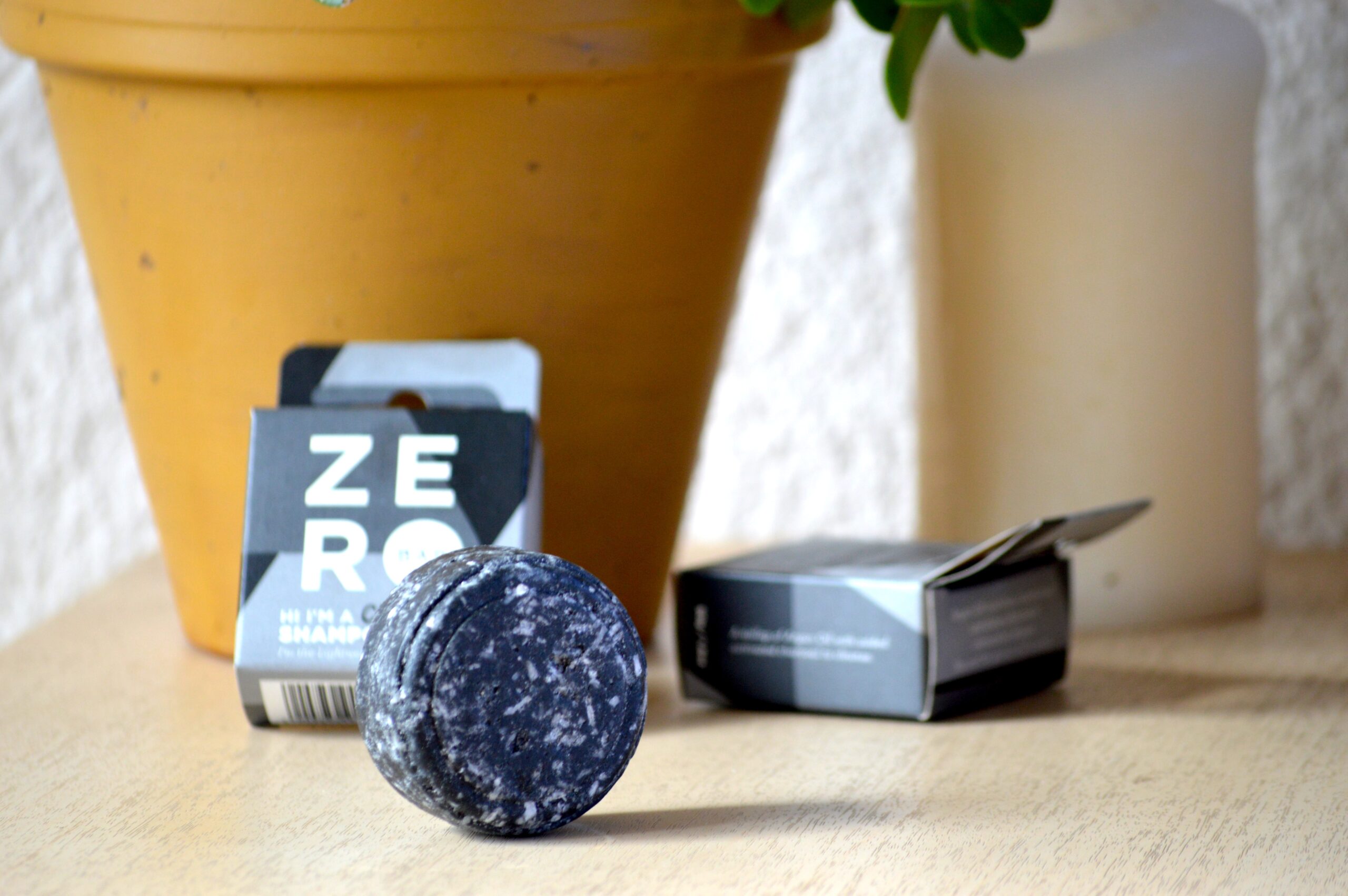
Making Refill Tablets
Find innovative production technology for making refill tablets and connect directly with world-leading specialists
The wave of liquid soaps and detergents in the 1950s revolutionized home and personal care. Cheap and convenient, these off-the-shelf products fit perfectly into the lifestyle of the time. A few decades later, though, plastic waste put the sustainability of hygiene products into question. Refill tablet production technology answers that by eliminating single-use plastic. Instead of picking up a new bottle every time, end-users complete the formulation process in a multi-use container and with a simple instruction: just add water.
Tell us about your production challenge
Apply wet granulation to facilitate the flowability of tablet materials in production technology
Before compressing the mixture into a tablet, granulate the fine particles to improve flowability throughout processing. The wet granulation technique introduces 1-4% water or solvent to the formula to bind particles together.
Add moisture-absorbing materials such as microcrystalline cellulose or silicon dioxide to remove any excess fluids.
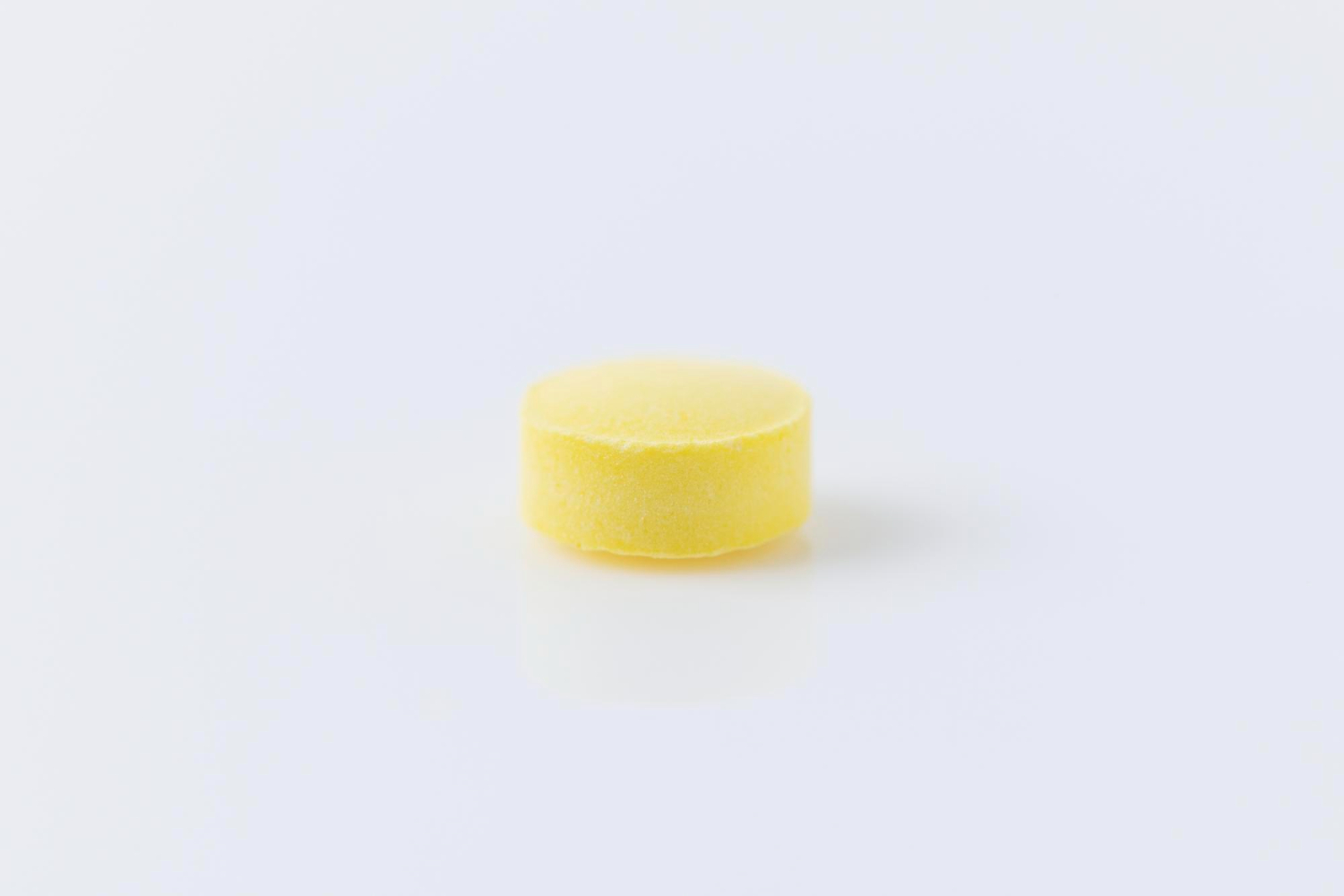
Pre-compress the mix before forming with compaction technology
The ease of use of refill products comes down to their physical form. Indeed, compression is the crucial step in refill tablet manufacturing.
Compaction technology presses the granulate into a cohesive mono-dose that can break up in the right liquid conditions. But excessive die-wall pressure on the particles could develop cracks later in the process. Subject the formula to pre-compression to prevent this kind of capping and lamination.
Enhance the sensory impact with your signature additives
Formulas for refill tablets vary by their intended use. For example, citric acid is a suitable cleaning agent in a bathroom cleaner mix, while sodium sulfate performs that action in a hand soap tablet.
The sensory effect is equally important. Calcium carbonate, among other additives, has a brightening effect; sodium laureth sulfate acts as a foaming agent. Mix scents and dyes to improve the consumer appeal of the refill tablets.
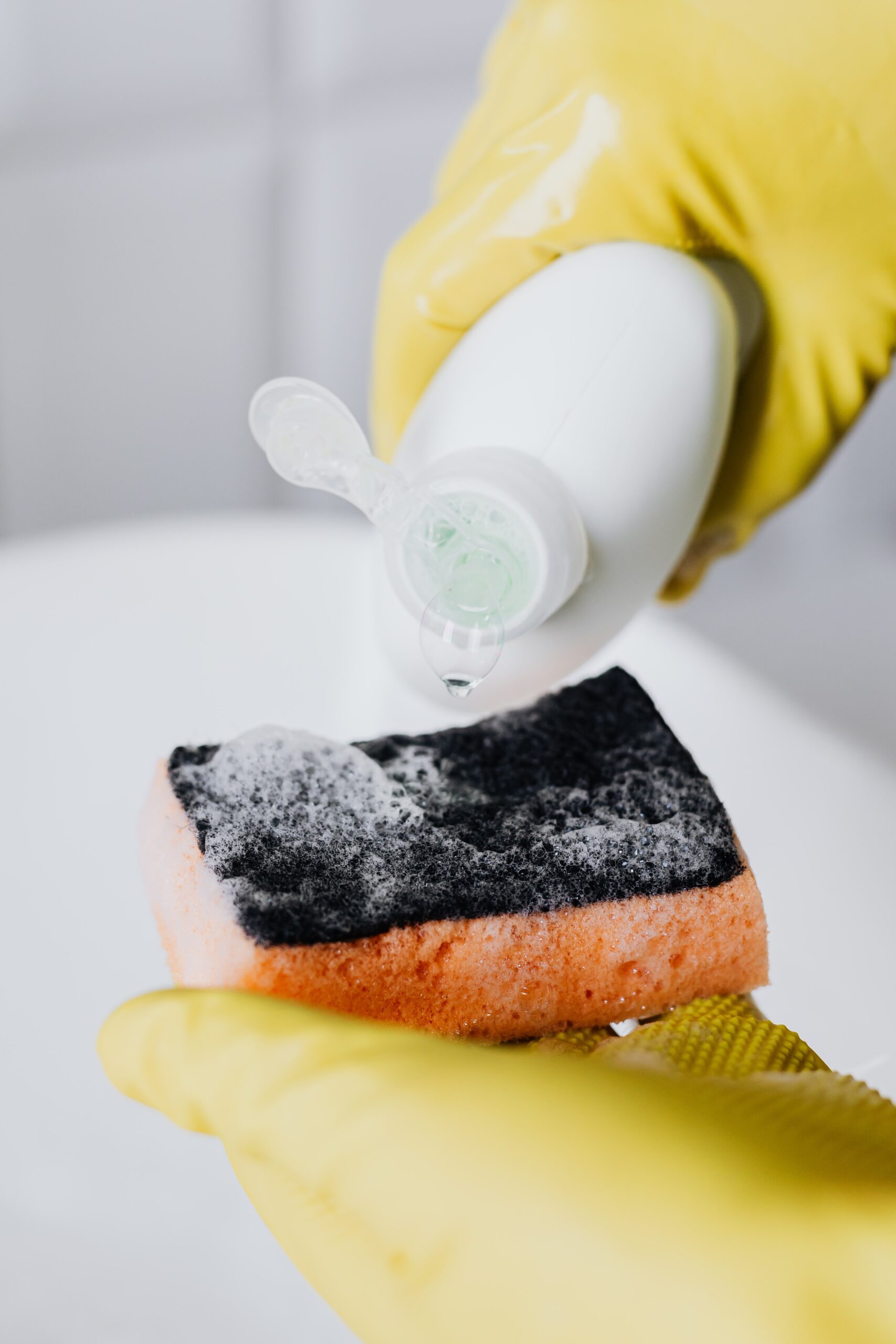
Add a disintegrant to ease tablet dissolution in water
The test of the refill tablet production lies in the dissolution of the dose. Once popped in its water container, the compacted formula must dissolve quickly and evenly, distributing the particles in the liquid.
Polyethylene glycol is an inactive ingredient that speeds up the disintegration of the tablet. Sesquicarbonates like sodium glycine carbonate are a class of petroleum-free alternatives that perform the same function.
Package refill tablets in water-tight wrapping film
One of the main advantages of refill tablets is that they significantly reduce water usage from the production line. Unlike liquid detergents and soaps, it is the final consumer that mixes in the water, decreasing the impact of large-volume transportation.
Wrap the tablets in humidity and air-resistant film to avoid premature dissolution. Individual packaging also makes storage and application easier for consumers.
Processing steps involved in refill tablets making
Which refill tablets technology do you need?
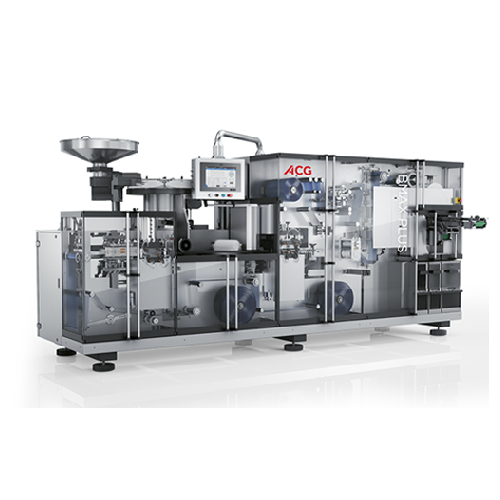
Flat forming and sealing blister packaging solution
Enhance your blister packaging process with a solution that ensures p...
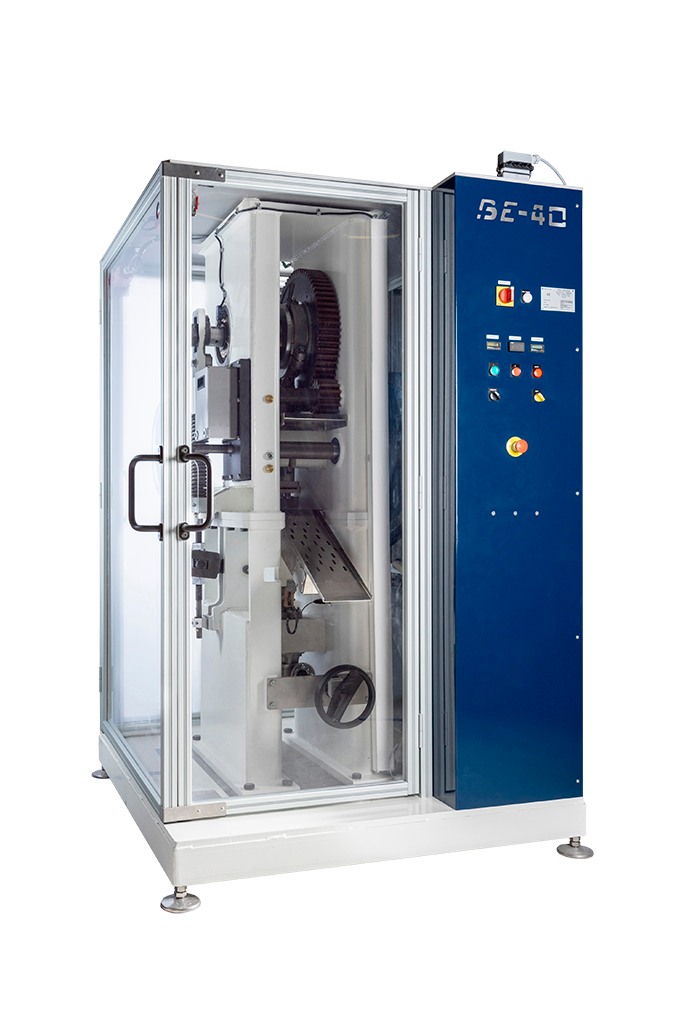
Eccentric press for refill tablets
Hundreds of different refill tablets, of various shapes or sizes, are on the market toda...
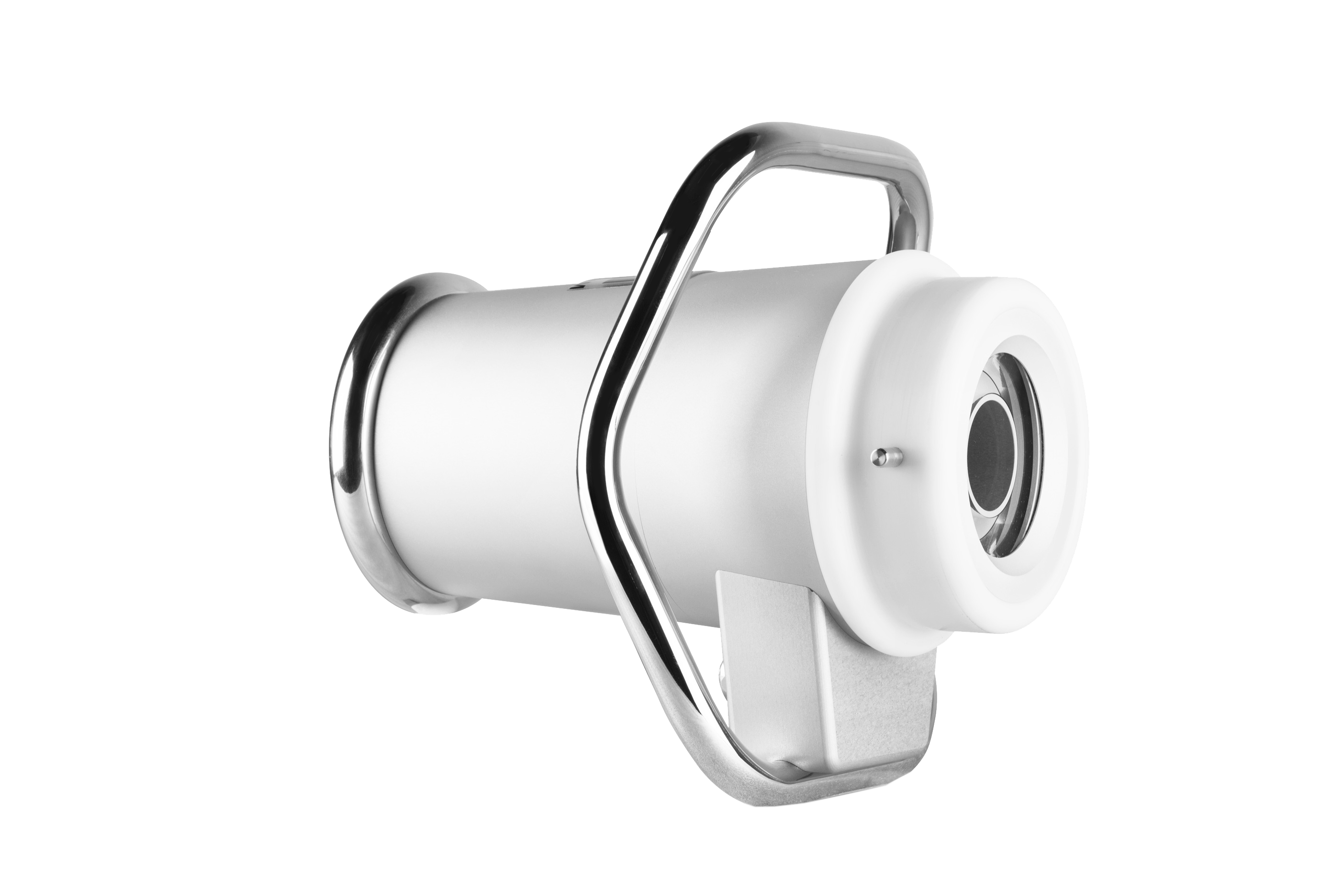
Particle analysation monitor
Products like granules, tablets and capsules require inspection at numerous steps in the produc...
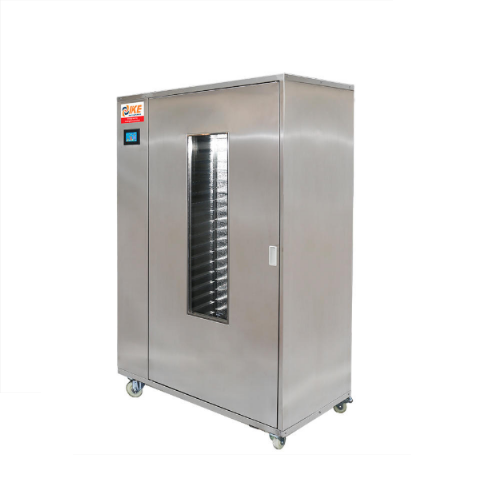
Industrial drying cabinet
The production of high-quality biltong and similar dried meat products can pose problems with main...
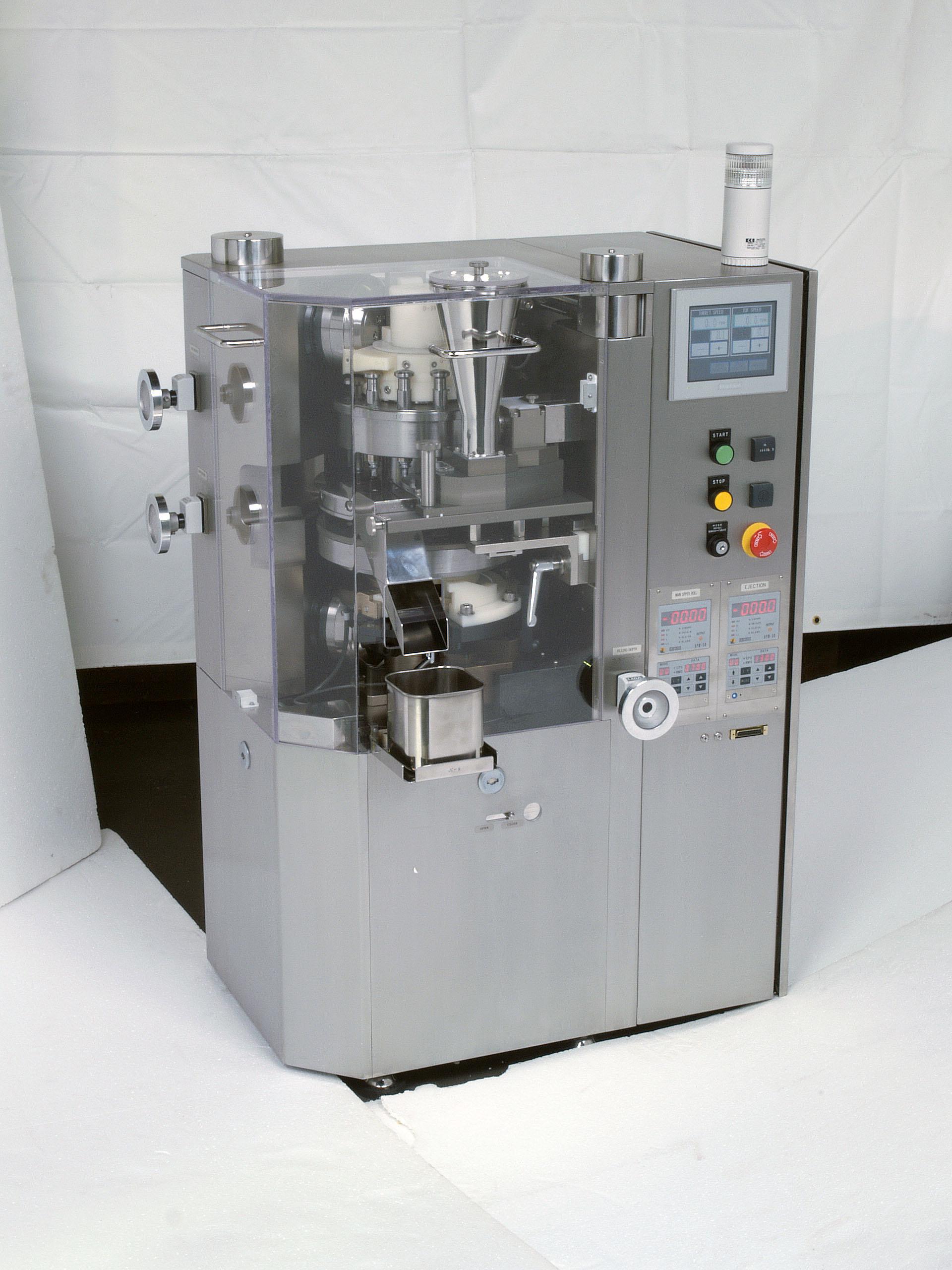
Laboratory Tablet Press
Pharmaceutical research and development projects may require small samples of high quality tablets fo...
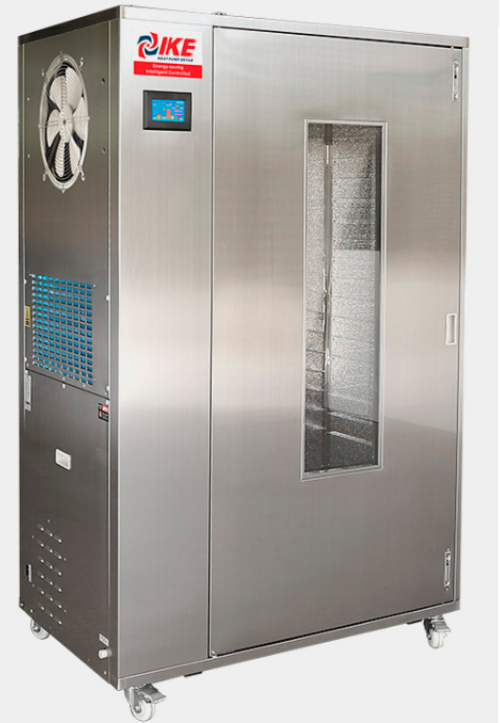
Industrial dehydration machine
Dried fruits are popular both as food in themselves and as ingredients. Traditional drying te...
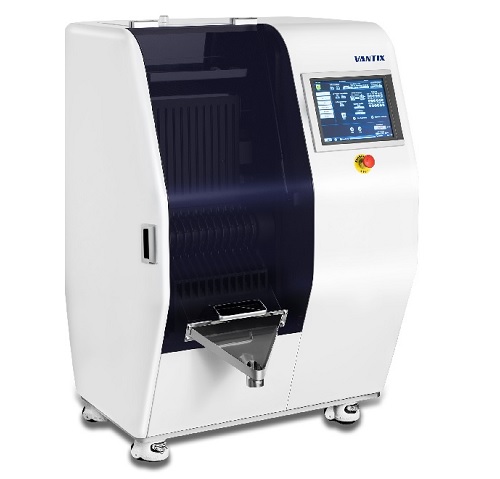
Capsule checkweigher
The production of pharmaceutical capsules requires that individual doses are checked for accuracy. In a ...
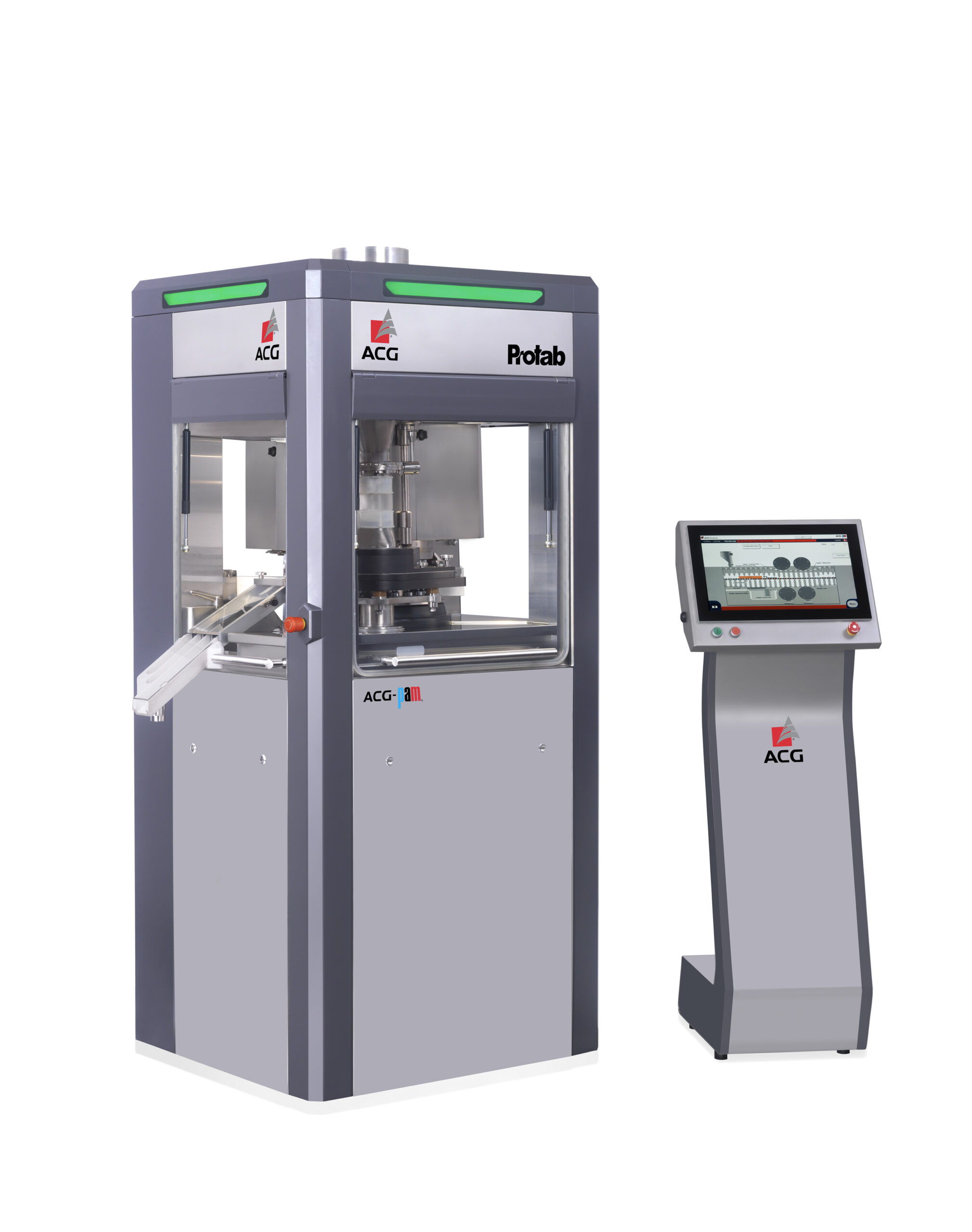
Single rotary tablet press
Creating batches of consistent high quality pharmaceutical grade tablets from your powdered ingre...
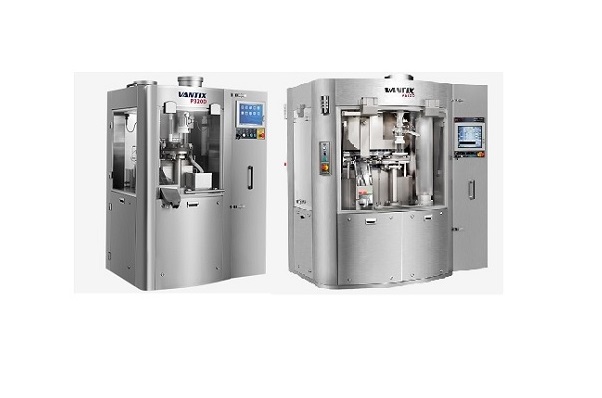
Single and double layer tablet press
High performance tablet presses that are capable of producing both single and double-l...
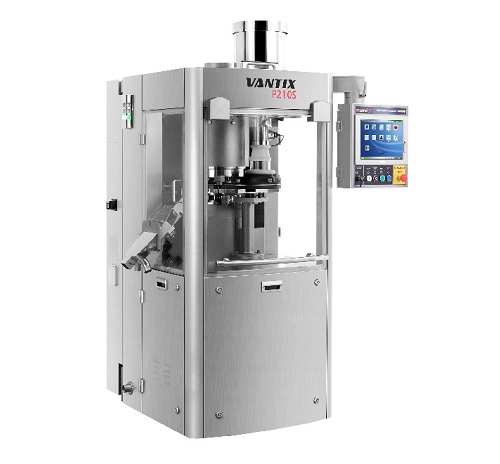
Rotary tablet press
For pharmaceutical tablet producers looking to reduce waste, costs and increase production volume, a hig...
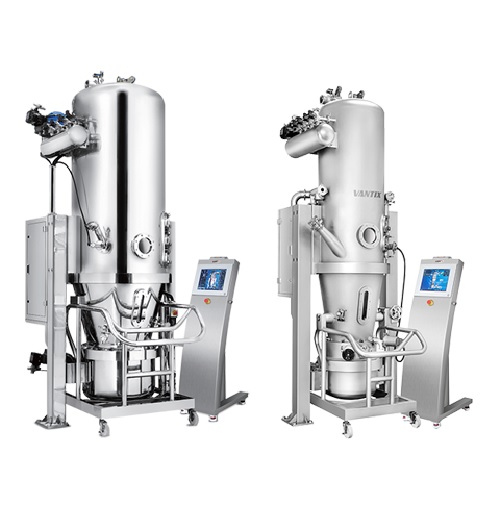
Fluid bed dryer for production scale
Fluidized bed drying (FBD) is a common process in the pharmaceutical industry for dryi...
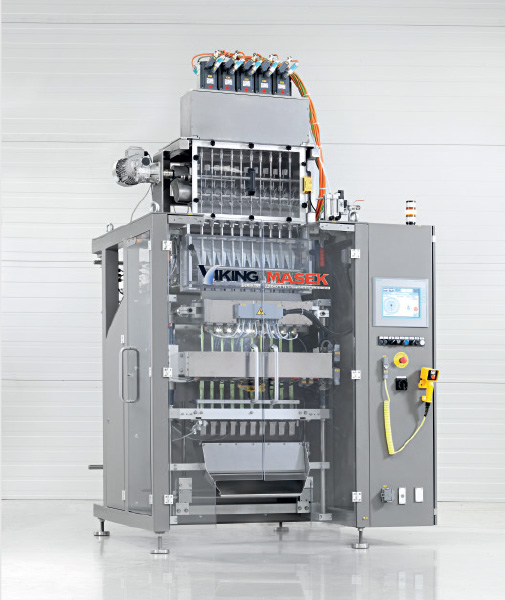
Stickpack Machine
If you are looking to pack your product into stick packs from 17 x 40 mm to 100 x 200 mm in size, you may b...
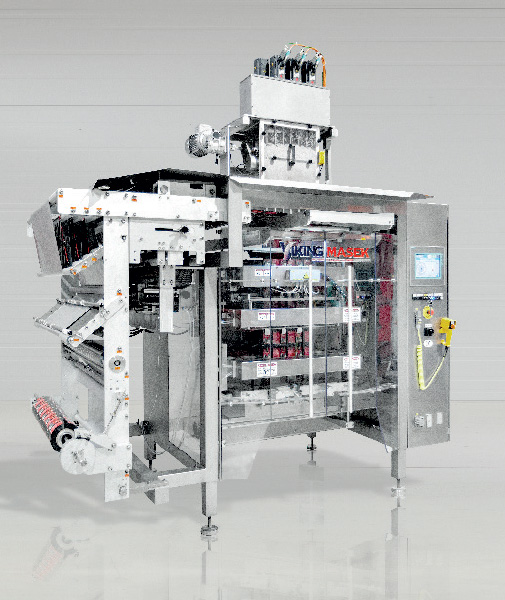
Sachet Machine
If you want to pack into eye-catching 4-side sealed sachets between 40×50 mm and 250×200 mm in size, ...
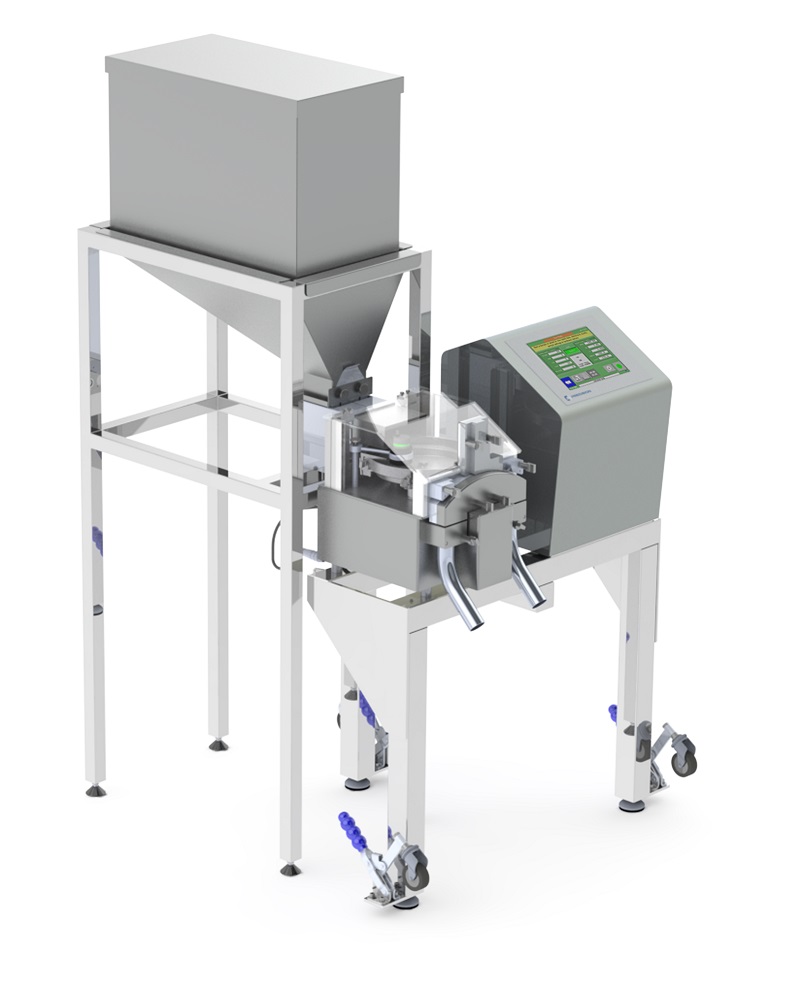
Versatile weight sorter for tablets & capsules
Saving costs and improved production efficiencies are possible by opti...

Vertical agitated dry media mill
A vertical agitated media mill is used for grinding ultrafine particles, in an agitated (or...
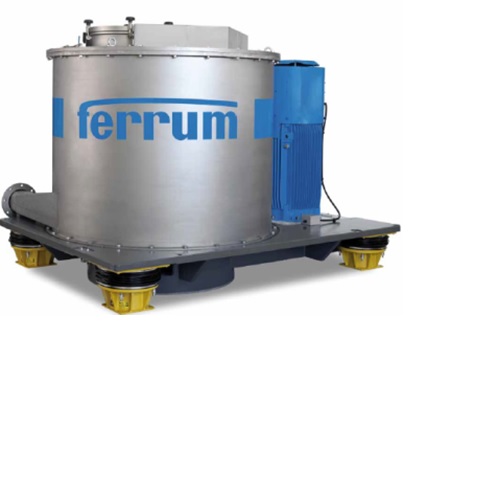
Gypsum centrifuge
Especially designed for flue gas desulphurization, applications in coal fired power plants and waste incine...