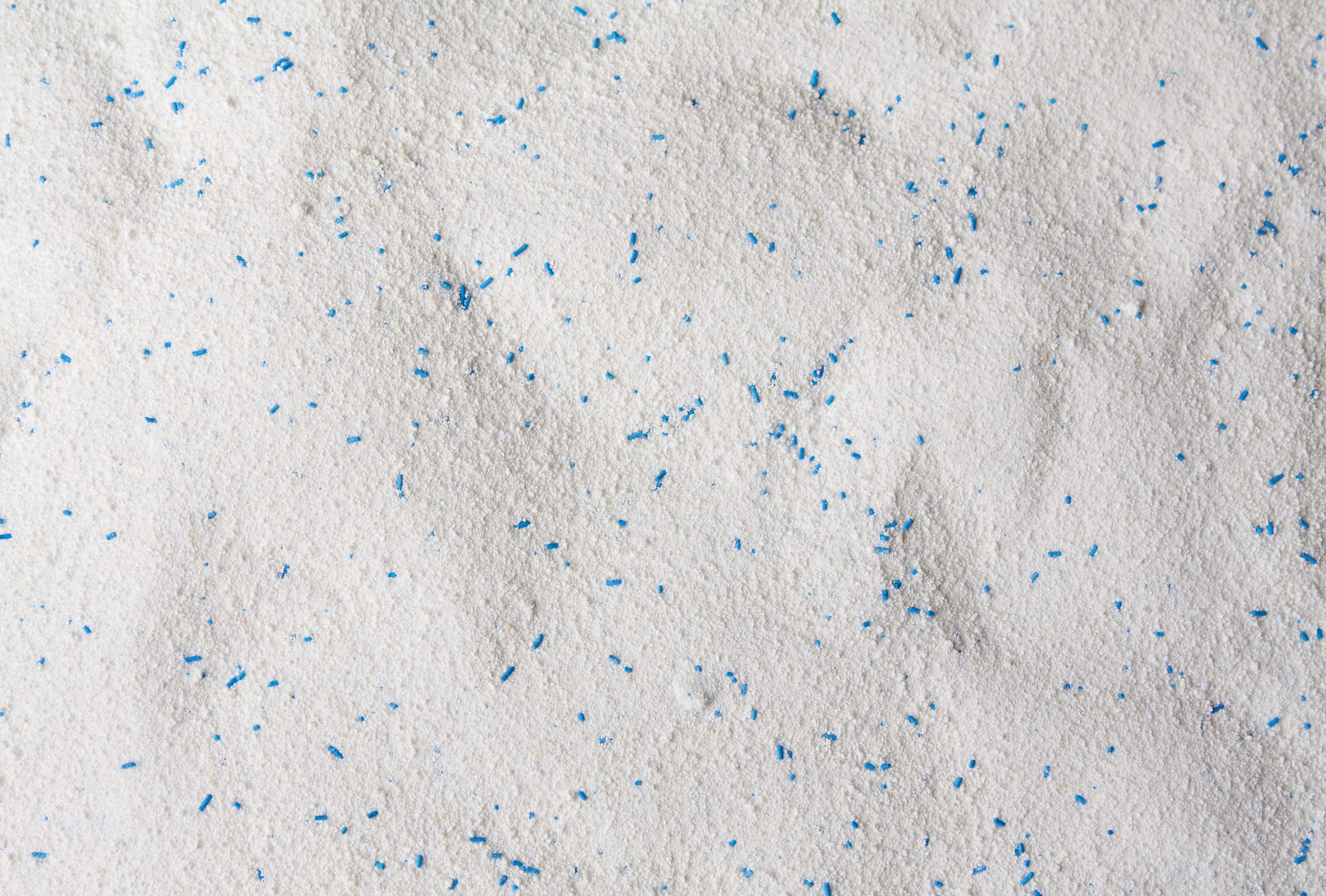
Detergent Manufacturing Equipment
Find innovative detergents equipment and connect directly with world-leading technology suppliers
Detergents are cleaning agents that help remove dirt and grease from porous and non-porous surfaces. Industrial production of detergents began after World War I. Still, it was after the 1950s and 1960s that the detergent industry grew exponentially due in part to the development of new detergent manufacturing equipment.
Innovative technologies for producing detergents
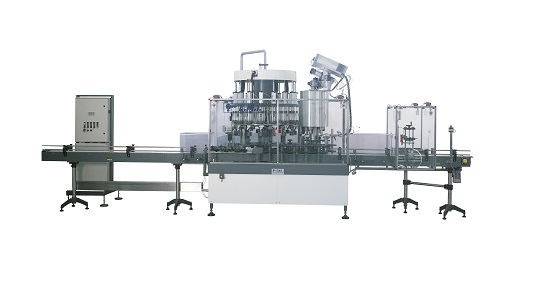
Liquid detergent filling machine
Filling of liquid detergents requires specialised equipment because of the foaming nature o...
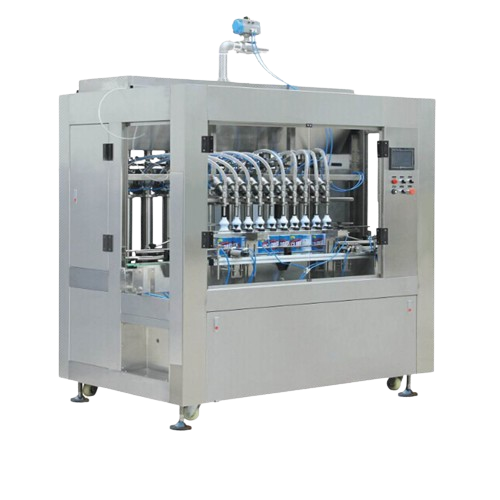
Automatic detergent shampoo filling solution
Streamline your filling process with precise volume control, achieving consis...
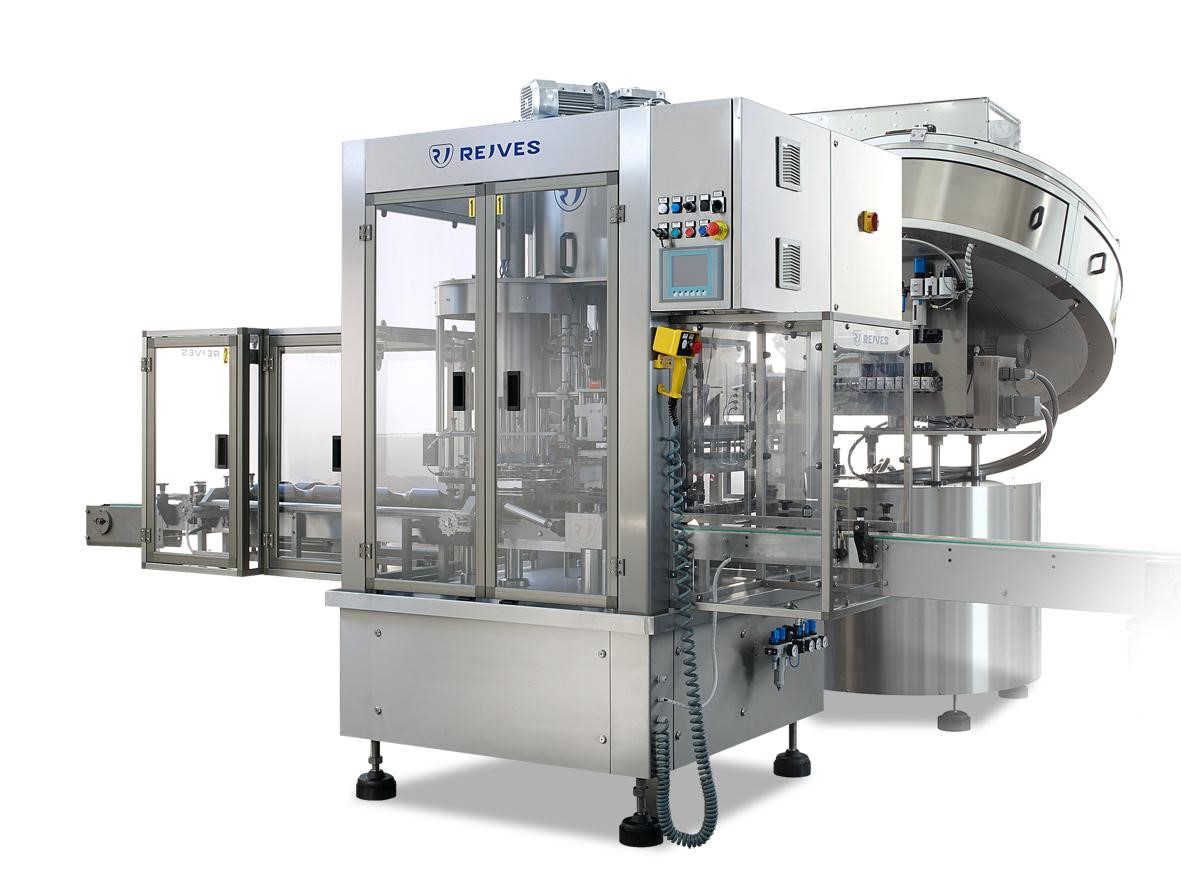
Hand sanitizer capping machine
Bottled products such as hand sanitizers, shampoos, and liquid detergents, have different cap...
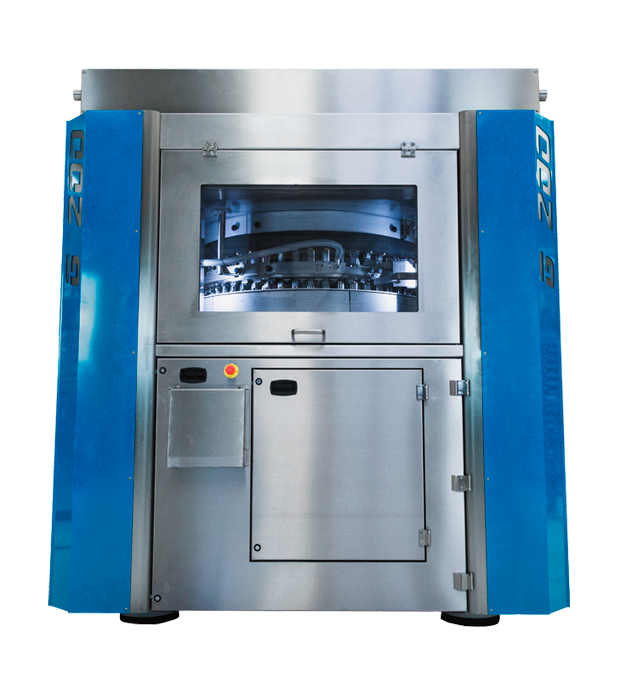
Three-layer dishwasher tablet press
Dishwasher detergent tablets come either in a single layer or multi-layer form. Multi-l...
Select your detergents process
Tell us about your production challenge
Dirty substances are generally related to hydrophobic fatty materials insoluble in water. However, detergents are amphiphilic, meaning they contain both non-polar hydrophobic (water-hating) and polar hydrophilic (water-loving) ends. This dual nature allows the detergent to grab the oily-greasy dirt stains and wash them away.
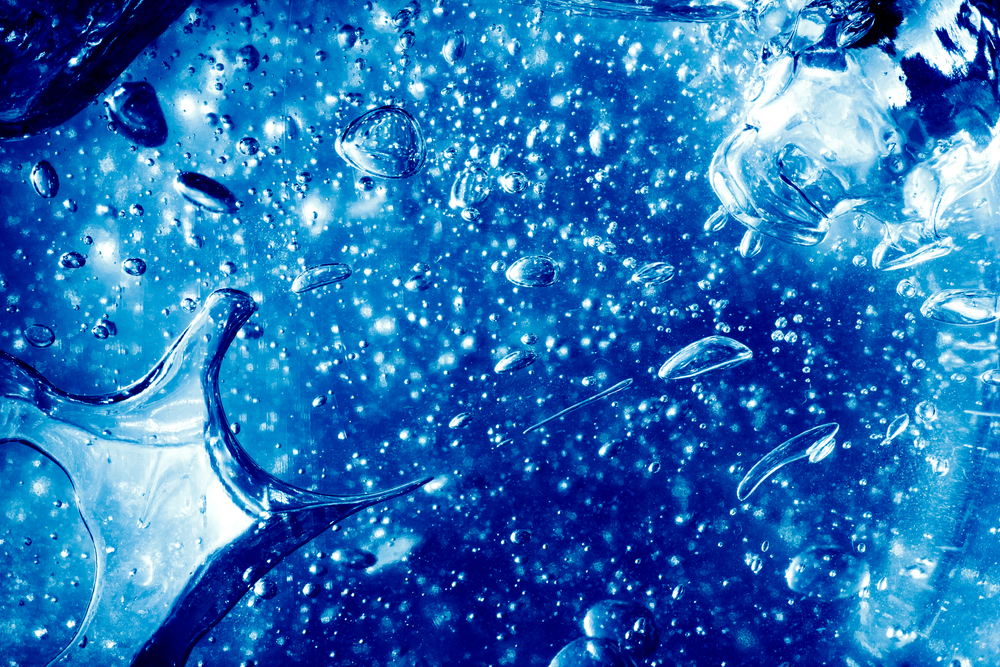
As surfactants or a mixture of surfactants, detergents have the ability to decrease the surface tension of water. This function facilitates the formation of dispersions, emulsions, and suspensions.
The most common detergent is soap, a sodium salt of fatty acids. To increase solubility, modern detergents contain alkyl-benzene sulfonates. In fact, these compounds (polar sulfonate group) are more soluble in hard water than soap (polar carboxylate group). Polar sulfonate is less likely to bind to calcium and other ions of the hard water than polar carboxylate.
Detergent manufacturing process
Detergent manufacturing involves mixing the raw materials in large tanks; the manufacturing process can be batch as well as continuous. Raw materials are selected based on the form and properties of the desired end product. It is essential to mix all ingredients thoroughly in a mixer machine to ensure that the chemicals are evenly distributed in the detergent.
Fillers, surfactants, disinfectant agents, and chemical agents are used as ingredients in detergent making. To give color, powdered pigments can be added. In hand soap production, for example, adding a preservative is critical to prevent the proliferation of bacteria if the soap is exposed to a substandard environment.
Liquid detergent, powder detergent, or laundry detergent?
Historically, when people referred to detergent, they usually indicated laundry detergent. It was only after the 20th century, due to the development of detergent making equipment, that the word detergent acquired a broader meaning with its liquid and powder form.
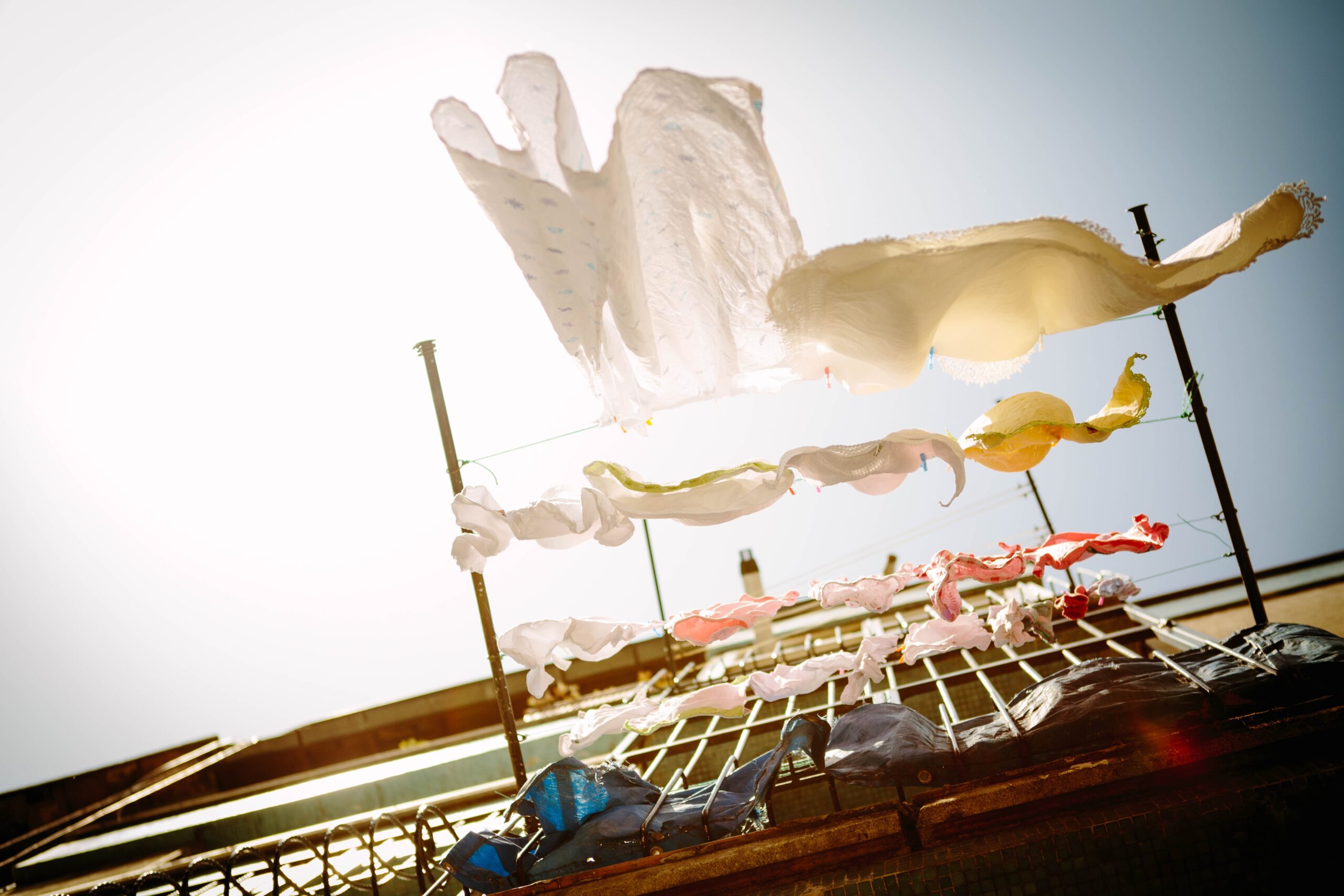
Laundry detergent
Wash, dry, fold, repeat. This is the daily formula for doing laundry. Helping us in this daily task is detergent which has a slightly different formula.
Producers can use three methods when making laundry detergent: dry mixing, agglomeration, or spray drying. The spry drying technique is the most used because it produces a lightweight, well-hydrated product that doesn’t cake. Pay attention to the pH range when producing the washing powder; the pH has to be 9-10.5. to ensure it is compatible with human skin and can clean effectively.
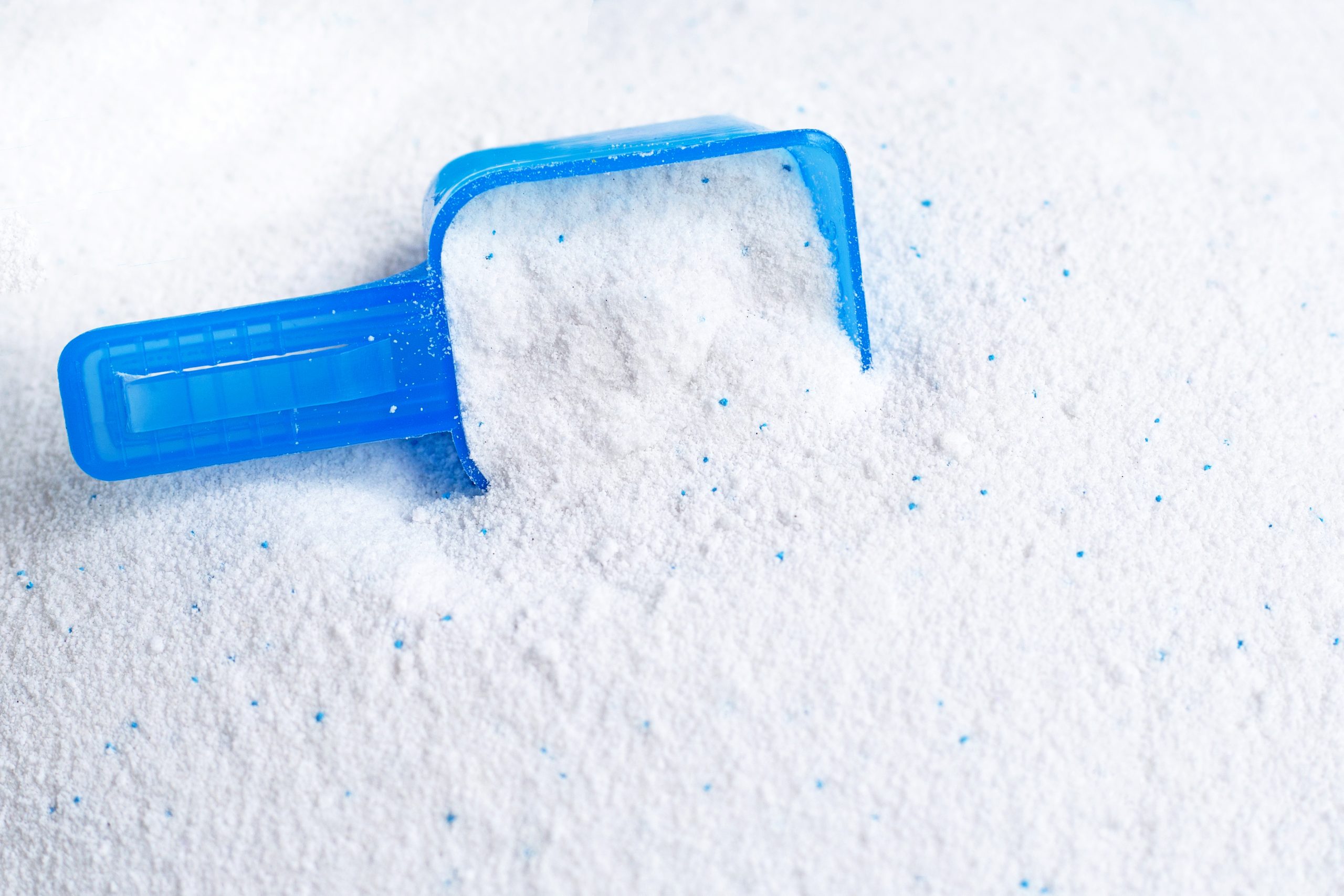
Powder vs. liquid detergent
The ingredients that make up powder detergents are builders, surfactants, and enzymes. This detergent is mainly used as a laundry detergent and is a more affordable choice because containing no water is lighter than liquid detergent, meaning that it has lower transportation costs. Powder detergent can be made by the agglomeration method and can be easily recognized by its granule-like appearance; however, the spry drying method is widely used in the detergent industry because it simplifies the process and improves the profit margin by turning a slurry into a dried powder in a single step.
Liquid detergents are nothing more than powders mixed with water and chemical solutions called solubilizers, making detergents dissolvable in water.
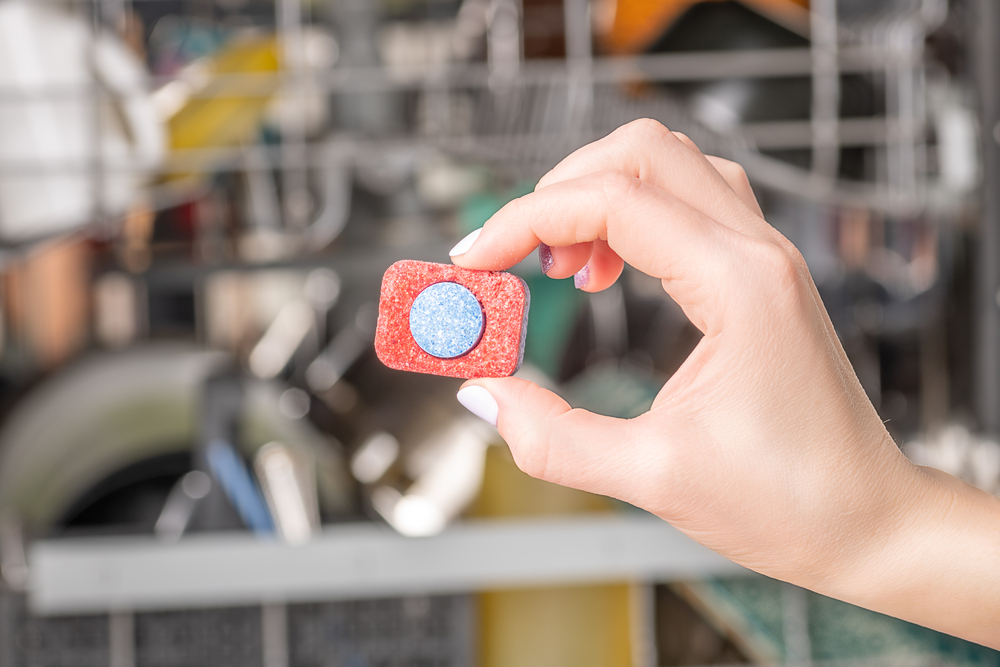
…And what about dishwasher tablets?
Dishwasher tablets are essential to make your dishes shine. The dishwasher tablet production always starts by obtaining granular detergent additives from a spray-dried slurry – Did we already mention that the spray-drying method is everywhere in the detergent making process?
After combining the granules with builders, water, surfactant, bleaching agent, dye, and fragrance, producers transfer it to a hydraulic or rotary press for the tableting process.
Packing your detergent products
When it comes to detergents, the packaging process depends on whether the detergent comes in liquid or powder form. For liquid detergents, a filling system pumps the liquid product into plastic bottles where a weighing device controls the correct filling level. After filling, a capping machine seals the bottles. For powder detergent, the packaging process begins by creating the bag or the pouch from a flat carton or laminated film. Then the selected container will be filled with powder detergent and sealed.
Detergent making videos
Detergent filling machine
Detergent capping machine
Which detergents technology do you need?
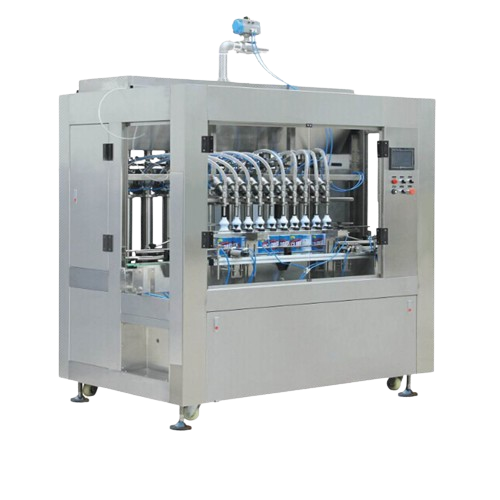
Automatic detergent shampoo filling solution
Streamline your filling process with precise volume control, achieving consis...
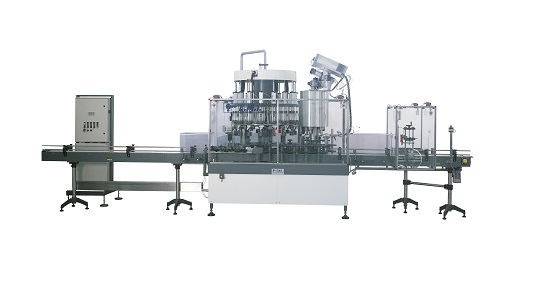
Liquid detergent filling machine
Filling of liquid detergents requires specialised equipment because of the foaming nature o...
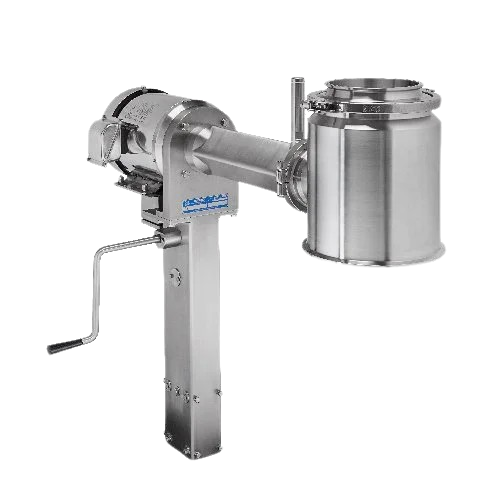
Cone mill for size reduction
Achieve precise particle size reduction and deagglomeration with minimal heat generation, ensur...
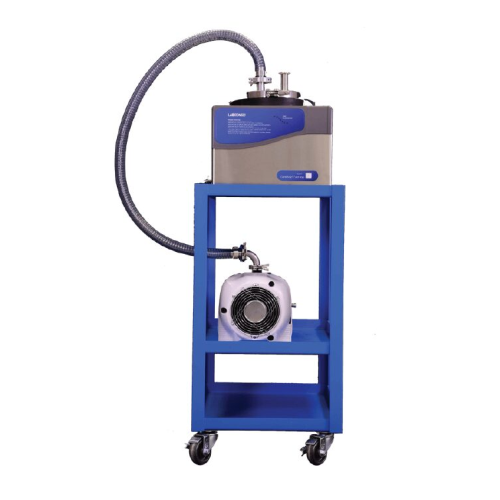
Laboratory vacuum cold trap for extract purification
Optimize your vacuum purging and drying applications with this advan...

Hybrid palletizer for bagged products
Optimize your palletizing process with high-speed robotic solutions designed to secur...
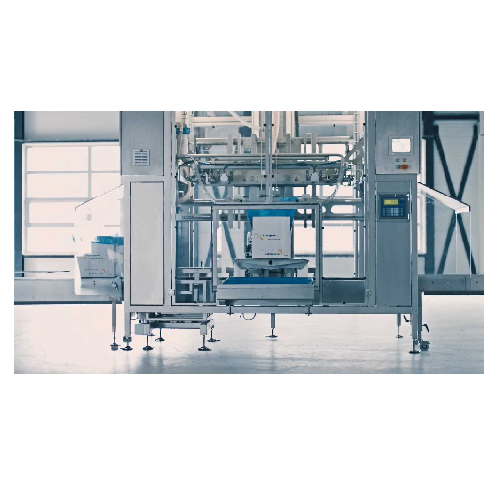
Automated bag folding for packaging
Streamline your packaging operations with a high-speed solution that seamlessly integra...
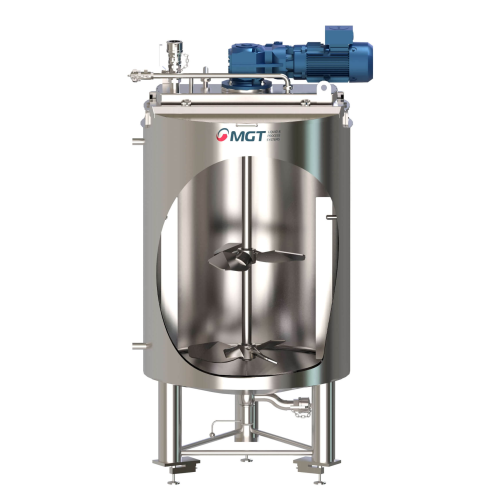
Mounting configurations for industrial agitators
Optimize your mixing processes with versatile agitators designed for effi...
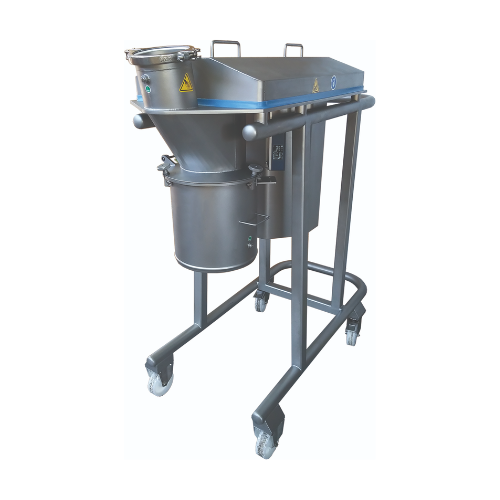
Versatile cone mill for uniform size reduction
Achieve precise particle size consistency and gentle deagglomeration across...
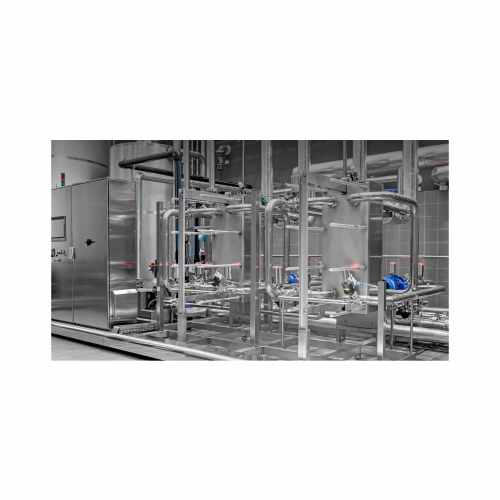
Automated system for cleaning in place (cip)
Ensure thorough, efficient cleaning of your production equipment with a syste...
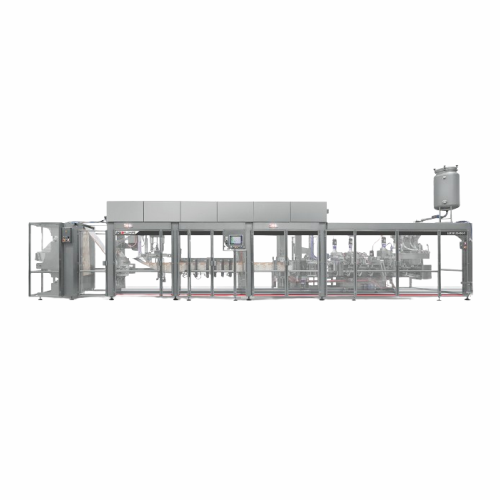
High-speed drift-dwell motion doypack forming system
Optimize your liquid packaging efficiency with a dual-motion system ...
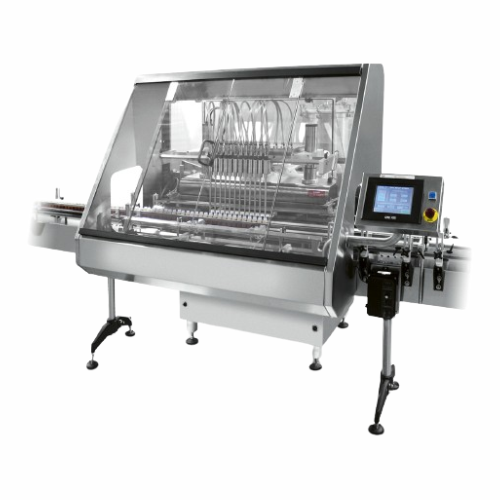
Positive displacement gear pump liquid filler
Optimize your liquid filling operations with precision gear pump technology,...
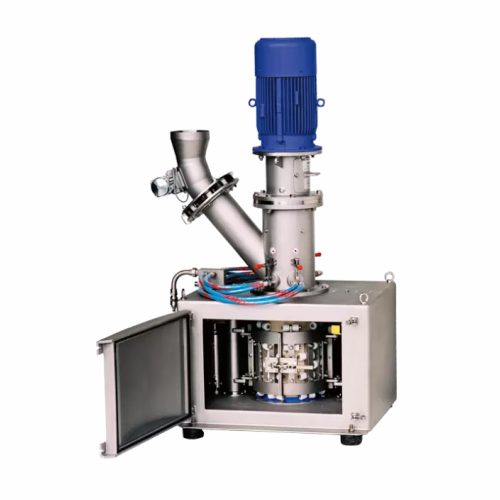
High impact mixer for powders and liquids
Achieve highly homogeneous mixtures with precision. This high impact mixer excel...

Production system for multi-chamber portion packs
Efficiently produce multi-chamber portion packs with high precision for...
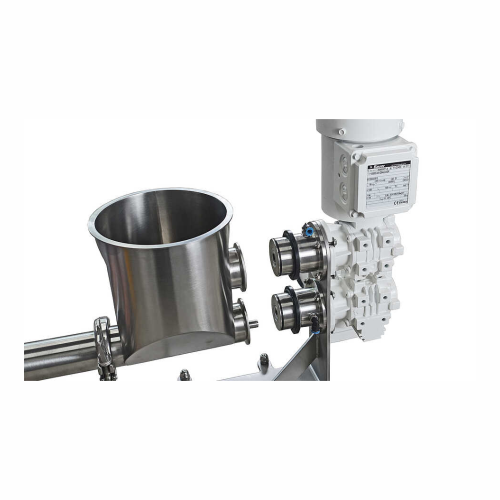
High-precision volumetric feeder for bulk materials
Achieve precise bulk material flow with a solution that ensures consi...
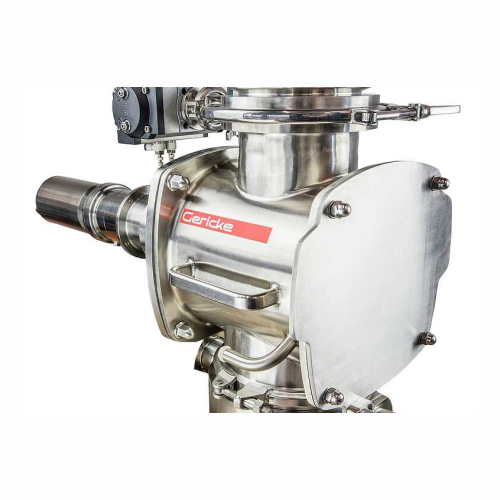
Mini batch blender for pharmaceutical solids
Achieve precise mixing homogeneity with the mini batch blender, perfect for l...
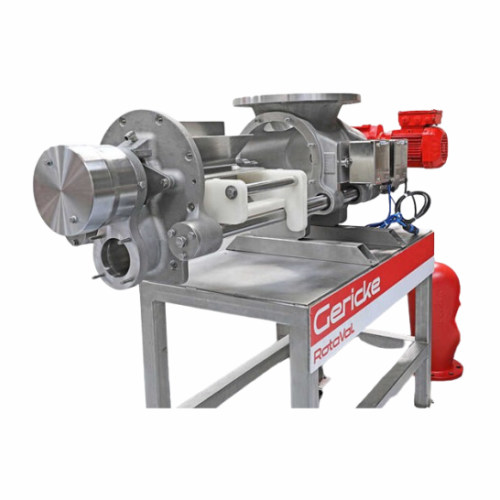
Quick-clean hygienic rotary valves
Ensure seamless cleaning and minimal downtime in your production line with rotary valves...
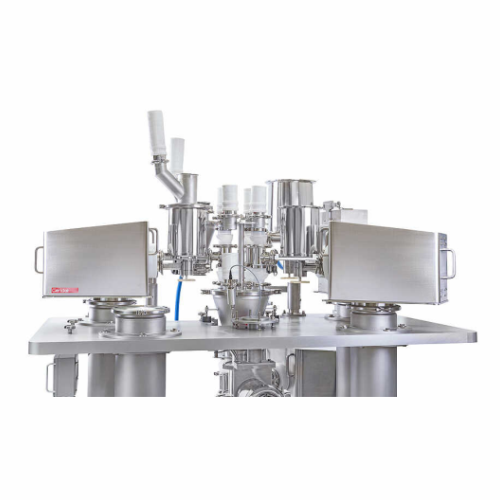
High-precision gravimetric feeders for industrial bulk solids
Achieve unparalleled accuracy in your production line with...
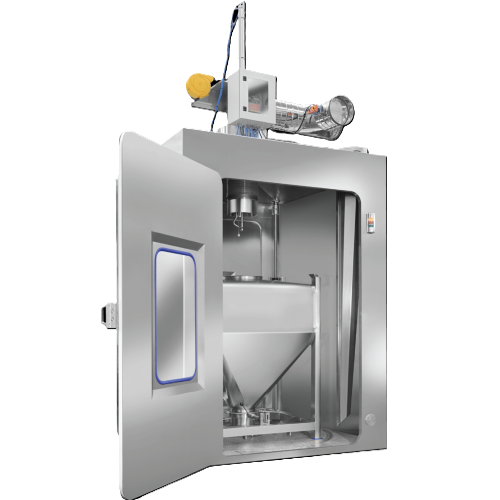
Internal and external bin washing cabinet
Streamline your sanitation process with automated bin cleaning that ensures thor...
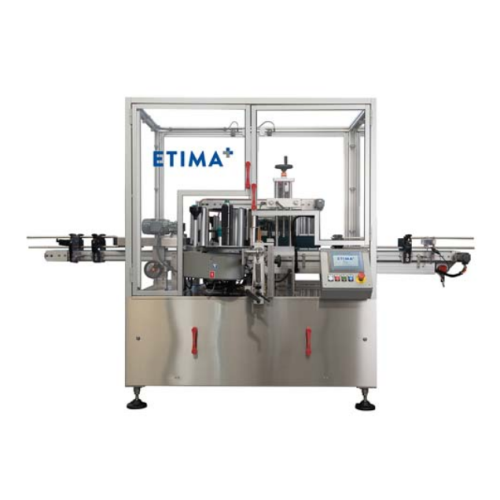
Multiformat high-speed labelling for self-adhesive labels
Achieve precision labelling on diverse container formats with ...
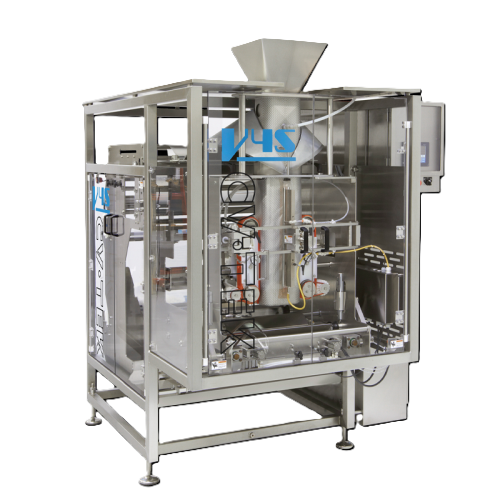
Vertical form fill seal packaging for high washdown environments
Ensure optimal packaging in demanding environments with...
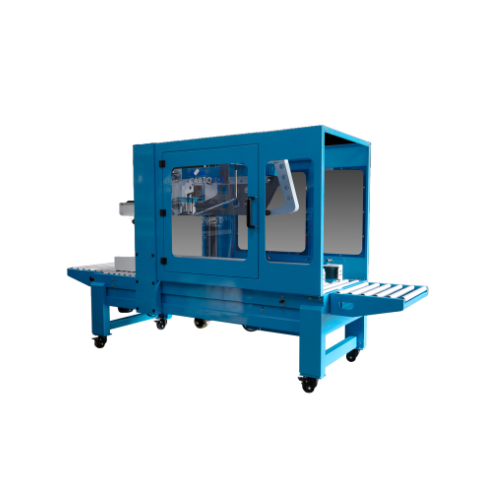
Automatic bag-in-box carton closer
Streamline your packaging line with a high-speed carton closer, designed to efficiently ...
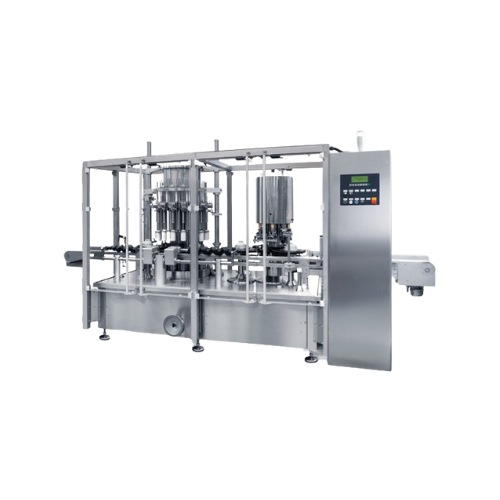
High speed continuous motion liquid filling and capping system
Achieve high-speed, precision filling and capping for liq...
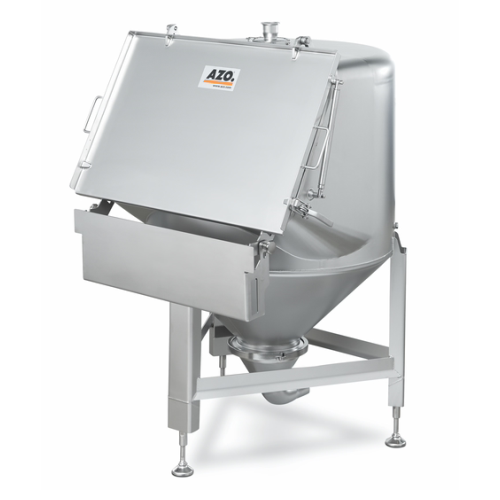
Hygienic feeding hopper for bulk solids
Ensure optimal hygiene in your powder and granular processing with a feeder that fa...
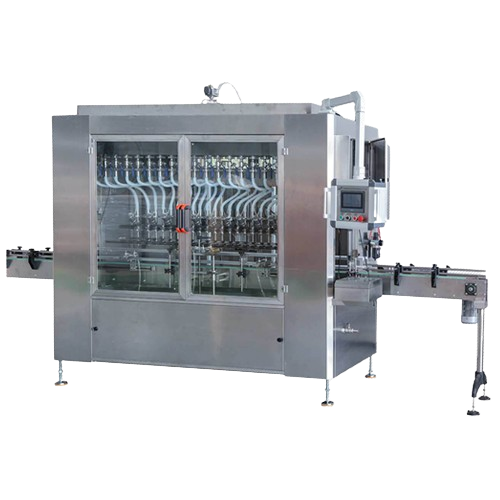
Automatic edible oil filling & capping solution
Streamline your liquid packaging operations with precise, high-speed filli...
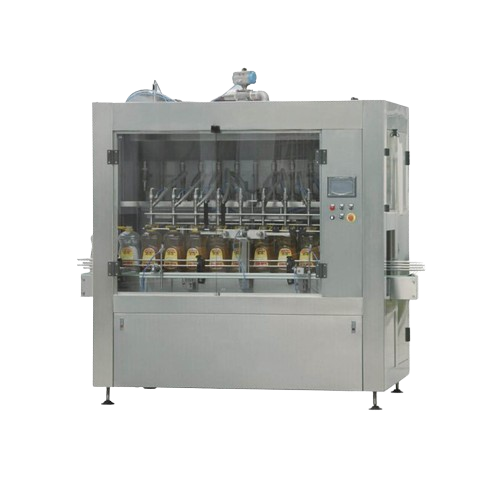
Automatic food cooking oil bottling solution
Ensure precise volumetric filling for a range of liquid products, enhancing y...
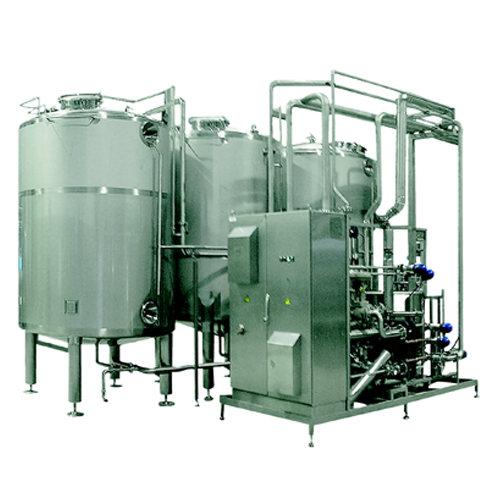
Automated Cip station for brewery cleaning
Ensure thorough hygiene and product integrity in your brewing process with a ve...

Powder dosing and weighing system
Optimize precision in pharmaceutical processing with a system designed to ensure accurate...
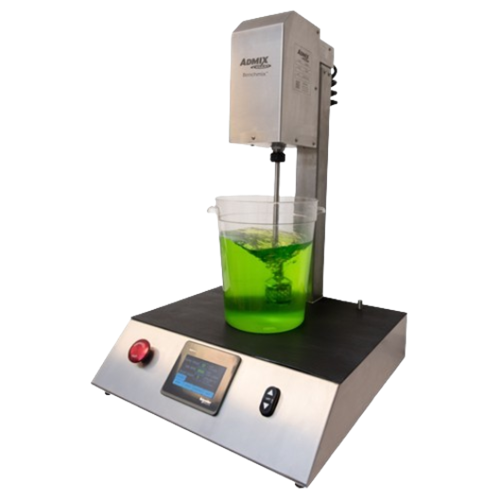
Benchtop mixer for lab-scale product development
Easily scale up your formulations with precise and repeatable lab-scale m...
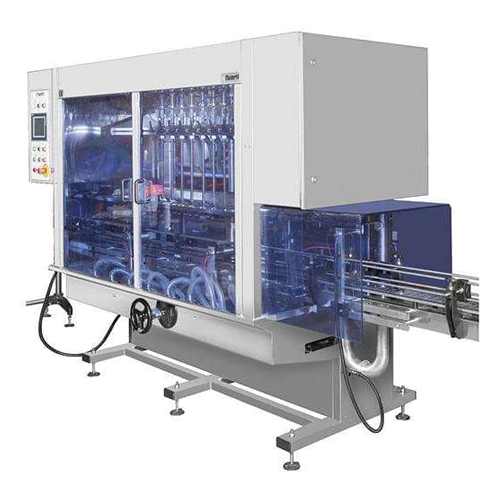
Automatic flowmeter filler for liquid packaging
Streamline your liquid production with precise filling capabilities, reduc...
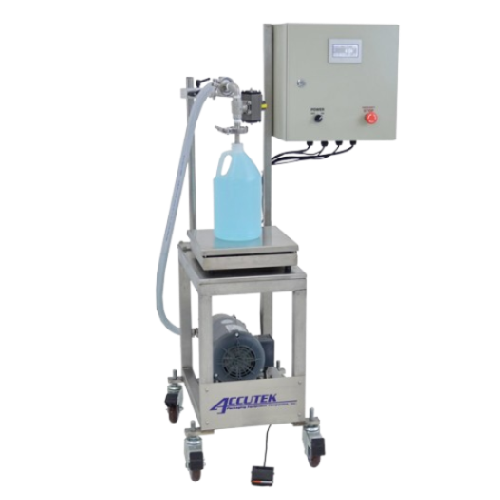
Accurate net weight filling for liquid and semi-liquid products
Ensure precise filling of diverse viscosities, from thin...
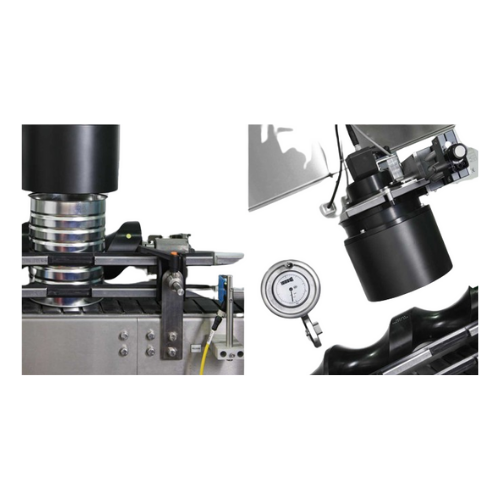
Container inspection and particulate detection system
Ensure product integrity and efficiency by accurately detecting and...
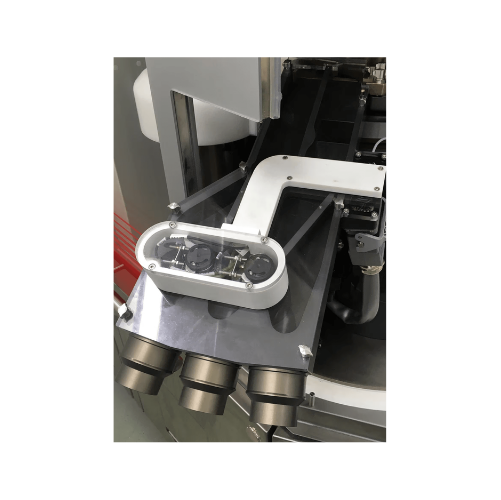
Rotary tablet press for abrasive powders
Achieve precise tablet sizing and bilayer production, even with abrasive powders, ...
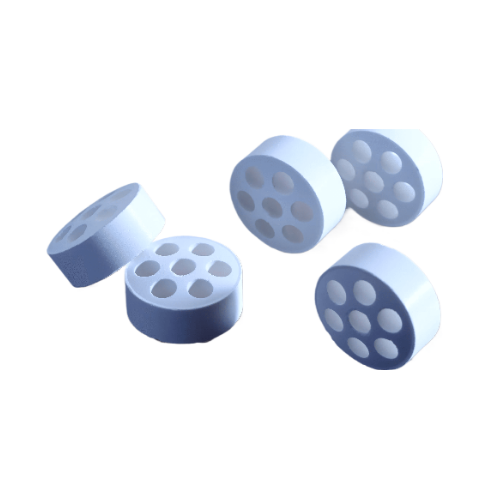
Rotary tablet press for large volume industrial tablets
Optimize your high-volume tablet production with a fully automati...
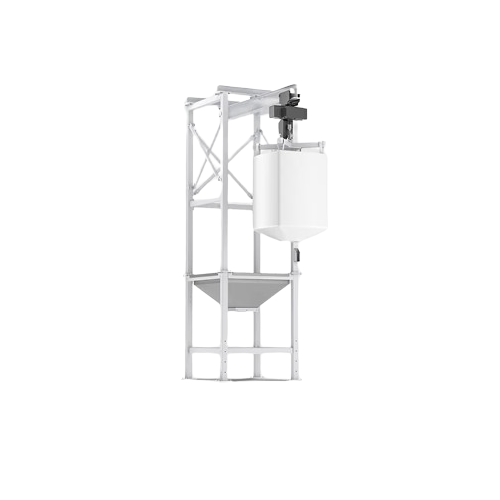
Big bag emptying station for bulk product handling
Streamline your bulk material handling with a station designed to effi...
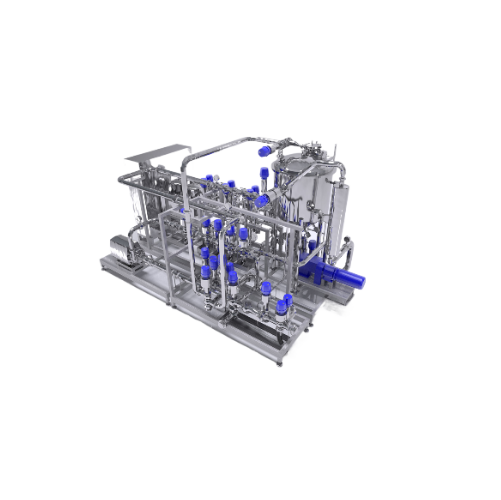
Tailor made mixing systems for personal and home care products
Achieve precise mixing for liquid formulations with conti...
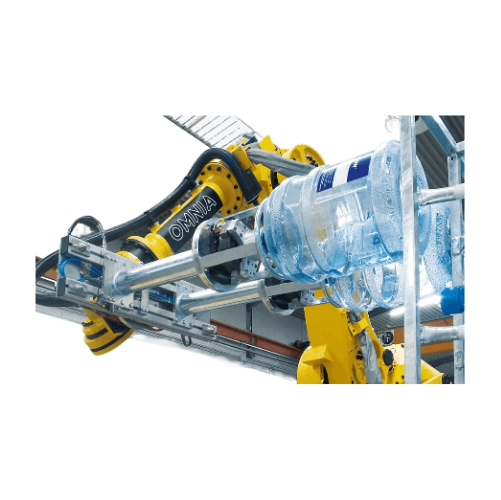
Robotic palletizer for food and beverage industries
Enhance your production line’s efficiency with a flexible robot...
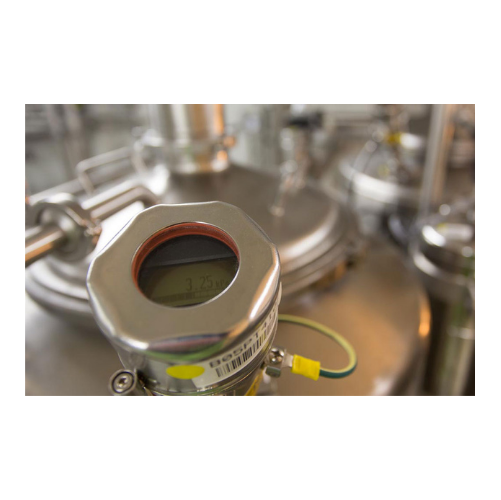
Powdered product shelf-life enhancement through inert gas packing
Extend the shelf life of sensitive powder products by...
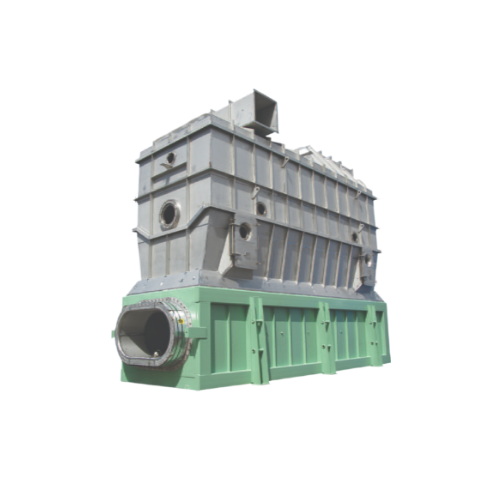
Static fluid bed dryer for powder and granular materials
Achieve optimal moisture control in powder and granular products...
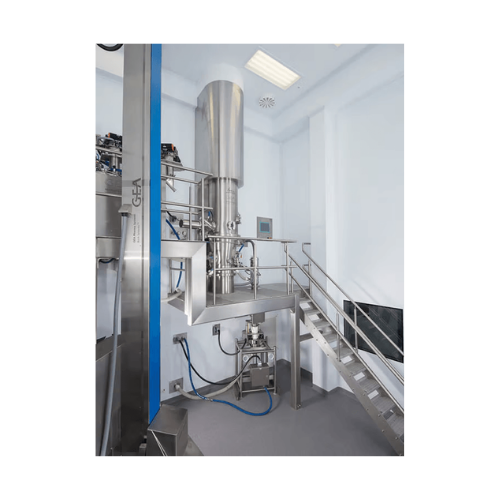
Cip for pharmaceutical process plants
Streamline your cleaning processes with integrated CIP systems to ensure precise and ...
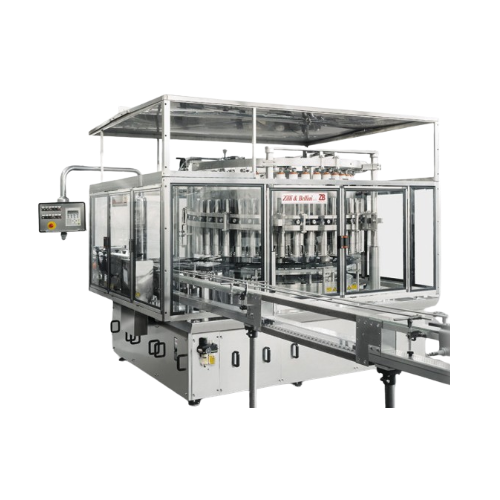
Rotary piston fillers with plunger for viscous products
Optimize your filling process with high-speed, rotary piston fill...
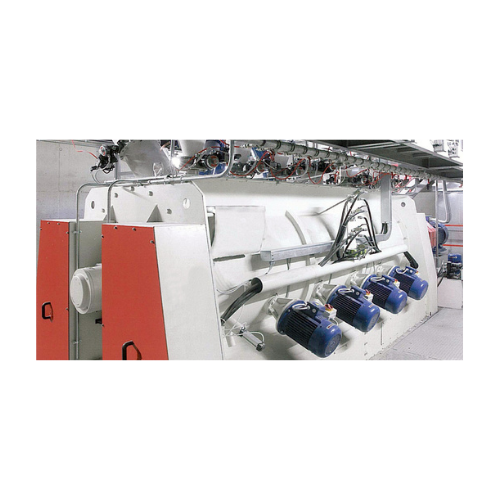
Batch-type single shaft mixers with bomb-bay discharge
When you need rapid, residue-free discharge in your batch mixing p...
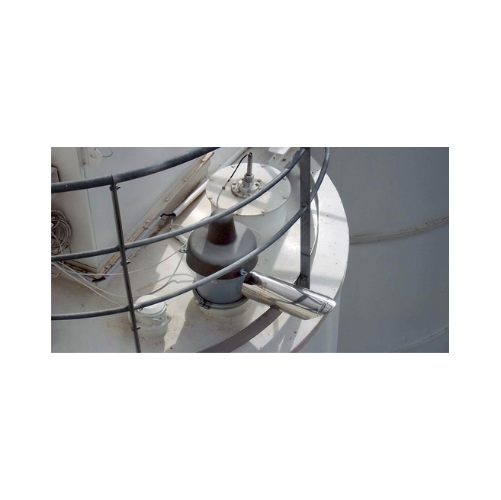
Membrane pressure relief valve for silo protection
Ensure immediate pressure stabilization in your bulk storage silos wit...
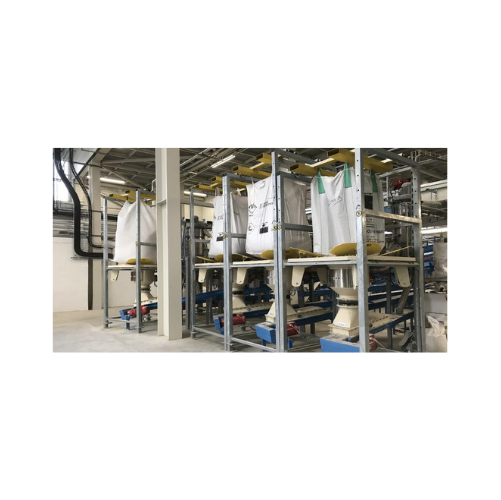
High flow rate Fibc discharger
Optimize your bulk material handling with a system designed for efficient and dust-free FIBC ...
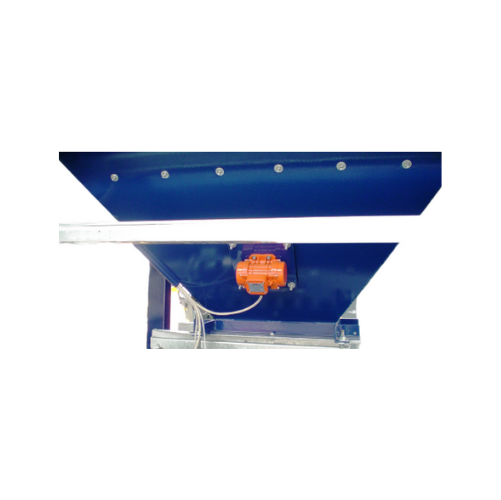
Industrial electric vibrator for bulk solids discharging
Enhance material flow efficiency and ensure consistent output ac...
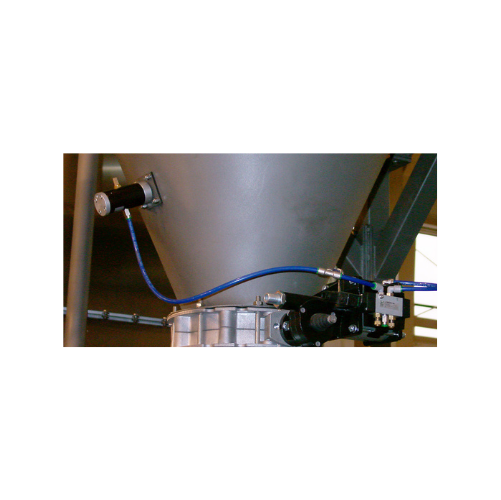
Pneumatic linear vibrators for bulk material flow
Prevent bridging and rat-holing in your production process with silent,...
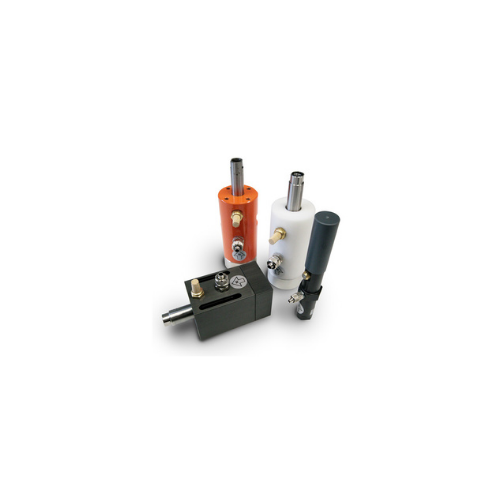
Cushioned pneumatic vibrators for bulk solids conveying
Streamline your material handling with precision vibration contro...
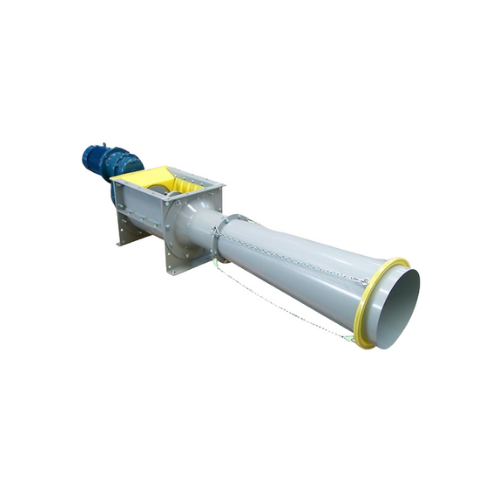
Waste bag compactor for bulk solids
Efficiently compact waste bags to a fraction of their volume, streamlining disposal whi...
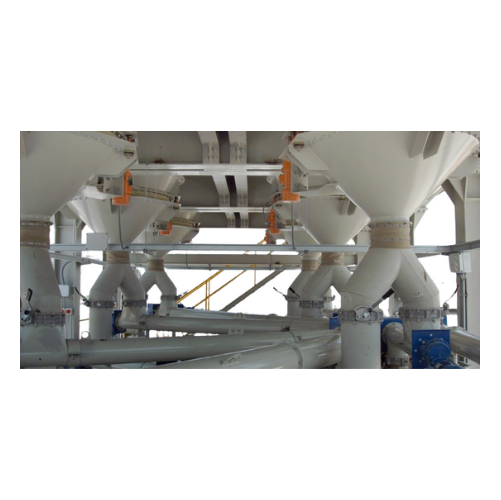
Vibratory outlet hopper for bulk material discharge
Struggling with material bridging and inconsistent discharge? Enhance...
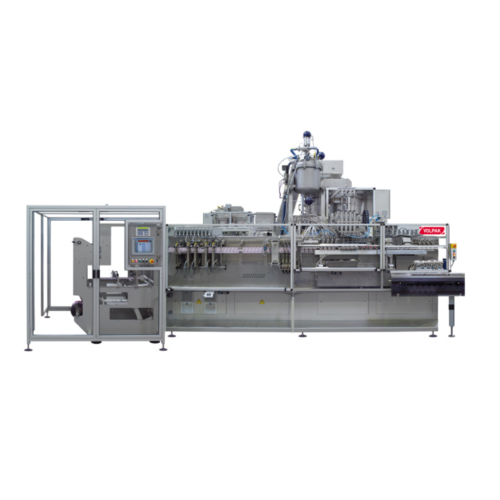
Horizontal flat pouching for top-cap pouches
For manufacturers aiming to streamline pouching operations, this high-speed h...
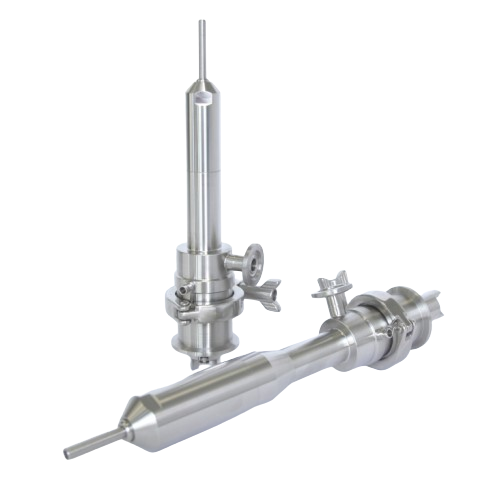
Accurate pharmaceutical dispenser for high-viscosity fluids
Achieve precise liquid dosing with ease, designed to handle ...
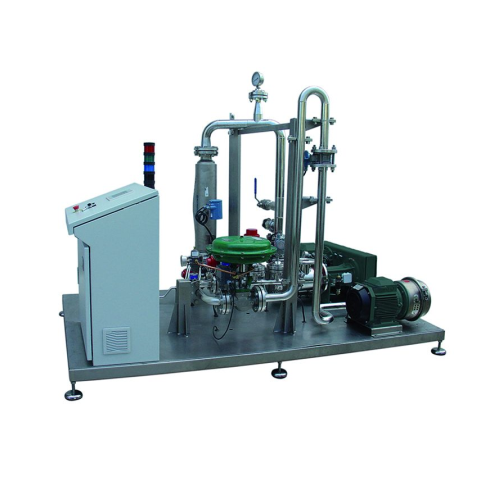
Complete mixing systems for industrial applications
Optimize your production efficiency and product consistency with adva...
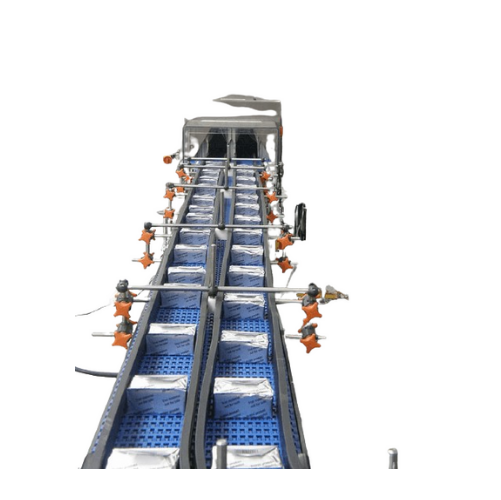
Industrial conveyor system for food and pharma applications
Optimize your production workflow with a versatile conveyor ...
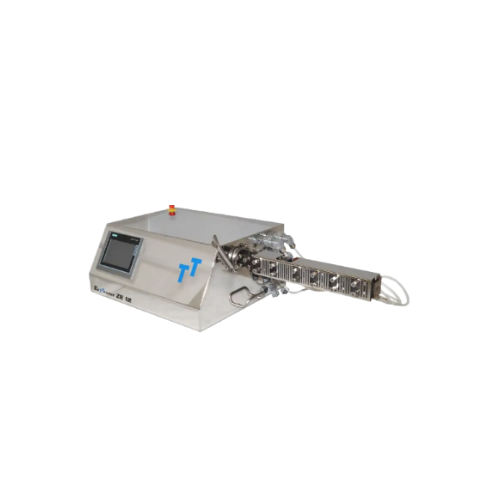
Table-top mini extruder for precision material processing
Achieve precise control over complex formulations with this fl...
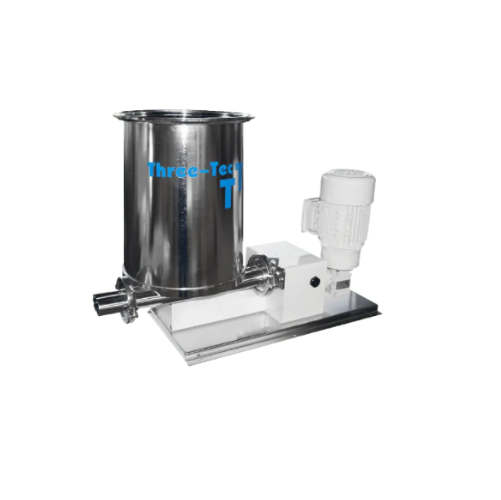
Volumetric twin-screw feeder for poorly flowing powders
For manufacturers dealing with powders that clump or cake, this f...
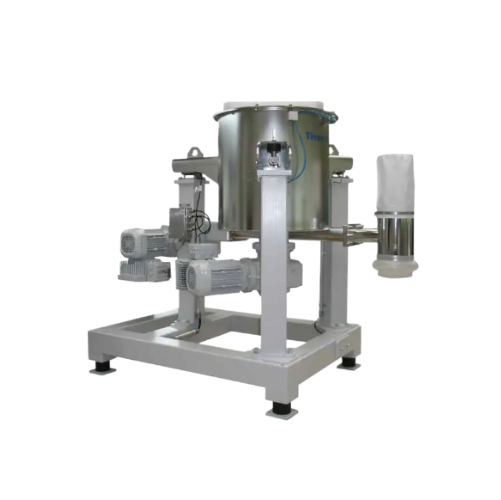
Twin screw feeder for poorly flowing powders
Optimize your process with precision feeding for powders that easily clump or...
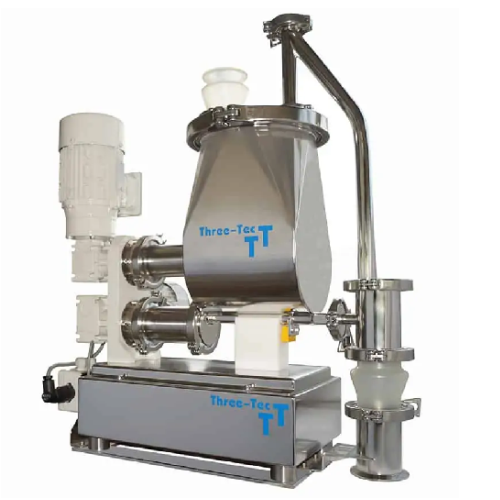
Quick change feeding devices for industrial applications
Experience seamless product transitions with quick-change feedin...
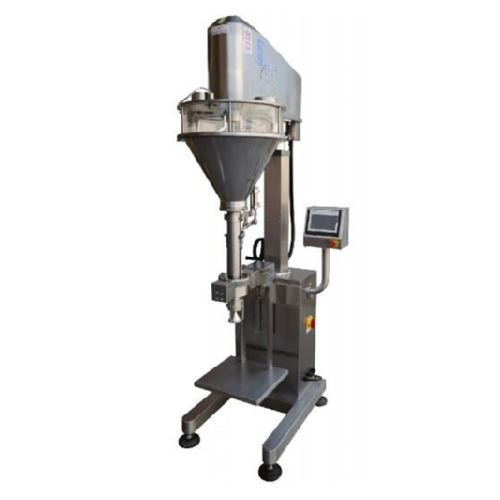
Powder auger filler for precise weighing and depositing
Ensure accurate and efficient powder filling with this innovative...
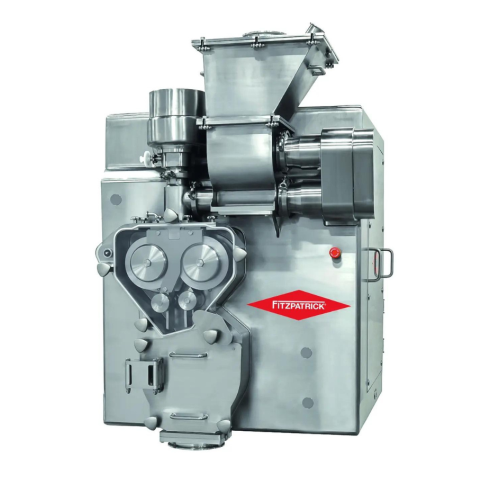
Dry granulation system for pharmaceutical powders
Streamline your powder processing with a dry granulation system that en...
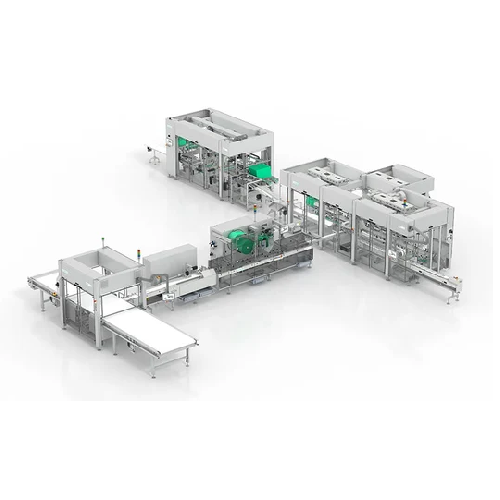
Horizontal flow wrapper for food packaging
Simplify your packaging process with our high-speed horizontal flow wrapper tha...
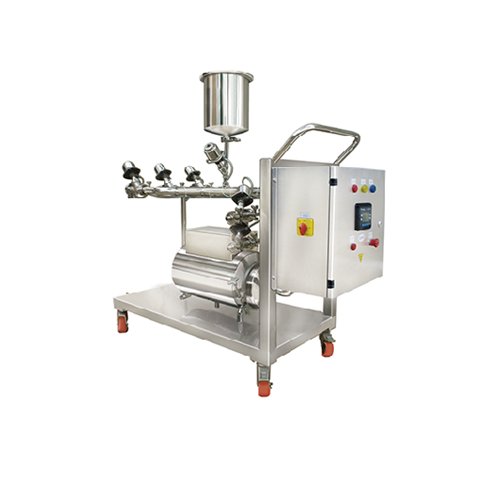
Wet granulation cleaning system
Ensure optimal cleaning and purification within your production line with a system designed ...
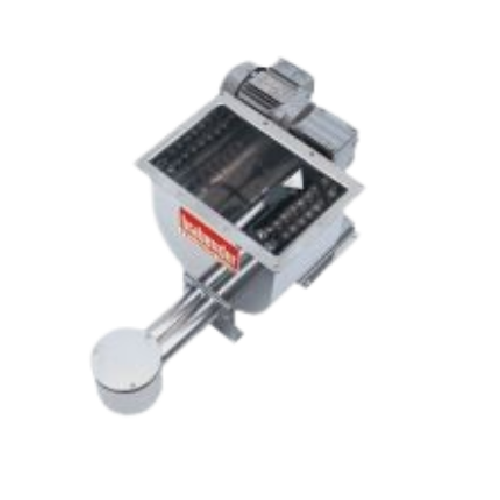
Twin screw feeder with stirring agitator for poor flowing powders
Optimize your processing line with a highly adaptable...
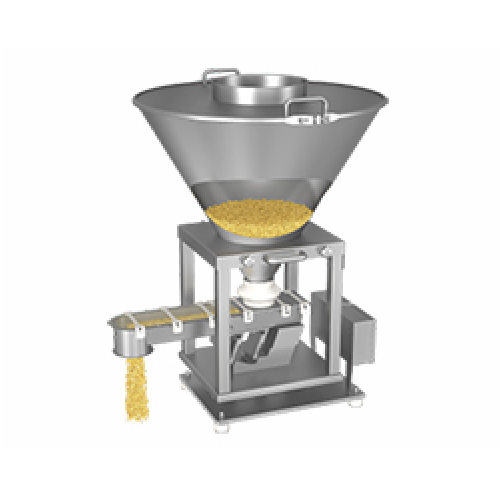
Vibrating tray loss-in-weight feeder for grained ingredients
Achieve precise and continuous dosing of free-flowing solid...
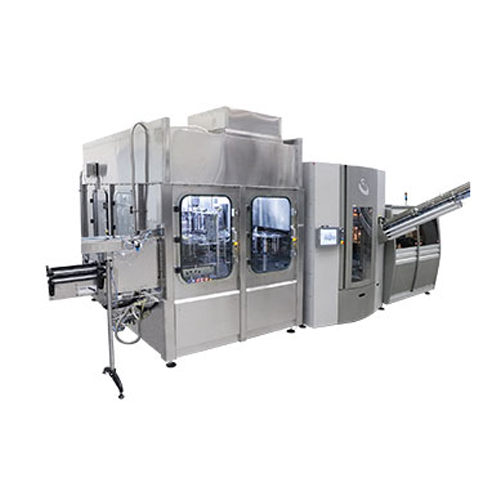
Integrated stretch-blow moulding, filling, and capping system for still liquids
Streamline your bottling process with ...
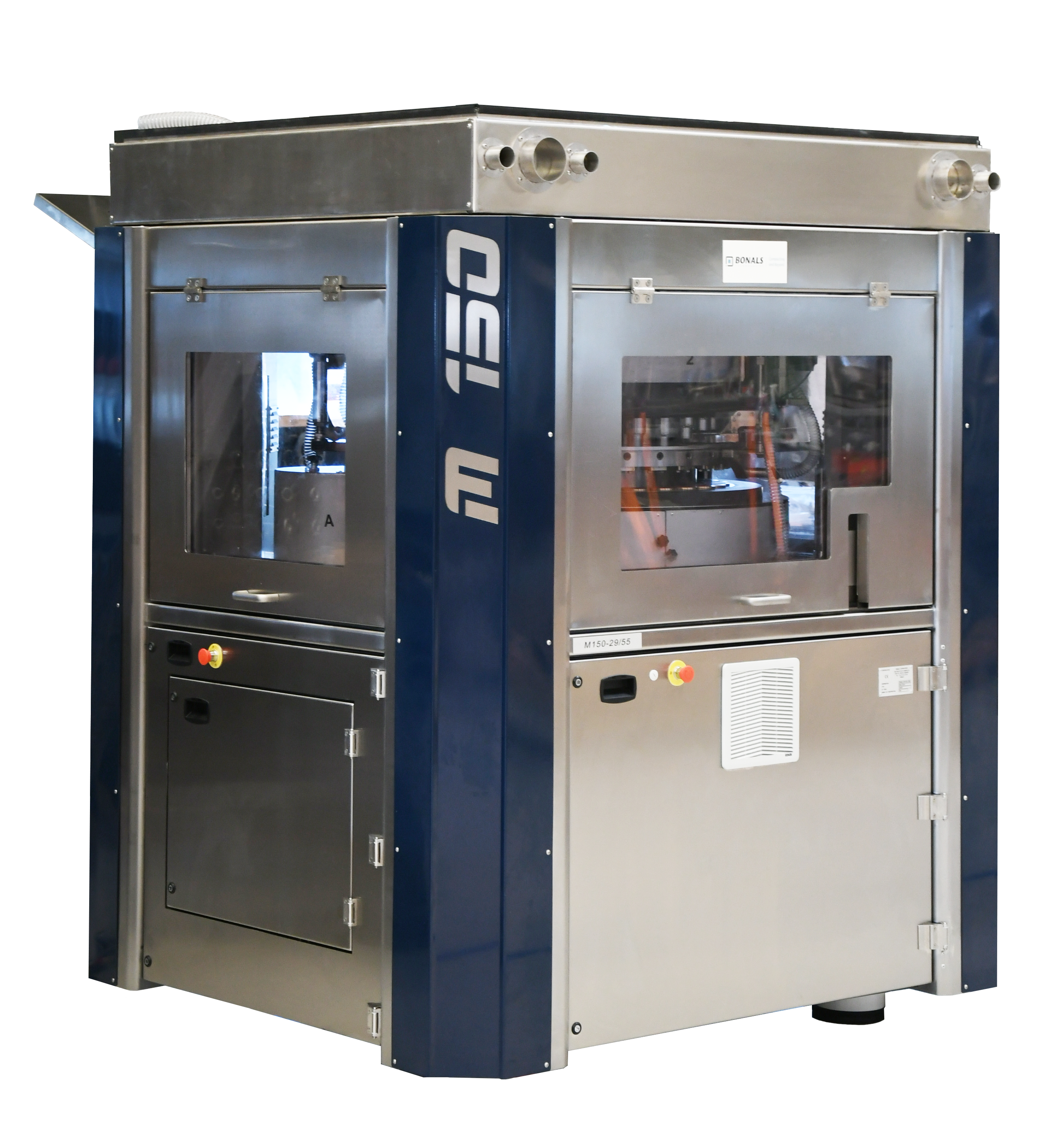
Fully automated dishwasher tablet press
The process of making dishwasher tablets that have more than one layer is very deli...
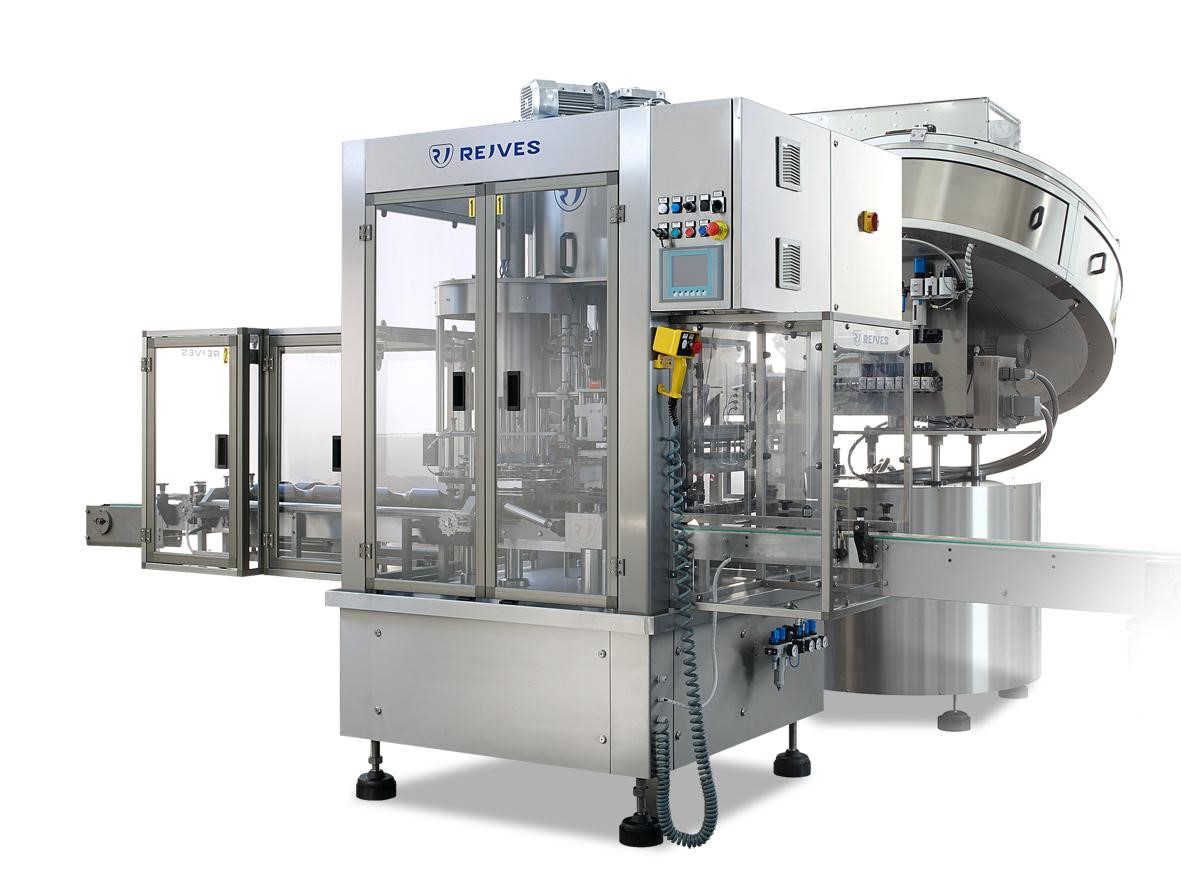
Hand sanitizer capping machine
Bottled products such as hand sanitizers, shampoos, and liquid detergents, have different cap...
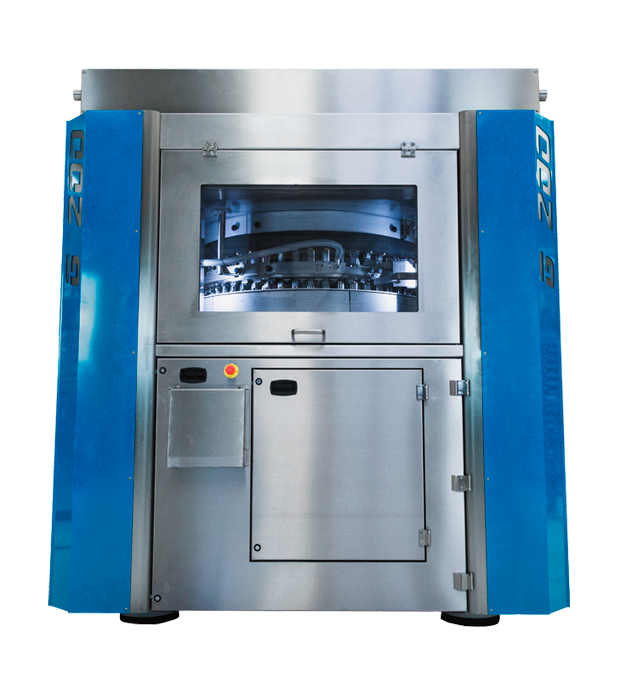
Three-layer dishwasher tablet press
Dishwasher detergent tablets come either in a single layer or multi-layer form. Multi-l...
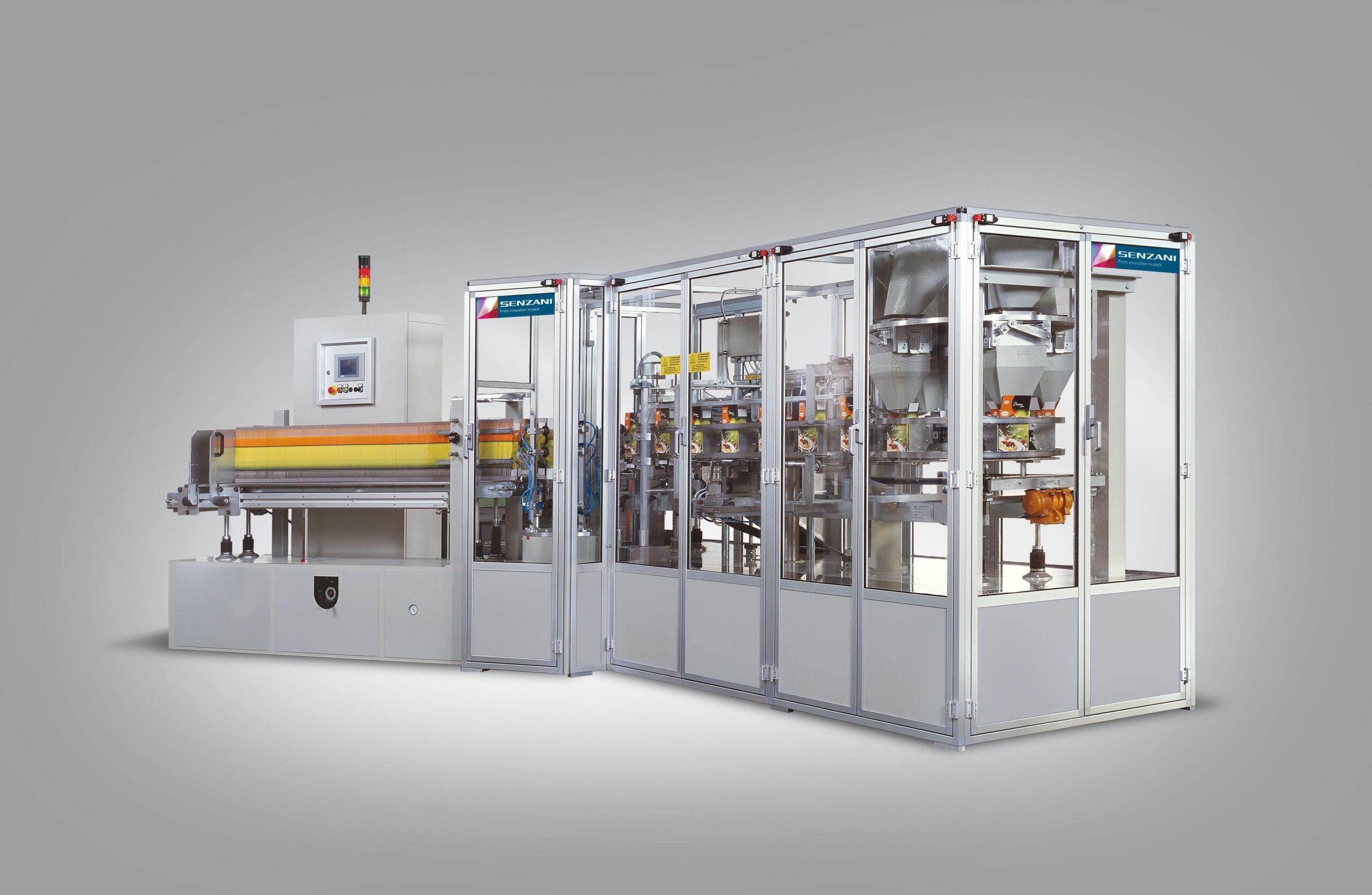
Vertical cartoning machine
In the food industry, a large number of bulk products like for example pasta, need to be packed i...
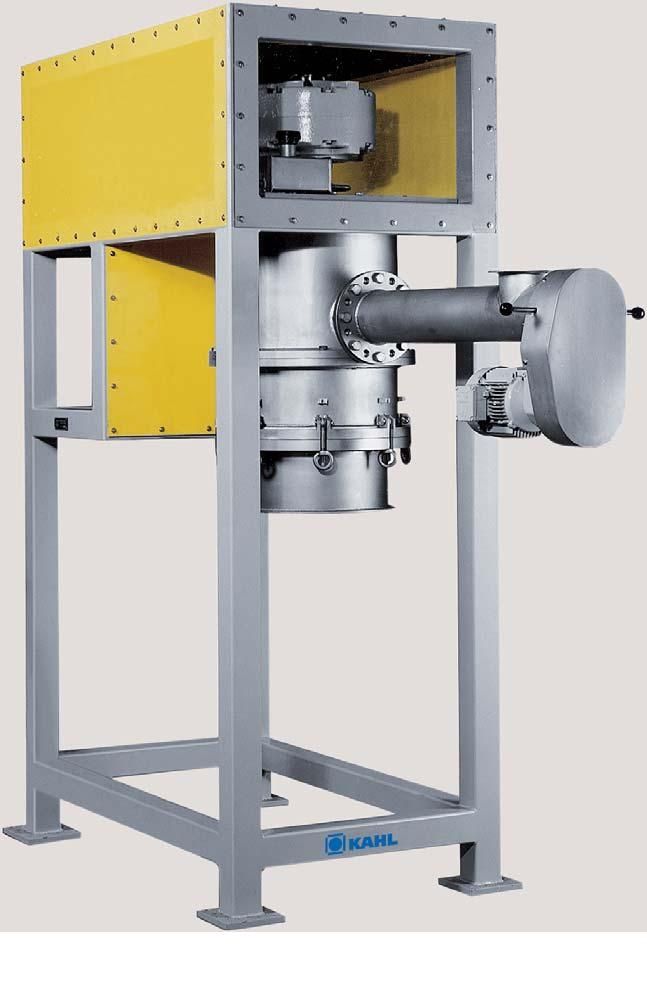
Pelleting press with overhead drive
Production of certain pelletized products requires working with output products of a pa...
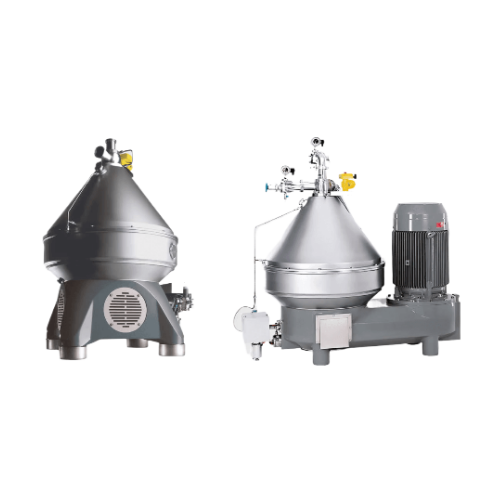
Separator for oil refining
Optimize your oil refining processes with a centrifugal separator that enhances purity by efficie...
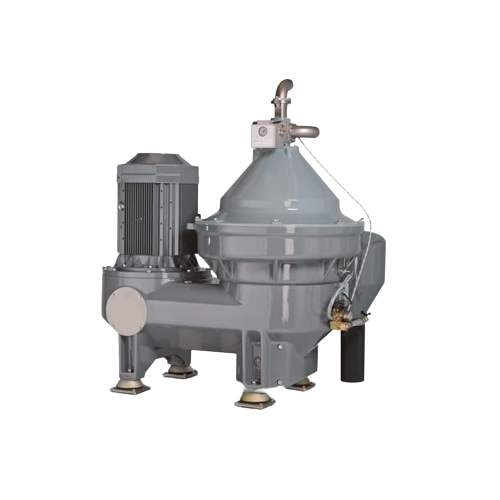
Clarifier for industrial fluids
Optimize fluid purity and extend equipment lifespan by efficiently separating contaminants f...
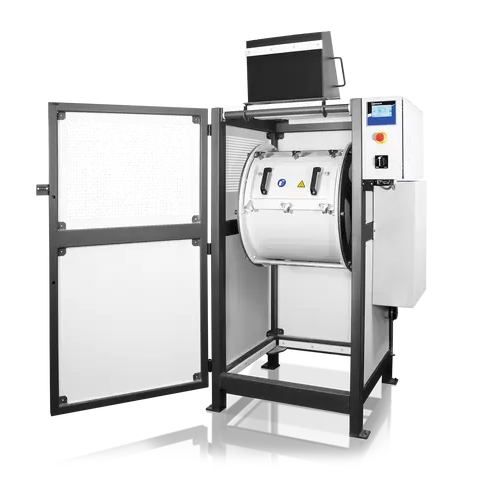
Drum mills for fine grinding of large volumes
Achieve consistent and precise pulverization of large sample volumes with dr...
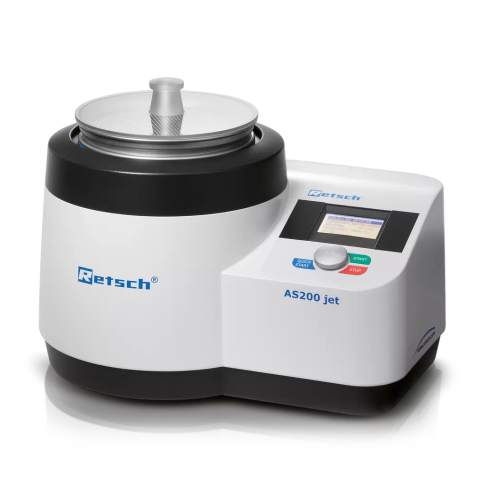
Air jet sieving system for powdered materials
Optimize particle distribution with precision air jet sieving, designed to e...
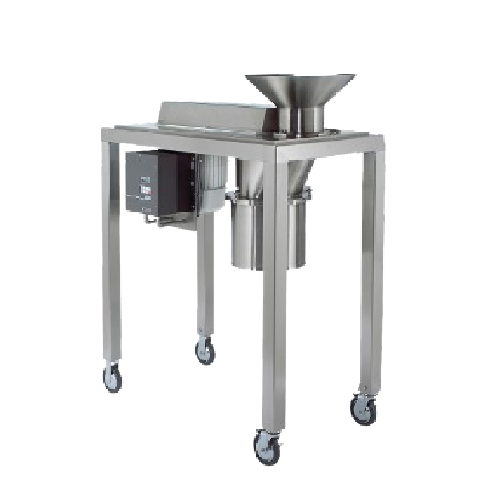
High efficiency milling solution for pharma and food industries
Achieve precise particle size control and enhance produc...
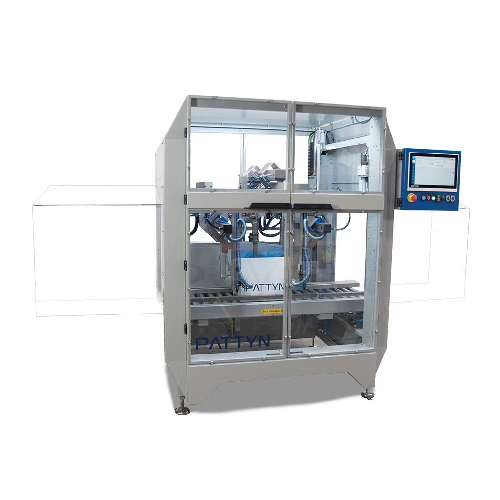
Automatic bag folding solution for bulk packaging
Enhance your production line efficiency and product protection by integ...
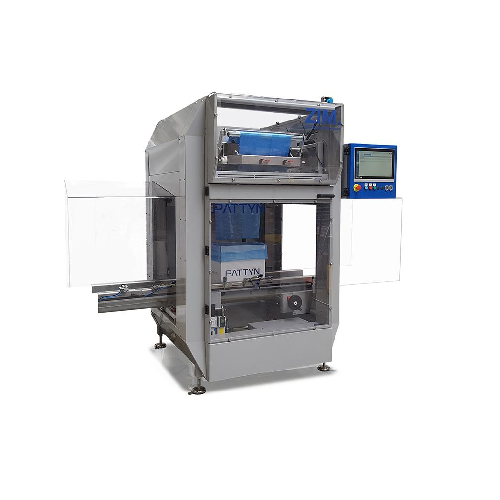
Automatic bag inserter for boxes and crates
Optimize your packaging line with a compact solution that seamlessly inserts p...
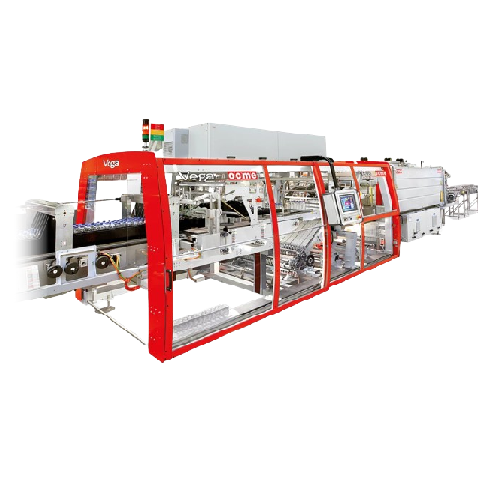
Shrink wrap packer for beverage and food industries
Optimize your production line efficiency with a versatile packer capa...
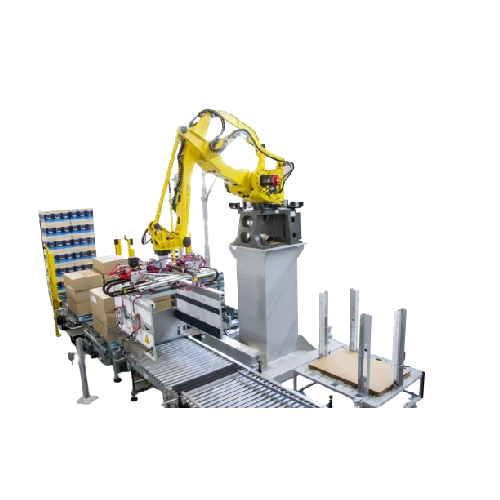
Robotic palletizer for row gripping
Optimize your palletizing efficiency with a robotic system designed for fast, continuou...
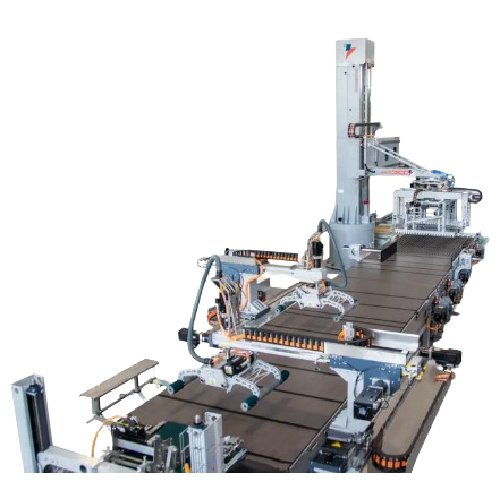
Single-column palletizer for medium to high production
Optimize your production line efficiency with a versatile single-c...
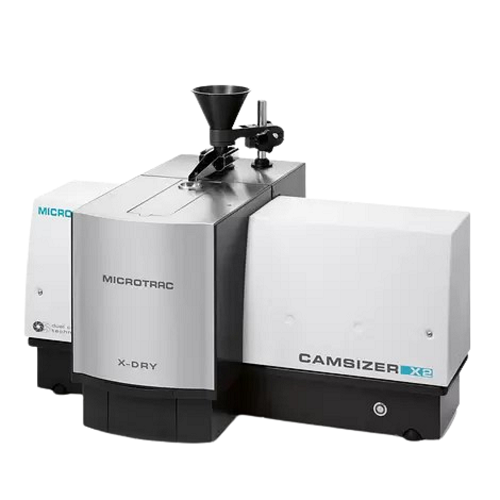
Particle size and shape analyzer
Achieve precise particle size and shape analysis from 0.8 μm to 8 mm with exceptional speed...
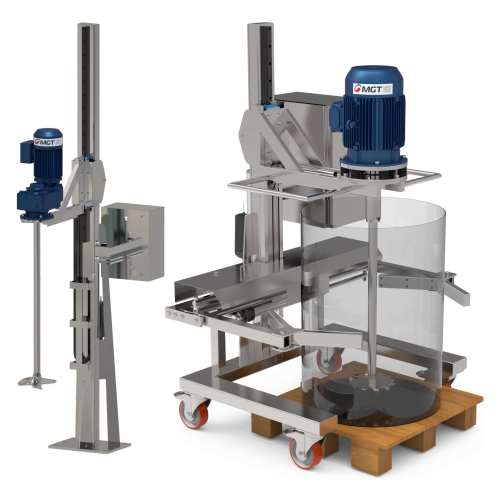
Pneumatic and electric lift for industrial mixing tanks
Enhance operational efficiency and safety with versatile lifts fo...
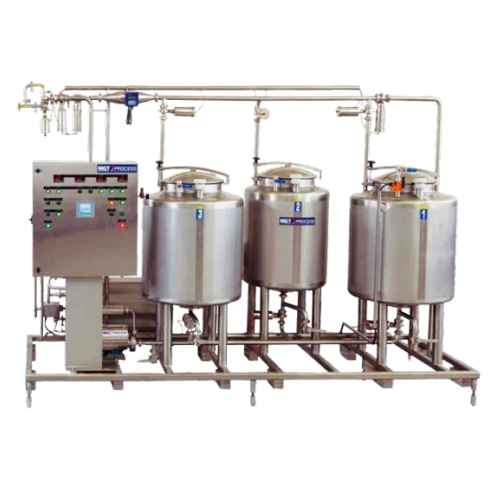
Cleaning-in-place (cip) systems for hygienic processing
Elevate hygiene standards in your liquid processing line with an ...
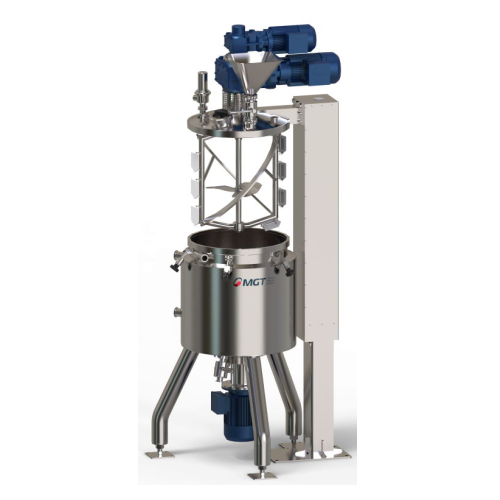
Vacuum mixing system for emulsion and homogenization
Achieve seamless emulsion and homogenization with precision: this sy...
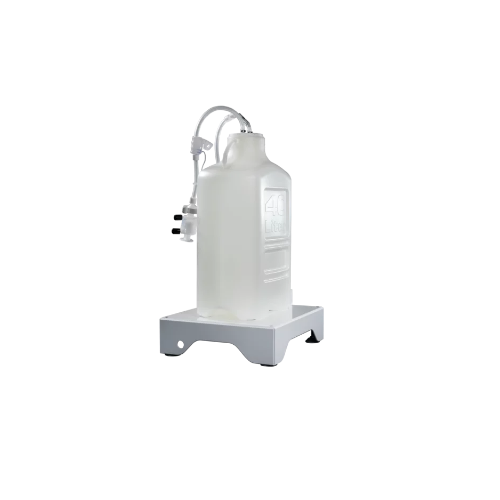
Single-use mixing solutions for downstream processes
Designed for safe and efficient one-time use, this mixing solution e...
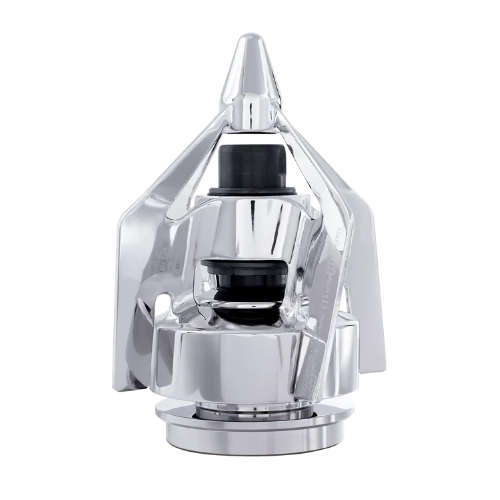
Versatile magnetic mixer for pharmaceutical and biotechnology applications
Optimize your biopharmaceutical mixing proc...
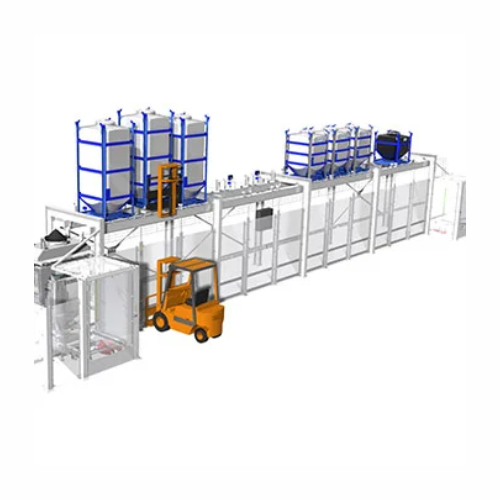
Flexible powder recipe formulation system
Streamline your batch production with efficient, dust-tight formulation and blen...
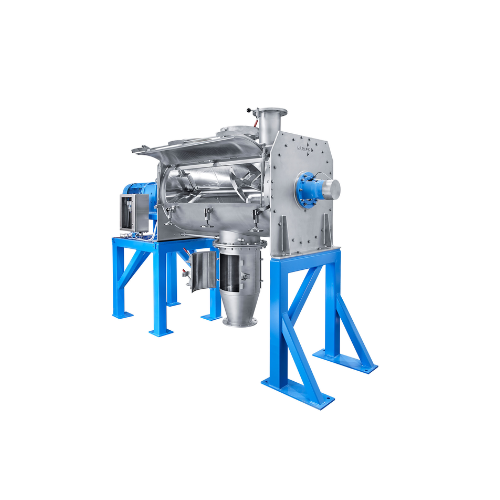
Ploughshare mixer for batch operation
Achieve superior mixing quality with a system designed for rapid batch operations. Ex...
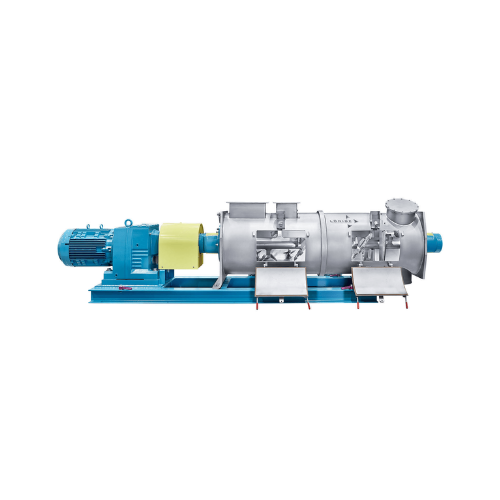
Continuous ploughshare mixer for diverse industrial applications
Enhance mixing efficiency and achieve precise particle ...
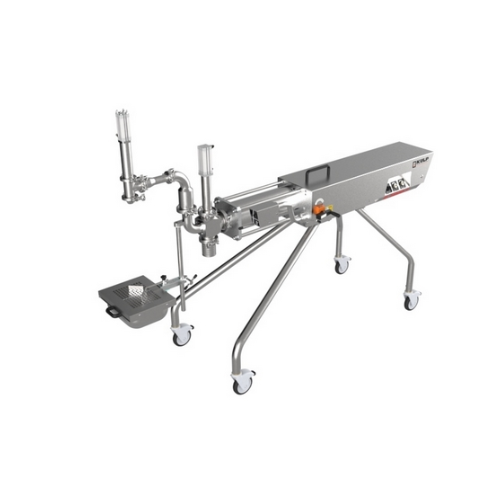
Volumetric filler for liquid and viscous products
Achieve precise and adaptable filling for a wide variety of liquid and ...

Jars and bottles rinsing solution
Ensure impeccable hygiene and particle-free cleanliness for your jars and bottles by inte...
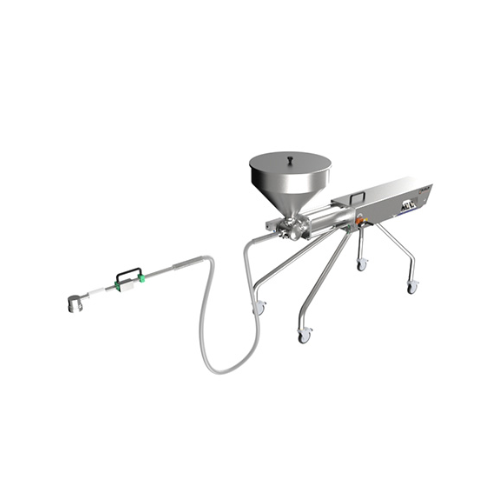
Volumetric filler for packaging liquids and semi-solids
Optimize your filling process with precision control and adaptabl...
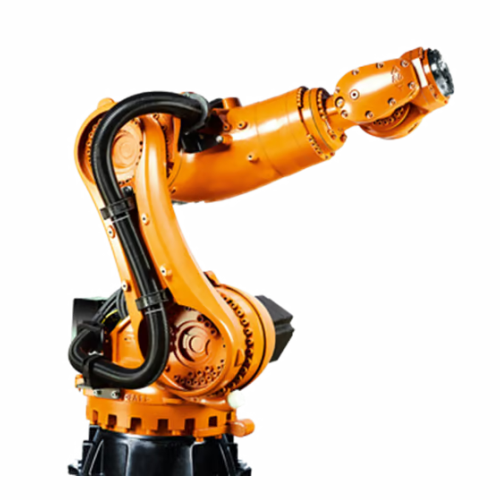
Spot welding robot for confined spaces
Optimize spot welding efficiency in tight manufacturing spaces with a compact robot ...
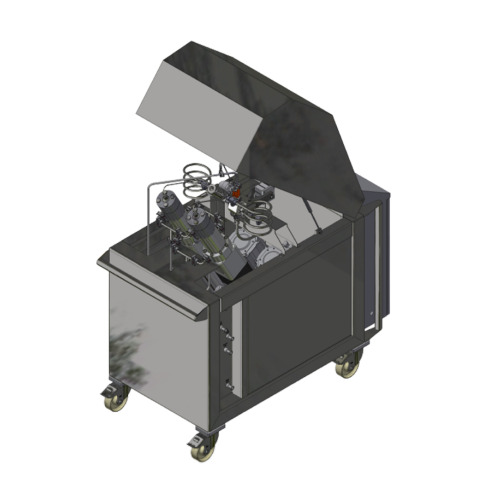
High pressure homogenizer for pharma applications
Achieve precise particle size reduction and stability in liquid formula...
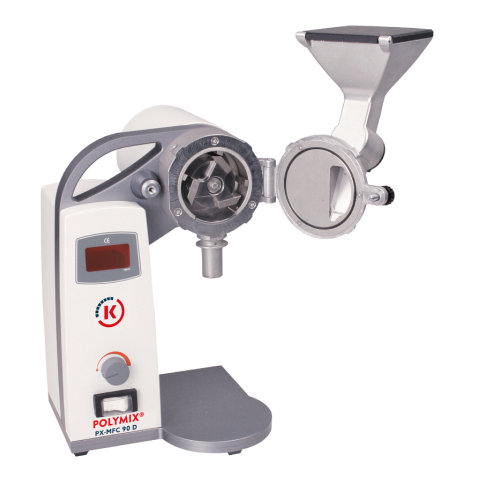
Dry sample preparation mil
Optimize your grinding processes with precision particle size reduction for various materials, en...
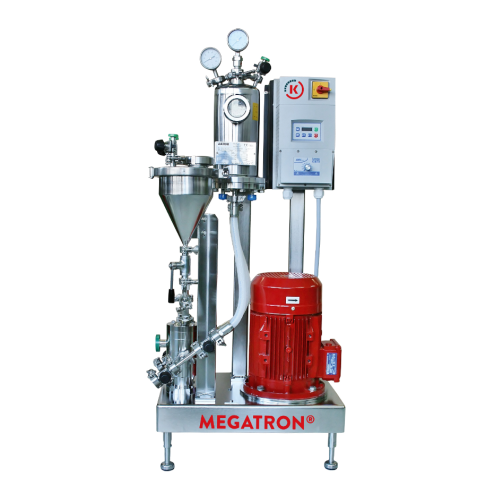
Powder induction system for high solid concentrations
Optimize your production line with this advanced system designed to...
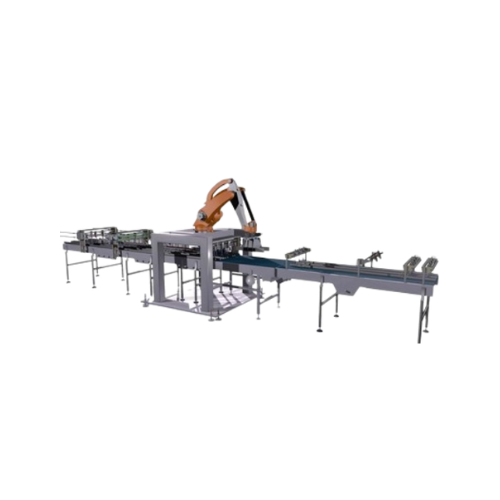
High-performance distribution and combining system
Streamline your packaging operations with a versatile system designed ...
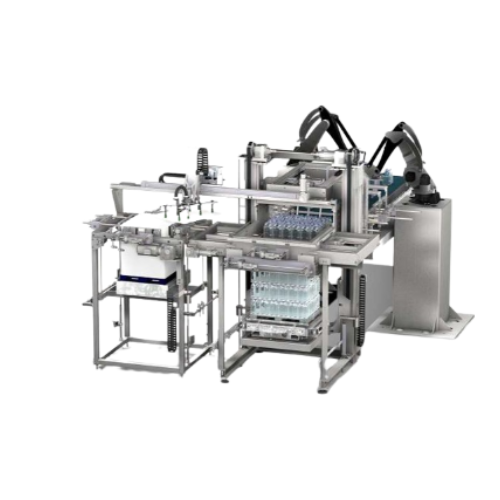
High-speed beverage industry palletizer
Optimize your palletizing process with a flexible, high-speed solution that adapts ...
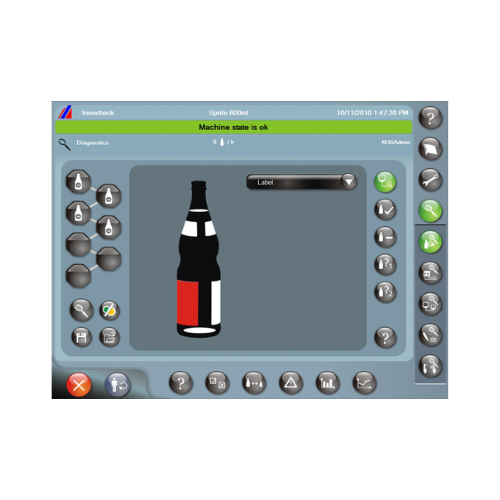
Label inspector for beverage and food containers
Ensure precise label application with high-speed inspection, crucial for ...
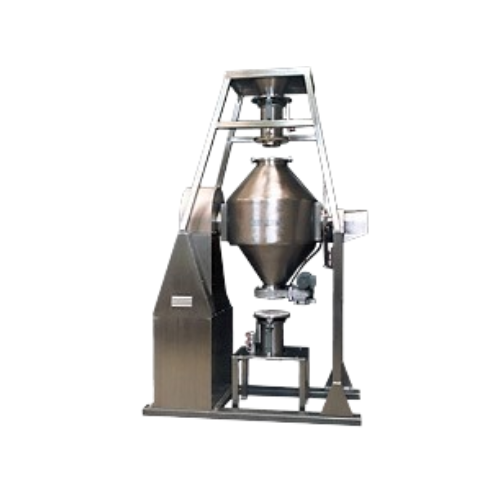
Double cone blender for fragile and abrasive material
Achieve homogeneous blends of fragile materials while minimizing da...
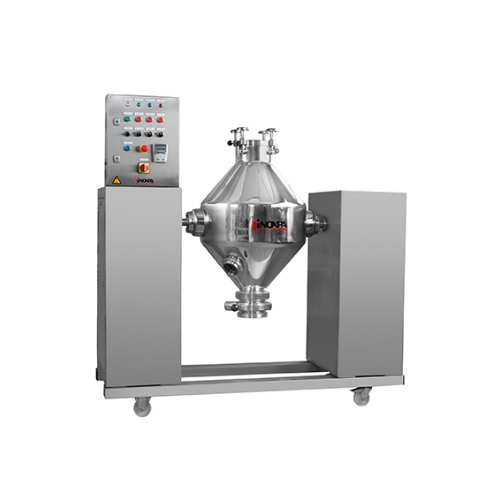
Double cone blender for homogeneous solid-solid mixtures
Need uniform blending for complex solid mixtures with diverse de...
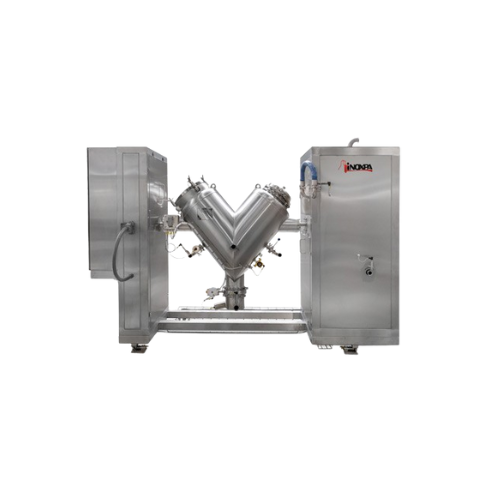
Industrial v-type solids blender for homogeneous mixture
Achieve precise blending of diverse powders and solids using the...
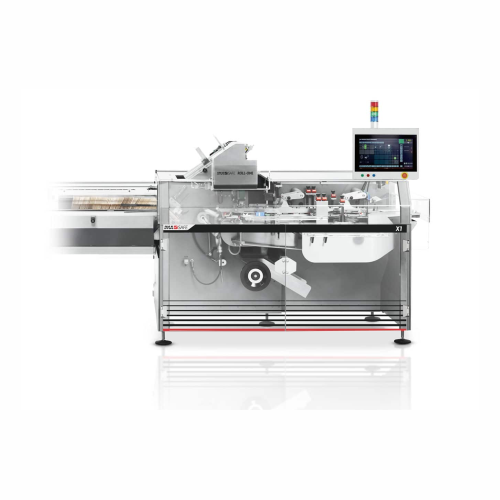
Intermittent motion cartoner for pharma packaging
Streamline your packaging line with versatile cartoning solutions that ...
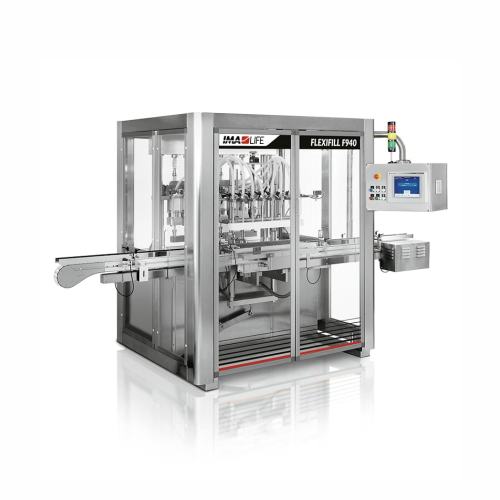
In-line filling system for pharmaceutical products
Ensure precise and flexible filling of liquids, from sterile saline to...

Bin tumbler for efficient mixing
Achieve precise blending and homogenizing of powders and granules with dual-inclination des...
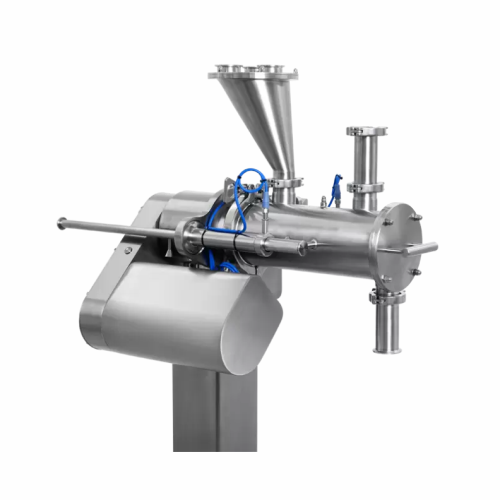
Continuous mixing for fine and cohesive powders
Achieve unparalleled mixing precision for cohesive powders while reducing ...
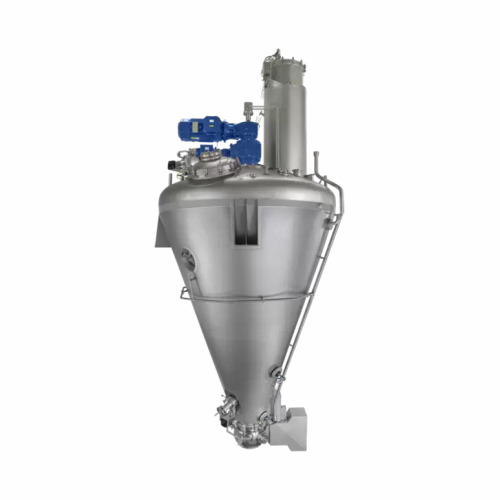
Vacuum dryer for powders and granules
Achieve precise moisture control for sensitive materials with a versatile vacuum dryi...
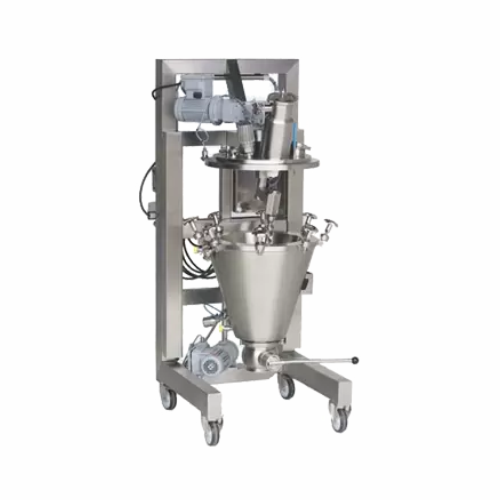
Laboratory vacuum dryer for heat-sensitive materials
Optimize moisture control in heat-sensitive materials with precise a...

Table roller mills for mineral raw material comminution
Achieve precise mineral raw material comminution and energy-effic...
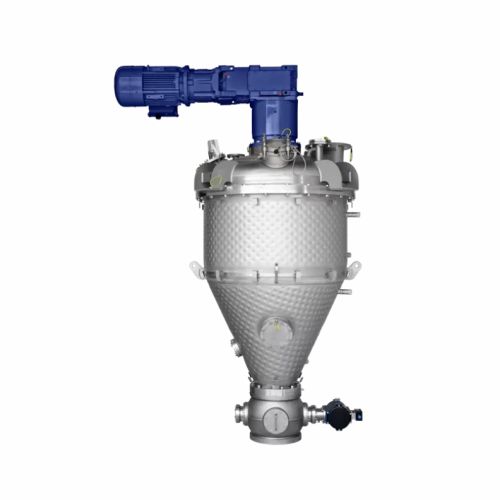
Conical paddle vacuum dryer for powders and granules
Achieve efficient drying of sensitive materials with this versatile ...
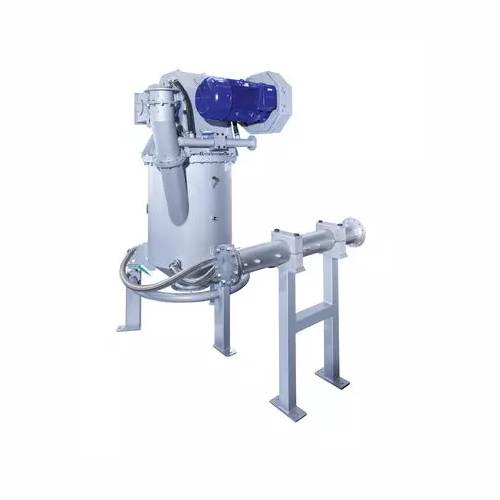
Fluidised bed opposed jet mill for fine particle processing
Achieve precise and consistent particle sizes with high-spee...
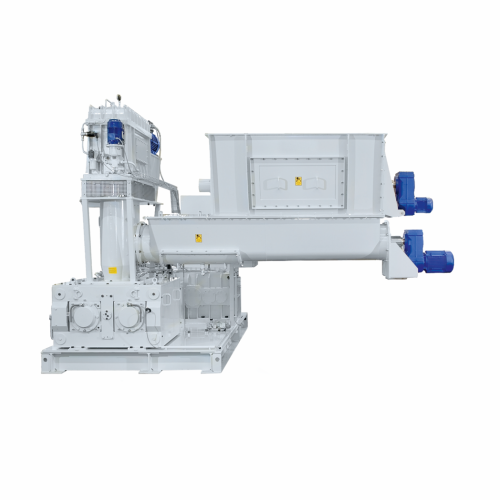
High-pressure roller compactors for chemical, food, and minerals industries
Achieve precise particle compaction and br...
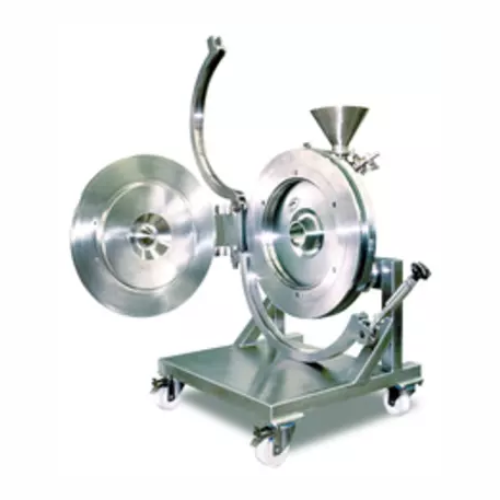
Spiral jet mill for superfine powder production
Achieve consistent ultra-fine powder with precise particle size control, c...
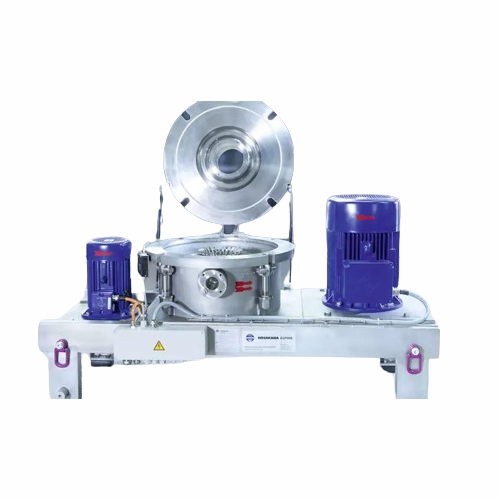
Classifier mill for ultrafine grinding
Achieve precise particle size distribution and contamination-free processing with th...
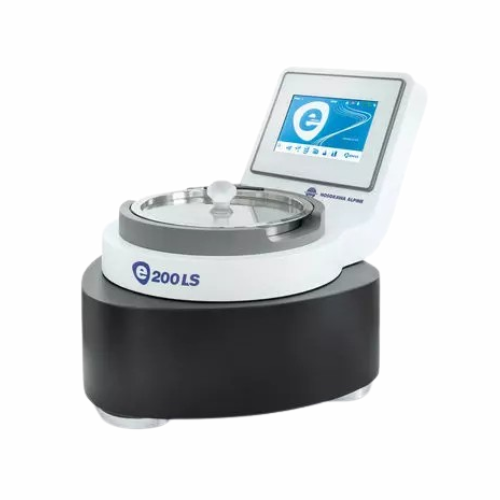
Air jet sieve for particle size analysis
Achieve precise particle size distribution effortlessly for your powders, ensuring...
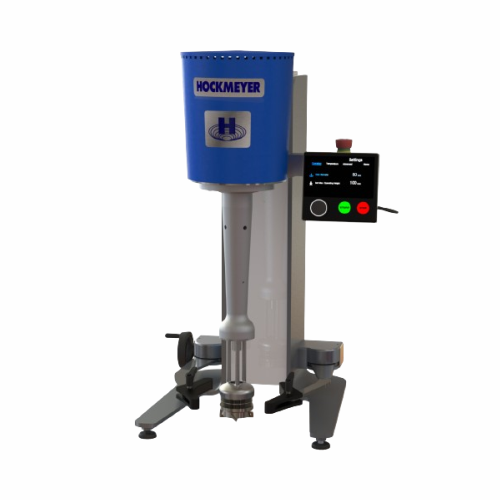
Lab-scale disperser and immersion mill
Achieve precise dispersing and milling with rapid changeover capabilities, ideal for...
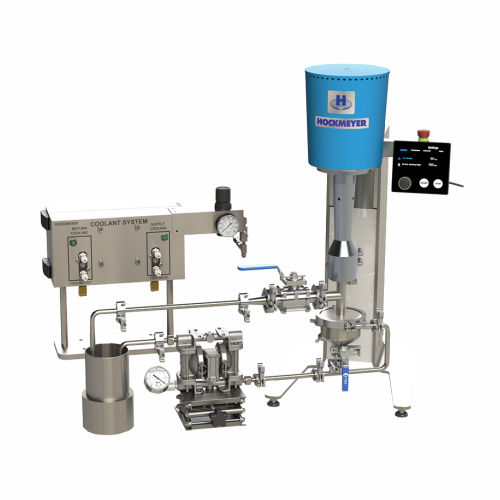
Laboratory vacuum milling for fine particle size reduction
Streamline your lab and pilot processes with high-speed vacuu...
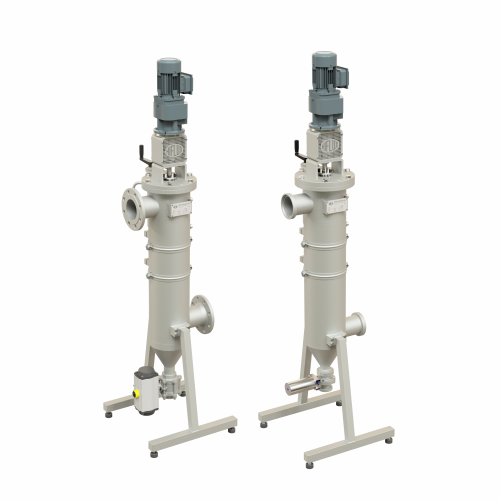
Self-cleaning filter for industrial and hygienic applications
Ensure continuous operation and minimal waste in your liqu...

Pre-breaker for initial material size reduction
Efficiently prepare your bulk materials for further processing by swiftly ...
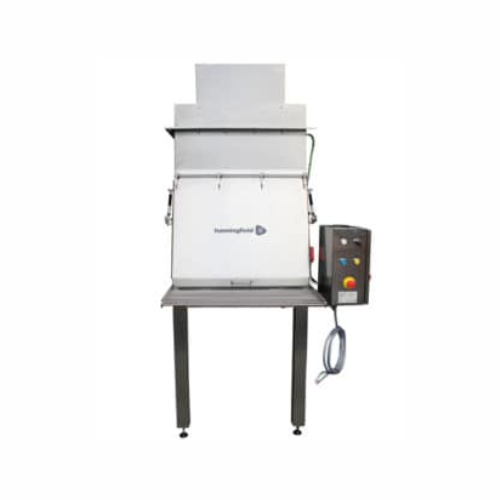
Dust control sack tip station for bag unloading
Ensure efficient powder unloading and minimize dust emissions in your prod...
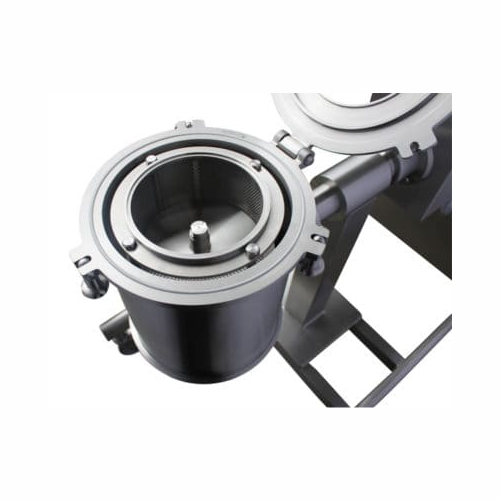
Centrifugal powder sifter for particle separation
Achieve consistent material quality with efficient powder sifting and d...
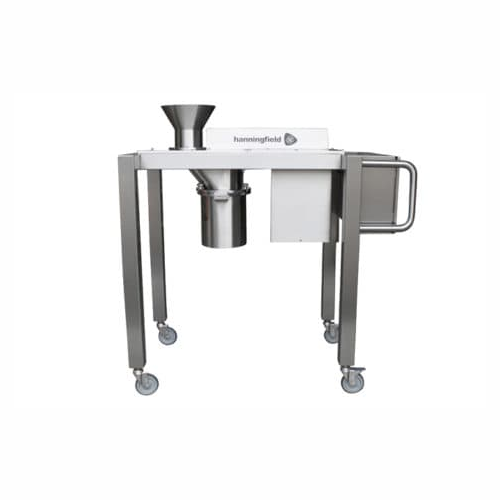
High capacity conical mill for powder processing
Optimize your milling process with a versatile solution that ensures prec...
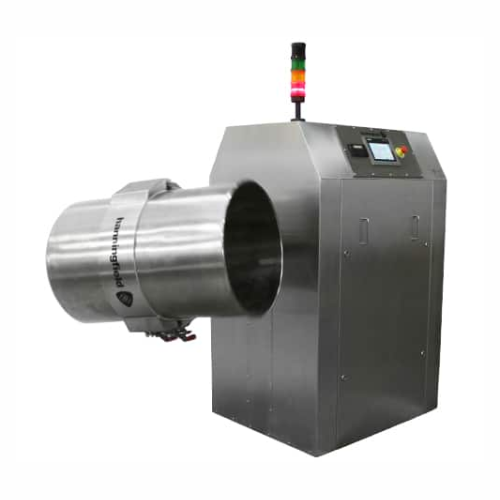
Industrial drum tumblers for uniform batch processing
Achieve precise mix uniformity in your batches with drum tumblers, ...
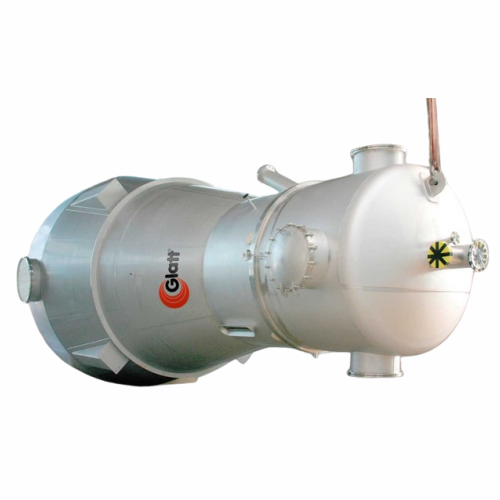
Fluid bed granulation system for food and chemical industries
Achieve efficient granulation and drying of liquids with c...
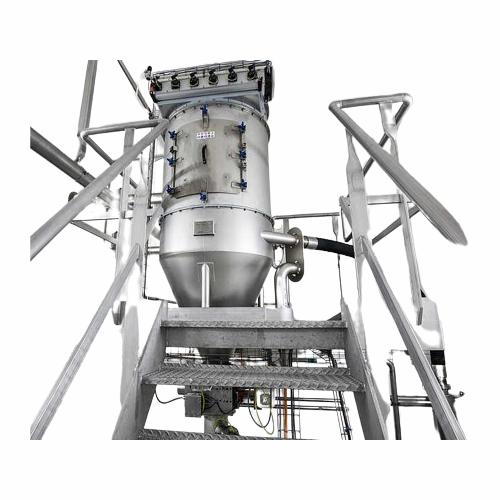
Vacuum pneumatic conveying for infant nutrition
Ensure efficient handling of delicate powders with a versatile vacuum pneu...
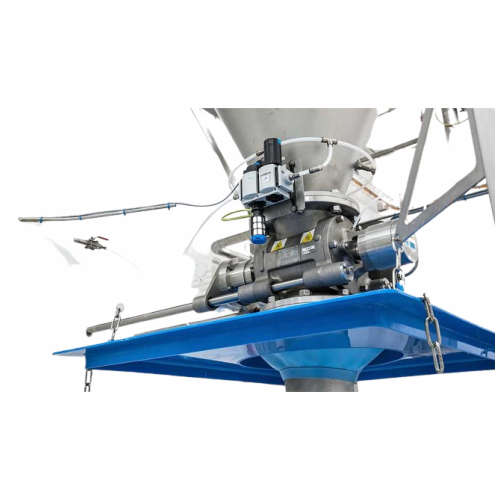
Heavy duty rotary valves for powder handling
Ensure precise material flow and safety in harsh processing environments with...
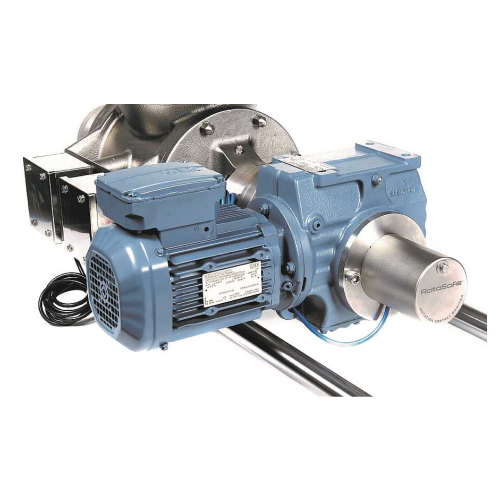
Contact detection system for rotary valves
Prevent product contamination and equipment damage with instant contact detecti...
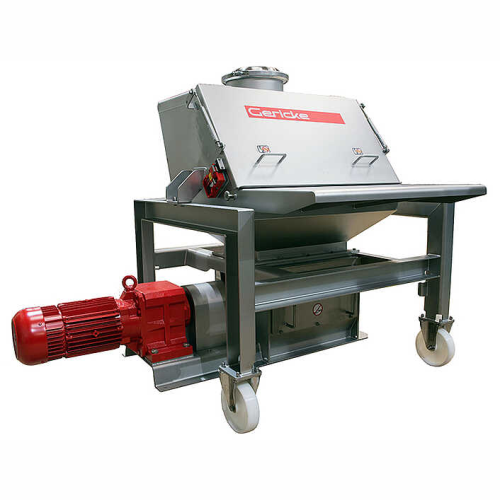
Sack tipping station for dust-free bulk material handling
Efficiently manage bulk materials while minimizing dust exposu...
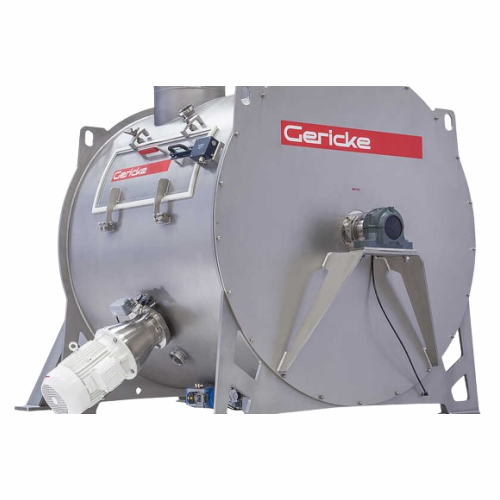
Single shaft batch mixer for chemical and pharmaceutical applications
Optimize mixing efficiency with rapid batch proce...
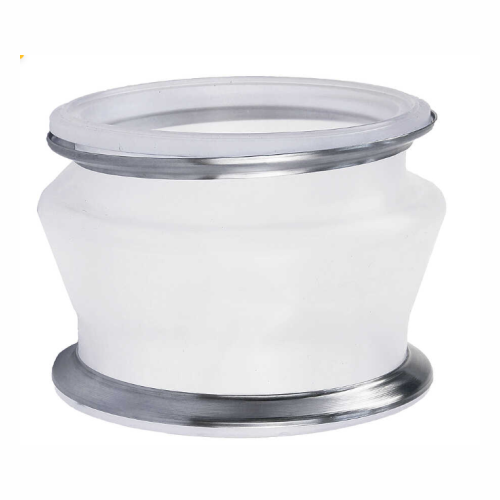
Hygienic flexible sleeves for tri-clamp connections
Ensure seamless, contamination-free transitions between processing st...
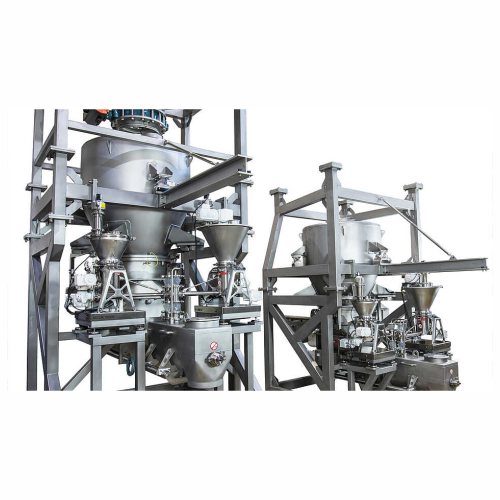
Continuous inline mixing for late product differentiation
Achieve seamless product differentiation with compact inline m...
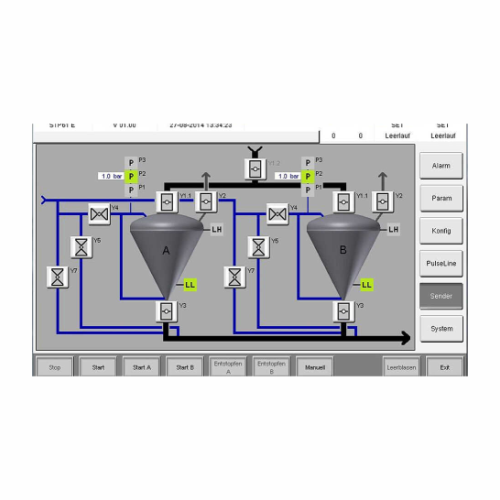
Conveying controller for dense phase conveying
Streamline your dense phase conveying operations with precise control and m...
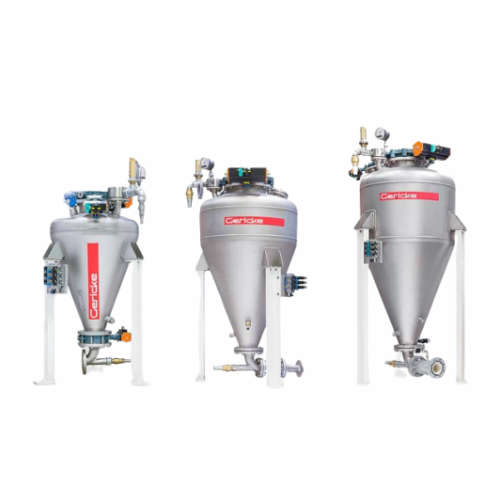
Dense phase pneumatic conveying system for powder transfer
Ensure gentle and efficient material transport with minimal m...
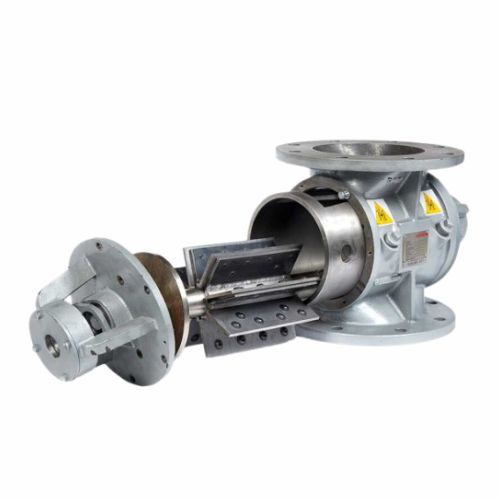
Pneumatic dilute phase conveying system for powders and bulk materials
Optimize your production line’s efficiency...
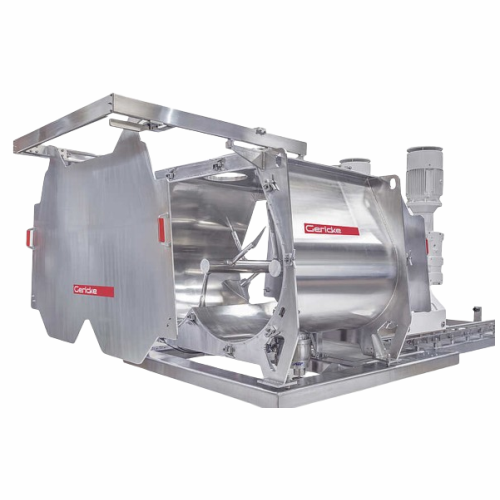
Double shaft powder batch mixer
Achieve high homogeneity and gentle handling with a double shaft mixer designed for efficien...
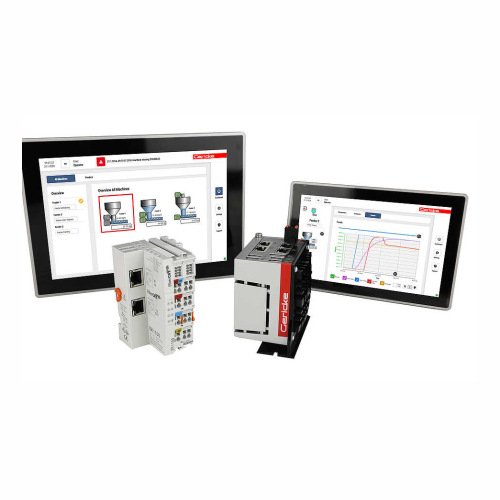
Universal controller for feeders in powder handling applications
Simplify and enhance your powder handling with precise ...
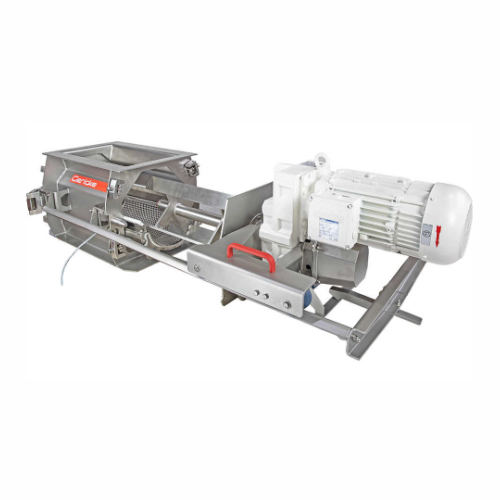
Deagglomerator for consistent particle size reduction
Struggling with inconsistent particle sizes or unwanted lumps in yo...
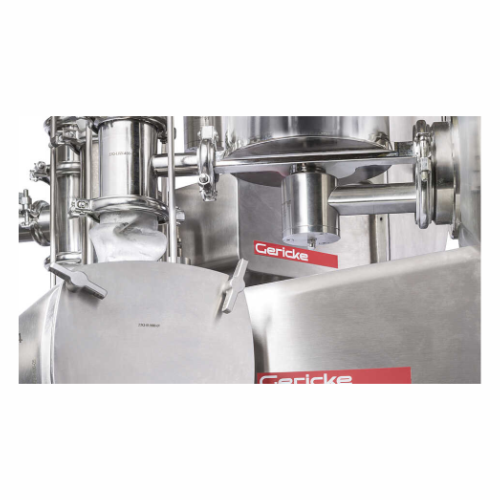
Continuous mixer for homogeneous blending
Achieve consistent product quality with precise mixing and blending, ideal for a...
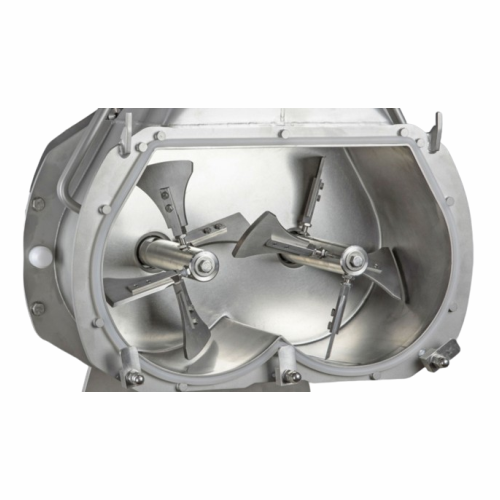
Laboratory mixer for r&d and small batch production
Achieve superior mixing precision for R&D and pilot production w...
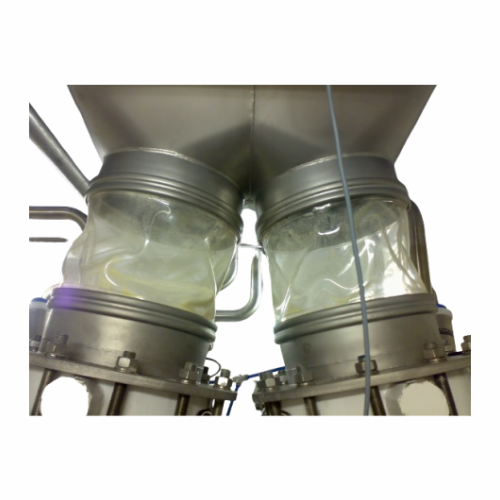
Hygienic flexible sleeves for food and pharmaceutical use
Say goodbye to contamination risks with this tool-free, quick-...

Big bag unloader for industrial bulk materials
Efficiently handle bulk materials with this modular unloading system, desig...
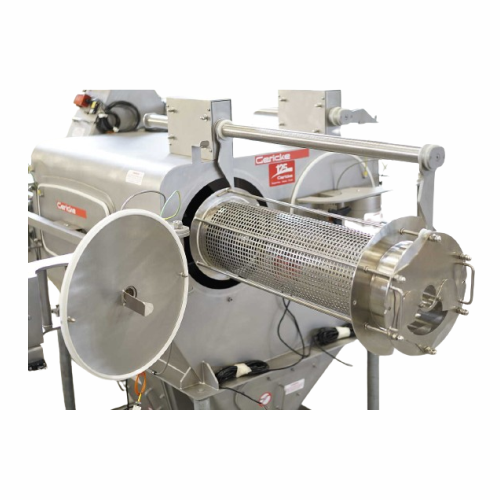
Centrifugal sifter for bulk solids and powders
Achieve precise particle separation and enhance product quality with a solu...

Continuous powder mixer for industrial applications
Achieve precise and efficient integration of powders, granules, and l...
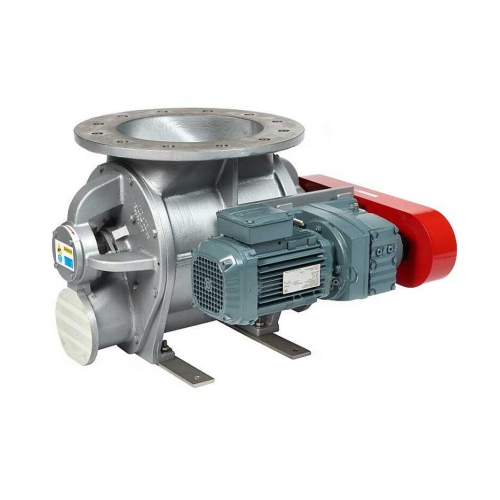
Heavy duty blowing seals for abrasive products
For operations dealing with abrasive materials under high pressure, these r...
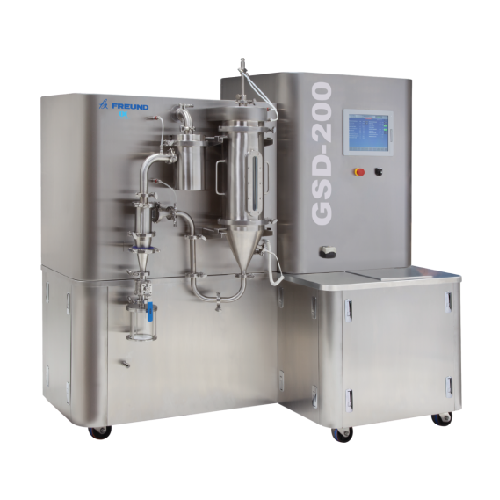
Laboratory spray dryer for sub-gram powder samples
Achieve precise control in developing fine chemical and pharmaceutical...
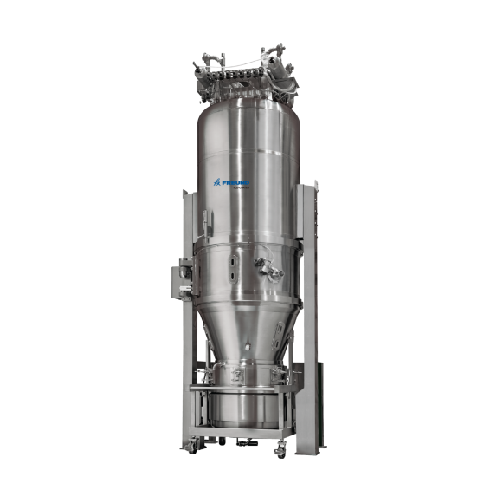
Fluid bed system for granulation and coating
Optimize your production with a multi-purpose fluid bed system designed for e...

Filter washing cabinet for industrial cartridge filters
Achieve hygienic standards with precision washing and drying of i...
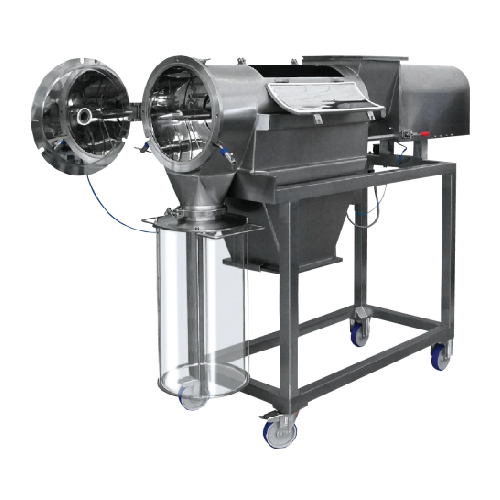
Centrifugal sifter for particle size classification
Achieve precise particle size control with high output efficiency, en...
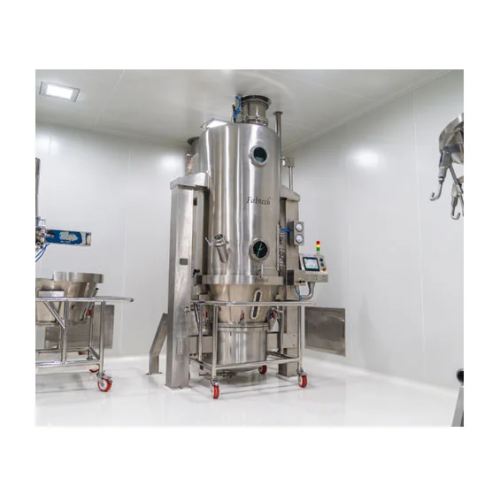
Fluid bed processor for granulation and coating
Fluid bed processors offer efficient granulation and coating, streamlining...

Ultraclean aseptic storage tanks for hygienic liquid food
Ensure your liquid products remain uncontaminated and maintain...
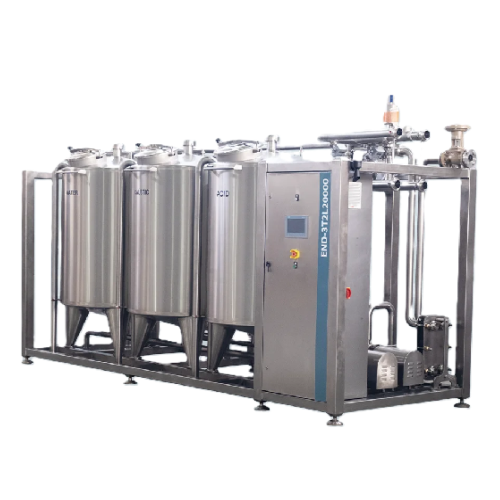
Automated cleaning in place (cip) systems for beverage processing
Optimize your production with automated CIP systems t...
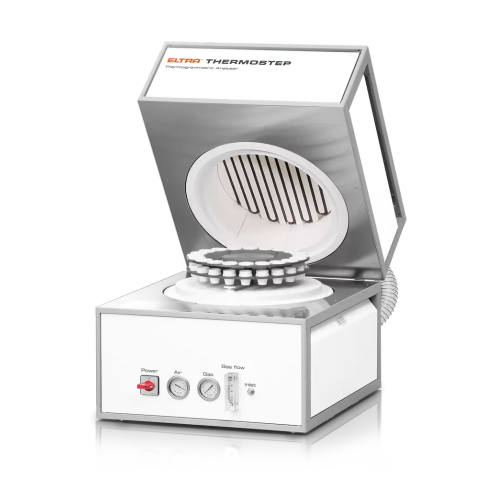
Thermogravimetric analyzer for moisture, ash, and volatiles analysis
Streamline your laboratory analysis with this solu...
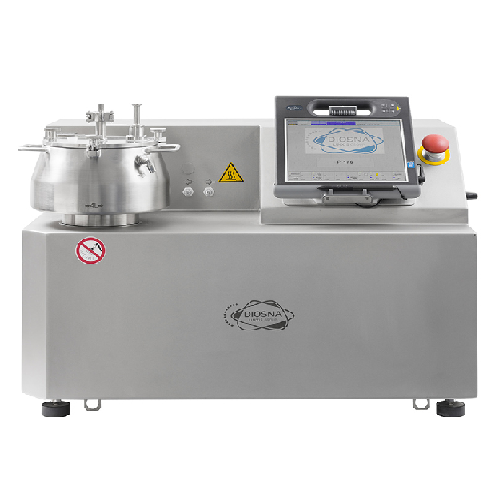
Compact laboratory mixer for high-shear granulation
Streamline your R&D processes with advanced mixing and granulati...
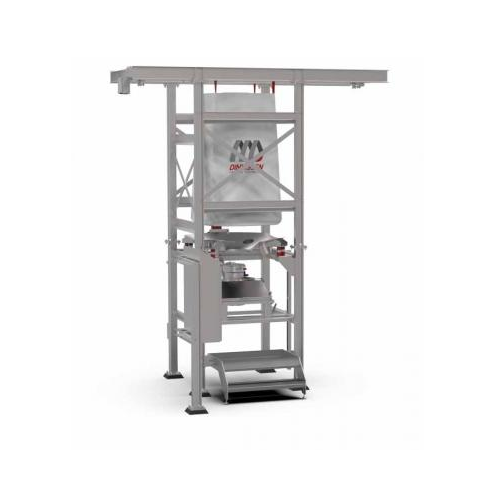
Modular big bag unloading station for various materials
For hassle-free handling of bulk materials, this modular solution...
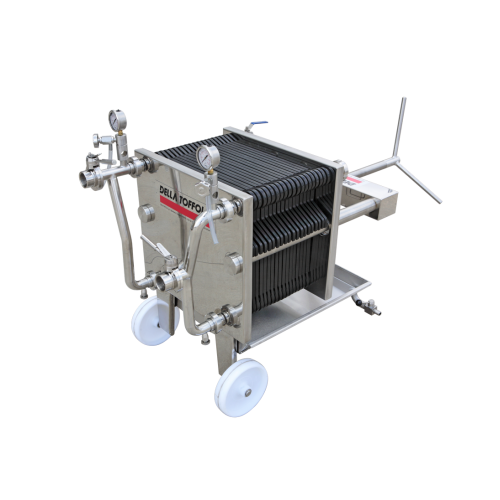
Industrial sheet filters for diverse liquid filtration applications
Achieve precise liquid filtration with adaptable sh...
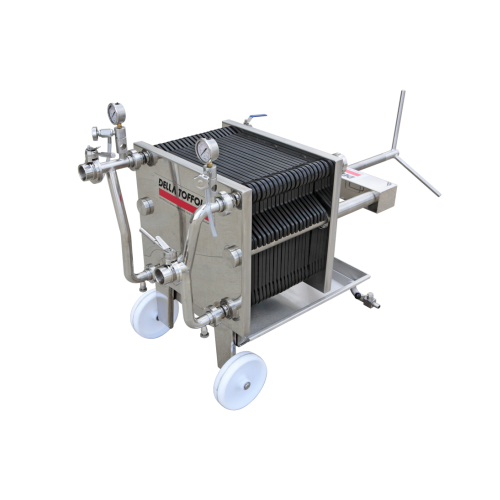
Sheet filters for wine and beer filtration
Enhance your filtration process with reliable sheet filters designed for high-q...
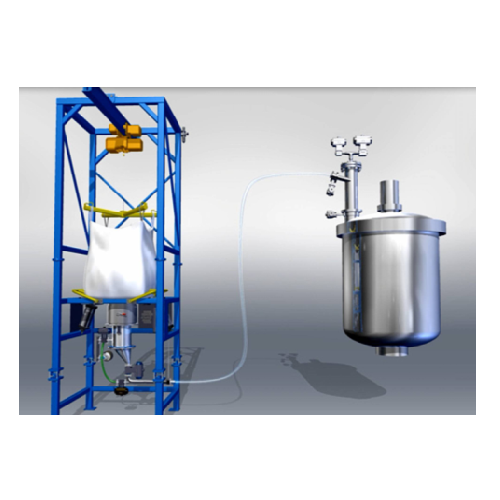
Big bag emptying station for powder handling
Ensure safe and efficient powder discharge with precision containment, adapta...
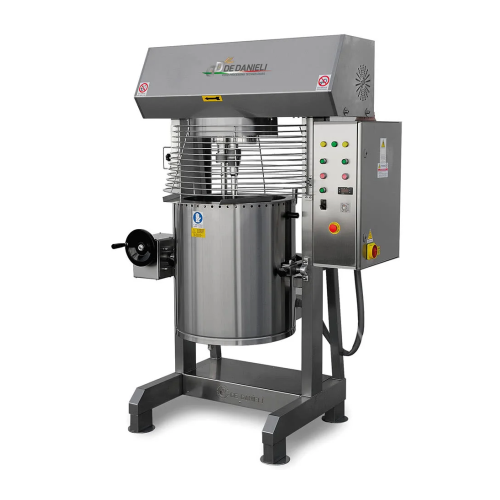
Industrial cooker for food processing
Enhance your production line with versatile cooking solutions designed for precise te...
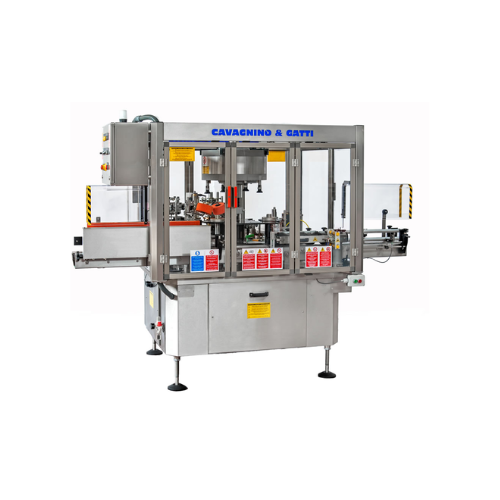
Compact wet glue labeling system for low volume production
Achieve precise, high-quality labeling with compact machinery...
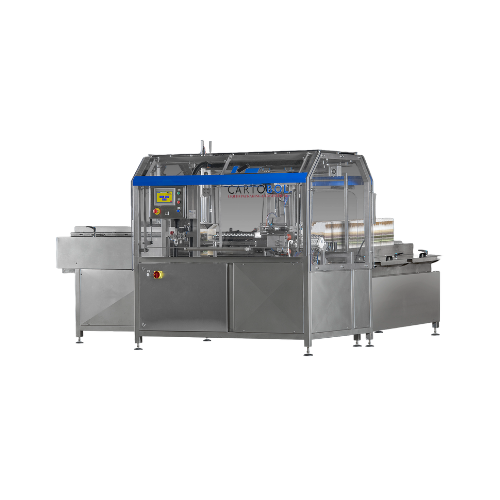
Bag-in-box carton erector
Experience seamless carton erection with advanced servomotor technology, enhancing both efficiency...
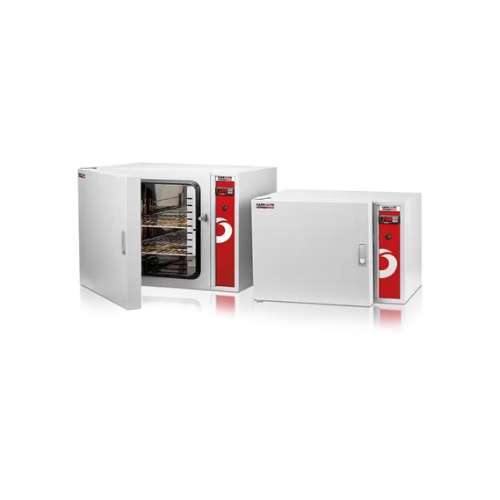
Laboratory oven for accurate thermal processing
Achieve precise thermal control for sensitive formulations, ensuring consi...
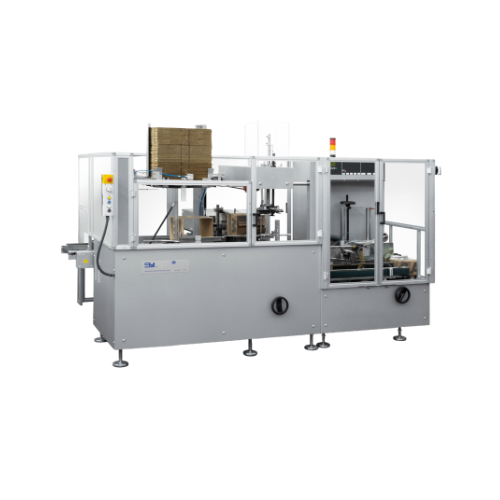
High-speed horizontal case packer for shipping cases
For high-demand production lines, this modular case packer streamlin...
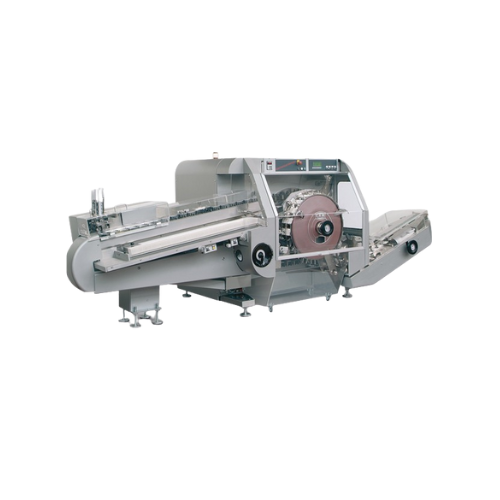
High-speed continuous motion horizontal cartoner
Achieve seamless high-speed cartoning with precision cartoner systems des...
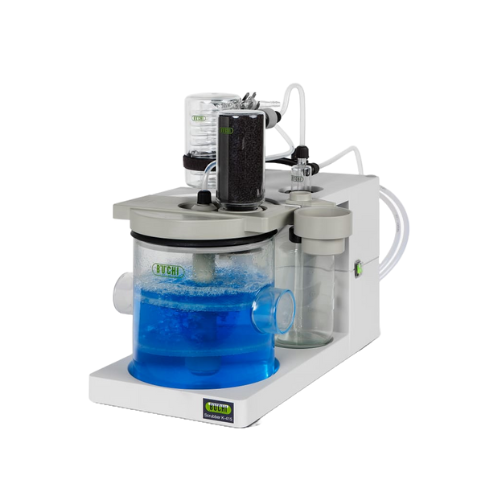
Industrial fume scrubber for safety compliance
Enhance workplace safety by efficiently neutralizing hazardous fumes and va...
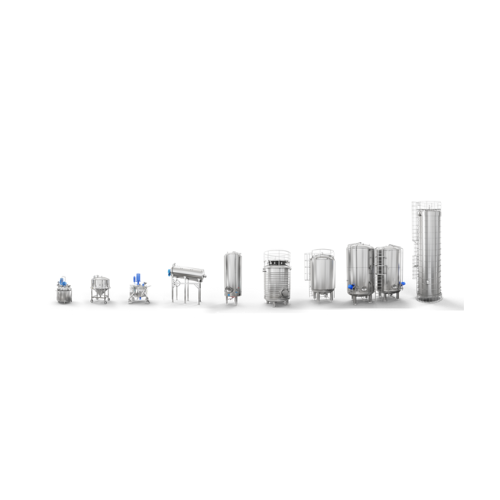
Industrial tanks for diverse applications
Efficiently manage your liquid production processes with customizable storage, m...
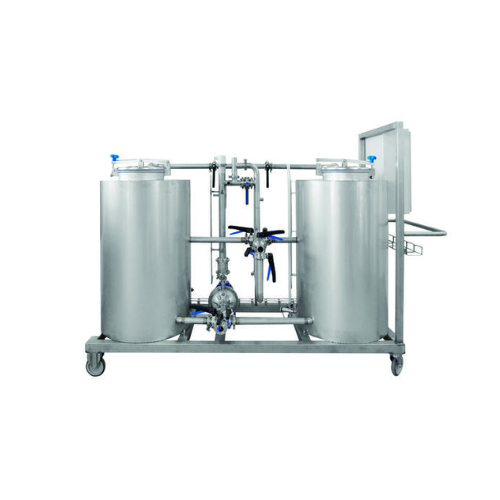
Mobile Cip plant for pipe and tank cleaning
Optimize your cleaning processes with this mobile CIP plant, designed for effi...
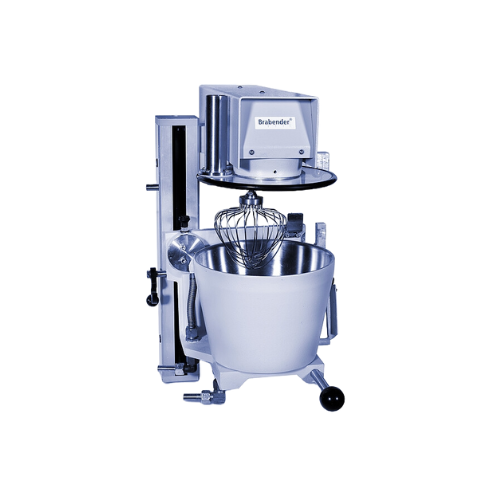
Planetary mixer for homogeneous material mixing
Achieve precise and consistent mixing of diverse materials from powders to...
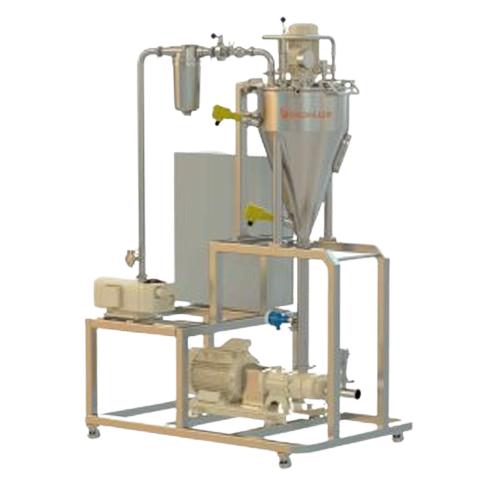
Vacuum deaerator for elimination of gases
Optimize your product quality by eliminating occlusive gases with this advanced ...
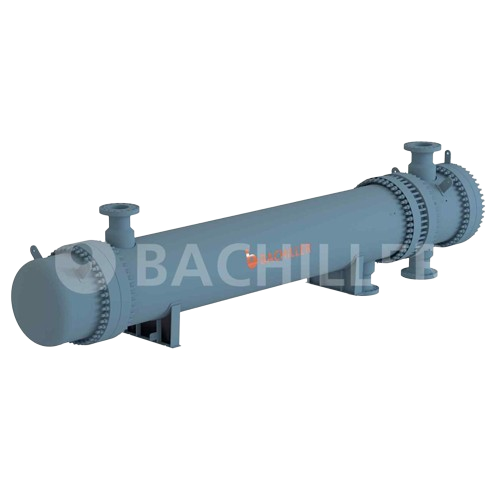
Shell and tube heat exchangers
Efficiently manage heat transfer in your production line with custom-engineered shell and tub...
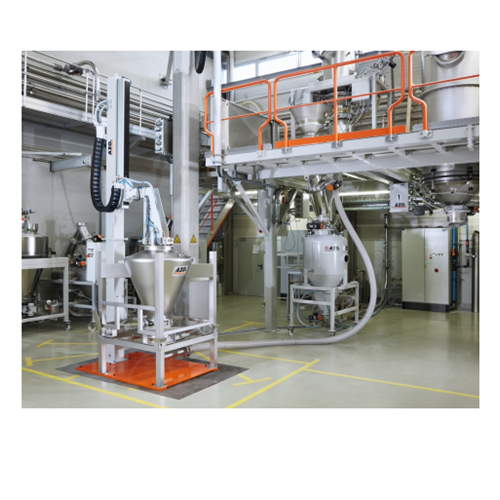
Dry cleaning container & hopper station
Effectively manage cleaning of rotation-symmetrical containers with minimal downtim...
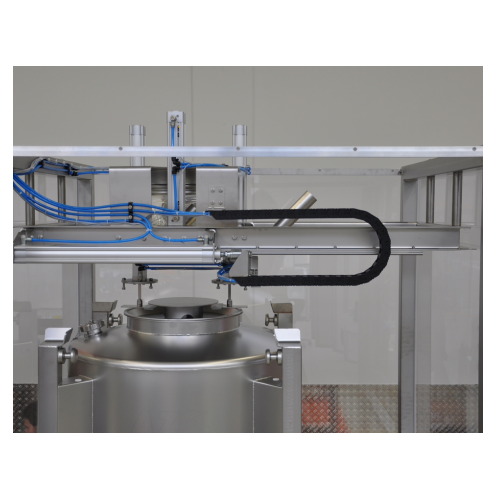
Dust-tight docking for dosing units to bulk solids containers
Ensure seamless, dust-free transfer and dosing of bulk sol...
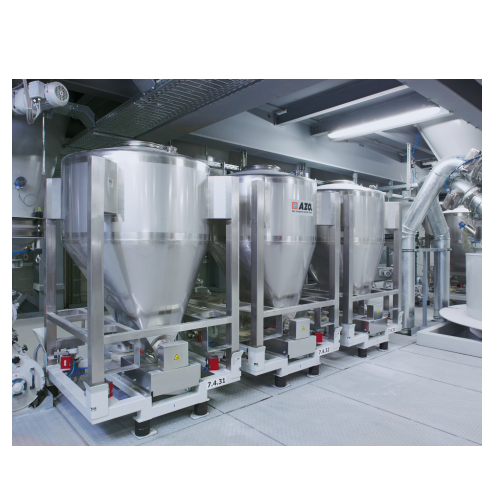
Precise dosing system for bulk materials
Ensure precise bulk material dosing with minimal dust, seamlessly switching betwee...
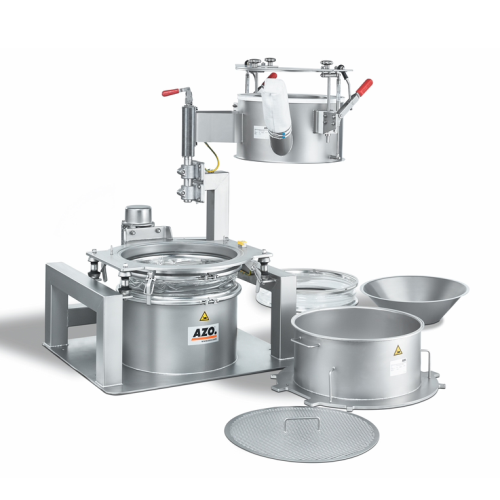
Big bag connection system for dust-free docking
Achieve dust-free docking and seamless discharging of bulk solids with an ...
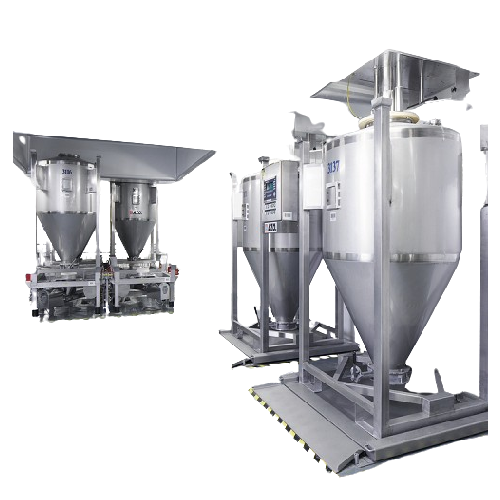
Automated bulk material handling system
Ensure precise batch tracking and efficient handling of challenging bulk materials ...
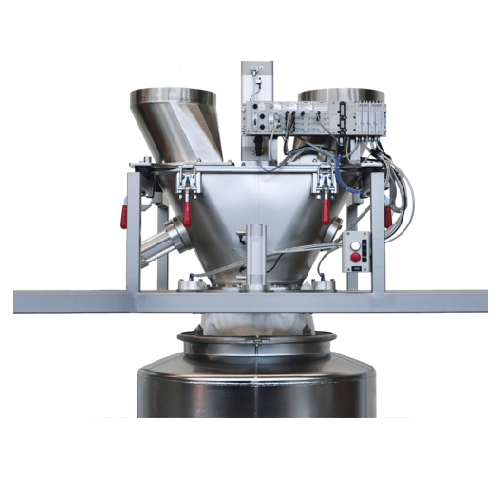
Contamination-free docking system for bulk solids
Achieve contamination-free transfer of bulk powders and granules while ...
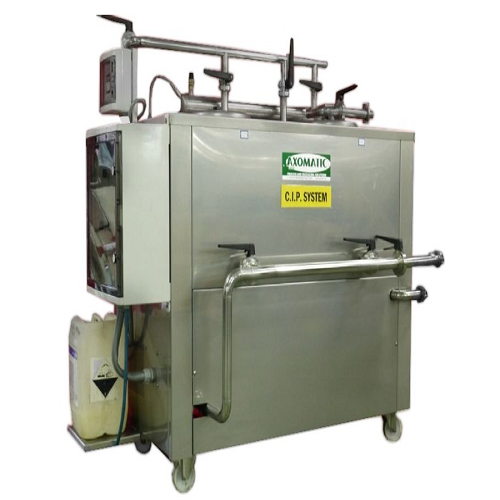
Cip clean-in-place system for undervacuum homogenizers
Ensure seamless sanitation for your undervacuum homogenizers with ...
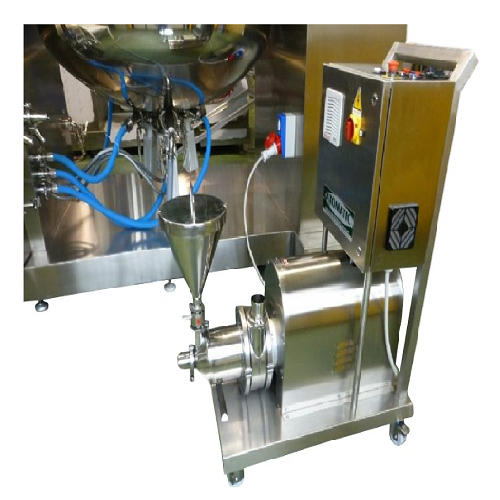
In-line external homogenizer for industrial fluid processing
Maximize fluid consistency and ensure efficient material di...
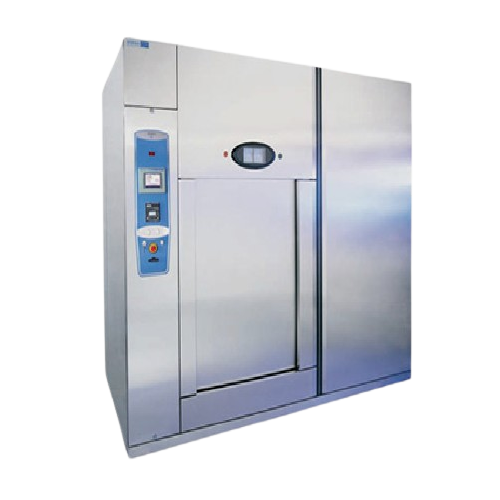
Gmp steam sterilizer for pharmaceutical applications
Ensure consistent sterilization and contamination control across you...
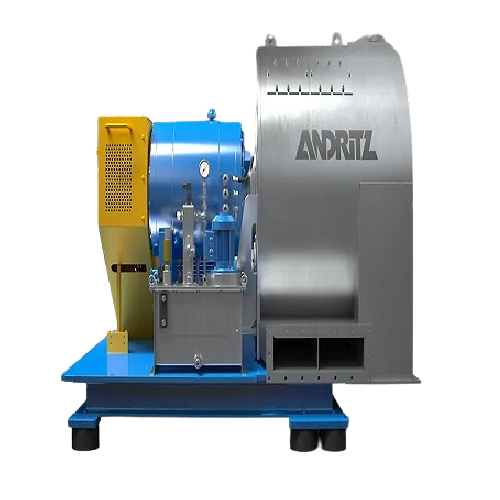
Screen scroll centrifuge for flexible dewatering
Ensure maximum uptime and consistent dewatering performance amidst variab...
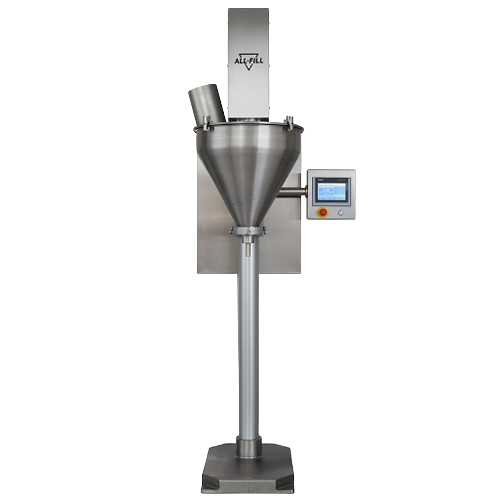
Volumetric filler for bags and rigid containers
Optimize precision filling of powders and granules with a versatile soluti...
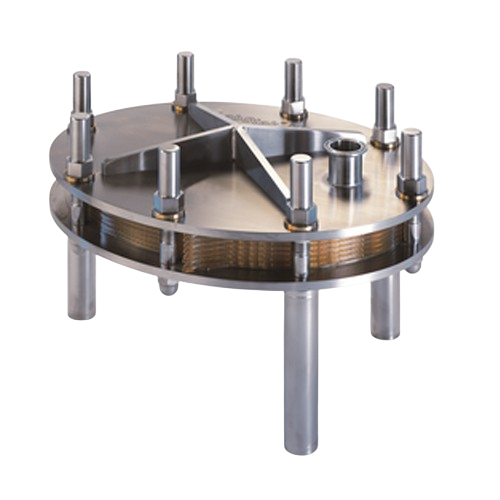
Ultrafiltration and microfiltration test unit
Streamline your filtration and membrane testing with a flexible, scalable un...
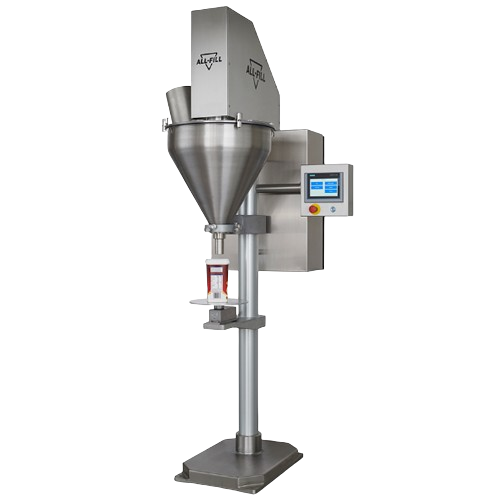
Gravimetric filling solution for inconsistent density products
Achieve precise weight accuracy in your filling processes...
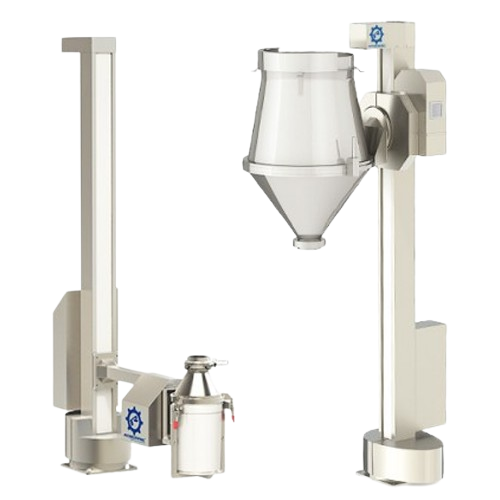
Lifting column for drums and bins
Optimize your powder handling operations with a versatile lifting solution designed for p...
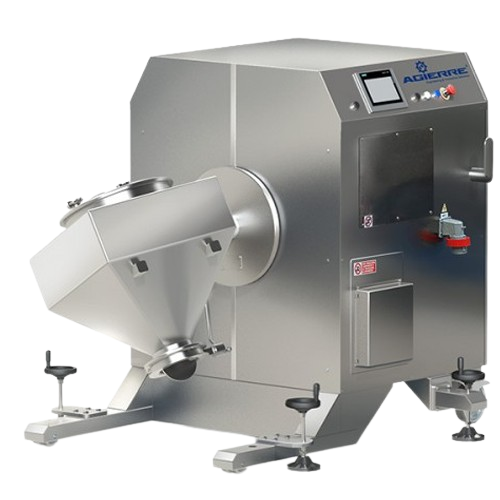
Mobile bin blender for mixing and homogenizing dry powders
Ensure thorough powder uniformity and eliminate cross-contami...
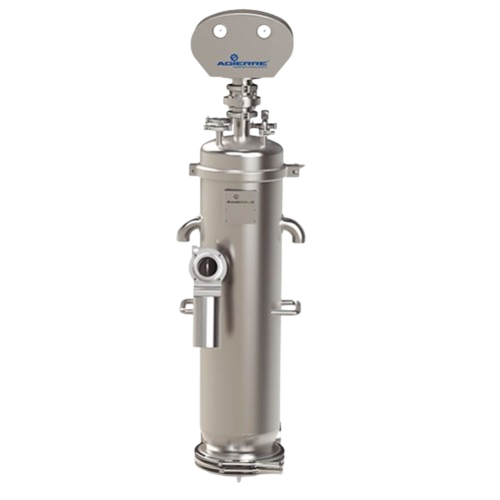
Vacuum conveyor for powder and granule transfer
Ensure efficient and contamination-free transfer of powders and granules w...
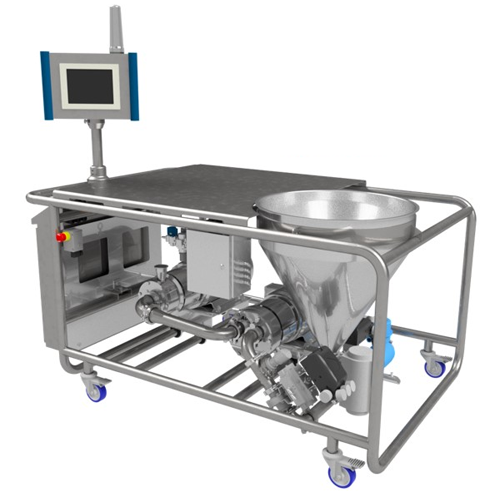
Automated powder induction and dispersion system for industrial mixing
Achieve rapid and efficient incorporation of pow...
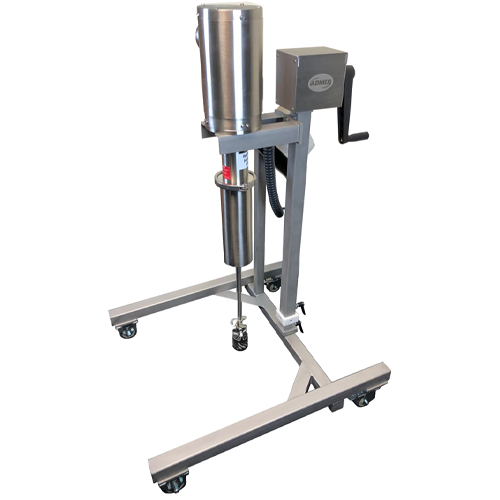
Pilot scale mixers for product development and small production runs
Optimize your mixing processes with precision cont...
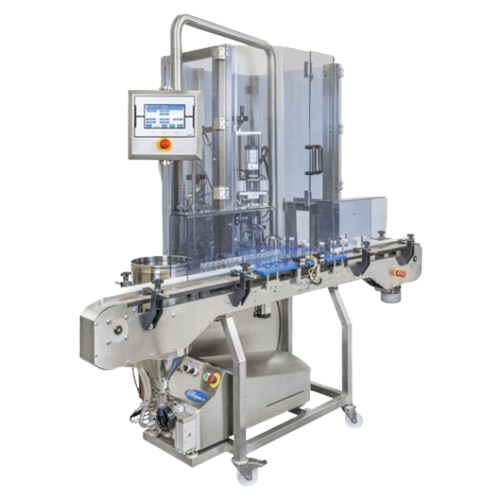
Filler and capper for bottles and jars
Optimize your production with a compact filling and capping solution that delivers f...
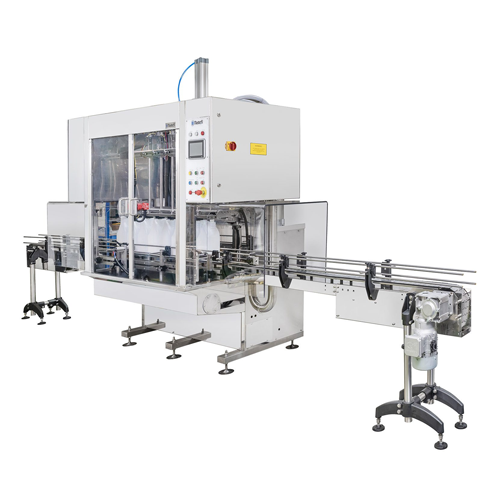
Automatic volumetric filler for liquid products
Optimize your production with this high-precision volumetric filler, desig...
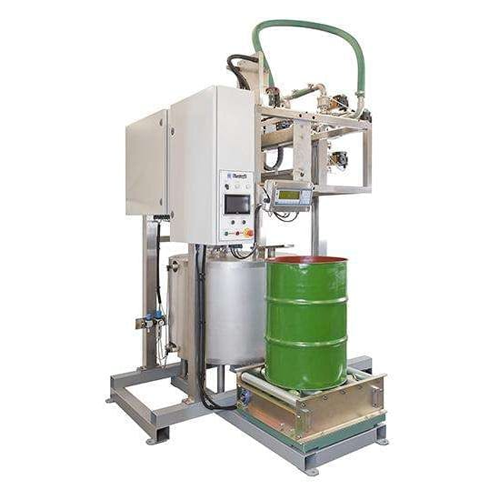
Drum decanting unit for high viscosity liquids
Efficiently decant high viscosity liquids like solvent-based paints and ess...

Semi-automatic flowmeter boom filler for large volume containers
Effortlessly handle large volume liquid filling with pr...
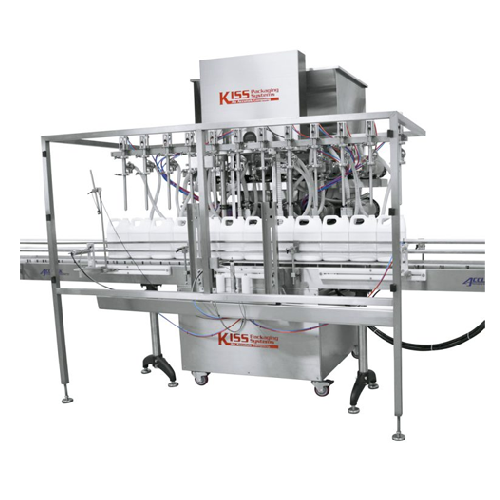
Automatic positive displacement filler for various liquids
Achieve precision and versatility in liquid filling operation...
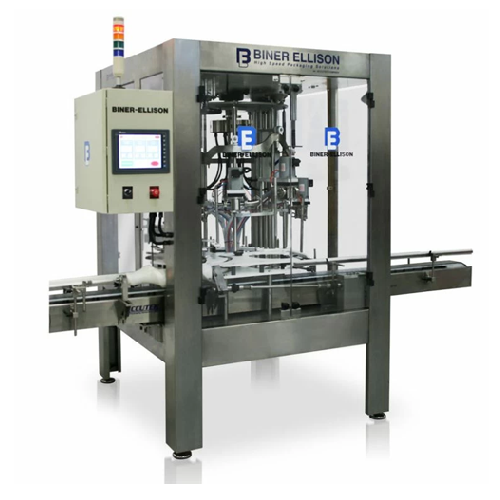
Automatic positive displacement bottle filler
Streamline your liquid filling operations with precision and flexibility, id...
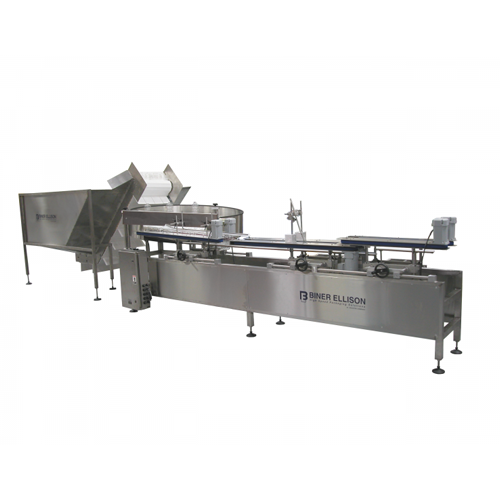
High-speed bottle orientator
Efficiently streamline your bottling process by ensuring containers are swiftly and accurately ...

Bottomless conveyor for 90° bottle transfer and coding
Efficiently connect disparate production systems in your bottling ...
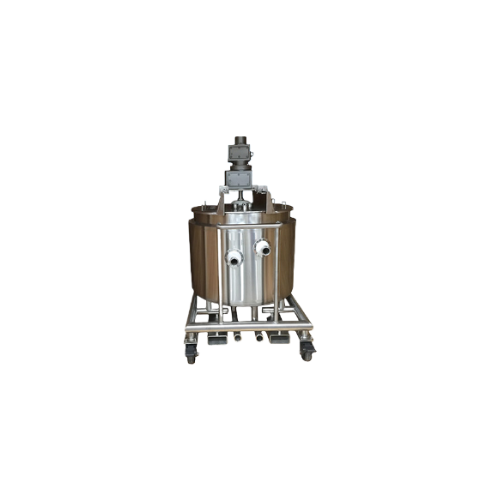
R&d vessels for research and development centers
Optimize your R&D operations with versatile vessels designed to hand...
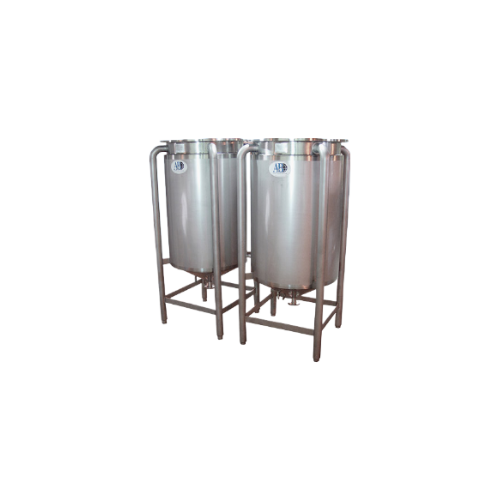
Customizable storage tanks for industrial use
Optimize your production with versatile storage tanks designed for precise c...
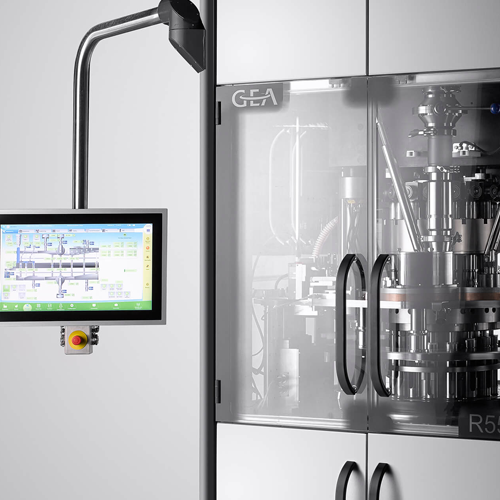
Heavy-duty tablet press for single & double-layer tablets
Maximize your tablet production with a high-speed solution cap...
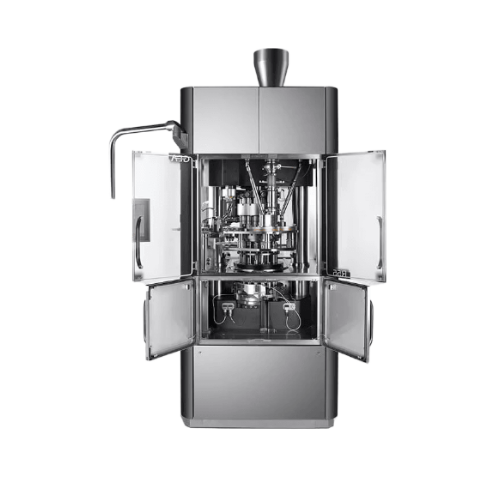
Industrial rotary press for single-layer tablet production
Optimize your tablet production with precision-engineered rot...
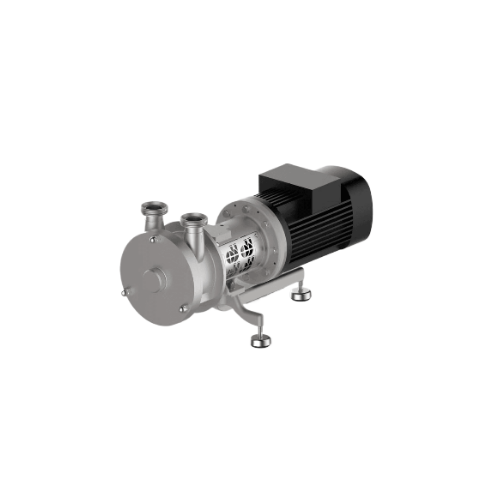
Self-priming side channel pump for high gas content media
When handling media with high gas content, achieving efficient...
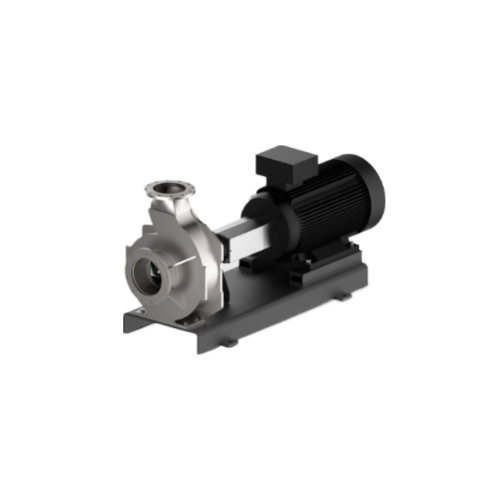
Single-stage centrifugal pump for heavy-duty applications
Optimize fluid handling with a high-efficiency centrifugal pum...

Fibc emptying stations for powder processing
Streamline your bulk powder handling with single-operator FIBC emptying stati...
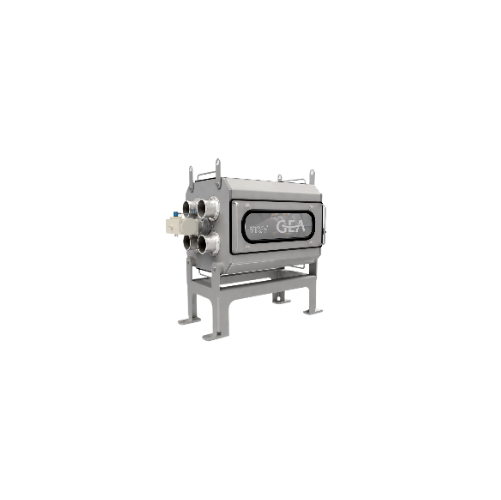
Rotary tube selector valve for powder conveying
Streamline your pneumatic transport system with a robust solution that div...
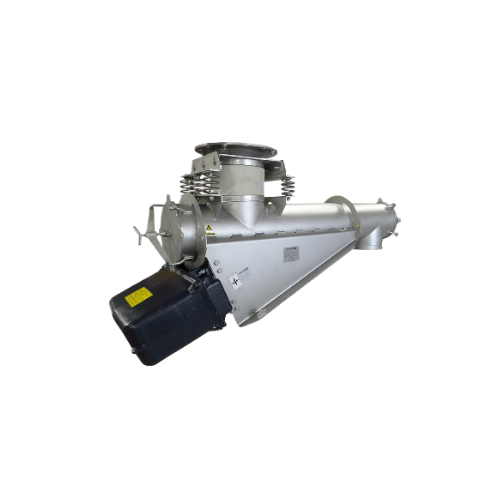
Vibrating feeder for food and pharmaceutical industries
Optimize your production line with precision dosing and gentle ma...
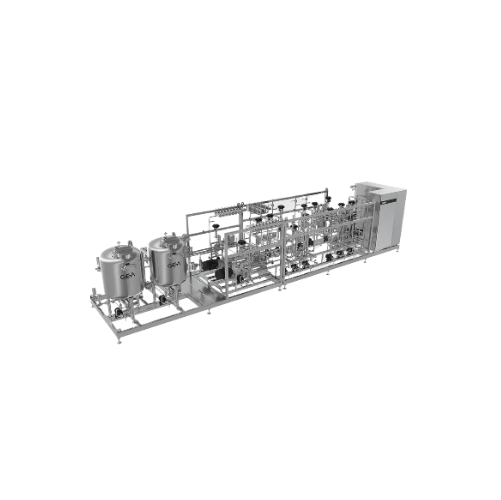
Continuous in-line blender for home and personal care products
Achieve precision and flexibility in blending liquid mult...
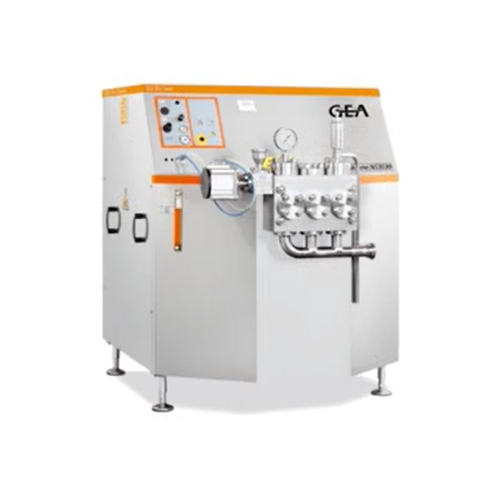
High pressure industrial homogenizer
Enhance liquid formulations with precision and efficiency—our high-pressure homogenize...
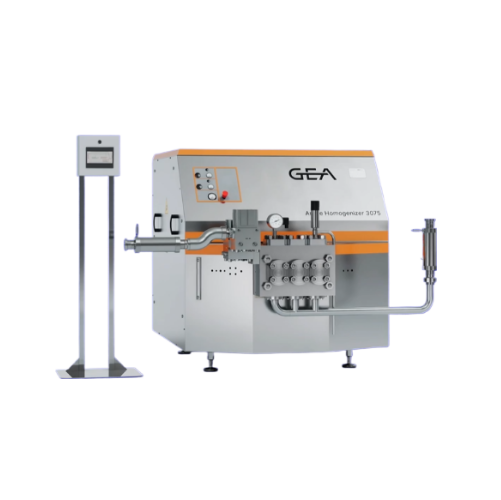
Inline real-time fluid quality monitoring system
Optimize fluid quality control with continuous, inline measurements that ...
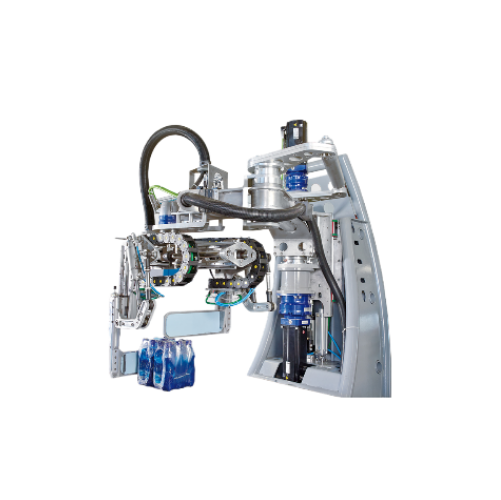
Layer preparation system for high-speed palletizing
Optimize your palletizing process with a system that ensures precise ...

Continuous leveler and sealer for powder packing
Enhance efficiency in powder packaging with a system that ensures precise...
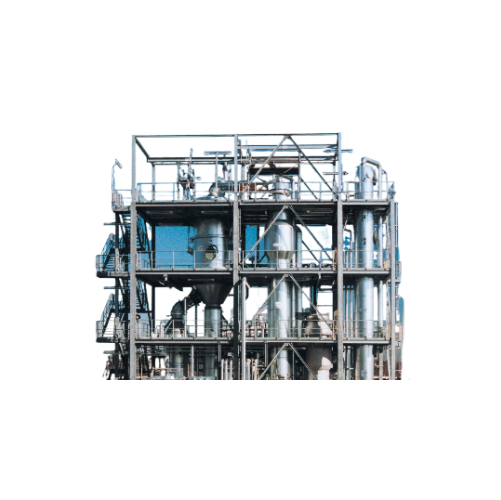
Forced circulation evaporator for highly viscous liquids
Optimize energy efficiency and minimize fouling in your evaporat...
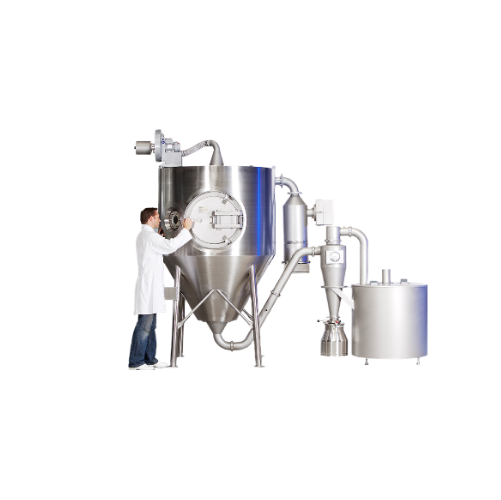
R&d spray drying solution for small batch production
Efficiently convert liquid solutions into precise, uniform powders f...
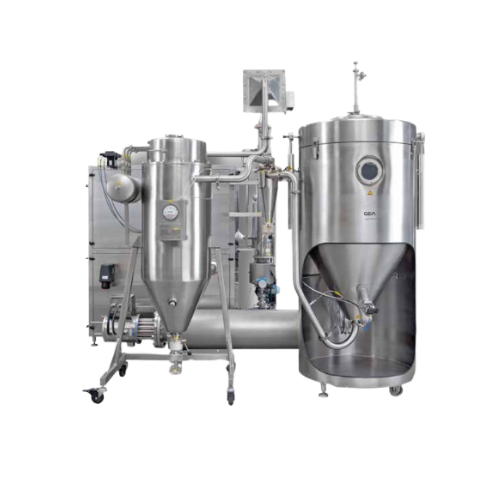
Spray dryer for food and dairy products
Achieve consistent drying for diverse powders and granulates with precision technol...
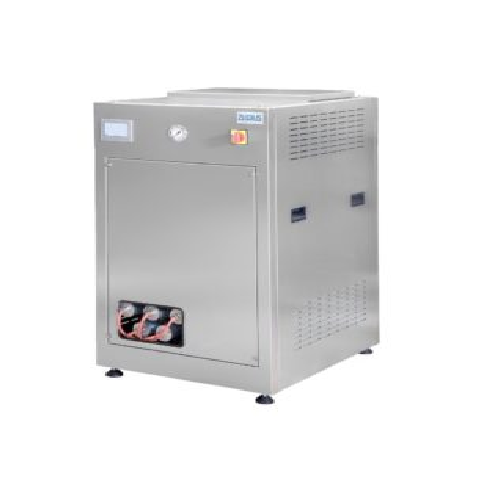
Pure steam generator for industrial applications
Ensure the highest levels of steam purity and precise pressure control fo...
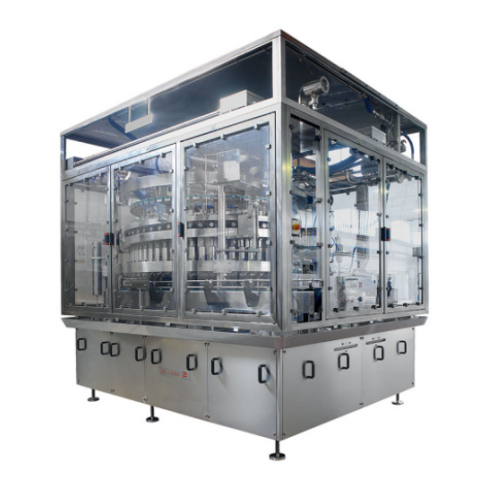
Rotary piston fillers for pumpable products
Optimize high-speed production lines with precision filling for diverse liquid...
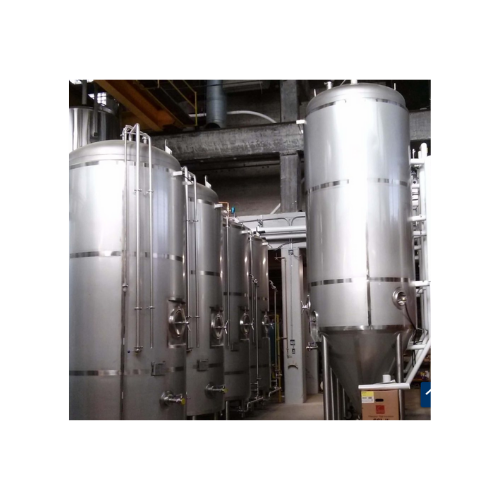
Bright beer tanks for breweries
Enhance your beverage production with precise carbonation and conditioning, ensuring excepti...
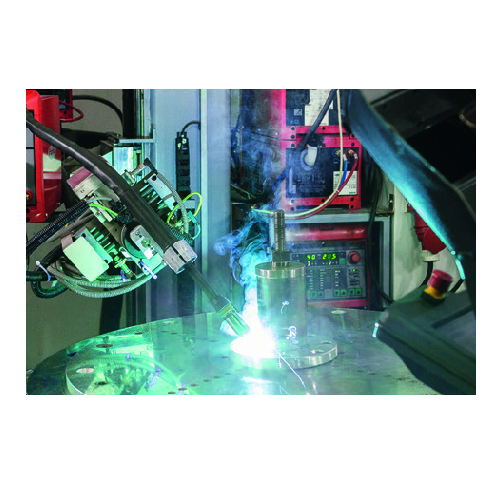
Traditionally welded silos for constrained installation sites
Ideal for facilities with limited space, these traditional...
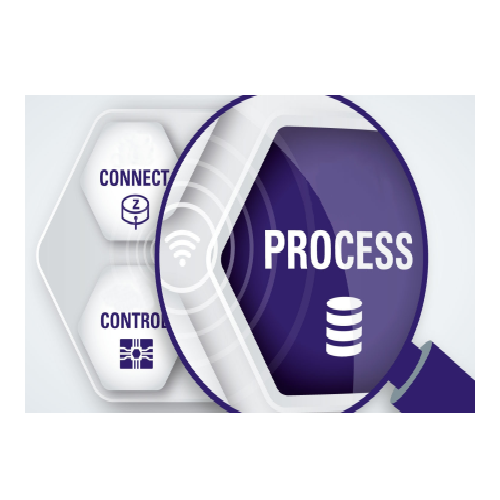
Autonomous process control for petrochemical and food industries
Streamline your production with autonomous control syst...
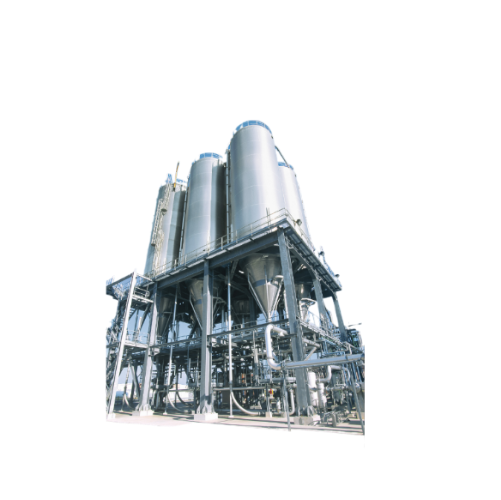
Advanced degassing and temperature control solution for process silos
Optimize your production line with precise contro...
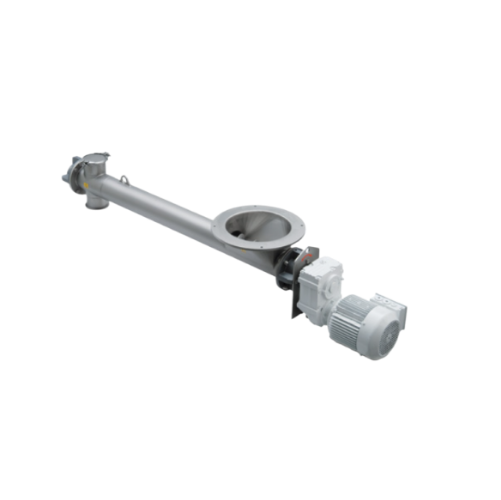
Dosing and conveying screw for dry bulk materials
Efficiently manage the precise dosing and conveying of dry, powder, and...
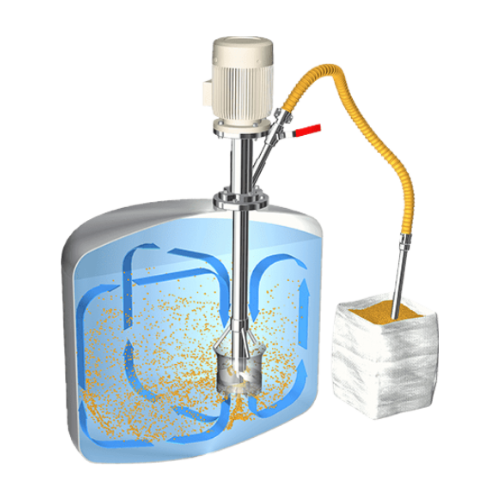
Low-dust powder induction mixer for liquids
Achieve dust-free induction and homogenization of powders in liquids with prec...
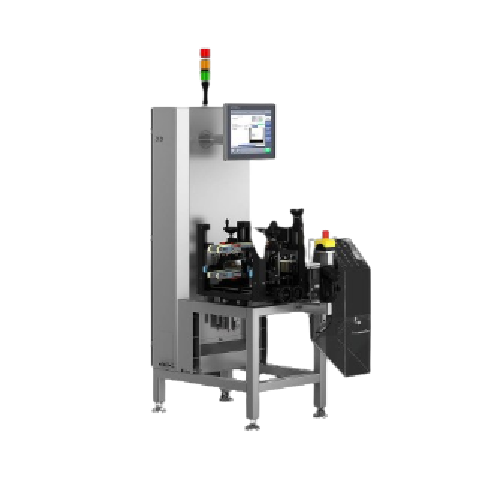
Compact serialisation solution for cartons
Optimize your packaging line with a versatile serialisation solution designed t...
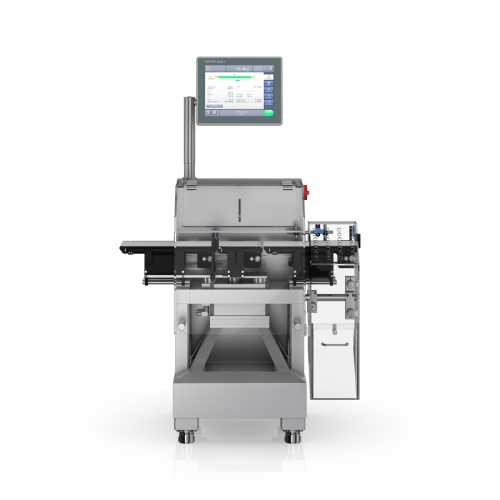
High-speed checkweigher for dynamic weighing
Achieve precision and consistency in high-speed production environments with ...
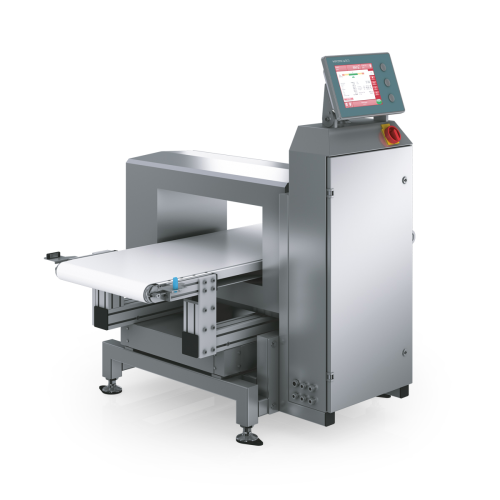
Checkweigher and metal detector for heavy loads
Streamline your inspection process by combining precision weighing with co...
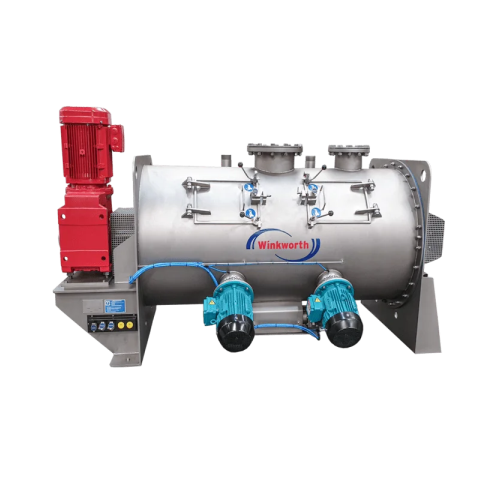
High-speed mixer for industrial mixing applications
Achieve rapid, consistent mixing and dispersion across diverse materi...
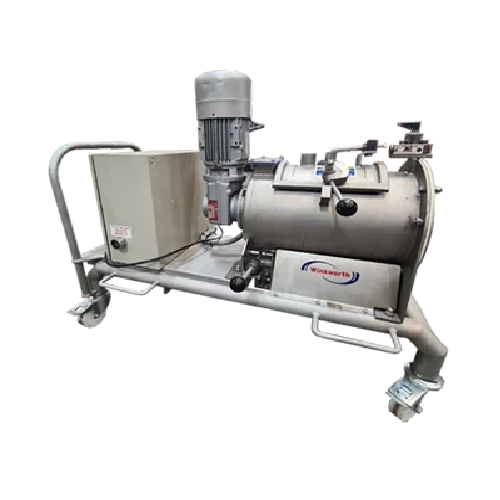
Industrial mixers for hire
Optimize your production line with versatile mixers designed for precision blending, heating, and...
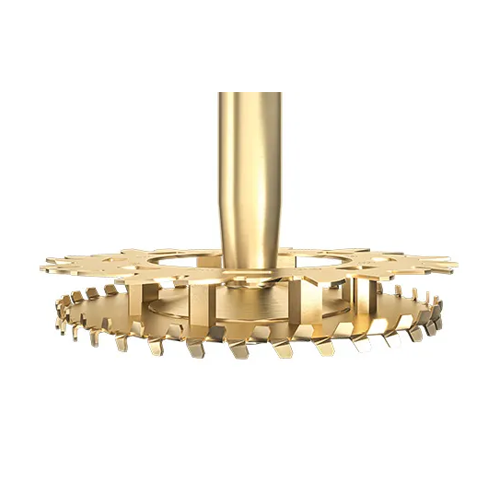
Mixer for high viscosity products
Enhance your production line with a versatile solution designed for precise mixing and di...
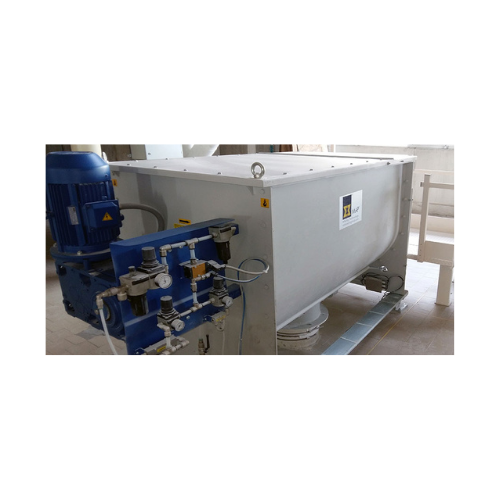
Single-shaft ribbon blender for homogeneous mixing
Achieve high-quality, precise blending of delicate and temperature-sen...
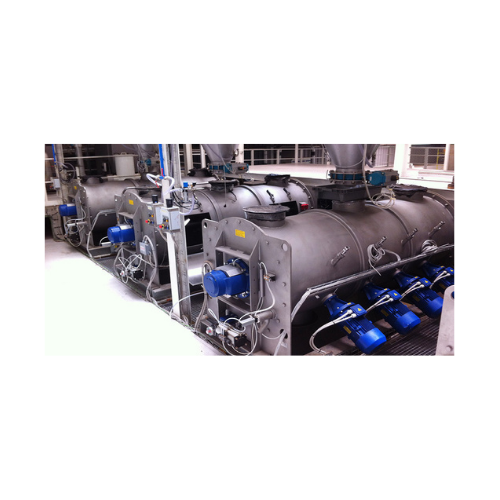
Batch-type single shaft mixer for industrial mixing
Achieve precise and uniform mixing with high-speed, single-shaft mixe...
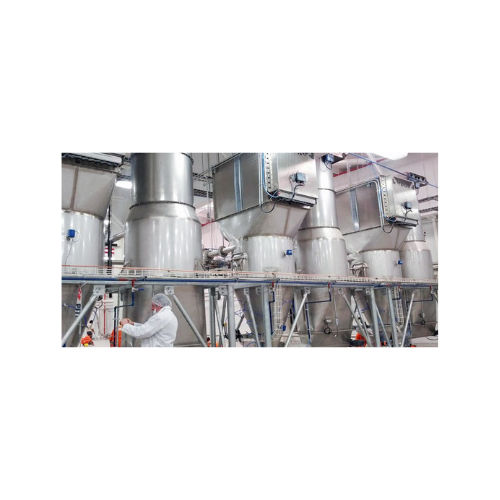
Atex-certified flanged polygonal dust collectors
Ensure dust control and compliance in explosive environments with our com...
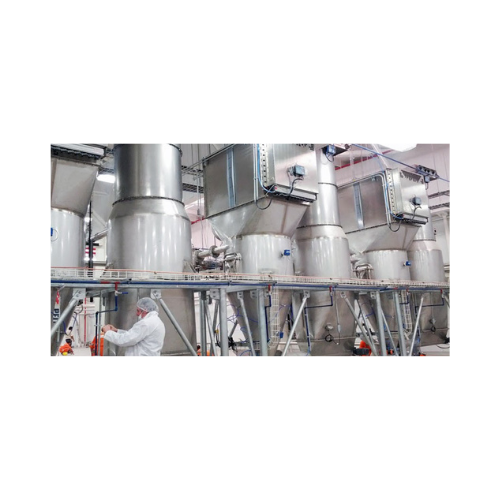
Industrial dust collection system for air filtration
Optimize air quality in your production line with this compact dust ...
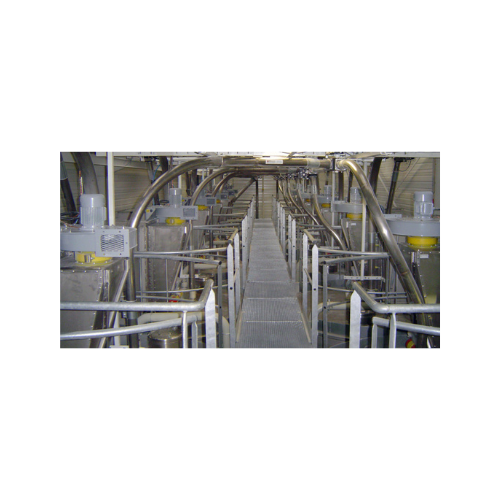
Atex certified flanged round dust collectors
Designed for potentially explosive environments, these flanged round dust col...
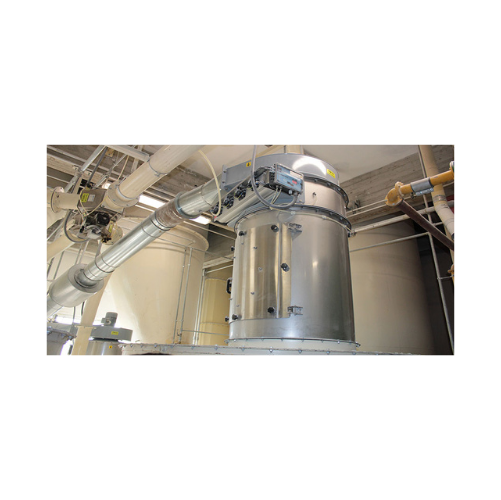
Food-grade round dust collectors
Maintain a clean production environment with this food-grade dust collector, designed to ma...
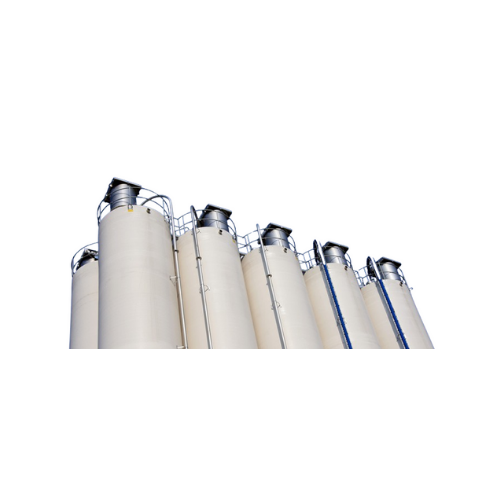
Flanged round dust collectors for industrial air filtration
Optimize your industrial processes with a dust collection sy...
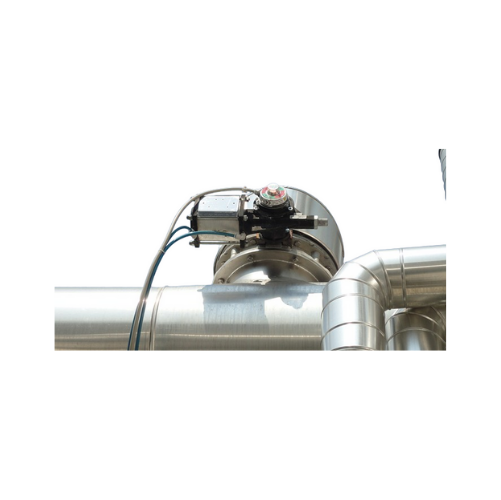
Fit-frame butterfly valves for dry bulk solids
Achieve precise control and minimize contamination in your dry bulk materia...
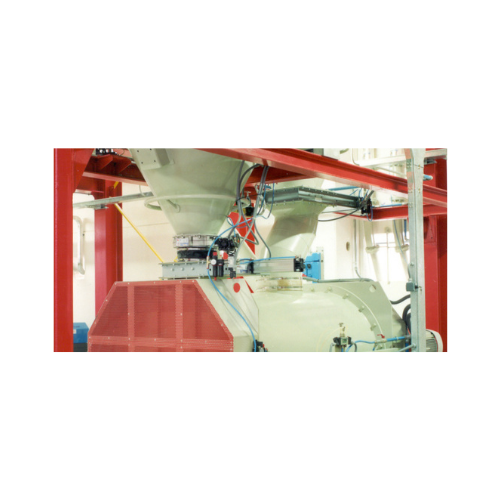
Butterfly valves for powders and granules
Ensure precise flow control and reliable sealing for gravity-fed or pneumatic sy...
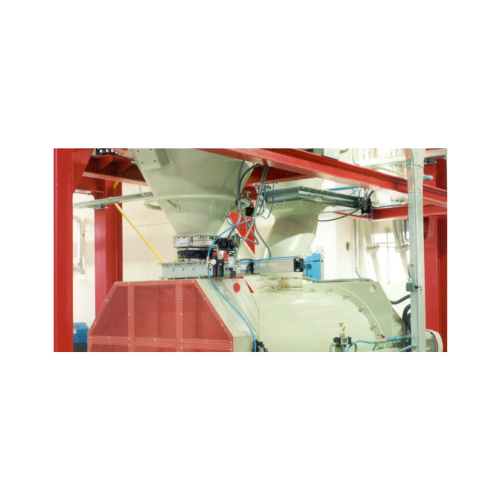
Butterfly valves for powder and granular material handling
Experience seamless material control with advanced butterfly ...
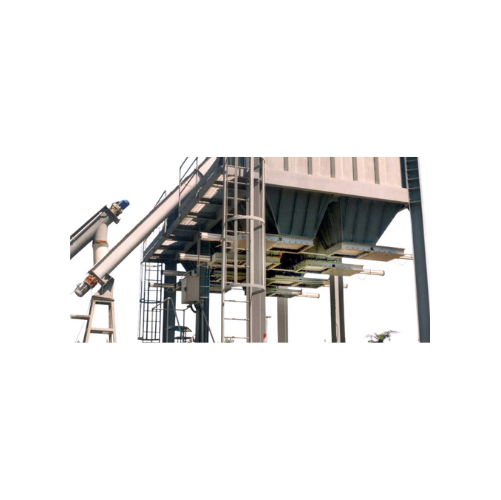
Industrial slide valve for heavy-duty applications
When managing gravity material flow in abrasive environments, achievin...
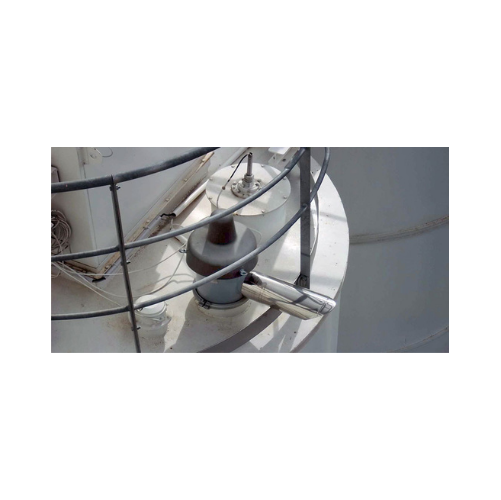
Membrane pressure relief valve for silos and bins
Ensure silo safety with our valve that instantly balances internal pres...
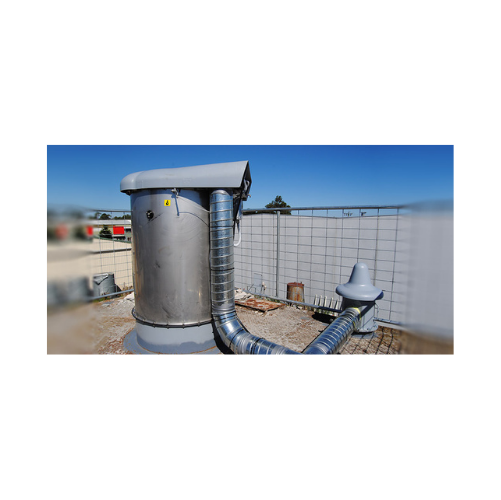
Low profile slide valve for controlling powder flow
Optimize your powder and granule flow management with precision-engin...
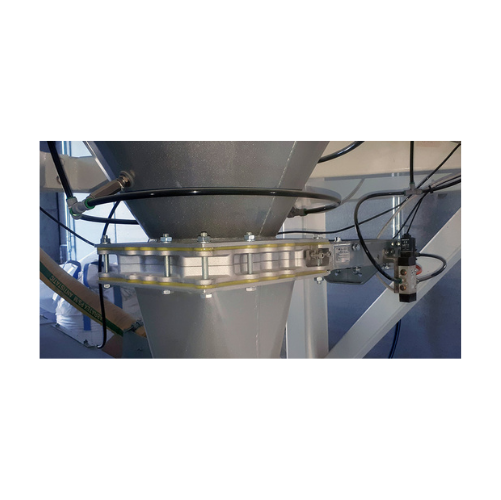
Slide valves for flow interception in powder and granular materials
Effectively manage the flow of powdery and granular...
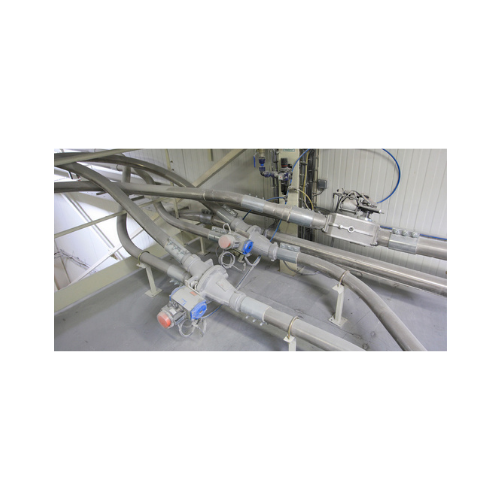
Flap diverter valves for pneumatic conveying
Streamline material flow in your pneumatic conveying system by effortlessly r...
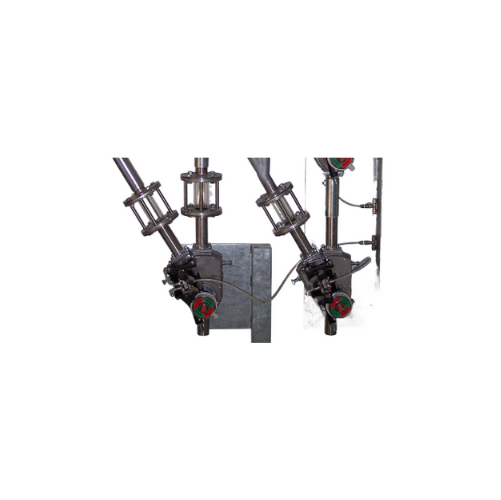
Diverter valves for pneumatic conveying lines
Experience precise flow control in pneumatic conveying with diverter valves ...
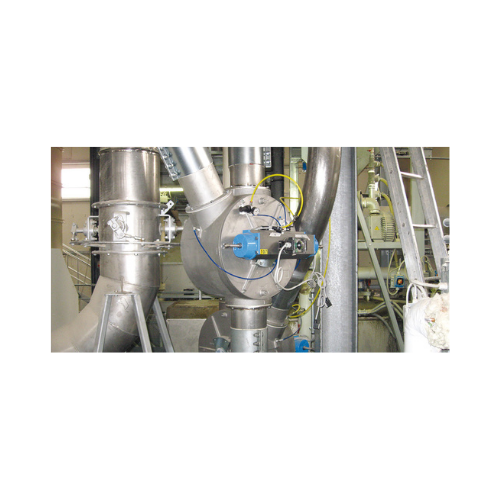
Drum-type diverter valves for pneumatic conveying
Optimize your pneumatic conveying system by effortlessly controlling th...
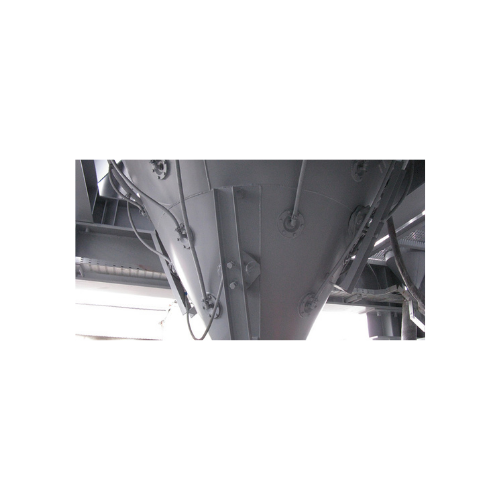
Vibro-aerators for bulk solids discharging
Optimize your powder flow and ensure consistent discharge with this advanced ae...
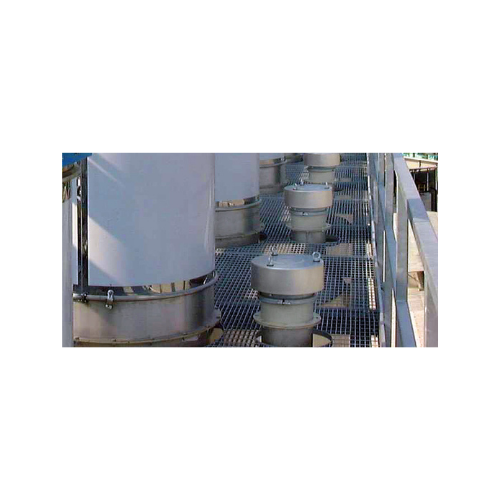
Silo overfill protection valves
When abnormal pressure threatens your silo’s integrity, reliable pressure relief becom...
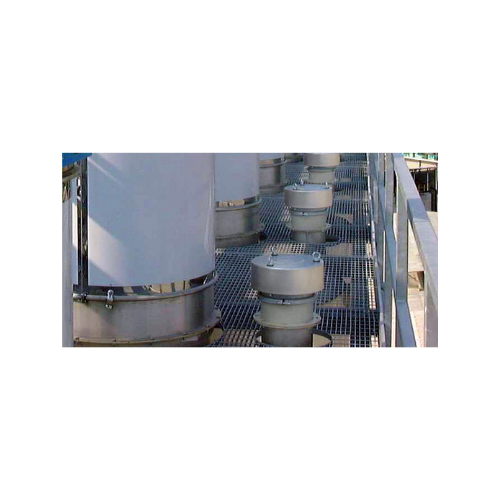
Spring-loaded pressure relief valves for silo overfill protection
Ensure safety and prevent costly overfills with press...
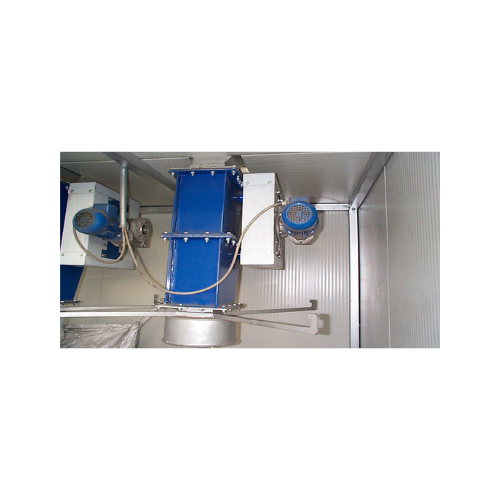
Double dump valves for high temperature granules
Ensure precise material flow and withstand extreme temperatures with thes...
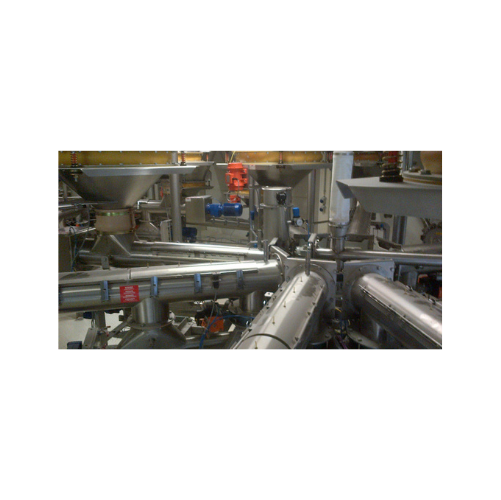
Stainless steel tubular screw conveyor for bulk solids handling
Ensure precise material handling with stainless steel tu...
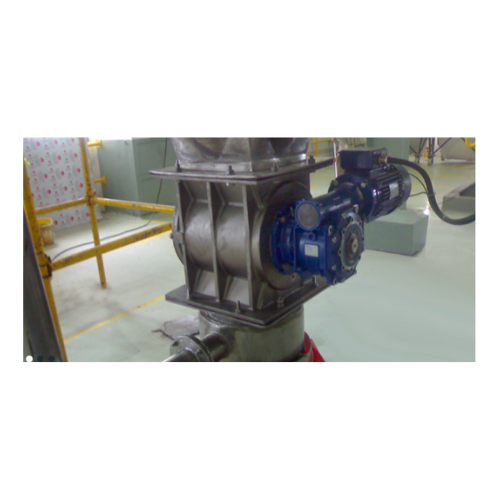
Drop-through rotary valve for powder and granular material feeding
Achieve precise control in discharging and feeding p...
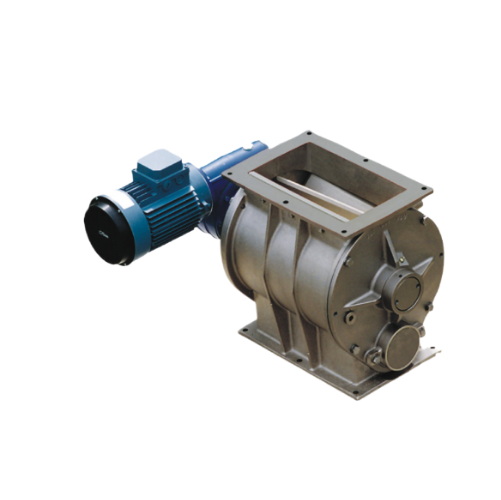
Drop-through rotary valve for precise powder and granule feeding
Ensure precise material handling with this drop-through...
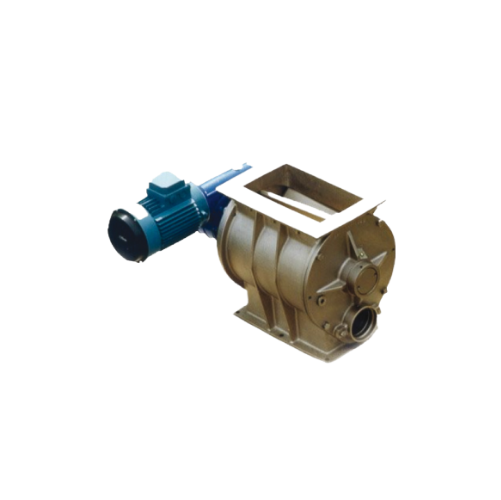
Blow-through rotary valves for pneumatic conveying
Optimize your pneumatic conveying systems with high-efficiency blow-th...
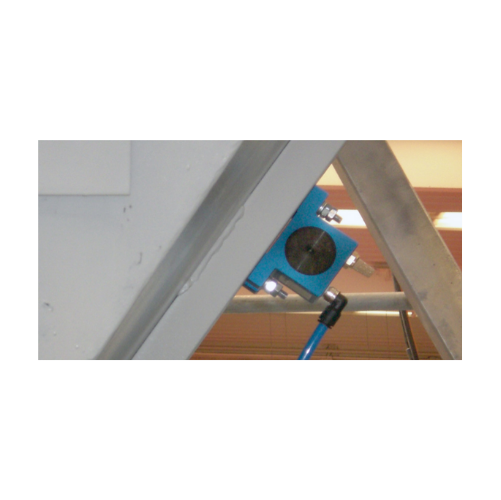
Rotary ball vibrators for fine powders and granular materials
Ideal for preventing material build-up and blockages, thes...
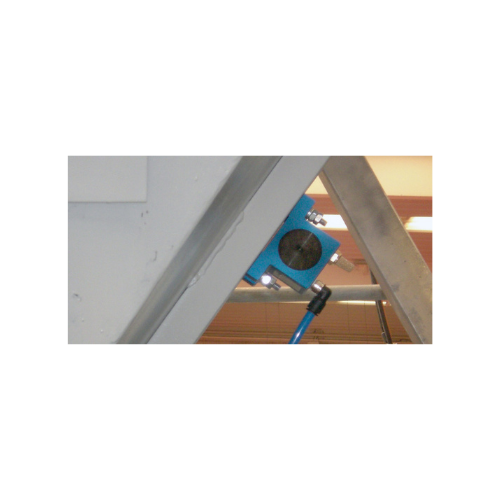
Rotary ball vibrators for aggregate reclaiming
Enhance efficiency in your production line with a solution that optimizes t...
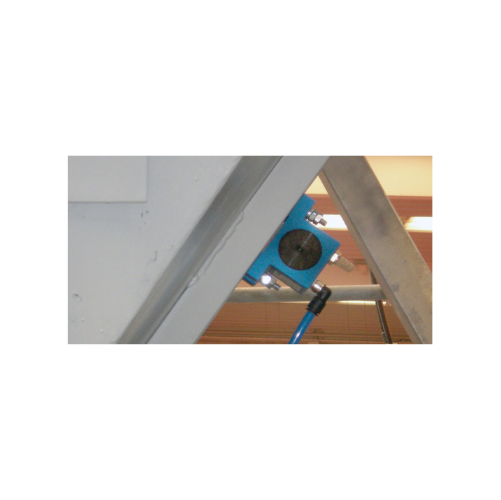
Rotary ball vibrators for bulk solids discharging
Ideal for enhancing material flow, this equipment efficiently handles f...
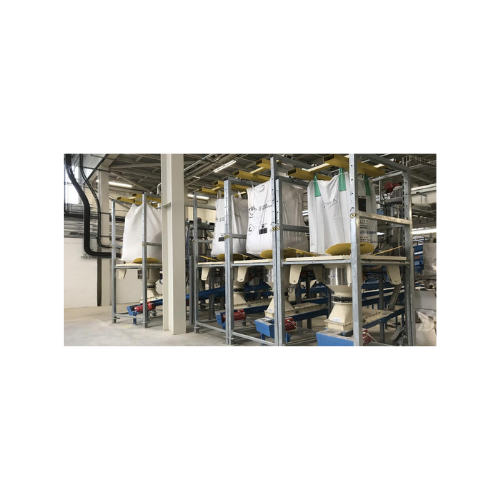
High flow rate Fibc dischargers for wastewater treatment
Optimize your material handling with efficient, dust-proof disch...
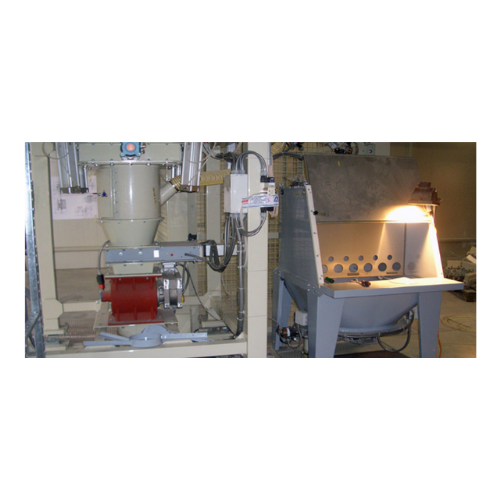
Manual bag opener for bulk solids discharging
Effortlessly open and empty bags while containing dust emissions, ensuring a...
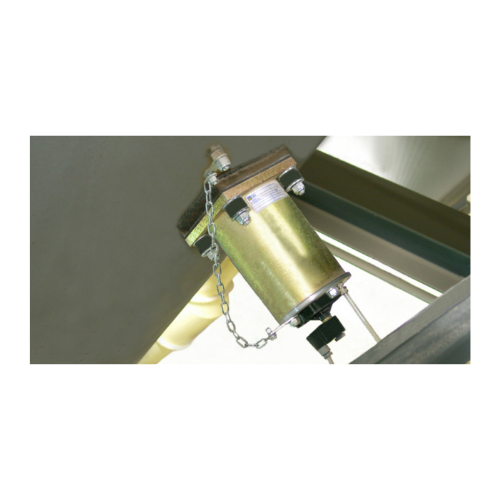
Single impact pneumatic hammers for flow aids
Combat material clogs and ensure smooth flow in your production line with pn...
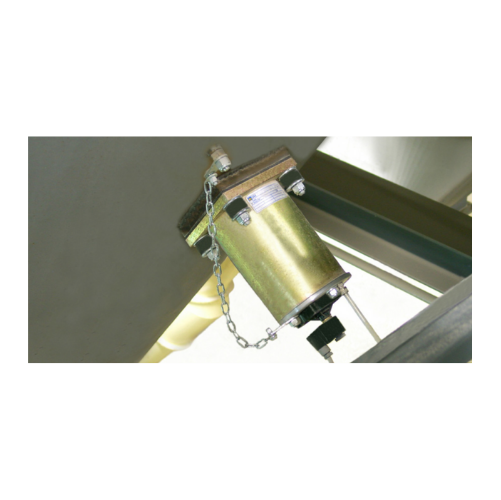
Pneumatic hammers for bulk solids discharging
Optimize your production efficiency and solve material flow challenges with ...

Pneumatic hammers for aiding material flow
Optimize material flow and eliminate blockages in your processing line with pne...
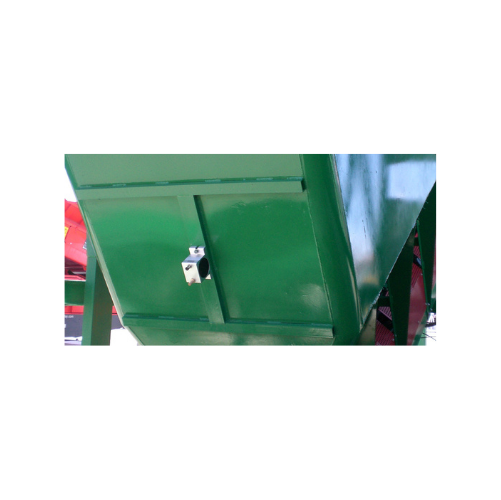
Industrial vibrator for high-frequency vibration
Achieve efficient material flow and compaction across various production ...
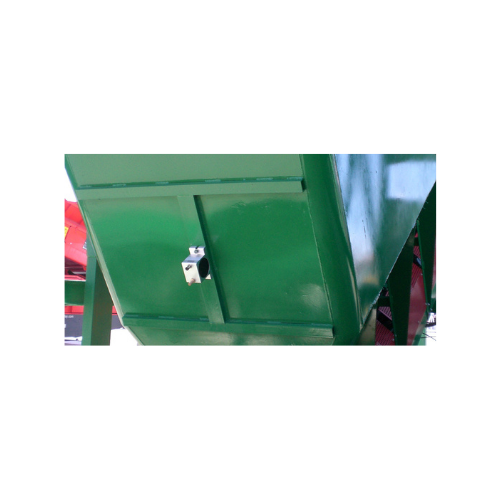
Rotary turbine vibrators for bulk solids discharging
Enhance the efficiency of material handling with high-speed, low-noi...
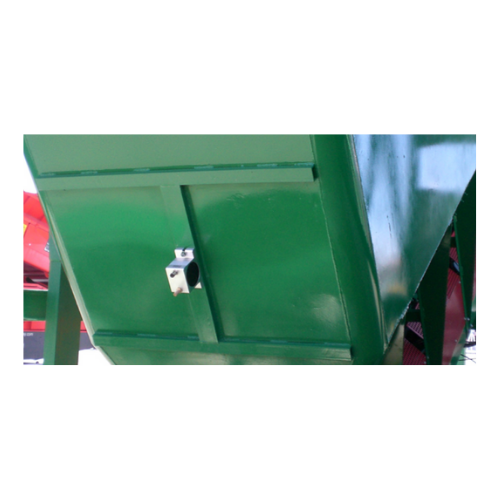
Rotary turbine vibrators for material flow aid
Optimize your production efficiency with high-speed, silent operation vibra...
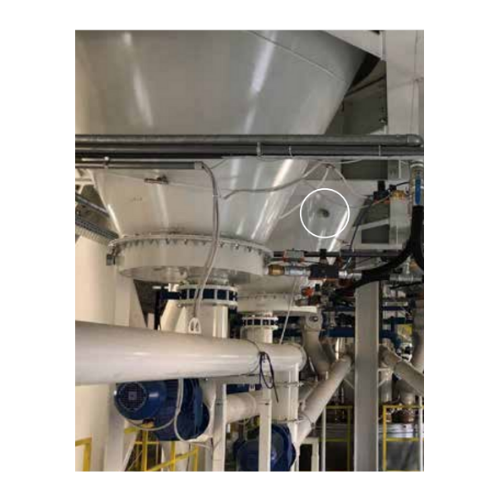
Continuous impact vibrators for bulk material removal
Combat material flow issues like bridging and rat-holing with our i...
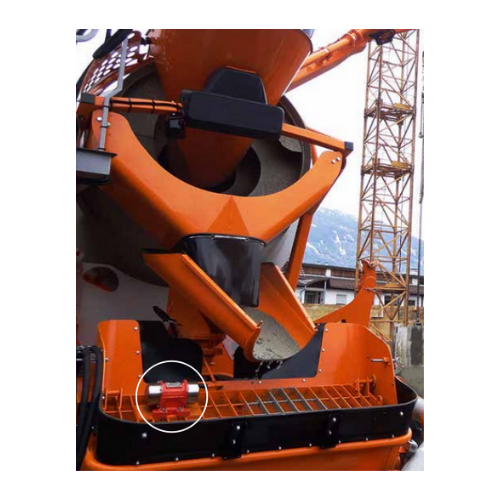
Continuous impact vibrator for aggregate reclaiming
Tackle material flow challenges head-on by preventing common issues l...
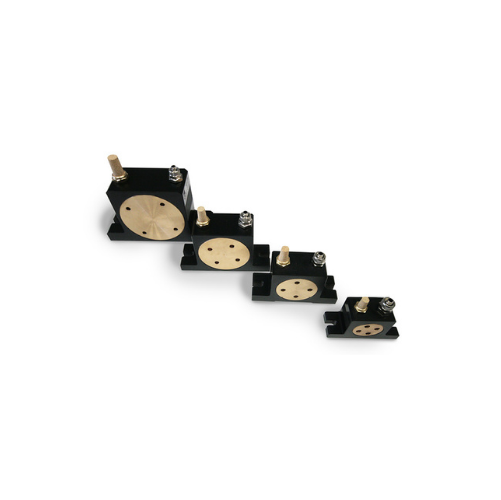
Rotary roller vibrators for material flow assistance
Enhance material flow efficiency in your production line with high-f...
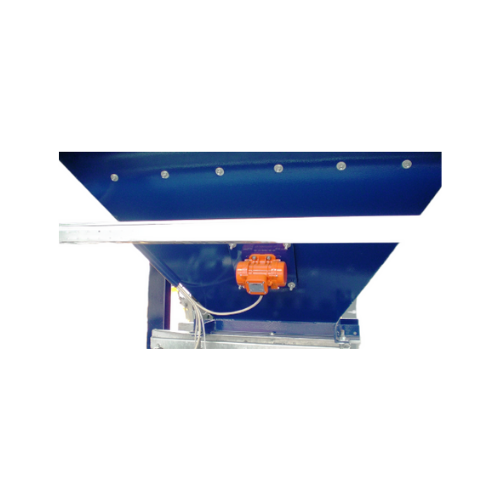
External electric motovibrators for industrial applications
Optimize material movement and improve discharge efficiency ...
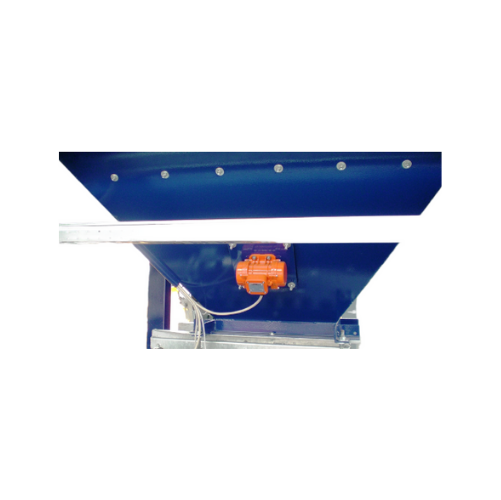
External electric motovibrators for bulk solids conveying
Enhance material flow efficiency and solve challenging dischar...
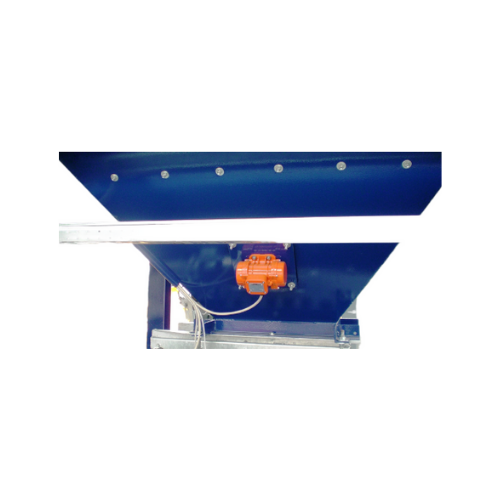
External electric motovibrators for industrial material flow
Experience enhanced material flow and precise material disc...
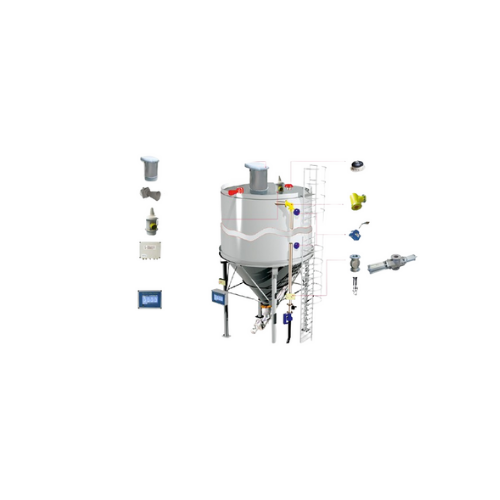
Silo overfill protection system
Prevent silo overfilling and excess pressurization with a system designed to safeguard silos...
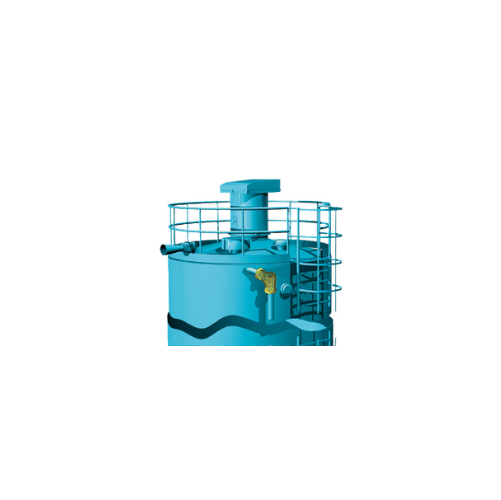
Silo overfilling safety system
Ensure safe silo filling with our system that prevents overfilling and excess pressurization,...
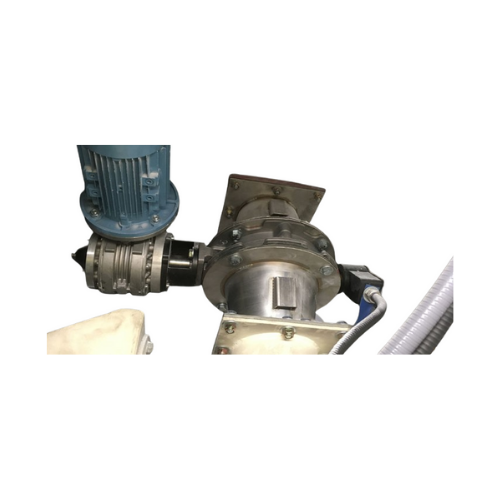
Lump breaking feeder valve for bulk material processing
Tackle bulk material flow challenges with a feeder valve engineer...
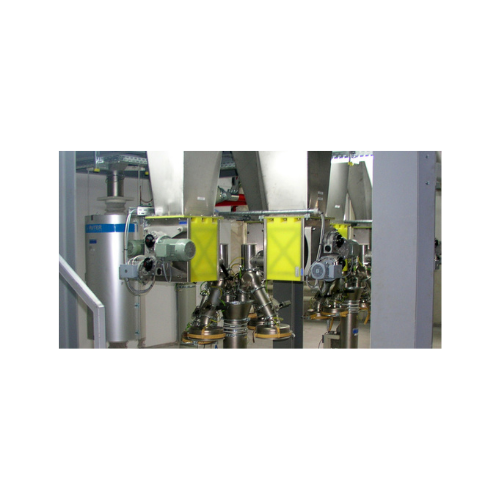
Micro-batch feeders for powder and granular material
Struggling with clog-prone powders? Gain precise control and consist...
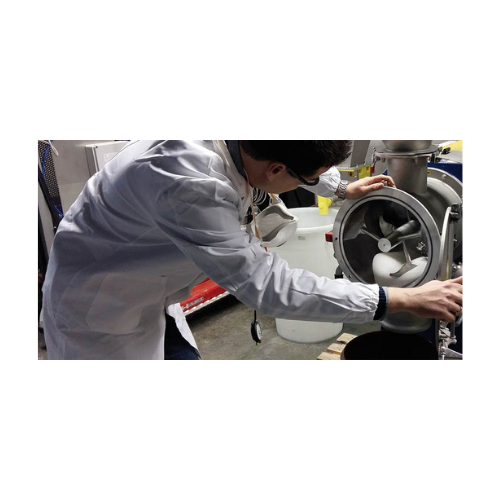
Laboratory batch mixer for small scale production
Achieve rapid and reproducible mixing results with this laboratory batc...
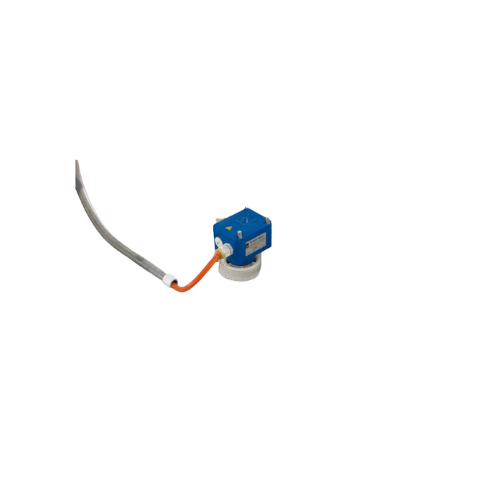
Bin level indicator for bulk solids
Ensure precise material level detection across your production processes, minimizing th...
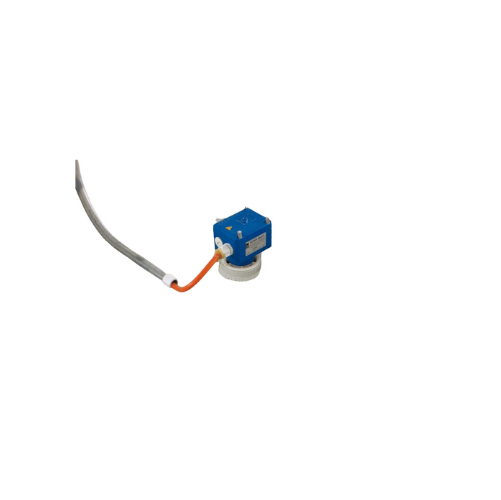
Bin level indicators for wastewater treatment
Ensure reliable material level monitoring in your silos and hoppers with ILT...
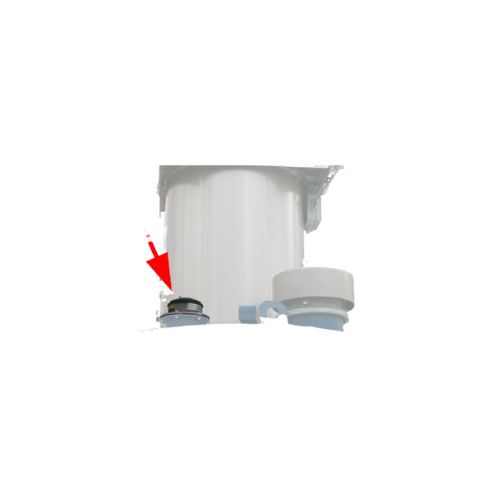
Electronic pressure meter for silo safety
Ensure the safety of your silos by efficiently monitoring internal pressure chan...
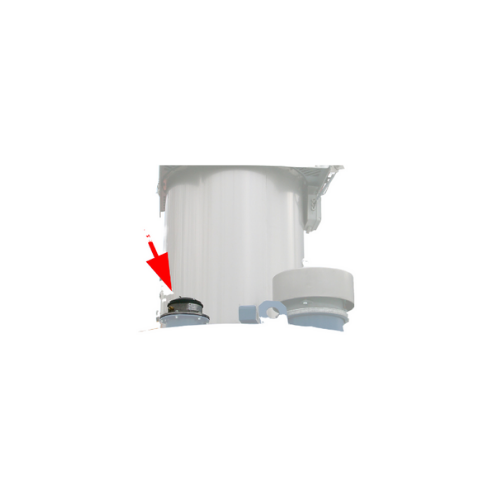
Electronic pressure meters for silo safety monitoring
Ensure precise pressure management in your systems with this advanc...
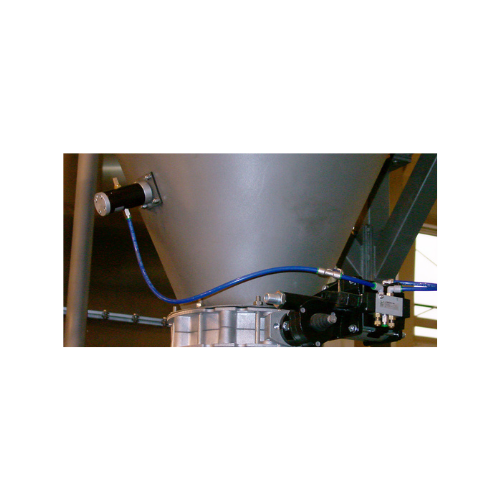
Cushioned pneumatic linear vibrators for bulk solids
Combat material bridging and rat-holing with silent vibratory techno...
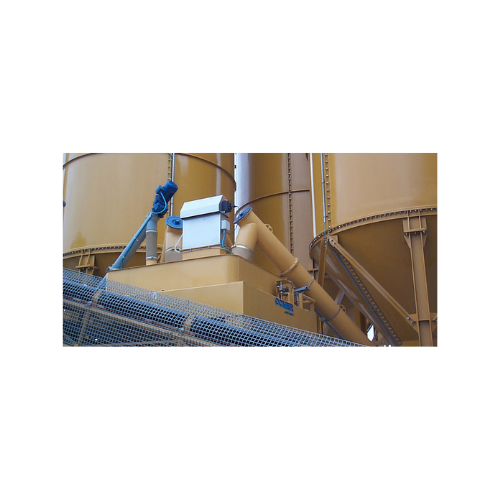
Hopper venting filter for efficient dust filtration
Achieve superior dust control and efficient material handling with a ...
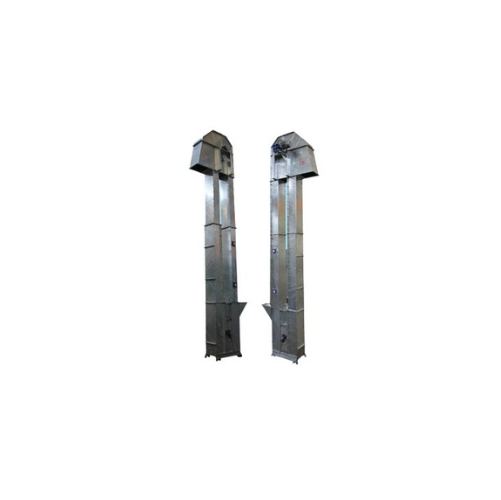
Vertical conveyor for fine aggregates and minerals
Optimize the handling of abrasive materials with a vertical conveying ...
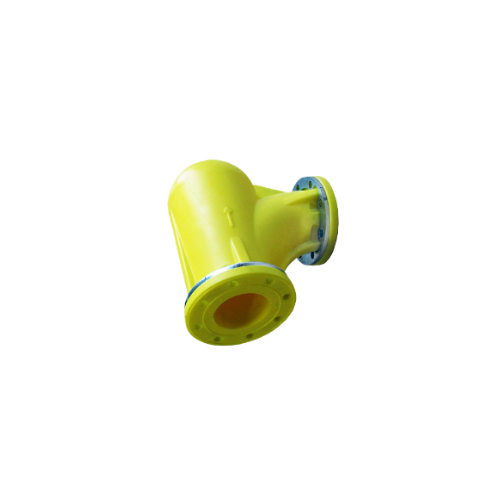
Anti-wear elbows for pneumatic conveying systems
Reduce wear and extend the lifespan of your pneumatic conveying systems w...
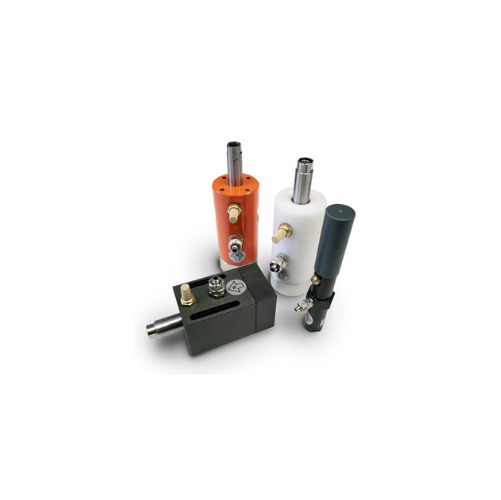
Cushioned pneumatic vibrators for coarse particle materials compaction
Enhance your material flow and compaction proces...
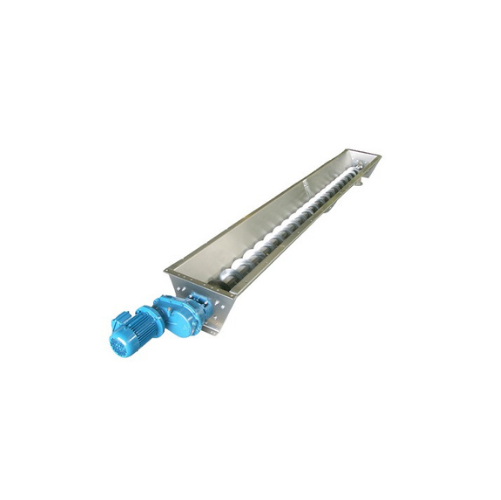
Stainless steel trough screw conveyor
Ideal for precise handling of powdery and granular materials, this solution ensures m...
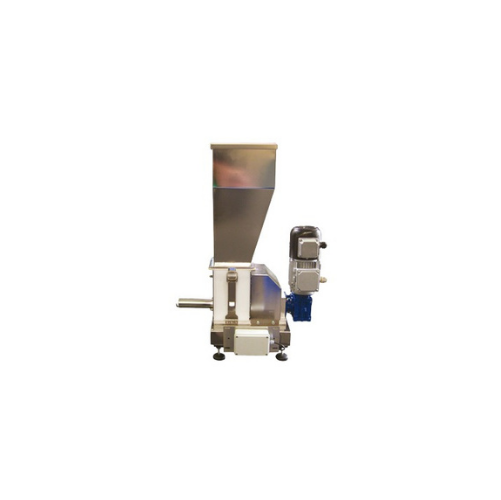
Loss-in-weight screw feeder for precise powder dosing
Achieve high precision in continuous dosing with this advanced scre...
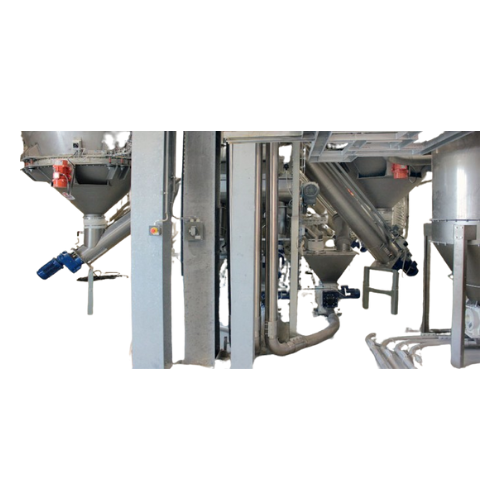
Food-grade bin activator for hygienic bulk solids discharge
Achieve consistent material flow and avoid contamination wit...
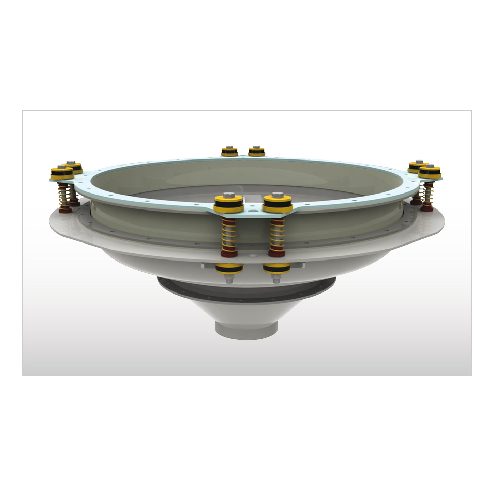
Industrial bin activator for smooth material flow
Enhance your material handling process with a solution that ensures con...
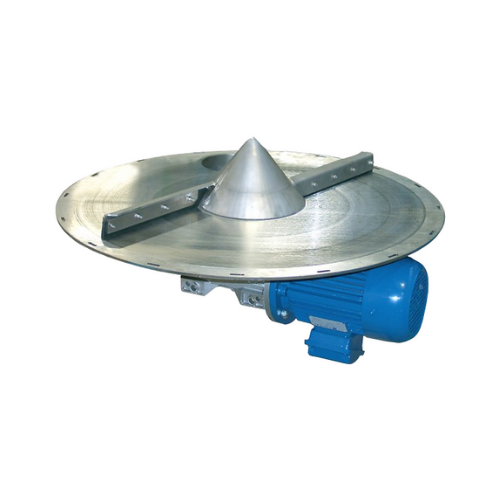
Rotary bin discharger for bulk solids
Efficiently manage bulk solids with a rotary bin discharger that minimizes residue an...
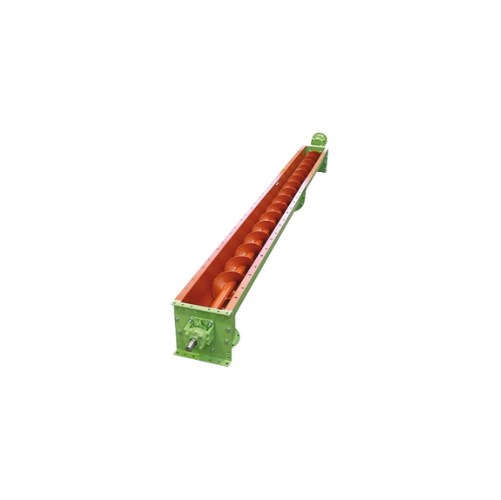
Trough screw conveyors for powdery and granular materials
Optimize your material handling process with a flexible screw ...
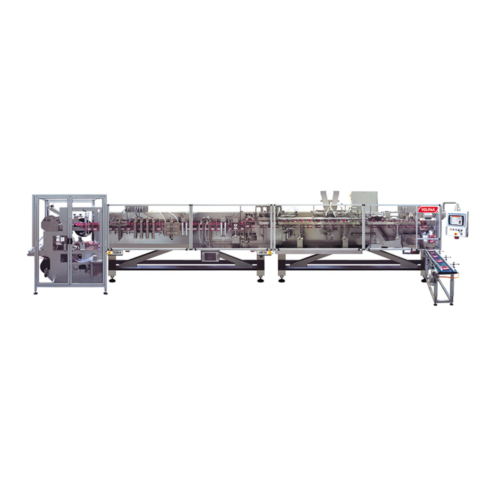
Stand-up pouch filling and sealing system
For packaging lines that demand quick, efficient, and flexible pouching, this hi...
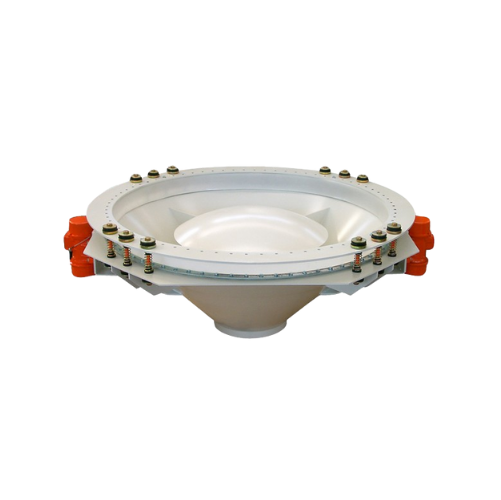
Vibratory hopper for bulk solids discharge
Ensure consistent material flow and prevent bridging in storage silos with this...
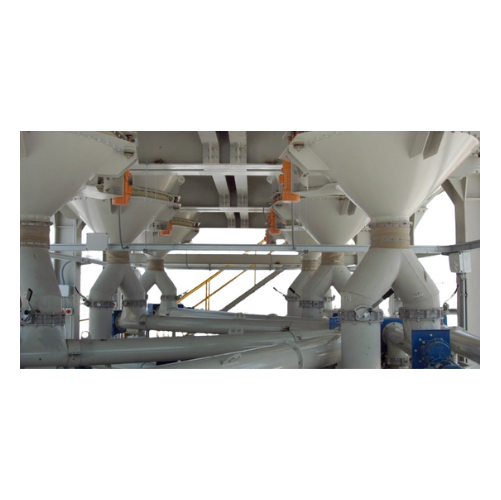
Bin activator for silo and hopper discharge
Ensure optimal material flow and prevent blockages in your storage systems wit...
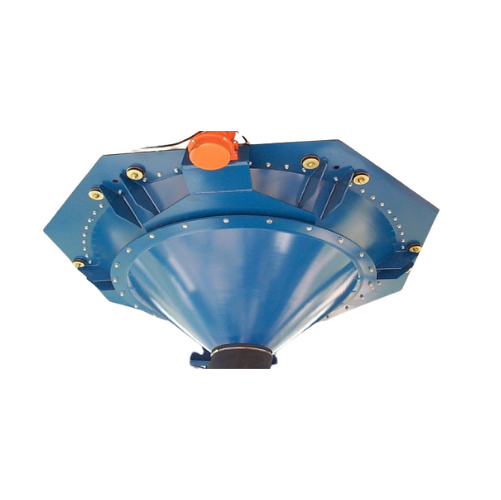
Vibratory outlet hopper for bulk solids discharge
Reduce material handling challenges with highly efficient vibration tec...
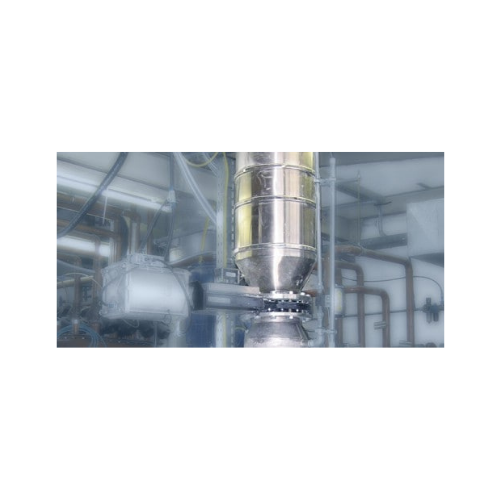
Powder locks for safe bulk material handling
Ensure containment and prevent contamination while processing sensitive bulk ...
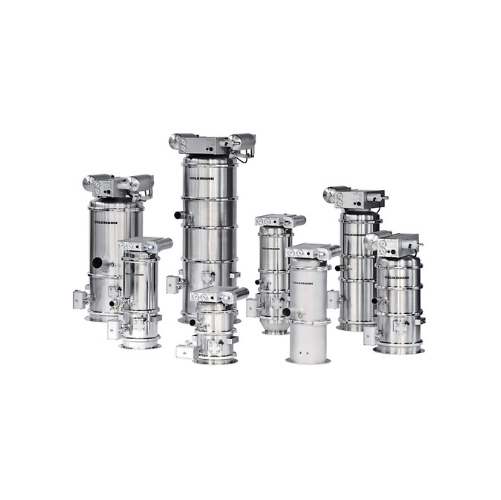
Powder handling vacuum conveyor system
Streamline your material transfer with a versatile vacuum conveyor system that ensur...
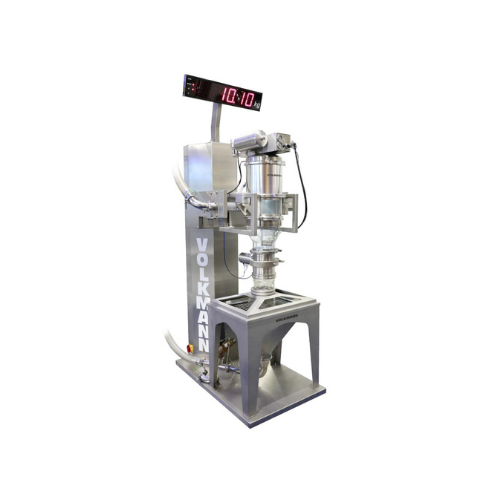
Integrated conveying and weighing system for bulk materials
Achieve precise material management with a solution that sea...
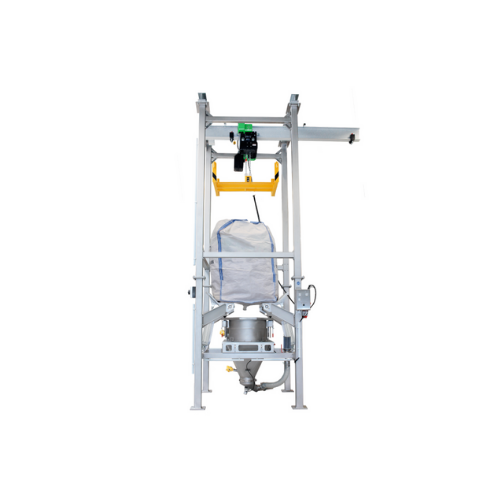
Big-bag unloading station for bulk materials
Facilitate seamless integration into your production line with efficient bulk...
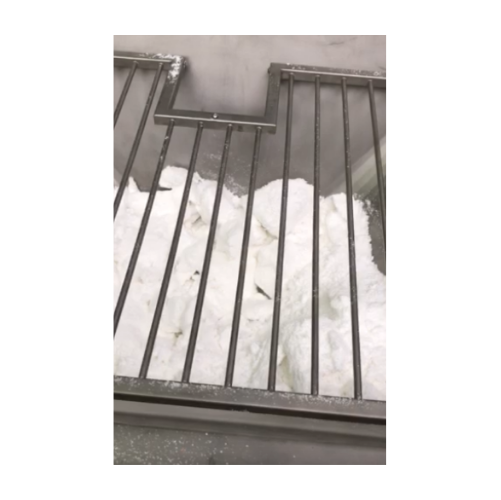
Lump breaker for breaking agglomerates and lumps
Effortlessly break down challenging agglomerates and clumps to ensure smo...
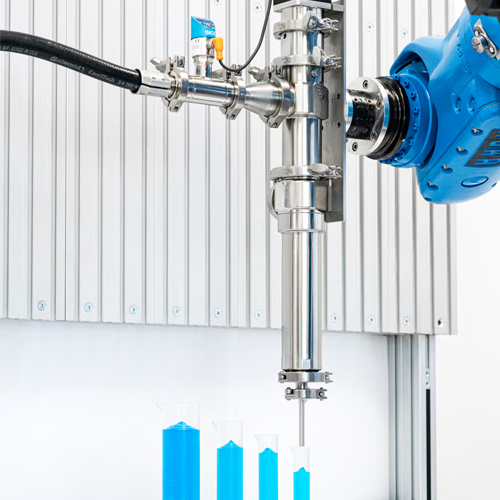
Dosing pump for liquids and pastes
Achieve precise dosing and filling of liquids and pastes with flexibility in dosing volu...

Dosing and filling pump for liquids and pastes
Achieve precise dosing and filling of liquids and pastes with compact, hygi...

Pressure monitoring solution for dosing processes
Optimize your production line by ensuring precise pressure monitoring, ...
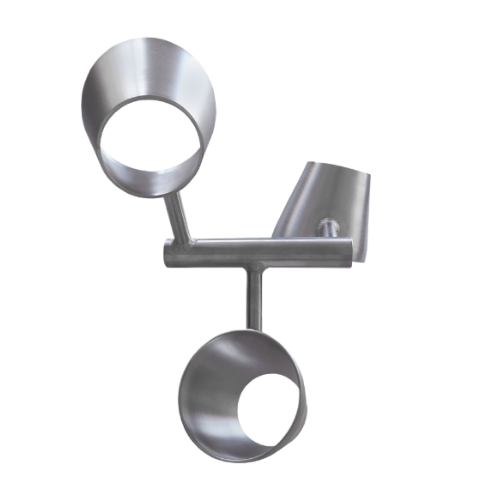
Side-mount agitator for large tank mixing
Achieve efficient mixing in large tanks with reduced energy consumption by lever...
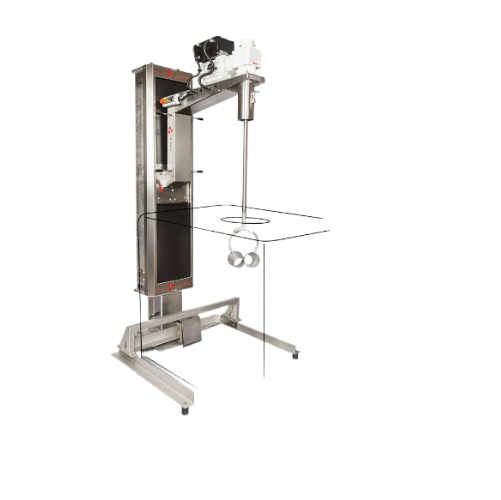
Adjustable integral stand mixer for transport containers
Achieve optimal mixing and stirring in diverse transport contain...
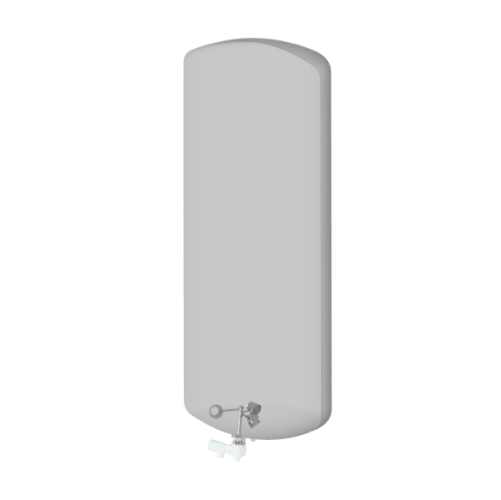
Tank agitator for low-level installation
Efficiently optimize your mixing processes with a bottom-entry tank agitator, desi...
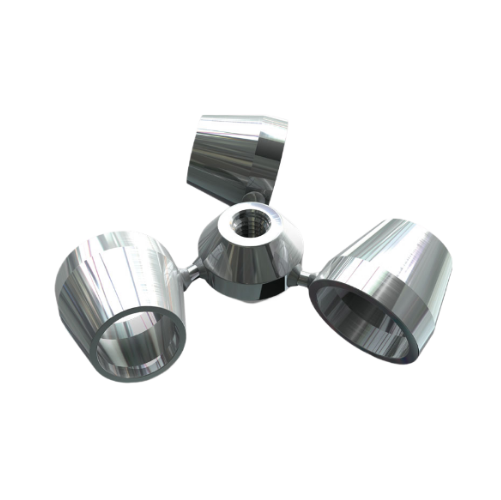
Homogenizer for low to medium viscosity media
Achieve uniform mixing and prevent air entrapment in low to medium viscosity...
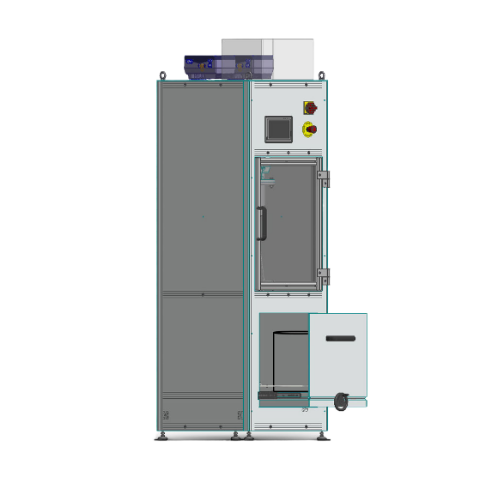
Semi-automatic stands blender for facade paints
Optimize your paint production with a versatile stirring system designed f...
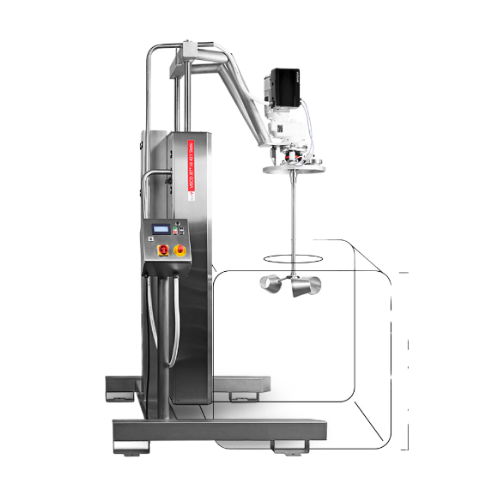
Industrial mixer for product-critical processes
When dealing with high-hygiene requirements and complex mixing tasks acros...
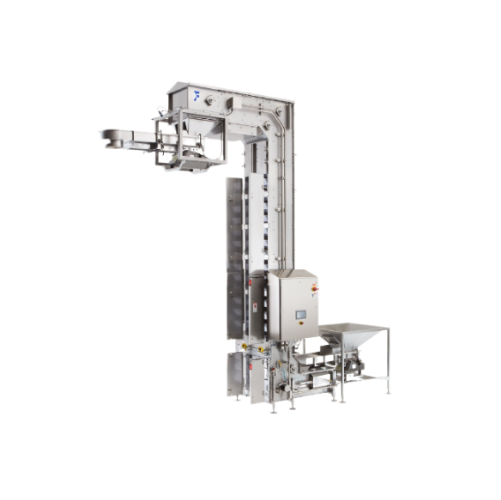
Automated infeed and outfeed systems for packaging lines
Streamline your production line by integrating reliable infeed a...
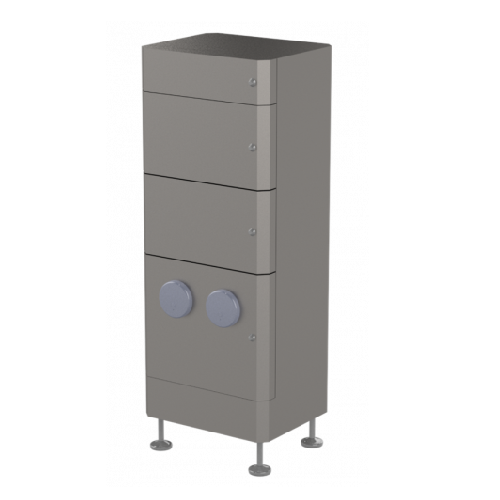
Supply air filter systems for industrial cleanrooms
Ensure critical air purity and operational safety in sensitive enviro...
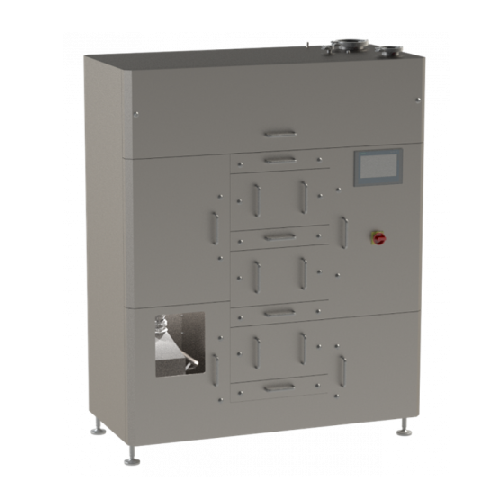
Compact dust extractors for cleanroom applications
Ensure safe and efficient dust extraction in cleanroom environments wi...
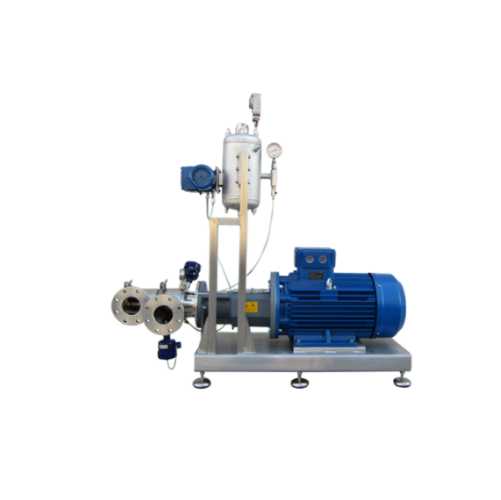
In-line mixer for liquid-liquid and solid-liquid processes
Optimize your mixing operations with an efficient solution th...
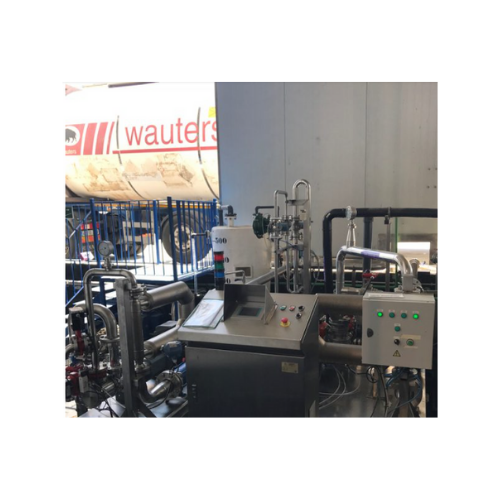
Complete mixing solutions for food, chemical, and cosmetic industries
Enhance your production line with precision mixin...
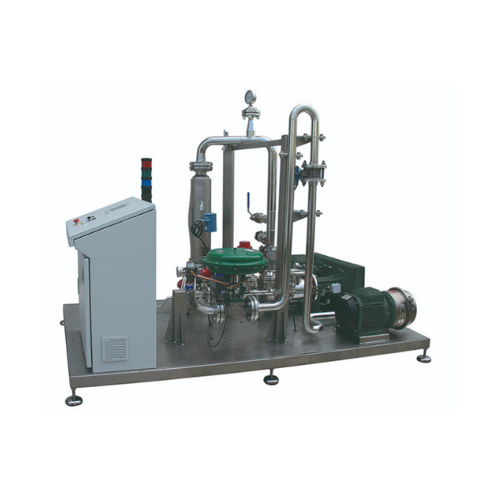
Complete mixing solution for food, cosmetics, and chemical industries
Optimize your production line with a system that ...
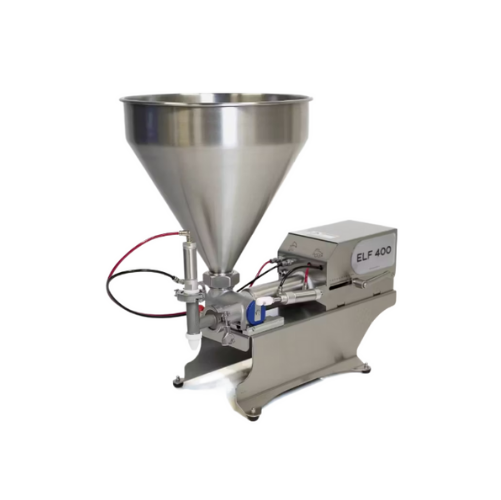
Single piston food filler
Achieve precise portioning and consistent product flow with a versatile solution perfect for handl...
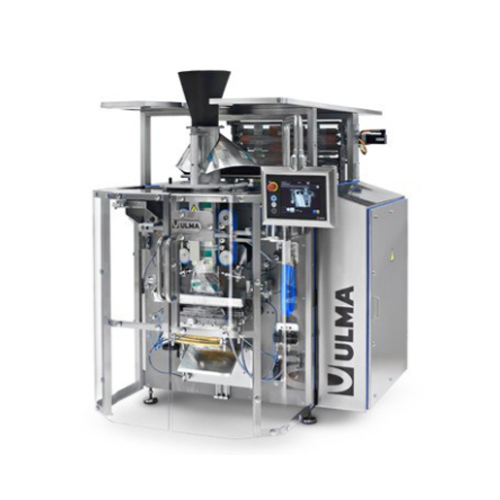
Vertical packaging system for medium-high speed applications
Optimize your packaging line with a system that delivers pr...
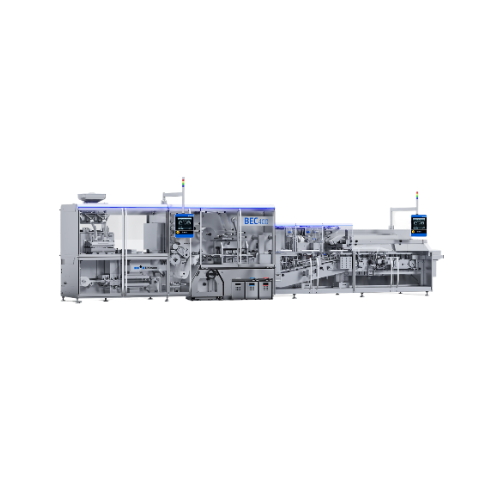
Fully automated packaging lines
Streamline your production with versatile packaging lines designed to handle a range of good...
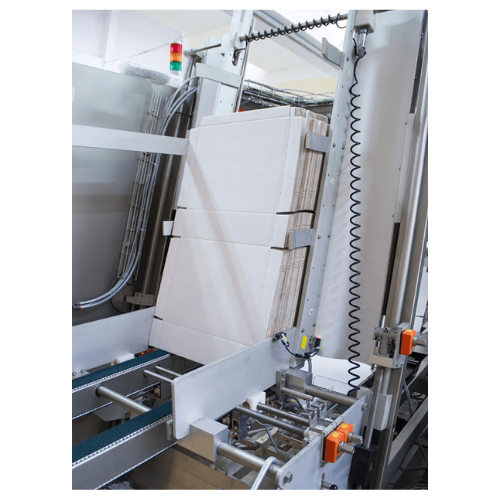
Automated wrap-around packaging system
Streamline your packaging process with a system that efficiently groups, folds, and ...
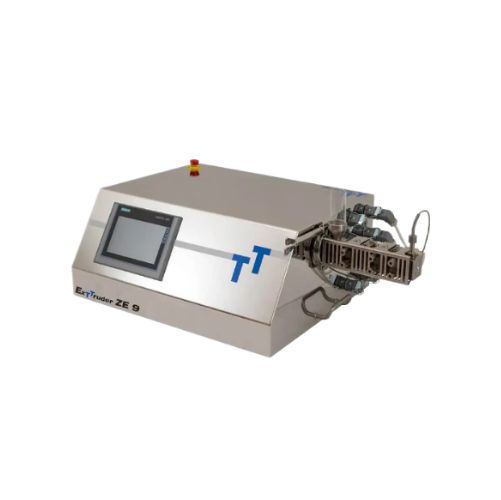
Mini extruder for small batch processing
Ideal for precise control in experimental formulations, this mini extruder streaml...
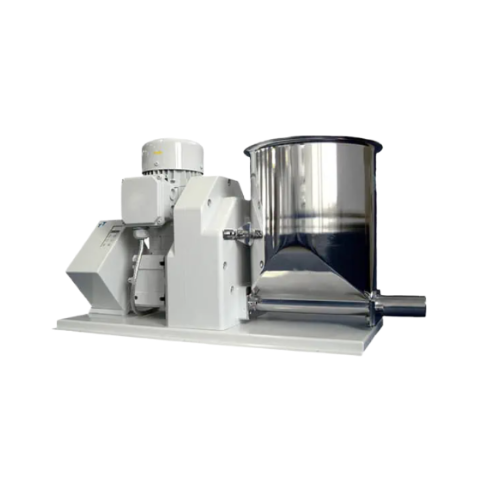
Volumetric twin screw feeder for powder and micro-granules
Optimize your production flow by ensuring consistent and prec...
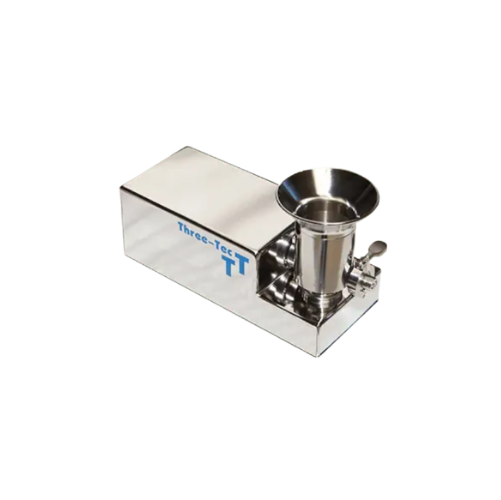
High-precision feeding system with load cell and weighing electronics
Achieve unparalleled accuracy in dispensing powde...
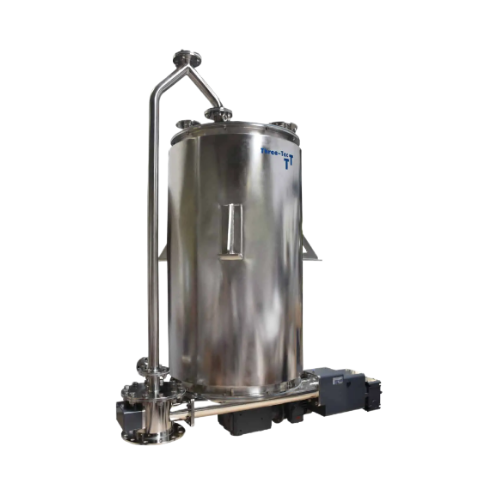
Twin screw feeder for bulk material handling
Optimize your bulk material processing with a solution designed for precise f...
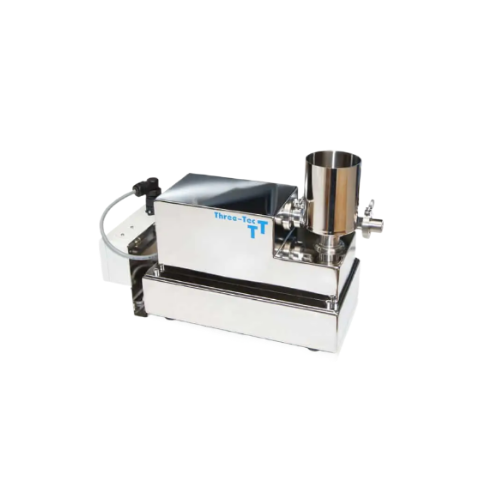
Precise volumetric or gravimetric powder feeder
For precise feeding of challenging powders prone to clumping and bridging,...
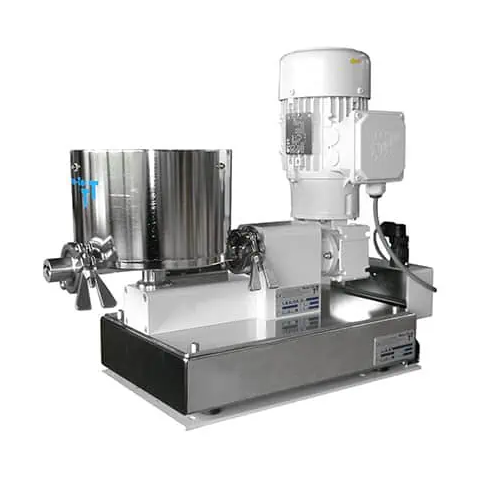
Volumetric flat-bottom twin-screw feeder for powders
When handling powders prone to clumping, a reliable feeder ensures u...
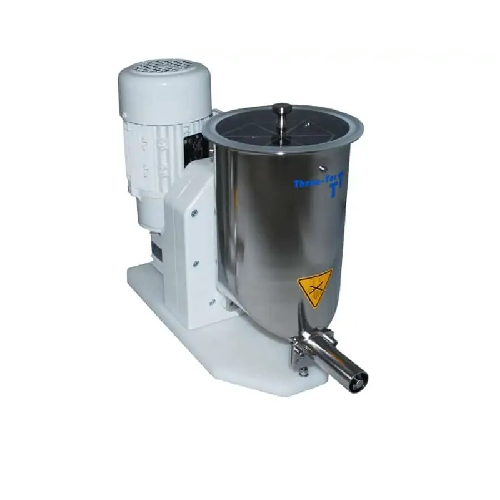
Volumetric single-screw feeders for free-flowing products
Achieve precise and continuous feeding of free-flowing powders...
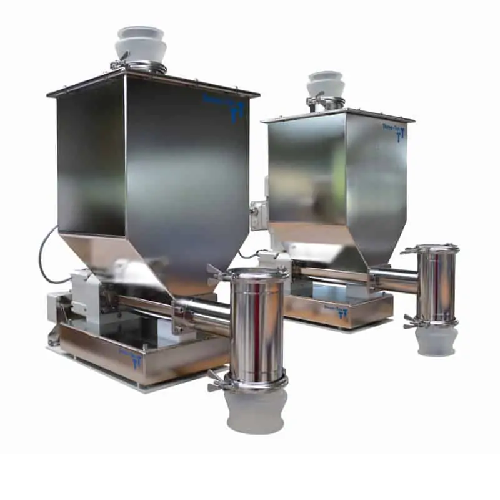
Gravimetric single-screw feeder for free-flowing products
Optimize your dosing precision for powders and granulates with...
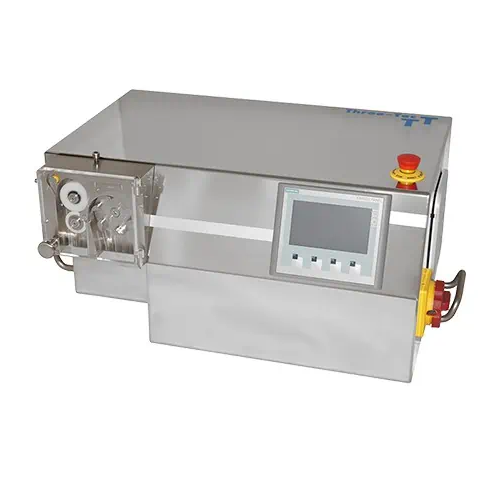
Granulator for processing strands into granulate
Optimize granule production with precise control over pellet size and ext...
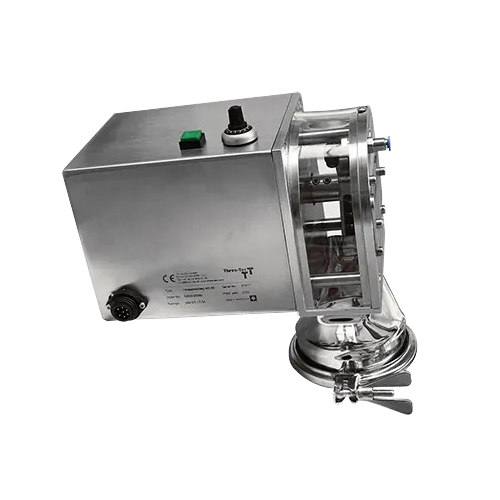
Hot cutter for processing extrudate into pellets
Efficiently transform extrudates into precise pellet sizes, enhancing you...
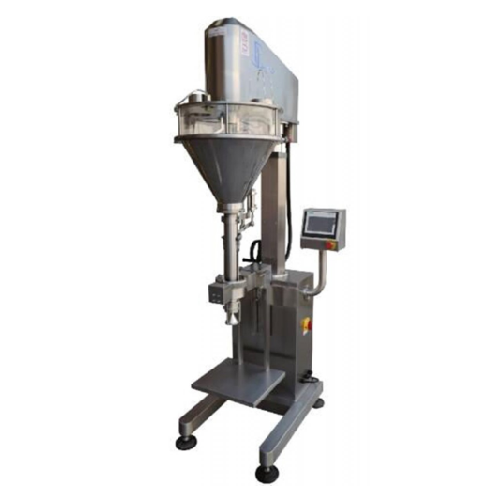
Gravimetric auger filler for powder weighing
Achieve precise powder filling with this gravimetric auger solution, ensuring...
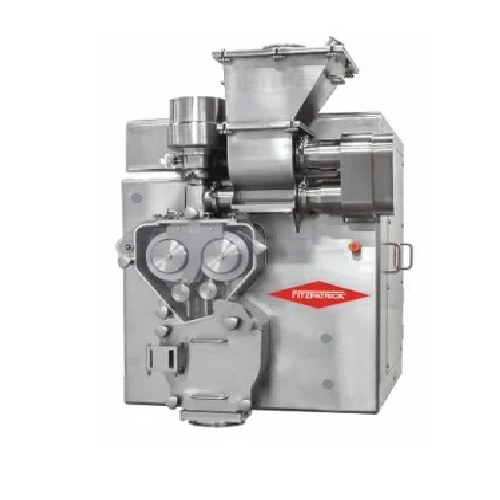
Roller compactors for dry granulation
Optimize your powder processing with advanced roller compaction, ensuring consistent ...

Automatic liquid filling solutions for various containers
Ensure precise liquid packaging for diverse container types, e...

Pneumatic syringe dosing system
Streamline your liquid dosing process with precision and efficiency, ensuring each applicati...
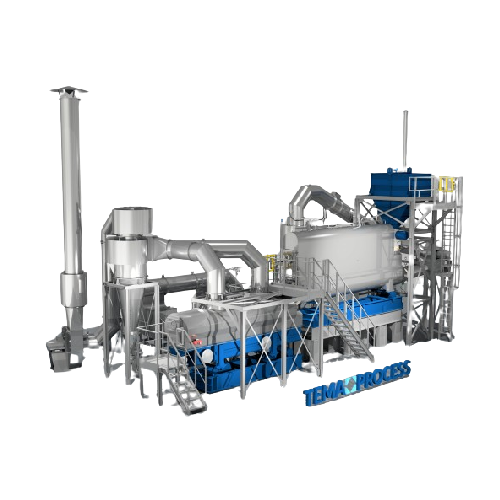
Vibrating fluid bed dryer for bulk materials
Ensure efficient moisture removal and thermal processing with this fluid bed ...
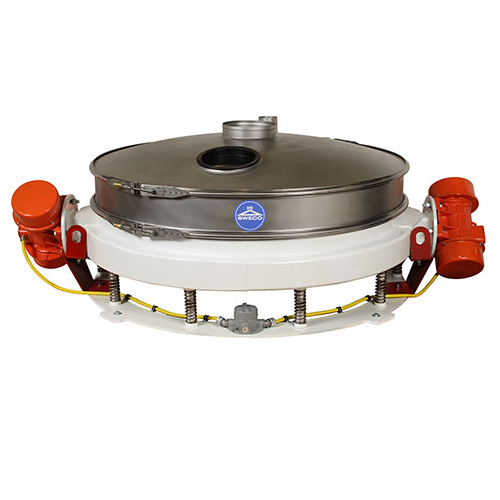
Low profile flow-thru separator for wet or dry scalping
Efficiently handle high-capacity separation with a compact design...
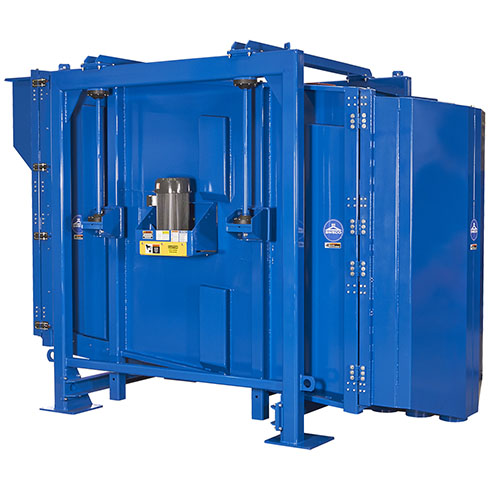
High-capacity industrial sifter for chemical and food processing
Achieve unparalleled screening precision and efficiency...
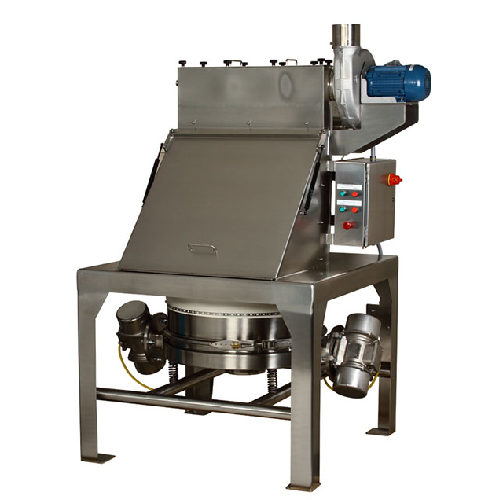
Round vibratory separation equipment - bag dump screener system
Enhance your material handling and safety by efficiently...
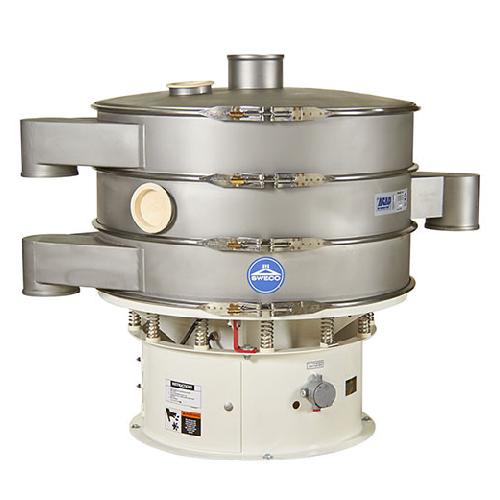
Round vibratory separation for various industrial applications
Ensure accurate material separation with a robust solutio...
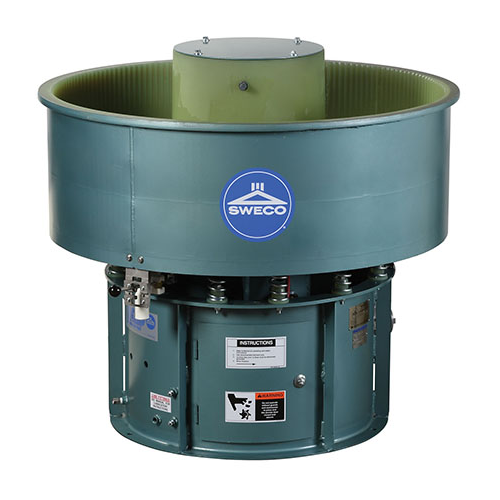
Vibratory finishing and deburring technology
Achieve precise surface finishing and deburring with advanced vibratory motio...
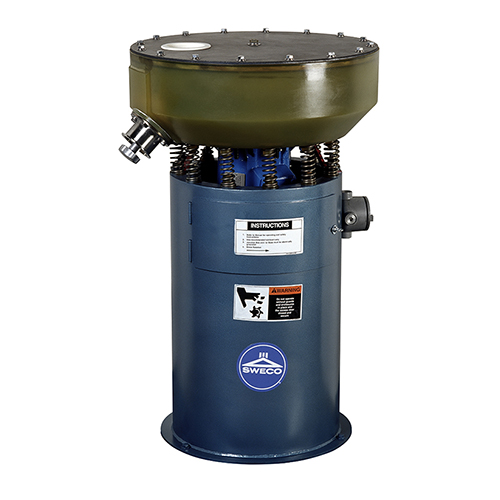
Sub-micron particle size reduction grinding mill
Achieve precise particle size reduction effortlessly with advanced vibrat...
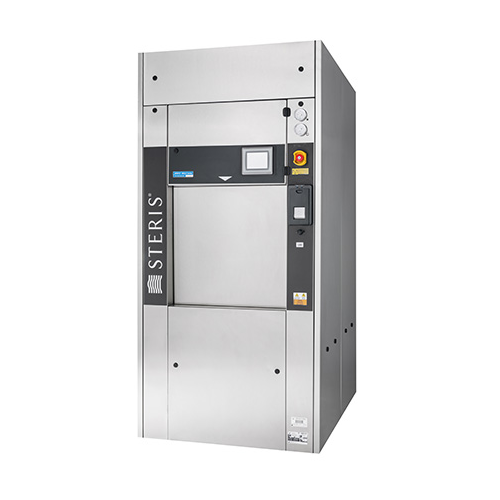
Medium steam sterilizer for laboratory applications
Ensure consistent and reliable sterilization of heat- and moisture-st...

Multiple-effect water still for pharmaceutical applications
Optimize your pharmaceutical water production with a system ...
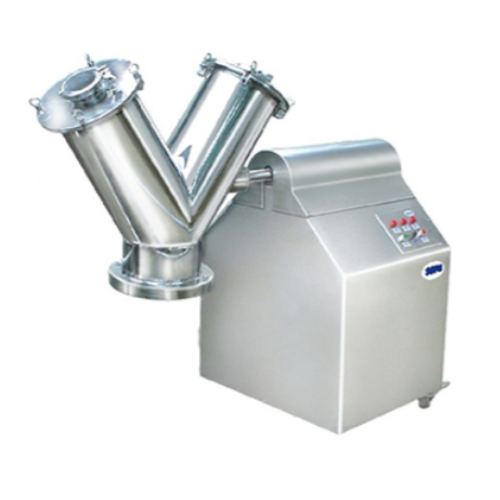
Industrial blender for uniform mixing
Optimize your process with precise mixing and consistent blending, ensuring uniformit...
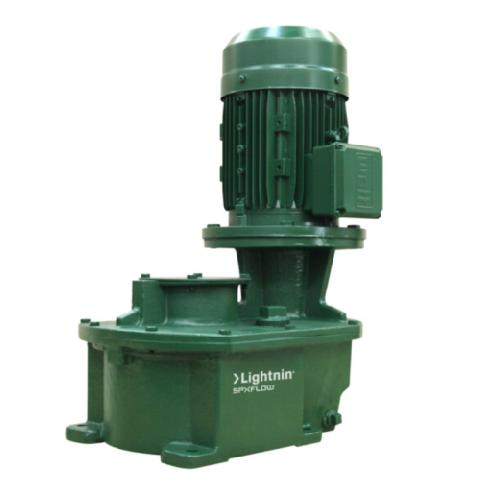
Medium torque mixer for chemical processing
Achieve optimal mixing efficiency and process consistency in demanding applica...
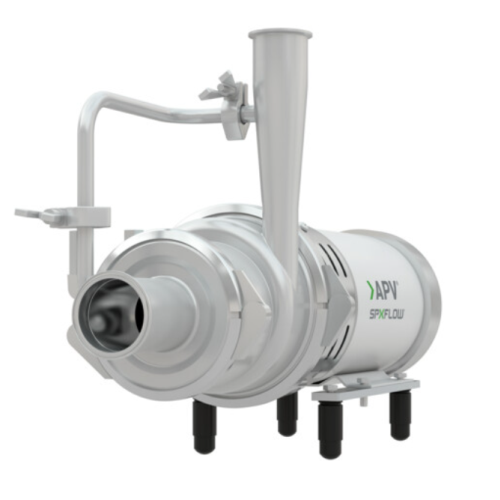
Self-priming centrifugal pump for entrained air handling
Effortlessly manage entrained air and foam in fluid processing w...
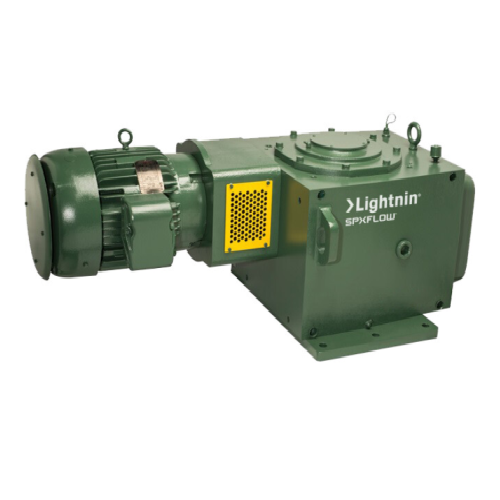
Medium torque top entering mixer for industrial applications
Optimize your mixing and blending operations with precise t...
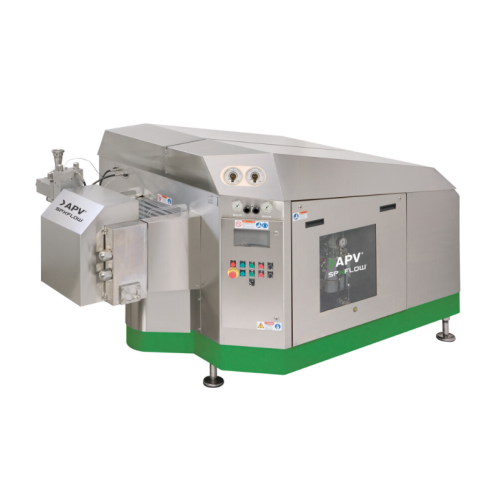
High pressure homogenization system for dairy and creams
Optimize your high-speed homogenization processes with precise c...
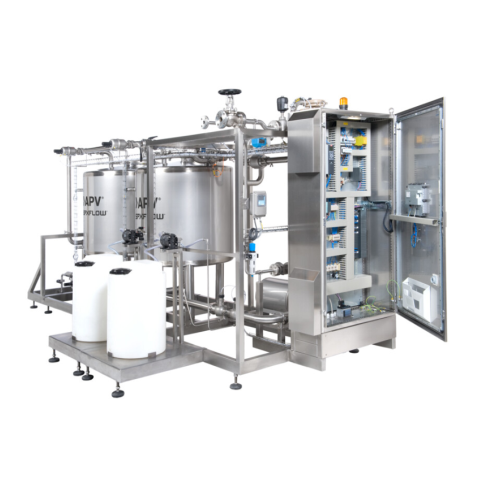
Clean in place (cip) system for industrial cleaning
Ensure optimal hygiene and production efficiency with a system that s...
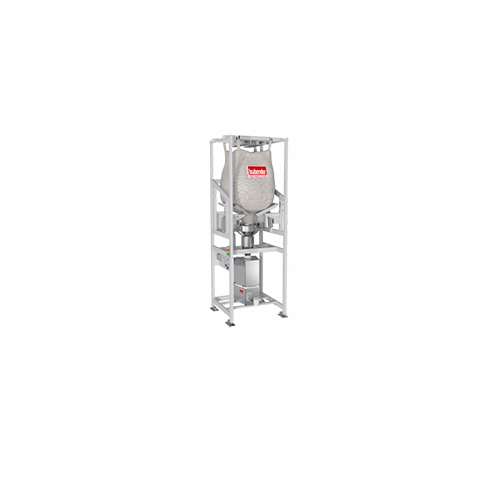
Bigbag discharge station with dust-free docking system
Streamline your production line with an efficient solution for man...
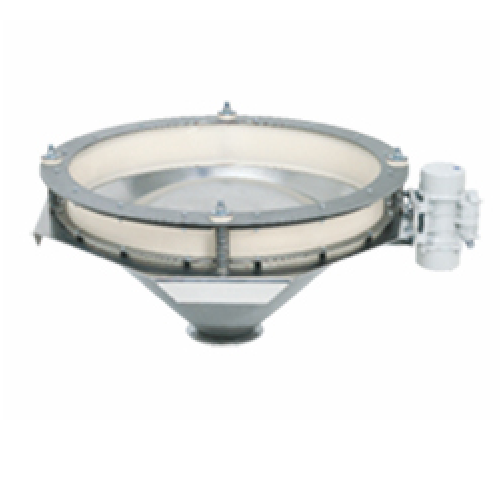
Bin activator for reliable bulk solids discharge
Ensure reliable flow and prevent compaction in your production line with ...
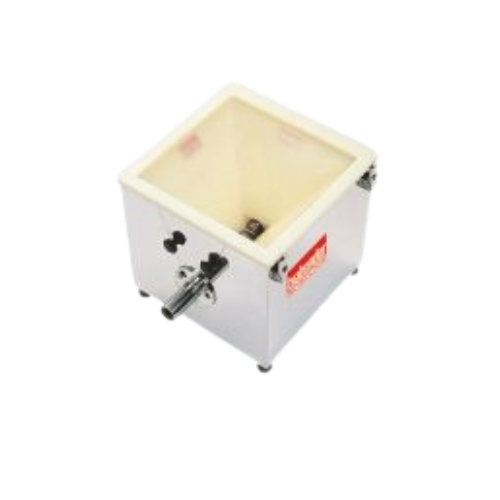
Volumetric feeder for flowable ingredients
Ensure consistent and precise dosing of diverse materials in your production li...
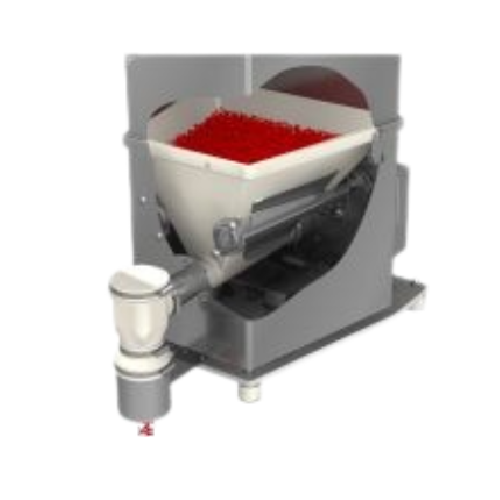
Volumetric feeder for consistent ingredient flow
Achieve precise and consistent ingredient dosing in your production line ...
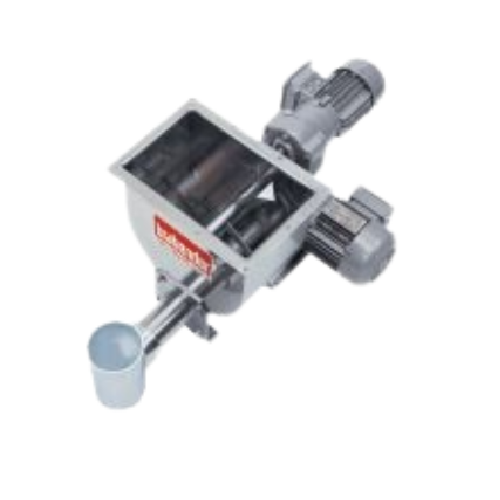
Single screw feeder with stirring agitator for powders and pellets
Ensure consistent mass flow and precise dosing with ...
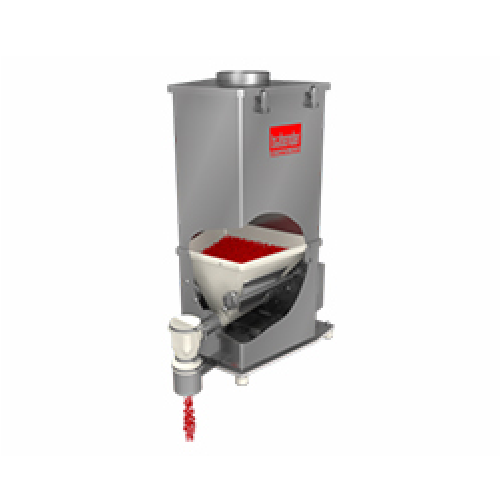
Loss-in-weight feeder for flowable ingredients
Achieve precise ingredient delivery with this feeder, designed to handle a ...
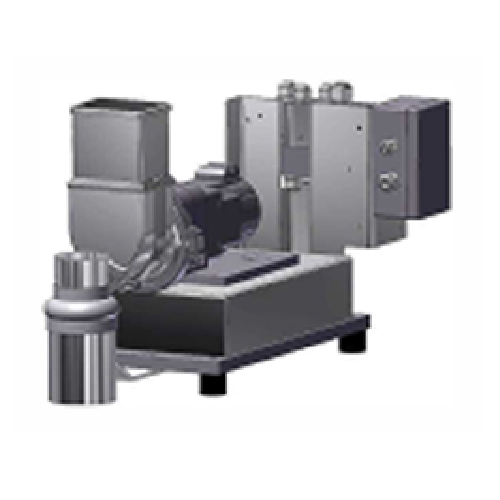
Laboratory loss-in-weight feeder for powders or pellets
Achieve precise dosing for lab-scale trials with this versatile f...
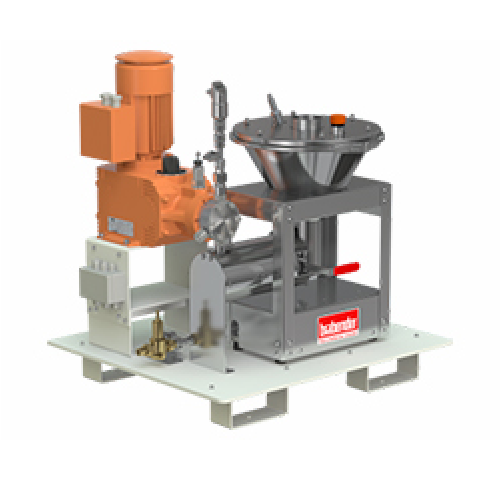
Loss-in-weight feeder for liquids
Achieve precise and continuous liquid dosing with high accuracy, adapting seamlessly to y...
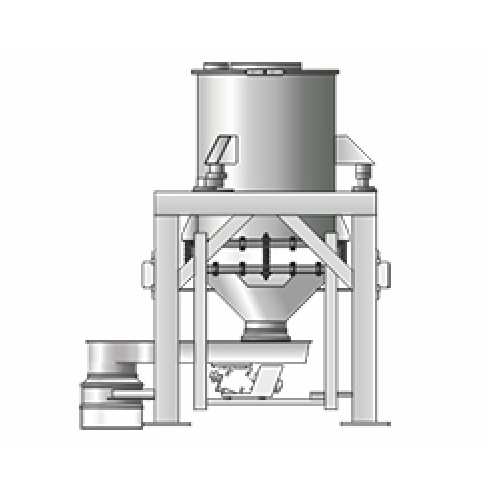
Loss-in-weight feeder for non-hygroscopic ingredients
Ensure precision in your dosing and weighing processes with this ad...
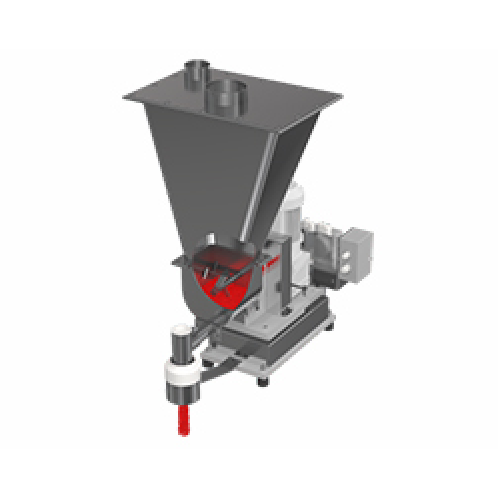
Single screw loss-in-weight feeder for powders and pellets
Ensure precise dosing and mixing in continuous automated oper...
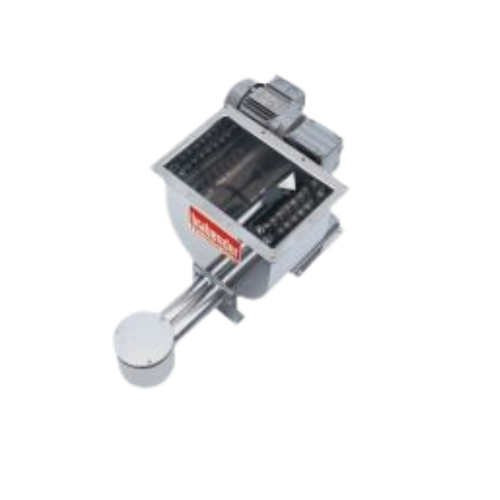
Twin screw volumetric feeder for poor flowing powders
Struggling with poor flowing or floodable powders? This twin screw ...
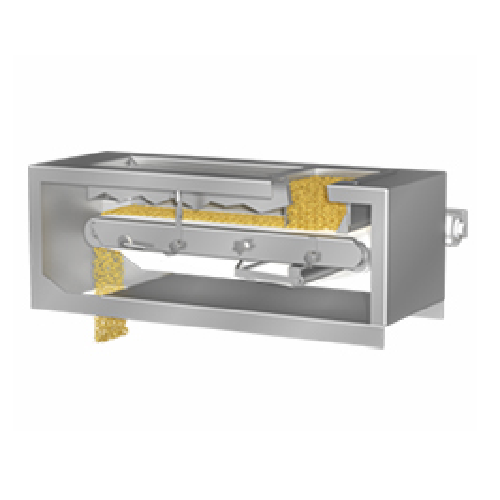
Weigh-belt feeder for industrial processes
Efficiently manage material flow and precision with a dependable weigh-belt fee...
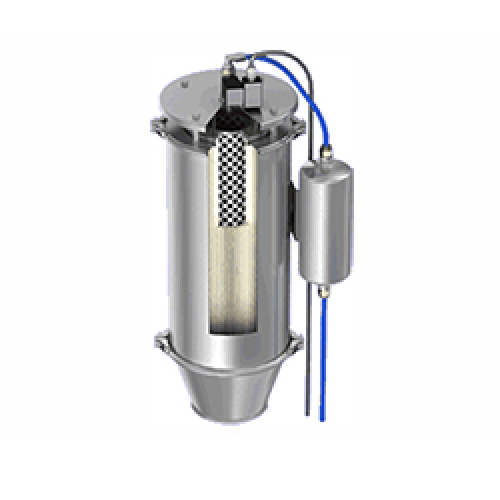
Dust filter for loss-in-weight feeder refill
Optimize your feeder operations by effectively filtering displaced air and mi...
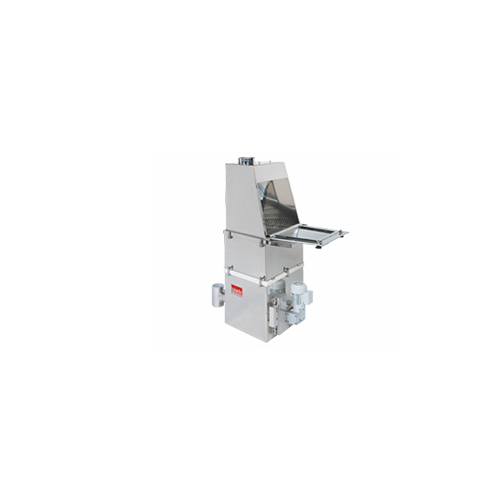
Bigbag discharge station
Efficiently manage bulk material unloading with this solution, which facilitates seamless dischargin...
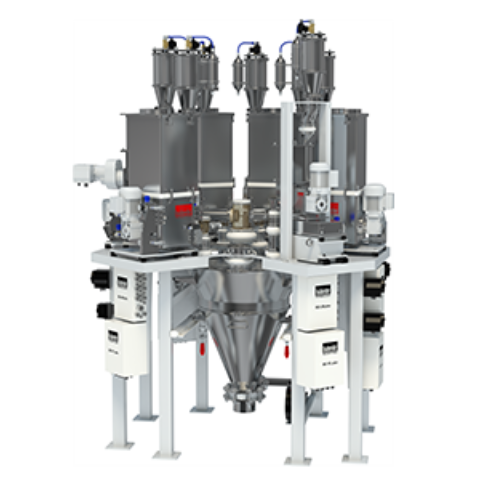
Hopper scale for precision batching
Achieve high batch accuracy with a central weighing hopper engineered for seamless inte...

Batch ingredient dosing system for high-accuracy weight control
Achieve precise weight measurement for multi-ingredient ...
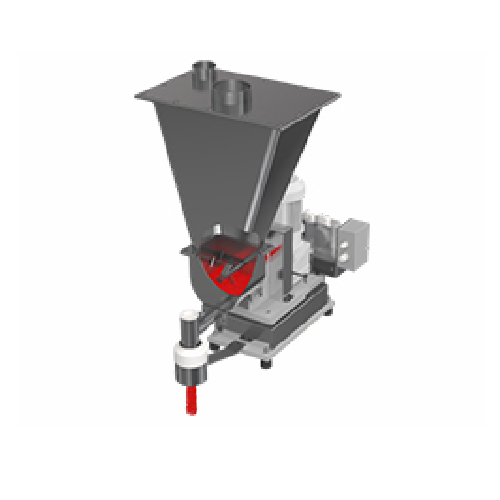
Single screw batch feeder with stirring agitator for powders and pellets
Ensure precise ingredient control and consiste...
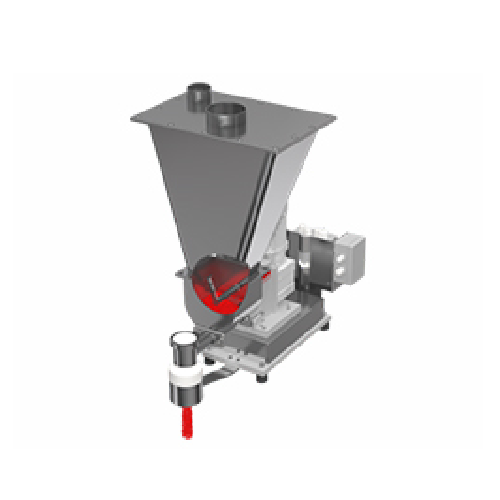
Double screw batch feeder for poorly flowing powders
Effectively manage challenging powders with precise batch dosing and...
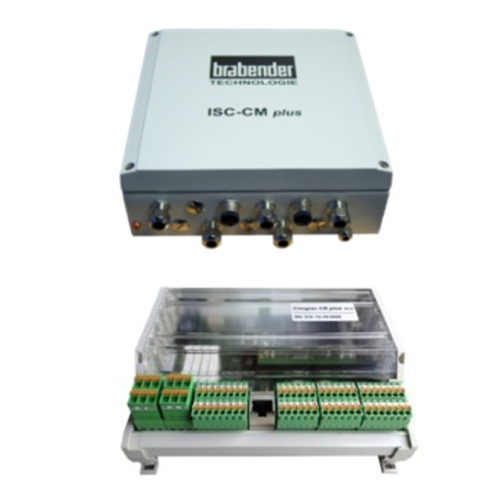
Feeder controller for gravimetric feeders
Optimize your dosing precision and monitoring accuracy with a versatile feeder c...
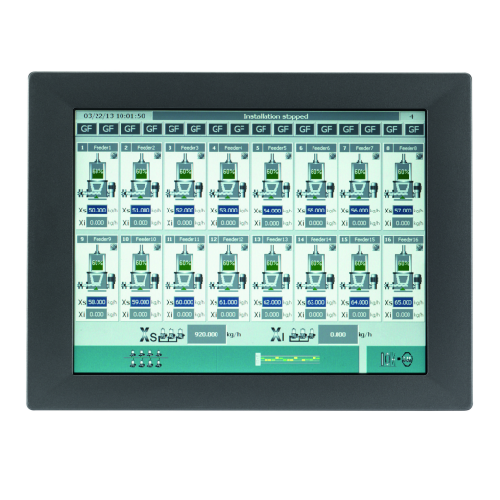
Gravimetric feeder operator interface
Efficiently manage up to 16 gravimetric feeders with a user-friendly interface, enabl...
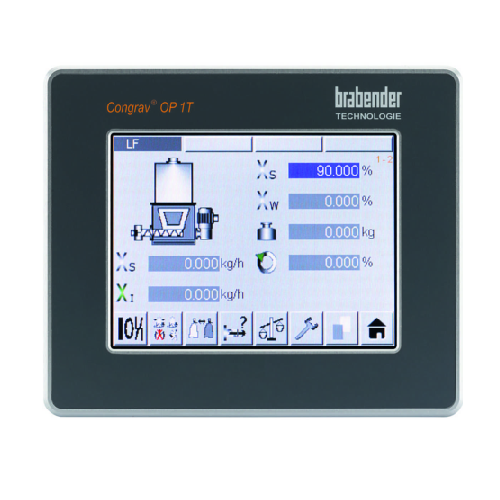
Single feeder operator interface for gravimetric feeders
Enhance precision in your dosing operations with an intuitive to...
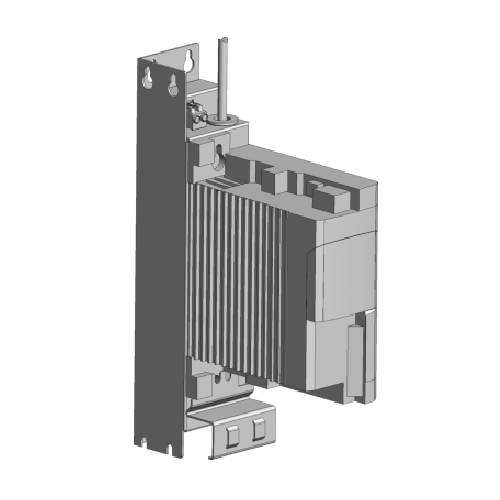
Speed controller for feeders
Ensure precise material flow by integrating this speed controller, ideal for managing both volu...
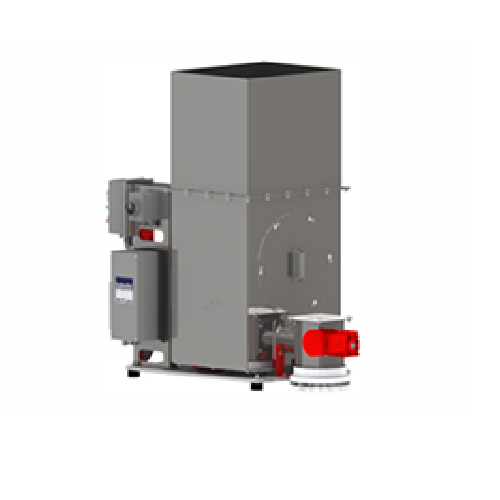
Loss-in-weight feeder for long and uneven fibers
Optimize feeding precision for challenging materials like long and uneven...
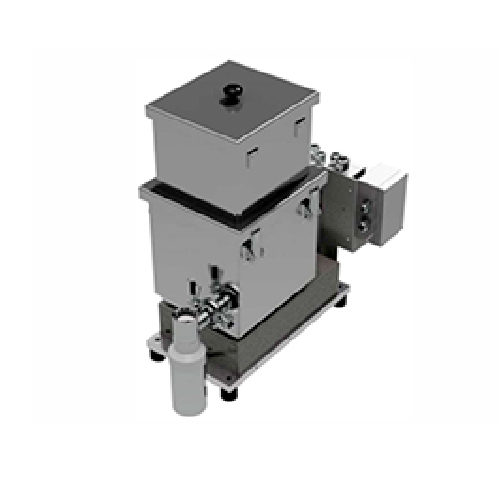
Loss-in-weight feeder for flowable particles
Ensure precise ingredient delivery with a feeder designed for high accuracy a...
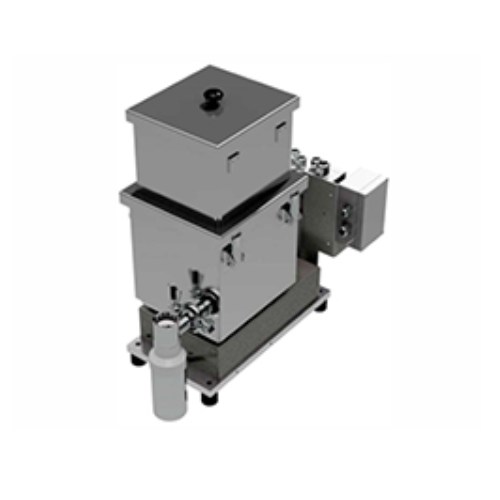
Batch feeder for bulk solids processing
Achieve precise batch dosing with this advanced feeder, designed to handle a variet...
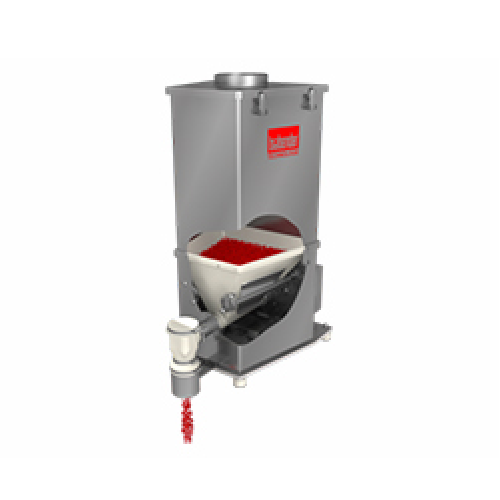
Precision batch feeder for flowable ingredients
Achieve precise ingredient control with a batch feeder designed for versat...
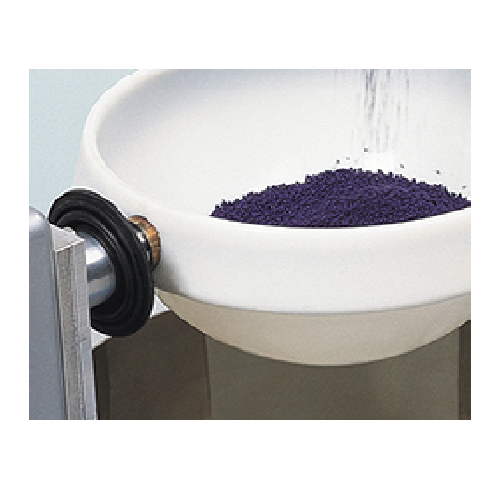
Microbatch dosing for precision ingredient measurement
Achieve precise ingredient dosing with our MicroBatch system, desi...
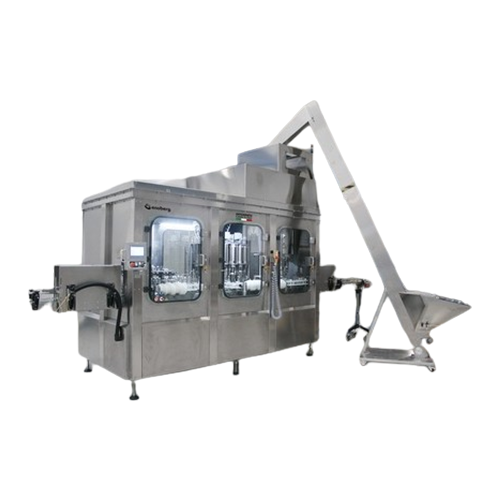
Hyper-clean electronic volumetric filler for Pet bottles
Enhance your liquid filling operations with precision and hygien...
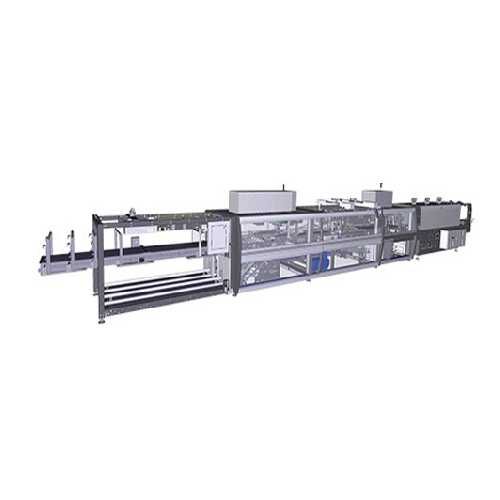
Combined packers with in-line infeed for plastic and glass containers
Streamline your packaging process with a versatil...
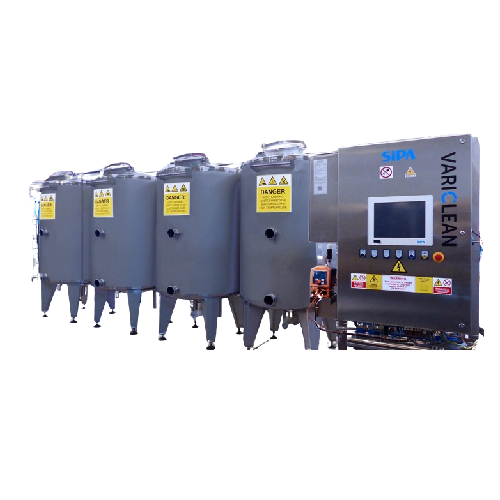
Cip sanitizing unit for food and beverage production
Ensure meticulous hygiene with a compact unit designed for seamless ...
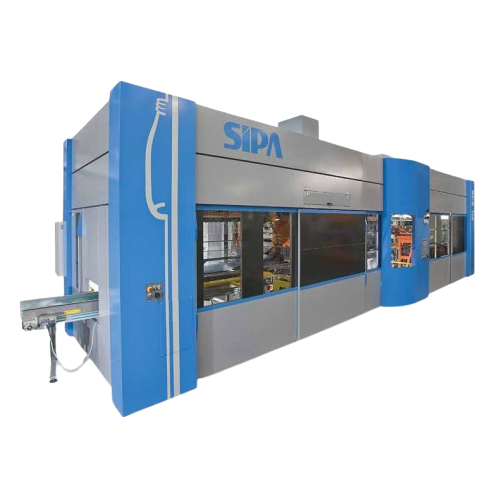
Single-stage plastic container production system
Eliminate multiple steps and minimize production costs with an integrated...

Injection stretch-blow molding system for Pet containers
For manufacturers aiming to produce versatile, high-quality PET ...
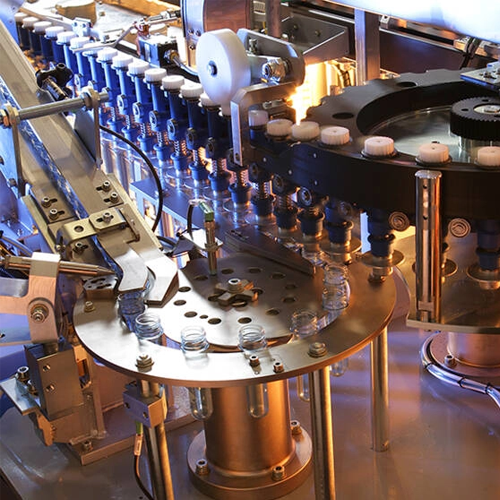
Linear blowing systems for Pet bottle production
Ideal for producers seeking versatile container solutions, this system en...
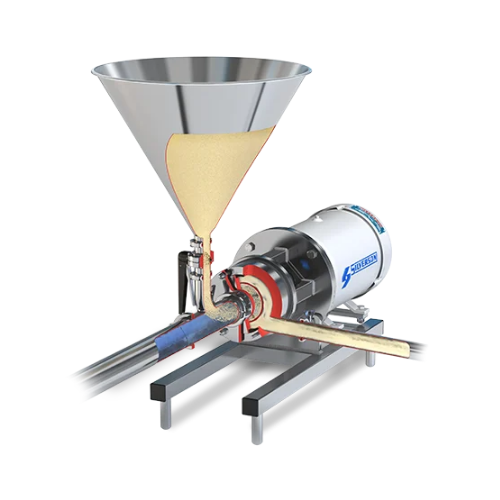
High shear powder mixing solution
Achieve agglomerate-free, homogeneous mixing of powders and liquids with high shear effic...

Laboratory scale powder/liquid mixer
Easily integrate powders into complex liquid formulations at a laboratory scale, ensur...
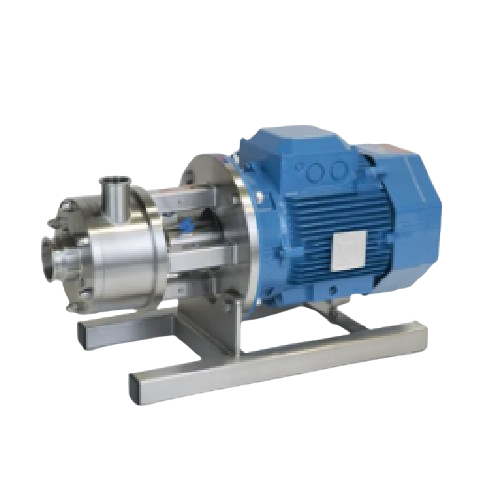
High shear mixer for efficient particle size reduction
Achieve rapid and precise blending and particle reduction in your ...
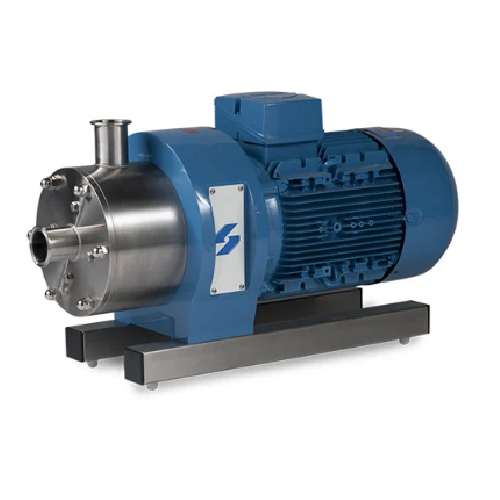
High shear inline mixer for continuous processing
Effortlessly streamline your mixing process with this solution capable ...
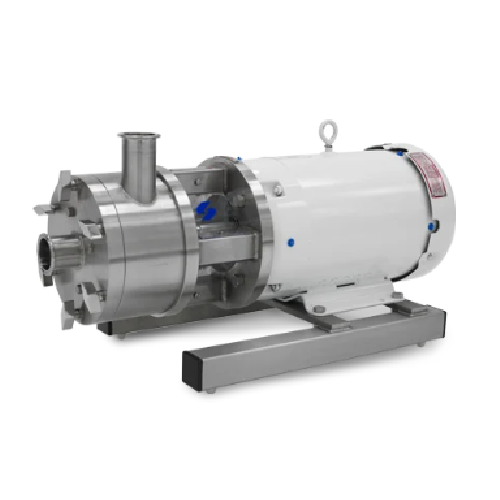
In-line ultra sanitary mixer for pharmaceutical and food applications
Enhance your liquid formulations with precision m...
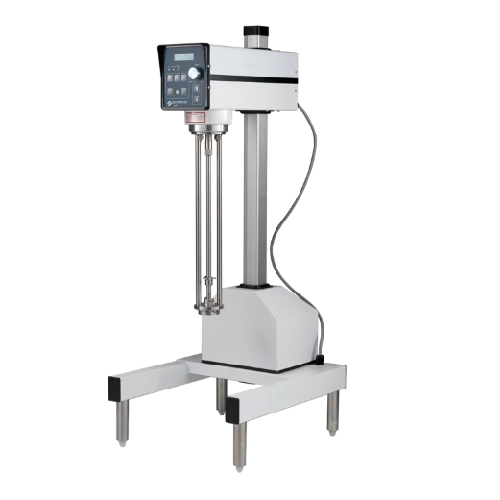
Pilot scale batch mixer for small scale production
Achieve precise control and consistency in small-scale production with...
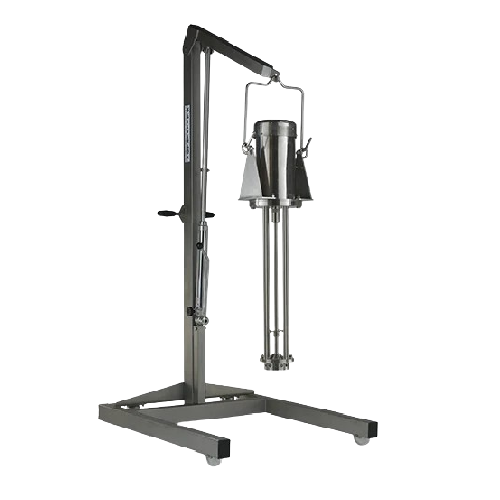
High shear batch mixer for industrial mixing
Optimize your production cycle with this high shear batch mixer, designed to ...
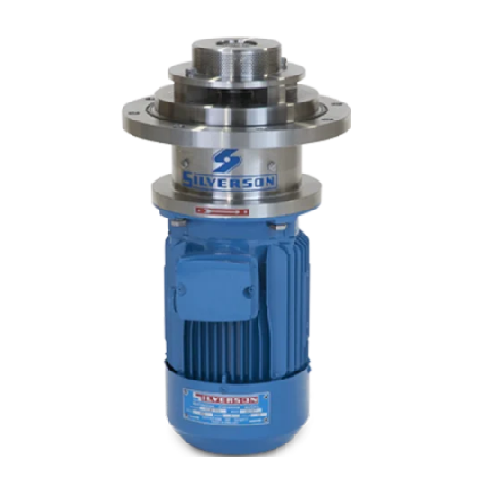
Bottom entry mixers for high viscosity products
Optimize your production line with mixers designed to handle both high and...
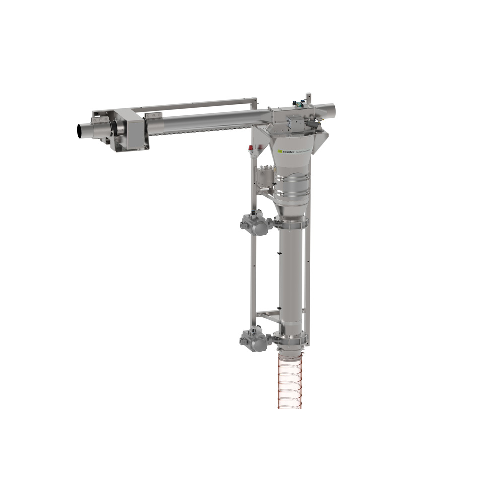
In-line metal detector for pneumatic systems
Ensure product purity and operational efficiency with a solution that effecti...
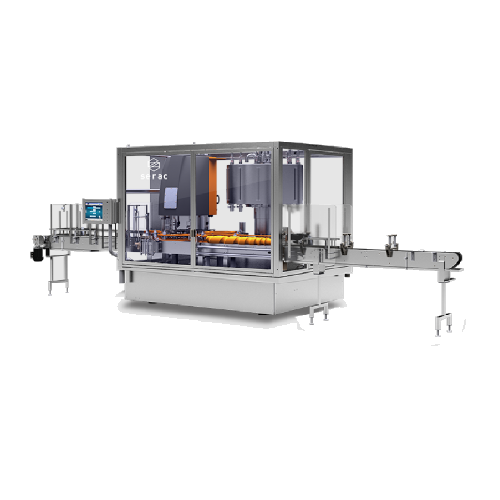
Versatile rotary filler-capper for liquid products
Optimize your liquid product production with a versatile solution that...
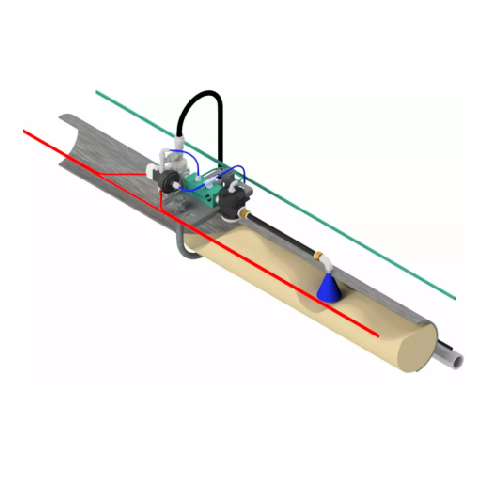
Injected density stabilizer for pneumatic conveying
Optimize your dense phase pneumatic conveying with a stabilizer desig...
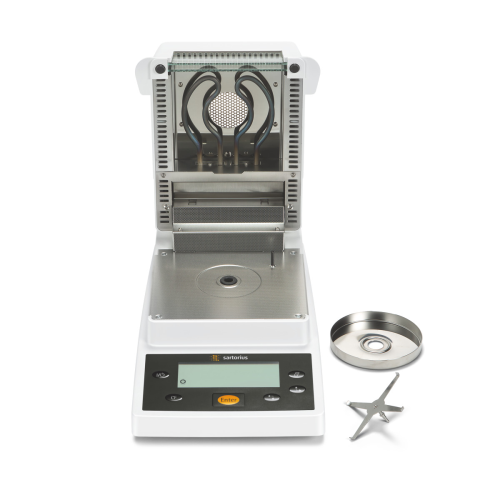
Infrared moisture analyzer for lab and production use
Achieve precise and reliable moisture analysis with minimal time an...
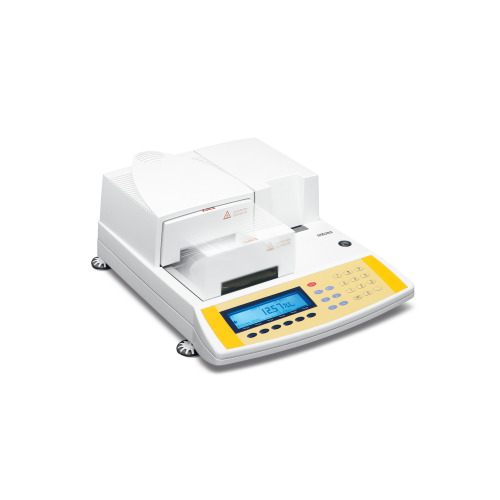
High-accuracy moisture analyzer for lab weighing
Achieve precise and reproducible moisture content determination for diver...
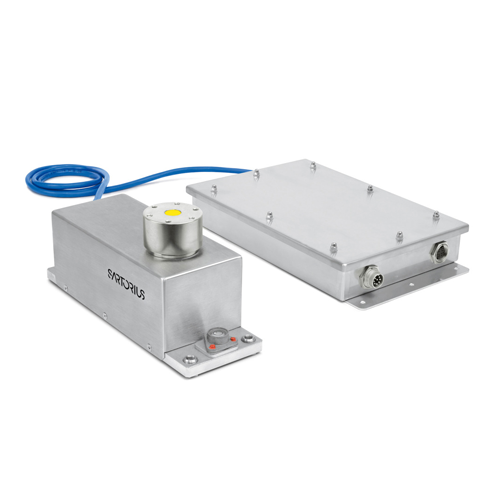
Explosion proof weighing cells for hazardous environments
Designed for hazardous environments, these weighing cells ensu...
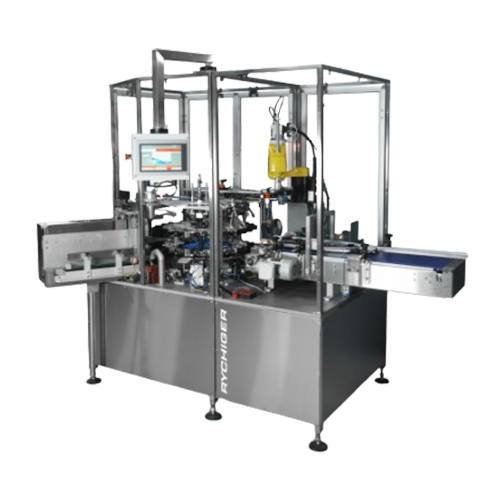
Cartoner for pharmaceutical products
Effortlessly streamline your packaging line with compact cartoning capabilities, ensur...
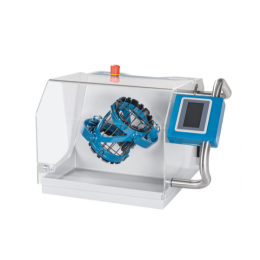
R&D shaker mixer for battery powders and chemicals
Material heterogeneity, agglomeration, and contamination are key param...
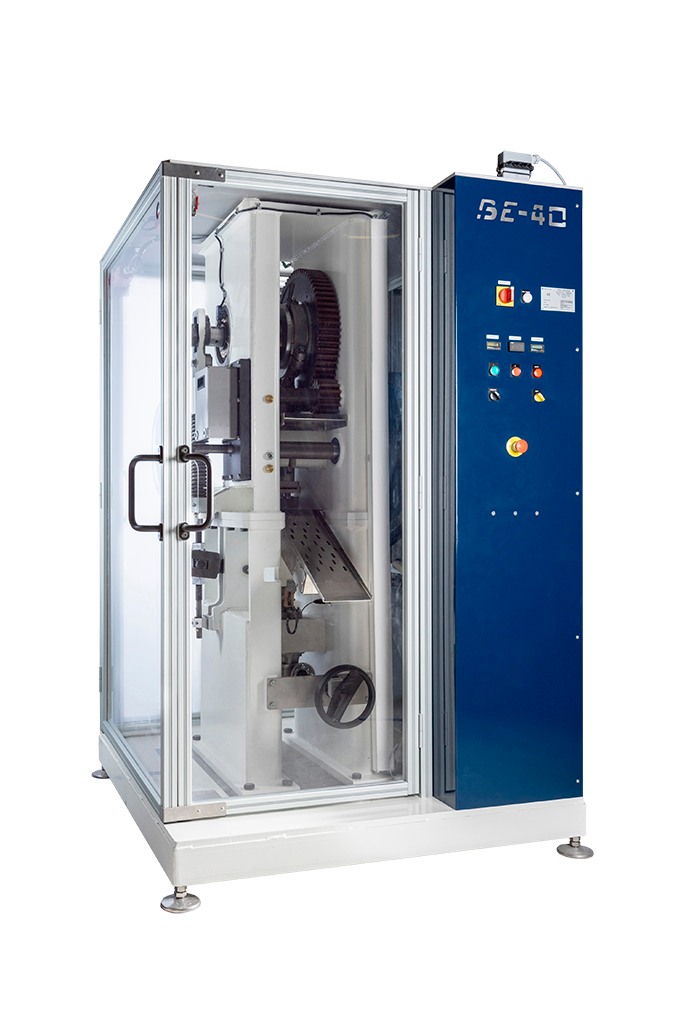
Eccentric press for refill tablets
Hundreds of different refill tablets, of various shapes or sizes, are on the market toda...
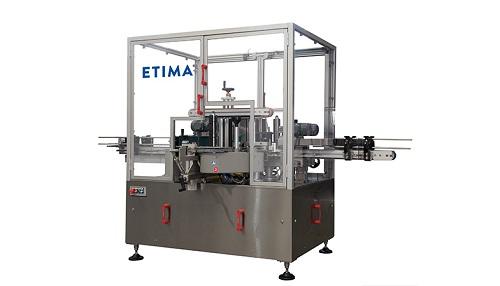
Self-adhesive linear labeling machine for bottles
It is vital to have precise and long-lasting labels on bottles to avoid...
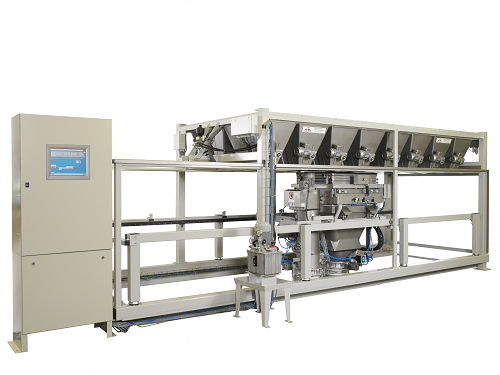
Micro powder dosing system
Micro dosing of powders and small components can be a major obstruction in the production process...
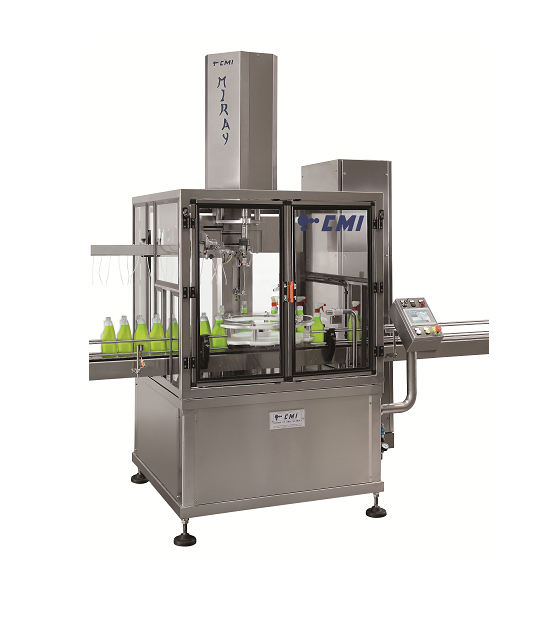
Automatic bottle capping machine
Traditional bottle capping systems are inflexible, limiting the scope of your packaging and...
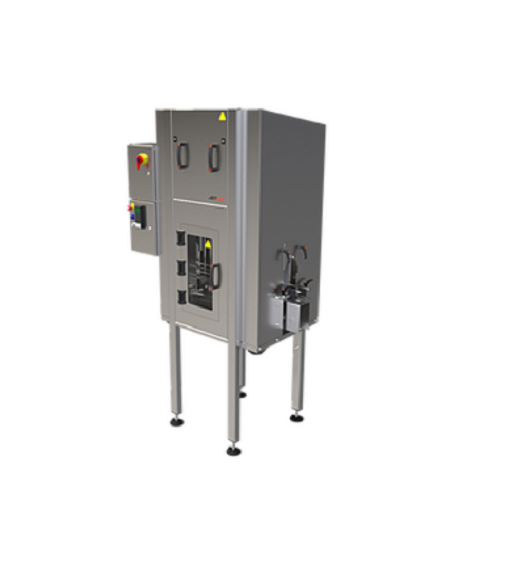
Air knife drying system for containers
In food or beverage production where a product is filled into jars, there is often r...
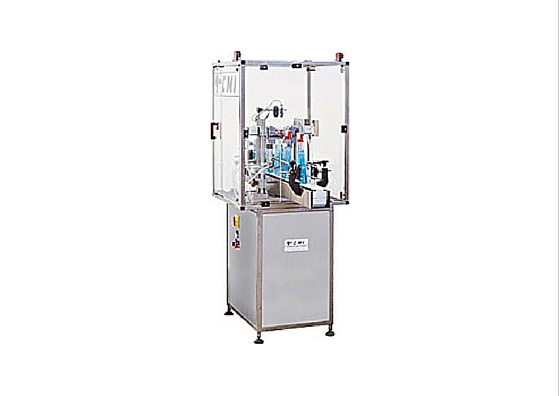
Semi-automatic trigger capping machine
Trigger spray bottle are the ideal capping solution for many chemical and household ...
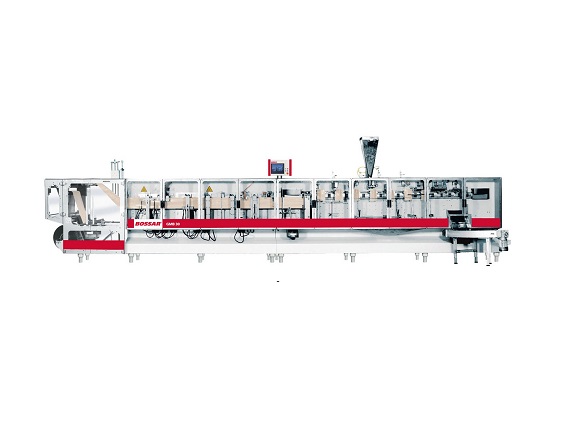
HFFS Machine for Large or Heavy Pouches
Traditional pouch-forming machines can struggle to maintain the position of the pac...
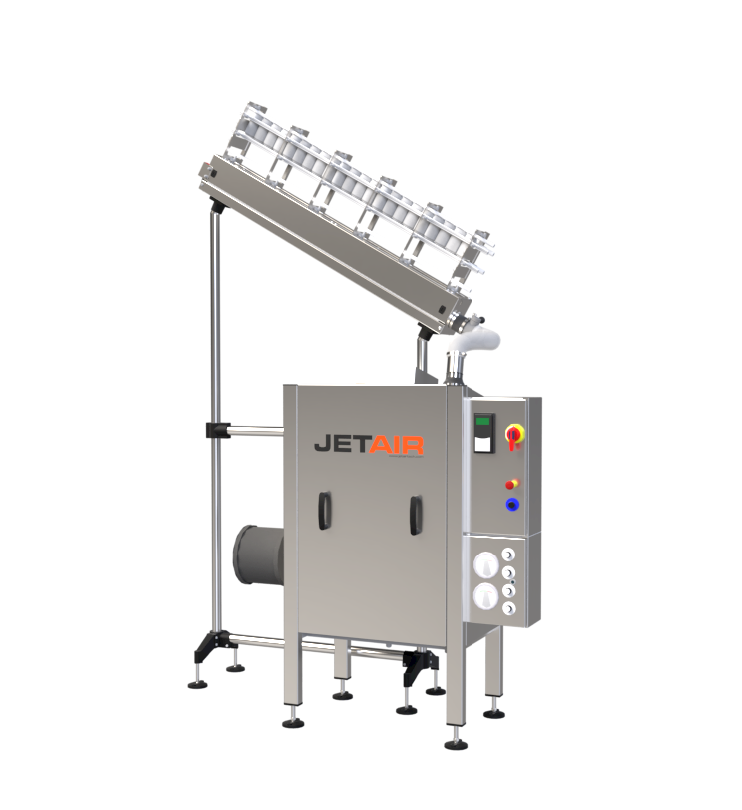
Air rinsing system for containers
Traditional water rinsing solutions for containers used in the food and pharmaceutical se...

Shrink sleeve applicator - 400 per minute
Flexible medium to high speed application of shrink sleeveing to containers is u...
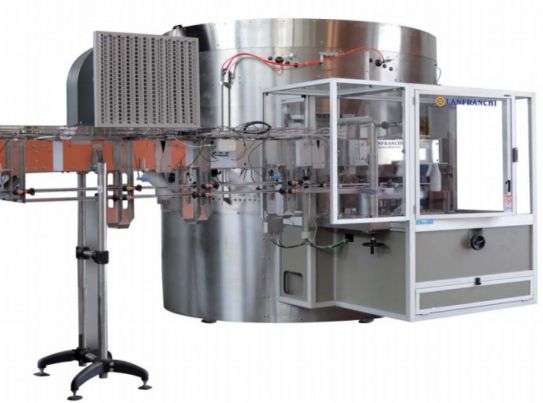
High-speed unscrambler for large bottles
Large volume plastic bottling plants need high-speed unscramblers suitable for lar...
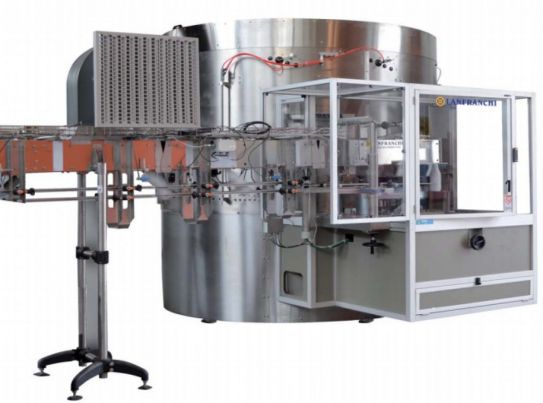
High-speed unscrambler for small bottles
Large-scale production of smaller volume bottled product needs a gentle, accurate ...
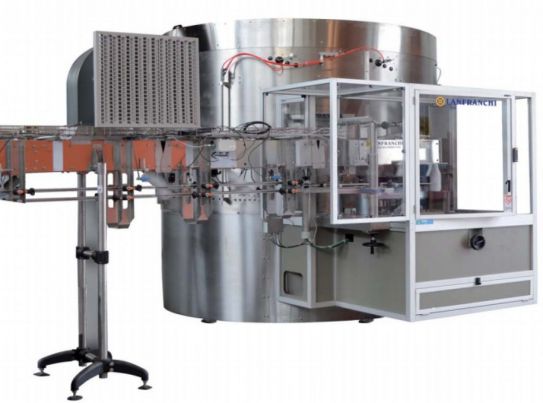
Low-speed unscrambler
Smaller plastic bottling lines need a lower cost, lower volume unscrambling machine that maintains gent...
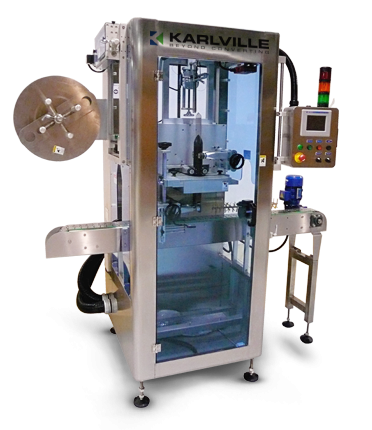
Low speed can sleeve applicator
Flexible automatic low speed application of shrink sleeving to cans is used in various indus...
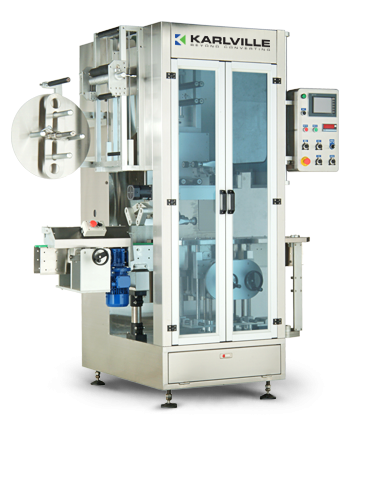
Low speed shrink sleeve applicator
A variety of industries require flexible addition of shrink sleeves to containers on the...
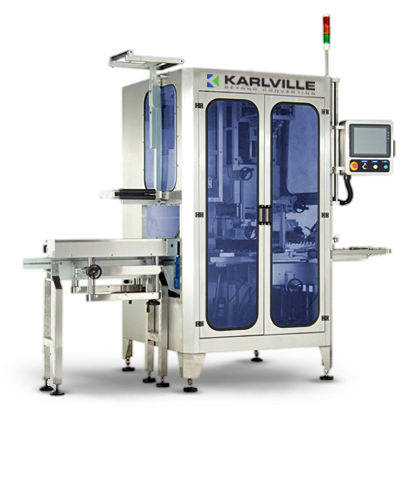
Shrink sleeve applicator - 600 per minute
Several industries require the flexible addition of shrink sleeves to containers...
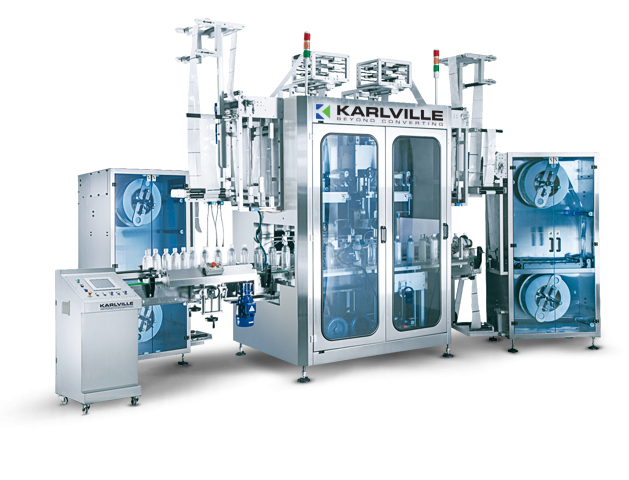
Shrink sleeve applicator - 800 per minute
High speed, in-line shrink sleeving systems require dual head capability with hi...
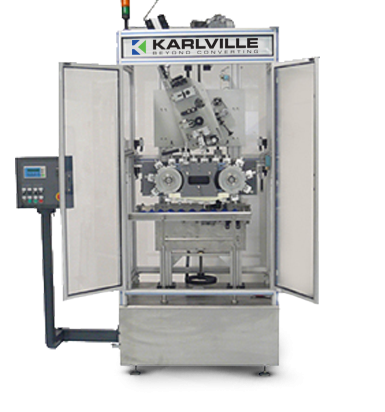
Tamper-evident sleeve applicator for caps
Reliability, continuity and changeover time are key success factors for tamper-e...
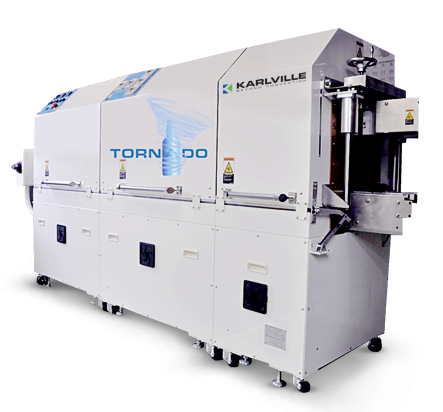
Energy efficient tunnel for sleeve application
Hot air application of shrink sleeves is much more efficient than tradition...