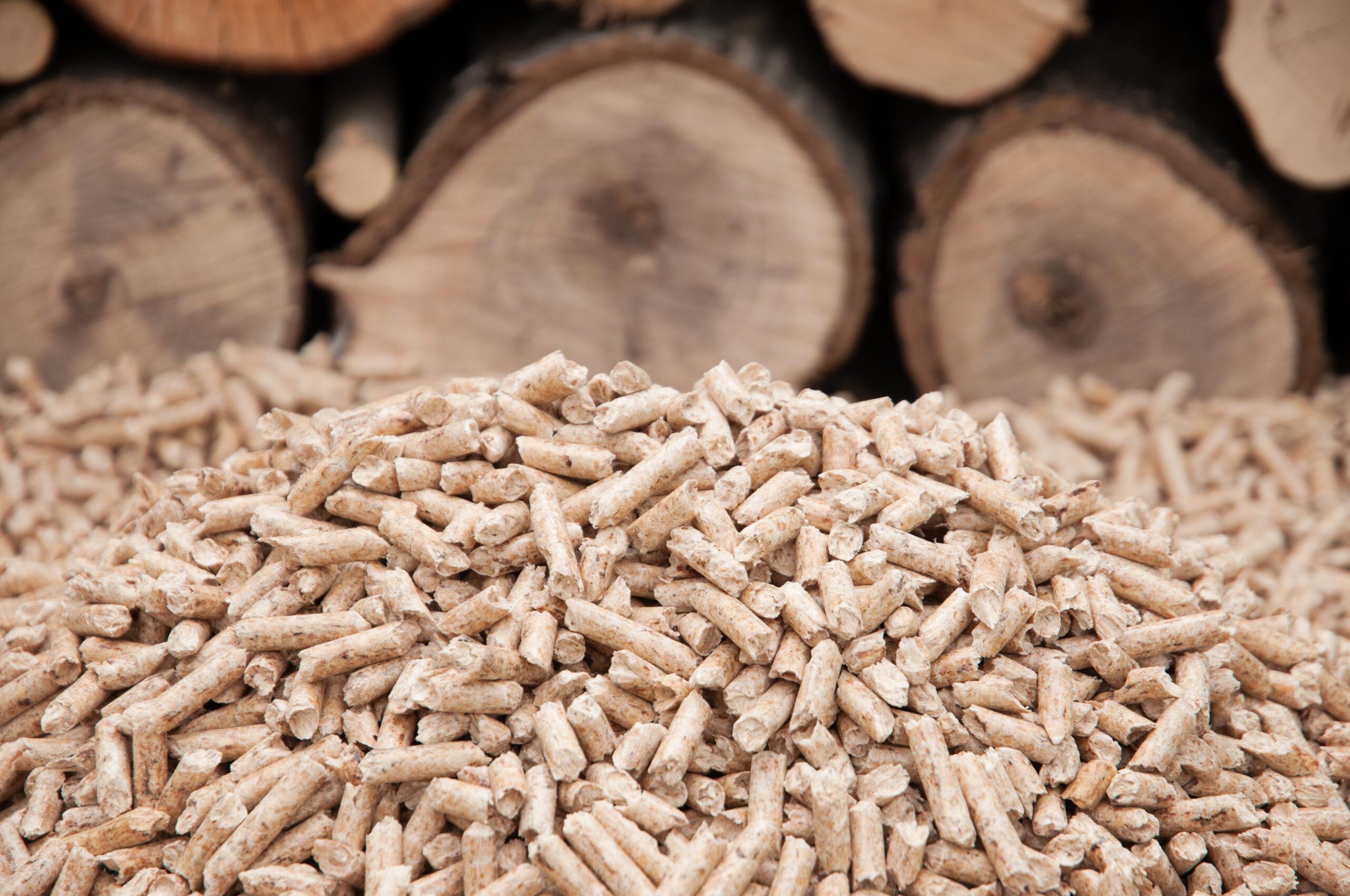
Pellet Fuel Equipment
Find innovative production technology for making pellet fuel and connect directly with world-leading specialists
As the worldwide demand for power keeps growing, the energy sector is diversifying its mix of sources. Pellet fuel offers a fossil-free alternative suitable for industrial and domestic sectors. But turning raw biomass, into pellets that comply with standards is a specialized process. Pellet fuel manufacturing equipment combines materials and additives to produce pellets of uniform size, density, and moisture content.
Tell us about your production challenge
Pre-treat biomass to remove water and contaminants
Pellet fuel is made from recycled biomass like wood waste (e.g., wood chips, sawdust & hardwood), agricultural residues (e.g., straws, corn stalks), and wastepaper.
Raw materials have different physical and chemical properties and must be pre-treated into a homogeneous feedstock material. Load the biomass onto the cleaning system to strip away the fibers. Dry the mixture in a heating cabinet or evaporator technology to decrease the moisture content. The pre-treatment of biomass is a crucial step in pellet production to ensure premium and quality pellets that meet the standards of governing bodies, such as the Pellet Fuels Institute in the US.
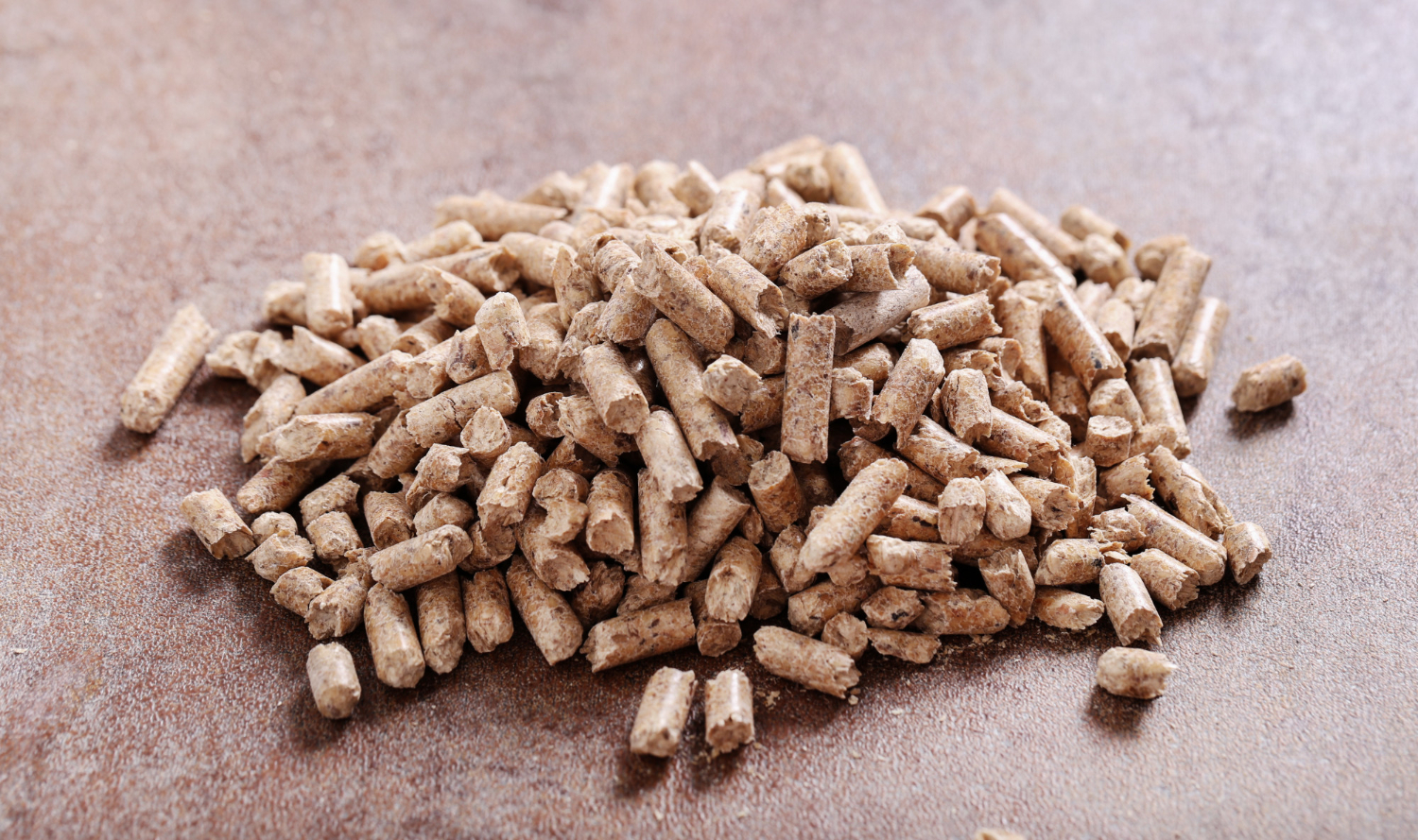
Mills are essential pellet fuel manufacturing equipment
Size reduction is a crucial step in the pellet production process. Smaller material particles facilitate homogeneous distribution in the feedstock mix and make the material easier to process.
Use a hammermill to crush the treated biomass into a uniform powder. This produces a balanced pellet with a high rate of burning efficiency. Heating pellets is a lot more efficient compared to traditional fossil fuels.
Harden the pellets by cooling them down after milling
Feed the treated stock to the pellet mill, which will be ground into a mass and pushed through a die to form the end product. The mill knives cut the pellets into the right shape and size.
Mix the ingredients in a pre-conditioner if you use additives such as fire retardants or binding agents. Straight out of the mill, pellets will be plastic. Bring the temperature down in a cooling chamber to solidify them into finished pellets.
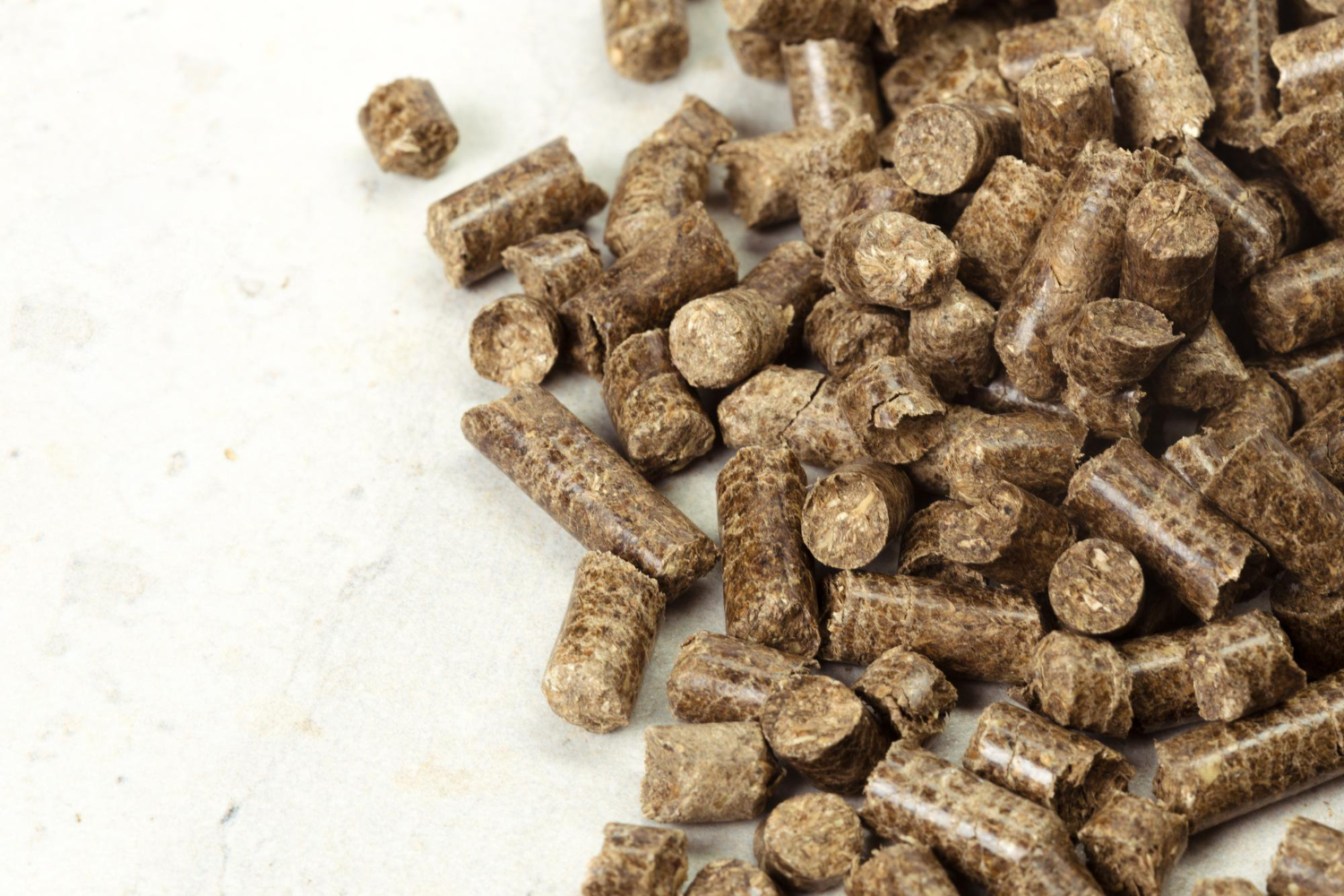
Manufacture economical pellets from torrefied wood
A torrefied wood pellet has a higher energy density (almost half) than its regular wood pellet cousin. Biomass like straw, hemp, and many more are also suitable for torrified pellets, opening further options.
This biofuel type is produced using the same pellet fuel manufacturing equipment. In the case of wood, it goes through the drying and milling process to get to a moisture percentage below 15%. But then, to produce torrefied pellets, the biomass is heated to 300°C in an anaerobic environment, reducing the mass and increasing energy content.
Make alternative pellet fuel from recycled waste
To fully harness the potential of bioenergy, fuel pellet producers seek to broaden the range of feedstock to non-woody biomass (e.g., dried green forage) and recycled waste. Agricultural leftovers, industrial food byproducts, and municipal solid waste can be integrated into bio-pellet production. However, it is important to ensure that organic wastes are pre-treated, to remove any contaminants from the material before processing it.
Which pellet fuel technology do you need?

Biomass baler for woody biomass collection
Optimize woody biomass management with a mobile solution that reduces noise, du...
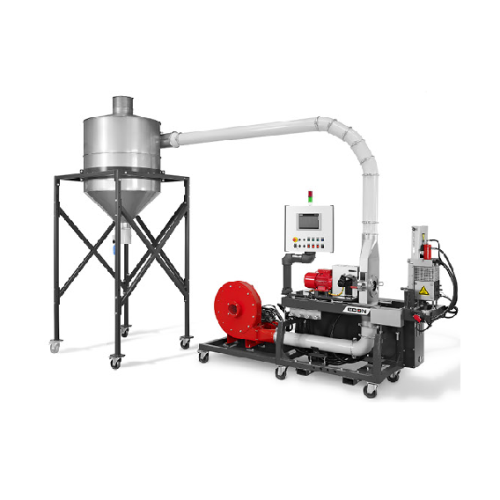
Air pelletizer for wood and natural fiber compounds
Optimize your pelletizing process with air-based cooling and conveyin...
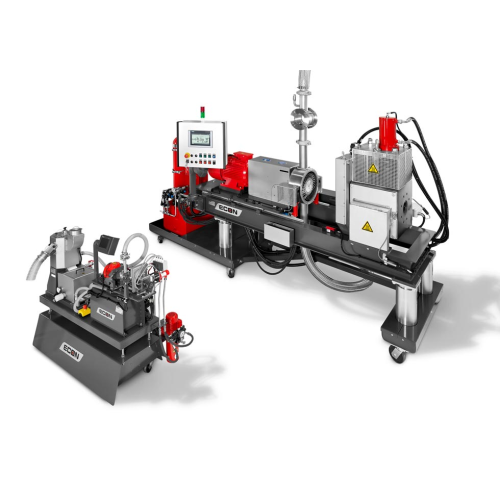
Underwater pelletizing system for thermoplastic materials
Optimize your thermoplastic pellet production with a reliable ...
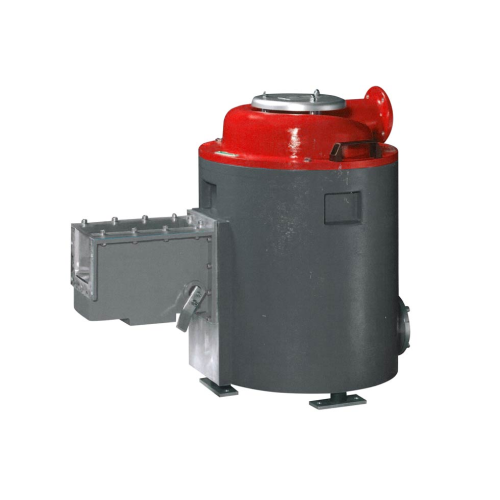
Pellet dryer for industrial recycling applications
Ensure precise moisture control for recycled plastic pellets and flake...
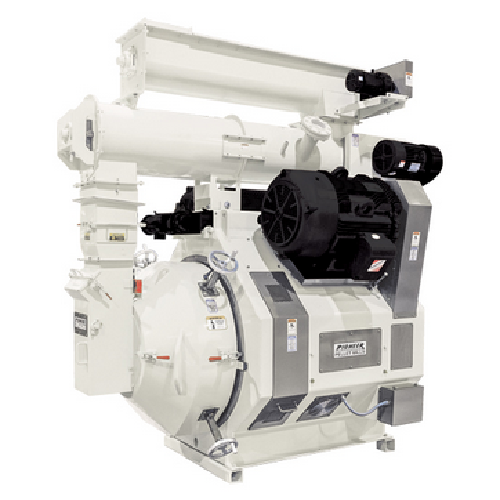
Pellet mill for noise-reduced pelleting
Optimize production with a pellet mill designed to minimize noise and enhance lubri...
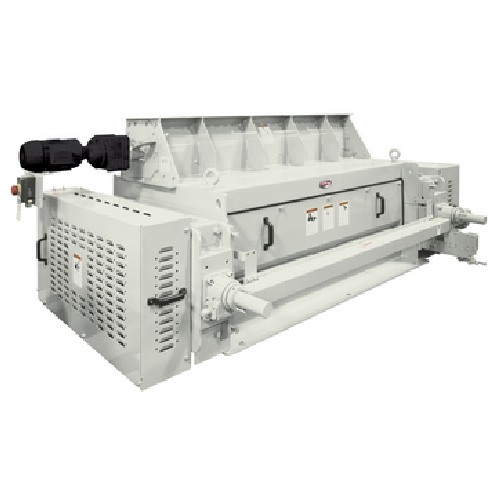
High-capacity pellet crumbler
Achieve precise pellet size reduction with this high-capacity solution, designed for effortles...
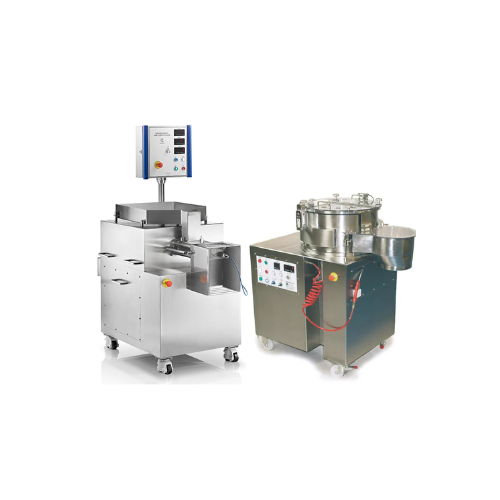
Pellet and bead extrusion and spheronization system 100 kg/hour
Optimize your production with a versatile system that se...
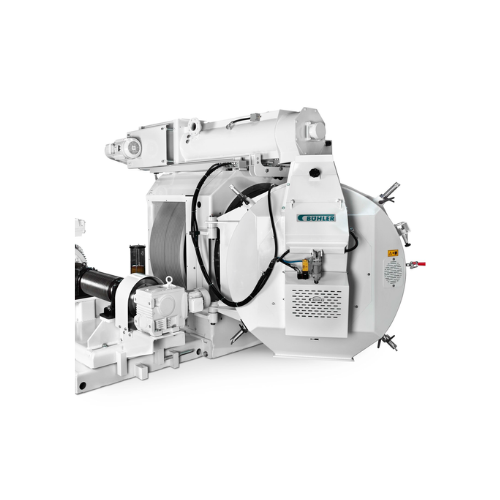
Pellet mill for biomass and sunflower hulls
Achieve high-speed, continuous production of durable pellets from varied mater...
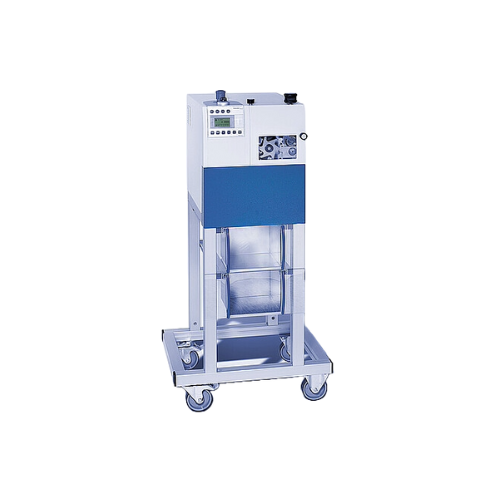
Pelletizer for consistent plastic pellet production
Achieve precise pellet sizes consistently with this flexible solution...
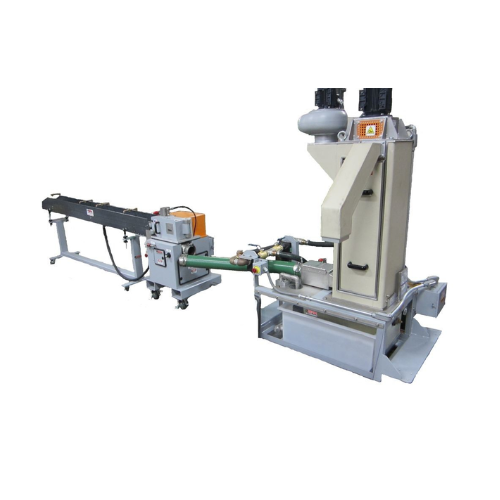
Automatic wet cut strand pelletizer for thermoplastic pellet production
Streamline your polymer pellet production with ...
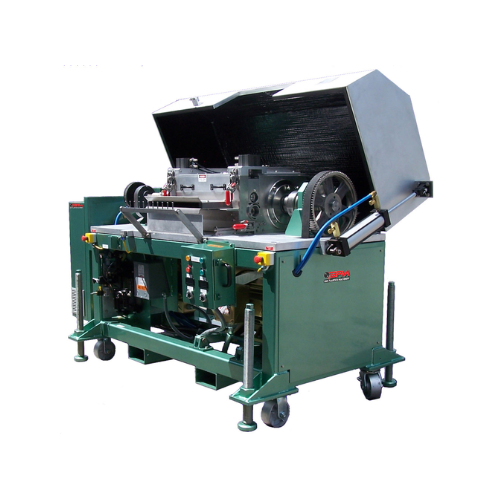
Pultrusion pelletizer for long glass fiber thermoplastics
Engineered to tackle the challenges of cutting and pelletizing...
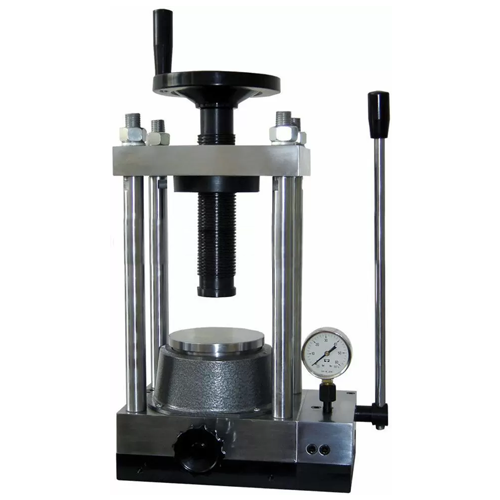
40-ton pellet press for laboratory applications
Achieve precise sample preparation with a 40-ton capacity, ideal for press...
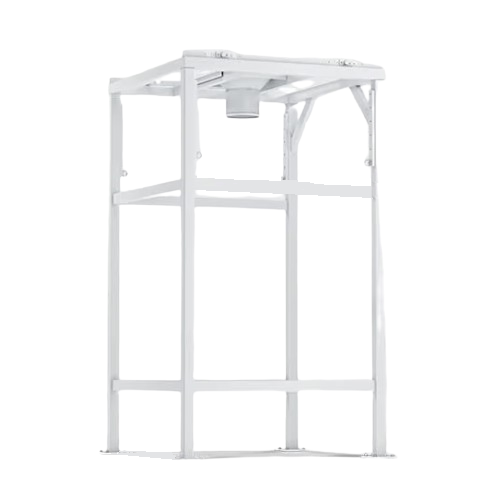
Big bag loading station for bulk product handling
Efficiently manage big bag handling with a system that combines hoistin...

Industrial rotary dryer for high moisture content materials
Achieve consistent drying performance with industrial rotary...
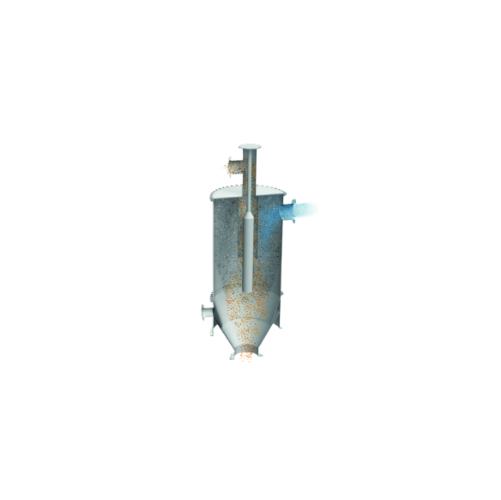
High-efficiency pellet dust separator
Achieve unparalleled separation efficiency in your polymer production line by removin...

Manure treatment system for livestock breeding
Optimize waste-to-value processes with advanced systems designed to efficie...
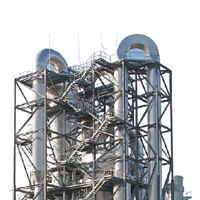
Exergy pressurized superheated steam dryer
Traditional dryers and heat transfer systems, like belt-, drum- or bed dryers a...
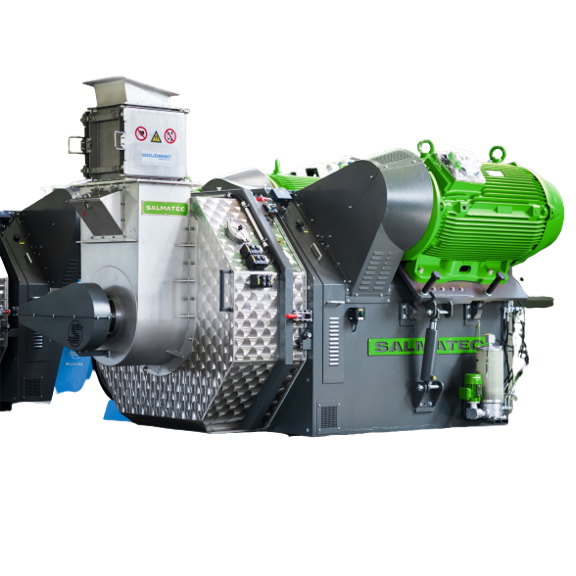
Complete pellet line
Large industries are shifting towards more environment-friendly technology, such as recycling wastes and...
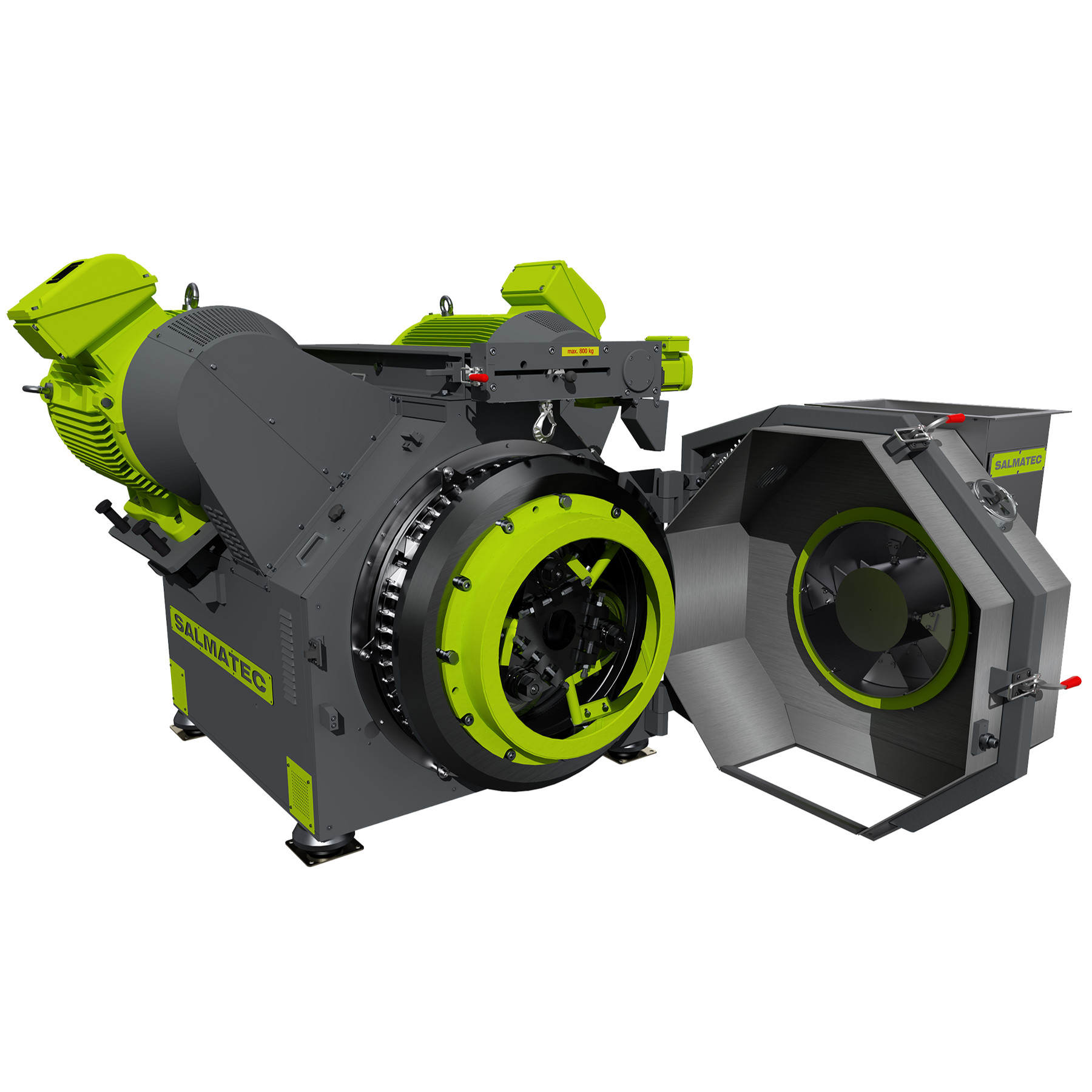
Industrial pellet mill
At the industrial level, the application areas of pellets range widely in fields such as feeds, biomas...

Evaporator for manure fertilizer
Traditionally, liquid manure processing can lose some important nutrients. An efficient ful...
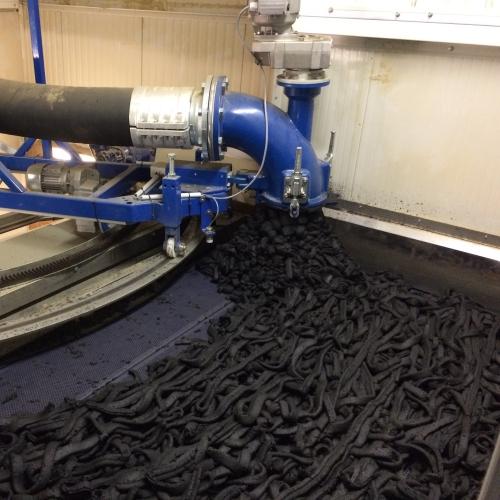
Belt dryer for sewage sludge
If your water treatment plant often facing difficulties with sewage sludge deposits, drying the...

Pelleting line for manure fertilizer
Manure fertilizer needs to be made marketable by making them visually attractive, with...
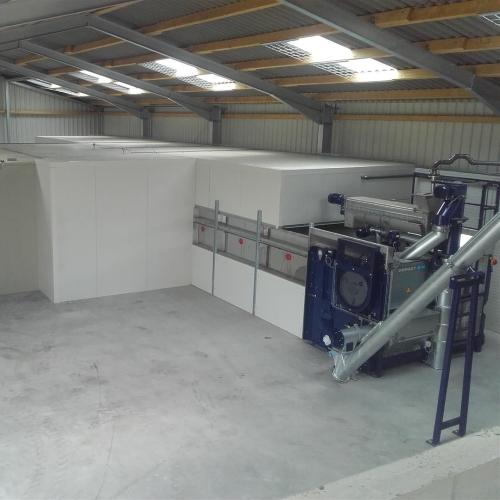
Belt dryer for digestate
The drying of poultry manure digestate requires careful and consistent moisture level control. A sus...
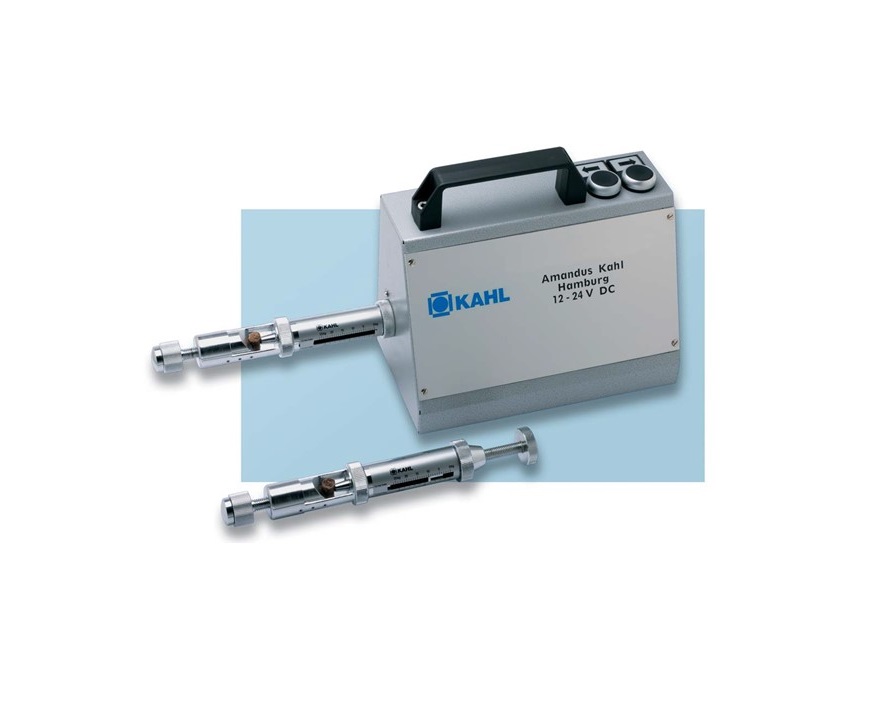
Pellet hardness tester
Control the quality of your pelletizing processes using a pellet hardness tester. Pellet hardness is o...
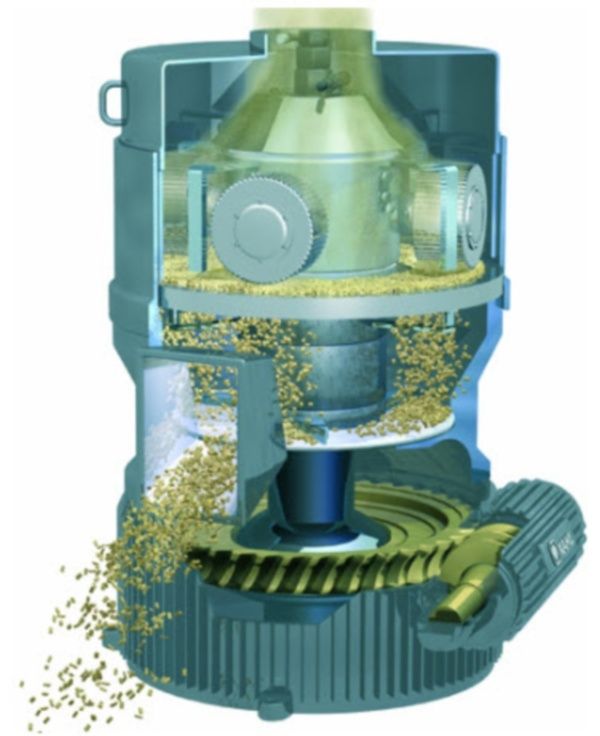
Pelleting press for biomass
Utilization of biomass for energy and other applications requires consistent and reliable compac...
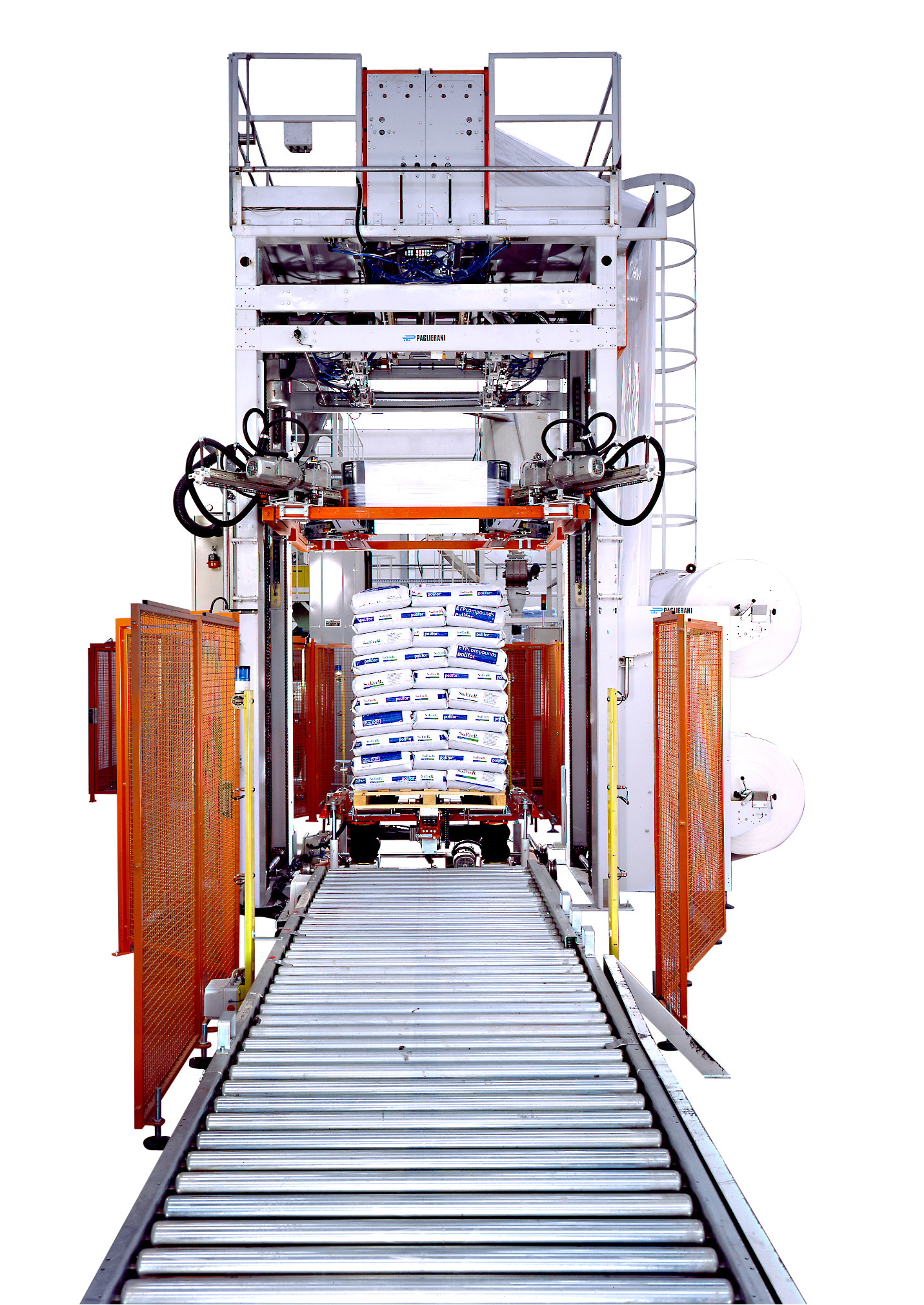
Stretch pallet hooder
Palletised loads need to be securely wrapped in order to protect them from shifting, crushing, ripped o...
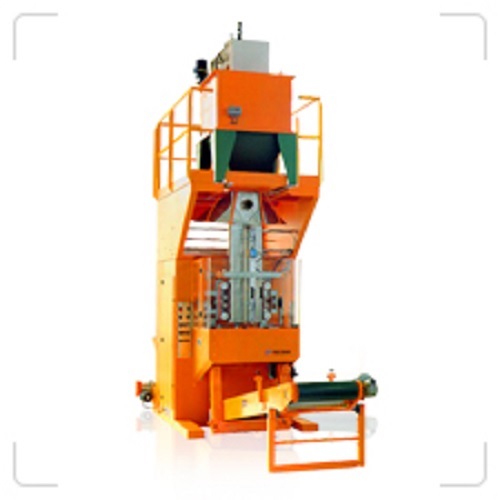
Vertical form, fill and seal machine for bags from 5 to 50 kg
To securely create, dose and pack larger quantities of mat...
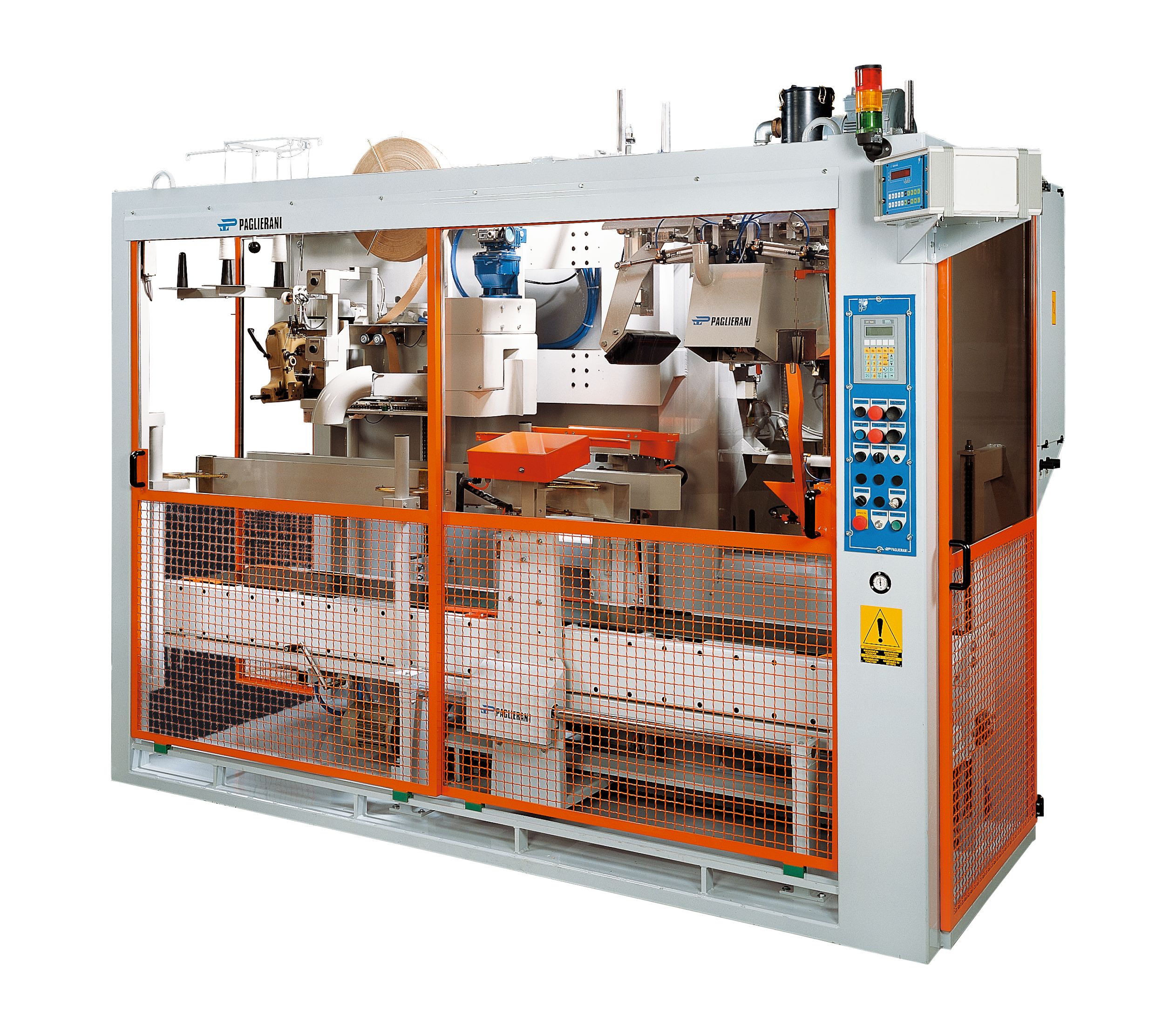
Automatic bagging machine for open mouth bags
Open mouth bags allow for a variety of different products to be packaged, wi...
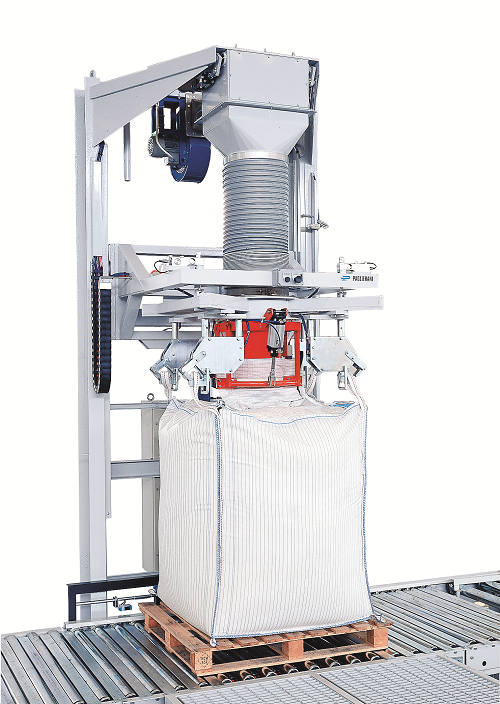
Big bag solutions
Management of big bags requires specialist handling and selection of cost-effective configurations for fill...
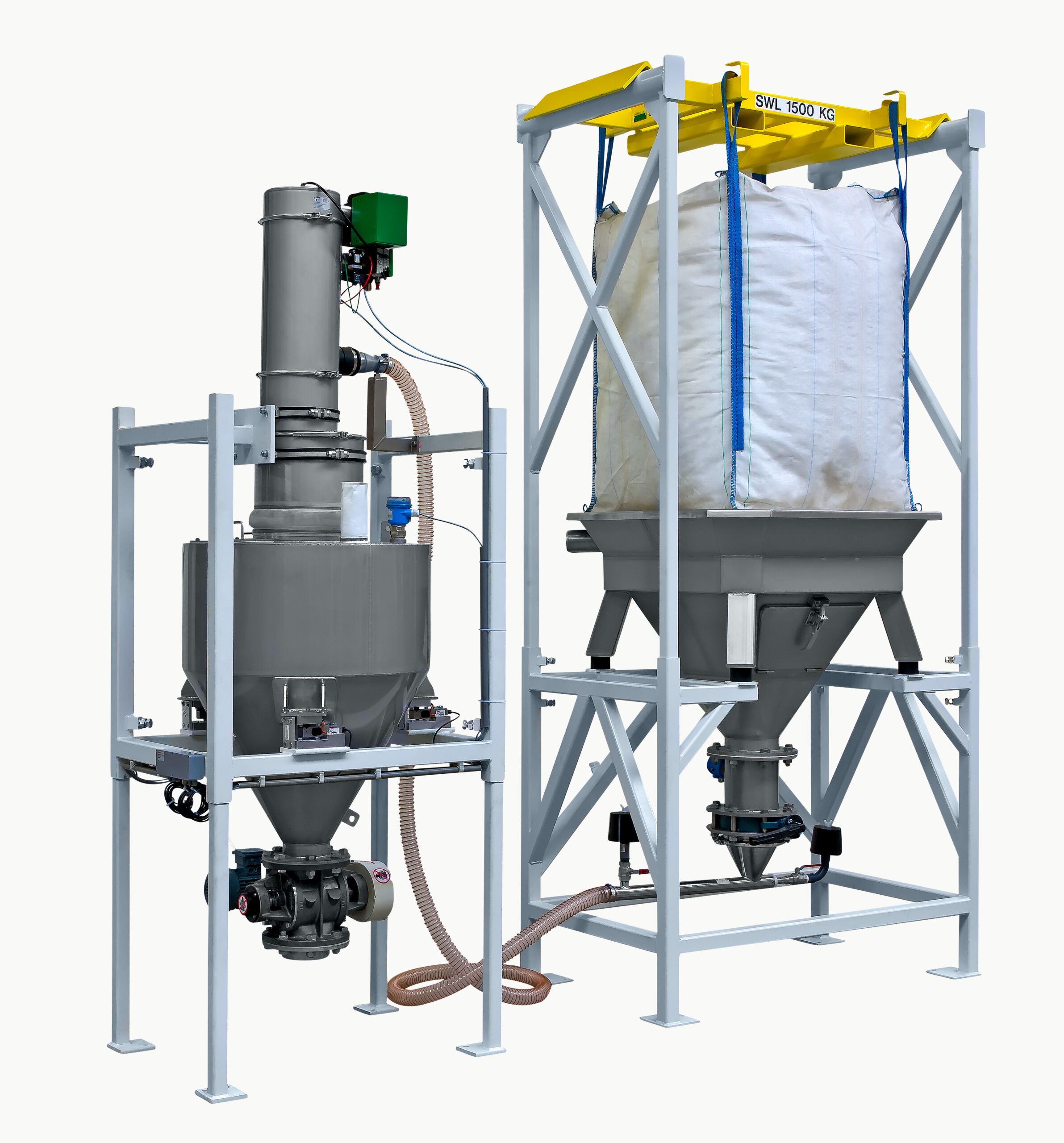
Big bag discharge system
Dust emissions, product loss and product contamination are the main risks when discharging products ...
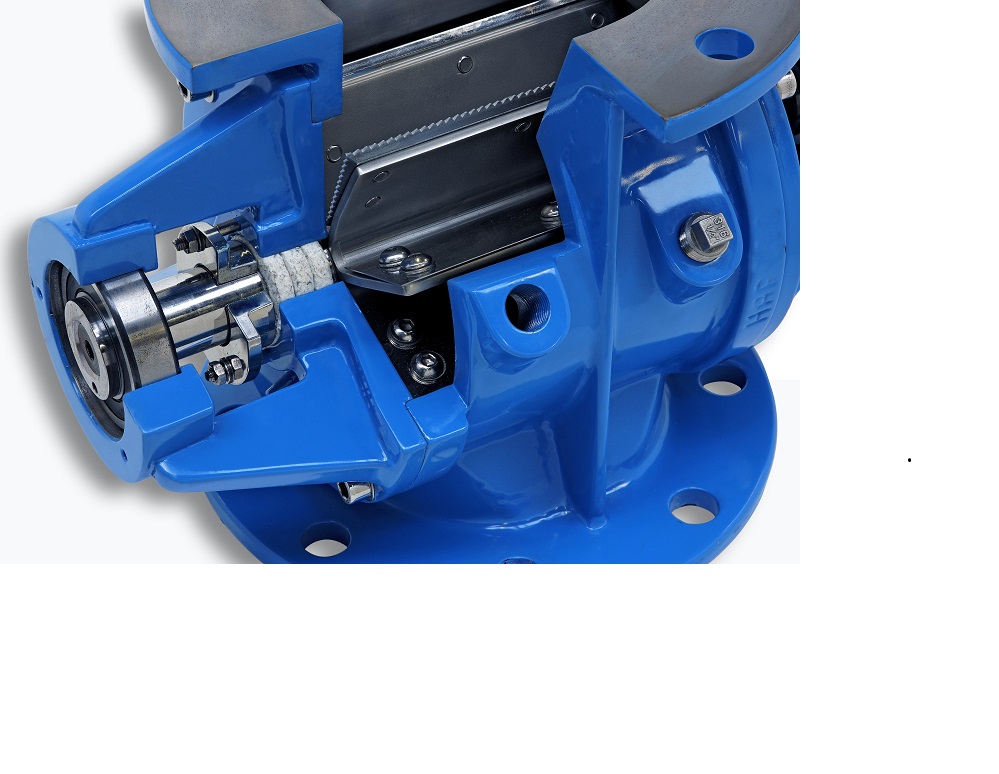
Heavy duty rotary valve
Handling powdered and granulated materials in pneumatic conveying systems requires consistent, safe v...
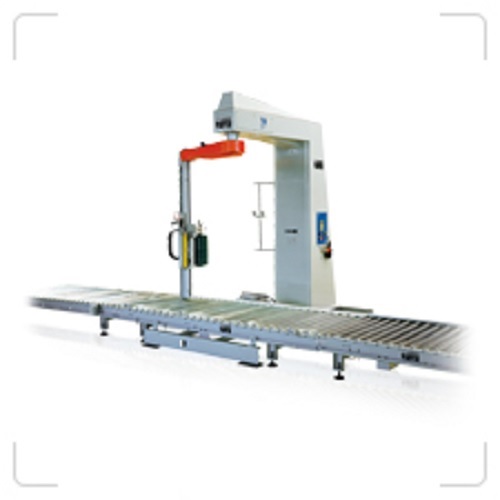
High speed stretch wrapping machine
Where high speed wrapping, without toppling, is required in tightly securing palletised...
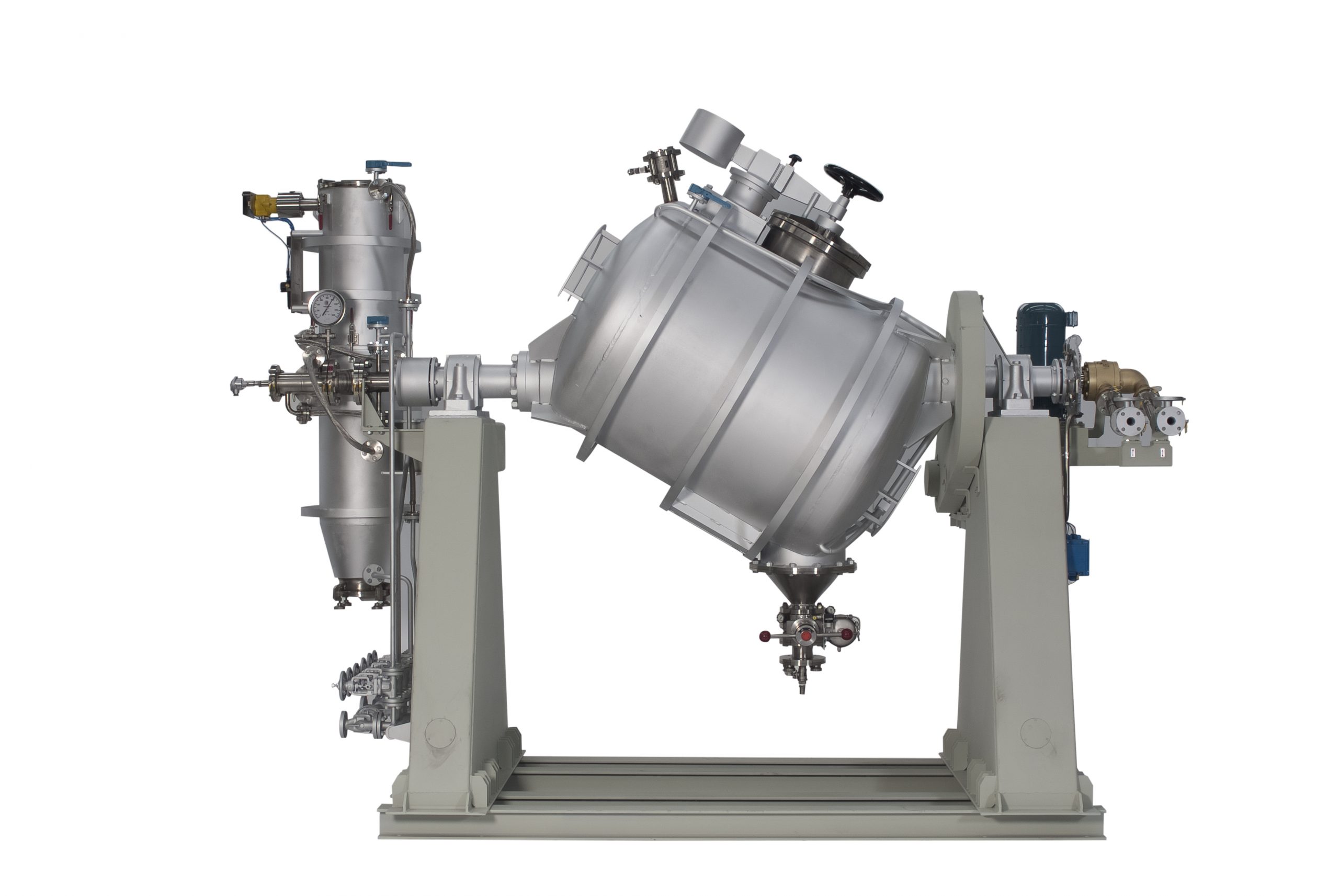
Tumble dryer for granulated plastics
Vacuum drying at high temperatures is important in the production of granulated plasti...
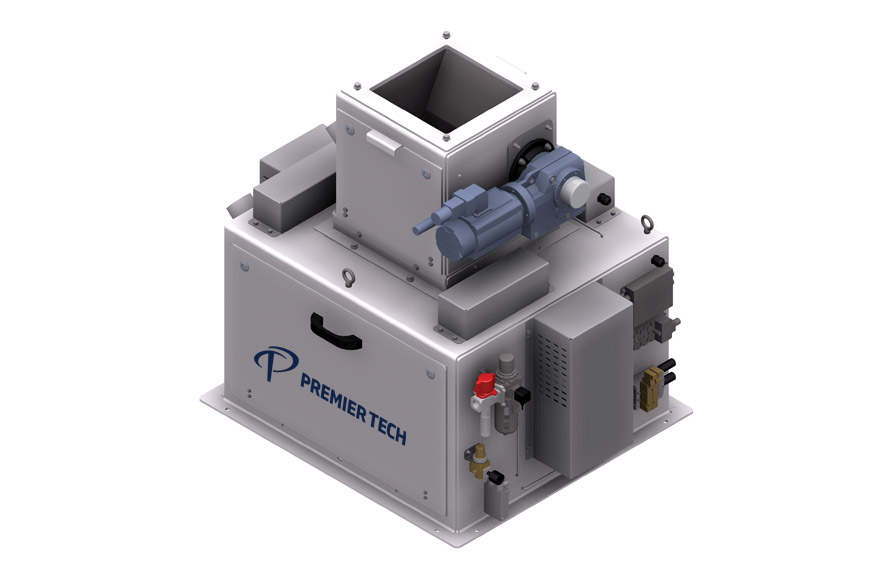
Electronic net weigher for high-capacity baggers
Electronic net weigher raises the industry’s standards to a higher level ...
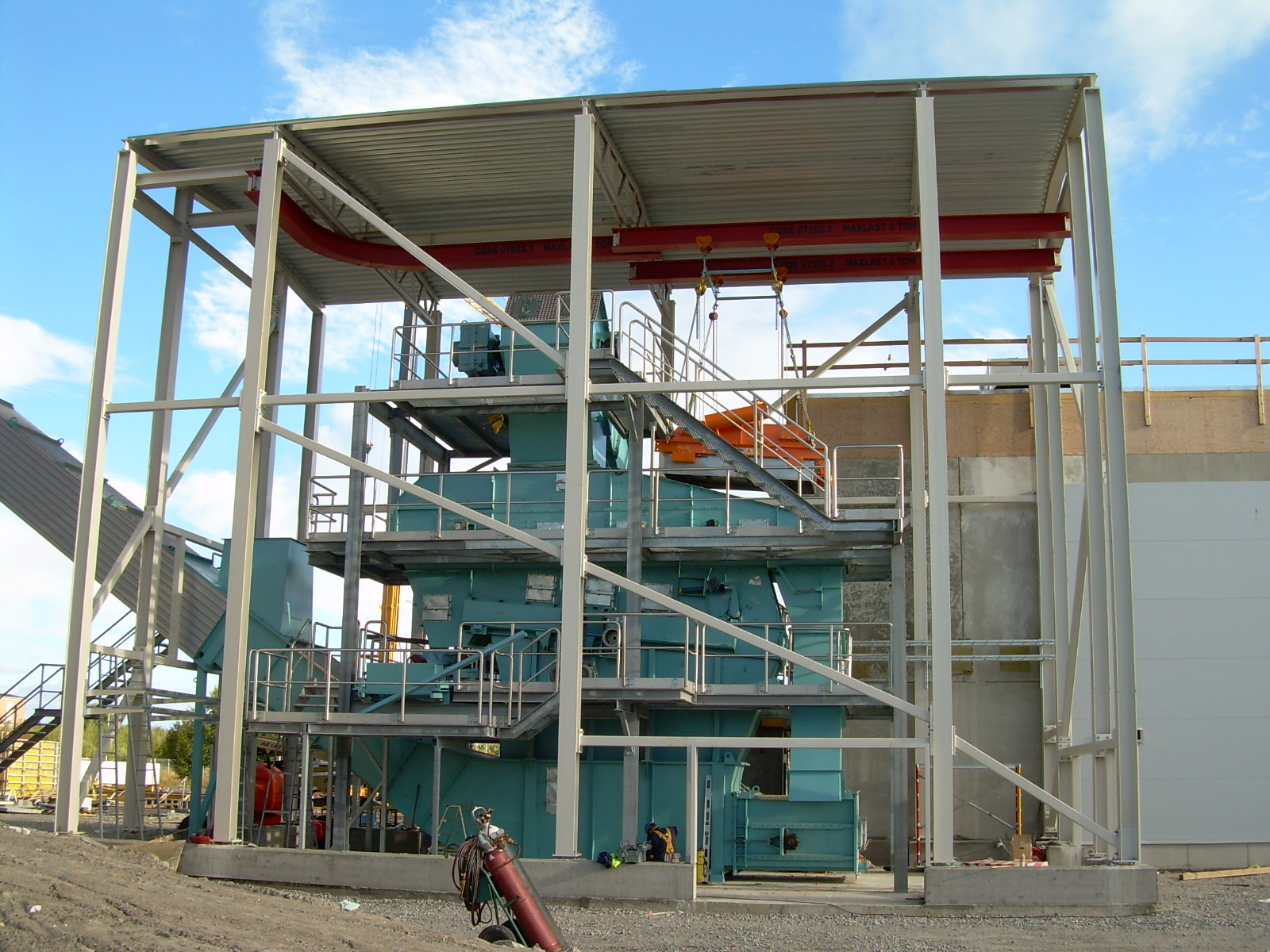
Solid biomass screening and crushing equipment
Biomass fuels come in many forms and often include impurities that can dama...
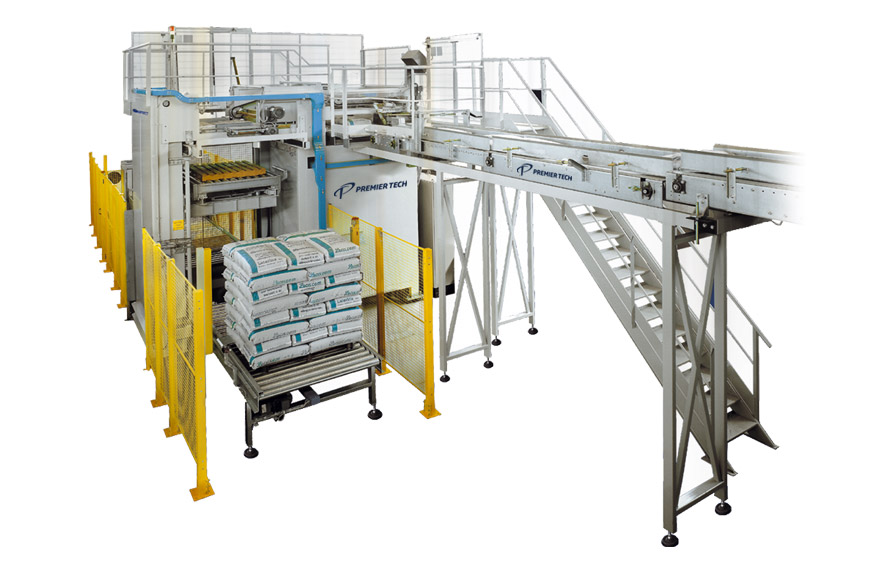
High-level layer palletizer
A palletizer that meets the middle and high-level needs of modern bagging lines. Quite suitable ...
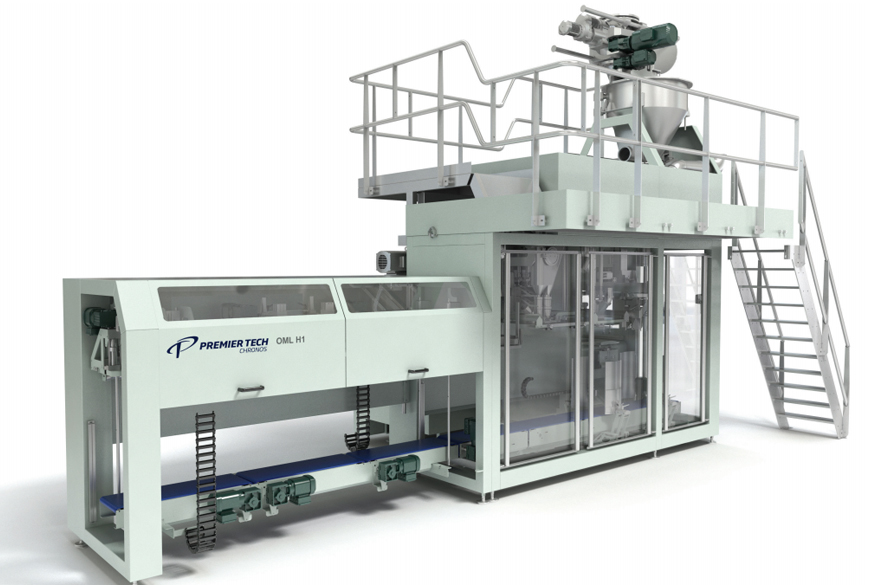
Hygienic open-mouth bottom-up baggers
Here are the open-mouth baggers that are specially designed for hygienic bagging of p...

Belt dryer for wood
Processing of wood and biomass into pellets or other volume reduced products requires careful and consist...
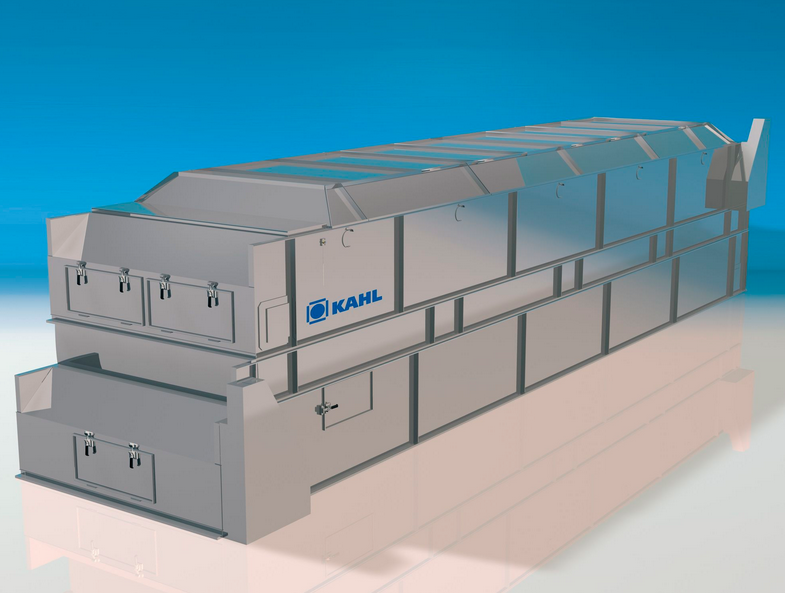
Belt dryer/cooler for pellets and granules
Many industries that process materials in pellet, powder, or crumble form need ...
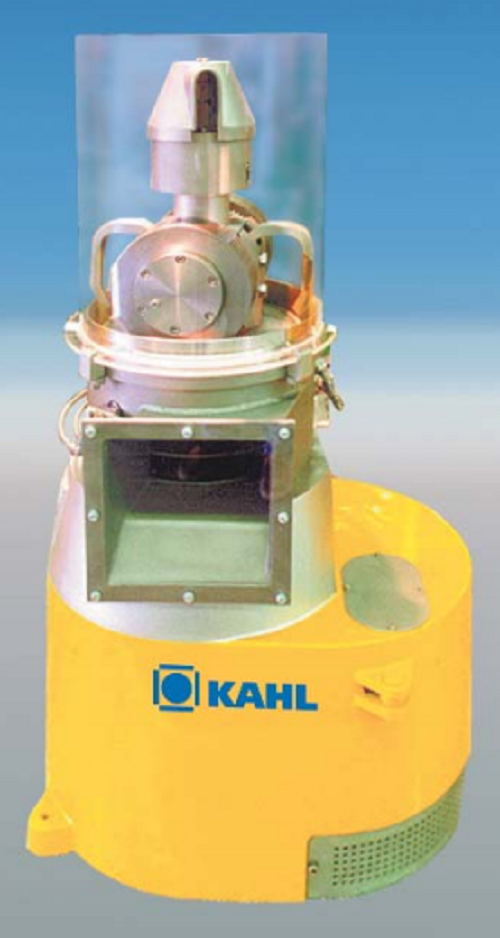
Small scale pelleting press
Many industries require reliable pelletizing equipment with smaller scale production capacities....