Horizontal bead mill for ultrafine particle grinding
Achieve precision in ultrafine grinding with a system that allows for rapid product changes and temperature-sensitive processing, tailored for high-demand applications requiring strict particle size control.
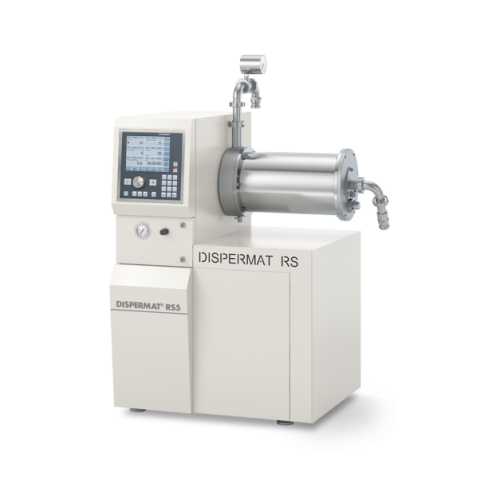
Efficiently Disperses Liquids and Slurries
The DISPERMAT® SC4 Dissolver from VMA-GETZMANN is engineered to master challenging dispersion processes with precision. This machine uniquely integrates a high-shear dispersing mechanism to ensure uniform particle distribution essential for diverse industries such as agrochemicals, automotive paints, and pharmaceuticals. Handling production capacities ranging from 30 to 600 liters, it seamlessly integrates into existing production lines with PLC-controlled operations for real-time process adjustments. The system’s energy efficiency is enhanced by its optimized motor control, contributing to reduced operational costs. Built with high-grade materials, the SC4 dissolver is available with corrosion-resistant options suitable for aggressive chemical environments. Maintenance is simplified with its intuitive design, allowing quick disassembly for cleaning, aligned with industry standards. Customization services are available to tailor the equipment to specific production needs, making it a versatile solution for complex dispersion applications.
Benefits
- Enhances product quality with uniform particle distribution.
- Reduces operational costs through optimized energy efficiency.
- Seamlessly integrates into existing systems with PLC control, minimizing manual intervention.
- Customizable configuration for tailored processing requirements.
- Simplifies maintenance, ensuring rapid cleaning and reduced downtime.
- Applications
- Sealants, Textile inks, Silicones, Aerospace coatings, Automotive paints, Printing inks, Coil coatings, Carbon materials, Pharmaceutical ingredients, Architectural coatings, Ceramic coatings, Food supplements, Artist colors, Nano materials, Wood coatings, Agrochemicals, Fuel cell materials, Automotive refinish paints, Polishing agents, Cosmetic ingredients, Battery materials, Food additives, Anti-friction coatings, Adhesives, Teflon coatings
- End products
- Aircraft anti-icing coatings, Lithium-ion battery electrodes, Non-stick cookware surfaces, Natural food colorants, Glazed tiles, Silicone rubber gaskets, Touch-up paints, Active pharmaceutical ingredients, Anti-aging serums, Interior wall paints, Fuel cell separators, Oil painting pigments, Probiotic powders, Quantum dots, Pigment-dyed fabrics, Painted metal coils, Abrasive polishing pastes, Piston skirt coatings, Screen printing inks, Varnishes for wood furniture, Conductive carbon composites, Automotive clear coats, Silicone sealants for aquariums, Herbicide granules, Epoxy adhesives
- Steps before
- Mixing, Emulsification, Pre-dispersing, Homogenization
- Steps after
- Filling, Coating, Packaging, Quality Control
- Input ingredients
- slurries, anode materials, cathode materials, raw materials, binders, pigments, active ingredients, excipients, liquid fertilizers, granulated fertilizers, water-soluble powders, spice particles, food dyes, conductive additives
- Output ingredients
- homogeneous distribution, dispersed slurries, coatings, ceramic pigments, screen printing inks, textile inkjet inks, automotive refinish paints, anode and cathode coatings, architectural coatings, emulsion paints, nano-scale particles, fine particles, high-quality dispersions
- Market info
- VMA-Getzmann is renowned for manufacturing high-quality dispersing, mixing, and milling equipment, particularly for the chemical, coatings, and inks industries, specializing in engineered-to-order solutions that emphasize innovation, reliability, and technical excellence.
- Power
- 0.3 - 55 kW
- Product Volume
- 0.05 - 2000 litres
- Control
- CN / C / SC / PLC
- Capacity
- 25 - 1000 litres/hour
- Milling Chamber Volume
- 5 - 30 litres
- Speed Adjustment
- Infinitely variable
- Automation
- PLC-controlled
- Batch vs. continuous operation
- Batch / Inline Continuous
- Automation level
- Manual / PLC / SCADA
- Energy efficiency
- 0.5–2 kWh/kg moisture
- CIP/SIP
- CIP 121°C / SIP 135°C
- Cleaning method
- CIP / Manual
- Abrasion resistance
- Yes
- Corrosive resistance (e.g. acids)
- Yes
- Cleanability
- Easy to clean
- Density/particle size
- 0.5–2.5 g/cm³ / 50–1000 µm
- Heat sensitivity
- Temperature-sensitive products
- ATEX certification
- Yes
- CE marking
- Yes
- Control panel type
- PLC / SC
- Control panel type
- CN / C / SC / PLC
- Integration possibilities
- USB, Wi-Fi, LAN (expected 2022)
- Cooling option
- Optional rotor cooling
- Design options
- Ceramic, plastic linings
- Sealing system
- Integrated pressurized sealing system