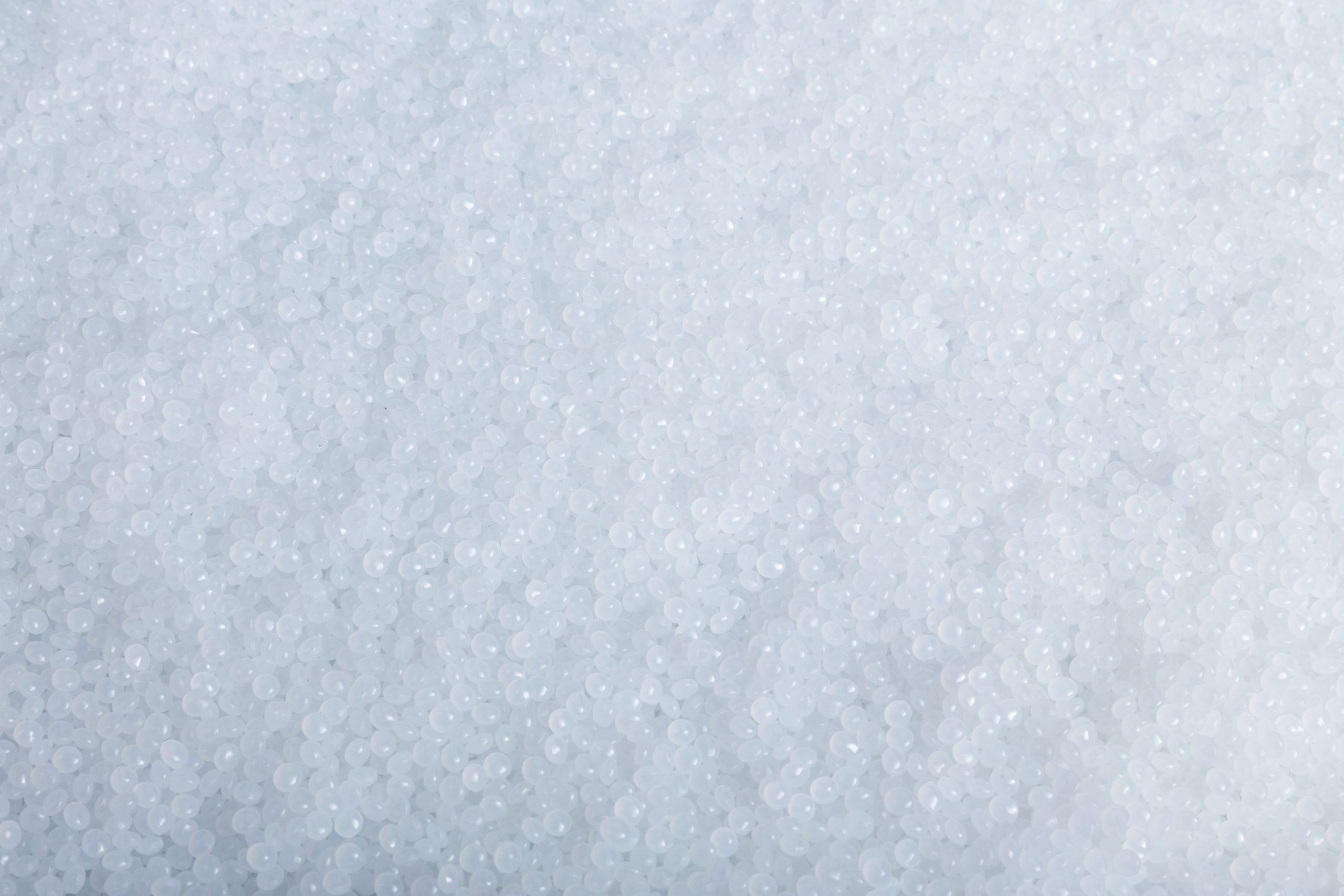
Making Polymers
Find innovative production technology for making polymers and connect directly with world-leading specialists
All plastics are polymers, but not all polymers are plastics. Polymer production is a multi-step process that transforms raw materials into products that we use in our day-to-day life with the help of polymer process equipment such as extruders, calenders and injection molding machines.
Select your polymers process
Tell us about your production challenge
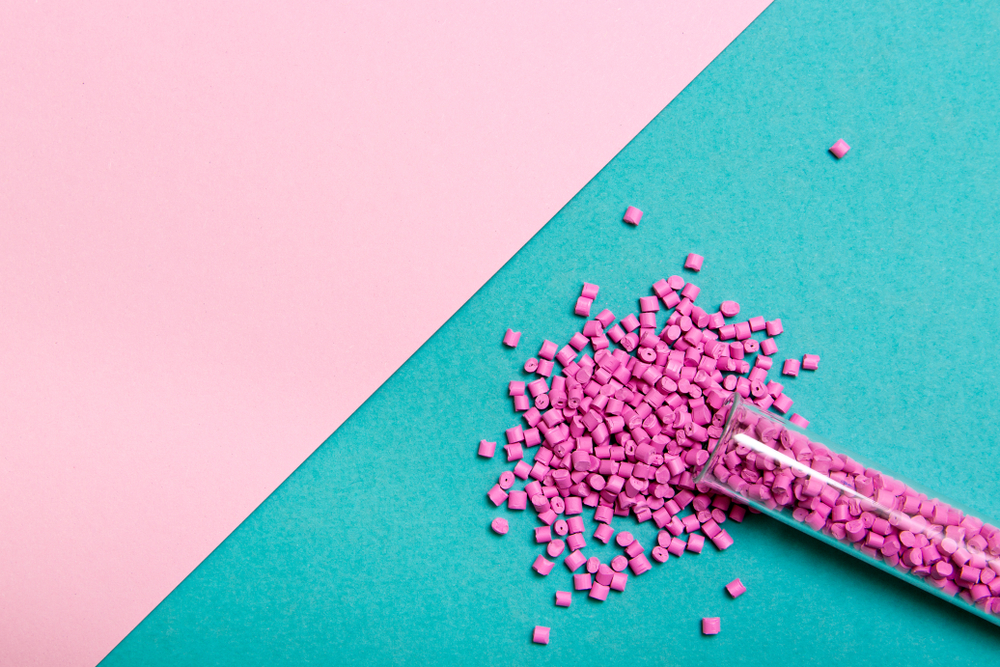
What are polymers?
Polymers are natural or synthetic substances composed of macromolecules that are multiples of simpler chemical units called monomers. Natural polymers are found in living organisms, including proteins, cellulose, nucleic acids and starches. On the other hand, synthetic polymers are derived from petroleum oil, with examples of nylon, polyester, and Teflon.
Addition polymerization vs condensation polymerization
There are two types of polymerization: addition and condensation polymerization. In the former, a polymer is formed simply by linking monomers together without co-generating by-products. The addition polymerization has three steps: initiation, chain propagation and termination of the chain. During addition polymerization, the monomers rearrange and form a new structure without losing atoms or molecules. It results in homo-chain polymers such as polyethylene, polystyrene and methacrylates.
During the condensation polymerization, monomers are joined by releasing other small molecules as a byproduct, for example, water or methanol, resulting in hetero-chain polymers. For instance, cellulose, starch, nylon and polyester are the results of this process. These polymers tend to be more biodegradable due to weaker bonds.
Manufacturing processes and polymer process equipment
Extrusion, calendaring…
Transforming polymers into practical products starts by adding additives according to the desired specifications. Polymeric materials in the form of powder, granules or melts are transformed into end products by extrusion. It is a process in which plasticized material is forced through an orifice and cooled once it achieves the favored shape.
Polymer process equipment includes a variety of extruders, such as ram extruders for short product lengths, gear pump extruders for pre-plasticized and low-viscosity materials and a single screw extruder which produces the majority of extruded products, especially those with a constant profile such as window frames.
Another widely used method is calendaring – processing molten polymers, mostly rubber and thermoplastic, by squeezing them between a pair of heated counter-rotating rolls in a machine called calendar, which can easily be set up to produce preferred thickness and size. This process is used to manufacture floor tiles, shower curtains, signs, and displays.
…and injection molding
Injection molding is the leading process for producing complex shapes, for example, toys, some musical instruments, or automotive parts. The process in the injection molding machine consists of four phases: plasticization, which transforms thermoplastic powder or granules into a homogeneous melt state, injection of melt from the plasticization unit to all parts of the mold cavity, setting of the melt in the mold cavity and ejection of the finished product from the mold.
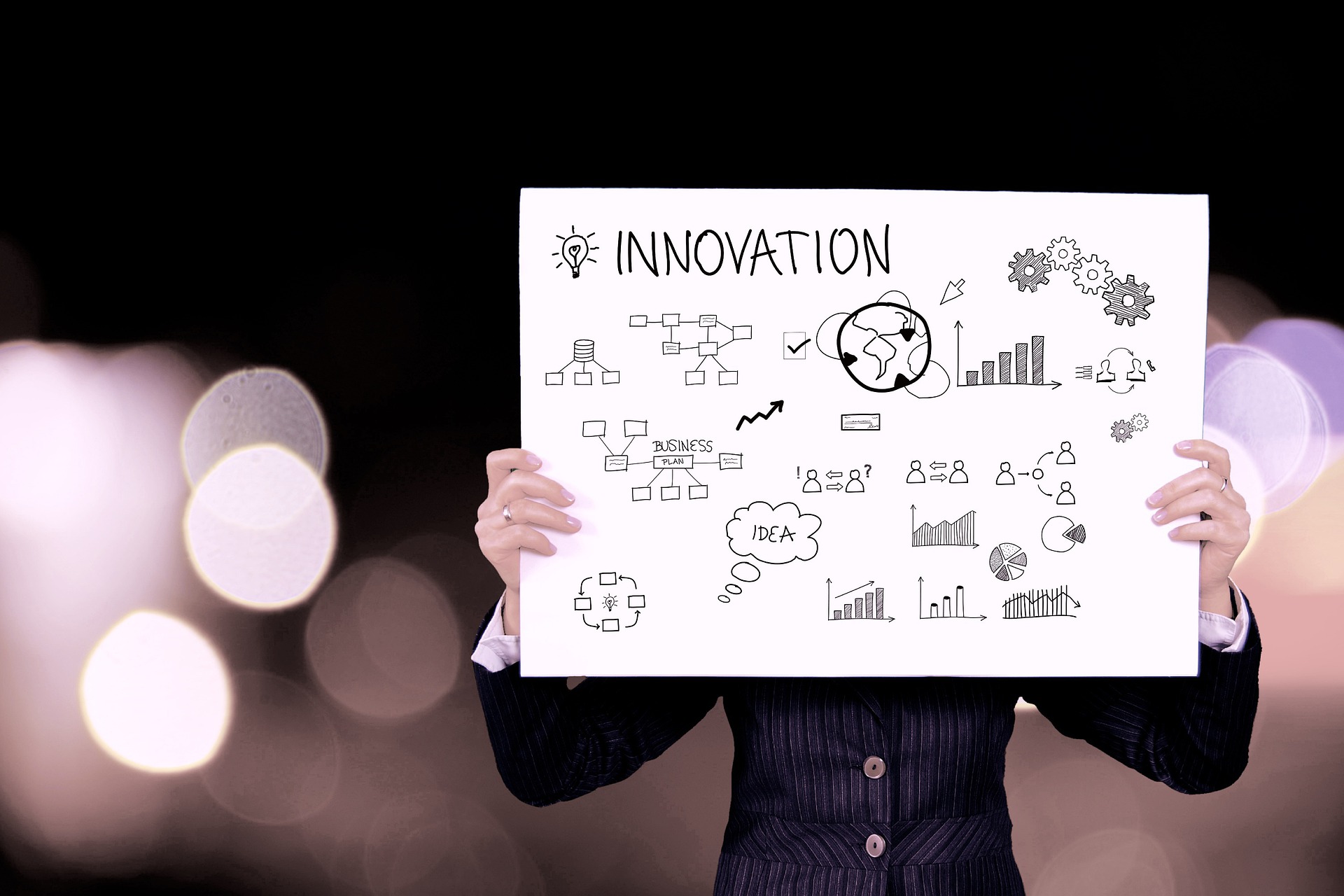
Technological Innovations: the versatility and future of polymers
Polymers can be used for various and unique products, some of them seemingly aiming to change our lives in the future. For instance, scientists from Defense Advanced Research Projects Agency developed a polymer foam that can be injected into an abdominal cavity and later easily removed to stop bleeding. Harvard University scientists found a way to inject polymers through needles, heal damaged tissue, and use polymers in robotics to add flexibility. Polymers can further be used to create artificial skin, ideal for prosthetics. Moreover, polymers might be an answer to cancer, as Duke University scientists tested a thermally responsive radioactive peptide polymer that is effective at controlling tumors. Other innovative applications are scratch repair, lotions against intense heat, and creating transparent soil.

Sustainable polymers as a solution
Sustainable polymers are materials that cater to consumers’ needs without damaging the environment. Namely, renewable sources, such as carbon dioxide, terpenes, vegetable oils and carbohydrates can be used to produce a variety of polymer end-products. Sustainable polymers can be made by fermenting the plant material to produce monomers, such as plant-derived sugar to lactic acid.
Another alternative is extracting chemicals from the plant like soybean oil or natural rubber. Finally, bioengineering and microbial pathways can convert plant molecules into monomers. Renewable polymers found their use in packaging, automotive parts and 3D printing. Sthereochemists strive to find a way to manufacture sustainable polymers while they keep the mechanical and physical properties of traditional plastics.
Economic and renewable – using CO2 to make polymers
The ability to use, and therefore reduce, CO2 emissions and convert them into usable products is the perfect example of renewability. Having significantly lower greenhouse gas emissions, CO2-based polymers are a striking sustainable alternative due to the source material being abundant, renewable, and inexpensive. As a very thermodynamically stable molecule, CO2 requires a significant amount of energy to be activated which is achieved with a specially-designed catalyst that reduces the energy barrier.
So far, there are two different approaches to introducing CO2 onto polymers. One is having CO2 participating directly in the polymerization process as a comonomer. The second approach uses CO2 for building blocks that are yet to undergo the polymerization process. This method could almost replace fossil raw materials as nearly all chemical products that use them can be produced from CO2.
Processing steps involved in polymers making
Which polymers technology do you need?
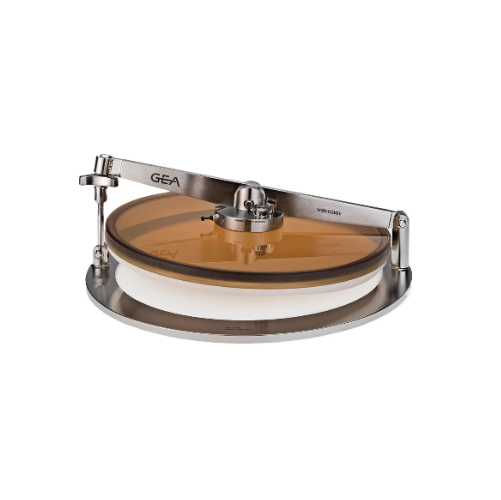
Sanitary cover for visual inspection
Ensure optimal hygiene and easy access in your production line with a transparent cove...
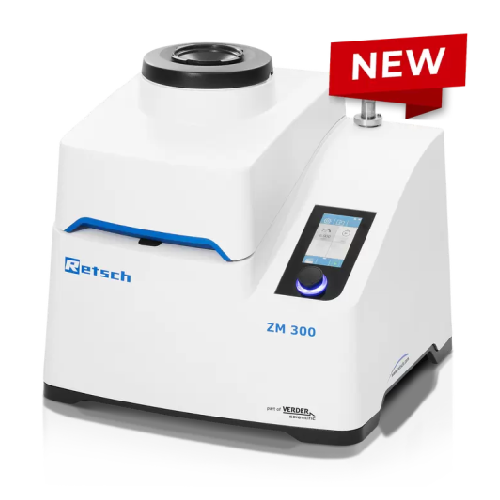
Ultra centrifugal mill for size reduction of soft and medium-hard materials
Achieve precise particle size reduction an...
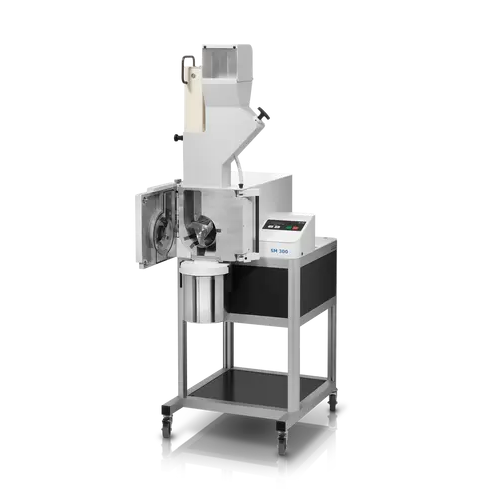
High-torque cutting mill for tough and fibrous materials
Tackle the toughest materials and ensure consistent particle siz...
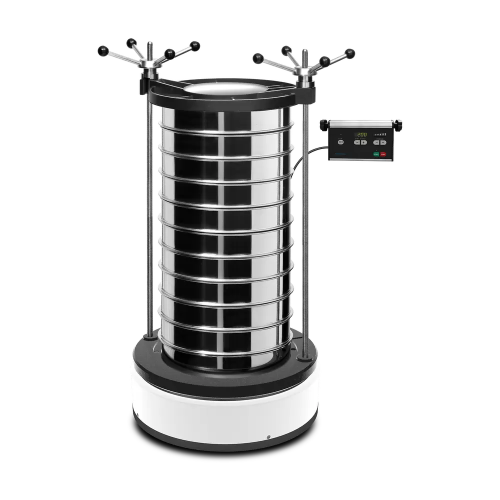
Laboratory sieve shaker for accurate particle size analysis
Streamline your material testing with a robust vibratory sie...
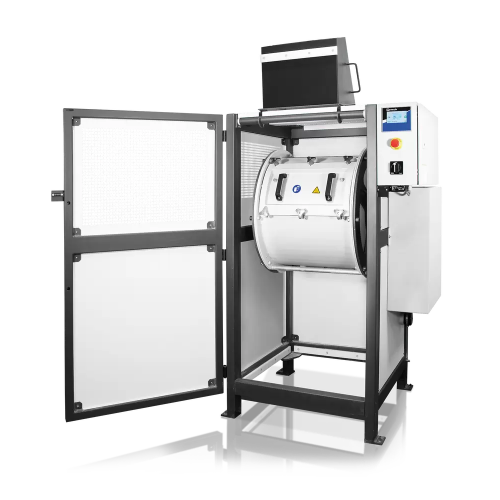
Laboratory drum mill for large sample volumes
Efficiently process large volumes of diverse materials into precise particle...
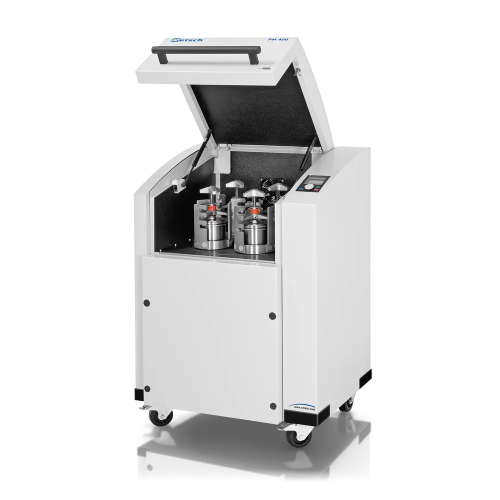
Planetary ball mill for high throughput grinding
For precise material engineering, achieve efficient size reduction, homog...
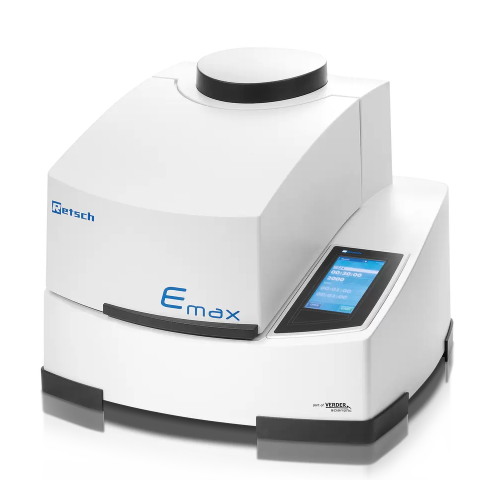
High energy untra fine ball mill
Achieve ultra-fine particle sizes rapidly with this high energy milling solution, designed ...
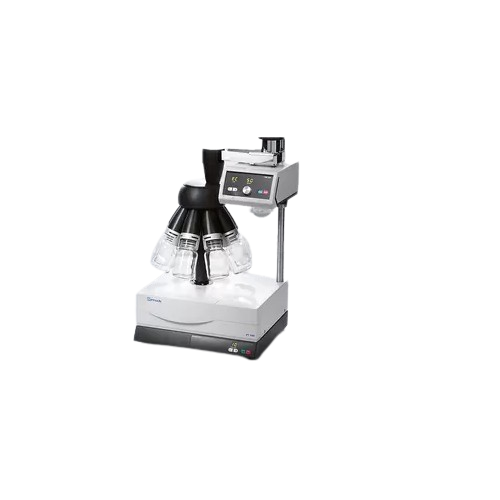
Sample dividing solutions for laboratory applications
Streamline your lab’s precision in sample preparation with so...
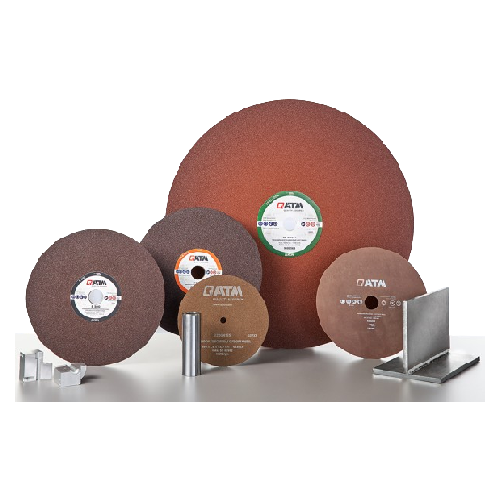
Premium cut-off wheels for metallographic sample preparation
Achieve precise cuts with minimal deformation and temperatu...
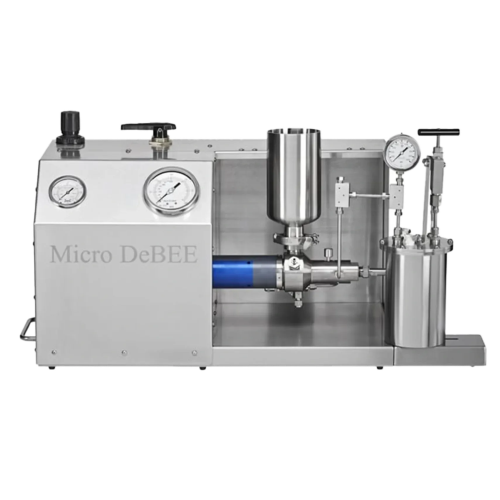
Laboratory homogenizer for nanoemulsions and dispersions
Elevate your laboratory capabilities with a bench-top homogenize...
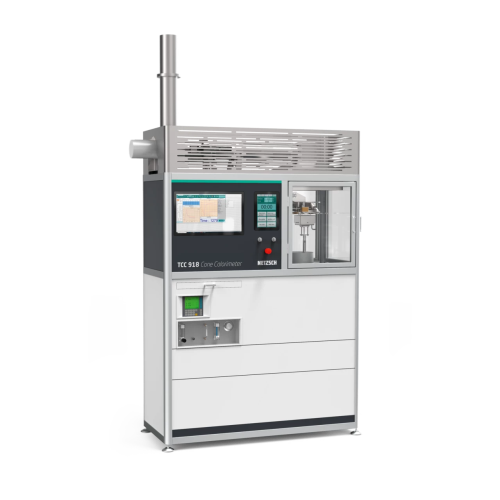
Cone calorimeter for fire testing and safety engineering
Ensure safety in your materials by precisely measuring combustio...
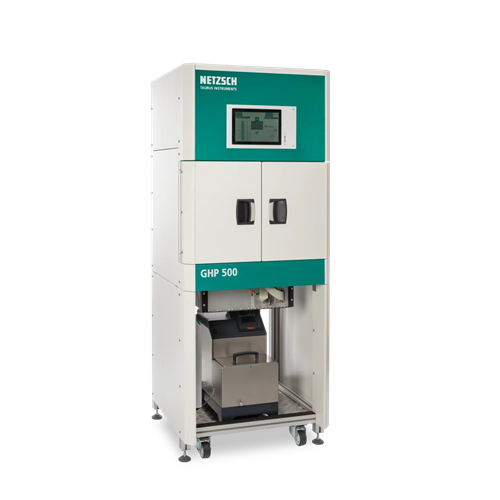
Guarded hot plate for thermal conductivity testing
Ensure optimal insulation performance with precise thermal conductivit...
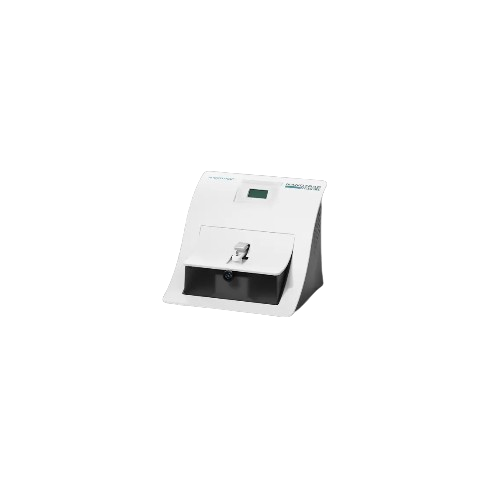
Nanoparticle size analyzer
Master precise nanoparticle and zeta potential analysis with dynamic light scattering technology,...
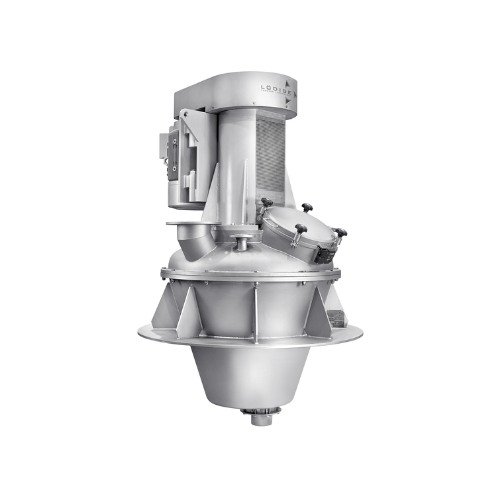
Wet mixer for viscous and paste-like products
Achieve high-quality mixing of medium to highly viscous products with precis...

Super high shear inline disperser for nanoparticle production
Achieve unmatched particle size reduction with cutting-edg...
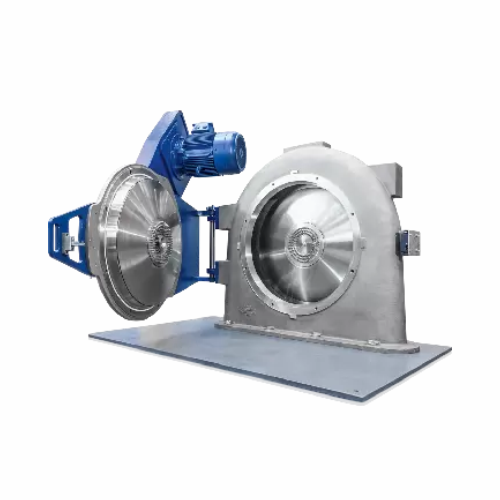
Industrial powder grinder
Achieve precise particle size reduction and classification with advanced equipment designed for co...
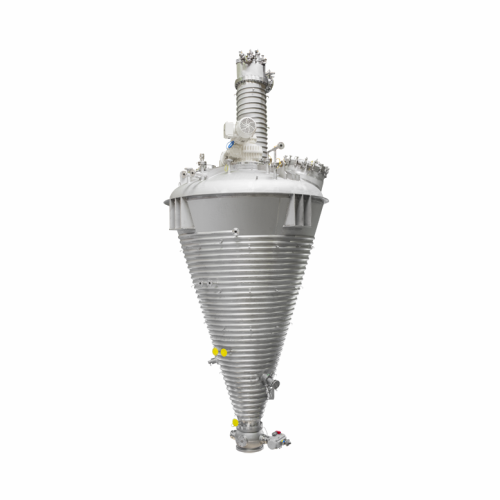
Vacuum dryers for powders and bulk solids
Achieve precise drying and mixing of sensitive materials with advanced vacuum te...
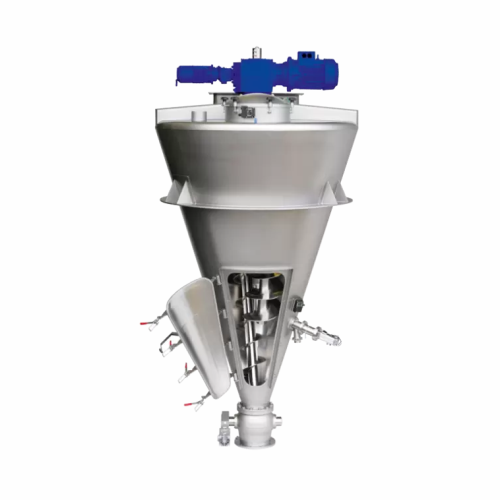
Batch mixer for segregative, free-flowing powders and pastes
Achieve precise and gentle batch mixing for delicate produc...
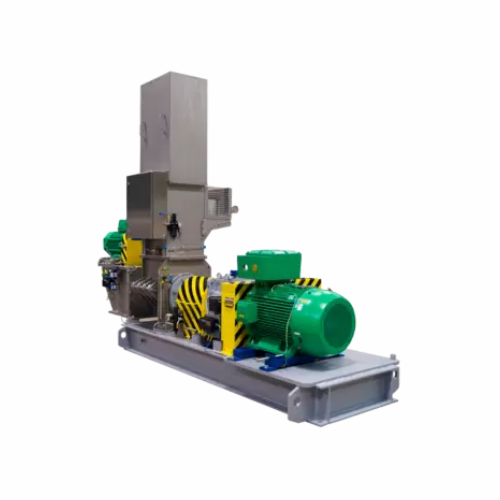
Choppers and disintegrators for industrial size reduction
Enhance your production efficiency by mastering size reduction...
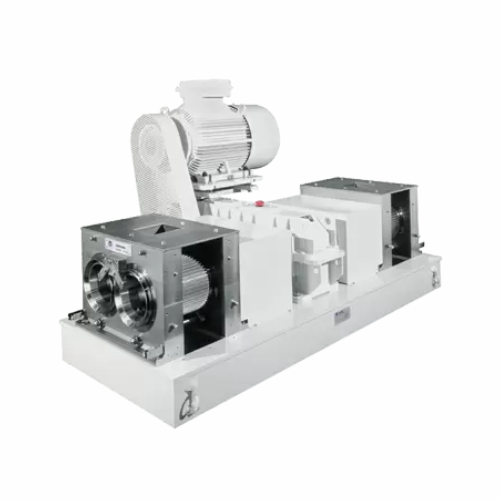
Compactors and granulators for powdery products
Transform loose powders into dense, free-flowing granules that enhance han...
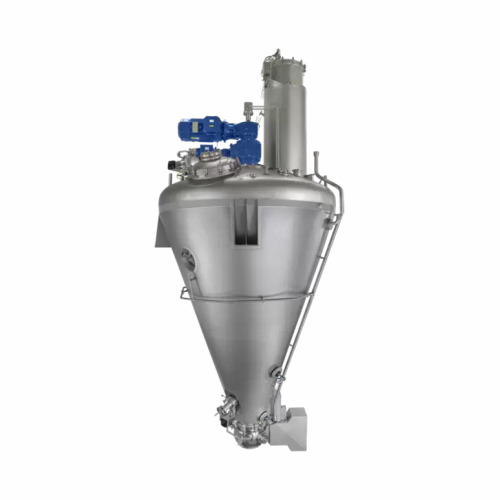
Vacuum dryer for powders and granules
Achieve precise moisture control for sensitive materials with a versatile vacuum dryi...
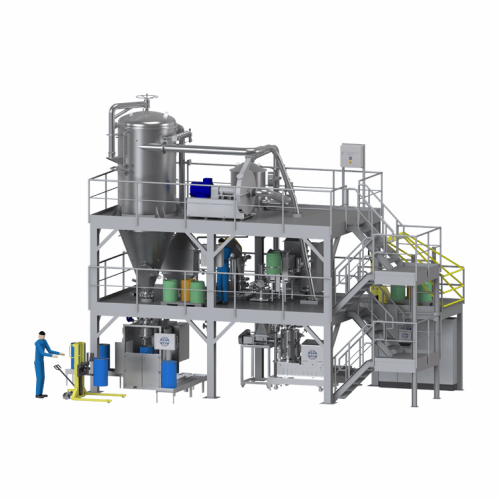
Drying systems for powders and bulk solids
Enhance your production line with precise control of moisture content in powder...
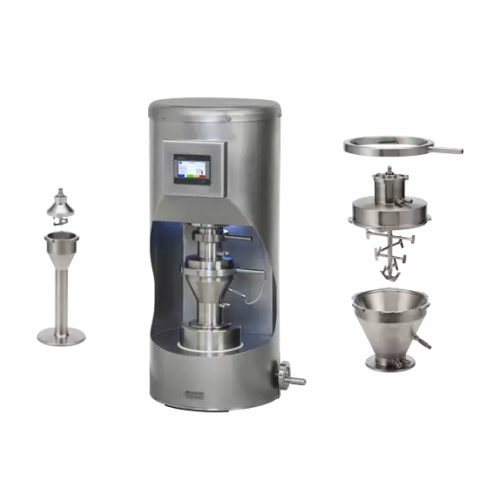
Lab mixer for powder formulations
Achieve precise particle mixing and coating with this stand-alone high-shear lab mixer, d...
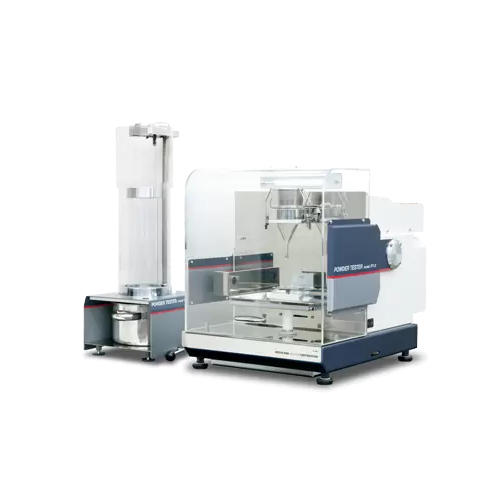
Powder characteristic evaluation
Ensure precise powder analysis and testing in your laboratory to optimize production qualit...
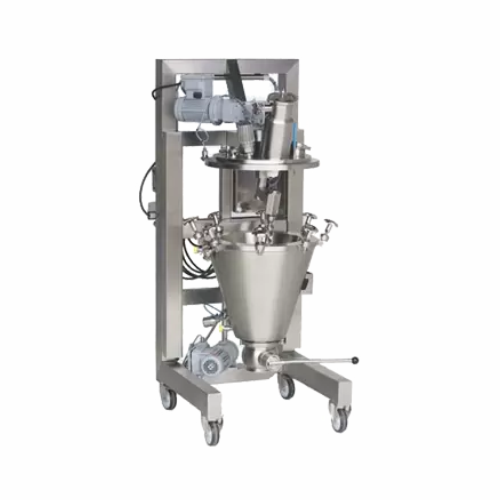
Laboratory vacuum dryer for heat-sensitive materials
Optimize moisture control in heat-sensitive materials with precise a...
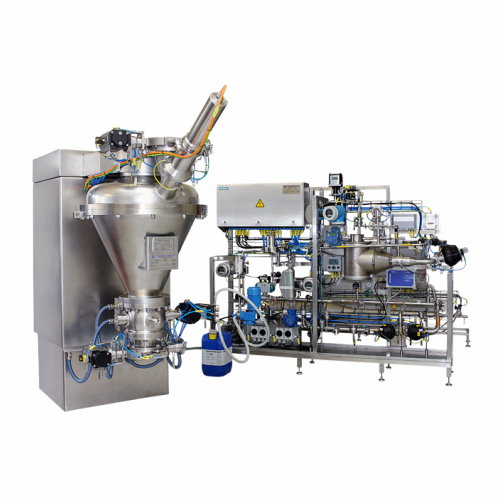
Cip/sip cleaning for solids processing systems
Ensure seamless transitions and maintain hygienic production environments w...
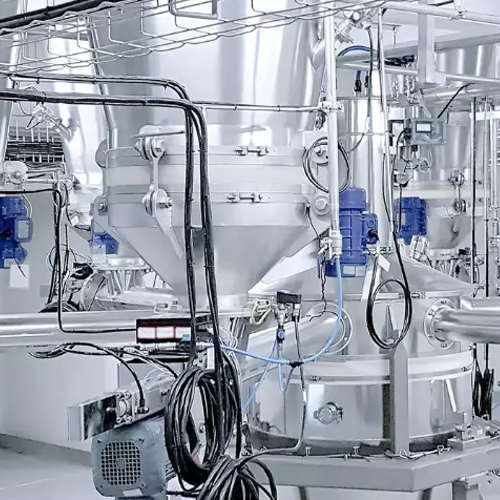
Conical screw mixer for powder blending
Achieve precise and homogeneous blending with the conical screw mixer, ensuring uni...
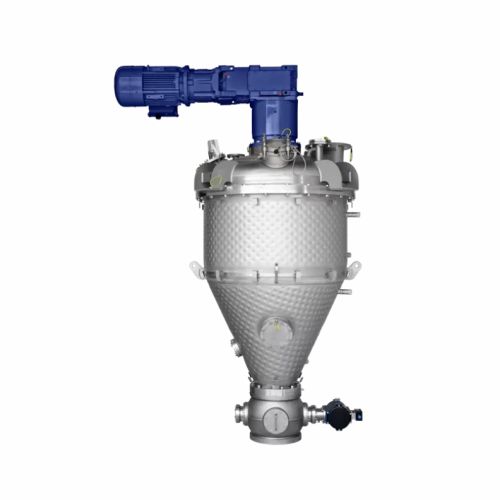
Conical paddle vacuum dryer for powders and granules
Achieve efficient drying of sensitive materials with this versatile ...
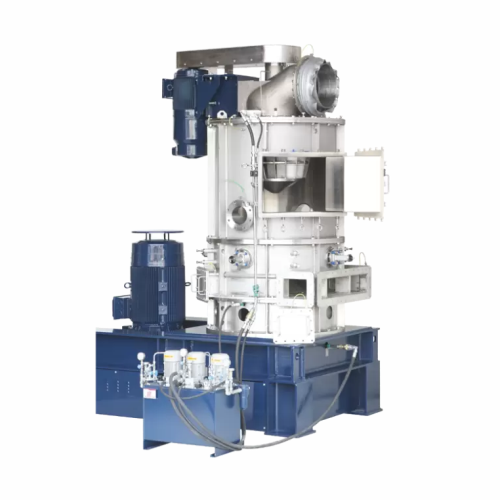
Ultra-fine powder flash drying system
Achieve rapid moisture removal and particle refinement with this integrated system, d...
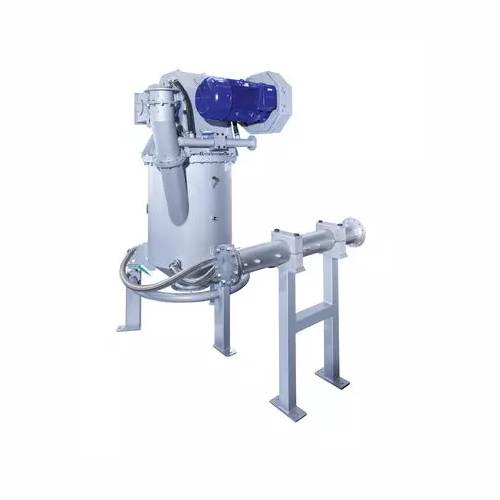
Fluidised bed opposed jet mill for fine particle processing
Achieve precise and consistent particle sizes with high-spee...
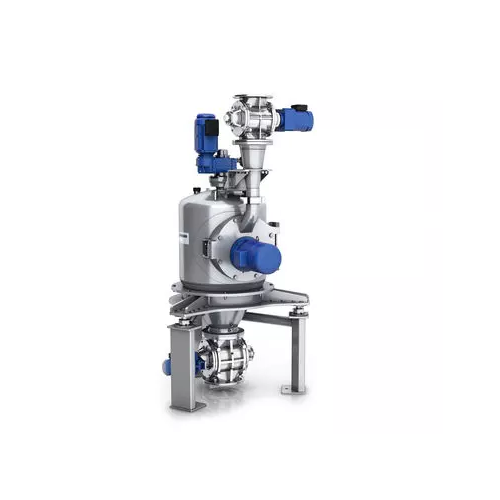
Fine impact mills for particle size reduction
Achieve precise particle size reduction with fine impact mills, essential fo...
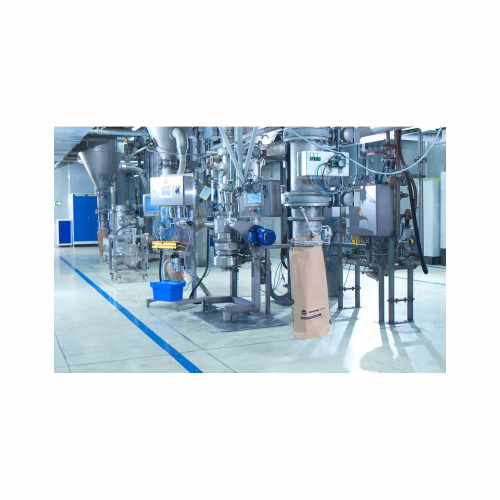
Air classifier for classifying industrial minerals
Achieve precise particle separation with advanced air classifiers, par...
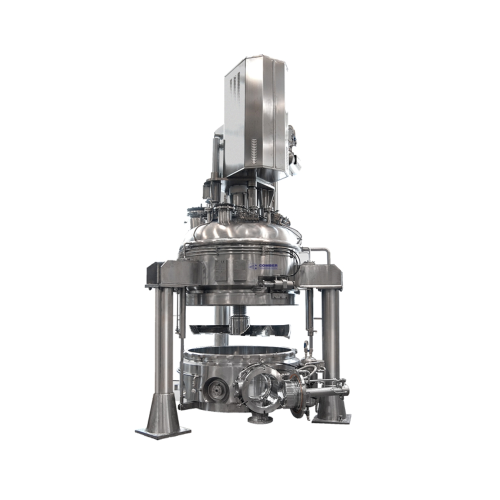
Vacuum pan dryer for heat-sensitive pasty products
When dealing with highly viscous, heat-sensitive products, efficient m...
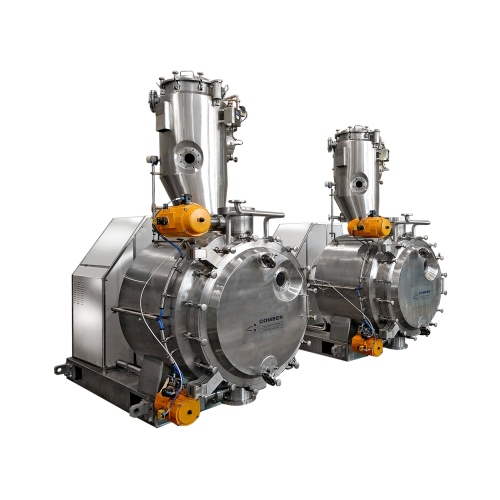
Horizontal vacuum paddle dryer for sensitive pharmaceutical ingredients
Achieve precise drying and mixing of sensitive ...
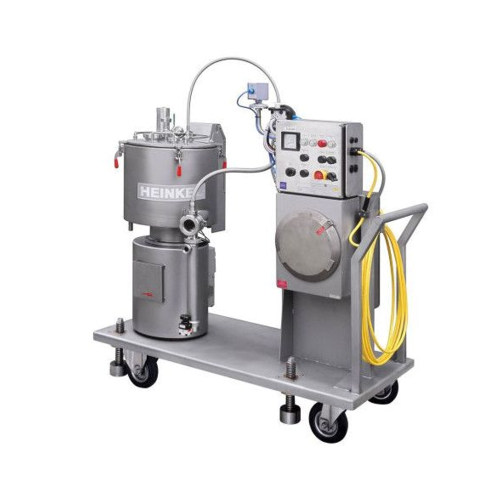
Vertical pilot plant centrifuge for chemical industry
Optimize your lab and pilot plant operations with this mobile centr...
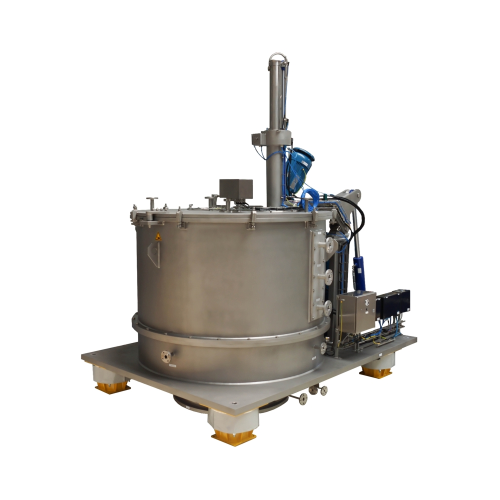
Vertical peeler centrifuge for chemical industry
Maximize throughput in continuous chemical processes with a versatile ver...
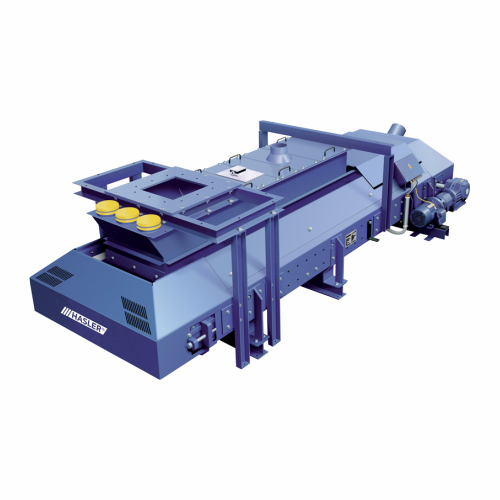
Powder belt feeder for accurate powder metering
Achieve precise powder metering with a specialized feeder that maintains d...
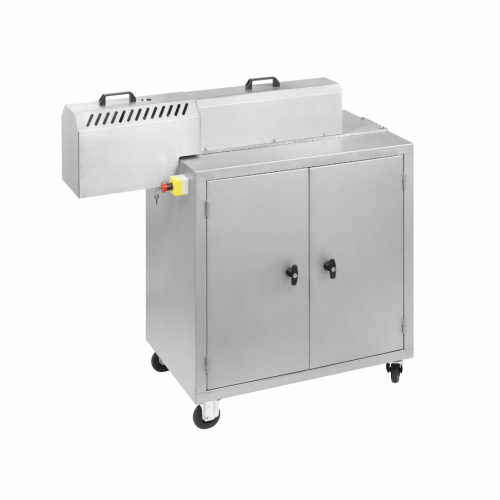
High-viscosity continuous industrial kneader for small volumes
Achieve consistent high-viscosity material processing wit...
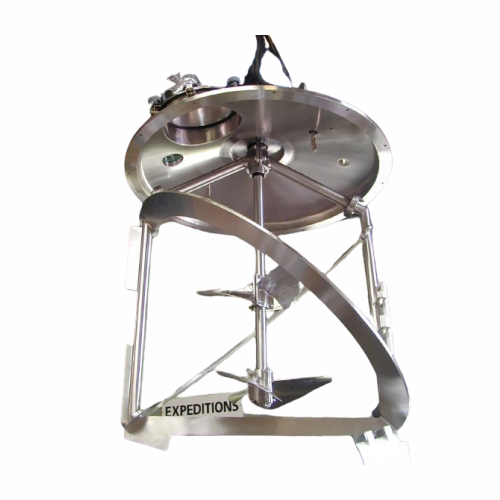
Coaxial mixer for high viscosity liquids
Achieve seamless blending of high-viscosity materials with a coaxial mixer designe...

Side entry mixer for industrial fluid mixing
Optimize your fluid mixing processes with high-speed side entry mixers, desig...

Wiped film evaporator for high boiling point materials
For challenging separations of high boiling, viscous, or heat-sens...
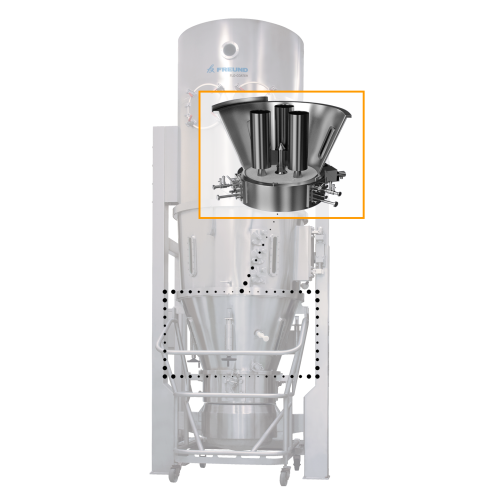
Wurster coating system for fine powders and pellets
Achieve precision coating for multiparticulate cores and mini-tablets...
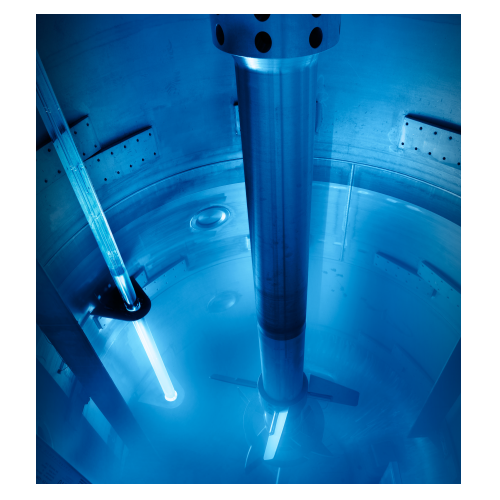
Industrial photochemical reactors for multiphase reactions
Optimize multiphase chemical reactions with light-activated p...
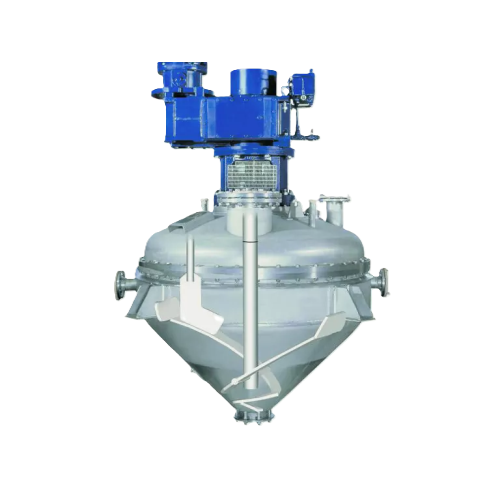
Vacuum dryer for free-flowing and pasty solids
Achieve precise drying and mixing with this vacuum dryer, optimizing heat t...
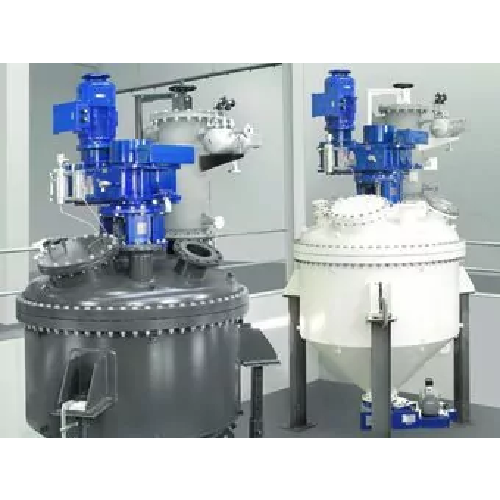
Vertical pharma vacuum blender for bulk solids
Optimize your mixing of fine chemicals and pharmaceutical powders with high...
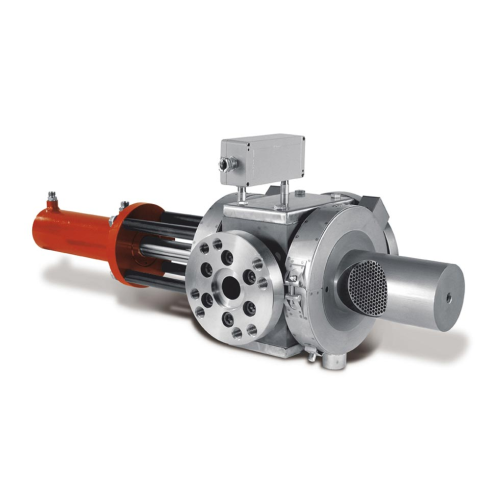
Discontinuous screen changer for low viscosity melts
Optimize your filtration process with a discontinuous screen changer...
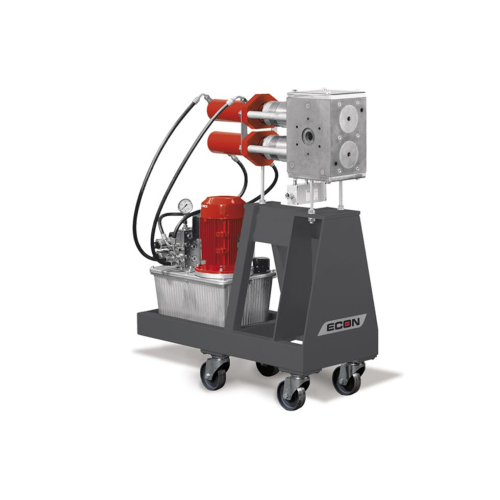
Inline screen changer for thermoplastics
Effortlessly swap filter screens during thermoplastic processing without halting o...
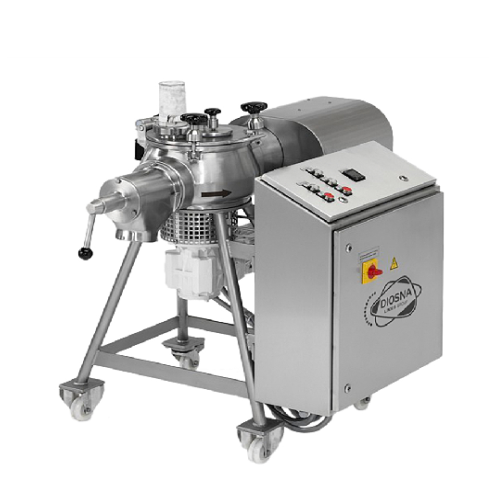
Versatile entry-level mixer granulator
Solve complex mixing and granulating challenges with this compact solution, offering...
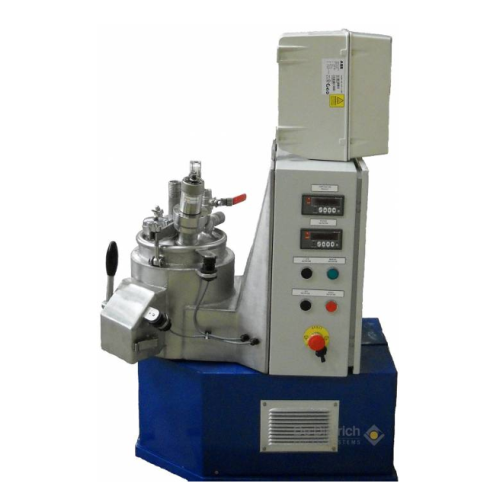
Powder blender for efficient mixing and discharge
Achieve precise mixing and efficient discharge with advanced powder ble...
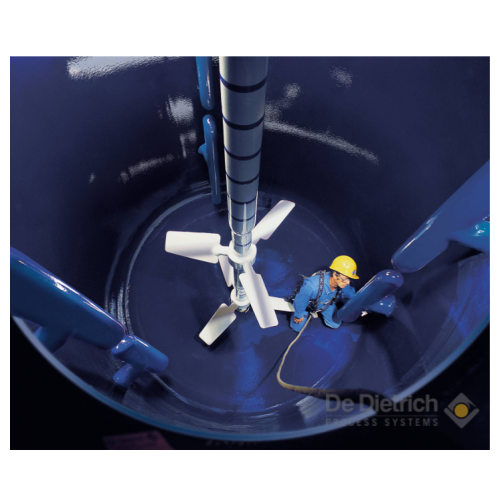
Glass-lined reactor for enhanced mixing performance
Optimize your chemical processes with a reactor that enhances mixing ...
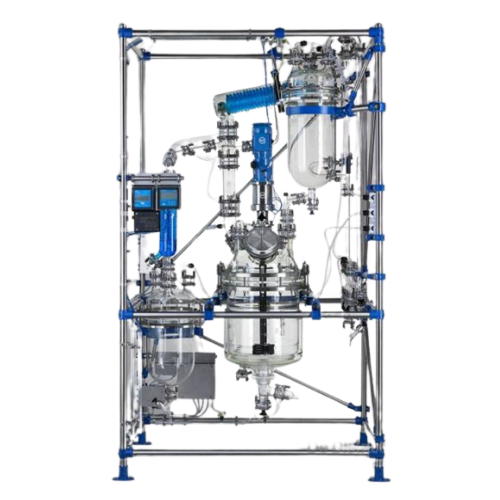
Industrial universal reactor for large-scale chemical synthesis
For chemical producers scaling past laboratory setups, t...
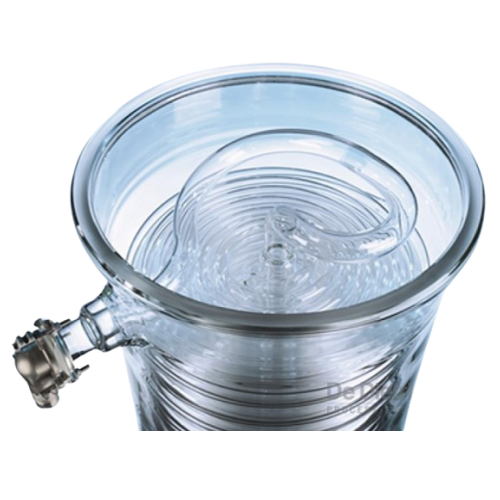
Heat exchanger for corrosive substance handling
Optimize your process of handling corrosive substances with a heat exchang...
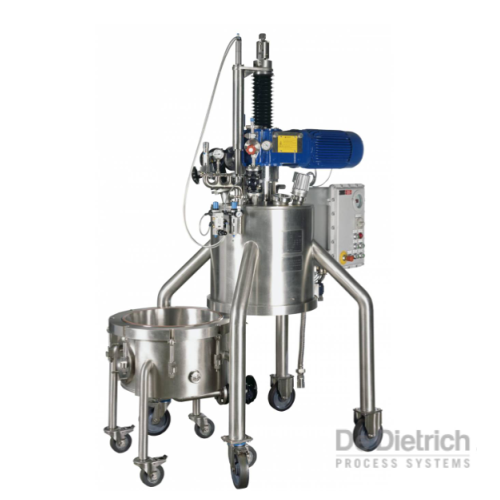
Pilot scale filter-dryer for pharmaceutical and chemical batches
Streamline small-batch production with a mobile filter-...
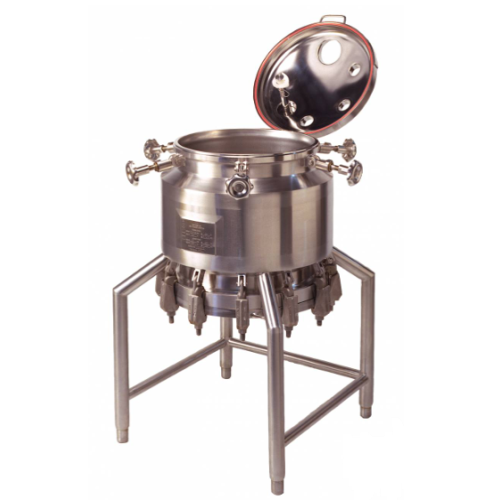
Static nutsche filters for liquid-solid separation
Achieve efficient separation of solids from liquids with precise contr...
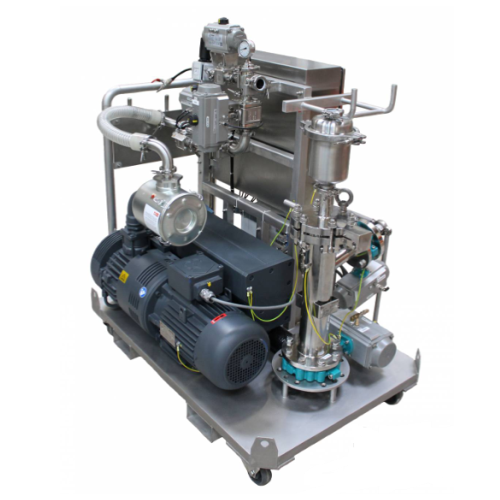
Mobile powder transfer system for pharmaceuticals and chemicals
Efficiently transfer and charge powders into various ves...
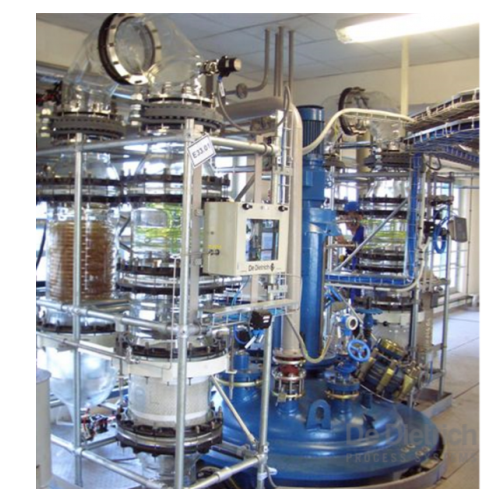
Distillation equipment for large reactors
Efficiently achieve high-purity separations and syntheses with distillation equi...
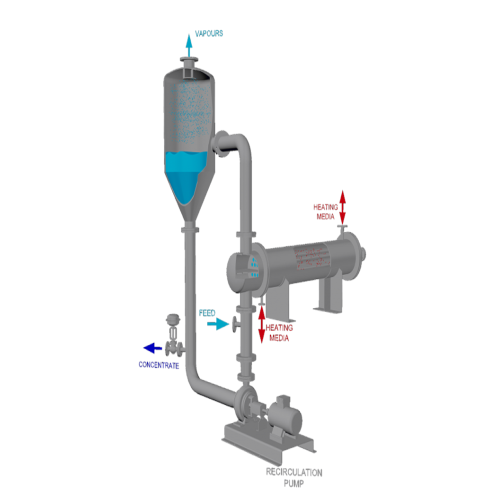
Force circulation evaporator for high viscous products
Optimize energy efficiency and manage challenging liquid compositi...
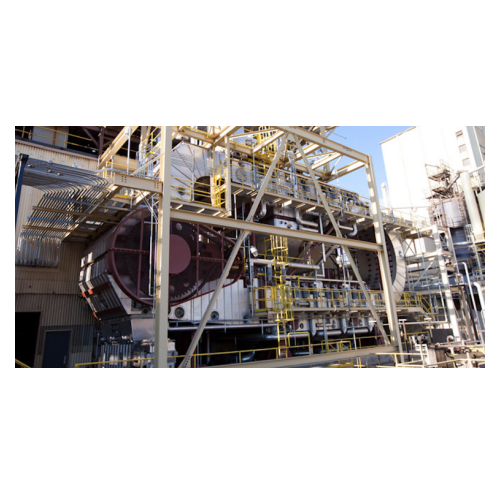
Percolation extractor for high-volume vegetable protein extraction
Optimize extraction efficiency across diverse materi...

Continuous vacuum dryer for protein products
Achieve precise moisture control and maintain product functionality with low-...
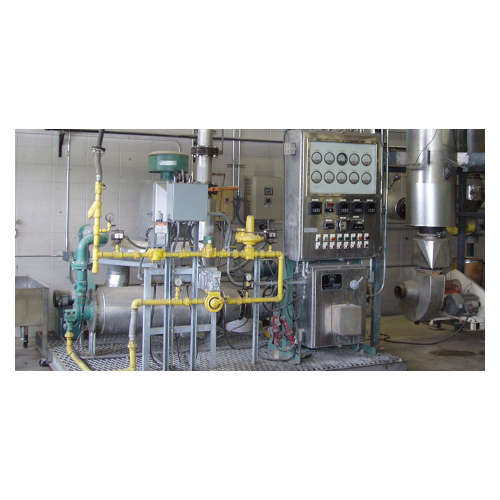
Vertical flash dryer for industrial drying applications
Optimize your production line with an energy-efficient vertical f...
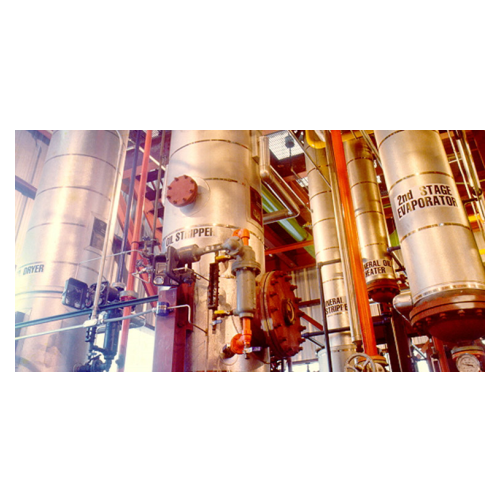
Mineral oil absorption system for solvent vapor recovery
Optimize solvent recovery and reduce atmospheric emissions with ...
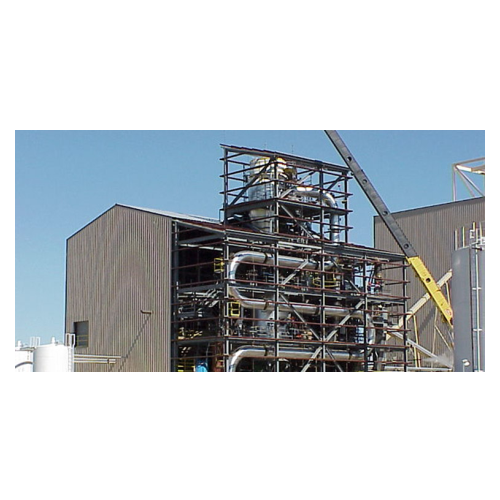
White flake desolventization for oilseed processing
Optimize your oilseed processing with a system designed to efficientl...
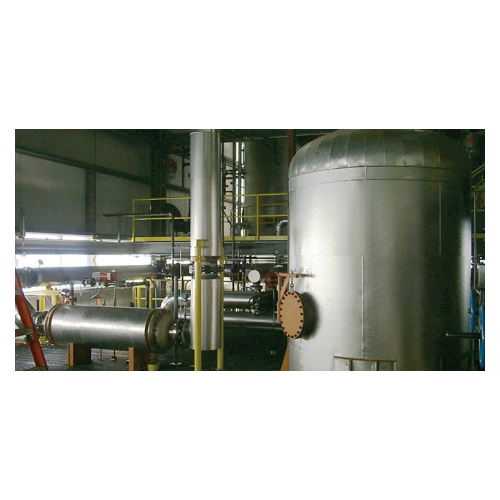
Zero effluent discharge system for solvent extraction plants
Eliminate wastewater in your solvent extraction process whi...
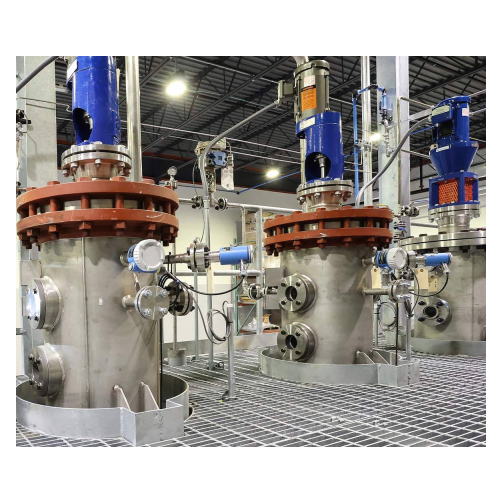
Biodiesel distillation process
Improve biodiesel quality by enhancing cold flow characteristics and removing impurities thro...
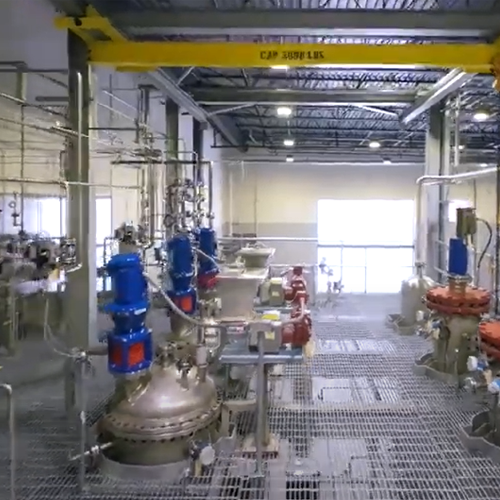
Renewable diesel pretreatment system
Extend hydrotreater catalyst life and boost plant uptime by optimizing feedstock purit...
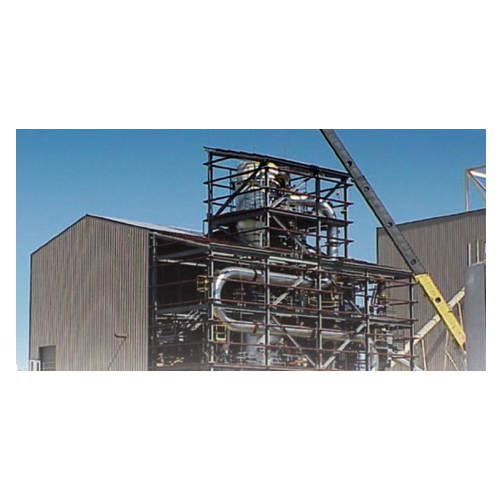
Flash desolventization system for oilseed processing
Achieve rapid desolventization with minimal heat exposure, preservin...
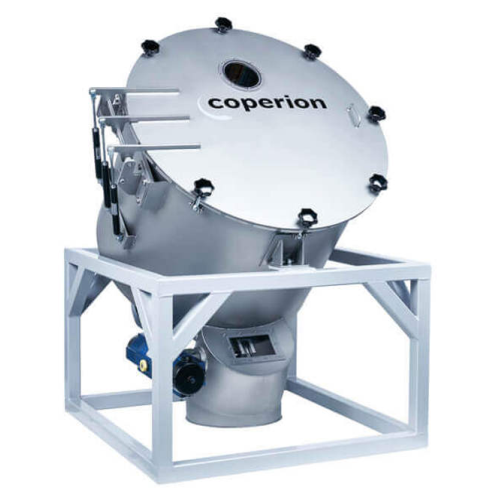
Bulk material mixer for high-speed homogenization
Achieve fast and gentle homogenization of bulk materials with a high-sp...

Filtration compounder for polymer recycling
Streamline your recycling process by integrating filtration and compounding in...
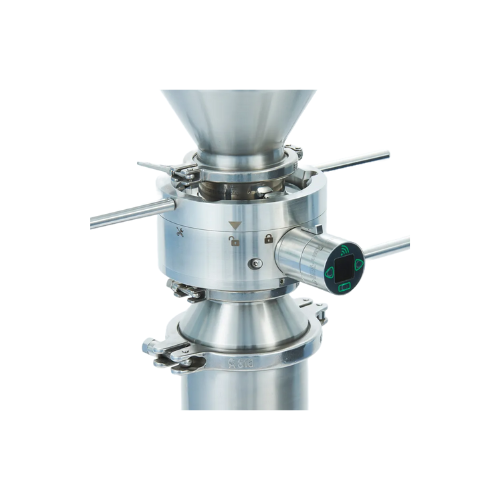
Aseptic transfer valve for sterility assurance
Ensure sterility and safety in your critical production processes with adva...
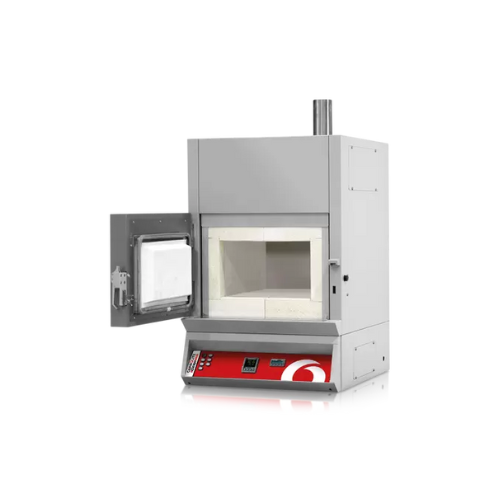
Ashing furnace for biomass with afterburner
Efficiently process high-smoke materials like biomass through advanced afterbu...
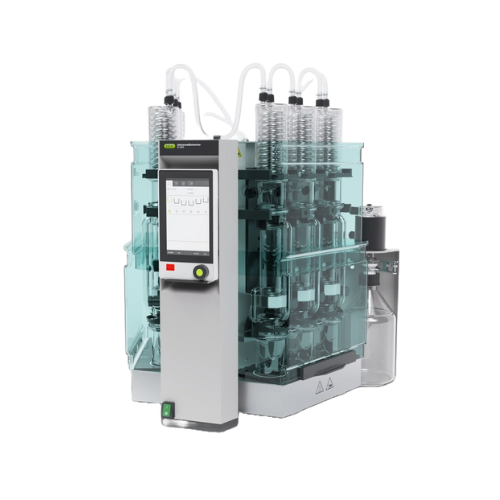
Multitasking extraction system
Effortlessly manage complex extractions with high-speed, reliable results, ensuring sample in...
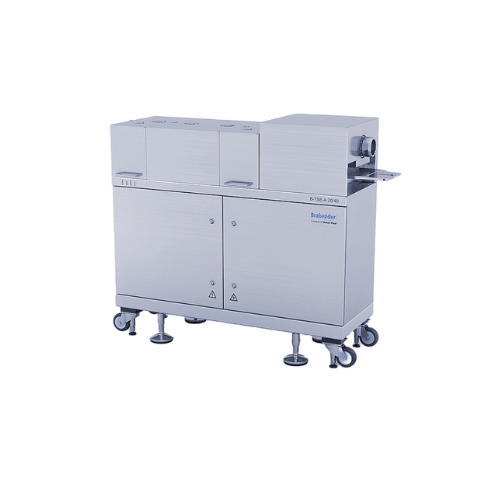
Lab-scale twin screw extruder
Optimize your material testing and production efficiency with our versatile twin screw extrude...
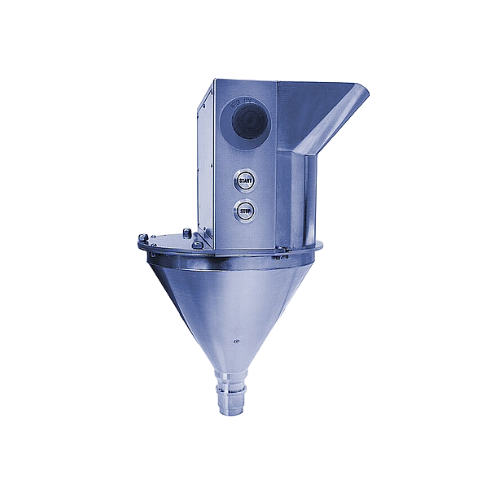
Vertical forced feeder for extruders
Enhance your extrusion process with a vertical forced feeder designed for precise dosi...
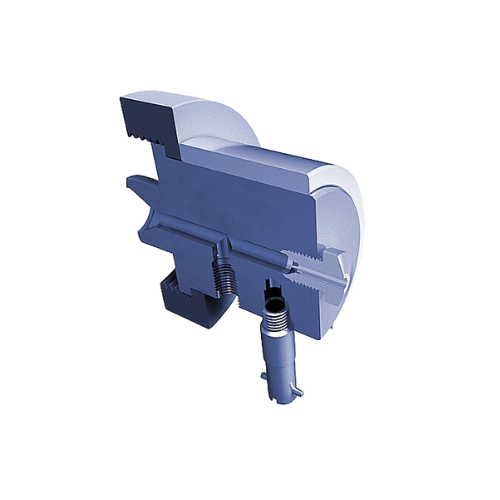
Round strand die head for precision extrusion
Achieve precise extrusion control across varied applications with our custom...
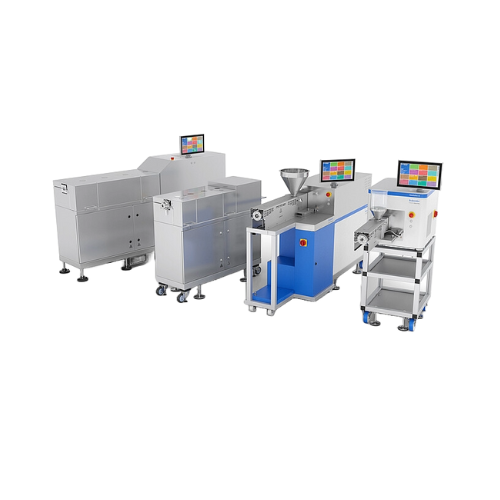
Lab- and pilot-scale twin screw extruders
Optimize your material development and testing with versatile extruders, ideal f...
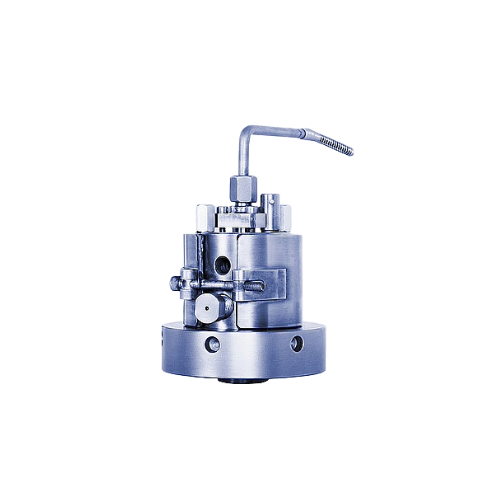
High-precision diameter measurement for round profiles
Achieve continuous, non-contact diameter measurement of round prof...
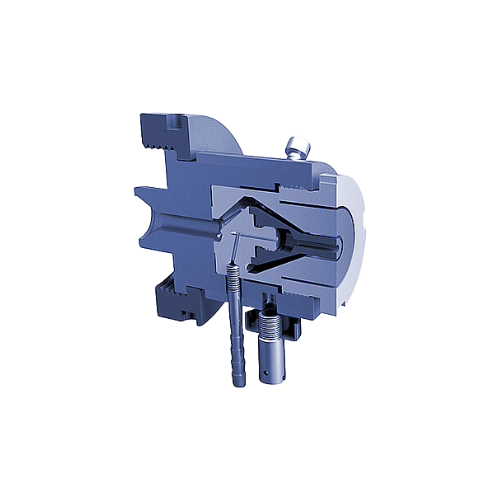
Tubing die head for pipe extrusion
Optimize your extrusion process with versatile die head options for producing high-quali...
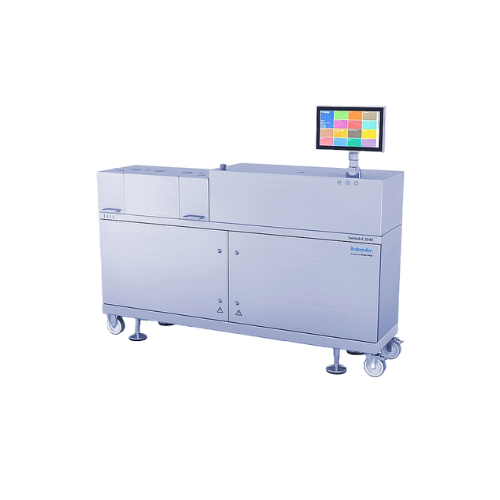
Small twin screw extruder
Optimize your lab and pilot production with a versatile twin screw extruder, designed for precise ...
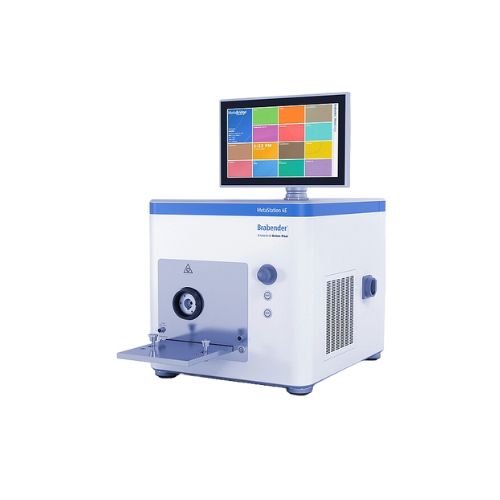
Modular torque rheometer for plastics and plastifiable substances
Optimize your material development and testing with a...
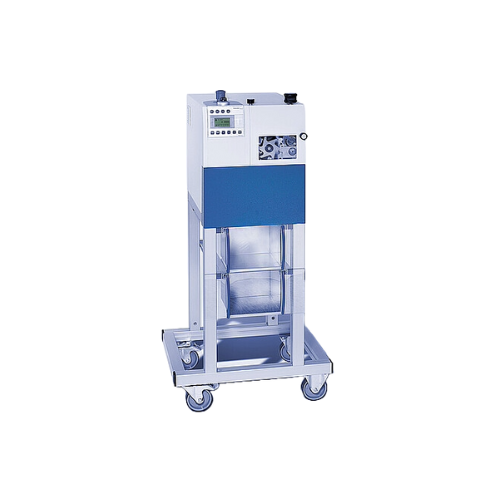
Pelletizer for consistent plastic pellet production
Achieve precise pellet sizes consistently with this flexible solution...
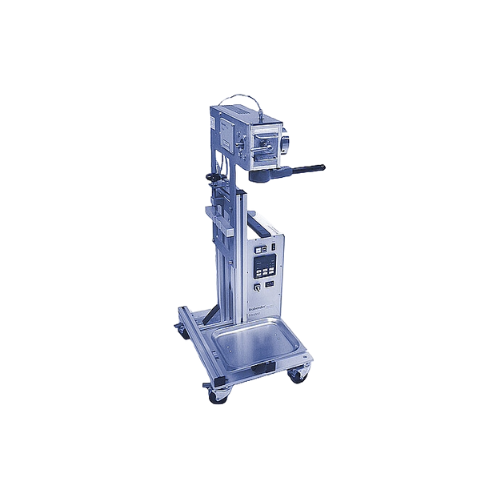
Filtration testing for spinnable polymer purity
Ensure the purity of your thermoplastic melts and spinnable polymers by ac...
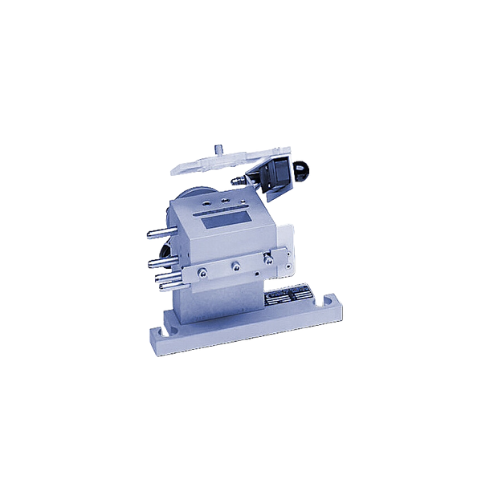
Measuring mixer for small grain samples
Optimize the precision of your formulation processes with a solution designed for p...
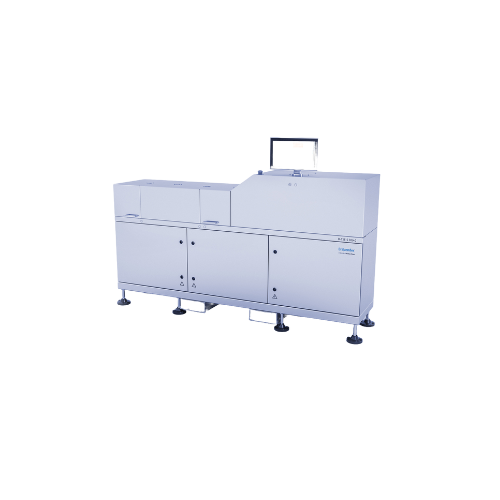
Lab- and pilot-scale twin screw extruders for small-scale production
Optimize extrusion techniques with lab and pilot-s...
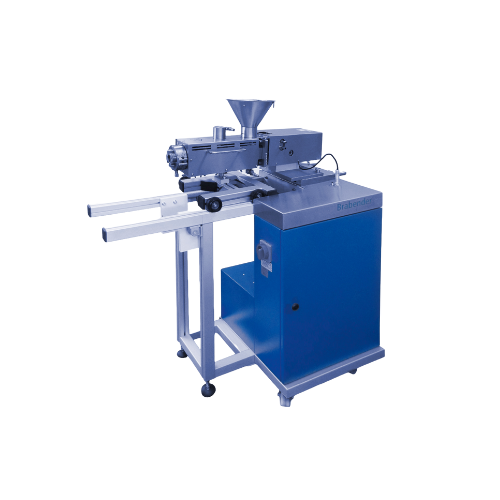
Conical twin screw extruder for shear-sensitive materials
Optimize the extrusion process for shear-sensitive materials w...
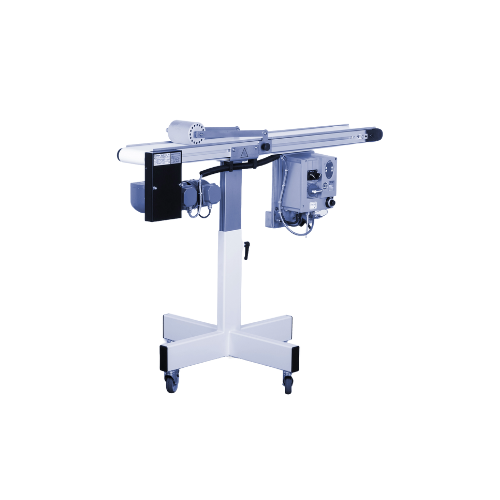
Conveyor belt for extruded profiles
Efficiently transport and convey extruded profiles with precision through adjustable sp...
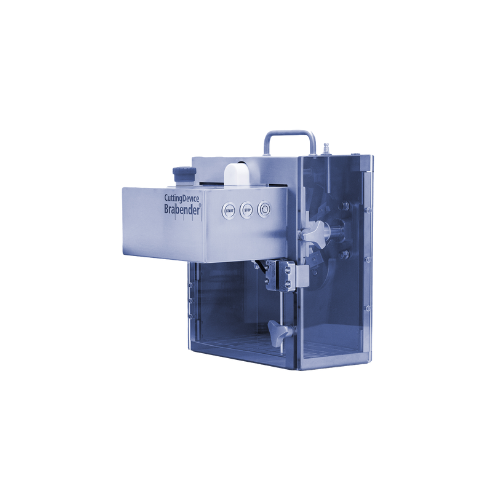
Laboratory cutting device for extrudates
For precise shaping of snack or feed extrudates, this compact cutting solution ens...
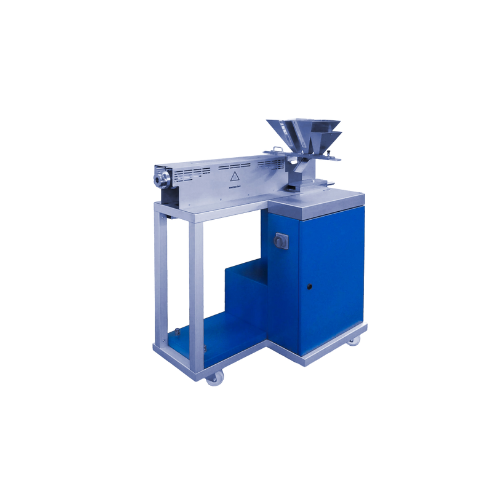
Polymer extrusion testing extruder
Optimize your polymer and plastic production with precise extrusion testing, simulating ...
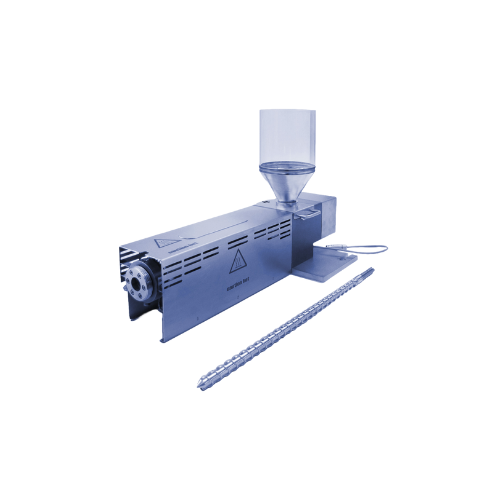
Polymer testing extruder
Effortlessly evaluate polymer and plastic product properties with precision, ensuring your materials...
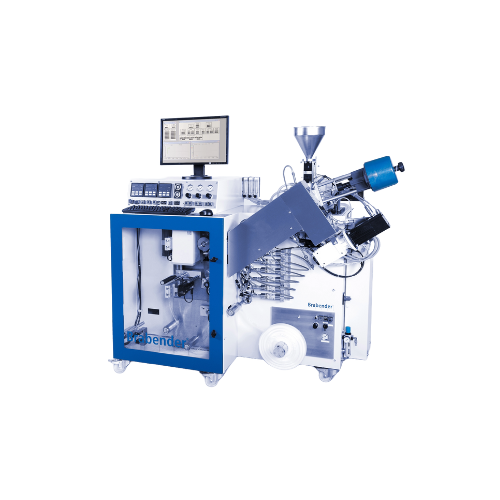
Automated polymer melt flow rate measurement system
Achieve precise polymer quality control by continuously analyzing mel...
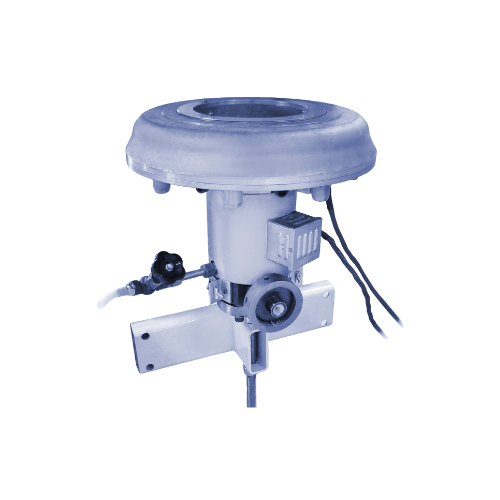
Blown film take-off unit for extrusion
Optimize your film production process with a versatile unit designed for seamless in...
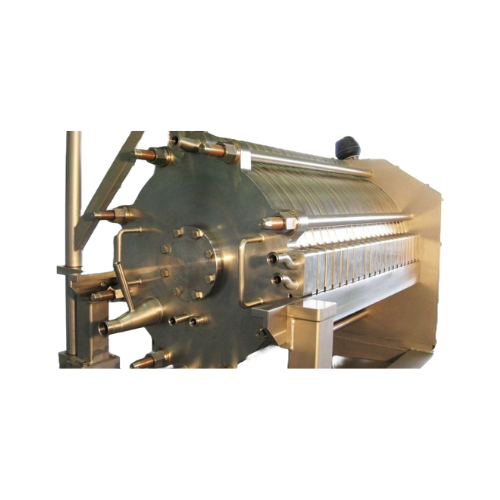
Crossflow filtration for microfine to nanoscale suspensions
Optimize your production line with advanced crossflow filtra...
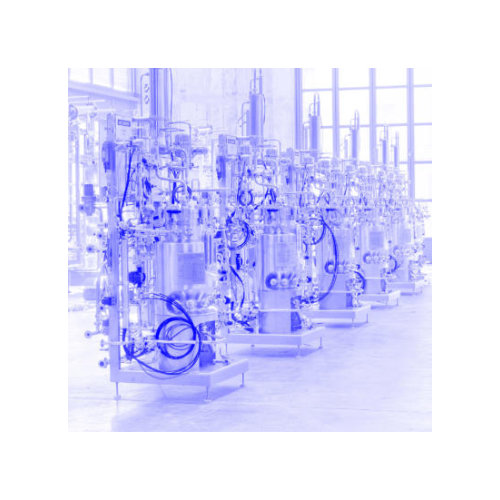
Modular bioreactor for low-volume production
Optimize your bioprocessing with a scalable solution designed for precise con...
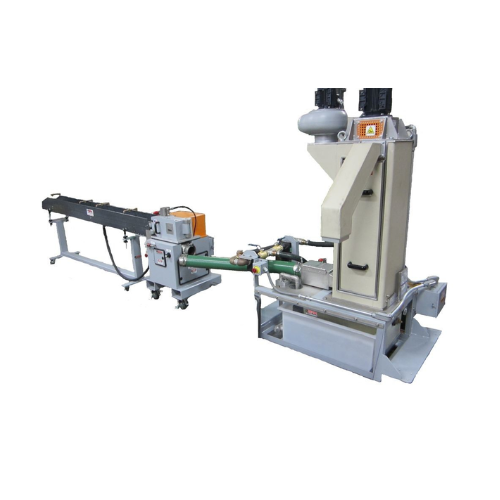
Automatic wet cut strand pelletizer for thermoplastic pellet production
Streamline your polymer pellet production with ...
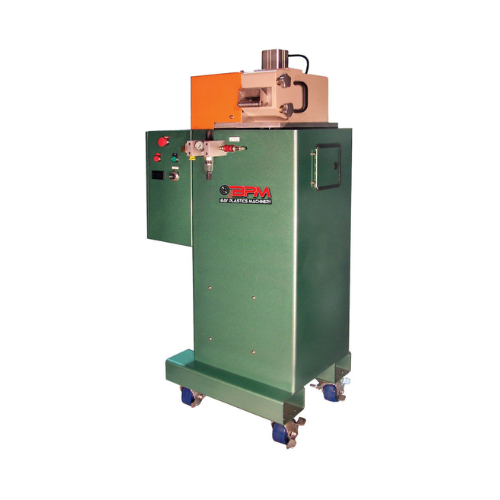
Strand pelletizer for small production lines
Achieve consistent and precise pellet sizes with our strand pelletizer, ideal...
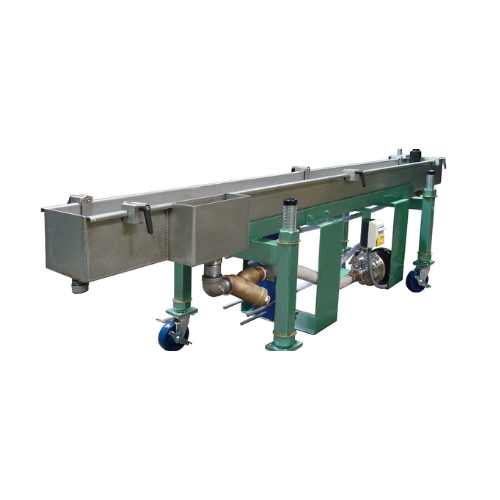
Industrial water bath for pelletizing processes
Enhance pellet quality and efficiency with a customizable water bath desig...
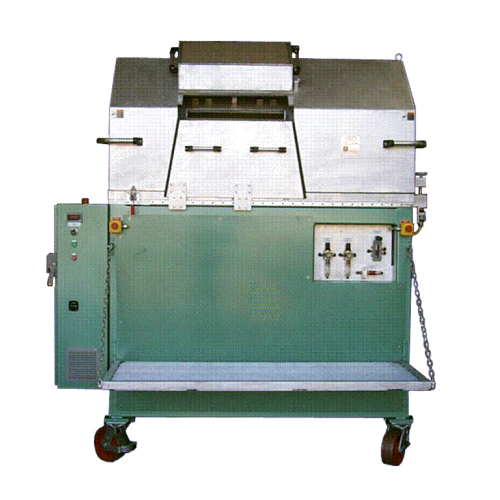
Dx strand pelletizer for plastic pellet production
Reduce operational noise while precision-cutting a wide array of therm...
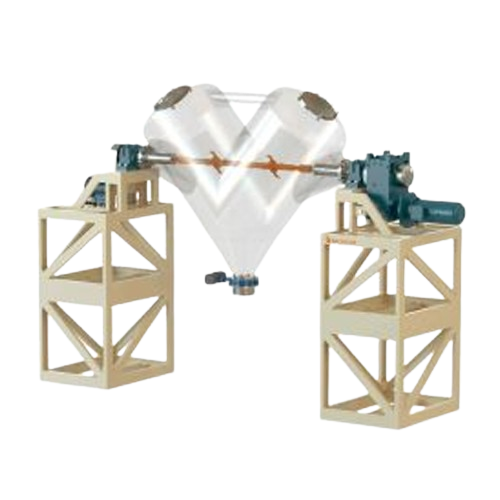
V shape mixer for solids and powders
Ideal for preserving the delicate structures of fragile materials, this mixer ensures ...
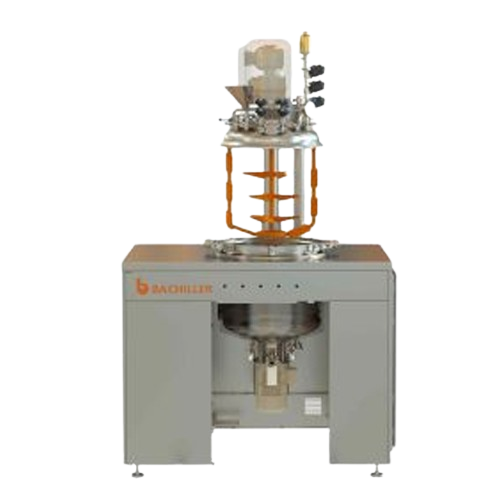
Laboratory vacuum mixer reactor for liquids and semi-solids
Achieve precise emulsification and mixing for high-viscosity...
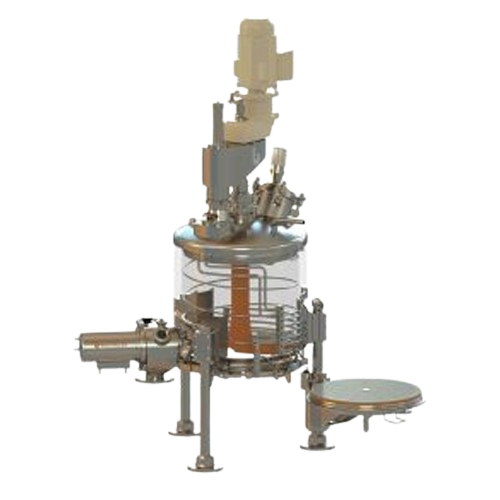
Agitated nutsche filter for solid-liquid separation
Ensure high-purity solid-liquid separation with minimized contaminati...
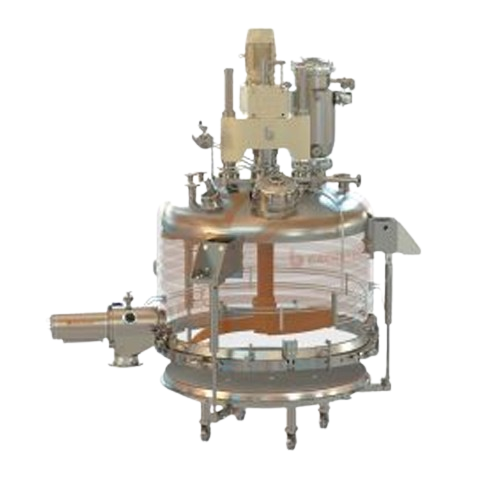
Agitated nutsche filter dryer for solid-liquid separation
Achieve high-purity solid-liquid separation with optimized thr...
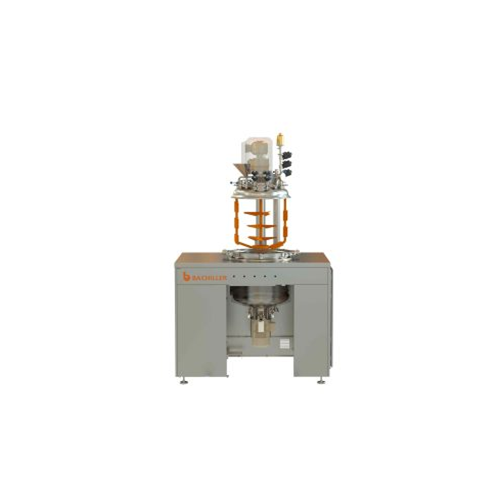
Vacuum mixer for liquid and cream processing
When dealing with high-viscosity liquids and creams, achieving uniform consis...
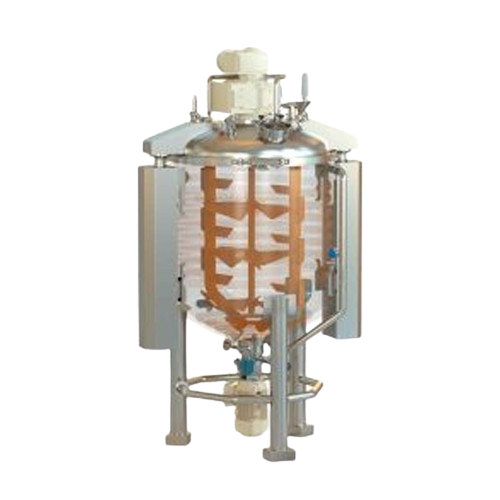
Industrial mixer for liquid and viscous products
Achieve precise mixing and homogenization of high-viscosity liquids and s...
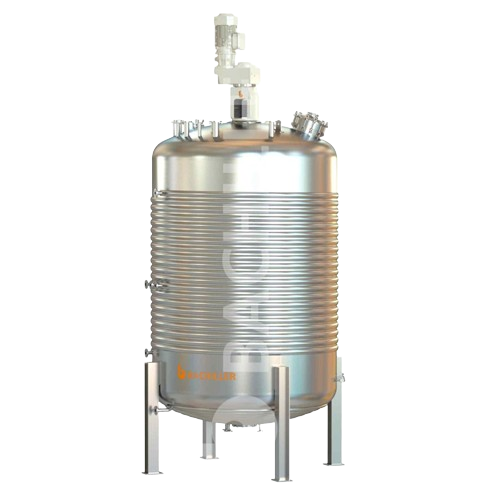
Stirred reactors with heating and cooling system
Optimize your production line with versatile stirred reactors, designed t...
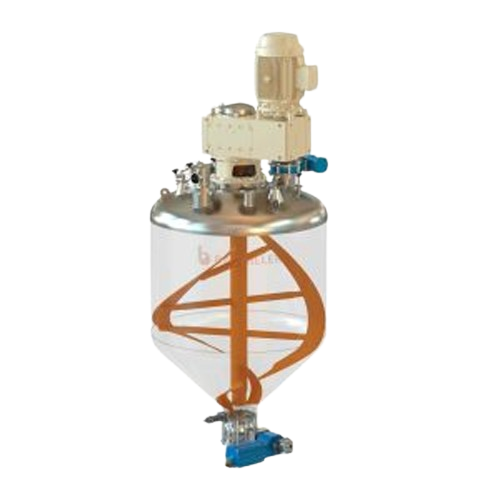
Vertical ribbon mixer for solids and powders
Achieve rapid, uniform mixing of powders and solids while preserving particle...
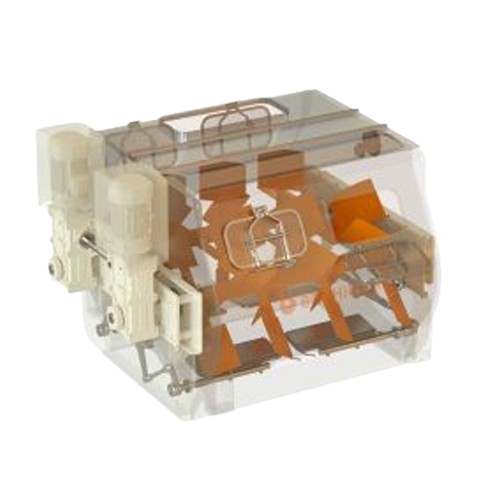
Double shaft paddle mixer for solids and powders
Achieve unparalleled mixing precision for fragile and diverse materials w...
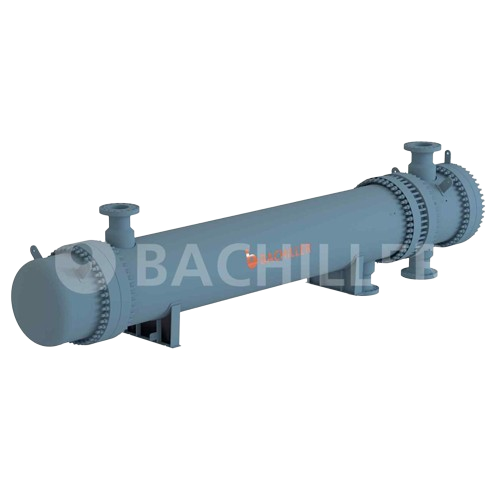
Shell and tube heat exchangers
Efficiently manage heat transfer in your production line with custom-engineered shell and tub...
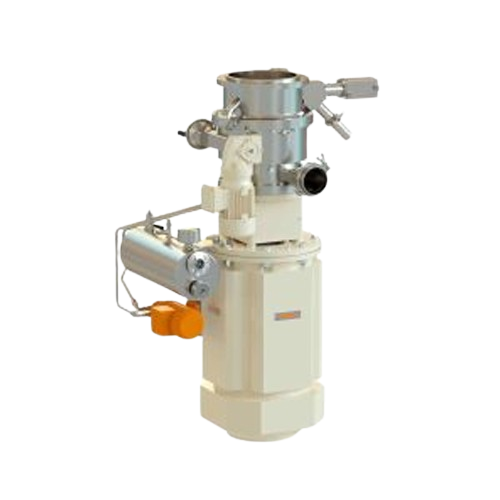
Homogenizer for high viscosity emulsion and dispersion
Achieve unparalleled dispersion and emulsification with a system d...
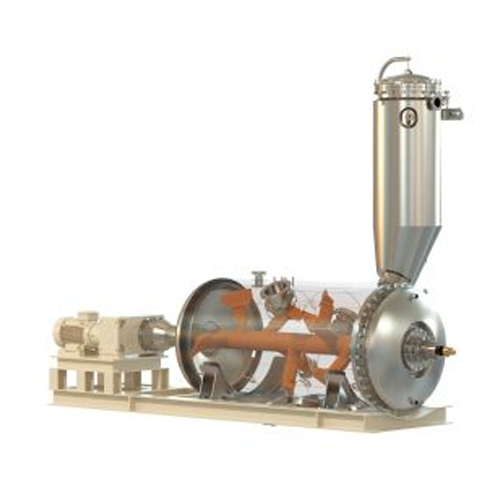
Horizontal vacuum paddle dryer for thermosensitive products
For high-viscosity products like active pharmaceuticals or p...
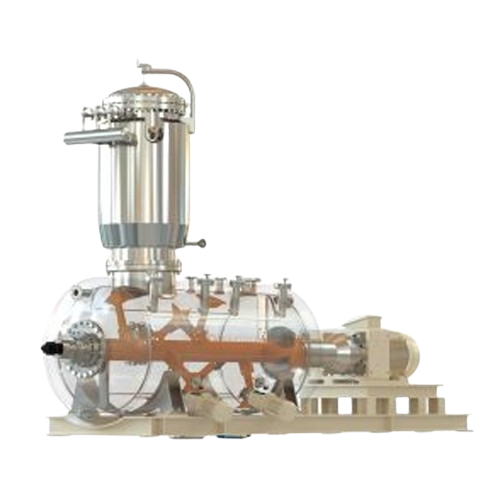
Horizontal vacuum paddle dryer for thermosensitive products
Achieve precise drying and mixing of high-viscosity, thermos...
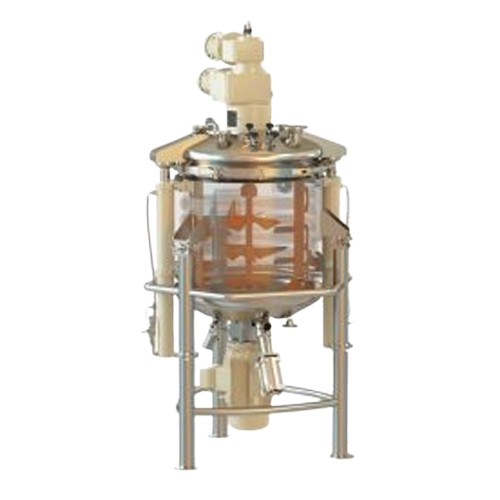
Industrial vacuum mixer and reactor for liquids
For manufacturers needing precise blending and stability, this advanced va...
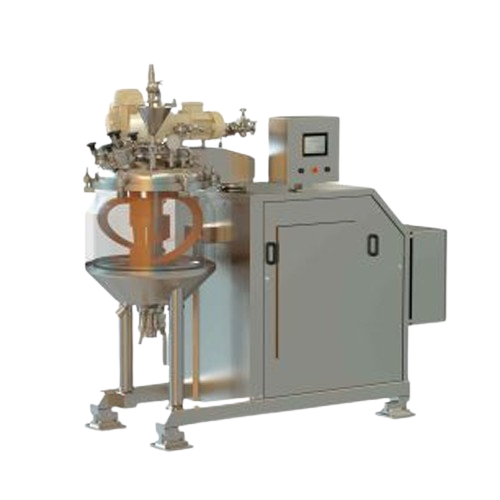
Vacuum mixer for liquids and semi-solids
Achieve precise mixing and homogenization of liquid and semi-solid formulations wi...
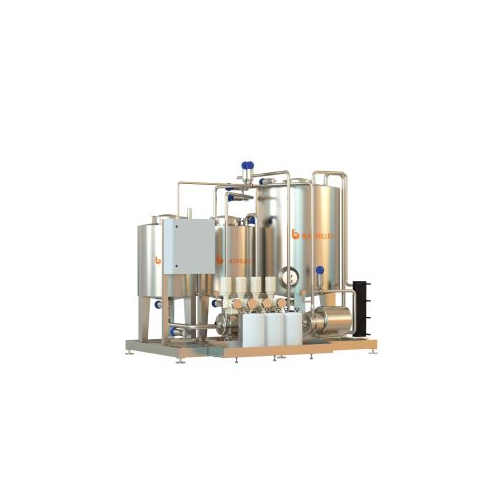
Cip system for process tanks
Ensure high-level cleanliness and compliance in your production line with an efficient in-place...
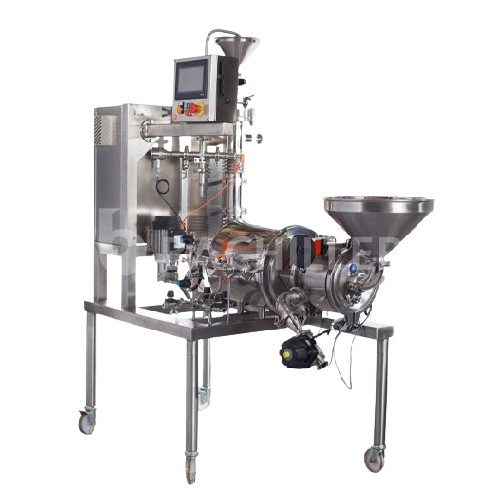
Colloidal mill for fine grinding and homogenisation
Optimize your liquid and semi-solid processing by achieving precise p...
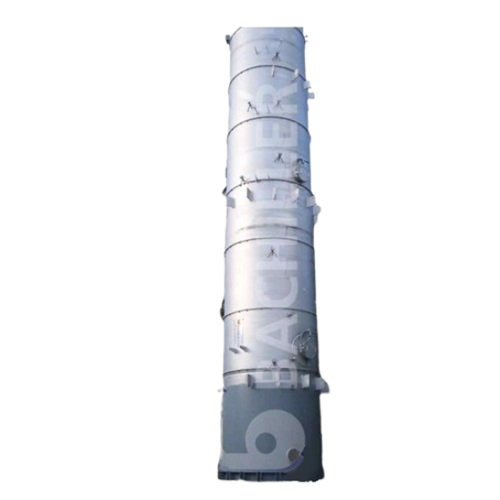
Industrial columns and towers for chemical processing
Optimize your chemical production with robust columns and towers, d...
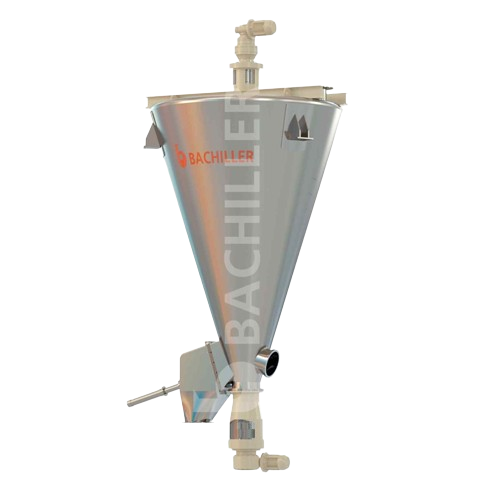
Conical screw mixer for solids and powders
Achieve precise homogenization of your solid and powder mixtures with minimal e...
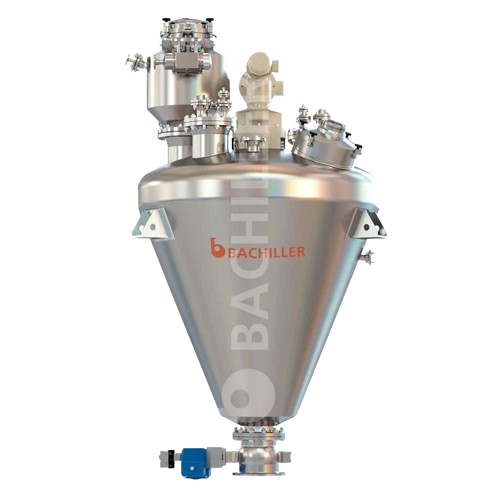
Vertical conical screw vacuum dryer
Achieve precise moisture control with ultra-vacuum batch drying, ideal for thermo-sensi...
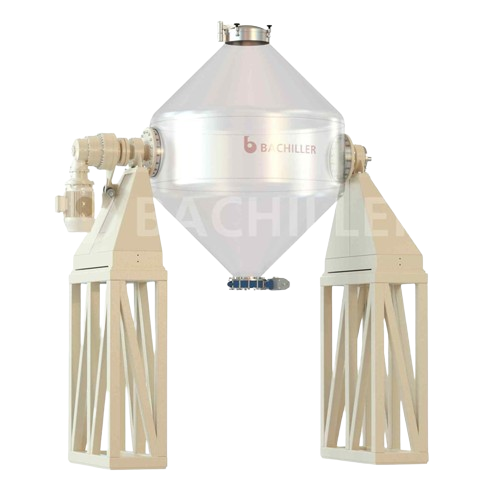
Double cone mixer for powders and solids
Ensure gentle mixing of fragile powders and solids with a low-speed, non-forced bl...

Double cone vacuum dryer for thermosensitive products
For precise drying of heat-sensitive powders, this double cone vacu...
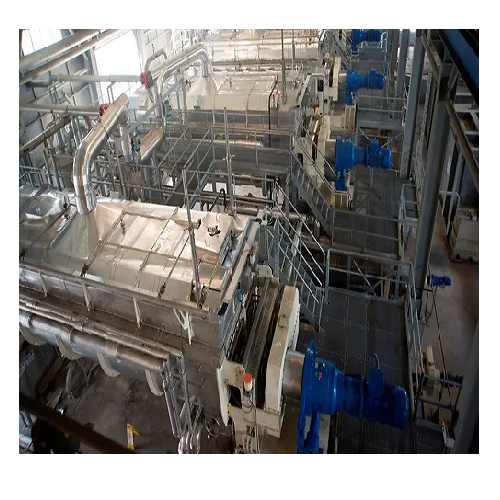
Paddle dryer for industrial sludge
Achieve consistent drying and pasteurization of complex materials with this advanced pad...
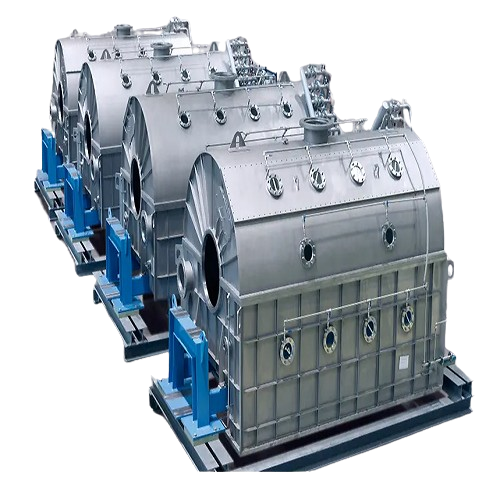
Advanced vacuum and pressure drum filters for high filtration rates
Optimize filtration and separation processes with h...
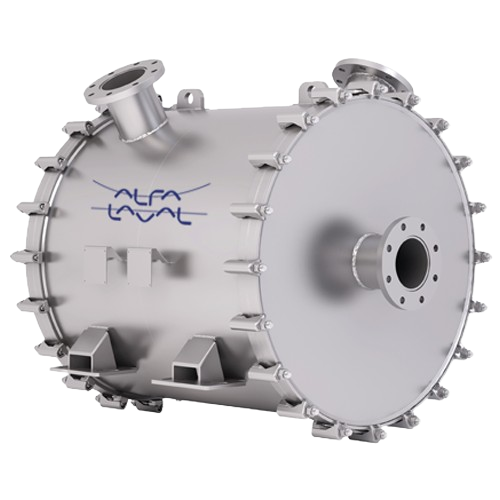
Welded spiral heat exchangers for dirty or viscous fluids
Handle your toughest heat exchange challenges with minimal fou...
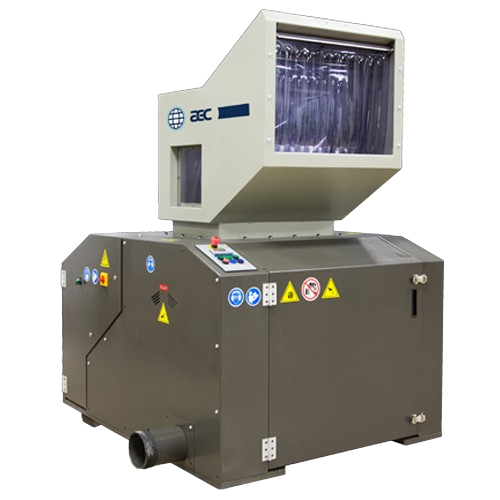
Beside-the-press granulators for injection molding
Optimize your plastic production by efficiently reclaiming resin with ...
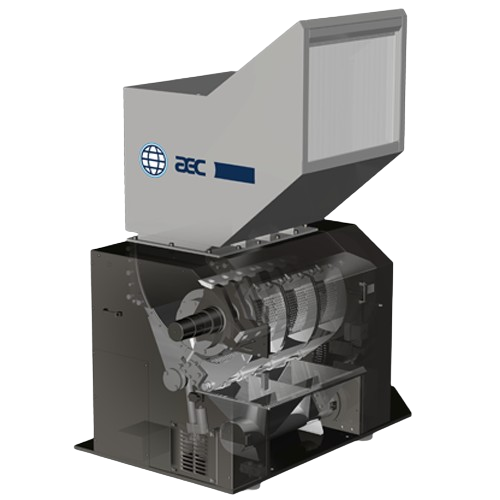
Central granulators for high-volume plastics recycling
Efficiently process large volumes of recycled plastics and industr...
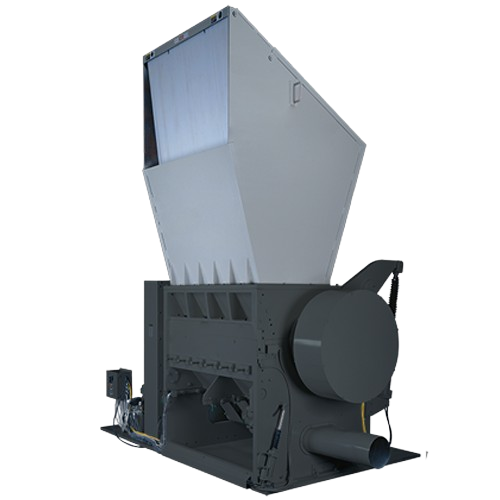
Heavy duty granulator for high-capacity size reduction
When tackling high-volume materials, rely on these industrial-grad...
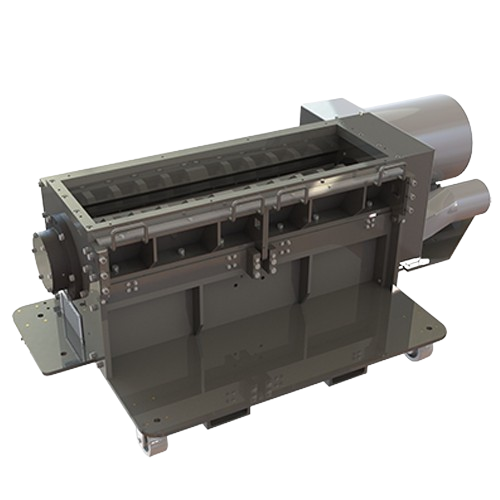
Thermoforming granulators for efficient material processing
Efficiently recycle and optimize your plastic waste by trans...
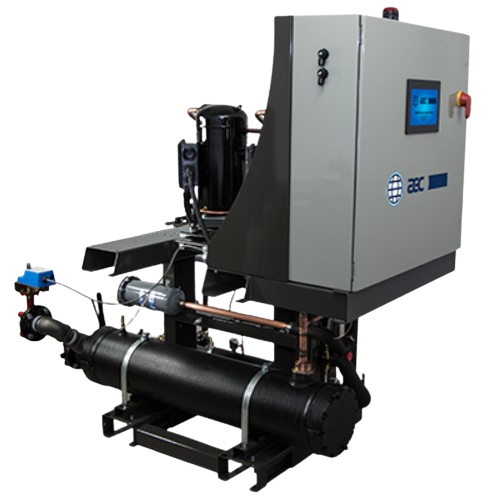
High efficiency central chiller for industrial cooling
Achieve remarkable energy savings with this modular chiller system...

Gravimetric batch blender for precise material handling
Achieve precision in blending complex regrind materials and polym...
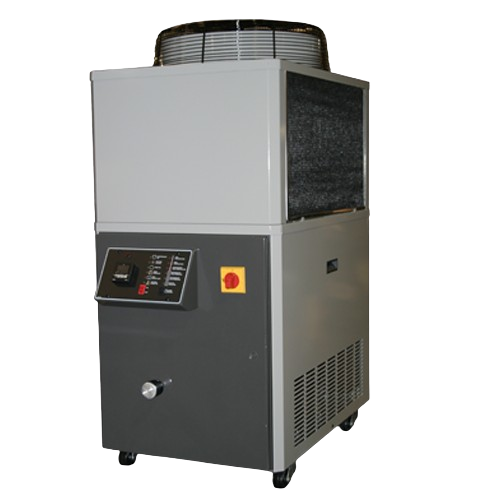
3.5 Hp air-cooled chiller for industrial cooling
Optimize your production with high-efficiency cooling, essential for main...
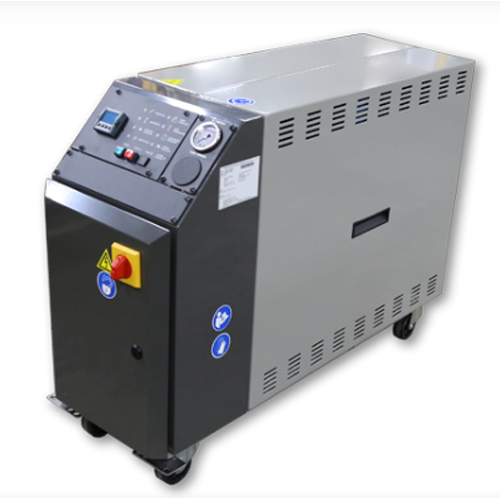
Positive/negative pressure temperature control unit for cooling circuits
Ensure precise temperature regulation and prev...
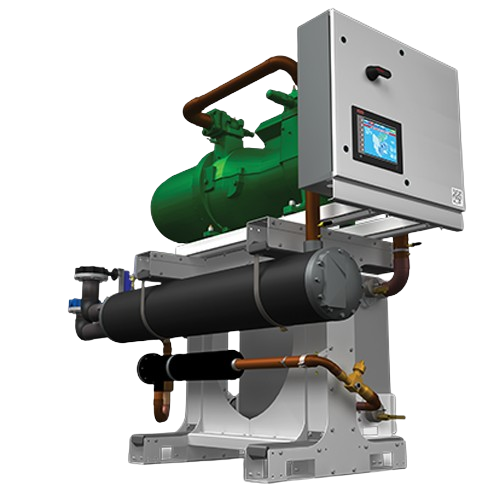
Central chiller for consistent process cooling
Optimize your production with modular central chillers offering scalable co...
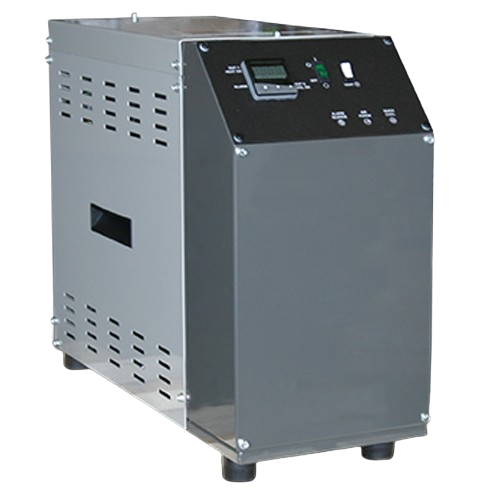
Compact water temperature control unit
Achieve precise temperature control in cramped production spaces, enabling consisten...
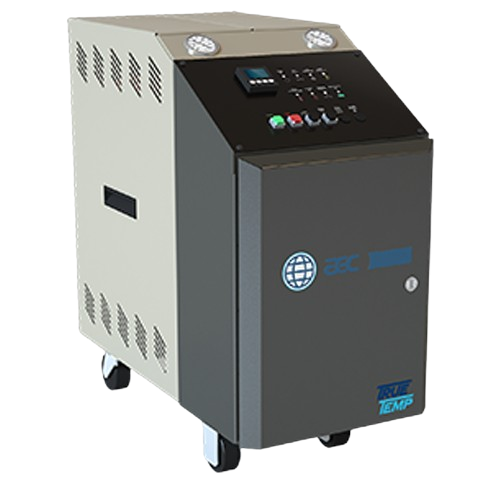
Water temperature control unit for production applications
Enhance your production efficiency by precisely managing wate...

Stainless steel drying hoppers for plastic processing
Optimize moisture control for thermoplastics with robust drying hop...
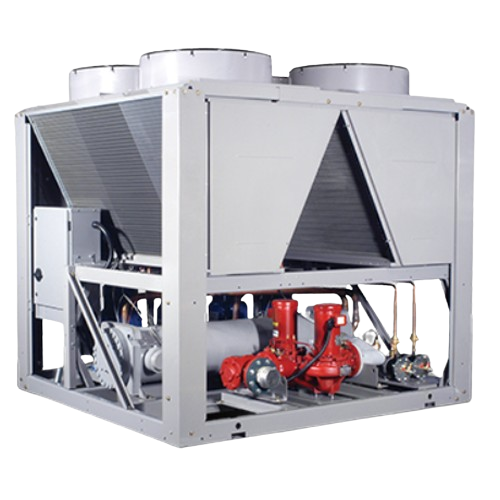
Outdoor central chiller for process cooling
For facilities needing reliable process cooling without sacrificing indoor spa...
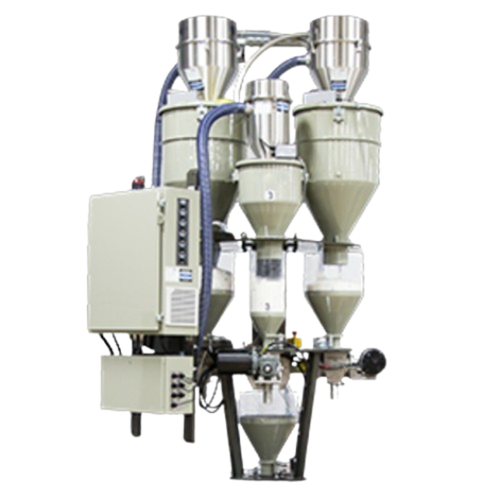
Continuous loss-in-weight blender for extrusion applications
Ensure precise ingredient ratios for extrusion processes wi...
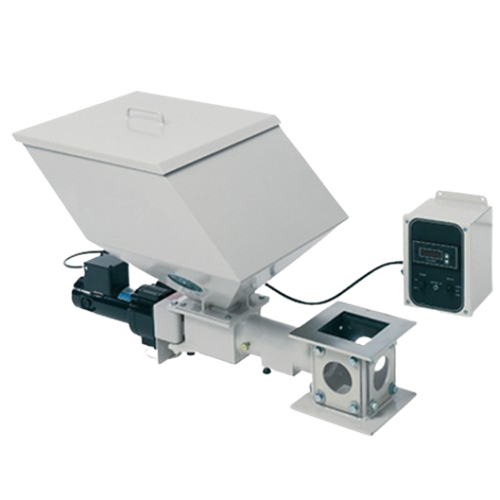
Volumetric additive feeders for injection and extrusion processes
Ensure precise and consistent blending of color conce...
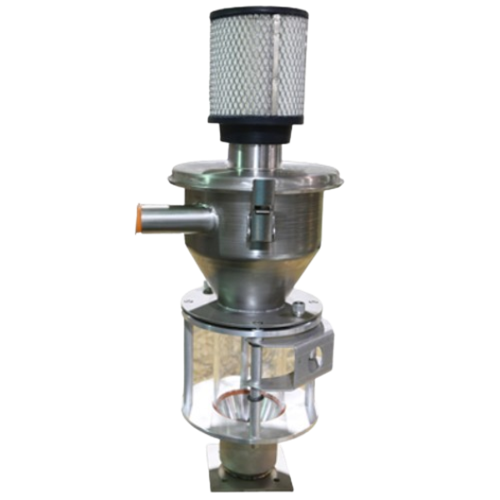
Compressed air loaders for material conveying
Efficiently convey diverse materials with minimal operator intervention, usi...
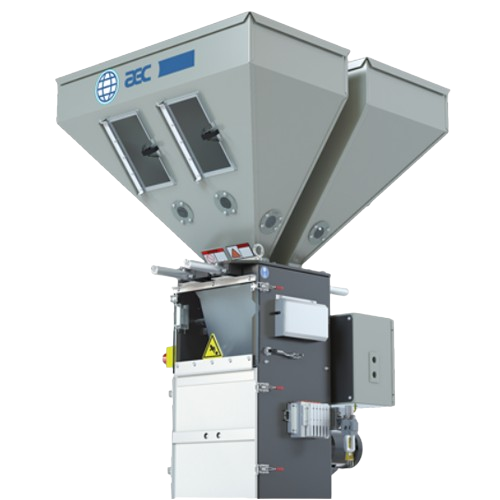
Gravimetric batch blender for injection molding and extrusion
Enhance your polymer blending precision with a solution ta...
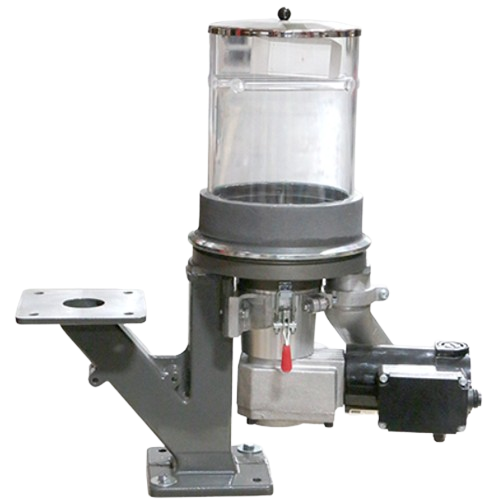
Digital doser system for plastics additive feeding
Achieve precise additive dosing for plastics, ensuring consistent qual...
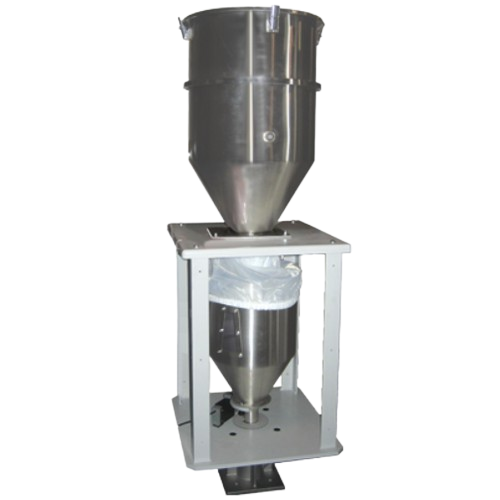
Extrusion control units for high precision manufacturing
Optimize your extrusion process with precision control over thro...
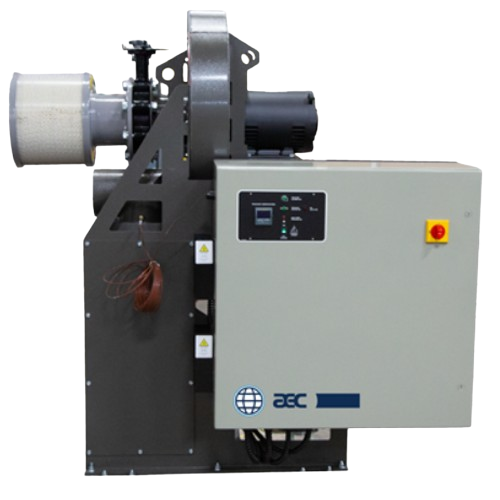
Hot air dryers for non-hygroscopic material
Ensure reliable material quality by effectively reducing moisture in non-hygro...
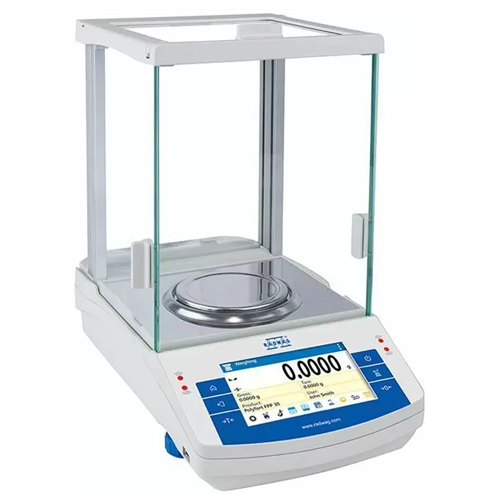
High precision analytical balance for laboratory use
Ensure precision and reliability in your laboratory measurements wit...
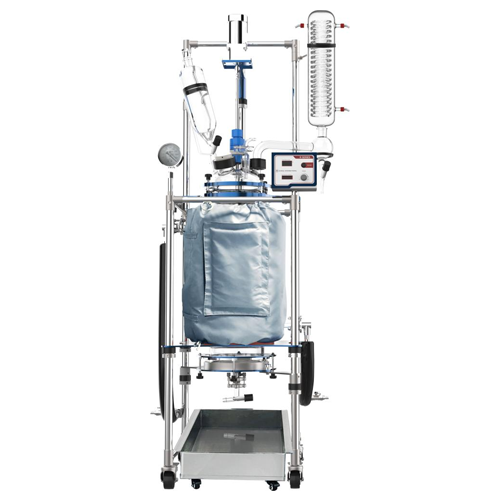
50l jacketed glass reactor for synthetic reactions
Achieve precise control over chemical reactions and material synthesis...
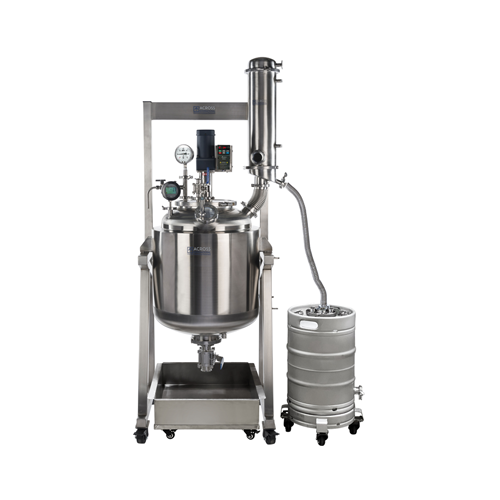
50l stainless steel dual-jacketed reactor for chemical processes
Optimize your laboratory’s efficiency with a dual...
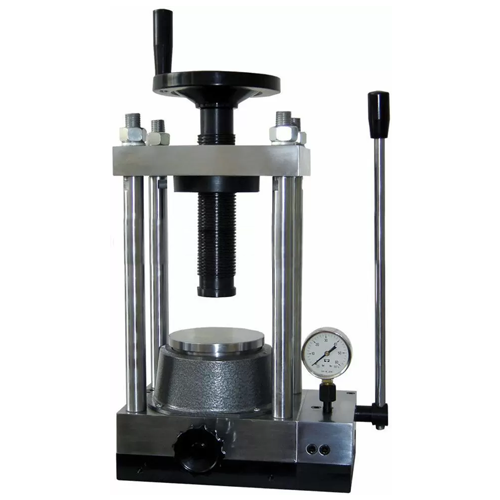
40-ton pellet press for laboratory applications
Achieve precise sample preparation with a 40-ton capacity, ideal for press...
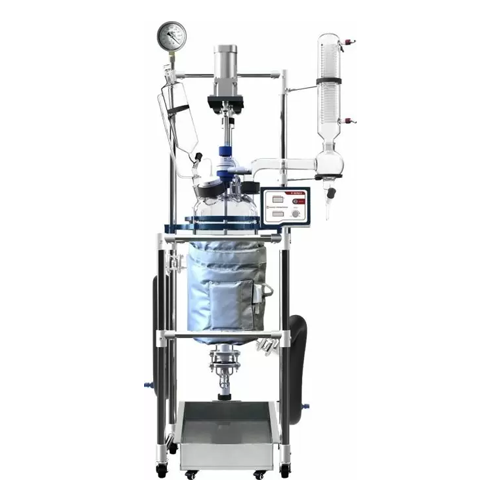
10l glass reactor system for synthetic reactions
Achieve consistent reaction control with efficient temperature and vacuum...
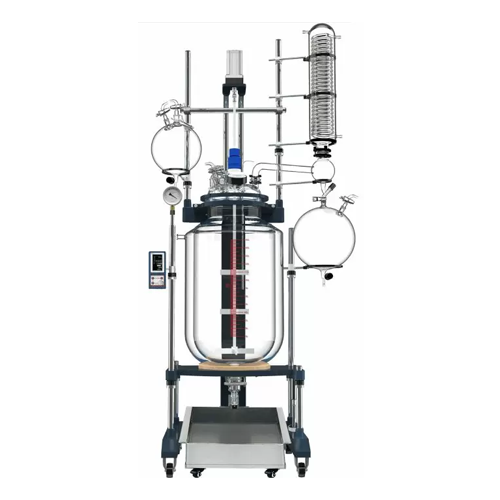
150l jacketed glass reactor for chemical synthesis
Achieve precise control over complex chemical processes with this sing...
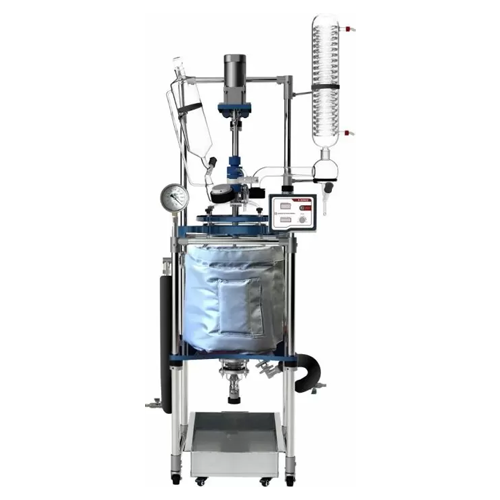
20l jacketed glass reactor system for laboratory synthesis
Achieve precise chemical synthesis and enhanced material reco...
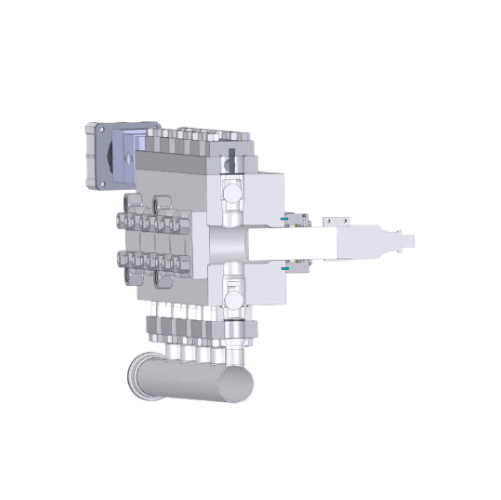
High pressure homogenization for polymer nanodispersions
Effortlessly handle challenging products with fibers or solid pa...
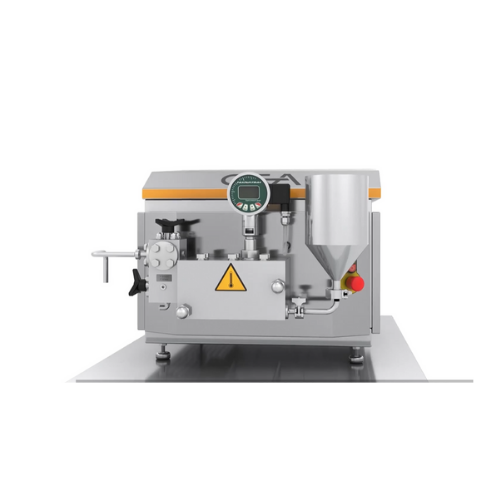
Laboratory homogenizer for small production processes
Optimize your production of nanoemulsions, vitamin suspensions, and...
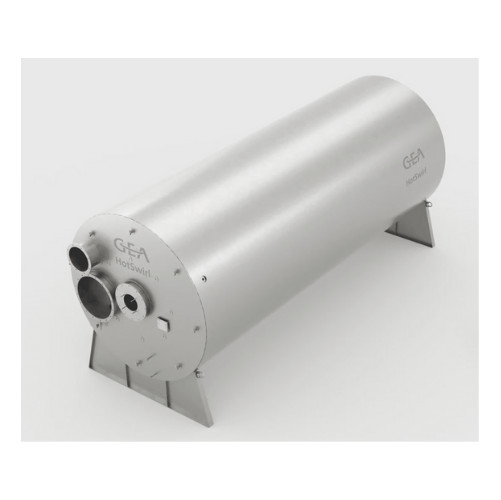
Industrial hot air system for spray dryers
Ensure consistent hot air delivery for critical drying processes, enhancing ene...
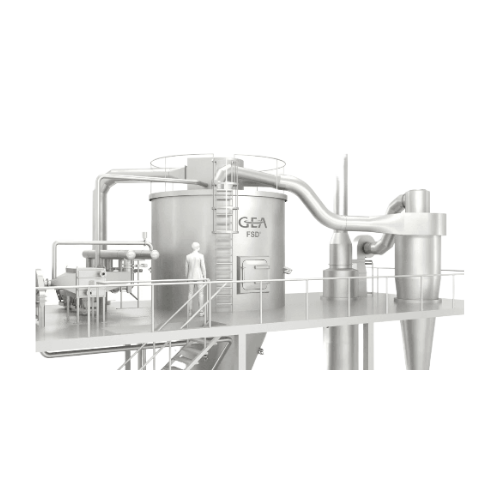
Spray dryers for ceramics and pharma products
Achieve consistent powder quality for heat-sensitive and sticky products wit...
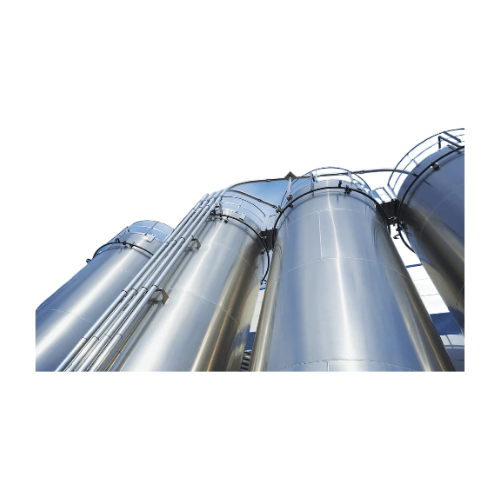
High-yield fermentation system for raw material processing
Achieve precise control in fermentation with advanced systems...
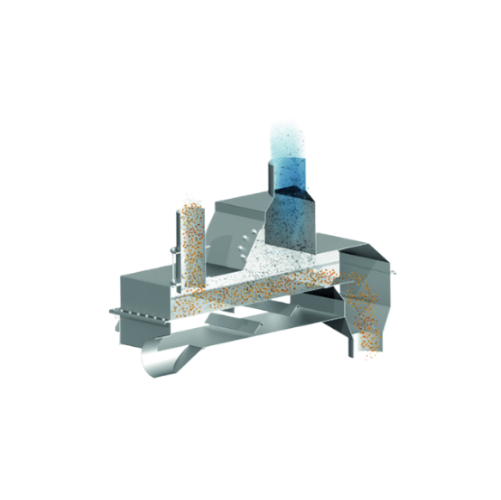
Vibratory pellet separator for dust and streamer removal
Achieve high-efficiency separation of dust and streamers from po...
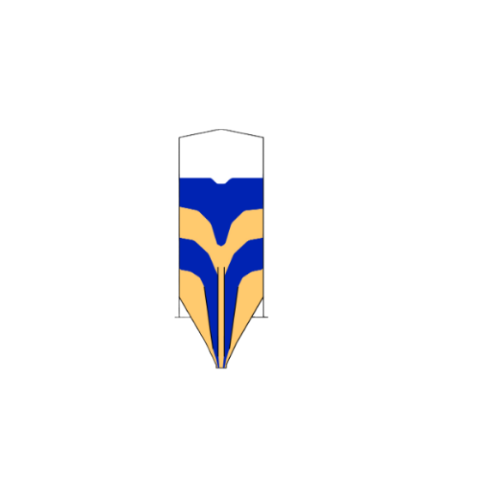
Blending silo for free-flowing and poorly flowing bulk materials
Achieve precise blending and mixing of diverse bulk mat...
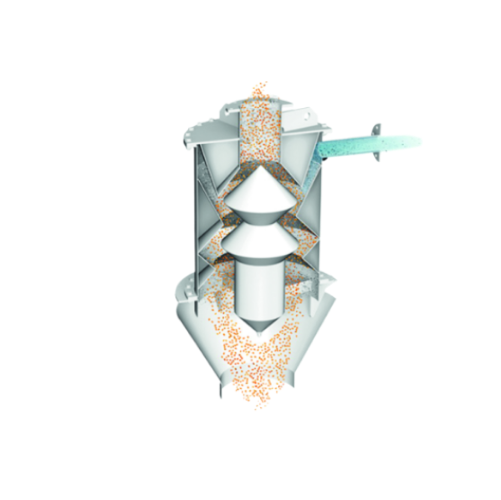
Air separator for polymers and plastics
Ensure high-purity plastic pellets by efficiently separating fine dust and streamer...
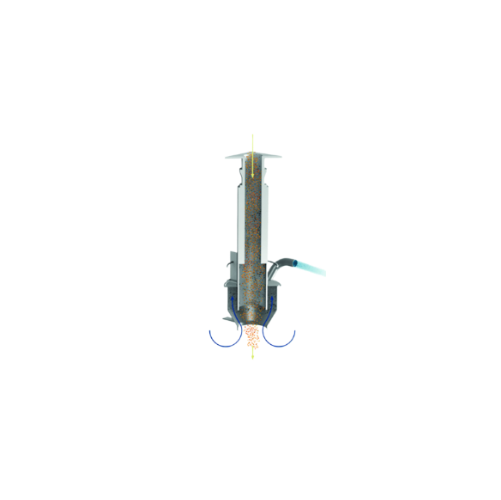
Gravimetric loading sifter for dust and streamer removal
Optimal for removing dust and streamers, this compact sifter ens...
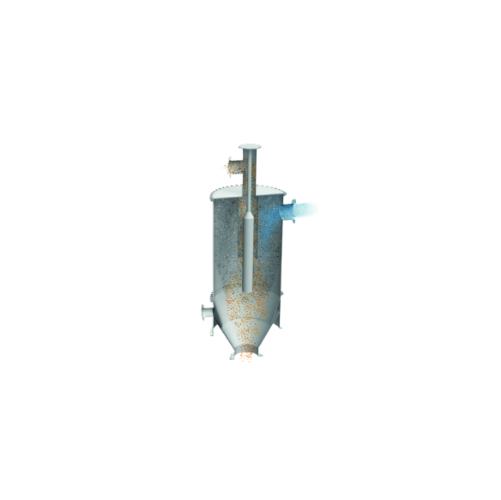
High-efficiency pellet dust separator
Achieve unparalleled separation efficiency in your polymer production line by removin...
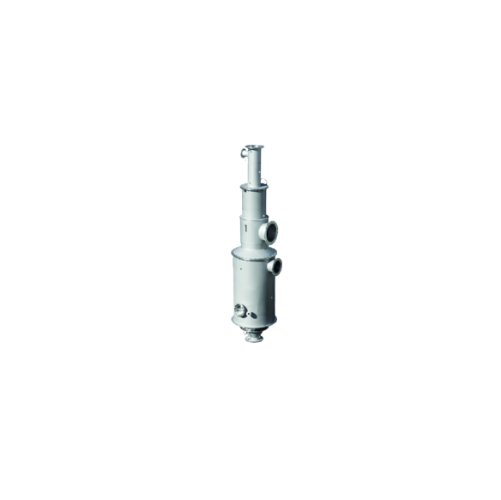
Counterflow separator for polymer pellet cleaning
Achieve unparalleled pellet purity with efficient dust and streamer rem...
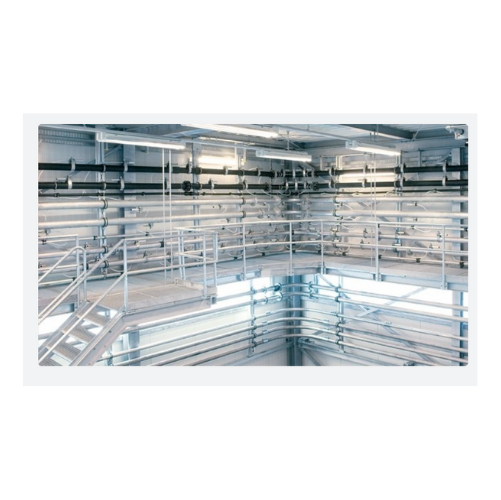
Industrial conveying system for carbon black and silica
Ensure dust-free conveyance of sensitive materials like carbon bl...
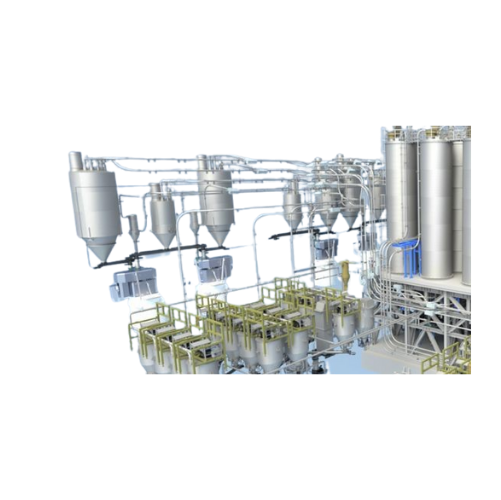
Dispersion paint production systems
Achieve 100% color accuracy and flexible production with our advanced system, ensuring ...
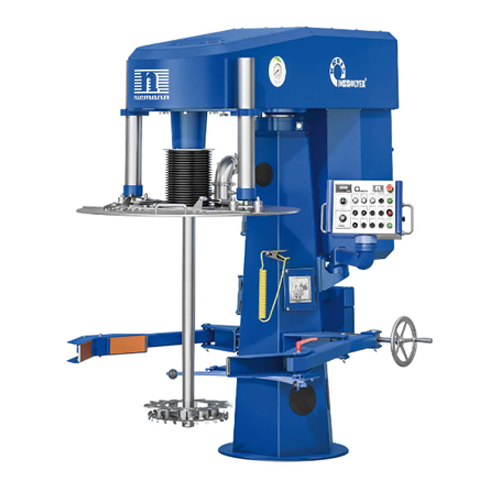
High-efficiency disperser for viscous products
Achieve precise control over the mixing and dispersing of high-viscosity ma...
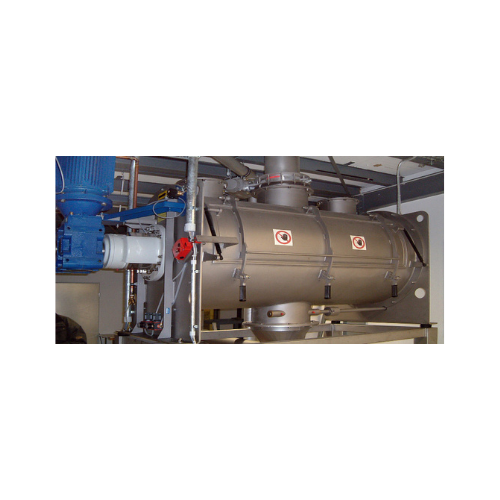
Batch-type single shaft mixer for efficient discharging
Optimize your material mixing and discharging processes with a sy...
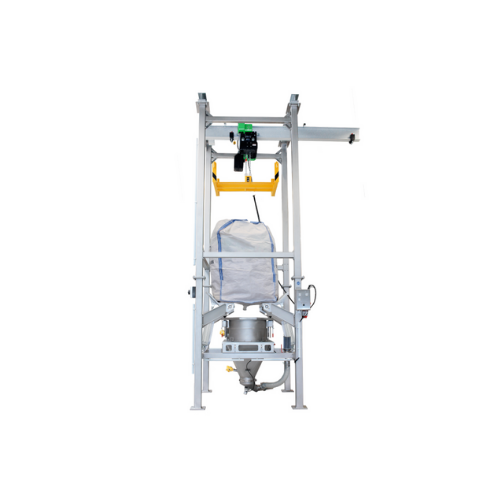
Big-bag unloading station for bulk materials
Facilitate seamless integration into your production line with efficient bulk...
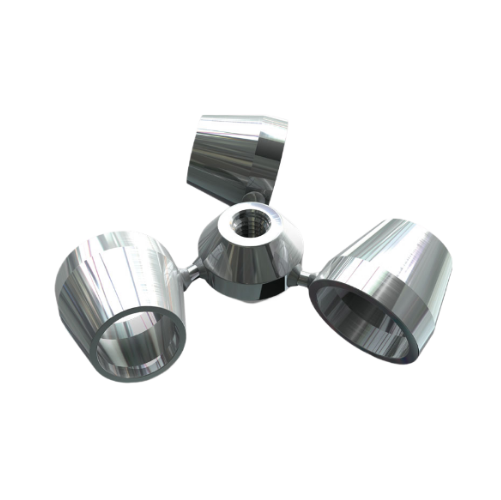
Homogenizer for low to medium viscosity media
Achieve uniform mixing and prevent air entrapment in low to medium viscosity...
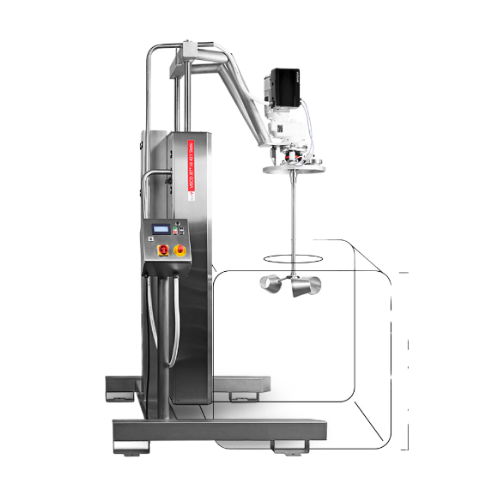
Industrial mixer for product-critical processes
When dealing with high-hygiene requirements and complex mixing tasks acros...
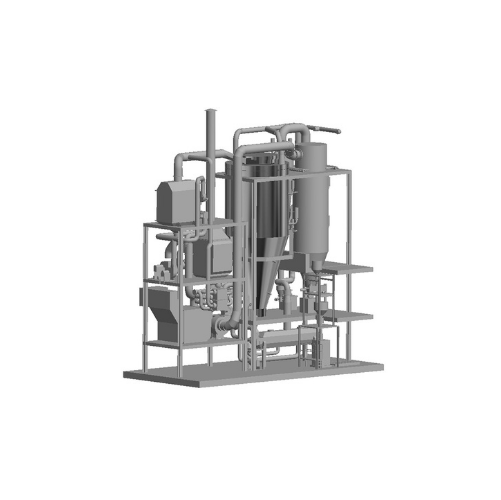
Spray drying system for heat sensitive products
For heat-sensitive products requiring precision drying, this spray drying ...
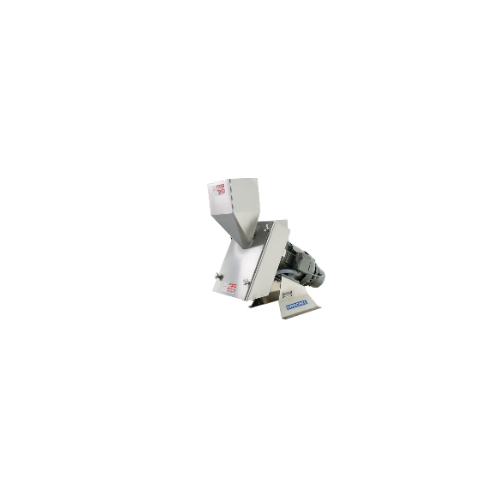
Industrial food processor for diverse applications
Optimize your production line with a versatile processor capable of ch...
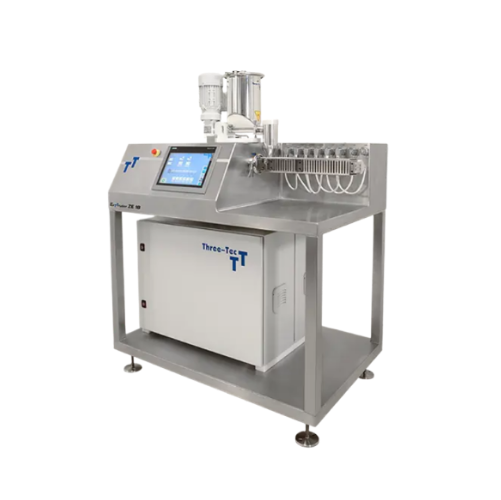
Twin-screw extruder for high containment applications
Achieve precise mixing of sensitive compounds with a twin-screw ext...
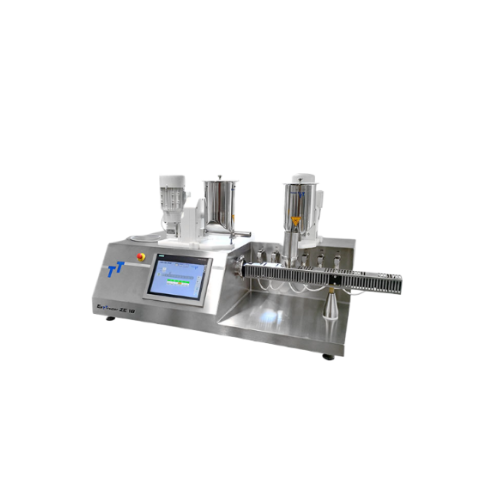
Table top extruder for customizable extrusion processes
Discover versatile extrusion capabilities for developing complex ...

Hybrid laboratory extruders for reproducible scale-up applications
Easily switch between screw diameters to enhance fle...
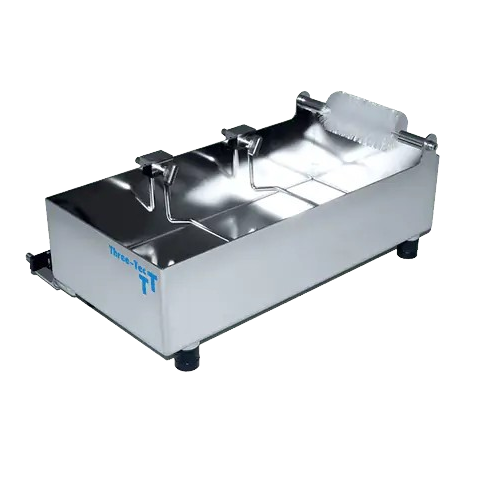
Cooling bath for efficient extrudate processing
Ensure optimal cooling for extrudates to maintain product integrity and en...
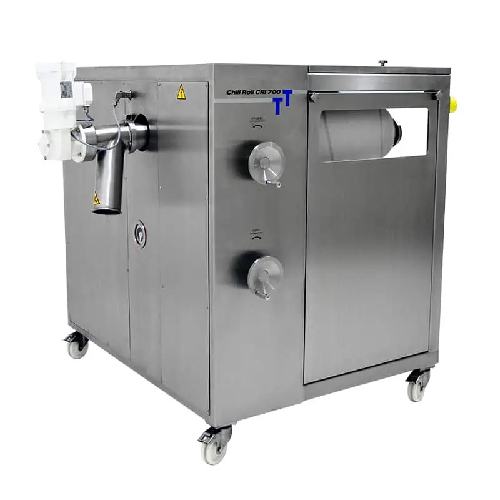
Continuous cooling roller for extrudates
Ensure rapid and efficient cooling of high-heat capacity extrudates with a compact...
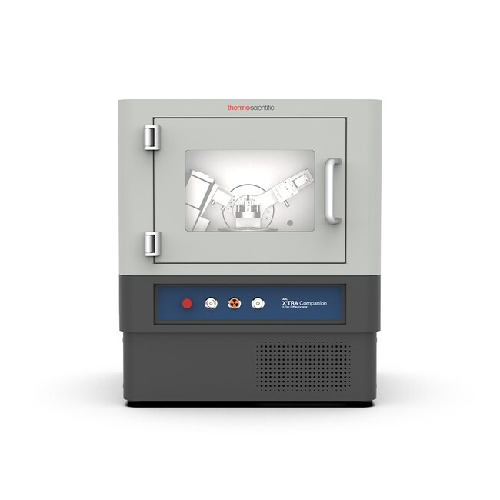
Benchtop x-ray diffractometer for routine analysis
Achieve high-precision phase analysis and crystalline characterization...
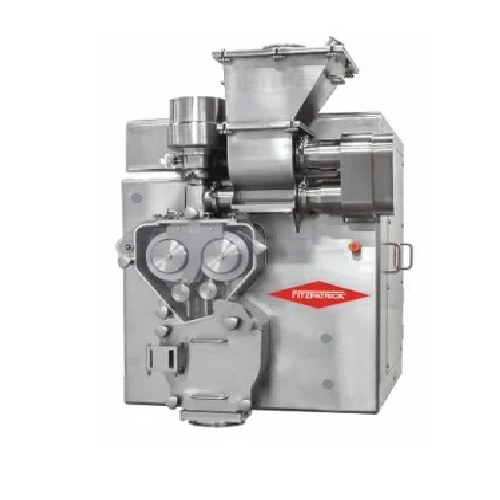
Roller compactors for dry granulation
Optimize your powder processing with advanced roller compaction, ensuring consistent ...
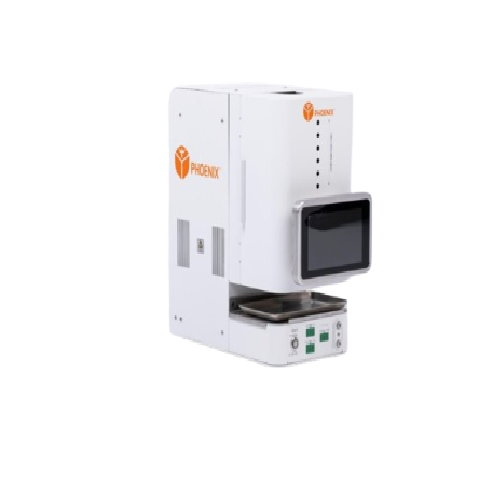
High-temperature and high-pressure flow reactor
Achieve unparalleled precision in high-temperature and high-pressure chemi...
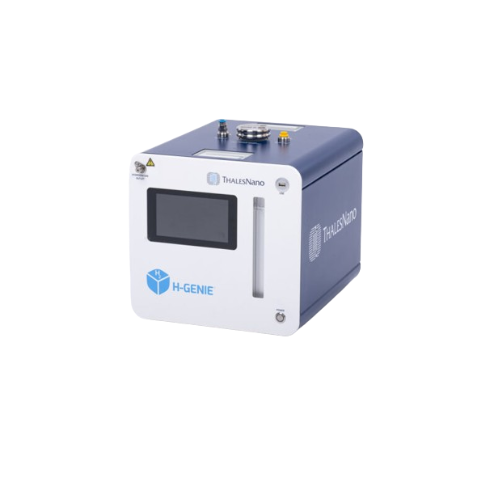
High-pressure hydrogenation reactor for chemical labs
Achieve precise high-temperature hydrogenation with integrated on-d...
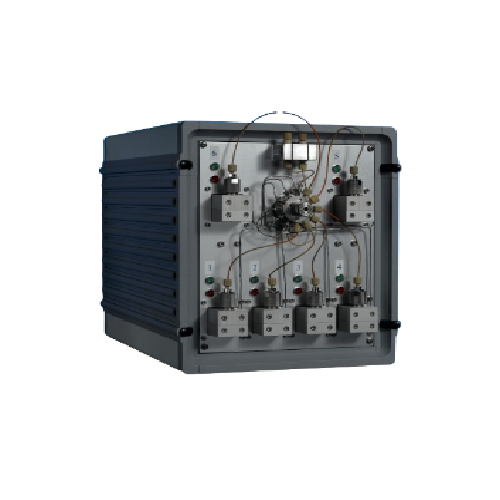
Catalyst cartridge switching system for flow chemistry
Effortlessly switch between multiple catalysts in a single run, op...
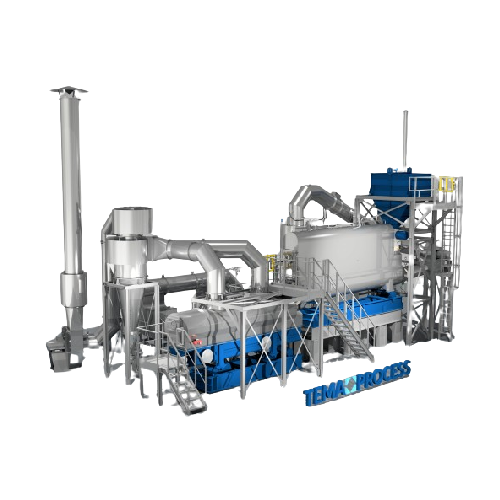
Vibrating fluid bed dryer for bulk materials
Ensure efficient moisture removal and thermal processing with this fluid bed ...
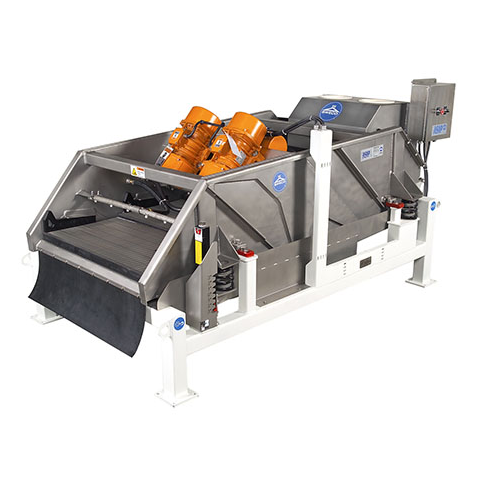
Multi-motion rectangular separator
Solve screen blinding effortlessly with an innovative system that combines elliptical an...
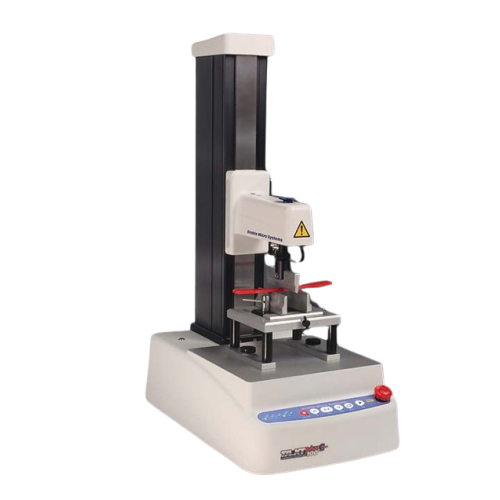
High-force texture analyser for precise measurement
Achieve unparalleled precision in texture analysis for high-force app...
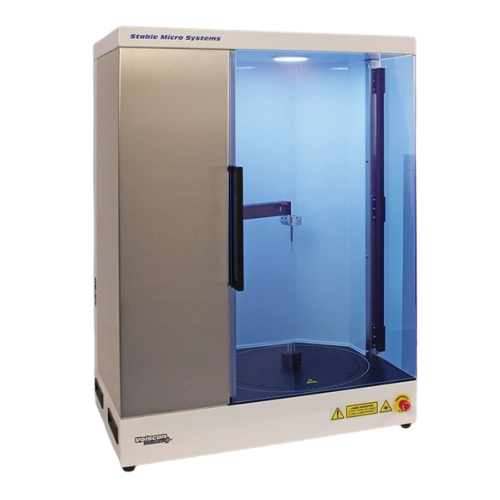
Laser-based volume measurement for bakery and solid products
For precision in product quality control, this laser-based ...
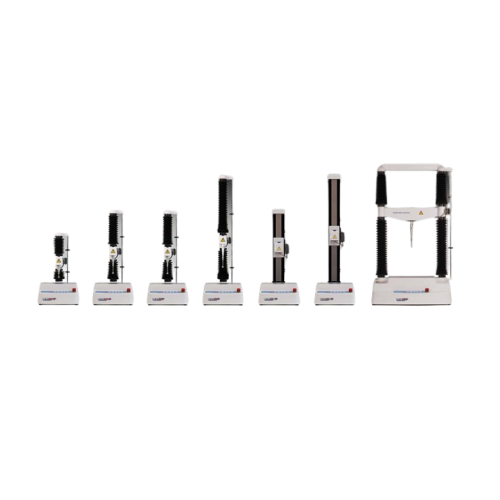
Portable texture analysis for low force applications
Easily perform precision texture measurements on low-force applicati...
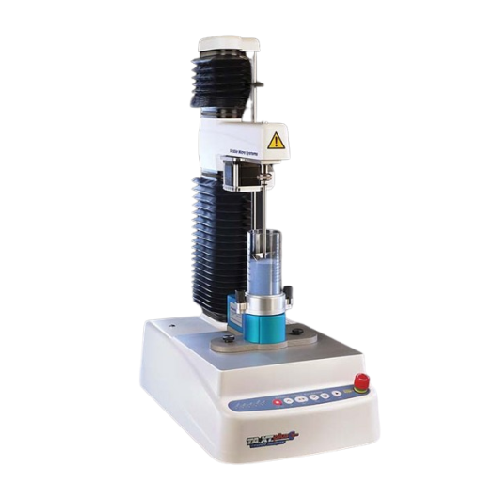
Powder flow measurement system
Achieve precise control over powder consistency and prevent process disruptions by assessing ...
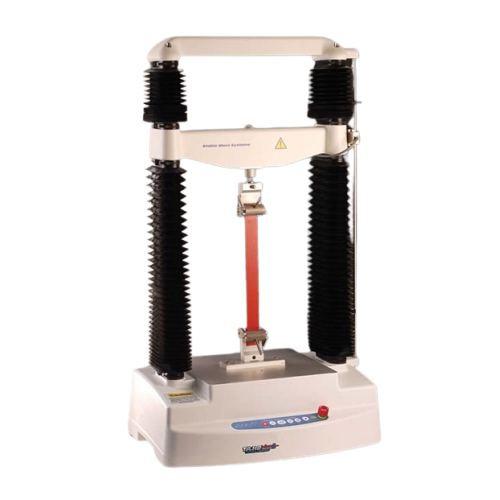
Texture analyzer for high force applications
Achieve precise texture measurement across a vast array of products with a so...
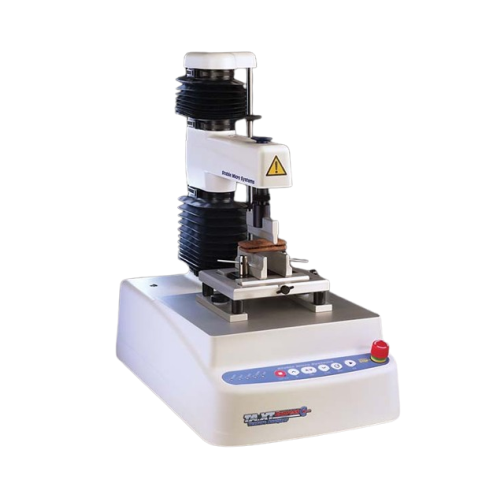
Entry-level texture analysis system for Qc applications
Perfect for quality control labs, this portable system streamline...
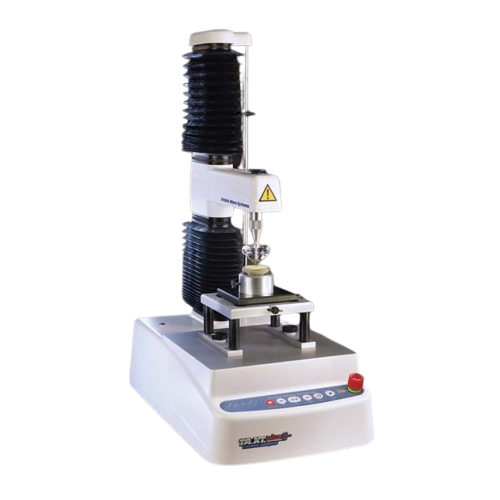
Texture analyser for food and cosmetics testing
Ensuring consistent product quality across diverse food and cosmetic appli...
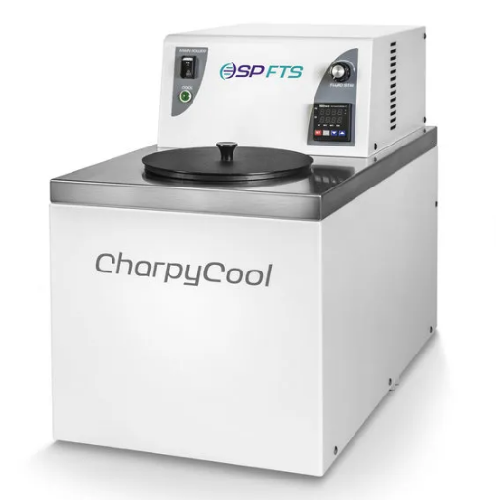
Low temperature bath for charpy impact testing
Achieve precise and stable low-temperature conditions for accurate Charpy i...
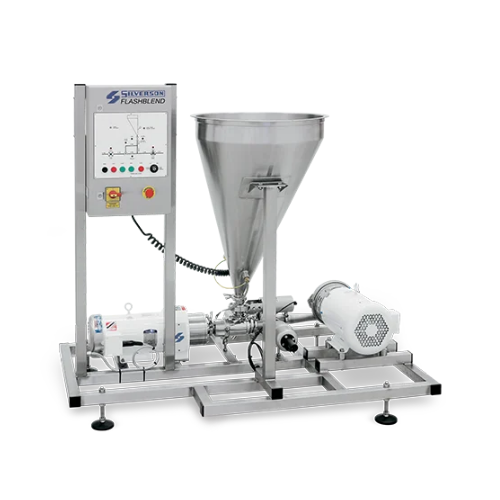
Powder/liquid mixing system for homogeneous dispersions
Struggling to integrate challenging powders into liquid formulati...
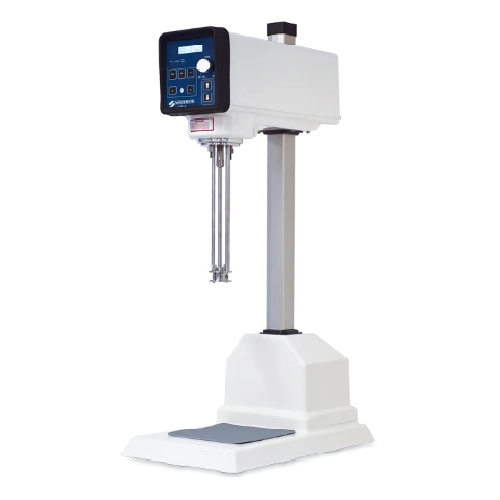
High shear lab mixer for laboratory work and r&d
Achieve unparalleled precision and consistency in laboratory and pilot-sc...
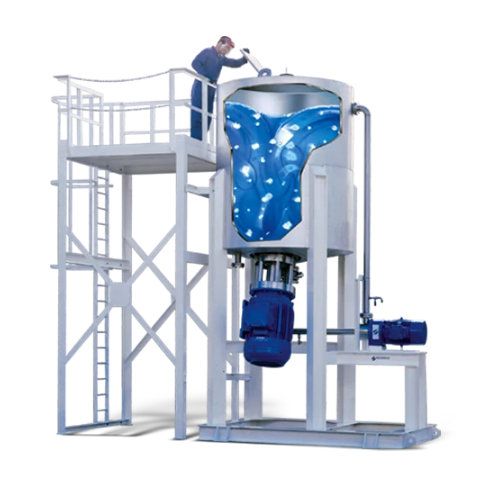
Disintegrator/dissolver mixing system for large solids
Streamline your process by transforming large, challenging solids ...
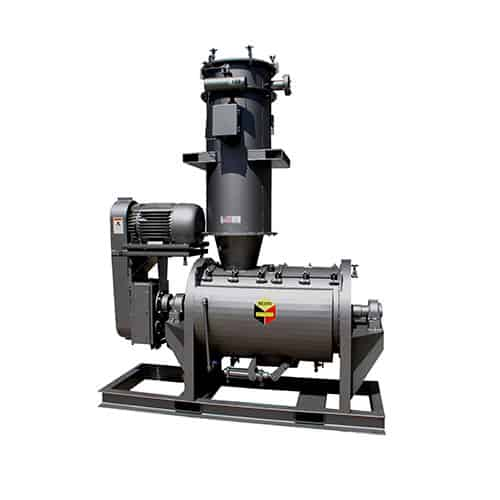
Industrial vacuum batch dryer for reducing moisture content
Achieve precise moisture control with a solution that handle...
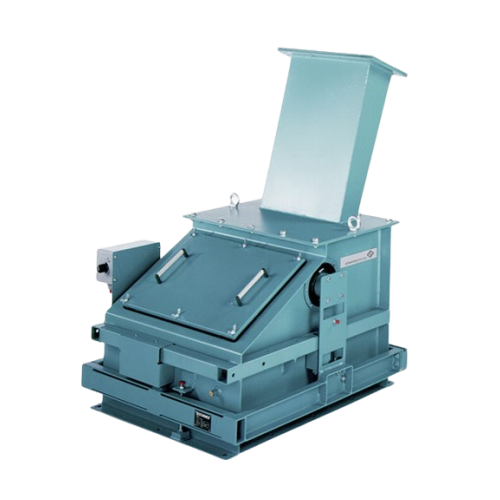
Solid flow meter for continuous bulk material measurement
Ensure consistent and accurate measurement of bulk solid mater...
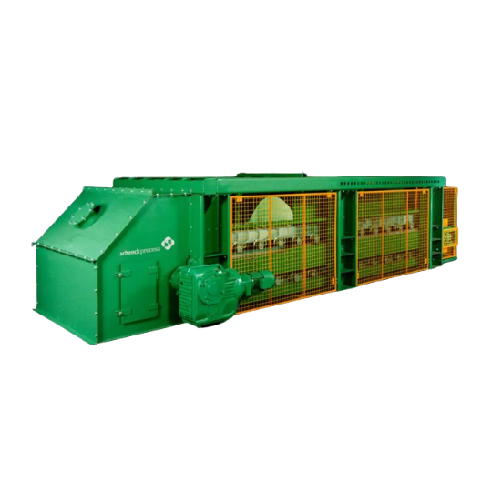
Apron weighfeeder for sticky bulk materials
Optimally handle challenging, sticky materials with precision and consistency ...
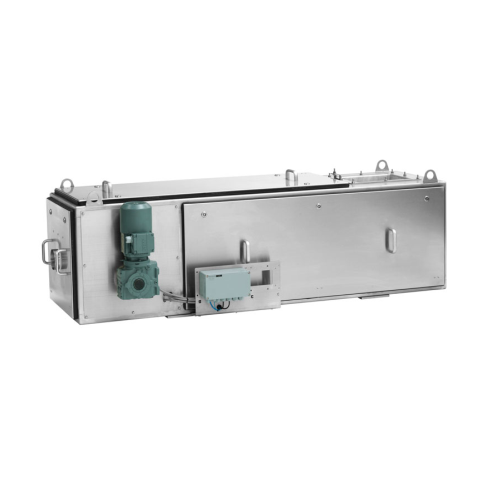
Continuous and batch feeding system for bulk materials
Achieve precise bulk material feeding with seamless integration in...
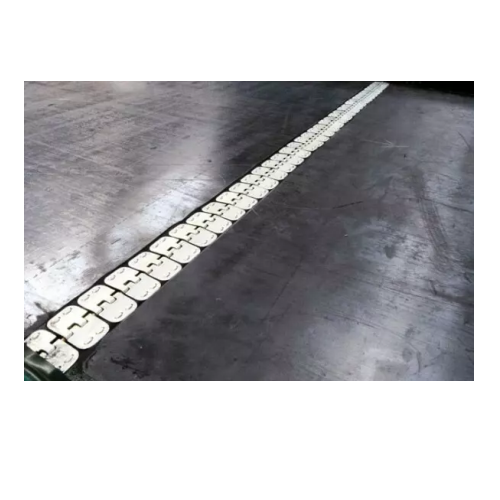
Optimal maintenance solution for industrial weighfeeders
Streamline your processing operations with a solution that minim...
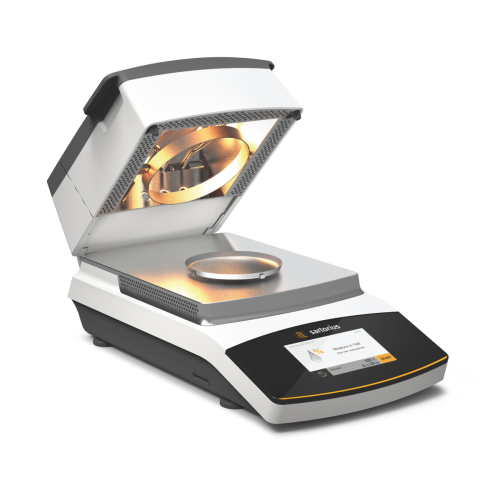
Fast and accurate moisture meter for various samples
Quickly determine moisture content in solids, liquids, and pastes wi...
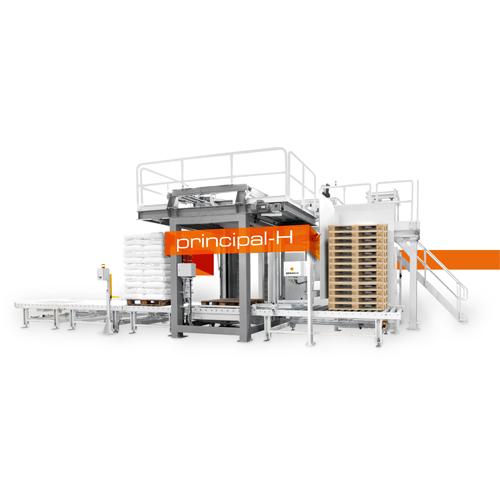
Automatic palletizer machine for bags and boxes
The effective placement and positioning of bags and boxes can be a challen...
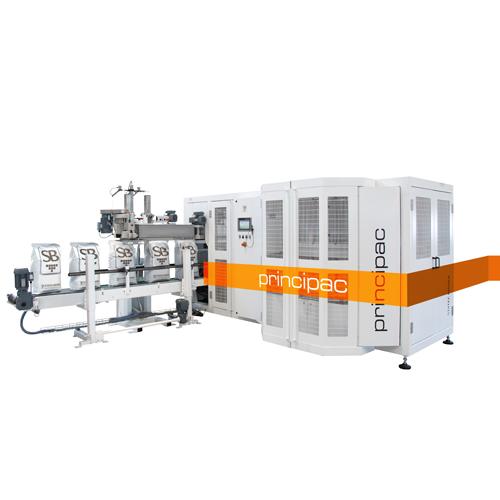
Open mouth bagging machine
If you are a manufacturer of fertilizers, bulk chemicals, sugar, seeds, or any grains it is likel...

Open mouth bag filling machine for powders
The packaging of powdery products such as flour can be challenging as it is cru...
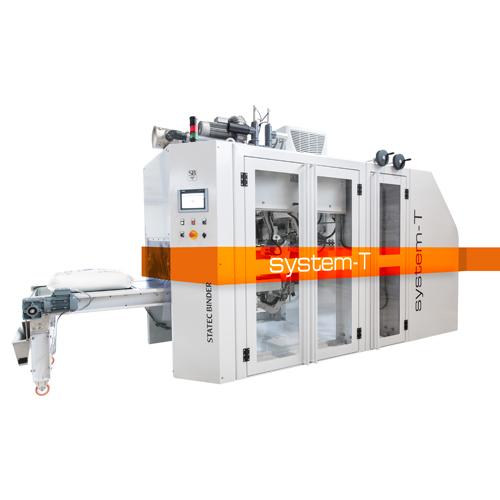
Form fill seal bagging machine
If you are in industries such as petrochemicals, fertilizers, animal feed, food, etc, you mus...
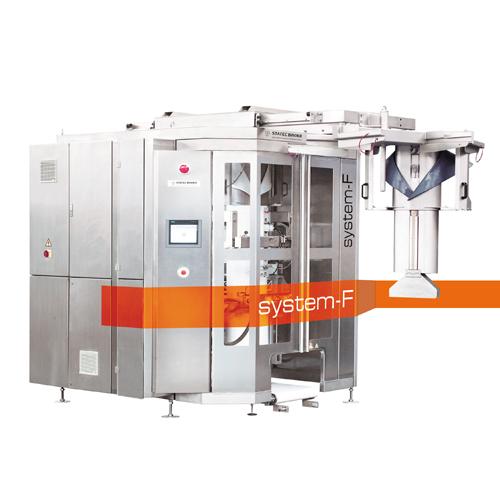
Vertical form fill seal machine
There is an increasing demand for a range of different package sizes of the same product. If...
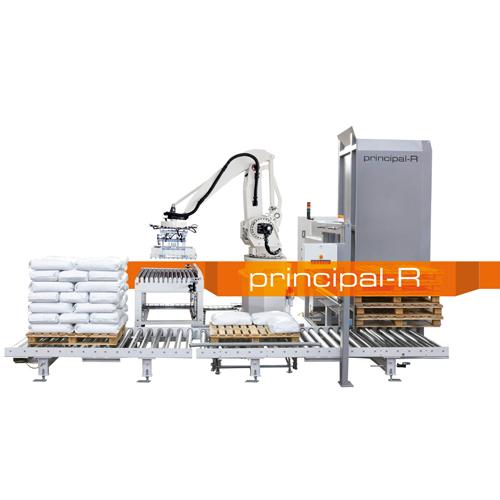
Robot palletizing system
If you are a relatively large-scale producer, packing and transporting large quantities of products ...
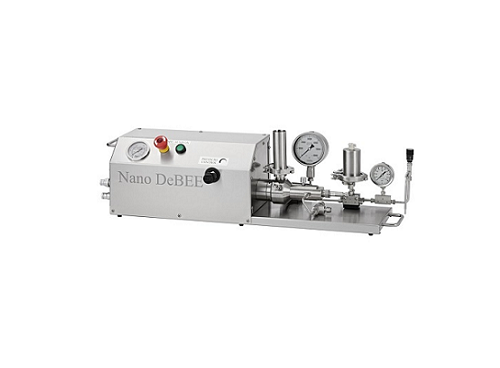
High pressure electric laboratory homogenizer
It’s vital that small units for experimentation can scale up with 100% accur...
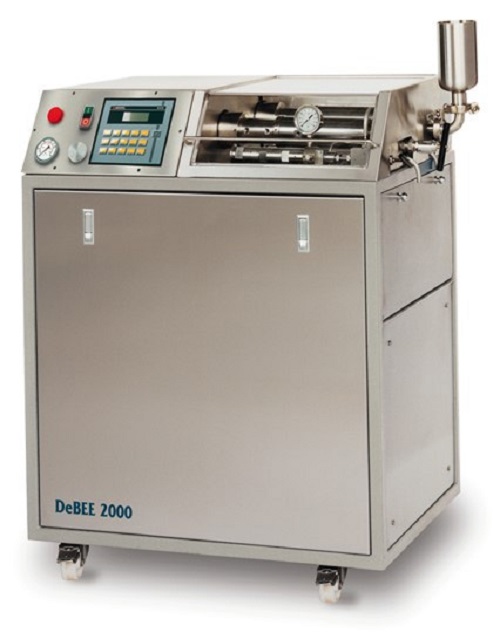
High pressure pilot homogenizer
Biotech and pharmaceutical development programs often require a mixing method that achieves ...
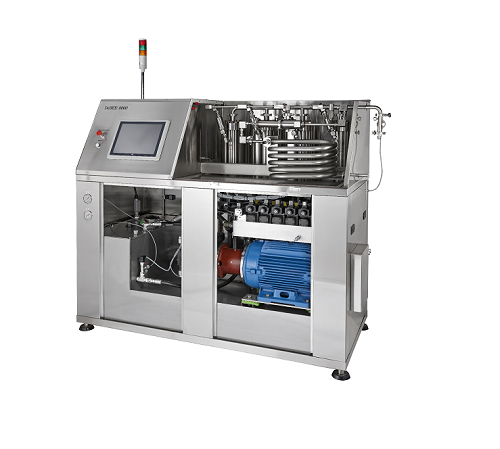
High pressure industrial homogenizer
For any industrial pharmaceutical process that relies on high pressure homogenization ...
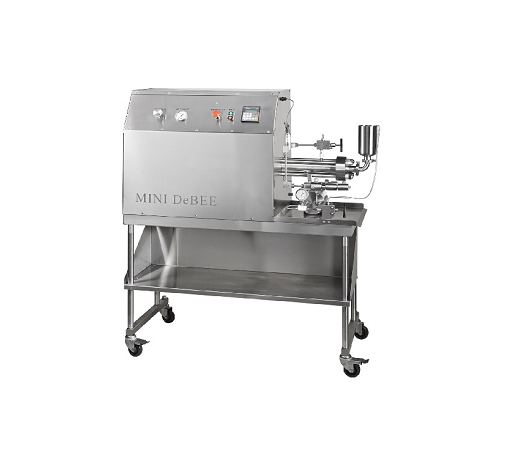
Pilot high pressure homogenizer
For maximum value, a high-pressure homogenizer that’s suitable for both laboratory and pilot...
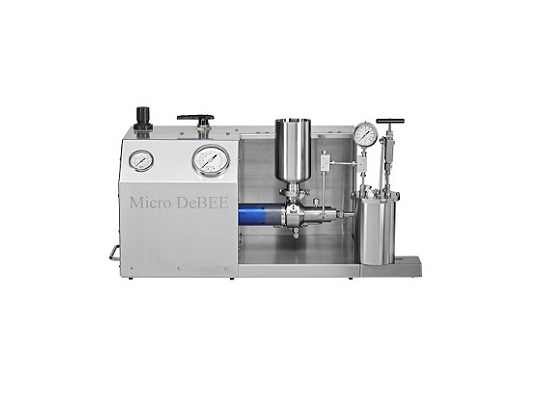
High pressure air powered laboratory homogenizer
Offering lab-scale to small pharmaceutical production scale output for in...
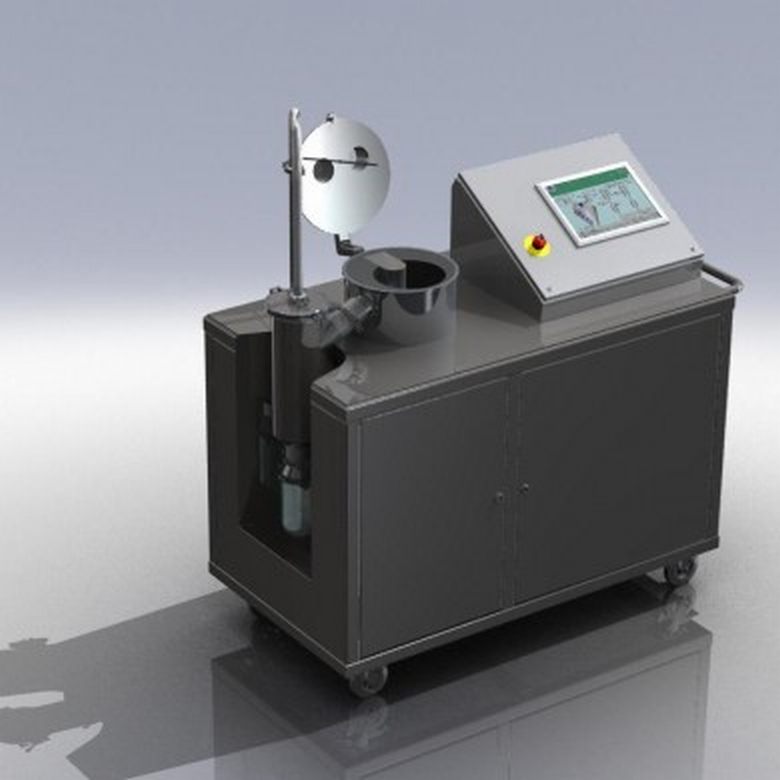
Laboratory scale active freeze dryer
The laboratory-scale active freeze-drying is used for dehydrating high-value products ...
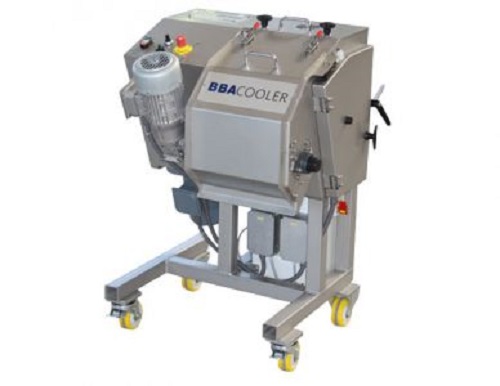
Drum cooler for laboratory hot melt processes
Do you need to cool molten masses to solid, thin film or flakes in an R&...
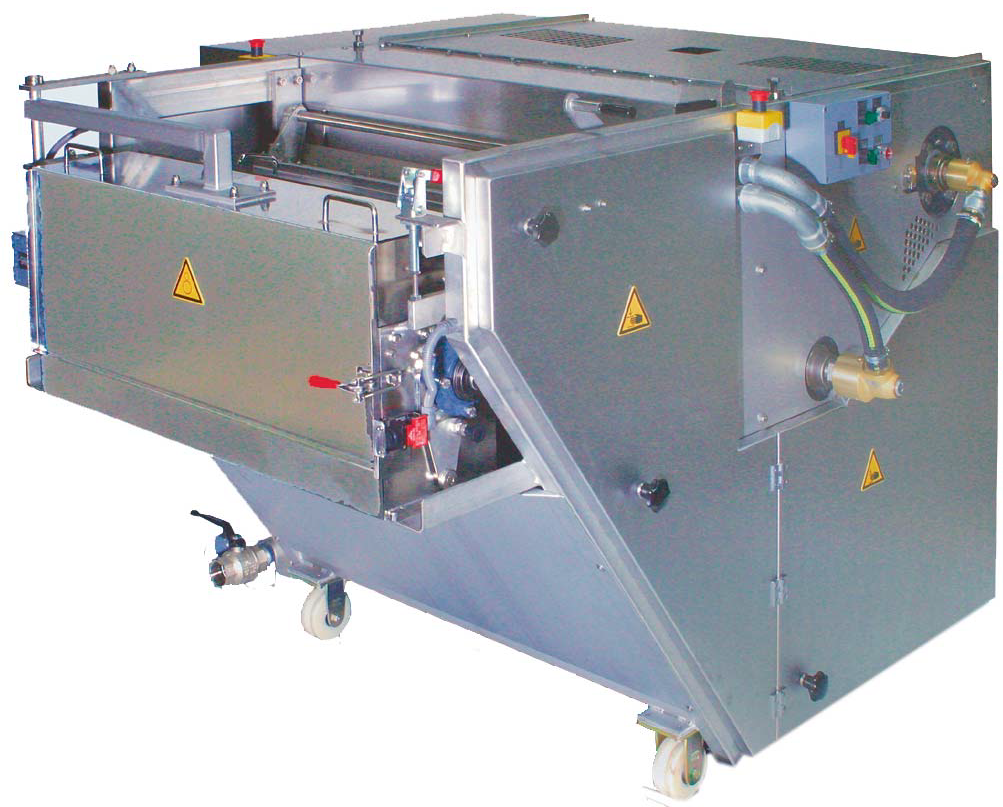
Drum cooler for hot melt processes
Medium-scale production of extruded hot melt masses benefits from reliable, efficient co...
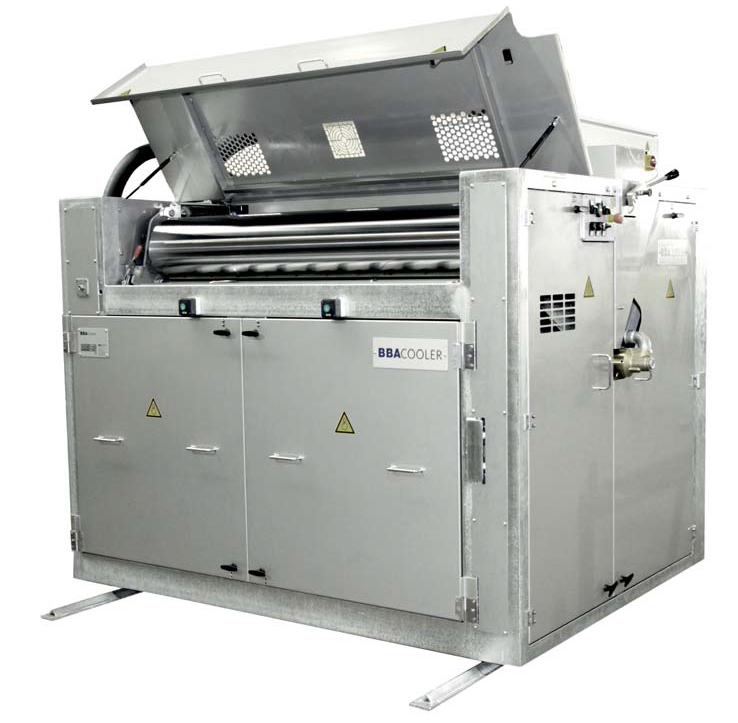
High capacity drum cooler for hot melt extrusion
Large scale cooling and extrusion of hot melt products on a continuous ba...
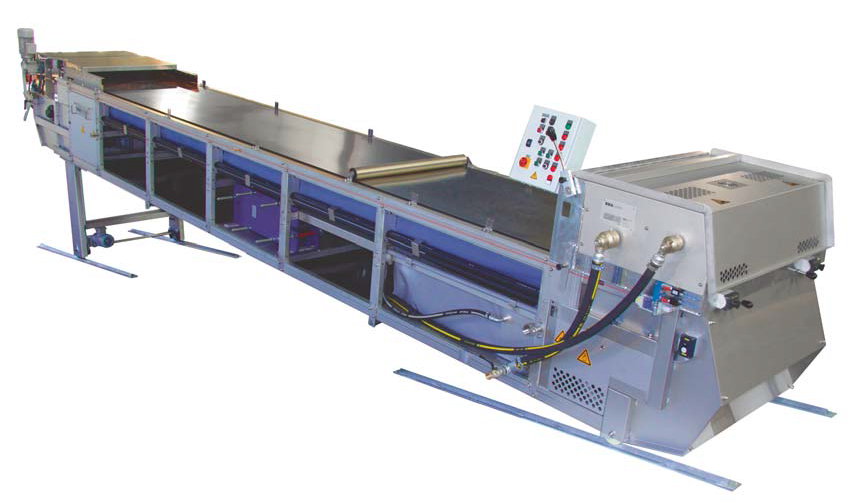
Steel belt cooler for hot melt extrusion
For producing high volumes of extruded hot melt product a flexible, high capacity ...
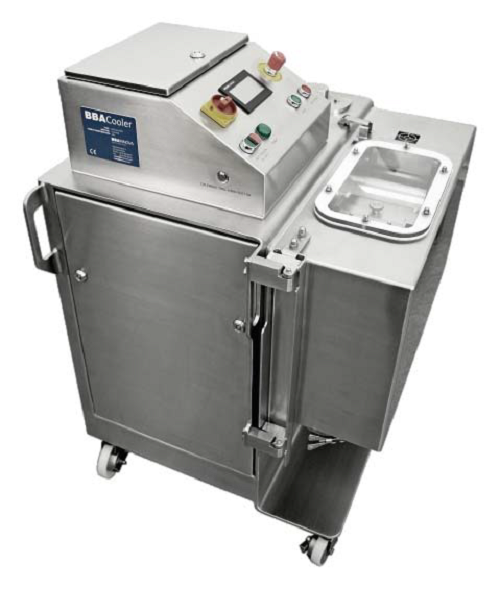
Laboratory GMP cooler for hot melt extrusion
Pharmaceutical R&D and laboratory extrusion of viscous hot melt masses re...
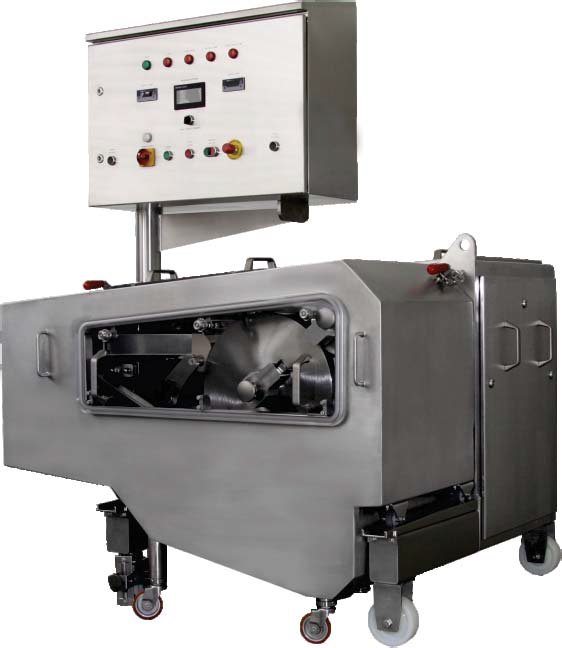
GMP cooler for hot melt extrusion
Pharmaceutical production of extruded hot melt masses requires a GMP designed, FDA approv...
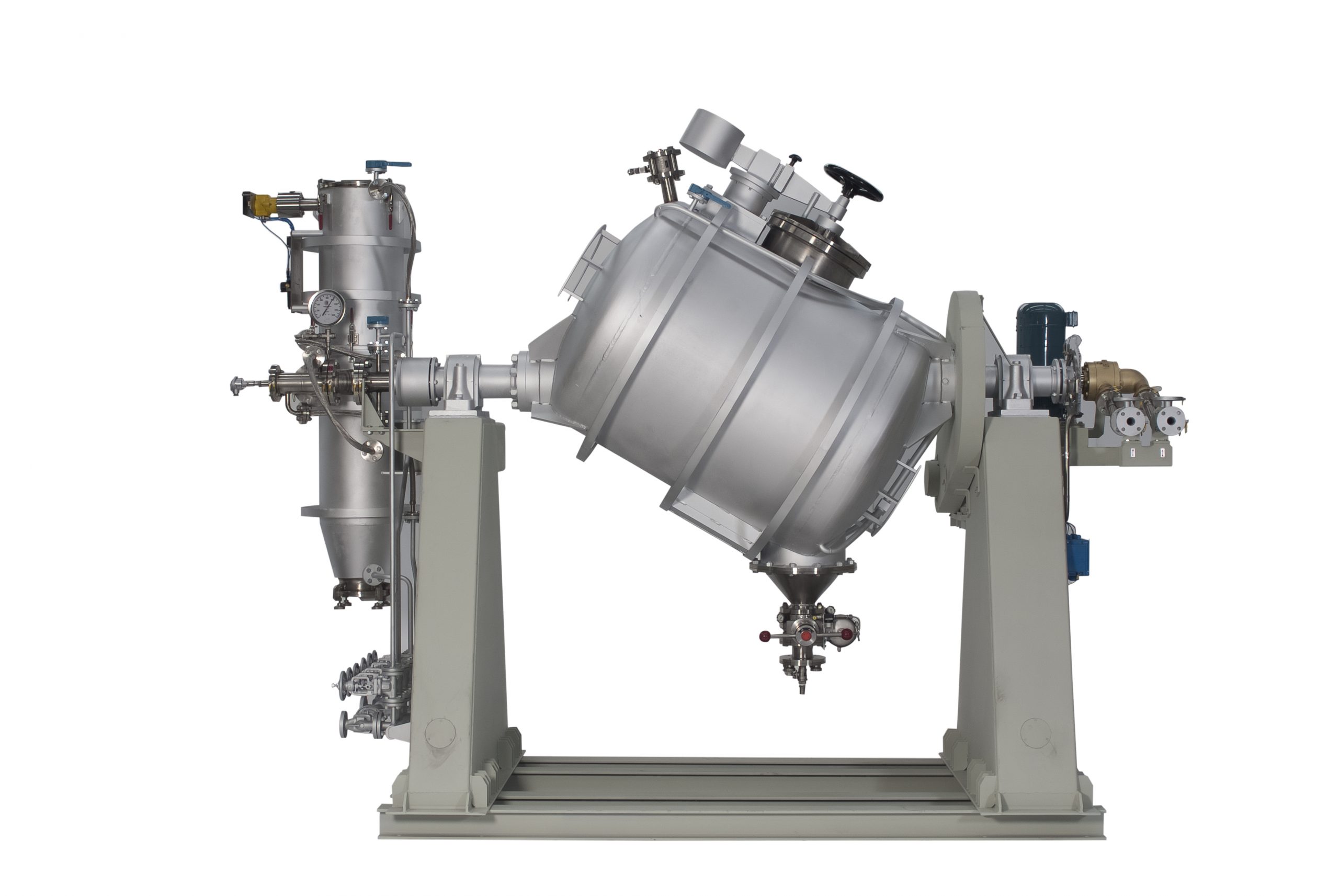
Tumble dryer for granulated plastics
Vacuum drying at high temperatures is important in the production of granulated plasti...
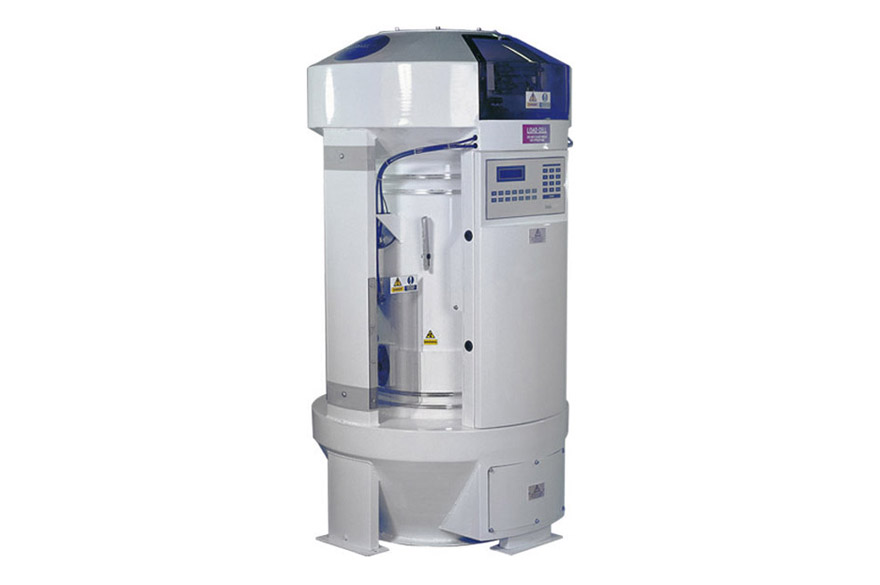
In-process weighing system for mills
When you need a throughput weigher for modern flour/grain milling applications, the we...
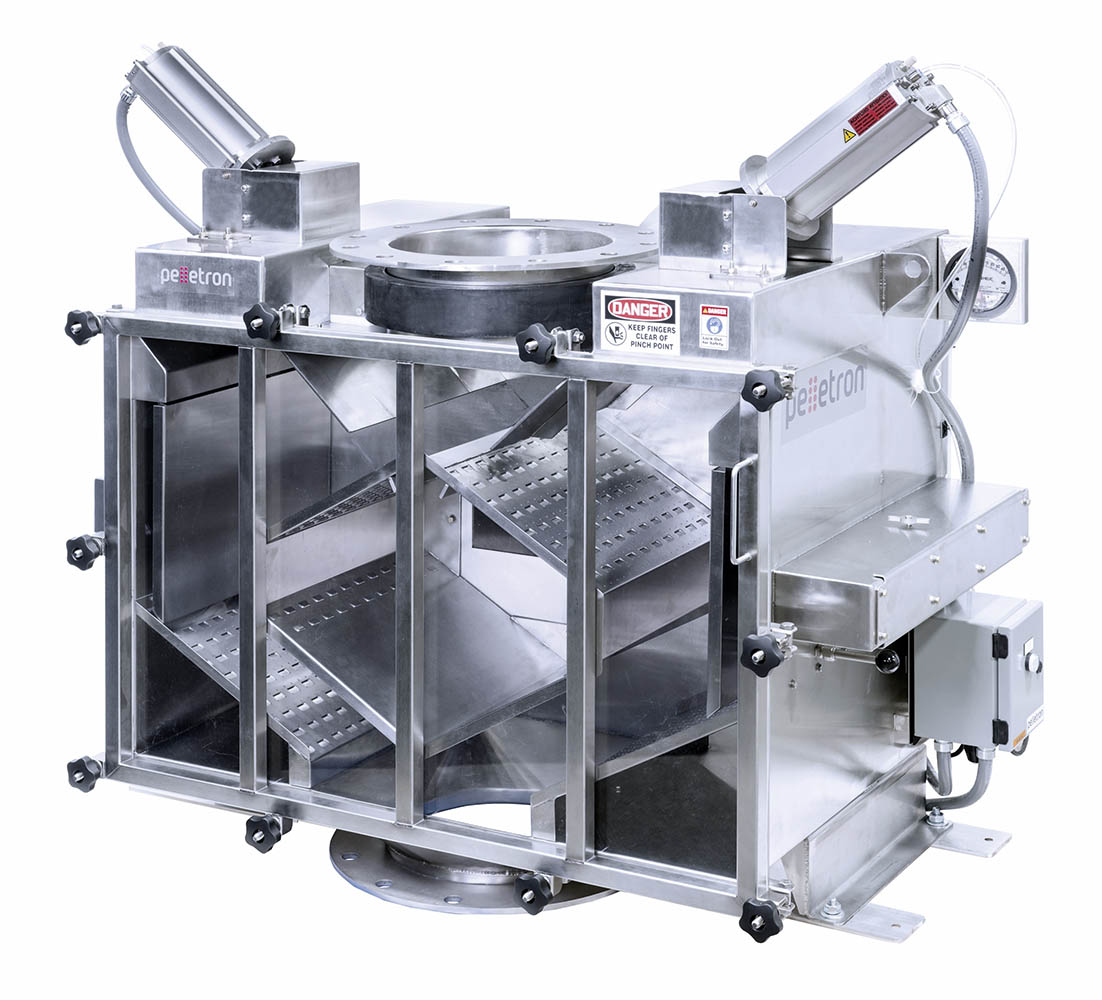
Deduster for plastic granules
Industries that use plastic granules see better product quality and decreased equipment wear a...
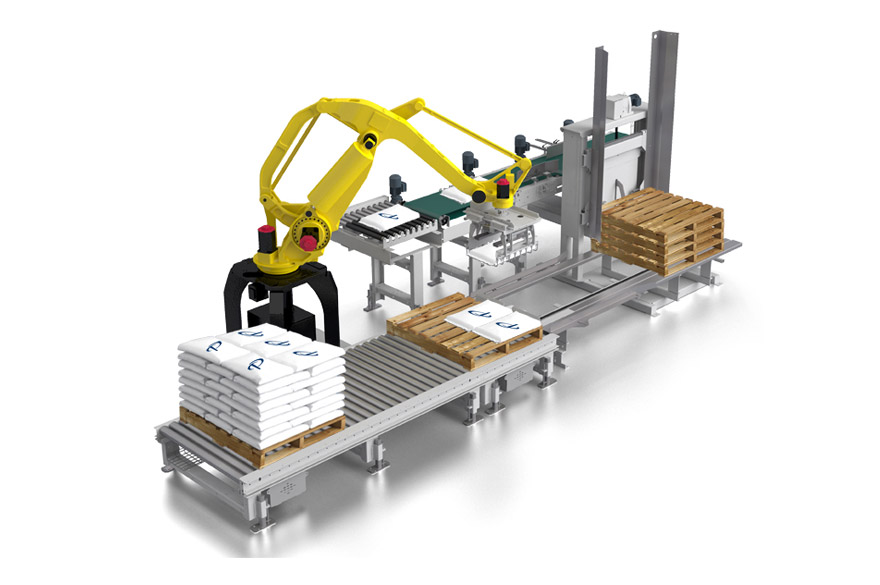
Robot palletizer
Palletize up to 1,800 large industrial bags per hour at a multi-pick-up configuration.
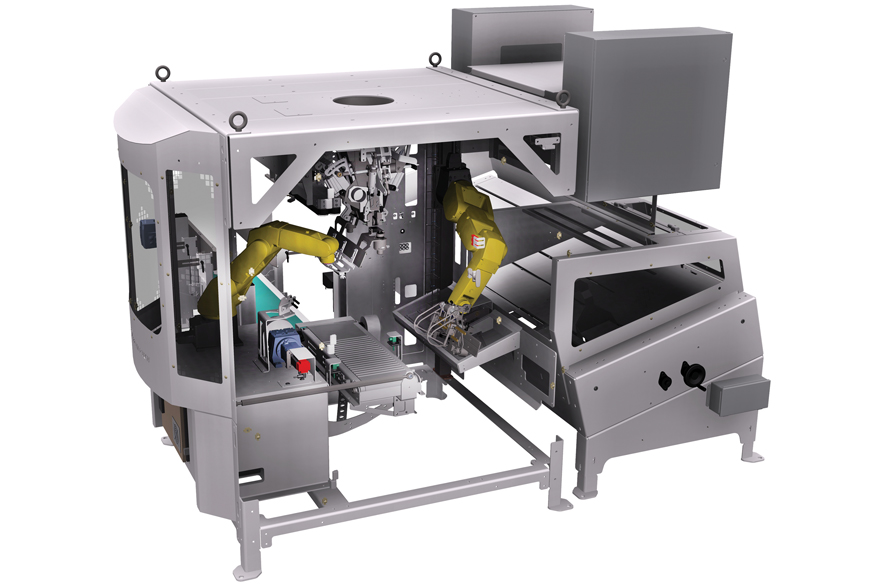
Versatile open-mouth bagger
If you want highly precise bagger for bagging multiple bag materials, here you go. This versatil...
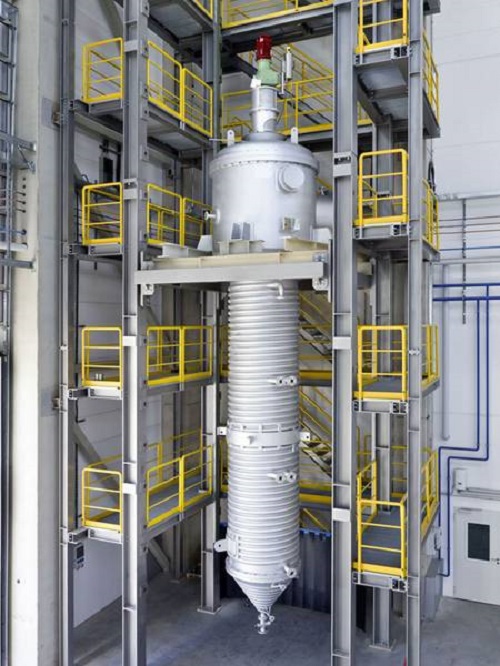
Wiped film evaporator
With wiped film distillation, a substantial decrease of boiling temperature is obtained by reducing the...
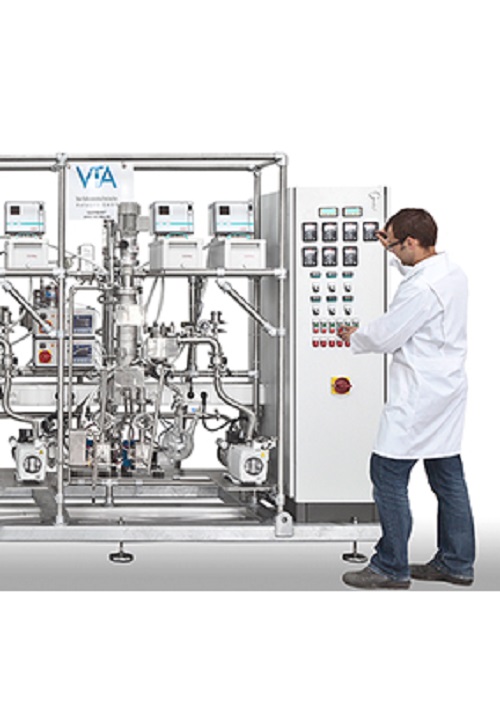
Pilot multi-stage distiller
If generating an scalable data and bring in results with small sample quantities of high-boiling...
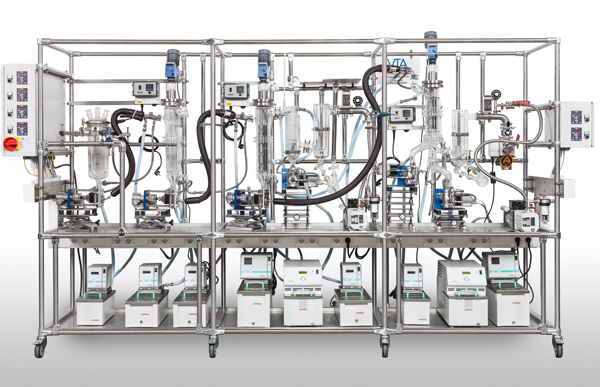
Laboratory multi-stage distiller
A laboratory multi-stage distillers that combines the wiped film and short path distillatio...
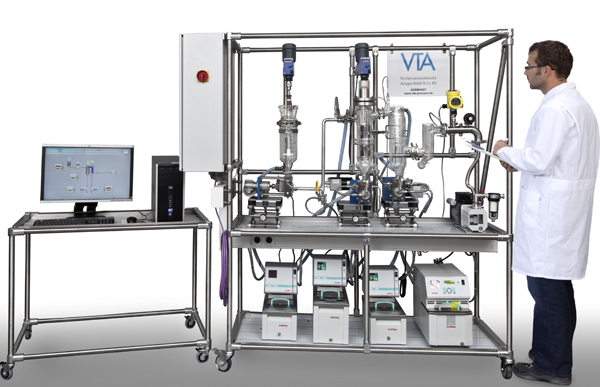
Laboratory wiped film distiller
Reach reliable conclusions testing the distillation of high-boiling or highly viscous materi...
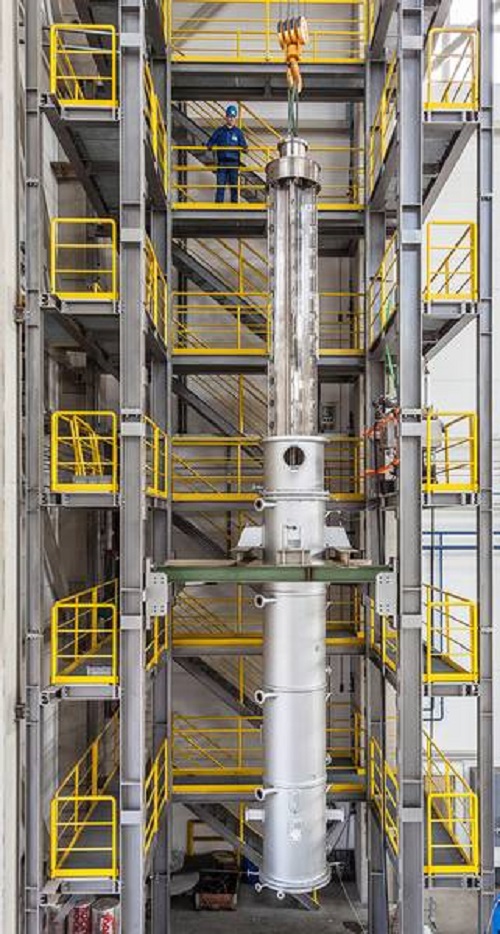
Thin film dryers
Dry dissolved or slurried crystallizing or amorphous products to a pourable powder.
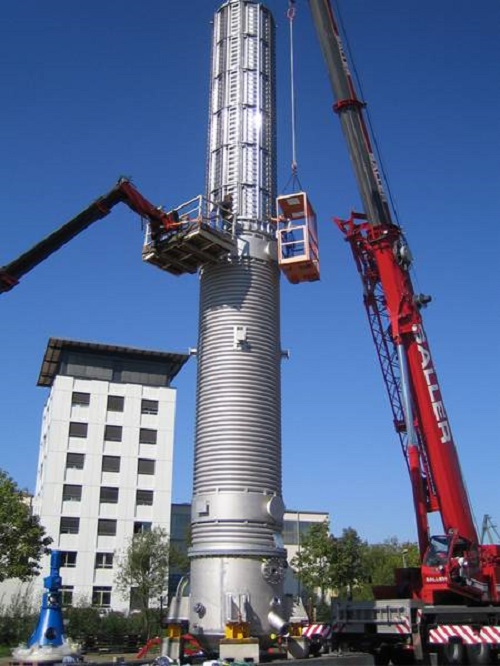
Short path evaporators
With short path distillation, a substantial decrease of boiling temperature is obtained by reducing th...
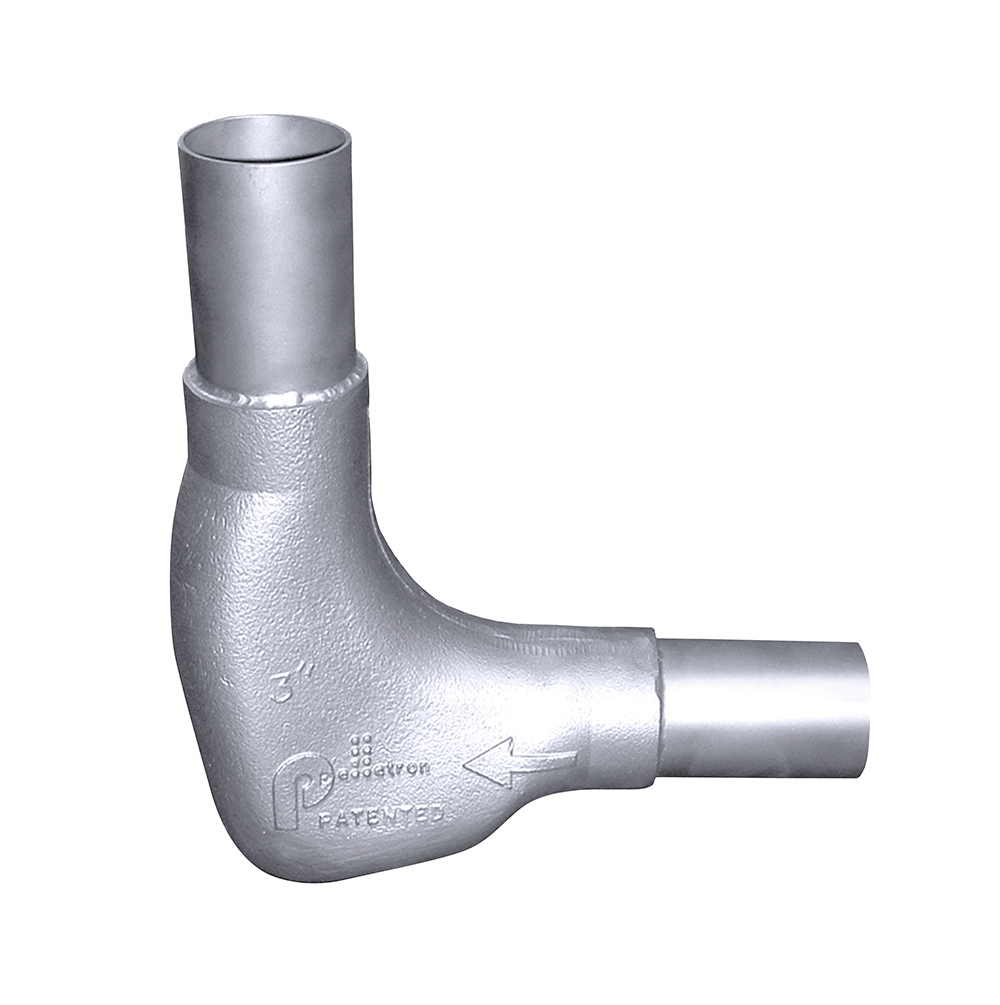
Pipe bend to reduce fines
A specialized pipe elbow for pneumatic conveying systems that virtually eliminates the friction an...
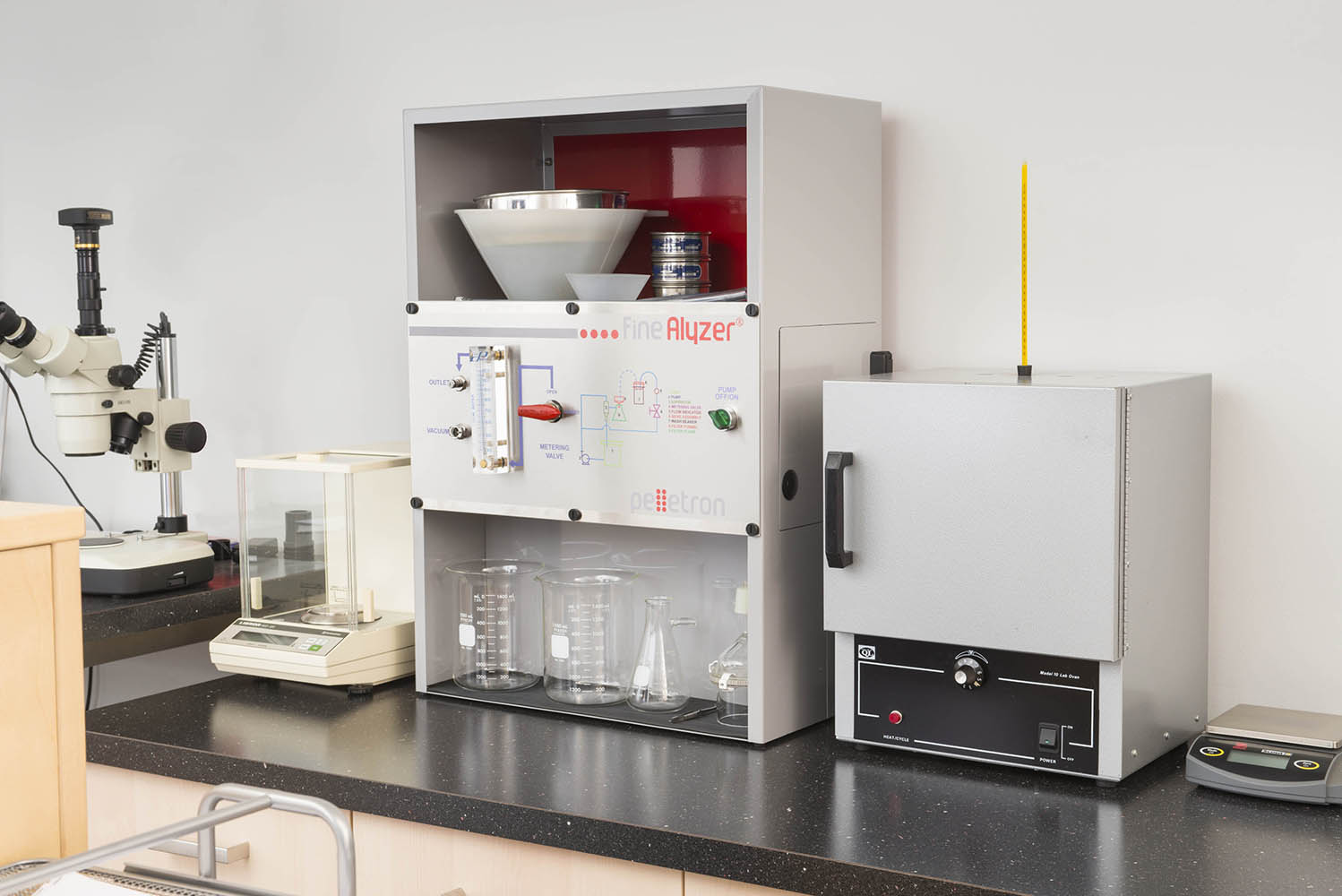
Laboratory granule dedusting analyzer
High quality clean bulk materials are used in many industries including plastics, foo...
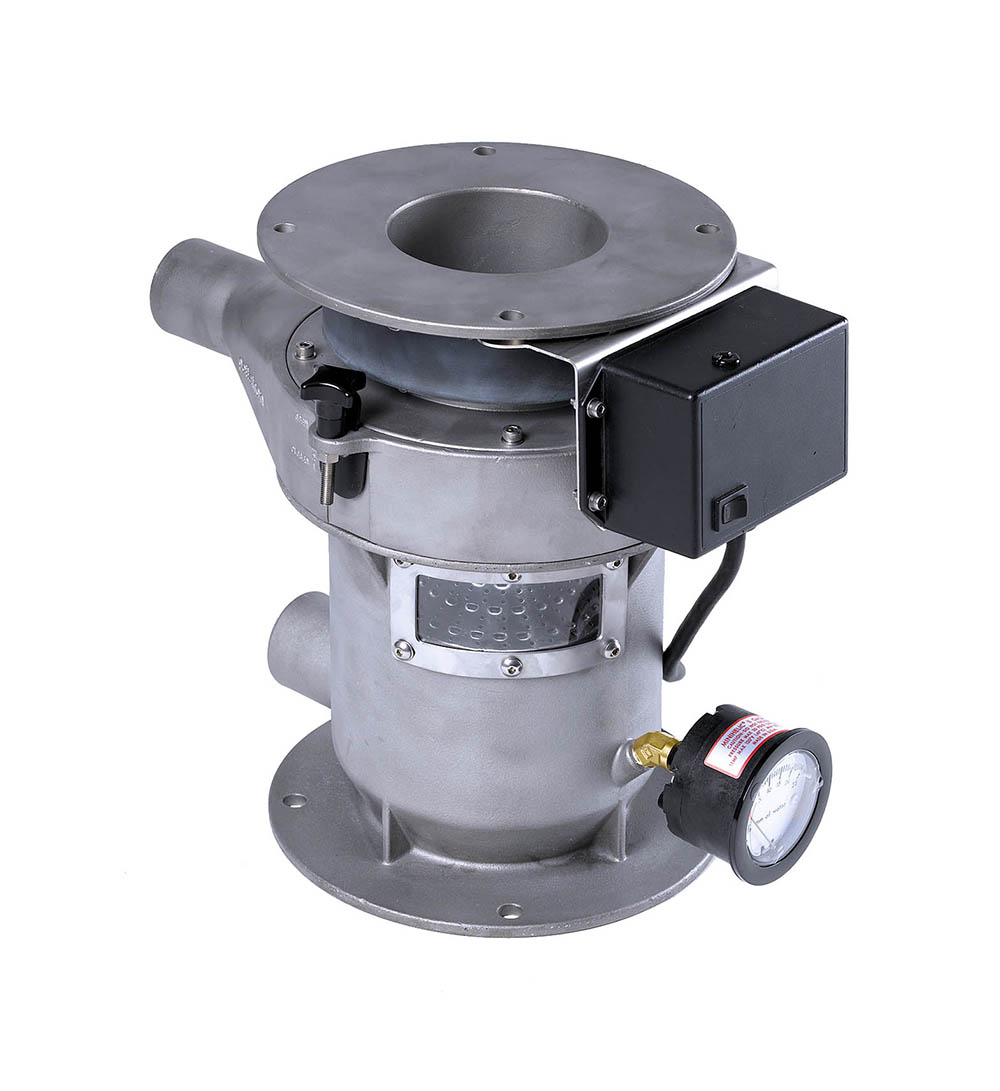
Small scale deduster for plastic granules
Industries that use bulk plastics see better product quality and decreased equip...
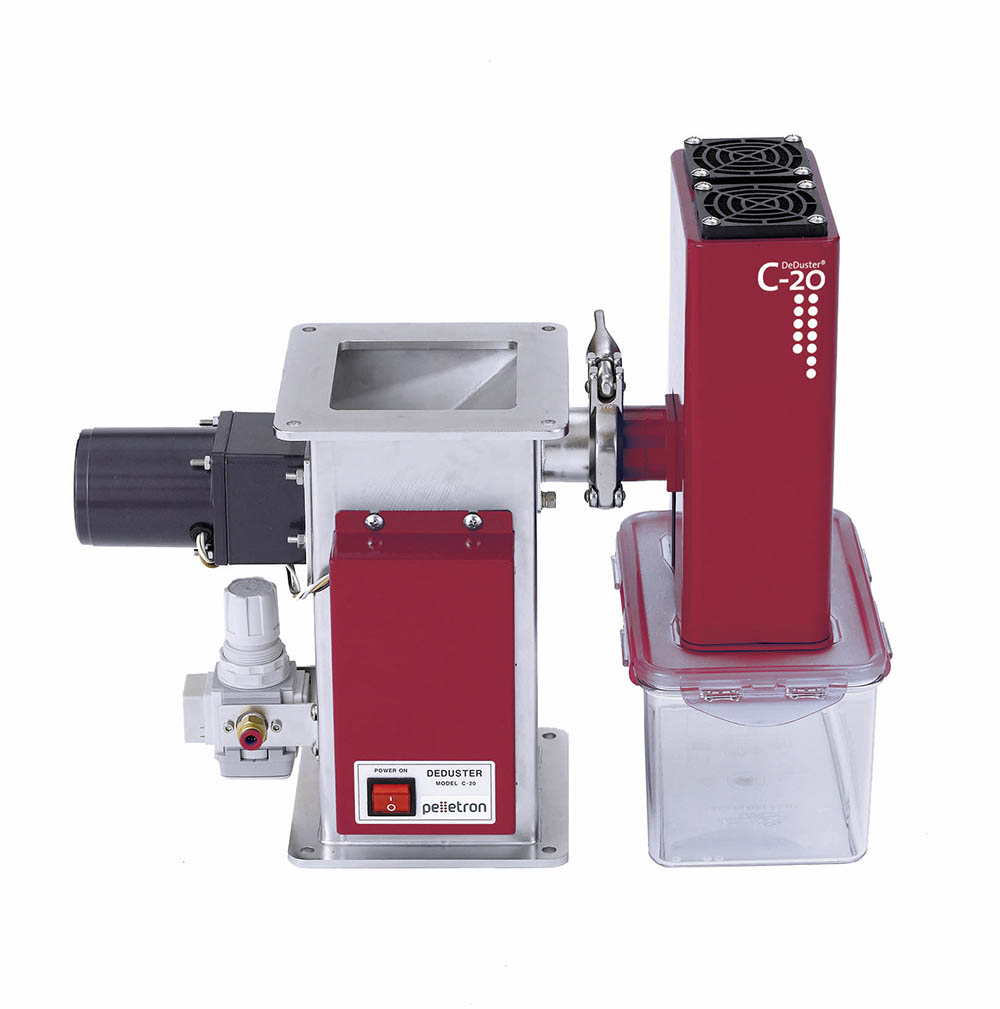
Deduster for injection moulding
High quality injection molded plastic parts require clean bulk resins free of dust and strea...