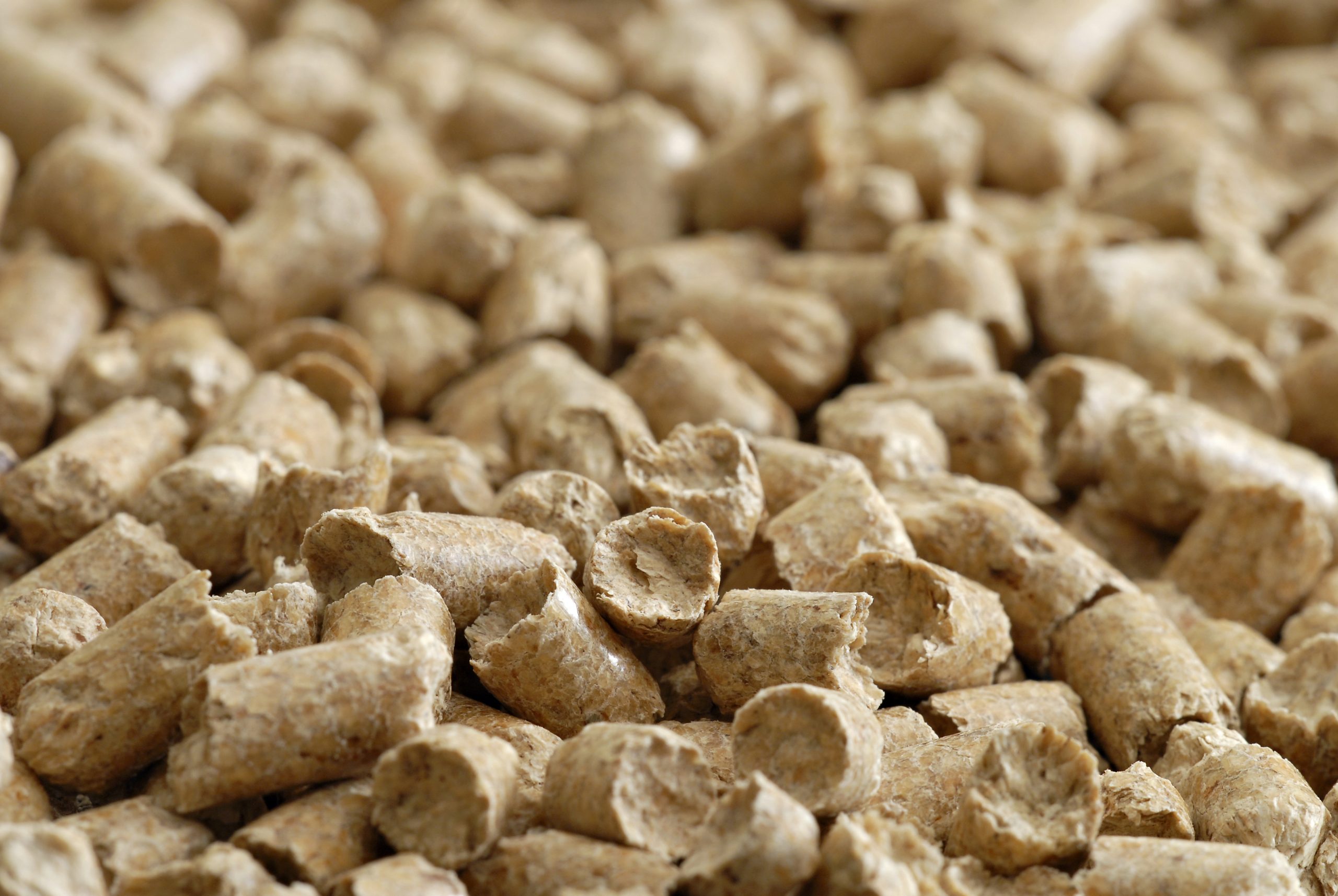
Feed Milling Equipment
Sometimes in a general overview, talking about feed milling equipment or feed milling process is talking about the entire production line or process to transform raw material into animal feed. This general overview includes storing and handling, milling or grinding, mixing, pelleting, and cooling. But here, we will focus on the milling or grinding process that reduces the particle size in animal feed production.
The feed milling can have two configurations in the production line: pre-grinding or post-grinding
There are two configurations of the grinding system in the animal feed production line: one is called pre-grinding and the other one post-grinding. The pre-grinding or pre-milling configuration happens before mixing the raw material, often used in places where cereals grains are available and at low cost. On the contrary, the post-grinding or post-milling happens after mixing the raw material and is used in places where cereals are expensive, and the formulated raw materials often vary due to their availability.
Choosing the best configuration depends on the raw material to use, its availability, the volume, and the dedicated space for storage.
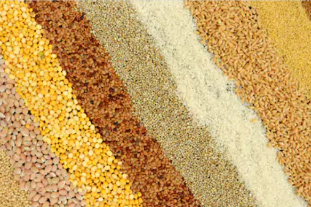
Pre-grinding is good when the facility produces one or few feed products
The pre-grinding or pre-milling system is not connected to the feed production line; therefore, the grinding capacity can be less than the capacity of the feed mill, and the production program can be different without affecting the process. These give the advantage of doing maintenance without affecting the animal feed production process. But the facility should produce one or few products in order to use efficiently the grounded material.
It is important to have a big storage capacity for each raw material grounded, so the milling equipment can operate at full capacity and for long periods. To have more flexibility to operate, you can have multiple milling equipment to process different single materials at the same time. With this configuration the hammer mills or rotor mills are smaller and have smaller motors than in post-grinding, meaning in most cases a lower requirement of horsepower, sometimes even with a lower overall energy consumption.
Post-grinding is the most common configuration in a feed mill plant
The post-grinding or post-milling system is the most common configuration in a feed mill plant due to its flexibility in terms of formulation. This process allows you to mill a wide range of materials simultaneously and keep a uniform particle size.
In the post-grinding, hammer mills need to have a higher capacity than the entire feed mill line not to affect the production capacity. This means higher horsepower requirement and higher energy consumption than in pre-grinding. But this is still a less expensive option for a feed mill facility.
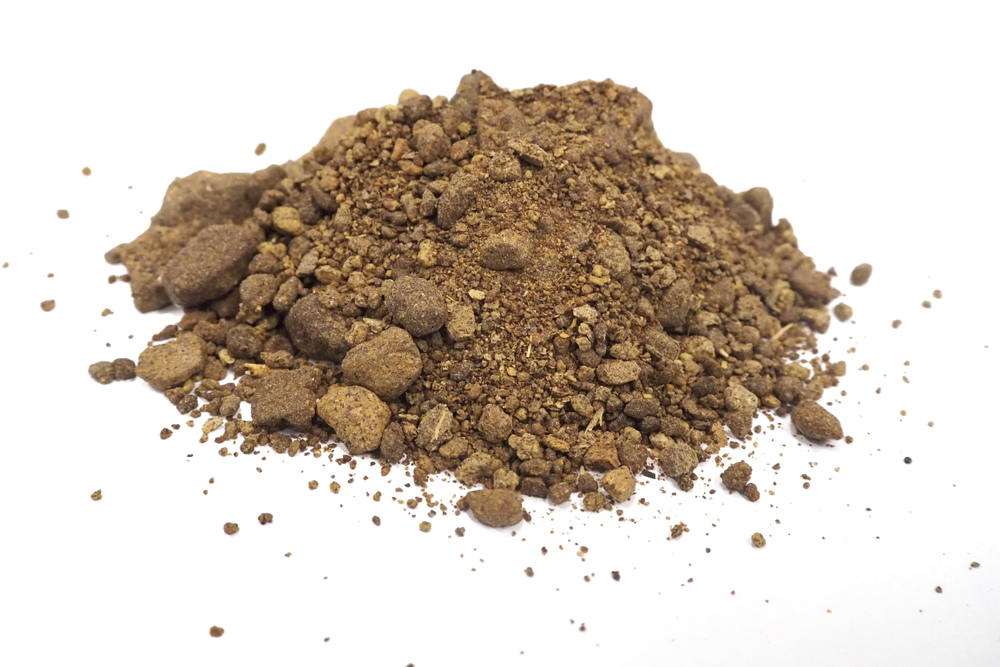
Size reduction needs to be according to the feeding animal palatability and digestibility requirements
The milling equipment reduces the size of the particles, removes some moisture, and in post-milling, it blends the materials. In the feed grinder machine, the gap between the hammer or the roller and the screen needs to be adjusted depending on the desired particle size, according to the requirements of palatability and digestibility of the livestock and the formulated raw materials. If you want fine particles the gap needs to be small, if you want coarse particles the gap should be bigger.
Producing fines requires more energy consumption and may cause quick wear in the hammer and the screen. Besides, dust can be formed from fines during the process, turning into an explosion hazard. But fine grounded material contributes to a better agglomeration and homogeneity of the mix, as well as easy absorption of fat and coating, thus a better pellet quality.
Aspects to consider in the milling process
The first aspect to consider in the milling process is the design of the process itself. Not only choosing the right mill machine but the related equipment to it, such as the feeder, the air extraction system, the conveyors, the controllers, and the magnets.
To choose the right equipment it is important to consider the physical characteristics of the raw materials to grind, the difference in size before the mill and after grinding, the moisture content, and the temperature sensitivity. At the same time, consider the mill technology; the operation requirements, maintenance, and safety.
Take into account the volume of material to grind per day and the different feed formulations, to decide the production capacity of the mill, which should be compatible with the capacity of the feeder, the air extraction system, and conveyors. Also, consider the requirements for speed and horsepower to choose the motor.
Use sensors and magnets for the safety of the operation
The safety of the operation requires the installation of a magnet before the milling equipment, to protect it from any piece of metal that can cause great damage to the machine. A metal detector for non-ferrous materials and a pre-cleaner will add extra safety to the process, and clean all of them on a regular basis.
Use sensors and switches that are able to stop the milling machine immediately if they detect explosion hazards and severe vibrations. Install sensors and controls for temperature, speed, volume, or weight to manage the overall operation. Nowadays automation will help with efficiency, productivity, and safety, as well as reducing the environmental footprint of the process.
Which feed milling technology do you need?
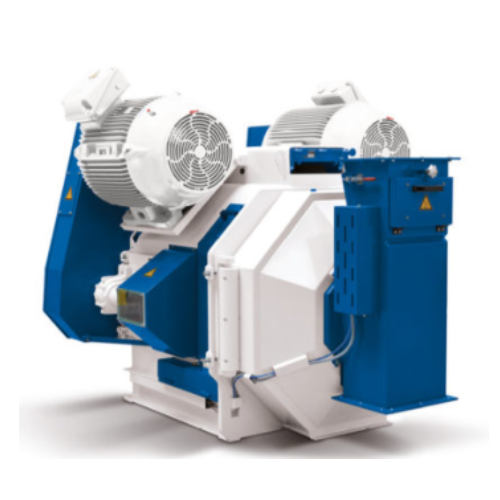
Pellet mill for high efficiency animal feed production
Achieve stable, vibration-free pellet production with enhanced ene...

Hammer mill for efficient particle size reduction in feed mills
Optimize your feed milling operations with this hammer m...

Pellet mills for feed, plastics, and industrial products
Optimize pelleting output across diverse materials with precisio...
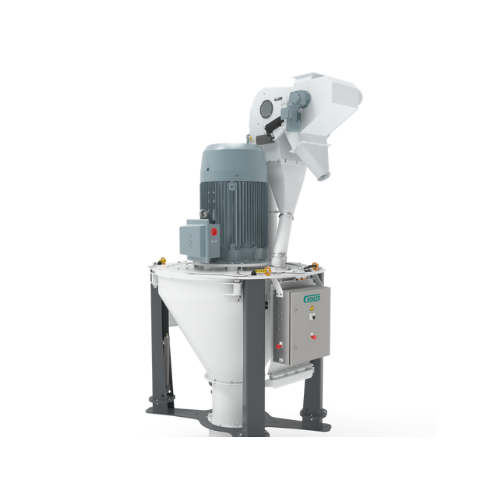
Vertical hammer mill for feed and grain processing
Optimize your milling operations and improve energy efficiency with th...
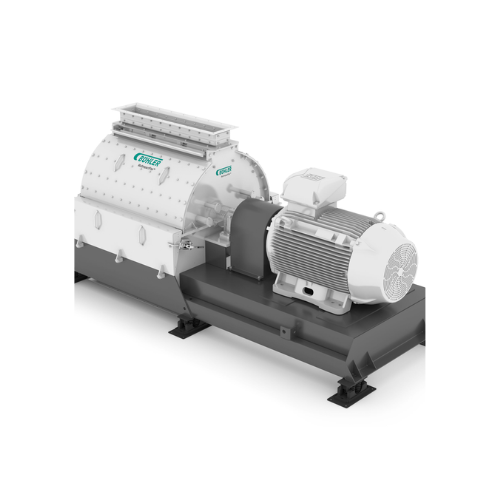
Hammer mill for fine grinding in food and feed industries
Achieve exceptionally fine particle-size distribution with a h...
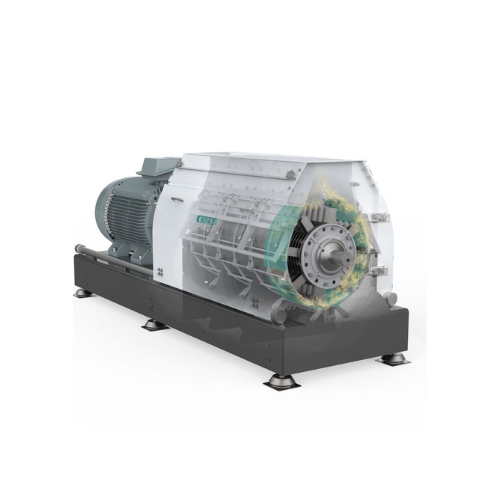
Industrial hammer mill for size reduction in food and feed processing
Achieve precise grinding and milling for diverse ...
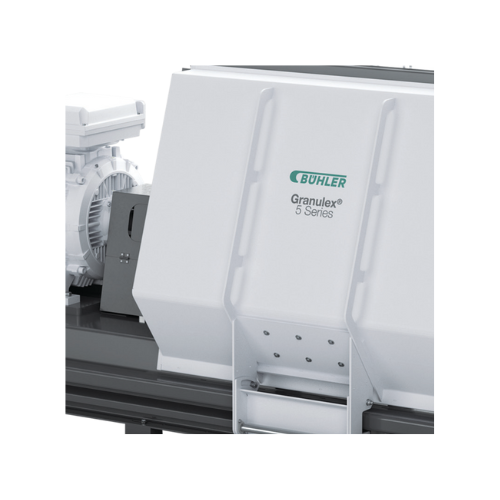
High-throughput hammer mill for animal feed production
Ideal for high-throughput operations, this hammer mill ensures pre...
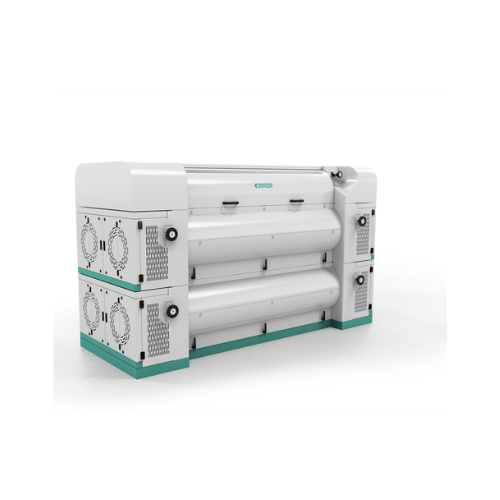
Cracking mill for oilseeds and feed
Enhance your production efficiency with a cracking mill that optimizes throughput and m...
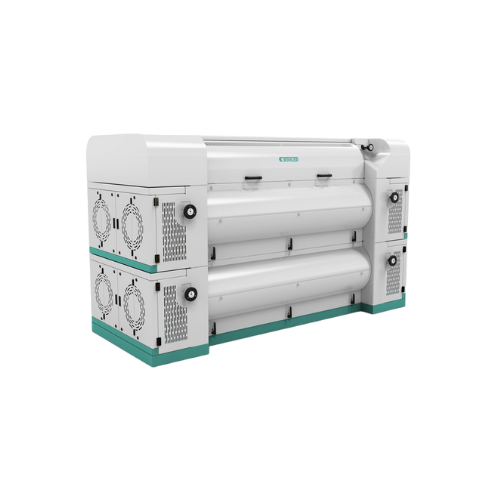
Cracking mill for oilseeds and feed processing
Maximize your production efficiency with advanced cracking and milling solu...

Hammer mill for size reduction in food and feed processing
Efficiently tackle size reduction challenges with a versatile...
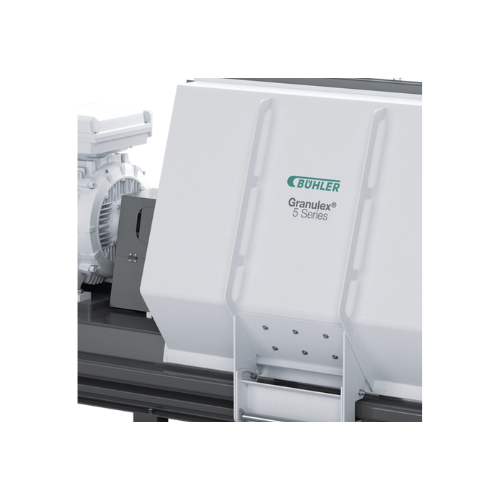
Hammer mill for animal feed grinding
Achieve precise granulation with high throughput and energy efficiency, while reducing...
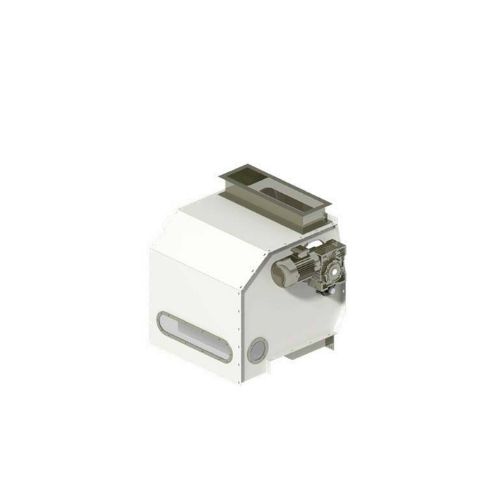
Hammer mill feeder for controlled grain processing
Optimize your feed production line with precise material control, redu...
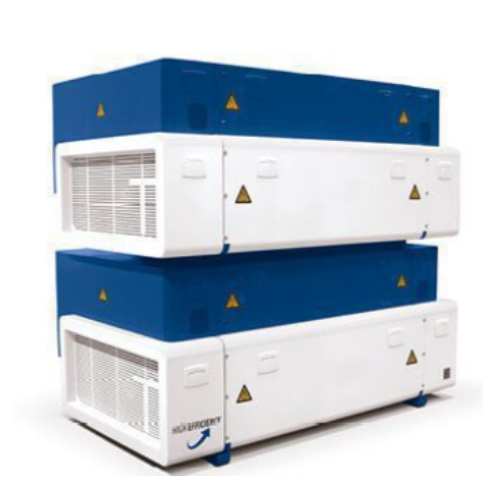
High efficiency roller mill for grain and oilseeds
Optimize your crushing and grinding processes with a versatile roller ...
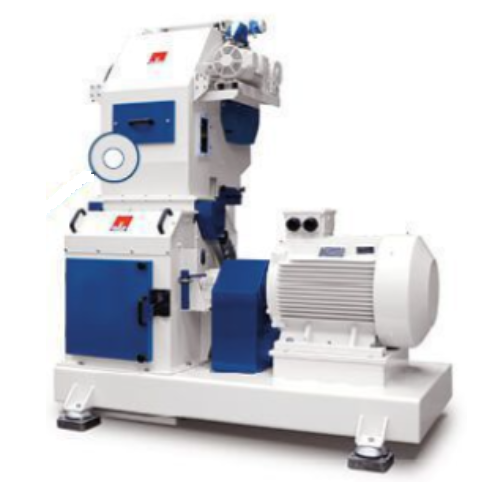
Industrial hammer mill for granulate grinding
Optimize the grinding process in feed production with a high-efficiency solu...
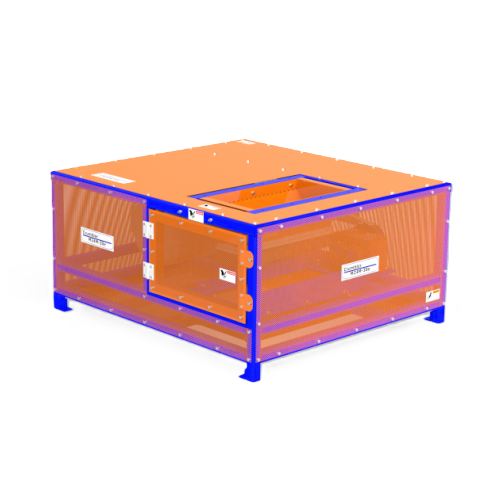
Rotary shear for wood chips and biomass processing
Efficiently transform diverse biomass materials into uniform particles...
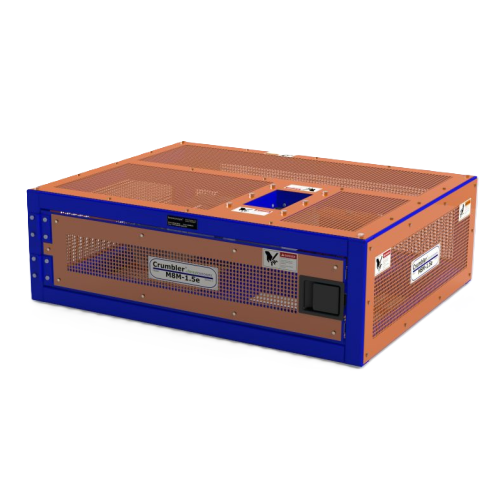
Micro-scale rotary shear for particle size reduction
Optimize your research with precise particle reduction, ideal for tr...
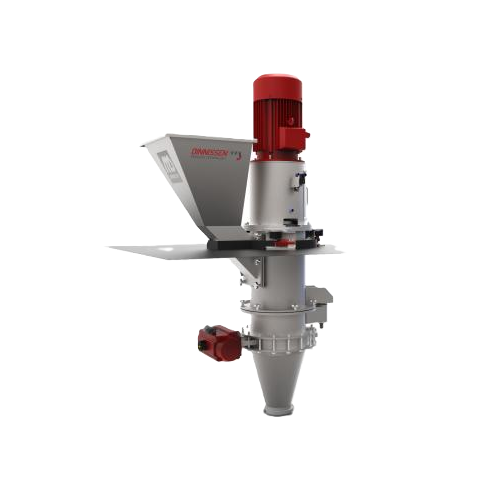
Industrial shredder for diverse material reduction
Achieve precise and efficient material resizing for diverse applicatio...
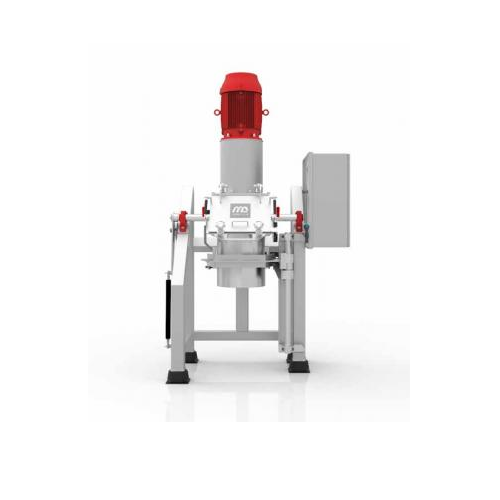
Industrial pulper for fresh produce
Achieve ultra-fine purees and pastes with this high-speed industrial pulper, designed t...
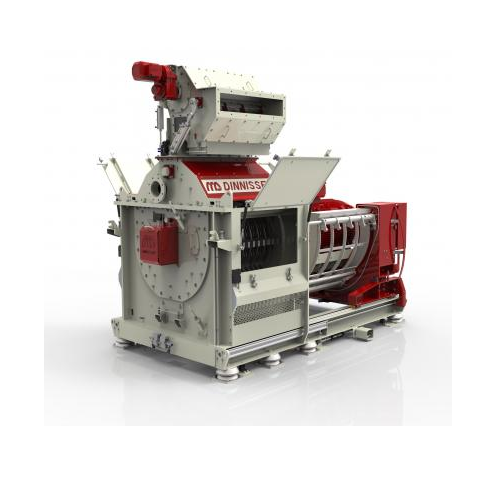
Fast screen exchange grinding solution for medium-hard products
Maximize your milling efficiency with a solution that al...
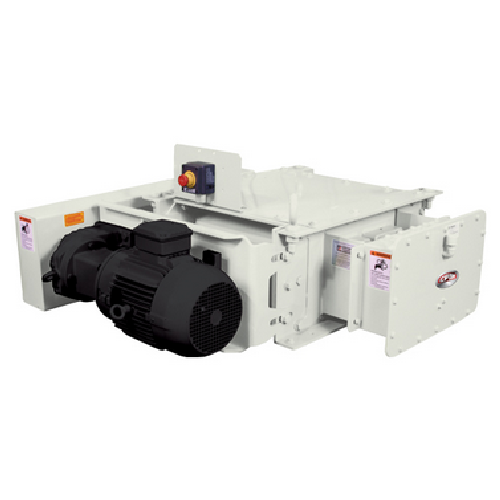
Industrial lump breaker for particle size reduction
Optimize your production line with an advanced solution for efficient...
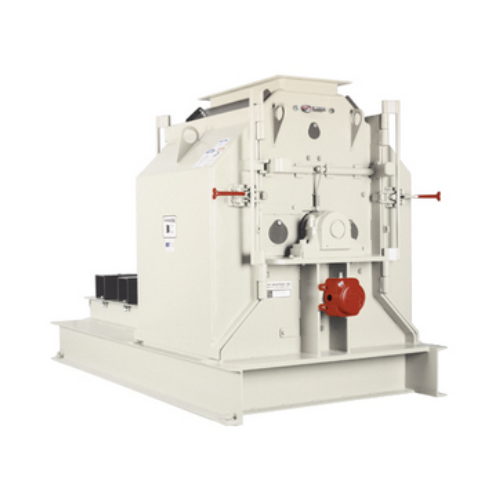
Hammermills for grinding tough products
Optimize particle size reduction with precision-designed hammermills that efficient...
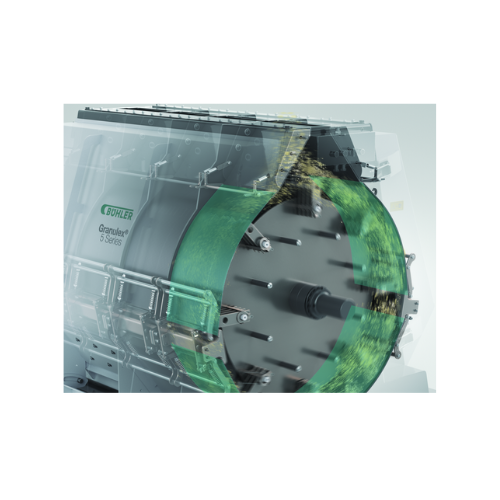
Horizontal hammer mill for grain processing
Optimize your grinding processes with our horizontal hammer mill, designed to ...
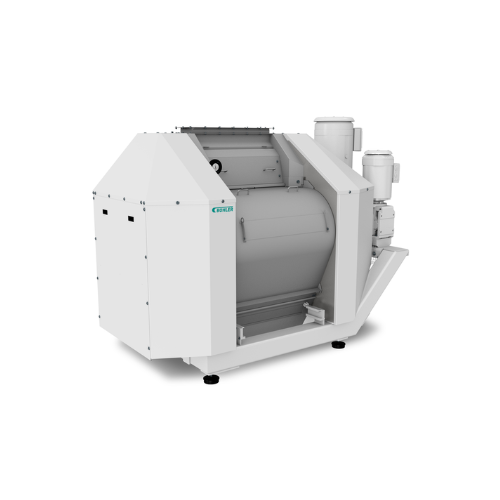
Industrial grain flaking mill
For efficient grain processing, achieve uniform flake quality with advanced temperature-contro...
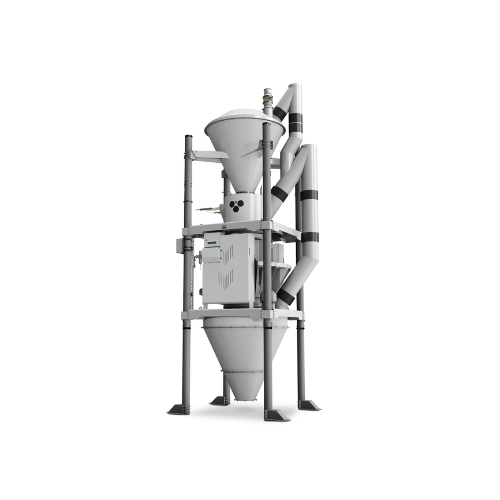
Fully automatic batch scale for powdery and granular products
Achieve precise and repeatable dosing for powdery and gran...
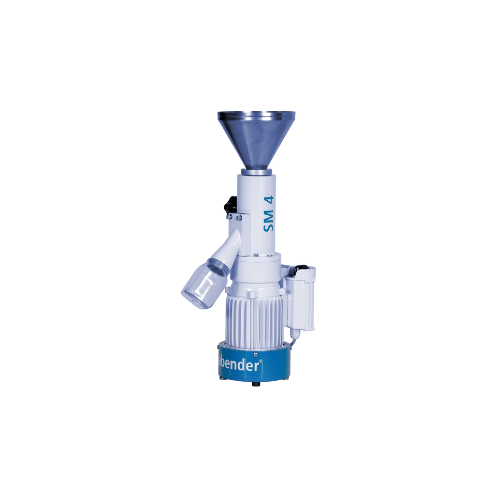
Industrial sample preparation mill
Ensure precise moisture, protein, and fat content analysis with this reliable milling so...
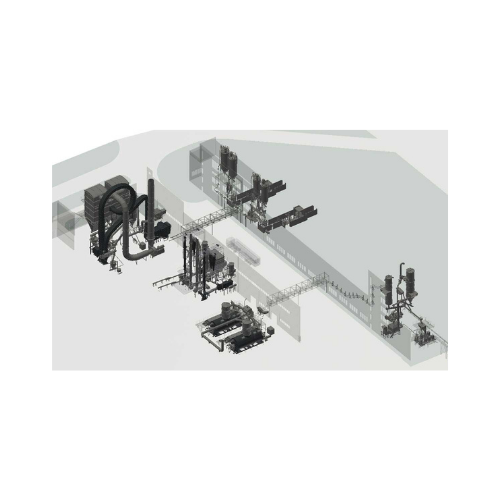
Wheat processing systems for industrial applications
Maximize efficiency in wheat processing with a system designed for p...
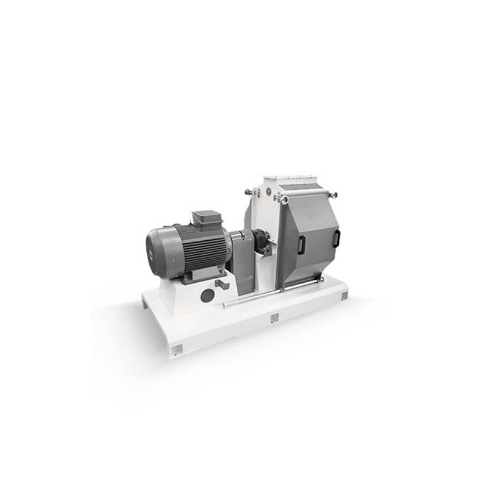
Hammer mill for grinding dry or low-moisture grains
Efficiently transform dry grains into high-quality feed and flour wit...
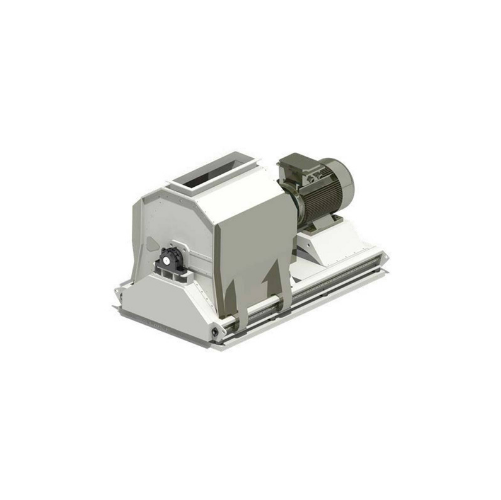
Industrial hammer mill for food industry grinding
Efficiently reduce raw material size with high-speed precision grinding...
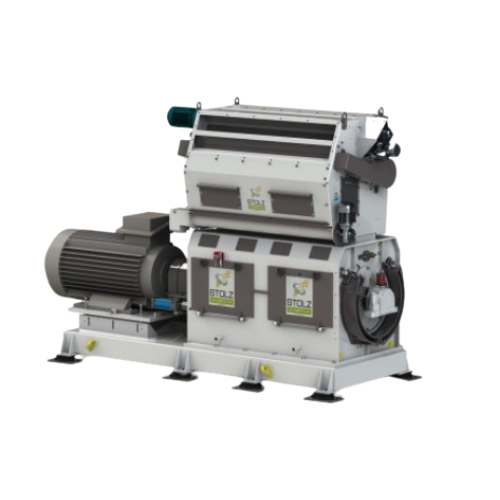
Industrial hammermill for fine grinding applications
Elevate your milling efficiency with hammermills designed for precis...
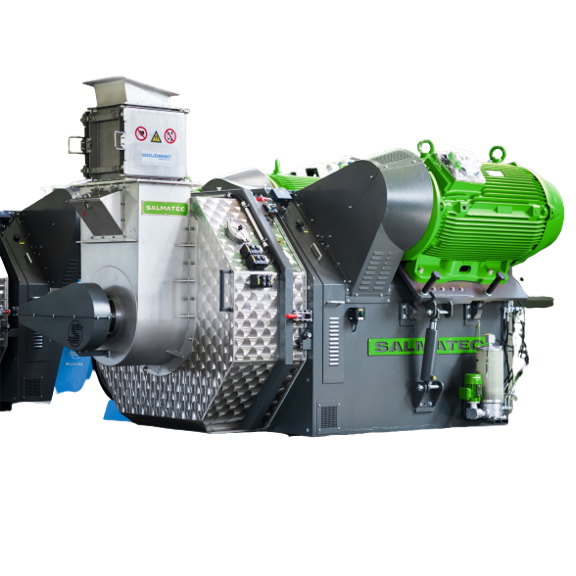
Complete pellet line
Large industries are shifting towards more environment-friendly technology, such as recycling wastes and...
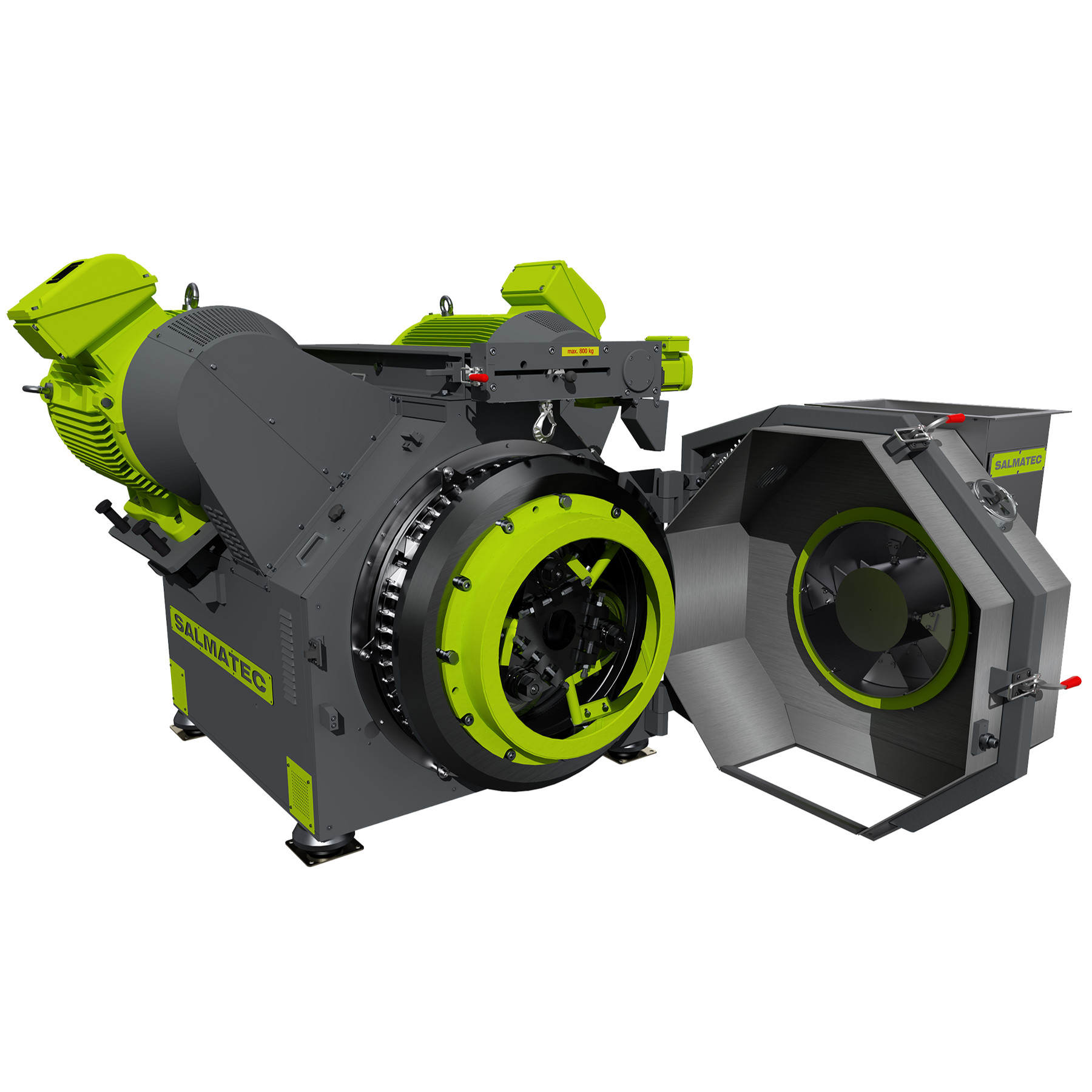
Industrial pellet mill
At the industrial level, the application areas of pellets range widely in fields such as feeds, biomas...
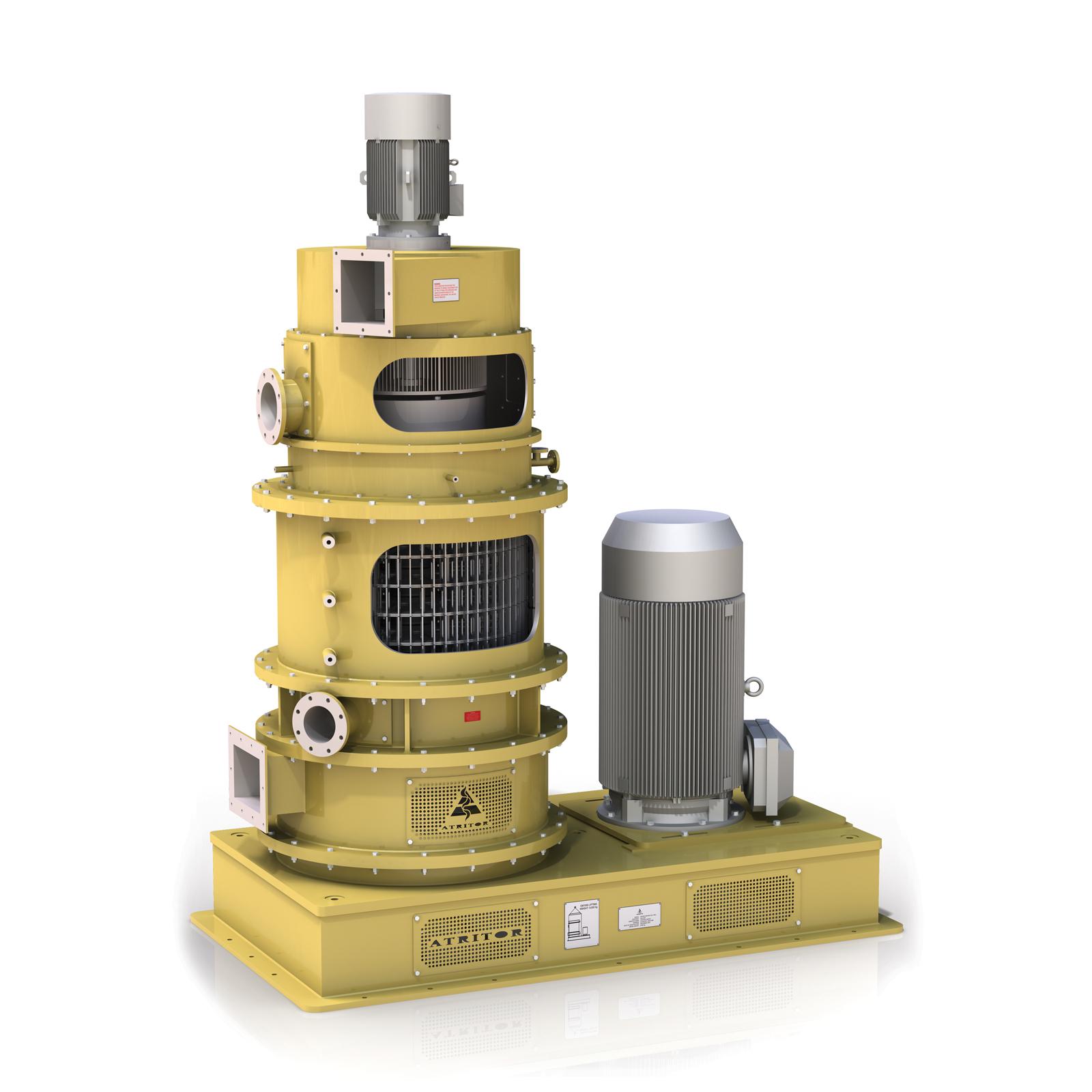
Milling and drying machine for fine powders
When you need to produce ultra-fine powders, the milling and drying process em...
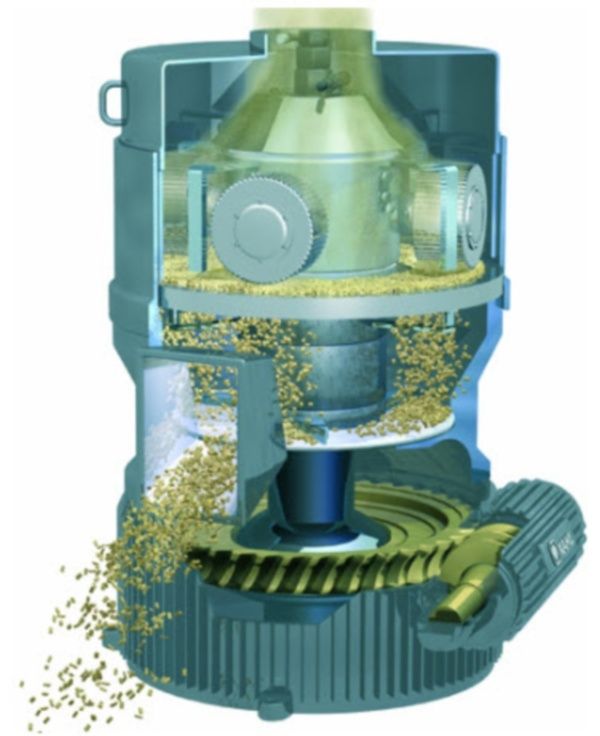
Pelleting press for biomass
Utilization of biomass for energy and other applications requires consistent and reliable compac...
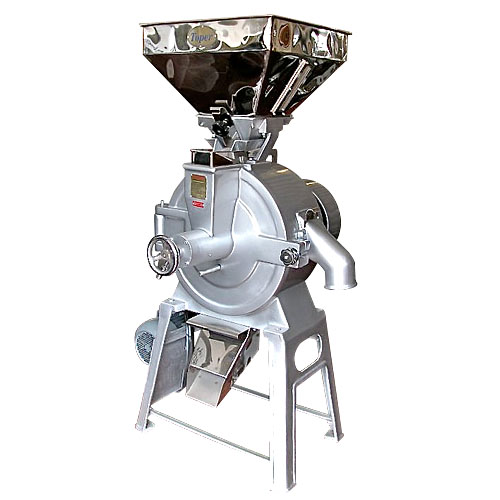
Stone mill for coffee beans
Traditional milling of coffee beans or seeds, with a stationary bedstone and a turning runner st...
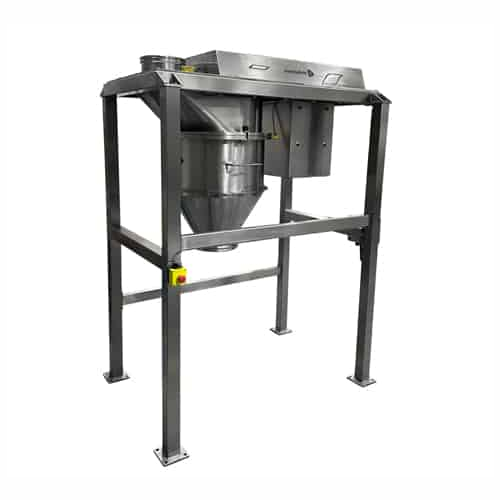
High capacity production milling for bulk materials
Optimize your production with our high-capacity milling solution, des...
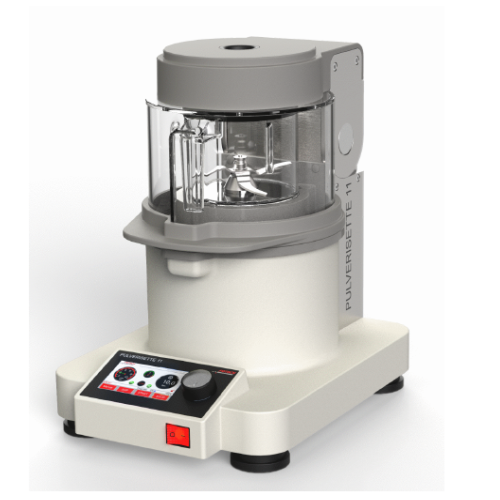
Laboratory knife mill for fast comminution
Achieve rapid and precise sample preparation with this versatile knife mill, de...
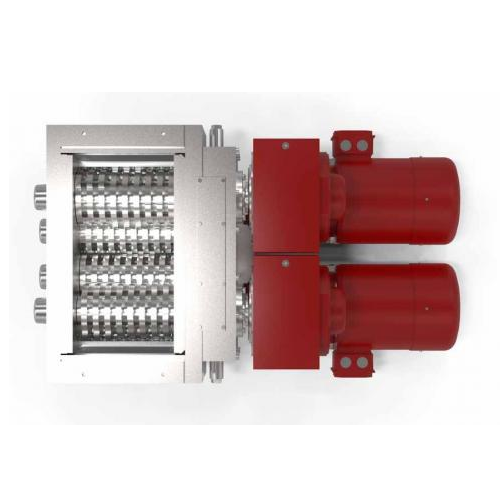
Industrial roller mill for grain size reduction
Achieve precise grain size reduction with minimal heat generation and opti...
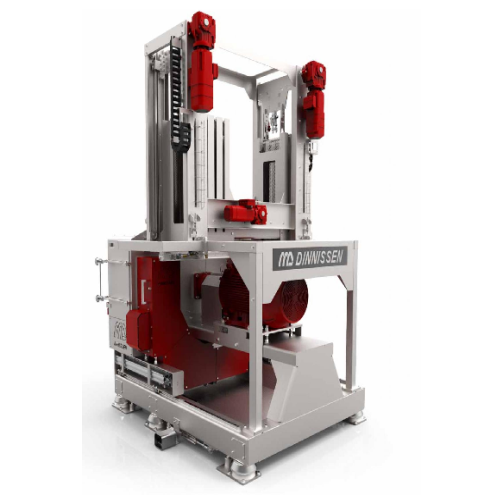
Hammer mill with automatic screen exchange
Optimize your milling operations with a high-speed solution that ensures seamle...
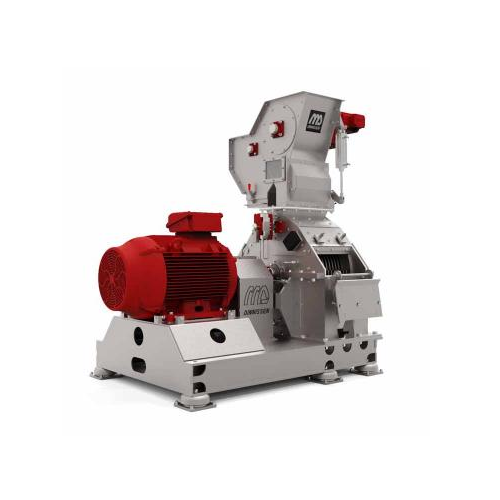
Industrial hammer mill for grinding and sifting
Ensure precise particle size reduction and consistent product quality with...
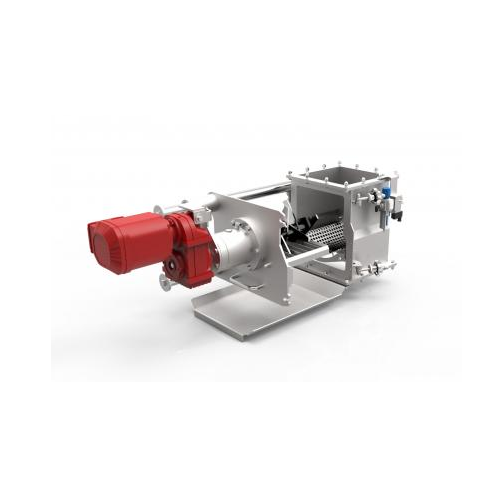
Industrial breaker for reducing large lumps and agglomerates
Efficiently break down challenging materials with a robust ...
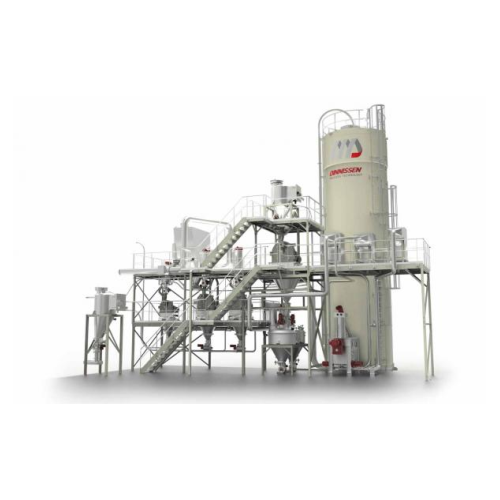
Centrifugal mill for fine grinding in industrial processes
Achieve exceptional fineness without overheating your materia...
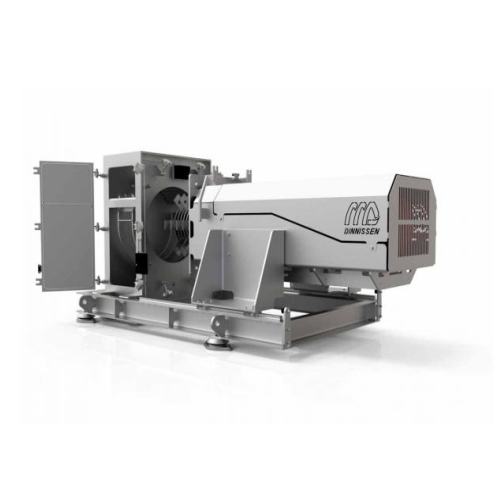
Hygienic industrial grinder for food and pharma applications
Achieve optimal hygiene and efficiency in your grinding pro...
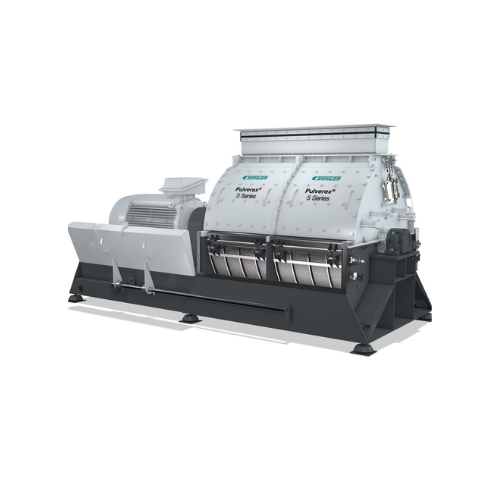
Industrial fine grinding pulverizer
Achieve consistent fine granulation at high capacity with reduced energy consumption, u...
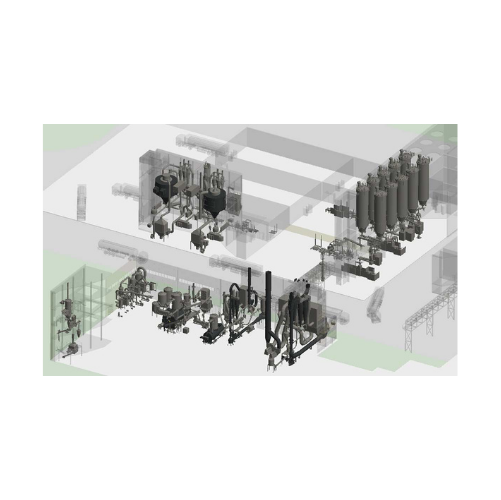
Corn wet milling plant drying systems
Optimize corn processing efficiency with integrated drying and dewatering systems des...
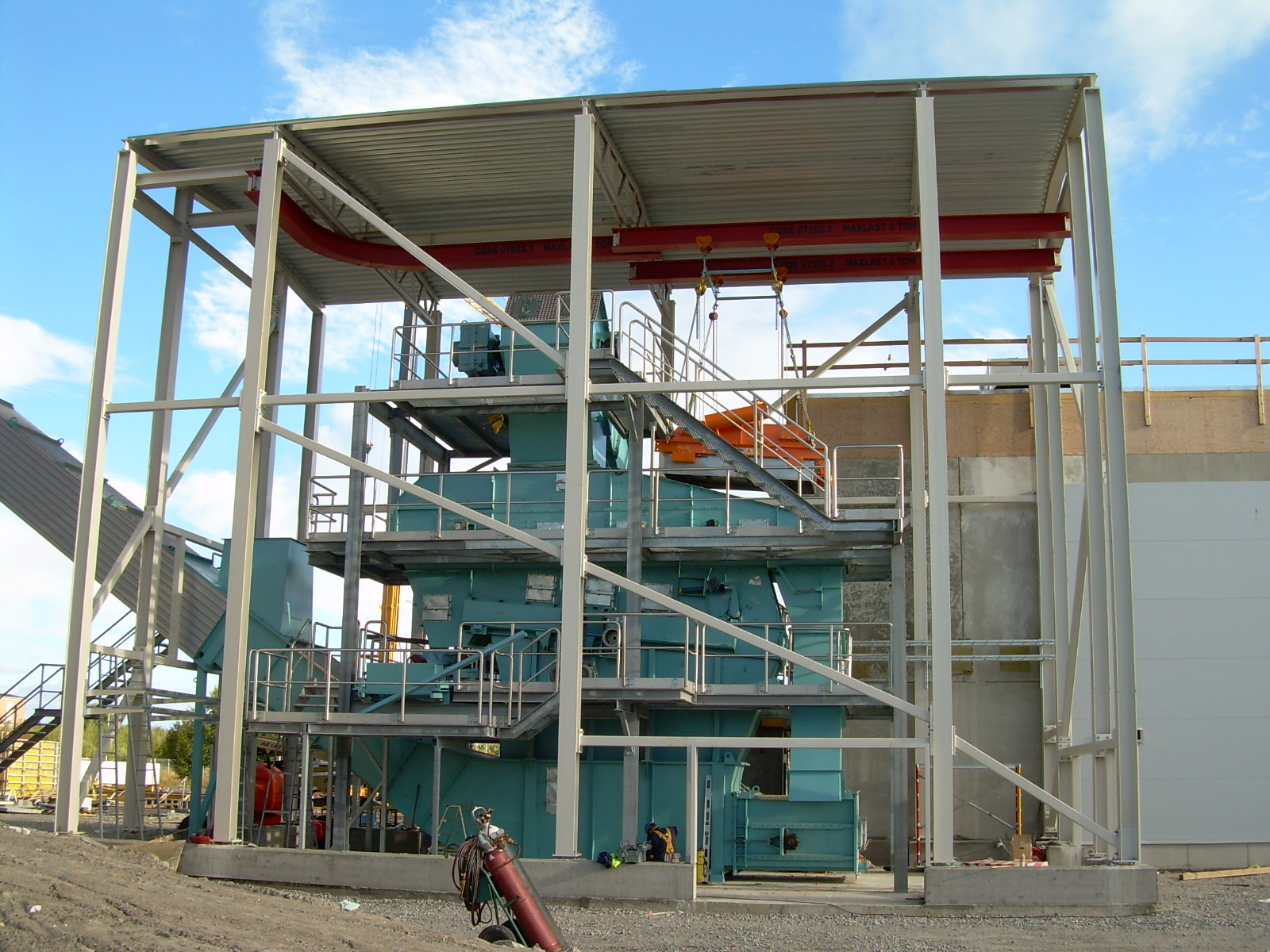
Solid biomass screening and crushing equipment
Biomass fuels come in many forms and often include impurities that can dama...
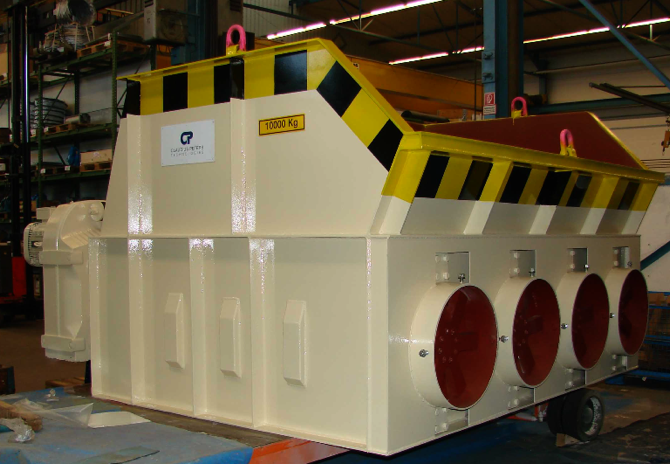
Reclaim crusher
Waste products and rejected materials are inevitably generated from any gypsum products manufacturing process....
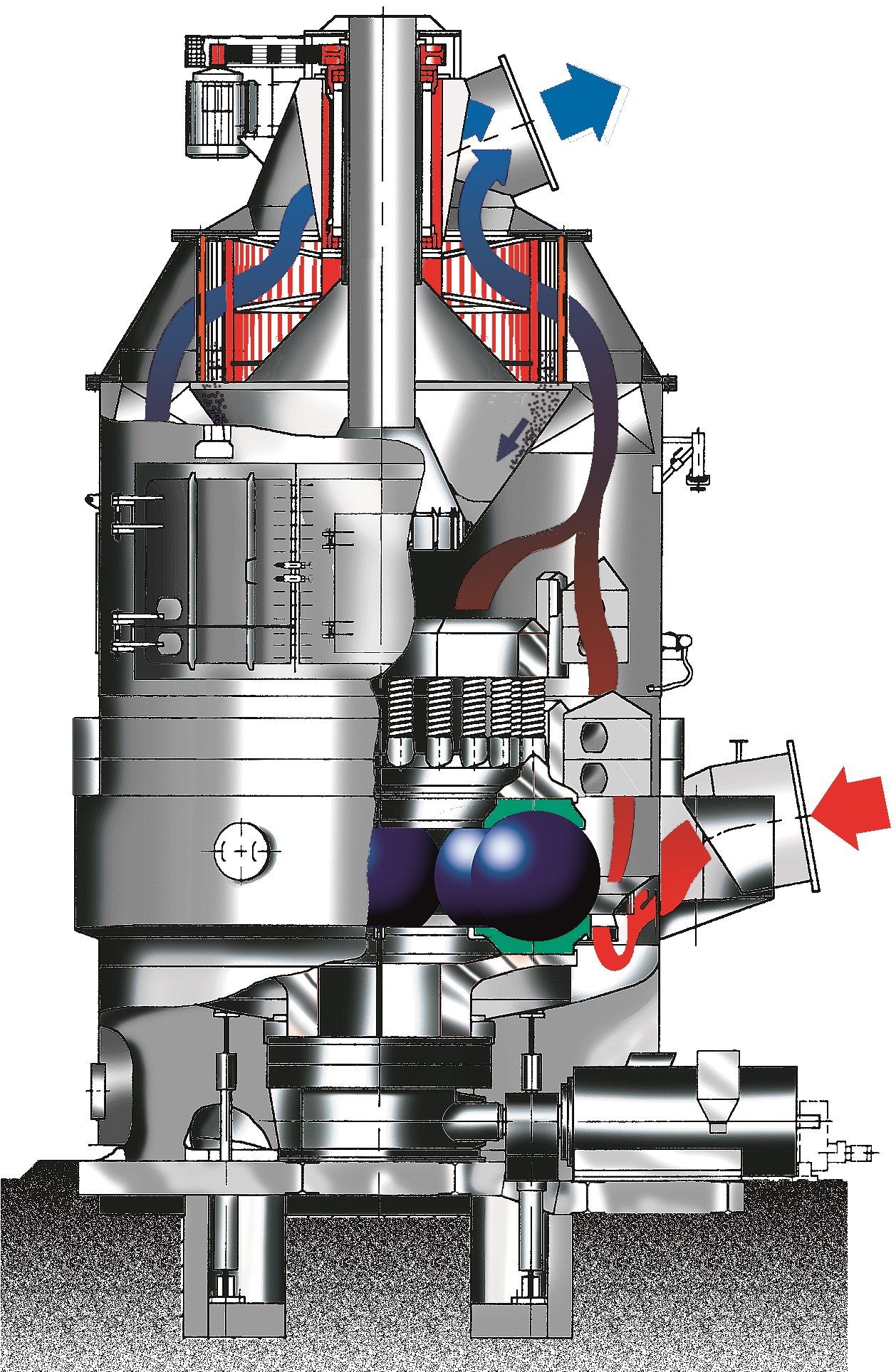
Mill for calcining gypsum
Quality of gypsum and stucco products are highly influenced by the quality of the calcining proces...