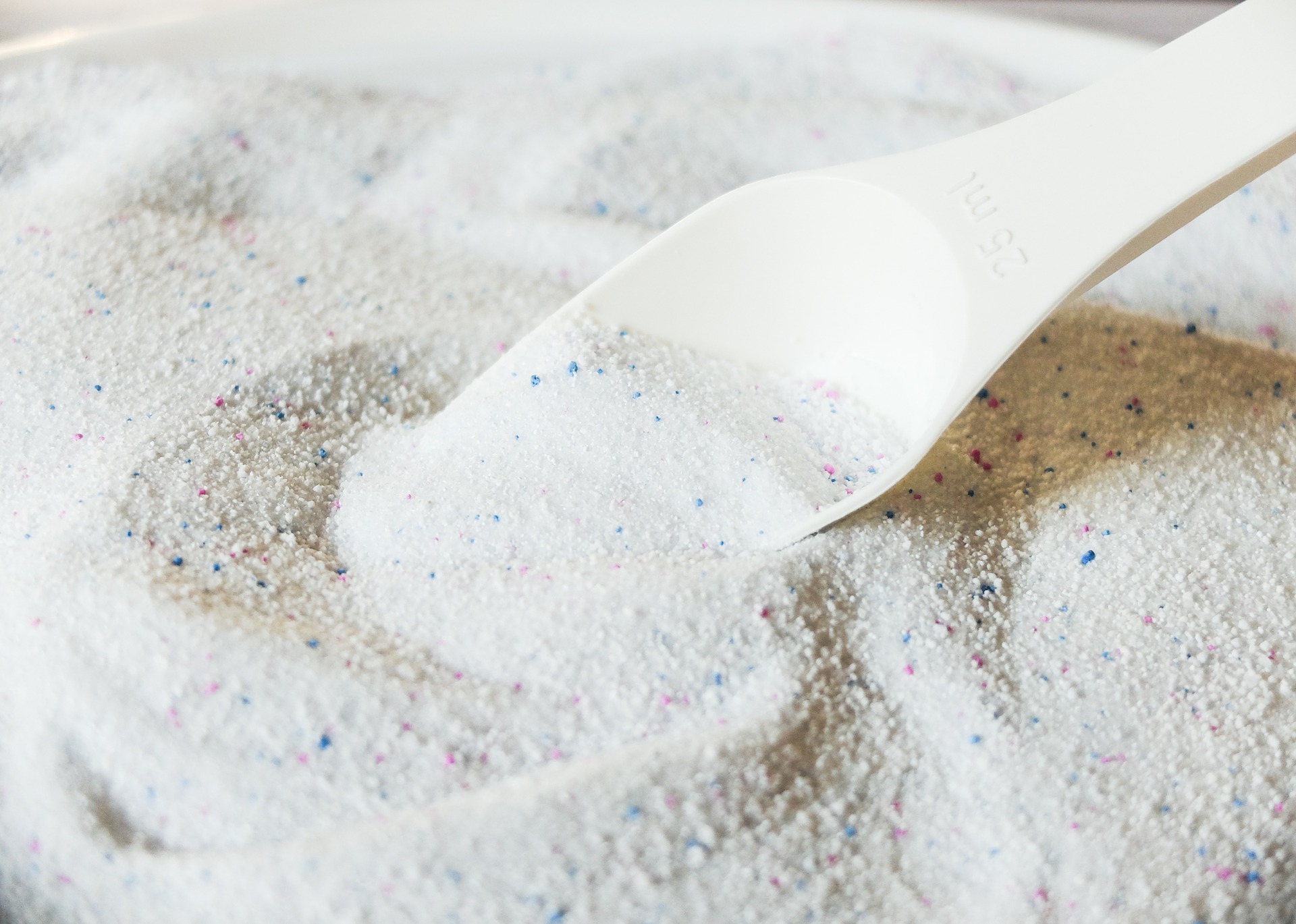
Making Powder Detergents
Find innovative production technology for making powder detergent and connect directly with world-leading specialists
Powder detergent is one of the most widespread washing solutions used in the laundry of fabrics. Since they contain no water, powder detergents are lighter than liquid detergent or pods, which results in cheaper transport and, thus, a more affordable choice for the end consumer. Although manufacturers can formulate their powder detergents differently, the detergent powder production process relies on a combination of builders, surfactants, and enzymes.
Select your powder detergent process
Tell us about your production challenge
The agglomeration process aka the mass detergent powder production process
The agglomeration process is a method used by large manufacturing companies due to its production capacity. Namely, it is a continuous process that can produce between 6,800 and 22,700 kilograms of detergent per hour. The detergent created by the agglomeration method can be easily recognized by its granule-like appearance. This detergent powder production process starts by mixing dry ingredients in an agglomerator.
Once the dry ingredients are blended into a fine consistency, liquid ingredients are added through nozzles in the agglomerator’s walls. The steady, continuous blending causes a heat-producing exothermic reaction which transforms the mixture into a hot, viscous liquid that reminds of gelatin. The jelly-like mixture leaves the machine on a drying belt and evolves into a texture that is easy to crush or crumble by being exposed to its own heat, air, and hot air blowers. The crumbled mixture is then pulverized to ensure the standard quality of the product.
The spray drying process: a pathway to the perfect formula
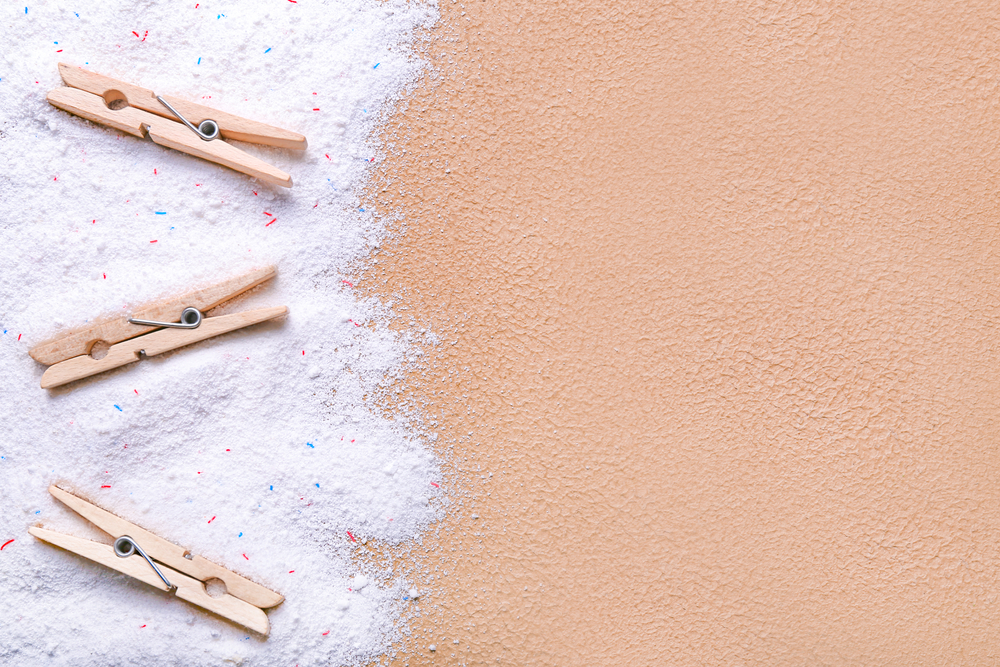
The spray drying manufacturing process creates a high-quality product characterized by lightweight properties, perfect dehydration and minimal risk of issues such as caking. Once dosed into a crutcher, the ingredients are mixed with processed water for up to one hour, creating the base powder slurry, which is aged for 30 minutes in the aging tank and passed through a self‑cleaning filter to break lumps. The high-pressure pumps spray the slurry up to the top of the spray drying tower, where the mixture is dehydrated by generating hot air in furnaces designed to obtain smokeless combustion.
The air flows from the bottom to the top of the tower, drying the slurry that is falling in the opposite direction. A mesh filters the dried powder to remove oversized particles. Since the base powder contains no enzymes, fragrances, or colorful speckles, these ingredients are added to the post-tower processing plant that performs the fine-tuning. This method is widely used for simplifying the process and improving profit margin by turning a slurry into a dried powder in a single step.

Sucrose - The secret ingredient in powder detergents
Sugar is one of the ingredients in the spray drying process as it provides the powders with a fine structure without utilizing sodium silicate. Although different kinds of sugars can be used, sucrose is the most preferred sugar due to its availability and cheapness. The use of sugar in powder detergent is to stabilize and persist bubbles. In other words, it creates a satisfactory structure without the need to utilize sodium silicate. Its use is more for aesthetics, as people expect detergent to foam and create bubbles, than adding efficiency to the product. According to the patent, the sugar level should be between 1% and 20% by weight of the spray-dried composition, although the most preferred sugar level is 5% to 15% by weight.
The environmental harm and green alternative
On average, powder detergents contain over 25 chemicals that are used to make clothes whiter, brighter and more fragrant. In most cases, these chemicals are toxic and destructive to human health and the environment. Released in waterways, the chemicals cause harm to aquatic life and fish whose gills, once in contact with surfactant micelles, impair the fish’s ability to absorb oxygen from the water.
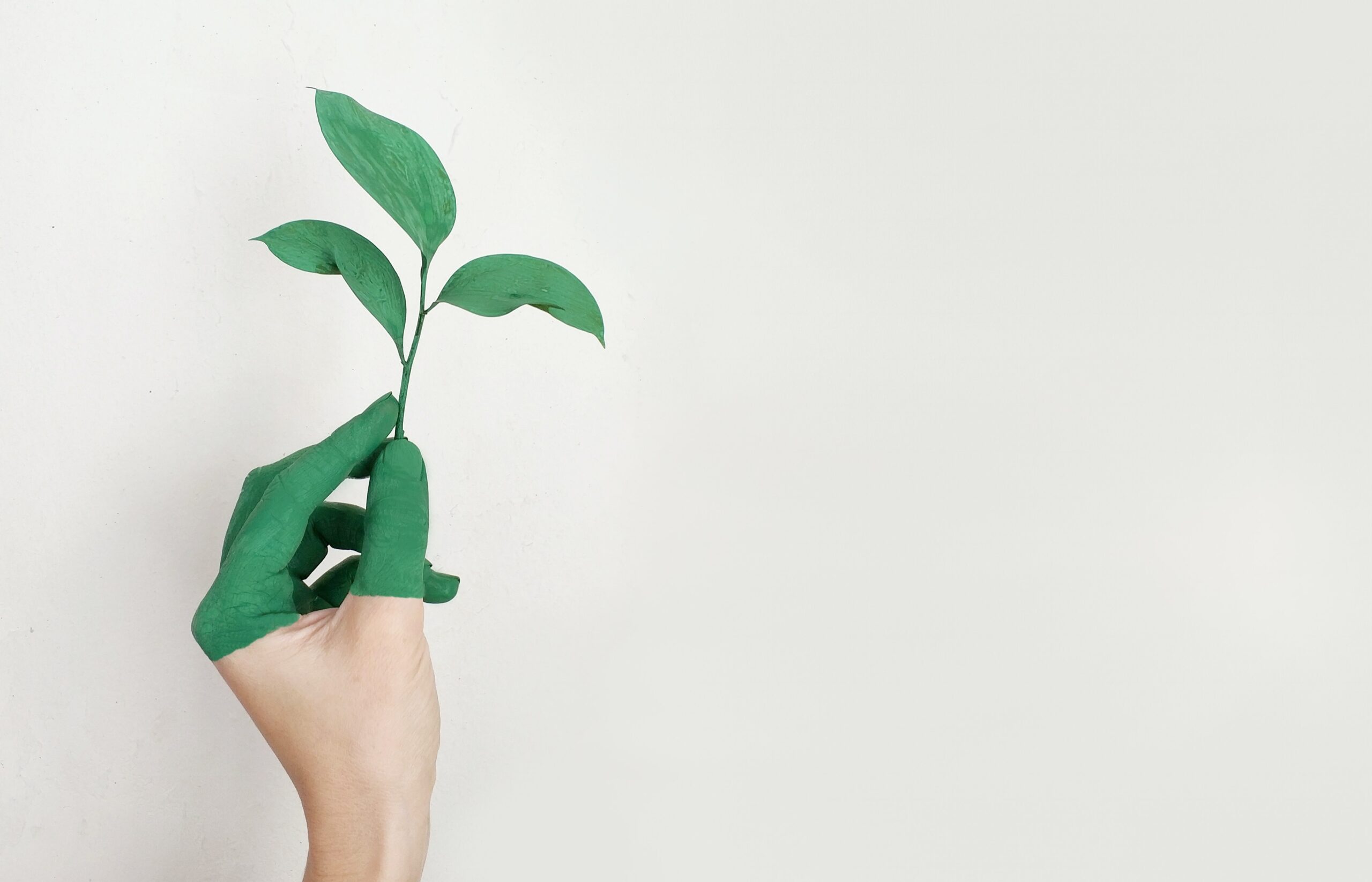
The main approach to making powder detergents green is striving to create alternatives to replace petroleum-derived raw materials with renewable raw materials, such as developing biobased solvents, surfactants, and detergent acrylates. For instance, recently there have been inventions such as commercial surfactants derived from algal oil or sophorolipid surfactants produced by fermenting sugar and nontropical vegetable oil such as rapeseed. Another green approach is creating detergents that can be efficient in cold water. Namely, energy use can be cut by 50% if laundry is washed in cold instead of hot water.
Processing steps involved in powder detergent making
Which powder detergent technology do you need?

Laboratory nutsche filter dryer for solid-liquid separation
Optimize your lab processes with a versatile benchtop filter...
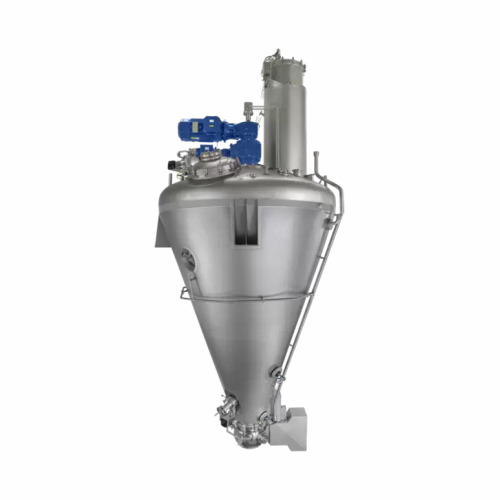
Vacuum dryer for powders and granules
Achieve precise moisture control for sensitive materials with a versatile vacuum dryi...
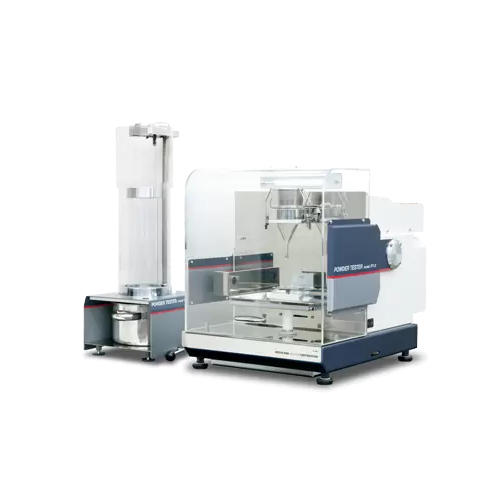
Powder characteristic evaluation
Ensure precise powder analysis and testing in your laboratory to optimize production qualit...
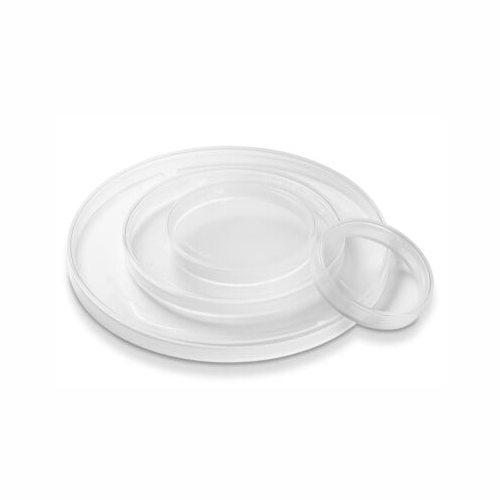
Silicone dust caps for dust-tight powder transfer
Achieve dust-tight containment and efficient powder transfer with flexi...
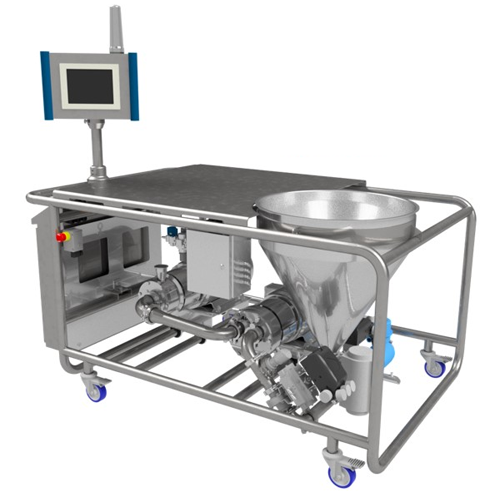
Automated powder induction and dispersion system for industrial mixing
Achieve rapid and efficient incorporation of pow...
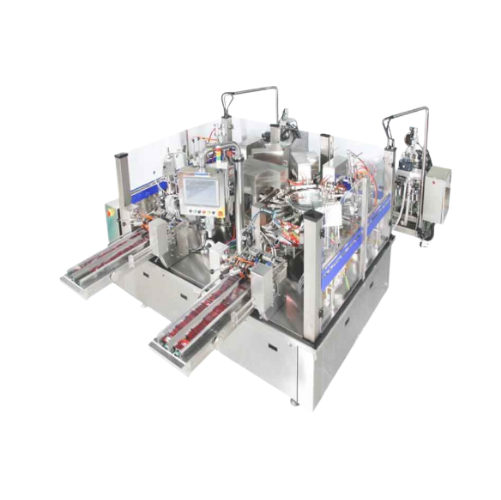
Automatic rotary premade pouch filler and sealer
Optimize your production line with high-speed pouch filling and sealing, ...
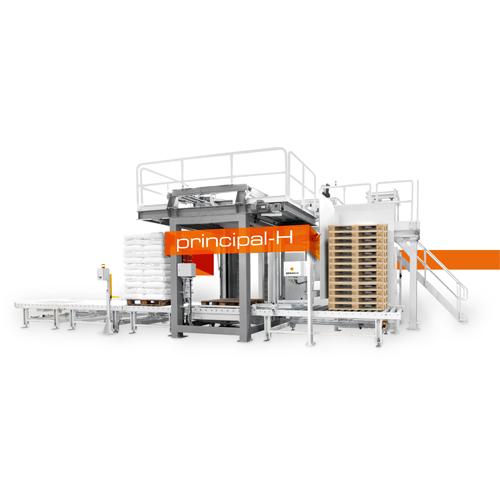
Automatic palletizer machine for bags and boxes
The effective placement and positioning of bags and boxes can be a challen...

Simple valve sack packer
Sometimes in the packing process, product leaks out of the top of a bag that has just been filled. A...

High volume particles separation sieve
For large scale production processes in the chemicals or food industries that requir...
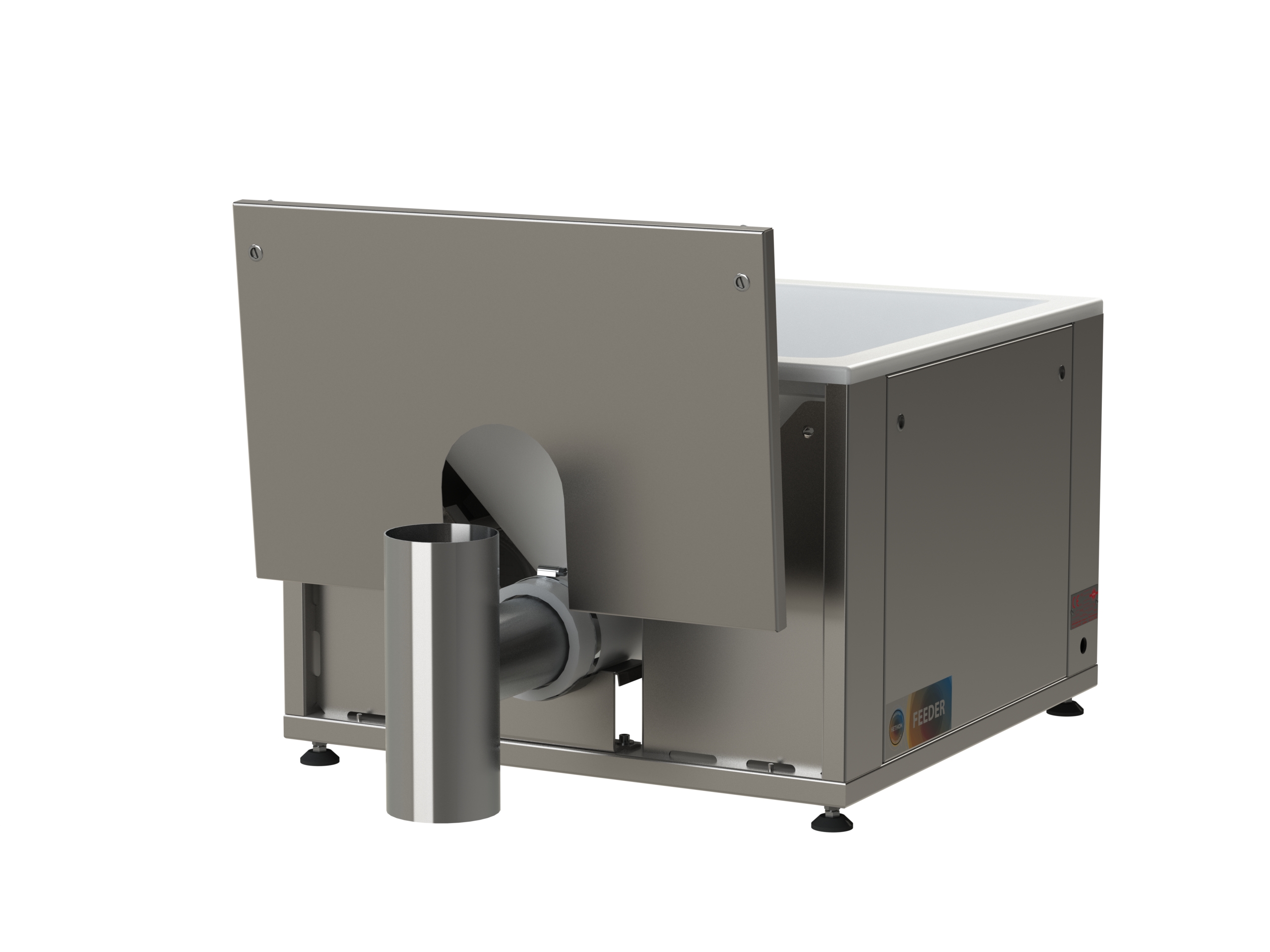
Feeder with flexible wall hopper
The varying properties of dry powder products mean that specialized feeders are required fo...
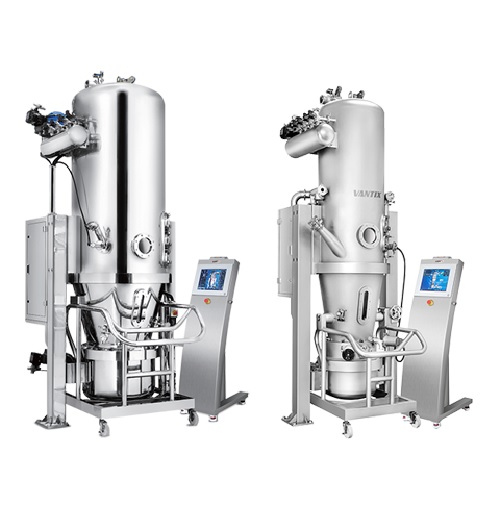
Fluid bed dryer for production scale
Fluidized bed drying (FBD) is a common process in the pharmaceutical industry for dryi...
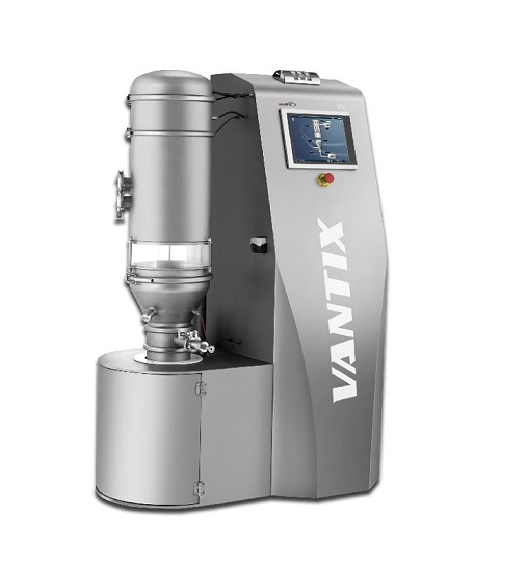
Fluid bed dryer for lab scale
Fluidised bed drying (FBD) is a common process in the pharmaceutical industry for drying compo...
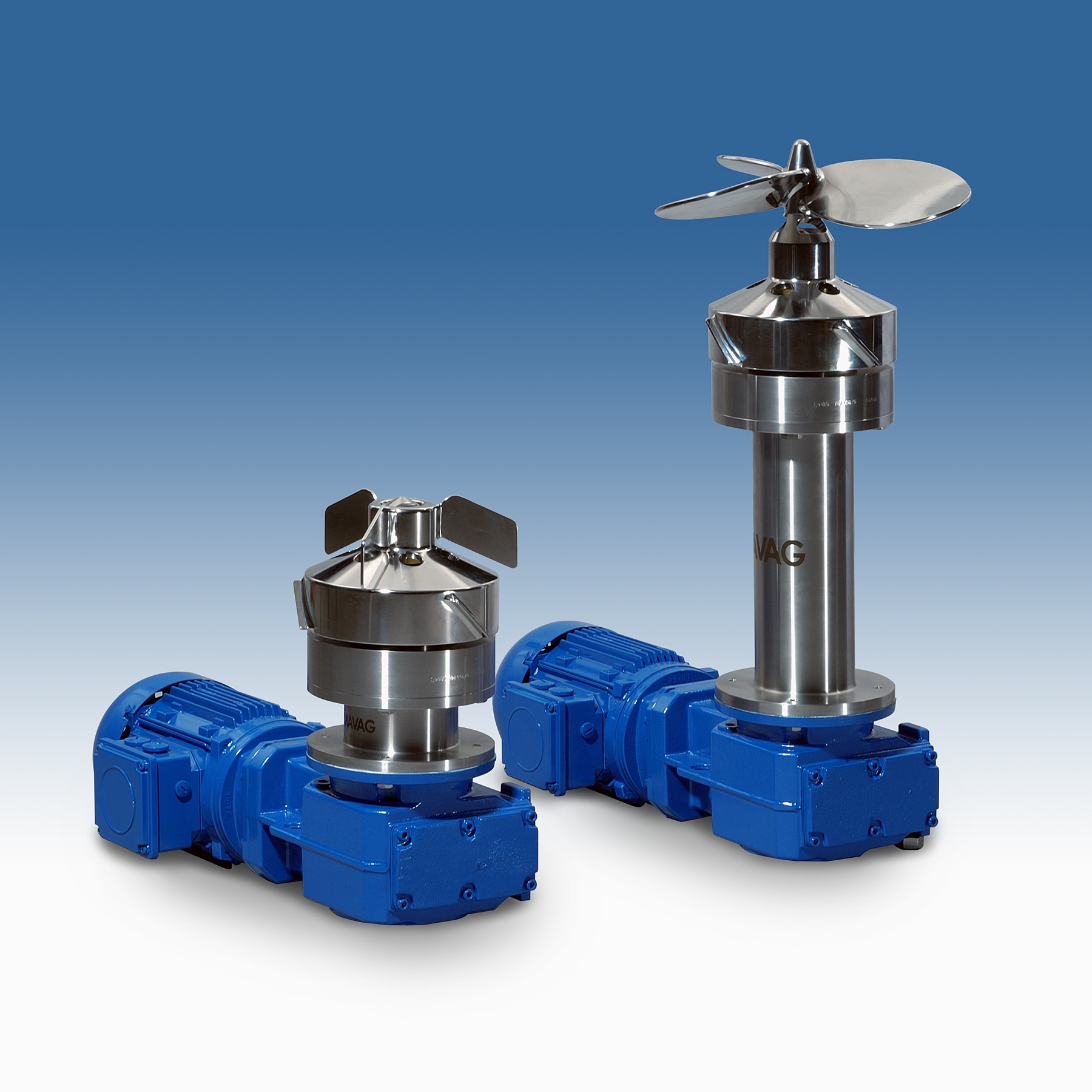
Magnetic agitator
Reliable mixing and agitation are essential to any quality production process that involves a fluid. This n...
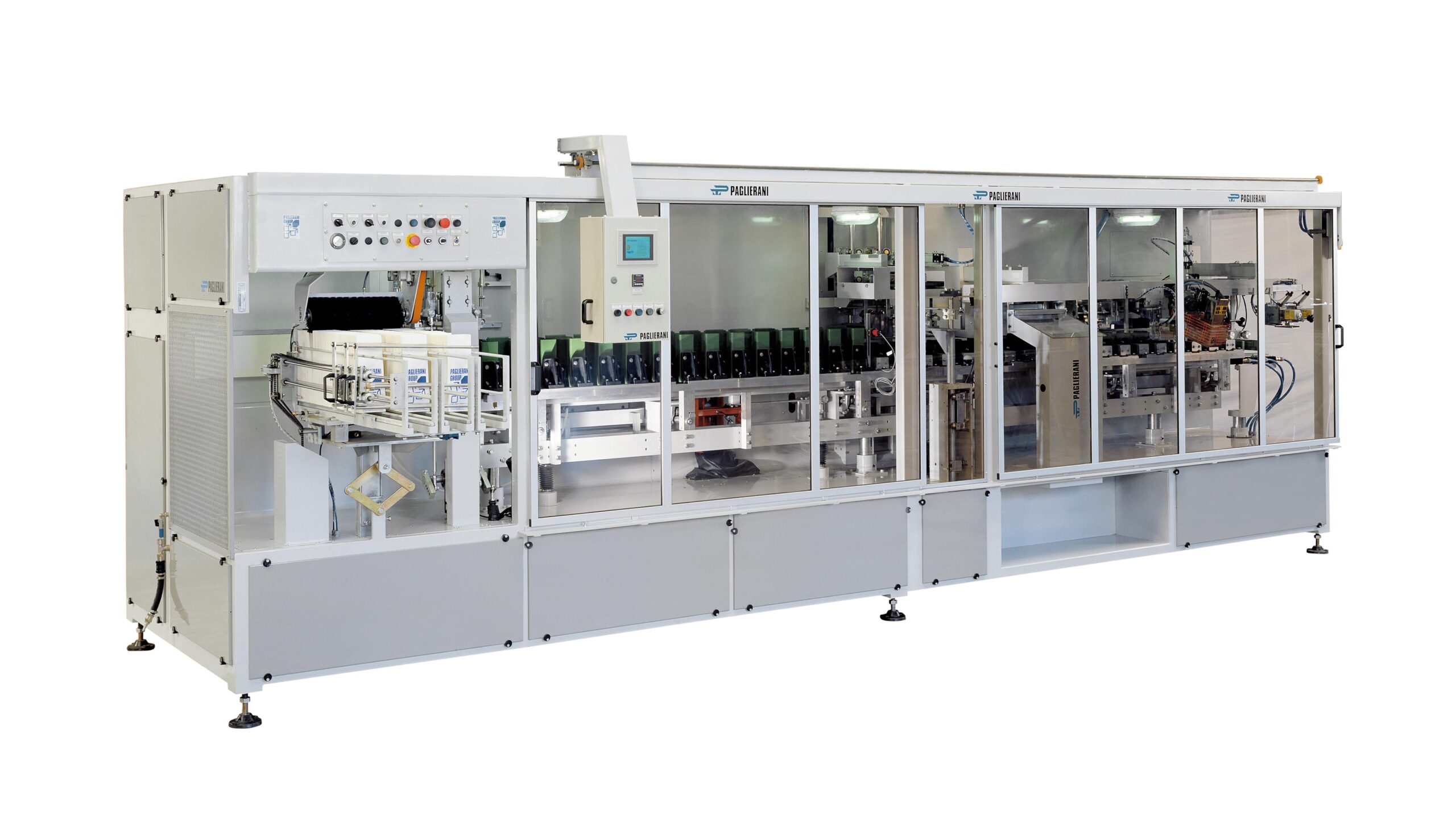
Packaging machine for preformed paper bags from 500 g to 5 kg.
Paper bag filling and closing for larger quantities of ma...
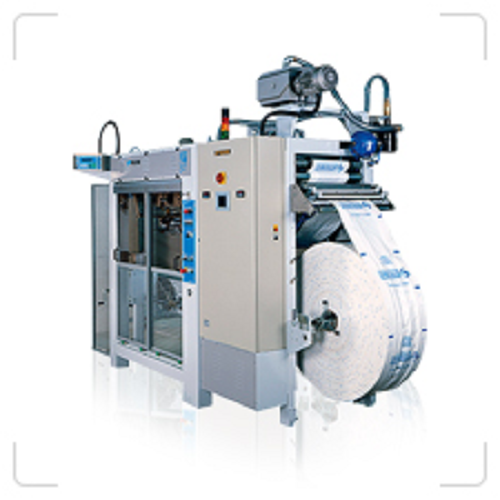
Horizontal form, fill and seal machine for bags up to 10kg
Bagging small quantities of solids or liquids, whether in pap...
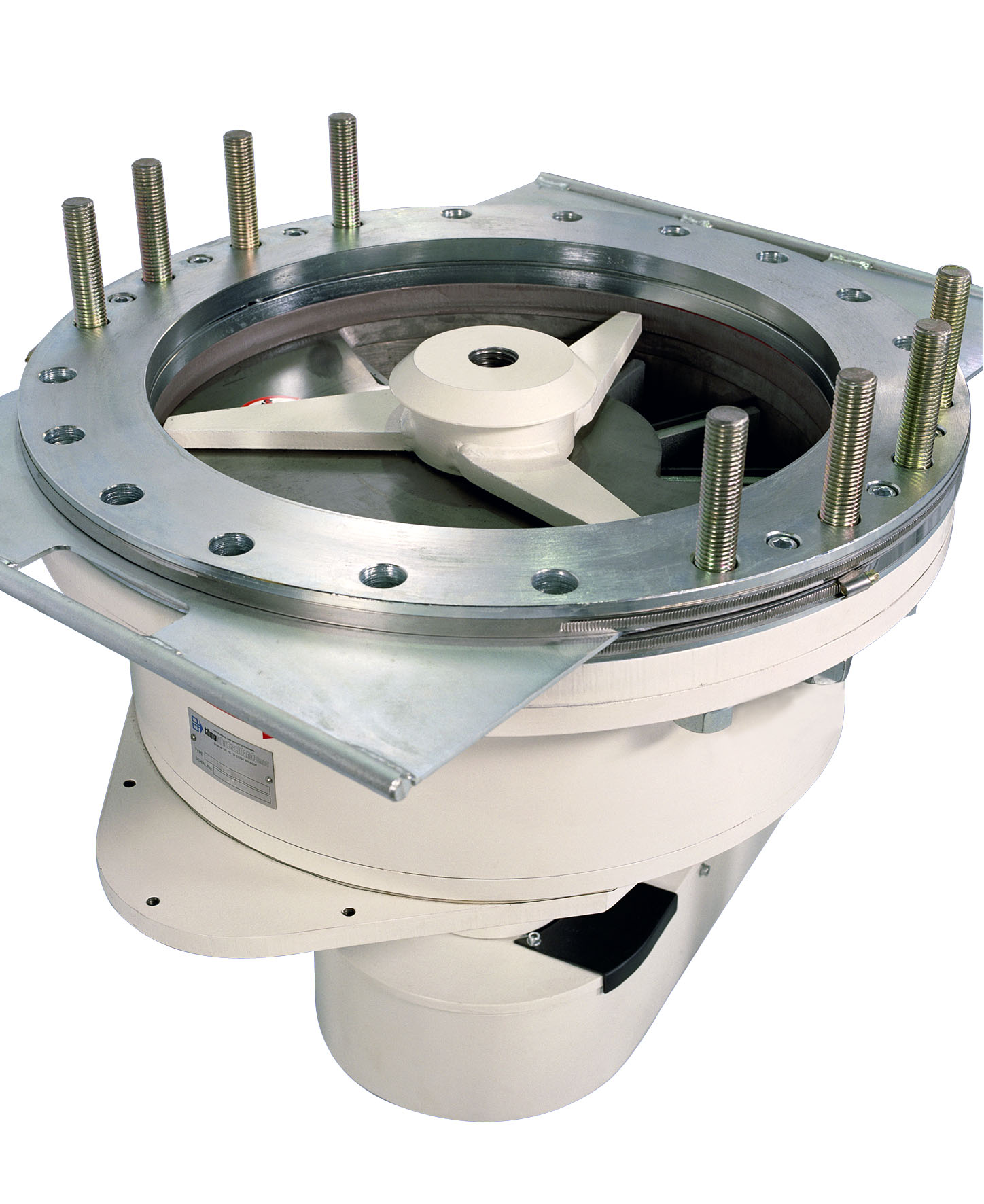
Special duty horizontal metering valve
Occasionally, there is no suitable standard valve available for a particular conveyi...
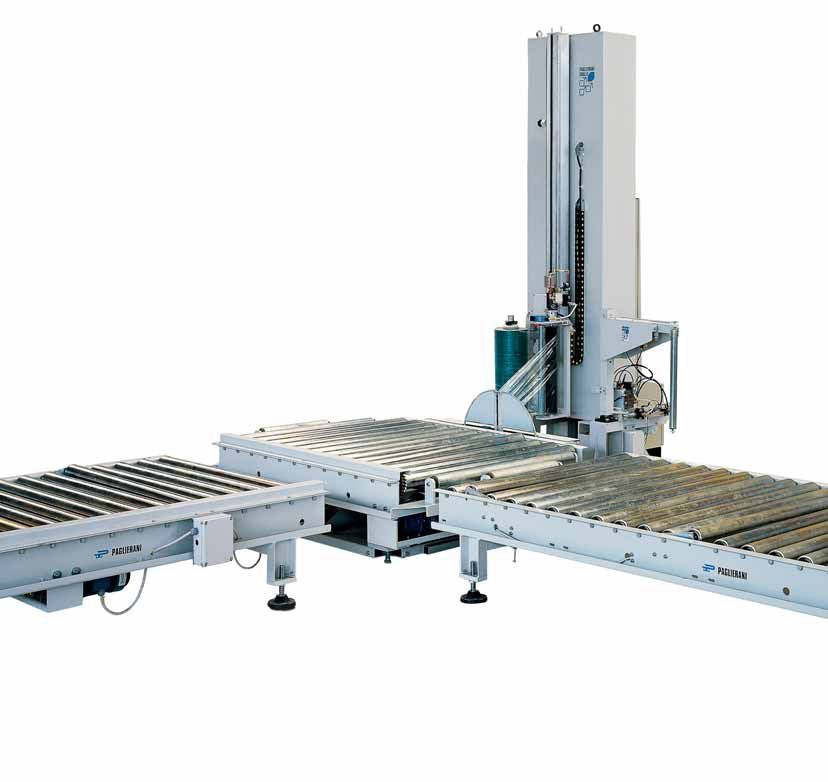
Automatic stretch wrapping machine for medium speed
For secure, automated stretch wrapping at medium speeds, the key is e...
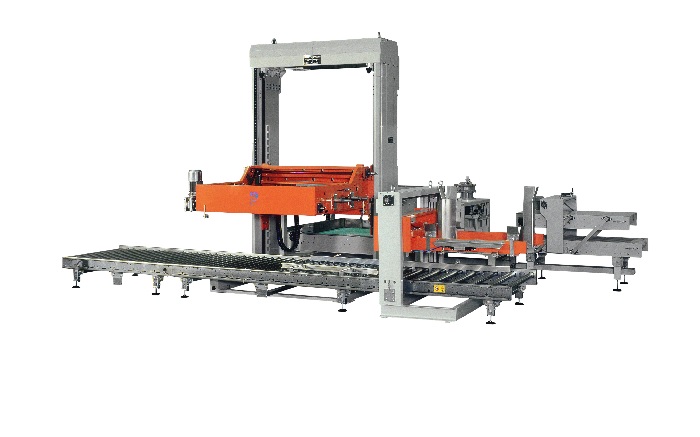
Traditional palletizer for bags
Packaging lines may require a single, flexible solution that can handle many different palle...
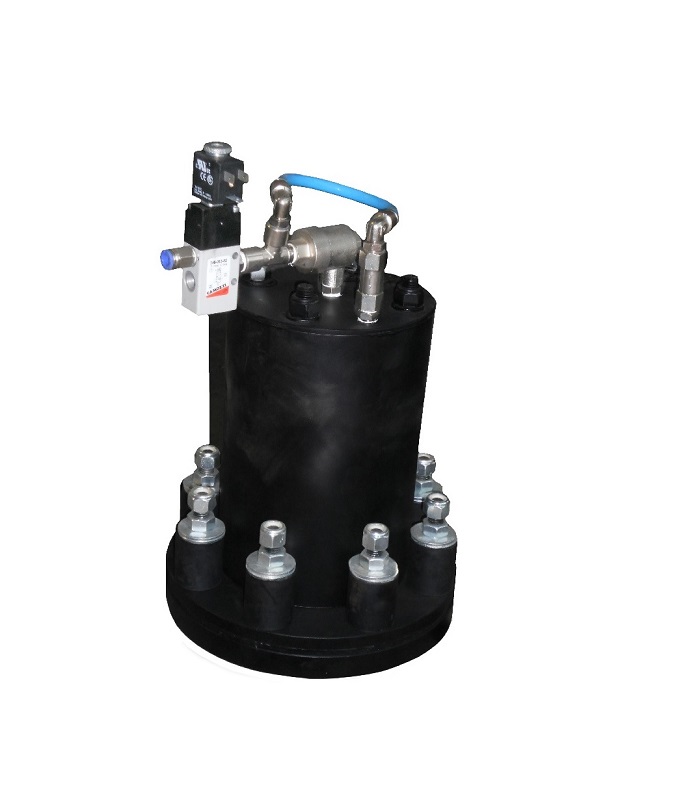
Airshocking hammer
Silos, hoppers, bins, and other containers can build up a layer of powdered product on the internal walls....
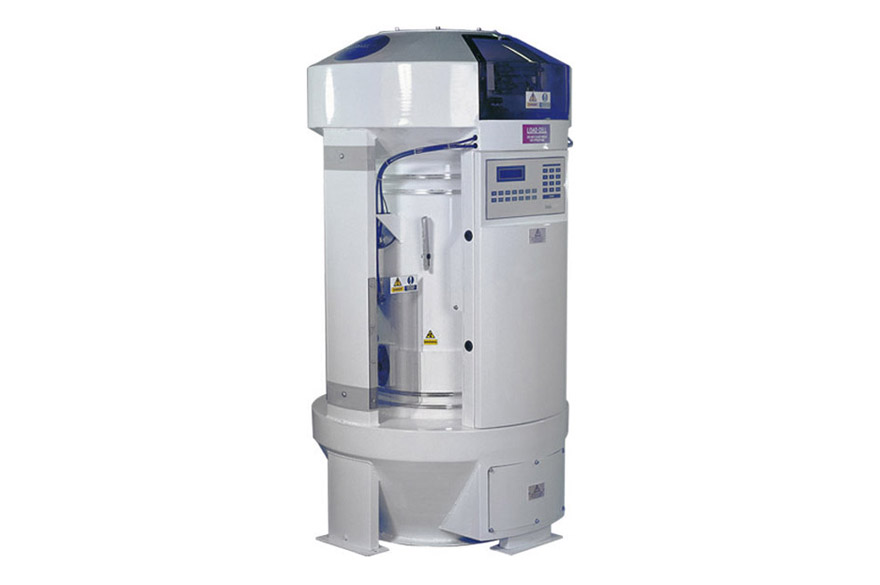
In-process weighing system for mills
When you need a throughput weigher for modern flour/grain milling applications, the we...
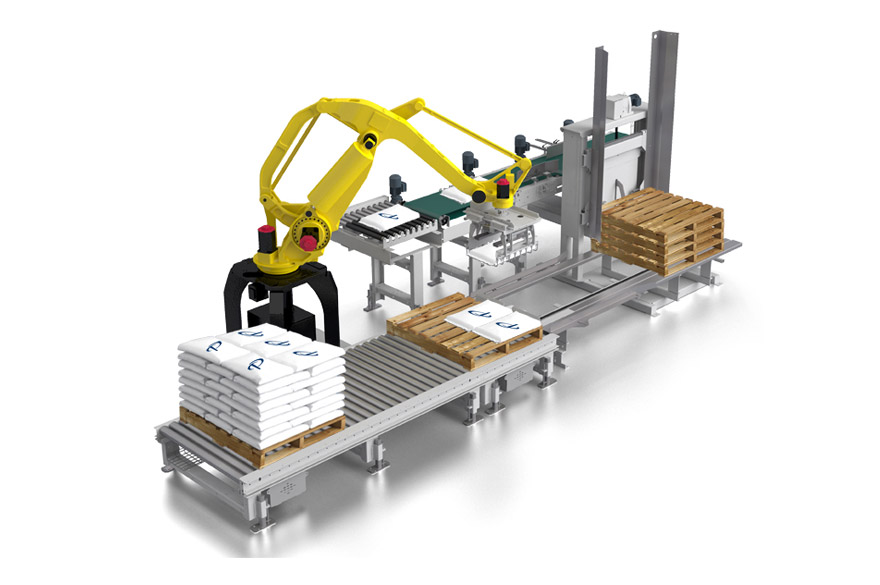
Robot palletizer
Palletize up to 1,800 large industrial bags per hour at a multi-pick-up configuration.
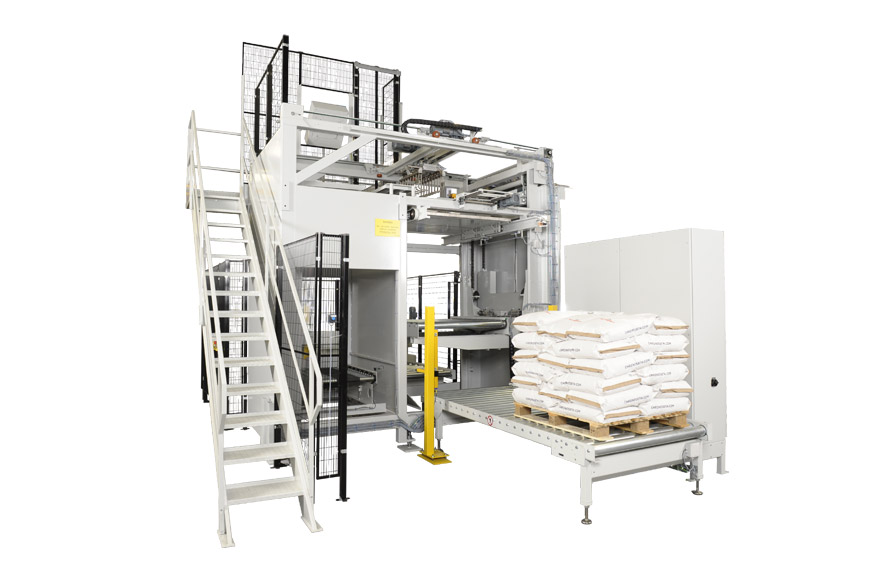
Compact palletizer
Choosing an accurate palletizer can be quite an advantageous move. This one is designed for euro, industri...
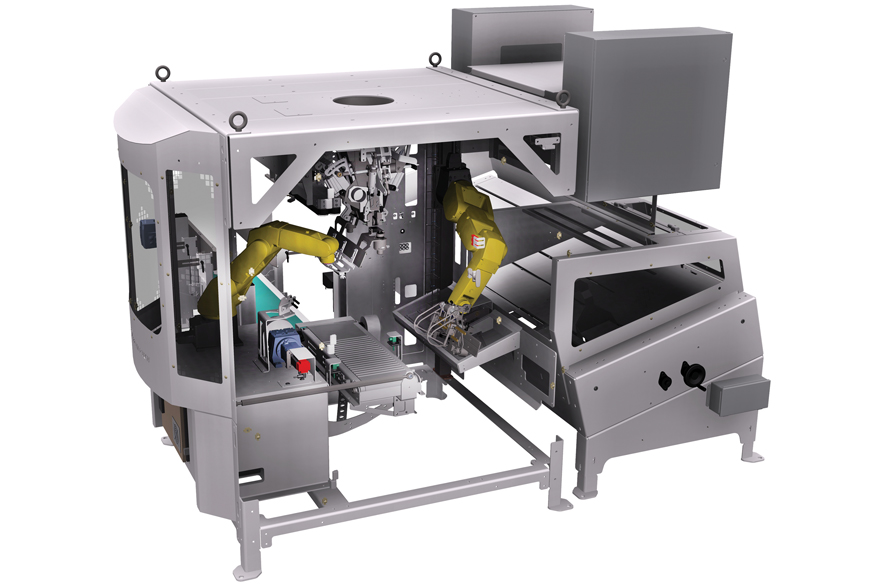
Versatile open-mouth bagger
If you want highly precise bagger for bagging multiple bag materials, here you go. This versatil...
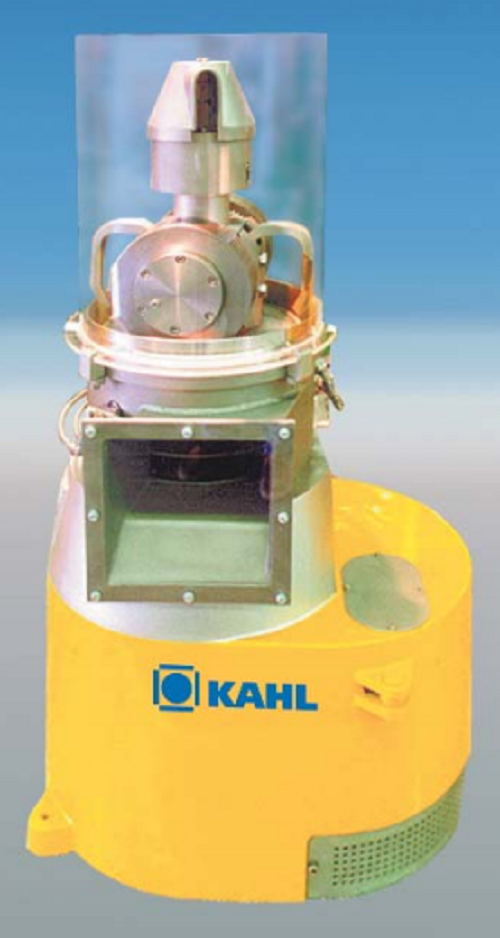
Small scale pelleting press
Many industries require reliable pelletizing equipment with smaller scale production capacities....