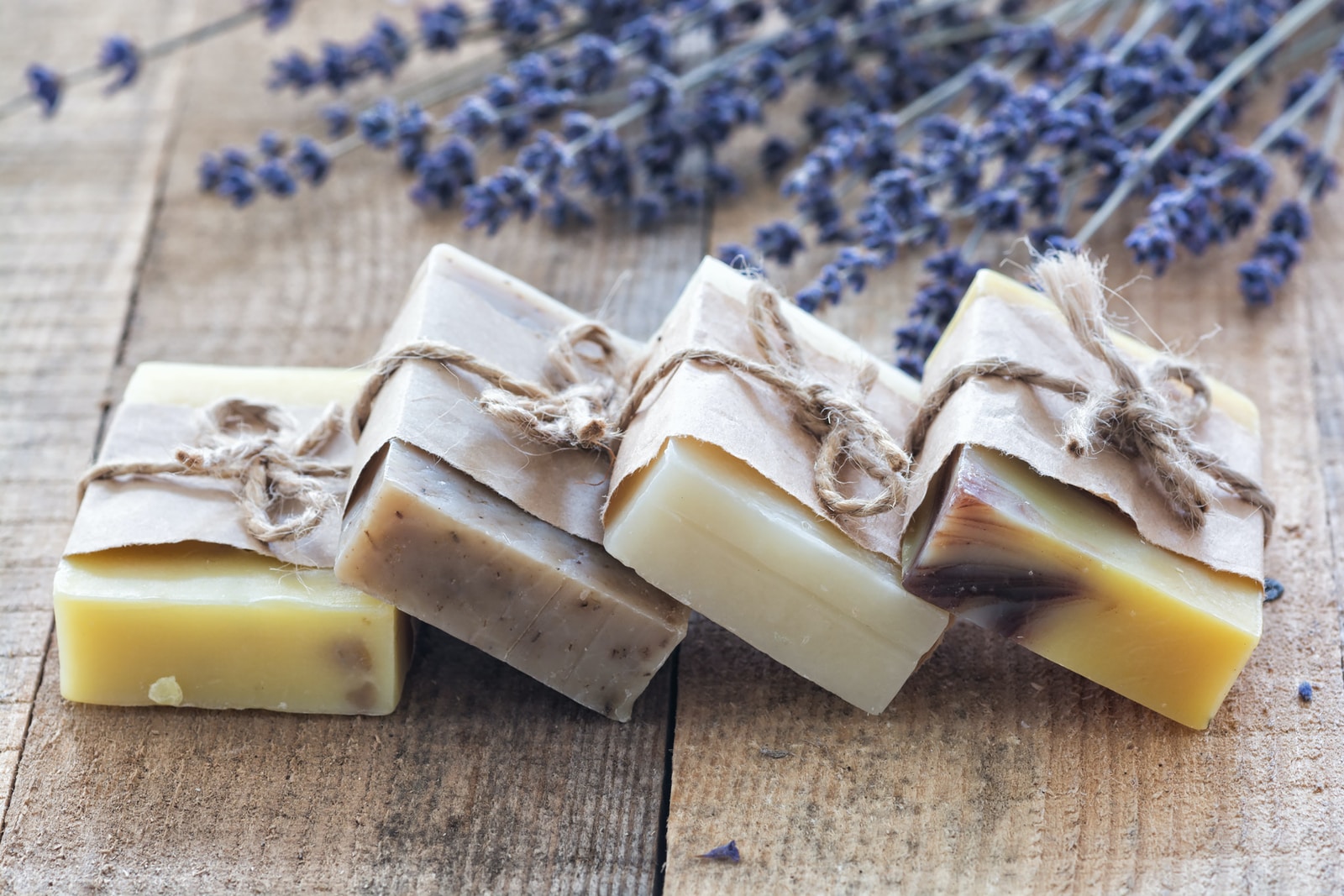
Making Hand Soap
Find innovative production technology for making hand soap and connect directly with world-leading specialists
Star-shaped, lavender-scented, yellow, green, in a dispenser, today’s hand soap comes in a variety of shapes, fragrances, and colors. But whatever type of soap you choose for your good hand-washing habits, the basis of all soap making is mixing animal fats or vegetable oils with an alkali - in this case, a strong base - in a kettle to produce a chemical reaction called saponification.
Stories about hand soap
Select your hand soap process
Tell us about your production challenge
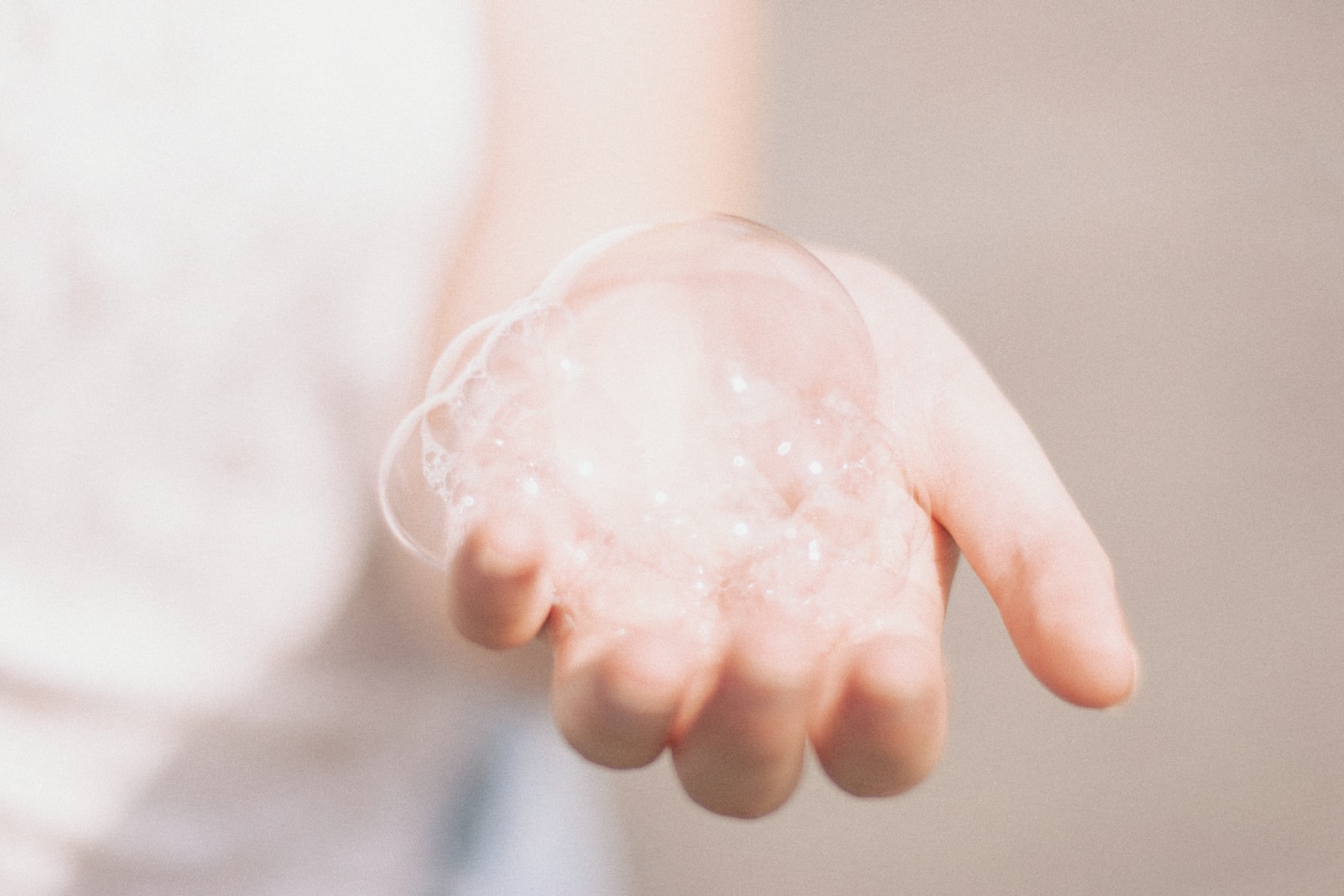
The chemistry behind soap making
Soap is a salt of fatty acids. Okay, but what does that really mean? To give these words meaning, we have to bring up some chemistry. Soap is the result of a chemical reaction called saponification. It happens when animal fats or vegetable oils are mixed with a strong base (sodium hydroxide or potassium hydroxide). The type of alkali determines the consistency of the products – sodium soaps are solid and potassium soaps are liquid or soft. When our strong base reacts with the triglycerides (the fats), it breaks the bonds in the triglycerides between the fatty acids and the glycerin. The fatty acids acquire sodium, becoming salt. So, from this chemical reaction, you get glycerin, which must be removed, and soap (salt of the fatty acid).
Small scale or large scale producers – Which process to choose?
There are two main methods for soap making: the kettle process and the continuous process. The kettle process is on a batch basis and it is very time-consuming. It takes from 4 to 11 days to complete the entire process. Due to time constraints, it is usually used by small to medium-sized manufacturers. If you are part of large manufacturers, the continuous process suits you best. In this case, the entire process takes a few hours instead of few days. But why there is this big time difference?
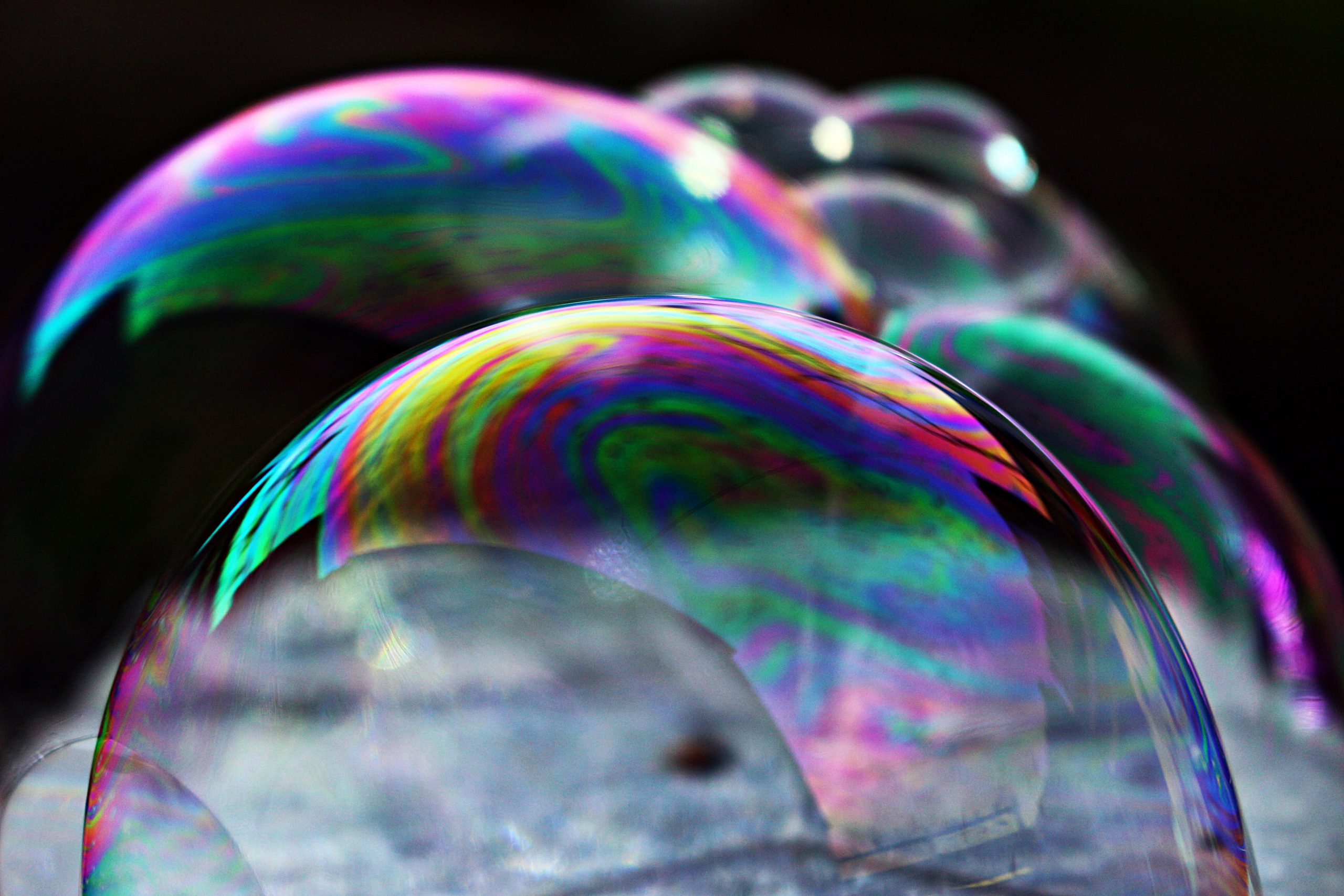
Soap making – The kettle process
To get saponification in the kettle process, you have to place animal fats or vegetable oils in a kettle and add gradually the alkali metal. From a perforated coil, steam jets are used to heat the mixture and encourage the chemical reaction to produce soap and glycerin. Treating the soap with hot brine (very salty water) causes an upper layer to form with soap curd and a bottom layer where glycerin settles. Glycerin is then pumped out of the kettle and treated for other uses. To remove impurities, you have to wash the soap left in the kettle and then boil it with water (pitching step). This creates again two layers: a top layer called net soap (70% soap and 30% water), and a bottom layer called “nigre” which are impurities.
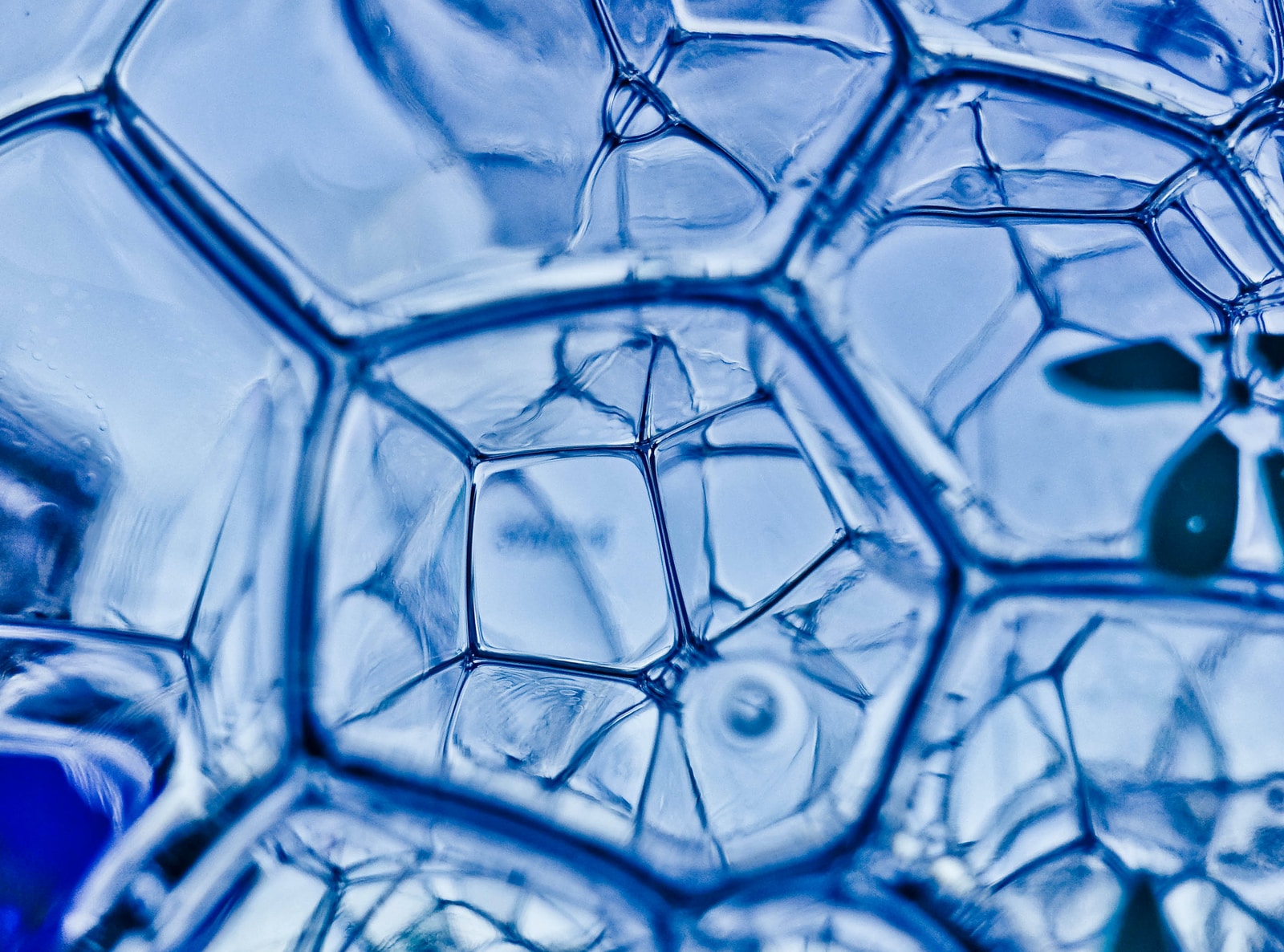
Soap making – The continuous process
The continuous process is quicker because manufacturers use fatty acids in saponification instead of natural fats and oil. Fatty acids do not have impurities and produce water instead of glycerin. The process starts splitting the fats into crude fatty acids and glycerin, using high-pressure steam. The splitting takes place in a stainless steel column called hydrolizer. Then fatty acids are distilled under vacuum. Only now you can use your alkali solution for saponification reaction to neutralize the fatty acids and produce soap and water. In this way, you can achieve complete neutralization without using excess alkali or brine to recover glycerin.
Finishing process for soap bars – What industrial soap making equipment do you need?
Regardless of which method you choose to follow, turning your soap into the shape you prefer requires finishing operations. After boiling, you need to cool your soap and let it solidify. Once solidified, soap is cut into ribbons that are in turn mixed and compressed by big rollers called mills. A blade scrapes the soap of the rollers and cuts it into denser ribbons that are sent to a hopper. Here an auger turns and pushes the soap in an extruder that shapes the soap in soap noodles. To create the different colors and fragrances, steel blades in a mixer mix the soap with color. Then, your colorful soap travels to a forming plate creating a long bar that will be cut into pieces called slugs. In the end, a dye press will shapes your hand soaps, creating these multi-colored and scented soap bars.
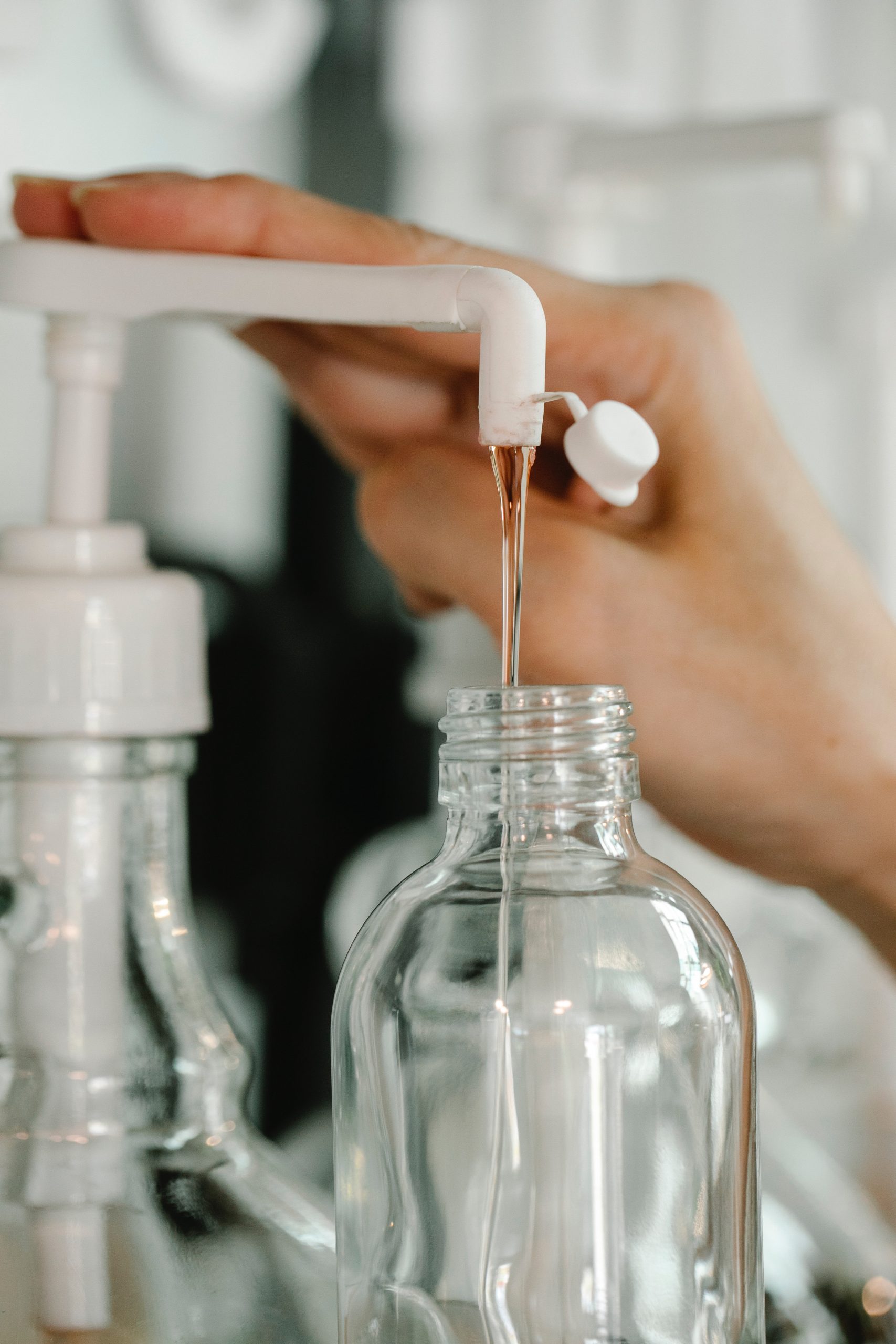
And what about liquid hand soap?
The difference between a soap bar and liquid hand soap lies in the alkali. To make the soap softer, you must use potassium hydroxide. However, to reach the liquid state you have to add water, which dilutes the concentration. Mind that water increases the chances of germs and bacteria growth, so disinfecting compounds and fungicidal solutions are added to your soap.
Filling and capping liquid hand soap
When your liquid soap is ready, you need to bottle it. Remember that after the process, your hand liquid soap is hot, so cool it before filling the bottle. You don’t want to melt your plastic bottle, do you? After cooling, your soap travels to storage tanks to await bottling. Meanwhile, through an infeed screw, bottles reach the filling station where several nozzles fill them simultaneously. The nozzles fill the bottles first slowly with a small layer of product and then with a second stage that fills them up much faster – this happens to avoid splashing and wasting of product. After filling, bottles reach the capping station, where first the dispenser pump is inserted in the bottles and then the chuck tightens and secures the cap through a fast rotation.
Processing steps involved in hand soap making
Which hand soap technology do you need?
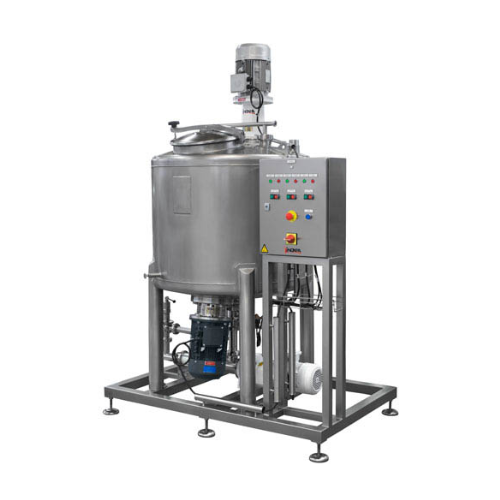
Hydroalcoholic gel mixing system
Ensure seamless production of hydroalcoholic gels with an advanced mixing system designed f...
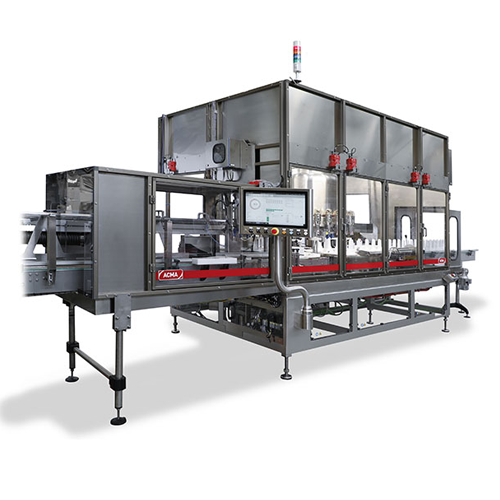
Rotary filler capper for personal care products
Ensure consistent filling and capping of liquid products with high-speed p...
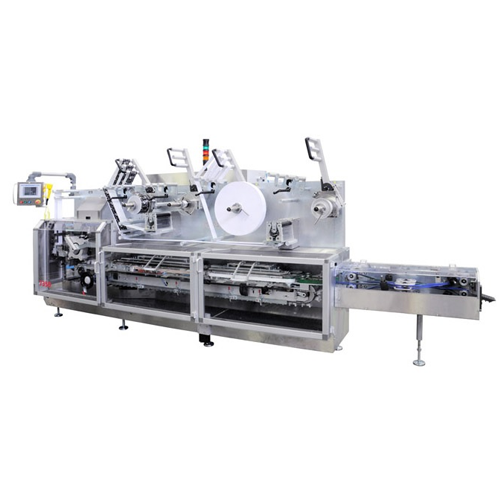
Soap bar fold wrapping solution
Ensure precise wrapping and sealing of soap bars with continuous motion, enhancing efficienc...
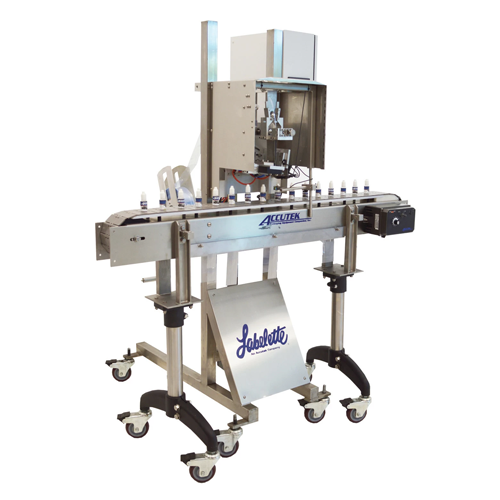
Tamper evident banding system
Ensure product integrity with a high-speed system designed to apply tamper-evident bands effic...
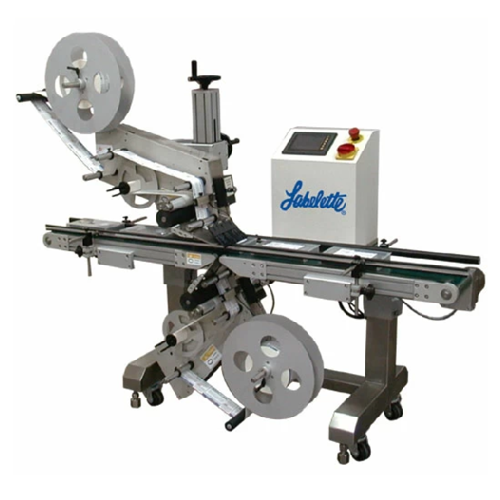
Dual head labeler for top and bottom label applications
Ensure precise and wrinkle-free labeling on containers and packag...
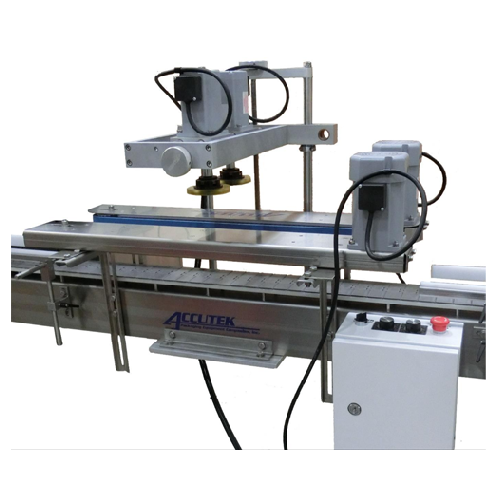
Retorquer for tamper-evident bottle caps
Ensure seal integrity and maintain tamper-evidence in high-speed production lines ...
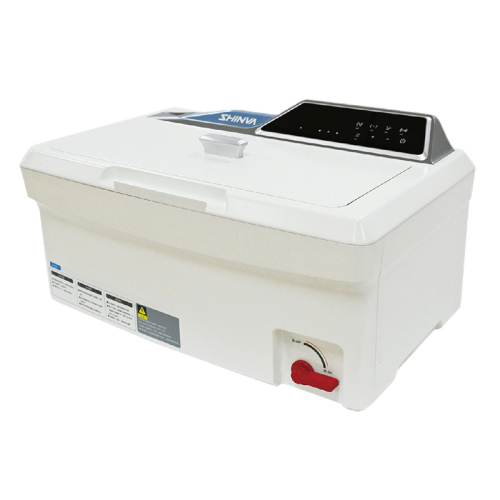
Tabletop ultrasonic washer for surgical instruments
Achieve thorough cleaning and disinfection of surgical tools and prec...
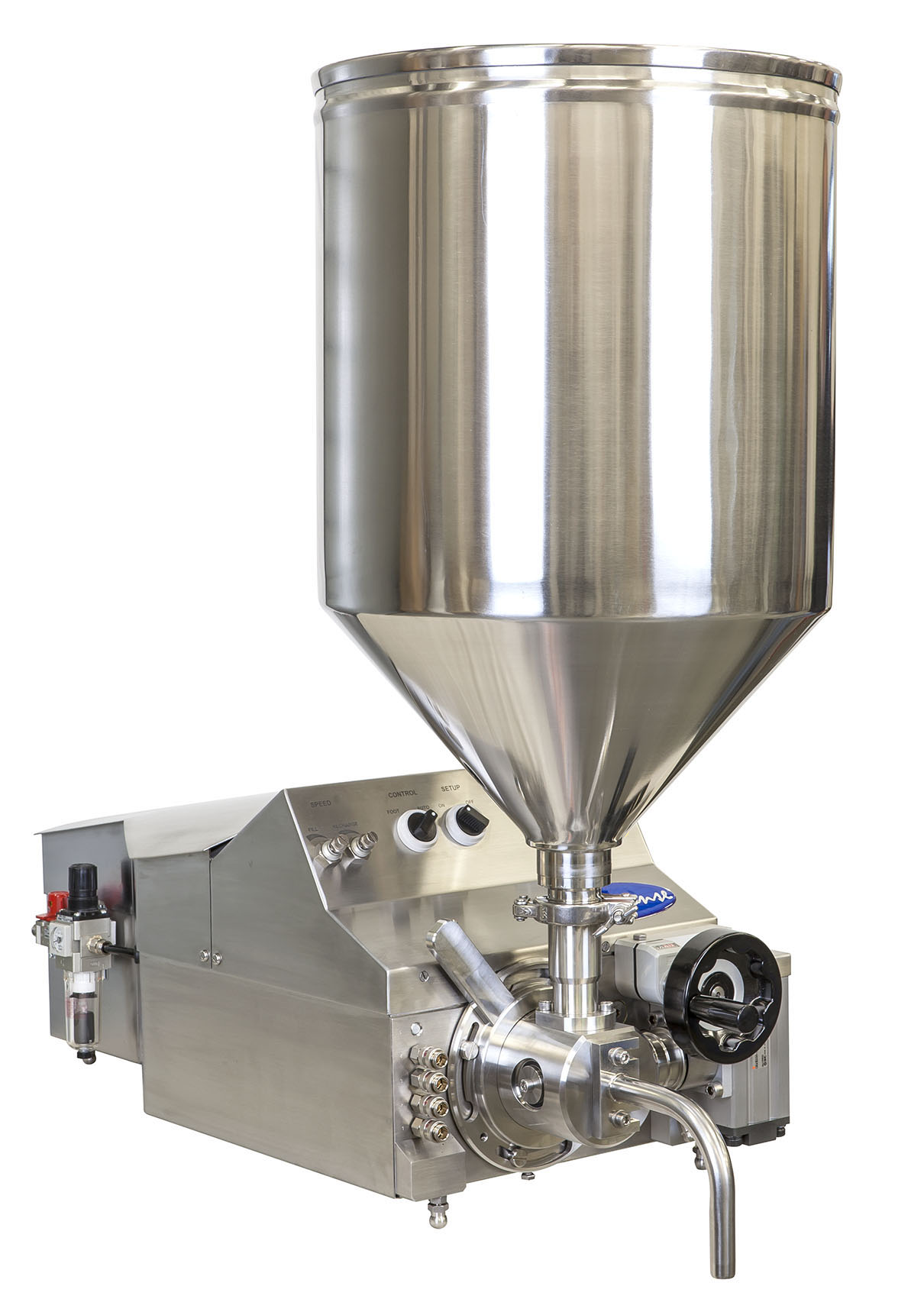
Semi-automatic filler
When you are a small or a medium-sized manufacturer the manual filling processes might often lead to in...
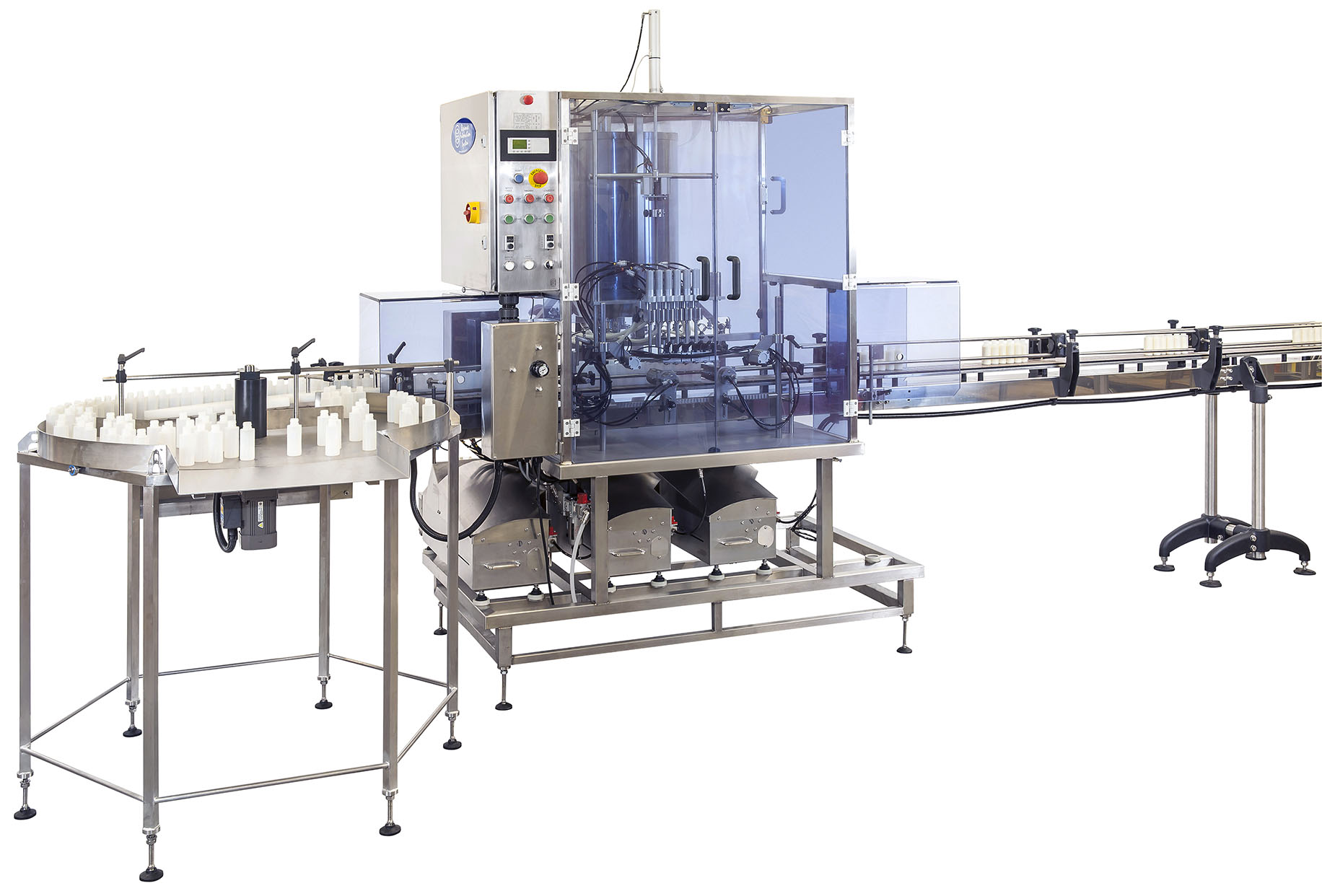
Up to four head automatic filling machine
When your consumer demand is increasing you will need new and more effective pac...

Hot air tunnel for shrink sleeve labels
Sleeves are very popular in food, beverage, Chemical and pharmaceutical industry be...
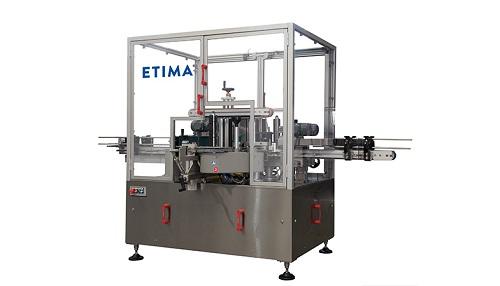
Self-adhesive linear labeling machine for bottles
It is vital to have precise and long-lasting labels on bottles to avoid...
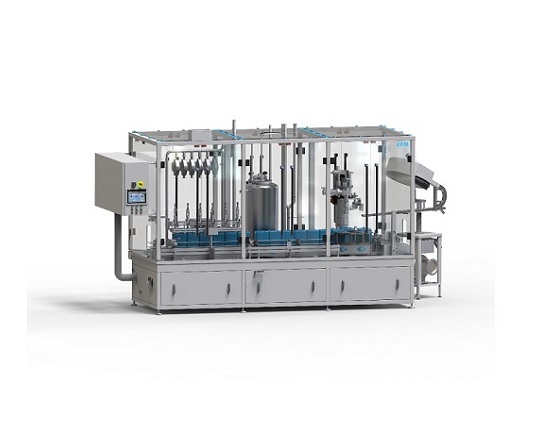
In-line monoblock linear filler & capper
In many food, chemicals and cosmetic industry processes it is vital to have a...

Flowmeter filler
For larger production runs of food, non-food and cosmetics industries, where accuracy and volume of filling i...
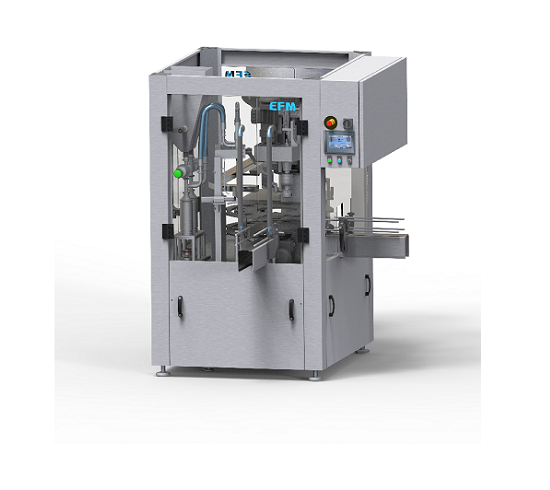
Compact monoblock filler
Filling and capping bottles and pots for food, chemical and cosmetics industries using separate mach...
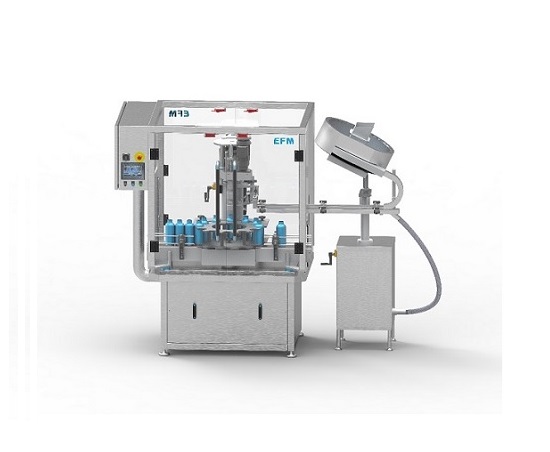
Single head capper
For the stand-alone capping of bottles of up to 30 litre capacity for smaller-scale production you need a ...
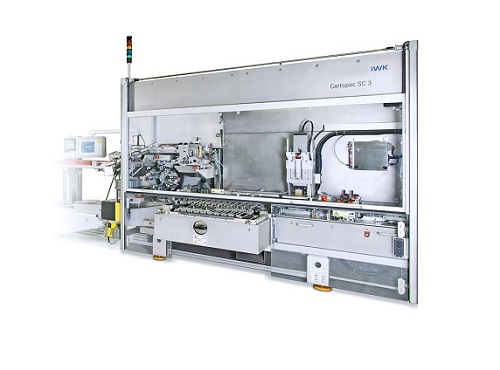
High-capacity horizontal cartoner for pharma and cosmetics appliances
Cartoners take carton blanks which are formed and...
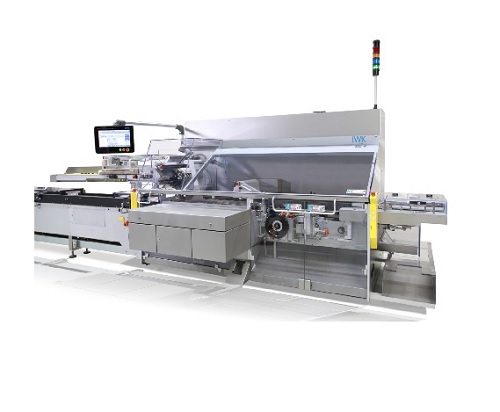
Automatic cartoner for applications in pharma and cosmetics
For high capacity production of cosmetics and pharmaceutical...

Horizontal cartoner for pharma and cosmetics
Most pharmaceutical and cosmetics products are packed in cardboard cartons fo...
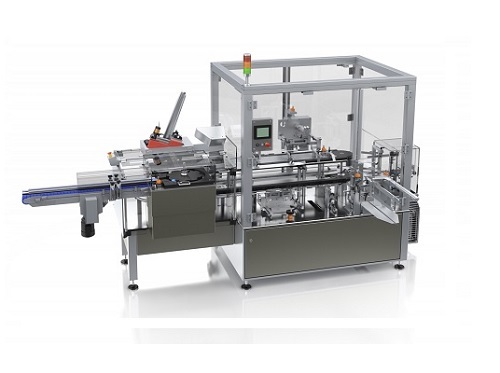
High capacity cartoner for pharmaceutical applications
Many pharmaceutical products are packed in protective and decorati...
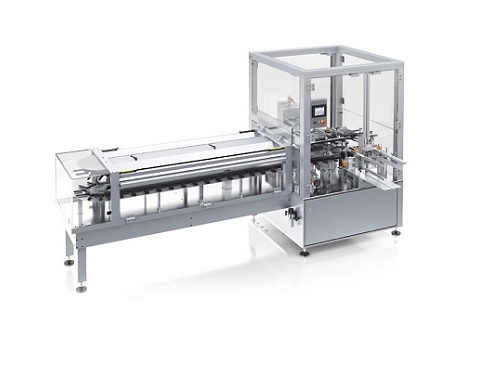
Vertical cartoner for pharmaceutical applications
Many pharmaceutical and cosmetic products are sold in protective and de...
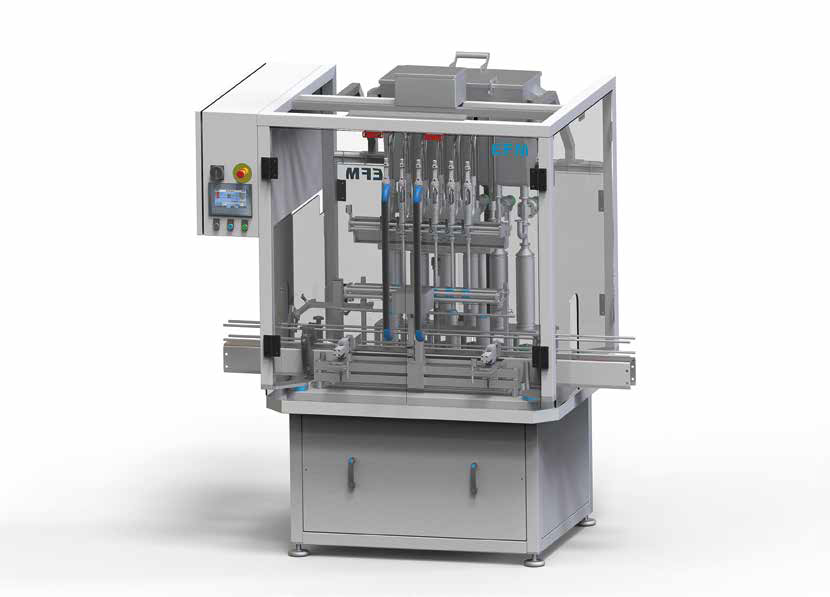
Servo controlled filler
For food and non-food liquid products that are high foam or have a high viscosity a specialist fillin...