Continuous tunnel dryer for tray carts
Efficiently dry diverse products with precision temperature control, ensuring gentle, uniform moisture removal for optimal quality in continuous production environments.
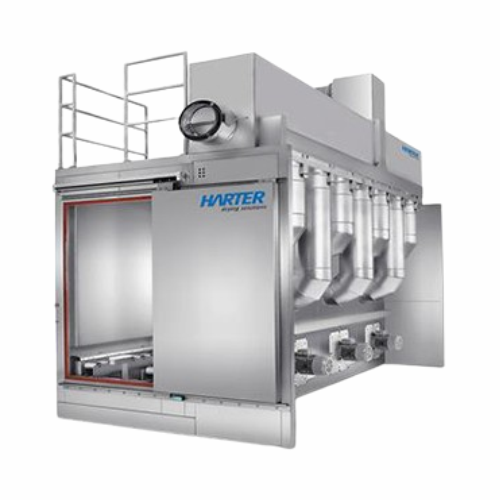
Dries and Conveys Products in Continuous Operation
The Tunneltrockner für Hordenwagen im kontinuierlichen Betrieb from HARTER drying solutions is a semi-automatic tunnel dryer designed for effective low-temperature drying while maintaining product quality. Utilizing a conveyor system, it ensures tray trolleys move continuously through the tunnel, offering consistent drying for a range of products such as caramel-coated popcorn, gelatin capsules, dried cannabis flowers, and sewage sludge. The system’s flexible configuration allows customization based on your specific production demands, accommodating various trolley sizes that can match Europallet dimensions or be tailored to your existing equipment.
This dryer excels in optimizing energy usage through precise temperature control, ensuring gentle yet efficient drying. Designed to integrate seamlessly into your production line, it supports both continuous and semi-automatic operations, enhanced by customizable speed settings to align with product-specific requirements. The robust construction is suited for diverse industries, including food processing, pharmaceuticals, and wastewater treatment, ensuring longevity and reliability under demanding conditions.
HARTER’s tunnel dryer provides significant energy savings with its ability to carry out low-temperature drying, thus reducing thermal stress on sensitive products while maintaining throughput. The equipment is engineered for easy integration and straightforward maintenance, featuring optional automated entry and exit of trolley systems, minimizing manual handling and enhancing operational safety.
Benefits
- Enhances product quality with gentle low-temperature drying, preserving material integrity.
- Increases production efficiency through continuous, automated processing of tray trolleys.
- Offers customizable configurations to fit existing trolley systems, reducing equipment costs.
- Saves energy with optimized temperature control, lowering operational costs.
- Improves safety and operational reliability with robust and adaptable design.
- Applications
- Animal feed, Surfaces, Industrial sludge, Packaging, Sewage sludge, Foods, Medical technology, Medicinal cannabis, Pharmaceuticals
- End products
- Gelatin capsules, Sterilized surgical instruments, Dehydrated industrial waste, Biosolids pellets, Caramel-coated popcorn, Pelletized pet food, Corrugated cardboard boxes, Dried cannabis flower, Metal sheets
- Steps before
- Purification, Grinding, Pre-treatment
- Steps after
- Packing, Quality Control, Storage
- Input ingredients
- Oberflächen, Lebensmittel, Tierfutter, Pharma, Medizintechnik, Medizinalcannabis, Verpackungen, Industrieschlamm, Klärschlamm
- Output ingredients
- Oberflächen, Lebensmittel, Tierfutter, Pharma, Medizintechnik, Medizinalcannabis, Verpackungen, Industrieschlamm, Klärschlamm, getrocknete Produkte
- Market info
- HARTER Drying Solutions is known for its expertise in energy-efficient drying technology, particularly using heat pump-based systems. They provide customized drying solutions for various industrial applications, focusing on energy savings and improved product quality.
- Automation
- Manual / Automatic
- Operating Mode
- Continuous / Semi-automatic
- Temperature Range
- Low temperatures
- Product Carrier
- Körbe / Hordenbleche on Hordenwagen
- Transport System
- Conveyor system
- Adjustable Speed
- Product-specific
- Size Compatibility
- European pallet size
- Bespoke Options
- Custom-sized Hordenwagen
- Flexibility
- Multiple product types and settings
- Drying Time
- Specific to product requirements
- Working Mechanism
- Continuous / Semi-automatic
- Product Handling
- Körben or Hordenblechen arrangement
- Load Flexibility
- Product adaptation via temperature/time
- System flexibility
- Adaptable to different products / tray sizes
- Control of Drying
- Product-specific speed adjustment
- Integration with Conveyors
- Automatic/manual loading into tunnel
- Continuous Processing
- Continuous or stepped tunnel processing
- Energy Efficiency
- Low temperature, efficient moisture removal
- Density/particle size
- 0.5–2.5 g/cm³ / 50–1000 µm
- Machine footprint
- Customizable to standard Euro pallet sizes
- Basket type
- Körbe or Hordenblechen in Hordenwagen
- Feed method
- Manual or automatic feed into drying tunnel
- Discharge method
- Automatically fed through conveyor system
- Customization capacity
- Flexible to different product dimensions
- Modular design
- Tailored to specific production needs
- Temperature setting
- Adjustable production-specific
- Layer capacity
- Variable based on production volume
- Control panel type
- Manual / Automatic
- Integration possibilities
- Custom Trolley Sizes
- Temperature control
- Product-specific
- Trolley size
- Standard Europallet / Customizable
- Operation mode
- Semi-automatic / Automatic