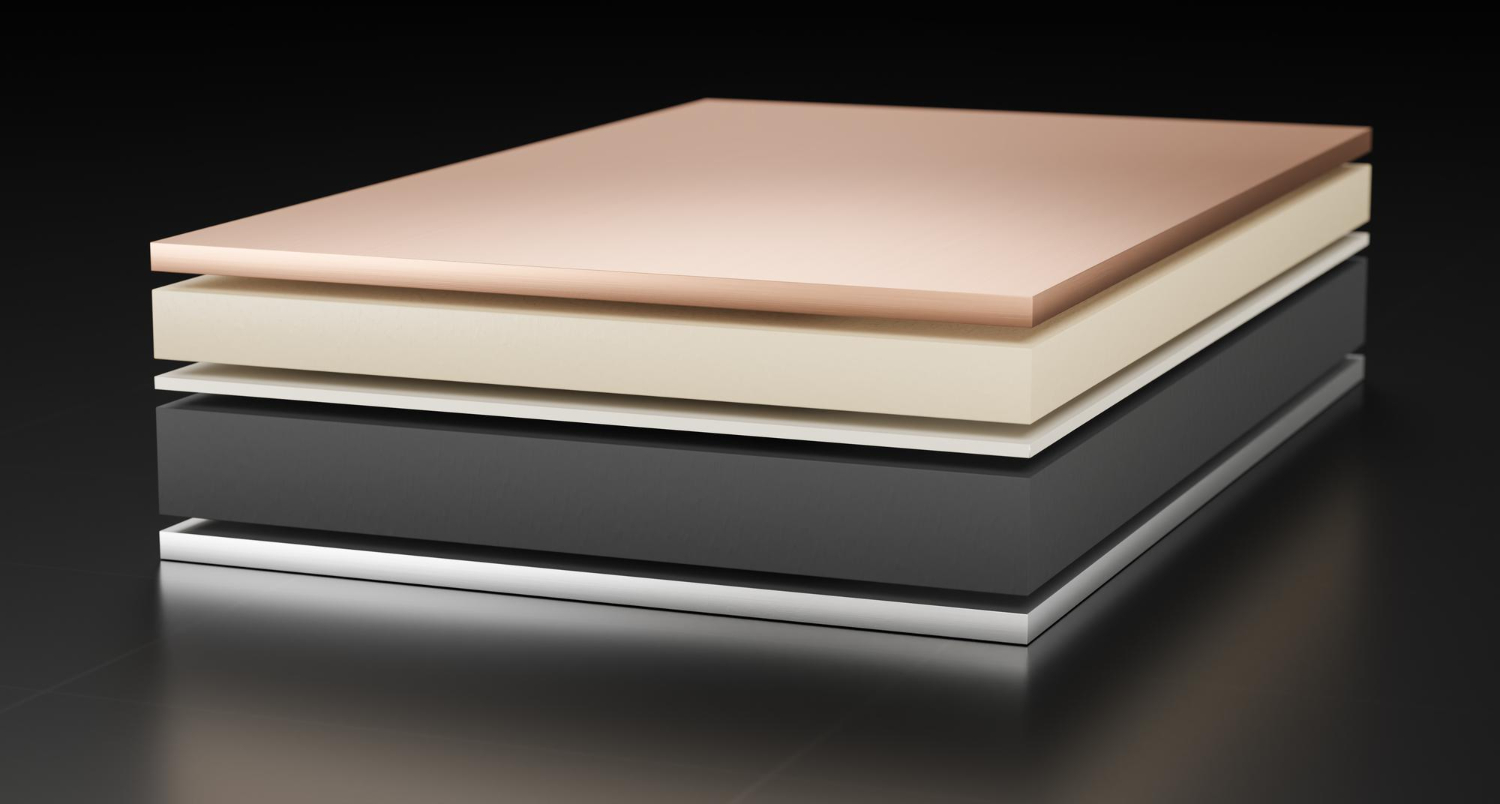
Making Solid-State Batteries
Find innovative production technology for making solid-state batteries and connect directly with world-leading specialists
The inventor of the lithium-ion battery predicted that solid-state batteries would become commercially available by the mid-2020s, making them an attractive option for energy storage in a wide range of applications, including electric vehicles. This battery type promises a marked improvement in safety, power, and environmental impact compared to current battery packs that use a liquid electrolyte. However, recent breakthroughs in the lab don’t automatically translate into mass production. The complex processing requires specially-designed manufacturing technology to make solid-state batteries a real solution, especially for the automotive industry.
Stories about solid-state batteries
Select your solid-state batteries process
Tell us about your production challenge
Distill lithium deposits under a vacuum to purify the metal for solid power
Lithium metal is the bedrock material of solid-state batteries. It is the lightest alkali metal and has the highest storage capacity. But lithium minerals are notoriously rare. Instead, the material is drawn from underground thermal waters and saline lakes.
The traditional extraction method concentrates the material together with other metal salts by evaporating the water from the natural brine. Treat the deposits to an ion exchange process that applies chelating resins that attract undesired metals. The remaining lithium metal is finally purified using vacuum distillation at around 550°C.
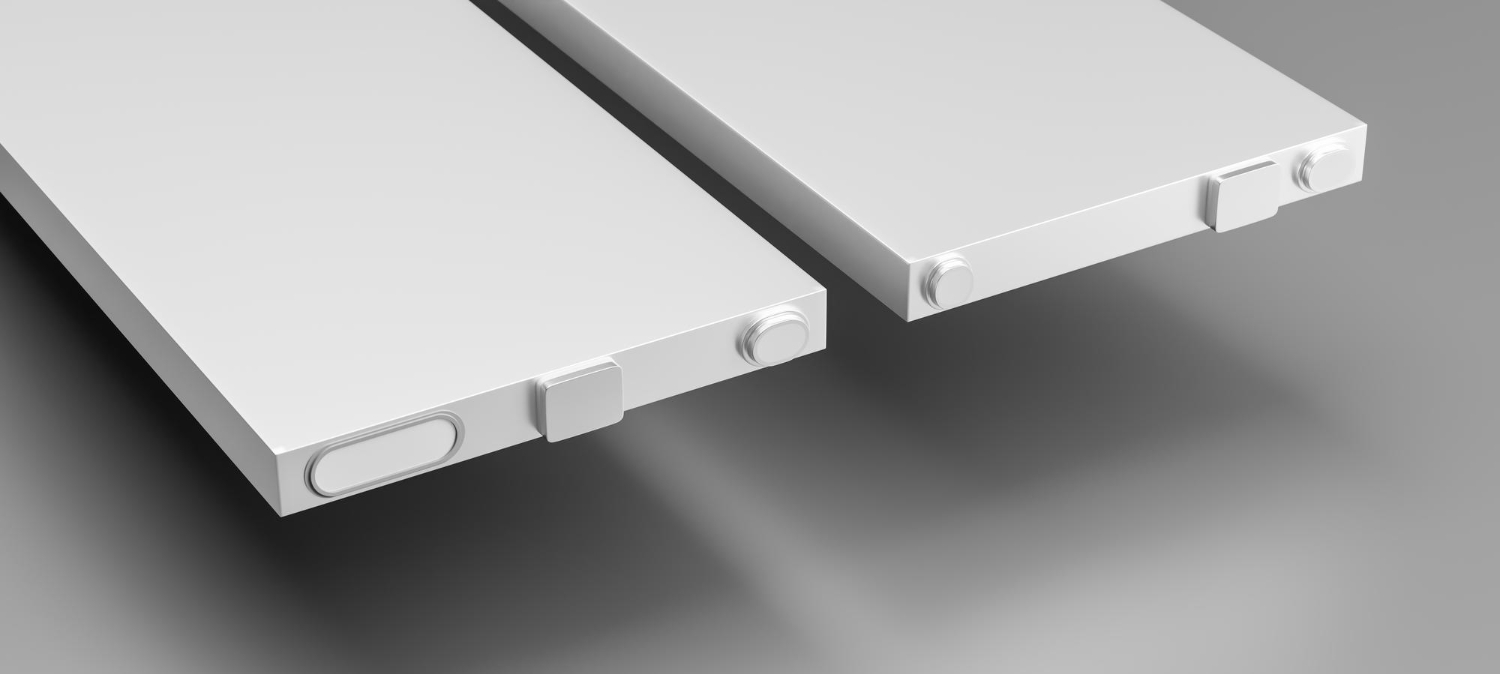
Increase energy density by compacting lithium into thin sheets
One of the innovations in solid-state battery design is stacking lithium strips around 20 microns wide. Lithium in batteries interacts with the electrolyte material forming a film (solid electrolyte interphase) that conduces ions but insulates electrons.
This technique lends batteries a longer lifecycle than a thicker slab of lithium metal and allows for fast charging. Passing the material through a roller compactor to reduce the thickness and form ultra-fine lithium sheets is a crucial step in the process.
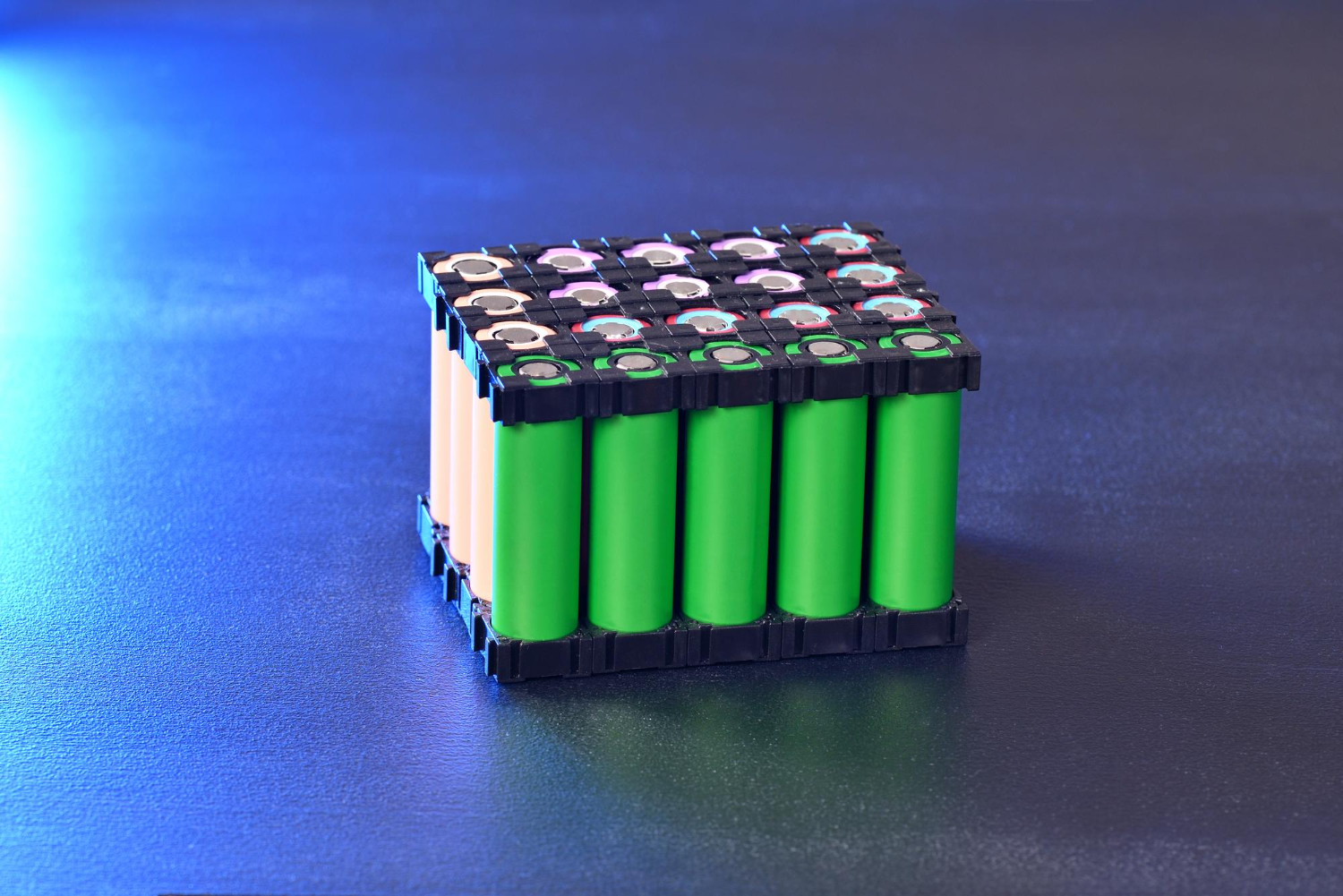
Exposure to moisture is a threat to solid-state battery manufacturing
A significant part of the research effort goes into developing electrolyte chemistries. Sulfide-type solid electrolytes gained much popularity thanks to their mechanical reliability in transferring ions between cathode and anode. Thus, making them suitable for electric cars.
But sulfides are prone to disintegration when they come into contact with moisture, making them challenging materials to handle. Monitor water levels throughout the production prosses using specialized moisture determination technology for solid-sate battery manufacturing.
Grind materials to increase their density and restrain void space
The solid layers between electrodes and electrolytes limit dendrite formation, one of the greatest disadvantages of lithium-ion batteries with a separator. But void space between the materials risks the growth of lithium filaments that cause short circuits in the battery system.
Filament growth occurs particularly in nigh-porosity substances. To prevent this, increase the density of materials by milling them into ultra-fine particles.
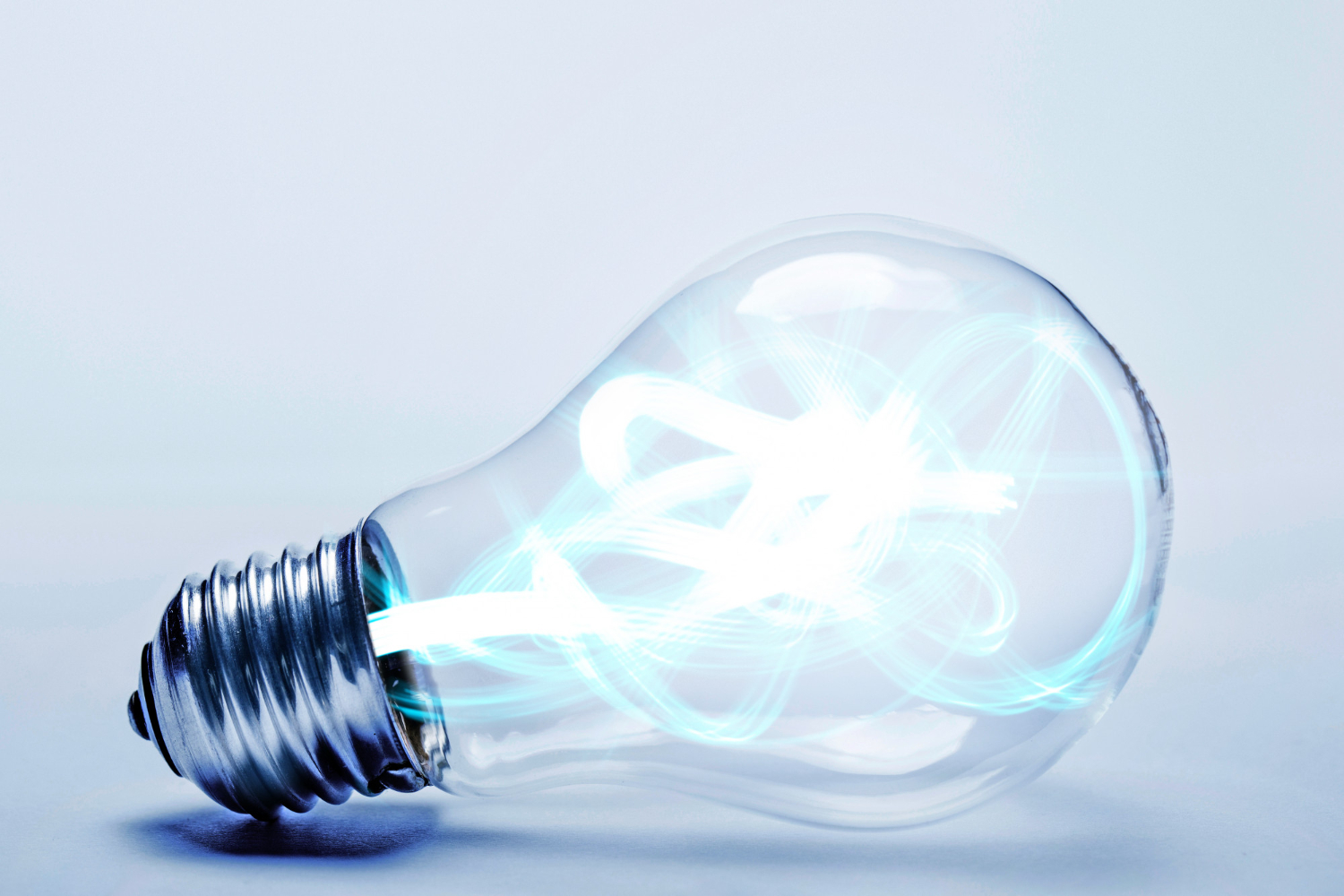
Deionize water for pre-extrusion slurry
One of the advantages of solid-state batteries over lithium-ion ones is that solid polymers allow high physical flexibility. Polymers can be manufactured into different form factors that suit the final battery design. This makes them an attractive option for manufacturers such as Tesla and other automakers.
A prominent processing technique is to mix the polymer material into a high-viscosity slurry and then extrude it into the desired shape. But failing to purify the water in the mix risks destabilizing the material’s conductivity. Use a deionized water system to purify the solution before turning it into a paste.
Incorporate ceramics to manufacture hybrid electrolyte material
The earliest electrolyte materials comprised solid polymers, but these have low ionic conductivity. Inorganic materials overcome this drawback; however, roll-to-roll manufacturing methods undermine their mechanical strength.
Novel materials combine inorganic substances with polymers to develop high-voltage tolerance. These inorganic polymer hybrid electrolytes (IPHE) score high on ion conductivity without giving up processability. An added advantage of IPHEs that incorporate ceramic as an inorganic material is that they can be designed for recyclability.
Processing steps involved in solid-state batteries making
Which solid-state batteries technology do you need?

Laboratory nutsche filter dryer for solid-liquid separation
Optimize your lab processes with a versatile benchtop filter...
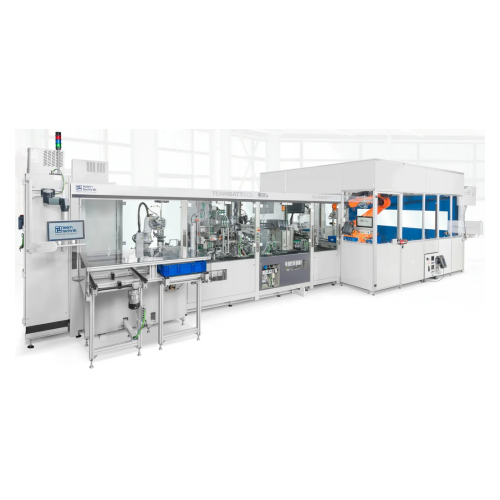
Production systems for battery cells with end-of-line testing
Optimize battery cell production with a flexible system of...
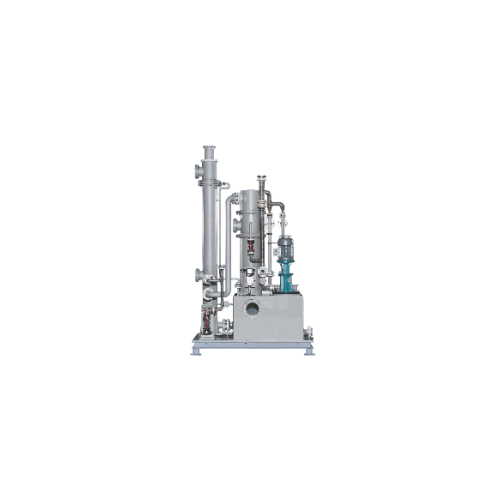
Aerosol separator system for industrial emission control
Enhance your emission control measures with our aerosol separato...
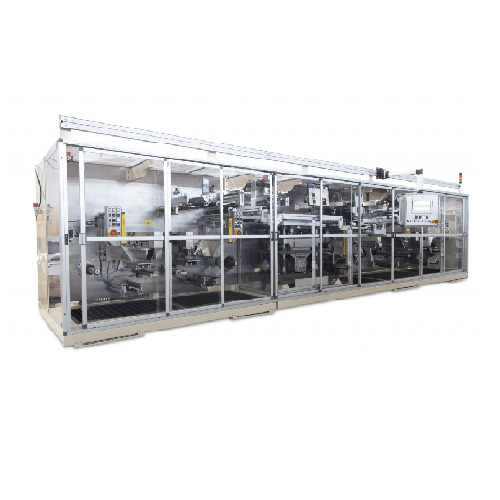
Roll to roll notching equipment for battery production
Optimize battery component production with precision notching, ens...
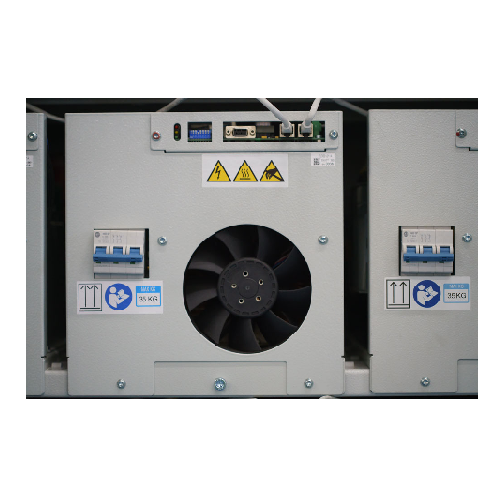
High-density battery chargers
Ensure your battery production line maintains optimal charge levels with precision and efficie...
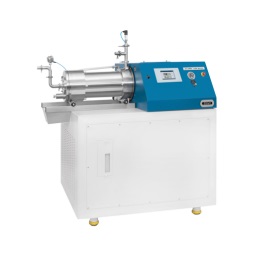
Ultrafine bead mill for battery materials
To facilitate the attainment of ultrafine particles and enhance electrode proper...
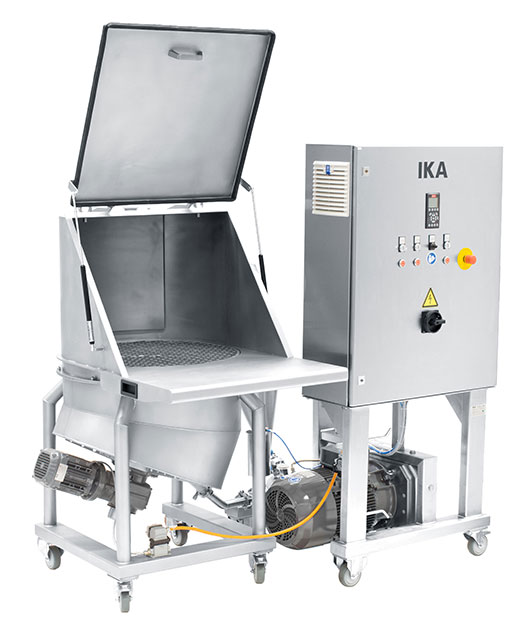
Inline solid-liquid mixer for battery production
In battery production, a critical phase entails mixing solids with liquid...
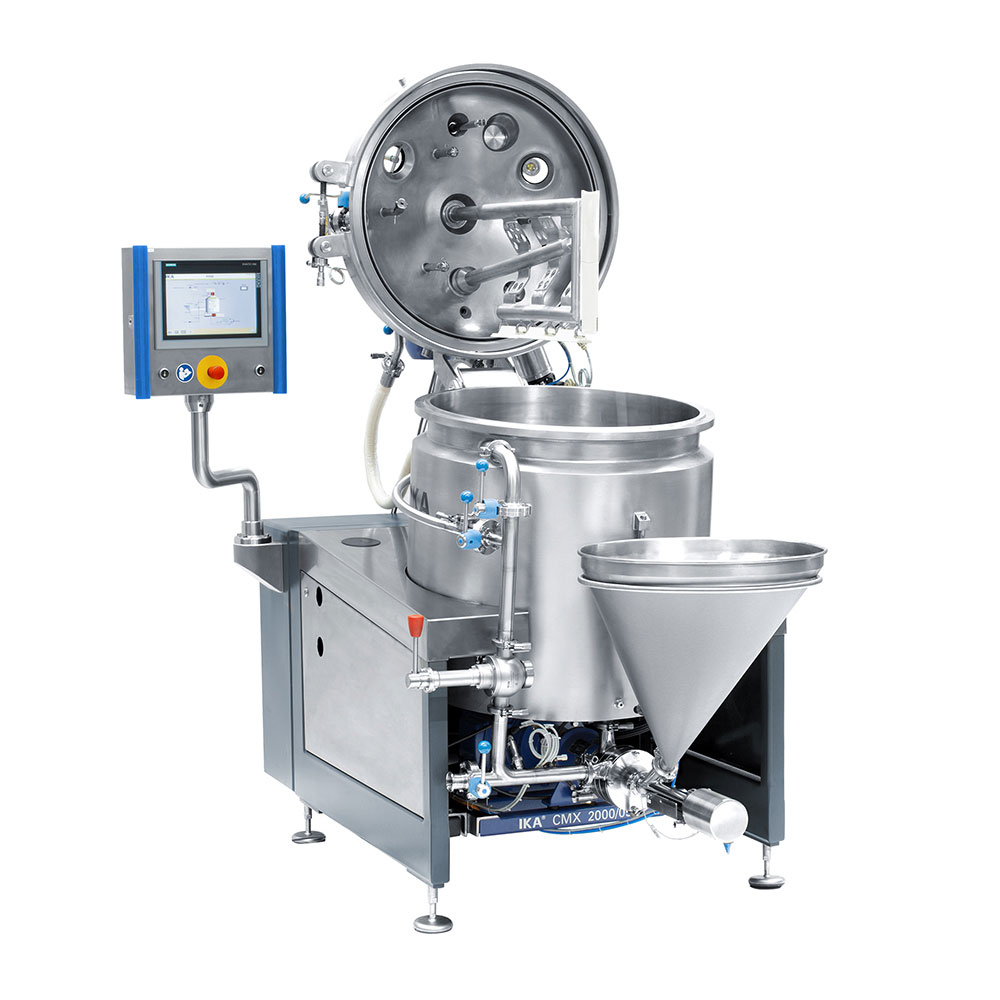
Compact Mixing Plant for Paints and Coatings
A smooth finish in paints and coatings depends on the grade of dispersal duri...
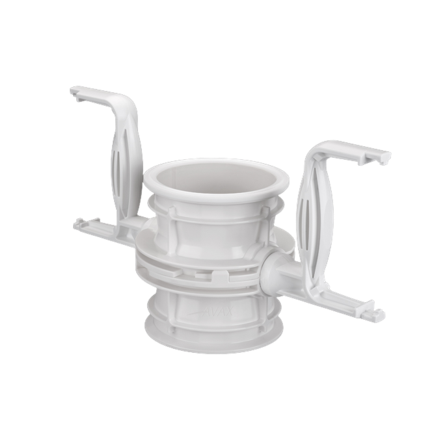
Single-use containment valves
From GMP and HSE perspective material transfer is critical for chemical and pharmaceutical for...
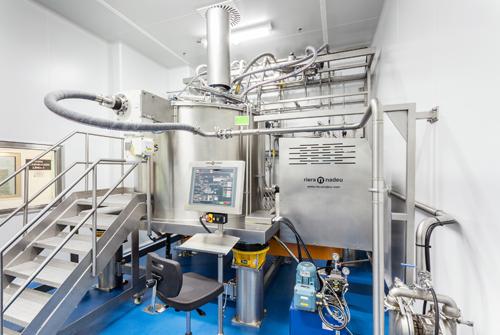
Automatic centrifuge for lithium carbonate
The battery industry requires high purity components. To obtain more than 99.5%...
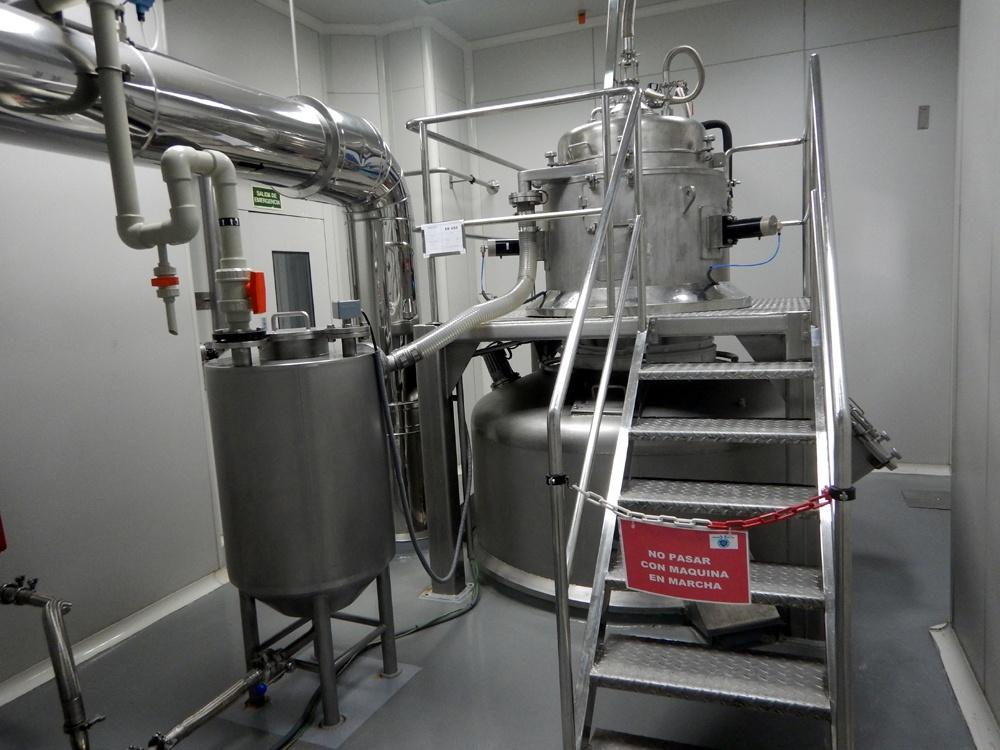
Continuous centrifuge for lithium hydroxide
Lithium hydroxide, a lithium compound used in making lithium batteries, is ind...
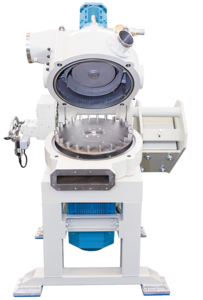
Classifier mill for powder coating
High-quality powder coatings are often required to manufacture equipment, appliances, an...
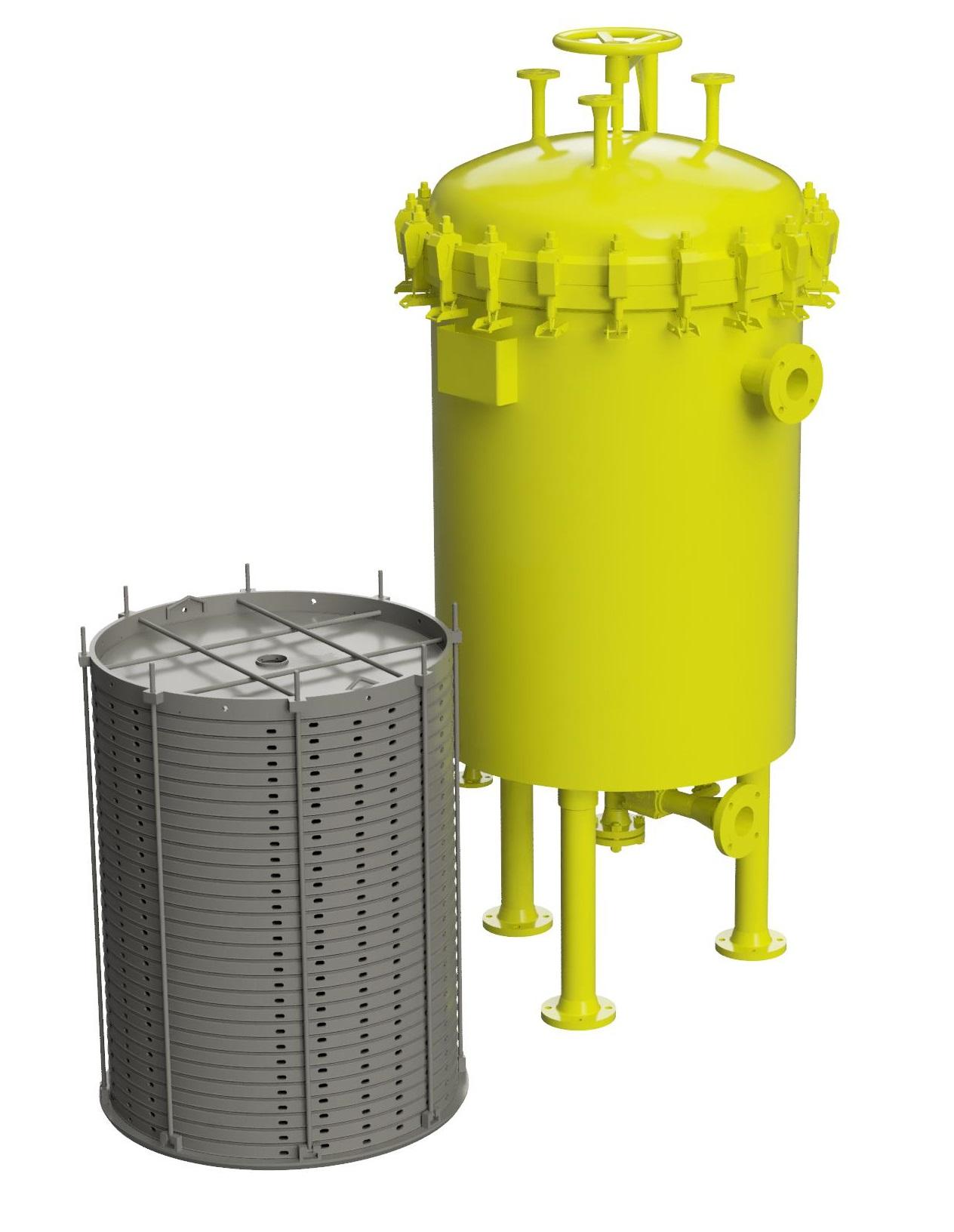
Industrial liquid filtration system
Systems for the filtration of liquids with suspended solid contents can be challenging ...
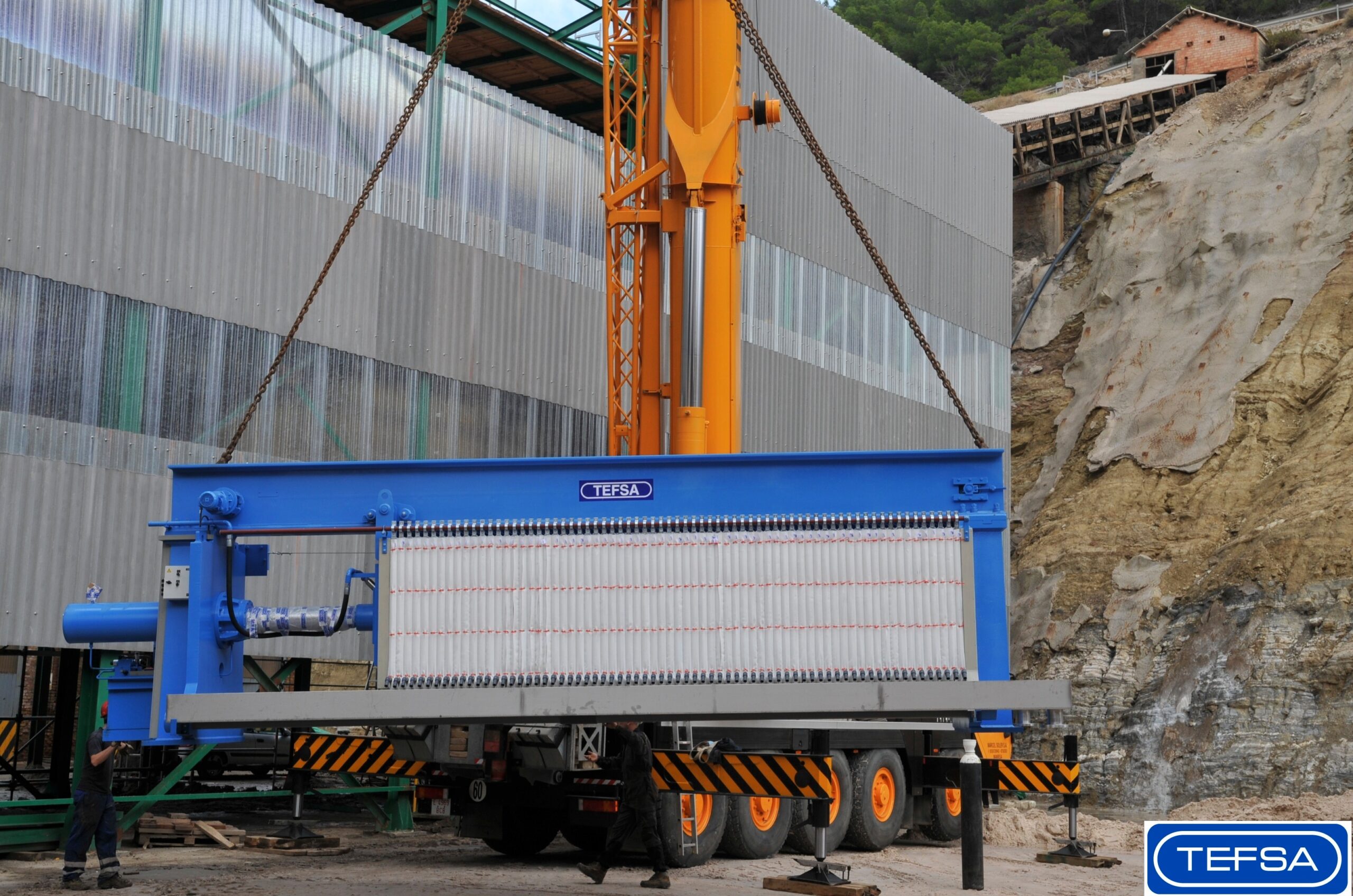
High yield filter press
When a saturated slurry or sludge must be dehydrated with high yield results mining and other heavy i...
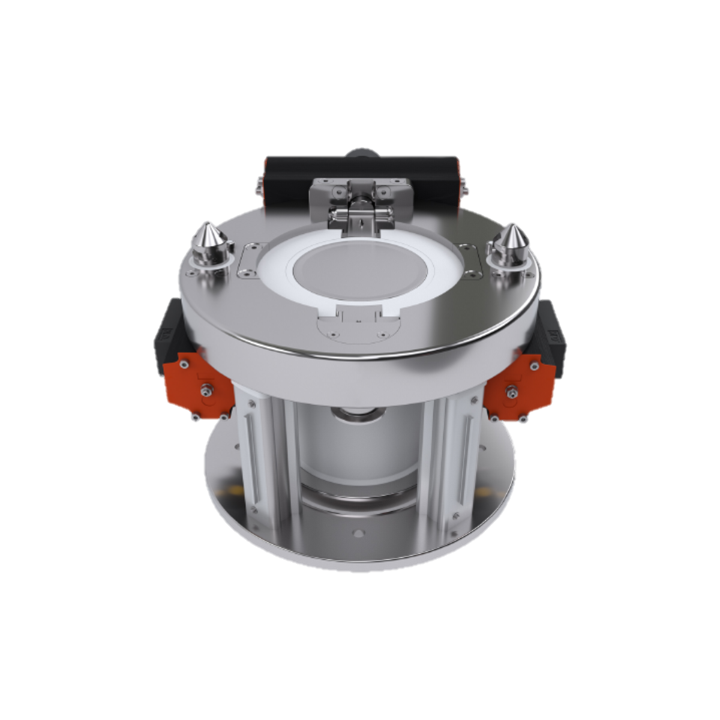
High containment split butterfly valve
Powder containment is the cornerstone of chemical and pharmaceutical manufacturing. ...
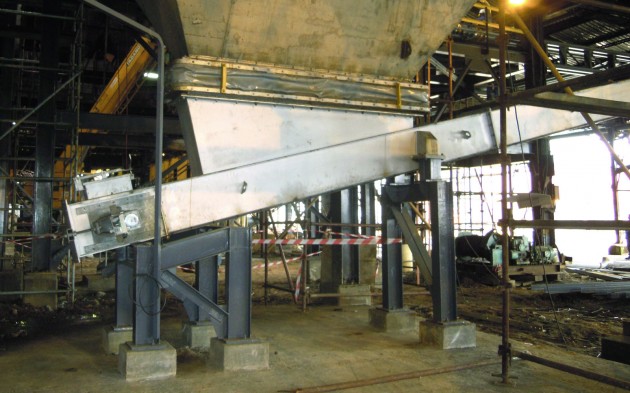
Dust and concentrate handling in smelting plants
Modern metal smelting operations involve extremely harsh conditions that ...
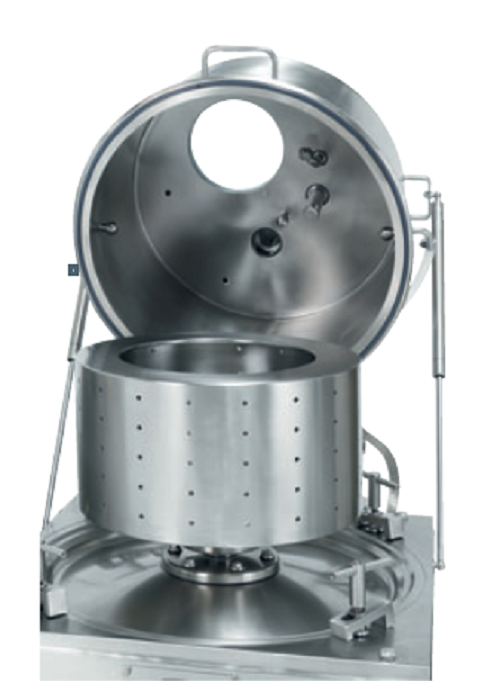
Isolator centrifuge
For transferring highly active pharmaceutical ingredients (HAPI) without contamination from the isolator ...