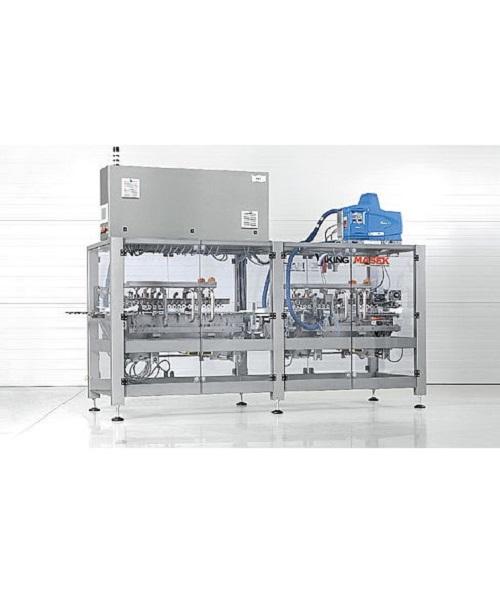
High speed carton closing machine
Choosing a carton closing machine becomes a significant consideration when the closing of...
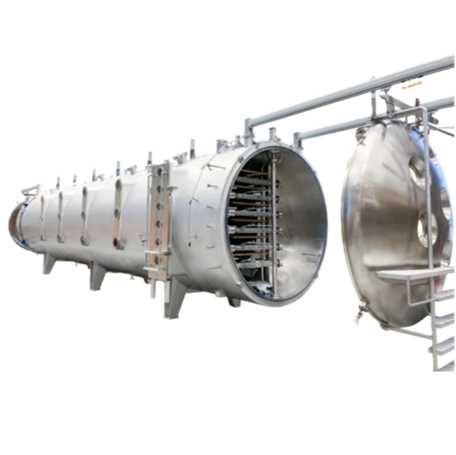
Vacuum belt dryer for instant drink powders
Extracting the essential acids and compounds from fruits and plants is a compl...
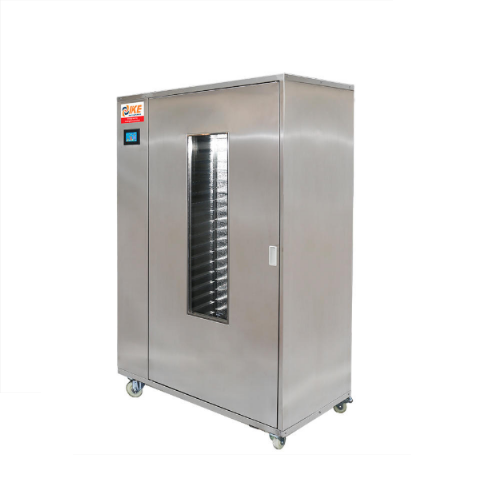
Industrial drying cabinet
The production of high-quality biltong and similar dried meat products can pose problems with main...
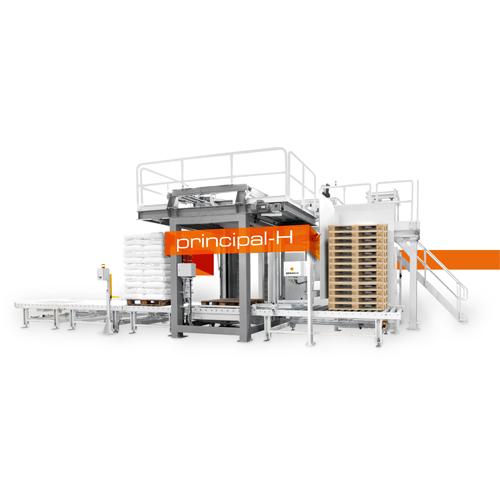
Automatic palletizer machine for bags and boxes
The effective placement and positioning of bags and boxes can be a challen...
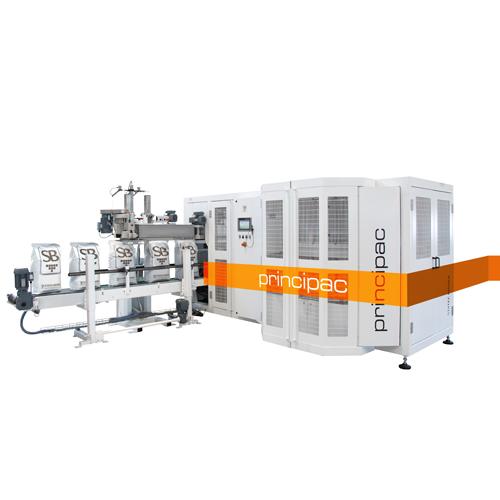
Open mouth bagging machine
If you are a manufacturer of fertilizers, bulk chemicals, sugar, seeds, or any grains it is likel...

Open mouth bag filling machine for powders
The packaging of powdery products such as flour can be challenging as it is cru...
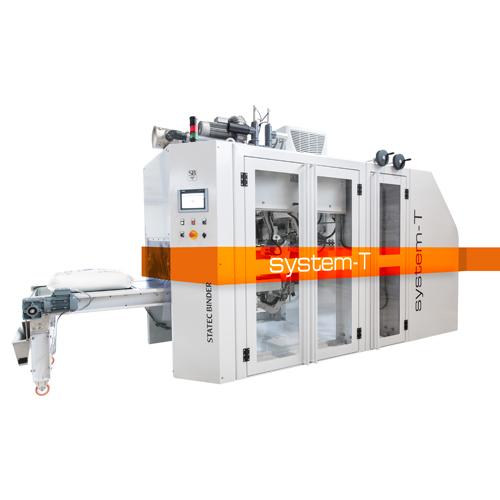
Form fill seal bagging machine
If you are in industries such as petrochemicals, fertilizers, animal feed, food, etc, you mus...
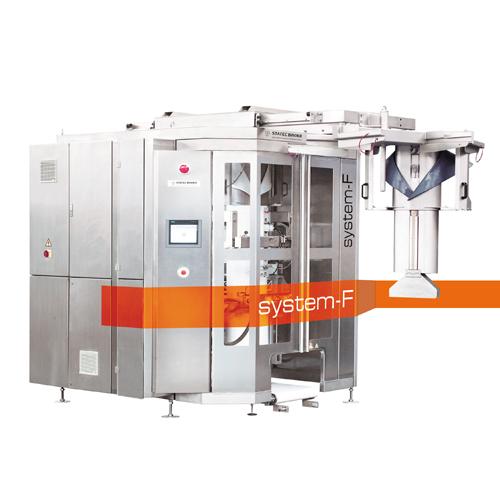
Vertical form fill seal machine
There is an increasing demand for a range of different package sizes of the same product. If...
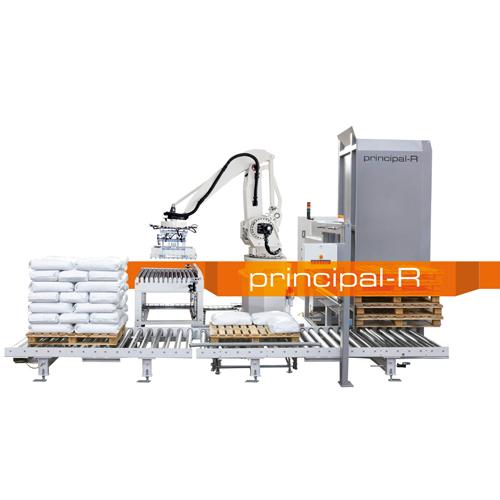
Robot palletizing system
If you are a relatively large-scale producer, packing and transporting large quantities of products ...
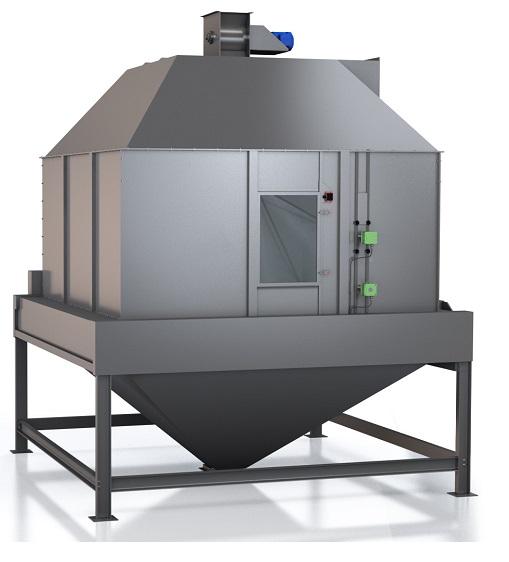
Continuous pellet cooler
Cooling is a very important and critical process for feed hygiene and pellet durability index. Pelle...
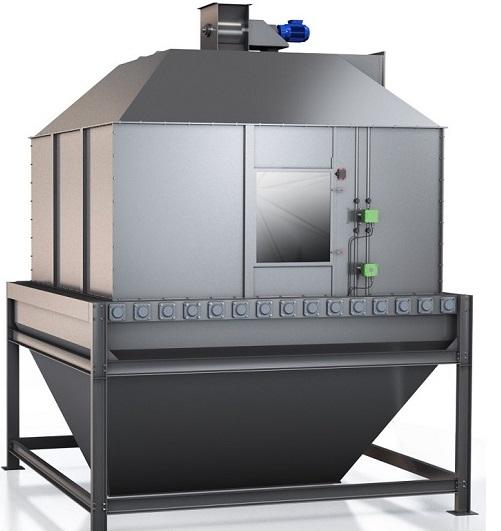
Gravity feed cooler
The food and feed industry has high food safety requirements making frequent cleaning and inspection nece...
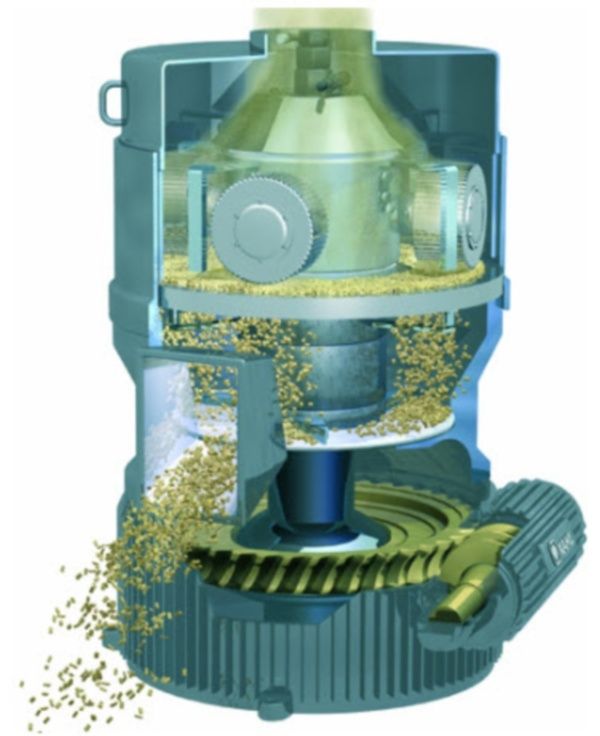
Pelleting press for feed and petfood
The production of agricultural feed and pet food products requires machines and plants...
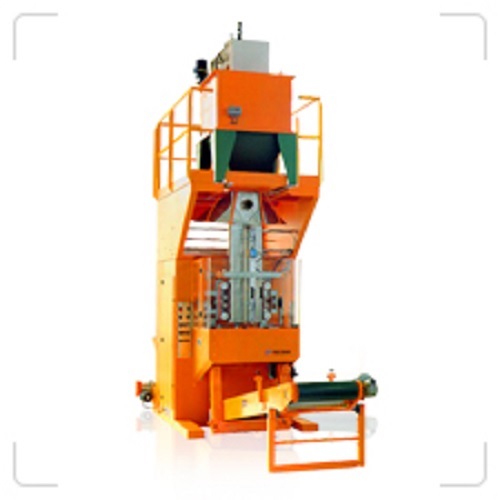
Vertical form, fill and seal machine for bags from 5 to 50 kg
To securely create, dose and pack larger quantities of mat...
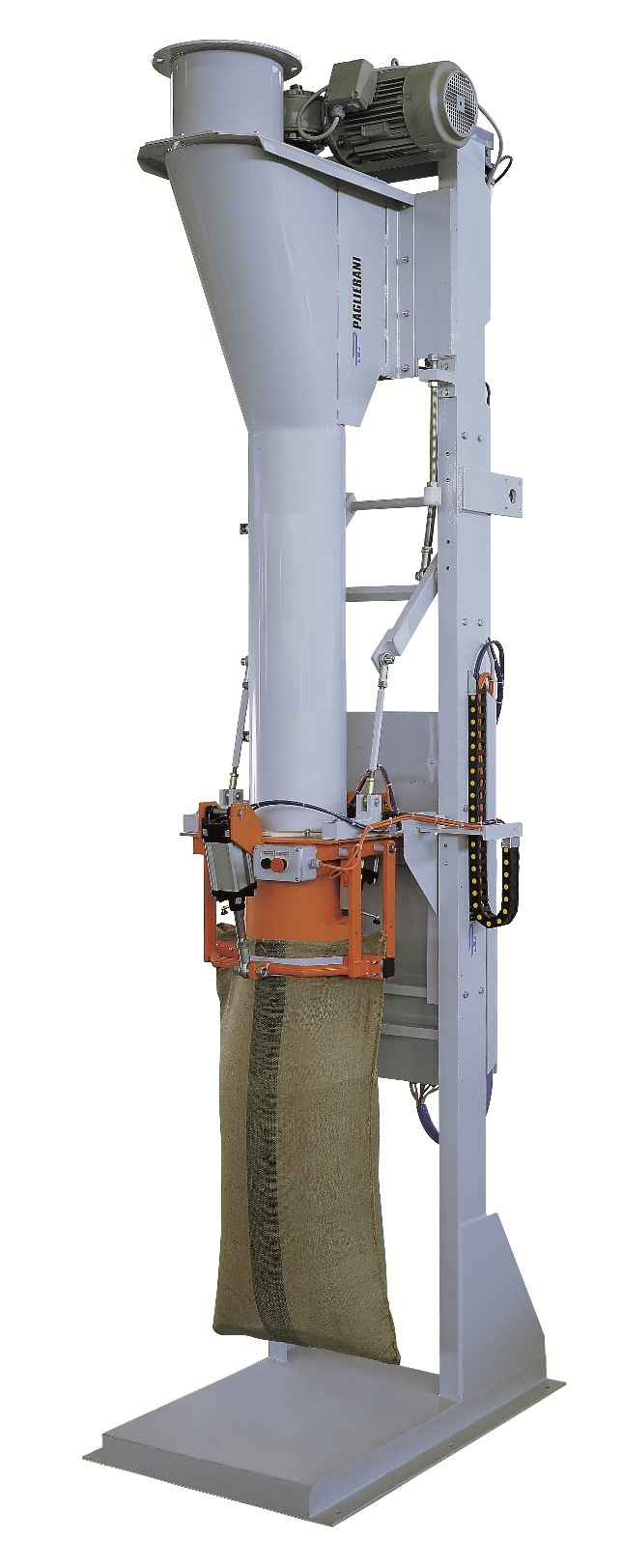
Bagger for open mouth bags
Where a stand-alone bagger is required for filling large, open mouth bags, a delivery method is n...
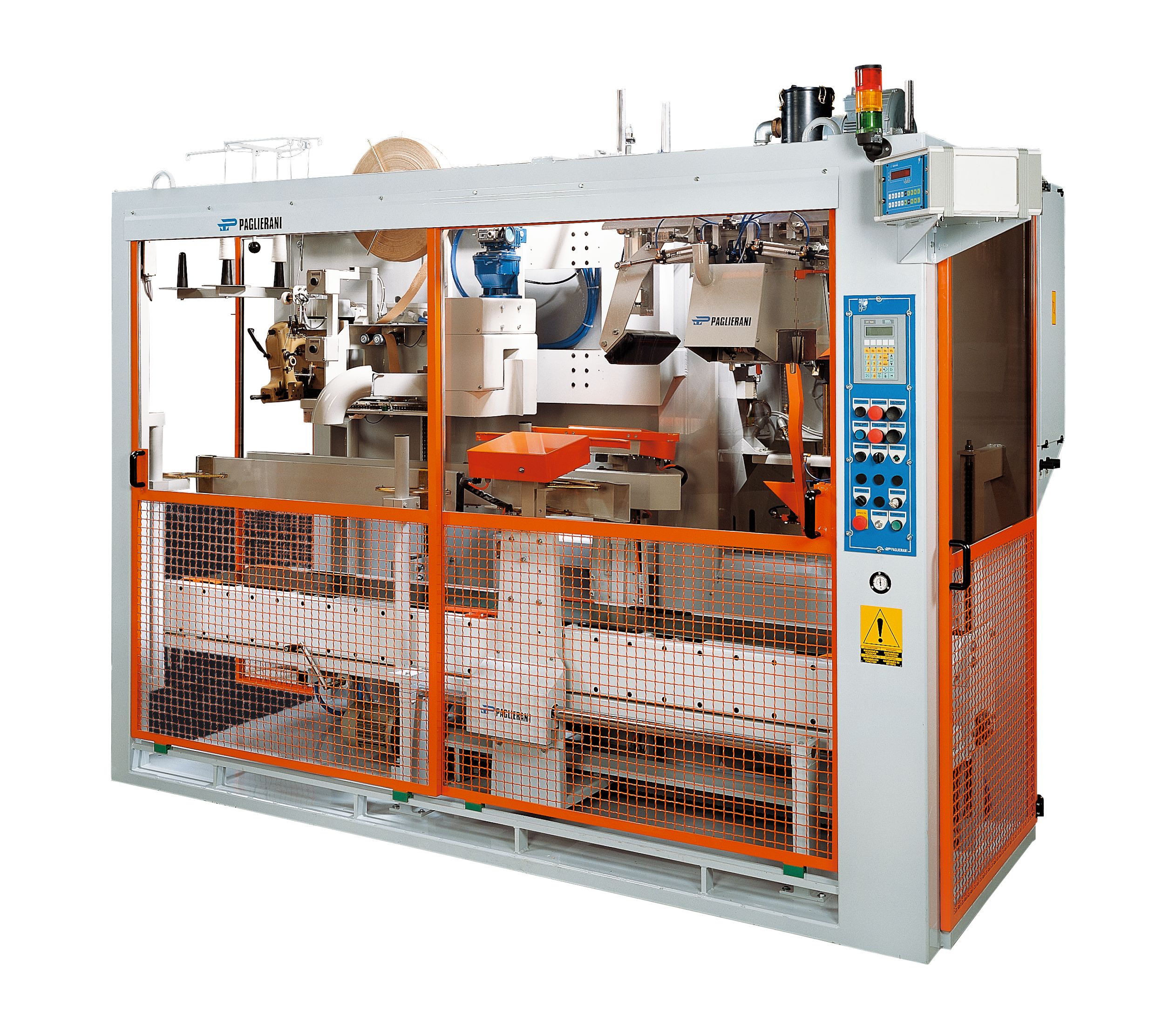
Automatic bagging machine for open mouth bags
Open mouth bags allow for a variety of different products to be packaged, wi...
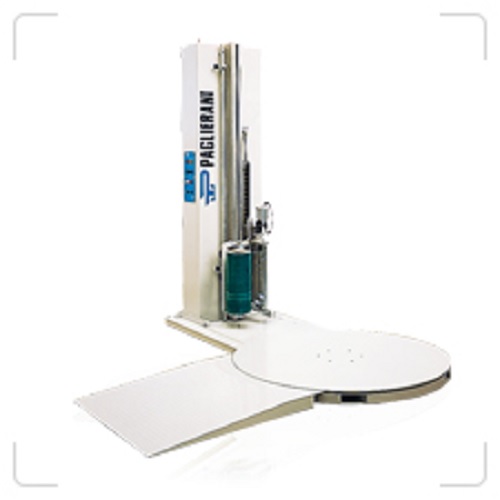
Semi-automatic stretch wrapping machine
At lower speeds, some level of automation is required to provide a cost-effective m...
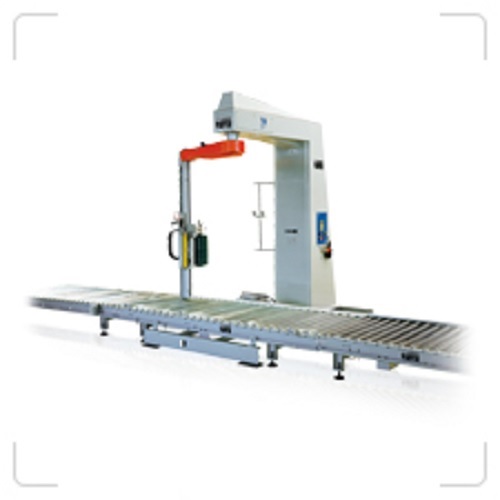
High speed stretch wrapping machine
Where high speed wrapping, without toppling, is required in tightly securing palletised...
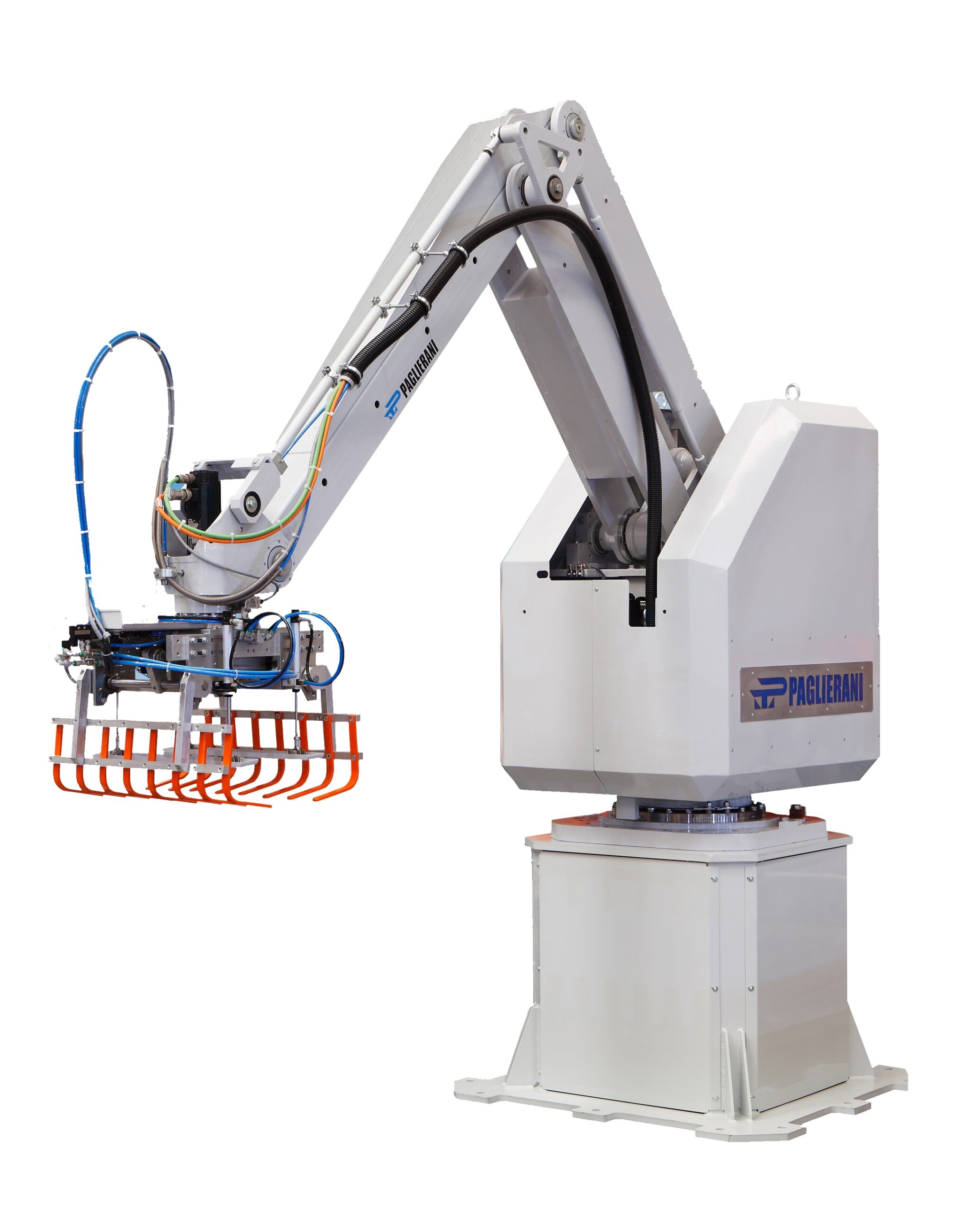
Palletizing robot arm
For high speed palletizing, palletizing high payloads, or just where greater flexibility is required, i...
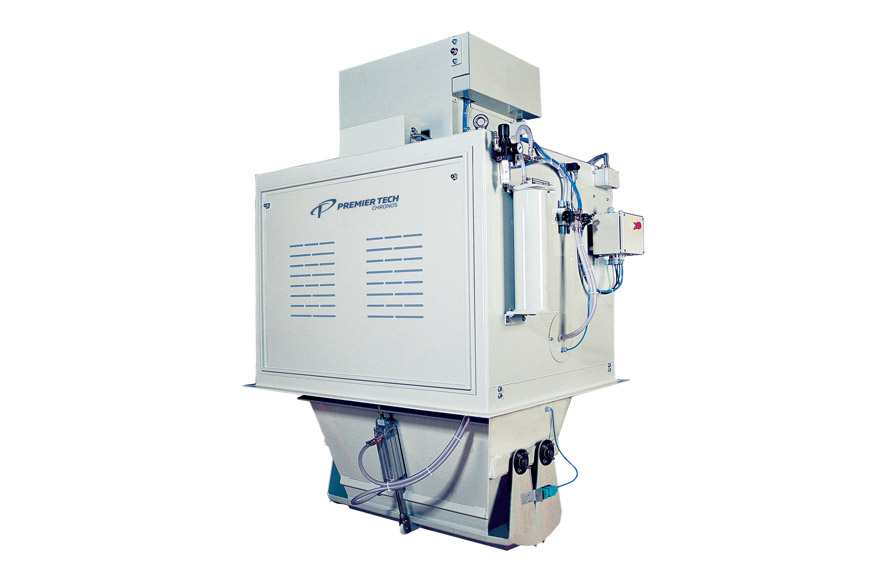
High-capacity bulk weighers
A checking weigher recognized for receiving and shipping bulk materials, typically in mills and ...
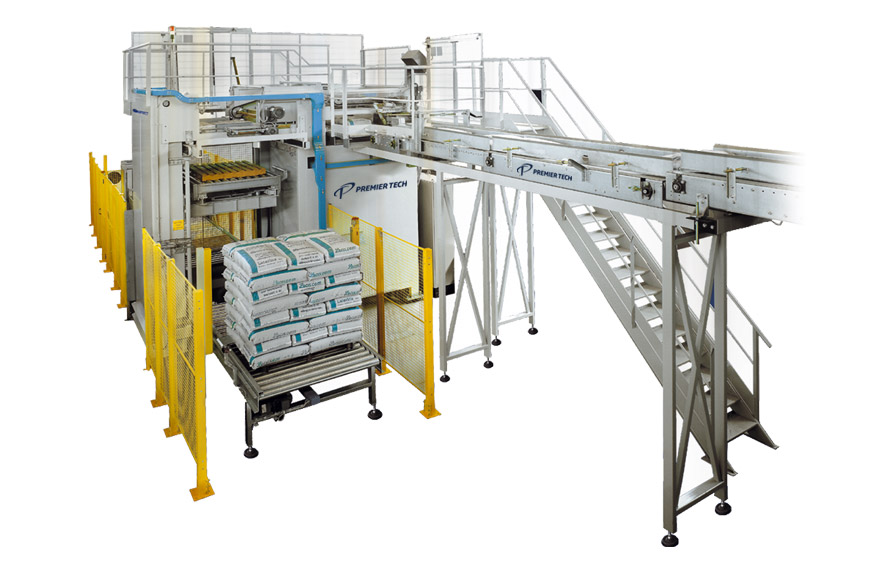
High-level layer palletizer
A palletizer that meets the middle and high-level needs of modern bagging lines. Quite suitable ...
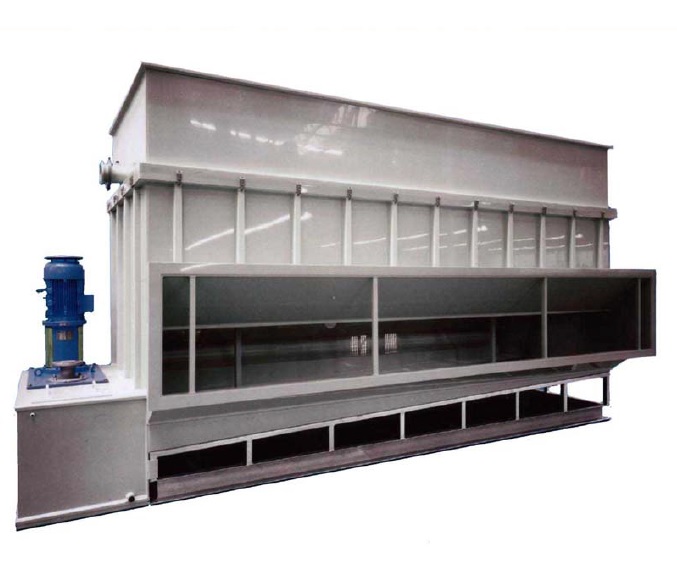
Air dehumidifier for bulk products
When your product or process is sensitive to humidity, using an air dehumidifier may res...
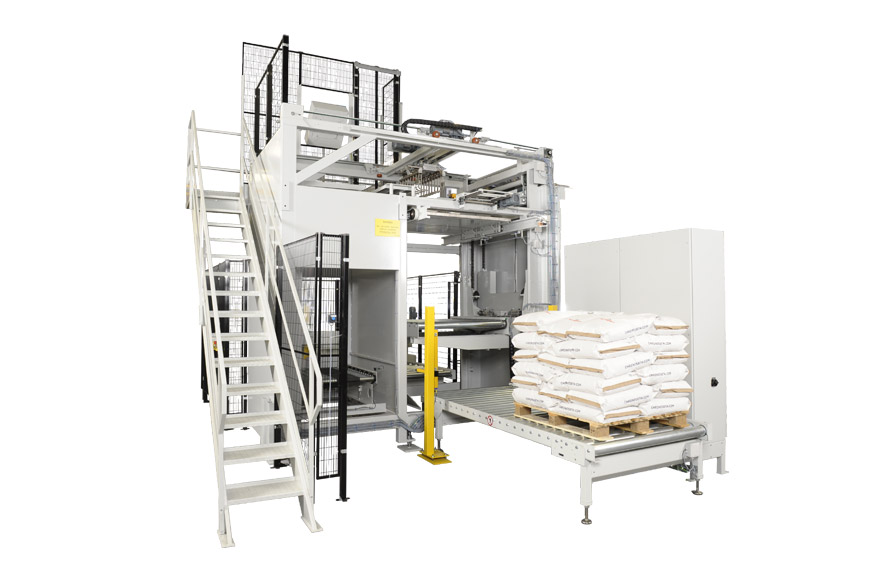
Compact palletizer
Choosing an accurate palletizer can be quite an advantageous move. This one is designed for euro, industri...
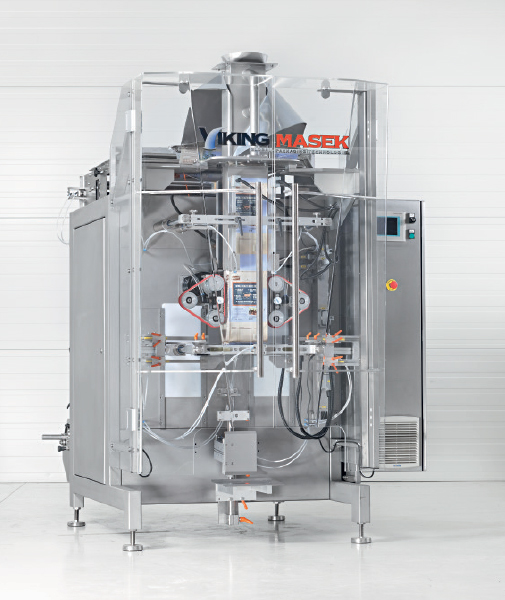
Continuous vertical bagger
Want a machine to pack unique bag styles such as quad-seal and Doy-pack bags at incredible speeds...
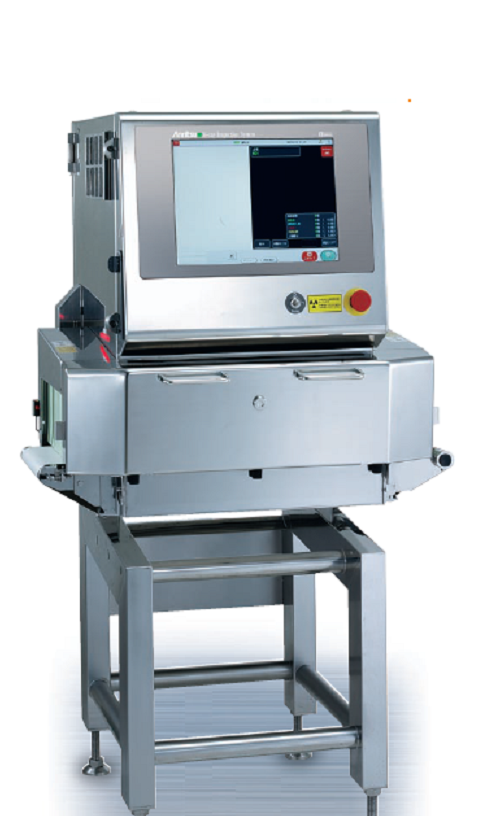
High sensitivity X-ray inspection system
This is the X-ray inspection system you need for detecting contaminants that are d...