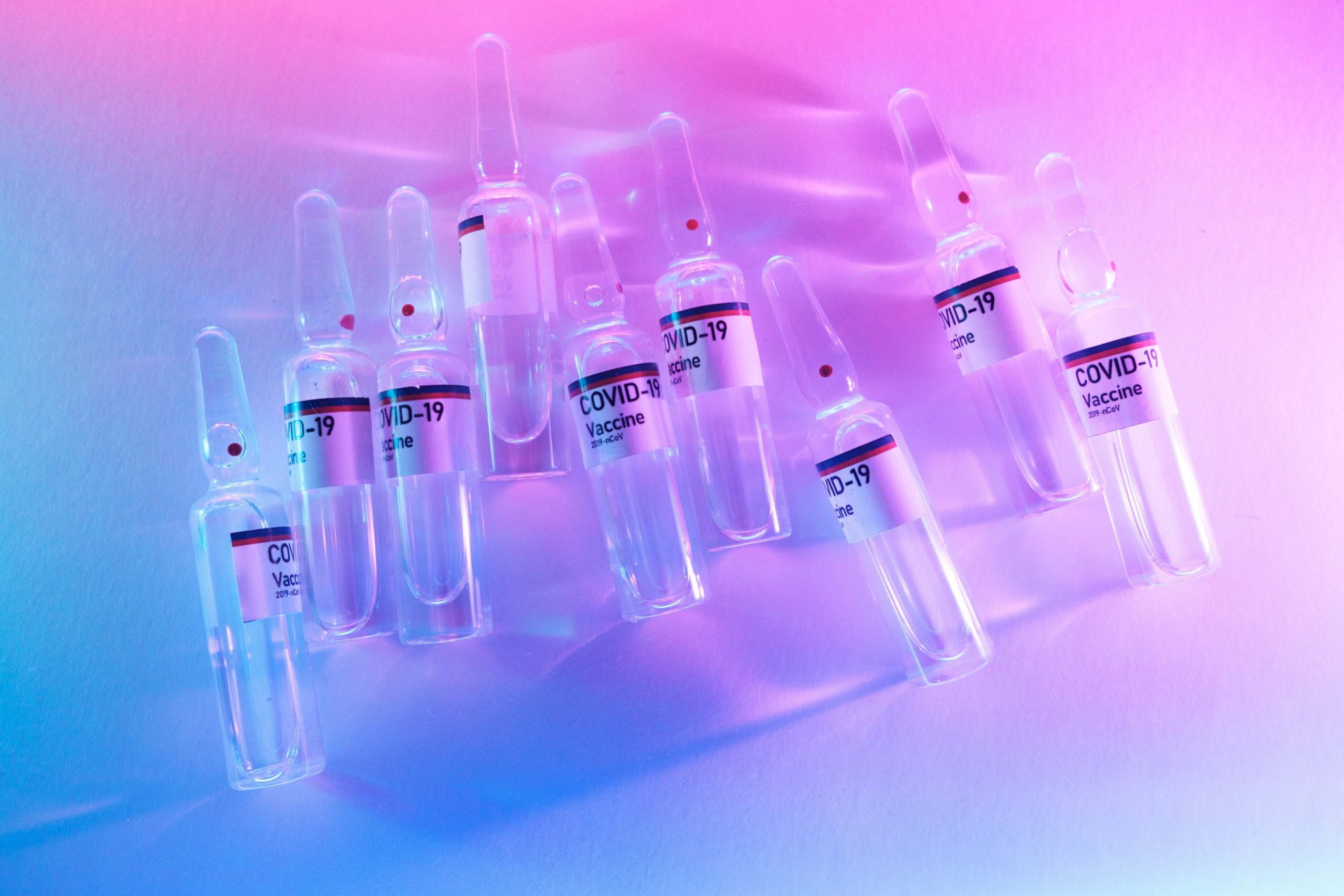
Ampoules Making Equipment
Find innovative production technology for making ampoules and connect directly with world-leading specialists
After being used to contain the blood of martyrs after death or to store the anointing oil of French monarchs, today ampoules are the first choice in packaging injectables. You create ampoules by melting the glass tube into the desired shape and seal them at the neck by melting the top of the glass tube. The only way for you to extract the contents from an ampoule is by breaking the glass at its breaking point, making it perfect for single dose applications only.
Technology picks for producing ampoules
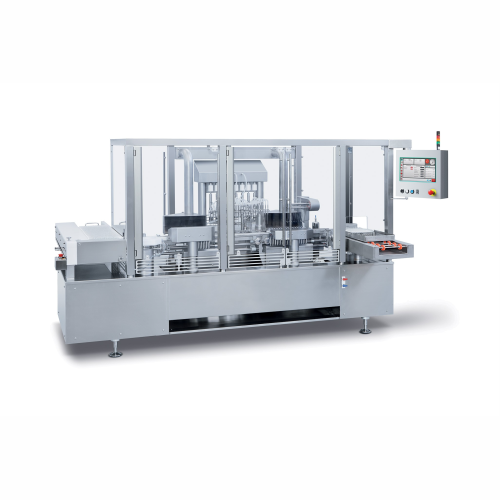
Aseptic ampoule filling and sealing solution
Ensure precise dosing and secure sealing of sterile liquid pharmaceuticals in...
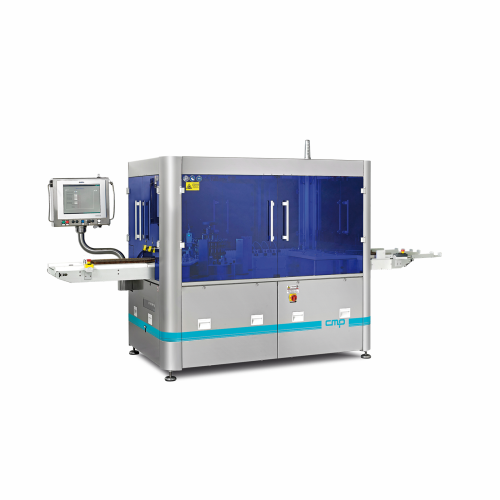
360 and leak Inspection system for glass containers
Ensure the integrity of every glass container with a comprehensive in...
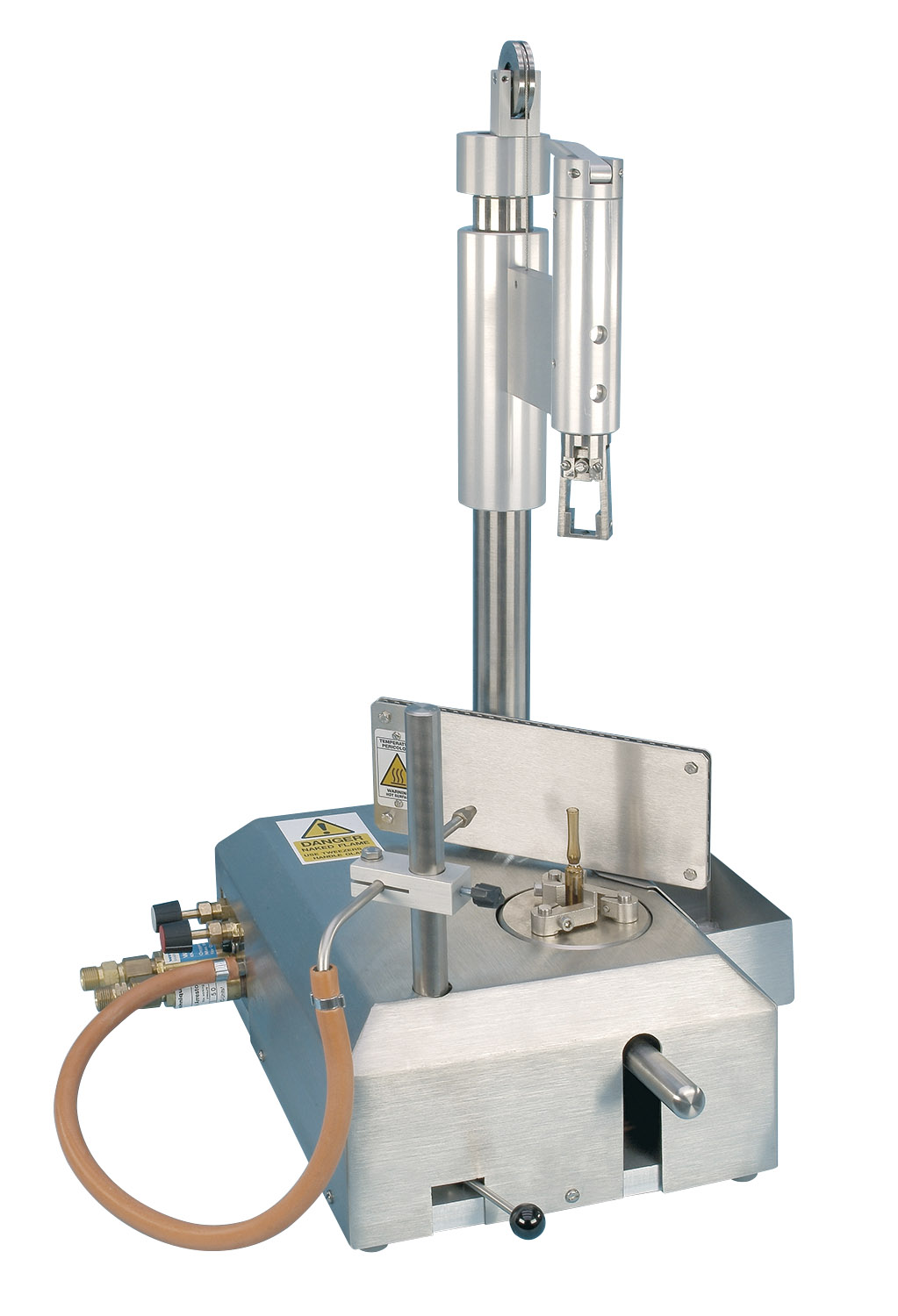
Benchtop ampoule opening and closing equipment
The procedure for opening or closing ampoules requires you to handle gas an...
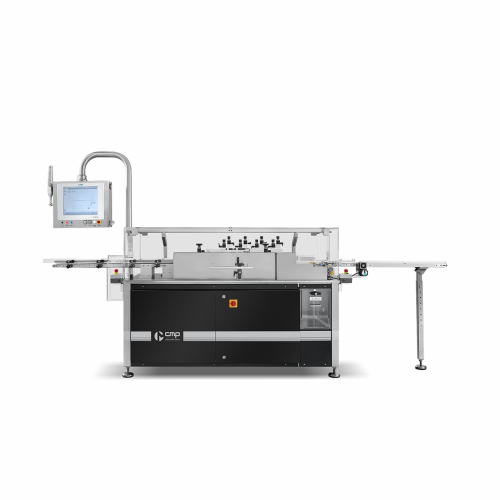
Inspection system for plastic ampoules in strips
Ensure the integrity of single-dose plastic containers with high-speed le...
Select your ampoules process
Tell us about your production challenge
Types of ampoules: shapes that fit the standards
Based on the shape of their head from ISO standards, you can count three types of ampoules: straight-stem (form B), funnel type (form C), and sealed (form D). ISO 9187-1:2010 specifies materials, dimensions, capacities, performance and packaging requirements for three forms of glass ampoule for injectable pharmaceutical products.
Straight-stem ampoules and funnel-types have open ends for the customers to wash and sterilize before filling and sealing. Sealed ampoules instead have dome-shaped closed ends, which means that ampoules are supplied already sterilized. This is done prior to the ampoule going through their respective filling and sealing machines. Customers have to open them with a sharp flame before filling them and then reseal them.
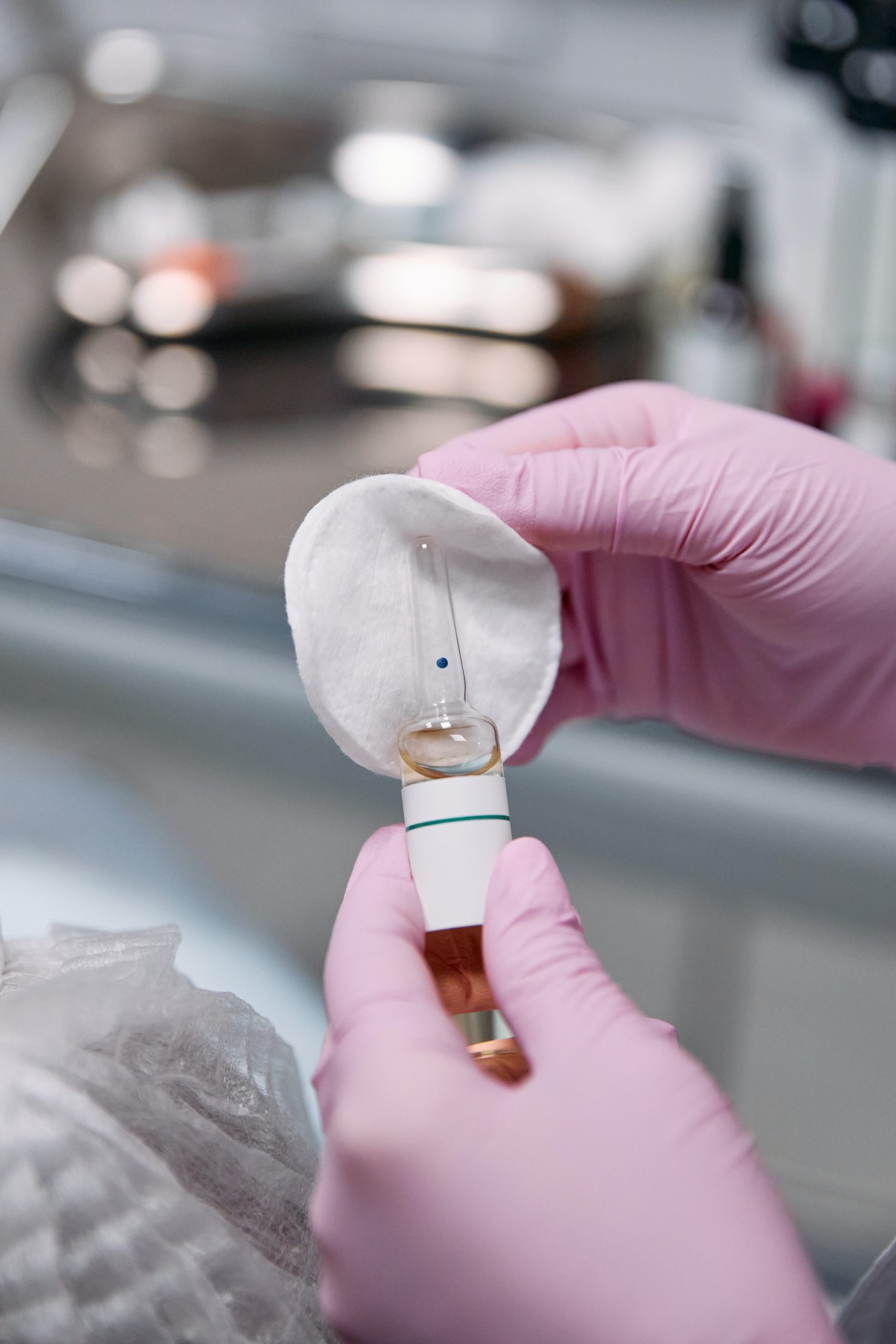
Ampoules also have different break systems. One point cut (OPC) refers to a small cut on the constriction of the ampoule and is paired with a colored dot mark for the position of the breaking cut. Color break ring (CBR) refers to an enamel ring applied around the constriction as a marker for the breaking cut. Scoring (SCO) refers to surface markings of the glass around the constriction part.
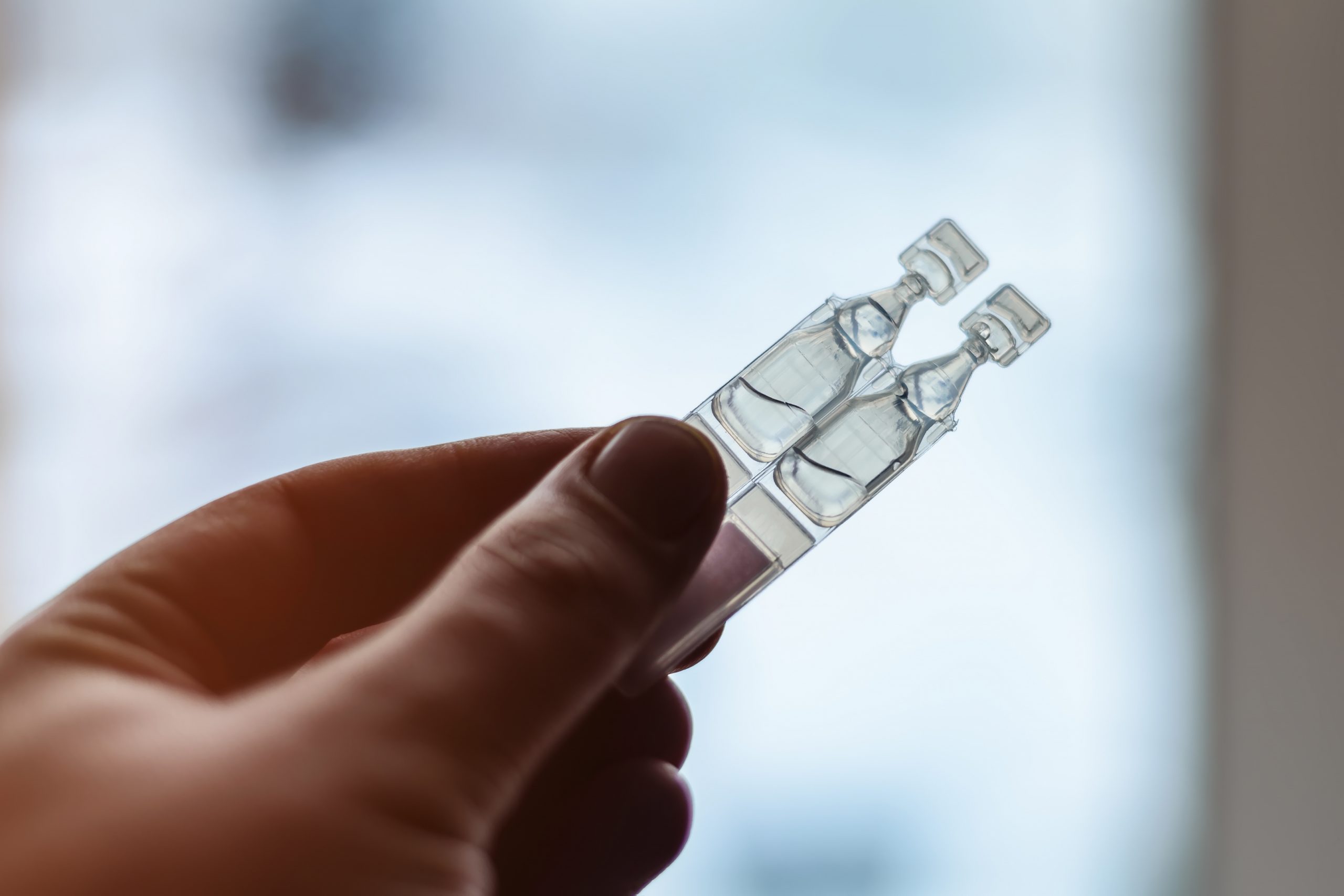
Plastic ampoules as a new possibility
Plastic ampoules are getting more popular in pharmaceutical companies. They are less costly to manufacture, easier to transport and store as they have better breaking resistance. Actually, they do not require tearing or cutting the top portion, because you can simply snap off the neck to open. Their manufacturing process offers more accurate dosages and prevents overfill of products, making it more efficient compared to glass.
Check the quality through ampoule inspection machine
Quality control for pharmaceutical products is a critical process. It requires multiple visual inspections to ensure that the products are not contaminated, and the packaging is intact and clean. You can opt for a fully automatic or semi-automatic inspection machine equipped with image sensors and magnifying cameras to check the correct fill level, detect contaminating particles, glass defects and container leakage.
Other options available for inspection machines include detecting product color using illumination and sensors, and container closure integrity using multiple cameras that check the position of the cap.
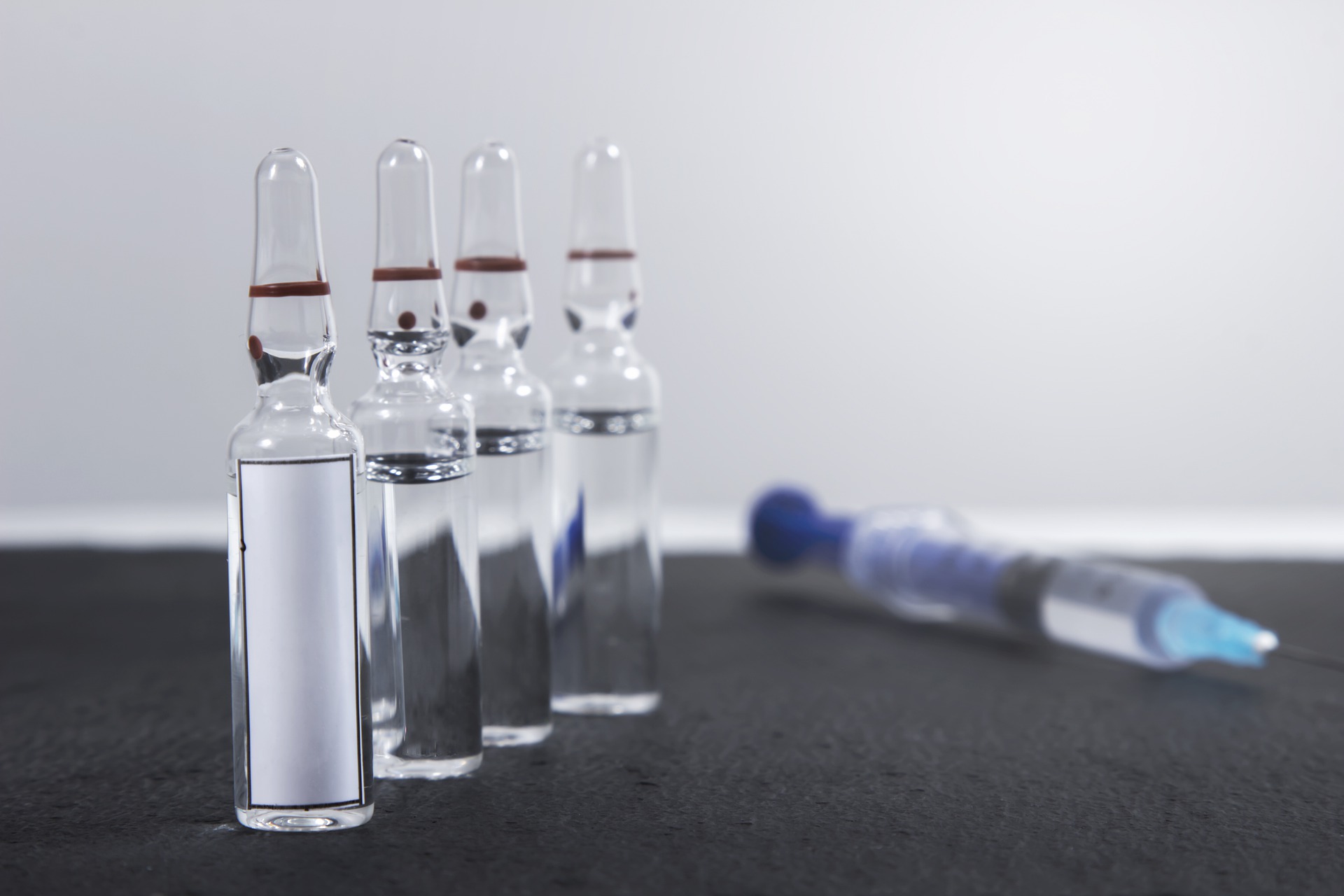
Color coding for identification
Have you ever noticed that ampoules have colored rings around their neck?
The colored rings are used as a code to identify the substance inside the ampoule. This makes it easier to sort them for the purposes of storage, labeling, and packaging. These rings are machine-readable for easier identification and printed by rotating discs using heavy-metal-free inks for safety reasons.
Difference between ampoules and vials
Ampoules are meant for single-use or single-dose applications since they are sealed at the neck with heat and you have to crack them open to extract the contents. With vials it is another story. You only need to remove the caps or pierce the rubber stopper with a syringe. As for the content inside, ampoules store unstable chemical compounds and highly volatile elements while vials are for storing stable compounds.
Specialised machinery for ampoule production
When it comes to the full production of making ampoules, specialised machines and manufacturing processes need to be followed. For example, all ampoule production lines and machinery should be made from high quality stainless steel. This is because the contents simply cannot be contaminated. The production process also includes the use of an ampoule filler, for liquid filling as well as Labeling machines and heating stations for sealing the glass.
Processing steps involved in ampoules making
Which ampoules technology do you need?
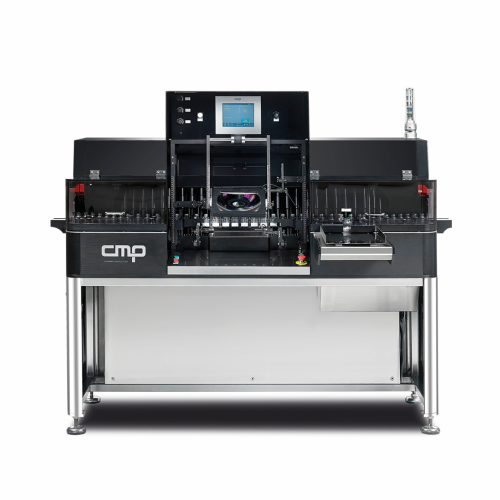
Inspection system for glass containers
Ensure precise inspection of liquid, freeze-dried, and powdered products in glass co...

External washing and drying system for ampoules and vials
Optimize your aseptic processing by seamlessly integrating a c...
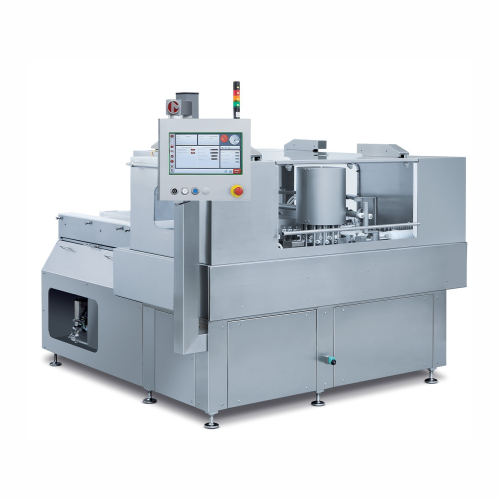
Industrial washing and sterilizing system for ampoules and vials
Ensure the highest hygiene standards in your liquid for...

Glass container Inspection line
Ensure precise quality control with a high-speed inspection line designed for glass containe...
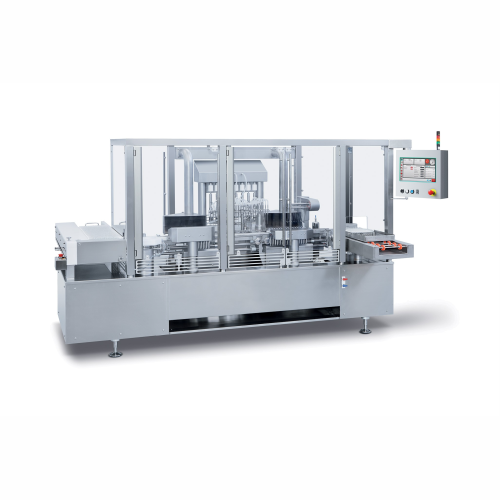
Aseptic ampoule filling and sealing solution
Ensure precise dosing and secure sealing of sterile liquid pharmaceuticals in...
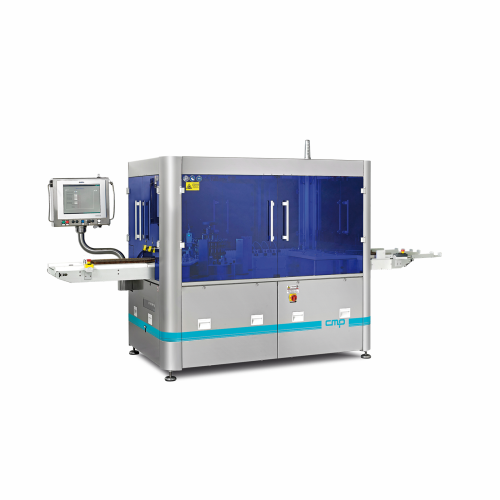
360 and leak Inspection system for glass containers
Ensure the integrity of every glass container with a comprehensive in...
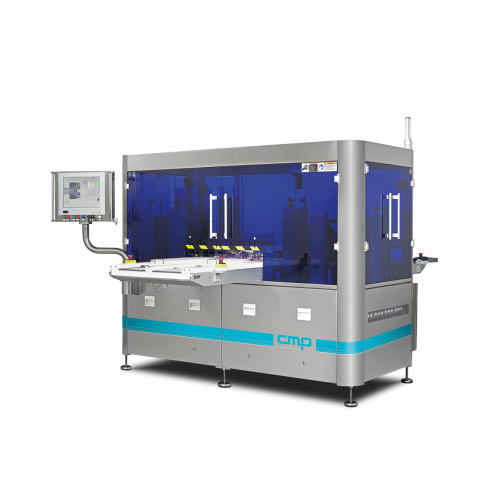
Glass container inspection system
Ensure product integrity with precision inspection for glass containers, detecting partic...
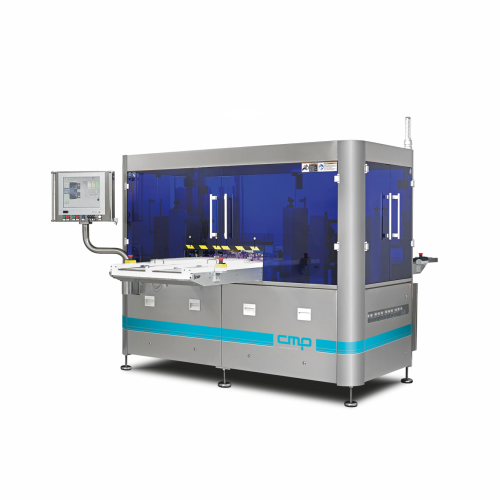
Inspection for glass containers
Ensure the integrity and quality of your liquid formulations with high-speed inspection and ...
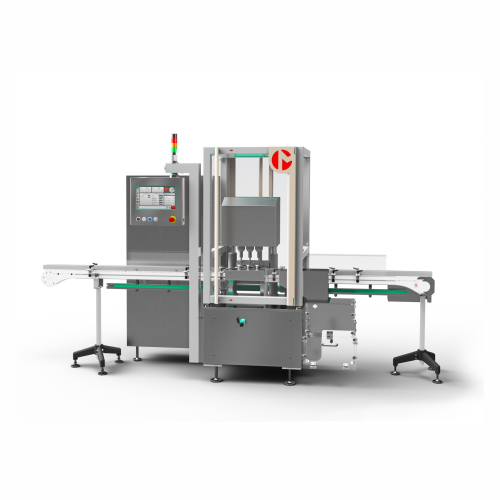
Filling and capping solution for bottles
Optimize your bottling efficiency with a robust solution designed to streamline fi...
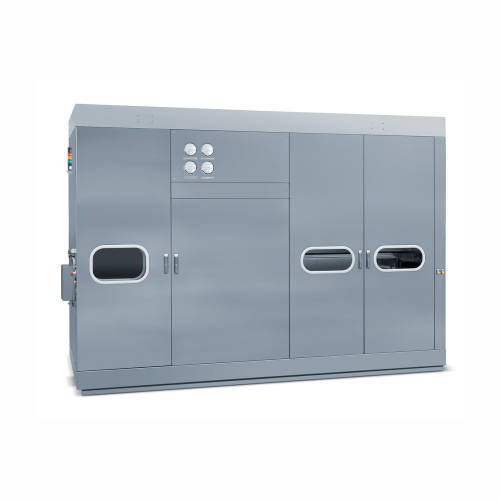
Depyrogenation tunnels for pharmaceutical containers
Ensure precise sterility and safety in pharmaceutical production wit...
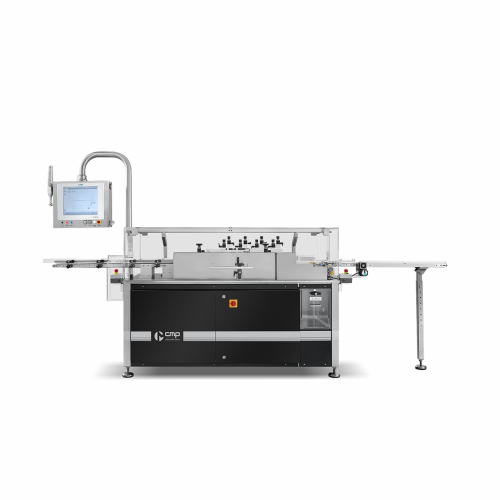
Inspection system for plastic ampoules in strips
Ensure the integrity of single-dose plastic containers with high-speed le...
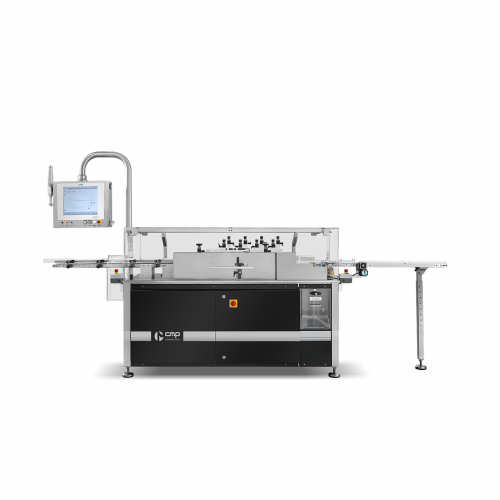
Leak testing for ampoules and vials
Ensure the integrity of sterile liquid containers with high-speed leak testing, detecti...
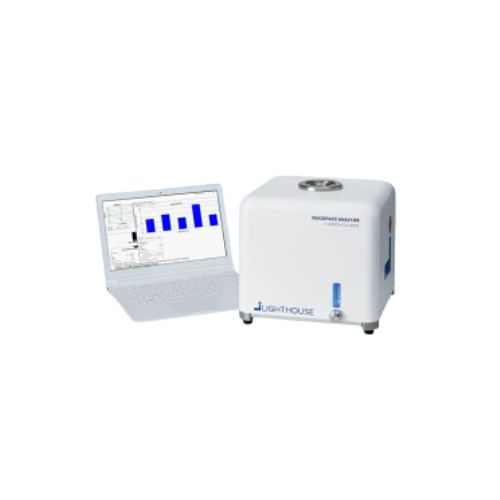
Carbon dioxide headspace analyzer for parenteral containers
Ensure accurate headspace gas analysis to maintain container...
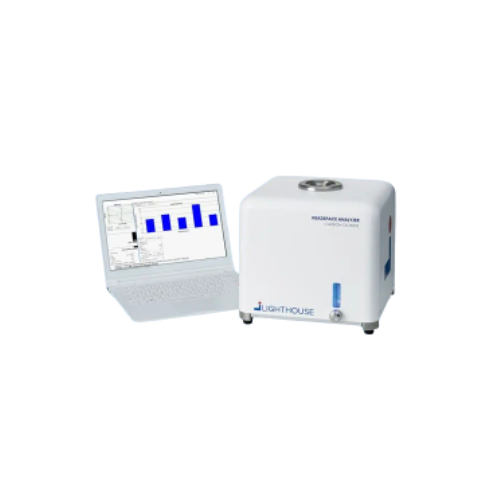
Oxygen headspace analyzer for container closure integrity testing
Ensure the integrity of oxygen-sensitive products wit...
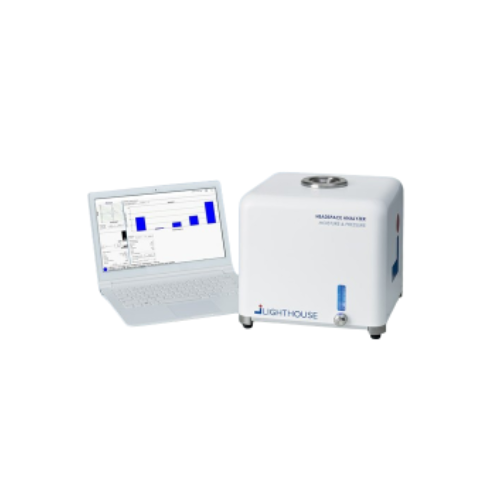
Moisture and pressure headspace analysis for sealed parenteral containers
Ensure accurate moisture and pressure assess...
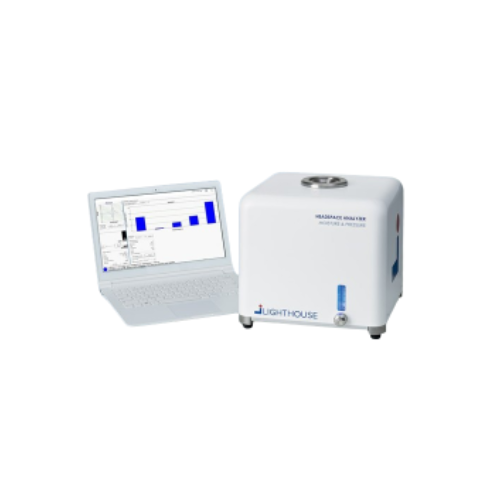
Water activity headspace analyzer for drug product samples
Ensure precise control of moisture levels across the entire p...
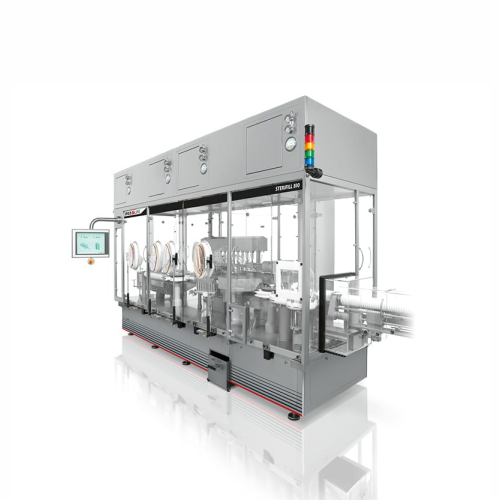
Ampoule filling and sealing system
Designed for high-speed sterile liquid filling and sealing, this system ensures precise ...
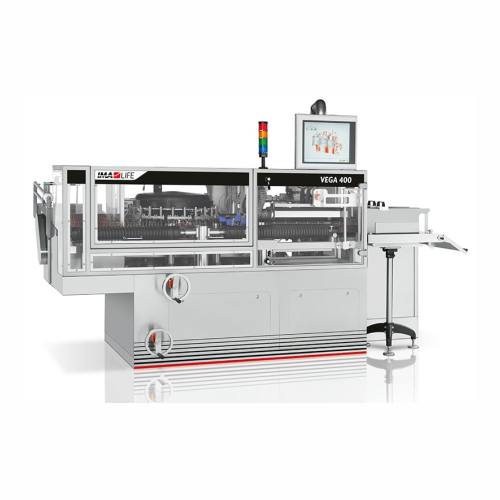
Ampoule external washer for decontamination
Ensure contamination-free glass containers with a high-speed solution designed...
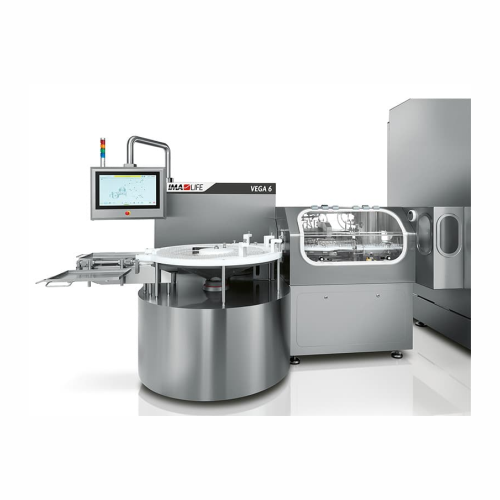
Rotary vial washers for parenteral containers
Ensure sterile and pyrogen-free parenteral preparations with a seamless wash...
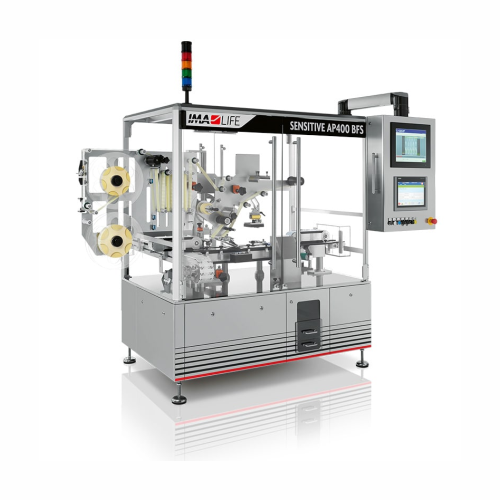
Labelling system for blow fill seal (bfs) strips
Ensure precise labeling and traceability for your blow fill seal containe...
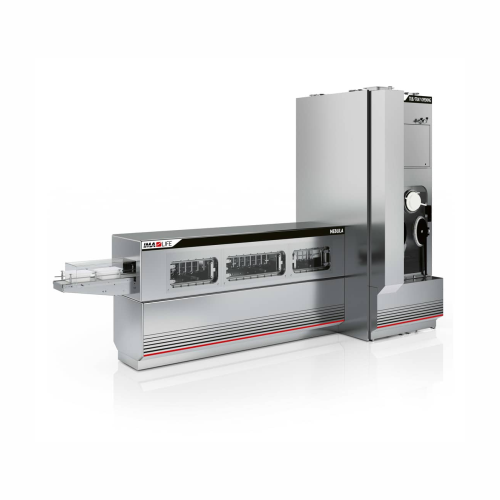
High-speed decontamination tunnel for pharmaceutical Rtu material
Ensure 100% sterility of ready-to-use materials with ...
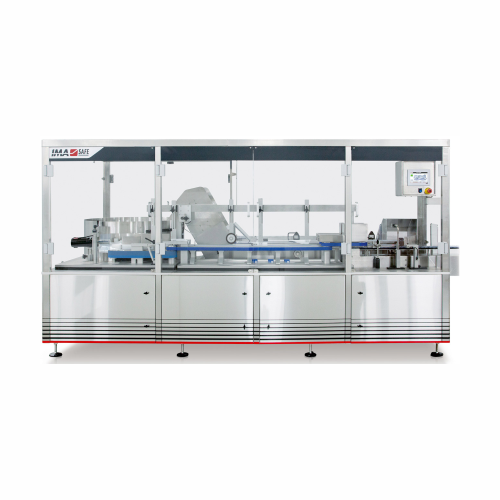
Linear bottle sorter and unscrambler
Streamline your bottle feeding with high-speed sorting, unscrambling, and inspection, ...
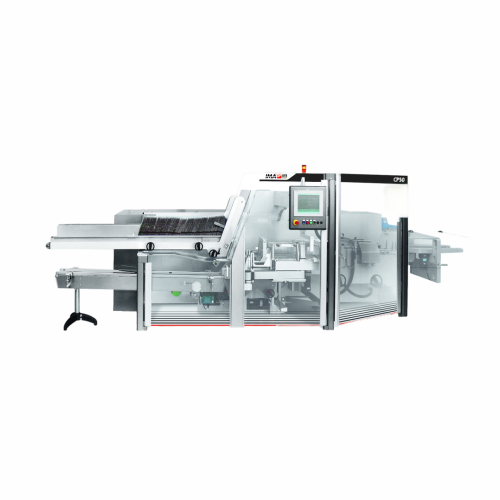
High-speed side loading case packer for small dimensions
Optimize your packaging line with a high-speed solution designed...
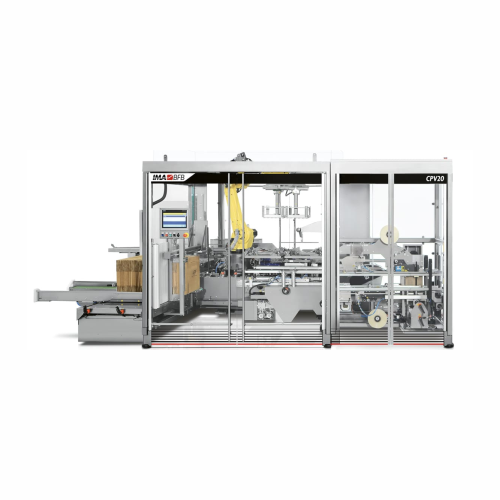
Top-loading case packer for pharmaceutical and cosmetic products
Ensure precision and flexibility in packaging with this...
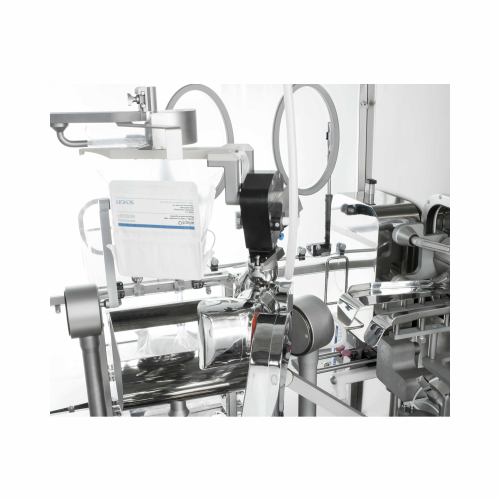
Robotic sterile package opening system
Achieve sterile precision with a fully robotic system that streamlines primary packa...
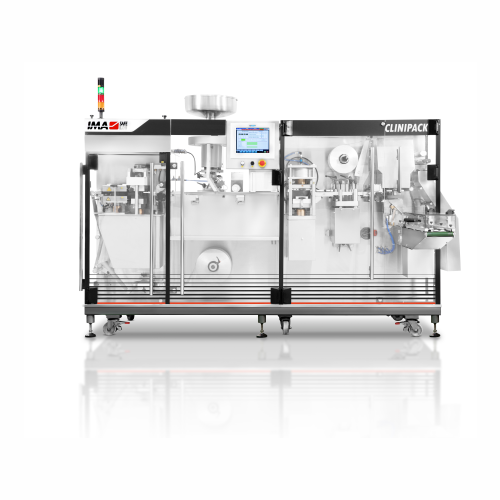
Thermoforming solution for clinical trials
Designed for precision and flexibility, this compact thermoforming machine stre...
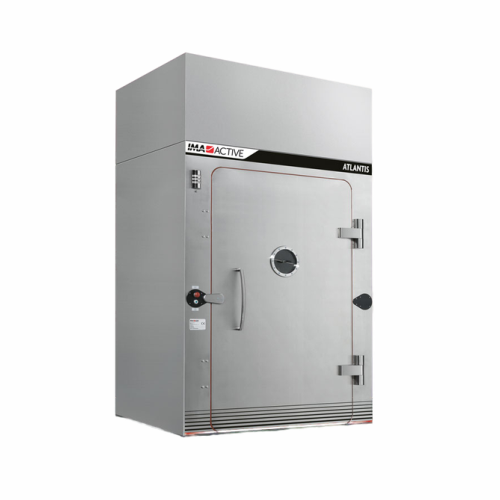
Pharmaceutical components washing station
Ensure optimal cleanliness with high-efficiency washing and drying of pharmaceut...
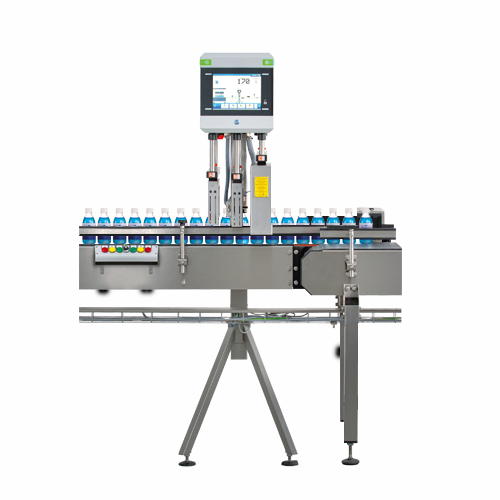
Compact full product inspection system for pharmaceuticals
Easily detect fill level inaccuracies, closure misalignments,...
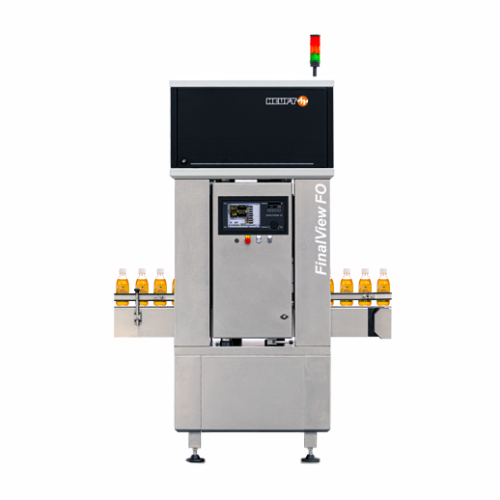
Final product inspection system for pharmaceutical containers
Ensure the integrity and precision of packaged pharmaceuti...
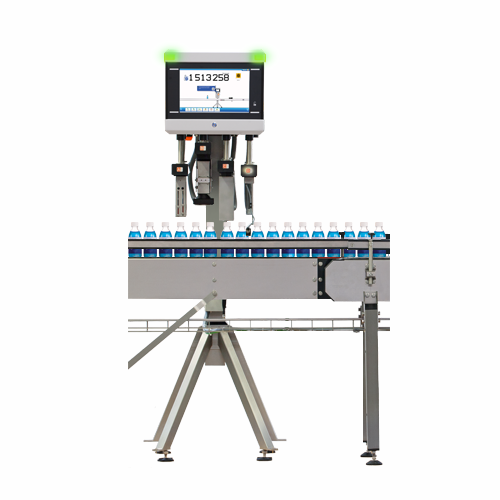
Full container inspection for pharma and food industries
Ensure precise fill levels and secure closures in your productio...
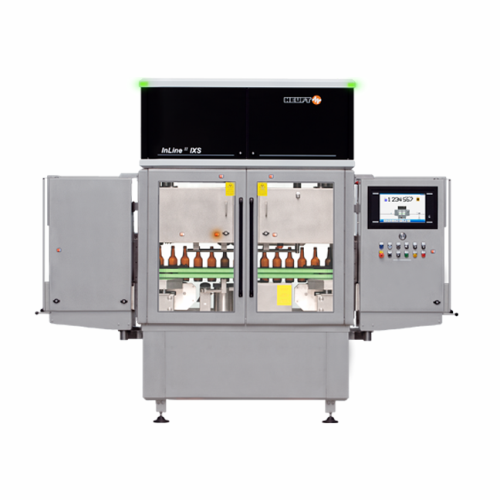
X-ray assisted empty bottle inspection
Enhance your production line with advanced X-ray and optical technology to ensure pr...
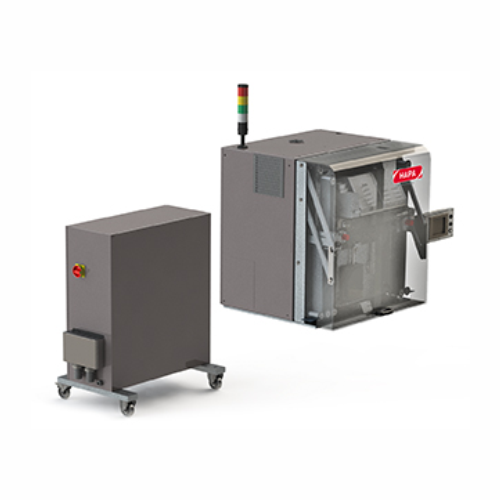
Uv Dod Cmyk label and packaging film printer
Achieve high-precision, on-demand printing for narrow-web packaging films and...
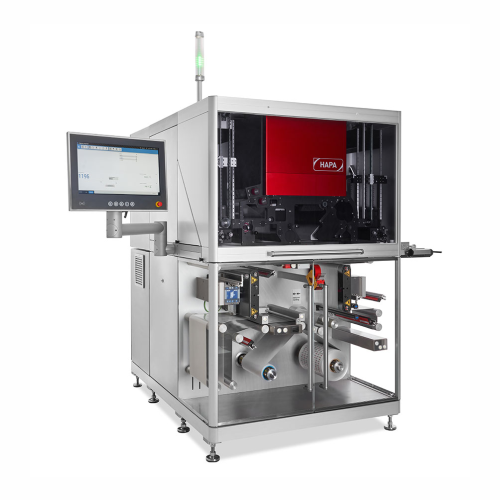
Inline digital printing system for pharmaceutical packaging
Enhance packaging precision and compliance with cutting-edge...
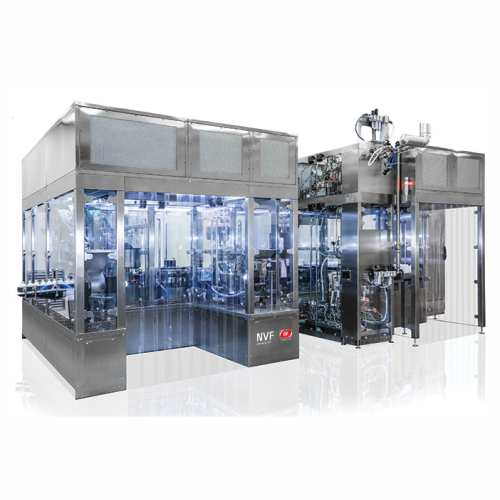
Sterile and nonsterile filling for injectable solutions
Efficiently fill and stopper injectable solutions in both sterile...
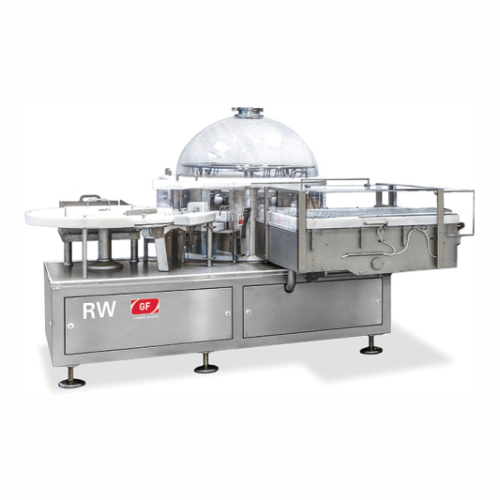
Rotary washer for pharmaceutical containers
Ensure optimal preparation of pharmaceutical containers with advanced rotary w...
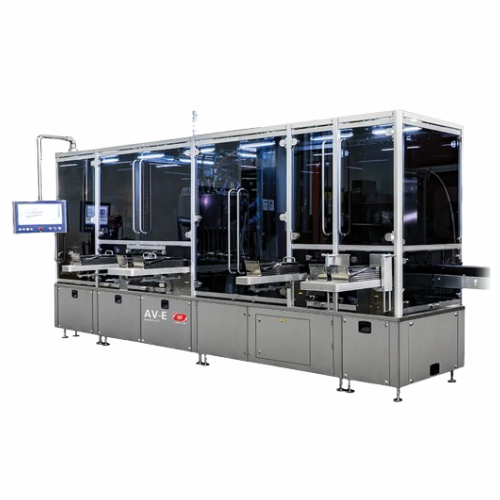
Optical inspection for ampoules, vials, cartridges, and syringes
Ensure product integrity and safety with this advanced ...
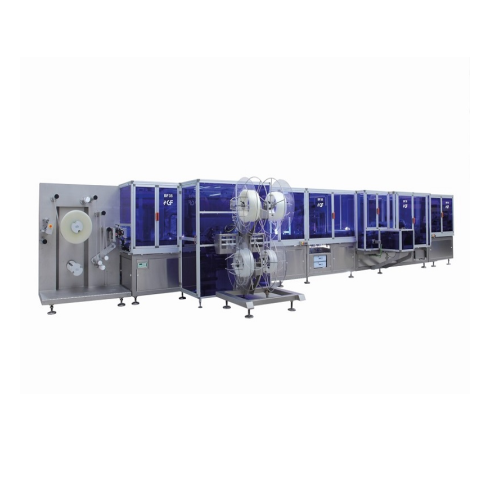
Bag forming system for pharmaceutical industry
For fluid pharmaceutical production, ensure precise formation and sealing o...
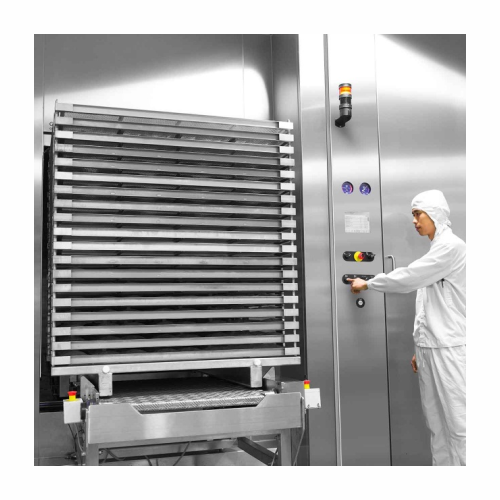
Pharmaceutical sterilization with steam/air mixture
Achieve sterile, dry, and ready-to-use pharmaceutical products with p...
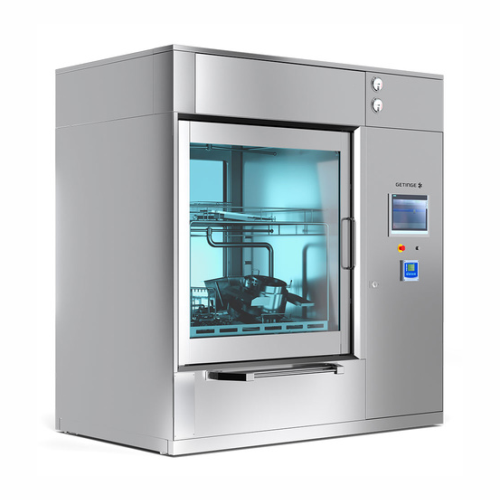
Cgmp washer/dryer for biopharmaceutical cleaning
Achieve optimal cleanliness with precise washing and drying for biopharma...
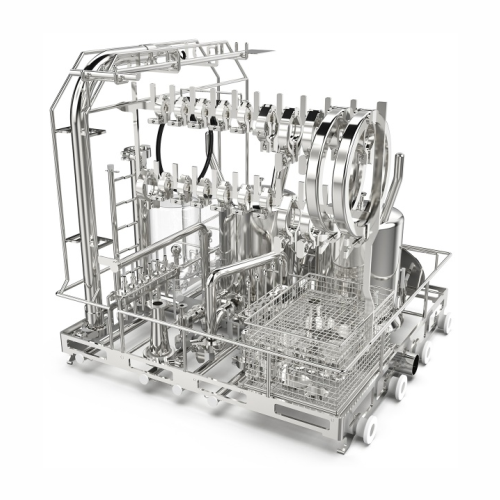
Loading solutions for Gmp washers
Ensure thorough cleaning and drying of biopharmaceutical components with modular loading ...

Liquid dispensing isolator for sterile environments
Maintain product sterility by utilizing a liquid dispensing isolator ...
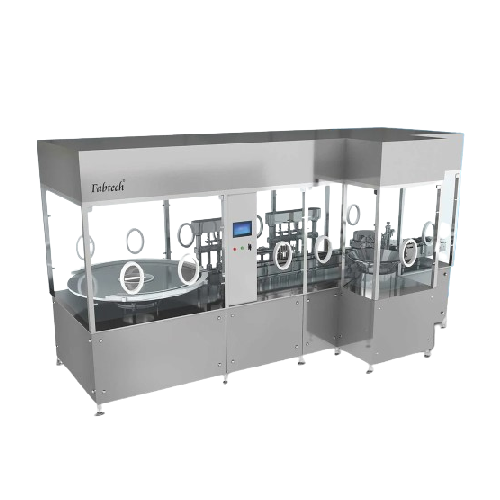
Pharmaceutical turnkey project consultants
Streamline your biopharma production with turnkey solutions that cover everythi...
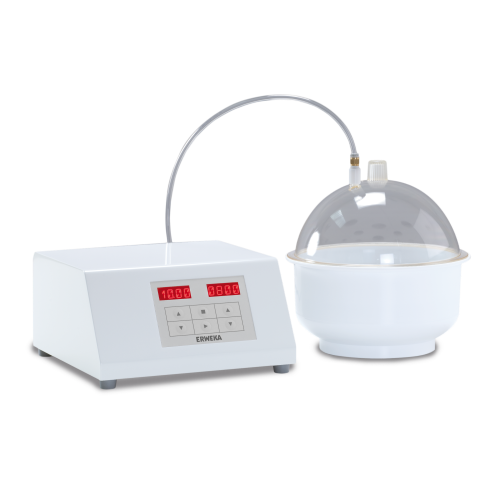
Blister packaging leak tester
Ensure airtight integrity in your blister packaging with precise vacuum and dye penetration te...
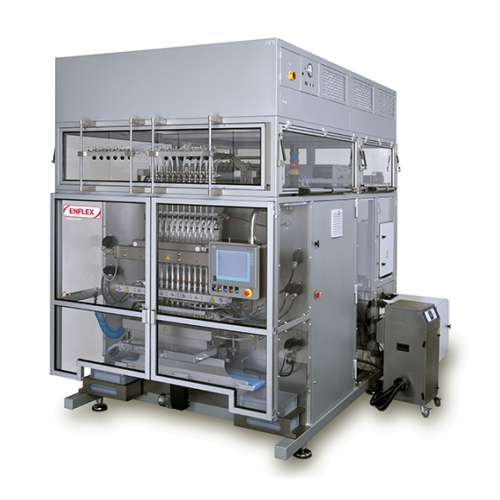
Intermittent stick pack machine for pharma and healthcare
Looking to streamline your packaging operations with high-spee...
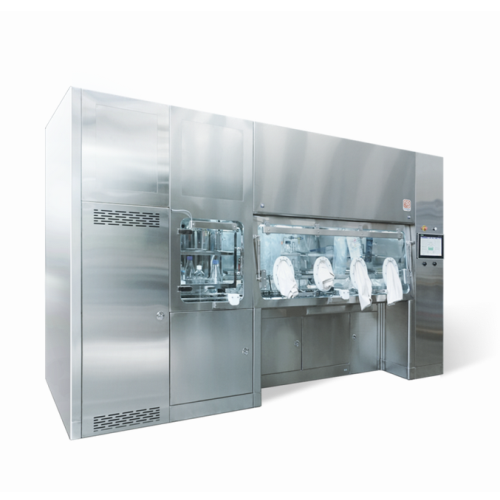
Modular sterility testing isolator for pharmaceuticals
Achieve uncompromised sterility with modular isolators designed fo...
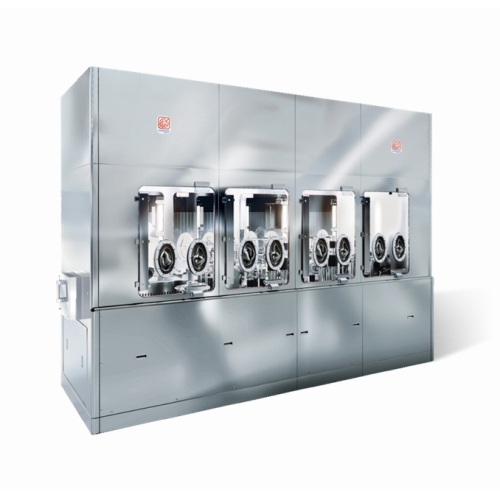
High quality sterile filling system
Experience unparalleled precision in aseptic filling with this advanced system, designe...
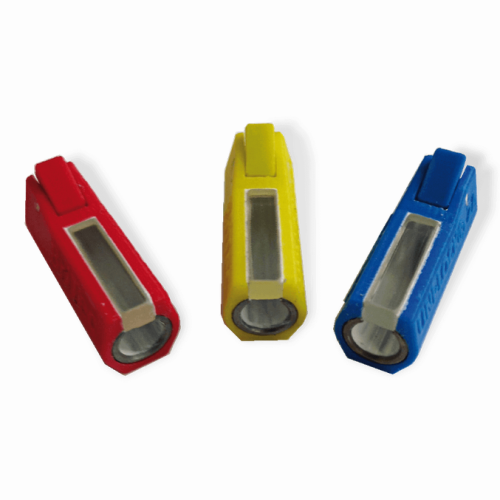
Tungsten syringe shield for radiation protection
Ensure precise radiation protection with a compact syringe shield designe...
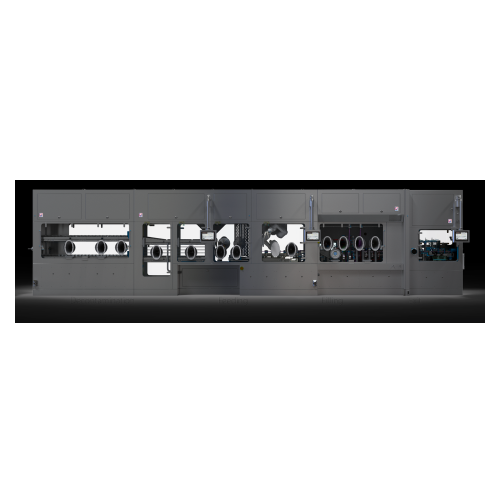
Automatic aseptic filling line for Iv bags
Ensure aseptic integrity and high-speed processing of IV bags with a filling li...
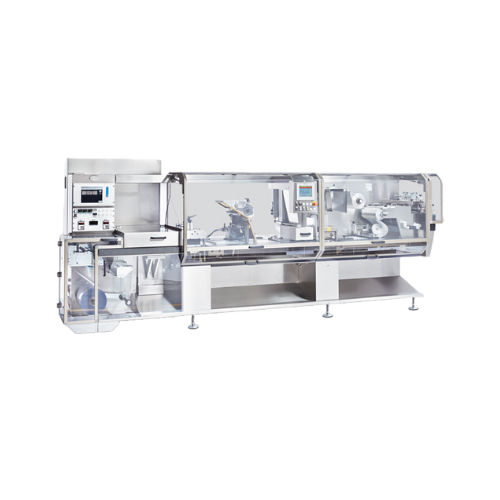
High speed blister packaging for pharmaceuticals
Need efficient packaging with quick format changeovers for various capsul...
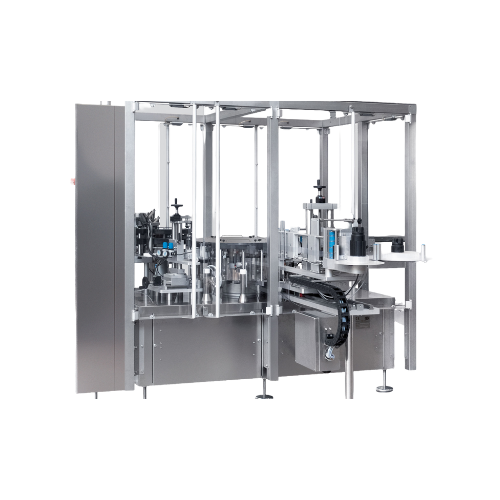
High-speed labelling solution for syringes and vials
Optimize your pharmaceutical packaging process with a cutting-edge l...
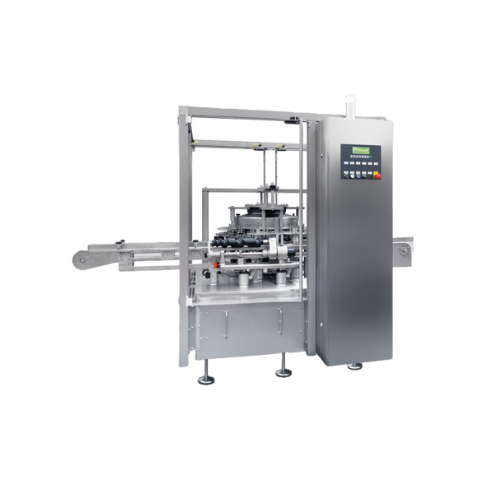
Rotary continuous motion bottle cleaning solution
Ensure pristine product integrity by effectively eliminating particles ...
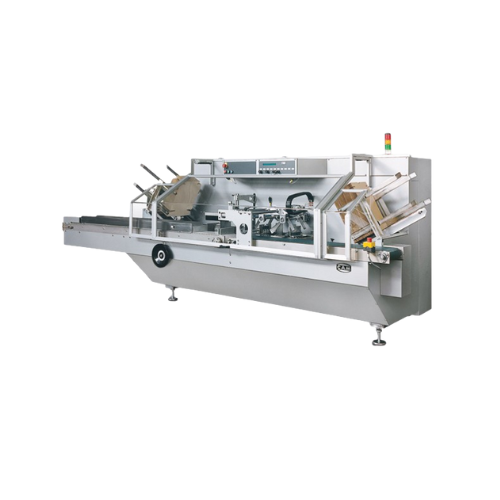
Tray and lid forming solution for food packaging
For manufacturers needing precision packaging, this machine seamlessly fo...
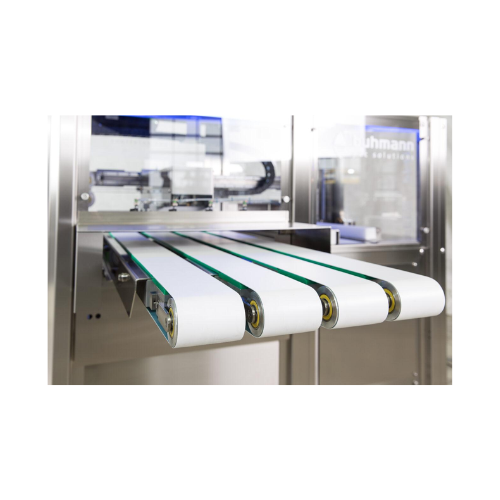
Conveyor system for aligning, sorting, and transporting products
Streamline your packaging line by efficiently aligning,...
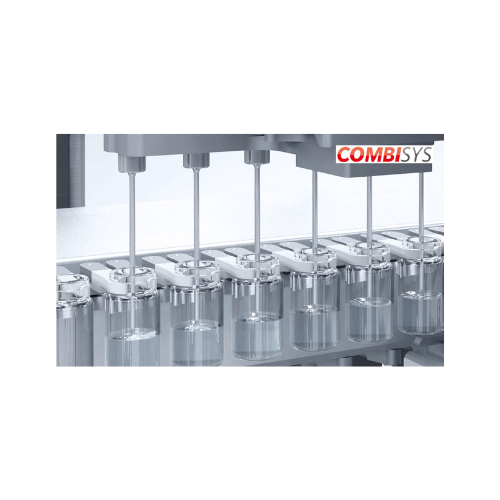
Combisys filling and closing system for pharmaceutical containers
Ensure precise filling and closing of pharmaceutical ...
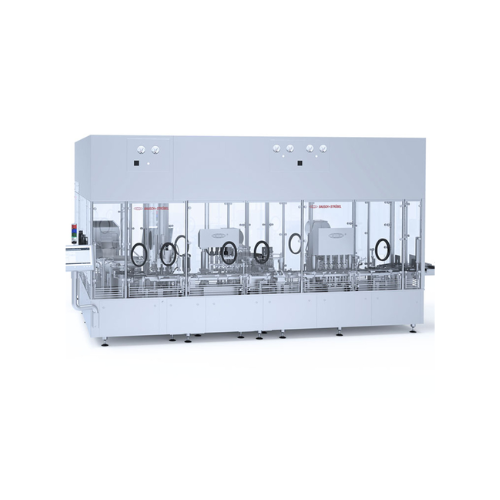
Filling and closing solution for plastic bottles
Efficiently sort, fill, and close a variety of plastic bottles with preci...
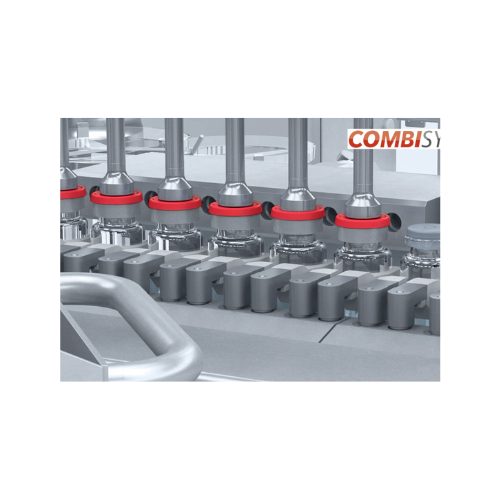
Automated vial closing system
Ensure reliable vial sealing with unparalleled flexibility and precision, optimizing your liqu...
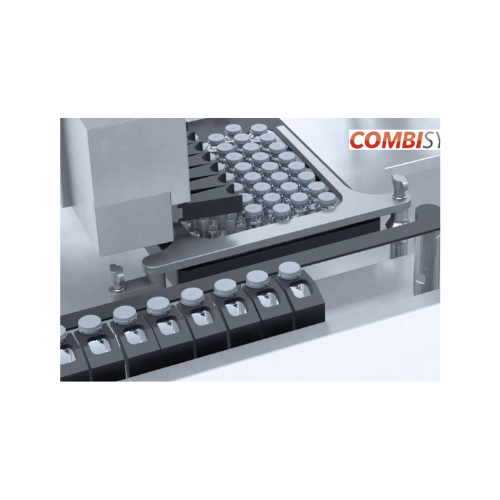
Automated container loading system for ampoules and syringes
Ensure precise loading and nesting of sterile containers in...
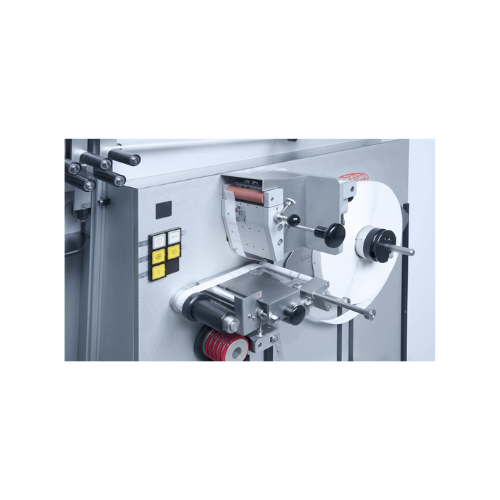
High-speed label splicer for continuous labeling
Ensure seamless production by integrating our label splicer solution, des...
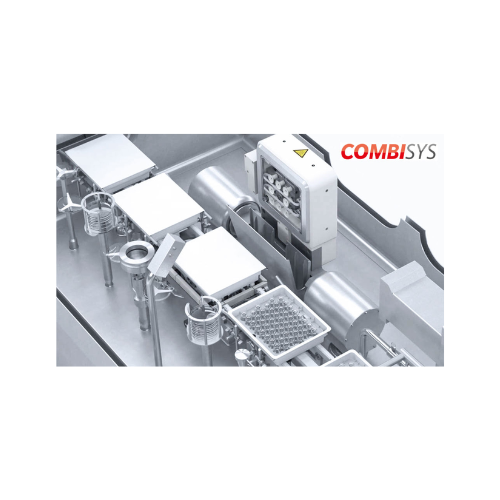
Automatic tub de-bagging and de-nesting solution
Efficiently prepare your RTU containers by seamlessly integrating de-bagg...

Tray loader for pharmaceutical containers
Maximize efficiency in aseptic fill-finish lines with precise and rapid tray loa...
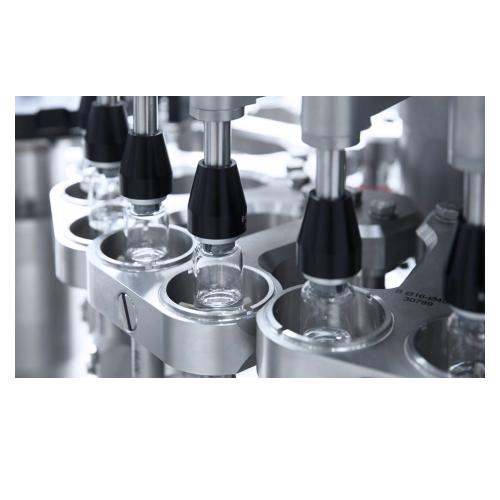
Container exterior cleaning for pharmaceutical applications
Achieve consistent cleanliness and dryness for your containe...
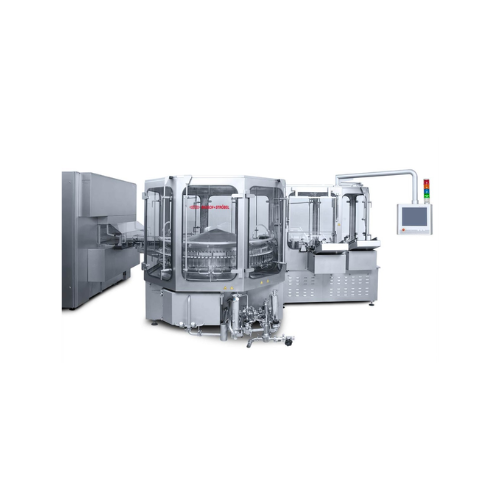
Compact cleaning system for glass and plastic containers
Ensure exceptionally thorough cleaning and gentle handling of di...
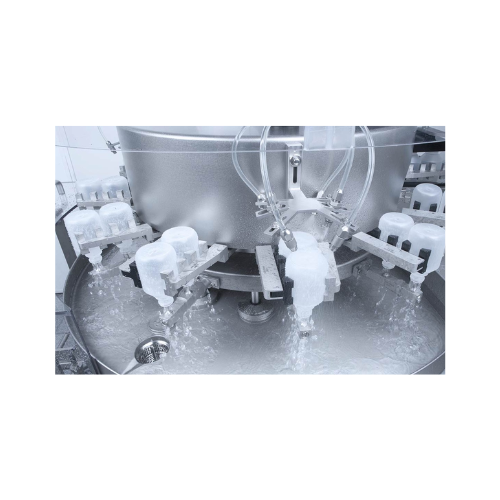
Vial and bottle cleaning system for pharmaceutical use
Ensure pharmaceutical-grade cleanliness for your vials, ampoules, ...
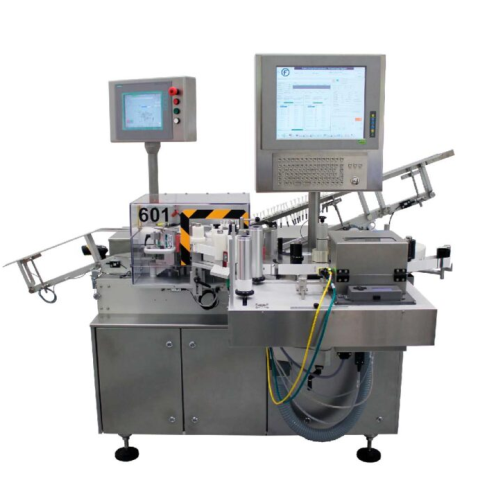
Automatic labeling system for pharmaceutical containers
Streamline your pharmaceutical packaging with precision labeling,...

Automatic vial labeling system
Achieve precise labeling at high speeds with a system designed for seamless integration into ...
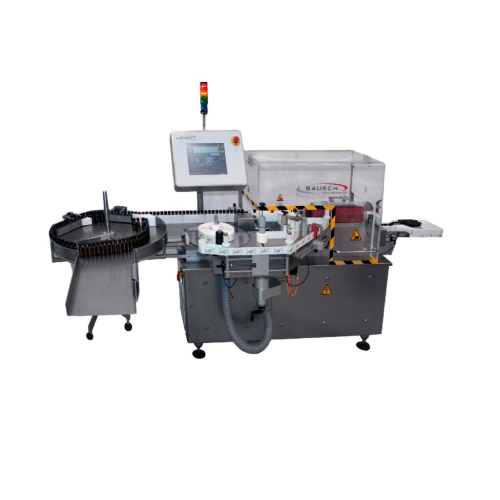
Fully automatic linear labeling system for bottles
Optimize your bottle labeling process with precision and speed, ensuri...
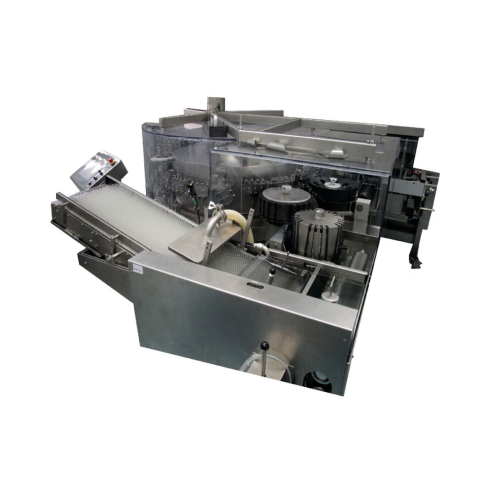
Rotary washing system for pharmaceutical containers
Achieve superior cleanliness and efficiency with a high-speed rotary ...
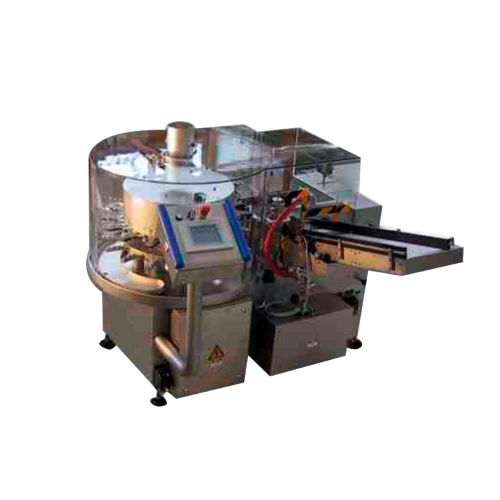
Automated washing system for vials, syringes, cartridges, and ampoules
Achieve sterile conditions with this high-speed ...

Semi-automatic washer for pharmaceutical containers
Achieve precise cleaning for pharmaceutical containers with a semi-au...
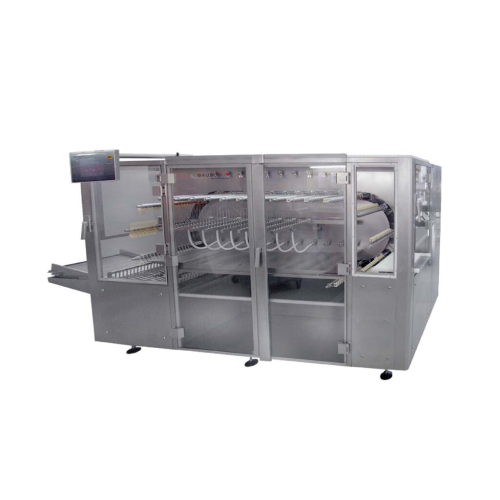
High-speed washing system for ampoules and vials
Ensure contamination-free ampoules and syringes with this advanced washin...
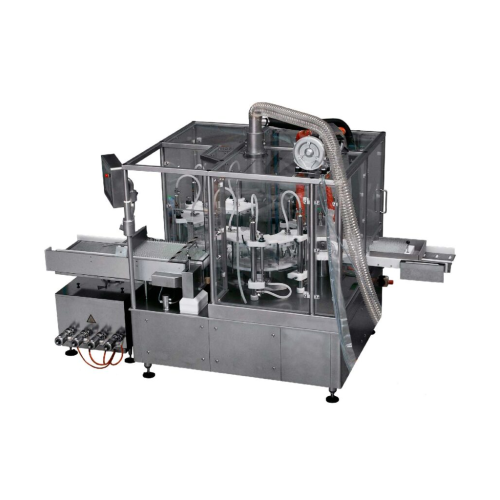
Automatic external washing system for ampoules and vials
Ensure optimal cleanliness of liquid medication containers with ...
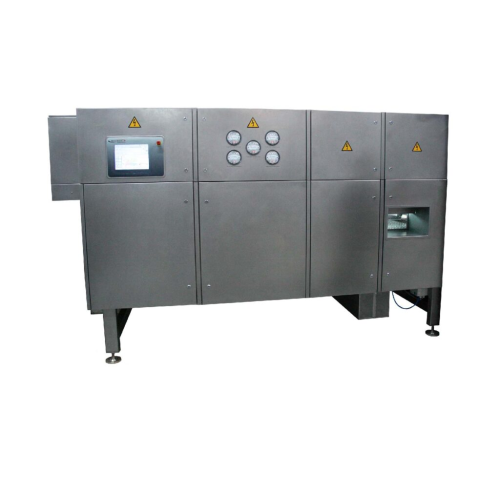
Hot air sterilization for glass containers
Ensure precise and uniform sterilization of glass ampoules, vials, and syringes...
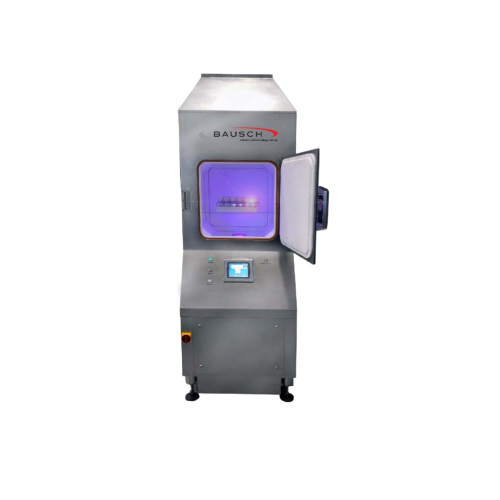
Sterile transfer chamber for pharmaceutical components
Ensure the sterility of your components rapidly with an enclosed c...
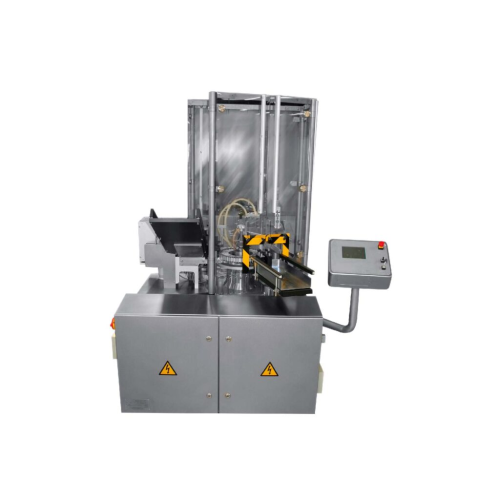
Filling and closing system for ampoules
Ensure precision and efficiency in your aseptic fill-finish operations with a compa...
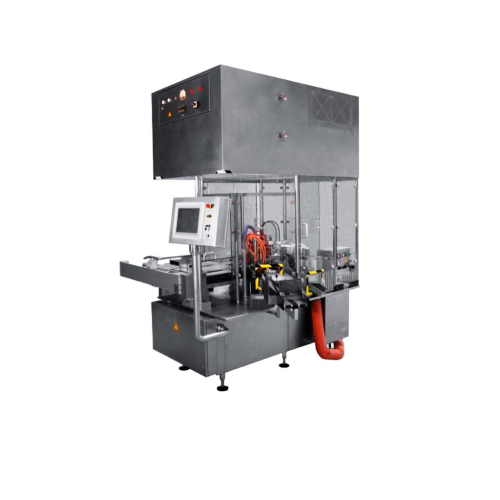
Ampoule filling and closing system
Optimize your production line with a high-speed system designed for seamless filling and...
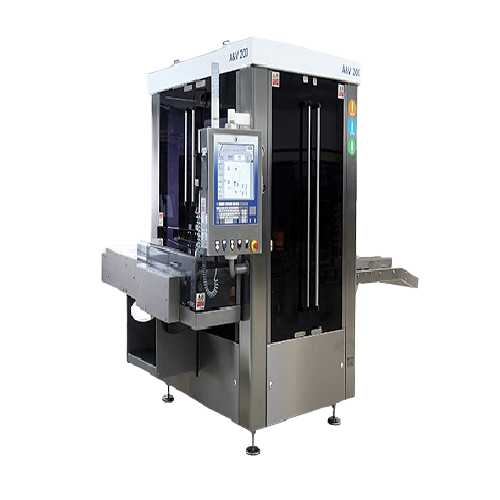
Automatic visual inspection for sterile preparations
Ensure the integrity of sterile products with precise visual inspect...
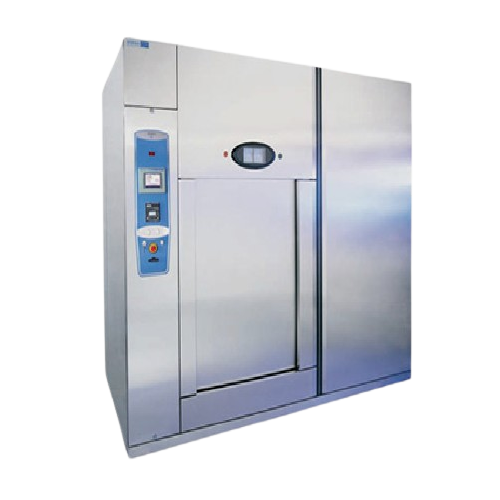
Gmp steam sterilizer for pharmaceutical applications
Ensure consistent sterilization and contamination control across you...
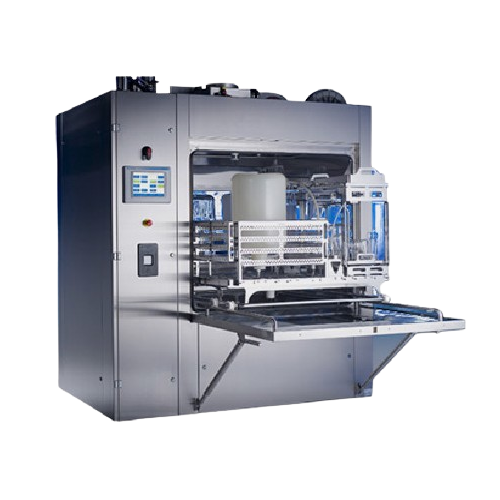
Gmp washer for pharmaceutical contamination control
Ensure verifiable cleaning and drying of critical components in bioph...
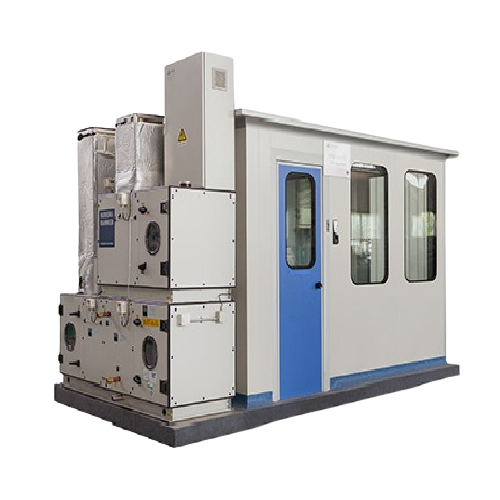
Customized Hvac system for pharmaceutical clean rooms
Achieve seamless sterilization and contamination control in clean r...
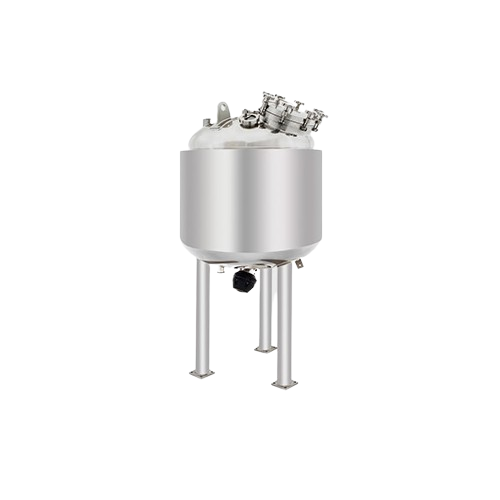
Wfi storage tank for pharmaceutical use
Ensure the integrity and sterility of Water for Injection in your pharmaceutical pr...
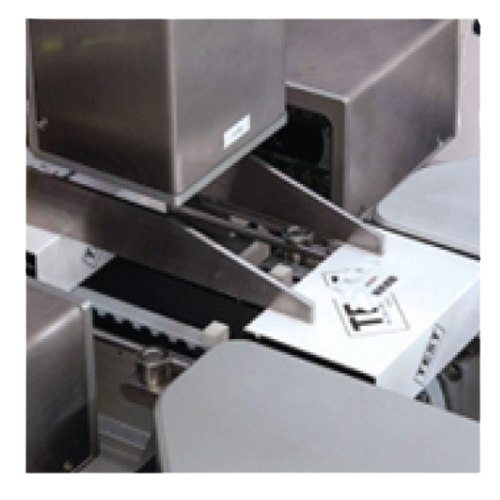
Serialization and inspection kit for packaging machines
Effortlessly enhance packaging integrity and compliance with high...
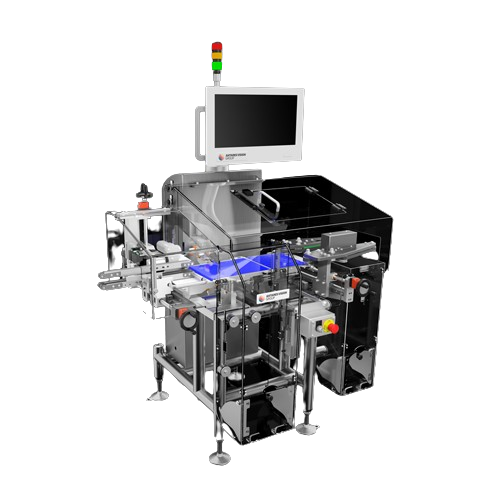
Pharmaceutical checkweigher for milligram-level accuracy
Ensure precision and compliance in your pharmaceutical packaging...
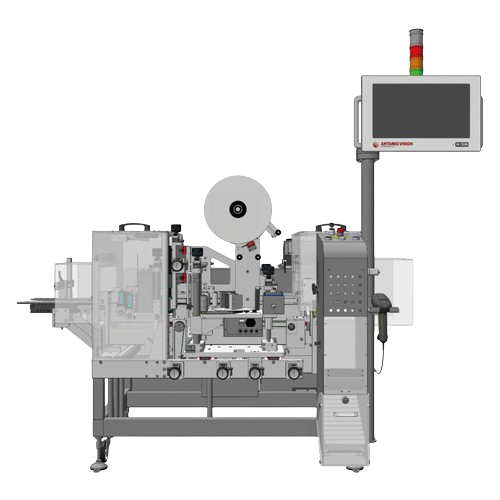
Automatic in-line serialization and tamper-evident sealing unit
Ensure seamless serialization and secure packaging with ...
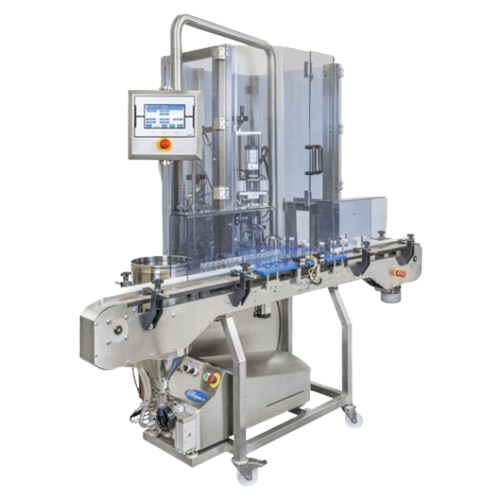
Filler and capper for bottles and jars
Optimize your production with a compact filling and capping solution that delivers f...
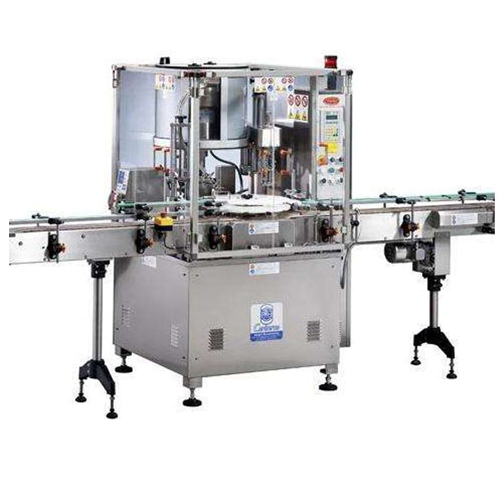
Compact filler and closer for vial processing
Efficiently streamline your vial filling and closing processes with a compac...
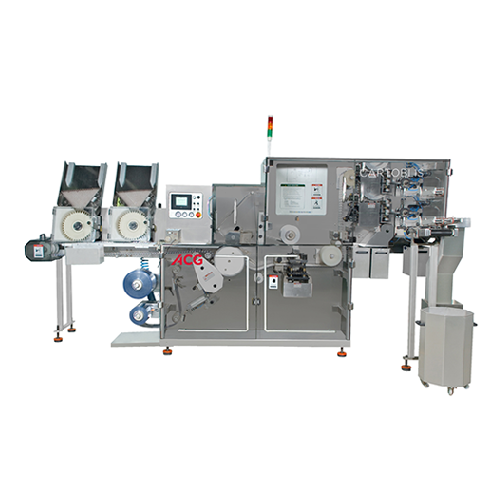
Blister packaging for solid dosage forms
Optimize your packaging line with high-speed, continuous blister packaging that en...
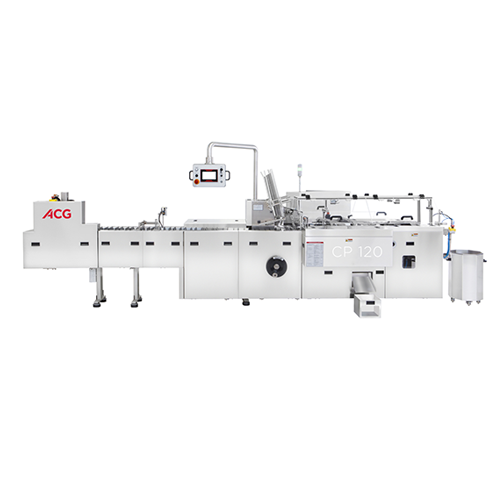
Continuous motion horizontal cartoner for blister packs
Effortlessly streamline your cartoning process with a continuous ...
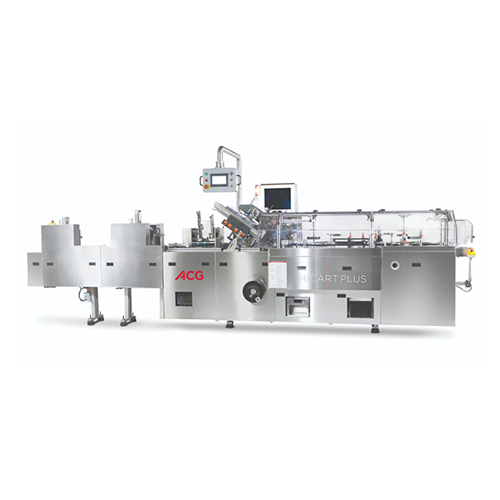
Continuous cartoning solution
Enhance your production line with efficient high-speed cartoning, designed to streamline packa...
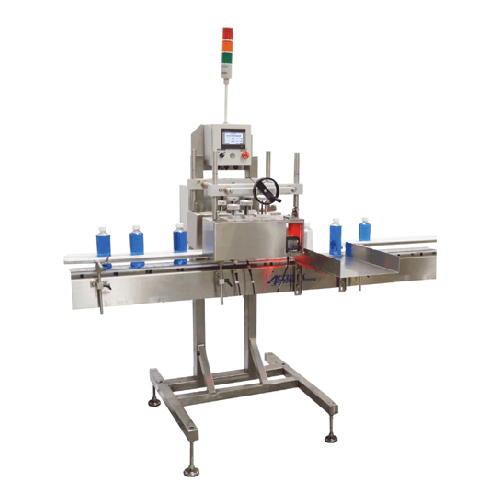
Inspection-rejection station for bottled products
Ensure your bottled and packaged products ship defect-free by automatic...
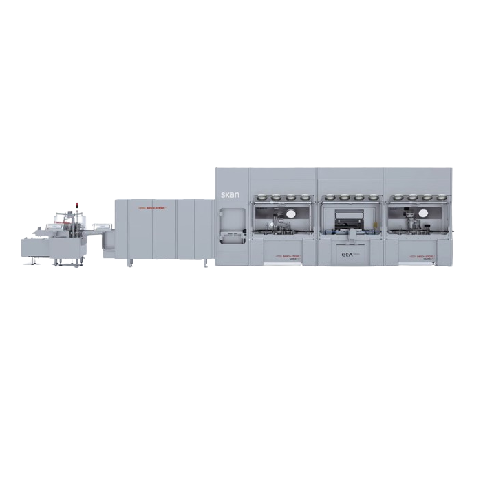
Freeze dryer for small-scale production
Optimize your production line with reliable lyophilization that ensures precise moi...

Laboratory freeze dryer for small batch processing
Ensure precise moisture control and stability in sensitive samples wit...
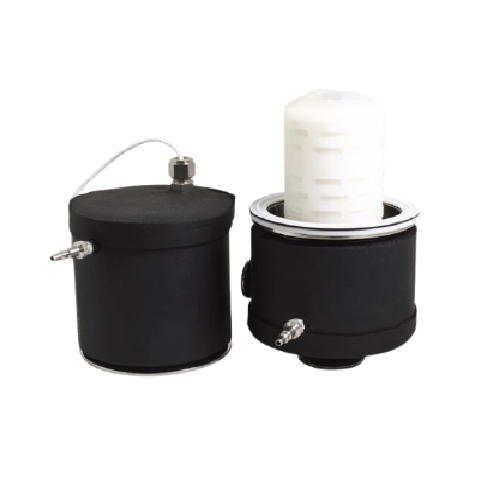
Large production autoclaves for laboratory and pharmaceutical use
Enhance your production line with our large autoclave...
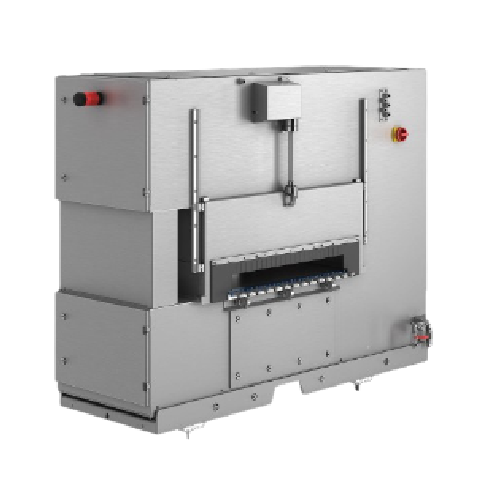
X-ray scanner for sealed container inspection
Ensure the integrity and quality of sealed containers while seamlessly integ...
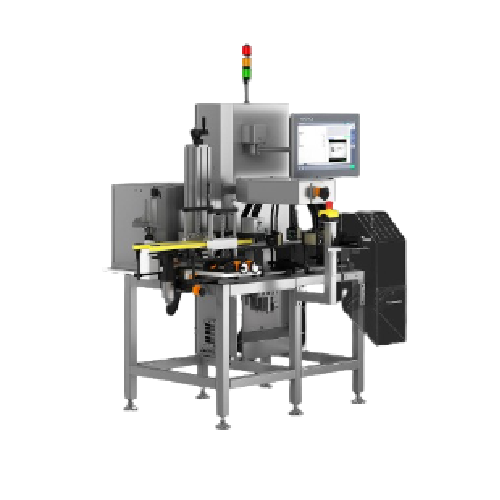
Bottle and vial inspection and coding system
Ensure seamless coding and inspection of vials and bottles with rapid 360° ev...
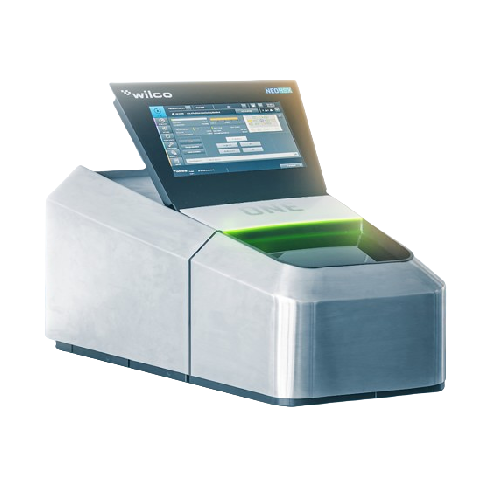
Lab headspace analyzer for small volume parenterals
Enhance your quality control with precise gas concentration measureme...
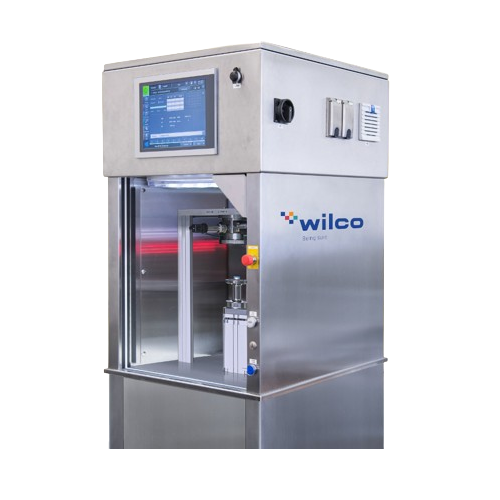
Headspace gas analyzer for large volume parenterals
Ensure the sterility and quality of injectable pharmaceuticals with p...
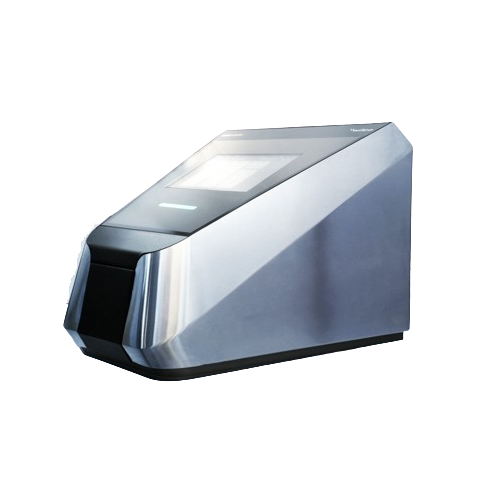
Headspace analyzer for small volume parenterals
Ensure precise gas concentration measurements in sterile pharmaceutical pa...
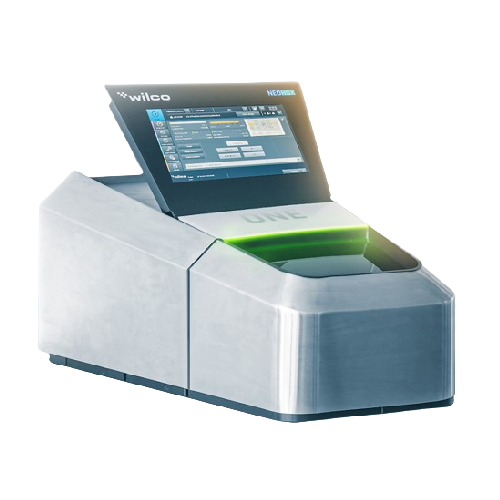
Headspace analyzing system for small volume parenterals
Ensure the integrity of sterile pharmaceuticals with precise head...
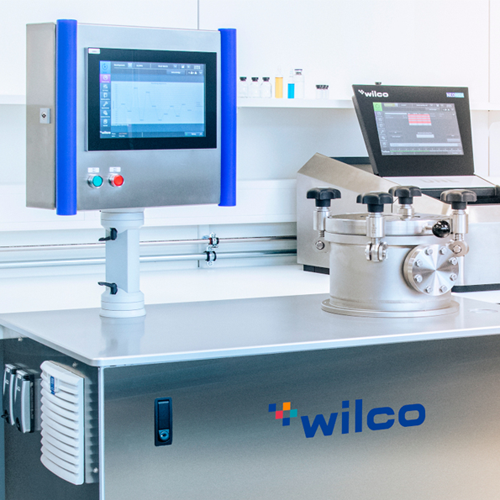
Headspace analyzation for small volume parenterals
Achieve unparalleled precision in gas concentration measurement for sm...
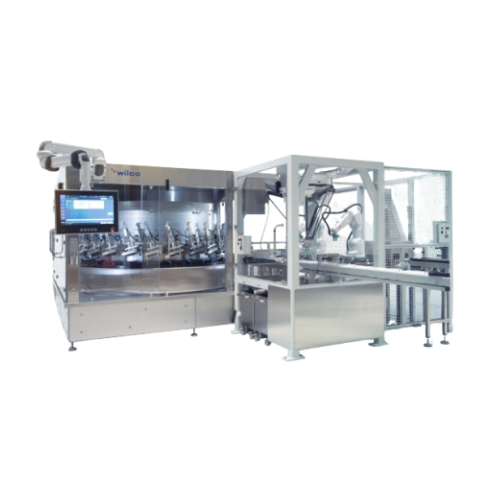
Automated container closure integrity tester
Ensure the integrity of your sterile pharmaceutical containers with high-spee...
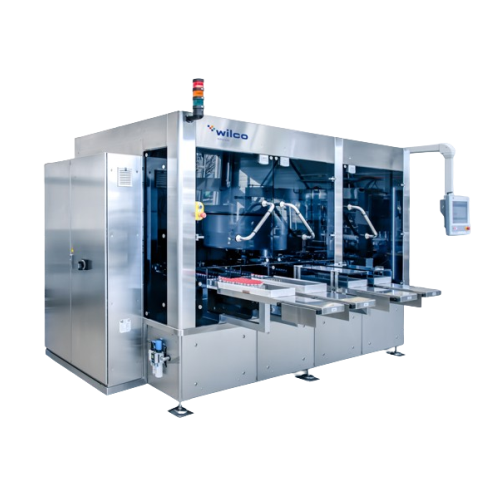
Automated Cci tester for primary packaging containers
Ensure the integrity of pharmaceutical packaging with precise and n...
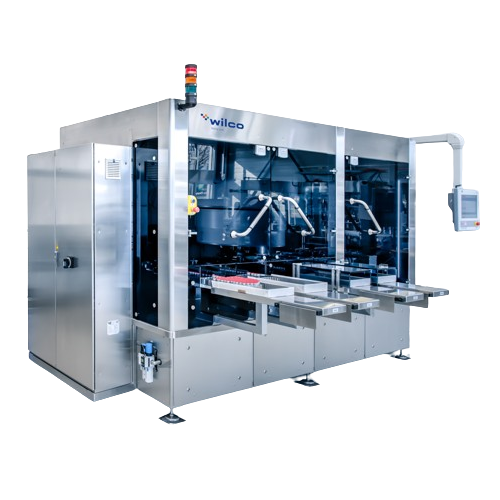
Non-destructive headspace analyzer for pharmaceutical packages
Ensure non-destructive and accurate headspace analysis fo...
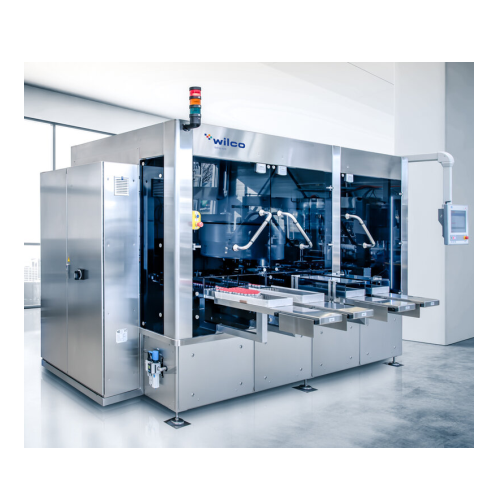
Automated headspace analyzer for small volume parenterals
Optimize container closure integrity with high-speed, non-dest...
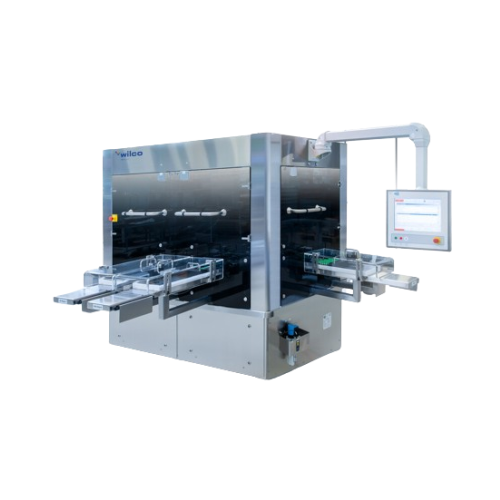
Automated headspace analysis for small volume parenterals
Ensure the integrity and quality of parenteral packaging with ...
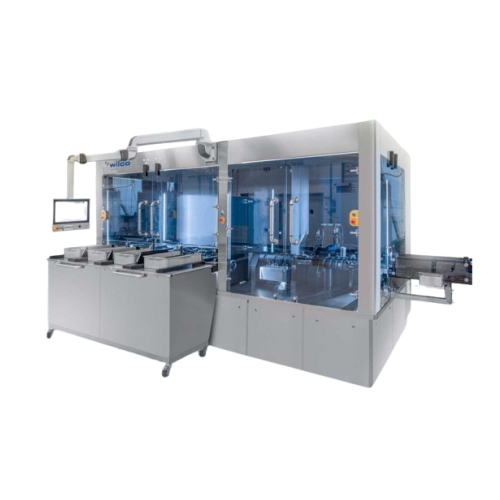
Combined Avi and Cci tester for vials
Ensure comprehensive quality control of parenteral products with an integrated soluti...
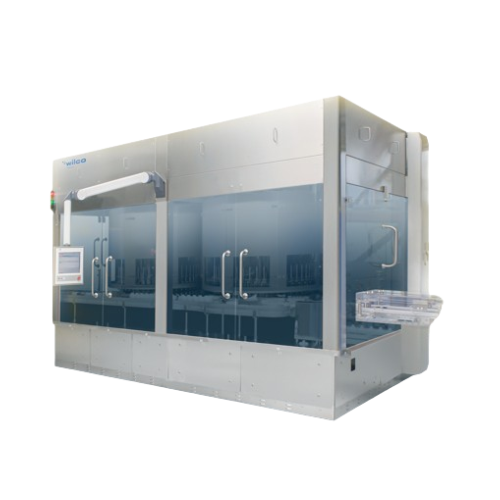
Combined visual and container closure integrity testing for vials
Ensure the integrity and quality of parenteral packag...
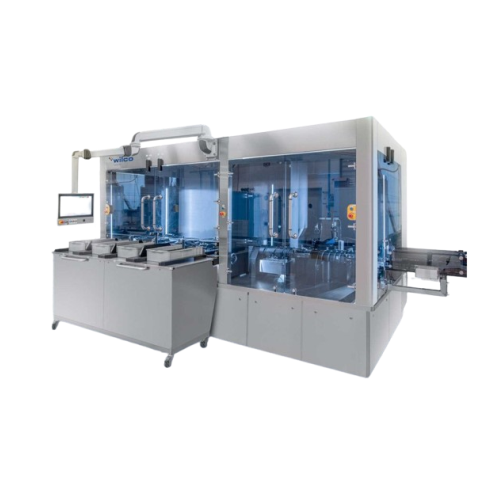
Combined visual and container closure integrity tester for vials
Ensure precise quality control of pharmaceutical packag...
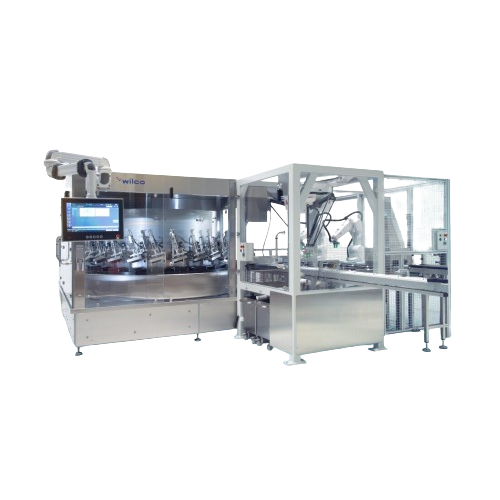
Automated container closure integrity tester for pharmaceutical packaging
Ensure the integrity of your pharmaceutical ...
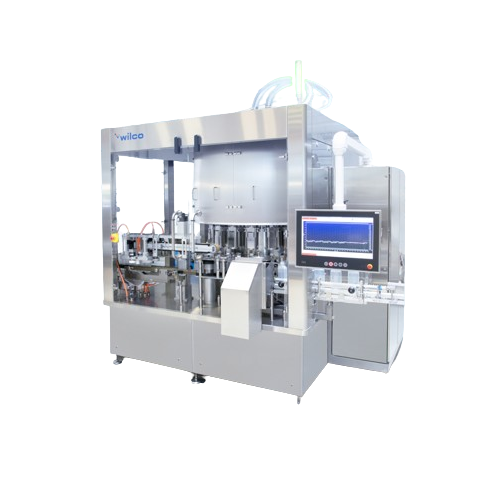
Automated Cci tester for pharmaceutical containers
Ensure the integrity of every pharmaceutical package swiftly with high...
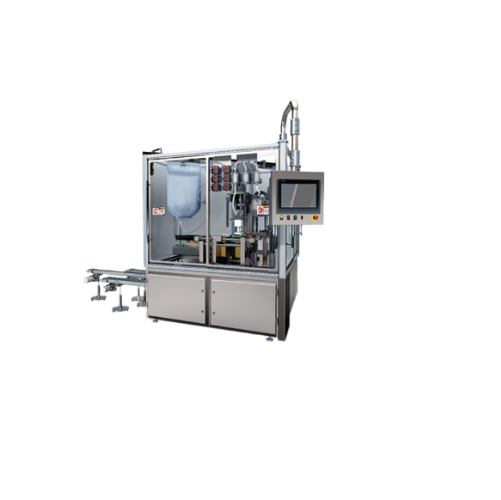
Blow/fill/seal packaging for laboratory and clinical trials
Streamline your small-scale pharmaceutical production with p...
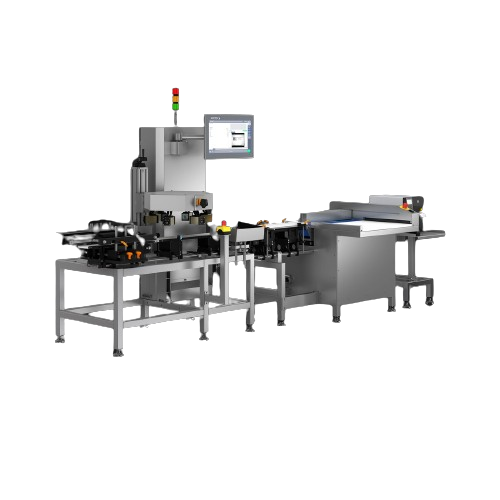
Omnidirectional inspection system for bottles and vials
Ensure precise serialization and aggregation with a 360° inspecti...
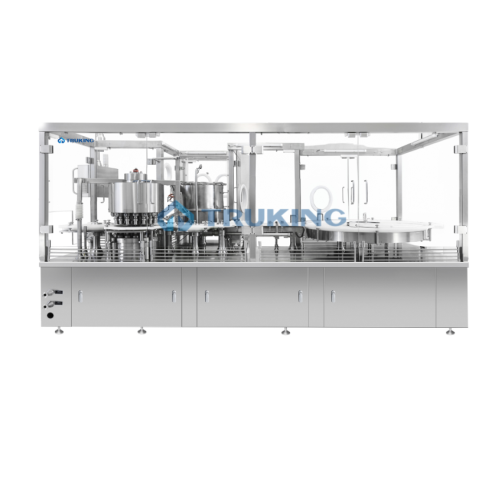
Vial capping machine for pharmaceutical production
Ensure precise and reliable vial sealing in high-throughput pharmaceut...
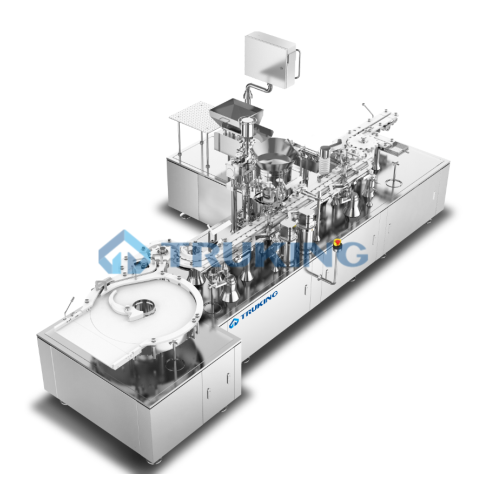
Vial powder dispensing system
Optimize your aseptic fill process with high-precision powder dispensing that minimizes contam...
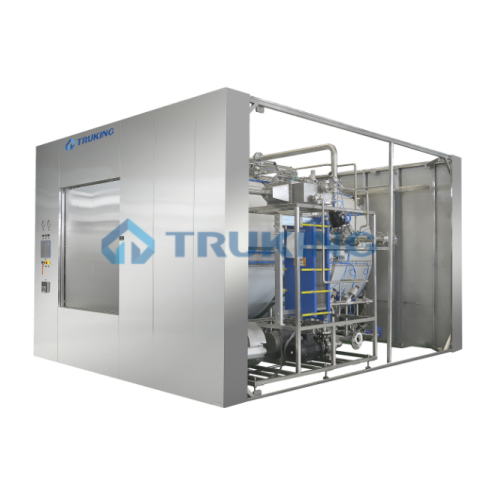
Superheated water sterilizer for pharmaceutical applications
Ensure precise sterilization with real-time monitoring and ...
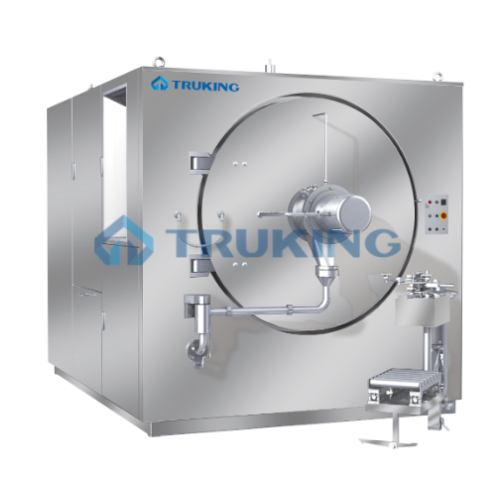
Washing machine for pharmaceutical rubber stoppers
Ensure sterile sealing and siliconization in rubber stopper processing...
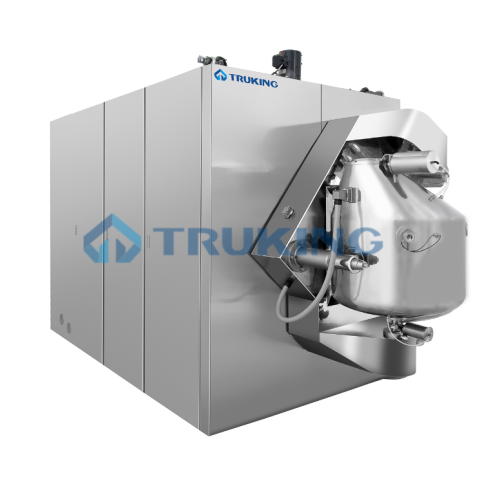
Washing machine for pharmaceutical stoppers and caps
Streamline your aseptic processing with precise washing, sterilizati...
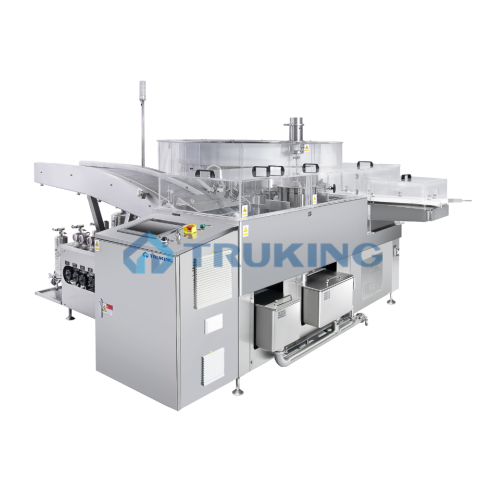
Vertical ultrasonic washing for pharmaceutical containers
Ensure immaculate cleanliness and sterilization of pharmaceuti...
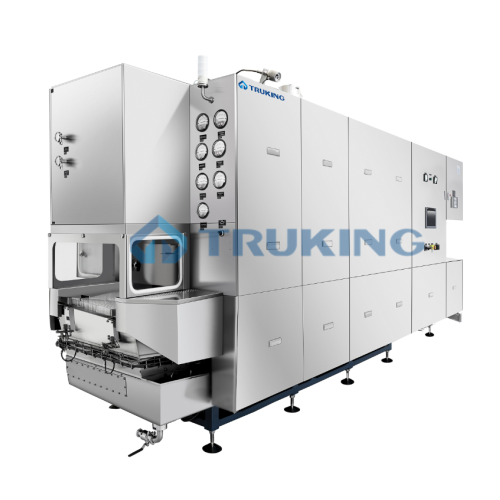
Sterilizing and depyrogenization tunnel for ampoules
Ensure sterile and pyrogen-free ampoules with precision control in d...
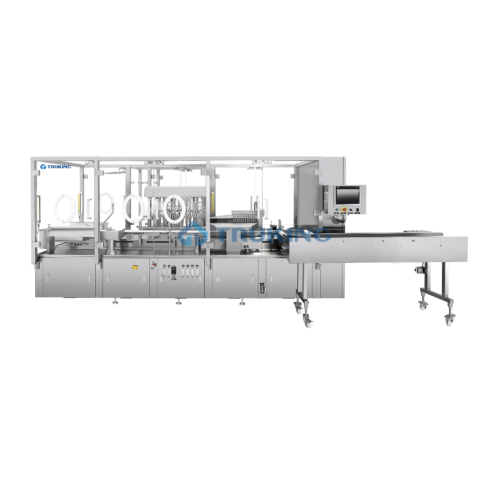
High-speed ampoule filling unit
Ensure precision and speed with this cutting-edge solution designed for efficient filling an...
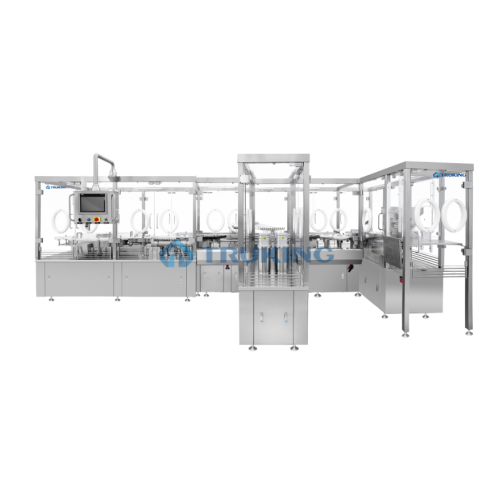
Vial filling and stoppering system for aseptic production
Streamline aseptic production by integrating high-speed vial f...
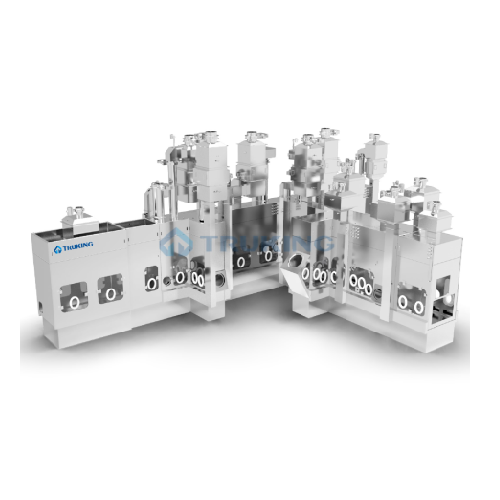
Pharmaceutical isolator system for aseptic production
Ensure aseptic conditions and operator safety with a robust isolati...
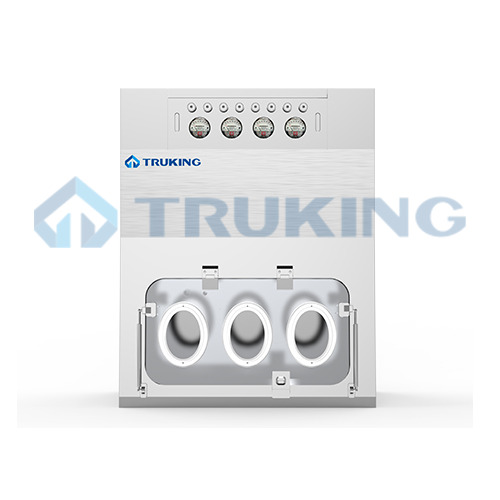
Feeding isolator for liquid preparation in pharmaceuticals
Ensure precise and contamination-free preparation of liquid p...
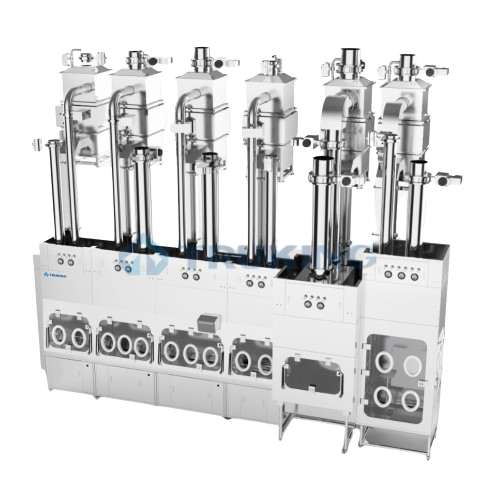
Active pharmaceutical ingredient isolation system
Ensure the aseptic production of pharmaceuticals while protecting perso...
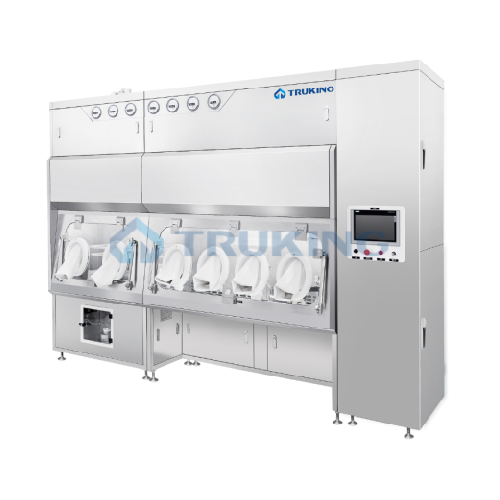
Sterility testing isolator for aseptic environment
Ensure precise sterility testing and prevent contamination with an iso...
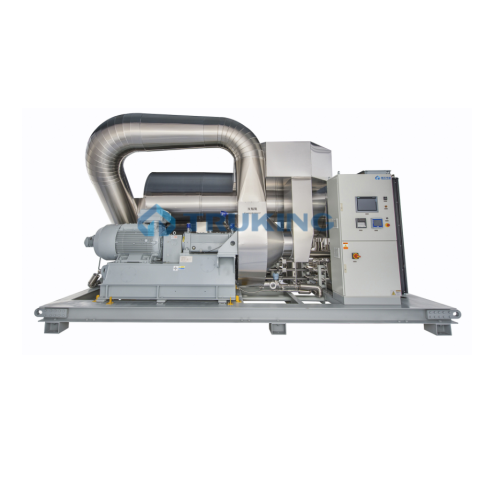
Hot press distilled water unit for pharmaceutical applications
Ensure superior water purity in pharmaceutical production...
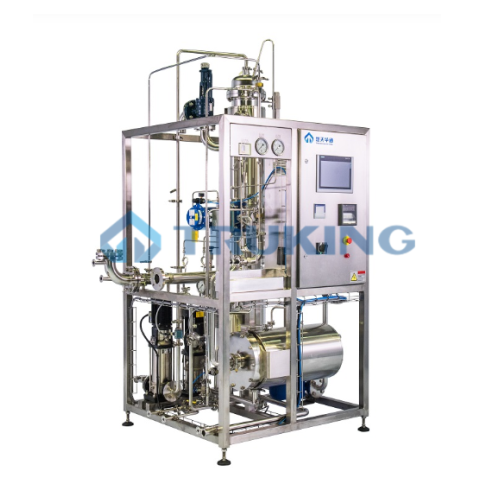
Pure steam generator for pharmaceutical and biotech industries
Ensure optimal steam quality and compliance with stringen...
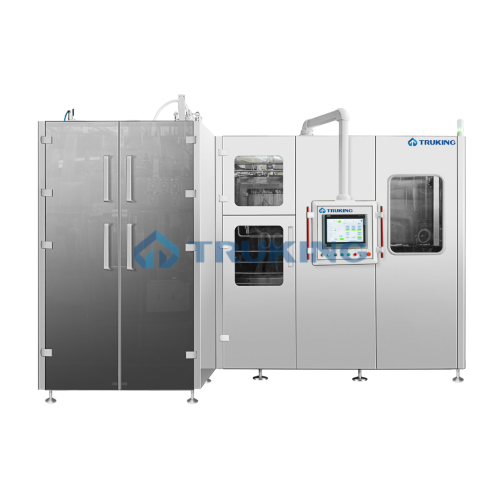
Aseptic blow fill seal system
Ensure sterile, high-speed production of liquid pharmaceuticals by integrating a cutting-edge ...
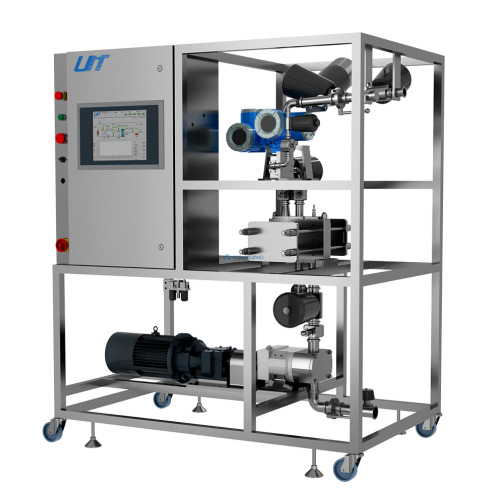
Production-level ultrafiltration system for industrial applications
Achieve precise concentration and separation of val...
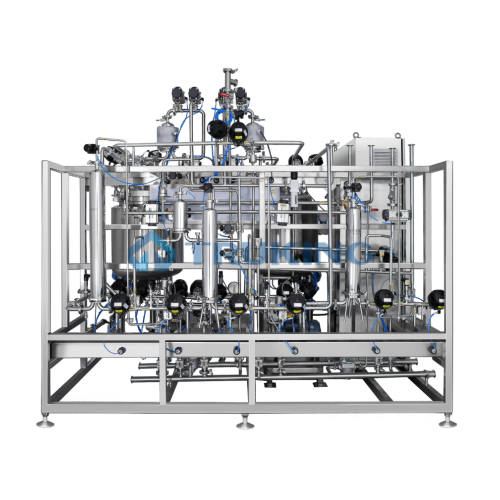
Pharmaceutical preparation system
Achieve seamless integration in pharmaceutical processes with a preparation system that o...
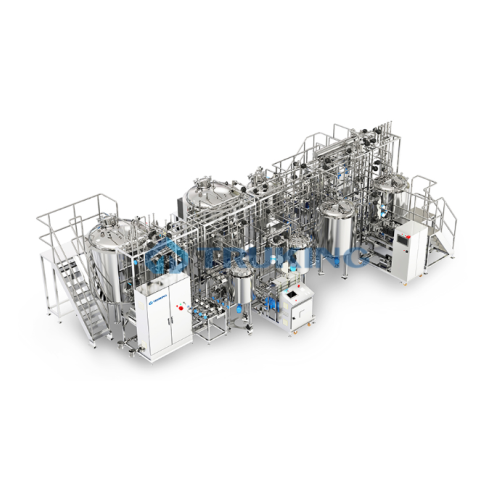
Complex preparation system for industrial microsphere production
Achieve precise particle size and uniform drug encapsul...
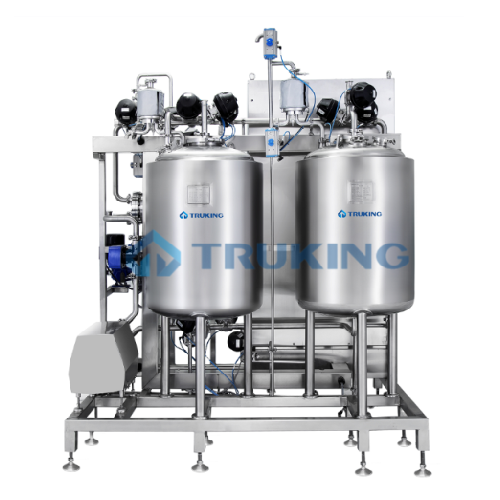
Comprehensive auxiliary system for online cleaning and temperature control
Ensure reliable and precise control in phar...
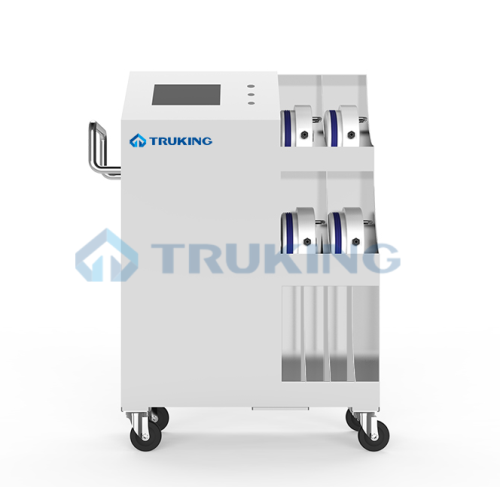
Isolator for sterility testing in pharmaceutical manufacturing
Ensure precise sterility testing with advanced isolators ...
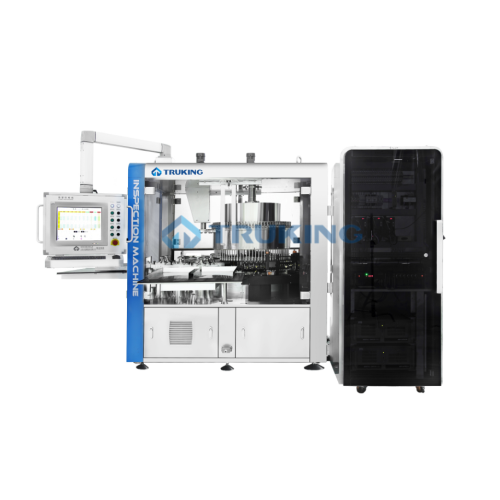
Automatic inspection system for ampoules and vials
Ensure precision in pharmaceutical production with a comprehensive ins...
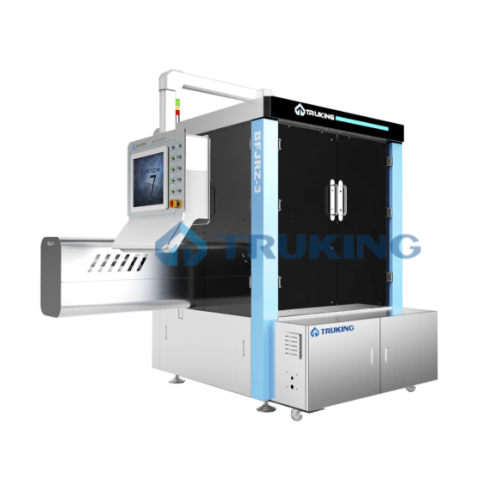
X-ray inspection for pharmaceutical vials
Ensure product purity by detecting contaminants in pharmaceutical vials with adv...
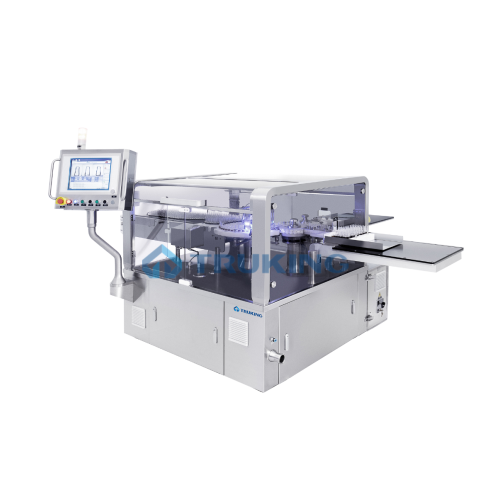
Automatic inspection system for sealing defects in ampoules
Ensure flawless ampoule sealing with a high-precision inspec...
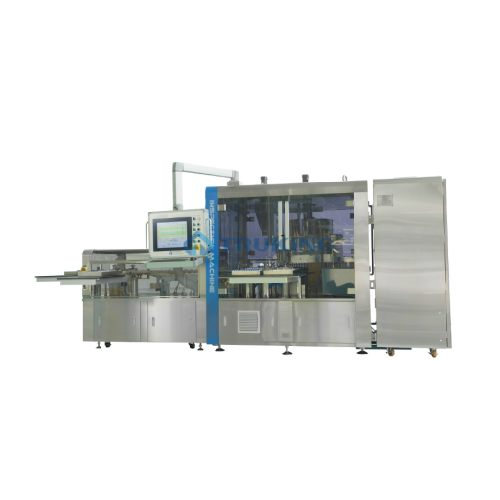
Automatic inspection and leak test for pharma containers
Ensure container integrity for injectables with high-speed inspe...
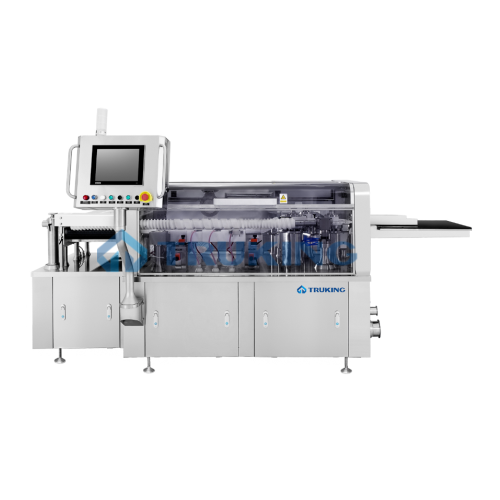
Automatic leak detection system for pharmaceutical containers
Ensure the integrity of pharmaceutical containers with pre...
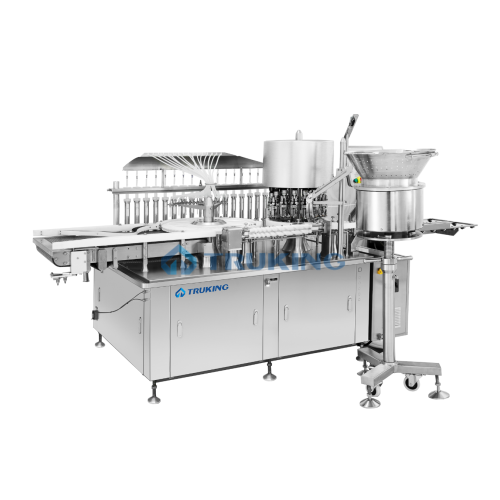
Oral liquid bottle filling & capping system
Streamline your liquid manufacturing processes with precise filling and secure...
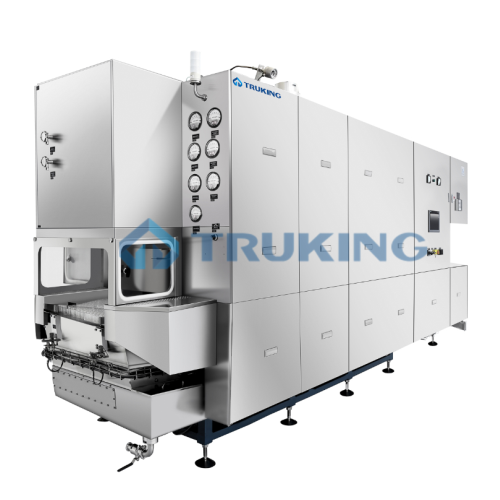
Sterilizing and drying tunnel for pharmaceutical vials
Ensure precise sterilization and depyrogenation of pharmaceutical ...
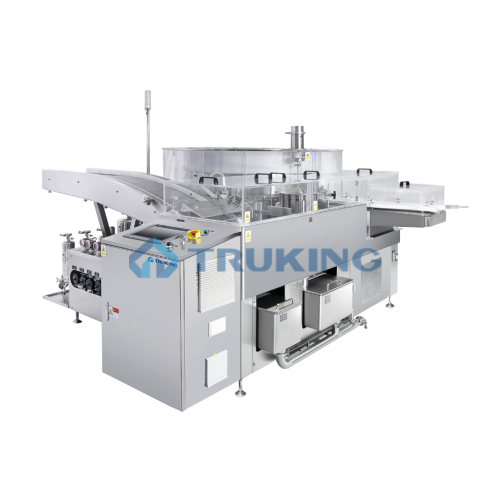
Vertical ultrasonic washing system for oral liquid bottles
Ensure optimal cleaning and sterilization with a compact vert...
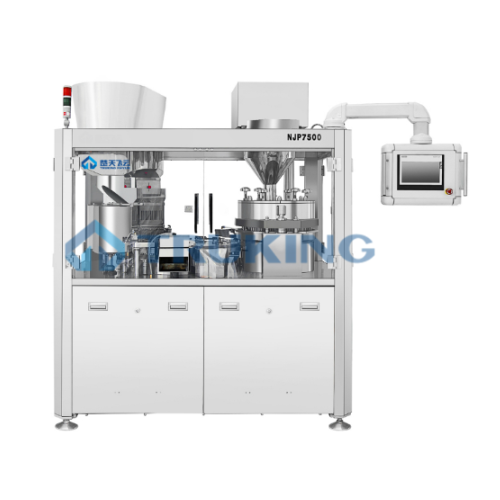
Fully automatic hard capsule filling machine
Enhance pharmaceutical production with precise capsule filling, ensuring opti...
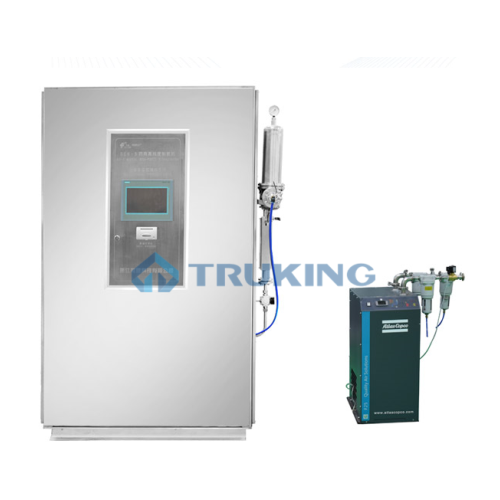
High-purity nitrogen generator for pharmaceutical and food industries
Achieve ultra-high purity levels in your producti...
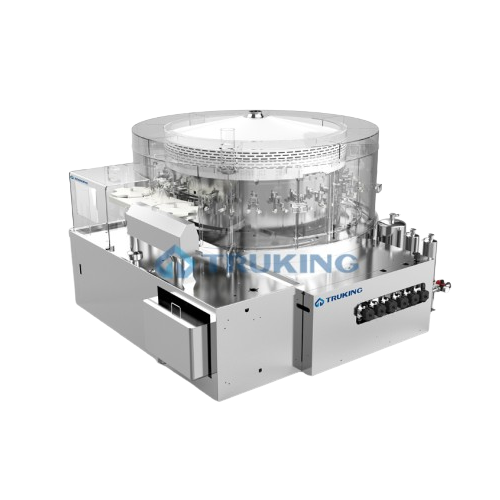
Industrial freeze dryer for pharmaceutical applications
Enhance your production line with precision cleaning solutions fo...
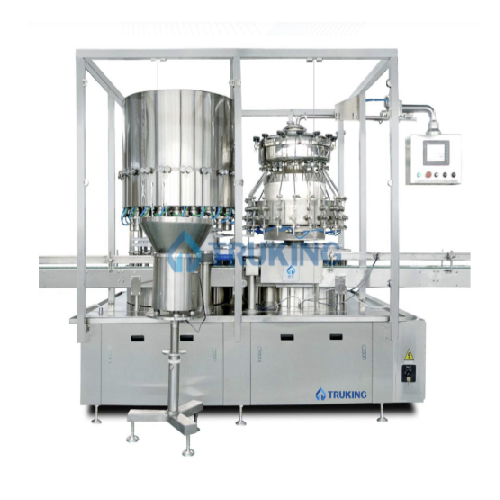
Gravity rotary filling for large infusion bottles
Ensure precise filling and secure stoppering of large infusion bottles ...

High capacity automatic blister packaging system
Streamline your production line with a high-speed blister packaging syste...
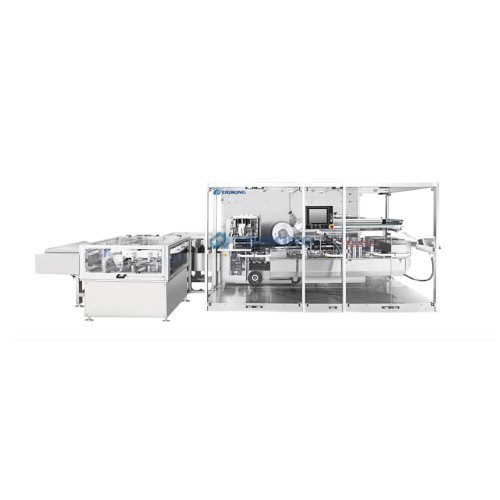
Secondary packaging cartoner for ampoules and vials
Optimize your aseptic production with efficient high-capacity carton ...
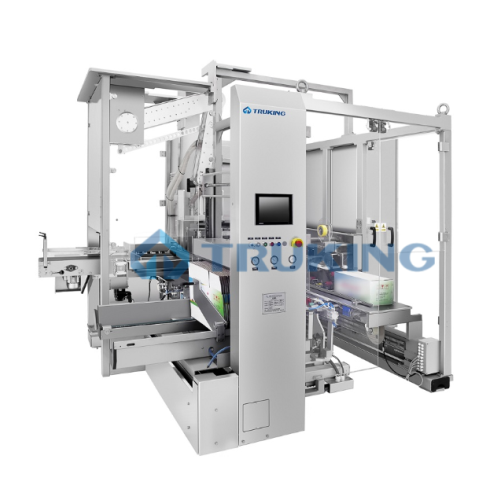
Automatic case packer for pharmaceutical industry
Optimize your packaging process with a versatile case packer designed t...
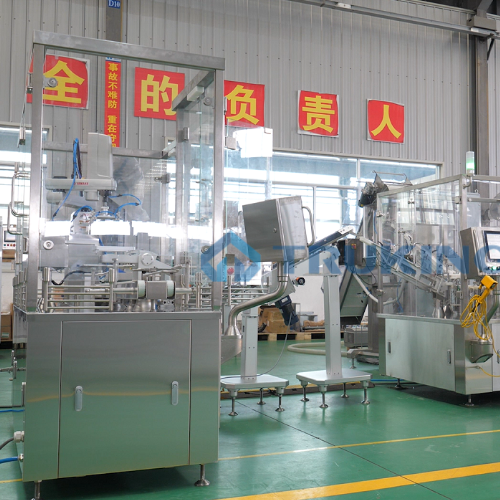
Pre-filled syringe plunger rod insertion and labeling system
Ensure precise labeling and efficient pre-filled syringe ha...

Large volume oral liquid filling system
Ensure precision and efficiency in liquid filling with a system designed to handle ...
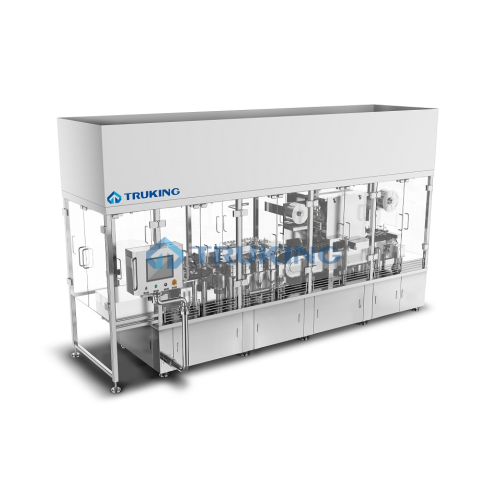
Diagnostic reagent filling system for accurate and efficient processing
Streamline the production of diagnostic reagent...
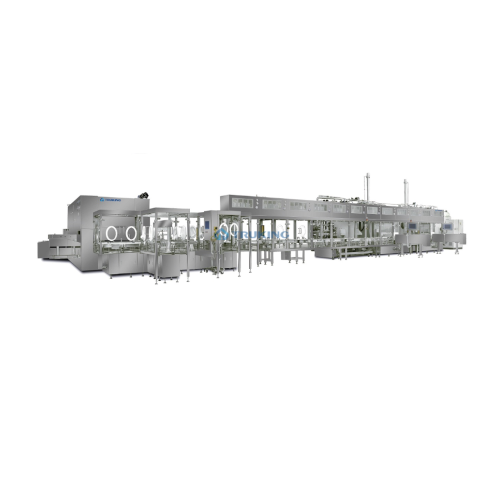
Auto loading & unloading system for freeze dryers
Efficiently manage vial handling in freeze-drying processes with automa...
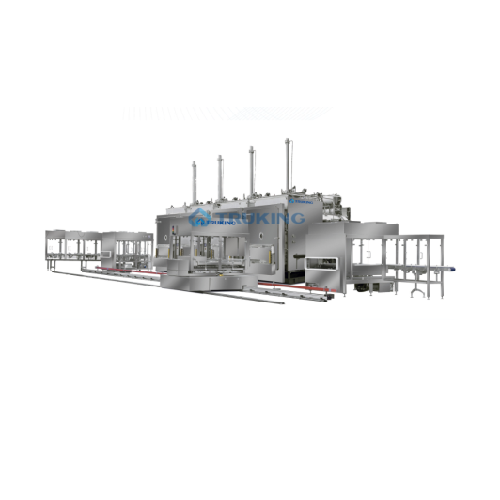
Mobile transfer loading system for freeze dryers
Streamline your lyophilization process with a high-capacity mobile loadin...
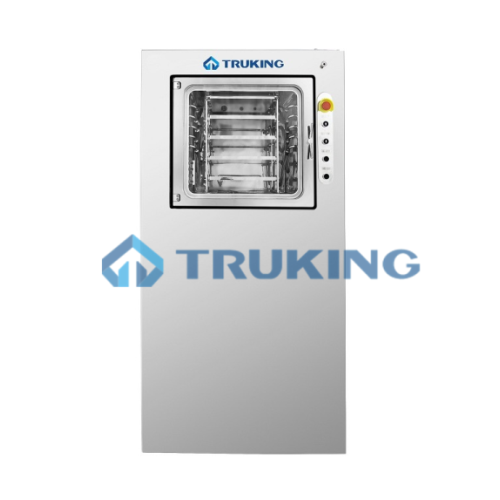
Laboratory freeze dryer for research and development
Optimize moisture removal with precision control during research and...
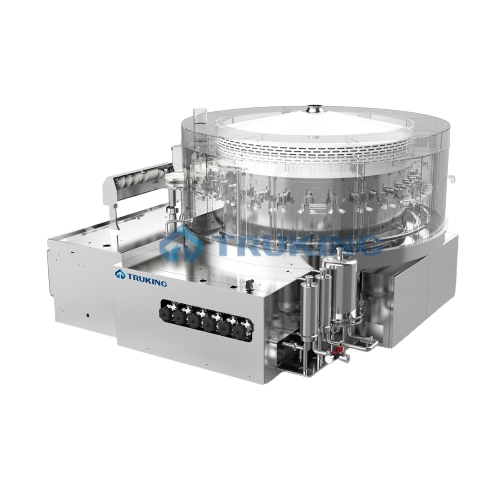
Ultrasonic pre-washing system for large infusion glass bottles
Optimize your cleaning process with an ultrasonic pre-was...
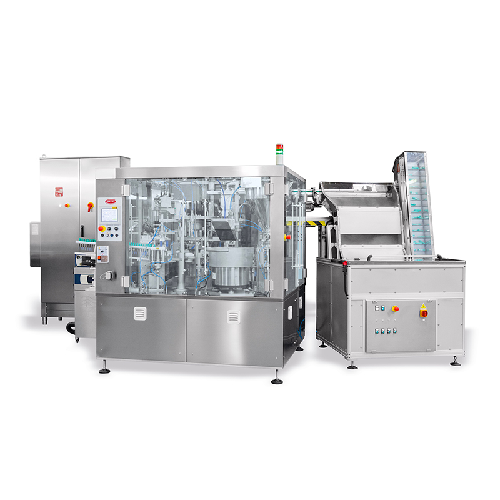
Automatic bottle filling and capping solution
When dealing with fragile or unstable bottles, precise filling and capping a...
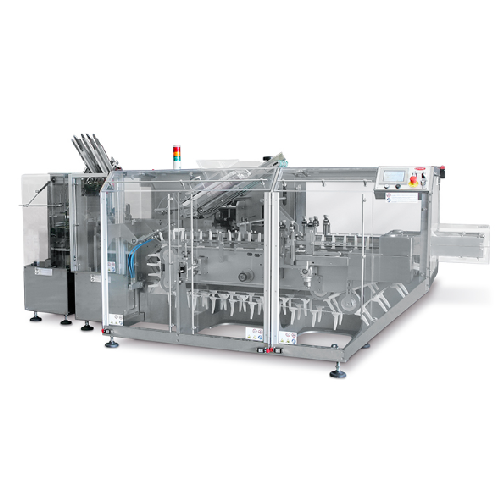
Horizontal cartoning machine for medium to high-speed production
Optimize your cartoning process with precise loading an...
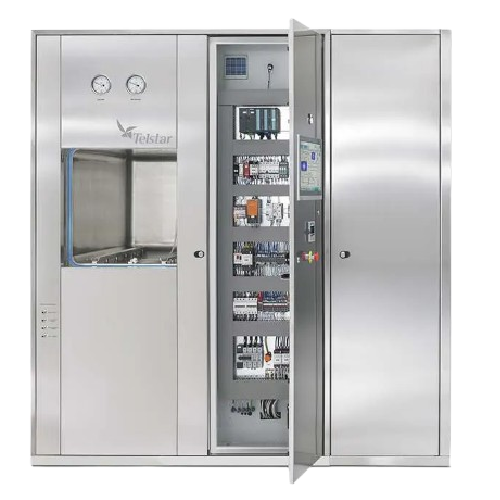
Saturated steam sterilizer for pharmaceutical production
Ensure sterility for a diverse range of pharmaceutical products ...
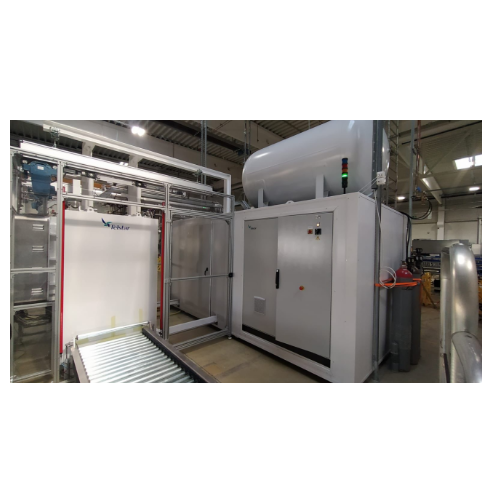
Leak detection and gas filling for electric switchgears
Achieve precise leak detection and efficient gas filling for elec...
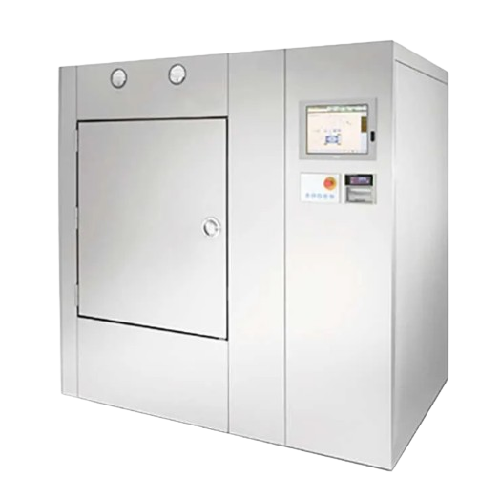
Dry heat sterilization and depyrogenation oven for glassware
Achieve precise sterilization and depyrogenation of glasswa...
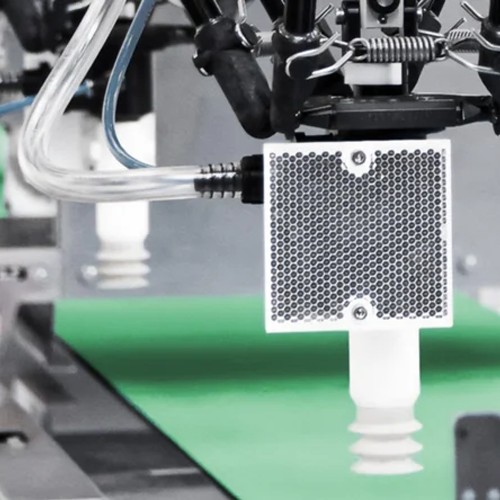
Robotic pick and place platform for food packaging
Enhance your packaging efficiency and product quality with a scalable ...
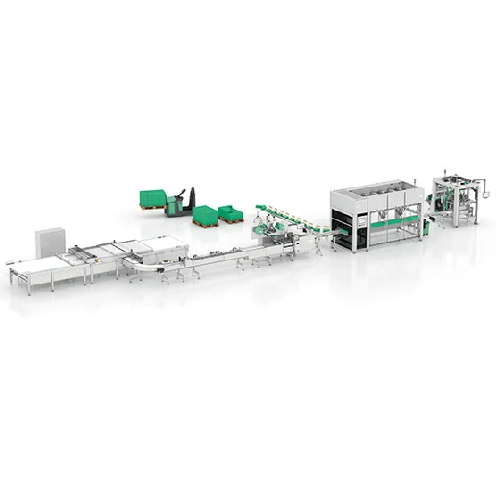
Automated visual inspection for pharmaceutical products
Ensure the integrity and safety of your parenteral products with ...
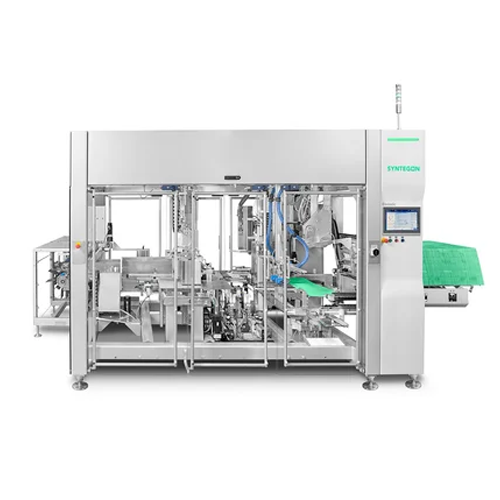
Case packer for diverse food products
Optimize your packaging line with this versatile case packer, capable of handling a w...

Biodecontamination system for small pharmaceutical enclosures
Achieve reliable sterilization in compact settings with th...
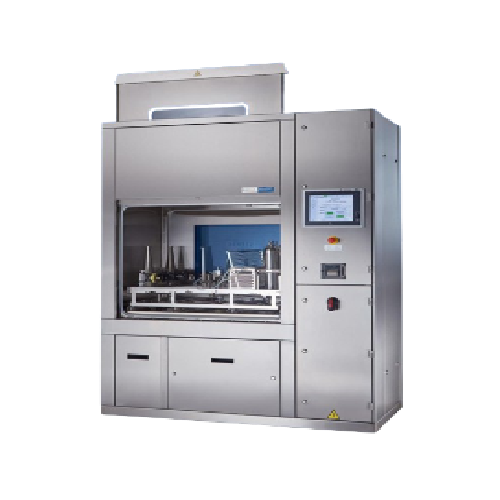
Pharmaceutical grade washer for biotechnology and pharmaceutical manufacturing
Efficiently clean and prepare your labo...
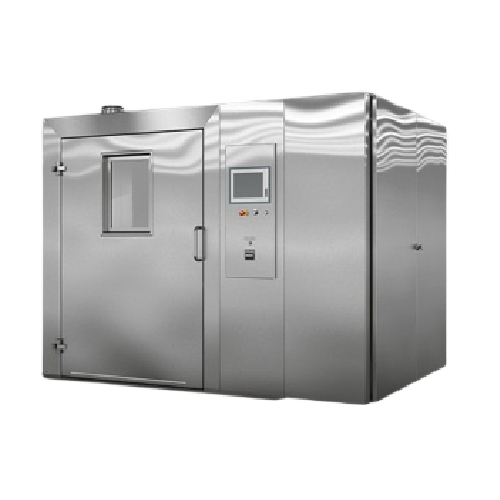
Pharmaceutical grade washer for large components
Ensure compliance and maximize productivity with a high-performance solut...
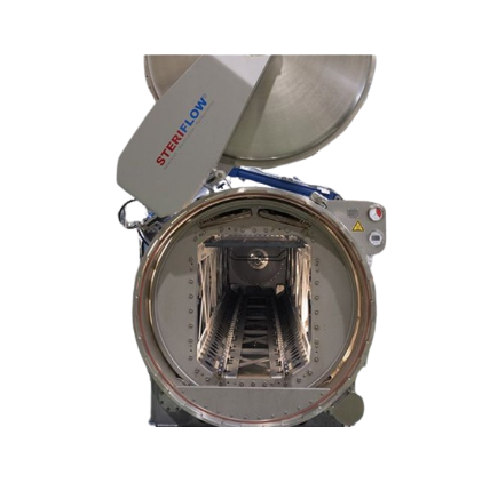
Static autoclave for pharmaceutical sterilization
Ensure reliable sterilization with a static autoclave that maintains cr...
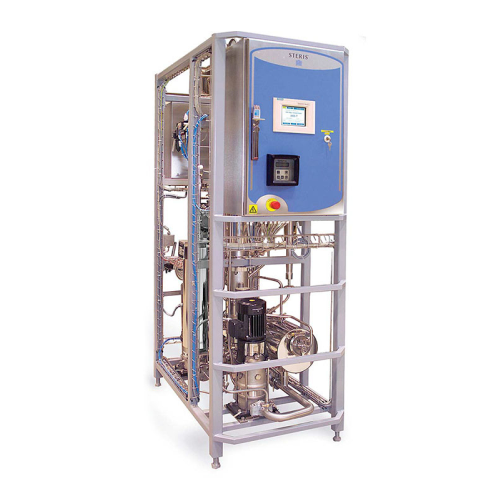
Pure steam generator for pharmaceutical applications
Ensure your sterilization process consistently achieves high purity ...
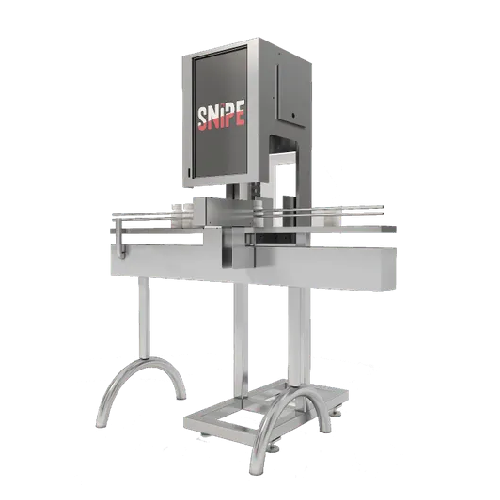
Bottle induction seal integrity inspection
Ensure uncompromised product quality by accurately inspecting and verifying the...
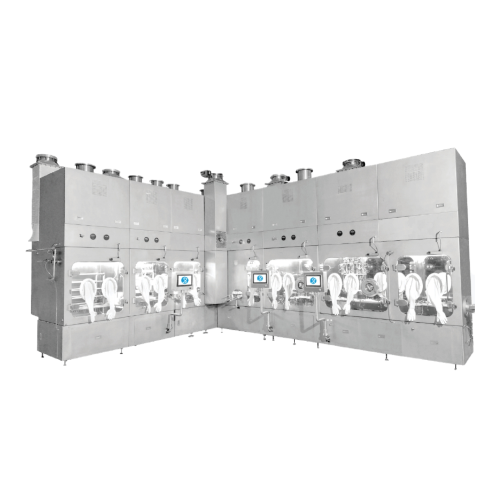
Ampoule filling and sealing line
Streamline your ampoule production with an integrated solution that expertly handles everyt...
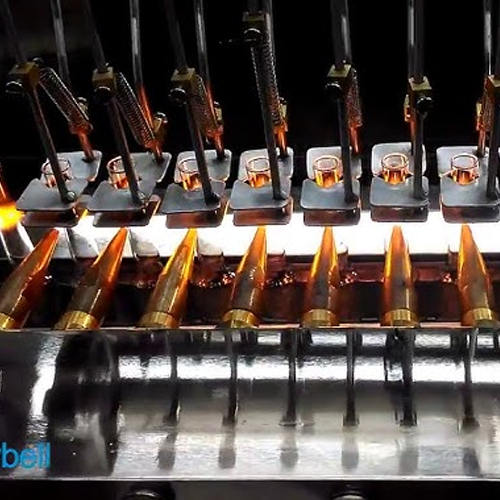
Triple combi filling and stoppering system for vials and ampoules
Optimize your liquid formulation process with a versa...
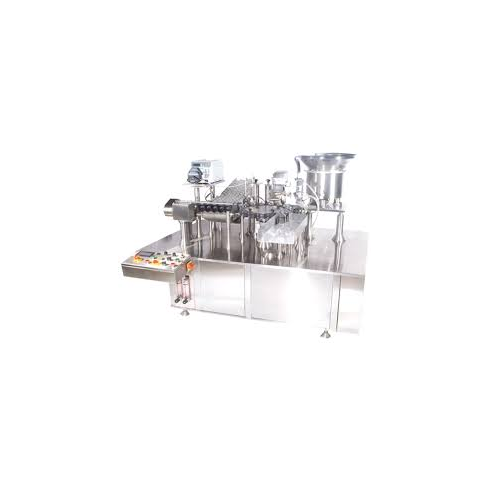
Combi r&d ampoule and vial filling equipment
Optimize your R&D operations with a versatile machine designed for preci...
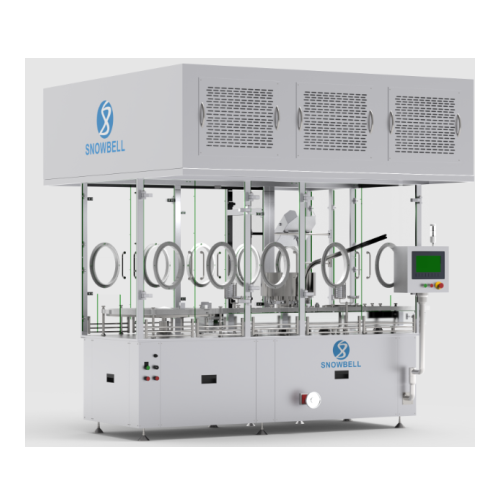
Vial washing system for internal and external cleaning
Streamline vial preparation with comprehensive washing, sterilizin...
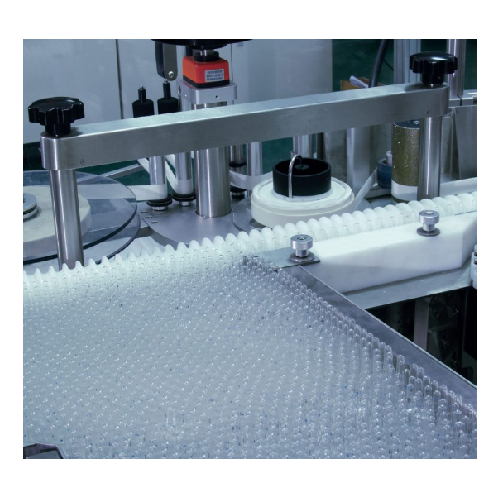
Pharmaceutical ampoule labelling system
Achieve precise and efficient labelling of ampoules with a high-speed system design...
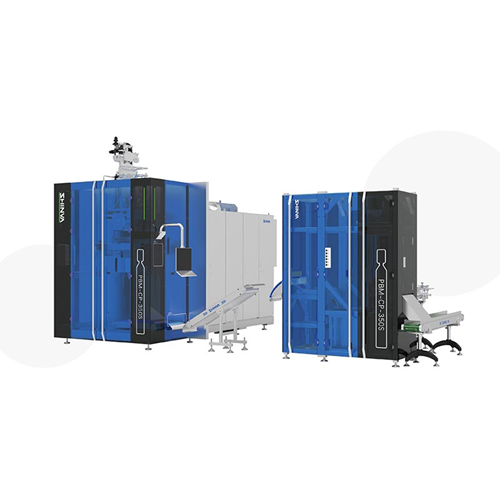
Single-mold continuous bottle Bfs solution
Optimize aseptic production with this advanced solution, offering superior ster...
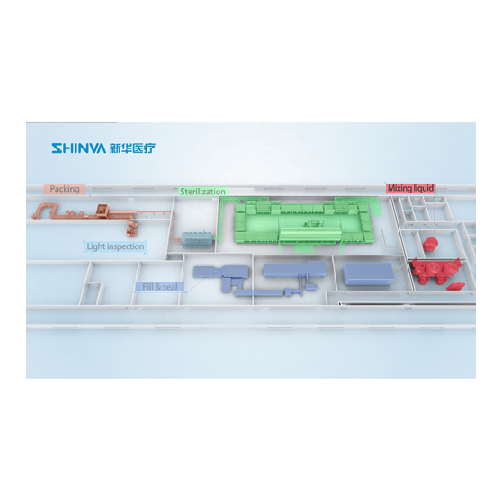
Plastic bottle blowing-filling-sealing system
Optimize sterile liquid packaging with integrated blowing, filling, and seal...
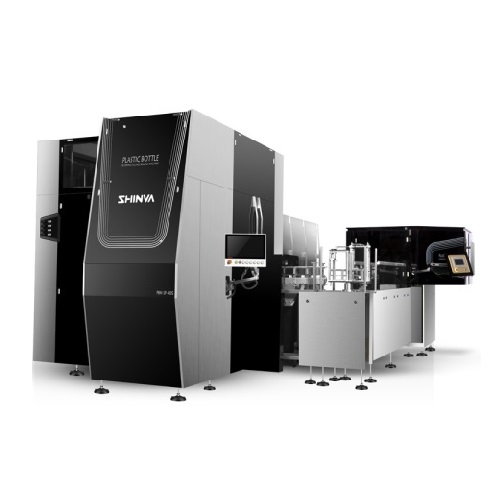
Blow-fill-seal system for small volume injection production
Ensure precise aseptic liquid packaging with integrated blow...
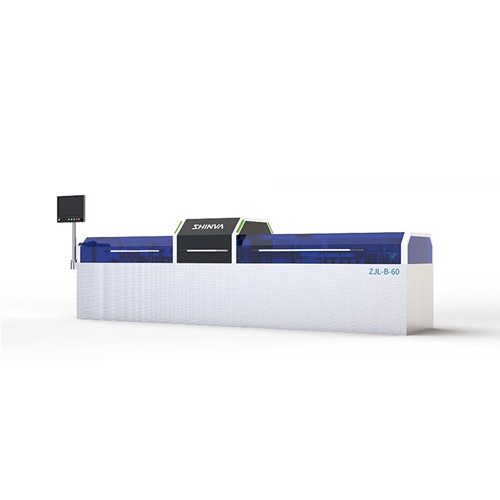
Plastic bottle Bfs leak detection solution for small volume injections
Ensure sealed integrity with precision leak dete...
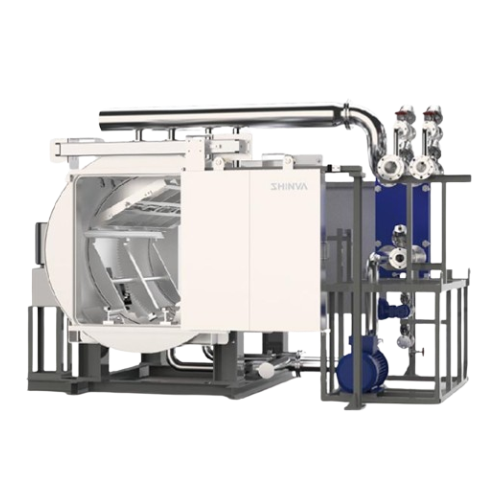
Moist heat sterilizer for liquid preparation
Ensure precise sterilization of pharmaceutical liquids and injectable biologi...
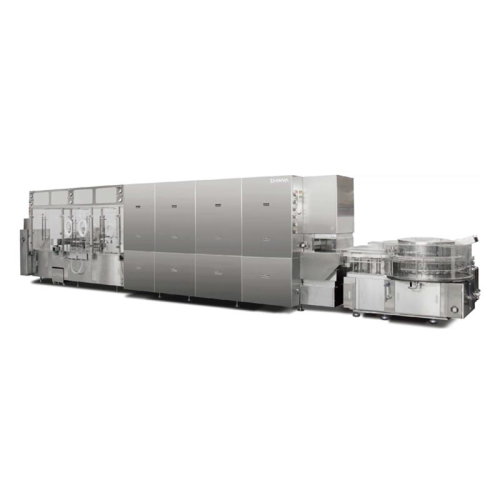
Ampoule washing, filling, and sealing line
Streamline your ampoule production with an integrated washing, filling, and sea...

Automatic light inspector for plastic ampoules
Enhance your quality control with high-speed, intelligent inspection, detec...
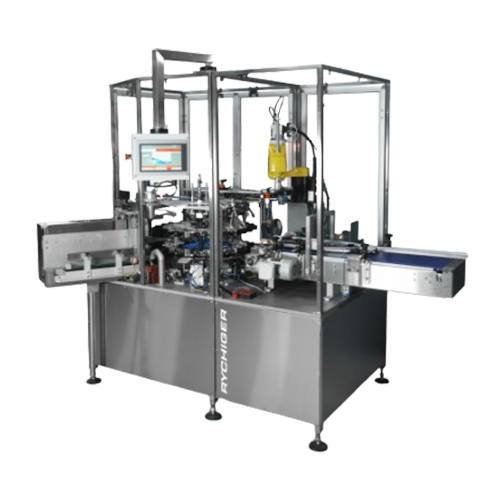
Cartoner for pharmaceutical products
Effortlessly streamline your packaging line with compact cartoning capabilities, ensur...
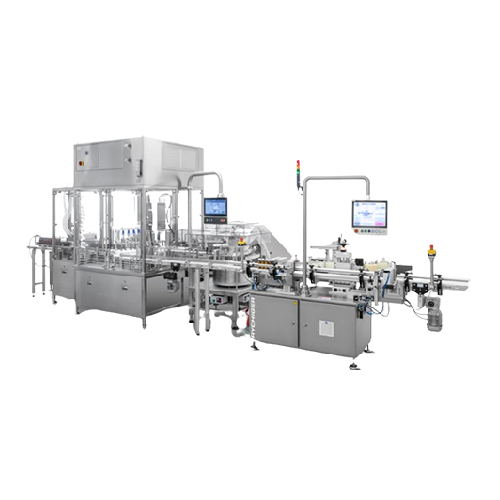
Rotary transfer system for pharmaceutical product filling
Ensure precise and hygienic filling of diverse pharmaceutical ...
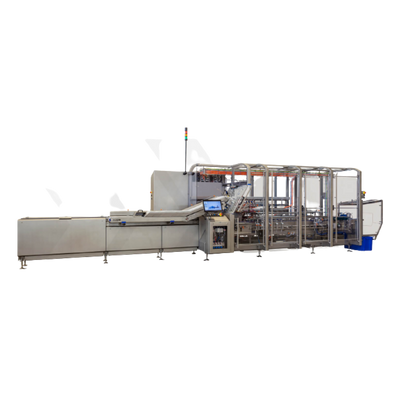
Hygienic Cartoning Machine For Pharma and Health Products
When packing single or multiple vials, ampoules or devices int...
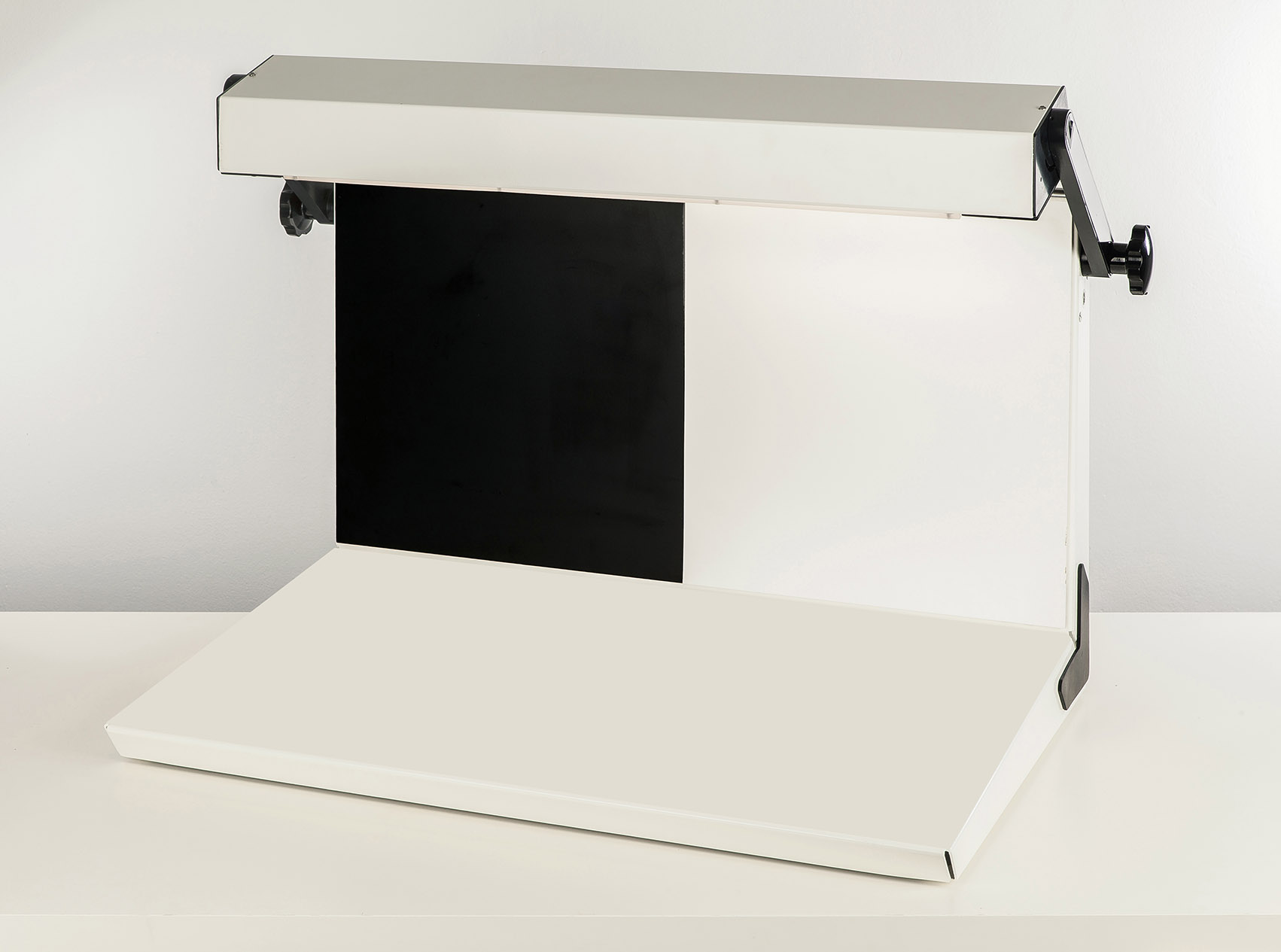
Laboratory liquid viewer for colored glass bottles
In the pharmaceutical industry, an inspection to detect any particulat...
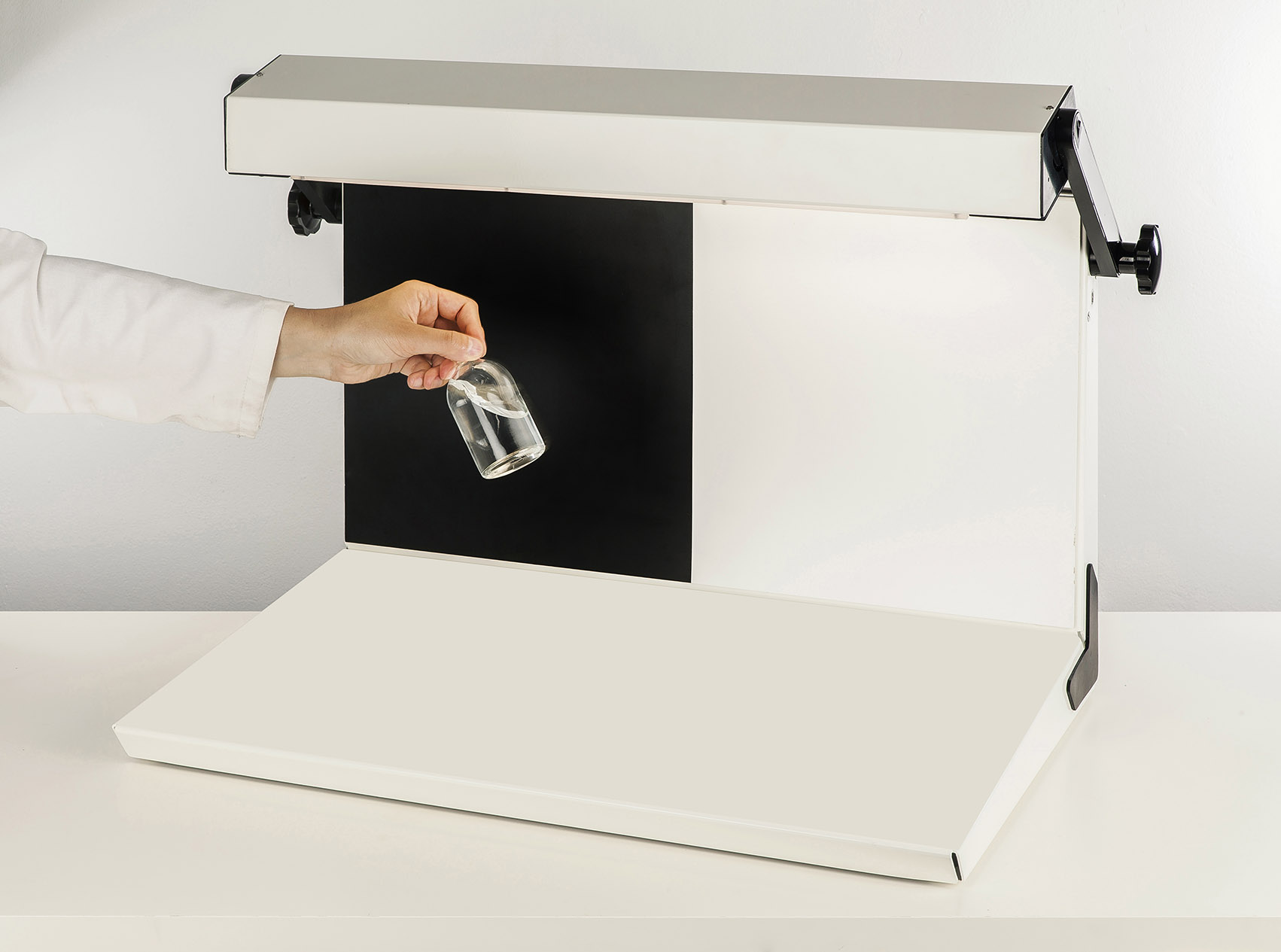
Laboratory liquid viewer for varying light conditions
In the pharmaceutical industry, you must inspect liquids in vials o...
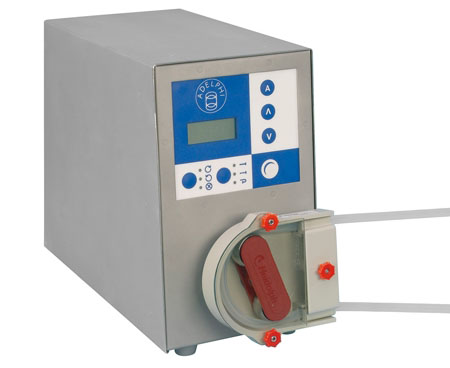
Benchtop peristaltic dispenser
When you fill vials and ampoules, high standards of hygiene are required to avoid the risk of...
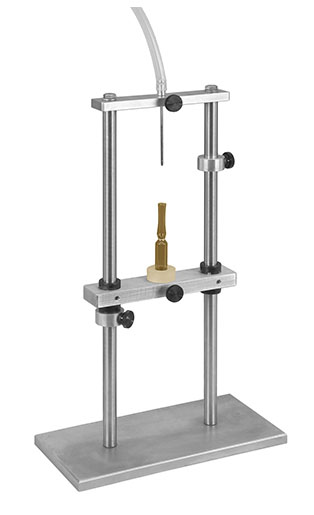
Manual ampoule filler
When you fill ampoules it is essential to avoid wetting the inside walls of the container, as it may af...
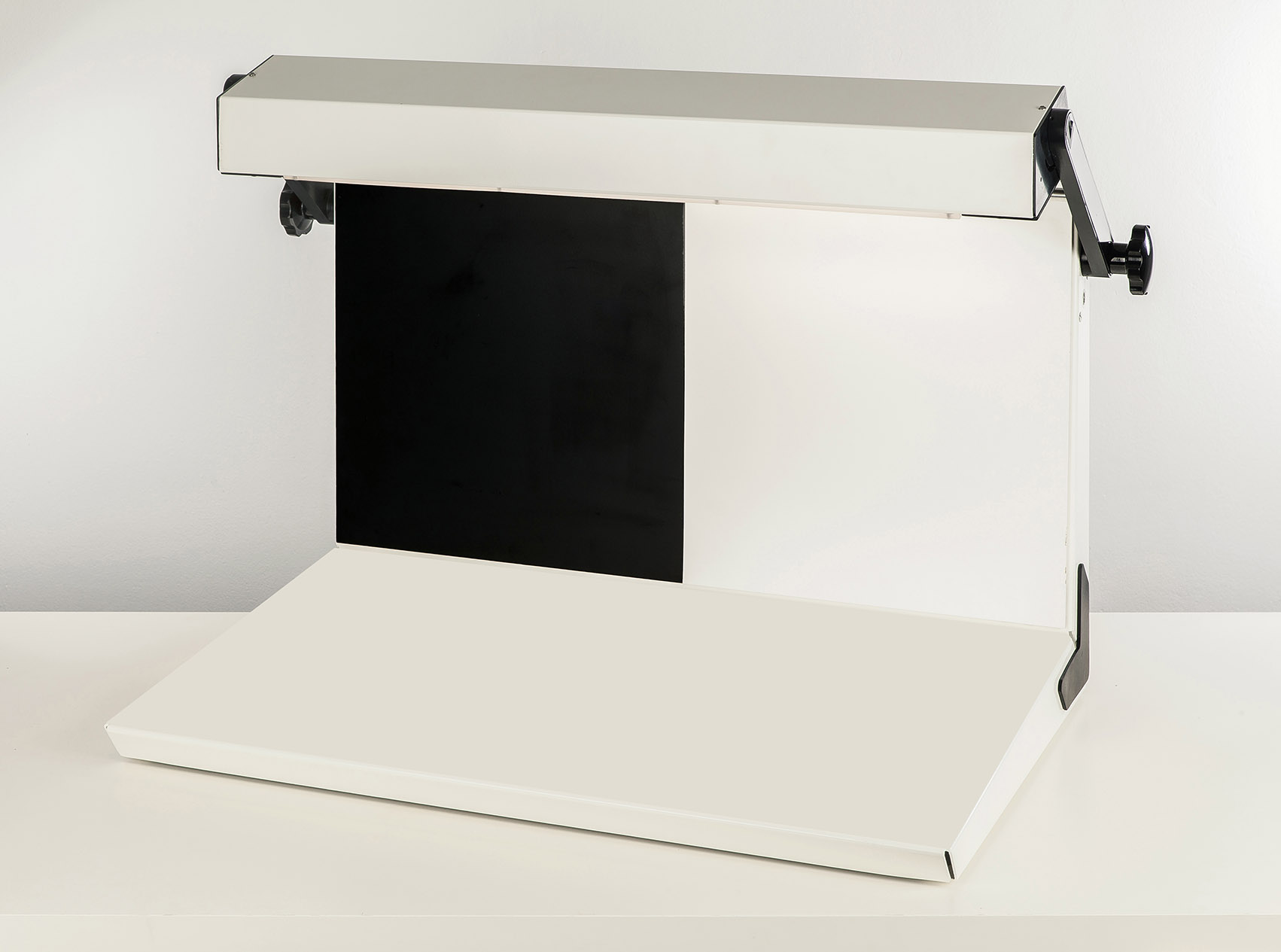
Laboratory liquid viewer for transparent glass bottles
Impurities like hair, fibers, or glass, sourced from the environme...
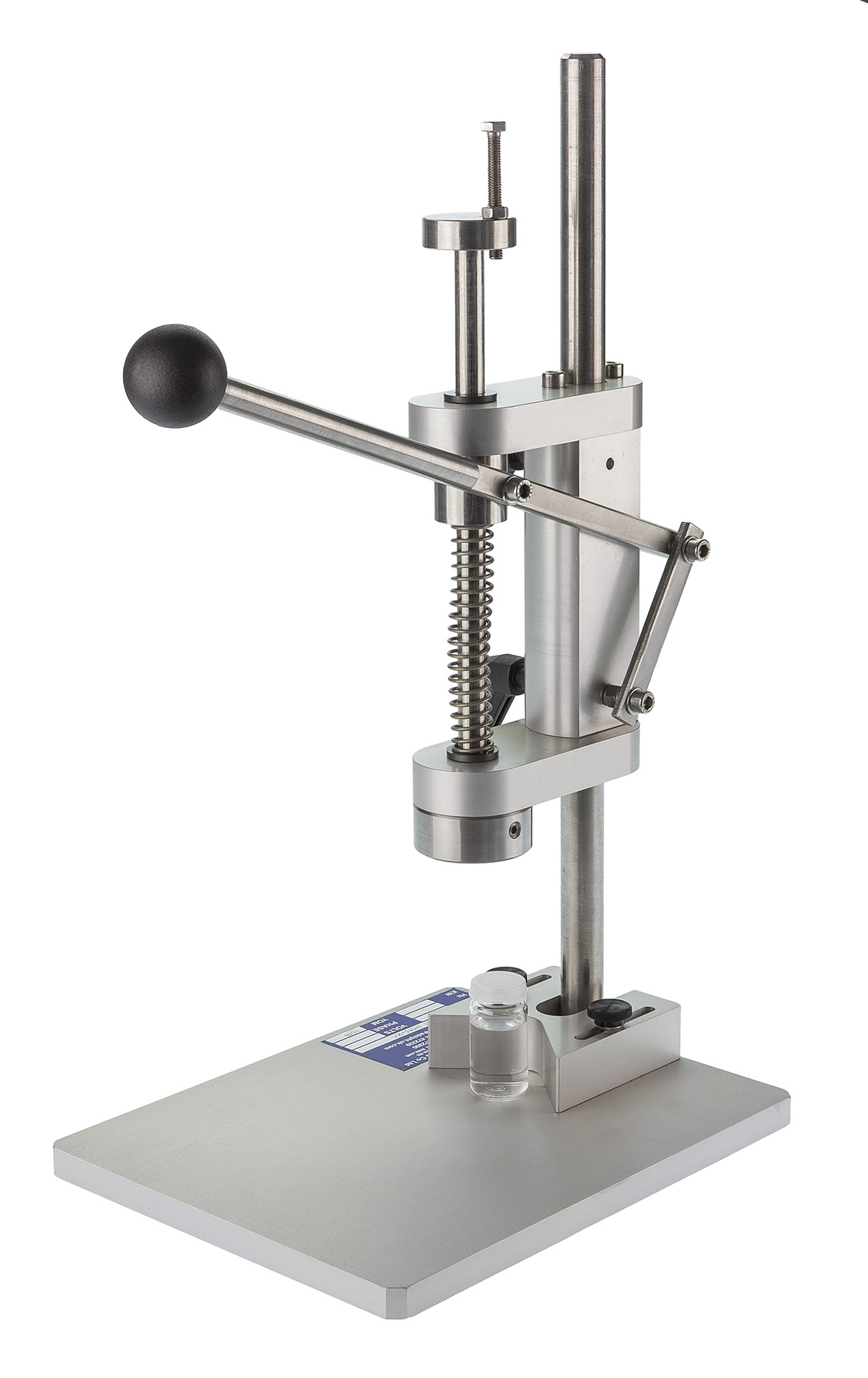
R&D bottle cap press
When you are a small-scale producer of liquids contained in bottles with press-on lids and caps you need...
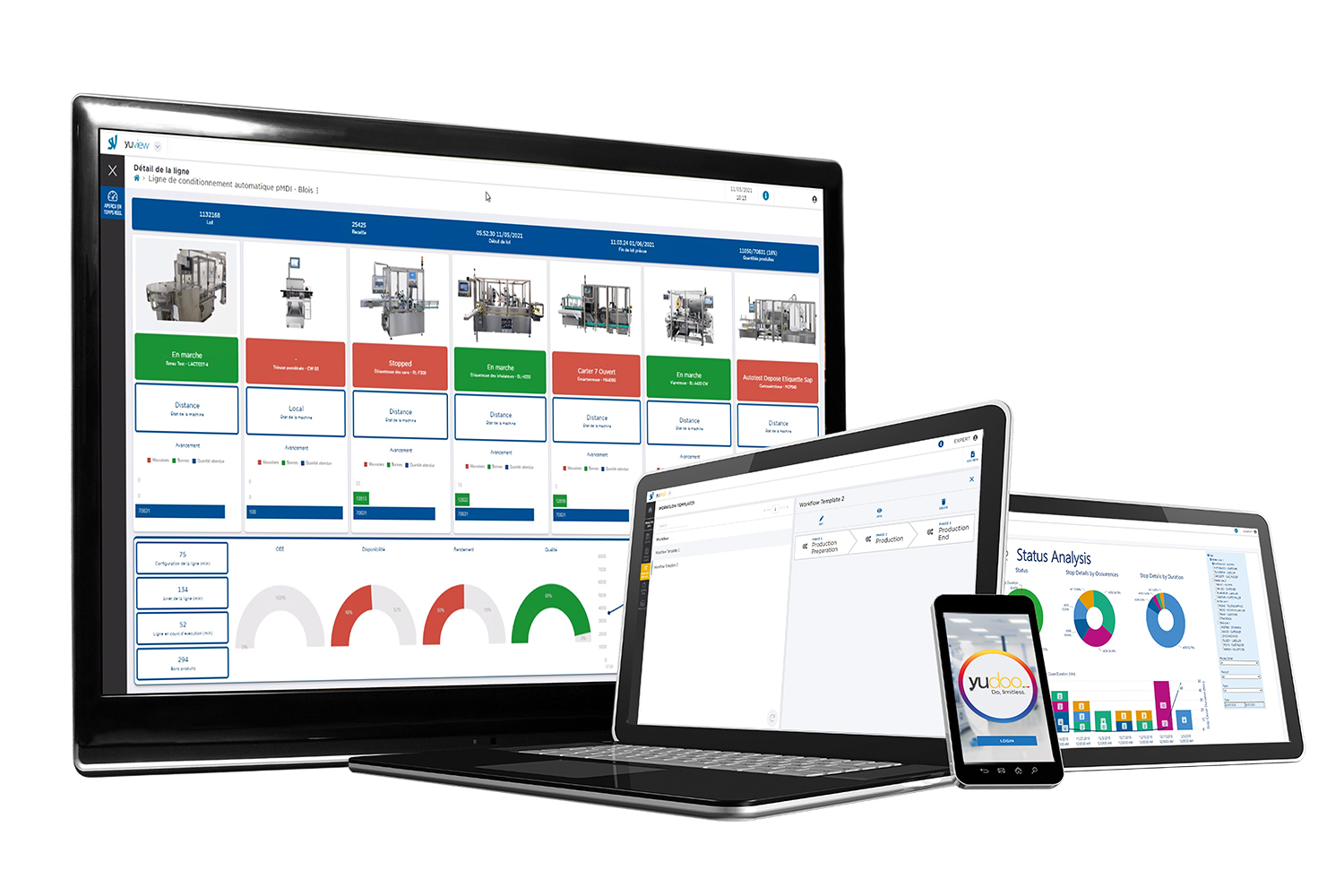
Pharmaceutical data management software
A typical pharmaceutical production handles numerous work flow activities like mana...
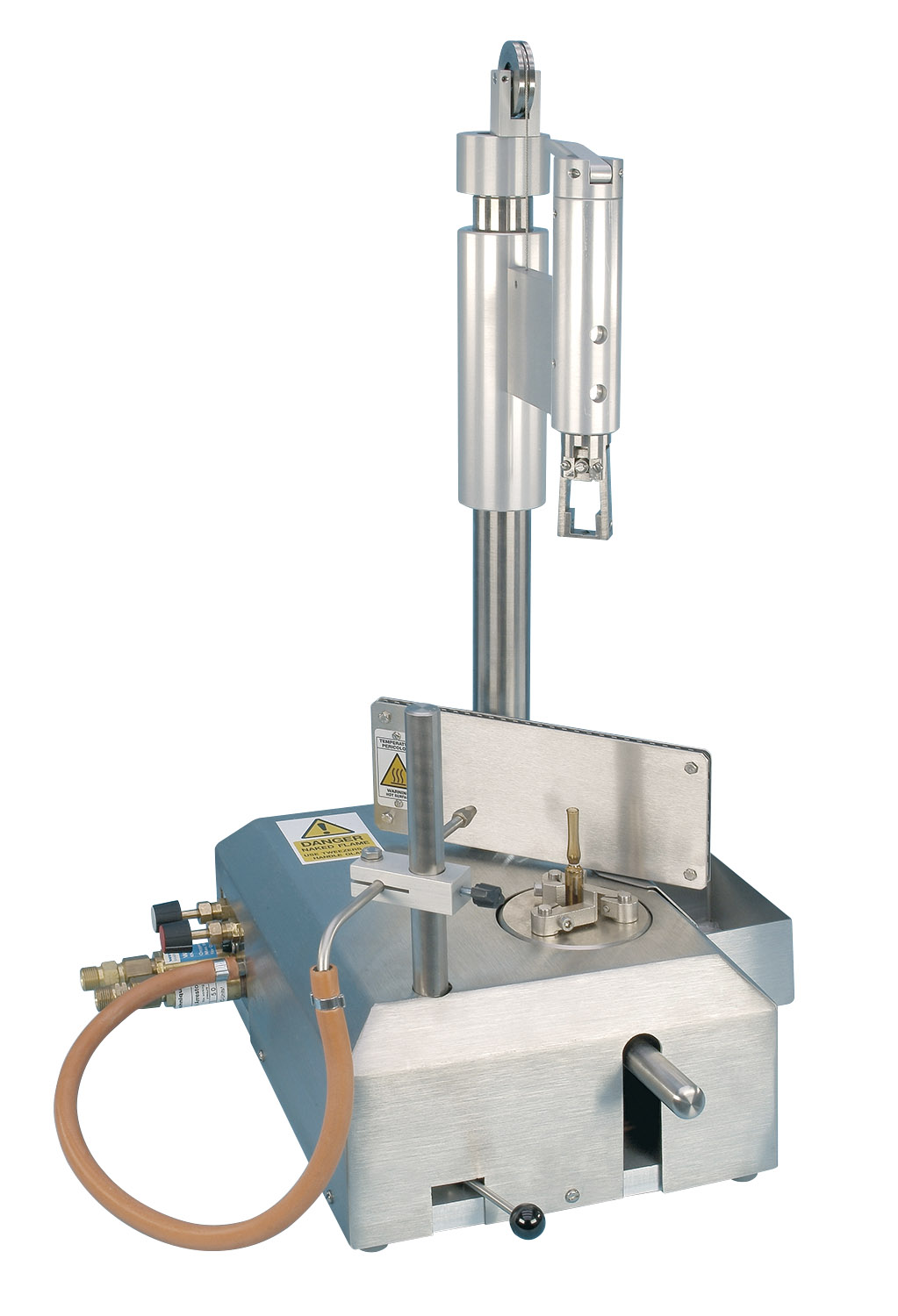
Benchtop ampoule opening and closing equipment
The procedure for opening or closing ampoules requires you to handle gas an...
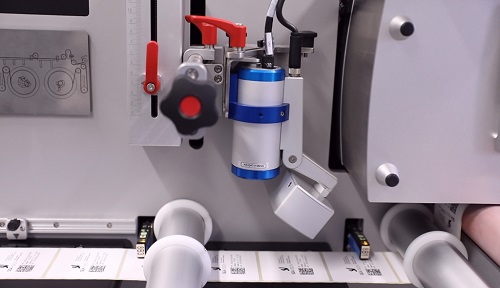
Serialized labels inspection and printing station
Labels are a key component in pharmaceutical packaging lines as they in...
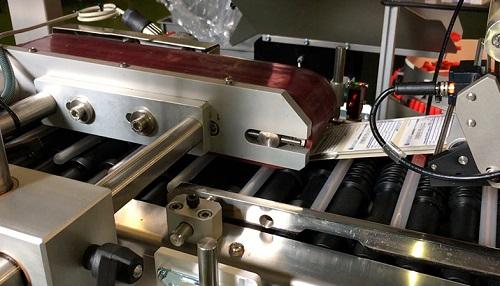
Labeling machine for ampoules
It’s essential for pharmaceutical companies to provide the highest quality ampoules to custome...
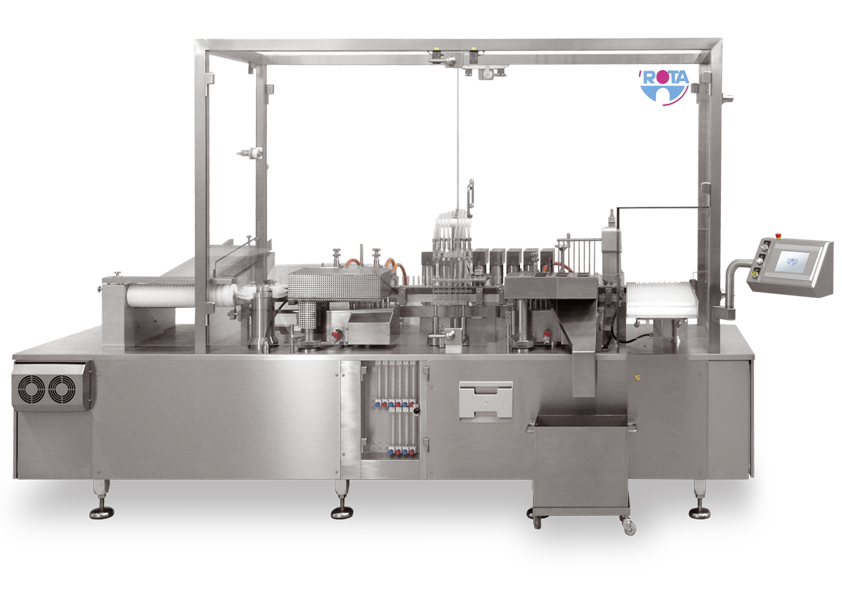
Ampoule filling machine
Filling ampoules or vials with parenteral fluids are an essential matter for which you need to consid...
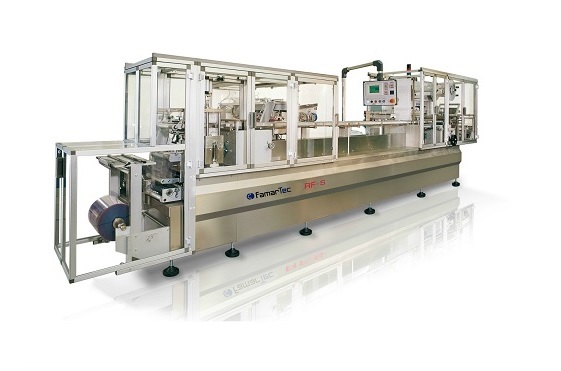
Packaging machine for syringes in trays
Pre-dosed syringes are rapidly becoming the method of choice for the delivery of in...
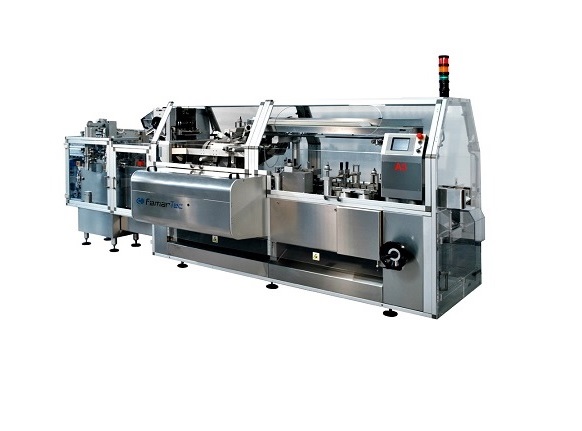
Continuous pack cartoner
High volume automatic cartoning is vital for large scale production of cosmetic or pharmaceutical pr...
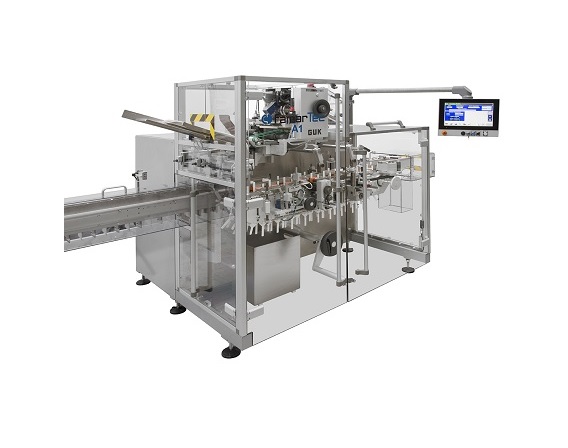
Horizontal cartoner for pharmaceutical applications
Automatic cartoning for cosmetic or pharmaceutical products is a requ...
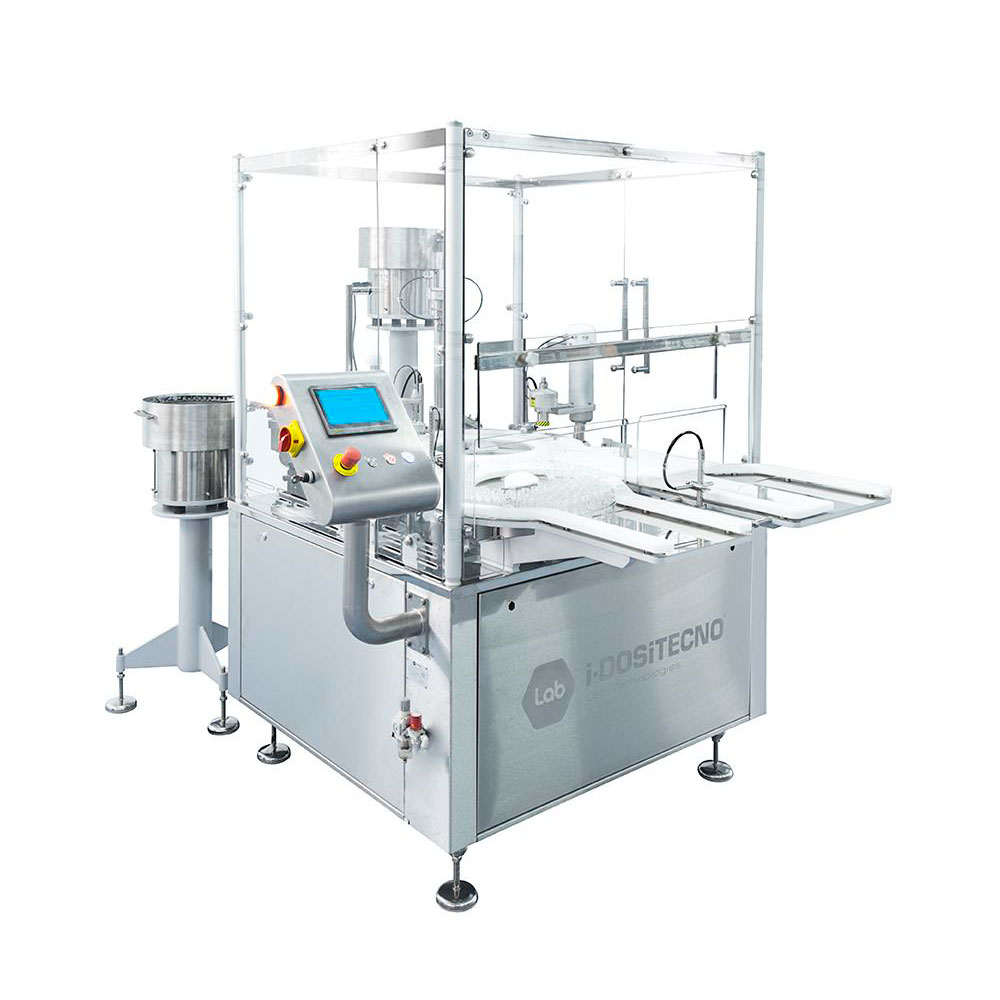
Start-up sterile filling line for injectables
For smaller-scale production of vials and syringes for the injectables marke...
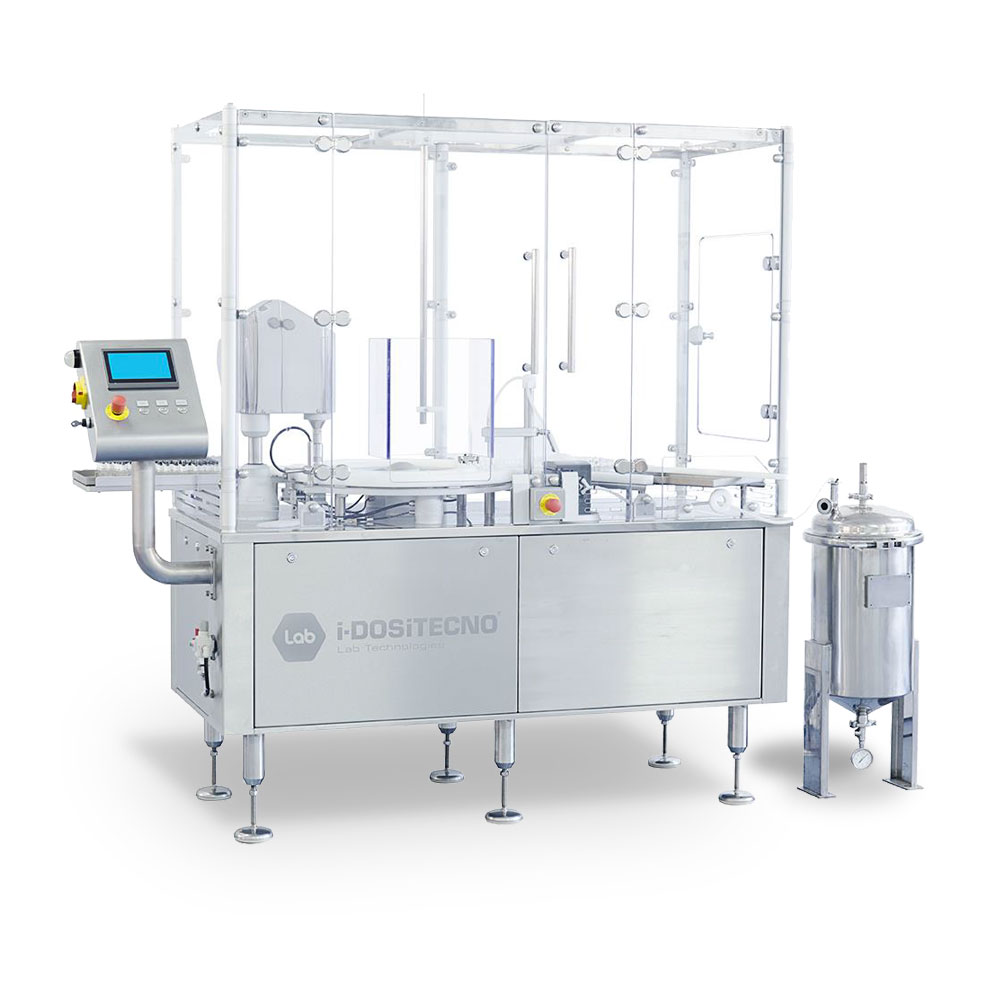
Table top sterile filling line for injectables
Where a compact solution is required for filling vials for the injectables ...
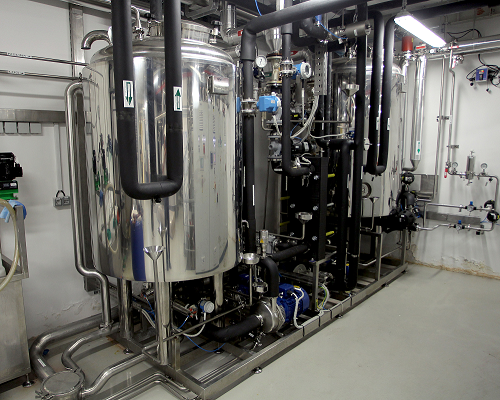
Cleaning and sterilization systems
An increasingly vital part of high quality pharmaceutical production is a dedicated Clea...
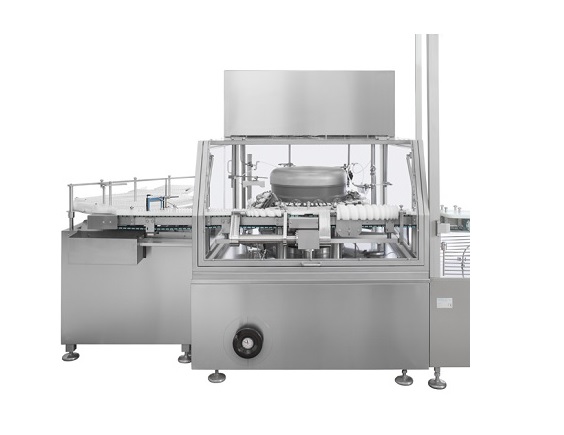
Rotary vial washing machine
When washing vial, ampoules, or cartridges for pharmaceutical production there is often a trade-...
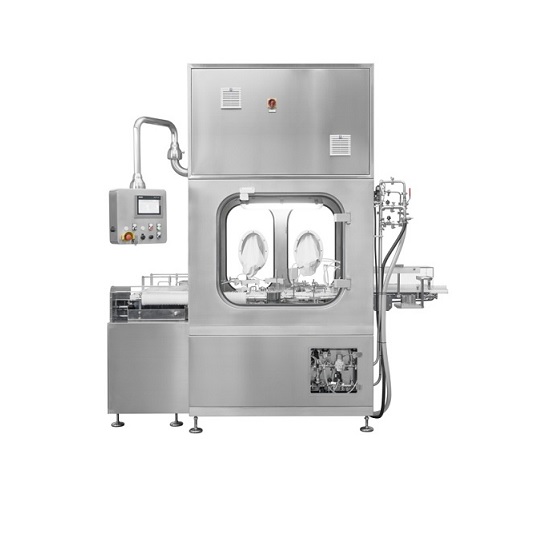
External vial washing machine
Exterior washing solutions for vials often suffer from high water consumption and low throughp...
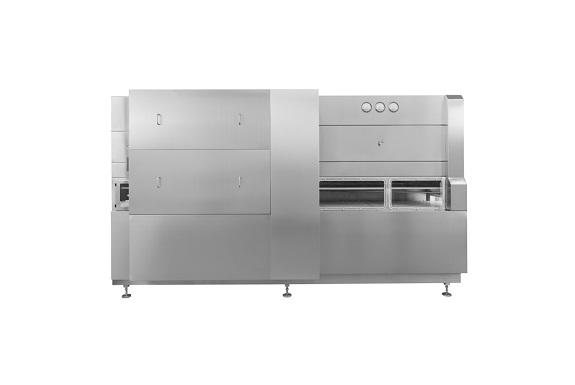
Vial sterilization tunnel
Sterilization of vials, ampoules and syringes before filling is a vital step in the production of ...
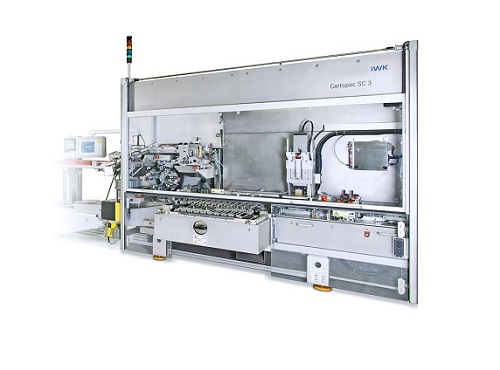
High-capacity horizontal cartoner for pharma and cosmetics appliances
Cartoners take carton blanks which are formed and...
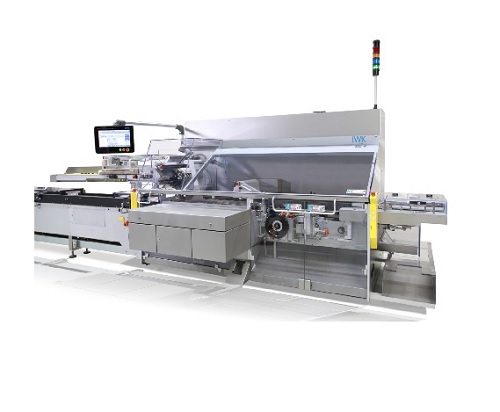
Automatic cartoner for applications in pharma and cosmetics
For high capacity production of cosmetics and pharmaceutical...
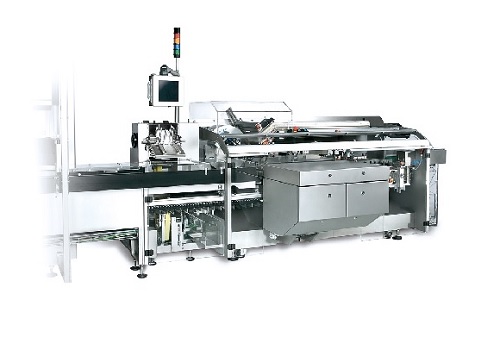
Pharmaceutical and cosmetic industry products cartoner
A large number of cosmetic and pharmaceutical products are packed ...

Horizontal cartoner for pharma and cosmetics
Most pharmaceutical and cosmetics products are packed in cardboard cartons fo...
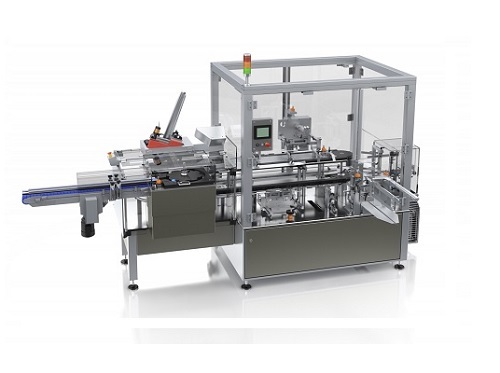
High capacity cartoner for pharmaceutical applications
Many pharmaceutical products are packed in protective and decorati...
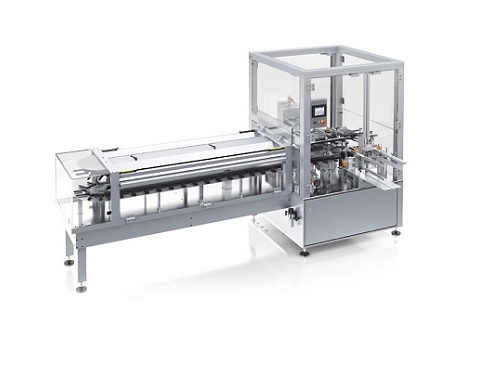
Vertical cartoner for pharmaceutical applications
Many pharmaceutical and cosmetic products are sold in protective and de...
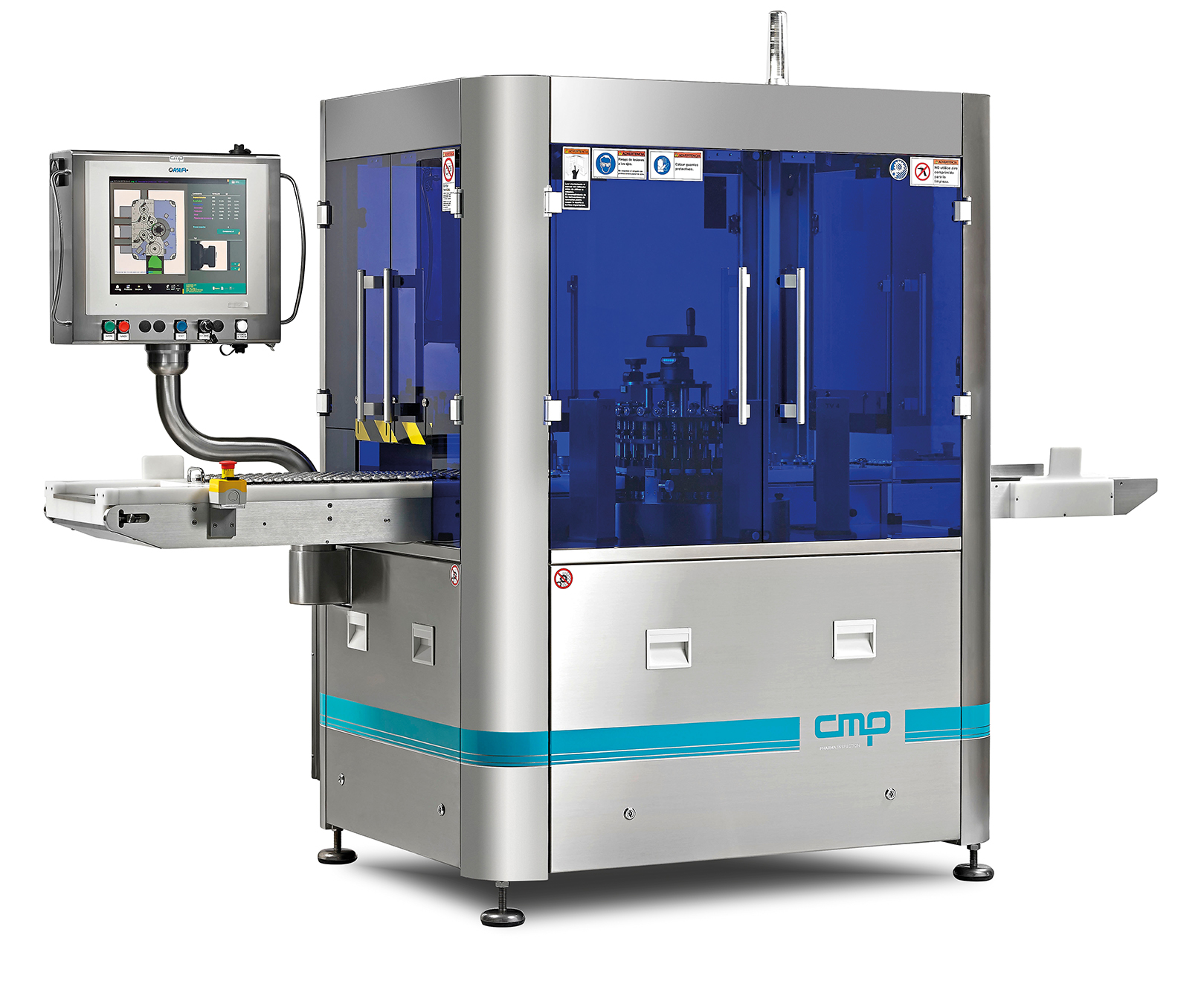
Flexible automatic inspection machine for ampoules, vials, cartridges
If you are looking to improve the efficiency of y...

Flexible automatic inspection machine for syringes
Manufacture of pre-filled syringes requires the highest quality inspec...
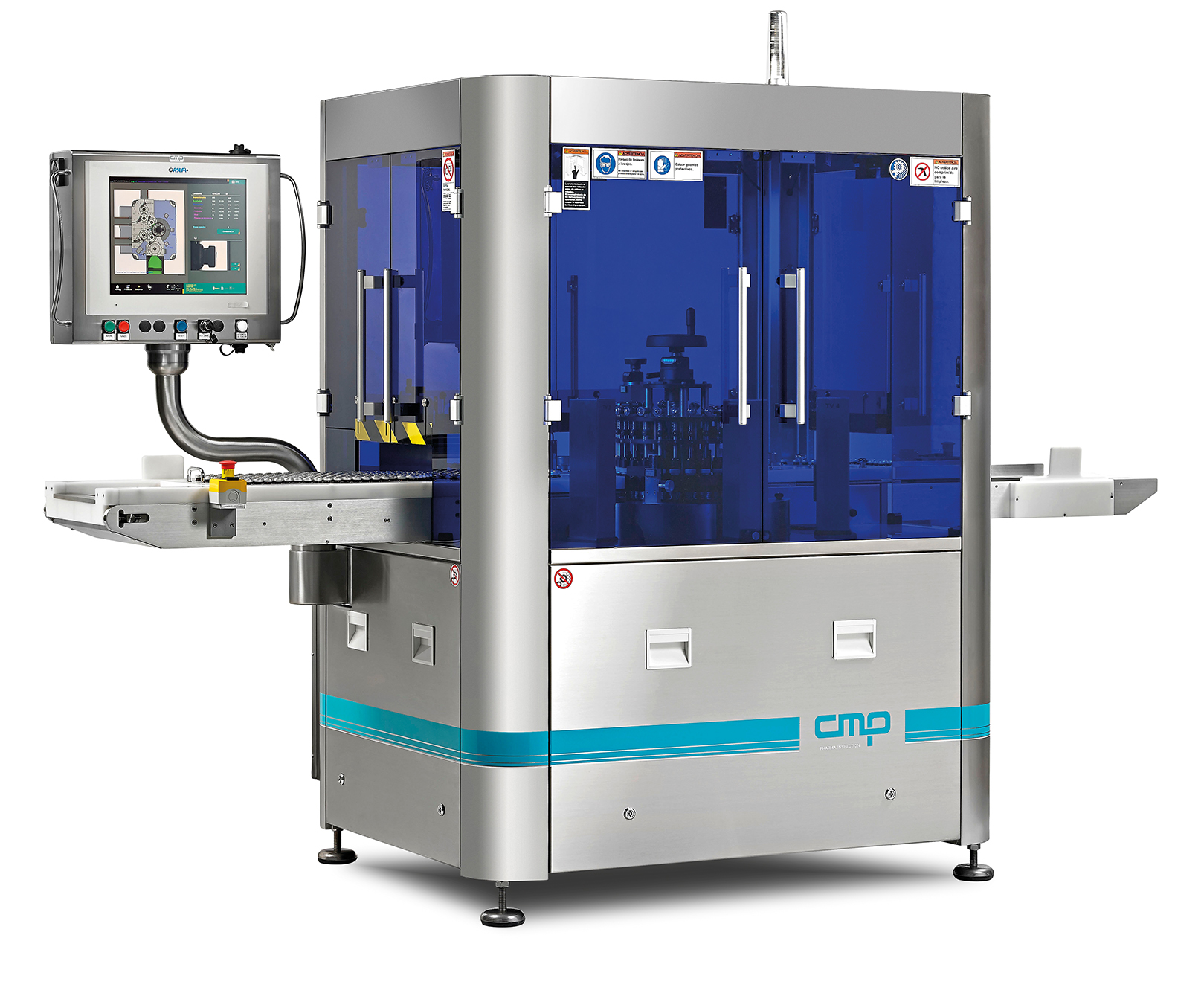
Small automatic inspector for ampoules, vials, or cartridges
Inspect small batch production of ampoules, vials, or cartr...
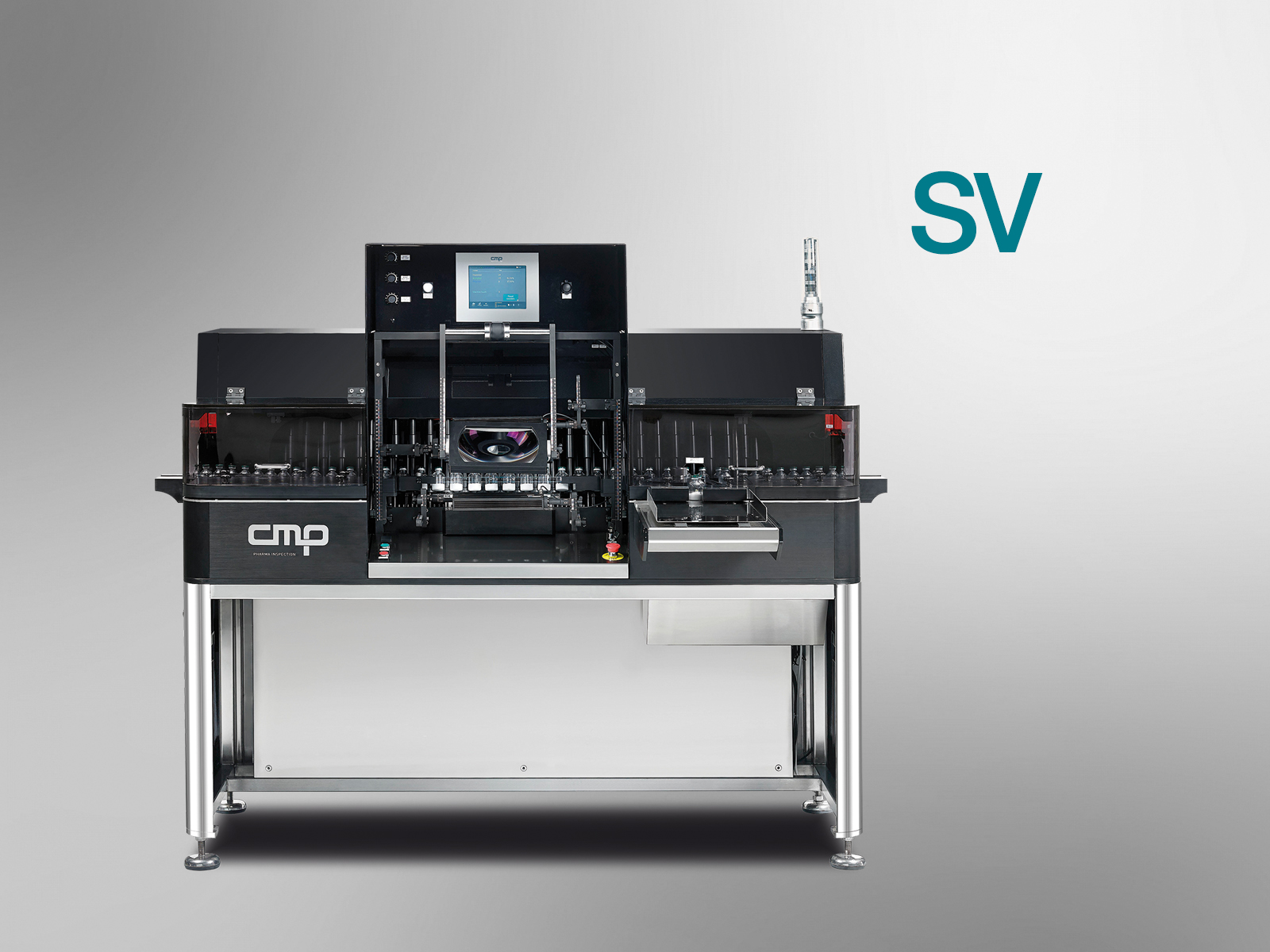
Semi-automatic inspection machine for ampoules, vials or cartridges
If you need to increase the efficiency of your manu...
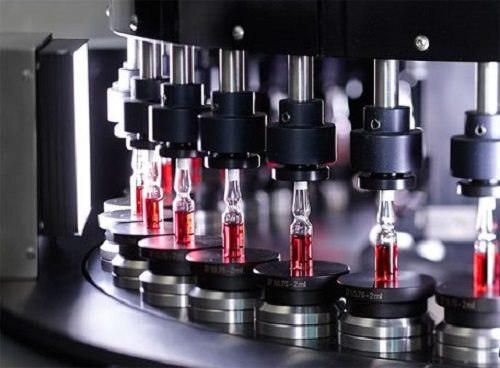
Visual and HVLD inspection for ampoules, vials and cartridges
Do you need to improve the efficiency and capability of yo...
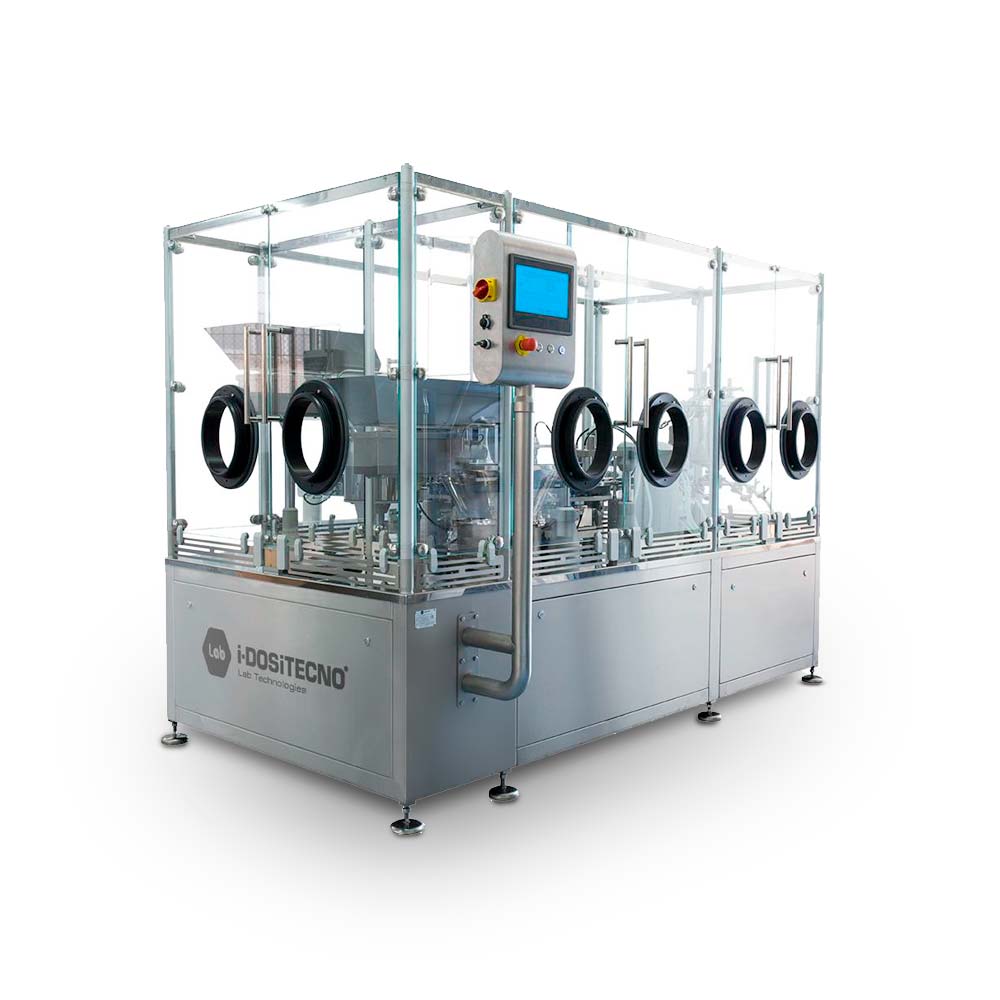
Sterile filling line for injectables
Sterile filling of liquids and powders for the pharmaceutical and cosmetic industries ...
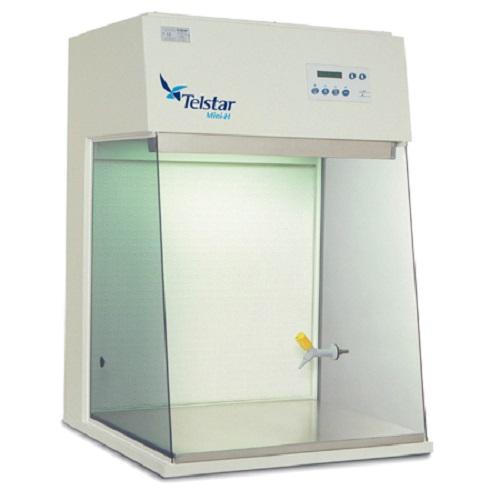
Compact horizontal laminar flow bench
HEPA filtered horizontal laminar airflow (cross-flow) creates an optimized free space...
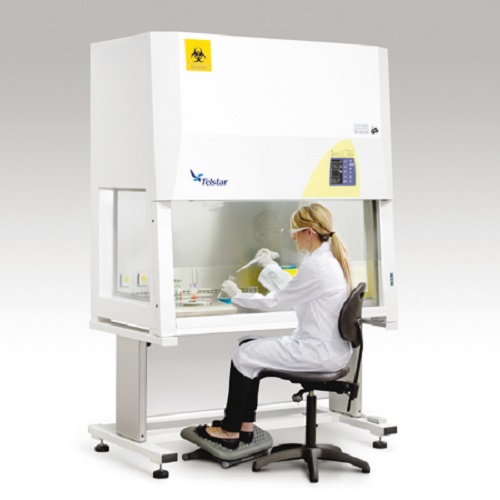
Microbiological safety cabinet class II
This handy device offers the most advanced features in product-operator protection ...
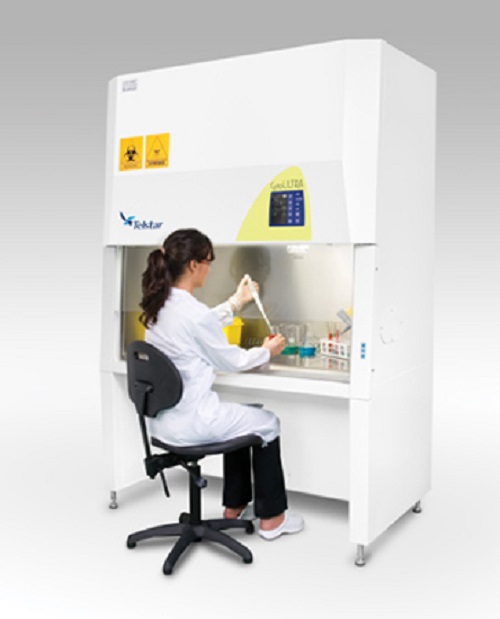
Biosafety cabinet class II for cytotoxic medicines
For the manipulation of hazardous substances utilized during the prepa...
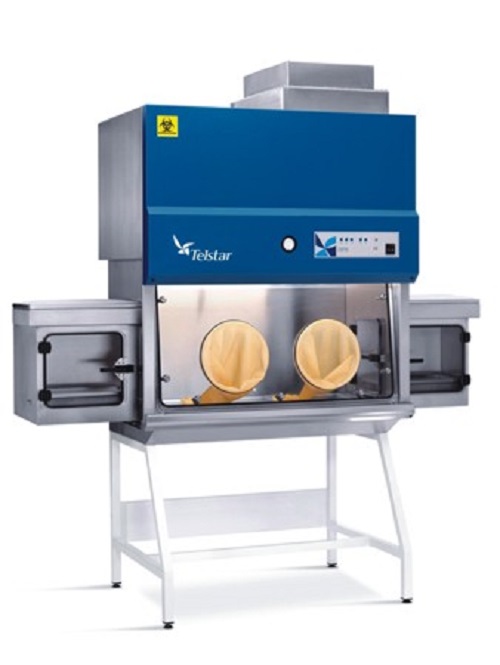
Positive pressure isolator
Ideal for products which have no biological risk but require high sterile conditions.
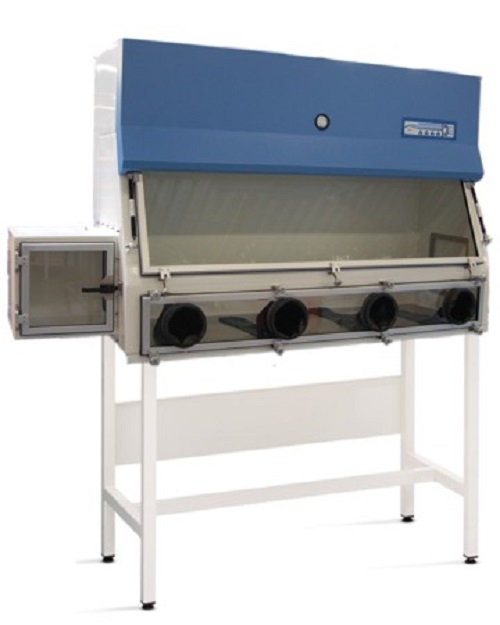
Biological safety cabinet class III
Specially designed for the handling of microbiological agents, when working with indige...
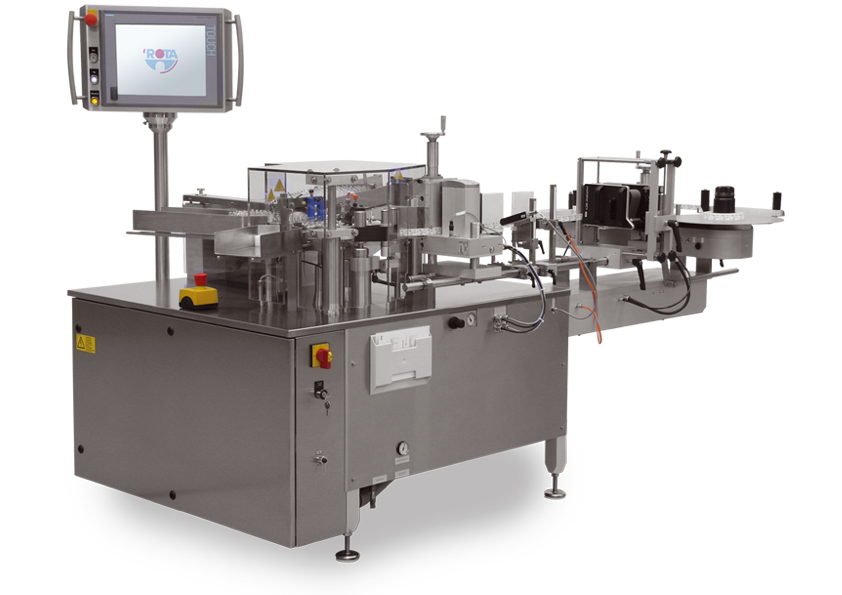
Labeling machines for pharmaceutical bottles
Labels for ampoules, vials and bottles are typically applied at the end of th...
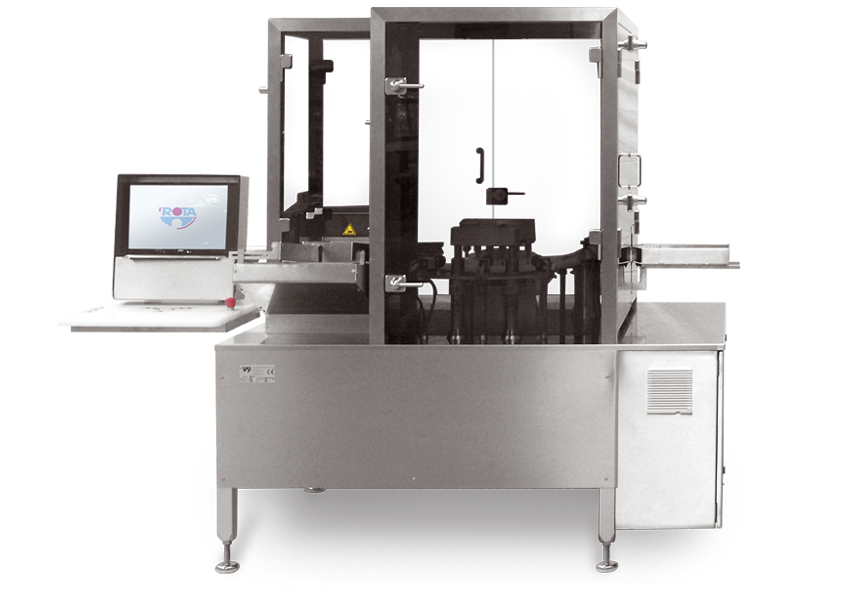
Pharmaceutical bottles inspection machine
For the visual inspection of small to medium batch-sizes of vials, ampoules or b...
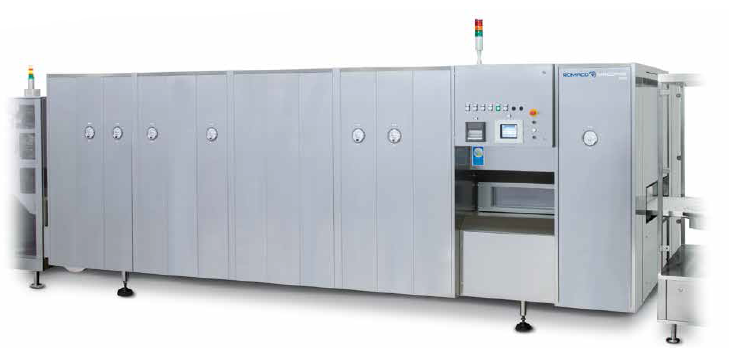
Depyrogenation tunnels for ampoules, vials and bottles
Sterilize and depyrogenize ampoules, vials, bottles and similar gl...
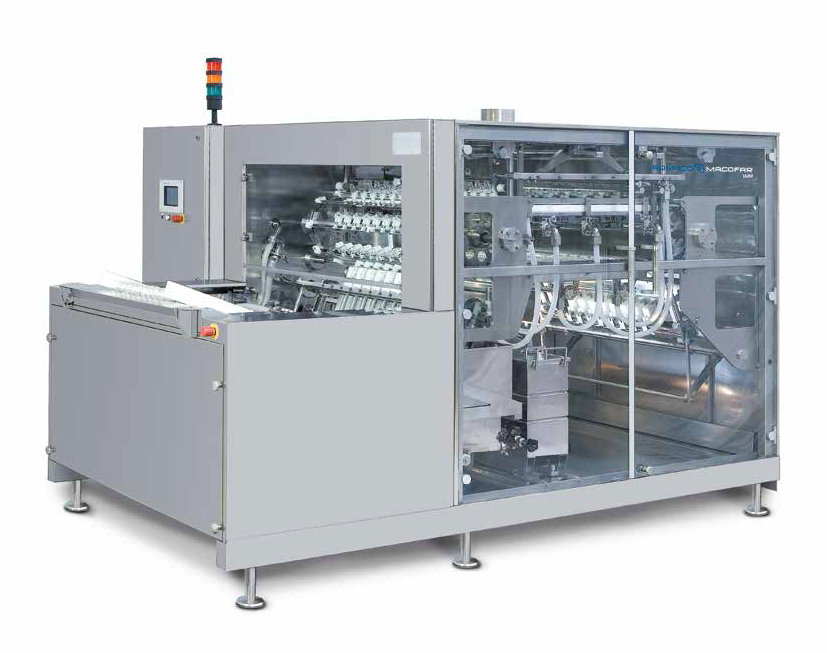
Automatic washing machine for ampoules
Automatic washing machine designed for cleaning ampoules and achieving a maximum out...
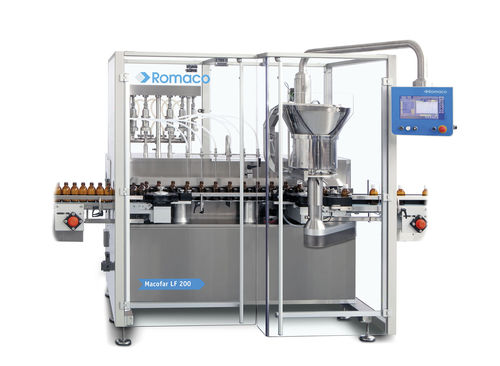
High-speed small volume liquid filler
Fill liquid pharmaceutical, nutraceutical and cosmetic products in ampoules and bottl...
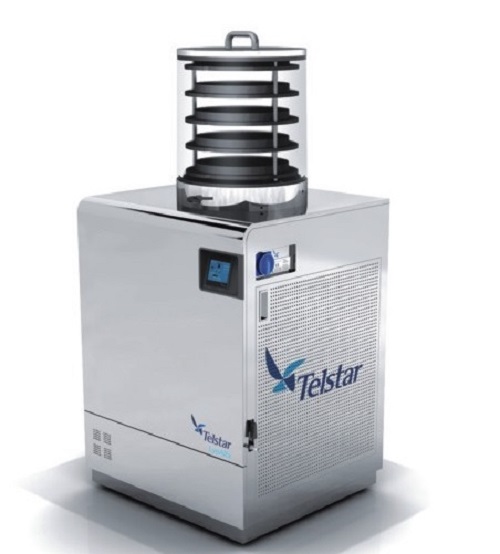
Compact laboratory freeze dryer
Particularly suitable for research centers requiring greater freeze drying capacity. Some of...
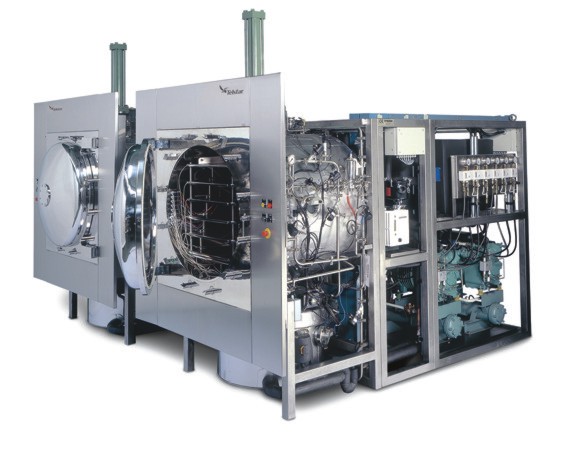
GMP freeze dryer
Designed to perform clinical trials, pilot, and small scale or large scale industrial drying processes, in ac...
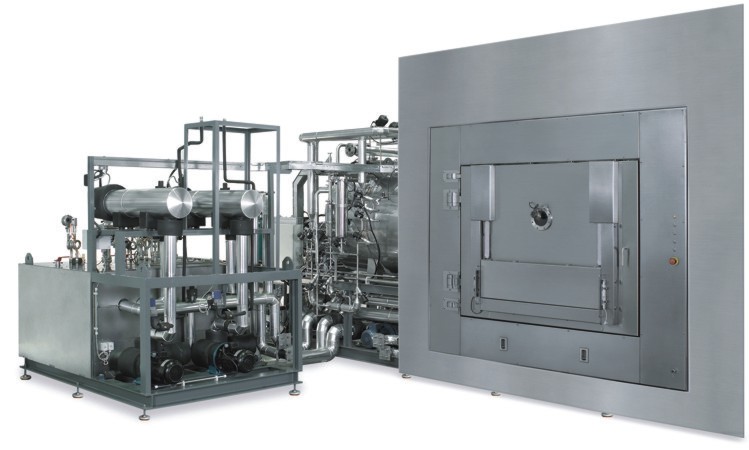
Custom engineered freeze dryer
For either bulk format or liquid in vials, ampoules or syringes, the Lyomega units are design...
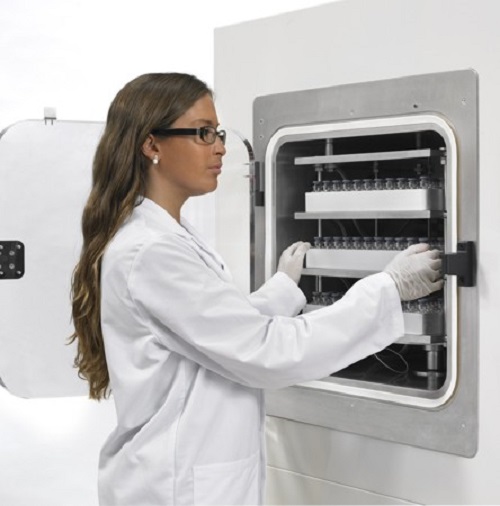
Pilot freeze dryer for scale up
Designed for biological, pharmaceutical and food products formulation and “scale up...
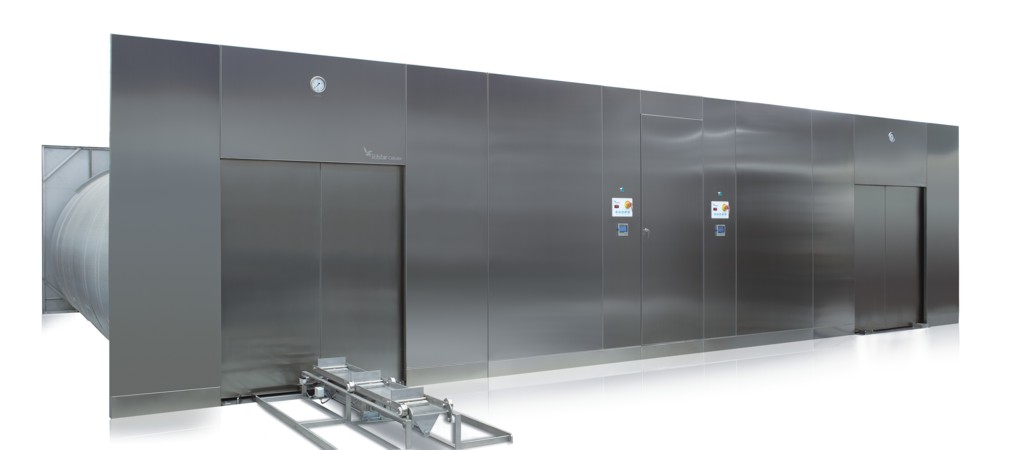
Superheated water shower autoclave
Specially designed for sterilizing large batches of parenteral solutions.
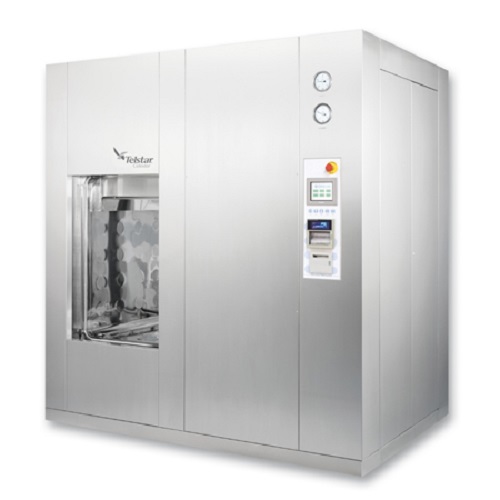
GMP autoclave
When sterilizing and dealing non-thermolabile products, you will want to get a hold of those resistant to the te...
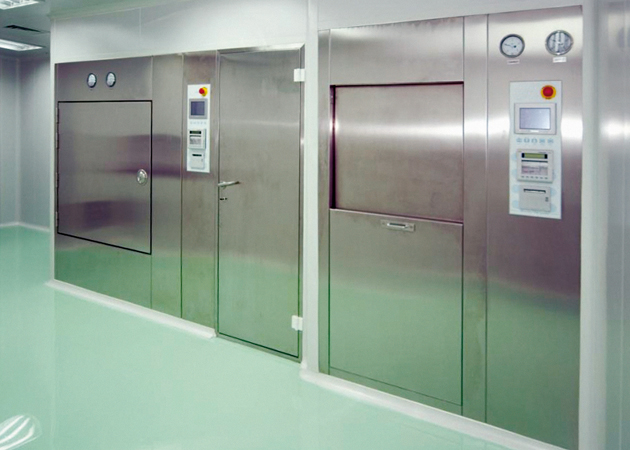
Dry heat depyrogenation oven
Specially designed for the drying and sterilization of glass containers, vials or ampoules, and...