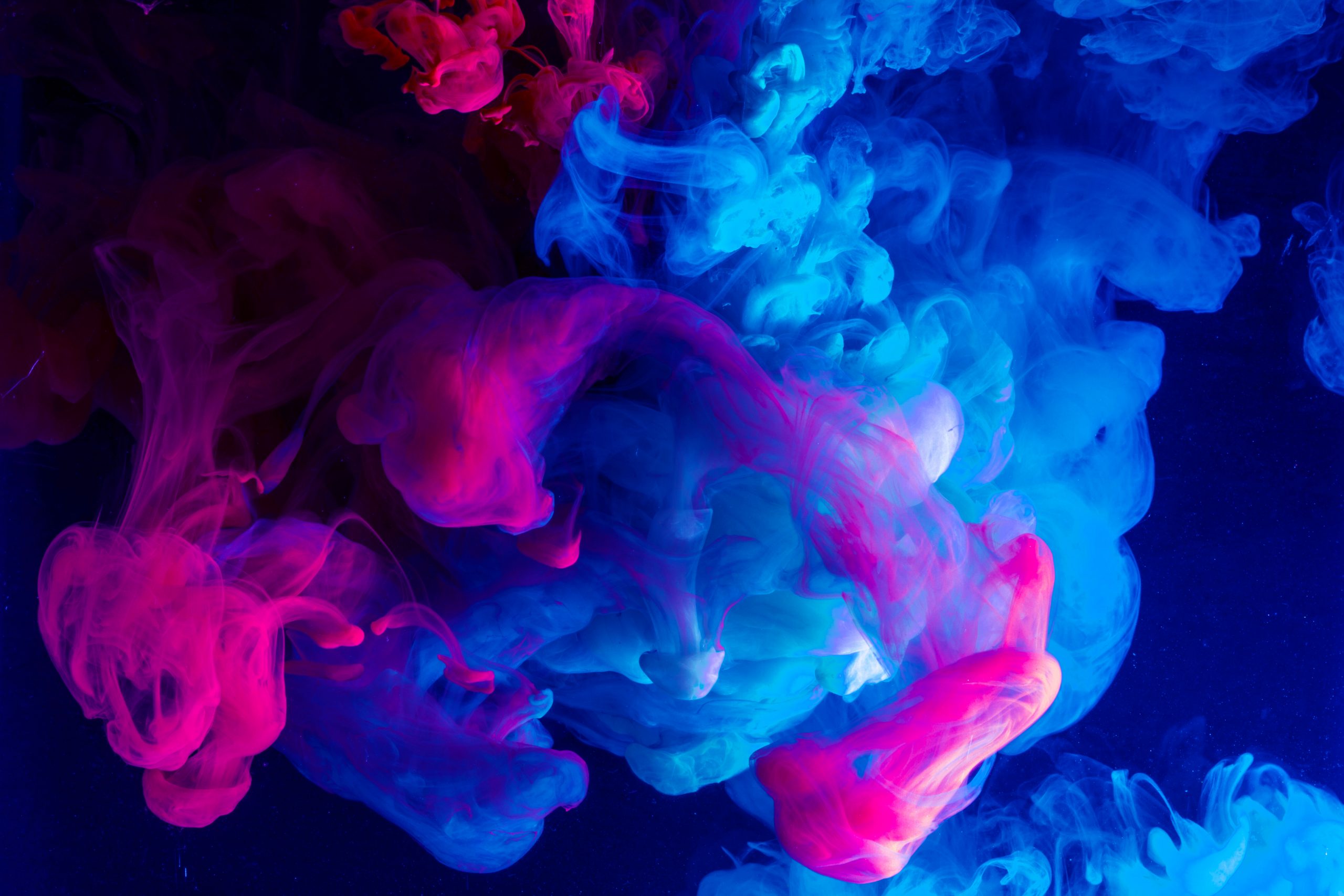
Making Ink
Find innovative production technology for making ink and connect directly with world-leading specialists
Colors present an enduring philosophical problem that generates lofty debates about subjectivism and consciousness. Meanwhile, ink manufacturing equipment turns colors into physical objects. Perhaps paradoxically, digitalization keeps fueling the use of printing ink. From custom clothing to secondary packaging to aircraft livery, inks are everywhere. Indeed, philosophical discussions are also primarily conducted in ink on paper.
Select your ink process
Tell us about your production challenge
Disperse the pigment particles with ink grinding equipment
One of the main challenges in the ink manufacturing process is the agglomeration of pigment solids. Once the pigment is mixed with the solvent, its particles tend to deteriorate the ink’s color properties.
Mill the formula to disperse the particles uniformly in the vehicle. A ball mill using steel beads distributes the solids evenly, developing colors to their maximum. High-shear ink manufacturing equipment like the three-roller grinder enhances gloss by breaking down agglomerates and reducing the surface area of particles.
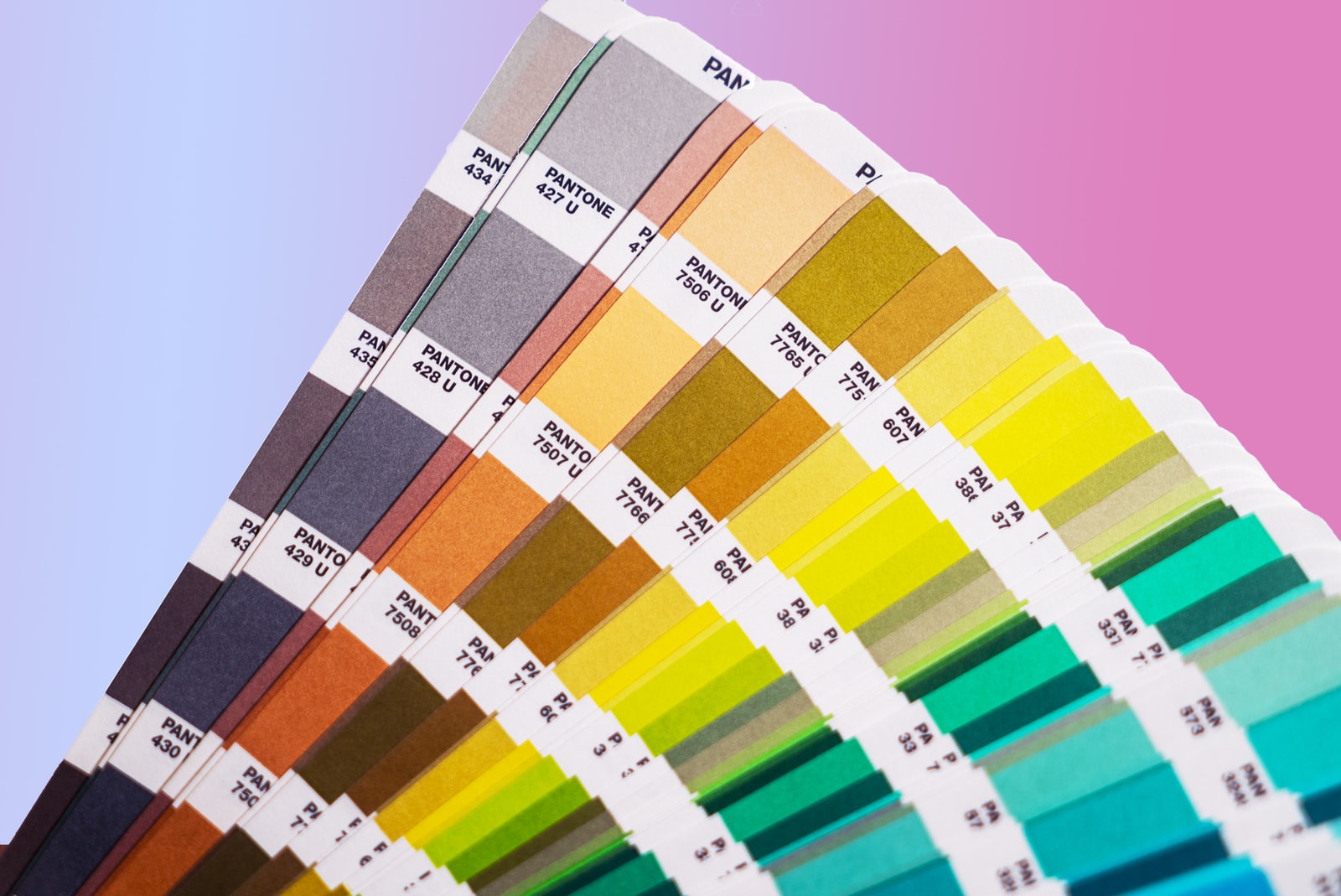
Blend pigment particles in a solvent-based varnish
The defining ingredient in inks is pigment. These particulate solids selectively absorb or reflect light to produce a color. But as insoluble materials, pigments do not automatically lend their tinge to other objects.
These colors are made transferrable by mixing pigments with a vehicle substance. Unlike dyes, pigment crystals do not alter their shape or characteristics when blended. But the vehicle’s composition affects the ink product’s properties – luminosity, viscosity, abrasiveness, and tackiness.
Select the base for solvent inks depending on their boiling point
The primary function of a solvent in an ink manufacturing line is to keep the final product in liquid form. Volatile solvents such as ethyl acetate have a low boiling point, are ideal for inks designed to evaporate quickly, and are often used in flexographic and gravure printing processes.
On the other end of the scale, inks made for screen-printing are based on solvents with high boiling points like butyrolactone and butoxyethanol. Solvents with moderate boiling points develop inks suitable for lithography.

Add a resin to improve the adherence of printing ink
The viscosity of the final product is critical, but ultimately, inks are produced to stick to surfaces. Inks need binders to grip to the medium, whether they visualize a serial number of a box of tablets or a pattern on a roll of wallpaper.
Formulate your vehicle with resins to turn the solution into a film when it is pressed in place. Cellulose derivates, acrylics, and rubber resins add gloss and resistance to the ink.
Treat oily media with high temperatures when formulating vehicles
Dissolve the solvent and binders in a mixer to formulate the base. Oleoresinous media like alkyds need to be heated at temperatures between 120°C and 260°C to reach complete dissolution.
When the primary formula is mixed, combine additives to modify the physical properties of the vehicle. Among these, plasticizers improve flexibility; chelating agents increase the viscosity, and waxes add rub resistance to the manufactured ink.
Which ink technology do you need?
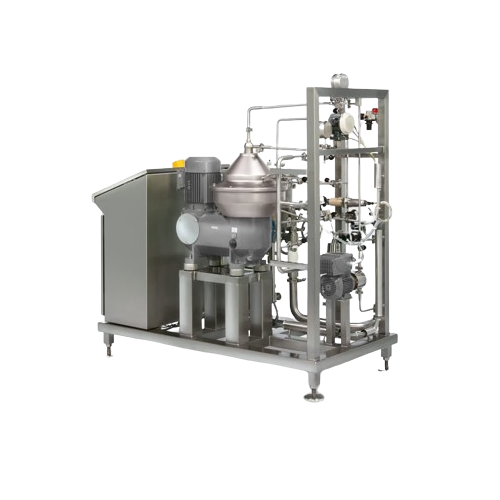
Clarifier for beverages
Enhance beverage clarity and purity with high-performance centrifugal separation, expertly designed t...
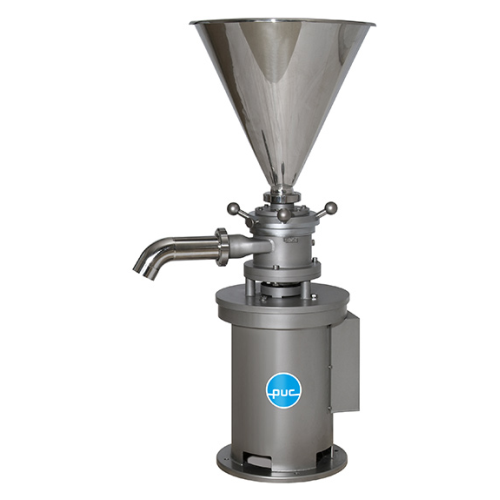
Vertical colloid mill for emulsifying and homogenizing
Optimize your production line with precise particle size reduction...
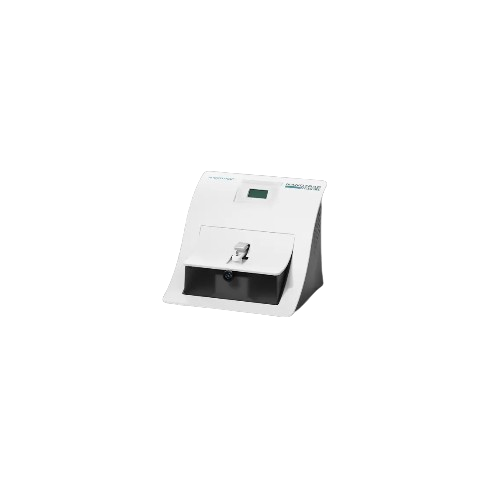
Nanoparticle size analyzer
Master precise nanoparticle and zeta potential analysis with dynamic light scattering technology,...
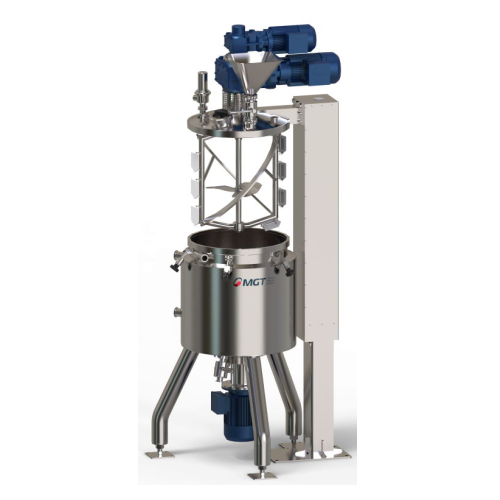
Vacuum mixing system for emulsion and homogenization
Achieve seamless emulsion and homogenization with precision: this sy...
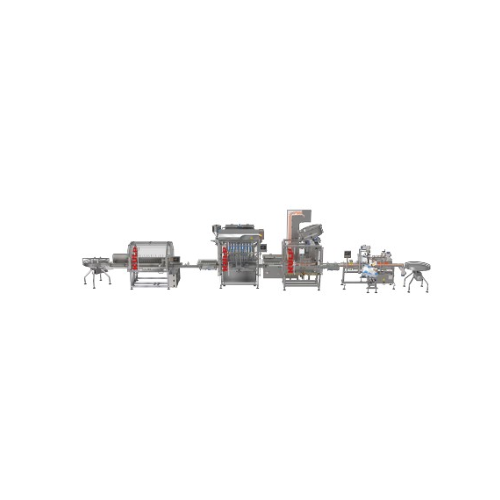
High capacity filling line for jars and bottles
Need to streamline your packaging line? This high-capacity solution proces...
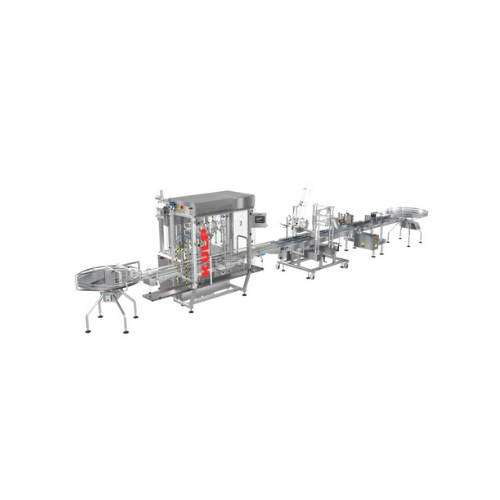
Large container filling line
Optimize your production line with a seamless solution for efficiently filling large containers...
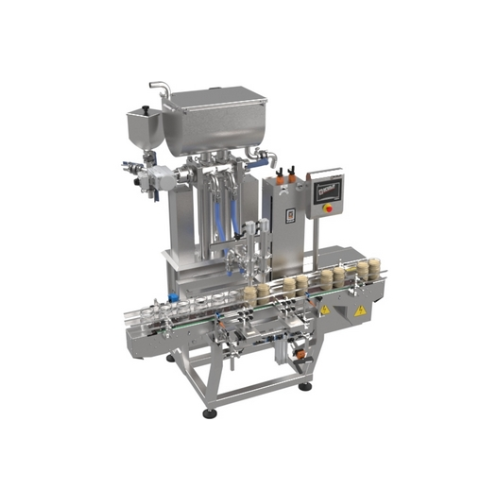
2-head liquid and viscous product filling system
Streamline your filling operations with precision and versatility designe...
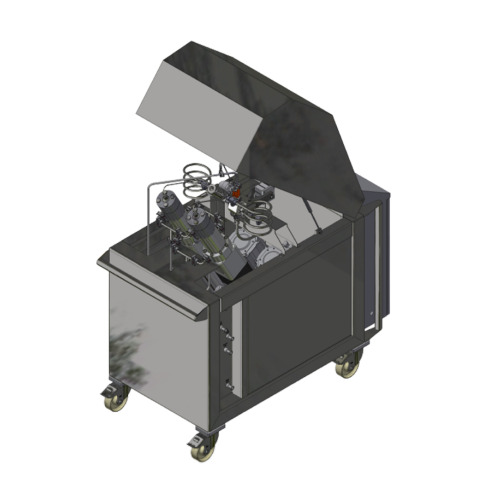
High pressure homogenizer for pharma applications
Achieve precise particle size reduction and stability in liquid formula...
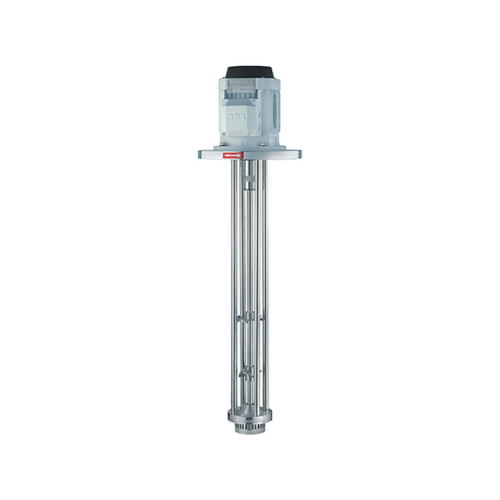
High shear vertical mixer for dispersion and emulsification
Achieve seamless emulsification and homogenization in divers...
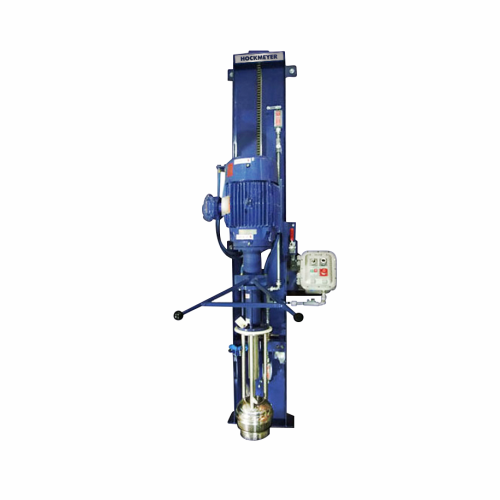
Immersion mill for pail and drum-sized batches
Streamline your production with a versatile solution that efficiently handl...
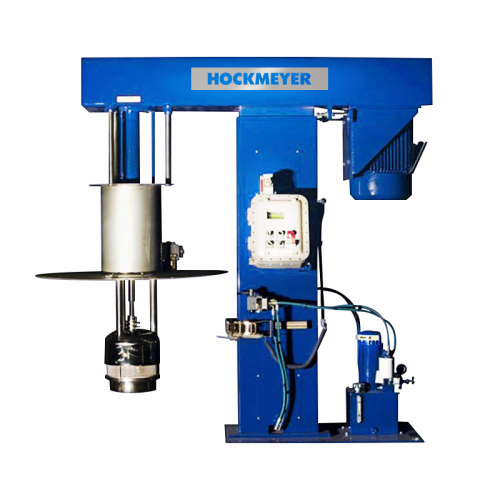
Immersion mill for particle reduction
Achieve streamlined particle size reduction and enhanced mixture homogeneity with imm...
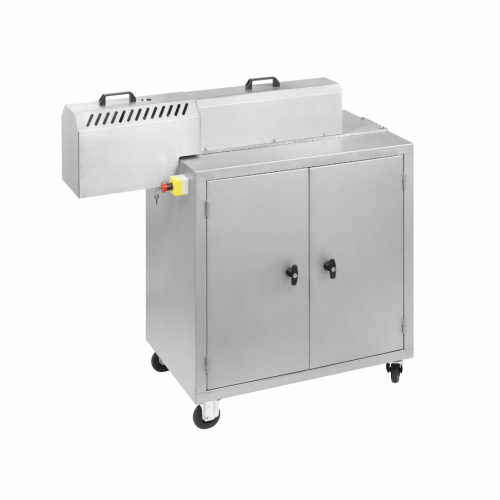
High-viscosity continuous industrial kneader for small volumes
Achieve consistent high-viscosity material processing wit...
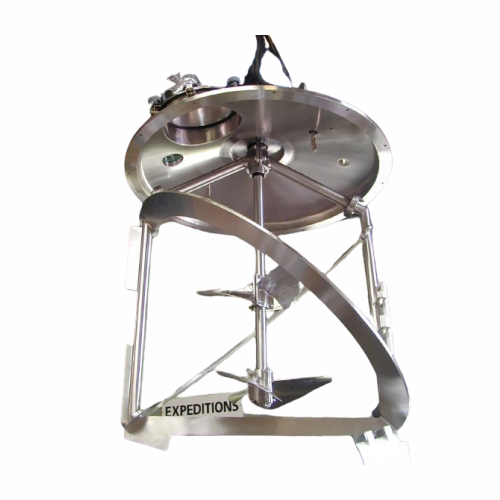
Coaxial mixer for high viscosity liquids
Achieve seamless blending of high-viscosity materials with a coaxial mixer designe...
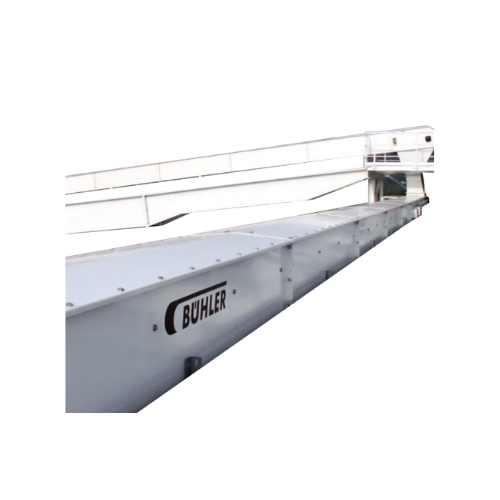
Heavy-duty trough chain conveyor for high throughput applications
Optimized for high-capacity operations, this robust c...
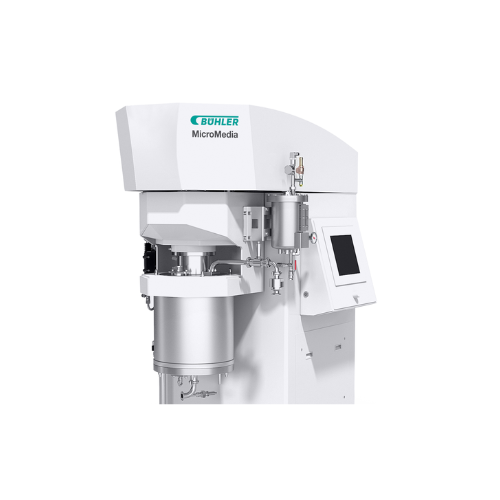
High-performance bead mill for wet grinding and dispersing
Optimize your production line with a bead mill designed for e...
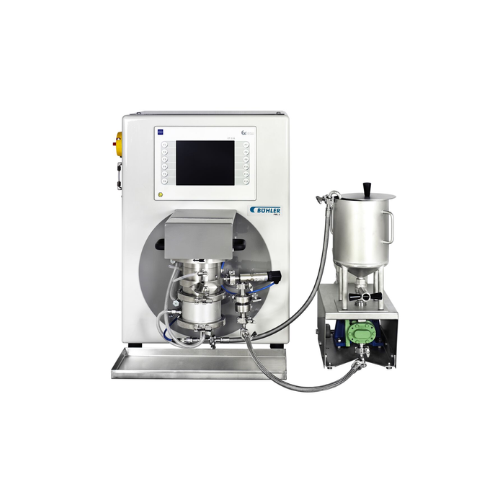
Laboratory bead mill for research and development
Optimize your laboratory processes with this flexible and modular bead ...
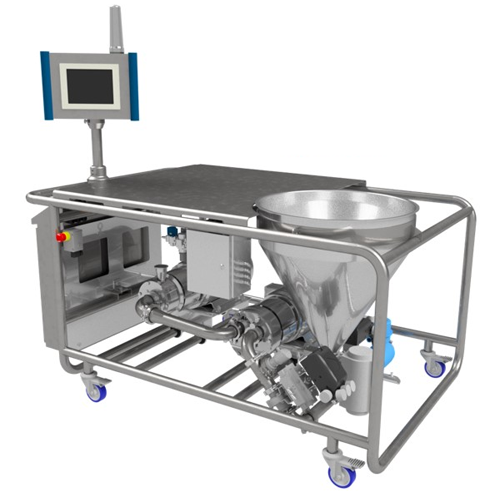
Automated powder induction and dispersion system for industrial mixing
Achieve rapid and efficient incorporation of pow...

Auto-indexing filler for aqueous solutions and light oils
Streamline your bottling process with this six-head filler, pe...
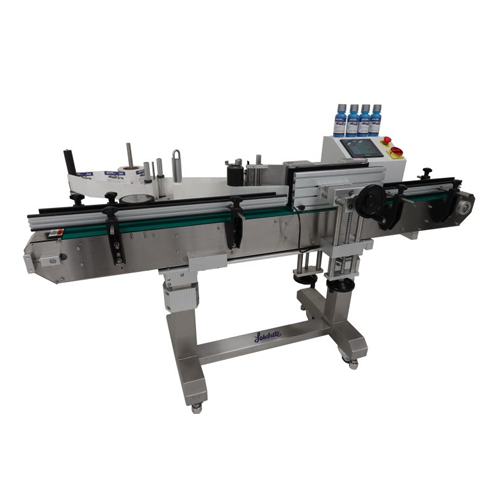
Automatic labeler for low profile containers
Optimize container labeling with precision and efficiency, addressing the cha...
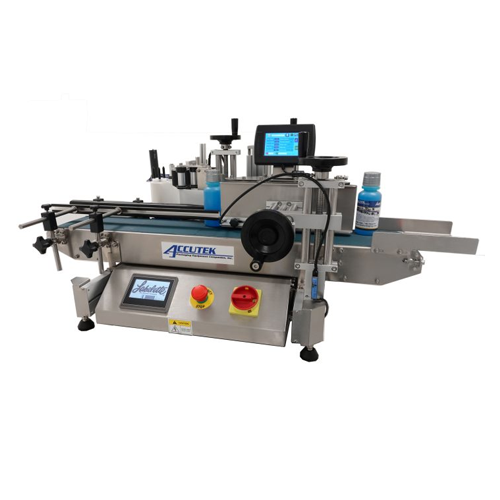
Tabletop labeler with integrated thermal printer for round containers
Efficiently label and print variable data on roun...
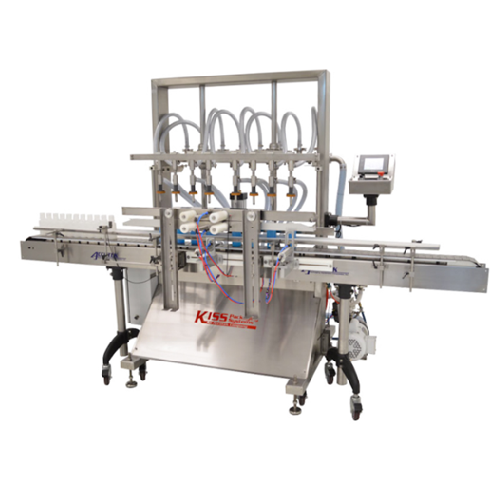
Automatic pressure overflow filler for low to medium viscosity liquids
Ensure consistent fill levels for low to medium ...
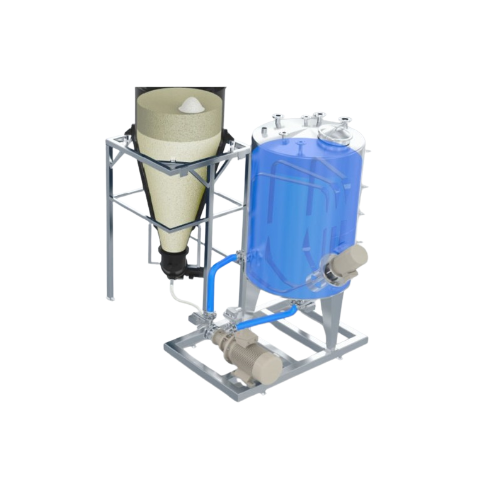
Powder wetting and dispersion system
Revolutionize your production with a system that seamlessly inducts, wets, and dispers...
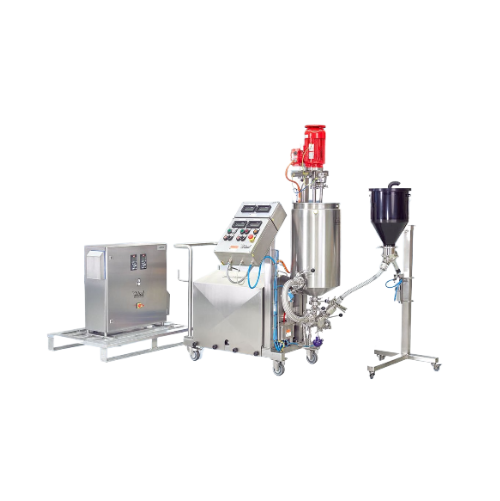
Laboratory disperser for powder induction and wetting
Optimize your pilot and laboratory processes with a high-speed disp...
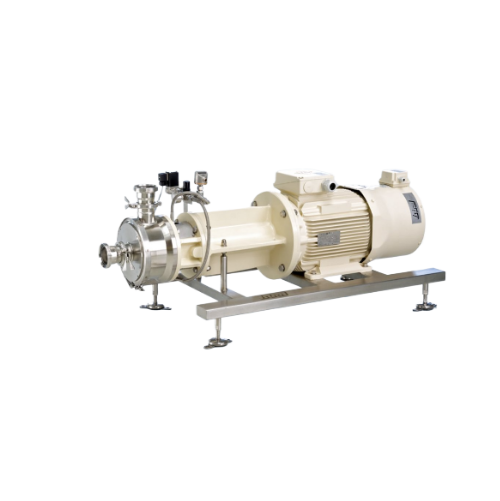
Inline disperser for homogeneous emulsions and suspensions
Achieve precise control over particle size and distribution w...
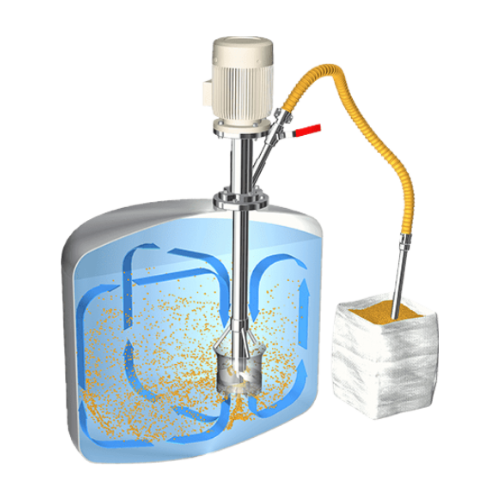
Low-dust powder induction mixer for liquids
Achieve dust-free induction and homogenization of powders in liquids with prec...
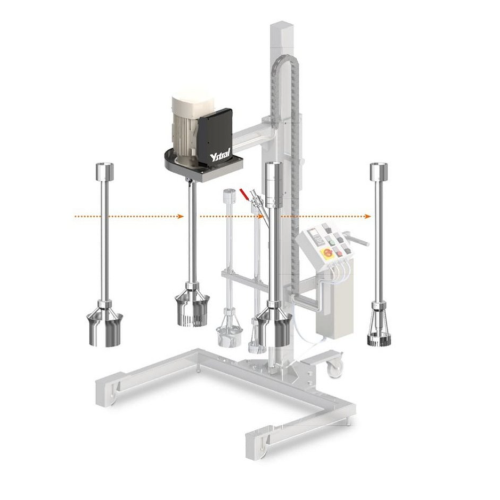
Multipurpose mixing equipment for chemical and pharmaceutical production
Achieve unparalleled flexibility with modular,...
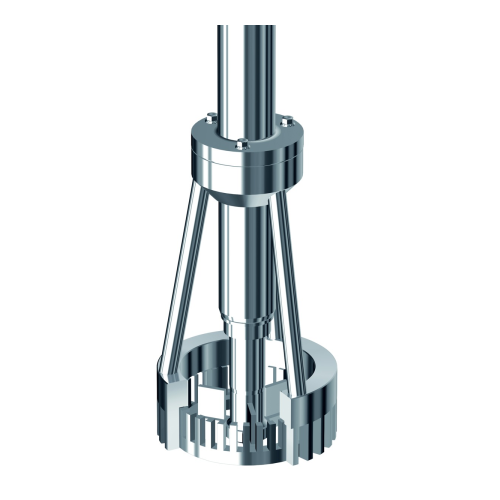
High-shear batch disperser for chemical and food industries
Achieve unmatched dispersion and emulsification precision wi...
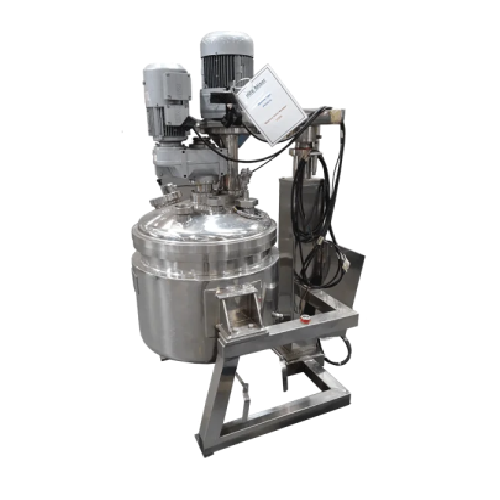
Mixing vessel for liquid, sauce, and cream products
Maximize efficiency in your production line with a versatile solution...
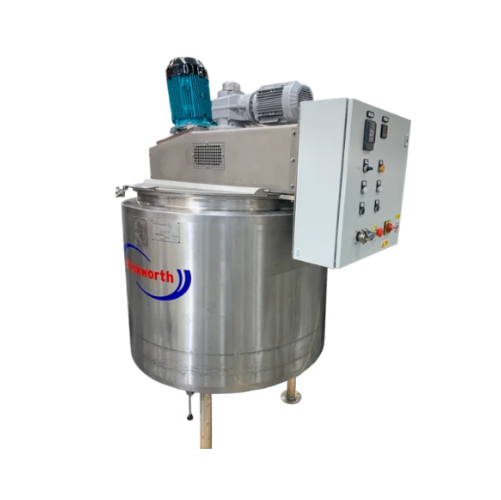
Pv processing vessels for liquid and cream mixing
Optimize your mixing operations with versatile processing vessels desig...
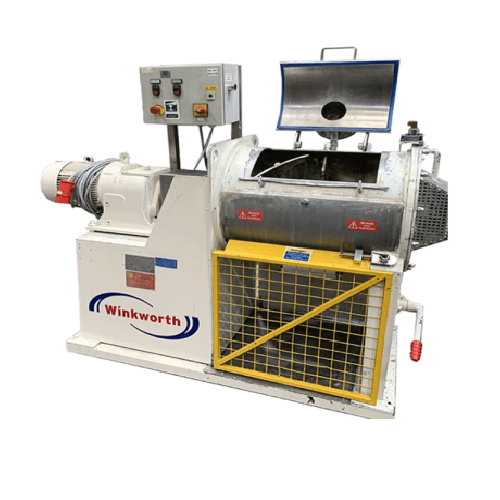
Industrial rapid turbulent mixer for homogeneous mixing
Achieve unparalleled homogeneity with rapid turbulent mixing, ess...
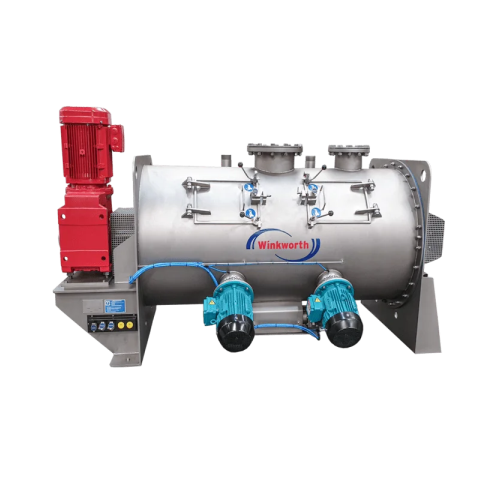
High-speed mixer for industrial mixing applications
Achieve rapid, consistent mixing and dispersion across diverse materi...
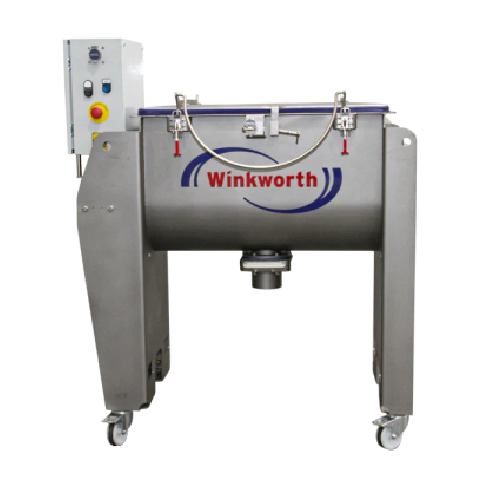
Horizontal shaft mixer for free-flowing materials
Achieve consistent mixing of diverse free-flowing materials with a reli...
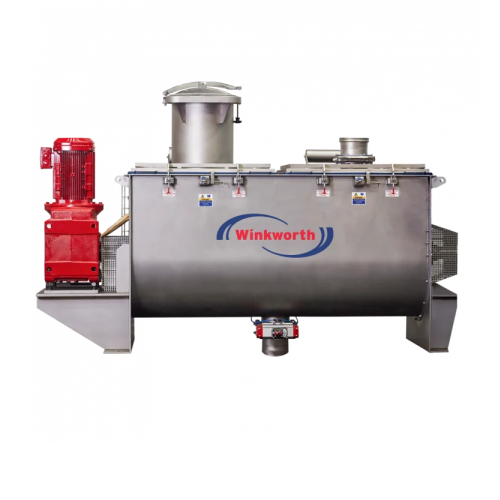
Efficient ribbon mixers for precise powder blending
Achieve consistent and uniform blending with this advanced U-Trough m...
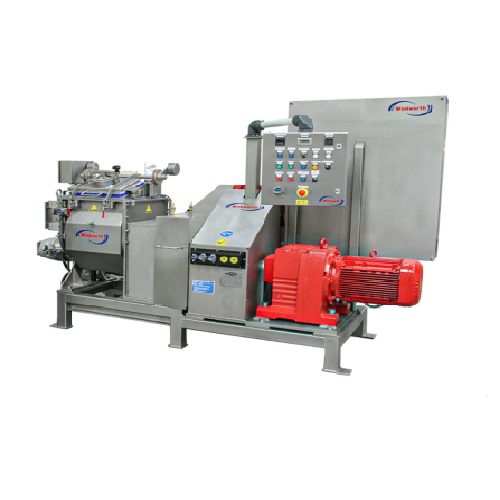
Industrial sigma mixer extruder for homogeneous mixing and extrusion
Achieve precise mixing and seamless extrusion of d...
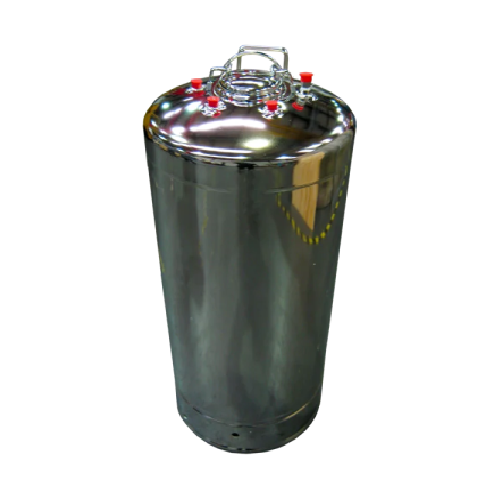
Pressure vessel for hazardous and non-hazardous liquids and gases
Ensure safety and compliance when handling hazardous ...
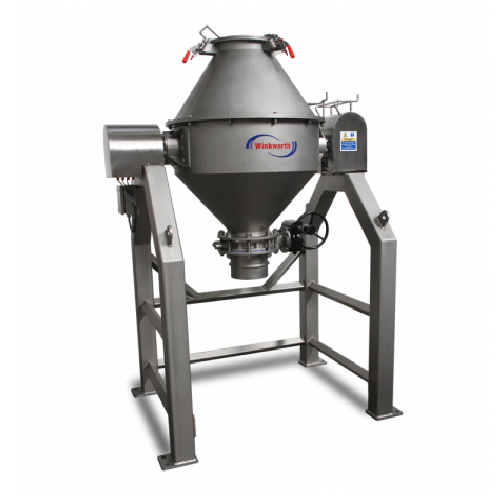
Double cone mixer for free-flowing material blending
Optimize your production with precision blending and gentle drying o...
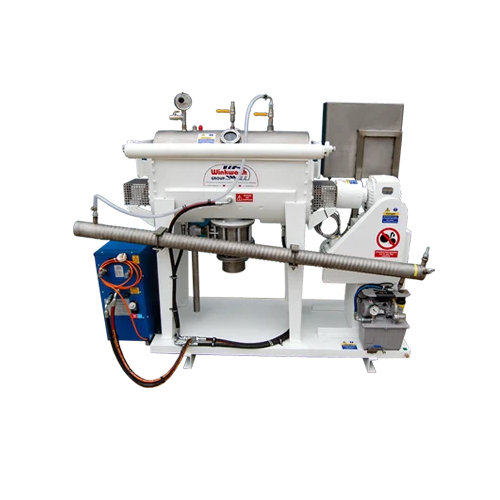
Industrial blenders for powder and granule mixing
Optimize your production line with advanced mixing solutions designed f...
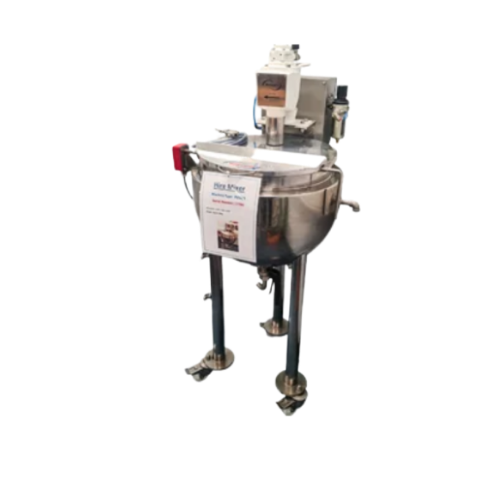
Pv mixing vessels for industrial hire
Optimize your production mix with vessels that ensure precise blending, heating, and ...
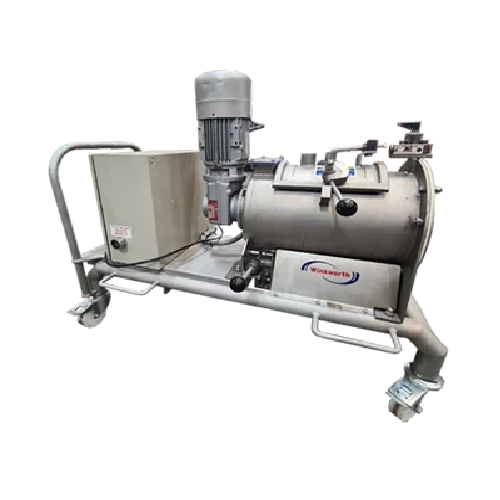
Industrial mixers for hire
Optimize your production line with versatile mixers designed for precision blending, heating, and...
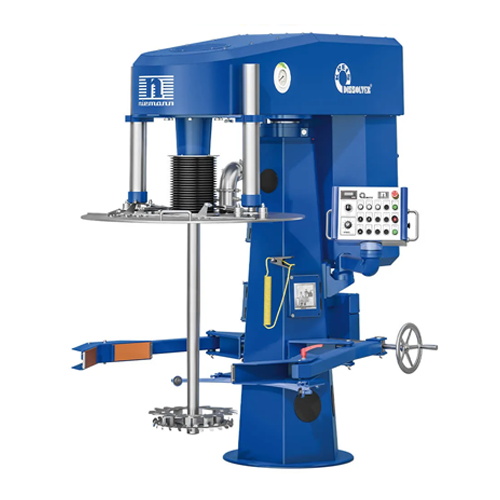
Dispersing system for high-viscous products
Achieve precise mixing and dispersing of high-viscous products with advanced f...
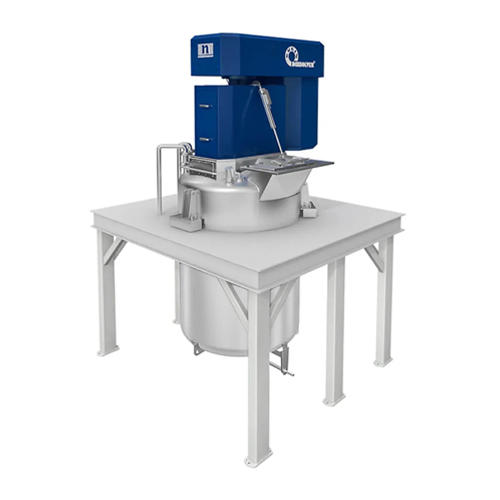
Top-mounted disperser for high-viscosity products
Achieve rapid, uniform dispersion of ultra-high viscosity materials wit...
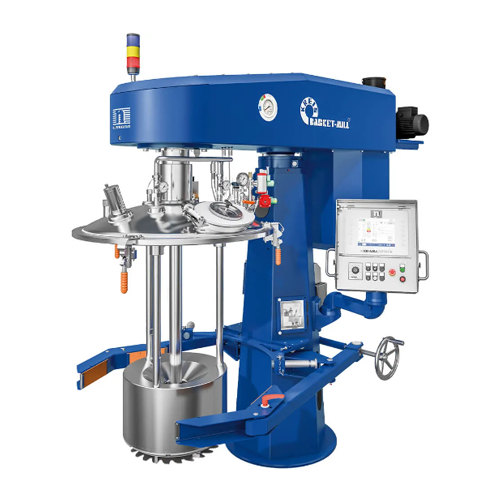
Basket mill for paint and varnish production
Achieve optimal particle size and product consistency with this advanced bask...
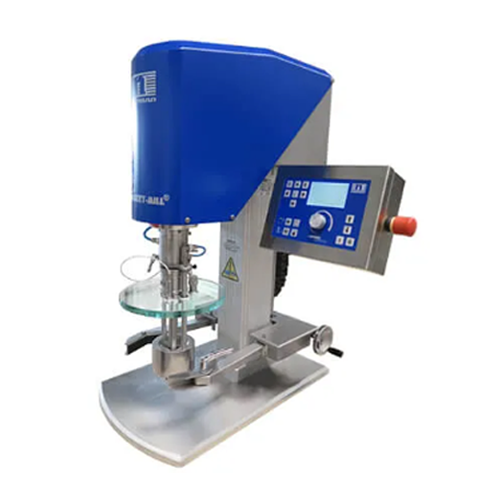
Laboratory basket mill for fine grinding in industrial applications
Optimize your laboratory’s efficiency with hi...
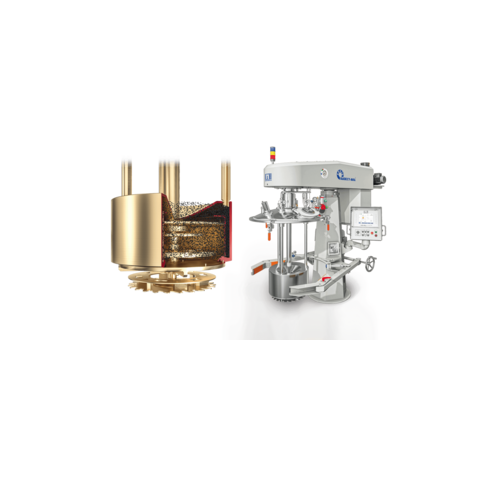
Milling beads for wet grinding in paint industry
Enhance product uniformity and grinding efficiency with specialized milli...
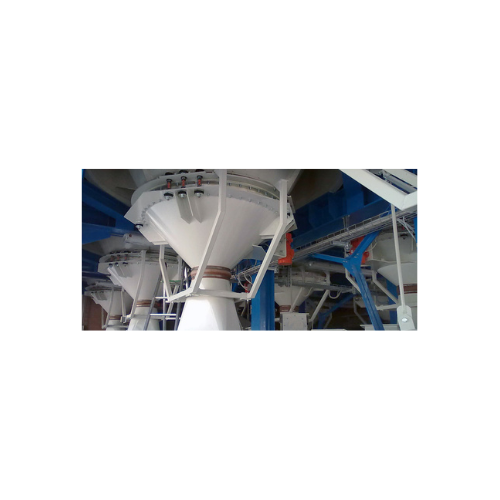
Bulk solids discharging and loading solution
Optimize your bulk material handling with equipment that ensures efficient an...
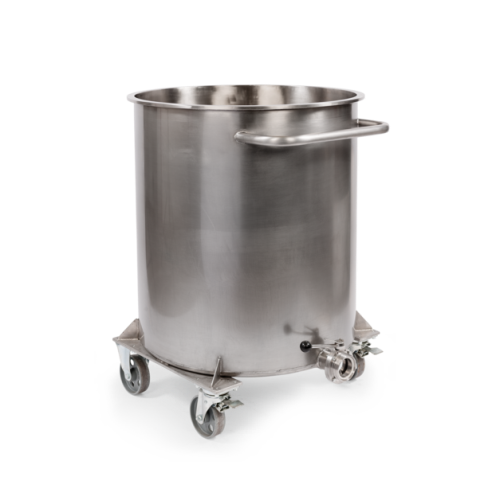
Industrial mixing dissolver for medium to large batches
Achieve precise mixing and dispersion of medium to large batch fo...
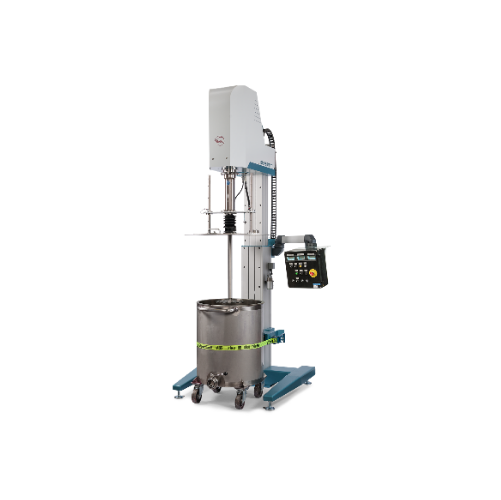
High-performance dissolver for large-scale production
Optimize your production line with precision-controlled dispersion ...
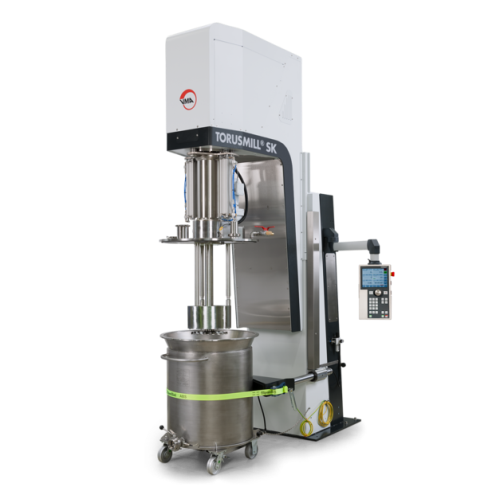
Vacuum basket mill for high viscosity products
Achieve efficient fine grinding of high-viscosity products while minimizing...
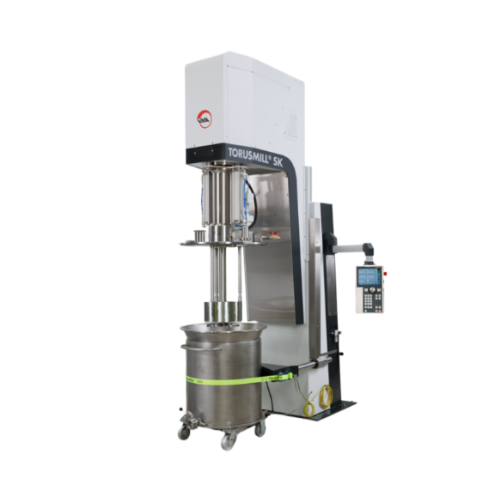
Vacuum dissolver for high viscosity products
Optimize your production with a vacuum dissolver designed to efficiently prev...

Vacuum dissolving system for high-viscosity products
Achieve flawless dispersion of high-viscosity substances under vacuu...
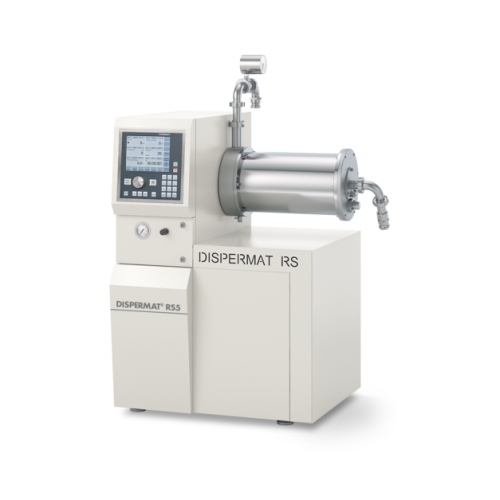
Horizontal bead mill for ultrafine particle grinding
Achieve precision in ultrafine grinding with a system that allows fo...
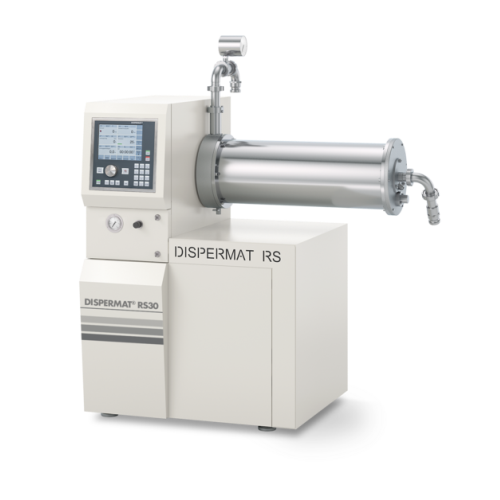
Horizontal bead mill for industrial nano grinding
Achieve precision in nano-scale grinding with this advanced bead mill, ...
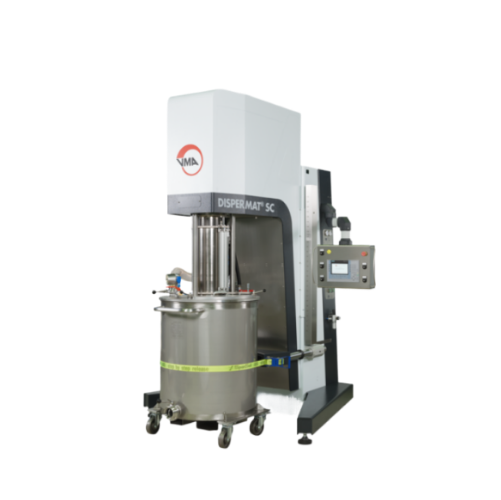
Modular basket mill for industrial dispersion
Effortlessly enhance your production efficiency with this versatile solution...

Industrial basket mill for medium viscosity products
Achieve precise particle size reduction and rapid pigment dispersion...

High-efficient industrial immersion mill
Achieve rapid, efficient dispersion and fine grinding in demanding production envi...
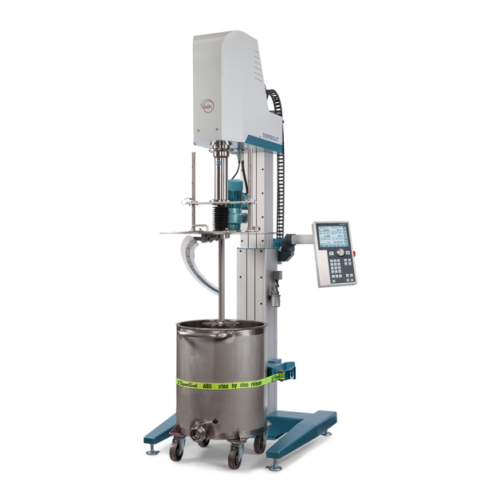
Dissolving system for high-viscosity products
Optimize the dispersion of high-viscosity liquids and pastes with this versa...
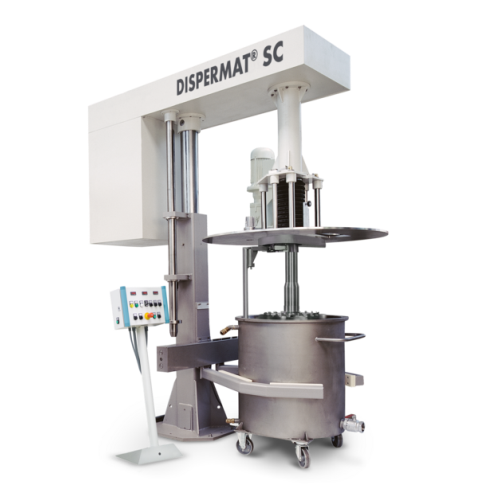
Industrial dissolver for high viscosity products
Optimize high-viscosity product dispersion with a robust dissolver design...
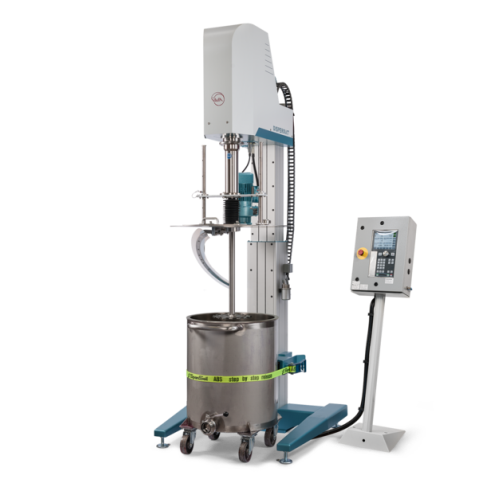
Explosion-proof dissolver with scraper for high viscosity substances
Ensure flawless dispersion with enhanced safety, d...
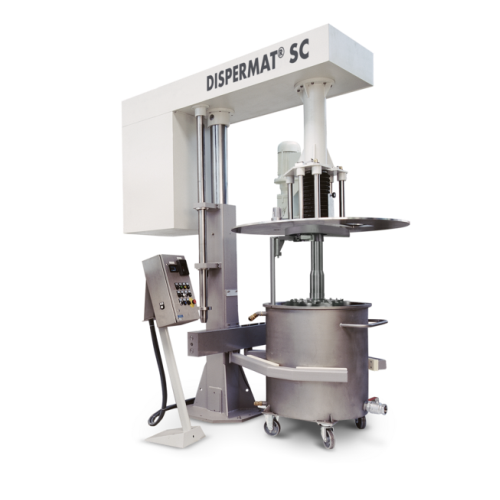
Explosion-proof dissolver for high viscosity products
Optimize your high-viscosity material processing with an explosion-...
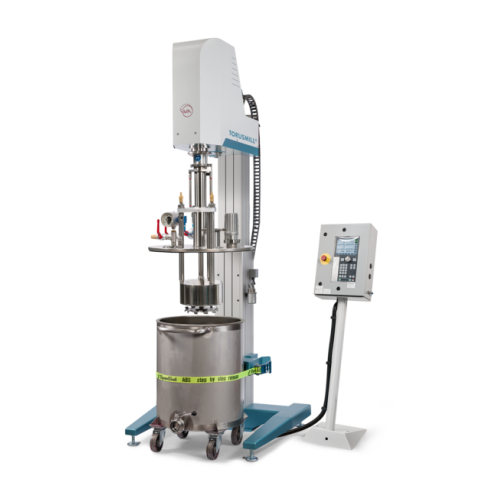
Vacuum basket mill for highly viscous products
Achieve precision in fine milling under vacuum to prevent air inclusions in...
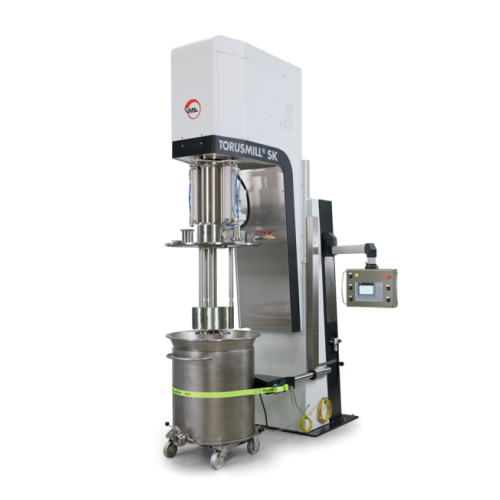
Vacuum basket mill for high-viscosity product milling
Achieve refined particle size and smooth texture in your high-visco...
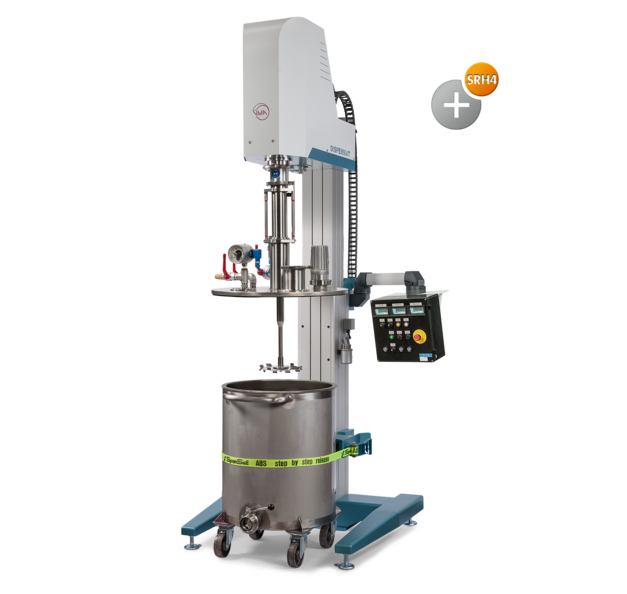
ATEX vacuum dissolver for high viscosity products
Ensure safe and efficient dispersion of high-viscosity materials under...
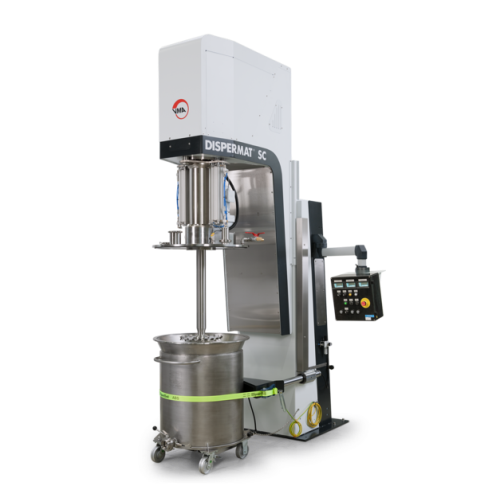
Explosion-proof vacuum dissolver for high-viscosity products
Optimize your production by eliminating air inclusions and ...
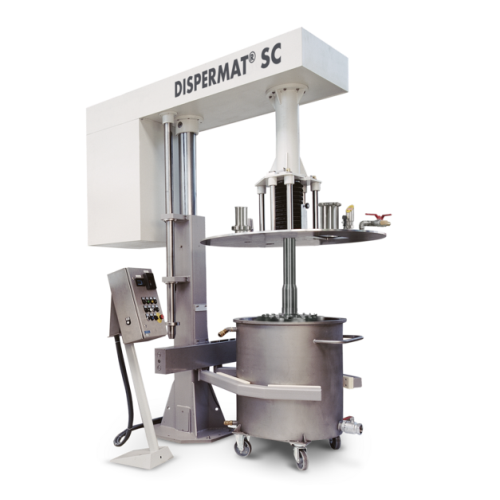
Explosion-proof vacuum dissolver for high viscosity products
Achieve precise dispersion of high-viscosity products under...
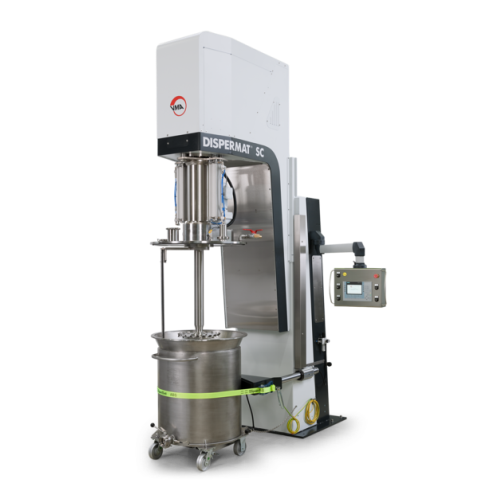
Explosion-proof vacuum disperser for high-viscosity substances
Achieve precise dispersion and eliminate air inclusions w...
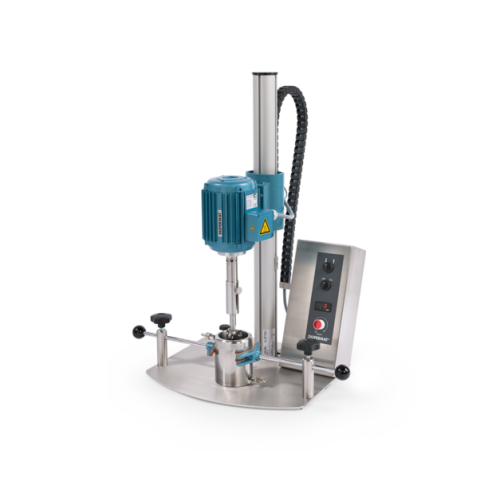
Laboratory stirrers for high viscosity materials
Efficiently mix and stir high-viscosity materials with ease, enabling pre...
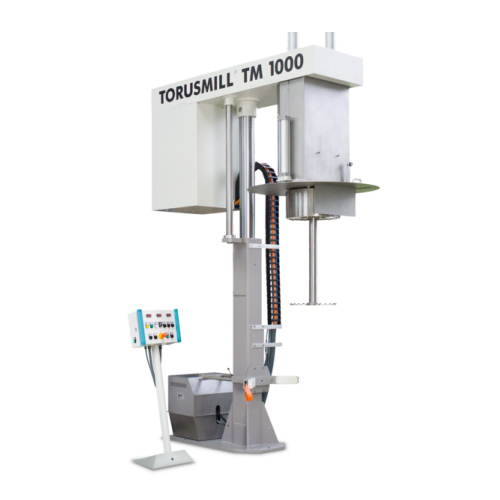
Basket mill with integrated dissolver for high viscosity products
Optimize your production efficiency by combining disp...
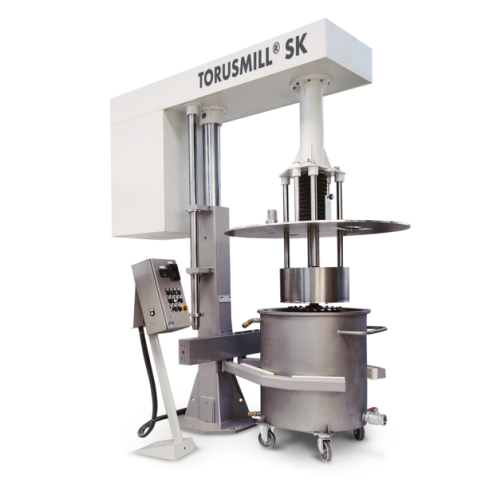
Explosion-proof basket mill for large scale production
Enhance your production line with an explosion-proof basket mill t...
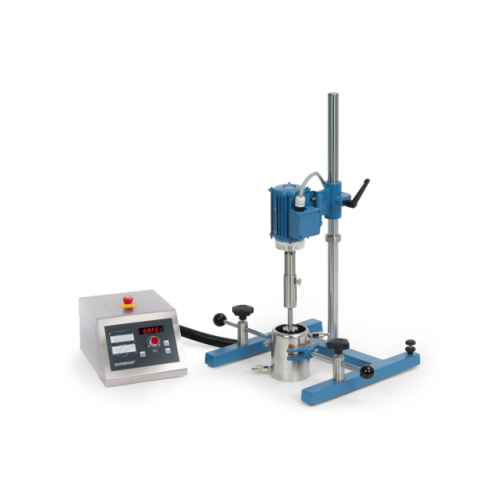
Lab and pilot plant dissolver for dispersion and fine grinding
Achieve efficient dispersion and fine grinding in laborat...
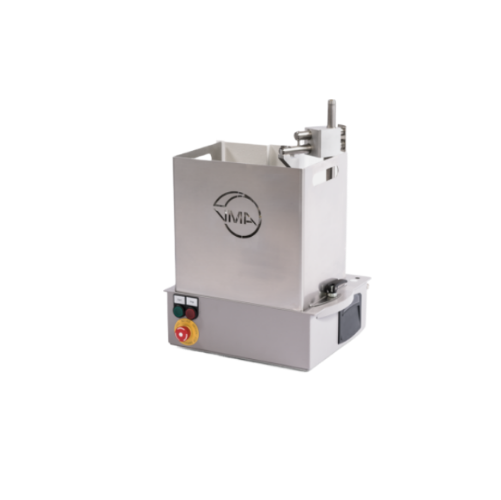
Industrial dissolver for high-viscosity materials
Efficiently disperse and mix high-viscosity materials with precision, e...
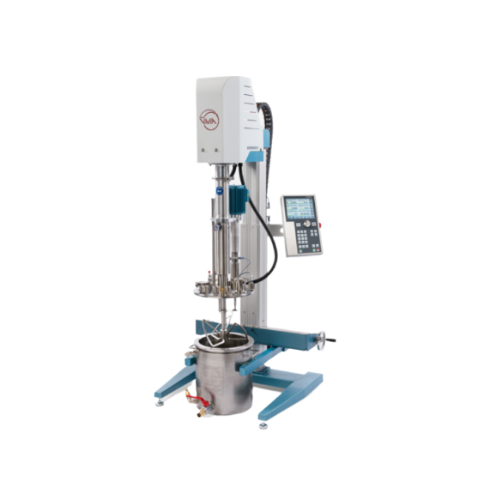
Vacuum dissolver for highly viscous products
Efficiently mix and disperse high-viscosity substances under vacuum to ensure...
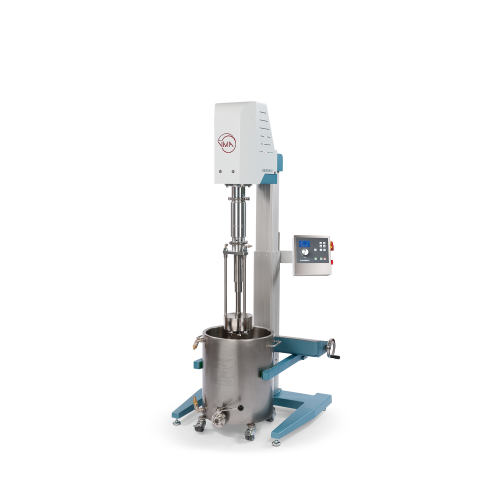
Entry-level vacuum dispersion system for laboratory applications
Achieve precise dispersion and milling with this versat...
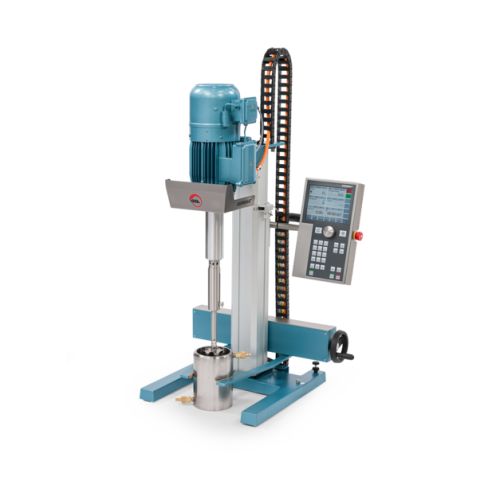
Rotary homogenizer for laboratory and pilot plant
For achieving optimal dispersion in complex formulations, this solution...
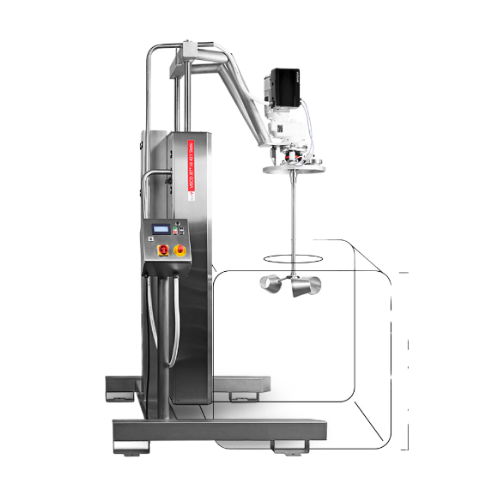
Industrial mixer for product-critical processes
When dealing with high-hygiene requirements and complex mixing tasks acros...
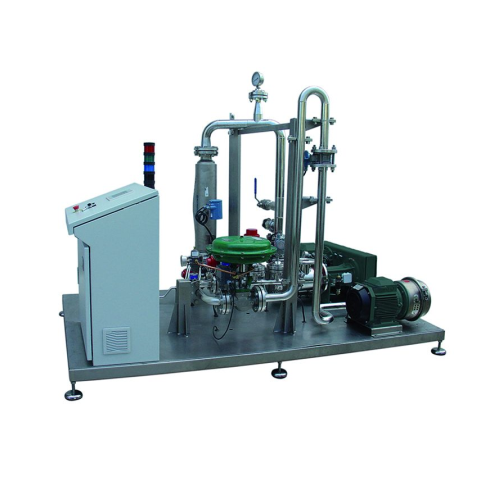
Complete mixing systems for industrial applications
Optimize your production efficiency and product consistency with adva...
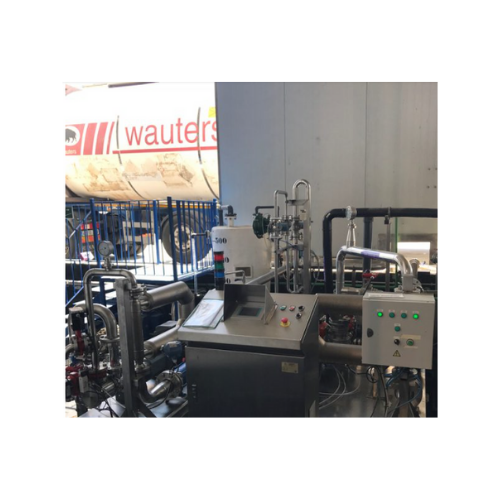
Complete mixing solutions for food, chemical, and cosmetic industries
Enhance your production line with precision mixin...
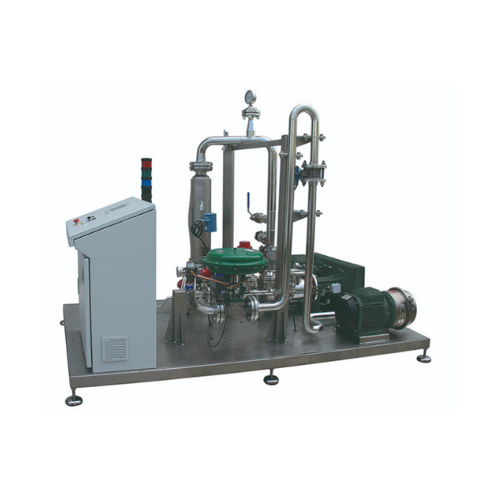
Complete mixing solution for food, cosmetics, and chemical industries
Optimize your production line with a system that ...
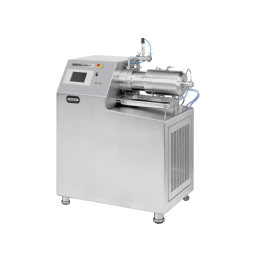
Ultra fine bead mill for nanosuspensions
Ensuring the quality, efficiency, and reproducibility of nanosuspensions throughou...
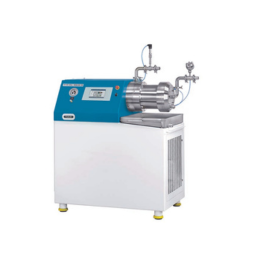
Self-cleaning bead mill for highly viscous materials
To prevent blockages, clogging, and cross-contamination coming from ...
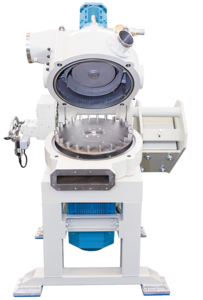
Classifier mill for recovered carbon black
Recovered Carbon Black (rCB) can be recycled back to the tire production chain ...
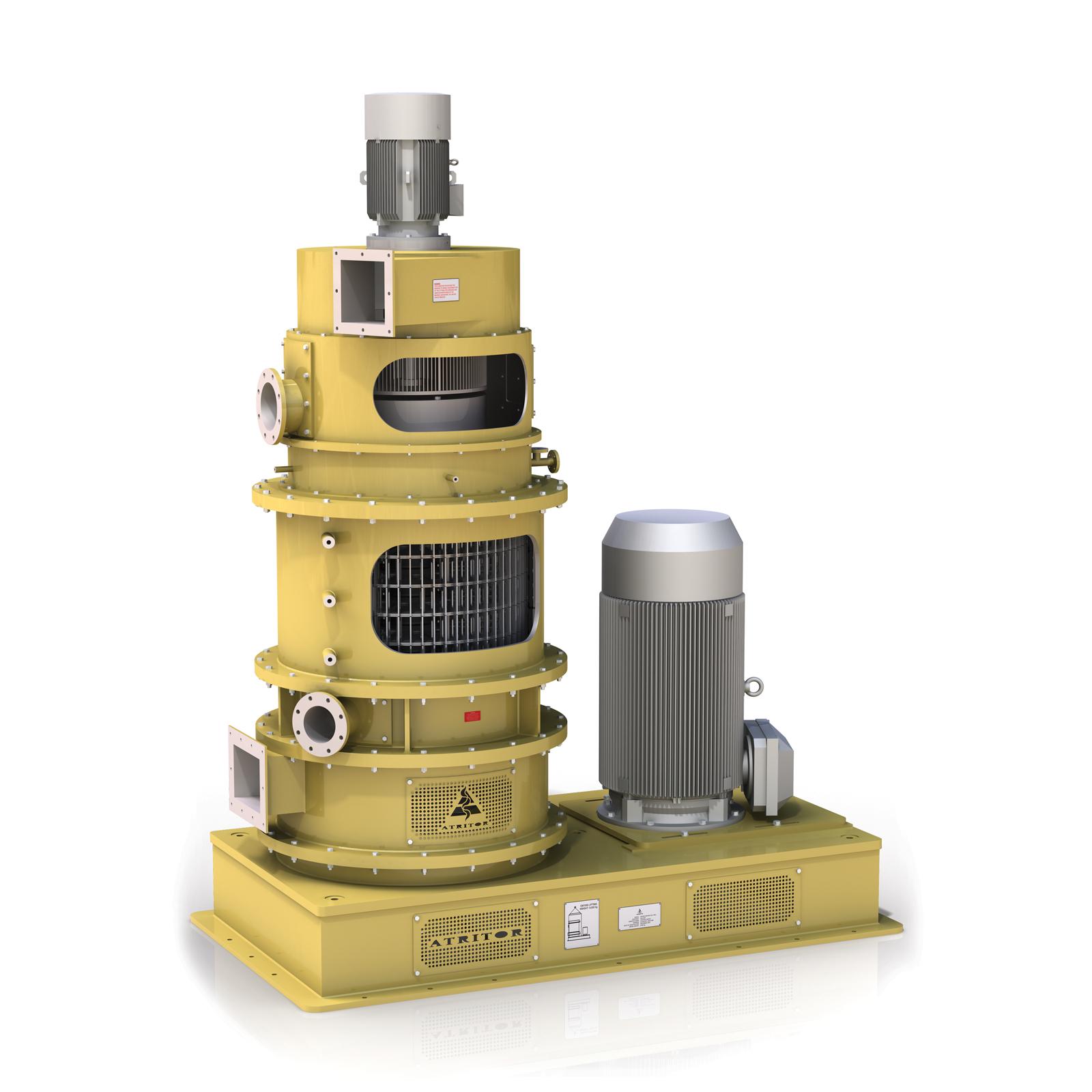
Milling and drying machine for fine powders
When you need to produce ultra-fine powders, the milling and drying process em...
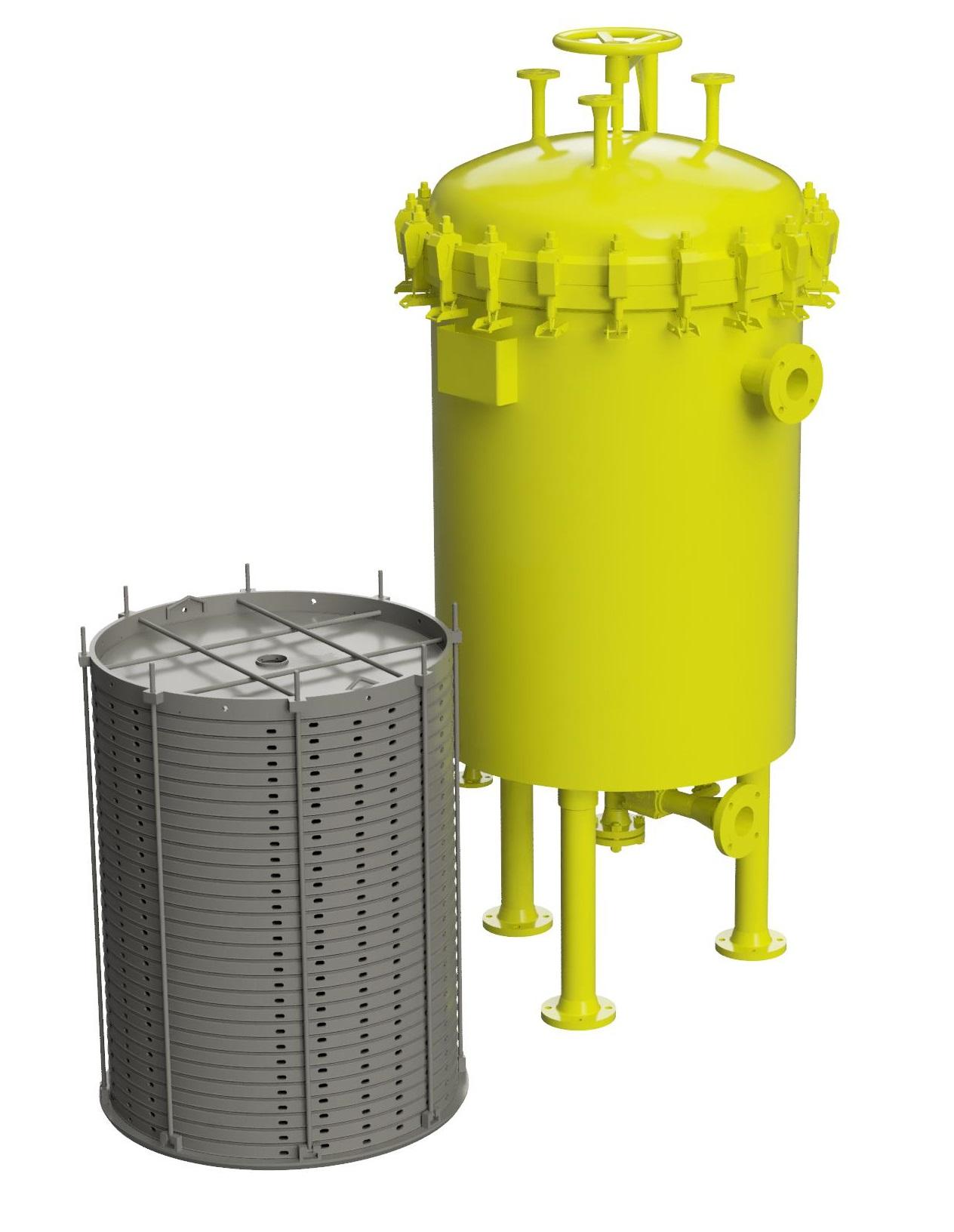
Industrial liquid filtration system
Systems for the filtration of liquids with suspended solid contents can be challenging ...
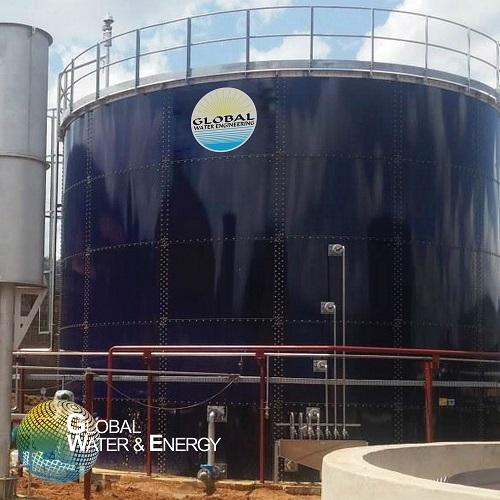
Anaerobic UASB wastewater treatment
If you need to remove organic compounds from your wastewater, the up-flow anaerobic slu...
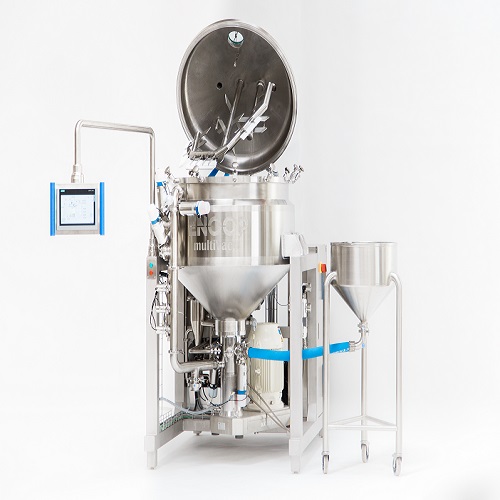
Vacuum based homogenizer
When producing liquid and viscous products such as mayonnaise, sauces, dressings and ketchup it’s vi...
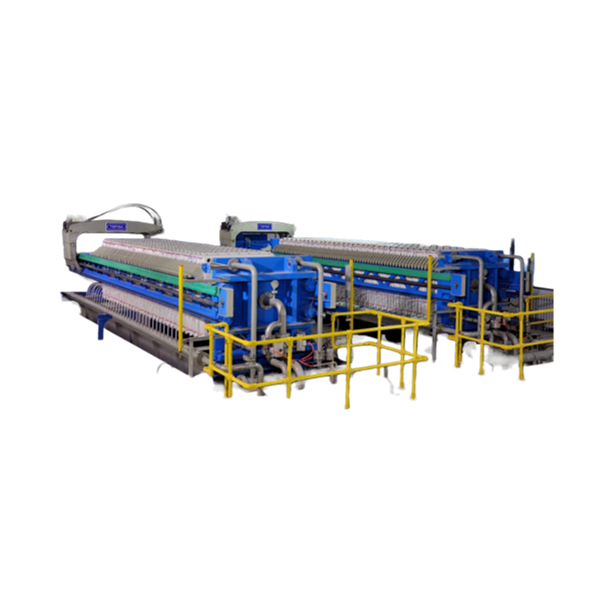
Side bar filter press
Production of dry cakes is required in a variety of industries and robust, low-cost side bar filtration...
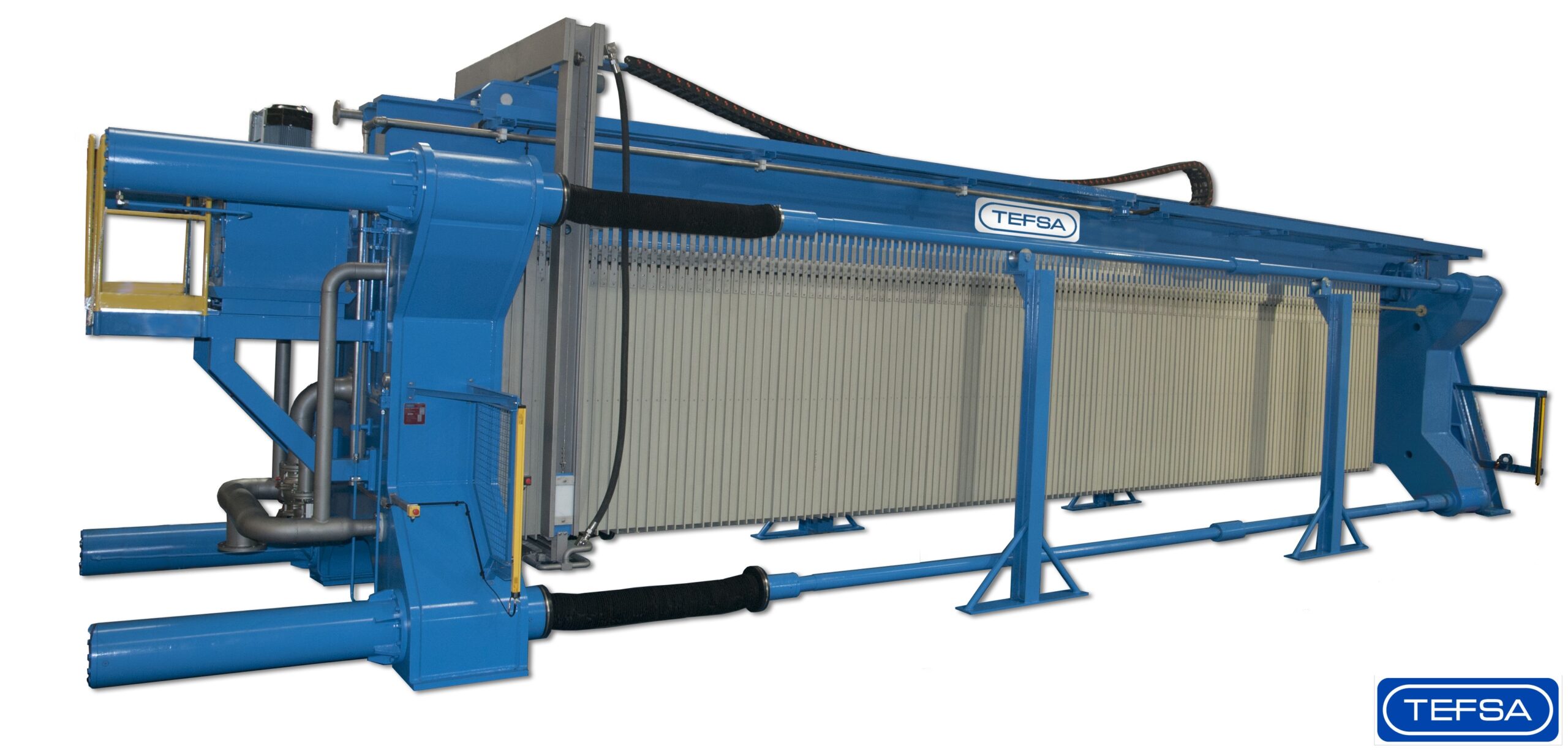
Overhead filter press
To name just a few of the myriad applications for overhead filter presses: industrial mineral industrie...
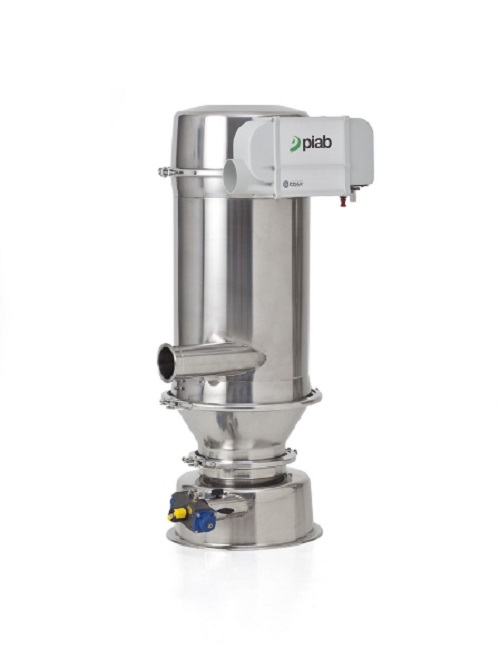
Premium vacuum conveyor
When you have a need to tailor make your conveyor and still have the high requirement on hygiene, e.g...
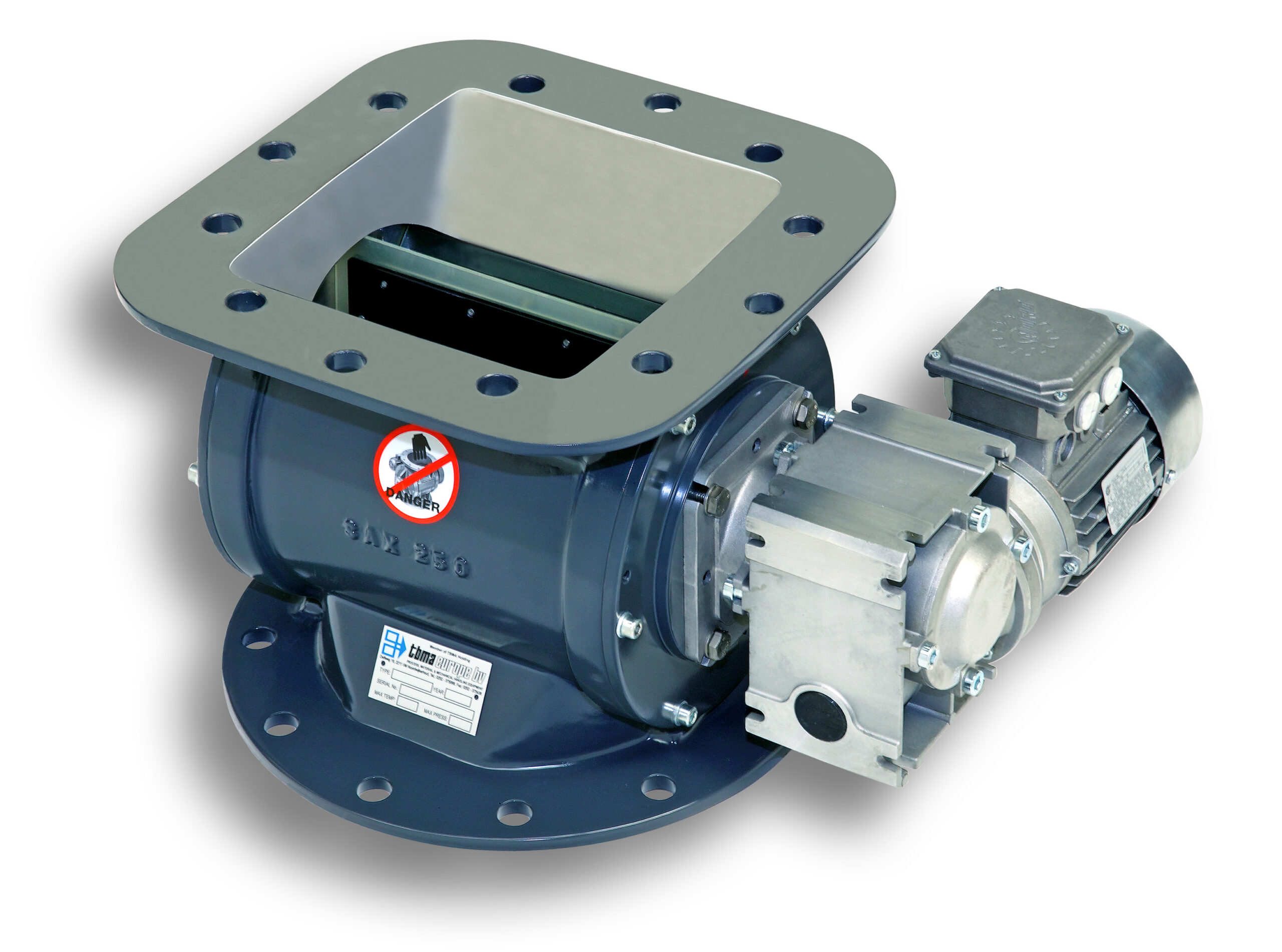
Light duty rotary dust valve
In some light industrial applications there is limited pressure differential for valve operation.
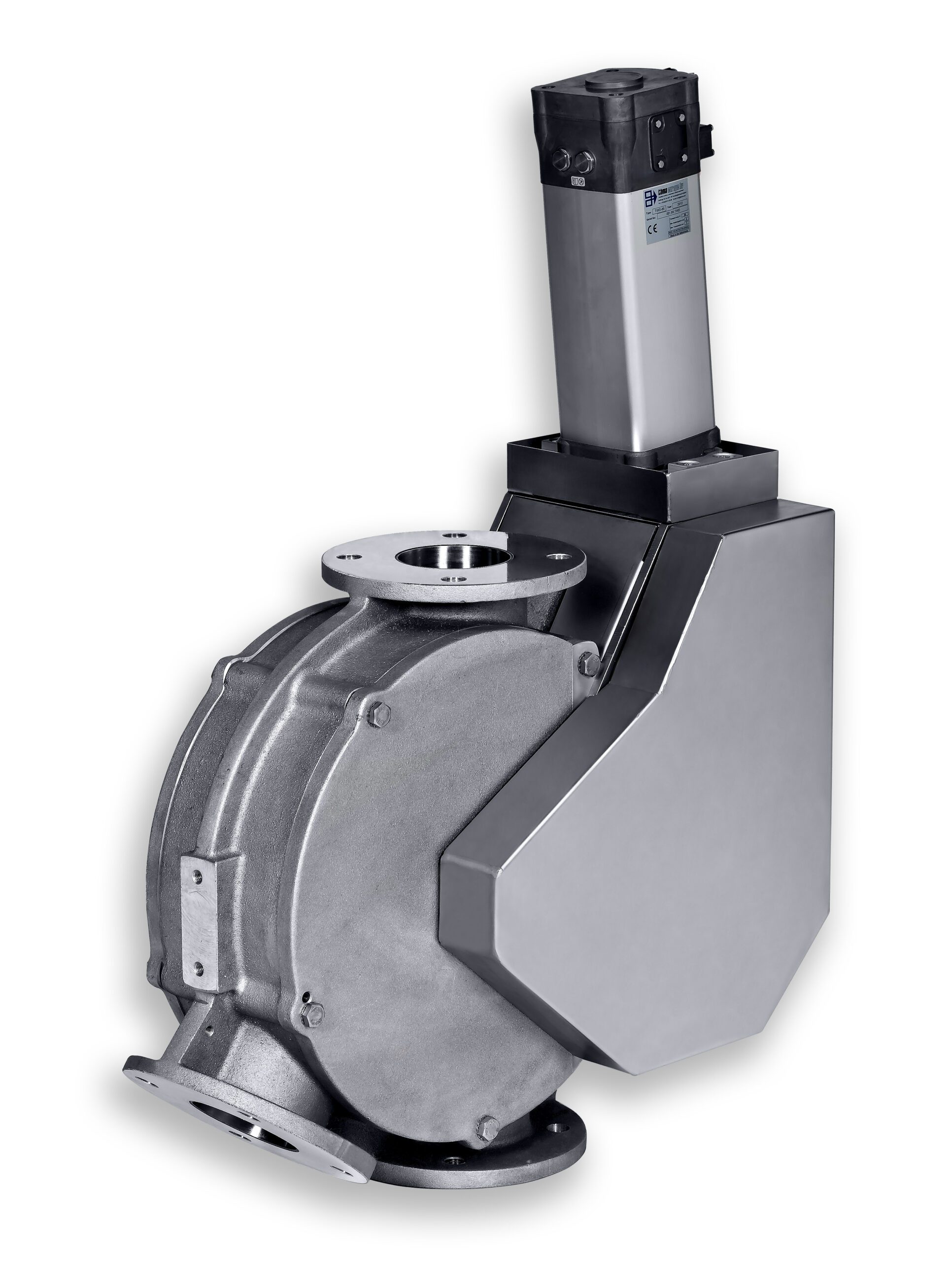
Dual channel plug diverter valve
Short switching times are often required when diverting or combining powder or granular sol...
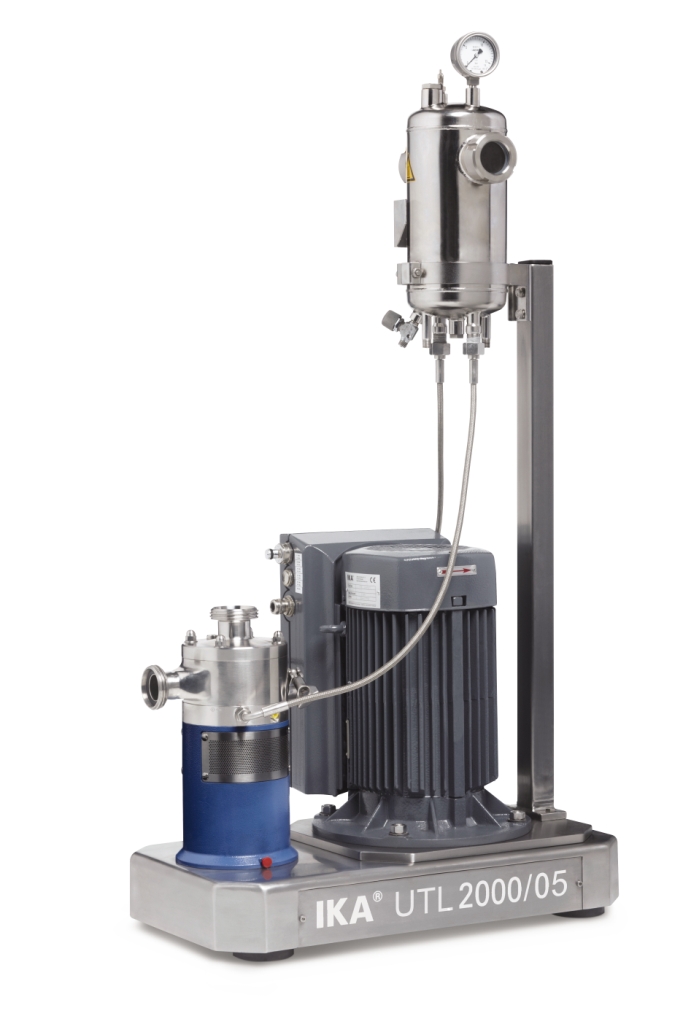
Dispersing machine for emulsions and suspensions
Equipment operating under the rotor/stator principal is often employed wh...
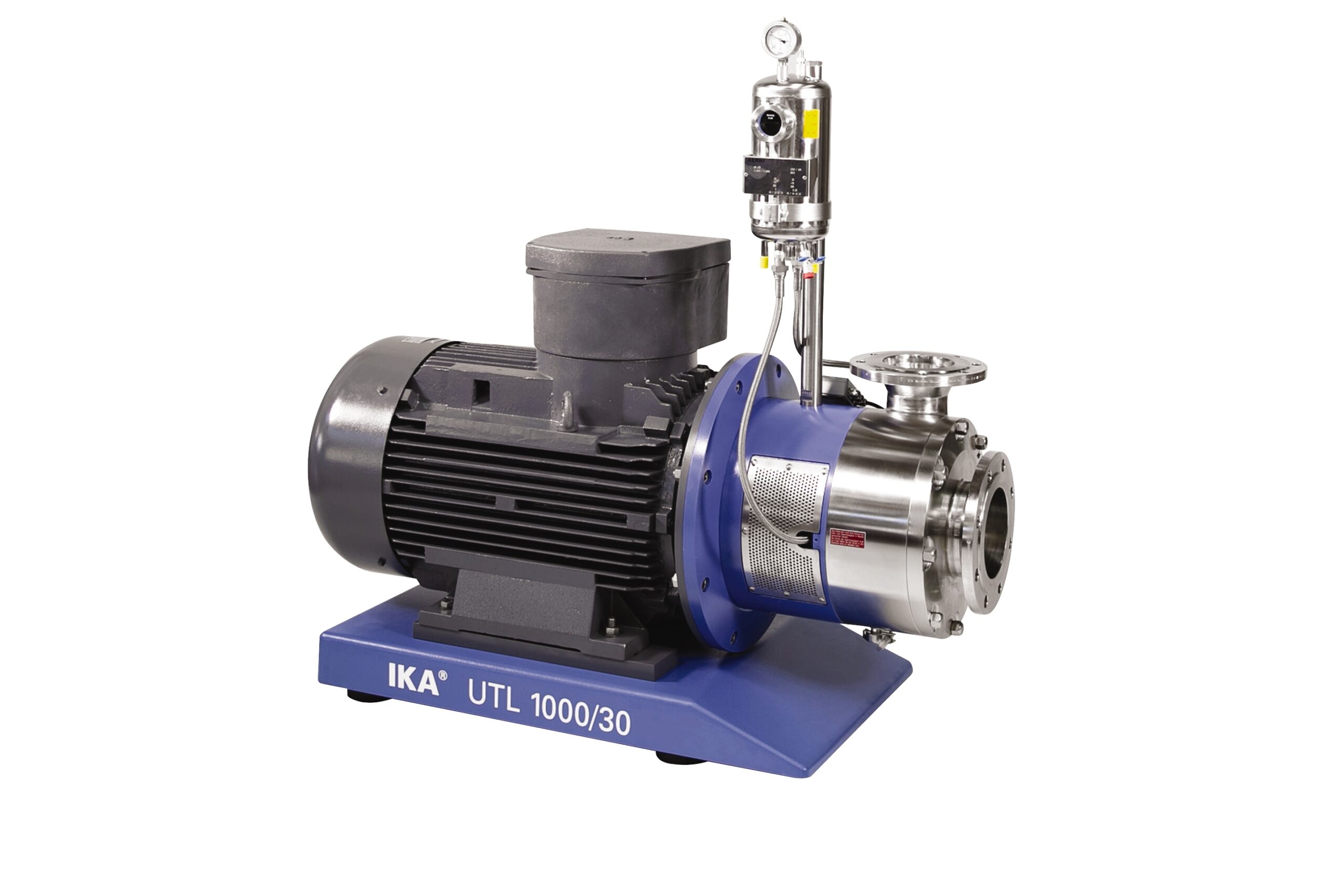
Economic dispersing machine for emulsions and suspensions
For products of medium viscosity and relatively consistent par...
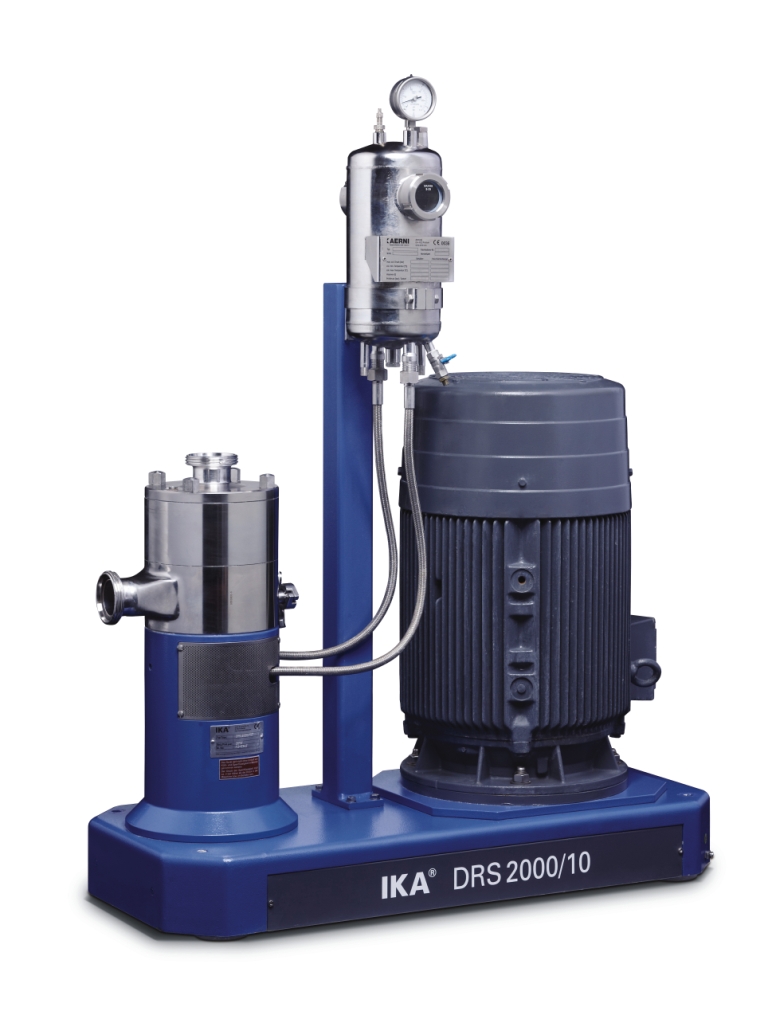
Ultra-fine dispersing machine for emulsions and suspensions
Producing the finest micro-emulsions and suspensions require...
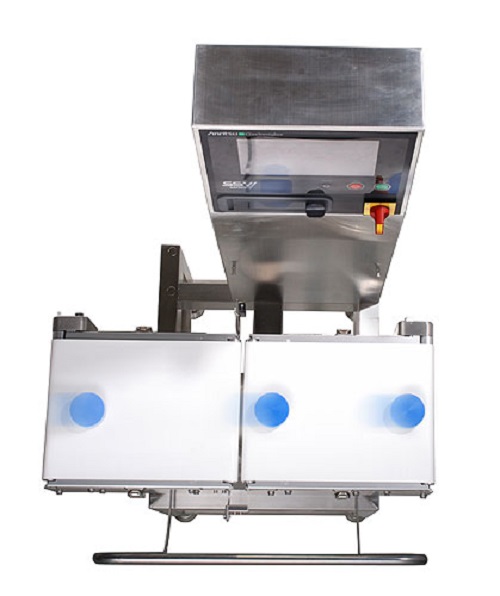
Versatile checkweigher
This Versatile checkweigher is equipped with a highly versatile strain gauge load cell. It is also sui...