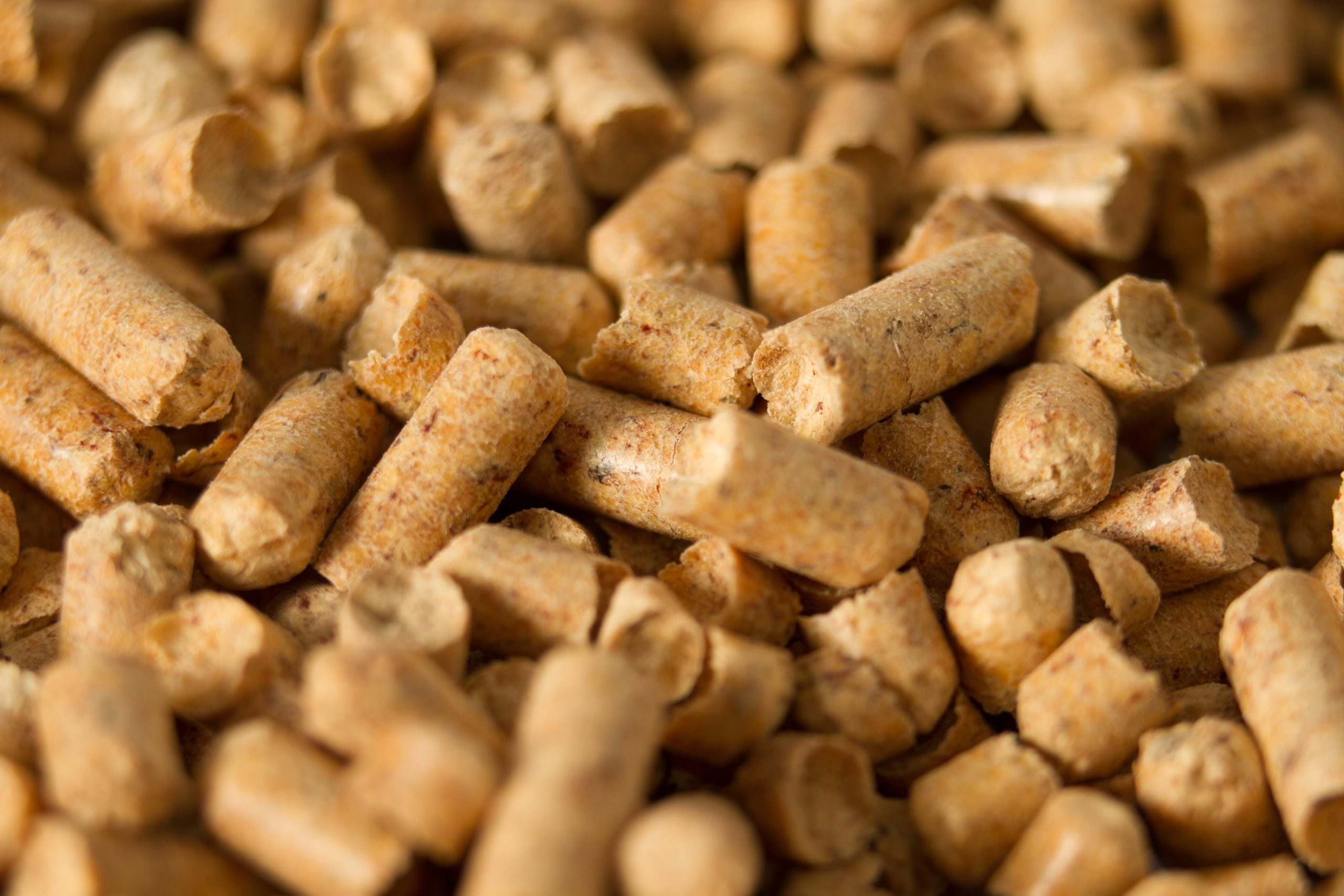
Wood Pellet Making Equipment
Find innovative production technology for making wood pellets and connect directly with world-leading specialists
Building a fire with wood sticks and logs is one of the most wholesome experiences. But it would take a lot of trees to heat up our homes. Instead, the fire-stoking power of plant material can be concentrated in a wood pellet, boosting its burning efficiency. However, wood pellet making equipment and machinery involves more than just the compaction of sawdust. Processing high-quality pellets from biomass can be as intricate as loading a fire-lay.
Stories about wood pellets
Select your wood pellets process
Tell us about your production challenge
Remove contaminants from primary materials to manufacture wood pellets
Residues from the timber industries are excellent raw materials for wood pellets. Plant material that cannot be worked into finished products, wood chips, sawdust and waste dust from sawmills find an alternative stream as pellets.
If your primary resource is pre-used wood, it must be stripped of paints, varnishes, and carpentry articles such as nails before processing. These chemicals and materials not only compromise the pellet’s quality but may become a hazard at the consumer end.
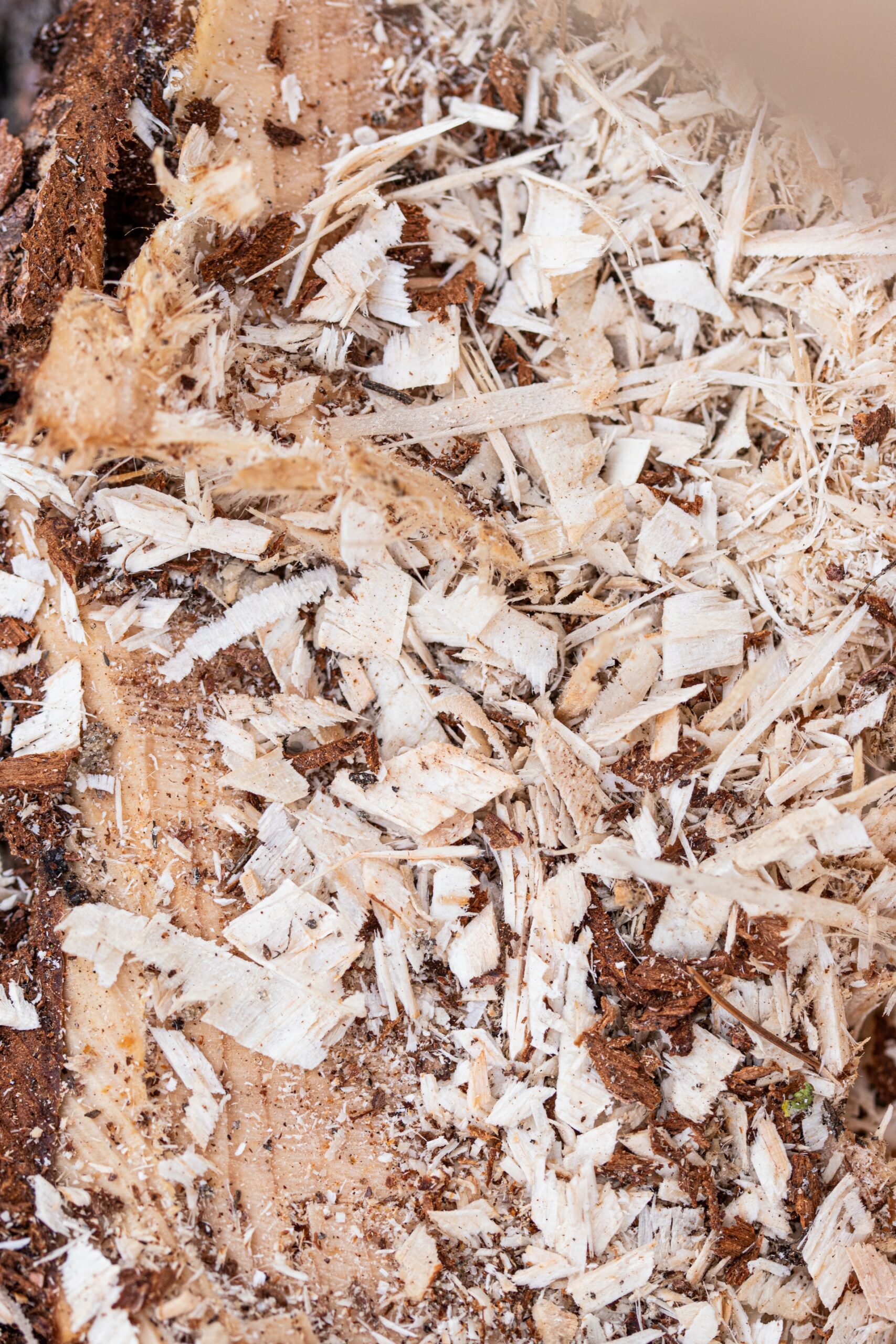
Grind the wood mixture in a hammer mill to produce a homogeneous pellet
Mill the material into uniform particle sizes, even if the by-products come from the same resource. Dissimilar particles weaken the structure of the wood pellets and could cause fracturing. Moreover, a heterogeneous mixture of grains promotes stickiness in the equipment, creating bottlenecks down the production line.
After grinding the input wood product, pass it through a hammer mill to ensure consistency in the final feed material.
Lower the moisture content in wood pellets with dehumidifying technology
Another critical step in wood pellet production is water reduction. Even if the material is stored in dry conditions, wood typically absorbs moisture from the atmosphere.
Select your drying equipment according to the manufacturing method. A heating cabinet integrates well into batch wood pellet manufacturing, while a belt dryer is better suited for a continuous process operation.
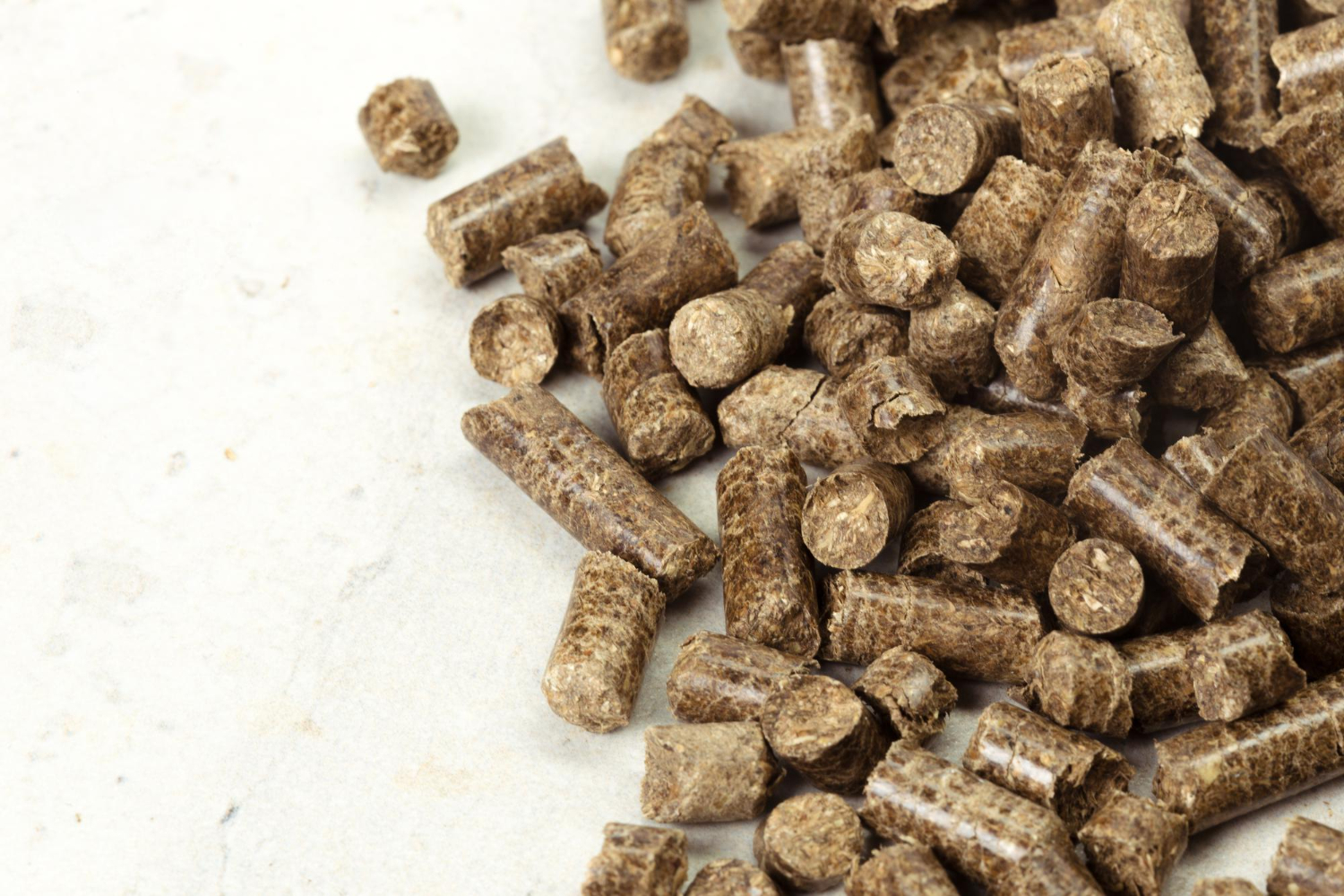
Ensure the correct wetness and dispersal of wood particles with a conditioner
Moisture removal is essential because particles cannot be compacted if soaked. But a wholly dehumidified pellet cannot hold together.
High-quality wood pellets have around 7% water content. Treat the wood mixture with conditioning equipment to ensure it is at the proper moisture level. Besides adding water, a conditioner disperses the particles into a homogeneous blend. These properties are crucial whether the end product is designed as industrial pellet fuel or for domestic use.
Wood pelleting making machinery must be compliant with sizing requirements
The wood pelleting machine compacts the conditioned wood material into strands. The internal heat of the technology fuses the particles, forming a solid. A series of knives cut the filament down to size at the other end. It is also worth mentioning that when starting a wood pellet plant, a choice between two types of machines needs to be made. That is between a flat die or ring die pelleting machine.
However, regulations around the sizing of wood pellets are generally stricter than for other applications, say pelleted feed or extruded plastic. The dimensions of wood pellets must be between 3.15 and 40.0 mm.
Processing steps involved in wood pellets making
Which wood pellets technology do you need?
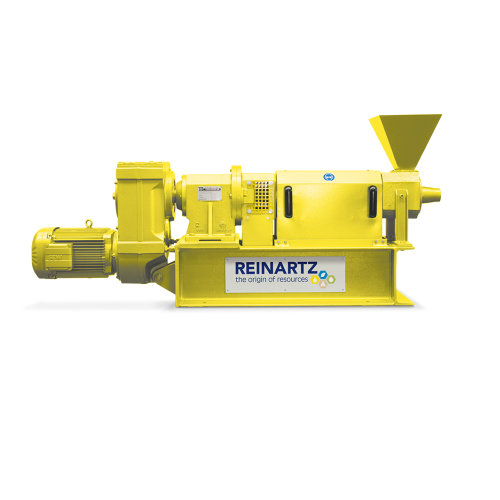
Efficient biomass screw dryers
Optimize biomass processing with screw drying technology that efficiently reduces moisture co...
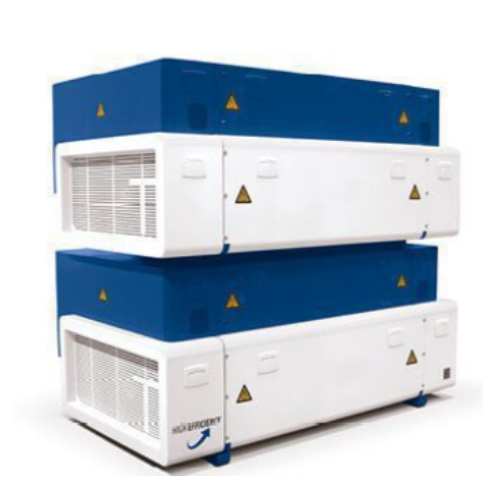
High efficiency roller mill for grain and oilseeds
Optimize your crushing and grinding processes with a versatile roller ...
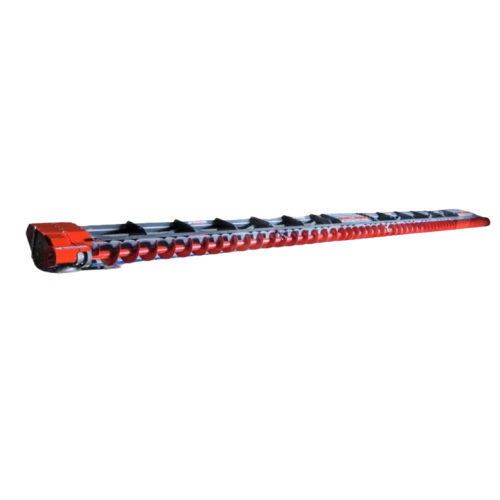
Silo unloader for difficult products
Tackle challenging silo extractions with a robust unloading system designed for high-s...
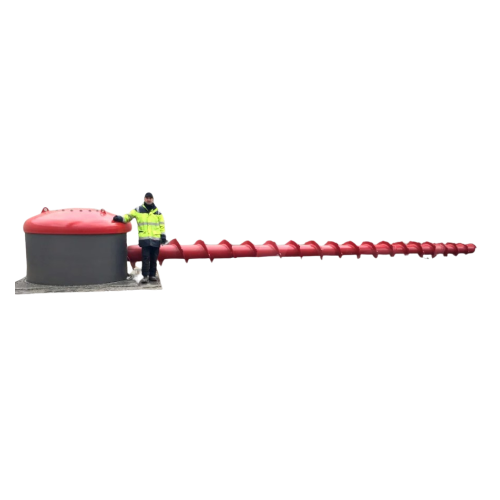
Unloader for non-free-flowing materials in flat bottom silos
Facing challenges unloading non-free-flowing materials? Thi...
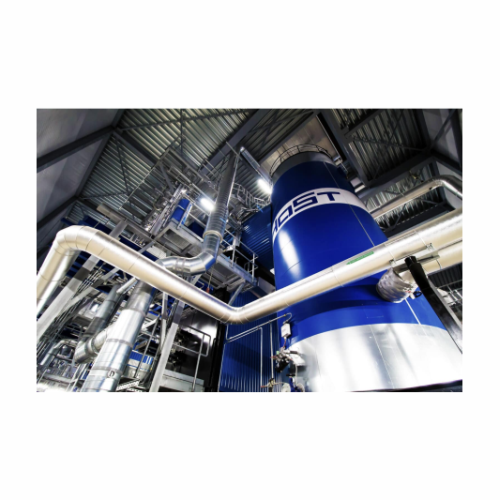
Industrial biomass hot water boiler
Ensure reliable and sustainable hot water generation for high-demand heating and indust...
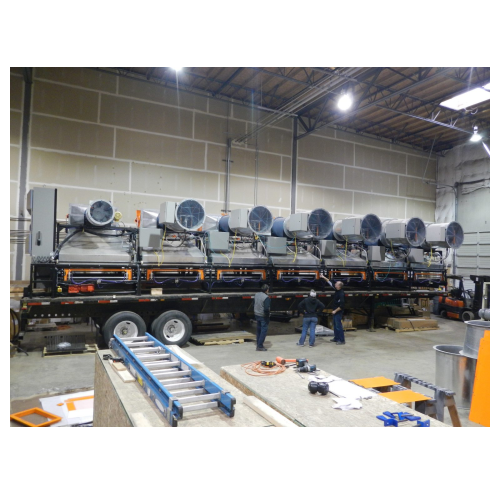
Downdraft dryer for biomass drying
Quickly reduce moisture content and energy consumption with a versatile dryer that reloc...

Biomass baler for woody biomass collection
Optimize woody biomass management with a mobile solution that reduces noise, du...
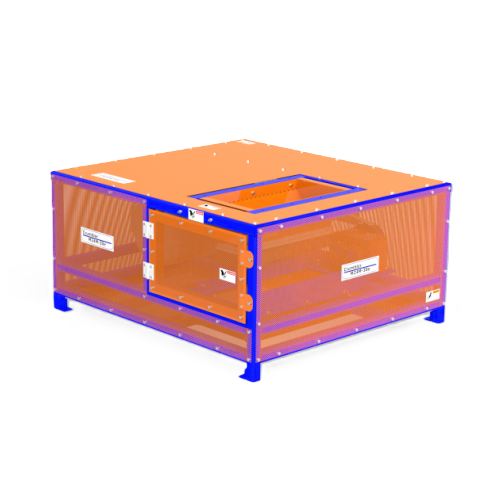
Rotary shear for wood chips and biomass processing
Efficiently transform diverse biomass materials into uniform particles...
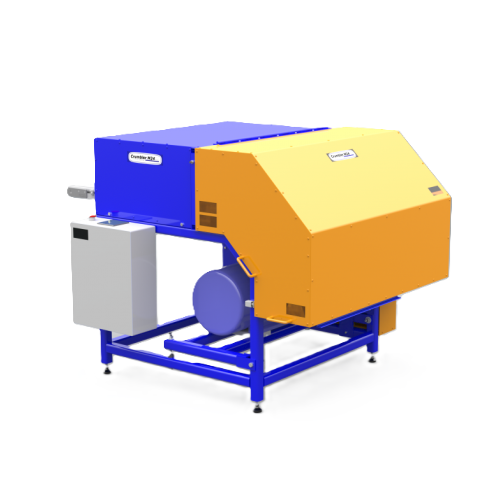
Pilot-scale commercial rotary shear for biomass processing
Optimize your biomass processing with efficient particle size...
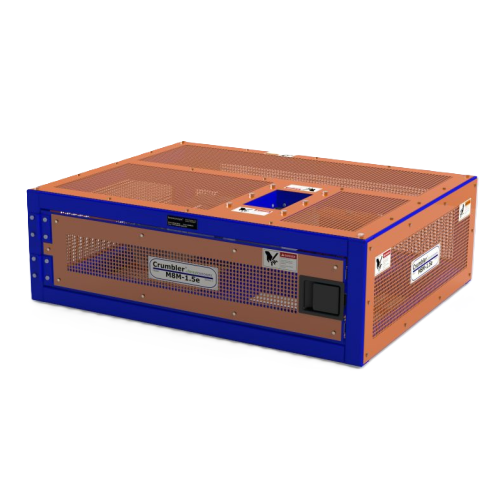
Micro-scale rotary shear for particle size reduction
Optimize your research with precise particle reduction, ideal for tr...

Advanced downdraft conveyor dryer for biomass feedstocks
Achieve precise moisture control and energy efficiency with adva...
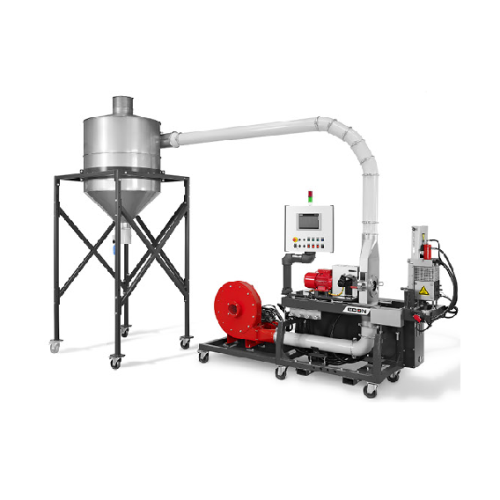
Air pelletizer for wood and natural fiber compounds
Optimize your pelletizing process with air-based cooling and conveyin...
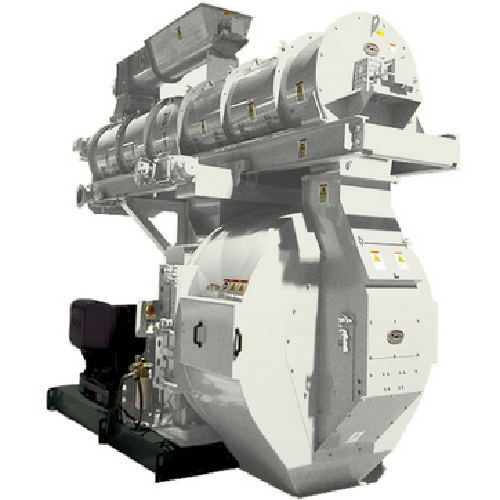
High-capacity ring-die pellet mill for animal feed production
Optimize your high-capacity feed production with this pell...
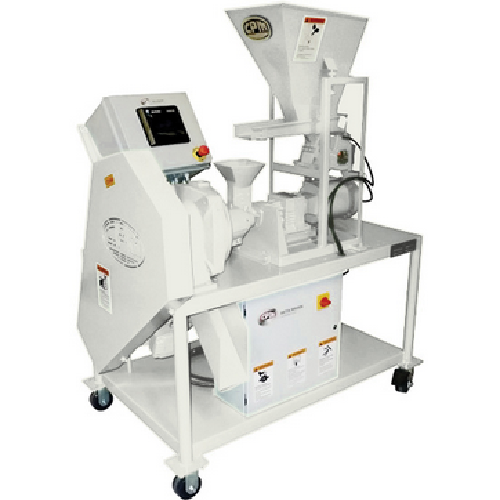
Laboratory pellet press for testing and formulation
Achieve precise pellet formulation and performance testing with versa...
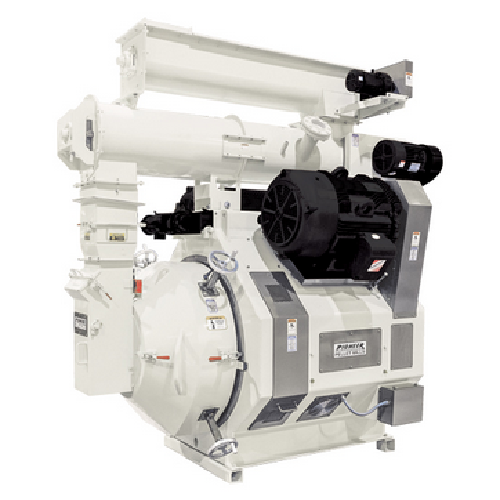
Pellet mill for noise-reduced pelleting
Optimize production with a pellet mill designed to minimize noise and enhance lubri...
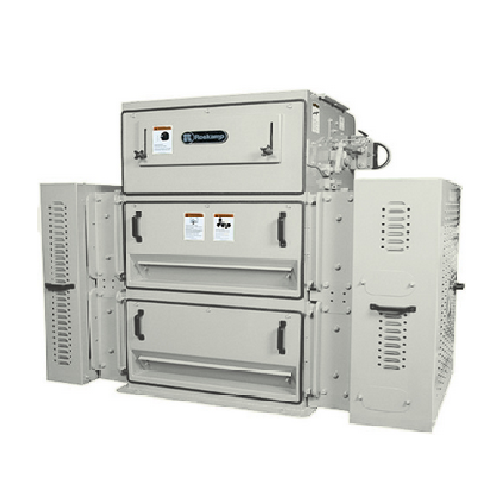
Roller mills for high-demand crushing applications
Optimize your production line with versatile roller mills designed to ...
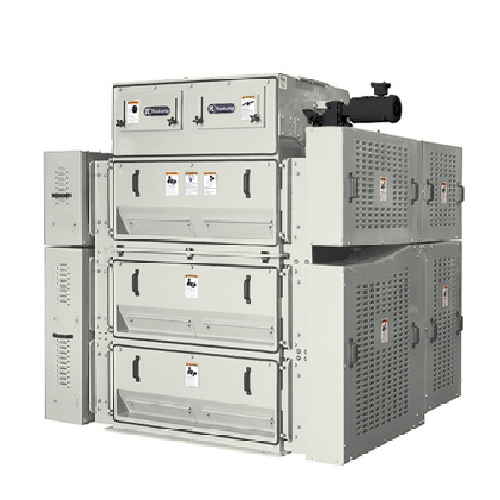
Heavy-duty roll crushers for crushing applications
Optimize your crushing and grinding processes with robust roll crusher...
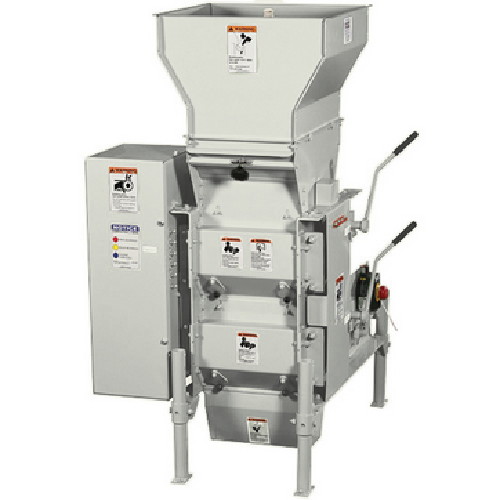
Efficient barley malt crushing with roller mills
Achieve precise particle size control in your processing line with a robu...
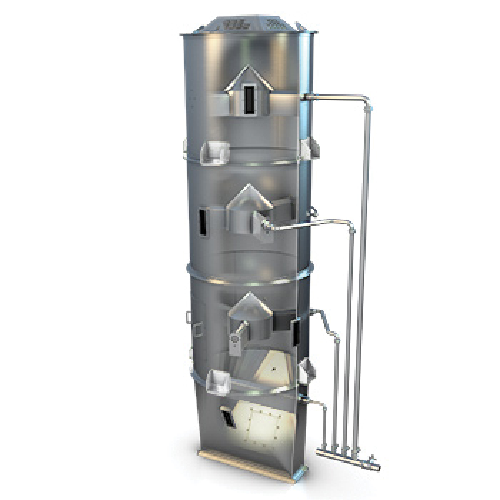
Steam chambers for grain expansion in steam-flaking
Ensure precise grain expansion with steam chambers, designed for unif...
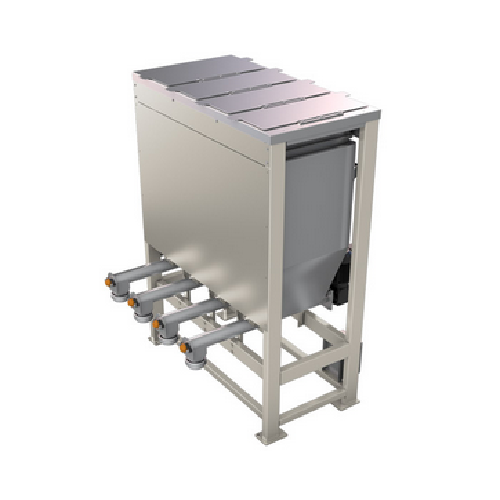
Loss-in-weight scale for micro ingredient batching
Enhance precision in your production line with advanced micro ingredie...
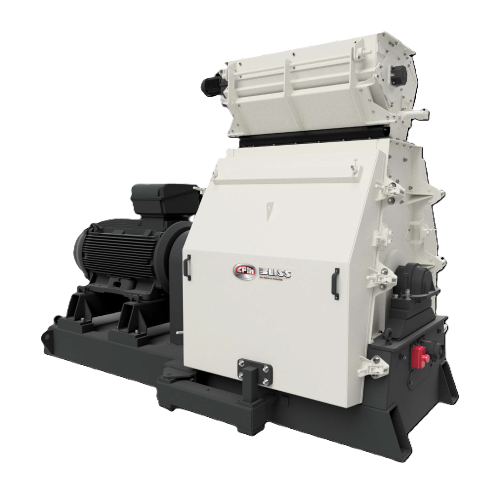
Industrial hammermill for size reduction
Optimize your production line with high-efficiency size reduction, designed to han...
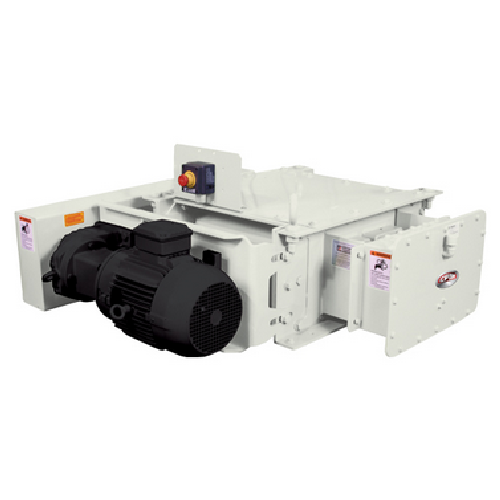
Industrial lump breaker for particle size reduction
Optimize your production line with an advanced solution for efficient...
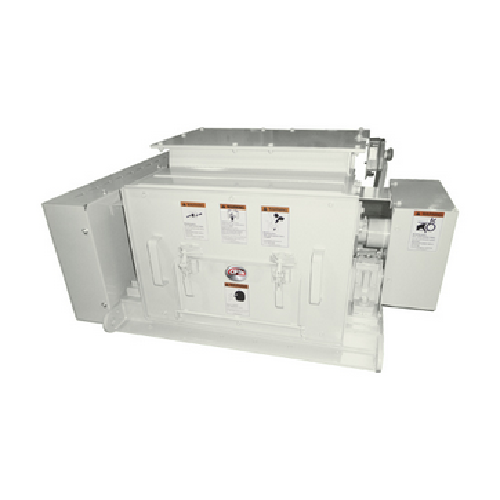
Heavy-duty crusher for 6-inch material
Efficiently tackle challenging crushing tasks with our solution designed to process ...
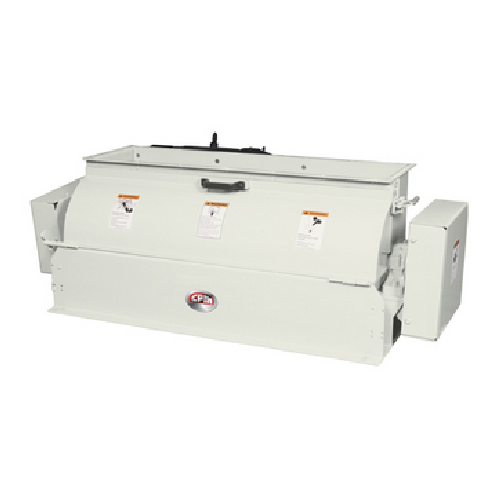
Industrial shredder for high-capacity shredding and delumping
Optimize production with precision shredding and delumping...
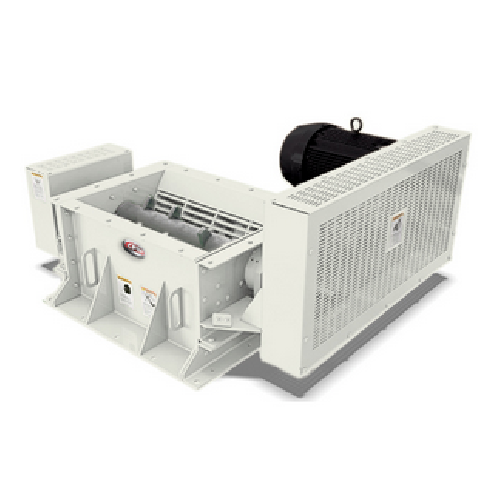
Industrial crusher for medium- to heavy-duty applications
Enhance efficiency in material size reduction operations with ...
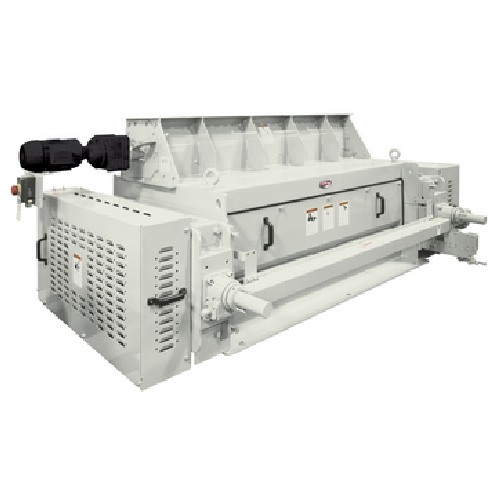
High-capacity pellet crumbler
Achieve precise pellet size reduction with this high-capacity solution, designed for effortles...
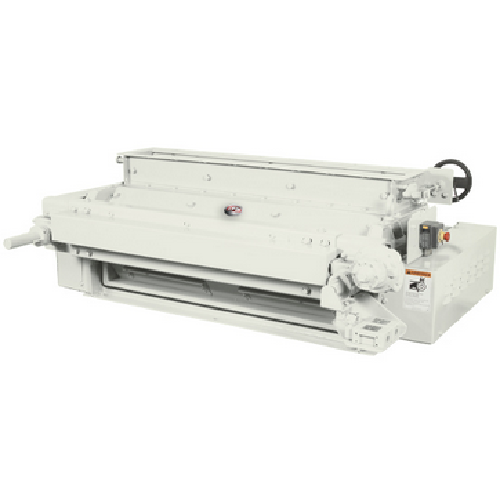
Pellet crumbler for animal feed pelleting
Optimize pellet size reduction with precise control and high efficiency, ensurin...
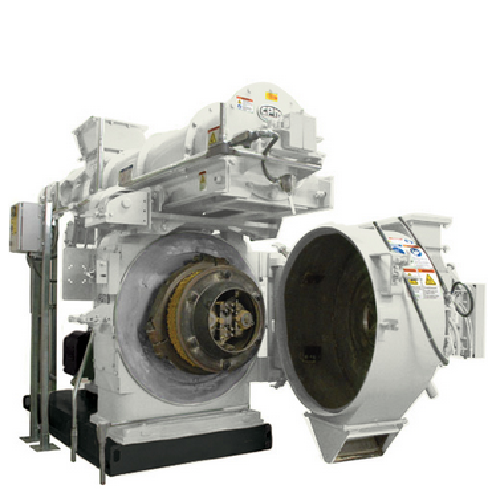
Small-scale pellet mill for animal feed production
Achieve precise pellet formulation for diverse feedstocks with an effi...

Pellet mills for feed, plastics, and industrial products
Optimize pelleting output across diverse materials with precisio...
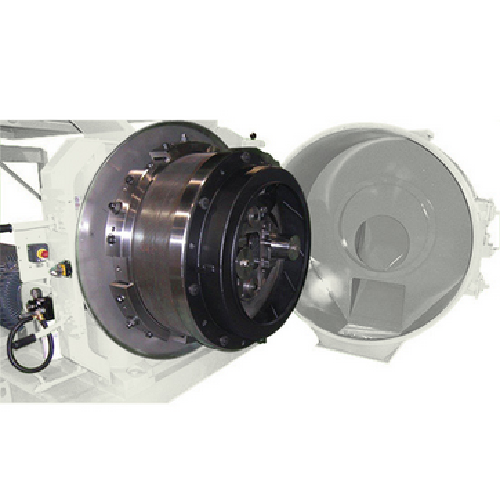
High-capacity pelletizer for oilseed meal processing
Maximize throughput and ensure consistency in your pelleting process...
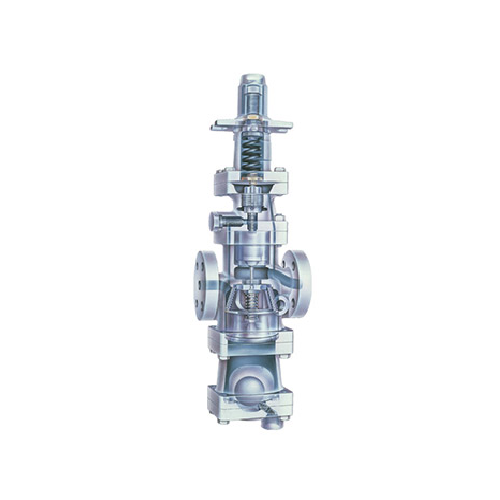
Industrial steam systems for conditioning
Efficiently deliver optimal steam conditioning for diverse feedstock, enhancing ...
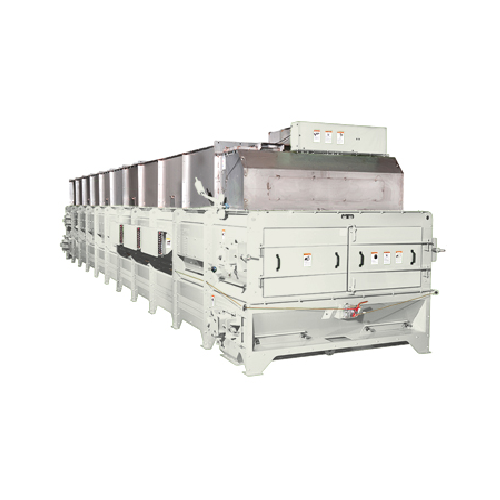
Heavy-duty horizontal dryer/cooler for pellets and meal
Optimize your production line with continuous high-speed drying a...

Industrial circular coolers for uniform product cooling
Achieve consistent cooling across your product range with circula...
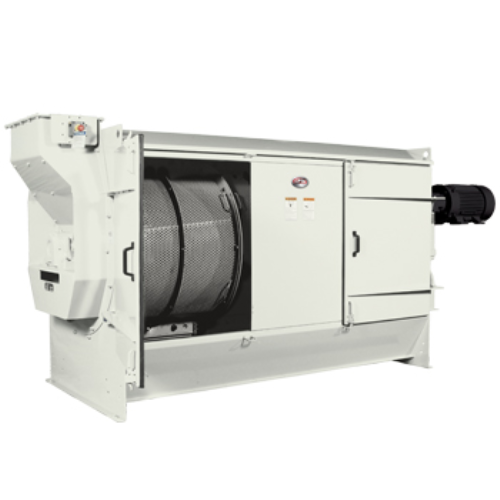
Gyro sifter for feed cleaning
Eliminate contamination and optimize product quality with high-speed screening and cleaning te...
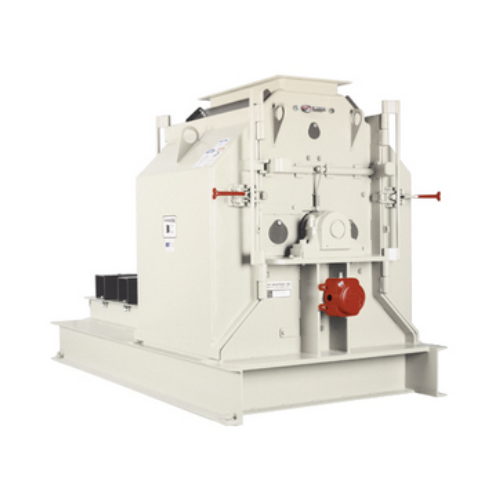
Hammermills for grinding tough products
Optimize particle size reduction with precision-designed hammermills that efficient...
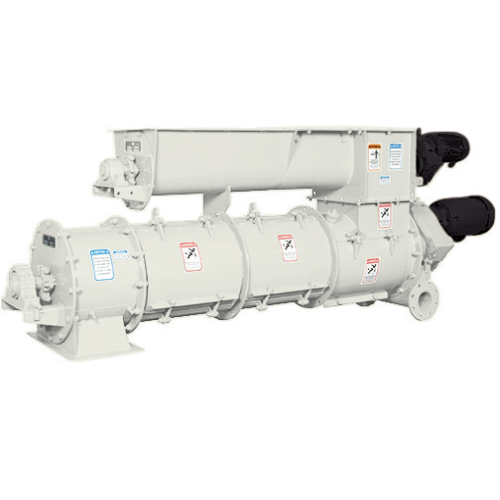
Industrial moisture and temperature control conditioner
Optimizing moisture absorption and temperature management, this c...
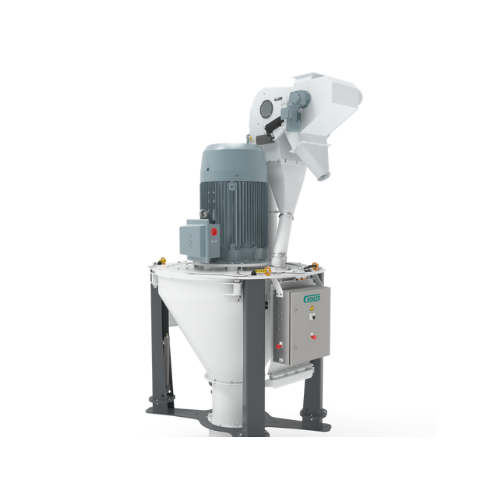
Vertical hammer mill for feed and grain processing
Optimize your milling operations and improve energy efficiency with th...
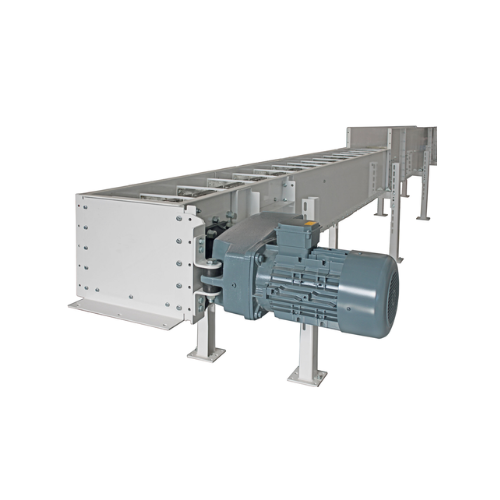
Chain conveyor for grain and floury products
Ensure seamless material handling with a versatile chain conveyor designed fo...
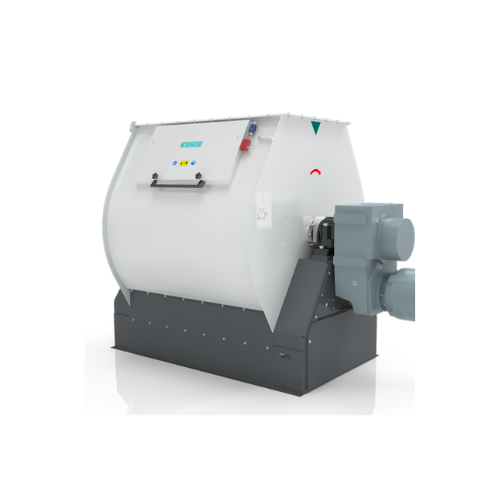
Batch mixer for animal feed
Streamline your mixing process with a high-speed batch mixer that delivers up to 20 mixing cycle...
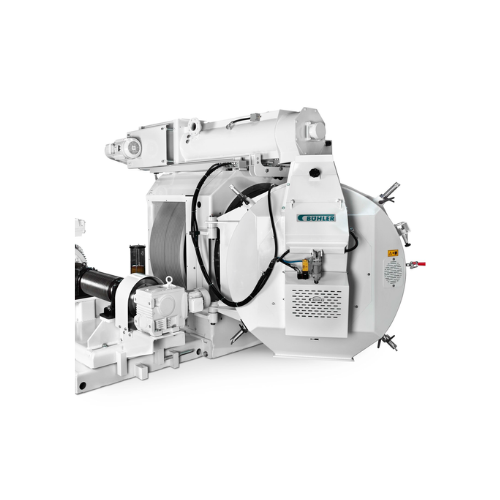
Pellet mill for biomass and sunflower hulls
Achieve high-speed, continuous production of durable pellets from varied mater...
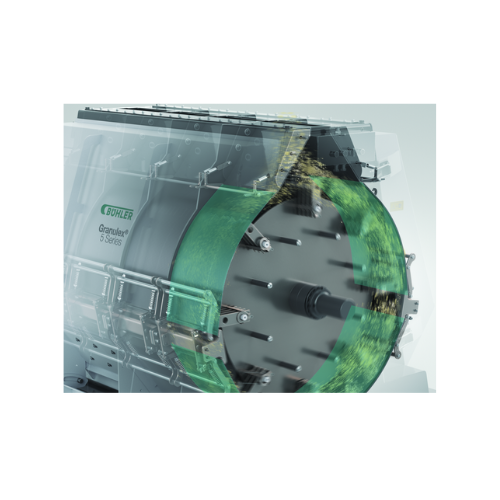
Horizontal hammer mill for grain processing
Optimize your grinding processes with our horizontal hammer mill, designed to ...
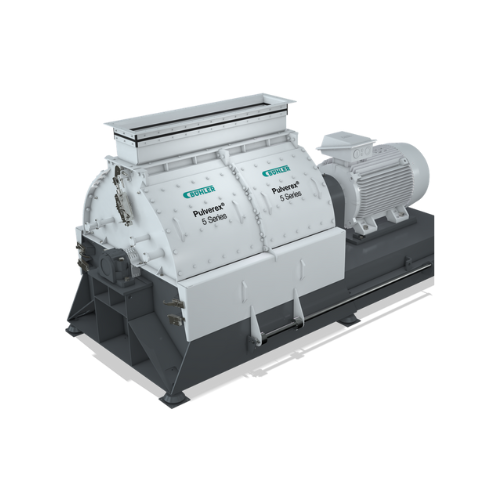
Pulverizer for fine grinding applications
Achieve optimal particle size distribution and enhance throughput with this adva...
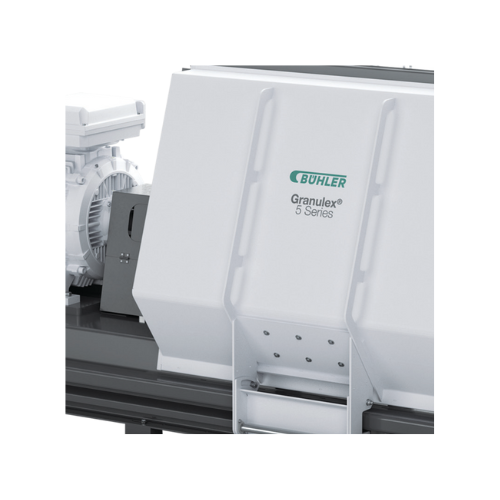
High-throughput hammer mill for animal feed production
Ideal for high-throughput operations, this hammer mill ensures pre...
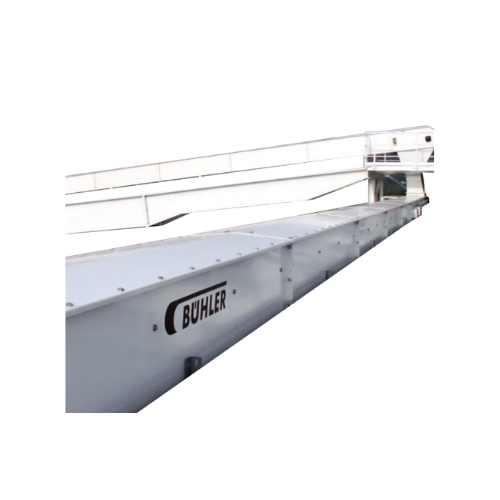
Heavy-duty trough chain conveyor for high throughput applications
Optimized for high-capacity operations, this robust c...

Discharge station for bags and big bags
Ensure consistent material flow and hygiene in your production line with a versatil...
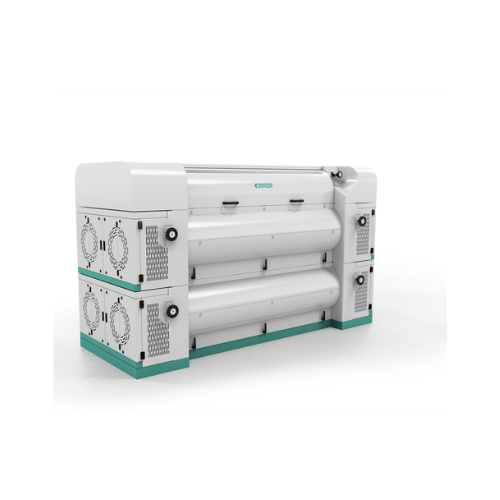
Cracking mill for oilseeds and feed
Enhance your production efficiency with a cracking mill that optimizes throughput and m...
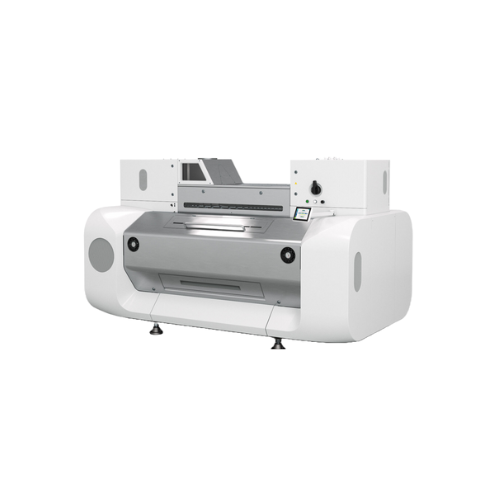
Integrated grinding system for wheat and grain
Optimize your grinding process with a system that delivers consistent parti...
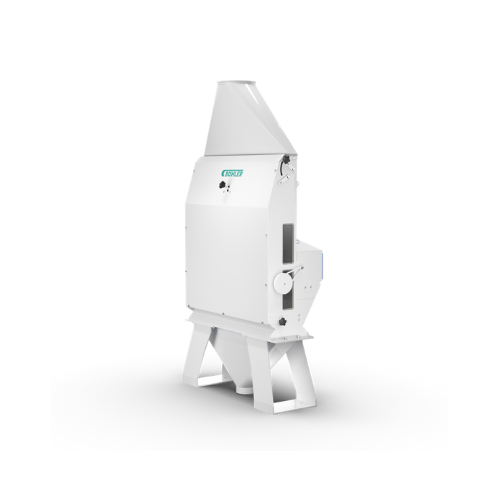
Aspiration channel for grain cleaning
Achieve superior product quality by efficiently removing light impurities from granul...

Hammer mill for size reduction in food and feed processing
Efficiently tackle size reduction challenges with a versatile...

Ultra-fine pulverizer for aqua feed and pet food
Achieve precise granulation with high efficiency for your feed and food p...
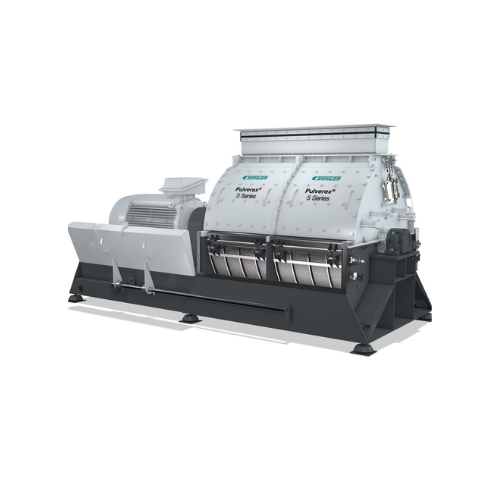
Industrial fine grinding pulverizer
Achieve consistent fine granulation at high capacity with reduced energy consumption, u...
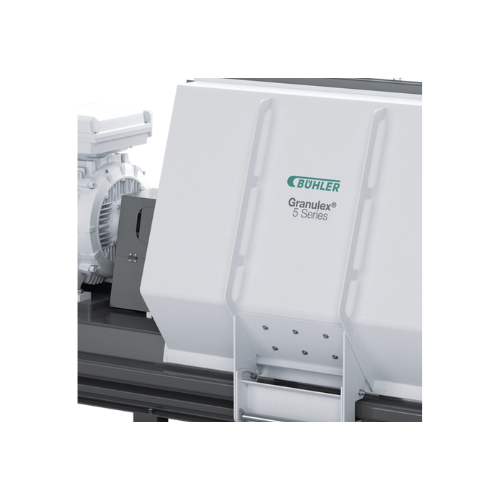
Hammer mill for animal feed grinding
Achieve precise granulation with high throughput and energy efficiency, while reducing...
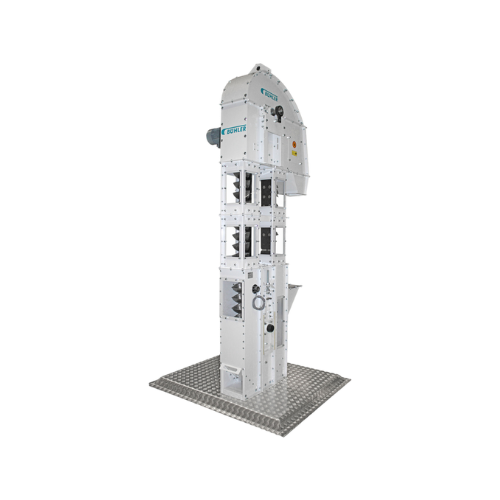
Vertical grain conveying solution for animal feed and bulk materials
Efficiently transport and elevate various bulk mat...
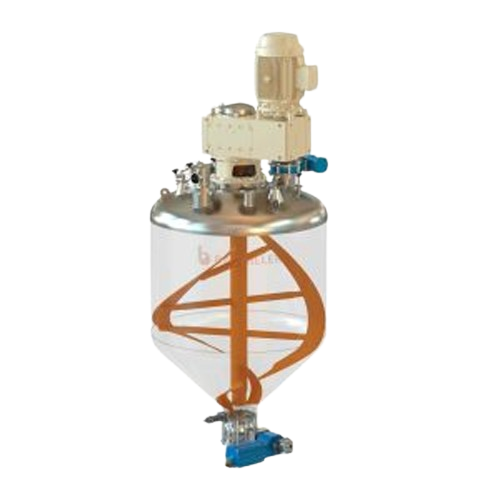
Vertical ribbon mixer for solids and powders
Achieve rapid, uniform mixing of powders and solids while preserving particle...
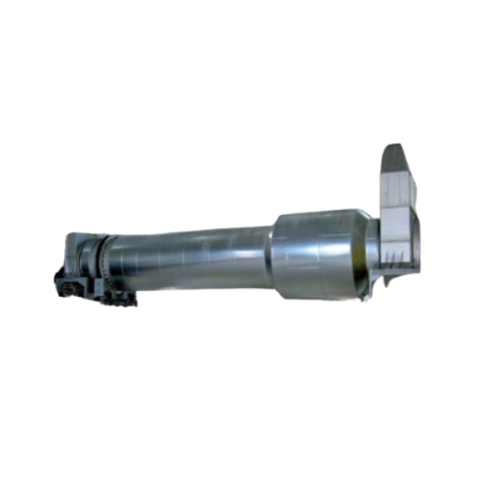
Indirect drying drums for solvent-based products
Optimize energy use and safety with our indirect drying drums, ideal for ...
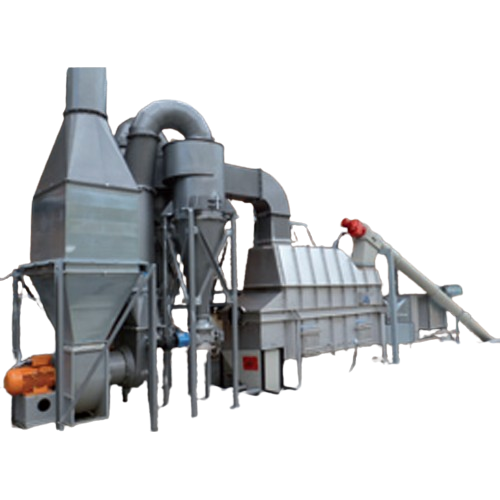
Biomass drying solution
Achieve efficient and gentle biomass drying with innovative heat exchange technology, ensuring optima...

Industrial drum dryer for bulk solids
Optimize your production line with high-throughput drying for varied particle sizes, ...

Retractable spiral chute for bulk material handling
Enhance the integrity of your products by gently transferring bulk ma...
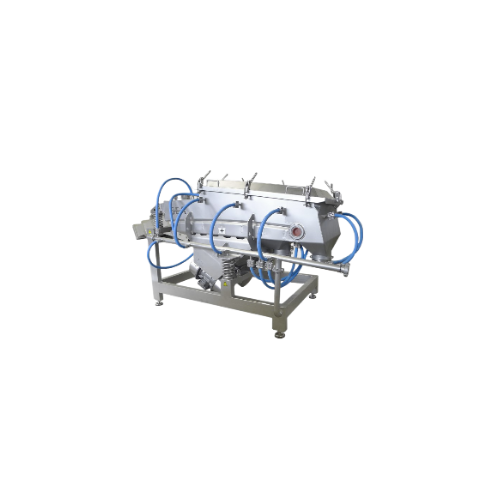
Industrial sifters for beverage processing
Optimize your beverage production with precisely engineered sifters that ensure...
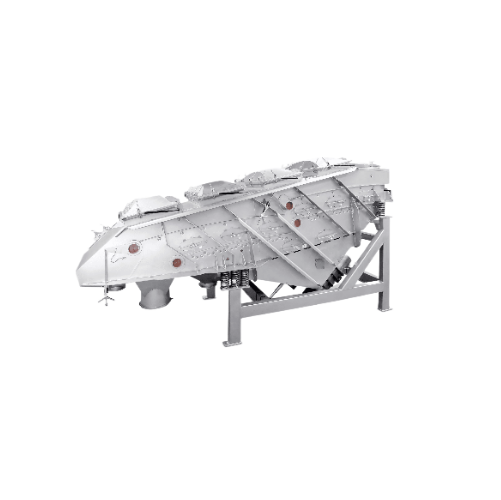
Vibrating sifter for chemical applications
Achieve precise particle separation with this vibrating sifter, ensuring optima...
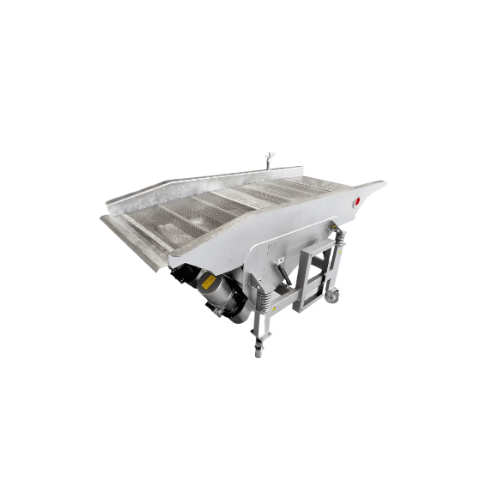
Food product sifter
Ensure precise separation with vibratory sifters designed for continuous operation, delivering gentle han...
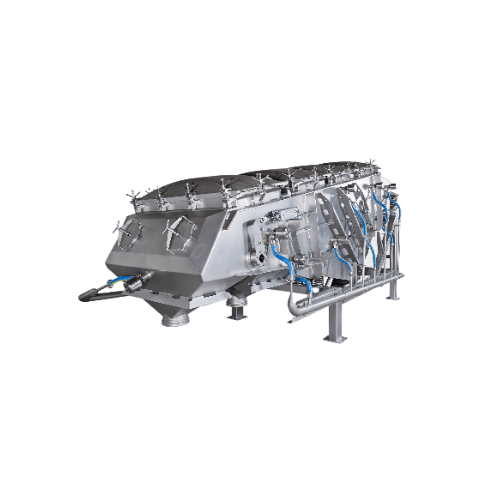
Industrial powder sifter with sanitary compliance
Optimize your powder processing with this versatile sifter, ensuring pr...
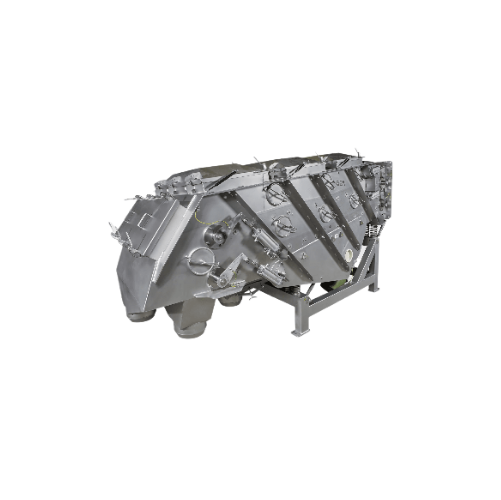
Sifter for pet food, fish feed, and animal feed
Achieve precise particle separation and enhance feed quality with this vib...
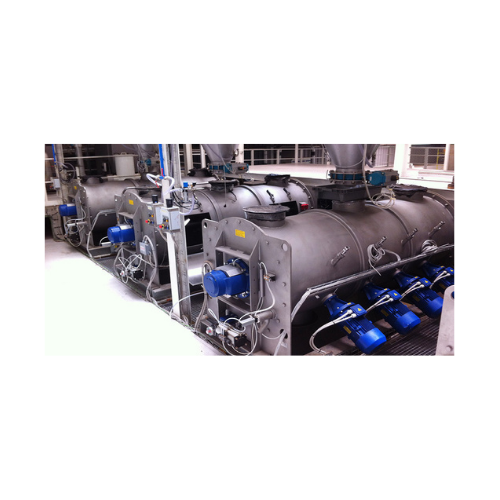
Batch-type single shaft mixer for industrial mixing
Achieve precise and uniform mixing with high-speed, single-shaft mixe...
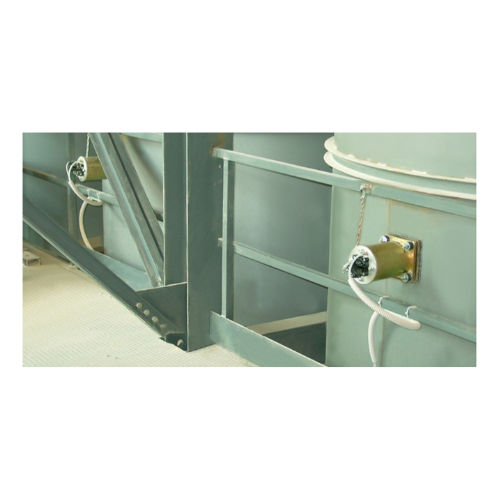
Air cannons for resolving bulk material flow issues
Solve bridging and rat-holing issues in bulk material storage with po...
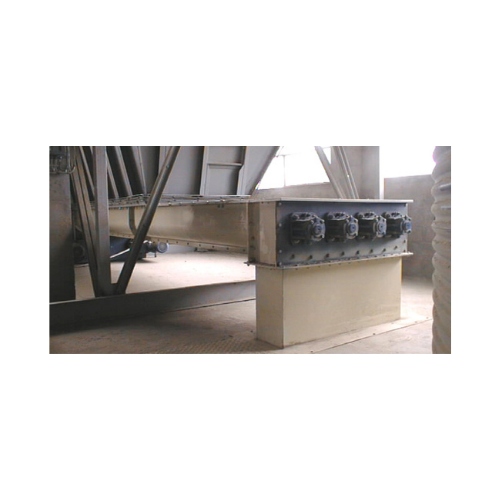
Live bin bottom for difficult material discharge
Efficiently manage the discharge of challenging materials like biological...
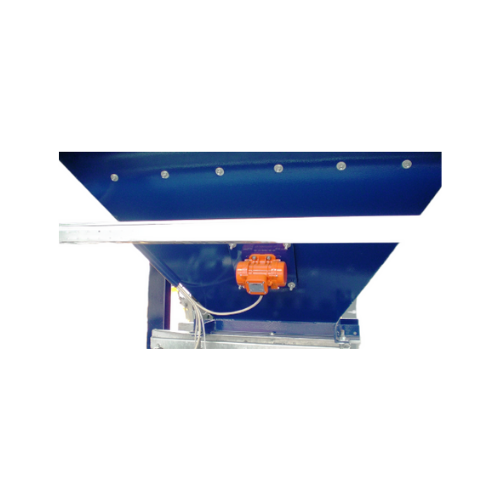
External electric motovibrators for industrial applications
Optimize material movement and improve discharge efficiency ...
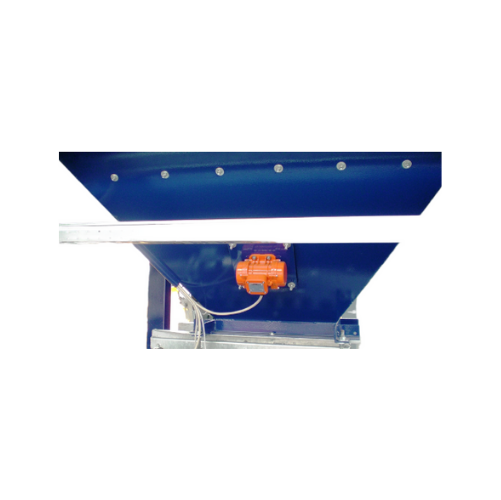
External electric motovibrators for bulk solids conveying
Enhance material flow efficiency and solve challenging dischar...
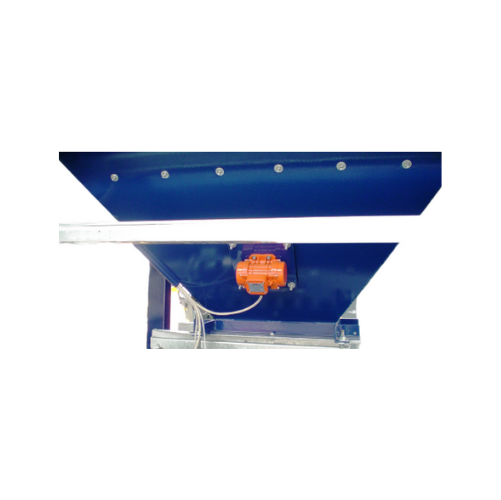
Industrial electric vibrator for bulk solids discharging
Enhance material flow efficiency and ensure consistent output ac...
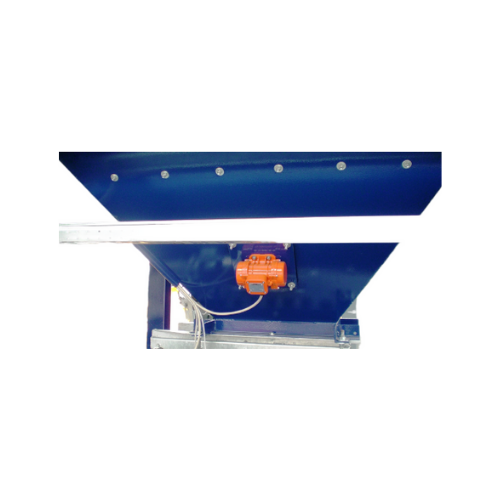
External electric motovibrators for industrial material flow
Experience enhanced material flow and precise material disc...

External electric motovibrators for hazardous materials
Ensure safety and efficiency in hazardous environments with relia...
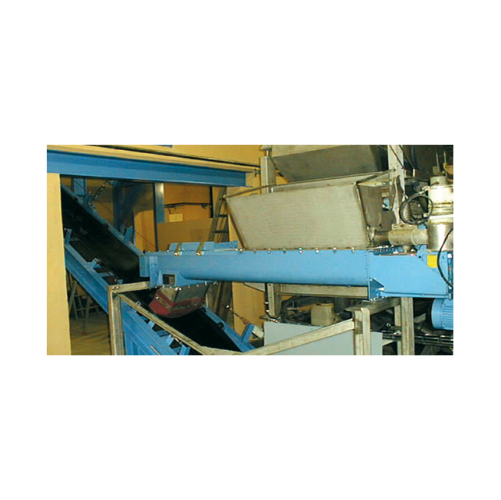
Continuous twin shaft paddle mixers for dust conditioning
Optimize your mixing process with twin shaft paddle mixers, en...
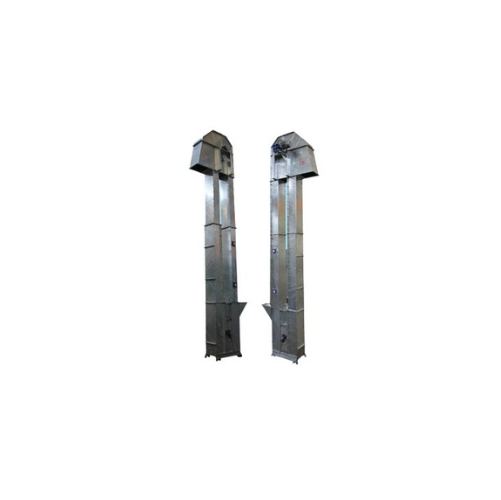
Vertical conveyor for fine aggregates and minerals
Optimize the handling of abrasive materials with a vertical conveying ...
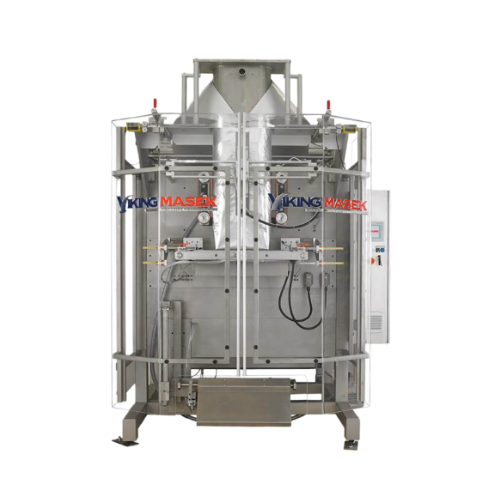
Vertical form fill seal for bulk bag packaging
Streamline your bulk bag packaging with efficiency and precision, ideal for...
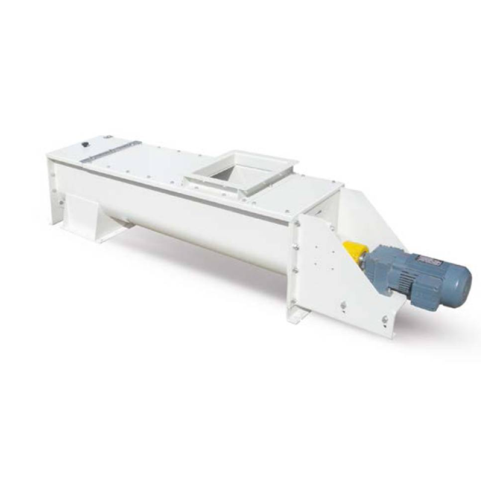
Screw conveyor for grain or finished products
Optimize your production line with a space-efficient screw conveyor designed...

Pellet mill for powdery animal feed products
Maximize plant efficiency and product quality with a versatile pelleting solu...
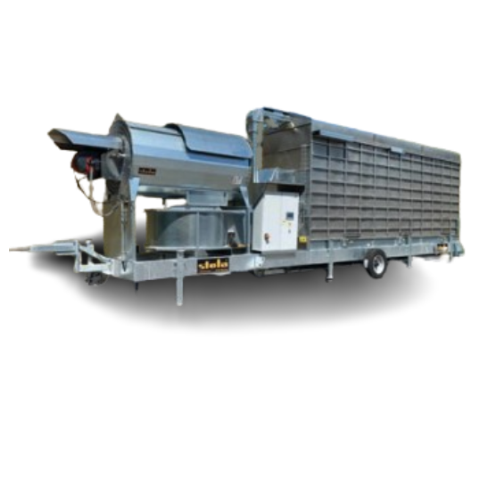
Mobile circulating dryer for agricultural products
Optimize your drying processes with a mobile circulating dryer, design...
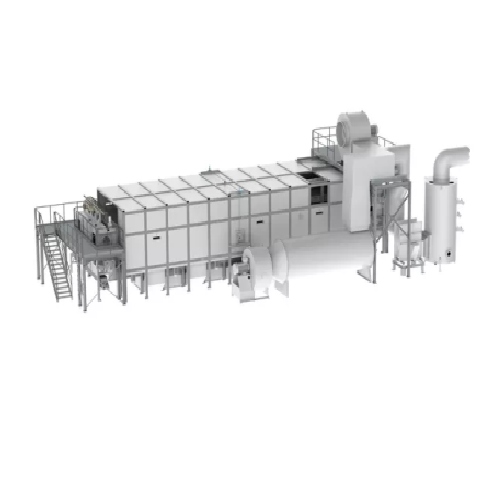
Slat conveyor dryer for industrial drying processes
Optimize your drying process with a robust slat conveyor system that ...
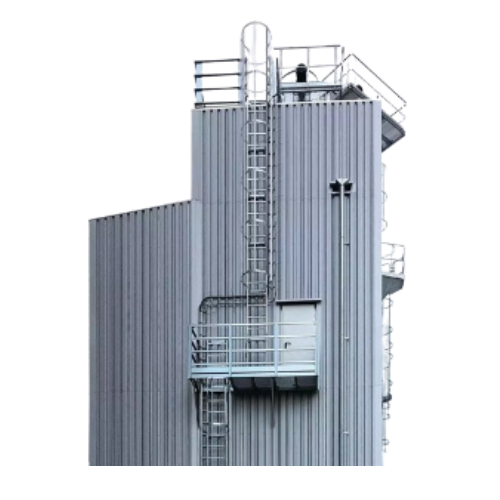
Stationary drying system for agricultural products
Optimize moisture control and energy efficiency in your drying process...
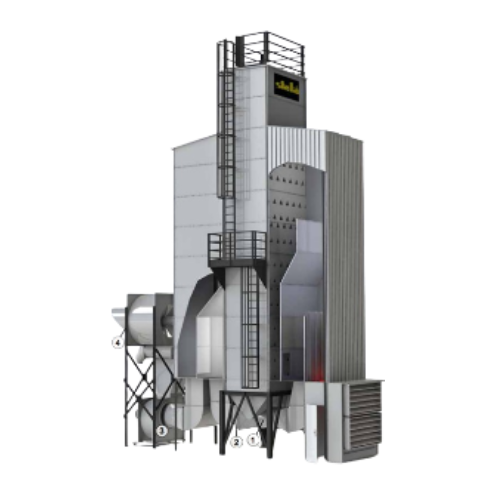
Stationary grain dryer with exhaust air system
Optimize your drying process with a system designed to handle diverse mater...
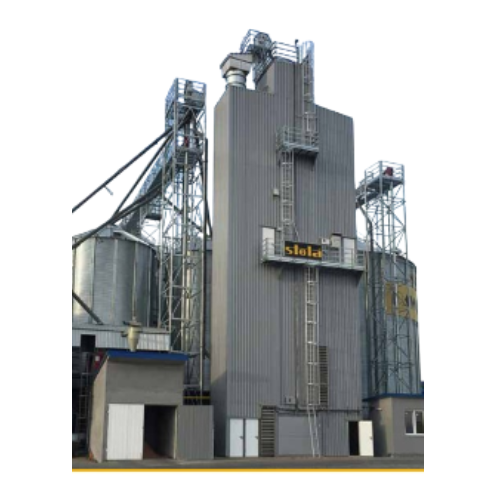
Grain dryer with air circulation system
Enhance efficiency and product quality with our versatile grain dryer, designed to ...
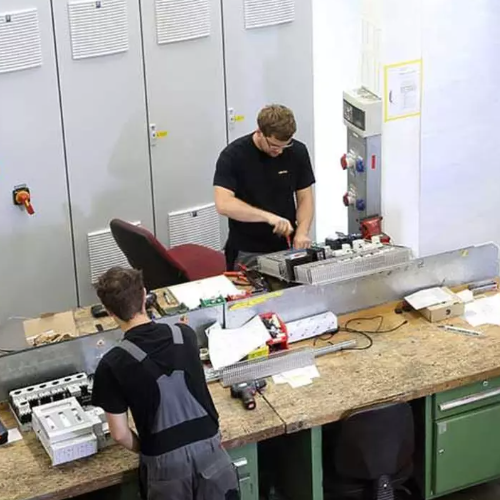
Low-emission belt drying systems for timber industry
Optimize moisture control and energy efficiency in drying processes ...
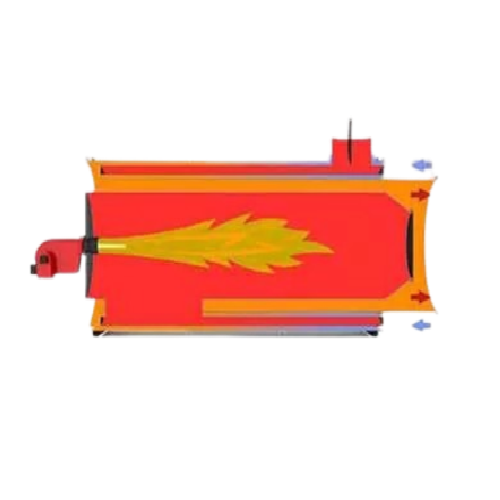
Industrial air heater for agriculture and industry
Optimize energy efficiency and maintain high air quality in your produ...
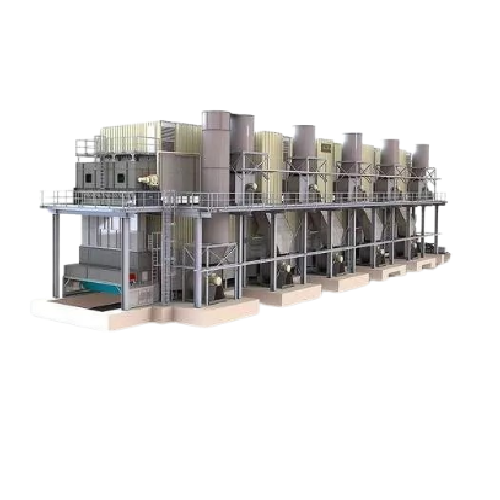
Belt dryer for sawdust
Optimize your drying process with advanced technology engineered for precise moisture reduction in div...
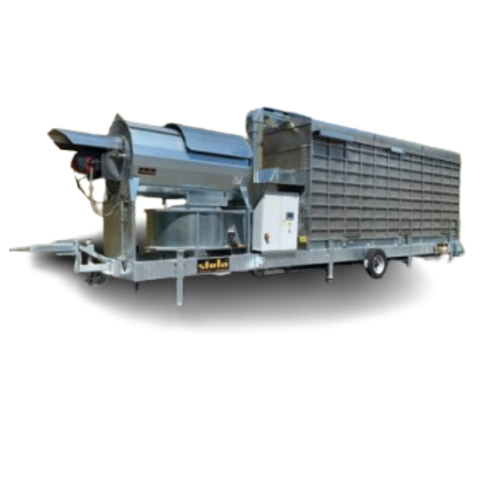
Hybrid dryer for agriculture and industrial applications
Achieve efficient moisture reduction in varied materials, from f...
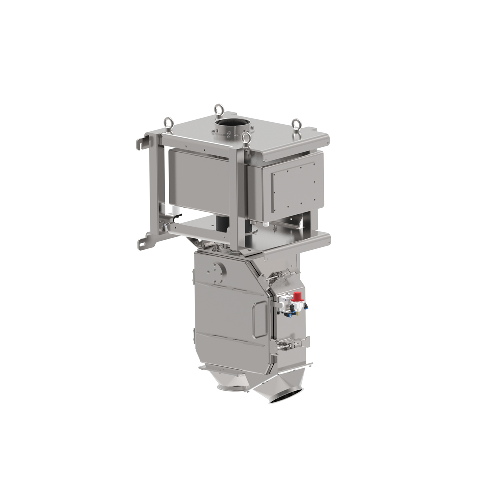
Metal detection system for powders & granules
Ensure product integrity and protect your machinery from metallic contaminan...
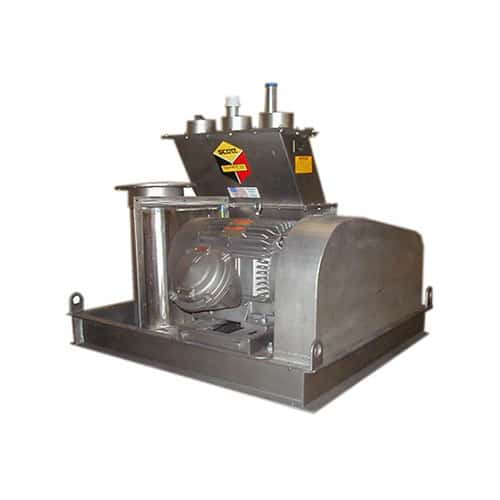
Shredder for fine particle size reduction
Optimize your production line with high-speed shredding technology designed for ...
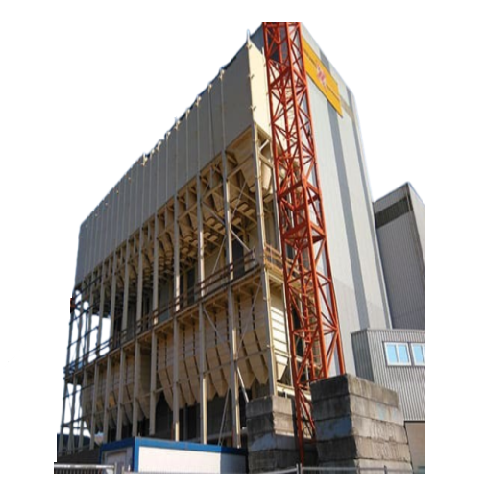
Sanitary modular bulk silos for efficient storage
Maximize your storage capacity and streamline assembly with a modular s...
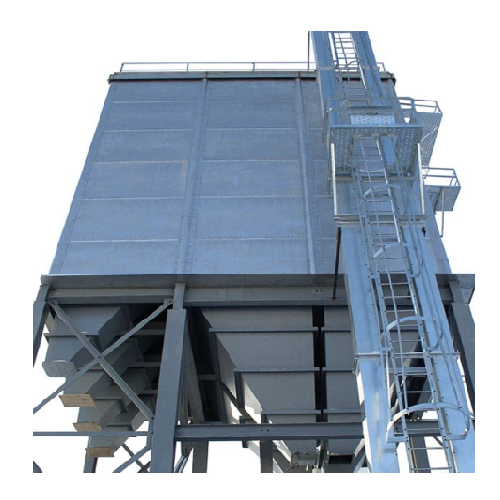
Modular bulk storage bins for efficient material handling
Maximize your storage efficiency with bolt-together solutions ...
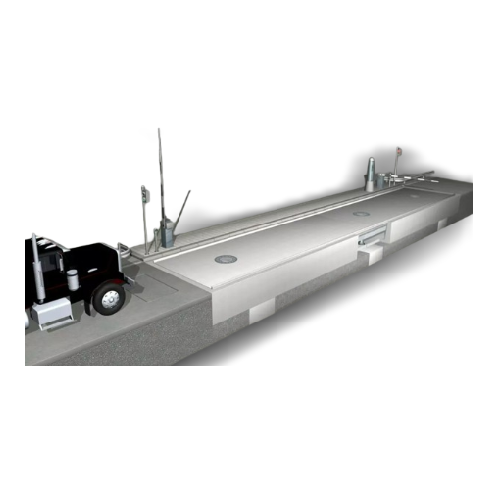
Pit scales for industrial weighing
Optimize material flow and ensure precise load determination with a robust pit scale sol...
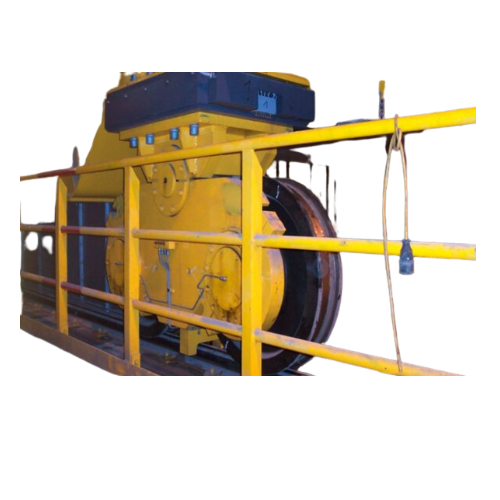
Crane scales for precise weighing in chassis
Optimize space with low-profile crane scales, ensuring accurate weight measur...
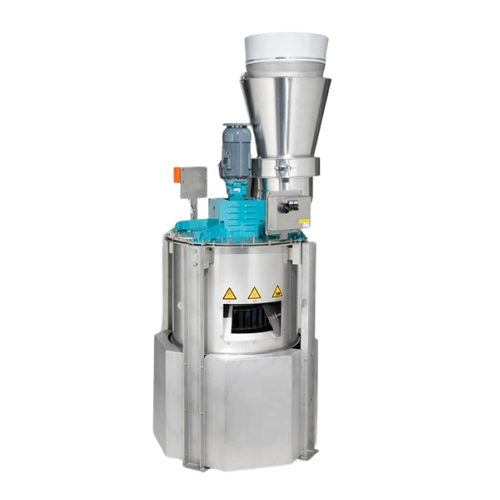
Mass flow rate feeder for bulk powders
Achieve precise control and consistent material flow in high-speed manufacturing env...
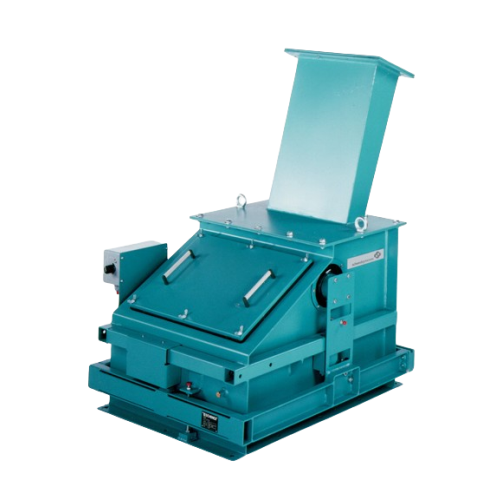
Solids flow meter for bulk solid streams
Ensure precise bulk material measurement with a system designed for accuracy and r...
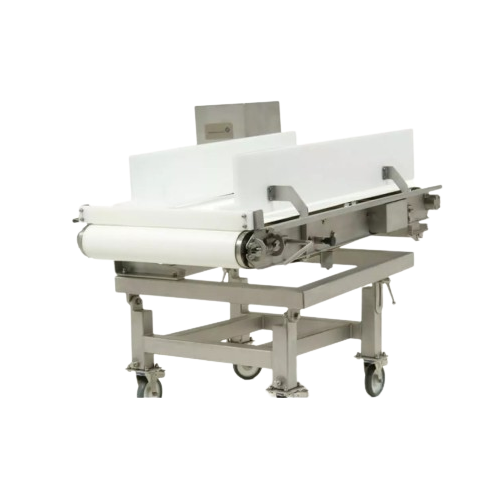
Industrial weighfeeder for hygienic applications
Achieve precise mass flow control with a hygienic design, ideal for appli...
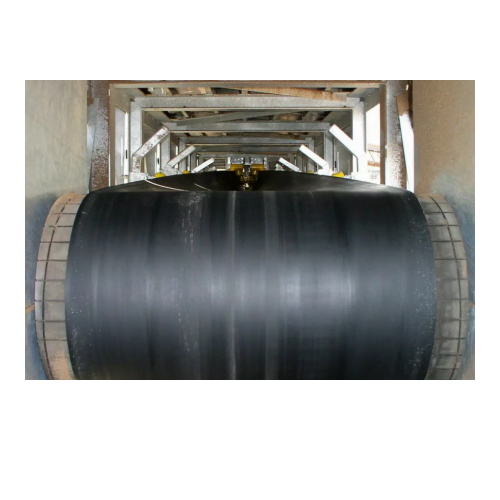
U-belt conveyor for bulk material transport
Optimize your high-speed bulk material transport with this space-saving convey...
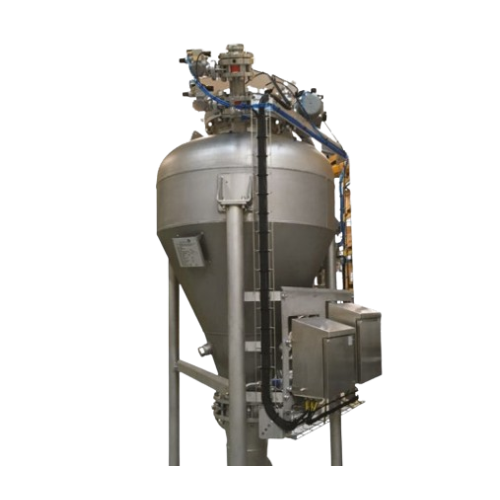
Dense phase pneumatic conveying accessories
Optimize material flow and reduce power consumption with dense phase pneumatic...
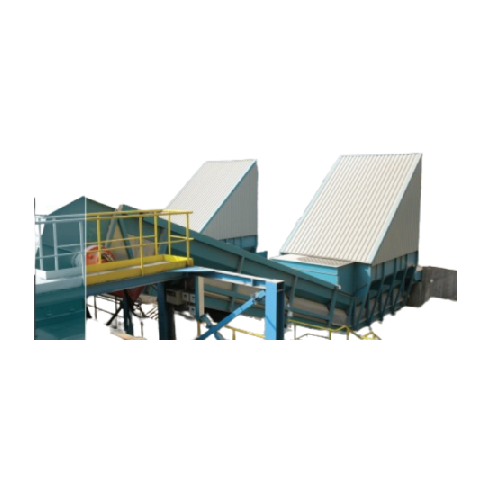
Bulk reception solution for industrial material handling
Optimize your operations with an above-ground bulk reception sys...
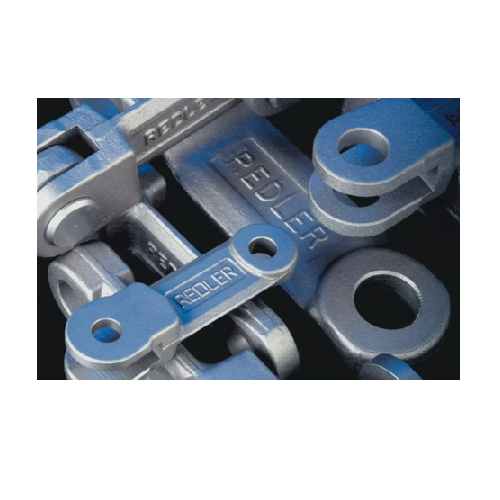
Drop forged chain for drag chain conveyors
Enhance your material flow efficiency with a robust drop forged chain designed ...
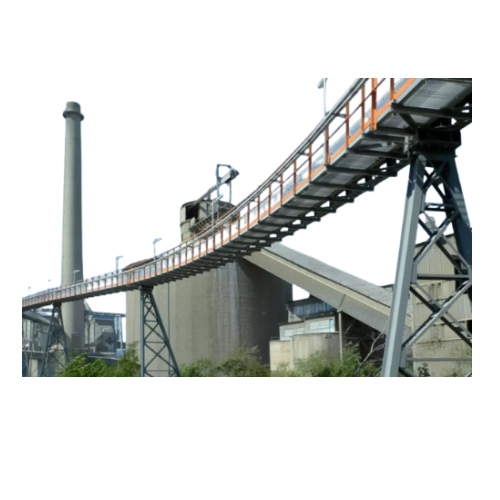
Tube belt conveyor for long-distance material handling
Ensure seamless and protective transport of bulk materials across ...
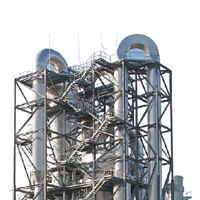
Exergy pressurized superheated steam dryer
Traditional dryers and heat transfer systems, like belt-, drum- or bed dryers a...
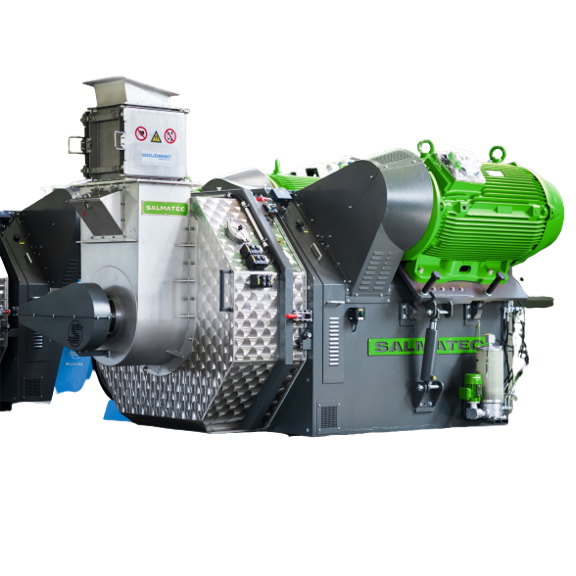
Complete pellet line
Large industries are shifting towards more environment-friendly technology, such as recycling wastes and...
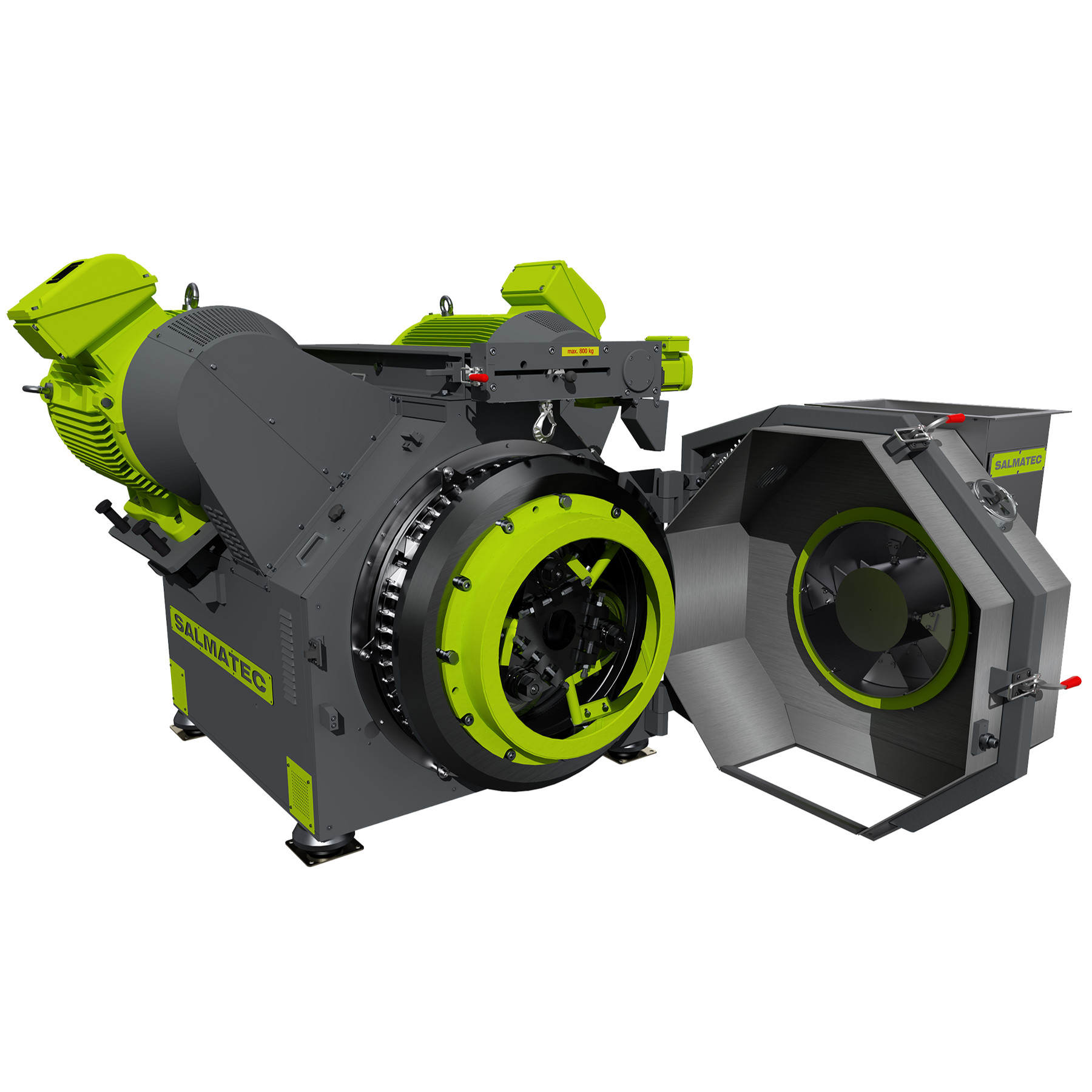
Industrial pellet mill
At the industrial level, the application areas of pellets range widely in fields such as feeds, biomas...
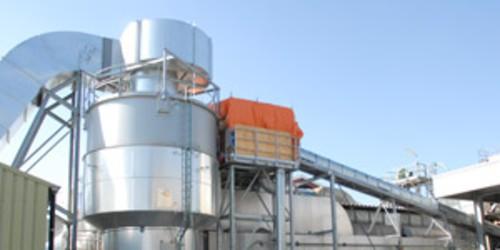
Wood chip gas syngas generator
The recovery of energy from biomass isn’t all advantages, it has its shortcomings as well. Bi...
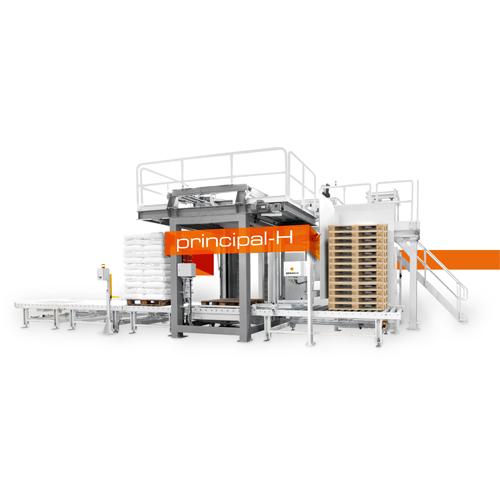
Automatic palletizer machine for bags and boxes
The effective placement and positioning of bags and boxes can be a challen...
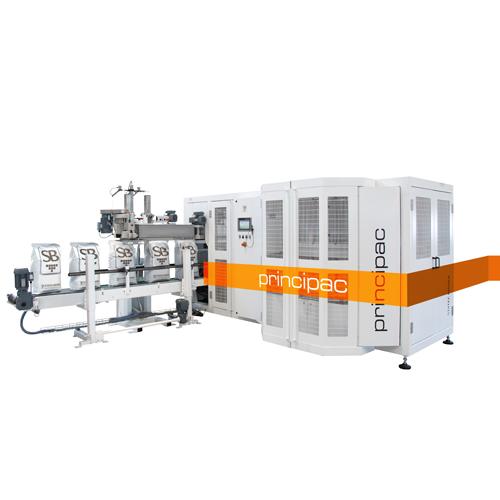
Open mouth bagging machine
If you are a manufacturer of fertilizers, bulk chemicals, sugar, seeds, or any grains it is likel...

Open mouth bag filling machine for powders
The packaging of powdery products such as flour can be challenging as it is cru...
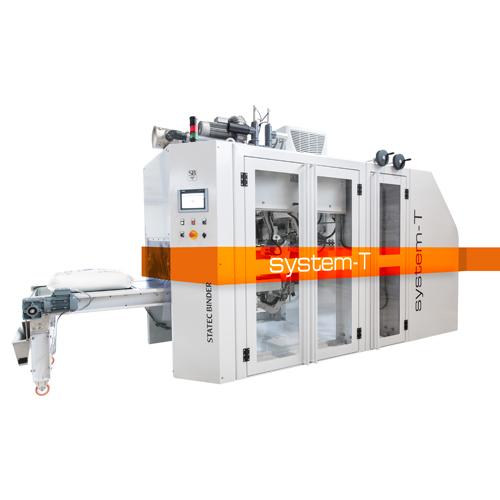
Form fill seal bagging machine
If you are in industries such as petrochemicals, fertilizers, animal feed, food, etc, you mus...
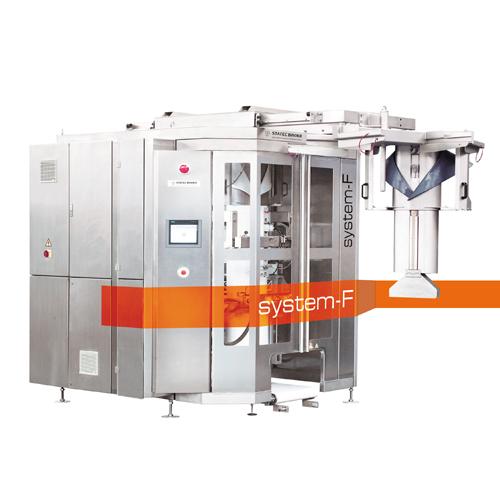
Vertical form fill seal machine
There is an increasing demand for a range of different package sizes of the same product. If...
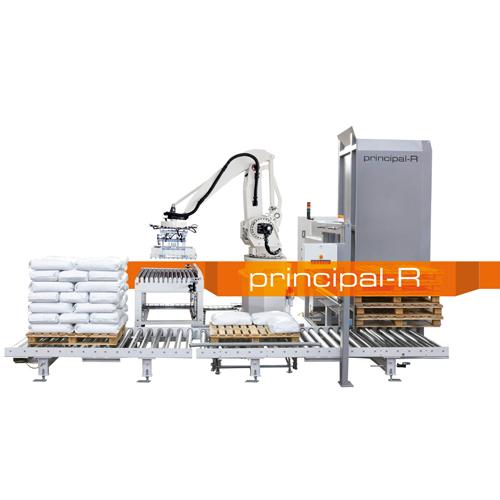
Robot palletizing system
If you are a relatively large-scale producer, packing and transporting large quantities of products ...
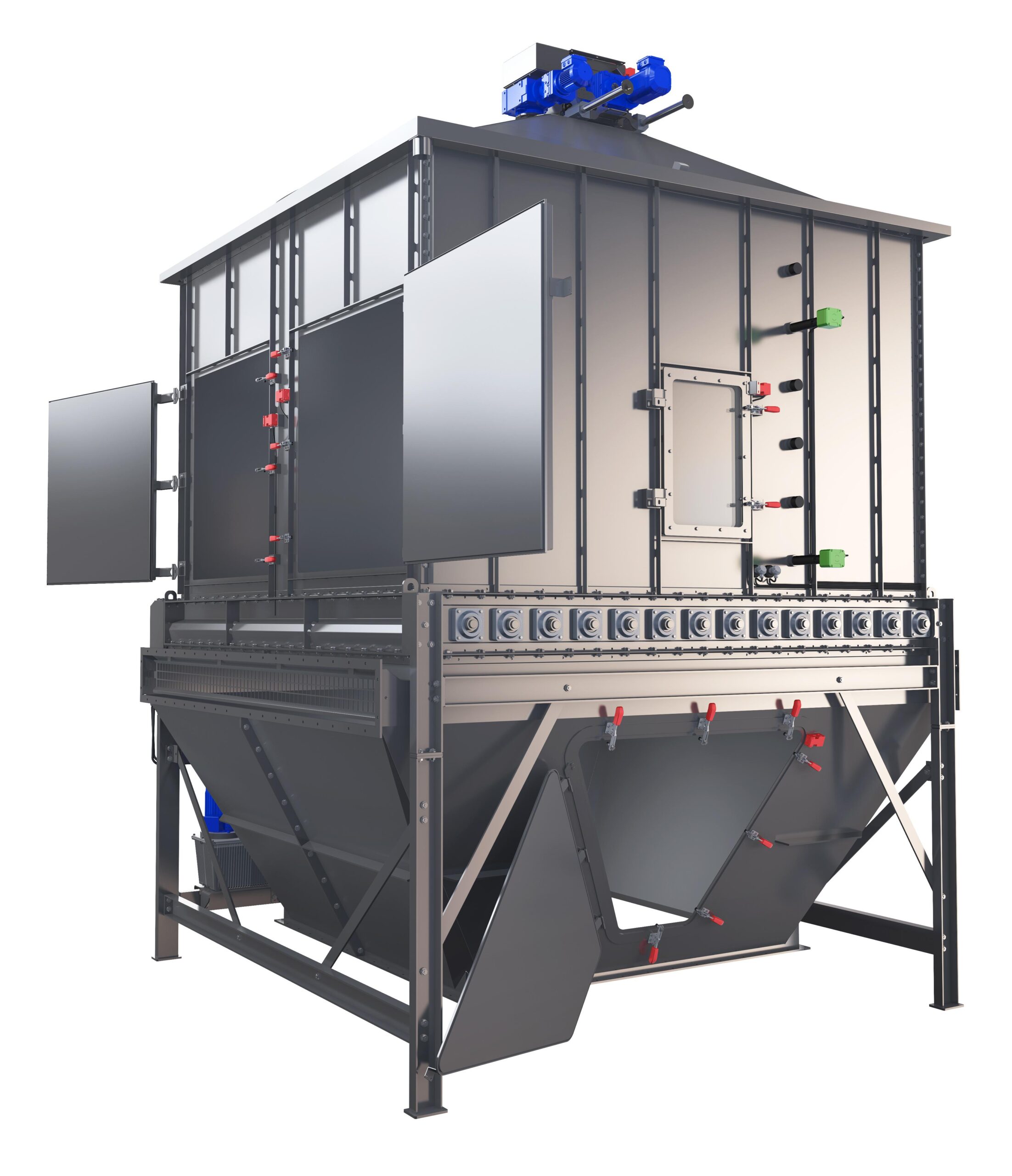
Counterflow pellet cooler
Food and feed industries require the highest standards of hygiene and sanitation. This entails fre...
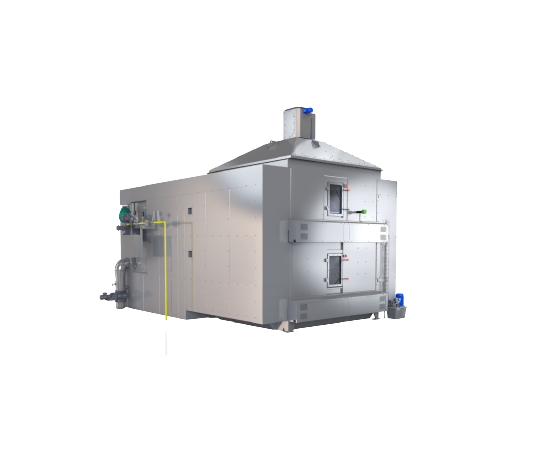
Continuous dryer machine
Traditional drying methods in the pet food, aquafeed, and extruded food industry can be the most ene...
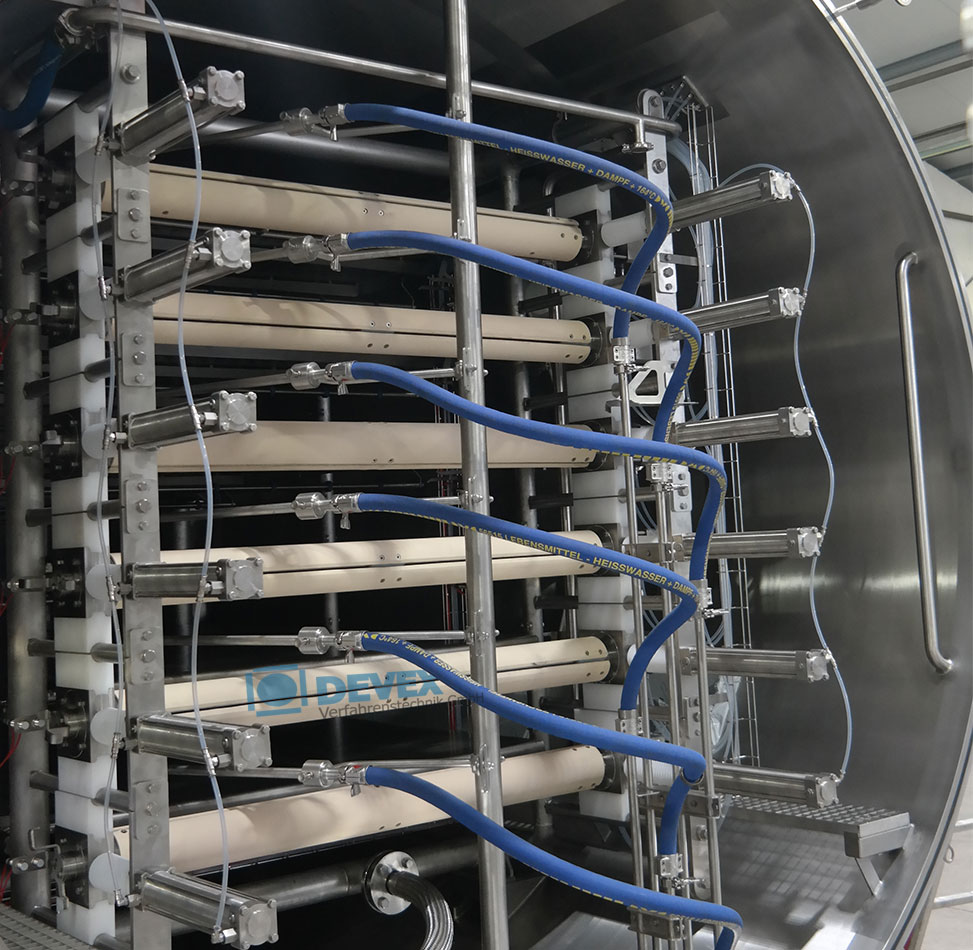
Continuous vacuum belt dryer
For gently drying liquid concentrates into granulates or powders, a vacuum drying solution is t...
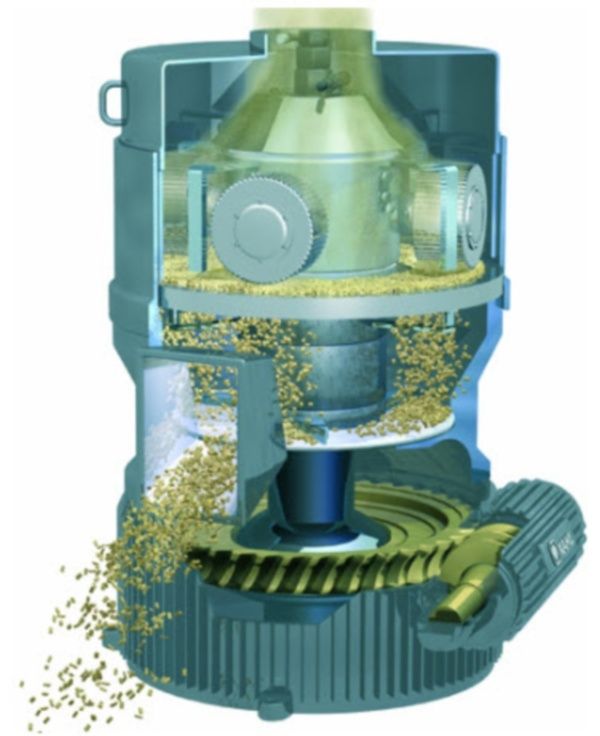
Pelleting press for biomass
Utilization of biomass for energy and other applications requires consistent and reliable compac...
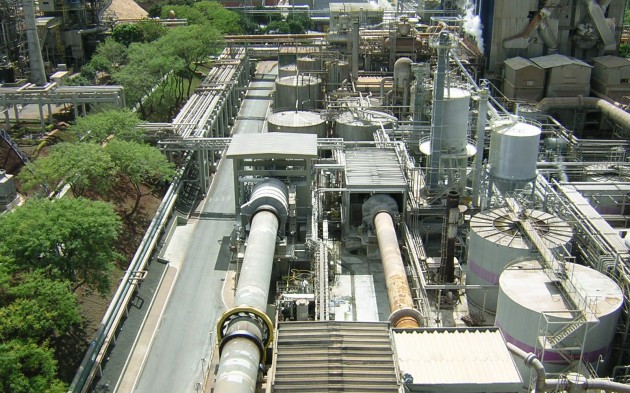
Conveyors for causticizing and lime kilns
Modern lime processing occurs on an extremely large scale and process interrupti...

Pneumatic conveying for industrial biomass boilers
Modern boiler plants have a wide variety of conveying needs. While tr...
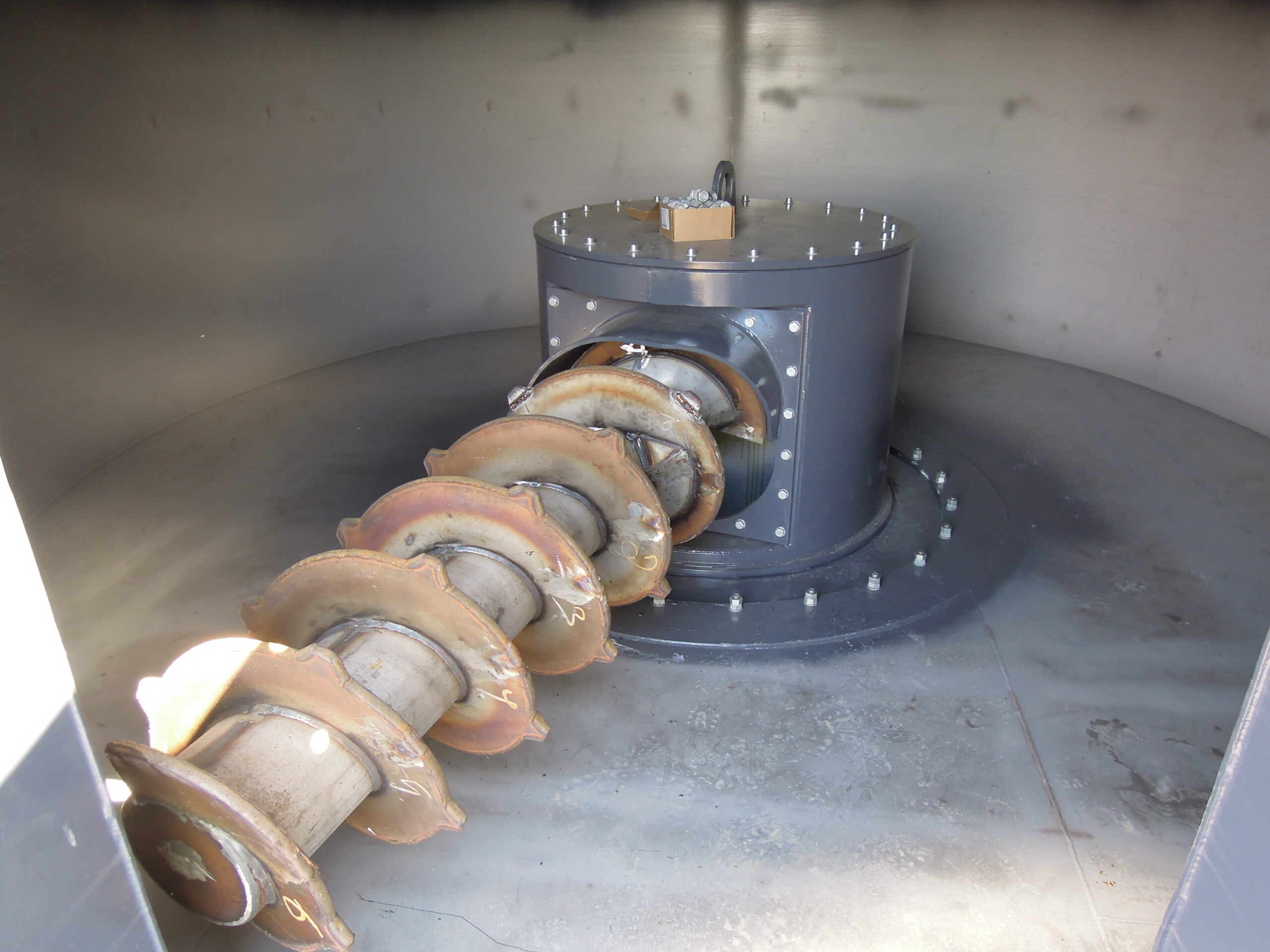
Solid biomass boiler feeding systems
Energy conversion from biomass requires efficient boiler operation which is largely in...
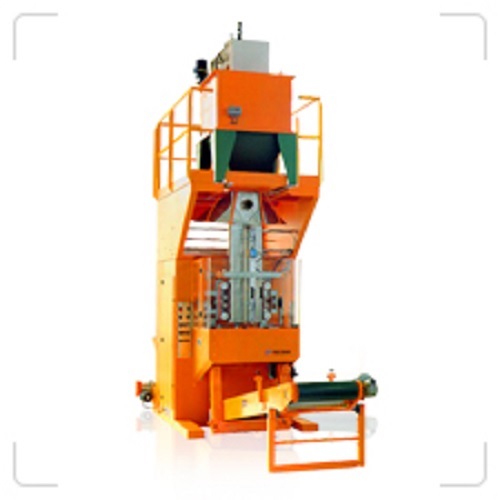
Vertical form, fill and seal machine for bags from 5 to 50 kg
To securely create, dose and pack larger quantities of mat...
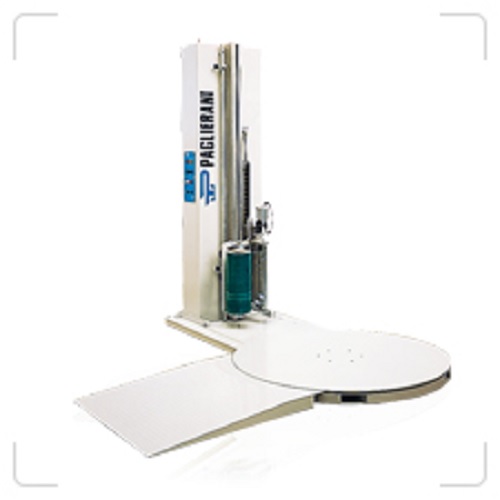
Semi-automatic stretch wrapping machine
At lower speeds, some level of automation is required to provide a cost-effective m...
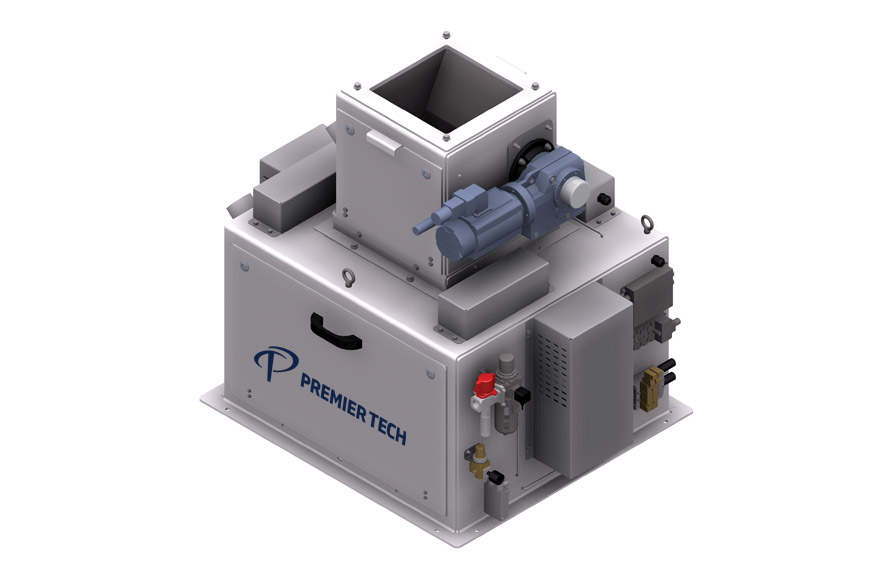
Electronic net weigher for high-capacity baggers
Electronic net weigher raises the industry’s standards to a higher level ...
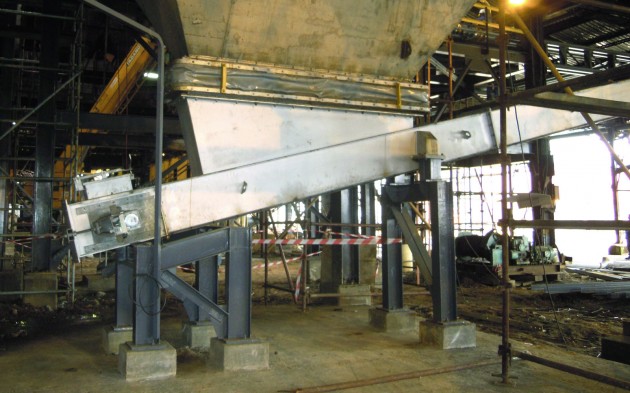
Dust and concentrate handling in smelting plants
Modern metal smelting operations involve extremely harsh conditions that ...
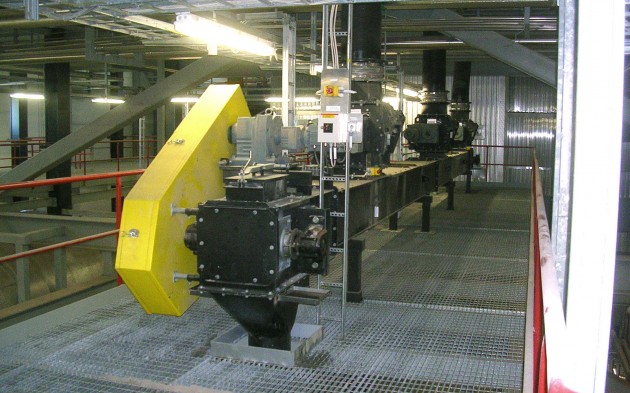
Conveyors for recovery boilers
Recovery boilers recapture energy otherwise wasted in organic byproducts of industrial proces...
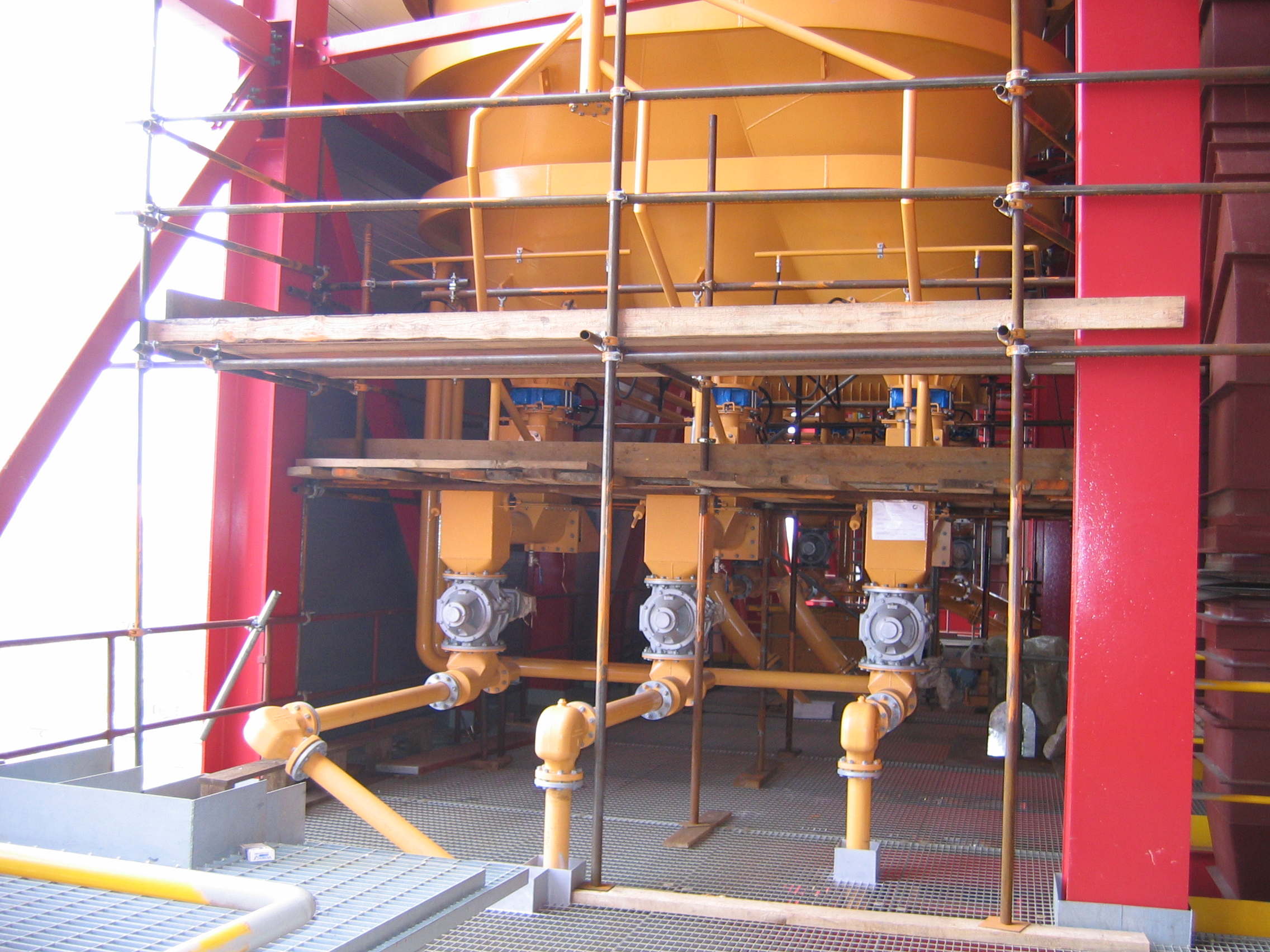
Additive and bed material feeding systems
Modern fluidized bed combustion furnaces require consistent and reliable deliver...
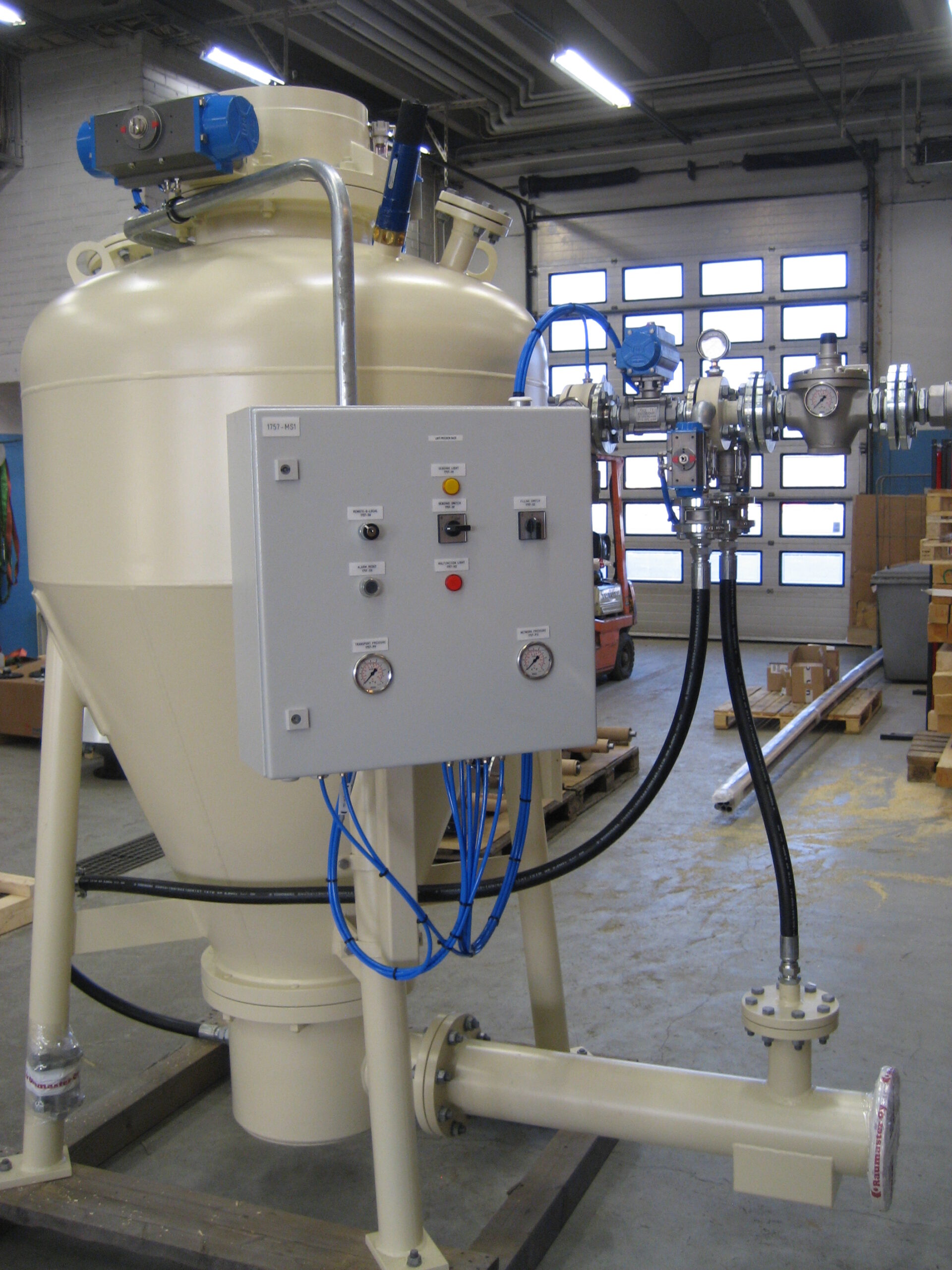
Ash handling systems for industrial biomass boilers
The increasing use of solid fuels including biomass for energy conver...
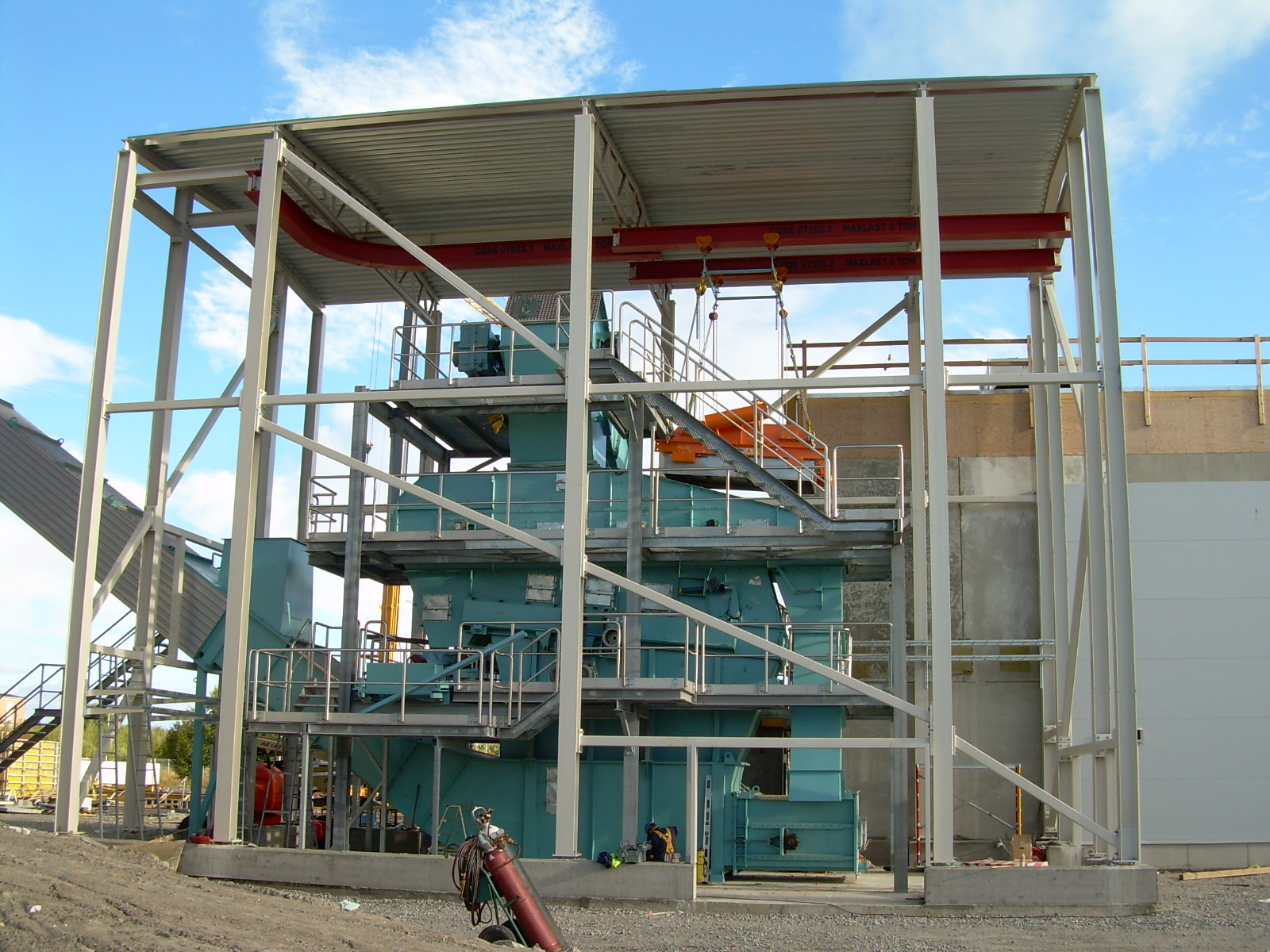
Solid biomass screening and crushing equipment
Biomass fuels come in many forms and often include impurities that can dama...
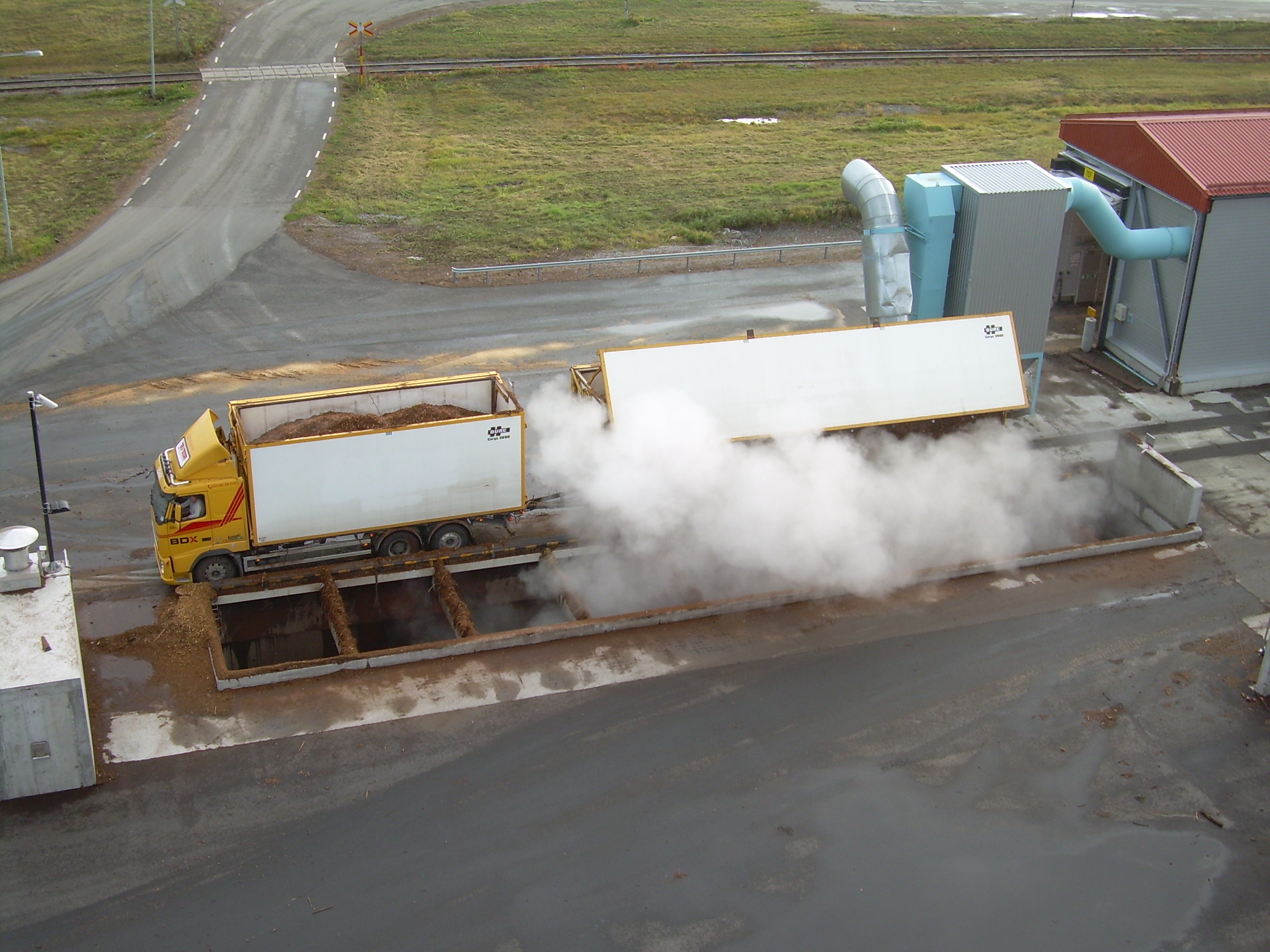
Solid biomass receiving systems
Biomass fuels come in many forms and are often handled in very large quantities. Shipment m...
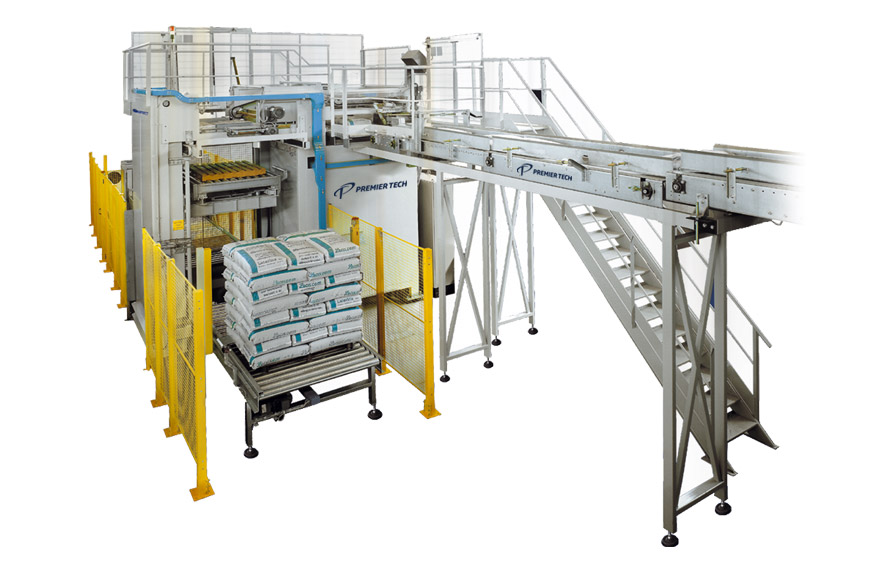
High-level layer palletizer
A palletizer that meets the middle and high-level needs of modern bagging lines. Quite suitable ...
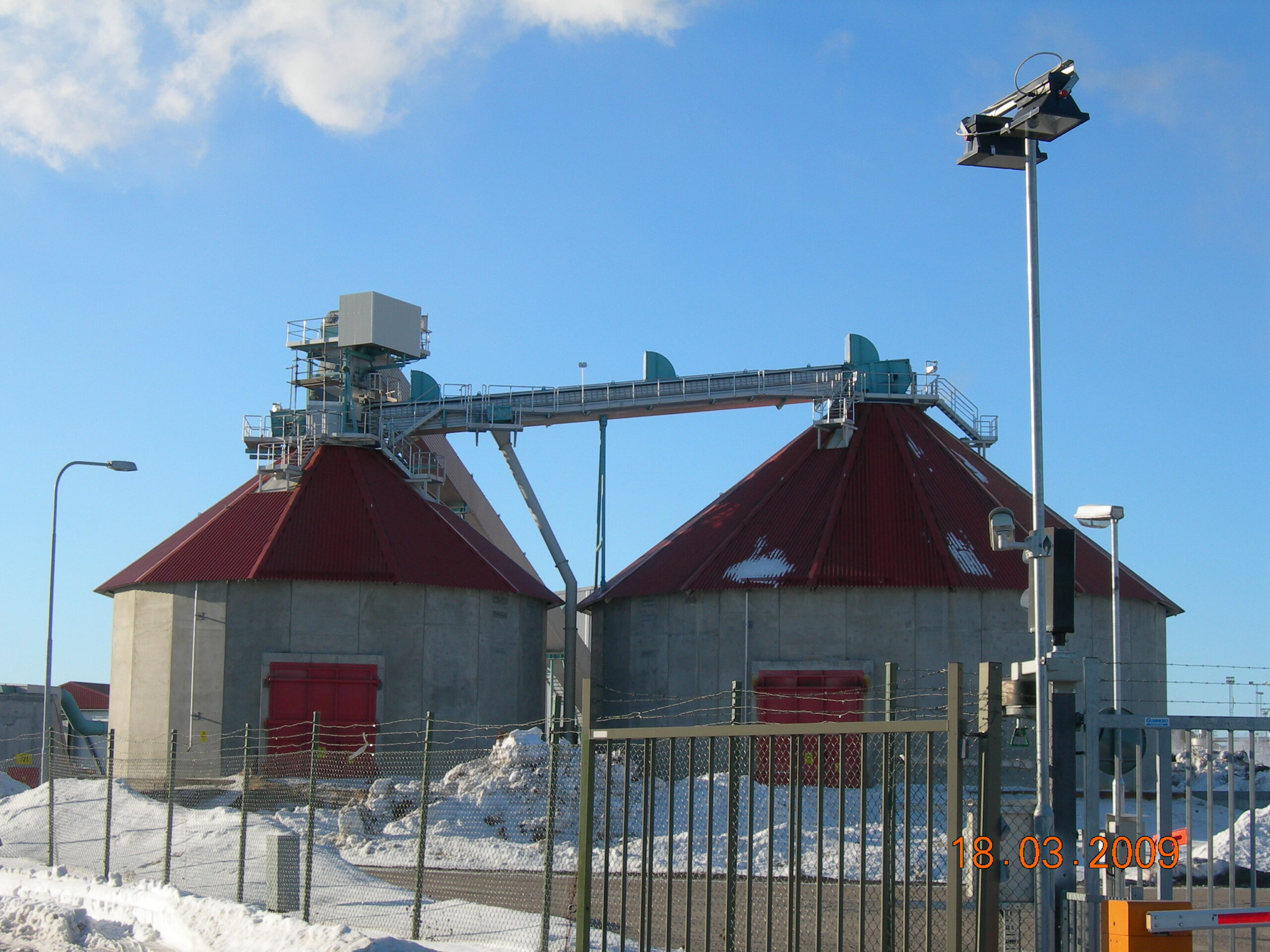
Solid biomass storage and reclaiming equipment
Biomass fuels must often be stored for additional preprocessing or prior to...

Manual bagger with gross weigher
This is a manual bagging set with an electronic gross weighing system to meet international...

Belt dryer for wood
Processing of wood and biomass into pellets or other volume reduced products requires careful and consist...