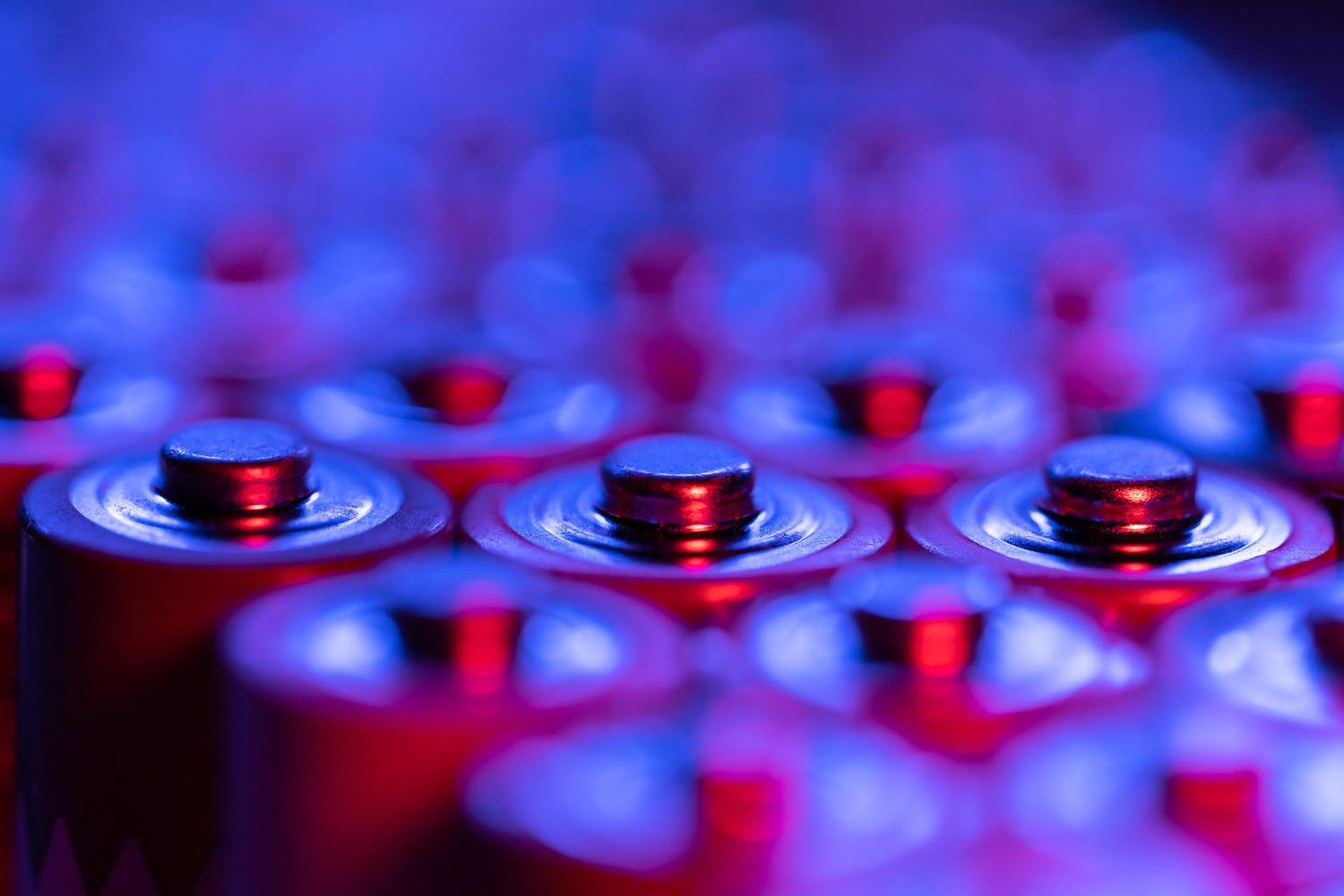
Lithium-Ion Battery Manufacturing Equipment
Find innovative production technology for making lithium-ion batteries and connect directly with world-leading specialists
Landline telephones in the 1980s were minimalist gadgets that kept getting slimmer in the 1990s. In contrast, cell phones in the same period were bulky and cumbersome. And once they lost their charge, they turned into a giant paperweight. Then came a revolution in batteries and automation with lithium-ion battery manufacturing equipment. Mobile phones packed more power, recharged faster, and endured more recharge cycles. Above all, they were light and small, making cell phones the inseparable companions they are today. But Lithium-ion batteries power much more than phones. As a result, the world is seeing steady growth in battery manufacturing equipment and lithium-ion production lines.
Tell us about your production challenge
Dry and refine lithium before processing the metal
The crucial element in lithium-ion battery production is, of course, lithium. The lightest material on earth is highly reactive, making it a prime candidate for this exchange of electrons.
The metal is obtained either from ore mines or extracted from lithium-rich pools. The former method is quarried and refined; in the latter, the water is removed by evaporators, and the metal is filtered from the remaining deposits.
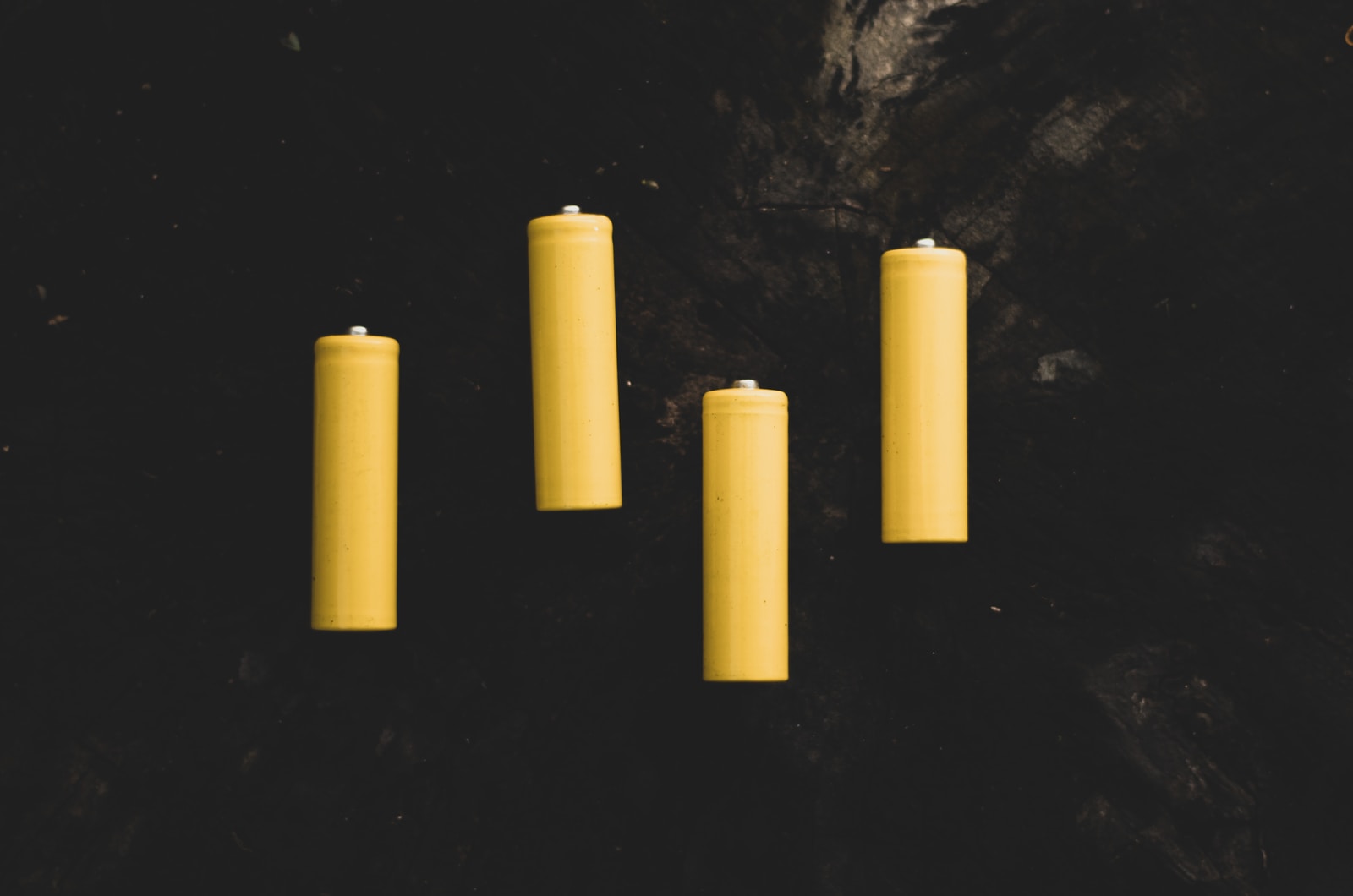
Stabilize lithium with a metal oxide
Lithium is a chemically unstable material, and it is worked into matrices with other metals to stabilize it. Engineers use multiple compounds to form these metal oxides for the cathode chamber. Nickel, manganese, cobalt, aluminum, and iron are the most widely used metals in the cell manufacturing process.
The anode chamber is typically made from graphite, a stable mineral that can hold the lithium ions discharged from the metal oxide.
Enlarge the surface area of lithium particles with fine milling technology
Before starting the formulation process, the raw metals need to be treated with a dryer to remove all moisture content.
Your dry materials are now ready for ultra-fine milling. Grind the metals into a powder to achieve a uniform particle size distribution that allows them to be worked more smoothly. Meanwhile, reducing particle size increases their surface area and produces a higher performance in batteries.

Form the lithium-ion mechanism into a battery cell
The graphite and metal oxides are coded onto current collector sheets, usually made of copper and aluminum on an assembly line. An electrolyte sheet sandwiched between them keeps them from coming into contact. It also serves as a barrier to electrons traveling from cathode to anode and back. Welding techniques, such as laser welding, are used to seal the battery cells, ensuring that they are safe and durable.
The pouch cell design is becoming increasingly popular, as it is lightweight and flexible, making it ideal for portable devices. Cell assembly is the process of assembling the different components of the battery cell, including the anode, cathode, and electrolyte.
The sheets are pressed together and wound around a steel cylinder, forming a compact cell. A typical battery pack module for electric vehicles consists of several lithium-ion battery cells packed together in an integrated unit. The whole is greater than the sum of its parts, and this solution generates electricity more efficiently than a large battery would.
Lithium-ion technology is changing electricity distribution methods
Advances in lithium-ion battery materials and technologies are fast-tracking electric mobility and promise to remodel electricity grids. The basic principle of the battery is that ions and electrons travel from a positive electrode (anode) to a negative electrode (cathode), creating an electric current on the way.
When the anode discharges all its ions, the current is interrupted, and the battery goes flat as the energy storage has been depleted. When you plug your battery-operated device into the wall socket, the positive charge pulls the ions to the anode again. With the development of advanced coater technology, battery manufacturers can now achieve a more efficient assembly line, with the ability to coat multiple layers of materials onto the current collector sheets in a single pass. This not only increases production speed but also improves product quality and consistency.
Which lithium-ion batteries technology do you need?
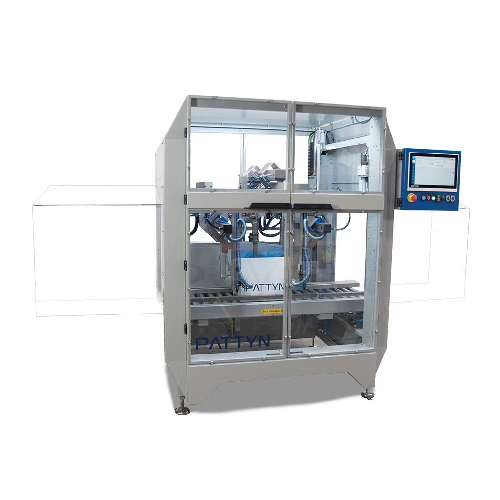
Automatic bag folding solution for bulk packaging
Enhance your production line efficiency and product protection by integ...
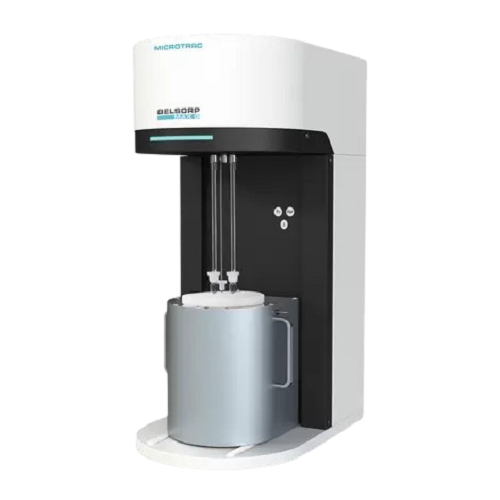
Specific surface area & pore size analyzer for materials
Achieve unparalleled precision in material characterization by m...

Laser diffraction particle size analyzer
Achieve precise particle size analysis with laser diffraction technology, ensuring...
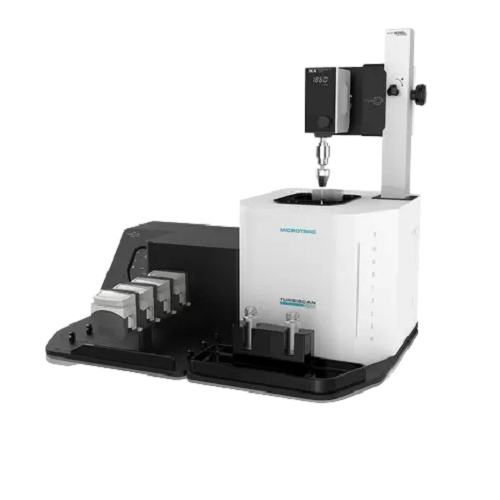
Stability analyzer for emulsions, suspensions, and foams
Accurately detect and quantify changes in dispersibility and sta...
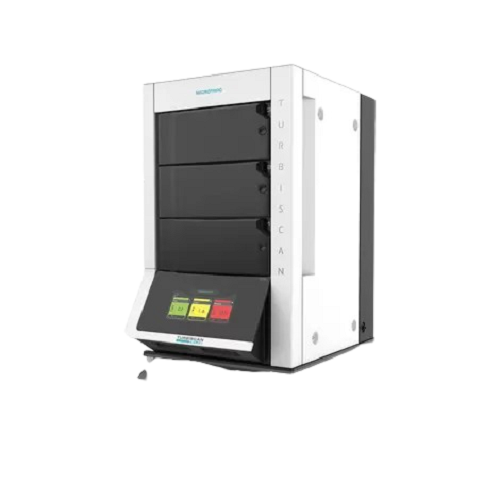
Multi-sample stability analyzer for emulsions and suspensions
Achieve precise, non-destructive stability analysis of emu...
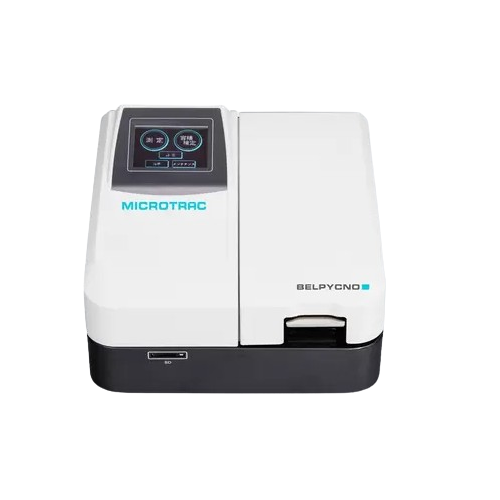
Gas pycnometer for true density measurement of solids and powders
Achieve highly precise density measurements of solid ...
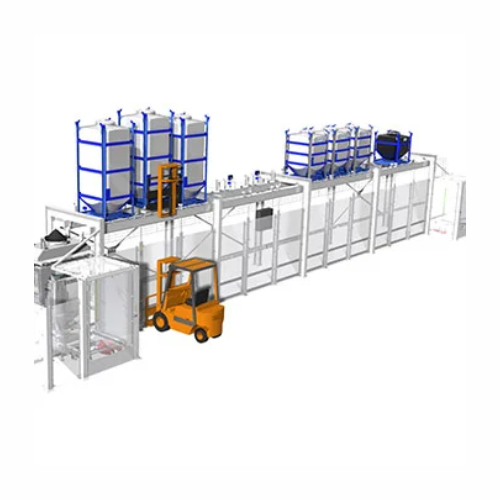
Flexible powder recipe formulation system
Streamline your batch production with efficient, dust-tight formulation and blen...
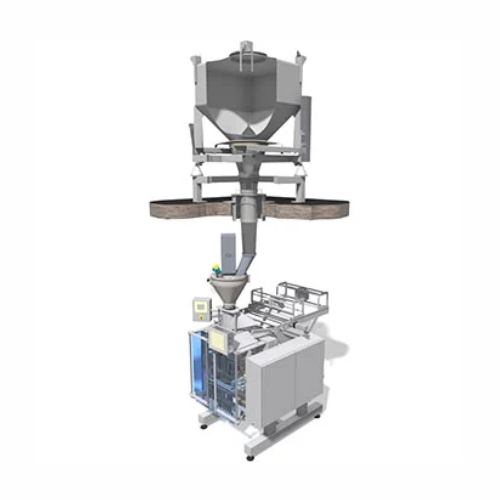
Powder packing module for consistent flow
Enhance your production efficiency with streamlined powder packing that ensures ...
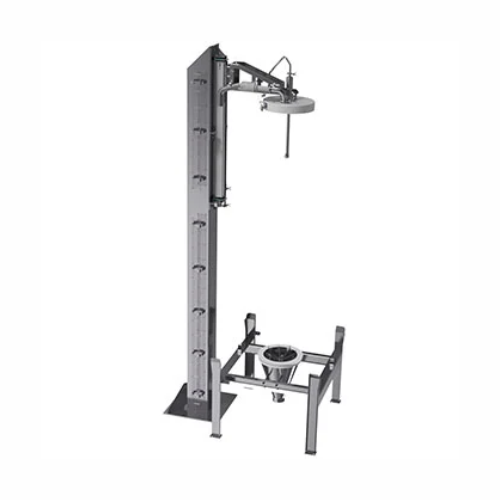
Ibc cleaning equipment for hygienic powder handling
Optimize cleaning efficiency and maintain hygiene standards with a ve...
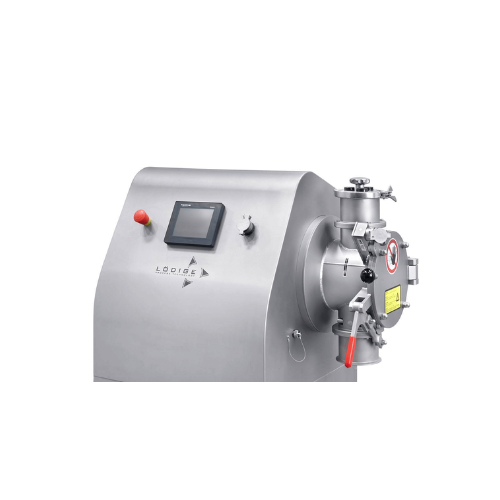
Laboratory ploughshare mixer for small-scale production
Achieve precise mixing and granulation for R&D and small-bat...
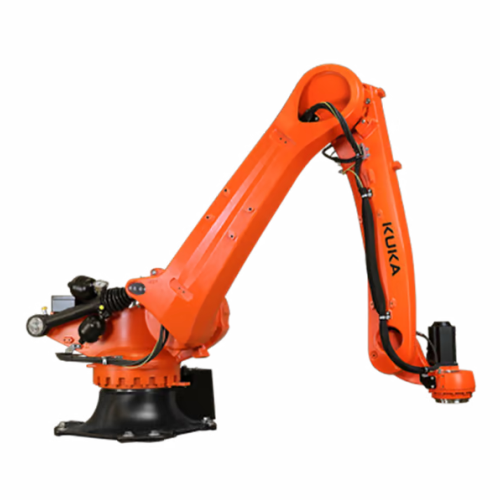
High-precision palletizing robot for industrial applications
Maximize efficiency and reduce floor space in your producti...
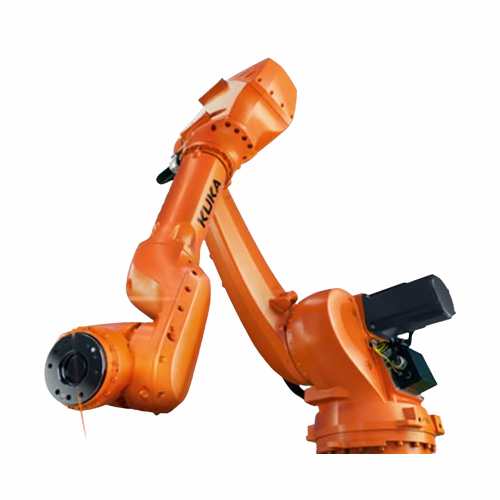
Flexible industrial robot for medium payloads
Optimize your production line with a versatile robotic solution that adapts ...

High payload industrial robot
Optimize your production with high payload robots designed to enhance flexibility and reduce o...
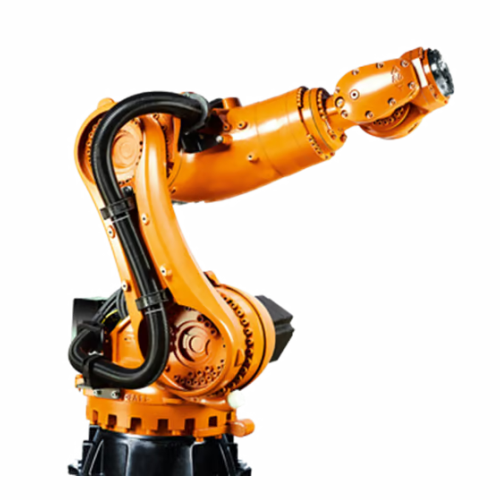
Spot welding robot for confined spaces
Optimize spot welding efficiency in tight manufacturing spaces with a compact robot ...
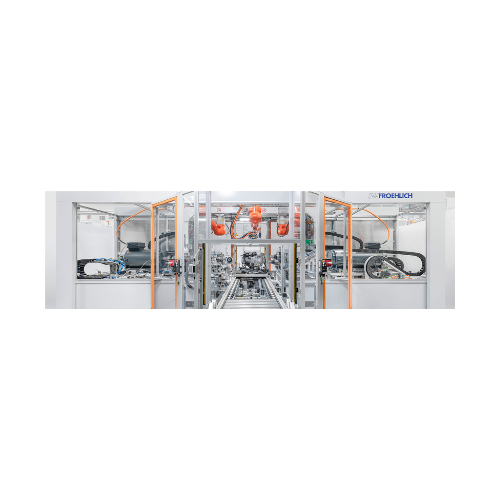
Automotive assembly and leak testing systems
Optimize your production line with versatile assembly and testing systems, en...
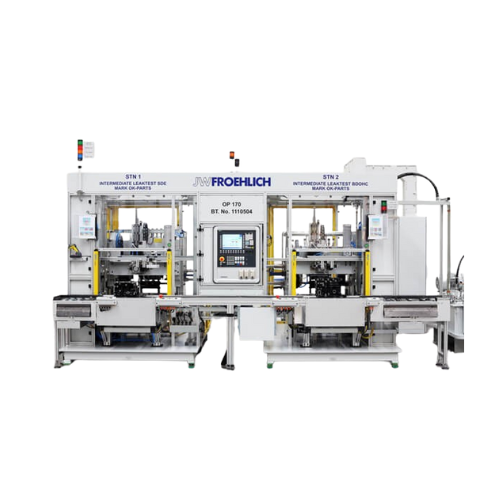
Cylinder block leak testing system
Ensure reliability and quality by detecting and addressing leaks in cylinder blocks with...
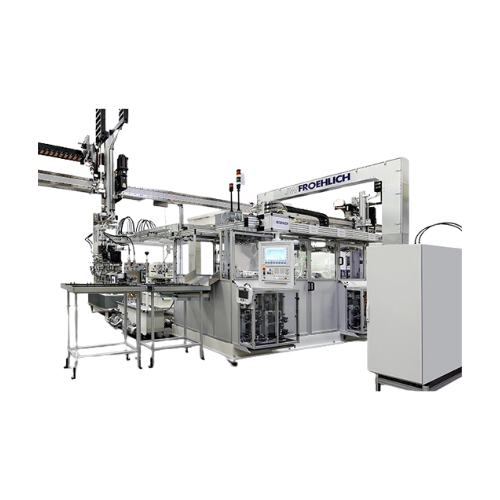
Function test for electro-hydraulic control units (ehs)
Ensure precise functionality and reliability in your production l...
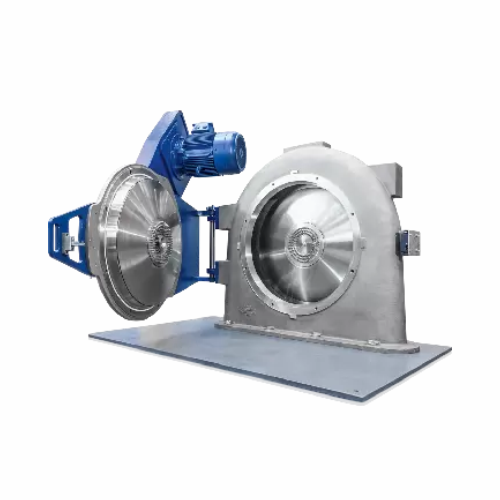
Industrial powder grinder
Achieve precise particle size reduction and classification with advanced equipment designed for co...
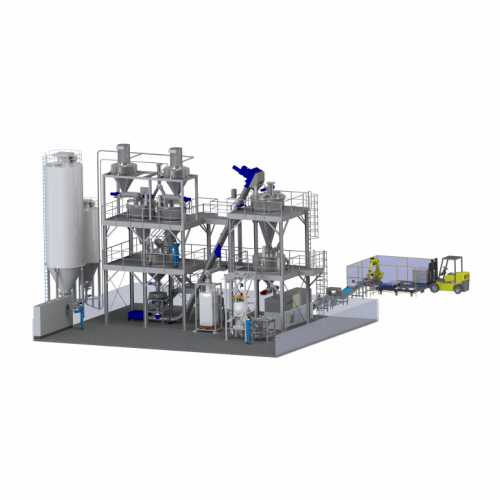
Powder mixing systems
Optimize your production line with precision powder mixing systems that ensure uniformity, enhance prod...
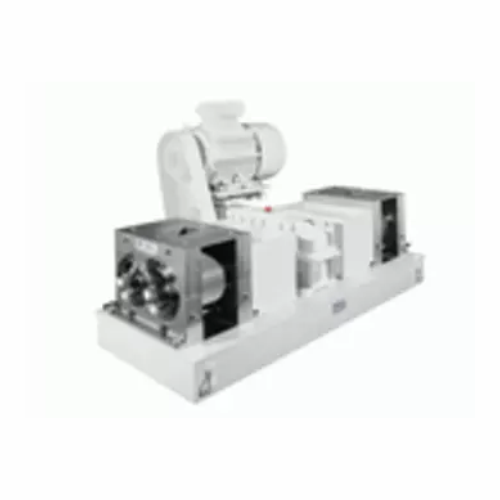
Gear pelletizer for stable cylindrical pellets
Achieve uniform pellet size and stability in your production line with a lo...
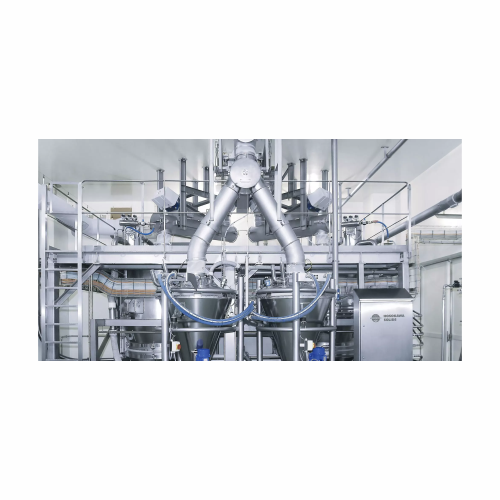
Pneumatic conveying system for bulk material handling
Efficiently transport bulk materials with precision through pneumat...
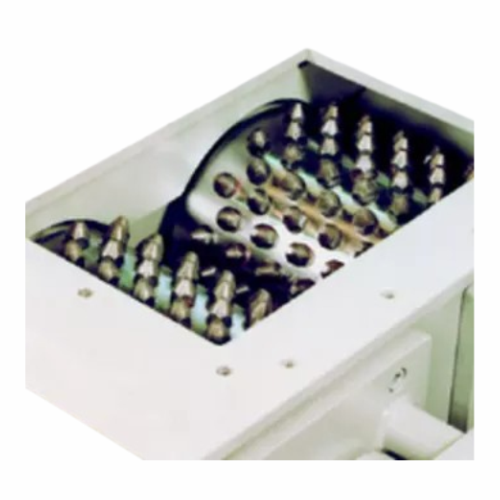
Industrial pre-crusher for coarse crushing
Optimize your production line by efficiently transforming clumped materials int...

Table roller mills for mineral raw material comminution
Achieve precise mineral raw material comminution and energy-effic...
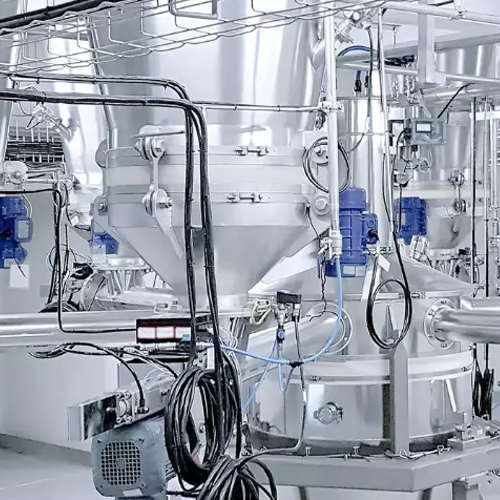
Conical screw mixer for powder blending
Achieve precise and homogeneous blending with the conical screw mixer, ensuring uni...
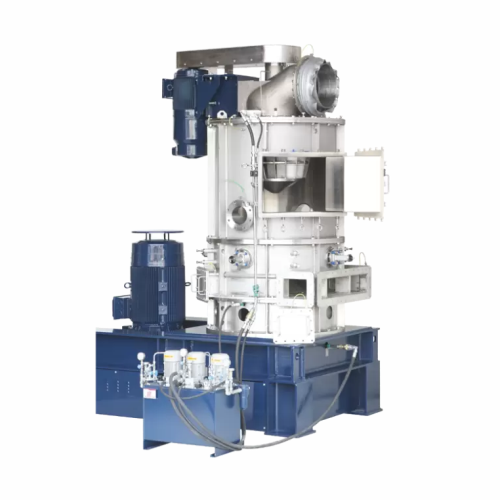
Ultra-fine powder flash drying system
Achieve rapid moisture removal and particle refinement with this integrated system, d...
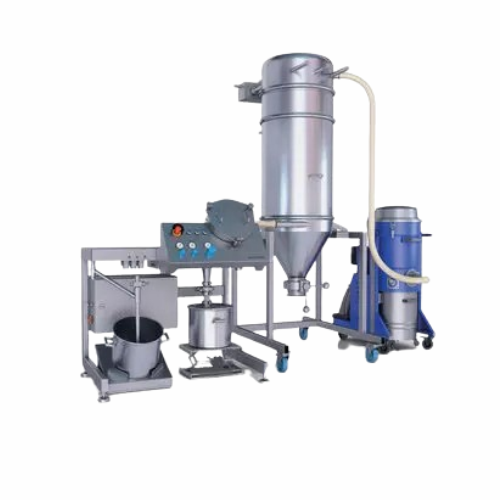
Spiral jet mill for ultrafine micronisation
Optimize your powder processing with precision-driven micronisation that ensur...
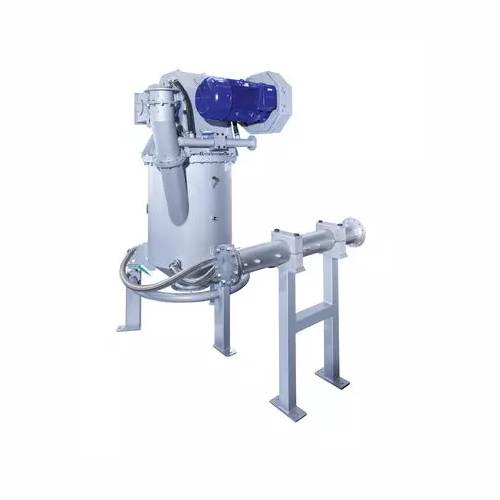
Fluidised bed opposed jet mill for fine particle processing
Achieve precise and consistent particle sizes with high-spee...
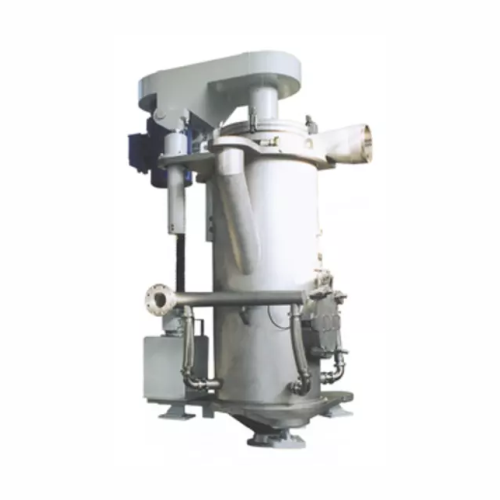
Jet mill for toner and pigment industries
Optimize particle size and distribution for high-demand applications with this h...
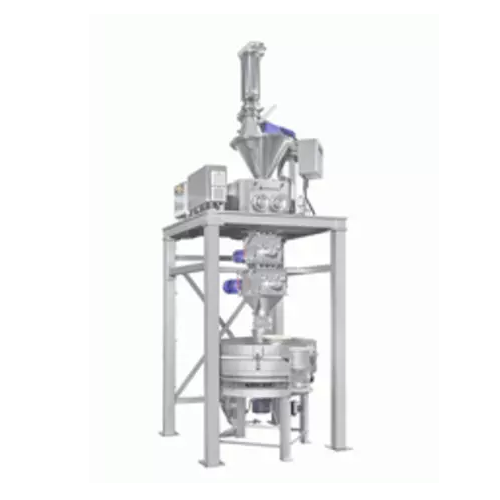
Roller press for fine-grained material compaction
Achieve optimal density and stability in your solid press agglomerates ...
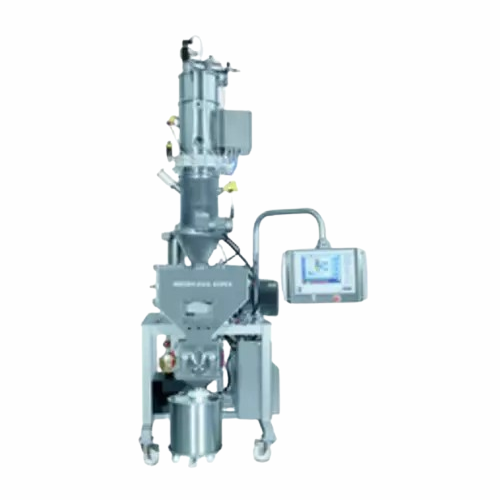
Compactor for powder processing
Designed for transforming powdered materials into uniform granules, this compactor enhances ...
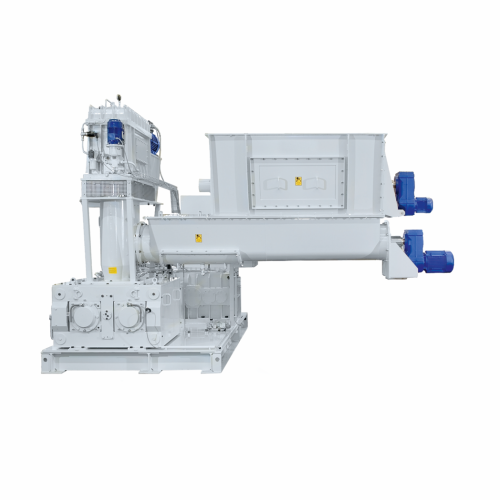
High-pressure roller compactors for chemical, food, and minerals industries
Achieve precise particle compaction and br...
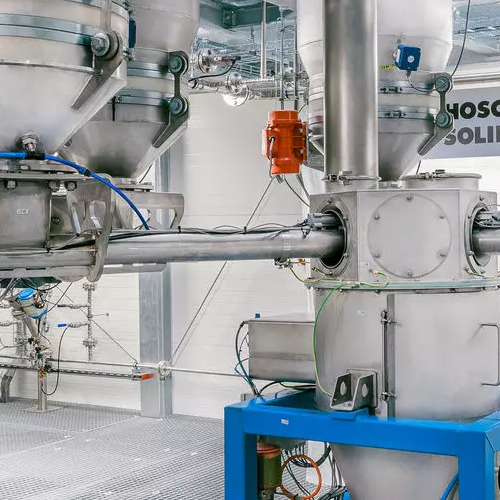
Mechanical conveying systems for bulk solids
Optimize your bulk material processes with advanced mechanical conveying syst...
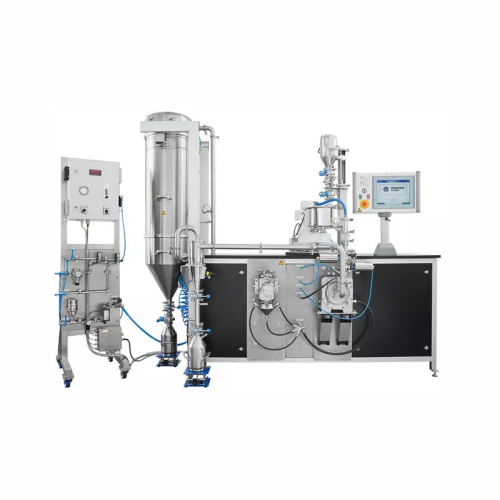
Multiprocessing system for flexible research and production
Optimize your process development with a versatile system th...

Pelleting and spheronizing equipment for chemical granulates
Optimize your production line with versatile pelleting and ...
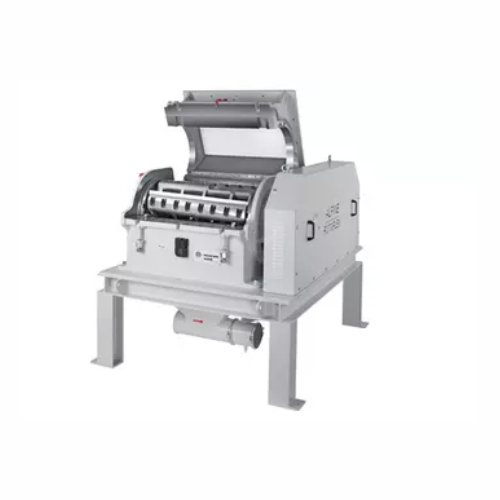
Industrial granulator for high-throughput plastic recycling
Facing challenges in efficiently recycling high-volume plast...

High-speed hammer mill for continuous operation
Achieve precise particle size reduction with high-speed hammer milling, id...
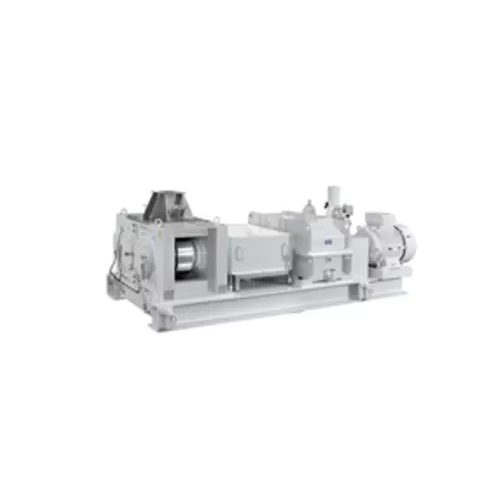
High pressure roller mill for medium-fine crushing
Achieve precision in particle size with high-pressure roller mills, id...
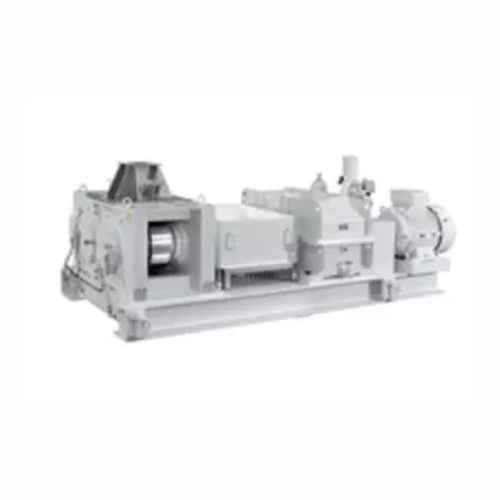
High-pressure roller mill for medium-fine crushing
Achieve precise granule distribution in medium-fine crushing applicati...
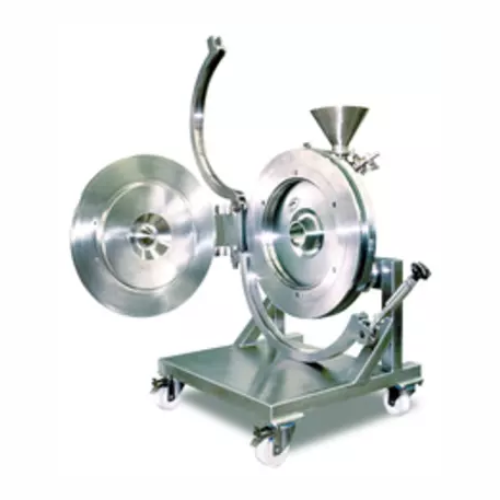
Spiral jet mill for superfine powder production
Achieve consistent ultra-fine powder with precise particle size control, c...
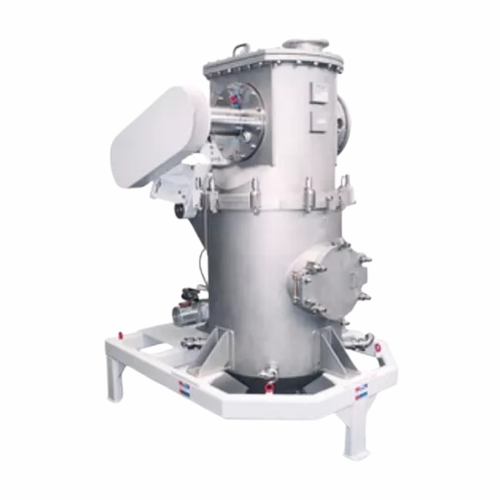
Fluidised bed opposed jet mill for ultrafine powder production
Achieve contamination-free ultrafine powder milling with ...

Sugar grinding and recrystallization system
Optimize your sugar production with a system that integrates grinding and recr...
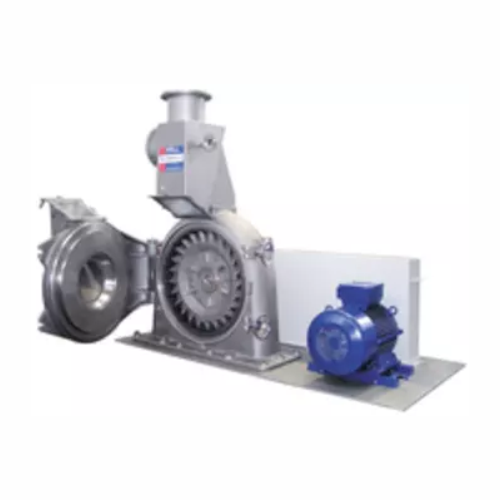
Versatile fine impact mill for soft materials
Achieve precision grinding with flexibility for a wide range of materials, e...
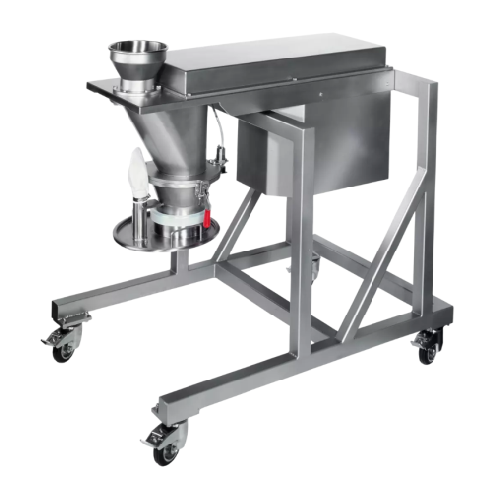
Flake crushers for gentle crushing of brittle materials
For processes needing precise granule control, our equipment ensu...
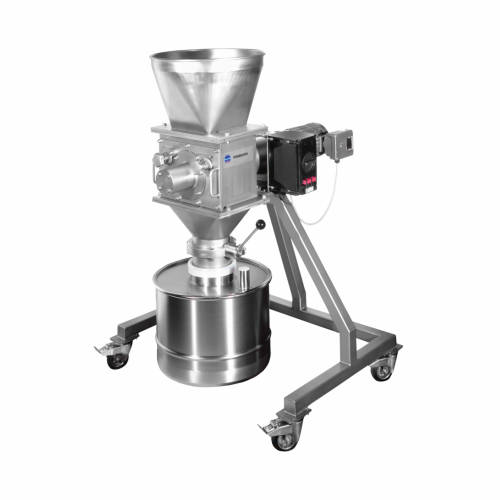
Flake crusher for hygroscopic substances and lumped salts
Efficiently turn fragile, aggregated materials into manageable...
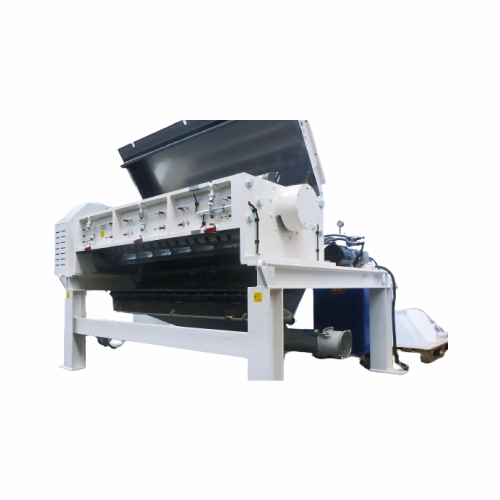
Industrial granulators for plastic recycling
Streamline your recycling operations with a solution that not only reduces en...
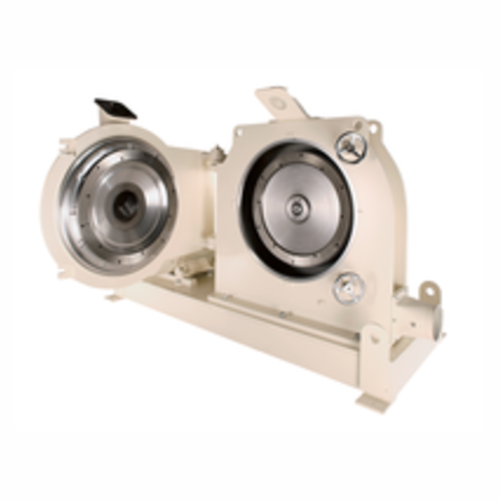
Fine cutting mill for soft to medium-hard plastics
Achieve precise size reduction and smooth particle shapes in plastic p...
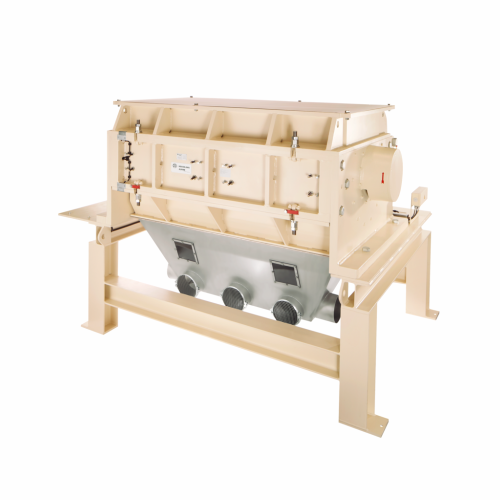
Compact granulator for plastic comminution
Optimize your plastic recycling operations with a compact granulator designed t...
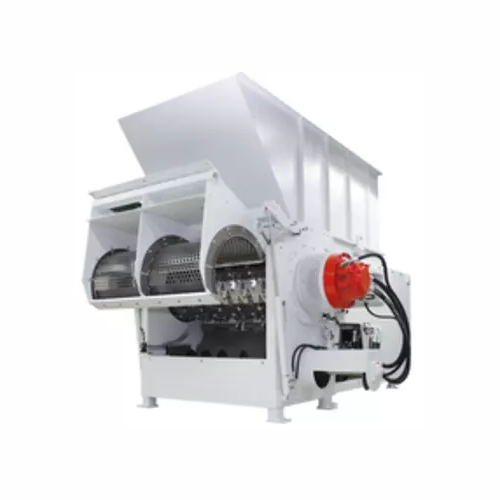
Heavy-duty shredder for difficult materials
Struggling with stubborn materials that resist conventional shredding? This ro...
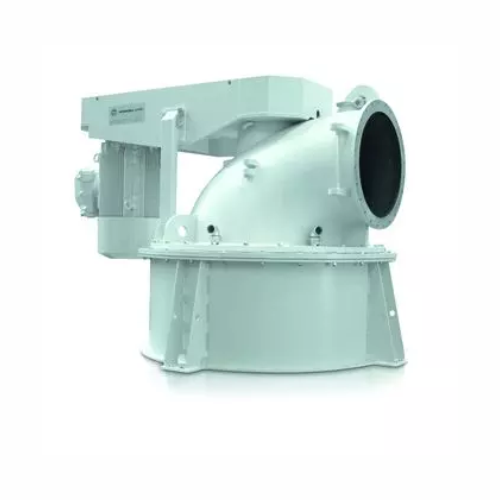
Air classifier for fine powder processing
Enhance your production line with precise particle size control and energy-effic...
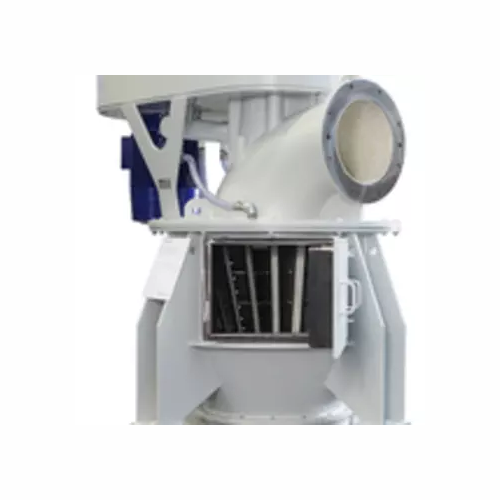
Ultrafine classifier for precise particle separation
Gain precise control over particle size with this ultrafine classifi...
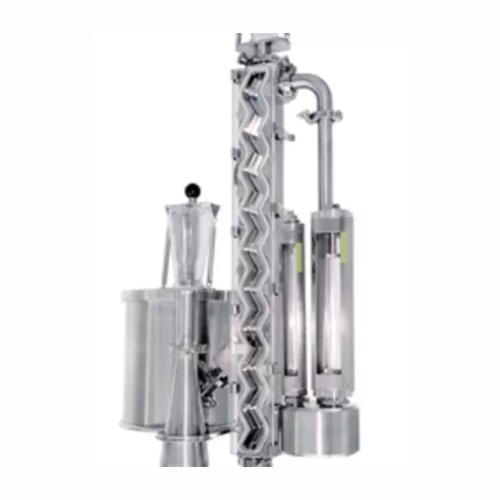
Gravity classifier for precise particle separation
Achieve sharp separations in particle processing with minimal maintena...
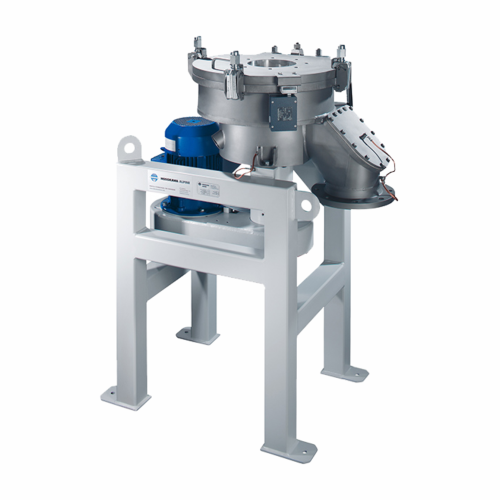
Ultrafine classifier for toner and pigments
Achieve unparalleled precision in classifying fine powders essential for high-...
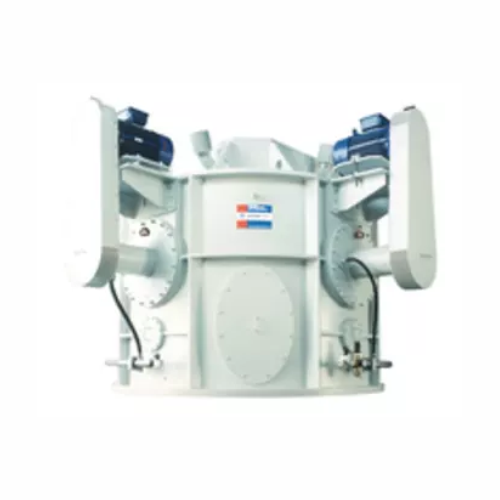
Ultrafine air classifier for powder separation
Achieve precise particle separation with technology designed to enhance you...

Ultrafine classifier for soft to medium-hard mineral processing
Achieve exceptional particle precision with an ultrafine...
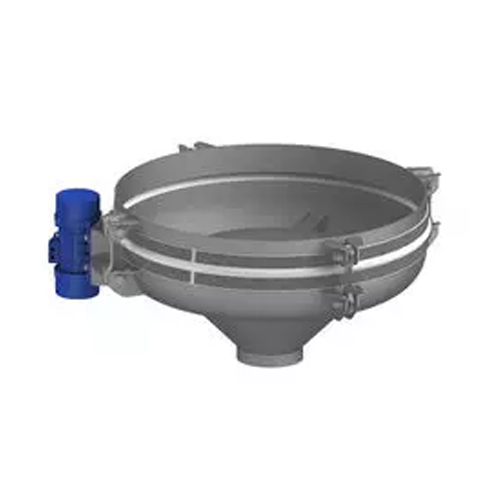
Discharge systems for difficult bulk materials
Achieve seamless bulk material discharge with our advanced systems that eff...
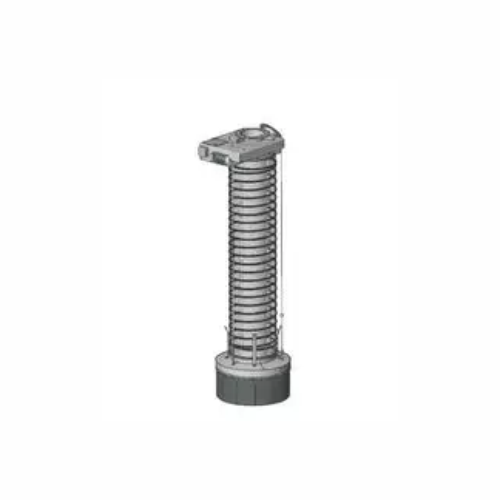
Automatic bulk material filling system
Ensure precise, contamination-free filling of various bulk materials with an advance...
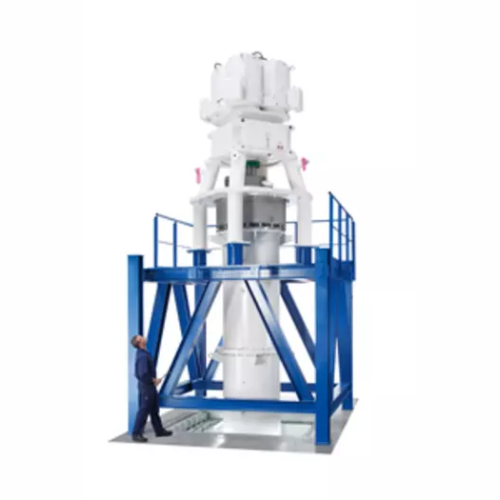
Ultrafine grinding mill for calcium carbonate slurries
Achieve precise particle size distribution in your mineral slurrie...

Ultra-fine dry grinding mill for glass and ceramics
Achieve ultra-fine particle sizes and energy savings with a dry grind...
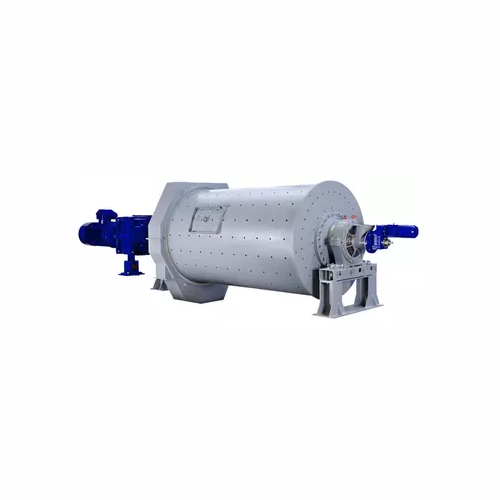
Ball mill for dry comminution of hard materials
Achieve ultrafine particle sizes and precise material breakdown with this ...
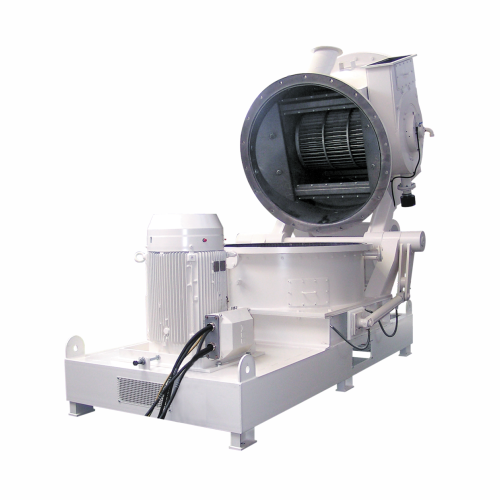
Classifier mill for ultra-fine grinding and precise particle size control
Achieve consistent ultra-fine particle distr...
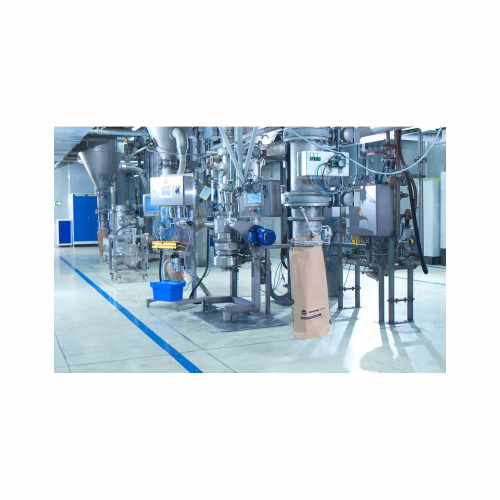
Air classifier for classifying industrial minerals
Achieve precise particle separation with advanced air classifiers, par...
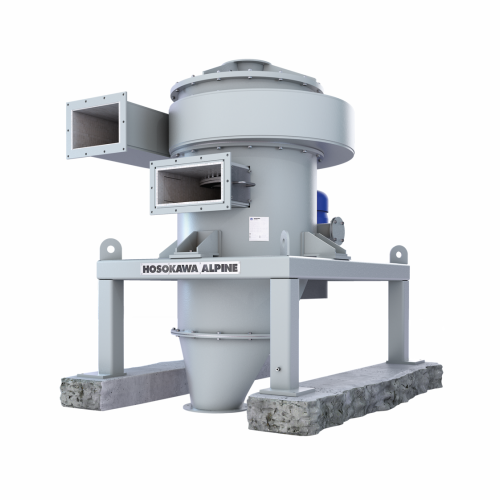
Air classifier for fine to medium-fine separation
Reduce energy consumption and wear while achieving high precision in th...
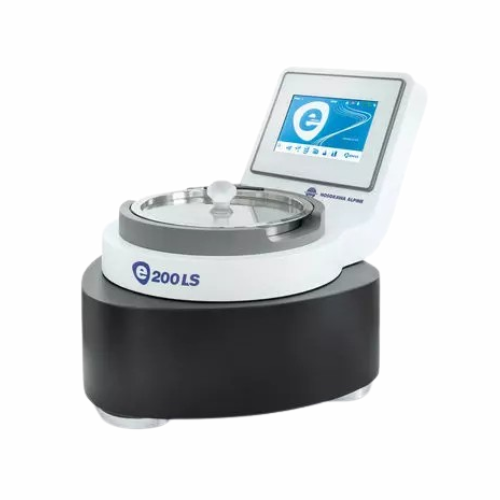
Air jet sieve for particle size analysis
Achieve precise particle size distribution effortlessly for your powders, ensuring...
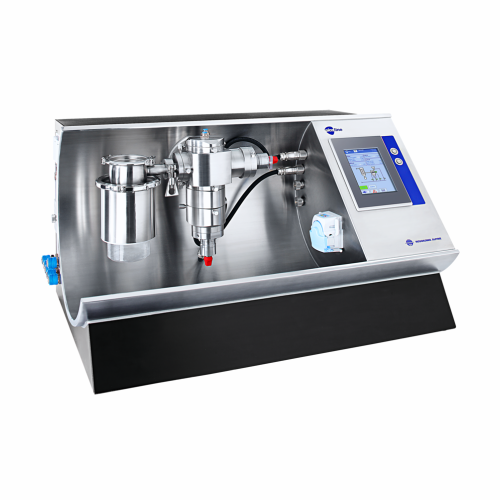
Laboratory system for powder and particle processing
When precision in powder processing is crucial, this versatile labor...
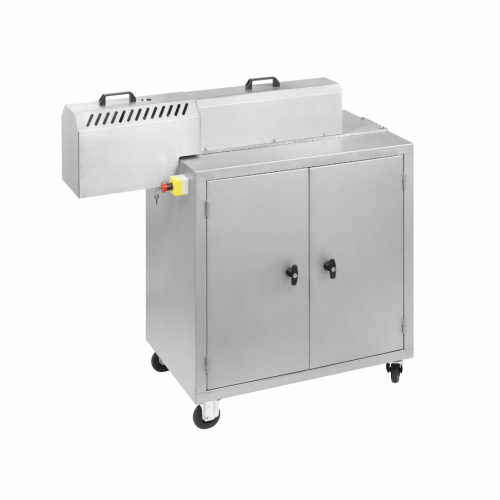
High-viscosity continuous industrial kneader for small volumes
Achieve consistent high-viscosity material processing wit...
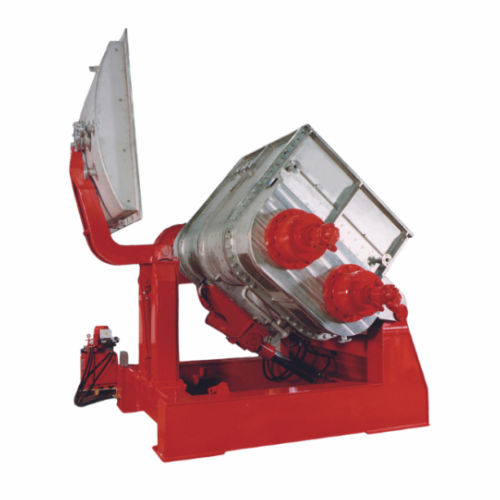
Double z-arm industrial extrusion kneader for high-viscosity processes
Optimize high-viscosity material processing with...
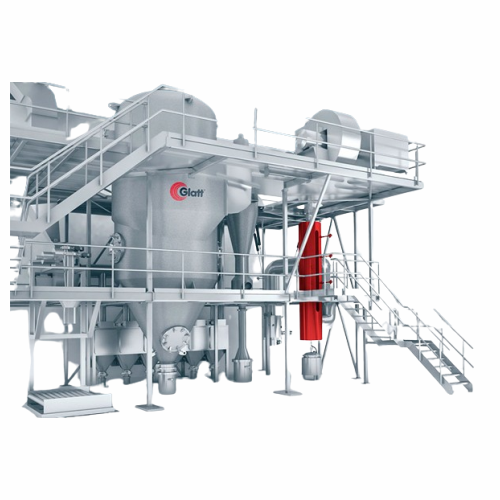
Powder synthesis reactors for nanometer and micrometer particles
Achieve precise particle control and enhance material p...
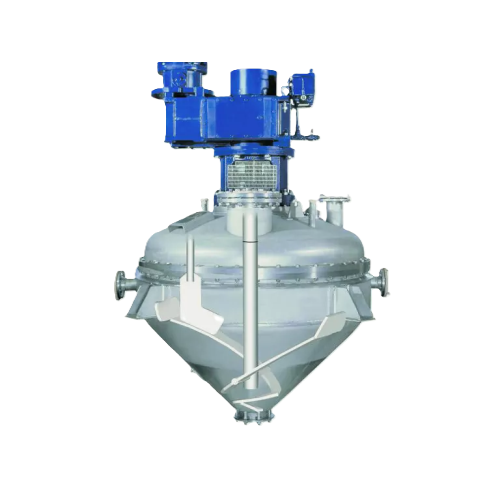
Vacuum dryer for free-flowing and pasty solids
Achieve precise drying and mixing with this vacuum dryer, optimizing heat t...
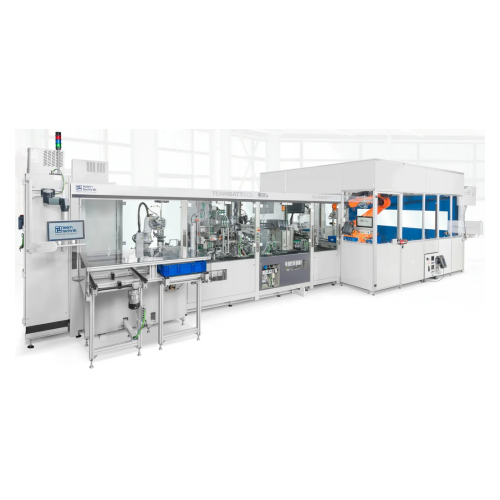
Production systems for battery cells with end-of-line testing
Optimize battery cell production with a flexible system of...
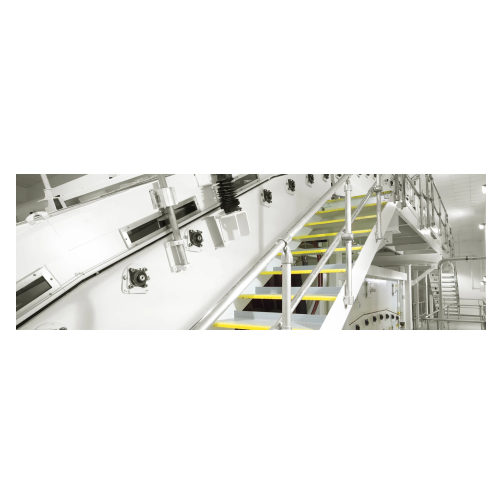
Roll support dryers for web transportation
Eliminate web curl issues and enhance drying precision for diverse materials wi...
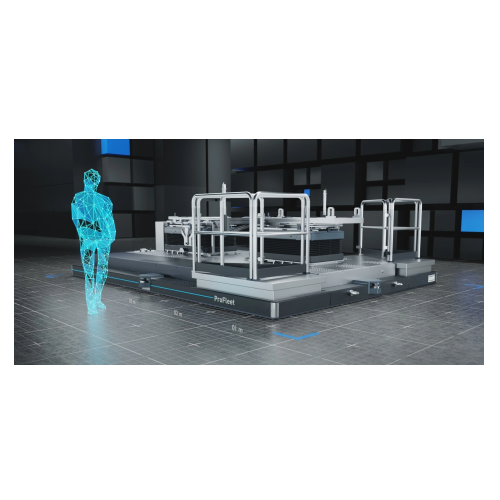
Compact Agv for trolley towing and load transport
Streamline your intralogistics operations with agile load transporters ...
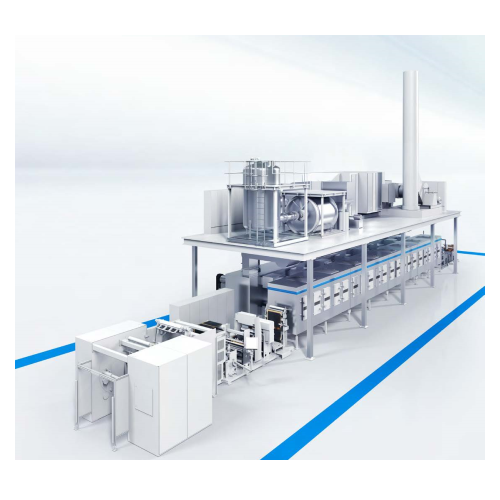
Battery electrode coating line
Optimize your battery production with a comprehensive coating line that enhances throughput a...
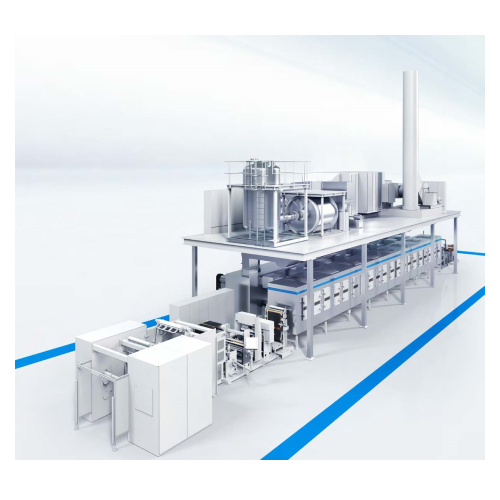
Electrode coating system for lithium-ion batteries
Achieve high-volume, precision electrode coating for lithium-ion batte...
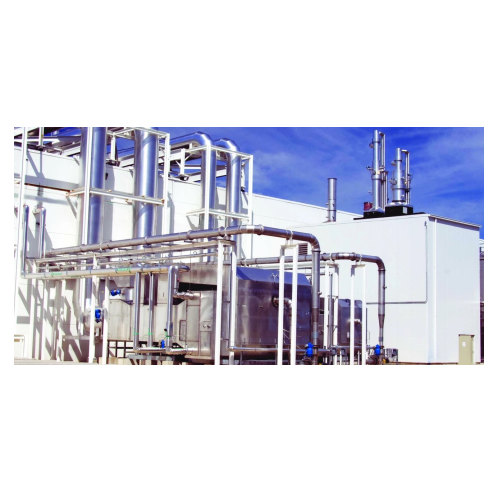
Solvent recovery systems for battery electrode manufacturing
Efficiently recover and purify solvents in battery electrod...
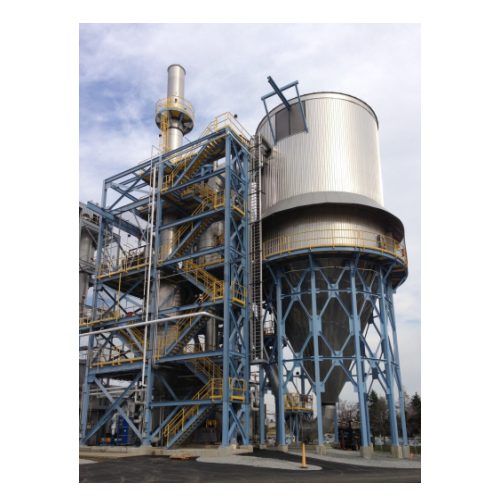
Spray dryers for lithium iron phosphate powder production
Optimize your lithium battery and electric vehicle production ...

Precision feeders and mixers for plastics processing
Achieve precise blending and feeding for plastics processing with mo...
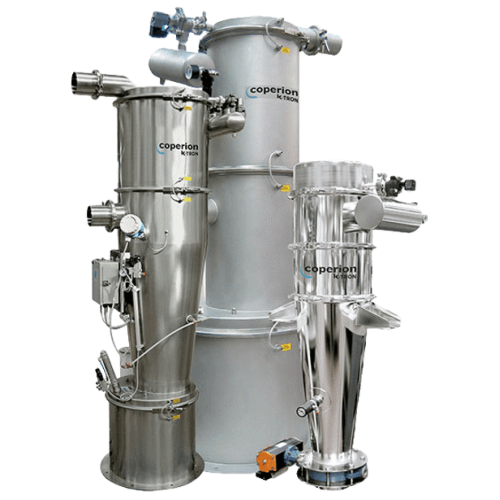
Sanitary bulk solids receiver for food and pharma
Ensure precise control over bulk solid transfer with a system designed ...
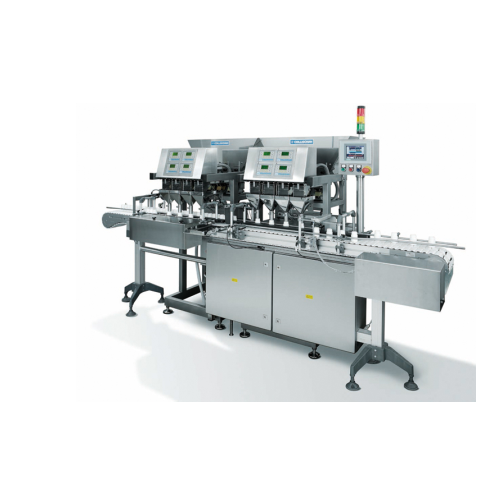
Complete packaging lines for various containers
Streamline your packaging process with versatile equipment capable of hand...
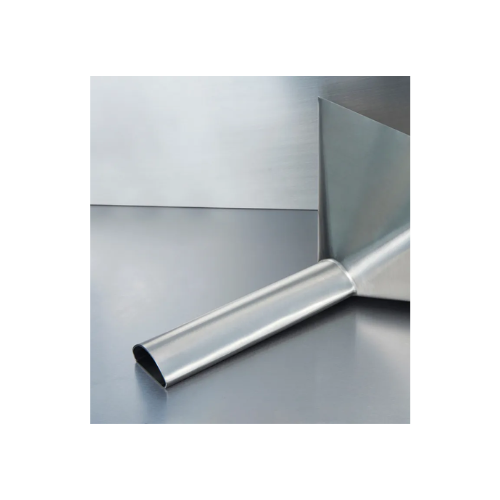
Powder dispensing funnel
Enhance powder handling accuracy while minimizing product loss with a precision-engineered dispensin...
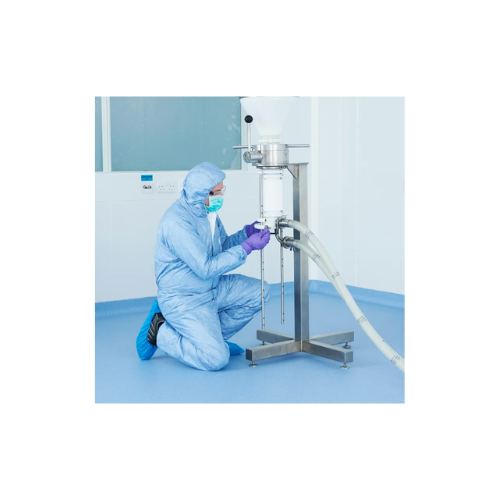
Bottle cleaning station for controlled environments
Ensure high-level decontamination of passive units and containers wit...
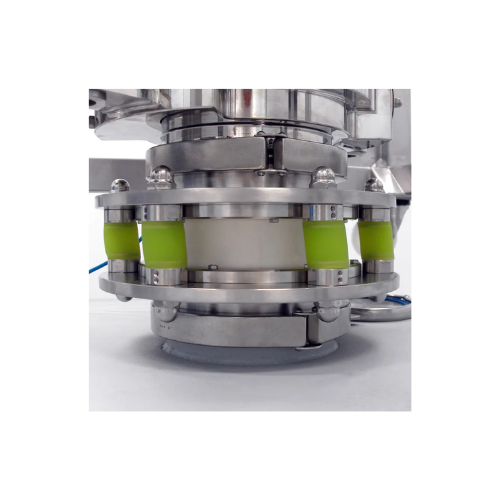
Bulk powder transfer safety device
Ensure stable and secure docking by minimizing equipment damage during powder transfer p...
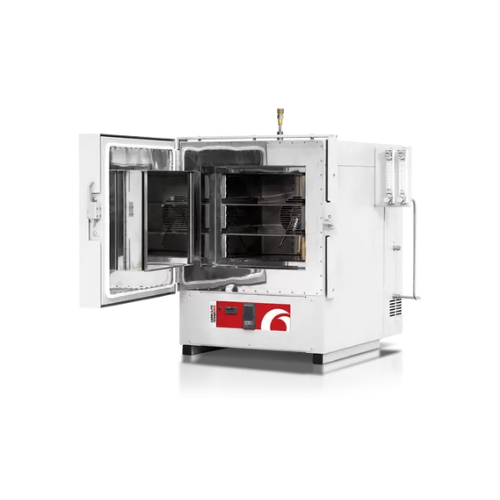
Controlled atmosphere oven for high-temperature applications
Achieve precise atmosphere control and uniform heating for ...
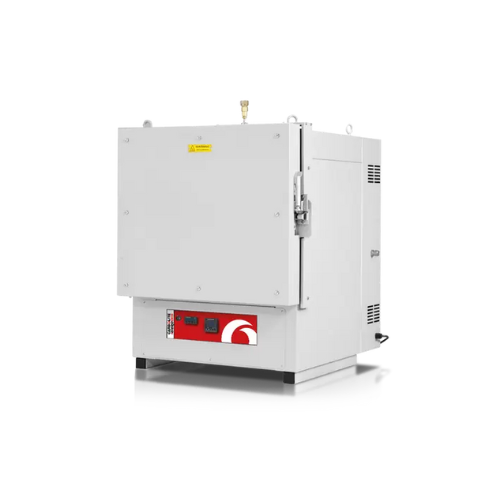
High temperature clean room ovens
Achieve precise environmental control for heating, drying, and sterilizing sensitive mate...
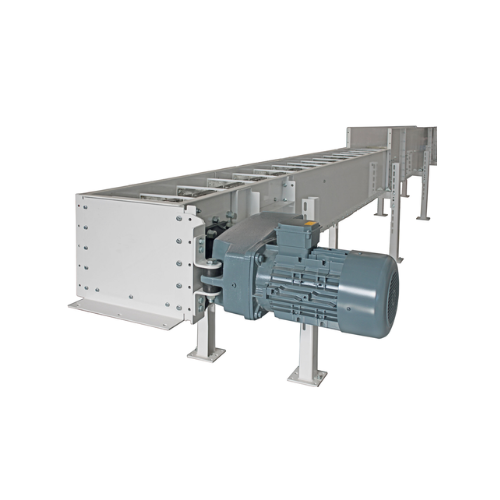
Chain conveyor for grain and floury products
Ensure seamless material handling with a versatile chain conveyor designed fo...
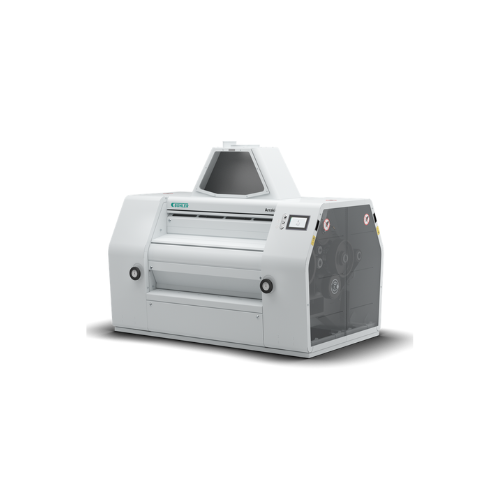
Four-roller and eight-roller mill for wheat and grain grinding
Optimize your grinding operations with this versatile rol...
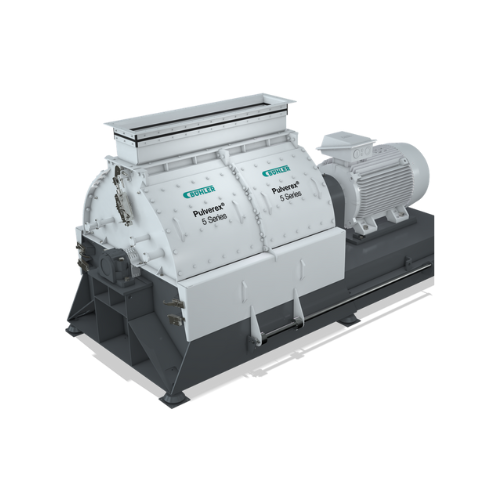
Pulverizer for fine grinding applications
Achieve optimal particle size distribution and enhance throughput with this adva...
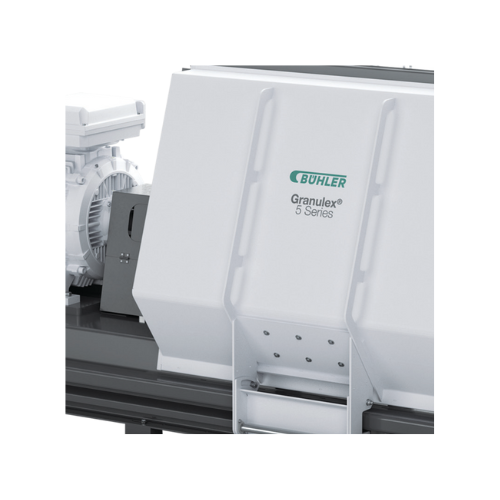
High-throughput hammer mill for animal feed production
Ideal for high-throughput operations, this hammer mill ensures pre...
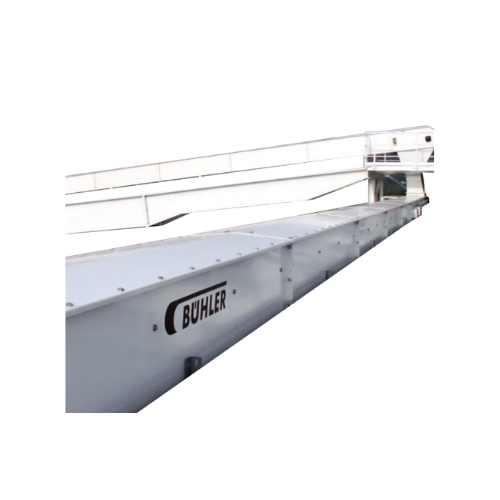
Heavy-duty trough chain conveyor for high throughput applications
Optimized for high-capacity operations, this robust c...

Twin-screw extruder for breakfast cereals production
Enhance your product range with flexible twin-screw extrusion techno...

Discharge station for bags and big bags
Ensure consistent material flow and hygiene in your production line with a versatil...

Control systems for wet grinding industry
Enhance precision and efficiency in your production line with advanced control s...
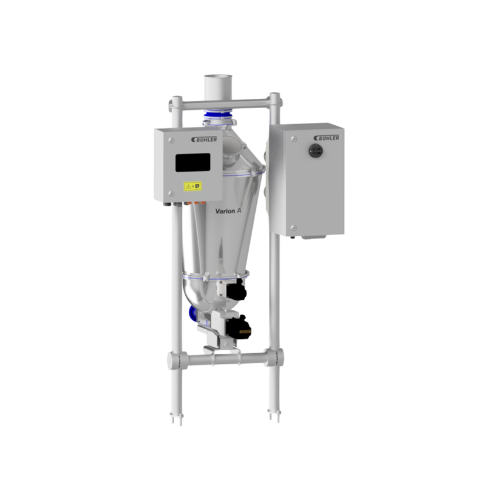
Batch scale for high accuracy weighing of powdery products
Achieve unparalleled precision in powder dosing with our batc...
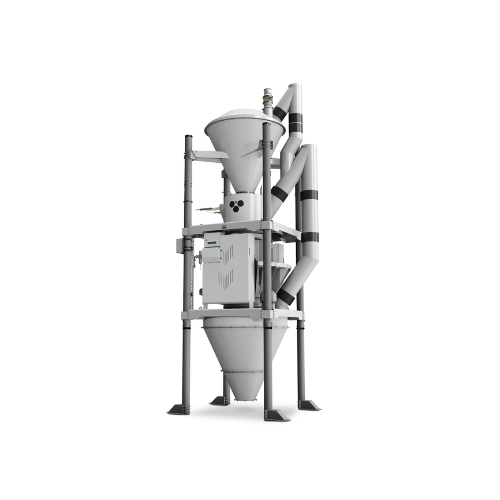
Fully automatic batch scale for powdery and granular products
Achieve precise and repeatable dosing for powdery and gran...
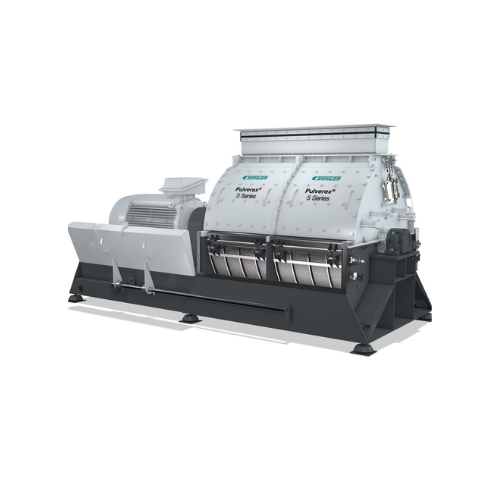
Industrial fine grinding pulverizer
Achieve consistent fine granulation at high capacity with reduced energy consumption, u...
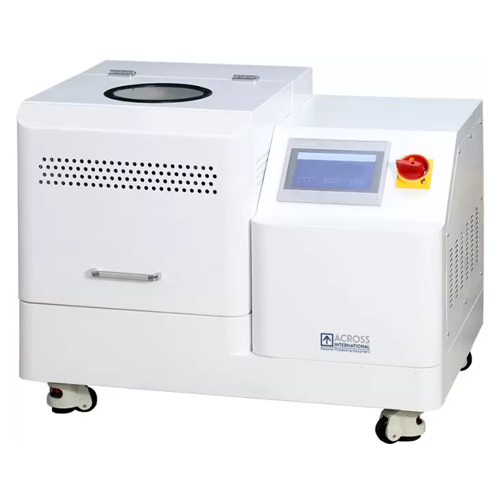
Planetary ball mill for powder material mixing and alloying
Achieve precise control in particle size reduction and homog...
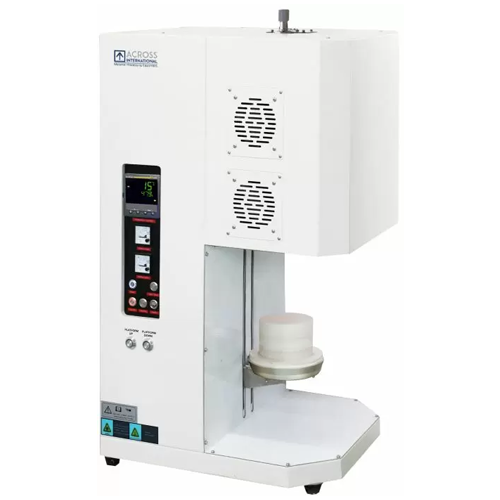
Table-top bottom loading furnace for high-temperature applications
For precise thermal processing and advanced experime...
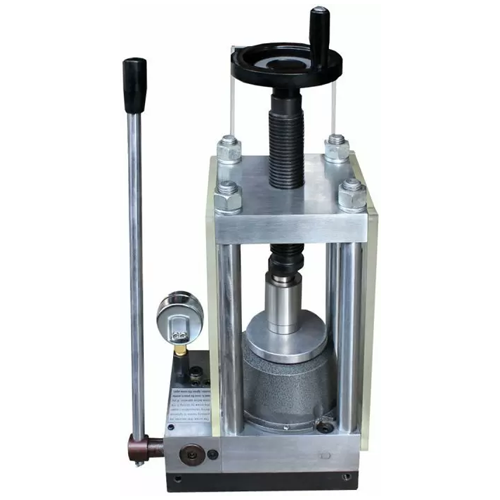
24-ton laboratory pellet press
Achieve precise pellet formation with reliable 24-ton pressing power, ideal for compaction of...
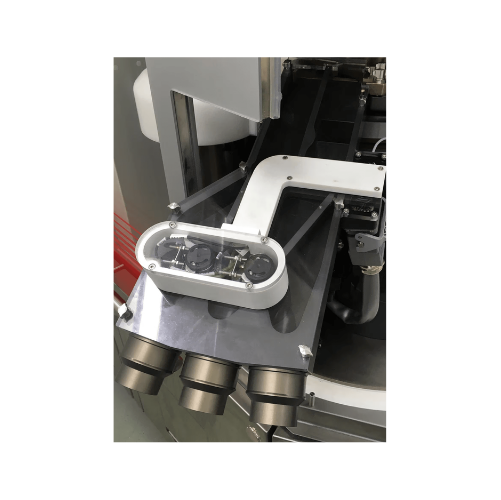
Rotary tablet press for abrasive powders
Achieve precise tablet sizing and bilayer production, even with abrasive powders, ...
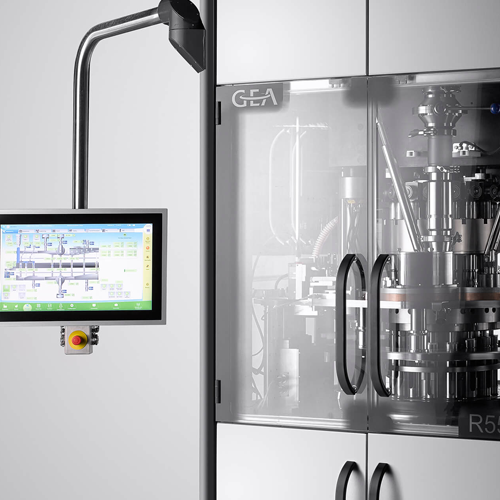
Heavy-duty tablet press for single & double-layer tablets
Maximize your tablet production with a high-speed solution cap...
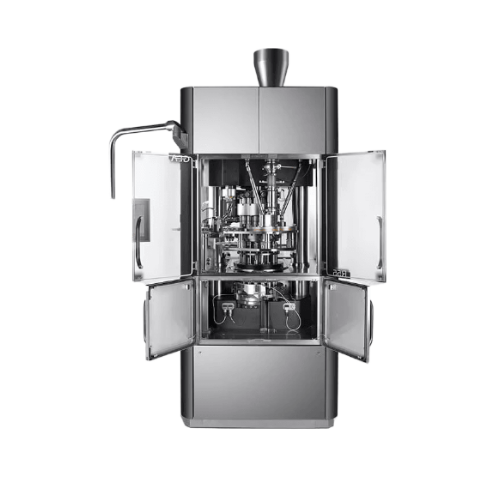
Industrial rotary press for single-layer tablet production
Optimize your tablet production with precision-engineered rot...
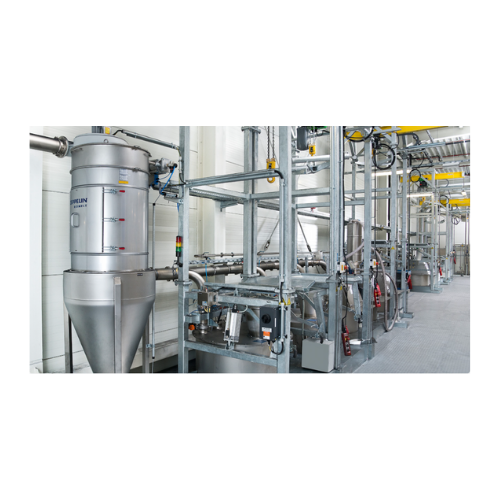
Battery production facilities with precision weighing
Achieve maximum product purity and precision in your production pro...
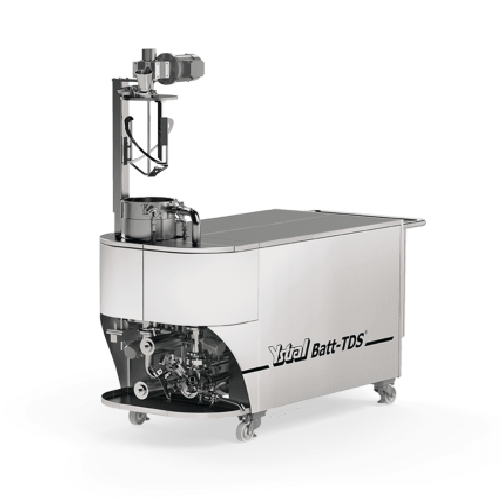
Inline disperser for lithium-ion electrode slurry mixing
Achieve highly efficient dispersion and homogeneity for battery ...
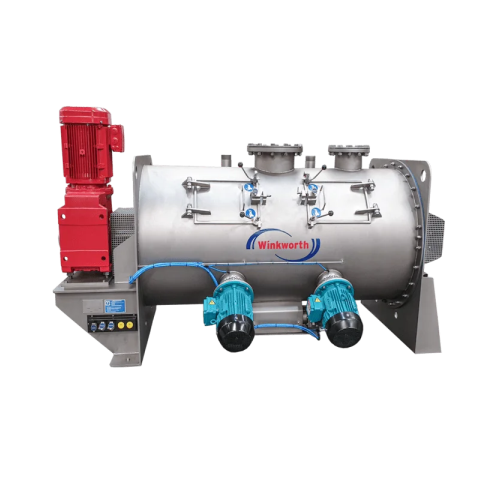
High-speed mixer for industrial mixing applications
Achieve rapid, consistent mixing and dispersion across diverse materi...
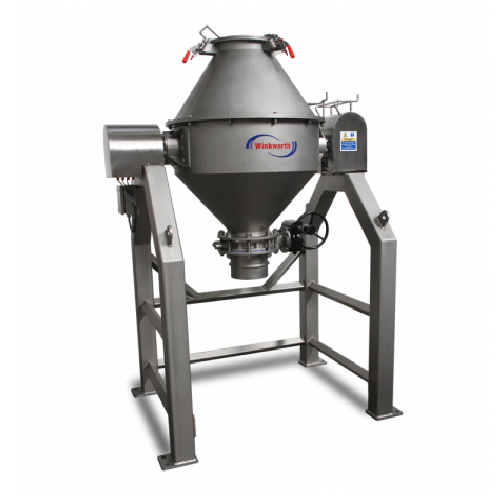
Double cone mixer for free-flowing material blending
Optimize your production with precision blending and gentle drying o...
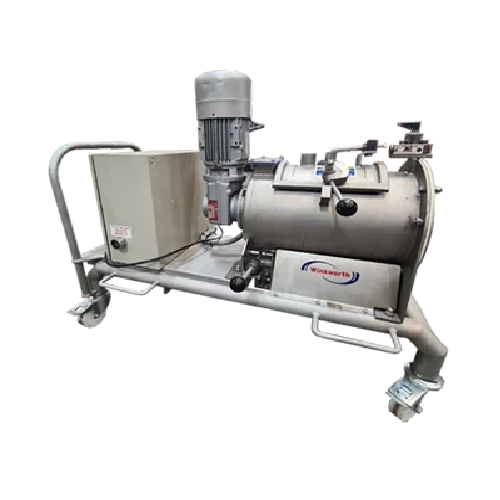
Industrial mixers for hire
Optimize your production line with versatile mixers designed for precision blending, heating, and...
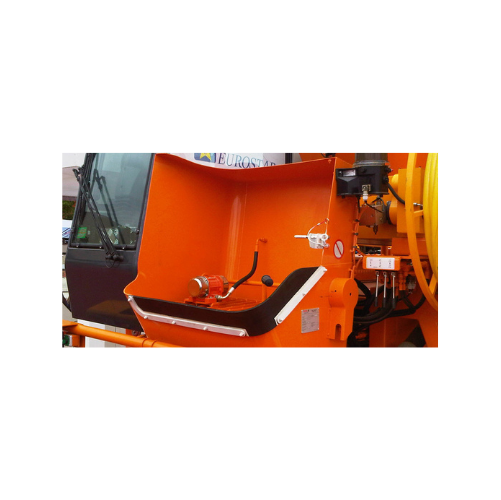
External electric motovibrators for hazardous environments
Ensure safety and efficiency in explosive environments with t...
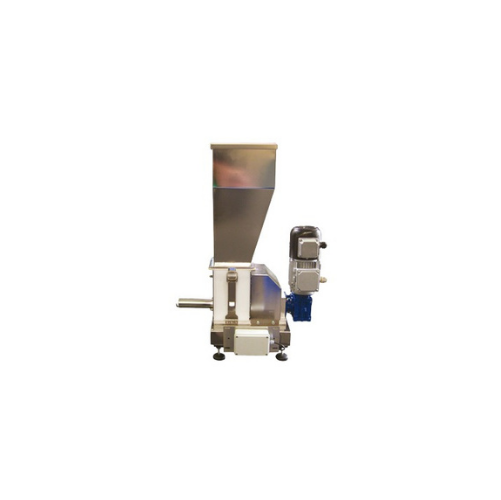
Loss-in-weight screw feeder for precise powder dosing
Achieve high precision in continuous dosing with this advanced scre...
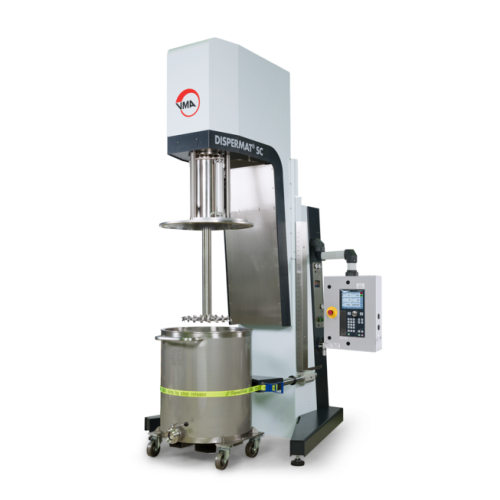
Explosion-proof production disperser for paint manufacturing
Ensure safe and efficient dispersion in volatile environmen...
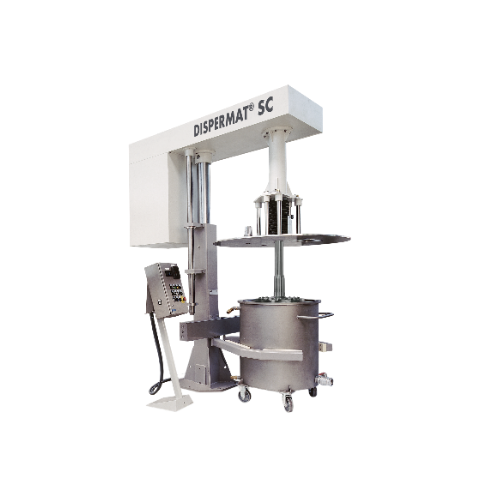
Explosion-proof dissolver for chemical processing
Ensure safe and efficient dispersion in volatile environments with this...
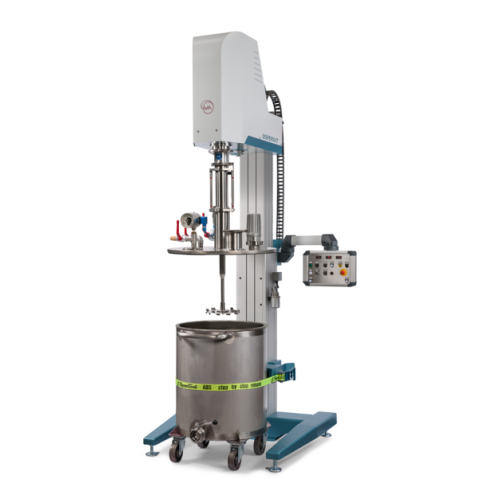
Vacuum dispersion system for high-viscosity products
Eliminate air inclusions during production with a modular vacuum sys...
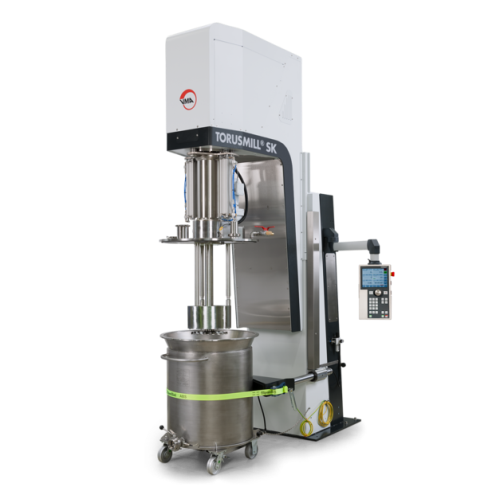
Vacuum basket mill for high viscosity products
Achieve efficient fine grinding of high-viscosity products while minimizing...
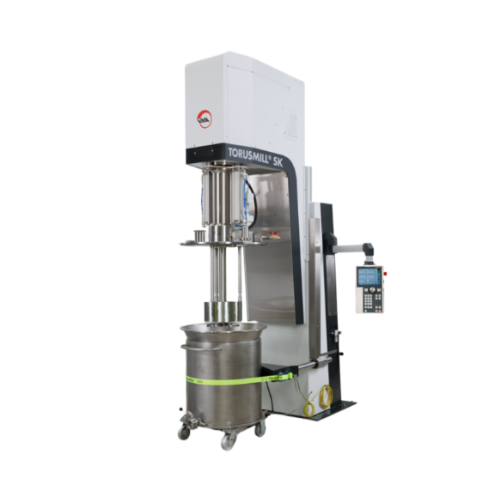
Vacuum dissolver for high viscosity products
Optimize your production with a vacuum dissolver designed to efficiently prev...
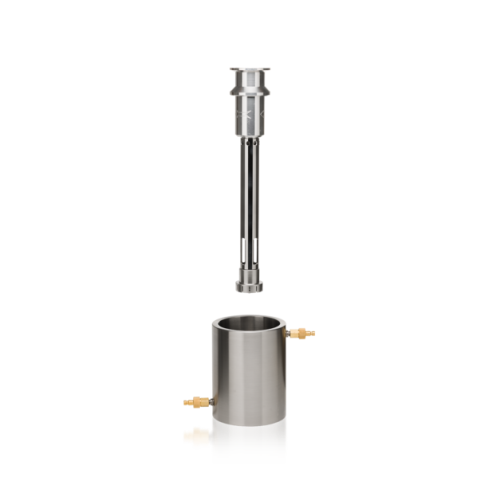
Vacuum dissolver for large batch production
Optimize your mixing processes with a versatile vacuum dissolver designed for ...
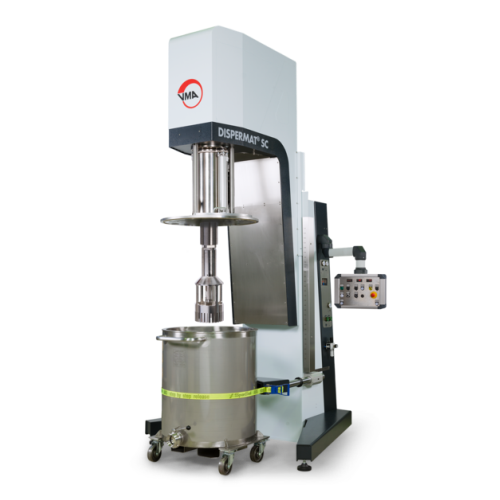
Rotary homogenizer for high shear mixing
Achieve precise homogenization of various viscosities with advanced rotor-stator t...
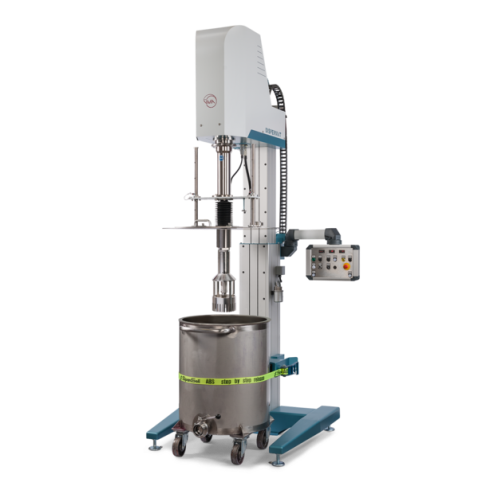
Rotor-stator homogenizer for high shear batch processing
Achieve ultra-fine particle distribution and stable emulsions wi...
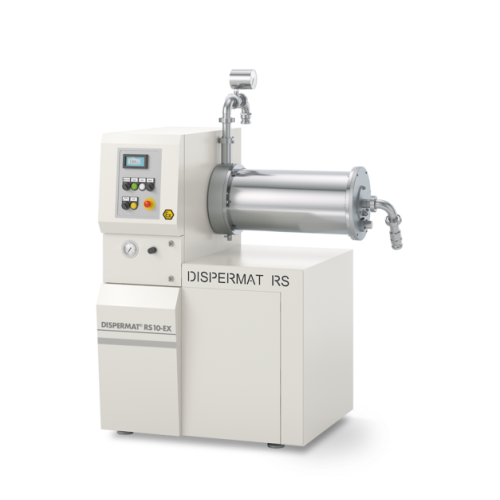
Explosion-proof bead mill for industrial grinding applications
For manufacturers seeking precise particle size control, ...
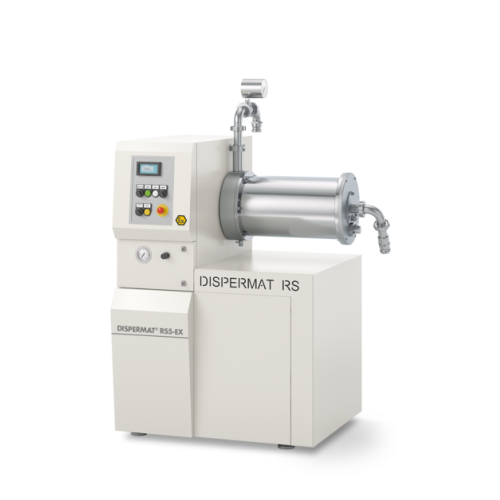
Explosion-proof horizontal bead mill
For manufacturers seeking precise particle sizing, this explosion-proof bead mill ensu...
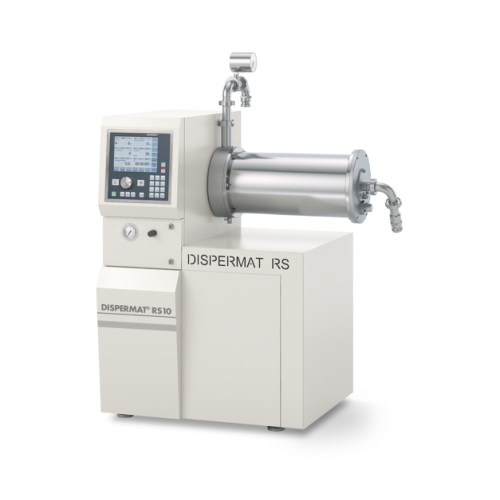
Horizontal bead mill for industrial production
Ensure ultra-fine particle size reduction in high-demand processes with thi...
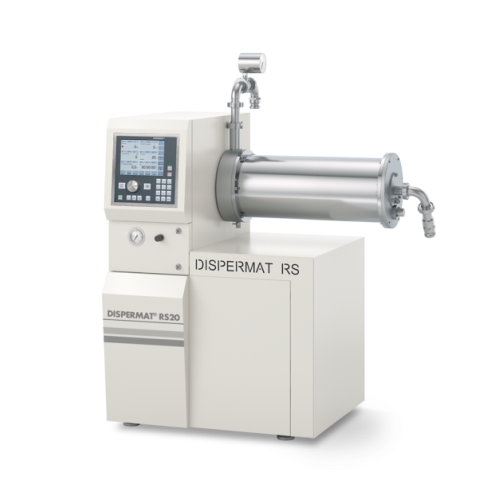
Horizontal bead mill for fine grinding in continuous process
Achieve ultrafine particle dispersion and consistent mixing...
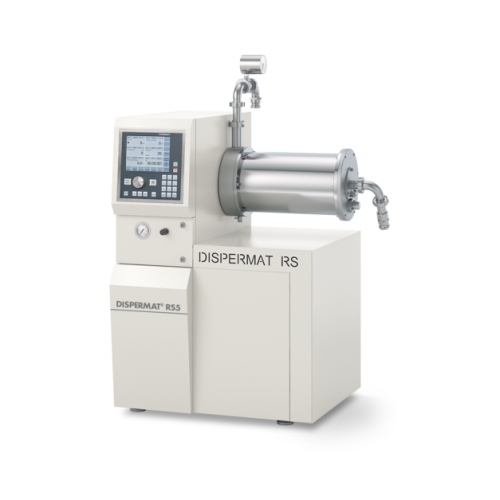
Horizontal bead mill for ultrafine particle grinding
Achieve precision in ultrafine grinding with a system that allows fo...
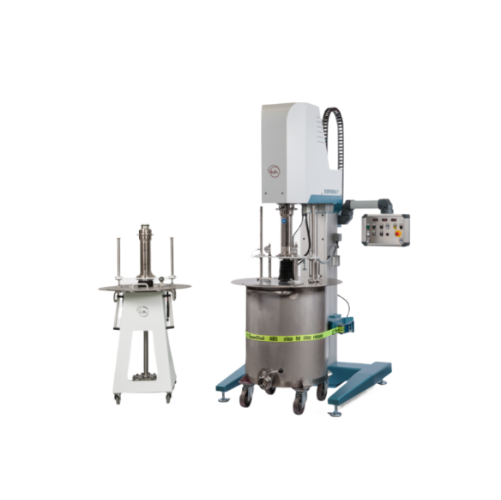
High-capacity dissolvers for industrial mixing
Enhance your production line with precision mixing, achieving consistent di...
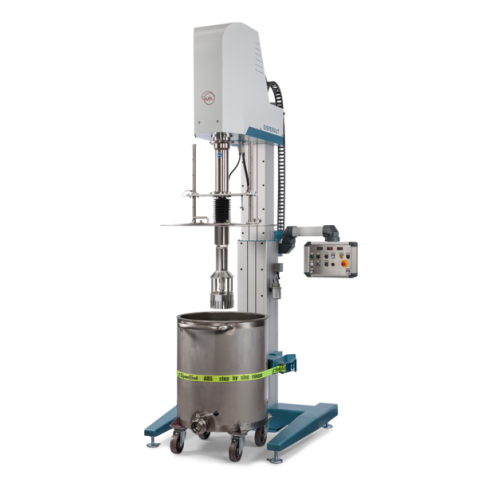
High shear batch process homogenizer for production
Achieve efficient emulsifying, homogenizing, and dispersing with prec...
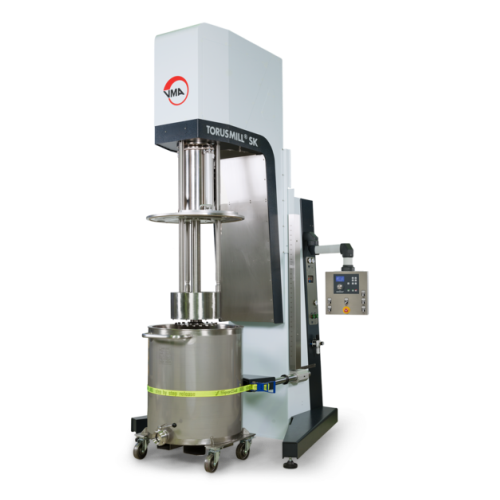
High-efficiency immersion mill for medium viscosity products
Achieve precise particle size reduction and superior disper...

High-efficient industrial immersion mill
Achieve rapid, efficient dispersion and fine grinding in demanding production envi...
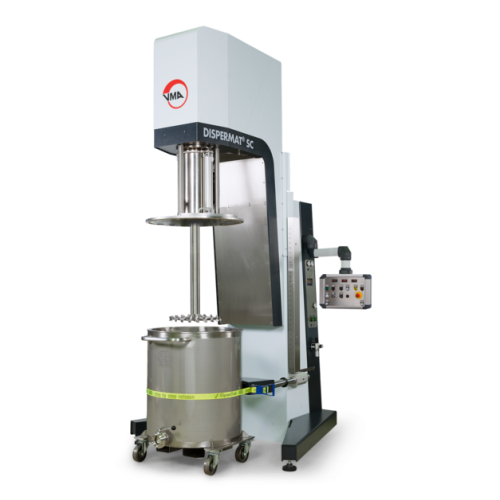
High-performance dissolver for industrial dispersion processes
Optimize your dispersion processes with this advanced dis...
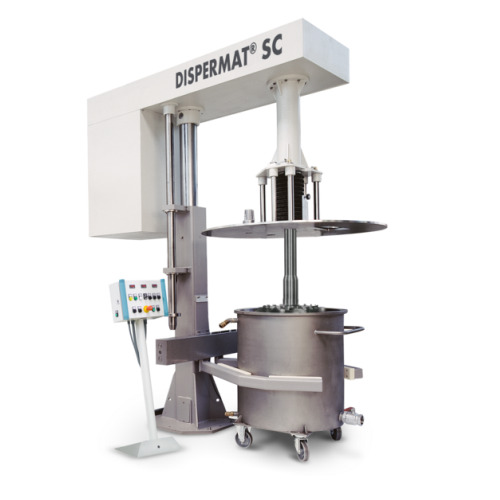
High-performance production dissolver for large batches
Achieve precise and repeatable dispersion for complex formulation...
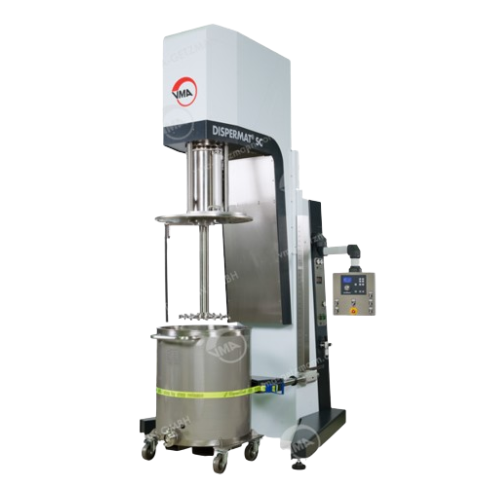
Production dissolver with scraper for high-viscosity products
Efficiently tackle high-viscosity material processing with...

Explosion-proof dissolver for high-viscosity products
Optimized for safely processing high-viscosity products, this explo...
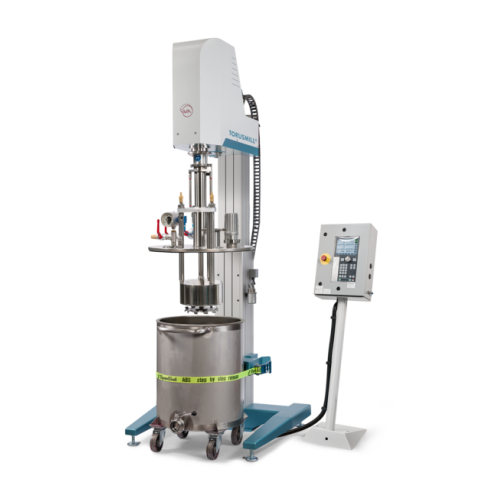
Vacuum basket mill for highly viscous products
Achieve precision in fine milling under vacuum to prevent air inclusions in...
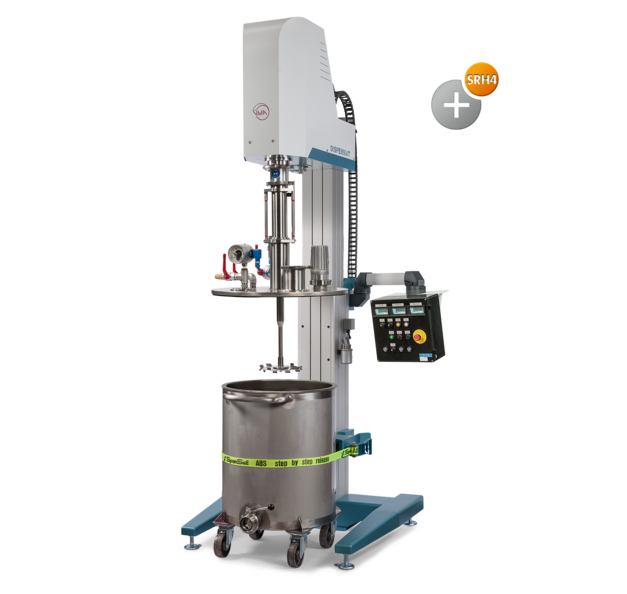
ATEX vacuum dissolver for high viscosity products
Ensure safe and efficient dispersion of high-viscosity materials under...
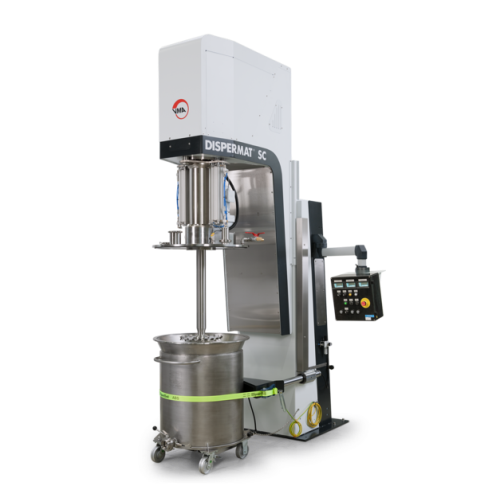
Explosion-proof vacuum dissolver for high-viscosity products
Optimize your production by eliminating air inclusions and ...
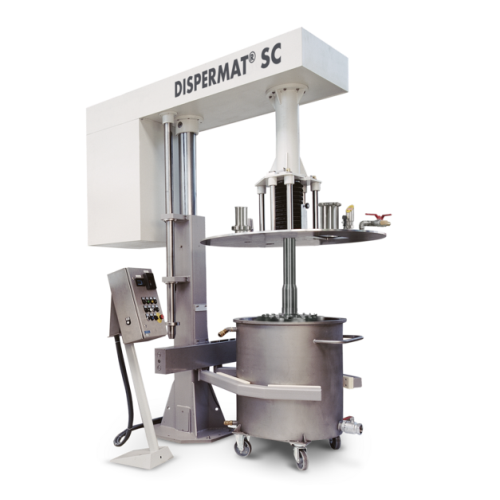
Explosion-proof vacuum dissolver for high viscosity products
Achieve precise dispersion of high-viscosity products under...
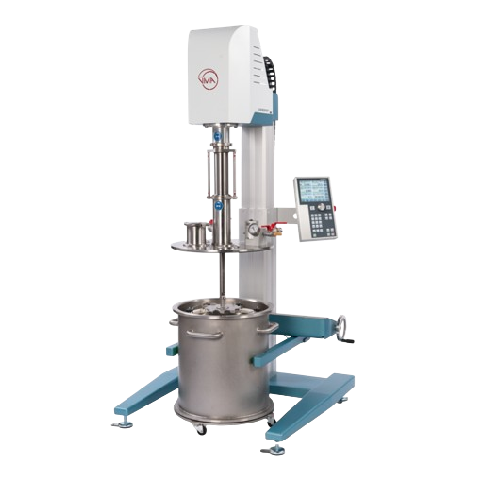
Vacuum dispersion system for single-walled containers
Optimize your production line with an adaptable vacuum dispersion s...
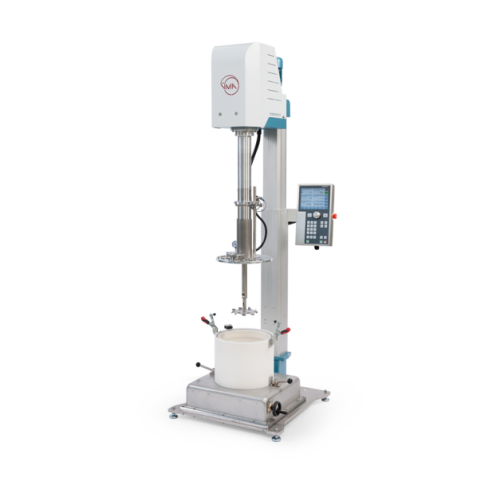
Laboratory vacuum dissolver
Experience precision vacuum processing for your high-viscosity formulations, ensuring optimal di...
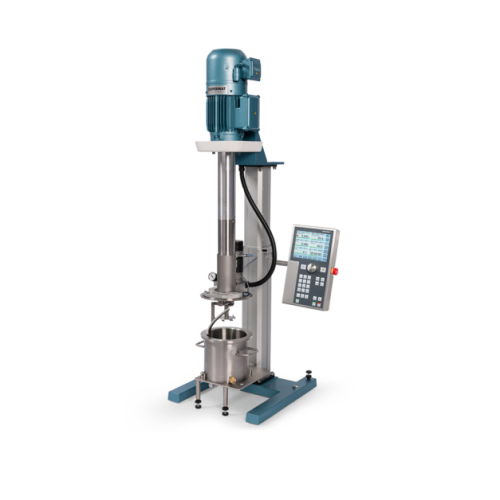
Vacuum dissolver for laboratory and pilot plant operations
Perfect for developing intricate formulations, this vacuum di...
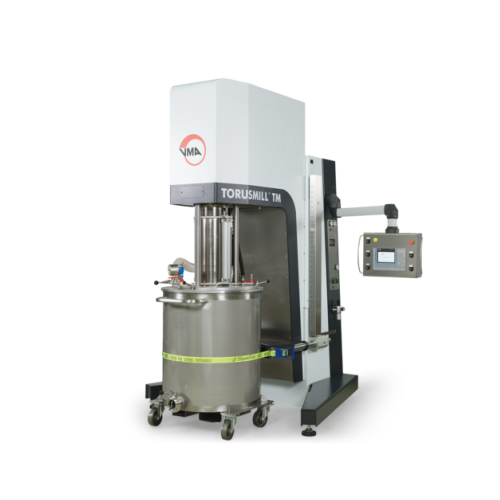
Dissolver for high-volume industrial dispersion
Achieve precise and efficient mixing with this dissolver, designed for sea...
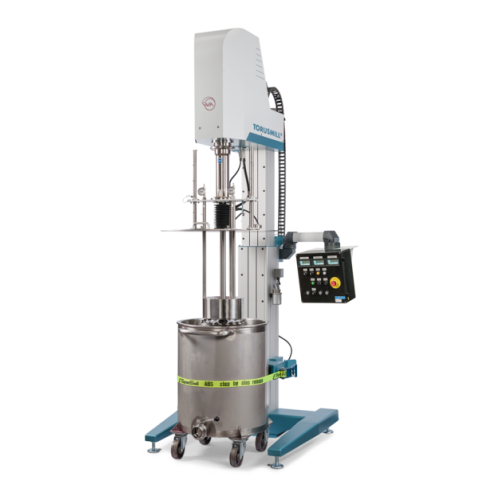
Explosion-proof basket mill for fine grinding
Achieve efficient and safe fine grinding with this innovative explosion-proo...
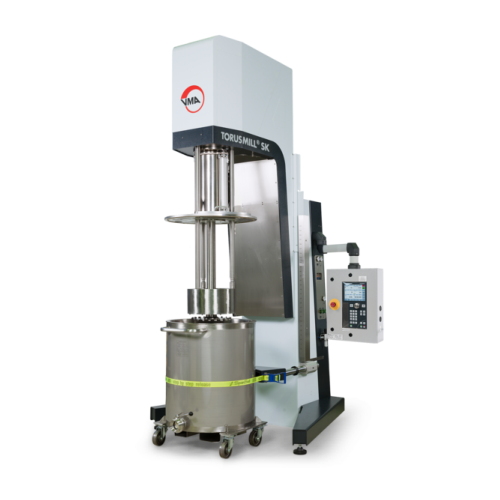
Explosion-proof immersion mill for paints and varnishes
Optimize high-performance coatings production with an explosion-p...
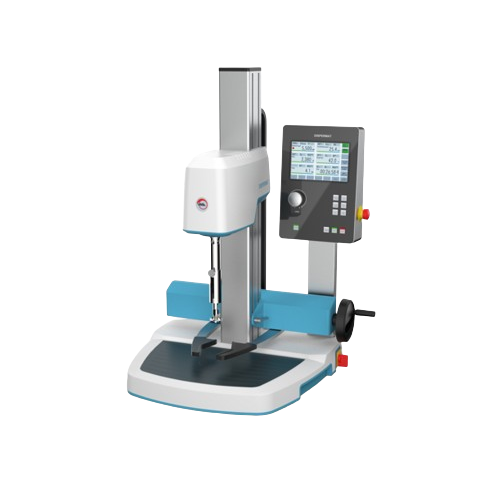
Laboratory dissolver for multiple applications
Efficiently streamline your laboratory processes with this versatile dissol...
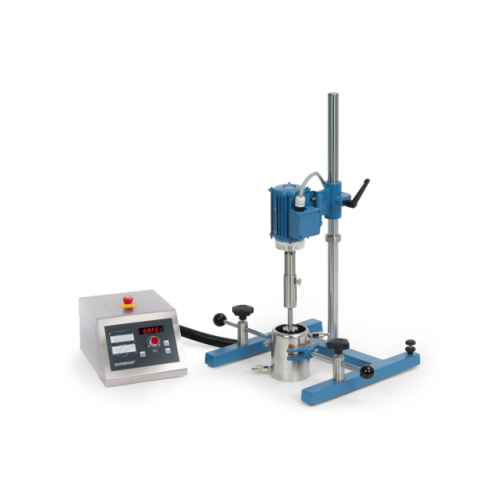
Lab and pilot plant dissolver for dispersion and fine grinding
Achieve efficient dispersion and fine grinding in laborat...
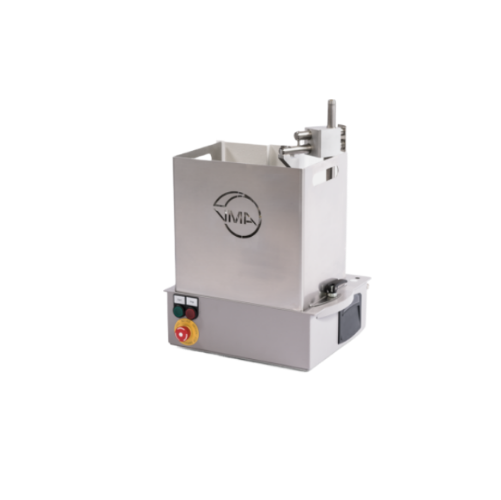
Industrial dissolver for high-viscosity materials
Efficiently disperse and mix high-viscosity materials with precision, e...
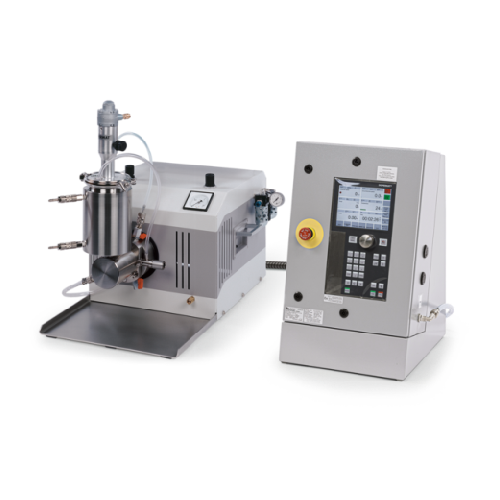
Explosion-proof horizontal bead mill for fine grinding
Ensure precise, explosion-proof grinding in hazardous environments...
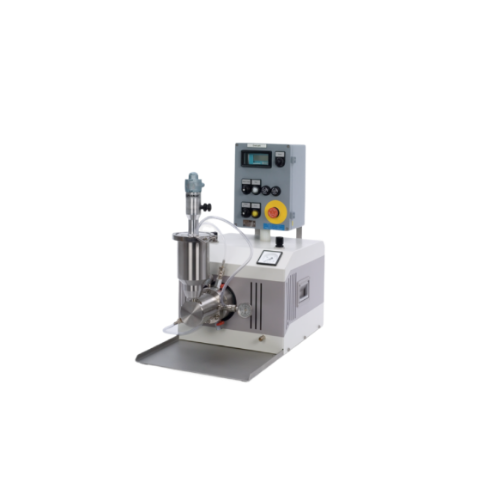
Atex horizontal bead mill
Ensure precision and safety in explosive environments with a robust solution that finely grinds an...
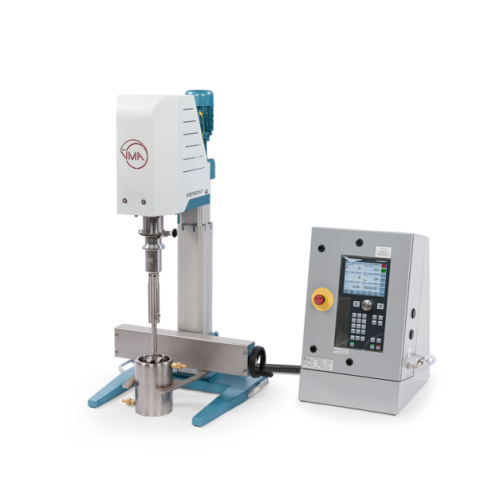
Explosion-proof dissolver for hazardous area mixing
When operating in hazardous environments, maintaining consistent and ...
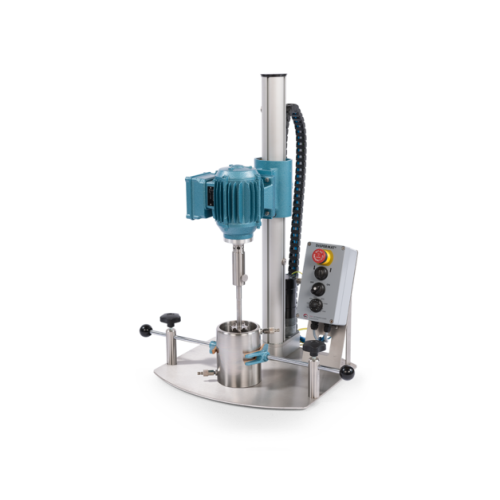
Explosion-proof dissolvers for laboratory use
Ideal for safely dispersing and mixing chemical substances in potentially ex...
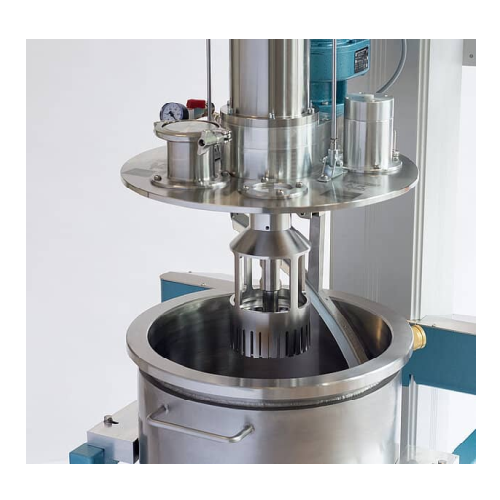
Efficient high-volume dissolver with scraper
For high-viscosity formulations, this advanced dissolver with integrated scra...
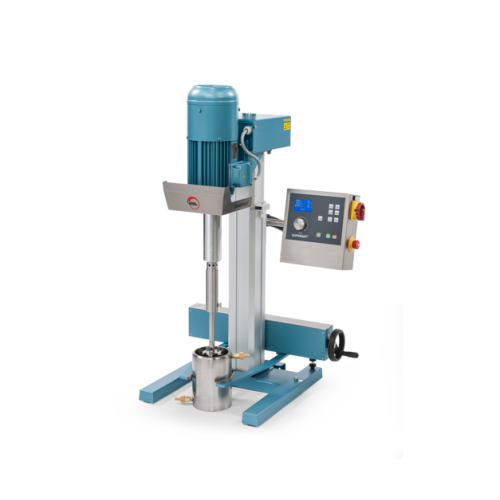
Lab stirrer for high-viscosity substances
Need precise, high-torque stirring for your complex formulations? This lab stirr...
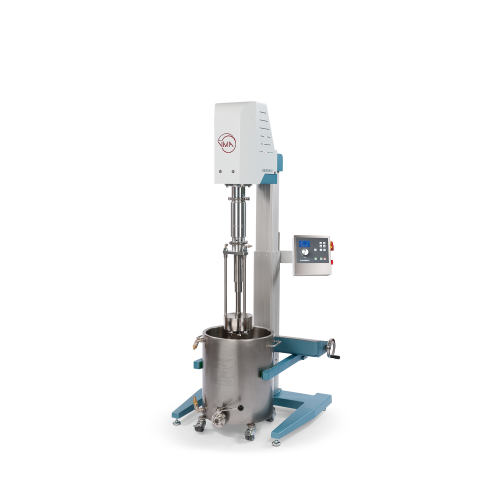
Entry-level vacuum dispersion system for laboratory applications
Achieve precise dispersion and milling with this versat...

Laboratory and pilot plant horizontal bead mill
Achieve precision milling with minimal product waste, ensuring consistent ...
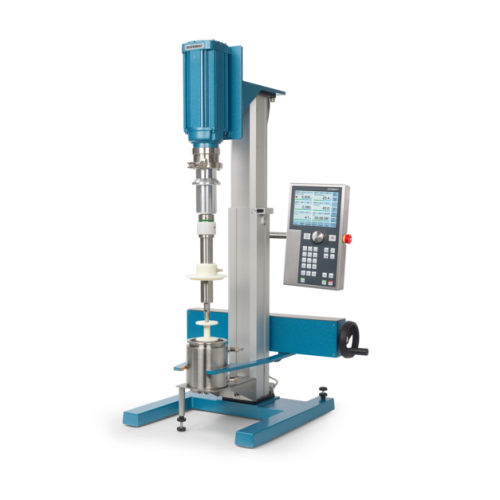
Laboratory disperser for small batch processing
Achieve precise dispersion and homogenization of high-viscosity mixtures w...
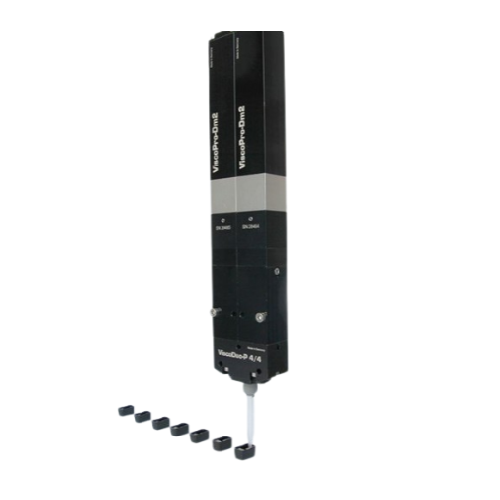
Precision 2k dispenser for automated systems
Achieve precise mixing and dispensing of two-component materials with minimal...
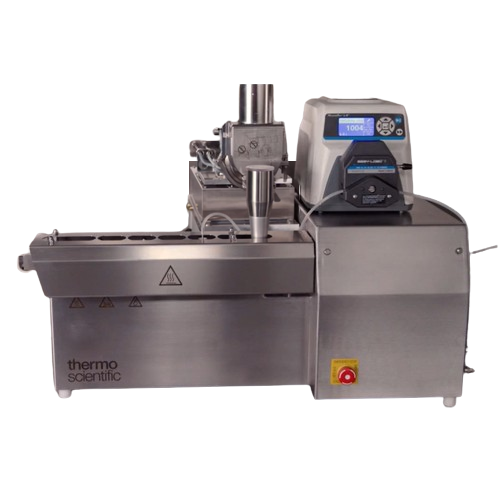
Glovebox for lithium-ion battery material processing
Ensure optimum material integrity with a solution designed to mainta...
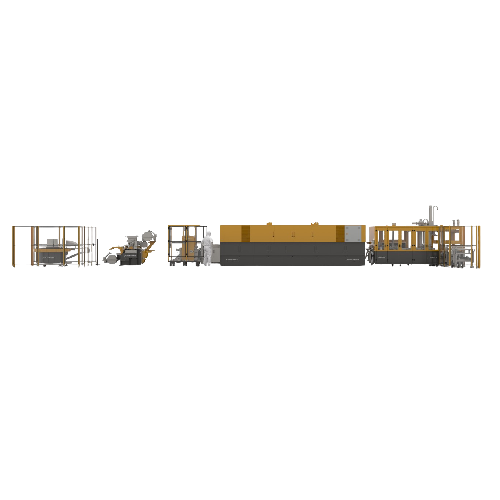
Pasting line for e-bike plates
Ideal for ensuring precision and consistency, this pasting line enhances the efficiency of ba...
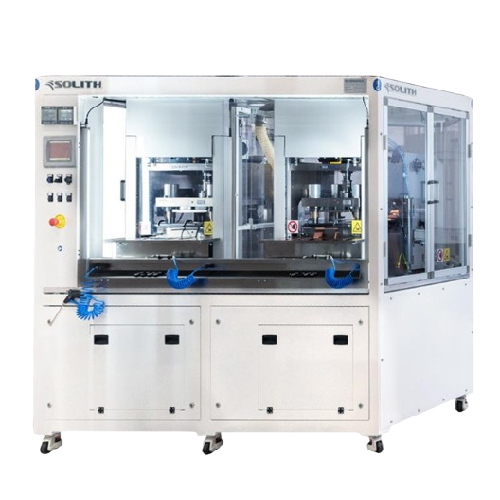
Pouch li-ion cell assembly line
Efficiently assemble high-performance lithium-ion pouch cells crucial for powering electric ...
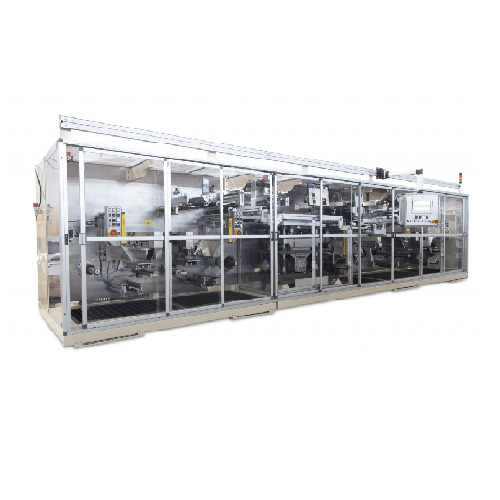
Roll to roll notching equipment for battery production
Optimize battery component production with precision notching, ens...
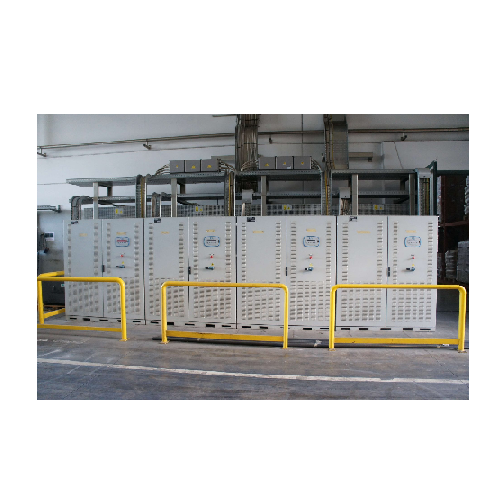
End of line testing for industrial batteries
Ensure battery reliability and safety in your production line with advanced t...
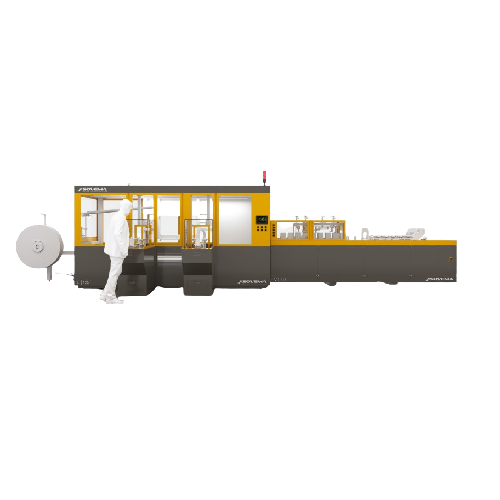
Enveloping and stacking solution for battery manufacturing
Streamline your battery production line with precision techno...
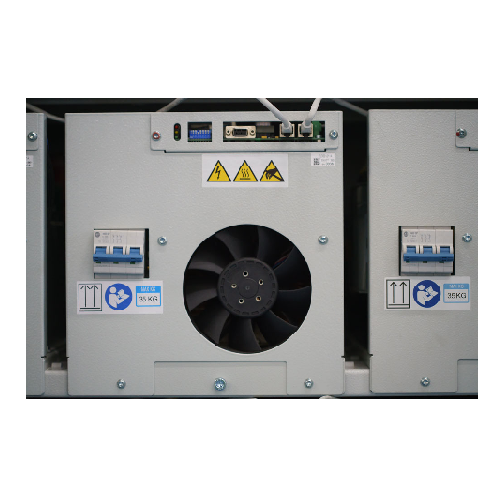
High-density battery chargers
Ensure your battery production line maintains optimal charge levels with precision and efficie...
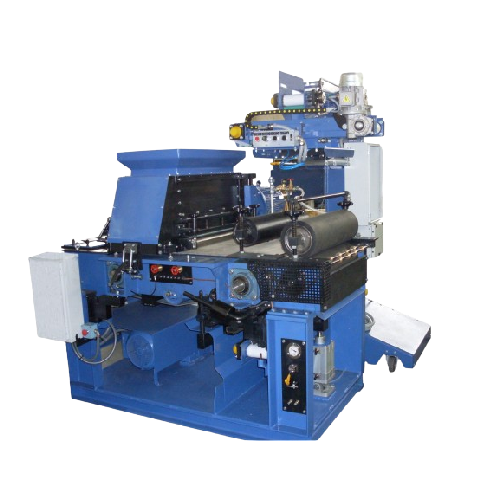
Industrial belt paster for battery manufacturing
Enhance battery production efficiency by precisely applying pastes to bat...
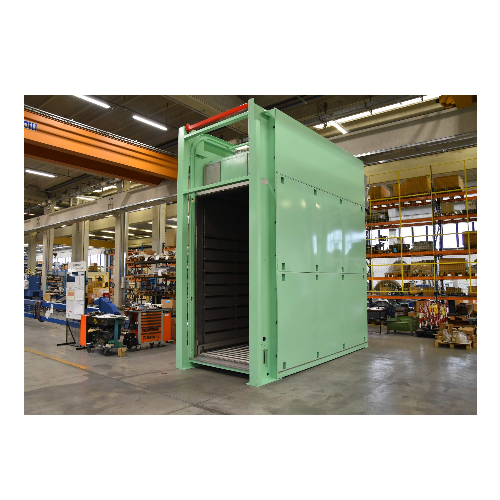
Industrial battery curing chamber
Achieve optimal battery performance with precise environmental control, ensuring the stab...
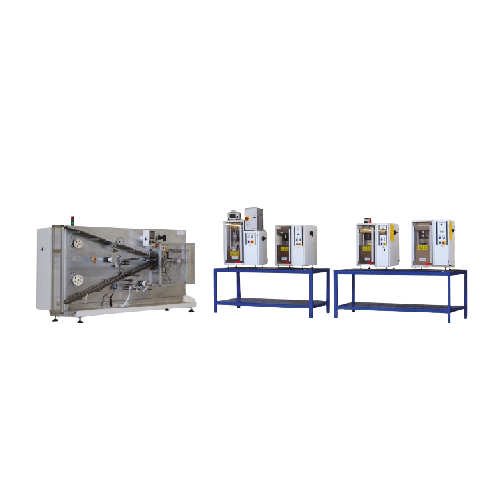
Industrial dry charge oven for battery manufacturing
Optimize your battery production with precision-engineered assembly ...
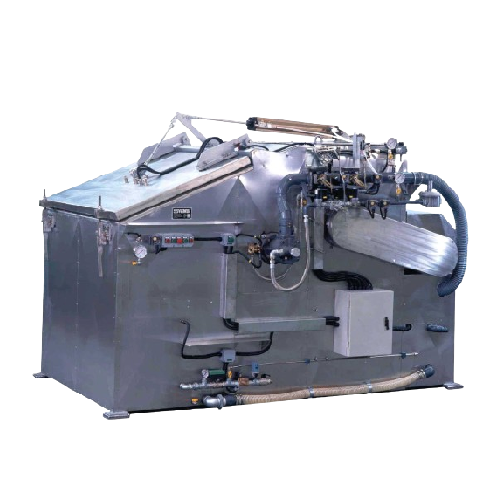
Eft chargers for industrial applications
Ensure optimal performance and longevity of lead-acid batteries with precise dry c...
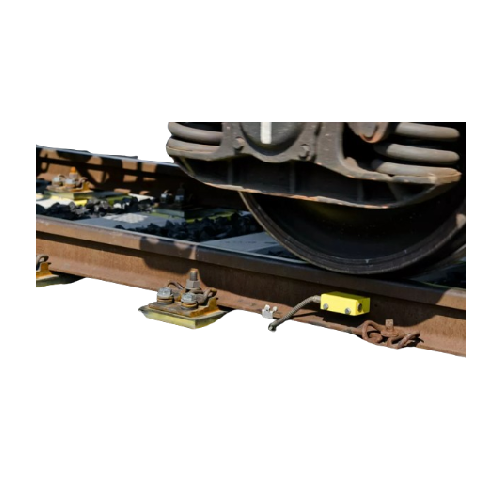
Dynamic weighing for solids and liquids
Ensure precision in rail transport with innovative dynamic scales that provide lega...
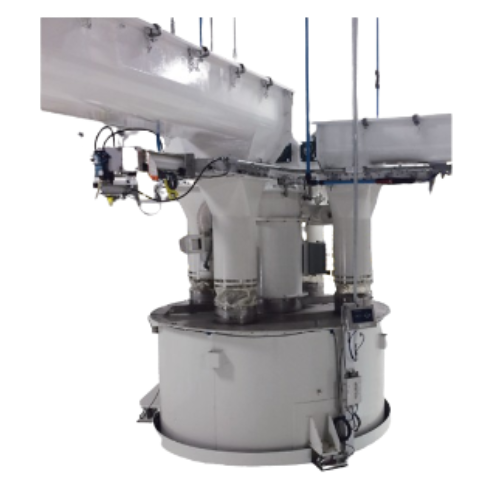
Scale hopper for bulk solid material handling
Ensure precise measurement and efficient transport of bulk solid materials w...
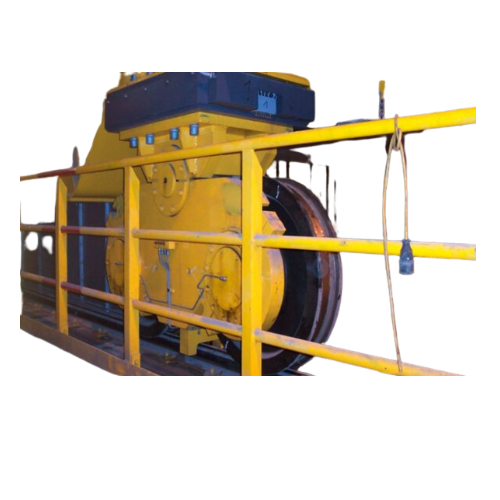
Crane scales for precise weighing in chassis
Optimize space with low-profile crane scales, ensuring accurate weight measur...
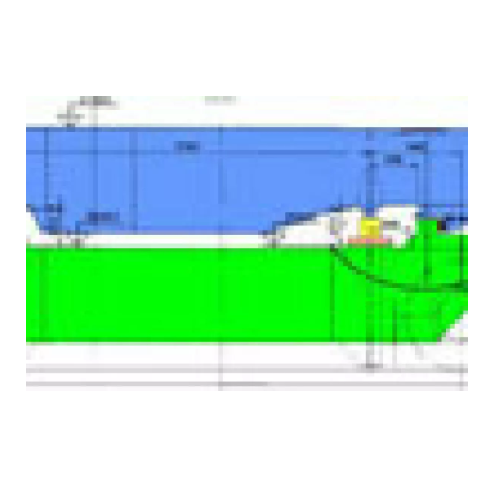
Crane weighing system for precision measurement
Ensure precise and temperature-resistant weighing during high-demand opera...
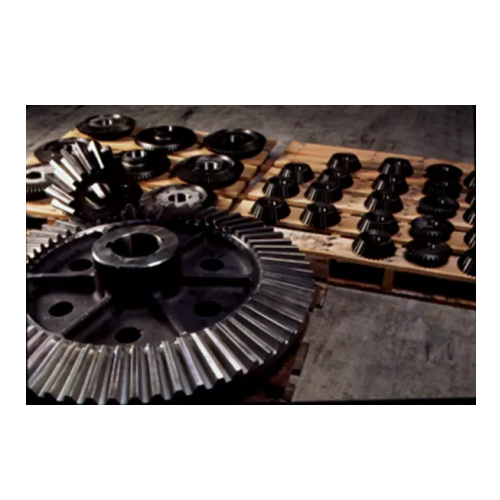
Industrial grinding mill replacement parts service
Optimize production efficiency with high-precision grinding solutions ...
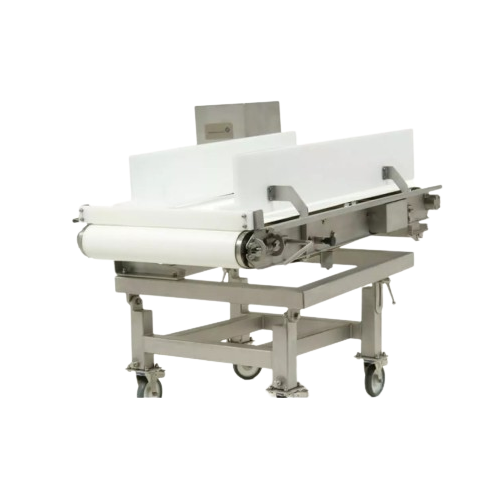
Industrial weighfeeder for hygienic applications
Achieve precise mass flow control with a hygienic design, ideal for appli...
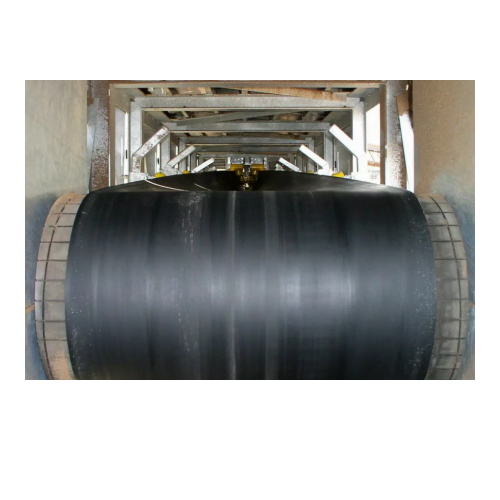
U-belt conveyor for bulk material transport
Optimize your high-speed bulk material transport with this space-saving convey...
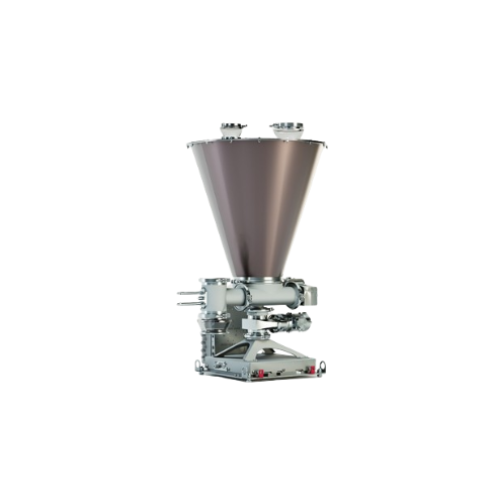
Loss-in-weight feeder for battery cell production
In battery cell production, achieving precise dosing and safe handling ...
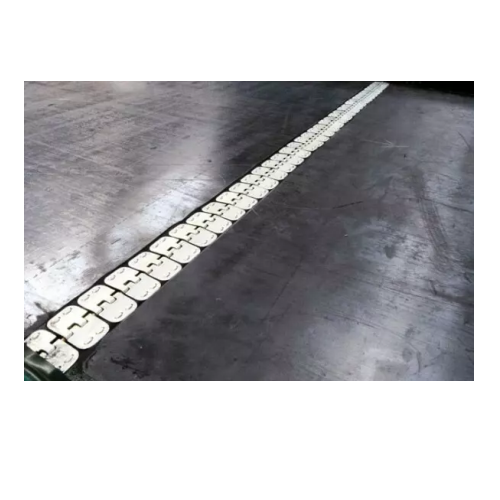
Optimal maintenance solution for industrial weighfeeders
Streamline your processing operations with a solution that minim...
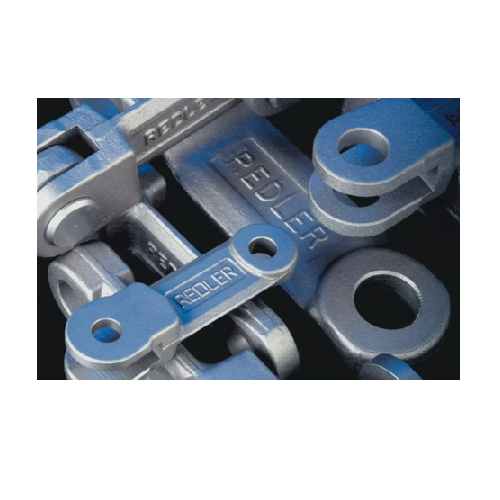
Drop forged chain for drag chain conveyors
Enhance your material flow efficiency with a robust drop forged chain designed ...
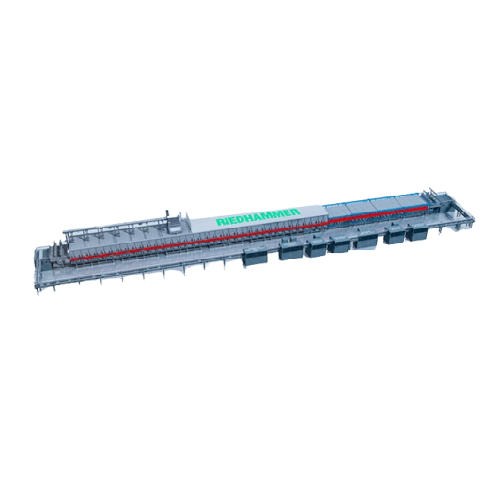
Lithium-ion battery powder processing solution
Optimize your lithium-ion battery manufacturing with advanced powder treatm...
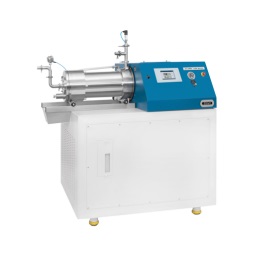
Ultrafine bead mill for battery materials
To facilitate the attainment of ultrafine particles and enhance electrode proper...
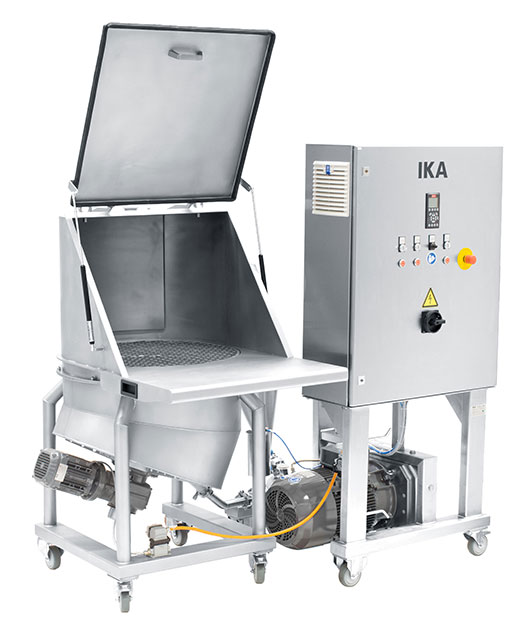
Inline solid-liquid mixer for battery production
In battery production, a critical phase entails mixing solids with liquid...
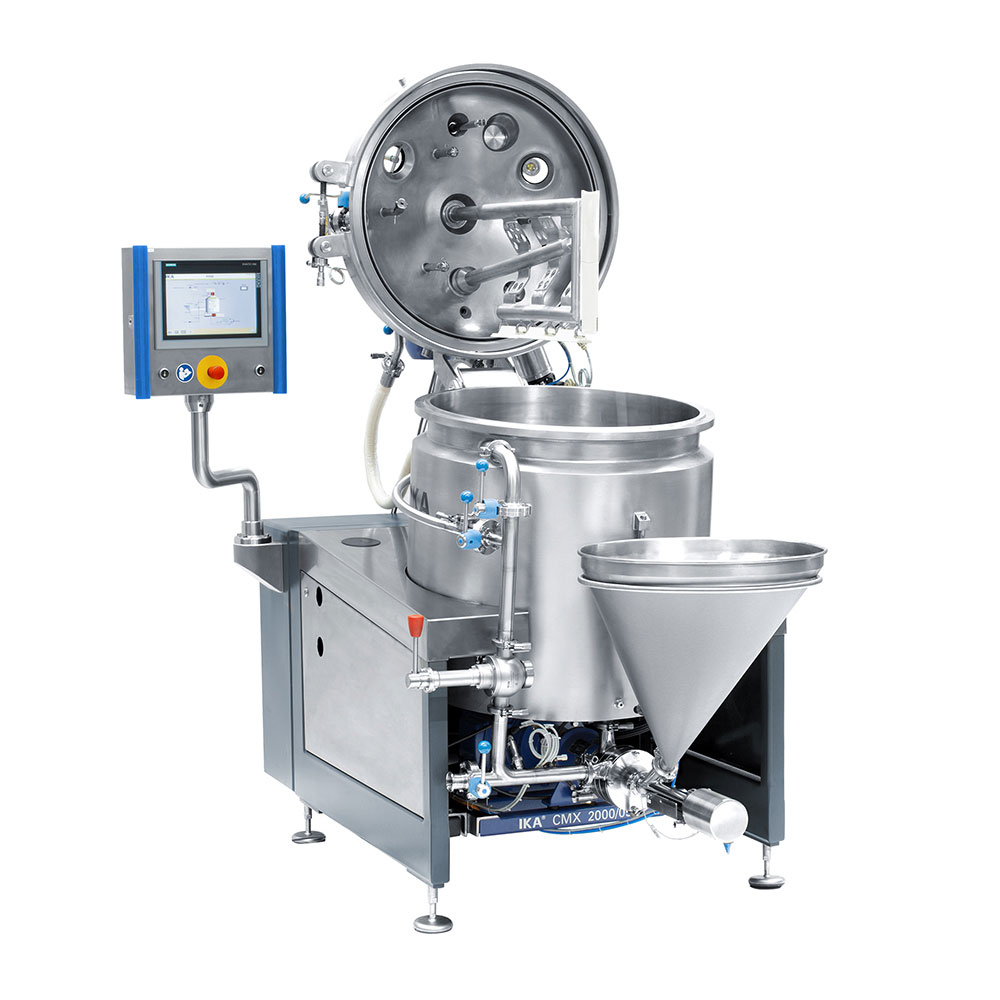
Compact Mixing Plant for Paints and Coatings
A smooth finish in paints and coatings depends on the grade of dispersal duri...
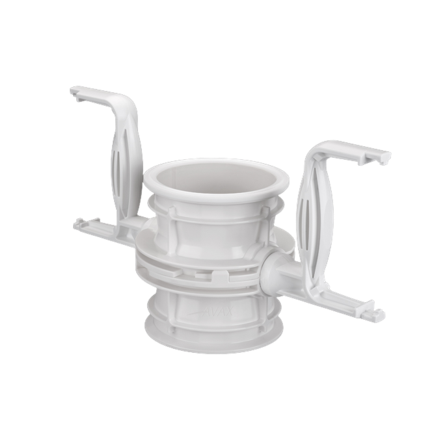
Single-use containment valves
From GMP and HSE perspective material transfer is critical for chemical and pharmaceutical for...
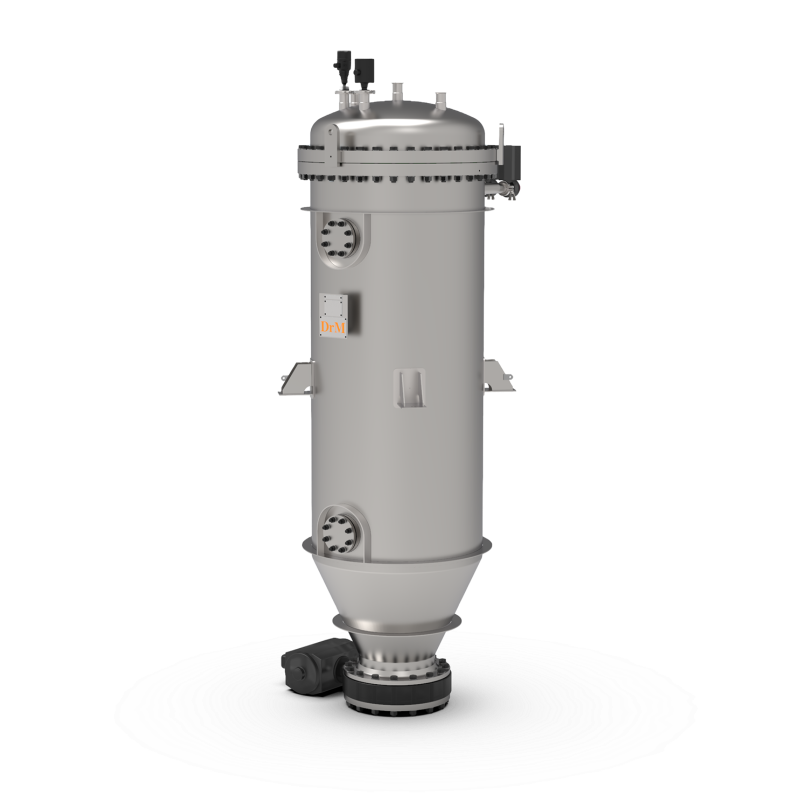
Self-cleaning candle filtration system
Separating solids from liquids by filtration requires frequent cleaning or replaceme...
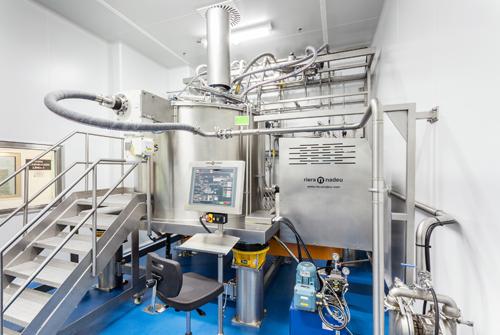
Automatic centrifuge for lithium carbonate
The battery industry requires high purity components. To obtain more than 99.5%...
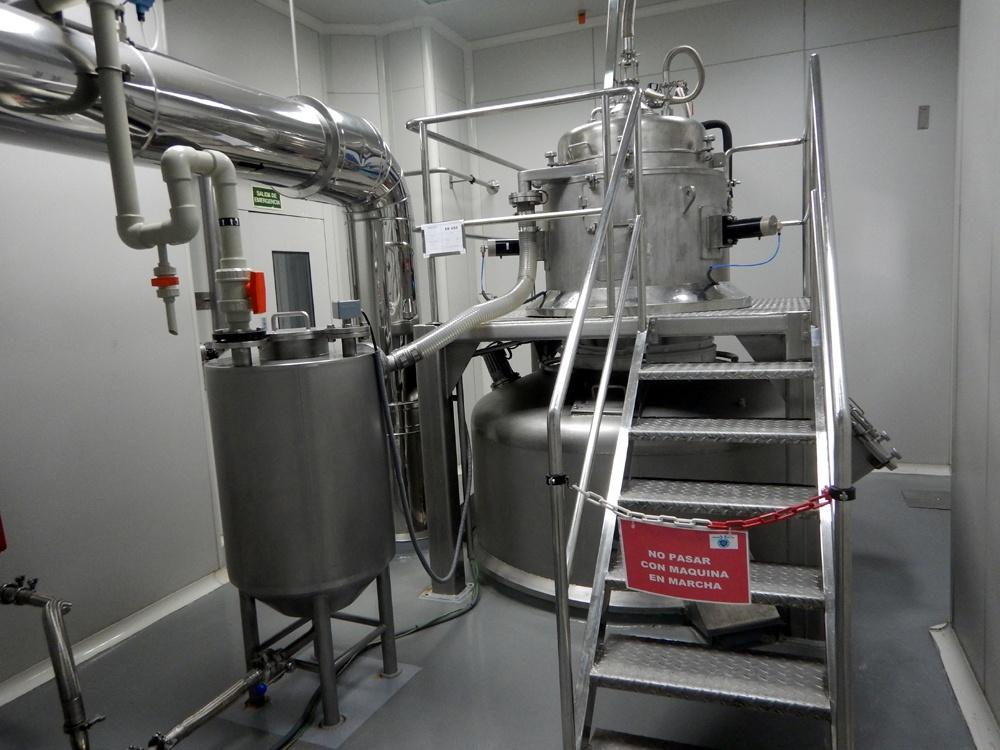
Continuous centrifuge for lithium hydroxide
Lithium hydroxide, a lithium compound used in making lithium batteries, is ind...

Open mouth bag filling machine for powders
The packaging of powdery products such as flour can be challenging as it is cru...
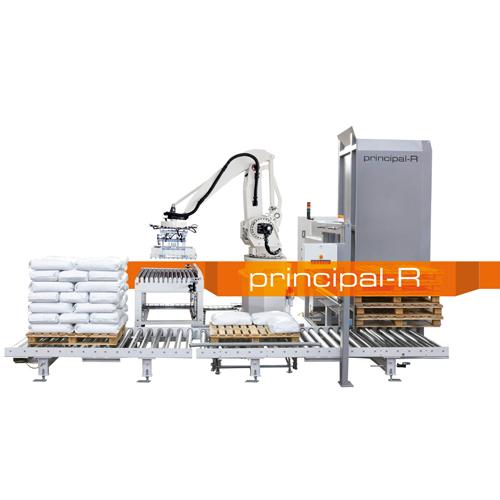
Robot palletizing system
If you are a relatively large-scale producer, packing and transporting large quantities of products ...
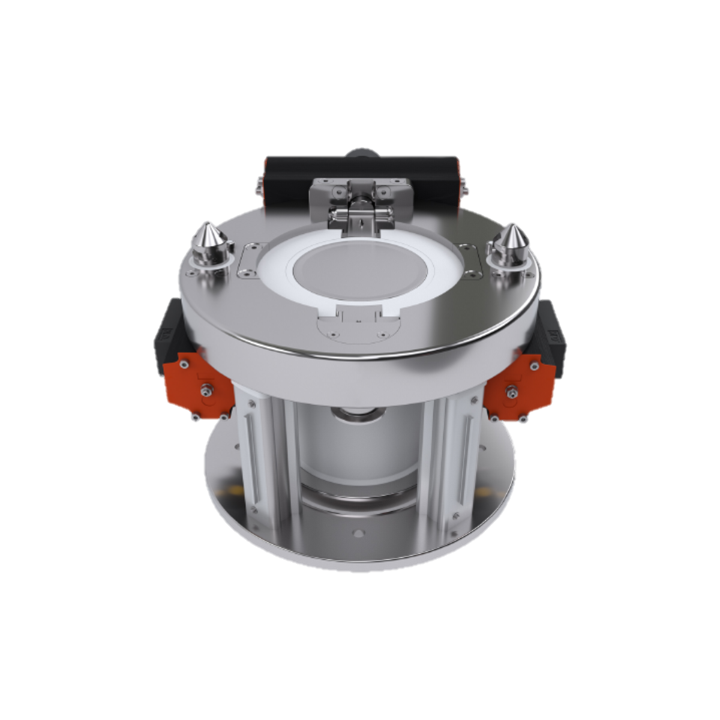
High containment split butterfly valve
Powder containment is the cornerstone of chemical and pharmaceutical manufacturing. ...