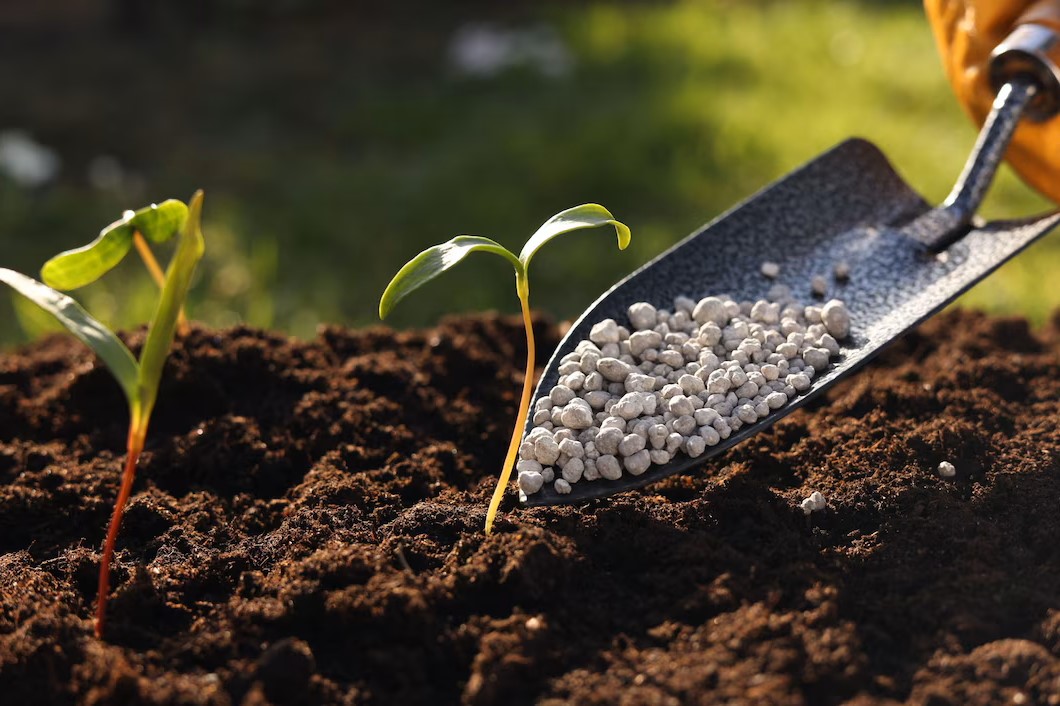
Organic fertilizer
Find innovative production technology for making organic fertilizer and connect directly with world-leading specialists
Let's navigate the complex world of engineered-to-order production technology together. Whether you're building a new process or optimizing an existing line, our platform connects you directly to the experts who can help. Use our curated catalogue to dive straight into the technologies that match your production goals. We continuously map out how production technology from suppliers around the world can help solve real production challenges. If you find something interesting, we introduce you directly to the specialists who know how to implement it. With more than 600 trusted machine manufacturers and over 20.000 technical experts in our network, you’re never far from the answers you need.
Tell us about your production challenge
Which organic fertilizer technology do you need?
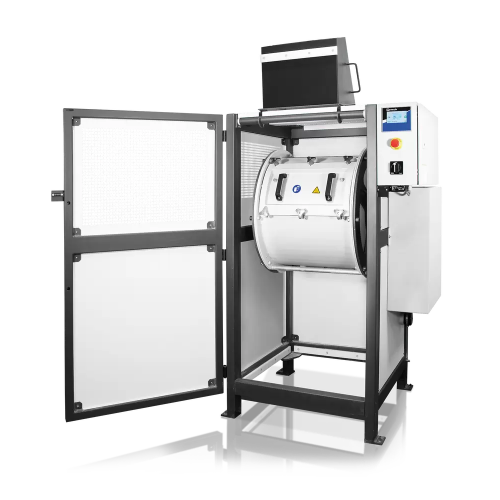
Laboratory drum mill for large sample volumes
Efficiently process large volumes of diverse materials into precise particle...
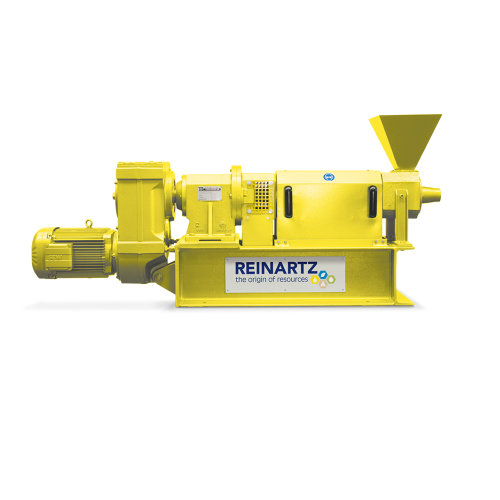
Efficient biomass screw dryers
Optimize biomass processing with screw drying technology that efficiently reduces moisture co...

Heat exchangers for efficient heat transfer in industry
Achieve precise temperature control across diverse viscosities wi...
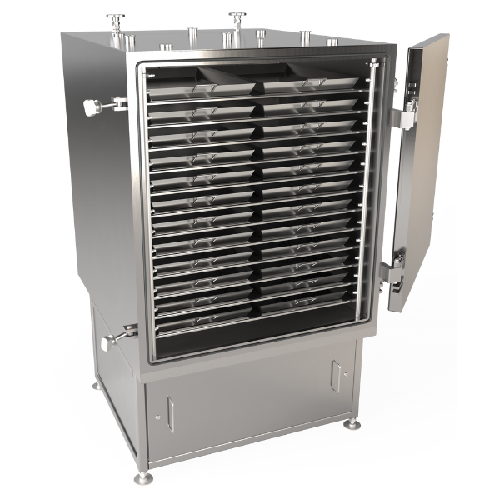
Continuous heat exchanger for soups and sauces
Optimize your soup and sauce production with a continuous heat exchanger th...
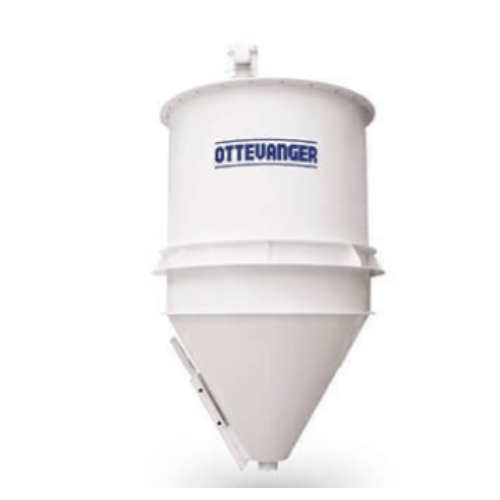
Vertical mixers for animal feed industry
Efficiently combine a variety of powdered and raw materials with precision, ensuri...
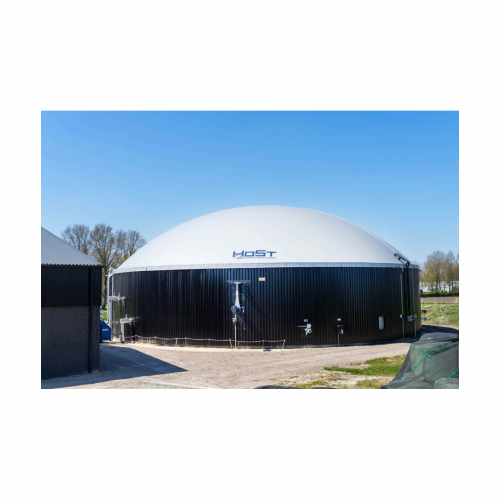
Organic residue and manure biogas plant
Transform organic waste into renewable energy while efficiently reducing carbon emi...
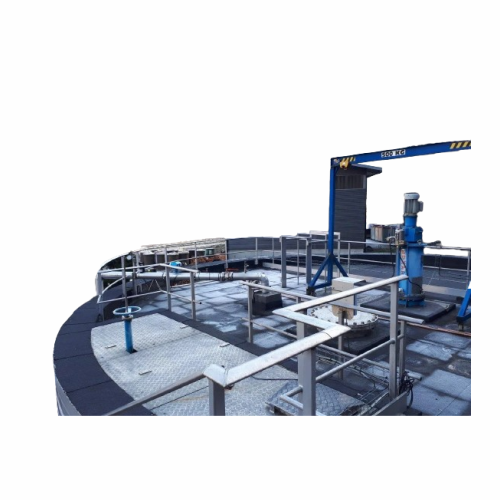
Agitator for biogas digesters in anaerobic digestion
Achieve efficient anaerobic digestion and optimal biogas recovery by...
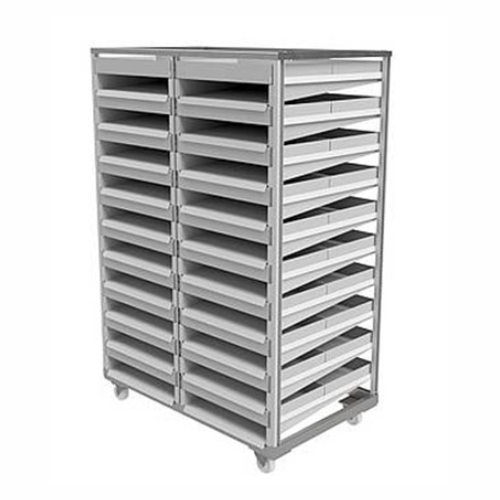
Flexible drying system for various industrial applications
Achieve precise moisture control across diverse materials wit...
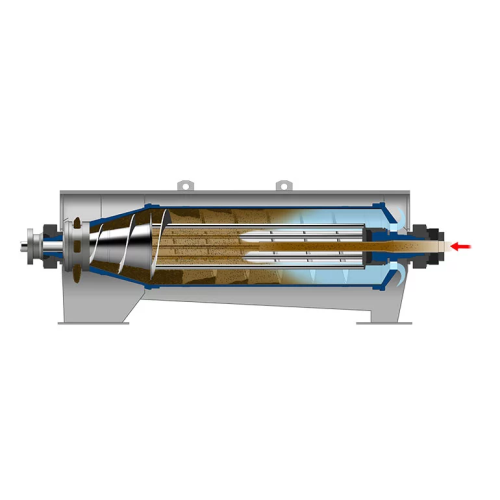
Advanced sludge dewatering for sewage treatment plants
Optimize sludge dewatering with a centrifuge that enhances separat...
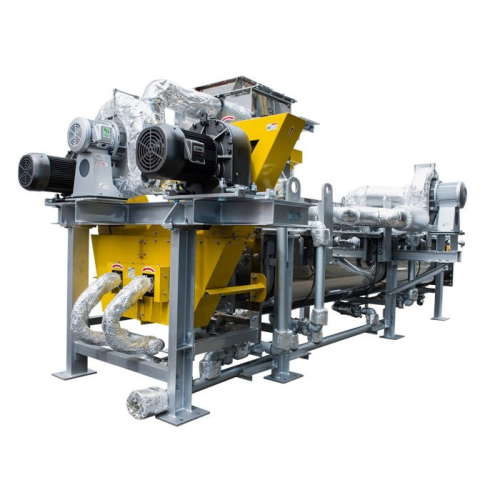
Sludge dryer for humid and pasty materials
Effortlessly manage pasty and sticky materials with a sludge dryer that ensures...
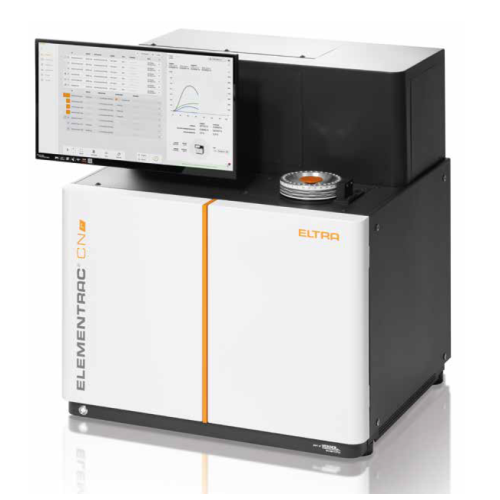
Carbon/nitrogen analyzer for organic samples
Optimize your lab’s efficiency with fast, reliable nitrogen and carbon ...
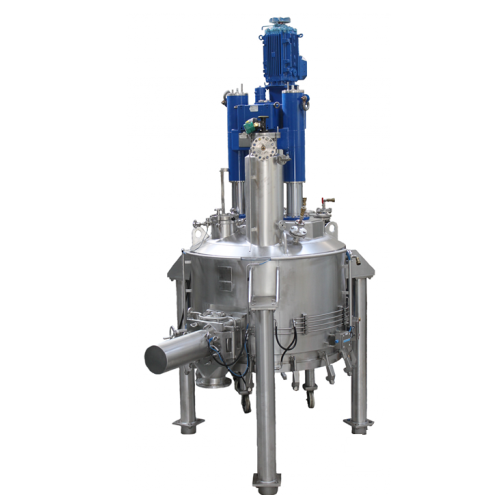
Agitated nutsche filter and filter-dryer for pharmaceuticals
Ensure precise filtration, washing, and drying of sensitive...
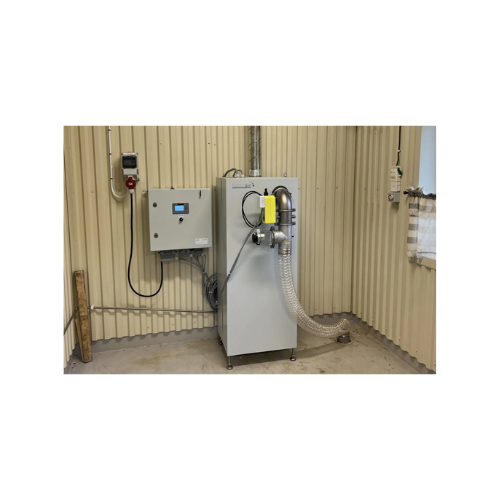
Catalytic system for industrial odour and Voc elimination
Tackle VOC and odour emissions with a versatile catalytic syst...
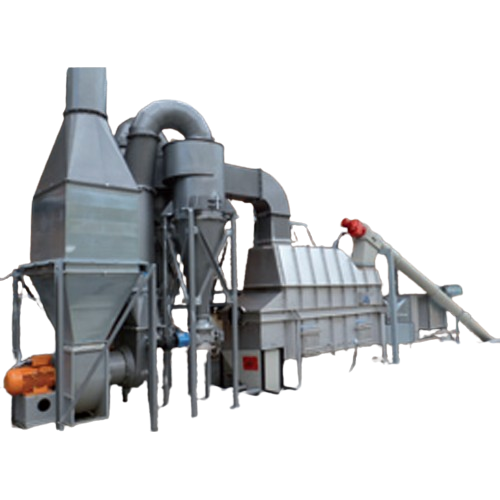
Biomass drying solution
Achieve efficient and gentle biomass drying with innovative heat exchange technology, ensuring optima...
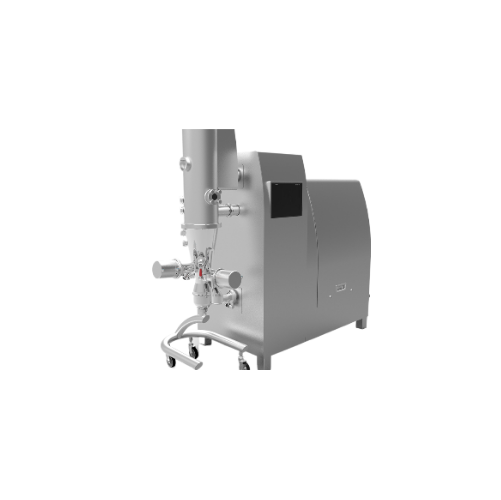
Screw press for vital wheat gluten dewatering
Optimize your production line with efficient moisture reduction for vital wh...
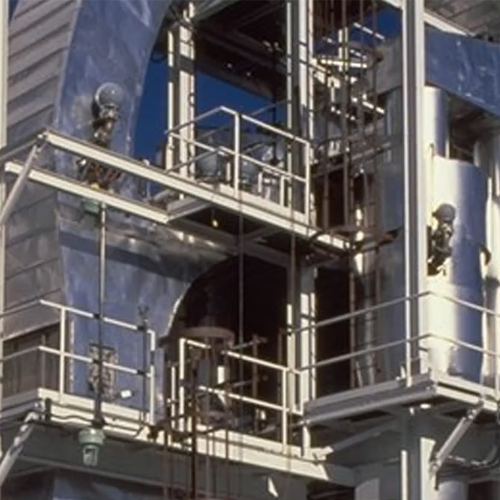
P-type ring dryer for thermally sensitive products
Optimize moisture control and prevent thermal degradation in your prod...
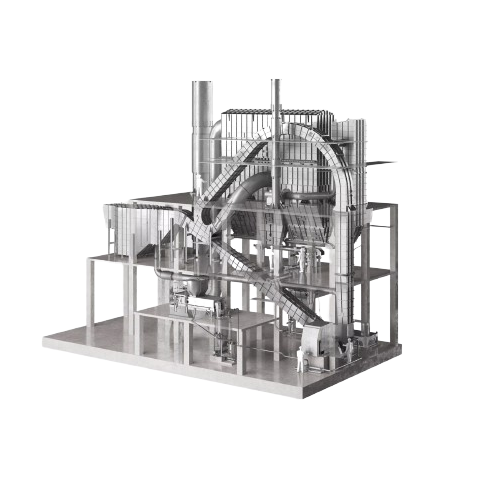
Industrial ring dryer for efficient particle processing
Control particle size and drying efficiency with precise recircul...
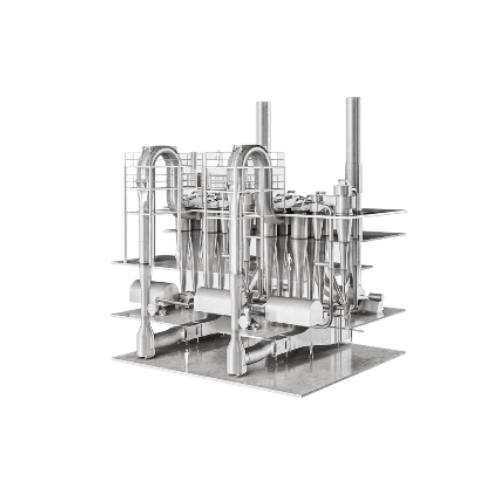
Flash dryer for industrial moisture removal
Optimize your production with rapid moisture removal, efficiently transforming...
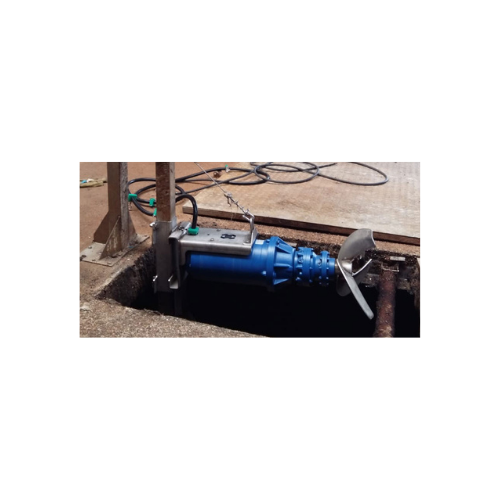
Biogas plant screw press separators
Maximize your renewable energy output and processing efficiency with cutting-edge solid...
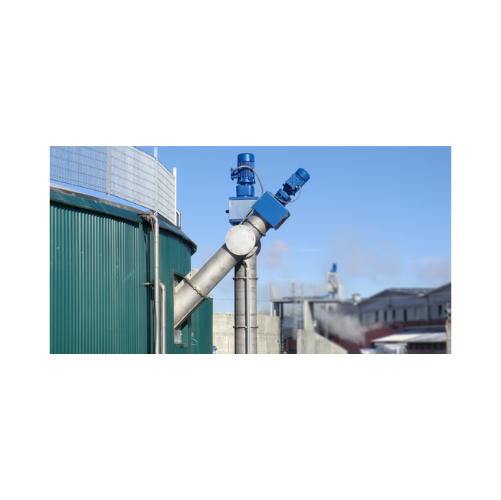
Biomass digester feeding system
Efficiently integrate biomass into your biogas production process with a system that seamles...
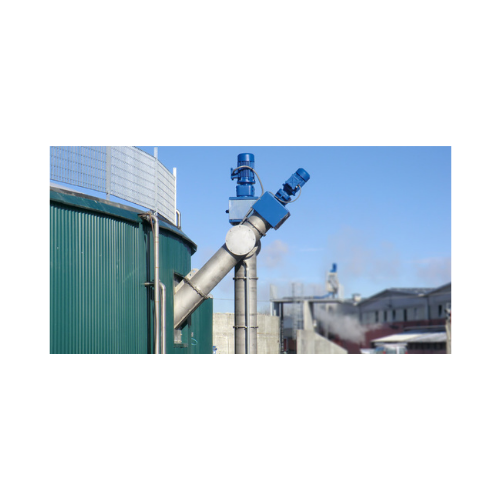
Bulk biomass digester feeding system
Optimize your biogas production with a versatile system designed for efficient biomass...
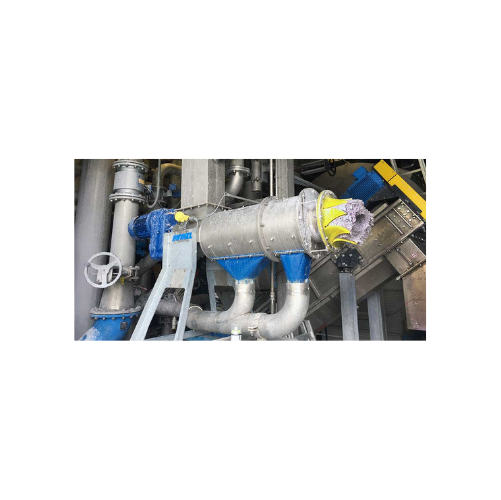
Pulp and paper screw press separator
Achieve high-efficiency solids-liquid separation in pulp and paper processing with a h...
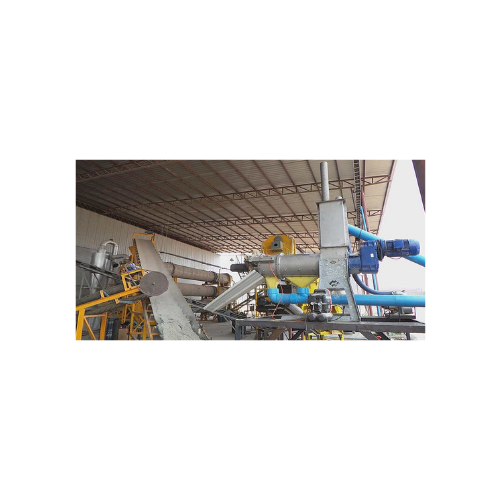
Tapioca horizontal screw press separator for biogas plants
Achieve high-efficiency separation and compaction of diverse ...
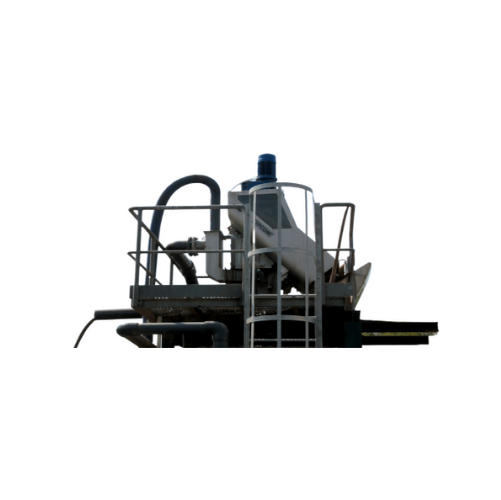
Screw press separator for slurries
Optimizing your separation process, this vertical screw press efficiently handles a wide...
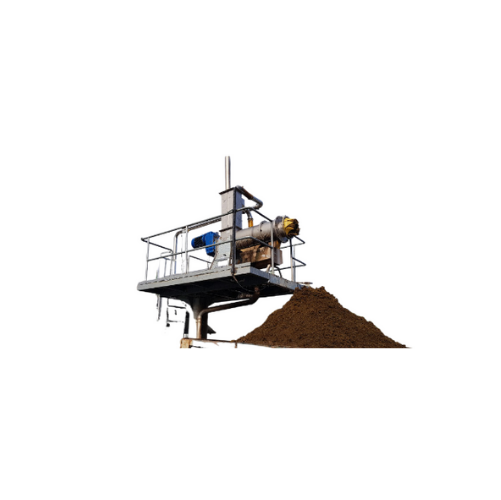
Cow manure screw press separator
Enhance nutrient recovery and reduce waste management costs with our robust screw press sep...
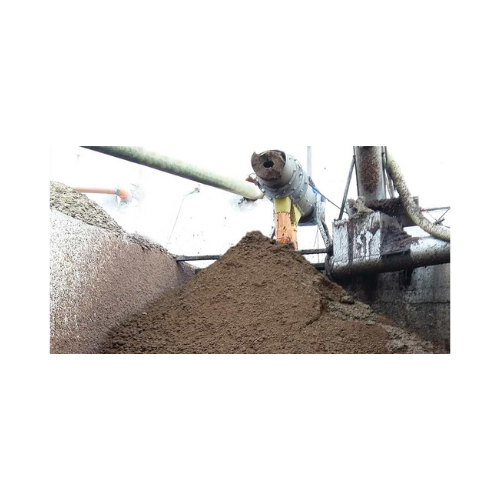
Horizontal screw press separator for pomace yield optimization
Enhance your production line by efficiently separating so...
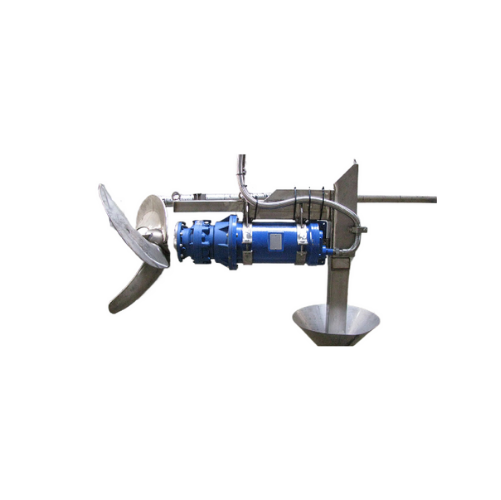
Submersible agitators for manure and wastewater treatment
Optimize mixing efficiency in manure and wastewater treatment ...

Continuous impact vibrators for bulk solids discharging
Optimize your discharging process with vibrators that effectively...
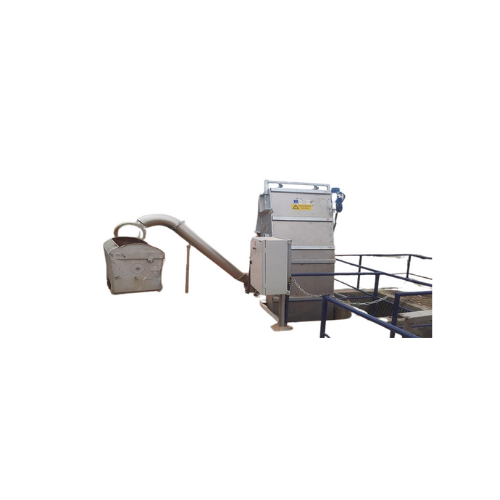
Bar screens for wastewater treatment
Efficiently remove coarse debris from wastewater streams with high-capacity sub-vertic...
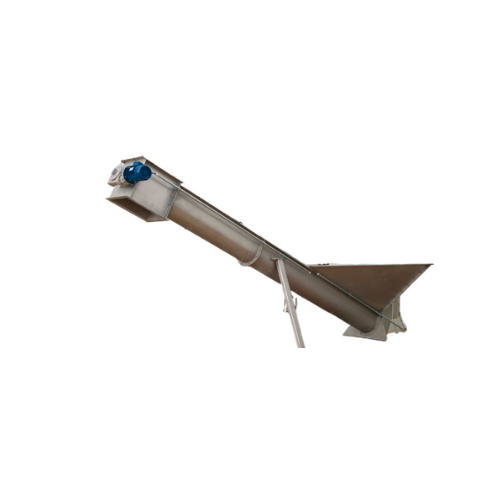
Grit classifier for wastewater treatment
Optimize your wastewater treatment process with a grit classifier that efficiently...
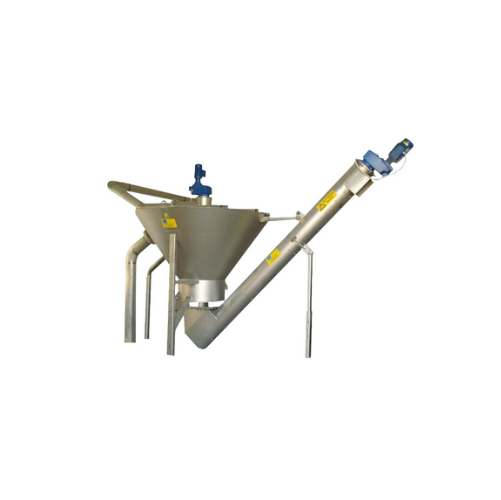
Sand washer for waste water treatment
Efficiently separate sand from wastewater while simultaneously reducing organic conte...
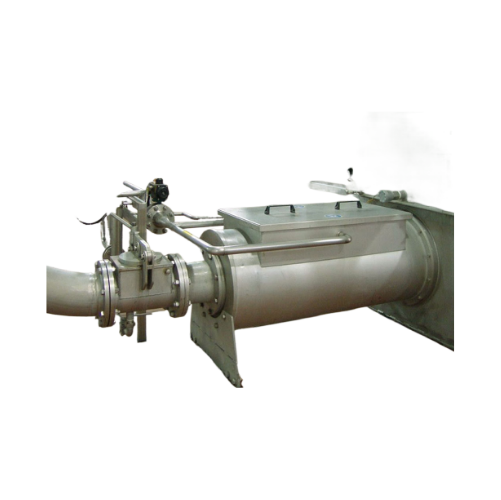
Wet spent grains pre-dewatering system
Optimize your brewery operations with a dewatering system that efficiently reduces m...
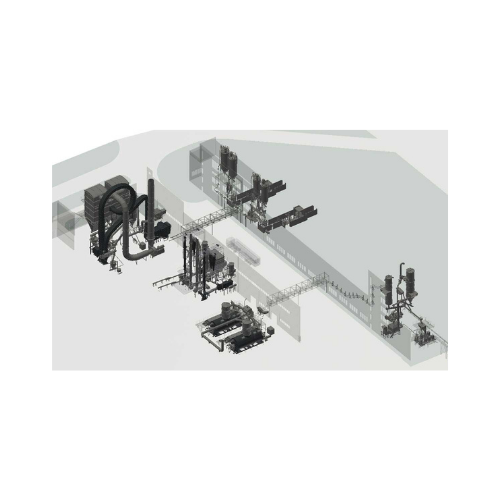
Wheat processing systems for industrial applications
Maximize efficiency in wheat processing with a system designed for p...
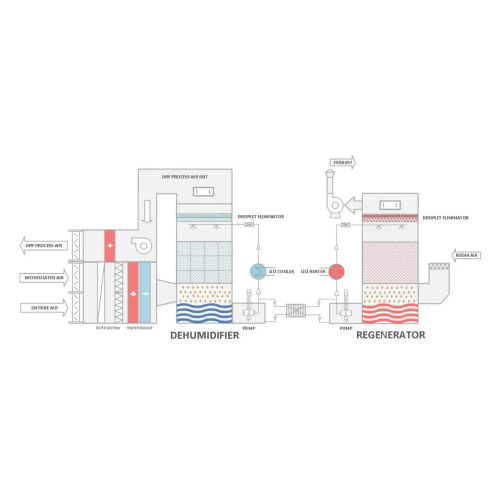
Industrial lithium chloride dehumidifier
Efficiently control air moisture and temperature with a solution that ensures prec...
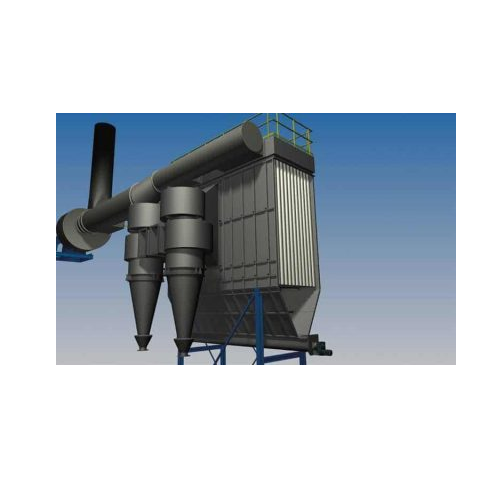
Industrial dust collection system
Optimize your process by efficiently capturing and removing airborne dust particles, ensu...
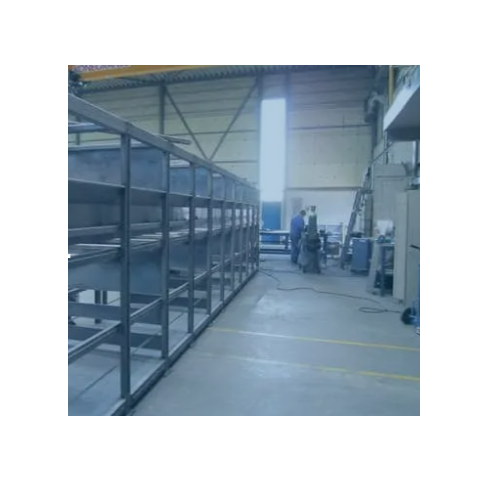
Continuous bulk fluid bed dryer
Achieve rapid and energy-efficient moisture removal across diverse materials with our advanc...
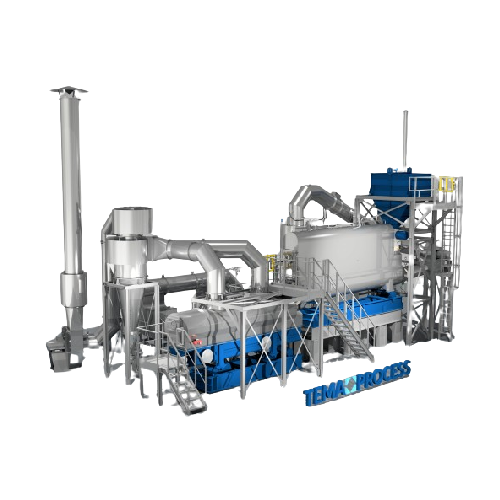
Vibrating fluid bed dryer for bulk materials
Ensure efficient moisture removal and thermal processing with this fluid bed ...
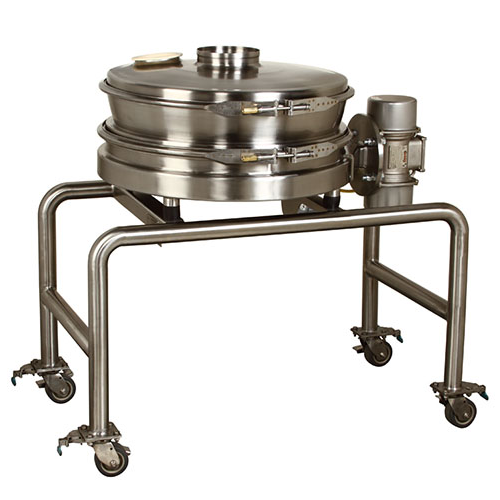
Sanitary separator for food processing applications
Ensure efficient separation and prevent contamination in food product...
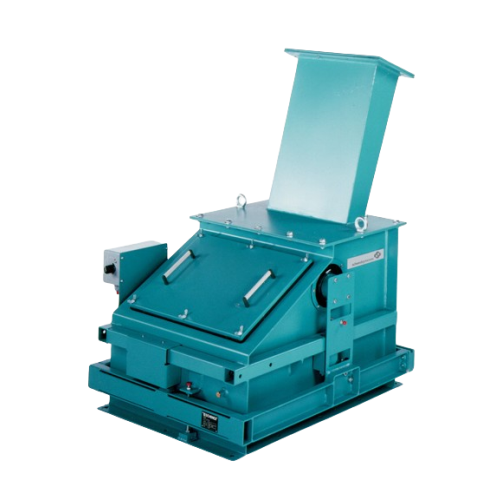
Solids flow meter for bulk solid streams
Ensure precise bulk material measurement with a system designed for accuracy and r...