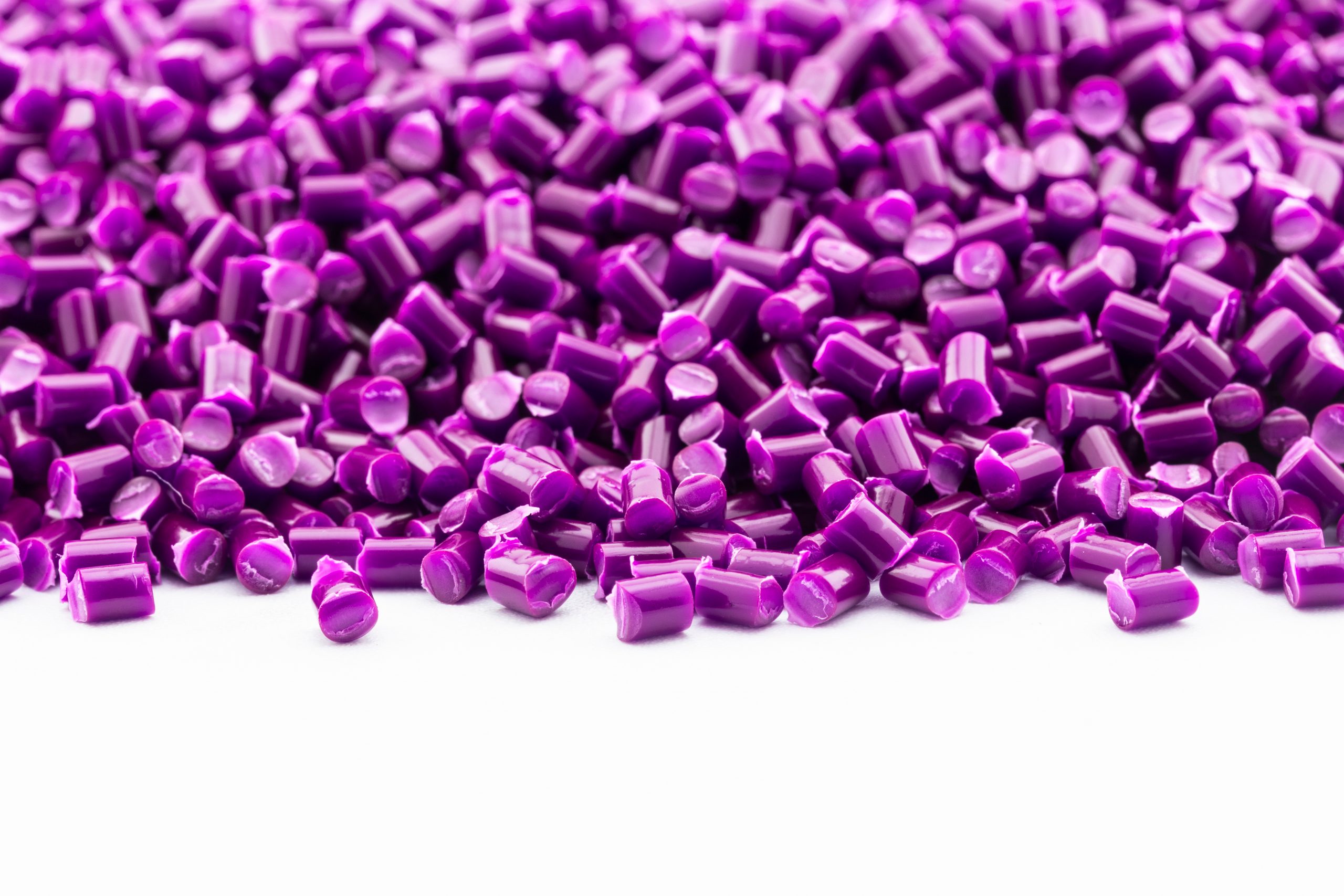
Making Masterbatches
Find innovative production technology for making masterbatches and connect directly with world-leading specialists
Also known as color concentrates for plastics, masterbatches are plastic granules that contain additives for coloring plastics. Their major purpose is to bring vibrance and improve the final product's appearance. In the process of making them, masterbatch production equipment is used to combine two major constituents—colorants and polymer-specific carriers.
Select your masterbatches process
Tell us about your production challenge
Choosing your masterbatch production equipment
The production of masterbatches involves mixing pigments and additives into a carrier resin or polymer for blending, then feeding the powder into a masterbatch extruder machine to form the final plastic product. The ingredients of the production process, such as pigments and resins, could vary depending on the customer’s need. The pigment concentration in each type of masterbatch differs even though they all fall within the range of 20- 75%.
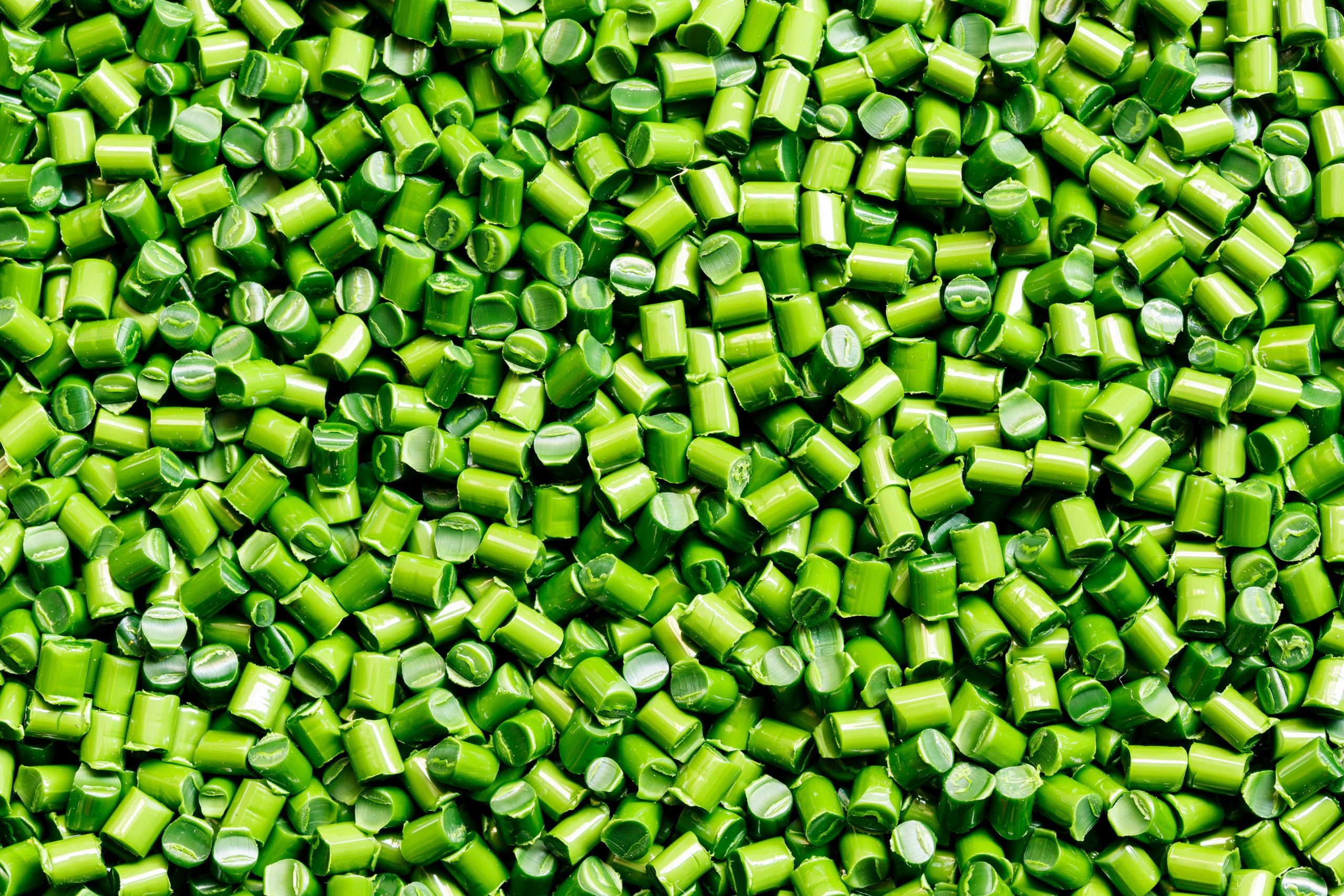
Polyethylene (PE), polypropylene (PP), or polystyrene (PS) resins can make masterbatches depending on the desired outcome. For instance, polyethylene resins are good in making food packaging materials that require reduced viscosity and increased melting point. Polypropylene is more chemically resistant than polyethylene, and better for making banners and floor graphics. Rigid polystyrene is an ingredient for making appliances.
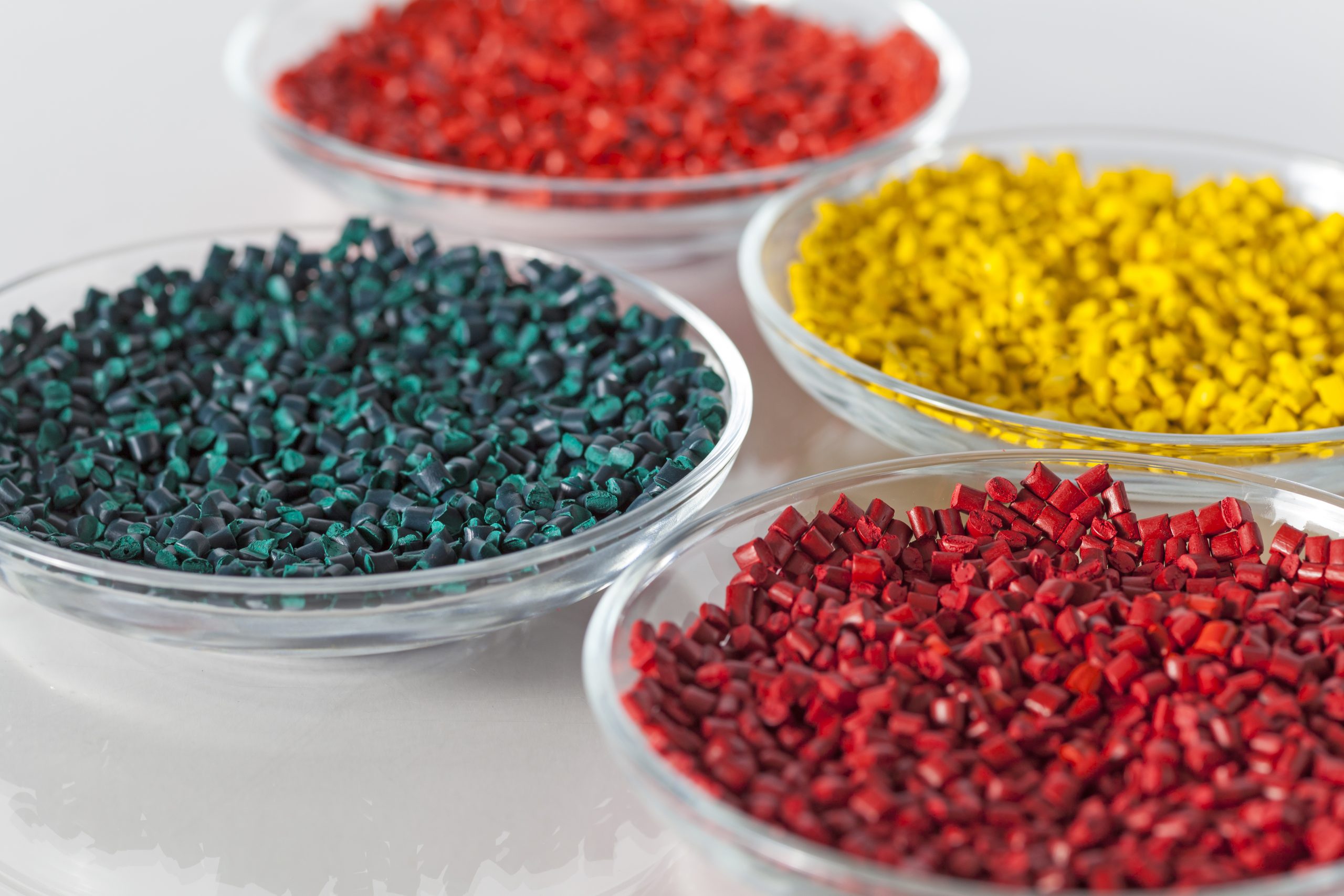
How to use it: applications of a masterbatch
Masterbatches have a wide range of applications in various industries and businesses. Their manufacturing process varies depending on the purpose they need to serve. This influences the type of additive to include in the masterbatch production equipment.
Masterbatches are an essential product for packaging, textiles, automotive, construction, electronics, and electricals. More specifically, they are applicable in making pipes and irrigation materials, non-woven fibers, thin and thick films, and blow moulding films.
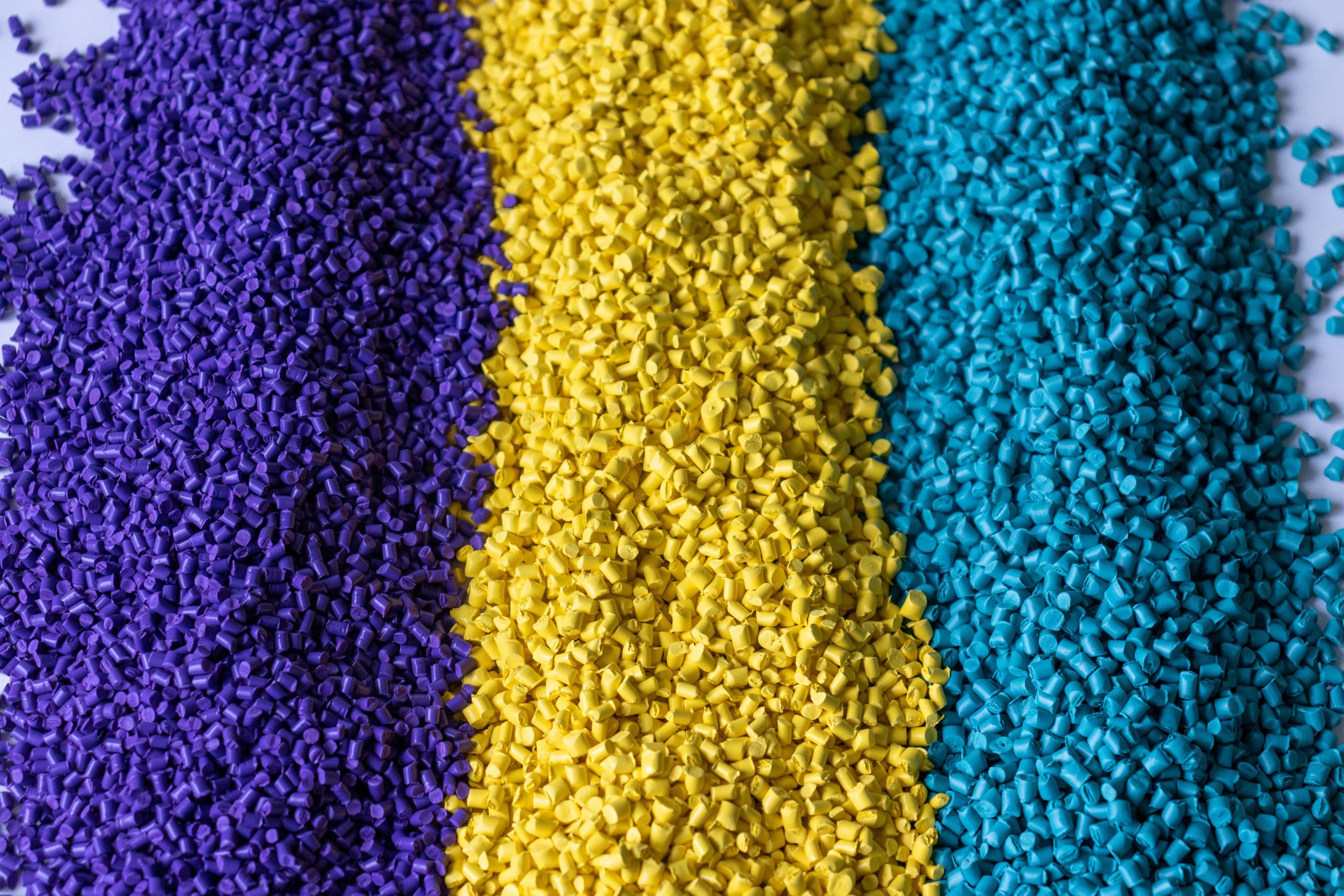
What defines a quality masterbatch?
Masterbatches need to meet certain criteria to be considered high-quality for the global market. First, its granule’s size must be uniform, with a size of approximately 3mm. It also needs to have stability and good color dispersion. Also, it must be produced with 100% virgin resin as this will ensure the end products have a smooth surface. Finally, a quality masterbatch must have good printability and durability.
Testing the masterbatch is essential to ascertain its viscosity, melting temperature, chemical resistance. In the United States, it must be in accordance with FDA’s suitability as part of standard quality control. In European and Canadian markets, it must meet the suitability standard of the European community and Food Inspection Agency, respectively.
Reducing the environmental impact of masterbatches
The use of plastics and masterbatches pose a high risk of pollution to the environment, as they are non-biodegradable. But it’s possible to make masterbatches that are more sustainable and eco-friendly.
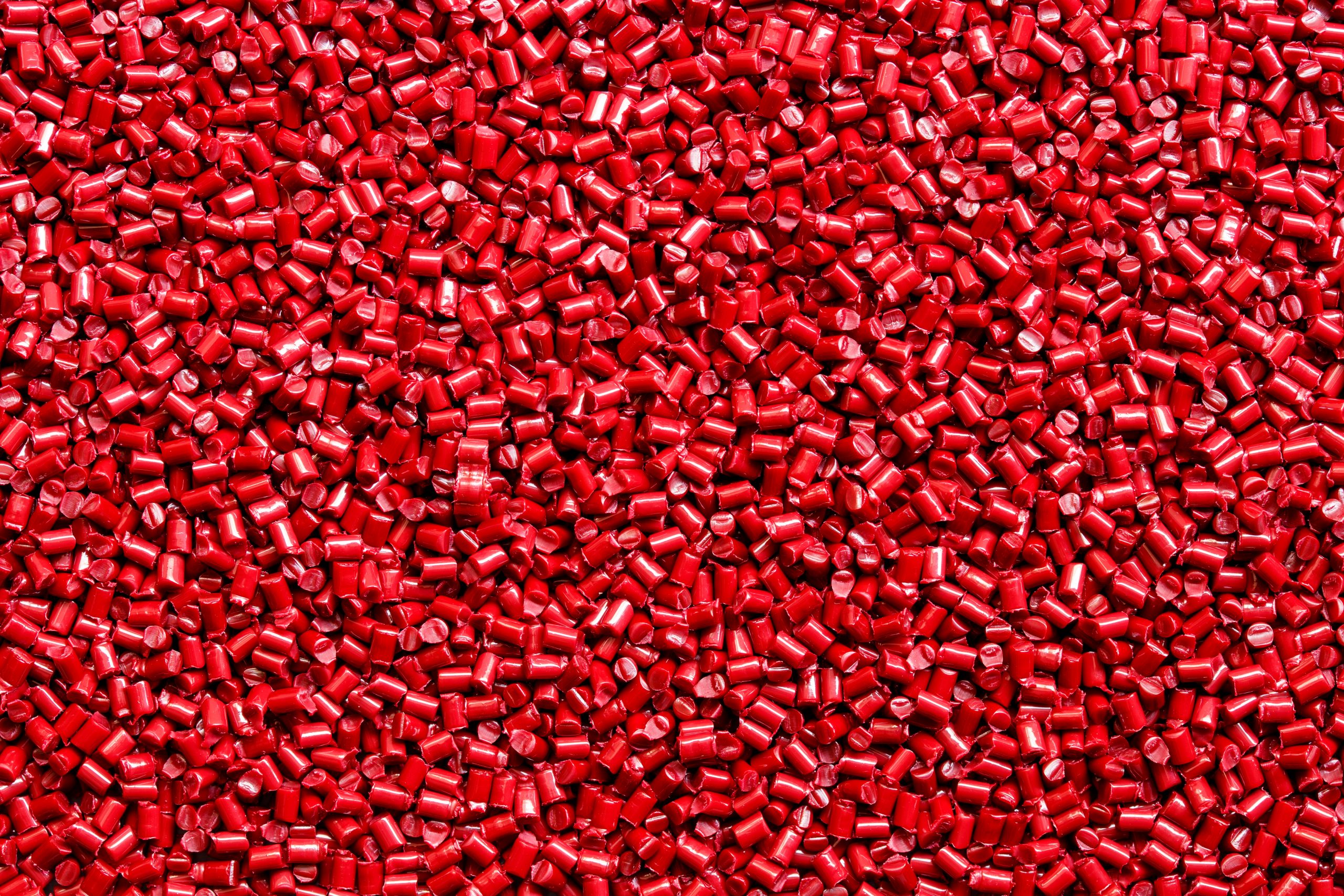
You can incorporate biopolymers into the masterbatch making machine as a way to produce a safe alternative. Biopolymers are strictly from plant sources like palm, rapeseed, sunflower, and coconut oils. They have unconditional approval from the FDA and EU and, because of their origin, they are highly suitable and safe for food packaging.
Another approach to reducing the negative impact of masterbatches is to use products that enable the recycling of polyethylene and polypropylene polymers.
Processing steps involved in masterbatches making
Which masterbatches technology do you need?
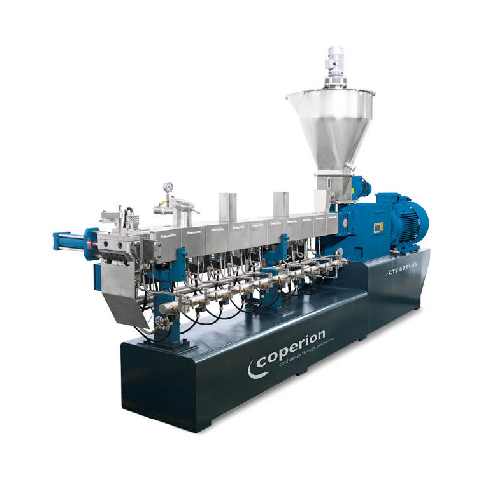
High-performance compounding extruder
Achieve precision in compounding and pelletizing with advanced extruders that ensure ...
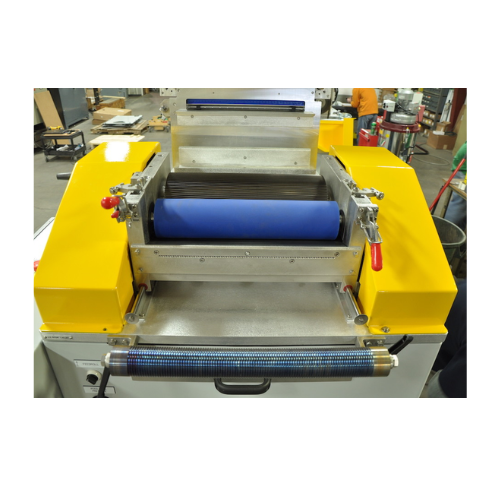
Micro pelletizer for thermoplastics
Achieve precision in micro pelletizing with a solution engineered to reduce turbulence,...
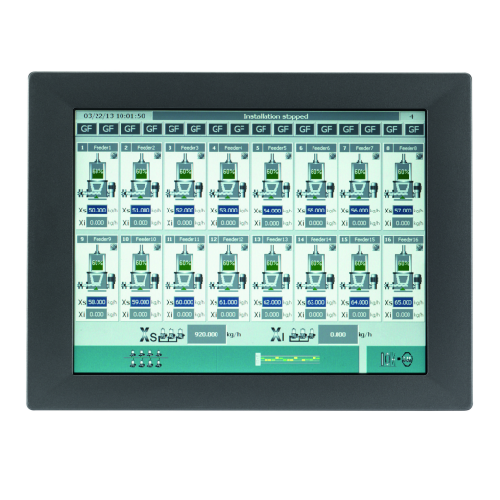
Gravimetric feeder operator interface
Efficiently manage up to 16 gravimetric feeders with a user-friendly interface, enabl...
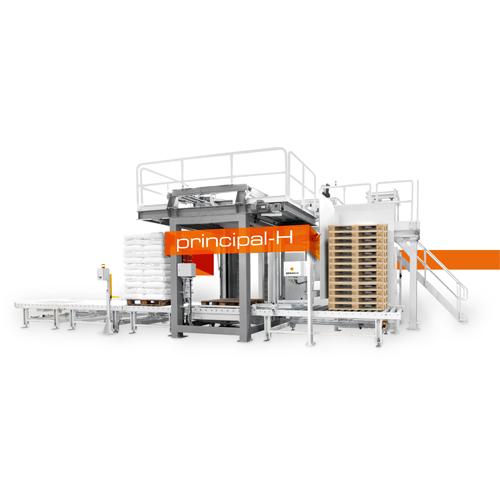
Automatic palletizer machine for bags and boxes
The effective placement and positioning of bags and boxes can be a challen...
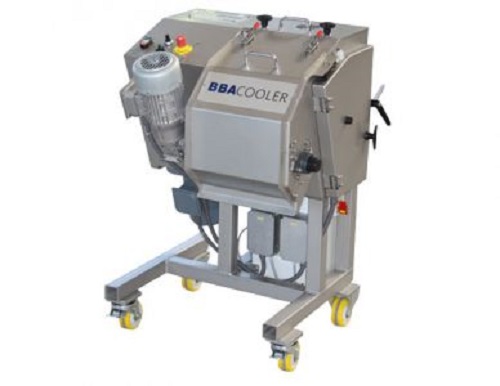
Drum cooler for laboratory hot melt processes
Do you need to cool molten masses to solid, thin film or flakes in an R&...
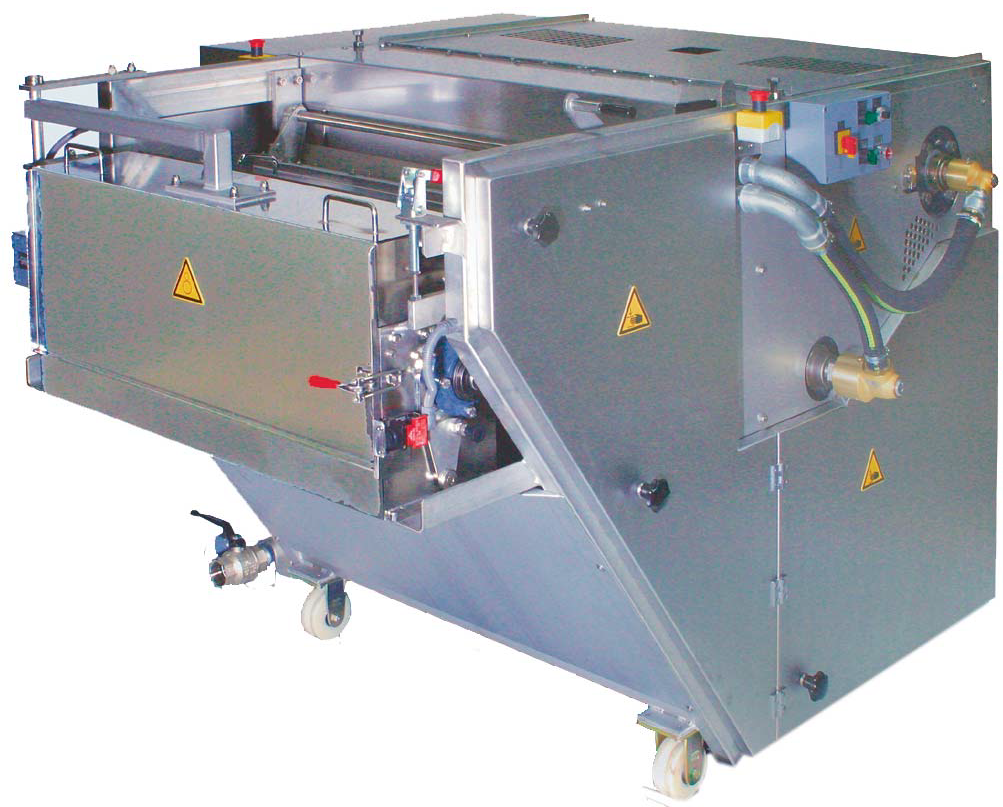
Drum cooler for hot melt processes
Medium-scale production of extruded hot melt masses benefits from reliable, efficient co...
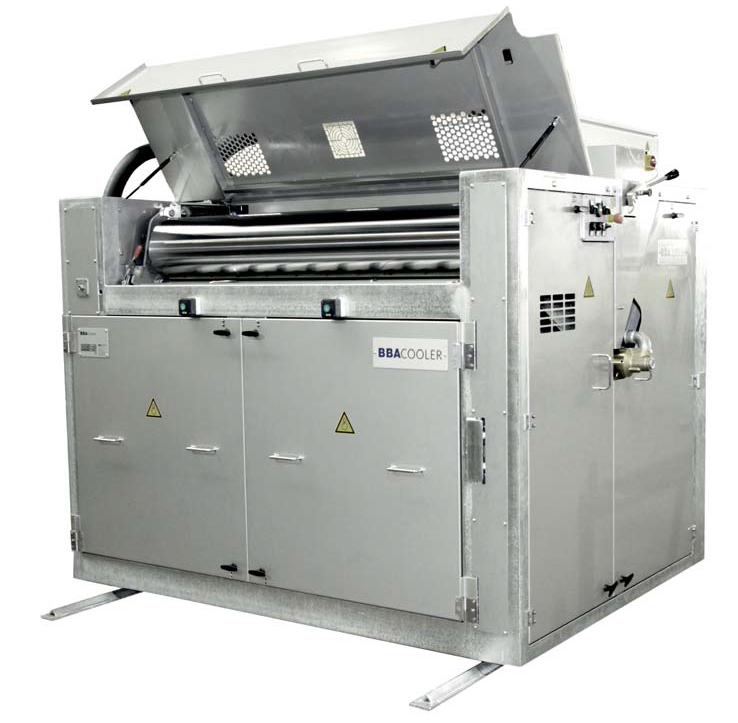
High capacity drum cooler for hot melt extrusion
Large scale cooling and extrusion of hot melt products on a continuous ba...
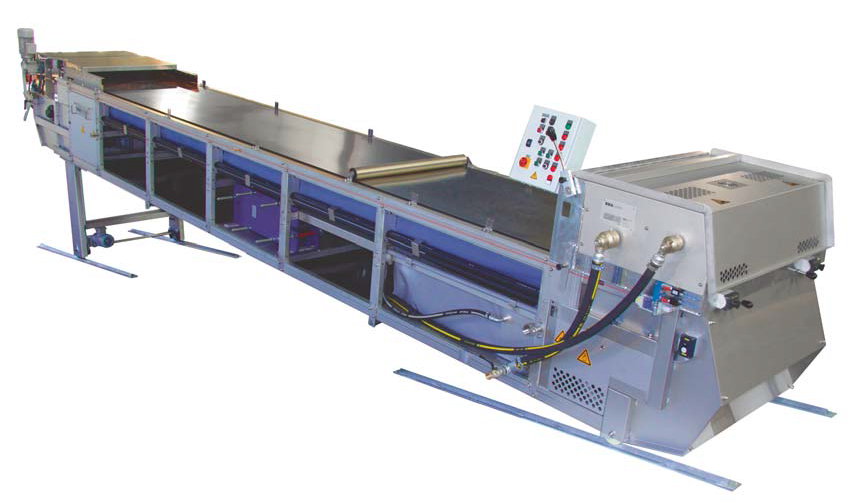
Steel belt cooler for hot melt extrusion
For producing high volumes of extruded hot melt product a flexible, high capacity ...
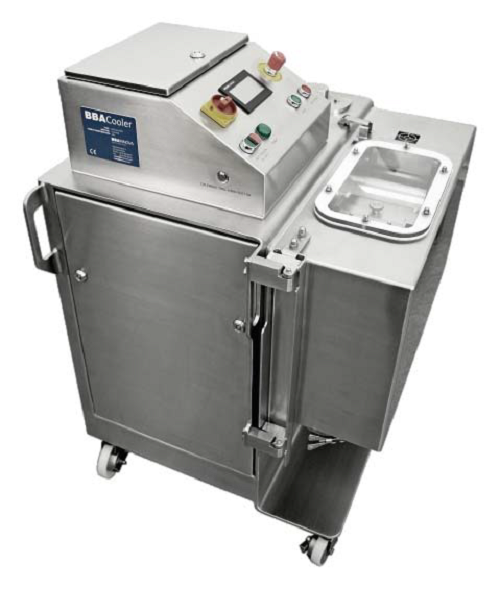
Laboratory GMP cooler for hot melt extrusion
Pharmaceutical R&D and laboratory extrusion of viscous hot melt masses re...
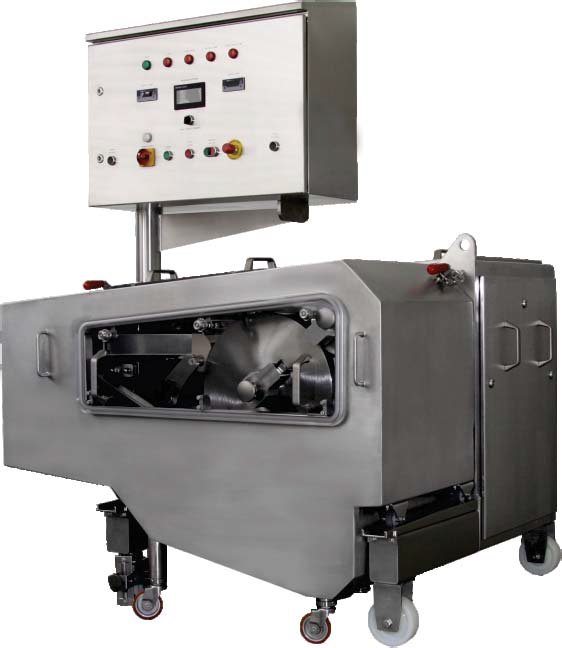
GMP cooler for hot melt extrusion
Pharmaceutical production of extruded hot melt masses requires a GMP designed, FDA approv...
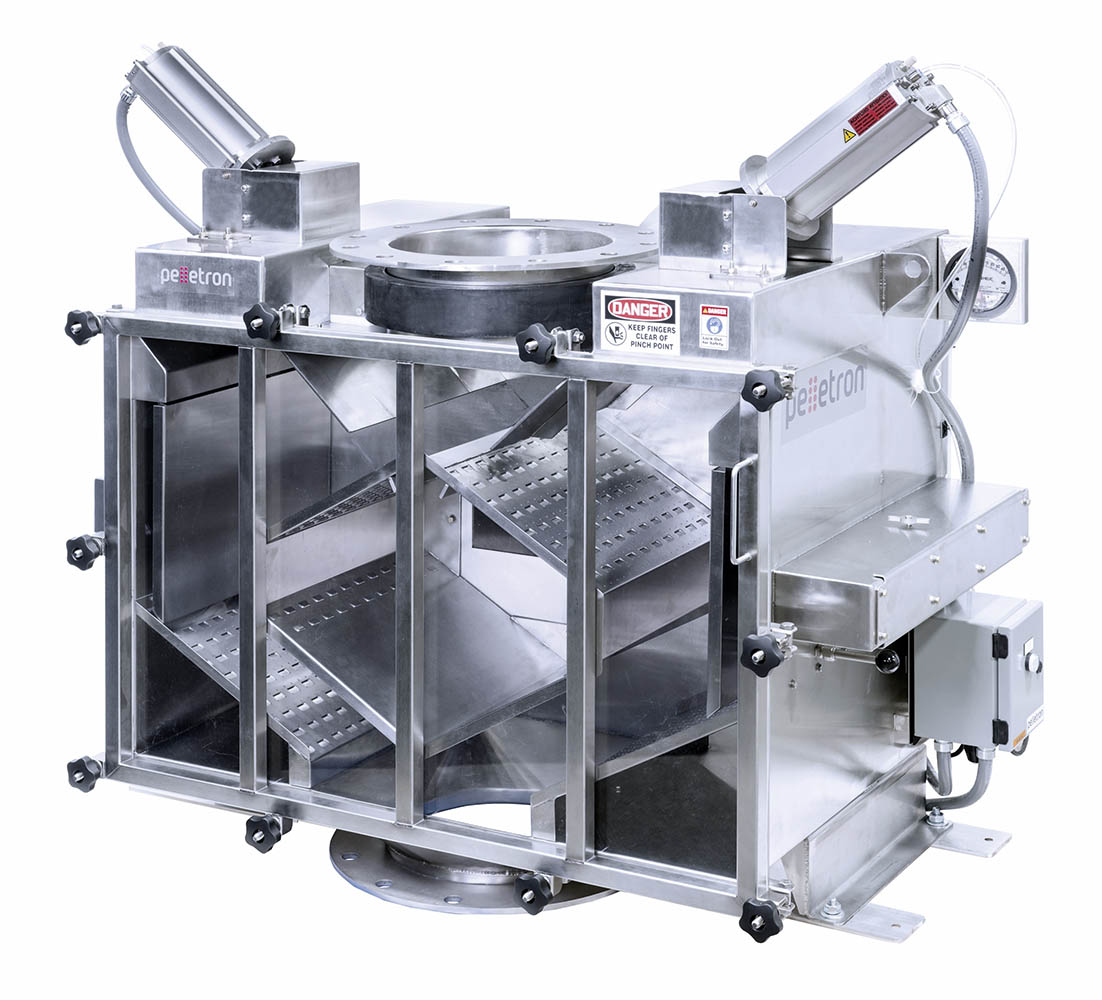
Deduster for plastic granules
Industries that use plastic granules see better product quality and decreased equipment wear a...
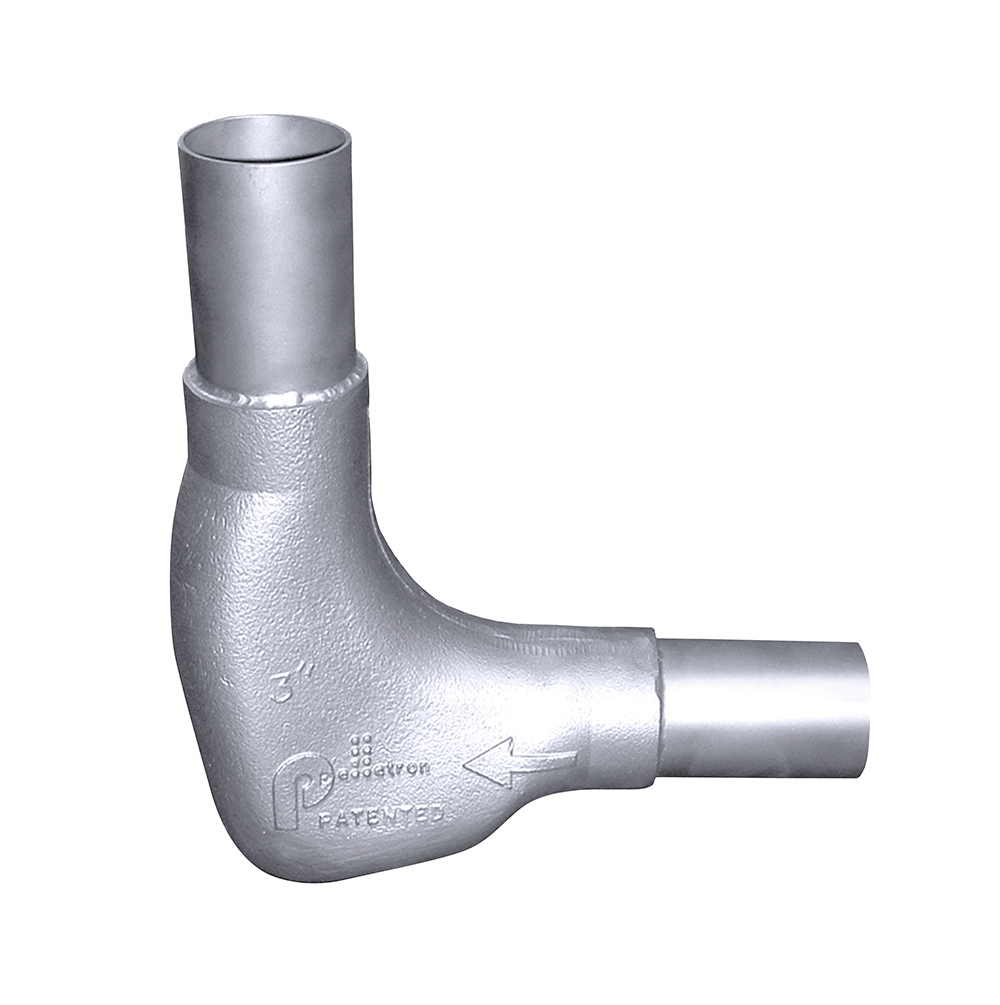
Pipe bend to reduce fines
A specialized pipe elbow for pneumatic conveying systems that virtually eliminates the friction an...
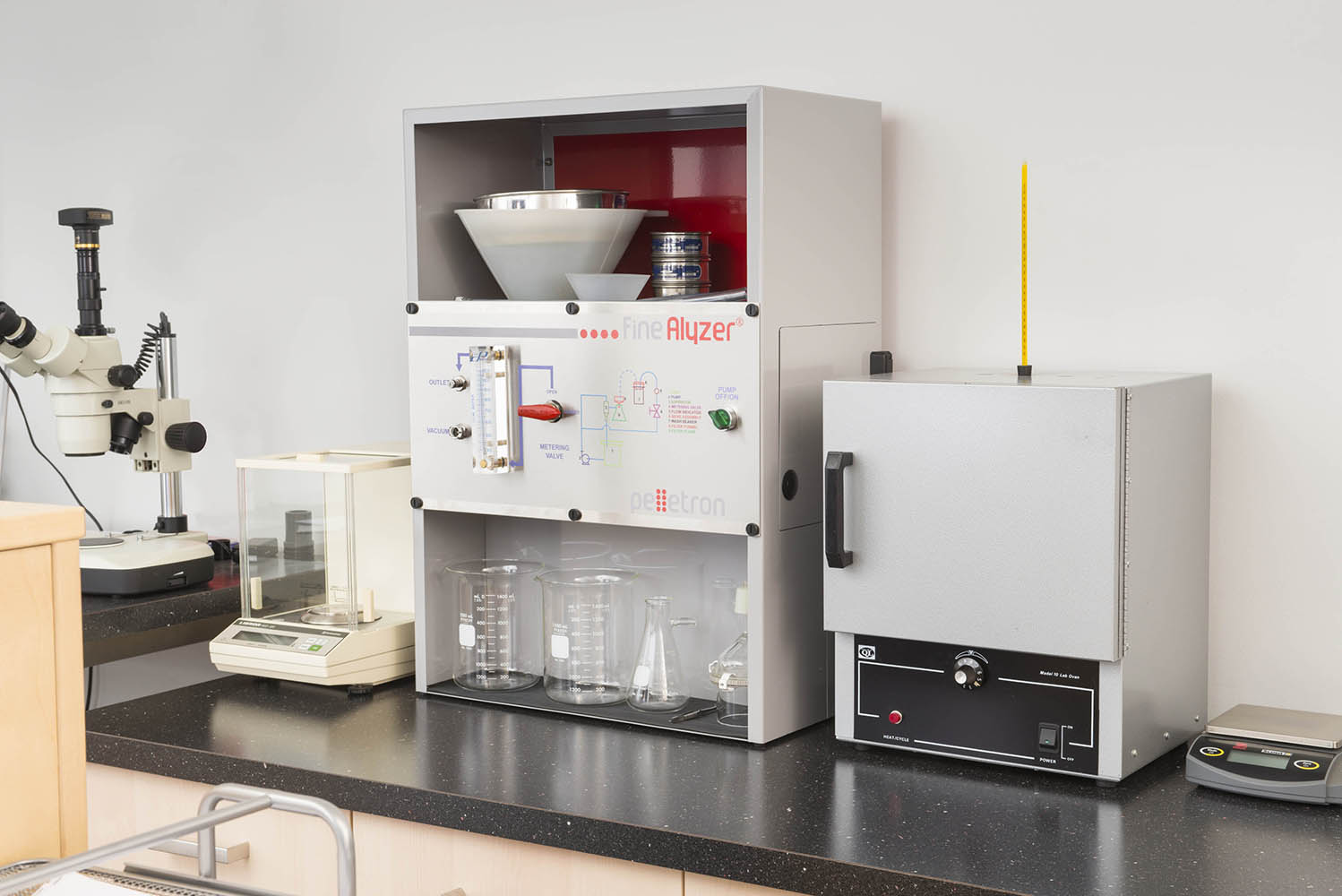
Laboratory granule dedusting analyzer
High quality clean bulk materials are used in many industries including plastics, foo...
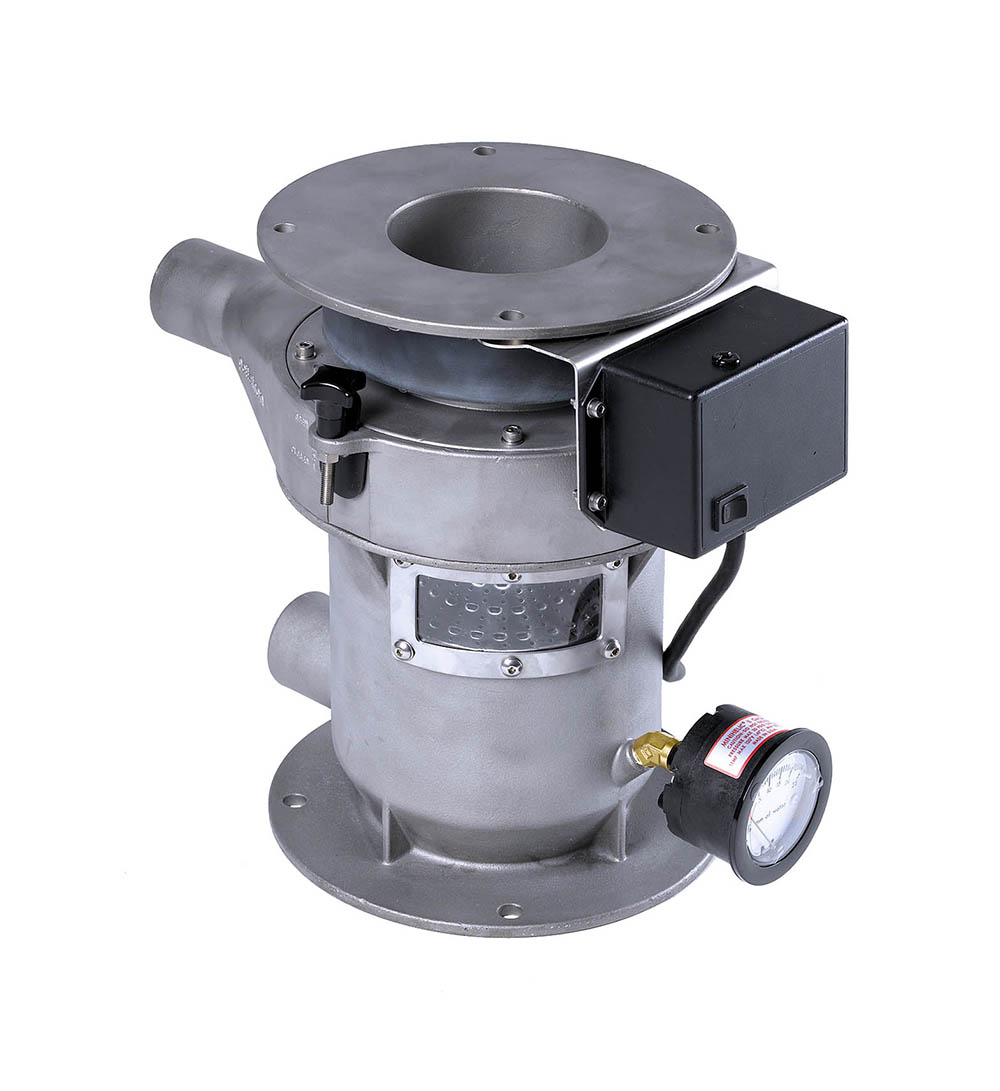
Small scale deduster for plastic granules
Industries that use bulk plastics see better product quality and decreased equip...
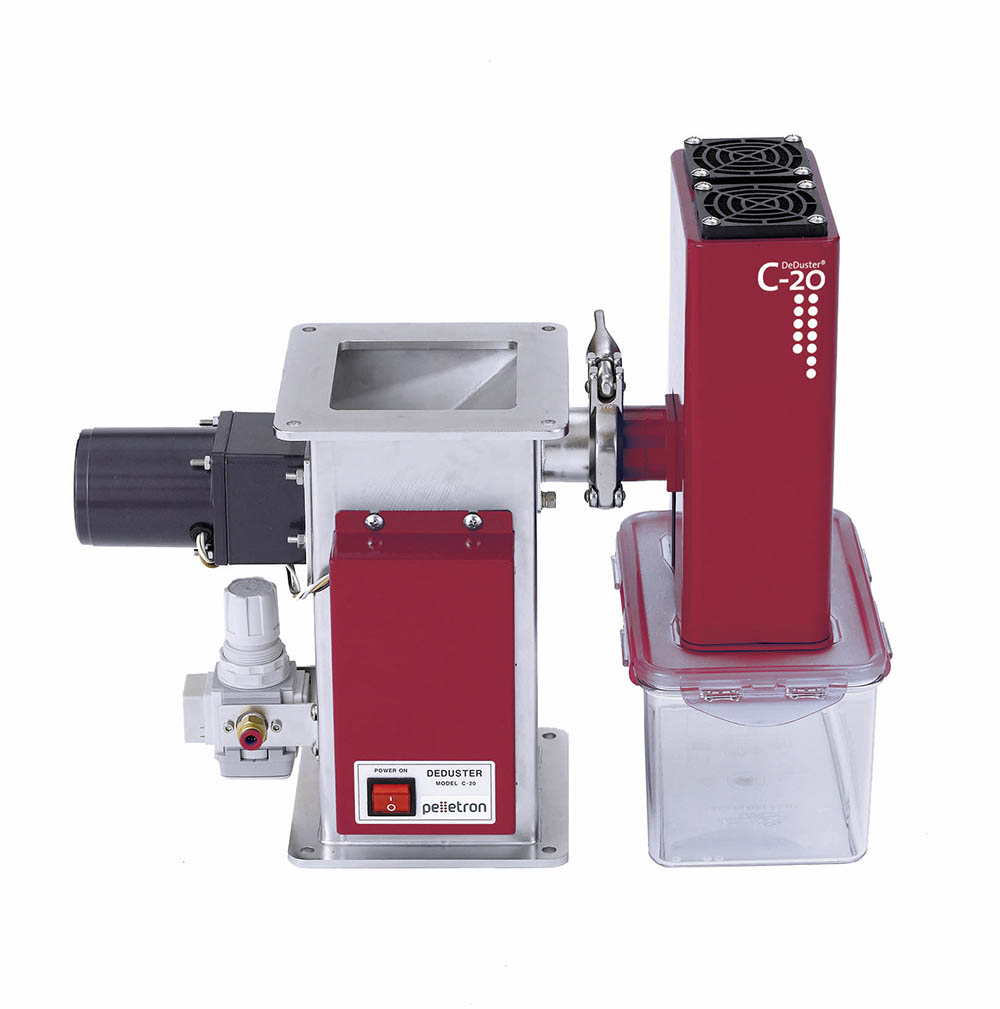
Deduster for injection moulding
High quality injection molded plastic parts require clean bulk resins free of dust and strea...