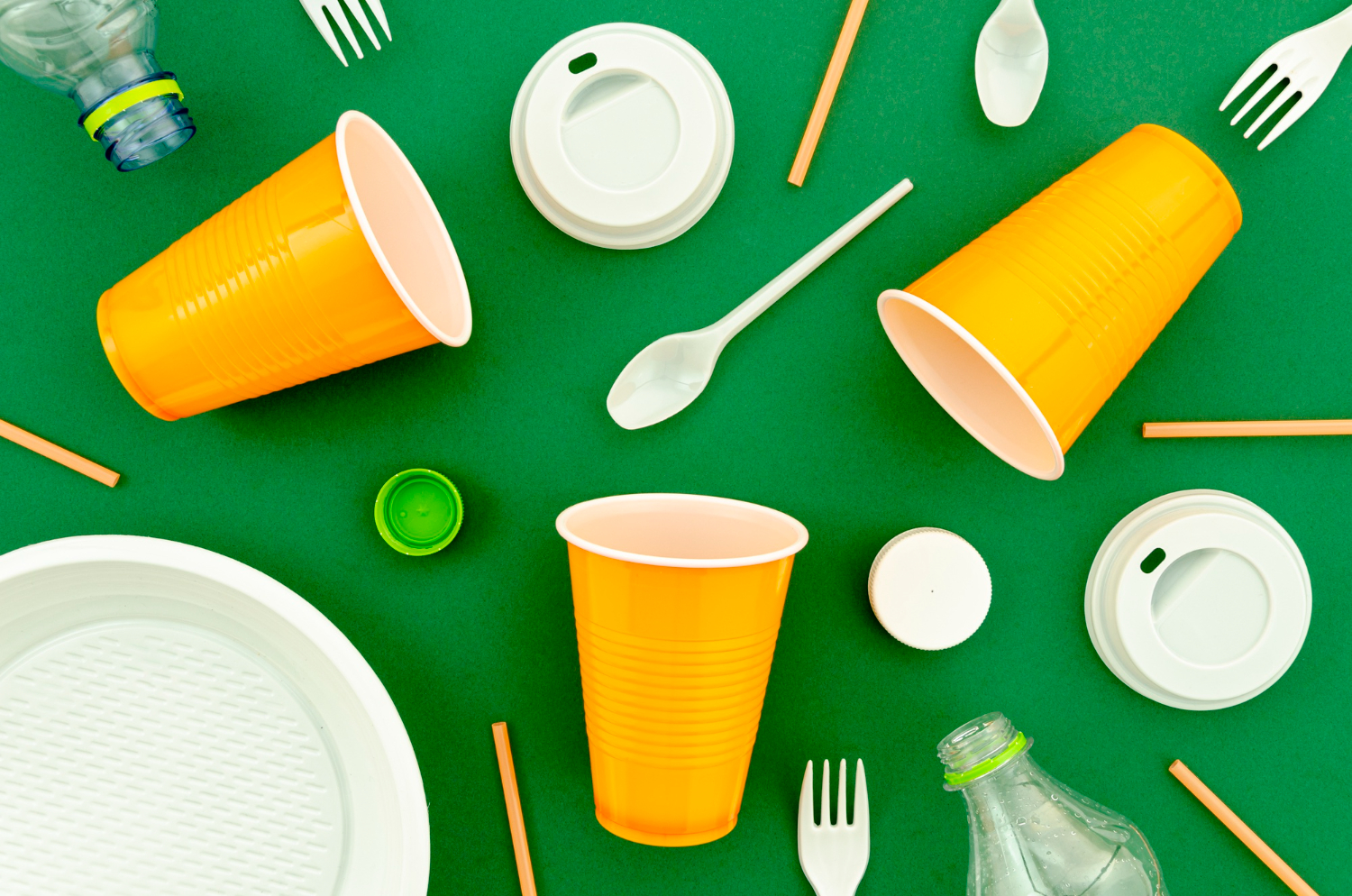
Making Recycled Plastic
Find innovative production technology for making recycled plastic and connect directly with world-leading specialists
The ubiquitous plastic shopping bag was first designed as a reusable carrier. Its inventor, Sten Gustaf Thulin, will have been appalled to see his creation turn into a single-use object. But this disposable tendency is common to all plastic materials, from screw taps to milk carton lining. With plastic recycling equipment, however, plastic waste can be reprocessed and given a second lease of life.
Stories about recycled plastic
Select your recycled plastic process
Tell us about your production challenge
Treat polyolefins with heat to depolymerize the plastic material
Plastics are synthetic organic polymers than be broken into the basic monomers and reconstructed into new material. The most widespread type of plastics, polyolefins, can be chemically depolymerized at high temperatures.
Heat the polymers to 380-480°C in a fluid bed heater until the chains start cracking and turn into gas. The monomer vapor is collected in a condenser and returned to liquid. Use catalysts like kaolin, quartz, or zeolite to improve heat transfer and decrease the temperature required for cracking.
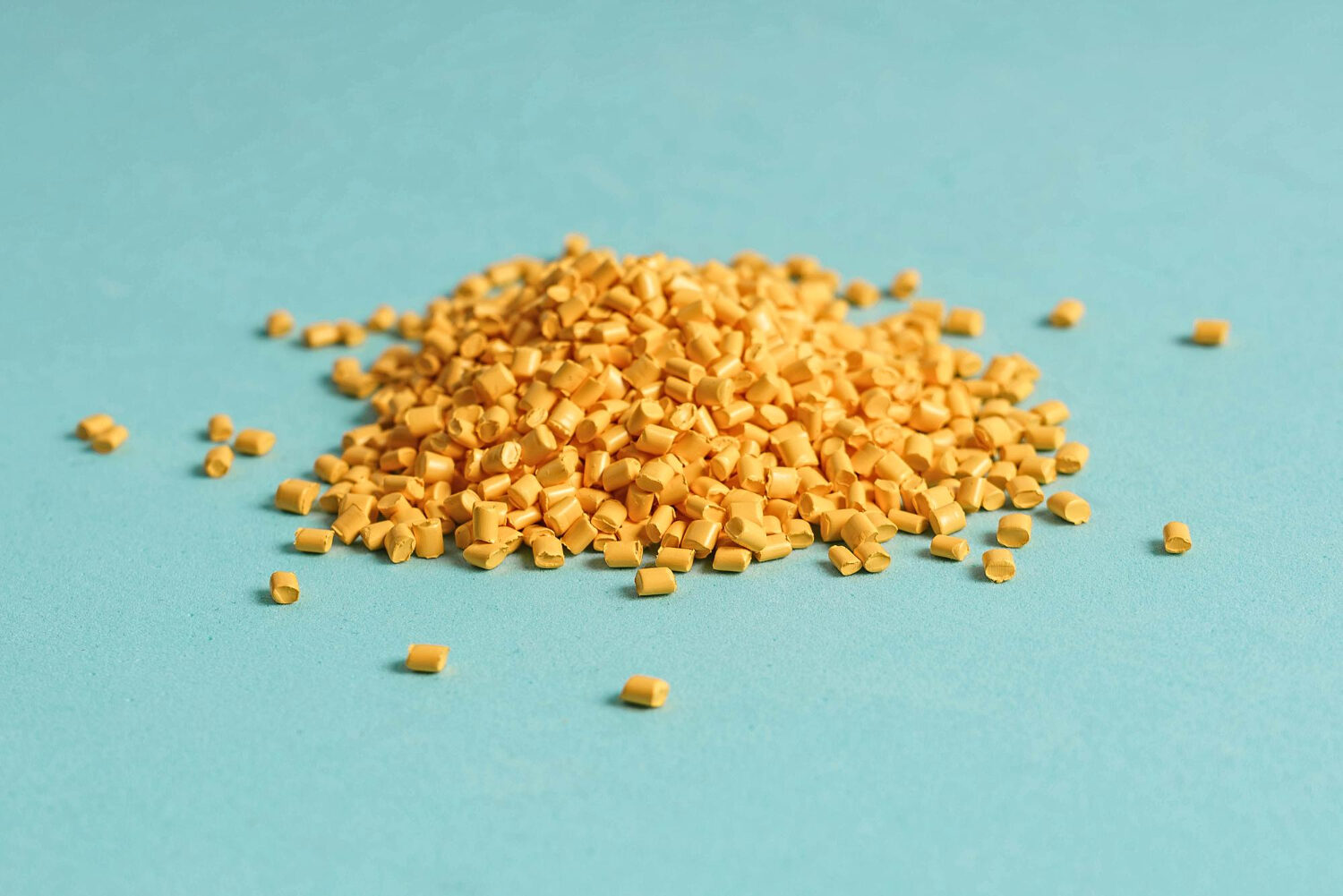
Mix additives in the recycling system to produce plastic pellets
The clean monomers are ready to be refabricated into new plastic material. Melt the material through an extruder to produce plastic pellets.
Depending on the intended use of the end product, the raw material feed can be compounded with other additives such as fire-retardants, impact-absorbers, or colorings. Pellets from recycled plastic are a suitable base to manufacture masterbatches for the industry.
Use a twin-screw extruder for tighter control over the pelletizing process
Polymer modelling of plastics follows a similar sequence whether it is manufactured through a single-screw or twin-screw extruder. However, a co-rotating twin screw extruder allows greater control over the plasticating process.
As the feed material travels along the screw, friction forces and heat transfer from the barrel begin melting it. This process accumulates in a melt pool nearer to the inner barrel, where the polymer is subjected to increasing pressure and flows out through the die.
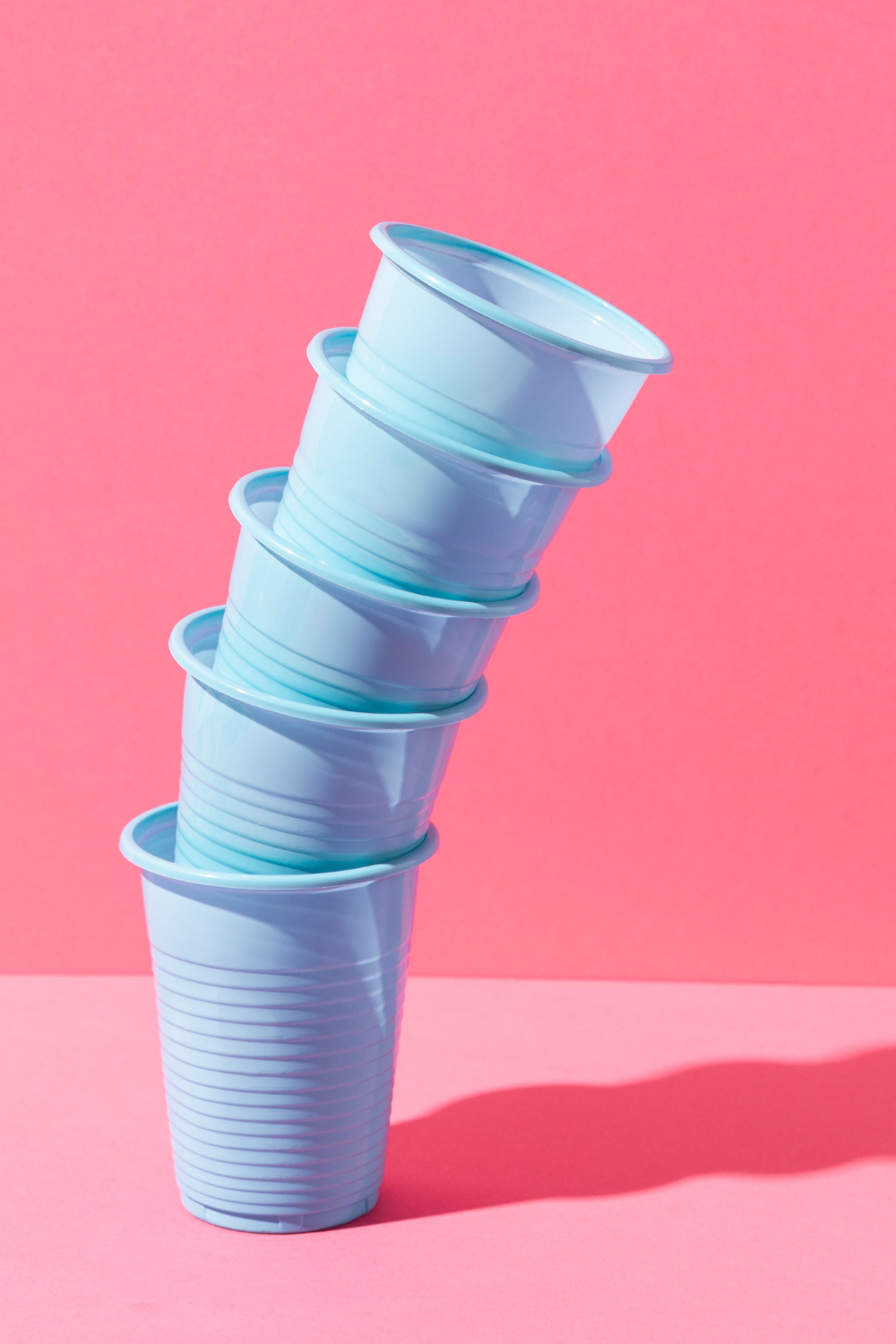
Separate the feed with specialized plastic waste processing equipment
Plastic types, for example HDPE, PVC and PET, all behave in different ways when subjected to mechanical and chemical processing. Separate the primary material into the right streams to prevent contamination down the plastic recycling production line.
A sink-float separator classifies the pieces by density. High-density plastic polymers sink when conveyed to a water-filled tank, whereas low-density pieces float. An alternative method is an optic scanner that sorts plastic pieces according to their capacity to absorb light.
Grind the plastic to improve the recycling process
Resize the feed material into uniform dimensions to prepare it for processing. Grind the plastic into flakes or filaments by passing the pieces through a shredder.
Besides making the stream more workable, reducing the size of the stream makes it easier to pick out impurities during the washing line stage. Contaminants such as metals or adhesive chemicals could compromise the quality of the final product. But resizing the feed material facilitates the segregation of valuable plastic from undesired particles.
Processing steps involved in recycled plastic making
Which recycled plastic technology do you need?
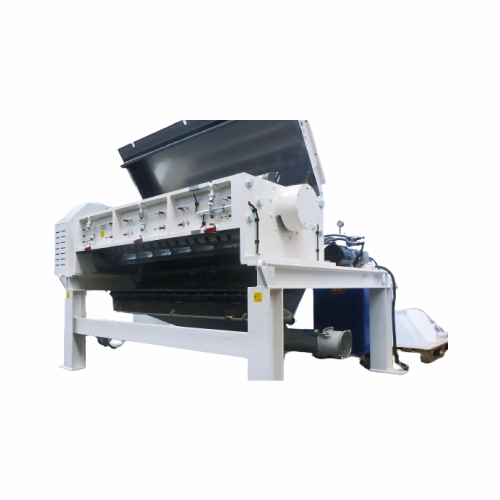
Industrial granulators for plastic recycling
Streamline your recycling operations with a solution that not only reduces en...
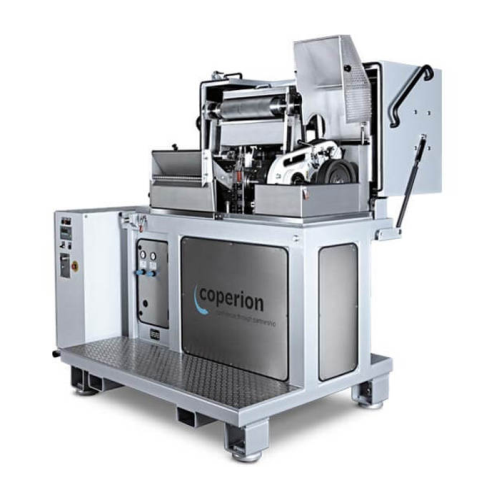
Industrial strand pelletizer for polymer processing
Optimize polymer pellet production with precision engineering, ensuri...

Filtration compounder for polymer recycling
Streamline your recycling process by integrating filtration and compounding in...
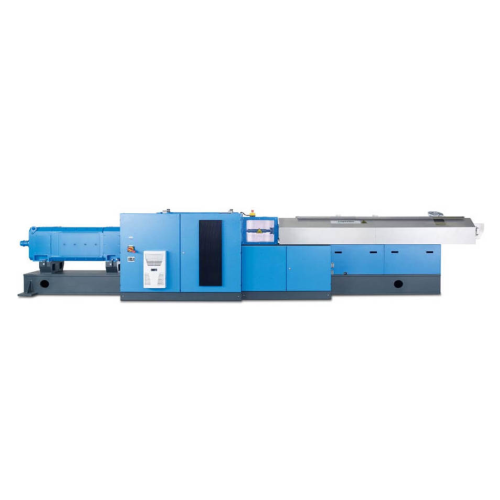
High throughput twin screw extruder for low bulk density products
When handling low bulk density materials, achieving m...

Optical sorter for coffee, grains, nuts, and plastic flakes
Ensure precise defect detection and foreign material removal...
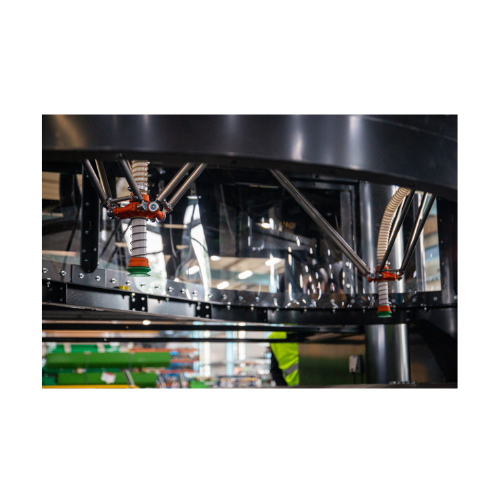
Automated sorting robot for material recovery facilities
Enhance your material recovery operations with AI-driven precisi...
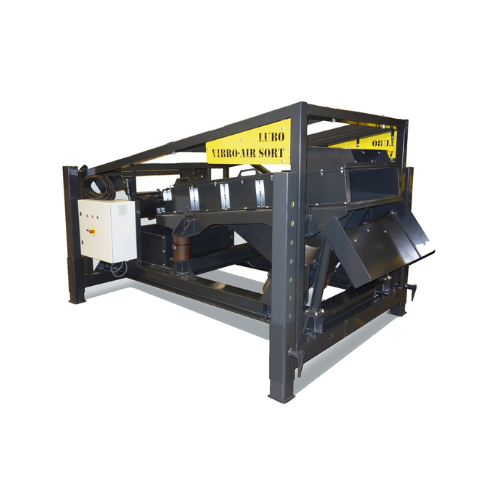
Density separator for recycling applications
Efficiently separate light and heavy materials with minimal density differenc...
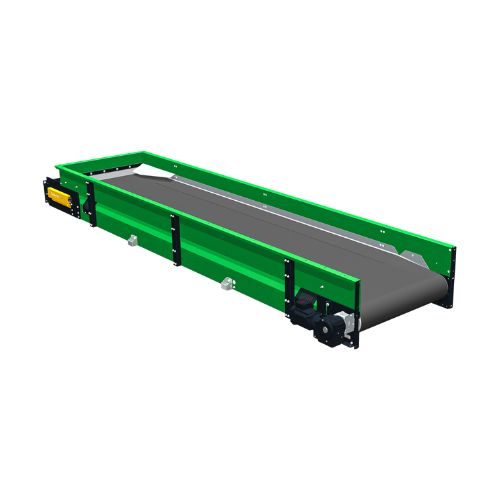
Sliding belt conveyor for sorting light, voluminous materials
Efficiently sort and convey light, voluminous materials wi...
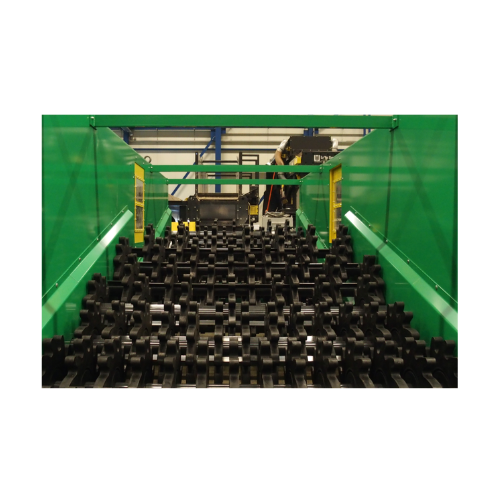
Occ screen for separating large cardboard
Efficiently separate large cardboard from mixed waste streams to streamline your...
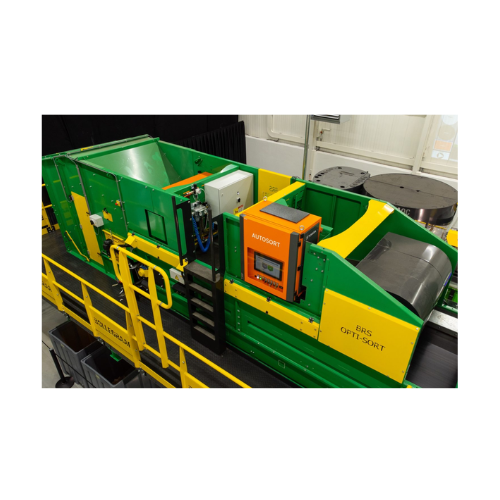
Integrated optical sorting unit for lightweight materials
Optimize your processing of lightweight materials by achieving...
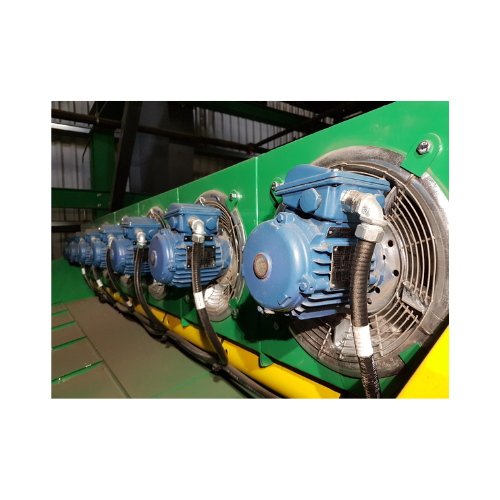
Optimize optical sorter performance
Enhance your optical sorting line capacity and material purity with advanced air displa...
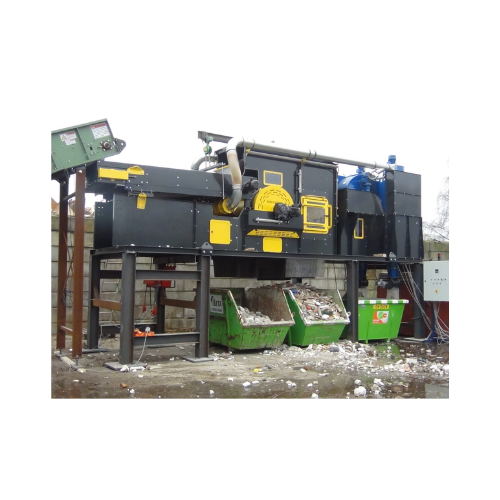
Air drum separator for heavy and light material separation
Effectively separate heavy and light materials with minimal e...
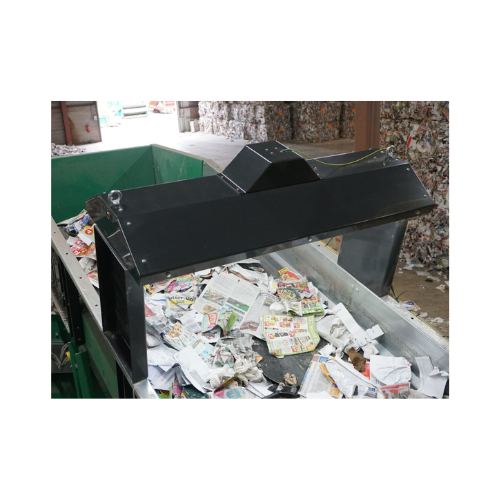
Optical analytics tool for material flow and composition
Optimize your waste management with real-time data analysis and ...
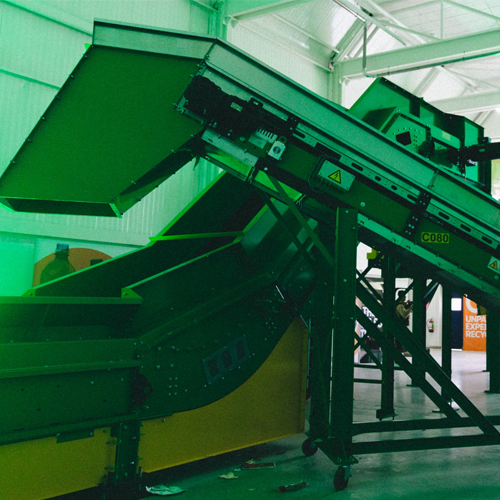
Belt feeder for waste sorting applications
Efficiently handle diverse waste streams and optimize resource recovery with a ...

Chain belt conveyor for waste paper and industrial waste
Optimize your waste processing with a robust chain belt conveyor...
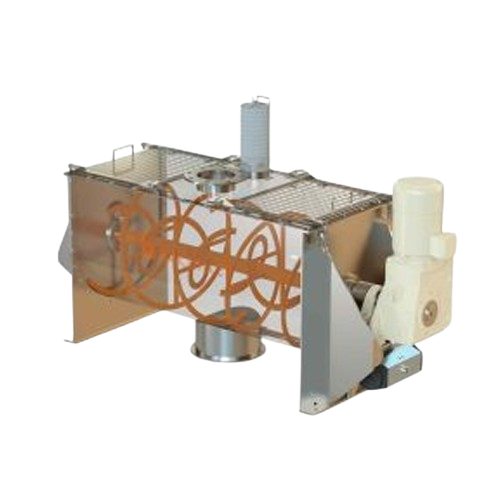
Horizontal ribbon blender for solids and powders
Efficiently achieve uniform blending of bulk solids and powders, ensuring...
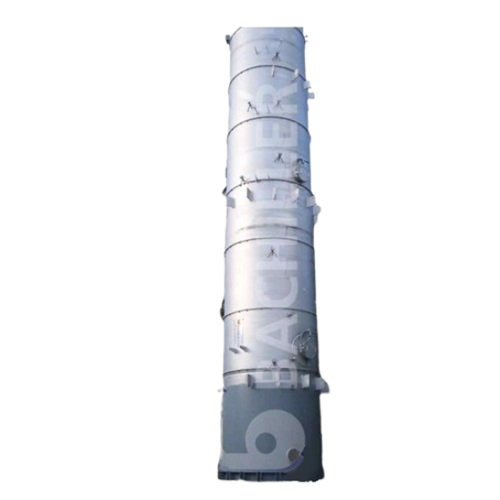
Industrial columns and towers for chemical processing
Optimize your chemical production with robust columns and towers, d...
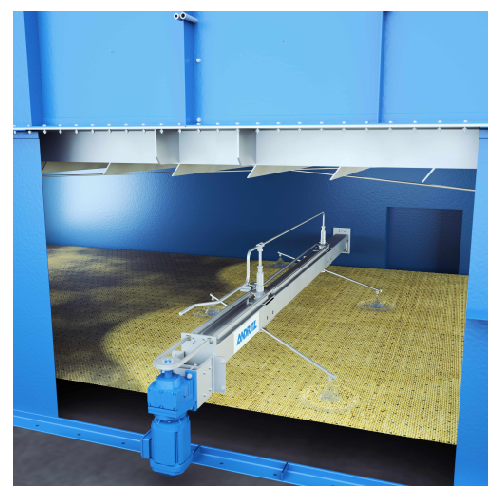
Belt dryer cleaning system
Maximize drying efficiency and product quality with an advanced belt-washing system designed to e...
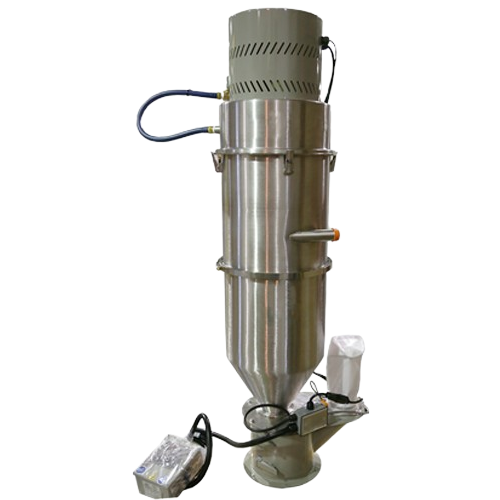
Powder hopper loaders for free-flowing materials
Efficiently transport free-flowing powders, including PVC and polyethylen...
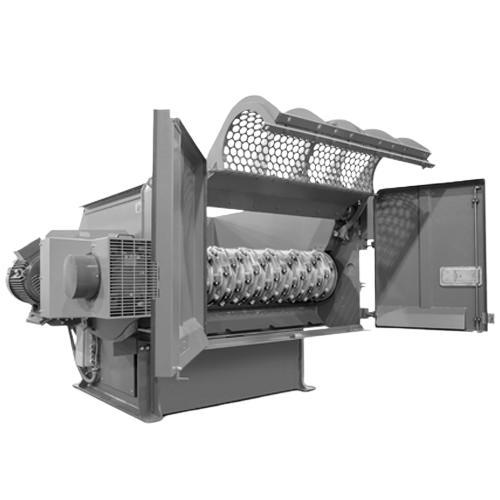
Industrial shredder for recycling and waste management
Efficiently transform challenging waste streams into valuable raw ...
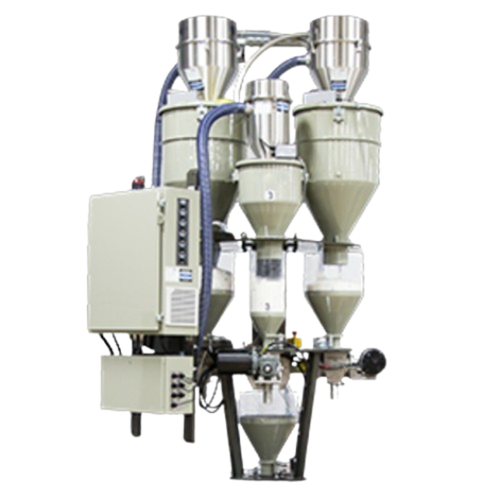
Continuous loss-in-weight blender for extrusion applications
Ensure precise ingredient ratios for extrusion processes wi...
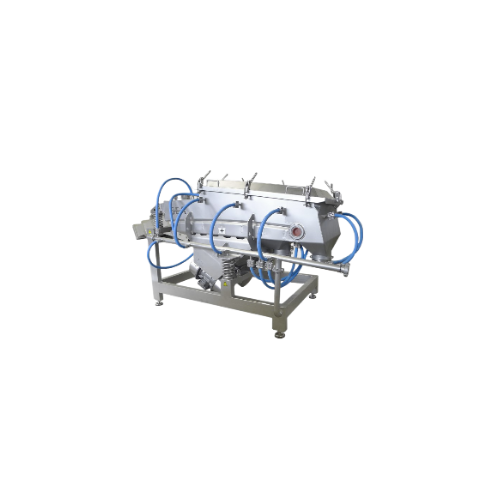
Industrial sifters for beverage processing
Optimize your beverage production with precisely engineered sifters that ensure...
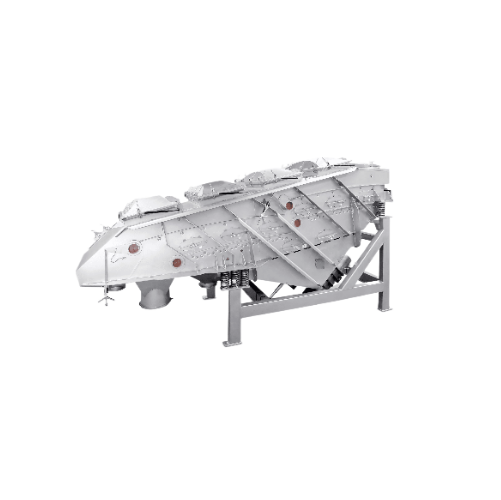
Vibrating sifter for chemical applications
Achieve precise particle separation with this vibrating sifter, ensuring optima...
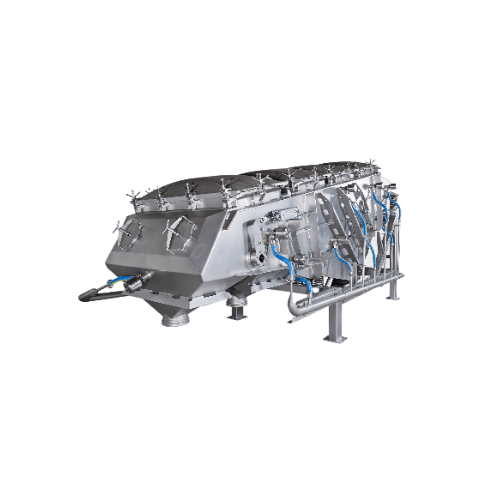
Industrial powder sifter with sanitary compliance
Optimize your powder processing with this versatile sifter, ensuring pr...
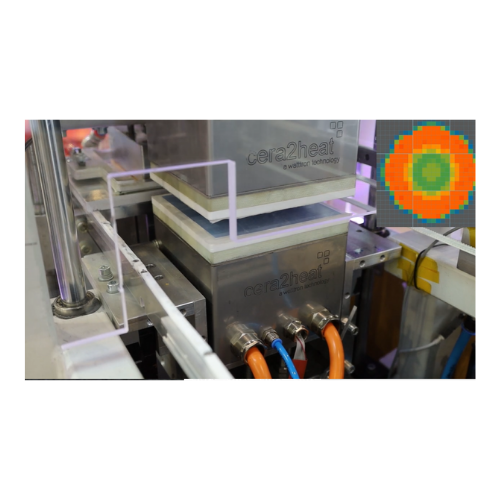
Heating system for sustainable moulded pulp packaging
Maximize material efficiency and sustainability by ensuring consist...
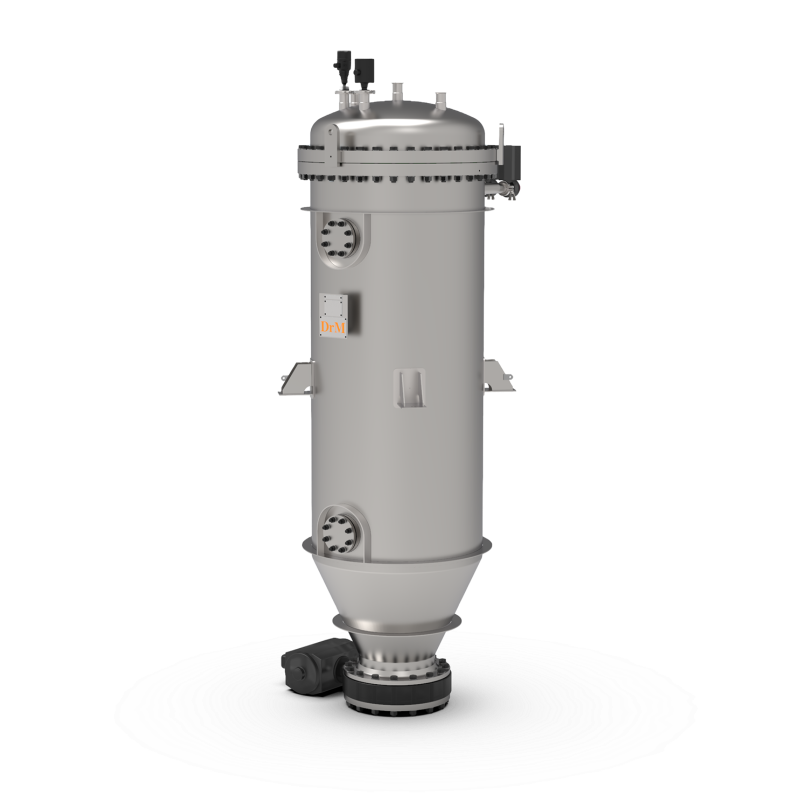
Self-cleaning candle filtration system
Separating solids from liquids by filtration requires frequent cleaning or replaceme...
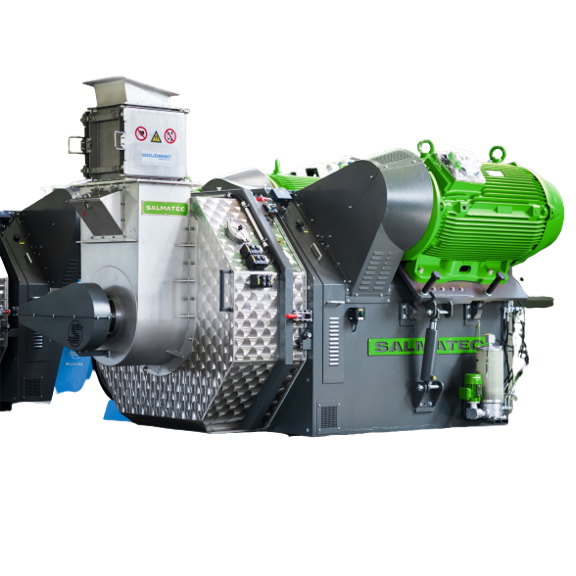
Complete pellet line
Large industries are shifting towards more environment-friendly technology, such as recycling wastes and...
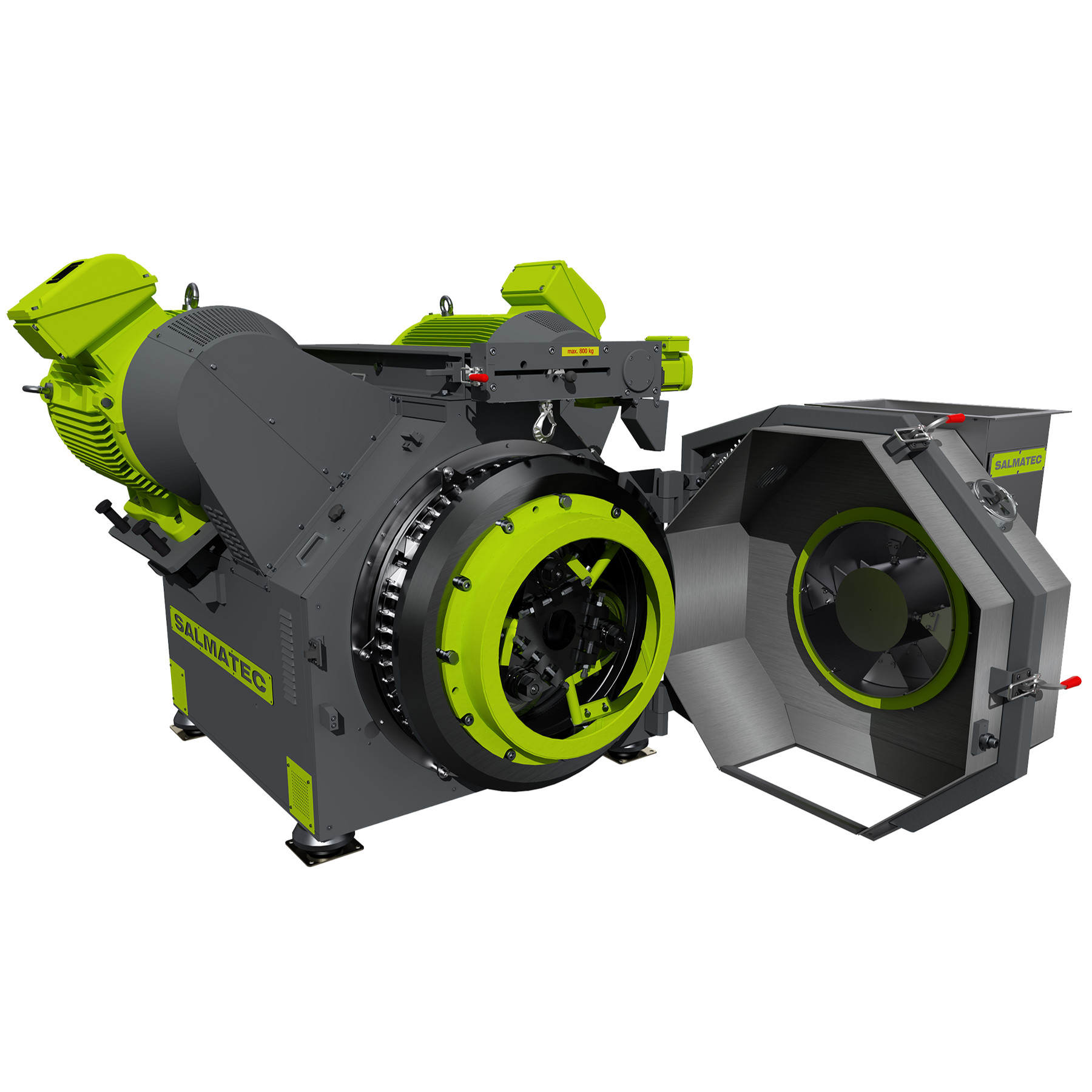
Industrial pellet mill
At the industrial level, the application areas of pellets range widely in fields such as feeds, biomas...
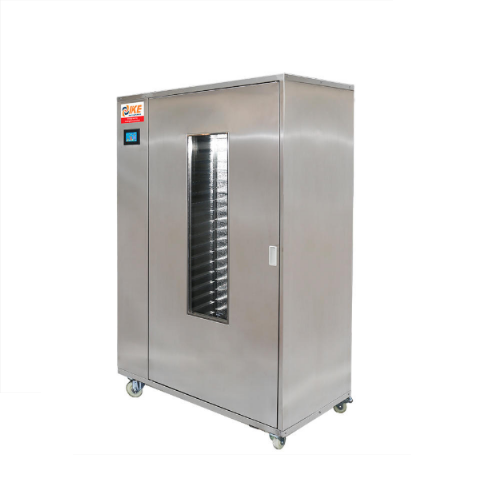
Industrial drying cabinet
The production of high-quality biltong and similar dried meat products can pose problems with main...
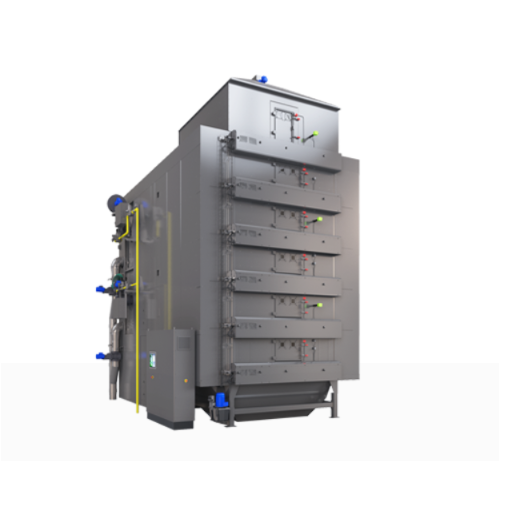
Recirculating batch dryer
Drying can be the most energy and time-consuming process in the food industry. This can have an ef...
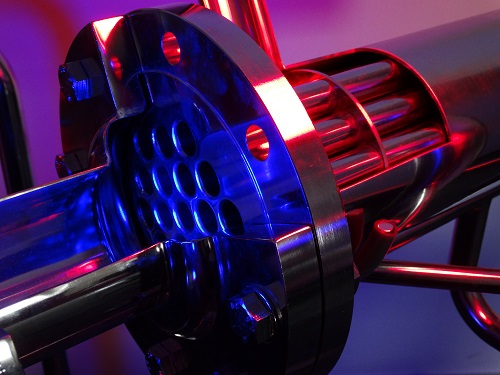
Shell and tube heat exchanger
Heating, cooling and tempering are important processes in the production of many products acro...
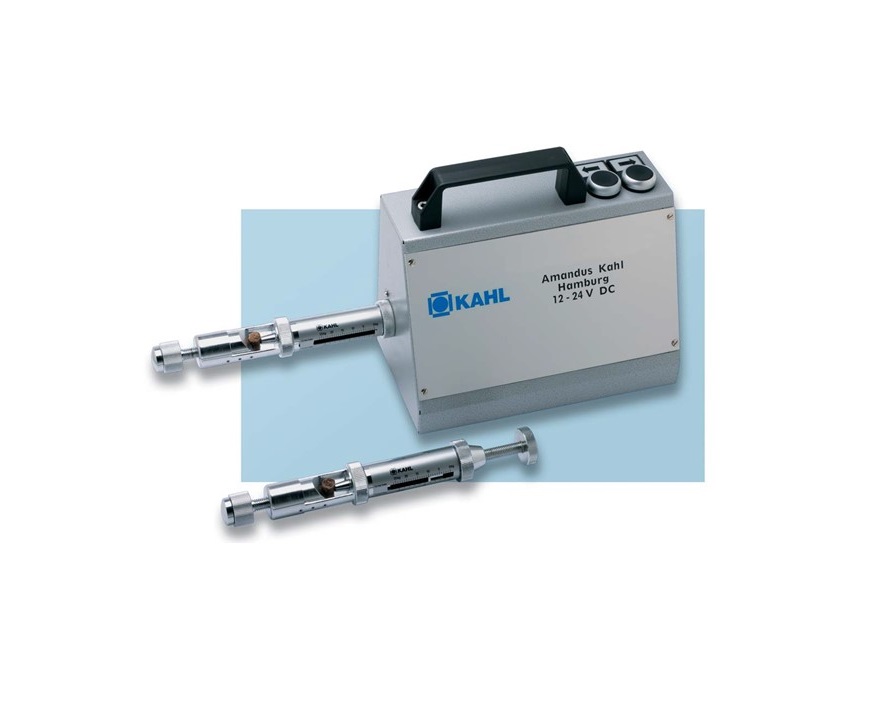
Pellet hardness tester
Control the quality of your pelletizing processes using a pellet hardness tester. Pellet hardness is o...
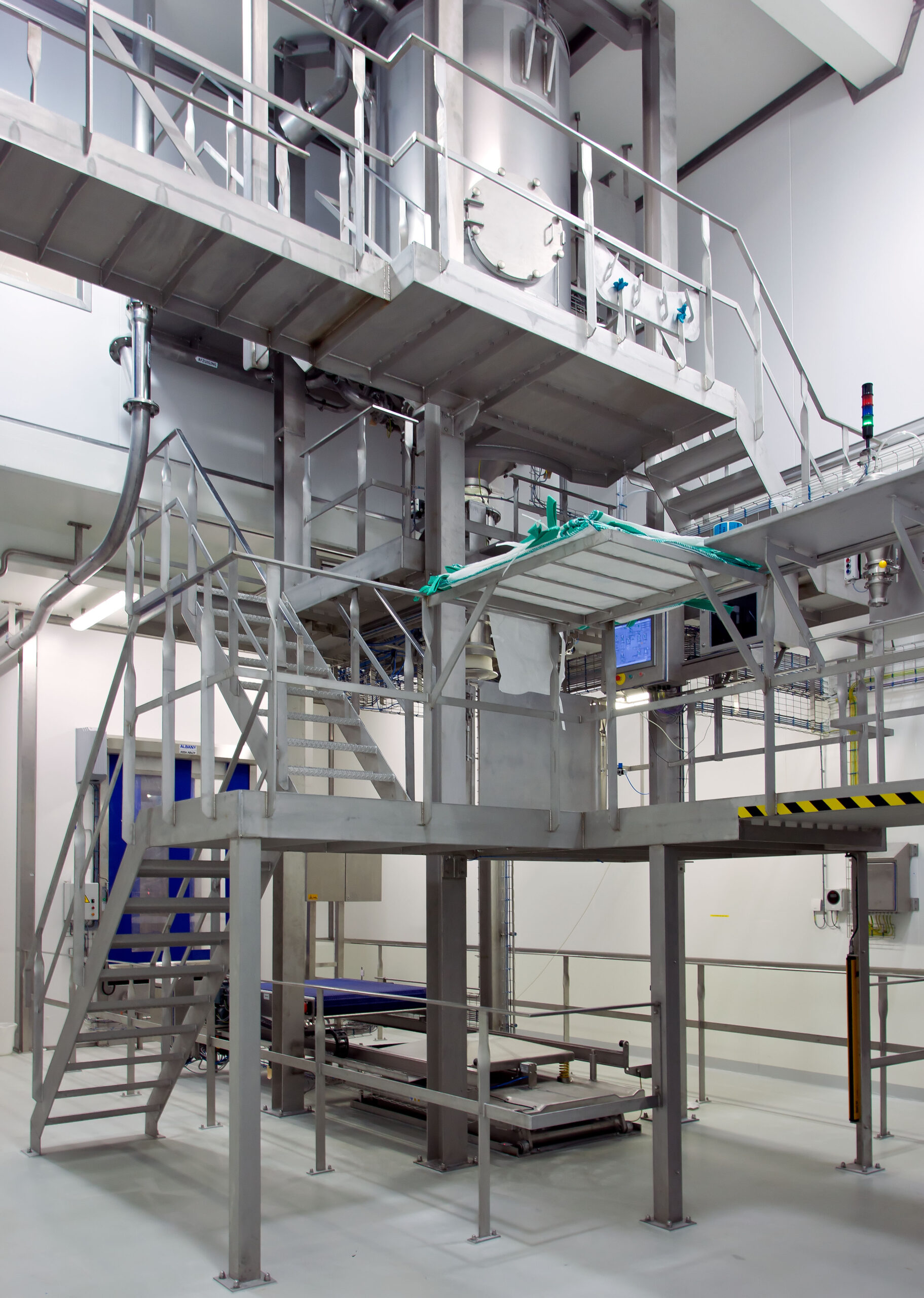
Hygienic FIBC handling line
There are many considerations when handling FIBC’s (Flexible Intermediate Bulk Containers)...
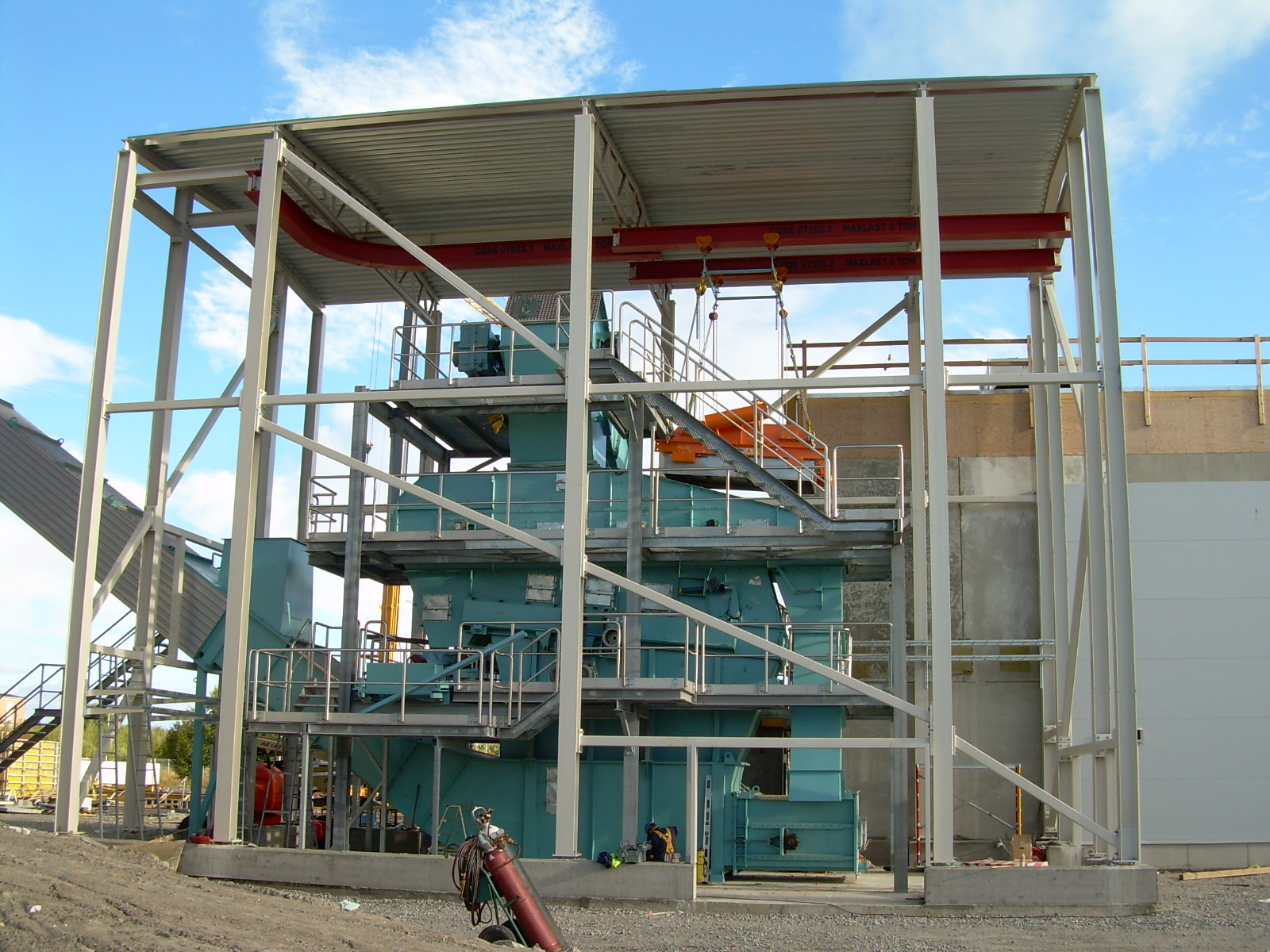
Solid biomass screening and crushing equipment
Biomass fuels come in many forms and often include impurities that can dama...
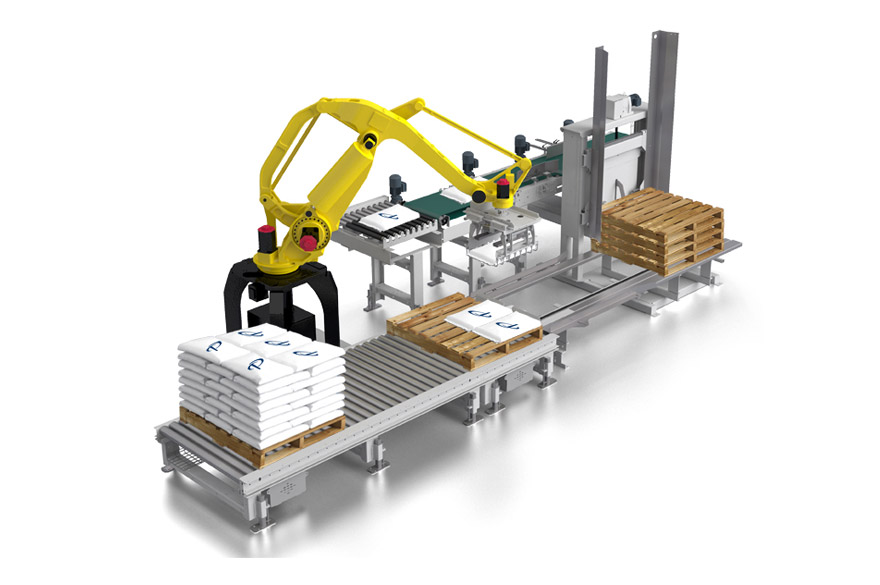
Robot palletizer
Palletize up to 1,800 large industrial bags per hour at a multi-pick-up configuration.
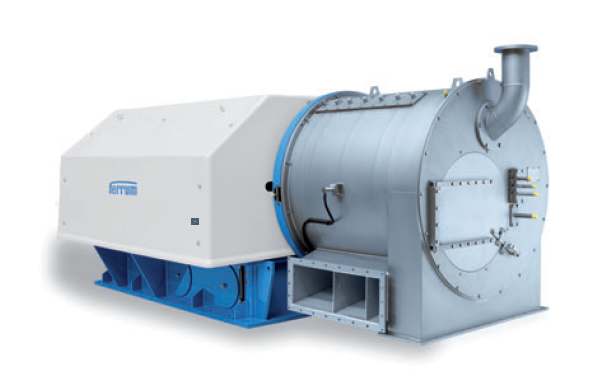
Pusher centrifuge
Pusher centrifuges are continuously operating filter centrifuges and can have several basket stages dependi...
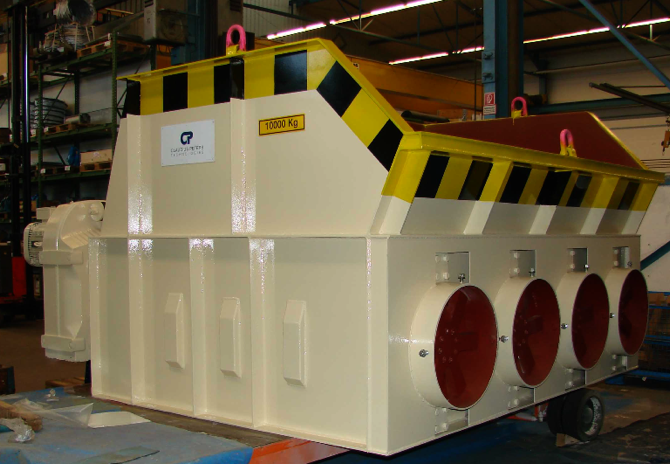
Reclaim crusher
Waste products and rejected materials are inevitably generated from any gypsum products manufacturing process....
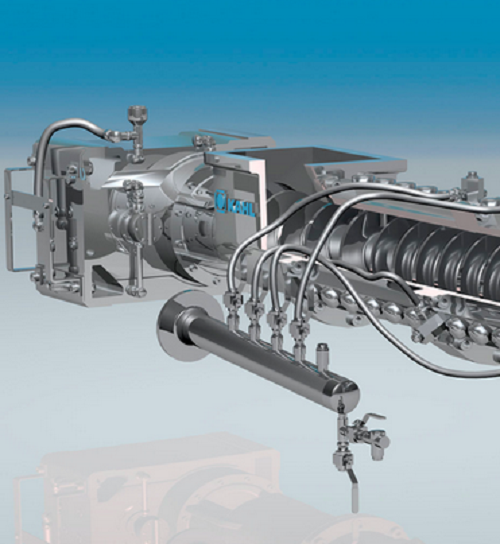
Extruder with annular gap expander
Products can be extruded with various shapes and characteristics by controlling the nozz...
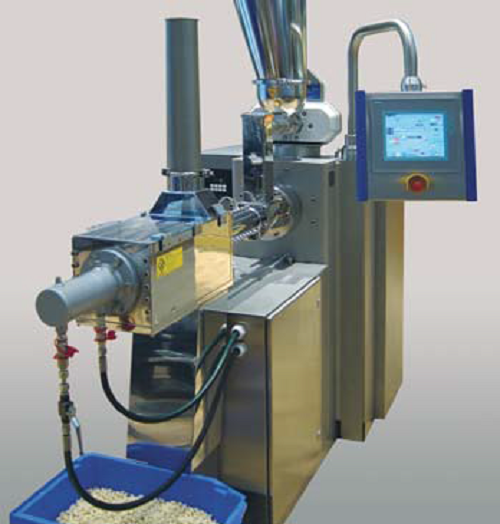
Laboratory extruder
Products can be extruded with a variety of shapes and characteristics by controlling the nozzle geometry ...
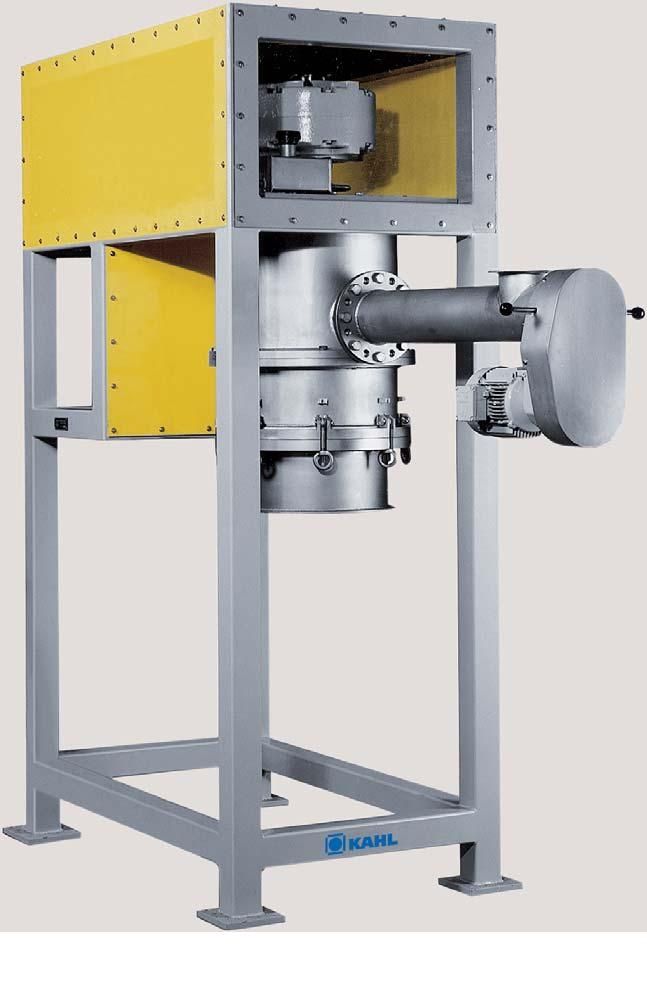
Pelleting press with overhead drive
Production of certain pelletized products requires working with output products of a pa...